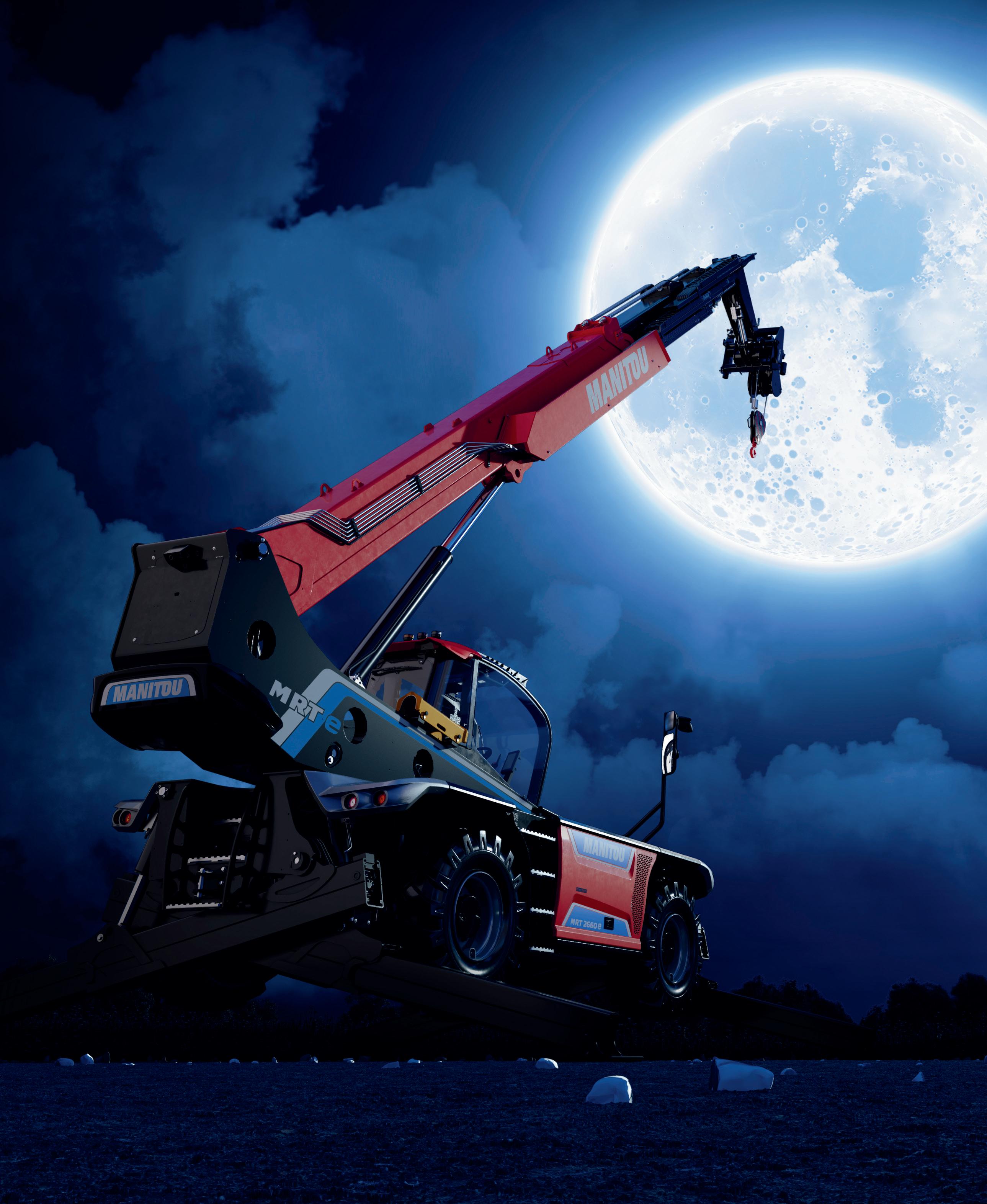
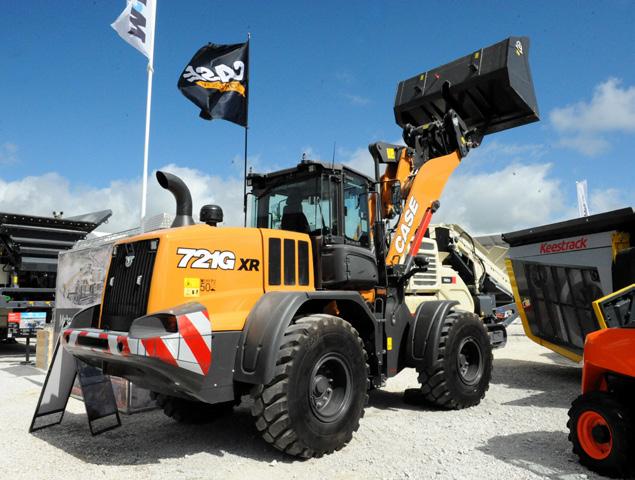
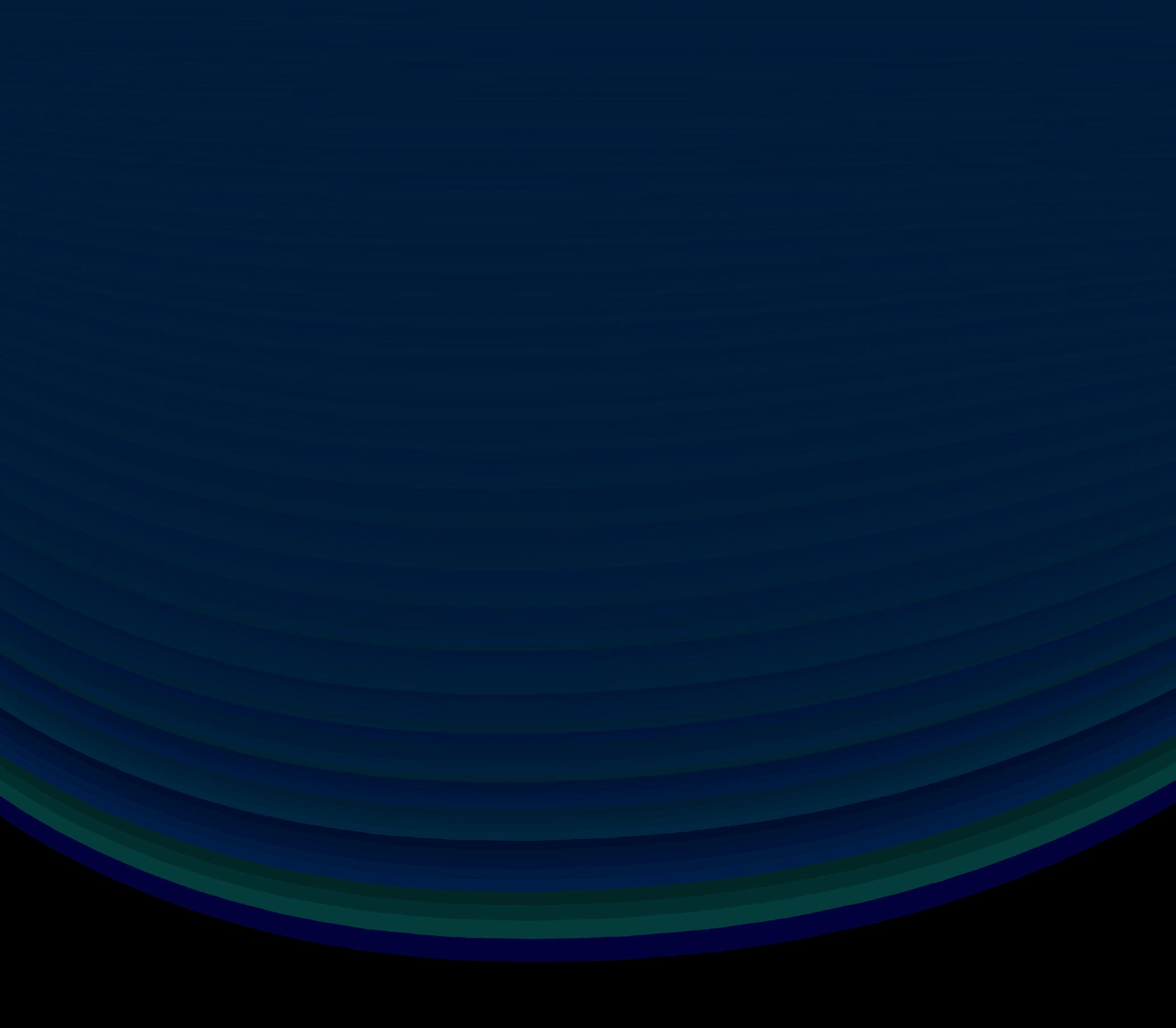
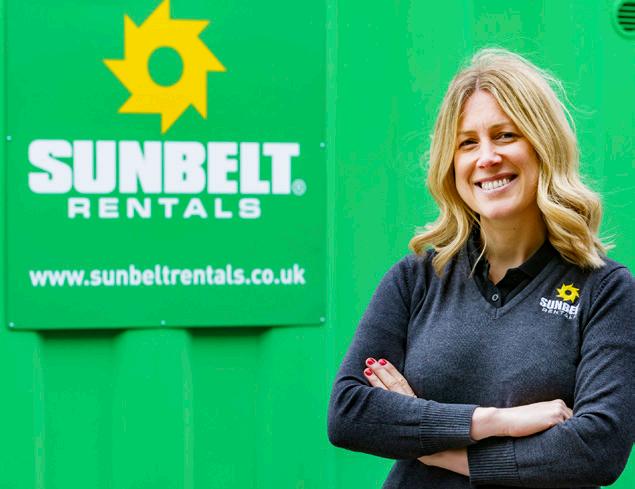
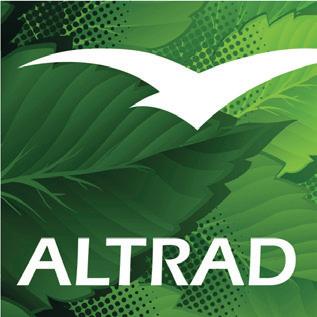











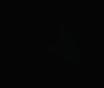










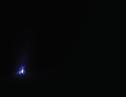








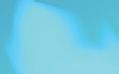

















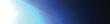








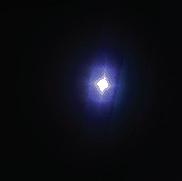








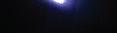


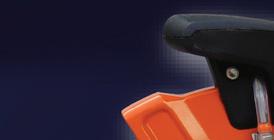
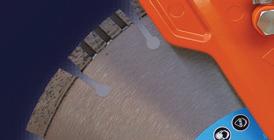
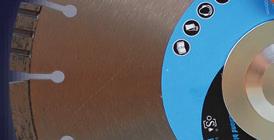
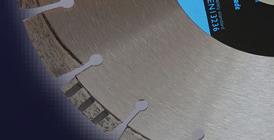
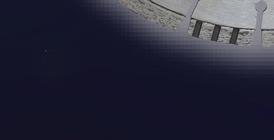





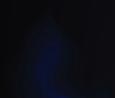









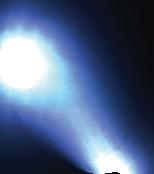
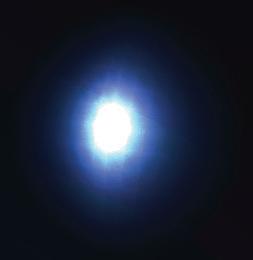















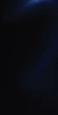


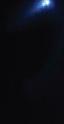

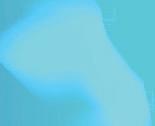

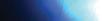
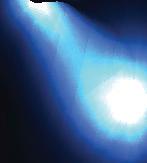
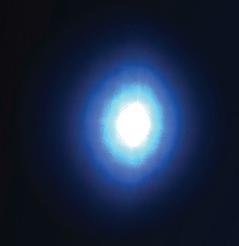

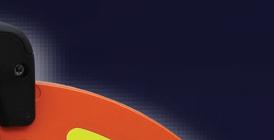
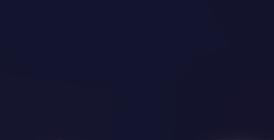
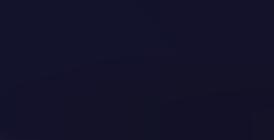
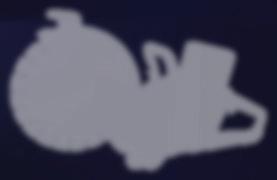
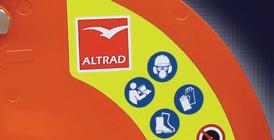
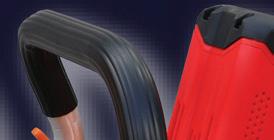
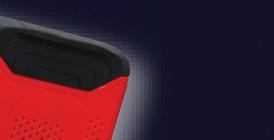
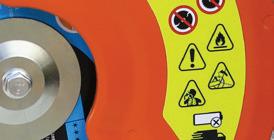
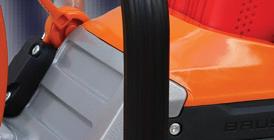
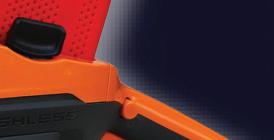
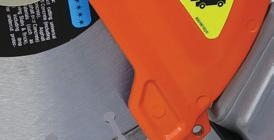
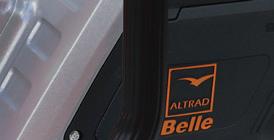
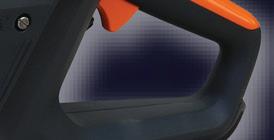
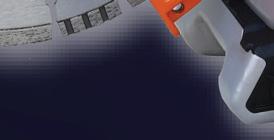
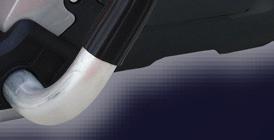
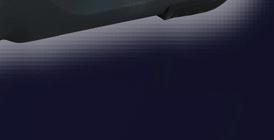



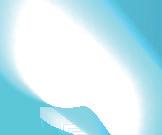
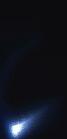

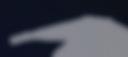

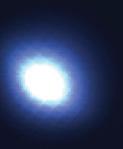


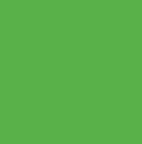







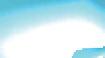













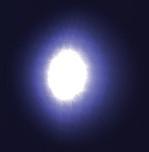


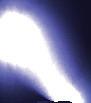

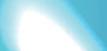


















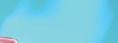







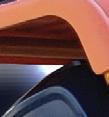






















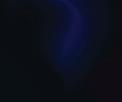

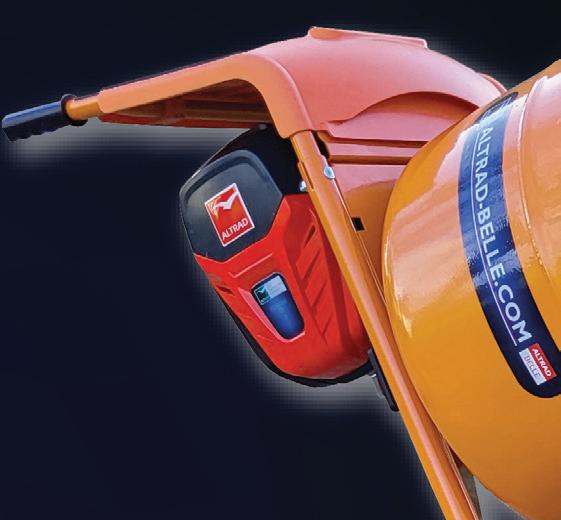

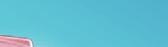
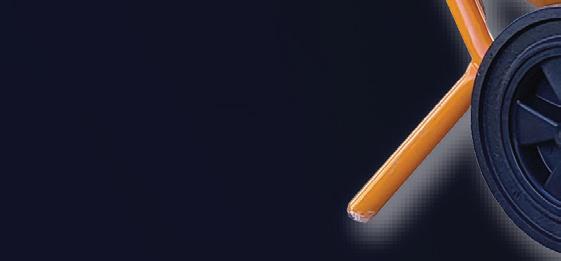
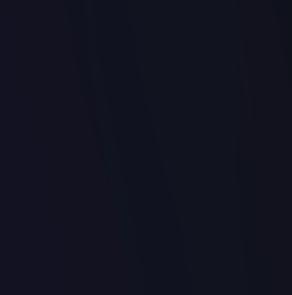
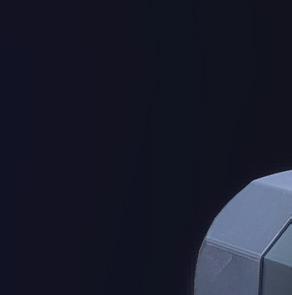


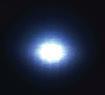







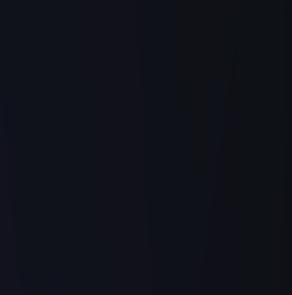





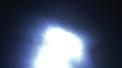

















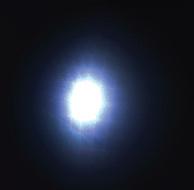


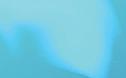














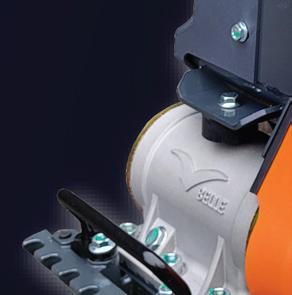


































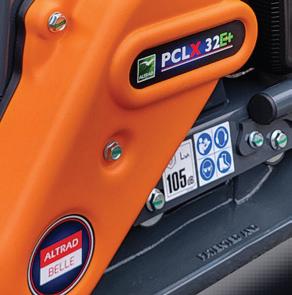

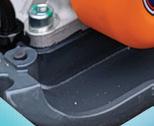



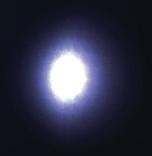









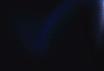
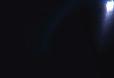





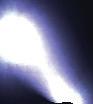

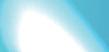



















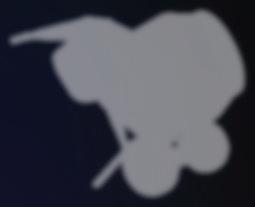






















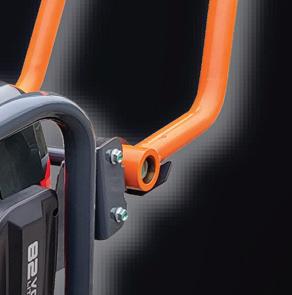
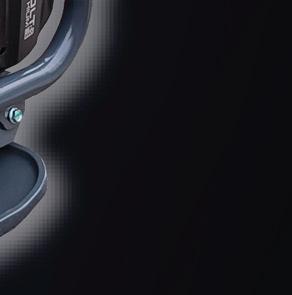
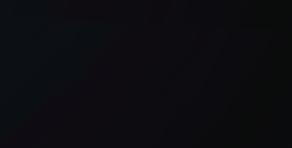









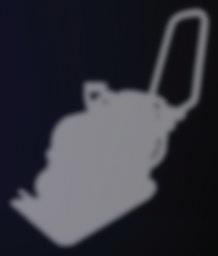








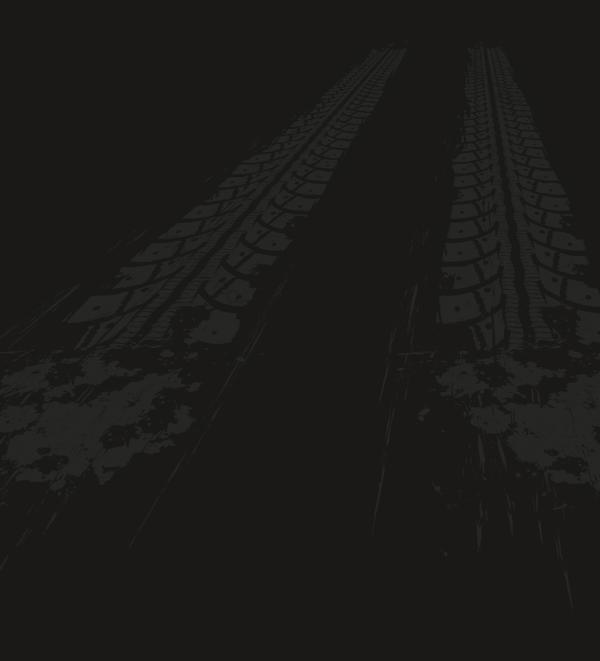




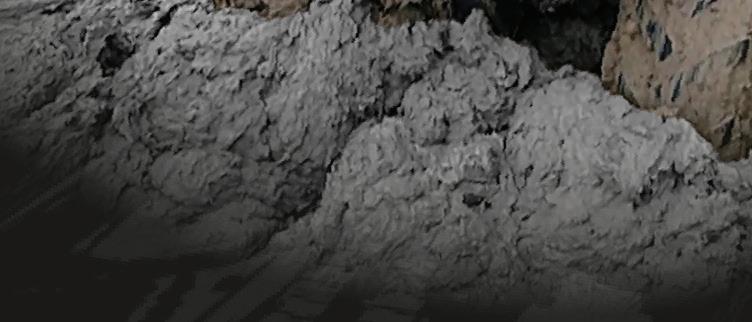
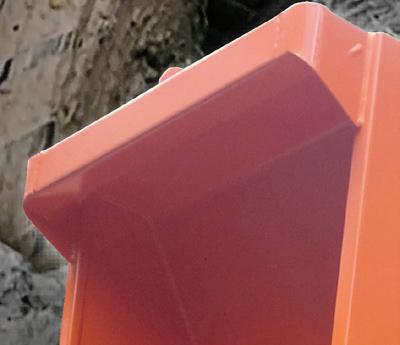

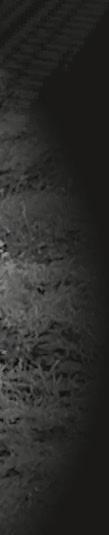
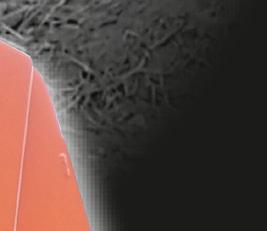
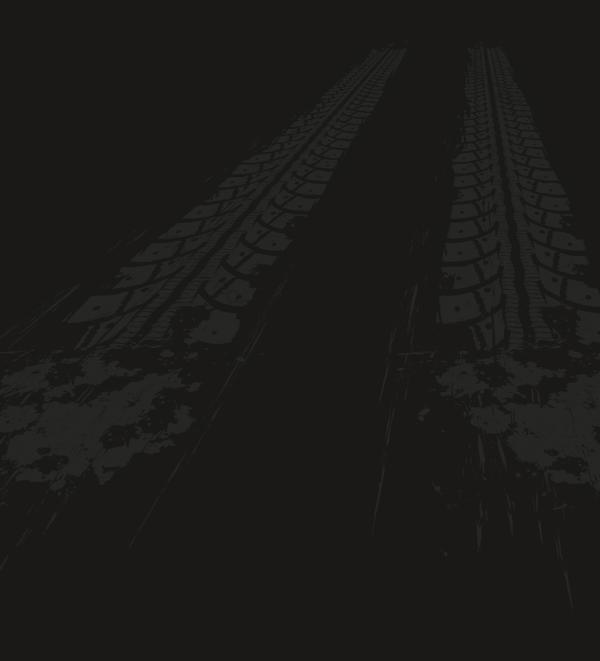

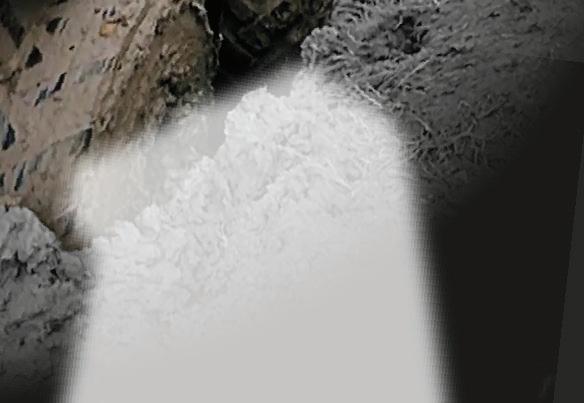
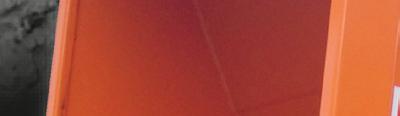
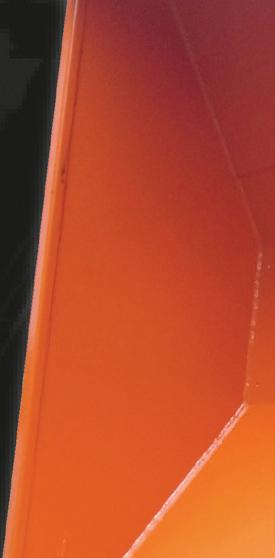
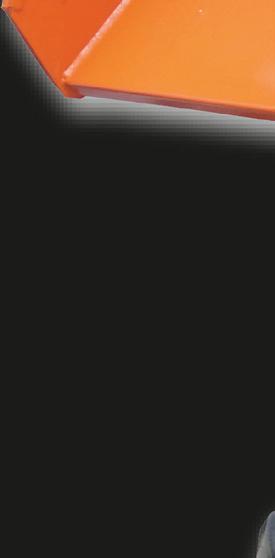
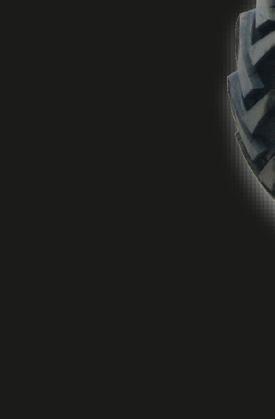
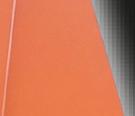
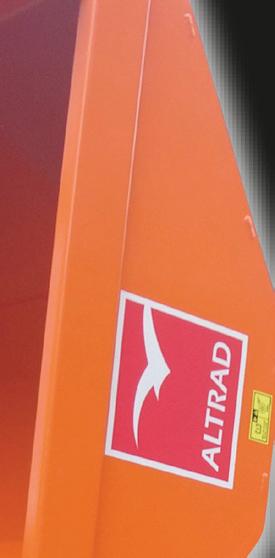
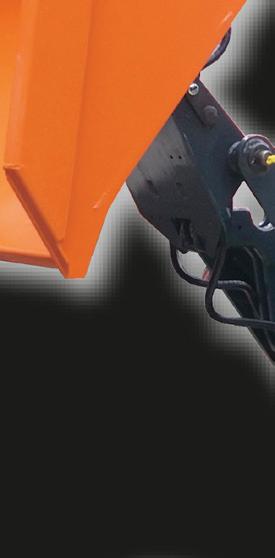
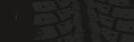
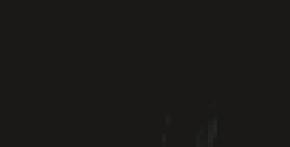
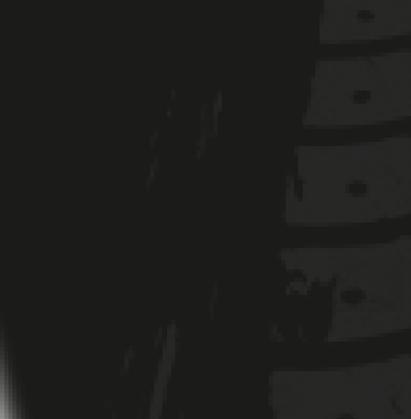
‘Best in Class’
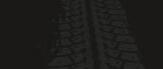

‘Best in Class’
What a summer it has been so far dear readers, and it’s long from over yet! After a fabulous time at Hillhead 2024, we are already gearing up for a busy autumn, but before the drear sets in again, let’s focus on enjoying the blue skies.
Manitou takes our front cover this month, and their focus is all on a sustainable and responsible future! They detail the machines from their range that help to achieve this goal without sacrificing safety or comfort. We also have not one. Not two, but THREE company profiles. TVH, Safety Shield and Southern Hoists are all delving into their histories as well as showcasing the very best of what they have to offer.
And speaking of putting a best foot forward, our Industry Corner this month is with none other than Sunbelt Rentals UK! Lorna and I had a fabulous time at their Go Greener day, and we can’t wait to tell you all about it!
And our travels don’t stop there! Not only did we all attend Hillhead 2024 (where I also spent the day with lovely Lana for her feature this month), but we have also been to the CPA Stars of the Future awards AND as far flung as Poland to visit the brand new LiuGong European hub!
Goodness, it’s been busy! At least we have all of you to share it with.
Happy reading!
Rebecca Phillips Managing Editor
Plant Planet is published by Kiwi Media and Promotions Ltd 2nd Floor, 41-42 Southgate, Chichester, West Sussex PO19 1ET +44 (0) 1243 345 323
Kiwi Media and Promotions Ltd. © 2024 all rights reserved.
Reproduction in whole or part is prohibited except with permission in writing from the company.
Note to contributors: articles submitted to the Editor for consideration must be the original work of the author.
Where photographs are included that are not the property of the company or contributor, permission to reproduce them must have been received from the owner of the copyright. Any views or opinions expressed within this magazine are not necessarily those of the company.
ISSN: 2631-4622
Registered in England No: 09910499
All advertisements are accepted subject to the Kiwi Media & Promotions’ standard of insertion. For a copy of Advertising Terms & Conditions, please write to: Darren Shelton, 2nd Floor, 41-42 Southgate, Chichester, West Sussex, PO19 1ET
www.sunbeltrentals.co.uk
DARREN SHELTON BUSINESS MANAGER
REBECCA PHILLIPS MANAGING EDITOR
MARTINA TONELLI MARKETING MANAGER
PHIL EVERY SENIOR SALES EXECUTIVE
LORNA COWLIN CONTENT CREATOR
CHARLOTTE WALSH BRAND MANAGER
STEVE WILSON DESIGN MANAGER
CHLOE TAPP MANITOU
HANNAH PASCOE
LISA
MAIKA
ELYSSA
KIRSTY ARCHBOLD-LAMING SOUTHERN HOISTS
BRIAN JONES HEAD OF CONSTRUCTION PLANT-HIRE ASSOCIATION (CPA)
Brian Jones is President of the CPA, the largest trade association for the plant-hire sector in the UK with circa 1,900 members. He has worked in plant-hire for over 50 years. Brian was elected to the CPA Council over 30 years ago and has been CPA President since 2017.
RACHEL LAMBERT @KINGSTON PR
Rachel Lambert is a PR consultant and the founder of Kingston PR, a business she started over 30 years ago. A former magazine editor, she is also a freelance writer covering a range of sectors.
LANA EDWARDS @TRACKLASS1
Working with plant machinery since she was 8 years old, Lana Edwards is one of the most well known and respected inluencers in the construction industry. She is the Number One Woman in Construction for Wales as well as a Top 100 Women in Construction for the UK.
We’ll send you an alert when you leave site without your tools.
EMBRACING
LIUGONG:
MANAGING EDITOR BECKS TRAVELS TO STALOWA WOLA TO VISIT LIUGONG’S BRAND NEW EUROPEAN HUB.
TVH HAS GROWN INTO A GLOBAL LEADER RENOWNED FOR ITS DEDICATION TO KEEPING CUSTOMERS’ OPERATIONS RUNNING SMOOTHLY UNDER THE MOTTO “KEEPS YOU GOING.”
AI IN PLANT
LORNA COWLIN LOOKS IN DEPTH AT AI’S PLACE IN THE WORLD OF PLANT MACHINERY.
KING’S AWARD HONOUR CELEBRATES INCREDIBLE JOURNEY OF SAFETY SHIELD GLOBAL FOUNDER AND TEAM.
HILLHEAD 2024
BACK IN BUXTON! THE FAMOUS QUARRY AND MINING EXHIBITION WAS BACK FOR ANOTHER STELLAR SHOW. RWM EXPO
THE COUNTDOWN TO THE RESOURCE & WASTE MANAGEMENT EXPO (RWM EXPO) IS ON!
SOUTHERN HOISTS
OPERATING FROM A SMALL YARD WITH A FLEET OF 15 AGEING MACHINES SOUTHERN HOIST SERVICES SET ABOUT BECOMING ONE OF THE MOST RESPECTED HIRE COMPANIES OF TODAY.
CPA STARS OF THE FUTURE
STARS OF THE FUTURE IS THE CPA’S AWARDS PROGRAMME FOR APPRENTICES AND TRAINEES IN THE CONSTRUCTION PLANT SECTOR AND IS THE PREMIER EVENT FOR RECOGNISING AND REWARDING APPRENTICES.
Manufacturer Sunward Europe debuted at Hillhead 2024 and made a good first showing with many machines sold in the three days.
On demonstration was the 21 - Tonne top of the line SWE215F-5A; this was sold on the second day of the show by Hamstead Plant, Sunward’s dealer for Warwickshire, Worcestershire, Staffordshire, Herefordshire and West Midlands and was delivered to the customer within one week.
The SWE215-5A worked on the quarry face for the three days and impressed a number of potential buyers.
The SWE 215F-5A is the perfect fit for large construction, quarrying or demolition work. Designed to be versatile and durable, with a long lifetime, the SWE 215F’s masterful design, Cummins EU Stage V B6.7 engine, and enhanced hydraulics system deliver power, smooth operation and high productivity.
In addition to the SWE 215F-5A, sales included the SWE 17F, SWE 25UF mini excavators and SWE 60UF compact excavators.
Rick Still the country manager for UK and Ireland said: “It was truly thrilling to connect with industry professionals from the UK and beyond. We would like to thank all attendees and dealers for making our first edition of Hillhead such a memorable and successful event.”
Sunward’s Hillhead debut also featured the “prototype” SWE 50UF mini excavator which will be available in the UK towards the end of 2024. This machine features a zero-tail swing for tight spaces, robust Kubota D1803-T engine, 5.3-tonne operating mass, and advanced seven-inch touchscreen for easy control.
Sunward launched the SWE 50UF mini excavator at INTERMAT in April and the response justified the company’s claims it is set to be a game changer, building as it is on the success of Sunward’s zero tail range which earned an iF Design Award. Complementing Sunward’s static display at Hillhead were four more excavators, including the 2.7-tonne SWE 25UF mini - the zero-tail version of the SWE 25F. Its unique zero-tail compact design makes it the perfect option for tight jobsites where power is required and its light weight makes it exceptionally easy to transport.
Sunward’s nine-tonne SWE 90UF-2PB compact excavator is the shortest ninetonne short-tail excavator (by almost 20 cm) available in the market. Developed especially for Europe, it combines a compact size with heavy-duty performance. Its very short-tail swing and two-piece boom allow it to work in a wide variety of urban tasks, including operating in confined spaces and along walls.
Sunward’s 16 tonne 155UF-2PB
medium short tail excavator, which made its UK debut at Plantworx 2023, was included in the Hillhead line-up. Also available with a mono boom, equipped with a Cummins engine with 90 kW/2200 rpm and a high-performance Hengli hydraulic system, it provides exceptional stability and high performance in its category.
An electric machine on Sunward’s stand was the two-tonne SWE 20FED electric mini excavator. Based on its bestseller in the European market, the SWE 20F, the cabbed/canopied SWE 20FED combines durability, reliability, performance and easy maintenance with exceptional value for money.
In addition to the excavators, Sunward’s stand included a 4.5-tonne SWTL 4538 compact track loader, which thanks to its suspended undercarriage system and tracks, offers excellent performance with outstanding drawbar power for operation on rough terrains like mulch, rock or dirt. It is also compact and versatile enough to be easily manoeuvrable in small spaces.
During Hillhead, Rick Still also shared Sunward’s plans to expand its dealer network and introduce larger equipment to the UK and Ireland.
And Joe Bayton, director of Hamstead Plant, shared his insights on why Sunward excavators are becoming a game-changer in the UK market due to their premium build, the exceptional support and unbeatable value.
Since 2013, Magni TH has always been committed to offering a range of innovative products capable of satisfying all market needs. Today, the company offers a wide line of telescopic handlers, comprising 40 models divided into three ranges: RTH, TH and HTH. At Intermat 2024, Magni launched different products, setting new market standards in terms of safety, technology and performance.
The brand new TH 3.6 is the most compact telehandler within the TH range. Originally designed for the construction and logistics sectors, offering a 3 tonnes capacity and a lifting height of 5.8 metres, it combines small size with impressive performance. Its low-level design makes it ideal for tight spaces while retaining optimal ground clearance on uneven terrains. These features, together with a Deutz Stage V engine of 55 kW (75 hp), gives it a top speed of 35 km/h. The fourwheel drive and steering, with hydrostatic transmission, makes up for superlative
stability and manoeuvrability with three steering modes: front, concentric and crab. This model is also equipped with the new compact cab, which maintains the same development approach followed in the TH range together with a new dashboard that optimises user experience through the ergonomic placing of the main controls. It also features USB ports (3.0 and c-type) for charging electronic devices and a handy cup holder. The new cab’s standard outfit is completed by the air-suspended seat, adjustable wheel column, heating and radio. Unlike other competitor models on the market, which only have the usual load cell mechanism, the TH 3.6 is equipped with a more sophisticated and precise tipping protection system to maximise performance and safety, in line with the whole TH range. That is the LMI (Load Moment Indicator), a technology that allows constant monitoring of the machine’s movements to prevent any kind of overload.
Moreover, Magni launched three new models derived from the
This feature is designed to optimise work when greater visibility is demanded and to guarantee the best level of comfort with an ergonomic position. Especially when handling delicate loads or using specialist attachments, greater visibility means safe and effective movements, even in the most complex procedures, such as the use of the tree cutting attachment. The hydraulic mobile support is able to raise the cab up to a height of 1.5 metres from standard position and tilt it between 0° and +16° for optimal control in conditions where movements must be exceptionally precise.
The recent general election on July 4th marked a monumental moment for UK, with the Labour Party securing its first electoral victory since 2005. Given the size of the majority, Labour has a clear mandate to deliver on the promises for change outlined in its manifesto.
Two key commitments, ratified in The King’s Speech, are building 1.5 million new homes and immediately updating the National Planning Policy Framework (NPPF). Both are particularly significant for the construction sector and therefore for Merlo. While these pledges are welcome, the devil will be in the detail on how they are implemented. That said, Merlo has welcomed this impetus to put housing and planning reforms at the heart of the new government’s agenda.
Merlo construction telehandlers: the best tool on site
Amidst this dynamic landscape, having the right machinery is crucial to meet the demands of a rapidly evolving market. The Merlo range of telehandlers, known for their manoeuvrability, market leading safety features and fuel efficiency all feature a hydrostatic transmission. Having offered exclusively hydrostatic drive since 1966, Merlo has perfected the precise control of both speed and torque, enabled the smoothest operation while delivering fuel savings of up to 18% when compared to other systems.
For the burgeoning housebuilding sector, Merlo’s range of construction handlers stand out as an indispensable asset for any construction site, offering the ideal solution. Merlo offers the perfect blend
of stability and reach with their bestselling P40.13 and P40.17 (up to 4tonne capacity, with 13m and 17m reach respectively) stabiliser equipped telehandlers.
With a range of Merlo produced attachments, these models are ideal for precise material placement in residential projects, providing the necessary lift and reach for a variety of tasks. For example, fly jibs for lifting and placing items like timber trusses and roofing joists whilst integrated man baskets are the certified solution for safe and efficient working at height during construction and finishing phases to name but two applications.
When it comes to general material handling around any construction site, Merlo’s compact 6m, 7m, and 9m telehandlers are indispensable. Their ease of use, tidy footprint and robust design make them ideal for a range of applications allowing for versatile manoeuvrability and efficient material movement.
a greater range of motion
Probably best known amongst Merlo products in the world of construction, is the rotating Merlo ROTO handler capable of positioning loads in a radius of up to 360 degrees. As well as being more cost effective than a crane, they also require less paperwork! Categorised as a telehandler, a ROTO can travel across sites or on the road, at up to 40km /hour. Merlo ROTO’s are equipped with stage V 170 hp engines and have an impressive lifting capacity of between 4 and 7 tonnes and with a reach of up to 35m. High specification S PLUS models have
dual hydraulic pumps and automatic management of the multi position stabilisers as standard. The ROTO range stands out for its hydraulic tilting cab, delivering exceptional comfort and safety for the operator.
While the market for heavy lifting in construction is niche, the range of Merlo’s high-capacity telehandlers are designed to handle heavy loads up to 12 tonnes with a maximum reach of between 8 and 18 m.
As the new government embarks on an ambitious construction agenda, the industry’s success will heavily rely on the efficiency and versatility of its machinery. Merlo’s construction range provides the essential tools needed to tackle the diverse challenges of modern builds. Merlo and the Merlo network of construction dealers, with a fully stocked UK parts warehouse, nationwide network of service engineers and support, stand as trusted partners you can count on, ensuring that your business can be equipped to excel in any dynamic and demanding environment. Investing in a Merlo is a strategic move towards sustained productivity, efficiency, safety and ultimately, success in the construction sector.
The safety of your rental equipment is paramount in the fast-paced construction industry. Project delays and serious on-site accidents can result from using unsafe equipment. The latest software can be a game-changer for construction firms and equipment rental companies that prioritise safety and compliance.
Access user guides: Instantly view detailed user guides to ensure the correct and safe operation of each item. Link directly to a portal containing official safety documentation unique to each machine and ensuring legal compliance. Verify equipment certificates: Scan QR codes to view essential certificates such as LOLER (Lifting Operations and Lifting Equipment Regulations) or PUWER (Provision and Use of Work Equipment Regulations), as well as other safety inspection certificates.
Scheduled Maintenance Alerts: Receive timely alerts for upcoming maintenance tasks to ensure no detail is overlooked.
Detailed Maintenance Logs: Centrally maintain comprehensive records of all maintenance activities, providing a clear audit trail and peace of mind for all equipment users.
To learn more about MCS, please visit: www.mcsrentalsoftware.com/en/ or scan the QR code FOR FURTHER
Automated Compliance Checks: Automate routine compliance checks to ensure that all equipment meets industry standards and regulations. By leveraging these features, construction firms and equipment rental businesses can significantly reduce downtime, enhance equipment reliability, and, most importantly, mitigate safety risks.
With software that has been designed specifically to meet the needs of the construction industry, you can take
advantage of robust features that allow for unparalleled benefits such as: Efficiency: Automate time-consuming tasks, allowing your team to focus on core activities.
Accuracy: Eliminate human error with automated processes and real-time data access.
Compliance: Ensure your equipment meets the latest safety regulations, protecting your business and employees. Join the growing number of construction firms and equipment rental businesses that trust MCS Rental Software to keep their operations and equipment safe and compliant.
Working with an electric loader is now more efficient than ever – even in extremely cold conditions. Avant Tecno presents the renewed e series and the third generation of fully electric loaders, whose unique battery technology further improves the capacity, pricing, safety, working time, durability, and lifespan of electric loaders. With a fully charged Avant e527, you can work all day.
Finnish compact loader manufacturer Avant Tecno has been at the forefront of the development of electric loaders for decades. Now, Avant is launching two next generation fully electric loader models, the Avant e513 and Avant e527, which will renew the Avant e series and replace their predecessors, the Avant e5 and e6 models. The new loaders will enter production in January 2024.
The new loaders are equipped with Avant OptiTemp® battery packs (13 kWh and 27 kWh) manufactured by Avant Tecno’s subsidiary Avant Power. The globally unique battery technology brings capacity to a whole new level, and the energy density of the batteries is among the best in the world.
The thermal management system of the patented lithium-ion batteries guarantees the same capacity in hot and extremely cold temperatures. Multi-level protection makes Avant OptiTemp® batteries very safe.
The new Avant e513 and Avant e527 loaders are almost identical, but the only difference lies in the capacity of the batteries. The Avant e513 (13 kWh) is a good choice for short-term continuous use on cattle farms, horse stables, greenhouses or DIY and leisure time, for example. The Avant e527 loader (27 kWh) with a larger battery is ideal for demanding professional use. Construction and demolition contractors will benefit from this model.
The fully electric Avants are ideal for working in confined spaces and on construction sites that have strict limits on noise and emissions.
When fully charged in the morning, the Avant e527 loader (27kWh) can be used for a whole working day. The maximum operating time of the machine is about 6 hours for medium-duty work, whereas for Avant e513, it is about 3 hours. The battery of both loaders can be fully charged with a fast charger in under 1.5 hours, allowing for long working days.
“For years, the market has been longing for fully electric loaders that would be more like diesel loaders in terms of functionality. Until now, operating time and pricing have been key issues related to electric loaders, but with Avant’s new e series, we solve them both,” says Jani Käkelä, CEO of Avant Tecno.
• Fully electric loader series. Zeroemission, very quiet. Low operating and maintenance costs.
• Two models: Avant e513 (battery capacity 13 kWh) and Avant e527 (battery capacity 27 kWh).
• Excellent capacity in hot conditions and severe frosts.
• Fast charge in under 1.5 hours. Type 2 charging, built-in 3 kW battery charger. The maximum charging current has been increased by 50% compared to previous Avant electric loaders.
• Two electric motors: one for driving hydraulics, and one for auxiliary hydraulics, boom, and steering. Thanks to the electric motor, maximum torque is immediately applied, which ensures excellent thrust.
• The further improved cooling system in the engine package keeps the machine’s heat under control even in soft terrain. Increased load resistance in short-term hard work.
• The updated multifunction display provides information on battery status, temperature, power consumption, operating hours, auxiliary hydraulics output, maintenance needs, and more.
MB Crusher, an Italian manufacturer, offers a comprehensive range of crusher buckets with 12 models available. These attachments cater to various machines, including mini excavators, wheel loaders, skid steer loaders, and backhoe loaders, as well as excavators ranging from 5 to 100 tons. With MB Crusher attachments, any heavy machine can be converted into a mobile jaw crusher.
The product lineup includes screening buckets, drum cutters, sorting grapples, and padding buckets. All MB Crusher
attachments are powered by the carrier’s hydraulic system, requiring only a plug-in to operate. They are easy to transport, have low maintenance costs, and do not need an additional operator.
Crushing and recycling are crucial in demolition and rebuilding projects. The push to maximize the use of available materials has led operators to utilize waste that was previously discarded or taken to disposal centres. To meet this need, MB Crusher’s product range is designed to facilitate on-site recycling of debris, simplifying the processes of crushing, screening, and handling aggregates, thus saving time and money.
We combine technological innovation with craft smanship to produce lifting solutions that rewrite the industry standards.
Our telescopic handlers are designed to overco me any challenge, thanks to unrivalled perfor mance, best-in-class visibility and groundbrea king technological innovations.
Their compact size makes TH models ideal for operation in tight spaces, with unbeatable agility in all operations.
We aim to enable you to work easily in a safe, comfortable environment, so you can be sure of performing at your best every day.
Construction sites are prime targets for machinery theft, causing delays and financial strain. ABAX, a leader in telematics, offers solutions to prevent and address these thefts efficiently. Here’s how ABAX recently helped Viper Hire Ltd quickly recover stolen equipment.
Viper Hire Ltd, a leading equipment rental company based in Somerset, faced a serious issue when a 0.8T 2024 Kubota K008-5 Digger and a Lumag dumper, collectively valued at over £17,000, were stolen from a job site. This not only disrupted their operations but also threatened significant financial loss. Fortunately, the company was already using ABAX’s telematics software.
Machinery theft is a major issue in the UK construction industry. According to the Chartered Institute of Building, over £800 million worth of equipment is stolen each year.
Less than 10% of this stolen machinery is recovered, making theft a significant financial burden on the industry. This highlights the importance of effective tracking and recovery solutions like those provided by ABAX.
ABAX’s telematics software provides real-time tracking and monitoring of machinery. Using GPS technology, the software gives precise locations of equipment. When the theft occurred, Viper Hire Ltd accessed the ABAX platform to find the stolen machines’ location.
Early the following morning, a Viper Hire employee checked the tracker and discovered the equipment’s location in Lancashire. With real-time GPS data from ABAX, the company quickly informed local authorities. Within hours, the police recovered the stolen machinery. This speedy recovery minimised downtime and losses, allowing the construction project to resume almost immediately.
ABAX offers extensive tracking solutions for the construction industry, covering vehicles, machinery, and tools. Their tool tracking solution stands out as a unique offering in the market. This software ensures that even smaller assets, which are often overlooked, are monitored and protected. By tracking tools, ABAX helps prevent losses that can accumulate over time and disrupt project workflows. Additionally, tool tracking helps prevent misplaced tools and those left on site, ensuring that all equipment is accounted for and available when needed.
ABAX’s telematics software doesn’t just help with theft recovery. It also aids in better asset management. The software provides real-time data on equipment usage, schedules maintenance, and offers performance analytics. This helps companies keep their machinery in top condition and operate more efficiently. After this incident, Viper Hire Ltd fully embraced ABAX’s software, using it to streamline maintenance and reduce operational downtime.
ABAX’s role in this recovery showcases its importance in the construction industry. By offering tools to protect and manage machinery, ABAX ensures businesses can continue their work with minimal interruptions. For construction companies, ABAX’s telematics solutions are a reliable way to safeguard assets and maintain efficiency.
Viper Hire Ltd shared their experience:
“The thieves cut through the wires on the tracker, thinking it would disconnect the device. However, the incredible battery life allowed us to track the machines all the way to where they had parked the van. If it wasn’t for that back-up battery, the machines would’ve been gone.” –Annie Burdick, Viper Hire Ltd.
IDE are so excited to announce that they are celebrating 30 years; that’s 30 years of manufacturing temporary power products, 30 years of experience working with various industries and driving forward innovative ideas to help customers reduce their carbon emissions onsite.
IDE have progressed significantly over the 30 years manufacturing temporary power distribution products, and in 2021 they became part of the Sdiptech group. Sdiptech provides value to customers in the infrastructure sector by offering high-quality technologies, solutions, and services to both the public and private sectors, primarily in Europe.
Currently IDE have over 70 members of staff at thier head office and manufacturing centre based in Cannock, where their temporary power products are built by experienced engineers. There are also three rental depots strategically placed in significant areas in the UK, giving customers flexibility as well as catering for their international customer base.
IDE is a trusted name within many industries, from events, construction sites and the TV and film sector. They have provided temporary power products to well-known large events, here in the
UK and internationally. They have also supported many temporary infrastructure sites. They have put together a fantastic team that continuously learn new skills and refresh current skills to ensure they create quality products and provide the best service to their customers.
The team specialises in combining sales, rental, bespoke design and manufacturing. They can work in partnership with the customer to make the very most of their power distribution assets and advise on important decisions. They are the trusted advisor; they take the time to understand the customer’s requirements and can design and build bespoke temporary power products for the customer’s site.
IDE’s offering is unique. They offer an unrivalled integrated service where they can help the customer find the right balance between buying and renting distribution boards and cables, considering any concerns they may have about capital and operational expenditure, or it could be about longerterm strategic advice. For instance, they can help the customer to plan, and future-proof their procurement needs, by ensuring they get the best from the power distribution set up and IDE’s expert services.
IDE are known for driving forward innovation and they have extended their carbon impact products team. Erica is the energy management and control system; the module can be placed into a distribution board, and it can then monitor and control energy consumption onsite by using an online dashboard. The team can then create reports based on the findings and suggest ways in which sites can reduce their costs, their energy consumption and carbon emissions. Their carbon impact products extend into temporary electric vehicle chargers making charging an electric car more accessible at events, festivals, on a film and tv production set or on a construction site. The temporary electric vehicle chargers are portable, robust and has optional payment methods.
IDE are so proud to celebrate 30 years in the temporary power market and will continue to provide excellent service, quality hand-built products as well as producing innovative products to align with their customers’ sustainability goals.
Utilising the latest technology and designed in the UK, we provide you with the latest safety solution for both your vehicle and sites.
Time pressures on getting work done is one of many contributing factors to incidents in industry today. At Fastview360, we want to help reduce incidents with safety systems that can warn operators and improve visibility around the equipment they are operating. Safety is the forefront of operations and using our technology can provide you with a harmonious solution.
Incidents happen, there’s no denying that – but what if you can achieve the first notification of loss rapidly and remotely? Using our dedicated dashboard, FV-Link, you can remotely collate video footage, details of the incident and the driver can add details too including more images and videos.
We can retrofit to any vehicle type with a variety of camera and tracking solutions. Working with customers, the solution provided is one that achieves what the customer wants to get from their products from cameras to sensor alerting system. Our hardware is tried and tested in many environments to ensure that it is fit for purpose and doesn’t let you down.
With both our vehicle and site solutions, we can integrate with existing systems to ease the migration to Fastview360. Our dedicated support and installations teams work to give minimal
disruption to your operations as possible. Good rapport with customers is essential and we believe this imperative to our ongoing work.
Site visits are essential as we utilise mapping procedures to advise on creating safe walkways. Health and Safety officers are key to assist with the initial planning though to implementation.
We are preferred supply partners of Avigilon products, part of the Motorola
group. This has allowed us to work closely with site health and safety officers to compile near miss reporting. Reporting of dangerous activity such as incorrect PPE, loitering, working at height, traffic flowing the wrong way supported by ANPR and other warnings can be sent directly to the Health and Safety officer with snapshot videos of the event. The solutions provided with FV-Link assist with insurance purposes, improving operator behaviour and increasing site safety.
Our vehicle and site products provide a robust solution for enhancing site safety through advanced monitoring, real-time analytics, and proactive incident management. By utilising the latest technologies available, you can significantly reduce risks, improve response times, and ensure a safer environment for all.
Don’t settle for second best
The telescopic handlers of the ROTO range allow 360 degree operation due to the rotating turret offering a greater range of action compared to a fixed telescopic handler. This model can be offered as a hybrid solution, allowing you to plug into an electric source on-site allowing emission & noise free operation.
PartsForMachines MD and CoFounder, Abhishek Tanwar comes from a background that includes working at management level in mining, banking, lubricants and construction equipment. He was well placed, therefore, to absorb the market situations across a variety of industries and become inspired by them.
“The construction and agricultural industries have some great machinery manufacturers, but the aftermarket seemed somewhat insular and dealercentric,” he explains, “We looked at both sectors in more detail and thought the opportunity existed for something that was more of a one-stop shop and, thus, the idea of PartsForMachines was born.”
Concept to reality took more than two years and in January 2021 partsformachines.com - the first purposedesigned e-commerce portal aimed at construction industry operators for their parts requirements and aftermarket needs - officially broke cover… and has been growing ever since.
From the outset, PartsForMachines’ emphasis was on the creation and delivery of a positive customer experience, built around a comprehensive, competitive product offer, with ease-of-use as its central tenet.
The four pillars on which PartsForMachines is based are “Easy to find; Easy to Buy; Great Service and Hassle-free Returns.”
As well as a five-star customer experience, (check their TrustPilot rating!) PartsForMachines makes sourcing spares and consumables more convenient, eliminating the need to travel off-site to purchase the required items, saving valuable time and effort, and reducing costly downtime.
With its launch coinciding with the latter stages of Coronavirus, it had the advantage, at the time, of making the whole parts buying process Covid-19 safe, and it quickly became obvious, with the volume of traffic coming to the site, that there were limitations to the original platform. Therefore, from early days,
PartsForMachines set to work building an upgraded platform, one that now incorporates a variety of widgets and other search tools to help customers find what they are looking for faster and more easily.
With the advent and increasing role of AI, however, PartForMachines is in the process of further upgrading the platform to allow for AI-enhanced features.
The other key factor in the PartsForMachines story is the role of the supplier partners. The company was keen to ensure that well-known, quality brands formed the core of its parts offer. The platform started with half a dozen and it is now approaching the fifty mark, as it increasingly moves towards its original aim of becoming a one-stop shop for the industry.
The Hire Exchange, the specialist business sales advisory for the plant and equipment hire sector, reports that in spite of tough trading conditions in late 2023 and the uncertainties prior to the recent election in 2024, the appetite for acquisitions remains strong and prospects for sellers in 2024 /25 look good.
Since their launch in 2020, The Hire Exchange have successfully completed 18 transactions with three more due to in 2024 and six more in process across sectors that include Plant Hire, Tool and Equipment, Powered Access, Genpower and Welfare.
Chris Harvey Co-founder of The Hire Exchange commented “Though early days, we sense a mood of greater optimism, even though interest rates are still high there are signs of these beginning at least to reduce.
The threat of tax rises is an issue of course as is the cancellation of some major projects due mainly to Government budget priorities, but with inflation under control, the new Government’s commitment to growth, housebuilding
and restoring stability, there is a feeling of greater confidence for investment and growth”
Demand for good hire companies is still high with trade buyers and investors appropriately adopting a long-term strategic approach, unencumbered by any shorter-term nervousness.
Asset backed lending and Asset Finance remain essential components in hire business growth and particularly in acquisition. So, while more expensive than in recent years and subject to greater lender caution, lending continues to be available and remains the life blood of the industry.
A good business is a good business, even if it has endured some market pressure. That said, prospective sellers should use this time to get their business in good shape to optimise its value.
This means ensuring that business is structured to reduce risk through maintaining an appropriate balance between turnover and debt and a focus on optimising margins and cash to maintain a healthy and steady level of EBITDA.
We are gratified that our reputation has grown for optimising value for sellers by
finding the right buyers but also amongst buyers by making acquisitions easier and presenting the best opportunities for them. In fact, an increasing number of buyers are inviting us to search out businesses that fit their strategic requirements. Good news for sellers who are our only client.
From a market demand point of view the good news is a sharp rise in interest in the hire sector shown by private and small fund investors. These include national and international businesses and High-Net-Worth Individuals who increasingly see the hire sector as a great place to invest with the security of asset backed operations.
If you are considering selling or acquiring a hire business we would be delighted to help. To learn more please visit: www.thehireexchange.co.uk or call 03303 230643
Safety, functionality, and productivity are three essential elements for large companies operating in the construction industry, especially with machinery. Ease of use, innovation, and practicality are essential for ensuring a sustainable and safe working environment for the operator.
DIECI has specifically designed its new rotating telehandler, the Pegasus 60.35, to fit in a market that’s increasingly attentive to work site safety and is on the lookout for high-performance equipment designed for lifting and transporting heavy loads with maximum precision.
This new range was created to facilitate work at the construction site, while at the same time offering maximum performance, comfort, and safety. The range consists of the Pegasus Essential, the Pegasus Classic, and the Pegasus Elite, the new top of the line solution with even greater performance.
Innovation begins with the Easy Tech System, a new hardware and software platform developed in-house by the DIECI R&D department, which ensures data processing capabilities comparable to that of the most modern vehicles. Guaranteeing greater performance and outstanding features:
• Greater precision and control of movement.
• Automatic boom movement, based on 6 selectable working modes (Normal, Soft, Heavy, Eco, Wall, Floor).
• Anti Tilt System-Pro, the new advanced
anti-tipping system with aggravating movements lock.
• Electronically controlled load-sensing pump, for an in-depth dynamic set-up based on the working conditions and equipment.
As evidenced by the innovative Easy Tech System, the advantages of Pegasus Elite begin with the cab, the interior of which has been completely redesigned with new smart control.This was to implement a new concept of machine control, thus ensuring simplified and safer features. This new smart and intuitive approach has led to the revamping of various interior aspects of the cab, starting with the controls, which are now digitally managed on a dual display:
• 4.3’’ display dedicated to the machine’s running functions;
• 12’’ multi-touch display dedicated to the machine’s operating status.
The advanced features implemented on the Pegasus Elite rotating telehandler can also be controlled from the display, allowing for the management of the following with just a few clicks:
• The six working modes;
• The connected equipment and the relative load diagram;
• The Soft Motion Function.
• The Easy Work System.
• The “limits” function.
Pop-ups and audible warnings visible on the display further protect the
operator, ensuring high levels of safety. The approach used for both screens is reminiscent of the automotive interface, facilitating the understanding of the parameters.The controls are suitable for the rental sector, and are easy to manage, even upon first use. The possibility of customising the display layout even allows the user to manage the screen based on their own operational needs.
All the new functions and individual controls have been implemented with a focus on control and visibility, making the Pegasus Elite rotating telehandler an extremely safe vehicle in any context, also thanks to:
• The 12’’ display.
• The reclining seat, to facilitate overhead operations.
• The LED work lights.
• The backlit keypads.
• The around-vehicle monitoring system.
Thanks to the new cab design, the Pegasus Elite rotating telehandler is an indispensable unit for large construction sites and more. Everything is centred around the operator, who will find everything they need to be completely satisfied!
CASE Construction Equipment is building upon the success of its motor grader heritage, with the introduction of the new D-series: 836D and 856D. Boasting many of the operator comfort and productivity benefits launched with the previous C-Series machines, the D-Series models take the operator’s cabin to a new level of comfort, with precision, intuitive moldboard control, powerful Dual Power engines and a comprehensive range of after-sales solutions.
CUSTOMER BENEFITS
Enhanced Operator Comfort - The D-Series graders feature a low-profile ROPS/FOPS cab, delivering unbeaten visibility. A reduced overall height facilitates easier transportation between job sites. Full width tinted glazing and a commanding view to the front and at
the moldboard, ensure optimum control, whatever the task.
There is a new touchscreen display, for all machine and maintenance info and to provide a monitor for the rearview camera. This customisable screen is located on top of a redesigned front console. A second console to the righthand side of the cab incorporates the ignition key, the new electronic hand throttle, a cup holder and USB charging ports. On the left-hand side of the cab there is a spacious storage compartment, which features a rubber strap and net.
The new Grader comes in both electrohydraulic joystick controls or mechanical levers, which means the driver has the ability to choose depending on their preference. Both machines come in standard with a heated and airsuspended seat.
The electro-hydraulic system uses highly precise, three-axis joysticks, which
are built into multi-adjustable armrests for maximum operating comfort. The joysticks are equipped with multiple roller switches and buttons, to control various machine functions.
These joysticks also provide accurate control of all moldboard operation, comfort steering options and TwinLift control, which allows the operator to control both lift cylinders from a single joystick.
Dual Power Performance – Powered by a Stage V six-cylinder FPT diesel engine, with Hi-eSCR2 emissions technology, the CASE D-Series graders deliver a dual power curve, with automatic switching as higher transmission ratios are reached. This ensures maximum power is available as travel speed increase, boosting productivity.
Compliant with HVO and other XTL synthetic fuels, the 6.7-litre diesel engine
features a maintenance-free Diesel Oxidation Catalyst (DOC) with Selective Catalytic Reduction (SCRoF) exhaust after-treatment system. An Ergopower transmission automatically delivers smooth shifting between gears, with allwheel drive models having a creep mode for compaction work, reducing the need for additional machines on site. Both the two- and four-wheel drive models are available with optional 24” tyres, ideal for uneven ground conditions.
Moldboard Control – D-Series graders can be tailored to the application with a choice of different moldboard widths, moldboard extensions, an overload clutch, a five-tooth ripper, additional counterweights and LED working lights. An A-shaped frame and central saddle provide maximum stability and versatility for the cutting edge.
The CASE moldboard design, on a roller-mounted encapsulated slewing ring, avoids any backlash and reduces wear, while supporting high mechanical torque for maximum control. With fewer greasing points, maintenance is reduced, boosting uptime and ensuring increased profitability for the customer.
The D-Series graders come ready to easily install a range of the most popular plug-and-play machine control systems to further boost productivity.
CASE Service Solutions – A range of connected and non-connected after-sales solutions ensures that your machine is working without unexpected maintenance costs and downtime.
Graders come with a CASE SiteWatch subscription – a tracking and fleet management tool, allowing customers to remotely monitor their equipment in use. Fleet managers can use geofencing to increase security and monitor unauthorised equipment use. With CASE SiteConnect this telematic transfer is enhanced by directly alerting dealers about machine performance and operating conditions, allowing proactive maintenance, quicker repairs as well as preventive service.
New D-series Graders benefit from CASE Care – a planned maintenance programme with genuine parts and lubricants which allows for certainty on the total cost of maintenance without any hidden surprises.
In addition, there are a range of services such as CASE Protect extended warranty and CASE Fluid Analysis to protect CASE Construction equipment and ensure uptime with extended warranty and other preventive programmes aimed at avoiding unexpected operating costs and optimising profitability.
Quick Specifications
836D – 836D AWD
Operating weight: 11,701-12,800kg
Engine: FPT Hi-eSCR2 Stage V
Power: 102/115kW Dual Power
Moldboard width: 3,050/3,355mm
856D – 856D AWD
Operating weight: 14,976-16,650kg
Engine: FPT Hi-eSCR2 Stage V
Power: 129/142kW Dual Power
Moldboard width: 3,350/3,665/3,960mm
To learn more about Kleenoil visit: www.kleenoil.co.uk
TIF YOU CHANGE THE HEAD OF A BRUSH AND THE HANDLE, IS IT STILL THE SAME BRUSH OR IS IT NOW A BRAND NEW BRUSH? BY THE SAME TOKEN – RATHER THAN CHANGING THE OIL
IT
opping up machine oil just adds to the particulate; the particles can’t be diluted – they just aren’t soluble, and they can’t be used up – indeed if they are allowed to travel perpetually around the system to cause abrasion and consequently even more particles!
And then there is the assumption that you’ve topped up the additives! Whilst, yes there is an element of this – if you are topping up dirty oil then the additives are used up even more quickly to try and balance and resolve the issues caused by the existing contaminants and sludges –so NO!
So then when to Change Hydraulic Oil?
As a general rule, hydraulic oil should be changed every 2,000 to 3,000 hours of use, depending on the operating conditions and the manufacturer’s recommendations… reasons why:
Contamination: Dirt, water, and other contaminants can build up in the oil and can cause wear and tear on components.
Oxidation: through contamination and moisture, the oil oxidises, resulting in the formation of sludge and varnish that may hinder system performance.
Additive depletion: The additives in the oil, which help improve performance and protect components, become depleted as they try to deal with the countereffects of the contamination.
Regularly changing hydraulic fluid as directed by the manufacturer is a standard process – but operators often leave this until a catastrophic failure
arises – often through dirty fluid. But why? Often because of time constraints, down time expense, labour restraints and of course simply the cost of the new oil with the cost of disposing of the waste oil.
But what if you constantly maintained oil to as clean & dry as new oil whilst in use?
Maintaining hydraulic fluid to ISO levels cleaner than new oil standards; and constantly dry, will stop the need for the additives to have to kick in and can therefore extend the oils life – alongside good condition monitoring oil doesn’t need to be changed until its condition tells you to! And, with good practise this could be a considerable length of time.
So how can this be achieved?
Cellulose depth filtration – continues to be the finest, affordable level of oil filtration. Cellulose is a natural form of filtration that not only removes particulate but also moisture in one simple application.
With fixed filtration on a routine filter change – oil life can be extended to offer considerable financial savings through lowered oil costs, downtime, component wear and breakdowns and waste disposal.
KLEENOIL will remove 99.95% water and contaminant down to 3 microns absolute. ISO 4406 Cleanliness Code –14/9 NAS 1638 Class 6
Onsite On Hire, a new showcase launched to show the very latest equipment innovations available for hire is full of important equipment suppliers showing their very latest carbon-busting products. Running alongside UK Construction Week, the construction event (1-3 October NEC, Birmingham) Onsite On Hire will show the very best tools, compact plant and equipment.
Visitors to Onsite On Hire will be able to see examples of products including solar welfare cabins, to help meet net zero targets on construction sites, solar/ hybrid generators and solar lighting sets plus hire/rental of energy management software that reduces energy consumption by 50%, with matching CO2 savings and cost reductions of 50% too. Other equipment will include the latest battery technology on a range of tools and equipment. There will also be the
latest electric powered mini diggers and dumpers; hydrogen/electric mobile work platforms including the HR15 H2E, part of Niftylift’s new Hydrogen-Electric range and the world’s first MEWPs (mobile electric working platforms) with hydrogen fuel cell technology. These pioneering machines offer zero-emission operation and unparalleled efficiency, delivering exceptional productivity while minimizing environmental impact.
Designed for performance and sustainability, Niftylift are setting new standards for environmentally conscious operations, making them the ideal choice for modern construction and maintenance projects.
Another Niftylift product is the HeightRider 12 Narrow Electric (HR12NE) one of a new generation of environmentally conscious self-propelled work platforms. With the ability to be driven from the cage while elevated, it delivers an impressive working envelope from a narrow-aisle, manoeuvrable chassis.
The HR12NE’s compact dimensions, make it ideal for working in a wide range of environments, but it’s particularly well suited to industrial locations such as factories and warehouses, where ‘narrow-aisle’ operation is required.
Another exhibitor, TCP, has a range of plant machinery and eco alternatives – such as hydrogen fuel-cell lighting and power provision, which have been designed to help sites reduce their environmental impact and improve health and safety. The TCP Ecolite Lighting Towers have silent operation, no harmful outputs, no ground spill risk and zero risk of contamination.
MHM Plant Group specialise in the rental of Trime solar/hybrid generators and solar lighting sets with Trime UK handling all UK sales of their generators and lighting towers.
Trime Group is a company that specialises in the design and manufacture of sustainable, energy saving equipment for the worldwide rental markets.
They have developed a wide range of innovative, versatile, compact and modern products suitable for multiple applications. Trime UK has significant knowledge in the lighting tower, power generation and equipment cleaning markets with individuals completing over 50 years of experience in developing and marketing environmentally sustainable lighting, generator sets and water saving machinery.
The Altrad Belle E+ 82v Lithium-Ion range is their innovative emission-free series of products that uses the latest battery technology to provide high performance and quality without engine emissions or the requirement of an onsite power source. The range includes the well-known Minimix 150E+ Cement
Mixer, the best-in-class DC 300E+ 300mm Disc Cutter, PCLX 32E+ & 40E+ Plate Compactors as well as the DUX E+ Poker Drive Unit.
Speedy Hire, the UK’s leading provider of tool, equipment, and plant hire services, is set to impress attendees at the ‘Onsite On Hire’ showcase this October with the Speedy Hire [Innovation Zone]. It will feature a selection of Speedy Hire’s extensive range of innovative equipment including low and zero carbon world-first product , designed to enable the industry tosignificantly reduce its carbon footprint. The showcase will highlight partnerships with Speedy Hire’s renowned supply
chain partners, including Niftylift, TCP, Makita, Milwaukee, Altrad Belle, JCB, AFC Energy, and more.
Onsite On Hire runs alongside UK Construction Week with more than 250 exhibitors showing latest products with 200 hours of CPD available, 300 industry speakers and dozens of workshops providing 3 packed days of information.
To learn more please visit: www.ukconstructionweek.com/ onsite-on-hire
Vertikal Days 2024 will be held on 11th and 12th September at its new venue, Newark Showground. Located in Nottinghamshire, the showground covers 126 acres, with the Vertikal Days event held on the 1km long Vulcan Runway. The site offers visitors a new layout with the largest exhibition space, both outdoor and inside the Marketplace than ever before.
It will be the 17th year for the Vertikal Days event (18 years since its debut at Haydock Park in 2007) and the Organisers have confirmed that the 2024 show is already a ‘sell-out’, growing year on year, and becoming the largest lifting equipment event in Europe for 2024.
Visitors won’t be disappointed with lots to see
Visitors this year can look forward to new product launches from the major crane, aerial lift and telehandler manufacturers, as well as the latest technological advances, from software to ancillary products. Twenty-seven ‘first time’ exhibitors will join the 2024 event which include producers of aerial parts, glasslifting, the latest generator technology and many more.
A few exhibitors will give live demonstrations from their stands so
visitors will see the latest product developments in real time. Look out for Tadano’s new hybrid crane demonstrating its battery power, and Torquer’s new HALO system which is being demonstrated on an Ainscough mobile crane. On the aerial side of things, IPAF will have a demonstration area in the centre of the showground promoting safe loading and unloading practice which continues to be the number one cause of accidents currently reported.
The show is dedicated solely to the lifting and working at height industry, and an ideal opportunity for rental companies, utilities, major contractors and end users who visit the show to see and hear about the latest developments. Staying true to its roots, visitors will also benefit from everything being complimentary, from parking and entry, through to refreshments and catering.
A full 24-page guide to the event will be published in the September issue of Cranes & Access magazine, which will highlight the many new product launches and a complete guide to every exhibitor.
Located centrally within the showground, the Marketplace Pavilion is almost a show within a show and will include an even more comprehensive mix of companies
displaying the very latest in ancillary products and services related to cranes, access equipment and telehandlers, such as safety equipment, software, innovative components, rigging solutions, training suppliers, financial solutions and electronics. It will also feature the main Marketplace café serving complimentary tea, coffee and soft drinks all day – a great place to network or simply sit for 10 minutes.
Associations already signed up include LEEA, IPAF and the CPA who will all be welcoming members and non-members to their stands. Both IPAF and the CPA will be holding meetings and details will be released closer to the time.
With sunshine in the logo, the team are always hopeful of bright weather, but we’re assured by the team at Newark that whatever the weather, the quality and reliability of the ground will serve us well.
Visitors can register and download their badge from the website: www.vertikaldays.net
By Rebecca Phillips
I’ll start by saying that this trip is very personal for me.
No, don’t worry. There’s no vendetta. This was somewhat of a homecoming for me. You see, my grandfather was in fact Polish and I spent the majority of my life continually explaining how to spell my Polish surname. That, and getting identified as other Eastern Europeans as ‘farm strong’ when carrying heavy things.
Thing is, I’ve never actually been there. I know, I know. Not good. But thanks to LiuGong, I got the chance. And what a chance it was! Barrelling down the highway and enjoying the scenery, I was none the wiser to what was in store. I’d heard from other editors at other open days that LiuGong know how to put on a show, so it was safe to say my expectations were high.
The day started with brilliant blue skies. Seriously, there is nothing that beats a continental summer. A short bus ride took us to the customer centre, where we were greeted with so many smiling faces and a signature LiuGong welcome pack, and led to the lounge for a coffee and rest before the show kicked off. And what a show it was!
After a warm and welcoming speech from Harry Mellor, the machines began to emerge from the warehouse, amidst smoke and grandeur like a mighty dragon from its cave. One by one, the lean green machines paraded before us, driven and showcased by the product team themselves. They each drummed in that LiuGong were the first to champion and pioneer electric vehicles, and always ensure that they deliver ‘high spec as standard.’ This duty of care is not only to the environment, but also the operator.
Let’s take a look at the incredible line up.
Comfort and ergonomics are key to the 9027FE, including a mechanical seat and climate control, which is certainly essential on a day like the day of the LiuGong event. The telematics system is top notch, giving the operator a better understanding of their machine and its needs.
Specifications
Operating Weight: 2,750 kg
Rated Storage Capacity: 20.6 kWh
Motor Rated Power: 16.5 kW
Standard Bucket Capacity: 0.08 m³
Arm Digging Force: 12 kN
Bucket Digging Force: 20 kN
Rated Voltage: 44.8 V
Shipping Length: 4,160 mm
Shipping Width: 1,550 mm
Shipping Height: 2,450 mm
Drawbar Pull: 21.1 kN
Second up was the 820TE. Unique leading feature: it has the option of 3rd and 4th spool auxiliary, as well as 3rd spool constant flow. It even has 5-7 hours of run time!
Specifications
Operating Weight: 6,400 kg
Rated Load Capacity: 2,000 kg
Standard Bucket Capacity: 1.2 m³
Rated Storage Energy: 70.5 kwh
Peak Power: 60 kw
Standard Breakout Force: 61 kN
Standard Dump Clearance: 2,618 mm
Fastest Total Cycle Time: 9.8 S
Wheelbase: 2,150
Transport L*W*H: 5833×2060×2515mm
Third was the 856HE, the biggest and most popular of the BEV range and easily competes with the Volvo and CAT models of similar ilk. It’s the world’s first pure electric wheel loader and proves that diesel is not a forever solution.
Specifications
Operating Weight: 19,800 kg
Rated Load Capacity: 5,800 kg
Standard Bucket Capacity: 3.5 m³
Rated Storage Energy: 423 kwh
Peak Power: 180 kw
Standard Breakout Force: 162 kN
Standard Dump Clearance: 2,977 mm
Fastest Total Cycle Time: 9S
Wheelbase: 3,525
L*W*H: 8615×2970×3500mm
Finally, we saw the brand new electric excavator, the 922FE. It comes with several features that make it a multipurpose machine, including high rise cabs for waste and recycling and tilting cabs for demolition. It had a 423 kilowatt hours battery, achieving a test run time of between 8-10 hours. There has been extensive safety test including puncture and rumble test, and all electrical components are covered by a 5 year warranty.
It was explained to us: “If we use the conversion of 1L of fuel for 4 kilowatts,
and compare it to a diesel 92, which is very fuel efficient, we can expect 11L per hour. This translates to 40 kilowatts per hour, which when divided equals out to 8 hours run time. Using a 40 kilowatt charger, you can charge it in 10 hours, but in demanding applications you can use a fast charger as the machine can receive up to 150 kilowatts an hour, meaning you can charge it in 3 hours. So, it meets the demands of a diesel machine, but with 65% less maintenance.”
It’s site-ready from the factory, with the high spec as standard. Quietest internal noise on ANY 20-tonne excavator, with only 65 decibels. They have listened
to their clients and operators. You can change joystick sensitivity and response as every operator is different and it’s something LiuGong takes seriously.
Specifications
Operating Weight: 24,100 kg
Rated Storage Capacity: 423 kWh
Motor Rated Power: 165 kW
Standard Bucket Capacity: 1 m³
Arm Digging Force: 105 kN
Bucket Digging Force: 152.5 kN
Shipping Length: 9,910 mm
Shipping Width: 3,090 mm
Shipping Height: 2,985 mm
Drawbar Pull: 220 kN
Training and safety are taken very seriously at LiuGong, and the presentation demonstrated this perfectly. Each new slide showed in great detail exactly which regulations and training certification LiuGong not only abided by, but ensured that their new operators for the BEV range would also adhere to. It wasn’t simply in operation either, this went right down to things such as the rubber gloves and shoes they could provide to protect against electric shock, with every piece of equipment clearly demonstrated. The care and attention given to training was remarkable, and a model example for others.
Committed as ever to the green initiative, we were shown a range of the most popular types of charging device, in the hope that we can do away with diesel altogether and create a better environmental solution in construction. Both stationary and portable were demonstrated, to suit all needs, with not only their own on display, but also two from partnered companies Kempower and EKOenergetykr.
Kempower Movable Charger
• For maximum power, connect the Kempower Movable Charger to a 63 A socket, though 32 A is also compatible.
• Maximum of 40 kW for a single DC fast charging point or 20 kW for two simultaneously.
• Supporting both CCS2 and CHAdeMO DC fast charging methods, it offers one or two DC charging points.
• The Movable Charger features a user-friendly touchscreen and integrated RFID reader.
• Monitor charging sessions on your mobile by scanning a session-specific QR code on the charger screen.
EKOenergetykr DC Mobile Charging Station
• 30 kW DC
• Charging station – Mobile
• Maximum charging current 100 A
• 1 charging point
• Possibility of adjusting the output power with 1 kW step
• Intuitive and versatile 7″ touchscreen with RFID
• Works independently of charging service providers
• Supports all electric vehicles It was fascinating to know that customers of LiuGong have had electric machines that worked through the snow and lasted 8 hours before needing to recharge! So even in extreme conditions they can keep going. In fact, they had a customer in Warsaw whose machine lasted 9 1/2 hours!
It wasn’t just the machinery that was infinitely impressive. The hands-on, all-in approach that every member of the LiuGong team had was staggering. I’ve not known a product team to understand the machines so intrinsically, let alone drive them around with all the nerve of a true operator. ‘We’re not workmates, we’re family,’ said Graham. ‘It honestly never feels like work.’ It was certainly impressive watching the product team climb aboard the plant and put it through its paces, and refreshing to see everyone muck in.
Howard Dale came and sat with me just before the demonstration to ask about my thoughts on their new hub. ‘It’s not an HQ,’ he assured me. ‘We don’t go for all that here. We want something really inclusive and designed for the people. So, it’s our European hub.’ And there was a certain something in the air that really encapsulated this notion. It was easy to have a talk with any of the LiuGong team (in multiple languages might I add) and the facility itself was just as impressive. From its fastidiously kept warehouse to its training facility, there wasn’t an area that hadn’t been designed with the user in mind.
Undercover, in the canopy, and with the smell of an awaiting BBQ to tempt us, we were all ready for the demonstration of the 4 machines we came here to see. It was certainly a feast for the eyes, our heads turned every which way as the 4 fantastic BEV machines showed us what they could do at the hands of their product team. Not only were we treated to another parade from the stars of the show, but we also got to witness an excavator race between the 922FE and the standard diesel model, to see which would dig a trench the fastest in the allotted time. I’m sure you’re not surprised to learn that the 922FE won! Quite the fun spectacle.
When the demonstration was over, it was time to kick back and relax with a lovely craft beer and a plate full of BBQ food, and watch the football on the big screen.
Above and beyond doesn’t even begin to cover the extent to which the LiuGong team went to host us. I’m sure everyone one in attendance would agree that we were exceedingly well looked after. We came away, not just with a signature LiuGong goodie bag, but also a wealth of information about how LiuGong’s commitment to sustainable solutions is changing the industry for the better.
I take my hat off to you all (my new LiuGong snapback, that is!), and thank you for the invite.
Since its establishment in 1969, TVH has been a specialist in parts and accessories for a wide range of machinery. Headquartered in Waregem, Belgium, TVH has grown into a global leader renowned for its dedication to keeping customers’ operations running smoothly under the motto “Keeps you going.” Today, TVH is also a key player in the market for small earthmoving equipment, including backhoe loaders, compact track loaders, mini excavators and skid steer loaders.
TVHs global footprint
TVH’s influence spans the globe, with consolidated sales exceeding €1.6 billion in 2023. The company serves 82,000 active customers across 184 countries, a testament to its extensive reach and reliable reputation. With more than 5,000 employees from 63 nationalities, TVH is proud of its diverse and multilingual team.
● Inventory: 49.5 million known references and 1.12 million different stock items
● Branches: 90 globally
● Orders: 21,000 processed daily
● Shipment Rate: 94% same-day
“The secret to our global success lies in our ability to combine local expertise with an expansive, reliable network,” says Mark Rogers, General Manager UK / Ireland. “This approach allows us to provide personalised service while maintaining high standards of quality and efficiency.”
The journey of TVH
TVH’s journey began in 1969 with founders Paul Thermote and Paul Vanhalst in Belgium. The company took its first step towards international expansion in 1987 by establishing operations in France. By 1995, TVH launched its first e-commerce offering, highlighting its commitment to innovation and customer convenience.
Some key milestones in TVH’s history include:
● 1990: First TVH representatives started their activities in the UK
● 1999: The incorporation of TVH UK Ltd took place
● 2002: Acquisition of Queensland Forklift Spare Pty Ltd
● 2003: Acquisition of System Material Handling in the US
● 2012: Expansion of agricultural equipment parts portfolio through Tractiv Group (Bepco branded)
● 2020: Launch of small earth-moving equipment (SEM)
● 2021: Formation of a partnership with D’Ieteren Group, which acquired 40% of TVH’s shares.
TVH has gained an important foothold in the small earthmoving equipment market. This category includes backhoe loaders, compact track loaders, mini excavators, and skid steer loaders, essential for construction, landscaping, agriculture, and various industrial applications.
Customers benefit from TVH’s extensive product range and parts inventory, ensuring access to quality components and accessories.TVH offers several quality levels through both OEM and our own house brands and alternatives. The quality of our parts are backed by robust quality control measures and advanced testing tools. Packaging is designed to minimise damage in transit, and supplier reliability is rigorously assessed.
One of the factors that sets TVH apart in the market is its ability to assist customers with a wide variety of parts for many makes and products. This capability is crucial to keep machines such as backhoe loaders and mini-excavators operating efficiently, as downtime can be costly for companies
relying on this equipment. TVH’s inventory management and logistical prowess ensure even hard-to-find parts are readily available, reducing customer waiting time and minimising operational disruptions.
In the digital age, TVH has embraced e-commerce to enhance customer experience. Over 88% of TVH’s orders are processed online, offering customers 24/7 access to inquiries and orders. The e-commerce platform allows users to search for parts by make, model, serial number or technical specifications and offers detailed product catalogues and 360° product images with zoom features.
This digital convenience is complemented by TVH’s impressive logistical capabilities, processing over 21,000 orders daily with a 94% same-day shipping rate.
TVH’s e-commerce platform is designed to be user-friendly, allowing customers to quickly find the parts they need and place orders with ease. Detailed product catalogues and high-resolution images help customers make informed decisions to ensure they get the right parts.
The company’s investment in digital tools extends beyond e-commerce. TVH also offers technical support through its online platform, providing customers with expert advice and troubleshooting assistance. This comprehensive approach to customer service ensures that TVH not only supplies parts but also helps customers maintain and optimise their equipment.
TVH’s global presence is supported by a local footprint in 28 countries and 90 branches worldwide. This extensive network ensures that customers receive timely and efficient service wherever they are. The company’s sales force includes 562 internal sales staff and 202 external sales staff, all dedicated to providing exceptional customer service and support.
Having a local presence in so many countries allows TVH to understand and respond to the unique needs of each market. This local approach is crucial in the equipment sector, where different regions may have specific requirements and preferences. TVH’s ability to tailor its services and product offering to these local needs has been a key factor in its global success.
Moreover, the company’s extensive network facilitates faster delivery times, as parts can be shipped from the nearest branch rather than a central warehouse. This logistical efficiency is particularly important for equipment used in time-sensitive projects where delays can be costly. By ensuring quick and reliable delivery, TVH helps its customers maintain productivity and meet their deadlines.
A key highlight of TVH’s local presence in the UK is its facility in Kidderminster. The site includes a 19,000 sqm warehouse with 17,578 pallet locations, 139,160 pick bins, and 63,122 SKUs. This local stock ensures quick and efficient delivery of parts and services to customers in the UK.
The Kidderminster facility is a testament to TVH’s commitment to serving the UK market. The expansive warehouse space and extensive inventory allow for efficient storage and rapid dispatch of parts, reducing lead times and ensuring customers receive their orders promptly. This local presence also means that TVH can provide more personalised service, understanding the specific needs of UK customers and tailoring solutions accordingly.
TVH’s excellence in product quality is embodied by its renowned brands and partnerships. TVH’s house brand TotalSource offers a wide array of parts and accessories for material handling, industrial, agricultural, and construction machinery. Bepco specialises in parts for major tractor brands, while CAM attachments provides high-quality attachments for various industries and machines. Energic Plus, another TVH
brand, is known for its superior battery charging equipment, including chargers, jumpstarters, maintenance products and regeneration systems.
TotalSource, TVH’s flagship brand, is synonymous with quality and reliability. The brand covers a broad range of equipment parts, allowing customers to find what they need regardless of the type of machinery. This extensive product range is especially valuable for companies using or equipping a variety of machines, as it simplifies the procurement process and ensures consistent quality across all parts.
Bepco, another key brand under the TVH umbrella, focuses on parts for agricultural machinery. This brand’s expertise in tractor parts makes it a valuable resource for customers in the agricultural sector. The combination of specialised knowledge and a broad product range enables Bepco to meet the diverse needs of its customers.
CAM attachments, known for their high-quality add another layer of versatility to TVH’s offering. Attachments such as sideshifters, fork positioners and bale clamps increase the functionality of equipment, allowing companies to perform a wider range of tasks with the same machines. This versatility is particularly beneficial in industries like construction and landscaping, where flexibility and efficiency are crucial.
Energic Plus focuses on battery charging equipment. Reliable power sources are essential for the operation of equipment, and Energic Plus provides the tools needed to keep these machines running. From chargers and jump starters to maintenance products and regeneration systems, Energic Plus offers comprehensive battery management solutions.
“We understand that the success of our company only exists if we are a trusted source of products and services which help you to be successful,” says Mark Rogers. “That’s why TVH has partnerships with top quality brands.To name a few: Albright: APP, Baldwin filters, Curtis, delta-q, Denso, Parker, Rexroth,…”
TVH’s service portfolio is designed to maximise the efficiency and lifespan of equipment. The company provides in-house engineering, manufacturing, and technical support to help customers find the right parts. Its manufacturing services include custom manufacturing, CNC workshops, electrical, hydraulic, and mechanical assembly, and engineering services. TVH also offers remanufactured parts rebuilt to original specifications, providing significant cost savings and environmental benefits. Comprehensive repair services cover electronic, electrical, hydraulic and drive and steering parts, all with a one-year warranty. TVH’s electronics department in Belgium, the largest in Europe, is the best-equipped service centre for the repair of electronic components for forklifts, mobile elevating work platforms and industrial vehicles.
“At TVH, we believe in providing more than just parts–we offer solutions that extend the life and efficiency of equipment,” says Mark Rogers. “Our comprehensive services, from custom manufacturing to repair and remanufacturing, ensure that our customers can rely on us for all their equipment needs.”
TVH University offers hands-on technical training, combining theory and practical applications, available both digitally and in person. This initiative ensures that both customers and employees are well informed in the latest technologies and best practices.
In charge of your batteries
TVH is committed to continuous improvement and sustainability.
GemOne, a telematics solution company under the TVH umbrella, is a prime example of TVH’s commitment to improving its services. The platform provides real-time data on equipment usage, performance and maintenance needs, allowing businesses to optimise operations and improve safety.
Battery Supplies, another key part of TVH’s strategy, offers a wide range of battery management products and services. Reliable energy sources are essential for equipment operation and Battery Supplies provides the tools needed to keep these machines running. From batteries and chargers to accessories and maintenance products, Battery Supplies offers comprehensive solutions for all battery-related needs.
As mentioned above, their house brand Energic Plus focuses specifically on battery charging equipment. Energic Plus provides the tools needed to keep machines running, including chargers, jumpstarters, maintenance products and regeneration systems, and offers comprehensive battery management solutions.
Sustainability is a core value at TVH, with ongoing efforts to reduce its carbon footprint and enhance solar energy production. TVH’s dedication to environmental responsability is reflected in initiatives to reduce energy consumption, promote recycling and support renewable energy projects. These efforts have earned TVH certifications from UNITAR and awards from Ecovadis.
“TVH’s sustainability initiatives not only benefit the environment but also enhance our reputation as a responsible and forward-thinking company,” says Mark Rogers.
TVH’s commitment to technical knowledge, continuous improvement and customer experience has made it a trusted partner in the market. With a robust local presence around the world, an extensive product range, and a dedication to sustainability and employee development, TVH continues to lead the way in ensuring the efficient and effective operation of offroad equipment worldwide.
Whether it’s a lift truck, industrial vehicle, construction or agricultural machine, TVH is the go-to source for parts and services that keep the machinery running smoothly, proving that they truly “Keep you going.”
Managing Editor, Becks, spent a day with the lovely Lana at the Hillhead Quarrying and Mining Show 2024 in Buxton. Here’s what they got up to.
Since I started at Plant Planet, (which is exactly one year to the day as I write this, so I’ll assume you’re all wishing me a happy anniversary - thank you very much!) the famous Hillhead show has been a hot topic of conversation. Everyone I spoke to, whether colleagues or clients, had a story to share. So, of course, this had rather built it up in my mind. I had pictured a sprawling labyrinth of exhibits, each one a feast for the eyes, beckoning me further into the dusty depths of this incredible quarry.
To be honest, I wasn’t that far off. Lucky for me then, that I had the most perfect guide to hold my hand around the show (and very often, my camera bag) … Lana!
Highlights were in abundance on our girl’s trip around the quarry. After a magical moment of running towards one another enroute to Plant Planet’s stand and a long-awaited reunion hug, we saw reminders of Lana’s genius everywhere around the show.
None more so, it has to be said, than the PlantWorx 2025 stand. Lana very proudly showed me the PlantWorx logo she, alongside James Herring tidying the edges and Ben Wade throwing Lana the material so she could ‘do her thing’, carved by feel alone in her excavator, displayed in all its glory as the backdrop to their stand. I knew there and then that we were in for a tremendous day.
When we weren’t window shopping for new plant equipment (a Liebherr digger, Dressta dozer and Hitatchi excavator were all in the proverbial basket), we were meeting and greeting everyone in the business to see what Lana could do to help. Despite not being an influencer (her insistence not mine), Lana is always ready and raring to use her platform to highlight the incredible work and/or products that people have to offer.
One of our early stops, for example, was to Leo Workwear. This impressive brand truly offers clothing to suit everyone, be it for height, weight, maternity or religious reasons. Leo ensure that their wearers are not only safe in their high-tech workwear, but comfortable as well. “There’s no ‘one size fits all here,” said the sales executive for Leo. “Everyone is an individual and that needs to be taken into account.” Lana was particularly passionate about this, as ill-fitting hi vis has been a burden since the moment she became an operator. “Everything always swamped me. It makes it impossible to move properly in the cab when the sleeves have to be bunched up so much, they get in the way. And don’t even get me started on work trousers.”
No matter who we met, Lana went with purpose. There were so many amazing companies she wanted to highlight for so many different reasons. In her opinion, Takeuchi Global, for example, make the best joysticks of any plant cab Lana has worked in. “They just fit right in my hand. There’s something about them.”
And let’s face it, any endorsement from Lana is a good one to receive.
I’ve always maintained that Lana is genuinely one of the most respected operators out there and scurrying around after her at the show proved this tenfold. Everyone we spoke to had only the most incredible things to say about her, and most of my time was spent nodding in enthusiastic agreement.
James Herring, the Rototilt Ambassador, who had worked with Lana previously and is quite the photographer and operator himself, assured me that “you will never find anyone more skilled, or as kind, as our Lana.” I had the same resounding reaction when we bumped into Lana’s longtime friend and colleague, Craig Coleman, known as Spike, at the JCB stand. The two of them chatted away about their previous adventures, reminiscing about their once matching Hitatchi excavators and lamenting their lost time. Demo drivers, influencers, sales reps, it didn’t matter.
Not only did so many new people eagerly want to meet Lana for the first time, but so many others wanted to catch up. And I can truly understand why.
Just in the relatively short amount of time that I have known Lana, she has been incredibly patient when teaching me about her world. I came to this job a relative newbie, and there has never been a question Lana wouldn’t answer, or a lesson she wasn’t dedicated to teaching.
And that brings me back to the topic we finished on at the end of our previous edition of Life with Lana: Mental Health.
Having the privilege of listening to all these incredible discussions has not only shown what an amazing bond Lana has with the people that have been a part of her life, but also how it’s those working relationships that have made the difference when it comes to the longevity of people’s construction careers.
Being an operator, is tough.
Of course, there are those like Lana that make it look easy. But the skill and time it takes to become that great takes years, not to mention a toll on the old stress levels
and physical wellbeing. The hours are long, the work is hard; it’s not all smiles like you see at these big exhibitions when everyone is dedicated to putting their best foot forward. So, why is it then, I hear you ask, am I highlighting this again now? Well, I’ll tell you!
Every single company that Lana brought to light at Hillhead was a company that put the operator first. Whether it was the incredibly comfortable cab in the Merlo Roto 50.30, or explaining how instrumental the Lighthouse Charity had been for a colleague of hers, she ensured I saw the best the industry had to offer. Even when, sadly, Lana had a bone to pick with certain companies, be they training institutions who had let bad operators slip through the cracks or perhaps a hire company who hadn’t delivered on a promise, Lana was gentle in her approach when highlighting the flaw. People’s wellbeing is most certainly first and foremost with this remarkable woman, and I for one believe she sets a fantastic industry standard we should all adhere to.
Take note, readers. Take note.
We believe that, with something as important as your nance, you need the personal touch, a single point of contact, one person, from start to nish.
At Sheppex you work with a specialist who knows your industry, the equipment, its suppliers, and understands your needs. Someone who is on your side, working on your behalf to arrange the best deal for your business.
This is why Sheppex is different
We can support a wide range of credit pro les, and specialise in providing unique terms to suit your nancial requirements, these can include:
• VAT deferrals • Long-term borrowing • Low start funding
• Reduced deposits • Seasonal payments • FX transactions
If you are fed up with trying to contact your relationship manager, or the lengthy application processes, then give Sheppex a call. Call one of the team
“See me as part of your team, working with you to nd and secure the right nance for the plant and equipment you need.”
Jonathan Asplin Construction Finance Specialist
Our products include:
Hire Purchase
VAT Deferral
Operating Lease
Re nance
Commercial Loan
Management Buy Outs/Ins
Stocking Finance
Invoice Finance
In today’s rapidly evolving industrial landscape, the shift towards sustainable and ecofriendly solutions has become more crucial than ever. This trend is driven by the need to meet stringent environmental regulations, reduce carbon footprints, and improve overall operational efficiency. Manitou, a global leader in the manufacture of material handling, personnel lifting, and earthmoving equipment, has risen to this challenge by developing an impressive range of electric machinery.
The MRT 2660 e represents a significant advancement in telehandler technology, combining versatility, power, and eco-friendliness to meet the diverse needs of modern job sites. Here are the key specifications of the MRT 2660 e:
● Lift Capacity: 6,000 kg
● Maximum Lift Height: 26 metres
● Maximum Reach: 21 metres
● Battery Type: Lithium-ion
● Battery Capacity: 360 Ah
● Charging Time: 4 hours (with fast charger)
Designed to excel with operator comfort and safety in mind, the MRT 2660 e is perfect for construction, renovation, industrial maintenance, and logistics. Its electric drivetrain ensures zero emissions, making it suitable for urban areas with stringent air quality regulations. Additionally, the low noise levels of the electric motor enhance the working
environment, particularly in noise-sensitive locations such as residential neighbourhoods, hospitals, and schools.
The 360-degree rotating capability of the MRT 2660 e allows operators to manoeuvre the machine with ease, reducing the need for repositioning and thus increasing efficiency. This feature is particularly beneficial in confined spaces where traditional telehandlers might struggle. The high lift capacity and extensive reach make it a versatile tool for a wide range of tasks, making it an invaluable asset on any job site.
Maximum versatility in the use of energy according to your working conditions. You have the option of adding an extra battery (in 100% electric mode) or a E-Xtra generator* (in hybrid mode). Your standard range up to 4 hours** can vary depending on your choice of option: up to 8 hours** with the additional battery or continuously with the E-Xtra generator.
*Heat engine that recharges the battery.
**Working autonomy depends on many factors: type of application, work cycle, weather, comfort options such as heating, ventilation, air conditioning and lighting, etc.
The 180 ATJe articulated boom lift is a prime example of Manitou’s commitment to combining performance with sustainability. Key specifications of the 180 ATJe include:
● Working Height: 16 metres
● Horizontal Outreach: 8.3 metres
● Lift Capacity: 230 kg
● Battery Type: AGM (Absorbent Glass Mat)
● Battery Capacity: 48V, 460 Ah
● Drive Speed: 6 km/h
Opt for a versatile, high-performance all-terrain lifting solution with the 180 ATJe 100% electric aerial work platform! Take advantage of its performance to optimise your operations on rough, uneven or muddy terrain or even indoors thanks to its zero emission energy. Its 4 steering wheels allow you to evolve in the most difficult terrains.
Equipped with transmission decks, this Manitou model has all the features to facilitate your work at height. Spacious and resistant basket, important ground clearance, active oscillating axle, 4 driving wheels, 4 steering wheels, continuous rotation as an option, and compared to the previous model, an increased load capacity of 408 kg.
Manitou’s MT 625 e compact telehandler is engineered to meet the needs of modern construction and industrial sites with a focus on sustainability and performance. Key specifications of the MT 625 e include:
● Lift Capacity: 2,500 kg
● Maximum Lift Height: 6 metres
● Battery Type: Lithium-ion
● Battery Capacity: 240 Ah
● Charging Time: 2 hours (with fast charger)
The MT 625 e’s compact design allows for excellent manoeuvrability in confined spaces, making it ideal for urban construction sites, agriculture, and industrial applications. Its electric motor provides smooth and responsive operation, enhancing operator comfort and precision. The zeroemission operation of the MT 625 e is particularly beneficial for projects with strict environmental regulations, ensuring compliance without compromising performance.
The quick charging time and durable battery of the MT 625 e enable it to handle demanding tasks without significant downtime. The low noise levels of the electric motor contribute to a quieter and safer work environment, reducing noise pollution and improving overall site conditions. The first 100% electric Manitou fixed telescopic handler, dedicated to construction applications!
The SE 0808 electric scissor lift is one of Manitou’s latest innovations, designed to provide safe, efficient, and environmentally friendly solutions for working at heights. Key specifications of the SE 0808 include:
● Working Height: 8 metres
● Lift Capacity: 230 kg
● Battery Type: Lead-acid
● Battery Capacity: 225 Ah
● Platform Dimensions: 2.3 x 0.8 metres
● Drive Speed: 4 km/h
The SE 0808 is engineered to meet the needs of various industries, including construction, maintenance, and facility management. Its compact design allows for easy manoeuvrability in confined spaces, while the robust lift capacity ensures it can handle heavy loads safely. The zero-emission electric drivetrain makes the SE 0808 perfect for indoor use or environmentally sensitive areas, aligning with modern sustainability goals.
The low noise levels of the electric motor also contribute to a safer and more comfortable work environment. Additionally, the scissor lift is equipped with non-marking tyres, making it suitable for use on delicate flooring surfaces. The SE 0808 features intuitive controls and a user-friendly interface, allowing operators to perform tasks with precision and confidence. Safety features such as emergency stop buttons, platform overload sensors, and guardrails ensure that workers can carry out their tasks securely.
The shift towards electric machinery is driven by the need for sustainability, efficiency, and compliance with environmental regulations. Here are several compelling reasons why businesses should consider Manitou’s electric range of machinery:
1. Eco-Friendly Operation: Manitou’s electric machinery produces zero emissions, making it ideal for indoor use and projects with strict environmental regulations. This helps businesses reduce their carbon footprint and contribute to sustainability efforts, enhancing their corporate social responsibility profile.
2. Reduced Noise Levels: Electric motors are significantly quieter than internal combustion engines, which is beneficial for work in noisesensitive areas and contributes to a safer and more comfortable work environment for operators and nearby personnel. This reduction in noise pollution can also improve worker satisfaction and productivity.
3. Lower Operational Costs: Electric machinery typically has lower maintenance requirements and operating costs compared to diesel or gasoline-powered equipment. This can result in significant savings over the machine’s lifetime, making it a financially sound investment.
4. Enhanced Precision and Control: Manitou’s electric machinery is designed to provide smooth and precise operation, which is critical for tasks that require accuracy and finesse. This improves overall productivity and reduces the risk of errors or accidents, leading to higher quality work and fewer delays.
5. Versatility and Flexibility: With a range of models designed for various applications, Manitou’s electric machinery can handle a wide array of tasks, from construction and maintenance to material handling and industrial operations. This versatility makes them a valuable asset for businesses looking to optimise their equipment fleet.
6. Innovative Technology: Manitou incorporates the latest advancements in battery technology and electric drivetrains to ensure their machinery offers superior performance and reliability. This includes fast charging times, long battery life, and robust lifting capacities, providing businesses with the tools they need to meet demanding operational requirements.
7. Safety Features: Safety is a top priority for Manitou, and their electric range includes numerous safety features to protect operators and enhance overall job site safety. This includes emergency stop buttons, overload sensors, and stable platform designs, ensuring that workers can carry out their tasks securely and efficiently.
8. Ergonomic Design: Manitou’s electric machinery is designed with operator comfort in mind, featuring adjustable seats, easyto-use controls, and excellent visibility. This reduces operator fatigue and improves overall productivity, leading to more efficient and effective operations.
9. Reduced Carbon Footprint: By choosing electric machinery, businesses can significantly reduce their carbon emissions and contribute to global sustainability goals. This not only helps the environment but also enhances the company’s reputation as a responsible and forward-thinking organisation.
Manitou’s electric range of machinery, including the MRT 2660e rotating telehandler, the 180 ATJe articulated boom lift, the MT 625 e compact telehandler, and the SE 0808 electric scissor lift, represents a significant advancement in sustainable construction and material handling solutions. These machines offer numerous benefits, including eco-friendly operation, reduced noise levels, lower operational costs, enhanced precision and control, versatility, innovative technology, safety features, ergonomic design, and a reduced carbon footprint.
Choosing Manitou’s electric machinery is not only a step towards a more sustainable future but also a strategic decision that can enhance operational efficiency, productivity, and safety. As industries continue to evolve and prioritise environmental responsibility, Manitou’s electric range provides the tools necessary to meet these challenges and excel in a competitive market.
For more information, please visit:
Rebecca Phillips and Lorna Cowlin travel to Wolverhampton College for another fantastic Go Greener Day with Sunbelt Rentals UK.
Let me start by saying, that right from the word go, Industry Corner has been my baby. Travelling far and wide to interview the best in the business has been so incredible, and every day I’m grateful that I was allowed to take this chance to launch such an amazing interview section in Plant Planet. So, naturally, I was very excited to be reunited with our friends at Sunbelt Rentals UK after their incredibly successful Go Greener Day last year, where the focus was sustainability in the construction and hire world. But you know what? It gave me the opportunity to step back and let someone else experience it for the first time.
There is nothing quite like a Sunbelt Rentals open day. It was actually my very first trip out of the office when I began that long year ago (where has the time gone, hey?), and it was being with this incredible company that my love of all things ‘interview’ truly sparked. So, what better starting point than that for our new writer, Lorna Cowlin, to make a start…
When I received a text from my best friend, our managing editor Rebecca Phillips, saying “want to go to Wolverhampton for your first work trip?”, I immediately messaged back “YES!” without even needing to know anything else. I was ready for my first big girl trip with my big girl job; officially becoming a woman in construction! So, when it came to the big day, I was raring to go.
I’ll admit, being new means my knowledge is limited, but my fascination is high; I’m keen to learn anything and everything I can in this field. So, when Becks and I arrived at the Wolverhampton Construction Skills College to attend the sustainable technology event with Sunbelt Rentals, I was like a kid in a candy shop. All around me were faces I had yet to meet, machines I had never seen before and noises I had only ever heard on a building site. Thank goodness I had Becky with me; I was too entranced to say anything!
Now, I must admit that it is hard to get my head straight with this event; there was so much innovative tech, inspiring stories and new information that it’s quite overwhelming to wrap my new-to-construction head around! But, as with anything, I suppose the best place to start is the beginning…
First stop was to meet with the lovely Hannah Pascoe, PR and Social Media Manager at Sunbelt Rentals. We enjoyed a catch-up, and she made me feel right at home. She explained the layout of the show, told us that we’d meet up with Charlotte Evans later on in the day. Before I knew it, Becky and I were off exploring.
We met with Steve Newton from Powered Access, a strong team of personable specialists. The years of experience of everyone in the team would make 100 years when combined! Not only did Steve explain everything he and his team did, but he also gave demonstrations and showed us the machinery and other kit.
Particularly interesting was the ‘little black box’, otherwise known in the industry as OverWatch™ by EQSS, which is secondary guarding for use with Scissor Lift EWPs. It works on the premise of detecting the operator’s position and movements, with respect to the EWP direction of movement, and uses the latest LIDAR and Inertial Measurement technologies, coupled with a powerful Wi-Fi enabled processor running EQSS proprietary AI and advanced sensor fusion algorithms. The OverWatch™ is the first truly usable, robust, unobtrusive and cost-effective secondary guarding solution presented to the market to date for Scissor Lifts.
• Real time measurement of the operator
• Spatial movement measurement of the EWP
• Smart AI algorithms for crush detection events
• Adaptive sensor fusion code for enhanced detection
• Small, robust and non-intrusive external sensor
• Wi-Fi configuration and diagnostics as standard
• Internal web page accessible by Wi-Fi
• Audio output with synthesised voice commands
• Multicolour RGB notification LED
• Simple aftermarket integration and installation
• Voice notification of movement direction
• Duck Through Doorway (DTD) Detection
• Wide operating voltage for 12V and 24V machines
• Optical inputs and solid-state highpower output
• Patented Concept and Technology
• Measurement of individual operator on dead man trigger
• Expandable hardware architecture for custom OEM control
• Real time data logging with event playback 8000+ samples
• Internal clock for time stamped event logging
• High Density, UV resistant ABS construction
• Rapid installation < 20 minutes for OEM supported models
• Automatic calibration, diagnostics and self-testing
• Functional Safety architecture to SIL1 / Plc
With the smell of pizza not too far off, we bumped into Steve again; only this time, with a different machine… a scissor lift. Becky and I gazed up into the sky to see Steve on the lift, nearly the same height as the two-storey college building next to him. Lowering himself, he came back down to the ground, stepping down the ladder to be back at our level, uttering four words only: “Wanna have a go?”
With jittery legs, I passed Becky my bag and climbed the ladder onto the lift. The higher we went, the smaller Becky got. Steve then handed me three bean bags and pointed to a bucket that was all the way back down on the ground.
I threw the first one but missed.
I threw the second one… it got in!
I threw the third one… and got that one in too!
Two out of three isn’t bad at all, especially when Becky went up and only got one. Not that it’s a competition or anything! But… I won.
The victory seemed short-lived, however, when Steve then pointed out my very clean steel-toe-capped boots, especially in comparison to Becky’s dirtied, well-loved ones, only further emphasising that I was just a small girl in a brand new, big world of construction!
Features
• With optional hydraulic levelling jacks, uneven terrain is no problem
• Enjoy enhanced versatility with true multi-terrain capability
• Double the duty cycle of other scissor lifts so you can stay on the job longer
• Boost efficiency with direct electric drive
• Rugged terrain tyres take you anywhere you want to go
• Minimal emissions
• Superior performance on or off slab
Specs
Make: JLG
Model: M4069
Height: 2.83 m
Width: 1.75 m
Length: 3.07 m
Weight: 5700 kg
Batteries: 8 x 6V, 370 A-h
Drive Speed Lowered: 3 mph
Drive Speed Raised: 0.5 mph
Gradeability: 35 (2WD) / 45 (4WD) %
Ground Clearance: 0.2 m
Hydraulic Reservoir Capacity: 32.18 Litres
Max Lift Height: 12.19 metres
Max Platform Height: 12.19 m
Maximum Drive Height: 9.14 m
Platform Capacity: 360 / 120 Extension kg
Platform Extension Length: 0.91 m
Platform Height Lowered: 1.73 m
Turning Radius (Outside): 4.88 m
Wheelbase: 2.32 m
Working Height: 14.19 m
Remove DIRT & WATER in the same mobile application
Affordable and easy to change out replacement cartridges
Kind to the planet – as a natural, sustainable product
Save waste costs, replacement value and labour
Simple ‘plug and play’ application
Site permanently on a problematic machine or on a rotational cleanse across your fleet
Whether it be to tackle one off contamination issues, or as a permanent fix to heavy use equipment to protect pumps, valves & cylinders etc.. or as a rotational cleanse on off-hire equipment.
KLEENOIL offer a completely free trial at your site ; with before and after independent oil analysis.
On the stand next door, Glyn Matthews then showed us this amazing app that brings site planning to real life! Sunbelt Rentals AR Equipment Visualiser is so user-friendly, and such a clever idea when it comes to construction machinery! Furthermore, to my feature article on AI in construction, this Sunbelt Rentals app is beyond innovative, super immersive and incredibly constructive. (I promise that awful pun was completely unintentional!) It uses augmented reality to create a 3D image of the equipment. The app helps you go through all the machines, equipment and tech you can hire from them to find the right item for you. Simply click on the item you would like to hire, then select “Place in Augmented Reality” and tada! That item is now on your camera, an AI version standing in front of you. It also includes other features such as virtual walkarounds and a vast amount of useful information about the equipment to make sure you make the right decision. Aside from my child-like glee, I can only imagine how incredibly beneficial and useful this app will be, making things so much easier.
Once again, I could barely say anything aloud as my brain was absorbing so much, but absolutely loving every minute. Since then, I have been playing around with the app when in the office, not only having a lot of fun with it, but also learning a lot and picking up the names of all the equipment. Five-star app from me!
Features
• Real-World Visualisation - Seamlessly place 3D models of equipment in your environment using your phone.
• Interactive Experience - Explore features and walk around virtual equipment for perfect placement.
• Detailed Information - Access essential specifications for informed choices.
• Easy Enquiries - Found the right tool? Enquire directly within the app.
• Enhanced Decision-Making - Visualise equipment in your space for accurate planning.
• Ease of Use - This intuitive app is user-friendly, regardless of tech expertise.
• Innovative and Free - Experience the latest in AR at no cost.
• Eco-Friendly - Minimise wrong deliveries, reducing costs and emissions.
Use these QR codes to download the app!
The wonderful Charlotte Evans, Senior Marketing Manager at Sunbelt Rentals gave us a tour around the rest of the site, pointing out many more incredible machines that Sunbelt Rentals provide. We even got to see the hydrogen generator; the zero-emission hydrogen power generator which Sunbelt Rentals are bringing to the market to help support customers with their net-zero goals
Known as ‘the ally of energy transition’, it is completely zero-emission, only releasing hot water and filtered air. It is also compatible with gas or diesel generators or can be hooked up to the grid, enabling end-users to make that allimportant transition at their own pace.
Specs
Dimensions - 3300 x 1100 x 2252 mm
Mass - 3.3 tons
Power - 110 kVA / 88 kW in ESP, 100 kVA / 80 kW in PRP
Output voltage - 400 VAC / 480 VAC
Frequency output - 50 Hz - 60 Hz
Protection index - IP43
This equipment had a back-up generator that was only used six hours over six months because the battery provided the extra power needed!
“Towards the back end of last year, we brought in different experts and suppliers with regard to hydrogen technology,” Charlotte told us. “So, we had EODev and we brought in hydrogen fuel supplier Hydrologic, who, I would say, are probably the premier supply chain partner. So, if you want to use hydrogen, Hydrologic would help you install it onsite as well as help you do your health and safety assessments. For us, we’re positioning ourselves as facilitators who can bring together the necessary parties and provide you with hydrogen generators. We can bring in Hydrologic. We can bring in fuel partners. We can bring in our own experts to design the whole solution for you. Sunbelt Rentals is the perfect partner.”
We also revisited (well, Becks did, it was my first time) Sunbelt Rentals’ incredible range of solar-powered options, including solar-powered CCTV!
Features
• Rapid Deployment: Quick and hassle-free setup
• Video Verified External Alarm System: Reliable security with verified alerts
• Monitored at ARC or Self Monitored: Choose the monitoring option that suits your needs
• Completely Wire-Free: No need for complex wiring or power sources
• Battery Operated: Ensures continuous operation
• Live Audio Announcements: Real-time audio feedback for added security
• Site-Specific Design: Tailored to your unique requirements
• Solar Charging for Control Unit: Eco-friendly, energy-efficient operation
• Warning Siren: Deters potential intruders and enhances security
• Weekly Rental Charges: Convenient and flexible rental options.
Specs
Make: Trime
Model: X-Eye Sunbelt Rentals Solar Height: 2482 mm
Width: 1150 mm
Length: 1150 mm
Weight: 1050 kg
Audio Horn: For out of hours intruder challenge
Battery Expected Cycle: 500
Battery Expected Life: 5,000 hrs
Battery Power Pack: 24V DC – 400 AH
Battery Quantity: 4
Battery Type: AGM
Camera: 4 x 60m White Light Static (4MP)
Colour: 1 X IP 4mp Turret Colour Camera
Detection Analytics: 8ch IP NVR Transmitter Recorder
Green Product: Yes
Mast Max Height: 6 m
Mast Rotation: Static
Solar Panels: 3 x 350 W
Despite the skies looking very grey and the wind picking up, it didn’t dampen the mood. Everyone was happy explaining, showcasing and demonstrating, and I was taking in as much as I possibly could.
Lunch was then served, and we chowed down on the super tasty pizzas that they provided, and before we knew it, Becky and I were off exploring again.
The Pegasus Elite ensures maximum safety and efficiency, ideal for demanding construction environments.
Anti-Tilt System-Pro: Advanced anti-tipping with dynamic load calculation.
Automatic Boom Movement: Six modes (Normal, Soft, Heavy, Eco, Wall, Floor) for optimised and safe movements.
Load-Sensing Pump: Dynamic adjustment based on working conditions.
Enhanced Cab Features: Dual display with real-time safety alerts and intuitive controls.
Soft Motion Function: Slows movements to reduce dynamic effects and shocks.
Easy Work System: Auto-adjusts loading capacity based on outrigger position for stability.
Operator Visibility and Control: 12’’ display for monitoring, with up to three cameras for around-vehicle monitoring.
Safe Access and Ergonomics: Four access ladders, walkway, and ergonomic controls for safe entry and operation.
LED Work Lights and Backlit Keypads: Enhanced visibility in low-light conditions.
Reclining Seat: Facilitates overhead operations for added safety and comfort.
We spent a large chunk of time with the Head of Social Impact, Sarah MacGregor, and Social Impact Managers, Jimmy Scott and Swati Patel. We didn’t get to meet Genna Booth, but we also heard from Sarah about all her hard work! This sector strives to encourage people to achieve their aspirations within their careers and life by supporting them. They help give them sustainable employment regardless of background. Hearing the passion from their stories, telling us why they do what they do and how it helps the children and adults they work with, I couldn’t help but feel emotional and in awe. This was truly inspiring work, and it was an utter privilege to hear their mission.
Jimmy Scott works on the Veterans Programme, which, whilst working alongside ‘Walking with the Wounded’, ‘Project RECCE’ and ‘Careers Transition Partnership’, help give veterans employment within this field, giving them necessary and transferable skills.
Swati Patel works with schools and colleges to help the children who are unsure of their future to feel more prepared. She educates them in important life skills, such as job interviews and work experience, ending in guaranteed employment for some of the students at the end of the programme.
Sarah MacGregor oversees a huge project, helping convicts and those in prison to retrain themselves to a truer lifestyle, settling back into the world of employment and working hard for a result. She explained to us that once some convicts are released, they reenter the world with very little money to their name; the money given to them sometimes isn’t even enough to get them back home. It even plays into Sunbelt’s environmental values, as the work they do with UK prisons has offenders planting and caring for trees, providing them not only with additional skills and values, but also a fund to aid them in their next steps after release. Sarah and her team provide a scheme that helps instil confidence into these people and despite their initial wrongdoings, gives the underrepresented a chance for redemption, a chance to live a fulfilling life.
They sum it up really well in their Social Impact brief:
Everything we do is the right thing. We are committed to working responsiblyit’s in our DNA.
“Our Sustainability Plan 2025 aligns with the UN Sustainable Development Goals and our sustainability strategy, Our Planet. We are committed to creating social impact and to achieving lasting legacies through our work. We collaborate with you and with our suppliers to help innovate and shape the next generation of environmentally friendly equipment.
We work with local communities around the UK, we help charities and help develop sustainable careers for disadvantaged groups. Our dedicated social impact team is working in line with Government recommended best practice, to capture the social value that we create.”
All of these stories echoed the same feeling to me: hope. Not only do Sunbelt Rentals provide services that make the world of construction easier to navigate, they also promote hope and wellbeing, highlighting the importance of a happy, settled future. It genuinely warmed my heart hearing about circumstances I was otherwise blind to prior and how they are overcoming it all. People are being helped, trees are being planted, the environment is in good hands. It further emphasised to me that if we all play our part, we really can make a difference. I walked away from their stand feeling full and light. Not only were Becky and I incredibly wowed by them, we were also recharged and motivated. All their hard work in the Social Impact Programme has also inspired a brand new section in Plant Planet… just goes to show you what happens when people come together as a collective! (Stay tuned for that new section, we can’t wait to share it with you!)
With achy feet, a full belly and a buzzing mind, Becky and I headed back to the minibus. We looked at each other with tired eyes and big smiles, knowing that our travels to Wolverhampton had been more than worth it.
I maybe a small girl in a big world of construction, but it’s no longer a scary world I know nothing about. It’s a world that is beckoning me in, telling me that there is so much more to learn.
Didn’t she do amazing folks?
I feel it’s appropriate to say a big thank you to Sunbelt Rentals UK. Not only did they welcome us both with open arms, provide us with incredible content, lunch, and a work buzz that lasted us all week long, but they have also inspired another new section for Plant Planet. I don’t want to give too much away right now, dear readers, but keep your eyes peeled in our December issue. You won’t be disappointed.
By Lorna Cowlin
So, when I was told that I’d be writing about artificial intelligence in construction, all I could think of was… eek. I also thought about how, instead of robots, it could in fact be diggers, cranes and excavators that come to life and fight against us. This is when I realised, I had perhaps taken it a little too far, and needed to research this a little more…
It’s hard not to feel uneasy when artificial intelligence (AI) is mentioned. The phrase can conjure up a sense of dread, with many of us worried that maybe one day this evil force will take over the world as we know it. Perhaps some of us have watched one-too-many sci-fi films about robots taking over human civilisation!
As a writer, it’s hard not to feel threatened by AI, especially with the rise of ChatGPT. It’s certainly something to keep a watchful eye on. We all seem to be unsure of whether it could help, or hinder, us. Artificial intelligence is a very broad term when it comes to technology, but to put it simply, AI is
When someone mentions ‘artificial intelligence’, I instantly think of the multiple Hollywood blockbusters about robots that although originally are made to help us, actually turn against us.
rather clever technology that enables computers and digital devices to learn how to perform tasks that humans can do, all minus one thing: a human touch. It’s developed to learn things that would normally require human intelligence, and after repeating said action over and over, at least a million times (and no, I’m not exaggerating!), this ‘machinelearning’ process has been completed, and continues to keep learning. In terms of construction, this can come in very handy…
By analysing the date from both electrical and building systems, AI can predict equipment failure and when maintenance will be needed. Using the machine-learning process, the system can pick this up prior to any dire need, alerting the issue before it has become a problem, therefore preventing mass delays. Whilst we all wish we could be this clever, we must admit that sometimes, our technology can be smarter!
A few years ago, when watching Mike Woolridge’s Royal Institution’s Christmas Lecture, I seemed to forget about my initial fears and found myself deeply fascinated in how these complex pieces of tech could learn nearly equal to that of a human brain. Woolridge discussed how even though AI still seems like such a futuristic concept, there’s so much around us in our day-to-day lives that we’ve become so accustomed to, it would be strange to think of a world without it.
However, it’s so easy to discuss the downsides to AI… I don’t want to get bogged down by that! When it comes to AI in construction, there’s an awful lot to be celebrated, and it’s worth noting the positive impact it can have in this industry. So, why do we need it? AI in the construction industry has many key ways in which it can help, but here are the top four most beneficial.
Not only can AI use its machine-learning technique to understand the process in which we do things, it can also help us out in terms of stock flow and scheduling! It can be used to allocate use of labour and materials, making the construction process run smoothly, thus making it more efficient and cost-effective. Not only this, but it keeps the
continuation of any project afloat, helping to prevent the prospect of failure or incompletion.
With AI’s machine-learning feature, this can help improve the quality of the work being done with minimal to zero human effort! By using AI-powered sensors and systems, defects and mistakes can be identified much quicker than a human could ever notice. This then assures that the right people will be addressed, and the issue overcome. This makes the process much faster all round, causing less delays and saving money.
Not only can AI learn how to do the job at hand within milliseconds, it can also recognise health and safety risks as well, identifying the risk before it has even happened. AI-powered cameras and sensors, either on the machines or sometimes even worn by workers, are there to monitor safety hazards and alert workers and other members of staff of the potential threats and dangers. AI can also register when safety protocols aren’t being acted out by the staff, so can signal when that needs to be improved. As a result, this can help reduce onsite accidents.
Unfortunately, there are a lot of jobs that can become tedious and repetitive, and therefore take away the focus from the more demanding roles. AI can be programmed to take over these roles, allowing the continuation of the project to run smoothly. It can be used to take data from a building system and analyse it to optimise air quality (especially indoors), energy efficiency and other important, yet trivial, tasks. This allows for better designs, construction and efficiency. This can also increase the length of projected time of a project, the extended lifespan allowing for better renovations and a more efficient outcome overall.
Like I mentioned earlier with Woolridge’s lecture, AI is around us even if we don’t realise it. Even little ole’ me, a content creator who works in an office, uses AI in my day-to-day job, and I certainly take it for granted as it’s so easy to miss! It can be as simple as sending an email with autocorrect, or social media platforms tailoring its approach to match its algorithm with my likes and interests on my feed. Without any of that, our jobs would be so much harder, so when it comes to the bigger industries and companies, it’s virtually impossible for them to not lean towards AI to lend a helping hand.
So, if AI can help office jobs like mine, then it can certainly help much larger scale jobs when onsite with heavy construction machinery! Down to the simple tasks such as robotic bricklaying and 3D printing, up to larger scale tasks
such as demolition, using heavy machinery and bigger onsite projects, the overall conclusion seems to show that AI is beneficial, suggesting it to be more of a friend rather than a foe.
AI has the capabilities to fuse together layers within the working world. Whilst the future for AI remains unclear (and perhaps we are right to be wary of it) it’s very unlikely it will replace the human workforce, only enhance. It has the power to alter the way we work, creating safer environments in the construction industry, making it more efficient.
Personally, I believe the future of AI is bright and promising! Within time, it’ll grow to become an integral, vital and valued part of our culture without disrupting or taking away any of our current harmony. Forget about those silly sci-fi films, forget about the idea of robots taking over our world, and embrace the positive changes within technology! It’s so easy to forget about how far technology has come even in the last twenty years, let alone since the first groundbreaking inventions. It unlocks new possibilities and opportunities to advance and to make our work systems, and perhaps even the world, a better environment. When used wisely, AI can help boost our creativity, safety and intelligence. We simply don’t know how far it could expand our own mind, our own horizons.
Whilst I agree that construction has, and will always be, a human business, I do also think that we shouldn’t shy away from what AI has to offer. Let’s embrace it.
You’ve worked hard for years. There’s been ups and downs but it’s all gone well. You’ve built the business, taken some risks, looked after your team and your customers and your family. So well done.
But maybe you’re thinking “what about me’’? What about the future, financial security, more time with the family, travel, leisure and yes, less stress?
Maybe it’s time to sell?
We can help. The Hire Exchange is the only specialist business sale advisory for the hire sector. We understand the market, we know the people and the right buyers for your business so we can optimise its value.
If you want know more about selling your business call Chris Harvey on 03303 230643, in strict confidence or visit www.thehireexchange.co.uk or email: info@thehireexchange.co.uk.
Jonathan Guest, the founder of Safety Shield Global, has spoken of his ‘unforgettable honour’ in meeting His Majesty, King Charles III at a special reception for winners of this year’s prestigious King’s Awards.
In recognition of his unstinting work on the delivery of construction site safety solutions, the Cheshire-based CEO joined business leaders from around the country at the royal reception at Windsor Castle.
Considered to be the highest commercial accolade possible for any UK business, the King’s Award was presented to Safety Shield Global for its ground-breaking work in developing an Artificial Intelligence safety system for plant machinery.
Devastated by the death of a close friend who had been crushed by an excavator on a construction site, Jonathan vowed to come up with a way to make the industry safer for its on-site workforce.
The tragic incident set Jonathan on a path to create a solution that would shield the countless vulnerable workers like his friend from the risk of People Plant Interface (PPI) – incidents of machines colliding with people.
From the very early tag detection systems using Radio Frequency Identification, to the use of AI human-form identification developed through technology initially utilised for collision avoidance in the automotive industry, the process for his research and development team has been a long but rewarding one, stretching back more than a decade.
Today’s Safety Shield technology has been fitted to more than 5,000 plant and machinery across the UK and Ireland, with zero people plant interface accidents reported. Its reliability has been confirmed through six ISO certifications and has been awarded an accuracy measure of 99.6% by independent testing bodies.
Acting as a third eye for the operator, visual and audible alerts are activated depending on whether the human form is within the amber (outer) zone or red (inner) zone, at which point a collision is imminent.
Proud recipients of a King’s Award for Enterprise: Innovation, Safety Shield earned royal recognition for their efforts in creating a safer construction site workplace as Jonathan looked back on what has been an incredible journey of discovery.
Speaking of his meeting with King Charles III, Jonathan comments: “Meeting King Charles at Windsor Castle was an unforgettable honour. His remarkable ability to connect with people was testament to his commitment to fostering enterprise and innovation.
“Windsor Castle provided a majestic backdrop for the reception and shaking hands with King Charles and discussing how Safety Shield is leading the way in construction site safety and innovation and the reasons for winning the King’s Award was a surreal experience that I will cherish forever.
“I am deeply honoured and humbled that Safety Shield Global has been awarded with The King’s Award for Enterprise: Innovation. This award represents recognition of the resolution, vigour, and dedication of our team.”
The unique human-form Artificial Intelligence detection system continues to deliver on the promise that CEO Jonathan Guest made to himself more than a decade ago.
Having joined the construction industry at the age of 16, Jonathan quickly worked his way up from labourer to a large diameter pipe layer for some of the UK’s leading pipeline and tunnelling companies, before starting his own construction company at the age of 20.
Running his business for 13 years, he became well known for delivering high quality pipeline, tunnelling and treatment works projects in the North of England for customers such as United Utilities.
It was during this time that a friend of Jonathan’s, working for another construction company was crushed and killed whilst working on site. He had over thirty years of experience on construction sites and worked for some of the leading companies in the UK as a site foreman.
His death not only affected his family and friends but also the plant operator and all his co-workers.
Jonathan and one of his employees, Richard Kerrison (now a director of Safety Shield) immediately started looking at ways to make the workforce safer on our sites. This led to the invention and development of the UK’s first RFID sensor and tag system for people and plant, these types of systems are still being used to this day.
The system was used by Jonathan’s construction company to keep the workforce safe by installing a sensor to the plant and a tag fitted to the hard hat of the workers. If the worker got too close to the plant the tag would vibrate and warn the operative and an alarm would sound in the cab of the plant to warn the operator.
However, a chance meeting with former Prime Minister Boris Johnson would eventually lead to Jonathan and his team developing the RFID system into a full human body detection system.
Whilst working on site in London, Jonathan was approached by the then mayor Boris Johnson during a routine site visit, who was so impressed with the RFID technology that he asked if it could be used on HGVs to alert for cyclists on the capital’s roads.
Further discussions at City Hall led to the system being developed further and tested by Transport for London and the transport research laboratory with the plan to install the tags on Boris Bikes around the city and placing sensors on the HGV’s.
a chance meeting with former Prime Minister Boris Johnson would eventually lead to Jonathan and his team developing the RFID system into a full human body detection system
TRUSTED BY GLOBAL LEADERS ACROSS A RANGE OF INDUSTRIES
KING’S AWARD FOR ENTERPRISE 2024: INNOVATION WINNER
Safety Shield has the solution
• The original and most advanced AI collision avoidance system
• Technology tailored to your plant and site
• Human form detection to alert operators of people close to plant
• Data reporting and real-time video to change behaviour on site
• 99.6% accuracy
Get in touch today to find out how we can create a bespoke system to help you save lives.
While the initial idea was rejected following opposition from London cyclists, the discussions had none-the-less sown the seeds of an idea that Jonathan and his team would pick up and develop into the state-of-the-art technology that is used today.
Introducing an Artificial Intelligence programme into the mix, they were able to design a system which could detect any cyclist or pedestrian using human form recognition instead of needing a wearable device or tag.
This solution was launched under the guise of ‘Cycle Safety Shield at City Hall’ and was later rolled out on London refuse vehicles, Sainsbury’s delivery trucks and testing also started on London buses.
The technology was picked up by many London councils and won multiple London and international transport awards.
In 2008, Jonathan closed his construction company and concentrated solely on the new technology and started a new in-house R&D company to further develop the system.
His vision was to adapt the new AI technology so that it was compatible for use in the construction industry, something which would prove extremely difficult and end up taking more than a decade to achieve.
Ever-changing environments, backgrounds, different types of hi-vis clothing, partially covered people, different items of plant and vehicles and many other factors meant the levels of accuracy were not high enough for the existing technology to make a difference.
In the last four years of R&D and testing Jonathan worked with Balfour Beatty and HS2 contractors as test partners which managed to speed up the process, during this time he also achieved the highest accuracy results of almost 99% and gained all the relevant ISO standards for the system to be able to work on plant with the highest accuracy and no interference to the plant itself.
With the help of his incredibly passionate Safety Shield colleagues, Jonathan officially launched the human detection
technology in 2018.
And while it may have been the end of one journey, it was also the start of another, as the technology continued to advance and the desire to come up with an even more reliable life-saving system saw them continue with their dedicated research and development programme.
This started with a couple of years of testing with many contractors to convince them that the system would save lives and help change behaviour on site.
This was, after all, a revolutionary system utilising technology that had never been used in construction before and people took some convincing.
By 2022, however, the industry was fully on-board and companies such as Balfour Beatty, HS2, Anglian Water, Countryside Developments, Vistry Group, Costain, Skanska, STRABAG, and many more were all adopting the technology.
Safety Shield has been instrumental in working with these types of companies to help write new plant specifications for this technology which has led to it being adopted and mandated by industry and has also opened a new market for other tech companies to develop similar entry level systems to meet the new demand.
The Safety Shield AI collision avoidance system is now being installed internationally with Safety Shield being the first company to invent, develop and introduce this type of system into the construction industry worldwide.
It has also moved into the rail industry and is working with Balfour Beatty to produce rail monitoring and collision avoidance solutions using the same technology.
Safety Shield Global continues to break new ground through its innovative AI technology, saving lives on a daily basis and making the industry a safer place for the generations of workers who will work with plant machinery in the future.
Its latest feature introduces an autonomous braking system which, by linking the Safety Shield AI mechanism with the plant operating machinery, steps in to put the brakes on and shut down the vehicle should the operator not react to the danger in time.
“My personal mission to stop plant hitting people began back in the early 2000s, when a friend was fatally crushed by an excavator on a construction site,” said Jonathan. “Any death or lifechanging workplace accident is one too many. I believe that these deaths are all avoidable – and AI offers the solution.
“More than ten years of research and development have gone into the creation of our systems. With Safety Shield, we
were the first to bring human detection technology to the construction industry. Today, what we produce is still the most advanced on the market.
“And even after bringing award-winning systems to market, we will never stop innovating and most importantly, listening to our customers.
“We are passionate about creating behavioural change in safety in the construction industry and that’s why we began. But our solutions don’t have to end there. The bespoke technology we produce can be applied to transport, rail or any type of machinery.
“We are constantly looking to the future as we believe that is the one way to ensure the longevity of our business. We know how fast technology moves so we have to be agile and constantly evolving.
“Although we specialise in technology, we see ourselves as a people-business. There’s a very human story at the heart of what we do.”
And the system is not only providing real-time life-saving results, but it is also enabling behavioural change among both the construction site management and its workforce.
A cloud-based monitoring system ensures every triggered alert – be it amber or red – sees information sent to a data centre which keeps all records, video footage and incident logs.
These can be viewed via an online portal and have proved invaluable in identifying trends, spotting specific issues and predicting likely incident hot spots on site. The video footage has prompted changes to site layout and specific awareness training.
The statistical impact is clear, with an average 65% reduction in red zone incursions around plant fitted with the AI collision avoidance system in 2022/23.
“Our next generation of construction professionals will enter the industry with knowledge and understanding of the very best safety practice when it comes to people plant interface,” continues Jonathan.
“On our tight, congested UK construction sites, I believe that AI technology with autonomous braking has the potential to completely eliminate collisions.
“Clearly, no technology is infallible. But I am optimistic that if AI collision avoidance systems with auto-stop become the norm, then we can achieve our goal of there being no fatal injuries as a result of workplace collisions.”
The King’s Awards for Enterprise was renamed last year to reflect His Majesty, The King’s desire to continue the legacy of HM Queen Elizabeth II, by recognising outstanding UK businesses.
The Award programme, now in its 58th year, allows successful businesses to use the esteemed King’s Awards Emblem for the next five years.
Back in Buxton! The famous quarry and mining exhibition was back for another stellar show, exceeding expectations and conjuring a crowd!
The 25th to the 27th of June brought sunshine, smiles and sensational exhibits. And, Plant Planet was thrilled to be back, catching-up with the biggest and the best in the construction and quarrying industry. It was also particularly special as it was the show debut for our brand new mini mag, Demolition Spotlight! Together, we put our best foot forward and demonstrated exactly what we have to offer the industry.
“Building on the momentum of the hugely successful 2022 exhibition, Hillhead 2024 was the most visited edition ever in terms of the volume of visits over the three days, with visitors spending more
time at the show than ever before and a record number attending for more than one day. In total there were a staggering 26,626 visits over the three days – marking an 8% increase from 2022.
“In terms of unique visitors, with 19,577 attendees from 67 countries (+6.2% compared with 2022) this year’s edition had the second highest ever number of trade visitors (only 2018 was higher at 19,753, although that show had less volume over the three days). Hillhead 2024 also recorded the event’s busiest day ever in its 42year history, with almost 10,800 visitors attending on day two of the show (Wednesday 26 June).”
As always, it was fantastic to catch-up with Merlo, whose signature bright green heralded visitors through the upper stands. With a flag waving from the top of their 30M high Roto 50.30 S Plus, it was easy for this long-established company to stand-out from the crowd.
While Lana and Graham chatted machine specifics, I got to meet new marketing manager Helen Selkin, whose passion for the company is evident in every word:
“There’s no company like Merlo on the market,” she told me as we sat down for a drink and looked out over the show. “Merlo prioritises operator safety and comfort; it’s at the core of our values.”
It was an absolute pleasure to attend the LiuGong press conference on the first day of Hillhead, kicking off the show in perfect style. The panel was made up of Dean Thornwell, Managing Director, Howard Dale, President of European Region, and Harry Mellor, Product Director. Their focus was on their continued ‘commitment to excellence’, as well as leading the change to electric vehicles across Europe. So not only did I get a wonderful goodie bag (I’ve named my toy digger Patsy), but we also got to hear so much about the incredible line-up of new products they have launched.
All set to a charming and well timed football theme, all of us in attendance were introduced to the incredible new winning team in the construction game, with particular emphasis on their new BEV range. To read more about that impressive range, make sure you read the LiuGong press day review on pages 34-38.
We were also treated to news on their brand new Portsmouth hub, which they moved into in January of this year. 94% of parts are stored there for the UK market, and sit in prime position at the port so that little transportation is required before heading to the end user. There was even a fantastic offer announced to those attending Hillhead, that for the limited span of the show, LiuGong would offer a 0% finance option! Now that is a late goal!
Arden’s UK team were a delight as they welcomed visitors to their stand. All of their attachments in their distinctive blue provided the perfect accompaniment to the blue skies; their incredible earthmoving kit speaking for itself as visitors piled towards the stand. Sales Manager Sean Donovan was particularly excited to show off their clamshell attachment range, which starts at 5 tonnes all the way up to 90 tonnes, and suits a variety of plant equipment. On top of this, they also had their multiprocessors that Arden is renowned for.
Wrapping up their global tour at the UK quarry was Swedish manufacturer, Steelwrist. My colleague, Phil and I, had a fantastic chat with Vice President of Global Marketing, Karl Serneberg, and Country Manager for the UK, Joe Westman, focusing mainly on their Open-S alliance. A joint initiative between two of the industry’s technology leaders, Steelwrist and Rototilt, the Open-S coupler is based on the established, symmetrical quick coupler standard for excavators (the S Standard) developed by Maskinleverantörerna, the Swedish trade association for suppliers of mobile machines. What the USBC has done for our handheld devices, so will Open-S for excavators!
It was amazing to see this piece on display at both Rototilt and Steelwrist, demonstrating how each other’s attachments fit perfectly with the Open-S coupler.
Karl had this to say: “It’s been designed by a council of engineers from all member companies, as we believe that the freedom to choose improves the conditions for new development. We also believe that closed systems create a lock-in effect that limits users’ ability to choose the best products. This way, we help end-users whilst also maintaining healthy competition between companies.”
Chatting with Andy Little at Rottilt, he too was excited by the possibilities it provided: “It’s fair to our customers. Without having to worry about couplers, they can focus their attention on getting the attachment that’s right for them.”
An incredible partnership to be sure!
Known as the trusted choice for mining and refining filtration, Donaldson is a global leader in providing advanced filtration solutions for the mining and construction industry. Specialising in equipment and dust collection solutions designed for challenging environments. The stand team were happy to talk visitors through their range of products, including essential filters for mining and construction machinery, such as air, lube, fuel, and hydraulic filters. These are crucial for maintaining the efficiency and longevity of heavy-duty equipment like excavators and dump trucks.
In the area of dust collection, Donaldson excels with systems tailored to mitigate airborne contaminants produced during operations, as their systems capture fine particulate matter, crucial for worker health and environmental compliance. Donaldson’s filtration solutions not only ensure operational efficiency and machinery durability but also enhance air quality and safety in mining settings.
Not only an innovative company, Donaldson also maintains a highly sustainable approach, as well as enhancing efficiency and environment for their end-users.
One of the most refreshing displays at the entire show, Air Spectrum heralded visitors from far and wide with its clever use of one of their misting sprinklers. Cooling everyone down and reviving them through the heat and dust, the team were then ready and raring to talk people through their incredible range.
Charlotte Walters, Marketing Manager, was pleased as punch to show us two of their machines working in tandem in the live demo zone. It perfectly demonstrated the power of water in dust suppression, particularly effective amongst the myriad of machines in that ring alone, as well as the dust from the working quarry.
It was fantastic catching up with our good friends at SMT, particularly following the highly successful trip to Volvodays in Eskilstuna. It was also exciting because of an announcement by Dynapac, who used Hillhead as their global platform to announce some very exciting news.
“During Hillhead, we officially announced SMT GB as an exclusive distributor for all Dynapac product lines in the UK,” said James Stephenson, Area Sales Manager for Dynapac. “We are really excited about this new partnership as it’s a bold and positive step for both firms. As a bonus, we’ve received new orders for some of the new and updated machinery models from our extensive product line-up. We had a busy Tuesday but Wednesday – as expected – was by far the busiest day.”
Amber Mills, SMT’s digital marketing specialist, was happy to tell us what a successful show they were having: “It’s honestly been such a lovely show so far. We have so much lined-up for next year and can’t wait to share it with everyone.”
We can’t wait to see it, stay tuned folks!
Enjoying a new location at the top of the hill, MB crusher’s stand was right next to the demonstration zone where their kit was being put through its paces, including their padding bucket and the sorting grapple. Particularly impressive was the new MB-HDS412 shafts screener. The ideal attachment for 10 to 14 tonne excavators, it is perfect for all sites. It combines efficiency and versatility in a compact piece of equipment, and is perfect for selecting material for covering pipes or trenches and creating the bedding; aerating packed soil; reclaiming and cleaning soils from various demolition debris, stones or roots, and moving materials of different types and sizes.
Hillhead was particularly standout this year as so many companies wanted to show off their electric ranges, and CASE was no exception. On display for the first time in the UK, was the CX15EV electric mini-excavator, alongside the other six mini-excavator models also making their UK debut: the CX12D, CX19D, CX25D, CX35D, CX50D, CX65TR. They also had the larger CX300E in action in the quarry, as well as the CX130E, CX210E, and CX250E models on their static stand. Certainly, an infinitely impressive line-up! On top of all that, CASE had wonderful interaction at their stand due to their mini operator challenge, where participants had to sit on the tiny excavator and use the arm to manoeuvre pipe from one fixing to another in the fastest time. It was a big success with guests, and certainly fun to watch!
How lovely it was to catch-up with everyone from CPA ahead of their Stars of The Future event. As always, everyone was all smiles, ready and raring to spread the good word about all of their tireless work for the industry. Not only did we talk to them about Stars of the Future (which was a resounding success by the way), but we also looked even further ahead to their annual CPA conference which will be held in November. Make sure you stay tuned for October’s issue which will have all the updates in our preview!
Who’s looking forward to PlantWorx, raise your hand? All of you? Thought so! We certainly are here at the office, and the PlantWorx stand got us all geared up for the big show next year. The 6th biennial construction machinery exhibition will be held from 23rd to 25th September 2025 at Newark Showground, a change from previous years. Personally, I am particularly excited as it will be my very first PlantWorx, and if my first Hillhead is anything to go by, it will be a RESOUNDING success.
VUE, the Manchester-based camera specialists showcased their Pedestrian AI solution that aims to significantly improve site safety through the use of their human-form recognition solution. It minimises blind spots around a vehicle or piece of machinery and proactively alerts operators and workers that are in areas of risk which could result in an injury or even a fatality. It differentiates between humans and static objects to prevent excessive alerting, and can detect a person with over 95% accuracy from something as small as a hand or foot.
Talk to the team at VUE today 0161 877 2257 or email hello@vue-cctv.co.uk
It’s important to remember that Hillhead is not all about big snazzy plant machinery displays; Hillhead encompasses everything that surrounds the machine, and that includes financing them. Paragon Bank PLC is a specialist lender and savings bank offering a range of products and services in the UK, and is part of the FTSE 250. Whether it’s new or used construction vehicles or machinery, either through purchase or lease, then Paragon is there to help. They have a wide range of flexible finance options that they were all too happy to discuss at their indoor stand.
Another finance team who shone was Aldermore. Aldermore is an award-winning bank, trusted and highly rated by over a quarter of a million customers for more than a decade. They helped focus the crowd’s attention to the business side of construction, helping to grow more than just a customer’s fleet, but their business too. With their range of specialist mortgages, savings accounts and business finance solutions, they aim to make your business dreams a reality. They even support in unlocking the cash tied-up in invoices, will fund an asset, bridge a finance gap, invest in commercial property or obtain finance for property development.
Bell Equipment were thoroughly excited to debut their new off-road water tanker at Hillhead. This new model, the B30E 27 000-litre Water Tanker, is built on the robust chassis of the acclaimed Bell B30E Articulated Dump Truck and can also be fitted with firefighting options for additional benefit. It’s the perfect addition to the mining and construction industry, as it is well-suited for dust suppression.
Bell Equipment Product Manager, Brad Castle, had this to say: “The centre of gravity has been kept low to reduce the risk of rollovers. Inside the tank is a fully engineered baffle system that prevents water surge and slosh, and provides increased stability for greater safety. The tank is also coated internally with a dual epoxy paint lining as standard to prolong the life of the tank.”
An industry leader in Fluid Solutions, United Rentals demonstrated to everyone at the show how they will also soon become a leader in Power Solutions. Whatever type of storage you’re looking for, United Rentals has the system for you. United Rentals products are designed with safety and quality as top priorities, have “plug and play” features and offer great versatility for a wide range of applications. This translates into unique benefits throughout the tank, pump, filtration and generator product lines.
Miller showcased their innovative quick coupler and bucket range, designed to perform in the most demanding environments. It was their buckets that truly stole the show, not only their 35t Extreme Rock bucket, but also five limited edition 20t heavy-duty buckets that were branded with the Lighthouse Club’s #MakeItVisible campaign colours. They were placed around the show, with one located at Miller’s stand, as well as their customers including Volvo SMT, Hitachi Construction Machinery, and CASE. Alongside this, Miller also sold Lighthouse Charity branded mini bucket models and footballs to raise additional money for the noble cause.
What a fantastic show it was! Completely living up to the hype, Hillhead 2024 exceeded all expectations, and wowed the record-breaking crowds day after day. Definitely a highlight in the exhibition calendar, we here at Plant Planet will certainly be looking forward to 2026 when we can return to the heart of mining and quarrying.
The countdown to the Resource & Waste Management Expo (RWM Expo) is on! As the UK’s largest gathering of resource, waste management, and recycling professionals, RWM Expo is set to take place on 11-12 September 2024 at the NEC, Birmingham.
The show offers an incredible opportunity for professionals across the entire resource spectrum to connect with the industry’s biggest players, learn from the sector’s brightest minds, and drive positive environmental change via discourse on sustainable resource management.
The event is free to attend for the first 20,000 registrants, so secure your free place at the forefront of environmental innovation, solutions, and knowledge exchange while you still can! Secure your free ticket here:
https://hubs.la/Q02CMDHn0
RWM Expo is at the forefront of resource, waste management and recycling, addressing critical issues such as resource scarcity, plastic pollution, and sustainable materials use. Attendees can expect to discover innovative solutions and technologies that promote recycling, waste reduction, and the circular economy, ensuring both ecological balance and long-term economic growth in the resource sector. Expect to see cutting-edge solutions from leading waste management suppliers, including waste service providers & operators, plant & machinery, sorting technologies, waste collections & transport, recyclers & reprocessors, material handling, skips & bins, and professional services & consultants.
RWM is spread across three halls, and includes a massive 10,000m2 outside area featuring spectacular displays of industry-leading machinery, live demonstrations of wasteprocessing equipment, refuse collection vehicles and street sweepers. The outdoor section of the show is the place to see apparatus working in its intended environment, as well
as a perfect area to relax and enjoy food, drink, and hear live music in the sunshine at the Inn on the Green!
RWM Expo is part of the broader Environmental Services & Solutions Expo (ESS Expo). This ultimate environmental event combines multiple specialised shows into a single, comprehensive platform under one roof, addressing key areas such as waste management, recycling, energy from waste, decarbonisation, water resource management, contamination, land development, and air quality control, together forming the UK’s largest environmental event with over 12,000 visitors. This unique format allows attendees to seamlessly explore a wide array of sectors and industries, all focused on addressing the most pressing environmental challenges of our time.
With free entry and access to all co-located shows through a single ticket, the RWM Expo provides an unparalleled opportunity for networking, learning, and collaboration across the entire environmental spectrum.
The five shows that make up ESS Expo are:
1. Resource & Waste Management (RWM) Expo
2. Energy, Fuels & Decarbonisation (EFD) Expo dedicated to sustainable energy generation, energy from waste, bioenergy, alternative fuels, energy management, and decarbonisation. It covers a broad spectrum of topics, including carbon capture, hydrogen technologies, and clean energy systems.
3. Water Resource Management (WRM) Expo focusing on water scarcity, flood and drought cycles, wastewater management, and water quality issues. WRM dives into wastewater treatment, point source treatment, and sustainable practices to ensure safe and accessible water resources.
4. Contamination & Land Remediation (CLR) Expo CLR addresses the remediation of contaminated sites, soils and materials, brownfield regeneration and greenfield development, geotechnical engineering and technologies, biodiversity and natural capital, and the management of hazardous substances.
5. Air Pollution Control (APC) Expo focusing on air quality management, emission reduction, stack monitoring, noise prevention, dust and odour control.
RWM & ESS attracts over 12,000 international visitors, uniting industry pioneers, visionary entrepreneurs, and eco-driven professionals to collaborate, learn, and inspire one another towards a greener future.
From Government, to Europe’s largest environmental services contractors, to big brands, RWM welcomes industry leaders from up and down the supply chain. Whether you are a business planning your net-zero strategy, a council looking to hear the latest regulatory updates or an equipment manufacturer launching a new piece of equipment, this is your platform to collaborate, network and learn with the people shaping the future of the resource sector.
• 12,000+ attendees
• 86% hold buying power
• 6,000+ companies
• 64 countries
• 26,000+ leads generated
• 17,000+ meetings
RWM Expo features an expert-led conference programme that includes interactive speaker presentations, lively panel discussions, workshops, and Q&A sessions. Attendees will have the chance to learn from industry leaders and gain insights into the latest trends and innovations across the entire resource and recycling spectrum.
Current headliners include Chris Packham MBE (one of the UK’s leading wildlife presenters and conservationists) and Mike Gunton, an icon of wildlife broadcasting as BBC Studios’ Creative Director and executive producer of record-breaking series, Planet Earth III.
The first 50 speakers have been announced, including the likes of Sony, EY, Biffa, Virgin Media O2, and the Environmental Services Association to name a few. More huge names will be revealed soon (think global brands and Government officials).
RWM & ESS Expo boasts 17 Stages, 350 speakers, live bands, DJs, live demos and a whole lot more. Discover a diverse array of stages and themes at the show, each designed to bring you the latest insights and innovations across the environmental sector. From high-level government discussions and cuttingedge technical sessions to interactive presentations and vibrant entertainment, the stages offer something for everyone. Attendees will benefit from a unique blend of learning, networking, and fun as they tackle the industry’s most pressing issues.
The stages range from the Net Zero Summit Theatre, which acts as the foundation for high-level discussions on environmental policies, strategies, and innovations, to the Green Skills & Future Talent Hub, which aims to nurture and develop the next wave of environmental professionals, to sector-specific technical theatres, and the ESS Live Stage, the heart of the event’s entertainment, featuring live bands and DJs.
Networking is the cornerstone of RWM Expo, with no shortage of options over the two days. With numerous opportunities to connect with peers, suppliers, and potential clients, attendees can engage in private meetings, AGMs, tutorials, member networking events, industry-specific forums, award presentations, breakfast briefings, and socials around the central bar, Inn on the Green, and ESS Live Stage. This is a prime chance for environmental leaders to build strong, lasting relationships and expand professional networks.
The expo offers live demonstrations of vehicles, equipment, and machinery, providing a hands-on experience with the latest technologies working in their intended environments. Workshops and talks will cover a range of topics, offering practical insights and solutions for everyday challenges in the environmental sector.
RWM Expo proudly features a variety of award schemes and initiatives that celebrate the achievements and contributions of outstanding individuals and organisations within the environmental sector.
Women in Resource & Sustainability: Taking place on the morning of day two, this inclusive networking platform is dedicated to celebrating and exploring the contributions of women in the resource, recycling, and waste management sectors. It offers a fantastic opportunity for professionals within the industry to share experiences, challenges, and success stories, fostering a supportive community and encouraging greater inclusion and diversity in the sector.
35 Under 35 Awards: This programme identifies the trailblazers in the environmental sector who are striving for professional excellence, promoting industry innovation, and giving back to their company or community. This programme invites individuals from waste and recycling, water management, energy, construction, and anyone connected to managing sustainability within their organisation to join an exclusive group of professionals under the age of 35.
The Environment 100 Recognition Scheme: Recognising our environmental leaders and sustainability champions, The Environment 100 shines a light on the trailblazers and visionaries driving forward environmental sustainability in the UK.
There’s so many reasons to come and check out RWM Expo – here’s just a few of them:
The first 20,000 tickets are free, making it an accessible event for all professionals interested in environmental services and solutions. Get yours while you still can: https://hubs.la/Q02CMDHn0
RWM hosts the most influential brands and world-class suppliers in the environmental sector, providing a platform to discover new products and services from its 550+ exhibitors.
As part of five shows in one, attendees get to explore the full environmental spectrum under one roof, gaining access to a wealth of knowledge and innovations. One free ticket gets you access to all five shows, as well as the outside areas, which you can freely walk between.
Be part of the discussion and discover environmental solutions that contribute to a more sustainable future. Learn from experts in the field and find out new policies, emerging trends, practices and leave with practical insights and methods that benefit your own operation.
From structured networking events to informal meet-ups, RWM offers numerous ways to connect and collaborate with industry peers and form professional connections. Check them all out on the website!
Don’t miss out on this incredible opportunity to be part of the beating heart of environmental excellence. With limited free tickets available, now is the time to secure your spot. Register via the website today and join us at the NEC, Birmingham, on 11-12 September 2024, for the UK’s largest environmental gathering. Be part of the conversation, explore the latest innovations, and connect with industry leaders.
For more information and to register, visit the website and follow their social media channels for the latest updates and announcements: https://hubs.la/Q02CMDHn0
The company began life in December 1992 under the leadership of Terry Barton, a man with a vision. Operating from a small yard with a fleet of 15 ageing machines
Southern Hoist Services set about becoming one of the most respected hire companies of today.
At the time there were very few companies offering hoist rental and installation, and there were no training courses or qualifications for such work, as it was a very niche market. Health and safety on sites was much less than today, and hoists provided a safe option to manual handling at height. By employing local people from mechanical backgrounds, the role of an Hoist Installer was simply a “learn on the job” role.
As a small specialist hire company, the fleet ranged from 150kg SWL up to 1200kg SWL capacity servicing clients across the South East and London from their base in Southampton.
In a rapidly growing industry SHS soon developed a strong reputation for the service and supply of hoists to the industry, supporting contractors on small projects in the local area.
Sadly Terry Barton passed away suddenly and the business was purchased by Claude Fenton Plant Hire in 2004. The investment provided further opportunity for growth and, with the backing and support of a larger company, SHS could drive forward full steam ahead with his vision. By adding larger hoists to the fleet, expanding the coverage area and bidding for major projects the team moved from strength to strength.
Director, Kirsty Archbold-Laming, was quick to seize the moment, with the team winning flagship projects and increasing the fleet size. The customer base quickly grew, with many of the main contractors in the industry using SHS directly.
Fast forward a few years, the market has expanded at speed, with more new builds restoration/regeneration projects and increasing skyscrapers. The UK has seen the need for more equipment on sites, and hoist selection is often one of the last considerations, however by offering guidance to clients and helping them plan, the project SHS continues to grow!
The company’s ethos of dedication, investment, development and commitment to training shows no sign of slowing down. Assisting industry associations, manufacturer development and continued support for their clients has seen the company grow further and expand its territory. The working areas expanded, covering nationwide which in turn has also taken the company to international projects including France, Netherlands and Italy.
The firm now has a fleet of over 120 hoists, including passenger/ goods and transport platforms, and prides itself on the company’s reputation not only within construction but also including projects in the event/entertainment industry. These include Harry Potter, Pirates of the Caribbean and Mission Impossible film sets, the Ryder Cup, Cheltenham Cup and various Royal occasions.
In addition to the development of the company, Southern Hoist Services is also a founding member of CHIG (Construction Hoist Interest Group), one of the specialist groups formed through the Construction Plant-Hire Association (CPA)
The group was formed in 1996 and has grown to 60 members today with rental companies, manufacturers, training providers, end users and health and safety advisors. It is an open forum to discuss problems and work together to find a resolution, whilst continuously improving the industry. It works with manufacturers to understand the customer needs and legislation to provide suitable equipment with safety at the forefront.
There are annual meetings for all to attend, and many Work Groups ongoing comprising members who give their valuable time and expertise to produce Best Practice Guidance, develop qualifications and discuss innovations.
With the wealth of expertise in CHIG, the sharing of knowledge with other associations, such as NASC (Scaffolding Contractors), Build UK (project contractors) and IPAF is a backbone for the construction industry. It really is simple – all differences are set aside to work together on issues and common values to make the industry better for all and improve standards in the UK.
SHS, along with other specialist hoist companies, championed a way forward for training and skills in a small but vital part of the industry, developing NVQ standards for hoist installers. As a founding member of the Construction Hoist Interest Group (CHIG), the safety standards and skills set have been developed to provide a safe environment for all involved. Kirsty has been the Chair of CHIG for since 2012 and is the only female to hold the position since its inception back in 1996.
She said: “I am so proud of CHIG and the wonderful group of people who give their time and effort to support the industry. Being in a male dominated role had its challenges when I started over 30 years ago, but to see how far we have come and the mutual respect shown between hire companies, safety professionals, manufacturers and the like is inspirational. It’s a different world to when we first started but the work CHIG has put into safe practices and assisting fellow members has been invaluable.”
Working closely within the work groups and with manufacturers directly has afforded the opportunity to design and develop models to suit the UK market, and as the UK has the strictest health and safety standards, this shows commitment from everyone. Current Guidance documents are available for download free from the CPA website www.cpa.uk.net
In addition to creating Best Practice Guidance, British Standards, Qualifications and Innovations, CHIG found there was a real need to educate contractors on equipment. With the increase in MCWPs, they were often mistakenly used in the same way as a typical construction hoist. This began a collaboration with IPAF over 10 years ago to produce a joint guidance document to ensure each piece of equipment was used by the contractors correctly.
With dedication from members through the work groups, joint training courses have been developed to help users and rental companies. The Construction Hoist Operator and the MCWP & Hoists for Managers courses provide much needed education for sites for planning, selecting the correct equipment and highlights the need for trained personnel to operate the machinery.
As we all know there is a skills shortage, and now the latest course has been launched for Hoist Installer training. This will help to attract people to a wonderfully diverse industry and give them the skills and understanding to enable them to undertake the qualifications sooner than expected. It is a role that should not be undertaken without the necessary knowledge, and health and safety must remain the most important item at any time. This is a starting point for entrants into the industry, which will lead to the existing higher qualifications CHIG developed with NVQ Qualifications. The qualification provides a high standard of knowledge with health and safety at the forefront.
The company is very proud to have nominated the first Hoist Installer (NVQ Level 2) for CPA Stars of the Future award, and even more so for their employee, Hayden Chappell, winning the award. It is a fantastic event held annually by CPA to celebrate the achievements of trainees and apprentices, and highlight what a wonderful industry it is to work in, with so many positions available.
It’s easy to see the future of construction by what we have achieved so far:
• The expertise and co-operation between rental companies, manufacturers and HSE has improved the industry and created a safer environment.
• Manufacturers have received assistance in developing equipment for UK markets to comply with the highest standards
• The collaboration between associations will spread the standards expected in the UK and perhaps on a global scale to ensure continued improvements in safety.
• Southern Hoist are also proud to be the first Hoist rental company to achieve IPAF Rental +
Kirsty Archbold-Laming, Director at Southern Hoist Services, had this to say:
“I am also involved in several committees and work groups throughout, including Construction Plant-Hire Association (CPA), Construction Hoist Interest Group (CHIG), IPAF UK & Ireland MCWP/Hoists, IPAf Rental + and British Standards Committee MHE/6 for Construction Hoists.
“I have always said I will have a pink hoist, and as difficult as lockdown was, it was particularly hard on charities who could not hold their events to raise money. Having lost my mum in 2011 to breast cancer, and doing the London Moonwalk many times since in her memory whist raising funds, I decided that we would raise money in construction to help the charity, and so Penny was born. Every time she is hired, 20% of the hire revenue is donated to cancer charities, and the amount of people that meet me and say “you have a pink hoist?!?!” is quite astonishing. Very proud of our Penny, and customers even request her, as she makes them happy too.”
Protect your pro tability with the proven results of ltration science. The right lters from Fleetguard on your equipment can help prolong engine life by removing contaminants that cause premature wear on critical components. You’ll get healthier engines, fewer breakdowns, lower repair costs and longer duty cycles.
The future of the construction plant industry is in safe hands judging by the outstanding quality of the entrants at this year’s Stars of the Future awards hosted by the Construction Plant-hire Association (CPA) today.
A total of 80 nominations were received for the CPA Stars of the Future apprentice and trainee awards 2024
The awards identify some of the industry’s brightest up-and-coming talent and its future leaders across various occupations including Plant Mechanics, Plant Technicians, Hire Controllers, Lifting Technicians, Plant Installers, Plant Operatives and Young Plant Operatives, as well as those who mentor the apprentices.
Almost 300 people attended the awards ceremony which was hosted at the Heart of England Conference and Events Centre in Fillongley, near Coventry, by former TV newsreader, presenter and journalist Merryn Myatt.
This was the 12th year of the acclaimed apprentice awards and this year’s nominations were judged by a total of 13 judges from the CPA and across the industry.
The CPA is the leading trade association for the construction plant sector in the UK, with over 1,900 members who supply around 85% of hired plant to the construction industry. The awards ceremony was held in association with event sponsors GAP Group and L Lynch Plant Hire & Haulage, and award sponsors and supporters ACOP Group, JCB, Liebherr, L Lynch Plant Hire & Haulage, M O’Brien Plant Hire, NOCN Group, Plant Planet, Southern Hoist Services, Sunbelt Rentals and Wolffkran.
On the day, the winners of each national category were as follows:
• National Plant Mechanic of the Year (Level 2) - Bethan Whittaker of KJ Services and Bridgend College
• National Plant Technician of the Year (Level 3) - Morgan Wardle of Banks Plant Solutions and Askham Bryan College
• Hire Controller of the Year - Millie Scott-Young of Sunbelt Rentals
• Young Plant Operative of the Year - Josh Jones of L Lynch Plant Hire & Haulage
• Plant Operative of the Year - Reece Stray of L Lynch Plant Hire & Haulage
• Lifting Technician of the Year - Zac Bradshaw of Commhoist
• Plant Installer of the Year - Hayden Chappell of Southern Hoist Services
• Individual Apprentice Mentor of the Year - Steve Gwynn of Sunbelt Rentals
• Group Apprentice Mentor of the Year - Dave Rogers of L Lynch Plant Hire & Haulage
• Best Personal Statement Award - Shannon Weiss of Finning UK and Finning Academy
• Judges’ Special Award - Tom Williams of CBL and Bridgend College
Stars of the Future is one of the CPA’s flagship events and one that we’re very proud of. We would like to congratulate all of the nominees and winners.
7TH NOVEMBER 2024 at the Heart of England Conference and Events Centre near Coventry
• Open to both CPA members and non CPA members
• Being co-hosted by former BBC TV presenter Merryn Myatt and content specialist Peter Haddock
• The essential event for the plant-hire industry
• Interactive panel debates discussing key topics such as innovation, decarbonisation, digitalisation, skills, business growth, succession planning and mental wellbeing delegate ticket price for CPA members. Email enquiries@cpa.uk.net for more info. 50% OFF
Book delegate tickets online at www.cpa.uk.net/events/ cpa-conference-2024 for £80 plus VAT including lunch.
The conference will run alongside a small, targeted exhibition. Contact Lisa Collins on 07968 840390 or email lisa@lisacollinscommunications.co.uk for further details.
Stars of the Future was originally introduced to recognise outstanding Apprentice Plant Mechanics and Plant Technicians, but the scope of the event has been extended over the years to reward other job roles in the construction plant sector. It is now widely acknowledged as the sector’s premier event for recognising and rewarding trainees and apprentices who are earmarked as future leaders of the industry.
CPA President Brian Jones said: “Stars of the Future is one of the CPA’s flagship events and one that we’re very proud of. We’d like to congratulate all the nominees and winnersit’s a tremendous achievement in itself for apprentices to be nominated by their employer or training provider for a Star of the Future award. Testimony to the success of the awards is that many previous Stars of the Future award winners have gone on to secure senior positions in the construction plant industry.
“We would like to thank all our sponsors, without whom we simply could not stage such an event or reward our winners so considerably. Award winners received some fabulous prizes, including tool kits, machine training courses, iPads, an overseas trip to visit a Liebherr crane manufacturing plant in Germany, another overseas trip to one of Wolffkran’s manufacturing facilities in Luckau, Germany, and a VIP day courtesy of JCB. Special thanks also go to each and every
one of our 13 judges for the time they took in going through all the nominations so thoroughly,” he continued.
Stars of the Future had a two-tier judging process – the CPA selection panel and a panel of external judges who decided the eventual winners of each category. The external judging panel included Arran Willis of Liebherr-GB, Siôn Morgan Jones of ACOP Group, Kirsty Archbold-Laming of Southern Hoist Services, Leigh Sparrow of Vertikal Press, Graham Black of Earthmovers Magazine, Tim Brownbridge of BAM Nuttall, independent judge Rob Allen, Georgina Williams of JCB and Sean Scarah of Balfour Beatty.
Graham Black, Editor of Earthmovers Magazine, who was part of the external judging panel, said: “It was a genuine honour to be asked to be a CPA Stars of the Future judge once again and the quality of the candidates was exceptional this year. Our job as judges was to identify the mega stars of the future and what often separates these high-achieving individuals is their video submission that they submit as part of their nomination.
“One of the reasons for this long-standing event is to attract more Plant Mechanics, Plant Technicians, Plant Operators and other occupations into our industry. Stars of the Future has been a great success and it was fantastic to see so many outstanding individuals in the room during the awards ceremony,” he continued.
The complete list of Stars of the Future 2024 category winners and those who were highly commended is as follows:
Plant Mechanic of the Year - North
Sam Ellis, Flannery Civil Engineering, Askham Bryan College - Winner
Plant Mechanic of the Year - Midlands
Luke Sutton, Synergy Hire, National Construction College East - Winner
Luke Divit, Marubeni-Komatsu, NSCG Stafford CollegeHighly Commended
Tyler Hartles, Marubeni-Komatsu, NSCG Stafford CollegeHighly Commended
Plant Mechanic of the Year - South
Josh Thomas, Liebherr-GB, NSCG Stafford College - Winner
Joe Mustey, Earlcoate Construction & Plant Hire, National Construction College East - Highly Commended
Luke Piggott, Vp Brandon Hire Station, Myerscough College - Highly Commended
Mike Kinnane, Sunbelt Rentals, Myerscough CollegeHighly Commended
Plant Mechanic of the Year - Scotland
Kai Blackburn, Ord Industrial & Commercial Supplies, National Construction College Scotland - Winner
Leeona McEwan, GAP Group, National Construction College Scotland - Highly Commended
Plant Mechanic of the Year - Wales
Bethan Whittaker, KJ Services, Bridgend College - Winner
Ethan Williams, KJ Services, Bridgend College - Highly Commended
National Plant Mechanic of the Year
Bethan Whittaker, KJ Services, Bridgend College - Winner
Josh Thomas, Liebherr-GB, NSCG Stafford College - Highly Commended
Plant Technician of the Year - North
Morgan Wardle, Banks Plant Solutions, Askham Bryan College - Winner
Ethan Hopwood, Allan J Hargreaves Plant Engineers Ltd, Preston College - Highly Commended
Thomas Joynt, Sunbelt Rentals, Myerscough CollegeHighly Commended
Subhaan Nawaz, Bachy Soletanche, Midland Group Training Services - Highly Commended
Plant Technician of the Year - Midlands
Courtney Price, SMT, Reaseheath College - Winner
Shannon Weiss, Finning UK, Finning Academy - Highly Commended
Oliver Voss, Watling JCB, National Construction College East - Highly Commended
Owen Van Greuning, Marubeni-Komatsu, NSCG Stafford College - Highly Commended
Plant Technician of the Year - South
Harry Totman, Liebherr-GB, NSCG Stafford College - Winner
Thomas Fuentes-Moreno, Vp Brandon Hire Station, Myerscough College - Highly Commended
Jack Southam, Southern Cranes & Access, National Construction College East - Highly Commended
Plant Technician of the Year - Scotland
Louie Masson, Pat Munro (Alness), National Construction College Scotland - Winner
Plant Technician of the Year - Wales
Tom Williams, CBL, Bridgend College - Winner
National Plant Technician of the Year
Morgan Wardle, Banks Plant Solutions, Askham Bryan College - Winner
Courtney Price, SMT, Reaseheath College - Highly Commended
Harry Totman, Liebherr-GB, NSCG Stafford College - Highly Commended
Hire Controller of the Year
Millie Scott-Young, Sunbelt Rentals - Winner
Lauren Jobson, Sunbelt Rentals - Highly Commended
Young Plant Operative of the Year
Josh Jones, L Lynch Plant Hire & Haulage - Winner
Lewis Ensor, L Lynch Plant Hire & Haulage - Highly Commended
Plant Operative of the Year
Reece Stray, L Lynch Plant Hire & Haulage - Winner
Lifting Technician of the Year
Zac Bradshaw, Commhoist - Winner
Plant Installer of the Year
Hayden Chappell, Southern Hoist Services - Winner
Arran Heath, Wolffkran - Highly Commended
Individual Apprentice Mentor of the Year
Steve Gwynn, Sunbelt Rentals - Winner
Bill Munday, Earlcoate Construction & Plant Hire - Highly Commended
Tony Jenkins, Marubeni-Komatsu - Highly Commended
Apprentice Mentor of the Year
Dave Rogers, L Lynch Plant Hire & Haulage - Winner
Jo Stamp, Sunbelt Rentals - Highly Commended
College of the Year
Bridgend College - Winner
Myerscough College - Highly Commended
Best Personal Statement Award
Shannon Weiss, Finning UK, Finning Academy - Winner
Award for Future International Development
Courtney Price, SMT, Reaseheath College - Winner
Judges’ Special Award
Tom Williams, CBL, Bridgend College - Winner
Hello one and all and welcome back to Demolition Spotlight! We have a jam-packed issue for you all this month! Not only do we have a review of our show debut at Hillhead, but we have so many incredible contributors supporting this issue!
Hughes & Salvidge have a wonderful case study about their project at the Royal Sussex County Hospital. And if that wasn’t enough, we are very lucky that their own Charlie Cawte is our Demo Report this month, telling us all about his extensive career in the demolition world.
Craig Evans of UKATA brings us our Demolition Dilemma this month, as he interviews Wayne Bagnall MBE about all things asbestos. And to top it all off, we have the ridiculously talented Paul Argent writing not one, but two articles for us! Here’s what Paul has to say about being a partner of Demolition Spotlight: “I’m pleased to be working with the Demolition Spotlight team to provide the magazine with over 35 years construction industry experience.” What an issue this is!
Happy reading!
Rebecca Phillips Managing Editor
DARREN SHELTON BUSINESS MANAGER
MARTINA TONELLI MARKETING CO-ORDINATOR
REBECCA PHILLIPS MANAGING EDITOR
LORNA COWLIN CONTENT CREATOR
CHARLOTTE WALSH BRAND MANAGER
STEVE WILSON DESIGN MANAGER
contributors
PAUL ARGENT RPA MEDIA SERVICES
CHARLIE CAWTE HUGHES AND SALVIDGE LTD
LUKE GOULD HUGHES AND SALVIDGE LTD
WAYNE BAGNALL MBE MSC CFIOSH HON-FIDE MCMI WAYNE BAGNALL CONSULTING
CRAIG EVANS UKATA
For all content related queries, please contact editor@demolitionspotlight.co.uk
For all sales related queries, please contact charlotte@demolitionspotlight.co.uk
Our unique capability to repurpose virtually all construction and demolition waste from site helps our public sector, local authority, commercial and residential clients achieve zero-to-landfill targets.
Demolition
Structural alterations
Site clearance
Soft strip
Asbestos management
Remediation
Earthworks & civils
Temporary works
Demolition & Enabling Works Waste Management Aggregates & Concrete
At R Collard Ltd we provide a full self delivery model, controlling all aspects of project delivery, allowing our clients to feel control and accountability while working together. We provide a one-stop-shop for all of our clients, contractors and developers alike. Our service proudly spans the breadth of the UK which utilises the group’s expertise, covering the initial consultancy and site investigation
through to the asbestos removal, soft strip, full structural demolition, earthworks and land remediation, allowing us to hand back a shovel ready site for the next phase of development!
In Eversley, at our head office, we have recently been working on the R Collard Ltd ‘Contracting’ rebrand and restructure. If you head to our website you will notice that what once was our ‘Demolition and Enabling’ section has been repurposed
to display the full ability of our now ‘Contracting’ division. By restructuring this space, it has allowed us to create the room necessary for us to convey our expert knowledge and strengths across all areas and sectors of contracting. Our ever expanding sights are keen to grow and expand nationally, especially across into the industrial sector and we hope that this rebrand helps us get there.
Exciting news from London as we are proud to announce that we have officially
completed on site at The Imperial Hotel in Russell Square. For this project, R Collard was awarded the role as principal contractor where we completed the soft strip, asbestos removals and demolitions to enable the refurbishment works at the hotel.
Over in Maidenhead we are in the final stages of the demolition of Broadway Car Park where we were once again on site as principal contractor. Here we are demolishing the nine storey, concrete framed car park down to ground level, followed by the removal of foundations and hardstandings alongside the demolition of the adjacent shop units.
In Hayes, we are thrilled to be completed with our works at Harlington School, Middlesex. This project involved the demolition and asbestos removal of the existing secondary school building down to ground, and the removal of foundations and hardstandings.
Following our successful performance on the initial demolition works, R Collard. We awarded the subsequent enabling package. This comprised of the cut and fill to formation level and the installation of 400mm of engineered fill in preparation for a new football pitch. For Phase 9 at Deepcut Army Barracks in Camberley, we are halfway through our demolition package while we are preparing for the following enabling cut and fill package.
In Reading, we are delighted to have been awarded the demolition and remediation package as the principal contractor at Vastern Road. This project is located in the town centre and is directly adjacent to the River Thames where our team will skillfully deliver soft strip, asbestos removal, demolition, piling mat and remediation works to demolish the existing structures to allow the site to be developed for residential and retail uses.
Over the next few issues of Demolition Spotlight, we will be keeping you up to date with the current happenings at R Collard, we have a few more awarded projects up our sleeves that we are eagerly waiting to share with you, along with more news and updates on our on site works. For the next two issues we will be further exploring our industry expertise by doing two separate deep dives into our ‘Demolition and Enabling’ and ‘Asbestos and Earthworks’ operations. Head to our website or our Collard Group LinkedIn page to keep informed in the meantime!
The National Federation of Demolition Contractors comment on the UK’s recent general election, and the need to focus housing redevelopment on brownfield sites.
We support the new government’s commitment to sustainable development and commitment to provide a significant improvement in planning for new housing. We firmly believe that prioritising brownfield development is a critical step in protecting our green spaces and promoting sustainability.
By focusing on the redevelopment of brownfield sites, we can significantly reduce the need for new construction on greenfield locations, which will in turn preserve valuable agricultural land. The demolition process plays a vital
role in this, as it allows us to unlock and recycle materials that can be reused in the creation of new housing and infrastructure projects. This approach not only minimises the consumption of new resources but also enhances the overall sustainability of development projects.
We are enthusiastic about continuing our work with the Ministry of Housing, Communities, and Local Government (formerly the Department of Levelling Up, Housing, and Communities) to support this cause by enhancing understanding of demolition’s role in sustainable development. Often misunderstood, the demolition industry is dedicated to sustainable practices that contribute to the efficient and responsible redevelopment of our urban areas.
We also welcome Sarah Jones to her
new role as Construction Minister in the Department for Business and Trade, alongside her role within the Department for Energy Security & Net Zero. We welcome the opportunity to collaborate with the minister and her team.
The NFDC looks forward to working closely with the government and other stakeholders to promote the benefits of brownfield development and to highlight the significant contributions of the demolition sector to a sustainable future.
To learn more about NFDC, please visit: www.demolition-nfdc.com FOR FURTHER INFORMATION
We firmly believe that prioritising brownfield development is a critical step in protecting our green spaces and promoting sustainability.
Areport by the Construction Industry Training Board (CITB) projects a shortage of over 200,000 skilled workers in the UK construction industry by 2025, underscoring the urgent need for effective recruitment strategies. As the problem escalates, both government support and internal industry initiatives are essential.
The shortage of skilled labour presents a significant challenge, and NDTG is making strides in tackling this issue.
The built environment sector has been proactive in promoting construction T Levels and apprenticeships to introduce a new generation into the workforce. However, to truly address the skills shortage, the sector must explore additional, untapped sources of talent, such as ex-offenders. According to the charity Unlock, around 12 million people in the UK have a criminal record. Despite significant labour shortages, only 30% of businesses employ ex-offenders, presenting a substantial opportunity for the industry.
One step at a time
The first initiative NDTG is employing in attracting untapped talent pools is with our combined efforts with the Ministry of Justice and the Prison Service. The CCDO card scheme provides an accessible way to get a job as an exoffender. But what it also allows for is a clear career trajectory. NDTG is
helping ex-offenders acquire valuable skills and qualifications that are highly sought after in the demolition industry whilst ensuring they stay within our industry with desirable pathways to more opportunities.
Some employers are hesitant to hire ex-offenders due to concerns about trustworthiness. However, the Ministry of Justice’s polling indicates that nearly 90% of businesses find ex-offenders reliable and punctual. Raising awareness about the positive contributions of exoffenders is essential to overcoming these notions. Our training programs have demonstrated that ex-offenders often possess transferable skills and a resilient attitude and work ethic. Exoffenders are keen to undo the negative preconceptions made of them.
Ex-offenders often bring transferable skills to the workforce. Our training programs have received positive feedback, with trainees showing enthusiasm and a strong desire to challenge negative stereotypes. By providing them with the necessary training and support, we’re helping break down the barriers for new career opportunities.
Existing initiatives like the Ministry of Justice’s Future Skills Programme provide crucial support for integrating
ex-offenders into the workforce. These programs should be widely promoted, and NDTG has gone further to enhance recruitment efforts and address the skills shortage. Our cross-mapped training allows demolition operatives to complete their demolition CCDO and construction SSSTS/SMSTS Site Safety Plus qualifications simultaneously. This initiative facilitates seamless and cost-effective development across construction and demolition.
Initially a response to the COVID-19 pandemic, NDTG now hosts online training programs as a cornerstone of our educational platform. We have made training more accessible and convenient, encouraging those joining the industry and those who want to progress through the CCDO card scheme.
By embracing these strategies and consistently focusing on how we can support recruitment initiatives, we can address the skills crisis and build a stronger, more resilient built environment sector. NDTG’s efforts in prisons, tapping into the potential of overlooked talent pools, exemplify our commitment to finding innovative solutions.
The global demolition industry is gearing up for this year’s World Demolition Summit (WDS), which is set to take place in Stockholm, Sweden, on the 6 and 7 of November.
Around 500 contractors are set to attend the event, which comprises a conference, awards dinner and networking opportunities.
Mark Coleman, CEO of Colemans – last year’s winner of the World Demolition Award for the Best of the Best Project of the Year, will take a keynote speaker slot at the conference.
Leila Steed, Programme Organiser for the World Demolition Summit, said: “I’ve had some very interesting conversations with Mark over the past several months.
“He’s someone that is incredibly passionate about innovation and, as a result, is spearheading a number of projects that could one day bring new avenues of opportunity to the demolition industry, and help to make it safer.”
Mark Coleman will be joined by other industry leaders, including Skanska’s Business Developer and circular working methods specialist Barbro Brattstrom Grujovic, and Bengt Borgen Hildisch, Senior Vice President of Decommissioning at Aker Solutions.
Experts from Thornton Tomasetti, Total Wrecking & Environmental, COWI, GreenDozer and the European Asbestos Forum have also been lined as speakers, with the full conference programme
expected to be published within the coming days.
Steed said: “The programme is very almost there. The last few presentations are now being finalised and people are starting to get really excited about it.
“This year is very special for us.
Demolition & Recycling International (D&Ri) magazine – the creator and organiser of the WDS – is celebrating its 25th anniversary.
“It’s an achievement that could not have been attained without the generous, passionate and steadfast support of our readers, clients, delegates, partner associations and, of course, our amazing WDS sponsors – many of which are headquartered in Sweden.”
These include Volvo Construction Equipment – the headline sponsor of the WDS since its inception 16 years ago, as well as Oilquick, Steelwrist, Epiroc, SMP, Brokk, and CEJN.
As part of its 25th anniversary celebrations, D&Ri is now giving away two free WDS tickets via a competition on its LinkedIn, Instagram, Facebook and X social media platforms.
The free tickets, which do NOT include travel and accommodation, have a total monetary value of US$1,800 for contractors and US$5,500 for OEMs.
One lucky winner – chosen at random - will bag both tickets, receiving free access to the WDS’s welcome drinks reception, the full conference and the
World Demolition Awards and Gala Dinner.
Steed said: “I’m so thrilled to be able to offer these tickets to our readers and event delegates.
“This competition is just one of several small ways in which we can demonstrate our gratitude to everyone that has supported us over this past quarter of a century.”
The WDS is run in partnership with the European Demolition Association (EDA), in association with the US National Demolition Association (NDA) and the National Federation of Demolition Contractors (NDFC), and with the support of Swedish demolition association, Branschorganisationen för byggnadsberedning (BFB).
To learn more about WDS, please visit: www.demolitionsummit.com
Martin Smith, aged 38 from Strathdee Properties in Craigellachie, has been crowned Scottish Plant Operator Challenge Champion 2024 after emerging victorious at the national competition in July.
The event, sponsored by the CITB, took place on July 27th at Errol Airfield in Perthshire, where 44 plant operators from all over the country undertook eight challenges designed to put their skills to the test. The eight challenges included the Backhoe Loader Challenge, sponsored by JCB; Telehandler Challenge, sponsored by Scot JCB; Selector Grab Challenge on an 8t Tracked Excavator, sponsored by Field and Forest Machinery; Trenching challenge on a 13t Tracked Excavator, sponsored by Blackwood Plant Hire; Lifting Challenge on a 20t Tracked Excavator Challenge, sponsored by SANY; Grading Challenge on a 20t Tracked Excavator, sponsored by Scot JCB; Attachment Challenge on a 14t Excavator sponsored by Geith and Morris Leslie and finally the Mystery Wildcard Challenge which turned out to be on a compact tracked loader from Manitou.
Martin Smith won £5,000 as well as an array of exclusive rewards from sponsors including Highland Industrial Supplies and Milwaukee.
Martin Smith finished first in the individual challenges Trenching and Loadall and placed first overall.
On being crowned Scottish Plant Operator Challenge Champion 2024, Martin Smith said: “It feels amazing to win, especially because I came into the plant industry late. When I first left school, I worked as a welder fabricator but growing up in Speyside, I was never far from plant machinery used in farming and I’d always been drawn to farming. When I started working for Strathdee Properties in 2011, it offered me the perfect balance because the company is involved in farming and property development, so before long I was behind the leavers on an excavator and I haven’t looked back since!
“I really enjoyed taking part in the Scottish Plant Operator Challenge; it was a great day out. The challenges were not easy but I am pleased with how I handled it and just delighted to have won.”
Thomasz Orkiszewski from Mouse Valley Training Ltd and a CPCS and NPORS Trainer and Tester, was one of the judges at the Scottish Plant Operator Challenge. Speaking about Martin, Thomas said: “Martin is a worthy winner. He excelled in the Trenching and Loadall challenges and kept calm and held his nerve to finish on top. Congratulations Martin!”
Speaking about the Scottish Plant Operator Challenge 2024, promoter Callum Mackintosh added: “What a weekend! This was the second edition of the Scottish Plant Operator Challenge, and the event is going from strength to
strength. We were honoured to have First Minister and MSP for Perthshire North, John Swinney, open the event. We welcomed visitors of all ages and from all over the country.
“A big thank you to Morris Leslie who once again allowed us to run the Scottish Plant Operator Challenge alongside the Vintage Working Plant and Tractor Weekend, a firm favourite with plant enthusiasts and local people. Congratulations to Martin Smith, a worthy winner who I hope will inspire other people, especially the younger generation, to consider a career in plant. Well done to all the operators who took part and thank you to all our sponsors, helpers and friends because without their support, this event would not happen.”
Thanks to the generosity of visitors to the Scottish Plant Operator Challenge and Vintage Working Plant and Tractor Weekend, £3,800 was raised on the gate for TASH4Ukraine, a charity based at Errol Airfield which works closely with volunteers and charities in Poland, Ukraine and the UK to provide practical, targeted aid to Ukrainians following the Russian invasion.
Hughes & Salvidge have been appointed the role of subcontractor for demolition works at Royal Sussex County Hospital, Eastern Road, Brighton, BN2 5BE
• Soft Stripping of all Buildings
• Asbestos Removal
• Mechanical Demolition of Superstructures
• Mechanical Demolition of Substructures
• Crushing of inert arisings
The asbestos enclosures were formed using the existing matrix of the building, and additional timber supports were installed where required. They were sealed using 1000-gauge polythene, adhesive tape, spray adhesive and expanding foam as required. Following the erection of the enclosures, a 3-stage air lock and separate bag locks were attached. Where possible, the non-asbestos ceiling tiles and supporting grid were lowered and cleaned for disposal as general waste. All cables and services within the work areas were cut out, cleaned, and again disposed of as general waste. The exposed pipe sections had a dilute solution of wetting agent applied to the localised area using a low-pressure hand pump spray bottle. Sufficient time was allowed for the surfactant to absorb until the dry material, former pipework, etc was wet as reasonably practicable before removal commenced.
The areas to be removed were needle-injected to ensure they were thoroughly wetted prior to removal with hand tools. The accessible loose material and debris were carefully removed via gloved hands and immediately bagged for disposal. The contaminated sections of pipework were double-wrapped in 1000-gauge polythene and sealed with adhesive tape, ready for cutting out into 2.5m lengths. All pipework was cold cut with a reciprocating saw and removed to enable a complete clean of the ceiling voids and provide better access to the walls and ceiling debris. All residue to the walls and ceilings was removed with the use of scrubbing pads with the hotspots of residue sprayed with a fibre suppressant via hand-held units. The works continued as described above until all the specific pipe and associated residue sections were cleaned/removed and all debris bagged.
Upon successful completion of the four-stage clearance procedure, the analyst issued a “Certificate of Re-occupation” to the client and our Site Manager for follow-on trades and inclusion in the H&S File.
Soft-striping of the Barry Building was completed to two sections ahead of mechanical demolition. A third section was completed during the structural demolition of the initial sections. All soft-stripping debris was initially segregated into appropriate waste streams stored internally and scheduled for removal during the mechanical demolition stage. This was due to the limited external space.
Several areas within the structure were designated for storage, with structural calculations performed to ensure the waste point loadings would not compromise the building’s structural integrity.
Scaffold handrail and harris fence panels were installed at any point that would become a leading edge to ensure safety. These handrails were then demolished with the structure to prevent labour from working adjacent to a created opening. The additional buildings followed the same process of softstripping.
During demolition, skips were moved, delivered to the work face, and positioned adjacent to the work area. Locations were agreed between all parties and recorded on the temporary works register.
Following the completion of asbestos removal and softstripping, structural demolition commenced. Initially, a singlestorey structure was removed to create a larger working area. Our ZX300 supported our high-reach equipment in reducing the four-storey sections. The Komatsu PC490 excavator was set up in a high-reach configuration with a 28m reach, and it handled the Barry building, which was approximately 16.5m in height. Demolition started on the southern elevation, progressing north and then west.
The excavator, equipped with a selector attachment, first removed the timber-pitched roof, lifting and lowering it to the ground floor. It then progressively removed the window units on the southern elevation within the machine’s reach, lowering them to the ground floor. The excavator reduced the height of the external masonry walls on the third floor, allowing the material to fall to grade after scraping it from the floors. The brickwork was reduced top-down in sections and progressively cleared from the floors to prevent overloading.
With the perimeter masonry removed to the third floor, the internal walls and intermediate floors were exposed. The excavator progressively reduced and removed the internal walls, lifting and lowering any remaining timber or stud
All soft-stripping debris was initially segregated into appropriate waste streams stored internally
partitions to the ground floor. The next intermediate floor was removed, followed by the external wall below. This process was repeated top-down, with the three identified basements backfilled with inert arisings as work progressed.
A second machine was present throughout the demolition to process the arising materials. Inert materials such as brick and concrete were stockpiled for crushing as works neared completion, while other materials, like general waste and metals, were removed to keep the site clear and maximise working space.
Throughout the works, one structure remained operational and required mechanical separation from the other structures. A fire exit route had to be maintained, and scaffold screen protection had to be installed to safeguard the live hospital’s air intake system.
Once a significant portion of the ground-bearing slab was exposed, machines equipped with impact hammers and buckets began removing the slab and foundations. They punctured the slab and foundations to break them into movable sections. Machines with buckets then lifted and stockpiled sections for further processing. Machines with pulverisers processed arisings further to separate concrete from reinforcing bars and load away respective materials.
All excavations and basements were progressively backfilled after foundation removal. The area was graded to match the surrounding site contours, and the footprint was tracked in by machine, leaving a flat site.
Site-won hard inert arisings were crushed on-site to produce aggregate for re-use. Concrete/hardcore was loaded into the hopper by an excavator, which is hydraulically fed into the crusher. The crushed material falls onto the conveyor where any reinforcement bar or other ferrous metal is removed by a hydraulic belt magnet fitted above the main conveyor. The crusher then discharges crushed aggregate and metal into two separate stockpiles. Metal was periodically loaded away into metal bins, and aggregate was regularly cleared and stockpiled in the client’s desired locations. Aggregate stockpiles were formed with a suitable angle of repose to ensure they remained stable and to mitigate any “land-sliding” of aggregate. The crusher is fitted with a dust suppression system, whereby water is sprayed onto the discharge conveyor to minimise dust. Arising stockpiles were dampened down at regular intervals to mitigate dust release. The area was left clean and tidy on completion.
other materials, like general waste and metals, were removed to keep the site clear and maximise working space
The famous quarry and mining exhibition was back for another stellar show, exceeding expectations and conjuring a crowd, and alongside it, we made our show debut!
Demolition Spotlight was thrilled to be able to meet the crowds at Hillhead 2024 and showcase everything we have to offer to the industry.
We caught-up with some fantastic people over the three days and can’t wait to tell you about them!
Catching-up with the team at BPH is always a treat and Hillhead was no exception. Their instantly recognisable purple attachments were out in full force, alongside a rather quaint toy excavator game which I definitely played on one too many times. We were delighted to show them their latest advert in the June issue of Plant Planet, and the guys on the stand were so excited they posed for a pic with a copy. It’s amazing to see their attachments at work, and they certainly made the most of their time at Hillhead.
Doyle’s Area Sales Managers were eager to assist their visitors with any questions, sales enquiries or even just to have a general chat. Doyle Machinery offers total solutions in Machinery and Equipment Sales, New and Used Machinery Sales, Short, Long Term and Contract Hire, Spare Parts, Servicing and Logistical Movements. They represent world-leading OEM brands such as: ARJES, EUREC, WILLIBALD, UFKES GREENTEC, STEINERT, BARFORD, SCREENBEE, MENART, SIBILIA and DUPUY. Their great dedication to transform vision into innovative and economical concepts was proven tenfold at Hillhead, and we can’t wait to see them at the next show.
Willie Doyle, Managing Director of Doyle Machinery, said Hillhead was a mustattend event: “We have a long history of exhibiting at Hillhead. With the UK and Ireland being our home market, the show is a great chance to catch-up with industry friends, colleagues, partners, and customers.
“It also serves as an excellent platform to engage with the wider industry and show how our latest product developments and innovations can help maximise the sustainability and profitability of businesses. Business aside, Hillhead is a fantastic opportunity to showcase and celebrate everything that’s great about quarrying, construction and waste-recycling.”
Red Knight 6 Ltd offer complete end-to-end solutions no matter the material recycling need. They are distributors of world leading crushing, screening and material recycling equipment to the UK and Ireland. Their variety of crushing solutions includes Rubble Master, who lead the world in impact crushers, giving greater flexibility in the type of material you need to produce. Rubble Master also had their new jaw crusher working in the demo area, which was incredible to see in action. RK6 also have a 19 tonne jaw crusher available from Nordmann and a variety of more compact jaw and impact crushers available from Komplet, meaning even the smallest of yards can keep on crushing.
They partner with Rubble Master, EDGE Innovate, MDS, Komplet, Nordmann, TrommALL and IMS to bring the very best equipment to the demolition, quarrying and recycling industries. All of their machine sales are underpinned by their sister company, RK6 Spares, who are dedicated to keeping machines up and running and are able to provide a wide range of spare parts at short notice from their warehouse.
Many companies had intuitive and well planned displays, but none more so than Hammerglass. Their simple interactive display clearly showcased their incredible product to full effects, with visitors trying their luck in a fair-like game. The object was simple; use a heavy rubber mallet to try and break the ‘glass’. And let me tell you, boy did people really try! On a sheet only 4mm thick, many an unlucky participant tried and failed to shatter the ‘glass’, a winning testament to this incredible safety venture.
Both Katarina Danielsson, PR and Content Creator, and Anders Rick, Marketing Director, were all too happy to talk us through Hammerglass.
“It started out as a security feature for buildings,” explained Katarina. “And now we are teaming up with many plant manufacturers who can see its safety benefit.”
“It works great for construction and demolition,” continued Anders. “Bars over glass affect visibility and small, but heavy, things can still get through and shatter real glass. This shows the need.”
Proof really was in ‘the pudding’, as I could think of no better way to demonstrate the might of such a fantastic safetyminded product.
It was a historical first appearance at Hillhead for Chinese manufacturer XCMG with their 40-tonne XE380E hydraulic excavator being put through its paces in the demo zone, as it is perfectly suited to our European workload. The XE380E is multifunctional, capable of demolition, construction and waste management. Not only that, but they actually debuted a staggering amount of new machines for the European market, all of which were proof of their commitment to sustainability, which was quite the hot topic for Hillhead 2024. On top of this, each machine was at the forefront of technology, with machines like the XC978 Loader showcasing its unique cooling system, making it perfect for intense work, like mining. XCMG proved their growing commitment to Europe, and we can’t wait to see what’s next!
At the top of the hill, INMALO triumphed in welcoming visitors to peruse their range of performance leading attachments and dust suppression solutions. Amongst them were MBI concrete and stone RP and MCP pulverisers, MBI Eagle 3 shear, Montabert hydraulic breakers, Rock.Zone RockCrusher bucket and finally their industry leading Motofog and MB Dust Cannon dust suppression ranges.
Sad to have missed out? They’ve actually done a roundup video which you can check out in this link here: https:// youtube.com/shorts/thmSR_ABdZE?si=12a0F0g_T6Bn9eOf
Starting off with a brand new stand location, SANY had a fantastic 3 days. The range they brought to both static and the demonstration zone was extensive, including telehandlers, tandem rollers and excavators. Following its debut at ScotPlant, the STH1840 telehandler was the most anticipated of SANY’s incredible line-up, showcasing its incredible Stage V Deutz engine for the enamoured crowd. The quarry face demo zone hosted two SANY excavators, the 50-tonne SY500H and 40-tonne SY390H crawler excavators, both wowing everyone for the entire span of the three day event. And it wasn’t simply the quarry face demo zone that got all the action. In crusher alley, the 30-tonne SANY SY305C was also put through its paces to demonstrate just how capable and high performing the SANY machines are. A fantastic show all round for this leading brand.
At Hillhead 2024, the BlakerTech stand showcased its advanced metal recycling equipment, prominently featuring the SandFlo and MagThro. The live demonstrations attracted significant interest, notably from overseas visitors as far afield as Israel and Sweden. The SandFlo, renowned for efficiently separating aluminium from mixed non-ferrous materials, was a highlight, driving inquiries and bookings for clients’ own material testing. These demonstrations underscored the practical efficiency of BlakerTech’s equipment in metal recycling. The team say they are enthusiastic about forming new partnerships to advance global metal recycling companies.
The UK’s need for bespoke storage solutions has increased massively over the past few years. We have seen massive sheds constructed to allow the storage of a huge variety of products to meet the needs of our growing next day delivery culture. Whilst many locations are suitable for these new developments, there are certain locations where the demolition and regeneration of a former site is more suited.
This is where specialist demolition companies like Bury based Hitec Demolition come in. Formed in 2019 by Mark Mates, the company have developed into delivering a variety of demolition solutions across the UK and find themselves as one of the go-to companies when it comes to the arduous task of demolishing fire damaged buildings. ‘We have successfully delivered numerous projects where buildings have been structurally damaged by severe fires,’ Mark comments. ‘Working closely with all interested parties to safely remove the structures and contents allowing investigators to carry out their works in the process, we seem to be one of the companies first on insurance company’s lists to call.’
Whilst this niche has helped the company to develop, traditional demolition contracts have, and remain, the company’s bread and butter works.
By Paul Argent
‘We like to create a good working relationship with many contractors, and this has seen us constantly receive repeat business from them,’ Mark explains. ‘One of these companies is UK wide developer Glencar who specialise in building the large warehousing complexes and sheds we see popping up.’
It is a project on the outskirts of Bolton where the two companies have come together again to demolish the former operating centre for the local electricity board. The huge group of buildings lie on a sloping site and comprise of a mixture of structures constructed over many years. Steel framed sheds with cement sheeting roof coverings sit alongside metal sheeted versions providing Hitec with a mixture of materials to deal with.
The huge site required additional security fencing installed before works could commence and with this completed, the team’s attention turned to the commencement of internal soft strip and asbestos removal. Such was the size of each shed; the respective teams were able to work at opposite ends of the site keeping each task separated.
With this work ongoing within the sheds, Mark started bringing in his fleet of machines ready to commence the structural demolition works. Whilst the ongoing strip out works were underway, the main contractor received bad news that despite employing the services of a hawk abatement team, seagulls had managed to nest on one of the large roof lights situated on a fully metal clad shed. ‘This will cause us some time delays as we will be unable to work within the vicinity of the nesting birds,’ Mark commented. ‘We have however been given the all clear to commence structural demolition around the rear of the building, well away from any nest sites.’
Mark has recently invested in updating the machinery fleet for the company and has added a pair of CAT excavators in the shape of a 336 and 352 with operating weights of 38 and 52 tonnes respectively. These join several Volvo excavators and a Komatsu PC490 high reach which will be used on some of the harder to reach areas.
The first task for the team was to remove a heavily reinforced concrete platform on the rear of the buildings.
This structure was built over the sloping portion of the site with the underside used for storage whilst the deck itself was used as a loading bay for the former occupier’s artic trucks to be loaded from the sheds. ‘It’s a well-built structure and will take a bit of muscle to knock it down,’ Mark explains. ‘Our plan is to demolish the outer ring beam with the floor slab following onto the next beam and simply carry this process on.’
With experienced operator and Plant Manager Keith Healey on the levers of the CAT 352 stripping cladding off th,e adjoining of,fice building, equally experienced Contracts Director, Dom Curran, used the smaller CAT 336 to remove security gates and fencing to the concrete platform to allow access to the ring beam.
Whilst the company is still relatively small, Mark knows that making the most of the assets they have can make a huge difference to the way they can operate and has decided to fit the fleet of excavators with Lehnhoff hydraulic couplers from Worsley Plant. ‘Initially it was seen as an expense we didn’t need,’ Mark explains. ‘But as we grew, we saw that in having an excavator fitted with the Lehnhoff allowed us to be almost as productive as we were with two machines on site. Instead of having machines waiting with a muncher whilst a first strips the cladding, it takes just seconds to swap the attachments over and carry on working. There’s no more climbing in and out of the cab to change hoses and getting covered in oil, it’s all done from the comfort and safety of the seat.’
This increase in efficiency is shown immediately as both Keith and Dom quickly swap between their Rotar selector grabs and either a shear or cracker within seconds allowing them to undertake each task quickly using the correct tools. ‘They’re a great bit of kit,’ Keith comments. ‘There’s no more making do with the tool you have fitted or taking hoses off, it makes life easier.’ Speeding up the job in safety is what the team at Hitec are about and with the fencing and gates removed, Dom quickly changes the selector grab for the Rotar RCC30 cracker
to attack the ring beam. A very common site across European countries where many buildings are constructed from concrete, the cracker is seen less often on a UK site. With a maximum jaw opening of just over 1.1m, the RCC30 is the ideal tool for taking on the concrete ring beam.
‘We have a good working relationship with the team at Worsley Plant who supply the majority of our attachments. We know we are buying good quality with the back up to match.’
With the two machines making good progress into the building, the main contractor’s groundworks teams will soon be able to commence their work on removing the concrete slabs and foundations before they start their new road building work.
Whilst the structural demolition will not task the Hitec team, they are finding that associated issues still remain for demolition contractors. ‘We still see disconnections of services as one of the biggest hurdles we have to face,’ Mark explains. ‘Time constraints are always an issue as no sooner do we start on site that we see many clients pushing to have a section handed over for the piling teams or such like. This job has thrown up the issue of nesting seagulls and whilst they will take a few weeks to hatch and fledge, we will still be expected to deliver the project on time and within our original budget.’
The demolition industry operates in a hazardous environment, with asbestos being a particularly significant threat. Asbestos can still be found in the fabric of many buildings to this day, and it was used in a wide range of products and materials. To protect workers and the public, asbestos training is paramount.
UKATA is committed to setting the highest standards for asbestos training. By our members adhering to stringent quality measures, the association ensures that training providers deliver exceptional courses. This commitment to excellence translates into a safer working environment, including the demolition industry.
The demolition industry faces many challenges and issues relating to asbestos; therefore, I sat down and discussed all things asbestos with UKATA member and demolition expert Wayne Bagnall MBE, a Director of Wayne Bagnall Ltd as a chartered safety engineer specialising in asbestos and demolition EHSQ consultancy, expert witness and training, actively writing industry guidance. He has co-authored BS 6187 Code of practice for full and partial demolition and written papers on legacy asbestos in concrete internationally: mwb@waynebagnall.co.uk
What are the challenges for asbestos training and health?
Asbestos training has evolved significantly. Earlier training methods relied heavily on theoretical classroom instruction with limited practical experience, often passing down suboptimal practices. Today, regulations and oversight bodies like HSE and UKATA have improved training standards. However, inconsistencies persist, such as inadequate refresher training and a lack of CPD among some asbestos surveyors. While progress has been made, the global asbestos crisis underscores the need for continuous improvement. By enhancing training methodologies, emphasising best practices, and monitoring performance, we can effectively reduce asbestos-related health risks. Ultimately, a global ban on asbestos is crucial to eliminate this deadly substance. Are clients providing adequate asbestos information? For buildings constructed before 2000, asbestos surveys are essential prior to any work that could disturb the building structure. A Management Survey is typically sufficient for maintenance and repairs, while a more intrusive Refurbishment and Demolition Survey is required for structural refurbishment, partial or full demolition projects. These surveys should be conducted by a UKAS-accredited organisation as strongly recommended by HSE in their guidance HSG264 to ensure quality, accuracy and reliability.
The survey provides crucial information about asbestos location, condition, and quantity, enabling appropriate control measures to be implemented. Unfortunately, contractors often
encounter poor quality or outdated surveys, hindering safe working practices. Adhering to regulations like the Construction (Design and Management) Regulations 2015 and utilising accredited and/or certified surveyors providing high-quality asbestos information is vital for protecting workers and the public from exposure and spread of asbestos. What must clients and contractors do before demolition relating to asbestos?
Clients must understand their duties under CDM regulations, including appointing competent contractors and providing accurate pre-construction information (PCI). For pre-2000 buildings, a UKAS accredited asbestos survey is essential. Effective communication and cooperation between client and surveyor are crucial and a requirement in HSG 264.
Demolition contractors must verify the accuracy of the asbestos survey and be prepared for unexpected additional findings. All asbestos removal work must be planned and executed in accordance with regulations, ensuring worker safety and environmental protection. Strict adherence to control measures, including licensed asbestos removal, independent air monitoring, and waste management, is paramount.
Both parties must maintain clear documentation and records throughout the project.
Despite existing regulations, asbestos exposure still occurs, often due to poor information, negligence or occasionally pressure to complete jobs quickly. This makes adequate training not only a legal requirement but also an essential practice for ensuring safety. Every demolition worker must receive asbestos awareness training as a minimum from a competent source before starting work. This training should cover the history of asbestos, health risks, identification of ACMs, and relevant legislation. It is crucial to emphasise that asbestos awareness training alone does not qualify an individual to work with asbestos – it is meant to help in recognising the asbestos risks and avoiding exposure.
Where work with ACMs is to be undertaken, a further level of training must be undertaken by all the operatives involved with practical elements etc, the work must be thoroughly planned to ensure compliance. This training is referred to as non-licensable work with asbestos and covers low risk tasks such as removing asbestos cement product, for example roof sheeting, and textured decorative coatings followed by a statement of cleanliness.
Any high-risk materials e.g. Asbestos Insulation, Coating and Insulating Board must invariably be removed by a HSE licensed contractor, and the area declared safe by an independent 4 stage clearance ahead of completing your tasks.
https://www.ioshmagazine.com/2022/03/29/bringinghouse-down-celebrating-life-demolition
To find a UKATA approved training provider, you can find a full list on our website: www.ukata.org.uk
For media enquiries, please contact: Victoria Castelluccio Events & Marketing Manager 01246 824437 victoria.castelluccio@ukata.org.uk
The UK Asbestos Training Association (UKATA) remains at the forefront of asbestos training, committed to raising awareness about the pervasive threat of asbestos and the critical importance of responsible management.
By Paul Argent
Worsley Plant are proud to have been supplying AW Demolition with attachments for almost a decade.
The Irlam based contractor started his journey with Worsley Plant when he purchased his first Rotar RG37 in 2014 and has since gone on to add numerous Rotar grabs, pulverisers and shears along with equipping his entire fleet of excavators with the Lehnhoff Lehmatic hitch system. ‘When I was looking for a second selector grab for my first machine, the build quality of the Rotar stood out for me,’ Managing Director Austin Wilkinson commented. ‘Not only was the build quality good, but the deal put together by the team at Worsley Plant made it a simple decision for me to buy it.’
The past decade has seen AW Demolition add over 30 Rotar attachments into the fleet including selector grabs, crackers and processors, around 25 Lehnhoff hitches which have been fitted to machines from 13 to 80 tonnes in weight and several Dynaset magnets. ‘Like the Rotar products, the Lehnhoff was well built and had a good pedigree,’ Austin commented. ‘Taking the first hitch really opened my eyes as to the time savings which could be made using such an attachment. It wasn’t cheap, but calculating the downtime from changing tools, repairing broken hoses and damage repairs made from using the wrong attachment, soon made the cost more bearable.’
As machines were replaced or brought in for overhauls, the Lehnhoffs were fitted until every machine now carries the fully automatic hitch. ‘We’ve found that before Lehnhoff we would have needed an additional machine on site just to keep up with production. Now we can reduce that number by one or two units depending on the size of the site and still maintain production levels,’ Austin explained. ‘Whilst the initial outlay may seem expensive, we can recoup this cost easily over a 12 month period.’
One of the latest additions to join the fleet is also AW Demolition’s first new machine, a LiuGong 933F. Supplied direct from the dealer to Worsley Plant’s yard in Middlewich, the LiuGong was fitted with a VL250 Lehnhoff hitch and Rotar RG40N with the selector grab being fully tested before the machine was sent to work in Manchester. ‘Whilst we will happily fit and test our products on site, it was nice to be able to have the machine in the yard for us to work on,’ Sales Director Adrian Nixon commented. ‘It has been a pleasure working with Austin and his team over the past decade and seeing him grow from a one man/one machine operation into one of the leading demolition contractors in the Northwest of England.’
With the new machine on site and undertaking the demolition of a former Premier Inn hotel, operator Kevin Gould was making full use of the Lehnhoff hitch as he was processing and sorting material from the remains of the building. ‘It’s a great piece of engineering and it gives me the ability to be far more productive than I was,’ he comments. ‘As I’m working my through the material if I find something that requires munching or cutting, it just takes a few seconds to swap my attachment over. Before it was easy to drop the tool, but you had to get out of the cab to swap hoses. This is okay when it’s a nice clean site but in the middle of winter, on a dark site, not so easy. Having the Lehnhoff has made my day easier and far safer.’
The former hotel was built of timber framed construction with a brick outer skin. Following a quick soft strip, the structural demolition commenced due to the tight time constraints for the commencement of the following piling works. ‘We would have liked to have spent more time undertaking a more thorough strip out but unfortunately we were unable to do so on the initial part of the project.’ Austin commented. ‘The second phase is already being stripped out to our higher standards.’
With Austin on the CAT high reach taking down the structure, it was left to Kevin to pick and sort through the material for onward recycling. ‘It can be a timeconsuming job,’ he commented. ‘But having the selector grab makes it a little easier.’ Segregating material into their relevant piles, Kevin works his way through the material occasionally pausing to load out a bulk skip to keep the site tidy. Having come across a large quantity of mattresses during their strip out works, some used and some new, the team contacted several local charities to hand out the expensive items free of charge. The used and soiled ones left over required specialist recycling although one or two were kept back to use as ideal sweeping brushes when picked up by the Rotar grabs. The site team headed by experienced Demolition Manager Melvyn Hall worked quickly to ensure the onward construction program was not affected by any delay in the demolition works. With Kevin ensuring the resulting demolition arisings were cleared on time, his next task was to remove the slab and foundations to allow a substantial piling mat to be installed. Austin commented: ‘We are being called on more and more to provide a complete package of ground reinstatement as well as demolition works.’
Whilst the arrival of the LiuGong is the first new excavator into the fleet, Austin is still a believer in having the right attachments for the job in hand. ‘I have always gone down the route of having the machines looking right, whatever their age but for me, it is the attachment on the end that does the work. If you have a cheap or poorly maintained attachment, the job is made harder.’
Six decades of experience provided by one of the UK’s leading Demolition and Decommissioning companies.
Demolition & Decommissioning
Dismantling & Asset Recovery
Decontamination
Airport Specialist
As a full-service demolition contractor, we work with our associated companies to offer the complete solution to our clients, providing significant cost savings via our complimentary offerings. The complete solution enables us to accurately forecast our waste arisings to achieve a recycling rate of over 97% on every project, limiting our impact on the environment and the communities we work in.
For this month’s Demo Report, Managing Editor, Becks is back on site with Hughes & Salvidge and this time, it’s all about one man: Charlie Cawte.
I’ll start by saying, that of all the people I have ever interviewed, Charlie might be the most at ease. I genuinely believe that something could accidentally explode near him, and he would give a simple nod, then go and deal with it as if it were no big deal. I was really excited to sit down with him and learn more in depth about this man who was as cool as a cucumber.
Arriving on site, I got to see the usual neat and tidy order that accompanies any H&S worksite, where Charlie led me through to the tearoom and made me a lovely strong cuppa whilst we waited for Luke Gould to arrive with us (traffic, am I right ladies and gents?!) Once the gang was altogether, we sat down and got to chatting…
Okay, let’s get the basic questions out of the way. How did you get started in demolition?
Charlie: Well, I was actually a butcher to start off with.
Oh really?
Charlie: Yeah, 14 years. I did my apprenticeship at Smithfield Market, which was two days a week, every other week, before I went full-time. Then, I guess, I just fell out of love with it. So, I decided to leave, and the very next day I had a job working for a subcontractor to H&SL. Basically, we would take the buildings down to ground level, then sell on all the materials like chimney pots, slates, timber and bricks. Then the boss at H&SL offered me a job with them directly, so I started on the Monday as a supervisor.
So quite a different start before demolition then?
Charlie: Absolutely.
What was it that kept you in demolition?
Charlie: I fell in love with the work. It really started when the managing director said, ‘do you want to go out and work at the airport? Only ten weeks.’ So, we went and out there, sorted all the inductions and all that, and basically took over from another contractor. So, there was a fair amount to tidy up and get to our standard. It’s much easier to start something right from the word go, but sadly that wasn’t the case there. But I liked the challenge. And after that, the higher-ups were so impressed with the work, that we won another contract. And then another. And then another. And fifteen years later, we were still there working on terminal five.
Wow! That’s quite the change in job.
Charlie: Certainly was. And at that point, it wasn’t all what I enjoyed. I was given a budget to take potential clients out, schmooze them a little, I guess. And the work was certainly coming in. We got some nice jobs, but it was so much back and forth. So much paperwork. I wanted to be on site with the lads, managing that side of things. The paperwork was never my strong suit. That’s when I handed that other side of things over to Danny. I said you do tenders, and all paperwork, and I’ll just run the site.
They’re quite different jobs though really, aren’t they? The contracts side and the site side.
Luke: Totally different. And it’s better we all stay where we’re suited to. That being said, a lot of it wouldn’t be possible if it weren’t for the extensive knowledge of folks like Charlie. We all learn so much from him.
Charlie: And you remember what I told you last time I saw you? What TEAM stands for?
Remind me, Charlie, you know what a scatterbrain I can be.
Charlie: Together Everyone Achieves More.
That’s the one! A very good parable. And actually having people in their areas of strength is far better than trying to get people to do things, no matter their knowledge base, that they’re not suited to.
Luke: Without Charlie, we wouldn’t have the gold standard we have today. Right from the word go, he shows everyone how a site should be run so it’s safe, tidy and orderly. And they take that with them wherever they go.
Charlie: Now, it’s just second-nature I guess, but that’s good. My motto is ‘don’t live like it, don’t work like it.’
And like you say, that must help when you’re having to go in and take over jobs from other companies, who haven’t run it that way.
Charlie: It certainly does. And it’s quicker. To be honest, the level of trust we have now, definitely makes things run smoothly. People at Head Office know I don’t ask for something unless I really need it. If I ring them and say, ‘I need a 44 cherry picker,’ there’s no question of why. It’s just ‘send us the method statements’ and that’s it. Luke: It’s your reputation Charlie, you’ve earned that trust.
You’re also one of the calmest people I have ever met. I’m sure that has something to do with it. No request you make would be unreasonable.
Charlie: There’s always a solution to every problem. Sometimes, it requires a step back to see what that is. No point in getting all het up about it. You also need to listen to other people’s opinions on it. I think a lot of people can get too big for their boots and think that they’re the only one with an answer, particularly when it comes to the young folk on site. I can remember plenty of times where, actually, someone with a fresh approach has been the one to give us the right way to go about something. That’s something I’d always advise people to do. Listen to the nippers, they have something to say!
It sounds like good advice to me. So then, what have been your best and worst jobs in your tenure?
Charlie: Best was definitely the old control tower at Heathrow. We worked on that for 12 months, taking down the south and west wings that connected the tower to the airport. That was alongside Laing O’Rourke who were building the new ramp. There was a lot of problem-solving there, which I really enjoyed. And our team was such a close knit one. We had this Polish weightlifter working with us, Jarek, and where the rest of us would take breaks up the 640 steps to the top of that tower, he’d carry boxes all the way to the top like it was nothing.
I know that name! My husband is a powerlifter and I swear I’ve heard him talking about a Jarek!
Charlie: I think he was an Olympic champion or competed in World’s Strongest Man.
That’s the one! How exciting!
Charlie: The entire team was amazing, but he always stood out.
I bet he did.
Charlie: I also worked with Jim Stevens, who’s a top site manager. And watching him work was a joy. He’s so particular about everything. Tightest ship I’ve ever seen. He knew his stuff and there was always a lot to learn from him. That was a real joy.
And your worst job?
Charlie: Definitely a slaughterhouse in Porchester. Every night we went home stinking and let me tell you that smell was something else. They’d never actually cleared the site, so it was filled with… erm… let’s just call it old produce.
That sounds absolutely disgusting.
Charlie: Oh it was.
Luke: I’m not sure we have any photos of that particular project…
Oh, that’s perfectly all right. I definitely don’t want to see that. My stomach isn’t strong.
Charlie: It’s for the best. It wasn’t pleasant. And it was just difficult, you know? There were no phones back then, so if I needed to phone the office it was off up the road to the nearest phone box. So, if I needed a new labourer or a lorry, there was always a wait. But honestly, that’s the only one that sticks out in my mind as a bad job, as it were.
No phones, sounds awful.
Charlie: I have a bit of a love/hate relationship with phones. They make the job easier, but nowadays, work breaks are just filled with everyone sat on their phones. In a room of eight people, I’d say seven are just sat on their phones. The banter has gone. And it means you miss chatting about the work. Things that could be resolved in a simple conversation are all done by email now, and it just wastes time.
Is that something you wish would change back?
Charlie: Yeah. Don’t get me wrong, the staff wellbeing for H&SL is amazing. They’re a company that cares. But phones are a general distraction. I think that goes for everywhere, not just the workplace. But you know what, I’m 70 next year. And I’m gonna keep going until I can’t work anymore. I love this job; I take pride in it. Particularly when I do get to pass on wisdom to the nippers. I’m only as good as the last lot of lads I worked with, and I reckon I’m lucky that I haven’t come across a bad bunch.
INMALO have supplied two models of the Eagle 3 to Hughes and Salvidge, one of which has recently been shipped off to their site in Portugal!
Eagle 3
· The shear is designed to demolish iron and steel structures or buildings, large means of transport such as aircraft or boats, tanks and cisterns.
The ideal tool for scrap and recycling of ferrous material destined for new life.
Redesigned jaws and increased cutting force allow for high level performance in metal cutting.
· Interchangeable tip and blades make maintenance simple and quick, keeping the tool at full efficiency.
The Speed-Valve reduces opening and closing times, improving productivity.
· The continuous hydraulic rotation enables precise positioning in high reach demolition and the double-row thrust bearing ensures high robustness and increases safety.
The quick and easy routine maintenance allows to reduce intervention times and costs.
Real-time tracking of equipment performance.
New Compact Frame: The new design features a smaller frame, a unique weight-performance-ratio and greater stability of the excavator thanks to the centre of gravity being moved to the rear.
Up To 30% More Cutting Force: The Eagle 3 line has been designed to increase the cutting force on all models, the new design of the jaws allows up to 9% larger opening to maximize work when scrapping.
New Water Jet Cut Jaws: Lower and upper jaws are cut with high-pressure water jet from 160 mm thick Hardox® steel plate and then completely milled to keep the mechanical characteristics of the steel unchanged and to avoid possible weakening due to high temperatures during both, the cutting process and the machining phase.
New Cutting System: A single integrated guide puck allows the upper jaw to use 100% of the cutting capacity even at difficult angles, such as when cutting tanks and reduces the deflection of the upper jaw. This results in increased productivity.
New Upper Jaw Design: Machined in every part, completely redesigned to operate with absolute stability and precision, made from a single element without welding; equipped with a new
type of exchangeable piercing tip that offers greater protection and reliability, with easier maintenance, reduced costs and downtime. The blade seats are milled from the solid to increase resistance.
New Oversized Cylinder: The cylinder is inverted to protect the rod inside, the enlarged bore develops more power by accelerating the cycles (opening and closing speed). Completely forged rod from the solid, ensuring superior resistance compared to a conventional cylinder. Equipped with premium quality seals that can last up to 3.000 hours.
New Armoured Plates: The most heavily used parts are armoured with interchangeable Hardox® 500 steel plates installed on the jaw profiles to avoid frequent maintenance operations that could affect the operational readiness of the shear The armouring allows the shear to resist any impact without altering their structure, maintaining a very high level of wear resistance. Once worn, the armoured parts can be replaced, restoring the longevity of the equipment.
Real-time Tracking: The Smart Box controls the attachment remotely thanks to 9 different sensors, including GPS, hour counter and shock detector.
Easy Maintenance: The EAGLE III series is designed to maximize its durability and to be maintained without complex interventions. The heavy-duty pivot components contribute to durability and long life, the central pin of the shear can be easily removed, directly on job-site with simple and quick interventions.
Shellplant Ltd of Earls Barton, Northamptonshire is proud to announce that it has secured an order from H.E. Services (Plant Hire) Ltd for the supply of over 100 Thwaites dumpers.
The order includes Thwaites’ market leading One Tonne Hi Tip dumpers. Compact in size, with a width of 1195 mm for optimum stability, these are ideal machines for working in confined spaces or where access is limited. They also benefit from user-friendly hydrostatic transmission which makes operation simple, together with an effective and efficient skip loader.
Additionally, the order comprises Thwaites 3 Tonne Powerswivel dumpers which are also fitted with hydrostatic transmission for simple operation. The machines are powered by a Yanmar Stage V 18.1 kW engine which provides, via the hydrostatic transmission, optimum traction and control. Like the Thwaites One Tonne machines, the 3 Tonne Powerswivel dumpers are very simple and straightforward to control making them the ideal choice for hire fleets.
These machines, which are fitted with immobilisers and trackers, are now available to hire throughout the UK via
H.E. Services (Plant Hire) Ltd network of 11 depots located across the UK mainland.
Shellplant and H.E. Services enjoy a long heritage in the industry, both trading since 1972. This was the year when Hugh Edeleanu (founder of H.E. Services) purchased his first secondhand excavator, marking the start of H.E. Services. Since then, H.E. Services has grown to become Europe’s largest excavator hire company. Driving this has been the company’s commitment to people, quality and service. Now with a fleet of over 3500 items of plant, and a policy of machine replacement at three years, H.E. Services can provide hires for a duration from one day to over 25 years, to anywhere in the country from Land’s End to John O’Groats.
Hugh Edeleanu, Chairman, H.E. Services (Plant Hire) Ltd, commented: “Thwaites dumpers have a long and good pedigree and have always been very well designed and built. We are proud to be purchasing British designed and British-built machinery from a very well-established British business that has an excellent dealer network in the UK to back up its top-quality products. Thwaites dumpers are always very well
accepted on-site and have a high level of safety features, with our customers giving us very good feedback on these machines.”
Julian Payne, Partner, Shellplant says: “We are delighted to receive this large Thwaites dumper order from H.E. Services and thank them for the business. We look forward to supporting H.E. Services with their ongoing service requirements for the dumpers, and, through high levels of customer service, to becoming a trusted supply partner in the future.”
Shellplant, an established supplier of new and used construction equipment, has been trading for over 50 years and represents many leading brands including Atlas Copco, Bomag, Kubota, Merlo and Thwaites, with a reputation within the industry for quality products and attentive customer service.
To learn more about H.E. Services: www.heservices.co.uk
To learn more about Shellplant: www.shellplant.co.uk
DISMANTLING
SOFT-STRIP/REFURBISHMENTS
FACADE RETENTION
SITE CLEARANCE/BULK EXCAVATION
Meet the Leguan 225
Get ready for the next generation of spider lifts. With faster boom hydraulics, greater working height, unrivalled up-and-over reach, and groud-breaking joystick controls the Leguan 225 is our most advanced spider lift to date. User friendly design, improved driving features and a steel-reinforced chassis guarantee premium performance even in the roughest terrains.