INDUSTRIAL DESIGN
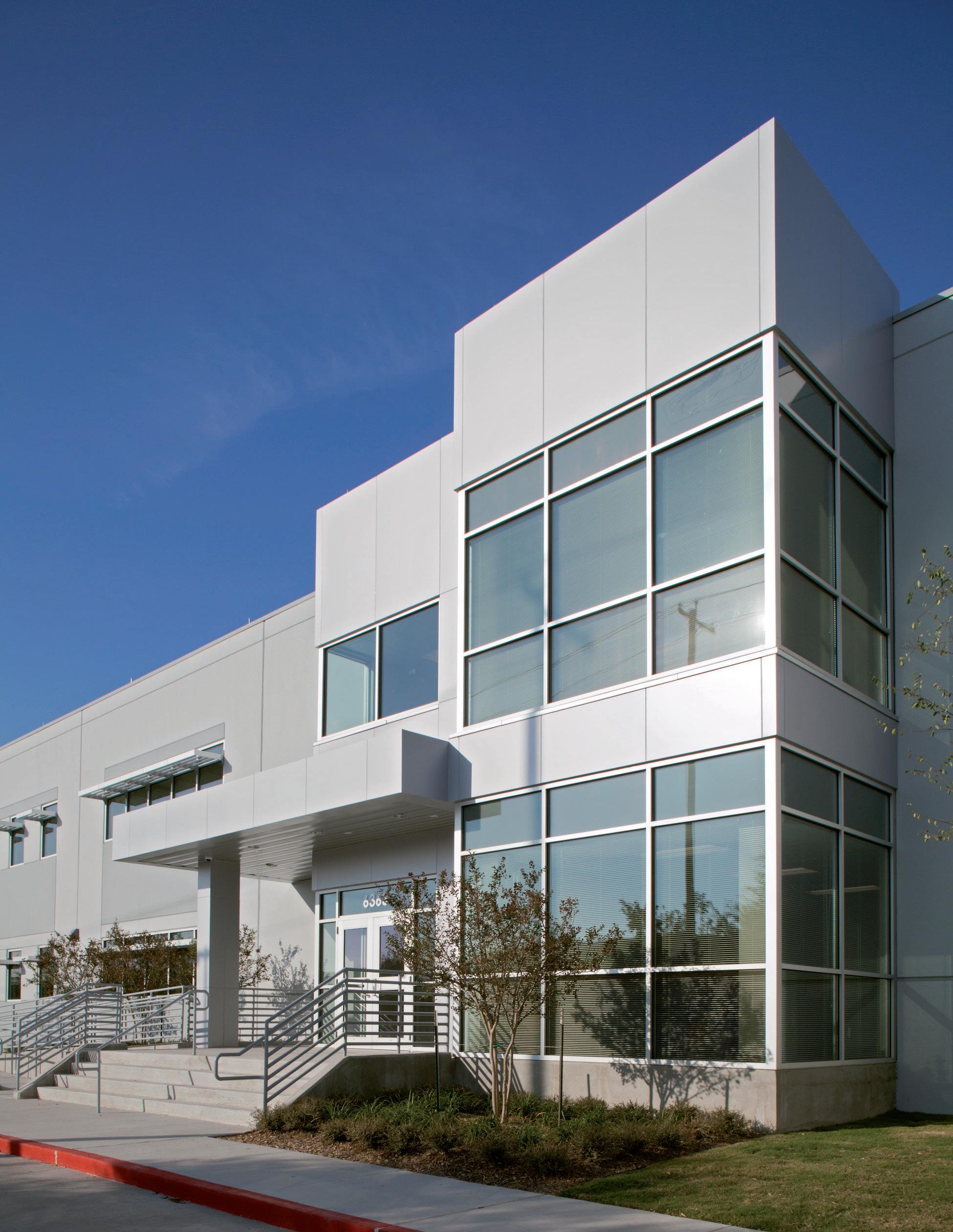
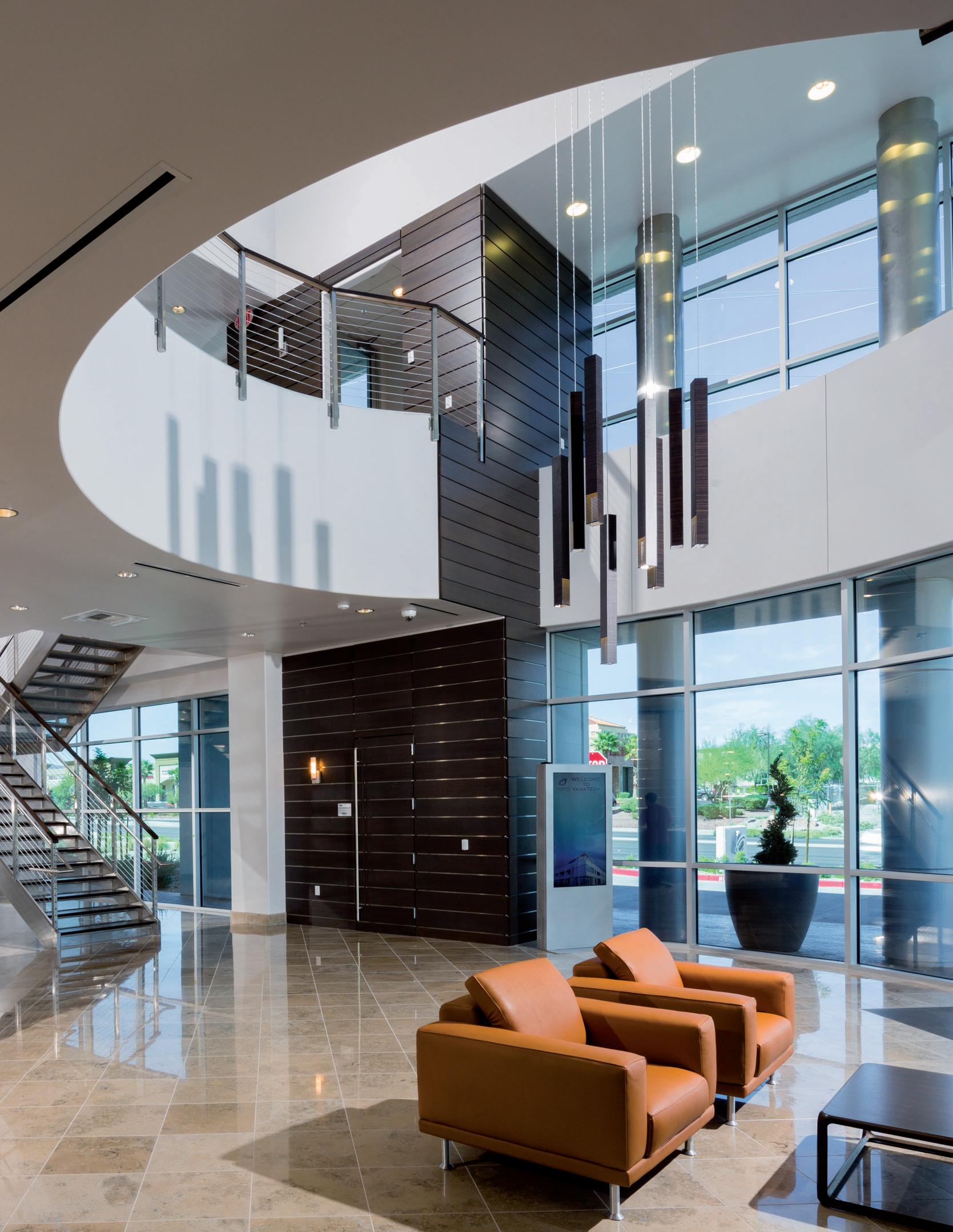
Founded in 1946, PGAL is an international design firm specializing in architecture, interiors, engineering, and planning for a diverse portfolio of public and private sector clients.
Renowned for outstanding client service and attention to detail, we balance innovative, responsive design solutions with a pragmatic, cost-conscious approach. This client-centered philosophy has earned PGAL repeat business and lasting relationships for more than 75 years.
We work with clients on projects large and small, developing long-term relationships based on partnership and trust. Every project decision is made to serve the client’s current and future needs.
Each assignment is led by one of our hands-on principals and embraced by a carefully selected project team of seasoned professionals. These core groups collaborate with a staff of more than 250 architects, engineers, designers, and planners across 13 regional offices to create landmark, award-winning projects that completely satisfy our clients’ goals.
Carnival Cruise Lines (CCL) selected PGAL to provide architecture and interior design services for an interior fitout of an existing 44,500-square-foot warehouse shell space into flexible rehearsal spaces.
The project includes five rehearsal spaces, eight band rooms, wardrobe area, scene storage, break-out lounge area with kitchenette, restrooms, and support spaces. The studio is highlighted by a dynamic, custom-designed LED light wall that forms the backdrop for their performances.
The space was also designed with the flexibility to expand the current space, providing an additional four dance studios, three vocal rooms, office and conference rooms, as well as provide an emergency generator to use the space as an emergency shelter.
PGAL served as prime architect in a design-build arrangement for this fast-track, complex drug delivery, and assembly project.
The 43,521-square-foot, two-story facility occupies an existing space and includes 9 Class 100,000 ISO Clean Rooms, gowning and packing areas, QC, and metrology. The building also has aseptic rooms, warehoused cold storage, partitioned drug storage rooms, standard warehouse storage for delivery devices, and circulation space.
The project required all cold rooms, clean rooms, and aseptic areas to be on emergency power. In addition, all cold storage rooms required redundant cooling.
PGAL also provided office, administrative, and conference space for SHL Group’s U.S. operations.
The FedEx Express Miami International Airport Facility was designed to support the integration of a new 67,000-square-foot temperature-controlled facility which forms an integral part of the FedEx global cold chain network. All aspects were considered in the design to support the integrity of temperature-sensitive flowers, healthcare, and perishable shipments.
The project involved an on-airport International Cargo/Parcel Building expansion, primarily consisting of 142,000 square feet of warehouse space with 27,000 square feet of new and expanded office areas. The new offices accommodate the expanded FedEx MIA operations and regional management, as well as the new Customs and Border Protection (CBP) operational/inspection offices. As a result, FedEx customers will now enjoy enhanced options when shipping critical and sensitive products between Central/South America, the Caribbean, and the U.S., plus other parts of the world.
The facility has temperature-controlled areas for -25°C to -10°C (frozen), 2°C to 8°C (cold) and 15°C to 25°C (controlled-room temperature) products; separate areas for healthcare shipments and other temperaturesensitive perishables (e.g. specialty foods, flowers, and seafood); a cross-dock station with direct trailer access to a cold (2°C to 8°C) environment; and a cold lock dual door design for precise temperature control.
The CenterPoint Energy Navigation Street facility was constructed on a 10-acre site and houses administrative offices, training, warehousing, construction and maintenance activities, shop, and operations that serve all of CenterPoint Energy’s six-state natural gas service territory. In addition, the facility is home to the company’s Mobile Energy Solutions, a portable, temporary natural gas supply available for pipeline integrity testing or emergency outages. The project includes 20,000 square feet of office/training area and another 100,000+ square feet of warehouse, shops, and storage facilities.
The project is concrete tilt-wall construction with high bay areas for the warehouse and shops and two-level space for the administrative/training areas. The project is the center of CenterPoint’s Gas operations, and all the maintenance crews are scheduled out of the facility, which requires a large amount of parking for employee cars with overlap for different shifts and the company service vehicles. The site includes a gas fueling station for the service vehicles and has exterior storage yards for daily and emergency service materials. The new 122,000-square-foot facility supports 225 natural gas employees that work in Houston’s East End, contributing to the ongoing revitalization of the community east of downtown Houston.
Located on 79 acres adjacent to the client’s main campus, this 265,000-square-foot Tier 3 module data center includes 100,000 square feet of raised floor area.
The client’s aggressive schedule required planning, design, and construction to be completed in 22 months.
The hardened facility is a cast-in-place concrete structure clad with precast panels designed to withstand a Category 5 hurricane. PGAL designed the structure to withstand temperature and shrinkage effects with no expansion joints and provided a 422-foot by 528-foot area of concrete roof plate.
The program included 35,000-square-foot computer room cells and 125,000-square-foot data center support space, as well as a 100,000-square-foot mechanical yard with 16 two-megawatt diesel generators.
This state-of-the-art, 365,000-square-foot Tier 3 data center reflects the client’s commitment to sustainability. Designed for 24/7 operations, the project includes a parallel, redundant, and scalable utility infrastructure. The core/shell houses four computer room cells, each designed with an electrical load capacity of 2.4 MW expandable to 4.8 MW. Other project components include administrative offices, meeting and conference rooms, and a mechanical and electrical yard. PGAL also coordinated the site electrical feed, which includes new overhead power from the CenterPoint substation to a new on-site substation, as well as a self-contained sanitary plant and potable well water system and detention area.
PGAL designed a Tier 2 operations center for the City of Baytown strategically located outside the 500-year flood zone and near a major thoroughfare for support purposes during an emergency situation. The facility encompasses 9-1-1 emergency communications and City Information Technology Services Department common areas. The communications department is a 24/7 operation that includes a dispatch center, consolidated radio/9-1-1 equipment room, communication coordinator office, and data center. The data center houses the City’s main servers, providing data storage and communications for all municipal buildings.
This 48,600-square-foot, mission-critical facility maintains critical call center equipment for all 9-1-1 emergency calls handled by 41 call taker locations in 49 cities across a two-county region.
The facility was designed to be fully self-supporting for ten days off the grid during a disaster and includes its own critical server rooms, power generation, water, food, and sleeping quarters. The hardened building can withstand a Category 5 hurricane and is protected with state-of-the-art security, audio-visual, and information technology systems. Program elements include training, administration, 9-1-1 support, and communications facilities.
The lobby’s slate flooring features warm autumn tones that blend with the interior setting and the metallic and neutral colors of the exterior architecture. The organic nature of the patterned woven carpet continues the lobby palette, while casework and doors introduce accents of cherry wood veneer.
The design team carefully chose interior materials to support the project’s LEED Silver design. For maximum efficiency, productivity, and security, PGAL positioned the boardroom, a large training room that can be divided into three rooms, the critical server, and support space on the ground level. The second floor accommodates private offices, a fitness facility and locker rooms, and the 24/7 command center.
The completed facility utilizes 40 percent less water and 18 percent less energy than a conventionally designed building, even with the advanced technological building systems. PGAL incorporated more than 40 different products or materials containing recycled content. In addition, 97 percent of the waste generated during construction was diverted from local landfills.
A state-of-the-art Tier IV data center will provide mission-critical services to the Greater Harris County 9-1-1 Emergency Network (GHC).
The 4,560-square-foot building is designed to serve as a Network Operating Center and backup disaster recovery center for the county’s administrative headquarters, the Tom Bass Building. The project also includes a separate equipment storage building, surface parking, and a separate radio communications tower.
As a Tier IV facility, the building has an A/B electrical gear/UPS, two generators with fuel storage, redundant AC systems and fiber feeds, plus potable water storage for up to two days of operation.
The data center is located on a new auxiliary campus that covers 40 acres of undeveloped land. PGAL’s design and engineering teams planned all-new utility services for the undeveloped site and road access with a low water crossing to support the new development, including a future 400-foot-high radio tower.
VadaTech is a computer manufacturing company serving the defense, aerospace, industrial, and telecom industries. PGAL provided complete architectural, design, and construction services for the company’s new headquarters and research, development, and manufacturing center.
Designed to Class A standards, the 71,500-square-foot building includes 20,000 square feet of office and support space plus 30,000 square feet of manufacturing and laboratory area.
PGAL designed the facility to support efficient production flow. Raw materials and parts now move from receiving to inventory, then to manufacturing floor preparation, assembly, wash, inspection, touch-up, and testing areas. Finished goods return to inventory immediately prior to shipping. As a result, raw material and finished goods inventory has clear separation.
At the client’s request, the new facility offers state-of-the-art efficiency and employee comfort and flexibility. Building components include conference rooms, engineering lab, manufacturing test lab, EMI chamber lab, environmental lab, and shock and vibration lab. The facility also houses shipping and receiving areas, inventory room, manufacturing area, administrative offices, kitchen areas, exercise room, and telecommunications room.
PGAL was charged with the renovation of a 30,000-square-foot maintenance and office/administration building for City of Houston. Renovations to the storage building comprising approximately 11,000 square feet were included in the project scope. Additionally, two bays and four pumps were added to the fuel bay area.
Project components include complete architectural/engineer design and construction administration services, office and administrative areas, conference and training rooms, lunch room, vehicle maintenance bays and equipment storage, site work, and drainage and utilities.
The state-of-the-art Frederick E. Giesecke Engineering Research Building (ERB) focuses on three areas: nanofabrication, materials characterization, and energy research. This 70,000-square-foot facility was delivered through a Public Private Partnership (P3) with The DDM Texas Group and Texas A&M University. The facility includes portable nanofabrication laboratories (prefabricated off-site), the Corrosion Science and Materials Reliability Laboratory, and research space for faculty, staff, and students working for the Texas A&M Energy Institute.
The building exterior establishes the architectural hierarchy of the interior; the single level portion giving way to the high bay construction. The expansive volume allowed for the insertion of the portable nanofabrication laboratory modules and the three-level conventional lab and office space, clearly defined with the extensive use of the curtain wall enclosure.
The interior office space utilizes an open concept with perimeter offices including full-height interior glass which brings the natural light into the deepest interior spaces for a healthy working environment for all inhabitants.
With a growing program and new researchers on board, Texas A&M University’s Chemistry Department needed to upgrade and modernize its facilities.
PGAL provided a master plan for upgrades to the department’s labs, systems, and support space.
Phase 1 included programming, planning, and renovation of the outdated Reed McDonald Laboratory. PGAL converted the outdated, 17,000-square-foot space into a state-of-the-art synthetic chemistry instruction and research environment. Workstations were replaced to effectively support organic and analytical laboratories.
The project also included code-related upgrades to bring the facility in line with current life safety requirements. Each floor includes new electrical and data rooms.
The build-out of the Southwest Airlines Cargo facility included 31,311 square feet of airline support program just south of the runway.
The two-story facility includes offices, maintenance and provisioning, and belly cargo space for the airline. The front entrance leads to the public cargo pickup lobby. Behind the lobby is the cargo space that includes flexible storage solutions and large roll-up garage doors for easy access to airside transport vehicles. Adjacent to the cargo area is a large space for additional storage and vehicle maintenance, separated by an industrial ice machine used for all outgoing Southwest flights.
Upstairs program includes flexible shared office space, locker rooms, and multiple break rooms for employees.
The addition and renovation of the University of Houston (UH) Main Campus Central Plant provides additional chilled water capacity to serve the needs of several UH projects to be constructed or planned in the near future. The addition adds three new 2,500-ton chillers to the existing system, and the four existing cooling towers were replaced with four new 5,000-ton ceramic cooling towers. A new 5,000-ton cooling tower was also added to accommodate the new chiller capacity. The addition includes 3,000 square feet of much needed administrative office space powered by rooftop photovoltaics, furthering the university’s sustainable agenda. PGAL and the university chose to use the facility as a learning tool rather than trying to hide the facility. With the central plant located in a prominent position on campus directly adjacent to the main library and along a new planned pedestrian plaza, the team designed the new addition as an aluminum and glass box to allow for the complete transparency of the inner workings of the central plant. The new cooling towers are designed as concrete structures with masonry exterior to blend with the building standards for all new structures. The transparent, open sides of the cooling tower create a “rain effect” with falling water that can be seen and heard by passersby.
The new CenterPoint Energy Rosharon Electric Service Center relocates and replaces the existing Hiram Clarke service center Located on South Main Street, Houston, Texas. The new location provides better access to the community and allows for the future growth of services required in the area. The new service center covers 20.63 acres, of which over 4 acres are newly paved drives and parking.
The project includes four buildings, including office space, warehouse space, Vehicle Garage, and a Vehicle Wash Building totaling approximately 50,000 gross square feet as well as a fuel island for service vehicles. The office and support spaces accommodate the 300 employees that pass through the facility daily and are primarily occupied at the start of the day/shift when employees gather to determine the workload for the day.
The warehouse space is directly adjacent to the office space and can accommodate storage shelving up to 12 feet high, with various sections separated to allow for specific storage areas to be isolated if needed for security purposes. In addition, the facility includes a continuously covered loading dock equipped to house up to 30 service vehicles alongside multiple ice stations for the service trucks. Designed as a drive-through facility, the Vehicle Service Garage allows for better traffic flow and can accommodate Larger service vehicles.
Our vision is to consistently enhance our value to clients by embracing their goals and delivering extraordinary results.