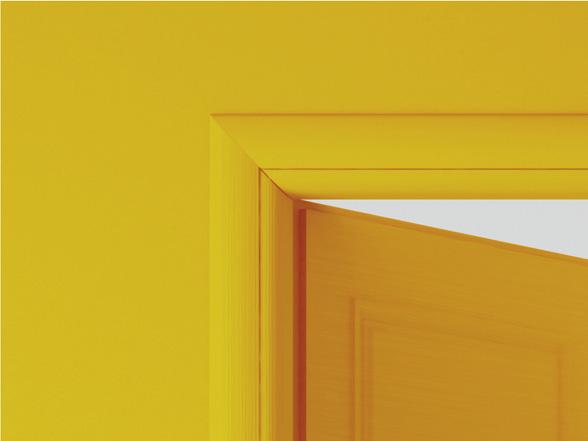
10 minute read
Collaborating on an environmental code


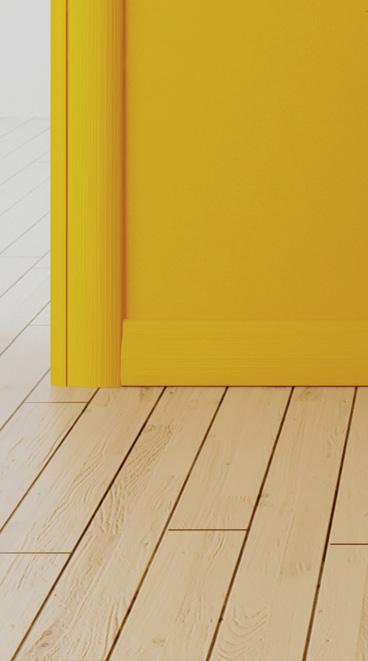


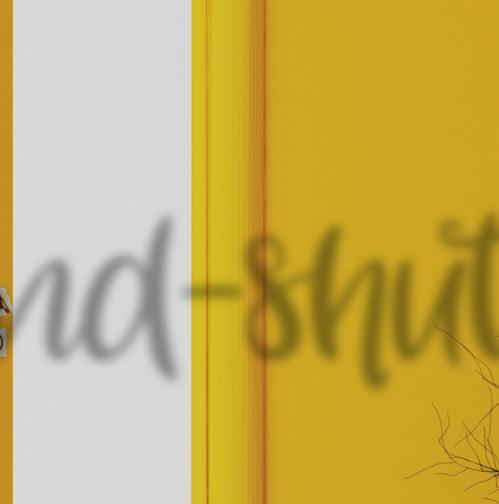

Morgan Sledd, Stark Solutions, USA, discusses the importance of both the correct style and ease of operation when it comes to pipeline closures.
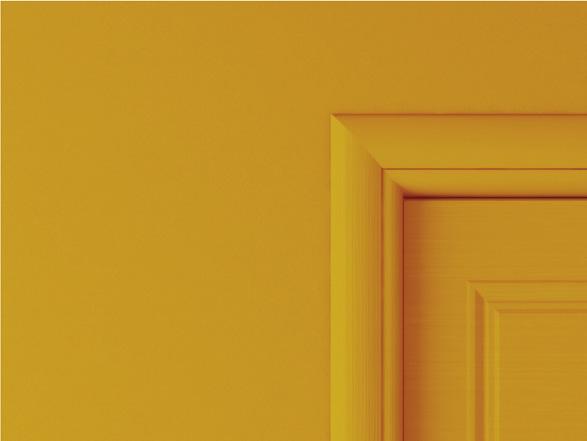
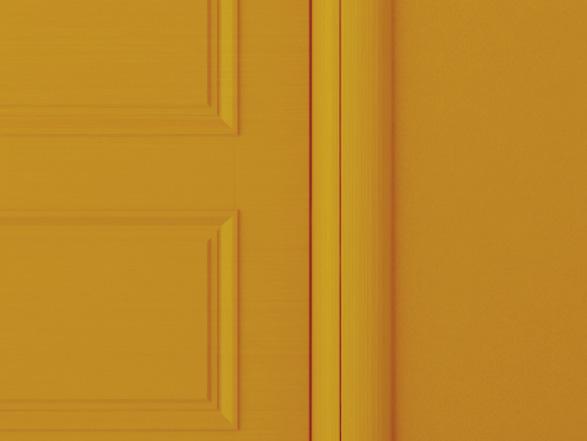
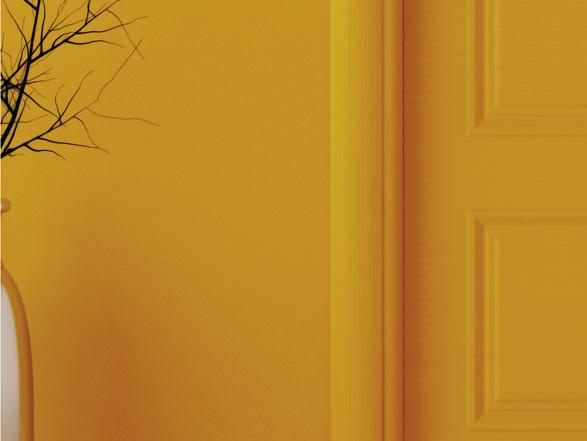
Pipeline integrity and maintenance depend upon ease of access to the inside of the pipelines. Today, that access could be in almost any part of the world; a residential area in middle America, the arid desert conditions of the Middle Eastern region, the cold climates of Canada or southern Australia, the corrosive offshore of the Pacific coastal nations, or even the wet and humid landscape of the tropical South American regions. It pays to have product options that fit your application, your media, and your region. Stark Solutions offers pipeline and pressure vessel quick opening closure solutions to meet those needs.

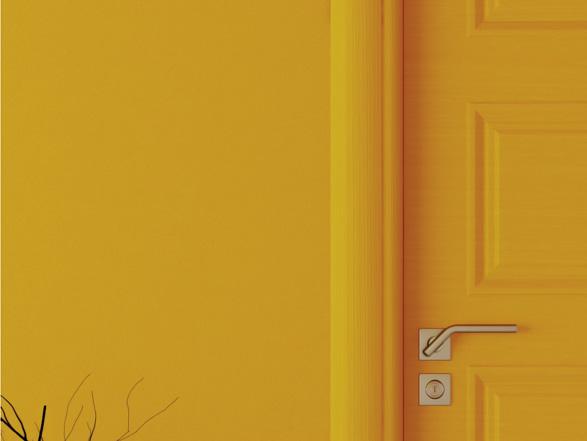
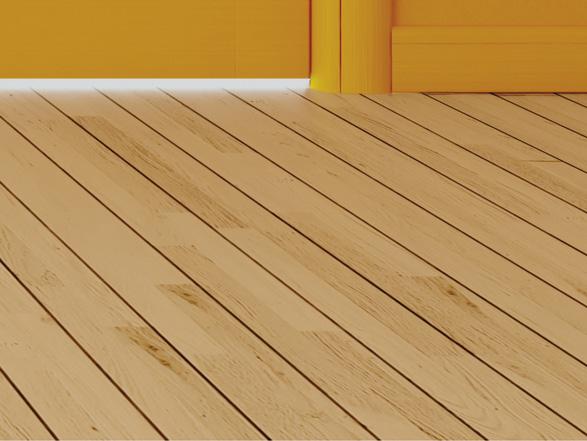
Quick opening closures Quick opening closures have been a mainstay in the oil and gas industry for many years. Starting off as flanged openings with a hinge or davit arm to support the removal of the blind flange, these openings were a means of entry into a pipeline or vessel for inspection and cleaning. Flanges have

a number of bolts that must be removed before the pipe can be accessed. Often times due to the size of the bolts, it requires large specialty tools to be used, which leads to extended down time to open while also factoring in an added potential for operator injury.
Another downfall is that flanges have no inherent safety features to alert the operator when lines are not properly vented. Once loosened, the media can directly escape, causing leakage and a potential safety hazard for the operator and anyone in the surrounding area. Closures have been designed to make access faster, easier and safer. Integrated features of closures set the operators’ safety as a top priority, by providing a warning device, such as a pressure alert valve (PAV), to alert the operator if there is internal pressure before they operate the closure. Once opened, closures are closed with minimal tooling and do not require extended procedures like the bolt tightening processes that are used on flanged connections. Closures, therefore, provide safety to the operator, and significant time savings overall.
Historically, quick opening closures have been offered in different form factors, with some of the most popular being the threaded closure, the clamp ring closure, and the internal door closure. The threaded closure has a cap that threads onto a hub, compressing an O-ring by turning the cap tightly. This closure type offers ease of access at an economical price point. The clamp ring closure has a door and hub held together by a clamp that closes onto both components from the outside. Access is quick and easy where frequent opening is needed. The internal door closure has a door that swings into the hub component, and then has a ring that expands inside the hub, securing the door in place. This closure style works well on large size pipes, higher pressures, and allows for additional customisations relatively easily. To answer the industry demands for these closure styles, Stark Solutions supports the market’s needs by manufacturing the S-500 threaded closure, the S-2000 clamp ring closure, and the S-3000 internal door closure.
S-500 threaded closure The S-500 threaded closure product offering draws on a long history in the oil and gas industry of providing an economical product for a wide range of uses. The simplicity of a cap screwing onto a mating hub allows the product to be easily used by operators who are either new to using this design or are already familiar with it. The hinging is bi-directional, allowing for ease of operation as well as flexibility on the project site. There are added features (including a raised square boss) to allow for more methods of opening without requiring a hammer or product impact. The proven O-ring sealing method allows for a wide variety of material options to meet the most demanding product and process requirements. The threaded product can be provided for the most common requirements as well as custom applications in sizes 2 in. to 52 in. (DN50 to DN1300).
S-2000 clamp ring The S-2000 clamp ring product line is made primarily for horizontal pipeline applications, conforming to the ASME B31.8 and B31.4 codes as well as the US DOT requirements, in addition to the CSA Z662 Cat 1 rules. Designed to be easily operated in the field, the latch mechanism and door hinging allow for simple, frequent operation common to pipeline applications. Hinging and opening latch assemblies have grease fittings for ease of maintenance lubrication to ensure trouble-free operation. These closures use an O-ring seal, safely located on the hub away from the through-bore, to help prevent damage or buildup during repeated pigging operations. Having an O-ring allows them to work with a wide variety of media profiles by simply specifying the appropriate O-ring material. This product is offered in sizes 4 in. to 48 in. (DN100 to DN1200). As the scale of the pipeline increases, so do the options for operation, to meet a wide variety of needs; from simple manual operation, to heavily mechanically advantaged operation, to designs that allow for ease of opening with only handheld power tools.
S-3000 internal door closure The S-3000 internal door closure product can be used equally well on pipeline or pressure vessel applications. Designed with a lockring component that prevents the door from being removed from inside the closure hub, any unlikely failure keeps the door firmly closed. This closure type can be manufactured in 6 in. (DN150), with no upper limit, to fit a number of applications. The internal door product is designed to come in O-ring or lip seal styles, depending on the design criteria and orientation. It has conveniently located handles and mechanical aids to ensure opening and closing are easy, no matter the size. The lockring components are visible during inspection to ensure there is no question about the state of the unit. Horizontal hinging can be specified either left- or right-handed. In addition, a variety of vertical hinging options are available, such as a wire rope winch, a chain hoist, a hydraulic cylinder, and more. This provides options for operators with different resources available at the job site. This closure also allows flexibility in the number of
Figure 1. From left to right: Stark Solutions’ S-500 Threaded Closure, S-2000 Clamp Ring Closure, S-3000 Internal Door Closure.
additional ports or taps available, as well as different hub weld bevel configurations.
Pipeline integrity ensures the safety and reliability of the pipelines. That extends to all aspects of the pipelines, including closures. To maintain the safety of the operators working with them, all of Stark Solutions’ closure products 6 in. (DN150) and above are provided with PAVs, and they can be provided on smaller units as well. These PAVs provide positive warning prior to opening the closure should there be any residual pressure left, as required by ASME BPVC Sec. VIII, Div.1 UG-35.2. With these PAVs, the operator can be sure the internal pressure of the unit has been properly vented before opening the closure. Additionally, only once the PAV has been properly operated can the closure be opened, keeping the operator safe in the event the pipeline had not been completely depressurised.
Customisation options are available to fit the specific needs of each customer on any of Stark Solutions’ quick opening closures. Closures can be provided with extended hubs, with flanges already welded on, or with lengths of pipe already welded on. Additional ports can be added for various gauges or valves in the cap/door or in the hub. Hub geometries can be customised with double bevels for ease of installation welding, or internal tapers to allow for use of smaller closure sizes on non-standard geometry projects. Internal weld overlay of stainless steel or Inconel metal can be provided, as well as sourcing pressure part raw materials out of various grades of stainless steel or duplex stainless steel. These material options allow for more corrosion resistance to internal media, and longer product life. Similarly, hinging and actuation components can be specified in various materials to allow for ease of use in environments that would typically cause severe external corrosion. On-site engineering staff can assist with other options as well during the product quote.
At its facility north of Houston, Texas, Stark Solutions machines all the pressure parts and performs all the assembly work. The facility is ISO quality certified and ASME certified with “U” and “R” stamps for Section VIII, Div.1 production. The Stark team supports their customers with Sales, Manufacturing, Quality Control, Engineering, and Service staff located together, working collectively, to ensure the best quality product reaches the customer with every order. Pipeline integrity is dependent on the reliability of the components the pipeline is constructed with. Not only should components be made from high quality materials with quality workmanship, but they should provide the operator with the safest and most efficient experience when using those components. For closures, that experience should include having the correct closure style for the location and application, as well as that closure having safe, easy, and quick operation..
AGRULINE XXL PIPES HDPE PIPING SYSTEM FOR HIGH VOLUME FLOW
OUTSTANDING LIFE SPAN Corrosion-free PE reduces lifecycle costs of large diameter pipes significantly FAST AND EASY INSTALLATION High flexibility, low weight and safe joining methods FOR HIGH-VOLUME FLOWS Compatible fittings and pipes available up to OD 3500 mm HIGH-QUALITY MATERIALS Selection of raw materials according to the PE 100+ Association guidelines EXPERTISE IN PLASTICS PROCESSING Decades of experience in plastics processing, research & development Heated tool butt welding machines from OD 20 mm up to OD 3500 mm
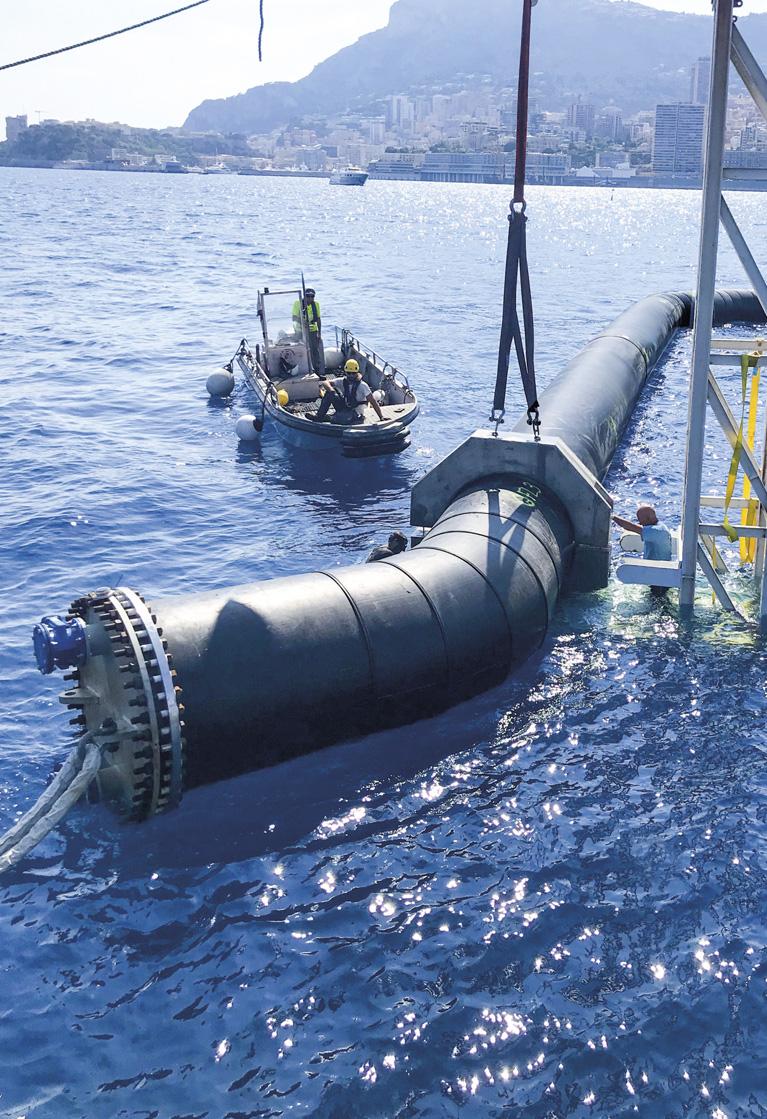
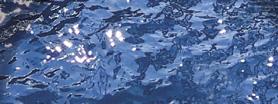
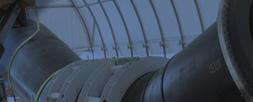

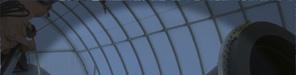
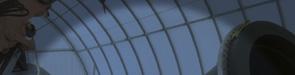

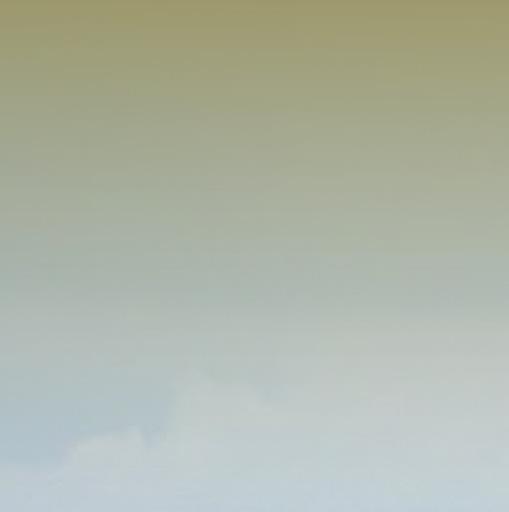
Nadine Robinson, Technical Adviser – Environmental Sustainability, International Marine Contractors Association (IMCA) presents a new voluntary IMCA Code that promotes environmental stewardship.
Working with its members IMCA has reached a significant landmark with its recently published ‘Recommended Code of Practice on Environmental Sustainability’ (IMCA ES 001), making it the first membership organisation in the industries IMCA serves to produce such a document. Reaction amongst members, and their clients, has already proved very positive, with one oil major representative declaring the IMCA Code has applications for other industries.
As a leading international trade association with some 700 member companies, IMCA represents the vast majority of marine contractors and the associated supply chain in the worldwide offshore marine construction industry. The association has a strong reputation for setting leading industry standards of technical and operating guidance; and is fully engaged in the energy transition to a sustainable, low carbon future, collaborating to advance environmental sustainability.
Through its ‘Code of Conduct for Members’, launched in 2018, all IMCA members commit to, and sign up to, adhering to applicable laws and complying with accepted standards of ethical and responsible business conduct, including those related to environmental protection.
In the new Code, we put pen to paper for the first time on what environmental sustainability means for our industry,
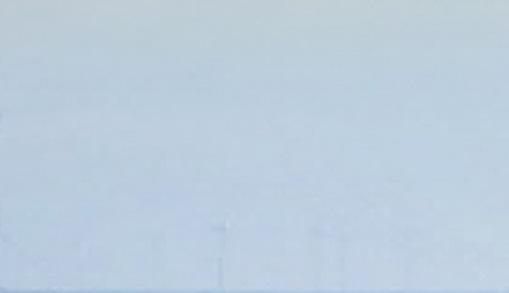
