gUMMY STACKS
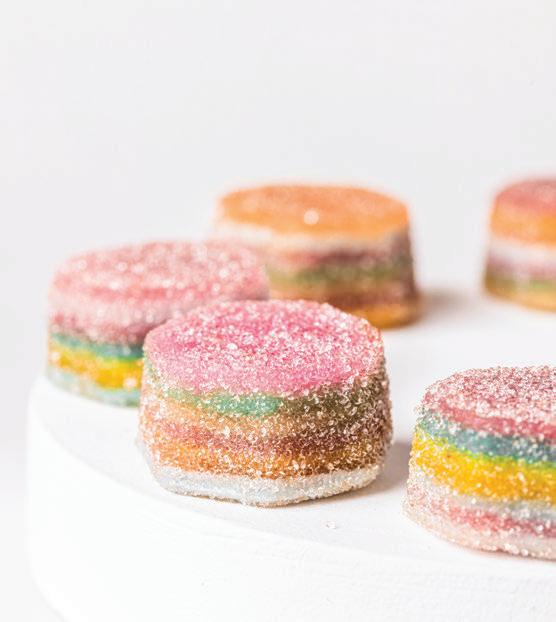

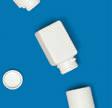
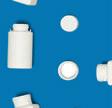
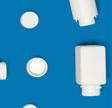
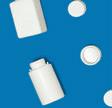
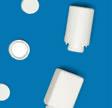
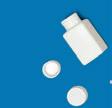
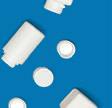
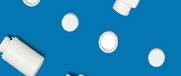
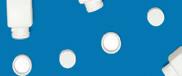

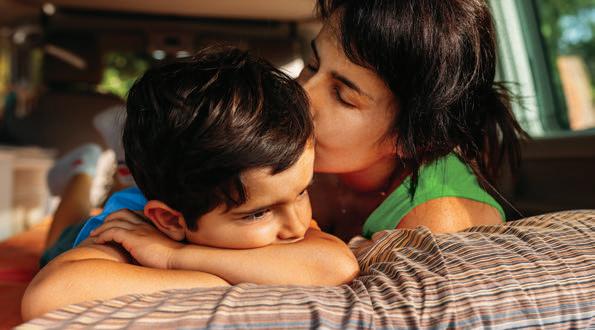























































































HEAT SEALING!
are the EXPERTS AT
engineer
TOSS!!
is
Based on a consumer questionnaire, ingredients are printed in stacks on in-house developed tech to offer a bespoke 28-day supply. The resulting colorful, customized gummies are packed in home-compostable wrap in a letterbox-friendly carton.
See an unmatched breadth of new technologies up close and in-person at McCormick Place in Chicago from Oct. 23 to 26, 2022.
A number of new robotic technologies meet the pharma industry’s need for greater automation, offering solutions for capping, pickand-place, and other processes.
Plan ahead for study startup timelines, expiry labeling on primary packaging solutions, and study administration methods.
From the[PACK]out: Regulations, regional acceptance, and validated packaging configurations all play a role. The challenges aren’t insurmountable but will require efforts from the packaging community.
Respondents to 2022 edition of IoPP’s annual survey are more confident about their prospects than they were at the outset of the pandemic. Employers are paying to retain already scarce labor.
In this Q&A, a machine safety expert discusses hazard identification and risk reduction. Though methodologies and approaches can differ, there are five key steps to risk assessment.
Keren Sookne
& BRAND GROWTH Mike Prokopeak
Melissa Griffen
Tim Hayes
DIRECTOR Jonathan Fleming
DESIGNER Maggie Wilson
Dave Bacho
Elizabeth Tierney, 815.861.2992
STRATEGY & COMMUNICATIONS Courtney Nichols
MANAGER George Shurtleff
SENIOR VICE PRESIDENT, DIGITAL & DATA David Newcorn
DIRECTOR, DIGITAL & DATA Elizabeth Kachoris
WEBSITES + UX/UI Jen Krepelka
PRESIDENT, SALES Wendy Sawtell
SENIOR DIRECTOR, CLIENT SUCCESS & MEDIA OPERATIONS Kelly Greeby
PRODUCT STRATEGY Alicia Pettigrew
David Newcorn
MARKETING Sharon Taylor
MARKETING MANAGER Amber Miller
SERVICES MANAGER Janet Fabiano
PARTNER AND EXECUTIVE VP, INDUSTRY OUTREACH, PMMI Joseph Angel
PARTNER Lloyd Ferguson
PMMI Media Group
N. Michigan Ave., Suite 1700
IL 60611
312.222.1010
312.222.1310
RECYCLE
Life sciences manufacturing has been tested the past two-plus years. PACK EXPO International in Chicago (Oct. 23-26) offers opportunities to tackle the next hurdles.
It’s been a trying few years for the life sciences industry, and the packaging community has risen to many exceptional challenges. A pandemic, skyrocketing product demands, and raw material disrup tions and price increases have caused much overtime and pivot ing by people in packaging. But it’s not all bad news. Newly confident, the workforce appears to be more risk-ready than last year according to IoPP’s salary survey. Check out our coverage on pp. 51.
Speaking of pivoting, our cover story highlights Nourished’s personalized supplement stacks produced by 3D printers. They switched packaging based on feedback not long after launch (pp. 26).
On the inspiration front, are you ready to step outside the facility and network in-person? Looking to evaluate new tech after two years of hunkering down with existing lines? Meet with your peers and suppliers to solve problems at PACK EXPO International, featuring the Healthcare Packaging Pavilion and Logistics Pavilion.
The show will feature tons (literally) of new machines and packaging technologies, ideas for reusable packaging, chances to network, and plenty more. When reviewing the show’s features (pp. 32), I was excited to see brand new opportunities like PACK Match to get unbiased, one-on-one guidance, in addition to the ever-popular educational and interactive sessions at the Innovation Stage and The Forum. Plus, Styx is headlining PACK gives BACKTM. Hope to see you there!
KEREN SOOKNE is the Director of Editorial Content of Healthcare Packaging. She may be reached at ksookne@pmmimediagroup or at linkedin.com/in/kerensookne
“Through PACK EXPO International, we were exposed to a new vendor that we wouldn’t have considered otherwise. It’s been helpful to be here and see new or alternative technologies, as well as newer models of equipment.”
— PREVIOUS ATTENDEE LIZ WICZER, EQUIPMENT & PROCESS ENGINEER, ABBOTTTHE NUMBER of Innovation Stage sessions at PACK EXPO International, plus eight sessions at the Reusable Packaging Learning Center and 15 sessions at The Forum.
“
It’s been very good for us in some ways… because we’ve been able to recruit some really excellent people from the remote world. On the other hand, it also makes it easier to lose people because when people can get a better offer, they don’t have to move. They just change the VPN that they tune into.”
THE PERCENTAGE of Americans that indicated they’re “comfortable” knowing drones will soon deliver items to their homes and businesses. Many think this will be in the next one to two years.
Source: Auterion
THE EXPECTED SIZE of the global biomaterials market by the end of 2022, driven in part by demand for implantable devices and the growth of chronic health issues from habits, inactivity, and aging populations.
Source: Future Market Insights
“
It has been well documented that healthcare workers regularly exposed to antineoplastic drugs face an increased risk of adverse medical conditions, making a truly-closed CSTD [Closed System Transfer Device] an essential component when preparing and administering these medications.”
THE DATE the FDA removed N95 respirators from the med device shortage list due to increased U.S. manufacturing, updates to the FDA’s supply chain assessment, and CDC/ NIOSH approval of new disposable N95s and reusable respirators.
A recent CBS News article discussed a social media trend that
attracted the attention of the FDA.
“One social media trend relying on peer pressure is online video clips of people misusing nonprescription medications and encouraging viewers to do so, too,” the FDA wrote. The trend includes cook-
ing chicken in NyQuil or similar over-the-counter cold meds. The FDA warns that breathing in fumes from boiling such medications can be harmful, not to mention eating the actual chicken.
The warning notes other dangerous social media trends such as consuming high doses of diphenhydramine to hallucinate, aka the “Benadryl Challenge.” The trend has led to both hospitalizations and deaths in young people. The FDA advises parents to discuss these trends and the associated risks with their kids.
President Biden delivered a speech at the John F. Kennedy Presidential Library and Museum referencing JFK’s famous moonshot speech from exactly 60 years prior. A TIME article noted Biden’s moonshot isn’t a literal race to the moon as JFK’s was, but rather a “Cancer Moonshot” initiative to combat the disease.
The President is looking to close in on the nation’s goal set in February to cut U.S. cancer deaths by 50% over the next 25 years, and to improve the lives of caregivers and patients dealing with cancer. In his speech, Biden pushed the private sector to lower drug costs, and improve data transparency. He also referenced new federally funded studies aimed at blood tests that can screen against multiple types of cancer, which would improve diagnostics and early detection.
(RTU) disposable syringes provide security, hygiene and dosing accuracy for medical injections. The NFL/2, manufactured by Dara and sold in North America by NJM, is a combination of filling and closing equipment for RTU disposable syringes in nests. The syringes are supplied pre-sterilized and ready to be processed, and therefore require no washing, sterilization,
If you’ve searched for equipment online lately, you know that it can be daunting to wade through search results—“cartoning equipment” at Google currently returns 33.8 million results!
Enter PMMI ProSource, the most authoritative online directory of validated machinery and material suppliers of packaging or processing equipment. Developed for end users like you, this free directory brings machinery, materials, and service providers to your fingertips by connecting you quickly to the validated members of PMMI who specialize in those solutions. Try www.prosource.org today and you’ll find:
1. Robust search tools. There are three ways to search using PMMI ProSource. Use the search bar at the top of the page to leverage ProSource’s robust and fast search engine or drill down by category from the home page. ProSource also allows you to search for machines by package type (i.e., vials, ampoules, blisters for tablets) and then narrow down results even further by selecting detailed filters, such as level of automation or configuration.
2. User-friendly experience. PMMI ProSource is a highly visual directory, using graphics of package types, machines, and materials to speed up the search. Product categories, features, and package types are also defined in plain language.
3. Validated and curated content. Another time-saving feature: a full-time editor at PMMI validates each supplier’s listing prior to publication and curates content for the end user. Unlike with the Google search, you can be confident that a ProSource search for “cartoners” will display vetted companies that have expertise in this area. Scan the directory’s categories to quickly find a supplier that matches up with your company’s budget and project requirements.
While you’re there, be sure to also check out ProSource’s ever-growing section of howto articles that can help you solve common problems in the plant. Recent articles have included The Top Five Considerations When Purchasing New Cartoning Equipment and Best Practices For Specifying Stretch-Wrapping Equipment. – Joseph Derr
Keep searching for new healthcare packaging suppliers at ProSource, the packaging and processing solutions finder.
www.prosource.org
The National Institute for Occupational Safety and Health (NIOSH), along with several partners, has recently released Protecting Temporary Workers: Best Practices for Host Employers. “Unsafe working conditions, unclear job assignments, inadequate training, and poor hazard communication put all workers, both temporary and permanent, at risk for injury and illness on the job. The best practices in this new resource are applicable across industries and occupations,” says a NIOSH release. The 21-page document also includes real-life implementation scenarios, as well as checklists. Additionally, staffing companies can access a complementary slide deck to educate their host employer clients about these best practices.
Visit hcpgo.to/tempwork —Keren SookneA recent FiercePharma article discussed Amgen’s plans to open a $365M smart facility in New Albany, OH, featuring its “most advanced” assembly and final product packaging capabilities. The planned 270,000 sq ft facility will eventually employ 400 people, and will support Amgen’s efforts as a founding member of OneTen, a group that focuses on hiring Black Americans into well-paying jobs. The site will lean heavily on artificial intelligence and automation in three areas: “advanced industrial automation using robotics and equipment automation; digital quality for automated inspection, testing, and real-time release of manufactured batches; and data availability to monitor and manage process and operational performance.” Construction is set to begin later this fall. (Image: Amgen)
—Tim Hayes
Insights provided at the ISTA Forum 2022 indicate that predictive technology for cold chain is becoming available, though challenges with the new process must be remediated.
High on the minds of the healthcare industry is the state of predictive technology for cold chain failures.
Transporting medicines and vaccines at appropriate, consistent temperatures is a persistent challenge with current real-time monitoring taking on a “passive role” as excur sions cannot always be acted upon in time.
According to a Technavio report, the global cold chain logistics market is expected to grow by $9.37 billion from 2021 to 2025 at a CAGR of 9.03%. Yet we’ve seen countless reports of vaccines damaged due to cold chain malfunction, such as improper distribution and shipping. Depending on a country’s infrastructure, many temperature-controlled drugs are estimated to lose their potency due to inadequate temperature control during transportation. In addition to effects on patients, all of this results in money loss for the industry as well.
As the pandemic has settled in and vaccines have been made to protect the global population, this concern remains of the utmost importance.
The current state of cold chain
The current industry practice is to use standard ambient profiles, lane ambient profiles, and lane risk assessments. Organizations base their decision of which shipper to use on these profiles. Custom ambient profiles can be made for a shipping lane over a period of a few years or more, which might provide better insight into the thermal stress the shipper could experience during transportation. However, this process is arduous and complex and these profiles cannot account for all real-world events.
Real-time monitoring devices can transfer real-time location and some amount of condition and sensor data, which can be accessed to inform on the package’s journey. Default settings can include geo-fencing and binary high/low threshold sensor parameter alerts, but these have incomplete insights and are not always actionable in real-time.
At the ISTA Forum 2022 TransPack & TempPack conference held in San Diego, CA, industry experts provided intel on the headway made towards predictive technology for cold chain transportation.
Saravan Kumar, CEO of MaxQ, presented his company’s latest research and technology at the Forum, called MaxTrace, which he refers to as “active prediction” technology. Being alerted to an excursion occurring in real-time doesn’t necessarily allow the brand owner or 3PL to intervene.
The company wanted to design a real-time monitoring system
that would generate alerts as soon as a breach was predicted— well in advance of the breach actually occurring—allowing suffi cient time to stop the temperature excursion. Such a system would increase efficiency, reduce wastage, confirm product safety, and ensure patient safety.
MaxTrace is a proprietary predictive cloud engine, designed to provide real-time actionable insights about the thermal life of each shipper and it creates a digital twin to accurately predict how long the box can maintain its required internal condition. This engine analyzes temperatures, journey duration, lane risk factors, exter nal weather data sources, machine learning intelligence, and more.
“We came up with a way to develop a cold chain container-specific digital twin, which we then deployed as a predictive cloud engine. It then takes all real-time signals and a bunch of different signals and variables, and it allows us to automate predicting and preventing temperature excursions,” said Kumar.
Kumar listed the following as the four key areas where excursion losses occur:
• conditioning error
To avoid these occurrences, MaxTrace gathers three performance indicators, which are the current state of the packaging, coolants, and insulation; lane parameters; and the expected ambient circum stance the container will face. “If we knew all three different param eters, to a certain extent I can predict what the performance of this container is going to be,” Kumar explained.
The function of the digital twin of the container, developed through a pseudo-analytical model, is to reflect the behavior of the container in real-time. This requires real-time input from IoT [internet of things] devices that are integrated with the container.
For the latest solutions, visit the following pavilions at the show:
+ The Healthcare Packaging Pavilion—West Building at booths W-12000 – W-20099
+ The Containers and Materials Pavilion—West Building
+ The Logistics Pavilion—North Building
+ The Reusable Packaging Pavilion—Upper Lakeside at booths LU-6700 – LU-6999
For more on the show, check out our PACK EXPO preview on pp. 34.
Arif Rahman, Director of Technology at MaxQ Research LLC, said, “The way we calibrate the system is we use qualification data that we have for the container and then we do trial shipments in realtime. With that, we can predict the future state of the container. But a pseudo-analytical model is rigid. To make it more flexible, we ingested external features and parameters that can help improve the accuracy of the model. For that, we added lean metadata, container metadata, weather forecasts, carrier milestones, and logistics disruptions, etc. And obviously you have the real-time data that is coming in through the IoT devices. All those are fed into the cloud engine to predict the performance of the container. This makes the model more agile, more adaptable, and the prediction becomes more accurate.”
This cloud engine is designed to provide predictions up to three hours in advance to allow for preventative actions for both active and passive containers, as well as for business and logistic process integrations, through rerouting and returning the shipments.
The goal is for the whole process to become totally automated through prediction and prevention. Benefits beyond excursion prevention include a scalable architecture that is container-agnostic, IoT device-agnostic, and accepting of a variety of data sources.
As a new process, there are challenges that the company is striving to remediate. The biggest challenge is validating the digital twinbased predictive model as it uses a wide range of factors. Real-time monitoring programs are also expensive, the agility of logistics processes to execute the prescribed action needs improvement, and it can be a challenge to help people understand that the SOP is dynamic.
↑ According to industry experts, cold chain transportation of medicines will benefit from predictive technology to help prevent excursions hours before they would take place.
Mark Maurice, Solutions Consultant at Sensitech , further explained that what’s missing are sophisticated workflows with
freight carriers and others within other indus tries. Someone must be available around the clock in the case the preventative action is required to head off a temperature excursion.
Regulatory compliance issues Maurice
touched on are:
• The sustainability of the monitors in using single- or multi-use real-time monitors . In the case of multi-use monitors, the devices would need to be
transported back to their origin. There could be a refurbishment process put in place where the device is taken to a local refurbish ment location. However, Maurice noted, monitoring systems that are reused will require upgrades in firmware and software as well as cell communications.
• Balancing the inventory of monitors as some may be lost or damaged. There is a cost to resetting and reconfiguring these devices. “You have to couple your sustainability plan with what it’s going to cost and balance that between multi-use in packaging and multi-use in monitoring,” Maurice said.
Maurice also emphasized that the way to manage shipments going through multiple climates is through machine learning. The ability to react quickly when an excursion is predicted is by having the optimal solution provided to the company through the machine learning intelligence. Humans on their own take too much time to come to the conclusion of what solu tion is the most efficient, according to Maurice. In the case of a universal pack-out, for example, analytics can lead a company to the most cost-ef fective seasonal shipper or right ship per considering where the product is being shipped to, managing both quality and cost. “But you can’t do that in your mind, right now, you can’t think of all those variables, the weight of the package, the qualifications, how long, which package to use,” Maurice said. “Predictive models can get us there.”
Multivariable analysis through machine learning is the future of monitoring, according to Maurice, as it would allow for the system to define the pack-out to use for a shipment, driving large quality and cost solutions.
New razor product for P&G brand Gillette is the first to use a recyclable, plantbased inner tray that uses color—a neon green Pantone.
ANNE MARIE MOHAN, SENIOR EDITOR, PACKAGING WORLDWith its new GilletteLabs with Exfoliating Bar razor product, Procter & Gamble brand Gillette has become the first to intro duce at scale a recyclable, plant-based inner tray from packaging supplier Footprint that incorporates color. As Footprint Vice Presi dent of Sales Solution Development Collin Euteneuer shares, when Gillette approached the company about designing a tray to hold the razor—a new concept that integrates an exfoliating bar into the razor’s handle—it was looking for a solution that would eliminate petroleum-based plastics entirely, would be recyclable, and would align with Gillette’s branding and style, including its brand colors. In the case of the GilletteLabs with Exfoliating Bar package, that color was a neon green Pantone.
Footprint is a materials science company that designs and devel ops plant-based fiber solutions for a range of applications, including frozen and shelf-stable foods, fresh meats and produce, foodservice packaging, cups and lids, and non-food applications, among others. Among the materials used are bagasse, or sugar cane, bamboo, soft wood, and hardwood, along with patented, proprietary barrier coat ings that enhance functionality for an application. One somewhat recent example of Footprint’s capabilities is a microwavable fiber bowl for frozen Healthy Choice meals from ConAgra.
Until the Gillette tray, applications using Footprint’s technology have been a kraft-like color or white. “This project was unique for Footprint in that it was the first dyed product produced in high volume, which required developing a wet-end process to support the color and achieve consistent color from part to part,” explains Euteneuer. “It was critical that we develop a product-safe dye so that Gillette’s branding style and color palette could be maintained.
“We also had to develop a technology to prevent fiber transfer to the product and create a coating solution that would prevent fiber transfer while also maintaining recyclability and the specific Pantone color of the tray.”
↑
The tray is made from bamboo and bagasse, which were chosen because the materials are local to the facility in Asia where the packaging is being manufactured.
Euteneuer explains that it’s critical when using dye in a molded fiber application to ensure it doesn’t transfer to the product or the consumer’s hands while at the same making sure it’s environmentally safe. “This was a learning process for us because we’ve never launched a product-safe dye solution at this scale before,” he says. “The packaging was built from the ground up and went through multiple iterations and experiments before we landed on our final product.” The process, he notes, took approxi mately six months.
Watch this video on brands looking to bio-plastics to replace some fossilbased plastic.
The tray is made from bamboo and bagasse, which Euteneuer says were chosen because the materials are local to the facility in Asia where the package is being manufactured. He adds that production engineering was customized to accom modate the manufacturing of the specialized fiber materials, maximizing line capability.
The new GilletteLabs with Exfoliating Bar prod uct was introduced by P&G in early 2022, with the razor held in the inner tray that is housed in a plastic-free, recyclable paperboard carton.
Installing a fifth filling line will help this leading manufacturer of commercial skin care products address the current demand for hand sanitizer and meet future customer needs.
The global hand sanitizer market is expected to reach $3.47 billion by 2028, up from $2.98 billion in 2020. Kutol Products, a maker of hand soaps, hair and body washes, industrial hand cleaners, and foam and gel hand sanitizers, plans to be a major player as this growth unfolds.
The Cincinnati-based company was founded in 1912, and it now produces under its own Health Guard® and Kutol® Pro brands as well as for private label brands. It’s no stranger to pandemics either, having operated through the 2009 swine flu pandemic. With the arrival of COVID19, says Vice President of Operations John Rhodenbaugh, “Our business exploded, just as it did during swine flu. With the previous experience gained by the entire Kutol team, we were able to apply lessons learned and make some good decisions this time around. We knew we had an idea of what was coming so we could plan, but we didn’t expect the demand to last so long.”
One key decision was to dedicate all of Kutol’s filling lines to handling only hand sanitizer for a while. All of the tanks and fill lines were converted to produce sanitizer throughout the pandemic. Such products are typically manufactured in an explosion-proof room, but when production expanded to the entire facility, safeguards were put in place to keep safety as a top priority. The second decision was to install a fifth filling line.
“We always planned on adding a fifth line, but COVID expedited our decision-making as it became very clear what product we
would be filling with that new line,” says Rhodenbaugh. “During swine flu, we grew as well and we sustained that business long term. We expected the same to happen this time with COVID. We realized if we wanted to sustain three to five times our usual volume into the future, whether that be two or 10 years from now, we would need another line.”
All four of the filling lines already operating at Kutol were anchored by machines made and installed by DTM Packaging, one of the Massman Companies . The newest of the four became operational in late 2018. “That line helped us out significantly through the pandemic,” explains Rhodenbaugh. “We made the decision to turn to DTM again for a high-speed fill line
↘ Shown here, though not to scale, are a 16-oz and 32-oz bottle filled on the versatile new line.
that would fill smaller sizes than our previous line and accommodate not just the hand sanitizer, but any of the products we produce.”
Kutol ultimately purchased a DTM fully integrated bottling line with a DTM Packag ing Purefil 2500 In-Line Walking Beam Flow Meter Filler, affectionally named “FillZilla”
by Kutol. The simple-to-operate machine features a clean hygienic design and a sanitary product path. An on-board pressure supply tank is equipped with dual-spray ball clean ing. Other design features include top-fill
anti-foam nozzles or bottom-up fill capability for filling foamy or high-viscosity products and quick changeover for a range of products and container sizes. Kutol runs PET, HDPE, PVC, or PETG containers in sizes from as small as 1 oz to as large as a half gallon on the new line. The filler can be used as a standalone machine or as part of a complete bottling line as was supplied .
Another significant design feature is that the filler is explosion proof, making it ideal for handling the alcohol present in hand sanitizer. According to Rhodenbaugh, if product were to spill on the line from the containers near an open spark or flame, there could be a fire. So at Kutol, the DTM filler is electrically closed, intrinsically safe, and in a classified area.
The bulk of business at Kutol is hand soap, so it’s not necessary for the four other DTM lines to be explosion proof. But Rhodenbaugh says that as the sani tizer portion of the company’s business has grown, it was important to have a safe fill line for those products.
During operation, empty bottles are poured into a bottle unscrambler from Pace, a ProMach company. A photo eye detects any down bottles and kicks them out.
Next is the eight-head filler, whose walking beam format results in contin uous-motion filling at speeds to 300 bottles/min. Immediately downstream is a capper, which is also supplied by DTM. A Cognex inspection system kicks off any bottle with a missing or cocked cap, and then each bottle is checked by a Wipotec checkweigher.
“We purchased it through DTM, but we worked pretty closely with Wipotec to make sure the side belts, for example, would be capable of properly handling such a wide range of bottle sizes,” notes Rhodenbaugh.
Pressure-sensitive film labels are
applied by a Nita labeler that does front and back or full-wrap labels. Then a vision inspection system from Cognex makes sure each bottle’s lot and date code—printed on each bottle by an ink-jet system from Videojet—is good before bottles proceed to a pack-off table for manual case packing. Cases are taped on a machine from Intertape Polymer Group.
While the DTM Purefil is capable of handling up to 300 bottles/min, Rhodenbaugh says Kutol will likely average about 80 to 120 bottles/min based on the bottle sizes and config urations. “There is definitely room for expansion on the line in the future,” he says. “But already we see an increase in capacity somewhere in the range of 200 to 400% compared to where we were. This boost in capacity will allow us to meet our growing needs, while keep ing Kutol’s TeamMate headcount the same.”
In addition to increased produc tivity, Rhodenbaugh says Kutol will benefit from using all DTM filling lines because the software and hard ware is the same, making it easier to train operators across all the lines. “All of the equipment behaves the same way,” notes Rhodenbaugh, “and all the buttons mean the same so the opera tors have a familiarity with the machin ery and can easily move from one line to the other and keep product running throughout the plant.”
Rhodenbaugh says Kutol also benefits from a long-term relationship with DTM. “DTM offers flexibility during the machine design-and-build process to cater to our filling needs,” he explains. In fact, DTM fully integrated and tested the Purefill before shipping it to Kutol.
“They offer ongoing support after installation,” adds Rhodenbaugh. “That’s why we’ve had them build filling lines for us since 2005.”
In turn, Kutol will count on the new Purefil line to offer ongoing support to its client base, which includes schools, business offices, medical facilities, and courtrooms that rely on these hand cleaning products. “We will
address our customers’ needs with our equipment throughout the pandemic and beyond,” says Rhodenbaugh. “We have a five- to 10-year vision for this new line to support our custom ers well into the future.”
1. Personalized gummy stacks are based on an online consumer questionnaire.
2. Ingredients are printed in 28-day batches by 3D printers developed in-house.
“Consumers don’t just want personalization, they demand it,” according to a McKinsey report citing COVID-19 and the surge in digital behaviors raising the bar for all players. There’s been a rise in personalized skincare, haircare, and more as consumers look to branch out from off-the-shelf offerings. But shorter, custom ized runs in healthcare can strain production capacity at legacy plants (if they’re even possible).
Meanwhile, 3D printing has been making its mark on life sciences and production, from faster prototypes and assembly parts for manufacturing to customized medical devices.
One supplement company founder saw a way to use 3D printing to deliver personalized gummies that meet demand for tailored vitamins. As Melissa Snover, Registered Nutritionist and Founder & CEO of Nourished, explains, “Everyone has different nutritional needs that should be catered to. Mass manufacturing vitamins has been the standard practice for decades, but it is not necessarily prac tical when introducing customized products, or when someone is looking for a nutritional regime to fit their specific needs.”
She feels that the current industry standard for personalization, picking separate tablets and packing them together, isn’t necessarily convenient, truly personalized, or sustainable.
In 2020, Snover launched Nourished’s personalized vitamins and “Life Stacks.”
The company uses 3D printing machinery to layer different mixes of active ingredi ents on top of each other to form a single product quickly, which is specifically suited to the consumer’s individual requirements. The stacks encompass made-to-order natu ral vitamins and ingredient combinations that are sugar-free, vegan, allergen-free, and plastic-free.
For Nourished, 3D printing itself is an integral part of their unique manufacturing ecosystem and the level of personalization they deliver to customers.
Customers take part in a quick two-min-
3. Gummies are packaged in home-com postable wrap in a letterbox-friendly carton.
ute consultation questionnaire, which generates recommendations for seven layers of nutrients (out of 35 options) that are best suited for the individual via a proprietary algorithm.
Once the customer completes the quiz—and the customer selects their coating flavor from six options including strawberry, pineapple, and cola—their personalized stack results are shown, displaying the suggested nutrients. Stacks are available for both one-time purchase and longer-term subscription. Each box contains 28 daily stacks.
As Snover explains, once the seven nutrients are selected, Nourished uses a proprietary 3D file and a movement instruction file within the 3D printer—this tells the printer what to create, how to move, and when to deposit the gummy material. “We use fused deposition modeling and seven print heads to create an industrial 3D printer capable of making a monthly supply of personalized supplements in just minutes. The machines utilize the normal X, Y, and Z axis with the addition of a four-rotation axis, together with an innovative plug-and-play cartridge retraction system,” Snover says.
↑ Nourished’s personalized vitamins and Life Stacks are 3D printed to layer different mixes of active ingredients, which are specifically suited to the consumer’s individual requirements.
The production team picks seven cartridges containing the seven active ingredients bespoke for each customer and loads these into the 3D printer for it to create a month’s supply of completely personalized stacks.
Nourished encapsulates all of the consumer’s chosen active ingredients into a patented vegan hydrocolloid gel, mean ing the body digests the Nourished stack like any other food for effective absorp tion of active ingredients. (The company guarantees that customers will receive at least 99.5% of the nutritional value of the gummy.) Snover notes, “To create each bespoke blend, we use seven plastic-free, food-grade syringes, which 3D print on a rotation method to encapsulate all of the active ingredients without them destroying each other.”
All stacks are produced at Nourished’s British Retail Consortium (BRC)-accred ited factory and are tested consistently by an in-house quality team. “Safety is our priority, and we make sure to sterilize and clean all utensils within our facilities and do not stock any other products which can cause cross-contamination,” she adds.
In product development, they found that the average consumer in the U.S. and UK was taking between five and eight vitamins and nutrients a day.
“After we discovered this, we did some research and found that given the current diverse food supply in the Western countries, very few people were deficient from micronutrients, except vitamin D and, in some cases, vegan iron/B12,” Snover explains. A deeper look into why they were buying supplements showed that consumers wanted to help support their lifestyle and achieve their goals. “This is why we ended up offering seven unique layers in each Nourished stack.”
While some supplements are affected by heat, light, humidity, and more, Snover notes that with 3D printing on demand, quick shipping, and a high threshold for thermal reversing (60° C), the stacks remain stable from production to consumption.
Next, Nourished packages each stack in home-compostable wrap ping, personalized with the customer’s name on it. They use a flow wrapper on-site at their facility in Birmingham. “We’ve saved more than 7,000 pounds of plastic waste, and it doesn’t stop there! Our packaging is 100% plastic-free, and our home-compostable wrappers made from wood pulp help to nourish the Earth’s soil,” explains Snover. (Editor’s note: Machine and packaging suppliers were not able to be shared.)
The set of 28 pouches is packaged in a paperboard carton. While the company originally designed their Nourished boxes to be able to display each stack individually, after launching in 2020, they received customer feedback that they would prefer a smaller, more compact box for their stacks.
“So, our design team began drafting up new packaging, which would still reflect our premium brand, but which would also be much more convenient for deliveries and storage. We introduced our letterbox-friendly box in May 2020, which is made from at least 90% recycled cardboard, which can be further processed or up-cycled many times,” Snover explains.
A sleeve is only added to the outside of boxes in a retail environment to differen tiate varieties. Direct-to-consumer orders are placed inside the letterbox-friendly box only—without tertiary packaging—to help reduce the company’s packaging and environmental impact.
“The production process does not include any artificial glue, and even the ink used is vegetal [water-based]. Furthermore, we researched extensively to find an ethi cal supplier based in the EU, which means the greenhouse gas emissions to import the boxes are extremely low compared to cheaper suppliers further afield,” she says.
The company is passionate about sustain ability and their responsibility to maintain a low carbon footprint. “Our individual flow wraps can be absorbed into the ground in just 32 weeks—they are certified with the TUV home-compostable standard, and even contain a biodegradable ink. Simply pop them into your home composting unit
and leave them to breakdown into the earth,” she says.
Not inclined to rest on their laurels, Snover says the team at Nour ished is consistently working to adapt and provide the best product possible in the most efficient manner. This is made easier by the fact that their printers are manufactured in-house. “We have a ‘printer farm’ where we are constantly building, optimizing, and developing our hardware. When we came up with the concept of Nourished, there wasn’t a manufacturing process available that would allow us to achieve the levels of customization we were so determined to achieve. So, we spent around 18 months in R&D creating our own prototype, which we have developed over time to 3D print our bespoke gummy blends,” she explains.
Manufacturing the product and printers in-house gives Nourished control over their own supply chain. Snover says, “It has allowed us to ramp up our production in response to consumer demand, adapt based on our valued customer feedback, and will also allow us to scale our business into new markets and regions in the future.”
Having launched in the UK in January 2020 and expanded into the U.S. market later that year, the 3D-printed vitamins can currently be purchased in either country through Nourished’s website. “We have plans for EU expansion, as we would love to offer even more
style,
vitamin stacks
goals,” explains Snover.
improve
also has several plans in the pipeline
the list of sugar-free, vegan nourishments
offer:
May, they launched their latest ingredient, Lutemax 2020, a nutrient designed to benefit eye health.
In the past year alone, they introduced ingredients that target menopause, PCOS, and sexual wellness.
As Snover says, “We will not be slowing down anytime soon. We want to place a focus on mental health and continue to add to our expanding list of nourishments.”
They’re also growing their facilities, with plans to open a new, 20,000-sq-ft manufacturing site (their third in Birmingham) to increase production capacity by 1,000%. “This year, we have begun our exciting partnership with Colgate and Patina which has been incredible,” she says. In their work with Colgate, the partners are teaming up to deliver stacks specifically for oral care. “There are some extremely exciting partnerships, new ingredients, and innovative product ranges launching soon!”
Having been an entrepreneur and business owner since she was 23, Snover is no stranger to overcoming challenges. “I am passionate about creating innovative solutions that make a real impact
on the end consumer, but creating the technology for Nourished was proba bly one of the biggest challenges of my career. Whenever you are creating a world-first, it can be a laborious task as there is no rule book or guide to refer to,” she says.
Nourished spent 18 months devel oping the hardware and trialing different formulations to encapsulate the active ingredients. As Snover explains, “We found some of the raw ingredients
Though she’s been an entrepreneur since starting her first company at the age of 23, Snover says, “It has only been since launching Nourished and raising funds from VCs for the first time that I have understood how much
of an issue funding is for female entrepreneurs, and particularly those in STEM. Women in STEM have received less than 1% of VC funding, and there is a need for more female role models in the STEM space. While there is a vast number of women leaving their mark, they do not necessarily get the recognition deserved, and their work is not highlighted throughout media as much as achievements by men in STEM. I am a proud supporter of women in business and STEM and have become a resolute mentor to help to inspire young people to study STEM fields.
“I believe there is a common misconception in STEM that in order for women to be successful in tech, you need to be a coder, when in fact you can be involved in the industry in other ways. As a CEO of a rapidly growing tech startup, I use a variety of material science, ingredient biology, additive manufacturing, algorithms, and decision-making engines online.”
really difficult to mask their natural flavors, especially ashwagandha, which has a partic ularly unpleasant taste. We spent a long time in the R&D lab testing different natural flavor ings, which would help to complement and
mask the wide range of 35 different vitamins, nutrients, and super-foods that we launched with, but we are extremely proud of the end result and the delicious 3D-printed stacks which we have today!”
Metal Detection X-Ray Inspection Checkweighing
Serialization SolutionsVision Inspection Track & Trace
Customized Material HandlingGlobal Field-based Service
us at Pack Expo Booth
ultimate brand protection, regulatory compliance, and an improved bottom line.
It’s more important than ever for the packaging and processing industries to reunite for in-person events—and PACK EXPO International (Oct. 23-26, 2022; McCormick Place, Chicago) is the most comprehensive packaging and processing show in the world in 2022. In response to the unprecedented demands on the industry, PACK EXPO International 2022 will offer more features than ever before.
It’s vital to come together and share innovations, connect with colleagues, hear from experts, and see machinery in action—and PACK EXPO International 2022 is the most efficient and effec tive way to do it all. No other event this year will showcase entire production line solutions and offer attendees everything needed to compete in a changing marketplace. Visit packexpointernational. com to search suppliers and plan your visit to the show.
• PACK to the Future Exhibit: Go PACK to the Future in an interac tive exhibit that celebrates the role of packaging and processing through history, and the impact it’s poised to have on our future. The curated exhibit includes historical equipment, mate rials, and photographs spanning 250 years, highlighting how the industry developed alongside civilization. This exhibit will be in the West Building at Booth W-20001.
• The PACK to the Future Stage will provide thought-provoking sessions on groundbreaking industry advancements and features free presentations
by industry experts on advances in pharmaceutical and canna bis packaging, wireless factory automation, sustainable alterna tives, smart packaging, artificial intelligence, and more (West Hall, Booth W-20025). Visit pwgo.to/7681 for more information.
• PACK Match at PACK EXPO International: This compli mentary consultation makes its PACK EXPO International debut, providing attendees personalized, one-on-one guidance to locate targeted solutions. For emerging and established brands, PACK Match Advisors are available for 30-minute virtual consultations to connect attendees with the right suppliers. Attendees complete an online form to indicate their challenges and ensure they are matched with the appropriate industry expert to use the service, and receive non-biased guid ance and recommended exhibitors to suit their business needs.
The HERMA 132M HC applies wrap around labels to bottles and vials at speeds up to 400 products per minute. The HERMA 132M HC is built ready to receive a wide range of print and vision systems and features a label reject system where any labels rejected by the vision system are automatically removed rather than being applied to the product. With over 100 fully validated systems successfully installed in the pharmaceutical industry you can rely on the HERMA 132M HC to fulfill your requirements.
Attendees must sign-up prior to Oct. 14 to take advantage of this service—assigned on a first come-first serve basis, meeting spots are limited. Visit pwgo.to/7683 to register.
• PACK Challenge: PACK Challenge, a brand new packaging competition sponsored by PepsiCo, brings six high school teams together for a head-to-head machine-building competition. PMMI will provide a build-to-print snack filler machine kit, designed specifically for this competition, along with an assembly (flight manual) to the qualifying teams. Each team will assemble the snack filler to the specifications at PACK EXPO International, and have the flexibility to be creative with add-ons. The winning school will be awarded $6,000 for overall Best in Show, with an additional three categories to compete in.
• At the Industry Speaks Stage, you can hear from experts in the PACK EXPO Partner Program covering multiple indus try verticals as they address the latest hot-button topics and industry trends, such as sustainability, remote access, supply
The annual Packaging & Processing Women’s Leadership Network (PPWLN) breakfast at PACK EXPO International will take place on Tuesday, Oct. 25, 7:30 to 9:00 a.m., in Room S-100 at McCormick Place. Hear from keynote speaker Dawn Hudson, former Chief Marketing Officer at the National Football League and former President and CEO of Pepsi Cola North America, who has led an impressive career spanning high-level posts in media, retail, consumer goods, consulting, and healthcare at some of the biggest corporations in the world. This year, the PPWLN networking event is sponsored by: Emerson, ID Technology, Morrison Container Handling Solutions, Plexpack Corp., Septimatech Group Inc., and SMC Corporation of America. RSVP for the breakfast at pwgo.to/7693
chain solutions, augmented reality, operational efficiency, and more within the Association Partner Pavilion at Booth N-4565.
• The Healthcare Packaging Pavilion: The name is the only thing that’s changed about this gathering ground for life science industries. The life sciences sector is an important focus for PACK EXPO International, and now this key market segment is positioned as it should be—as an integral part of PMMI’s flagship show. This “show within a show” in the West Building will house innovations for pharmaceuticals, biopharmaceuticals, nutraceuticals, and medical devices (Booths W-13000 to W-20099). Visit pwgo.to/7685 for more information.
• The Logistics Pavilion: New for 2022! Logistics represent a crucial part of the product journey from manufacturer to consumer—and they’re among the top five searches on the PACK EXPO website. With the boom in e-commerce, the Logis tics Pavilion in the North Building will be the place to find targeted solutions related to the supply chain, including warehousing, fulfillment, distribution logistics services, and transportation providers. Visit pwgo.to/7686 for more information.
• The Forum at PACK EXPO: Take advantage of free, unique, interactive learning sessions throughout the show. The Forum at PACK EXPO will feature 45-minute sessions on the latest industry trends. Sessions will be interactive, including activities, small group discussions, and Q&A sessions in the North Hall at Booth N-4543. Visit pwgo.to/7687 for full schedule.
• The Innovation Stages: On the show floor, the three Innovation Stages present free 30-minute seminars on breakthrough technologies and techniques focused on a wide range of indus try-specific solutions. Innovation stages are located in the North Hall at Booths N-4560, N-4580, and N-4585. For more information, visit pwgo.to/7688
• See also the PACK to the Future Stage and Industry Speaks Stage mentioned previously, along with the Processing Inno vation Stage. These are all free to attendees and conveniently located on the show floor.
• The Reusable Packaging Pavilion: Sponsored by the Reus able Packaging Association, this pavilion showcases sustain able packaging solutions to help reduce waste, cut costs, and gain supply chain efficiency. It’s located in Upper Lakeside at Booths LU-6700 to LU-6999. Don’t miss the Reusable Pack
aging Learning Center at LU-6737.
• The PACKage Printing Pavil ion features digital printing and converting, labeling, and coding and marking technologies.
• The Containers and Materials Pavilion is a destination for the latest in sustainability, recyclability, e-commerce, and consumer convenience.
• The Showcase of Packag ing Innovations® Sponsored by WestRock: Booth W-20052 features winning entries from worldwide packaging competi tions.
• PMMI U Workforce Develop ment Pavilion: This one-stopshop in West Hall offers resources to strengthen and grow your work force. Browse the workshops and register at pwgo.to/7692
• Association Partner Pavilion: This pavilion offers key resources, insights, and expertise from lead-
For those unable to attend PACK EXPO International in person, limited aspects of the live event will be available online via PACK EXPO Xpress Registration gives you:
+ Access to create a personalized schedule via My Show Planner
+ Ability to search products and exhibitors, including matchmaking capabilities and opportunities to connect with exhibitors in their online showrooms
+ On-demand access to some educational content during and after the show
Visit pwgo.to/7700 to register for PACK EXPO Xpress. You also have the ability to upgrade your registration to attend in-person—after Sept. 30, it will cost $130. If you’re able to upgrade to in-person, you’ll be glad you did.
ing associations dedicated to advancing the packaging and processing industry at Booths N-4510 to N-5101.
Plus, check out the Technology Excellence Award finalists and vote at the show, online,
or via the mobile app.
Band Styx Headlines PACK gives BACKTM: PACK EXPO’s annual event, PACK gives
BACK, returns to the show bigger and better than ever! Headlining band Styx takes center stage at McCormick Place and tickets are $95 each (or buy nine and get the tenth free). The event is sponsored by Rockwell Automation
and proceeds benefit the PMMI Foundation, which provides financial support for packaging and processing education. For more information or to buy tickets, visit pwgo.to/7695
Young Professional’s Networking Event:
The Emerging Leaders Network will host an evening event at Punch Bowl Social in downtown Chicago, spon sored by Beckhoff Automation LLC Visit pwgo.to/7696 to register.
Emerging Brands Summit (ESB): Launching this year, this one-day event features educational content and table top exhibits. The new program is aimed at founders and leaders of startup manufacturing companies looking to scale their brand to larger production through either in-house facility buildout, or outsourced relationships with contract manufacturers and packag ers. The ESB occurs on Sunday, Oct. 23, from 8:45 a.m. to 5:30 p.m., at McCor mick Place, Room S-100. Visit pwgo. to/7699 to learn more.
The Industry Meets at PACK EXPO gathers industry partners and their audiences as they host meet ings, conferences, and receptions in conjunction with the show (learn more at pwgo.to/7697). This includes the Contract Packaging Association’s Meet & Greet Reception, IoPP’s Medical Device Packaging Class, AIPIA’s Smart Packaging event, and the Flex ible Packaging Association’s Emerging Leadership Council & Reception.
Download the free PACK EXPO International Mobile App , spon sored by ProMach, in advance of the show to start developing your show plans. Search exhibitors, products, and sessions; create and save a personal agenda; use the interactive mapping tool; and engage with My Show Planner.
Attendees should also visit pack expointernational.com and use My Show Planner to check the sched ule of booth activities, add itinerary sessions, plan routes around the show floor, search exhibitors by keyword or product category, schedule meetings in advance with exhibitors, and more. See you this October in Chicago!
Company Booth
3CK Srl W-18024
All Packaging MachineryS-2366
ABRE - Brazilian Packaging Association W-20052, N-6003
Accurate MachinesW-13055
ADE, Inc. W-19025
AIC Muller USA W-19023
Airnov Healthcare PackagingW-14041
Alconox Inc. W-13005
Amcor Flexibles North America S-3705, S-3814
Amcor Healthcare PackagingW-16031
AMETEK MOCON W-13020
Antares Vision North AmericaS-3756
APPS Inc. W-19029
AROL North AmericaS-3732
Ascend Packaging Systems, LLC W-17015
AstroNova Product Identification W-17013, N-5612
Atec US LLC, Sterile Technology W-15034
Atlas Vac Machine W-17001
ATS Automation Tooling Systems Inc. W-16049
Automatic Liquid Packaging Solutions (ALPS) W-16050
Avery Dennison Corporation LL-9830
AWS Bio-Pharma Technologies, LLC W-18023
Aylward Enterprises, LLCW-16021
Bandall America W-20000, LU-7141
Bausch Stroebel Machine Company Inc. W-17010
BAUSCH Advanced Technology Group W-14025
BELL-MARK S-1626
BellatRx Inc. S-1637, W-18032
BERGAMI PACKAGING SOLUTIONS SRL W-17039
BOLONDI CLEANING HEADS
S.N.C. DI Manfredi Dante E Fabrizio.
W-17017
Bonfiglioli Engineering S.r.l. W-15023
Breve Angela Srl W-18024
Breve C.E.A. W-15043
Brightly Software W-18031
Bruker Corporation W-15006
C2sense W-15036
Company Booth
Campak/Tecnicam, Inc.W-16023
Chase-Logeman Corporation S-3920
Closure Systems International, Inc. S-3430
Colamark USA W-16055
Colimatic USA, Inc. W-13016
Columbia Machine, Inc.N-4721
Columbia/Okura N-4721
Constantia lexibles - Pharma W-15031
COPA-DATA W-15058
Countec Co., Ltd. W-19020
Cremer W-13014
Curia (formerly AMRI) W-15028
CURTI USA CORPORATIONW-20006
Custom Etch W-17053
Custom Powder Systems/ Integrated Containment Systems
W-15051
CVC Technologies W-16027
Dara Pharmaceutical Equipment W-17002
DDL, Inc. W-14050
Delta Modtech S-2908
Di Mauro Flexible PackagingW-12057
Domino Amjet Inc. S-3506, EB-51
Dorner Mfg. Corp. N-5725, EB-67
DPSS Lasers Inc. W-13004
Drug Plastics & Glass Company, Inc. W-17019
Dycem Corp W-15048
EBAC Industrial ProductsW-17023
EFP, LLC W-18027, N-5381
Elektromag Inc. W-13008
Esco Technologies W-16046
Esko Brand Solutions W-17046
ESS Technologies, Inc.W-16013
Essentra Packaging W-15059
Eurotrol W-13027
ExxonMobil W-23060
Felins USA, IncorporatedW-19019, S-3842
ette Compacting America, Inc. W-15000, W-15002A
Flexible Packaging Association ( PA)
Company Booth
FP Developments, Inc.W-15020
Franz Ziel USA Inc. W-13039
FreeThink TechnologiesW-14046
FREUND-VECTOR CORPORATION W-15044
Gardner Denver Industrials Group W-18050
GEMCO W-17035
Genesis Packaging Technologies W-16016
Glatt Air Techniques Inc. W-14003, W-15002C
GRANDPACK W-17067
groninger W-18001
Hamamatsu Corporation W-20028
Harpak-ULMA Packaging LLC S-3448, S-3449, EB-13
Harro Hofliger, Inc. W-14001, W-15002B
Heat and Control, Inc.N-4704, N-4706
Heinlein Plastik-Technik Gmbh W-19005
HERMA US, Inc. W-17016
Herrmann AG W-14022
Heuft USA, Inc. W-15014, LU-6712
HTI Plastics W-14026
HUBEI MELON PLASTIC Co., Ltd. W-14048
IL Pharma Packaging Co.W-20004
IMA North America Inc.S-2514
INOVINOX USA, LLCW-14045
Institute of Packaging Professionals (IoPP) W-20052, N-4523
IWK Packaging Systems, Inc.W-16049
James Alexander Corporation W-15018
Jones Healthcare GroupW-13049
Kahle Automation W-15035
Key International, Inc. W-19018
Keystone Folding Box Co.W-13047
Keystone Package Testing W-14008, N-6078
KISICO GmbH W-15056
Klöckner PentaplastW-16018, W-24022, EB-59
KOCH Packaging Systems, Inc.W-13012
W-20052, N-4533
ormost uji Corporation S-2766 Formpak Inc. W-13040 oster Corporation W-20024
Körber W-14027
KORSCH America Inc.W-14009
Kraemer US LLC W-13037
L.B. Bohle W-14009
Company Booth
Lepel Corporation W-12044
Lifoam W-23035
Lighthouse Instruments W-18043
Liveo Research Inc. W-15010
Locked4kids - Ecobliss Packaging Group W-15016
Luminer Converting Group W-20012
M.O. Industries, Inc. W-15022
M&O Perry Industries W-18036
M3 Automation W-13045
MACTEC Packaging Technologies W-20034
Marchesini Group USA Inc. W-17005
Markem-Imaje S-2930
Medical Packaging Inc.W-14004, EB-63
Mesa Laboratories, Inc. W-14024
Mettler Toledo Product Inspection S-1714
MG America, Inc. W-15003
MGS Machine Corp.S-2501
MHI - Maruho Hatsujyo Innovations W-13018
Mikron Corporation Denver W-13017
Morrison Container Handling Solutions N-4906, EB-55
Multivac Inc. W-18002, N-4745
NeoCeram W-16022
New England MachineryW-15001, S-2530
Nikka Densok USA W-16024
NJM Packaging W-17002, N-5650
Orkin Commercial ServicesLL-9511
Ossid - ProMach, Performance Packaged N-5330
Oxford Lasers Inc. W-14034
PACK EXPO International/ PMMI N-4550
PACKWORLD USA N-5913
Pacmac Solution Pvt LtdW-18029
PallayPack, Inc. S-4275
Panelmatic, Inc. W-15046
Paxiom Group S-2153
Paxxus N-6161
Pentapack NV W-17003
Perlen Packaging W-15029
Pester USA Inc. W-18013, S-2989
Pfeiffer Vacuum W-19012
PharmaMed W-14028
Company Booth
Pharmapack North AmericaW-15045
Pharmaworks LLC W-17002, N-5650
PKB W-19001
PMMI Media Group W-20052, N-4550
Pneu-Con Inc. W-13040
Polycine Gmbh W-20022
Precitec W-12054
Preco, LLC W-14006, LU-8713
Premio Inc. W-20032
Procepack W-14055
Prodieco & Natoli Engineering W-13013
ProMach Pharma W-17002, N-5650
Prosys Innovative Packaging Equipment Co. S-3664
PSnC/Avanti W-18034
PTI - Packaging Technologies & Inspection W-20014, S-3106
QT9 Software W-19009
Quantum Packaging Technologies Inc W-15042
RAUMAK North America Inc. W-14047
Res-Tek, Inc. W-15012
Romaco Group W-18030
Rommelag Engineering W-18006
Rotzinger W-16045, S-2392
Sanner of America, Inc. W-15052
Sarg USA W-15050
Scanware Electronic GmbH W-13031
Schreiner MediPharm W-15047
Schubert North America LLCW-19008, LU-8730
SEA Vision USA W-18016
Sellaempaq W-19007
Sepha Ltd. W-14019
Serpa Packaging SolutionsW-17002, N-5548
Shawpak W-19030
Shibuya Hoppmann Corp.S-2446
SIGMA CAP SEAL W-20018
Sonoco S-1640, W-18020
Sonoco Alloyd S-1640
SOTAX W-13009
Span Tech LLC N-4734
Spee-Dee Packaging Machinery S-2022, EB-11
Spirax Sarco W-18038
Spookfish Innovations Private Limited W-17033, N-4884
Company Booth
Starview Packaging Machinery N-5728
Staubli Corporation W-18025
Steriline S.r.l W-17030
Sterimed Inc. W-13053
STERIS Corporation W-18068
Stevanato Group W-15039
Swiss Can Machinery W-13023
SWISS Pavilion (by Switzerland Global Enterprise)
W-13023, W-14022, LU-8403
Syntegon Packaging Technology, LLC S-3514, EB-15
Systech - Dover Europe SARLS-2930
Technoflex W-15030
Tedelta North America LLC W-18009
TekniPlex Healthcare W-13043
Telstar W-19011
TM PACKAGING (CAMBODIA) CO. LTD W-16068
Uhlmann Packaging Systems W-13010
Universal Machine and Engineering Corporation W-19013
Universal Pack, S.R.L. W-16048
Viscotec W-15038
VMI W-17037
Volpak, S.A. S-2501
Weckerle GMBH W-16054
Weiler Engineering, Inc. W-16017
Wexler Packaging Products, Inc. W-19019, S-3842, LU-8847
Wilco Precision Testers USA LLC W-17010
WIPOTEC-OCS, Inc.S-4172
Wisesorbent Technology LLC W-12045
WLS (formerly Weiler Labeling Systems) W-17002, N-5650
WORK Microwave Gmbh W-20038
Xyntek Inc., A CXV Global Company W-15060
Here we feature a selection of companies exhibiting in the Healthcare Packaging Pavilion and beyond. For full listings, visit: packexpointernational.com
MULTIVAC offers individual packaging solutions & automated lines for medical and pharmaceutical products. Our solutions cover all the functions of packaging, handling, labeling and marking, quality inspection, box packing and palletizing. Using MULTIVAC Clean DesignTM packaging equipment ensures that sterile medical product are packed reliably in cleanroom environments.
Visit our Pack Expo Booth W-18002 in the Healthcare Packaging Pavilion or contact us today to learn more about our specialized healthcare solutions.
1. New robotic technologies meet the pharma industry’s need for greater automation.
The pharmaceutical market requires robots that offer extreme accuracy while being engineered to hygienic standards. According to a recent report from Grand View Research, the global phar maceutical robots market size was valued at $162.7 million in 2021 and is expected to expand at a CAGR of 9.2% from 2022 to 2030. Says the report, “The growing need for automation in manufacturing units, coupled with the high costs of new drug discovery, is significantly increasing the demand for robotics in clinical trials, drug discovery, and laboratories for automating the procedures. In addition, key companies are introducing technologically advanced robotic machines, which has further led to the tremendous growth of the market. With rising demands for precision, output, and faster turnaround times, automation and robotics have gained traction in the phar maceutical industry.”
According to a 2022 report from PMMI— The Association for Packaging and Processing Technologies, Pharmaceutical Manufacturing Trends Shaping the Future, three out of four pharmaceutical companies interviewed for the report are using robotics along their line, and over half predict they will implement more robots/cobots in the future.
Currently, traditional robots, as opposed
2. Solutions have emerged for capping, pickand-place, and other processes.
3. Some new options offer energy savings compared to previous designs.
NOP (No-Plastic Program) means we promote eco-friendly plastic substitutes for the packages manufactured on IMA machines. rough the research and testing of alternative processes and materials, together with our partners, we foster plastic-free and sustainable, compostable, biodegradable or recyclable packaging solutions.
According to these objectives, IMA established OPENLab: the Group’s network of technological laboratories and testing area, dedicated to the research on sustainable materials, technologies and production optimization processes.
Discover more about IMA NOP on ima.it/imazero and IMA OPENLab on ima.it/open-lab
cobots, account for the largest share of the market, at 63.7%, says Grand View. Appli cations include pick-and-place material handling, loading and unloading, packag ing, palletizing and depalletizing, storing and retrieving, product placement, stack ing, cutting, scribing, sorting, process-toprocess transferring, and precision spot welding.
Designed for ultra-high precision for tasks such as assembly, pick-and-place, and intricate small-parts handling processes is Epson Robots’ new GX Series of SCARA robots for the medical device, electronics, and consumer electronics industries. The two robots that make up the series, the GX4 and GX8, incorporate Epson’s Gyroplus vibration reduction system and rigid arm design for fast settling times. The robots are available with multiple arm configurations, with 250- to 350-mm reach for the GX4 and a 450- to 650-mm reach for the GX8.
According to Epson, the high-power-den sity SCARA robots are equipped with larger motors to handle heavy workloads at fast speeds. The GX4 can handle payloads up to 4 kg, and the GX8 up to 8 kg, both from a small form factor. The robots are also equipped with Epson RC+ industrial auto mation development software that streamlines automation so operators can design complex and robust robotic solutions with a simple interface, advanced integrated solutions, and an advanced 3D simulator.
Built for demanding environments, the GX robots are available in Standard, Cleanroom (ISO3), and ESD (electrostatic discharge) models; new standalone ESD models are available. The GX8 also supports IP65, which means it protects against low-pressure water jets from any direction, as well as condensation and water spray.
Another new SCARA robot-equipped solution geared toward the pharma market is ESS Technologies ’ Robotic Capping System. The system integrates one, two, or three Fanuc SR-3iA robots with an ESS-designed gripper-style EOAT (end of arm tool
ing) to pick caps from a feeder track, place them on a test tube, bottle, or vial, and apply a pre-torque before the containers convey to a final torque station—all at speeds to 120/min. The system can accommodate multiple cap sizes and torque or pressure requirements, push-on caps, and pucked containers, such as test tubes with rounded bottoms or irregularly shaped bottles.
During operation of the system, a timing screw drive and conveyor place the container in position for precise cap placement. The robots are programmed to act in coordination, each capping one container at a time. After the robot places the cap, the containers convey to a final torque station that fully tightens the cap to the exact requirements. Push-on-style caps are tamped into place at the final station.
According to ESS, Allen-Bradley controls and a color touchscreen HMI allow the operator to easily select the cap size to be run on the system, and optional automatic system runout programs make size change
↑ 3P innovation’s R500/R1000 capsule filling system integrates Stäubli’s smallest six-axis robot, the TX2-40 with a Stericlean design.
→ For hygienic pick-and-place applications in pharmaceutical as well as food and electronics environments is a new robot from Kuka Robotics, the KR 3 DELTA.
↙ Epson Robots’ new GX Series of SCARA robots have been designed for tasks such as assembly, pick-and-place, and intricate small-parts handling processes.
over fast and efficient—typically 15 minutes or less.
Fanuc’s compact SR Series SCARA robots can be integrated into existing systems. The robotic capper can also be ordered with ESS’s FC Series in-line filler/capper machines to create a fully automated, high-speed filling and capping line. Cap placement inspection with automatic reject ensures that uncapped containers or containers with skewed caps are removed from the production stream for rework.
For hygienic pick-and-place applications in pharmaceutical as well as food and electronics environments is a new robot from Kuka Robotics, the KR 3 DELTA. The ceiling-mounting, parallel-arm robot offers a reach of 1200-mm, a maximum payload capacity of 3 kg, and cycle times as low as 0.5 sec. According to Kuka, an encapsulated gear unit and self-lubricating ball joints increase reliability and reduce maintenance.
The KR 3 DELTA uses a corrosion-resistant, stainless steel shell that protects against dust and moisture. The design accepts alkaline or acidic high-pressure cleaning and disinfection up to 100 kPa (kilo pascal) for simplified upkeep and shorter downtimes. Food sector-certified for material safety according to international guidelines, the robot carries IP67 high-protection certification, with A4 IP69K for axis 4.
Kuka has paired the KR 3 DELTA with its KR C5 micro controller, which the company says uses nearly 35% less energy than preceding designs. Kuka adds that the scalable, easy-to-install controller requires less space, offers increased safety, and integrates seamlessly into existing production environments.
For lab-scale environments, engineering firm 3P innovation has introduced the R500 and R1000 range of robotic capsule and device powder fillers, which
allow customers to eliminate “formulation for filling” steps and reduce pre-clinical timescales, fast-tracking to Phase III. In the center of the fully automated machine, with a footprint of just 1 x 1 m, is Stäubli’s smallest six-axis robot, the TX2-40 with a Steri clean design.
Explains David Johnson, Marketing and Sales Director of 3P inno vation, “We designed this machine for pre-commercial production, enabling the manufacturer to fill powders in a scale that is needed for pre-clinical testing.” No minimum batch size is required, and the dose size can easily be changed.
World’s 2022 Robot
Report.
The R500/R1000 is able to fill vials, capsules, syringes, cartridges, and custom containers with a variety of challenging powders like pure APIs (Active Pharmaceutical Ingredients), spray-dried and engineered particles, delicate biologics, freeze-dried powders, and solid dispersions (“drug-in-polymer”). The R500 fills capsules at speeds to 500/hr, the R1000 at 1,000/hr, with high accuracy and no need to change the hardware when the product is changed, according to Stäubli. Dosing accuracy is ensured by gravimetric Fill2Weight technology developed by 3P innovation. Containment and full cGMP compliance are achieved with the integrated isolator housing, ensuring a controlled and sterile environment. The Stericlean TX2-40 robot includes a fully enclosed structure with special seals, keeping airborne particles to a minimum. The robot’s completely smooth surface, protected by a high-resistance coating, eliminates retention areas, and all connections run through the base of the robot. All of this, says Stäubli, ensures that the TX2 Stericlean range can with stand the cleaning processes common in pharma ceutical and other applications.
1. The new setup will require only one or two submissions through the clinical trials informa tion system (CTIS) platform.
Regulation EU No 536/2014 on clini cal trials—a binding legislative act for each member state, overruling national law—came into force on January 31, 2022, to simplify clinical trial preparation and activation.
With it will come many changes that will impact study startup processes and timelines, expiry labeling on primary and secondary packaging, and study adminis tration methods such as direct-to-patient.
2. If an addendum is not issued, Annex VI’s un intentional effect on labels may require a con glomerate of solutions to meet requirements.
3. The direct-to-patient method removes a de gree of complexity and burden for the patients participating in clinical trials.
An XTalks webinar panel discussion, “How to Avoid Significant Delays in Multi-Country Studies Due to EU 536/2014 Clinical Trial Regulation,” made note that before the regulation, most tasks required to start enrolling patients could largely be planned and managed independently, with minimal coordination between study, coun try, and site project managers. This previous method put the focus on the first country and site approved, knowing additional activ ities would follow, which made for decen tralized, unsophisticated planning and management. The regulation, however, represents a paradigm shift to last country and site ready, with any missing content required for the study, country, or site approval delaying all countries and sites. This can significantly impact study timelines.
↑ Regulation EU No 536/2014 on clinical trials comes with many changes that will impact study startup processes and timelines, expiry labeling on primary and secondary packaging, and study administration methods such as direct-to-patient.
required clinical sponsors to contact potentially over a hundred different regulatory agencies to get the study up and running, whereas the new setup will require only one or two submissions through the clinical trials information system (CTIS).
Elvin Thalund, Director, Industry Strategy, Oracle Health Sciences, explained in the webinar that the previous study startup dynamic, at least as far as it concerns European countries and sites,
Though this simplifies one aspect of study startup and won’t allow each member state to enact its own laws and interpretations of directives (creating specific challenges for clinical sponsors as
done previously), it does require more time before clients can begin enrollment. Where the previous method took six to eight and a half months, the new method will take eight to 11 months to identify sites, select sites based on feasibility and need, and activate them. This is because the new EU regulation will not allow the selection process and activation process to run in parallel.
Instead, the new regulation splits the submission process into two parts:
• Part 1: the reporting country, which is an EU regulatory submission, requiring submission of study material and product material
• Part 2: the member states concerned, which is a country regulatory submission, country IRB or IEC submission that requires submission of recruitment material, patient material, principal investigator, facility information, indemnity, and localized study material
The critical elements, as noted by Thalund, are first the product, study, and localized study material; and then the principal investigator and facility information. As a regulation, the timeline is inflexible and fixed and aligned across all member states, causing clinical sponsors to adapt in order to operate within the framework.
If the timelines are not met by the clinical sponsor, then the submission lapses and delays and can even require a restart. So if a Part 1 timeline is missed, it affects the whole trial timeline, and if a Part 2 timeline is missed, it only affects the country of that particular submission. Though if that country is critical for the study, the delay will obviously affect the entire study.
Other important factors that can affect a study timeline include (1) the individual member states’ final decisions as each can reject Part 1 and Part 2 decisions, and (2) substantial modifications, which must be submitted after the initial Part 1 submission is complete. The regulation does not allow for partial approvals.
Pierre Omnes, Executive Director, Site Start Up and Regulatory, Syneos Health, explained that individual Part 2 applications can be submitted at different times based on the amount of information available for the desired sites after the conclusion of the Part 1 acceptance. He cautioned to include as many countries in Part 1 as you think will be useful first as you don’t need to wait for the decisions to be granted in all countries to submit Part 2 applications, as long as they were included in Part 1. To include a country not listed in Part 1, you must follow the additional member state procedure, which
has different criteria.
In the first part of a webinar series on the evolution of clinical trial packaging put on by Essentra Packaging—a global manufacturer of cartons, leaflets, and labels that specializes in the pharmaceutical industry, as well as beauty and personal care—called “The Implications on Clinical Trials Labeling Due to Annex VI Changes and Patientricity,” experts discussed changes, issues, and potential solutions for Annex VI expiry labeling.
When the EU 536/2014 Clinical Trial Regulation was born, Annex VI had an unintended effect on expiry labels which presents various challenges to sponsors. Annex VI chapter nine stipulates that the expiration date is required to be printed on the label.
Joe Monteiro, Technical Account Manager Clinical Trials, Essentra Packaging, listed in the webinar a number of challenges that this poses for sponsors:
• Increased cost of rework, especially around kits, which have multiple primary containers per kit, each required to have an updated expiry label
• Purchase of new labels for relabeling, which must be performed in a controlled GMP-compliant environment under quality QP release—this also brings depos under careful consideration concerning site capability
• Added cost of releasing supplies
• Potential for labels on the outer pack being broken during relabeling, increasing risk of damaged packs
• Biological drugs taken out of cold storage for pack labeling,
↑
which increases the risk of damage to the drug
• Careful selection of label materials and adhesives for cold temperature applications
• Consideration of space available on small primary containers, such as syringes and vials—consider futureproofing the design for relabeling
in managing multiple sets of supplies, it could be considered in the interest of not disrupting your entire supply chain.
A pilot study conducted by Essentra provides another solution in unique packaging designs. The challenge set was to relabel the expiry dates on vials that had already been packed and sealed, with out compromising the tamper-evident label or causing damage to the pack.
Monteiro explained that the industry had been proactively search ing for and providing guidance on potential solutions to these chal lenges, though he points out that no one solution will be a fix-all. Oftentimes, sponsors will need to apply multiple solutions to fit their needs.
Though the long-term solution would be an amendment to the regulation for the expiration date to be on the primary packaging, a solution suggested by the European Federation of Pharmaceutical Industry and Associates (EFPIA) published in a white paper describing risk-based concepts on interim solutions on expiry labels is to label the primary container with the initial expiry date and include a statement referencing the outer pack for the most current expiry date. This solution, however, is only for consideration as it has not been accepted by the European commission.
Non-profit industry group, TransCelerate, whose mission is to collaborate across the biopharmaceutical research and development community, proposes an electronic label solution with a basic single panel, which would contain product information and a barcode. A participant could then scan the barcode using a smart device, which would link them to all necessary information regarding the medicine they are taking. However, this solution is not yet accepted from a regulatory standpoint, but a dual strategy of an e-label and a conventional label on the same pack may serve to introduce the concept into the sector.
The International Society for Pharmaceutical Engineering (ISPE) has also published a white paper that mentioned e-labels as a potential solution as well as operational strategies, such as limiting the batch sizes and the use of just-in-time labeling, which would entail keeping supplies at a central packaging site and printing labels with the latest expiry date just prior to distribution. Sponsors will need to keep in mind additional time for printing, packaging, and releasing the product. This option is applicable for small volume studies but may prove risky and inefficient for medium- to largesized studies.
Another solution discussed by Monteiro: labeling supplies based on countries and regions, which would entail an alternative packaging arrangement with an EU-only supply of products that are labeled with the expiry date. Though this adds additional complexity
“We decided to do a carton design, which would encompass a single and a multiple ampoule pack presentation,” said Monteiro. “The solution we came up with was a cradle design, which ensured tamper-evident integrity. The carton consisted of an internal panel opening, which would allow for the primary container labels to be overwritten or relabeled. It also consisted of a hinged close wraparound cover for lightfastness, transport stability, and, importantly, product security.”
Essentra successfully manufactured, released, labeled, and packed 20 cartons with vials stored under cold ambient temperature condi tions. The company was then able to relabel the vials without break ing the tamper evident seal or damaging the packs. No additional packaging was required for the vials in relabeling.
Diarmuid Wilson, Essentra’s Business Development Director Clinical Trials, discussed in the same webinar the impacts of directto-patient (DtP) due to Annex VI as well as the COVID-19 pandemic.
Throughout the beginning of the pandemic, the impact of lockdowns and other factors, including a focus on COVID trials, resulted in a decrease of clinical trial startup, which recovered in the first half of 2021, thanks, in part, to DtP. This patient-centric approach removes a degree of complexity and burden for the patients participating in the clinical trials. As a flexible solution, DtP use during the pandemic was intended to eliminate subjecting patients to addi tional risk while maintaining continuity of care by preventing treat ment delays.
Wilson said biopharma companies have particularly been adopting this administration method and that many more sponsors plan to include some form of DtP or hybrid solution in their future proto cols. A review in the U.S. on 2021 data quoted in the webinar indicated a significant drop in patient recruitment when further than 41 kilometers (~21 miles) from sites. According to a 2014 study by ISPE, 78% of patients say they would prefer to have medications delivered to their home versus traveling to a clinical site.
Wilson listed the benefits of DtP over traditional trials:
• Traditional trials aren’t always convenient for patients due to location, schedule, and lifestyle, which can lead to under-enrollment and high dropout rates. The COVID pandemic has also made patients more unwilling or unable to travel.
Potential for added waste and delays to the additional packaging requirements that Annex VI may present
• The DtP approach can expand patient demographics, reducing geographic barriers, which then makes it more viable to address
diseases.
• DtP has potential for supporting patient compliance and
increase
reducing
ery, the secondary packaging needs to mirror the approach. The packaging also needs to ensure the quality of the medicinal products or placebos, taking into account variables such as temperature, humidity, and light sensitivity.
Seeking secondary packaging partners with capabilities that support improved timelines is a suggestion Wilson said can minimize sourcing complexity. He lists other areas that will impact the packaging and communication
costs.
• Sponsors will no longer need to store clinical and ancillary materials for the duration of trials.
• DtP can reduce sourcing, cost, and expiry relabeling of bright stock, also minimizing waste (in traditional trials, shelf life is limited and subject to ongoing stability programs), often there is a need for continuous expiry extension.
“As illustrated in the traditional supply model inventory, our finished inventory is built up and stored at a central location and batch-shipped to a clinical site. Most common with the patient-centric approach via DtP, clinical supplies are first sent to the clinical site, who will then arrange shipment to the patient’s home. The alternate model bypasses the clinical site alto gether, and instead uses a central phar macy to distribute the supplies directly.
Hybrid models are also common,” Wilson explained. He summarized, “Potentially, the model may deliver effi ciency, shorter timelines, and reduced costs.”
Wilson went on to describe issues surrounding cold chain. Demand for biologic, cell and gene, and orphan therapy trials is expected to be highly variable and material is often in short supply and very expensive. Typically, sponsors will have to pool supplies in a regional hub-and-spoke network to expedite order management. To support the flexibility of this trial deliv
options that will need to be considered for the trial:
• Transportation
• Timing definite
• Product safety in the home
•
•
•
•
of
He
these
be addressed as early on in the trial as possible to better meet goals and timelines. DtP brings in another line of considerations not previously included in packaging briefs, which revolve around what bringing a trial into the home means for patients and their families as well as satisfying regulatory demands within that environment. Clinical trial companies can manage these considerations on their own, or by turning to focused packaging suppli ers who can provide valuable insights and structure.
Wilson explained that in the case of a packaging design center, the focus is split into three care areas: the design element, packaging rationalization for supply chain and shipping optimiza tion, and enhancement of added value features or smart packaging options.
For the design element, Wilson suggested “having experienced tech nical experts [to] develop conceptual packaging [for briefs]. Coupled to that process, it’s beneficial to have a set of grounded solutions previously trialed and tested, which can shortcut devel opment and address questions that are not directly related to the specific parameters of the trial in question, but speak to the ability to be agile and flexible.” These solutions could include cold chain, or predesigned book or label presentations that can match required presentation and language needs.
Smart packaging options will become increasingly important as DtP drives further AI and adherence parameters, and can include solutions such as RFID or NFC labels to capture transmitted data, time or temperature indicators, or have child-resistant (CR) parameters included. Abiding by regulatory stan dards, these technologies and pack aging solutions will enhance the trial environment, Wilson asserted.
1. Regulations, regional acceptance, and validated packaging configurations all play a role.
2. The challenges aren’t insurmountable but will require packaging community effort.
3. Hybrid models may be an opportunity to limit paper without completely removing the option.
At the[PACK]out this May in Austin, TX, industry professionals participated in a sustainability panel, which included talk of eIFUs (electronic instructions for use).
When asked about the challenges around implementing paperless options, the panel—moderated by Jamie Pero-Parker, PhD, Sustainability Sector Lead at RTI Innovation Advisors—focused on three main hurdles.
Regional acceptance: Samantha Smith, Engineering Director – Product Stewardship at Medtronic, explained that regional acceptance can be an issue. “We have a good handle on North America, in general. Once you get out into regionality—there’s a bit of a struggle to get the right folks to answer the right questions to get eIFUs in play,” she said. “Then we have SKU proliferation. We don’t want to carry a SKU for a high-volume product for too many different countries. We’ll want to make sure that we’re reducing our inventory so we’re not carrying SKUs for several different regions just to have the right IFU. So how can we come up with a hybrid model, so that we can use a limited amount of paper?”
While North America and Europe may be receptive, Smith said, “Once you get out into the smaller regions, they have a lot of regulations and getting those folks on board with understanding” is tough. She said you have to keep asking, “Why do you think you need the paper IFU?” and keep digging with a lot of “whys.” A lot of times, you find out they don’t actually need it, she noted.
Operation: Kevin Kane, Packaging Engineering Manager at Stryker, said it’s also important to consider the challenges of re-verification, as some products have an IFU placed in a specific position that might affect sterilization and/or performance with packaging.
Removing that IFU could pose a challenge or disrupt operations.
Regulations: Of course, regulations are on everyone’s mind when considering life science packaging updates. Lindsay Smaron, Senior R&D Packaging Engineer at Boston Scientific, noted, “On the regulation side, in Europe they allow eIFUs on products that are implantable devices. But from an EU perspective (not country-specific), they’re not really keen on opening up the regulation to allow it on all the other devices. There was a survey about five or 10 years ago where we allowed it in implantables. Through MedTech Europe, we as an industry are pushing back and doing a survey to doctors to reevaluate that [to allow eIFUs for other devices].”
Regulators may not see paper IFUs as an issue because they’re not hearing it from their customers, she explained. But their customers (on the political side) are different than device manufacturers’ customers (doctors). It will take effort on the part of device manufacturers to help regulators understand that it’s a positive thing that they allowed eIFUs on implantables and to press on for change for other device eIFUs.
The annual Institute of Packaging Professionals (IoPP) Salary Survey is always a revealing benchmarking tool. But this year, the 2022 edition offers a particularly interesting snapshot of an industry and a workforce in flux. After two years of survey respondents telling us they were reacting to pandemic uncertainty by hunkering down, staying put, and avoiding the risk of seeking greener pastures, the most recent crop of responses shows that an increasing number of respondents have recently found, or are likely to seek, new employers. Given an already tight labor market and the more recent “Great Resignation” trend, this pushes soaring salaries even higher, meaning management will have to invest in order to retain talent. Furthermore, it appears those employers are willing to make that investment in employees in younger and earlier age and experience cohorts than ever.
Personalized medicine is now more than a concept – it is driving real change in the pharmaceutical industry today.
ΖQVWHDGRIDGRSWLQJDRQHVL]H WVDOO
DSSURDFKWDLORUPDGHSUHYHQWLRQDQG
WUHDWPHQWVWUDWHJLHVDUHGULYLQJJURZWK
LQPHGLFLQHVWKDWDUHWDUJHWHGDWGH QHG
JURXSVRISDWLHQWVZLWKWKHDFWLYH
VXEVWDQFHGRVHDQGWLPLQJDOORSWLPL]HGWR
DFKLHYHDQHQKDQFHGUHVSRQVHZKLOHDOVR
ORZHULQJWKHULVNRIDGYHUVHH HFWV1
)RUSKDUPDFHXWLFDOFRPSDQLHVWKHVKLIW
WRDPRUHSHUVRQDOL]HGIXWXUHSUHVHQWV
VLJQL FDQWRSSRUWXQLWLHVEXWWKHUHDUH
DOVRFKDOOHQJHVΖQPDQXIDFWXULQJDQG
SDFNDJLQJVXSSO\FKDLQVIRUH[DPSOHWKH
GHPDQGIRUODUJHVFDOHSURGXFWLRQZLOO
HQGXUHEXWKLJKHUOHYHOVRISHUVRQDOL]DWLRQ ZLOOXOWLPDWHO\FRUUHVSRQGWRDUHGXFWLRQLQ EDWFKVL]HV
ΖQGHHGWKHUHLVHYLGHQFHWKDWDVVHPEO\
DQGSDFNDJLQJOLQHVWRGD\DOUHDG\IDFHD JURZLQJUHTXLUHPHQWWRPDQDJHDKLJKHU QXPEHURIVPDOOHUSURGXFWEDWFKHVZLWK WKHWUHQGWRZDUGVVL]HVRIEHORZ LWHPVVHWWRFRQWLQXH
$PDMRULPSOLFDWLRQRIWKLVVKLIWLVWKH
LQFUHDVHLQEDWFKFKDQJHRYHUVQHHGHG
%DWFKFKDQJHRYHU%&2WLPHFDQYDU\
EXWDWLPHIUDPHRIEHWZHHQWZRDQG
IRXUKRXUVLVQRWXQW\SLFDOWRHQVXUHDOO
processes are conducted in accordance ZLWKVWDQGDUGRSHUDWLQJSURFHGXUHV623V
DQGLQFRPSOLDQFHZLWKUHOHYDQWUHJXODWRU\
JXLGDQFH:LWKVPDOOHUEDWFKHVPHDQLQJ
PRUHFKDQJHRYHUVWKHQHWUHVXOWLVIRU SURGXFWLYLW\RQWKHOLQHWRGLPLQLVKRYHU WLPH
2QHSRWHQWLDODQVZHUWRWKLVFKDOOHQJH LVWRLQFUHDVHFDSDFLW\+RZHYHUWKLVLV
FRPSOLFDWHGE\WKHQHHGWRIDFWRULQUDPS
XSWLPHΖWDOVRKDVWKHSRWHQWLDOWREHFRPH XQVXVWDLQDEOHDVEDWFKVL]HVUHGXFHIXUWKHU DQGWKHSUHVVXUHRQDYDLODEOHUXQQLQJWLPH
LQWHQVL HV0RUHRYHULWGRHVQRWVROYHWKH
URRWFDXVHRIWKHSUREOHPWKHOHQJWKRI FKDQJHRYHUWLPH
Come visit
learn more
$W6WHYDQDWR*URXSRXU1H[W
*HQHUDWLRQ3DFNDJLQJ6ROXWLRQKDVEHHQ
GHVLJQHGVSHFL FDOO\WRDQVZHUWKLVLVVXH
LQDSSOLFDWLRQVLQYROYLQJWKHODEHOOLQJ
SDFNDJLQJFDVLQJDQGSDOOHWL]LQJRIPHGLFDO
GHYLFHV7KLVPRGXODUV\VWHPIDFLOLWDWHV
EDWFKFKDQJHRYHUVZLWKDQH[WUHPHO\
KLJKGHJUHHRIDXWRPDWLRQWRGUDPDWLFDOO\
UHGXFHWKHWLPHLQYROYHGIUHHLQJXS
SURGXFWLRQFDSDFLW\DQGHQDEOLQJEDWFKHV
WREHSURGXFHGXVLQJORZHUPDFKLQH
VSHHGVIRULPSURYHGTXDOLW\6SHFL FDOO\
WKHHɝFLHQFLHVWKDWFDQEHUHDOL]HGYLDWKH
1H[W*HQHUDWLRQ3DFNDJLQJ6ROXWLRQPDNH
LWSRVVLEOHIRU%&2WREHUHGXFHGIURP
VHYHUDOKRXUVGRZQWRXQGHUPLQXWHV
$FULWLFDOHOHPHQWRIWKHV\VWHPLVWKH
IDFWWKDW]HURLQWHUYHQWLRQLVUHTXLUHG
IURPRSHUDWLYHVΖQVWHDGDXWRPDWHG
ORJLVWLFVDUHXVHGWRFRQYH\SDFNDJLQJ
PDWHULDOVIURPWKHZDUHKRXVHWRD
VWDJLQJDUHDFORVHWRWKHSURGXFWLRQOLQH
%HFDXVHWKH\DUHLQFORVHUSUR[LPLW\
WKHPDWHULDOVDUHLPPHGLDWHO\DYDLODEOH
WREHORDGHGLQWRPDJD]LQHVXVLQJ
URERWLFVVDYLQJDVLJQL FDQWDPRXQWRI
ZDVWHGWUDQVSRUWDWLRQWLPH$IWHUDEDWFK
SURGXFWLRQF\FOHLVFRPSOHWHPDJD]LQHV
DUHHPSWLHGRIODEHOOLQJDQGSDFNDJLQJ
PDWHULDOVZKLFKDUHVHQWWRZDVWHDQGWKH
OLQHLVSUHSDUHGIRUWKHIROORZLQJEDWFK
*03DQGUHJXODWLRQVVWLSXODWHWKDW
PDWHULDOVIURPRQHEDWFKPXVWEH
SK\VLFDOO\VHSDUDWHGIURPDQRWKHUWRDYRLG
WKHULVNRIFURVVFRQWDPLQDWLRQ:KHQVXFK WDVNVDUHPDQDJHGE\RSHUDWLYHVIROORZLQJ 623VWKHUHLVQRZD\WRHUDGLFDWHWKHULVN RIKXPDQHUURUHQWLUHO\%\DXWRPDWLQJWKH
SURFHVVKRZHYHUWKHUHLVIXOOWUDFHDELOLW\
RIDOOHOHPHQWVWKURXJKWKHUHFRUGLQJ
RIXQLTXHLGHQWL HUVHULDOFRGHVDQGWKH
PRYHPHQWRIEDWFKPDWHULDOVLVYDOLGDWHG
WKURXJKRXWHYHU\VWDJH
7KDWLVQRWWRVD\WKDWRSHUDWRUVDUH
UHPRYHGIURPWKHSURFHVVHQWLUHO\
ΖQVWHDGWKHHPSKDVLVRIWKHLUUROHOHDQV
PRUHKHDYLO\WRZDUGVPRQLWRULQJWKH
SURFHVVPDQDJLQJWKHFROOHFWLRQRILQ SURFHVVFRQWUROΖ3&VDPSOHVDQGKDQGOLQJ
DQ\UHMHFWVWKURXJKDVVLVWLYHOLQHFOHDUDQFH
VXSSRUWHGE\YLVLRQWHFKQRORJ\
2YHUWLPHDVWKHGHPDQGVRQDVVHPEO\
OLQHVLQFUHDVHLQFRPSOH[LW\DQGLQWHQVLW\
WKHLQQRYDWLYH1H[W*HQHUDWLRQ3DFNDJLQJ
6ROXWLRQDOORZVIRUJUHDWHUHɝFLHQF\
SURGXFWLYLW\DQGSHUIRUPDQFHTXDOLW\
E\DXWRPDWLQJEDWFKFKDQJHRYHU$QG
EHFDXVHDOOPDFKLQHU\FRPSRQHQWVDUH
PDQXIDFWXUHGDQGLQWHJUDWHGE\6WHYDQDWR
*URXSSKDUPDFHXWLFDOFRPSDQLHVKDYH
WKHDVVXUDQFHRIDVLQJOHVRXUFHRIVXSSO\ WRDQVZHUWKHSURGXFWLRQFKDOOHQJHV
EHLQJSUHVHQWHGE\PHGLFLQHȇVPRUH
SHUVRQDOLVHGIXWXUH
What were the top predictors of a salary? After the obvious job function variable—corporate management makes more than operators on average—the three factors of experience, education, and age are the most accurate salary predictors.
• Of the 31 respondents who reported not having an undergraduate degree, nearly half (45%) of them earn more than $100,000. That gure was 36% in 2021 and 25% in 2020. Lack of an undergraduate degree is becoming less of an impediment to success , but more education still correlates with higher salaries, more raises, and better security.
• Those without undergrad degrees earned an unweighted average of $100,970, the rst time in PW ’s tenure with this study that they’ve averaged six gures. That’s up 6% from $95,380 in 2021, which was up 12% over 2020’s reported $84,500. Perhaps this is an indicator of the tightening labor market, and the need to look outside of the usual undergraduate degree talent pools. Still, the biggest salary gains are to be made once a degree is earned.
• The biggest salary jump based on education, a 22% salary increase, was reported between a high school/some undergraduate ($100,970), and an undergraduate degree ($122,630). Average salaries increase by 18% from undergraduate to graduate degree, and 21% from graduate to doctorate. Note: only 11 respondents reported having a doctoral degree, so it’s a small sample size.
• Certi ed Packaging Professionals earned an average of $134,310 in 2021, as reported in 2022, 15% more than their non-CPP peers who reported an average of $116,590.
• People without undergraduate degrees are less likely to have gotten a raise in the past year (2021). Only 42% of those without undergraduate degrees reported getting a raise, compared to undergraduate degree holders (76% got a raise), graduate degree holders (66%), and doctoral degree holders (80%).
• People with undergraduate degrees feel more secure in their jobs. 56% feel very secure and 35% feel somewhat secure. Respectively, those numbers are 48% and 29% for those without undergraduate degrees.
• Those without undergraduate degrees are the least optimistic about earning more in 2022 than in 2021. Only 52% of them expect to do so, compared to undergraduate degree holders (66%), graduate degree holders (73%), and doctoral degree holders (60%).
• In prior years, the largest experience-based pay jump was between the 3- to 5-year range and the 6- to 10-year range. This was 23% last year. This year, respondents say that biggest jump happens even earlier on the experience continuum. A jump of 23% is reported between the ≤2-year range ($95,700) and the 3- to 5-year range ($111,560). We see another strong, but less pronounced pay jump (17%) happening between the 3- to 5-year range ($111,560) and the 6- to 10-year range ($128,240). This means that employers appear to be willing to promote and pay more and more quickly for talented, but less experienced employees than they have in previous years.
• Just as we saw last year, we see another major pay jump as respondents move from intermediate experience ranges to the >20 year mark. This is to be expected since there are some large salaries among careers that have spanned more than 20 years, and may include careers upwards of 40 years.
• Of the six experience cohorts, the three most experienced (10-15, 16-20, and >20 years) are less likely to expect to earn more this year than they did the previous year, and more likely to expect to earn less this year than the previous year. Perhaps this is evidence of plateauing salaries at later stages of careers, and limited upward mobility. After 20 years or more in an organization, people may have advanced as far as they can, and as such salary gains may not be as dramatic.
• Of the six experience cohorts, the three least experienced (≤2-, 3- to 5-, and 6- to 10-years) are all 99% con dent in at least earning the same as last year. Respectively, 79%, 83%, and 85% expect to earn more.
• Bonuses are a different story. People at the lower experience levels are less con dent in bonuses, and less likely to have received one in the last year. Of respondents with ≤2 years of experience, 47% got a bonus last year and expect to get them this year. Of the 3- to 5-year experience range, 57% got a bonus last year and expect to get one this year. All other experience cohorts were near or above 70%, both in receiving a bonus last year, and expecting one this year. It appears that con dence in bonus correlates with greater experience.
• Experience still pays. The lower experience cohorts do see big salary gains earlier than ever (after ≤2 years), and those jumps, at least as a percentage, are not as dramatic among the 10+ year experience cohorts. Still, those who traverse the plateau and make it to the >20-year cohort see on average a 16% salary jump after 20 years. A chart on pp. 56, titled “Biggest Salary Gains Happening Earlier than Ever” illustrates this dynamic, and how it’s changed in recent years.
• The largest average salary increase, a 44% jump from $91,740 to $132,440, occurs between the 18-34 cohort and the 35-44 cohort. Average increases thereafter slow to 10% from 34-44 to 45-54, and 16% from 45-54 to 55-64, then we see a sharp drop off in salaries in the >65 years of age (-32%). This is perhaps due to emeritus status, reduced hours, semi-retirement, etc. in the >65 age group.
• This survey once again illustrates that while the highest salaries are certainly among the older and more experienced ranges, the largest percentage gains are to be had early on; in fact earlier on than ever. Also, there may be some diminished salary returns toward the end of a career, perhaps due to limited upward mobility/plateauing, compounded due to planned responsibility reductions. Among unprompted, write-in concerns, Ageism/Staying Relevant again makes an appearance among 3% of respondents.
• Of the 18-34 cohort, 87% expect to earn more than last year, re ecting the most con dence in a raise of any age cohort. This re ects the greater upward mobility of younger ages. Only 67% of the 55-64 cohort and 38% of the >65 cohort, (about 2/3 and 1/3, respectively) expect to earn more next year.
• Of the 18-34 cohort, 90% are very or somewhat secure in their jobs, exhibiting higher job security con dence than any other age cohort.
• 30% of the youngest cohort, aged 18-34, make more than $100,000 per year. That’s up 4 percentage points from 26% as reported last year. That cohort also earned 3% more in 2021 ($91,740 reported in 2022), than last year. The previous year, they had earned 8% more in 2020 ($88,980, reported in 2021) than they did in 2019 ($82,560, reported in 2020). Salaries among the youngest cohort continue to grow at or more quickly than the overall averages.
• 33% of the oldest 65+ cohort earn less than $100,000, perhaps indicating reduction in hours or responsibility. They also earn 32% less ($116,250) than the next youngest cohort, 55- to 64-year-olds, who report making the most of any age group at $170,580.
• The average salary reported by women ($113,970) now trails that of men ($127,900) by 22% in 2021 (reported in 2022), meaning the gender pay gap among respondents on this survey, is growing. This gap was 17% in 2020 (reported in 2021), and 16% in 2019 (reported in 2020).
• Men (72%) and women (70%) reported receiving a salary increase last year at nearly the same clip. The reported size of the raise was similar, too, though women were more likely to report the lowest raise range: 79% of women, and 74% of men reported a ≤5% raise. Meanwhile, only 13% of women reported a 6-10% raise, compared to 20% of men. While these are similar, men reported slightly more raises in general at the outset. Then, the percentage increase of those raises was slightly higher among men. These factors compound to help widen the gap.
• Both men and women reported having received a bonus last year at the same rate, and their expectations for future bonus are about the same. Women are slightly more secure in their jobs, also.
• While the at- rst-glance parity on all of these metrics is encouraging, women aren’t reporting quite as many or as high of raises as their male counterparts, which only grows the wage gap. Not to mention, even if there were parity on these metrics, that wouldn’t translate to equality considering that women begin with the disadvantage of a lower average salary as a starting point.
• Women skew younger than men, with 43% being in the 18-34 cohort. Only 23% of men are in that cohort.
• Women are less experienced than men, with more than half (56%) having less than 10 years of experience. Less than a third (29%) of men report having less than 10 years of experience. The experience gap among respondents is even wider than it was last year, when 49% of women claimed 10 years or less experience, compared to 33% of men.
• More women (61%) than men (52%) report having an undergraduate degree only. However, among those with undergraduate degrees, 31% of men and 24% of women report a graduate degree, so a big-picture takeaway is that women and men report roughly equal levels of education.
• 19% of women respondents are engineers, compared to 28% of men. Current programs attracting women to STEM education aim to bridge that gap.
• 5% of women respondents are in corporate management positions, compared to 9% of men. Programs aimed at training women for leadership positions hopefully should help toward more equal representation in this job function.
• Women (21%) are more concentrated than men (11%) in sales and marketing roles.
In the middle of what’s been called the Great Resignation, what exactly does it mean when unPACKed with PMMI podcast guest Dr. Jessica Kriegel says, “There is a war on talent, and the talent won.” Beyond a catchy quote, it’s a statement she hopes will open the eyes of industry leaders in all sectors.
The age and experience distribution of women in packaging is a big factor in the now 22% gender-based salary gap. Women less frequently report their job function as engineering or corporate management, a reality that many programs are working to change via youth programs exposing women and girls to STEM subjects and leadership skills. The good news, as it was last year, is that the survey re ects a younger and less experienced cohort of women—with collectively comparable educations—that should eventually emerge into the upper age and experience echelons they previously didn’t inhabit. But if women remain concentrated at their current experience, age, and job duty distribution, that doesn’t bode well for gender pay equality. It is not clear whether the process of women matriculating into higher pay categories is just aggravatingly slow, or if women’s experience, age, and job duty distribution is stickier, more xed, than we had hoped and anticipated. Compounding the problem, men report slightly more, and slightly higher salary increase raises.
The biggest takeaway is that the balance of power has shifted away from the employer and toward the employee. One illustration of this can be found in write-in answers. When asked what keeps them up at night regarding job security, 23% of respondents said “Nothing,” an unprompted, specific answer that’s reinforced by 84% of respondents telling us they are somewhat or very secure when asked about job security in a multiple-choice question.
In this year’s results, we’re seeing a shift toward new job-seeking and greater risk-taking. This increased mobility among employees is forcing employers to up the stakes to retain them. The overall average salary reported by the respondents went up to $130,070, up 7% from last year and an all-time high in Packaging World’s (PW) reporting on the survey. Pharmaceutical and nutraceutical average salaries fared even better than that overall figure, with the average salaries of $165,200 and $148,214, respectively. But the dollar figures aren’t just going up evenly across the spec trum of age and experience. Employers are using a strategy of rewarding promising newer and younger employees with bigger, earlier salary jumps, hoping to lock them in.
Pharmaceutical and medical industry respondents are also most bullish about receiving a rasie this coming year, with 84% and 82%, repectively, expecting to earn more next year than this year.
one-stop shop for solutions targeted to pharmaceuticals, biologics, nutraceuticals, medical devices and more. Discover new innovations to scale up production, ramp up e-commerce, streamline operations and increase usability in the Healthcare Packaging Pavilion.
1. Machine suppliers and end users must identify hazards and reduce risks.
2. The methodology in the B155.1 standard is recommended for its ease of use.
In this Q&A, Bruce Main, PMMI Technical Advisor and President of design safety engineering, inc. (pictured), and Sean Riley, Senior News Director, PMMI Media Group, discuss risk assessment for packaging and processing machines.
Sean Riley: We hear “risk assessment” a lot. What exactly is it in layman’s terms?
Bruce Main: It’s basically a safety assessment. It’s a type of analysis where you look to identify hazards associated with machinery or equipment. It guides you through a process to develop risk reduction measures to make sure that you achieve acceptable risk.
Sean Riley: When did this become a topic for machinery in particular? When did PMMI first integrate risk assessment into the B155.1 standard?
Bruce Main: Let’s start with the last part first. The B155.1 first integrated risk assessment in the 2000 edition of that standard. The reason that it was done then was because of where it came from. The risk assessment process really got legs in the 1995-1996 timeframe
3. Though methodologies/approaches can differ, there are five key steps to risk assessment.
when the European Union issued the Machinery Directive, which is a law in Europe that requires that machine suppliers or builders do risk assessments. Because of that, and because many PMMI members were shipping machines to the EU, we needed a methodology to do this. That’s where this really came from.
Sean Riley: Is that something I can do on my own or do I need to bring someone in to do one?
Bruce Main: Well, it’s intended to be something you can do yourself. As a builder of a machine or a supplier of the machine, the Machinery Directive is intended that you can self-certify. Who’s required to do this under the Machinery Directive? The law in Europe says the machine supplier is required to do it.
Now, under B155.1, we operate in a bit of a different legal environment, so there’s requirements in the B155.1 standard that both the supplier of the machine is required to do a risk assessment and the user of the machine is also supposed to do a risk assessment. The machine supplier looks at the machine as they build it and its intended use, and the user of the machine looks at how that machine is used within a facility and the hazards that might be associated with the facility.
Sean Riley: Do they bring that to each other to make sure they
mesh or is that something that’s done independently?
Bruce Main: If it’s an off-the-shelf type of machine, a labeler, there may be very little collaboration, whereas if your supplier is building you an integrated bottling line, then quite a bit of collabora tion will go on and that risk assessment may be done collaboratively for both the machine as well as the installation.
Sean Riley: Besides one being from the supplier and one being from the purchaser, are there different ways to do a risk assess ment?
Bruce Main: Yes, there are many different ways to do risk assess ments. That’s one of the great things about risk assessment is there’s lots of flexibility. The key thing is that you need to identify hazards and reduce risks to an acceptable level. Those are the very fundamental pieces and there’s lots of different ways to do it in different industries. The semiconductor industry has a methodology, the robot industry has a methodology, the machinery methodology is available—the B155.1 follows the machinery methodology as well. There’s a whole bunch of different approaches to risk assessment and there’s flexibility in how you can do it.
Sean Riley: Okay, so if I’m a packaging company, does PMMI have one that they suggest, the method that I should follow?
Bruce Main: The methodology that’s illustrated in the B155.1 stan dard is the one that we recommend. We do that because it’s easy to use and easy to learn. It provides enough structure and granularity to help you identify hazards without getting down a rabbit hole and getting lost. When I say there’s lots of different ways to do it, there’s also lots of different ways to overdo it, if you will.
Sean Riley: Okay. Could you give me some key steps on how I would do a risk-assessment process?
Bruce Main: Yes. There are five key steps. When we look about at the different methodologies and the different approaches to risk assessment across several industries, and I’ve had the opportunity to do that because I’ve written a couple books on this topic of risk assessment, what you see is the commonalities: the first step is you need to identify hazards, second is to assess the risks, third is reduce the risks to an acceptable level, fourth is to document your results, and fifth is to follow-up to make sure you’ve done what you said you’re going to do.
Of those five steps, the first one, identify hazards and the third one, reduce risks to an acceptable level, are the most important parts because if you don’t identify hazards, you can’t achieve acceptable risks, you’re going to potentially miss something and if you don’t reduce risk to an acceptable level, you’re missing the point.
What is most interesting is the second step, assessing risk. There are great efforts made by engineers all over the world trying to get away from the subjectivity of it. That’s one of the challenges of risk assessment is that fundamentally, you want to keep your Operator Safety on the goal and identify hazards and reduce risk to an accept
able level. The scoring of risk is really not that important and it’s sometimes overemphasized.
It’s different for the application. If we’re making cotton balls, we have one level. If you’re making steel, it’s entirely different level. The hazards are different, the risks are different. It’d be great if somewhere in industry from above we said, “Okay, you need to get to be a seven. If you get seven, you’re good, and if you’re more than seven, you’re not,” but it really depends on the application.
Sean Riley: How do I get started? How do I integrate risk assessment into my process?
Bruce Main: Well, you need to form a team. That’s usually the best way. Get the resources to understand what’s going on. B155.1 is certainly a great place to start. There are tools available. The PackSafe software is a tool that we have developed and is offered for sale for companies to use. It guides them through the process, lets you know what to do next, and how to make decisions about what you need to do. It’s not an expert system, it doesn’t tell you what to do, but it tells you what to think about. That’s one of those tools that will help you work through this process. The standard is something that is a very good resource.
PMMI offers risk-assessment training—Fred Hayes and I have done the risk-assessment training for many years. This is a two-day session where we talk about the different topics of risk assessment, products, liability aspects, aspects related to control systems, and even OSHA enforcement. We spend a fair amount of time working with the PackSafe software, getting people to do risk assessments in the training session. There’s a lot of resources available.
Introduction to Standards Development is a free program developed by PMMI to benefit businesses by providing insights related to standards participation. With knowledge of standards development, machinery can be designed, operated, and maintained in accordance with applicable requirements. Machinery export marketers also gain a tremendous benefit related to meeting requirements in effect at global destinations.
This program is designed to increase awareness of how standards can assist in meeting business objectives. In addition, the ability to participate in standards development supports a competitive solution for the global marketplace.
The course is not industry-specific; it raises the importance and value of standards work within all industries. It features examples related directly to packaging and processing machinery.
Visit the free program at: pmmi-standardstraining.com/
Riley: What are the legal implica
doing a risk assessment, whether
in Europe or the U.S.?
Bruce Main: Well, let’s start with Europe
there’s a law. The Machinery Direc
tive is the law that requires that you do risk assessments. If an OEM is shipping a machine into Europe, you have to do risk assessment as required by the law. That’s just what you have to do.
In the U.S., we have the standard, the B155.1 standard. That’s not a law, it’s just a consensus standard. It’s a situ ation where you don’t have to do it by law, but the standard’s going to be what is used to measure your performance in the court of law if somebody were to get hurt, so you really need to be doing risk assessments. It’s going to be hard to defend a company if they’re not doing it, primarily because it’s been required now for almost 20 years.
Sean Riley: Are there other reasons for people to do risk assessments that would help in the design of their machinery that isn’t just eliminating hazards?
Bruce Main: We have seen situa tions, and I want to say almost every project that I work on, where what comes out of the risk assessment is one of two things: You either have hit a home run and you’ve identified all the hazards and you’ve got it solid and you’ve got a great machine and now the confidence in your design goes up, or we’re able to identify small changes that can actually improve the productivity, the throughput, the ease of use, the speeds, you’re just making better machines. One of our customers commented, “When engineers’ confi dence goes up, costs go down.”
Let me give you an example. If you need to change a pump or a motor on a machine and the design of the machine is such that it’s buried inside the middle of the machine and in order to get to it, you have to dismantle the machine, that can really impact your downtime, but if you identify that task—and there’s safety implications to all this—but if you make it so that you can actually get to the pump or the motor, get in and get out and make that change and do it relatively quickly, that impacts [the end user’s] ability to produce.
+ The enhanced FA1 pick and place feeder for blister machines features a new vibratory feed track, with gentle handling to virtually eliminate particulates in a compact footprint
+ It feeds even difficult-to-handle solid doses such as fragile, unusually shaped, and orally dissolving products up to 80 cycles/min
WLS
+ Designed for installation on virtually any WLS labeler, the applicator applies thermochromic vaccine vial monitor (VVM) labels that change color when exposed to an out-of-tolerance temperature for a set amount of time
+ Running up to 600 parts/min, the VVM applicator is suited to vials, bottles, or other containers that hold temperature-sensitive products
+ This 12-pocket system fills gummy products (particularly nutraceuticals) into glass, paperboard, or plastic containers at speeds up to 70 bottles/min
+ It includes magnetic funnels that do not require fasteners, and easily integrates with a weigher or counter
NJM
+ The enhanced Bronco® 130 pressure-sensitive labeler can be configured to apply single, dual, wraparound, and/or multi-panel labels to round, square, rectangular, and/or oval bottles in a variety of sizes
+ Running up to 250 bottles/min, the inline, servo-driven system features new software capabilities and printer options for flexibility
WIPOTEC-OCS
+ The new Traceable Quality System Modular Design (TQS-MD) uses a “building block” concept for compatibility with a broad array of products
+ Employing one user interface, functionalities can include weighing, marking and verifying, labeling, metal detection, and serialization/aggregation integration (among others), for a “one system, many capabilities” approach
SIGNODE
+ With belt speeds up to 155 ft/min, the LDX-RTB 4.0 semi-automatic random case sealer features patented technology for processing of void-filled and over-stuffed cases with a pneumatic top cartridge
+ Maintenance is simplified with easy access to motors/electrical/belts
products can improve all areas of
production line while reducing workforce needs and giving you more flexibility to run different product sizes. From filling and capping to check weighing and inpection, we can help solve throughput
Century Parkway, Ste. 200, Mount Laurel,
Antares Vision’s Print & Check EVO is among the most widely used integrated serialization solutions on the market. Quick and easy to integrate into packaging lines, the unit occupies just 705mm of oor space as it prints and veri es on carton aps. Upper and lower conveyors keep cartons stable for reliable printing and unsurpassed veri cation accuracy. The Print & Check EVO can handle cartons up to 120mm wide and 200mm in height at a maximum speed of 300 units per minute.
Ideal for small- to mid-sized production, the Mini Man ual Station maximizes manual aggregation produc tivity and, among other bene ts, e ciently supports post-lot reworking operations in warehouses and distribution centers. Following the situation-speci c recipe – for example, the number of cartons per case – the Mini Manual Station aggregation unit issues the upper level, “parent” container label once the preset quantity of items has been scanned into the system. The unit features an ergonomic design for easy, multipoint access and an always-on handheld scanner for fast, reliable code reading.
08054
The high-resolution AV Print Inspector vision system provides inline layout inspection for webs and labels at speeds up to 80 m/min, and can be incorporated into new or existing labeling, printing or packaging machines. Antares Vision created the system to meet increasingly sophisticated and print-on-demand appli cations. The technology supports quality control across a wide range of layout features including 1D/2D barcodes, optical character recognition (OCR) and veri cation (OCV), color check, and pattern matching. It can de ne as many as 40 unique regions of interest, each with inde pendent parameters and reportable defect statistics
Digital Factory is a comprehensive software tool designed to monitor equipment performance and e ciency throughout the production process. The solution satis es pharmaceutical companies’ increasing desire to leverage data initially generated to comply with serialization mandates in the US and abroad. By tracking various key performance indicators (KPIs), it stream lines data into a user-friendly dashboard for intuitive operator decision-making. Information collected from production and packaging lines can then be used to improve business processes at all levels.
Antares Vision Group guarantees protection of products, people and brands through inspection systems for quality control, Track & Trace solutions for anti-counterfeiting and supply chain transparency, smart data management tools for maximized e ciency and digita lization of the supply chain, from raw ma terials to the nal consumer. The Antares Vision Group is active in the pharmaceu tical market, Life Sciences (biomedical devices and hospitals), beverage, food, cosmetic and consumer-packaged goods. The Group reaches over 60 countries in the World with complete and exible solutions, hardware and software.
With twenty years of experience in vision technologies, the Antares Vision Group is supplier to ten of the leading pharma ceutical companies, more than 25,000 inspection systems ensuring product safety and quality, 6,500 quality controls and more than 3,500 serialization mod ules on lines installed around the world.
In 2020, Antares Vision Group expanded their capacity services through the acqui sitions of Convel, Adents, Applied Vision and Applied Vision, and rfxcel in 2021, and ACSIS in 2022.
The Load Transfer Station (LTS) product line, o ered by Columbia Machine, helps to reduce contamination from entering production areas, streamlines operations & reduces costs. Columbia manufactures a complete line of pallet transfer solutions including stand-alone stations to fully automatic solutions that allow pallet load transfer to be completed in less than one minute, without requiring the operator to leave the safety of the forklift.
Columbia Machine’s LTS solutions come standard with the latest safety features. These include Category 3 electrical safety components, upstacker guarding with A-B SensaGuard RFID interlocked door switches, multiple emergency stops, and muted light curtains on the automat ed systems. Every Columbia Machine LTS has been engineered to exceed the requirements of pharmaceutical processors who are working to meet FSMA regulations.
Columbia’s LTS is capable of transferring products
that are packaged in cases, super sacks, glass vials, pails, barrels, drums and bags from one pallet type to another, including Plastic, Chep and GMA pallets that are commonly used in both receiving and shipping applications.
To ensure that all Columbia equipment works smoothly with upstream and downstream ma chinery, complete systems integration services are available—including project management, controls, installation, wiring, commissioning and preventive maintenance plans. As a family-owned company with a total commitment to customers, employees and a long-term nancial perspective, Columbia is your premier partner for load transfer solutions.
Columbia Machine, Inc.
The Load Transfer Station (LTS) product line is part of the Palletizer Division of Columbia Machine, a leading American palletizer manufacturer. For more than 80 years, Columbia has manufactured complete palletizing and material handling solutions.
The mission at Columbia Machine is to be the preferred supplier of engineered product solutions in the targeted markets we serve. We provide excep tional customer value through strategic marketing, innovative product devel opment and unparalleled customer service. We value safety, integrity, trust, fairness, professionalism and teamwork in relationships with our customers, employees, business partners, suppliers and shareholders. We “always” see our business through “the eyes of our cus tomers,” and provide them with superior solutions through innovation, quality, reliability and continuous improvement.
PHONE
For over 40 years Delta ModTech has been a leader in web converting and packaging innovation. We are dedicated to providing exible automation solutions for converters and manufac turers worldwide.
Delta ModTech systems feature a variety of processes including heat-seal pouching, rotary die cutting, laser cutting, tight tolerance registration, printing, laminating, coating and drying.
The packaging solution for process applications where speed, exibility and consistent seal quality are important. For the manufacturing of:
• Heat-seal/Cold-seal pouches
• Resealable pouches
• Liquid dispense pouching
• Sachet lling
We’ve developed several solutions to meet the pack age and pouching needs of our customers and their end users. Our experience with building machines to meet the demands of the most stringent speci cations will give you con dence in meeting your production goals.
• Mod-Track® Vision Inspection – Part-in-pouch, closed loop registration, date/bar code reading, rejecting
• Reject conveyors/marking equipment
• Part handling Conveyors for: stacking, shingling, sorting, turning, etc.
• Printing for date, lot and bar code printers – inkjet, thermal transfer, laser, etc.
• Case packing and cartoning integration
Packaging and Pouching Machine Speci cations
• Web Width: 10” (254 mm), 13” (330 mm), 18” (457 mm), Custom Widths Available
• Max speed – Reciprocating Packager: 13” 80 ft/min (24 m/min)*, 18” 55 ft/min (16.75 m/min) *
• Seal Repeat – Up to 24” (609 mm)
• Control System: Delta ModTech INTELLI-MOD® control system
• Drive System: Servomotor Control
• User Controls: Touchscreen HMI Pendant Arm
• Cabinet Construction: Welded Steel Frame, Alumi num Front Plate
* Process Dependent
Now with Frontier Coating Technology - In 2016, Delta ModTech acquired Frontier Industrial Tech nology (now Frontier LLC). Frontier has successfully developed custom coating and drying solutions for 30 years. This partnership allows us to provide turnkey solutions from lab scale to production.
We deliver web converting and packaging systems for the most complex and demanding jobs in the medical, pharmaceutical, label, RFID and cosmetic industries. Our systems are designed to meet your application requirements, improve your pro tability, and reduce your risk.
Serving our customer’s has always been Delta’s highest priority. We focus on quick, e cient solutions to keep your machines running to their full potential. To back up this philosophy, we have a full-service sta on call, made up of Engineers and Technicians. We have the pro cess knowledge and proven modules to ensure the longevity of your machine.
Care
care
Battery
Ad
www.deltamodtech.com
4071 Albany Street, McHenry, IL 60050
Dispense Works is one of a few USA manufacturers that builds the robotic product line in its entirety. This includes controls from board level and all software and rmware.
PHONE EMAIL
WEBSITE www.dispenseworks.com info@dispenseworks.com 815-363-3524
Dispense Works Inc., located in McHenry, IL, leads the industry with the best built, most industrial ized robotic dispensing machines available. From compact benchtop designs to full scale produc tion machines, we have the equipment to t your needs. These systems are quickly becoming the “operator’s choice” with features that rede ne the terms simple, easy and operator friendly.
Over 15 years ago we decided to create a true le based control system that can be built on, expanded, and updated in the future. Unlike many “me too” solutions, this type of software provides our customers with not only hundreds of pre-programmed functions, the entire control system may be upgraded in the future as new features arise by just downloading one le. This investment has evolved into a truly unique control system that simply out distances the competition. Seamless communication including Ethernet and RS232 connectivity, dual USB ports, large CF card memory.
With manufacturing requirements being more challenging and demanding than ever, having
information such as production data and history les automatically logged with information including dates, cycle times, etc., is increasingly important.
Our machines o er an industry proven control sys tem which combines real time motion control, I/O logic and vision with a rich list of pre-programmed functions in a tightly integrated package. No external PLCs, valve controllers or PCs required.
Today, our systems are hard at work in many different industries, such as Pharmaceutical, Food, Healthcare, Chemical, Industrial and other Packaging Industries, setting new benchmarks for performance. This multi-industry experience and success can be combined and applied to address your specific application whether standard or customized. All of our products are 100% designed and manufactured at our US facility. All software and machine firmware including the sub-systems for motion control vision software, etc., are developed and main tained in house as well.
Our ongoing commitment to developing the best solutions in uid applications has made us the First Choice in robotic dispensing systems as we move forward with new product development.
We are constantly challenging existing “methods” with a new generation of ideas and can provide better solutions to help you meet and exceed your dispensing needs. Whatever your industrial dispensing requirement, Dispense Works already has or can develop a solution.
See Our Ad on Page 30 www.dispenseworks.com
ESS Technologies, Inc. designs, manufactures, and installs automated packaging lines for manufacturers of pharmaceuticals, diagnostics, cosmetics, and consumer packaged goods.
Founded in 1993, ESS is now a part of the Pac teon Group, providing one source for end-of-line packaging solutions. As an authorized FANUC system integrator, ESS can design-in, install, and support all your end-of-line automation needs.
ESS also designs custom robotic end-of-armtooling (EOAT), which allows the precise handling of components and packaging materials. Our packaging line solutions include:
• Fillers / Cappers, Inline or Monoblock
• Horizontal Cartoners
• Vertical Cartoners
• Top, Bottom and Side Load Case Packers
• Tray Erectors and Loaders
• Wrap Around Case Packers
• Robotic Pallet Cells
• TaskMate Robotic Systems®
The ESS team has designed packaging lines for the following industries: Pharmaceuticals, animal health, diagnostics, medical device, cosmetics, nutraceuticals, and consumer products. Our robotic systems, fillers-cappers, cartoners, case packers, and palletizers are engineered to meet all applicable standards and production require ments. ESS is a UL-certified builder of electrical panels. We do not lock any portion of the PLC or robotic code in our controls, and ESS provides all OEM part numbers in the Bill of Materials.
ESS engineers work closely with our customers to understand the level of automation required, physical limitations, OSHA requirements, flexi bility, and future expandability. The result is an ergonomic and cost-effective production line that requires minimal operator training and can be easily retrofitted for future applications. ESS . has extensive experience integrating serialization systems to meet pharmaceutical serialization mandates.
ESS and all the Pacteon Group com panies bring integrity, pride, account ability, customer focus and teamwork to every packaging line we install. Our people and these principles form the Pacteon Promise: We make it right.
Key ESS Team Members
VP and General Manager
Tim Cokeley
Director of Operations
Paul Landers
Director of Engineering
Michael Morgan
Global Business Development
Walter Langosch
Midwest-Northwest Regional Sales Manager
Mike Witowicz
Northeast Regional Sales Manager
Brad Wol
Southeast Regional Sales Manager
Matt Kent eld
Southwest Regional Sales Manager
Mike Sires
Field Service Manager
Andrew Franz
Mechanical Engineering Manager
Steven Easter
Electrical Engineering Manager
David Sandoval
See Our Ad on Page 43 www.esstechnologies.com
As a market leader in exible packaging, Formost Fuji has been providing horizontal wrappers and baggers that are EFFICIENT, RELIABLE, and SIMPLE to operate for over 55 years.
Our Horizontal Flow Pack Wrappers are built with the end-user in mind having an easy to operate HMI that includes graphics and step by step instructions. The HMI can be customized for simplicity with icons or photos representing each product for a one touch changeover. This innovative ow wrapper has a simple to thread lm process that saves time and a shortened lm route that saves money. The center n seal unit tilts down allowing easy access for sanitation and maintenance.
B16 Box Motion End Seal Technology o ers four times the sealing pressure and longer dwell time with improved design. This provides high perfor mance hermetic seals on di cult to seal lms.
The Swing Arm Rotary End Seal Option for Hor izontal Wrappers provide increased dwell time
and seal quality at high speeds, allowing exibility for a wide range of product and lm sizes.
The Formost GTS Bagger provides performance proven technology with speed, versatility and dependability. Built to run up to 90 bags per minute, it is ideal for gently bagging a wide range of products including medical drapes.
Proven superior design and engineering are combined with the latest technology to bring you the High-Speed Box Motion horizontal wrapper. Capable of packaging speeds up to 400 per minute (application dependent), the high-speed box motion wrapper boasts high e ciency, tight wrapping, low vibration, and direct drive servos.
Formost Fuji provides sustainable, and e cient packaging solutions for the healthcare industry. Items such as masks, IV bags, inhalers, blister packs, syringes, tube sets, and many other med ical and pharmaceutical products are wrapped and bagged on performance proven Formost Fuji equipment.
First and Formost, we strive to put you the customer rst. Meeting and exceeding your expectations is our gold standard. Whether it be in design, manufacturing, or service, you can expect Formost Fuji to deliver a solution you are proud of. Throughout 55 plus years in this business our ideals have remained the same; build it right and deliver on time, all at a value to our customers.
Our team of experienced people listen to you, and understand your needs.
Horizontal Wrappers
Baggers
Automation Solutions
Special Applications
715 Church Road, Elmhurst, Illinois 60126 USA
PHONE
info@guk-vijuk.com 630.530.2203
WEBSITE www.guk-vijuk.com
GUK packaging-line equipment runs on the packaging line’s drive or can be equipped to run independently.
In-line lea et folding enables immediate insertion of lea ets into product cartons, along with the product. The NEW servo-driven GUK Cartonac 2005 has a hinged feeding table for easy access to the fold plates and rollers, and improved suction rollers and air blasts on the feeder table allow e cient feeding of folded products—up to 3 panels thick. It is a simple upgrade from the Cartonac 91 or Cartonac 2000. The Cartonac 2003DS is PLC con trolled for quicker, easier setup, and the feeder and folder is servo driven for better control and greater speed.
The GUK–Sigma Pick & Place Station precisely tips at or 3-dimensional (and di cult-to-handle) items onto products in production lines.
GUK PA21 Lea et Feeders feed inserts (and outserts) in-line for insertion into or cartons, handling lea ets up to 8 mm thick, depending on the model. The GUK PA15 Lea et Feeder feeds lea ets, turned 90º, and can be mounted parallel to the packaging line to save space. It is also used with gluing or tabbing equipment in o -line lea et/outsert bundling systems.
GUK RS Roll-Fed Folders o er economical lea et production, as roll printing saves paper, cutting, and labor costs—while minimizing probability of lea et mix-up.
Make spine-glued booklet lea ets on the GUK FA53 Folder. Fold up to 28-3/4 inch sheets for larger medguides on the GUK FA73 Folder. Choose from a number of G&K–Vijuk Outsert Systems with varying capabilities of folding outsert lea ets with from up to 90 panels to up to 350 panels.
Meet TRACK & TRACE requirements with the G&K–Vi juk CTM Coding and Serializing Station on MV Outsert Systems. Print industry standard 1- and 2-dimensional codes using black or UV inks. A 3-camera system veri es the dimensional qualities of outserts, and veri es and logs the printing and print quality of the codes.
Save time and labor with the GUK–Sigma PPM Auto Stacker, which automatically collects outserts and packs them compactly into trays that move in, then move out when full, in continuous production.
World leader in outsert-producing machin- ery, G&K–Vijuk has been special izing in miniature-lea et folding solutions for over 40 years.
Member of the GUK Group headquartered in Germany (manufacturer of folding machinery since 1949), we continue to assess the needs of the pharmaceutical industry, as shown by recent developments in machinery to fold a greater number of panels and fold wider sheets—both for more print space on a single lea et— and machinery for bundling lea ets for dispensing even more information on two to four lea ets.
GUK recently acquired MB Bäuerle, manufacturer of automated folding and inserting systems in Germany, and Sigma Engineering, manufacturer of pick and place product-handling machinery in the Netherlands, to further our goal to pro vide innovative, time-saving equipment to improve our customers’ e ciency in providing products and services for their customers.
Providing safeguards that help ensure your products match the prescription.
Anywhere along the line, protect your consumer and your equipment. E cient detection of foreign objects is critical to consumer safety, brand survival, and will also protect machinery and prevent downtime. We o er a complete line of metal detectors, checkweighers, and Xray inspection systems from our strategic partners: CEIA® and Ishida.
CEIA, is a world leading innovator of industrial metal detection systems for products such as powders, cap sules, tablets, and liquids. Quality control is at the core of CEIA development of the most advanced electronic and mechanical technologies for detection of contaminants accidentally present in products.
CEIA metal detection systems are:
• Industrial metal contaminant detection
• Fully-HACCP and GMP compliant
• ISO 9001 certi ed and constructed of EC and
FDA approved materials
• Available for free-falling product applications
The Ishida X-ray (IX) series raises the bar in performance and usability with a global range that meets all local territory standards. O ering customers easy mainte nance and stress-free operation, the range includes a robust fail-safe system that prevents a contaminated product reaching the consumer in the event of a power outage or breakdown, helping to minimize the potential for costly recalls.
All models o er exceptionally sensitive foreign body contaminant detection and additional bene ts such as the ability to identify damaged and missing products or components, helping the pharmaceutical industry achieve a rapid return on investment. Quick commer cial returns are also achieved by ensuring that high quality product leaves the factory gate, safeguarding reputations.
Ishida also o ers high-precision weight checking you can depend on. Checkweighing is key for delivering what your consumers expect by providing accurate veri cation of a package’s weight or count and detect ing missing components. Rely on a range of features to handle di erent products and incorporate new functions to meet the latest requirements. Promote quality control and customer satisfaction with Ishida’s extensive know-how in weighing technology.
Rising to the challenge, advancing processes, and helping to bring the best products to the world using science, technology, and creative thinking.
We are process and product technologists committed to advancing pharmaceutical and other industries with science and imagination. Whether you measure success by e ciencies, improvement, or innovation, count on us to deliver results.
Providing sales, service and spare parts expertise across the globe for metal detection, X-ray and checkweighing anywhere along a production line, Heat and Control works closely with strategic partners to bring new technologies and solutions that meet the strictest of quality standards.
To view the entire line up of pharmaceutical solutions o ered please visit: www.heatandcontrol.com/solutions/ pharmaceutical
See
Ad
10 www.heatandcontrol.com
Vial labelling at 400 PPM with zero downtime
has introduced continuous labeling capa bilities for its 132M HC Wrap-around Labeler. The continuous operation is made possible by two new modules – EasySplicer and EasyCutter – that can be retro tted onto existing machines. The new add-ons allow label and backing paper reels to be changed or disposed of without production interruption. Con sidering that reels on high-speed labelers such as the HERMA 132M HC require replacement approximately every 10 minutes, the result is signi cantly improved output through downtime elimination. With the new EasySplicer and EasyCutter modules, label reels can be changed, and the backing paper reels disposed of, without the machine coming to a standstill.
The new add-ons allow label and backing paper reels to be changed or disposed of without production interruption. Considering that reels on high-speed labelers such as the HERMA 132M HC require replace ment approximately every 10 minutes, the result is signi cantly improved output through downtime elimination. With the new EasySplicer and EasyCutter modules, label reels can be changed, and the back ing paper reels disposed of, without the machine coming to a standstill.
The HERMA 211 HC Wrap-around Labeler is de signed to meet demand for a fully FDA-compliant
labeler in a highly compact footprint. The semi-au tomatic unit is particularly helpful in the transition from clinical trials to full production, as well as for the smaller-batch manufacturing typically found in biopharmaceuticals settings. The HERMA 211 HC is suitable for labeling a wide range of cylindrical products including syringes, tubes, glass vials and ampoules. Capable of applying approximately 30 labels per minute, the HERMA 211 HC can handle webs as wide as 80mm, and products ranging in diameter from 10-120mm.
The HERMA 500 Label Applicator is an IOT-en abled machine utilizing real-time metrics to optimize production e ciency and consistency, even in a multifactory setting. Capable of achiev ing labeling speeds up to 200m/min, the HERMA 500 can handle label widths between 80-320mm and roll diameters from 300–600mm. HERMA has enjoyed impressive sales of its signature HERMA 400 Label Applicator, selling more than 4,000 of the label applicators in 2018 alone – half of which were provided to original equipment manufactur ers (OEMs). The HERMA 500 is a next-generation label applicator that builds upon its predecessor’s best features and integrates Industry 4.0 connectivity. Exceptionally fast, the HERMA 500 has a maximum speed of 650ft/minute, and also o ers short make-ready time and industrial-grade Ethernet connection.
Peter Goff CEOHERMA US Inc. is a subsidiary of HERMA GmbH, a Germany-based provider of labeling machinery and self-adhesive labels and materials to the global packaging marketplace. HERMA GmbH’s comprehen sive range of products spans the labeling production process to include labeling machinery, a variety of adhesive materials, and nished self-adhesive products.
In the United States, HERMA is best known for its equipment. HERMA’s exible label ing machines are designed, developed, and built for integration into industrial processes, while its self-adhesive paper and lm compounds are manufactured with unsurpassed precision. The compa ny’s range of nished adhesive products includes labels for a broad set of industries, including healthcare and pharmaceuticals, automotive and electrical, chemicals, food, cosmetics and logistics. The company’s three divisions comprise nearly 1,000 personnel.
Established in 1961, IMA is world leader in the design and manufacture of automatic machines for the pro cessing and packaging of pharmaceuticals, cosmetics, food, tea and co ee.
Its position of leadership is the result of signi cant investments in R&D, regular and constructive dialogue with the end-users in its sectors and the Group’s ability to expand internationally, conquer ing new markets. Its history features a constant growth that has enabled the Group to close the year 2021 with consolidated revenue of about 1.7 billion euros. Exports accounted for about 87%. The Group, whose Chairman is Alberto Vacchi, has more than 6,200 employees, around 63% in Italy and 37% abroad, and is present in about 80 countries, sup ported by a sales network made up of 28 branches (Italy, France, Switzerland, the United Kingdom, Germany, Austria, Spain, Poland, Israel, Russia, the United States, India, China, Malaysia, Thailand and Brazil), representative o ces in central-eastern Europe and more than 50 agencies. IMA has 53 manufacturing plants in Italy, Germany, France, Switzerland, Spain, UK, USA, India, Malaysia, China and Argentine. The IMA Group owns more than 2,700 patents and patent applications in the world and has launched many new machine models over the last years. In 60 years in business, IMA has built up highly qualifying values such as experience, re liability, an extensive presence in the global market and a strong capacity to respond to the requests of end-users; which now enable it to propose innova tive solutions as well as high quality products.
At PACK EXPO Chicago, on our booth 2514, we will present our technological innovations for the Pharmaceutical and Food sectors, along with our Corporate projects IMA Zero and IMA Digital - aimed at highlighting the Group’s commitment towards sustainability and digitalisation.
During the show, discover more about our OPENLab: the network of technological laboratories and testing
areas, dedicated to the research on sustainable materials, technologies and production optimisation processes. The dedicated workstation on our booth will welcome visitors with their material’s samples to share their needs with our experts, learning how the IMA Group can support the businesses’ sustainable path.
Stop by the IMA Digital corner: discover how to generate more e ective and e cient internal processes, creating value by using empowered machines and services designed to deliver predictive and personalised customer experiences throughout the value chain.
Technologies on show for the pharmaceutical sector:
• IMA Safe C40 blister packaging machine
• IMA Safe Comadis C1075 automatic tube lling machine
• IMA Perfect Pack Stick 360 vertical intermittent motion stick packaging machine
• IMA BFB CPH2-RP4 integrated case packingpalletizing machine
Technologies on show for the food sector:
• IMA Tea&Herbs CT11 tea bag packaging machine
• IMA Petroncini TMR25 roaster machine
• IMA Sprea co SR6N capsule lling and sealing machine
• IMA Ilapak Carrera I-500 ow wrapping machine
• IMA Ilapak Vegatronic 6400HD vertical bagging machine
• IMA Ilapak WA 16-25 multi-head weigher machine
• IMA Ilapak Delta 6000 R inverted ow wrapping machine
• IMA Delta Systems Eagle ow wrapping machine and feeding system machine
• IMA Ilapak V3600 wicket bagger machine
• IMA Hassia F600 form ll and seal machine for sachets
• IMA Intecma cutting tool for multipacks
Discover more about the Group’s presence on show
https://ima.it/en/exhibition/packexpo-chicago
Over the years, IMA has seen continu ous and multidisciplinary growth in the design and production of a complex of machines and equipment. The Group is aware of the potential for innovation and service provided by the rich net work of subcontracting and component manufacturing that IMA has created in more than sixty years of activity.
Having correctly identi ed its potential and developed products and services for its end-users, IMA has achieved a leadership position in international markets, investing in those new tech nologies that will allow an improve ment in the quality of life on the planet in the future, thanks to the reduction of food waste and greater access by the population to increasingly e ective drugs, besides an increasing respect for the environment. Through the work of its people, IMA aims to create wealth and well-being, interacting with the so cial and natural environment, inspired by corporate social responsibility and sustainability.
HELP PEOPLE MAKE A MATERIAL DIFFERENCE
Jadex Inc. is a US-based manufacturing and material science company utilizing innovation and technology to develop sustainable products that serve the medical, industrial, and consumer markets. The range of products includes cus tom-designed plastic components, engineered nylon resins and mono laments, zinc products, and temperature-controlled products that solve both medical and consumer challenges. Jadex Inc. operates out of 19 facilities across the US, UK, and Puerto Rico and has approximately 1,800 employees.
Jadex is the parent company of Alltrista®, Lifoam®, LifeMade®, Shakespeare®, and Artazn®.
Inventors of the world’s first foam ice chest, Lifoam® has been a pioneer in thermal protec tive products for both industrial and consumer use for nearly 60 years. Now, Lifoam® works with companies who are looking to reduce the environmental footprint of their cold-chain
shipping operations by providing leading-edge sustainable solutions marketed under their Envirocooler™ product line. Envirocooler™ EVG utilizes additive-infused expanded polystyrene (EPS) that breaks down in a landfill in less than four years while maintaining the thermal and material properties of traditional EPS. Made from 100% biobased materials, Envirocooler™ with Bioffex™ technology allows for landfill degra dation in less than four months without leaving microplastics behind.
For nearly 50 years, Alltrista® has been striving to positively impact people’s lives with their products. Experts in the design and manufacture of rigid packaging and custom molded solutions, Alltrista® specializes in innovative, high-vol ume, precision manufacturing for the medical, pharmaceutical, nutraceutical, specialty, and high-end consumer markets. By incorporating new technologies, such as Compression Blow Forming (CBF), Alltrista® can o er reduced base material, lightweight packaging that minimizes impact on the environment while maximizing cost and e ciency.
As a material-science thought leader, Jadex™ is driven to provide essential product solutions that protect the health of our con sumers and the environment. We are focused on cutting-edge innovations that provide our customers with the most sustainable and responsible ways to deliver everyday necessi ties -- how, where, and when they’re needed.
The CATALYST for change; enabling cus tomers & consumers to use materials more sustainably.
MAKERS of essential materials and products that not only we cannot do without, but also that there is no future without.
Making sustainable solutions PRACTICAL for our customers and their consumers, today and tomorrow.
PHONE
Klockner Rd., Gordonsville, VA 22942
lms.com
lms.com
Focused on delivering its vision: The Sustainable Protection of Everyday Needs, kp is a global leader in rigid and exible packaging, and specialty lm solutions, serving the pharmaceutical, nutritional supplement, medical device, label lm, and durable application markets. With a broad and innovative portfolio of packaging and product lms and services, kp plays an integral role in the customer value chain by safeguarding product integrity, protecting brand reputation and improving sustainability. kp’s “Investing in Better” sustainability strategy solidi es its commitment to achieving ten clear targets for long-term improvement by increas ing recycling and recyclability of products, cutting carbon emissions and continuous improvement in employee engagement, safety, and diversity, equity and inclusion. kp has earned a gold rating from EcoVadis, the leading platform for environmental, social, and ethical performance ratings, putting kp in the top 3% of companies rated in the manufacturing of plastics products sector.
Founded in 1965 kp has 31 plants in 18 countries and employs over 5,900 people committed to serving customers worldwide in over 60 locations. Collaboration is integral with each opportunity. With a cooperative approach, kp’s expert techni cians visit you on-site to consult, troubleshoot, train, and provide all the necessary solutions to help optimize lm performance. You can also work together with a designated team at the kp i.center, designed speci cally, to serve the pharmaceuti cal, nutritional supplement and thermoforming industries. Equipped with state-of-the-art ma chinery and expert sta , kp is dedicated to help you improve current packaging and create new sustainable solutions.
In order to achieve our vision – sustainable protection of everyday needs – we must use our core values and core behaviors in everything that that we do, to create a culture. With our core culture in place we will use this to achieve our strategic imperatives, to add value to our customers, create partnerships and be an employer of choice. Generating these goals our customers will endorse our strategic value proposition in becoming global leaders in recycled content products and high-barrier protective packaging, with the best talent in the industry to achieve best-in-class productivity for our customers.
We are a leading supplier of primary and secondary packaging machines and lines to the pharmaceutical, biotech and cosmetic industries. Established in 1992, our 23,000-square-foot North American Headquar ters supports the USA, Puerto Rico, and Canada and is backed by 2,500 Marchesini sta members world wide. This modern facility is equipped and sta ed to meet the ever-increasing demands of today’s sophis ticated and quality-conscious packaging clients.
Our Group provides stand-alone machines and complete lines to handle the entire packaging pro cess of pharmaceuticals and cosmetics. The nished product is a combination of craftsmanship integrated with robotics and new technology.
Thanks to 30 years of experience in the sector, our team of experts comprehensively analyze and de ne the customer’s packaging requirements to translate technical challenges into e ective unique solutions. By combining the most-advanced tech nology with our knowledge and understanding of the pharmaceutical, cosmetic and consumer products industries, we have made solving packaging challenges our specialty.
All precision packaging machinery available through Marchesini Group USA has been manufac tured to meet the highest level of quality certi cation using established production benchmarks and testing procedures. We provide a wide range of ma chines and lines: our solutions are characterized by high quality, reliability, exibility and customization.
We provide solutions for liquid products in aseptic, in vials, ampoules, bottles or syringes, from washing, lling and capping solutions to end of line.
We provide solutions for tablets or pills in bottles or blisters. We have a wide range of counting, lling and thermoforming machines and lines as well. We also have a wide range of complete packaging machines for products in stickpack, sachets and medical devices too. Our solutions also include labeling and inspection machines, cartoners and case packers. We also produce a wide range of cosmetic packaging machinery in which clients are supported by our Beauty organization located at the company’s head quarters in Bologna.
At Marchesini Group, customer service is not a department. It is a commitment to our company philosophy and a realization that our steady growth can only be maintained through customer care. Whether our customer’s packaging solution requires a new installation or a modi cation or retro t, we are here to help optimize productivity and maximize uptime to get the best results and the highest output. Quality control and testing procedures are maintained at every stage of product development and manufacture.
Our customer care service, like our custom packaging solutions, is tailored to t our customer’s speci c requirements. The Group consolidated its remote after-sales support services, by developing X-CARE, a complete kit of services - which can also be used individually. These services include X-FAT (testing via streaming) and X-SAT (Final Line Acceptance carried out at the customer site thanks to the MIMO system of video cameras), which join the Live Assistance and Teleservice real time remote assistance services.
“It has been almost fty years since my father, Massimo, developed the rst cartoning machine branded Marchesini.
He started his business in his garage at home, in Pianoro, just outside Bologna, but soon expanded thanks to the abilities of a man who had worked for years as a skilled technician for a leading manufacturing company of automated machines.
Over time, we have grown without giving up the quality that characterizes the made in Italy production. Today we export 90% abroad, thanks to our employees, collaborators, suppliers and to the entire supply chain.
The packaging industry is indeed one in continuous evolution and to re main competitive we have to constantly deal with technological innovation. We are the right partner where cus tomers will nd the best cutting edge solutions for their speci c needs.”
Maurizio Marchesini PresidentOur Ad on Page 35 www.marchesini.com
METTLER TOLEDO | www.mt.com/pi
METTLER TOLEDO
Product Inspection Division
813-889-9500 www.mt.com/pi pi.marketing@mt.com
Key Pharmaceutical Contact: Robert Conrad Sales Director Pharma 813-889-9500
Robert.conrad@mt.com
PHONE
EMAIL WEBSITE www.mt.com/pi pi.marketing@mt.com 813.889.9500
METTLER TOLEDO is your single source for product inspection solutions o ering Safeline metal detectors and x-ray inspection systems, Hi-Speed inline check weighers, CI-Vision machine vision systems and PCE Track & Trace, serialization, and aggregation solutions. Our broad product inspection line ranges from very basic and economical systems to sophisticated, state-of-the-art systems with customized material handling solutions. Depending on your speci c requirements, our systems can ensure perfect product presentation, create codes, verify package and label integrity, ensure weight range compliance, provide tamper-evident sealing, detect physical contaminants and inspect contents inside the closed package.
METTLER TOLEDO PCE Systems are available to mark packs with individual serial numbers for full traceability of the production or packaging process and collect critical corresponding process data. All packaging formats from single cartons and bundles through to shipping cases and ready to ship pallets can be marked and veri ed.
METTLER TOLEDO CI-Vision inspection systems en sure that products consistently meet manufactur
ers’ quality standards and speci cations resulting in per fect product presentation every time.
METTLER TOLEDO Safeline metal detection systems prevent costly recalls by ensuring your products are free of ferrous, non-ferrous and stainless steel contaminants which can be introduced during processing.
METTLER TOLEDO Safeline x-ray inspection systems can detect ferrous, non-ferrous, stainless steel, glass and stone contaminants, detect mass and check for missing or damaged product inside closed packages.
METTLER TOLEDO Hi-Speed dynamic checkweigh ing systems ensure 100% quality control, minimize costly giveaway and give you total peace of mind.
We also o er connectivity and data management solutions and global service support for increased productivity and pro ts brand protection, and regulatory compliance.
Manufacturing Facilities: 1571 Northpointe Parkway Lutz, FL 33558
1571 Northpointe Parkway Lutz, FL 33558 USA www.mt.com/pi
We know moving your containers e ciently is key to packaging success. Our objective is simple: perfectly move your container for the application you need every single time. No two containers are the same, so your handling systems shouldn’t be either. We expertly move containers to make lling, capping, labeling, check weighing, metering, indexing, code dating, and just about everything else - easier.
Before arriving at your plant for instal lation, each custom designed has been tested and approved. So, you can have peace of mind throughout the whole process that our service, commitment, and support starts day one. Leading the industry in fast service and expert fol low up, when you work with Morrison, you’re working with a team of dedicat ed solution providers that are excited to enhance your plant productivity and container throughput.
Morrison Container Handling Solutions designs innovative packaging solutions for your unique container handling needs.
Innovation, in the pursuit of greater line e ciencies, has kept Morrison Container Handling Solutions the leading manufacturer of custom container handling equipment for over 50 years. Our services are all backed with design expertise and our legendary Support Built In®, our customer service philosophy, for any questions you have or technical support you need before, during, and after installation.
Our mission is to utilize our experience and design innovation to provide exible and responsive solu tions to the packaging industry. We strive to be the industry standard by providing an exceptional work environment that allows us to meet our customers’ needs and exceed their expectations with our promise of Support Built In®.
Utilizing a variety of our product lines to create custom integrated systems or single solutions that
solve container handling challenges, we approach every line with a unique opportunity to improve throughput and container handling.
As the leading manufacturer of timing screws in North America, we custom design not only screws but also drive units, change parts, down bottle reject integrations, can openers, and Auto Adjust Rails® . These solutions address a variety of line related productivity issues from the perspective of your container. For customers looking for robust solutions, we can provide turnkey systems that handle their containers for a variety of packaging applications complete with controls.
With PMMI Certi ed Trainers on sta , as well as a team of Field Service Engineers and Container Handling Experts, we back all our products with Support Built In®, so every step of the way, you’ll have a partner, from design, to install, to spare parts, and maintenance.
We look forward to being a partner in your productivity. With over 50 years of knowledge and experience, we are determined to analyze problems and provide solutions for your container handling needs – with Support Built In ®.
The thermoform packaging equipment with MULTIVAC Clean Design™ are solutions for sensitive pharmaceutical and biotech products, such as combination packs, pre-fill syringes, ampoules, vials and injectors. This GMP-compliant equipment concept separates the process area and equipment for maximum control and reliable packaging.
The thermoform packaging equipment with MULTIVAC Clean Design™ provide a high level of flexibility in terms of formats, packaging materials and process validation. The quick conversion of the equipment, for small and medium batch sizes, can be achieved by a simple format change.
The modular construction makes a high level of flexibility possible in the equipment design.
The innovative equipment concept allows the process area to be strictly separate from
the equipment. Transparent enclosures with large-area doors guard against direct access and environmental influences. At the same time, they provide perfect visibility and cleanability.
The thermoform packaging equipment with MULTIVAC Clean Design™ are equipped with the proven MULTIVAC IPC control to guarantee reliable and reproducible packaging outcomes. The aim of the design in all equipment with MULTIVAC Clean Design™ is maximum visibility and the avoidance of cross contamination.
Accordingly, particular emphasis was placed on equipment design with the following features:
• Strict separation between the product processing area and the equipment technology area
• Visibility of all process-related areas
• De ector plates in the inside of the equipment
• Widest possible avoidance of hidden voids
• Minimum gap dimensions
• Cable and pipe work routing in enclosed ducts
MULTIVAC is passionately focused on contributing to our customers’ success by delivering innovative and reliable solutions and superior support services.
MULTIVAC is the global leader in thermoforming packaging equipment. Our equipment can package a wide range of products e ciently and cost-e ectively, including medical and pharmaceutical products, food, industrial and consumer goods.
Our product range is the broadest in terms of size, performance and equipment: compact equipment for small volumes, high-speed equipment for large volumes and specialized machines along with packaging technologies such as printing and labeling, quality inspection and packaging line automation.
Our sales and technical service professionals are committed to helping our customers achieve their goals with the world’s most innovative and reliable packaging solutions.
us.multivac.com
HEALTHCARE
PHONE EMAIL
www.NJMPackaging.com info@NJMPackaging.com 1.800.811.6990
NJM Products Include:
Line Integration – NJM can integrate a tablet, powder or liquid packaging line. As part of this service, we provide equipment and then integrate turnkey systems at the customer’s plant, and o er in-plant training, documentation and validation support.
Unscramblers – NJM unscrambling equipment is compact and ideal for packagers. Our unscrambler is designed for round, rectangle, square or oval bottles.
Cappers & Retorquers – NJM cappers include inline belt, inline disc and rotary continuous models. Our compact design makes our cappers easy to incorporate into your packaging operation. We also supply retorquers of inline belt or inline disc type.
Cottoners – NJM cottoners are simple yet precise, with a guillotine tearing device as standard equip ment, and options such as missing cotton detection and wisp detection.
Labelers – NJM labelers are customized for labeling applications, and all are built in the same way: robust,
reliable and versatile, with electronic controls and up-to-date container handling features.
Liquid Filling & Closing – Aseptic liquid lling & closing systems for the pharmaceutical liquid dose industries are o ered by our partner, Dara Pharmaceutical. NJM is Dara’s exclusive sales partner in the USA and Canada.
Print & Apply – NJM print & apply labelers label cases, cartons, bags, pallets, drums and tires. They can be purchased individually, or as part of a turnkey system that includes case erecting, taping, and check weighing. RFID tagging is also available.
Tablet Counters – NJM o ers tablet counters from our partner, Cremer. Cremer counters feature thoughtful design, robust construction, quality and accuracy. Cremer tablet counters are also simple to take apart for cleaning, without tools.
Serialization – Our Track & Trace systems manage the collection and aggregation of serialized units of production and enable customers to e ectively satisfy FDA requirements.
NJM, part of ProMach Pharma Solutions, has been a trusted automated packaging sys tems manufacturer, integrator, and support resource for over a century. We o er a broad range of technologies and applications, specializing in the needs of pharmaceutical, nutraceutical/vitamin, and personal care product packagers. Complementing NJM’s manufacturing and integration expertise, we supply quality packaging line equip ment from other leading manufacturers.
The full range of NJM’s services – manufac turing, representation of NJM’s distributed brands, and integration – makes NJM a one-stop packaging solutions provider o ering expert knowledge and experience from the earliest stages of planning through implementation and production. NJM’s extensive portfolio includes unscramblers, tablet counters, bottle lling, cottoners, cappers, liquid aseptic processing/ lling equipment, labelers, printers and coders, end-of-line equipment, as well as custom solutions and software. With this portfolio and over 100 years of successful experience supporting our customers, NJM is a premier single source provider for fully integrated lines and serialization solutions.
Industries Served:
• Pharmaceutical Oral Solid Dose
• Pharmaceutical Liquid Dose
• Nutraceuticals & Vitamins
• Personal Care
College Rd, Battleboro, NC 27809 USA
PHONE
www.ossid.com
Ossid LLC, a ProMach brand, is committed to providing our customers with a superior line of medical packaging machines. Ossid is the leading manufacturer of high-speed packaging and labeling equipment, including tray overwrappers and sealers, weigh price labelers, ow wrappers, case scales, and horizontal form ll seal machines. Working with customers in the medical industry, Ossid provides sterile, safe, and e ective packag ing equipment solutions.
There’s nothing standard about medical devices. Ossid understands the unique and complicated requirements of the medical industry and strives to meet those needs with precision and safety at the forefront of the design. That’s why Ossid’s line of horizontal form ll and seal (HFFS) machines are exible to t your specialized needs, no mat ter the speci cations. If you can imagine it, our team of engineers, with a combined 75 years of experience, will work to design it.
Ossid’s medical HFFS machines are versatile; packaging both exible and rigid medical
package types and are built in accordance with UL 508A standards and AMI sanitary principles. These machines o er many features and bene ts including an auto web aligner, static eliminator, hinged upper tooling, servo actuated presses, and a robust framework and guarding package. These HFFS machines are ideal for packaging medical devices, dental kits, syringes, pharmaceuticals and other products.
In addition to HFFS machines, Ossid also is the US master distributor for the Reepack brand of ow wrappers. Flow wrappers can provide a packaging solution ideal for products such as medical mask, alcohol wipes, and more.
Our comprehensive customer service program, including service technicians, parts and training teams know how to help you keep your equip ment running at maximum efficiency. Ossid helps its packaging customers protect and grow the reputation and trust of their consumers. ProMach is performance, and the proof is in every package.
Our mission at Ossid, LLC is to provide our customers with cost-e ective packaging and labeling solutions. Ossid works to give our customers a complete exible packaging solution. Providing customers with excellent service nationwide, we can respond quickly to customers experiencing downtime needs and o er preventive maintenance programs to reduce overall downtime concerns. Our goal is to build long term relationships with our customers. Our committed sales, service and aftermarket parts teams work collectively to quickly and e ectively assist customers with their needs. As part of the ProMach Flexibles & Trays business line, Ossid helps our packaging customers protect and grow the reputation and trust of their consumers. ProMach o ers end to end capabilities nearly everywhere on the packaging line. ProMach can o er solutions for any customer project or application needs by providing best in class stand-alone equipment from industry leading product brands, partial line integrations, and complete large multi-brand turnkey packaging line integrations. ProMach is performance, and the proof is in every package.
Packworld USA o ers a complete line of precision-controlled heat-sealing equipment engineered with the advanced TOSS Technology – The Optimum Sealing System. Designed speci cally for today’s medical device, biotech, and pharmaceutical markets, Packworld USA machines produce validatable, repeatable, and consistent seals on all types of medical pouches and related polymeric products. Complementing the line of straight bar heat sealers, Packworld USA also o ers machines equipped with Vacuum & Purge and Seal & Cut capabilities for a variety of materials and pouch shapes.
What sets Packworld USA apart from all the rest is its use of the high response, state-of-art, TOSS Technology. All their sealers come equipped with advanced TOSS® PIREG® Heatseal Temperature Control. Unlike other sealing methods, only the PIREG® controller uses Variable Resistance Con trolled (VRC) technology to monitor the resistance on the heatseal band responding in milliseconds to adjust temperature precisely over the full length and width of the heat-sealing element accurately up to 500°C.
Packworld USA’s energy and engineering resources are dedicated to designing heat seal machines
meeting today’s stringent validation requirements of the FDA/GMP/NIST demanded by the medical, pharmaceutical, and bio tech industries. You can be sure they’ll meet your needs no matter the appli cation with validatable, repeatable, and consistent seals from one machine to another, from the rst pouch to the last.
Packworld USA continues to develop and incor porate additional advanced features. The touch screen interface provides graphical display of time/ temperature/pressure, password protection, recipe storage, data logging, multi-point calibration, and the ability to run in 21 CFR Part 11 compliance. Vacuum/purge, automatic knife cut, safety gates, electronic adjustable stand heights, and automatic bag stretching are all possibilities on Packworld USA precision heat sealers.
Along with its line of validatable pouch sealers, Packworld USA also specializes in the design and manufacturing of custom heat seal tooling for applications requiring contoured shaped heating elements. Packworld USA is so con dent in the quality of their machines their entire line is backed with a 30-Month Warranty.
From the start, Packworld USA’s sole mission has been to rede ne conven tional impulse heat sealing by employ ing the advanced, Variable Resistance Controlled (VRC), TOSS Technology in every machine it builds. Today our entire company is committed to the design and engineering of precision VRC heat sealing machines that are validatable, repeatable, and consistentcapable of producing “Perfect Seals… Every Time”.
Our entire team is driven by Pack world USA’s core values: quality, trust, honesty, integrity, respect for the individual, teamwork, partnerships, and excellence.
Added together, Packworld USA, with their complete line of benchtop, vacu um/purge, and seal/cut heat sealers has become one of the world’s most recog nized brands of high-quality heat-seal ing machines in today’s medical device, biotech, and pharmaceutical markets.
See Our Ad on Page 3 www.PackworldUSA.com
The Paxiom Group designs, builds and delivers state-of-the-art packaging machines around the world. Manufactured through our WeighPack, EndFlex and ValTara brands, and supported by Paxiom Service, our primary, secondary and endof-line solutions are engineered to fit almost any production requirement and budget.
We’re not a typical packaging machine company. We’re a single-source provider, meaning you get ONE point of contact for design, manufacturing, service and integration. And since we take full responsibility from line layout design, manufacturing and testing through to factory acceptance, installation and technical support, you get peace of mind that your investment is safe.
We’ve delivered thousands of machines to our clients since 1991, but we know that investing in
packaging automation is not just about the machine. It’s about the people you work with, the company behind the machine and their infrastructure, longevity and support. That’s why we aim to create long-lasting partnerships based on trust and a genuine desire to see you succeed.
From weighing, filling, bagging, flow wrapping and labeling to cartoning, case erecting, tray forming, case packing and robotic palletizing, we are confident we have the right automation solution for your business.
Let us design a system to increase your production rate and save you valuable time, labor and resources. Come meet us in person and see our solutions first-hand in Las Vegas or at one of our Xperience Centers near you.
We are much more than our machines.
We know that investing in packaging automation is not just about the machine, it’s about creating long-lasting partnerships based on trust. We believe in doing things right the rst time.
While we take pride in designing and building solutions to meet the demands of today, we are always planning for the needs of tomorrow. We are committed to developing the products that our clients will need as they continue to grow.
Our sta of over 300 professionals is dedicated to nding the right system for your business. We use our decades of expertise to carefully evaluate each customer’s distinct application and o er an ideal solution.
Honesty, transparency and respect are at the core of everything we do, and we back up these words with our actions. Our roots in this industry run deep and our reputation for reliability, openness and accountability brought us to where we are today.
Pharmaworks, A ProMach Product Brand | www.Pharmaworks.com
HEALTHCARE PACKAGING PAVILION WEST #17002, PACK EXPO NORTH #5650
2346 Success Dr., Odessa, FL 33556 USA
Pharmaworks, part of ProMach Pharma Solutions, is the premier supplier of blister packaging machinery for North America and has a worldwide installed base. Backed by the power of ProMach, Pharmaworks can turnkey any size blister project from our expanded production facility in Odessa, FL.
PHONE
WEBSITE www.Pharmaworks.com Sales@Pharmaworks.com 1.727.232.8200
Pharmaworks Products Include:
• NEW: TF1 Blister Machine – A simple and cost-e ective blister packaging solution. The TF1 blister machine is perfect for entry-level packagers where budget matters.
• TF1e Blister Machine – Features a compact footprint, quick changeover, and the latest in servo technology. The TF1e is perfect for small, medium, or clinical production.
• TF1pro Blister Machine – The latest in blister packaging technology, the TF1pro is built for today’s demanding cGMP and changeover requirements.
• TF2 Blister Machine – A medium output workhorse that is great for deep-draw medical devices and consumer products.
• TF3 Blister Machine – All the features expect ed in a high output machine.
• TF4 Blister Machine – With ultra-high output production, this machine is perfect for high volume projects.
• BlisterMate – A standout semi-automated blister machine that is great for R&D, low volume type production.
• Vision Systems – Scanware blister and print vision inspection systems.
• Ci6 Cartoner – The ultimate in pharma-grade intermittent cartoning.
• Feeding Systems – Pharmaworks provides a variety of feed systems featuring pick & place, ood feeding, dedicated, and custom robotic technology. All of our feed systems can be integrated with virtually any intermittent blister machine.
• Blister Machine and Cartoner Rebuilds –Not ready to invest in new blister packaging equipment? Pharmaworks is the clear leader with over 20 years of experience rebuilding and upgrading third-party equipment.
• Tooling & Change Parts – As the leading OEM, Pharmaworks is the go-to source for tooling any of our packaging machines as well as a variety of third-party equipment.
For 20 years, Pharmaworks has set ourselves apart from other OEMs by not only selling our line of blister machines and equipment, but by rebuilding and upgrading other OEM brand equipment. This uniquely positions Pharmaworks to be a full-service provider for our packaging customers.
Industries served:
• Pharmaceutical
Medical/ Medical Device
Animal Health
Nutraceutical & Vitamin
Personal Care
Consumer Products
NJM
WLS
ProMach Pharma Solutions is four brands, within one company, that collaborate to provide total pharma solutions. ProMach Pharma o ers more than a century of experience in designing, manufacturing, integrating, and supporting the most sophisticated and advanced pharmaceuti cal and medical packaging solutions in the marketplace. ProMach’s technologies can meet the most challenging requirements with minimal downtime, higher productiv ity, and true pharmaceutical packaging per formance, with compliance built right in.
Industries Served:
Pharmaceutical Oral Solid Dose
Pharmaceutical Liquid Aseptic Processing
Medical / Medical Device
Nutraceutical & Vitamin
Animal Health
Food
Complete Turnkey Line Integration
Beverage
Consumer Products
Personal Care
Cartoning, Case Packaging & Robotic Palletizing with
Integration
High-Speed Pressure Sensitive Labeling
ProSys is a premier manufacturer of manual, semiautomatic, and fully automatic equipment for lling Cartridges, Squeeze Tubes, Syringes and Rigid Containers. A global supplier of lling equip ment since 1985 with U.S. sales, manufacturing and customer service facilities located in Southwest Missouri.
Squeeze Tube Filling Machinesspeeds from 15 to 300 per minute.
Syringe Filling Machinesspeeds from 20 to 300 per minute.
Airless Pump Filling Machinesspeeds from 15 to 300 per minute.
Cartridge Filling Machinesspeeds from 10 to 250 per minute.
Building Quality, Integrity & Value In Our Team, With Our Customers, and in The Equipment We Design, Build & Deliver.
Tool-free Release System for Simple Changeovers
“Digital Readout Indicators” for Fast & Accurate Adjustments
On-line Service & Support
Recipe Storage
Creams,
to 3 Million
Romaco is a leading international supplier of pro cessing and packaging equipment specializing in engineering technologies for pharmaceutical products. The Group provides individual ma chines, lines and turnkey solutions for manufac turing, filling and packing powders, granulates, pellets, tablets, capsules, syringes, liquids and medical devices. The company also serves the food and chemical industries. Through its various technologies, Romaco is committed to sustain able production and to systematically reducing CO2 emissions.
The Romaco Group has its headquarters in Karlsruhe (Germany) and operates from five European business sites, with a broad portfolio comprised of seven established product brands. Siebler and Noack (Karlsruhe, Germany) supply blister, heat-sealing and rigid tube filling ma chines like the integrated Unity 300 blister pack aging line for the low to medium speed segment. Macofar (Bologna, Italy) markets technologies for filling sterile and non-sterile powders and liquids. Promatic (also Bologna, Italy) specializes in cartoners, track & trace systems and case packers. Kilian (Cologne, Germany) is a leading manu facturer of tablet presses such as the KTP 1X, designed as an all-in-one instrument for research and development activities. Innojet (Steinen,
Germany) is in the business of granulating and coating fine solid particles. Tecpharm (Barce lona, Spain) offers tablet coating technologies. Romaco also runs six laboratories in Germany, Italy, Spain and China. Through its laboratory expertise, the solution provider is the point of contact for customers worldwide, for example, to develop new products.
More than 850 highly skilled and committed Ro maco employees are dedicated to the develop ment of future product technologies and to the continuous implementation of internal improve ment processes. The Romaco Group’s multi-brand system solutions are sold worldwide through eight Sales & Service Centers and a dense net work of local agent organizations. Over 12,000 installations delivered by Romaco are currently in use in more than 180 different countries.
We enable our customers to produce more sustainably in order to meet legal requirements, be future-proof and ensure long-term success. In this e ort, we are guided by the principle that “avoidance is better than reduction is better than compensation” – meaning that the technologies provided by us help to prevent carbon dioxide emis sions, excessive material consumption and energy wastage or, if that is not possible, to reduce or o set them through suitable measures.
Supplying end-to-end solutions for the entire process chain – from granulation, tableting and coating to lling and packaging – is another important part of our commitment to being a sustain able partner for the pharmaceutical, chemical and food industries.
300 Corporate Drive, Suite 10, Blauvelt, NY 10913
PHONE
EMAIL WEBSITE www.schreiner-medipharm.com info@schreiner-medipharm.com 845.848.9000
Pack Expo Premiere: Sustainable Labeling Solutions
At Healthcare Packaging Expo Booth W-15047, Schreiner MediPharm will debut sustainability-minded versions of two popular solutions. One is a more sustainable Pharma-Tac label for infusion bottles, with an integrated hanger and removable documentation parts. The other is a more eco-friendly version of an Autoinjector-Label, featuring an anti-slip functionality. For both, Schreiner MediPharm utilized lm materials that are either recycled or produced from renewable raw materials.
Robust RFID-Label features an integrated RFID tag secured via the label’s special construction, avoiding damage to RFID chips due, for example, to mechanical impact during manufacturing or handling. This assures RFID chip perfor mance from production to nal use – especially on round containers with narrow radii.
Cap-Lock is a combination of cap adapter and label that rm ly seals pre lled syringes for reliable rst opening indication. The specially constructed plastic cap adapter is positioned atop a syringe’s primary closure to equalize any di erence in diameter between syringe body and closure. A label with integrated perforation for tamper evidence wraps around the syringe body and bottom part of the cap adapter.
Needle-Trap features a safety mechanism incorporated
into a self-adhesive syringe label – allowing needles to be safely secured after use. The cost-e cient solution suits existing dispensing systems and uses standard secondary packaging. Detachable label parts, gradu ation and counterfeit protection features also can be integrated.
Customized Seals for Tamper Protection
Schreiner MediPharm develops tailor-made closure seals optimally adapted to the respective application and packaging material. The sealing solutions provide reliable tamper evidence and irreversible rst opening indication. They can be combined with analog and digital authentica tion features for counterfeiting protection and enhanced product security.
Multi-functional Features for Autoinjector-Labels
Schreiner MediPharm o ers customizable features for its Autoinjector-Labels, including irreversible rst-opening indication with anti-recapping functionality. An integrated NFC chip o ers interactive user support and clear digital indication of label opening.
Smart Blister Enhances Medication Adherence Schreiner MediPharm has developed a smart blister pack to enhance medication adherence by clinical trial participants. When patients push tablets from the pack, real-time data such as medication type, extraction time and speci c cavity is stored and transmitted to a database via smartphone app or reader.
Schreiner MediPharm is a global leader in the development and manufacture of innovative specialty labels with valueadded bene ts that have set the standard in the highly demanding healthcare and pharmaceutical industries. Schreiner MediPharm’s expertise is based on 70 years of experience as a high quality supplier and reliable partner to the biggest names in the healthcare market. Schreiner MediPharm has its world headquarters in Oberschleissheim, near Munich, Germany, and U.S. headquarters in Blauvelt, New York, 30 miles from New York City.
Schreiner MediPharm develops and produces customer-speci c, intelligent labeling solutions with value-added functions that simplify the dispensing and administering of pharmaceuticals to enhance safety and reduce process costs. The company’s products include specialty peel-o labels; labels with integrated hangers; multi-page labels; brand protection and RFID solutions; and functional syringe labels.
Spee-Dee® Packaging Machinery, Inc. sup plies lling solutions and checkweighers for the food, pharmaceutical and nutra ceutical industries. Designed for speci c applications with simplicity in mind, SpeeDee systems achieve accurate, reliable lling and weighing, and are backed by a commitment to service and quality. Since 1981, companies around the world have trusted Spee-Dee llers and checkweighers to improve e ciency, productivity and pro tability.
Since 1981, Spee-Dee has earned a reputation for building reliable, accurate and durable dry filling systems. Customers trust Spee-Dee to improve efficiency, productivity and profitability. Our test lab is second-to-none and offers the ability to simulate your full production line at our facility.
Servo technology eliminates time-consuming manual maintenance. Ideal for dry fill appli cations such as powdered drink mixes, sports nutrition, nutraceuticals and more.
Fill rigid containers with ease and accuracy. Changeovers are a breeze with patented mag netic funnels and all tool-less change parts. An open design allows 360 degree access. Ideal applications include nutraceutical gummies and powders. Stream gummies without bridging, guaranteeing an accurate fill, every time, with our patented streaming system.
Electro-Magnetic Force Restoration (EMFR) weigh ing technology is ten times more accurate than strain gauge models. Tool-less belt changes, USB port for easy data collection and calibration by your technician - all in a small footprint. Sanitary, heavy-duty and inclined models available.
Quick-change cups are easily inserted in minutes, cleaning and maintenance are straightforward and user-friendly. Automatic or manual ne tuning available to adjust the ll weight for volume and weight accuracy. Designed to handle a variety of applications from simple hand- lls to interfacing with automatic equipment. Speeds up to 140 lls per minute.
Unique tare/gross weighing system that tares the jar weight and veri es the gross weights. Easily inte grates with a variety of multihead weighers. Reach speeds up to 40 jars per minute as you ll jars with a range of 1 to 28 grams of cannabis ower.
See Our Ad on Page 47 www.spee-dee.com
PHONE
Sterimed o ers a complete product range designed for single-use medical device packaging.
•The most extensive selections of polymer rein forced breathable top web materials and associat ed sealing technology on the market (Polybond®)
•Flexible formable and non-formable medical lms optimized for our top webs (Ethyform®, Ethy ex®)
•Inner protection solutions – secondary barrier systems inside the primary package (Ethywrap®)
•Full range of preformed materials for MDMs
We are actively accelerating our innovation e orts and developing sustainable packaging solutions that meet the healthcare industry’s regulatory requirements.
Pack Expo will be the rst time we introduce Polybond® CGP 85, an innovative solution for rigid packaging counterparts.
Polybond® CGP is mainly composed of materials from renewable resources and bio-sourced carbon. Cellulose contributes to an e cient sterilization process; synthetic
binders are used for optimal mechanical characteristics, bringing Polybond® CGP closer than ever to polyole n plastic material capabilities. It is the material of choice when you want to reduce your plastic footprint and contribute to reducing waste on planet Earth.
Medical Header Bags are used for packing bulky items – from gowns, and drape sets to custom procedure kits intended to be sterilized with EO and irradiation.
They are proposed by many suppliers, thanks to their relatively easy manufacturing lm & polyole n process.
Header Bags by STERIMED are di erent, the breathable window is made of Polybond® BGP, Sterimed’s in-house developed, cellulose-based substrate made of 66% bio-based carbon. Polybond® BGP is now replacing the 100% fossil carbon plastic polyole n of conventional header bags.
Sterimed’s success is based on broad expertise and experience. We support our customers step by step from the product design, and validation process, to education and knowledge sharing.
STERIMED Infection Control - World wide leader 100% focused on steriliza tion packaging & infection control.
Thanks to direct contact with end-users in the medical devices manufacturing industry and in hospitals across the globe, STERIMED provides customized solutions, products, and expertise. STERIMED provides a global product o ering utilizing industrial facilities across 3 continents through 10 man ufacturing sites and 22 distribution centers and sales o ces.
Our unique know-how and global industrial setup make us the partner of choice for companies looking at outsourcing industrial activities such as printing, slitting, sheeting, or ther mo-bonding materials.
Today 1 in 4 medical devices, in the world, is packaged using a Sterimed sterile barrier material.
Ad on Page 6 www.sterimed.us
www.stevanatogroup.com
Founded in 1949, Stevanato Group is a leading global provider of drug containment, drug deliv ery and diagnostic solutions to the pharmaceu tical, biotechnology and life sciences industries. Stevanato delivers an integrated, end-to-end portfolio of products, processes and services that address customer needs across the entire drug life cycle at each of the development, clinical and commercial stages. Stevanato’s core capabili ties in scienti c research and development, its commitment to technical innovation and its engineering excellence are central to its ability to o er value-added solutions to clients.
Thanks to its unique approach as a one-stopshop, Stevanato Group is able to o er an unprec edented set of integrated solutions to pharma and healthcare companies for a faster time to market and a reduced total cost of ownership.
As a global player in the industry, we blend our 70-year expertise and your needs to support you all the way from clinical trials to high volume production with our manufacturing solutions, comprising vision inspection machines, assembly
systems, packaging and end-of-line equipment. Stevanato Group’s wide range of capabilities provide an unparalleled advantage for building out end-to-end solutions, all from one source, for di erent inspection requirements and drug delivery device projects.
With an holistic problem-solving approach, we unlock the potential of your business, delivering high-yield solutions designed and manufactured to reduce downtimes and increase OEE.
We operate out of US o ces for local pre- and after-sales support; contact us today.
We cooperate deeply with our partners all over the world, providing our know-how, re sources and enthusiasm to turn every project into an achievement.
We are fully committed to be the best, objective-focused partner in the research and delivery of innovative solutions to support the success of our customers.
And we never stand still.
In fact, it’s our continual innovation and pioneering of new trends in pharmaceutical glass packaging that ensures we produce the world’s most advanced solutions year after year, enhancing the level of product integrity that can be guaranteed to patients and always seeking to exceed customer expectations.
Systech provides exible identi cation and traceability solutions to achieve compliance and detect supply chain threats. With thousands of implementations across the globe, we understand the full spectrum of challenges associated with regulatory compliance. Systech pioneered serialization, and we remain the trusted provider for the world’s leading pharmaceutical companies. Our comprehensive brand protection suite delivers the real-time, actionable product data and digital connectivity needed to help you meet the requirements and achieve compliance anywhere in the world.
Proven, full-stack platform
Systech delivers full-stack capabilities that can be deployed rapidly on any line, site or enterprise in any region. Our serialization and traceability software solutions are con gurable for unbeatable ease of implementation and speed to accommodate changing demands and meet regulatory compliance.
• Create unique product identi ers, automate pallet labeling and aggregate every packaging level for seamless traceability
• Provide site-level master data, serial number management, event reporting and o ine serialization packing operations
• Establish enterprise-level connectivity with comprehensive track-and-trace and compliance integrations
Secure, end-to-end supply chain tracking
Mixing and matching traceability tools from di erent vendors can be overwhelming and costly. Systech provides a single, simple solution for generating, managing and reporting product data in a diverse supply chain ecosystem. Our traceability solution makes it easy to create a compliant system of record for your products in changing regulatory environments.
• Get item transfer visibility and secure data exchange across your global supply chain
• Create, modify and order the processing of data based on your requirements
• Establish multiple levels of user restrictions and redundancy for everyone in your supply chain
Non-additive, digital connectivity Product authentication at the individual item level is the most e ective way to prevent counterfeiting and diversion. Systech’s non-additive e-Fingerprint® technology turns your existing package barcode into a unique digital identi er for an extra layer of protection. Each product becomes instantly connected to verify authenticity and gather actionable supply chain insight.
• Connect physical products to the digital supply chain for item-level authentication and traceability
• Detect product counterfeiting and diversion issues in real-time
• Deliver/receive item info using a smartphone
Systech delivers end-to-end traceability and identi cation solutions that empower our customers with actionable information across the supply chain to keep products authentic, safe and connected.
To be the platform that delivers transparency across the supply chain, providing businesses with the right information to know exactly what is happening at every stage.
PHONE
TekniPlex is a globally integrated company that pro vides innovative solutions through materials science and manufacturing technologies, employing over 7,000 personnel throughout its worldwide opera tions. One of two major company divisions, TekniPlex Healthcare provides medical device components and a multitude of materials science solutions that lead to a healthier, more sustainable world. Its solutions are utilized by prominent brands in the medical, pharma ceutical, and diagnostics sectors.
Comprehensive Solutions Platform: To deliver the most suitable solution for each application, TekniPlex Healthcare o ers a robust set of capa bilities including cleanroom production, polymer compounding, extrusion of both lms and tubing, coating, lamination, injection molding, printing and slitting, among others. With a broad materials set at its disposal, including PVC, PP, PE, PVdC, polyesters, TPEs & TPUs, Tyvek®, Aclar®, COC & COP, various papers and foils, TekniPlex pairs extensive process capabilities with materials science to meet the ever-evolving demands of the healthcare industry.
TekniPlex Healthcare manufactures precision med
ical tubing solutions for a wide range of single-use medical device applications, including intravenous (IV) administration, hemodialysis devices, insulin delivery, cardiopulmonary bypass equipment and wound drainage. Our medical-grade tubes are used worldwide in hospital, clinic and home settings.
TekniPlex Healthcare also supplies high-value components, materials, and solutions in its extensive line of PVC and TPE medical-grade compounds. Suitable for extrusion, injection and blow molding processes, these compounds are engineered to deliver ideal solutions for speci c applications.
TekniPlex Healthcare also supplies top and bottom sterilizable web packaging materials, exible lms, lidding foils, thermoformable blister barrier lms, pouch materials, and unit and multi-dose containers for medical devices, pharmaceuticals, animal health and other healthcare and personal care products.
© 2022 DuPont. All rights reserved. DuPont™, the DuPont Oval Logo, and all trademarks and service marks denoted with ™, or ® are owned by a liates of DuPont de Nemours, Inc. unless otherwise noted. Aclar® is a regis tered trademark of Honeywell International.
Improving patient health is the only mission that matters. With a global reach, TekniPlex Healthcare’s deep understanding of the overall pharma ceuticals and medical landscape helps it produce exemplary barrier properties for drugs and precision medical devices for interventional and therapeutic procedures. The division’s ever-evolv ing portfolio helps meet demands for high-leverage medicines and mis sion-critical healthcare products that bene t care providers and patients.
Partnership breeds success: TekniPlex Healthcare takes on its customers’ most complex challenges, aiming to deliver better patient outcomes by manufac turing both standard and customized products that allow for less invasive procedures, reduced pain, faster heal ing, and safer drug delivery.
See Our Ad on Page 21 www.tekni-plex.com
Gateway Drive, Elgin,
PHONE
Weiler Engineering, Inc., a leading provider of aseptic custom Blow/Fill/Seal liquid packaging equipment for pharmaceutical and healthcare applications, is committed to the highest standards of excellence and to further expanding products and systems to enhance patient care. Weiler’s proprietary ASEP-TECH® B/F/S packaging machines produce shatterproof, durable, aseptically-packaged products in one uninterrupted operation. This hands-free manufacturing process ensures that parenterals, ophthalmic solutions, and respiratory drugs reach the marketplace sterile, in the most cost-e ective manner possible - every time. The ASEP-TECH® System is the culmination of 60 years of innovation in machine design and sterile process development, producing the most advanced aseptic liquid packaging process machinery available today.
The Weiler design incorporates the three-step process of blow molding, aseptic lling, and hermetic sealing of liquid products in one sequential operation on a compact machine frame. Weiler’s patented electronically controlled ll system, automatic sterilization system with integral data collection, and lter integrity test system are provided as standard equipment for each machine con guration. Each
machine is also equipped with a HEPA air shower to ensure a Class 100 environment under dynamic conditions in the nozzle shroud area.
Weiler’s latest innovation is the NEW compact ASEPTECH® LAB+ Blow/Fill/Seal machine, which is ideal for Stability and Clinical batches for pharmaceutical products and/or small development batches using advanced aseptic technology. This revolutionary small footprint design focuses on ease of changeover and product range exibility.
The versatile ASEP-TECH® LAB+ machine features servo-driven motion controls and a modular platform that o ers options such as Single-Use Technology (SUT) or conventional Clean-in-Place (ClP) and Steam-in-Place (SIP) technologies, a new patent pending Grade A lling zone and Particulate Matter Removal (PMR) system.
ASEP-TECH® Blow/Fill/Seal machines are proudly manufactured in the USA, designed and built by Weiler Engineering, Inc. in a 162,500 ft², state-of-theart manufacturing plant. Weiler’s manufacturing facilities and corporate o ces are conveniently located near Chicago’s O’Hare International Airport.
FACTS:
• Recognized as an advanced aseptic technology by the USFDA
• 63 years serving global markets
• Experience gained from 25 years operating a captive pharmaceutical CMO
• Close operation with regulatory authorities – compliance is key!
• Quality + Operational Know-how + Integrity
• Focus on the science of the technology for maximum customer bene t
• Simplicity of design to maximize product exibility and minimize footprint
• Optimum service support throughout the markets we serve = high customer satisfaction!
See
Ad
www.weilerengineering.com
N. Church Street, Moorestown, NJ 08057 USA
PHONE EMAIL WEBSITE www.WeilerLS.com WLS@ProMachBuilt.com
Rotary Labelers – Pressure-sensitive labelers for labeling a variety of product shapes vertically.
Vertical In-line Labelers – Pressure-sensitive labelers for labeling a variety of cylindrical products vertically.
Horizontal In-line Labelers – Pressure-sensitive labelers for labeling a variety of cylindrical products horizontally.
Label Heads – Pressure sensitive label heads with label print and inspection options including serialized codes and RFID tags.
New! Label Presence Inspection – WLS’s new VialView label presence inspection stand-alone station is ideal for verifying label presence prior to nal packaging.
HEALTHCARE
#17002,
Label Coders – For stand-alone or integrated high-speed coding of labels, including serialized codes.
Label Printers – Autonomy® drop-on-demand digital ink label printers with UV curing and full label inspection.
Vial Coders – For code printing on vials or bottles using ink jets or lasers.
Documentation & Certi cations – DDS, FAT, SAT, IQ/OQ and Trace Matrix documents as well as UL, Seismic and CE certi cations.
Field Service – US and European eld service team also o ering equipment training courses and maintenance contracts.
ProMach Pharma now o ers sales and service capabilities through our European o ce.
About WLS
WLS, part of ProMach Pharma Solutions, is an industry-leading designer and manufacturer of high-speed rotary and in-line labeling machines and serialization, coding and label printing solutions for the pharmaceutical and medical packaging markets as well as the food, beverage, personal care, and consumer markets. With over three decades of experience, our mission is to improve our customer’s labeling capabilities and ensure that our labelers provide them with the highest possible OEE.
Industries Served:
Pharmaceutical
Medical/Medical Device
Nutraceutical & Vitamin
Food
Beverage
Consumer Products
Learn more about WLS at WeilerLS.com
Our Ad on Page 15 www.WeilerLS.com
Antares Vision Group 7, 64 www.antaresvision.com
Columbia Machine, Inc. 6, 65 www.loadtransfer.com
Delta ModTech 18, 66 www.deltamodtech.com
Dispense Works Inc. 30. 67 www.dispenseworks.com
ESS Technologies, Inc. 43, 68 www.esstechnologies.com
Formost Fuji Corp. 24, 69 www.formostfuji.com
G&K-Vijuk Intern. Corp. 56, 70 www.guk-vijuk.com
Heat and Control, Inc. 10, 71 www.heatandcontrol.com
HERMA US Inc. 33, 72 www.herma.us
IMA - S.p.A. 41, 73 www.ima.it
Jadex Inside Front Cover, 74 www.jadexinc.com
Klockner Pentaplast 19, 75 www.kpfilms.com
Marchesini Group USA 35, 76 www.marchesini.com
METTLER TOLEDO 31, 77 www.mt.com/pi
Morrison Container Handling Solutions 62, 78 www.morrison-chs.com
MULTIVAC Inc. 39, 79 us.multivac.com
NJM, A ProMach Product Brand 11, 80 www.NJMPackaging.com
OSSID 48, 81 www.ossid.com
PACK EXPO Emerging Brands Summit Insider Back Cover www.EmergingBrandsSummit.com
PACK EXPO International 57 www.PackExpoInternational.com
Packworld USA 3, 82 www.PackworldUSA.com
Paxiom Group 61, 83 www.paxiom.com
Pharmaworks, A ProMach Product Brand 12-13, 84 www.pharmaworks.com
ProMach Pharma Solutions, A division of ProMach 9, 85 www.ProMachPharma.com
ProSys Servo Filling Systems 25, 86 www.prosysfill.com
Romaco Group 36, 87 www.Romaco.com
Schreiner MediPharm, A business unit of Schreiner Group LP Back Cover, 88 www.schreiner-medipharm.com
Spee-Dee Packaging Machinery 47, 89 www.spee-dee.com
Sterimed Holding 6, 90 www.sterimed.us
Stevanato Group 52-53, 91 www.stevanatogroup.com
Systech, by Markem-Imaje 5, 92 www.systechone.com
TekniPlex 21, 93 www.tekni-plex.com
Weiler Engineering 49, 94 www.weilerengineering.com
WLS, A ProMach Product Brand 15, 95 www.WeilerLS.com
a workshop tailored to
company?
most reliable and
in North America
from the buyer’s perspective.
directory of packaging and processing technology
include:
Plain-language lters so it’s easy to nd what you need.
Type-ahead keyword search.
by machine
desired package type.
c lters that are
to each product category.
You’re looking for...
you looking for packaging or processing solutions and you don’t know where to start?
With decades of combined CPG experience working for companies like PepsiCo, Dannon, General Mills, Del Monte, Nestle, and Kraft, our advisors are available for one-on-one private consultations to provide personalized advice for YOUR brand’s specific need.
Scott has worked at both Nestle and Del Monte, where he had a 20-year career, most recently VP R&D, Quality & Operations Services.
Mark had a 35-year career in packaging at Abbott Labs, where his last position was to lead global engineering
Eric Greenberg is an attorney with a practice in food and drug law, packaging law and commercial litigation, and is adjunct faculty at Chicago-Kent College of Law and Cal Poly, and is legal columnist for Packaging World.
Jamie has worked at General Mills, Campbell Soup, Del Monte Foods, and JUST, and is now CEO of Catapult Commercialization Services.
Tony brings a 40 year-career working with Frito-Lay, Ocean Spray Cranberries, Diageo, Dannon, and PepsiCo
Diane has had a long career in CPG, the bulk of it at Kraft Foods, where she held several Director and VP roles, overseeing at various times engineering, operations, global supply chain, and global safety and sustainability