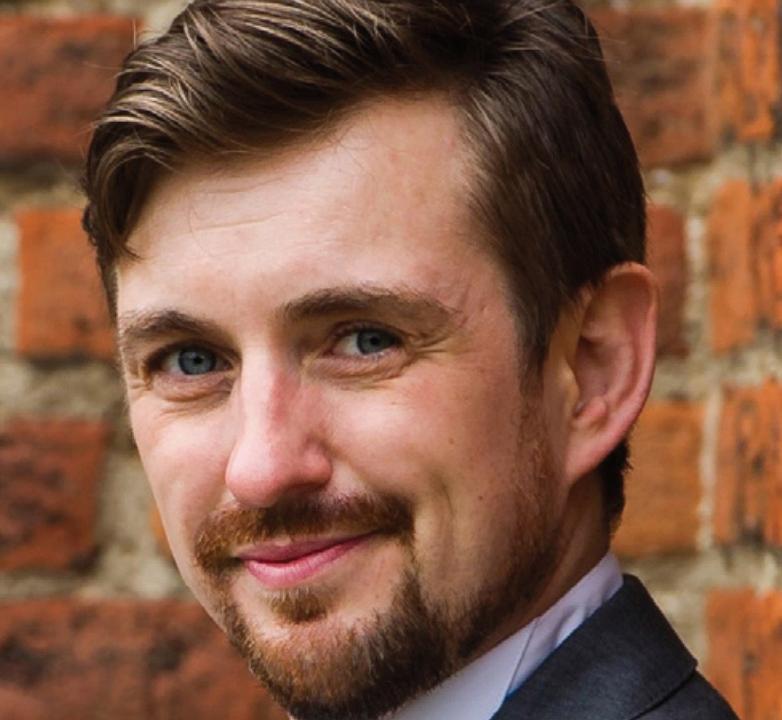
2 minute read
Chemical Industry
By Mark Victory - Senior Editor, Recycling at ICIS
Advertisement
The increased use of partially sorted 90% mixed polyolefin bales by the mechanical recycling sector is pushing pyrolysis-based chemical recyclers towards other feedstocks to avoid competing with the mechanical recycling chain.
Pyrolysis-based chemical recyclers are increasingly investigating the use of PVC-screened reject bales, which currently predominantly serve the refuse-derived fuel (RDF) market, to avoid direct competition with the mechanical recycling sector.
Although there is an absence of comparable life cycle assessments (LCAs) that can show the environmental impact of chemical recycling compared with mechanical recycling, virgin production and alternatives, it is broadly agreed that mechanical recycling has a lower environmental impact than chemical recycling.
Because of this, many chemical recyclers aim to avoid material that can be efficiently used in mechanical recycling to ensure that the processes are complimentary.
In 2021, mechanical recyclers have been increasingly using mixed polyolefin bales – typically with a minimum 90% polyolefin content - because of a shortage of sorted monomaterial polyolefin bales,. These are the same mixed-plastic waste bales that chemical recyclers have, until now, predominantly been sourcing. There are a variety of reasons why monosorted bale supply is tight, including: • Substitution of virgin in the first half of the year due to shortages in that market • Changing virgin plastic packaging material choices, the impact of COVID-19 on sorting centres • Structural shortages of collection and sorting capacity • Projects delayed by the onset of the coronavirus pandemic • Additional demand ahead of the introduction of plastic packaging taxes in Spain, Italy and the UK in 2023 • An extended construction peak season due to delays to project completion dates • Ambitious sustainability targets from the packaging sector, which go beyond what is available at current collection, sorting and reprocessing capacity
With polyolefin bale shortages expected to last at least into 2022, mechanical recyclers sourcing mixed polyolefin bales is unlikely to prove a temporary phenomenon, until sufficient additional collection and sorting infrastructure is built.
The shift in mechanical recycling purchasing patterns is causing pyrolysis-based chemical recyclers to explore other mixed-waste bale grades, with RDF reject bales a primary focus. Along with tight PVC tolerances, pyrolysis-based chemical recyclers also typically aim to limit PET content in a bale – because it needs transesterification to depolymerise and because it produces oxygen in the reaction – as well as nylon and flame retardant content.
As a result, they prefer lighter-fraction waste, which broadly matches what is currently being sent to RDF.
Limiting chlorine content in RDF-suitable reject bales is becoming more challenging for waste managers due to the increased presence of PVC content and the rising use of polyvinylidene chloride (PVDC) in products such as films and cheese trays.
At the same time, downstream tolerances are becoming stricter, with bales for RDF use needing to contain below 1% chlorine and bales for pyrolysis typically targeting chlorine content below 0.1% to prevent corrosion.