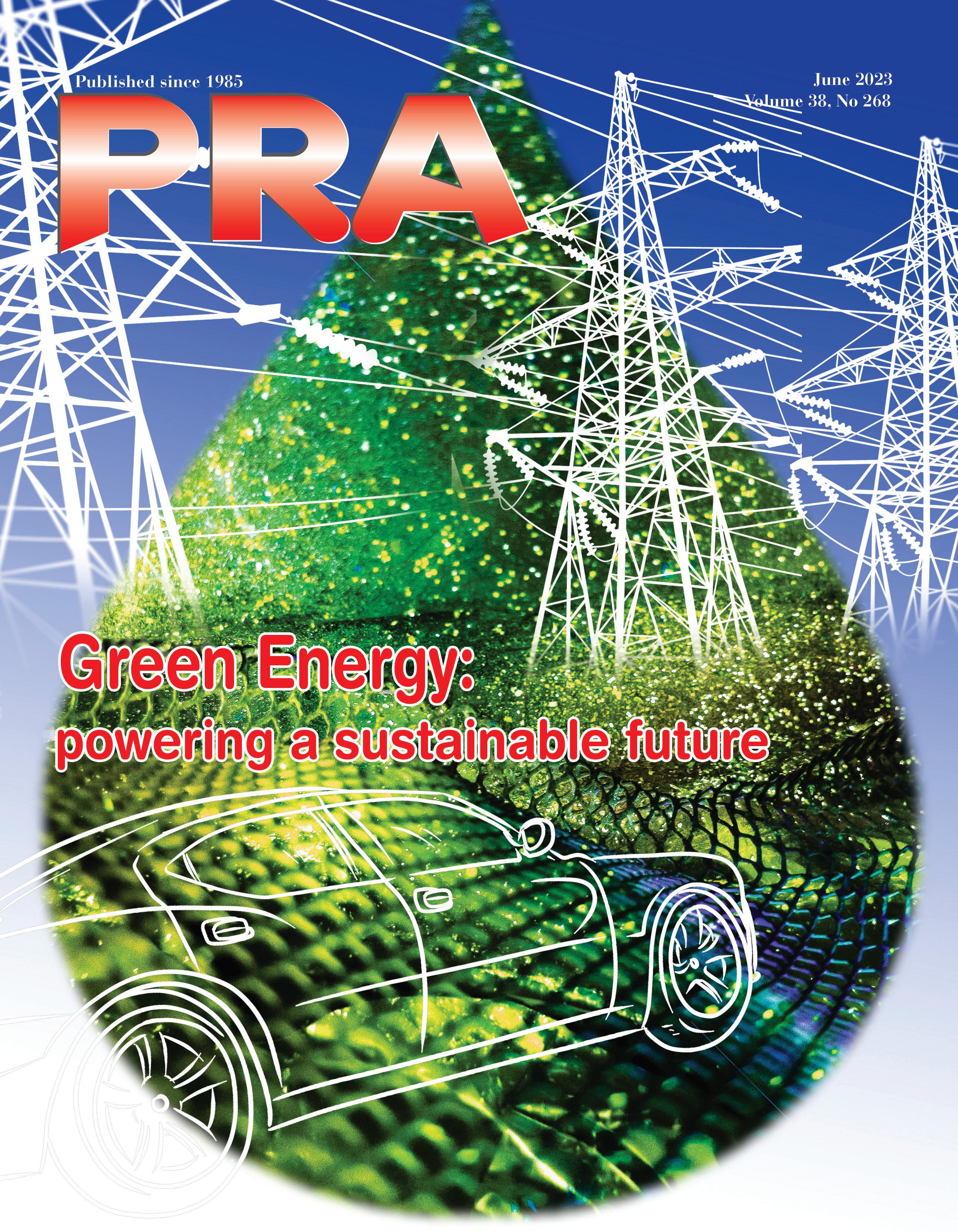

10 Renewable Energy
Asian countries are making a mark in renewable energy with green hydrogen since increased use of green hydrogen has the potential to improve energy security, spur regional growth, and promote global cooperation in the fight against climate change
15 Additives
A new range of additives are helping plastics producers meet the enhanced requirements for high quality recycled materials
18 Country Focus
Thailand is stepping up efforts to curtail carbon emissions with its path towards an electric vehicle landscape
2 Industry News
6 Machinery News
7 Materials News supplements
Tooling: Victrex/Tool Gauge will produce aircraft parts using hybrid overmoulding; a new stack mould system for thinwall packaging is the highlight from oerlikon hrSflow
packaging: The consumer products sector is looking into the use of more sustainable packaging options, such as reusable packaging
machinery: Global injection moulding technologies industry leader, husky Technologies, recently commemorated the next phase of expansion in India, at its new offices and existing chennai campus. We find out more about the company’s plans
Gloves: malaysia's glove makers are benefiting from streamlining of operations, new investments, and net-zero collaborations to mitigate the impact of low demand, a glut of gloves and expensive raw materials
publisher/editor-in-chief
Arthur Schavemaker
Tel: +31 547 275005
Email: arthur@kenter.nl
Associate publisher/executive editor
Tej Fernandez
Tel: +6017 884 9102
Email: tej@plasticsandrubberasia.com
senior editor
Angelica Buan
Email: gel@plasticsandrubberasia.com circulation
Stephanie Yuen
Email: stephanie@taramedia.com.my
permits
ISSN 1360-1245
printer
United Mission Press Sdn Bhd (Co. No: 755329-X) 25 & 27, Jalan PBS 14/14, Taman Perindustrian Bukit Serdang, 43300 Selangor, Malaysia.
is published 4 (four) times a year in English by Kenter & co publishers’ representatives bV.
Whilst every effort is made to ensure that the information contained in this publication is correct, the publisher makes no warranty, expressed or implied, as to the nature or accuracy of such material to the extent permitted by applicable law.
© 2023 Kenter & co publishers’ representatives bV No part of this publication may be reproduced, stored or used in any form, or by any means, without specific prior permission from the publisher.
prA is circulated free to trade readers in the plastics and rubber industry. Airmail subscriptions are available at uS$160 within Asia and uS$250 to all other countries outside Asia.
is a member of Abc (Audit bureau of circulation)
www.plasticsandrubberasia.com www.rubberjournalasia.com
www.injectionmouldingasia.com
www.plasticsandrubberasia.cn
Green energy is the new buzz word with countries focusing on renewable energy sources to lead the path towards lowering carbon emissions
• Japanese chemical firm Asahi Kasei has invested in Israeli start-up specialising in 3D printing software Castor Technologies Ltd . In addition to utilising Castor’s software and services, Asahi Kasei will pursue synergies between its CAE technical service for plastic products and Castor’s software.
• Auto parts firm
Faurecia , a company of the Forvia group, French tyre maker Michelin and Stellantis have entered into an agreement for auto maker Stellantis to acquire 33.3% stake in Symbio , a specialist in zeroemission hydrogen mobility. Faurecia and Michelin will remain shareholders with 33.3% stakes each.
• Japanese firms
Toyobo Co Ltd (51%) and Mitsubishi Corporation ( MC ) (49%) have launched operations at their new joint venture company, Toyobo MC Corporation ( Toyobo-MC ), which will specialise in manufacturing and sales of functional materials.
• French multienergy company TotalEnergies has
accepted an offer from Pacific Avenue Capital Partners for the acquisition of three product lines (Wingtack, PolyBD and Dymalink) developed by its affiliate Cray Valley The transaction includes four production sites in the US, the Cray Valley Italy affiliate and portfolio of customers.
• German conglomerate Henkel has sold its business activities in Russia to a consortium of local financial investors, including Augment Investments , Kismet Capital Group and Elbrus Services , for EUR600 million. All acquirers have established and longstanding business relationships in Western countries and are not subject to EU or US sanctions.
• Italy’s Versalis – Eni 's chemical company and a shareholder of Novamont (36%) – will acquire the remaining 64% of Novamont’s shares currently held by Mater - Bi – a company controlled by Investitori Associati II and NB Renaissance .
• Maire Tecnimont ’s subsidiary NextChem has acquired a 51% stake in MyRemono , a newly established
company to which Biorenova transferred patents, assets, including a demonstration plant, and contracts related to CatC, a depolymerisation technology to recover monomers (building blocks for the plastic value chain) with ultra-high levels of purity from PMMA, (known as Plexiglass).
• US materials firm DuPont has acquired Spectrum Plastics Group from private investment firm AEA Investors for US$1.75 billion in cash. Previously, DuPont had been hot on the heels of acquiring Rogers Corp , which did not materialise, and has now settled for a smaller deal for a specialty plastics manufacturer that focuses on the growing biopharmaceutical market.
• Materials firm Arkema ’s planned acquisition of German thermal interface materials firm Polytec PT will strengthen its Bostik’s product offer to serve the fastgrowing batteries and electronics markets.
• US industrial firm Hillenbrand Inc ., which also has machine firm Milacron in its portfolio, has acquired the Schenck Process Food and Performance Materials ( FPM ) business, a portfolio company of Blackstone , for US$730 million. Headquartered in Kansas City, FPM has over 1,300 global employees and sells to customers in over 150 countries, with 85% of revenues generated in North America.
• Austrian flexible packaging firm Constantia Flexibles , Indian private investment company Premji Invest , and Indian packaging supplier SB Packagings , have finalised the joint venture to create one of the largest packaging platforms in India and South Asia.
• Packaging firm Alpla Group has strengthened its commitment to the UK market with the acquisition of the packaging business iTEC Packaging ( Mansfield ).
• Sulzer Chemtech (GTC Technology) has started up the world’s largest facility for styrene extraction from pyrolysis gasoline (pygas) derived from naphtha cracking. Located in Zhejiang Petroleum & Chemical’s integrated refining and petrochemical complex in Zhoushan, China, the unit uses Sulzer Chemtech’s proprietary GT-Styrene licensed technology to produce 100,000 tonnes/year of styrene.
• Speciality polymers maker Kraton Corporation is to expand its SBS supply capability at its Belpre, Ohio, facility by 24 kilotonnes/year by 2025.
• Spanish multinational firm Repsol has broken ground on its EUR657
million expansion project at its Industrial Complex in Sines, Portugal. The project includes a linear PE and PP plants with a production capacity of 600,000 tonnes/year.
• Flex P Films Egypt, a subsidiary of Indian flexible packaging materials company Uflex, is building a US$110 million, 30,000 tonnes/month-capacity PET plant in SIDC Industrial Park, owned by Orascom Industrial Parks, in Egypt. Phase 1 is scheduled to start in 2024, and Phase 2 by mid-2025.
• China Petroleum & Chemical Corp. (Sinopec) subsidiary Hainan Baling Chemical New Material Co has started up a SBC plant in Hainan, China. The US$280 billion, 170,000-
Extrusion lines for separator film
Lithium-ion battery separator films manufactured on SML’s extrusion lines are based on a dry process, which ensures excellent chemical and thermal stability, tensile strength as well as low film thickness.
tonne/year plant will produce 120,000 tonnes/year of SBC and 50,000 tonnes/year of SEBS products.
• German chemicals firm BASF will establish compounding capacities for its certified compostable biopolymer ecovio in Shanghai, China, to be available for customers throughout the region Asia-Pacific from mid-2023.
• Belgian firm Fost Plus and recycler Morssinkhof Plastics Belgium will build a 40,000-tonne/year recycling plant to convert PP, PE, and HDPE packaging waste. The EUR30 million plant will be built at the Kristalpark III business park in Lommel, and be operational from 2024.
• German materials firm
Covestro is building a 25,000 tonnes/year compounding plant for PCR polycarbonates at its integrated site in Shanghai.
Covestro also inaugurated a new production line for TPUs that will be used for production of paint protection films (PPF) at its site in Changhua, Taiwan.
• Italian materials firm RadiciGroup has opened a EUR35 million site in Suzhou, China, to double capacity for manufacturing engineering polymers.
• German materials firm Evonik is doubling its global capacity for Vestamid E, polyether block amide (PEBA), with expansion of its production plant in Shanghai, and an optimisation project at its facility in Marl, Germany. Construction
lines
at the Shanghai site starts in fall 2023 and will increase the company’s ability for the polymerisation of PEBA.
• US-based manufacturer of thermoplastics, composites, seals, and engineered components Greene Tweed has invested in a new manufacturing facility in Cheongju-si, Chungcheongbuk-do, South Korea, with construction to be completed in early 2024.
• South Korean chemical firm Jaewon Industrial will open a new chemical recycling plant in the US to serve lithium-ion battery manufacturers and the EV supply chain. It will invest US$102 million to locate its first operations in Indiana, buying 30 acres of land to build a 65,000sq-ft facility to disperse conductive slurry and a facility for recycling 100,000 tonnes/year of n-methylpyrrolidone (NMP).
• Japanese chemical firm Kuraray Co recently opened its isoprene plant in Map Ta Phut, Rayong Province, Thailand. Operated by Kuraray GC Advanced Materials Co and Kuraray Advanced Chemicals (Thailand) Co, the plant will produce Genestar heatresistant PA9T, Septon HSBC, and the 3-MPD.
• US firm Penn Color has expanded its presence in Asia since the opening
of its technology centre in Singapore in January, and now with the opening of a world-class facility in the Pluak Daeng Subdistrict, Rayong Province, Thailand, to supply colourant and additive masterbatches to markets in the region.
• Japan’s Fujifilm Corp. has broken ground on a new EUR30million expansion at its electronic materials manufacturing site in Belgium, to grow semiconductor materials manufacturing capabilities in Europe.
• US-headquartered West Pharmaceutical Services, a supplier for injectable drug administration, recently inaugurated its facility in Jurong, Singapore, a part of West’s commitment to invest more than US$350 million globally in 2023.
• US-based coatings provider PPG has announced a US$44 million investment to upgrade five powder coating manufacturing facilities in the US and Latin America, to increase overall capacity, add production capabilities for bonded metallic powders, improve processing times with automated packaging, and enhance capabilities to produce small, medium and large batches.
• Swiss chemical firm Clariant has opened its new CHF80 million
Catofin catalyst production site in Jiaxing, Zhejiang Province, China, adding on to the existing nearby catalyst plants in Jinshan and catalyst R&D centre within the One Clariant Campus in Shanghai.
• South Korea’s SK Geo Centric and China’s Zhejiang Satellite Petrochemical (STL) are to build the fourth ethylene acrylic acid (EAA) manufacturing plant in Jiangsu, China, with completion by 2028, an investment of US$300 million and a targeted capacity of 50,000 tonnes/year.
• US recycler PureCycle Technologies Inc has reached mechanical completion of its first PP purification plant in Ironton, Ohio. The facility will begin operational pre-startup, safety review processes, and the march toward initial pellet production, which is currently anticipated to commence in the second quarter of 2023.
• Technip Energies has been awarded a contract by Ningbo Juhua Chemical & Science Co for a 1,3-propanediol (PDO) plant with a capacity of 72 kilotonnes/year and a 150 kilotonnes PTT plant in Ningbo, China.
• Alujain National Industrial Co. has selected Lummus Technology’s C3 Catofin PDH technology for its
new propylene plant in Yanbu, Saudi Arabia. The 600,000-tonnes/year integrated propylene, PP complex will be connected to Alujain’s existing PDH/PP facility; with an investment of US$2 billion and startup expected in 2026.
• WR Grace & Co, the supplier of polyolefin catalyst technology and PP process technology, has announced hitting another milestone in the Asian market, with the start-up of a 500 kilotonnes/year PP reactor line by PetroChina GuangDong PetroChemical Company (PetroChina GuangDong), a subsidiary of PetroChina Group, the world’s second-largest petroleum company. The plant will produce homopolymer, random copolymer, and impact copolymer PP resins. This marks the fourth Unipol PP technology plant startup for PetroChina, which includes PetroChina Guangxi (200 kilotonnes/year), PetroChina Fushun (300 kilotonnes/year), and PetroChina Sichuan (450 kilotonnes/year).
• Grace has also signed a new license with PetroChina Guangxi Petrochemical Company (PetroChina Guangxi) to develop a 400,000-tonne/ year single reactor line using its Unipol PP technology. The anticipated start up is in 2026.
• Speciality materials firm Trinseo has inaugurated its PC dissolution pilot facility in Terneuzen, the Netherlands.
• Japan’s Tosoh Corporation is building a facility to recover 40,000 tonnes/year of CO2 from the combustion gas released during manufacture at its Nanyo Complex, in Shunan City, Yamaguchi Prefecture. The recovered CO2 will be converted into feedstock for the isocyanate products, including for MDI, a raw material for polyurethane.
• An inauguration ceremony held recently marked the completion of the
capacity expansion for VAE dispersions and VAE dispersible polymer powders at German firm Wacker Chemie’s Nanjing site in China. Wacker invested around US$100 million in its integrated production site for the expansion measure.
• Japanese chemical firm Nippon Shokubai recently inaugurated its US$200 million acrylic acid (AA) facility with a production capacity of 100,000 tonnes/year in Cilegon, Indonesia. Nippon Shokubai Group manufactures superabsorbent polymers (SAP) for disposable diapers and AA which is the raw material for SAP.
• Toyochem Co., the polymer and coatings arm of Japan’s Toyo Ink Group, has completed construction of a new polymer pilot facility at its Kawagoe Factory, a manufacturing complex located in Kawagoe City, Saitama Prefecture in Japan. The new facility, which came online in April 2023, is engaged in the prototyping and medium-scale production of advanced polymers and their composites
• South Korean chemical firm LG Chem has broken ground on its fourth carbon nanotube (CNT) plant in South Korea, to more than double output of the material in the next few years. It is located in LG Chem's Daesan
complex, in Seosan, and will boost the firm’s total CNT production capacity to 6,100 tonnes.
• Bombay-listed Indo Rama Synthetics (India) Ltd, which is 32%-owned by Thailand’s integrated chemical producer Indorama Ventures, has started up commercial operations at its 230,000-tonne/ year PET plant in the western Maharashtra state in India.
• Indorama Ventures has tied up with French biotech company Carbios to form a joint venture for the construction of what it says is “the world’s first PET biorecycling plant” in France.
Discover our first-class solutions for a wide range of customized plastics recycling processes:
+ from size reduction, washing, separating, drying and agglomerating of plastic waste through bulk material handling, feeding, mixing and extrusion all the way to compounding, pelletizing, deodorization, storage and packaging
+ fulfilling highest product quality standards and maximum reliability
+ delivering highest throughput rates with maximum efficiency
PLASTICS RECYCLING TECHNOLOGY. EFFICIENT. SUSTAINABLE. RESPONSIBLE.
With the expansion of electromobility, the market for lithium-ion batteries is gaining rapidly in importance – and with it the demand for separator film. This is one of the most critical and expensive part in a lithium-ion battery, accounting for 15-20 % of the overall costs.
Over the last ten years, Austrian extrusion machinery maker SML has delivered more than 90 cast film lines for the production of premium separator film.
“It uses the efficient and environmentally friendly dry process. With this vast experience gained, we know in the meantime what really matters in this business,” Alexander Bruckmüller, Product Manager at SML explains.
But which functions does a separator basically have in a lithium-ion battery? Its main purpose is to keep the two electrodes apart to prevent electrical short circuits. Simultaneously, the separator allows the transport of ionic charge carriers that are needed to close the circuit during the passage of current in an electrochemical cell.
To fulfill these functions, separator film in lithium-ion batteries must meet a number of requirements:
• Free from gels, as any surface defect, unmolten or burnt particle in the film can cause holes after stretching. And this in turn causes short circuits.
• Thin-gauges and uniform thickness: Battery separator film (BSF) must be thin to facilitate the battery's energy and power densities. To support many charging cycles, its thickness must be uniform.
• Optimum porosity enables the electrolyte to be thoroughly moistened and ensures facile ionic conduction. Generally, commercial separators with pores of 1 micron or less have a porosity of 40-50 %.
• Adequate mechanical properties: to withstand physical stress caused by external compression and electrode expansion.
• Chemical stability: the separator must be an electronic insulator; additionally it must be electrochemically stable in the face of redox reaction potentials.
• Ability for a thermal shutdown at temperatures which are slightly lower than that, at which thermal runaways occur. During a shutdown, mechanical properties must be retained.
• Dimensional stability: the ability to keep shape over a wide temperature range without curling or warping, lying completely flat. Minimum thermal shrinkage in all directions.
Cost-efficient manufacturing using the dry process SML’s cast film lines for separator film fulfill these requirements “100%”, says the firm.
“Separator film can be made of different materials and can be produced in different processes. The most common processes are the dry and the wet process, and the most common raw materials are polypropylene (PP) and polyethylene (PE),” continues Bruckmüller.
On SML’s cast film lines, separator film is manufactured using the dry process. Compared to the wet production method, the dry process has significant advantages:
• Lower material costs: in the dry process, rather standard PP or HDPE resins are used. While in the wet process, relatively expensive, ultra-high molecular weight polyethylene (UMWPE) is applied.
• Fewer production steps: the dry process is more straightforward compared to wet process.
• More environmentally friendly: no solvents are required to create the pores, as it is necessary in the wet process.
• Much lower energy consumption: it is not necessary to evaporate the solvent and dry the film afterwards.
Next to the electromobility market, dry process separator film is in high demand for large-scale electricity storage at wind and solar power plants.
In this edited version of a white paper by TotalEnergies Corbion, a 50/50 joint venture between TotalEnergies and Corbion, the company explains why its Luminy PLA family of bioplastics qualifies as sustainable under the EU taxonomy regulation.
Thailand, where Netherlands-based TotalEnergies Corbion has been operating a 75,000-tonne/year PLA plant in Rayong since 2018, is the second largest global exporter of sugarcane. Planting sugarcane is the starting point for Luminy PLA production.
After growing and harvesting the sugarcane, it is brought to a sugar mill to extract the sugar, which is fermented using microorganisms to produce lactic acid, an organic acid also produced by the human body.
TotalEnergies Corbion converts the lactic acid into PLA, a biopolymer that manufacturers can use in multiple applications from packaging to 3D printing to electronics.
Different regional and international standards exist to measure biobased content in plastic materials. Typically, these rely on the carbon dating technique known as C14, which determines the origin of the carbon in the material. Carbon is the key building block of our planet, and roughly two sources of carbon exist: carbon from renewable resources or carbon from fossil resources. Biobased materials have a C14 activity of 100%, and fossil-based materials have an approximate 0% C14 activity.
In Europe, EN16875 is a regulation that specifies a method of determining the biobased content in products using the C14 method, while in the US, the US Department of Agriculture’s BioPreferred programme strictly monitors third-party certifications and manufacturers’ claims regarding biobased content.
Thus, Luminy PLA is certified 100% biobased according to EN16785 and USDA BioPreferred programme.
As our population grows and global demand on resources increases, arable land will become scarce. It is, therefore, essential to use the most efficient crops available. Agricultural yields per hectare of arable land vary based on the type of crop and region. Sugarcane and sugar beet provide the highest carbohydrate yields per hectare of land used.
TotalEnergies Corbion sources its lactic acid from fermentation specialists and global market leader in lactic acid Corbion that says it predominantly uses the highest-yielding feedstocks regionally available: raw sugar from cane is used by its factories in Thailand and Brazil, dextrose from corn is used by its lactic acid production plant in the US, and raw sugar from sugar beet is used by its factories in Europe.
In addition to bioplastics production, lactic acid produced in these factories is also used in food ingredients, biochemical ingredients, and medical biomaterials.
Feedstock efficiency scores highly for PLA
In addition to crop yields, it is important to have an energy-efficient conversion from raw sugar to polymer. The term ‘feedstock efficiency’ as used here describes the conversion ratio of feedstock weight to final plastic polymer weight and is a combination of a theoretical efficiency (which differs per type of bioplastic) in combination with production efficiencies. This means that different types of bioplastics, produced using different production processes, will require different amounts of feedstock.
In terms of feedstock efficiency, PLA is one of the most efficient biopolymers: yielding 1 kg of PLA polymer for 1.6 kg of fermentable sugar feedstock. Other bioplastics can require 2.5-3 times more sugar feedstock to produce the same amount of plastic.
Ultimately, feedstock efficiency has a positive impact on land use. Additionally, all environmental impacts related to agriculture are correlated with the amount of feedstock used.
TotalEnergies Corbion produces PLA bioplastic made predominantly from raw sugar from cane in Thailand. Over the years, both Corbion and TotalEnergies Corbion have significantly improved the internal process yields and as mentioned above, is able to produce 1 kg of PLA using just 1.6 kg of raw sugar.
TotalEnergies Corbion also says that the European sugar beet and Thai sugarcane used as feedstocks for the production of its PLA bioplastics are “always GMO-free”.
Meanwhile, TotalEnergies Corbion's production plant is certified ISO 14001-Environmental Management System, ISO 9001 Quality Management System and ISO 45001 Occupational Health and Safety Management System.
TotalEnergies Corbion sources lactic acid from Corbion, and Corbion's Cane Sugar Code has been developed to describe expectations of its cane sugar suppliers to fulfil responsible sourcing commitment. The code is based on the definitions for sustainable sugarcane and derived products as set out by Bonsucro , a global, non-profit, multi-stakeholder organisation founded by WWF in 2005 to advance a more economically, environmentally, and socially responsible sugarcane sector.
Corbion’s code of conduct for cane sugar suppliers includes a general supplier code, applicable to all Corbion suppliers, as well as specific extensions directly relating to sugarcane farming in Thailand and Brazil.
A benchmarking study indicates that Corbion’s Code contains a broad set of robust principles and criteria that is well aligned with the principles and criteria laid down by Bonsucro and other relevant standards (RSB, ISCC, SMETA) for addressing raw materials, ethical and social compliance.
TotalEnergies Corbion Luminy PLA produced in Thailand fully complies with EUTaxonomy regulations, meaning that it qualifies as a sustainable material within the framework of reducing environmental impact and mitigating climate change in the region. For plastics users, this demonstrates that they can substantially reduce their Scope 3 GHG emissions by replacing fossil-based plastics with PLA.
The EU taxonomy, which came into force on 12 July 2020, is a classification system with technical screening criteria for defining the specific requirements and thresholds for an economic activity to be considered as significantly contributing to a sustainability objective.
This provides companies, investors, and policymakers with appropriate definitions of which economic activities are environmentally sustainable. It also helps the EU to scale up sustainable investment and to implement the European green deal.
Today’s feedstocks for bioplastics are grown on arable land. Land use for bioplastics production is minimal and does not compete with food productions in any way through 2027.
The European Bioplastics Association publishes annual market size data for the current and future years. Using these growth rates, one can estimate the overall impact of the bioplastics market on land use.
The data shows that, for example, in 2027, land used for growing feedstocks for bioplastics will account for only 0.058% of global agricultural area, a figure from which we can conclude that bioplastics do not negatively impact food production, a conclusion also supported by various independent reports, including those from the n ovaInstitute , Wageningen University and Research Centre and IfBB
Thai raw sugar production is in the range of 12 million tonnes/year. Thailand has 16.81 million ha of arable land. In 2020/2021, the land used for sugarcane is estimated to be 1.75 million ha. This means that 10.41% of the arable land in Thailand is used for sugar production.
TotalEnergies Corbion has a production capacity of 75 kilotonnes of PLA; 1 kg of PLA requires 1.75 sq m of land, while 75 kilotonnes of PLA require 13,312 ha, which is 0.08% of Thai arable land and 0.8% of Thai land used for sugar production.
Production of biobased Luminy PLA has a 75% reduced carbon footprint, including biogenic carbon, compared to conventional plastics.
The starting point for the Global Warming Potential (GWP) of PLA is the CO2 absorption from the atmosphere by the growing sugarcane. According to the biomaterial storage approach, the amount of CO2 fixated in the PLA material is 1,833 kg CO2/tonne of PLA.
Global net emissions from PLA production are 2,334 kg CO2/tonne of PLA, which makes the carbon footprint of PLA production 501 kg CO2/tonne PLA when deducting the carbon uptake. The biggest contributor to the GWP in the PLA production process is in the production of lactic acid. This is mainly due to the energy consumed and the chemical usage.
The GWP of the sugar cane production is influenced by fertiliser usage, the plant burning, and the fuel used in machines and equipment. Finally, the sugar mill impact is negative due to the highest gain from heat
and electricity produced from by-products.
Since 2021, TotalEnergies Corbion has also been offering a version of its Luminy PLA grades with recycled content. Collected post-industrial and post-consumer PLA waste are depolymerised via hydrolysis producing lactic acid. The lactic acid is then reprocessed in the polymerisation line to produce new PLA, which are said to be of the same quality as the virgin material.
Currently, bioplastics represent less than 1% of the more than 390 million tonnes/year of plastic produced. However, according to the latest market data compiled by European Bioplastics ( EUBP ) in cooperation with the nova-Institute, global bioplastics production capacities are set to increase from around 2.2 million tonnes in 2022 to approximately 6.3 million tonnes in 2027. This represents a significant potential reduction in atmospheric CO2.
PLA bioplastics play an important part to reach a truly circular plastics economy by providing additional end-of-life options compared to traditional plastics.
In addition to being biobased, PLA can be organically recycled via industrial composting, creating valuable biomass, which in turn, facilitates plant growth and closes the cycle.
Additionally, innovative biobased materials can be transformed back into feedstock using established mechanical or advanced recycling methods.
Advanced recycled Luminy rPLA is sourced from used PLA and maintains the same certified characteristics, meaning that its product life cycles can be endless.
Asian countries are making a mark in renewable energy for lower to zero carbon footprint, with green hydrogen, says Angelica Buan in this article.
Going net-zero: the society’s impossible dream? A net-zero economy appears to be a Utopian future where everything is balanced and there is no climate issue. However, the push for a net-zero economy has never been more urgent than now.
In a net-zero scenario, total greenhouse gas (GHG) emissions, such as carbon dioxide (CO2), are countered by measures that either eliminate or capture an equivalent amount of CO2 from the environment. The use of renewable energy could help the world move to a net-zero economy.
Similarly, low-emissions products and processes that replace traditional high-emissions options, such as expanding production of electric vehicles instead of internal combustion engine (ICE) vehicles and production processes fueled by green hydrogen, will take the forefront.
Green hydrogen, which is produced through electrolysis from renewable electricity, can play a critical part in the worldwide transition to a low-carbon economy. It can be produced from renewable sources, eliminating reliance on fossil fuels and energy imports.
Green hydrogen can help to decarbonise difficult-to-abate sectors like heavy industries, transportation, and power generation. These industries can dramatically lower their carbon footprint by replacing fossil fuels with green hydrogen.
By 2050, industries like iron and steel, chemicals, cement, transport and aviation will account for up to 42% of total clean hydrogen demand. According to Deloitte 's 2023 global green hydrogen outlook, it can reduce cumulative emissions by up to 85 GtCO2eq by 2050, which is more than double the global CO2 emissions in 2021.
Carbon neutrality means having a balance between emitting carbon and absorbing carbon from the atmosphere in carbon sinks. Removing carbon oxide from the atmosphere and then storing it is known as carbon sequestration. In order to achieve net zero emissions, all worldwide GHG emissions will have to be counterbalanced by carbon sequestration
With a steady reduction in carbon emissions, it is predicted that by 2050, coal energy production, which accounts for a fifth of worldwide GHG emissions, will practically disappear, but electricity consumption would more than double. To meet the rising demand for electricity, renewable energy output is likely to rise.
According to McKinsey 's report titled The Netzero Transition: What it Would Cost, What it Could Offer , production of hydrogen and biofuels would rise more than tenfold between 2021 and 2050. Other industries, for example those that manage carbon with carbon capture and storage technologies, could also grow.
Increased use of green hydrogen has the potential to improve energy security, spur regional growth, and promote global cooperation in the fight against climate change.
According to the Asian Development Bank ( ADB ), Asia-Pacific has accounted for more than half of global hydrogen investment by 2021, with an increasing number of nations in the region adopting national-level hydrogen programmes to speed up decarbonisation.
There is no doubt that the region has a huge potential market for green hydrogen. Nonetheless, a few critical factors, such as high production costs affecting investment viability, could prevent green hydrogen from fully contributing to the region's energy transition.
According to the Deloitte research, global investment in hydrogen in 2020 was only US$1.5 billion, or 0.5% of the record US$500 billion in renewable energy investment that year. Nonetheless, the region has mapped out strategic investment plans to develop green hydrogen infrastructure.
India’s energy autonomy plans hinge on renewables
India has set a goal of becoming energy independent by 2047 and net-zero by 2070. According to data from Invest India , the government's investment promotion energy platform, India ranks fourth in the world in renewable energy installed capacity, as well as fourth in wind power capacity and solar power capacity, according to the REN21 Renewables 2022 Global Status Report.
At the COP26 climate summit, the country also committed to an increased target of 500 GW of non-fossil fuel-based energy by 2030.
In 2022, India had the largest year on year growth in renewable energy additions, at 9.83%. Foreign investment in this industry is strongly encouraged, with up to 100% FDI permitted under the Electricity Act of 2003.
India has set its sights on becoming energy independent by 2047 and achieving net zero emissions by 2070
According to the Union Cabinet-approved National Green Hydrogen Mission, the country plans to produce 5 million tonnes/year of green hydrogen by 2030. The mission's goal is to make India a world leader in green hydrogen production and supply by generating export opportunities for green hydrogen and its derivatives and supporting R&D projects in this sector. It also intends to add on renewable energy capacity addition of around 125 GW; and a reduction in annual GHG emissions of about 50 million tonnes/year.
Nonetheless, according to a report by the Institute for Energy Economics and Financial Analysis , investment in India will need to more than double to US$30-US$40 billion/year for the country to meet its aim of 450 GW of renewable energy capacity by 2030.
Singapore is taking major steps with green hydrogen as it works toward its net zero goal by 2050. Depending on technology advancements and the development of alternative energy sources, hydrogen is expected to supply up to 50% of the country's power demands by 2050.
Green hydrogen's potential and widespread implementation are hampered by high production costs. This challenge spurred the National University of Singapore ( NUS ) to establish a dedicated research institute.
The S$25 million Centre for Hydrogen Innovations ( CHI ), which is said to be the first of its kind in Southeast Asia, intends to develop breakthrough technologies that would make hydrogen commercially viable as a green energy source. These capabilities, in turn, will help Singapore position itself as a game changer in enabling a hydrogen economy, one in which hydrogen is one of the key commercial fuels used to power Singapore's energy demands. The centre began operations in July 2022.
CHI, led by Professor Liu Bin, who also founded the NUS Green Energy Programme, which focuses on carbon capture, will conduct research on making green hydrogen affordable for Singaporeans and provide solutions to the country's reliance on fossil fuels as a source of energy.
Singapore may need to import hydrogen from regional sources due to limited solar and water supplies. CHI intends to conduct
import cost analysis and supply chain analyses to ensure cost-effectiveness and to maintain downstream commercial applications of hydrogen inexpensive. The Centre will also concentrate on creating solutions to enable the safe transportation of hydrogen imports.
As part of a watertight strategy, CHI will also look into innovative technologies for local hydrogen production, such as electrolysis of water and methane pyrolysis powered by solar energy as a renewable energy source, to ensure national energy security in the event of supply chain interruptions.
CHI will also collaborate closely with policymakers, governmental agencies, and industry partners to investigate and develop hydrogen fuel uses.
Some of these uses include commercial and transportation fuel cells, as well as clean feedstock for the chemical sector. Initially, CHI will conduct hydrogen-related research with the goal of developing disruptive technologies such as hydrogen carriers (chemicals that contain hydrogen that can be extracted) and infrastructure.
Ammonia is a well-known hydrogen transporter as well as potential carbon-free fuel. However, the extraction of hydrogen from ammonia faces technological challenges. Led by Associate Professor Yan Ning of the NUS College of Design and Engineering's Department of Chemical and Biomolecular Engineering, the team will seek to create more energyefficient and environmentally friendly techniques of extracting hydrogen from ammonia.
Meanwhile, to increase local on-demand hydrogen production, Associate Professor Wang Qing and his team from NUS CDE's Department of Materials Science and Engineering developed a type of redoxflow battery system that can combine electricity storage and hydrogen production via specially formulated chemicals powered by renewable energy such as solar. This enables steady hydrogen production and electricity storage, which might be used to charge electric vehicles or to power Singapore's electrical infrastructure.
Another innovative project will be led by Assistant Professor Lum Yanwei and Assistant Professor Wang Lei from NUS CDE's Department of Chemical and Biomolecular Engineering, who will look into how hydrogen could be converted directly from water into a high energy density liquid hydrogen carrier, bypassing the step of extracting hydrogen from water to form hydrogen gas, potentially avoiding the safety risks and costs associated with shipping, storing, and utilising hydrogen.
In a related development, Keppel Infrastructure , a subsidiary of Keppel Industry , is developing a 600MW combined cycle gas turbine (CCGT) power plant and has awarded an engineering, procurement, and construction (EPC) contract for the plant's construction to a consortium comprised of Mitsubishi Power Asia Pacific and Jurong Engineering
The Keppel Sakra Cogen Plant, Singapore's first hydrogen-ready power plant will be constructed in the Sakra region of Jurong Island and will be owned by Keppel Sakra Cogen ( KSC ) Pte Ltd.
Keppel Asia Infrastructure Fund ( KAIF ) and Keppel Energy will each own 70% and 30% of KSC, respectively. Furthermore, KSC and Keppel Energy
will enter into a turnkey contract for the development of the KSC plant, which is scheduled to be completed in the first half of 2026.
It will initially run on natural gas as its principal fuel and is also designed to run on fuels with 30% hydrogen content, with the potential of switching to run totally on hydrogen. Furthermore, as a CCGT power plant, it will be capable of producing steam for use in industrial processes for Jurong Island's energy and chemical customers.
CCGT is claimed to be the most efficient among Singapore's operating fleet, saving up to 220,000 tonnes/year of CO2, when compared to Singapore's average operating efficiency for equal power generated.
In addition to the EPC and LTS contracts, Keppel Infrastructure’s subsidiary, Keppel New Energy , signed an MOU with Mitsubishi Heavy Industries to conduct a feasibility study on the development of a 100% ammonia-fueled power plant on a selected site in Singapore.
Indonesia is determined to improve its carbon emissions index. It plans to reduce emissions by approximately 32% on its own by 2030, and 43.2% with foreign assistance during the same period, through its Green Hydrogen initiative.
According to the Ministry of National Development Planning , Indonesia's existing renewable energy capacity is relatively small, but its potential is substantial, with a total utility-scale renewable energy potential estimated at 442 GW in 2018, of which just 2% had been utilised.
Pertamina and Tepco intend to tap into Indonesia's immense geothermal potential for both electricity development and the production of ammonia and green hydrogen
Significant partnerships are also anticipated to hasten Indonesia's achievement of its emissions target. For instance, the state-owned electricity utility of Indonesia, PLN ( Persero ), is working with France Hydrogene to develop hydrogen technology that can take advantage of Indonesia's natural resources. PLN intends to construct a hydrogen plant to replace fossil fuel-based diesel generators.
In a related development, PT Pertamina Power Indonesia and Tokyo Electric Power Company Holdings ( Tepco ) signed an MOU on the development of green hydrogen and green ammonia. This agreement covers the conduct of verification surveys, joint selection of hydrogen production areas, identification of market segments, market development, and other matters in Indonesia. Together, the two companies will provide technology, ammonia manufacturing, transportation, and green hydrogen at low cost. Both companies prioritise the domestic Indonesian market during the commercialisation phase, and also target the export market to Japan and other countries in the medium to long term. The project will be able to tap into Indonesia's immense geothermal potential for both electricity development and the production of ammonia and green hydrogen.
The major themes that are characterising the entire plastics and rubber industry and its market will be a focus at PLAST 2023, scheduled for 5–8 September at the Fiera Milano fairgrounds in Rho-Pero. The spotlight is on innovation and opportunities offered by developments in production paradigms in a circular-economy perspective that, together with sustainability and energy savings, represent the key themes at PLAST 2023.
These themes are central not only in the products, services, and systems on display, but also as regards the fair itself, this year aiming to achieve the best performance in terms of sustainability. A part of this process has been made possible by Fiera Milano, which has taken a sustainable event management system approach involving control of logistics, wastes, and food services to reduce the environmental impact, including CO2 emissions, associated with the organization and conduct of PLAST 2023.
Promaplast, the organiser of PLAST, aims to represent a virtuous example of this concern and to observe the core rules of sustainability that are now considered an objective that can no longer be postponed. One of the aspects characterising this approach is installations that meet standards of ecodesign and food services such as those put forward by the Fondazione Banco Alimentare, which is closely attuned to the associated issues.
And that is not all. For the first time, Promaplast offers the possibility of implementing a carbon footprint assessment process in time to allow companies to
announce their initial results already at PLAST 2023. The calculation of a company’s carbon footprint is the most immediate and universally accepted method for representing and communicating the environmental impact of an organization. The process uses the parameters developed by the United Nations Intergovernmental Panel on Climate Change (IPCC), applying internationally recognised protocols (GHG Protocol and ISO 14064). Expressing a company’s activities in terms of atmospheric carbon dioxide equivalents is a measure of concern for the environment and demonstrates the commitment to meeting the core rules of sustainability that are now considered an added value.
Together with technological innovation, the theme of sustainability will pervade the six halls of the fair, part of an exhibition that covers everything from materials to processing, from finished products to services and the most advanced solutions developed by manufacturers of plastics and rubber processing machinery, equipment, and moulds.
After having introduced in May 2022 the exhibition-convention GREEPLAST – focused on the sustainability of materials, technologies, and transformation processes for plastics and rubber – PLAST 2023 too will showcase innovation in the key of green: from increasingly sustainable and environmentally friendly materials to machinery with reduced energy consumption for processing bio-based and recycled polymers and from processes that make it possible to use less raw materials without compromising on performance to sorting and recycling systems.
The event has over 1,200 exhibitors already having reserved their stands and official buyer delegations are expected from at least 30 countries. Early registration is open for professional operators who wish to engage with specialised products, systems, and services and full-spectrum responses to their needs in terms of products, technology, solutions, and business opportunities.
For further information: info@promaplast.org - www.plastonline.org
A new range of additives are helping recycled plastics producers meet the enhanced requirements for high quality recycled materials, says Angelica Buan in this report on additives.
Additives are required to increase both the utility and quality of polymers; improving plastics' flexibility and workability with plasticisers, strengthening with reinforcements and fillers; improving their flowability with lubricants, and incorporating antistatic and conductive properties.
While additives can provide a variety of benefits to plastics, certain additives can be hazardous to the environment as well as posing risk to human health and ecosystems when these additives are exposed to heat or weathering, or that some may release heavy metals into the environment during the production, use, or disposal of plastics.
Even more, some additives used in plastics, such as fillers, pigments, flame retardants, and plasticisers, can contaminate the recycling process. During recycling, plastics are typically sorted and processed based on their resin type. If additives are present, they can interfere with the sorting process, making it difficult to separate and process different types of plastics effectively.
The disruption in the recycling process can hinder efforts to reduce plastic waste and promote a circular economy.
Every year, around 400 million tonnes of plastics are produced, with packaging accounting for approximately 40% of the total. Only a small portion of this is recycled, with the vast majority ending up in landfills and incinerators after only one use, or being dumped into the environment.
Thus, the development of new recycling additives is vital for increasing not only recycling rates but also the quality of recycled plastics.
Demand for recycled polymers is increasing, owing mostly to rising consumer awareness and effective regulations. According to McKinsey's Advanced Recycling: Opportunity of Growth report, more than 80 global consumer packaged goods (CPG), packaging, and retail companies have made public commitments to achieve recycled content in their packaging ranging from 15 to 50% by 2025.
With the market shifting toward high-quality recycled plastic, additives are assisting recyclers in improving the quality of recyclates.
Evonik's Tego additive portfolio is designed to conserve energy during the mechanical recycling process while simultaneously improving polymer quality, allowing the plastics value chain to be transformed into a value cycle
The Tego Cycle additives line from German specialty chemicals manufacturer Evonik attempts to convert plastic waste into valuable plastic materials. At a plastics recycling show in Europe in May, Evonik introduced a variety of additives, which can help customers enhance processes and raise the quality of recycled polymer and final plastics.
The Tego additive portfolio is designed to conserve energy during the mechanical recycling process while simultaneously improving polymer quality, allowing the plastics value chain to be transformed into a value cycle, Evonik said.
High costs and the technical challenge of producing quality polymers are causing comparably low recycling rates, according to Alper Aksit, Marketing Manager Compounds & Circular Plastics Region EMEA, Evonik, who also mentioned that Evonik’s initiatives like the Circular Plastics Program, which combined with its Tego additives can help speed up the plastic industry's transformation into a fully circular economy.
During the wet stage, Evonik's antifoams and wetting agents can be utilised to improve the efficiency of washing, separation, deinking, and drying processes, resulting in significant energy savings. Furthermore, during the compounding (dry stage), Evonik's odour absorbers, compatibilisers, dispersants, and processing aids help to optimise processing and polymer properties, resulting in lower costs and a considerably greater quality of recycled plastic content.
In addition, Evonik has also introduced its new organo-modified siloxane-based Tegomer Polymer Processing Aids (PPA) for converters wanting to replace typical PPAs made from fluoroelastomers in PE and PP processing.
Similarly, additives maker SI Group offers its Evercycle additives platform, which debuted in 2022 at a major trade show in Germany. According to SI, Evercycle enables process stability, colour control, and lower acetaldehyde levels for PET recycling and conversion. Its benefits for recycling polyolefins include process stabilisation and performance improvement, allowing for higher recycled content.
By enabling more plastics to be recycled back into the economy, making it possible consumer brands to increase the amount of recycled content, and allowing for multiple uses of their products to increase the sustainability of their products, SI's formulated additive solutions advance the transition to a more circular economy, according to Irfaan Foster, Market Development Director at SI Group.
Joey Gullion, Chief Commercial Officer at SI Group commented that the business continues to invest in innovation and provide new environmentally friendly products like Evercycle additives to the market, showcasing its capacity to assist clients in the shift to a circular economy.
Mechanical recycling recovers and reuses valuable materials from waste goods, reducing the need for virgin resources. Furthermore, it diverts waste from landfills and incineration plants, reducing the amount of waste that ends up in these disposal locations. When compared to other forms of recycling, mechanical recycling uses less energy and does not require chemicals. As a result, mechanical recycling fits into the circular economy paradigm of creating high-quality recycled plastic with a low carbon footprint.
German chemicals firm BASF offers the IrgaCycle additive solution for mechanical recycling that addresses recyclers' and converters' concerns about recycled plastic quality and processing performance as a result of impurities in recovered plastics and polymer contaminants that accelerate polymer degradation, impairing material properties.
BASF's new IrgaCycle range aims to increase the percentage of recycled content in a variety of end-use sectors such as packaging, automotive and mobility, and building and construction
Dr Thomas Kloster, President of BASF's Performance Chemicals division, noted that the new IrgaCycle range aims to increase the percentage of recycled content in a variety of end-use sectors such as packaging, automotive and mobility, and building and construction. These solutions address specific quality issues associated with recycled resins, such as limited processability, poor long-term thermal stability, and insufficient protection against outdoor weathering.
Solutions such as IrgaCycle PS 030 G, IrgaCycle PS 031 G, IrgaCycle PS 032 G, IrgaCycle UV 033 DD, and IrgaCycle XT 034 DD increase the mechanical qualities of polymer recyclates. The ready-to-use products are simple to add into the recycling steps.
Dr Volker Bach, Global Lead Innovation at BASF Plastic Additives, noted that the granulated nondusting product form ensures safe and convenient dosage while conversion or compounding of recovered material.
Preventing the degradation of manufactured plastic parts' physical, chemical, and mechanical properties used to be an enormous challenge for recycled plastic manufacturers. Today, new additives are boosting recyclate stability, increasing the use and value of recycled materials.
Brüggemann , a German chemical manufacturer and family-owned polymer additives provider, has introduced three additives to improve the stability of polyolefin recyclates. These additives are said to produce recyclates with improved mechanical and processing qualities, eliminating the requirement for virgin material. Bruggolen R grades are delivered as dust-free additive blends in compacted granule form for convenient and homogenous distribution.
Bruggolen TP-R2090 is designed for PP recycling and can be used to recycle post-industrial and post-
consumer waste; Bruggolen TP-R8895, with its higher acid scavenger concentration, is ideal for recycling PP from battery casings. Both additives provide quality recyclates that are not possible with ordinary re-stabilisation, according to Brüggemann.
For PE recycling, Brüggemann has developed Bruggolen TP-R2162, which also contains the new repair technology and is particularly suitable for LLDPE recyclates used in film extrusion.
Finding methods to collect, sort, and recover these types of materials is becoming increasingly vital for the industry that use them as well as consumers, according to Smithers’ report, The Future of Mono vs MultiMaterial Packaging to 2028 .
Multi-material packaging is made up of different materials that have been combined, such as plastic, metal, and paper. While multi-material packaging provides benefits in terms of product protection and aesthetics, it can be difficult to recycle due to sorting complexity, contamination - which can degrade recycled material quality and disrupt the recycling platform, limited recycling infrastructure, additional costs associated with sorting, separating, and processing these complex materials, and compatibility issues due to different melting points or chemical compositions.
To address these challenges, masterbatch supplier Ampacet has introduced Revive 962 E, a compatibiliser masterbatch that enables recycling of multi-material packaging consisting of polyolefin and technical polymer components.
Brüggemann
The repair mechanism in this case produces film with higher initial mechanical strength while reducing defects. Brüggemann claims that even at low dose levels of 0.3%, laboratory tests have shown an increase of about 25% in tensile strength and 10% in elongation at break.
For the first time, it is possible to repair defects in molecular chains that emerge during processing or subsequent use and degrade quality. Re-stabilisation not only protects the recyclate from additional damage, but it also repairs the polymer chains, resulting in mechanical strength that is closer to that of virgin polymer, according to Brüggemann.
The Bruggolen R grades complement the company’s broad portfolio of additives for mechanical recycling of polyamides, and that include long-term heat stabilisers, process stabilisers, flow improvers, reactive chain modifiers, nucleating agents and other process auxiliaries.
Traditional multilayer composite films are difficult to recycle due to the necessity to separate the individual film layers. Furthermore, many countries lack adequate systems needed to recycle complex laminates.
Ampacet's Revive 962 E, a compatibiliser masterbatch enables recycling of multi-material packaging consisting of polyolefin and technical polymer components
The product enables the use of recycled material in quality film applications as well as an alternate end-oflife disposal option to landfill disposal. It also allows for better utilisation of recycled plastics and helps to reduce the consumption of virgin materials, says Ampacet.
On the other hand, US-headquartered manufacturer of specialised polymer materials Avient offers its PCR Color Prediction Service, which assists brand owners in understanding what colours are achievable based on the amount of PCR used in PET resins; and its new polyolefin antioxidants, Cesa Nox A4R recycling additives. Both are intended to improve the customer experience when working with PCR content for packaging materials.
The PCR Color Prediction Service uses technology to determine if colours are possible in a new application that contains PCR content through prior colour matching. This technology, said to be the first of its kind for the plastics sector, also determines how much PCR content can be added to an existing application without affecting its signature colour.
Avient's Cesa Nox A4R enhances PCR content stability and prevents oxidation, which can create defects such as black spots, gels, and discolouration in post-consumer polyolefins
Avient measures resin qualities with proprietary software to identify the range of colours that can be successfully reproduced in a specific PCR-based material. According to Avient, this premium service simplifies and accelerates the selection of desired
colours for polymers with PCR content, eliminating time-consuming trial and error while also providing flexibility to clients who may need to transition from one PCR content source to another.
Meanwhile, the Cesa Nox A4R enhances PCR content stability. It is based on a special formulation that prevents oxidation, which can create defects such as black spots, gels, and discolouration in post-consumer polyolefins. This antioxidant can be added early in the recycling process to PCR content or introduced into virgin resin to prepare it for future recycling. Packaging, automobile parts, and consumer goods are among the applications for the stabilised polyolefins.
According to Norbert Merklein, Vice President and General Manager of Color, Additives, and Inks at Avient, the additives range tackles any barriers that arise during the recycling process or when customers want to incorporate PCR content into existing or new applications.
The company also says it is accelerating its additive innovations in order to contribute to the circular economy and assist clients in meeting their sustainability goals.
Thailand is not cutting corners in policies and investments when it comes to its electric vehicle (EV) sector. It is, in fact, speeding up the growth of its EV sector as part of its commitment to lowering carbon emissions, adds Angelica Buan in this report.
Putting the brakes on carbon emissions
Thailand, dubbed as the Detroit of Asia, being the top automotive producer in the ASEAN and the 11th largest car manufacturer globally, aims to achieve carbon neutrality by 2050, and net zero emissions by 2065.
It has pledged to reduce greenhouse gas (GHG) emissions by up to 25% by 2030 in accordance with the Paris Agreement at the 26th UN Climate Change Conference (COP26).
According to the Ministry of Natural Resources , Thailand has pursued decarbonisation in the transportation sector, which produced close to 76 million tonnes of carbon emissions in 2019.
In 2022, after the Covid-19 limits were lifted, transportation-related carbon emissions increased to 79.6 million tonnes. Thailand's transportation carbon emissions from oil and natural gas combined exceeded
28.3 million tonnes from January to April 2023, representing a 3.51% increase over the same time last year, according to Ministry of Energy data.
Industry players have stepped up to the challenge of reducing carbon emissions. Shell Company of Thailand recently collaborated with the Electricity Generating Authority of Thailand ( EGAT ) to conduct research of clean energy technologies such as carbon capture and storage (CCS), carbon capture utilisation and storage (CCUS), and renewable energy generation. The study focuses on reducing GHG emissions and propelling Thailand towards its net-zero emission goal by 2065.
As part in the country's carbon neutrality commitment, EGAT has implemented the "Triple S" approach, which includes source transformation to
increase renewable energy share in the mix, and the development of new technologies to support renewable electricity generation.
It is also focusing on increasing the reforestation of 160,000 ha of land and a study of CCUS technology. Other than that EGAT supports mechanisms to encourage public participation in GHG gas reduction through energy saving projects; as well as through EV deployment.
The collaborative study will address renewable energy, CCUS, hydrogen fuel, and ammonia as alternate power generation sources.
Thailand will, however, continue to rely on fossilfuel electricity generation to provide energy security and meet domestic demand. The outcome of this collaboration will be applied to power plants and other future EGAT initiatives aimed at Thailand's development and global environmental challenges.
Thailand is about to change lanes in its energy mix, which is now dominated by natural gas. The National Energy Plan (NEP) 2022 includes measures to minimise carbon emissions. With more renewable energy on the horizon in the coming years, it is only fitting to promote the use of EVs on a larger scale, with the country on track to produce 30% of domestic EVs by 2030.
Thailand has implemented a number of policies to encourage the use and production of zeroemission vehicles (ZEVs), railway expansion, and the development of public transportation systems.
Thailand's National EV Roadmap is aimed at transforming the country into an EV hub within the ASEAN region, with targets of producing 250,000 EVs, 53,000 electric motorcycles, and 3,000 electric public buses by 2025, and increasing EVs' share of total domestic vehicle production to 50% by 2030 - up from the previous 30% based on the 30@30 policy.
This amounts to having every EV sold in the country made locally by 2035 and increasing the overall number of EVs to 2.5 million by 2040, according to Chandler MHM ’s 2023 Thailand Energy Transition outlook report.
Accelerating the deployment of EV charging points and accompanying infrastructure, as well as power grid management and the production of EV parts, batteries, and storage, are all priorities.
As well, tax breaks have fueled local demand for EVs while also attracting investment in the EV sector.
Counterpoint Research 's Global Passenger Electric Vehicle Model Sales Tracker indicated that Thailand accounted for over 60% of Southeast Asia's EV sales volume in the third quarter of 2022, followed by Indonesia and Singapore.
Battery electric vehicles (BEVs) accounted for 61% of sales, with plug-in hybrid electric vehicles (PHEVs) accounting for the remainder.
Well-positioned as a regional EV hub
Thailand's rise to prominence as a key EV hub for OEMs in the region and around the world has been accelerated by highly favourable government policies that support the entire automotive industry value chain, including the production of batteries, driving systems, and other EV-related infrastructure such as power grid management systems.
Home-grown Thai entrepreneurs are already building EVs and developing the infrastructure to power them. Energy Absolute , a listed Thai company with a market value of US$10 billion, is selling electric buses and boats, has an electric car ready to launch and is building what to date is the country's biggest network of charging stations.
Other local companies, including start-up MuvMi and long-established water transportation operator Chao Phraya Express Boat Co ., are replacing the country's iconic but previously heavily polluting "tuktuk" auto rickshaws and diesel-powered fast river boats with emission-free electric versions.
Many OEMs are establishing manufacturing facilities in Thailand, where incentives such as tax breaks are in place for both investors in the EV supply chain and vehicle purchasers.
Automaker Mercedes-Benz has rolled off its completely electric Mercedes-EQS in Bangkok, leaving a mark in Thailand's progress from a traditional automobile making base to a regional forerunner in EVs, the Board of Investments ( BOI ) stated.
The German luxury carmaker not only chose Thailand as its first location in Southeast Asia to manufacture the EQS, but also to build high-performance lithium-ion batteries that can power the vehicle for more than 700 km on a single charge.
Other automakers, according to BOI, have signed up for a government incentive plan to promote EV sales and production in Thailand, under which the government is offering subsidies ranging from US$2,000 to US$4,400 per vehicle depending on the model and battery capacity.
Foxconn Technology Group , the world's largest contract electronics business has picked Thailand as one of its first two locations in the world to develop EVs. Foxconn is collaborating with Thailand's state-owned oil and gas firm, PTT , to launch Horizon Plus , a joint venture that expects to invest between US$1-US$2 billion to build finished automobiles for other manufacturers using Foxconn's modular platform and software.
With production set to begin in 2024, the partners hope to be producing between 150,000 and 200,000 vehicles/year by 2030 at Thailand's Eastern Economic Corridor (EEC), an areabased initiative encompassing an integrated infrastructure that will position Thailand as a vital gateway to Southeast Asia, China, and the rest of the Asia-Pacific.
Combined, Chinese vehicles accounted for nearly 78% of the Thai EV market in the first quarter of this year, with the rest of the market shared by models from Tesla and Volvo . This is spurring on Chinese EV auto makers such as Hozon New Energy Automobile that has tied up with Thailand's Bangchan General Assembly . Construction started in March on Hozon's plant, which has a designated production capacity of 20,000 vehicles/year and is due to start operating early next year.
Meanwhile, BYD , China's biggest EV manufacturer, is building its first overseas EV plant in the country, with Thai industrial developer WHA Group . Located in Rayong, the plant, which started construction in March, is scheduled to see vehicles roll out in 2024, with a capacity of 150,000 EVs/ year. It will serve as a hub for BYD's EV production and sales in Thailand and neighbouring member countries of ASEAN.
Leading Chinese EV maker BYD is expected to launch its Thai-made EVs in the country next year
In a related development, PTT, in collaboration with partners PTT Oil and Retail Company ( OR ), Bangkok Industrial Gas Company ( BIG ), Toyota Daihatsu Engineering and Manufacturing ( TDEM ), and Toyota Motor Thailand Company ( TMT ), has opened Thailand's first hydrogen fueling station (HRS) for fuel cell electric vehicles (FCEV) in the Bang Lamung district of Chonburi province.
Supercharging for BEV manufacturing Investment in BEV manufacturing and charging is also gaining traction to assist Thailand's EV ecosystem. The government estimates that some 900 public quick chargers have already sprung up throughout the country. That figure is forecast to rise to 4,400 public quick chargers by 2025, 12,000 by 2030 and 36,500 by 2035.
Meanwhile, PTT”s wholly owned subsidiary, Arun Plus and Contemporary Amperex Technology ( CATL ), a Chinese lithium-ion battery manufacturer signed an agreement to explore possible cooperation and development prospects in ASEAN battery-related business and secure long-term energy storage system technology in Thailand and global markets. With this deal, CATL will authorise Cell-to-Pack (CTP) technology to Arun Plus. The CTP technology directly integrates cells into packs without modules. The partners also intend to supply batteries to Horizon Plus, as well as other EV brands.
In related news, Nuovo Plus , a joint venture formed by Arun Plus and Global Power Synergy Public Company ( GPSC ) to produce and distribute lithium batteries under the G-Cell brand, is in a joint venture
with Gotion Singapore with an authorised capital of nearly 600 million baht. Nuovo Plus, whose plant is located in Map Ta Phut Industrial Estate in Rayong Province, controls 51% of the company, while Gotion owns 49%.
The joint venture, NV Gotion , plans to import, assemble, and distribute battery modules, battery packs for energy storage systems, and EVs. According to reports, the initial production capacity will be 1 GWh/ year, and this will be increased to 2 GWh/year by 2025. Thus, Thailand is setting aggressive targets for the infrastructure required to support its zero-emission ambitions.
Victrex/Tool Gauge to produce aircraft parts using hybrid overmoulding
Tool Gauge , a US manufacturer of plastic and metal assemblies for global aerospace original equipment manufacturers (OEMs), and PEEK/PAEKbased polymer solutions provider Victrex have announced that they will collaborate to develop a new co-moulding technology for the aerospace industry. This new technology will use formed carbon composites combined with carbon filled thermoplastics.
“The aerospace industry continues to increasingly adopt thermoplastic materials as they lower aircraft weight, reduce time and waste from machined metals, and provide sustainable goods for our future,” explains Jim Lee, General Manager of Tool Gauge.
“As part of this collaborative project with Victrex and UW, we aim at replacing machined aluminium components used in commercial aircrafts that are currently expensive and take months to produce with new thermoplastic composite versions,” he explained.
The fabrication of the proposed thermoplastic utilises hybrid overmoulding where thin sheets of carbon fibres are combined with Victrex’s LMPAEK polymer, creating a unidirectional tape.
This material is then stacked and consolidated into one panel with the application of heat and pressure, with small pieces cut from the panel. Finally, the short-fibre reinforced PEEK compound is injection moulded onto the insert. A fusion bond
similar to a weld forms between the PEEK compound and LMPAEK composite insert as the molten PEEK melts the surface of the insert. As the part cools, the PEEK compound and LMPAEK composite solidify as one piece.
The hybrid overmoulding process creates a part that is mechanically stronger and stiffer than a part only made with PEEK compound due to the continuous fibre reinforcement used in the composite insert.
The hybrid overmoulding combines injection moulding with thermoforming to create a finished part that is lighter, cheaper, produces less waste, can be produced faster, and has superior fatigue performance.
“As a solution provider, Victrex firmly believes that the path to innovation lies in understanding customers’ needs and pioneering solutions where PEEK and PAEK deliver a strong advantage,” adds Jonathan Sourkes, Head of Market and Business Development for Victrex.
He concludes that through this, the company will continue to be at the forefront of technological advancements.
Designed to withstand high filling pressures, the new compact stack mould, engineered by the hot runner manufacturer Oerlikon HRSflow for thinwall packaging applications, is equipped with the new Xd nozzle series.
The patent-pending solution, soon available on the market, enables fast injection and cycle times in a stable process with high part weight consistency, says the Swiss firm.
Oerlikon says a demo tool equipped with this new technology is available at its test lab, which is equipped with six injection moulding machines – from 50 to 1,000 tonnes.
The new stack mould has also been developed to process PCR resins and sustainable compounds according to future needs which are increasingly connected to circular economy.
The tool has been designed to produce a 210 ml single-serving cup in R-PP with a weight of 6.3 g and a thickness of 0.3 mm. The mosaic frame on the part walls, patented by Collomb , allows a robust structure despite the part weight reduction.
The new Xd nozzle series ensures a stable injection process and the maximum productivity at a lower cost per unit.
Moreover, assembly and maintenance are simplified and efficient thanks to a plug-and-play installation thus avoiding long and costly downtime. The system, which enables the use of smaller injection moulding machines, fits a maximum plate thickness of 220 mm and a minimum distance of 260 mm from gate to gate of coaxial nozzles.
Oerlikon is a leading provider of comprehensive polymer processing plant solutions and high-precision flow control component equipment. The division provides polycondensation and extrusion lines, manmade fibre filament spinning solutions, texturing machines, BCF and staple fibre lines as well as nonwoven production systems.
It also develops and produces hot runner systems and multi-cavity solutions for the injection moulding industry. Its hot runner solutions serve business sectors, inclu ding automotive, logistics, environmental, industrial applications, consumer goods, beauty and personal care and medical.
Hot runner specialist Oerlikon HRSflow has developed a compact stack mould for thinwall packagingThe consumer products sector is taking steps to look into more sustainable packaging options, such as the usage of reusable packaging, says Angelica Buan in this report.
Growing volume of waste from fast food packaging
Comfort food: who can resist the nostalgic, feel-good sentiments that these familiar, yet typically high-calorie meals elicit? Despite the fact that healthy eating has become a lifestyle rather than a fad, individuals continue to crave comfort food, which include anything from hot soups, warm casseroles, and baked goodies to fast food meals, store-bought ready-to-eat (RTE) meals and snacks, and ready-to-drink (RTD) beverages.
The convenience of RTE and RTD products is, unsurprisingly, a big growth driver in the comfort food market. However, this increase also contributes to the growing volume of packaging waste.
Often, convenience food is packaged in single-serve or individual wrapping that is discarded after each use. This packaging often includes several layers of packing to preserve freshness, avoid spills, or prolong shelf life.
However, over-layering not only increases waste production but also makes recycling more challenging. Of concern is that these packaging materials typically are not recyclable or biodegradable.
Plastic leads as main packaging material
Of course, plastic is the most often used packaging material, followed closely by paper, glass and metal.
According to the United Nations Environment Programme ’s ( UNEP ) 2021 Global Assessment of Marine Litter and Plastic Pollution, plastic materials can be problematic since they can take years to degrade in the
oceans, posing dangers to humans and natural ecosystems as marine litter. It added that almost 85% of plastic packaging waste ends up in landfills or as uncollected trash, where it is likely to wind up in the oceans.
Despite a poor reputation for biodegradability and recyclability, technologies have evolved to produce sustainable plastics or polymers that meet the criteria for reusable packaging as well as renewable plastic alternatives.
While recycling has traditionally been a means to reduce packaging waste, it has its drawbacks, one of which is the high expense of an inefficient recycling collection and sorting system.
According to the UNEP report, the yearly loss in the value of plastic packaging waste during sorting and processing is projected to be between US$80 and US$120 billion.
Thus, reusable packaging has recently been promoted as a more effective solution. Reusable packaging is intended to eliminate the use for single-use packaging, which contributes considerably to waste that ends up in landfills or pollutes waters and natural environments. Switching to reusable packaging can save resources, reduce energy usage, and reduce greenhouse gas emissions from packaging manufacturing and disposal.
Reusing or using reusable packaging is said to be a more effective option than using or remanufacturing single-use packaging, which uses up to 80% more water during its lifecycle from production to recycling to disposal, while also helping to reduce greenhouse gas emissions by 60%, according to the Reusable Packaging Association
This is despite the fact that recycling packaging waste has gained popularity and is commonly opted for as the cornerstone of waste management policies.
According to the Ellen MacArthur Foundation’s Reuse: Rethinking Packaging research, transforming 20% of plastic packaging into reuse models is a US$10 billion economic opportunity that benefits customers and is an important step toward addressing plastic waste and pollution.
According UNEP’s 2021 Global Assessment of Marine Litter and Plastic Pollution report, plastic materials can be problematic since they can take years to degrade in the oceans
There is evidence that the market is becoming increasingly responsive to purchasing sustainable products and that it tends to favour businesses that move toward sustainability.
Based on a 2022 poll conducted by Trivium Packaging , a metal packaging provider, more consumers are indicated to be favouring sustainable packaging such as refillable and reusable containers, compared to the previous survey conducted a year ago.
According to the 2022 Global Buying Green Report, which is based on a study of over 15,000 customers from Europe, North America, and South America, the majority, or 86%, are prepared to pay more for sustainable packaging, especially among younger consumers (those under 45 years old).
Pepsi has introduced new packaging goals to double down on scaling reusable packaging options. PepsiCo also invested over US$3.2 billion to acquire SodaStream, the world’s leading reuse platform
Expanding reusable packaging is backed by major food and beverage companies due to the benefits they provide to the environment and to meet consumer demand. For instance, Coca-Cola and PepsiCo , who have long been “rivals” in sales and product development, now share the same goal of making their packaging sustainable.
To begin with, PepsiCo’s Positive (pep+) sustainability strategy pledges to double the proportion of all beverages sold in reusable packaging from 10% to 20% by 2030.
While recyclable and reusable packaging help to reduce waste, recyclable packaging is used once, then placed in the recycling bin. This is what is known as single-use packaging. Reusable packaging helps reduce waste by using materials repeatedly
The survey also found that overall consumer demand for sustainable packaging is still high, with 74% of respondents interested in buying products in refillable packaging and 70% of respondents identifying as “environmentally conscious,” which is a 3% increase from the survey results from the previous year.
According to Trivium, which has been growing the use of infinitely recyclable metal in packaging and delivering a range of innovative solutions to improve packaging sustainability, refillable packaging is proving to be a versatile and valuable for consumer products.
However, the results of the survey did not dampen the growing appetite for recyclable packaging, but rather highlighted the benefits of refillable packaging in extending the packaging’s life.
Similarly, consumers are less likely to purchase things that are “harmful to the environment.” Major brands are, nonetheless, making efforts to match packaging attitudes of consumers.
In 2018, the beverage firm invested more than US$3.2 billion in SodaStream , an Israeli carbonated drink startup and developer of im-home sparkling water machines. By increasing recycled content in its packaging, it hopes to cut virgin plastic per serving by 50% by 2030 and achieve Net Zero by 2040.
PepsiCo has also collaborated with a number of partners, including the Closed Loop Partners NextGen Consortium , to develop new infrastructure to support reuse and refill models.
Coca - Cola also intends to significantly boost its use of reusable packaging. By 2030, the company aims to have at least 25% of all beverages globally across its portfolio of brands sold in refillable/ returnable glass or plastic bottles, or in refillable containers through traditional fountain or Coca - Cola Freestyle dispensers
Similarly, Coca-Cola has created its own sustainability plan for packaging. The American beverage company announced in 2022 that it will increase its use of reusable packaging, as well as bottle collection and recycling efforts, with the goal of having at least 25% of all beverages sold in refillable/returnable glass or plastic bottles, or in refillable containers through fountains or freestyle dispensers by 2030, as part of its World Without Waste initiative.
Refillable beverage containers, according to the company, have high levels of collection and a low carbon footprint. Returnable glass bottles and refillable PET bottles now account for more than half of product sales in more than 20 markets, and more than a quarter of sales in another 20 markets.
Meanwhile, as part of its efforts to promote circular packaging, Coca-Cola has expanded the distribution of refillable 2-l and 1.5-l PET (RefPET) plastic bottles in South Africa. Before being recycled and manufactured into new PET bottles, the bottles can be cleaned, refilled, and reused.
It has also collaborated with Carrefour , a French retail chain corporation, to pilot a circular shopping system called Loop in France, where consumers can order products and beverages delivered to their homes in customized packaging that is collected, cleaned, refilled, reused, or recycled.
Furthermore, it has also teamed up with Burger King , an American fast food burger restaurant chain, and TerraCycle , a US-based recycling business, for a pilot programme to reduce waste.
Since recycling rates have remained so low that 90% of plastic waste is not recycled, focusing on reuse and durability-based solutions may be adequate to reduce plastic waste.
While this is an ideal situation, it is not simple. Upstream Solution ’s New Reuse Economy report stated that shifting to a reuse economy where packaging is a “service rather than a product” will necessitate re-imagining and recreating supply chains as well as investing in and building the infrastructure to support it.
It noted that, among other things, a lack of infrastructure is a barrier to scale reuse. Private and public investments in interoperable collection, logistics, and washing infrastructure that can service numerous firms at the same time are required. This will require brands and reuse service providers to standardize their reusable packaging formats.
The growth of reusables is also being hindered by convenience norms and a perceived lack of consumer interest for and engagement in reuse solutions. Furthermore, unless regulations are put in place to limit single-use products, reusables are becoming less and less appealing as more consumers still tend to choose the low cost and convenience of disposables.
Perhaps the most significant challenge is reorienting consumer preferences to more sustainable solutions.
There are also plans by Coca-Cola to recycle all of its primary consumer packaging by 2025 and to employ 50% recycled material in packaging by 2030.
Accelerating the reuse of plastic packaging can significantly reduce waste. According to the World Economic Forum ’s ( WEF ) Consumers Beyond Waste project, even 10% to 20% reuse can already eliminate the equivalent of half of yearly plastic ocean waste.
Consumers are concerned about the affordability, convenience, and safety of reusable packaging, according to the WEF’s Future of Reusable Consumption Models report. Businesses are concerned about a lack of infrastructure, financial viability, and how to achieve adequate brand differentiation.
Consistency in incorporating reusables as part of the product or service, on the other hand, will gradually improve consumer awareness about choosing reusables over disposables, and responsibility over convenience. In that regard, the industry must lead by example.
Global injection moulding technologies industry leader, Husky Technologies , recently commemorated the next phase of expansion to the company’s India facilities with ceremonies at its new offices and existing Chennai campus. We spoke to company officials to find out more about the expansion plans for Husky in the country and localisation of products/services.
PRA : Please provide us an update on your expansion plans in India, such as increased capacity and capability for producing hot runners as well as increased local OEM parts team and inventory.
Husky : Our expansion plans in India aim to increase both our capacity and capabilities to better meet the growing demands in the region. We are witnessing many of our key customers investing and expanding in this part of the world, and we are dedicated to ensuring that we are aligned with their growth strategies.
Our expansion will focus on bolstering the technical engineering and manufacturing capacity of our hot runner and controller product lines. This will enable us to offer more efficient local support, ensuring that we can respond effectively to our customers’ needs.
To enhance customer satisfaction and improve service responsiveness, we have implemented a strategic plan by expanding our local OEM parts inventory and establishing a dedicated team of highly skilled service technicians positioned across the country. This expansion enables us to better support our local customers by enabling the availability of OEM parts closer to them. With a comprehensive inventory on hand, we can swiftly address customer service needs, minimising downtime and maximising operational efficiency. Our team of expert technicians, stationed strategically throughout the region, possess the knowledge and expertise required to quickly troubleshoot and resolve issues, enabling a prompt and effective resolution.
This expansion will also reinforce our local after sales support for Husky integrated systems, providing our customers with comprehensive and efficient service. In essence, these initiatives underline our commitment to supporting the regional growth of our customers in India and throughout South Asia.
PRA : Is this new expansion in India to cater only to the Indian or South Asian markets?
Husky : While our capacity expansion in India will certainly enhance our ability to serve the local market, the growth in our capacity and capabilities is intended to bolster our global footprint and enable us to respond efficiently to other rapidly evolving South Asian markets.
PRA : Please expand on “the first ICHOR integrated medical injection moulding system that produces blood collection tubes locally.” What is this system and what does it entail?
Husky : Husky’s ICHOR integrated injection moulding system is specifically designed to manufacture blood collection tubes (BCT). The recent start-up of this system at CML Biotech in India, one of the largest BCT manufacturers in the country, marks its debut in the Indian market.
The ICHOR system will enable CML to improve their process efficiency, part quality, weight variations, and cycle times. Based on Husky’s proven PET technology, with integrated robot and auxiliaries, one HMI and advanced hot runner, this system offers unmatched levels of productivity, precision, efficiency and provides end-to-end visibility on the BCT manufacturing process.
The ICHOR system is also equipped with Advantage+Elite, Husky’s proactive, predictive, and transparent monitoring solution. This realtime monitoring capability ensures that system performance is fully optimised and allows for potential issues to be identified and addressed before production is impacted.
PRA : With regards to the the Advantage+Elite technology, what advantages will it provide for customers in India?
Husky’s ICHOR integrated injection moulding system is specifically collection tubes manufacturers in the country, marks its debut in the
Husky : The newest addition of our Advantage+Elite, proactive, predictive and transparent, remote monitoring centre in India offers several advantages. We are situated in closer proximity to customers, enabling us to serve the Indian region more effectively. We are equipped to support our regional customers in their local language.
Advantage+Elite offers Indian customers local support with global expertise and an optimised remote monitoring solution, with the goal of delivering increased convenience, accuracy and satisfaction.
PRA : Is Husky planning on collaborating with or developing technologies specifically for the ASEAN markets?
Husky : Husky is indeed actively exploring collaborations and investing in technology development to meet the specific needs of the ASEAN markets. Our approach is rooted in gaining insights directly from our customers, including those across South Asia, such as India, Singapore, Malaysia, Philippines, and Vietnam. This invaluable feedback shapes our innovation and product development, ensuring that our technologies are designed to address our customers’ evolving requirements.
For instance, in the hot runner space, we are currently collaborating with customers in India to advance Side Gate product development. This collaboration is just one example of how we are tailoring our solution offerings to meet the unique needs of specific regional markets.
In the medical space, we aim to bring our integrated system to ASEAN countries. This system, which is a result of our comprehensive understanding of the global medical manufacturing sector, could prove extremely beneficial to the region.
Additionally, our advanced medical tooling technologies have already won us numerous customers in various countries. We are enthusiastic about the prospect of introducing these technologies to other markets within the ASEAN region, thus helping local medical manufacturers enhance their capabilities and competitiveness.
In essence, Husky’s strategy for the ASEAN market is centered on continuous innovation, collaboration, and localisation of our technology offerings, all aimed at meeting the specific needs of our customers in the region.
PRA : What challenges do you see arising in the medical manufacturing sector in India, in particular, and in Asia in general, in the near term, and how will Husky be able to address them?
Husky : The medical manufacturing sector in India and across Asia is encountering an increasingly complex landscape of challenges, set to shape the industry in the near term.
– Competitive Pricing and Market Rivalry : The Indian market is highly price-sensitive, with intense competition from many local manufacturers and importers offering similar products, which adds to the pressure to keep costs low. Furthermore, India is striving to increase its share in the global market.
– Localisation and Low Volume Requirements : A significant shift towards localisation in Asian countries means that medical manufacturers often face demand for lower volume runs, especially in Southeast Asia. This change is moving away from the approach of engaging larger, often exportoriented companies.
– Quality Consistency : The increased need for competitive pricing has created a significant challenge for some producers to maintain consistent quality.
– Time to Market : Bringing products to market swiftly, while maintaining high quality and cost efficiency, remains crucial.
– Equipment Uptime, Parts Quality, and Service Availability : As our customers’ products are vital to healthcare, there is a high priority placed on these factors.
At Husky, we are strategically positioned to help our customers navigate these challenges. Our innovative medical technologies can support manufacturers in producing high-quality parts cost-effectively, while also maintaining optimal equipment uptime. Our deep experience in various medical parts production aids our customers in their time-to-market strategies, minimising risk and accelerating their speed of execution.
Through our strong service availability, we were able to support several of our Indian customers during the pandemic, helping them bring their products to market quickly and effectively to combat the health crisis.
As the landscape of the industry evolves towards increased localisation , we remain committed to delivering solutions that meet these changing demands, ensuring our customers remain competitive, while delivering high-quality medical products.
To stay connected and continue to get updates on Husky’s India expansion progress, follow us on social media, or visit www.husky.co
Malaysia’s glove makers are benefiting from streamlining of operations, new investments, and net-zero collaborations to mitigate the impact of low demand, against the backdrop of a glut of gloves and expensive raw materials, says Angelica Buan in this roundup of the sector.
The rubber industry is Malaysia’s second-largest commodities sector after the oil palm sector. The industry’s growth engine is the glove sector, a significant consumer of natural rubber. The sector saw record high demand for gloves during the Covid-19 pandemic. The World Health Organisation (WHO) had said that 89 million medical masks, 76 million examination gloves, and 1.6 million medical goggles were required per month to respond to the health crisis then.
Malaysia, a major global provider of rubber gloves, benefited from the spike in demand. Already, the country supplies 65% of the world’s requirements for gloves.
According to the Malaysian Rubber Glove Manufacturers Association (Margma) , global demand in 2022 was 399 billion gloves and Malaysia supplied almost 256 billion of these gloves. The value of export revenue was RM23.6 billion.
Since 2019, the Malaysia Rubber Council (MRC) has also observed an increase in demand. Glove exports totalled RM17.9 billion in 2019, more than doubling the previous year’s figure of RM35.2 billion. Exports increased by 55.4%, but declined by 65% to RM19 billion in 2022.
Meanwhile in 2023, glove exports were worth RM3 billion in the first quarter. Following the relaxation of pandemic restrictions, demand has certainly dropped.
The Malaysian glove sector’s first-quarter results were less impressive, earning it an “underweight” rating from Kenanga Research , and in its June sector outlook, it indicated that Malaysia’s glove sector was struggling with fewer sales, higher pricing, and lower plant utilisation.
According to the research firm, outdated production facilities are also being decommissioned, which may relieve supply pressures in the sector.
On the other hand, there is still an excess of glove supplies, which implies that low prices and low plant utilisation will continue to afflict the market in 2023. As Margma predicted, this and other aforementioned problems are anticipated to hound the industry in the next quarter.
Nonetheless, according to Kenanga, the demand-supply imbalance will eventually improve, reaching equilibrium in 2025 when virtually no new capacity will be added while worldwide demand for gloves continues to climb. According to the analysis, global demand for rubber gloves is expected to expand at a rate of 12%-15% per year through 2023, despite persistent overcapacity.
MIDF Research noted that challenges for glove makers will persist in the near term, as excess supply of gloves in the market continues to affect the industry’s average selling price and low utilisation rates, which fell from 35%-40% in the fourth quarter of 2022 to 32%-35% in the first quarter of 2023, less than half the rate in 2019.
The rising cost of raw materials has put a damper on production costs as well. According to MIDF Research, prices have risen for butadiene by 25%, acrylonitrile by 10%, and natural rubber latex concentrate by some 4.5%, mainly due to rising demand for synthetic rubber in downstream applications such as vehicle tyres, paint, shoe bottoms, and others.
Prices will remain high due to lower NR latex concentrate production throughout the rainy season and higher demand for butadiene and acrylonitrile.
Local players are treating the issue with optimism and sternness as they navigate difficult waters.
The top glove producer in the world, Top Glove , which implemented “quality and cost optimisation initiatives”, has decommissioned obsolete production lines and temporarily halted production at 17 of its 49 factories (43 in Malaysia, five in Thailand, and one each in China and Vietnam), among other measures it has taken, including implementing a manpower restructuring, to consolidate its operations amid weaker global glove demand.
The decommissioning of production lines eases the production capacity by 5 billion pieces of gloves, bringing Top Glove’s total production capacity to 95 billion pieces of gloves.
Top Glove has devised a turnaround strategy targeted at increasing sales volume, improving quality, consolidating facilities, improving employee efficiency, strengthening cash flow position, and optimising supply chain.
Despite the challenging business environment, Top Glove stated it remains upbeat about the longterm prospects for gloves in the healthcare and food industries.
Meanwhile, Hartalega expects to improve its operational efficiency and focus more on its production lines at its facility in Sepang to cater for future expansion.
Nonetheless, with new investments focusing on environmental sustainability, the sector is primed for improved possibilities in the future.
A major player, Kossan Rubber Industries , in collaboration with Malaysia-based climate-tech solutions firm Pantas , recently established the Greening Value Chain Programme (GVC), which aims to help and incentivise carbon emission control among Kossan’s small and medium-sized company (SME) suppliers.
The programme, which was previously launched by Bank Negara Malaysia (BNM) in conjunction with the Finance Day at COP-27 in Egypt, allows suppliers to access BNM’s RM2 billion Low Carbon Transition Facility (LCTF) to fund SMEs’ working capital or capital expenditures related to low-carbon practices at an affordable rate.
To mitigate is losses, Top Glove is adopting cost optimising measures, including decommissioning obsolete production lines and temporarily stopping production at 17 out of its 49 factoriespersist for another two years before easing in 2025
Meanwhile, close competitor, Hartalega Holdings is also decommissioning its Bestari Jaya facility, in Selangor, which the glove manufacturer claims, has grown inefficient and is limited by outdated technologies, as well as higher energy, maintenance, and labour costs. The decommissioning of the Bestari Jaya complex, which has four manufacturing plants and has been operational since 2004, is planned to be completed by the end of 2023.
The decommissioning is expected to reduce operating expenses, improve cost optimisation, and boost operational efficiencies. Following the procedure, the business anticipates a RM347 million impairment loss for the fiscal year 2023, as well as a RM70 million provision for retrenchment costs and contract obligation charges in 2024.
Kossan, in collaboration with climate-tech solutions provider Pantas, has rolled out a green value-chain programme to assist and incentivise carbon emission management with its SME suppliers. Pantas will assist the SMEs to begin measuring GHG emissions and report on sustainability indicators
Pantas will support SMEs in measuring GHG emissions and reporting on sustainability indicators in a consistent and efficient manner to assist in meeting national carbon reduction targets.
The Joint Committee on Climate Change (JC3)supported programme will provide SMEs with free access to Pantas’s carbon accounting software solutions, as well as training and consultation services from GVC service provider partners such as Malaysia Green Technology and Climate Change Corporation (MGTC), Credit Guarantee Corporation Malaysia (CGC), British Standards Institution (BSI), and AmBank .
Currently, eight of Top Glove’s Malaysian factories have solar energy systems, with plans to add on 16 more by 2023. Top Glove’s total solar capacity will rise from 5.34MW to 15.47MW as a result of this PPA, saving about 13,000 tonnes/year of CO2 emissions.
Beefing up investments; with sustainability criteria Even so, Margma expects global glove demand to hit 300 billion pieces this year, as a result of favourable regulatory requirements, increased healthcare awareness, an ageing population, and general population expansion.
This has provided the impetus for Mölnlycke , a Swedish medical device company and long-time Malaysian market entrant, to open a new surgical glove plant in Malaysia with a total investment of EUR50 million. The new plant started production last year, generating 500 new local job positions.
The 14,620 sq m facility, located on a 29,164 sq m tract of land in Kulim Hi-Tech Park, Kedah, has a production capacity of 50 million pairs/year of surgical gloves and 200 million pairs/year of medical gloves when it reaches full capacity in 2026.
As part of its commitment to reduce its operational carbon emissions by 50% by 2030, Mölnlycke says the manufacturing plant was built in partnership with Engie for energy solutions and Veolia Water Technologies for wastewater treatment solutions to ensure best-in-class energy and wastewater management at the new plant.
Shizen Malaysia has executed a second long-term Power Purchase Agreement for a rooftop-based solar PV plant with Top Glove. The project will contribute to reducing Top Glove’s average electricity cost while lowering its carbon footprint
In a similar effort, Top Glove agreed to a 20-year
Power Purchase Agreement (PPA) with renewable energy developer Shizen Malaysia , a subsidiary of Japan’s Shizen Energy , for the glove maker’s solar power system, with the goal of lowering carbon emissions by 25% by 2025.
Shizen Malaysia will install and operate a 10-MW peaking grid as part of this cooperation, and Top Glove will buy the power generated by Shizen Malaysia for a period of 20 years.
Both companies have previously worked together on rooftop solar power projects, such as the one on the rooftop of Top Glove’s facilities, which has a capacity of 10MW and enables it to deliver renewable energy to its factories.
Mölnlycke, which entered the Malaysian market in 1990, has three more factories in the country, all of which are fully powered by green electricity, two of which are for the production of surgical gloves and one for packing.
New investments and capacity expansion plans like this indicate that the sector’s recovery is just around the corner.
Mölnlycke’s latest plant in Malaysia optimises energy consumption by tapping digital energy management to monitor how energy is being used and where it is being lost. The new plant in Kulim is also equipped with a solution for wastewater treatment provided by Veolia, enabling water recovery and reuse
4 – 7 JULY
MTA Vietnam
Venue: SECC, HCMC, Vietnam
Tel: +84 28 3622 2588
Email: mtavietnam@informa.com
Website: www.mtavietnam.com
13 – 15 JULY
M'sia Pack & FoodPro
Venue: MITEC, Kuala Lumpur, Malaysia
Tel: +60 (3) 91321922
Email: mtavietnam@informa.com
Website: www.mimf.com.m
25 – 27 JULY
Plastics & Rubber Hanoi
Venue: ICE, Hanoi, Vietnam
Tel: +84 28 3622 2588
Email: plasticshanoi@informa.com
Website: www.plasticshanoi.com
2 – 4 AUGUST
UTECH Asia | PU China
Venue: Poly World Trade Centre Expo, Guangzhou, China
Tel: +1 313 446 5869
Email: lcrawford@crain.com
Website: www.puchina.eu
14 – 17 AUGUST
9th Cambodia Intl Machinery Industry Fair (CIMIF)
| Camboplas
Venue: Diamond Island Convention & Exhibition
Ctr, Phnom Penh, Cambodia
Tel: + 886-2-2659-6000
Email: akai@chanchao.com.tw
Website: www.chanchao.com.tw/CIMIF
17 – 19 AUGUST
Propak India
Venue: Bombay Exhibition Centre, Mumbai, India
Tel: + 91 9820209795
Email: mehraj.waghu@informa.com
Website: www.propakindia.com
23 – 25 AUGUST
Interfoam Vietnam
Venue: Ho Chi Minh City, Vietnam
Tel: +86 21 6323 2733 Fax: +86 21 6323 2733
Email: katelyn.xue@interfoam.cn
Website: www.interfoamvietnam.com
5 – 8 SEPTEMBER
PLAST
Venue: Milan, Italy
Tel: +39 02 8228371 Fax: +39 02 57512490
Email: info@plastonline.org
Website: www.plastonline.org
6 – 8 SEPTEMBER
NEPCON Vietnam
Venue: International Center for Exhibition, Hanoi, Vietnam
Tel: +84 286 287 3355
Email: nepconvietnam@rxtradex.com
Website: www.nepconvietnam.com
13 – 15 SEPTEMBER
China International Brush Making Industry Exhibition (CIBRUSH)
Venue: Shenzhen, China
Tel: +86 10 5867 7299 Fax: +86 10 5867 7126
Email: cibrush.ouyang@hjtexpo.com
Website: www.cibrush.com
20 – 23 SEPTEMBER
T-PLAS
Venue: BITEC, Bangkok, Thailand
Tel: +65 6332 9644
Email: ailing@mda.com.sg
Website: www.tplas.com
20 – 23 SEPTEMBER
Pack Print International
Venue: BITEC, Bangkok, Thailand
Tel: +65 6332 9620 Fax: +65 6332 965
Email: ppi@mda.com.sg
Website: www.pack-print.de
27 – 30 SEPTEMBER
Vietnam PrintPack
Venue: SECC, Ho Chi Minh City, Vietnam
Tel: + 886-2-2659-6000
Email: exfdp@chanchao.com.tw
Website: www.chanchao.com.tw/ VietnamPrintPack
4 – 5 OCTOBER
International Trade Fair for Composite Materials, Technologies and Products - Kompozyt Expo
Venue: Krakow, Poland
Tel: +48 12 651 90 79 Fax: +48 507 044 186
Email: molka@targi.krakow.pl
Website: www.kompozyt-expo.pl
Publishing Office / Scandinavia, Benelux & France
Postbus 130, 7470 AC Goor, The Netherlands
Tel: +31 547 275005 Fax: +31 547 271831
Email: arthur@kenter.nl
Contact: Arthur Schavemaker
Regional Office
B6-11, Menara Indah, Jalan 9, Taman TAR 68000 Ampang, Selangor, Malaysia
Mobile: +6017-8849102
Email: tej@plasticsandrubberasia.com
Contact: Tej Fernandez
China & Hong Kong
Room 6B, Floor 6, Building HengLong, No. 50 Renming Zhong Road, Zhangjiagang, 215600 China
Tel: 0512-58919146
Fax: 0512-58919145
Mobile: +86-17751702720
Email: henry.xiao@matchexpo.com
Contact: Henry Xiao/Zhu Wei
Malaysia (Print, Web, Digital Advertising & Conferences)
Tara Media & Communications
Mobile: +6017 610 1270
E-mail: yokepeng@taramedia.com.my
Contact: Yoke Peng
Southeast Germany, Switzerland & Austria
Verlagsbüro G. Fahr e.K
Breitenbergstrasse 17
D-87629 Füssen, Germany
Tel: +49 8362 5054990
Fax: +49 8362 5054992
Email: info@verlagsbuero-fahr.de
Contact: Simon Fahr
North-West Germany
JRM Medien+Verlag
Minkelsches Feld 39
D-46499 Hamminkeln, Germany
Tel: +49 2852 94180
Fax: +49 2852 94181
Email: info@jwmedien.de
Contact: Jürgen Wickenhöfer
Malaysia. India, Indonesia, Singapore, Thailand, Australia, New Zealand, Korea & Philippines
Tara Media & Communications
B6-11, Menara Indah, Jalan 9, Taman TAR 68000 Ampang, Selangor, Malaysia
Mobile: +6017-8849102
Email: tej@plasticsandrubberasia.com
Contact: Tej Fernandez
Italy, Spain & Portugal
MediaPoint & Communications Srl
Corte Lambruschini, Corso Buenos Aires, 8, Vo Piano - Interno 9, 16129 Genova, Italy
Tel: +39 010 570 4948 Fax: +39 010 553 0088
Email: info@mediapointsrl.it
Contact: Fabio Potesta
Taiwan 宗久實業有限公司
Worldwide Services
11F-B, No.540 Sec.1, Wen Hsin Rd., Taichung, Taiwan
Check out the Advertisers' page on our website.
Information is categorised by the YEAR & DATE of publication for easy reference.
For further details, email us at: news@plasticsandrubberasia.com
Tel: +886 4 23251784 Fax: +886 4 23252967
Email: global@acw.com.tw
Contact: Robert Yu 游宗敏
USA & Canada
Plastics Media International
P. O. Box 44, Greenlawn, New York 117430, USA
Tel/Fax: +1 631 673 0072
Email: mjm@4m-media.com
Contact: Michael J Mitchell
www.plasticsandrubberasia.com
www.rubberjournalasia.com
www.injectionmouldingasia.com
www.plasticsandrubberasia.cn
2023
2-4 August 2023
PU China / UTECH Asia is the most established annual event for the polyurethanes market in the region. Visiting the UTECH Asia / PU China exhibition is completely FREE of charge and allows you to see the latest technology available to the Asian polyurethanes market.
Interested in exhibiting at the show? Scan here and get in touch!
Organised by