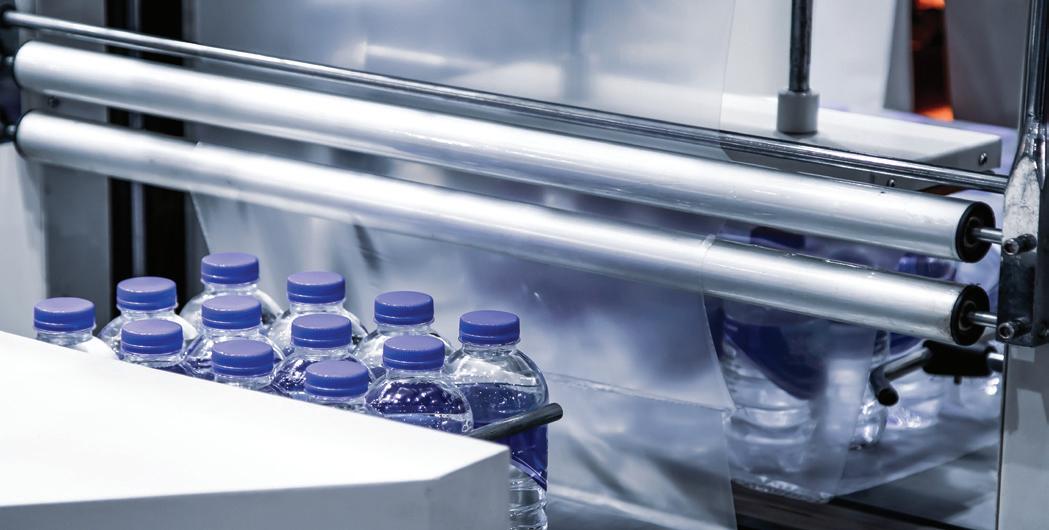
46 minute read
Film Technology
Film Technology ExxonMobil’s latest Exceed grades exceed performance levels
US firm ExxonMobil says it has developed a new series of Exceed XP performance polyethylene (PE) grades that deliver “remarkable” mechanical performance with a combination of low density and fractional melt index (MI).
Advertisement
Exceed XP 7021 and Exceed XP 7052 offer the value chain a combination of attributes that is currently not available in a single resin. This includes high levels of elasticity and holding force, puncture energy (up to 2.3 J/mil) and dart impact resistance (up to 900 gm on a 25.4 micron film).
The grades are targeted at stretch hood packaging, collation shrink, primary packaging, and greenhouse applications that previously were not possible.
Researched and trialled
It says that research and tests indicate that Exceed XP 7021 and Exceed XP 7052 also offer a combination of fractional MI and low density (0.911- 0.912 g/cm3) that is not available in the market today. This makes films with enhanced bubble stability and creates opportunities to increase output for converters.
Producers of stretch hood packaging films can now benefit from both high elastic recovery and high holding force. Thanks to the performance of Exceed XP 7021 and Exceed XP 7052 a compromise is no longer necessary, helping to enhance pallet stability for product protection and safety. The new performance PE grades also offer high puncture and dart impact resistance for less breakage, while delivering low haze which improves barcode and QR code reading. Ease of processing leads to excellent gauge control and the high elasticity provides forgiveness for less than perfect gauge profile.
Michael Vinck, Global Polyethylene New Products Marketing Manager, ExxonMobil said, “Tests undertaken in collaboration with Signode, an industry- leading OEM and manufacturer of Lachenmeier stretch hood equipment, resulted in a single resin Exceed XP 7-based solution. Although the film was co-extruded, it is a mono- material PE film contributing to its recyclability.”
Meanwhile, manufacturers of collation shrink films can offer their customers energy savings opportunities with the new grades, which enable high shrink speeds at temperatures as low as 120°C. Films can protect sensitive products from excessive heat. The removal of cardboard trays is possible in many applications. “Films which exhibit MD and TD shrinkage at low temperatures, and can be processed on traditional blown film lines, are a rarity in the market,” said Vinck.
Primary packaging films made with Exceed XP 7021 and Exceed XP 7052 can help seal packages at low temperatures without blocking issues. Customers can reduce anti-block levels to improve coefficient of friction (COF) control and optical properties for better brand promotion. Designed for low seal initiation temperature (SIT) packaging applications, these PE polymers also enhance packaging toughness with flex crack, extreme dart and puncture, while offering good optical properties.
“Flex-crack resistance is so high, tests undertaken by ExxonMobil resulted in an average of 1 hole per ten thousand cycles,” said Vinck. “The combination of fractional MI and a 0.912 g/cm3 density helps prevent seal thinning without the addition of LDPE when compared to conventional sealing resins.”
Greenhouse films that are tough, clear, and soft can now be fabricated by converters due to the extreme dart and puncture resistance offered by the Exceed grades. As a result, the greenhouse films have better integrity, reducing the risk of failure and premature breakage during installation and in-service. “Films made with these new grades offer farmers the opportunity to enjoy longer and better growing conditions for potentially higher crop yields, helping to meet the growing population’s need for food,” said Vinck.
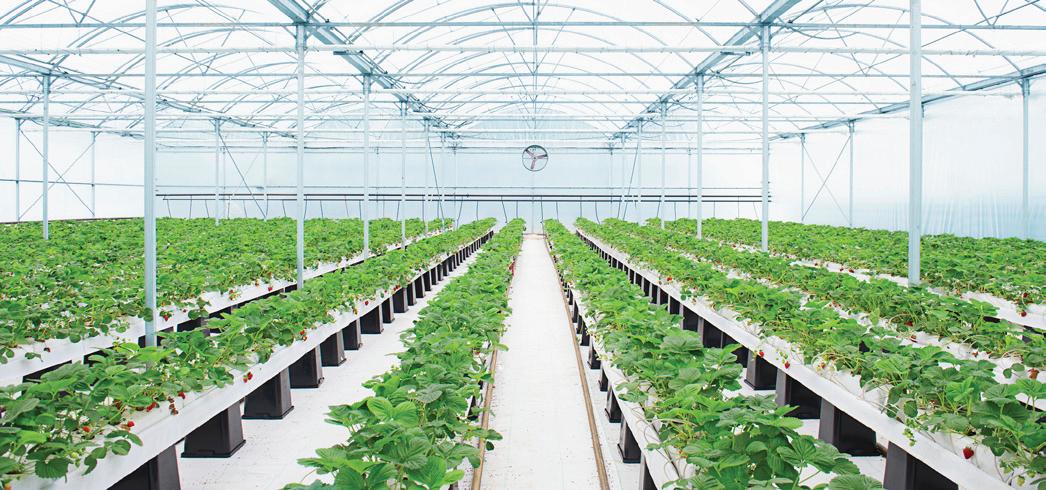
Greenhouse films feature remarkable softness and clarity combined with dart and puncture resistance for integrity
He adds, “Extending the extreme performance of our Exceed XP portfolio to ‘never seen before’ levels, these new grades are designed to help the value chain create innovative solutions to meet specific applications needs.”
“We are currently working closely with our value chain partners to develop film formulation solutions that many in the industry believe would only happen in the future but which, through collaboration, we are making possible today,” Vinck concludes.
Consumer Electronics
New innovations to level up electro-technology
High-performance electro-technology solutions are on the rise, in a world where speed, efficiency, and dependability are key benchmarks. These new innovations provide manufacturers with options for meeting consumer demand while emphasising product safety and longevity of service life, adds Angelica Buan in this report.
Avient’s ECCOH LSFOH grades for industrial and telecom cables, fulfil the performance requirements of fibre optics, telecommunications infrastructure, and comply with the new IEC 60794-6 standard
When it comes to cutting-edge electronic gadgets with high-performing functionalities, customers are not leaving shopping carts empty. And it’s not for the reasons we may think. The days of owning gadgets as a status symbol or buying the most recent gizmo to keep up with the Joneses are long gone.
In today’s fast-paced world, consumer electronics have become indispensable to consumers everywhere. With electronic devices, we are able to communicate, interact, plan our daily lives, and get our fix of entertainment.
Nonetheless, today’s consumers also expect a more robust user experience. Thus, market players are investing in R&D to introduce new advanced engineering materials and specialised grade compounds with properties that meet the performance, functionality, safety, and long service life requirements of consumers.
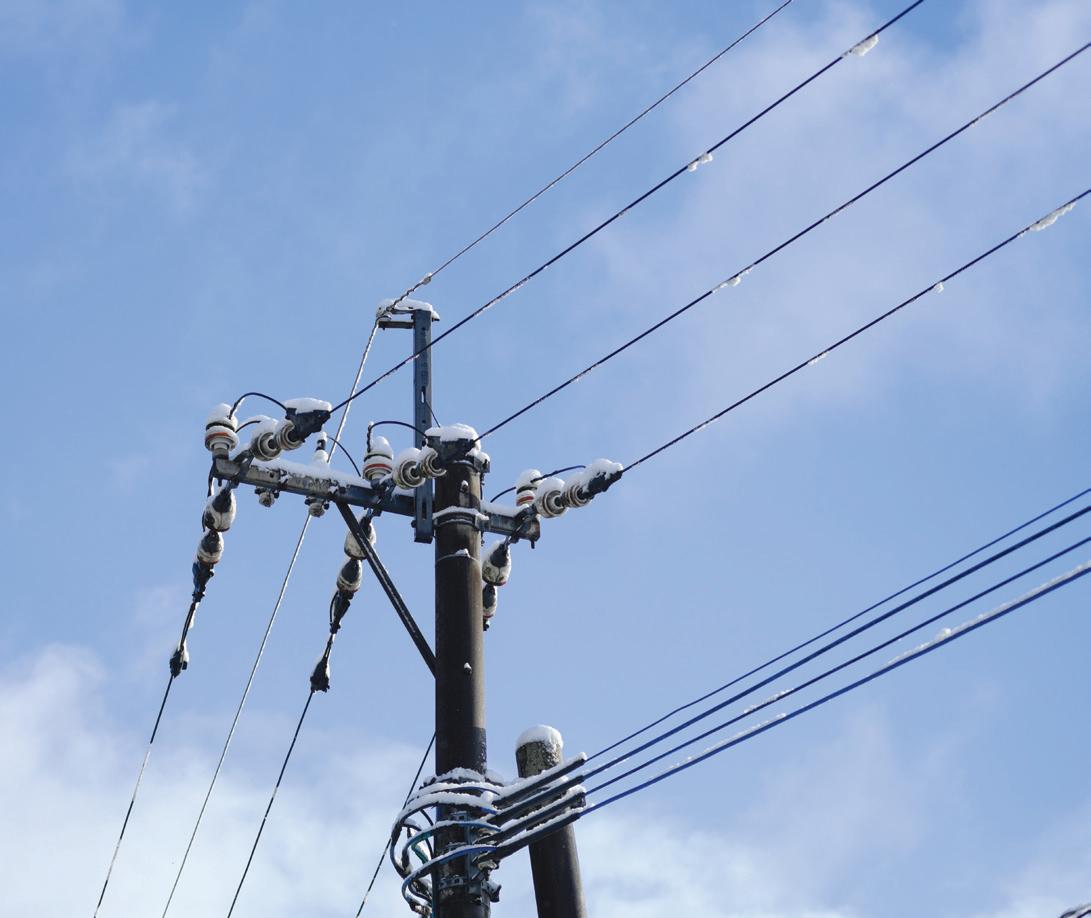
Low smoke solution for fibre optics application
Cables and wires, which are the vital arteries of electronic devices and electrical conduits, are prone to fire hazards. Used for cable jacketing in the wire and cable industry, low smoke-free halogen materials are thermoplastic or thermoset compounds that emit limited smoke and no halogen when subjected to heat or exposed to fire.
These flame retardant (FR) compounds address consumer concerns about fire safety and toxicity, as well as the growing demand for FR plastics in the construction, electrical and electronics, and transportation sectors, and government fire safety regulations.
Traditional materials like polyvinyl chloride (PVC) and fluorinated ethylene propylene emit less dense smoke and hardly any highly toxic gases called halogens. Thus, halogen-free, low-smoke cable cables are used in a variety of applications, including poorly ventilated areas and other potentially dangerous environments.
US manufacturer of specialised polymer materials Avient, formerly known as Polyone, has launched its new ECCOH LSFOH (low smoke and fume, zero halogen) grades for industrial and telecom cables, which fulfil the performance requirements of fibre optics, telecommunications infrastructure, and the new IEC 60794-6 standard.
Its latest offering, ECCOH 5565 and ECCOH 5978 UV, two new cable jacketing formulations, help extend the life of cables, it said.
Withstanding up to 20,000 flex fatigue cycles, ECCOH 5565 has flexibility and environmental stress cracking resistance (ESCR), making it ideal for power and control cables in industrial machinery, heating and air-conditioning systems, and plant engineering systems, where flex resistance is required during installation or use.
It also has good temperature resistance, operating over a wide temperature range of minus 40-80°C, as well as water absorption resistance. This makes it suitable for use in dry optical fibre cable applications or where additional cold resistance is required, such as indoor and outdoor duct cable applications, powerto-the-antennas, or 5G hybrid cables.
High flame retardancy and good char forming properties are combined with a high ESCR in ECCOH 5978 UV formulations. This makes them more effective in aerial drop cables, which are frequently subjected to constant stress from the clamps that keep them in place. This formulation can be used on direct buried cables and other duct or indoor applications that require extra flame and low dripping performance, as well as where cable fixations and movements put extra stress on the cable jacket.
Safety standards compliance with FR resins
With the implementation of safety standards, substandard electronic products are being pushed out of the market. This is beneficial to consumers. As well, with the implementation of the International Electrotechnical Commission’s new IEC 62368-1 consumer electronics safety standard, many manufacturers are looking for higher- performing FR materials.
Consumer Electronics
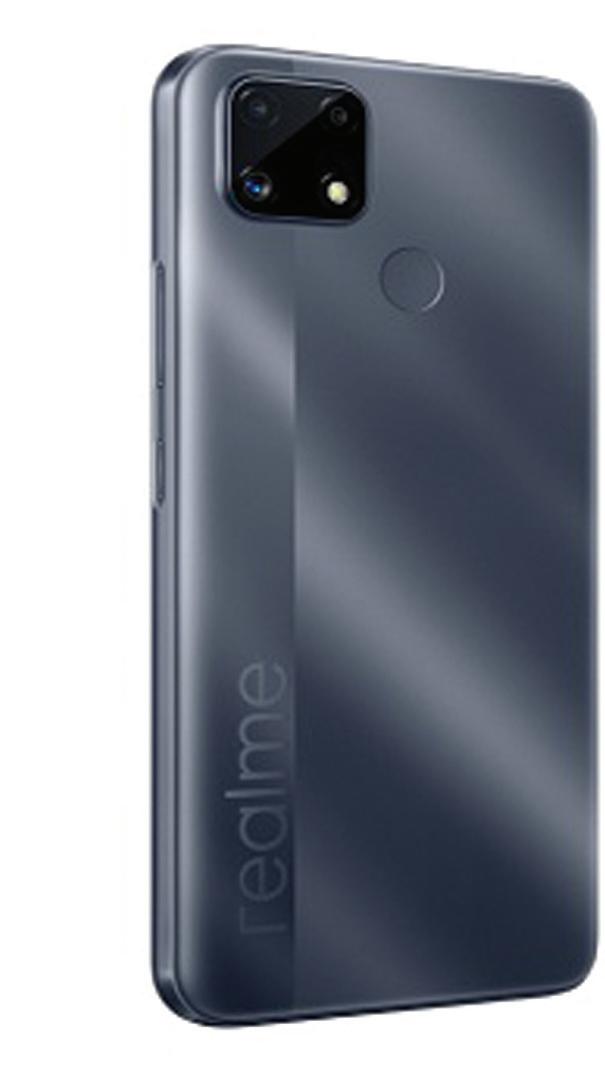
Realme uses chemical company Sabic’s new LNP Elcres EXL7414 copolymer resin for the battery enclosure of its C25 phone to achieve UL 94 V0 FR compliance at 0.6 mm
Sabic’s new LNP compounds offer enhanced anti-static performance for applications regulated under the EU’s increasingly stringent ATEX directive governing equipment used in explosive atmospheres
Chinese smartphone manufacturer Realme has chosen chemical company Sabic’s new LNP Elcres EXL7414 copolymer resin for the battery enclosure of its C25 phone to achieve UL 94 V0 FR compliance at 0.6 mm, as required by the new IEC standard. The C25 phone was designed to be thin (9.6 mm) and light (209 g).
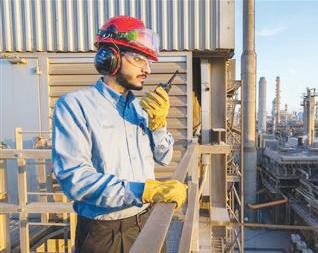
Furthermore, the new LNP copolymer resin’s flame retardance supports its potential use in ultra-thin-wall components, which could help save device weight and space in ever- thinner designs. The LNP copolymer resin also has good flow for thin-wall moulding, ductility to resist drop damage, and chemical resistance to withstand UV-cured painting.
Realme created an ultra-thin-wall battery cover to reduce product weight and maximise space for internal components while still adhering to the IEC standard.
It was the first consumer electronics company to use Sabic’s FR resin, a PC-based copolymer material that replaces standard PC while providing improved FR capability defined as UL 94 V0 at 0.6mm. LNP Elcres EXL7414 resin uses a non-chlorinated, non- brominated FR formulation as part of its safety value.
Sabic has also introduced LNP Stat-Kon and LNP Stat-Loy compounds, with enhanced anti-static performance for applications regulated under the EU’s increasingly stringent ATEX directive governing equipment used in explosive atmospheres. The new technologies can potentially replace less-effective metals and coated or filled polymers in electronics enclosures, automation equipment, equipment housings, lighting fixtures, safety gear and hand-held devices such as flashlights.
The two new products are based on Sabic’s LNP copolymers technology. Stat-Kon compound is said to be an advanced material that provides exceptional electrostatic discharge (ESD) protection while retaining impact resistance to safeguard sensitive electronics and offers processing ease.
Meanwhile, Stat-Loy D3000IEU6 compound is a colourable product that offers opportunities to reduce costly secondary painting operations and also adding aesthetics as previously ATEX applications were mainly in black.
TPU for high-strength, flexible applications
When compared to other types of polymeric films, thermoplastic polyurethane (TPU) films have a higher elongation and characteristics like high strength, flexibility, toughness, and ease of application, making it a better choice for demanding film applications.
Elastollan TPU from Germany-based chemical firm BASF is more than that. The company has launched a new Consumer Electronics toolkit that includes a collection of Elastollan TPU wearables and mobile phone protective cases.
Six classic Elastollan designs are featured in the collection, featuring scratch, UV, and discolouration resistance, as well as good transparency and ease of colouring. The protective cases can also be made with biocontent, thereby meeting the sustainability goals of consumer electronics brands.
The watch strap collection combines style with everyday wear and tear resistance, BASF said. The collection of textured straps made with Elastollan, developed with Singapore-headquartered Meiban’s laser texturing Innovation Meiban Skin (IMS) technology, has a soft touch feel and abrasion/UV resistance.
Consumer Electronics
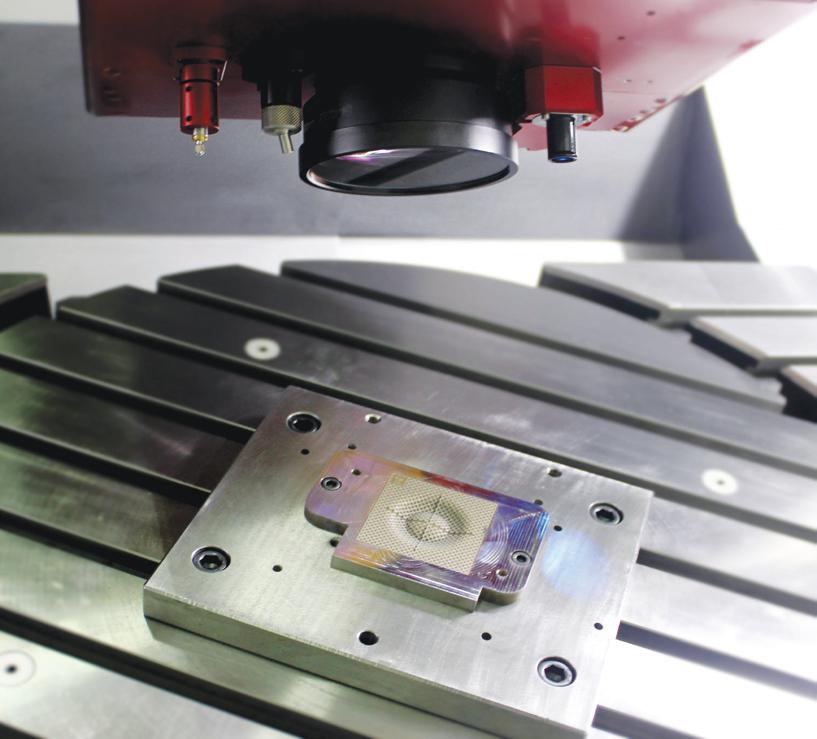
BASF’s Elastollan soft touch feel TPU series is made possible with Meiban’s Innovative Meiban Skin IMS technology
The innovation serves a much greater purpose for users as they can quickly visualise interactive 3D constructs for a richer and more immersive experience, according to BASF, through using mixed reality devices. Remote collaboration and streamlined creative workflows of ideas and concepts also largely owe to advanced technology.
Advancement in microelectronics
Global semiconductor equipment investments for front end fabrications are expected to reach nearly US$100 billion in 2022, driven by digital transformation and other secular technology trends. This is in line with meeting surging demand for electronics, according to the World Fab Forecast report released by SEMI, an industry association made up of companies involved in the electronics design and manufacturing supply chain.
In terms of regional fabrication equipment spending in 2022, South Korea will lead with US$30 billion, followed by Taiwan with US$26 billion, and China with nearly US$17 billion. With roughly US$9 billion in fabrication equipment spending, Japan will take fourth spot, while spending in the Americas and Southeast Asia is expected to exceed US$6 billion and US$2 billion, respectively.
This development underpins a collaboration between DuPont Electronics & Industrial and Kempur Microelectronics to supply microlithography materials in China to meet the country’s demand for advanced photoresists and other lithographic materials.
The collaboration will enable Kempur to quickly supply a wide range of lithographic materials to support customer growth.
Kempur, which was founded in 2004, is one of China’s largest photoresist manufacturers, with a portfolio that includes photoresists and other supporting materials for integrated circuit fabrication, as well as resists for lightemitting diodes (LED) fabrication and other applications.
DuPont is a global supplier in materials for semiconductor fabrication, with a diverse array of established products for lithography at multiple wavelengths, including 193nm (ArF), 248nm (KrF) and i/g-line photoresists, as well as spin-on carbon (SOC), antireflective coating materials (BARCs), advanced overcoats and ancillaries.
Meanwhile, at the back of an increased demand for printed circuit boards (PCBs) and advancements in connectivity and automotive electronics, DuPont debuted Circuit Materials Innovations at a China-held show earlier this year to keep up with emerging trends like PCB miniaturisation and a growing demand for highspeed data and signal transmission. Flexible PCBs and low-loss materials will continue to gain popularity as consumer electronics become smaller, thinner, and more multifunctional
The High-Density Interconnect (HDI), Substratelike PCB (SLP), and IC Substrate segments of DuPont Interconnect Solutions’ broad product portfolio are designed for fine- line applications. The Riston DI95 Dry Film, a multi-wavelength DI dry film photoresist developed for pitch 70m HDI tent/etch process, is one of the new products. It allows for fine patterning with high yields.
Pyralux GFL Sheet Adhesive is a proprietary B-staged modified polymer adhesive with low-loss properties for high-performance applications and excellent mechanical resilience for high-yield circuit fabrication.
Pyralux GFL is primarily utilised to bond flexible inner layers or rigid cap layers in flexible and rigid-flex constructions; and the Interra HK 04J, a thin laminate with a polyimide dielectric, is designed to function as a power and ground plane in printed wiring boards (PWBs). It is ideal for applications such as embedded capacitance technology for PWB or semiconductor packaging, and high-speed digital applications for reduced impedance.
DuPont said that these technologies enable miniaturised devices and improve the functionality of electronic components while enhancing high reliability and productivity.
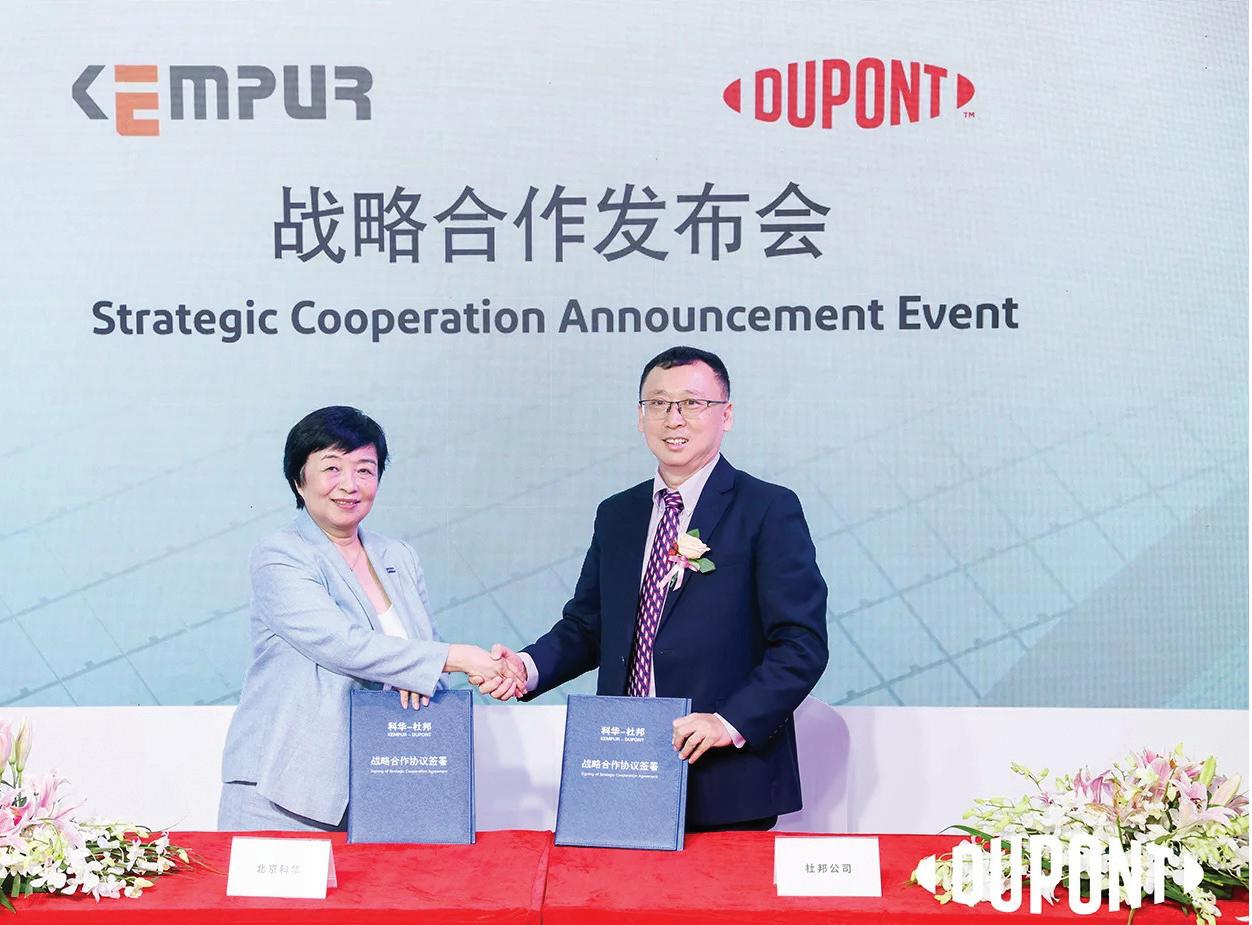
DuPont Electronics & Industrial and Kempur partnered up to supply microlithography materials in China to meet the country’s demand for advanced photoresists and other lithographic materials
Advertorial
Plastics industry’s efforts to comply with China’s “Dual Carbon” targets
China has embarked on a road towards a “dual carbon” target where it commits to reach its carbon peak by 2030 and move forward to achieve carbon neutrality by 2060. As the world raised concerns over climate change, countries are exerting efforts and directing resources to curb carbon and greenhouse gas emissions. Having the world’s biggest industrial production, China’s role in meeting its “dual carbon” goal is crucial and its commitment has been well received around the world.
To reach its “dual carbon” goal, China has introduced policies encouraging technological innovations that are aimed at encouraging smart production, utilising renewable energy, increasing recycling and usage of biobased and recycled materials. More investments have also been directed towards “green manufacturing” projects as green manufacturing is one of the strategic objectives under the ‘Made in China 2025’ plan. The government has also been supporting some industries that have shifted to products that contribute to reduction in carbon emission, such as the production of new energy vehicles (NEV) like electric vehicles.
Plastics manufacturing at a turning point
China’s plastics manufacturing operations are largely dependent on fossil fuels, hence carbon emissions from these plants remain high. A report from the WWF Global states that in 2021, researchers estimate that the production and incineration of plastics will amount to over 850 million tonnes of greenhouse gases into the atmosphere. As plastics factories resume their production following the pandemic, emissions from these factories have surged.
But the commitment of the plastics industry has not waned and will continue to inspire innovations. Given that each stage of plastics production produces greenhouse gas emissions that affects the environment, a growing number of companies in the plastics industry are taking urgent steps to reduce their carbon footprint, either through the use of more efficient and smarter production process, shift towards renewable energy such as solar energy to power their plants, plastics recycling and re-use of recycled materials as inputs.
Leading global companies are supporting China’s goal to reduce carbon emissions. DSM announced that it is accelerating its efforts to reduce its total greenhouse gas emissions (including Scope 1, 2, 3 upstream) and the carbon footprint of its products by 50% by 2030, from a 2016 baseline. In its drive towards 100% renewable electricity, DSM Engineering Materials plants in Europe and China are already fully powered by renewable electricity. In addition, it has committed to developing and rolling out bio- and/or recycled-based alternatives for its entire portfolio by 2030; specific grades are already available for all major product lines.
Sabic has announced the successful implementation of another project under its TRUCIRCLE program to speed up its move towards a circular plastic economy. Allied Bakeries, a UK-based supplier of bakery products, has introduced bread bags made by St. Johns Packaging using Sabic’s certified circular polyethylene (PE) in the packaging of their Kingsmill No Crusts 50/50.
A collaboration between Ineos Styrolution and travel luggage maker TUPLUS enabled the latter to utilise Ineos’s Terluran ECO GP-22 MR50, a fully recyclable ABS grade containing 50% of recycled post-consumer waste electrical and electronic equipment (WEEE), to produce its travel luggage.
The contribution of Clariant to China’s carbon neutrality goal is through its MegaMax catalyst series for CO2-based methanol production which aims to help China reach its carbon neutrality target. Capturing and converting CO2 emissions is a cornerstone of the technology roadmap for addressing climate change. Synthesising methanol from CO2 is a particularly valuable approach because methanol forms a building block for thousands of chemical products such as plastics, paints, cosmetics, and fuels — including providing an energy storage carrier for hydrogen.
At CHINAPLAS 2022, the highly efficient machines, recycling technologies and other production techniques that will help plastics manufacturers achieve their goals of reducing their carbon emissions are among the highlights. On-floor demonstrations of well-known Chinese and overseas exhibitors, and consultations with technical experts will further help visitors as they explore viable options.
For more information, visit: www.chinaplasonline.com.
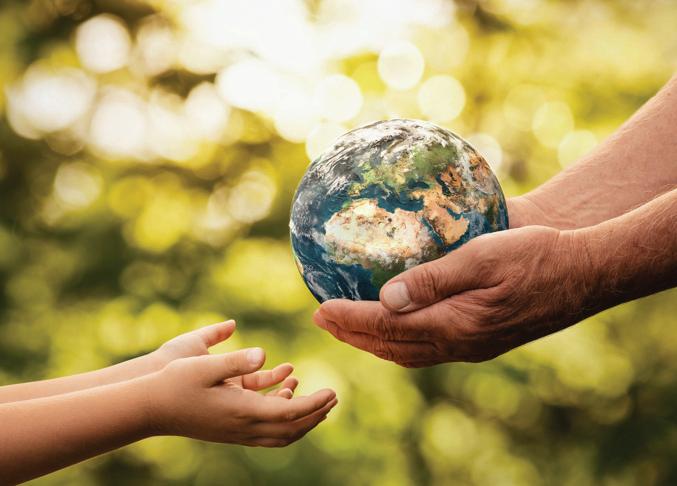
Automotive
EVs on growth trajectory path; Asia jumps on bandwagon, too
Electric vehicle (EV) growth has jumped by an astronomical 140% in 2021 as automotive makers target 40 million units/year by 2030, with 32% of the global market now covered by commitments to end sales of fossil fuel-powered vehicles, and 20% covered by national policies. Meanwhile, Thailand and Indonesia are poised to be EV hubs in Asia.
Growth spurt based on commitments
Passenger electric vehicle (EV) sales are set to jump over 80% in 2021, to 5.6 million units, against the back of unprecedented industry and government commitments around the world over the last two years, according to the Zero-Emission Vehicles Factbook, a report published by BloombergNEF (BNEF), at the request of the UK COP26 Presidency and in partnership with Bloomberg Philanthropies.
The Factbook documents the progress that has been made towards global net-zero emissions in the road transport sector, and shows that the future is brighter than ever for zero-emission vehicles.
In the first half of 2021, sales of passenger EVs (including battery electric, plug-in hybrid and fuel cell vehicles) were 140% higher than the same period in 2019, reaching 7% of global passenger vehicle sales. This compares with just 2.6% in 2019, the year of the last UN Climate Change Conference.
Fleet growth of vehicles
The total global fleet of passenger electric and fuel cell vehicles now totals nearly 13 million, of which 8.5 million are true zeroemission vehicles (ZEVs), either battery electric or fuel cell (still, fuel cell vehicles account for a fraction of that total). The latter figure is up from just 4.6 million at the time of COP25.
At the same time, by 1H 2021, the global fleet of zeroemission buses has increased by 22% since 2019, and it is expected that 18% of all municipal buses on the road to be zero-emission at the end of 2021.
What is more, the future looks brighter than ever. A review of industry outlooks shows that zero-emission vehicle forecasts have been raised across the board.
BNEF says its own forecast for the global ZEV fleet in 2040 has been raised from 495 million vehicles in its 2019 forecast, to 677 million in its 2021 Electric Vehicle Outlook.
The International Energy Agency (IEA) has raised its 2030 battery EV fleet forecast by 7% since 2019, while the Organisation of the Petroleum Exporting Countries (OPEC) has raised its 2040 estimate for the global electric and fuel cell vehicle fleet by 11%.
Factors pushing growth
Underpinning these stronger forecasts are a range of factors, including improving battery technology and costs, faster roll-outs of charging infrastructure, a wider range of vehicle models on offer to customers, and longer range and faster charging speeds available on the newest vehicles. Each of these factors is discussed in detail in the report.
The report was launched in time for Transport Day of COP26, where a coalition of government and global car industry leaders working towards 100% zero-emission new car, van and HGV sales by 2040, will come together, helping to keep 1.5 degrees within reach.
In an Annex to the report, BNEF finds that automotive makers committed to reaching 100% zero-emission vehicle sales by 2035 and now account for 32% of the global market. The Annex finds that similar national targets account for 20% of passenger vehicle sales. US state-level targets to phase out sales of internal combustion engines now cover a quarter of automotive sales in the country (which currently does not have a national phase-out target). Additionally, the combined national targets, ICE phase-out targets and interim ZEV sales targets of China, India, and the US, reach nearly 41% of the global passenger vehicle market. This is up from just 8% in 2019. Ambitious targets are increasingly being matched by policies and regulations stimulating market growth for zero-emission vehicles. The European Union’s proposed CO2 emissions standards imply that EVs should account for 25%-32% of sales in the bloc by 2025, and 60%-83% by 2030.
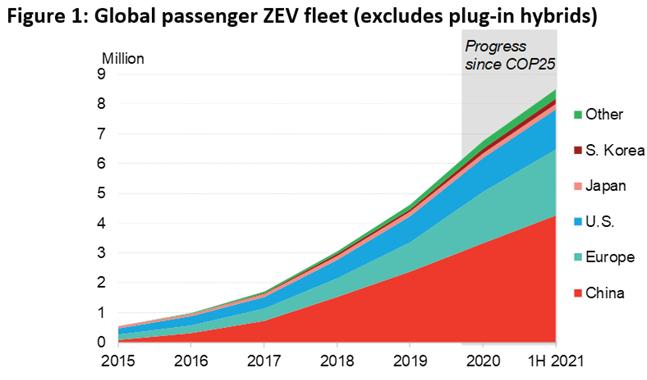
Automotive
Source: BloombergNEF.
Proposed fuel economy rules in the US imply a 24% market share for EVs by 2026, on the way to a 50% share by 2030 under US President Biden’s executive order.
Elsewhere, China is targeting 20% new energy vehicles by 2025, increasing to 40% by 2030.
Thailand/Indonesia to be EV hubs in Asia
It is not just in China that the momentum is rising. In Southeast Asia, Thailand and Indonesia are positioned to become EV ecosystem hubs, according to Roland Berger’s 10th edition Automotive Disruption Radar (ADR).
The Thai government’s National Electric Vehicle Policy Committee had set the new EV policy in March 2021, which provides clear emphasis on zero-emission vehicles (ZEVs). This announcement is designed to enable 50% of vehicles produced in Thailand to be ZEVs by the end of this decade and 100% by 2035.
Recently, Thai Prime Minister Prayut Chan-o-cha had reiterated this ambitious goal at the 2021 COP26 in Glasgow, Scotland.
The Thai government’s commitment to promoting ZEVs has sparked interest among industry players, with talk on potential investment on EV-related joint-ventures and plant investments.
Most recently, Taiwanese electronics firm Foxconn announced plans to produce up to 200,000 EVs/year in Thailand, in a joint venture with Thai-based gas and petroleum business company PTT Public Company Limited, to start in 2023/4.
Indonesian EV regulations attract industry players
The Indonesian government has announced a national strategy with targets to achieve 2.2 million EVs and 13 million electric bikes on the road by 2030.
The country is slated to benefit from US$1 billion worth of investment following plans by Hyundai Motor and LG Energy Solutions to build a battery cell manufacturing site with 10 GWh capacity in Karawang. The plant is due to open in the first half of 2024 and aims to leverage Indonesia’s significant raw material resources, especially nickel.
In the electric two-wheeler segment, Gojek and Gogoro in cooperation with state-owned oil/gas firm Pertamina will conduct a pilot of four battery swapping and 250 electric scooters in Jakarta, with an eventual scale of up to 5,000 units.
“Keen industry interest and activities are a clear signal that Thailand and Indonesia would be very interesting to watch in their journey towards automotive and transportation electrification and transformation,” said Roland Berger Southeast Asia Partner, Udomkiat Bunworasate.
Sales demand-driven not based on environmental concerns
On the demand side, customers are showing strong interest to purchase EVs. In general, short-distance car trips are the main reason for wanting to buy an EV, and action for the environment comes second. Interestingly, the environment was not a key concern based on the ADR survey results in 2020.
Based on the latest ADR survey, 80% of Thai respondents and 75% of Indonesian respondents indicated interest to purchase a battery electric vehicle as their next car. Thai and Indonesian consumers also scored higher than the global average in listing short-distance car trips and action for the environment as the two top reasons for wanting to buy an EV.
Key concerns in both countries were also in line with global respondents, who were mainly deterred from purchasing an EV due to the higher price tag compared to internal combustion engine (ICE) cars and limited availability of charging facilities.
Roland Berger says its ADR is the only established tool in the market measuring the change in the automotive industry. The platform ranks countries based on 26 indicators to measure the level of innovation, progressive digitalisation, and electrification in the automotive industry.
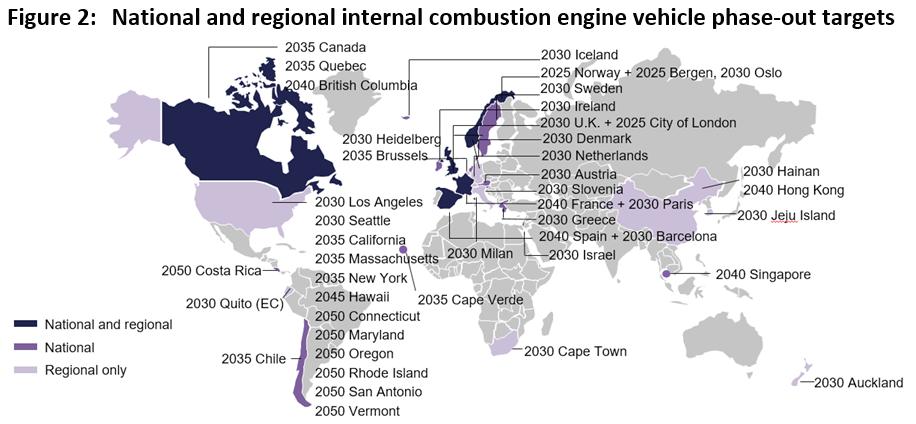
Machinery News
New machinery adds to personal touch
In an industry that thrives on personalised (rather than online) meetings, machinery makers at the recent Fakuma show, held in Friedrichshafen, Germany, were finally able to meet customers and partners face-to-face, after the past two years of no shows, and launch new machines, too.
Positive vibes from exhibitors
With exhibitions having been cancelled or postponed as a result of the Covid-19 pandemic, companies breathed a sigh relief at the recent Fakuma show. Christoph Schumacher, Director of Marketing at injection moulding machine maker Arburg, said, “Our expectations were more than met: the quality of the trade visitors and their interest in our exhibits and innovations was very high. Many decision-makers came to our stand to discuss specific projects.”
Arburg displays variety of machinery and technology
Arburg had the largest trade fair stand and many new products on display, combining major topics of the future – digitalisation as well as sustainability and resource conservation in 2021 – with its declared aim of increasing customers’ production efficiency.
As is well known, the “arburgGREENworld” programme brings together all aspects of resource conservation and the circular economy. At its stand, Arburg used several applications to demonstrate how resources can be conserved and materials recycled. Examples included the processing of transparent biobased P 12, a bio-plastic consisting of 39% renewable raw materials based on castor oil. This material was used to create the well-known Uvex sunglasses on a turnkey system based on an Allrounder 520 A.
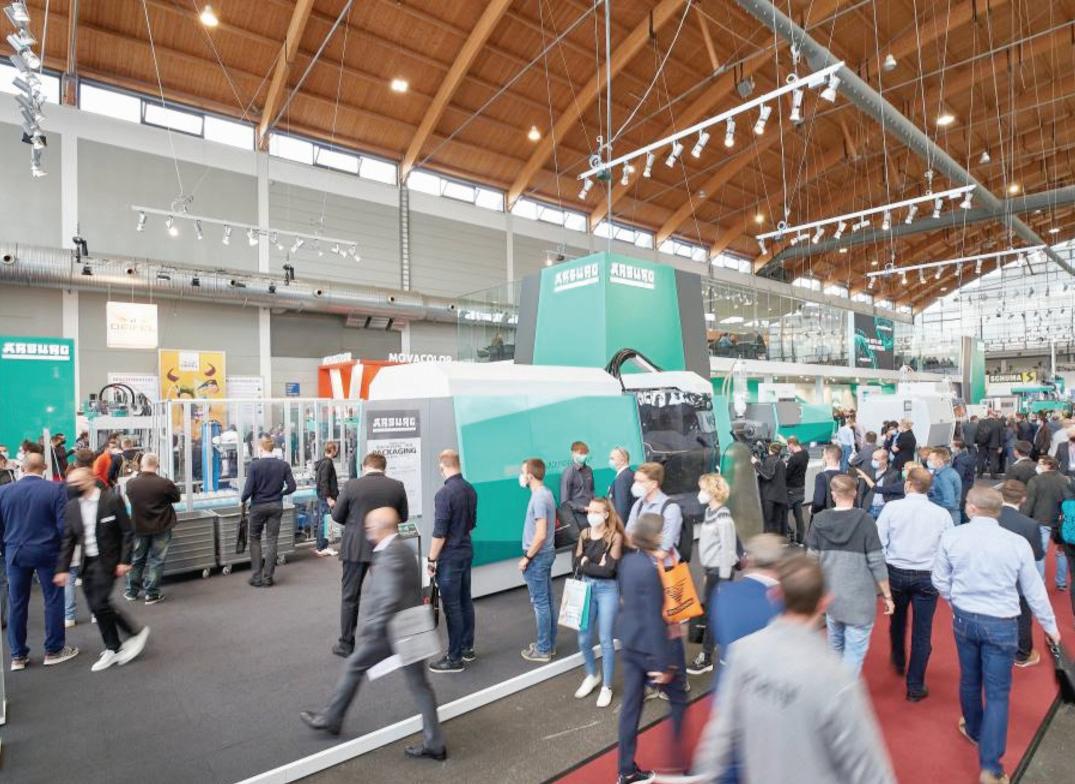
Arburg displayed a cross-section of its diverse range of products and services at Fakuma
Meanwhile, compatriot company, Austrian machine maker Engel, also said Fakuma 2021 was a great success. Christoph Steger, CSO of the Engel Group, said, “The automotive industry has come back with a bang, and the investment backlog has cleared. Even if the Corona pandemic is still preventing some travel, Engel’s stand was well attended.“ He also said visitors came not only from the automotive industry, but also the medical technologies, packaging and technical moulding sectors.
Peter Kochs, Director Sales & Business Development, Europe, of Ferromatik Milacron, said, “Our team met in person with a significant number of injection moulding prospects as well as existing customers from Europe and abroad.“
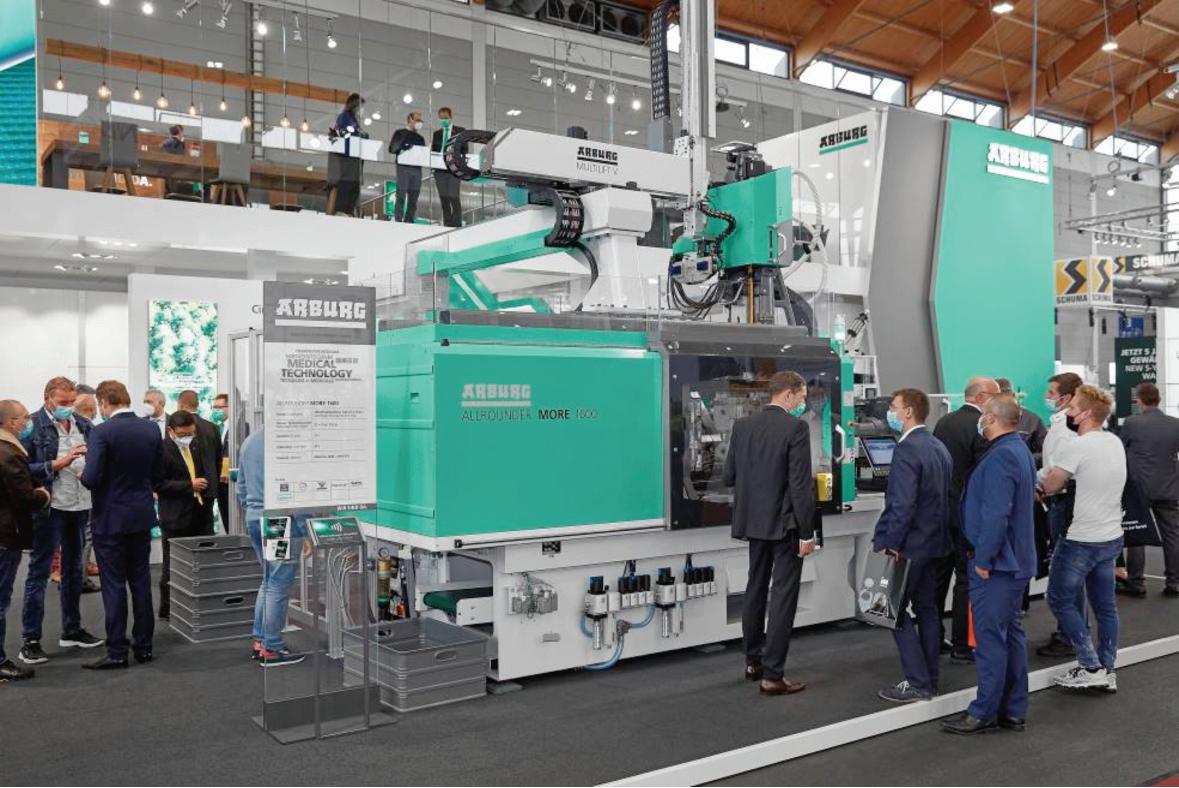
The new Allrounder More multi-component machine made its world debut at the show
Post consumer recyclate (PCR) was used on an Allrounder 1300 T rotary table machine at the stand of Arburg’s partner, Lauffer.
In the case of recyclates, the sharply fluctuating quality of the material places high demands on injection moulding machines and injection moulding processes. To address this, Arburg has put together a new “recyclate package”, which premiered at Fakuma. The package includes various control functions and special plasticising features to enable recyclates to be processed reliably. The recyclate package is available for all Allrounders and can also be retrofitted to older models.
Just how sustainability and digitalisation interact was demonstrated by the “CurveCode” and “HolyGrail” marking technologies as innovative solutions for separating plastics by type and returning them to the materials cycle.
Arburg’s new Allrounder More machine series also made its first debut at an exhibition. The series covers the two sizes 1600 and 2000 and caters to multi- component
Machinery News
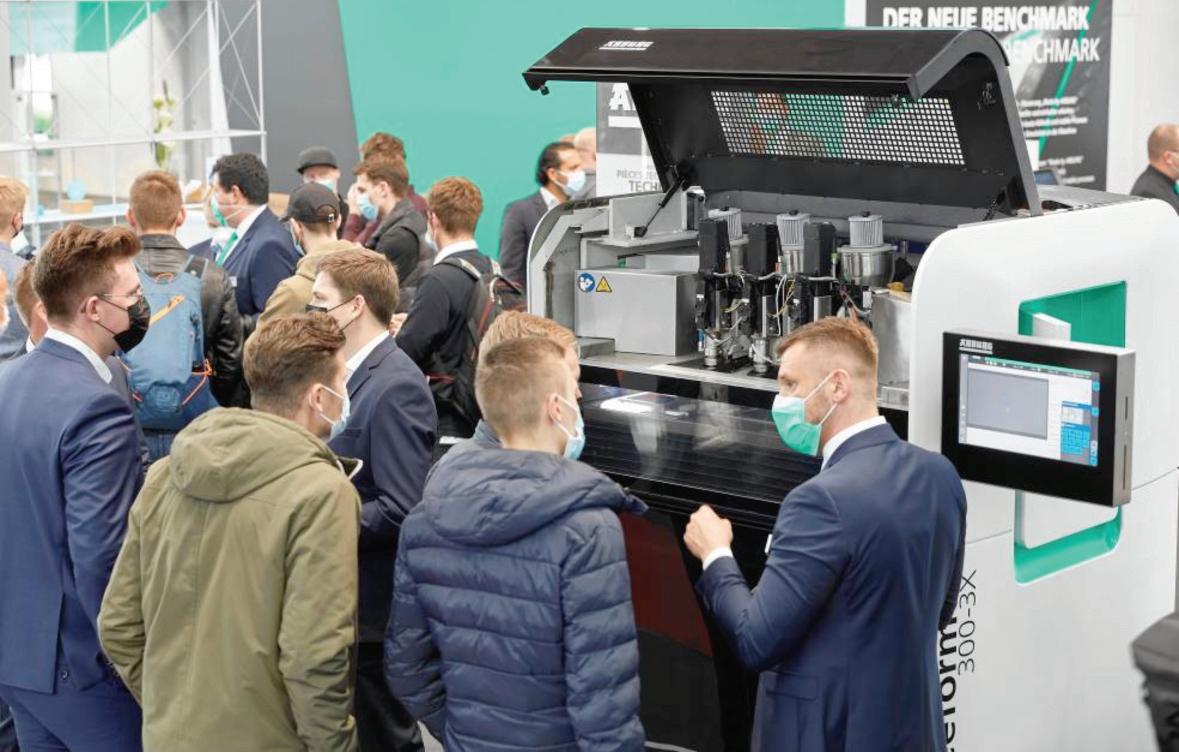
Lukas Pawelczyk (right), Department Manager Sales Freeformer at Arburg, explains the freeformer’s potential to visitors
injection moulding, with a flexible design to offer more space for larger moulds and ejectors, more modularity in its assembly, and ease of use via the Gestica control system. An Allrounder More 1600 produced a complex lab-on-a-chip for medical technology at the trade fair.
Other focal points were the Gestica control system and the planetary roller screw drive – both “made by Arburg” and benchmarks in the plastics industry. Arburg also highlighted its drive element, the planetary roller screw drive as an important part of the drive train, which is a central feature for the performance and durability of an injection moulding machine and accordingly a “seal of quality”.
Additive manufacturing also played an important role at Fakuma. A live presentation was given of the processing of high-temperature material Ultem on a freeformer 300-3X. In addition, a large number of components demonstrated the potential offered by Arburg Plastic Freeforming for the medical technology and automotive sectors, where Arburg is working on exciting projects together with partners and customers.
Also prominently represented on Arburg’s stand was sister company innovatiQ and its LiQ 320 printing system, which processes liquid silicone (LSR) using the LAM (liquid additive manufacturing) process.
Engel leveraging the full potential of its machines
At Engel’s stand, solutions for more sustainability in injection moulding and further digitalisation of production processes met with great interest, since “the two topics are closely linked”.
Compared to the last Fakuma, Engel’s stand was larger with additional space used to present digital products and solutions.
The Austrian firm presented a closed process chain for PP involving the production of mono-material food packaging using IML thin-wall technology and the production of protective covers from label offcuts.
At the same time, thee-speed 420 machine celebrated its world premiere. “Hybrid and all-electric injection moulding machines are seeing deployment in an increasing number of applications,” says Steger.
Demanding precision applications gave insights into the performance of the various hybrid and all-electric machine series.
In this regard, two machine exhibits that Engel presented on site in Friedrichshafen was the production of pipette tips on an all-electric e-mac and the manufacture of microcomponents from LSR on an all-electric and tiebar- less e-motion TL.
Moulders get first look at Milacron’s new eQ all-electric
Germany’s Ferromatik Milacron announced a new addition to parent copany Milacron’s all-electric eQ -Series CE, now available to injection moulders across Europe at Fakuma. The new Milacron 150-tonne eQ-series injection moulding machine was displayed with a 24-cavity HDPE moulded cap application with a 2.7 cycle time
The eQ series is a high-precision electric machine, which is said to combine accuracy and reliability across all processes. Optimised energy consumption through regenerative power recovery system stores energy during motor braking and allows up to 70% reduced melt stress.
The machinery supports additional specialised processes like thin wall moulding and multi-component moulding. This machinery line can be requested by moulders across Europe and Asia, said Milacron.
Some highlights of the machine are: screw diameter of 18-90 mm; maximum energy efficiency thanks to regenerative servo drive technology; low maintenance costs; series-standard overvoltage protection device; latest servo drive technology for increased efficiency throughout the entire injection process; improved kinematics of the toggle joint combined with steering of the closing force into the tool centre and latest Milacron control generation Mosaic G3.
Ferromatik Milacron has a new addition to Milacron’s all-electric eQ -Series CE available to injection moulders across Europe
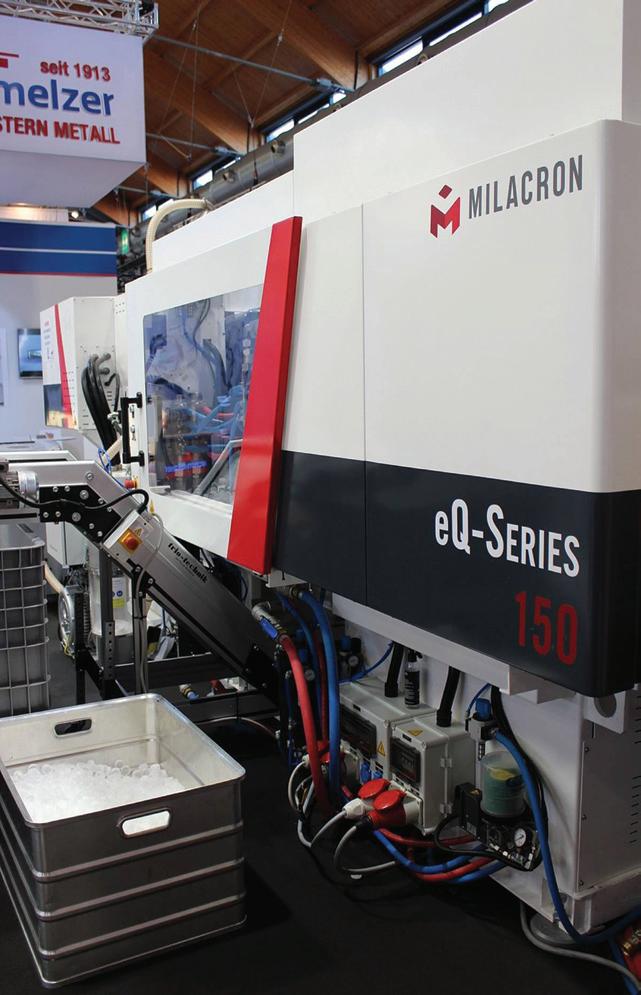
Industry News
• Japanese tyre maker
Bridgestone Corporation has withdrawn from the conveyor belt business. It said that it plans to reduce its production and sales volume gradually to minimise the impact to the operations of its customers and suppliers, and will withdraw from the business completely by the end of 2024.
• US-based specialty chemicals firm Eastman Chemical
Company’s tyre additives business has been acquired by an affiliate of private equity firm One Rock Capital
Partners. The acquired company will operate under the name Flexsys.
• Munich-based chemical company Wacker Chemical has acquired a 60% stake in Chinese manufacturer of organofunctional silanes Sico
Performance Material ffor
EUR120 million.
• Swiss elastomers firm Datwyler has sold its German subsidiary, an online distributor, Reichelt to German private equity firm Invision. Reichelt made
CHF188.8 million in 2020 in online distribution of electronic components.
• US-based industrial technology company EnPro Industries has sold its polymer components business to private equity firm
Edgewater Capital Partners.
The polymer components business is headquartered in
Texas, with two production facilities in Texas and a smaller site in Pennsylvania, and is part of Enpro’s sealing technologies segment. The organisation will be renamed Altamira Material
Solutions.
• UK’s Fenner Precision
Polymers, a Michelin Group
Company and supplier of reinforced polymer technology, has acquired Lumsden Corporation, a manufacturer of industrial conveyor belting and wire cloth for the quarry and mining industry, as well as related solutions for a wide variety of applications including food processing, heat treating, mining, glass treating, printing and canning.
• US carbon black supplier
Cabot Corporation is to acquire
Tokai Carbon (Tianjin) from
Tokai Carbon Group for US$9 million. The carbon black manufacturing facility was commissioned in 2006 and is located in close proximity to Cabot’s current carbon black and specialty compounds facility in Tianjin,
China. The acquisition is expected to support the growth of Cabot’s battery materials product line.
• German technology firm
Continental is to acquire
Swedish polymers firm
Trelleborg’s printing solutions business, headquartered in Lodi
Vecchio, Italy, to complement its surface solutions and printing technology portfolio.
• Swedish industrial group
Indutrade is to acquire all of the shares in Czech silicone moulder Silroc CZ, which has annual sales of approximately
CZK85 million.
• Polytek Development
Corp. a US manufacturer of specialty polymers for coating, mould making, and casting applications and portfolio company of Arsenal Capital
Partners, has acquired
Specialty Resin & Chemical, a supplier of mould making, casting, coating products, epoxy and PU resin, rubber, silicone, and related accessories. a RM50 million financing facility from HSBC Amanah Malaysia Bhd to finance its purchase of Nobel Synthetic Polymer Sdn Bhd and Nobel Scientific Sdn Bhd, collectively known as the Nobel Group, which manufacture chemical derivatives for the rubber sector, coatings, and related products. The agrochemical company said the facility is expected to increase its consolidated gearing from 0.52 times to 1.21 times.
• India’s Apollo Tyres is now manufacturing its Vredestein brand of tyres in India for the superbike and premium and luxury passenger car segments.
The tyre manufacturer had acquired the European brand in 2009 and launched it in
India with a range of imported tyres. Apollo had previously said that it planned to locally manufacture tyres from the premium brand in India.
• Norway-based silicon-based materials supplier Elkem is investing EUR36 million in new specialty silicones supply for customers in Europe, the Middle East and Africa (EMEA) and the Americas.
The company will upgrade and debottleneck its silicone upstream plant in Roussillon,
France, by a 20,000-tonne capacity expansion, bringing the effective silicone intermediates capacity from Elkem’s upstream plant in Roussillon, France to 100,000 tonnes/year.
• Zhongce Rubber Group (ZC Rubber), a Chinese tyre manufacturer, plans to leverage 5G technology to improve data network platform innovation and data-driven manufacturing process reengineering. Through network collaboration, flexible production, and service expansion, it said that it will improve core competitiveness
and company value, as well as develop a replicable 5G Smart Factory platform for the tyre industry.
• End-of-life tyre (ELT) recycler
Pyrum Innovations has started the expansion of the production capacity of its pyrolysis plant at its headquarters in Dillingen,
Germany. To date, the plant consists of one production line, which has been operating on an industrial scale since May 2020, producing pyrolysis oil, recovered carbon black and pyrolysis gas from more than 7,000 tonnes of ELTs during this period. The addition of two more production lines will triple processing capacity to approximately 20,000 tonnes/year of ELTs.
• The joint venture between
German chemicals firm Evonik and Chinese company Wynca,
Evonik Wynca (Zhenjiang)
Silicon Material, is startingup its new fumed silica plant.
Located in the Zhenjiang
New Material Industry Park in Jiangsu province, the plant is Evonik’s first fumed silica production site in China.
• Polish chemical firm
Synthos is constructing a new 120 kilotonnes/ year butadiene extraction unit with associated logistic infrastructure in Plock,
Poland. The commissioning of the butadiene extraction unit and first production are scheduled for 2024. Air Liquide
Engineering and Construction
is licensing the BASF NMP
Butadiene Extraction technology and has been awarded with the overall engineering, procurement and construction services and supplies for the project.
• Italian bicycle tyre maker
Vittoria Group is constructing a new factory in Thailand.
Industry News
The US$20 million investment will see its local subsidiary Lion Tyres Thailand (LTT)’s factory premises grow from 36,00052,000 sq m in the Bangpoo industrial district, near the current LTT headquarters. Operations will start at end of 2022 and allow Vittoria to double the total output capacity of tyres over the coming years.
• In line with its restructuring plan, Bridgestone Corporation is consolidating its plants for automotive seat pads in Japan, which are now manufactured in four plants owned by its group companies, out of which three plants are owned by
Bridgestone Chemitech Co (BSCT), and one plant owned by Bridgestone Diversified
Chemical Products (BDCP).
It will close the BSCT plant in
Ageo, Saitama Prefecture, in the fourth quarter of 2023 and consolidate operations within the three remaining facilities for automotive seat pad production – BSCT’s Nabari and Hofu sites as well as BDCP’s Tosu plant.
• Indian tyre maker BKT has started trial production at a new facility in Waluj, Maharashtra, following an investment of
US$65 million. Spanning an area of 22 acres, BKT’s latest plant is situated 5 km from an existing
BKT plant, also in Waluj.
Around 500 employees will work at the facility where small and medium diameter tyres will be manufactured for machinery working in the agricultural and industrial sectors. It will have an estimated production capacity of 30,000 tonnes/year of off-highway tyres (OTRs).
• Trelleborg Group is expanding geographically by establishing manufacturing operations in
Russia, Vietnam, Japan and
Morocco, with an investment of
SEK300 million over five years. 2
Trelleborg Sealing Solutions
will begin manufacturing sealing solutions for the large domestic Russian market in the third quarter of 2022. The production site, located in Yesipovo near Moscow, will manufacture high-performance seals for the transportation equipment and aerospace market segments, among others.
• Italian tyre maker Pirelli is investing US$36 million in its
Silao, Mexico, manufacturing site to raise production capacity from 6.6-7.2 million tyres/year.
The facility employs over 2,700 people and services the local and greater North
American markets.
• US firm Lion Elastomers will be expanding the emulsionbased facility in Texas, US, to manufacture NBR (nitrile butadiene rubber), to support the domestic demand. Major markets include general mechanical goods, automotive parts, oil and gas field supplies, medical devices, and personal protective equipment.
• Carbon black supplier Orion
Engineered Carbons will convert a reactor line at its plant in Louisiana, US, from manufacturing soft carbon black to producing hard carbon black, commonly used in tyre treads. It will increase supply by 30,000 tonnes/year by mid-2022.
• Russia’s PJSC Tatneft has signed a license and engineering agreement with Italian chemical firm Versalis relating to technologies for the production of NBR and carboxylate styrene butadiene rubber latexes (XSBR). The plants to be built at the Togliatti industrial site will produce 70,000 tonnes/year of NBR and 30,000 tonnes/year of XSBR.
Glove Sector
Glove sector gains an upper hand in PPE market
Consumption for rubber gloves has gone up amid workplace safety concerns and the management of emerging infectious diseases like the recent Covid-19 pandemic. Meanwhile, the nitrile butadiene rubber market has responded positively with improved supply.
NBR latex is known for its multiple advantages, such as high performance in extreme temperatures, oil resistance, and personal protection, making it suitable for use in a wide variety of industrial applications.
Growing reliance on PPE, a gain for the NBR latex
Industrialisation is gradually spreading across the globe, leading to the emergence of industry-focused economies all over the world. As a result of this expansion, there has been an increase in workrelated risks, prompting various authorities such as the Occupational Safety and Health Administration (OSHA) to mandate the provision of efficient safety equipment to workers, particularly in high-risk industries such as healthcare and chemical.
Notably, during the Covid-19 pandemic, the importance of having dependable and high- quality PPE (personal protective equipment), particularly gloves, was emphasised. Gloves are an important component of the coronavirus defense protocol because they protect health workers from disease transmission while they are treating patients.
This trend is poised to boost the nitrile butadiene rubber (NBR) latex industry, which is expected to exceed US$4 billion by 2027, according to Global Market Insights (GMI) estimates.
Demand for medical gloves accelerates NBR output
Gloves are inevitable medical devices, shared Toms Joseph, former Joint Director (Economics) at Rubber Board, Kottayam, Kerala, India, and Economist at the
Association of Natural Rubber Producing Countries
(ANRPC). Throughout those periods of rising and falling rubber glove shares, and until the NBR glove technology was developed and patented in 1990 by Neil Tillotson and Luc DeBecker, natural rubber (NR), nitrile, and vinyl gloves remained the most common types used in the medical sector, Joseph said in an article.
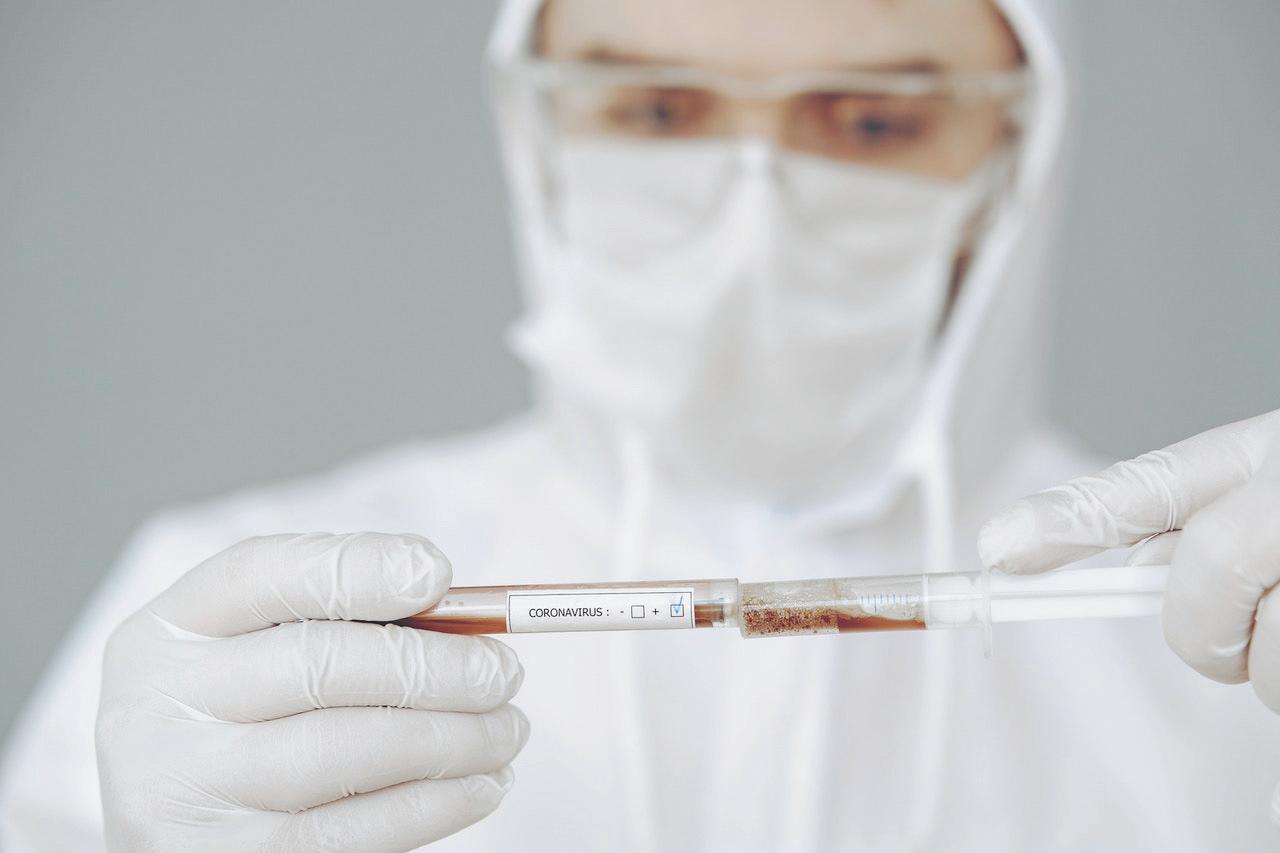
The development of blood and body fluid safeguards to all patients bolstered demand for medical rubber gloves
Rubber product factories began producing rubber gloves on request from hospitals and other healthcare facilities. Medical gloves eventually became required PPE for healthcare providers, patients, and others to ensure barrier protection by reducing the risk of pathogen exposure. Gloves are also worn by employees in spas, salons, and other places where physical contact is possible, Thomas said. Medical rubber gloves (including surgical rubber gloves) are regulated as Class I Reserved Medical Devices in the US, and the FDA inspects them to ensure that performance criterion, such as leak resistance, tear resistance, puncture resistance as well as biocompatibility, are met. In a similar vein, GMI stated that Gloves are vital PPE in the coronavirus defense protocol because they protect health increased demand for raw materials, such workers from disease transmission while they are treating patients as NBR latex, has contributed to the high

Glove Sector
demand for effective PPE gloves. When compared to its conventional counterparts, NBR latex is quickly replacing NR as the preferred alternative due to its performance efficiency and versatility. While nitrile latex gloves are widely used in both non- medical and medical applications, the NBR latex market in the medical gloves segment is growing.
NBR latex demand, which treaded around 1 million tonne/year in 2019, nearly doubled to 1.9 million tonnes in 2020 owing to increased use of protective gloves during the pandemic. As a result, major manufacturers have ramped up their production of the material globally to meet the demand for medical PPE to combat emerging virulent diseases like the Covid-19, GMI said.
Medical gloves in epidemics, pandemics
Meanwhile, Thomas adds that medical gloves have been in high demand for some time, because of advances in healthcare facilities in invasive medical procedures such as surgeries; longer life expectancy, and hygiene awareness.
During outbreaks of epidemics, however, the demand for medical gloves skyrocketed. This was true of the epidemics/pandemics during the recent decades such as AIDS (Acquired Immunodeficiency Syndrome ) in 1981 onwards, SARS (Severe Acute Respiratory Syndrome) in 2002-2003, Bird Flu in 2003-2004, Swine Flu in 2009-2010), Ebola in 2013, and now Covid-19.
Until the early 1980s, reliable information on HIV/AIDS transmission and infection was not available. In 1983, the US Centre for Disease Control and Prevention (CDC) issued “Blood and Body Fluid Precautions,” the first time the term AIDS was used. The World Health Organisation (WHO) launched the Global AIDS Program in February 1987, and the CDC provided the “Universal Precautions” on dealing with blood and body fluids when managing the disease in August 1987.
The development of blood and body fluid safeguards to all patients bolstered demand for medical rubber gloves, resulting in a jump in US glove imports (particularly disposable examination gloves) from 3.9 billion pieces in 1989 to 25.29 billion in 1998. Because of the rapid increase in demand for rubber gloves, several countries increased their glove production capacities.
In the case of the Covid-19 pandemic, demand for gloves was so high that it spawned a new generation of glove tycoons, as a result of a new round of massive investment. The outbreak of the pandemic increased the demand for gloves from around 350 billion to around 400 billion.
Thomas said that even with new investments and full utilisation of global capacity, only about 420 billion pieces/year are being used at full capacity, and with demand expected to continue to rise rapidly, a deficit is expected in the near future.
With regards to pricing, higher demand and sporadic shortages drove up the cost of raw materials like NR and nitrile latex on the global market. Glove manufacturing costs have also risen as a result of Covid restrictions and protocols, as well as plant closures due to worker infections.
However, the rise in glove prices and resulting increase in net profit of major glove companies has multiplied. Surgical, examination, and other disposable gloves (HS 401511 and 401519) had a global export value of US$16.71 billion in 2020, up from US$8 billion in 2019, according to Thomas.
Wide scope of applications to drive NBR growth
NBR latex gloves are used in a wide range of industries, including chemical, mining, automotive, and metalworking. According to GMI’s projections, the NBR latex industry in the industrial segment will grow at a CAGR of nearly 10% through 2027, owing to the product’s suitability for PPE in key industrial uses.
In the workplace, nitrile latex gloves can protect the wearer’s hands from potential hazards like liquids, abrasive materials, and cuts. They’re particularly useful in applications involving caustics, alcohol, oils, chlorinated solvents, greases, and other chemicals.
With the demand for protective gear expanding at such a breakneck pace, major players in the NBR industry are concentrating their efforts on increasing output.
For example, in September, American Nitrile, an Ohio-based company, announced the opening of a new advanced production facility in the US dedicated to the production of nitrile gloves for use in industrial, government, and healthcare applications.
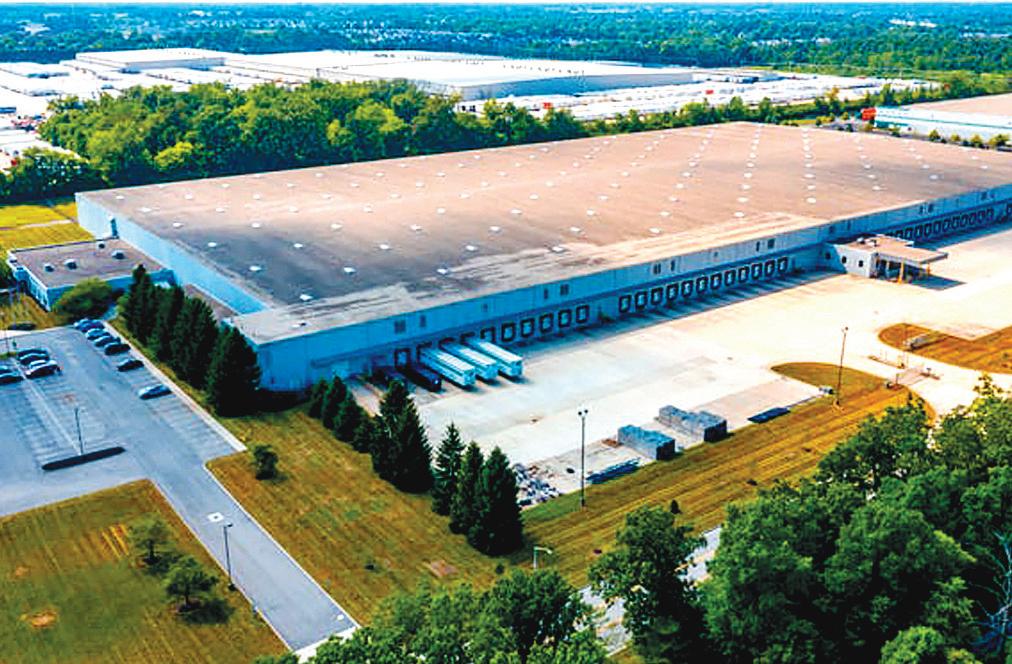
Glove Sector
During the same period, India-based producer performance emulsion polymers Apcotex announced a capacity expansion plan to increase nitrile latex production at its existing India- based plants by 60,000 tonnes/year. The plants, which are expected to be completed by late 2022, will be designed for maximum manufacturing flexibility for existing industrial and healthcare protective products, as well as to improve the quality and quantity for nitrile gloves in the coming years.
Strategic alliances to address supply-demand deficits
Strategic moves such as collaborations and partnerships will not only increase these companies’ visibility in the global business landscape, but will also help them meet the safety needs of industrial end-users as they evolve.
Blue Star NBR and American Glove Innovations (AGI)-Blue Star Manufacturing joint venture Blue Star-AGI, announced in October this year, is one such partnership. The companies pledged a US$714 million investment to build a production facility for NBR and nitrile gloves in Virginia. The investment was part of the companies’ effort to increase the production of exclusively “Made in America” protective nitrile gloves as well as raw materials, which are currently primarily produced in Asia.
Malaysia’s is arguably the largest glove maker in the world and the glove industry consumed RM6.6 billion worth of NBR in 2020 and roughly 70% of it or RM4.6 billion was imported from China, South Korea, Japan, Thailand and other countries.
Thus, Malaysian companies are also stepping up in the NBR market. Petronas Chemicals Group (PetChem), a Malaysian chemical company, announced in June its collaboration with South Korea’s LG Chem to build an NBR production plant at the Pengerang Integrated Complex (PIC) in Johor, with a production capacity of 200,000 tonnes/ year upon completion. This strategic collaboration, according to PetChem, came at an ideal time, as the demand for nitrile latex gloves has been steadily increasing.
Another Malaysian player Hong Seng Consolidated Bhd (formerly known as MSCM Holdings Bhd) has also kicked off the construction of a NBR plant in the state of Kedah. It is aimed to be completed in stages over four phases with the targeted full production capacity of 960 kilotonnes/ year. The first phase of 240 kilotonnes/year is expected to commence its commercial production by the second quarter of 2024. The company says it will contribute up to 20% of the world’s total NBR supply (upon full completion of the plant) and will help Malaysia reduce its dependency on NBR imports. NBR latex has shown its viability as a material of choice for manufacturers and distributors expanding into novel application domains over the years. Because of the material’s technical similarities to conventional natural rubber, it is undeniably positioned as a superior alternative.
Petronas Chemicals Group and LG Chem have tied up to build an NBR production plant in Johor
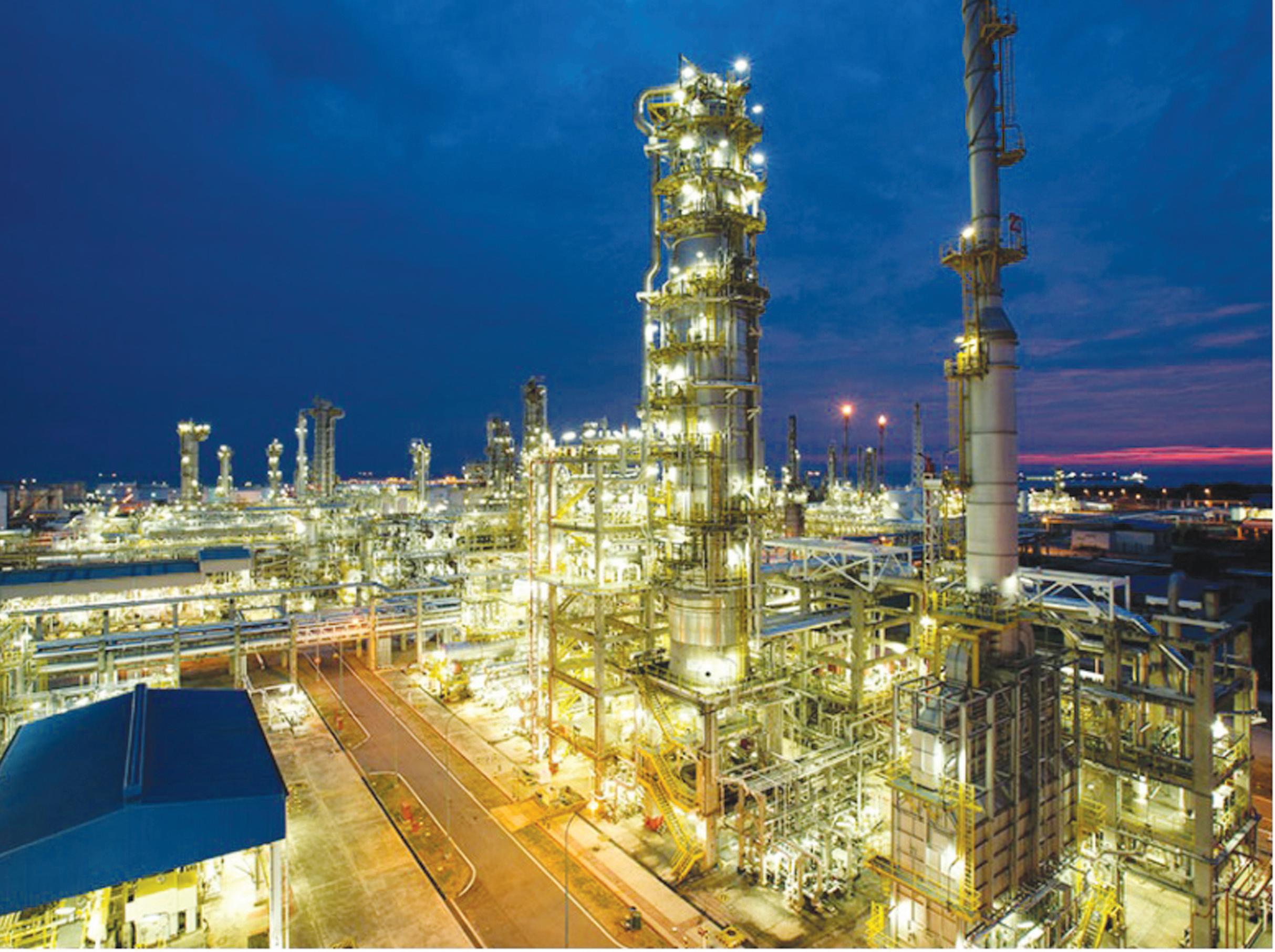
2021
1 - 4 DECEMBER Plast Eurasia Istanbul
Venue: Tuyap Fair Convention and Congress Center, Istanbul Tel: +90 (212) 867 11 00 Fax: +90 212 886 93 92 Email: info@plasteurasia.com Website: www.tuyap.com.tr
1 - 10 DECEMBER VietnamPlas Online Expo | Vietnam PrintPack Online Expo
8 - 9 DECEMBER E-PACK Europe
Venue: Amsterdam & Online Tel: + 44 (0) 1372 802000 Email: eventseu@smithers.com Website: www.smithers.com
9 - 11 DECEMBER China Machinex India
Venue: Bombay Exhibition Cetre, Mumbai, India Tel: +91 (022) 2660 5550 Email: sharon@winmark.co.in Website: www.chlmx.com
2022
12 - 15 JANUARY IPF Bangladesh
Venue: ICCB, Dhaka, Bangladesh Tel: +886-2-2659-6000 Fax: +886-2-2659-7000 Email: exfdp@chanchao.com.tw Website: www.chanchao.com.tw/ipf
25 - 27 JANUARY Oman Plast
Venue: Oman Convention & Exhibition Centre, Muscat, Oman Tel: +968 24788804 Fax: +968 24788845 Email: info@omanplast.net Website: www.omanplast.net
25 - 28 JANUARY Interplastica
Venue: Moscow, Russia Tel: +49 211 4560 436 Fax: +49 211 4560 7740 Email: ErbenC@messe-duesseldorf.de Website: www.interplastica.de
9 - 12 FEBRUARY T-PLAS
Venue: BITEC, Bangkok Tel: +65 6332 9643 Email: lindatan@mda.com.sg Website: www.tplas.com
8 - 10 MARCH JEC World
Venue: Paris Nord Villepinte Tel: +33 (0)1 89 20 40 64 Email: jecworld@jeccomposites.com Website: www.jec-world.events
8 - 11 MARCH PLASTIMAGEN Mexico
Venue: Centro Citibanamex, Mexico City Tel: +52-55-1087-1650 Email: carmen.sanchez@tarsus.mx Website: www.plastimagen.com.mx
14 - 16 MARCH Plast Alger
Venue: CIC Algiers Tel : +49 6221 45 65 19 Fax : +49 6221 45 65 25 Email: f.detjen@fairtrade-messe.de Website: www.plastalger.com
16 - 18 MARCH Manufacturing World Japan
Venue: Tokyo Big Sight, Japan Tel : +81-3-3349-8506 Email: mfg-japan.jp@rxglobal.com Website: www.japan-mfg.jp
25 - 28 APRIL Chinaplas
Venue: National Exhibition and Convention Center, Shanghai, PR China Tel: +852 2811 8897 Fax: +852 2516 5024 Email: chinaplas@adsale.com.hk Website: www.chinaplasonline.com
ADVERTISERS’ ENQUIRIES
Check out the Advertisers' page on our website.
Information is categorised by the YEAR & DATE of publication for easy reference.
For further details, email us at: news@plasticsandrubberasia.com
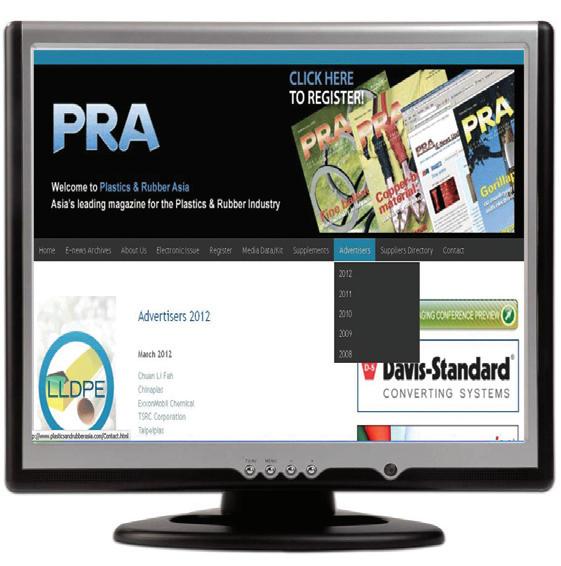
PRA Digital issue is available ONLINE!
www.plasticsandrubberasia.com
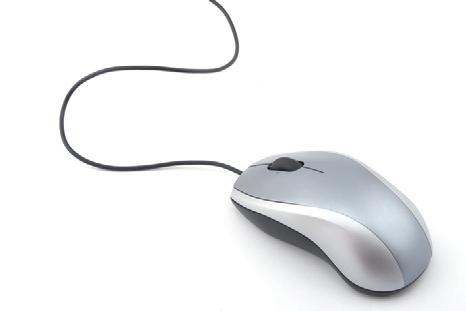
INTERNATIONAL OFFICES
Publishing Office/Scandinavia, Benelux & France Postbus 130, 7470 AC Goor, The Netherlands Tel: +31 547 275005 Fax: +31 547 271831 Email: arthur@kenter.nl Contact: Arthur Schavemaker
Regional Office
SQ9, Block A, Menara Indah, Taman TAR, 68000 Ampang, Selangor, Malaysia Tel: +603 4260 4575 Email: tej@plasticsandrubberasia.com Contact: Tej Fernandez
China & Hong Kong
Room 803, No.2, Lane 3518, Road Bao'An, District Jiading, Shanghai Tel: +86 13341690552 Mobile: +86 17751702720 Email: henry.xiao@matchexpo.com Contact: Henry Xiao/Zhu Wei
China
Bridge Media 亚桥传媒 Room 206, #1, 569 Shilong Rd, Shanghai, China 200237 Tel: +86 21 3368 7053 Mobile: +86 138 1643 7421 Email: lagopoah.yang@bridgemedia.cn Contact: Lago Poah Yang 杨旋凯
Southeast Germany, Switzerland & Austria
Verlagsbüro G. Fahr e.K Breitenbergstrasse 17 D-87629 Füssen, Germany Tel: +49 8362 5054990 Fax: +49 8362 5054992 Email: info@verlagsbuero-fahr.de Contact: Simon Fahr
North-West Germany
JRM Medien+Verlag Minkelsches Feld 39 D-46499 Hamminkeln, Germany Tel: +49 2852 94180 Fax: +49 2852 94181 Email: info@jwmedien.de Contact: Jürgen Wickenhöfer
Malaysia. India, Indonesia, Singapore, Thailand, Australia, New Zealand, Korea & Philippines
Tara Media & Communications SQ 9, Block A, Menara Indah Jalan 9, Taman TAR, 68000 Ampang, Selangor, Malaysia Tel: +603 4260 4575 Email: tej@plasticsandrubberasia.com Contact: Tej Fernandez
Italy, Spain & Portugal
MediaPoint & Communications Srl Corte Lambruschini, Corso Buenos Aires, 8, Vo Piano - Interno 9, 16129 Genova, Italy Tel: +39 010 570 4948 Fax: +39 010 553 0088 Email: info@mediapointsrl.it Contact: Fabio Potesta
Taiwan 宗久實業有限公司 Worldwide Services 11F-B, No.540 Sec.1, Wen Hsin Rd., Taichung, Taiwan Tel: +886 4 23251784 Fax: +886 4 23252967 Email: global@acw.com.tw Contact: Robert Yu 游宗敏
USA & Canada
Plastics Media International P. O. Box 44, Greenlawn, New York 117430, USA Tel/Fax: +1 631 673 0072 Email: mjm@4m-media.com Contact: Michael J Mitchell
www.plasticsandrubberasia.com www.rubberjournalasia.com www.injectionmouldingasia.com www.plasticsandrubberasia.cn
