HybriDfMA Secure-Prisons System
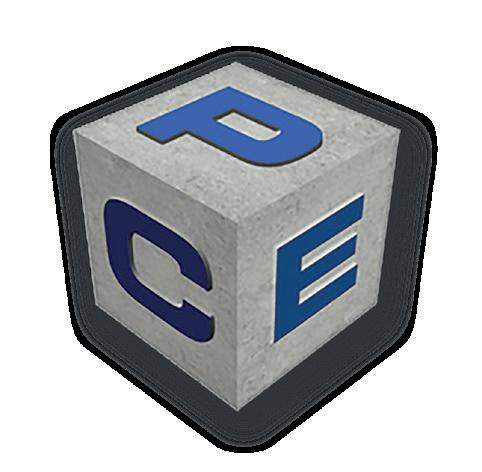
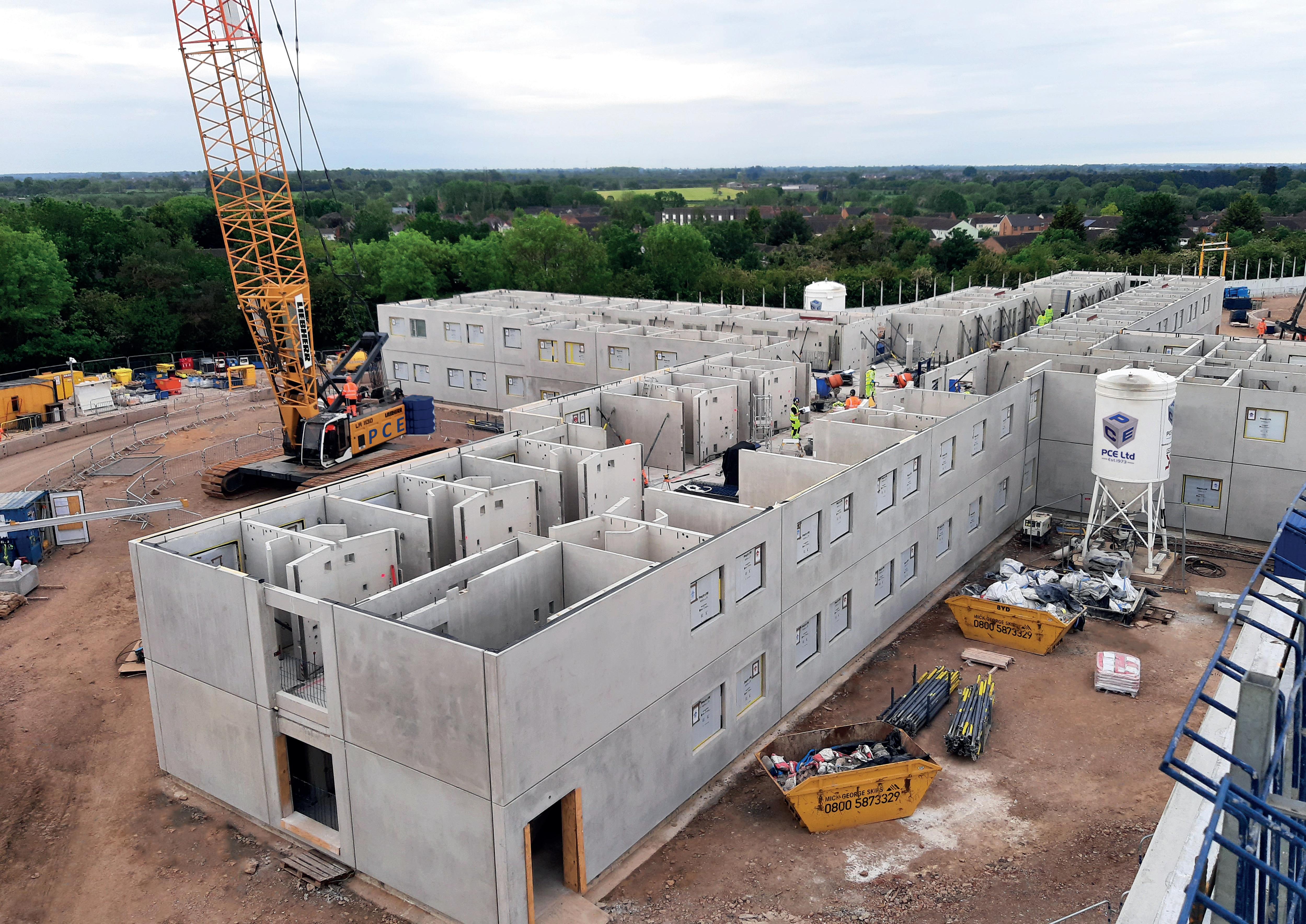

INTRODUCTION
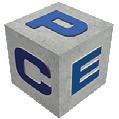
Following successful delivery of the award-winning HMP Featherstone, and more recently, HMP Five Wells, PCE has positioned itself as a market leader for the design and delivery of high quality, high security, modernised prisons.


As such, it was the ideal specialist design and build contractor to partner Main Contractor, Lendlease, in the delivery of HMP Fosse Way, situated in Leicestershire, on behalf of the Ministry of Justice (MOJ). Fosse Way is a near 2,000 capacity Category C Resettlement prison, focusing on rehabilitation and prisoner reintegration. Like HMP Five Wells, Fosse Way forms part of the Government’s New Prison Programme (NPP).

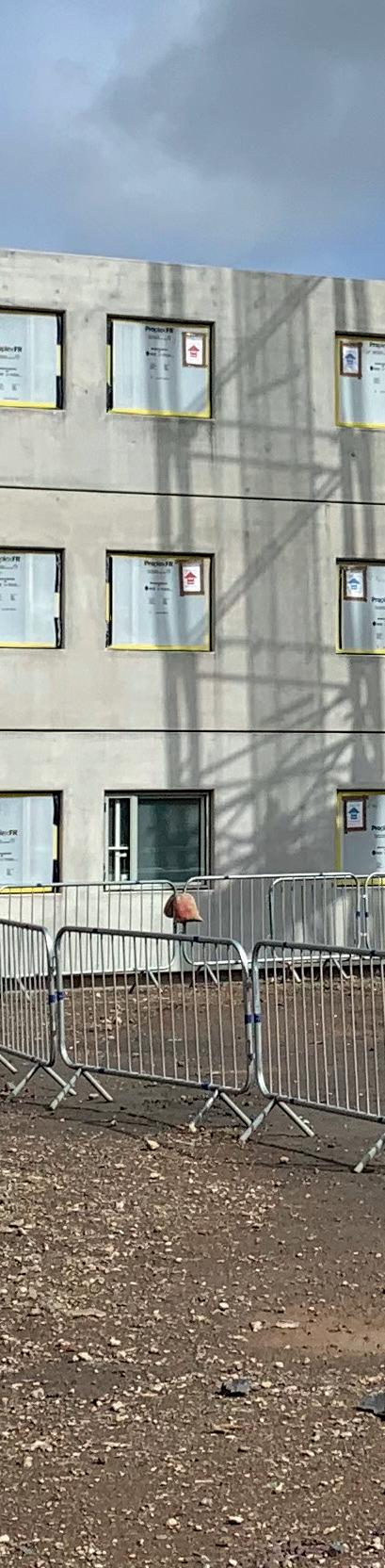

PROJECT OVERVIEW
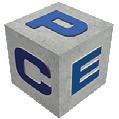
Fosse Way is a true hybrid superstructure. Its construction involved 23 different architectural, steel, and reinforced precast component types used to design and build the 7 four-storey hybrid houseblocks, 1 PCC Care and Separation Unit (CaSU) and an entrance building, comprising of three separate spaces. The project covered nearly 48,000 m2 of floor space and over 30,000 m2 of varied façade.
The implementation of PCE’s HybriDfMA Secure Prison and HybriDfMA Frame systems, part of its suite of HybriDfMA systems, delivered significant benefits in terms of speed and scale. With industry-leading safety, quality, efficiency, and value, the project was completed in a total of 38 weeks, 6 weeks faster than the target date.
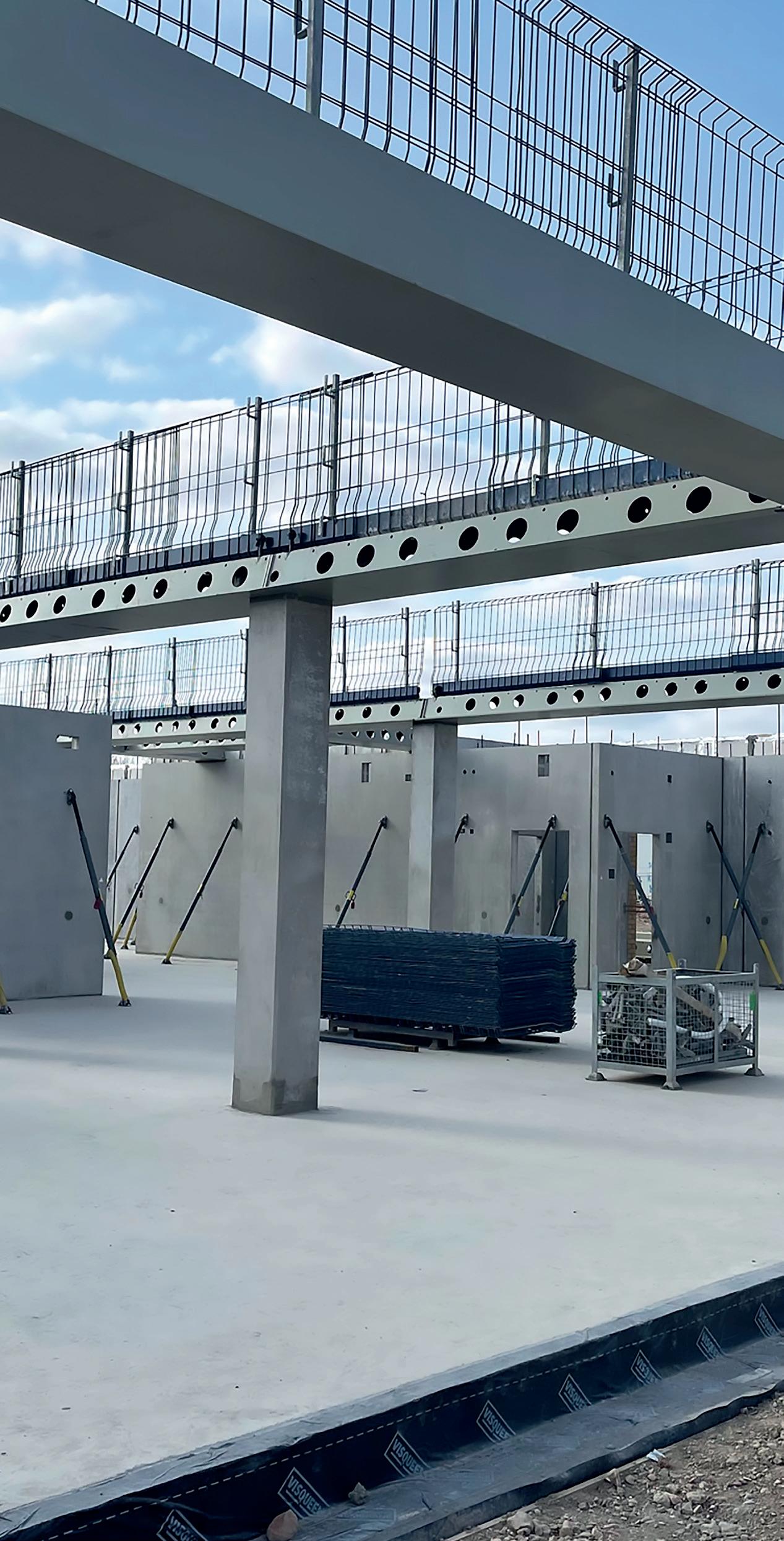
Utilising a lessons learned philosophy and culture of continuous improvement, PCE were able to build on the successes of Featherstone and Five Wells, delivering elevated excellence and expected construction across the HMP Fosse Way project. By integrating the latest Modern Methods of Construction and offsite manufacture, PCE leveraged its digital capabilities, data-driven insights, and the innovative HybriDfMA Secure Prison system to expertly coordinate the design, manufacturing, logistics, and assembly of the superstructure. This ensured an expedited project programme, whilst simultaneously reducing waste, site deliveries, streamlined onsite workforces, and reduced carbon through smart design.
Key Metrics:
• Completed in 38 weeks – 6 weeks ahead of schedule
• Project spanned over 48,000m2 of floor space with nearly 30,000m2 of varied façade
• Circa 14,000 offsite manufactured components, totalling 54,000 tonnes
• 74,000 M&E, security, and utility integrations
• Daily lifting of circa 285 tonnes
• Average of 74 hybrid units installed daily
• 45 cells installed per week, or 9 per day
• Average workforce of 70 onsite operatives
• Reduced waste, deliveries, and required onsite personnel
PROJECT VALUE
CLIENT
MAIN CONTRACTOR
ARCHITECT
STAGES B-E STRUCTURE & CIVILS
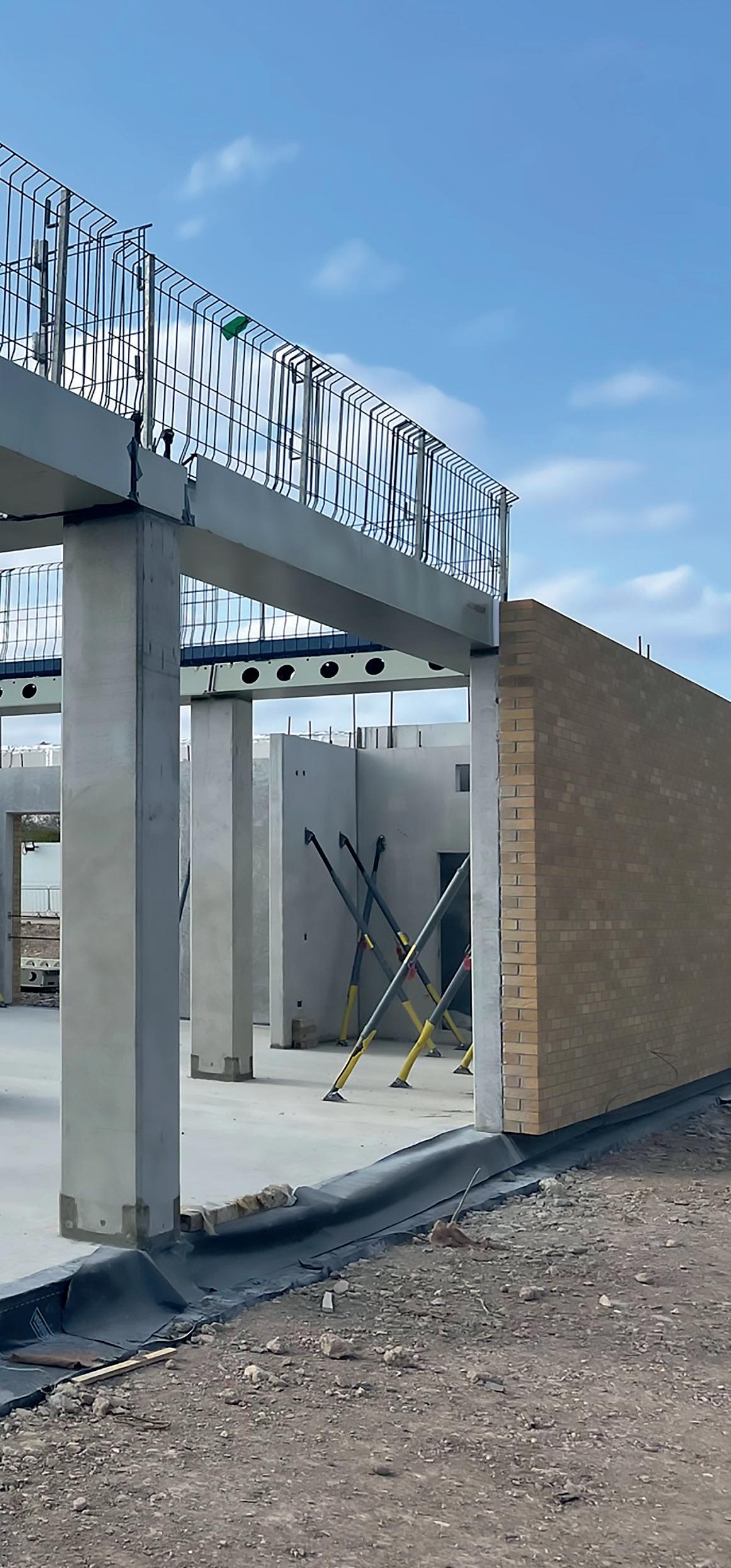
M&E CONTRACTOR
£37m Ministry of Justice Lendlease Pick Everard Pick Everard
CHT
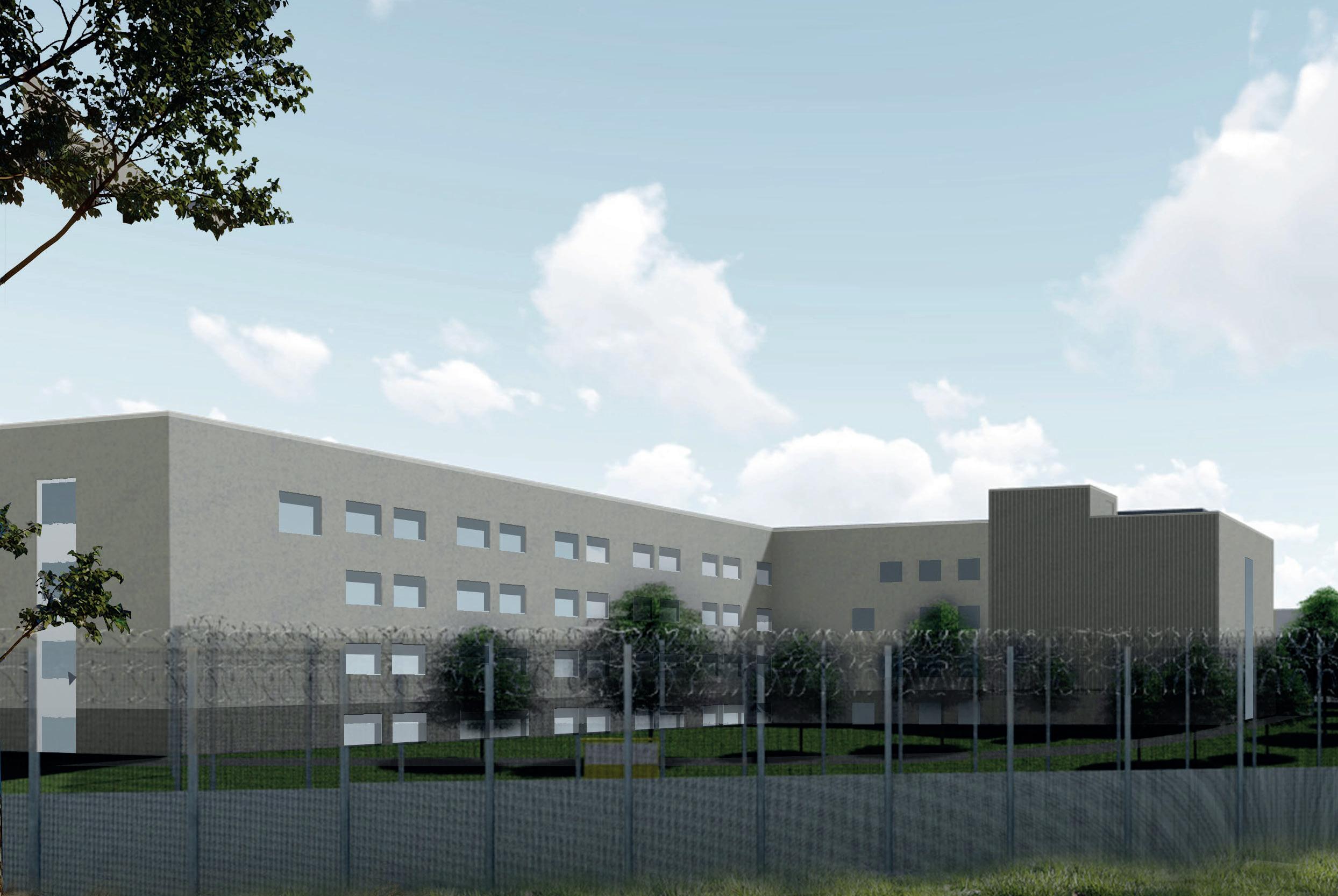
STRUCTURAL COMPONENTS
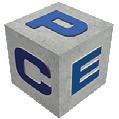
Duct Wall Unit Cell Roof/ Floor Unit Corridor Wall Unit
The cactus shaped Duct walls were cast vertically using PCE’s steel moulds so that all the visible faces were formed against the mould faces, providing a high-quality finish. Moulds were set with steel formers to enable the connection for sinks, toilets and vents, and radii and skirting recesses to ensure accuracy of key detailing.
Cell roof/floor components spanning two cells and associated ducts were cast flat on steel tables in their final orientation, ensuring a high-quality finish to the cell ceiling and a floated finish to the upper face, which formed the plant room floor. Magnetized steel formers were fixed onto the moulds to create the main roof light opening.
The intricate corridor walls were cast from steel vertical moulds so that all the visible faces were formed against the mould faces to provide the required high-quality finish. PCE’s bespoke profiled steel formers for the cell and riser door were set into the vertical mouldage at standard position, with specific key positions set within the moulds for containment of them, ensuring they could be positioned accurately and held firmly during concrete placement.
Structural Facade Panel
External walls were cast flat on variable steel tilt tables, ensuring a high-quality finish to the internal cell face and a floated finish provided for the cavity face. Tilt tables minimised unnecessary handling-reinforcement that would otherwise have been required to turn the unit vertically into its delivery orientation.
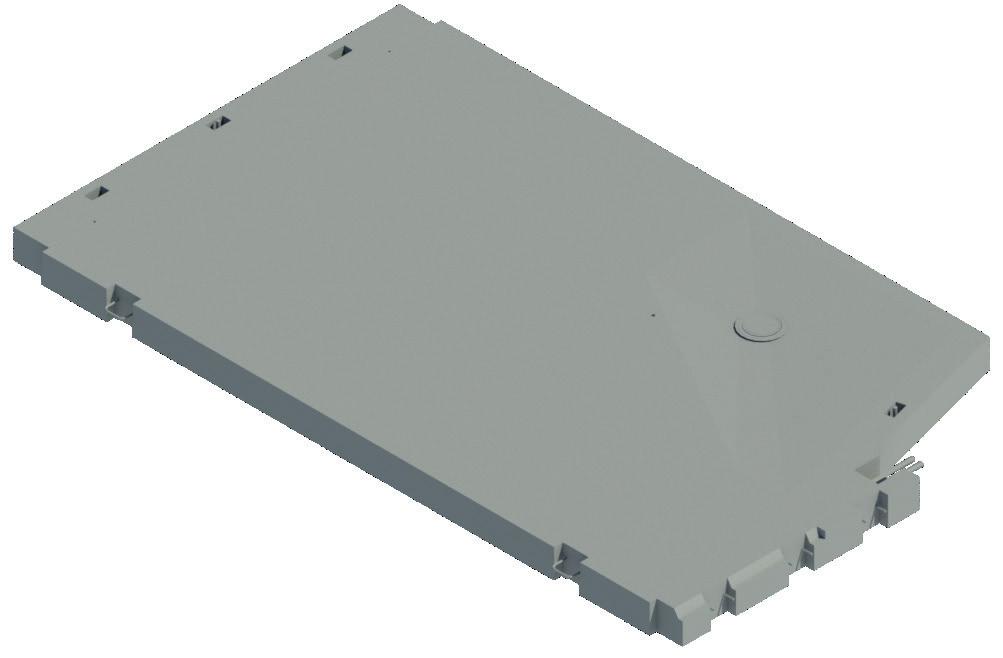
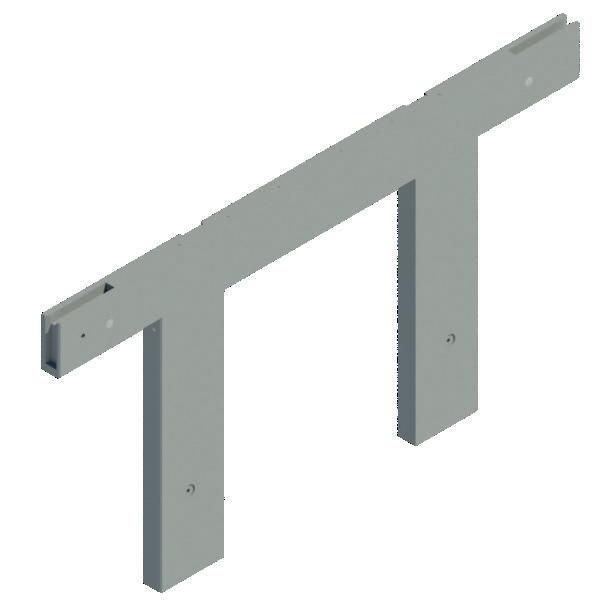
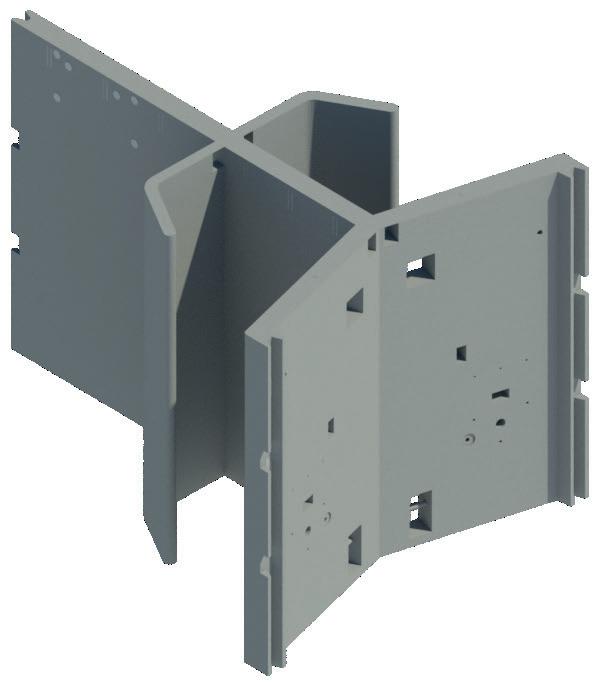
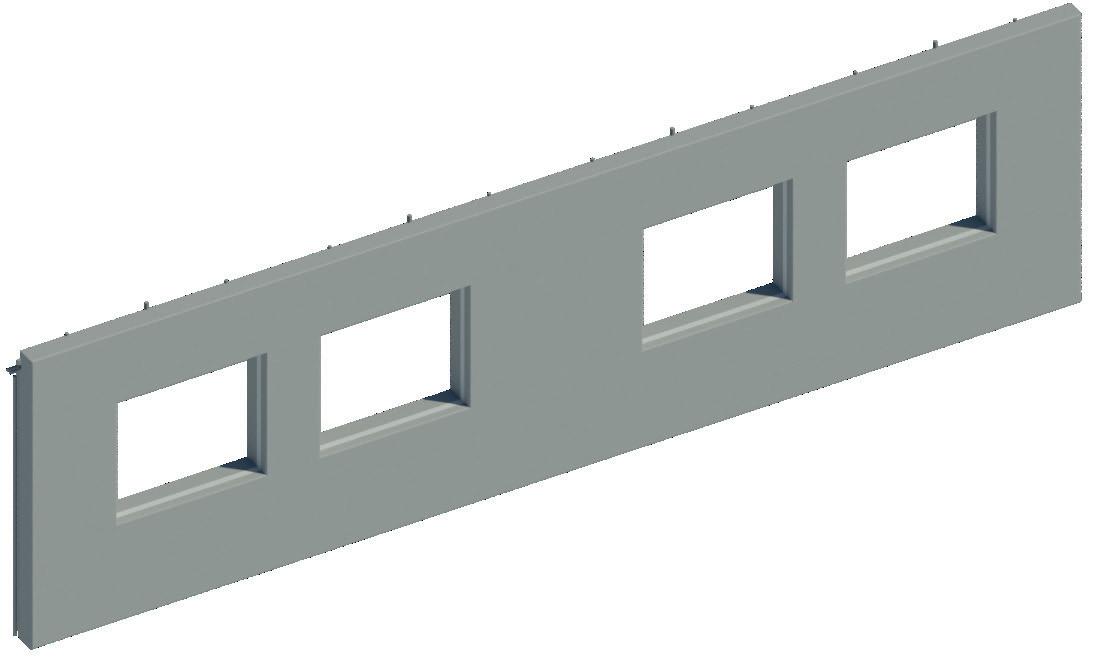
Circular Column Unit

Circular columns are utilised in the main association area, with a direct decoration finish. This required a mouldage strategy that delivered a crisp finish with no imperfections. The columns are erected utilising column shoes, allowing units to be sat in the temporary condition, without the need for propping sockets in the seen finish face.
PCE’s HybriDfMA SecurePrison Systems Kit-of-Parts
PCE have developed a portfolio of standardised structural system solutions across different sectors and structure types, built around an interchangeable ‘kit-of-parts’ philosophy. Components are predetermined, creating optimisation with refined and proven geometric features and limits. Whilst standardised for repeatability and predictability, precision engineering ensures a scope of flexibility, allowing PCE to accommodate client configurability to suit specific use requirements. Designed with smart connectivity, components interface and interact with precision, forming a complete structure, with ease, speed, and the highest quality.
The Secure-Prison System ‘kit-of-parts’ consists of just five common components; three types of wall units, two floor/roof units and a façade panel. The walls sit between and to the front and rear of the cells, forming with the cell roof to create a robust monolithic concrete structure, with a central access corridor between the lines of cells. Repetitive use of the key components, complete with integrated M&E and security features, enables fast, reliable, and assured construction of the Secure-Prison houseblocks.
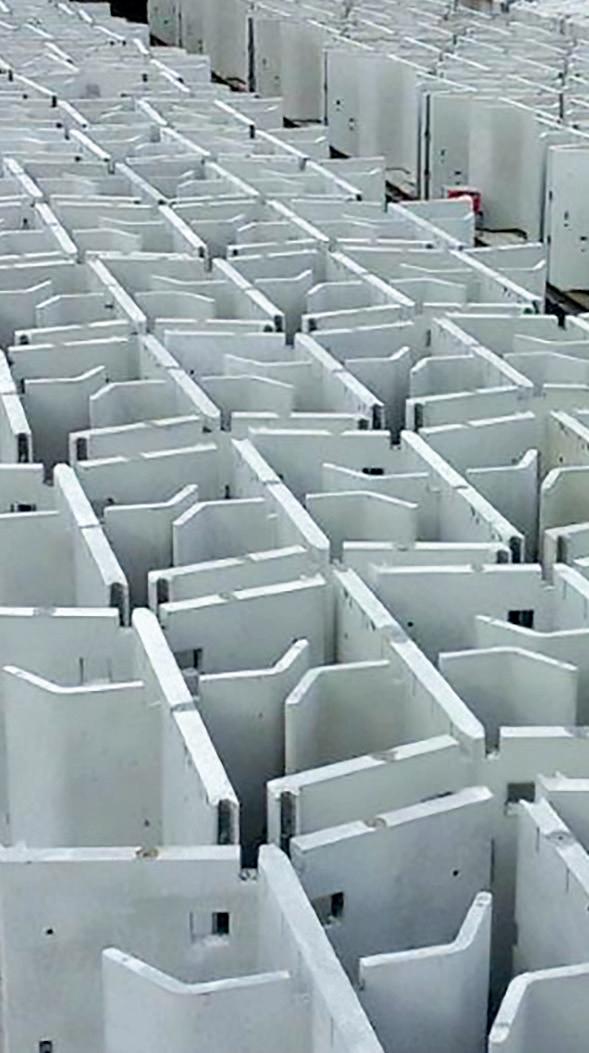
SITE LOCATION
Located on the pre-existing footprint of the now demolished HMP Glen Prava, the Fosse Way development is found off Tigers Road, running adjacent to an old military barracks. The name Fosse Way derives from the historic Roman road, running through Leicester as it connects key areas across the country. The immediate surrounding environment includes local businesses, housing, a school, and protected natural land, all of which factored into the logistical and operational considerations for deliverance of the build.
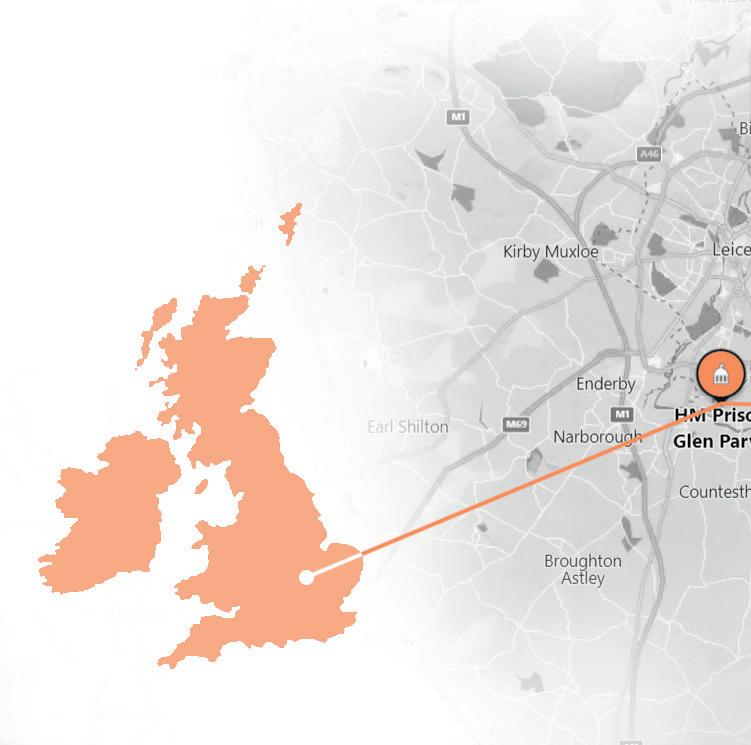
HMP Fosse Way, 10 Tigers Road, Wigston
LE18 4TN
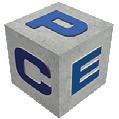
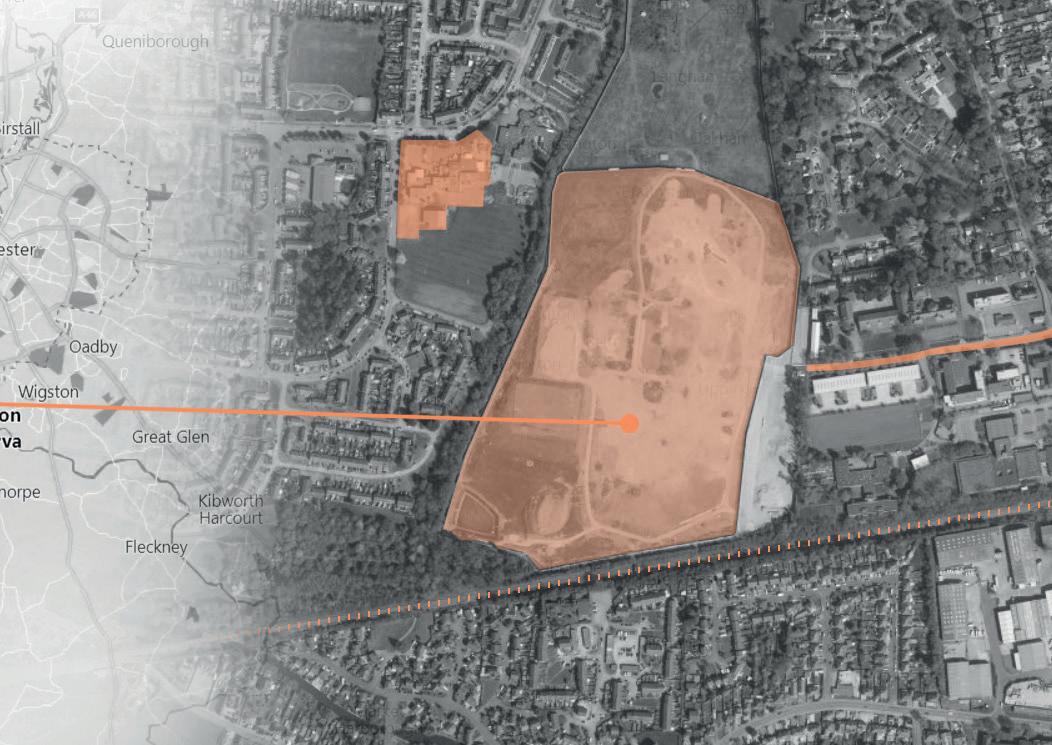
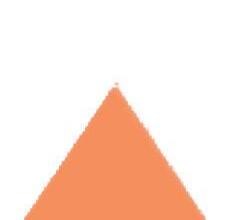


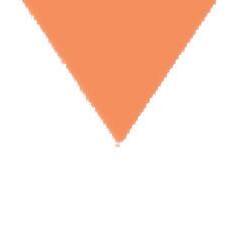
OFFSITE MANUFACTURE
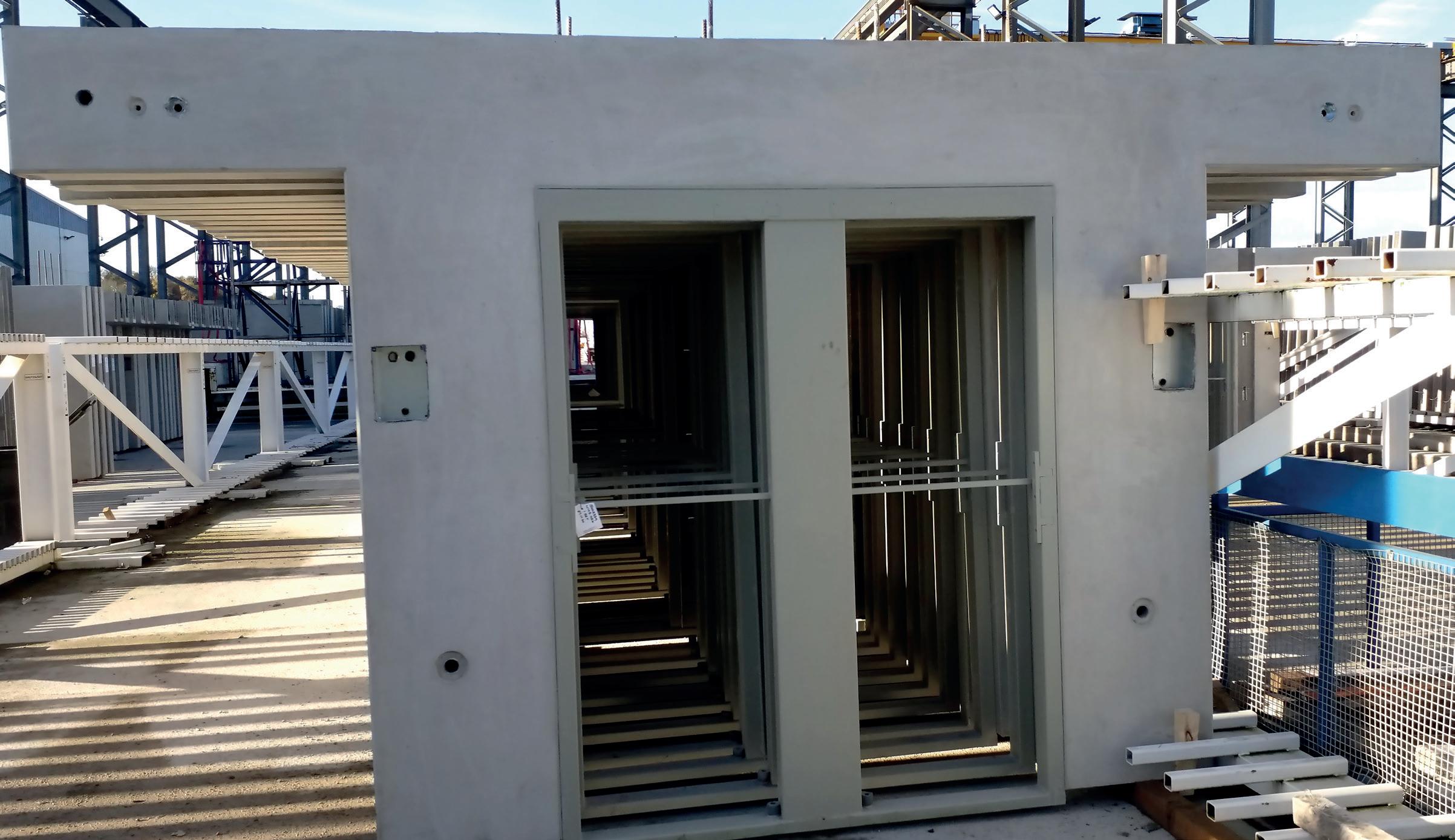
PCE’s offsite supply chain model facilitates increased flexibility, speed, and scale. It provides PCE with extensive access to a broad supply chain, combining expertise and capacity to deliver varied, high quality, highly predictable, and highly controlled production requirements, regardless of scale.
For Fosse Way, this resulted in PCE collaborating with 10 of its offsite supply chain partners across 10 months to deliver 13,961 offsite manufactured elements of precast concrete, structural steelwork, and composite structural steel/reinforced concrete beams, totalling around 54,000 tonnes. In addition, manufacturing saw production of nearly 30,000m2 of varied façade, including direct decoration, exposed concrete, and golden thatch bricks.
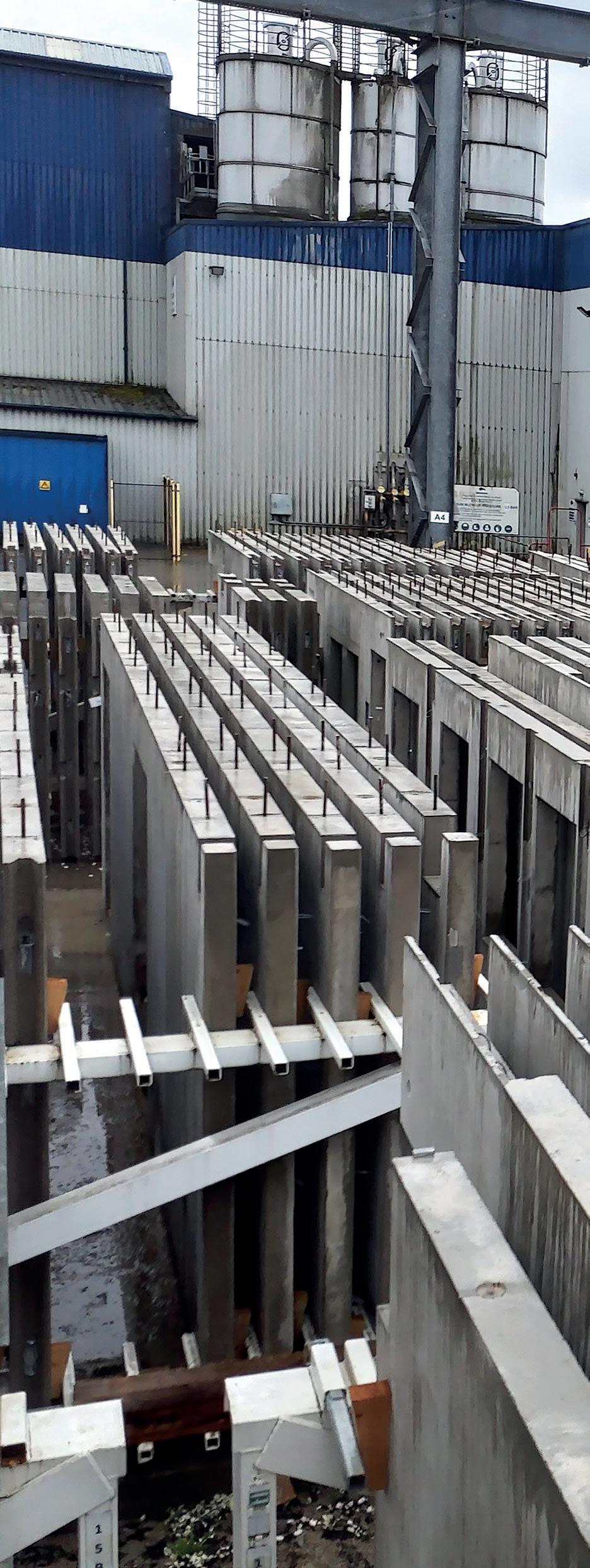
The comprehensive modular solution incorporated 74,000 M&E, security, and utility integrations, including underfloor heating mats, shower trays, shower heads and conduits. All were cast in and fully coordinated to align with the riser modules for wider service distribution.
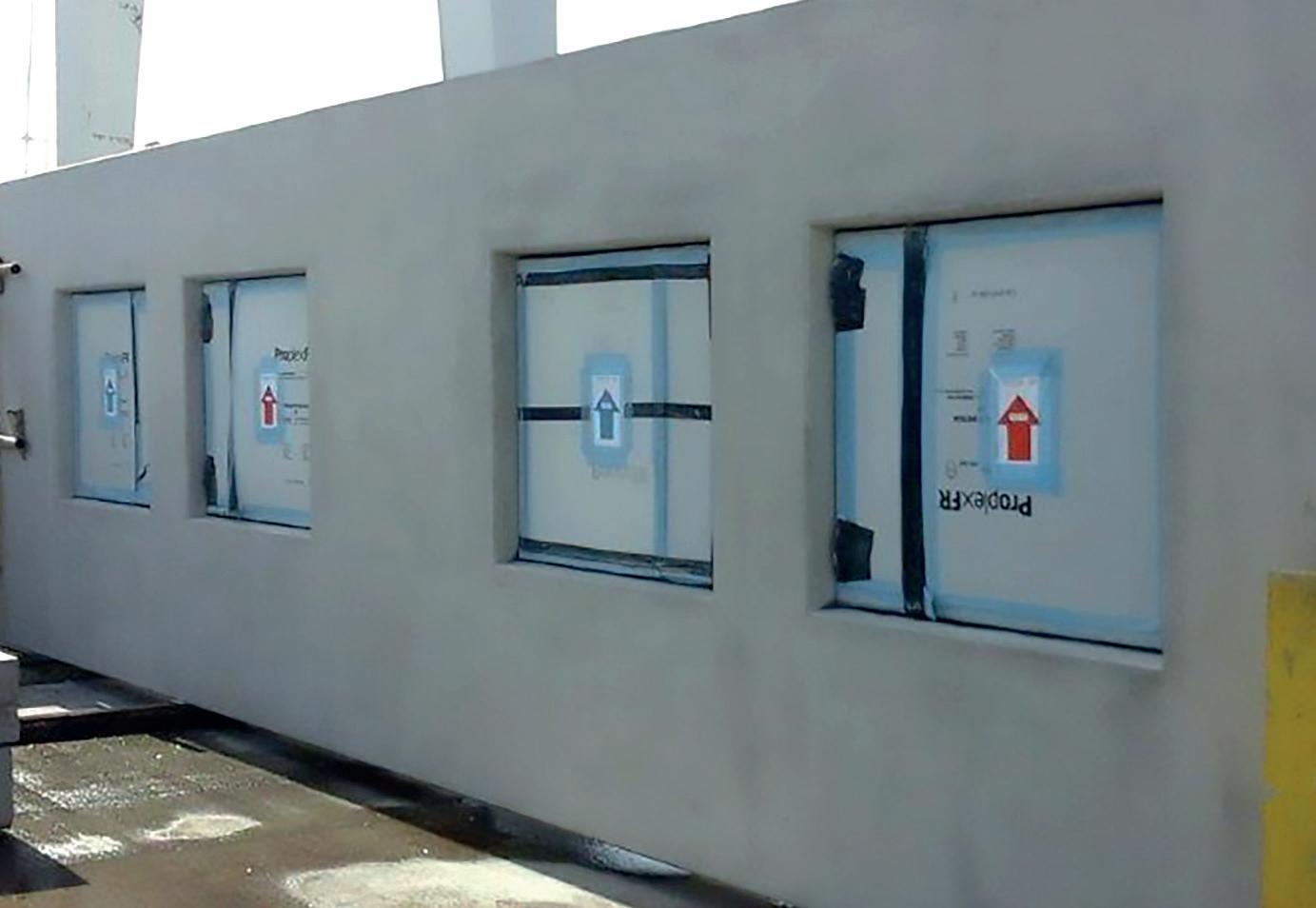
Manufacturing on such a scale required a robust, well considered manufacturing, coordination, and offsite storage strategy. Cutting edge digital capabilities helped diligently coordinate the logistics behind the operation. In addition, PCE’s Precast Coordinators were positioned across the supply chain, collaborating closely with suppliers to ensure PCE’s high level specifications are met and adhered to. The offsite emphasis also ensured reduced carbon footprint and risk across manufacturing, with significantly reduced waste, onsite operatives, and onsite operations.
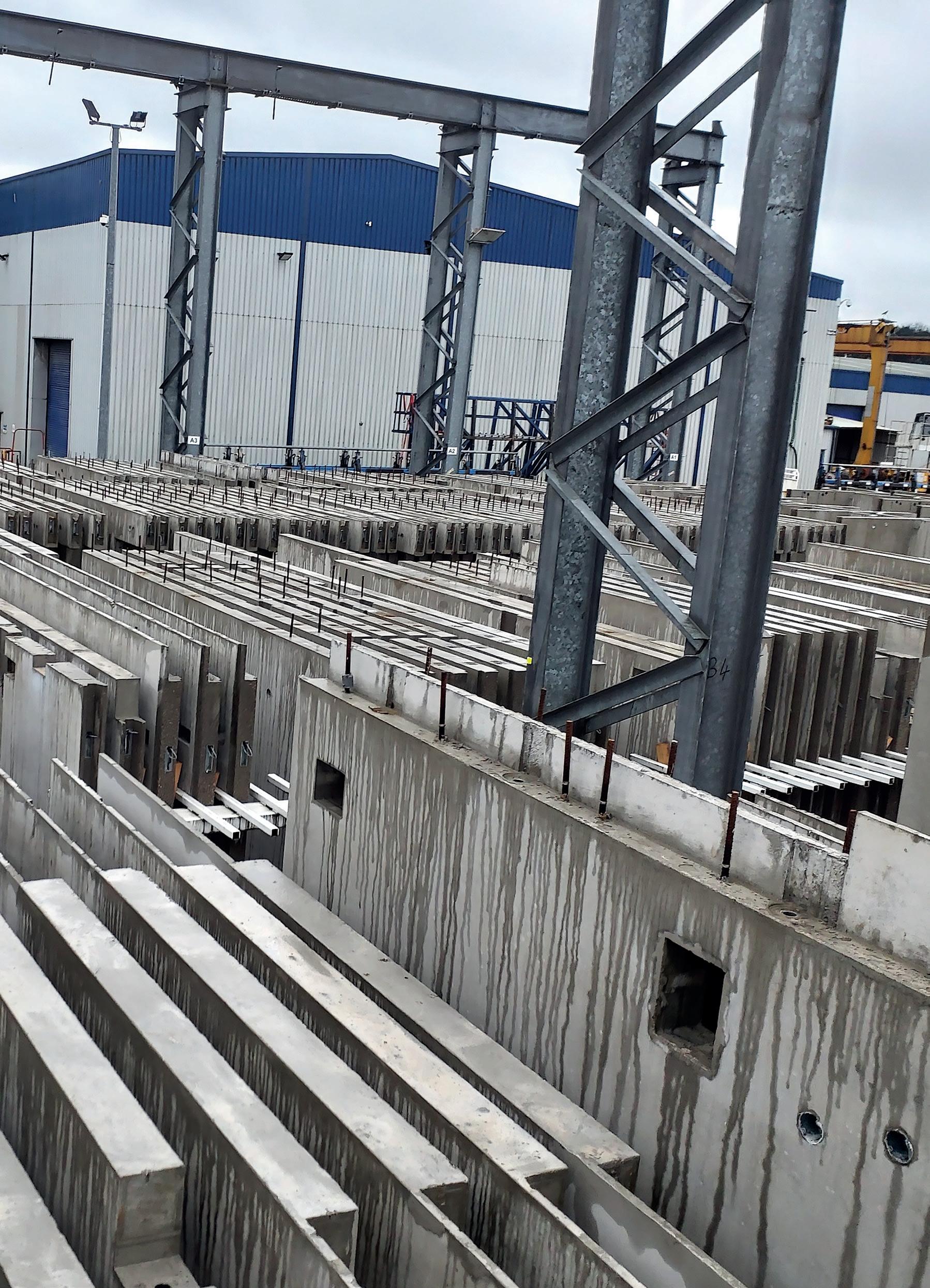
BRICK-FACED CLADDING
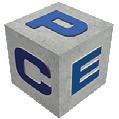
The HybriDfMA Frame system used for the main entrance building incorporates a bespoke façade panel unit using brick slips on the outer side of the panel to achieve the desired architectural intent. The Golden Thatch brick was chosen for its aesthetics and the ability to produce two slips from one brick, reducing costs, waste and carbon footprint. Bricks, mortar and mastic seals were sampled and signed off having met both the architects desired intent and planning requirements.
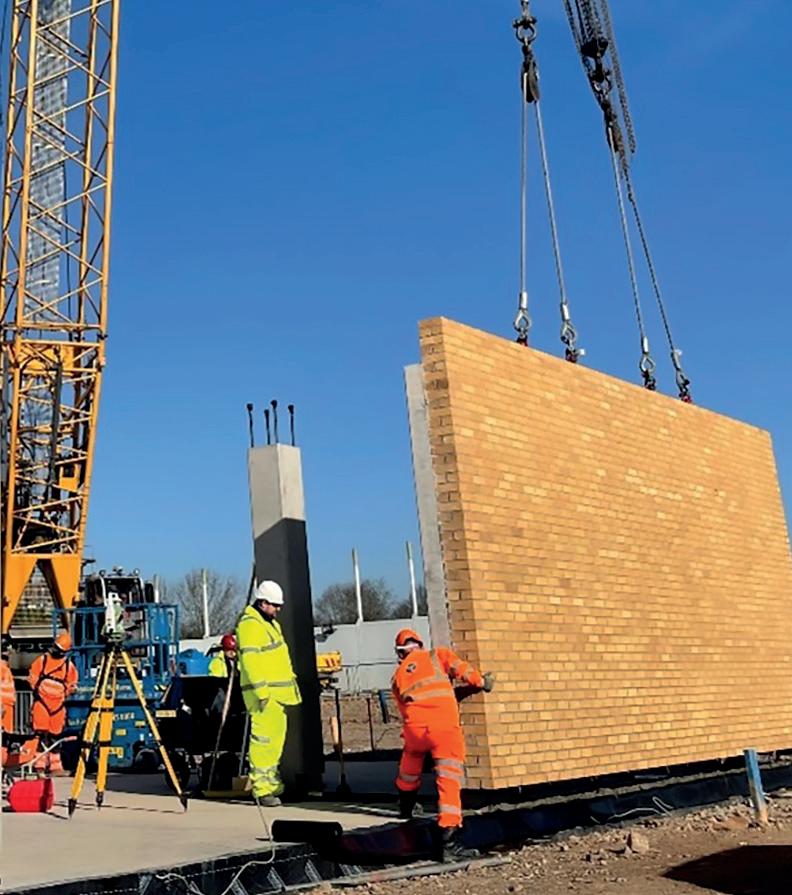
Working closely with the clients M&E contractor, PCE were able to facilitate concealment of the lightening protection from the roof level back down to the earthing rods behind the mastic seals, maintaining visual integrity.
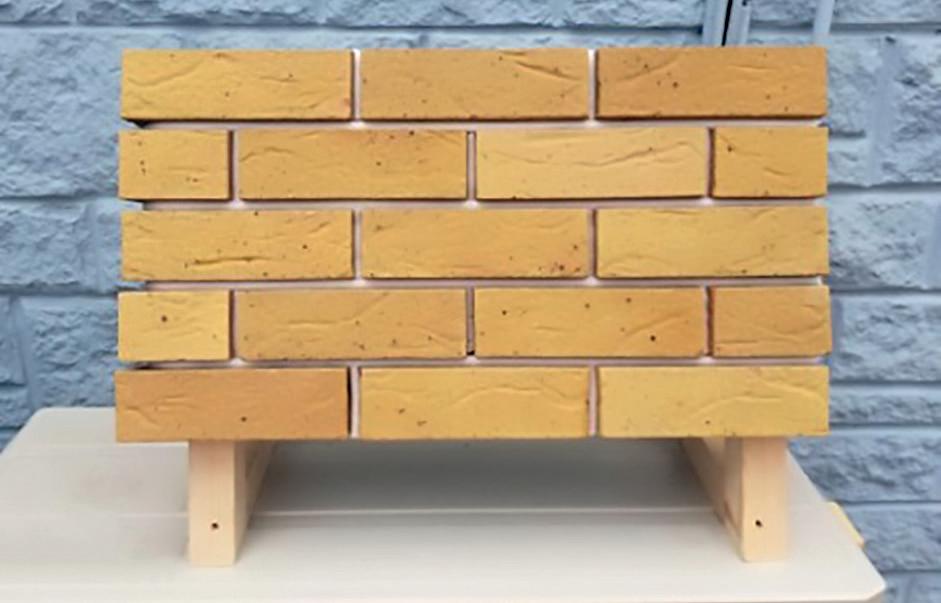
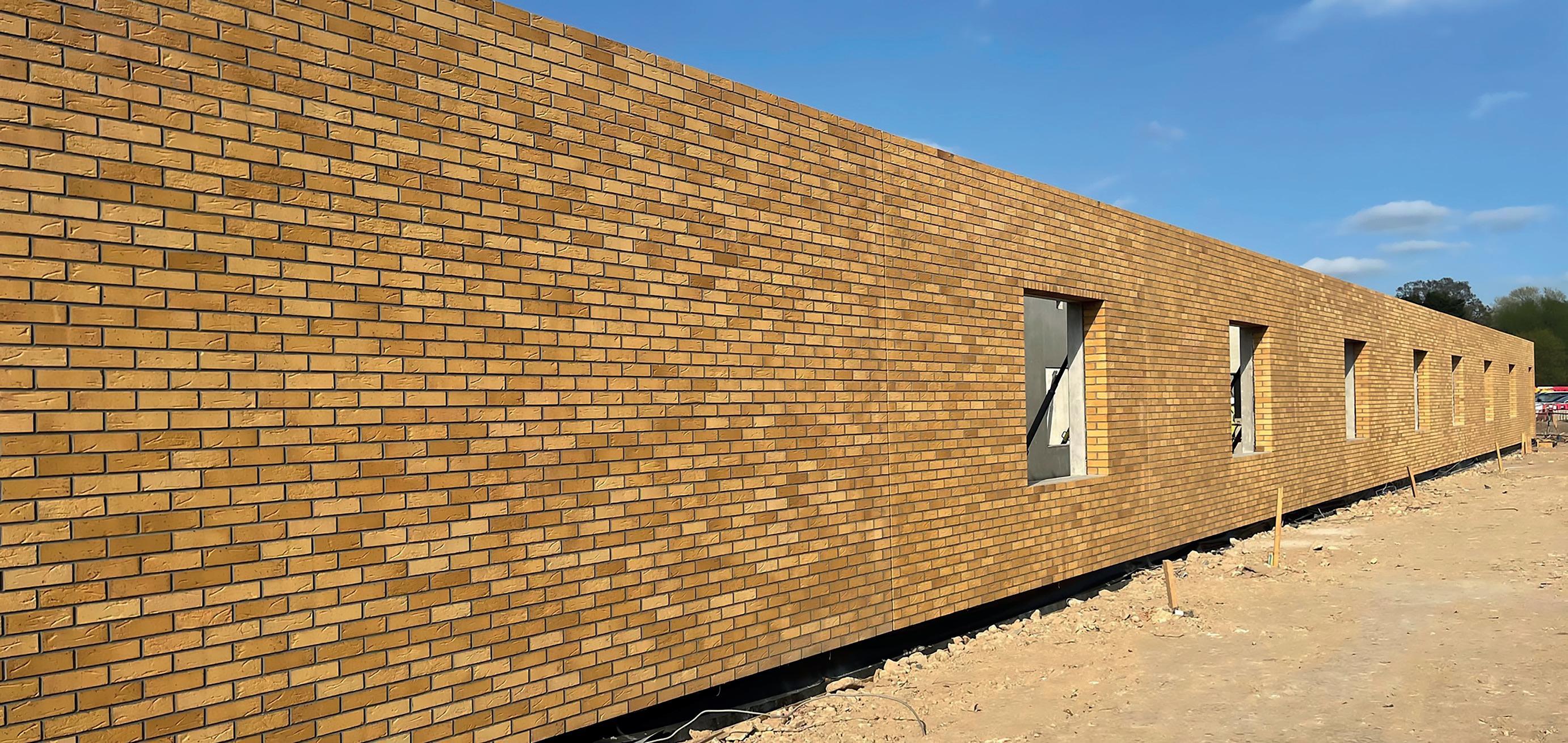
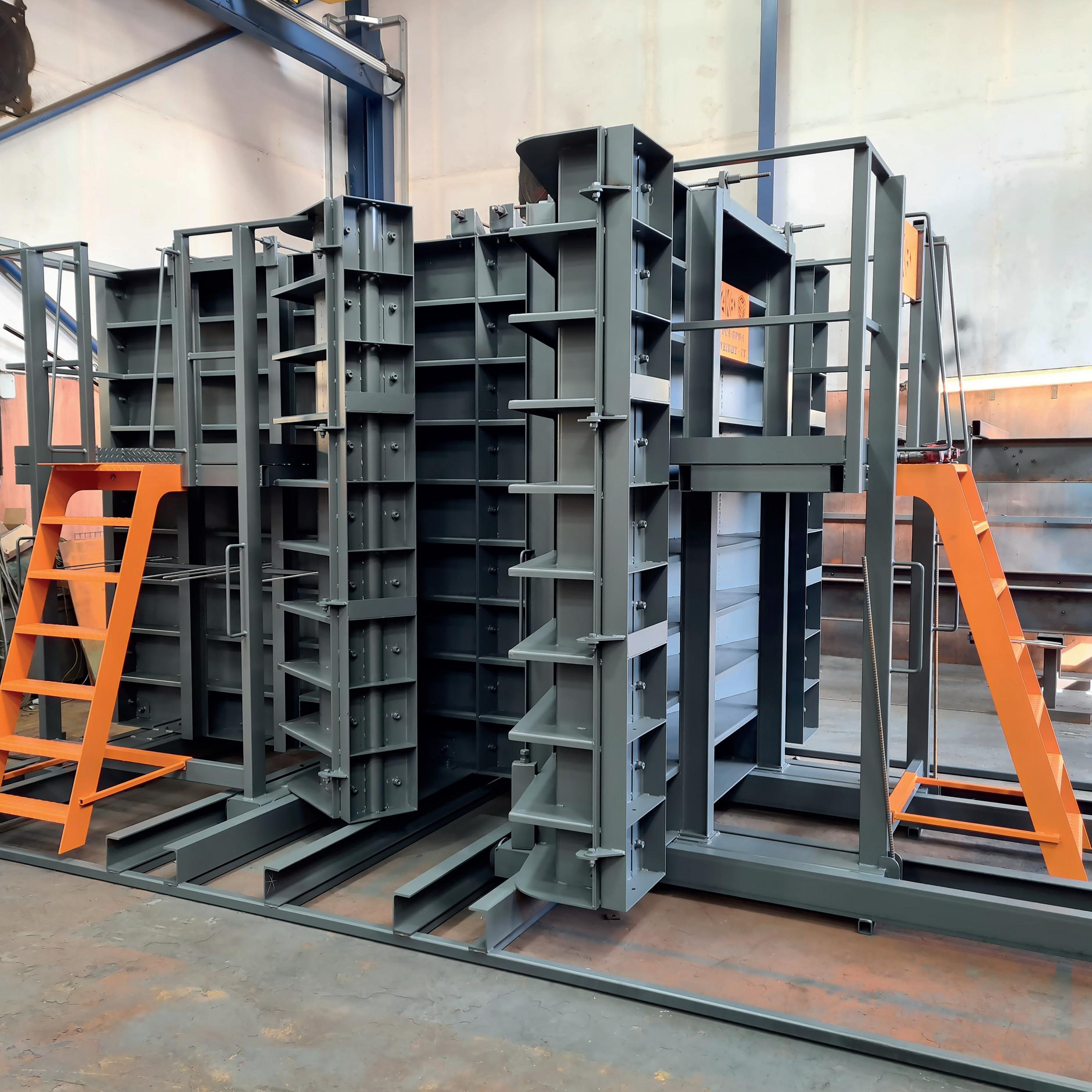
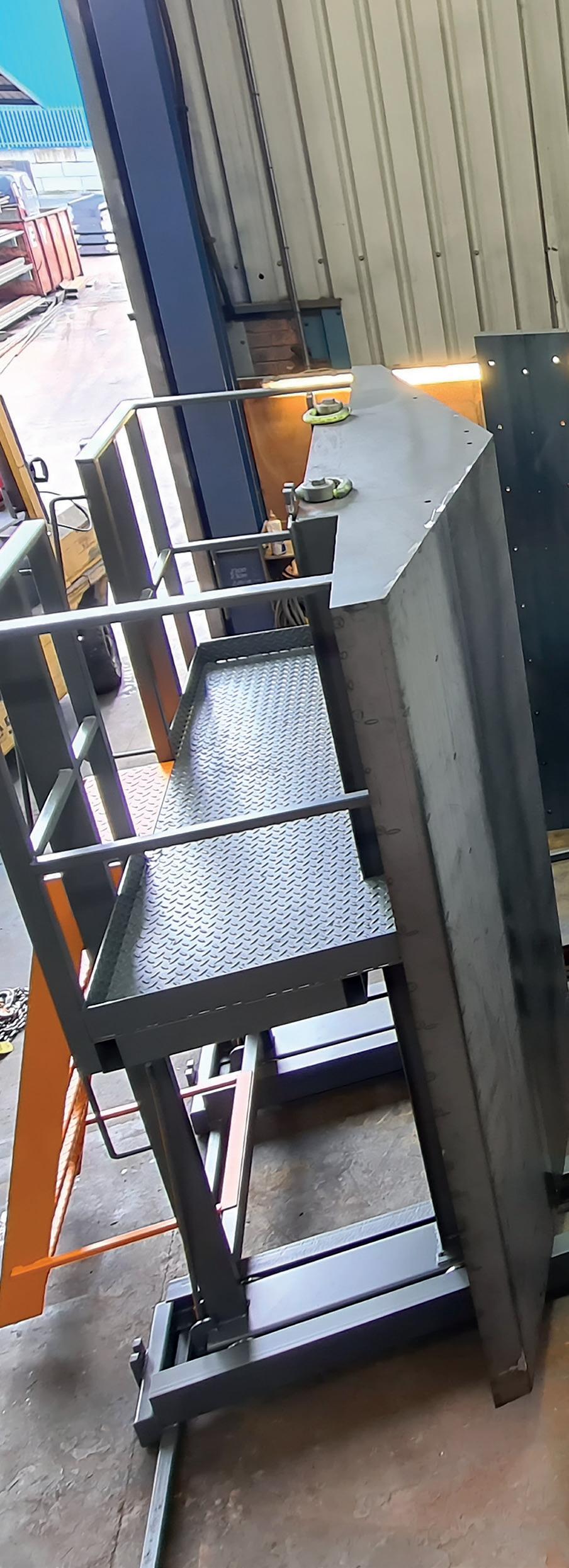
MOULD INVESTMENT
PCE has developed bespoke moulds to ensure consistency, repeatability, accuracy, and quality in manufacturing custodial sector components. Moulds ensured all respective constituent parts were accurately integrated, including structural ties, builders-work openings, and encast M&E items. This provided efficiencies for follow on trades throughout the project fit-out stage.
The images to the left show the custom built mould for the SecurePrison Duct wall unit, which was used to cast all the Duct Wall components.
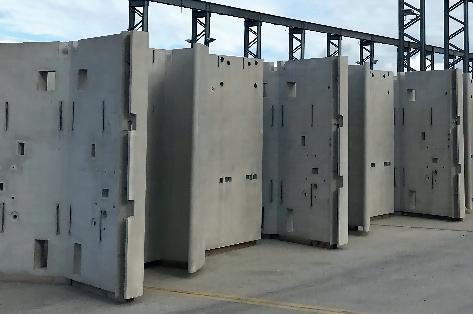
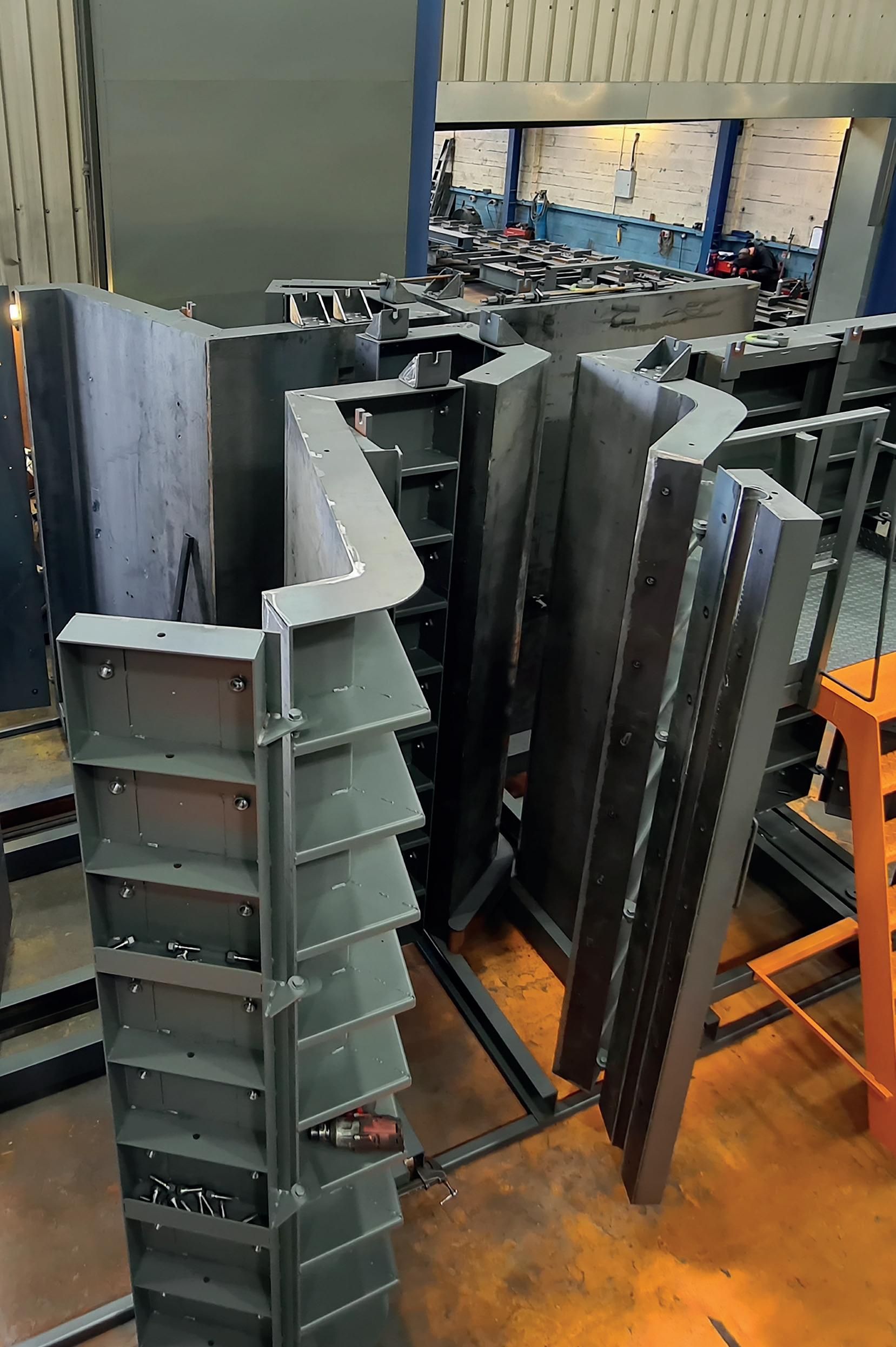
SUPPLY CHAIN MAPPING
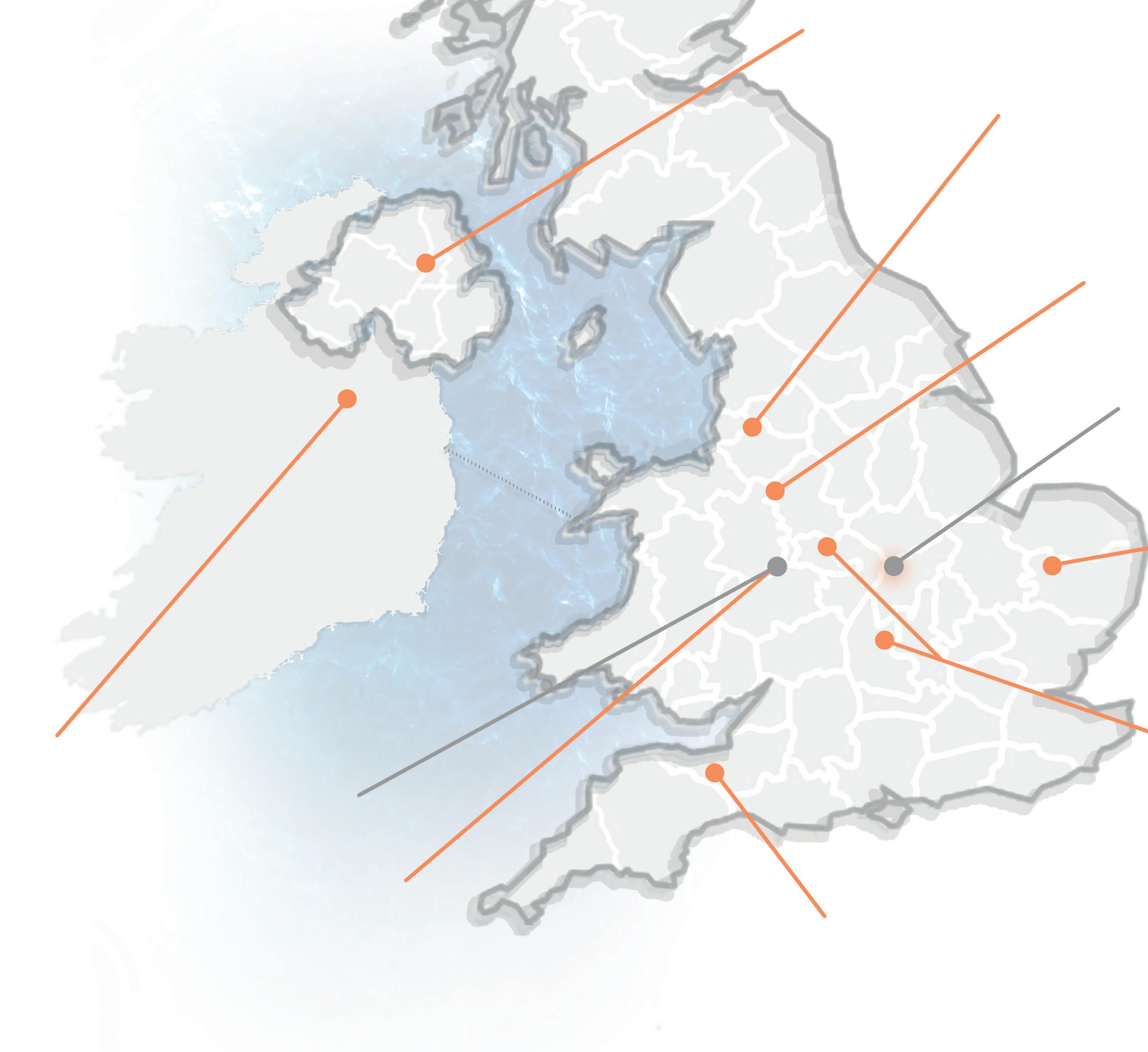
Critical to the success of delivering the project was the alignment of the carefully selected PCE supply chain partners with the ‘kit-ofparts’ requirements. Around 14,000 precast concrete components were manufactured within 10 months.
Cell Roof Units
PCE Head Office
PCE Ltd
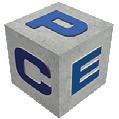
Square Columns, Beams
SWP
Circular Columns, Roof Upstand Walls, Roof Upstands
Oranmore
Cell Floor Units, Misc Floor Units, Hollowcore
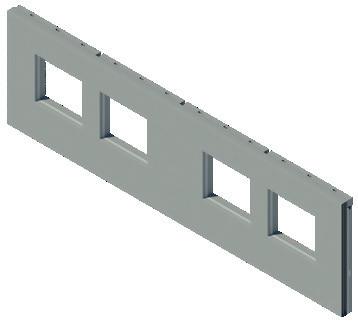
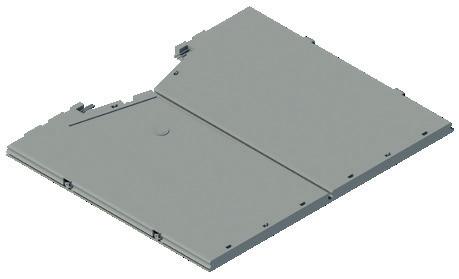
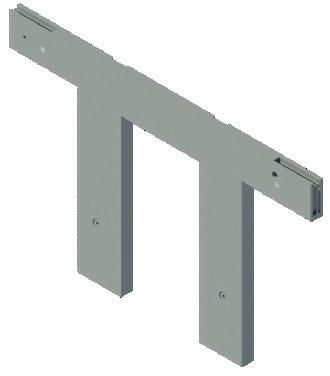
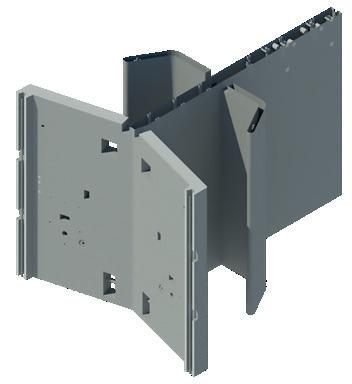
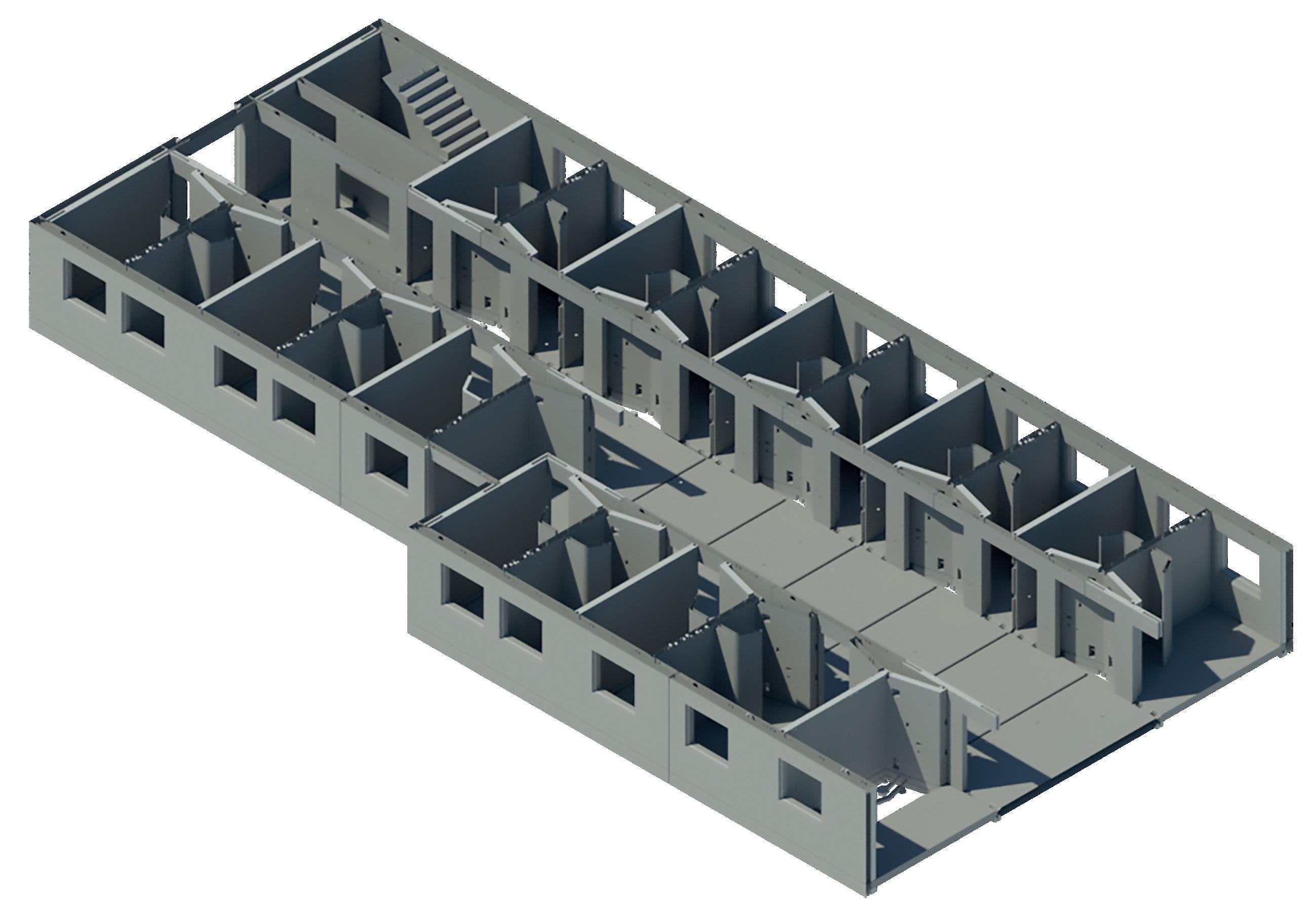
Forterra
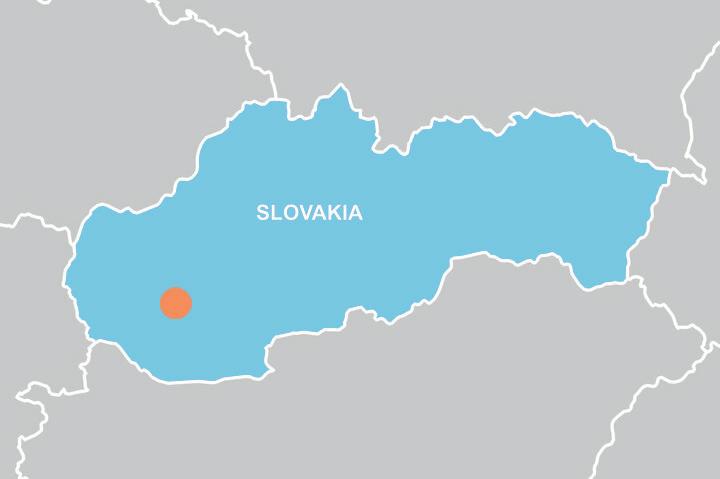
Duct Walls, Corridor Walls, Internal Wing Walls, Sandwich panels, Cell Floor Units, Misc Floor Units, Stairs, Landings, Parapets
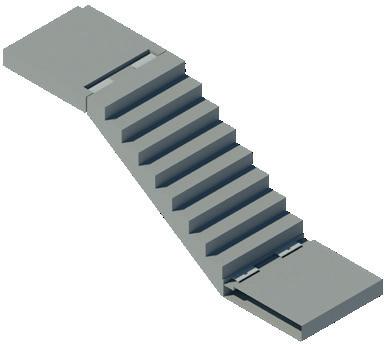
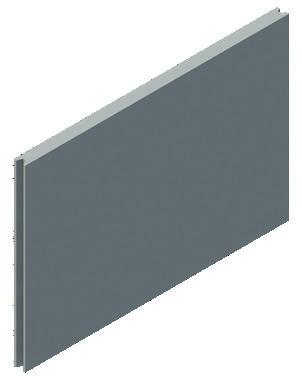
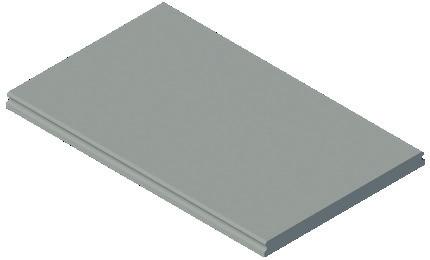
Stairs
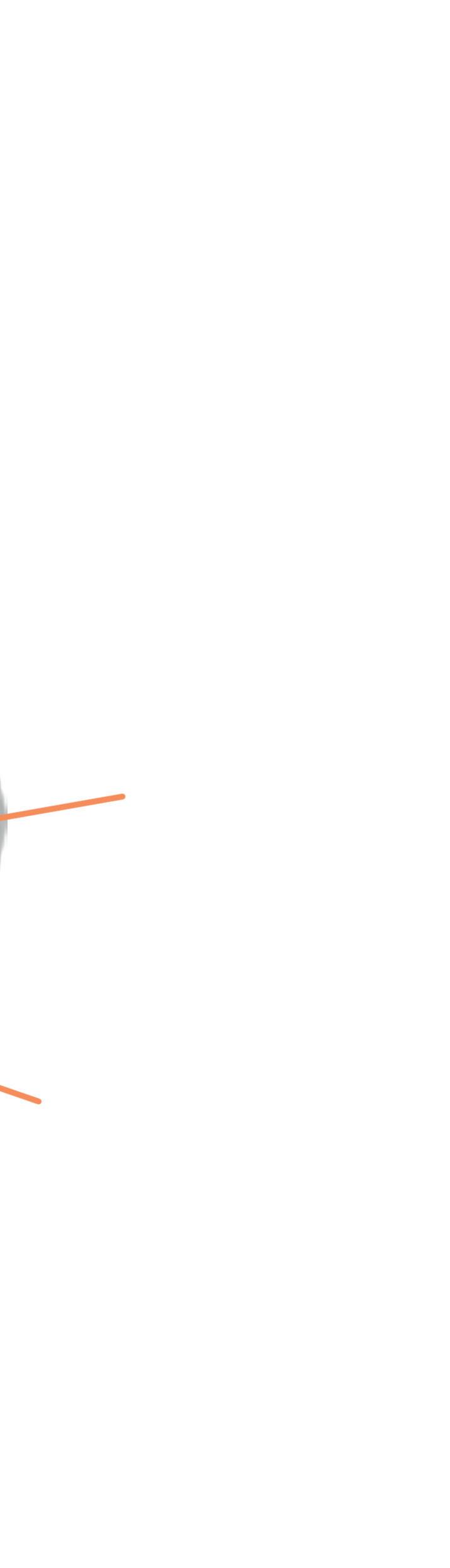
COMPONENTISED MODEL

PCE’s digital approach enables both the design and project team to track and monitor the projects progress at each stage of development. Over 1,600 detailed manufacturing drawings were produced by PCE’s in-house design team directly from the 3D structural model, helping resolve all interface and manufacture coordination requirements including the scheduling of integrated components cast into precast concrete elements. This ensured an accurate distribution of components to the relevant manufacturing factories.

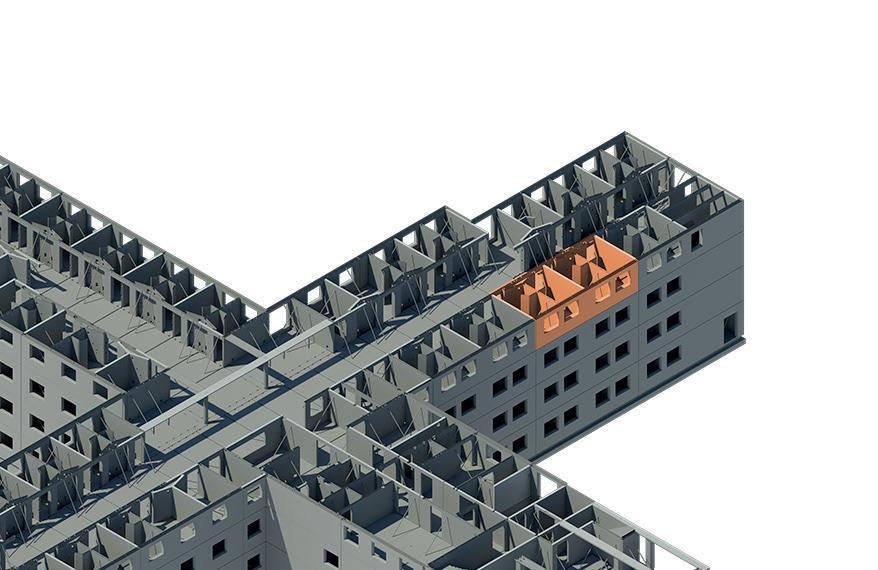
Secure-Prison System cell created from PCE’s Kitof-parts - expanded

Secure-Prison System cell created from PCE’s Kitof-parts - constructed
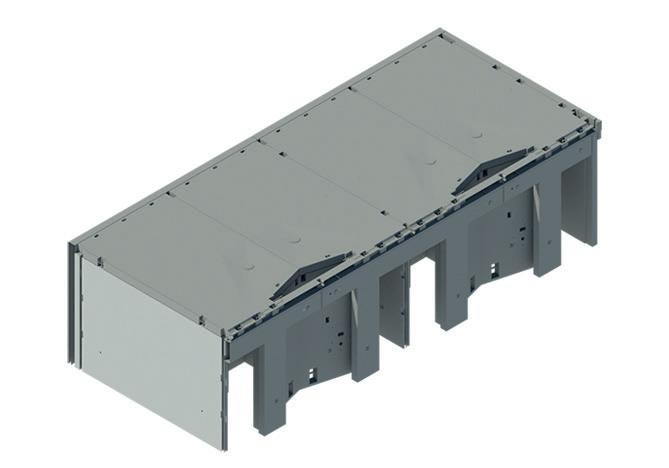
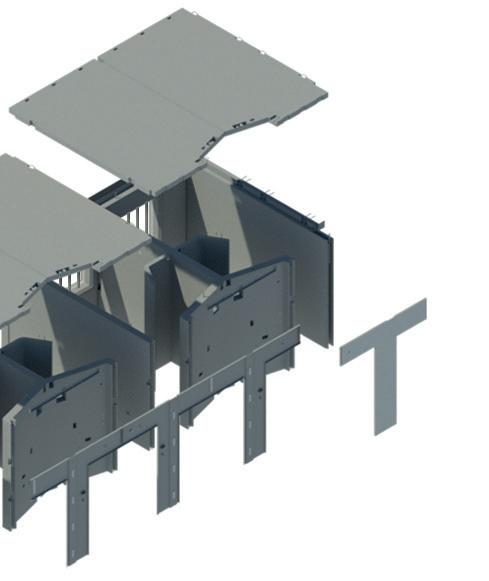
ASSEMBLY CONNECTIVITY

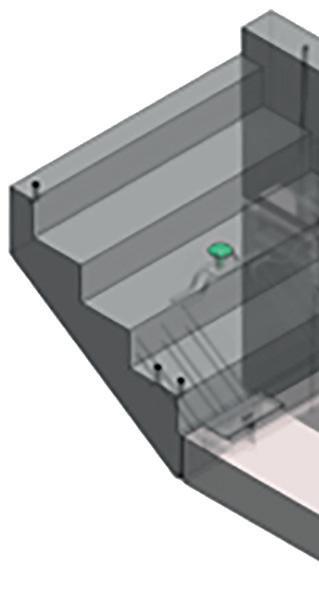
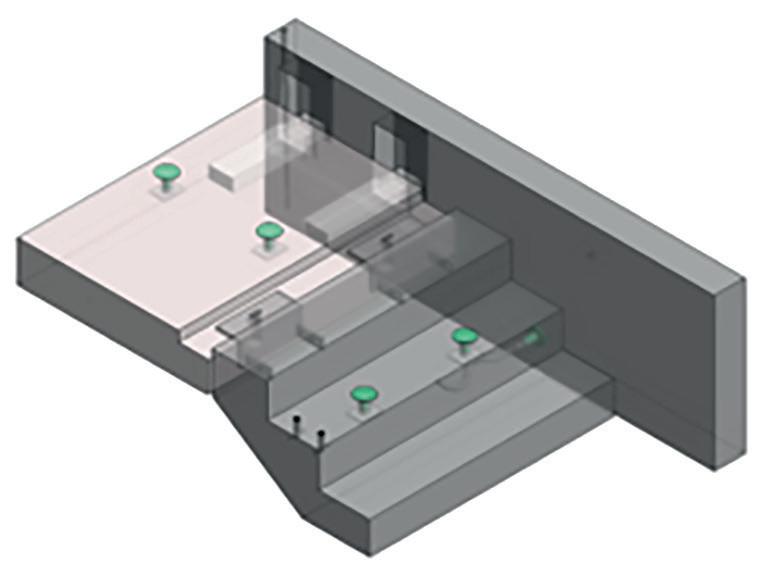
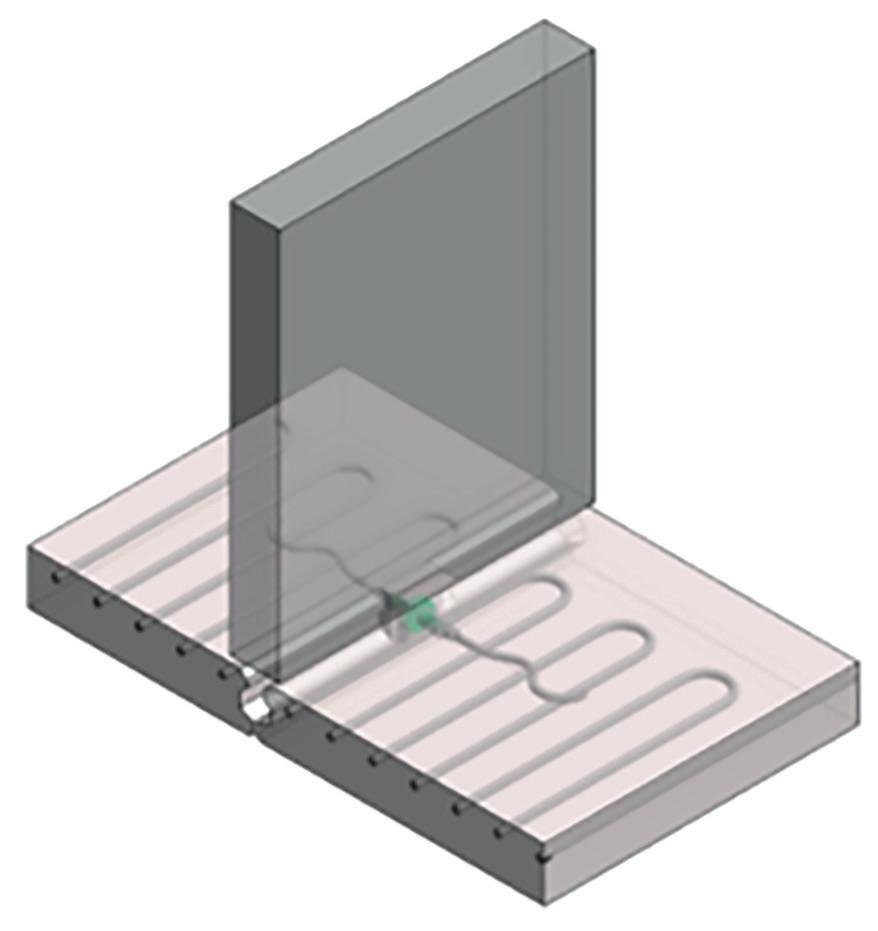
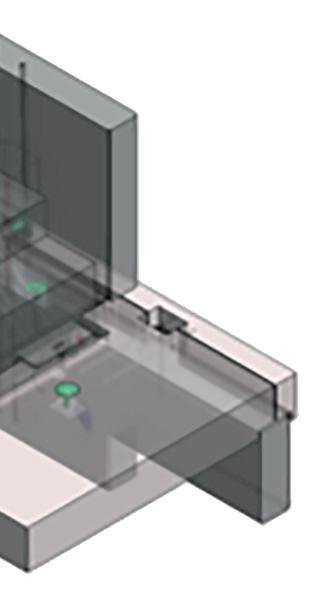

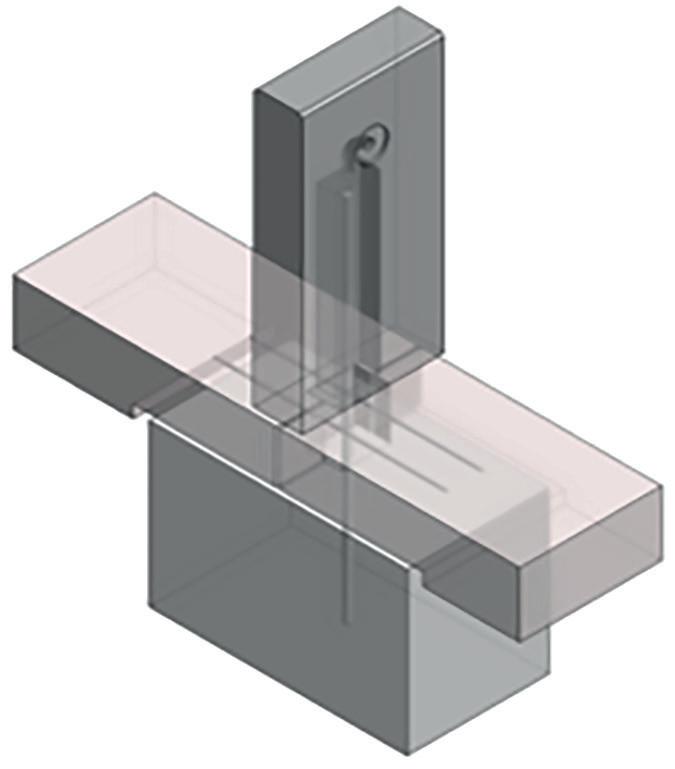

DESIGN JOURNEY
After successfully delivering HMP Five Wells, PCE set out to build on lessons learnt, adopting new innovations and design developments to improve its already high standards, reduce on-site waste, and increase efficiency throughout the project lifecycle. This journey began with a focus on design innovation, examining structural connections, element interfaces, methodologies of build, fabrication processes, and health and safety implications.
Stage 1
PCE’s Secure-Prison system ‘kit-of-parts’ are used to create prison cells that are repeated to create houseblocks. Designers can easily interchange these ‘kit-of-parts’ components and vary the size from the optimum to create their own unique solutions.

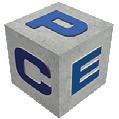
Each component is for production that handling, and temporary site temporary propping
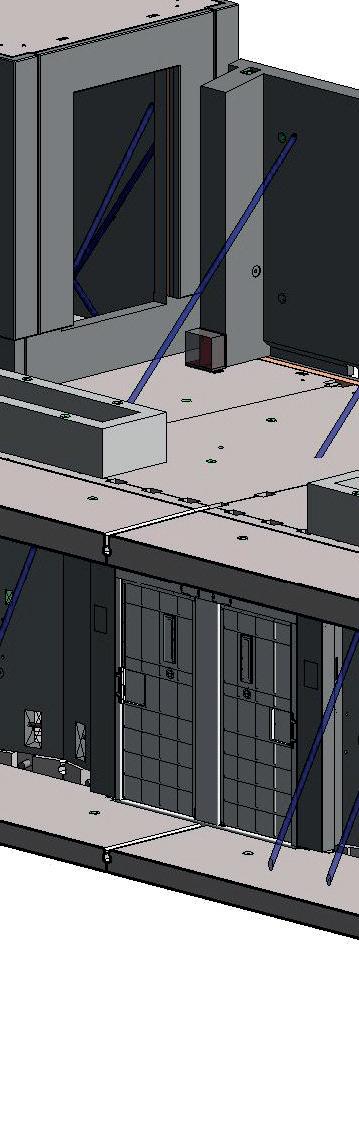
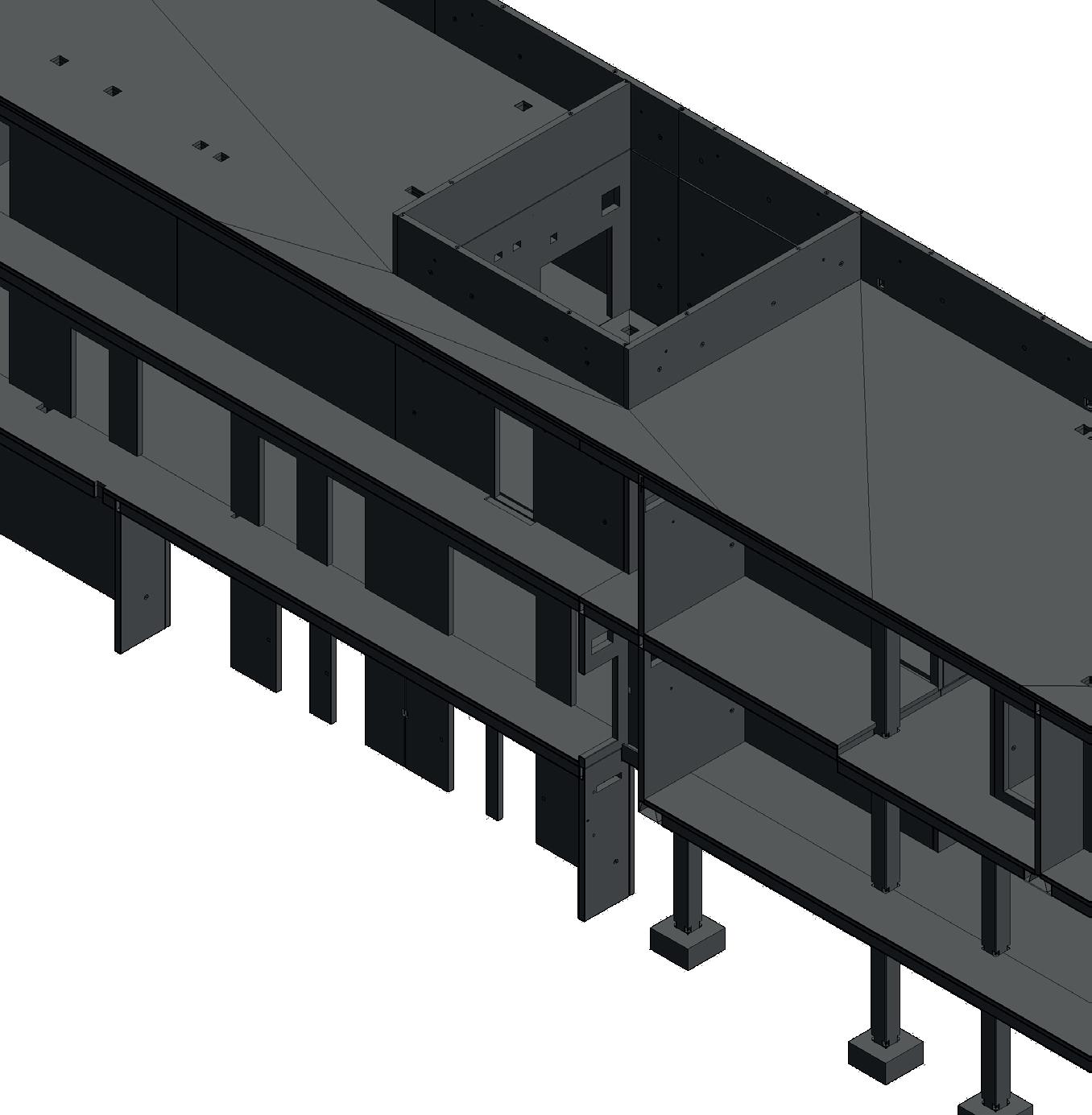
is completed with cast-in components that are required for connectivity, lifting/ temporary works requirements, including onpropping and fall prevention provisions.
Final drawings are sent off to manufacture for the concrete to be poured into bespoke moulds with castin components.
Stacking and handling methodologies are predetermined with respect to finishes and temporary loading conditions, ensuring units arrive on site to the required quality standards.


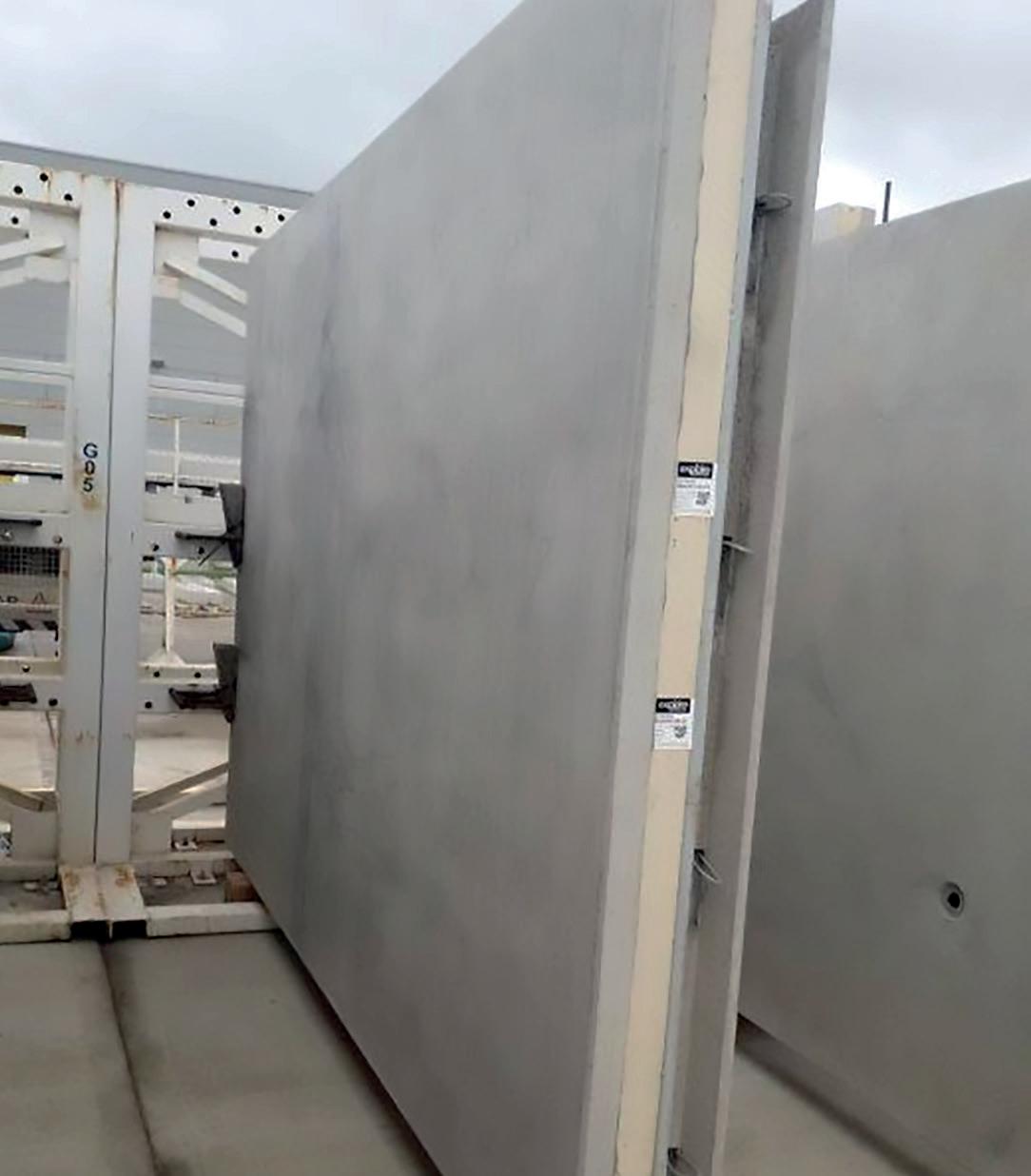
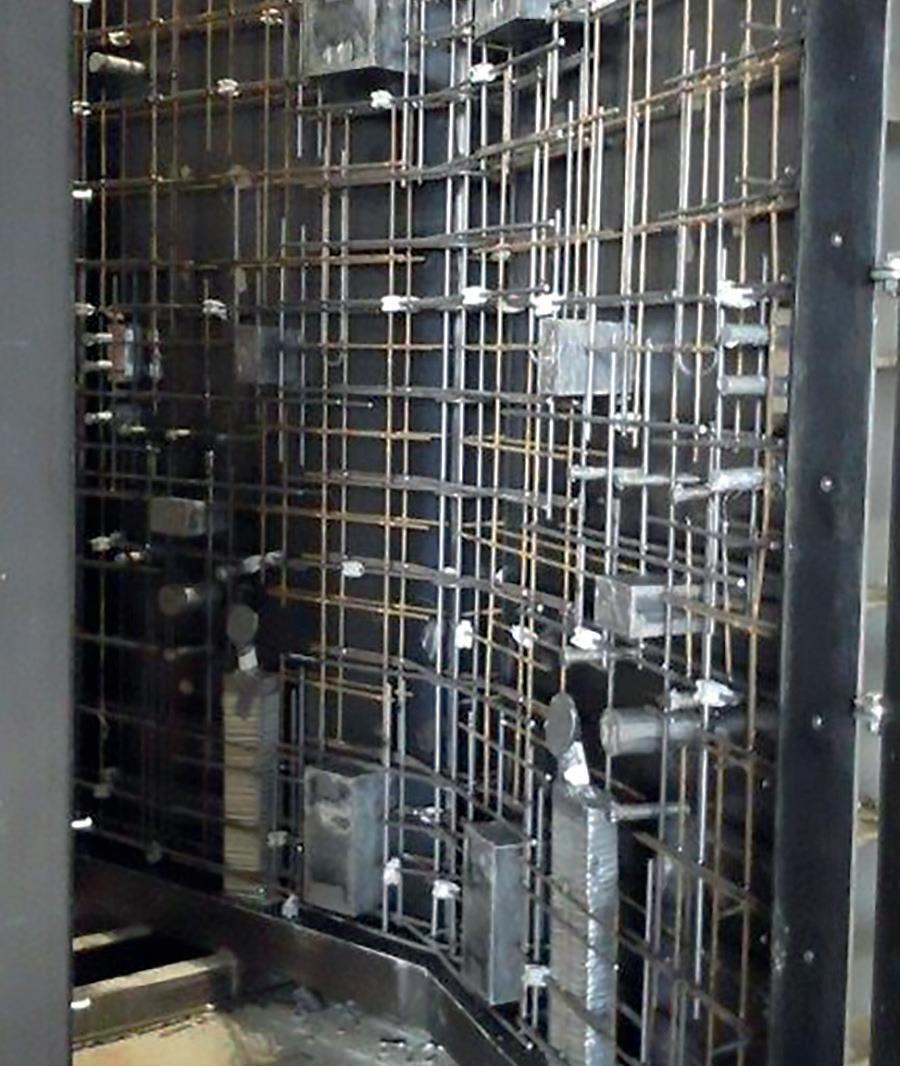
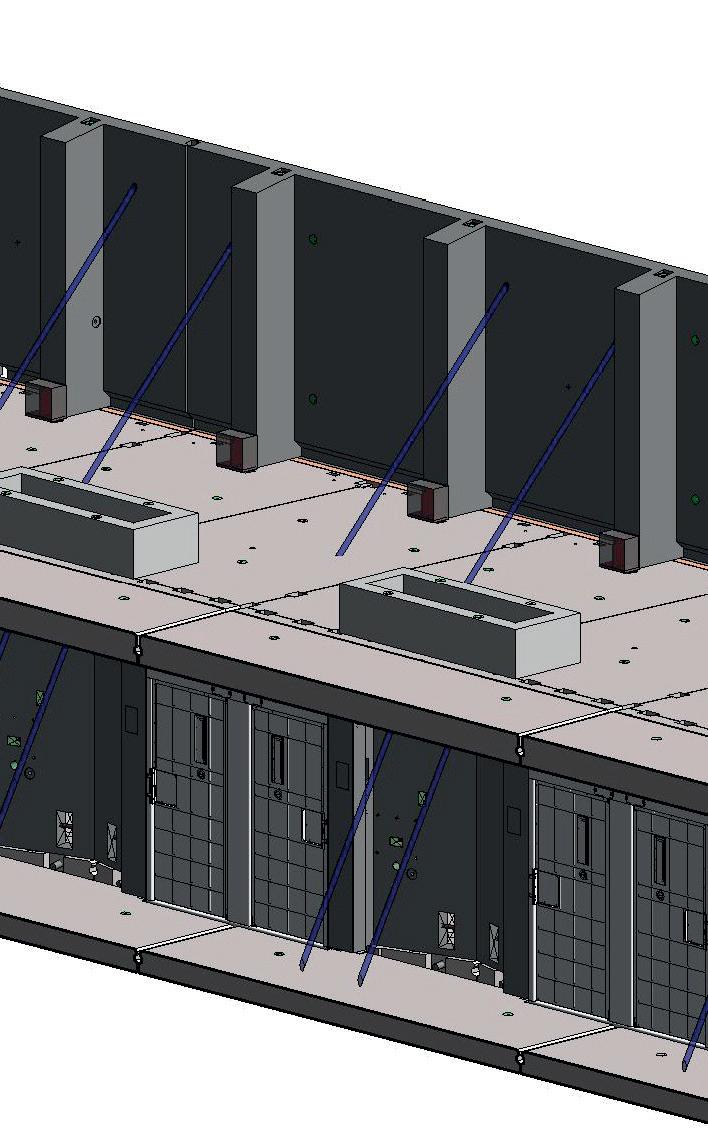
Benefiting developed utilising liaison keep enabled and any Working PCE‘s of plan possible, the significantly double
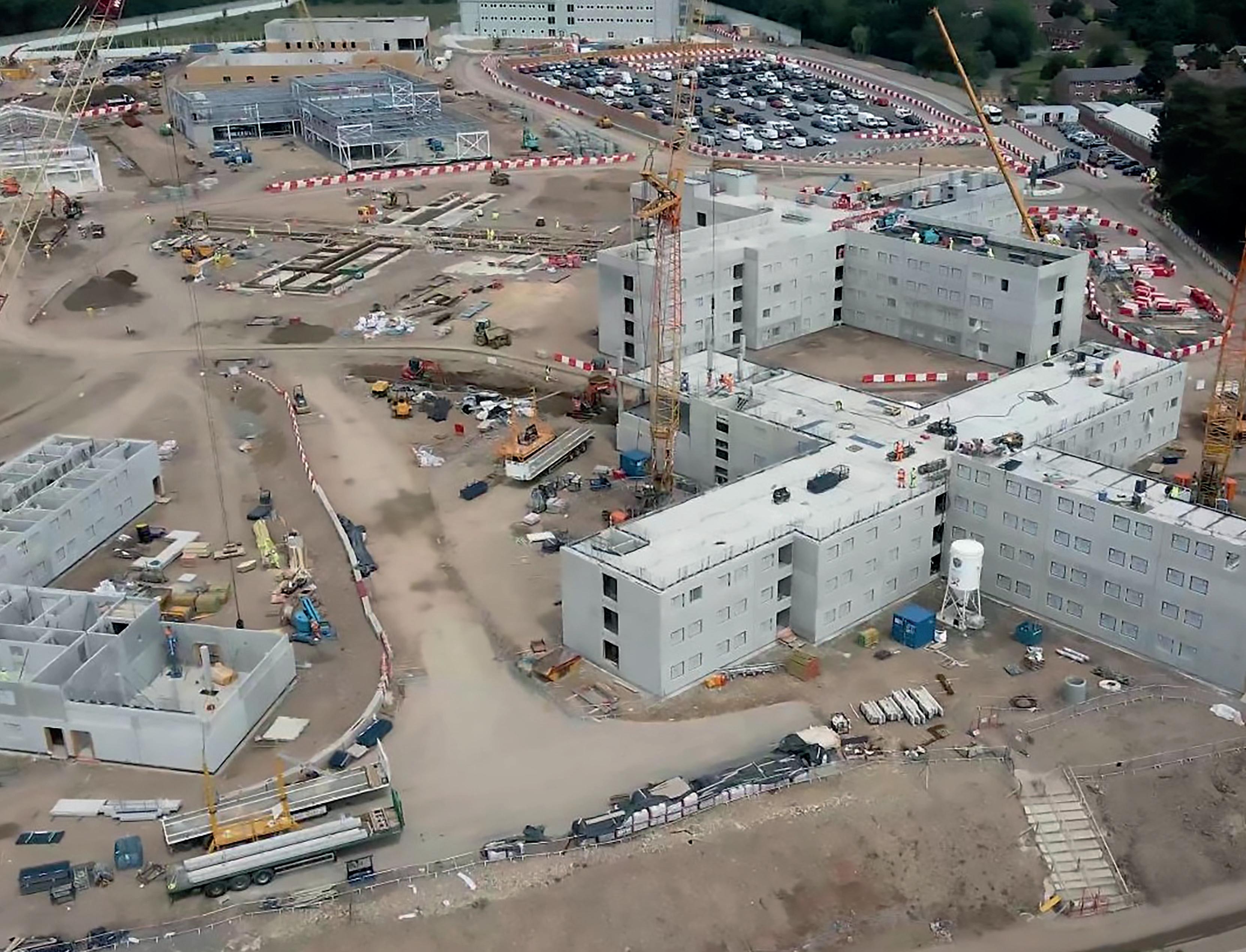
SITE LOGISTICS
Benefiting from a wealth of experience, PCE developed a coordinated logistic strategy utilising a site holding yard, with constant liaison with supply chain partners helping keep a modest stock of units on-site. This enabled just enough flexibility to manipulate execute new installation plans, should any unforeseen circumstances arise.
Working in conjunction with hauliers, PCE‘s vast experience and understanding complex logistical strategies helped plan individual loads, ensuring that where possible, components are lifted directly from the vehicle to the final place in the build, significantly reducing on-site storage and double handling whilst executing an efficient just-in-time delivery strategy.
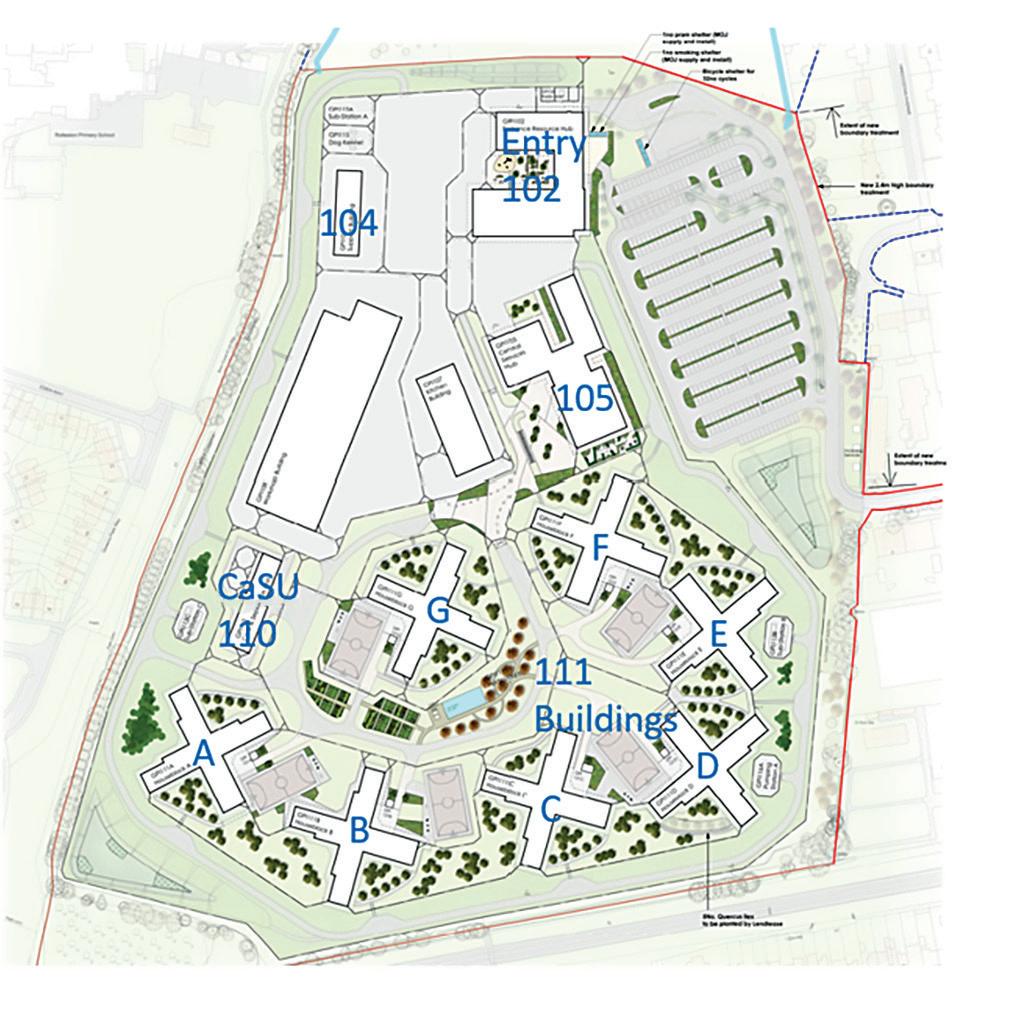
START OF THE
To enhance the assembly stage of the a significant development in its structural by adopting an innovative new silo-fed negated the need for additional palletised usage, as well as minimising resource timber waste. It also had the indirect logistics, including reducing fuel and reducing associated waste by over also reduces noise disruption by almost manual handling of bagged materials, get go.
Pre-construction on-site surveys were connectivity points prior to PCE taking footprint to avoid revisits by other
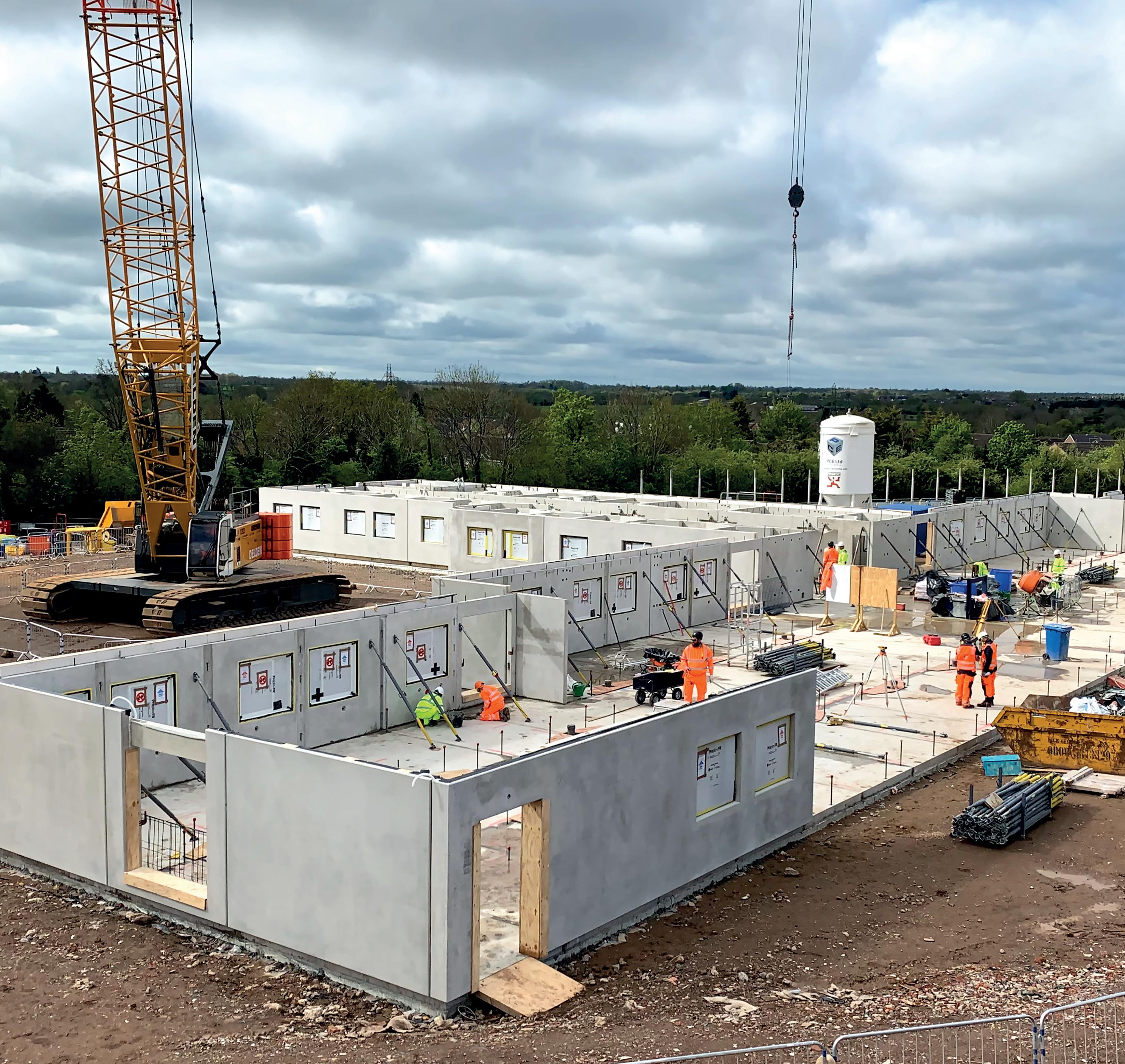
THE BUILD
the project, PCE implemented structural grouting methodology silo-fed system. The new system palletised deliveries, reducing fuel resource including paper, plastic, and indirect benefit of reducing waste and skip collections. Whilst 50%, the innovative silo system almost a third, as well as reducing materials, creating efficiencies from the were conducted, checking all taking ownership of the building trades.
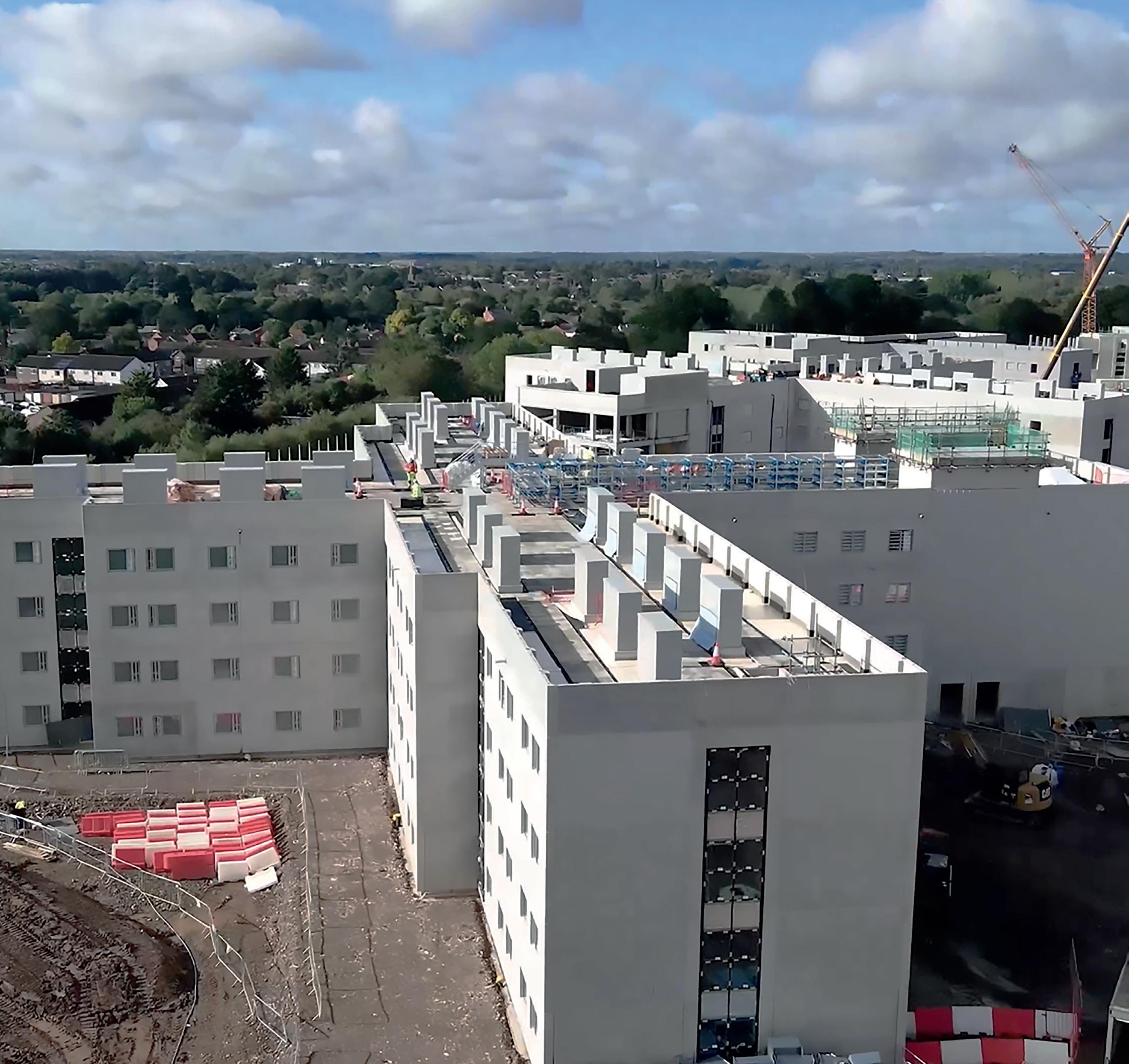
ASSEMBLY WITH SAFETY AND SPEED
The HybriDfMA systems employed ensured efficiencies extended throughout assembly. Optimal standardised construction techniques ensured speed of assembly with reduced risk. Lifting operations equating to around 285 tonnes of material and circa 74 hybrid units installed daily. On average, PCE installed 45 cells per week, or 9 cells per day, each with unwavering consistency and quality. PCE’s streamlined, efficiency-driven approach ensured its highly skilled, multidisciplined workforce, which averaged circa 70 onsite operatives across 7 cranes, ensured cells were delivered securely at a rate of around 45 per week, or 9 per day.

PCE’s HybriDfMA systems inherently prioritises safety for everyone involved in manufacturing and on-site assembly. Risk is meticulously identified at every turn and either eradicated through design, or controlled through PCE’s innovative safe systems of work and safety processes.
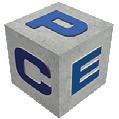

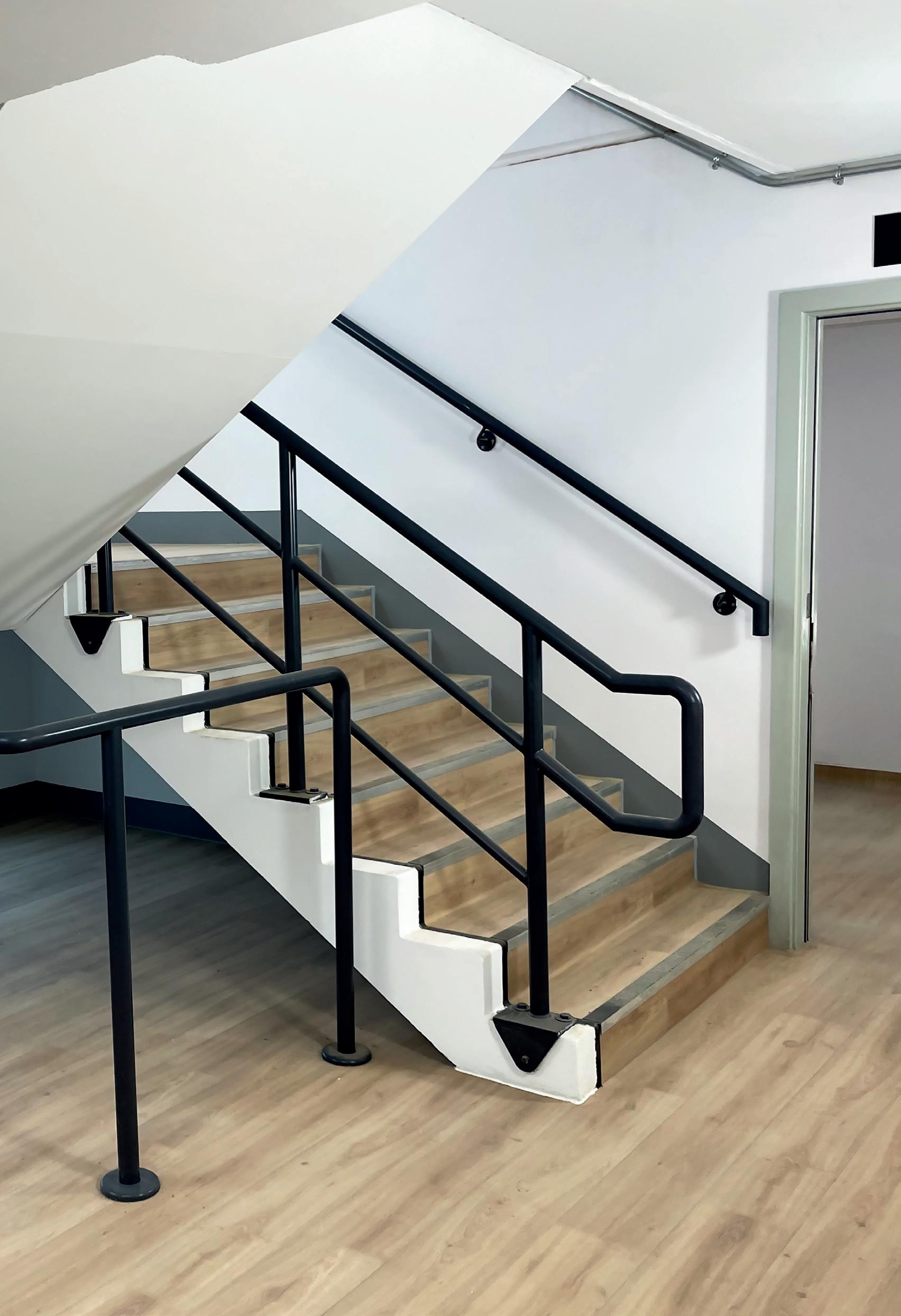

INSIDE THE HOUSEBLOCK
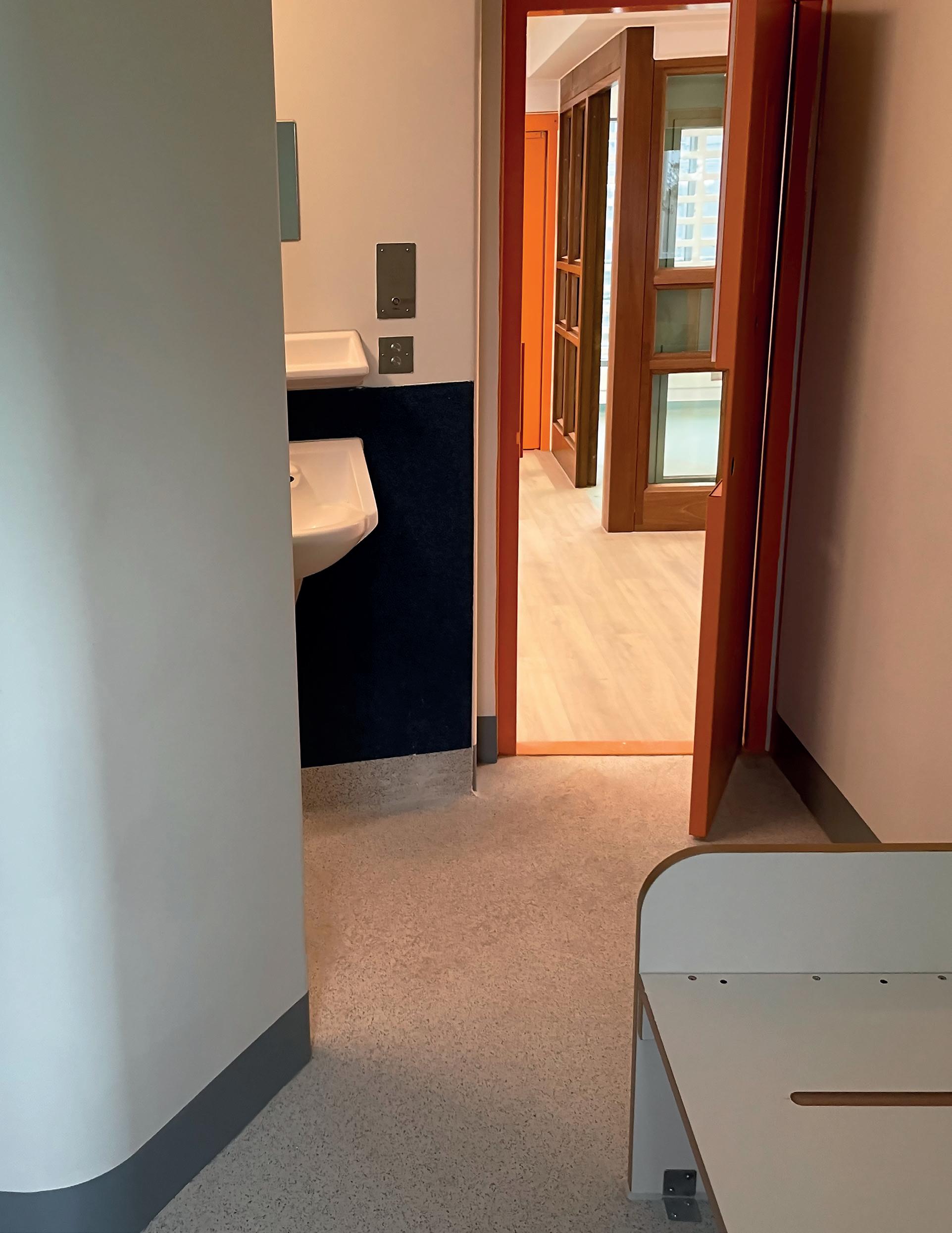
Precast concrete components are optimized to minimize follow-on work. Secure-Prison system cell M&E utility conduits and shower trays are cast-in during offsite production. This enhances serviceability and security, whilst self-compacting concrete is used for the cell duct, corridor wall, and door components. Doing so ensured a high-quality finish whilst limiting blowholes per unit, improving security and the overall cell aesthetics.
Units featuring barless windows were secured and sealed with toughened glass to reduce noise, prevent waste disposal, and restrict access to prohibited objects, meeting new MOJ category C standards. The barless windows, complete with adjustable ventilation, are specifically designed for casting into four-cell wide external precast concrete façade panels. PCE collaborated with supply chain partners to improve window quality by tightening tolerances during manufacture to compliment casting strategies, ensuring a crisper element interface when placed into moulds.
Smart integration and connectivity were key to the overall success of the project delivery programme. Throughout assembly, M&E riser modules were installed through an opening in the roof of the houseblocks, spanning vertically across all four floors of the structure. These pre-assembled riser modules integrate key services through all floor levels in a compact modular form. Installing and fixing the modules on-site instead of using traditional methods saved on both cost and time.
COMPLETING THE
Despite a 6-week delay due achieved an accelerated programme, which benefited the client by trades.
After successfully delivering PCE’s secure system ‘kit-of-parts’, demonstration of the expertise
With another completed project, within the design, production primed to push the boundaries improvement and detailed information offering further advancements and digital tracking in the years
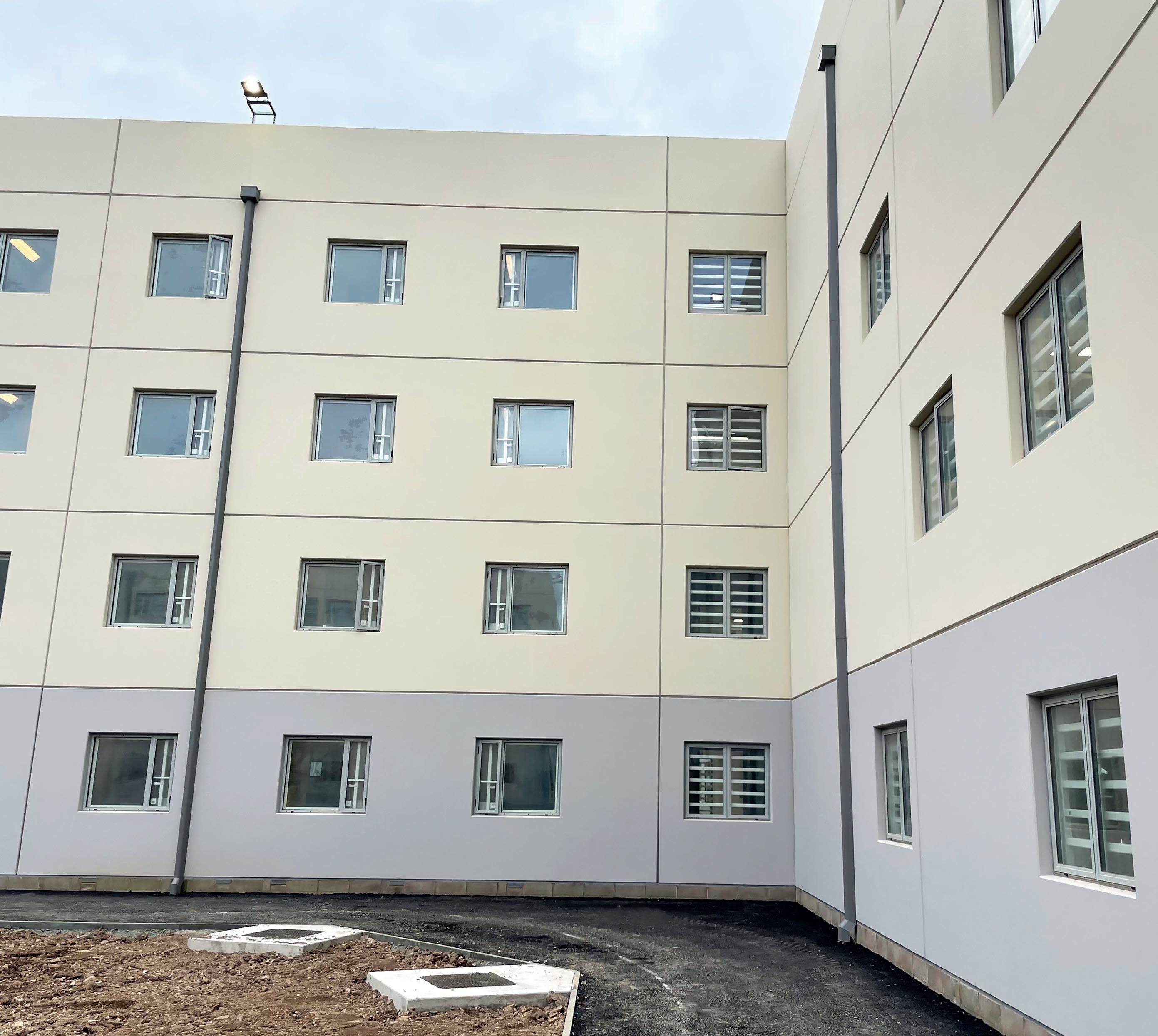
The Ministry of Justice commented:
‘‘PCE have demonstrated of Justice and the Government’s manufacture at the rate programmes. The success Whitehall with growing Methods of Construction including reducing embodied agenda.’’
COMPLETING THE BUILD
to preceding trades and the pandemic, PCE programme, recovering lost time plus 2 weeks by enabling early engagement with follow-on
delivering a multitude of custodial projects utilising ‘kit-of-parts’, HMP Fosse Way is yet another expertise PCE brings to the custodial sector. project, and the implementation of innovation production and construction on site, PCE is now boundaries even further in this field with continuous information at its core, and look forward to advancements in efficiencies, carbon-reduction, safety years to come.
commented:
demonstrated an absolute commitment to the Ministry Government’s priorities by supporting precast needed to support challenging construction success of delivery is now promoted across interest in the way PCE have utilised Modern Construction to deliver pace, quality and innovation embodied carbon to support the sustainability
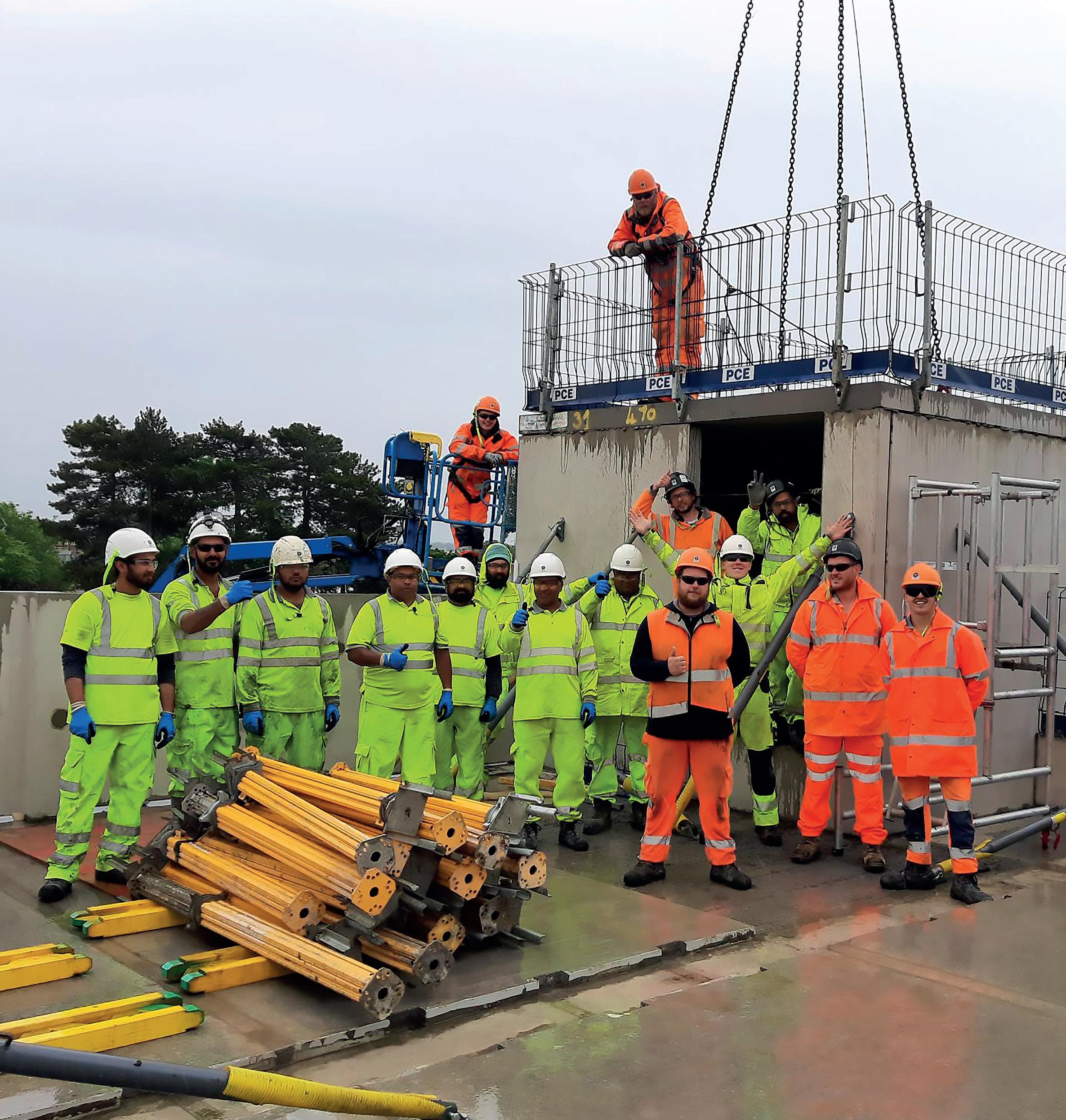
DIGITAL TRACKING
PCE implemented an electronic system to monitor the life cycle of products for enhanced efficiencies, waste reduction, and real-time reporting. The PCE delivery report system captures delivery timings and product quality on construction sites through real-time electronic reports completed by offloading crews using mobile phones. PCE’s on-site assembly philosophy is based on programmed just-in-time deliveries, with all offsite manufactured components being delivered with zero defects.
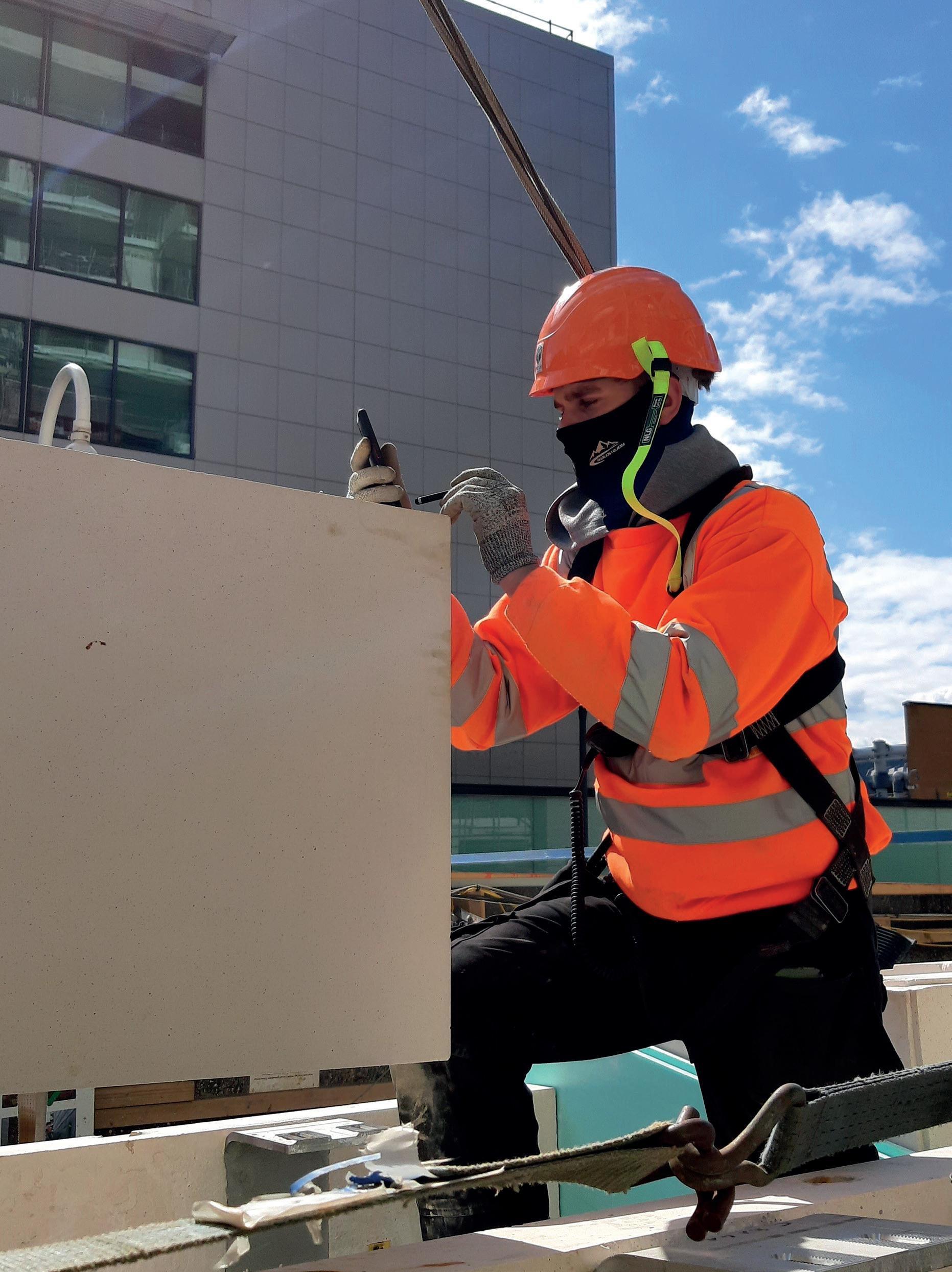
The system enables accurate, easy, and rapid reporting of offloading durations, visible defects or damage, incomplete or late loads, etc. It provides quick and detailed, verified electronic time-stamped data to analyse performance and quality of deliveries, helping determine continuous improvement opportunities to maximise efficiency and minimise cost. PCE’s IT department continues to consider improvements to the system and its integration with other parts of the PCE digital world, acting on feedback from site operatives to improve the delivery report system further.
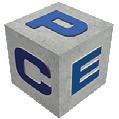
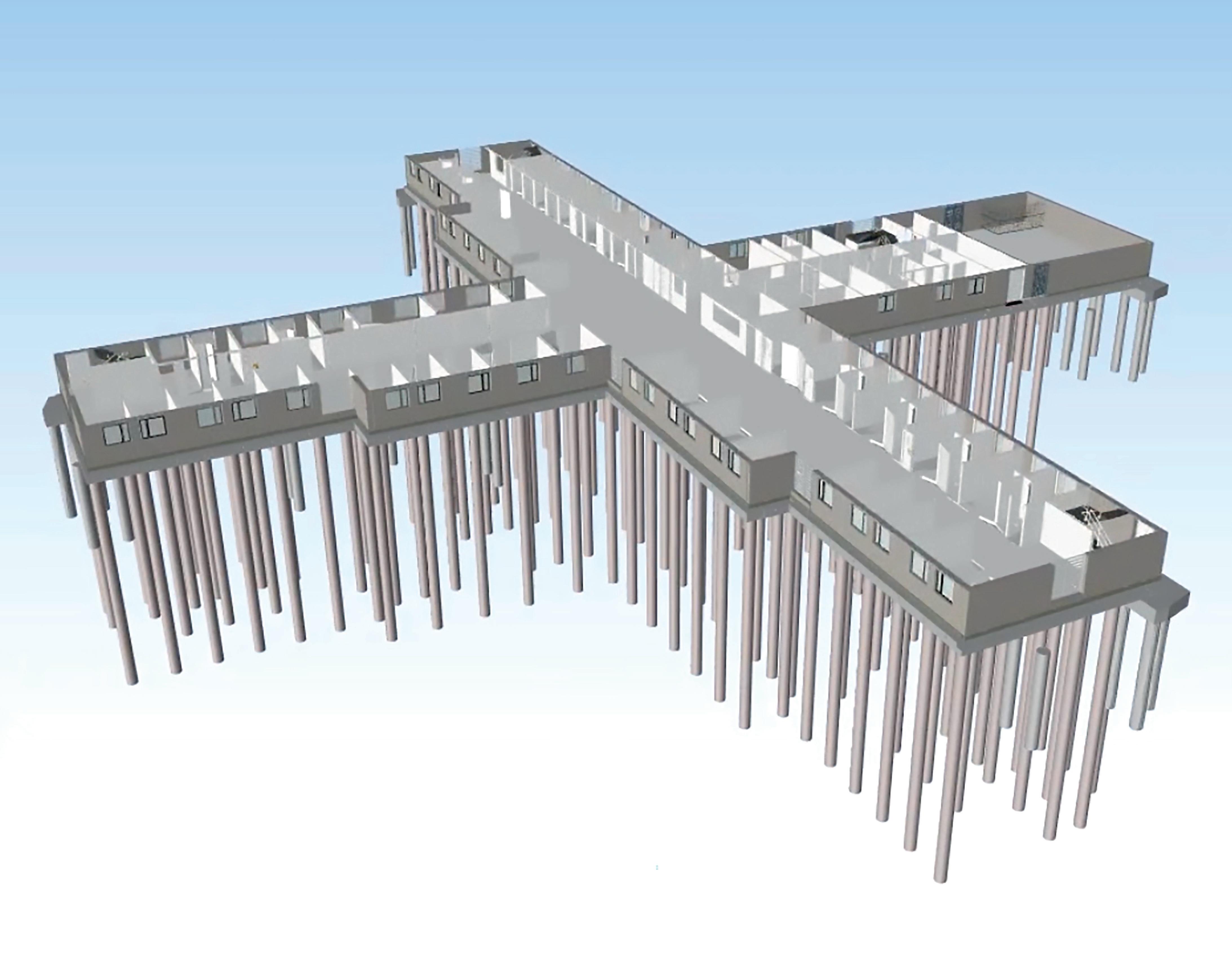
PROJECT INNOVATION
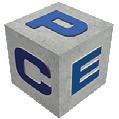
A PCE employee identified an opportunity to innovate through adapting a piece of machinery, and collaborated with PCE’s Operations Plant Engineer to design, develop and deliver the ‘grout wand’.
The grout wand allows users to ‘gun in’ the slab soffit to wall apex connection with a M330 grout pump, significantly increasing productivity and efficiency by approximately 250%, whilst bringing massive health and safety benefits. The wand eliminates the need to work from height, reduces the need for manual handling, and lessens the risk of HAVS, greatly reducing risk to employees, which is of significant importance to PCE. It also allows PCE to do the job in a much more cost-effective manner and ensures consistency of mixing the product to the necessary specification.
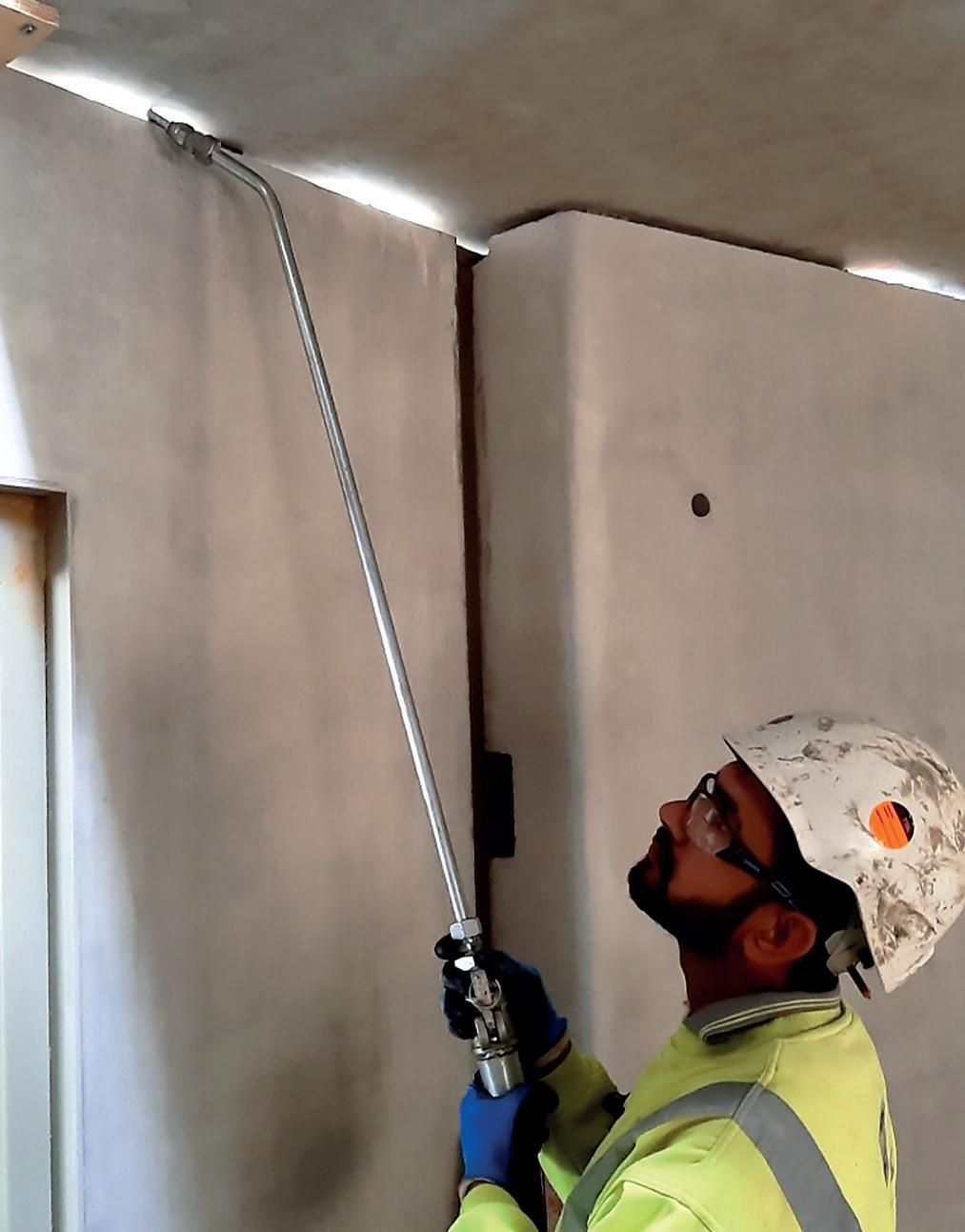
HMP Fosse Way also saw the use of PCE’s SlingSafe, a patented safety system providing efficient and safe offloading by preventing site personnel from falling from delivery vehicles. Designed and engineered within in the UK, SlingSafe features a unique dual boom and dual safety harness system to prevent slips and falls. With many of all reportable UK work-related accidents occurring near vehicles, PCE believes the system has the potential to reduce injuries and fatalities across many industries.
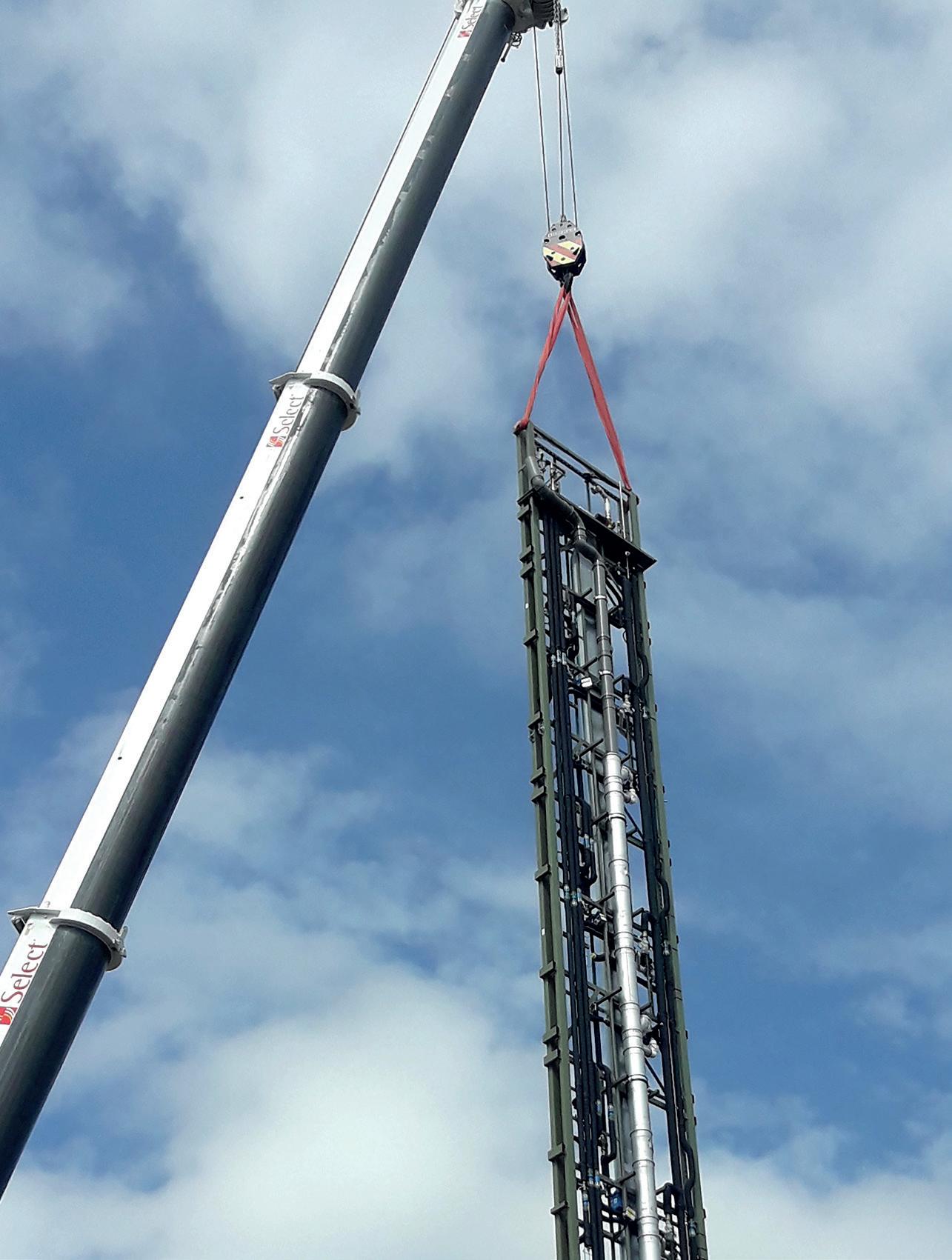
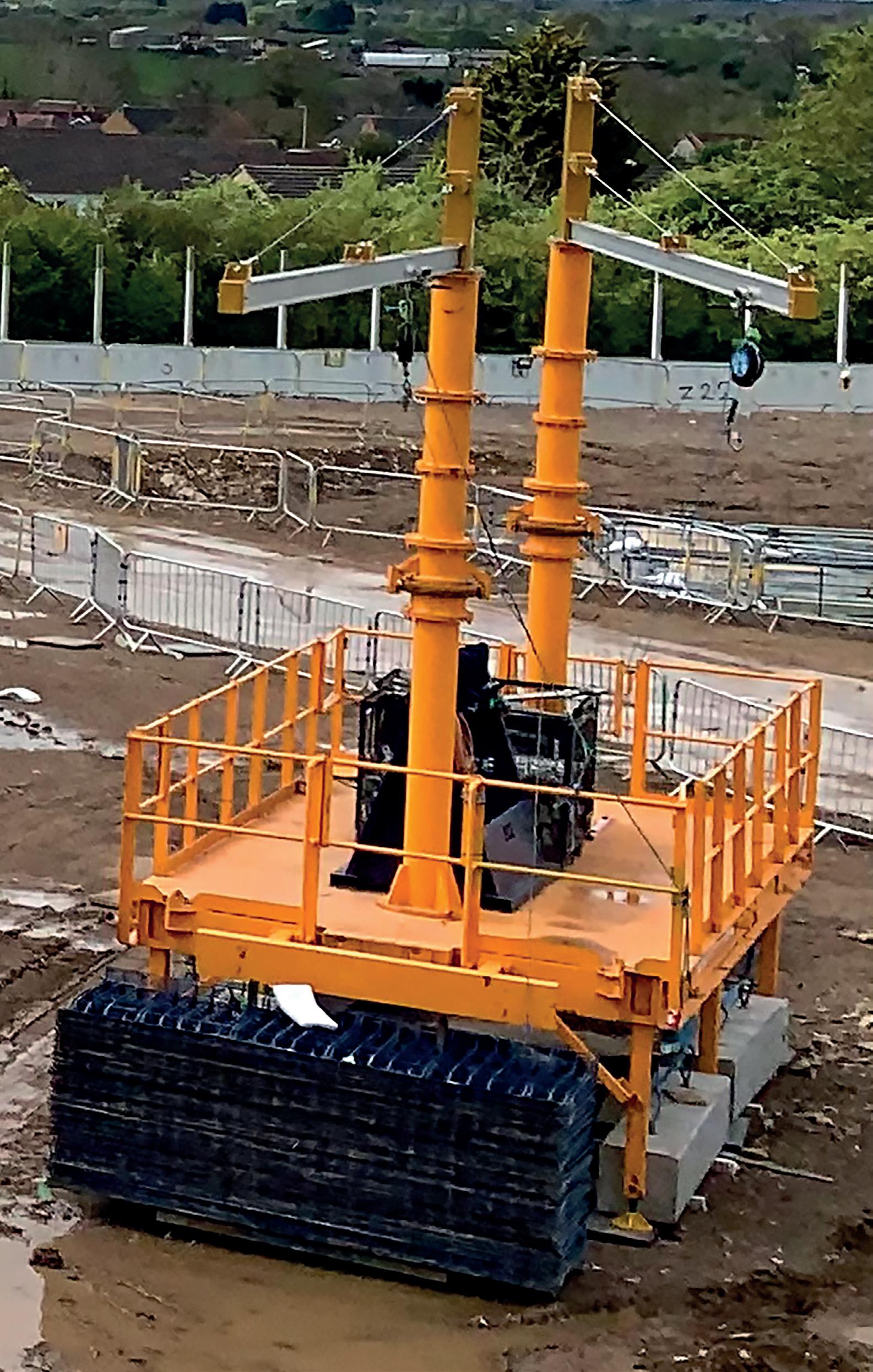

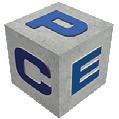
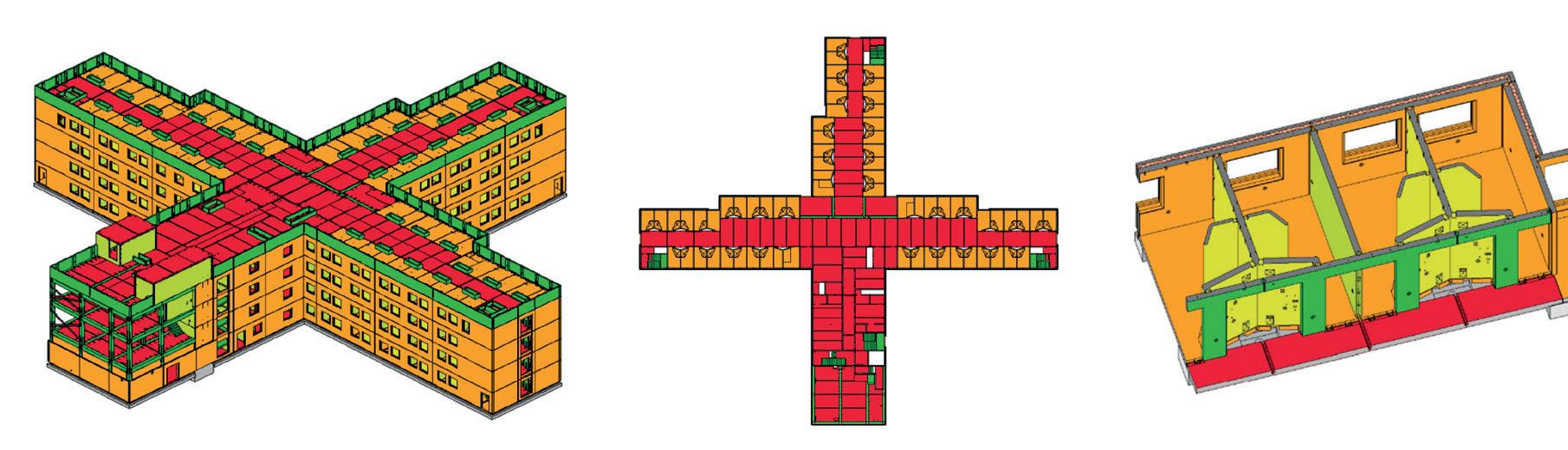

DECARBONISING PRECAST CONCRETE


PCE used its expertise to ensure the final structure was completed with a minimised amount of embodied carbon, helping achieve sustainability standards and environmental efficiency. The Fosse Way project has also extensively supported the government-funded ‘Decarbonising Precast Concrete’ initiative, in which PCE is a key partner, as a guideline for even more efficient and sustainable prison design and build.

Many tests took place during the build to ensure future concrete mixes are to a standard that fit the overall carbon reduction needs, which was greatly assisted by the creation of a carbon calculator. Due to high strength requirements for lifting, a more specific concrete mix had to be created than the one chosen for the original design specification. In addition to an improved mix, design, logistics, and assembly improvements created a potential 21 % reduction in carbon verses the benchmark design mix.
The initiative proved pivotal, with research indicating that optimized strategies could save up to 40% embodied carbon against the benchmark, whilst delivering significant commercial and programme benefits. PCE continues to develop eco-friendly and sustainable structural solutions to support future client needs and to progress towards its goal of becoming carbon neutral.
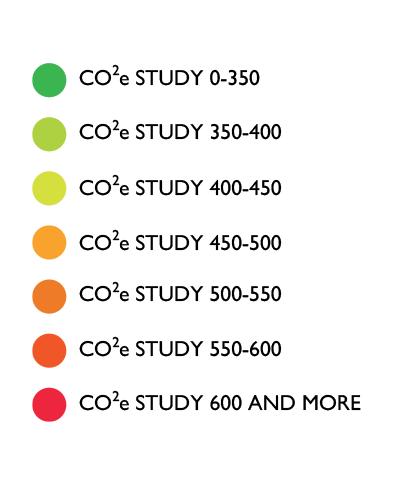
OUR PEOPLE
During project delivery, at its peak PCE employed around 90 personnel either directly or through specialist sub-contracts. This included 5 ROTL (Release on temporary License) individuals as PCE assisted with their rehabilitation back into society. The appreciation and management of people, their skill sets and backgrounds was something which took careful and meticulous planning, which resulted in some fantastic results and allowed individuals to increase their knowledge and further develop their skills.
PCE Project Manager at HMP Fosse Way, Dan Gallagher commented:
“At the heart of every project we deliver, are the people we employ and work with, and this project is no exception. The project has delivered fantastic results which reflects the hard work and dedication from the whole team, raising the bar once again for project delivery, with a big thank you to everyone involved!”
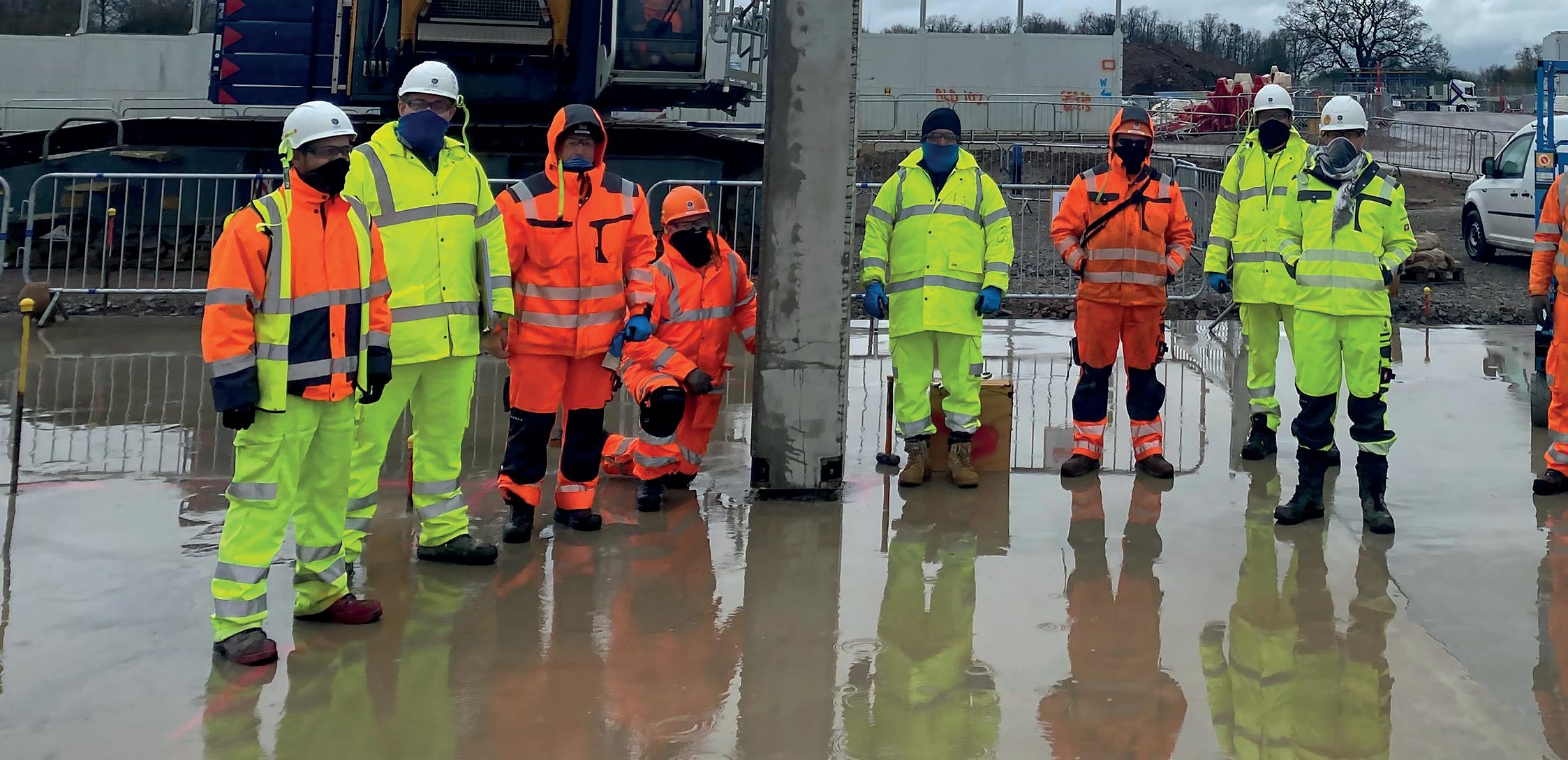
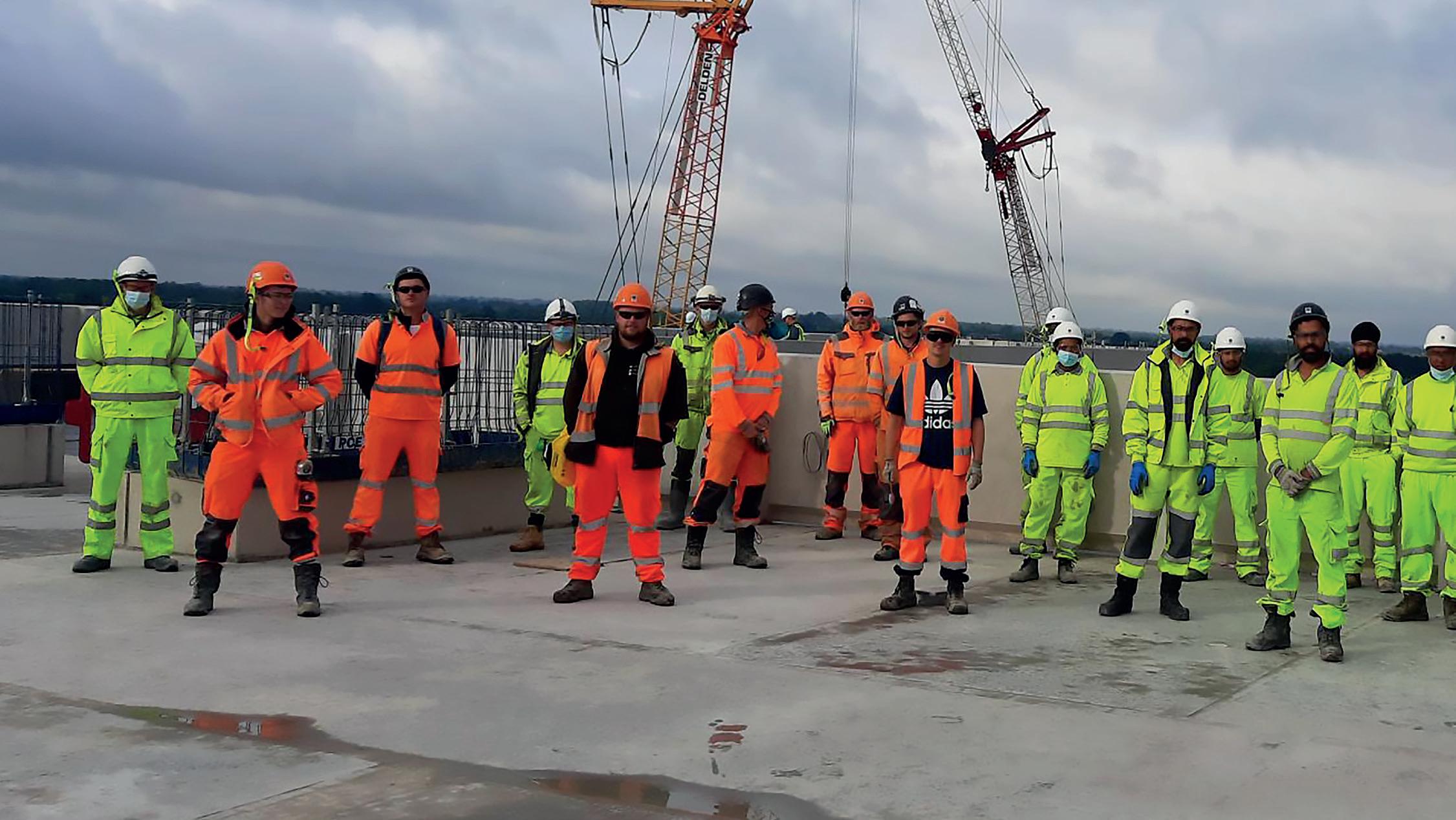
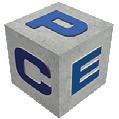
Our Employee Ownership Trust (EOT)
Being an EOT business means PCE are equally owned by its employee partners. As business owners, our people take ownership for PCE’s continued success and enjoy the rewards that come with it; the more successful our business, the more reward we collectively enjoy.
We recognise that for PCE to be successful, we need our people to be at their best, which is why we have established a culture built around development and succession planning, investing into our workforce and providing challenging, inspiring and rewarding careers for our people to realise their potential.
Our people are given the tools and support to develop their careers, increase their knowledge, skills and experiences to help drive our EOT forward, and ultimately, enjoy the rewards we share for our collective success. It’s this culture that has been installed, that enables us to deliver great projects, such as HMP Fosse Way.
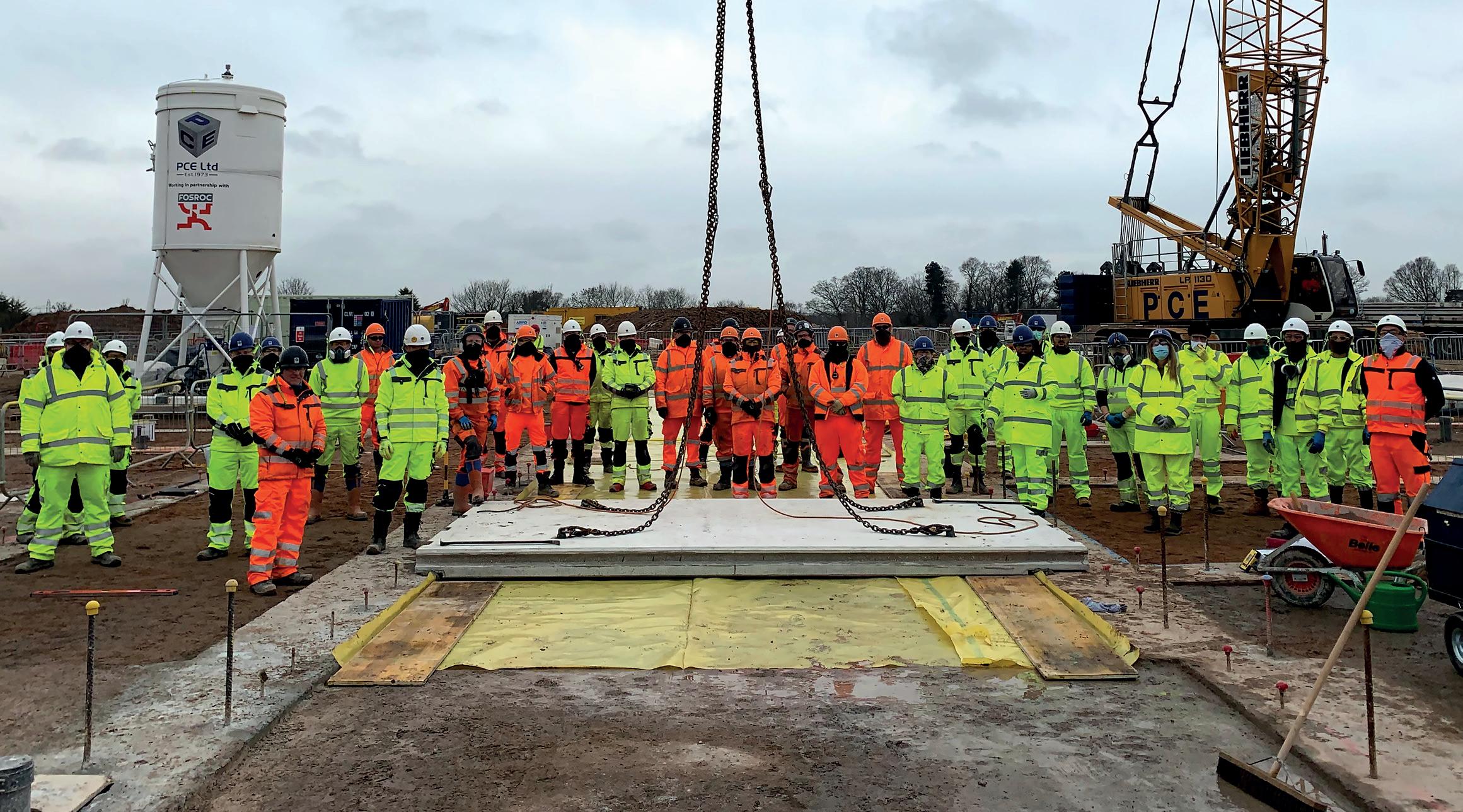
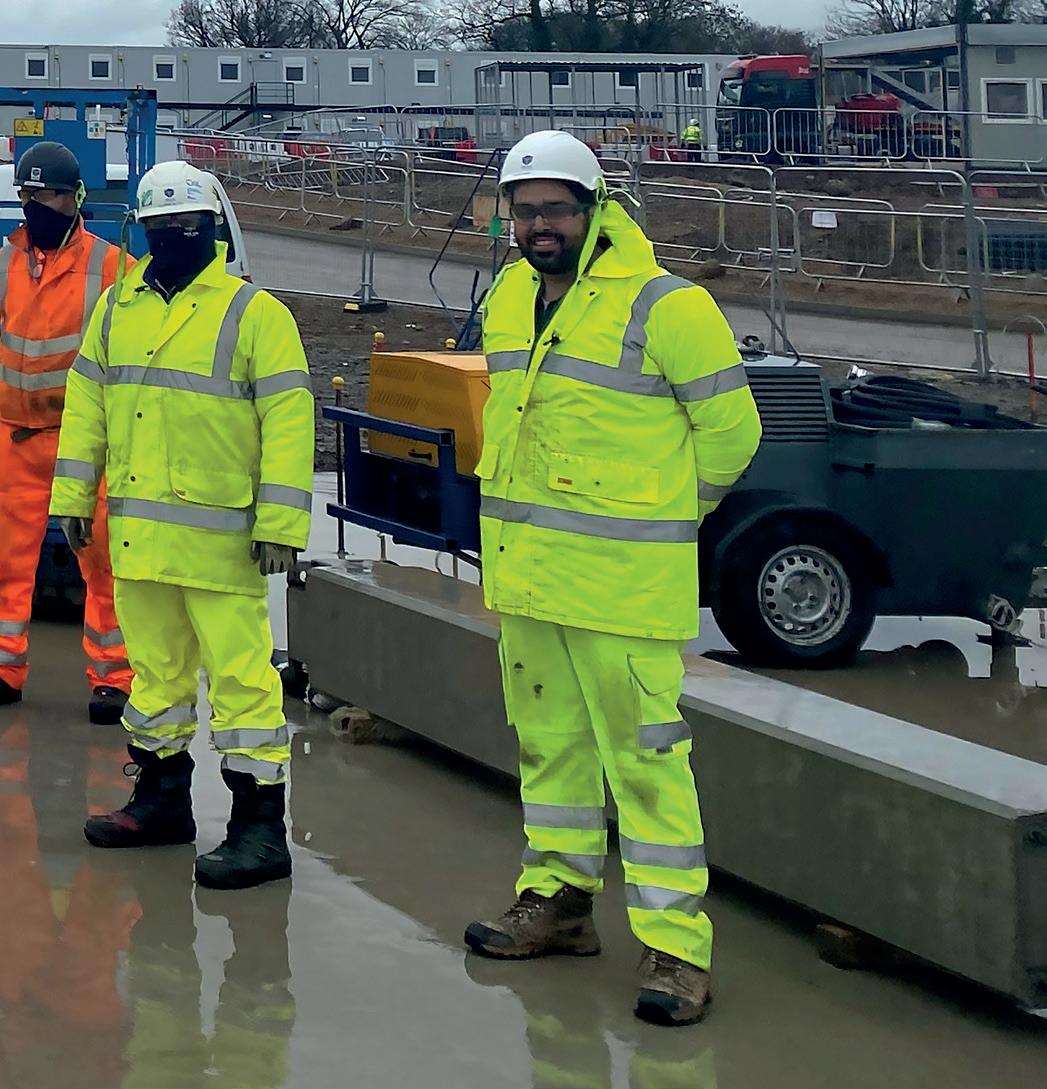
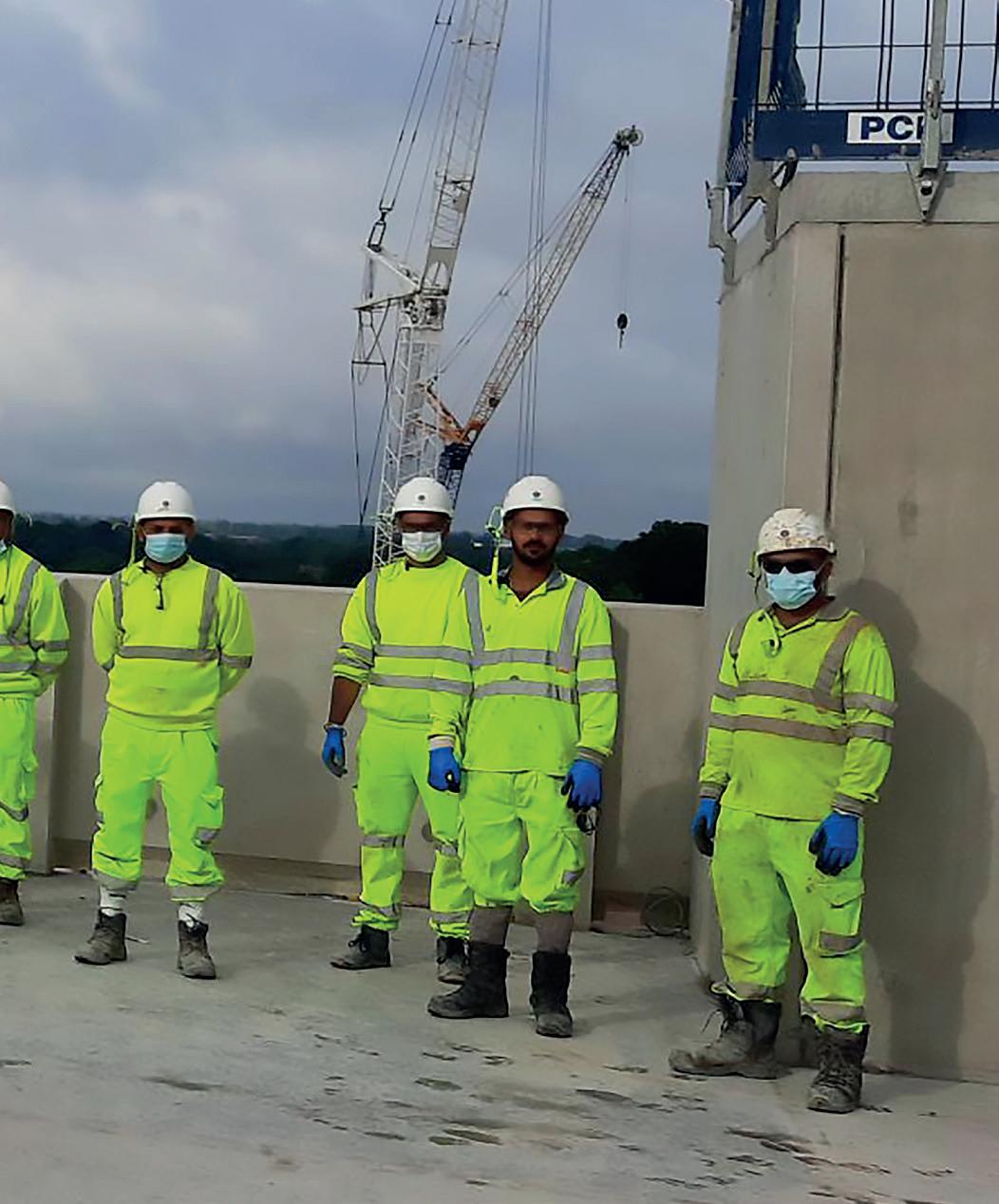