MARCH 2023
A Quarterly Supplement of
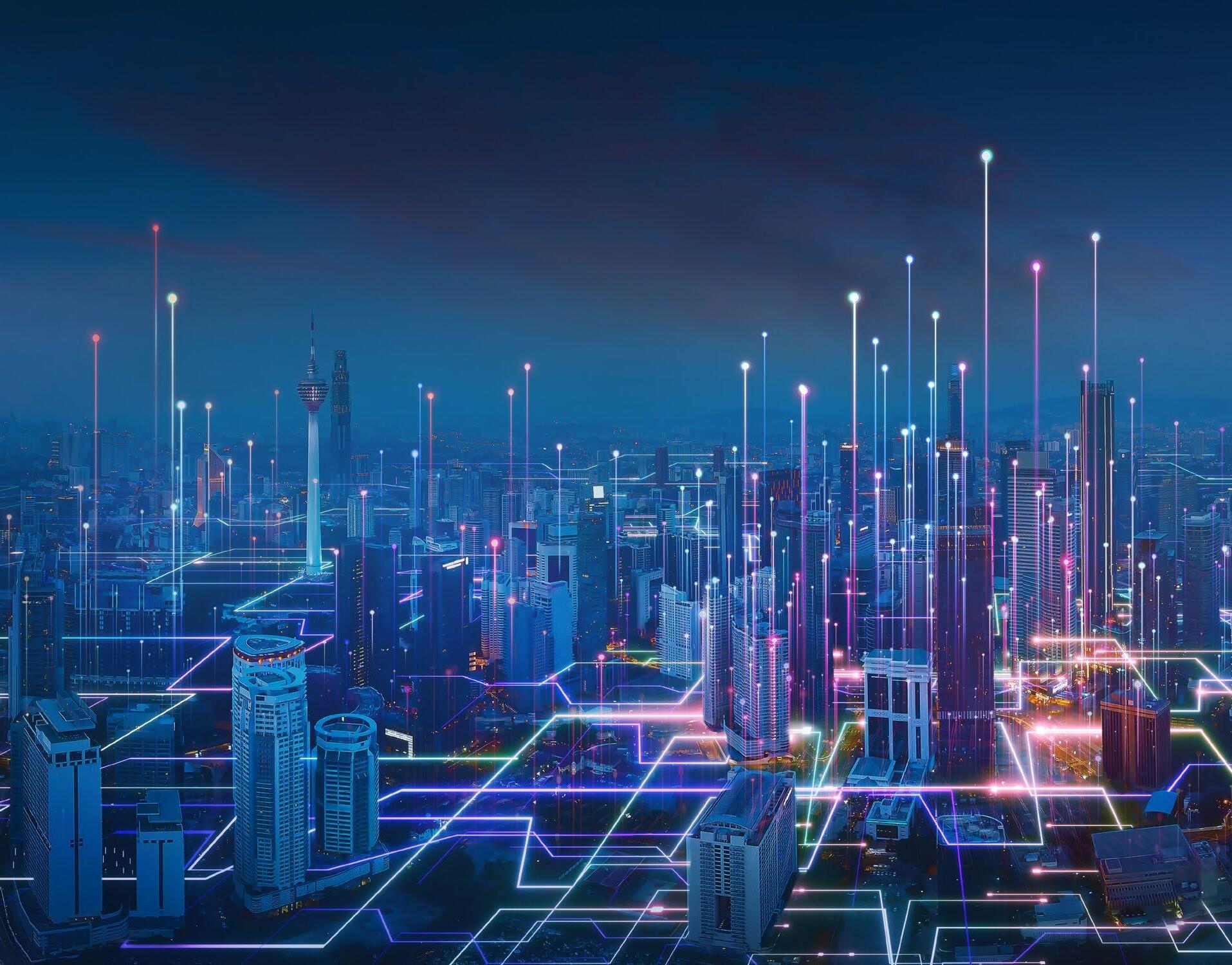
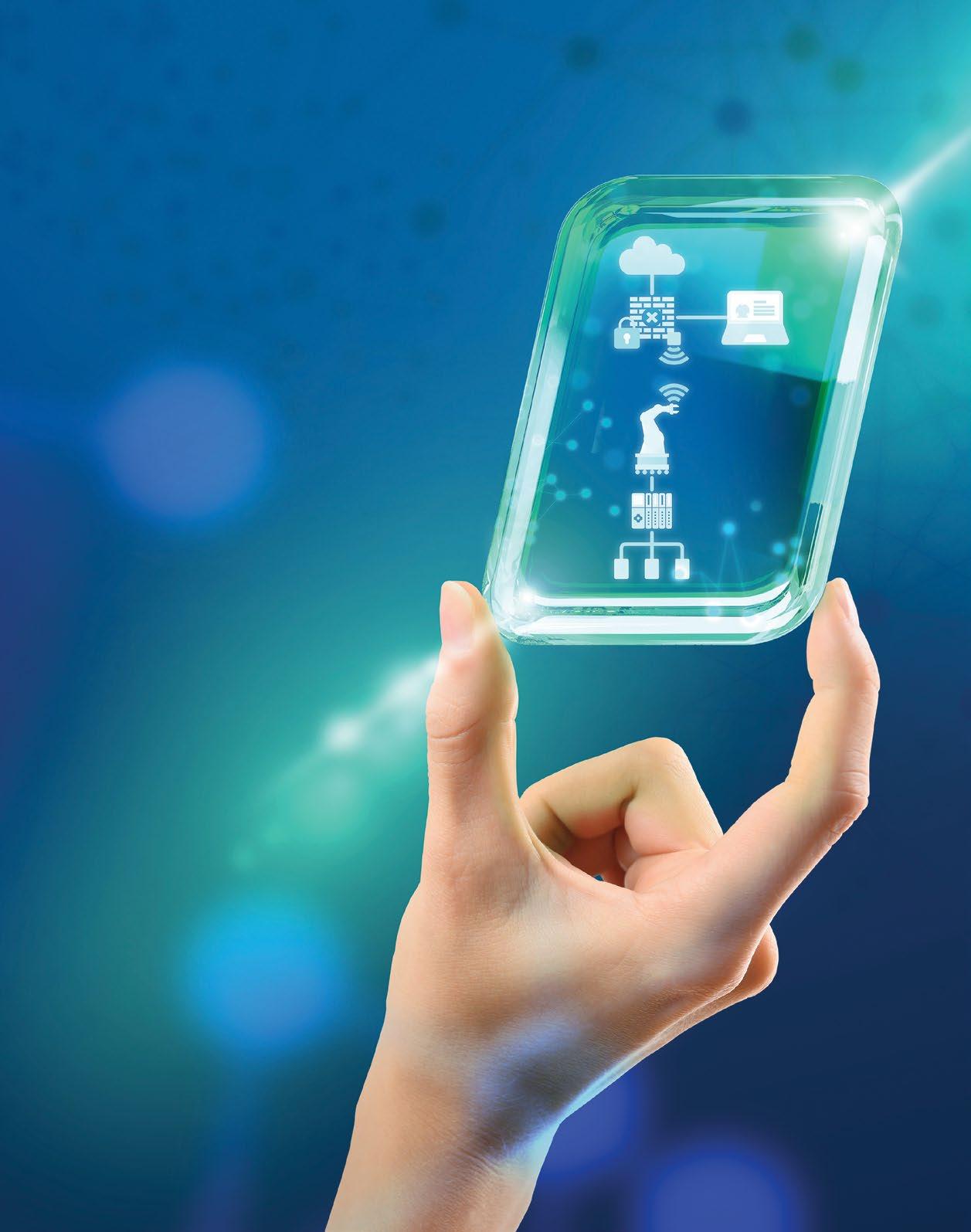



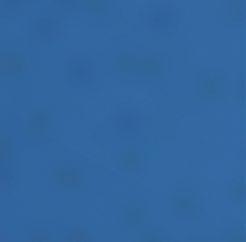
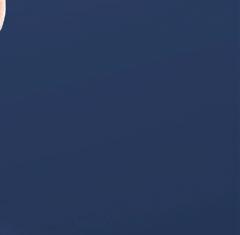
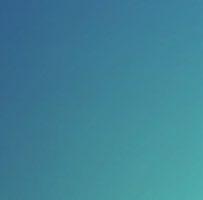
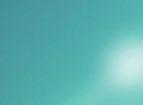

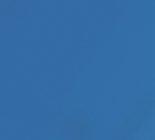

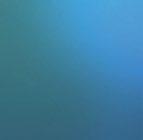
A Quarterly Supplement of
An inside look at Festo’s electric and pneumatic automation solutions for intralogistics.
Amid overlapping global crises and countless marketplace upheavals, companies from every sector are looking to shore up their operations against future disruptions. Industry insiders have long seen improving asset health monitoring and maintenance as a winning strategy to achieve resilience, agility, and efficiency.
In addition to reliable components and ready-to-install systems, Festo also offers productivity tools, global sup -
port, and custom solutions. Partnering with Festo ensures interoperability of components and assists in bringing OEMs and integrator solutions to the market faster, with less engineering overhead. OEMs and integrators become more productive with Festo.
Festo offers the world’s most complete electric automation product range. Standardizing on reliable and interoperable Festo electric automation components not only provides design symmetry, but it also streamlines design and acquisition, lowers inventory, and ensures global technical support. Key intralogistics components include EMMT series servo motors for controllability and path accuracy in positioning applications. The EMMT’s space-saving single-cable solution significantly reduces installation effort.
The Festo Simplified Motion Series (SMS) represents an engineering breakthrough that achieves the simplicity of pneumatics with the benefits of electric automation. SMS axes offer an alternative to more expensive and complex traditional servo motion. SMS takes proven ball screw axes, toothed belt axes, mini slides, electric cylinders, piston rod, and rotary actuators and integrates them with an onboard servo drive. Users commission two-position functionality via onboard push buttons with no additional software needed. When controlled with IO-Link, which is a standard feature of SMS axes, positioning along the axis length is infinitely variable.
EGC series axes are ideal for linear gantries and cantilevered axes. Linear actuators in the ELGA family deliver speed, acceleration, and accuracy in the most demanding applications. CMMT, a compact servo drive series, offers precise force and speed. Auto-tuning supports easy commissioning and automatically optimizes control behavior of rotary and linear motion.
The company offers innovative and high-quality pneumatic solutions from servo pneumatics to the world’s first intelligent valve terminal, the VTEM, to the industry leading DFSP stopper cylinder. Festo pneumatic components include air preparation, tubing, flow control valves, high flow valves, valve terminals, sensors, mini slides, guided drives, direct interchangeability ANSI NFPA cylinders, and metric and imperial round and compact cylinders.
Festo’s core range of components meets most application needs and is guaranteed to be in stock for quick shipping. The availability of core components lowers supply chain risk. Festo has taken its core products concept to a higher level with the new Festo Pneumatic Essentials program. Festo Pneumatic Essential is a one-stop-shop for the 16 most-applied pneumatic components. These components feature innovative compact design for today’s smaller footprint machines and competitive prices.
The Festo Automation Experience (AX) is a new artificial intelligence platform for predictive maintenance, predictive quality, and energy optimization. Using advanced analytics, Festo AX maps data to learn a component, machine, product, or energy system’s healthy state. Festo AX provides early warnings with actionable information to correct anomalies when data begins trending out of normal.
Festo servo drives, integrated drives, remote I/O systems, and valve terminals are integrated directly and seamlessly into both electric and pneumatic automation systems.
OEMs and integrators combine Festo electrics and pneumatics into larger environments using Ethernet-based protocols, such as EtherNet/IP, EtherCAT, Profinet, and Modbus. Festo function blocks simplify integration with Rockwell, Beckhoff, Siemens, Omron, and others.
Festo emphasizes connectivity to Ethernet-based protocols through IO-Link. Its most advanced remote I/O solutions, including CPX-E and CPX-AP-I with their IO-Link masters, enable fast connection to host PLCs, enabling connection of the widest possible range of automation components from Festo and third-party suppliers.
CPX-AP-I, a new generation decentralized I/O, connects valve terminals and digital and analog I/O to the integrated system. CPX-AP-I can accommodate more than 80 digital and analog input blocks, valve manifolds, and IO-Link master modules per system, with cable lengths up to 50 meters (164 feet) between modules. Because of the extended distances available between modules, CPX-AP-I is ideal for intralogistics systems, where moving valves closer to actuators is essential for reducing cycle time.
Using Festo online engineering productivity tools, such as
Handling Guide Online, for configuration and selection, engineers can quickly and easily define mechatronic 1D, 2D or 3D kinematics. They can also select the matching motor and servo drive or valve terminals, plus the remote I/O system, and be assured of component interoperability. These tools reduce design time from hours to minutes and ensure interoperability of components.
Festo Didactic—the educational arm of Festo—takes lifelong learning and mechatronic technical training to a new level. Festo Didactic provides lab-based equipment that replicates real world automation to two-year educational institutions and audits and trains at customer sites. The Festo Learning Experience (Festo LX) is a new online portal to make it easier to create individual learning experiences for personnel.
Electrics, pneumatics, seamless connectivity, productivity tools, AI, and training taken together make Festo the intralogistics partner that boosts productivity.
A conversation with Phil Marshall, CEO of Hilscher North America, highlights the trends worth watching during industry’s digital transformation.
Q: What are one or two specific technologies and/or megatrends that will be shaping and enabling development of the IIoT in 2023 and beyond?
A: The Industrial Internet of Things (IIoT) requires quality communications, making both message queuing telemetry transport (MQTT) and Open Platform Communications Unified Architecture (OPC UA) key technologies. These technologies enable future IIoT developments and allow other technology solutions to work. MQTT is a communications protocol with very low overhead, which makes transferring massive amounts of information into cloud-based systems manageable. OPC UA is a universal way to exchange data between systems, supporting that flexibility on a system-to-system basis.
MQTT and OPC UA must also go hand in hand with security. Cybercriminals will continuously find attack vectors; to block threats, a collective effort is required. This means that embedded, layered security spanning every link in the communications chain—from the component manufacturer to
the end user—is essential. This is where IEC 62443 comes in. With more than 30 years of communications experience, Hilscher has long supported security through products such as our netX 90 communications controller.
The netX 90 enables security functions to be embedded into automation products, protects CPU activity with “root of trust” techniques and isolates communications from applications to ensure that neither can be affected by the other. Its successors will be similarly enabled in order to match network security requirements as they evolve. We recently announced that the netX 90 supports Common Industrial Protocol (CIP) Security, an important next step for North American automation vendors.
Q: What are the specific technical benefits these technologies provide that will enable new IIoT application successes versus what is possible with typical applications today?
A: IIoT is evolving but it has not seen the quantum leap that many predicted. Instead, it has taken a decade to become mainstream
because automation users are conservative about change, particularly concerning security. In addition to that hesitation, early IIoT implementations were cumbersome and extremely expensive. These issues led many users, such as small machine builders, to be disinclined to get involved. Today, powerful IIoT solutions are both far less expensive and far more flexible.
The reality is that automation users have always pushed for better and more effective ways to operate and manage assets. Today, they recognize that they cannot compete unless they start offering IIoT features with their equipment. The latest products on the market today offer plenty of opportunity to deploy cost-effective solutions in innovative ways.
ers continuous access to machine condition and performance. From a performance perspective, this opens exciting opportunities to improve processes such as enhancing workflows, increasing product quality and boosting manufacturing flexibility. Better monitoring can also uncover potential failure mechanisms that may be addressed before the failures cause downtime. Additionally, the digital twin version of a machine becomes a reality, enabling off-line diagnosis, process improvement and system design.
Q: What challenges for automation and control engineers do these technologies address?
A: Now, IIoT spans the entire manufacturing hierarchy. At the highest levels, global interaction of systems allows companies to manage their enterprises better and more effectively across global markets. And at the lowest levels, processing the data from sensors mounted on machines can help manage equipment more efficiently and send this data to where it can most effectively be used—locally or globally.
Gathering sensor-level data via smart IO-Link modules deliv-
These technologies also allow vendors to monitor their machines from anywhere in the world. This presents new business opportunities because vendors can take greater responsibility for their equipment, wherever it may be. Machine rental, rather than purchase, becomes an option that is paid for on a per-use basis—which is an attractive option as staffing levels decrease and skills and experience are lost. Machine providers can also support continuous quality improvement and online upgrades.
Q: Given that the IIoT is already more than 10 years in the making, what is your assessment of the progress and overall impact of the IIoT on industrial automation and Smart Manufacturing?
A: So far, IIoT has moved forward at a pace that I would expect. But now, I see it accelerating as the possible added value of new solutions become clearer. For a product vendor like us, it offers
exciting new opportunities too. Our netX family, especially the netX 90 system on a chip, has become the foundation of a new range of Hilscher IIoT solutions called netField.
Our 30 years of communications experience plus the security offered by netX allows us to broaden our product range to include a variety of processing solutions that deliver fast results at the point of greatest need. These can be edge or cloud-based solutions and they are suitable for virtually any class of user. Furthermore, all of this can be delivered at a far lower cost than before.
In effect, products like netX and netField are typical of a new generation of IIoT solutions that are less costly, more versatile and easier to deploy. And, these solutions operate without compromising performance or security. Huge IT infrastructure is no longer needed to implement IIoT since solutions can now be tailored to exact needs and budgets. Fewer IT skills are required, existing software can often be reused, and users can focus on what they know best—their own processes—by utilizing solutions that are user-friendly and less expensive than any previous offering.
ward as always. Solutions will become better and more secure while added value will continue to grow as users become more and more familiar with the options. It is certain that with the type of scalable and cost-effective IIoT solutions on the market now, users will become smarter in the ways they utilize the features. Innovation will play its usual role and the manufacturing world is likely to find plenty of new opportunities to exploit.
Q: What are key next steps and/or technologies that will enable more rapid development of IIoT applications?
A: Semiconductor developments will continue to drive IIoT for-
It’s common knowledge that lifecycle management for machines can save time, effort, and resources. It can also increase reliability, decrease unplanned downtime, and extend the life of machines. The same is true for automation components including PLCs, robots, and HMIs.
By Rob Ruber, senior product manager, and Tim Hider, product marketing manager, Mitsubishi ElectricToday, it’s not enough to have high-quality automation components. Advanced engineering software is now an essential ingredient for remaining competitive. When selecting engineering software, look for these essential attributes.
• A single programming environment for every phase of development—from design, to programming, debugging, and maintenance;
• Advanced diagnostics for quickly identifying, communicating, and resolving issues even before team members arrive at the machine; and
• Advanced simulators that not only let you simulate the PLC logic, but also the HMI and 3D digital twins.
This stage is all about reducing time-to-market. For the design stage, look for these time-savers:
• Intuitive drag & drop functionality makes configuration and programming much easier;
• Custom function blocks & libraries make it easy to standardize and reuse code across different machines;
• Advanced simulation makes it possible to program while the mechanical system is in design; and
• Modern HMI makes it possible to create advanced screens that intuitively communicate changes in status, which expedites testing.
Startup is all about reducing time-to-commission. A key way to reduce commissioning time is to create easy access to the data needed to fine tune your machine to the needs of the application. Web pages and other user interface tools give you access to the information needed to make adjustments. They can also tell you how those adjustments have affected your process.
For the startup stage, look for:
• System recorder module that simplifies troubleshooting by capturing and recording all program state changes based on a trigger;
• HMI VFD/servo templates, so operators have access to key VFD (variable frequency drive) and servo data for quicker install and troubleshooting;
• PLC and HMI web server visualization, so you can accelerate troubleshooting with pre-built system webpages;
• Custom web pages and interfaces that enable more efficient staff training by allowing staff to dial in a machine’s unique needs at a unique site; and
• Support for multiple languages, so startup tools can be used around the world.
During the operate stage, reducing downtime is key. All machines will go down at some point. Your software should have advanced diagnostic tools that help you quickly identify, communicate, and offer resolutions to team members before they even arrive at the machine. All of this is now possible and will only get better in the years to come.
One important capability at the operate stage are event recorder modules. These modules record and sync up the program state changes (electrical) and a camera (mechanical) for a set amount of time before and after an event takes place. This will give you a full digital and electrical record of what took place before and after an event and is key in identifying root causes for even the most elusive errors.
Other key capabilities to look for include:
• Predictive maintenance for monitoring critical sensor data and providing feedback when anomalies occur. Look for techniques such as high/low process control and guard band as well as advanced capabilities like MT or MLR. You should also be able to visualize feedback on the HMIs or the software should be able to send alarms via text or email via an IoT gateway.
• HMI backup and restore so that when lightning strikes, you can quickly download your VFD parameters from the HMI.
• Enterprise system integration for issuing service tickets and informing maintenance staff the way they want to be informed.
• HMI mobile and reporting capabilities for remote/offsite monitoring via tablet or PC and reporting events or operational anomalies.
The final stage is all about having actionable data to drive intelligent business decisions. For the optimize stage, look for:
• Advanced data collection, which requires high-bandwidth connectivity for sharing vast amounts of data;
• Advanced data reporting that can produce the reports in real-time, so you have them when you need them;
• Advanced data analysis enabled by artificial intelligence; and
• Advanced process optimization for communicating data analysis back to the components to enable continuous improvement cycles.
Trouble-free engineering is possible with component-level lifecycle management. It can improve every phase of development and help you deliver high-quality, low-maintenance machines at scale. It can also help you mitigate risk in the technology lifecycle, extend your machine’s period of profitability, lower service costs with predictive maintenance, and increase customer loyalty.
DataHub® is the only broker that parses and manages MQTT data intelligently. Data coming from multiple devices can be filtered, aggregated and processed, monitored and secured while ensuring data consistency from the field to the dashboard.
If you’re using MQTT for IoT, be smart! Get the DataHub Smart MQTT Broker.
How a unifying “Theory of Everything” could be developing in industry via industrial networking, sensing, location, and programming technologies.
By Michael Bowne, executive director, PI North AmericaIn my schooling, I studied physics for my major. The Holy Grail in this field of study is a Theory of Everything: a unifying theory of the forces that govern quantum mechanics and those that govern relativity (gravity). It makes me ponder if there will someday be a unification of industrial networks; one network to rule them all: from the IT side to the OT (operations technology) side. Maybe this will come to pass—though I expect it to be a very long way away.
Then again, maybe not… Quantum mechanics and relativity separately have enabled immense advances in our civilization. Each is a different tool to solve different problems. The same situation exists in industrial networking today: different tools, purpose built for different use cases.
This strategy has certainly worked well for the most successful network in the history of humanity: the Internet. Here we use specialized protocols like FTP, HTTP or VoIP to accomplish different tasks.
Similarly on the OT side, we have specialized technologies like IO-Link, Profibus, Profinet, omlox, and others under the PI (Profibus/Profinet International) organization umbrella. These others include the Standard Robot Command Interface (SRCI) or Modular Type Package (MTP).
But just because these technologies accomplish diverse tasks, doesn’t mean they can’t be combined to solve unique usecases:
• IO-Link + Profinet is an obvious combination. IO-Link enables intelligent sensors to provide semantically rich data beyond a
simple process value. Profinet can then transport this data with high determinism, while enabling other protocols to coexist plainly on the same Ethernet-based infrastructure. It is the perfect pair for a myriad of use-cases: OEE (overall equipment effectiveness) tracking, predictive maintenance, remote monitoring, and more.
• Profinet + SRCI is another obvious combination. The SRCI enables the programming of robots directly in the PLC. It harmonizes all the various libraries from different robot vendors into a single library. It is embraced by all the major robot companies extant today. The use of robots in industrial automation continues to grow rapidly. Therefore, the combination of easy robot programming (SRCI) with takeit-for-granted high speed communication (Profinet) makes perfect sense.
• With SRCI + omlox we can begin to solve unique use cases. It’s not just stationary robots that have grown in usage, but also autonomous mobile robots (AMRs). To track their location in a vendor-neutral way, omlox specifies open interfaces for high-accuracy, robust, location tracking via Ultra-Wideband. Combined with the SRCI to easily program the robots, we now have helped make AMR integration easier.
• And with omlox + IO-Link we can solve unique challenges with open standards. The combination of omlox with RFID tags can be thought of as two sides of the same coin—omlox
for location data and RFID for identification data. But in brownfield installations where many tags already exist, another solution presents itself: RFID tag readers with IO-Link. Combine these with omlox, and now these data can be linked to both identify and track the location of tags rather transparently.
Will we ever see one network to rule them all? Perhaps. It certainly would be an elegant solution. But would it be practical? Perhaps not. In the meantime, just as physicists have looked to combine theories as a bridge towards a Theory of Everything, so do we in industrial networking begin to combine technologies. The principal difference: In industry, it’s not just theory, it’s reality.
•
B l - y :
• Secure boot and cryptography Encryption via SSL/TLS for HTTPS, OPC UA, MQTT, VPN
• IEC 62443 compatible Enables layered security for Defense-in-Depth design
• Built-in diagnostics Monitor operating conditions for predictive analysis
• Multiple processors Logical separation of communication and application tasks
gl y:
IEEE 802.3cg standard
• 10 Mbit speeds and intrinsically safe with Ex equipment
Internal xMAC processors
• Enable protocol specific switching between two channels
Supports SPE
L mo f om H ls :
• Connect external PHY devices via MII interface
B l - y call 1.630.505.5301 email: info@hilscher.us or visit www.hilscher.com, www.netIOT.com
Partitioned design
• Restricts software access to on-chip peripherals on either side
Minimum ten-year availability
IO-Link sensor networks
• Connect two 10 Mbit channels with SPE port up to 1,000 meters
Real-time Ethernet connections
• Pair existing 100 Mbit RTE with 10 Mbit SPE
Switch Capabilities
• Use netX 90 as a switched device between 100 Mbit RTE and 10 Mbit SPE
TepSys quickly transitions from manual to automatic data collection and distribution using DataHub software from Skkynet.
Hydroelectric power plants in Japan have been vital to the national energy supply for many years, and today’s demands for low-carbon energy make these resources more valuable than ever. To maximize production, plant executives across the country are taking a critical look at their outdated business systems. Many tasks in these plants are not automated and must be carried out manually. On-site operators and other staff often send status reports by email or verbally over the phone. Production data arrives
late or in fragments, making it difficult, and in some cases impossible, to create a coherent picture of what’s happening. Without site-wide trend charts and other analytical tools, management has little knowledge of the real-time operational status of the plants. This leads to inefficient plant operations, high manpower requirements, and increasing costs.
The Tepco Systems Corporation (TepSys) of Tokyo, Japan, recently completed a digital transformation project to upgrade data collection, storage, and visualization for a customer operating a hydroelectric power plant in central Japan. Without disrupting existing equipment or business procedures, TepSys was able to quickly transition the company from manual to automatic data collection and distribution, saving time and manpower, and providing a platform for advanced data analytics.
Last year TepSys was asked to solve this kind of problem. One of its customers needed to upgrade their data collection and utilization methods, which at that time relied on members of the control group sending emails and making regular phone calls to the company’s main offices to inform them of the latest status of the power generation system. This had been working reasonably well for a long time, but it was not very efficient.
Although engineers and managers at these plants are typically aware of the inefficiencies, modernizing and digitalizing is difficult. Business systems and control devices are often inseparably tied to the plant machinery, making them very costly to replace. What is required is a way to automate and provide data visualization without disrupting existing systems or equipment. The ideal solution is one that is quick to implement, integrates well with the systems in place, and—as much as possible—is free from errors. Mistakes are not an option.
What management wanted was to feed the data from their plant control systems directly to dashboards on the desks of headquarters maintenance and operations personnel, allowing them to make timely and accurate decisions and forecasts. They also wanted the option of sending supervisory control commands back to the control systems, if needed. The project had to be implemented in a short time frame, at minimal cost, and provide exceptional performance. And since this was critical infrastructure, it had to be secure.
To meet these requirements, TepSys turned to BellChild Co. Ltd., a system integration company located in Osaka specializing in security, robust infrastructure, and advanced operations capabilities. “After looking over the specifications for this project, we suggested DataHub software from Skkynet as the best solution,” said Mr. Fujiwara, general manager of the
iBress Division at BellChild. “DataHub technology offered three key advantages: connectivity, high-speed data storage, and visualization. Being secure by design makes it ideal for use in the energy sector.”
The TepSys team installed DataHub software on their selfhosted TepCube cloud service, and connected most of the control systems and plant equipment to it via Modbus TCP. Other data was logged to CSV files, which were read by the DataHub instance, then aggregated with other data into a single, universal data set. The team quickly configured InfluxDB, a real-time data historian, to collect the data and provide
high-speed access for retrieval. They were able to easily build screens to display this logged data with the DataHub WebView HMI. “We had a pilot system running in a few days,” said Mr. Hiroki Suga, TepSys project manager. “Other approaches required combining multiple pieces of software and building an HMI, meaning high development costs and longer implementation times. The DataHub solution was the most cost-effective way to combine business automation and on-site visualization of the whole system.”
The final turn-key solution was approved and handed over in a few months, and the project was a resounding success. Plant management have streamlined their business procedures and enhanced data analytics. Staff now spend less time travelling to read data meters, and more time planning what systems to access and how to improve their operation. “Our business procedures have changed significantly, and we have been able to make things more efficient,” said the lead plant engineer. “Until now, we would go to the site to check the data as needed, but now we decide what data we need by ourselves, and we link that data to the DataHub. As more of us begin using WebView we expect greater improvements in the future.”
TepSys credited customer and supplier involvement as key to the success of the project. “We spent a lot of time listening to plant engineers and managers, and adjusted project specifications accordingly,” said Mr. Suga. “Using a basic design,
we confirmed the necessary DataHub functions and configuration with BellChild in advance, and then proceeded step by step, confirming at each point how to best implement DataHub features.”
BellChild expects to be working closely with TepSys to expand their use of DataHub technology. The need to integrate OT (operations technology) with IT is being felt throughout the Japanese industrial sector.
“We are counting on continued support from BellChild as we offer the OT-to-IT model from this project to other customers at power plants, factories, and similar facilities,” said Mr. Kouichi Nishikata, manager of the power control system division at TepSys. “DataHub advantages of rapid implementation, secure design, and built-in HMI, all in a single off-theshelf package, will ensure they get a top-quality system at a reasonable cost.”