
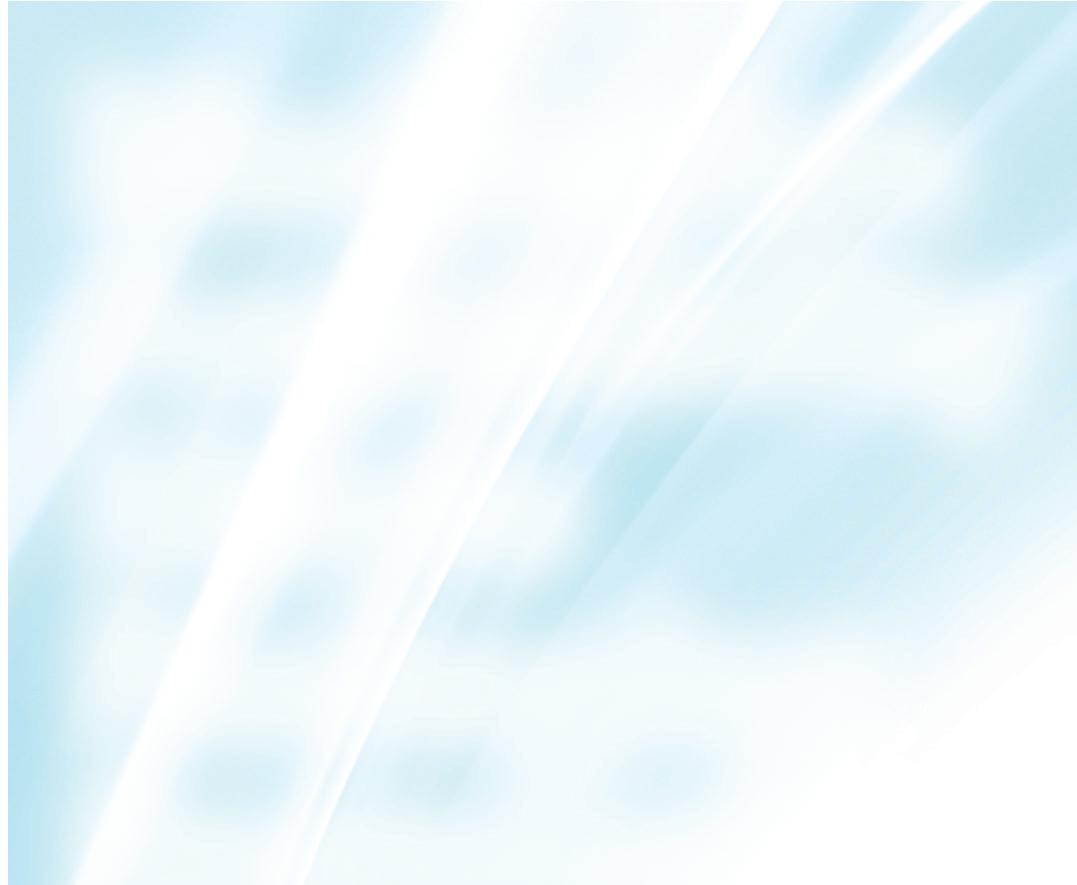
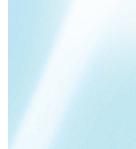

The 2024 IoPP AmeriStar winners focus in on decreasing plastic waste, enhancing usability, and reducing materials | 12 The Role of AI in Human Factors | 22
PHARMACEUTICAL PACKAGING
Community Poll: What ranks as your biggest sustainability hurdle?
12 Medication Accessibility Meets Packaging Sustainability
SnapSlide Rx achieves both medication accessibility and reduced use of plastics, while earning 2024 IoPP Ameristar Honors.
PACKAGE DESIGN
14 Achievements in Healthcare Packaging
The Institute of Packaging Professionals (IoPP) unveils its 2024 AmeriStar Award recipients.
REGULATORY
16 The Impact of the Chevron Deference in Pharmaceutical Packaging
The Chevron Deference has recently been overturned, resulting in potentially less bureaucratic control over regulated industries, such as the FDA.
WORKFORCE
18 Prominent People in Packaging: Ron Yakubison
Yakubison discusses his role at Merck & Co., Inc., Rahway, NJ, USA (hereinafter “MSD”), the evolution of pharmaceutical packaging, and the unique position of integrating packaging materials and machinery expertise.
MATERIAL DEVELOPMENTS
20 Bamboo Toothbrush Launches with Recyclable Packaging
Colgate-Palmolive has relaunched its bamboo toothbrush with compostable handle packaged in a recyclable paper-based tub and lid pack.
TECHNOLOGY
22 Q&A: The Role of AI in Human Factors
Louisa Harvey shares how embracing AI in the right way might shape how devices and packaging can be better targeted to patients.
MACHINERY/PACKAGING/FILLING
26 Nonprofit Civica Installs New High-Value Filling Lines for Essential Medicines
A new isolator-integrated vial filling line and nest filling line allow the company to produce many different forms of injectables to pivot based on need.
TRANSPORT PACKAGING
32 Barrier May Mitigate Dry Ice Supercooling Effects in Transit
How might a vented CO2 barrier prevent supercooling in dry ice packouts?
PACK EXPO PREVIEW
38 PACK EXPO International Sets to Amaze
Witness an unparallelled range of solutions and engage with industry thought leaders at the largest international packaging and processing show of 2024.
www.healthcarepackaging.com
EDITOR-IN-CHIEF Elisabeth Cuneo
ecuneo@pmmimediagroup.com
CONTRIBUTING EDITOR Joseph Derr
ART DIRECTOR Norman Smith
CREATIVE DIRECTOR David Bacho
VICE PRESIDENT, SALES John Schrei jschrei@pmmimediagroup.com
SENIOR MANAGER, PRINT OPERATIONS Lara Krieger lkrieger@pmmimediagroup.com
FINANCIAL SERVICES MANAGER Janet Fabiano jfabiano@pmmimediagroup.com
PMMI Media Group
PRESIDENT David Newcorn
VICE PRESIDENT, DIGITAL Elizabeth Kachoris
SENIOR DIRECTOR, MEDIA OPERATIONS Kelly Greeby
DIRECTOR, DIGITAL MEDIA Jen Krepelka
DIRECTOR OF CONTENT Kim Overstreet
SENIOR DIRECTOR, EVENTS Trey Smith
FOUNDING PARTNER AND EXECUTIVE VICE PRESIDENT, INDUSTRY OUTREACH, PMMI Joseph Angel
PMMI Media Group 401 N. Michigan Ave., Suite 1700 Chicago, IL 60611 www.pmmimediagroup.com
PMMI The Association for Packaging and Processing Technologies 12930 Worldgate Dr., Suite 200, Herndon VA, 20170 Phone: 571.612.3200 | Fax: 703.243.8556 | www.pmmi.org
Healthcare Packaging® (ISSN # 21543666) is a registered trademark of PMMI, The Association for Packaging and Processing Technologies. Healthcare Packaging® is published twice annually by PMMI with its publishing office, PMMI Media Group, located at 401 N. Michigan Ave, Suite 1700, Chicago, IL 60611; 312.222.1010; Fax: 312.222.1310. Copyright 2024 by PMMI. All rights reserved. Materials in this publication must not be reproduced in any form without written permission of the publisher. Applications for a free subscription may be made online at www. healthcarepackaging.com/subscribe. Paid subscription rates per year are $55 in the U.S., $80 Canada and Mexico by surface mail; $130 Europe, $200 in all other areas. Single copy price in U.S. is $20. Free digital edition available to qualified individuals outside the United States. POSTMASTER; Send address changes to Healthcare Packaging®, 401 N. Michigan Avenue, Suite 1700, Chicago, IL 60611-3789. PRINTED IN USA by Quad. Volume 19, Number 2 The opinions expressed in articles are those of the authors and not necessarily those of PMMI. Comments, questions and letters to the editor are welcome and can be sent to: editors@healthcarepackaging. com. Mailing List: We make a portion of our mailing list available to reputable firms. If you would prefer that we don’t include your name, please write us at the Chicago, IL address.
Questions about your subscription or wish to renew? Contact circulation@pmmimediagroup.com
PLEASE RECYCLE THIS MAGAZINE Remove inserts or samples before recycling.
on G&K–Vijuk MV outsert systems!
• Start small, folding up to 90 panels…or go big, folding up to 350 panels…or a size in between.
• Fold larger-size outserts or medication guides by specifying or adding the new GUK FA73 Folder— folding sheets up to 730 mm wide.
on the G&K–Vijuk Coding and Serializing Station!
• Print a unique code on each outsert for traceability with print and dimensional verification.
• Log all verification results, good and bad, for an accurate record of existing numbers for tracking and compliance.
• In-line or off-line.
My name is Liz Cuneo, and I am the new Editor-in-Chief here at Healthcare Packaging.
For those of you who understood the Austin Powers reference, I hope that got a chuckle. For others, the title may seem confusing, but either way…
My name is Liz Cuneo, and I am the new Editor-in-Chief here at Healthcare Packaging. You’ve likely seen my name hit your inbox a few times by now, but alas, here I am in print, in the magazine you’re holding (or scrolling through online). This is my inaugural issue, and as such, I have taken extreme care to bring you some of the best articles, news headlines, and new products that will hopefully get you interested and inspired by the latest happenings in the pharmaceuticals, biologics, medical devices, and nutraceuticals packaging realm. Don’t miss coverage of the 2024 Ameristar winners, including our cover story on one of the winners: SnapSlide Rx. Plus, read how AI can help create better medical device
packaging and how to prevent dry ice supercooling. You’ll also read about the upcoming PACK EXPO International and some of the machinery and material developments on display there. For those who will be attending, I look forward to meeting as many of you as I can (look for me on the show floor or at our community forum event- more details to come). For those who won’t be attending, visit our website for coverage of the show before, during, and after the event. Got a story idea, bone to pick, or just want to say hello? Drop me a line.
Liz Cuneo is the Editor in Chief of Healthcare Packaging. She may be reached at ecuneo@pmmimediagroup.com.
CONNECT with me on LinkedIn, scan the QR code.
“WESTERN HEALTHCARE is currently far too reliant on single-use disposable plastic medical devices. It’s one of the main reasons why the sector consumes around 15 million tonnes of plastic globally every year.”
Dr Ameera Patel, CEO of TidalSense, in an article in Medical Plastics News, “Ending the Trade-Off Between Patient Safety and Sustainability.”
“ “IF WE ONLY THINK about ‘how can I turn a glass bottle back into a glass bottle?’ That’s not the way nature works, leaves don’t turn back into leaves… when a leaf falls in the autumn, maybe 5% of those molecules might end up back as leaves the next year, but it’s really a system of flows.
”Dr. Dayna Baumeister, co-founder of Biomimicry 3.8, a consultancy that helps companies innovate packaging and products with cues from nature.
THOSE IN THE PLASTICS INDUSTRY and healthcare sector understand the crucial role of plastics in saving lives. Plastics has been a trusted material for many years, relied upon by pharmaceutical companies, medical equipment manufacturers, laboratories and research facilities, and healthcare professionals.
Dr. Perc Pineda, The Plastics Industry Association Chief Economist.
72%
of consumers said they would switch brands if a product or package was Ease of Use Certified, according to a past Nielsen Ease of Use Survey.
77%
of consumers believe that product information is important when making a purchase and 79% of shoppers are more likely to purchase products with a scannable barcode/QR code, according to a 2024 GS1 US consumer survey.
96%
of C-Suite leaders said they had high expectations for AI increasing productivity, yet 77% of employees said those same tools had added to their workload, says a new study from The Upwork Research Institute.
80%
of healthcare providers and 84% of supplier organizations expect supply chain challenges to worsen or remain the same over the next year, according to Premier’s 2024 Supply Chain Resiliency survey.
Visit us at Booth #S-2438
for Free Code : 14U32
PMI is proud to present our new intermittent cartoner, VARIO-SIF II.
Engineered with cutting-edge all-servo technology, the VARIO-SIF II delivers extremely safe and reliable packaging of a wide variety of products across various industries. Over 500 units have been across various industries. Over 500 units have been installed in numerous fields such as food, pharmaceutical, health nstalled in numerous fields such as food, health and wellness foods, and chemical products. The VARIO-SIF II is a reliable, refined low-maintenance cartoner. Additionally, the VARIO-SIF not only reduces change over time, but also increases reproducibility.
According to a study from Custom Market Insights, the demand of global sterile medical packaging market size & share was valued at approximately $25.2 billion in 2023 and is expected to reach $27.3 billion in 2024. It is then expected to reach a value of around $63.6 billion by 2033, at a compound annual growth rate (CAGR) of about 9.4% during the forecast period.
• A notable global trend in sterile medical packaging is the growing emphasis on ecology and environmental responsibility. As concerns about plastic contamination and environmental degradation develop, there is a greater need for sterile medical packaging solutions that decrease waste, lower carbon footprints, and employ eco-friendly materials.
• By material, the plastic segment held the highest market share in 2023 and is expected to keep its dominance during the forecast period 2024-2033.
• By end use, the pharmaceutical segment held the highest market share in 2023 and is expected to keep its dominance during the forecast period 2024-2033.
PACK EXPO International (Nov 3-6) Chicago, IL
Pharmapack Europe (Jan 22-23) Paris, France
MD&M West (Feb 6-8) Anaheim, CA
2025 ISTA Forum, TransPack, TempPack (March 24-26) Orlando, FL
PDA Week 2025 (April 6-11) Palm Springs, CA
The PACK OUT (May 13-15) Coronado, CA
The Arthritis Foundation announced its partnership with Target in the development of Ease of Use® Design Guides for product and packaging design, which the companies claim is the first of its kind. These Ease of Use Design Guides serve as resources for engineers and designers in the requirements definition and design development stage for easy-to-use products and packaging developed in the United States. The guidelines are based on the Arthritis Foundation’s Ease of Use Certified® program, which recognizes products and packaging that have been independently tested, approved, and certified as easy to use for people who live with mobility limitations.
CORDENPHARMA is investing $978.7 million over the next three years to grow its peptide technology platform. Plans include two major expansions occurring in parallel in the U.S. and Europe, including both existing facilities and new constructions designed and built according to the pharmaceutical industry’s most stringent quality and technical standards for short and long peptide manufacturing, including Biologics License Applications (BLA) requirements. This is the result of rapidly increasing demand in the Diabetes and Obesity Glucagon-like Peptide 1 (GLP-1) agonist medications market, and comes off the back of multiple, long-term, multiyear contracts.
TMR (Transparency Market Research) reports that the desiccant market is projected to grow to $552.6 million in 2023. It is projected to grow at a 5.7% CAGR from 2024 to 2034, and by 2034, the market is expected to hit $1.0 billion. The rise of e-commerce and the need for effective moisture control in packaging during shipping and storage is boosting the market. The development and commercialization of bio-based desiccants offer new opportunities, aligning with the global shift toward green and sustainable products. Innovations in packaging solutions that incorporate desiccants, such as active packaging, can open new avenues for growth. The increasing application of desiccants in healthcare products beyond pharmaceuticals, such as in medical devices and diagnostics, provides additional growth potential.
Several major bandage brands are adding insult to injury by including per- and polyfluoroalkyl substances (PFAS, also known as forever chemicals) in their products. That’s according to a report from The Guardian, citing new research conducted by parent buyer’s guide site Mamavation’s EPA-certified laboratory. Mamavation tested 40 types of bandages from major brands including Band-Aid, CVS Health, Walmart’s Equate brand, and more, and found that 26 contained over 10 ppm of organic fluorine, a marker for PFAS. The chemicals are linked to several negative health effects including decreased fertility, developmental effects in children, and increased risk of some cancers.
A rise in melatonin overdoses among children has prompted calls from the Council for Responsible Nutrition (CRN) to follow new child-safe packaging guidelines, according to a report from ABC News. In March, the CDC reported there were about 11,000 emergency room visits involving children five and under who took melatonin unsupervised between 2019 and 2022. The CDC previously announced that cases of children overdosing on melatonin had increased by 530% from 2012 to 2021, ABC News reports. In response, the CRN announced a new set of voluntary packaging and labeling guidelines for both melatonin and gummy form melatonin supplements, as detailed on the association’s site.
Heritage Store, part of Nutraceutical Corp., issued a recall earlier this year of its Hydrogen Peroxide Mouthwash in Wintermint and Eucalyptus Mint flavors due to a lack of child-resistant packaging, as reported by CNN and others. The Consumer Product Safety Commission (CPSC) website states that the mouthwash contains over 3 grams of ethanol, requiring child-resistant packaging under the Poison Prevention Packaging Act (PPPA). The CPSC warns that the product, packaged in 16-oz bottles, poses a poisoning risk if swallowed by young children. The packaging features brown bottles with white lids and pink and white labels featuring the Heritage Store logo and flavor information.
The diabetes drug Ozempic has been a hit for manufacturer Novo Nordisk. But its meteoric rise in popularity brings with it concerns for the patent holder due to emerging reports of patient harm and the widespread availability of counterfeit versions worldwide. That’s why the Denmark-based drugmaker is taking a proactive approach, testing suspect products and collaborating with authorities to try to uncover the origin of the fake versions. A recent Reuters article discussed how Novo Nordisk’s CEO, Lars Fruergaard Jorgensen, is addressing the situation through collaborative efforts with the U.S. Food and Drug Administration (FDA) and other authorities in numerous countries.
San Francisco-based Teal Health received breakthrough designation to accelerate review of its at-home cervical cancer screening device. “The Teal Wand is a proprietary device designed to enable people to easily, comfortably, and confidently collect their own vaginal sample for cervical cancer screening from their home or health clinic, without the need for an invasive exam,” the company reports. Users collect their sample at home and then mail it to a laboratory for testing on an FDA-approved diagnostic test for primary screening of high-risk HPV (human papillomavirus). Teal Health provides a patient portal for users to view test results, access health providers, and (when appropriate) receive assistance in securing follow-up care or procedures.
For nearly 40 years...
Providing a range of today’s finest packaging and processing equipment.
• Capsule fillers
• Capsule check-weighers
• Capsule banding machines
• Pouch fillers
• Cartoners
• Tray formers
• Case packers
• Palletizers
• Packaging line integration
• Metal detectors for capsules
• Bottle unscramblers
• Bottle fillers/cappers
- Tablets/capsules & liquids
• Bottle labelers
• Bottles: Carton coding, verification, serialization
• Bin blending equipment
• Material handling equipment
• Blister machines
• Thermoformers
• Washers
• Sterilizers
• Depyrogenation
ISTA Pharma Committee and Thermal Modeling/ Simulation Working Group recently authored a white paper that delves into the differences between thermal modeling and thermal simulation and discusses how these tools can be used to assess the performance of thermal shipping systems. After a comprehensive overview of current tools and their applications within the temperature-controlled supply chain, the white paper highlights the potential benefits of using thermal modeling/simulation to improve efficiency, reduce risk, and enhance product and patient safety. The white paper concludes that while thermal modeling/simulation can be a valuable tool for optimizing the storage and distribution of temperature-sensitive products, it is important to carefully assess the risks and regulations associated with its use. “Possible uses for thermal simulation within our sector are limitless,” said Richard Peck of RP Pharma Consulting and a co-lead of the white paper during an ISTA Connect Meeting in August promoting the release. Download this and other white
UK-BASED Tower Cold Chain has introduced a new live tracking and monitoring feature for its parcelsized KTEvolution containers in 26- and 57-liter sizes. Powered by ELPRO, this solution offers real-time monitoring of temperature, shock, tilt, altitude, and location. The ELPRO logger alerts users to temperature deviations, enabling immediate intervention and reducing costs. The live tracking feature provides end-to-end visibility for temperature-sensitive pharmaceutical shipments, crucial for high-value or direct-to-patient deliveries. Customers can now optimize cold chain processes, mitigate risks, and enhance quality assurance and compliance with real-time IoT data. Tower’s latest offering follows other value-added services launched earlier in 2024, including the Tower Control Center, an online portal that enables customers to access comprehensive shipment data, documents and the ability to utilize a journey simulation tool, aiding in efficient planning and risk mitigation.
Ultra-lightweight hybrid design for easy and efficient cleaning of hard to reach areas.
SnapSlide Rx achieves both medication accessibility and reduced use of plastics, while earning 2024 IoPP Ameristar Honors.
By Liz Cuneo, Editor-in-Chief
SnapSlide® Rx from SnapSlide LLC launched this year out of the company’s headquarters in Scranton, PA. SnapSlide Rx is a no-torque child-resistant cap with a patented sliding mechanism that enables single-handed operation on prescription pill bottles. This inclusive design benefits individuals with limited mobility or dexterity, enhancing medication access and safety. The state-of-the-art closure mechanism integrates seamlessly into existing pharmaceutical packaging, meeting stringent safety standards. It’s these achievements that have netted the company a 2024 IoPP AmeriStar Award.
The new medication package is the brainchild of Rocky Batzel, Inventor & CEO of SnapSlide. While he was attending medical school, the young entrepreneur sought to find a solution
to a family problem. As Batzel explains, his mother pointed out the difficulty his grandmother had trying to open her pill bottles herself. This led him to research the traditional pill bottle package, and child-resistant closures, which he realized hadn’t changed much in over half a century.
He also realized that people with limited dexterity, such as those with arthritis, struggle with these closures as well. The idea to make SnapSlide Rx one-hand operable came to him when he saw an amputee struggling to open a wine bottle. Batzel knew that making the closure one-hand operable would help the millions of people who struggle to independently open their own medication bottles. He also wanted the cap to remain on the bottle during opening, and while being easy to open, would also be child resistant. These goals are what led to the development of a sliding mechanism for the cap.
“The primary goal was to improve access to medication for those with limited dexterity, such as individuals with one arm or suffering from arthritis,” says Batzel.
Whether it is people with a broken arm, suffering from a stroke, a spinal cord injury, or amputees, SnapSlide helps people be more independent by allowing for single-handed operation.
If improving medication accessibility was the primary goal of SnapSlide Rx, sustainability and simplicity were the next goals. Batzel says he sought out to create a scalable solution with a simple design and reduced plastic use.
“By removing the need for threads, we’ve reduced the plastic used in both the cap and bottle. This results in significant plastic
SnapSlide’s design reduces the plastic used in both the cap and bottle—about 25% per unit.
savings—about 25% per unit. Given the industry’s scale, this translates to millions of pounds of plastic saved annually,” says Batzel.
Additionally, the reduced plastic usage improves shipping efficiency, saving on cardboard boxes and truckloads.
The manufacturing process is similar to traditional methods, involving injection molding for both the cap and the bottle. The cap and slider then come together with some automation equipment. Then, the bottles and caps ship to pharmacies where the same filling and labeling methods apply.
“The simplicity of SnapSlide allows it to be scalable and cost-effective, making it a viable solution for the industry,” says Chason Sordoni, COO of the company.
An invention is never without its trials, or resistance, as Sordoni and Batzel describe how pharmacies and over-the-counter (OTC) companies are often set in their ways, making them hesitant to adopt new technologies.
“One of the significant challenges has been overcoming resistance to change within the industry,” says Sordoni.
But one thing that may help spur change is the overwhelmingly positive feedback from consumers and pharmacists alike.
“I have received heartfelt thanks from individuals with disabilities who can now open their medication bottles independently,” says Sordoni.
He says that pharmacists have also expressed appreciation, noting that it makes their jobs easier and helps them better serve their communities. During a recent conversation, a pharmacist mentioned that he often has to send delivery
drivers back to customers’ homes to help them open bottles that they can’t open themselves.
The company’s next target is the OTC market, which includes products like acetaminophen and ibuprofen. Since this market requires an induction seal, the team at SnapSlide are in the process of developing a specific solution for the bottle.
Then the company must focus on scalability, working on optimizing production processes to handle large volumes efficiently. The goal is to be fully prepared to scale up as more pharmacies and OTC companies adopt SnapSlide. Overall, the focus remains on creating solutions that are both user-friendly and environmentally sustainable. They believe that the principles behind SnapSlide can be applied to a wide range of products, making everyday tasks easier for millions of people.
SnapSlide’s design has been recognized in the Drug & Pharmaceutical category of the recent 2024 IoPP AmeriStar Honors. Read about more of the Ameristar winners in the pages that follow.
IoPP’s 2024 Professional AmeriStar Awards:
The Institute of Packaging Professionals (IoPP) unveils its 2024 AmeriStar Award recipients. In the pharmaceutical, medical device, and nutraceutical space, eight winners have emerged:
CATEGORY: DESIGN EXCELLENCE
CATEGORY: MEDICAL DEVICE
This product integrates cutting-edge in-mold label technology, creating a striking visual appeal with transparent polypropylene substrate and deep, pink-colored recycled polypropylene. The standout feature is its unique 3-piece cap: a light pink inner cap, a clear matte over-cap, and a dark pink hanging loop for easy shower storage. The compact design and hanging loop enhance usability, making it ideal for shower storage and travel. The Shower Stick’s pink color scheme and prominent ‘W’ logo align with the Will Perform body lotion range, enhancing brand visibility.
Intuitive’s Da Vinci Xi Endoscope Packaging System’s design exemplifies a holistic approach to sustainability, cost reduction, and efficiency. The system sets a new standard in medical device packaging, highlighting how thoughtful design can deliver substantial economic and environmental benefits, enhancing operational efficiency while demonstrating a solid commitment to sustainability.
This flexible, sustainable pouch replaces traditional rigid trays, enhancing shelf visibility and user experience. The design reduces non-renewable energy demand, carbon footprint, and water consumption, aligning with Bayer’s sustainability goals. The custom carry handle and ample printable space offer user-friendly and informative packaging.
CATEGORY: MEDICAL DEVICE
Plastic Ingenuity’s packaging solution ensures robust protection for sensitive pipette tips, which is crucial for highly automated diagnostic machines. Initial straight wall designs failed drop tests, prompting the incorporation of ribbing, flutes, and structural enhancements to the PET base and lid. This solution exemplifies innovation in protective packaging design and maintains the integrity of sensitive medical diagnostics.
CATEGORY: SUSTAINABLE PACKAGING
Dymapak’s metal-on-metal seal ensures 100% curbside recyclability, eliminating mixed materials. The mono-material design offers essential barriers, enhancing sustainability while maintaining functionality and safety. This pioneering closure raises the bar for child-resistant packaging.
This eco-friendly packaging features a PaperFoam® tray and a PharmaLock™ Easy Seal+ paperboard lid, eliminating single-use plastic waste. The new design fits more products on the shelf, enhancing retail efficiency and e-commerce durability. It improves consumer convenience with an intuitive peel-back lid, maintaining operational efficiency with existing equipment.
Centrum transitions its gummy vitamin portfolio to 100% post-consumer recycled PET, significantly reducing reliance on fossil fuels and cutting virgin plastic consumption by 646 metric tons. This shift supports a circular economy, maintaining product safety and quality while combating plastic pollution and mitigating climate change.
CATEGORY: DRUG & PHARMACEUTICAL
SnapSlide® Rx from SnapSlide LLC SnapSlide® Rx introduces a no-torque child-resistant cap with a patented sliding mechanism that enables single-handed operation. This inclusive design benefits individuals with limited mobility or dexterity, enhancing medication access and safety. The state-of-the-art closure mechanism integrates seamlessly into existing pharmaceutical packaging, meeting stringent safety standards.
See the full list of 2024 AmeriStar Award winners at IoPP’s website: www.iopp.org/i4a/pages/index.cfm?pageid
The
Chevron Deference has recently been overturned, resulting in potentially less bureaucratic control over regulated industries, such as the FDA.
The Supreme Court of the United States (SCOTUS) recently ruled on a case involving a long-standing precedent. In this case the justices voted 6 to 3, along ideological lines, to overturn the Chevron Deference. This ruling has the potential to impact all industries that are regulated by a federal agency, including the pharmaceutical, food, medical devices, and cosmetics industries.
CHEVRON
The Chevron Deference was established by a Supreme Court ruling in 1984 (Chevron USA vs Natural Resources Defense Council) and gave federal agencies the ability to interpret federal statues in cases of ambiguity. To understand the implications of overturning this 40-year precedent it is important to recall the role of the three branches of government. The legislative branch writes the laws; the executive branch executes the laws; and the judicial branch interprets the laws.
This could potentially result in lower operating costs for Life Science companies and a shorter time to bring new products to market.
of ambiguity exist because the congressional acts that created and defined the roles of the FDA are not specific enough to cover every conceivable scenario. This is where the Chevron Deference comes in. The Supreme Court ruling in 1984 stated that in areas of ambiguity the deference goes to the federal agency to determine what is appropriate to deliver on their congressional mandate. In essence, the Executive Branch of the government is empowered to determine if a rule or regulation is within the scope defined by Congress.
was established by a Supreme Court ruling in 1984 and gave federal agencies the ability to interpret federal statues in cases of ambiguity.
“ ”
The FDA was created by an act of Congress in 1906 to regulate the food and pharmaceutical industries. Subsequent legislative action expanded the FDA’s scope and regulatory authority. Congress gave the FDA authority to protect public health by ensuring the safety, efficacy, and security of food, drugs, medical devices, and cosmetics. Thus, the FDA has the authority to enact rules and regulations to achieve their mandate. Some of the regulations might be considered to go beyond the role defined by the statute or it might be ambiguous whether a particular regulation is within the scope of the congressional legislation. These areas
In June, the U.S. Supreme Court overturned the Chevron Deference, which means that the Judicial Branch will now play a role when there is a question or concern whether a regulation goes beyond the Congressional statute. From a practical perspective, it is important to consider what impact this will have on the regulated industries including the packaging industry and the federal agencies that create the regulations. It is likely that there will be many more legal challenges to regulations imposed on industries. The FDA and other federal agencies will have to tread more carefully. They will have to get more industry feedback before enacting a new regulation to insure it will not be challenged, or if it is challenged, it can withstand judicial scrutiny.
1 . Uncertainty- When a federal agency enacts a new rule or regulation, there will be uncertainty about whether it will be
challenged in court, and ultimately if it is challenged how the courts will rule. Overall, there will likely be more legal challenges.
2 . Less agility and adaptabilityFederal agencies will not be able to move as quickly as they did previously. They will have to work with the regulated entities and perhaps reach a compromise before new rules are enacted.
“THE FDA and other federal agencies will have to get more industry feedback before enacting a new regulation to insure it will not be challenged, or if it is challenged, it can withstand judicial scrutiny.
”companies as well as a shorter time to bring new products to market.
5 . Less informed decision makingSubject matter experts at federal agencies might have less influence in interpreting statues. Decisions on regulations requiring analysis of complex data and information will be made by judges who may not have the background to comprehend all the aspects of the particular regulation.
3 . Less power for federal agencies- Some critics have argued that the 1984 SCOTUS Chevron vs NRDC ruling gave too much power to the executive branch of the government. This latest ruling from SCOTUS will shift power from the Executive branch to the Judicial branch.
4 . Less bureaucratic control over regulated industries, such as the FDA. The impact that this has on Life Science companies will be seen in the coming months and years. It could potentially result in lower operating costs for these
Ultimately federal agencies and industry will have to work together more closely to ensure patient safety is not impacted. Specifically for the packaging industry, it is not only the FDA that is impacted but also OSHA and the EPA.
Patrick Gavit is a retired biochemist from Takeda Pharmaceutical Co., a Japanese multinational biopharmaceutical company. Gavit has 40 years’ experience in the Chemical and Biotech industries and is Six Sigma Blackbelt certified.
Yakubison discusses his role at Merck & Co., Inc., Rahway, NJ, USA (hereinafter “MSD”), the evolution of pharmaceutical packaging, and the unique position of integrating packaging materials and machinery expertise.
By Liz Cuneo, Editor-in-Chief
In this new regular feature, Healthcare Packaging is interviewing some of the best and the brightest in the industry to learn more about their careers, their thoughts on what has changed over the years within the industry, and what challenges are arising.
Ron Yakubison is the Executive Director, Packaging Solutions and Strategy Implementation, part of Packaging Tech Ops at MSD. He started as a summer intern at the company in 1991, returning to officially start his career in 1992, and he hasn’t left yet. Since then, he has held 16 positions during his 32-year career at MSD, ranging in various roles in packaging engineering, package design, and operations. Yakubison’s passion is packaging, and it shines through his successful career at MSD while also being a part time lecturer with Rutgers School of Engineering. Read on for how he got into the industry, how to best optimize a package, and his insights into what makes packaging in biopharmaceuticals so unique.
Q UESTION: How did you get into packaging?
I discovered packaging during my third year at Michigan State University. Initially, I was in material science and engineering. I have always been mechanically inclined, and my family had a tool & die business, so my plan was to eventually work there. But I switched to packaging due to its diverse applications and opportunities. And I eventually ended up in pharmaceutical packaging. The interesting thing about pharmaceutical, specifically, is that you’re always reinventing something, always working on something new, that’s part of the excitement.
One of my key values is that I wanted to work at an American company, it’s a core value of growing up in the Detroit area, and at the time, MSD had maintained Fortune’s Most Admired company since 1987.
Q: What unique challenges does pharmaceutical packaging face today?
Ensuring patient safety and compliance is paramount. As products become more complex, packaging must meet stringent requirements to maintain product integrity and efficacy, especially for home-administered treatments.
Q: I understand you have a background in both packaging materials and machinery… Is this atypical for someone in your position?
It is atypical. Most professionals specialize in one area. However, having knowledge in both fields provides a comprehensive understanding of the entire packaging process, from design to implementation.
If you think about packaging, it’s packaging components, machinery, and the process of how it all gets together. Many people go into package design/development and focus in on the design. The equipment engineer is more of a mechanical engineer— they need to know a little bit about the design/ components but focus more on the equipment. At a lot of companies, that’s two different groups.
I have always had an interest in both. In my career, I was responsible for package design, but I became more and more interested in the equipment. At the beginning of my career, my projects gave me significant opportunity to travel to sites and suppliers, accelerating my development of packaging processes and problem solving. A foreign assignment in the Netherlands also enhanced my shop floor understanding and capabilities, while understanding how to work in a different culture.
Q: Sometimes there is a disconnect between the material side of things and the machinery. Would you agree?
“
” THE FUTURE PRODUCTS in our industry’s pipelines continue to get more complex while regulatory expectations continue to drive new ways of working with the packaging design, process, and equipment.
—Ron Yakubison
Yes. Once someone becomes an equipment engineer, they typically never change, and very few know the packaging materials intimately. But knowing both sides allows for better package optimization. Same goes for package development professionals; it is difficult to optimize the design without knowing about the equipment and the packaging process.
Q: How has your background in both packaging materials and machinery influenced your career?
Understanding both components and machinery has been crucial. By developing my packaging knowledge broadly across all aspects of packaging, it has allowed me to have a more comprehensive view that has been pivotal in driving packaging strategy at MSD. This dual expertise has allowed me to optimize packaging designs effectively. What are we mostly optimizing the packaging for? For us, its ensuring patient safety with compliance packaging. Asking a patient to dose themselves with a sterile product (say a syringe) presents challenges. Then there are the human factors of getting all that to work. And then understanding the population as far as literacy (instructions for use).
I have had mentors and sponsors throughout my whole career and being at a large company allowed me to continue to grow. My love for packaging continued to grow, too. I made the decision early on that staying in packaging was more important than advancing my career. I have been lucky that I have been able to accomplish both during my time at MSD.
Q: What has changed the most in the industry over the last 32 years?
In general, the industry has moved from high-volume solid dosage products to more niche, sterile products. The rigor of science and the understanding of root causes in packaging has
significantly improved from years past. At MSD, we’re known for digging into the science of almost anything. The level of understanding, the science of packaging today vs. ten years ago is night and day. The maturity of what goes into a good package vs. an OK package vs. a great package—that bar continues to rise across all industries, and I believe biopharmaceutical packaging in some ways is driving that.
Q: What do you see as the biggest challenge or biggest opportunity in the pharmaceutical industry? How does packaging help alleviate this challenge?
What’s important is having detailed understanding of the environment(s) that the package will be used in and a comprehensive understanding of all the different items the package needs to solve for in its life cycle. A good packaging professional needs to take all these items into consideration and find the correct balance based on business and product needs.
The future products in our industry’s pipelines continue to get more complex while regulatory expectations continue to drive new ways of working with the packaging design, process, and equipment. As we continue to expand the markets where these products serve, it is important to manage the added complexities these markets have to the package and distribution, by leveraging standards and focus on more sustainable transportation methods.
The goal of pharmaceutical packaging is to make sure the patient receives safe, quality, compliant product, and will prepare and use the product per the instructions provided. This includes ensuring the package provides all the needed protections, which could include moisture, light, temperature, oxygen, shock, vibration, and compression protection while the product travels through the supply chain.
Colgate-Palmolive has relaunched its bamboo toothbrush with compostable handle packaged in a recyclable paper-based tub and lid pack.
This year, Colgate-Palmolive has relaunched its bamboo toothbrush featuring a compostable handle that is 100% natural and biodegradable, is made out of sustainably grown bamboo, and comes in a recyclable paper-based tub and lid-style packaging.
“We are constantly looking for ways to develop innovative products with the environment in mind,” says Sukhdev Saini, the Global Packaging Leader at Colgate Palmolive.
To do that, the toothbrush’s handle is made from 100% sustainably grown bamboo. To protect it from water damage, it is coated in natural beeswax. The toothbrush also features charcoal infused floss-tip soft bristles that clean hard to reach areas. If the bristles are removed, the bamboo handle is completely compostable.
The product’s packaging is made of 100% paper, which is unique for toothbrushes that often come packaged in plastic.
HERE, we’ve gathered a handy list of suppliers offering a range of sustainable offerings, from recycled content to multi-use materials, and more. Scan the QR code to download this researched list today.
For more information scan the QR code
Because user experience and usability are so important, Saini says that care was taken to ensure its usability.
“ We ensure that this package is easy to open and use for consumer convenience, ” says Saini.
To be sure that customers can still understand what the product looks like (in lieu of the traditional clear blister pack), Colgate developed new graphic designs that feature high-quality renderings of the toothbrush that showcase the appearance and effectiveness of the toothbrush to the customer, without the need for a plastic blister or window.
The new packaging was rigorously tested to ensure it meets the same product protection requirements as plastic blister packaging. A paper-based inlay was developed to hold the brush firmly in place, preventing damage to the bristles during transport. This, combined with secondary packaging made entirely out of paperboard material, enables the packaging to successfully meet the International Safe Transit Association (ISTA) testing requirements. A new manufacturing line was installed to manufacture the toothbrush’s new paper-based tub and lid packaging.
Sustainable packaging solutions built and supported locally
Blister Machines
Custom Automation/ Product Handling
Rebuilds
Vision Inspection
Cartoning
nimal
Are we blocking innovation by not accepting AI? Louisa Harvey shares how embracing AI in the right way might shape how devices and packaging can be better targeted to patients.
By Keren Sookne, Contributor
It’s important to see devices and packaging as one system, one unit.
LOne area that AI can help is in how companies mine existing data.
ouisa Harvey, the principal & founder at Harvey Medical (a ClariMed company), is passionate about the usability of medical devices. She founded Harvey Medical in 2012, Healthcare Fieldwork in 2016, and co-founded the Medical Human Factors Network in 2018, with the mission to raise the bar of medical human factors work in the UK.
[Editor’s note: answers have been edited for brevity.]
1. What are some of the ways that a pharmaceutical or medical device manufacturer could target experiences or device/packaging designs to regions or patient populations with help from data and AI?
Everything I speak about today is pertaining to both the devices and the packaging. I think it’s really important to see devices and packaging as one system, one unit. A user should instantly feel a continuous energy between the device in question, the packaging, and any other materials.
Sometimes there’s a bit of a disconnect. People might really love the packaging and they feel excited to open the box of their life-saving medication—then the vibe they get when they actually see their medical device and use it isn’t quite there.
There is a huge amount that we can do with AI in the areas of research that I work in, both human factors and market insights/ UX. One of the big differences is going to be the way that we can mine existing data. Many pharmaceutical and medical device companies have a whole wealth of data contained in final study
With AI, packaging and the device can be targeted to people who struggle to take their meds.
reports, market insight studies, raw audio/video files, and human factors reports. AI looks for patterns, patterns that might not have been immediately obvious if a human was to wade through thousands of pages.
Companies could feed all that existing data into a system, then find out trends and current research topics. This in essence would be classified as synthetic data. But be mindful that synthetic data does not live. It is only as current as the data, so companies should continue to feed the system with new insights. Preferably the raw data files, as emotion tracking could retrospectively be used on the videos to provide greater context to responses. It’s important to remember to get the informed consent right in all studies going forward to ensure any further analysis is ethical and responsible.
2. Do you think companies are hindered by lack of data or incomplete data? Do they already have access to data sets they can feed in?
It depends on the size of the company. For big pharmaceutical and medical device companies, I’m sure there’s a lot that can be harnessed. But for smaller companies, they don’t have that and there isn’t anything readily available. They could use HE75 standard, which is full of rich information on how to develop your device with a bit on packaging, too. But that’s really all that they have access to, and various literature searches. The beauty of AI is that it should be capable of pulling competitor information swiftly from databases such as the MAUDE database and others, so companies (regardless of size) can learn what ‘mistakes’ have been made with competitor devices so they can be ahead of the game.
“SOMETIMES there’s a bit of a disconnect. People might really love the packaging and they feel excited to open the box of their life-saving medication—then the vibe they get when they actually see their medical device and use it isn’t quite there.
”—Louisa Harvey
3. What’s an area that you think device and pharma companies could improve upon?
I think that there’s been a lack of market insight (UX) work done early on in many of the devices that I’ve seen lately. We like to make sure they are put in front of users right from exploratory. For example, you’re speaking to people who live with the condition, who are going to be opening the package and using the device, right through to doing the human factors validation testing at the end stage, which is where we’re looking at whether the device is safe, easy, and effective for use.
Because that end stage is regulated, people are very much focused on that part, whereas the answers to create a differentiating trialblazer is much earlier than that. You’re almost glued with the wrong device if you don’t speak to non-biased users early on. As researchers, I think we are often not asked to ask the right questions by the companies that we work with. We educate and advise how these questions might look, and I think there’s a lot to be done in that respect to make sure you’re really able to design and develop things that are truly novel.
It’s the same with packaging, too. I’m very rarely asked to look at packaging until the end of the design process, where I’m suddenly given the final packaging and instructions for use with the device. I would’ve liked to have had an input early on to make sure that that energy throughout the system is relayed across all the materials within it. When you’re brought in at that last minute, you’re under quite a few constraints in terms of making any changes.
Sometimes just not having an idea is better. I would rather people come to me and say, “What is going to be the future device in this area?” and not even give me a concept for use. Because it inhibits us immediately—as soon as a participant that we’re testing sees that [concept device], they are completely drawn into that device design, instead of really enabling inventive thinking.
4. That can be counterintuitive. Many people in life sciences feel an invisible pressure to “know the answers” right at the outset, where there’s a lack of curiosity or freedom to admit where they’re not really sure.
I think AI will help with that, too, because it will enable us to pull together all sorts of common themes off huge reams of datasets, which a human just wouldn’t be able to do in the amount of time available. So, I’m hoping that we’ll get innovation turned around a lot quicker than what we’ve been seeing.
5. What sorts of regulatory hurdles might there be to using AI for targeted design purposes. Data needs to be in a sanitized form before it enters any models, correct?
Absolutely. Any data that comes out of research studies is always anonymized if you’re doing everything correctly. Even at the point of the participant turning up, they’re given a participant number. So, it’s already anonymized to a certain extent, and there’s a lot that goes into that to make sure that the person isn’t identifiable.
But beware of pitfalls, for example if you’ve got an orphan indication, where there’s only five people in the world with that condition, it could be obvious as to which person was talking about it [based on demographics]. So, you have to be very careful to make sure that it is truly anonymized.
There’s a whole raft of privacy and ethics involved in this particular scenario. I’m sure there’ll be more and more documents coming out about how to appropriately use data and ask for people’s consent.
In terms of regulatory perspective, a lot of devices we’re now seeing contain AI. I was just looking at the FDA website the other day to see how many contain AI and it’s a huge proportion of what they’re now approving, so we need to be really aware of that. Across the globe, regulators are looking at plans and pathways to work out how devices should be developed responsibly when they contain AI and how that testing is going to take place. There will be quite a lot of regulatory changes that are going to be happening in the near future.
6. In terms of the ethics questions that you run into, is patient consent the main focus or are there other hurdles?
AI in general can inherently produce bad outcomes, which people have seen all over the news, and TV programs like Bleeding Edge, which has created immense social distrust. There is always an inherent risk when anything is connected.
As a global specialist in non-destructive and deterministic CCIT solutions, we work with major pharmaceutical companies, alongside smaller organisations and CDMOs. These companies have chosen our innovative technologies over blue dye for:
• Non-destructive methods
• Accurate, rapid pass/fail results
• Vacuum decay & Pressure decay
• ASTM / USP 1207 compliance
• 21 CFR Part 11 reporting
Are you ready to switch to non-destructive and deterministic CCIT for better quality assurance?
Live demonstrations
Join us at Pack Expo
West Hall, Booth #W-16064
“
THE BEAUTY OF AI is that it should be capable of pulling competitor information swiftly from databases such as the MAUDE database and others, so companies (regardless of size) can learn what ‘mistakes’ have been made with competitor devices so they can be ahead of the game.
—Louisa Harvey
”
However, I do think that we could be blocking innovation by not accepting AI. I feel very strongly that being able to use AI is already proving to be amazing in the field of medicine. I’ve felt for a long time that market insights and human factors haven’t been recruiting the right people to take part in research, no matter how stringent the screening criteria. My colleague and I, alongside two amazing software developers developed an app—when people are screened to take part in studies, we can detect whether they’re likely to adhere to the medication as prescribed or not.
We can really target the materials, packaging, and device to those people who would inherently struggle to take their medication. For a long time, I’d started to see a pattern of people
turning up for research that are the sorts of people who would take their medication regardless of what their device or packaging looks like.
At Pharmapack, we were speaking about sensory concepts, as well. I think that’s a huge area that’s not being looked into. But yet, it is looked at in the consumer world. Particularly with regards to packaging, there are perfect opportunities to enhance the energy of the system by stimulating other sensory factors.
For example, even as you open the box, there’s a certain scent that makes you feel relaxed about taking the medication. I’m sure there’s some sensory innovation to be had there as well.
Civica is on a mission to deliver quality generic medicines—including insulin—at low cost. A new isolator-integrated vial filling line and nest filling line allows the company to produce many different forms of injectables to pivot based on greatest need.
By Keren Sookne, Contributor
Invest in premium equipment to deliver affordable drugs. It may seem counterintuitive. But it’s how nonprofit innovator Civica is approaching its mission to deliver quality generic medicines to patients in need. They are the only pharmaceutical company created for the express purpose of preventing and mitigating drug shortages.
I remember covering Civica’s talk at the PDA Annual Meeting in 2019. Having recently launched, they had identified a set of generic drugs to focus on and were working to contract with
manufacturers or sub-contractors to produce drugs in established facilities. Their long-term goal was to produce their own nonprofit drugs. Just five years later (not long in the pharma world), here they are starting engineering and exhibit batches in their own new injectable drug facility in Petersburg, VA.
When they needed to purchase two filling lines for the facility, they turned to groninger, Germany-based provider of filling and closing machines, and Switzerland-based SKAN, known for their isolator technology. The new isolator-integrated vial filling line and nest filling line allow Civica to produce many different forms of injectables to be able to pivot based on greatest market need. They’re even filling a pen product in a nested tub cartridge successfully.
Jason Winfield, Director of Engineering, Biologics at Civica, credits the executive leadership team for prioritizing the approach to “do things right the first time.”
While it may be tempting to save money upfront in production, if this leads to rejects due to filling accuracy or quality issues, that ultimately costs more down the road and negatively impacts sustainability. Rejecting substandard product is the responsible thing to do, but if you can eliminate rejects from the outset, you save all the commodities you used in the process.
Selecting lower-cost equipment from lesser-known manufacturers didn’t fit with Civica’s mission to positively impact the supply chain with quality medicines. Plus, with deviations costing thousands and market recalls costing in the millions, they wanted to engineer out nonconforming product ahead of time. “This is where I give thanks to my executive leadership team. There was never a question of quality, compliance, and reliability of products. They know that if you do it right the first time, it’s more financially sound in the long run because you avoid rejected batches,” says Winfield.
Civica purchased the integra, a bulk vial filling line that processes vials up to 400 units/min with 100% In-Process-Control (IPC). A special priming mode eliminates product losses during start-up, while the IPC and run empty mode prevent losses during production and at the end of a batch, respectively.
Civica currently can process over 10 different vial sizes on the line, from 2R (2 mL) through a 50 mL molded glass vial, including multiple configurations for 10 mL vials. Matt Clifton, business development manager at groninger, explains that the integra utilizes a servo-driven walking beam, and there are no format parts needed for the 2R through 30R vial range for quick changeover. “At our stoppering station, we use a vibratory bowl that does not need to be changed for any stoppers,” he adds.
“You may have heard of the high five test—ideally, one isolator glove can touch the outstretched glove on the other side. For the integra, groninger worked together with SKAN to give the machine a slim design, requiring gloves on only one side of the isolator. Its compact design allows for fast decontamination and short cycle times, boosting productivity.
For cartridges, the In Process Control (IPC) helps prevent losses during production.
me is really exciting because we were all but told it can’t be done and we did it. I’m really pleased that the consistency of the fill leads to the consistency of the plunger placement, which leads to consistent matchup at the pen assembly, and it’s really exciting to do something like that to serve the patients.”
They purchased a pre-sterilized cartridge in a tub complete with aluminum overseal and combi cap. “You’re filling it from the back end. Then you have to either vent-tube or vacuum-assist place that stopper. So stopper placement is going to be a variability of the accuracy of your fill,” Winfield says. “If your fill is not accurate, then your plunger placement is going to be moving on the backside.” Accurate plunger placement is key to preventing rejects, and pens are a costly part of the assembly. In order to get better
THE SKAN ISOLATOR for me is the number one in the industry, and groninger’s capabilities with their syringes, both from filling accuracy and plunger placement, is I think next to none on that prefilled syringe line. —Jason Winfield
”The groninger DFVN 2005 is a ready-to-use (RTU) nested filler with an integrated isolator that can fill and close vials, syringes, and cartridges. “We still have plans to fill prefilled syringes on that line,” explains Winfield. “But because of the nested configuration, we were able to quickly pivot to cartridges for our insulin program. Having the nested tub capability was an easy transition to the 3-mL cartridge from the prefilled syringe formats. We fill both a 1-mL stake needle as well as a 1-mL short luer lock prefilled syringe.”
Civica has successfully filled a pen product in a nested tub cartridge, with both water and their insulin molecule. “That to
plunger placement, Civica could have switched to mechanical placement, but that wouldn’t offer them the same flexibility in what they could fill. “We’ve gotten really good feedback from our pen assembly manufacturers on that cartridge filled pen almost to unbelief. They can’t believe vacuum-assist stoppering is performing that well. So, to hear our pen supplier compliment that process and those cartridges that have been filled on our line—it really made the engineering team and the MSAT team feel good here.”
A standalone Material Transfer Isolator from SKAN with an integrated skanfog decontamination system performs a fast, automated decontamination cycle to transfer material to either line. SKAN also provided glove testing equipment.
groninger nest filling line with SKAN isolator.
An additional technology that Civica utilizes to quantify a container’s experience on the production line is a drone from SmartSkin Technologies. The intention of the drones is to eliminate damage and improve yield by providing insight into the forces experienced on the lines that may damage glass. The SmartSkin drones can be utilized during commissioning and qualification or during a product turnover to ensure proper setup prior to sterile containers being introduced to the line.
Civica opted to purchase groninger’s overhead SCADA system. “It sends batch recipe data down to each one of the individual machines and collects the batch report that we can use for disposition, which makes for less paperwork in my cleanroom,” says Winfield. “What’s great about that is if you have a fill line like our vial line that has a washer, a tunnel, a filler, a capper, and an accumulation station, I don’t have to rely on an operator to make
“WITH RESPECT to space, we designed the space the right way. It’s like no other facility in the world. People have room to move, to move their pallets around. We have a third bay where we’re putting a third filling line in dedicated for cartridges in the insulin pen,” says Winfield. “The executive team said, ‘That’s it. We’re not going to cram anything else into this facility because if we do, we risk quality and compliance, ease of operations, ergonomics, and safety. We’ll go somewhere else.’ I’m excited to hear about that.” He feels that the vial filler sits in a small footprint relative to what else is out there, but that small footprint didn’t take priority. “It was really the ease of operations, the reliability of the machines, and also the U.S. presence that we have from both companies to support any mechanical challenges that just happen in operations.”
the right entry in each one of those HMIs because the SCADA is doing it from the top down. There’s a lot of great details with the integration between the units.”
The lines offer Civica the flexibility it needs to produce many different products and formats in the future to address drug shortages and lower the cost of essential medicines. Additionally, both lines are designed to minimize product loss, ensuring optimal use of valuable pharmaceutical ingredients.
This efficiency is vital for Civica, which is preparing for its first rollouts of biosimilar insulin products on the equipment. “The lines are open to the widest possible range of products and as a standard include nitrogen capability, vacuum filling, and vacuum stoppering. Civica is targeting an under-utilized market where they need the drug products so quickly, so the intent behind both of these machines is to be able to produce whatever is needed,” says Clifton.
Both groninger and SKAN offer virtual capabilities, and the degree to which they’re used depends on a manufacturer’s openness and comfort level. “It’s certainly beneficial for emergency scenarios—such as if the SCADA is not connecting with one of the PLCs—to allow techs from either company to remote in and help as Civica continues to learn its equipment,” says Winfield. “Most of the time we find out that it was a simple IP address issue. We’re learning in our automation space. But we get great support, whether it’s remote or onsite, from both companies.”
One of Winfield’s primary objectives was to avoid using many vendors across filling lines and isolators. “Civica was a young company as we started the design, and we had a lot of executives who had experience with groninger and SKAN. They are industry leaders from a technology and reliability standpoint in our
most important application, which is sterile filling,” he adds. “Equipment prep upstream, and secondary packaging and visual inspection downstream are also critical. But primary container closure is where my sterility assurance rests, and it is the most important thing we do.”
Notably, groninger and SKAN, who have a 20-plus year relationship, partnered to develop the integrated technology years before a customer was even involved.
Typically, a manufacturer goes through a lengthy user requirements specification and subsequent design process, choosing the best-in-class filler and isolator which will be integrated as a last step. As Clifton says, the duo developed and integrated the system based on historical user requirements they’d seen then coupled that know-how with the latest technologies.
Marc Suter, head of sales, North America at SKAN, says, “We’ve predefined certain interfaces, how we work together, and we have a contract in place that details who is responsible for what. That really helps going into the individual project.”
Because the line is not completely custom, Civica benefits from the companies’ experience throughout multiple builds. Suter says prototyping is done beforehand, and they even have predefined slots for prefabrication, so when they begin a project, they aren’t starting from scratch.
Initial design began in 2020, with groundbreaking in 2021, so the team had to overcome pandemic-related challenges. Midway through 2020, they started ordering the longest lead equipment, beginning with the filling line and the isolators, which coincided with COVID shutdowns.
Normally face-to-face ergonomic studies would be conducted in person, so they had to get creative and learn quickly. “We implemented two different ways of doing this. We implemented virtual reality for the vial line. For the second line, we built a one-to-one model,” says Suter. “groninger and SKAN met at our premises because we were able to travel across the border from Germany to Switzerland. We had our colleagues from Civica patched in remotely. We put different cameras around the model, and went around with tablets showing details—we had to be creative to overcome these challenges and keep the momentum of the project.”
Winfield notes that commodities such as single use bags and syringes were hard to procure during these startup phases. “But within two years, all four pieces of equipment—both fill -
ing lines and both isolators—were installed to the site and had FATs performed.”
Richmond is a young, but growing pharma hub. One of the challenges Winfield knew they were going to encounter was with hiring and training personnel. “We knew that we needed to be a center of excellence with training our staff,” he says.
Now that they’ve performed engineering batches with the actual molecule on both the nested and vial lines, they’re in the process of hiring and developing more staff. He appreciates groninger’s multilevel training opportunities with onsite trainers. “Our training program is ongoing. But people love knowing the impact we’re having to patients and the opportunities we have to serve. Nearly every day they’re telling you something different they learned to do, or they’ll bring an idea of how we could potentially make an improvement. That engagement is what builds our culture in Petersburg that we’re excited about.”
The equipment suppliers also felt the passion for improving access to life-saving medication on U.S. soil. This marks the first time groninger and SKAN have worked together to benefit a nonprofit in the U.S. “There was a lot of buy-in to the patient-centric mission—that was the unique flavor overall for this project, the direct concern for patients,” says Clifton. “I think that Civica felt like they owed it to the patient, in addition to the automation portion, to deliver efficiency. I think they wanted to present a different model. In addition to the model, there were no compromises. They didn’t look to minimize scope or quality.”
Suter adds, “What’s struck me—even without starting to produce insulin yet—is they’ve already made an impact on the industry. You’ve seen competitors dropping their prices already because of the example they’re setting. I’m just waiting for the moment when our lines are up and running and filling the affordable insulin. I’m really looking forward to that.”
By Keren Sookne, Contributor
Dry ice doesn’t melt—it sublimates, meaning that it changes straight from a solid to a gas.
IKEY TAKEAWAYS
Supercooling is where dry ice drops below -78.50C and can lead to temp. excursions that can compromise product integrity.
n temperature-sensitive pharmaceutical packaging and transport, the use of dry ice is a common practice for maintaining low temperatures. Unlike traditional ice, dry ice doesn’t melt—it sublimates, meaning that it changes from solid to gas without ever entering a liquid state. However, the phenomenon of supercooling, where dry ice drops below its typical sublimation point of -78.5 0C, poses significant challenges and can lead to temperature excursions that can compromise product integrity.
Could applying an outer barrier to the shipper mitigate these risks? At ISTA’s TempPack, Kristin Deltano, senior product development engineer at Cold Chain Technologies, LLC, presented early data on CO 2 -impermeable, vented barriers around shippers. Results showed promise in lessening temperature excursions and tests are ongoing.
Deltano explained that the sublimation point of dry ice can change depending on the partial pressure of the CO 2 in the
Data reveals the potential of CO2 barriers in packaging to manage supercooling.
shipper. Partial pressure is the pressure exerted by one gas in a mixture of many gasses. If this partial pressure drops, for example when CO 2 gas escapes from gaps in the shipper—then so, too, will the sublimation point of the dry ice. This can result in multiple issues for a manufacturer:
• When dry ice in a shipper sublimates faster than expected, the system may supercool below the temperature a pharmaceutical product can withstand.
• The system may not meet the expected duration of the shipper because the dry ice sublimates too quickly in the shipment.
Research into supercooling has looked at dry ice surface area, vibration, pressure, convection, and shipper orientation as possible causes. Among these, convection, dry ice surface area, and shipper orientation were the biggest factors leading to this phenomenon. As a refresher, convection is the heat transfer process where warmer substances rise and colder, denser
substances sink. This phenomenon causes dense CO2 gas to escape from lower gaps in the shipper, and this can lead to a drop in pressure and subsequent supercooling.
It’s commonly understood that a “This Side Up” label is not a guarantee that a package will remain upright in the unpredictable world of shipping. Packages may fall over, or they may be stacked sideways or upside down for long durations, and this can impact shipper performance. But why would a shipper supercool faster on its side?
CO 2 gas escapes from gaps in the shipper, leading to a drop in pressure of the system. Deltano explained that for a multi-panel shipper, using a six-piece EPS cut sheet or vacuum insulated panels (VIPs), gas can escape through the gaps in any orientation resulting in supercooling risk. No matter how tightly the panels are packed together, there is still some form of a gap that gas can move through.
For a molded shipper with its only gaps at the top—between the lid and the base—CO 2 gas can prematurely sneak out of the gaps in the top when it is laid on its side or upside down, inducing supercooling. “Upright, the gas can just build up within the system until it meets that lid gap. On its side, that gap is now oriented towards the ground and the CO 2 is going to flow right out of it,” said Deltano.
So, molded shippers will see their worst supercooling when placed on their side or upside down because of the gap between
the lid and the base. Multi-paneled shippers, like molded shippers, will see the worst supercooling on their side or upside down because the gap between the lid and the base is larger than the gap between the side panels that have been tightly pressed together.
“Most excursions below -90 0 C were actually caused by an upright shipper falling to its side during transit, which is an incredibly common occurrence,” she said.
A team at CCT conducted a series of tests to explore how different configurations of CO2 barriers could mitigate this effect. Deltano said that while it may be tempting to simply plug up all the gaps to prevent CO2 leakage, she noted that dry ice is a hazardous material that typically requires specialized handling. The system must have some ability to vent when needed to prevent a dangerous buildup of pressure that can lead to explosion.
They tested a CO 2 impermeable barrier—a polyethylene bag— around shippers built with insulated panels, which would block any gaps in the system, with a vent opening at the top.
The experiment involved three identical six-paneled insulated shippers. As alluded to above, multi-paneled shippers typically experience more supercooling than molded shippers, because molded containers will only see supercooling on their side or upside down. Multi-paneled shippers can see supercooling no matter the orientation.
• The first, a control shipper, had no barrier.
• The second, labeled the Base Sleeve, covered five sides but left the top open.
• The third was the Base Sleeve + Overhang, encasing all six sides except for a small vent hole at the top.
The shippers were filled entirely with dry ice and left in the lab’s ambient conditions at 20 0C. Thermocouples were placed on the same inner sidewall to record temperatures throughout the test duration. Seventeen hours into the test, they tipped the shippers onto their sides so that the side with the thermocouple
became the bottom. “Then, 40 hours into the test, we shook the shippers. We took weights at three points: the beginning, right before tipping, and at the end,” she said.
The control shipper never recovered from its initial supercooling, dropping 100C below the barrier samples to approximately -900C, indicating a clear difference in performance due to the presence of CO 2 barriers. Weight loss rate showed that the control shipper had a higher rate of sublimation, implying a shorter duration.
Between the two samples with barriers, differences were minimal initially. However, tipping the shippers on their sides introduced new dynamics. With its open top, the Base Sleeve saw a significant temperature drop as CO 2 escaped easily. In contrast, the Base Sleeve + Overhang maintained better pressure and experienced less temperature fluctuation with its higher vent hole from the ground.
“Both sleeve samples saw a dip in temperature when tipped,” explained Deltano. “The Base Sleeve saw a larger dip because the CO 2 could escape easily, whereas the Overhang sample maintained some pressure due to its vent hole placement.”
BY USING a CO2 barrier to control gas flow, we can reduce temperature drops and mitigate the rate of dry ice sublimation, Deltano said. “ ”
The findings revealed the potential of CO 2 barriers in managing supercooling. “By using a CO2 barrier to control gas flow, we can reduce temperature drops and mitigate the rate of dry ice sublimation,” Deltano said.
This early research highlighted that both placement and size of vent holes make a difference in maintaining desired temperatures and durations. The Base Sleeve + Overhang, with its strategically placed vent, outperformed the base sleeve in shipper duration aspects.
When asked if there are concerns that the vent could be blocked in transit via misapplication or neighboring shippers and create an overpressure situation, Deltano noted that they are still looking into particular vent sizes and blockage potential. If the vent is blocked by corrugate, gas can still escape because that material is CO 2 permeable.
Research remains ongoing with different materials. A paper barrier was shown to have a small effect on supercooling mitigation, but the effect was not as pronounced as the polyethylene bags used in this study.
Across the industry, manufacturers are looking to shift to sustainable transport packaging materials. The addition of new materials should always be weighed with the risks of product damage and waste.
Witness an unparallelled range of solutions and engage with industry thought leaders at the largest international packaging and processing show of 2024.
Get ready to dive into the heart of innovation – the packaging and processing industry is coming together like never before at PACK EXPO International. Prepare for an unmatched experience where you can connect with colleagues, gain insights from experts, and witness cutting-edge technologies and machinery live and in person.
Attending PACK EXPO International is not just an opportunity; it’s a necessity to stay informed on the industry’s latest developments. Explore a vast array of packaging and processing solutions, covering over 40 vertical markets and tailored to every product, production line, and supply chain need. With 2,500 exhibitors spread across 1.3 million net sq ft of space, it’s the largest PACK EXPO International to date, and the largest gathering of packaging and processing suppliers, ideas, and industry professionals this year. There’s no better way to stay ahead of the curve and drive your business forward.
Visit www.packexpointernational.com to learn more and plan your visit to the show.
McCormick Place Convention Center November 3-6, 2024 Chicago, Ill.
9 a.m.-5 p.m. Sunday, Monday, Tuesday
9 a.m.-3 p.m. Wednesday
Registration pricing: Registration is $30 until October 11, after which the price will increase to $130.
Making its PACK EXPO International debut, Sustainability Central will take an expansive look into packaging sustainability and what it means to brands. That includes expert speakers and actionable, sustainable solutions in manufacturing, materials, design, and more.
Expert representatives from leading companies will share insights on various packaging sustainability topics and practical strategies for brands to boost sustainability. With over 20 educational sessions, attendees can learn from experts at Amazon, Clorox, Conagra, Dr. Bronner’s, Dow, Merck, Nestlé, the Consumer Brands Association, and more well-known companies and organizations.
Sustainability Central will also feature kiosks from Virginia Tech, the University of Florida, Clemson University, PMMI Business Intelligence, AMERIPEN, and others, highlighting their latest research, innovations, and best practices. Find it in the West Hall at Booth W21020. Visit hcpgo.to/434 for more information.
Emerging Brands Central is a valuable resource for brands seeking to expand their reach and scale operations. An evolution of the Emerging Brands Summit, this educational stage offers easy access to industry experts as they share insights on topics including product development, packaging innovation, and scal-
March 10-12, 2025
Atlanta, GA
Discover solutions you won’t see anywhere else in the Southeast. The exciting new PACK EXPO Southeast 2025 unites all vertical markets in one dynamic hub, generating more innovative answers to your production challenges. Don’t miss this extraordinary opportunity for your business!
ing strategies. Attendees can participate in these free 30-minute sessions, which promise to deliver up-to-the-minute, practical advice for scaling operations. Emerging Brands Central will be located in the West Building at Booth W20049. Learn more at hcpgo.to/435
The PACK EXPO Scavenger Hunt will transform the show into a dynamic and interactive journey, with an opportunity to win $1,000.
To participate, attendees must download the mobile app and enter the unique codes found at each of the 10 show specialty areas within all four buildings of McCormick Place. Attendees who complete all stops will be entered for a chance to win $1,000. Three winners will be selected.
Attendees can access the scavenger hunt via the PACK EXPO International Mobile App, sponsored by ProMach, Inc.
For more pavilion information and to find exhibitors within every pavilion at PACK EXPO International, visit hcpgo.to/436.
The Healthcare Packaging Pavilion is a top destination for life sciences companies. It’s a “show within a show,” housing innovations for biologicals, medical devices, nutraceuticals, and pharmaceuticals. Find the Healthcare Packaging Pavilion in the West Hall.
Logistics is a crucial part of the product journey from manufacturer to consumer, and it’s more important than ever with the boom in e-commerce. The Logistics Pavilion will be the place to find targeted solutions related to the supply chain, including distribution, warehousing, transportation, material handling, docking, and inventory management. Due to high attendee demand, this year’s Logistics Pavilion will be four times larger than 2022! Find it in the North Building.
This exciting area features the latest innovations in digital printing and converting, labeling, coding, and marking technologies. Year after year, the PACKage Printing Pavilion continues to be attendees’ first stop for the digital printing, converting, and labeling solutions they need to enable cost-effective customization, short runs, and on-demand traceability and variable data packaging. Find The PACKage Printing Pavilion in the South Hall.
The Association Partner Pavilion houses leading associations from the PACK EXPO International Partner Program. These organizations are dedicated to advancing the packaging and processing industry and offering significant resources, insights, and expertise. Find and engage with them all in one central location in the North Hall. Participating associations can be found at hcpgo.to/437.
Register to gain access to over 150 free educational sessions and learn from industry-leading experts. Six different types of sessions cover the most pressing topics in packaging and processing, all conveniently located on the show floor to ensure participants don’t miss a beat.
Learn the latest industry developments with up-to-the-minute content. Three Innovation Stages will present free, 30-minute seminars on breakthrough technologies and techniques focused on a wide range of industryspecific solutions.
Scan QR code for a direct link to sessions listed.
THE PACKAGING & Processing Women’s Leadership Network (PPWLN) serves to recruit, retain, and advance women’s careers in packaging and processing. Each PACK EXPO, the PPWLN hosts a networking event to address a timely issue facing women in the industry.
The annual PPWLN Breakfast is back during PACK EXPO International, Tuesday, November 5 at 7:15-9 a.m., in Room W-375 at McCormick Place. It’s the perfect spot to mingle, munch, and start your day with energy and inspiration from guest speaker Lisa Sun, founder and CEO of retail brand and lifestyle company GRAVITAS.
Sun will blend her personal story, experiences from her data-driven insights from 11 years at McKinsey & Company, and the story of the launch of GRAVITAS to showcase the power of confidence, innovation, and a strong vision. Beginning her career at McKinsey & Company, Sun is no stranger to the corporate world’s highs and challenges. Her transformation from receiving critical feedback to launching a sizeinclusive apparel brand shows just how powerful embracing your unique “superpower” can be.
The PPWLN Networking Breakfast is sponsored by BW Packaging, Emerson, ID Technology, Morrison Container Handling Solutions, Plexpack Corp., Schneider Electric, and Septimatech, Syntegon Packaging Technology, LLC. Register here, hcpgo.to/438.
Made in the USA
Streamline your Produc∶on with a Complete Solu∶on for Automated Assembly
From compact benchtop designs to full scale producঞon machines. We have the equipment to fit your needs!
THE TECHNOLOGY Excellence Awards are back at PACK EXPO International 2024, and it’s up to you to vote for the winner. These awards recognize the most innovative technologies not yet shown at any previous PACK EXPO event. More than 100 solutions suppliers submitted nominations for this year’s awards, which were reviewed by top industry professionals and narrowed down to three finalists in each of four categories.
New this year, voting will begin online on October 28, a week before the show starts, and continue through noon on Tuesday, November 5. In-person attendees are encouraged to visit the finalists’ booths and vote via the official show app or online. Winners will be announced after noon on November 5. For a complete description of the finalists’ technologies, visit the Technology Excellence Awards page at hcpgo.to/440.
Gain valuable insights from industry experts tuned into the hot topics affecting packaging and processing. Speakers will cover multiple industry verticals, and speak on the latest trends including sustainability, remote access, supply chain solutions, augmented reality, and operational efficiency.
Scan QR code for a direct link to sessions listed.
PMMI U is offering its popular training workshops in Chicago to coincide with PACK EXPO International.
• Risk Assessment Workshop: November 1-2, 2024
• Certified Trainer Workshop: November 3-4, 2024
• Field Service Essentials: November 3-4, 2024
Visit hcpgo.to/442 to browse and register for these workshops.
New to the show? Stop by the First-Time Attendee Lounge, sponsored by ProMach, Inc. This lounge is dedicated to first-time attendees searching for products and solutions for their businesses. Receive personalized attention, including assistance from the show staff in locating products, introductory education sessions presented by industry experts, complimentary refreshments, and a place to charge devices. Visit it during show hours in the South Building at Room S-102.
The Attendee Resource Center is an online gateway with information and resources to help attendees maximize their time and get more ROI from attending PACK EXPO International.
Download the Attendee ROI Guide, use the justification letter template, watch explainer videos, explore additional search tools to find the best solutions at the show, and much more. Find it at hcpgo.to/439.
Download the free PACK EXPO International Mobile App, spon-
sored by ProMach, Inc., to your smartphone to navigate the show like a pro.
• Look up exhibitors, products, and educational sessions.
• Create and save a personal agenda of what you want to see and do.
• Navigate from booth to booth with the interactive map.
• Get news and notifications about demos, giveaways, and more.
• Join in on the Scavenger Hunt and enter to win $1,000.
• Access your agenda anywhere.
Take advantage of My Show Planner in the PACK EXPO International Mobile App or online at www.packexpointernational.com to create a personalized collection of “must-sees” and track interests before, during, and after the show.
My Show Planner features a personalized resource planning tool and directory and appointment scheduling capabilities. Add exhibitors and sessions of interest and even schedule meetings in advance with exhibitors to maximize your time at the show. Visit hcpgo.to/441 to get started.
TekniPlex
TekniPlex Consumer Products introduces its new ePress Seal liner, said to be the first and only pressure-sensitive seal utilizing expanded polyethylene (EPE). The ePress Seal is more flexible and resilient than polystyrene (PS) foam, offering greater resistance to compression and better maintaining its shape to provide longer lasting gasketing properties. Lightweight and easy to remove, the liners are suitable for nutritional supplements and are recyclable in regions where the polyethylene (PE) recycling stream is available.
Qosina, Polestar Technologies
Qosina announces the addition of iDOT Single-Use Sensor Bag Ports from Polestar Technologies to its extensive portfolio. These integrated Disposable Optical Transducer (iDOT™) gamma-stable bag ports offer non-invasive monitoring and come pre-calibrated for plug-and-play use. Polestar’s iDOT sensor configuration allows for simple integration of pH and dissolved oxygen (DO) monitoring to single-use bags, including bioreactors. They feature a POE bag port with sensing film, using materials that meet USP Class VI requirements.
Pharmaworks
R.A Jones
R.A Jones announces the debut of the Celestion™ MTX TopLoad platform at PACK EXPO International 2024. The Celestion™ MTX represents the latest advancement in flexible automation, integrating advanced robotic technology to address a wide range of packaging needs. It is a versatile TopLoad packaging platform designed to handle a diverse range of products, including pouches, wraps, round products, and kits.
CCL Healthcare, Controlant
The Saga Card represents an IoT innovation aimed at enhancing supply chain transparency. It integrates a printed battery, cellular modem, and sensors to actively track medications throughout the supply chain. Real-time data provided by the cellular modem and sensors ensures compliance with FCC regulations. Additionally, the device automatically deactivates once the medication reaches its designated point of use.
Pharmaworks, a ProMach product brand, introduces its new enhanced TF1e blister machine at PACK EXPO International in Booth W-16017. Now with auto-adjusting stations utilizing laser feedback, an extended heater station and more, this compact machine can handle more challenging packaging films like 100% recyclable, mono-materials and achieves a new thermoforming depth of up to 40 mm. With more production versatility, the enhanced TF1e helps manufacturers and contract packers optimize product quality, reduce labor, and improve profitability.
Capmatic unveils the Patriot SF, said to be the world’s smallest tablet and capsule bottle packaging line. Designed with precision and efficiency in mind, Patriot SF boasts features tailored to streamline operations in the pharmaceutical, healthcare, and nutraceutical industries. With a compact, balcony-style design, Patriot SF minimizes footprint while maximizing accessibility, requiring only one operator for seamless functionality. Its recipe-driven system ensures quick and repeatable changeovers, enhancing productivity without compromising quality.
Berry Global, Inc.
Berry Global Group, Inc. introduces a range of special closures and couplings which can be used in conjunction with its popular Politainer™ combi pack. This provides a closed system that facilitates the safe and easy dispensing of sensitive liquids without coming into contact with air. Available in sizes from one to 30 litres, Politainer comprises a polyethylene container held within a sturdy cardboard outer. The container collapses as product is emptied, which helps to ensure almost complete evacuation of the container while preventing air from entering.
Keystone Folding Box Co.
Keystone Folding Box Co. introduces a new paperboard blister wallet with push-through opening functionality. Ideal for hard tablets, the company’s Push-Pak™ allows intuitive push-through dosage access and a tighter, more condensed blister arrangement that reduces the package’s overall size. The blister wallet also provides highest-possible F=1 child resistance while remaining easy to open for seniors and consumers with dexterity challenges.
Syntegon
Antares Vision Group
Antares Vision Group launches DIAMIND Sentry, a solution allowing pharma companies to efficiently manage the substantial uptick in exceptions stemming from traceability mandates. The sophisticated system was developed by rfxcel, a business unit of Antares Vision Group providing supply chain visibility solutions. The cloud-based platform allows manufacturers, wholesalers, and dispensers to quickly identify and resolve product data exchange errors. Importantly, the system’s advanced exception management capabilities do not require platform upgrades, clearing the way for rapid deployment and immediate operational impact.
Syntegon’s Settle Plate Changer (SPC) for automated viable monitoring in the aseptic filling process is a patented robotic solution that will support customers in complying with the latest Annex 1 for new and existing equipment. Syntegon’s SPC robotic solution reduces downtime and contamination risk in aseptic filling by 80%, and it can be seen at PACK EXPO International 2024 at Booth 18099.
At PACK EXPO International 2024, you’ll find new technology and materials from hundreds of exhibitors that specialize in pharmaceuticals, biologics, nutraceuticals, medical devices and more. No other show delivers as many solutions for versatile packaging that will keep your products safe and effective.
Anti-Counterfeiting Technologies
Sustainable Materials
Smart Packaging & RFID
Digital Printing
This special section of company profiles includes select companies who will be exhibiting at PACK EXPO International, November 3–6, 2024. These profiles highlight the companies, the markets they serve, and the packaging equipment, products, and services they offer.
Phone email Website
Complete, Visible Validation for Medical Pouches
Validatable Band Sealers
Supplied with verification ports for process validation of pressure, speed, and temperature. Embossing coder available. 3/8” wide hermetic seal.
A pressure wheel can be added to provide flat seals on Tyvek® pouches. Dual heating and dual cooling bars offer faster sealing of difficult materials. Compressed air is required. Seals Tyvek® pouches at up to 40 feet per minute.
Shown with synchronized conveyor to support pouches while travelling through dual heating and cooling zones. www.allpackagingmachinery.com
• Tabletop Model
Designed for lightweight products and smaller pouches. Topstop guide shown is an available option to assist with seal alignment.
• Fully Framed Stand Model
Includes crank handle for height adjustment of sealing head to position over existing variable speed conveyor.
• Conveyorized Model
PRESIDENT, CHIEF APPLICATIONS ENGINEER: DAN WOOD
SALES & MARKETING MANAGER: LYNN MIRANDA
All Packaging Machinery Corp. manufactures medical pouch sealing machinery with validation features. Additional machinery lines include USDA-approved vertical and horizontal conveyorized band sealers, bag loaders and tabletop portable band sealers.
APM machinery is user friendly and manufactured to be durable and efficient. With over 75 years of successful packaging experience, our quality machinery is proudly made in The United States of America.
www.allpackagingmachinery.com
See our ad on page xx of this issue
200 Century Parkway Suite C, Mount Laurel, NJ 08054
Phone
Website
856-780-3465
sales.us@antaresvision.com
www.antaresvisiongroup.com
Antares Vision Group’s range of Inspection Machines is designed to guarantee your product’s quality, integrity, and safety and meet regulatory requirements. Our new generation of vision technologies allows product inspection of any container and product content from any angle during different production phases.
AV Group’s Prefilled Syringe Inspection Machine can handle up to 400 pieces per minute, processing SVP glass and plastic syringes up to 24mm in diameter. It inspects liquids with various viscosities, from water-like products to emulsions and gels. An added camera mounted on a secondary carousel yields 100% inspection of the syringe surface.
Fast, smooth single-point handling minimizes the risk of product breakages and scratches, thanks to individually motorized grippers and guideless conveying with vacuum-operated starwheels. The VRI VI series specializes in precise,
high-speed vial inspection of up to 400 liquidfilled glass containers per minute, combining sophisticated particle and cosmetic detection with technology-driven closure integrity verification. The unit can inspect liquids in various viscosities, including water-like, oily, suspension, gel, emulsion, lyophilized, and powder products. Vials are also checked for cosmetic defects such as crimping quality, flip-off color, neck-shoulder sidewalls, and stopper position. Molded glass and plastic containers also can be inspected.
Antares Vision Group is a world leader in track-and-trace solutions. It provides solutions to major global pharma manufacturers (more than 50% of the Top 20 multinationals) and government authorities to monitor their supply chains and validate product authenticity.
Antares Vision Group leads the way in transforming supply chains with advanced traceability, inspection, and data management solutions. We foster Trustparency® by enhancing safety, quality, efficiency, and sustainability across multiple industries.
Our DIAMIND ecosystem streamlines production with a data-centric approach, integrating digital identities with physical products for seamless operation from production lines to global supply chains. It ensures product integrity and traceability from raw materials to consumers, powered by AI for top efficiency and accuracy.
AV Group serves Life Sciences (pharmaceuticals, medical devices, and hospitals), Beverage, Food, Cosmetics, Chemicals, and Packaging industries globally, with over 1,300 professionals in 60+ countries and 40+ international partners.
Phone email Website
www.colbertpkg.com sales@colbertpkg.com
Colbert Packaging is a dynamic high-volume producer of sustainable paper-based packaging, serving the pharmaceutical, healthcare and consumer goods industries. We produce offset and flexographic printed folding cartons, formed paper trays, pressure-sensitive roll labels and informational package inserts. Our in-house services include structural design, full-service prepress, paperboard sheeting, ink blending/ matching and die making/cutting.
Our packaging solutions are more sustainable by nature, simply by using paperboard. Downstream, we know that our secondary packaging materials are 100% recyclable, and most are compostable. We’ll work with you to design earth-friendly, secondary packaging solutions that satisfy today’s sustainability requirements. Everything from right-sizing materials to 100% inline vision inspection for fully integrated quality control, sets you on a course to The Total
Package. Add to the equation fully recyclable paperboard, along with water- and agri-based inks, coatings and adhesives, and you’ll have The Total Package in One Clean Carton®!
Is product tampering or counterfeiting a concern? To better protect our customers’ pharmaceutical and healthcare products with secondary packaging, we are committed to an ongoing investment in the technology and expertise required to design and manufacture customized solutions. We offer a complete array of overt and covert security features designed to guard against fraud risks.
Explore our paper-based, recyclable, secure, and brand-worthy solutions for ALL your packaging needs.
What packaging challenge can we help YOU solve today?
For 65 years, independent family-owned Colbert Packaging has built a diverse product offering and a commitment to producing safe, smart and sustainable paperboard packaging solutions. Under the leadership of CEO Nancy Colbert MacDougall, the company owns and operates two manufacturing facilities in the Midwest, including Kenosha, WI, and Elkhart, IN. Colbert’s continual investment in cutting edge printing and finishing equipment and technology provides customers with top-quality service, and a place where employees find opportunity for career growth and fulfillment.
For product marketers, Colbert Packaging applies industry heritage, innovative technology, and design to create Safe, Smart, and Sustainable delivery solutions in which our customers’ products shine.
8445 Bunker Lane Blvd. NW, Ramsey MN
Phone email Website
800.279.3358 • 763.755.7744
contact@deltamodtech.com
www.deltamodtech.com
For over 40 years Delta ModTech has been a leader in web converting and packaging innovation. We are dedicated to providing flexible automation solutions for converters and manufacturers worldwide.
Delta ModTech systems feature a variety of processes including heat-seal pouching, rotary die cutting, laser cutting, tight tolerance registration, printing, laminating, coating and drying.
Seal to print registration — The packaging solution for process applications where speed, flexibility and consistent seal quality are important. For the manufacturing of:
• Heat-seal/Cold-seal pouches
• Resealable pouches
• Liquid dispense pouching
• Sachet filling
Improve your capability — We’ve developed several solutions to meet the pouching needs of our customers and their end users.
• Mod-Track® Vision Inspection – Part-inpouch, closed loop registration, date/bar code reading, rejecting
• Reject conveyors/marking equipment
• Part handling — stacking, sorting, etc.
• Printing for date, lot and bar code printers
• Case packing and cartoning integration
Packaging & Pouching Machine Specifications
• Web Width: 10” (254 mm), 13” (330 mm), 18” (457 mm), Custom Widths Available
• Max speed – Reciprocating Packager: 13” 80 ft/min (24 m/min), 18” 55 ft/min (16.75 m/min)*
• Seal Repeat – Up to 24” (609 mm)
• Delta ModTech INTELLI-MOD® controls
• Drive System: Servomotor Control
• User Controls: Touchscreen HMI Pendant Arm
• Welded Steel Frame, Aluminum Front Plate
We deliver web converting, packaging and coating systems for the most complex and demanding jobs in the medical, pharmaceutical, label, RFID and cosmetic industries. Our systems are designed to meet your application requirements, improve your profitability, and reduce your risk.
Service and Support — Serving our customer’s has always been Delta’s highest priority. We focus on quick, efficient solutions to keep your machines running to their full potential. To back up this philosophy, we have a full-service staff on call, made up of Engineers and Technicians. We have the process knowledge and proven modules to ensure the longevity of your machine.
EQUIPMENT SOLUTIONS FOR A VARIETY OF PRODUCTS: Diagnostics, Drug Delivery, Ostomy, Wound Care, Personal care, Electronics, Battery
715 Church Road, Elmhurst, Illinois 60126
Phone email Website
630.530.2203
info@guk-vijuk.com
www.guk-vijuk.com
To save time and labor, invest in GUK packaging-line equipment that runs on the packaging line’s drive. GUK–Vijuk Cartonac Leaflet Folders enable you to fold leaflets inline and immediately insert them into cartons along with the product. The servo-driven GUK Cartonac 2005 has a hinged feeding table for easy access to the fold plates and rollers. Improved suction rollers and air blasts effects efficient feeding of products— up to 3 thicknesses. The PLC controlled Cartonac 2003DS sets up easily and quickly and is servo driven for better control and speed.
Pre-folded leaflets can be fed in-line for insertion into cartons with GUK PA21 Leaflet Feeders. The PA15 model can rotate leaflets 90º for feeding, while mounted parallel to the packaging line to save space. These may also be used with gluing or tabbing equipment in offline leaflet bundling systems.
GUK–Sigma Pick & Place Stations precisely tip flat or 3-dimensional items onto products in
production lines.
Make spine-glued booklet leaflets on the GUK FA53 Folder. Fold large med-guides on sheets up to 28-3/4 inch wide on the GUK FA73 Folder. Choose from a number of G&K–Vijuk Outsert Systems with varying capabilities — from folding outserts with up to 90 panels, to up to 350 panels.
Meet TRACK & TRACE requirements with the G&K–Vijuk CTM Coding and Serializing Station. Print unique or standard 1- and 2-dimensional codes on outserts. A quality verification system logs all results, good and bad, for a tab on missing numbers in a series. Save time and labor with the GUK–Sigma PPM Auto Stacker, which automatically collects and packs outserts compactly into trays.
GUK RS Roll-Fed Folders save paper, cutting, and labor costs—and the probability of leaflet mix-up.
World leader in outsert-producing machinery, G&K–Vijuk has been specializing in miniature-leaflet folding solutions for over 40 years.
Member of the GUK Group headquartered in Germany (manufacturer of folding machinery since 1949), we continue to assess the needs of the pharmaceutical industry, as shown by recent developments in machinery to fold a greater number of panels and fold wider sheets—both for more print space on a single leaflet; and machinery for bundling leaflets for dispensing even more information on two to four leaflets.
GUK recently acquired MB Bäuerle, manufacturer of automated folding and inserting systems in Germany, and Sigma Engineering, manufacturer of pick and place product-handling machinery in the Netherlands to further our goal to provide innovative, time-saving equipment to improve our customers’ efficiency.
21121 Cabot Blvd, Hayward, CA 94545
Phone email Website
510.259.0500
info@heatandcontrol.com
www.heatandcontrol.com
Providing safeguards that help ensure your products match the prescription. Anywhere along the line, protect your consumer and your equipment. Efficient detection of foreign objects is critical to consumer safety, brand survival, and will also protect machinery and prevent downtime. We offer a complete line of metal detectors, checkweighers, and X-ray inspection systems from our strategic partners: CEIA® and Ishida.
CEIA Metal Detection - CEIA, is a world leading innovator of industrial metal detection systems for products such as powders, capsules, tablets, and liquids. Quality control is at the core of CEIA development of the most advanced electronic and mechanical technologies for detection of contaminants accidentally present in products.
Ishida X-Ray - The Ishida IX Series raises the bar in performance and usability with a global range that meets all local territory standards. Offering customers easy maintenance and stress-free operation, the range includes a robust fail-safe system that prevents a contaminated product reaching the consumer in the event of a power outage or breakdown, helping to minimize the potential for costly recalls.
Ishida Checkweighers - Ishida offers highprecision weight checking you can depend on. Checkweighing is key for delivering what your consumers expect by providing accurate verification of a package’s weight or count and detecting missing components. Rely on a range of features to handle different products and incorporate new functions to meet the latest requirements.
Rising to the challenge, advancing processes, and helping to bring the best products to the world using science, technology, and creative thinking.
We are process and product technologists committed to advancing pharmaceutical and other industries with science and imagination. Whether you measure success by effciencies, improvement, or innovation, count on us to deliver results.
Providing sales, service and spare parts expertise across the globe for metal detection, X-ray and checkweighing anywhere along a production line, Heat and Control works closely with strategic partners to bring new technologies and solutions that meet the strictest of quality standards.
Phone email Website
908.362.9266
info@james-alexander.com
www.james-alexander.com
James Alexander Corp. has added 18,000 square feet to its warehousing capacity, providing more space for servicing pharmaceutical (OTC & Rx), medical devices, health & beauty products, first aid and diagnostics sectors.
JAC’s patented single-use plastic ampoules are available in a variety of colors and applicators, offering singlehanded activation in a customizable format. JAC’s glass ampoules can be filled and assembled in single-use swab or dropper packages, and its novel winged device, THE ACTIVATOR™, provides easier activation for these glass formats. Other services include autoclave sterilization for glass ampoules, blister packaging and formula compounding.
James Alexander Corp.’s plastic ampoule combines style and ease of use through singlehanded activation. With a gentle squeeze, the inner membrane ruptures, allowing contents to
be dispensed. Available in sizes up to 5ml, and a range of colors and applicators.
James Alexander Corp.’s unit-dose swabs offer the stability of glass in one- or two-part systems for convenient application of pharmaceuticals and health aids. JAC also produces single-use glass ampoules for inhalation and dropper tip assemblies for liquid dispensing.
Safe and easy to use, the DuoDispersion System® tandem dropper or swab can hold two separate liquids, or a powder and a liquid; each formula is sealed in its own ampoule until the point of application. It can hold a combined volume of 1.2mls. Two versions are available: a dropper tip and a swab for topical application.
Located in northern New Jersey, James Alexander Corporation (JAC) is a leading contract manufacturer and custom filler of single-use crushable glass and plastic ampoules. Founded in 1976 by Francesca Fazzolari and Alexander Davidson, JAC is a privately-owned, ESOP company that still services several of the same customers it originated with 45 years ago.
JAC’s manufacturing facility features unique, company-designed equipment and produces its patented plastic ampoules, among other products. The company makes great efforts to ensure that most of its components are made in the USA, aligning with its goal of investing in local communities, regional job markets and the American manufacturing sector at large. Currently, James Alexander is developing new and innovative materials for JAC’s plastics ampoules. Among other aims, the goal is to make the containers compatible with alcohol-based liquids.
3585 Klöckner Road, Gordonsville, VA 22942
540-832-3600
kpinfo@kpfilms.com
www.kpfilms.com
Focused on delivering its vision: The Sustainable Protection of Everyday Needs, kp is a global leader in rigid and flexible packaging and specialty film solutions, serving the pharmaceutical, medical device, and shrink sleeve label markets, amongst others. With a broad and innovative portfolio of packaging and product films and services, kp plays an integral role in the customer value chain by safeguarding product integrity, protecting brand reputation, and improving sustainability. kp’s “Investing in Better” sustainability strategy solidifies its commitment to achieving ten clear targets for longterm improvement by increasing recycling and recyclability of products, cutting carbon emissions and continuous improvement in employee engagement, safety, and diversity, equity and inclusion. kp has earned a gold rating from EcoVadis, the leading platform for environmental, social, and ethical performance ratings, putting kp in the top 3% of companies rated in the manu-
facturing of plastics products sector. Founded in 1965, kp has 31 plants in 18 countries and employs over 5,700 people committed to serving customers worldwide in over 60 locations.
The sustainable protection of everyday needs, is not just a slogan to kp, it is a way of life. We have invested heavily across all the market segments we service, in the development and production of recyclable and recycled content packaging films. Chief among these markets is the pharmaceutical blister films market. We are proud that our kpNext® R1 pharmaceutical blister film was the first to market as a completely recyclable blister film in the RIC 1 recycling stream and remains the top choice for many major brands globally! We have since expanded the kpNext® family to include a certified recyclable polypropylene blister film with enhanced barrier characteristics called kpNext® RB5. When it comes to sustainable packaging for pharmaceuticals, think of kp and kpNext® brand of products.
43 Fairfield Place West Caldwell, NJ 07006
Phone email Website
973.575.7445
sales@marchesiniusa.com
www.marchesini.com
For 50 years, Marchesini Group has been creating customized machines and lines for the packaging of pharmaceutical, biotech and cosmetic products. Founded in 1974 by Massimo Marchesini, the multinational company with a turnover of 591,000,000 euro and 2,800 employees is celebrating its 50th anniversary this year focusing on the future. The Group is present in 116 countries worldwide, including the USA, a strategic area where the subsidiary Marchesini Group USA has been operating for over 30 years. Established in 1992, the 23,000-SQFT North American Headquarters supports the USA, Puerto Rico, and Canada markets. This modern facility is equipped and staffed to meet the everincreasing demands of today’s sophisticated and quality-conscious packaging clients. Thanks to 30+ years of experience, the team of experts comprehensively analyzes and defines the customer’s packaging requirements, translating technical challenges into effective and unique
solutions. By combining the most advanced technology with expertise and the needs of the pharmaceutical, cosmetic, and consumer products industries, Marchesini Group USA provides stand-alone machines, complete lines, and turnkey solutions for the full packaging of products, solving all challenges. From the processing to primary and secondary packaging, up to the end of the line: all the solutions are characterized by high quality, reliability, flexibility and customization. Furthermore, customer assistance is central: whether the customer’s packaging solution requires a new installation, a modification, or a retrofit, the team is here to help optimize productivity and maximize uptime to achieve the best results and the highest output.
Fifty years have passed since my father, Massimo, developed the first Marchesini cartoning machine in the garage of our home in Pianoro, just outside Bologna. We then expanded rapidly, and over time we have grown without compromising the quality that characterizes Made in Italy production. Today, we export 90% abroad, thanks to our employees, collaborators, suppliers, and the entire supply chain.
The packaging industry is indeed a sector in constant evolution, and to remain competitive, we must continually embrace technological innovation. In recent years, we have invested heavily in artificial intelligence to provide machines and lines increasingly capable of preserving product quality and improving production performance. We are the right partner where customers will find the best cutting-edge solutions for their specific needs.
Maurizio Marchesini, President of Marchesini Group
1571 Northpointe Parkway, Lutz, FL 33558
Phone email
Website
813.889.9500
pi.marketing@mt.com
www.mt.com/pi
METTLER TOLEDO is your single source for product inspection solutions offering metal detectors, x-ray inspection systems, checkweighers, and machine vision systems. Our broad product inspection line ranges from very basic and economical systems to sophisticated, stateof-the-art systems with customized material handling solutions. Systems can ensure perfect product presentation, create codes, verify package and label integrity, ensure weight range compliance, detect physical contaminants and inspect contents inside the closed package.
CI-Vision machine vision systems perform accurate label and package quality inspections on all types of packaging, including label quality, 1D, 2D, and alphanumeric text, proper sealing, cap and lid placements, and tamper band presence.
Safeline metal detection systems are extremely sensitive, easy to use, and prevent costly recalls by ensuring your products are free of ferrous, non-ferrous and stainless-steel contaminants which can be introduced during processing.
Safeline X-ray inspection systems can detect contaminants including stone, glass, and ferrous, non-ferrous, and stainless-steel metals, as well as detect mass and check for missing or damaged product inside closed packages.
Hi-Speed checkweighers are available in a wide range of sizes and configurations to handle nearly any container type or package design at high speeds to ensure accurate product delivery, reduced giveaway, and an optimized production process.
An OMAC member, we are committed to connectivity as well as data storage and retrieval, with methods including EthernetIP and OPC, as well as METTLER TOLEDO’s ProdX data collection. ProdX facilitates the collection and storage of production data across multiple lines and facilities. All data is easily accessible and exportable to other systems, facilitating compliance with all regulatory requirements.
Our solutions supported by the most comprehensive engineering solutions, product testing, and training in the industry, with 24/7 telephone support and nationwide field service.
• Capsule fillers
• Capsule check-weighers
• Capsule banding machines
• Pouch fillers
• Cartoners
• Tray formers
• Case packers
• Palletizers
31 Kulick Rd, Fairfield, NJ 07004
Phone email Website
973-808-8185
sales@mgamerica.com
www.mgamerica.com
Headquartered in Fairfield, New Jersey, MG America is a subsidiary of MG2 of Bologna Italy, a company that was founded in 1966 and today is one of the world’s three leading manufacturers of capsule filling equipment.
MG America is a leading supplier of an innovative family of precision-crafted processing and packaging machinery that includes capsule fillers, material handling, primary packaging equipment, secondary packaging equipment, checkweighing/weight control systems, tablet & capsule inspection, and line integration solutions. From sales, field service and spare parts to machine trials and local service/support representation, MG America offers a true “Partnership for Success.”
Packaging equipment from MG America can be found throughout North America in industries such as pharmaceutical, medical device, diagnos-
tics, nutritional products, and OTC products. Our lineup of premier, European-made machinery has earned a global reputation for reliability, precise performance, and superior craftsmanship.
• Packaging line integration
• Metal detectors for capsules
• Bottle unscramblers
• Bottle fillers / cappers
• Tablets/capsules & liquids
• Bottle labelers
• Bottles – Carton coding/ verification/serialization
• Bin blending equipment
• Material handling equipment
• Washers
• Sterilizers
• Depyrogenation
173 Technology Drive, STE 150 Irvine, CA 92618
Phone
Website
info@movitherm.com (949) 699-6600
www.movitherm.com
Maintaining consistent seal quality can be a daunting task. Manual inspection methods are not only time-consuming but also prone to human error, leading to missed defects and compromised product integrity. This often results in wasted products, increased costs, and dissatisfied customers. Traditional inspection methods struggle to keep up with high production speeds, making it challenging to detect and address seal issues promptly.
MoviTHERM’s TSI System is an advanced, automated solution designed to ensure the highest quality in packaging seal inspection. Utilizing thermal imaging technology, the TSI system detects and rejects faulty seals in real-time, while also measuring your process variability. This dual functionality allows you to not only maintain consistent seal integrity but also gain insights into your production process to achieve greater efficiency and reduce wasted product.
Process variability refers to how much your sealing process deviates from the norm. If your sealing process isn’t consistent, it creates varying thermal profiles. Our system can then easily distinguish between a good seal (one that will keep your product safe and fresh) and a bad seal (one that might fail and lead to product loss). However, if your process has excessive variability, it makes it harder to detect finer defects. While our system can still catch major seal issues, smaller ones might slip through unnoticed.
But there’s good news! Even if your process has a lot of variability, our TSI system can help you “dial in” and monitor your process. By providing direct thermal feedback, we can help you adjust and reduce variability to an acceptable level. Once you achieve this consistency, you can ensure your products meet the highest quality standards.
MoviTHERM, Advanced Thermography Solutions was founded in 1999. The company has 100% focus on infrared imaging for scientific and industrial applications. MoviTHERM sells thermal imaging cameras, enclosures and accessories as part of their distribution model, but also offer off-theshelf, turnkey thermal imaging solutions for packaging seal inspection, early fire detection, machine condition monitoring, and non-destructive inspection. Services include custom system design and software development, consulting, feasibility studies and OEM Product Design.
Contact information: Eric Hughes Regional Sales Manager (949) 699-6600 Ext. 125 e.hughes@movitherm.com
MULTIVAC is passionately focused on contributing to our customer’s success by delivering innovative, reliable solutions and superior support services.
11021 N Pomona Avenue Kansas City, MO 64153
Phone email
Website
800.800.8552
info@multivac.com
www.multivac.com/us
MULTIVAC is your partner for healthcare packaging, labeling, inspection and handling solutions. Our packaging machines are the perfect machine for every pack.
MULTIVAC is one of the world’s leading suppliers of packaging solutions for a wide variety of medical and pharmaceutical products, as well as consumer and industrial goods. Our portfolio covers virtually all packaging design, performance, and resource efficiency requirements. In addition, it encompasses an extensive range of packaging technologies, automation solutions, and labeling and quality control systems.
All MULTIVAC machines can be integrated into holistically designed systems thanks to our comprehensive line solutions. To ensure maximum line operating and process reliability, high efficiency, and low Total Cost of Ownership (TCO). With this in mind, we are consistently driv-
ing forward digitalization – through real-time analysis tools such as MULTIVAC Smart Services targeted towards predictive maintenance and machine learning. Thinking and acting sustainably, we are dedicated to the responsible use of resources and energy in terms of manufacturing our products and their use at your site.
Ultimately, we see ourselves as a partner who makes a decisive contribution to your business success – whether you are a start-up or a large company, when you decide on a MULTIVAC packaging solution, you opt for the highest level of quality and efficiency, comprehensive customer care, and perfect service. As a worldwide group with 85 subsidiaries, we are closely linked with our customers and their markets, allowing us to identify trends and developments early. As our customer, you benefit from our highly qualified sales and service team in your area.
MULTIVAC is the global leader in thermoforming packaging equipment. Our equipment can package a wide range of products efficiently and cost-effectively, including medical and pharmaceutical products, food, industrial and consumer goods. Our product range is the broadest in size, performance, and equipment: compact equipment for small volumes, high-speed equipment for large volumes, and specialized machines for producing applications, including specialized machines for producing applications such as MultiFresh™ packaging.
Our sales & technical service professionals are committed to helping our customers achieve their goals with the most innovative and reliable packaging solutions.
5600 Kieran, Montreal, QC H4S 2B5
Phone email
Website
800.811.6990
info@NJMPackaging.com
www.NJMPackaging.com
NJM Products Include:
Line Integration – NJM can integrate a tablet, powder or liquid packaging line. As part of this service, we provide equipment and then integrate turnkey systems at the customer’s plant, and offer in-plant training, documentation and validation support.
Unscramblers – NJM unscrambling equipment is compact and ideal for packagers. Our unscrambler is designed for round, rectangle, square or oval bottles.
Cappers & Retorquers – NJM cappers include inline belt, inline disc and rotary continuous models. Our compact design makes our cappers easy to incorporate into your packaging operation. We also supply retorquers of inline belt or inline disc type.
Cottoners – NJM cottoners are simple yet precise, with a guillotine tearing device as standard equipment, and options such as missing cotton detection and wisp detection.
Labelers – NJM labelers are customized for labeling applications, and all are built in the same way: robust, reliable and versatile, with electronic controls and up-to-date container handling features.
Liquid Filling & Closing – Aseptic liquid filling & closing systems for the pharmaceutical liquid dose industries are offered by our partner, Dara Pharmaceutical. NJM is Dara’s exclusive sales partner in the USA and Canada.
Tablet Counters – NJM offers tablet counters from our partner, Cremer. Cremer counters feature thoughtful design, robust construction, quality and accuracy. Cremer tablet counters are also simple to take apart for cleaning, without tools.
Washing, Sterilization, & Decontamination Equipment – NJM is the exclusive North American representative for Steelco’s Pharma and Biopharma products.
NJM, part of ProMach Pharma Solutions, offers a broad range of technologies and applications, specializing in the needs of pharmaceutical, nutraceutical/vitamin, and personal care product packagers. Complementing NJM’s manufacturing and integration expertise, we supply quality packaging line equipment from other leading manufacturers.
The full range of NJM’s services – manufacturing, representation of NJM’s distributed brands, and integration – makes NJM a one-stop packaging solutions provider offering expert knowledge and experience from the earliest stages of planning through implementation and production. NJM’s extensive portfolio includes unscramblers, tablet counters, bottle filling, cottoners, cappers, liquid aseptic processing/filling equipment, labelers, printers and coders, washing, sterilization, & decontamination equipmemt, end-of-line equipment, as well as custom solutions and software.
4000 College Rd, Battleboro, NC 27809
Phone email
Website
Ossid LLC, a ProMach brand, is committed to providing our customers with a superior line of medical packaging machines.
Working with customers in the medical industry, Ossid provides sterile, safe, and effective packaging equipment solutions. There’s nothing standard about medical devices. Ossid understands the unique and complicated requirements of the medical industry and strives to meet those needs with precision and safety at the forefront of the design. That’s why Ossid’s line of thermoform fill and seal machines are flexible to fit your specialized needs, no matter the specifications. If you can imagine it, our team of engineers, with a combined 75 years of experience, will work to design it.
Ossid’s medical device thermoformers are versatile; packaging both flexible and rigid medical package types and are built in accordance with UL 508A standards.
These machines offer many features and
benefits including an auto web aligner, static eliminator, hinged upper tooling, servo actuated presses, and a robust framework and guarding package. These machines are ideal for packaging medical devices, dental kits, syringes, pharmaceuticals, and other products.
In addition to thermoformers, Ossid is also a master distributor for the Reepack brand of flow wrappers. With four styles to choose from, flow wrappers can provide a packaging solution ideal for products requiring a hermetic seal or a simple dust covering. Let our team guide you to the best packaging solution for your application.
Our comprehensive customer service program, including service technicians, parts and training teams know how to help you keep your equipment running at maximum efficiency. Ossid helps its packaging customers protect and grow the reputation and trust of their consumers. ProMach is performance, and the proof is in every package.
Our mission at Ossid is to provide our customers with cost-effective packaging and labeling solutions. Ossid works to give our customers a complete flexible packaging solution. Providing customers with excellent service nationwide, we can respond quickly to customers experiencing downtime needs and offer preventive maintenance programs to reduce overall downtime concerns. Our goal is to build long term relationships with our customers. Our committed sales, service, and aftermarket parts teams work collectively to quickly and effectively assist customers with their needs.
ProMach can offer solutions for any customer project or application needs by providing best in class stand-alone equipment from industry leading product brands, partial line integrations, and complete large multi-brand turnkey packaging line integrations.
2037 East Maule Ave, Las Vegas, NV, 89119
Phone
Website
702-450-0808
info@paxiom.com
www.paxiom.com
Paxiom is a leading provider of primary, secondary, and end-of-line packaging machines with more than 30 years of industry expertise. Designed and manufactured through our WeighPack Systems, EndFlex, and ValTara brands, and supported by Paxiom Service, our state-of-theart packaging solutions are engineered to fit a wide variety of production requirements, spaces, and budgets.
Our group has delivered over 7,000 packaging machines and fully automated systems throughout the world while creating long-lasting relationships built upon hard work, integrity, and exceeding customer expectations.
Our packaging automation technology includes net weigh filling, multi-head weighing, auger filling, optical counting, vertical/horizontal form fill & seal bagging, premade pouch bagging, flow wrapping, container unscram-
bling, container filling, capping, induction sealing, labeling, cartoning, corrugated case or tray forming, robotic case or tray packing, sealing and closing, robotic palletizing as well as conveying, printing, check weighing and inspecting etc.
We engineer packaging solutions to automate all the stages of your healthcare packaging processes including bottle weigh filling, capping, induction sealing, labeling, bagging, wrapping, check weighing, cartoning, case or tray forming as well as robotic case/ tray packing, and palletizing for retail display, merchandising and distribution within the nutraceutical and pharmaceutical industries.
Follow us on social media: Linkedin, Instagram, X, TikTok: @paxiomgroup
FaceBook: @paxiomXperience
Visit our website Paxiom.com to watch all our real-life application videos and customer installs. Come visit our Las Vegas Xperience Center to see, test, and operate our packaging machines in person.
Our mission is to customize complete turnkey solutions to meet almost any production need. We have a deep lineup of automated packaging machines from upstream weigh fillers and baggers to downstream case packers and palletizers.
We engineer and manufacture the machines you need to fully integrate your automated packaging line, giving you the peace of mind that comes from one vendor taking complete line responsibility. Let’s start your system today!
Learn more about our brands: weighpack.com, valtaratec.com, endflex. com, canapasolutions.com
32 Case Street, Poland, NY 13431
Phone email Website
800.848.8483
perfex@perfex.com
www.perfex.com
Perfex Corporation is a world leading manufacturer of innovative cleaning tools for controlled environments. Established in 1924, PERFEX® celebrates 100 years of excellence fueled by passion and dedication.
Our founder believed cleaning tools should be designed to eliminate associated safety issues, to this day we develop each product with the same idea in mind. Reliable tools, made from quality materials, to meet and exceed the demands of today’s hygienic concerns.
PERFEX is the pioneer of TruCLEAN® mopping systems, a first-of-its-kind design specific for ultra-high sanitation areas, cleanrooms, laboratories, and controlled environments. Manufactured in the United States, TruCLEAN mopping systems include autoclave compatible stainless-steel components and temperature-resistant polypropylene buckets.
TruCLEAN mopping systems are lightweight, ergonomic and easy to use on floors, walls, and ceilings. Available in multiple configurations and colorways, suited for large or small area cleanrooms of any grade. Capture and isolate contaminants to ensure the delivery of pure cleaning agents, NO more dirty water or weakened solutions.
TruCLEAN cleanroom mops incorporate specialized materials to promote economical and consistent cleaning methods without leaving residual contaminants. TruCLEAN Sponge is the first mop designed specifically for use in controlled environments and remains as the benchmark for critical cleaning professionals worldwide.
NEW - TruCLEAN Sterile includes sponge mops and mop covers gamma sterilized and validated per AAMI standards for healthcare products.
PERFEX also manufactures a complete line of color-coded brooms, brushes, and squeegees hygienically designed to prevent cross contamination. Our patented heat-fused brush fiber design eliminates fiber fall-out and areas for contaminants to collect.
Our experienced team is committed to providing you with the most effective cleaning systems available in the industry today. Perfex representatives are readily available for on-site evaluations, product support, and technical advice.
Perfex products can be found in diverse industries across the globe such as pharmaceutical, semiconductor, bioengineering, medical device, and life sciences. We keep our mopping supplies well stocked to ensure the safety of your workplace in emergency situations.
our ad on page 11
2346 Success Drive, Odessa, FL 33556
Phone
email Website
www.Pharmaworks.com
Pharmaworks Products Include:
• TF1 Blister Machine – A simple and costeffective blister packaging solution. The TF1 blister machine is perfect for entry-level packagers where budget matters.
• TF1e Blister Machine – Features a compact footprint, quick changeover, and the latest in servo technology. The TF1e is perfect for small, medium, or clinical production.
• TF1pro Blister Machine – The latest in blister packaging technology, the TF1pro is built for today’s demanding cGMP and changeover requirements.
• TF2 Blister Machine – A medium output workhorse that is great for deep-draw medical devices and consumer products.
• TF3 Blister Machine – All the features expected in a high output machine.
• BlisterMate – A standout semi-automated blister machine that is great for R&D, low volume type production.
• Vision Systems – Scanware blister and print vision inspection systems.
• Feeding Systems – Pharmaworks provides a variety of feed systems.
• Blister Machine and Cartoner Rebuilds –Pharmaworks is the clear leader with over 20 years of experience rebuilding and upgrading third-party equipment.
• Tooling & Change Parts – Pharmaworks is the go-to source for tooling for any supplier’s equipment.
Pharmaworks, part of ProMach Pharma Solutions, is the premier supplier of blister packaging machinery for North America and has a worldwide installed base. Backed by the power of ProMach, Pharmaworks can turnkey any size blister project from our expanded production facility in Odessa, FL. For 20 years, Pharmaworks has set ourselves apart from other OEMs by not only selling our line of blister machines and equipment, but by rebuilding and upgrading other OEM brand equipment. This uniquely positions Pharmaworks to be a full-service provider for our packaging customers.
Industries served:
• Pharmaceutical
• Medical/ Medical Device
• Animal Health
• Nutraceutical & Vitamin
• Personal Care
• Consumer Products
850 Pratt Blvd, Elk Grove Village, IL 60007
Phone
Website
847-437-1427
sales@pmikyoto.com
www.pmikyoto.com
Based in Chicagoland since 1993, PMI has continued to expand our operations and product offerings as customer demand increased. We have worked to ensure our customers have been satisfied with the quality machines built, installed and continuously supported by our team of qualified engineers and technical professionals. Our headquarters in Elk Grove Village, IL, houses our engineering, manufacturing, engineering and testing facility next door.
Our parent company is committed to the advancement, support and service of the global packaging industry with best-in-class products and service offerings. Backed by and experienced team of 400 engineers from Kyoto Seisakusho, our engineering team will continue to advance our product lines and our tradition of well-built packaging equipment, including :
Horizontal Cartoners
Vertical Cartoners
Case Packers
Robotic Systems
Intergrated Systems
We take pride and go extra mile to make sure that your machine meets and exceeds your expectations. Our philosophy of designing rugged, well-crafted machines will assure your highest efficiencies with minimum cost of ownership while your machine runs for many decades. It is common to find PMI machine running at high efficiencies 20 years after installation. PMI KYOTO machines are built to last
426 East Fountain Road Webb City MO 64870
Phone email
Website
417.673.6542 info@prosysfill.com
ProSysFIll.com
ProSys is a premier manufacturer of semiautomatic and fully automatic equipment for filling, Squeeze Tubes, Syringes, Airless Pumps, Cartridges, Jars, Containers & Hot Melt applications for the Pharmaceutical industry. A global supplier of filling equipment since 1985 with U.S. sales, manufacturing and customer service facilities located in Southwest Missouri.
FEATURES & BENEFITS
• Fill Accuracy of +/- 0.1% by Volume
• Turnkey & Custom Designs
• Air-Free Vertical Bottom-Up Filling
• Custom Mix Solutions (Eliminates Batching)
• Drum & Pail Presses
• SERVO Solutions
• Explosion Proof Controls (Class 1 Division 1&2, ATEX 0&1)
• Tool-free Release System for Simple Changeovers
• “Digital Readout Indicators” for Fast & Accurate Adjustments
• Multiple Service Technicians for Less Down Time & Preventive Maintenance
• On-line Service & Support
• Recipe Storage & Recall
• Creams, Lotions & Viscous Pastes to 3 Million Centipoise
• Designed & Built in the U.S.A.
MAJOR MARKET GLOBAL INSTALLS
• Pharmaceutical
• Cosmetic
• Chemical
• Adhesive/Sealant
• Lubricant
• Food
Building Quality, Integrity & Value in Our Team, With Our Customers, & in the Equipment We Design, Build & Deliver.
FLEXIBLE COMBINATION SYSTEMS
• Plastic & Metal Tube Filling Systems
• Tube & Airless Pump Filling Systems
• Tube & Cartridge Filling Systems
• 10, 14 & 30 oz. Cartridge Filling Systems
Squeeze Tube Filling Machines speeds from 15 to 300 per minute.
Syringe Filling Machines speeds from 20 to 300 per minute.
Airless Pump Filling Machines speeds from 15 to 300 per minute.
Cartridge Filling Machines speeds from 10 to 250 per minute.
Custom Filling Systems
36
Unit 25 Carrowreagh Business Park, Carrowreagh Road, Dundonald, Belfast, BT16 1QQ
Phone email Website
+44 2890 48 48 48 / USA 616-888-9081
info@sepha.com
https://sepha.com
Sepha provides a range of innovative leak testing solutions, deblistering machines, and small-scale blister packing machines for pharmaceutical and healthcare products.
CCIT & Leak Test Solutions
Sepha offers a range of non-destructive and deterministic CCIT & Leak Test solutions for various types of parenterals, blister packs and medical device packaging.
Key features:
• Enable to identify leaks as small as 1μm
• In line with ASTM standards & USP 1207 guidelines
• Can form part of 21 CFR Part 11 compliant system
Small-scale Packaging Solutions
Sepha offers a range of blister packaging machines, that can handle thermoform and cold-form materials, to package tablets, capsules,
medical devices and other products. Designed with full 21 CFR Part 11 capabilities.
Ideal for:
• Clinical trials and stability studies
• Package development
• Low volume production of specialist drugs
Deblistering solutions:
Sepha provides a range of automatic, semiautomatic, and manual deblistering machines for the safe recovery of drugs from all blister pack types.
Key characteristics:
• Suitable for push-through, child resistant and peelable blisters
• Deblistering capacity up to 60 blister packs per minute
• Handles thermoform/alu and coldform/alu blisters
• No product or foil contamination
With over 40 years’ experience in the pharmaceutical packaging industry, Sepha has a great understanding of the packaging requirements and role primary packaging plays in bringing new drugs to market.
We have established a global reputation for innovation and development of tailored, highquality equipment for use in the manufacture of pharmaceutical blister packs, parenterals, medical devices and healthcare products.
In line with our philosophy to ensure quality and safe products for patients and their families, we have partnered with hundreds of pharmaceutical companies across the globe. We understand their needs to ensure product security through package integrity and the importance of extended shelf life and speedto- market. Their success is our success.
The owners, management, and staff of Starview are dedicated to designing and manufacturing packaging machines in North America with the highest quality fit, and finish backed up with industry leading customer service.
Phone
Website
514-920-0100 ext.310
sales@starviewpackaging.com
www.starviewpackaging.com
Starview Packaging Machinery, Inc. is the leading manufacturer of packaging machinery for high-visibility packaging with over 30 years of supplying standard and custom packaging systems to our customers. Providing the Medical Device and Pharmaceutical Industry with innovative packaging machines for:
• Medical Device Packaging
• Pharmaceutical Packaging
• Blister & Clamshell Packaging
• Customized Packaging Equipment
• Integrated Automated Systems
We design, engineer, and manufacture a comprehensive line of manual, semi-automatic, and automatic sealing machines. Available in shuttle, rotary, carousel, and inline conveyor configurations, a variety of standard and custom sealing areas are available to meet the specific requirements of customers and maximize
productivity. Machines are configured to suit the specific application such as carded packages, sterile medical device packages, or pharmaceutical wallet packages.
Our distinct competitive advantage is in providing a complete range of both standard and customized quality packaging systems backed by solid machine designs, robust machine construction, and superior service. Starview offers many value-added features for our machines such as product sensing, print-ing and/or verification, hydro-pneumatic cold seal presses, robotic product loading, automatic packaging materials loading, automatic inline fold-over, finished package unloading with reject features. Quick-change mechanisms for tooling sets, on-screen sealing press adjustments, machine performance tracking, and ANSI Class 4 safety make Starview machines an excellent choice.
Starview’s directive is to produce a full range of sealing machines for medical device packaging, pharmaceutical packaging and retail high visibility packaging. We offer standard machines with an array of custom and in demand options to provide our clients with machines to match their manufacturing requirements. We are fast, efficient and client focused. We invite you to come and experience the Starview Advantage.
1395 Gateway Drive, Elgin, IL 60124 USA
847.697.4900
www.weilerengineering.com
Weiler Engineering, Inc., a leading provider of aseptic custom Blow/Fill/Seal liquid packaging equipment for pharmaceutical and healthcare applications, is committed to the highest standards of excellence and to expand products and systems to enhance patient care. Weiler’s proprietary ASEP-TECH® B/F/S packaging machines produce shatterproof, durable, aseptically-packaged products in one uninterrupted operation. This hands-free manufacturing process ensures that parenterals, ophthalmic solutions, and respiratory drugs reach the marketplace sterile, in the most cost-effective manner possible - every time. The ASEP-TECH® System is the culmination of 64 years of innovation in machine design and sterile process development, producing the most advanced aseptic liquid packaging process machinery available today.
The Weiler design incorporates the threestep process of blow molding, aseptic filling, and hermetic sealing of liquid products in one
sequential operation on a compact machine frame. Weiler’s patented electronically controlled fill system, automatic sterilization system with integral data collection, and filter integrity test system are provided as standard equipment for each machine configuration. Each machine is also equipped with a HEPA air shower to ensure a Class 100 environment under dynamic conditions in the nozzle shroud area.
Weiler’s latest innovation is the NEW compact ASEP-TECH® LAB+ Blow/Fill/Seal machine, which is ideal for Stability and Clinical batches for pharmaceutical products and/or small development batches using advanced aseptic technology. This revolutionary small footprint design focuses on ease of changeover and product range flexibility.
ASEP-TECH® Blow/Fill/Seal machines are proudly made in the USA, designed and built by Weiler Engineering, Inc. in a 140,000 ft², stateof-the-art plant. Weiler’s facilities and corporate offices are located near Chicago’s O’Hare Airport.
INNOVATION DRIVEN BY SCIENCE!
FACTS:
• Recognized as an advanced aseptic technology by the USFDA
• 65 years serving global markets
• Experience gained from 25 years operating a captive pharmaceutical CMO
• Close operation with regulatory authorities – compliance is key!
• Quality + Operational Know-how + Integrity
GOALS:
• Focus on the science of the technology for maximum customer benefit
• Simplicity of design to maximize product flexibility and minimize footprint
• Optimum service support throughout the markets we serve = high customer satisfaction!
WLS, part of ProMach Pharma Solutions, is an industry-leading designer and manufacturer of high-speed rotary and in-line labeling machines and serialization, coding and label printing solutions for the pharmaceutical and medical packaging markets as well as the food, beverage, personal care, and consumer markets.
Phone email Website
Rotary Labelers – Pressure-sensitive labelers for labeling a variety of product shapes vertically.
Vertical In-line Labelers – Pressure-sensitive labelers for labeling a variety of cylindrical products vertically.
Label Heads – Pressure sensitive label heads with label print and inspection options including serialized codes and RFID tags.
Label Presence Inspection – WLS’s new VialView label presence inspection stand-alone station is ideal for verifying label presence prior to final packaging.
Label Coders – For stand-alone or integrated high-speed coding of labels, including serialized codes.
Label Printers – AUTONOMY® is a high-speed, full-color, stand-alone digital label printer with integrated full-label inspection system. Printing variable and serialized data with label artwork.
Vial Coders – For code printing on vials or bottles using ink jets or lasers.
Documentation & Certifications – DDS, FAT, SAT, IQ/OQ and Trace Matrix documents as well as UL, Seismic and CE certifications.
Field Service – US and European field service team also offering equipment training courses and maintenance contracts.
With over three decades of experience, our mission is to improve our customer’s labeling capabilities and ensure that our labelers provide them with the highest possible OEE.
Industries Served:
• Pharmaceutical
• Medical/Medical Device
• Nutraceutical & Vitamins
• Food
• Beverage
• Consumer Products
All Packaging Machinery Corp. 10, 48 www.allpackagingmachinery.com
Antares Vision Group 35, 49 www.antaresvisiongroup.com
Colbert Packaging Corporation 29, 50 www.colbertpkg.com
Delta ModTech 25, 51 www.deltamodtech.com
Dispense Works Inc. 41 www.dispenseworks.com
G&K-Vijuk Intern. Corp. 2, 52 www.guk-vijuk.com
Heat and Control, Inc. 53, OBC www.heatandcontrol.com
James Alexander Corp. 7, 54 www.james-alexander.com
Klöckner PHP 55 www.kpfilms.com
Marchesini Group USA Inc. 43, 56 www.marchesini.com
METTLER TOLEDO 57, 72 www.mt.com/pi
MG America, Inc. 9, 58 www.mgamerica.com
moviTHERM 17, 59 movitherm.com
Multivac, Inc. 60, IFC www.multivac.com
NJM Packaging 37, 61 www.njmpackaging.com
Ossid 34, 62 www.ossid.com
Paxiom Automation, Inc. 3, 63 www.paxiom.com
Perfex Corporation 11, 64 www.perfex.com
METTLER_TOLEDO-HalfPage-Horizontal_8x5.25-v01.pdf 1 9/3/2024 1:58:21 PM
Pharmaworks LLC 21, 65 www.pharmaworks.com
PMI KYOTO 5, 66 www.pmikyoto.com
PMMI 39, 46 www.pmmi.org
ProSys Fill LLC. 36, 67 www.prosysfill.com
Sepha Ltd. 24, 68 sepha.com
Starview Packaging 42, 69 Machinery Inc. www.starviewpackaging.com
Weiler Engineering, Inc. 31, 70 www.weilerengineering.com
WLS 71, IBC www.weilerls.com
P u | | M | B | M ...
Inspection and foreign object detection systems that offer unparalleled sensitivity for pharmaceutical products to protect
• CEIA high sensitivity metal detection; ferrous, non-ferrous, stainless steel
• Ishida X-ray for foreign object and product defects
• Ishida precision checkweighing for weight verification
• Powders, capsules, tablets, liquids
Heat and Control® offers a complete line of metal detectors, checkweighers, and X-ray inspection systems for pharmaceutical products from the leading manufacturers, Ishida and CEIA®. Technical support, demonstration, and testing is available in North, Central and South America.
Nov. 3-6, 2024 Booth N-6106 McCormick Place Chicago, IL, USA