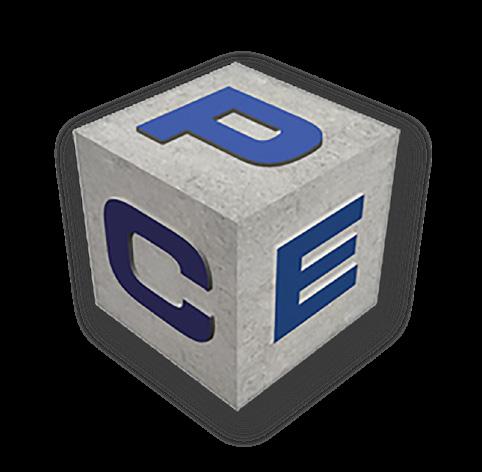
Assembly Building C
HybriDfMA Frame System


Structural Components
Supply Chain Mapping
Offsite Manufacture
Quality Control
Site Logistics
Frame Design Architectural
Façade Panels
Start of the Build
Completion of the Build Site
Digital

Structural Components
Supply Chain Mapping
Offsite Manufacture
Quality Control
Site Logistics
Frame Design Architectural
Façade Panels
Start of the Build
Completion of the Build Site
Digital
PCE Ltd was pleased to have been awarded a contract by Galliford Try to design, manufacture, and construct a HybriDfMA office building frame using offsite manufactured structural steel and precast concrete components together with insitu reinforced concrete. Building C of the central Bristol Assembly development is a 14-storey tower adjacent to the River Avon for property developer Bell Hammer working with insurer, AXA. The project architect was AHMM, with consulting engineers ARUP.
The HybriDfMA framed building provides 92,000 sq.ft. of office space utilising PCE’s experience of Modern Methods of Construction (MMC). Building C is the second and tallest of three units built from a phased construction programme. The Assembly development will also include a new public area, with connections through the site and a new floating pontoon. This development created a new destination for Bristol and a new type of people-friendly workspace. The plan draws from the character and context of the site, integrating it into the city.
Assembly Building C exemplifies excellence in construction as a prestigious HybriDfMA framed office building. Its innovative Hybrid design approach has allowed PCE to think creatively, embracing new ideas to develop a versatile ‘kit of parts’. This not only enhances the visual appeal of structures like Building C, but also seamlessly merges precast concrete and steel with an emphasis on standardisation, repeatability, and predictability. This integration enables the construction process to be faster, safer, and more efficient, evident in the meticulous attention to detail throughout the entire design journey.
The project embraces the early stages of Modern Methods of Construction (MMC) to ensure extensive incorporation of offsite precast concrete manufacturing. This streamlines the production and delivery process, whilst ensuring the highest levels of quality and control. Notably, the building features exposed architectural precast concrete sandwich panels. These form an integral part of the main core towards the north, alongside other precast concrete elements such as twin and solid walls. These reinforced precast concrete components are deliberately left unpainted, showcasing their raw beauty, a feat that required meticulous design considerations to ensure the building blends harmoniously with the iconic Bristol skyline.
To achieve this ambitious vision, a total of 44 architectural sandwich panels, over 400 reinforced precast concrete twin and solid walls, and more than 1000 hollowcore units were expertly manufactured at various locations throughout the UK. Collaborative partnerships with suppliers played a crucial role in attaining the desired high specifications, minimising the need for extensive on-site finishing works as well as reducing material consumption and waste.
MAIN CONTACTOR
ARCHITECT
M&E ENGINEERS
CONSULTING ENGINEERS
Wayne Scannell, Senior Project Manager for Galliford Try commented:
“I highly recommend PCE Ltd for their exceptional pre-construction support, delivered by knowledgeable staff members who greatly enhance the effectiveness of the wider project design team. Their project management team were collaborative, wellcoordinated and personable, fostering a positive working environment. The operatives demonstrated remarkable dedication, with a clear focus on health and safety. I would definitely welcome the opportunity to work together with PCE again in the future.”
26% Reduction In Embodied Carbon 0
Plasterboard Used
13 Days Per Level Installed
32 Weeks Constructing
75% Structure Exposed
92,000 sq.ft Office Space
12 Site Operatives
2,460 Off-site Manufactured Components
330 Product Deliveries
17 Tonne Architectural Panels
14 Storey Tower
0 External Scaffolding
Systemised DfMA delivery of ‘unique’ hybrid structural solutions. PCE’s HybriDfMA approach enables fast and safe onsite assembly of unique structural frame and imaginative façade solutions using offsite design and component manufacturing processes, providing great value high quality buildings. This systems ‘kit of parts’ can be easily configured to suit unique designs ensuring ease of assembly.
• Existing designs easily and efficiently configurable utilising PCE’s Frame system approach
• Optimised component geometry improving carbon efficiency
• Optimised structural grid through the use of long span solutions
• Seamless integration of façade and M&E systems
• Enhanced safety through removal of back propping, improved access, and improved working from height
• Streamlined critical path and construction efficiency through early access for follow on trades
• Industry leading quality and predictable tolerances due to systemised approach
• Fire resistant along with excellent thermal and acoustic performance
• Reduced carbon through smart design
• Offsite expertise for highest quality and control
• Kit of parts with flexible material interchangeability
• Up 50% reduction in construction programme
• Up to 90% reduction in waste
• Up to 80% reduction in site deliveries
• Up to 80% reduction in on-site personnel
• Improved productivity
• Digital twin and data driven insight
Precast architectural facade panels
17 tonne precast architectural façade panels with Rekli pattern finish. Cast with a large diameter window fixed at the manufacturing factory to compliment the installed units and give clear views internally of the exposed precast concrete stairs and core.
PCE’s HybriDfMA Systems combine MMC and DfMA principles with modular construction and optimised to offer high quality, repeatability, and enhanced predictability. Assembly alternations by the clients request. In all, some 44 architectural and sandwich panels, 249 steel Deltabeams with 9,000m² of reinforced structural topping came together
200 tonnes of structural steel columns for the length and breadth of the structure at each level providing stability of the building.
Precast solid walls were cast flat on variable steel tilt tables, ensuring a high-quality finish. Tilt tables were used to minimize unnecessary handling reinforcement that would otherwise have been required to turn the unit vertically into its delivery orientation.
Twin-wall cores provide lift shafts as well as
construction and material flexibility. Systems are based on standardized ‘kit of parts’, refined Assembly Building C was built from the Hybrid Frame system ‘kit of parts’ with bespoke 200 tonnes of steel columns, 440 twin and solid walls, over 1,000 hollowcore floor units, to showcase a first class PCE HybriDfMA framed office building for the centre of Bristol.
Twin-wall lift cores provide stair and as frame stability.
Deltabeam
Deltabeams were used compositely with reinforced structural concrete to support the floor structure without any down stands.
Precast hollowcore floor unit
300mm deep prestressed concrete hollowcore units, designed to work compositely with the 200mm deep reinforced structural topping.
screed
140m³ of insitu concrete was poured into a rebar cage on each floor before assembling the next. This totaled 9,000m² of reinforced structural topping for the entire building.
chain partners supplied the project with architectural and sandwich panels, 200 columns, 440 twin and solid walls, over floor units, 249 steel Deltabeams and reinforced structural topping.
Techrete Solid Slabs
Creagh Hollowcore
Oranmore
Solid Slabs, HRS, Steel Cages
Solid Wall, Twin-wall
The PCE HybriDfMA design mindset allows their designers to think out of the box to incorporate new ideas provided by a ‘kit of parts’ approach, and through the manufacturing phase we see that ethos being put into practice. Building C is an integration of traditional double height steel columns, precision composite steel/ concrete Deltabeams and prestressed concrete flooring components all of which has been manufactured using Building Information Management (BIM) processes to very tight tolerances. Exposed architectural panels with their Rekli pattern acid etched finish showcase a spectacular front to the building along Narrow Plain, Bristol.
Collaborative partnerships with suppliers played a crucial role in attaining the desired high specifications, minimizing the need for extensive on-site finishing works as well as reducing material consumption and waste. Structural elements were manufactured offsite in controlled factory environments, delivered ‘just in time’, and assembled directly from the delivery vehicle. Ancillary components such as reinforcement, fixtures, fittings, edge protection, and riser protection were delivered with their respective units or sequenced as part of the construction cycle to minimize handling and optimize efficiency. Offsite installation of windows into architectural panels eliminated the need for scaffolding and reduced on-site trade activities. Furthermore, feature balustrades for stairs were fitted to stair flights offsite, eliminating the requirement for on-site installation.
PCE always strive to provide the appropriate component materials to ensure structural integrity, appearance, and client value to build state-of-the-art buildings and are proud of their dedication and commitment to working closely within their Offsite manufacturing factories. Engagement and good communication between PCE and their manufacturing factories ensures there is a complete understanding of the specification. PCE’s Precast Quality Co-ordinators are present in the factories to offer first-hand contact advice, assistance, and ensure that PCE quality assurance requirements are being met. They help to organise the units that are offered up as samples, where the whole project team, including representatives of AHMM, Galliford’s, PCE and factory management all agree and sign off on the finished aesthetics, shape, and tolerances of the first units cast. This sets the benchmark for all following units to be manufactured by. With Modern Methods of Construction
at the forefront of planning for Assembly C, the project team at PCE considered every avenue where they had planned tasks that were traditionally completed on site and looked to amalgamate these into an Offsite manufacturing solution. One of the main benefits of taking this approach was the large reduction in the need to carry out onerous tasks usually done on-site. An example of this is the steel reinforcement cages that were fitted to the structural steel Peikko Deltabeams as well as leading edge handrail posts offsite rather than after the beam had been erected into position. The major advantages of this is less work at height on a leading edge, better quality of the steel fixing in the factory, and speed as well as the importance the safety of the PCE multi-disciplinary workforce.
Developing and controlling a highly detailed pre-planned ‘just in time’ delivery process, to the heart of one of the largest urban regeneration areas in the UK is second nature to the PCE construction team.
All city centre developments have their unique challenges with logistics - and the Assembly Building C site is no exception, with an extremely tight overall footprint and access only available off the cobbled street of Cheese Lane with zero space for storage of delivered components.
A fully developed design solution, coordinated with all disciplines and an integrated onsite delivery approach, was crucial. Engagement with offsite factories and suppliers was paramount; site space was limited, allowing only one delivery at a time. Therefore, PCE scheduled each unit delivery with precision months in advance. This required communicating the build sequence to factories with detailed loading plans showing each unit on every load
Initial engineering design work for the 14-storey tower commenced with the team utilising their experience in HybriDfMA Frames to provide structural expertise and know-how, enabling PCE’s structural technicians to initiate and deliver first class digital Building Information Models. Throughout the design engineering phase for the building, calculations for the principally steel framed structure with its complexity of steel columns and composite concrete/steel beams integrated with other precast concrete elements were diligently carried out to generate robustness, stability, and temporary works analysis models. These models, by giving attention to detail in the design process, fully considered the structures ability to withstand the design dead, imposed and wind loads to ensure valued engineering buildability and to reduce the amount of temporary works, bracing, etc, and resultant foundation loads.
Composite concrete/steel Deltabeams span between the circa 200 tonnes of structural steelwork columns for the length and breadth of the structure at each level with the North precast concrete core structure providing the overall stability of the building. The suspended floor plates are formed from prestressed Hollowcore flooring incorporating an insitu concrete topping.
The structural design of Assembly C was heavily influenced by sustainability considerations. The architectural vision aimed to reduce the number of building elements, with many left exposed without additional finishing. This required streamlining the structures’ ‘kit of parts’ while ensuring the concrete’s colour complemented the architectural vision. The result is an aesthetically pleasing and environmentally friendly outcome.
Maximizing available space was also a priority in the design process. A key criterion was minimizing solid ceiling coverage, allowing for exposed structural soffits. These considerations also fed into the servicing design, with free hanging rafts positioned to obscure VRF units whilst allowing other high-level services to be exposed.
Exposed architectural precast concrete formed part of the main core to the combined with other precast concrete solid and twin wall components. placed by PCE’s Engineers and Technicians to detail in the design of the architectural the visually exposed finishes to ensure building, complementary to the Bristol was a key demand of the city planners Bristol Development.
For a successful HybriDfMA project, in the detail: PCE’s attention to the and management of such features ensure that. Following the manufacture components, they only need to be vehicles and fixed into their final structure.
The HybriDfMA design mentality think out of the box to incorporate by a ‘kit of parts’ approach. This appealing structures, like Assembly ability to merge precast concrete, structural steel in a design that provides built faster, safer, and more efficiently, value.
concrete sandwich panels the North of the building concrete elements including Great importance was Technicians on attention architectural panels and all ensure a stunning, visual Bristol skyline, which planners for this prestigious project, the eye is always the refinement features enables them to manufacture of the hybrid be lifted from the delivery place within the mentality allows designers to incorporate new ideas provided allows for more visually Assembly Building C, by the concrete, insitu concrete and provides a building to be efficiently, giving added client
As with all PCE projects, the construction phase of PCE’s HybriDfMA delivery is significantly aided by proper planning and preparation. The offsite solution ensured that the majority of construction activity way completed offsite. This improves quality, logistics, and onsite efficiencies which in turn, facilitates a faster build. In readiness for the onsite phase, many precast components were pre-fitted with necessary features, such as secure hand railing. This enabled the site team to hit the ground running as soon as components arrived to site.
The first units to arrive on site were the 17 tonne architectural panels that adorn the front of the 14-storey building.
These units were just part of the whole HybriDfMA structural ‘kit of parts’ approach, marrying up with precast concrete panel elements forming the cores and stairwells, as well as structural steel columns, Deltabeam composite structural beams with prestressed hollowcore floor units and insitu structural topping.
As 11 out of the 13 levels were virtually identical, it was clear that this project would provide significant efficiency opportunities due to the repetition of offsite manufactured components. This enabled the PCE site team to develop a construction plan and programme which provided each day’s onsite assembly sequences for every level. These were drilled down to one-hour slots over the thirteenday per level cycle and were identical in task requirements and timings from one level to the next. Not only did the finalised schedule give clear direction to the onsite workforce regarding the operations scheduled for completion on any given day, it gave the offsite manufacturing facilities plenty of notice with their production planning and delivery scheduling, to ensure the right product arrived at site on the correct day and at the right time.
The Assembly Building C project demanded meticulous attention to detail, particularly the delivery and installation of its structural components, which had to meet exceptionally high-quality standards. This included a range of elements such as precast twin and solid wall components, steel columns, and exposed soffits, as a significant portion of the structure would remain visible without cosmetic finishes. Notably, the precast concrete hollowcore floor units exhibited a symmetrical herringbone effect, with joints aligning seamlessly through the core and walls.
Each floor level, comprising 84 precast concrete hollowcore floor units, 18 steel columns, composite construction Deltabeams, 35 twin and solid walls, two sets of stairs and landings, 3 façade architectural wall units, and 140 m³ of insitu concrete, was structurally completed within a tight timeframe of less than 13 working days. This feat was achieved with a team only 12 operatives.
Furthermore, the project introduced an innovative modular riser wall system designed specifically to enclose theoretical risers. This forward-thinking solution, constructed progressively, integrates seamlessly with the frame construction using a modular panel system, providing a fire-rated enclosure.
To streamline operations, careful planning of crane lifts was essential. This included choreographing the placement of loose reinforcement and other supplies to ensure consistency across all floor levels, facilitating easy access for the onsite team. Strict tolerances were upheld through the use of metal jigs, manufactured and employed to swiftly and accurately position bars for structural connections, thereby averting potential clash issues as assembly progressed.
In contrast to traditional practices involving separate specialist contractors, PCE’s multiskilled workforce delivered a comprehensive turnkey mixed structural material frame project, providing clients with added value and a seamless construction experience.
in exceptionally
structure
columns, 18 landings, completed team of
Safe access of personnel to each floor level as the assembly of the building progressed, was of paramount importance. During the planning stage, PCE liaised with PERI regarding the deployment of its proprietary systems, enabling access to each level through the four lift cores with the system projecting past the working level as the building progressed upwards. This enabled the erection crew operatives the opportunity to remove lifting gear from the top of the next level of walls at chest height, instead of working from additional platforms.
Due to the shape of the stair cores, PCE and Peri designed a special platform that split into three parts. It could be lifted out in less than ten minutes, with its repositioning for the next level in the same time frame.
An example of PCE’s safety-focussed approach was to factory install reinforcement cages to the edge delta beams and to pre-install leading edge protection. This approach alone removed in the region of 1400 man-hours on-site steel fixing and significantly reduced the risk of working at the edge of the structure. It saved precious crane time and helped ensure PCE could consistently deliver a 2.5 week floor cycle.
Mindful of sustainability, PCE manufactured structural components with an emphasis on simplifying tasks, reducing waste, and enhancing safety. For instance, a key strategy involved leaving the structure exposed, eliminating extra finishes and linings, thereby reducing onsite activities and carbon emissions through decreased material usage.
The floor construction features a composite system with hollowcore planks and a sustainable structural topping that significantly reduces concrete usage, incorporating up to 40% cement replacements for maximum sustainability. Furthermore, the structure was erected without back propping and falsework, making onsite activities smoother and cutting down material usage. These efforts vividly demonstrate PCE’s unwavering commitment to sustainability, rendering project delivery both efficient and environmentally responsible.
For instance, a key strategy involved leaving the structure exposed, eliminating extra finishes and linings, thereby reducing onsite activities and carbon emissions through decreased material usage. Taking the right steps through design enabled zero use of plasterboard across the project, helping work towards its BREEAM rating of excellent.
PCE achieved significant sustainability improvements in project delivery by implementing smart strategies in design and offsite manufacturing, surpassing traditional onsite methods. By embracing a systematic, offsite Design for Manufacture and Assembly (DfMA) approach, PCE ensured smooth operations with fewer onsite workers, minimised disruption, and achieved a remarkable waste reduction of up to 90%. Additionally, careful just-in-time delivery scheduling further slashed site deliveries by up to 50% and reduced onsite storage needs.
PCE’s digital delivery system optimized construction processes for the Assembly C project. elements underwent detailed 3D modelling, ensuring precise coordination and real-time This facilitated seamless progress monitoring across design, fabrication, and assembly facilitated lifecycle tracking and real-time issue resolution.
Fabrication drawings and manufacturing programs were synchronized with assembly automated progress tracking linked to the BIM model. Onsite, digital inspections and assurance checks were conducted, with all documentation digitally linked for auditable Assembly C, PCE’s digital delivery has evolved and expanded. Use of cutting-edge digital has taken project and component tracking to new heights.
project. Design real-time project tracking. assembly stages. Metadata assembly sequences, with and real-time quality auditable tracking. Since digital twin technology
PCE were delighted to have won Best Use of Concrete Technology at the Offsite Awards 2023 for Assembly Building C. The structure showcased exposed concrete in its raw, unadorned form, a feat that required meticulous design considerations to ensure the building blends harmoniously with the iconic Bristol skyline.
Manufactured offsite, the precast concrete’s smooth finish underlines the highest material standards and precise delivery techniques. This exemplifies the level of detail achievable through offsite solutions, allowing the project to meet the high specifications and architectural vision. The exposed concrete also eliminated the need for additional finishes and linings, significantly reducing on-site activities and carbon emissions through reduced materials.
It was not just the striking visuals of the exposed concrete that distinguished Assembly C. The whole process, from meticulous design and just-in-time logistical planning, to the high-performance properties of the highly-crafted concrete, ensured the project stood out.
PCE are delighted to have received such recognition for this innovative structure. The success of the project couldn’t have been achieved without the contribution and collaboration of the consultant team, including Structural Engineers Arup, Architectural Designers AHMM, Main Contractor Galliford Try. A special thanks also to the suppliers who manufactured the products that met and surpassed PCE’s high quality standards including Peikko, Creagh, Explore, SWP Precast, and Acast.
The entire project and the journey was a testament to the detailed planning and endeavours of the entire PCE team throughout all the processes required, and benefitted from the increasing use of digital information controls that the company is continuously developing.
Complications were inevitable and from them valuable lessons were learnt and new approaches developed, enabling PCE to continue its desire in pushing well beyond the normalities of Modern Methods of Construction, honing project delivery, logistics and onsite efficiencies.
Being an EOT business means PCE are equally owned by its employee partners. As business owners, our people take ownership for PCE’s continued success and enjoy the rewards that come with it; the more successful our business, the more reward we collectively enjoy.
We recognise that for PCE to be successful, we need our people to be at their best, which is why we have established a culture built around development and succession planning, investing into our workforce and providing challenging, inspiring and rewarding careers for our people to realise their potential.
Our people are given the tools and support to develop their careers, increase their knowledge, skills and experiences to help drive our EOT forward, and ultimately, enjoy the rewards we share for our collective success. It’s this culture that has been installed, that enables us to deliver great projects.