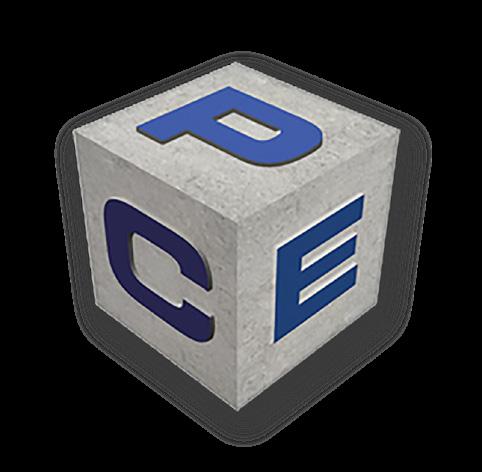
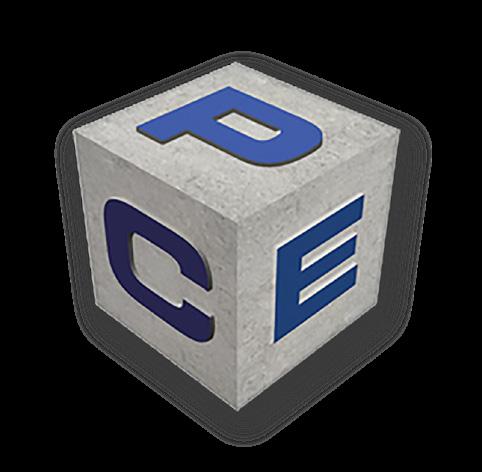
Golden Jubilee National Hospital
Hybrid Frames System
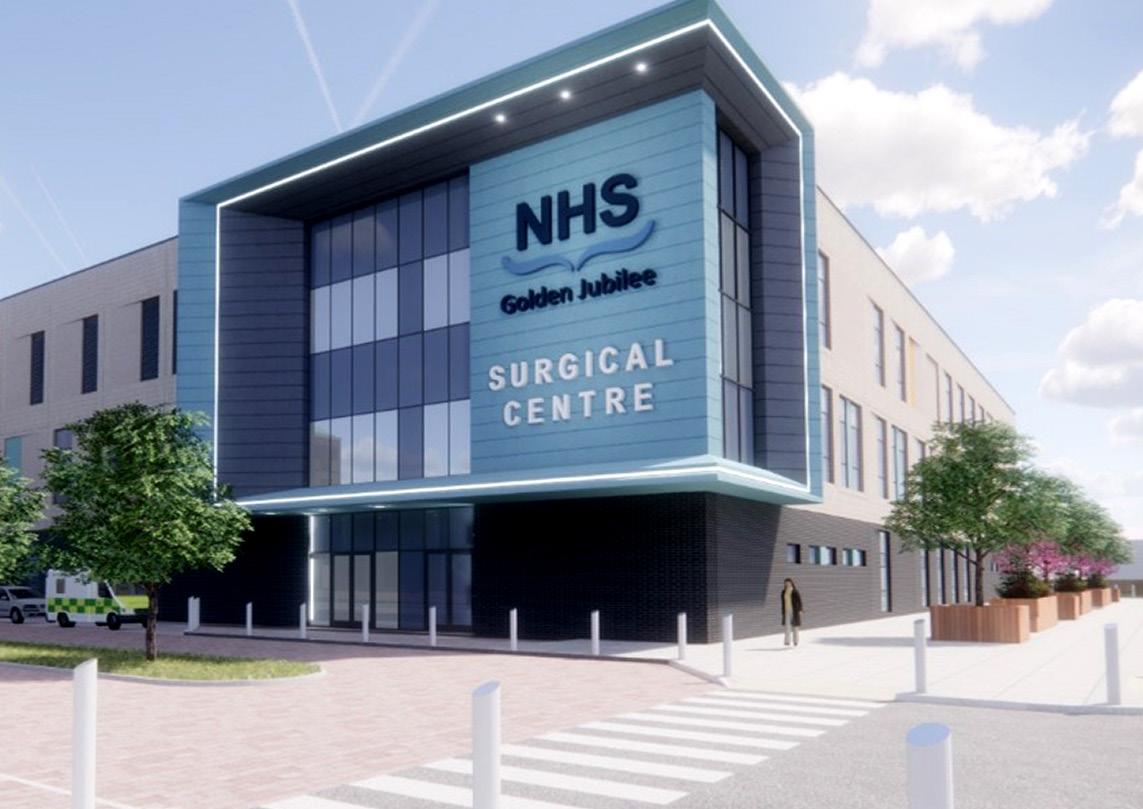
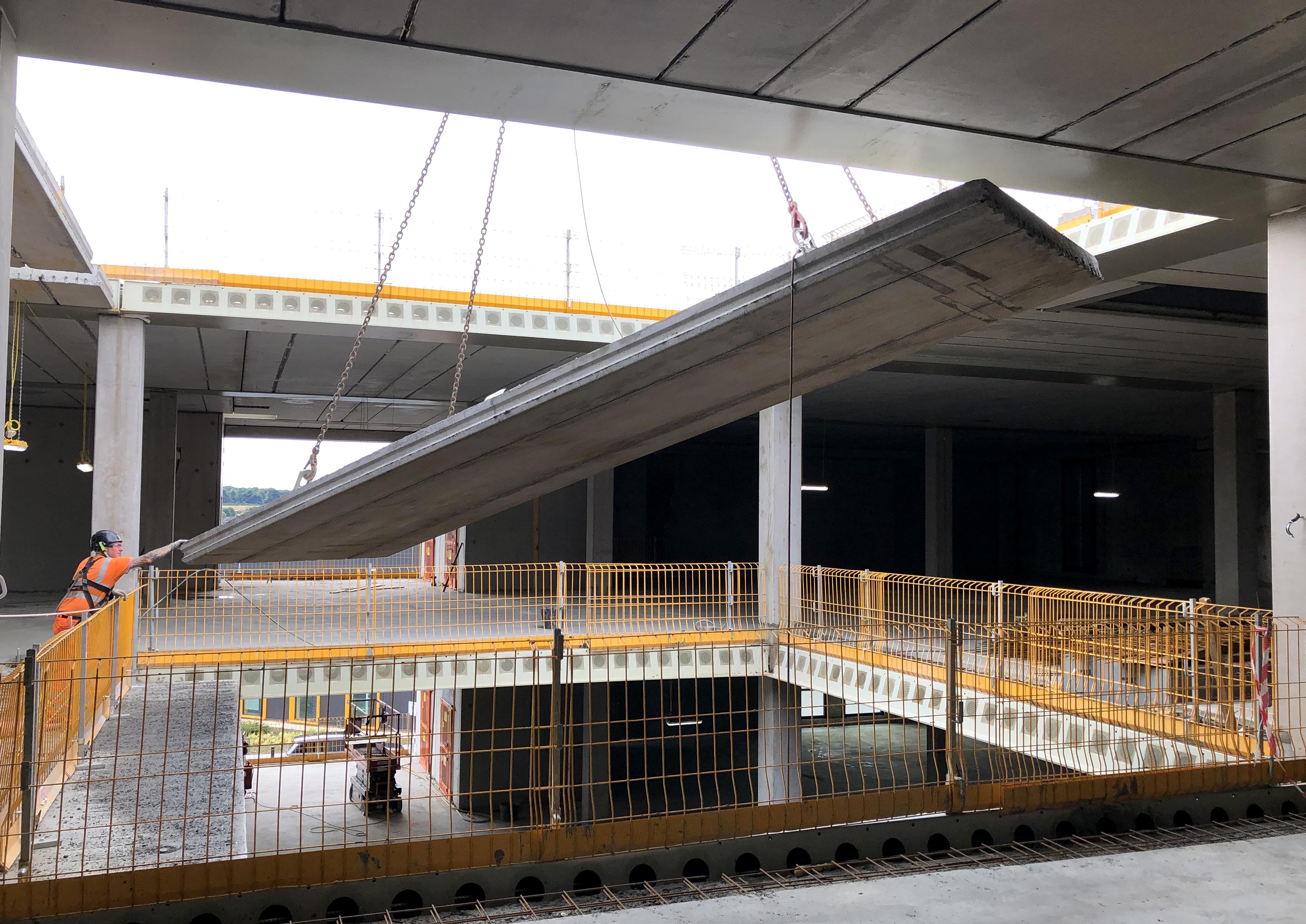
INTRODUCTION
As part of the Scottish Government’s investment of £200 million to meet demand for elective procedures during the 2020’s, the NHS Golden Jubilee Foundation, responsible for Glasgow’s Golden Jubilee hospital, created a business plan to expand its services so that it could treat more patients than ever before.
Phase Two of the Foundation’s plan was the delivery of a new three-storey building to form a Surgical Centre extension providing additional operating theatres for orthopaedic surgery, a day case surgery admission unit, an outpatient pre-operative assessment area, diagnostic space and supporting accommodation.
The original Stage 3 design intent was for a posttensioned in-situ concrete structure with traditional brickwork façade. However, Kier Construction Scotland, who were appointed as Main Contractor, quickly considered how the scheme could be improved through the incorporation of Modern Methods of Construction (MMC) approach.
The use of MMC techniques enable the development of construction that meet the NHS Health Technical Memoranda (HTMs). HTMs give comprehensive advice and guidance on the design, installation, and operation of specialised building and engineering technology used
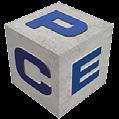
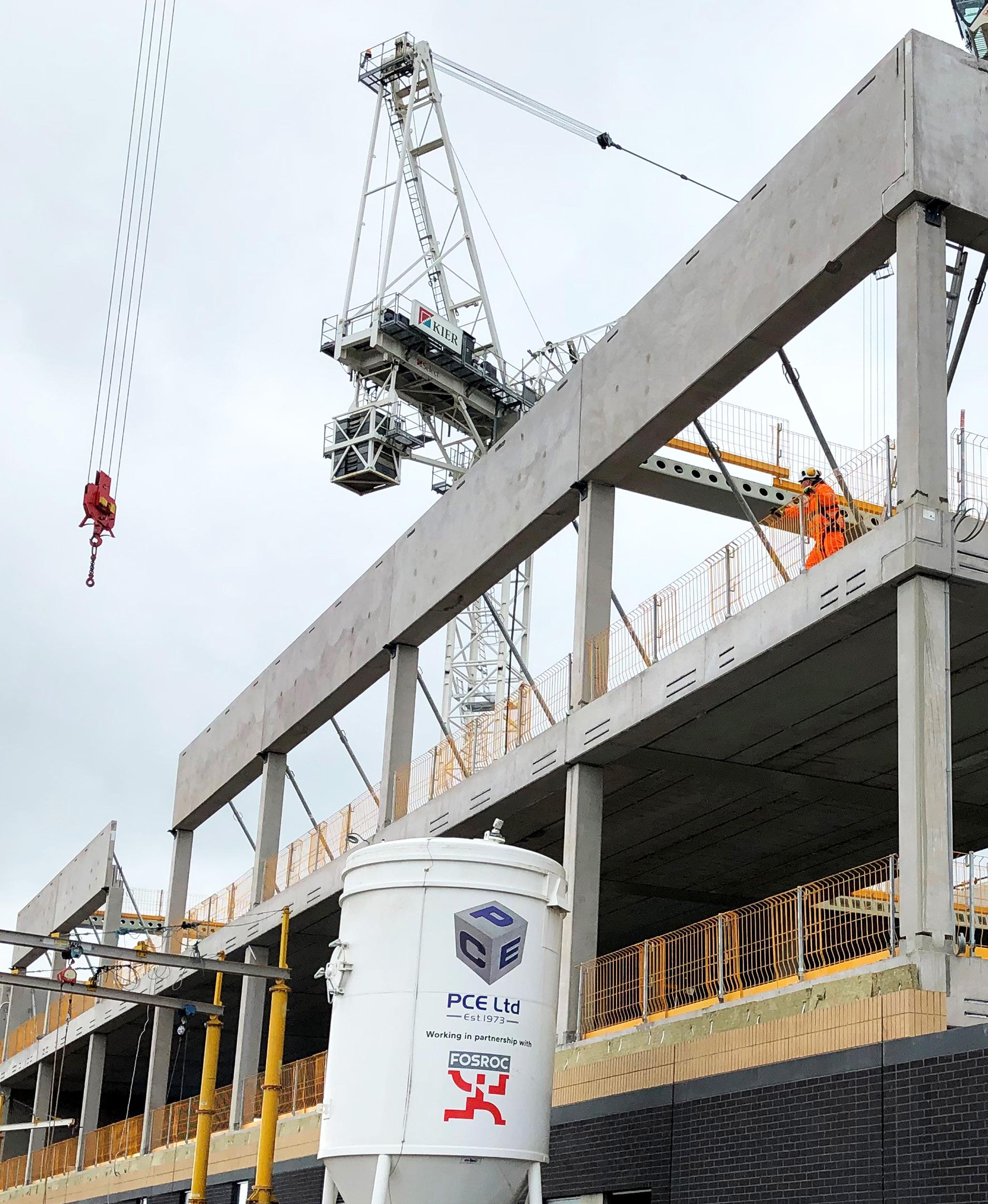
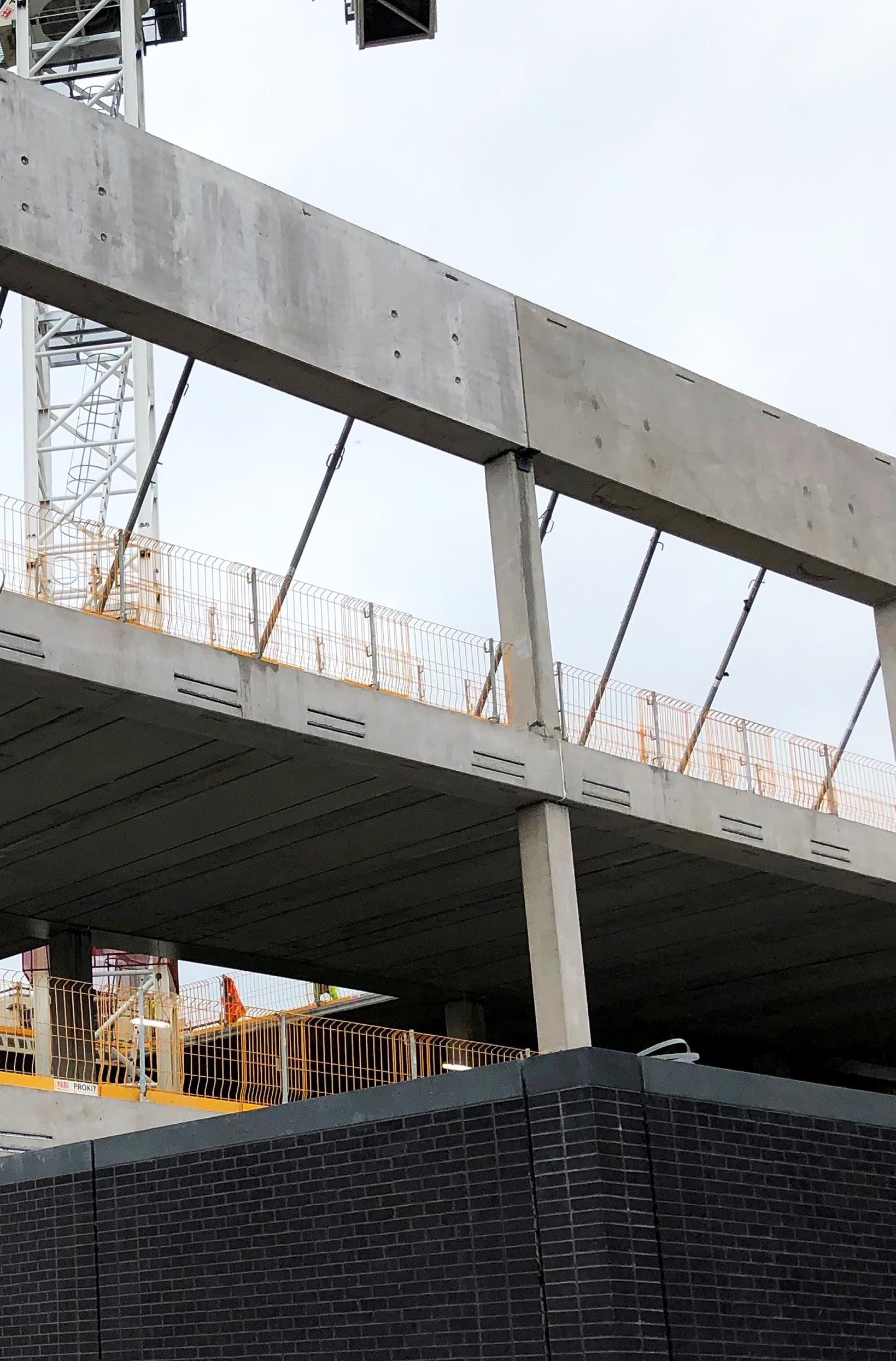
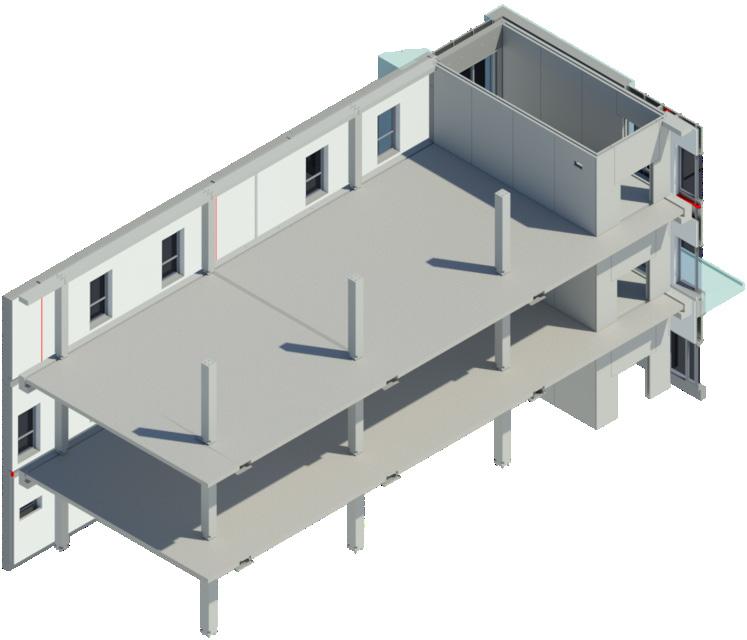
in the delivery of healthcare projects. With design drivers accommodating differing uses such as clinical wards, theatres, M&E plant, etc, a flexible structural grid approach can be achieved allowing for future changes. The use of digital techniques in the design and build, as well as subsequent building use, is paramount as is ensuring the best sustainable options, especially with reduction in carbon footprint and achieving Net Zero Carbon as the NHS has now committed to completely eradicating its Core Carbon Footprint by 2040.
PROJECT OVERVIEW
Kier Construction Scotland approached PCE Ltd to develop and deliver a design and build scheme using PCE’s innovative HybriDfMA Frame System. Use of the system solution would ensure an accurate replication of the layout, performance characteristics, and usage flexibility of the original Stage 3 post tensioned in-situ design, including a modular non-loadbearing brick faced precast concrete panel façade, whilst incorporating the added benefits of a reliable and predictable modular ‘kit of parts’ approach to MMC delivery. The revised approach accepted by the client and delivered by PCE resulted in structural completion in just 15 weeks, 12 weeks faster than the original in-situ strategy.
The Surgical Centre extension was to be built adjacent to the existing, fully functional hospital building, with all site deliveries required to pass through the hospitals existing ground level car park. The build location was also close to a nearby housing estate. Whilst PCE’s system solution adds significant value in terms of speed and scale, it also brings standout logistical benefits. For the Golden Jubilee project, this resulted in around 350 fewer site deliveries, thus reducing both noise and dust disturbance. Further, the reduced onsite workforce and programme reduction saved over 50,000 on-site operative hours. Such benefits were particularly pertinent not just to the client, but to hospital users and the neighbouring residents, given the sites close proximity. It also helped provide a lower carbon footprint when compared to traditional construction methods.
Integrating a modular offsite manufactured façade solution, which was assembled on site concurrently with the frame, was just another aspect of the well-developed construction impact mitigation strategy. It resulted in the removal of activities and trades from site. This ensured increased commercial and operational efficiencies, whilst maintaining unhindered functioning of the existing hospital. The modular façade approach was developed with the architects to allow the delivery of ‘large format’ precast concrete cladding panels. These panels encompassed the brick and decorative concrete finishes, as well as a pre-installed glazing system fitted at the factory prior to delivery of the façade panels to site.
A requirement of the suspended floor construction was to ensure that a low vibration susceptibility would be achieved due to the sensitive equipment within the operating theatres. PCE’s experience and expertise across the healthcare and bioscience sectors would ensure it was well equipped to design and deliver a structure that reliably and consistently adhered to all requisite performance requirements.
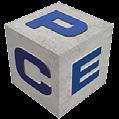
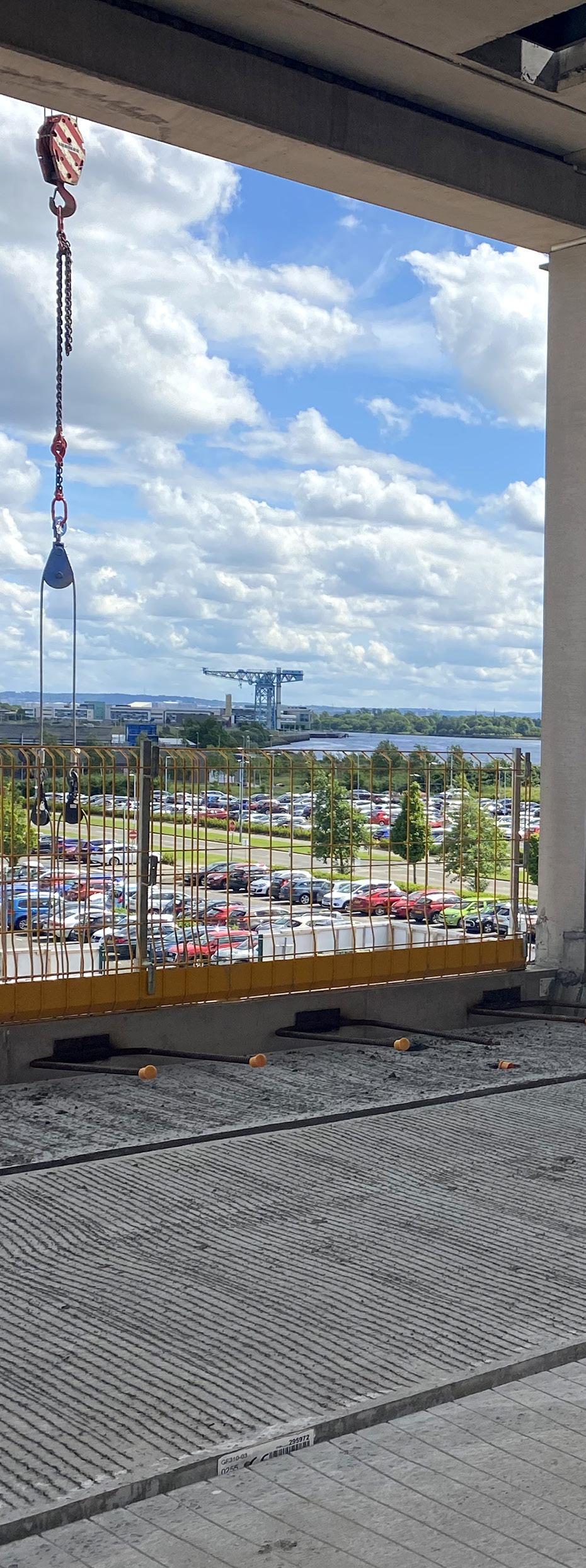
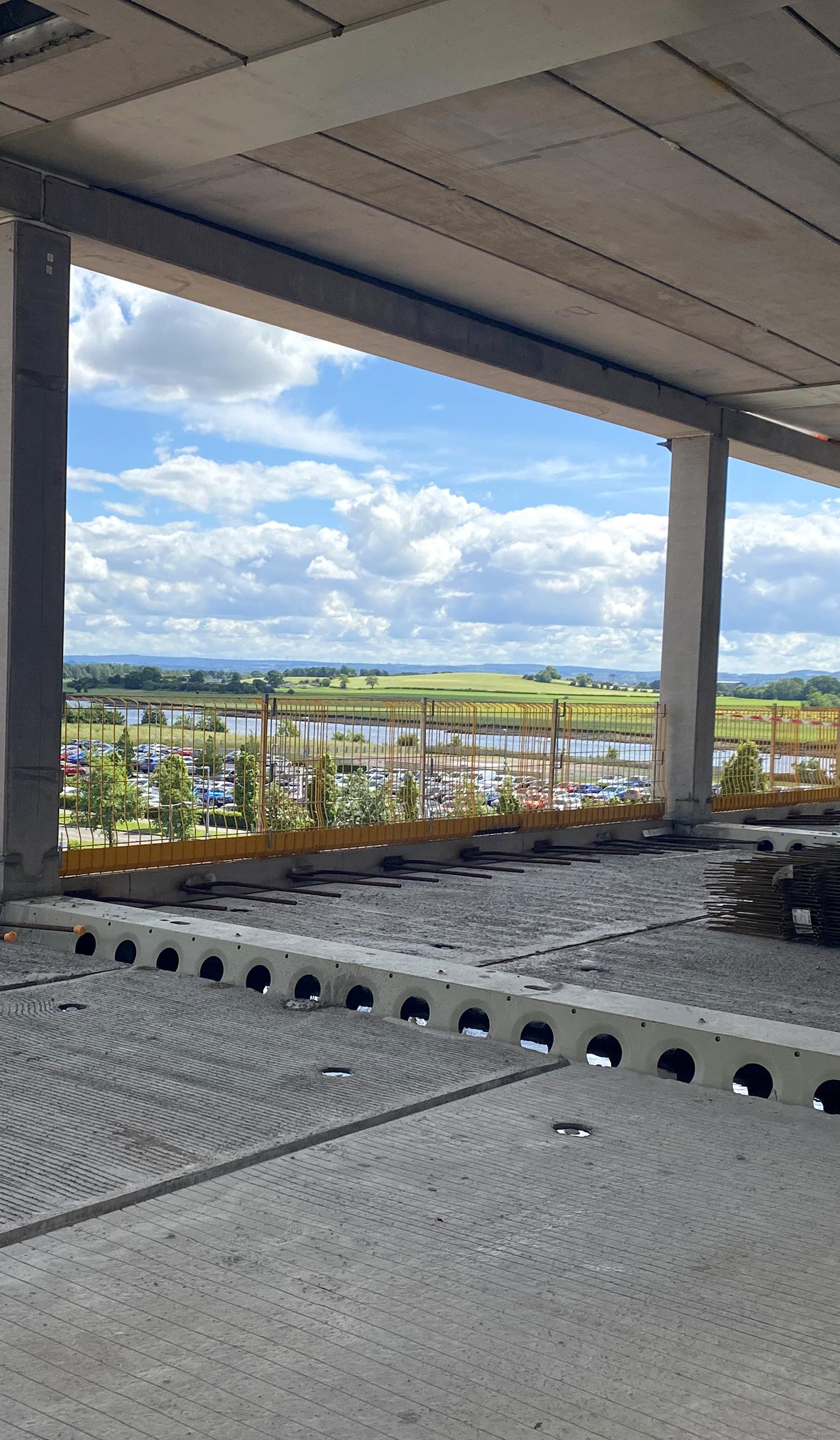
PROJECT VALUE
CLIENT
MAIN CONTRACTOR
ARCHITECT
CONSULTING ENGINEERS
COST CONSTULTANT
M&E ENGINEERS
PCE LTD PROJECT MANAGER
£36m
Golden Jubilee Foundation
Kier Construction Scotland IBI Group
Curtins Glasgow AECOM
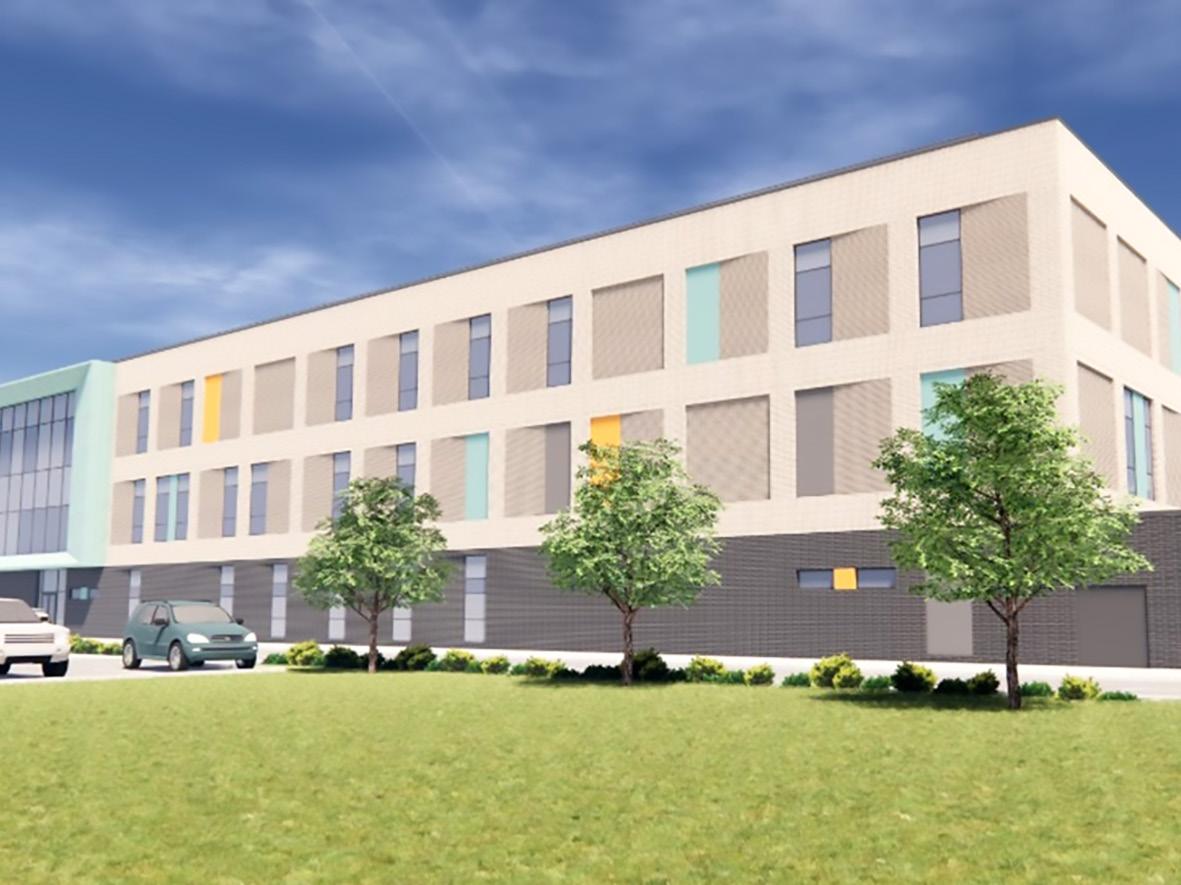
TUV SUD & NG Bailey
Adam Clarke
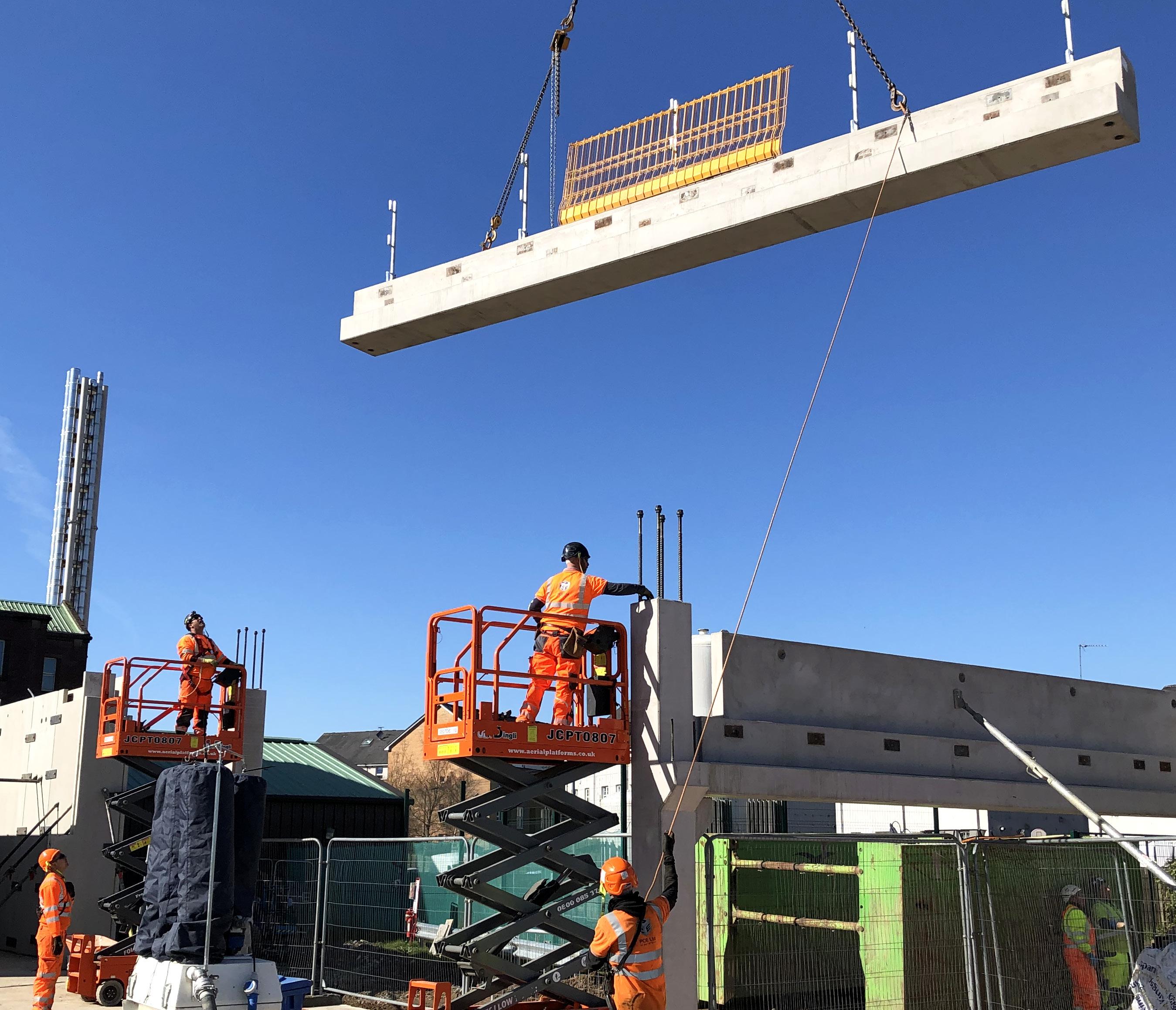
BUILDING
The three-storey building area of 3,500m2. The structural and a 400mm structural to interface with the existing precision engineering 50mm between where
The use of composite construction prestressed concrete floor beam downstands. With soffits, the fixing of M&E any desired subsequent with greater ease and with precast stairs and stability by distributing and provided safe access Other precast concrete core capping units, ancillary
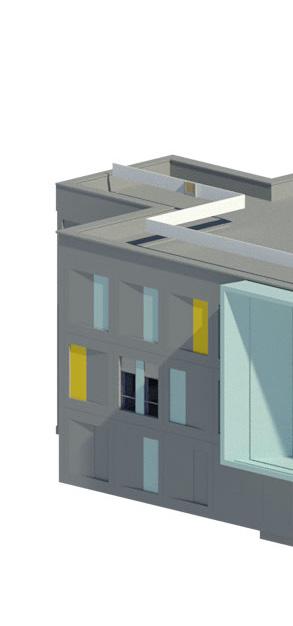
BUILDING DETAILS
building has a suspended floor and roof area of 7,650m2 and a façade structural arrangement was based on a standardized 8.4m2 grid structural floor zone. The 4.5m storey height allowed the new building existing hospital without the need for steps and ramps. PCE’s and installation accuracy was evidenced, with a gap of just the new structure interfaced with the existing one.
construction concrete/steel Deltabeams supporting precast floor units gave a flat soffit for the floor plate, resulting in no With the precast floor components having channels cast into their M&E services was simplified and made faster. This will also allow subsequent change of use requirements in the future to be achieved efficiency. Precast concrete twinwall components, together and landings, form the lift and stair cores. This gives the building distributing lateral forces back to the ground floor slab and foundations, access and egress for site personnel during the assembly phase. concrete components include columns, edge beams, parapet beams, lift ancillary walls, and roof plinths to take the M&E plant.
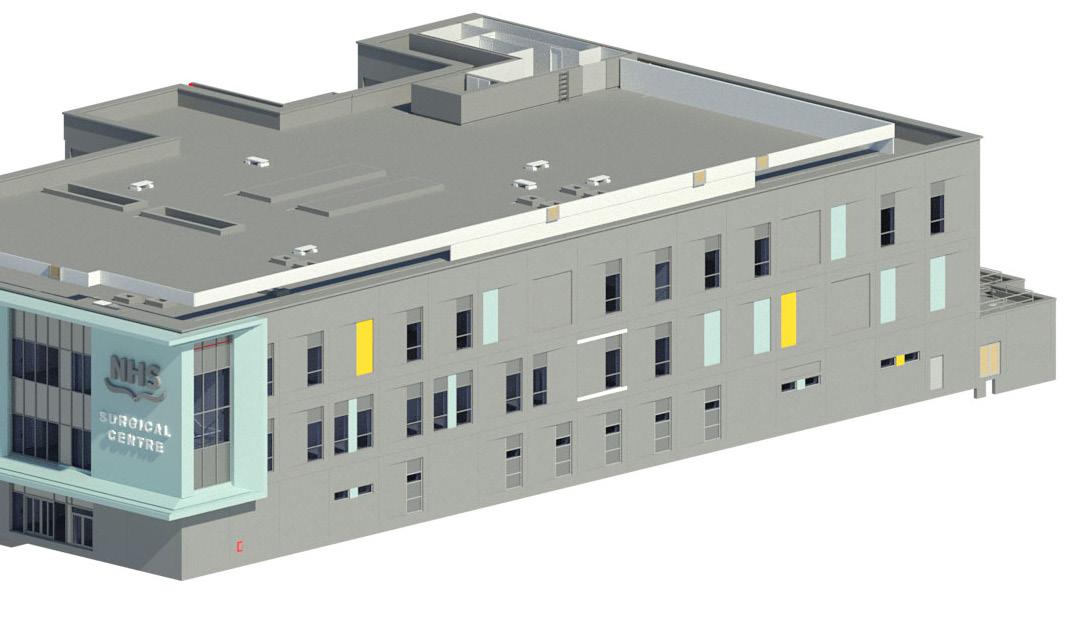
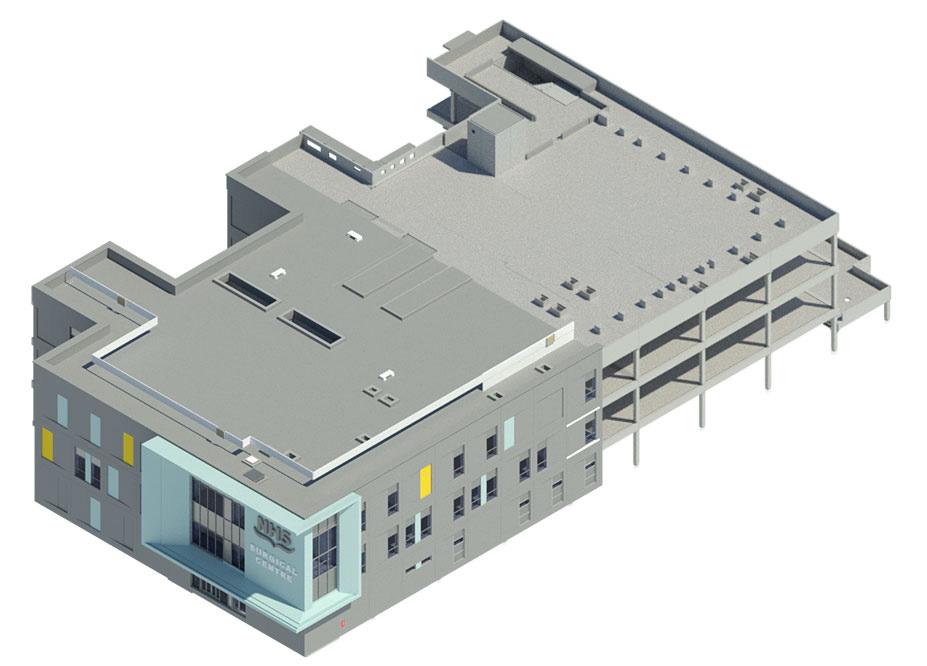
A total of 1,184 structural components were manufactured offsite in quality-controlled factory environments. In addition, a total volume of 1,350m3 of in-situ reinforced concrete was also used.
To clad the structure, a further 177 offsite manufactured façade panels were produced. These components used Himley black wirecut dragfaced facing brick between ground and first floor level, with Sandlewood wirecut dragfaced facing brick for the upper two levels, with units having complementing reconstructed stone bandings and mullions as required. During the design process the façade units were maximised in line with the lifting capacities of the projects two CTL430 tower cranes, together with the structural grid and storey height. This minimised the number of external joints, the resulting panel dimensions being up to 4.5m high, with a maximum weight of 16.13tonnes. All glazing and louvre units were installed at the façade panel manufacturers factory prior to delivery, saving time, the need for external access to the envelope, whilst reducing the number of people working on site.
SITE LOCATION
Golden Jubilee Hospital is located in Clydebank, near Glasgow, Scotland. Phase Two is located at the North-East corner of the original existing hospital complex.
Golden Jubilee National Hospital, Agamemnon St, Clydebank, G81 4DY
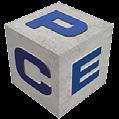
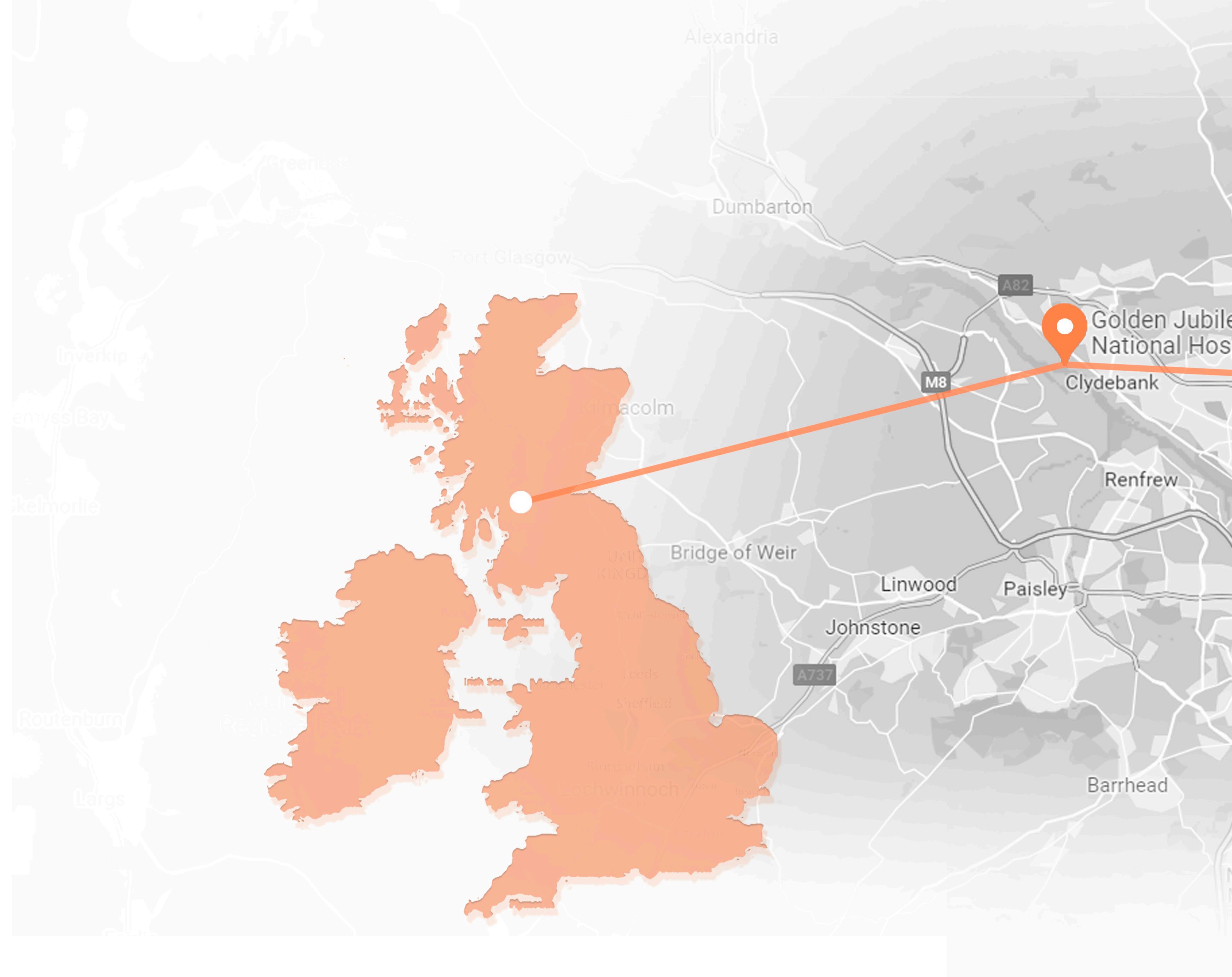
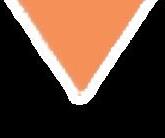
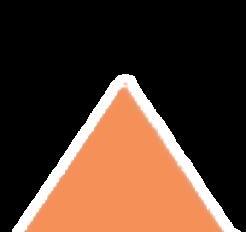
Hospital grounds
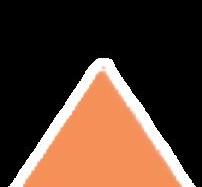
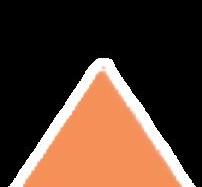
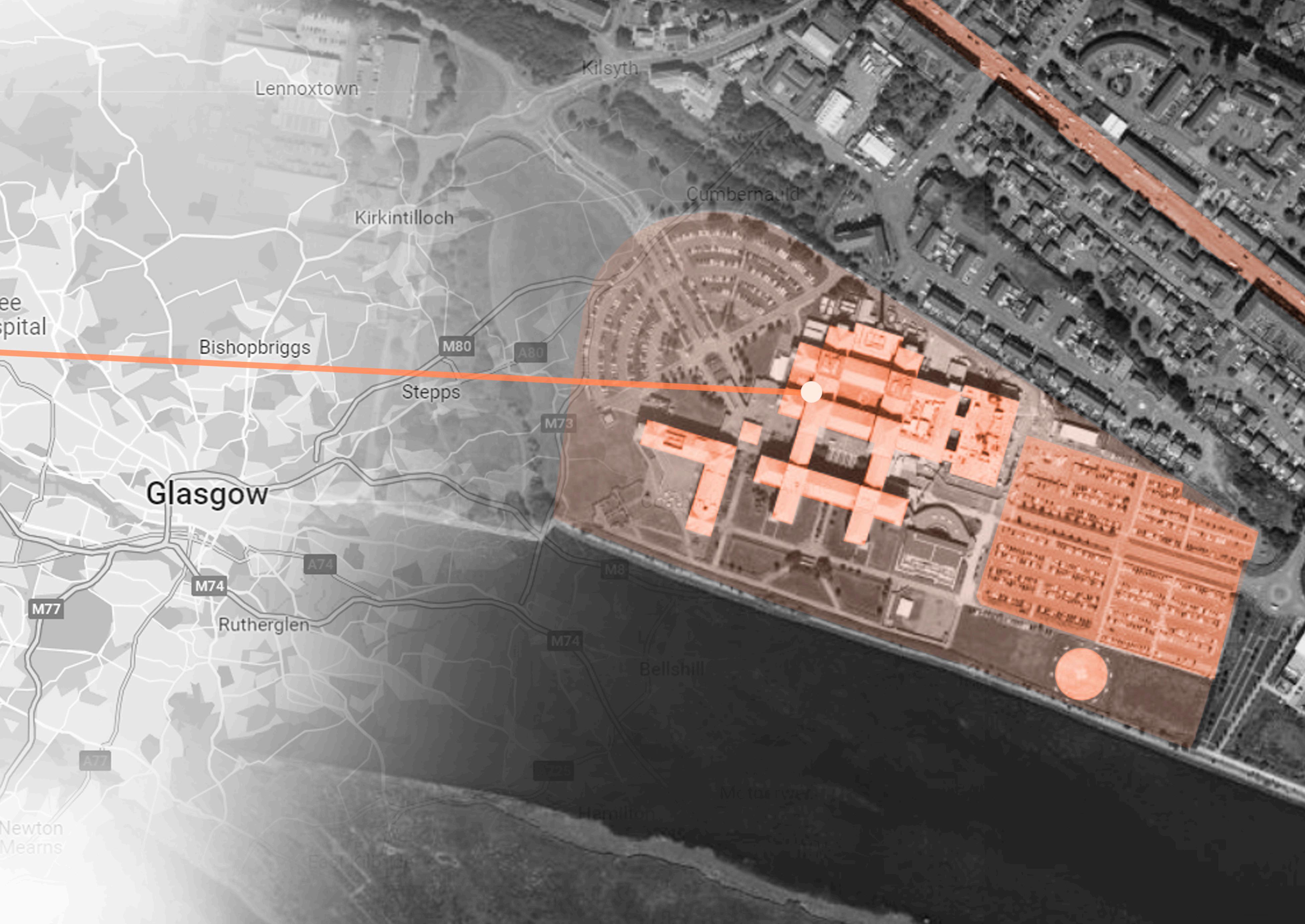
buildings
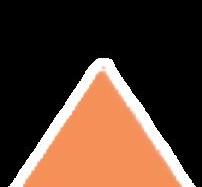
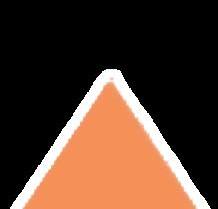
Operational hospital heli-pad
A814
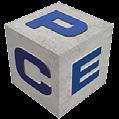
STRUCTURAL COMPONENTS
Precast Square Column
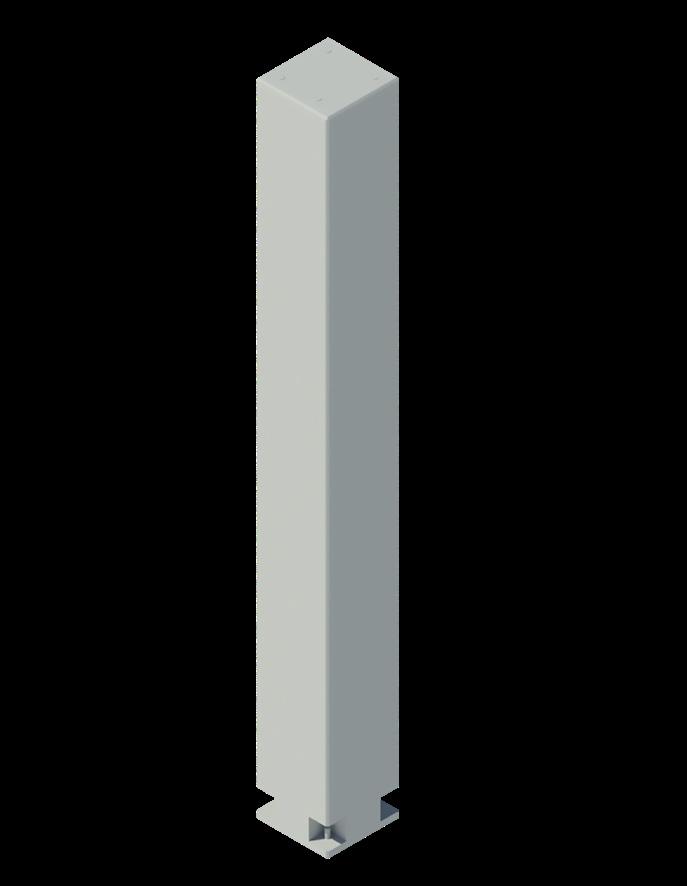
Precast concrete Columns were a key part of the structural frame design adopted.
Deltabeam Stair and Lift Cores
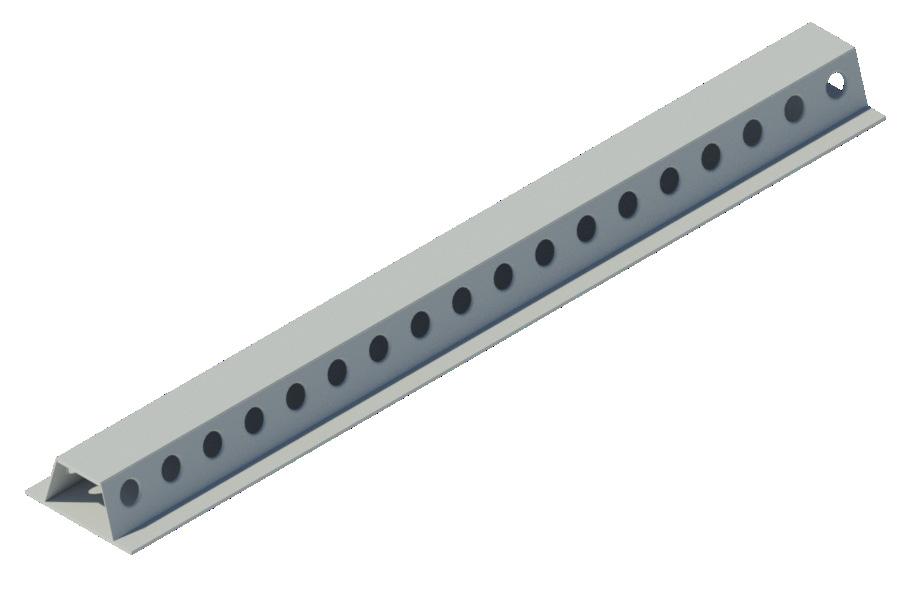
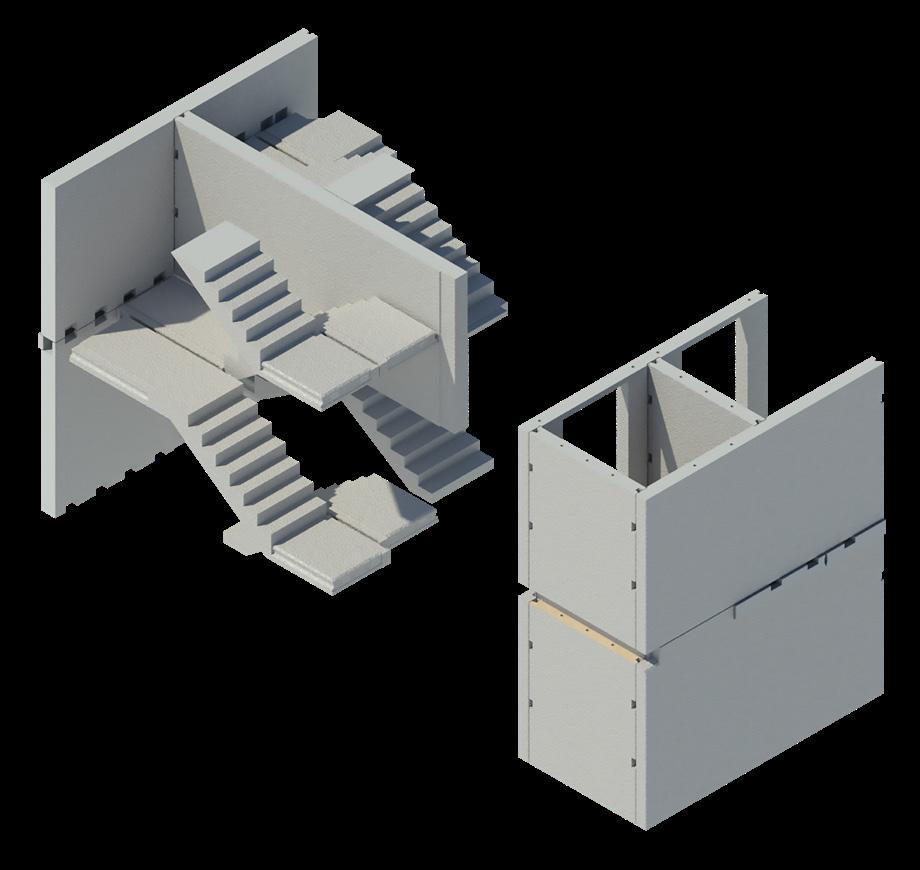
Deltabeams used compositely with reinforced structural concrete to support the floor structure without any down stands.
Providing Stair and Lift Core Units as well as frame stability.
PCE developed a business structural system philosophy built around the selection of interchangeable ‘kit of parts’. Each component’s smart connectivity allows it to ‘plug into’ the next to create the complete structure. The Frame System ‘kit of parts’ consists of just six common components; square column, Deltatbeam, pre-stressed floor units, stair/lift cores, edge beam and a non-structural facade panel.
Precast Edge Beam
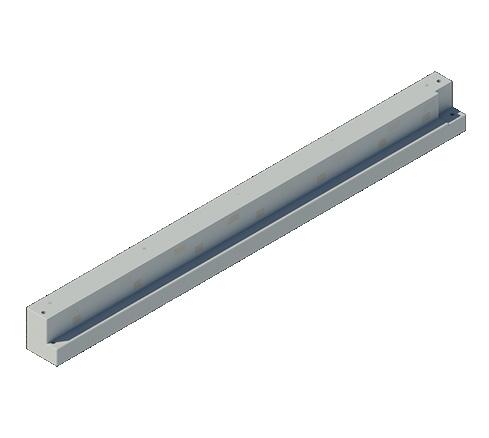
Precast Concrete Edge Beams were used to simplify interfaces with the façade whilst efficiently controlling deflection limits.
Pre-stressed Floor Unit Non-Structural Facade Panel
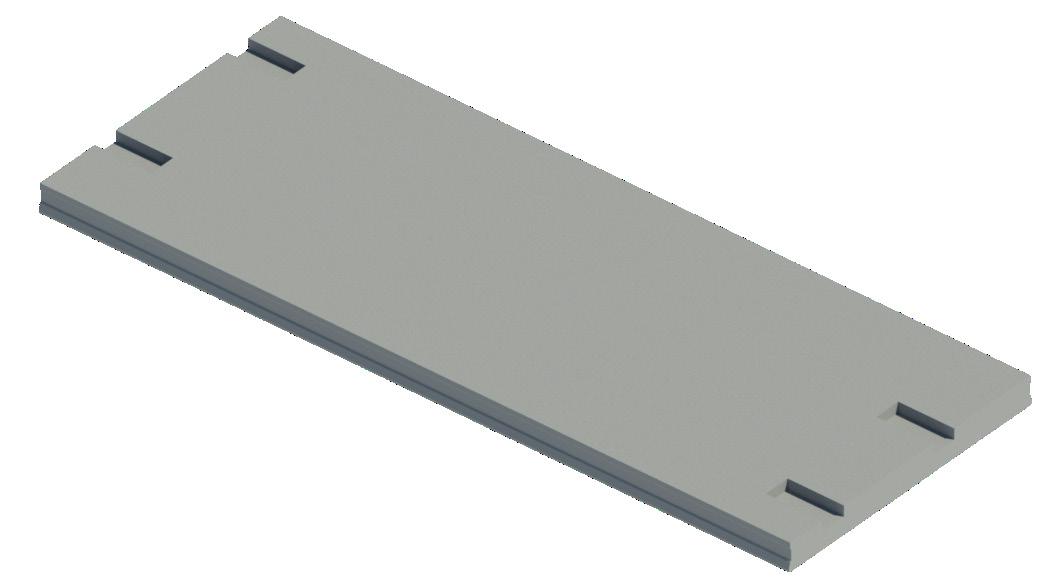
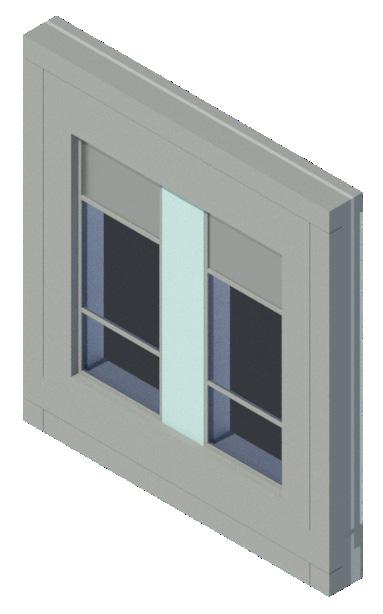
200mm deep pre-stressed concrete Floor Units, designed to work compositely with the 200mm deep reinforced structural topping.
Offsite constructed external pre-glazed panels with brick finish.
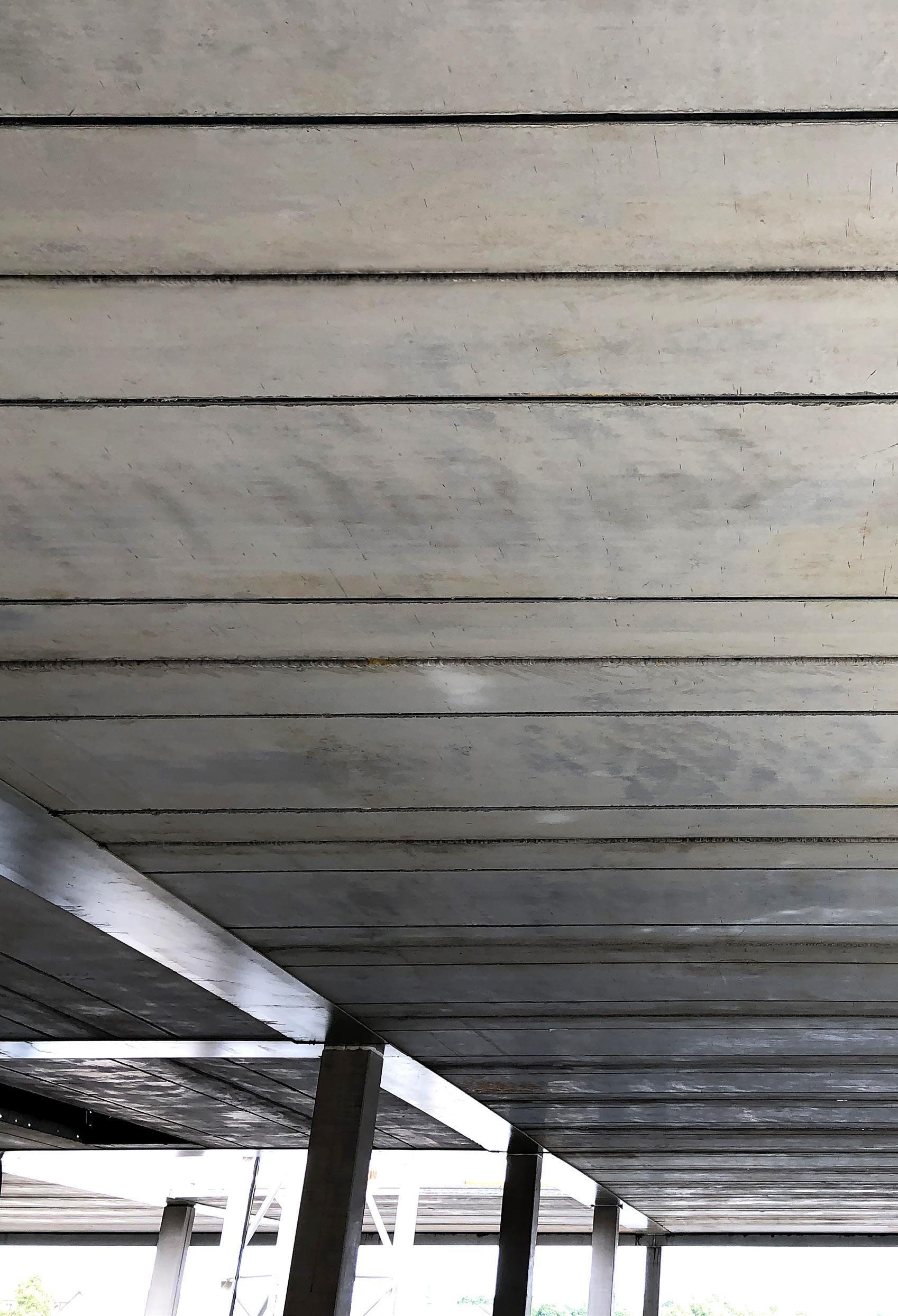
LOW VIBRATION FLOORPLATES
It was of particular importance in the design process to ensure that the floor areas of the operating theatres had a very low susceptibility to vibration, due to the sensitive equipment that would be used within them. The suspended floors had to achieve a vibration response factor of no more than 1.0.
Capitalising on its pervious experience and success across the healthcare and biosciences sectors, where such requirements are frequent, PCE ensured it’s HybriDfMA Frame system solution catered unequivocally for the required technical performance of the structure. The resultant floor plate design resulted in reinforced precast concrete edge beams and internal composite concrete/steel Deltabeams supporting 200mm deep solid prestressed concrete floor units acting compositely with 200mm of insitu reinforced concrete topping.
To prove the exceptionally low vibration requirements had been met, a fullscale test of the dynamic properties of one of the floors after construction was carried out using an array of shakers and accelerometers, coupled with specialist software. The results clearly showed that the PCE HybriDfMA Frames System solution adopted gave a much stiffer floor plate than predicted using typical conservative design assumptions.
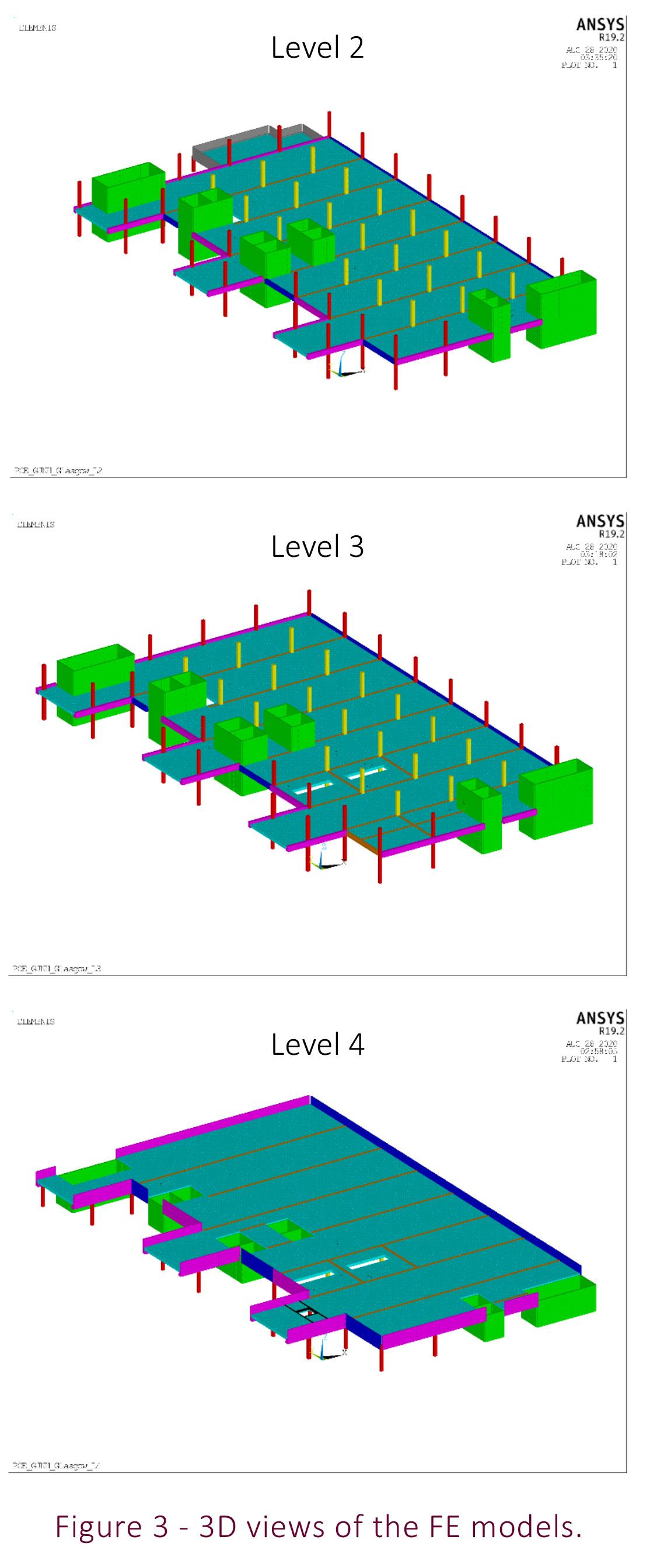
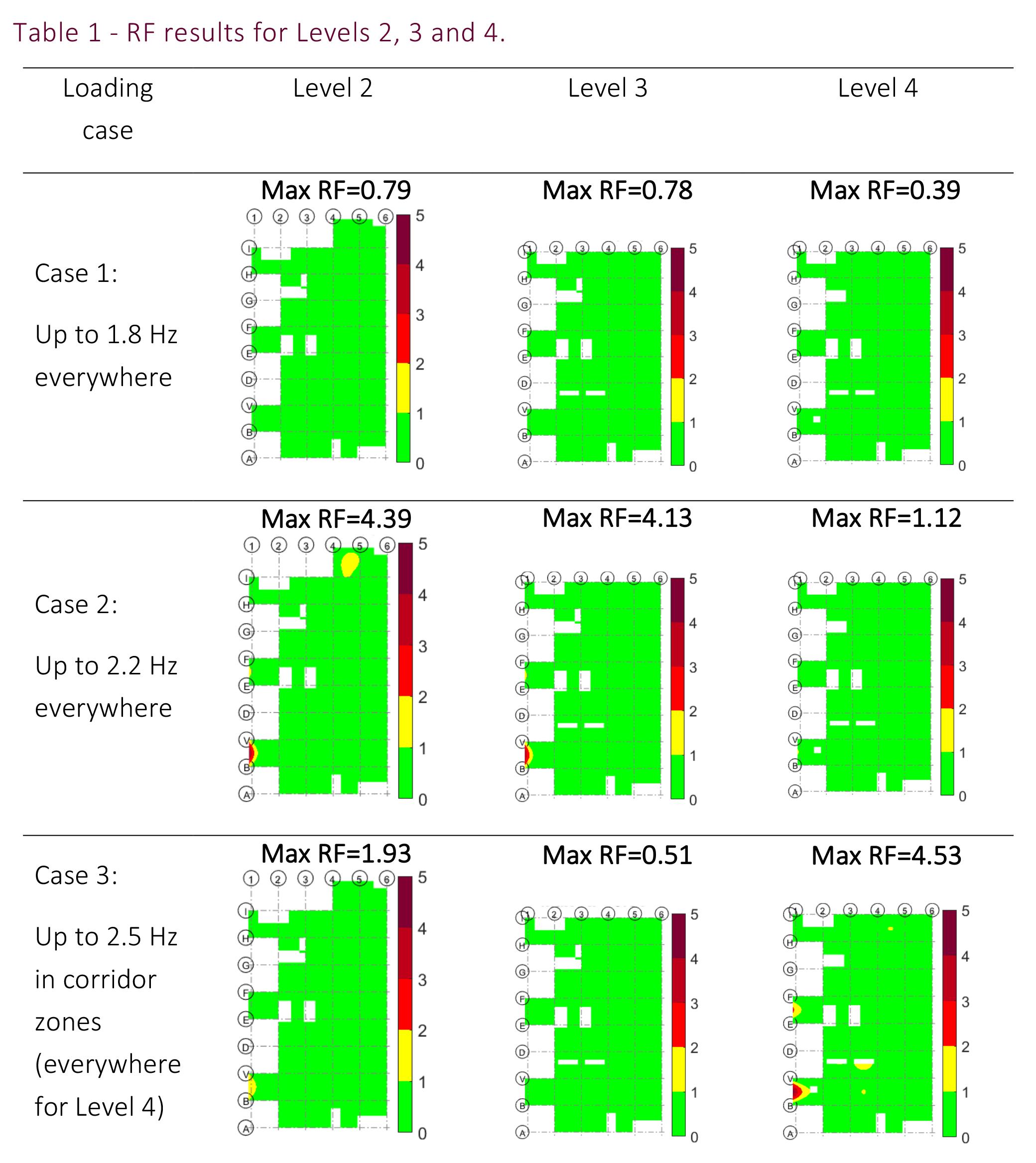
OFFSITE MANUFACTURE
The superstructure and façade components were configured as a ‘kit of parts’ and manufactured offsite at specialist factories across PCE’s supply chain. The project team, including the supply chain, collaborated to test and agree on the aesthetics, shape, and tolerances of the manufactured elements which set the benchmark for offsite manufacturing.
From there, PCE’s in house quality inspection team worked closely with the offsite supply chain manufacturers to ensure high quality and compliance of components produced, without exception. These robust quality systems and factory-controlled conditions guaranteed the highest levels of accuracy and consistency, ensuring the speed, efficiency and predictability of the assembly phase.
PCE’s flexible supply chain model enabled maximum utilisation of its supply partners strengths, whilst minimising any delivery risks through using multiple manufacturers. This was particularly important for the Golden Jubilee project as most of the manufacture occurred during the early stages of the Covid pandemic.
The offsite manufacture of the brick faced cladding panels also resulted in a 50% reduction of the total number of bricks required, compared to traditional masonry construction, as they were cut in half prior to casting into the face of the panels.
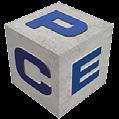
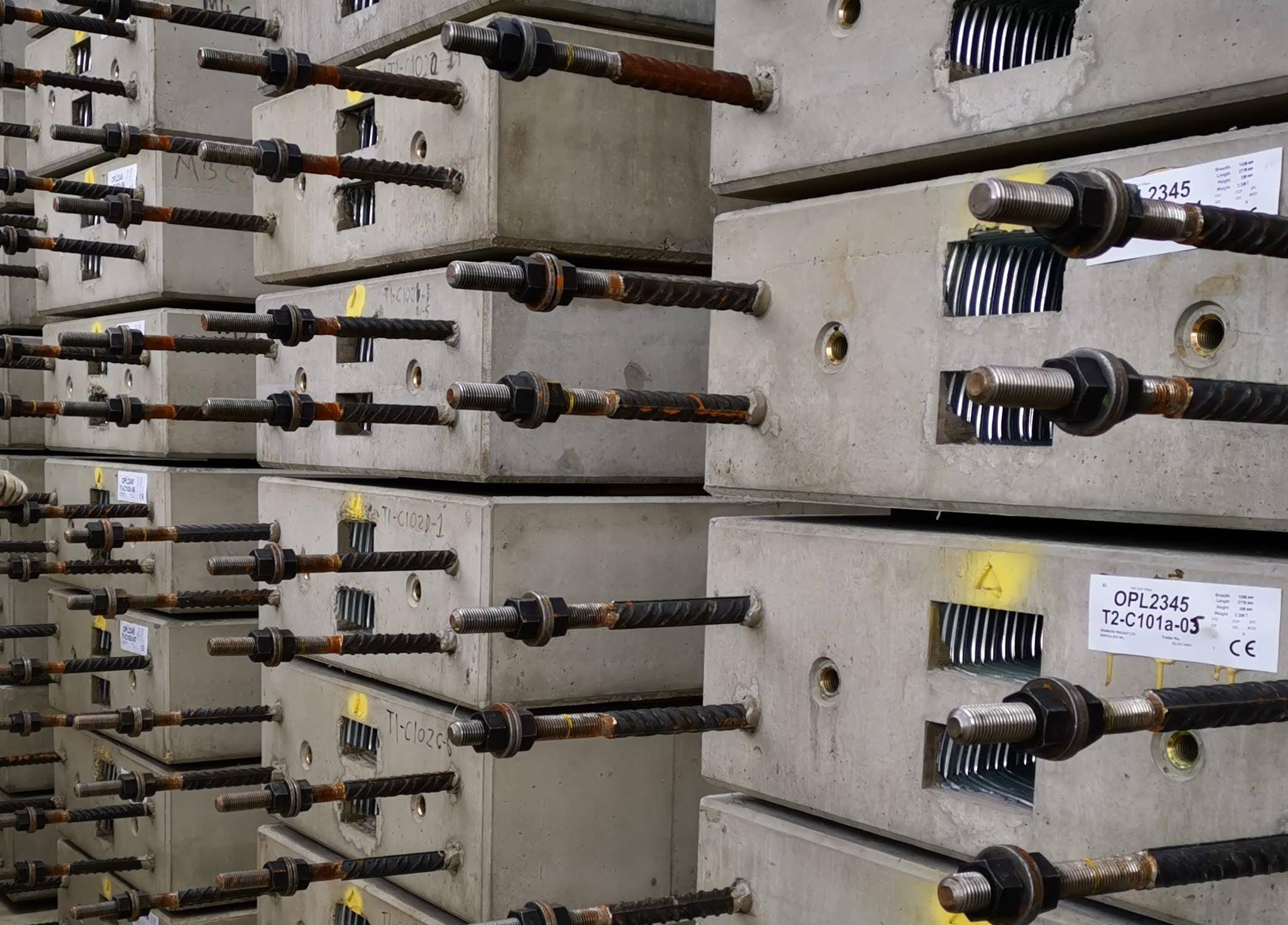
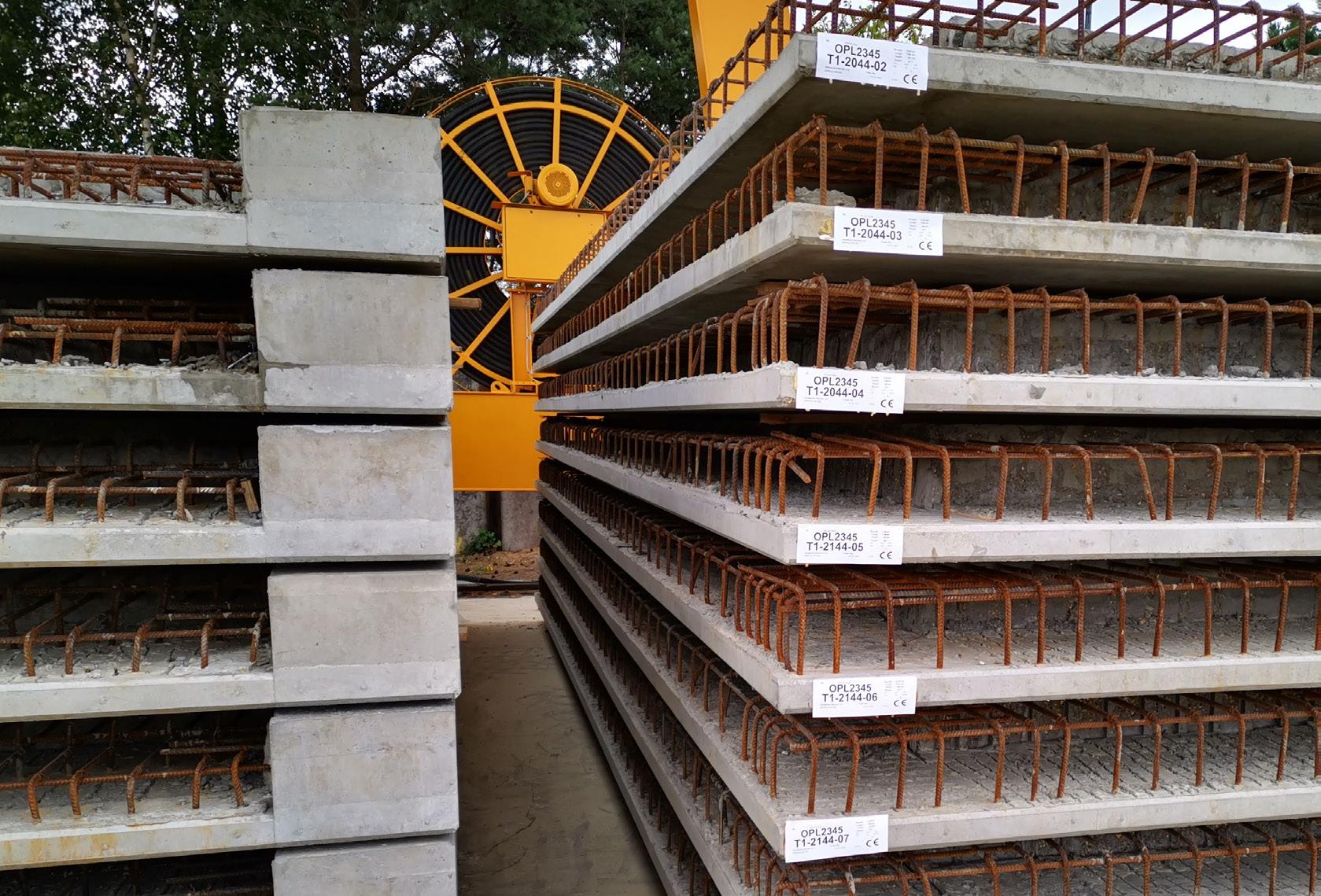
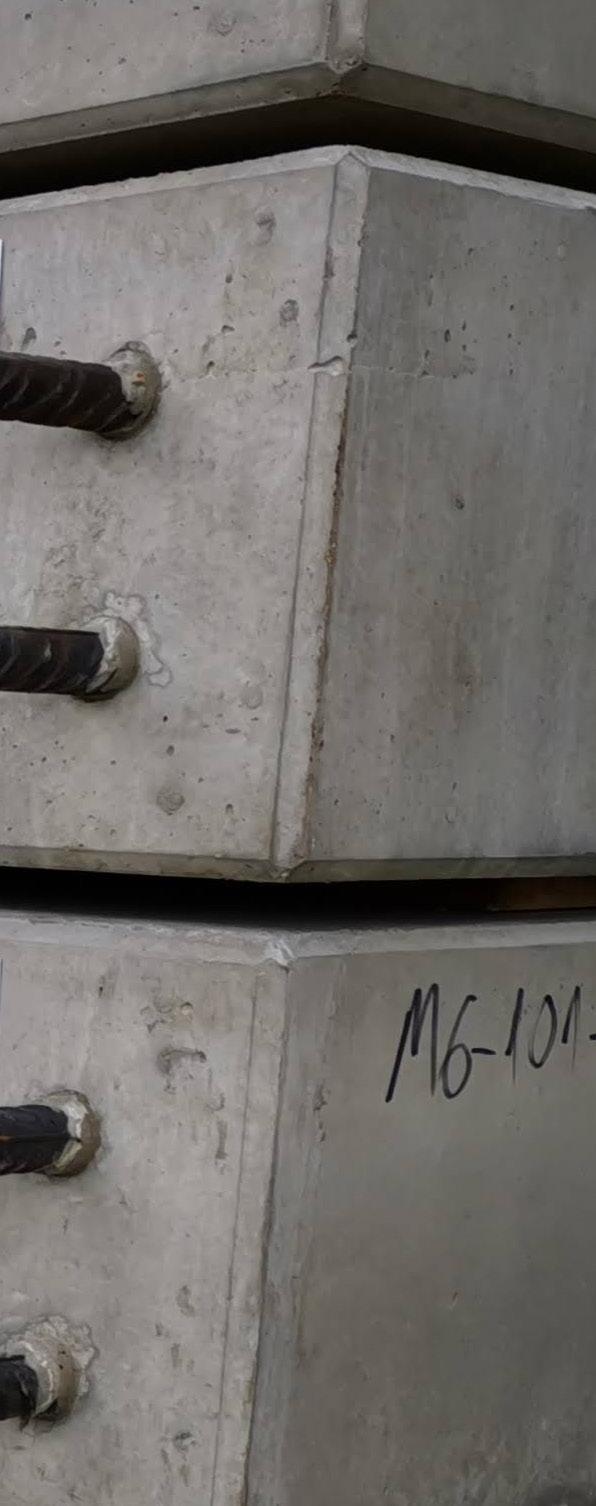
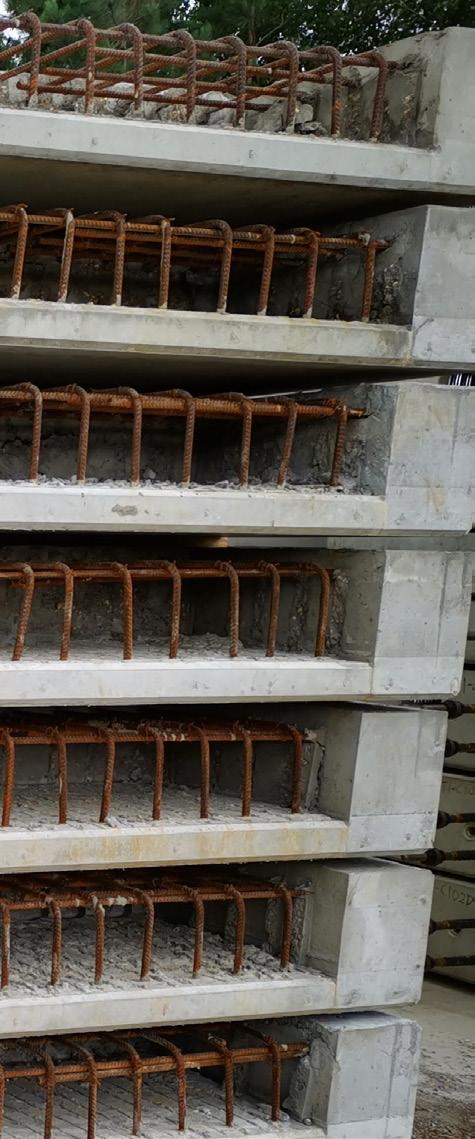

Golden Jubilee
National Hospital
SUPPLY CHAIN MAPPING
Central Rebar
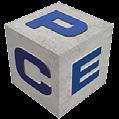
Techrete Loose Steel Rebar and Prefabricted Reinforcement Cages
Flood Precast
Pre-stressed Floor Units
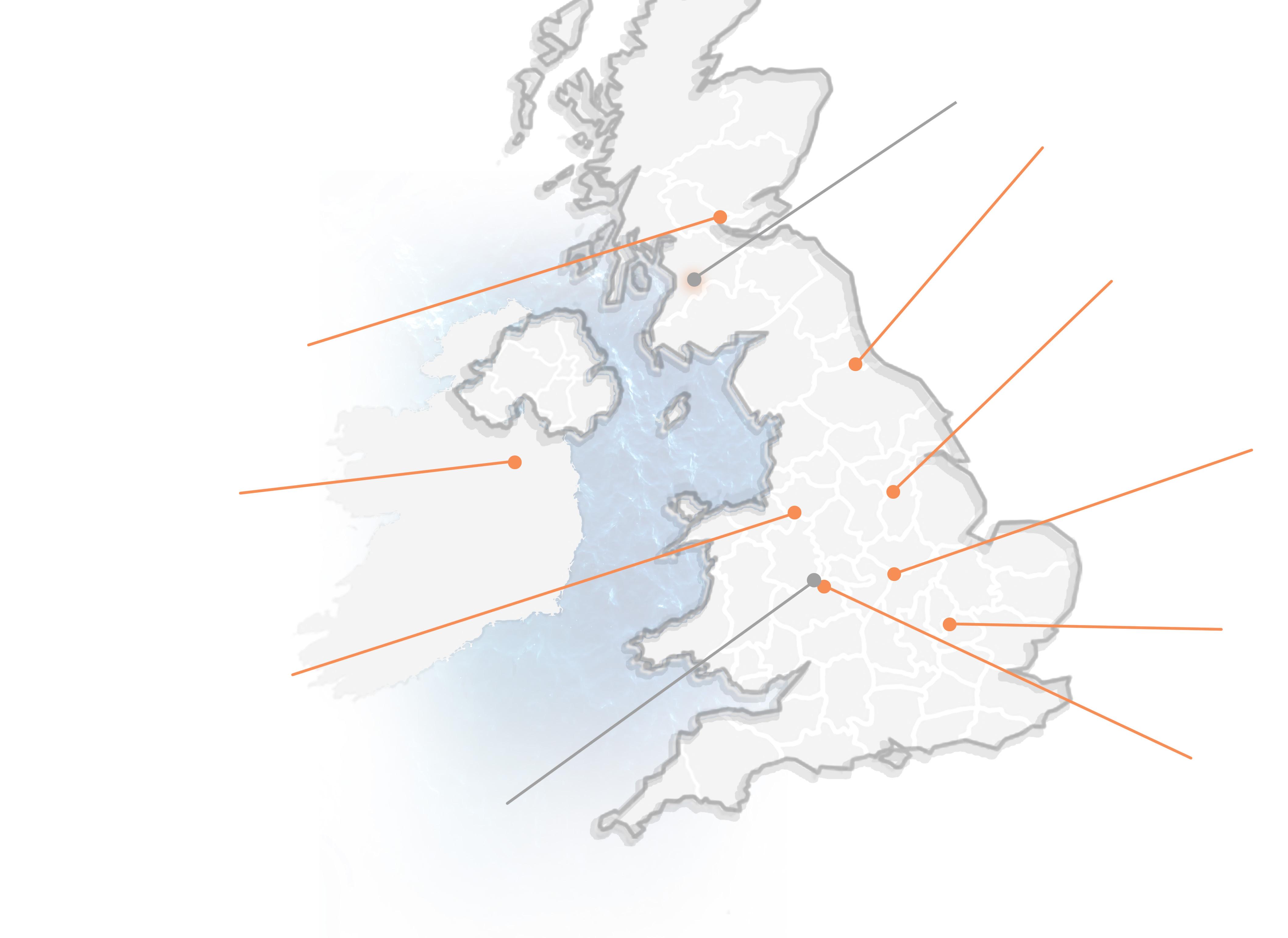
FP McCann
Columns, Beams, Stairs, Landings, Parapet Beams, Lift Capping Slabs, Roof Plinths, Ancillary Walls
PCE Head Office
Peikko
Harris Manufacturing
Twin-Walls
Deltabeams
Structural Steelwork
Ambar
RiserSafe
Techrete
Brick Faced
Cladding Panels
RiserSafe Modules
Manufacturing
Structural
Steelwork
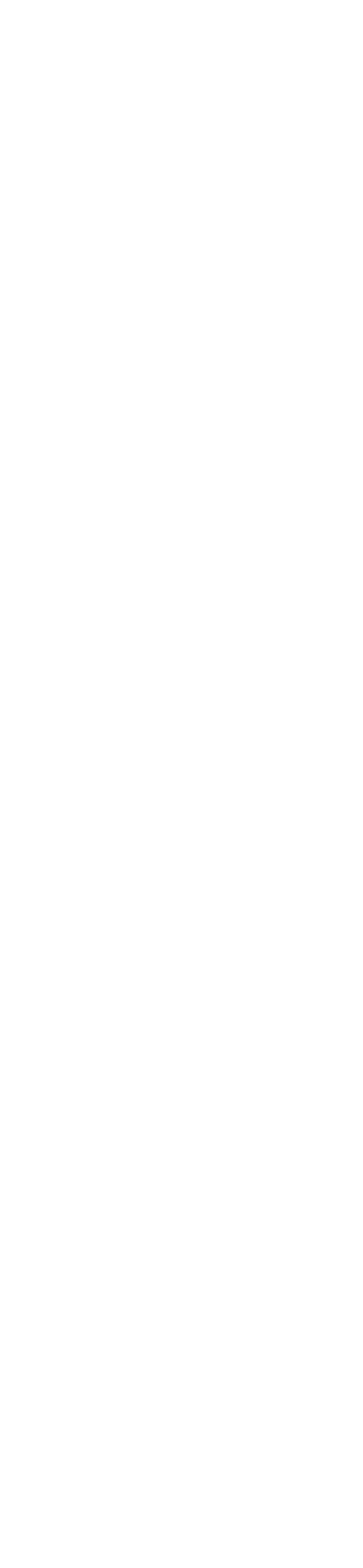
The 1,184 offsite manufactured components were produced in 8 different factories within the UK and Europe. Ready mixed concrete and reinforcement for the in-situ works was sourced locally to the project.
Pre-stressed Floor Unit
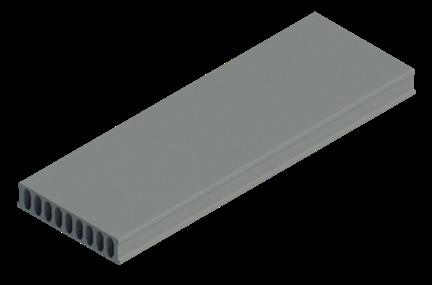
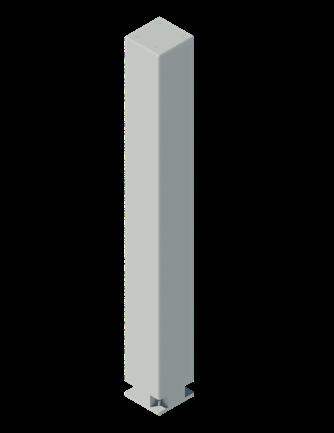
Stair and Lift Cores
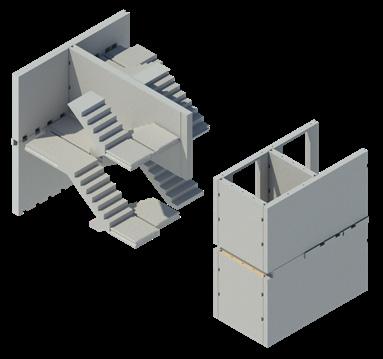
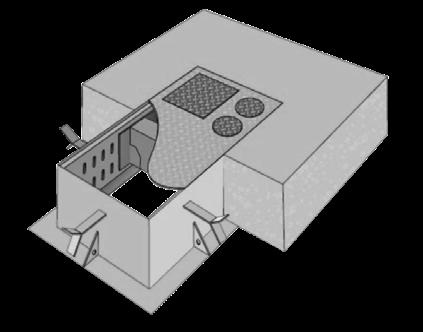
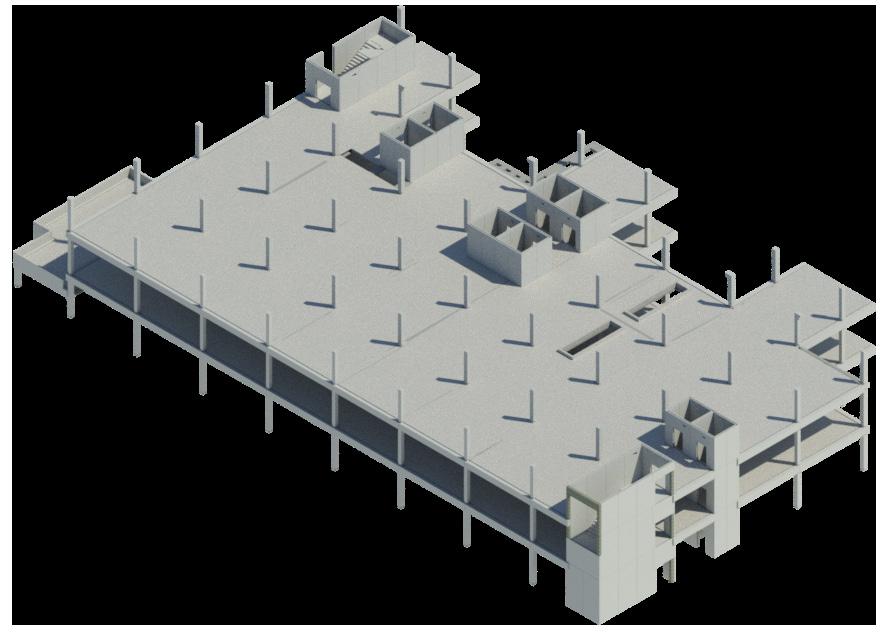
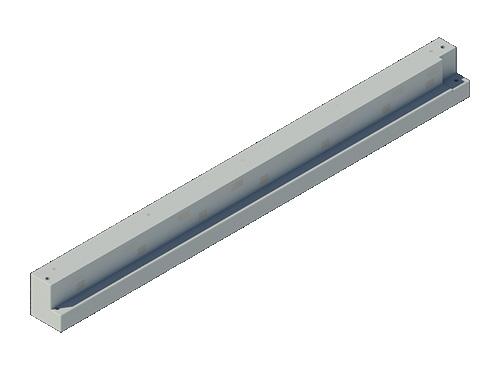
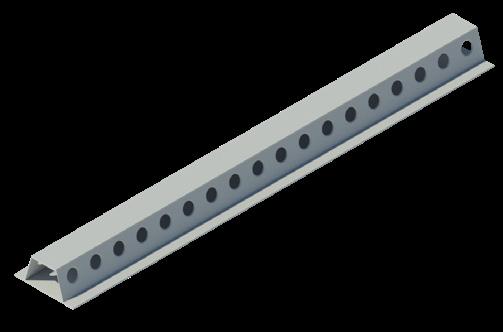
RiserSafe Module
Precast Square Column
Precast Edge Beam
Ambar Kelly
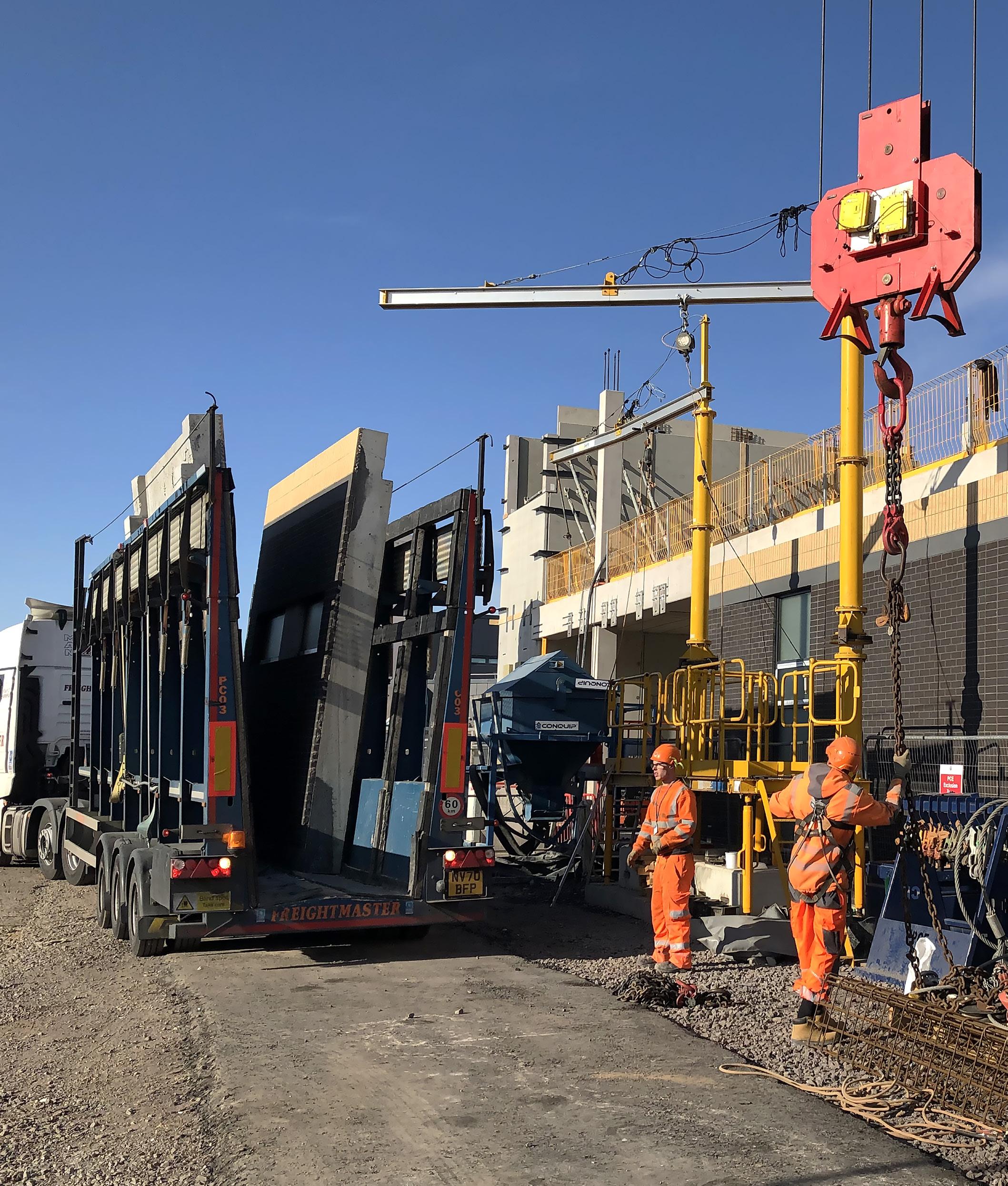
SITE LOGISTICS
PCE’s digitally coordinated, meticulously planned logistic schedules ensured timely, streamlined delivery of the 612 offsite manufactured components. Loads were scheduled and sequenced in such a way that facilitated efficient ‘just in time’ deliveries. Upon arrival to site, units were installed directly from delivery vehicles to their intended positions. This lean approach removed the need for site storage and double handling, saving on time and reducing the risk of damage in on-site transit.
The structure was assembled using two CTL 340 tower cranes carefully positioned within the building footprint of a confined site with a relatively small footprint. The efficiency enhancing nature of PCE’s HybriDfMA Frame System approach streamlined the project, improving logistics and onsite operations. It reduced the size of on-site workforce required and the number of delivery vehicle movements. This greatly reduced the potential of physical and noise disruption to other users of the Golden Jubilee Hospital.
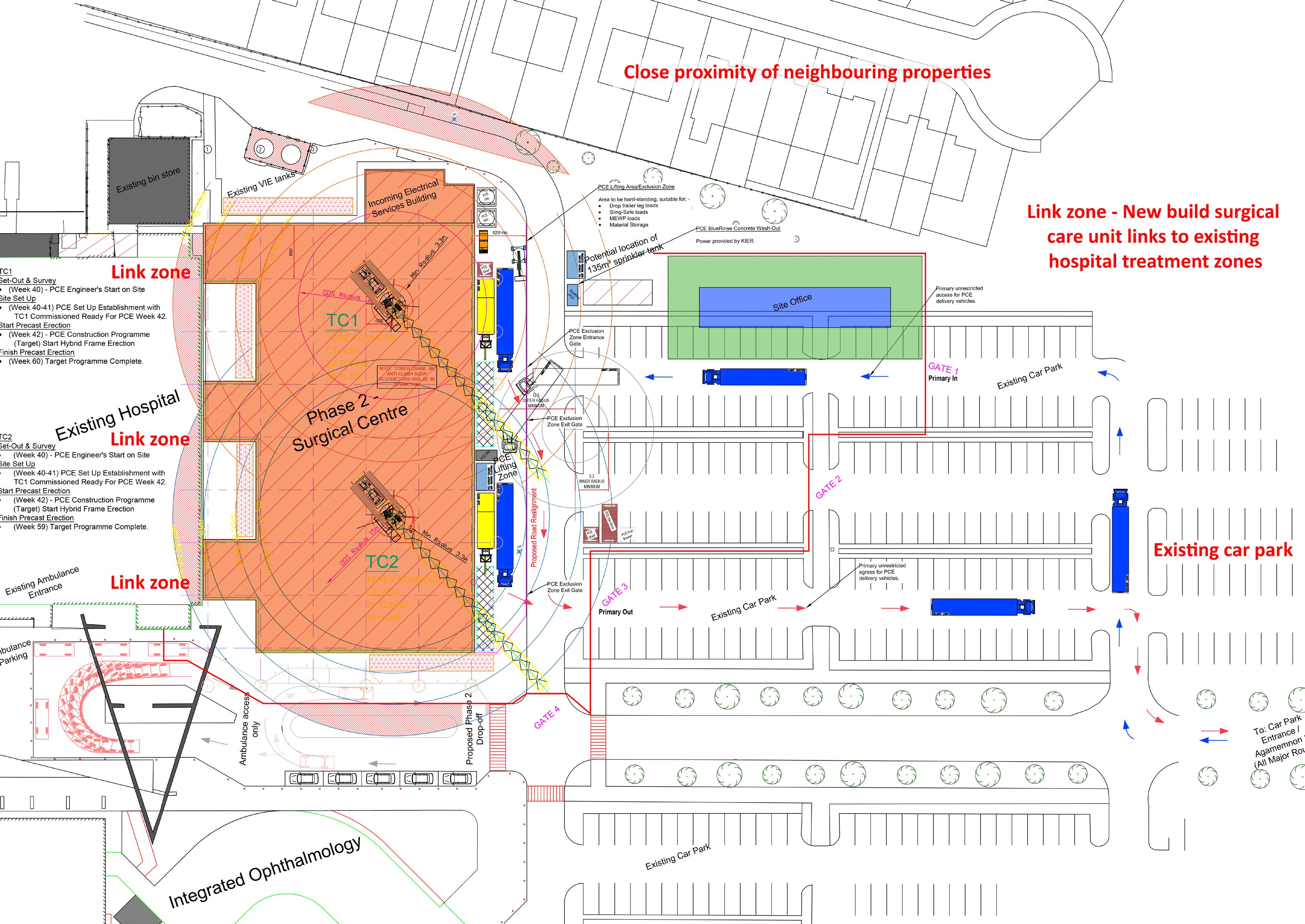
STRUCTURE ASSEMBLY
The assembly phase commenced with the installation of the ground to first floor frame structure. This consisted of precast square columns, structural steel Deltabeams, and precast concrete edge beams. Precast concrete twinwall components, stairs, landings and lobby stairs formed the stability cores, providing vertical circulation/access through the building during the assembly phase. The precast prestressed concrete floor plate was installed working away from the staircores, ensuring safe access for PCE’s highly skilled, multidisciplined construction operatives. Twinwalls were structurally concreted, and floor units were structurally tied to the supporting beams to provide enough lateral stability in the temporary condition to allow the build to progress efficiently.
After the next level of superstructure was constructed, the final structural topping activities could progress on the floor level below, unhindered by any inclement weather.
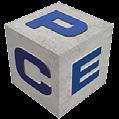
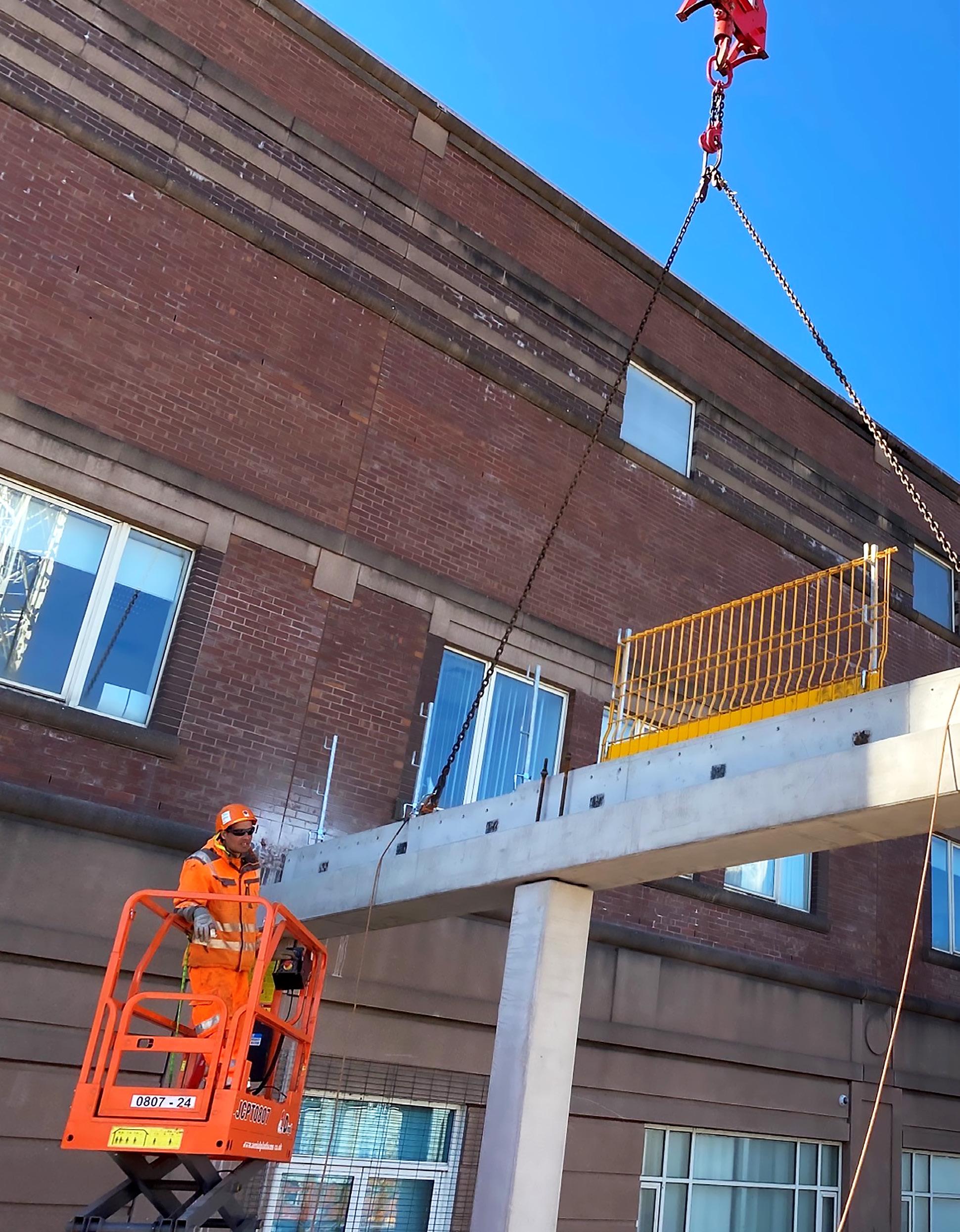
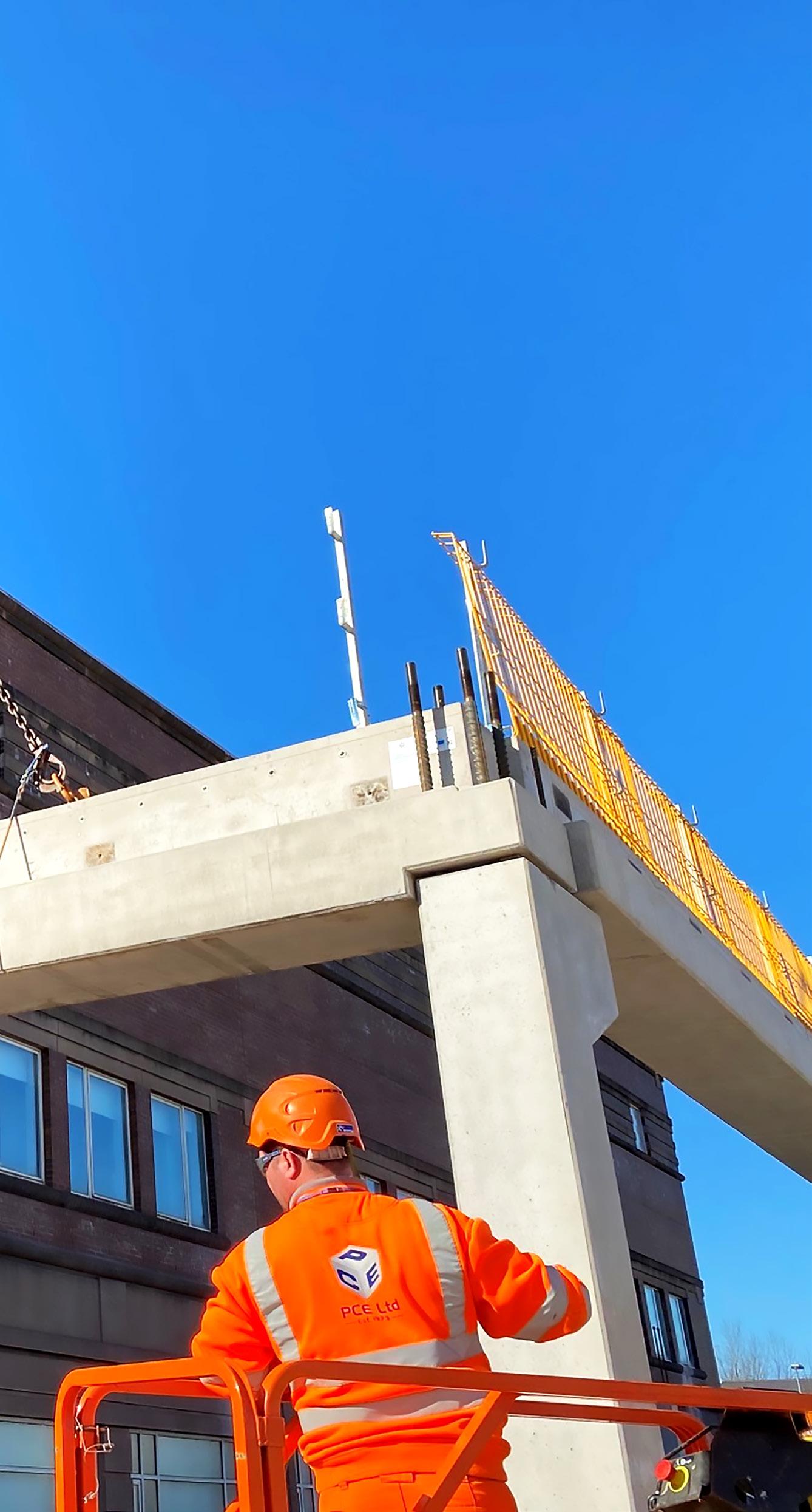
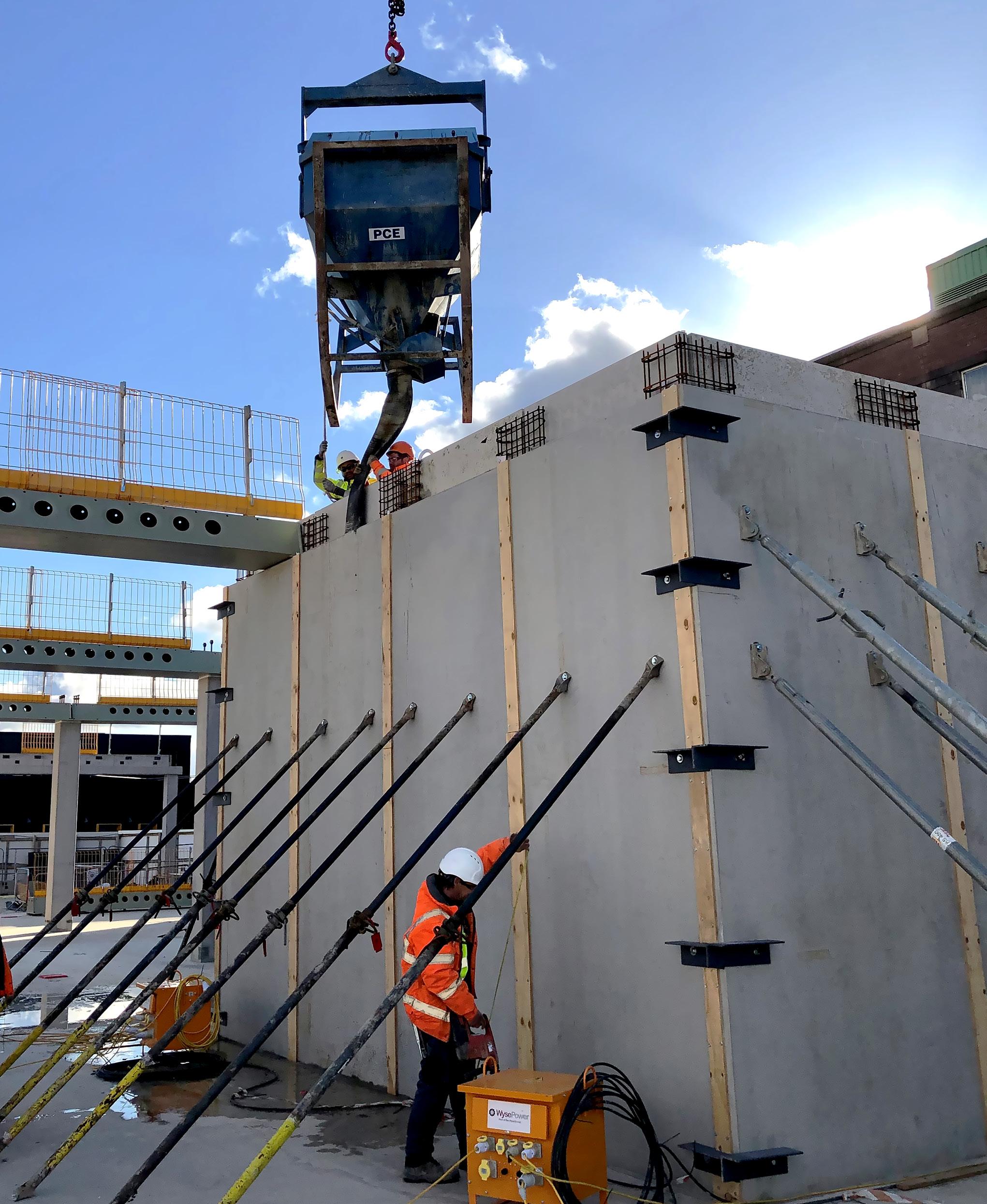
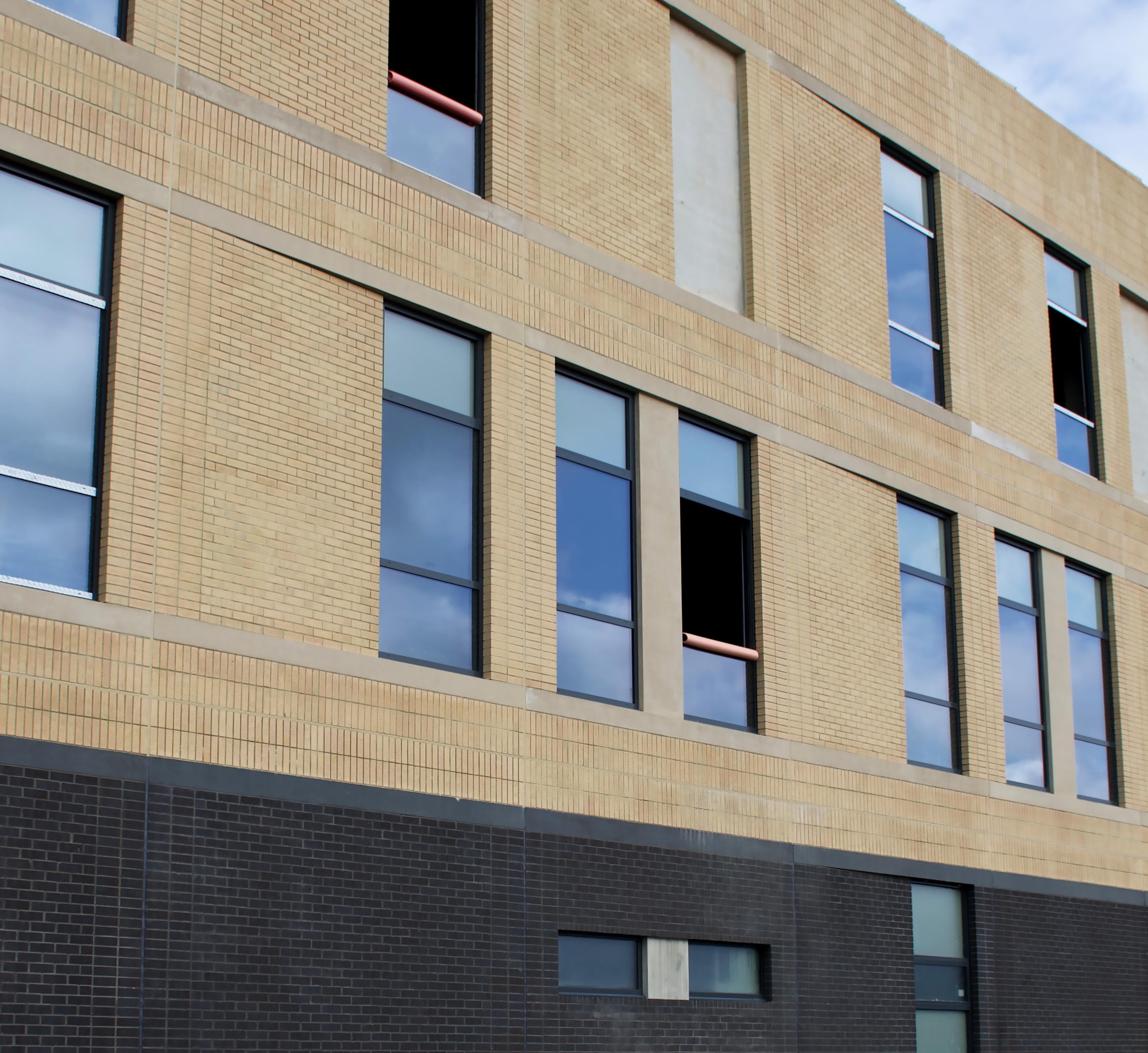
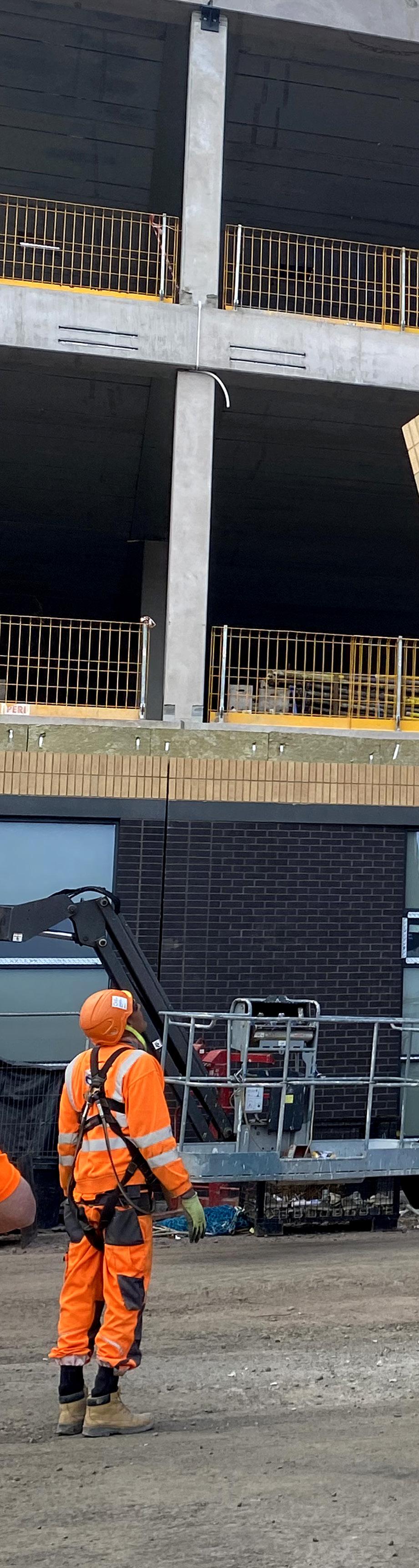
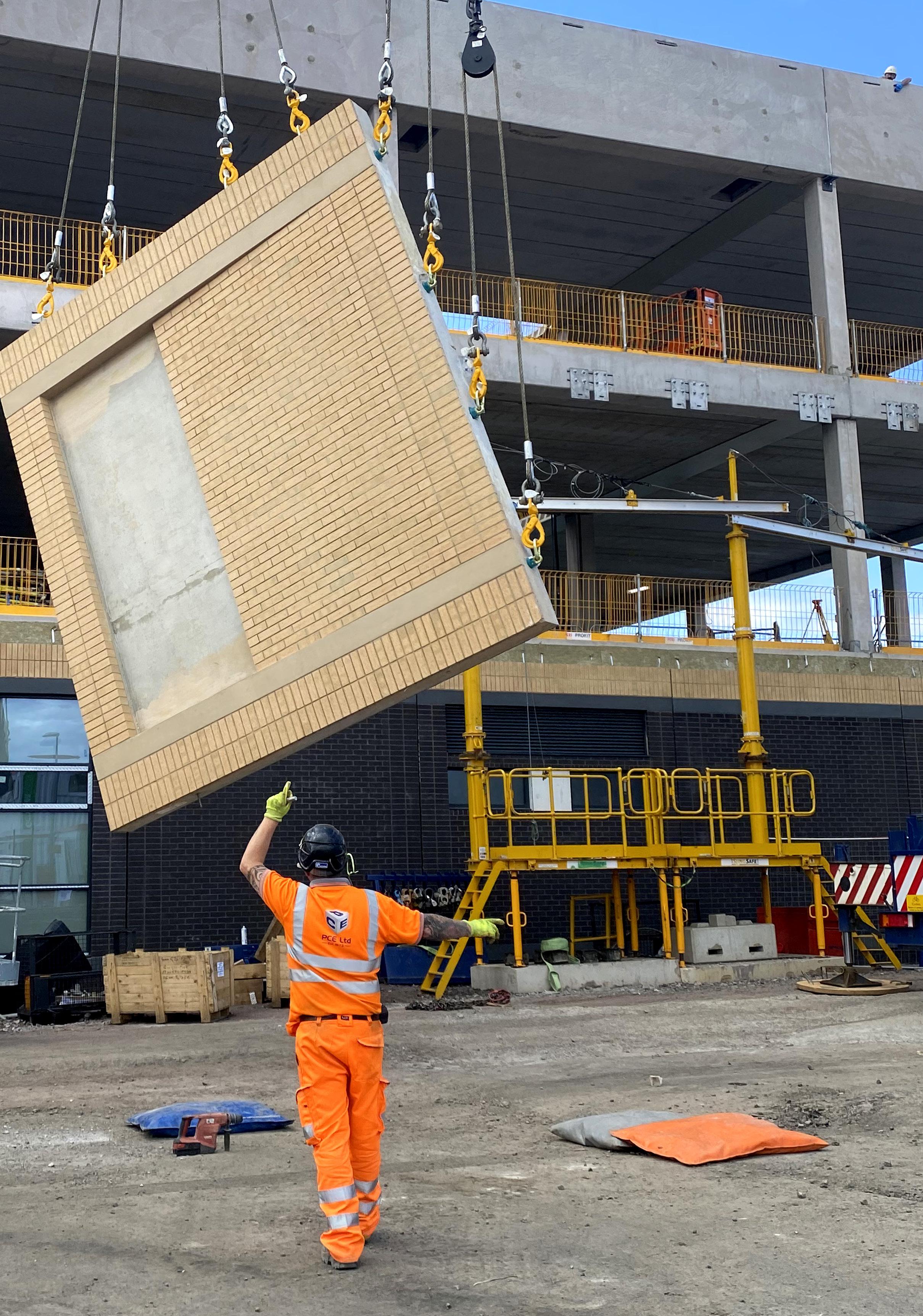
FACADE ASSEMBLY
The offsite engineered and manufactured façade panel dimensions were maximised in line with the lifting capacities of the project’s two CTL430 tower cranes and the structural grid. The resulting panel dimensions being up to 4.5m (high) x 4.25m (wide) x 0.29m (thick) with a maximum gross weight of 16.13 tonnes meant that they had to be delivered to site in landscape orientation.
Once delivered in ‘landscape’ orientation, these units needed to be rotated through 90 degrees prior to their installation. This was achieved by careful and coordinated use of one of the sites tower cranes, combined with a 90tonne all-terrain mobile crane.
Benefiting from the company’s expertise to maintain the highest levels of safety, all lifting operations and processes were designed to be fully compliant with respective legislative guidance.
After panel installation had been completed, external joints were mastic sealed to form a watertight shell to the building.

SITE SAFETY
PCE maintained its excellent attitude and approach to ensuring the safest working practices. It’s systemised approach, standardised methodologies, and highly skilled team helped reduce health and safety risks. The project recorded zero RIDDOR incidents, whilst PCE was recognised for its commitment to safety throughout.
Commended as ‘outstanding’ by Kier’s project management, it was noted:
‘‘PCE on-site supervisors were extremely aware of site requirements and adapted in the form of on-site daily briefings where information was disseminated to the workforce any safety issues were addressed immediately in the form of Toolbox Talks.’’
PCE’s Project Manager for Golden Jubilee, Adam Clarke, commented:
“The Golden Jubilee project demonstrates what can be achieved with a skilled multidisciplinary workforce committed to high SHE standards along, with the support and collaboration from the Kier project team. The team have proven that high risk operations can be safely co-ordinated on a daily basis within a fully operational hospital complex.”
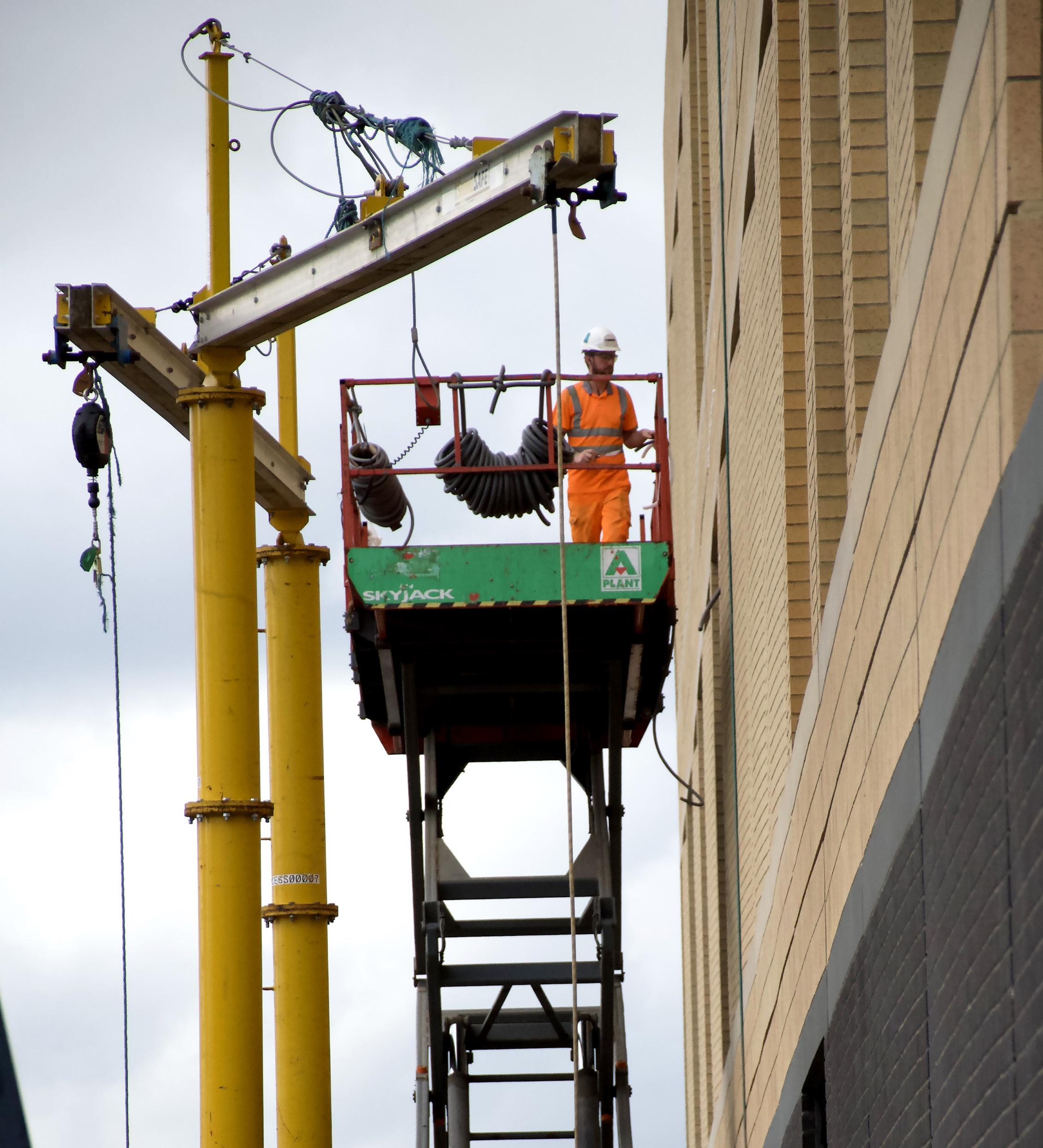
COMPLETION OF ASSEMBLY
The assembly of the structure and façade were completed by two of PCE’s specialist installation teams in a 15 week on site programme, 12 weeks quicker than what would have been achieved with the original Stage 3 traditional construction design proposal. This was a notable achievement considering the new facility links directly to the existing hospital, which remained fully operational during the entire build.
Such a significant improvement to construction programme is testament to the speed benefits achieved through PCE’s HybriDfMA approach, which facilitates faster construction without sacrificing structural integrity, safe working, and quality. It not only results in reduced waste, resource, and improved onsite efficiencies, it also means buildings can become operational much sooner, adding increased client value.
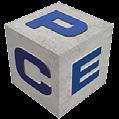
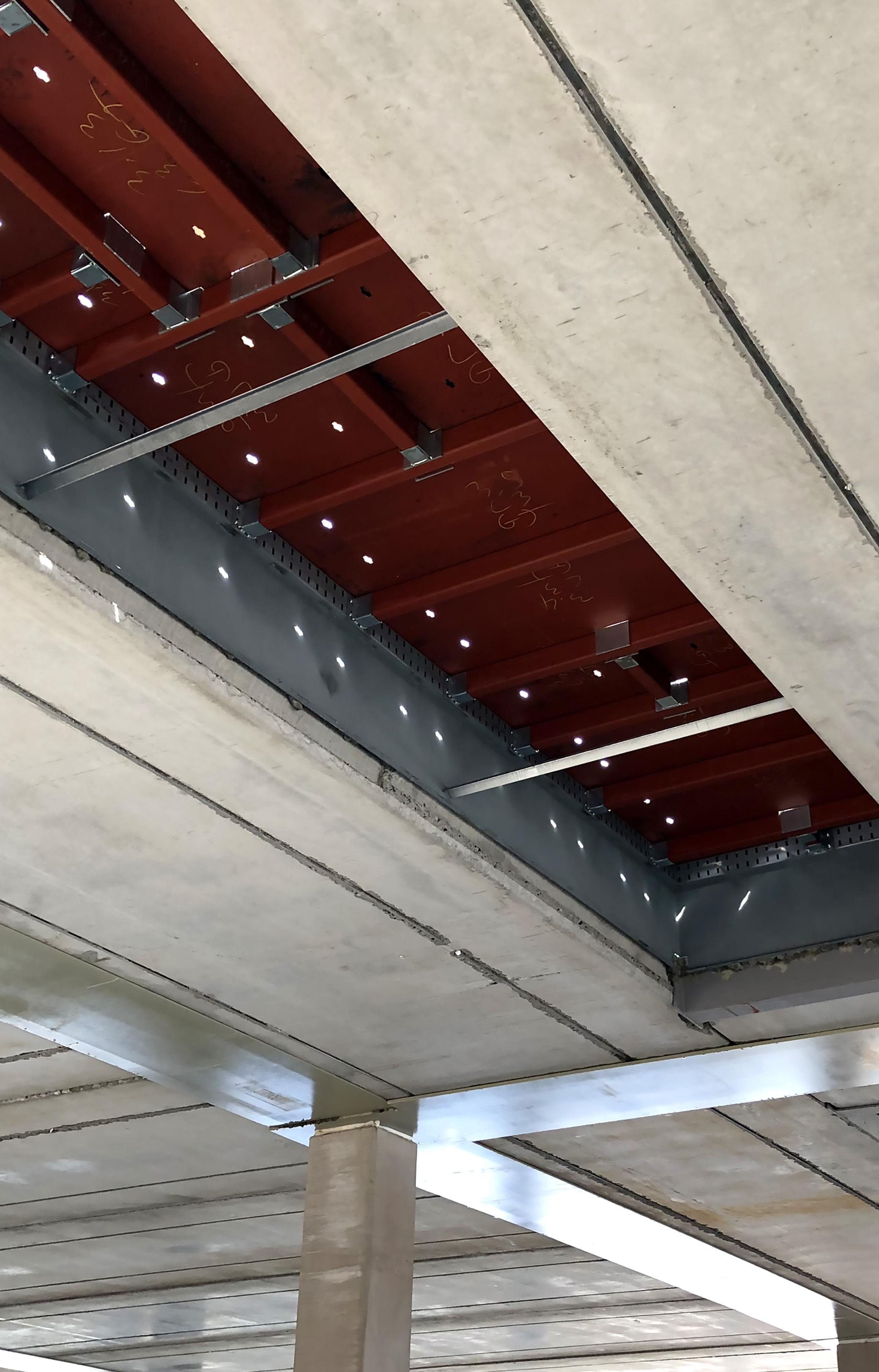

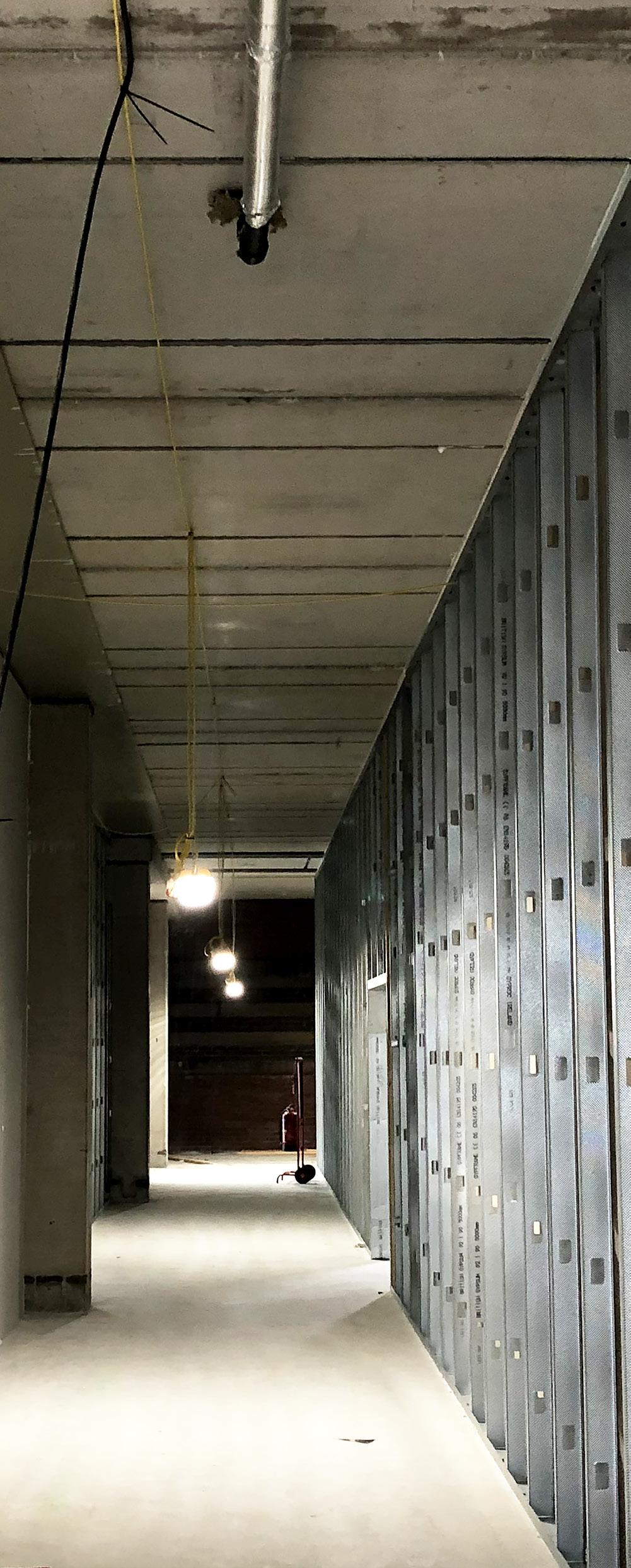
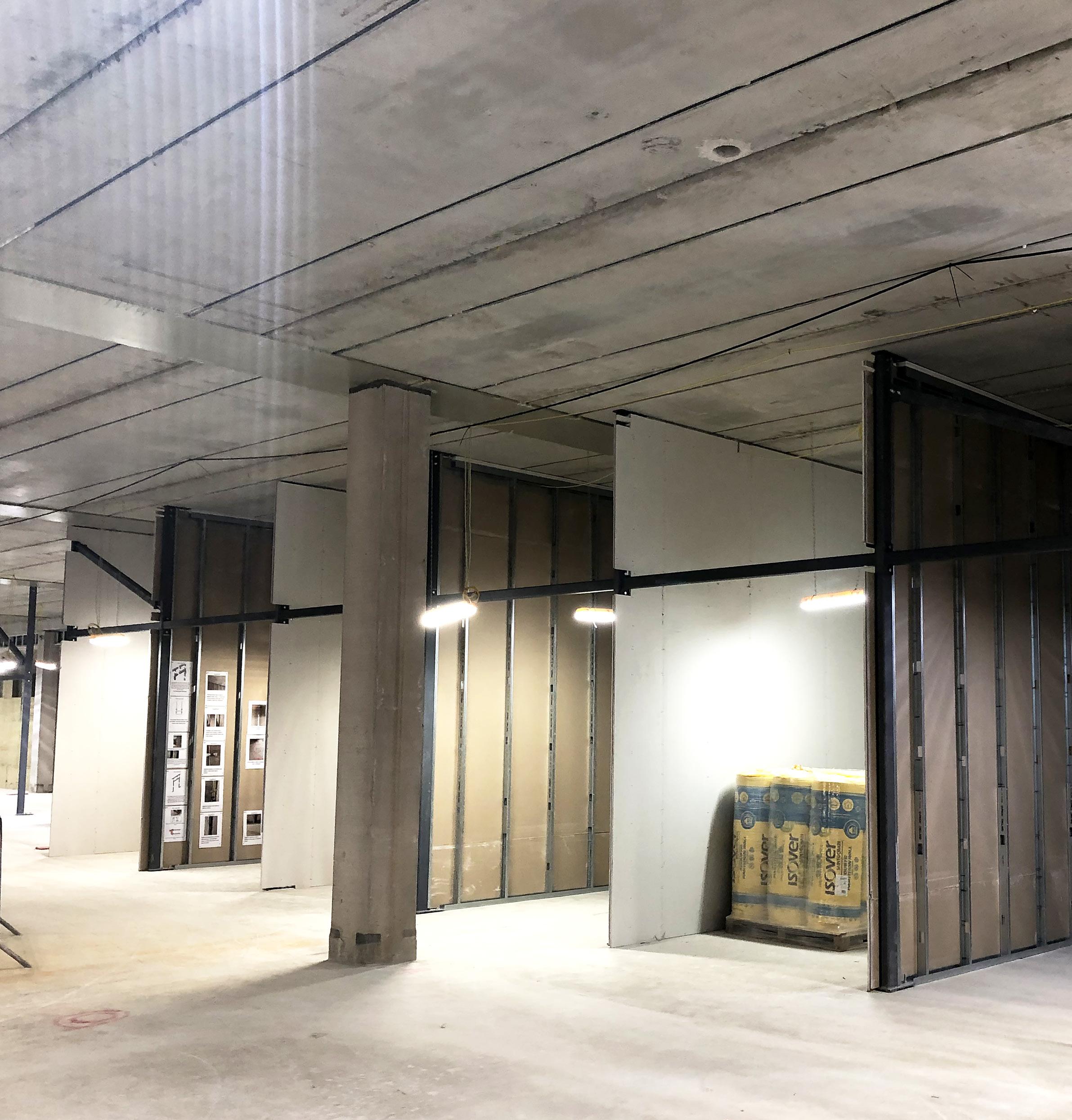
BIM AND DIGITAL
The use of Building Information Management and digital applications were key to the project’s success. Advanced digital capabilities enabled the coordination of complex design, ensuring a coordinated and cohesive design, manufacture, logistics, and assembly strategy.
Digital proficiency is a fundamental element to the PCE model. Continuous improvement is made to PCE’s data-driven insight and system approach, and the Golden Jubilee project helped facilitate further developments across PCE’s digital offering.

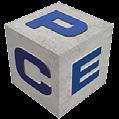
Ynomia Digital Twin
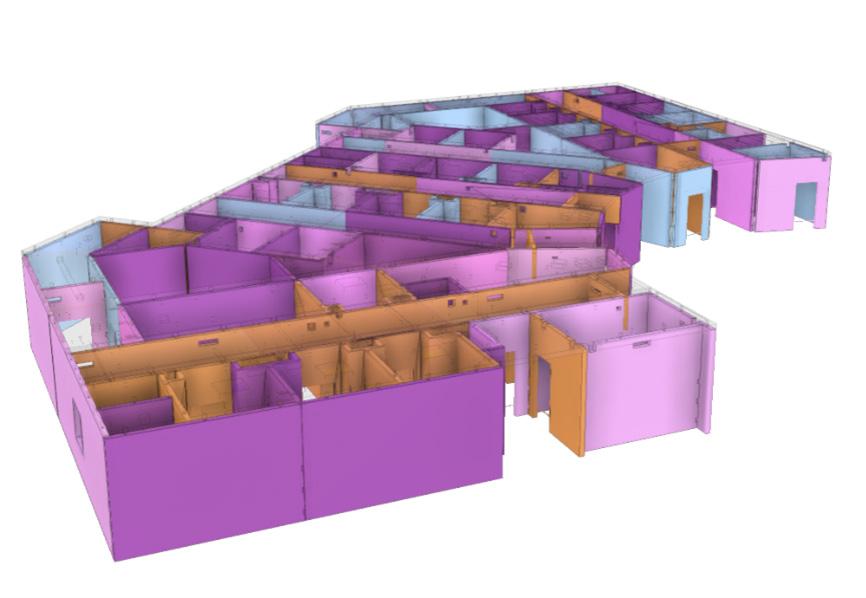
Design and manufacture stage

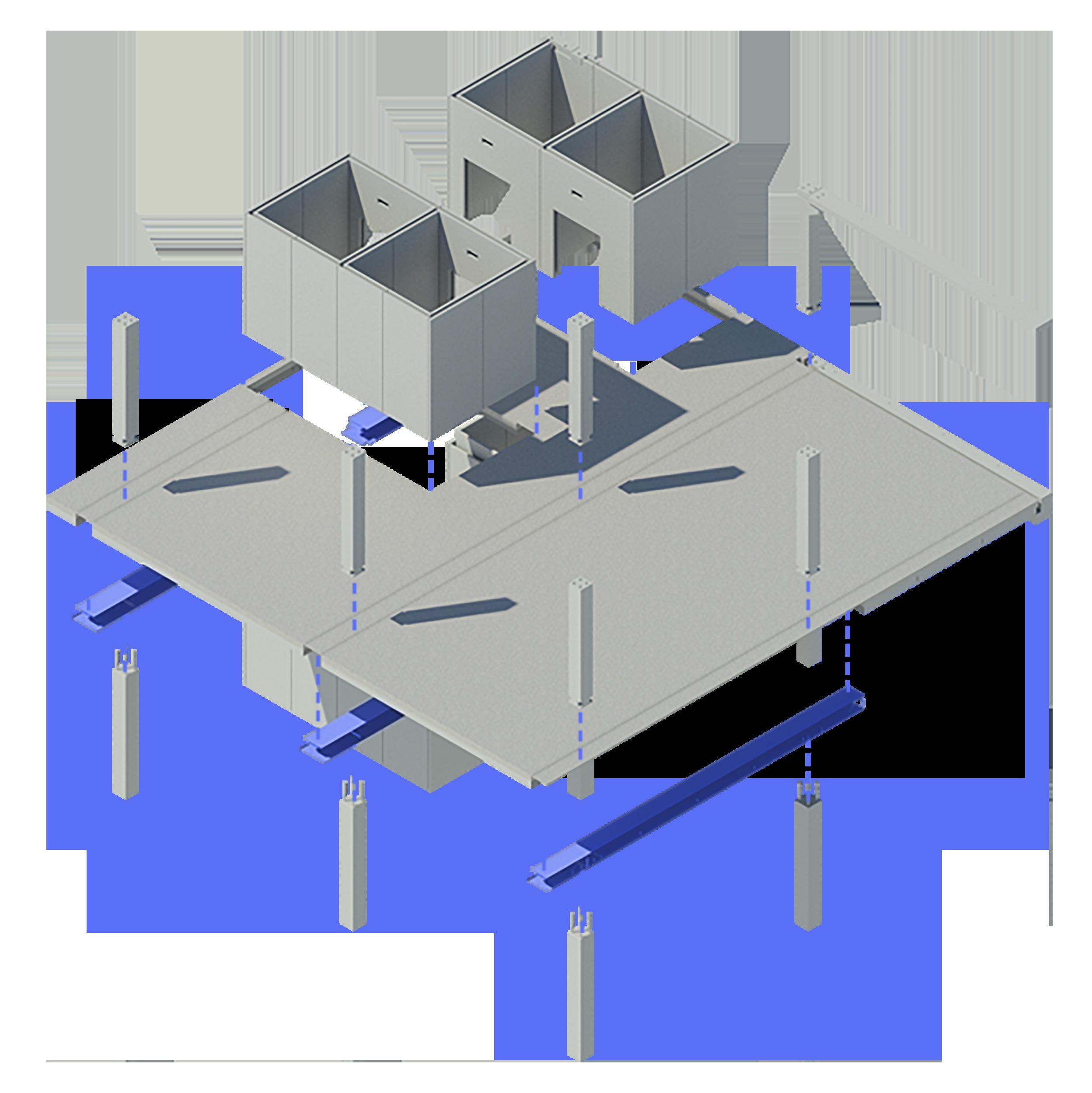
Installation complete Golden Jubilee Hospital kit of parts
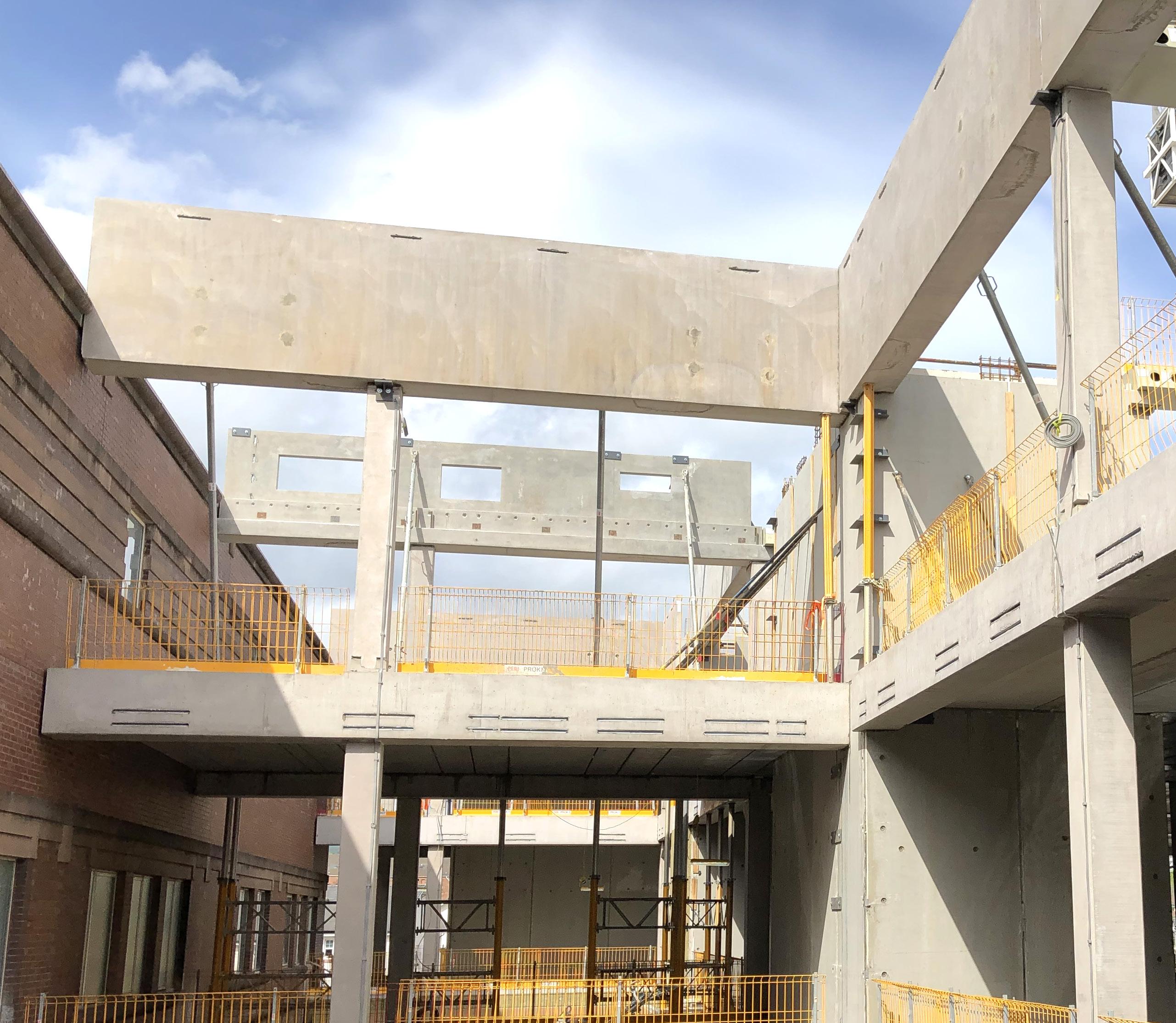
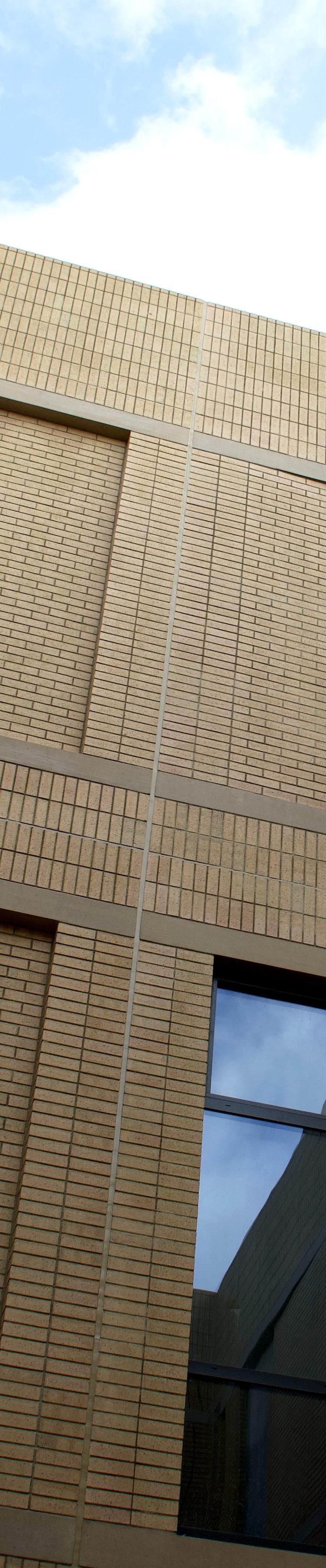
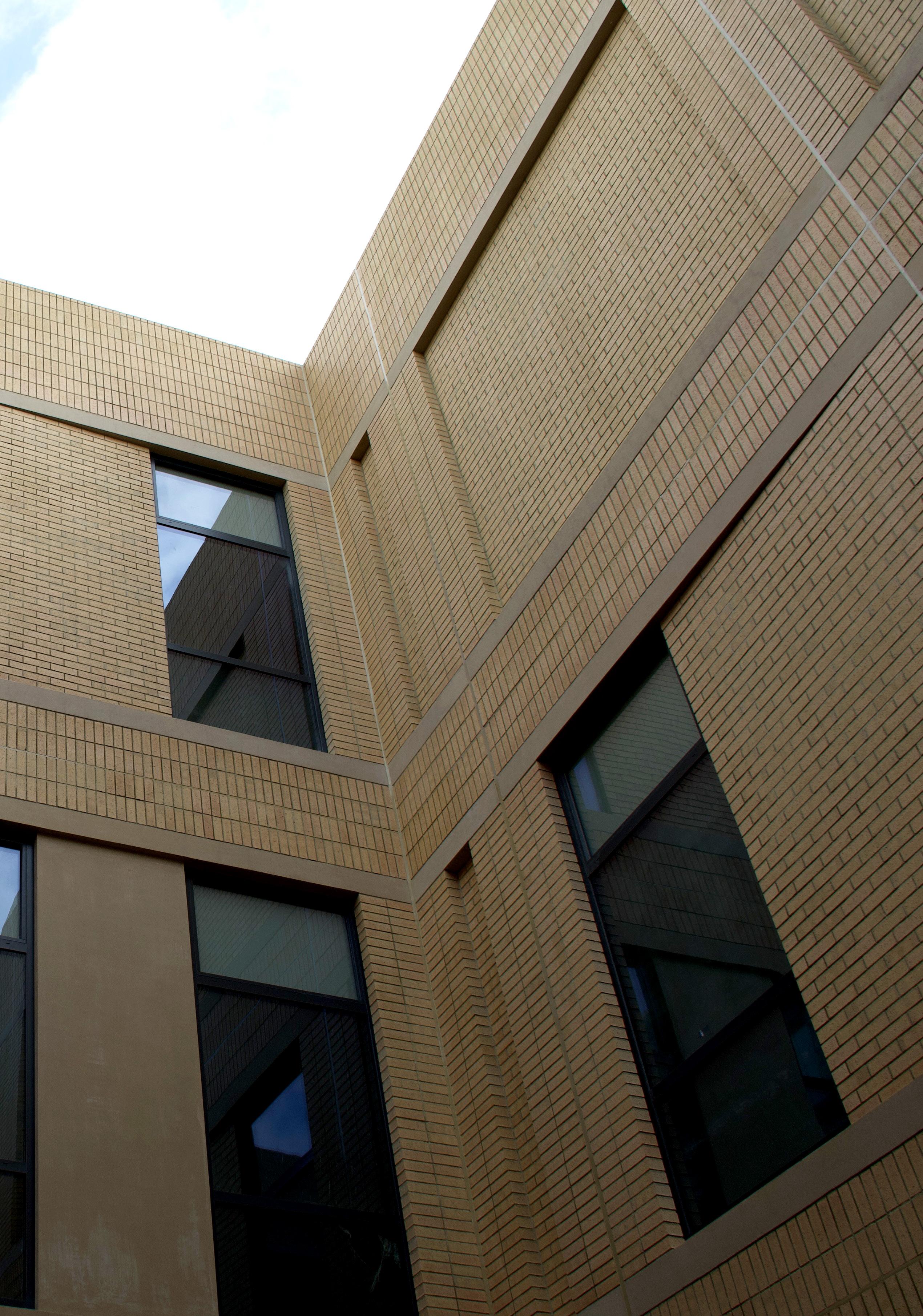
DECARBONISING PRECAST CONCRETE
PCE used its expertise to ensure the final structure and façade was completed with a minimised amount of embodied carbon, and reduced carbon footprint, thus assisting in the achievement of the required sustainability standards and environmental efficiencies for the project.
When approaching matters on sustainability, PCE is at the forefront of the Offsite construction industry. All of our employees are encouraged to play their part in delivering projects with a reduced carbon footprint, from receipt of enquiries through to the final project handover.
Externally the company is collaboratively involved with industry and government research initiatives to progress new sustainability ideas and techniques.
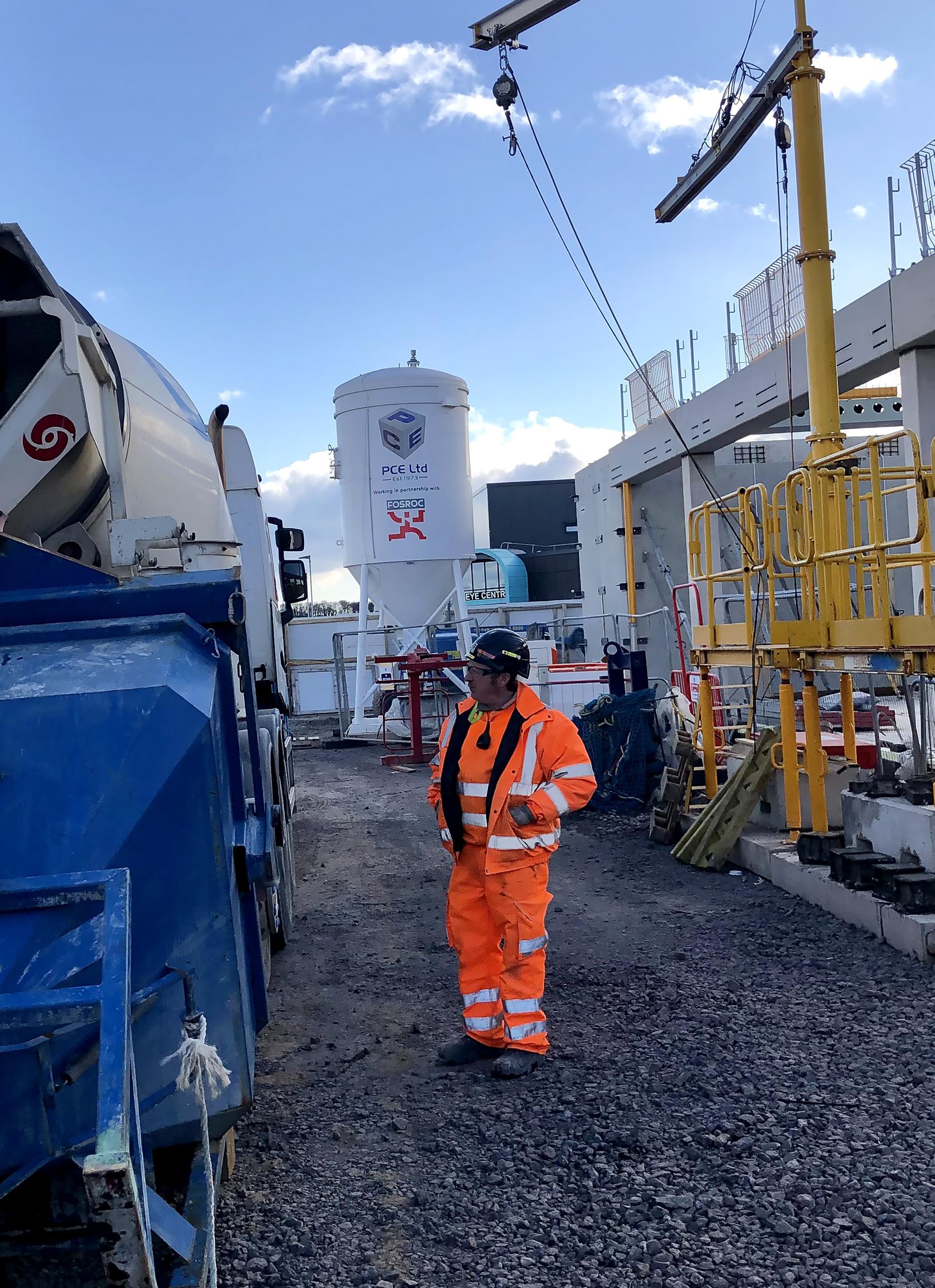
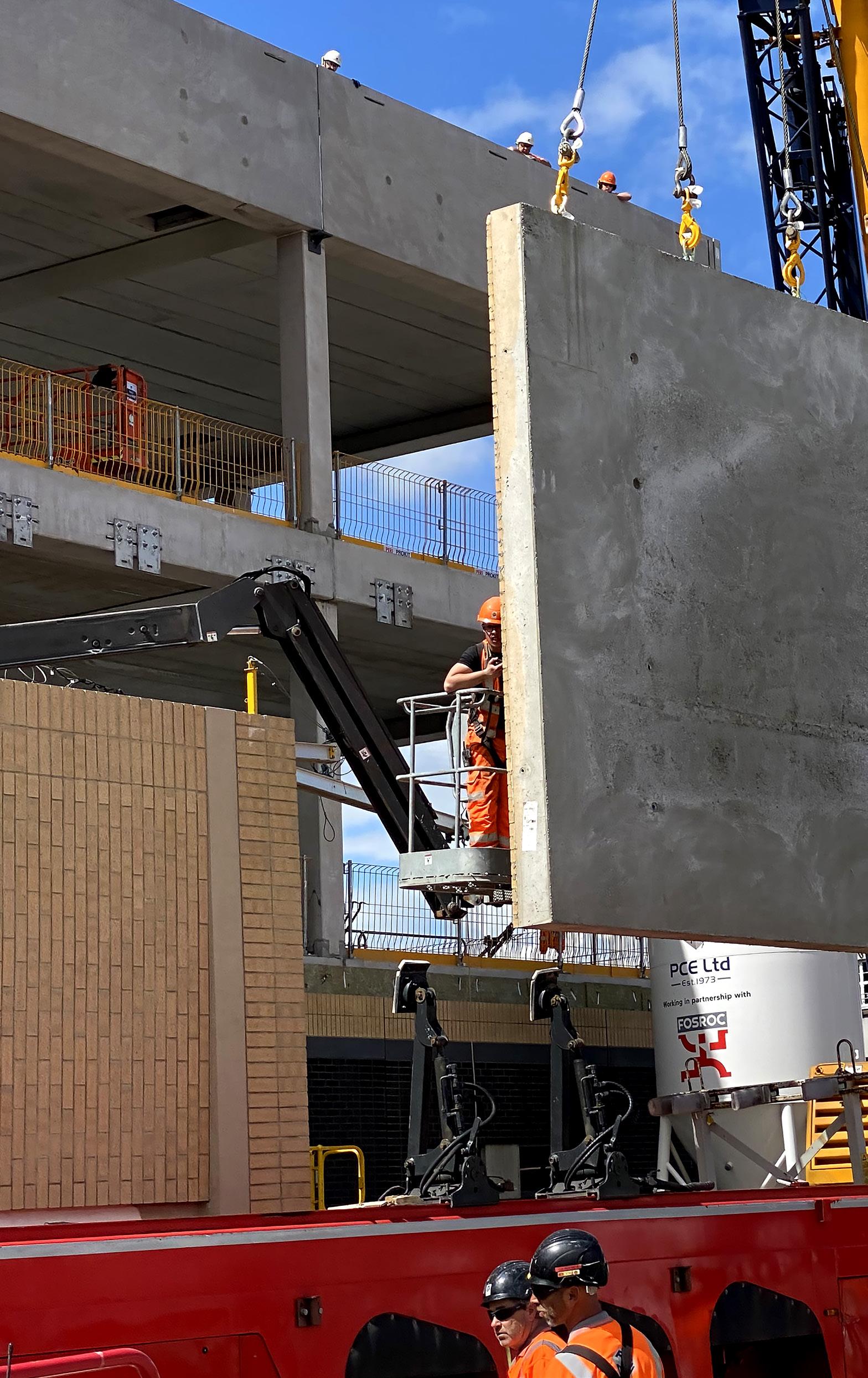
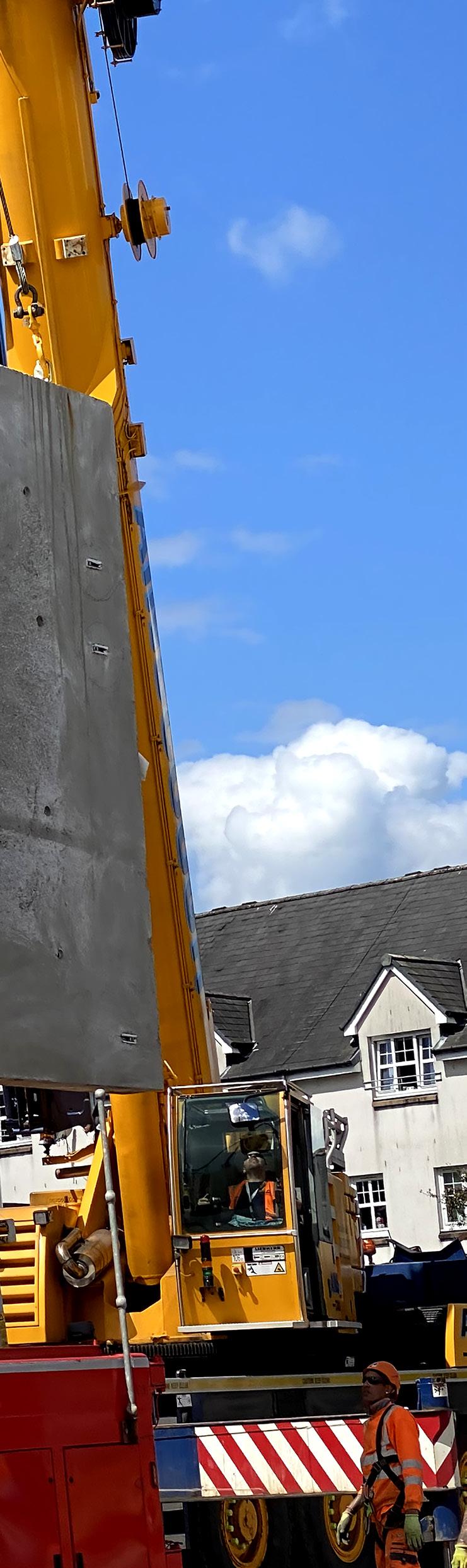
PROJECT DELIVERY
The success of PCE’s HybriDfMA solution to the design and delivery of NHS Golden Jubilee Foundation’s Phase 2 is clear to see. In addition to the impressive performance statistics, the project generated positive feedback from multiple stakeholders.
Andrew McTavish, Operations Manager Scotland for Kier, had the following to say:
“The building has been seen by many different clients, CEO’s and consultants and everyone has had the same thing to say, “This is how we should be doing it”. They have been astounded by how fast the structure was constructed and also the quality of the finish. From my own personal view, I enjoyed every minute working with PCE Ltd, The professionalism the team showed throughout the time in pre-con and construction was second to none. Without question I would use this type on construction every project if I could. The building will be and is currently being seen as the most cutting edge project in healthcare in Scotland, and I am asked about this project at most meeting and conferences I attend.”
Kier Construction Scotland passed on feedback they received from the fit-out trade contractors used on the project: ‘’It’s (PCE’s HybriDfMA Frame System) great, the flat soffits and the building being close to watertight had allowed them to work productively during the fit-out works. Keir set out to make this project a first for healthcare in Scotland using MMC and it has delivered in every way. Keir should hand over the project in 2023 as planned despite the assembly of the structure and façade occurring during the Covid Pandemic.’’
PCE adopted a team ethos from the first day on site which continued throughout the project. Two of PCE’s site operatives were also commended for exceeding the expected delivery of Kier’s values of Collaborative, Trusted and Focus. During the works, PCE consistently operated with their positive approach in creating the right safety culture, sharing experiences and safe working practices with the wider team during the hybrid structural frame and façade panel installation. This was recognised by Kier as enabling the project to become more efficient while working collaboratively and without incidents.
Key Metrics:
• Site Man Hours reduced by 50,000
• Site Deliveries reduced by over 350
• Programme reduction of 12 weeks
• Significant reduction in waste
• Reduced number of on-site follow-on trades
• Risk reduction through the removal of scaffolding,
• working at height and temporary works.
OUR PEOPLE
As always, the PCE team spirit was strong on project Golden Jubilee, from the design team in the office, the manufacturing team in the supporting factories and the construction and projects team on site. Despite the Covid pandemic challenging Scottish weather, the rain could not dampen the team’s morale, who not only delivered a project that surpassed expectation, but did so being noticed by the Client, with PCE being recognised and rewarded for their outstanding contributions to safe working on site.
Project Manager Adam Clarke was quick to note the efforts of the entire PCE team, stating: “The efforts of all at PCE continue to amaze. No challenge proved too steep and at every turn, the team rallied together to overcome and achieve. I couldn’t be happier with their continued efforts throughout the project and thank them for their support. Well done to all involved on another successful PCE project!”
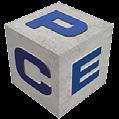
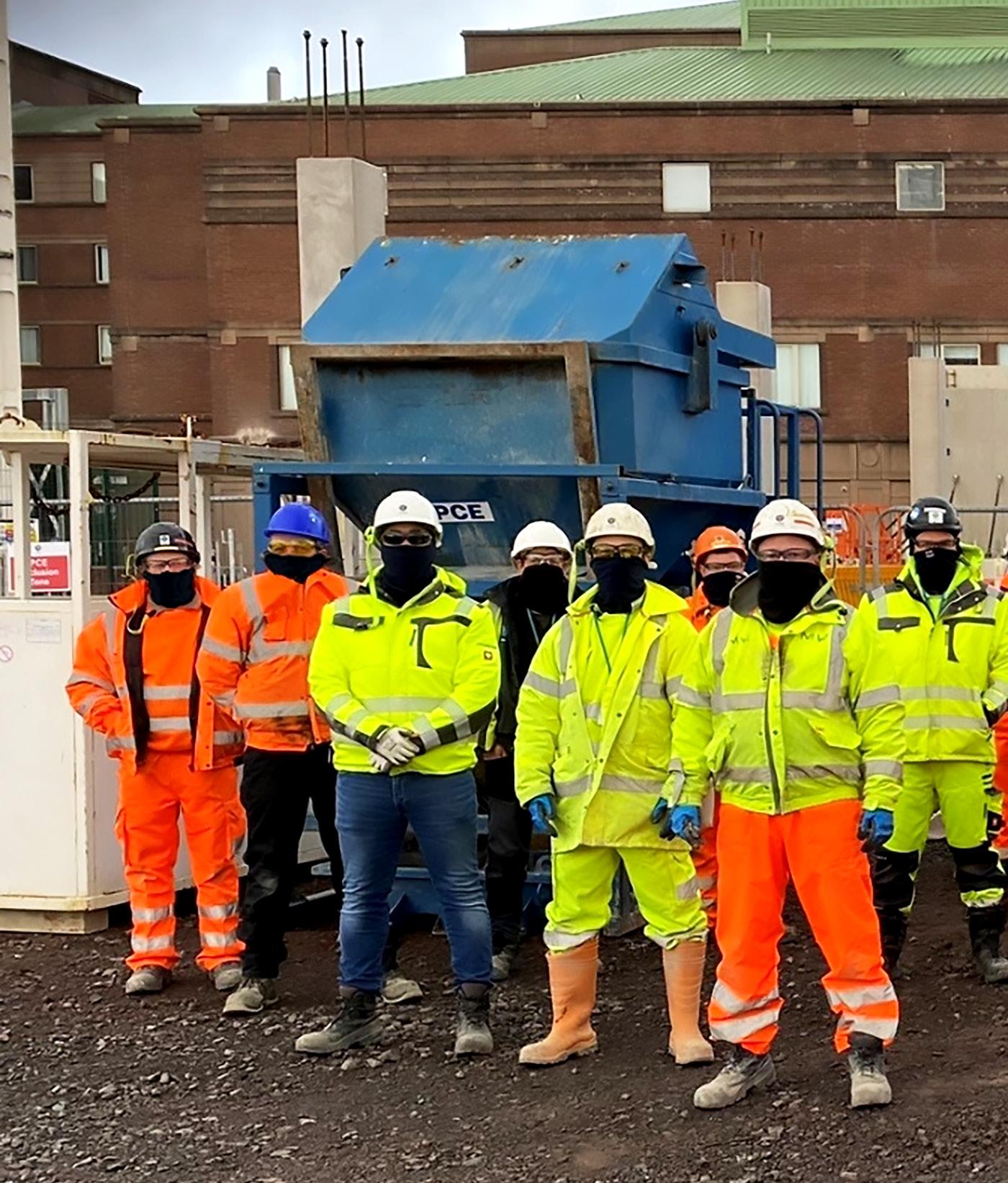
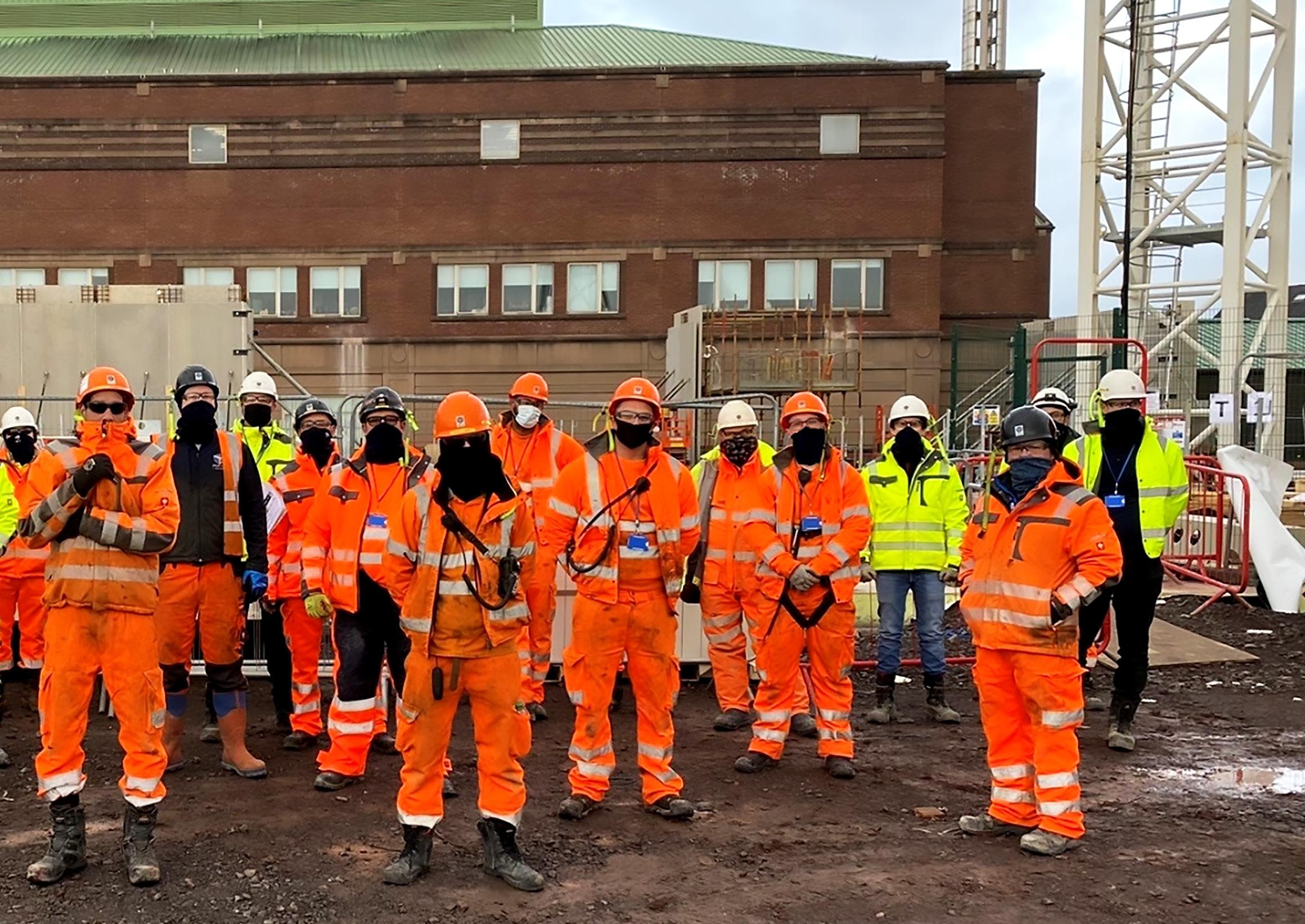