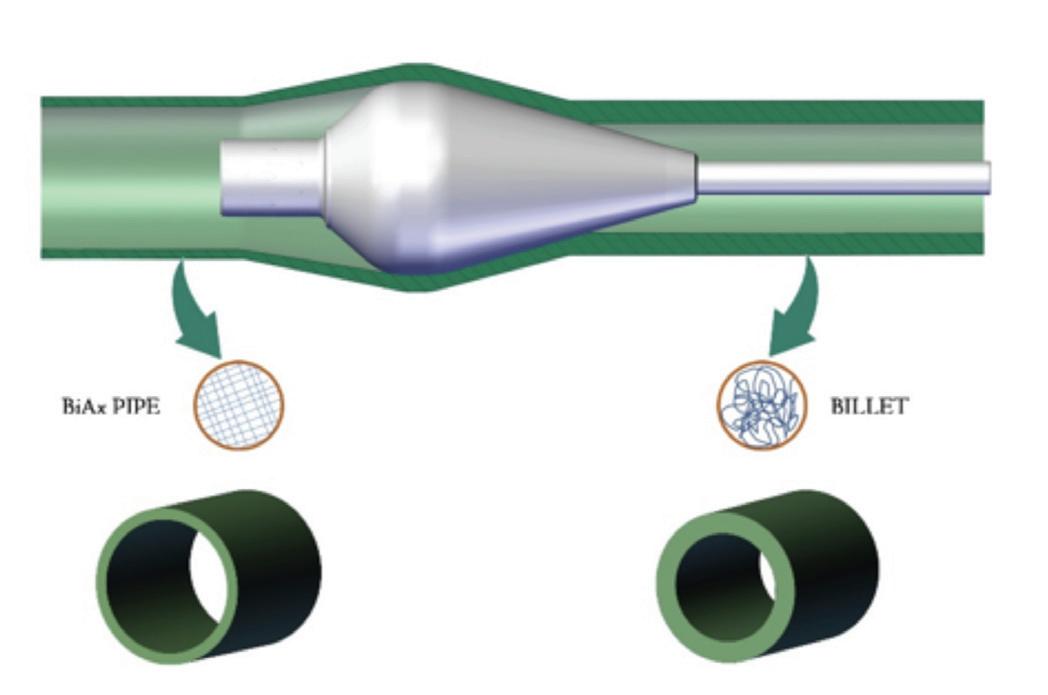
6 minute read
Pipe Sector
PiPe industry
Pipe sector pushes envelope for sustainability
Advertisement
With the imminent pressure on the plastics sector for sustainability, materials makers are introducing biomaterials for pipes, or the use of less material in pipe technology.
Sabic introduces new PO pressure pipe technology
With the urgent need for more durable and reliable as well as cost-efficient and sustainable pipe systems to meet the potable water and sanitation needs of an ever-growing global population, chemical firm Sabic has developed a new BiAx pipe technology and range of dedicated PE and PP resins. These are said to mark a significant leap forward in the performance profile of polyolefin pressure pipes.
BiAxPIPE BILLET
Sabic has developed a new range of PE and PP resins that offer improvements in key performance properties for biaxially stretched pressure water pipes
Together with Italian pipe manufacturing equipment specialist Tecnomatic and German PPR pipe systems supplier aquatherm the technology is being advanced from concept to reality.
Since the introduction of polyolefins for pressure pipes, continuous efforts have been made to improve the performance levels and expand the application scope of polyolefin pipes. Sabic says it has now succeeded in optimising the formulation of dedicated PE and PP resins for biaxial stretching that will allow manufacturers to boost the key properties of pressure pipes to unprecedented levels. The new resins in combination with the BiAx stretching technology will enable a new generation of lighter and stronger as well as energy and cost-efficient pipe systems.
The new technology is said to offer improvements over incumbent polyolefin pipes across the entire range of performance criteria. Higher resistance against internal pressure enables wall-thickness reduction and thus can reduce material use by at least 30%.
In addition, the smooth inner wall surface reduces the energy required for pumping. The technology renders the pipes more abrasion resistant and prolongs their lifetime. Combined, these characteristics provide a major leap forward.
The new PE and PP pipes promise better resistance to disinfectants, a lower coefficient of linear thermal expansion (CLTE) and improved low-temperature impact strength.
As part of these joint efforts, Tecnomatic has installed a fully integrated continuous BiAx pipe extrusion line for evaluation, trials and optimisation of the process. On this line, pipes are first conventionally extruded with thick walls and small diameters, then drawn over a heated mandrel and stretched in two directions to obtain larger diameters and thinner walls. This gives them their characteristic BiAx properties. Another partner in this project is aquatherm and it is targeting to introduce Sabic’s advanced biaxially oriented pressure pipe technology in a wide range of diversified application areas.

PiPe industry
Pipe system with renewable raw material
Ultra Rib 2 Blue is a new generation of PP sewer pipes with a significant carbon footprint reduction, achieved thanks to its composition of over 50% of raw material coming from certified renewable feedstock.
The pipe is a collaboration between Swedish pipe maker Uponor and materials supplier Borealis, which supplies its Bornewables, a portfolio of circular polyolefin products manufactured with renewable feedstocks.
The specifications of Ultra Rib 2 Blue are the same in terms of properties and performance as the standard Ultra Rib 2. The pipes are manufactured at Uponor's ISCC PLUS (International Sustainability & Carbon Certification) certified factory in Fristad, Sweden. As part of this certification, customers receive a sustainability declaration of the amount of renewable raw material in their delivery of Ultra Rib 2 Blue following the mass balance approach. metric pressure pipes, fittings and valves produced in Europe. The sustainable PVC resin, made using tall oil, a waste product from paper production, will see up to 90% reduction in the CO2 emission during production versus conventional PVC while still maintaining the highest quality, durability, and recyclability, the company adds.
The PVC piping systems from GF, first produced in 1955, have been tried and tested for more than 65 years. Today, they include pipes, fittings, valves, actuators, and measurement and control technology used across industries in over 100 countries for the most demanding applications.
To achieve the biggest impact, the PVC resin used for pipes, fittings and valves is successively adjusted to use up to 20% bio-attributed PVC. The sustainable PVC resins meet the same stringent performance criteria as GF's conventionally produced PVC grades. To verify the correct use, an independent certification body is appointed to audit the production plants and supply chain which processes the bioattributed PVC-U. "With the introduction of bio-attributed PVC into our material mix, we are transitioning toward more sustainably sourced products," announces Jens Frisenborg, Head of Business Unit Industry/Utility at GF Piping Systems. "By adding renewable raw material, with identical chemical and mechanical properties, to our valves, fittings and pipes, we provide our customers with unrivalled quality, while also supporting them in achieving their own sustainability goals." Insensitive, flexible to plan, easy to install, and reliable: these properties Jens Frisenborg, Head of BU Industry/Utility at GF of piping systems are in demand in numerous Piping Systems, adds that industrial areas: in the company is transitioning drinking water treatment, toward more sustainably microelectronics production, sourced products in sewage treatment plants, in shipbuilding, and the food industry.
GF adds that PVC piping systems are suitable for use in almost every branch of industry, saying “it is not only their durability that makes them so versatile but also their easy installation”. Now with bio-attributed PVC, GF concludes that it is ensuring they are more sustainably sourced.
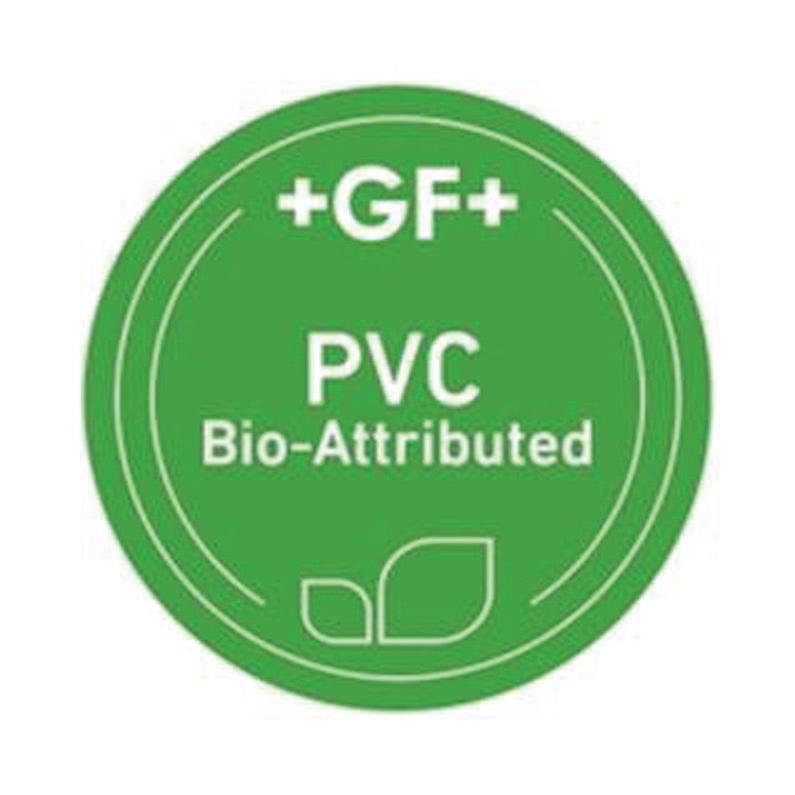
The reduction in CO2 footprint is achieved by partially replacing fossil feedstock with renewable feedstock, unsuitable for human consumption (waste and residue streams), and traceable back to the first collection points. The chain of custody created by the ISCC PLUS certification makes that Borealis’ Bornewables portfolio and Uponor’s Ultra Rib 2 Blue meet the sustainability standards of ISCC PLUS.
Furthermore, the partners add that data transparency is at the core of Ultra Rib 2 Blue and the Uponor Blue sustainable offering line. To help organisations to meet their sustainability goals, the products are backed with independently verified data. "We are pleased to collaborate with Borealis to create a plastic pipe with up to 70% reduction in carbon footprint. We are delivering on our promise to offer the highest quality now in a sustainable product. Our customers can be confident they are making the right decision for the future of our environment," says Sebastian Bondestam, President of Uponor Infra.
Robin Bresser, Head of Marketing, Pipe at Borealis, adds, “The Bornewables portfolio represents a key step in our efforts to offer products decoupled from fossil-based feedstock, with the aim of providing a solution to the climate challenge.”
Uponor and Borealis have introduced the Ultra Rib 2 Blue, which is based on Borealis Bornewables consisting of over 50% renewable raw material, reducing the carbon footprint by up to 70% GF’s label for the new, bio-attributed PVC products
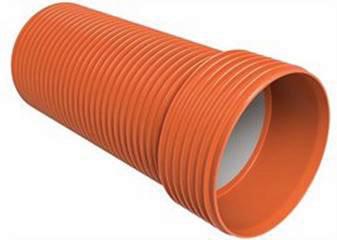
GF introduces bio-attributed PVC
As a pioneer of pressure piping, GF Piping Systems (GF) has announced the introduction of bio-attributed materials to all of its polyvinyl chloride (PVC-U)
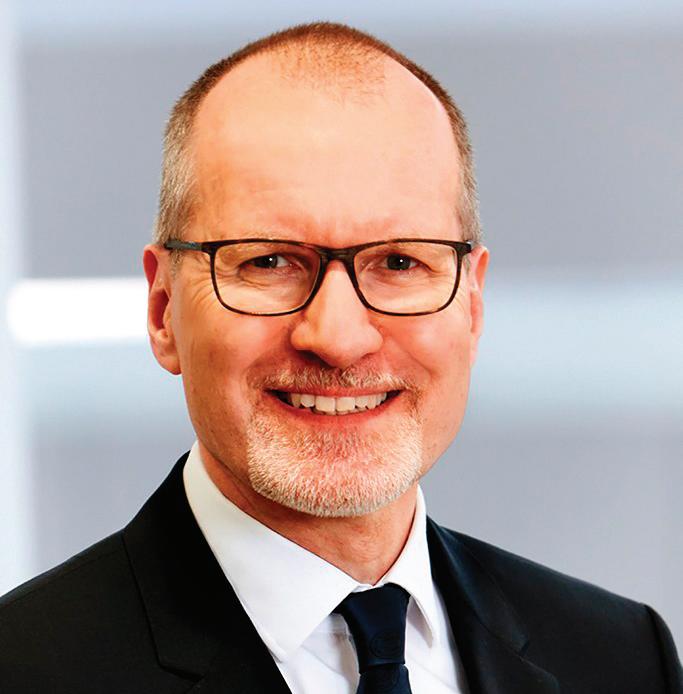