University of Warwick

HybriDfMA Frame System
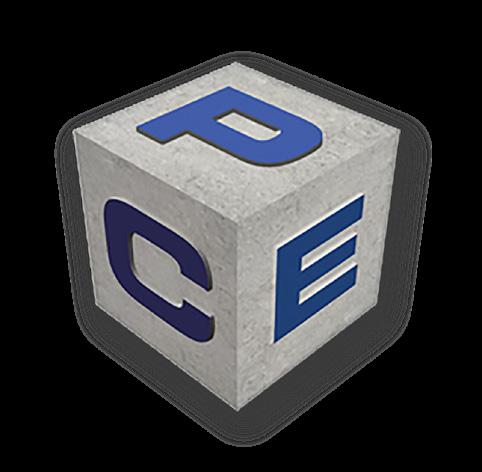

PCE was instructed by Willmott Dixon Construction Limited to provide the structural frame of the new £54M state of the art five storey research building for the University of Warwick, located on the Gibbet Hill campus. The development was appointed in benefit of 300 biomedical researchers from across the School of Life Sciences and Warwick Medical School to fight human diseases. PCE was the preferred specialist for the project providing the client with a System build Frame Solution using the proven HybriDfMA approach. This includes delivering a time efficient and safe construction method with a multi skilled site team and offsite engineered products. The Hybrid Frame was built with a mixture of precast concrete components including columns, beams, solid walls, Hollowcore Flooring, Delta Beams and stairs and landings, including structural concrete topping.
PCE was the preferred specialist for the project, having been instructed by Willmott Dixon Construction Limited to provide the client with a System build Frame Solution using their proven HybriDfMA approach. This delivered a time efficient and safe construction method with a multi skilled site team and offsite engineered products. The development brings together nearly 300 biomedical researchers from across the School of Life Sciences and Warwick Medical School to fight human diseases. PCE’s HybriDfMA frame system, replaced an in-situ concrete frame which was specified up to Stage 3 of the design process.
CLIENT
MAIN CONTACTOR
ARCHITECT
PROJECT MANAGER
CONSULTING ENGINEERS
PCE LTD PROJECT MANAGER
£3.2M
University of Warwick
Wilmott Dixon
Fairhursts Design Group
Turner & Townsend
Peter Brett Associates
Craig Billyeald
The Hybrid Frame solution used for this project consisted of precast concrete columns, concrete beams, Deltabeams, hollowcore floor units, solid walls, stairs and landing units and a structural concrete topping. In total, delivery vehicle movements were limited to just over 300 within the live University campus compared to over 450 if a fully onsite insitu concrete option had been used.
The Hybrid Frame solution used for this project consisted of precast concrete columns, concrete beams, Deltabeams, hollowcore floor units, solid walls, stairs and landing units and a structural concrete topping. In total, delivery vehicle movements were limited to just over 300 within the live University campus compared to over 450 if a fully onsite insitu concrete option had been used.
Thorough quality checking of Offsite engineered components is an essential feature of PCE Ltd’s HybriDfMA construction approach. Frequent validations help ensure that the client’s and PCE’s expectations of high standards are continually maintained. The projects then Design, Manufacture and Construction Coordinator Jordan Shaw regularly spent time in the offsite manufacturing facility, carrying out rigorous standard testing procedures on the components that were delivered and installed at the University of Warwick Interdisciplinary Biomedical Research Building. A National Quality Audit carried out by the Main Contractor for the project, Willmott Dixon Construction, included an inspection of the manufacturing and construction quality systems and procedures put in place by PCE and its supplier, resulting in a score of 98.3% being achieved. This score is a reflection of both the thorough quality assurance and checking procedures carried out within the Offsite manufacturing facility, along with the exceptional quality management and assurance by the construction team on-site.
PCE’s then Design, Manufacture and Construction Coordinator Jordan Shaw commented,
“Throughout the country for all of our Willmott Dixon projects as well as other PCE contracts, we have Precast Coordinators and engineers like myself who regularly check precast components at manufacturing facilities. The checking procedure takes place starting from the design stages, checking that the fabricated reinforcement cages accurately conform to the requirements of the design drawings, as well as Pre and Post concrete pour inspections to really ensure that the required accuracy and quality is achieved throughout all of the manufacturing stages.”
During the construction stages, Jordan appeared in Willmott Dixon’s video Get it right – offsite which focussed on offsite construction product quality management for the University of Warwick’s Interdisciplinary Biomedical Research Building.
Efficiencies and assembly obtained by HybriDfMA
off-site manufactured concrete and components
Warwick University some of the walls that and then turned for installation.
were the largest Delta Beams our multiskilled coordinated a fully operational Campus site. onsite insitu reduced the concrete usage over 850 tonnes. significant delivery vehicle during the phase therefore structures content.
Efficiencies in the design process assembly solution were by the use of PCE’s HybriDfMA approach of using manufactured precast and structural steel components together. On the University project were the largest finished can be made, delivered turned on site ready installation. Also installed largest structural steel Beams in Europe, which multiskilled workforce coordinated safely installing on operational University site. The addition, insitu reinforced concrete the initial expected total usage for the project by tonnes. This provided a significant reduction of over 100 vehicle movements to site the structure’s assembly therefore minimising the structures embodied carbon
The construction of the project began the precast concrete frame including the architectural ribbed or board marked finished wall panels. The M&E seamlessly slot into the building during the build with the precast components having ‘cast-in’ fabrications. This was made simple by the very tight tolerances between the concrete and timber frame, allowing glulam beams to be directly bolted on. Over 1,400 individual structural elements were manufactured offsite and delivered on just 208 delivery vehicles. The HybriDfMA solution also required 630m³ of reinforced insitu concrete to be used on site for the formation of structural composite concrete and steel beams along with structural floor toppings.
The 4 composite action steel and concrete beams each required 12m³ insitu concrete to complete them, bringing the final weight of each to approximately 48 tonnes. Temporary edge protection was pre-installed steel Deltabeams at ground level prior to their erection in order to at height risks and to allow safe access for the installation of prestressed Hollowcore planks between the large beams. Holding down bolts for connected to the beams, which support the 3 storeys of Offsite manufactured frame structure above, were also prefabricated onto the Deltabeams manufacture.
12m³ of on-site beam element pre-installed to the reduce working prestressed concrete for the columns manufactured Deltabeams during their
The Interdisciplinary Biomedical Research Building project for the University of Warwick where Willmott Dixon is the Main Contractor extended the range of structural innovation for PCE’s HybriDfMA Offsite Design and Build systems. The erection of 4 steel and concrete composite action beams using structural steel Deltabeams manufactured by the Peikko Group to form part of the roof and transfer structure over the clear double storey height lecture theatre was a prime example of this. The structural design solution for the building developed by PCE included some of the most heavily loaded Deltabeams to be produced. At 16 meters long with a delivered structural steel weight of 18 tonnes they are also the heaviest ever to be manufactured.
The digitally engineered and Offsite manufactured structural frame features areas of high quality exposed precast concrete which are visible from inside the building. The team commenced installing some of the nine-metre-high architecturally finished pre-cast concrete Auditorium and Core wall panels near the very start of the build. These walls were cast using a Reckli form liner system to produce wave and board marked effects to the surface of the panels, giving a high quality exposed concrete finish. This was applied to both sides of the units in some areas. These exposed finishes formed an important architectural feature in various areas within the building including the café area, the auditorium and around the cores.
PCE Ltd’s project and construction teams at University of Warwick were praised for the Health & Safety standards which they are achieved on site early on in the build, resulting in record scores on the third site audit conducted by Willmott Dixon. A visit by Willmott Dixon’s Group Safety Inspector Bob Walls was a huge success. The high-risk operations, working at height, excavations, working around live services, general tidiness of the site and the attitude of the workforce was all superb in Bob’s terms. This was the third audit during this period, one more final visit was conducted between then and Christmas. It was noted; “The scores so far this period are very high, and set the bar for the region, competing amongst the highest nationally, so no pressure on the final one PCE!’’
PCE’s Construction Director Karl Hubbard commented,
“The Warwick University project demonstrates just what PCE’s off-site engineered HybriDfMA systems are capable of, we have some of the largest finished walls that can be made being delivered to this project that are then being turned on site ready for installation.
“We will also be installing the largest structural steel Delta Beams in Europe on this project, all of which our multi skilled workforce will be coordinating and safely installing on a fully operational University Campus site.
“All of this along with high levels of safety and quality can only be achieved by having a committed and skilled workforce, the off-site planning and fruition of the plan is outstanding and a real credit to all involved.
“Well done from all at PCE, please continue to maintain the high standards that are currently being achieved.”
PCE Ltd, as part of tradition, celebrated the milestone of the topping out of their structural frame project for the Interdisciplinary Biomedical Research Building at the University of Warwick. The celebration took place on-site with the Main Contractor Willmott Dixon and representatives of the client, University of Warwick. The representatives spoke extremely highly of the quality and value of PCE’s off-site HybriDfMA solution which had significantly contributed towards the project achieving the target of 50% pre-manufactured value for the complete development. The milestone of structural completion was a combination of 6 months on-site assembly works by PCE’s multi-skilled site team and an overall period of 13 months from design commencement through off-site manufacture. The collaborative nature of working within a large Project team helped PCE to overcome many interesting design, manufacture and onsite challenges. The main challenge being extreme inclement weather. It was important to fix this drawback to maintaining progress for critical follow on trades.
One of the benefits System construction assembly. Over structural components on the project the clients high requirements
aspirations. The building was of on-site assembly skilled site team. with a period commencement manufacture. start of the build, architecturally Auditorium and interior wall panels form liner system board marked sides in some formed an important in various areas
benefits of HybriDfMA Frame construction is the speed of Over 1,400 off-site manufactured components were assembled project in just 24 weeks, meeting high visual architectural requirements and off-site manufacture
The biomedical research completed in only 6 months assembly works by PCE’s multiteam. This was in combination of 13 months from design commencement through to off-site Specially installed, near the build, were the nine-metre-high architecturally finished pre-cast concrete and Core wall panels. These panels were cast using a Reckli system to produce wave and marked effects to the surface, on both cases. The exposed finishes important architectural feature areas of the building.
Responsible for the structural design, offsite component manufacture and on-site assembly, PCE used their expertise to ensure the resultant structure was completed minimising embodied carbon and ensuring environmentally and sustainability efficiencies. On this occasion, the project won the Green Building Project of the Year Award at the recent BusinessGreen Leaders Awards which recognises the most innovative and inspiring green building projects, which have pioneered new designs, techniques, and technologies in pursuit of improved environmental performance. PCE continues to be at the leading edge in developing eco-friendly and sustainable structural solutions for their clients, including having been a partner in a recent Government funded research initiative, ‘Decarbonising Precast Concrete’, the findings of which are already being implemented into ongoing projects.
Working in conjunction with main Willmott Dixon, specialist design structural frame contractor PCE Ltd their Frames System Offsite HybriDfMA parts’ approach to ensure that the structural concrete and steelwork finished structure was delivered, the pandemic, ahead of initial programme to the very high visual architectural required. It also met the University’s considerations of minimising environmental impacts during construction and Carbon footprint. Included within over 1,400 precast concrete components individual 250mm thick architecturally storey-height wall panels up to 6m 3.6m wide and weighing 20 tonnes. the precast frame components using Granulated Blastfurnace Slag to reduce contents by 35%, with up to 50% cementitious materials used in the structural toppings, a large saving carbon content of the concrete was
Efficiencies in the design process assembled solution obtained by use HybriDfMA approach also reduced expected total concrete usage for by over 850 tonnes with a significant of over 100 delivery vehicle movements during the structure’s assembly phase.
main Contractor and build Ltd used HybriDfMA ‘kit of the resulting steelwork portion of the even during programme and architectural quality University’s key environmental embodied within a total of components were architecturally finished 6m in height, tonnes. With using Ground reduce cement 50% supplementary the onsite saving in embodied was obtained. and final use of PCE’s reduced the initial the project significant reduction movements to site phase.
The site team of only 18 people installed over 1,300 bespoke offsite engineered precast concrete elements, some of the largest structural steel Deltabeams to ever be used in Europe, as well as insitu reinforced concrete to complete the frame in a period of 22 weeks. The Offsite engineered HybriDfMA solution together with close logistical control by the site team ensured that transport vehicle movements were kept to a minimum which has helped support the University of Warwick in their battle against parking and traffic issues as well as helping to reduce the projects carbon footprint.
Managing Director Nickie Brown commented,
“When you see your teams, receiving such recognition and appreciation from our client partners regarding our employee’s commitment, efforts and drive, it reminds me what great ethics and passion our people have. People, Quality, Innovation and Health & Safety is our USP, so it fills me with joy when others point this out to us!”
The hybrid solution resulted in a saving of 200kg/m² of concrete which saved c.850t of concrete overall.
PCE Ltd’s Interdisciplinary Biomedical Research Building project for the University of Warwick was shortlisted for the 2020 Offsite Awards in two categories, following nominations by NG Bailey. PCE was also delighted to have been nominated for a number of 2021 Offsite Awards: PCE was nominated in the category for “Best use of hybrid technology” and the Main contractor Willmott Dixon was nominated for “Education project of the year”. The research building won “Best use of concrete technology” at Offsite Awards 2021. PCE Ltd provided the structural frame of the £54M state of the art five storey Interdisciplinary Biomedical Research Building for the University of Warwick, located on their Gibbet Hill campus – a project which was recognised as displaying the “Best use of concrete technology” at the 2021 Offsite Awards.
Nickie Brown, PCE Managing Director said,
“The Warwick project is yet another consecutive prestigious Offsite Award and thus is a great reflection on how our business has developed over the past few years as well as a great message to our current and future clients as to what PCE can do and, equally importantly, how we deliver value.”
The University of Warwick featured in issue 30 of the Offsite Magazine. The publication. It focuses on Main Contractor Willmott Dixon‘s desire to “de-risk” challenges, including the physical constraints of the site, exposed concrete finish transfer structures”.
This is the third University project where PCE has been responsible for the has featured in Concrete Quarterly in the past two years, the other two being Summer 2020), and Leeds University Sir William Henry Bragg Building (CQ Construction has won yet another Award for their Warwick University Interdisciplinary
The new Interdisciplinary Biomedical Research Building (IBRB) housing both Brown was featured in the Spring edition of the worldwide acclaimed Mineral
article, called Meeting the Hybrid Challenge is on page 74 of the “de-risk” the project as a result of being faced with a number of significant finish requirements and the “complexity of the temporary works and
design and build of the structure using their HybriDfMA approach that being the International award winning Kingston University Town House (CQ –(CQ – Winter 2021). PCE Ltd is delighted that Main Contractor Willmott Dixon Interdisciplinary Biomedical Research Building project completed in 2021.
both the medicine and life sciences departments with Architects Hawkins Mineral Products Association, Concrete Centre’s, Concrete Quarterly magazine.
PCE’s multi skilled onsite construction team who have were responsible for the construction of the company’s HybriDfMA Frame System structure for the University of Warwick IBRB building, was awarded a one thousand pound cheque from Main Contractor Willmott Dixon in recognition for going above and beyond with their efforts and performance on the project. The team worked extremely hard to ensure the client’s expectations were met, especially during the harsh weather conditions at the time, with the rain, snow and wind making progress difficult. The efforts shown by the team are a great example of providing what good looks like, a philosophy close to the core of PCE’s business, and demonstrates what can be achieved by the company as partners with passion, determination and not prepared to accept second best.
PCE’s Project Manager Craig Billyeald commented, ‘’The structural frame was constructed on site with a workforce averaging at just 18 multi-skilled PCE operatives. In total over 23,000 man hours of accident free working were recorded by the PCE site team. This reinforces the safety systems and pre-planning incorporated within PCE’s design, off-site manufacture and construction activities, proving again that the PCE philosophy and commitment throughout our business is focused on safety being the priority.”