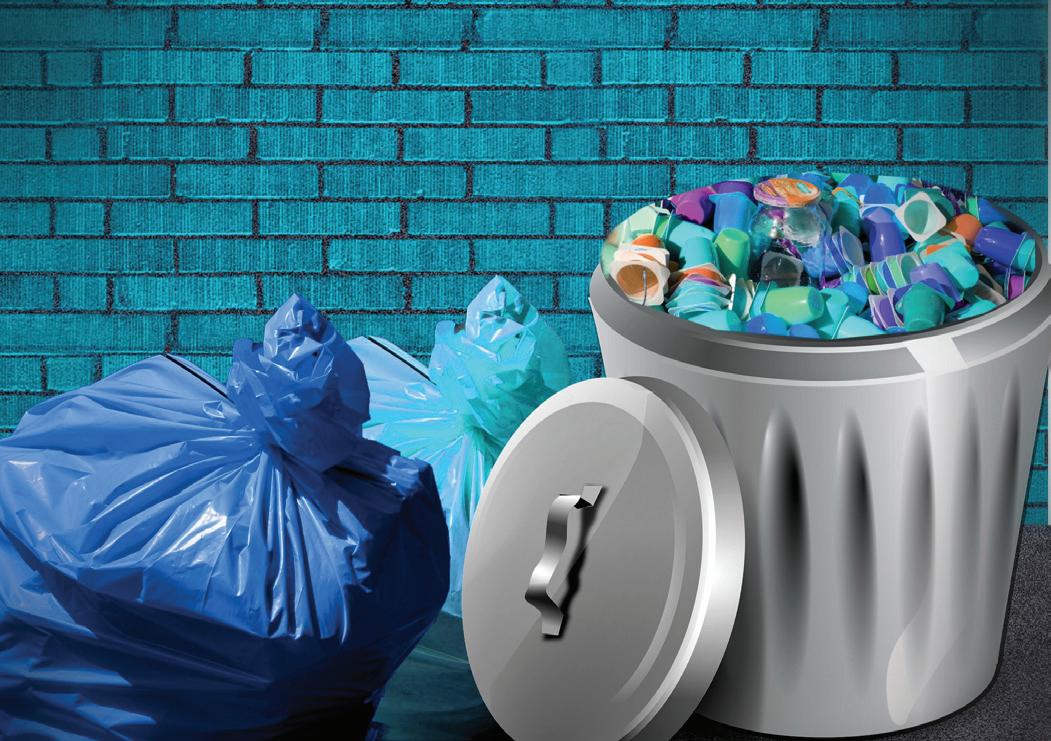
9 minute read
Materials News
Materials News Advancing recycling to tackle plastic circularity
The uptake of chemical recycling is on the rise since it offers an increased recycling rate, and higher value product output, says Angelica Buan in this report.
Advertisement
The amount 300 million tonnes isn't just a number; it's the amount of plastic waste produced annually around the world. To make matters worse, the amount of waste generated is expected to increase by 3.4 billion tonnes by 2050, a consequence of growing urbanisation, population, and economies.
What will happen to this waste is now up to us. Regardless of whether the recycling infrastructure has improved or expanded, research still finds that only about 20% of waste is recycled each year, with vast amounts still being dumped in landfills.
Finding a long-term, sustainable solution to waste plastic has been elusive for a long time. The proliferation of green initiatives has, in many cases, failed to deliver the promised targets, while conventional recycling and reuse strategies have not been able to recover the material value of plastic waste.
Now, the notion of plastic circularity has been provided with some sort of a solution whereby using effective recycling processes, the recovery of high-value products, such as oil, gas, and chemicals, is a possibility.
Partnerships on chemical recycling
According to a report by Wood MacKenzie, the sustainability of the plastic value chain is dependent on how the sector manages plastic waste. It recommends boosting investments in chemical recycling, as doing so might raise recycling rates by 50% by 2040.
Only about 20% of waste is recycled each year, with vast amounts still being dumped in landfills, according to studies
Chemical recycling, also known as advanced recycling, has been compared to mechanical recycling, and which WoodMac says is the best option to recover value from end-of-life plastic by converting it into other usable, even food-grade applications.
Pyrolysis is a chemical recycling process that breaks down longer chain polymers into shorter chain materials by heating plastic waste without oxygen. These products can then be processed further into chemicals or fuels. Pyrolysis can recycle low-quality plastic waste that cannot be recycled using traditional mechanical recycling methods. Additionally, pyrolysis does not degrade the final plastic's quality and requires less intensive waste sorting.
Hence, chemical recycling’s ability to increase recycling rates is sufficient justification for its implementation in order to promote sustainability.
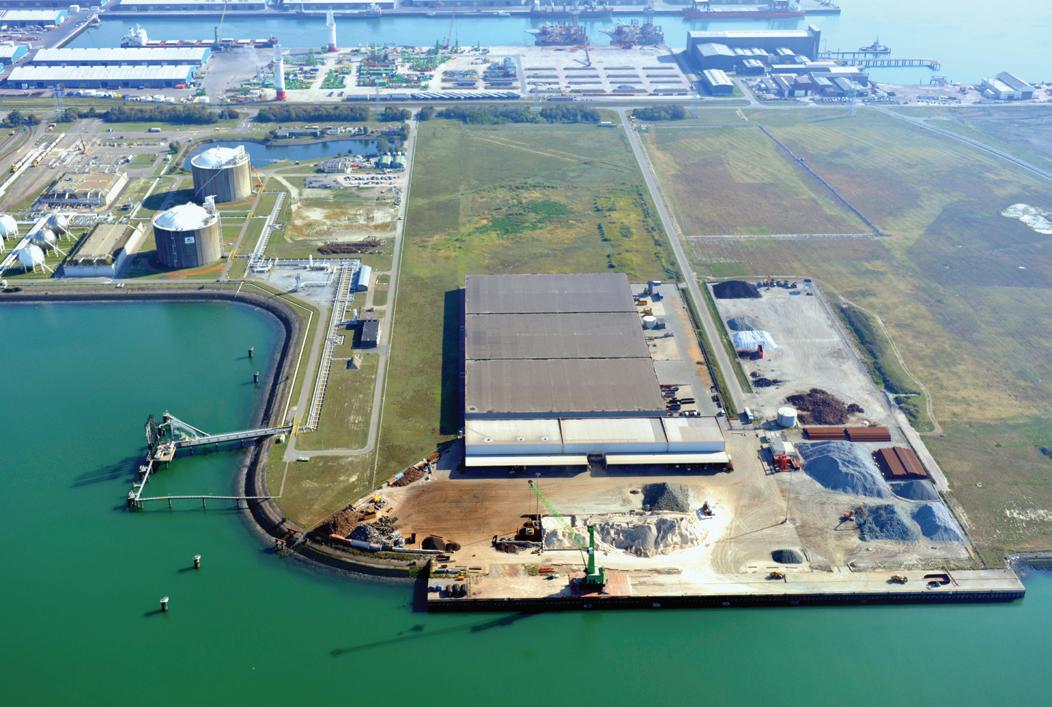
Neste and Ravago are establishing a chemical recycling facility in Vlissingen, North Port
Thus, a number of tie-ups have been seen, with two leading European companies, Neste and Ravago, joining forces to focus on chemical recycling. The partners stated that their goal is to increase global processing capacity and catapult the joint venture into a global leader in chemical recycling of mixed plastic wastes.
The joint venture between Neste, a Finnish renewable oil refining company, and Ravago, a Belgian plastics producer, will establish a chemical recycling facility, with a processing capacity of about 55,000 tonnes/year of mixed plastic waste, and intended to be the starting point of joint global chemical recycling activities, in
Vlissingen, the Netherlands’ North Sea Port. The plant will be built upon US-based Alterra Energy's thermochemical liquefaction technology.
Elsewhere, Anglo-Dutch gas/oil company Shell’s corporate venture arm and BlueAlp Holding have formed partnership to develop, expand and deploy BlueAlp’s plastic waste to chemical feedstock technology, which has already been developed to a commercial scale. The technology transforms tough to recycle plastic wastes into a recycled feedstock, such as pyrolysis oil that can be used to make sustainable chemicals.
Shell's goal of recycling 1 million tonnes/year of plastic waste in its global chemicals plants by 2025 will be aided by this investment.
Blue Alp/Shell’s joint venture will build two new conversion units in the Netherlands under the terms of the agreement, with Shell taking a 21.25% equity stake in BlueAlp. To start-up by 2023, these units are expected to convert more than 30 kilotonnes/year of plastic waste and supply 100% of the pyrolysis oil as feedstock to Shell's Moerdijk and Rhineland crackers.
Shell, which has had a successful pilot using pyrolysis oil at the Moerdijk petrochemicals plant since August 2021, along with increased use of recycled feed at its Norco petrochemical complex in the US since November 2019, is looking to licensing two more units for use in Asia to supply the Shell Energy and Chemicals Park in Singapore.
Materials News
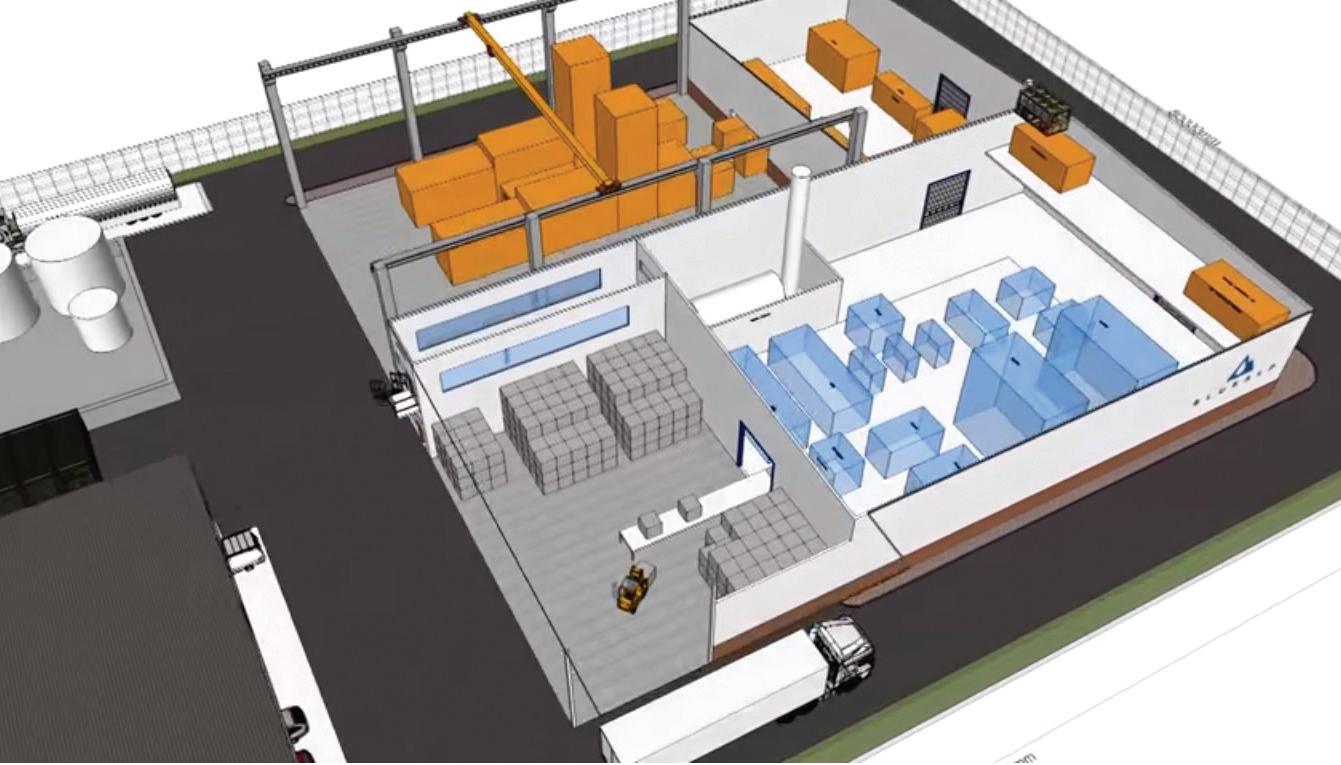
BlueAlp and Shell have teamed up to develop, expand, and deploy BlueAlp's plastic waste to chemical feedstock technology
From plastic grocery bags to jet fuel
Demonstrating the efficiency of hydrocracking technology to convert plastics to fuel, Washington State University researchers have devised a novel method for converting plastics into compounds for jet fuel and other valuable hydrocarbon products. At moderate temperatures, their
IMPROVED QUALITY REDUCED DOWNTIME REDUCED SCRAP RATE IMPROVED QUALITY REDUCED DOWNTIME REDUCED SCRAP RATE
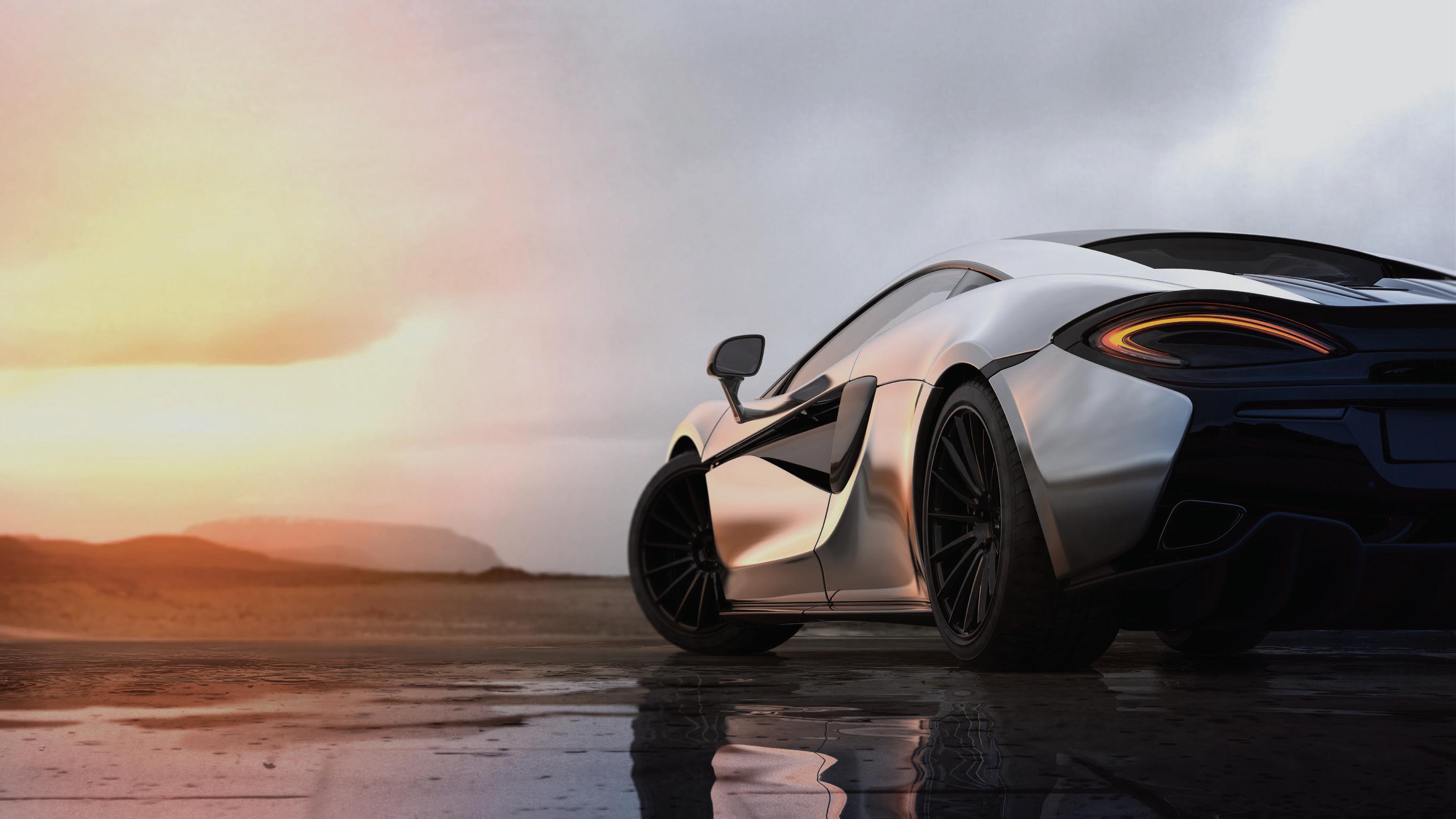
Chem-Trend is the most proven partner in the world for release agents, purging compounds, and other process chemical specialties. With decades of proven experience in manufacturing for automotive parts such as gaskets and seals, noise vibration harshness components, transmission belt, car bumper, car doors and more, we have helped provide greater efficiency, higher-quality products, lower downtime, reduced scrap rates, and more predictability, as well as greater leaps in innovation. For free trial, please contact us at our website or +65 6736-0113.
Materials News
method was able to transform 90% of plastic into these compounds. Processing conditions can also be fine-tuned like adjusting the time, temperature or amount of catalyst used to create desired products.
Funded by the Washington State Research Foundation and the National Science Foundation, the innovation, which was published in the journal Chem Catalysis, used a catalytic process to efficiently convert PE waste to jet fuel and high-value lubricants within an hour at a temperature of 220°C, which they claim is more efficient and lower than temperatures that would be typically used.
The researchers, led by graduate student Chuhua Jia and associate professor Hongfei Lin in the Gene and Linda Voiland School of Chemical Engineering and Bioengineering, stated that they are working to commercialise this breakthrough technique.
Meanwhile, researchers from California State Polytechnic University say that plastic grocery bags can also be a viable resource for fuel. Pyrolysis, or the thermochemical decomposition of carbon-based matter in the absence of oxygen, was utilised to heat- convert the plastic to a vapour, which then met a catalyst and transformed into the desired fuel-like product. Their work has been published in the Journal of Renewable and Sustainable Energy by AIP.
Mingheng Li, one of the study's authors, explained that the catalyst is important in this pyrolysis process since it just takes one step to get to the required fuel product at relatively low temperatures.
Li explained that the catalyst was prepared by immersing a zeolite substrate in an aqueous solution containing nickel and tungsten and drying it in an oven at 500°C. The synthesized catalyst was used with a labdesigned, single-stage pyrolytic reactor that ran at a specified temperature of 360°C to degrade a variety of plastic supermarket bags.
Other organic wastes, old motor oil, and municipal solid wastes could potentially be processed using the catalytic process to produce useful energy products.
The researchers' next steps will be to explain the breaking mechanism that occurs on the surface of the catalyst and to optimise diesel fuel production from diverse mixed plastic waste.
Levelling up on recycled waste for circular polymers
US-based Dow Chemical has taken plastic circularity to the next level by recycling waste plastics into feedstock oil for the production of circular polymers. This is in line with its recent announcement of its advancements to reduce plastic waste, cut carbon emissions, and provide customers with recycled plastic products that perform similarly to fossil fuel- derived virgin plastics.
Dow's collaborations include the ones it has with Dutch pyrolysis company Fuenix Ecogy Group, Dutch energy company Gunvor Petroleum Rotterdam, US-based environmental technology company New Hope Energy, and UK-based recycling technology company Mura. All of these will enable Dow to begin supplying fully circular polymers to customers in 2022.
With Fuenix, Dow is expanding its initial agreement with the company, which began in 2019 to scale circular plastics production through advanced recycling, by building a second plant in the Netherlands that will process 20,000 tonnes of waste plastic into pyrolysis oil feedstock, which will be used to make new plastic at Dow's Terneuzen site.
Dow’s collaboration with Mura supports the rapid scaling of its new HydroPRS (Hydrothermal Plastic Recycling Solution) advanced recycling process. The world's first HydroPRS plant is under construction in the UK, with the first 20,000-tonne/year line expected to be operational in 2023.
Recently, Dow tied up with Gunvor to purify pyrolysis oil feedstocks derived from plastic waste and beginning in 2021, Gunvor will supply cracker-ready feedstock to Dow. To ensure that the pyrolysis oil feedstocks are of sufficient quality to produce new polymers, the purification process is required.
Meanwhile, Dow and New Hope Energy, a company that converts used plastics into pyrolysis oil feedstock, agreed to a multi-year supply agreement for pyrolysis oil feedstocks.
In the meantime, Dow is expediting the design, engineering, and construction of a purification unit in Terneuzen to provide additional capacity to purify pyrolysis oil feedstock derived from plastic waste.
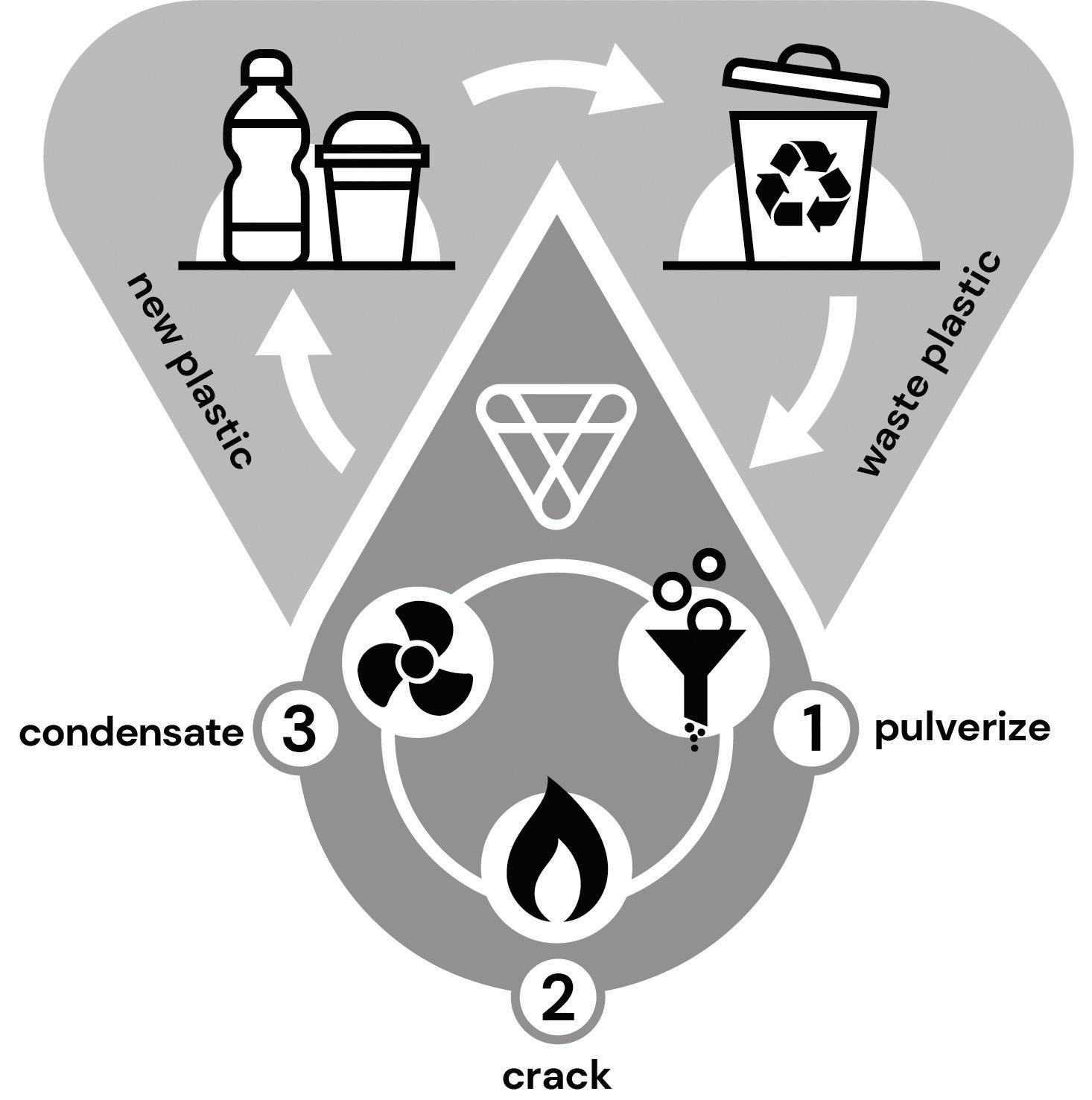
Dow is expanding its Fuenix deal with the construction of a new plant that will convert 20,000 tonnes of waste plastic into pyrolysis oil feedstock for Dow's Terneuzen facility
Materials News
Sustainable packaging material promises lower carbon footprint
German chemical firm BASF is also advancing the pyrolysis technology, as evidenced by its ChemCycling project. The company, also a co-founder of the Alliance to End Plastic Waste, cooperated with Quantafuel and Remondis this year on chemical recycling of wastes and joint investment on a pyrolysis plant. The German firm also acquired US-headquartered Zodiac Enterprises, which recycles precious metals from industrial scrap to expand its chemical catalyst recycling and capability.
Meanwhile, Styropor EPS (expandable polystyrene) was recently chosen by Europe's largest home appliance manufacturer for its packaging needs. BSH Hausgeräte GmbH will use Styropor BMB, which is made from chemically recycled (Ccycled) plastic waste, as a packaging material for selected large appliances from its luxury brand Gaggena.
BSH is initially testing the packaging at its Dillingen production site in Germany, and plans to expand its use for all large appliances globally.
Pyrolysis oil has simply replaced fossil raw materials in the production of packaging foams that have become so well-known over the last 70 years. The oil is extracted by BASF's partners from plastic waste that would otherwise be used for energy recovery or disposed of in landfills. At the start of the value chain, BASF uses the required amount of oil to make new plastics.
Because recycled and fossil raw materials are mixed in the manufacturing process and cannot be distinguished, the recycled portion is assigned to Styropor Ccycled using a mass balance approach. Ecoloop, an independent certification programme, has certified both the allocation process and the product itself. When compared to conventional Styropor, the production of Styropor Ccycled packaging saves at least 50% of CO2, says Ecoloop.
In the future, BASF and BSH intend to strengthen their collaboration by looking into the use of alternative raw materials.
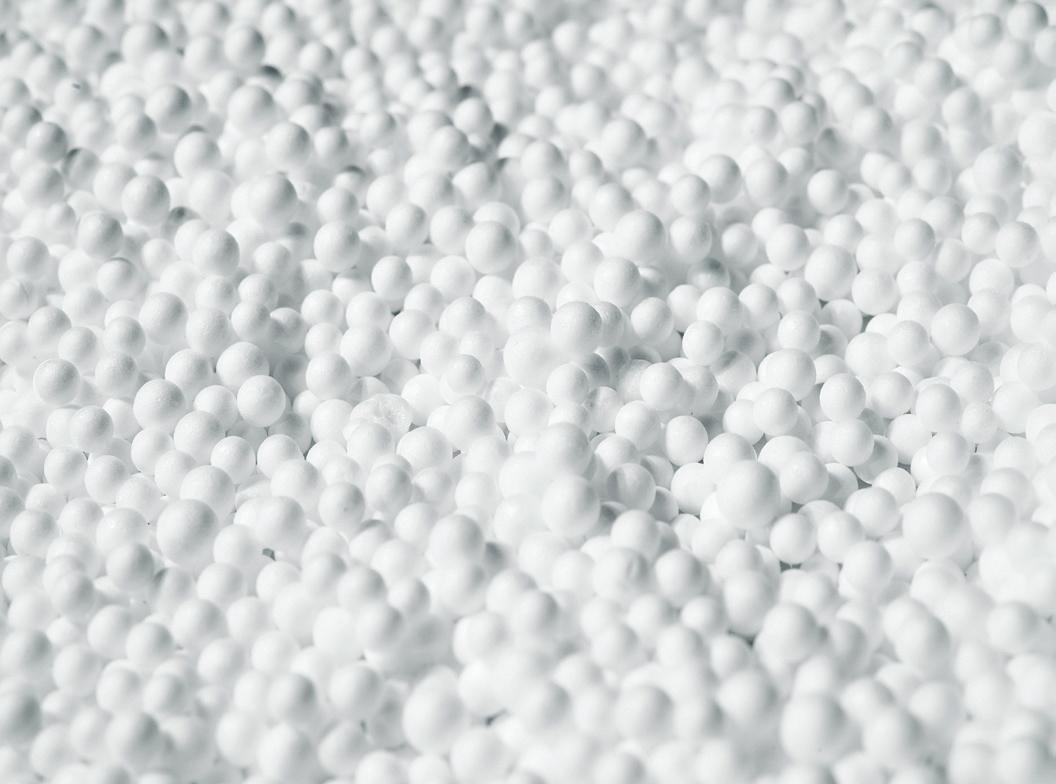
For its home appliance packaging, BSH Hausgeräte uses BASF's Styropr EPS, which is made from chemically recycled (Ccycled) plastic waste
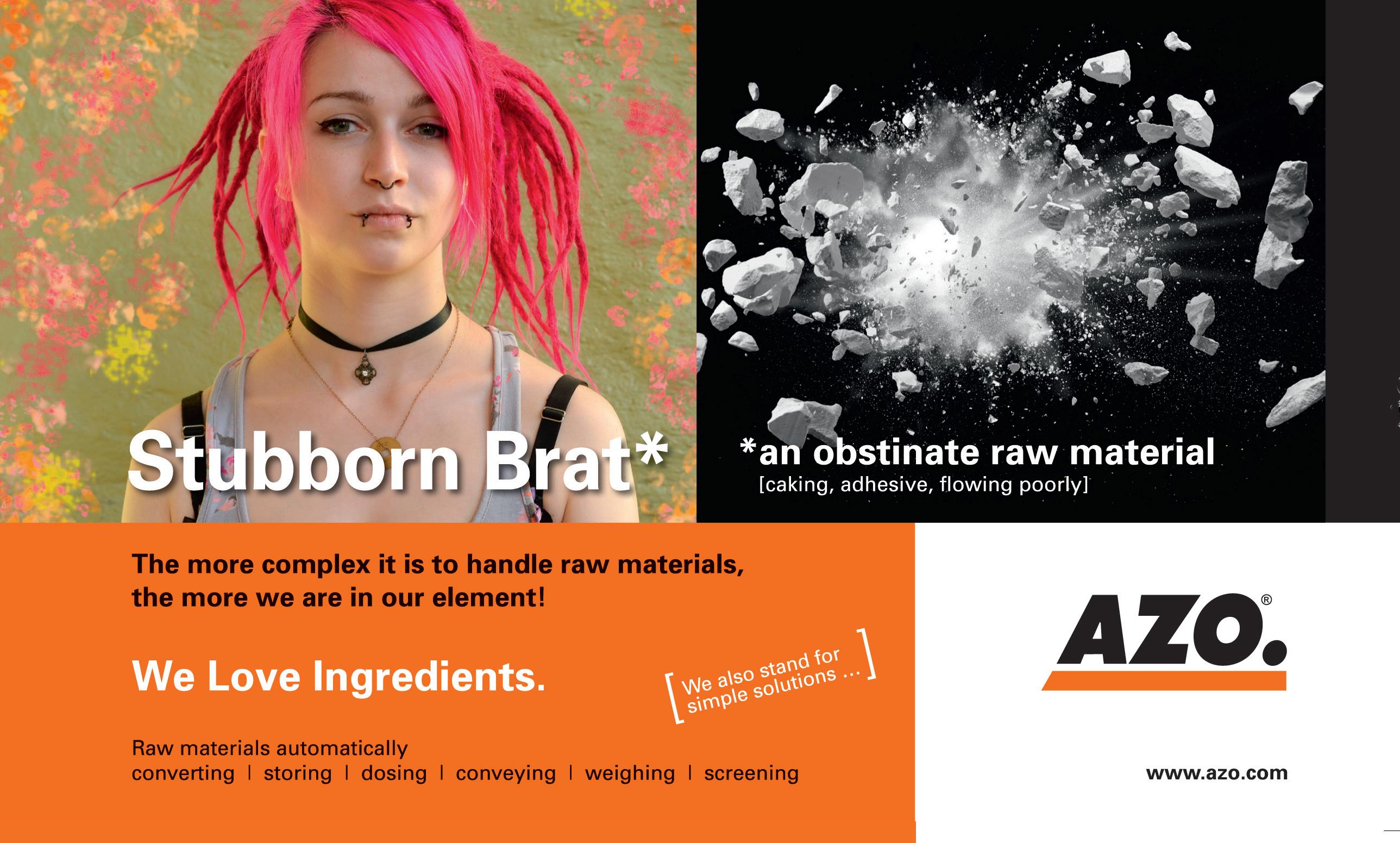