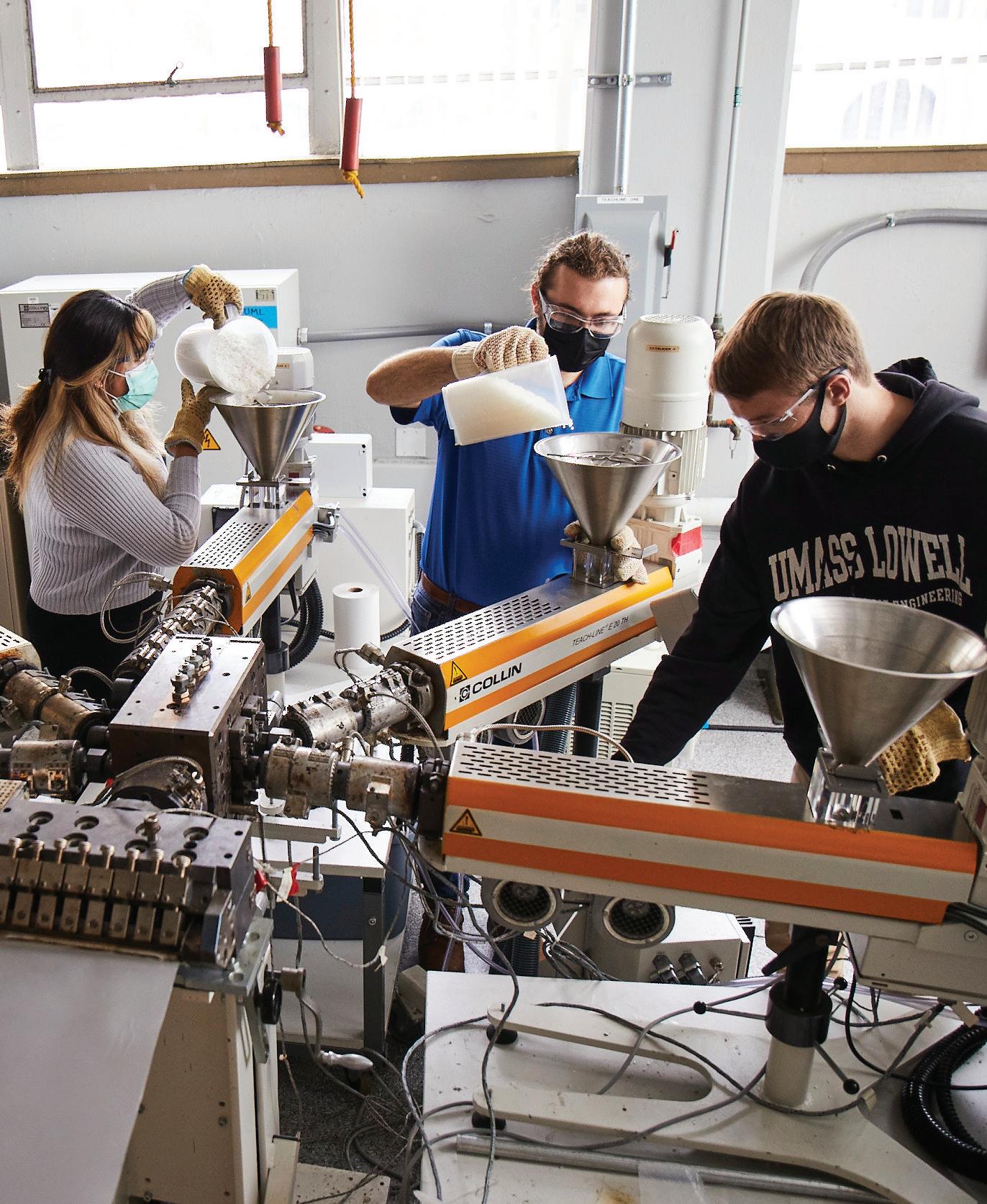
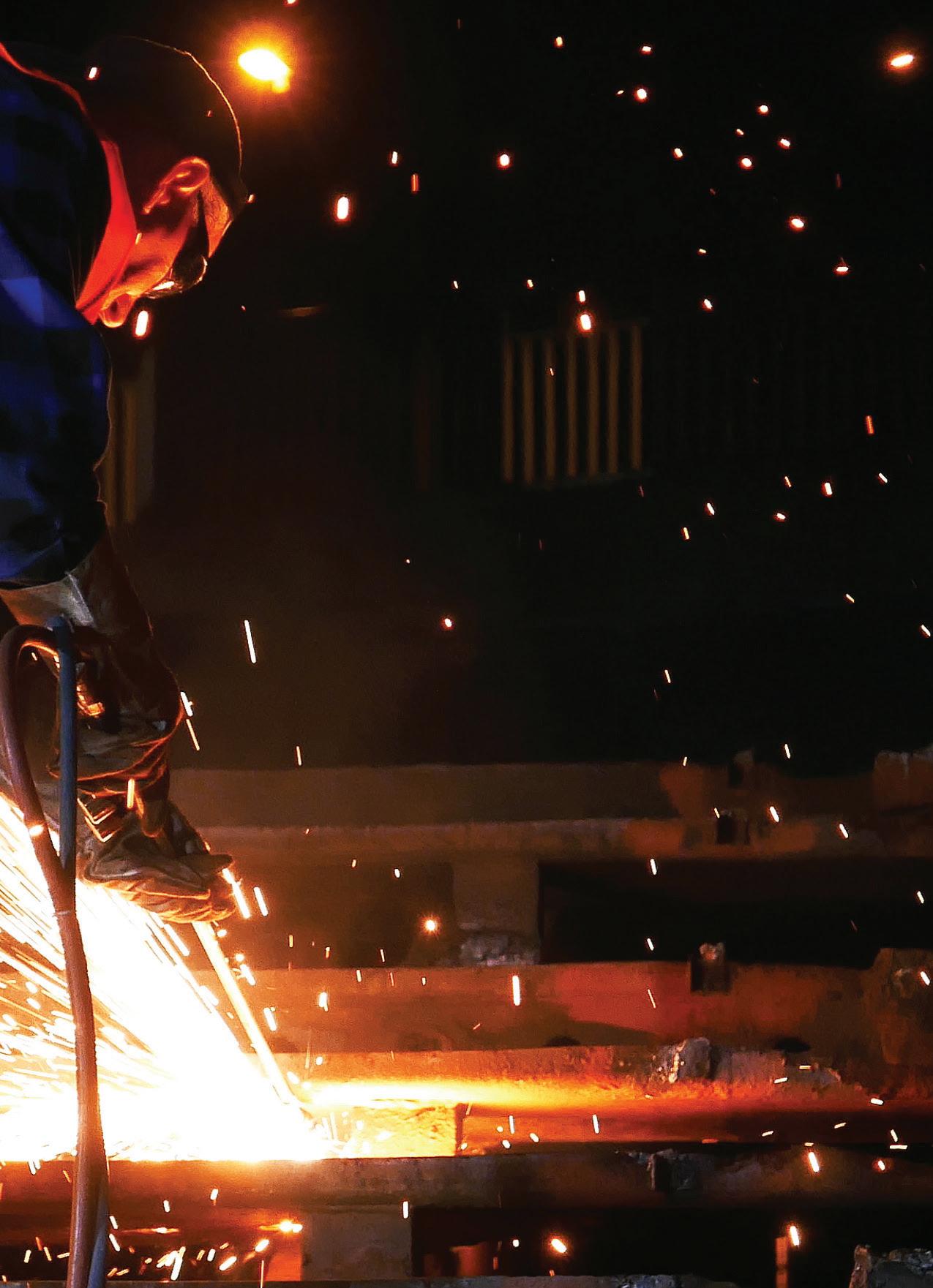
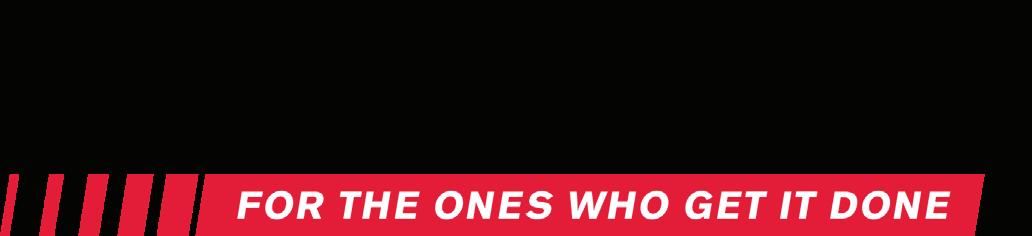
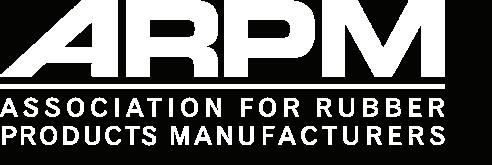
Just recently, I visited a well-known fast-food restaurant to grab a quick lunch; at least, that was my intention. As I entered the establishment, I noticed a small line of people who seemed both perplexed and frustrated waiting to place their food orders.
As I took my place in the queue, I began to notice the reason for the frustrated looks. As time grew, so did the line, and remarkably, customers using the drive-through service were leaving their cars and entering the restaurant to collect their food orders. As this was happening, the stress level of the four employees behind the counter was growing at an exponential rate. They were bumping into each other, arguing in front of the customers, insulting each other and incorrectly handing off orders.
Since I had nothing else to do while in line, I began to wonder: “Where’s the manager? Where is the leader of the pack? Why isn’t the person in charge taking action to fix the obviously broken process?” The answer: He was loading chickens in the oven. He was so consumed with working “in” the business,that he did not recognize he actually was losing business. He was so consumed “in” the process of maintaining inventory levels that he could not see the obvious.
Good business leaders understand the value of working “on” the business rather than “in” the business; however, most also understand how easy it is to be consumed with the reality of meeting customer demands. Today’s rapid pace of business, overloading responsibilities and lean staffing levels often put working “in” the business far out of balance with working “on” the business for many leaders.
Although it may sound silly, are you loading chickens in the oven as a leader, manager or influencer of people? Are you taking time to work “on” your operation instead of working
Letha Keslar, ARPM“in” your operation? If you are, the fix is easy. Great leaders schedule time to work on important matters because they understand that urgent matters always will outnumber the important ones. Just as the restaurant manager was focused on the urgency of ensuring proper levels of oven-roasted chicken, a brief step away from the urgent to focus on the important would have added to his bottom line!
I know that over 600 rubber and plastics manufacturing business leaders will converge in Indianapolis to work “on” their businesses at the Benchmarking and Best Practices Conference. Mark your calendar to join them, October 4-6! (Chickens are not allowed to attend!)
See you in Indianapolis! n
“GOOD BUSINESS LEADERS UNDERSTAND THE VALUE OF WORKING “ON” THE BUSINESS RATHER THAN “IN” THE BUSINESS; HOWEVER, MOST ALSO UNDERSTAND HOW EASY IT IS TO BE CONSUMED WITH THE REALITY OF MEETING CUSTOMER DEMANDS.”
ARPM Team
Strategic Advisor Troy Nix – tnix@arpminc.org
Executive Director Letha Keslar – lkeslar@arpminc.org
Managing Director Kaitlyn Triplett – ktriplett@arpminc.org
Marketing Director Marcella Kates – mkates@arpminc.org
Analytics Director Tony Robinson – trobinson@arpminc.org
Director of Publications Susan Denzio – sdenzio@arpminc.org
Analytics Lead Andrew Carlsgaard – acarlsgaard@arpminc.org
ARPM Officers and Board of Directors
President
Travis Turek, Bruckman Rubber Corporation
Vice President
James Wideman, MBL (USA) Corporation
Treasurer
Marel Riley-Ryman, Southern Michigan Rubber
Secretary
Joe Keglewitsch, Ice Miller LLP
ARPM Board of Directors
Rich Balka, Home Rubber Company
Bill Bernardo, Ebco, Inc.
Kirk Bowman, The Timken Company
Russ Burgert, Maplan Rubber Machinery
Aaron Clark, Danfoss
Joe Colletti, Marsh Bellofram
Randy Dobbs, Sperry & Rice
Ryan Fleming, Freudenberg-Nok Sealing Technologies
Doug Gilg, Continental ContiTech
Diya Garware Ibanez, Fulflex, Inc.
Seth Johnson, Zochem LLC
Donovan Lonsway, BRP
Jon Meigan, Lake Erie Rubber & Manufacturing
Mike Rainey, HBD Industries Inc.
Mike Recchio, Zeon Chemicals L.P.
Brandon Robards, Ace Extrusion
Vice President, Editorial: Dianna Brodine
Editor: Lindsey Munson
Vice President, Design: Becky Arensdorf
Graphic Designer: Hailey Mann
The Benchmarking and Best Practices Conference will host over 600 rubber and plastics professionals in Indianapolis, Indiana, on October 4-6. The conference is anchored with best practices and leading benchmark presentations derived from the industry’s most notable sources of statistical information. A new feature to the event this year is an exclusive automation hall where the industry’s thought leaders in automation will exhibit their technological advancements and automated achievements.
The Conference team is pleased to welcome the following keynote speakers:
As the master of ceremonies for the Benchmarking & Best Practices Conference and known for his spirit, enthusiasm and belief in American manufacturing, Nix will deliver an opening address on lessons in leadership and the importance of becoming more in tune with one’s inner self. Nix’s tagline “America Is What America Makes” is an essential ideal that motivates those attending to strive for excellence.
Mark Scharenbroich
With his career working in both industry and education, Scharenbroich discovered how some of the best organizations and team leaders built a culture that encourages people to perform at a higher level through greater engagement.
An update from Washington, D.C., Nashashibi will provide insights and updates on the latest from policymakers, trade talks with allies, efforts to increase taxes and regulations and what steps lawmakers are taking to address workforce and supply chain challenges.
A prominent keynote speaker around the world, Brown delivered a TEDx talk in 2015 with over 5 million views to date. Brown started her career as an engineer at General Electric, working in both R&D and manufacturing, developing technology for which she holds a US patent. Brown is fluent in Spanish, is a certified Six Sigma Black Belt and holds degrees in chemical engineering, spanish and business.
Laurie Harbour, Harbour Results, Inc.The past several years have shown that it is challenging to predict the future of manufacturing – to say the least. Harbour is going to share how companies can use their MAPP Plastics Benchmarking data to create a roadmap to improve flexibility and de-risk their business.
YOU DON’T WANT TO MISS THIS EVENT! | Early bird pricing ends August 19! Register and learn more: www.arpminc.com/conference.
Please note, this agenda still is a work in progress. The Conference Committee wanted to share the general timeline of the event to assist attendees with travel arrangements. All times are EDT.
Wednesday, October 4
11:00 AM Young Professionals Board Meeting
1:00 PM Young Professionals Pre-Con
1:00 PM Various Sponsor User Groups/Pre-Con
1:00 PM Sponsors/Exhibitors Move In
4:30 PM Sponsors Meeting
4:30 PM Registration Open
5:00 PM Building Leaders of Character Alumni Reception
5:30 PM Industry Welcome Reception
(adjourns at 7:30 PM)
5:30 PM The 2023 Champion Pin Disbursement
Thursday, October 5
7:00 AM Breakfast
8:00 AM Conference Welcome and Keynote Troy Nix
8:20 AM Keynote Mark Scharenbroich
9:30 AM Networking Break Amongst the Sponsors
10:00 AM Keynote Casey Brown
11:00 AM BC LABS Session One
12:20 PM Lunch and Learn with Keynote Casey Brown Or Networking Lunch
1:00 PM BC LABS Session Two
2:30 PM Networking Break Amongst the Sponsors
3:00 PM Omar Nashashibi, Franklin Partnership
3:45 PM Laurie Harbour, Harbour Results
4:20 PM Keynote Jason Young
5:00 PM Members’ Choice Reception (adjourns at 7:30 PM)
Friday, October 6
7:00 AM Breakfast
8:00 AM Peer to Peer Networking
9:00 AM BC Labs Session Three
10:00 AM Networking Break Amongst the Sponsors
10:30 AM Innovation Awards Ceremony
11:00 AM Keynote Dr. Jennifer Golbeck
12:00 PM What’s Next? 12:15 PM Conference Adjourned
This year’s event will take place at the Indianapolis Downtown Marriott, 350 W. Maryland, Indianapolis, IN 46225.
A room block has been secured for the event. Book at www.arpminc.com/ conference.
AMCO Polymers
Americhem Engineered Compounds
Aurora Plastics
Bear Industrial Group
Beaumont Technologies, Inc.
Benesch, Friedlander, Coplan & Aronoff, LLP
Captive Solutions and Options
Chase Plastic Services, Inc.
Colors For Plastics, Inc.
Conair
DELMIAWorks
Federated Insurance
Frigel
Globeius
Grainger, Inc.
Harbour Results
iD Additives, Inc.
INCOE Corporation
Kallan Sales Development
LS Mtron
M. Holland Company
Management Recruiters of Tallahassee
Mantle, Inc.
MBS Advisors
Moldex3D
Noble Plastics
Partnership
Paulson Training
Programs, Inc.
Plante Moran
Plastics Business
Polysource, LLC
Progressive Components
Prophix Technologies
Purgex Purging Compounds
RapidPurge
Rapid Robotics, Inc.
RJG, Inc.
Routsis Training
SIGMASOFT® Virtual Molding
Stout
Synventive Molding
Solutions/Thermoplay
US Compliance
Vive Marketing
WayPoint Marketing Communications
Wipfli, LLP
With thousands of rubber manufacturers in the US, there are bound to be common quality issues faced by plant managers. There also are bound to be common-butoverlooked ways, as well as uncommon ways, to address those issues. Here are a few ideas for tackling quality issues; they might be just the ticket or they might be food for thought that will spawn an entirely new quality control approach.
For some production jobs that call for a cleanroom, rubber manufacturers might benefit from thinking outside of the box. Instead of brick and mortar for a hard-wall cleanroom, how about a mobile version that can be moved from work cell to work cell?
● A mobile cleanroom can be constructed with a tube steel frame on casters, clear vinyl curtain walls, a plastic strip doorway, ceiling tiles for a roof, light fixtures and fan-
powered HEPA filters for a positive-pressure HVAC system.
● Mobile rooms do not take the place of all permanent cleanrooms, but they are a flexible option that can work in some situations and can be especially useful for secondary operations.
● A mobile cleanroom has low complexity and high flexibility when compared to a traditional cleanroom and can be constructed in days or weeks. A mobile cleanroom with a simple design costs much less than permanent construction while delivering more flexibility.
● The cost of the HVAC equipment will be the biggest variable and will depend upon the ISO class standard that must be met.
● The only obvious downside is that manufacturers enjoy a much higher level of control over a traditional cleanroom as compared to a mobile counterpart.
● A frame on casters means that the cleanroom can be
moved to surround a single production machine or part of a machine, to shroud a critical assembly line or to contain an entire production line.
What to keep in mind: Seek a mobile cleanroom manufacturer that can build to spec to meet certifications; consider how to maintain the hygiene and integrity of the room, as well as maintenance of the HVAC system; factor in the need for HVAC that meets ISO standards and for particle count equipment to confirm the HVAC capacity; and remember to plan for training/protocols specific to the nature of a soft-wall cleanroom.
While it is hard to beat the human brain for breadth of knowledge, imagination and adaptability, a human brain tasked with performing visual inspection over and over all day long inevitably will experience fatigue, lose concentration and eventually make mistakes. Some sources cite an upto-30% failure rate when humans attempt to catch quality defects, and poor quality control that leads to high scrap rates can take a big bite out of a manufacturer’s revenue.
● A computer vision inspection system paired with a robotic arm consistently can pick up parts, position them precisely to scrutinize and capture images from multiple angles, and assess the parts’ quality at multiple points simultaneously with superb high-resolution vision.
● Vision-enabled robotics simply don’t get tired, get
distracted, get bleary-eyed or slow down. And they have an unmatchable knack for recognizing defective similarities and patterns – machine learning – to help guide design and production improvements.
● Considerations for implementing a computer vision inspection system include choosing the correct lens for the size of the part being scrutinized and installing the proper lighting for illuminating a matte or shiny, an opaque or transparent, or a smooth or textured part and for revealing the tiniest flaws that may occur.
● The software managing the system must be capable of collecting and storing visual data and able to use machine learning and number-crunching needed for this part or that certification or those customers.
● Each inspection configuration will be put through its paces for a validation test – fed a large number of parts with a known number of variable defects – to ensure that the machine catches as near to 100% of the defects as possible.
Vision system vendors are ready to customize solutions and construct systems that meet rubber manufacturers’ every requirement.
“It’s better to start small and consistent than large and inconsistent.” So says Paul Akers, author of “2 Second Lean,” who preaches the good news that it is not necessary to embrace the entire lean discipline and all of its rules and principles.
“2 Second Lean” simplifies lean into concepts that the entire manufacturing plant’s workforce can understand, embrace and use. Implementing a scaleddown version of lean – just a few essentials – can offer a real payback, and smaller bites of lean are easier to grasp and implement.
● A mantra of “2 Second Lean” is empowerment; rather than empowering only designated problem solvers –aka management – to make helpful change, empower everyone on the plant floor and in the offices to make the little changes that add up to big improvement.
● Morning meetings, during which all employees learn about the company’s financial state, its latest successes and its biggest challenges, can be very brief but immeasurably valuable. With an overview of the company’s health in mind and empowered to “fix what bugs you,” employees at every level can walk the plant
floor on the hunt for little problems that can be fixed with small improvements.
● Improvement examples include organizing tool areas with the “a place for everything and everything in its place” mindset or standardizing how a process is done so that more consistency leads to less error and scrap. For a job with a learning curve for newbies, how about making a short video, uploading it to YouTube and posting a QR code at the workstation so employees can scan the code, watch the video on their phones and then get to work?
● Along with empowerment, “2 Second Lean” depends upon employee engagement. Respect each individual’s value, and offer them chances to learn, grow, advance and teach.
● Engaging and empowering workers often helps cultivate a company culture that keeps veteran workers on the payroll and attracts new employees.
By introducing “2 Second Lean” and inviting everyone to climb aboard as a constructive critic and changemaker, manufacturers can make big gains. n
This article was based on ideas that were shared at the 2023 MAPP/ARPM Engineering & Quality Forum on April 20-21, a veritable breeding ground for innovation. Thank you to the presenters, including “Master Class – Mobile Cleanroom,” by Rob Zimmerman, Westec Plastics; “Why Computer Vision Systems Beat Human-Based Inspection Every Time,” by Ed Chan, Mandy Dwight and Nick Keyes, Rapid Robotics; “Master Class – 2 Second Lean Journey,” by Shawn Gross, Viking Plastics.
More information: www.arpminc.com/events/
Most customers believe they have a practical understanding of whether a product fits its purpose. For example, a garden hose should not burst when the water is turned on. But because this concept is so key and disagreement so frequent, most suppliers go to great lengths to confirm a product works as customers believe it should.
So, how does a supplier determine a product is usable for its purpose?
Testing. For a garden hose, it might be a burst test – that is, pressurize a hose until it bursts (all very safely, of course). But how about a hydraulic hose operating under much higher pressure, sitting in the sun all day, rubbing up against a part of the bulldozer body at -40° C or perhaps 125° C?
The manufacturer of a hydraulic hose – for example, a fiber-reinforced hose for oil-based hydraulic fluids – has a much bigger burden confirming the product works as stated. Technological products typically are tested at three levels.
First, there’s development testing. At this stage, everything about the product could be new and untried. The raw materials, the subcomponents made by a second-tier supplier, the manufacturing technique and the design geometry all might be different from earlier models. Perhaps it has new rubber formulations for the hose cover and interior. The cover rubber will need to be tested for the effects of ozone, temperature and abrasion. The interior rubber will be tested for the effect of the hydraulic oil and temperature. Related tests will be run on other subcomponents, like the fiberreinforcing material. With this information, the designer makes prototype hoses for testing the geometry (diameters, wall thicknesses), the manufacturing technique (die size, adhesion and cure parameters), and finally, the finished product (flexibility, vacuum, abrasion and pressure). The idea is to find tests that mimic the products’ working environment and elicit the same failure characteristics as in the field. For products that last years, it is necessary to accelerate the aging/failure process. Consider a car engine crankshaft seal. If tested on a car, a seal will last 10 years or more – a long
time to determine whether a design is good or to test several design ideas. Even when accelerated, a seal test in the lab lasts nearly six months.
The next level of testing begins once designers believe they have a working product (and many times, before). The goal is production qualification. A production batch is run, then parts are tested to determine whether the supplier reliably can make the product to specification, and if not, whether any defective parts before they are shipped. This leads to the last type of testing can be caught: Periodic tests run to confirm nothing has changed in the material, design or manufacturing process since the original qualification testing was done.
This test sequence is logical but complex to execute when the same hose goes to several customers and each could have a different set of tests to meet their requirements – or no tests at all. For a typical hydraulic hose, ISO 1436 (and the 10 other ISO test methods it references) outlines how the hose is tested. Hoses are tested for bend radius, burst pressure, low-temperature flexibility, cover adhesion, lining adhesion, vacuum, abrasion, ozone, fluid resistance for cover and lining and several dimensional features. If there is a change in the product material, design or manufacturing process, some or all the tests need to be run again.
The ISO 1436 does not stop there. Certain tests are expected to be run at intervals based on time (every 24 months), length of manufactured hose (every three kilometers) and warehouse production lot. As complex as this seems, without the standard there would be an even larger spaghetti bowl of individual supplier-customer test programs and conditions. Currently, the responsible ISO group – TC45/SC1 – is working on clarifying these test requirements and retest intervals.
Until now, the hydraulic hose has been used as an example. Test protocols like ISO 1436 exist for welding, steam, ammonia, oil suction and gasoline hose (all ARPM standards). And even further, test methods exist for most critical rubber products on the market today – many captured by one of the standards writing groups. All of them are efforts to ensure a product is merchantable or better. n
Getting job applicants in the door and converting them to employees is just the first step in ensuring a manufacturing plant is fully staffed to meet its customers’ needs. A focus on retention is critical, and human resources professionals in five rubber companies across the US have created game plans within their companies to fuel, engage and build long-lasting relationships with employees.
Albert Levalle is the human resources manager for La Habra, California-based VIP Rubber & Plastic Company. VIP Rubber has been manufacturing custom rubber extrusions, plastic extrusions, rubber sheet products, molded rubber products, plastic pipe and tubing in the US since 1961. Daniel Gifford, human resources manager, and Sandy Burnett, human resources generalist, oversee recruitment and retention activities for Bando USA, Inc., Bowling Green, Kentucky, a supplier of automotive and industrial power transmission and conveyor belts.
Garware Fulflex USA, Inc. (Fulflex), Brattleboro, Vermont, is a manufacturer of rubber sheets and elastic tapes, and Anne Meyer serves as its human resources manager. Fernando Gauna is a human resource recruitment specialist at R.E. Darling Co., Inc. (REDAR), a composite manufacturing company in Tucson, Arizona. And at Ebco, Inc., Elgin, Illinois, Bill Bernardo is the CEO who leads the familyowned and engineered-driven company supplying OEM customers with elastomer solutions.
From review incentives to rewarding excellent attendance and safety records, companies prioritize employees by creating a sense of value, recognizing hard work and encouraging growth opportunities.
REDAR encourages employee participation in engagement activities, Gauna said: “Giving employees outside opportunities away from work creates an environment that allows teams to build a deeper respect for one another. The company offers a variety of activities, including a Family Feud game show night, wellness challenge and classes from Zumba to boot camp, appreciation week and family events.”
In addition, REDAR executives do quarterly lunches with newly hired employees as a time to get to know one another and gather feedback on the process of onboarding, team orientation, training and everyday work experiences.
Fulflex’s new hire orientation used to be a few short hours. Meyer said, “HR paperwork would be filled out, they would watch a few safety videos and take a quiz, then take a facility tour and start training.” To help new hires feel more at ease, confident in their new role and acclimate as part of the team, the company recently restructured its new hire orientation. Now it’s a full day of fun, learning and engagement activities, including lunch with peers and managers, to provide a oneto-one experience with full safety training with videos and quizzes, policy and procedure overview, harassment training, benefits review and more.
New hires also are engaged in a 30-, 60- and 90-day HR review so there is continued communication and the opportunity for the new hires to provide their feedback on what’s working and what is not so Fulflex can facilitate continued improvement with onboarding, etc. All of this is done with specific personnel, such as the human resources manager, HR administrator, department managers and anyone who would be a guide for the employee. Engagement is important for both new hires and tenured employees. Fulflex provides monthly grinders and salads for all staff, attendance raffles and birthday cards that include a gift card from a company favorite, Dunkin Donuts.
Ebco adds fuel by conducting a 90-day review of its new hires. If employees meet or exceed expectations in that review, they could receive a bonus. Bernardo said, “We want to be competitive when it comes to getting top-notch talent, so we pay at or above published pay rates for the county and state. We also offer tickets to sporting events and have monthly massages available, among many other incentives.”
Once on board at VIP, an employee immediately becomes part of the family. By choosing to invest in its employees –not only through a benefits package but also through personal touches such as birthdays, department parties, a summertime bash and holiday time off – VIP has seen the reward within its culture. Levalle shared, “Each department is like a family. They get to celebrate big life events from anniversaries to awards given for safety, training, etc., all with a dedicated budget from the company.”
Bando has a Gain Sharing Bonus program where employees are recognized for going above and beyond in their day-today work. “The program is about contributing to the ‘gain’ of being better as an employee, department and facility,” Gifford said. “It allows employees to step up and be a leader, whether it’s showing up for work every day, following safety procedures, speaking up if there’s an unsafe situation or helping their department to succeed in its goals. It assists in creating a culture of self-accountability, positivity, hard work and reward.”
As an industry, rubber companies are facing the same human resources challenges and market labor lows. A company’s front line is looking for emerging trends to help alleviate internal tensions, grow a balanced organization and retain skilled and seasoned employees, all with a common goal of meeting customer expectations. Together, in the trenches, companies share leading ways to adopt the power of communication, fine-tune safety protocols and change the status quo of culture.
From an open-door policy to creating a work-life balance among employees, Meyer receives many knocks on her door a day! When she gets a knock, Meyer typically responds with one of the following lines: “I’m never too busy for you, come on in,” “We’ll do this together” or “We’ll stay here until we get it done.”
“My door is always open. I will drop what I’m doing if an employee needs anything, right down to a personal crisis. I want to hear about it,” Meyer said. She knows this level of connection shows employees they are valued and have a workplace that cares. Culture is a huge part of Fulflex but building it is not always easy. She said, “I give everyone an
equal amount of respect, no matter what level of position. Employees know that what they say to me will be held in confidence, and many reciprocate the same level of compassion and care, saying, ‘I’m happy you’re here.’ That’s when you know you’re doing something right.”
Fulflex’s Vice President of Operations Don Venice holds a State of the Business monthly meeting plant-wide for all three shifts. This meeting comes with complete transparency to employees, with Venice presenting on sales, new policies, safety and so forth. Managers occasionally will contribute to the meeting by addressing issues, concerns and successes. The presentation then is posted in the plant’s main hall for all employees to return and read – communication is key.
At REDAR, employees know of the open-door policy, and it’s used from the bottom to the top level; however, one of the most intriguing and useful systems the company put in place is its ethics hotline. Gauna shared, “This is an anonymous messaging system for employees to report any issues or concerns. In addition, we do two surveys a year, companywide, with minutes of paid time for employees to tell us about their experience with the company and provide us with feedback on what has been going well and what we need to improve.”
Like the other HR managers, Levalle has an open-door policy, and on a typical day, he can be found on VIP Rubber’s facility floor making rounds with the employees – watching, listening and having conversations. He said, “My department always has an open door; our office is on the main floor where the action is and that was one thing I changed when I started last year. The old HR department used to be upstairs.”
“BY CHOOSING TO INVEST IN ITS EMPLOYEES... THROUGH PERSONAL TOUCHES SUCH AS BIRTHDAYS, DEPARTMENT PARTIES, A SUMMERTIME BASH AND HOLIDAY TIME OFF – VIP HAS SEEN THE REWARD WITHIN ITS CULTURE.”
Gifford shared, “My office is so close to the employee break room, I can hear the microwave or employee conversations. This is important to me to be available, and employees frequently do utilize my open door.” Beyond human resources and its open-door method, Gifford heavily relies on the production managers to get a pulse on employees through weekly gatherings with each shift. These usually are done by standing in the aisle and having an open dialogue among the teams. From those gatherings, HR receives feedback, managers can address concerns and questions, safety practices are mentioned and put top of mind, and teams bond with each other.
Meyer said safety is a big challenge for Fulflex. “We don’t have a designated on-site safety representative to offer “As a team, we review the situation. Employees just want to be heard, listened to and given a sense of value. With that, as a company, we’ve provided Psychological Safety training by partnering with our insurance broker,” said Meyer.
Meyer strongly believes it starts with a culture of mutual respect and accountability, from the top-level employees to the lower level. She said, “The workplace culture must shift. If you see something, say something.” Meyer began making the shift in developing a “Stop and Spot” observation card. She said, “It’s a simple checkbox card with categories (i.e., behavioral, PPE, Line-of-Fire, etc.,) that an employee fills out and drops in one of the multiple safety observation boxes located throughout the facility. Whether the card is filled out for recognition or a safety concern, it’s encouraging all employees to come forward and look out for themselves and their co-workers. Every Friday, Fulflex has a safety meeting and, instead of gathering with a small committee, it’s required for every person in the building to attend, as each employee is considered to be a member of the Safety Committee.
Gauna shared that REDAR is passionate about recognizing its employees and that safety is a top priority. “Yes! We celebrate work anniversaries, give out safety awards and do ‘near miss’ monthly drawings for employees who participate in notifying our EHS department of ‘near misses,’” he said.
Ice Miller focuses on meeting the needs of our clients quickly, efficiently and cost-effectively. Ice Miller attorneys with rubber industry experience can assist with your greatest legal challenges. Contact Josef Keglewitsch at 614-462-2279 or josef.keglewitsch@icemiller.com for more information.
300+ lawyers in Columbus and other offices
icemiller.com
Every day, VIP does essential safety walks in its fast-paced environment. Levalle said, “We make sure the facility is compliant and meets OSHA standards. Safety is a significant piece of VIP’s culture. HR gets on the facility floor, holds discussions and takes issues on the spot – and responds accordingly. It is important every employee feels safe at work.”
Each year, Bando dedicates an entire week to safety, known as its Safety Week. During this week, all of Bando’s parent companies are invited to be involved and participate, whether at the US facility or from afar. Gifford said, “With
“...GIFFORD HEAVILY RELIES ON THE PRODUCTION MANAGERS TO GET A PULSE ON EMPLOYEES THROUGH WEEKLY GATHERINGS WITH EACH SHIFT.”
all of Bando’s locations across the world partnering together to have Safety Week, it is important to engage employees through friendly competitions, such as who has the best safety slogan or who can identify the most potential safety hazards, and then we fix them, among many other games. We dress up in hard hats and safety vests! We partner with local insurance companies that donate items to employee gift bags. It’s a big week to stop and remind each other about safety practices, have fun as a company and show that Bando values its employees. It’s also a week where HR and leadership are out engaging, connecting and interacting with employees;
it’s a time for employees to have conversations beyond the facility walls.”
For Meyer, it’s about the small wins and finding what makes employees tick by offering attendance rewards and benefits that are outside the box. She said, “It’s about the team – if you don’t come to work, your teammates are burdened and production can be negatively impacted. It affects the team morale and the company entirely.” Recently, Fulflex had a working day of perfect attendance, so as a reward and to show employees the importance and appreciation of showing up, pizza was provided for all shifts.
Gifford knows all too well the challenges with employees not showing up. He said, “Bando struggles with attendance, and we’ve tried to combat it with a point system.” Bando’s point system has proven effective in combating poor attendance, building morale and culture and proactively pushing employees to have self-accountability and a team mentality. On day one, employees are given a specific amount of points that can either grow or be taken away. An employees points increase for good attendance, following best safety practices, going above and beyond for the company, and so forth but
decrease for poor attendance and so forth. Employees can turn points into rewards. The company’s goal in the next year will be to get fully staffed by filling the generational gap and cross-training specific job roles. So, if attendance is an issue in specific roles, Bando will be prepared to prioritize the needs within the facility and place employees appropriately.
“We’re at a turning point with the market, customer orders and employee morale that is showing leadership it’s time to make a few critical adjustments. We believe that through the highs and lows of it all, and as labor settles, employees will see a profession and career and not just a job,” Gifford said.
VIP Rubber shared its top five human resources trends that employees find valuable and meaningful:
1. Communication – From the onboarding process to a tenured employee, communicating and listening are essential to creating a value-based foundation for each employee. It’s about the connection between HR and employees.
2. Security (employee value and financial) – Everyone wants personal and financial security, fair job responsibilities and a fair wage.
3. Safety – VIP is in constant motion every day to make sure all employees are safe on the job. The maintenance team can be called on at any time to jump in and fix a machine, clean up a spill, etc. There’s a level of respect that comes with safety because employees are not just looking out for themselves but also for their team and the entire company.
4. Engagement and respect from every level – Levalle said, “It starts at the top. VIP is led by amazing leaders who are great people; they come down to the facility floor, walk around and talk with employees. Their example trickles down to the bottom line.”
5. Benefits for the employee and family – Offer quality benefits for the employee and family. Create an employee buy-in to form a sense of ownership and value between the company and the employee.
The human resources department is the cornerstone of every company. As front-line workers who battle the labor market lows, HR teams put forth every resource to retain employees and cultivate a culture of positivity and teamwork. It is in working together and sharing methods that shines a light on recruiting and retention issues. “Culture is why employees show up,” Levalle said, “they realize they are on a team and play a vital role on that team and for the company. Every person has a job to do, and if that person doesn’t show up, it brings down production and productivity.” n
ARPM’s purpose states that “ARPM is a giving organization comprised of the rubber industry’s most successful manufacturing companies. We are committed to shaping the industry through continuous evolution of improving leading-edge training and setting product standards.” One way the ARPM leadership teams are embodying this purpose is through the development of the ARPM Training Academy.
According to the Association for Talent Development (ATD), companies that offer comprehensive training programs have 218% higher income per employee than companies without formalized training. But it doesn’t stop there. These companies also enjoy a 24% higher profit margin than those who spend less on training.1 For years, companies have struggled with the Return on Investment (ROI) for investing in the training of employees. However, these statistics illustrate how devoting more resources to training will save a company time, money and resources and enhance the company’s technical depth – which are all reasons why the ARPM Training Academy was created.
Rubber industry professionals have expressed a need for in-depth technical training, and ARPM was able to facilitate a Seals Product Design and Manufacturing training course in June 2023. While the foundation for this course lies within ARPM’s industry-leading best practice documents and product standards, Joe Walker of Elastomer Technologies and ARPM’s Training Academy director, took the lead in developing the agenda and bringing in industry veterans with over 140 years of combined experience in the rubber industry. This course was an industry first and, due to the technical depth of the instructors, became the industry’s most powerful training event offered.
Attendees spent five days immersed in comprehensive training in rubber science, product design (for static and dynamic sealings) and producibility. One attendee shared, “These were some of the best, most knowledgeable and experienced people to teach this kind of class.”
When ARPM shared with the industry that a training course of this depth was going to be offered, Walker stated to the members, “The quality of a company’s associates directly is related to their knowledge of materials, design, products and processes that are the fundamental backbone of the products that are being delivered to the customer. The ability of these associates – design engineers, commercial teams or process designers – to respond to the voice of their customers is key to a company’s reputation in the industry.”
Ensuring the associates have the skills and knowledge needed to succeed is the responsibility of the company. Walker continued, stating, “The most effective way to enhance the quality of these associates is to have them gain experience from industry experts. By making use of the knowledge of these experts, who come from a variety of industry-leading companies, this program allows associates, and therefore the company, to benchmark their own internal knowledge base and practices. It evaluates and implements industry-wide best practices to gain enhanced knowledge and demonstrate an investment in the company and its associates. It is not common to have an assembly of such industry experts as ARPM has gathered to provide this comprehensive series of training in sealing technology. There simply is no more efficient or cost-effective way to invest in associates and enhance a company than through this industry first.”
In early June, eleven world-class organizations sent their leaders to participate in the Seals Product Design and Manufacturing training, investing in their employee continuing education and knowledge base. The ARPM
Training Academy, in essence, amounts to focused industry graduate studies for products. The 13 rubber industry leaders who completed these studies were left with enhanced product knowledge, along with a certificate of completion to showcase the time they committed to investing in themselves.
ARPM celebrates the companies that are investing in their employees and the employees who are investing in their continuing education. Congratulations to all the attendees of the Seals Product Design and Manufacturing training:
● Dana Incorporated
● Datwyler Group
● Eagle Elastomer
● Ebco, Inc.
● Engineered Seal Products
● Grace Technology and Development
● Precision Associated, Inc.
● Rainbow Rubber Extrusions, Inc.
● Safran Landing Systems
● Tremco, Inc.
● Uni-Grip, Inc.
Training and development are recognized investments. ARPM will continue to foster the ever-evolving need for new training opportunities for the rubber industry through the ARPM Training Academy. n
References
1. http://businesstrainingexperts.com/knowledge-center/ training-roi/profiting-from-learning/
August 2-3, 2023 – Human Resources Forum
August 16, 2023 – PFAS – A Deeper Dive
August 23-24, 2023 – Peer Networking
September 18, 2023 – ARPM Building Leaders of Character Program
October 4-6, 2023 – Benchmarking and Best Practices Conference
October 18, 2023 – ARPM Connects at the International Elastomer Conference
November 9, 2023 – Stockwell Elastomerics Plant Tour
November 15-16, 2023 – Finance Forum
For the most up-to-date information and to register for events, visit www.arpminc.com/events.
the importance of providing immediate feedback and how it should be delivered; conquering communication challenges by applying time-tested military methods to relay objectives and key mission points; and being equipped to better improve organization performance with After Action Review tools.
Registration is limited to 35 participants on a first-come, firstserved basis. For more information, questions or to register, contact info@arpminc.org.
HR Professionals in the manufacturing industry continue to face challenges in hiring, retaining and engaging employees. ARPM is hosting the annual Human Resources Forum (virtually), August 2-3, 2023, to facilitate discussions on best practices and challenges facing the industry today.
Presentations will cover company culture, training best practices, hot topics in compliance, career paths, apprenticeship programs and much more.
For more information and to register, visit www.arpminc. com/events. Can’t attend the event? Submit registration and receive access to all recordings and event materials.
After years of research, ARPM partnered with Thayer Leadership to create the Building Leaders of Character Program, starting September 18, 2023. Thayer Leadership at West Point builds leaders with a simple premise: Character is foundational to the ability to lead. Combine this with knowledge and action, and it unleashes the “whole” leader every organization needs.
Building Leaders of Character Program 1.0 is made up of 18 virtual sessions over a 14-week span. During the program, attendees will become more robust in holding people accountable; developing and maintaining trust; pulling people together to meet organizational objectives; understanding
Stockwell Elastomerics, Philadelphia, Pennsylvania, will host ARPM’s fourth-quarter plant tour on November 9. Plant tours offer the opportunity for APRM members to visit other member facilities, see how others are approaching challenges and help the host company see new areas of opportunity. Being able to attend member-hosted plant tours is one of the top benefits of being an ARPM member.
During this plant tour, attendees will have the opportunity to listen to the Stockwell Elastomerics team discuss how it has remained an employee-owned company, its safety and continuous improvement initiatives and how it has successfully implemented a return-to-work program.
In the spirit of continuous improvement, attendees will have the opportunity to walk away from this plant tour with several implementable best practices and solutions to challenges the rubber industry is facing.
There are a limited number of spots reserved for nonmembers on this tour. Interested in seeing what a plant tour is all about? Reach out to ktriplett@arpminc.org.
The ARPM Training Academy is a dynamic technical training resource that teaches fundamentals and advanced topics for the rubber industry. Rubber industry professionals came together June 5-9, in Columbus, Ohio, for the Seals Product Design and Manufacturing training course facilitated by ARPM. The Training Academy course was a success thanks to partners, including Freudenberg-NOK Sealing Technologies and MAPLAN, and lunch sponsors, including Akron Rubber Development Lab, DESMA and SIGMASOFT Virtual Molding. For more information, visit www.arpminc.com/training-academy.
Akron Rubber Development Lab; DESMA and SIGMASOFT
Virtual Molding. For more information, visit www.arpminc.
ARPM works to ensure that the interests of the United States Hose, Belt and Seals manufacturers are kept as a priority on the world’s stage and holds positions on Technical Committees of ISO through its membership in the American National Standards Institute (ANSI). Through the support of ARPM’s two technical experts and several volunteers, ARPM is able to oversee the developments and modifications of global standards while providing feedback and governance on suggested changes to international standards. Additionally, ARPM fosters a relationship with the Mechanical Power Transmission Association (MPTA), the Conveyor Equipment Manufacturers Association (CEMA), the Association for Hose and Accessories Distribution (NAHAD) and the Compressed Gas Association (CGA).
All the product standards go through a revision by ARPM’s technical committees every five years, to follow the ANSI requirements. In the last month, ARPM announced two newly updated sealing standards – OS-4: Application Guide for Radial Lip Type Shaft Seals and OS-15: Measuring Radial Lip Seal Torque and Power Consumption.
ARPM provides over 120 product standards at no cost to members, including the new versions as they are updated. To view the full list of product standards, visit www.arpminc.com/publications
Please join ARPM in welcoming the following new members!
R.T. Vanderbilt Company Tremco, Inc. Qualiform, Inc. n
The
This executive leadership program is open to mid-to-senior-level leaders, across the rubber industry, who want proven, practical tools to be a more effective leader.
The experience includes an assortment of applied academic classroom modules, interactive experiential sessions, mentoring with expert faculty, networking time with other participants, and inspirational speakers.
Register your leaders today!
"THIS LEADERSHIP PROGRAM EXCEEDED MY EXPECTATIONS. I WOULD HIGHLY RECOMMEND IT FOR ANY LEVEL OF LEADER DESIRING TO GROW AND IMPROVE THEIR SKILLS."
- VICE PRESIDENT ENGINEERING
The 2023 Environmental Health and Safety (EHS) Summit was held on May 24-25 in Columbus, Ohio, where the Association for Rubber Products Manufacturers (ARPM), announced the winners of the Safety Awards. The EHS Summit is an annual event hosted by ARPM and is designed to share best leadership and safety practices with industry professionals who want to achieve world-class safety within their companies.
The Safety Awards Program is comprised of two awards: the Safety Achievement Award and the Safety Best Practice Award.
The prestigious Safety Achievement Award is broken down into four award levels: Gold Achievement, Silver Achievement and Honorable Mention. The award is a way to recognize safety in the industry and award facilities that have achieved a level of safety performance above the industry average.
The award requirements are based on data reported on a company’s annual Occupational Safety and Health Administration (OSHA) 300 Log of Work-Related Injuries and Illnesses. This data is reported by an employer through the Log and the Incident Report only if a recordable workrelated injury or illness has occurred, including death, days away from work, restricted work or transfer to another job, medical treatment beyond first aid, loss of consciousness or a significant injury or illness diagnosed by a physician or other licensed healthcare professional.
Recognizes worksites with no occupational injuries or illnesses.
● BRC Rubber & Plastics, Bluffton, Indiana
● BRC Rubber & Plastics, Ligonier, Indiana
● Hamilton Kent LLC, Winchester, Tennessee
● Mechanical Rubber Products Co., Inc, Warwick, New York
● Zeon Chemicals L.P., Hattiesburg, Mississippi
● Zochem ULC, Brampton, Ontario
Silver Achievement Award
Recognizes worksites with no occupational injuries or illnesses involving lost workdays or restricted work activity.
● Blair Rubber Company, Seville, Ohio
● BRC Rubber and Plastics, Hartford City, Indiana
● Zochem LLC, Dickson, Tennessee
Honorable Mention Award
Recognizes worksites with the lowest incident rate based on size (1-199 employees and over 200 employees).
● Eagle Elastomer, Cuyahoga Falls, Ohio
● Prospira America, Upper Sandusky, Ohio
Safety Best Practice Award
Recognizes the “best practices” that an organization implemented to increase overall safety.
● Hamilton Kent LLC, Winchester, Tennessee
● Contitech Canada, Inc., Mississauga, Ontario
● Zeon Chemicals LP, Hattiesburg, Mississippi
ARPM Managing Director Kaitlyn Triplett said, “The Safety Awards Program recognizes leaders in the rubber industry for committing to and achieving excellence in safety and These companies are making safety a top priority and have gone above and beyond to ensure their most valuable asset – their employees – are safe on the job. Congratulations to all of our 2023 Safety Award Winners!” n
More information: www.arpminc.com/ehs
A S S O C I A T I O N F O R R U B B E R P R O D U C T S
M A N U F A C T U R E R S
B e n c h m a r k i n g | I n d u s t r y S t a n d a r d s |
T r a i n i n g | N e t w o r k i n g | a n d m o r e . . .
L i s t e d i n R u b b e r a n d P l a s t i c s N e w s " T o p 5 R u b b e r
I n d u s t r y A s s o c i a t i o n s Y o u S h o u l d K n o w . "
V i s i t a r p m i n c . c o m f o r m o r e .
Orion S.A. (OEC), Grand Duchy of Luxembourg, a specialty chemicals company, announced it entered an exclusive distribution agreement with ChemSpec, Orrville, Ohio, a specialty chemicals supplier. Effective July 1, 2023, ChemSpec represents Orion’s rubber and premium rubber carbon black product lines for mechanical rubber goods throughout the US and Canada. ChemSpec is a subsidiary of Safic-Alcan, which also is a partner with Orion overseas. ChemSpec has a wide range portfolio of products to offer the rubber industry, and the Orion carbon black line enhances its value to the end user. For more information, visit www.orioncarbons.com.
Trelleborg Healthcare & Medical, Plymouth, Minnesota, a provider of innovative, reliable engineered polymer solutions for demanding medical, biotech and pharmaceutical applications, hired Scott Ryan as general manager for its Northborough Biopharma Center of Excellence in Massachusetts. Ryan is responsible for operational strategy and oversight of all critical management functions. In addition, he leads site operations including production, building repair, maintenance, security and safety. Ryan has more than 35 years of progressive diagnostics, clinical manufacturing, quality and process development leadership experience. Before Trelleborg, he served as senior director of a high throughput plasmid manufacturing company and led operations of a genetics laboratory. Ryan earned his Master of Science degree in Clinical Laboratory Sciences Management from UMass Lowell in Lowell, Massachusetts. For more information, visit www.trelleborg.com/healthcare
Smithers, Akron, Ohio, a provider of testing, consulting, information and compliance services, announced the hire of Chad Atzemis as a senior consultant. As part of Smithers’ rubber technical consulting team, Atzemis leads efforts to expand its technical consulting offerings into additional markets and enhance the team’s capabilities. The technical
consulting team at Smithers guides everything from raw materials analysis and product engineering to laboratory testing and field performance. Before joining the team at Smithers, Atzemis was COO at Lianda Corporation. Atzemis serves on the Ohio Rubber Group board and holds a Six-Sigma Green Belt.
Additionally, Smithers announced its sponsorship of the University of Akron Formula SAE Team. Recently, it hosted the team at the Smithers Tire & Wheel Test Center for a tour of the facilities and a discussion about laboratory testing for automotive components. The University of Akron has participated in Formula SAE for over 30 years. Students are challenged to incorporate their classroom knowledge into effective automotive designs by designing, building and racing a Formula One-style racecar. The experience empowers students to confidently enter the workforce and make significant contributions to the automotive industry after graduation. The team placed eighth out of 89 teams at Formula SAE Michigan in May 2022, with top 10 finishes in the endurance and design events. The sponsorship from Smithers will support the design and creation of the car, as well as shipping costs and travel expenses for overseas competitions. For more information, visit www.smithers.com
Ice Miller, a full-service law firm that spans eight offices, welcomed 31 summer associates to the firm in its Chicago, Indianapolis, Columbus and New York offices. Law students from 21 law schools joined the firm for this year’s 10-week, in-person program. The summer associates have opportunities for substantive legal work, skills-based training, pro bono work and networking events. Each summer associate is paired with an associate mentor. For more information, visit www.icemiller.com
Grainger, Lake Forest, Illinois, a broad-line distributor of maintenance, repair and operating (MRO) products serving businesses and institutions, has expanded its long-standing
educational assistance program to include part-time team members and partnered with new institutions to provide high-quality degree programs, with some offered at no cost. From day one, all team members are eligible to apply to the program, which provides up to $5,250 per year toward a qualifying degree. For annual tuition above that, Grainger splits the cost – covering 50% – with no limit. This also includes specialized technical certifications, such as HVAC and OSHA training.
In addition, Grainger is expanding its relationships with accredited institutions and has partnered with Western Governors University and the University of Phoenix to
offer team members a high-quality education. For more information, visit www.grainger.com.
Stern Rubber Company, Staples, Minnesota, a manufacturer of custom rubber products offering full services from design to quality assurance, has expanded its product portfolio to include agricultural flails. These flails are compressionmolded natural rubber products used for defoliating sugar beets. Stern Rubber took over this business from Premier Products in 2021. For more information, visit www.sternrubber.com n
•
The manufacturing industry in the US continues to face workforce recruitment challenges. Colleges and universities are helping to address the shortage by offering rubber processing-oriented subject matter, often in conjunction with their plastics and polymer programs. What are institutions offering, and what might they need from industry partners to support their programs in ways that better fill the industry’s needs? Inside Rubber surveyed universities in the Upper Midwest, on the East Coast and on the Gulf Coast to get insight into the rubber processing education available.
How many students are enrolling in the rubber processing-oriented programs each year?
Unfortunately, not that many. If we are talking about kids that specifically go into the bachelor’s program or come over for the minor, it usually is between two and four a year.
Once they have finished their education, how quickly are those students getting hired?
Very quickly, since we are the only school in the country that actually offers a rubber-specific program at the bachelor’s level.
What practical experience is required as part of these programs? Internships?
Students are required to do an internship for the associate degree and one for the bachelor’s degree as well. The students usually find them on their own, but we always have companies reaching out to the university and making offers, which we post for the students to see.
How is Ferris State partnering with the manufacturing community in your area?
Ferris State University, www.ferris.edu, is a four-year public institution located in Big Rapids, Michigan. Ferris State started its Rubber Technology program in 1998. Marc Guske, program coordinator/associate professor, Plastics & Rubber Tech, School of Design & Manufacturing, answered questions for this article.
What does Ferris State institution offer in rubber processing-oriented certificates or degrees?
We offer a Rubber Minor (often paired with an Industrial Chemistry or Plastics major), an associate degree in Plastics and Polymer Engineering Technology that includes rubber coursework, and a Bachelor of Science degree in Rubber Engineering Technology.
Some manufacturers let us go into their facilities and do field trips. The rubber industry can be a little secretive, so we appreciate that they will let us do that. I have a good rapport with local companies; if I need chemicals or bales of rubber, I am able to get donations fairly quickly. And some of our recent alumni have done a really good job of guest lecturing and bringing their expertise back to share with the students.
What additional support do you wish you had for these programs?
More students would be great. The low volume of students is, I think, the same problem that everybody is facing; for whatever reason, when high school kids think about going to college, they don’t seem to be considering engineering or the plastics and rubber fields. Plastic gets a lot of bad publicity, as we all know, but when it comes to rubber, I think people just don’t really think about rubber parts being as necessary and ubiquitous as they are. It’s rather hard to find a cool rubber part among the tires and hoses and belts. O-rings aren’t sexy, but they definitely are critical.
How is your institution promoting these programs?
Most of our recruiting efforts are focused on high-school-age prospects. Every semester we invite the high schools within an hour’s radius of Big Rapids to come on campus for a half day. We pay for the bus, and the students get free lunch. We give a lecture about what our programs are all about, and then we have rotations where the kids go to the plastics lab, then to the rubber lab and then do hands-on chemistry experiments. This approach seems to pay big dividends. When we survey incoming freshmen, we get a lot of kids who say, “Oh, yeah, when I was in ninth grade, we came here and so then when I was thinking about where I wanted to go, studying this at Ferris State just kind of clicked.”
What do you think should/could be done to get more students to enroll?
We have an upcoming event that likely will expose some more people to our programs. The Michigan Rubber Group will hold its technical meeting at Ferris State on September 20, 2023. That will be an opportunity for people in the industry to meet with the Michigan Rubber Group, to see what they do and see our lab facilities, and network. We will have some students presenting at that meeting.
The University of Houston, www.uh.edu, is a four-year public institution located in Houston, Texas. Andy Chang, MBA, program director II, Subsea Systems Institute, UH Energy – Chancellor/President’s Division, described what the U of Houston has to offer.
What does your institution offer in rubber processingoriented certificates or degrees?
We have Rubbers in Extreme Environments, a short course for a certificate that is a micro-credentialing program that offers an understanding of the challenges of how rubber behaves and fails in extreme conditions, along with solutions to prevent failure and develop better materials. The program is geared toward industry professionals and rising seniors in a bachelor’s degree program or graduate student – business, engineering or technology preferred.
How many students are enrolling each year?
It is not a regular program. We offered a course for an industry in March 2023, where more than 50 people participated.
What practical experience is required as part of these programs?
We accept both industry professionals and university students into the program. There are minimum requirements for both groups:
● Industry professionals must have several years of relevant industrial experience.
● Students either must be rising seniors in a bachelor’s degree program or graduate students – in engineering or technology preferred.
The course is lecture-based. Minimum science or engineering background is needed, with a few years of experience in the industry.
How is your institution promoting these programs?
Rubbers in Extreme Environments is of great relevance to industries that use rubbers in extreme environments. We, therefore, focus our promotion on companies in these sectors. We also promote our programs through newsletters, social media and other means that reach out to a wider audience, both in academia and to the industrial sector. We will be offering our next program in November.
What do you think should/could be done to get more students to enroll?
Reach out more. As discussed in the first question, there is a growing need for rubber materials in harsh environments. Greater understanding of that need, and of the opportunity that exists in addressing it, is key to getting more students to enroll. Our main approach to increasing enrollment is through growing our relationships with companies that are active in these applications for various types of rubber materials.
As part of the University of Wisconsin-Milwaukee, the School of Continuing Education, www.uwm.edu/sce, is the largest provider of professional development in southeastern Wisconsin. Aaliyah Schoclet, program manager, engineering, School of Continuing Education, answered these questions.
What does your institution offer in rubber processingoriented certificates or degrees?
The School of Continuing Education offers non-degree certificates in Elastomers Technology, with courses such as Bushing Design for Automotive and Commercial Applications, Molding of Rubber and Design of Rubber Molds, RPA Testing of Rubber Processability and Dynamic Properties and others.
The Elastomer Technology Certificate focuses on recent technologies, advancements in the field and strategies to improve elastomer designs. It benefits anyone designing, manufacturing or working with synthetic rubbers. Students
receive firsthand knowledge from current industry professionals to address real-world challenges. Learning outcomes include proficiency in analyzing methodologies of process variation and control; the ability to assess elastomer material selection, dispensing methods and the molding process; skill in integrating knowledge of elastomer processing equipment, including pumping, shaping, curing and monitoring; the ability to describe different types of manufacturing limitations within the injection molding process; proficiency in evaluating the principles and techniques of designing molds and molded part design; and competence in applying problem-solving techniques and strategies to address situations the student currently faces.
How many students are enrolling in the rubber processing-oriented programs each year?
Our classes are geared toward industry professionals and vary based on industry needs.
How is your institution partnering with the manufacturing community in your area?
We provide customized courses to the manufacturing community. Plus, our instructors are manufacturing professionals in the community with real-life experience who are at the center of growth and change in the rubber processing industry. I also am an active member of the Women in Manufacturing (WiM) organization.
How is your institution promoting these programs? Our comprehensive marketing plan focuses on driving traffic to our website and these programs. From SEO to targeted email campaigns and social media marketing, engineers and other professionals are learning about our programs. We also get a lot of referrals from local companies and past students. Plus, we are working to build connections with key manufacturing businesses.
What do you think should/could be done to get more students to enroll?
It is not about what we should/could do but what we do. We focus on building relationships within the community.
The University of Massachusetts Lowell, www.uml.edu, is a four-year public institution located in Lowell, Massachusetts.
Amy Peterson, Ph.D., associate professor and associate chair for master’s studies, provided information about the education options at UMass Lowell.
What does your institution offer in rubber processingoriented certificates or degrees?
We offer a graduate certificate in Elastomeric Materials. Additionally, MS students can complete a specialization in Elastomeric Materials by completing the courses associated
with the graduate certificate in Elastomeric Materials. Specific courses related to rubber processing include Processing with Elastomers, Rubber Technology, Thermoplastic Elastomers and Design with Elastomers. In addition, thermoset rubberbased experiments are offered as part of the Plastics Process Engineering Labs for the BS degree and the Graduate Polymer Lab required for all MS and Ph.D. students.
We also have a student chapter of the ACS Rubber Division. The students attend the International Elastomer Conference each fall, sponsored by the ACS Rubber Division.
How many students are enrolling in the rubber processing-oriented programs each year?
The Elastomeric Materials graduate certificate program was just reinstated this academic year, so we do not have good data yet. We have a number of students involved in elastomer research projects.
Once they have finished their education, how quickly are those students getting hired?
Since the Elastomeric Materials graduate certificate program was just reinstated, we do not have good data specific to rubber processing yet. The ACS Rubber Division members and the New England Rubber and Plastics Group keenly are interested in recruiting students. In general, students are hired very quickly.
What practical experience is required as part of these programs? Internships?
All of our degree programs include required laboratory courses, which give our students valuable hands-on experience in polymer synthesis, plastics processing and characterization. Our BS and MS programs also have optional co-op programs, which give students the opportunity
to apply the knowledge they’re learning in classes to realworld challenges in a work environment, while also earning money. Many of our students continue working at their co-op employers after their co-op ends, either by working part-time during the school year or by returning to that employer as a full-time employee after graduation. Students also may work on industry-sponsored research projects in elastomers.
How is your institution partnering with the manufacturing community in your area?
UMass Lowell students and faculty regularly attend and present at the International Elastomer Conference and the local ACS Rubber Division section – the New England Rubber and Plastics Group (NERPG). NERPG generously has supported student travel.
We have sponsored research projects and student internships with local industry. Additionally, several (local and non-local) manufacturers are members of SHAP3D, our 3D printingfocused, National Science Foundation-sponsored IndustryUniversity Cooperative Research Center, with particular interest in the thermoset elastomer project.
What additional support do you wish you had for your programs?
We always are grateful for additional support, whether it be internships, sponsored research, equipment or something else. Specific to rubber-related teaching and research, we would like to have a new Banbury mixer.
How is your institution promoting these programs?
Our admissions offices organize regular open houses (including virtual ones for graduate programs) and webinars. That being said, many of our programs are promoted through word of mouth – we offer the oldest and largest ABET-
accredited Plastics Engineering program in the country, so our alumni do a lot of work promoting us actively through conversations and passively through their successes.
What do you think should/could be done to get more students to enroll?
At the graduate level, we have greatly increased our online options to allow working professionals and those who don’t live in the Lowell area (or don’t want to deal with traffic) to complete our graduate certificates and MS. Our graduate certificates can be completed online. Additionally, as of this year, we have an online pathway for our Plastics Engineering MS. To ensure that students graduate with that critical hands-on experience, the online MS includes a two-week on-campus residency to be completed during one of the summers a student is enrolled in the program. During this residency, students will be full-time in our labs. In this way, we can maintain the hands-on strength of our program, which is critical to our industry stakeholders, while still making the degree program achievable for people working full-time.
Specific to rubber processing, we think that better articulation of the importance of elastomers to many products is needed. Elastomers are critical to soft robotics, stretchable electronics, tires and barrier materials, just to give a few examples. Students often are unaware of the interesting, impactful jobs that are available in this field. n
The changing dynamics between employers and the US workforce over the last few years have affected wages and salaries for nearly every job in the manufacturing industry. While wages and salaries in the US rubber manufacturing industry can vary depending on several factors, including job role, skill level, experience and geographical location, the recent trend has skewed toward higher wages for workers amid increased demand for products and services post-2020. These observed increases partly are due to near double-digit inflation and a decreased supply of workers.
According to the US Bureau of Labor Statistics, workforce participation hasn’t rebounded from pre-pandemic levels as of May 2023 and still is 2.5 million workers short when compared to February 2020. Unemployment spiked to over 14% at the height of the pandemic but has been comparable to pre-pandemic levels since early 2022. A reported 0.56 ratio of unemployed persons per open position as of April 2023 is at a record low and has been maintained since late 2021. Low unemployment, plentiful job openings and relatively low participation have made somewhat of a buyer’s market for workers in the past few years, who constantly feel the pressure to find higher wages to offset inflation. However, inflation is slowing in the current year, and potential economic headwinds could see that trend slowing in the second half of 2023.
The 2023 ARPM Wage and Salary Report provides valuable insight into salaries across the rubber industry. The industry offers a range of employment opportunities across numerous sectors, including medical, consumer goods, industrial rubber product manufacturing, and rubber product wholesale and distribution. Additionally, individuals with specialized knowledge in areas like polymer science, materials engineering, automation or rubber technology may earn higher wages than others at similar levels due to the demand for their expertise. Geographical location also impacts wages within the industry, as certain regions with a strong concentration of manufacturing facilities (and competition for workers) or a higher cost of living may offer higher wages to attract and retain skilled employees.
In the 2023 report, 54 of the 67 historically tracked positions (81%) increased median compensation (up from 76% in the previous year). The average increase year-over-year for those positions was approximately 6%. The remaining 13 positions decreased in median salary – averaging around 3% lower than in 2022. The most substantial salary increases between 2022 and 2023 were for apprentices (19% increase), automation engineers (16% increase), warehouse directors and managers (15% increase) and quality directors and managers (13% increase). Conversely, the most substantial median wage decreases were for information systems managers (8% decrease), continuous improvement managers and directors (6% decrease) and sales engineers (6% decrease) (see chart 1).
A new trend for 2023, was that white-collar workers who were directly not involved in the plant’s day-to-day operations most often saw declines year-over-year compared to those closer to operations or engineering. Moreover, having a high-demand specialty gives certain segments of
While the average yearly wage increase seems relatively high, inflation likely accounts for much of this. The consumer price index (tracked by the Bureau of Labor Statistics) peaked a year ago, in June 2022, at around 9.1%, but this has been falling since then and sits at 4.1% as of May 2023, remaining twice as high compared to pre-pandemic levels). Inflation, on average, sits at 5.3% for 2023 (see chart 2), and comparing that 5.3% to the approximately 6% growth on average for positions tracked in the Wage and Salary Report, inflation is likely the driving factor for the general increase. Also, despite these year-over-year increases, processors report slightly lower hiring demand overall than last year.
In 2022, 92% of those surveyed said they would be hiring new employees over the next 12 months, and this dropped to 87% in 2023. While this only is a 5% decrease compared to the previous year, there may be some concern that a recession is likely around the corner due to recent government intervention to curb consumer demand and inflation. Hiring
new roles more slowly than in the previous few years or maintaining a consistent level of employment may prevent any future reduction in workforce. If the recession hits and unemployment increases, employers can likely expect to see the trend in rising wages tail off or potentially decrease as demand for new employees decreases and hiring slows.
The salary and wage increases observed in the 2023 report are not surprising, given the current state of the economy and inflationary pressures. Depending on the situation, processors may need to adjust to remain competitive in the labor market or risk losing valuable resources and incurring additional costs to replace departed employees. If conditions remain favorable toward workers, there will continue to be some degree of movement in the market. Knowing the going rate for those positions is imperative to attracting and retaining the necessary talent to keep operations steady in an uncertain economy. Likewise, if the market shifts toward employers in a recession, processors need to only adjust to the current market if it fits the current needs of their business. The 2023 ARPM Wage and Salary Report contains a detailed breakdown of all 67 industry positions, an analysis of benefits and data on additional forms of compensation to help prepare regardless of market conditions. n
To discover the latest wage and compensation rates, along with the most recent workforce management benchmarks covering shift differentials, overtime, PTO and more, visit www.arpminc.com.