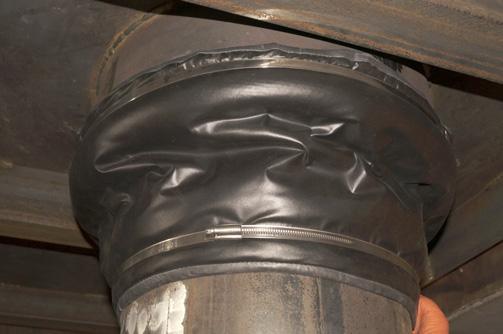
9 minute read
An open-and-shut case
entire manufacturing line – from developing the material and small-scale testing, qualifying and full-scale compounding to manufacturing and delivering finished products. Most of the material development has been customer-driven, as well the need for fire protection materials in offshore installations.
Fire protection is often divided into two types of systems – active fire protection (AFP) is either triggered by a sensor when exposed to, for example, smoke and heat, or you must manually activate to operate. These systems include sprinkler, deluge, water spray, fire extinguishers and more. The other type is the passive fire protection (PFP) system, which exists as an integrated part of a component or as part of a structure on buildings, offshore oil platforms, or ships. PFP contains the fire within an area, thus limiting the fire and smoke spread in a given time period.
When it comes to extending the life of assets and supporting operations, the focus on technical safety in oil and gas production has increased immensely during the last few decades. The solutions must demonstrate excellent performance across a range of fire scenarios, often in conjunction with higher heat load, and documented success through certification, type approvals and test reports that illustrate not only fire protection properties, but also provide installation and handling information.
Due to the need for PFP in different applications in the oil and gas segment, the Firestop technology was developed. The material was developed to protect risers, transporting oil and gas in offshore installations, in the event of fire. If a crack happens in a gas-filled pipe, and a gas leak occurs, a small spark can transpire into a severe jet fire scenario. Thus, the Firestop material was developed to handle the harshest fire scenario that the industry could foresee.
The material was later qualified for use in several other applications and architectural PFP seals has been a large area of development. Since structures and equipment rarely have the same requirement with regards to fire ratings, dimensions and movement, they often need to be tailormade and designed for each installation.
Sealing and elastomers Elastomer-based, passive fire protection seals offer a flexible connection between rigid metal sections. Capable of handling large displacements, they connect modules, maintaining a fireproof partition, absorbing misalignments, angular deviations and eliminating concentrations of stress. Elastomer-based seals used in escape tunnels and door seals offer protection of door frames and connecting fire-safe escape areas.
The benefits of elastomeric seals include: ) Elimination of the propagation of vibrations, dynamic loads and deviations caused by a fabrication process.
) Customisation to fit any shape and size to suit individual project requirements.
) Installation on a variety of structures.
In areas where drainage is required, elastomer-based seals can be made as a drain gully that supports the design of a closed deck, eliminating the need for fireproofing of process deck structures. Drain gullies allow hydrocarbons spillage from process modules to drain, eliminating the requirement for multiple drainage boxes and integrated overflow. As the properties of each material vary, finding the most effective material and technical solution for a project is crucial.
Passive fire and corrosion protection in the offshore industry Factors to consider when choosing the right material include the potential source of a fire, duration, temperature, and blast, along with qualifications, certificates, and material properties.
The objective of PFP is to prevent or mitigate the serious consequences of fire: ) Prevent escalation of fire to adjacent areas.
Figure 1. Pipe penetration seal (HPT).
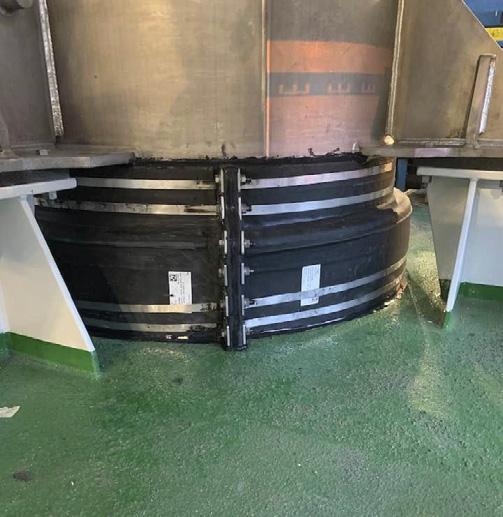
Figure 2. Radial firestop seal.
) Ensure a temporary refuge is intact for a specified amount of time.
) Protect people from the fire (heat and smoke) and make escape or evacuation possible.
) Protect essential systems and equipment.
) Maintain structural integrity for a set period.
The most extreme fire scenarios are hydrocarbon, jet fire and high heat flux – all distinctive to topsides on offshore platforms. Elastomer materials can be used alone or in various combinations to meet specific requirements. Vipo specialises in developing bespoke combinations to meet industry requirements and has, over decades, developed and adapted rubber materials to meet the harsh environmental and safety requirements in the offshore industry.
Elastomer-based materials are also well suited for protection against corrosion. External corrosion in carbon and low-alloy steel is a serious challenge in the oil and gas and other highly corrosive environments. Vipo has developed a rubber-based material that provides sealing against corrosion. The steel is rubbed or sand blasted, then primer and or adhesive is used before the rubber is applied by machines or by hand. It is completed through a vulcanisation process, by cross-linking the rubber to the steel providing excellent bonding. This gives corrosion protection superior to any paint system available. Testing advances and qualifications During the development of any new PFP material, manufacturers must ensure the solution is qualified against the harsh fire
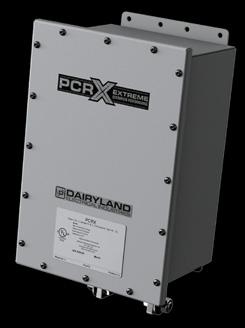
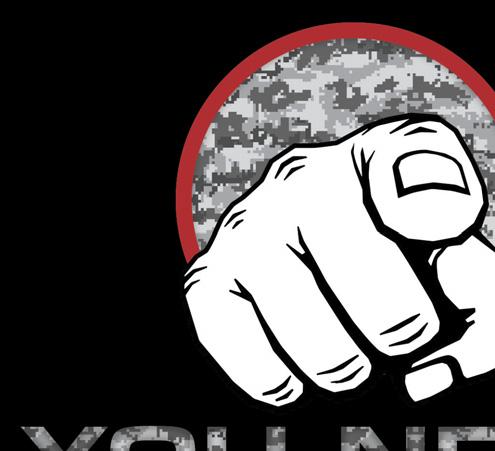
Developing a bespoke sealing solution for pipe penetration Seals can also be used in conjunction with wall penetrations where the customer has a need to be able to inspect the steel structure, and thus a requirement for a flexible, re-mountable solution that must also withstand tough fire.
Vipo’s Pipe Penetration Seal (PPS) is a thin and flexible seal, consisting of layers of tough and durable materials that offers protection against fire, blast and weather. With a thickness of approximately 10 mm, requiring minimal space, the wrap-around seal closes the pipe penetration and allows movement of the pipe during operation. Seals are tailormade to fit a wide range of different applications, geometries, and sizes, and are easily installed and dismantled with hand-held tools.
PPS is made in one piece with an overlapping joint and is typically fixed and secured with stainless steel hose clamps that are easy to remove for inspection, and can be reused, reducing wastage as seals are not damaged during the processes. The material can also be used to seal in other applications and can be fixed by bolting it to structure or it can be tailor-made as wraparound jackets to fit any geometry, structure or component.
MEET THE PCRX
Expanding on our industry-leading decoupler designs, the PCRX’s new camouflage technology uses sophisticated solid-state power electronics to deliver fast, accurate readings during interrupted survey testing.
Learn more about the next generation of Dairyland decouplers: Dairyland.com/PCRX
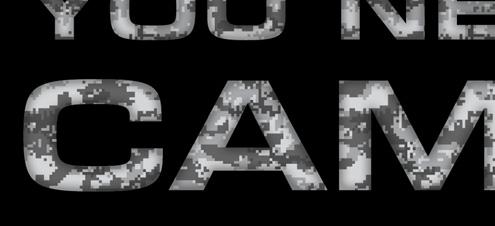

requirements in the given industry, such as cellulosic, pool fire, hydrocarbon fire (HC fire) and jet fire. In recent years, the industry became gradually more aware that a jet fire has a higher heat load than permitted in standard jet fire testing. This required the development of an extended jet fire test, also known as high heat flux (HHF) testing.
Fire classifications are characterized by heat fluxes around 150kW/m2 with temperatures reaching approximately +1100˚C in hydrocarbon fires, and around 250kW/m2 with temperatures around +1200˚C for jet fires. Hydrocarbon, or pool fires, may occur when combustible liquids (oil, gas) leak from a pipeline, forming a fluid pit or reservoir which ignites. Fire integrity in these cases, is measured using H-fire ratings, showing the material’s ability to resist fire and remain intact during a given time frame, usually for 120 minutes.
The heat fluxes given for a jet fire are dependent on different boundaries such as type of fuel, a mix of fuel/ oxygen, and flame size. The ISO22899 standard describes a set-up with a pressurised gas release giving a severe combination of erosive forces and heat. This mixture can be highly destructive to some PFP systems, resulting in potential failure of the system to act as a barrier between areas. The test setup is sufficient when giving an indication of the performance of a wide range of PFP materials and systems, with the heat flux achieved limited to 250kW/m2 . The now recognised higher heat flux and temperatures of jet fires created the need for new HHF testing standards to be created. For both jet fire and HC fire testing, standards have been developed over decades and are well known to the industry, including ISO834,
ISO22899, IMO FTP Code. HHF testing, often performed sequentially with HC fire testing, currently has no standardised test protocols or programmes, and it is often left to individual suppliers to demonstrate HHF material or system compliance. Vipo’s operation in Norway has created a large-scale bespoke HHF testing rig to assess its rubber based PFP materials in higher temperatures and heat fluxes. A chamber measuring 3 x 3 x 2.7 m with pressurised gas input to the same standard as stated in ISO22899, was constructed. For comparison, Vipo’s standard hydrocarbon jet fire test chamber was built and operated in accordance to ISO22899 measures 1.5 x 1.5 x 0.5 m. Air is added to the chamber to higher the temperature, creating a high heat flux environment of 350kW/m2 with a temperature of approximately +1300˚C.
Conclusion Sealing technology has come a long way and is still undergoing rapid development in specific industries operating within demanding environments. Material choice, specifically when dealing with active and passive fire protection systems, is a crucial element to maintaining and protecting structures. Elastomers are a common choice when developing solutions to sealing challenges due to their distinct properties. Due to the nature of where seals are often used, the demanding environment requires the highest level of testing and qualification. Therefore, when developing new, innovative sealing technologies and solutions, it is necessary for engineers around the world to be very aware of both what exactly the seal is being used for, and the range of material options and their specific properties.
Figure 3. Vipo’s 350kW/m2 Jet fire test rig.
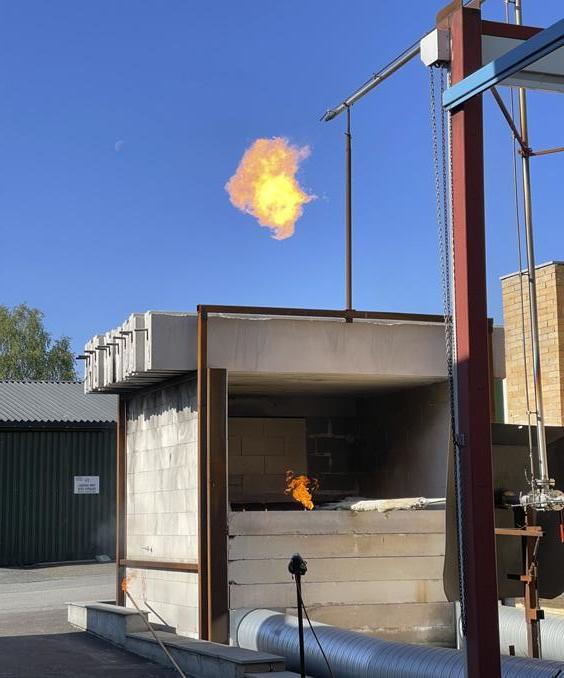
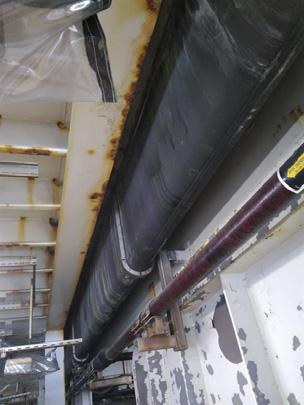
Figure 4. Drain gully firestop seals.
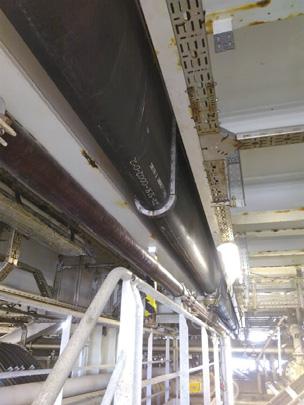
Wherever you are, World Pipelines is with you.
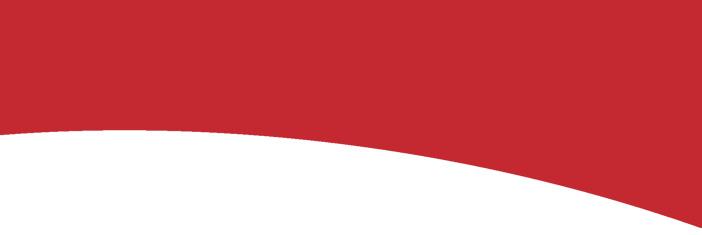
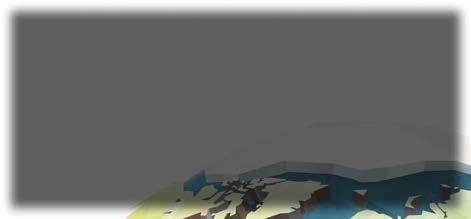
The print issue is distributed to a global audience of industry professionals (verifi ed by ABC). Register to receive a print copy here: worldpipelines.com. magazine/world-pipelines/register
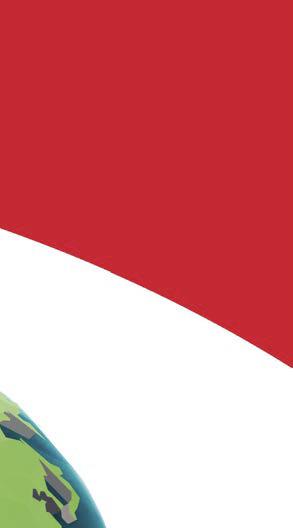
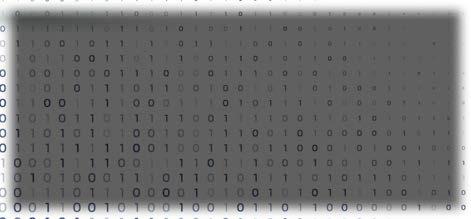
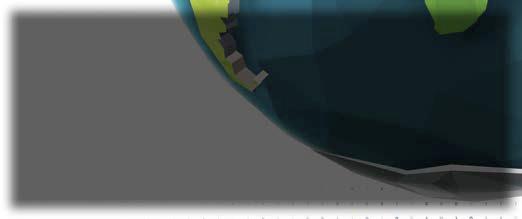
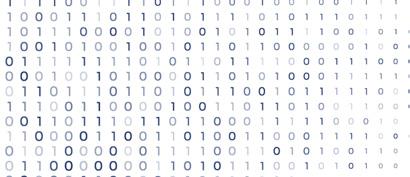
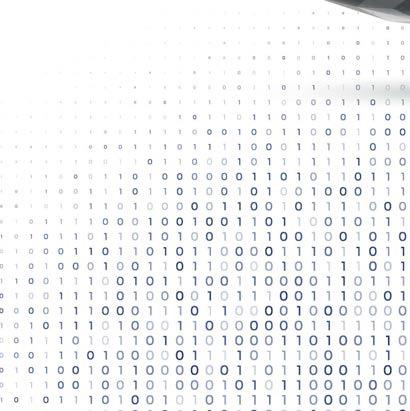
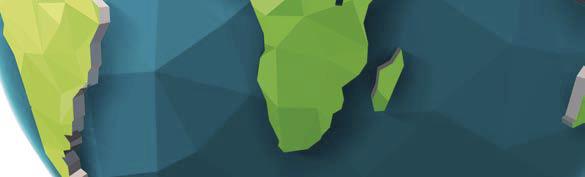
Prefer to read the issue online? The digital fl ipbook version is available here: worldpipelines.com/magazine/world-pipelines
Download the World Pipelines app for Android (Google Play) or iOS (App Store) to access World Pipelines from your mobile device.
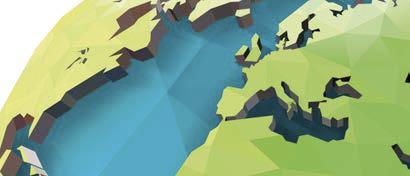
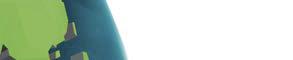
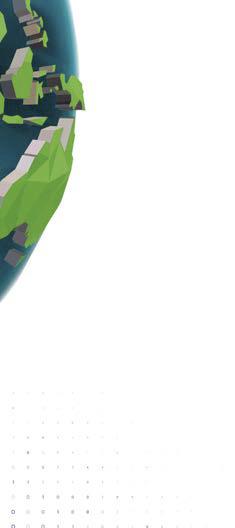
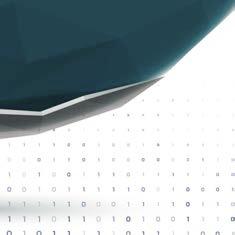
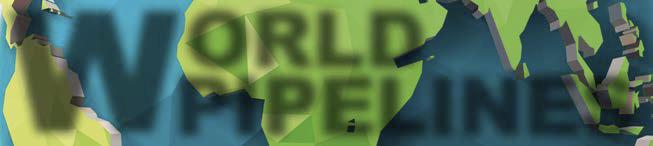