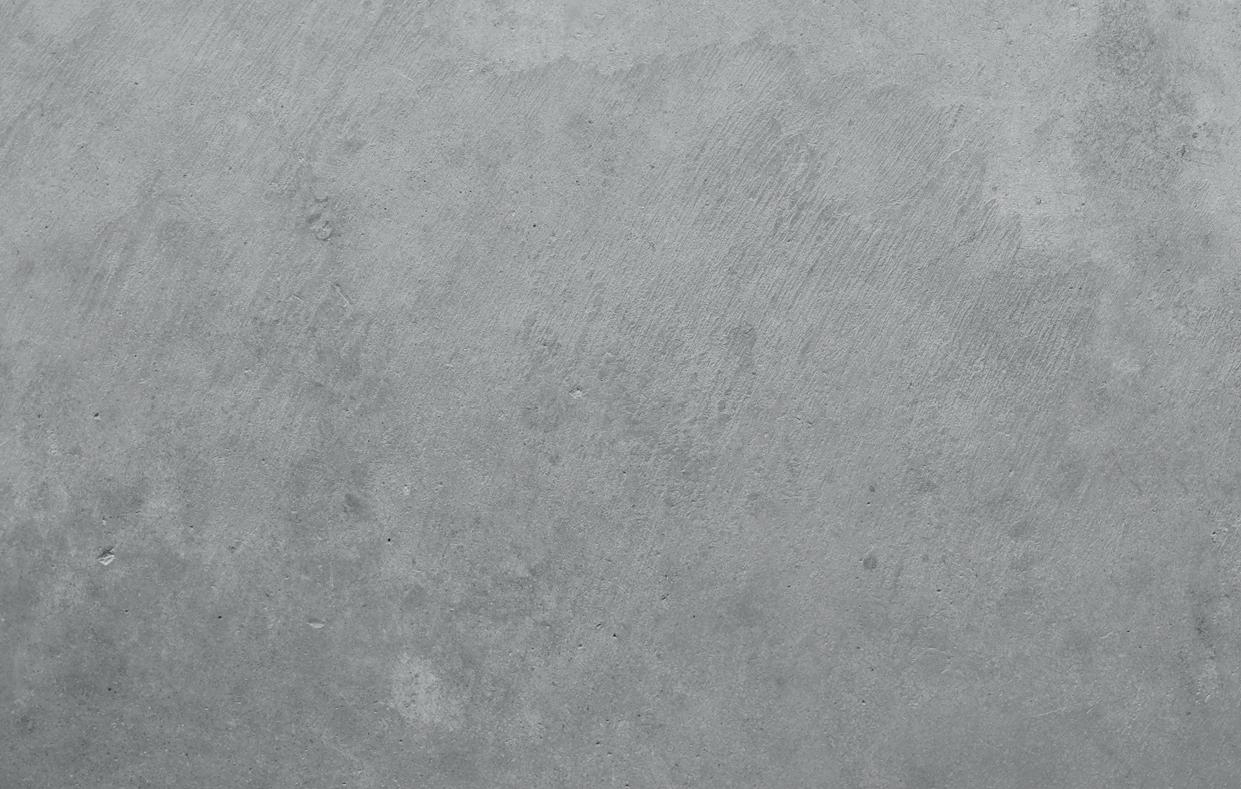
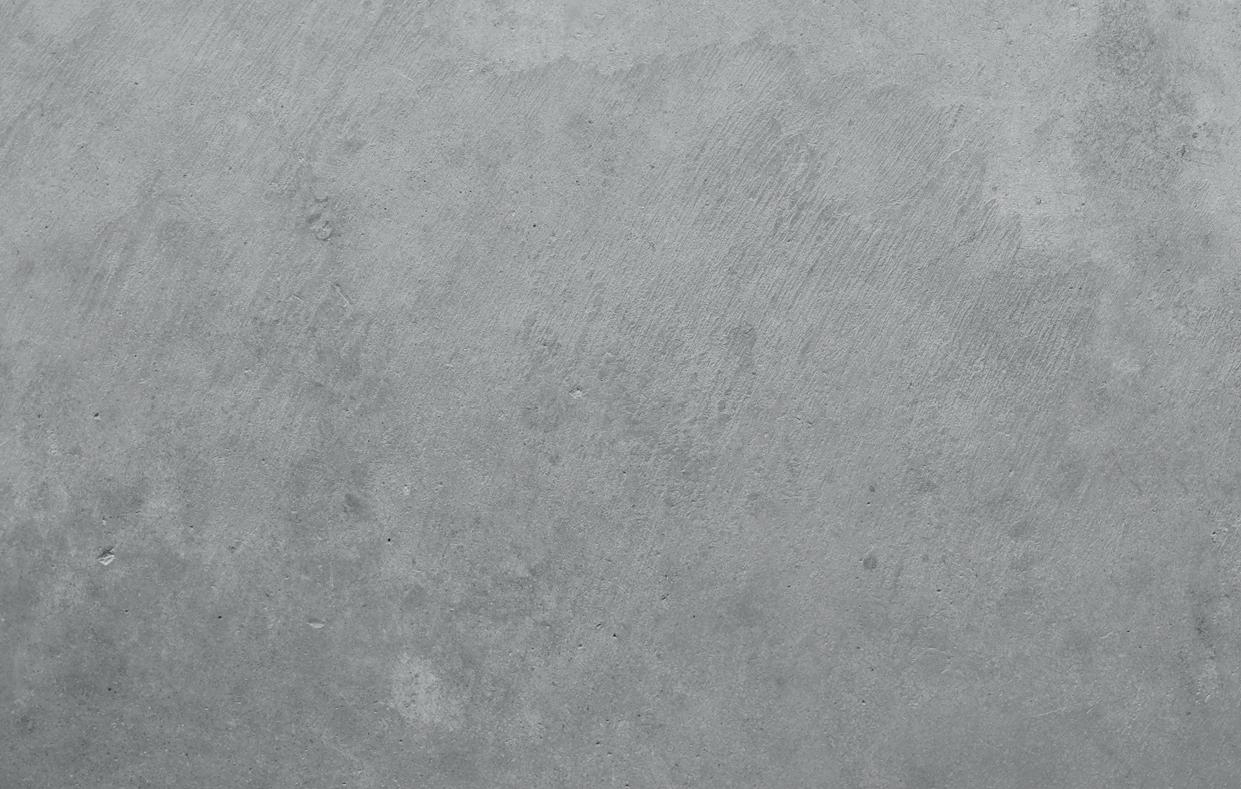
Anglian Demolition
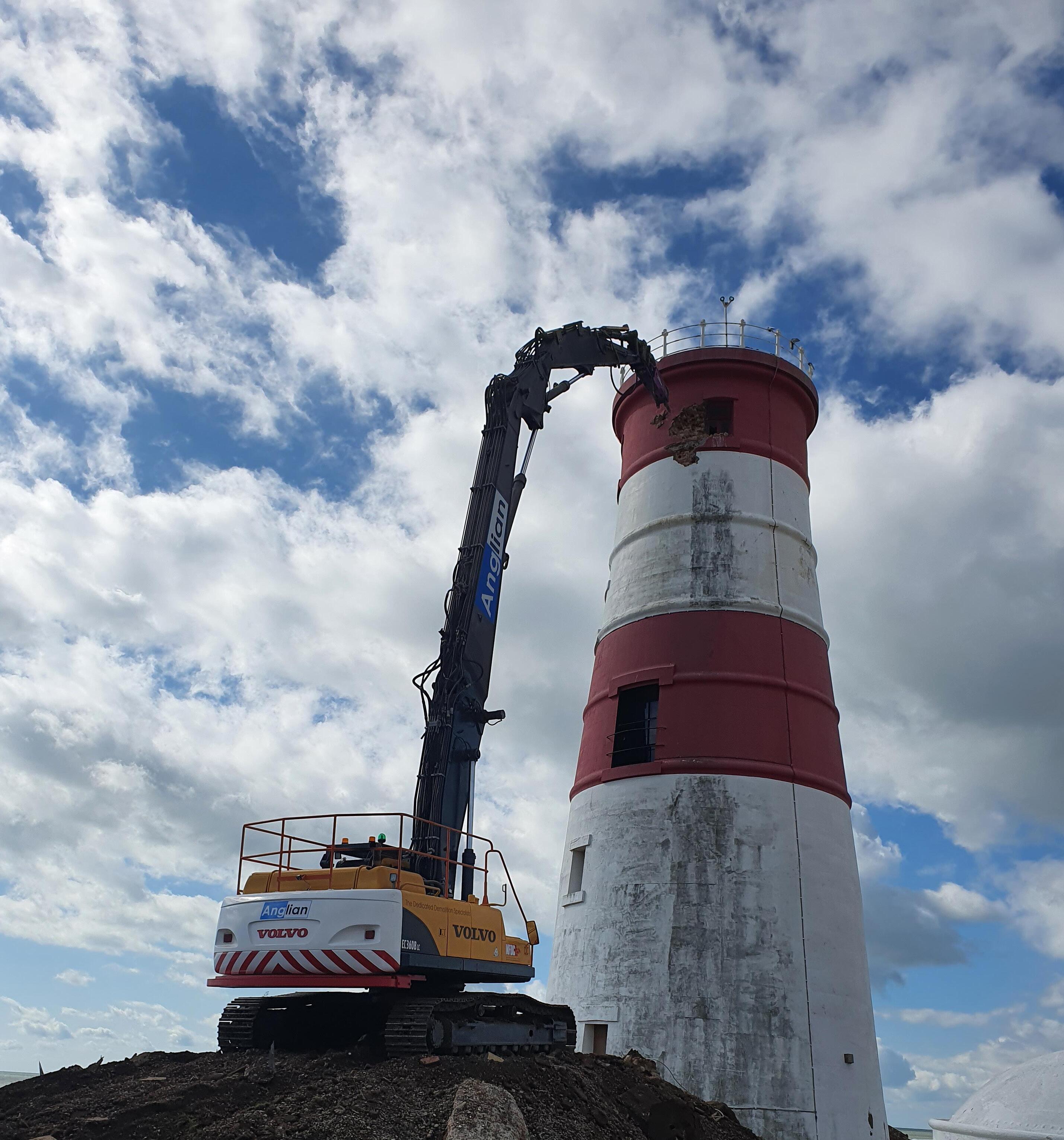
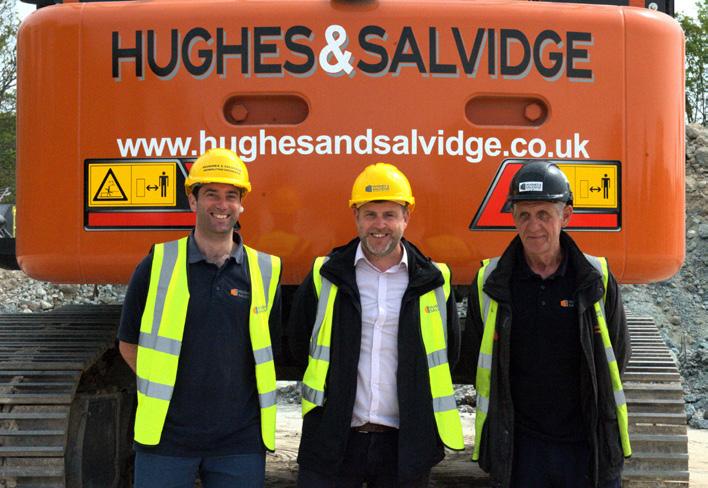
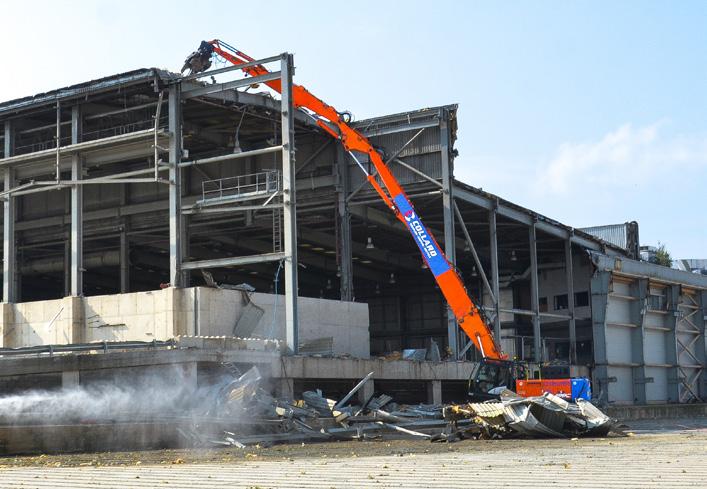
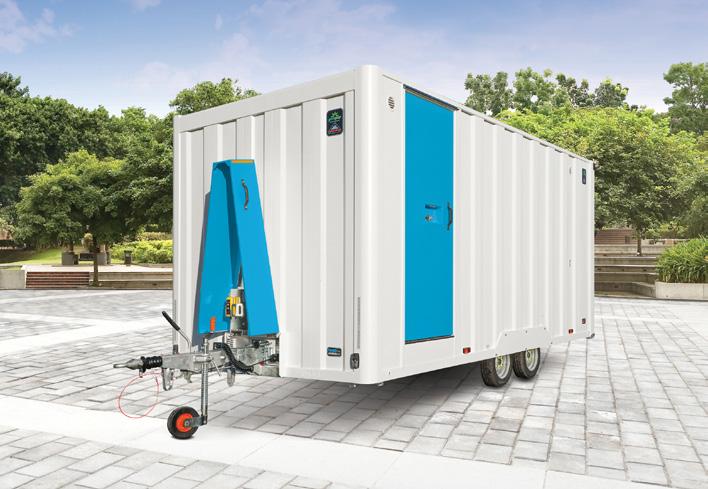
Autumn has finally arrived! And with it another issue of Demolition Spotlight. Aren’t you lucky? This issue is just as packed as the last, with Anglian Demolition light(house)ing up our front cover and being the subject for our Demo report. Andy Elvin takes us through his time in demolition and what lead to him becoming a senior contracts manager.
Hughes and Salvidge become the topic of a conscious companies feature, where we look at their incredible work on the Hilsea Eco Bus Station. We also have not one, but two articles from the fantastic Paul Argent, bringing you stories direct from the heart of the industry. On top of all that, we have news stories from R Collard and Genquip!
Awesome Autumn our team
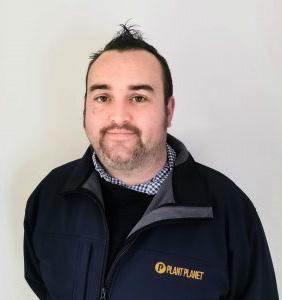
DARREN SHELTON BUSINESS MANAGER
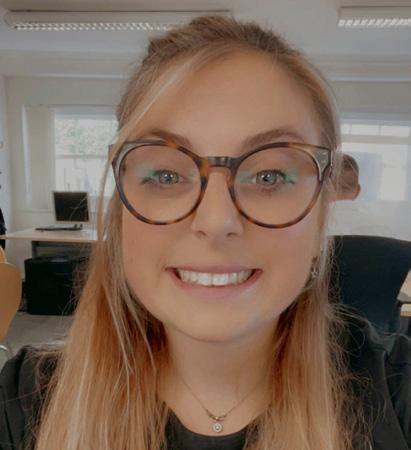
MARTINA TONELLI MARKETING CO-ORDINATOR
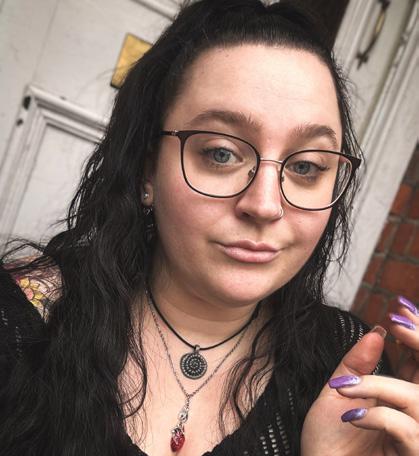
REBECCA PHILLIPS MANAGING EDITOR
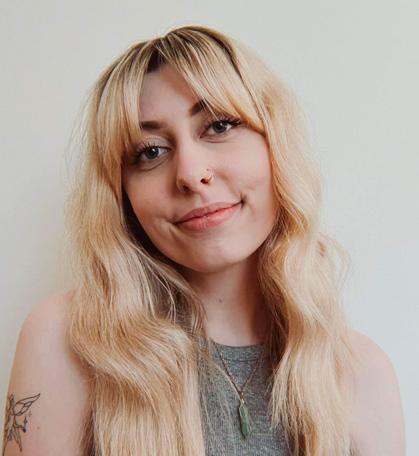
LORNA COWLIN CONTENT CREATOR
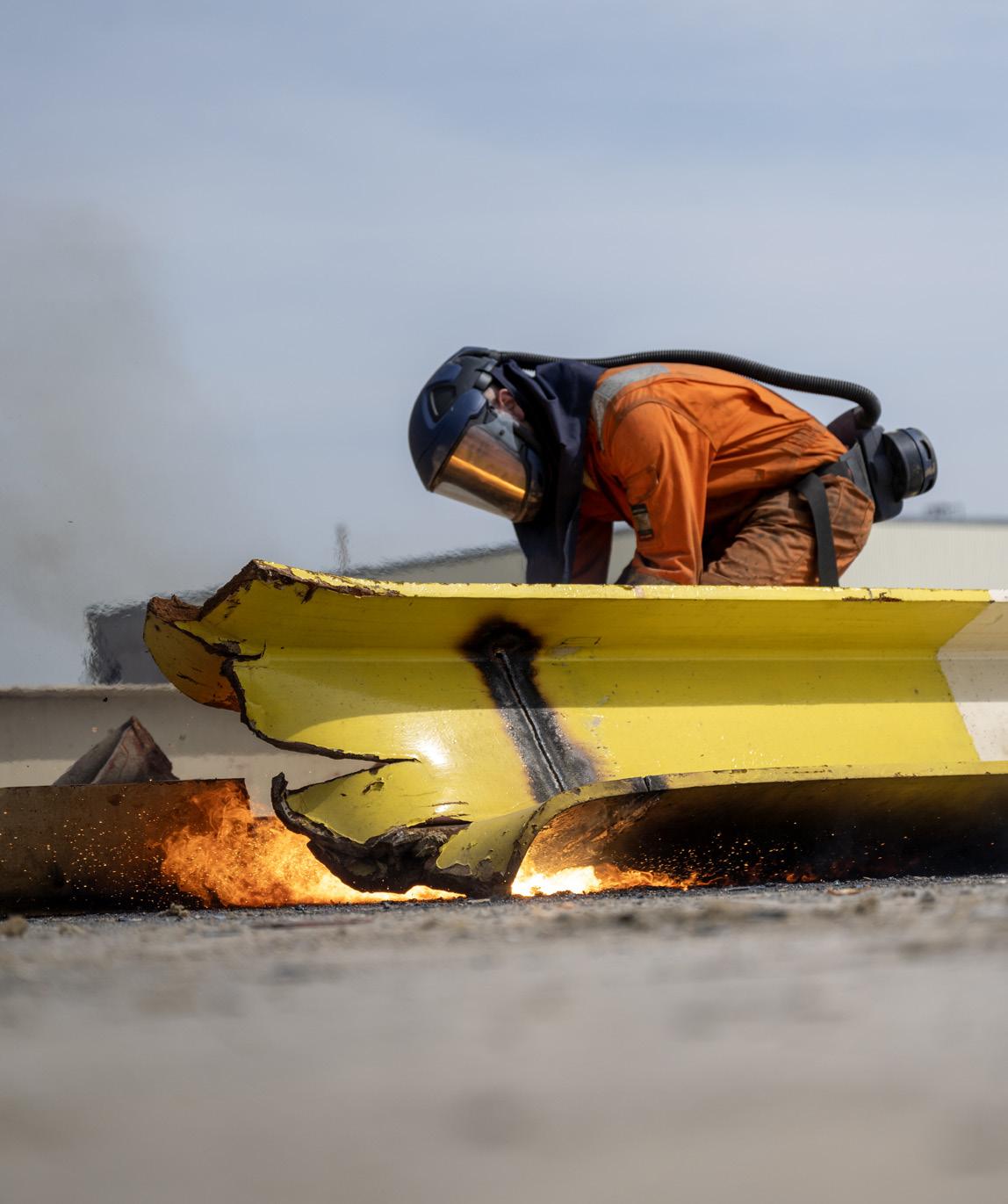
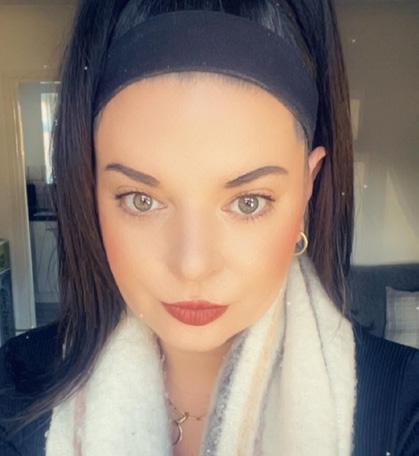
CHARLOTTE WALSH BRAND MANAGER
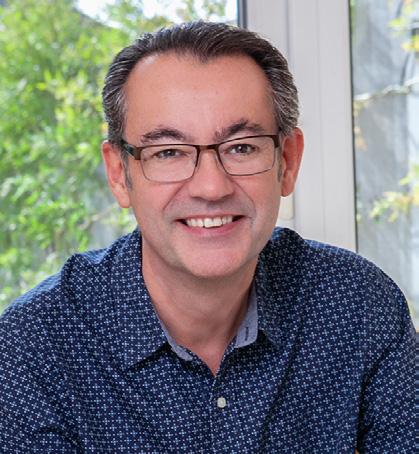
STEVE WILSON DESIGN MANAGER
PAUL ARGENT RPA MEDIA SERVICES
ANDY ELVIN ANGLIAN DEMOLTION
LUKE GOULD HUGHES AND SALVIDGE LTD
PETER BEACH GENQUIP UK LTD
For all content related queries, please contact editor@demolitionspotlight.co.uk
For all sales related queries, please contact charlotte@demolitionspotlight.co.uk



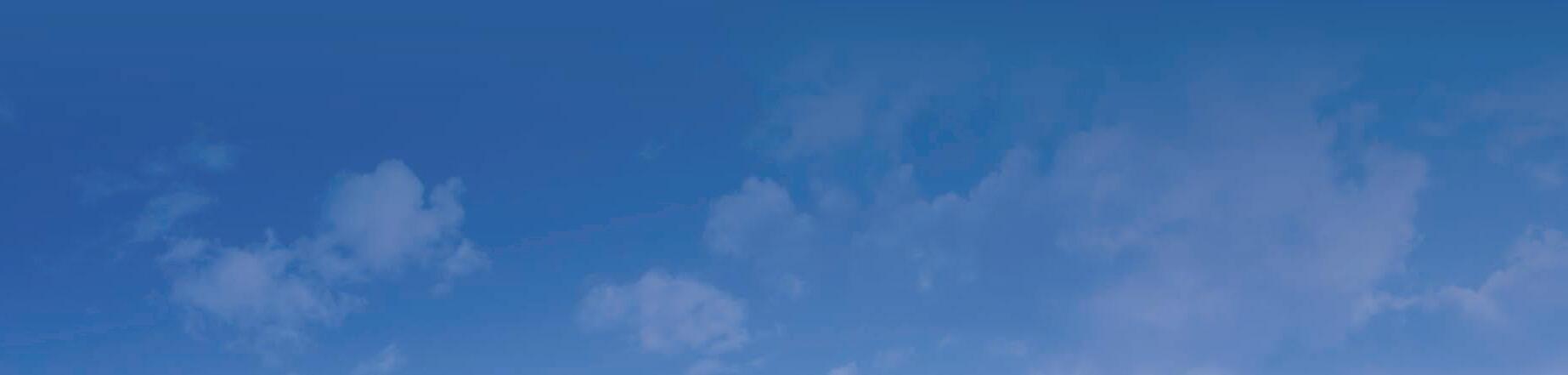
iRange hybrid power revolutionising welfare accommodation.
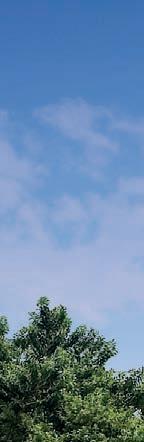
Owners and end users are impressed by the near-total reduction in carbon emissions, running costs, and noise pollution. No wonder, respected rental industry authorities have honoured the iRANGE with an array of prestigious green awards and nominations.












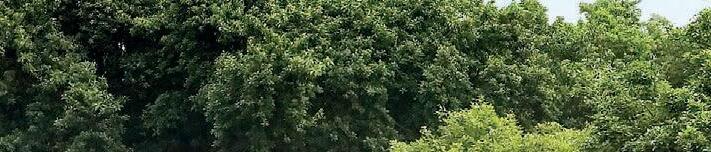




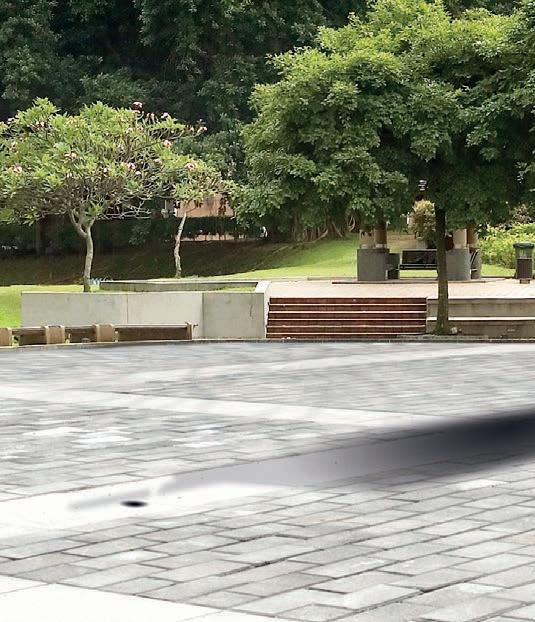
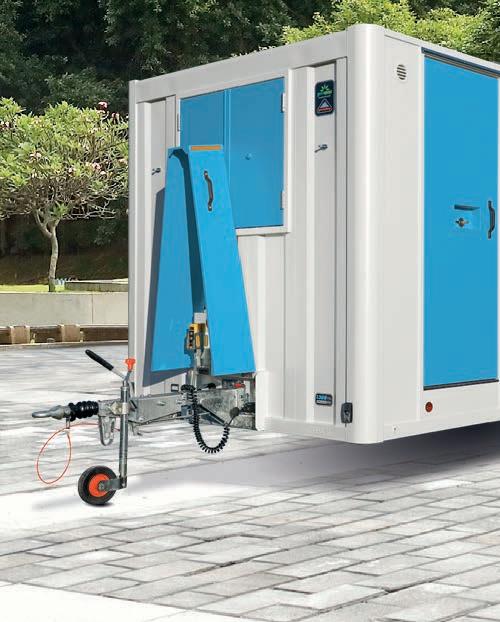
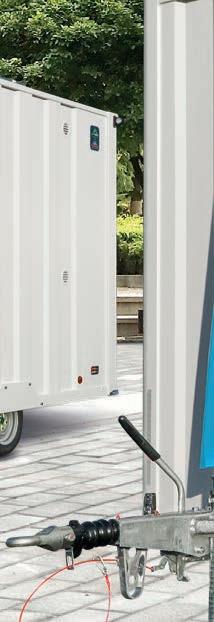
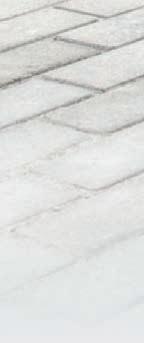
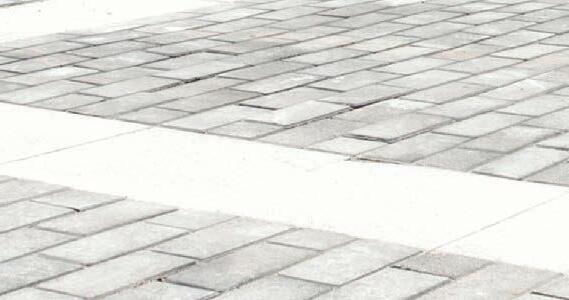
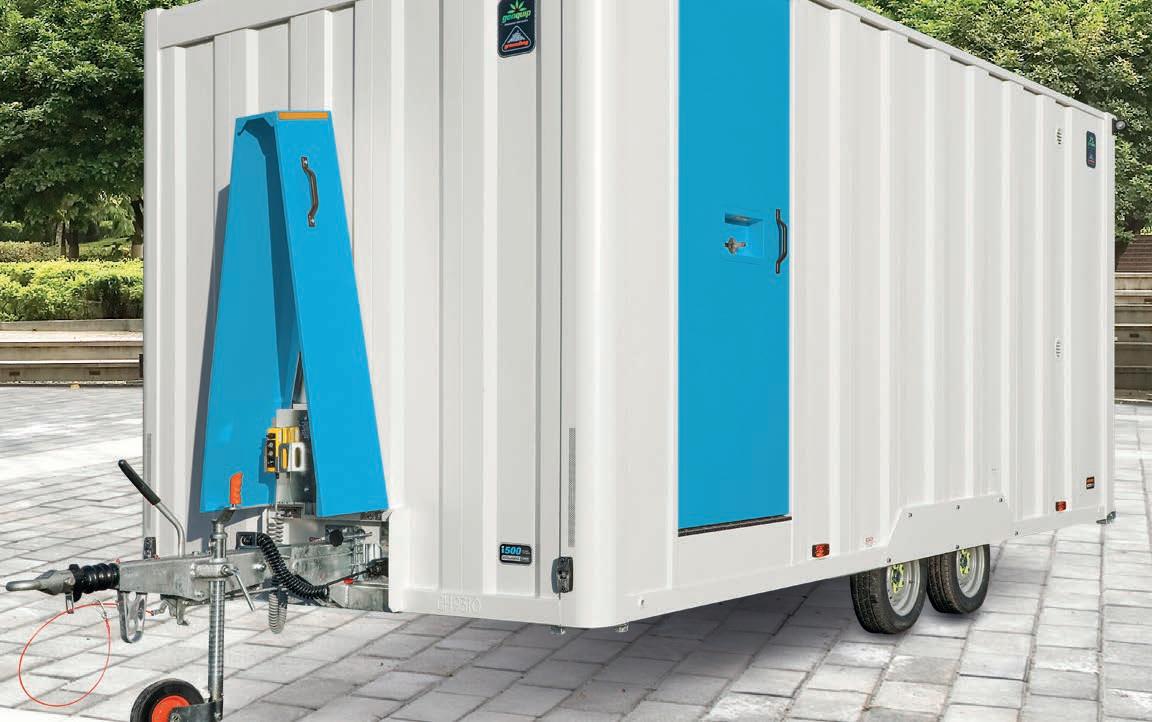




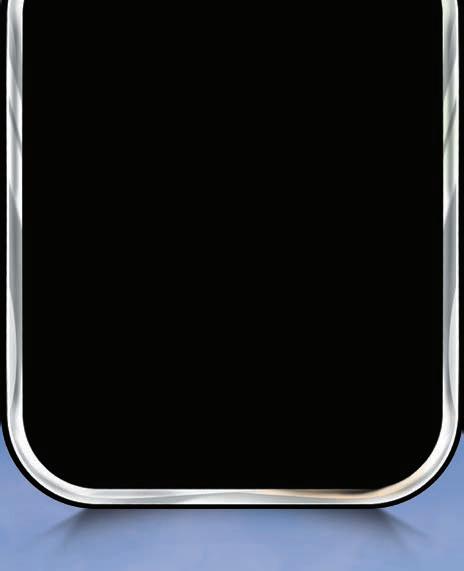







The iRANGE eliminates the need for fuel throughout the summer months and can achieve up to 100% reduction in carbon emissions - only running when the battery levels require the utilisation of the on-board power unit.*

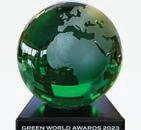









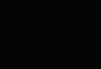







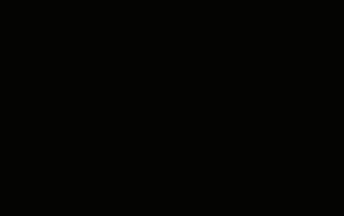
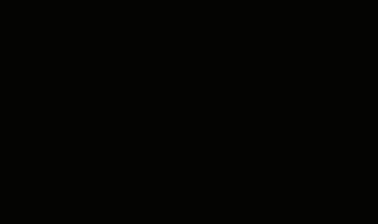
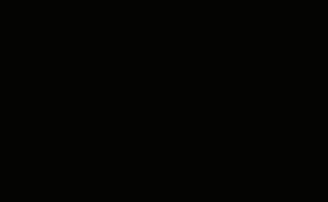
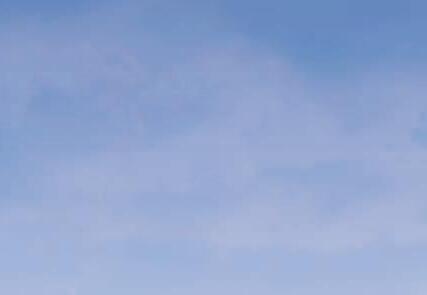
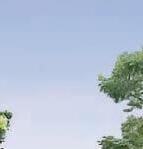
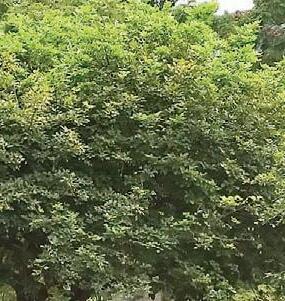
Scan for more information on the iRANGE
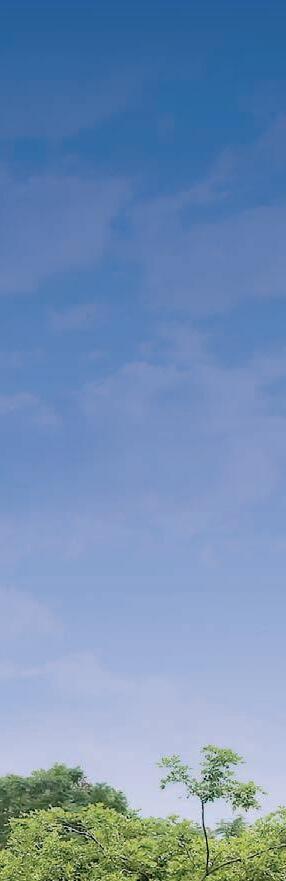


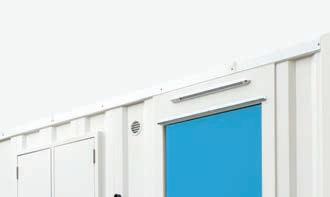
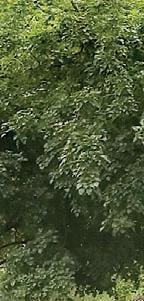
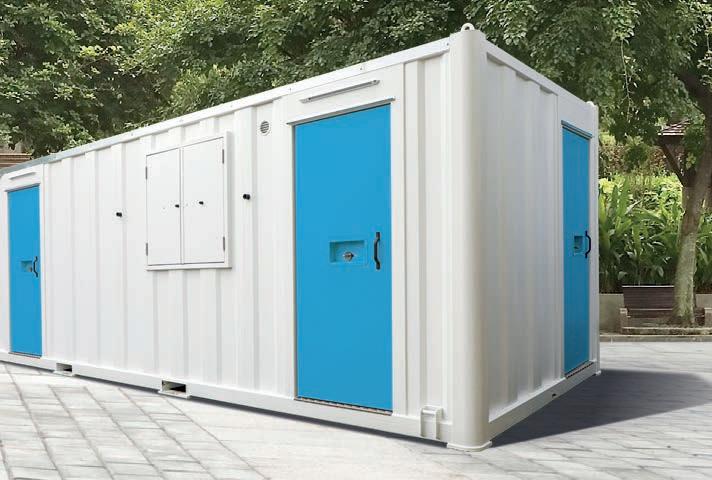
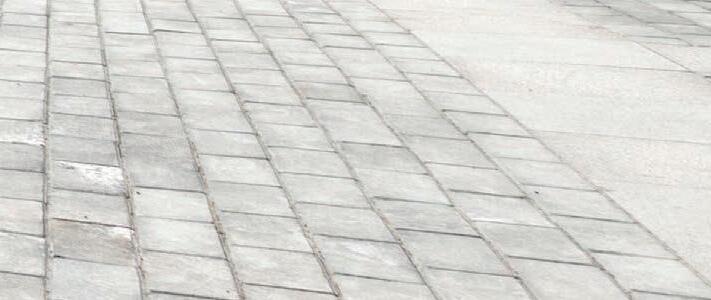

Environmental features give owners and end users savings by way of reduced fuel usage, 90% reduction in onboard power unit servicing, longer running life, fewer breakdowns and massively reduced noise pollution.
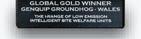
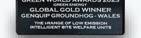
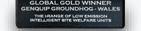

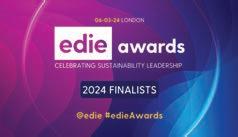
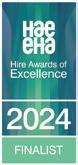
* During the winter period and night use the power unit will still be required, with a reduction in running of up to 90% when compared to our Fusion Pulse welfare unit.

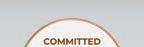



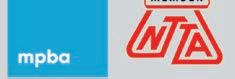

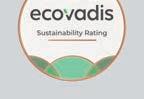
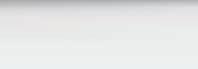
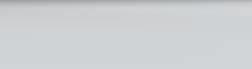
Collard Group – The One-Stop-Shop A demolition and enabling deep dive
At Collards, we provide a onestop-shop for all of our clients, contractors and developers alike. Our service spans the breadth of the UK which utilises the group’s expertise, covering the initial consultancy and site investigation through to the asbestos removal, soft strip, full structural demolition, earthworks and land remediation, allowing us to hand back a shovel ready site for the next phase of development!
Last issue we announced our award of the demolition and remediation package in Vastern Road, Reading. This week, we have been putting up our Collard branded monarflex and we look forward to sharing
more of this site with you soon. We are thrilled to announce that we have been awarded a contract at the Mechanical Biological Treatment Facility in Basildon, Essex. We will be demolishing the entire facility to slab while below level structures will be left and voids and pits infilled. Collards are very proud to be undertaking an industrial project of this scale, and we will be sharing more details on this over the coming weeks. Over in Harvest Hill, Maidenhead we have been progressing with a large earthworks cut and fill package. With 80,000m3 of fill being imported, this site will be developed into residential housing. Another project we are pleased to update you on is in Watchmoor Park, Camberly. There are five buildings on this site where
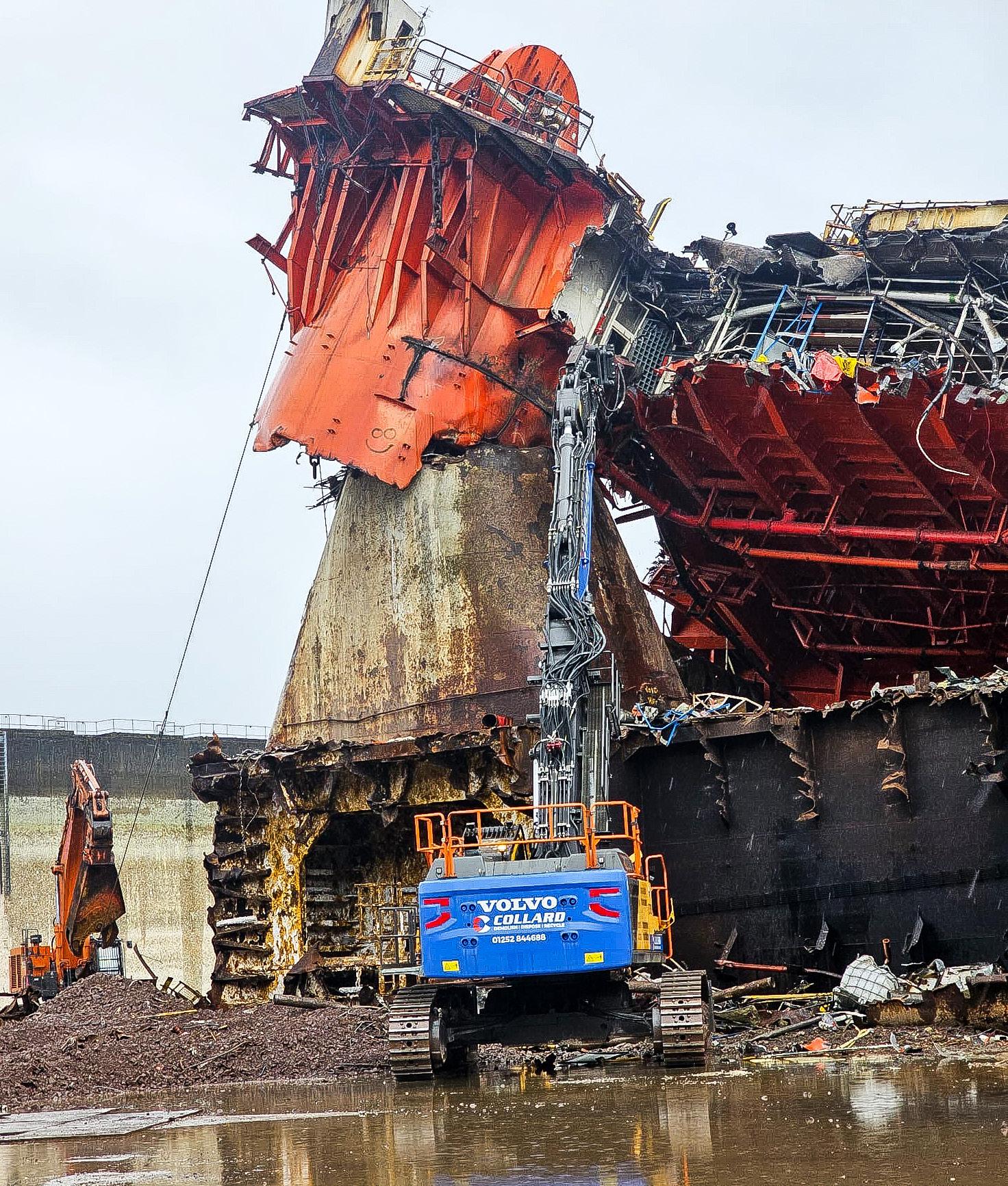
we are working to remove the asbestos, strip-out, demolish and grub-foundations. Collards will be crushing arisings to stockpile on site for the future office and warehousing development. In the north of Scotland, our Volvo EC750 excavator is working to dismantle a decommissioned deep sea oil rig from the 1970s. Over a three-day journey, we transported this machine 650 miles to break down the gigantic 11,200 tonne rig.
We are excited to share that we have had three new apprentices start their journey with us recently. They are currently joining us at operative level, and we look forward to them moving through and up the ranks of the business. Currently, we have a team of evergrowing apprentices at different stages
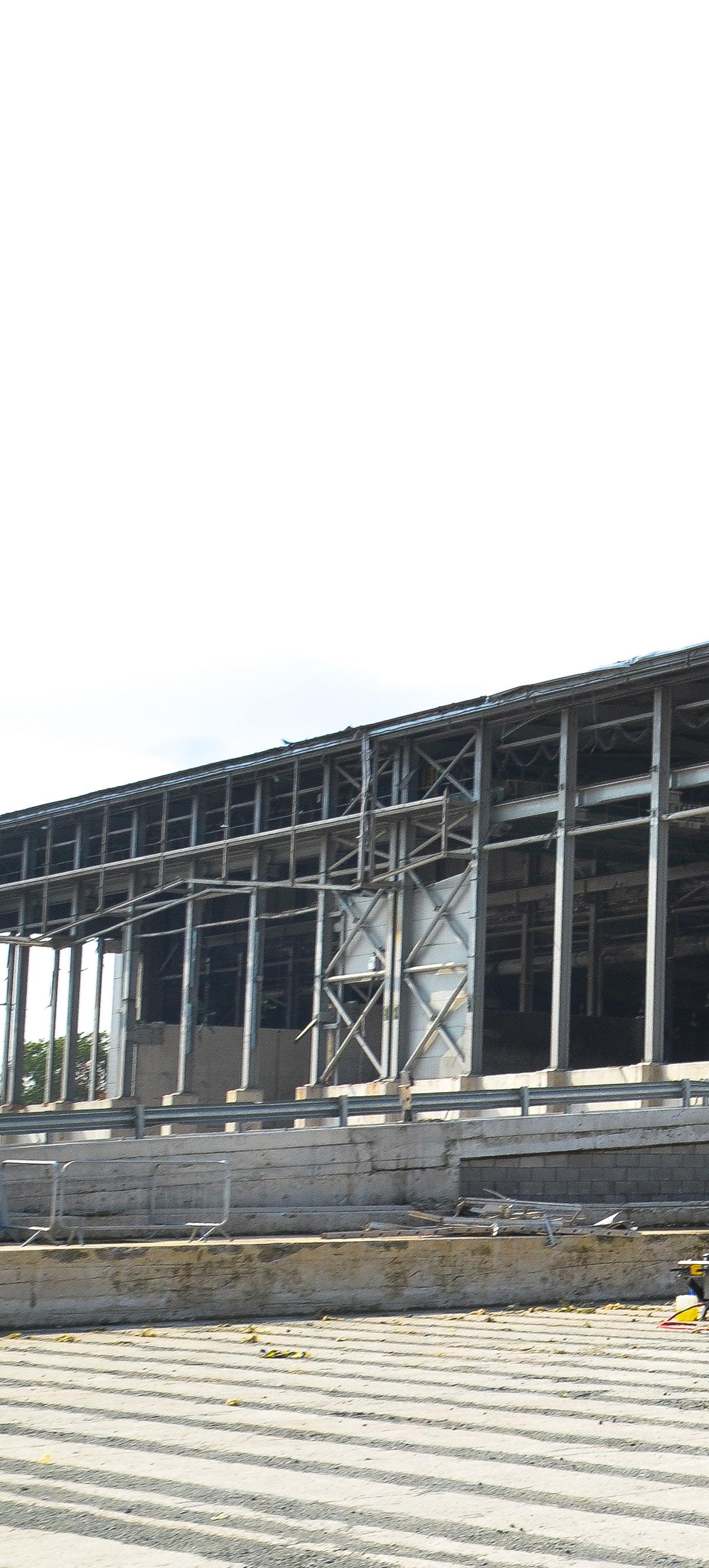
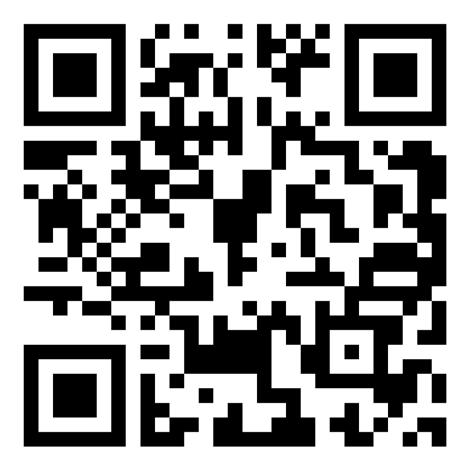
of their development with us. This is part of our ’30 before 30’ target to support the youth in the industry. We are proud to be investing in the up-and-coming talent and there is more outreach for next gen coming in the future which we are keen to share our thoughts and plans for!
In our contracting department, our demolition and enabling team is staffed with a skilled and varied team to ensure a smooth-running operation. From early tender stage to completion, we have the best people capable of keeping our clients satisfied. In our work winning team we cover business development, bid coordinating and estimators to get the work through the door and on the table for our operations team. In operations we are covered from contacts managers and quantity surveyors to our in house HSQE team to keep the job on track and operating safely at all times. Our HSQE are dedicated to taking care of the health and safety needs for the whole business, specialist team members with backgrounds and 1st hand experience in demolition enables
them to provide proactive and relevant insight into bespoke Health and Safety systems for the group. To learn more about our people, head to our website to ‘meet the team’. At Collards we often implement 3D modelling into our tenders to set us apart from the pack when it comes to winning projects, this allows our clients and stakeholders to get a great visualisation of exactly what we will be carrying out on site. We’ve found that our efforts and care at early tender stage sets a great first impression and a precedent for our working standards. At Collards we understand that a successful project requires meticulous preparation, our demolition and enabling services are designed to pave the way for smooth project execution while addressing critical preparatory tasks that set the stage for your main construction phase. We offer bespoke design and installation of temporary structures, expert façade retention, a range of section 278 works to cover highway improvement and urban regeneration along with stats diversions where we excel in the safe management
of live services and utilities on site. Because Collard Group are able to offer an end-to-end solution to our customers through our circular economy model, we find that the financial stability of the group allows us to leverage opportunities outside the capacity of regular demolition companies. This model also means we are able to be incredibly self sufficient due to little need to subcontract out works as the group can complete a project from start to finish independently. In the next issue, we will be diving into Asbestos and Earthworks in more detail while keeping you up to date with the current headlines at Collards. Give our QR code a scan to have a look at our socials and website to learn more about us and what we have to offer!
To learn more about R Collard Ltd, please visit: www.rcollard.com
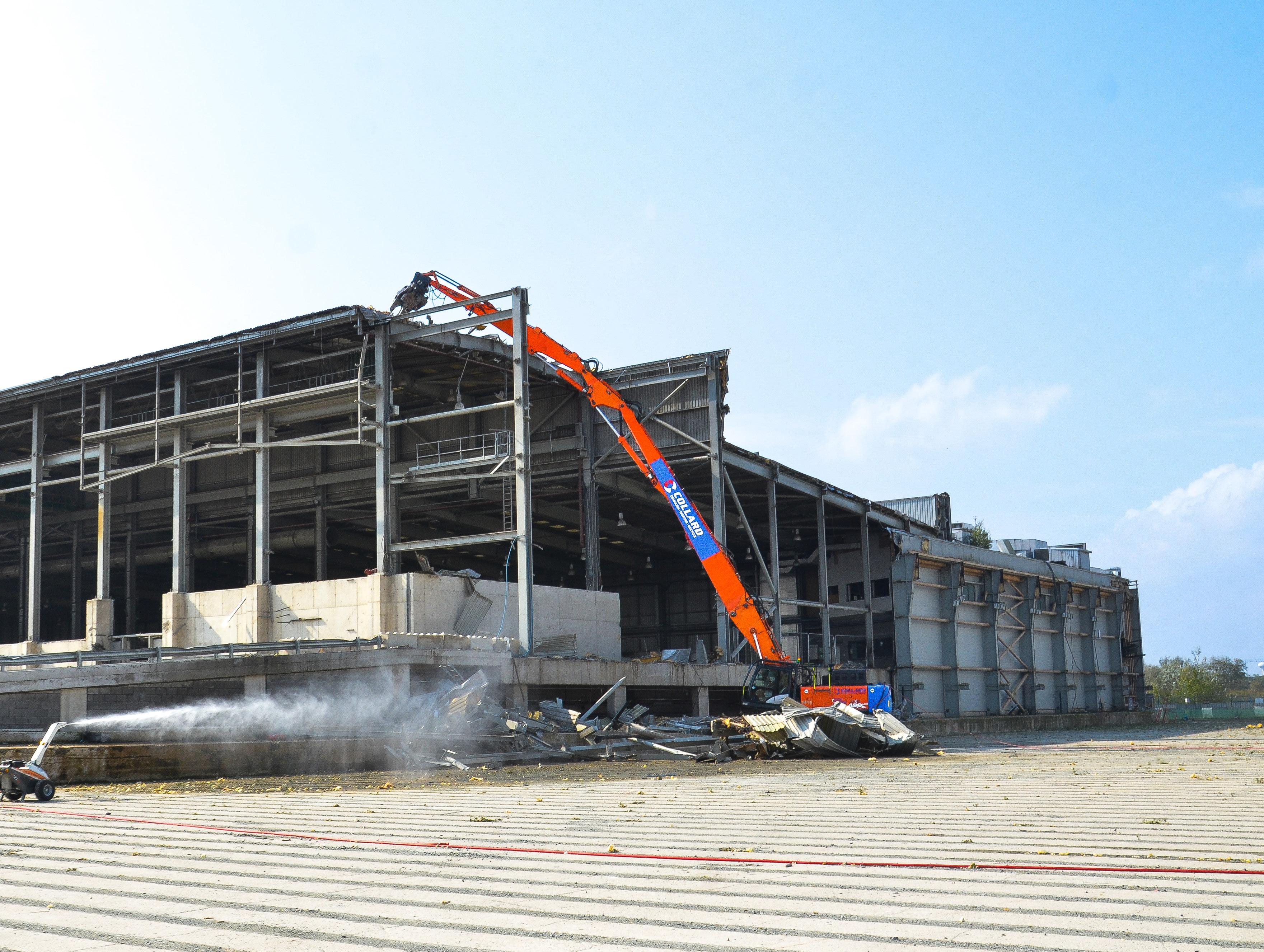
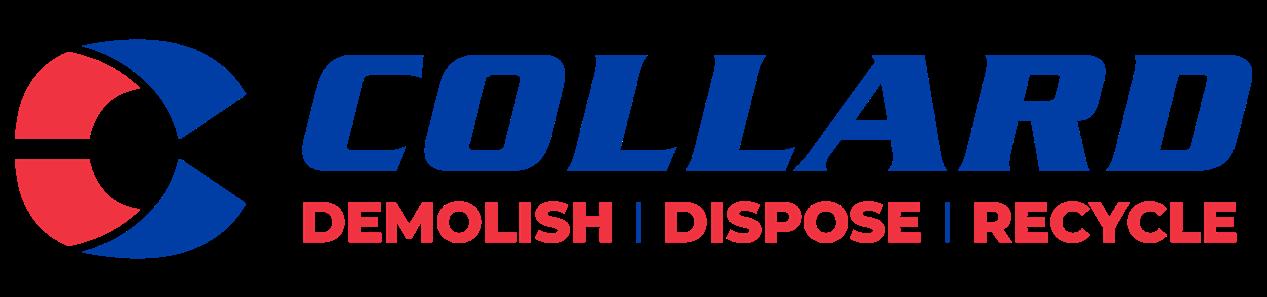
GOING GREEN
Everybody wants to reduce carbon emissions and that is what Genquip-Groundhog clients are asking for. However, there are still issues with hire rates versus costs. The challenge for the hire companies is that a lot of their customers want the best unit but don’t want to pay a higher rate for it; that is still a major issue.
Genquip-Groundhog aim to try and use the right language around sustainability. Net Zero is a huge challenge for welfare units, there will still be some emissions, but you can significantly reduce them. We believe it is important because people have grown wise to being greenwashed.
Our ethos at Genquip-Groundhog is to help you achieve realistic carbon reduction.
We are serious about sustainability. We have recently joined the EcoVadis global sustainability platform to continue driving down our emissions and measure our progress against our peers. We also have our own Sustainability plan which we have worked on for over 2 years. https:// www.groundhog.co.uk/sustainability.php
In the same vein, we believe more honest conversations around what is achievable with solar on welfare cabins. A solar-only welfare unit does not work 52 weeks a year in the UK. Our welfare units are often in use 24 hours a day and a welfare unit used in Cornwall in summer is going to perform a lot differently to one used in Glasgow in winter.
Due to market demand, we continue to manufacture a mixture of solar and diesel-powered welfare units.
Another challenge is that people like what they know. We launched the Fusion Pulse about 12 years ago and have probably made around 6,000 of them. It was so successful that people are reticent to move to a new product.
The transition to more sustainable cabins is also requiring wider investment in skills. An experienced fitter used to working with diesel has no idea what they are looking at when it comes to servicing a lithium cabin. It is a whole new ball game that requires investment in technical expertise, both at the factory and out in the field. As an industry we are no longer just manufacturing a metal box and adding a diesel generator, it is much more technical.
It is an interesting market at the moment. There is more competition because the market has really taken off in the past 20 years. There are probably 100,000 units in the UK now and we have produced about 20,000 of them.
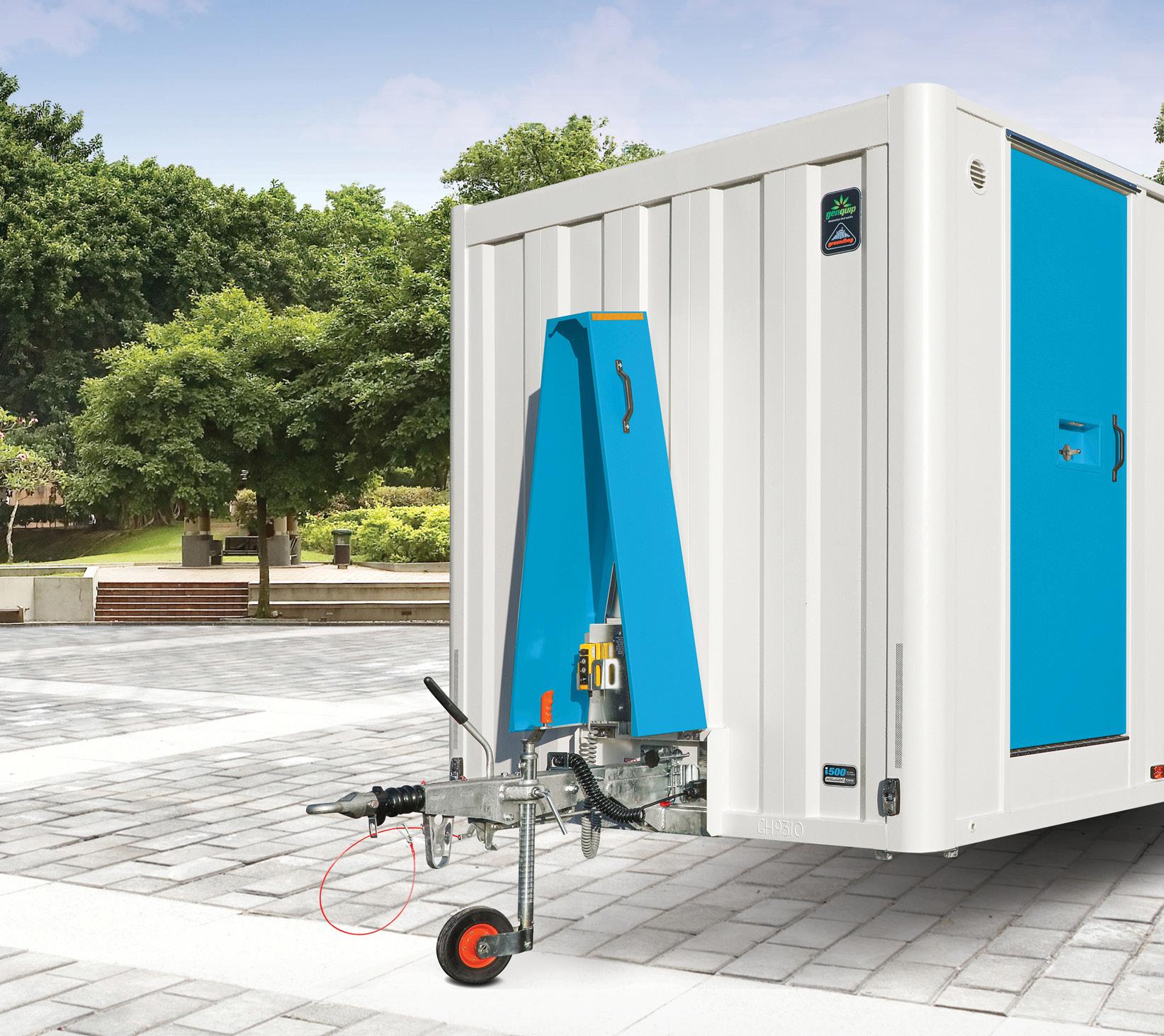
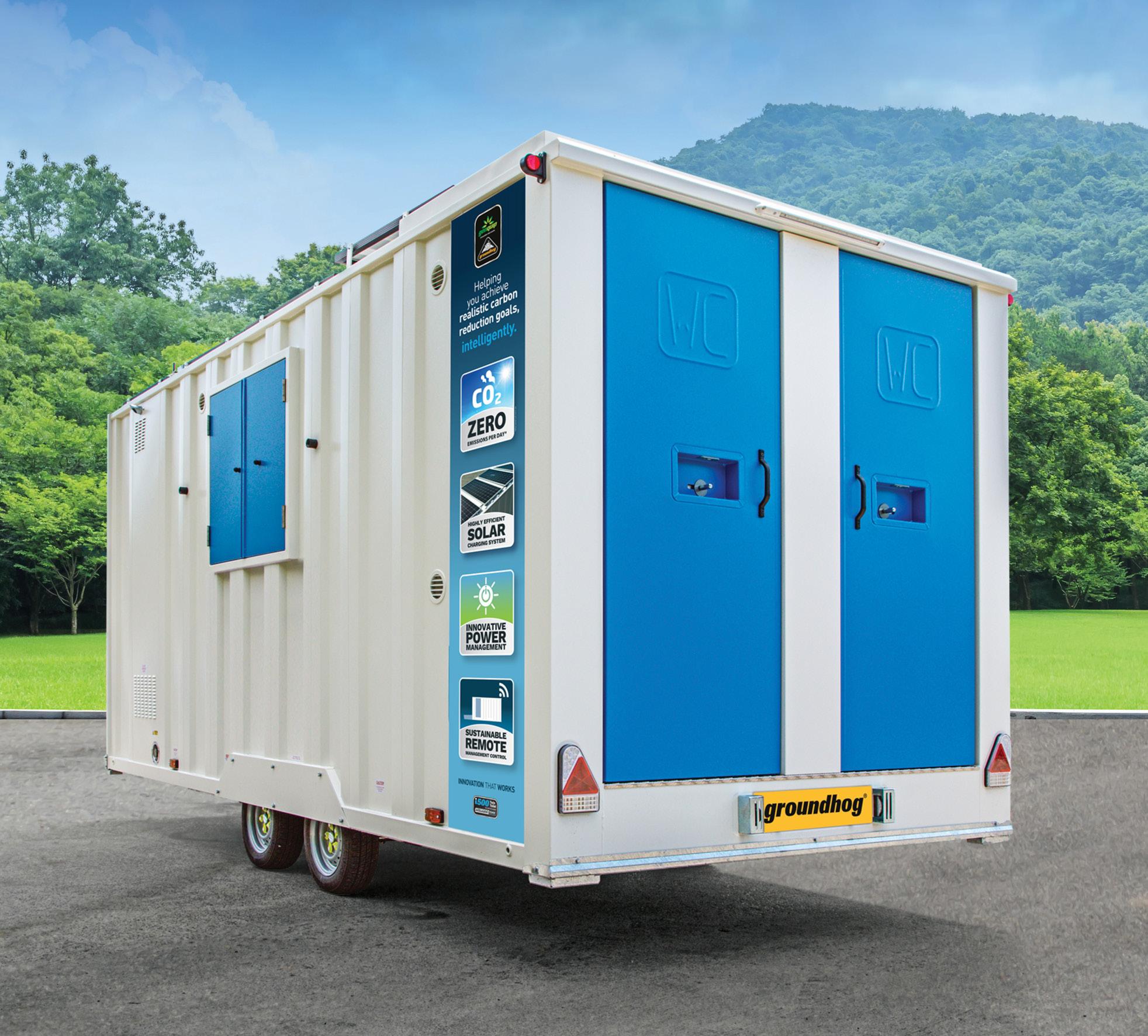
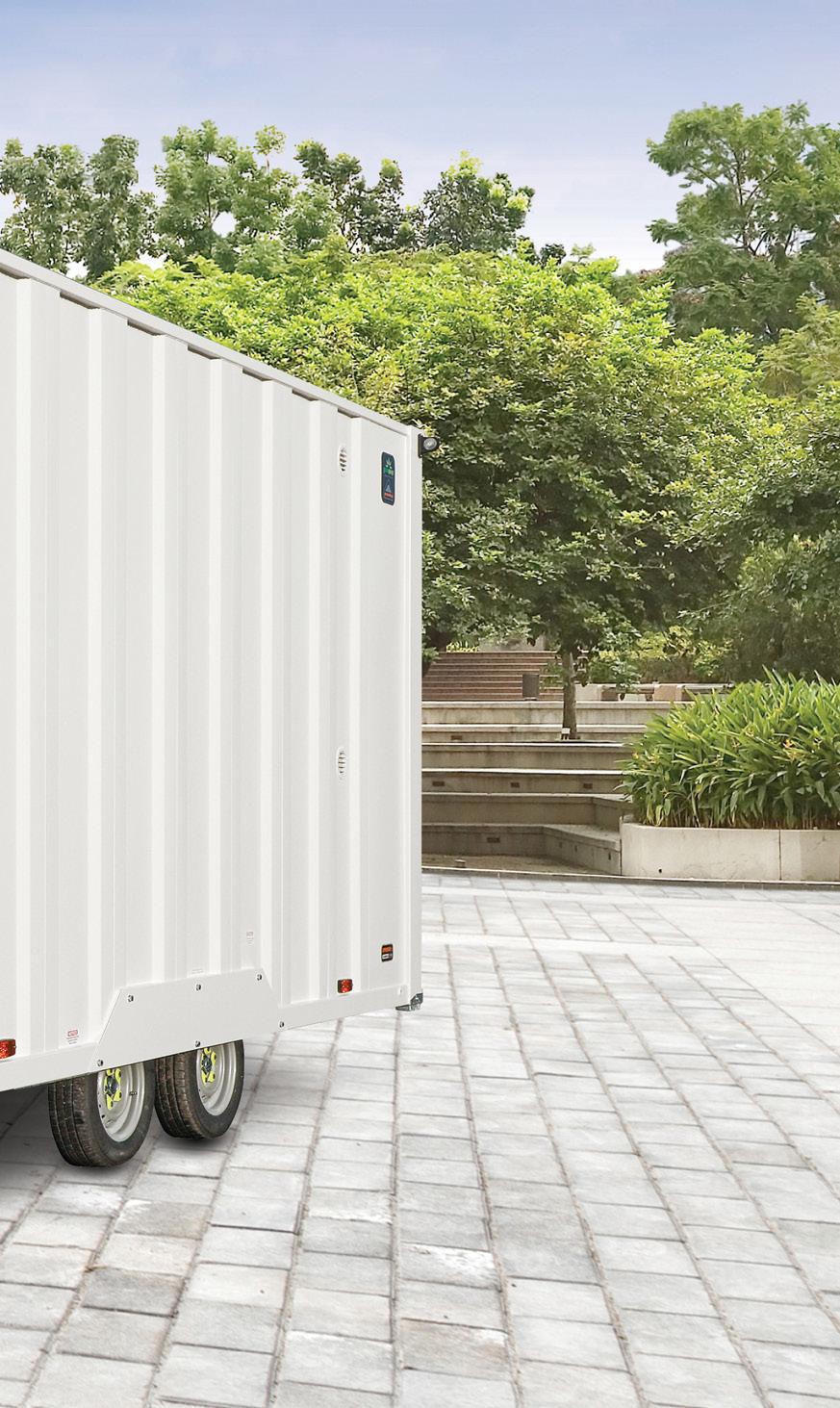
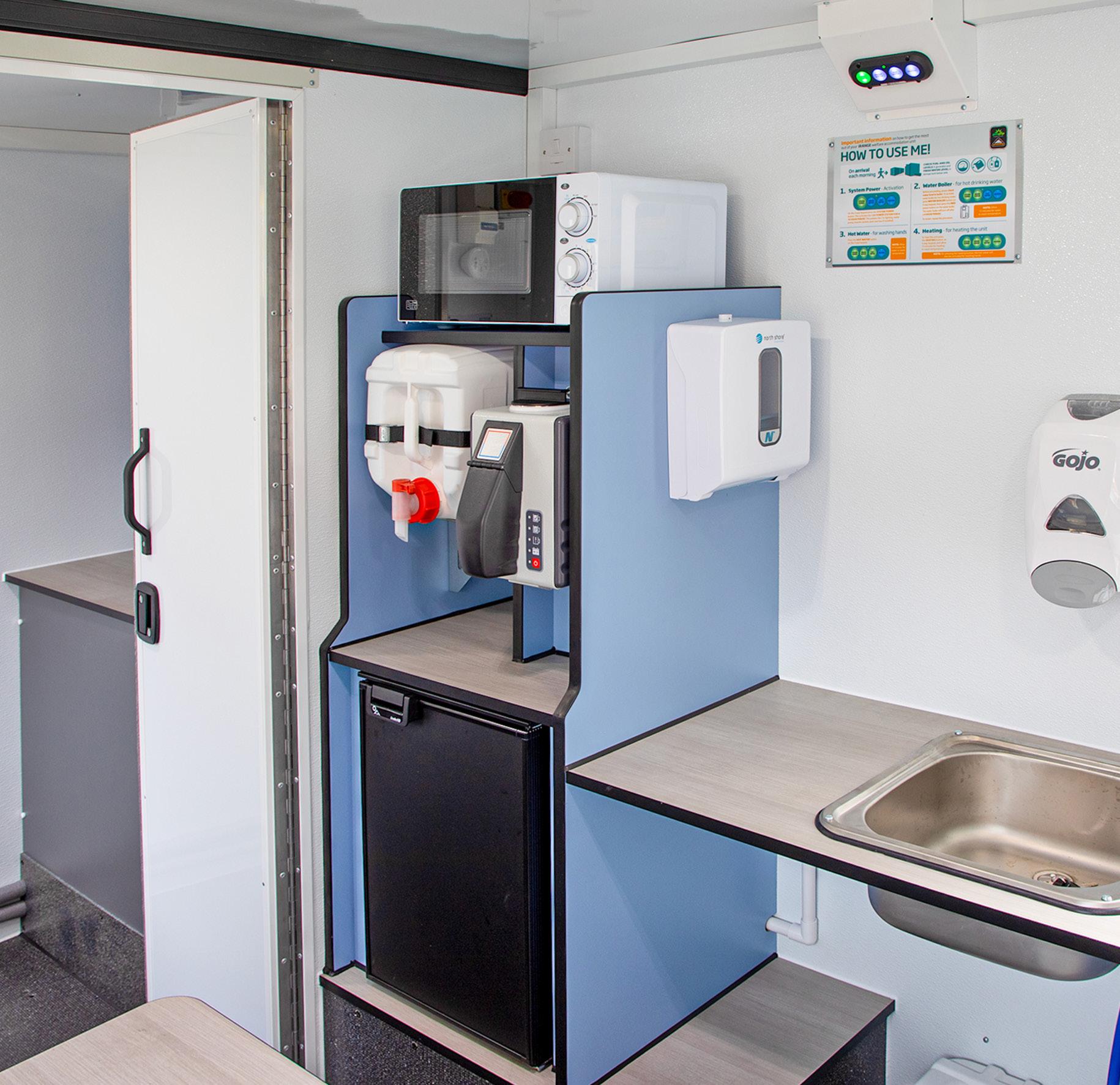
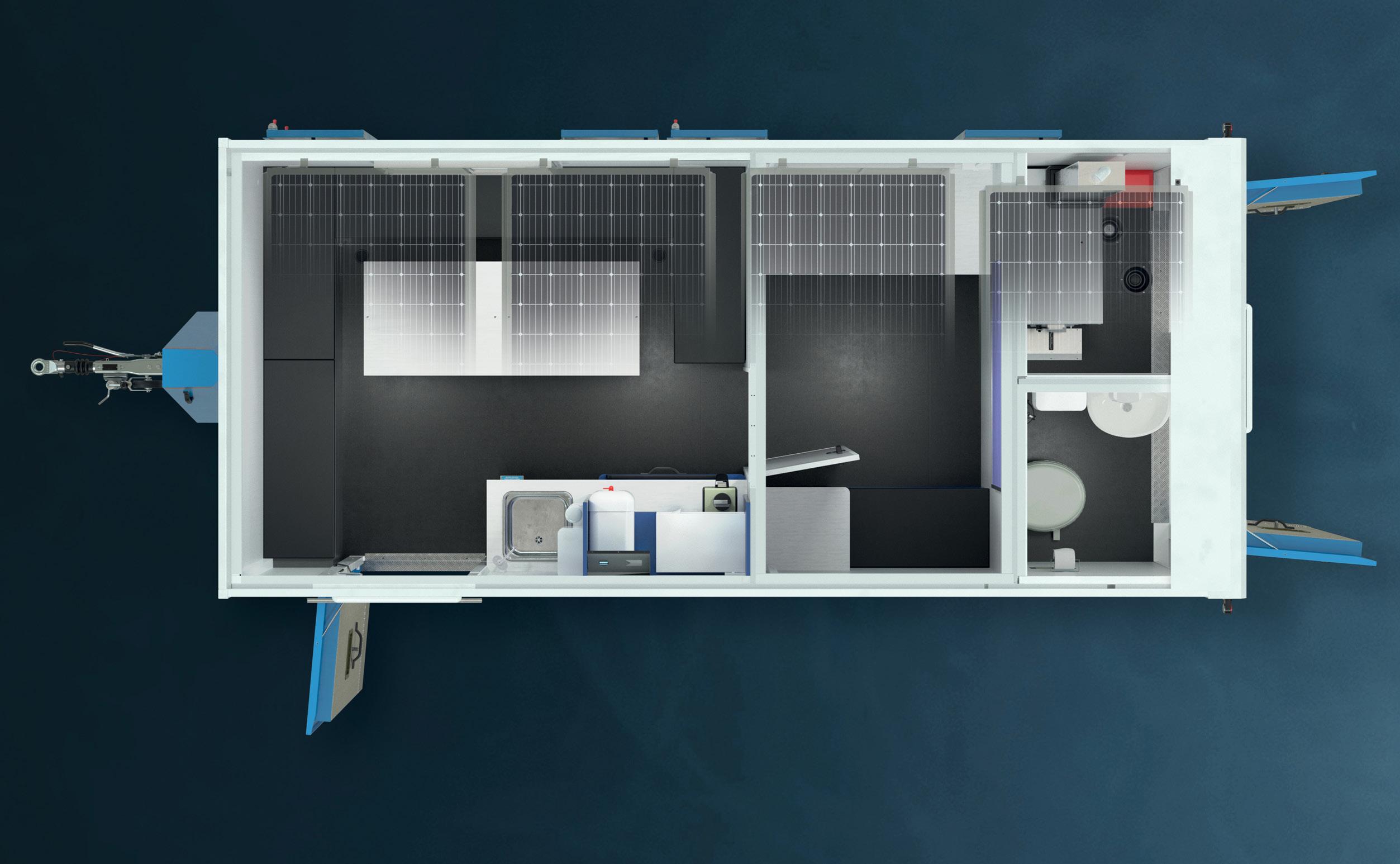
SUCCESS IN SAUDI!
The last few years have been significant ones for Hughes and Salvidge and our wider divisions. In 2023 we achieved a record turnover of over £40million and celebrated the 30th anniversary of K&B Crushers, our concrete crushing division. Moving into 2024, we are celebrating Hughes and Salvidge being 60 years old as well as our move to bigger and better offices. During that time, we have also been branching out to new locations and challenges, undertaking our first project abroad in the Kingdom of Saudi Arabia (KSA).
To secure this project, we completed an extensive tendering process which included visiting the site in KSA with a strong team of our Managing Director, Cost Engineer, Operations Director, SHEQ Manager, and Structural Engineer, to ensure the project was commercially and logistically feasible. Post-tender, multiple meetings were conducted via Teams with the team in KSA to finalise all aspects, leading to a contract award in 2023.
Following award, our full team tackled the task of organising the logistics of conducting our first project overseas. Our plant, workshop, and equipment were prepped by our in-house fitters, ready to be shipped to Dubai and then loaded onto another ship to Dammam, a port just south of our project located
in Jubail. Our Accounts team worked closely with our external Accountants and trusted advisors to establish PE (Permanent Establishment) status in KSA and understand the tax laws, both for the company and our employees.
Our Project Administrator and Business Development Manager supported each other in gathering the correct information regarding applying for work visas and arranged all paperwork and Embassy appointments with the project team.
Our Health and Safety team arranged for additional training to take place so our specialist team had the correct and appropriate qualifications/cards for conducting their work in KSA. They also arranged for new Hughes and Salvidge PPE specifically designed for working in warmer climates.
Once in KSA, our team on the ground sought out a compound in Jubail, alleviating the need for hotels and reducing the project costs.
The project was the first major demolition project undertaken by our client, and was undertaken whilst the surrounding plant and Industrial City remained operational. Our Senior Management team alleviated any concerns by producing work- and area-specific Method Statements and attending daily meetings with the client’s team.
The scope of works included:
• Separation works from the retained plant.
• Full structural demolition around a live teal plant.
• Installation of protection scaffold screens.
• Checks of service disconnection.
• Removal of a 50-metre styrene column.
• The removal of residual products.
• Three months of manual enabling works.
• Demolition of redundant plant and structures to slab.
• Mechanical demolition of the reactor plant including the removal of 5x 70-tonne reactor vessels.
• Site finishing works to hand over a safe, obstruction-free site to the client.
The project was completed by our top Machine Operators, Cost Engineer, Project Manager and Site team who fully embraced life in KSA during the 8-month project, visiting Riyadh, Jeddah and nearby Bahrain during their time on this project.
FOR FURTHER INFORMATION
To learn more about Hughes and Salvidge, please visit: www.hughesandsalvidge.co.uk
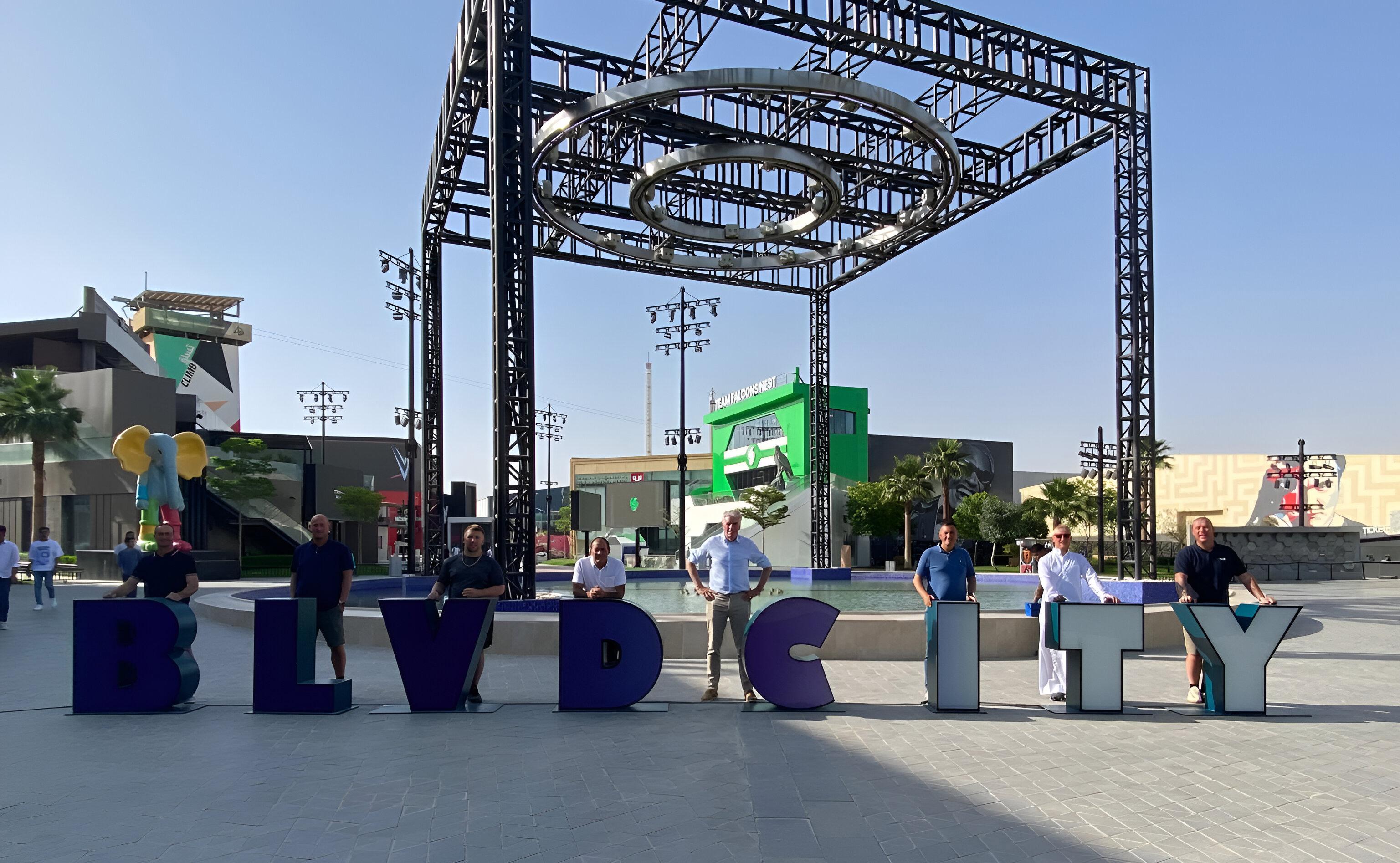
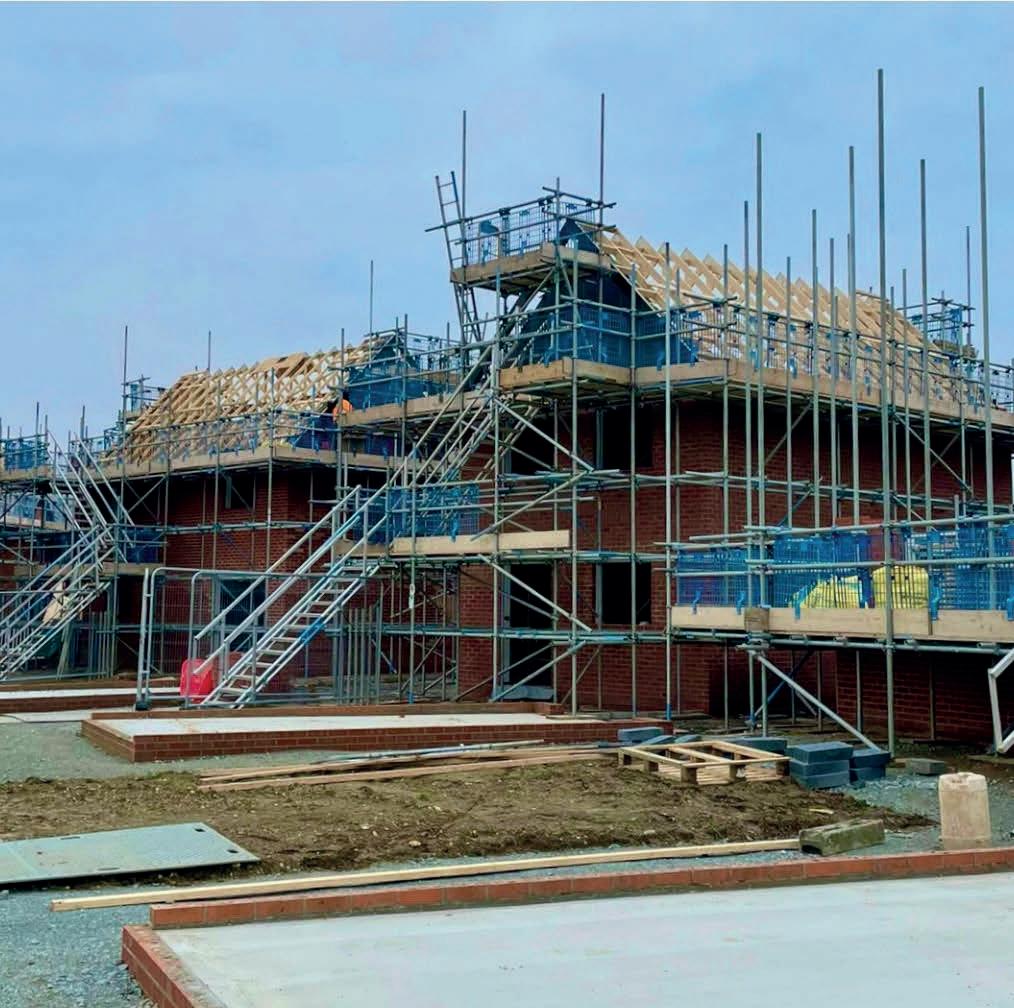
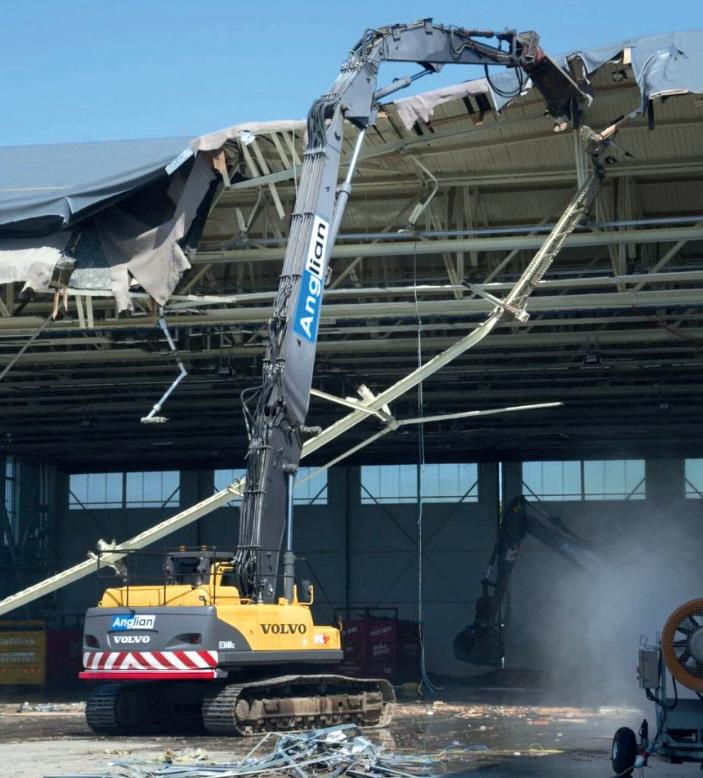
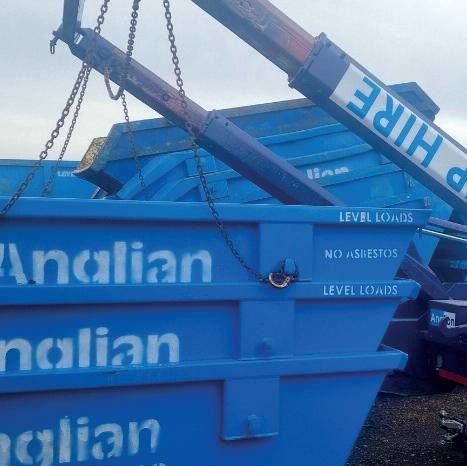
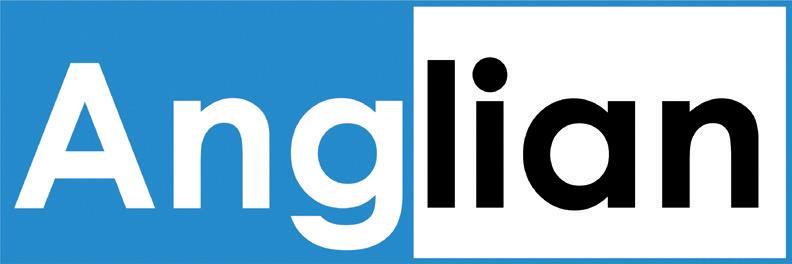

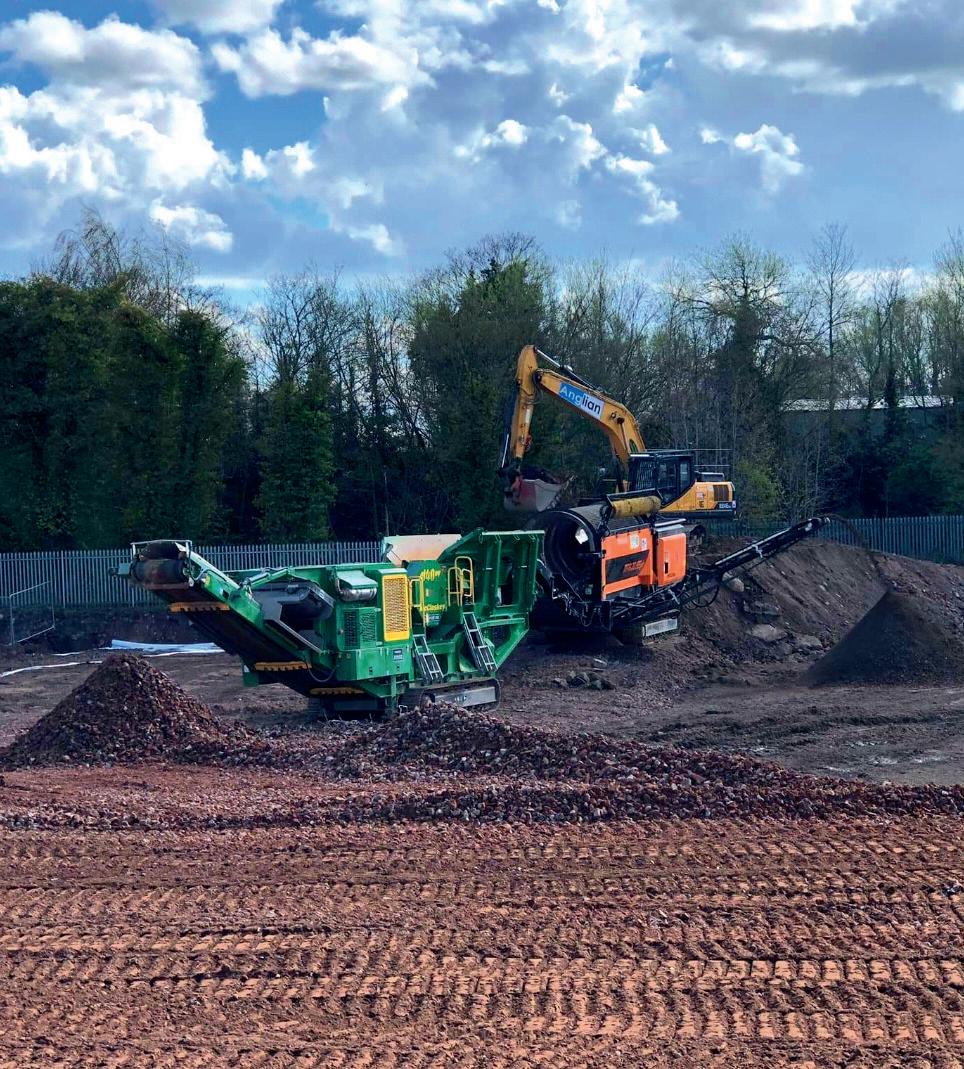
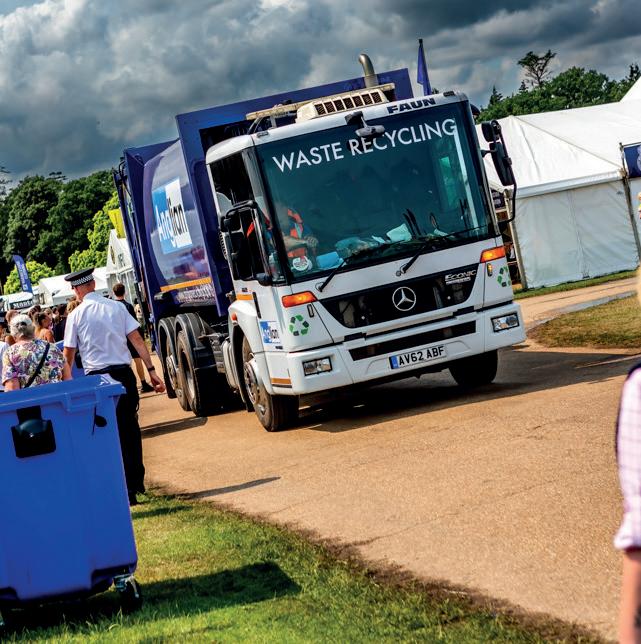
Conscious Companies // Hughes and Salvidge
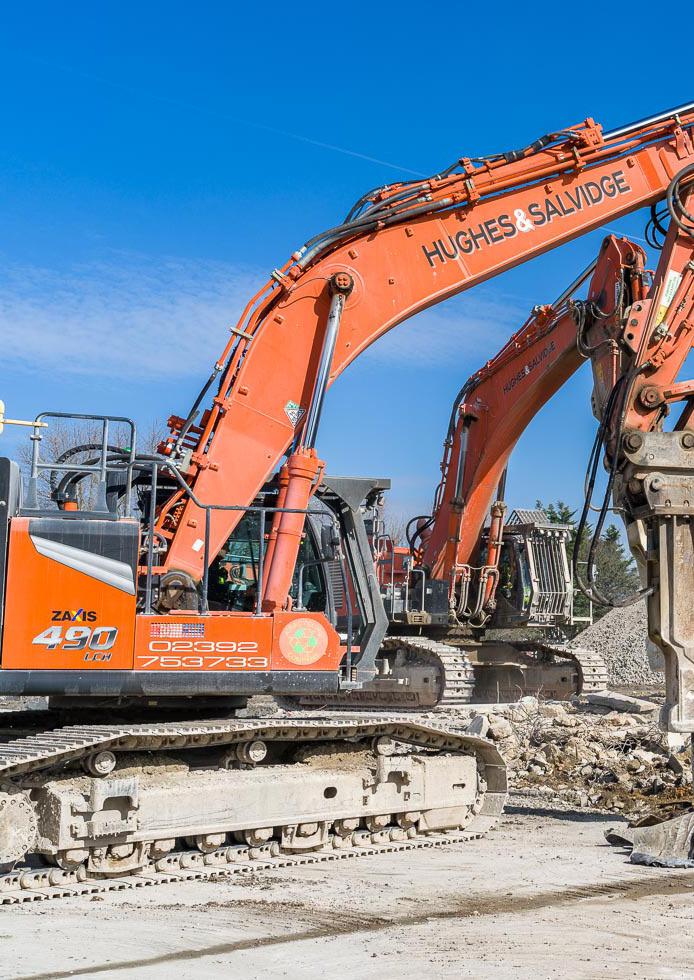
Rebecca Phillips travels to Hilsea to check out one of the latest Hughes and Salvidge demolition projects and learns just what an ostensibly conscious company they truly are.
DEMOLITION!
Quite a powerful word, isn’t it? And I must say, not the first one that springs to mind when thinking of an ecominded conscious company. Anything construction or demolition based usually screams unnecessary waste, and the struggle to remain environmentally friendly is certainly very prevalent.
It was a particularly lovely surprise then, to meet the guys at Hughes and Salvidge. I have been to a lot of different worksites in my time, but nothing beats a H&SL site. Not only is there a real buzz of community amongst the workforce, but the site itself is impeccably tidy. It’s a key indicator of just how much they care about everything they set their hand to, something that was further proven when we started our tour of the site.
We were lucky enough to not only have Site Manager, Charlie Cawte and Marketing Manager, Luke Gould to show us around, but the unexpected pleasure of Operations Director, Danny Byng also, who happened to be there at the same time as us. Rather fortuitous if you ask me, as we had the ear and wisdom of three distinct areas of the company.
By the time we were on site with them in early May, they were very near to the end of the project. None of the original structure remained, and there were only a few machines left clearing the last of the rubble. What started as a 7 storey structure was now completely flat and levelled ground; a fantastic showing for 10 months work.
After our amazing tour and mini photoshoot that the boys were kind to indulge me in, we sat down in the tea room for a little catch up about the project.
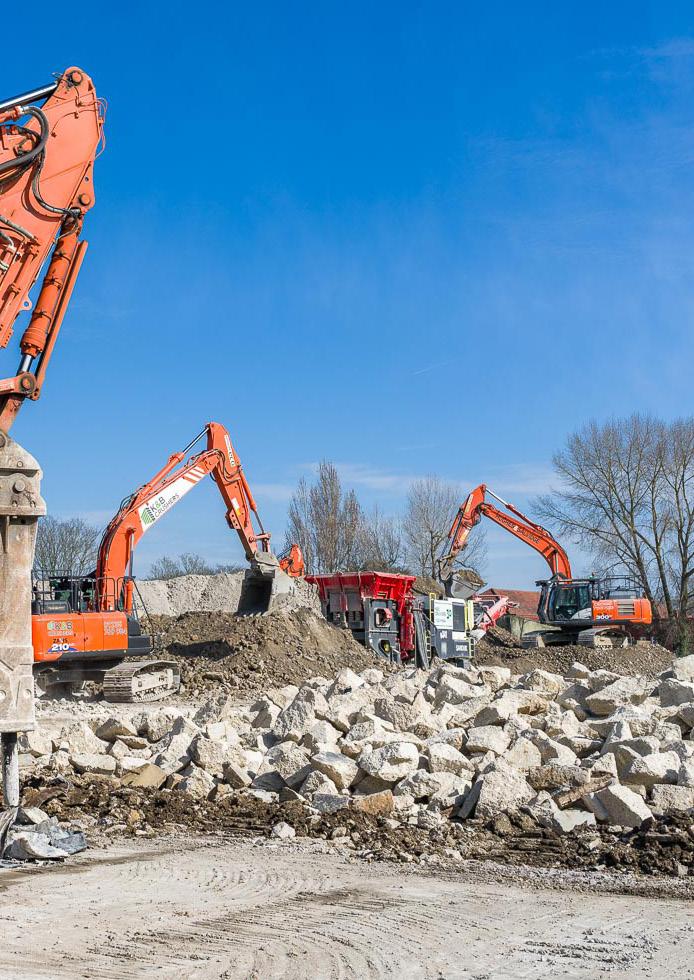
So, let’s kick things off. When did this project get started?
C: It started in August 2023 and is still ongoing though in the final stages of wrapping up.
Did you have an estimation for how long the project would take?
C: Not so sure about a specific estimation. I mean, the building came down pretty much on time. There was an issue with electrics, and the stat supply of SSE took forever to turn off the power so that slowed things down. And it was always an unknown what was in the ground, especially the area we are now. That made things a bit tricky.
Have you found that weather has played a part in that too?
C: Um, the wind has certainly not been in our favour. It’s definitely a pain when trying to keep the dust down, though the rain actually helped with that a lot.
L: Yeah, sorry to the cricket, but we needed that rain.
Poor cricket! So, you were saying earlier you started on the back end of the site?
C: That’s right. We were soft stripping that end while the asbestos survey was being carried out at the front end. That meant we didn’t have to delay and could work in tandem. We had three machines working at the back to take the canopy down, so it had to be very carefully planned.
demolition spotlight // case study
Sounds like a good way of doing things.
C: We’re a good team. And you know what TEAM stands for? Together, everyone achieves more.
And how much of that waste went to landfill in the end?
L: Under 1% of arisings went to landfill, Blimey! That’s incredible.
L: Thank you. We take sustainability incredibly seriously. Also, around 20,000t of concrete was crushed and recycled and 1000s of tonnes of metal was recycled.
C: We’ve also protected a 5m deep tidal culvert under the site, including a 3m area around it throughout the site as it acts as a passage for waters from the main road as well as being critical for the local floodplain.
Sounds like you really are committed to a greener solution.
L: Absolutely. We have our ‘Green Hands Initiative’ which we are really proud of, and our website details exactly what that means. But it’s small changes we try to make that can end up making a big difference.
Such as?
C: Well, we try our best to avoid disrupting nature. For every tree we take down, we plant a new one. And honestly, I don’t like taking trees down. Trees belong to the earth. They’re its lungs.
I think that might be my new favourite quote of all time.
C: *I have to interject that at this point, Charlie simply gave the coolest most nonchalant shrug* It’s the simple truth.
L: We do also try to use green plant machinery where possible. It can’t always be done, but it’s definitely a conscious effort on our part.
You must be excited to be a part of such an ecofriendly project then?
L: Absolutely. It’s wonderful to know that from start to finish, it’s an eco-project.
A spokesperson from First Bus South had this to say of the project:
“First Bus South have invested £20m in a new depot, which once complete, will create a purpose-built electric bus depot of the future with the capability to run a fully electrified bus fleet of up to 90 vehicles.
The new depot for Hilsea is due to complete by the end of 2025 and will provide First Bus South with the capability to operate a full zero emission bus fleet across Portsmouth by which will save 5000 tonnes of CO2 emissions every year.
More than 300 local people will benefit from temporary employment in construction roles in the project.
Once complete, Hilsea depot’s electric charging infrastructure will also be open to local businesses, following successful B2B models by First Bus in Glasgow and Leicester, where companies such as Open Reach, DPD and Police Scotland benefit from the use of our infrastructure to support their own transition to EV fleets. We are also looking at the potential to provide B2C charging to car users (with a successful trial currently taking place in our Cornwall depot) which will benefit local businesses and the wider community.”
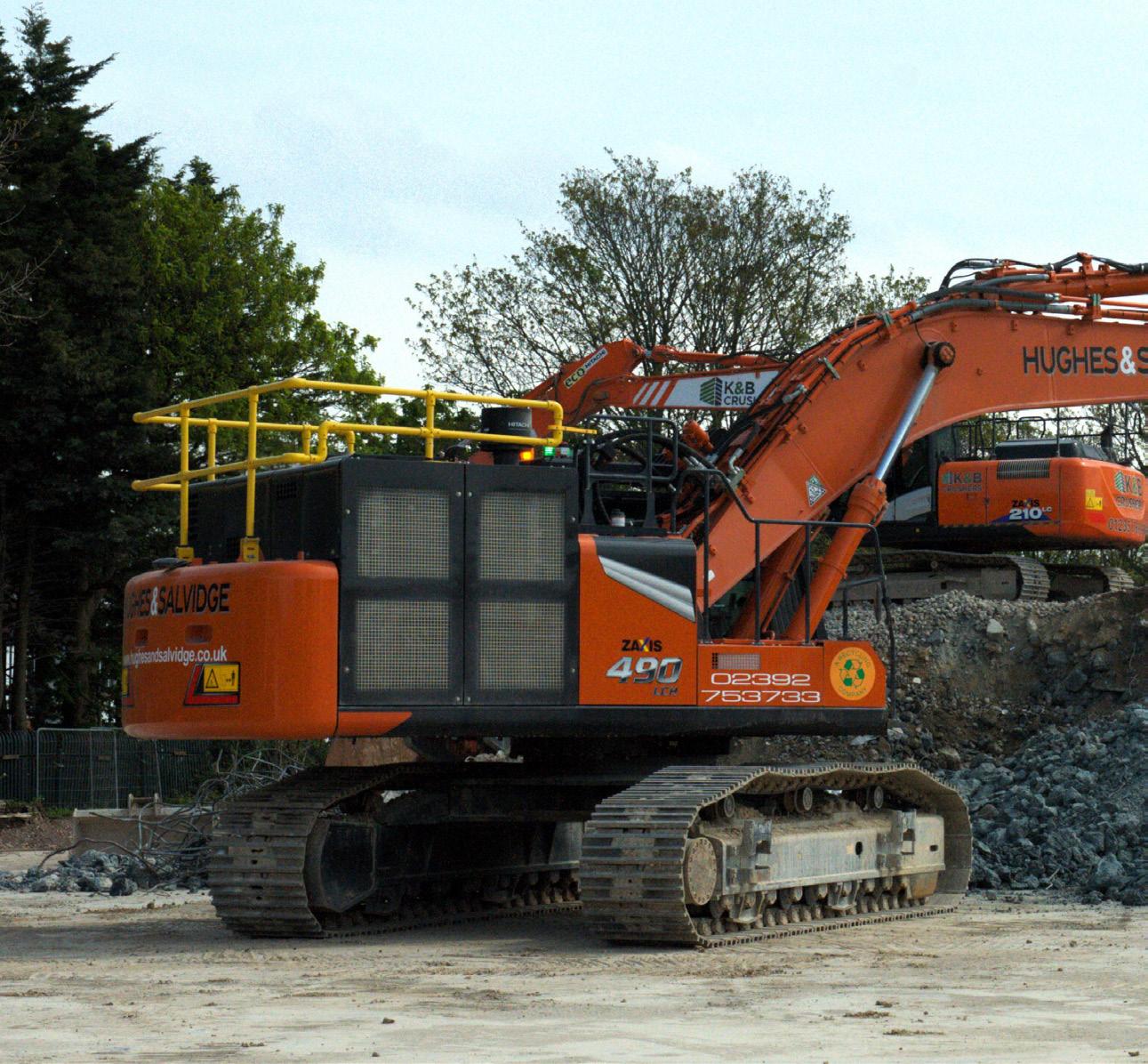
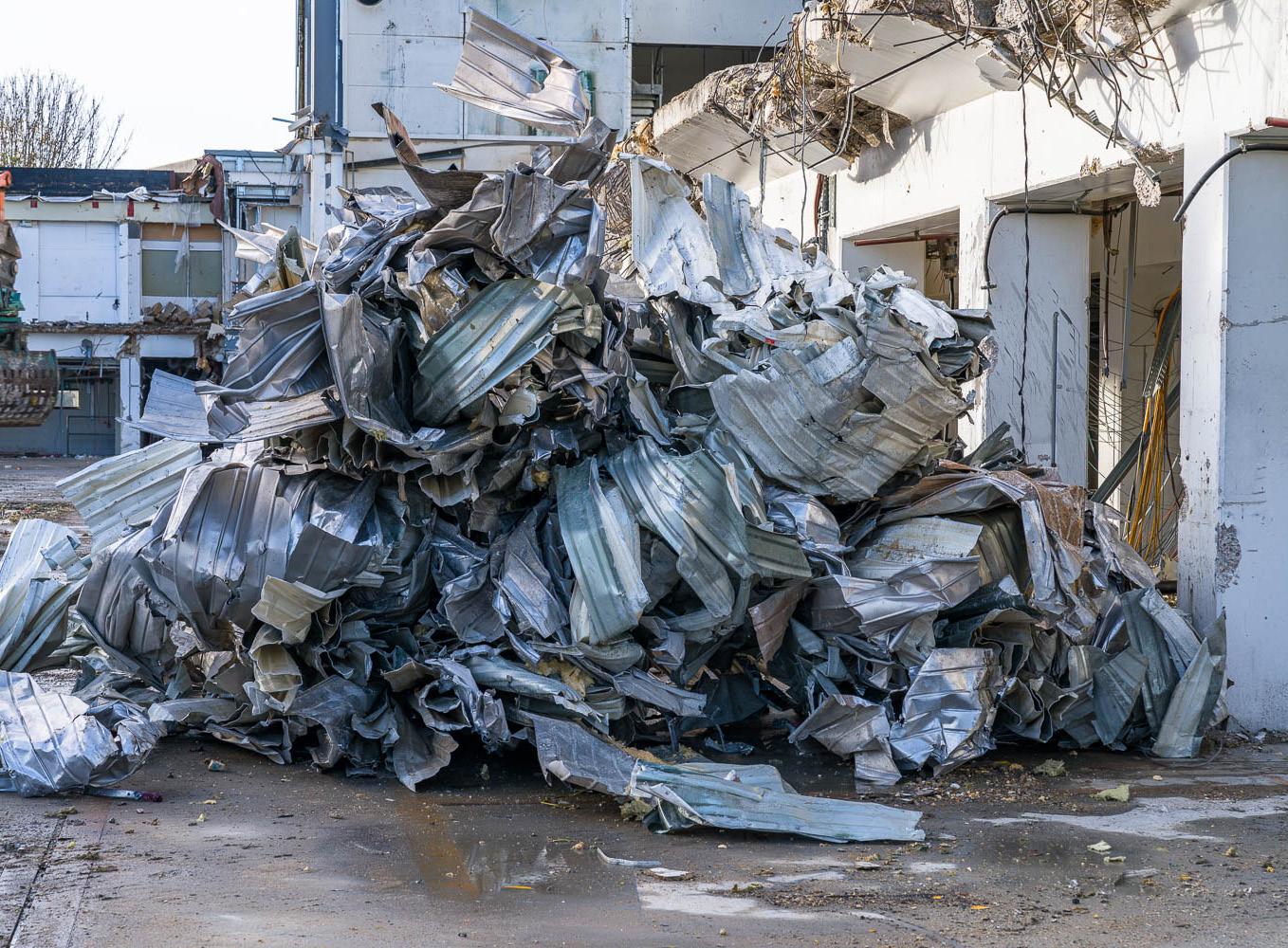
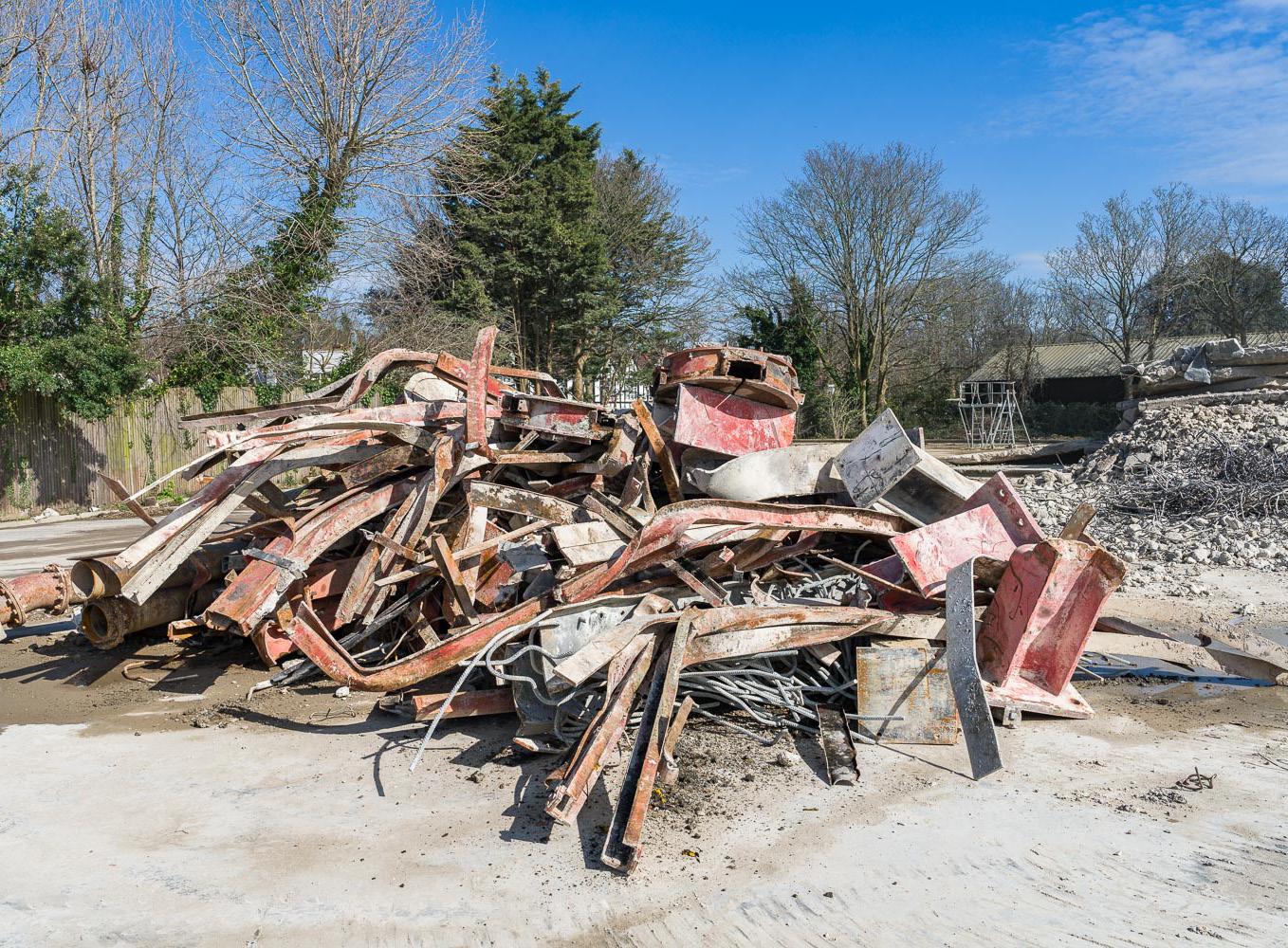
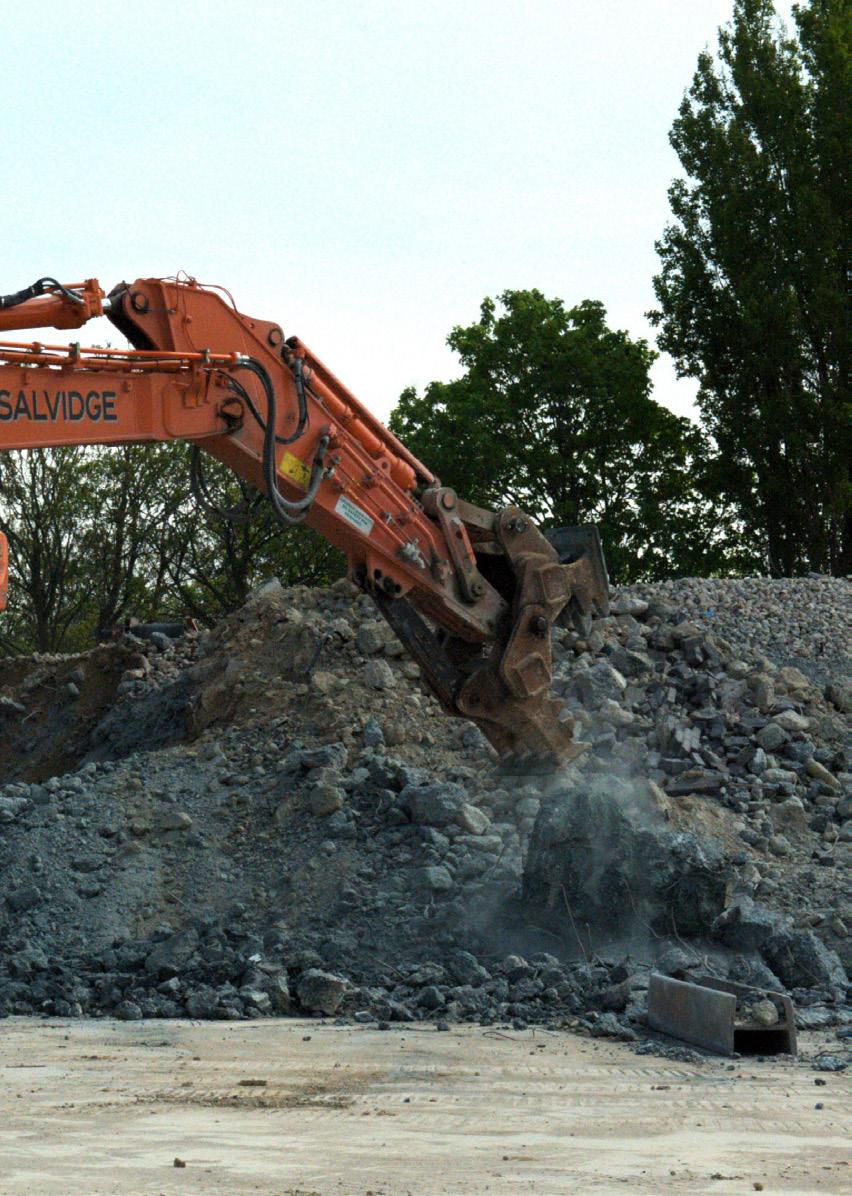
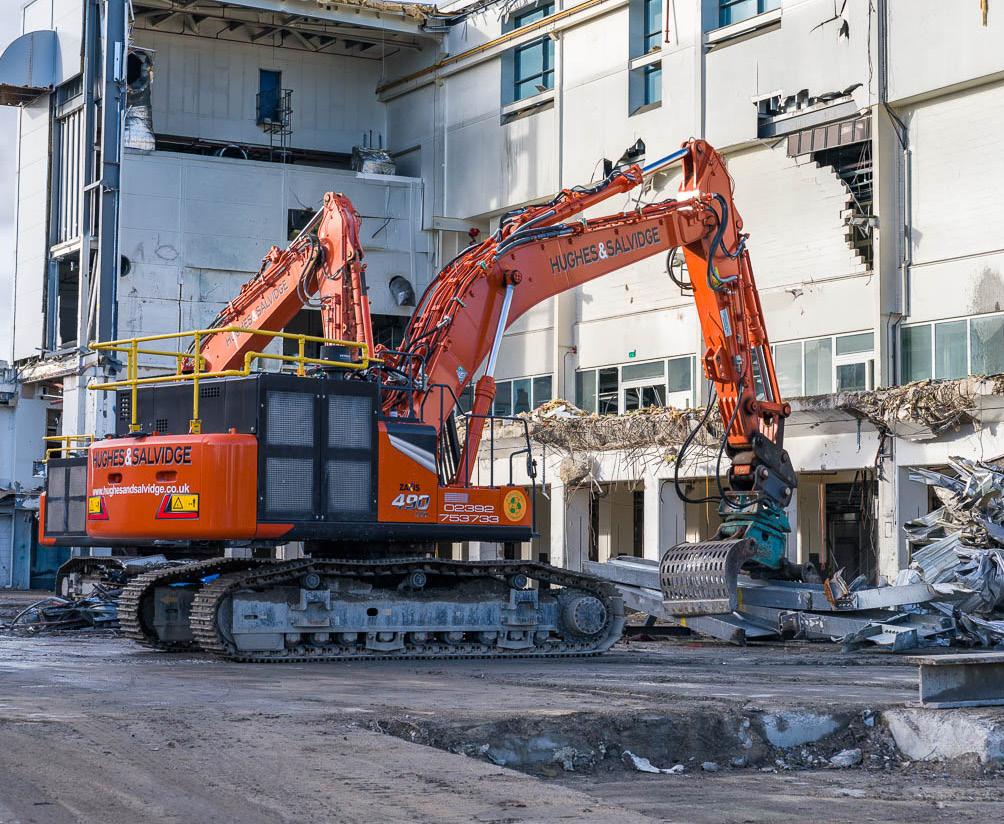
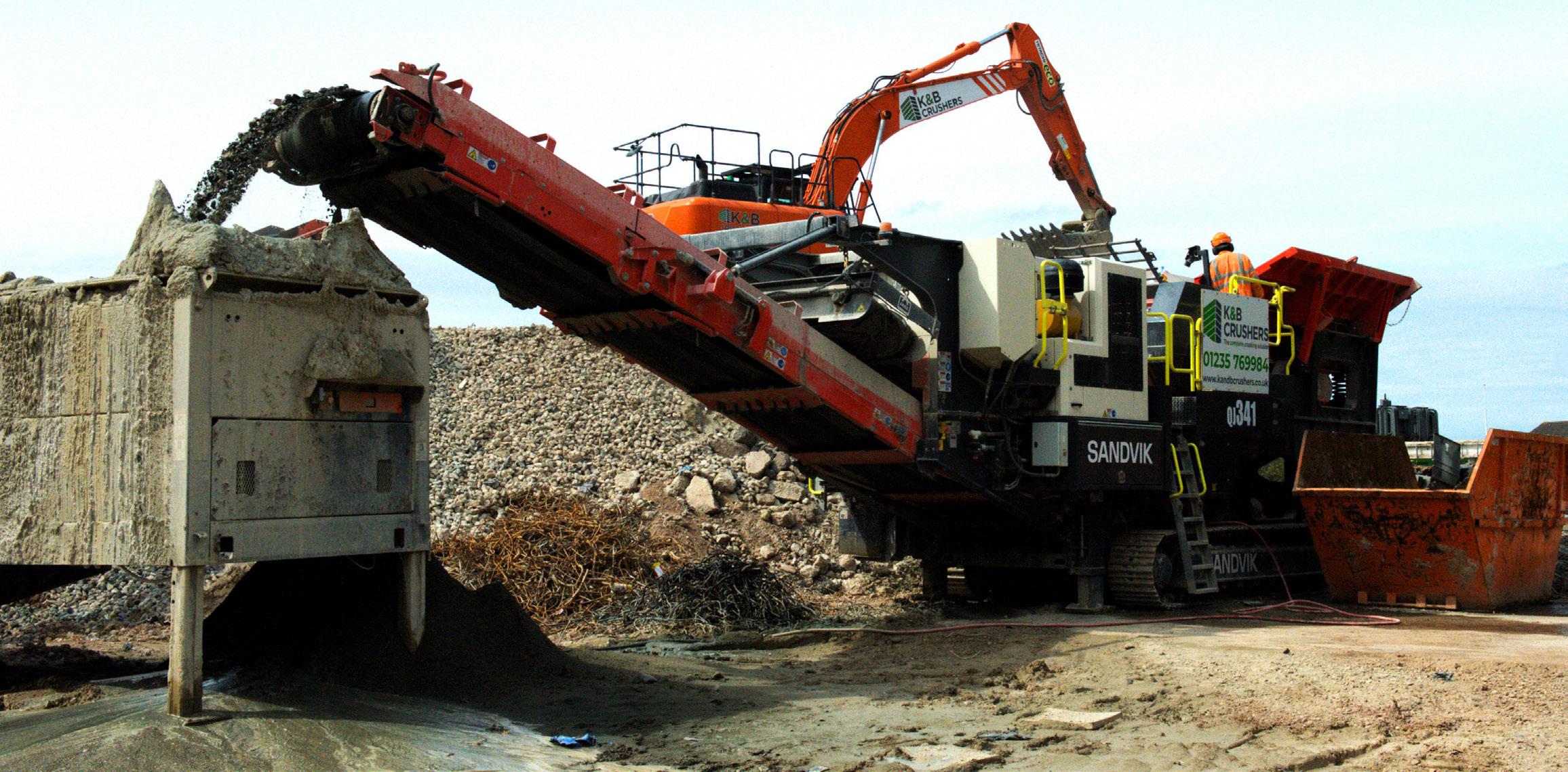
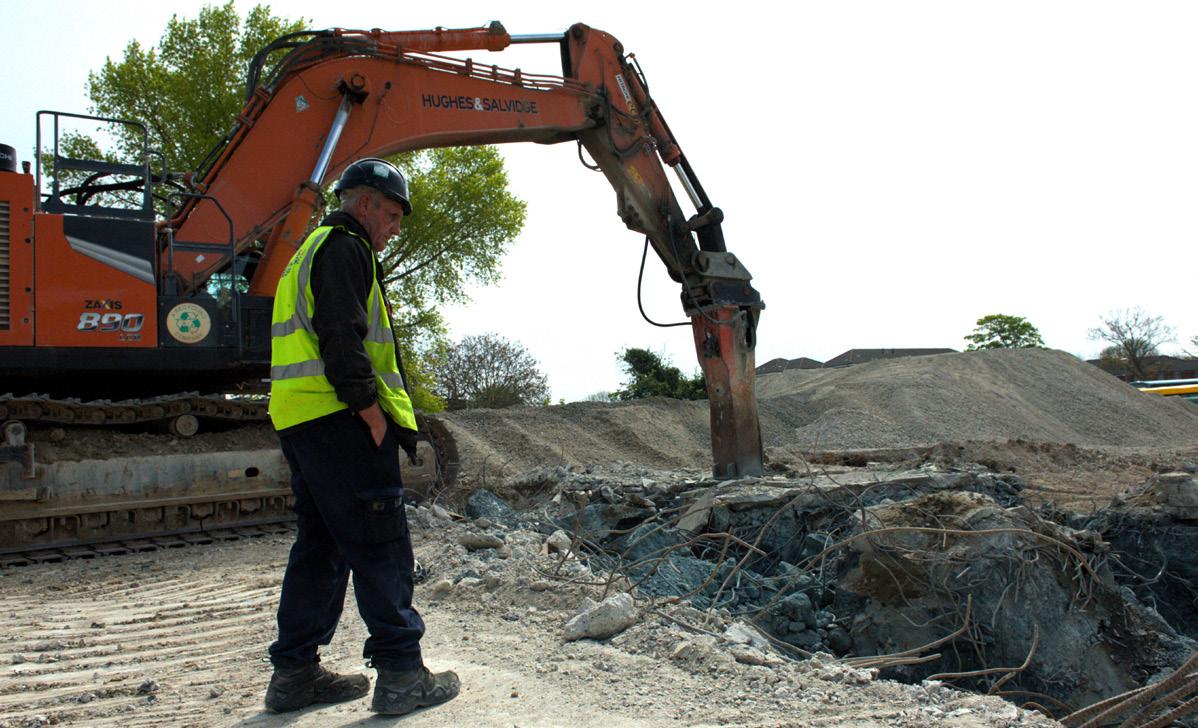
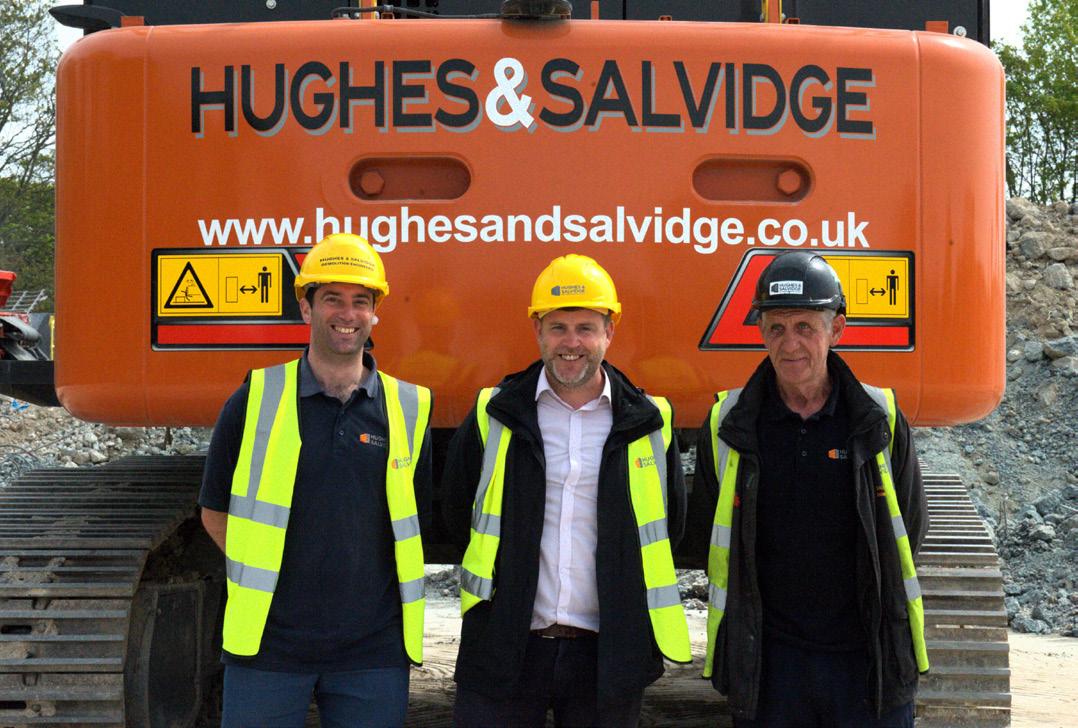
demolition spotlight // case study // Hughes and Salvidge
Here is a closer look at the Green Hands Initiative!
“Our key performance categories for this initiative are COSHH, Waste, Sustainability, Procurement, Environment, Health and Wellbeing, and Community.
Each category covers one of the main targets currently identified through our existing Environmental Management System.
Each performance category is made up of a series action points that allow us to see what we are doing well and provides us with steps for positive reinforcement, improvement and development.
Our Green Hands Initiative includes a scoring matrix that enables our SHEQ team to monitor performance on site. Employees volunteer to be ‘Environmental Champions’ on each of our sites to support and embed the initiative in everything we do.”
Waste
• Reduce the use of single use items, both plastic and paper.
• Recycling bins available with clear and informative signage about what can be recycled.
• Ensure office furniture is relocated at the end of each project.
• Ensure waste is segregated to ensure loads are not contaminated when removed from site. -We aim to recycle 100% of demolition arisings.
• Utilise associated companies to reuse demolition arisings, for example – K&B Crushers.
• Ensure Site Waste Management Plan is readily available and EWC and SIC code crib cards are included.
• Keep accurate records of all removed waste and recycling to ensure 100% traceability.
Sustainability
• Ensure recycled paper and stationery is used in both offices and sites.
• Reduce water usage by targeting areas of demolition.
• Install water tracking (e.g. water meters).
• Recycle water used on site.
• Keep accurate records of water, fuel, gas, and electricity usage.
• Reduce CO2 emissions by minimising traffic movements and not allowing machines or vehicles to idle when not being used.
Environment
• Install noise, vibration and dust monitors.
• Prevent contamination to waterways by using witches hats and pads over drains.
• Ensure Natural England has given confirmation of demolition works.
• Tree and flora protection in place and secure.
• Clear information on invasive plants and protected species displayed on sites.
• Liaise with the Environment Agency and other relevant parties to ensure procedures to protect are in place.
• Clean footwear for working near waterways.
Hughes and Salvidge are a genuinely forward thinking company, who care about every aspect of their work. The extensive track of long-term worker retention, their commitment to sustainability and general welfare of any people in contact with their projects sets a new standard for not only demolition companies, but everyone across the board. It was a true pleasure to visit their site, and I can’t wait for the next visit!
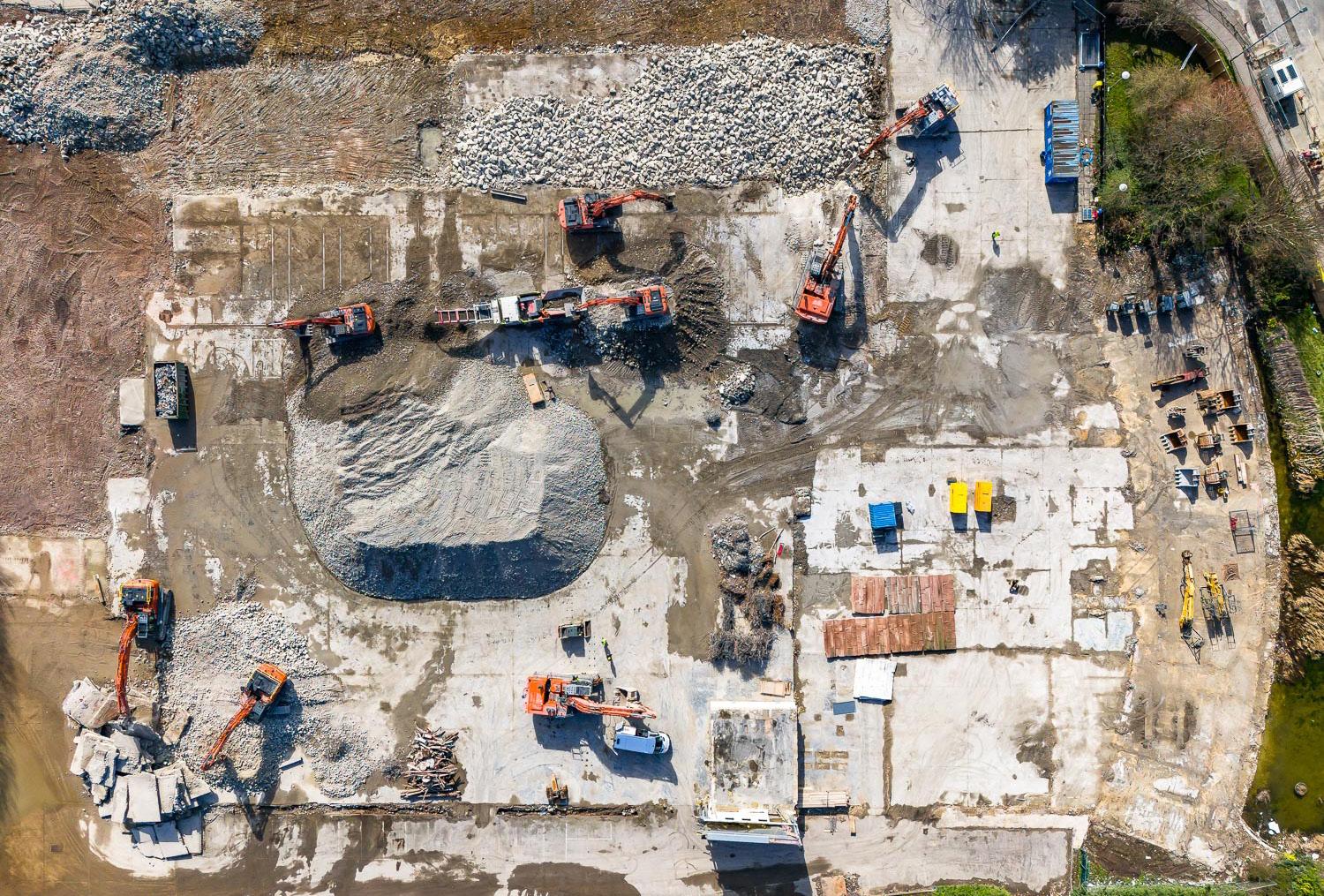
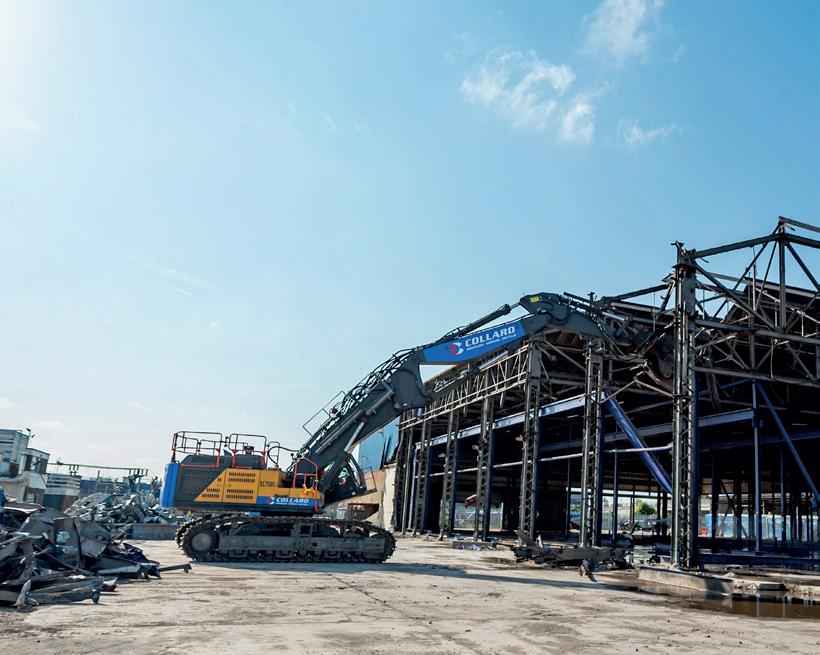
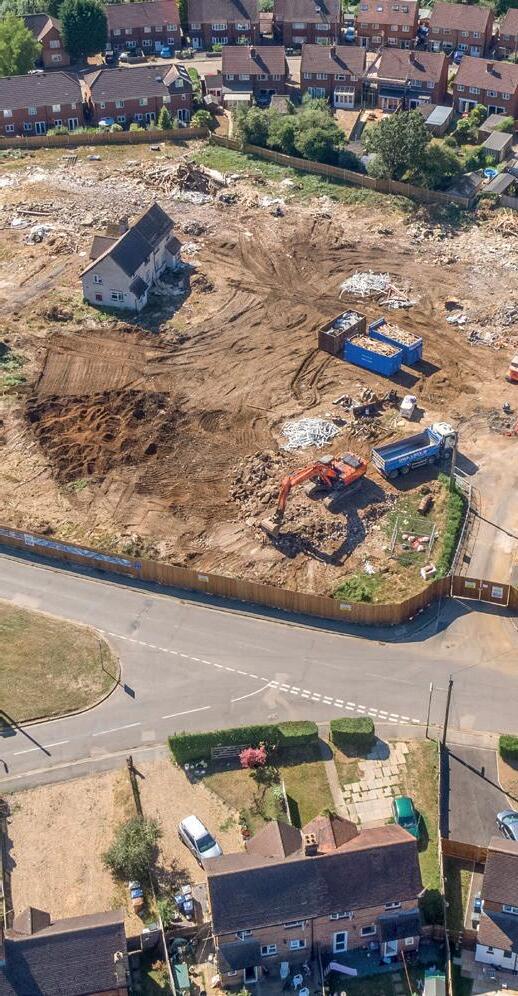
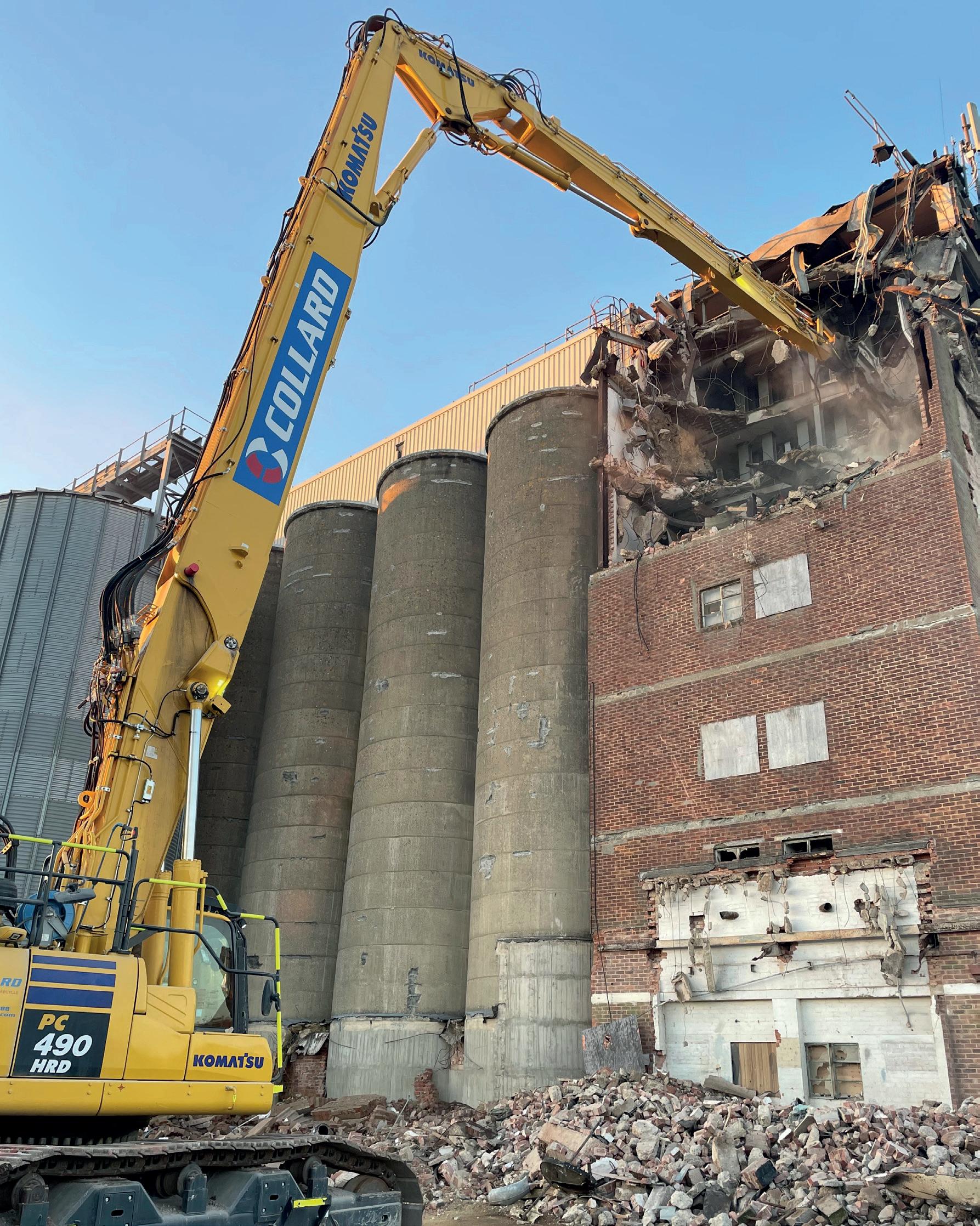
LEADERS IN DEMOLITION AND WASTE MANAGEMENT
Demolition & Enabling Works
Zero-to-landfill
Our unique capability to repurpose virtually all construction and demolition waste from site helps our public sector, local authority, commercial and residential clients achieve zero-to-landfill targets.
Demolition
Structural alterations
Site clearance
Soft strip
Asbestos management
Remediation
Earthworks & civils
Temporary works
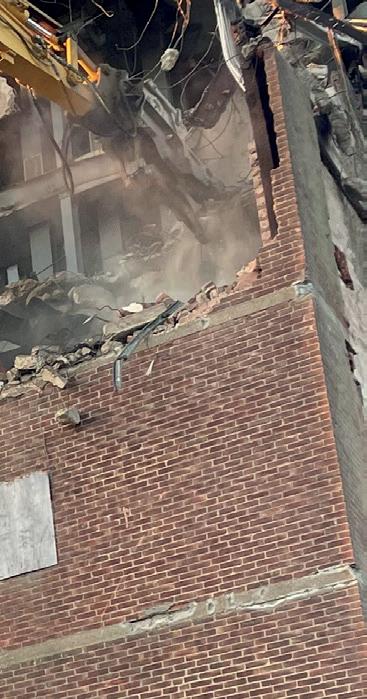
Waste Management Aggregates & Concrete
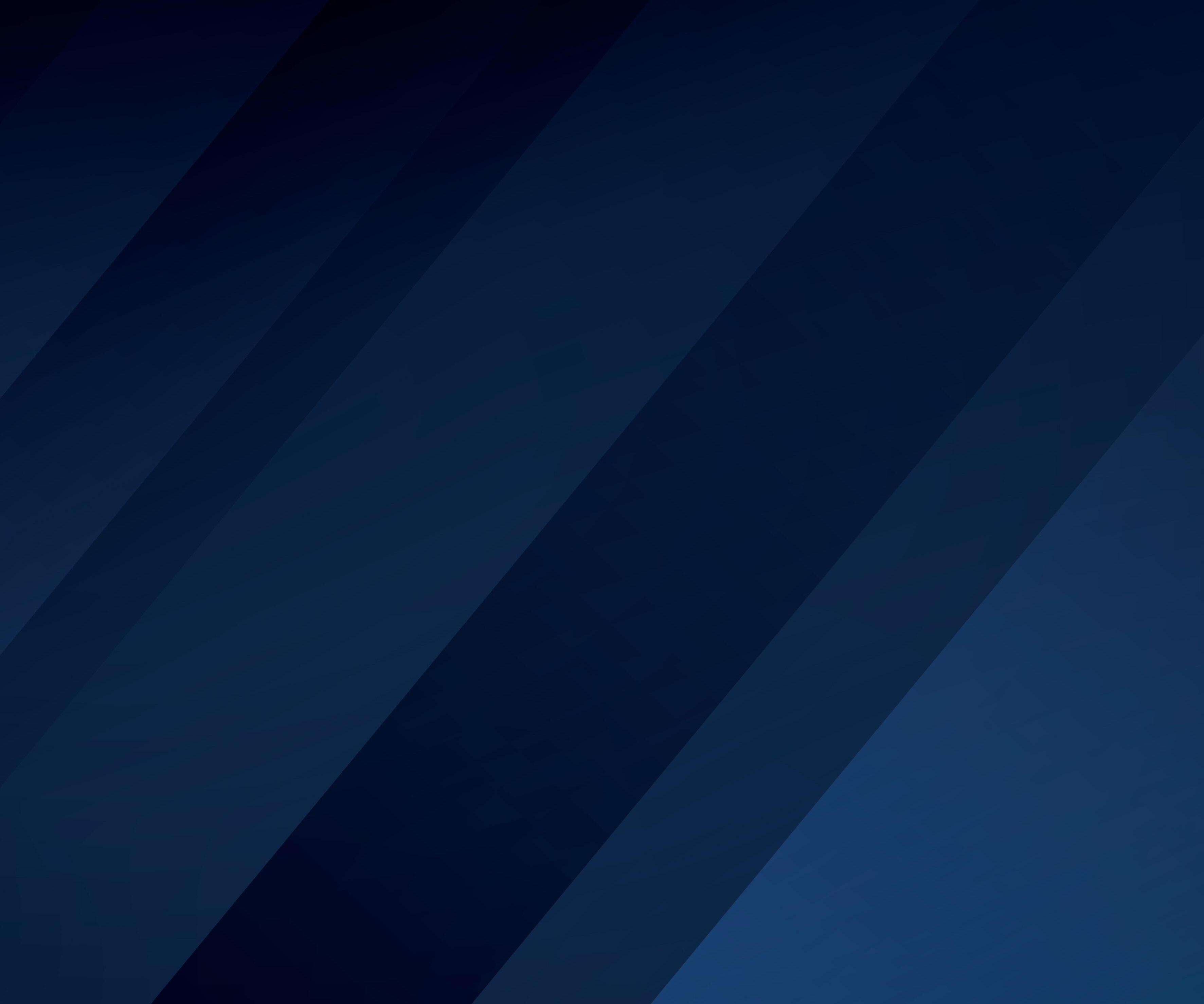
Anglian Demolition
Managing Editor Rebecca sits down with Andy Elvin, Senior Contracts Manager for Anglian Demolition.
The best way to start is always the simplest; When did you get started in demolition?
I’ve been in demolition for around 18 years, and with Anglian for ten years. I actually started off on the ground, then moved to plant operating. I went from supervisor to project manager and now I’m in senior management.
Wow, so you really have done all the steps now get you where you are today. So, what did your first role entail?
Well, for my very first job, I was known as what’s called a chicken picker. It wasn’t long after, I went into plant operation and built up my experience in earthworks. I just loved working on machines and really found my comfort zone there.
And how long have you been working as senior contracts manager for Anglian? How did that career progression come about?
I joined Anglian in 2014 as a plant operator but was quickly given the opportunity to move into a supervisory role. I thoroughly enjoyed the transition and then went on to earn a CCDO demolition gold card before progressing to project manager on-site.
After I’d been at Anglian for five years, I was one of three team members specially selected by Anglian for career development into a senior management role. I felt honoured to be given this opportunity and grabbed it with both hands. I became contracts manager in 2020 and was promoted to senior contracts manager two years later.
Knowledge from the ground up is something that certain contracts managers aren’t going to have, because some people just go straight into a managerial role. Do you find that really helps you with what you’re doing?
Massively! As senior contracts manager, it’s essential to have an understanding across the trades and so my hands-on industry experience stands me in good stead. I’ve spent plenty of time on the ground doing various types of projects, from top-down to standard demolition, so I understand all aspects.
Each project has so many different elements and my experience helps to plan how every aspect of the demolition will be undertaken at each stage. I know what the capabilities of the machines will be, what size machine will be needed and what attachments will best serve. I also understand the day-to-day challenges my guys have on site – I’ve been there and done that too!
At Anglian, we’re really fortunate to have an experienced team on the ground that I can call on as needed. Sometimes it’s good to get another viewpoint or have someone to talk certain elements through with.
Especially if, as you say, you’ve got such a good team as well to back you up.
You’re only ever as good as your team below you. Ours at Anglian is second to none.
In terms of qualifications, did you do yours first? Or was it all work based?
I completed all my qualifications alongside being on site. I’ve done my standard CPCS qualifications, followed by my gold card and NVQ Level 7 black CSCS card. The NDTG gold card training was from a supervisory level and, of course, I’ve done all the training required for my current role.
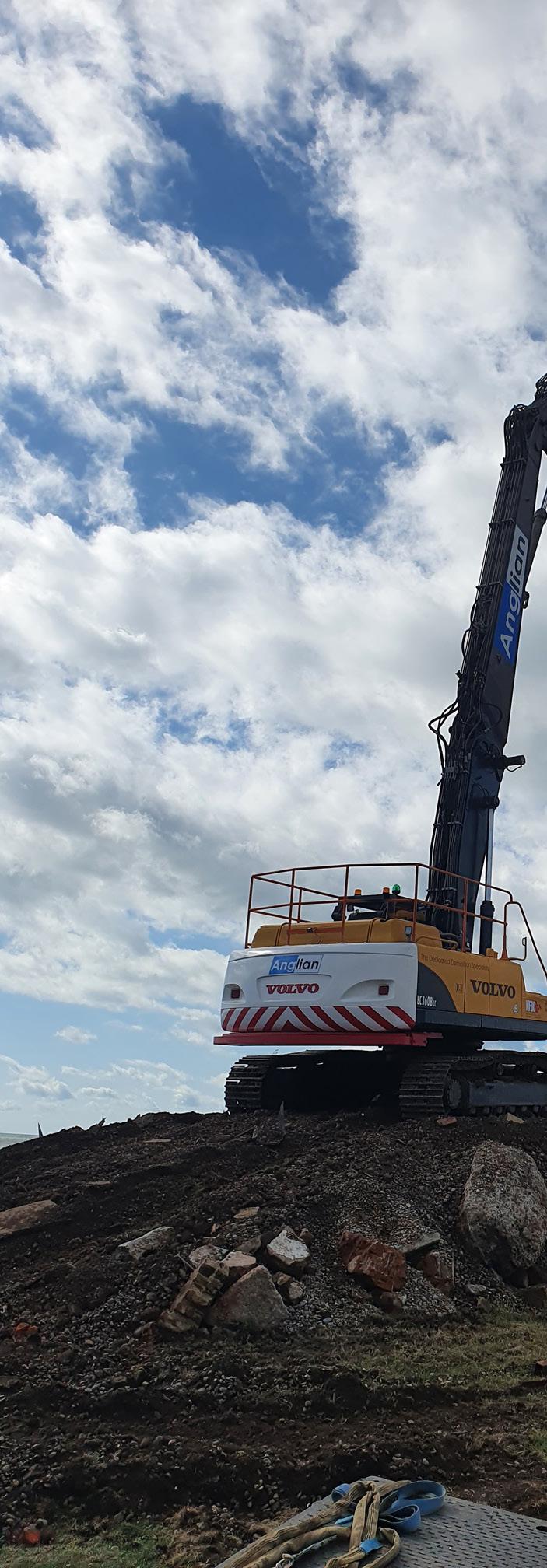
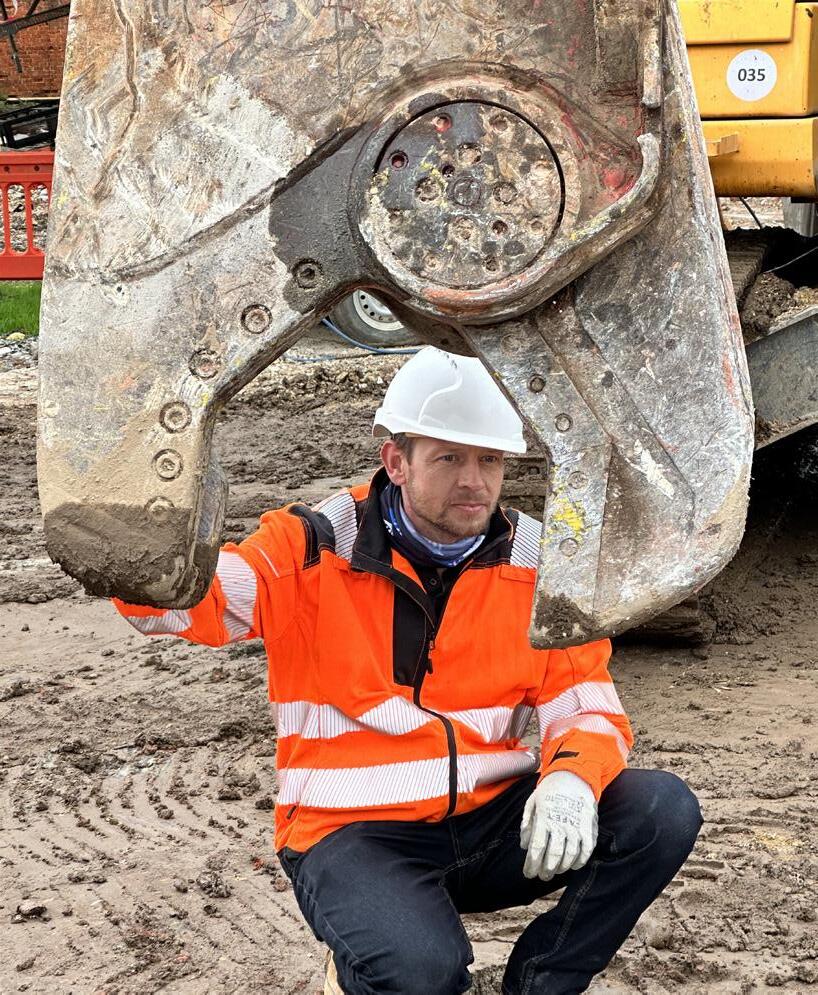
andy elvin
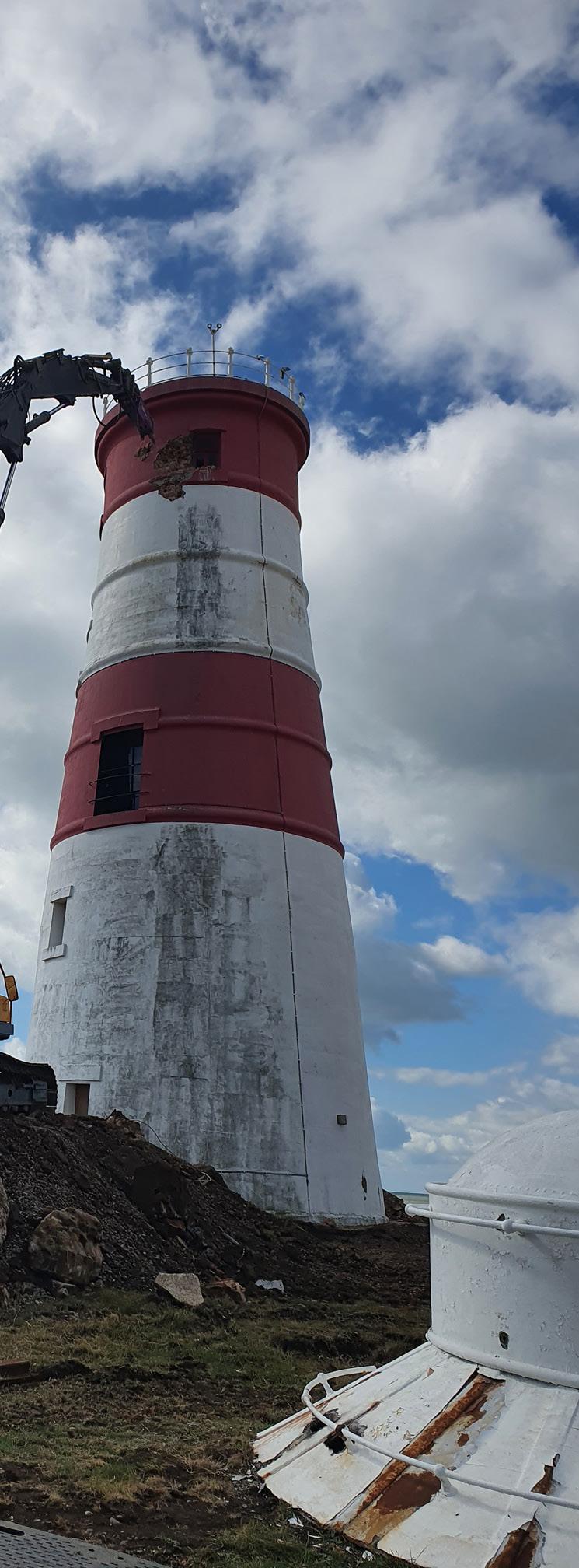
Do you think that your practical knowledge helps you more than that? Or do you need both?
In a role like this with so many variables and moving parts, I’d always say that practical knowledge was vital. Qualifications are essential of course, but the hands-on experience of completing projects is something you can’t really study for. During my career, I’ve spent hundreds of hours on-site working on and observing all manner of demo jobs. It’s this experience which means I know how the building is going to come down and enables me to write the method statement for that specific project. With demo, there isn’t a one size fits all approach so it’s skills and knowledge you have to rely on.
That’s something that really sets you apart from other people and something that is a big selling point for Anglian.
Absolutely. We’ve got an experienced demolition side, but Anglian also has divisions for asbestos surveys and removal, scaffolding, earthworks and remediation and waste recycling. We offer this all in-house, meaning that no matter what project a client comes to us with, we can cover the lot. We provide a one-stop-shop, but equally each division are specialists in their own right which clients can call on individually too.
We also work a lot with other contractors – for example, providing skips for their projects and processing their waste, or erecting scaffolding for them to work from.
That must be helpful having all of that in one, so you can offer clients a complete package.
It is brilliant for us, because when we tender for a project, and there’s different elements – from a special scaffold to waste – we can do it all. Anglian can organise and manage the entire project, which also means a clear outlook on costs. I’m not waiting on a subcontractor to come in or to finish up. We have eyes on everything. It’s much neater and tidier that way, for us as well as the client. Our divisions work hand in hand too to deliver the best service – for example, we segregate all the waste from our demo projects on-site and bring it back to our facility for processing and recycling.
Definitely. So, in your career, what’s been your absolute highlight?
For me personally, it was stepping from the site into the contract manager role. At this point I knew Anglian really believed in me. When I was on site, I genuinely thought I had another ten years there, because I was only around about 35 at the time. I always thought I’d move on around 45-50. But then the opportunity arose in the business, and I took it. Not only was it a change in my career, and it also showed me that my directors believed in what I was doing and saw I had what it took to progress to the next level. They valued everything that I’d done so far.
Do many follow a similar career path to yours?
I’m not so sure. Very often, when you have demolition men on site, they’re usually perceived to be these rough, hard, tumbled gentlemen. And it’s rare for these individuals to be given the opportunity to come in from that side of the business to become someone who stands in front of a client and sells them the company and its services. As a business, Anglian is keen to recognise potential and give staff who work hard and are keen to progress their career the opportunity to do so. I’ve been fortunate here and definitely grabbed it with both hands. I’ve not looked back!
So where is your next jump in your career?
It’s an exciting time at Anglian and I’m really enjoying my current role. I have lots that I want to do with my current team. I’m looking forward to continuing my journey here, achieving my goals and helping to drive the business forward.
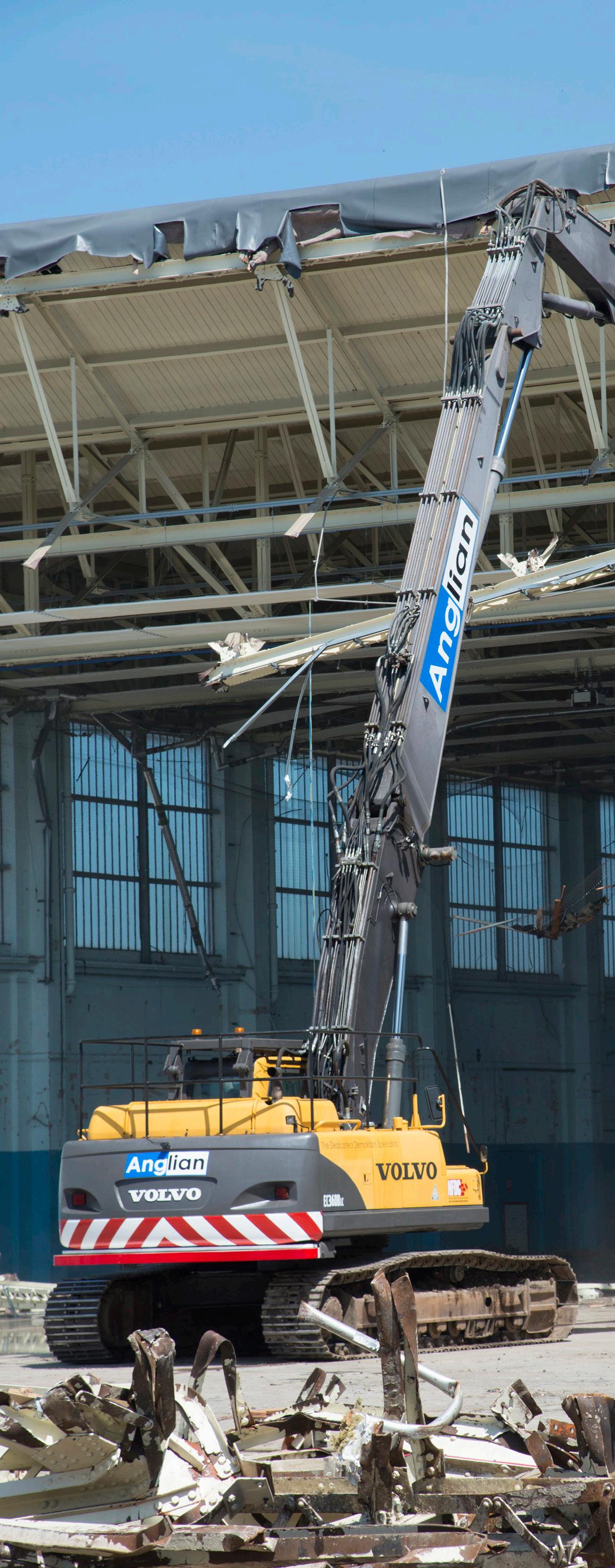
What would you say has been the biggest challenge that you faced in your career?
The biggest challenge was definitely the transition from site to office. I think a lot of businesses and a lot of industries are the same - when you are working on site, you have such a drive to achieve a specific goal in a specific time to a specific budget. You’re so focused on the job in hand on site that you often don’t realise the other factors going on behind the scenes to make the project run as it needs to. That was the biggest eye opener for me; learning that other side of it and realising all the different things required from a contracts perspective before a site job can even start, but also as it progresses and even after completion.
Is that something you’ve talked to the guys on site?
Absolutely – I’ve been on both sides and now I’m the conduit between! I’m always open and honest with my guys.
That must be really good for camaraderie.
Everyone works together. I genuinely believe Anglian has the strongest demolition team now that the business has ever had. There’s a lot of things that people often don’t understand in demolition. People just think you go in and knock stuff down. There’s so many different types of skills you need, whether it be disconnecting buildings, demolishing buildings, soft stripping buildings. You need such an array of knowledge to be able to undertake the roles people don’t get. Our team at Anglian has this expertise in spades.
Demolition and construction are both really in need of workforce. Do you think the skill set is too daunting for a lot of people?
There’s a lot of factors affecting the number of new people coming into the industry - not just skillset as skills are something you can usually learn. It’s a real shame to see this as it’s such a rewarding career.
Either way, I suppose it’s important to put the information out there so people can make an informed choice.
100%. We are always keen to talk to potential new recruits and enable them to find out more about working at Anglian. This year, we’ve taken on eight younger generation team members. After six months, when they come to you and I go, ‘this is in my blood! I love demolition!’, I know they’ve got the bug just like I did at that age. It is one of those careers that when you’re in, you’re in. You can’t extract yourself from it, because it uses such an array of knowledge and variety of tasks all the time. Every day is different and you’re always learning as construction and demo processes continue to evolve. It’s such a brilliant industry to be part of.
Demolition then, as a general business, seems to drive a thirst for knowledge and a passion for the art of demolition?
Yes, the machine drivers especially. I have so much respect for them. They have to know every aspect of the business, not simply how to operate a machine. Otherwise, how would they be able to separate the different types of waste as they go? What’s the best way to take down each specific building section? What attachment is needed? There is so much to know. These are the guys that usually impart their knowledge to help bring on the next wave of employees and they’re vital to the continuity of the business in future. Learning on the job is the best way to learn, and for anyone to take time out of their busy schedule to teach too is just incredible.
I’ll say! Sounds like you really do have an incredible team! We do. We really do.
DEMOLISH. CRUSH. RECYCLE.
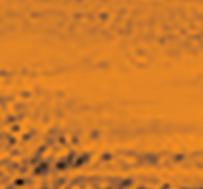
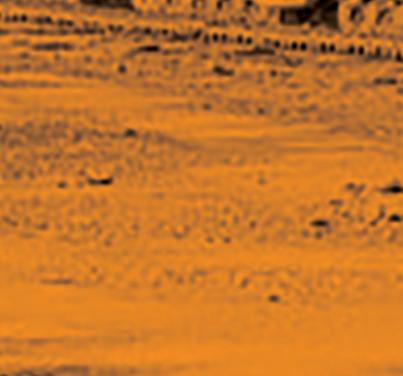
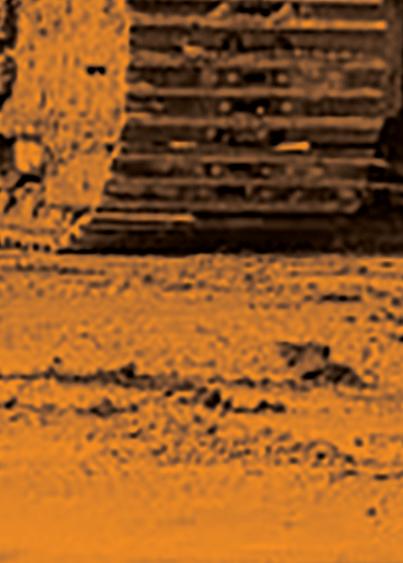
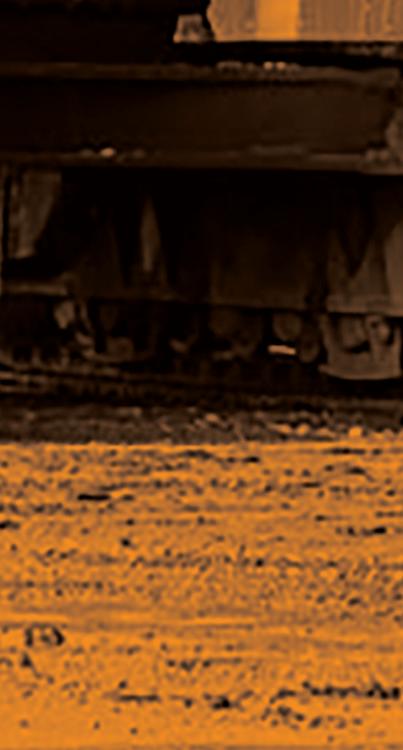
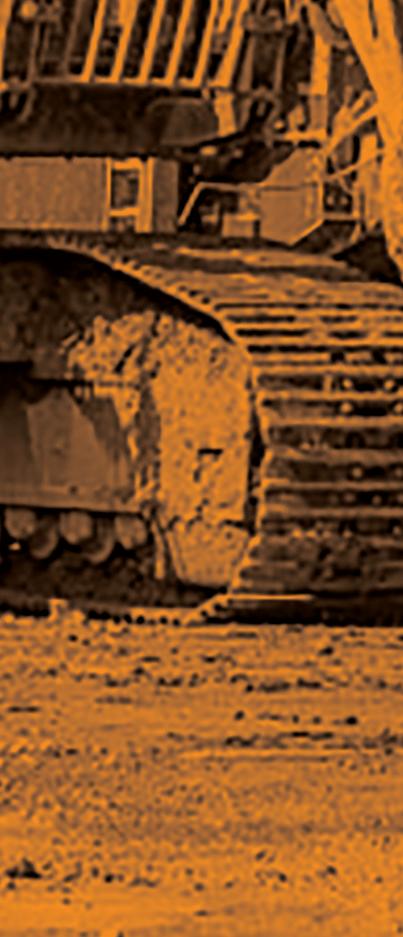
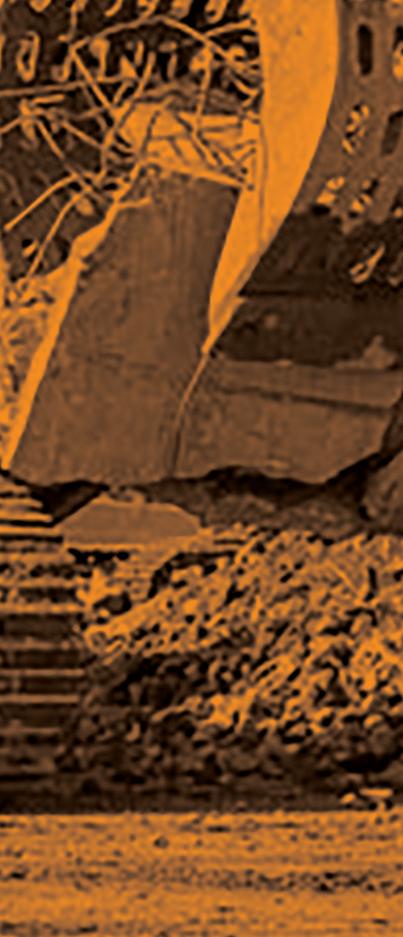
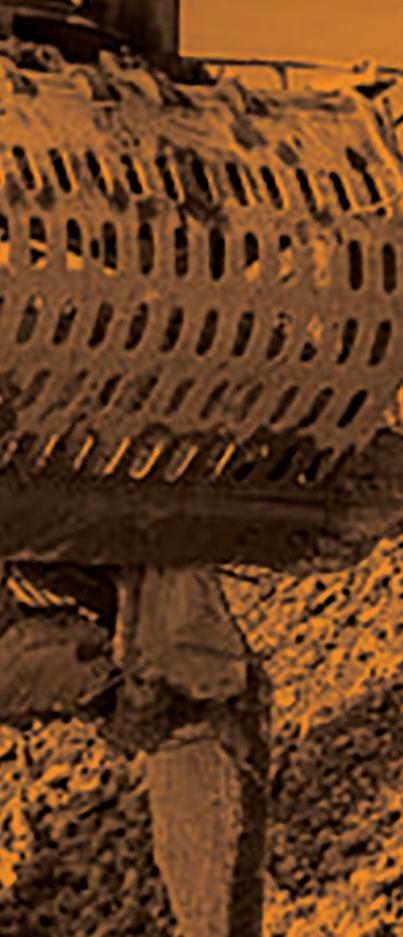
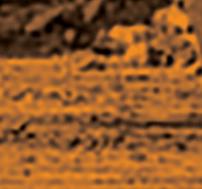
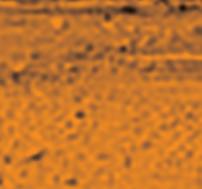
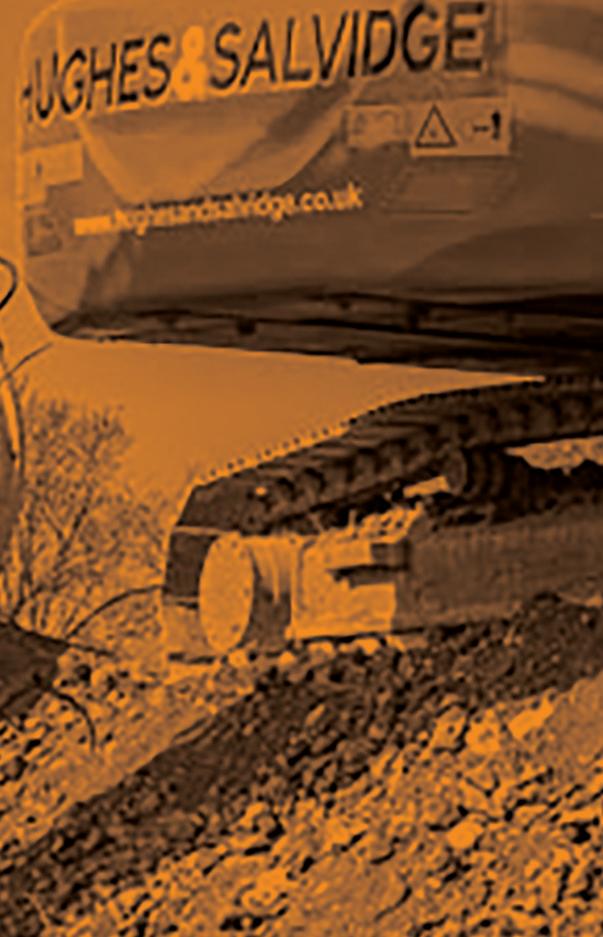
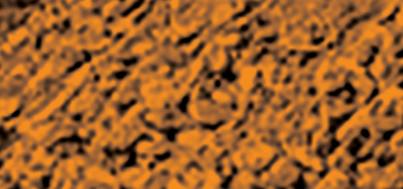
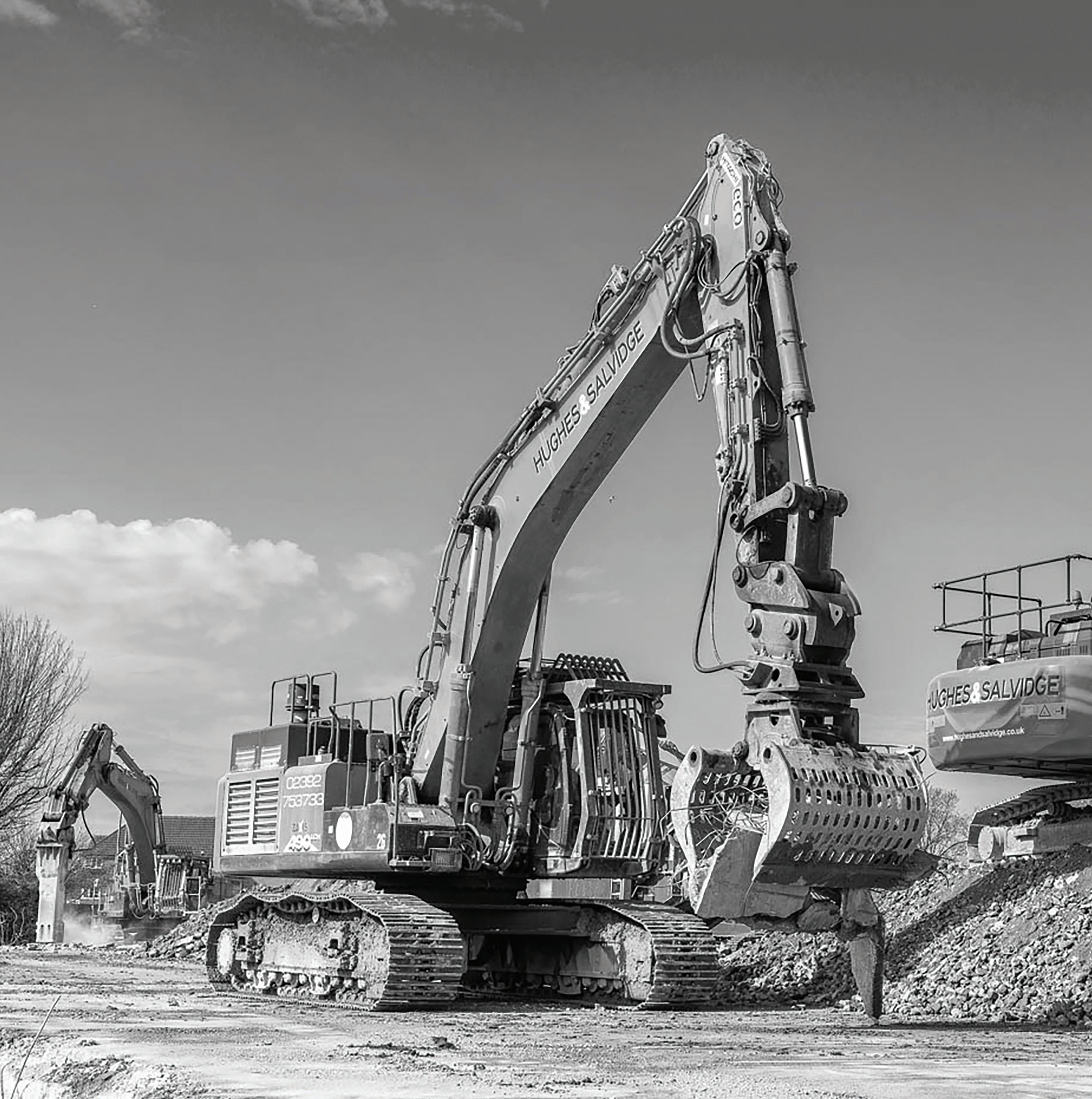
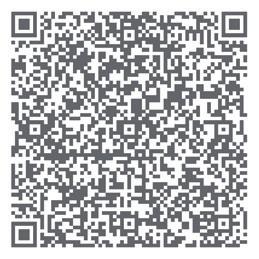
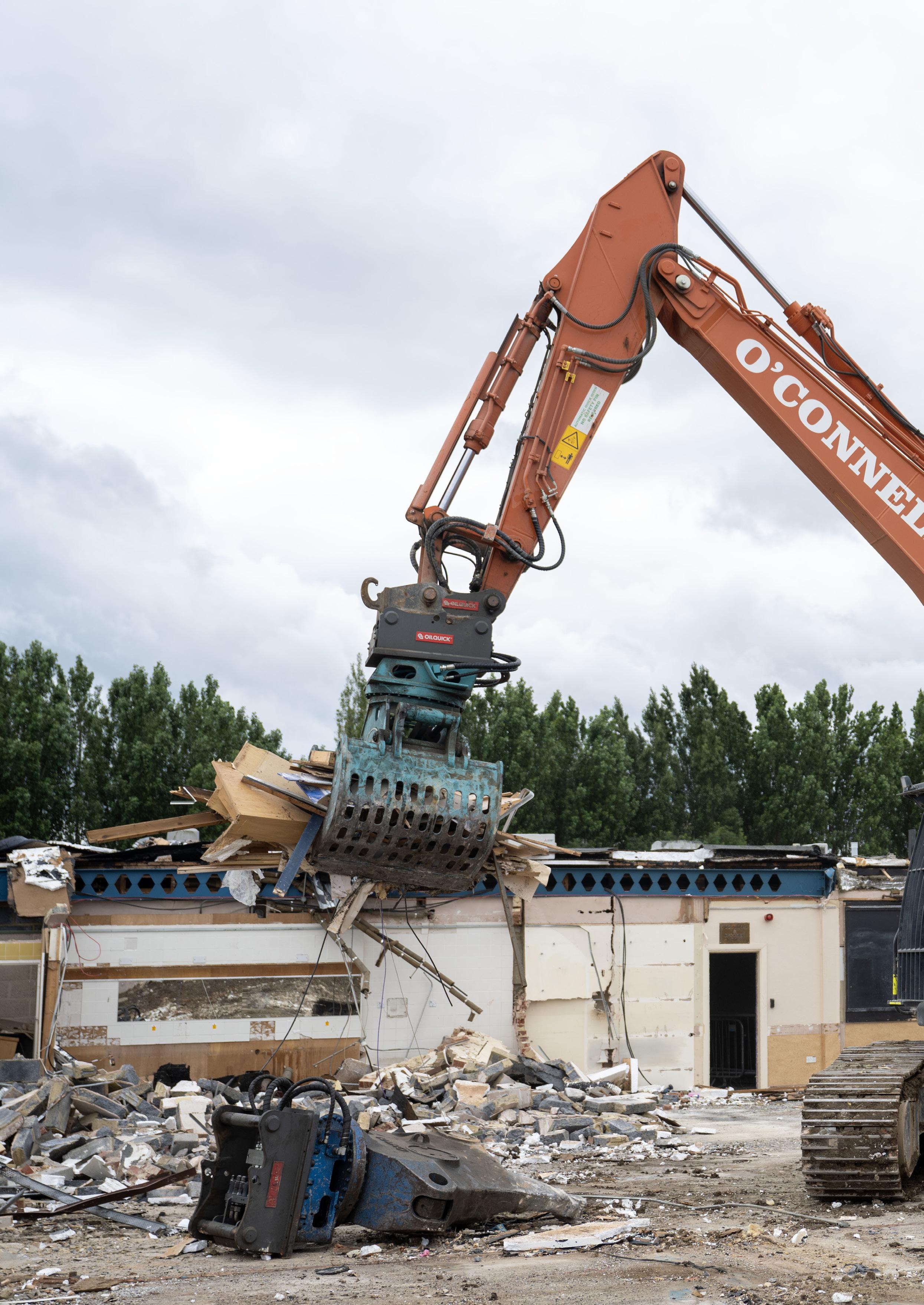
Scoring Goals with O’Connells
By Paul Argent
One of football’s most iconic names, Queens Park Rangers have recently started the upgrading of their training facilities in Hounslow, Middlesex. Whilst their training grounds feature the latest in 4G pitches and perfectly manicured grass fields, the indoor training and welfare facilities didn’t quite match up.
Supporters and retail investors part-funded the £20million build alongside the club’s owners to provide first-class facilities for every team under the QPR banner to train at a single site for the first time. The purpose-built training ground is at the heart of the Board’s strategy to nurture homegrown talent and its long-term commitment to making the club self-sustainable. The facility is named in memory of co-owner Ruben Gnanalingam’s father, Tan Sri Gnanalingam - affectionately known as TSG.
G. Gnanalingam, who sadly passed away in July 2023, was the founder and executive chairman of Westports Holdings Berhad who, for over 30 years, led the major Malaysian port from its humble origins to a major transhipment gateway in South East Asia. He took a keen interest in QPR after Ruben became a shareholder in 2011, supporting the club from his home in Malaysia while attending fixtures when possible. With development a cornerstone of the new training facility, TSG is also an acronym for three key values that have been applied as part of the club’s development strategy - train, succeed, grow.
With the extensive new development completed ready for the 2023-24 season, the owners applied for planning permission to clear the existing structures on the site and level the land.
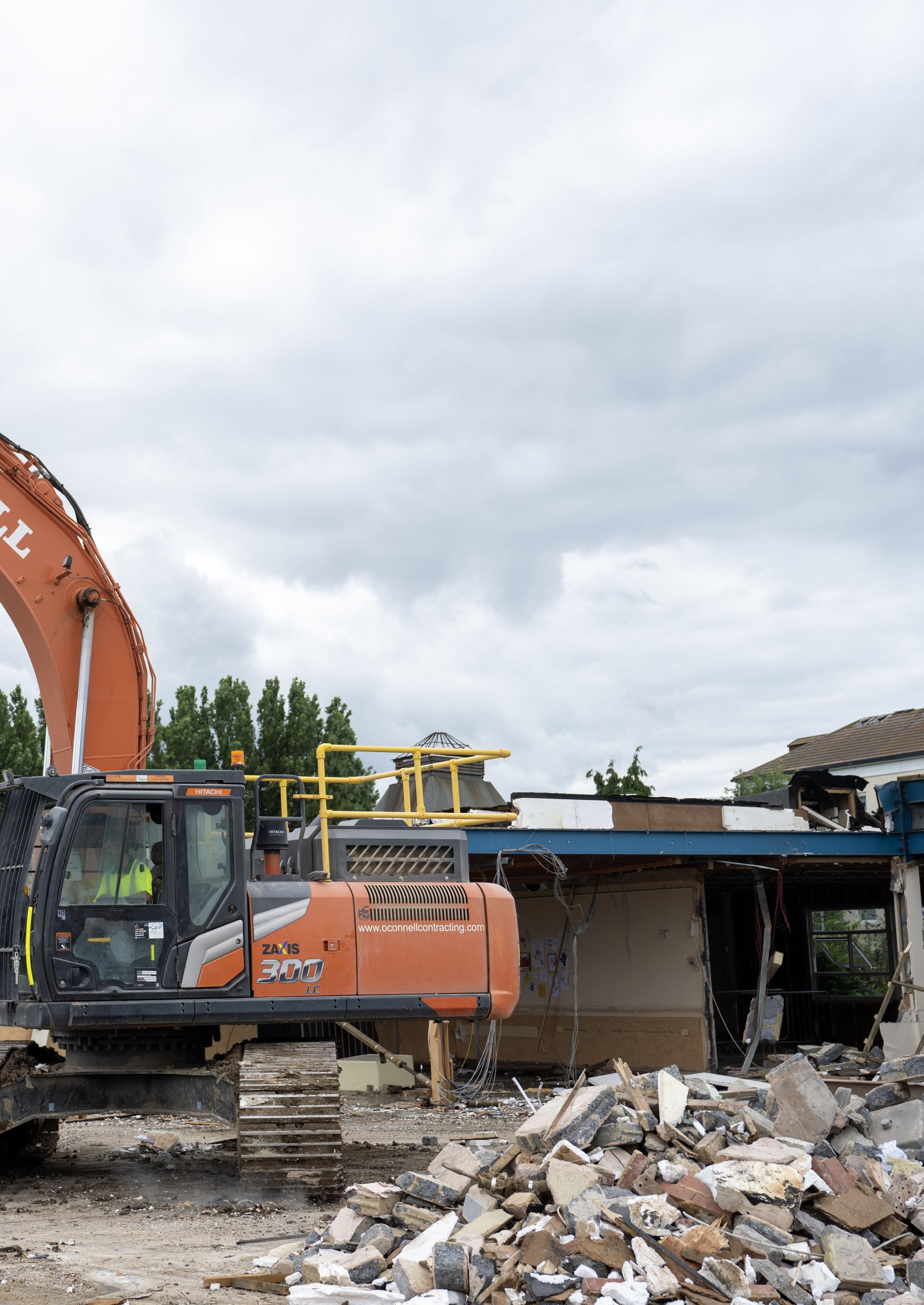
Following on from the completion of other successful work on the development side of the land, locally based O’Connell Contracting were signed up for the work. O’Connell Contracting was formed in 2013 by Declan O’Connell and began as an independent construction management consultancy based in Stanmore, North London. Delivering a variety of works over the years has seen the company change from offering consultancy solutions to delivering projects in their entirety across the residential and commercial sectors.
The work at TSG has seen O’Connells deploy a small team of men and machinery to carefully demolish the mixture of buildings they found on site. Following a comprehensive soft strip and asbestos removal program, the company was able to commence work on the structural demolition works. Closely surrounded by residential properties and with the TSG now up and running, mitigation works were put into place to ensure noise, dust and vibration issues were kept to a minimum throughout the contract period. One of the most important pieces of equipment was the trailer mounted Dehaco dust suppression system which was used extensively to ensure the adjacent pitches and their respective players were kept free from airborne dust particles.
The company favours Hitachi excavators and runs a fleet of the Japanese made machines up to 35 tonnes in weight. Recent additions to the fleet have been made in the purchase of OilQuick hydraulic couplers allowing the quick and easy changing of attachments. ‘We have invested in three OilQuick hitches for our dedicated demolition machines to allow us to become more productive and efficient.’ Declan O’Connell commented. ‘They have allowed us to reduce the number of machines we have to put on site which means lower overheads for us in terms of transport, fuel costs and operators. There is also the huge benefit of being able to change the attachment to ensure the correct one is being used at all times. This again reduces any damage to the attachment and reduces downtime.’
The project at Hounslow saw Declan use a ZX3007 and a ZX350-6 excavator to demolish a range of structures including the indoor basketball and handball courts, indoor and outdoor shooting ranges, six outdoor tennis courts, the club house, the first team changing rooms, and the sports centre. The mixture of construction methods used on the array of buildings meant the teams
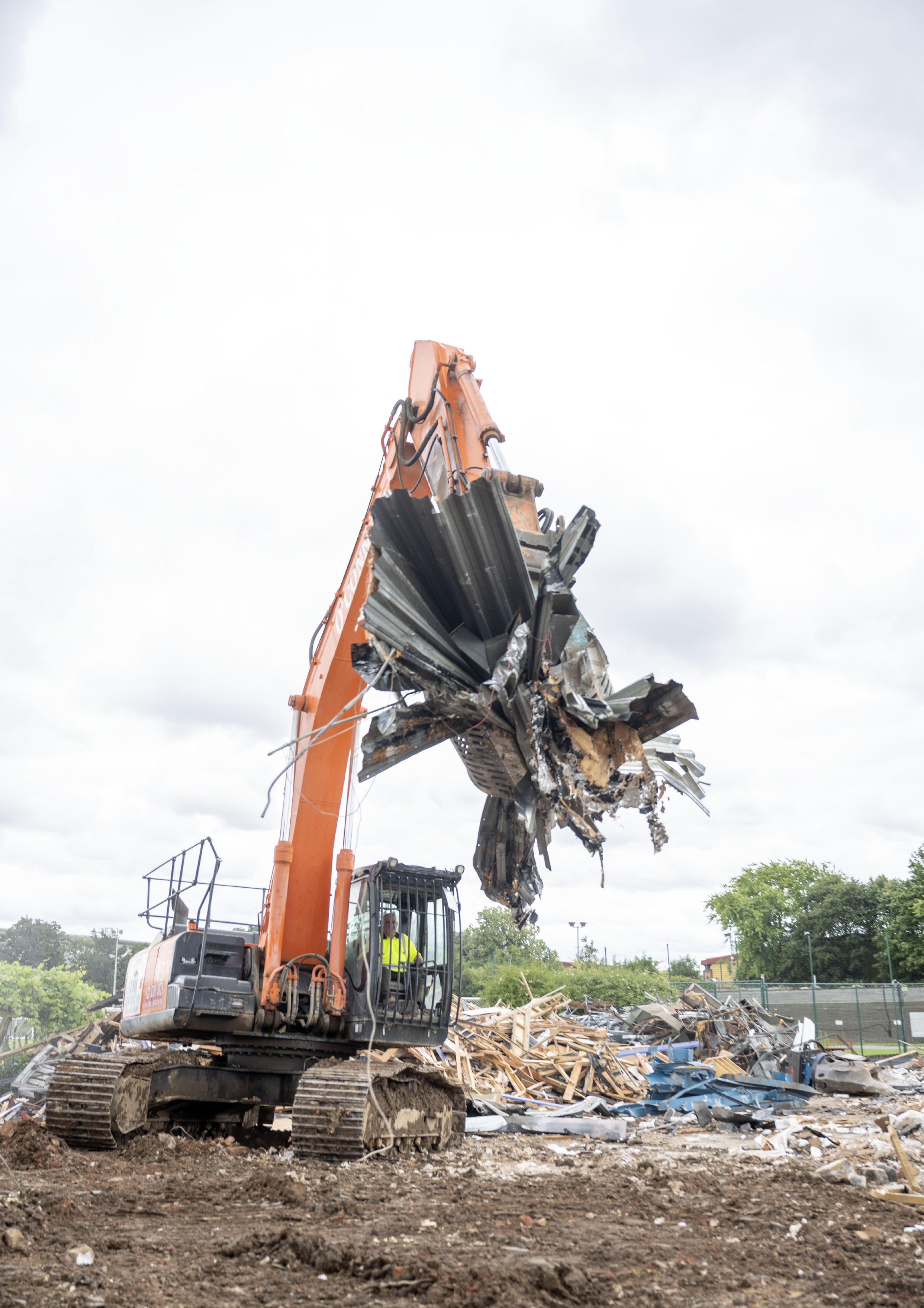
had to contend with a variety of materials to dispose of. Large areas of felted flat roof were dropped safely to the floor where one of the excavators carefully peeled back the bitumen felt to allow it to be segregated and disposed of accordingly. With the roof coverings removed, a quick attachment changeover to one of the Okada shears allowed the lightweight steel trusses to be snipped and dropped before being five-footed for onward recycling. As the buildings were safely demolished the ability to change attachments quickly saw the piles of material for recycling and disposal quickly loaded into bulk skips.
With the buildings demolished and the materials cleared away, O’Connells were tasked with the removal of all below ground obstructions to a depth of 1m to ensure the ground was ready for any potential future development to take place.
‘We are very proud to have been asked to undertake this prestigious project.’ Declan commented. ‘As we had been involved in the development phase of the works, being asked back by the developer and club itself goes a long way in building up the reputation of our company and enhancing our reputation for collaborative working to obtain the best outcome for all parties.’
Steeling the Spotlight
Steel. A common material found in almost every building. Recycling steel has been a common part of any demolition contractors remit for many years.
With a varying price on this commodity, demolition companies have been reaping the rewards for the segregation and separation of ferrous and non-ferrous metals for decades, but as the world moves forward we are now faced with looking at alternatives for the recycling of steel which has traditionally involved coal fired blast furnaces.
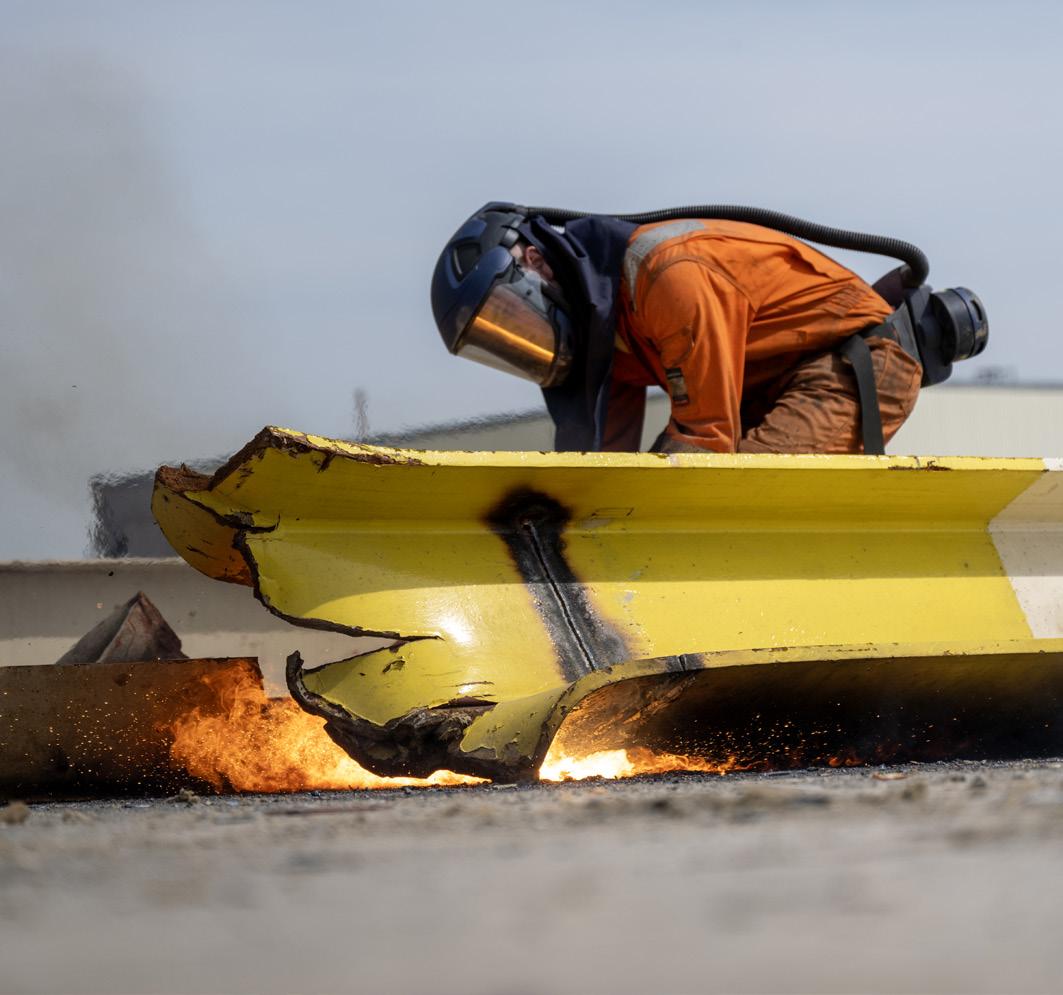
By Paul Argent
The recent closure of one of the UK’s largest blast furnaces in Port Talbot has highlighted the issue of carbon heavy steel manufacture and recycling. Yes, we have the more environmentally friendly option of electric arc furnaces, but as an industry, is there another option of dealing with the sometimes-substantial volumes of steel coming from a demolition project?
The Alliance for Sustainable Building Products (ASBP) lead the DISRUPT 1 and DISRUPT 2 projects. Standing for the Delivering Innovative Steel ReUse ProjecTs, DISRUPT 1 and 2 is aimed at exploring the innovative reuse of structural steel in construction and encouraging the adoption of new circular economy business models. Whilst many contractors may look at this as another gimmick, there are several forward thinking demolition contractors and recycling companies putting it into practice and reaping the rewards for being at the forefront of this dynamic change in the industry.
Steel is one of the most widely used and resource intensive materials used in construction. Although commonly recycled at end of life, the reuse of steel is minimal despite the apparent environmental, carbon and circular economy benefits. The high value of steel at end of life can be realised by being reused in a wide range of construction applications.
One of the main barriers identified during the first DISRUPT project which is preventing the significant uptake of steel reuse is the lack of available material generated during refurbishment and demolition projects. There are several reasons for this including a lack of incentives to reuse rather than recycling, and the need for new enabling processes and business models.
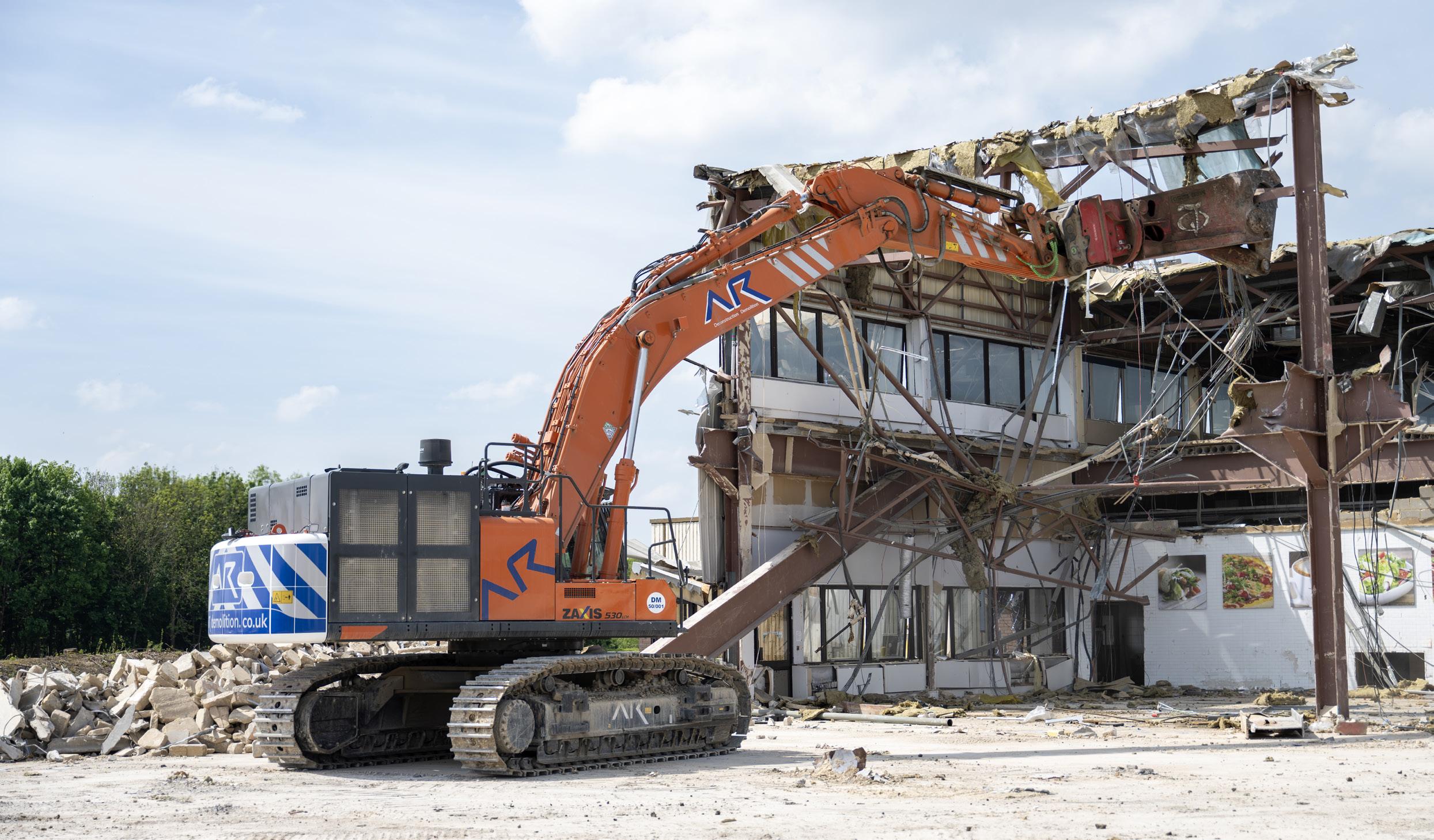
DISRUPT II has addressed this key barrier by working with the demolition industry, through one of the key sector bodies, The Institute of Demolition Engineers; one of the largest stockholders of reclaimed steel, Cleveland Steel and Tubes Ltd; and a number of demolition contractors from across the UK, to establish the crucial evidence that is needed to enable more steel to be reclaimed. This will be supported by the larger value chain – clients, designers, engineers and contractors.
One of the UK’s foremost demolition contractors, Leicestershire based AR Demolition, have been at the forefront of DISRUPT 2 on their huge Swindon project where they have been tasked with the demolition of a former car manufacturing plant.
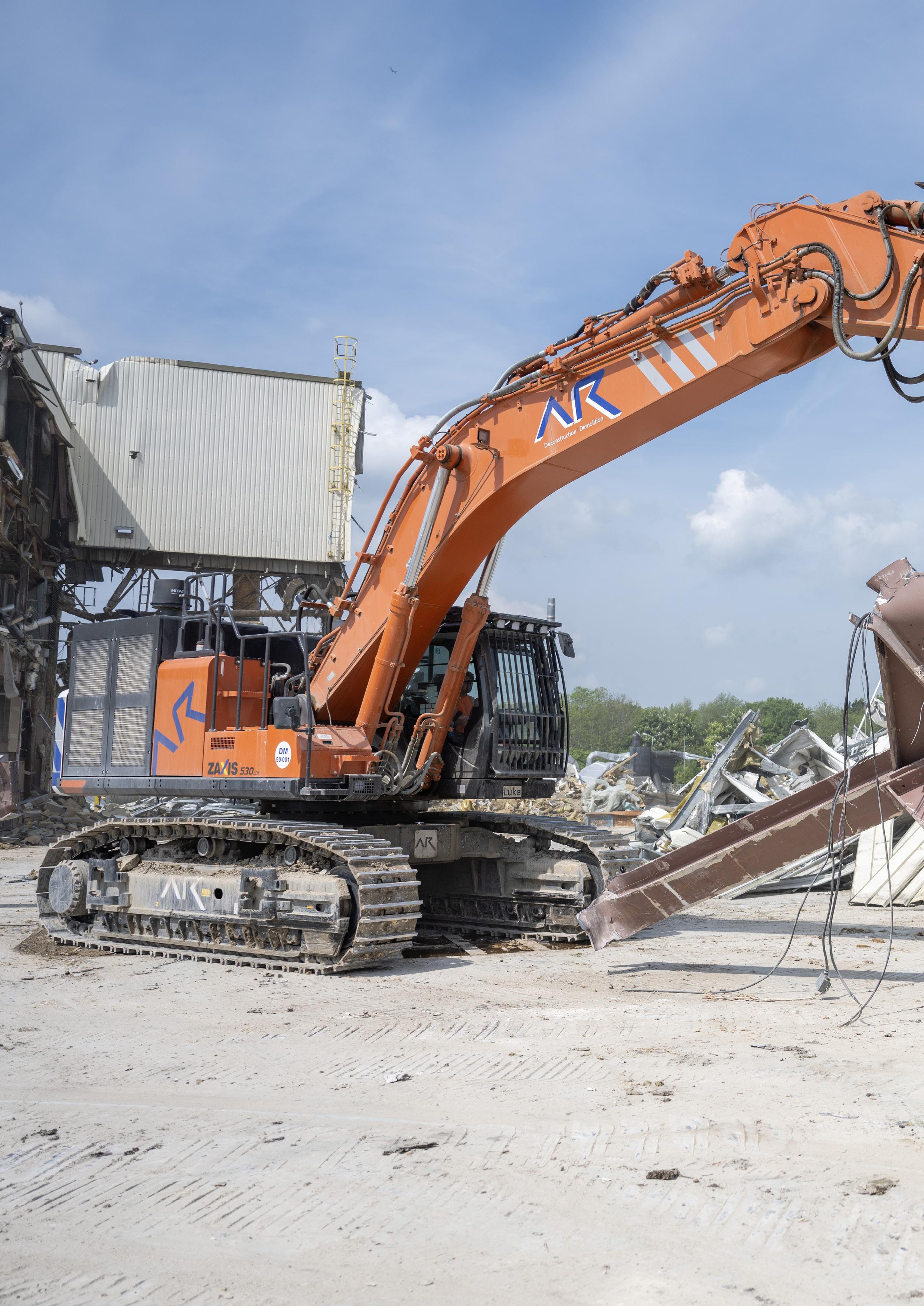
The plant was constructed in 1985 and extended at regular intervals in the intervening years prior to its closure in 2021and consisted of a huge variety of steel framed buildings. Seeing the benefit of reusing steel, AR Demolition’s CEO Richard Dolman took the commercial decision along with his recycling partner Ward, to undertake a substantial volume of steel salvage and reuse across the entire plant. ‘We identified steel which could be reused at an early point in the project clearly marking it for reuse.’ Richard explained. ‘Our operators are used to taking down a building with the view of the steel being five-footed and removed form site. With our Site Managers using toolbox talks and regular site meetings, we planned the works around the
salvage of sections as opposed to scrapping them.’
Whilst the envelope of the buildings was removed in the normal fashion, the pre-identified steel sections were then carefully cut down leaving them in as long a length as possible. As AR Demolition’s excavator fleet use OilQuick couplers it was then a quick change of attachment allowing the selector grabs to carry the steel sections to a dedicated lay-down area adjacent to the building being demolished. In this area a highly skilled burning team would remove any cleats, node points or damaged sections of material to leave a completed I beam of a certain length. ‘We weren’t tied to providing steel of determined length so long as it was over 4m.’ Richard explained. ‘The length and height of the beams
and columns we were dealing with on almost every building made this an easier task to identify the pieces we could reuse.’
Once each section was cleaned and cut to length, it was then stockpiled ready for transport. The resulting damaged ends and node points could then be treated as traditional scrap.
‘We have found the task of separating and processing the steel for reuse to be no more costly than traditional methods.’ Richard points out. ‘We are very lucky that we have sufficient storage space here which allows us to stock a large volume of material at any one point. Smaller projects will need their logistics plans to be robust to allow for
Once each section was cleaned and cut to length, it was then stockpiled ready for transport. The resulting damaged ends and node points could then be treated as traditional scrap.
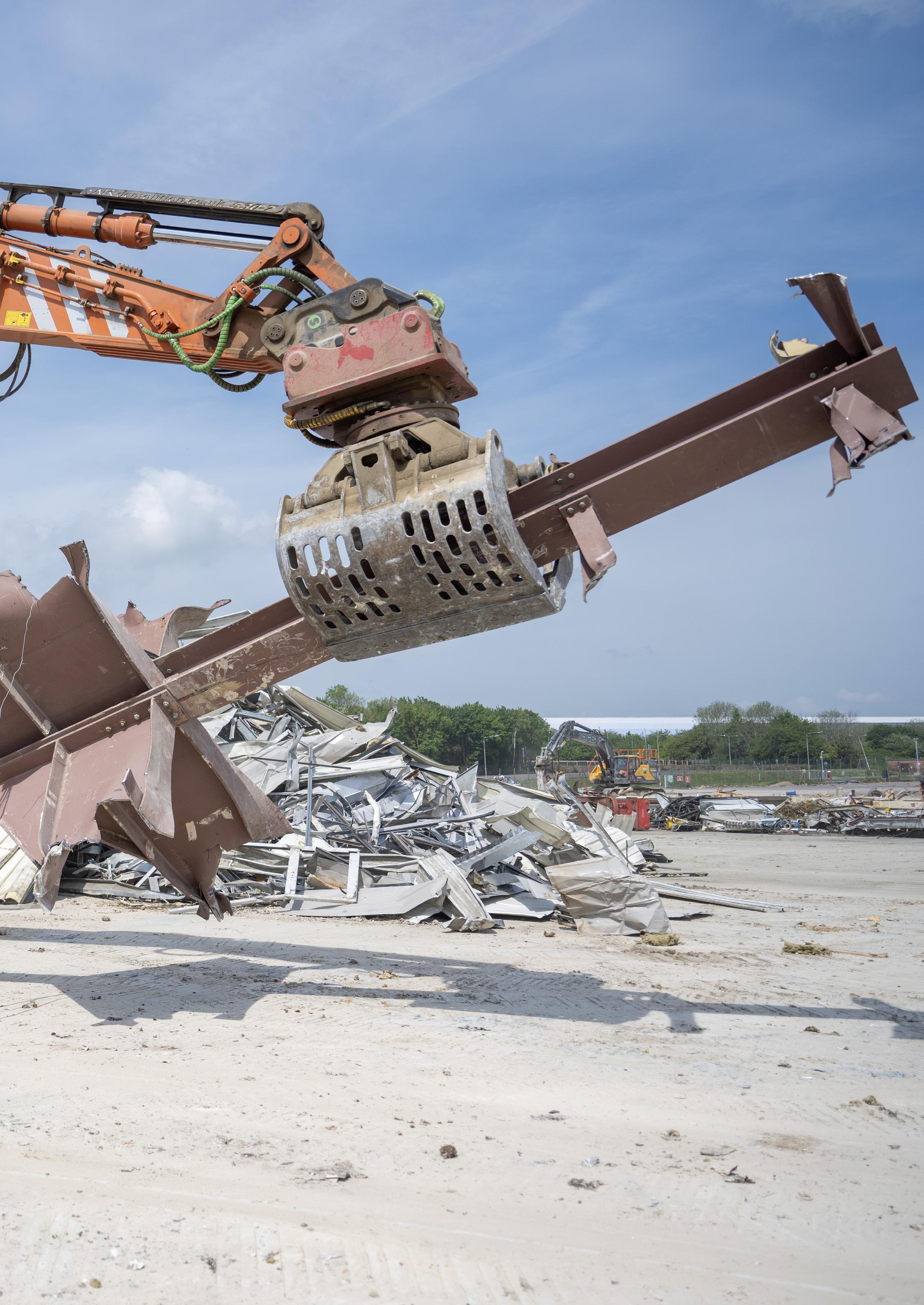
material to be sipped or stored depending on the available room on site.’ As for the financial difference between reuse and recycling, Richard is rightly very cautious about putting figures on the table. ‘We have looked very closely at the figures involved and the returns we can expect to make.’ He comments. ‘We have to look at the bigger picture of the cost of recycling and the demands it puts on the environment. Being able to reuse steel sections which ultimately may have been cut down, melted and remade into similar sections makes the environmental gains for DISRUPT to be very beneficial.’
a cost effective yet comprehensive 2D solution to machine control
With over 20 years of experience delivering cutting edge technology to the construction industry, Pat Bulcock and Claire Plant’s newest venture, S Type X have added what they believe to be a gamechanger for the market.
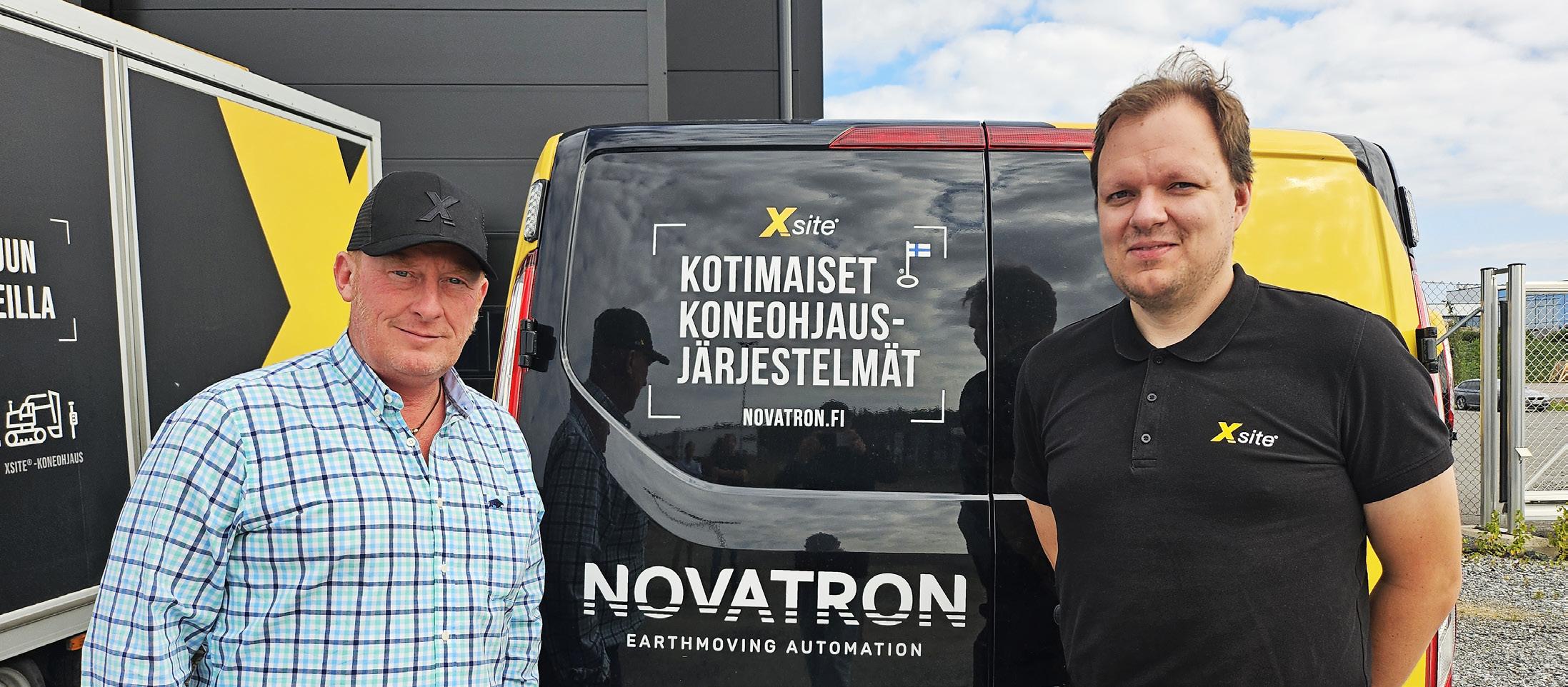
With the popularity of machine control systems growing, S Type X have recently been appointed as the UK and Ireland dealer the Novatron Xsite® range of machine control systems. ‘We believe there is a place in the market for the system which can offer users a wide range of machine control solutions.’ Bulcock comments. ‘We have had many years of experience working alongside some of the leading manufacturers and whilst we could compete alongside them with Xsite®, we wanted to offer a simple and accurate solution to small and medium sized operators, many of which don’t require the complex packages supplied by other brands. This is the reason we have decided to launch Xsite®Easy, a cost effective yet comprehensive 2D solution to machine control.’
The Xsite®Easy system offers users a simple and easy to follow menu system in the 5 inch in-cab monitor allowing them
to quickly and accurately set up their machine. The system offers fast and accurate measuring of depth, distance, and slope and with real-time visualization of the bucket and targetlevel orientation, the operator can quickly reduce time and costs on site. The system has been developed to suit a wide range of applications and comes with full tiltrotator integration and waterproof G series sensors allowing it to be used in dredging applications.
‘We are very excited about bringing Xsite®Easy to the UK and Irish markets.’ Bulcock said. ‘The industry has been needing a high quality and robust system like this this for a long time.’
S Type X are the UK’s leading dealer for a range of construction and agricultural equipment aftermarket parts including light bars, buckets and hitches and a range of customisation accessories.
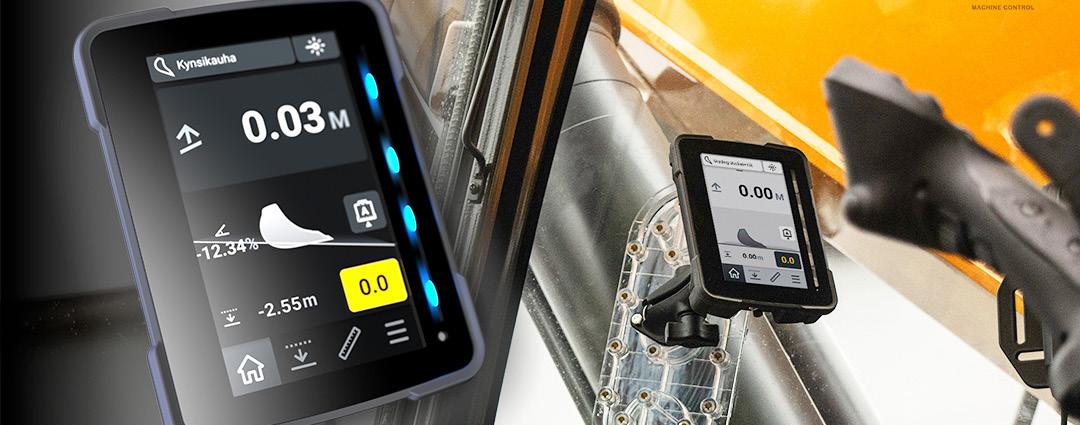
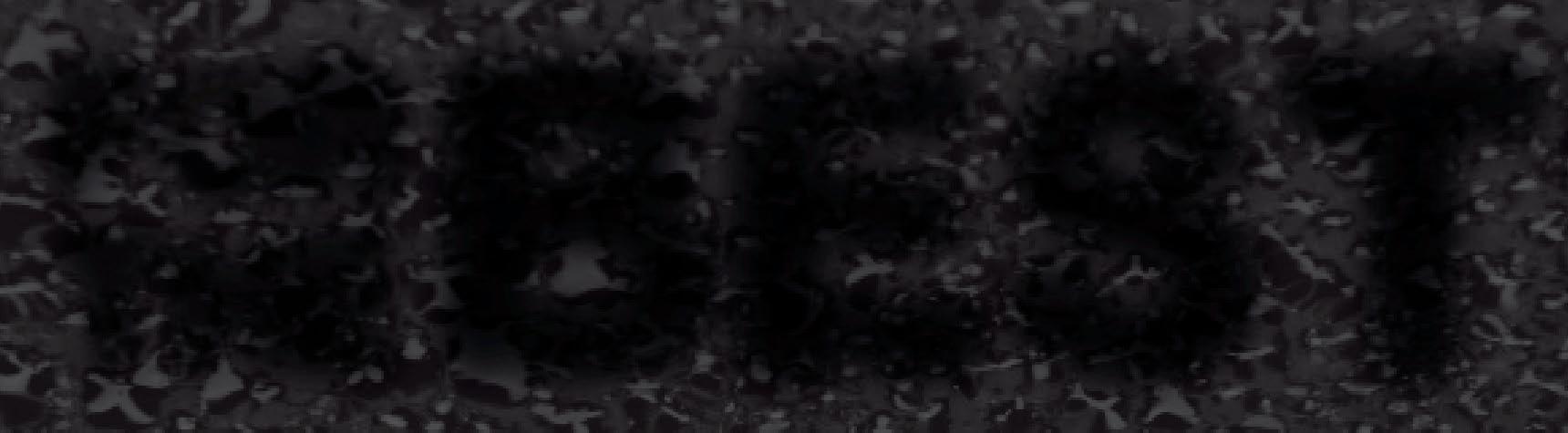
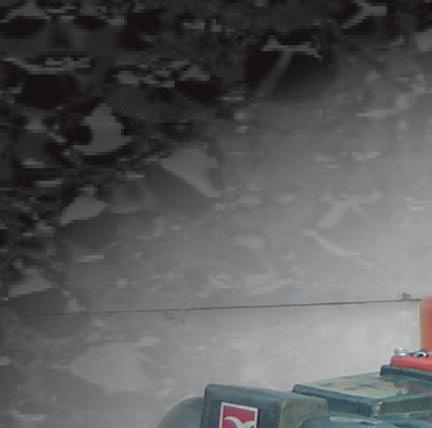

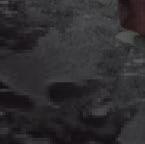
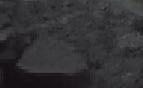
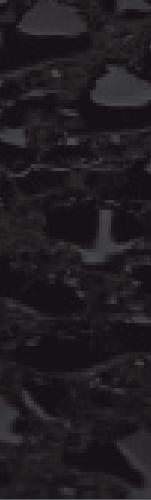
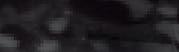



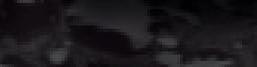

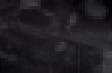

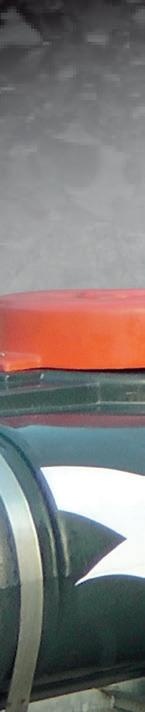
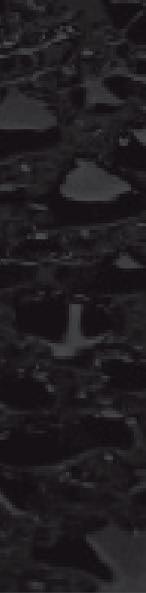

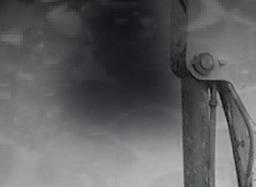
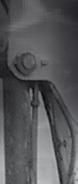


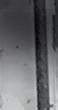

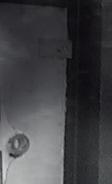
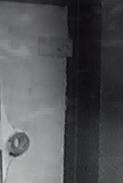
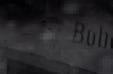

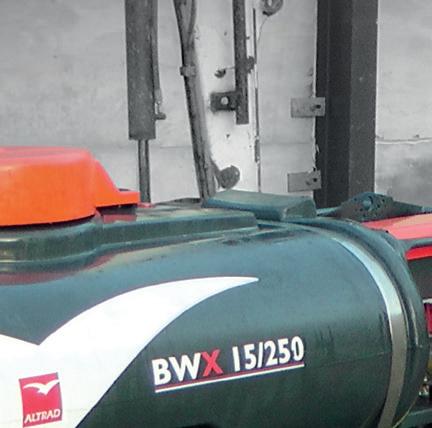
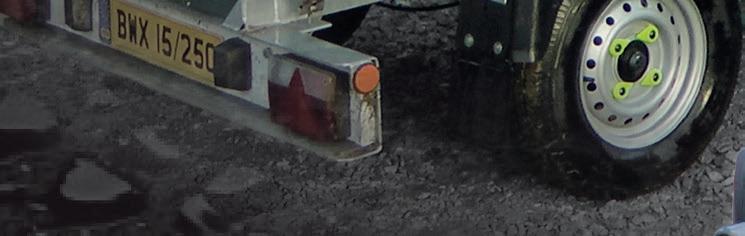

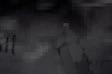


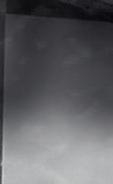
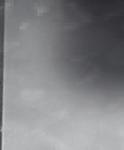

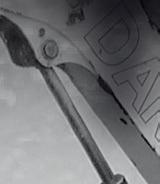
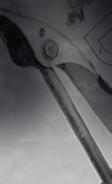




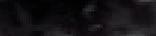
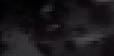

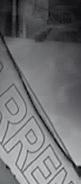
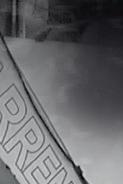

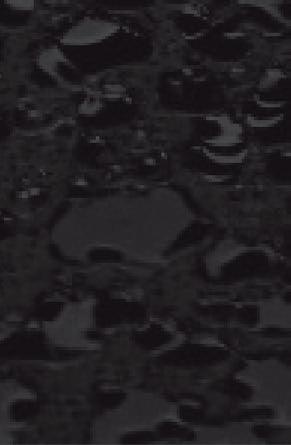
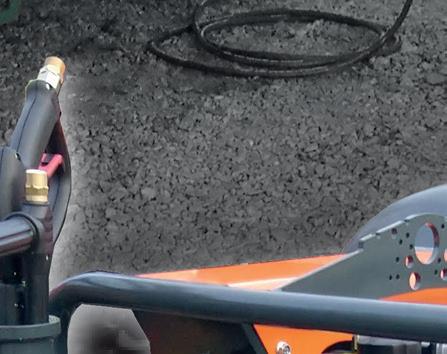

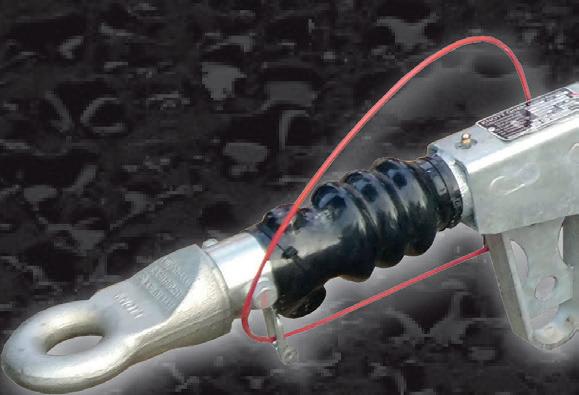
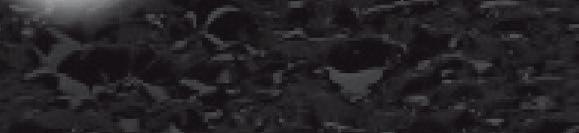
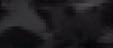


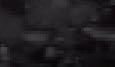

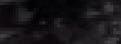
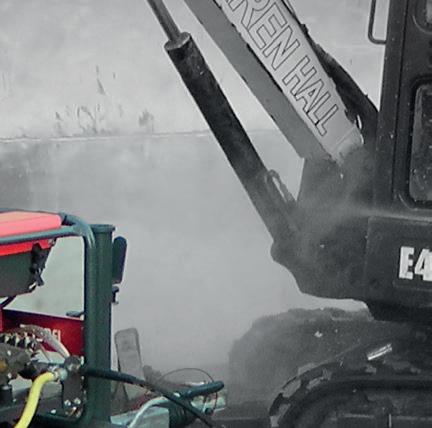
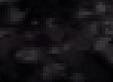
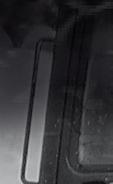
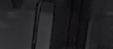
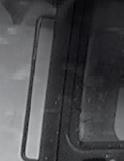


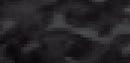
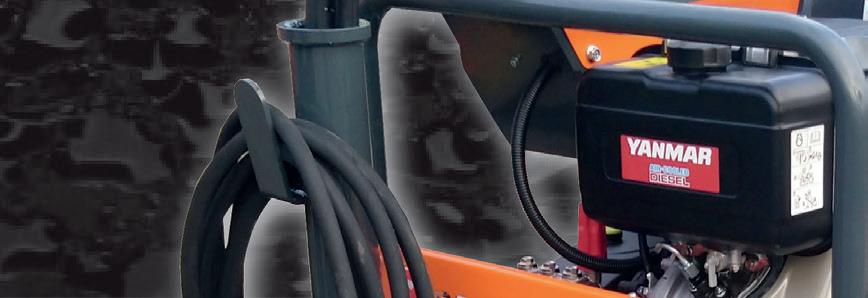
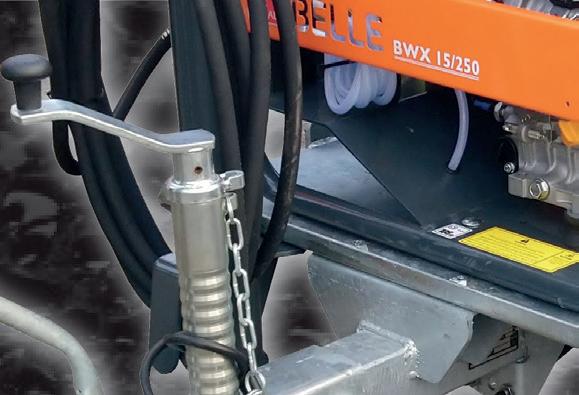
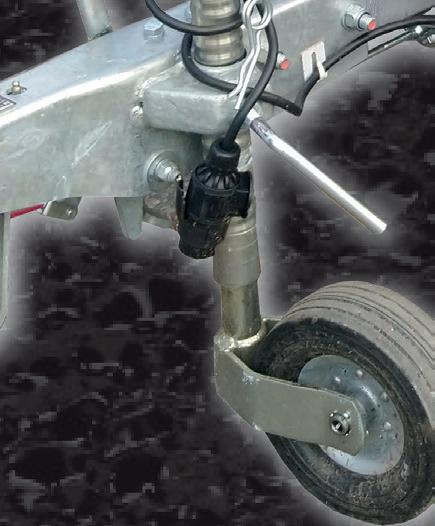

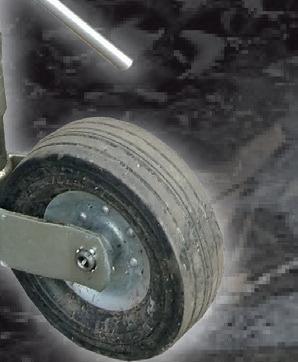
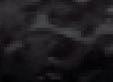
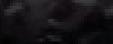

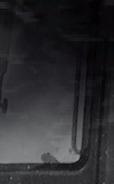

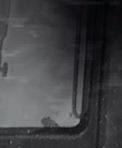

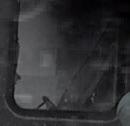
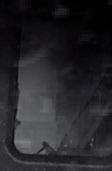

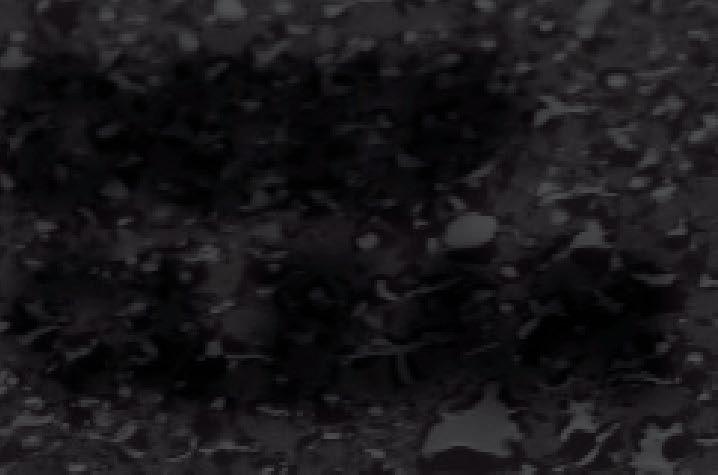
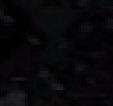
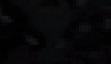

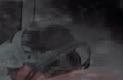
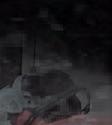
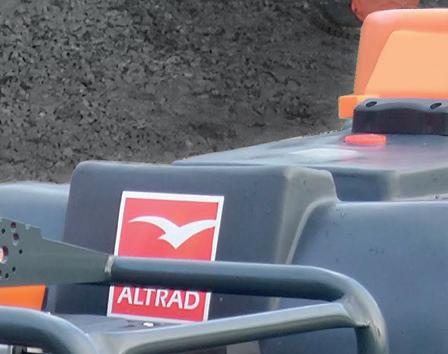
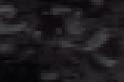
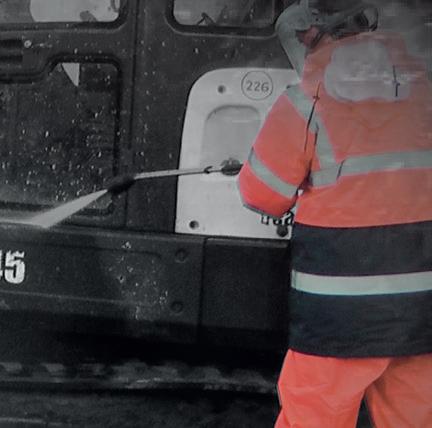

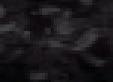
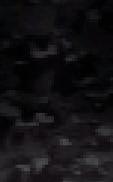
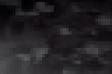
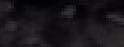
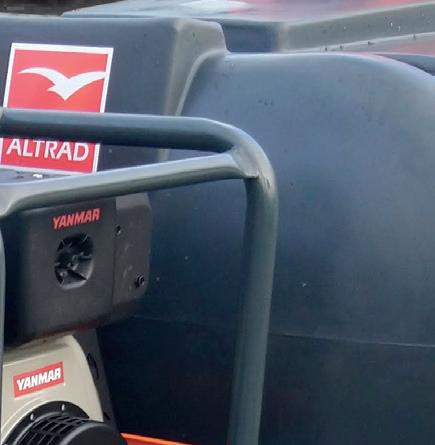
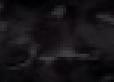
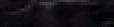

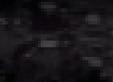
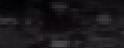


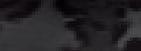
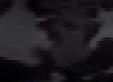
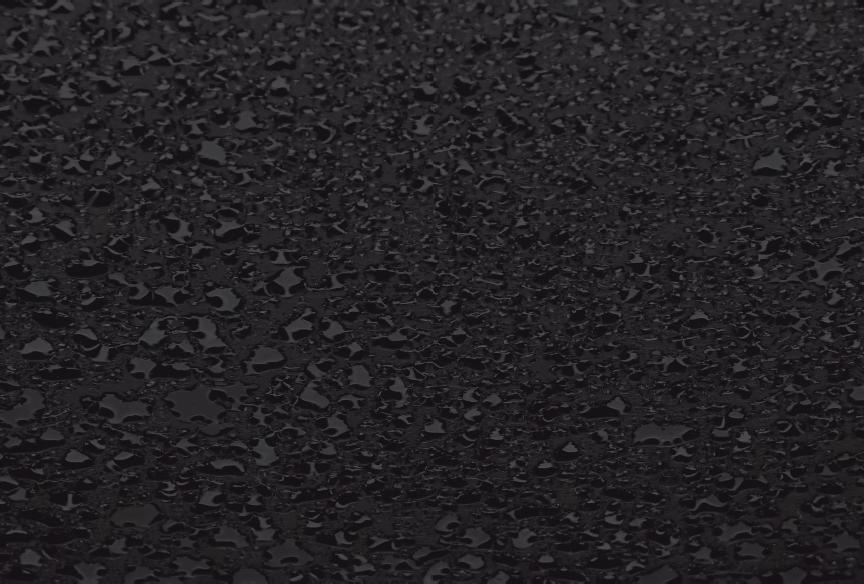
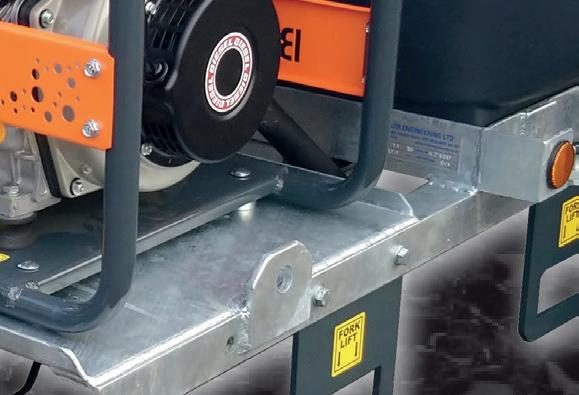
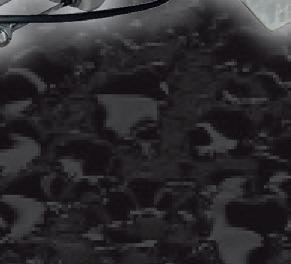
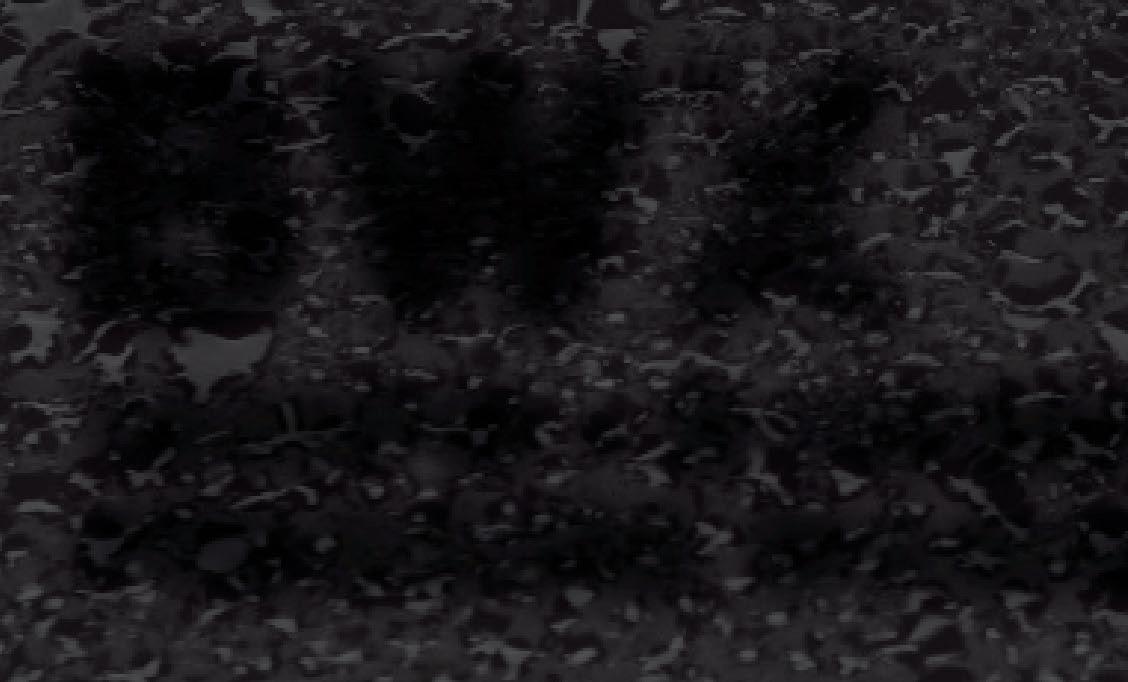
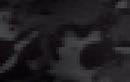

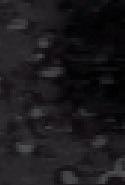
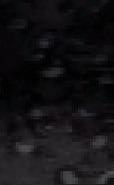
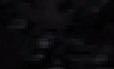

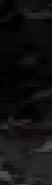
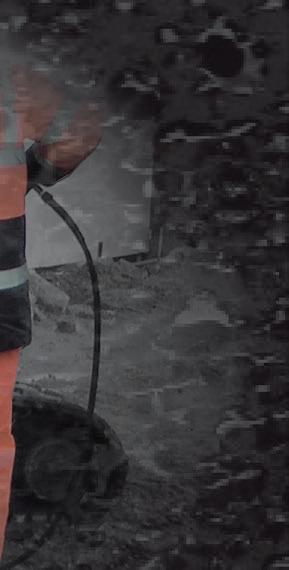
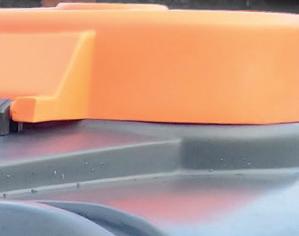
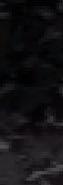

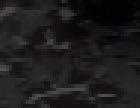
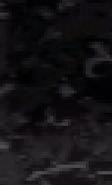
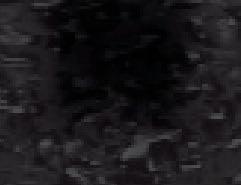
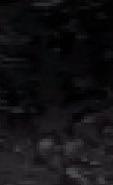
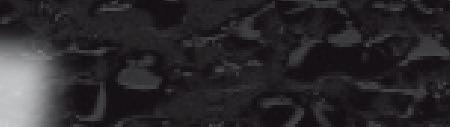
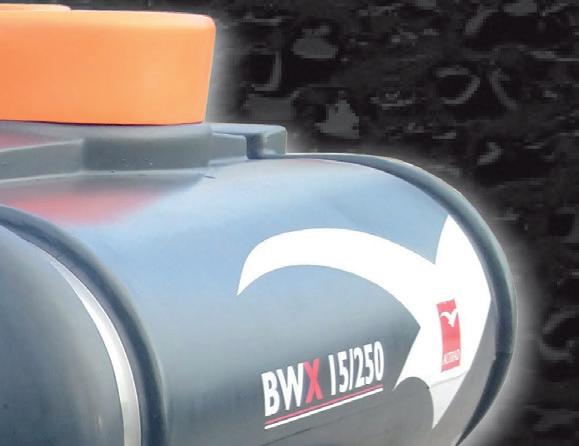
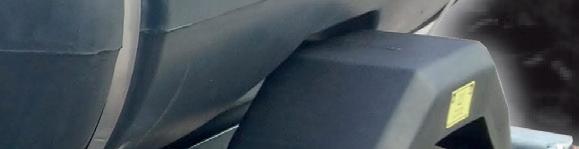
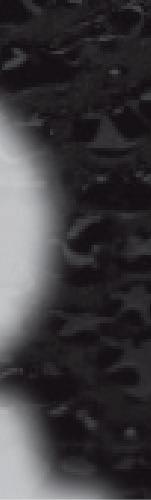
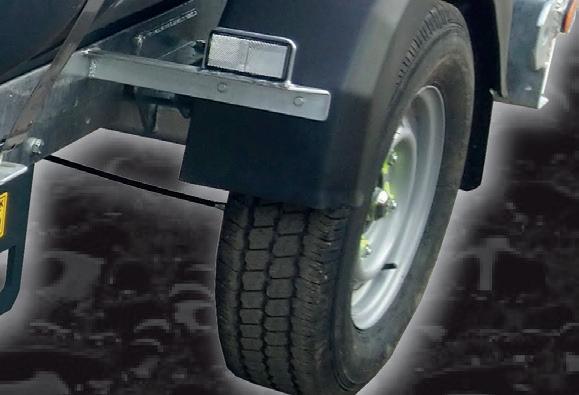

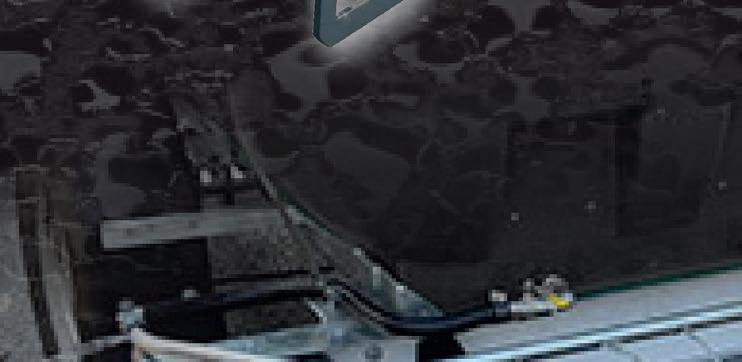

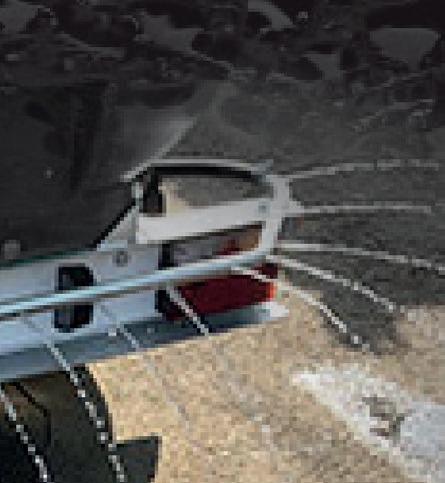
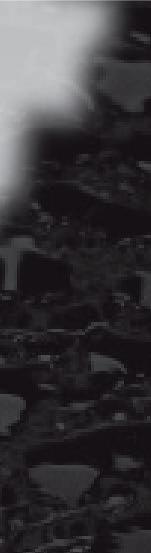
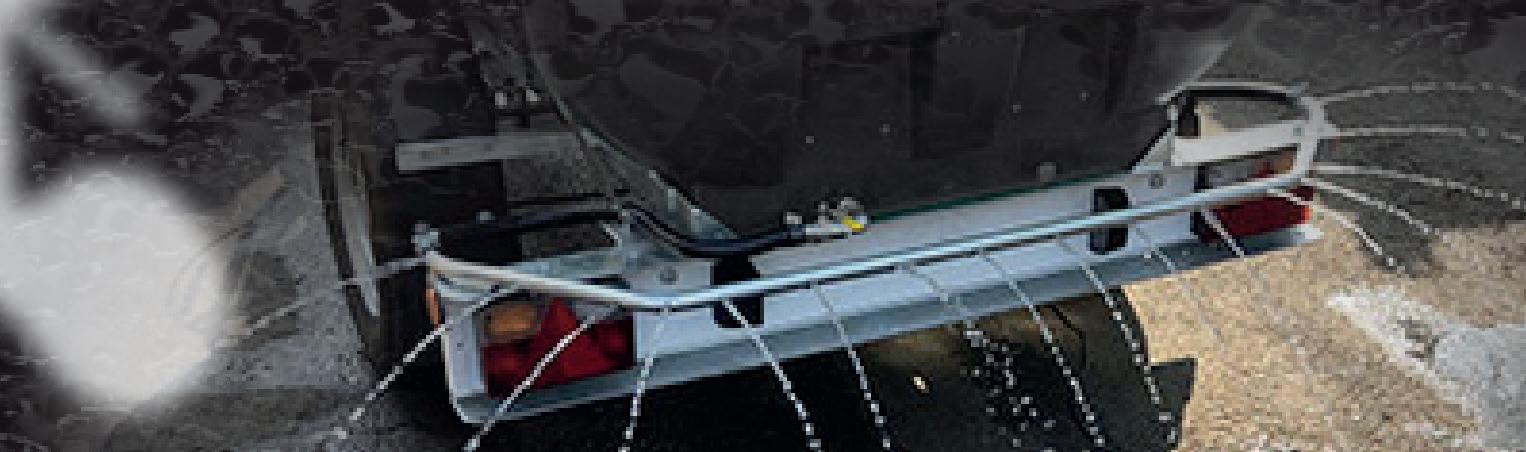

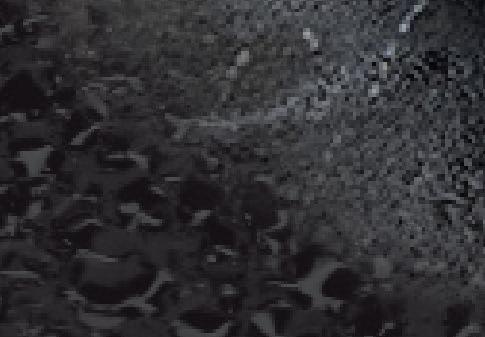
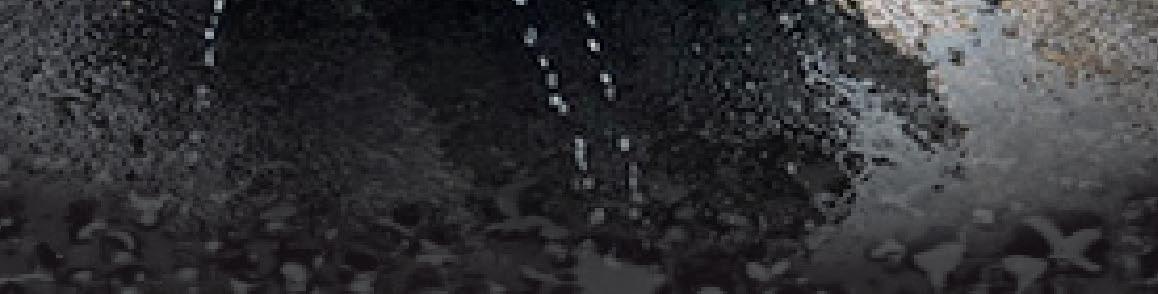
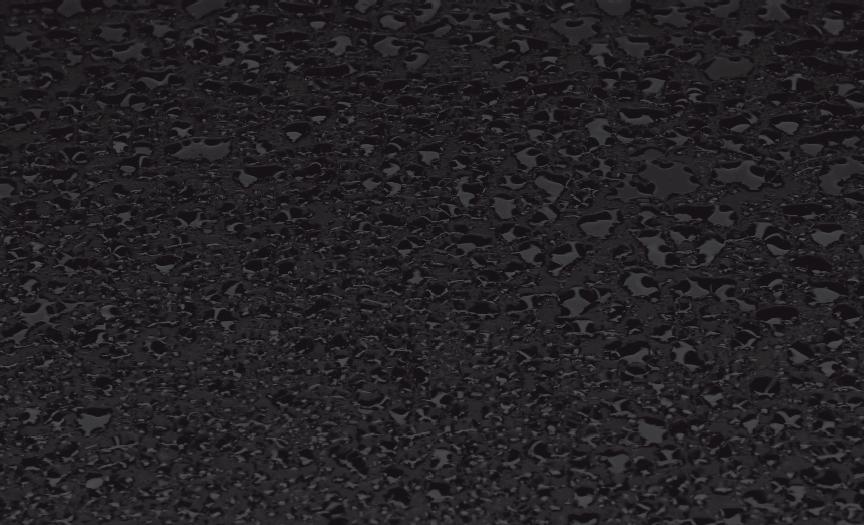
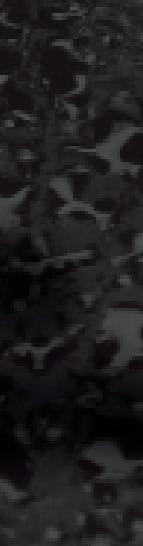
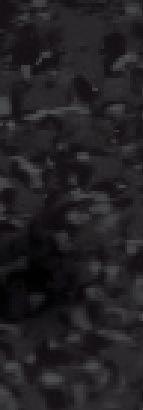

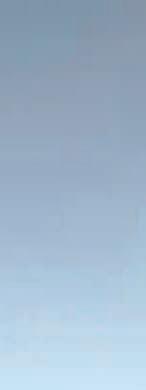
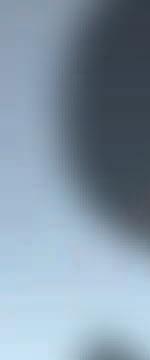
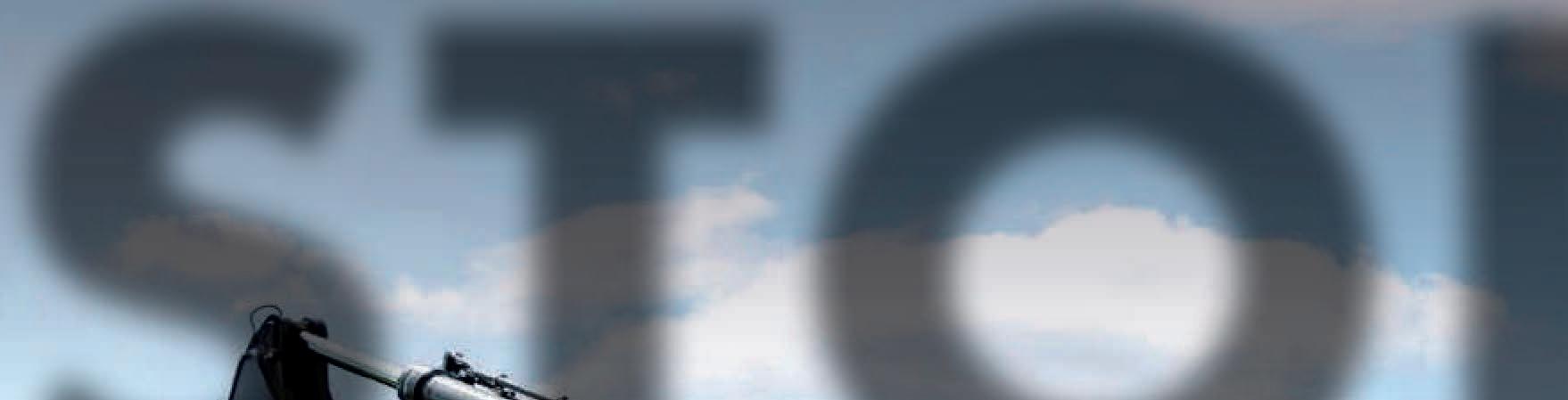
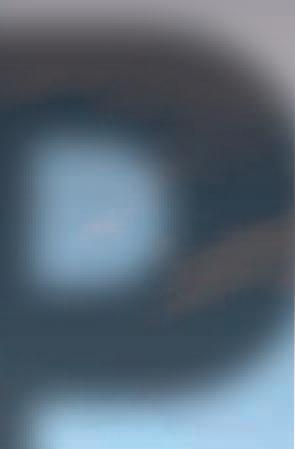

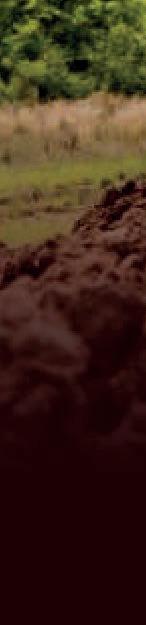

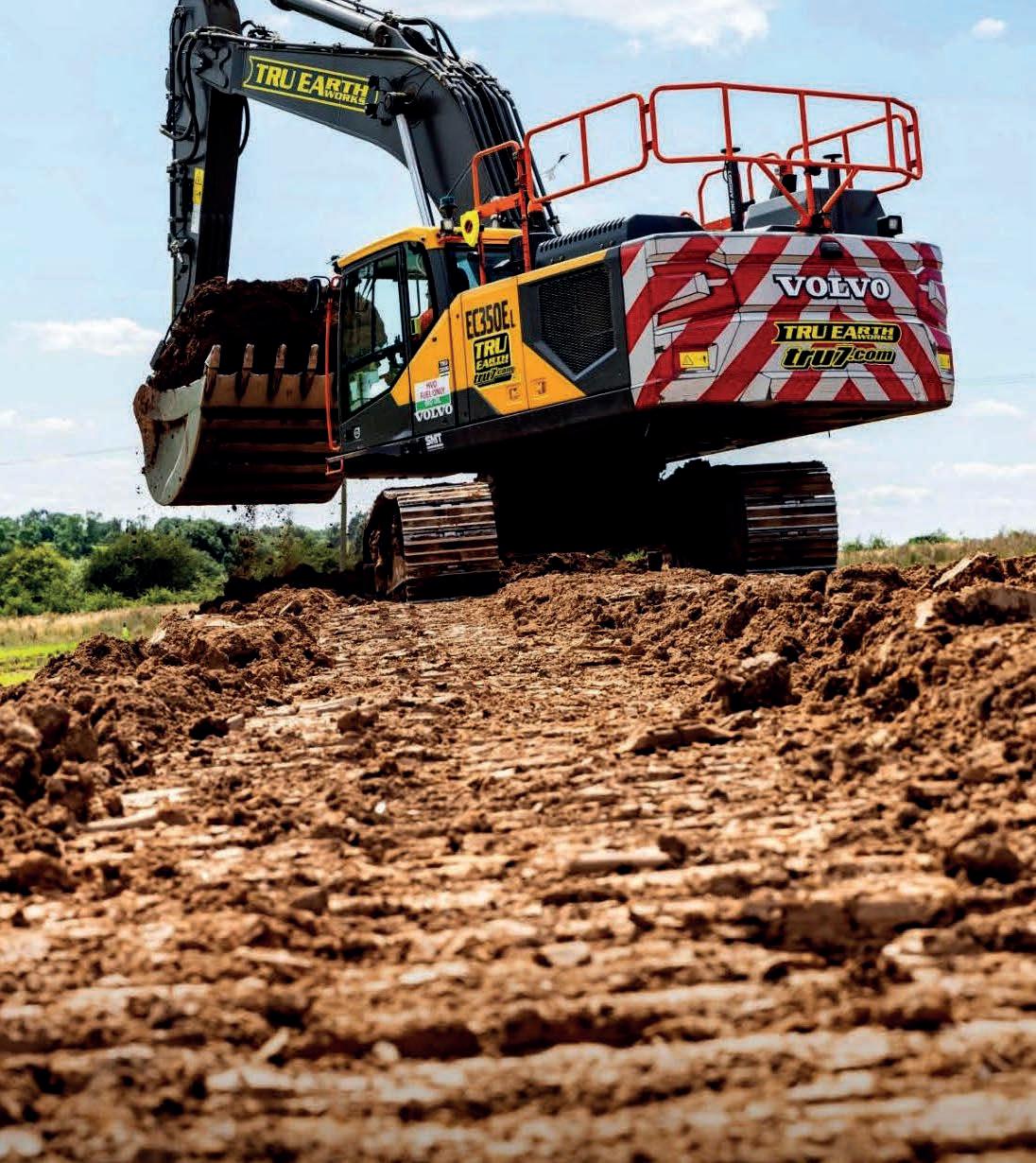
Take control of on-site safety with Safety Shield
Safety Shield is the only solution that:
• Has proven records of on-site and independent testing
• Is based on 10+ years of research & development
• Has UK and European testing and certification




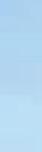
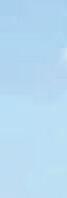


IN THEIR TRACKS STOP ACCIDENTS
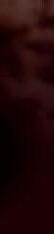

• Has gained relevant ISO standards
• Has a 99.6% accuracy rate
Winner of the King’s Award for Enterprise: Innovation
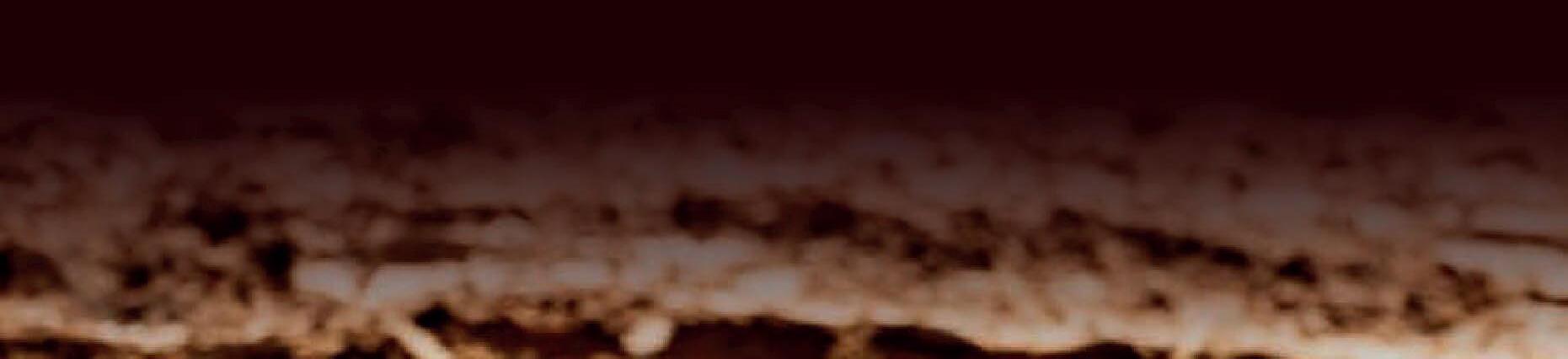

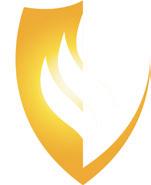

Mandated by tier 1 contractors and on projects including Balfour Beatty and Anglian Water
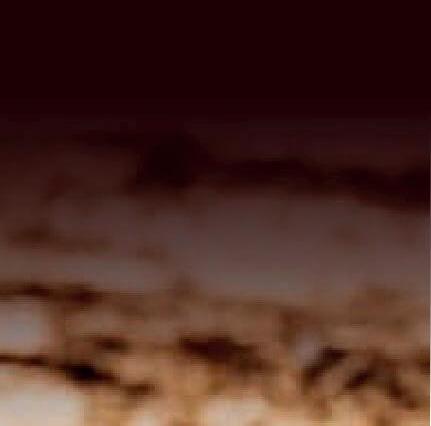