NEWS BRIEF
Vote by noon
Voting for the Technology Excellence Awards closes at noon today (see story, p. 40). A video by PMMI Vice President, Trade Shows Laura Thompson introduces the 12 finalists (see packexpolasvegas.com/the-show/ technology-excellence-awards-finalists). Choose your favorite in each category: Food/Beverage, General Packaging & Processing, Personal Care/Pharma and Sustainability. Winners will be announced this afternoon. SD

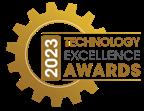
Streamlined automation
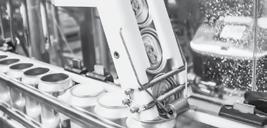
Bosch Rexroth (Booth SL-5964) demonstrates streamlined automation with a ctrlX AUTOMATION-powered, multitech layout consisting of a VarioFlow plus conveyor, which delivers high accuracy with unprecedented speed, and a Kassow collaborative robot. With more than 225 years of engineering expertise, the company’s comprehensive, harmonized factory automation portfolio offers advanced yet easy-to-use components and digital engineering tools. Customized support addresses the most intricate engineering challenges. SD
Paperboard tray line uses less material
Marchesini Group USA (Booth SL-6701) exhibits a Paperboard Tray Line with a newly designed tray. The innovative tray design Marchesini developed generates a savings of around 50% in paperboard and glue and occupies about 30% less space, saving in the final carton/shipper pack configuration, compared to current designs on the market. SD
Pressure check
Force Sensor from Teledyne TapTone (Booth S-4126) detects leaks and low pressure in containers dosed with liquid nitrogen, carbonated beverage containers and aerosol containers. Parallel belts transport the container at speeds up to 2.67 m/sec. (525 ft./min.). As containers move past, a sensor measures the tension on the sidewall. The system can check pressures up to 11 bar or 160 psi. SD
PMMI Foundation distributes $200k
PACK gives BACK™ and Golf Tournament raise funds.
PACK EXPO Las Vegas attendees relaxed on Sunday before the show opened playing in the Golf Tournament and attending a private PACK gives BACK™ performance of O™ by Cirque du Soleil®, an aquatic and acrobatic extravaganza at the Bellagio Hotel & Casino. Both events raised funds for the PMMI Foundation, the charitable arm of PMMI, The Association for Packaging and Processing Technologies (Central Lobby).
The 128 players in the Golf Tournament fundraiser enjoyed 18 holes at the Bali Hai Golf Club, right on the Las Vegas Strip, along with breakfast, sponsored by Festo (Booth SL-6160), and lunch, sponsored by Morrison Container Handling Solutions (Booth C-1651)
This year’s PACK gives BACK event drew a soldout audience of 1,800 and was generously supported by Title Sponsor Rockwell Automation (Booth SL-6127).
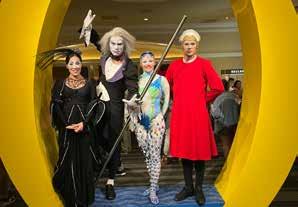
The money raised at the Golf Tournament and
PMMI unveils State of Industry, global trends

At a media lunch yesterday, PMMI, The Association for Packaging and Processing Technologies (Central Lobby) reported on the state of the industry, provided show updates and described global packaging trends.
The annual State of the Industry report notes shipments topped $10.2 billion in 2022, a 12.4% growth rate on top of an even stronger 2021. However, backlogs are declining and growth in 2023 is expected to be substantially lower, but still a healthy 3.4%. The report attributes the slowdown to “economic uncertainty and a high interest rate environment,” which

(Continued on page 8)
Sustainability Central debuts
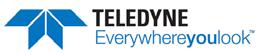
Interactive destination offers resources to improve sustainability of brands.
Anew, not-to-be-missed area of the show floor, Sustainability Central (Booth N-9455) and the accompanying Sustainability Stage (Booth N-9967) (see schedule, p. 16), offer an interactive destination where attendees can find ideas and material-agnostic information to improve a brand’s sustainablity profile.
Sustainability Central, presented by PMMI, The Association for Packaging and Processing
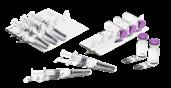
PACK gives BACK events at PACK EXPO International and PACK EXPO Las Vegas support PMMI Foundation’s scholarship programs. The proceeds from PACK gives BACK events provide $5,000 scholarships each year to six students attending a North American college or university. (Continued on page 4)
(Continued on page 10)
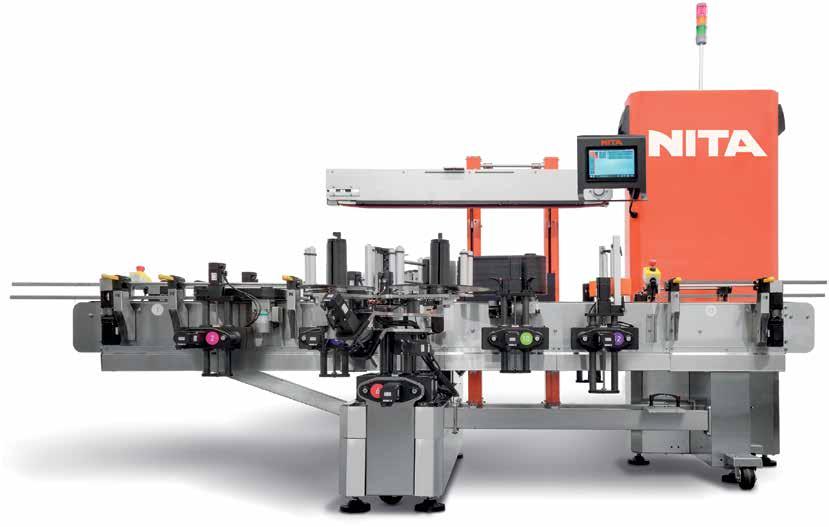
It is time to experience












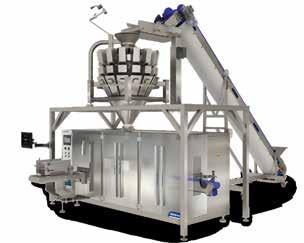
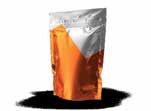

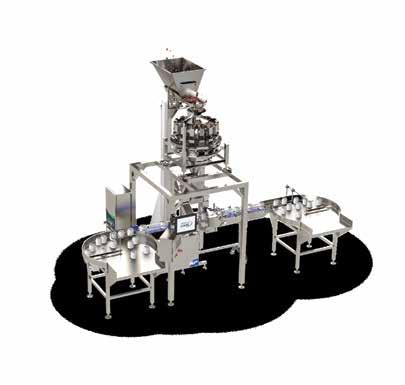
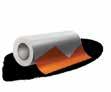
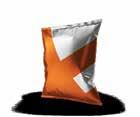
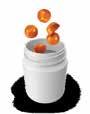
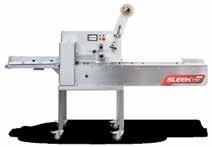


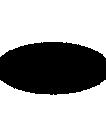


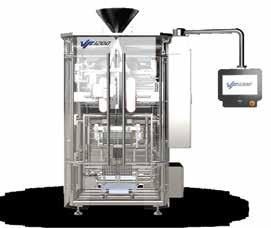
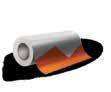
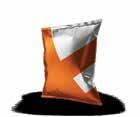
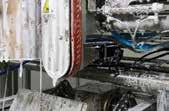
Holograms display fillers, case packers
Alongside the eye-catching machines running live at Syntegon (Booth C-2800), two immersive holograms are displaying other technologies from the company’s portfolio Osgood liquid-filling machines and Elematic case packers. The holograms’ educational visuals and voiceovers will show the viewer all that the machines have to offer. Displaying yet another way Syntegon thinks outside of the box—or carton. SD
Never forget
PMMI, The Association for Packaging and Processing Technologies (Central Lobby), recognizes the significance of PACK EXPO Las Vegas 2023 opening on Sept. 11th. To honor the men and women who gave the ultimate sacrifice that day, PMMI will match donations up to $50,000 to the Tunnel to Towers Foundation. Built upon the mantra, “While we have time, LET US DO GOOD,” the Tunnel to Towers Foundation supports our nation’s fallen and catastrophically injured first responders, military heroes and their families. Donate at packexpolasvegas.com/T2T-donation. SD
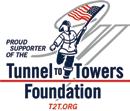
Spirals use vertical space
Spirals move products up, down or either direction in minimal space. Options from Ryson International (Booth C-4736) include Narrow Trak, mass flow and unit load spirals. Many spirals ship in one piece and are pre-tested, minimizing installation time and cost. The company also offers bucket elevators, which transport bulk materials horizontally and vertically. SD
sponsors hotel shuttle
Free transportation to the convention center is available daily from 7:00–11:00 a.m. and to show hotels from 2:00–6:00 p.m. on Monday and Tuesday and 2:00–4:00 p.m. on Wednesday. Buses to the hotels depart from outside the Central Hall. Shuttle buses are sponsored by Amicus Spend Management (Booth SU-7699A) SD
Boosting sustainability
Hitachi Industrial Equipment & Solutions America (Booth N-9520) has improved the environmental profile of its shipping processes and embraced sustainable packaging for the UX2 continuous inkjet printers manufactured at its Hitachi Taga facility. Expanded polystyrene, which is unrecyclable in several countries, has been replaced by 100% fiber-based corrugated and laminations. These materials are entirely recyclable yet offer equivalent efficiency and protection for the printers. Sustainable packaging will be expanded to other products. SD
has prompted end users to spend more conservatively. The report states, “While projects have not largely been canceled, they are being delayed while the market is in a ‘wait and see’ mentality.” This will result in a further slowdown in 2024 with a growth rate of only 0.5% anticipated. However, much stronger growth in the 6–8% range is expected for 2025–2027.
A significant portion of this growth will come in secondary packaging equipment, especially for warehouse applications, which are experiencing a need to automate. This is due to growth in eCommerce, mixed pallets, case packing and shrink wrapping.
NEW FEATURES, UPCOMING SHOWS
Jim Pittas, president & CEO, PMMI, encouraged editors to take advantage of new show features including Sustainability Central (Booth N-9455) and its Sustainability Stage (Booth N-9967) (see schedule, p. 16), the Logistics Pavilion also in the North Hall, the Healthcare Packaging Pavilion in the South Lower Hall and the Industry Speaks Stage (Booth C-1141) (see schedule, p. 24). He also discussed upcoming shows including PACK EXPO East (March 18–20, 2024; Pennsylvania Convention Center; Philadelphia), PACK EXPO International (Nov. 3–6, 2024; McCormick Place; Chicago) and the launch of PACK EXPO Southeast (March 10–12, 2025; Georgia World Congress Center, Atlanta).
GLOBAL TRENDS
The media briefing concluded with an overview of global packaging trends and challenges by Pierre Pienaar, president of the World Packaging Organisa-
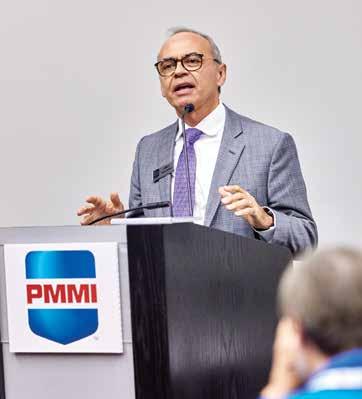
tion (Booth C-1246). According to Pienaar, the top five trends for the last 12 months have been sustainability, smart packaging, on-demand packaging, artifical intelligence and nanotechnology. He concluded, “Sustainability is the only way forward. We’ve made a difference to society and changed industry focus but each of us has to do it. We are at a crossroads.”
For more info, visit packexpolasvegas.com, pmmi.org, worldpackaging.org. SD
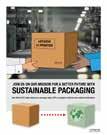
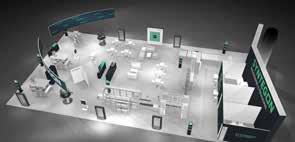
New ink dries quickly on PE
HP (Booth N-10054) adds another solvent ink to its portfolio with the introduction of the HP 2600 solvent print cartridge. The new ink broadens the array of substrates and applications compatible with thermal inkjet (TIJ) technology. Meanwhile, HP continues to invest in its TIJ 2.5 platform.

Available now via HP Partners, the new HP 2600 solvent ink is optimized to print on both treated and untreated polyethylene*, which often is specified for flexible food packaging.
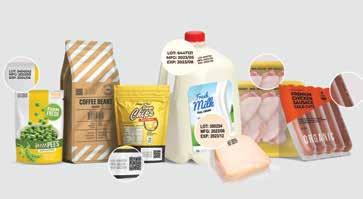
Designed with efficiency in mind, this latest ink formulation was developed with a fast, stable dry time of less than 3 sec. on every substrate tested. The HP 2600 ink also provides outstanding durability on polyvinyl chloride, as well as on other films such as biaxially oriented polypropylene.
Paired with HP Partner’s TIJ-based coding and marking printers, the HP 2600 solvent cartridge can
provide easy-to-use and low-maintenance advantages to end users to address labor shortage issues and increase production line efficiencies.
For more info, visit hp.com/thermalinkjet. SD
* CCL and Blueridge used during the testing at HP
Secondary & End of line
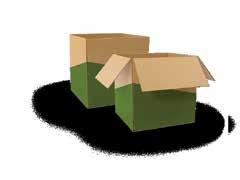





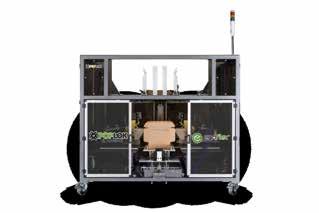








When the choice is yours, why not choose more? A leading provider of primary, secondary, and end-of-line packaging machines, Paxiom has more than 30 years of industry expertise. Operating from seven global facilities, with a passionate and focused staff of professionals with the strongest national service presence, the ability to provide systems integration, and an installed base that included more than 7,000 machines across the world. Paxiom. Get more.
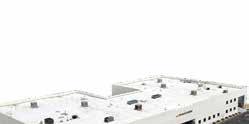
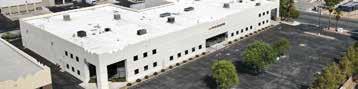

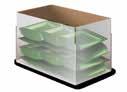



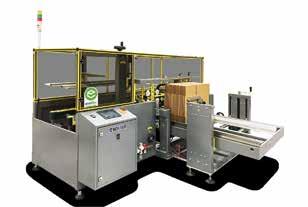



Students race to complete tasks
The annual Amazing Packaging Race competition, sponsored by Emerson (Booth SL-6107), will take place tomorrow. Teams from colleges, trade schools and universities will take on tasks assigned by two dozen exhibitors. “We are thrilled to be part of this hands-on event that celebrates technology and innovation, two principles deeply rooted in Emerson’s heritage,” says Emerson vice president Jay Gatz. At the conclusion of the race, First, Second and Third Place teams will be recognized. Each First Place team member wins $1,000; Second Place and Third Place team members receive $500 and $250, respectively. SD
Tequila maker boosts output
At Sauza Tequila, visualization and control technology from Rockwell Automation (Booth SL-6127) has boosted production 16%, the equivalent of 107 million L of tequila, and cut water consumption 75%. The technology supplied by Tecno Productos, gold-level member of Rockwell’s PartnerNetwork™, manages operations from recipe and batch management through equipment cleaning and automatically generates reports required by regulators. SD
Onebutton changeover
PLC-controlled, servo-driven, fully automatic labeler from Quadrel Labeling Systems (Booth C-1655) changes over with the press of a button. The new design reduces changeover time to less than 2 min. and is available on ProLine models. SD

Custom-printed cartons
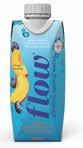
Flow Beverage debuts five custom spring water cartons for select Live Nation Canada venues. The designs represent the first commercial use of Tetra Pak Custom Printing from Tetra Pak (Booth C-4340). The premium inkjet-based carton package printing technology combines customizable printing for limited editions and other promotional campaigns with the environmental benefits of paper-based beverage cartons. Ola Elmqvist, executive vice president Packaging Solutions, Tetra Pak, concludes, “Digital printing opens a world of opportunities for brands . . . and it is an ideal solution for startup businesses launching a new product.” SD
Multi-protocol servo drives
Festo (Booth SL-6160) introduces the CMMT MP family of multi-protocol servo drives, which can be configured as EtherNet/IP, EtherCAT, PROFINET and Modbus TCP. The multi-protocol strategy reduces drive inventory, improves engineering productivity and simplifies tech support. To choose the protocol, engineers log into the drive using the free online productivity tool Festo Automation Suite, select the protocol from a drop-down menu and configure the unit. SD

SEPTEMBER 12, 2023
Map leads to digital transformation
New project, People First initiative, needs volunteers.
The new Digital Transformation Roadmap from the OpX Leadership Network (Central Lobby) helps consumer packaged goods companies and OEMs make the transition from manual to digital processes.
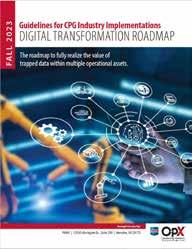
Written by technology experts from companies like Rockwell Automation (Booth SL-6127), Siemens Digital Industries (Booth SL-6351) and Emerson Discrete Automation (Booth SL-6107), the document explains why companies should implement the IIoT (Industrial Internet of Things) and provides a step-by-step process that includes obtaining data, structuring data, understanding what the data means and taking action. It’s available for free download on the OpX Leadership Network website.
Yesterday, at the Executive Council Meeting of the OpX Leadership Network, its People First Task Force reported on its research to identify resources for improving the work environment, working conditions, career pathing, scheduling and compensation. The Task Force found current tactical measures are not adequately preventing turnover and call-offs, nor filling open positions.
“A new, more strategic approach is needed to align our manufacturing processes to succeed in the future labor market,” says Bryan Griffen, director, Industry Services, PMMI, The Association for Packaging and Processing Technologies (Central
Lobby), and convener of the OpX Leadership Network.
As a result, OpX decided to convene a new Solutions Group to develop the strategies and tools that will lead the industry to a stronger, more diverse and dynamic workforce. The Solutions Group is asking for volunteers with technical and human resources expertise to participate in this revolutionary work product.
The People First initiative is an outgrowth of the Workforce Engagement work product, published by OpX in 2015. Its goal is to overcome difficulties in hiring and retaining personnel by shifting opinions that manufacturing is dark, dirty and dangerous to an understanding that it is advanced, technological, valuable to society and a worthwhile career.
Griffen, who has served as managing director of the group is departing and will be succeeded by Tom Egan, vice president of Industry Services, PMMI. For more info, visit opxleadershipnetwork.org. SD
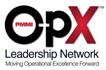
Publisher
PMMI Media Group
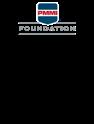
Editorial Director
Hallie Forcinio
Associate Editor
Barbara Rook
Production Manager
Mary Thorne
Art Director
Debi Friedmann
IT/Production Support
Manny Dominguez and Olga Minkevich
Photographers
Miles Boone and Edyta Sokolowska
Advertising Sales Management
Dave Newcorn, President, PMMI Media Group
John Schrei, Vice President, Sales, PMMI Media Group











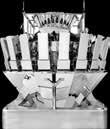
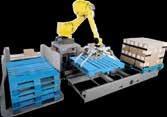


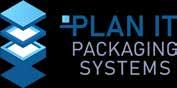

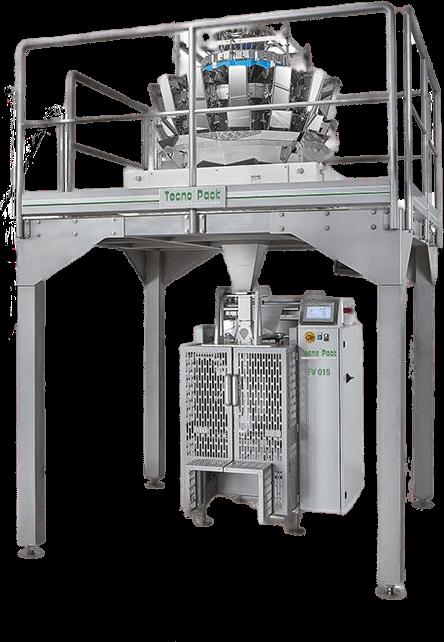











DISCOVER THE FUTURE OF PACKAGING
SUSTAINABILITY
SEPTEMBER 12, 2023
(Foundation Continued from page 1)
During the past year, the PMMI Foundation has awarded nearly $200,000 in educational scholarships to students pursuing careers in the packaging and processing industry.
“The PMMI Foundation scholarships embody our commitment to fostering the future of our industry, and we take immense pride in paving the way for aspiring industry leaders to excel,” says Kate Fiorianti, director of Workforce Development, PMMI. “These scholarships not only recognize the dedication and passion of the recipients but also showcase the unwavering commitment from PMMI to foster excellence in our industry.”
Scholarship recipients fall into several categories. PMMI Member Family Scholarships ($5,000 per student) support immediate family members of PMMI member company employees who are interested in packaging and processing as a career choice.
NORTH HALL, Booth N-9455
Attain a complete understanding of packaging sustainability and what that means for your brand.
Reshape Your Brands Impact
Explore 6 key areas of packaging sustainability encouraging you to think outside the box.
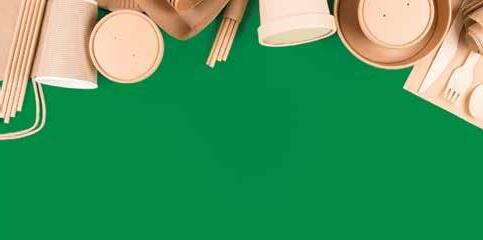
• Manufacturing
• Material
• Design
• Logistics
• Recovery
• Analytics
Find Inspired Ideas
Talk with top universities about their projects centered around sustainability and the circular economy.
• Michigan State University
• Wisconsin Stout
• Indiana State University
PMMI Memorial Scholarships honor Claude S. Breeden, Glenn Davis and Art Schaefer and provide financial assistance to students attending two-year colleges in North America.
2023 PACK EXPO SCHOLARSHIP RECIPIENTS
HALEIGH GARTNER
Clemson University, Packaging Science
JULIANNE HOM
California Polytechnic State University, Packaging Value Chain
MARISSA RUPERT
Pennsylvania College of Technology, Automation and Engineering, Mechatronics
CADEN SAND
Alexandria Technical and Community College, Mechatronics
JEFFREY SANTOS
Hennepin Technical College, Automation and Robotics Engineering Technology
SIERRA SETON
Toronto Metropolitan University, Graphic Communications Management
2023 MEMBER FAMILY SCHOLARSHIPS RECIPIENTS
MICHAEL BESKE-SOMERS
University of Vermont, Mechanical Engineering
GAVIN FRANZ
Michigan State University, Electrical Engineering
IAN HOHN
Colorado State University, Computer Engineering
TRENTON HOHN
University of Iowa, Chemical Engineering
RILEY HOSKINS
University of South Carolina - Darla Moore School of Business, Business
ARYEH LEVY
Tulane University, A.B Freeman School of Business
NORAH MALLOY
Saint Catherine University
SAM MANAK
University of Wisconsin Whitewater, Business
CHAD REXON
Rowan UniversityCollege of Business, Marketing
BEN ROBSON
University of Wisconsin Parkside, Business
CHRISTIAN SHORT
Florida Polytechnic University, Mechanical Engineering
JOCELYN SIOUI
The Pennsylvania State University, Finance
ROBERT WALL
Purdue University, Mechanical Engineering
ALEXANDRIA WALL
Purdue University, Mechanical Engineering
RYAN WOLFE
Shippensburg University, Accounting/Finance
2023 MEMORIAL SCHOLARSHIPS
RICARDO CARRANZA
Gateway Technical College, CNC Programming
ALEXANDER KONG
Booth: N-9967
Get Insights from Experts
FREE sessions on how to make your brand more sustainable.
JEFFREY GANDY
Hennepin Technical College, Robotics Engineering
AUSTIN HOLDERNESS
Hennepin Technical College, Mechatronics A.A.S
STEVEN JONES
Metropolitan State University, Computer Science
KARAN KARADENNAVAR
Rochester Institute of Technology, Print and Graphic Media
Hennepin Technical College, Automation Robotics Engineering Technology
BENJAMIN PEDERSEN
Hennepin Technical College, Automation Robotics and Engineering Technology
THOMAS WELLS
Dunwoody College of Technology, Automation and Controls Engineering Technology
(Continued on page 10)
Vertical Conveying. Simplified.






Spiral Conveyors & Bucket Elevators
















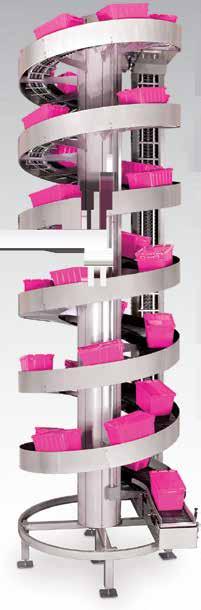
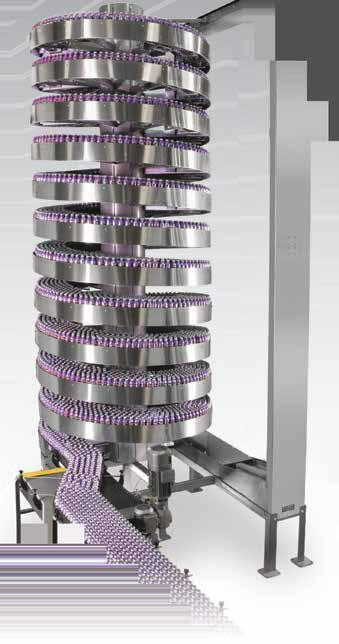
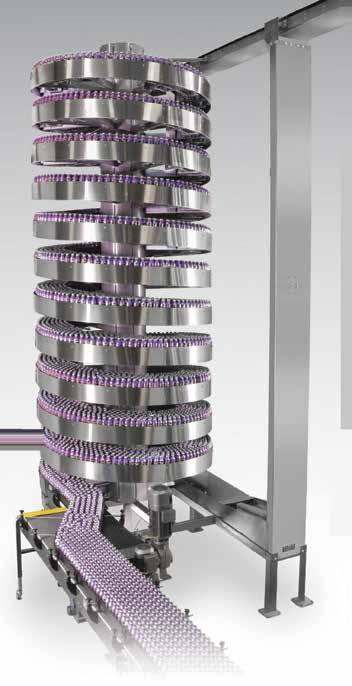



Unit Load Spirals convey cases, totes and packaged goods smoothly on our slat style belts and come in 9 standard slat widths ranging from 6” to 30”. Available in powder coated carbon steel, stainless steel, wet environment and freezer versions.
Mass Flow Spirals handle full and empty bottles, cans and jars in mass up to 2,000 units per minute. Available in 4 different slat widths ranging from 6” to 20”.
Narrow Trak Spirals are super compact and designed to handle smaller loads. Our 6” and 9” wide nesting slats can end-transfer small cartons and packages or side-transfer small bottles and containers in a single file or in mass at speeds in excess of 220 FPM.
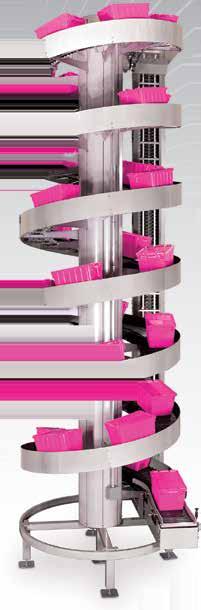
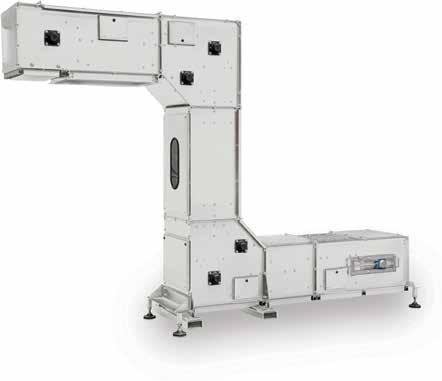
Ryson’s Bucket Elevators combine vertical and horizontal transportation of bulk materials in one integral unit.
Our Bucket Elevators are designed for gentle handling and well-suited to transport a broad range of bulk products. They are completely enclosed with overlapping pivoting buckets, that prevent spillage and helps mitigate foreign debris.
They can be configured with multiple inlets or outlets that can be controlled individually. Available in three standard bucket sizes, yielding capacities up to 300, 700 or 1,800 cubic feet per hour. They can also be delivered in powder-coated carbon-steel, or stainless-steel for wet environments.


All Ryson equipment is modular and built to order. No matter the application, the Ryson team is up to the challenge of finding solutions for your conveying needs. For application assistance or more information, give us a call or visit www.ryson.com
Check out our running equipment at Pack Expo | Booth C-4736






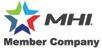

www.ryson.com





























(757) 898-1530

Ryson Spiral Conveyors need less floor space than conventional conveyors and are faster and more reliable than any elevator or lift.
pavilion
hotspots
find targeted solutions
NORTH HALL
The Containers and Materials Pavilion
Find new sustainable materials, flexible packaging, printable films and more. Also see award winning packages at:
PACKage Printing Pavilion
Explore technology that makes customization, promotions, small runs, on-demand production and smart packaging cost effective.
The Logistics Pavilion
Find supply chain solutions including warehousing and dock equipment and systems, inventory management and control, distribution logistics services and transportation.
The Processing Zone
Find front-of-the-line solutions for food and beverage processing and discover ways to increase safety, improve efficiency and achieve total system integration.
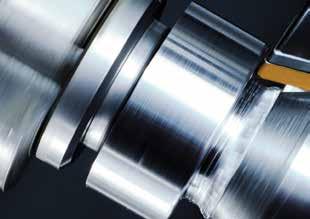
SOUTH UPPER HALL
The Confectionery Pavilion
Uncover specialized equipment and integrated systems for your candy, chocolate, mints and gum production lines.
Sponsored by:
The Reusable Packaging Pavilion
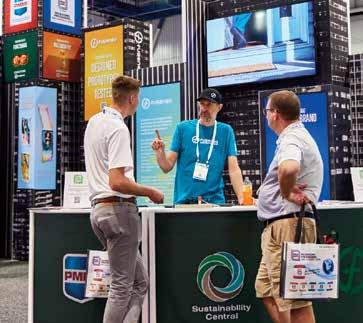
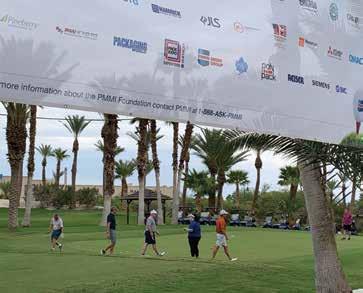
Discover reusable assets that not only reduce waste but also provide more reliable protection for your production and can be part of a smart supply chain.
Sponsored by:
SOUTH LOWER HALL
The Healthcare Packaging Pavilion
A one stop shop for solutions targeted to pharmaceuticals, biologics, nutraceuticals, medical devices and more.
SEPTEMBER 12, 2023
(Foundation Continued from page 8)
Other $5,000 awards include the Electrical Engineering Scholarship, awarded to Gavin Boomsma from Michigan State University; the Mechanical Engineer Scholarship, given to Nathan Gessler from Colorado Mesa University; the Processing Scholarship, bestowed on Supriya Korade, who is studying Food Process Engineering at the Illinois Institute of Technology; and the Packaging & Processing Women’s Leadership Network Scholarship, recognizing Molly Coonfield, a Mechanical Engineering student at Montana State University.
Finally, the $5,000 Chuck Yuska Scholarship, established in honor of PMMI’s former president & CEO of 28 years, recognizes a student representing innovation in the packaging industry. This year’s recipient, Lexi McFarlane from California Polytechnic State University, San Luis Obispo, is studying Packaging Value Chain.
For more information, visit pmmifoundation.org. SD
Technologies (Central Lobby) and curated by Fuseneo, highlights key areas of packaging sustainability.
“We want to present all options and help brands make decisions from equipment to logistics to materials,” says Brent Lindberg, founder and Head of Curiosity at Fuseneo.
(post-consumer recycled) cushioning machine from Pregis. HC Renew PCR cushioning features an 80% PCR message and provides the same protection and durability as traditional air cushions but reduces carbon emissions by 40%, fossil fuel usage by 65% and water usage by 70% when compared to cushioning film made with virgin resin. A How2Recycle® store drop-off label provides clear guidance on proper disposal.
Recovery participants include Pact Collective, Plastic Bank, Purecycle, Recycled Material Standard, SCRAPP, SmartLabel, Terracycle/Loop, Tetra Pak and WMU. Logistics participants include AIM, CAPE, Flock, MagicLogic and Sifted. Analytics participants include AMERIPEN, Atlantic Packaging, EarthShift Global, ISU and Trayak/Compass.
Also available at Sustainability Central, the PACK EXPO Sustainability Solutions Finder, a targeted, curated list of sustainable solutions, created by PMMI Media Group (Central Lobby)
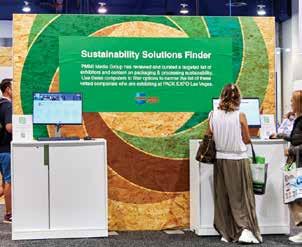
For more info, visit packexpolasvegas.com/green, fuseneo.com. SD
A range of sustainability advances are displayed including yet-to-be-commercialized options from university researchers at Cal-Poly, Indiana State University, Michigan State University and Wisconsin Stout.
Other Sustainability Central participants are divided among manufacturing, materials, recovery, logistics and analytics innovators. Manufacturing participants include Atlantic Packaging, BW Pack, Compass, CMC Automation, Emerson, Festo, PMMI, Rockwell and Schneider.
Materials participants are Ahlstrom, Amcor Rigid Packaging, Atlantic Packaging/CruzFoam, Ball, Billerud, DOW, Ecovative, Envision, Evoware, Flexible Packaging Association, Graphic Packaging, PaPack, Paperfoam, Pregis, Printpack, Smyth, Sonoco, Sway, Temperpack and TIPA.
One materials participant, Pregis, demonstrates how an inside-the-box shipping solution meets the growing demand for circular packaging with its AirSpeed® hybrid cushioning (HC) Renew™ PCR
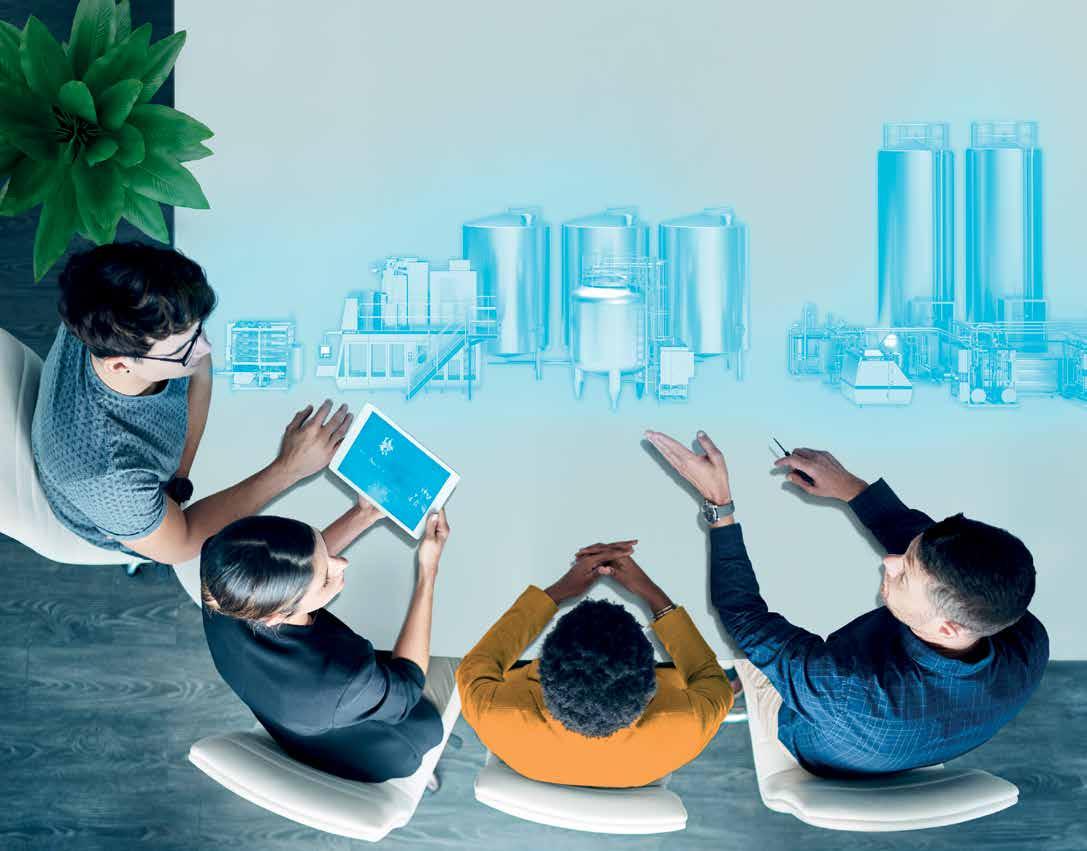
SEPTEMBER 12, 2023
Use vertical space
Kick back and dine for leSS!
Kick back and dine for leSS!
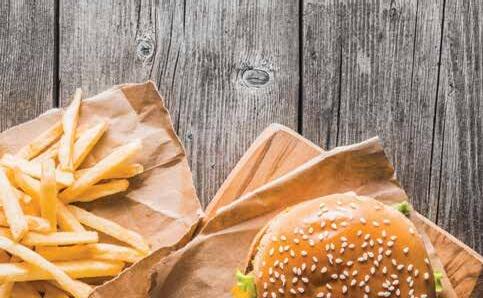
Visit
Spiral conveyors from AmbaFlex (Booth C-5238) move product to different levels but also can provide portal access, buffering, dynamic accumulation, etc.
Open Daily Open Daily In North Hall
back of the show floor
11:00 AM - 3:00 PM Monday - Wednesday
Refuel Relax Return
FIRST-TIME ATTENDEE LOUNGE
Perhaps even more important to line efficiency is the potential to move some processes overhead to utilize every inch of available floor space. When designing or upgrading layouts, using vertical space opens up untapped potential. For example, elevating products a few meters and returning them to floor level for the next step leaves space for additional machines, walkways, or other applications.
South Upper Hall Room S-220
HOURS OF OPERATION:
Monday – Tuesday: 8:00 am – 5:00 pm
Wednesday: 8:00 am – 3:00 pm
If your badge says “First-Time Attendee” stop by to:

• Ask questions of show staff
• Access product locators
• Enjoy refreshments and comfortable seating
• Attend special sessions
MONDAY, SEPTEMBER 11
8:30 am PACK EXPO 101: Navigate the Show Like a Pro
1:30 pm Bringing Your Products to Market Using Contract Packagers & Manufacturers
TUESDAY, SEPTEMBER 12
8:30 am PACK EXPO 101: Navigate the Show Like a Pro
1:30 pm How to Make Your Product’s Packaging Environmentally Friendly
WEDNESDAY, SEPTEMBER 13
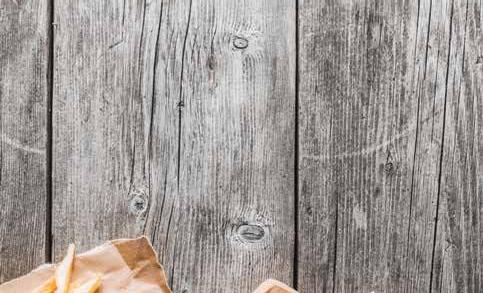
8:30 am PACK EXPO 101: Navigate the Show Like a Pro
One dairy plant wanted to add a bundling machine. Putting it on an overhead plateau with a stainless-steel SpiralVeyor 1xSV300 unit on one end and a SpiralVeyor 1xSV600 unit on the other eliminated the need to rearrange the line. The flow of ice cream pints moves upward to the bundler, and bundled product travels back down for the next step. The systems are washdown-compatible and occupy a 30% smaller footprint compared to alternative options. A 1-min. maintenance program enables engineers to complete most maintenance tasks within minutes and maximizes uptime.
For a nutraceutical project, AmbaFlex worked with DCC Automation (Booth SL-6269) to provide multiple washdown-compatible stainless-steel SpiralVeyor SV300-900 systems, which occupy 1.2 sq. m of space and deliver the high throughput required.


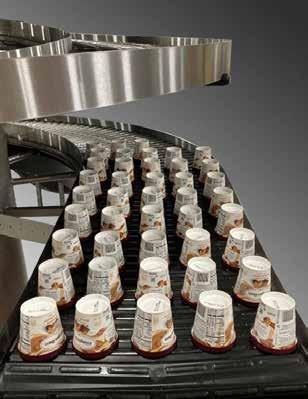
PLUS, an Exclusive Networking Reception on Tuesday 4:30 pm – 5:30 pm. Your First-Time Attendee Badge is your access pass.
Sponsored by:
Booth C-3222
In another dairy plant upgrade scenario AmbaFlex and DCC Automation collaborated to provide a subzero-compatible, moisture-resistant stainless steel SpiralVeyor to move ice cream from the packaging machine on the ground floor to a high-level palletizer in a minimum of space.
On production lines where one or more machines stop and restart frequently, an accumulation system can be used to smooth product flow. This prevents backups and line slowdowns. In some cases, it also can eliminate some of the stopping and restarting because when a downstream machine goes down, product can be diverted to the spiral while engineers fix the glitch. One installation of the AccuVeyor AVo spiral offers 90 m of accumulation (roughly 8 min. of extra storage). When the glitch is fixed, the spiral’s direction is reversed and product returns to the main line on a last-in/first out basis.
For more info, visit ambaflex.com, dccautomation.com. SD
Compact spirals offer high throughput.Ice cream pints travel to a new bundling machine, installed on an overhead plateau to eliminate the need to rearrange the line. Nutraceutical line benefits from compact, washdown-compatible spiral capable of high throughput. An offline, reversible spiral holds 8 min. of accumulation and minimizes line stops.
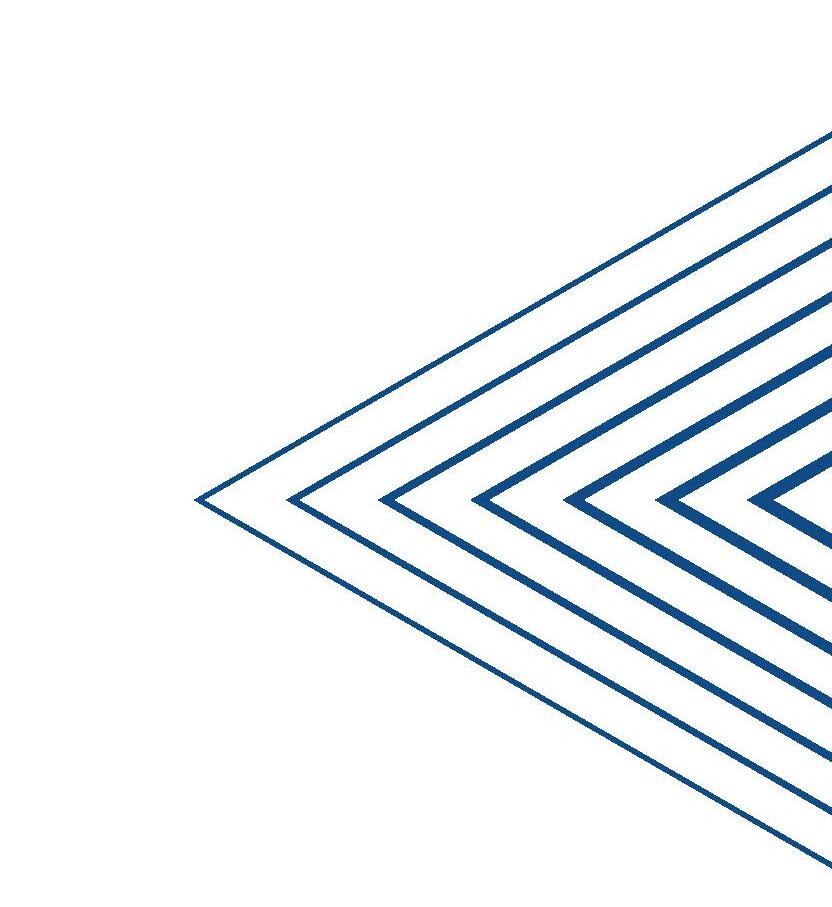
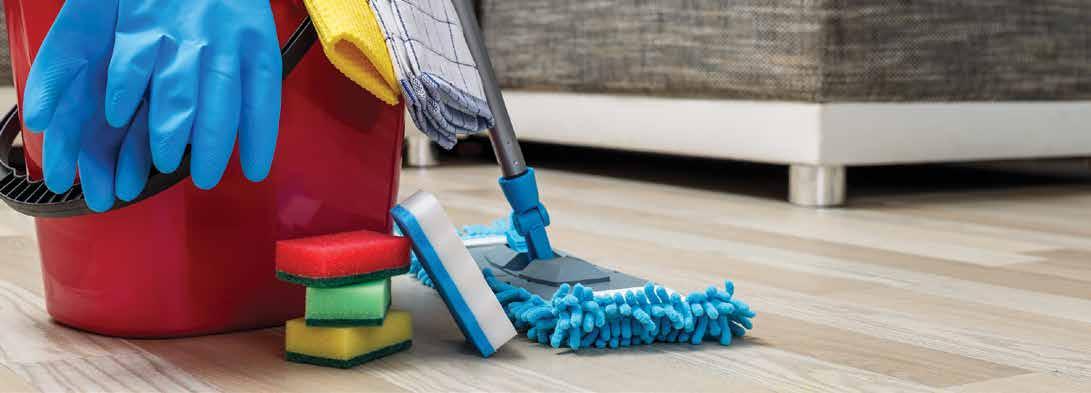

Say











































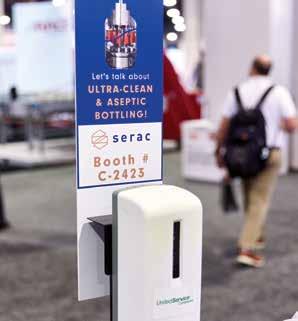
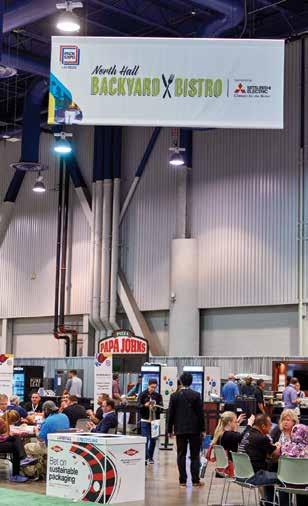

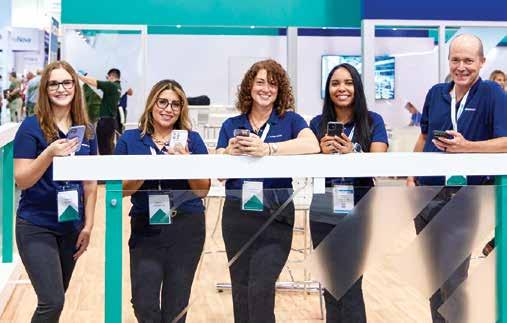
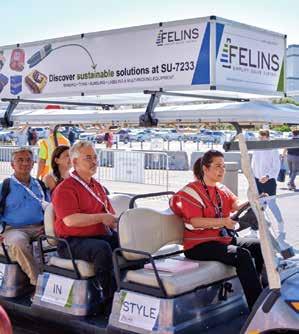
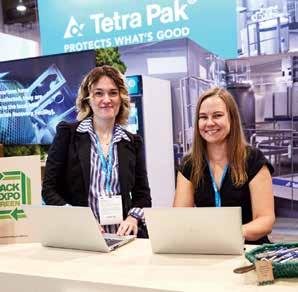
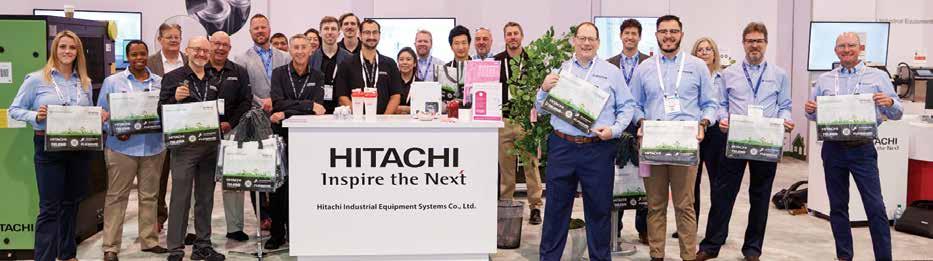
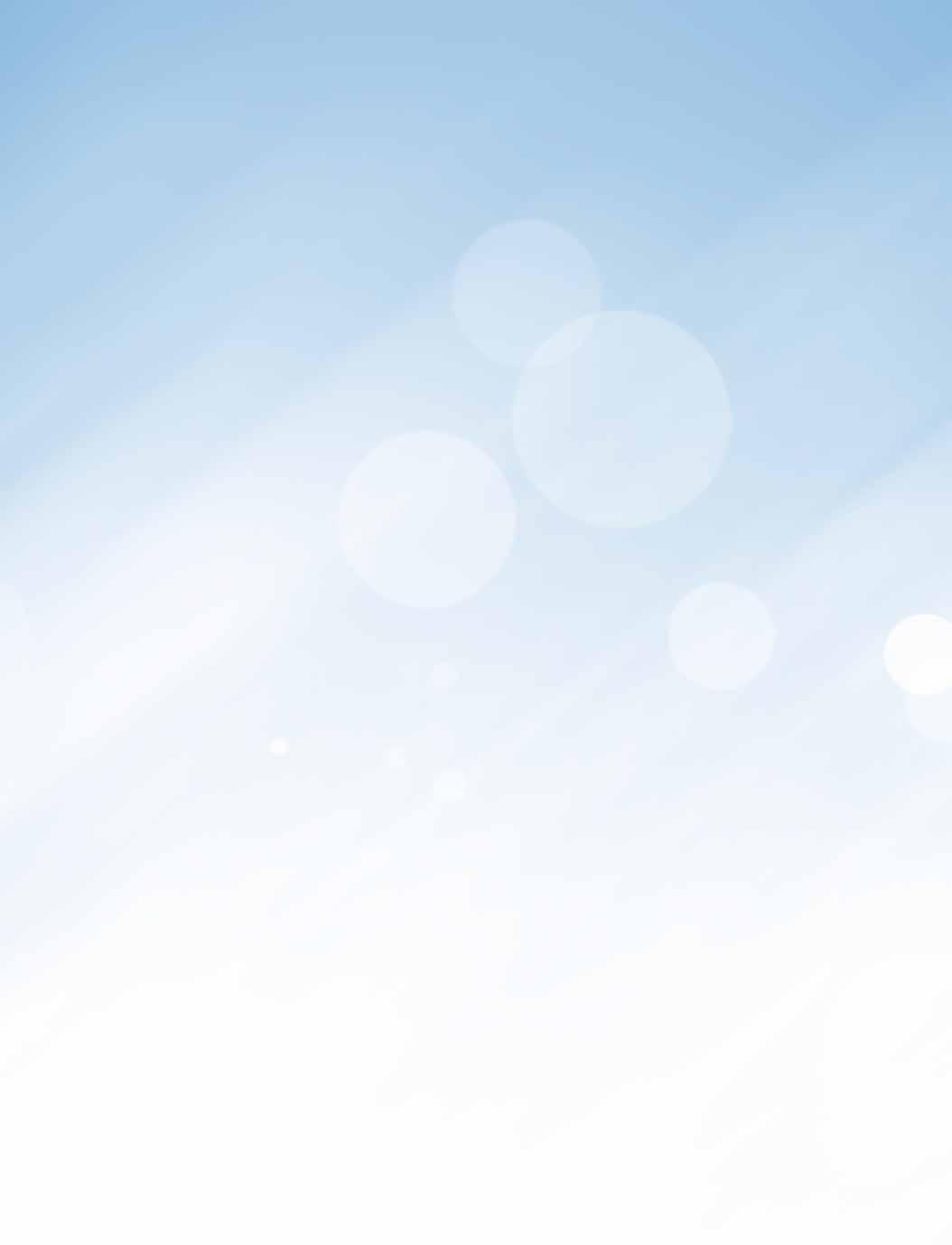
We s et the st a nd a rd fo r susta i nable therm oforme d pac kagin g. Rea c h you r goals quic ke r with ou r SC S Global c ertified 100% pos t- c onsume r re cycled m a ter ia l .
We s et the st and ard fo r susta inable therm oforme d pac kagin g. Rea ch you r goals quic ke r with ou r SC S Global certified 100% pos t- consume r re cycled m ater ial .
Per fec t i n b oth the food and reta i l mar kets , we h ave an in-s toc k o rcus tom solution fo r you r pac kaging needs .
Per fec t i n b oth the food and reta il mar kets , we h ave an in-s toc k o rcus tom solution fo r you r pac kaging needs .
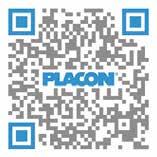
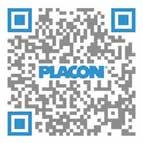
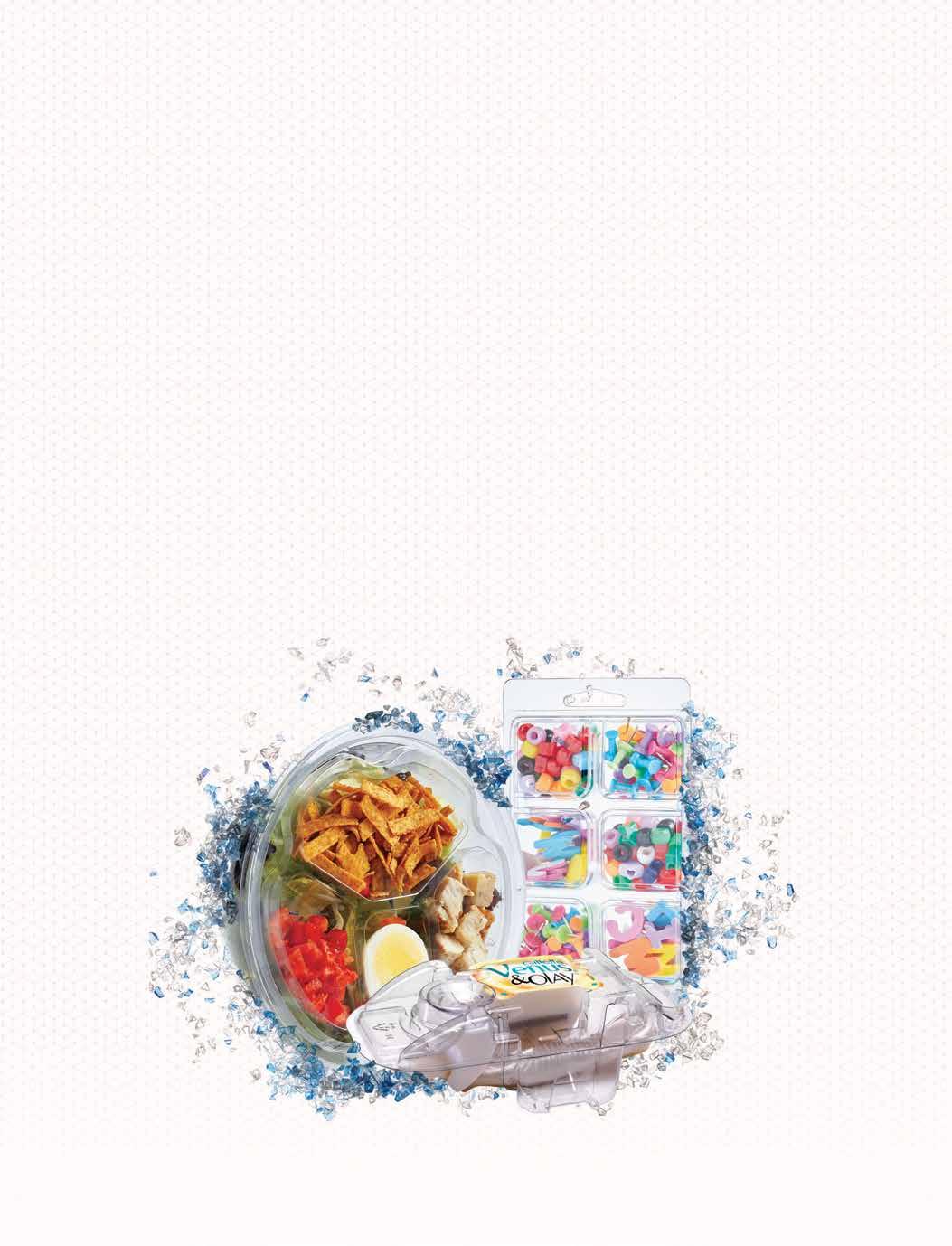
SEPTEMBER 12, 2023
Sustainability Stage debuts
Anew show feature, Sustainability Central in the North Hall, houses the Sustainability Stage (Booth N-9967) where attendees will learn from more than a dozen industry experts about how to improve the environmental profile of their brands.
Topics include logistics, labeling, waste reduction, sustainable design and transitioning to more sustainable materials. with an opening presentation on Monday by Daniella Souza Miranda, global business director, Circular & Renewable Solutions at Dow (Room S-116), the show’s official Sustainability Partner. Session descriptions, times and locations are listed below. Updated schedules
Sustainability STAGE
may be found on the show website or via the show App, sponsored by ProMach (Booth C-3222)
Other free educational opportunities on the show floor include the new Industry Speaks Stage (Booth C-1141) (see schedule, p. 24), the Innovation Stage (Booths C-2051, C-2058, C-2151) and the Processing Innovation Stage (Booth N-10511) (see schedule, p. 30), plus The Forum — An Industry Knowledge Exchange (Booth C-2158) (see schedule, p. 58)
Schedule as of August 23, 2023.
For more info, visit packexpolasvegas.com. SD
TUESDAY, SEPTEMBER 12, 2023
STYLE
THAT FITS: BUILDING YOUR PACKAGING WARDROBE
10:00-10:30
AM
Building the perfect wardrobe goes beyond mere chance; it requires the expertise to choose the best silhouette, fabrics and accessories. Step onto the fashion runway and hear insider style secrets, empowering you to curate a well-coordinated packaging wardrobe considering materials, shapes, textures and colors that will bring your packaging to life.
Brent Lindberg Founder & Head of Curiosity FuseneoNEW BOTTLE, SAME SPRITE
11:00-11:30
AM
Sprite’s status as one of the biggest and most recognized brands in the world can largely be attributed to its crisp lemon-lime taste and its iconic green bottle. As of 2022, Sprite, Seagram’s, Fresca, and Mellow Yellow have transitioned from a green to clear polyethylene terephthalate (PET) bottle in North America. This move marks The Coca-Cola Company’s commitment to a World Without Waste by making it easier to recycle PET packaging into new bottles, thus supporting a circular economy. For Sprite, this was no easy feat as the brand is associated with predominantly green packaging. Through detailed consumer research and technical expertise, Coca-Cola was able to make the switch to a more sustainable package. Join Noah Wigington as he takes us through the process of understanding the consumer mindset when transitioning to sustainable packaging and the positive impact it can make on the recycling stream.
Noah
WigingtonGlobal Packaging Development & Innovation Lead
Coca-Cola
ALTERNATIVE SUSTAINABLE MATERIALS: THE FUTURE OF PACKAGING
12:00-12:30 PM
As alternative materials enter the packaging landscape, it is critical that they are designed and engineered to both provide relief from their problematic predecessor and function and protect as a replacement. Manufacturers are demanding alternatives but need a level of confidence not always accessible within
the framework of a startup. Collaborations like that of Atlantic Packaging and Cruz Foam promote innovation and application ingenuity. Hear how a great idea can turn into a viable replacement when validated through industry standards and endorsed by a sustainable leader like Atlantic Packaging.
Kyle Pischel
Dir, Packaging Solution Center
Atlantic Packaging
Toby Corey Exec Chairman & COO
Cruz Foam
BEYOND SUSTAINABILITY: LEAD THE SHIFT TO CIRCULAR PACKAGING
1:00-1:30 PM
An estimated 11 billion kg of plastic pour into our waterways and devastate our ocean. Rather than seeing plastic as waste, we need a way to reveal its inherent value and recognize its true worth in changing our lives. Plastic Bank, founded in 2013, is a social enterprise that provides an opportunity for the world to collect and exchange plastic as a currency. This idea has spurred a global Social Recycling movement that has stopped 80 million kg of plastic waste from entering the ocean, while empowering collection communities in vulnerable coastal areas of Southeast Asia, Latin America and Africa to find a path out of poverty. Learn how recycling can be socialized by being part of a greater purpose-driven movement—for individuals and institutions alike. Plastic pollution endangers more than 800 species, including us. Hear how you can become part of the solution.
David Katz Founder & ChairmanPlastic Bank
LIKE, SUBSCRIBE AND FOLLOW THE MOST SUSTAINABLE SOLUTIONS AT PACK EXPO
2:00-2:30 PM
This foursome plus moderator will provide a “CliffsNotes” version of can’t-miss innovations seen around the show. The panel will provide colorful commentary on the innovations in sustainability seen around PACK EXPO. Learn what these innovations mean for the packaging industry, and how they might be helpful for your own organization.
Brent Lindberg - Moderator Founder & Head of CuriosityFuseneo
Cory Connors
Dir, Sustainable Packaging
Landsberg Portland
Adam Peek
Sr VP, Sales
Meyers
Evelio Mattos
Creative Dir, Packaging
International Direct Packaging
Jonathan Quinn
Dir, Mkt Development & Sustainability
Pregis
CLOSING THE PACKAGING LOOP: ADVANCING THE CIRCULAR ECONOMY
3:00-3:30 PM
Explore successful examples and challenges associated with advancing circular economy practices. From sourcing renewable key inputs, energy considerations and decarbonization to recycling and recovery, companies are considering how to minimize waste and keep materials in circulation while regenerating nature. With billions of packages in circulation around the world daily, this session considers the significant potential impact of packaging and provides tactics for driving progress toward a more sustainable future.
Christopher Davidson
VP, Sustainability
WestRock
COLGATE-PALMOLIVE’S SUSTAINABILITY & SOCIAL IMPACT STRATEGY
4:00-4:30 PM
At Colgate-Palmolive, we are really proud that Colgate is in more homes than any other, so we can, and will, create a healthier, more sustainable future for all. To achieve this mission, Colgate has developed a Sustainability and Social Impact Strategy with 11 actions ranging from Accelerating Action on Climate Change to Designing Sustainable Products. This session covers the strategy, actions and examples of how Colgate is embedding sustainability across its value chain.
Cecilia Coates
Global Sustainability - Climate & Water Lead
Colgate ∆
MAKE IT SMARTER AT PACK EXPO 2023
BOOTH C-5033
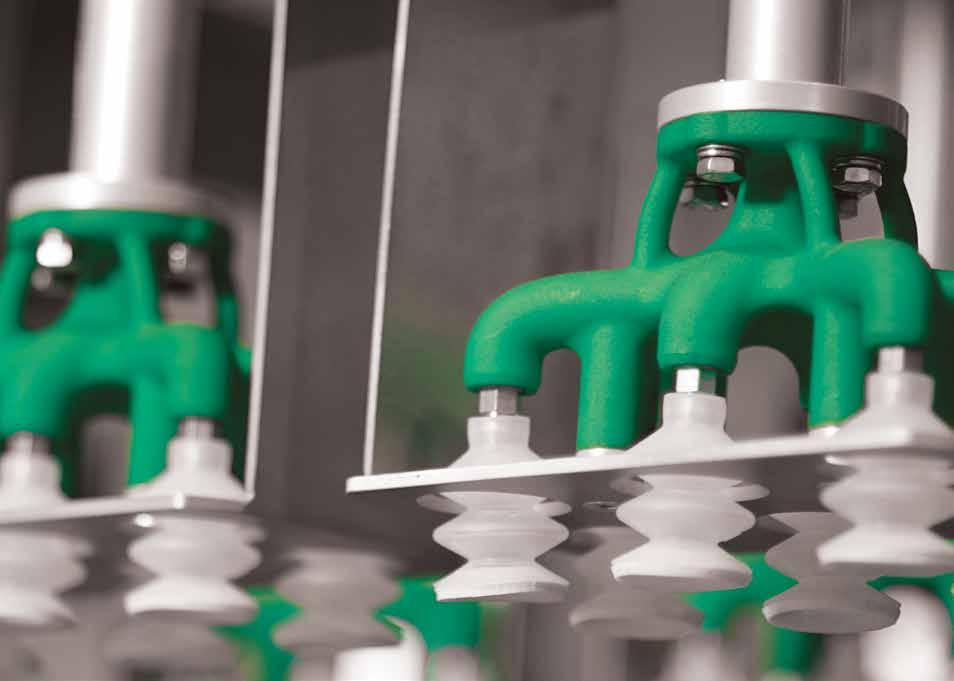
SEPTEMBER 12, 2023
LEVERAGING SUSTAINABILITY IN PACKAGING COST OPTIMIZATION
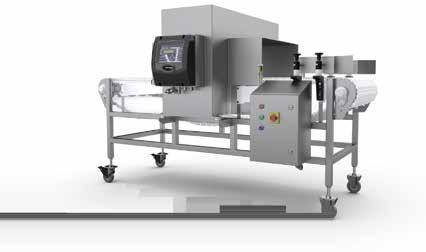
10:00-10:30 AM
As the consumer goods and packaging industry faces several headwinds coming out of Covid, including an uncertain economic situation, softening demand, supply chain challenges that haven’t fully been resolved, etc., sustainability often takes a back seat to cost optimization and other performance improvement levers. There are, however, ways to incorporate sustainability into these initiatives to continue to make progress against goals and commitments, as well as not have to sacrifice either objective. Join members of the Roland Berger team as they discuss how to incorporate sustainability thinking into cost optimization and provide examples of its value creation.
Rebecca Marciniak
Dilhani de Silva
Roland Berger
ALL TOGETHER NOW: UNLOCKING PACKAGING’S CIRCULAR FUTURE
11:00-11:30 AM
It’s time to go beyond broad recyclability claims and design packaging that is actually being recycled into valuable post-consumer recycled material. But how can brands transform from passive producers of waste to active participants in a circular economy? By embracing a systems approach that engages materials suppliers, reprocessors, materials recovery facilities and machinery makers to shed light on all the links of the circular supply chain. From advanced recycling to reuse and refill and monolayer materials, we’ll explore the ways stakeholders can take their recyclability claims from promise to reality.
Matt Reynolds
Chief Editor, Packaging World
Anne Marie Mohan
Senior Editor, Packaging World

Sean Riley
News Editor, Packaging World
PMMI Media Group
INTENTIONAL DESIGN FOR SUSTAINABLE AND RECYCLABLE PACKAGING STRUCTURES
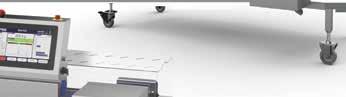
12:00-12:30 PM
To meet the combination of growing consumer demand and an escalating regulatory environment, Michelman helps customers transition to more sustainable solutions for their packaging needs. We will discuss how to transition from film-based substrates to fiber-based substrates that will enable improved end-of-life options for final structures in existing recycling streams—all while maintaining excellent barrier performance!
Talia Collins
Mgr, Global Research & Development
Michelman
Toby Corey
Exec Chairman & COO
Cruz Foam SD
Wherever you are and whatever your industry, there’s a PACK EXPO event to provide solutions you need today and the inspiration for tomorrow.
March 18-20, 2024
Philadelphia, USA
June 4-7, 2024
Mexico City, Mex.
Nov. 3-6, 2024
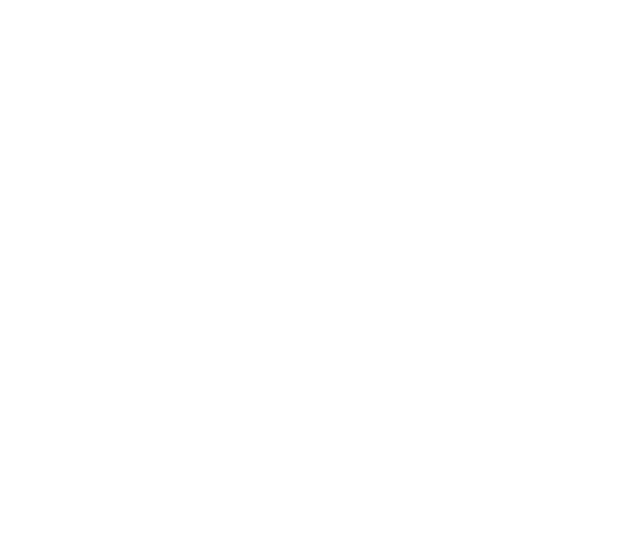
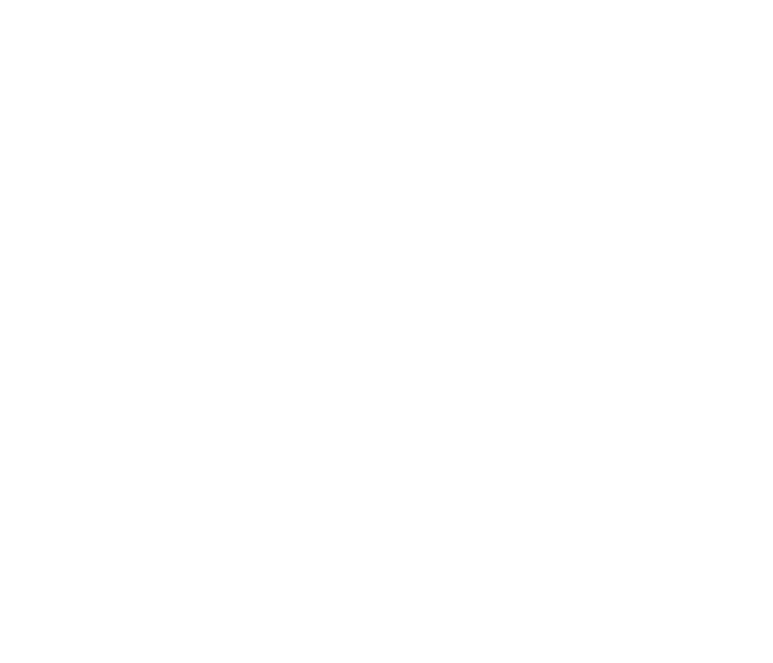
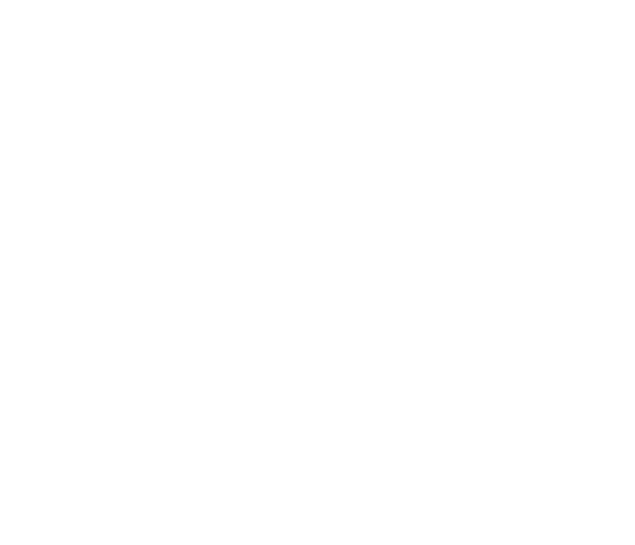
Chicago, USA
March
June
Sept.
Partners bring knowledge to show Partner
Program links attendees to wide array of organizations.
Approximately 30 organizations are partnering with show organizer PMMI, The Association for Packaging and Processing Technologies (Central Lobby), for PACK EXPO Las Vegas, connecting attendees to leading associations from all segments of packaging and processing.
“The Partner Program is one reason why PACK EXPO Las Vegas is the most comprehensive packaging and processing event in North America in 2023,” says Jim Pittas, president & CEO, PMMI. “These organizations bring targeted knowledge to the show floor and give attendees actionable information to improve their operations.”
Participants in the PACK EXPO Partner Program exhibit in the Partner Pavilion or elsewhere on the show floor.
New this year, the PACK EXPO Las Vegas Partner Plus Program gives groups the opportunity to present sessions on the Industry Speaks Stage (Booth C-1141) (see schedule, p. 24) or to co-locate meetings with the show under the banner, Industry Meets. For example, the Cold Pressure Council (Booth C-1153) has scheduled its Annual Conference on Tuesday, Sept. 12, 2023, at the Las Vegas Convention Center and a Board of Directors meeting the next day. Other Industry Meets participants include: the International Bottled Water Association (offsite);
MHI Automation Industry Groups; Composite Can & Tube Institute (Booth C-1350); Contract Packaging Association (Booth C-1256); Institute of Packaging Professionals (Booth C-1154); and OMAC - The Organization for Machine Automation and Control (Booth C-1255). The latter plans a public General Session and a Workgroup meeting at 10:00 a.m. and 11:00 a.m., respectively, on Tuesday, Sept. 12.
The Industry Speaks Stage, another first for PACK EXPO Las Vegas, offers an opportunity to hear experts representing Partner Program participants discuss hot topics and trends including automation, high-pressure pasteurization, digital transformation, contract manufacturing/packaging, flexible packaging, modern warehousing and logistics, machinery standards and sustainability.
“As part of the PACK EXPO Partner Program, we are looking forward to seeing our members and meeting potential members while talking to brand owners, packaging designers, label printers, molders and others who are learning more about the advantages of in-mold labeling and decorating technology,” says Dianna Brodine, managing director at the In-Mold Decorating Association (Booth C-1347). “In addition, we are releasing white papers about the sustainability and recyclability of in-mold labeling/dec-
INDUSTRY MEETS
Cold Pressure Council (Booth C-1153)
Composite Can & Tube Institute (Booth C-1350)
Contract Packaging Association (Booth C-1256)
Institute of Packaging Professionals (Booth C-1154)
International Bottled Water Association
MHI Automation Industry Groups
OMAC - The Organization for Machine Automation and Control (Booth C-1255)
orating processes and presenting an Industry Speaks session on the subject [4:30 p.m., Monday, Sept. 11].”
For up-to-date schedules and Partner Program Pavilion details, check the PACK EXPO Las Vegas mobile App, sponsored by ProMach (Booth C-3222), or the show website.
For more info, visit packexpolasvegas.com, promach.com. SD
PARTNER PROGRAM PARTICIPANTS
3-A Sanitary Standards (Booth C-1353)
AIM (Booth SU-8306)
AMERIPEN (Booth C-1151)
Anuga FoodTec Family (Booth C-1158)
ASD Turkish Packaging Manufacturers (Booth C-1145)
Association for Roll-to-Roll Converters (Booth C-1351)
Association of Plastic Recyclers (Booth C-1157)
Australian Packaging and Processing Machinery Association (Booth C-1150)
CANAINCA
Cold Pressure Council (Booth C-1153)
Composite Can and Tube Institute (Booth C-1350)
Consumer Brands Association (Booth C-1248)
Contract Packaging Association (Booth C-1256)
Flexible Packaging Association* (Booth C-1348)
Foil & Specialty Effects Association* (Booth C-1346)
Foundation for Supply Solutions (Booth C-1152)
International Bottled Water Association
In-Mold Decorating Association* (Booth C-1347)
Institute of Packaging Professionals* (Booth C-1154)
Instituto Argentino del Envase (Booth SU-8135)
International Society of Beverage Technologists (Booth C-1354)
MHI Automation Industry Groups
National Confectioner’s Association (Booth SU-7201)
OMAC – The Organization for Machine Automation and Control (Booth C-1255)
OPC Foundation (Booth C-1250)
PLCopen (Booth C-1253)
Reusable Packaging Association* (Booth SU-8000)
SNAC International (Booth C-1146)
The Tube Council of North America*
UCIMA – Italian Packaging Machinery Manufacturers Association (Booth C-1149)
U.S. Department of Commerce (Booth C-1159)
World Packaging Organisation* (Booth C-1246)
SSV Series Drum Motors
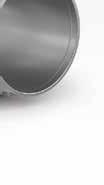
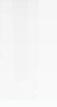

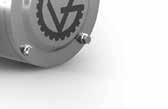


Maintenance-Free, Efficient & Space Optimized Conveyor Belt Drive Solution

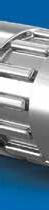
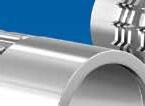

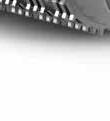



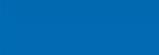
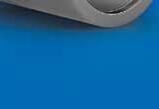
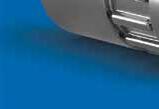

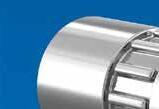







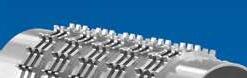

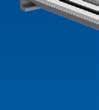



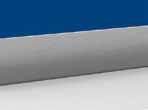
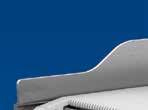

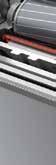

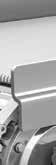
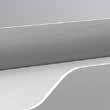
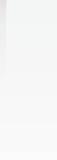

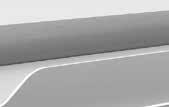

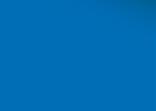

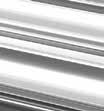
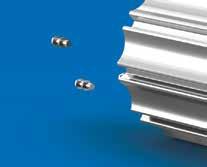

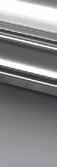
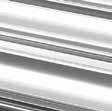
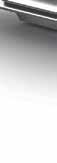

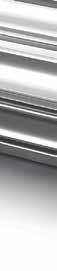
ELIMINATE Drive Sprockets
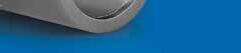
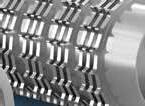
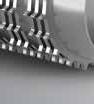

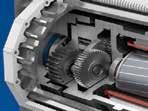
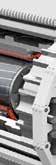
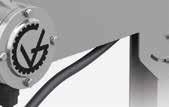


ELIMINATE Product Build-Up



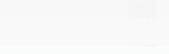

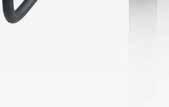
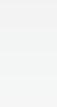

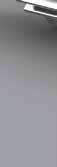
ELIMINATE Bacterial Harborage
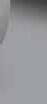
The new patented SSV-XP Drum Motor features an interchangeable profiled sleeve that can be removed and exchanged for another profiled sleeve to match the belt required on the conveyor without changing the drum motor.
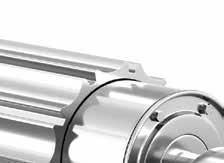
SEPTEMBER 12, 2023
Showcase displays award winners
Visit The Showcase of Packaging Innovations®, sponsored by WestRock.
The Showcase of Packaging Innovations® (Booth N-9550), sponsored exclusively by WestRock (Booth C-2023), features award-winning packages from competitions around the world.
“The Showcase of Packaging Innovations is a traditional and treasured component of PACK EXPO,” says Jim Pittas, president & CEO of PMMI, The Association for Packaging and Processing Technologies (Central Lobby), the show organizer. “We are most grateful to WestRock for sponsoring this facet of the show once again. Being able to view an array of innovative packaging in one place is inspiring and gives attendees ideas to take home and adopt to make their packaging more environmentally-friendly and consumer-friendly.”
Ten organizations are participating in this year‘s
Showcase, which is located in the North Hall straddling the boundary between the Containers and Materials Pavlion and the PACKage Printing Pavilion.
Sustainability plays a role in many of the award winners. A judge for the Flexible Packaging Association competition, Gary Borges, associate professor, University of Wisconsin-Stout, explains, “Sustainability is growing tremendously . . . Post-consumer recycling is a trend that we saw. And we’re seeing an increase in paper structures that . . . we can send to our paper waste streams at home. So, we’re seeing all of these innovations taking place. It is pretty impressive.”
For more info, visit packexpolasvegas.com, westrock. com, dow.com, flexpack.org, fsea.com, imdassociation. com, iopp.org, profoodworld.com, reusables.org, tube.org, worldpackaging.org. SD
At the Flexible Packaging Association, the RESCUE!® Outdoor Disposable Fly Trap earned the Highest Achievement Award. It also won a Packaging Excellence Gold Award, a Technical Innovation Silver Award and an Expanding the Use of Flexible Packaging Award. The flexible packaging, produced by Glenroy for Sterling International, is easy to use: Cut along the dotted line at the top to expose the trap entrance, add water and hang. The pouch construction protects the consumer from the powerful attractant inside. Once the trap is full (collecting up to 20,000 flies), the consumer simply discards it.

In the ninth annual Sustainability Excellence in Manufacturing Awards, organized by ProFood World, a PMMI Media Group (Central Lobby) publication, First Place in the Program Category honors a certified carbon-neutral brand made in a zero-waste Conagra Brands facility in Fayetteville, AR.
PARTICIPANTS
Dow (Room S-116)
Dow Packaging Innovation Awards
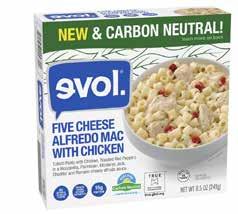
Flexible Packaging Association (Booth C-1348)

Foil and Specialty Effects Association (Booth C-1346)
In-Mold Decorating Association (Booth C-1347)
Institute of Packaging Professionals (Booth C-1154)
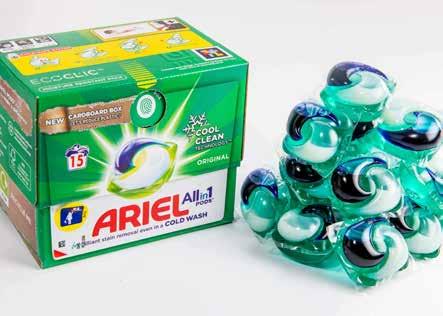
ProFood World (Central Lobby)
Sustainability Excellence in Manufacturing Awards
Reusable Packaging Association (Booth SU-8000)
The Tube Council of North Ameria WestRock (Booth C-2023)
World Packaging Organisation (Booth C-1246)
In a competition sponsored by the In-Mold Decorating Association, label supplier MCC Verstraete and molder Jokey Group were honored with the Best In-Mold Label Award for an interactive in-mold label with a digital watermark. Designed for De Dames van Akkkerlust, a new ice cream brand, the intelligent feature adds value in the packaging journey—from tracking and authenticating products to boosting customer engagement to digitally sorting the package for recycling. The sustainable packaging is designed to reflect the nature of the ice cream, which is made on a sustainable farm from 100% organic milk.
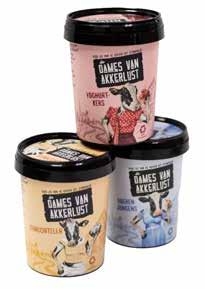
The Best of Show Award in the 2023 AmeriStar competition, sponsored by the Institute of Packaging Professionals, revolutionizes single-use packaging with a focus on sustainability and consumer satisfaction. Annie’s certified industrially-ompostable molded fiber cup offers functionality equal to a plastic thermoform and broadens the use of molded fiber into shelf-stable products. The packaging offers a 45% reduction in carbon footprint and is direct-printed via a flexographic process. A spray coating made from a renewable formula offers grease and water protection. Improved convenience and warmth retention enhance the consumer experience. The package also won an AmeriStar Award in the Sustainable Packaging category.
The top prize in the Dow Packaging Innovation Awards, the Diamond Award, went to Procter & Gamble for its G ECOCLIC® box for liquid laundry capsules. The patent-pending cardboard packaging scores for sustainability and child safety. The carton consists of FSC-certified materials with a minimum of 70% recycled fibers, and its dimensions and design fit 50% more packs per pallet. The certified child-resistant design also is easy to open even for people with dexterity limitations and sight or cognitive impairments. A reassuringly loud ‘one click’ closure signals the pack is closed.
IMA creates eCommerce division
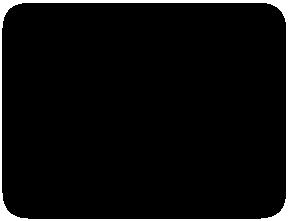
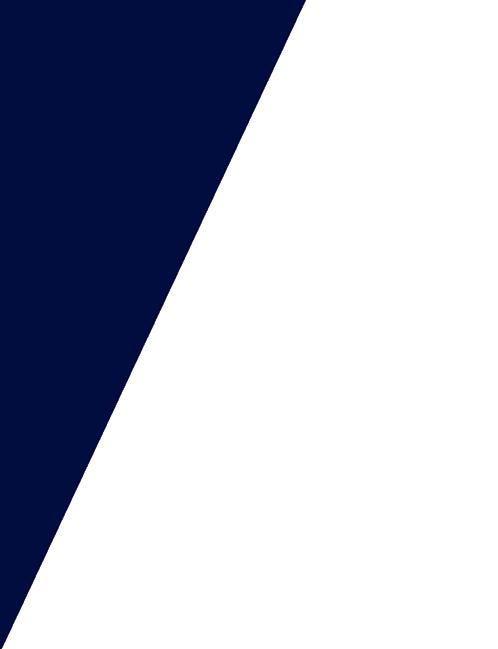





E-CO Flex machine right-sizes boxes, conserves corrugated.
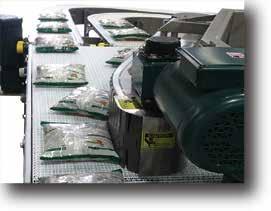
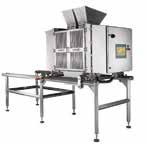


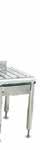









Anew division established by the parent company of IMA NorthAmerica (Booth C-3200, C-3400) serves the increasing demand for online shopping with technologies to automate the packaging process.
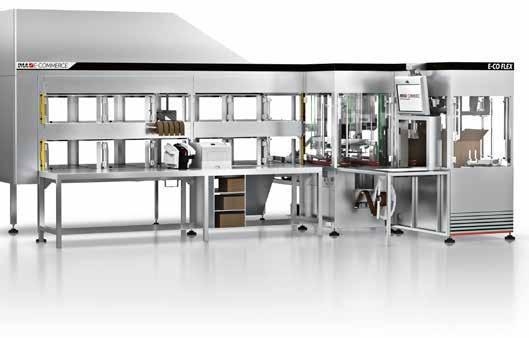






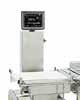

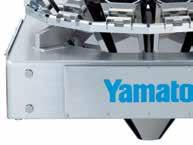
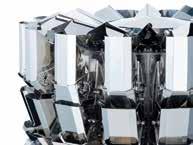




The first model in the IMA E-COMMERCE line, the E-CO Flex machine, simplifies e-fulfillment packaging by connecting to the end user’s warehouse management system and selecting the best fit-to-size box for the products to be packed.
Once the most suitable box is identified, the blank is automatically picked from the magazine, erected and bottom-sealed using water-activated tape. Tape is applied on an integrated, proprietary water-activated tape dispenser from Intertape Polymer Group, which serves as the exclusive distributor of the E-CO Flex machine in the U.S. and Canada.
The pre-assembled container is presented to the operator, who simply inserts the items to be shipped and secures them with the required amount of dunnage. The operator reinserts the open-faced box into the machine where the remaining void is measured. If necessary, the E-CO Flex machine is capable of automatically reducing the height of the box and then closing it, adapting flap-folding to the new box dimensions.
Automated packaging solutions, such as the E-CO Flex machine with right-sizing capabilities, allow e-tailers to combine multiple stations into one unit. By reducing the cubic footage of cases to a minimum, dimensional (DIM) weight pricing can be safely implemented, resulting in reduced material usage. This can reduce corrugate consumption while eliminating the need for void fill in compliance with the latest sustainability policies adopted by IMA Group.
For more info, visit ima.it. SD
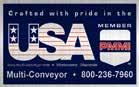
Editor’s Note: The original version of this article was posted on March 20, 2023 by Packaging World.





Industry Speaks Stage features PACK EXPO Partners
Anewcomer to the free educational programming at PACK EXPO, the Industry Speaks Stage (Booth C-1141), located in the Central Hall, draws experts from the PACK EXPO Partner Program, which includes various technical and industry groups.
The 30-min. presentations focus on topics such as automation, standards, developments in high-pressure processing, sustainability, flexible packaging, contract manufacturing/packaging, warehouse automation, in-mold labeling/ decorating, metallic labels/cartons, automatic identification and data capture, beverages and snack food.
DIGITAL TRANSFORMATION SUCCESS USING OPC STANDARDS
10:30-11:00 AM
Real-world examples from end users highlighting their digital transformation journey when using OPC technologies.
Mike Clark DirOPC Foundation North America
THE CONTINUING PATH OF HPP INNOVATION
11:30-12:00 PM
The current widespread use of high-pressure pasteurization (HPP) technology has been a journey driven by innovation. Join us to learn more about the foundations of its current success and the expanding opportunities that lie ahead.
Rick Marshall VPShape Process Automation
Session descriptions, times and locations are listed below. Updated schedules may be found on the show website or via the show App, sponsored by ProMach (Booth C-3222)
Other free educational opportunities on the show floor include the new Sustainability Stage (Booth N-9967) (see schedule, p. 16), the Innovation Stage (Booths C-2051, C-2058, C-2151)/Processing Innovation Stage (Booth N-10511) (see schedule, p. 30), plus The Forum — An Industry Knowledge Exchange (Booth C-2158) (see schedule, p. 58). Schedule as of August 23, 2023.
For more info, visit packexpolasvegas.com. SD
TUESDAY, SEPTEMBER 12, 2023
FLEXIBLE PACKAGING INDUSTRY: POLICY DRIVING INNNOVATION
1:30-2:00 PM
Learn about the current state of the flexible packaging industry and discuss legislative, regulatory and other factors driving innovation in the space, the second fastest growing segment of the packaging industry in the U.S.
Alison Keane Pres & CEO Flexible Packaging AssociationDYNAMIC GROWTH: CONTRACT PACKAGING AND MANUFACTURING INDUSTRY
2:30-3:00 PM
gies and sustainability. Discuss recent FSEA studies on the repulpability/recyclability of metallic-transfer decorating on paper/board.
Jeff Peterson Exec Dir Foil & Specialty Effects AssociationEND-TO-END AUTOMATION IN MODERN WAREHOUSING AND LOGISTICS
4:30-5:00 PM
ADVANCING
THE PACKAGING INDUSTRY WITH AIDC TECHNOLOGY
12:30-1:00 PM
By embracing automatic identification and data capture (AIDC) technologies, the packaging industry is witnessing significant advancements in traceability, data management, quality control and consumer engagement. These technologies empower businesses to optimize operations, streamline supply chains, enhance customer experiences and maximize competitiveness in a rapidly evolving market. Hear an overview of the technologies changing the market and learn about the role AIM plays in helping advance the packaging and AIDC industry.
Michael Allen Business Development Dir AIM North AmericaViewing data from the Contract Packaging Association’s State of the Industry Report, member feedback and its Request for Quote platform, dive into the changing demands of this dynamically growing industry. These essential providers of capabilities and services address the needs of emerging and legacy brands launching food and retail products. Explore how CoMans and CoPacks add value as consumerand market-driven needs impact the packaged goods supply chain. Understand how brands are adapting to meet new challenges with strategic CoMan and CoPack partnerships and accelerating time to market.
Ron Puvak Exec DirContract
Packaging AssociationSUSTAINABILITY AND METALLIC DECORATING FOR CARTONS AND LABELS
3:30-4:00 PM
Sustainability as it relates to decorative metallics is on the forefront of the minds of brand owners and others in the print and packaging industries. The Foil & Specialty Effects Association (FSEA) has taken important steps to generate pertinent, accurate information about metallic transfer-decorating technolo-
This overview of the automation journey starts at initial strategy and design, moves to implementation of automation technologies and ends with the continuous monitoring and optimization of these systems. Take an in-depth look at the challenges and opportunities presented by end-to-end automation in warehousing and logistics, focusing on the significance of strategic planning and meticulous design in successful implementation. View a blueprint for a successful transition toward automated operations. Then, navigate toward the nuts and bolts of logistics automation, showcasing technologies that enhance productivity, reduce errors and contribute to overall business growth. Lastly, highlight the indispensable role of sensor intelligence in ensuring operational efficiency and safety in automated systems. Examples of intelligent sensor systems demonstrate how these technologies provide crucial data, support real-time decision making and empower businesses to remain agile and responsive in the face of changing market dynamics. Lastly, the presentation will highlight the indispensable role of sensor intelligence in ensuring both operational efficiency and safety in automated systems.
Chris York
Chief Technology Officer
Slate River Systems
Nils Hart
Exec Dir, Business Development
Murata Machinery USA
Susan Nangle
Consulting & Digital Solutions
SICK ∆
NEVER BEEN SO EASY
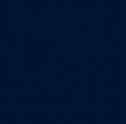
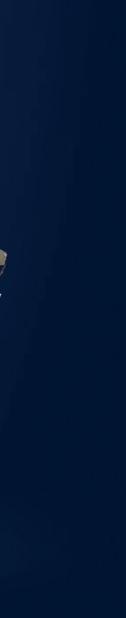

SEE US AT BOOTH SU-7412
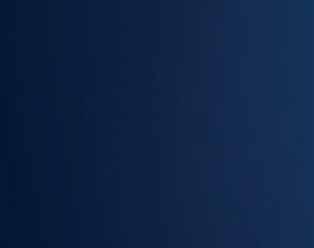

TOTALLY AMERICAN WITH AN ITALIAN HEART
Ronchi America proudly presents the SIRIO/S capper, built in Atlanta, GA. This SIRIO/S capper includes all of the Ronchi features and is FAT ready within 12 weeks or less. The SIRIO/S capper is also capable of being synchronized with the US built Ronchi EXACTA/R 18 filler.
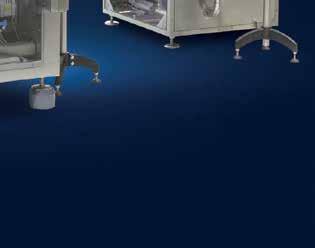

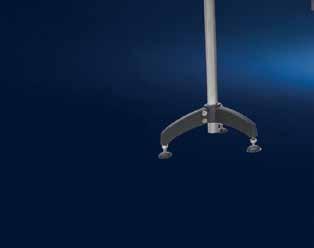
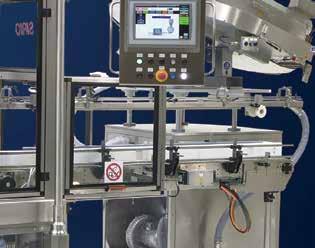
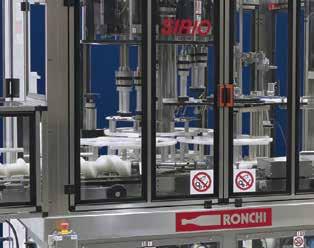
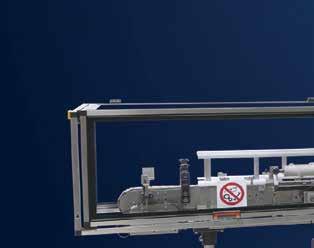
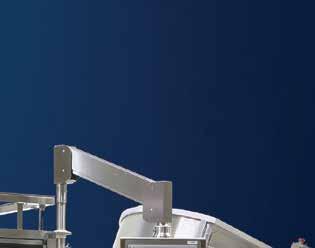
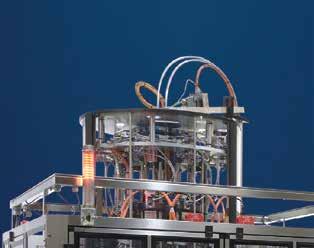
SEPTEMBER 12, 2023
THE PACKAGING POLICY PRECIPICE— CHALLENGES OR OPPORTUNITIES
10:30-11:00 AM
The U.S. remains at a critical precipice on packaging and environment policy with significant new laws continuing to be passed and implemented on packaging producer responsibility, labeling, recycled-content mandates and more. Join a fast-paced discussion about what’s happening and how to engage with the ensuing challenges and opportunities.
Dan Felton Exec Dir AMERIPENWEDNESDAY, SEPTEMBER 13, 2023
SUSTAINABILITY INTO PACKAGING AND PROCESSING MACHINERY

11:30-12:00 PM
Examine the global and regional perspectives of sustainability and circular design, showcasing initiatives, programs, regulations and roadmaps from Italian packaging machinery manufacturers.
Riccardo Cavanna PresUCIMA - Italian Packaging Machinery Manufacturers’ Association
Learn from winning manufacturers
Session presents Manufacturing Innovation Award winners.
Meet this year’s winners of ProFood World’s Manufacturing Innovation Awards (MIAs) today at 4:00 pm in a presentation on the Processing Innovation Stage (Booth N-10511)

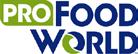
Each year, ProFood World’s editors choose three new or renovated food or beverage plants as Manufacturing Innovation Award (MIA) winners.
Winning companies “have a lot of ideas about what it means to optimize a safer, more productive, more sustainable food processing system,” says Aaron Hand, editor-in-chief of ProFood World
One of this year’s winners differs from the usual award recipient and represents a considerable shift in how the world might need to look at food production going forward.
MyForest Foods makes a bacon alternative from mycelium, which is essentially the root system of mushrooms. That in itself puts the company on the avant garde end of the food spectrum. But even for a mycelium producer, its Swersey Silos operation in Green Island, NY, takes an innovative approach to the growth of the ingredient. It’s a vertical mycelium farm. Within that vertical farm, MyForest teases the
mycelial fibers with the same kind of refreshing dew they would experience on the forest floor after a cool night. A gentle breeze also simulates the whoosh of the wind through the trees at sunset.
By orchestrating the environmental factors carefully, MyForest is able to grow the natural mushroom textures and flavors it is after—in accelerated timeframes (12 to 16 days vs. 12 to 16 weeks). The structures thus grown resemble whole pork bellies and are exactly the right size to slice off strips of mycelium bacon for further processing at another facility.
As it happens, another MIA winner plays in the plant-based space as well, producing milk alternatives, as well as ready-to-drink teas and whey-based protein shakes, among other beverages. SunOpta’s aseptic production facility in Midlothian, TX, does some 90% of its business in co-manufacturing, with state-of-the-art, high-speed lines that provide the
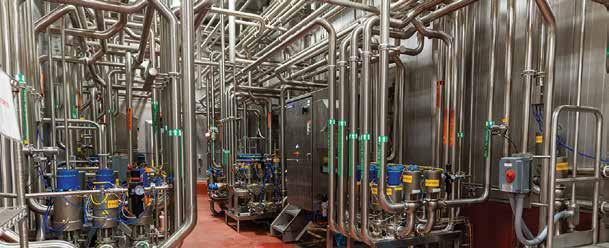
WHAT CAN THE ISBT OFFER YOU, THE PROFESSIONAL IN THE BEVERAGE INDUSTRY?
12:30-1:00 PM
The vision of the International Society of Beverage Technologists (ISBT) is to be the premier global beverage industry technical association, which drives sustainable growth, resolves challenges and leads productivity innovations. ISBT offers the global industry a platform to network and help the industry thrive. Come learn what this 75-year-old society offers its members and their companies in a global format.
Ron Puvak Marketing Committee ChairInt’l Society of Beverage Technologists SD
flexibility needed to run more than 100 stock keeping units. The new operation combines the best of existing operations for worker comfort, safety and efficiency, sanitary design, the flexiblity to expand into new formats, operational productivity and sustainability. Like its other facilities, it relies largely on equipment from Tetra Pak (Booth C-4340)
The third MIA winner is a 295,000-sq.-ft. greenfield turkey processing plant started up by Prestage Foods, a subsidiary of the family-owned Prestage Farms. The highly automated operation in Camden, SC, houses the Western Hemisphere’s only scaled European-style air-chill turkey processing model, a major improvement over traditional water-chill processing. The facility also features highly automated systems and advanced food safety and traceability protocols.
For more info, visit profoodworld.com, packexpolasvegas.com. SD
Targeted ERP system wins award
Food/beverage companies benefit from purpose-built software.

For food and beverage (F&B) companies, an enterprise resource planning (ERP) system, designed especially for these industry sectors, offers signficant benefits vs. generic ERP systems. In fact, according to Aptean (Booth N-10902), a developer of ERP and other systems, F&B firms running a purpose-built ERP system generate higher revenue (5.3% higher in 2022).
Aptean’s targeted ERP system recently earned Frost & Sullivan’s Customer Value Leadership Award in North American ERP Software for F&B Industry. Frost & Sullivan notes the system goes beyond traditional ERP capabilities, providing features and functionalities that help end users remain cost-effective and make informed business decisions. Its modular approach adds value by allowing users to implement and configure the specific capabilities they require, providing a scalable and simplified path to growth.
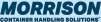
“The beauty of Aptean’s approach and its products is that the company does not see F&B as a monolithic category. Aptean has designed its products to meet the needs of different F&B verticals and sub-verticals, allowing each customer to deliver the highest
quality products, thus enabling exceptional customer value,” says Sankara Narayanan, industry principal at Frost & Sullivan.
Aptean’s comprehensive suite of integrated applications include warehouse management, transportation and shipping management, e-payment, sales and customer management, electronic data interface, manufacturing execution, enterprise asset management and product lifecycle management.
Specialized capabilities and functionalities of the Aptean F&B ERP system include:


• Bi-directional ingredient tracking and allergen management
• Expiration tracking and tools enabling supply/ demand balancing for food waste reduction
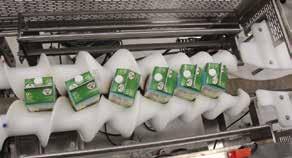
• Automatically calculated catch weight values tracked through solution to invoicing
• Lot tracing, ingredient-level tracking and product origin management

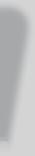

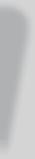

• Visibility into production activities through a collaborative forecasting and planning module
• Grower settlement calculations and pricing automatically calculated using grade-out/ pack-out methodology
Flexible Automation
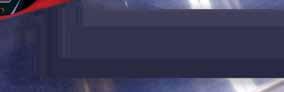
TO IMPROVE YOUR THROUGHPUT SOLUTIONS




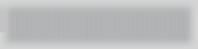
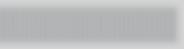


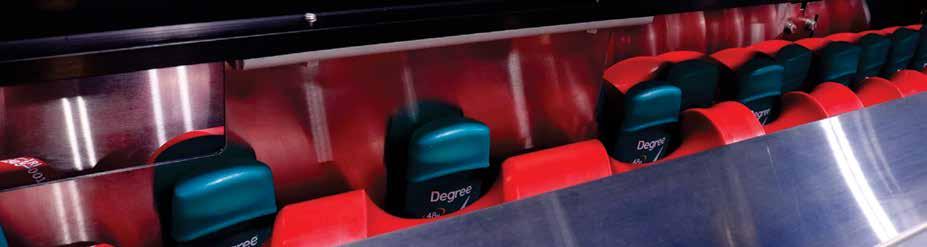
• Deep lot profitability features that show detailed costs for haulage, labor, machinery, duty, rework and more
• Supply chain management that supports a wide range of product variations, including weight, breed, cut, age, variety, region of origin and packaging.
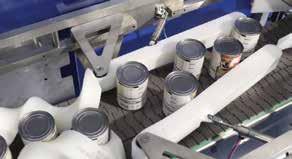
Aptean also offers professional services and support as well as resources to guide F&B companies toward digitalization, manage costs and quality, boost profitability, reduce waste and enhance the sustainability of production and distribution operations.
The company also offers targeted ERP solutions for other sectors, including fashion and apparel, industrial manufacturing, imports/distribution/retail, processing manufacturing and equipment dealer management.
With both Cloud and on-premise deployment options, Aptean’s products, services and unmatched expertise help businesses of all sizes to be Ready for What’s Next, Now®. Headquartered in Alpharetta, GA, Aptean offers a global presence with offices in North America, Europe and Asia-Pacific.
For more info, visit aptean.com. SD
PFAS-free
oxygen
absorbers debut
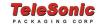
Address tightening regulatory environment for PFAS.
In response to an ever-stricter regulatory environment for per- and polyfluoroalkyl substances (PFAS), Mitsubishi Gas Chemical (MGC) (Booth SU-7490) is launching PFAS-free AGELESS oxygen absorbers.
Dubbed as “forever chemicals,” PFAS have been widely used in industry and consumer products worldwide since the mid-20th century. Once favored for their oil- and water-resistant properties, PFAS have recently been under public scrutiny for their
Academic scholarships to students pursuing careers in the industry.

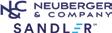


Summer Manufacturing Camps
To educate and inspire the future manufacturing workforce.
Financial assistance for educational programs
such as FIRST robotics teams and curriculum development at local colleges and universities.
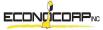
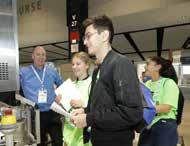
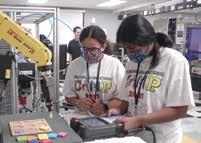
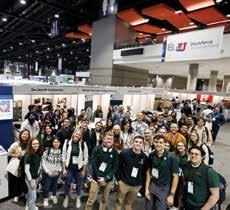
and more…
inability to breakdown in the environment and potential adverse health effects. As a result, legislators around the world have enacted laws banning PFAS in products, including packaging, putting pressure on manufacturers to find alternatives.
MGC has revolutionized its oxygen absorber technology by replacing PFAS with a proprietary formula, which meets new, stringent global regulations without compromising quality, performance or safety.
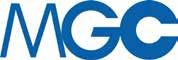
“To develop a brand new, PFAS-free solution for our customers within such a short stretch of time is a truly herculean feat,” says Sean Hael, sales and marketing GM at Mitsubishi Gas Chemical America. “PFAS-free AGELESS supports companies’ advancement toward long-term sustainability goals and complies with evolving regulations, all while providing the same performance and efficacy that our customers know and trust.”
PFAS-free AGELESS oxygen absorbers are oil-resistant and can deoxidize the interior of sealed packages to maintain flavor, color, fragrance and nutrition of freshly prepared food, as well as dramatically extend shelf life. PFAS-free AGELESS oxygen absorbers can create a 99.9% oxygen-free package within 24 hr.*, which keeps a variety of foods fresh without the use of unhealthy preservatives—drastically extending product shelf life, reducing waste and improving product quality.
PFAS-free AGELESS oxygen absorbers protect and preserve a variety of products, including processed meats, meat snacks, baked goods, dried fruits, coffee, pet treats, pharmaceuticals and nutraceuticals. For more info, visit AGELESS.mgc-a.com. SD
* Absorption time can range up to 72 hr. based on size and type.
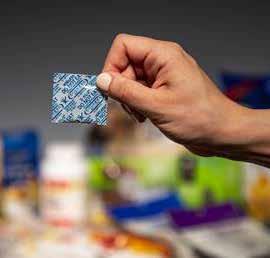
nce again, Lenze Americas (Booth C-4803) is sponsoring lounges for exhibitors and PMMI members at PACK EXPO Las Vegas. The lounges provide meeting space, seating, refreshments and a chance to take a break away from the busy show floor.He explains, “This year’s industry growth and numerous new features at PACK EXPO Las Vegas will make the show floor incredibly busy. As a result, these lounges will be highly sought after by exhibitors and PMMI members as a valuable space to relax and network.”
The respite space will be especially welcome this year as the PACK EXPO Las Vegas show floor is expected to be extra busy with 30,000 attendees touring nearly 1 million sq. ft. of floor space to visit more than 2,300 exhibitors.
For more info, visit packexpolasvegas.com, lenze.com. SD
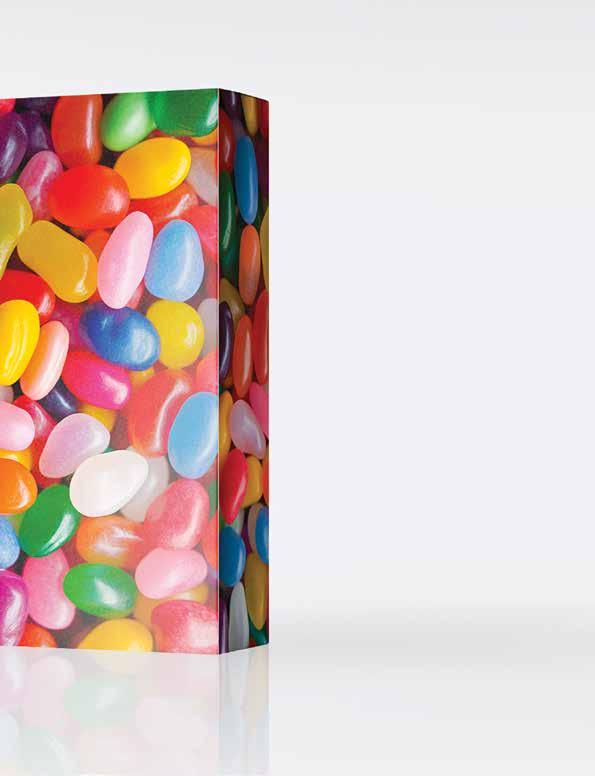
The Exhibitor Lounges are located in rooms S-215 and N-114. The two PMMI Member Lounges are located in rooms S-222 and N-101.
“Lenze Americas understands the significance of providing members and exhibitors with a dedicated space to rejuvenate amidst networking with attend ees at their booths. We take pride in our continued sponsorship of these lounges this year,” says Paul O’Connor, Lenze Americas.
“We are grateful to Lenze Americas for support ing this resource again,” says Jim Pittas, president & CEO, Processing Technologies (Central Lobby) nizer of the PACK EXPO family of trade shows.
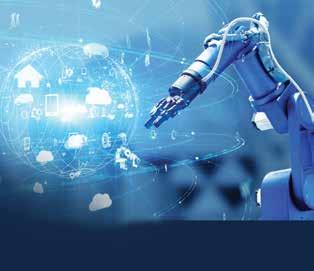
Future Innovators
Students demo self-built robots
THE ‘BOTS ARE TAKING OVER PACK EXPO Las Vegas!
R
UP TO REDUCED WEIGHT VS. CONVENTIONAL ALTERNATIVES
obotics teams from Las Vegas-area high schools are demonstrating the robots they have built along with design, engineering, assembly and troubleshooting skills at The Future Innovators - Robotics Showcase (Booth N-9769), sponsored by Bastian Solutions (Booth N-10343)Come see Vegas-area high school students showcase their “bot skills”. Interact with the bright minds of the future and ask questions about their innovative robot designs.
Located in the North Hall in Booth N-9769
Monday - Tuesday | 9:00 am - 5:00 pm
Wednesday | 9:00 am - 3:00 pm
Demos are scheduled throughout each day of the show. Stop by to see what these teams have built, watch their robot in action, ask questions and tell the students about career opportunities in manufacturing and engineering.
This annual event is designed to open doors for a new generation of packaging professionals and encourage participation in STEM studies. It’s one of many student-based activities at PACK EXPO Las Vegas, which also includes the winners of the 2022 PACK Challenge (Booth N-9026) from Waterford Union High School and the Amazing Packaging Race, which is sponsored by Emerson Discrete Automation (Booth SL-6107) and occurs on the final day of the show.
For more information about supporting student programs, visit the PMMI U booth at N-9000.
Produced by:
For more info, visit packexpolasvegas.com, bastiansolutions.com, emerson.com/en-us/industries/automation/ food-beverage. SD
MORE THAN
YOUR
BOOTH N-9216
35% metsagroup.com/metsaboard AVERAGE PAPERBOARD
SHOWCASE
Innovation Stages offer free educational sessions
The always-popular Innovation Stage program returns to PACK EXPO Las Vegas with four platforms: the Processing Innovation Stage (Booth N-10511) in the North Hall, plus three Innovation Stages (Booth C-2051, C-2058, C-2151) in the Central Hall. Exhibitors and subject matter experts will present more than 60, 30-min. sessions about the latest technology breakthroughs and best practices.

Topics range from automation, digitalization, artificial intelligence (AI) and cybersecurity to food
DATA-DRIVEN SUSTAINABILITY
10:00–10:30 AM
Innovation Stage 2 | C-2151
Smart factories are leading the way when it comes to leveraging data to improve operations, reduce costs and increase environmental sustainability. As Industry 4.0 continues, we look at the positive impact automation can have on tackling cybersecurity, efficiency, safety and sustainability in smart factories.
David Eifert Sr Business Development Mgr Phoenix Contact USAREVOLUTIONIZING OEE IN CHANGEOVER AND PREDICTIVE MAINTENANCE
10:00–10:30 AM
Innovation Stage 3 | C-2058
Dealing with the challenges of increasing productivity despite employee turnover? See how to improve OEE by getting the correct data to make the right decisions, implementing smart devices and Guided Changeover to reduce planned and unplanned downtime, increase machine optimization and reduce product and packaging waste.
Greg Molinaro Dir, Packaging, Food & Beverage Americas BalluffTHE JOURNEY FOR THE STEAM SYSTEM DECARBONIZATION
10:00–10:30 AM
Processing Innovation Stage | N-10511
Steam systems can deliver significant sustainability benefits through energy and water savings. Learn how we help identify and implement solutions that support and contribute to achieving net-zero goals, through system efficiency, connected insights and decarbonization options—throughout the steam system—from generation to point of use.
Alex Rosa Sr Mgr, Applications Sales & Support Spirax Sarco

safety, workforce challenges, sustainability and technology innovations. Highlights include sessions by WestRock (Booth C-2023) (sustainability), Syntegon Packaging Technology (Booth C-2800) (gloveless fill/finish), Siemens Digital Industries (Booth SL-6351) (digital twins), Delkor Systems (Booth C-3840) (robots), Soft Robotics (Booth N-10311) (AI-enabled food picking) and Metsä Board (Booth N-9216) (zero-waste packaging). Session descriptions, times and locations are listed on the following pages. Updated schedules may be
TUESDAY, SEPTEMBER 12, 2023
ROBOTS IN THE WORKFORCE
10:30–11:00 AM
Innovation Stage 1 | C-2051
Advancements in robotics are revolutionizing industries with flexible and affordable automation. Learn how implementing robots can replace multiple lines, how modular scalable systems can grow along with operations without capping future capabilities and how to recognize automation opportunities and create a system that satisfies retailer demands for various packaging formats.
Rick GesslerVP, Engineering Delkor Systems
CIRCULARITY WITHIN REACH: LIGHT-BLOCKING SHRINK SLEEVES
11:00–11:30 AM
Innovation Stage 2 | C-2151
As leading brands seek to eliminate problematic plastic in their packaging, recyclable solutions are top-ofmind. For some markets, particularly dairy, beverage and nutraceuticals, a recyclable option has been out of reach. GreenLabel BlockOut shrink sleeves provide a light-blocking, recyclable labeling alternative for transparent polyethylene terephthalate containers.
Tyler MatusevichDir, Sustainability
Brook + Whittle
THE NEXT FRONTIER FOR AI VISION IN CPG: MONITOR ASSET HEALTH
11:00–11:30 AM
Innovation Stage 3 | C-2058
CPG faciliites have used cameras and other vision technology for years for quality assurance and security. Now, there’s an exciting frontier for vision: AI-enabled, real-time asset health monitoring. This session walks through how this technology works and how it unlocks productivity.
Mauricio Casares
Smart Factory Improvement Mgr
Schneider Electric
found on the show website or via the show App, sponsored by ProMach (Booth C-3222).
Other free educational opportunities on the show floor include the new Sustainability Stage (Booth N-9967) (see schedule, p. 16), the new Industry Speaks Stage (Booth C-1141) (see schedule, p. 24) and another popular standby, The Forum—An Industry Knowledge Exchange (Booth C-2158) (see schedule, p. 58).
Schedule as of August 23, 2023.
For more info, visit packexpolasvegas.com. SD
WHY YOUR MIXING PROCESS SHOULD BE FULLY AUTOMATED
11:00–11:30 AM
Processing Innovation Stage | N-10511
We all have heard the term “lights-out bakery.” The concept is to build a bakery where lights are not needed because the line is fully automated, and no personnel are required to operate the equipment. Today’s continuous mixing technology is already close to the “lights-out” goal.
Jim Warren
VP, Exact Mixing
Reading Bakery Systems
MGRIPAI: EASY-TO-INTEGRATE
AI-ENABLED FOOD PICKING
11:30–12:00 PM
Innovation Stage 1 | C-2051
Soft Robotics’s new UI allows integrators to utilize artificial intelligence (AI) with the click of a button. Optimize bulk picking and remove the need for bulky singulation machines. Learn how easily our food automation solution can be programmed to handle variance between applications and optimized to increase yield.
Harley Green
Strategic Business Dir
Soft Robotics
RECYCLABLE LABEL FILMS WILL SUPPORT A CIRCULAR ECONOMY
12:00–12:30 PM
Innovation Stage 2 | C-2151
SmartCycle label film is produced from a polyethylene terephthalate (PET) that has similar properties to traditional, non-recyclable films but is recyclable along with the PET bottles being labeled. This innovation for the labels market will have long-lasting environmental benefits.
Justin RentmeesterMkt
Development Mgr, Labels North AmericaKlöckner
Pentaplast∆


12,
TARGETING HEAT IN PACKAGING SYSTEMS FOR HIGHER PERFORMANCE
12:00–12:30 PM
Innovation Stage 3 | C-2058
The utility operating cost of a packaging machine is largely driven by the heating systems needed to seal or form packages. Design choices can impact thermodynamics, reduce operating costs and help improve uptime. A new heater design demonstrates a 25% reduction in energy consumption and better process control—without any customer design changes.
Jeff Wheeler VP of OperationsNexthermal
ADDED-VALUE LAMINATING ADHESIVES FOR SUSTAINABLE SOLUTIONS
12:00–12:30 PM
Processing Innovation Stage | N-10511
The latest innovations in laminating adhesives meet the continuous challenges of regulations and circular economy and highlight the impact of adhesives within the flexible packaging structure. Close teamwork among all stakeholders is the key to success.
Michael Reed PresMORCHEM
PRODUCTIVITY BOOST: UNLEASHING DATA VISIBILITY
12:30–1:00 PM
Innovation Stage 1 | C-2051
Data visibility is critical. Certifications, material locations, maintenance records . . . knowledge leads to productivity and helps keep facilities running more efficiently. Learn how BR Code scannable tapes and labels, together with the free BitRip mobile app, can put critical data at your fingertips . . . without expensive equipment and systems.
Scott
Sommers VP, Insights & InnovationShurtape Technologies
WINNING FORMULA: FIBERBASED PACKAGING WITH CONSUMER APPEAL
1:00–1:30 PM
Innovation Stage 2 | C-2151
As sentiment around environmental sustainability increases, consumers are looking hard at consumption habits and the waste that their purchases generate— and the role packaging plays is central to this. Learn how to win consumers with waste-reducing, recyclable packaging, made from renewable resources.
Jeannine Scherzer Global Mktg Dir Chuck Tarlton Innovation Dir Graphic Packaging InternationalROLE OF ADHESIVES IN SUSTAINABLE PACKAGING FOR CONSUMER
1:00–1:30 PM
GOODS
Innovation Stage 3 | C-2058
Sustainability is the way forward, and innovative, sustainable packaging for consumer goods is becoming more prevalent in the marketplace. Learn about approaches to thoughtfully using adhesives in the design and production of sustainable consumer goods packaging.
Melissa Seburg Mktg Mgr
H.B. Fuller
HUMAN AND PET FOOD: MAKING FOODS SAFER AND HEALTHIER THROUGH HPP
1:00–1:30 PM
Processing Innovation Stage | N-10511
High-pressure processing, or HPP, is a non-thermal process for foods that inactivates pathogens and eliminates the need for preservatives, while maintaining nutrients and flavor. Learn about how HPP works, trends and examples of commercial food and beverage applications.
Dr. Vinicio Serment
HPP Applications & Food Processing Specialist



Anthony Zapata
Business Development
Hiperbaric - High Pressure Processing
EMPOWERING YOUR WORKFORCE WITH FLEXIBLE MANUFACTURING
1:30–2:00 PM
Innovation Stage 1 | C-2051
Are you struggling to keep your workforce effective and deal with the high mix of demands from consumers? Suffering from quality issues after changeovers? More adaptable equipment is needed.
Justin GarskiAmericas OEM Segment Mgr - Packaging Rockwell Automation
THE TRICKLE-DOWN EFFECT OF RIGHT-SIZED PACKAGING
2:00–2:30 PM
Innovation Stage 2 | C-2151
Minimize risk and reduce cost while being more sustainable with right-sized packaging. When it comes to packing and shipping, you can make efficiencies in larger factors such as operations and system design but also in smaller details like automated box sizing and packing processes.
Jack Dean Solutions Acct Exec
Bastian Solutions
GO ALL IN: WINNING THE BET ON CIRCULAR SOLUTIONS
2:00–2:30 PM
Innovation Stage 3 | C-2058
Dow will showcase its holistic approach to improving
the life cycle of packaging, from production to recycling, emphasizing the positive impact of closing the loop. The first step toward a packaging circular economy is to design for end-of-life to ensure the package can be efficiently recycled or repurposed, thus reducing waste to landfill and promoting resource recovery. Incorporating post-consumer recycled (PCR) materials, such as the innovative REVOLOOP technology, enhances circularity in packaging applications, supporting environmental, social and governance (ESG) and PCR incorporation legislation. Minimizing carbon footprint is the ultimate ESG goal, achieved through the use of low-carbon or biobased materials and lightweighting, which reduce energy consumption during production and transportation. Together we can accelerate the move to a circular future.
Michelle Sauder
Mktg Dir, Food & Specialty Packaging
Heather Turner
Mktg Dir, Industrial & Consumer Packaging
Rennisha Wickham
Sr Mktg Mgr, Rigid Packaging
Dow
NEW TRENDS AND APPLICATIONS IN HIGHPRESSURE PROCESSING (HPP)
2:00–2:30 PM
Processing Innovation Stage | N-10511
HPP offers greater profitability than conventional processing, fresher taste (not altered by heat, chemicals or irradiation), the “clean” label consumers are demanding, longer shelf life due to drastically reduced spoilage and enhanced food safety since the extreme pressure inactivates pathogens.
Dr. Errol Raghubeer
VP, Food Science & Technology
JBT - Avure HPP
THE KEY TO SUPPLY CHAIN SUCCESS: EFFECTIVE YARD MANAGEMENT
2:30–3:00 PM
Innovation Stage 1 | C-2051
Today’s shipping yards face overwhelming challenges that go beyond manual tracking methods. See how leading logistics operations are leveraging effective yard management practices to ditch spreadsheets, paper and radios while improving the bottom line by millions of dollars per year.
Colin Mansfield
Dir of Sales & Mktg
Yard Management Solutions
ADDING INTELLIGENCE TO YOUR MAGNETIC SEPARATION EQUIPMENT
3:00–3:30 PM
Innovation Stage 2 | C-2151
Protecting the purity of your product reduces the potential risk of a recall, damage to brand reputation and financial liability. Adding “intelligent” technology to

SEPTEMBER 12, 2023
TUESDAY, SEPTEMBER 12, 2023 (CONT’D)
your magnetic separation equipment protects equipment and reduces downtime, maintenance costs and risks of fire or explosion.
Frank Reda Sales Mgr - Americas Magnetic Products
CABINETLESS PACKAGING MACHINE CONTROL
3:00–3:30 PM
Innovation Stage 3 | C-2058
The advantages of cabinetless machine design are clear. New technologies that combine all control functionality in IP65/67 form factors help shrink machine footprints by 75% and reduce component count. Review real-world examples that demonstrate how to successfully design cabinetless packaging machines.
Eric ReinerIPC
Product MgrBeckhoff Automation
PLUG-AND-PRODUCE CASE STUDY OF MODULAR PRODUCTION IN R&D LABS
3:00–3:30 PM
Processing Innovation Stage | N-10511
Merck is automating its laboratory environment and digitalizing production at its global headquarters in Darmstadt, Germany, in response to market demands for ever-shorter lead times and customized products. Modular production and relying on an industry standard called Module Type Package (MTP) are key.
Giuseppe MeninLife
SciencesCOPA-DATA
& Process Industry Mgr
WORKFORCE CHALLENGES AND THE IMPACT OF THE NEXT GENERATION
3:30–4:00 PM
Innovation Stage 1 | C-2051
Discuss current challenges impacting the packaging workforce, the importance of academia and the role technology plays when it comes to shaping the next generation of leaders in the industry.
Matthew Wright CEO & FounderSpecright
HOW PACKAGING INNOVATION IMPACTS TESTING SOLUTIONS IN 2023
4:00–4:30 PM
Innovation Stage 2 | C-2151

Protect brand and product via collaboration with a partner that provides equipment and services to manufacturers, laboratories and production lines. Learn about the latest research that describes the current state of packaging, factors that are driving the industry forward and roadblocks to innovation.
Greg Wright Global VP, Sales & Mktg Industrial Physics3D BIN PICKING WITH COLLISION-FREE ROBOTS
4:00–4:30 PM
Innovation Stage 3 | C-2058
The combination of 3D Vision for robot guidance (SICK), advanced path planning (Realtime Robotics) and robots (Mitsubishi Electric Automation) solves the most demanding 3D bin-picking problems more accurately/faster than ever before.
Nick LongworthBusiness
SICK
Consultant,Matthew Somerville
Dir
ofIndustrial Robotics
Sales, North America
Realtime Robotics ∆
Come see Vegas-area high school students showcase their “bot skills”.
Interact with the bright minds of the future and ask questions about their innovative robot designs.
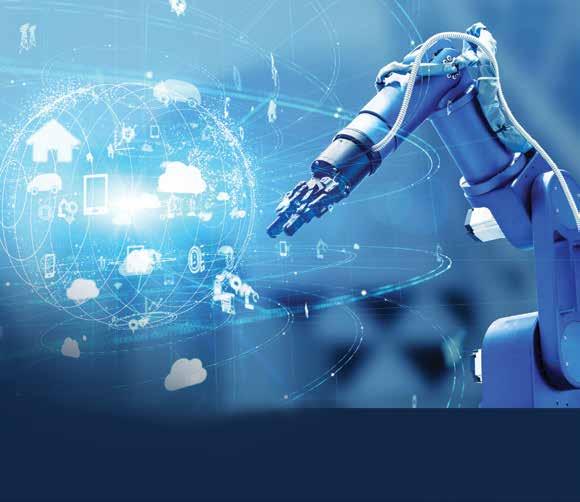
Located in the North Hall in Booth N-9769
Monday - Tuesday | 9:00 am - 5:00 pm
Wednesday | 9:00 am - 3:00 pm
For more information about supporting student programs, visit the PMMI U booth at N-9000.
SEPTEMBER 12, 2023
LEVERAGING DATA TO ENABLE CRITICAL SUPPORT FROM YOUR OEM
10:00–10:30 AM
Innovation Stage 2 | C-2151
In today’s challenging environment, it is becoming critical to leverage your OEMs for your operational success. How do we capture, organize and make data available outside manufacturing equipment to enable this much-needed support from machine builders? Let’s start with the basics: data-ready machines supporting performance management.
Steve MulderAmericas OEM Mgr
Rockwell Automation
HIGH-BARRIER RETORTABLE POLYPROPYLENE SOLUTIONS
10:00–10:30 AM
Innovation Stage 3 | C-2058
“Monomaterial packaging” is one of the buzzwords in the flexible packaging industry, since current multi-material packaging is not easy to recycle. PP GL Barrier film is a key component to make recyclable retort pouches.
Chris
WardVP, Toppan Packaging Innovation Ctr Toppan Group
THE JOURNEY TOWARD SUSTAINABLE PACKAGING WITH ONEBARRIER
10:00–10:30 AM
Processing Innovation Stage | N-10511
The journey toward sustainable packaging progresses with oneBARRIER monomaterials, a family of recyclable polymer- or paper-based substrates.
Chris Marshall
Area Sales Mgr BOBST
AI IS TRENDING, BUT FIRST YOU NEED GOOD DATA
10:30–11:00 AM
Innovation Stage 1 | C-2051
Before packaging operators look to artificial intelligence or machine learning to solve their most pressing problems, they need a strong product and packaging data foundation through digitized specifications.
Matthew Wright CEO & Founder SpecrightPACKAGING SUSTAINABILITY INTO YOUR LINE EFFICIENCY
11:00–11:30 AM
Innovation Stage 2 | C-2151

WEDNESDAY, SEPTEMBER 13, 2023
Industrial digital transformation enables new approaches to efficiency. Whereas traditional approaches break out production efficiency (measured in OEE) from energy management key performance indicators, a sustainability-oriented OEE integrates the two. Currently being tested, this approach offers significant promise in driving decarbonization.
Miguel
NajeraVP, CPG
Schneider Electric
TRANSPORT SYSTEMS EVOLVE, TAKE ON PICK-AND-PLACE FUNCTIONS
11:00–11:30 AM
Innovation Stage 3 | C-2058
An entirely new way to think about robotics relies on intelligent linear transport systems. Wireless movers can be equipped with powered end effectors that result in a low-profile, flat multi-robot system that’s fully embedded into packaging machinery instead of attached as a separate, standalone robot module.
Jeff Johnson U.S. Mechatronics Product Mgr Beckhoff Automation


WAREHOUSE AUTOMATION
2024 TRENDS AND INNOVATION
11:00–11:30 AM
Processing Innovation Stage | N-10511 2024 will be the year automation comes into its own. Warehouses are ready, the technology is falling into place, and all that’s left is for you to jump in and start benefiting. But, before making any investment, it’s good to know where we are today, and what’s coming.
Sriram Sridhar Chief Revenue OfficerAddverb
SUSTAINABILITY — WHAT DOES IT MEAN IN PACKAGING MATERIALS?
11:30–12:00 PM
Innovation Stage 1 | C-2051
Sustainability continues to be a hot topic. Understanding how materials can affect the sustainability curve is challenging and requires a holistic approach. Hear about new developments and improvements of materials specific to thermoforming and tray-sealed package design for food.
Gregg Poffenbarger Business Unit Dir - Materials MultivacPACKAGING DESIGN AND QUALIFICATION FOR A CIRCULAR
ECONOMY
12:00–12:30 PM
Innovation Stage 3 | C-2058
Address the impact consumer demand for sustainable products has had on CPG and retail. Get your roadmap to use Virtual Twin technology to accelerate sustainable and profitable packaging models to plan the circular logistical journey to develop and qualify packaging of the future.
Raymond Wodar
Global Dir, Business Consulting, CPG & Retail Industry
Dassault Systèmes
DIGITAL READINESS: HOW TO UTILIZE THE RIGHT
TECHNOLOGY
12:00–12:30 PM
Processing Innovation Stage | N-10511
The food and beverage industry has shifted focus to Cloud-based software. This shift has delivered decisive benefits, as roughly 75% of food and beverage companies have seen key performance indicator improvements. Digital readiness is essential.
Jack Payne
Solution Consulting Dir, Food & Beverage Aptean REDESIGN. REPURPOSE. REVOLUTIONIZE: INNOVATIONS FOR ZERO-WASTE PACKAGING
12:30–1:00 PM
Innovation Stage 1 | C-2051
The circular economy will soon guide all consumption. As the need for packaging grows, we must use design for easy recycling or purposeful re-use. Learn from winners in this year’s Better With Less—Design Challenge.
Nathan Pajka
Sustainability Mgr
Metsä Board SD
AMICUS SPEND MANAGEMENT (BOOTH SU-7699A) FOR SPONSORING THE SHUTTLE BUSES.
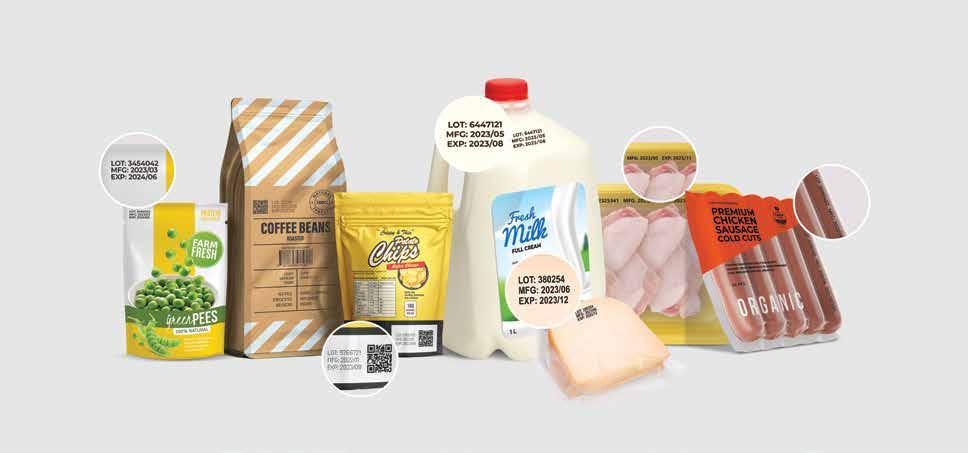
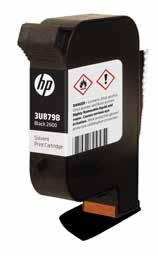
Moving toward circularity
Success
Packaging has always been a balancing act. Consumer packaged goods (CPG) companies must weigh cost versus performance and market appeal versus machinability. As interest in sustainable packaging has grown, brand owners also must balance circularity with price, safety, distribution requirements, material availability and overall environmental impact. This requires a dialogue among stakeholders about packaging design, material choices and end-of-life disposal options.
To begin this conversation, PMMI, The Association for Packaging and Processing Technologies (Central Lobby), and AMERIPEN (the American Institute for Packaging and the Environment) (Booth C-1151) have published 2023 PACKAGING COMPASS: Evaluating Trends in U.S. Packaging Design Over the Next Decade and Implications for the Future of a Circular Packaging System. The study and accompanying infographic identify key trends in packaging design and materials and the implications of these trends on legislation and the recovery systems for CPG companies.
“By releasing this deep dive into the trends driving the circular packaging system, we hope to facilitate an industry dialogue that will help close the gap between design needs and recovery needs,” says Jorge Izquierdo, vice president, market development, PMMI. Based on extensive research and analysis, the study’s goal is to spark a conversation on trends, present forecasts for the coming decade, and recognize the role of multiple stakeholders in advancing a circular packaging system.
The 10-year forecasts and materials sales projections indicate plastic packaging, particularly the flexible pouch format; recycled-content packaging, primarily paper and plastic; and compostable packaging will experience the highest demand, although the latter represents a small share of the market. De-
TOP THREE KEY MATERIALS
Compostables
spite the disparity in usage, these three formats have the same hurdles to overcome: a lack of end-of-life recovery infrastructure as well as effective legislative and investment strategies.
A survey of 394 CPG brands and retailers shows:
• 75% use plastics in packaging
• 61% use paper
• 14% use glass
• 13% use metal
Projections show plastics will grow across every category, and the use of flexible film will expand at a 4-6% compound annual growth rate (CAGR), slightly above the 3-4% CAGR for plastics overall. Plastic films offer significant operational and sustainability benefits. Tensile strength delivers more protection with less material. Light weight and compact footprint reduce carbon emissions during distribution. Highly customizable materials run efficiently on filling lines and reduce overall cost and cycle time. Consumers appreciate the format’s light weight, reduced shelf space requirements and potential for easy-opening and resealing features.
Although usage continues to grow, figures from the Recycling Partnership show only 1.9% of the U.S. population has access to flexible film recycling. Most of this film is recovered from retail drop-off programs, but consumer participation in these programs is low.
Recycled Content
As a result, establishing a circular economy for flexible films will necessitate a substantial expansion in recycling infrastructure that involves better collection, sortation and end-of-life reprocessing, potentially including widespread use of chemical recycling.
The report explains chemical recycling is an emerging technology that reverts materials to their original monomers. Its adoption could enhance opportunities for the circular reuse of flexible films by increasing collection, lowering sortation requirements and improving recycled resin quality by reducing contamination, color or scent concerns, thereby simplifying the regulatory acceptance of recycled resins for food-contact applications.
Compostable packaging has a projected CAGR of 15-16% during the next decade and is receiving a lot of attention because of a perception that it offers a less-complicated end-of-life option. However, composting also suffers from a lack of infrastructure. According to statistics from the Sustainable Packaging Coalition, only 27% of the U.S. population has access to curbside composting programs, and only 11% of those composting programs accept packaging.
To realize the full circular potential of compostable packaging, the U.S. needs to increase consumer access to composting by investing in the collection of compostable materials and in expanded access to composting facilities that accept food scraps along with packaging. As the U.S. looks at investments into the necessary collection and processing infrastructure, the most immediate impact is likely to be attained if closed systems like stadiums, foodservice outlets and cafeterias were implemented before household collection programs.
Recycled-content packaging is a popular path toward circularity. Design for recycling guidelines have been developed by several organizations and are helping the packaging industry choose combinations of polymers, labels and additives that do not hinder a package’s recyclability. Many brand owners use these guidelines to help meet commitments to increase the use of recycled content.
Unfortunately, a disconnect between strong demand and insufficient supply and processing capacity for recycled resin must be overcome. Like flexible packaging, potential solutions lie in simplified and improved collection, better sortation techniques and
greater capacity for end-of-life reprocessing. Chemical recycling could be a potential way to increase capacity as well as recycled resin quality.
IMPROVING INFRASTRUCTURE
Achieving a circular economy depends on improving the infrastructure for collection, sortation and end-of-life reprocessing. Policy changes will be needed to achieve these objectives. According to the report, establishing a circular economy will depend on the development of:
Extended producer responsibility (EPR)
EPR programs shift financial and operational responsibility for end-of-life management of products to producers instead of taxpayers and the government. As of spring 2023, four states (California, Colorado, Maine and Oregon) have enacted EPR requirements, and more states are considering EPR bills. However, a national law would overcome a patchwork of differing state requirements and simplify compliance.
The research within this study indicates EPR programs should include a focus on ways to improve the quality and quantity of recycled materials. Key considerations should explore how best to invest in the composting infrastructure, including packaging, and
Fast Lead Times
address how to handle hard-to-recycle materials by investing in collection and sortation technology and supporting end-market development. The data also show package design needs to consider many factors beyond design for recycling. Leveraging EPR to help balance all the design variables should create benefits for each stakeholder.
Universal Access
Providing all households with convenient and consistent access to recycling and composting services would increase collection.
Standardized Definitions
Definitions for commonly used terms like recycling and composting would ensure stakeholders are communicating a consistent message and reduce consumer confusion.
Alternatives to Material Bans
Material bans can prevent CPG companies from choosing the optimum packaging material and actually increase a product’s environmental impact. Shifting from material bans to dialogs about collection, sorting and reprocessing gives brand owners the freedom to pick the best option.
Recovery Innovation
Federal investments into programs uncovering
emerging science and data are needed to drive efficiencies across packaging design and waste management.
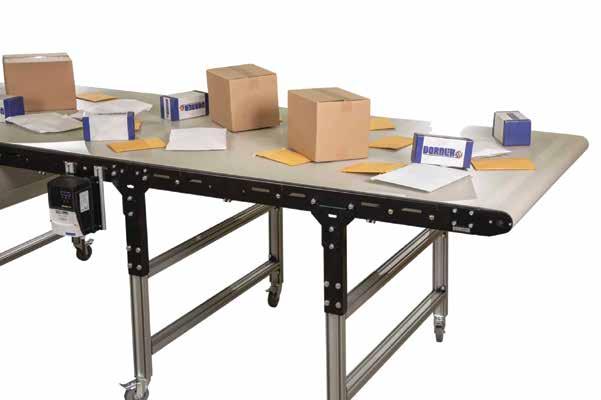
Data Collection
Consistent data collection will help measure and benchmark the performance of a circular packaging economy.
Reusables Infrastructure
Reusables are another promising option to achieve circularity. However, as with other options, infrastructure is lacking, and investment is needed. According to the report, successful reusable packaging programs depend on redesigning distribution systems for reverse logistics. This will involve establishing safe and hygienic drop-off or pick-up collection points, which are convenient to consumers, and equipping production lines for washing and refilling.
Currently, the adoption of reusables poses a daunting challenge for many packaging companies due to the costs to develop and scale a system to achieve a significant impact. A collaborative strategy that incentivizes innovation is needed. Understanding the challenges and opportunities of reusables will require participation from a wide range of stakeholders.
CONCLUSION
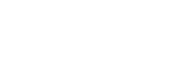
A circular economy can be achieved by focusing on how best to invest in recycling and composting infrastructure across the U.S. and tying that dialog to what is happening with packaging design and the multiple variables packaging designers must juggle. Success will depend on how well members of the packaging value chain understand each other’s challenges and opportunities.
For more info, visit pmmi.org, ameripen.org. SD
Multihead weighers 101
Choose the right combination scale for your application.
The first multihead weigher was introduced to the packaging industry in the 1970s. Since then, there have been quite a few technological advancements made; however, design-wise, the exterior appearance of these scales has not changed too much. Even though they look similar, you can’t just use any combination scale for any application. What features and components do you need to consider when choosing the right combination scale for your application?
PRODUCT-SPECIFIC QUESTIONS
To ensure you buy the best scale for your application, start by asking these five questions:
• What type of product(s) do you want to run on the scale?
• What are the characteristics of the product(s)? (Shape, piece size, stickiness, fresh vs. frozen, etc.)
• What level of sanitation is required? (Washdown vs. wipe-down)
• What are your requirements for target weight(s) and speed(s)?
• What packaging equipment will be under the scale? (vertical form/fill/seal, tray line, pouch machine, jar line, etc.)
Discussing the answers to these questions and providing as many product details as possible will help you and a scale manufacturer determine the best weighing equipment for your application.
Yamato (Booth SL-5949) recommends you make a product matrix to determine the product(s) and target weight(s) you want the scale to run. Know this before you even begin researching multihead weighers. Providing more detail related to the immediate—and future—needs of a scale will likely save you time and money in the long run.
HOW WILL YOUR PRODUCT RUN?
Multihead weighers use vibration to move product down the feed pans to the feed buckets. If you cannot start and stop the movement of product on the top of the scale, then a multihead weigher is not going to be a viable weighing solution. Take this into consideration and be prepared to send samples to the scale manufacturer for testing for runnability.
PRODUCT-CONTACT SURFACES
The first important detail to consider for your multihead weigher is the product-contact surfaces. The product-contact surfaces are just that—any surface that your product will contact. Different surfaces are used on a scale depending on the characteristics of the product(s) being run.
Most combination scale manufacturers offer their scales with at least two options for product-contact surfaces, such as smooth and embossed.
Smooth-polished contact surfaces suit free-flowing products such as dry snacks, nuts, hard candies
and seasoned items.
Embossed contact surfaces are used for harderto-move products because they minimize the surface area that contacts the product. Some manufacturers, like Yamato, offer multiple levels of embossing to further maximize movement through the scale.
PRODUCT-SPECIFIC CONFIGURATION
Once the ideal product-contact surface has been determined, it is time to look at four other areas of the multihead weigher that require product-specific configuration. This includes the scale’s top cone, linear feed pans, bucket size and door type, and collating chutes and funnel.
Top Cone: When product is added to the scale, it lands on the top cone and is distributed through vibrations out to the linear feed pans. The rigidity, moisture content, stickiness and shape of the product determine the texture and angle of the top cone. Products like leafy greens require a steep, embossed top cone to stop product from piling up in the center of the scale. Smaller products like jellybeans or nuts require a flat top cone so the product will not roll or move too quickly down the scale’s linear feed pans.
Linear Feed Pans: The next step is to determine what type of linear feed pans will be best for moving the product into the buckets. Like with the top cone, the scale vibrates to move product along the linear feed pans. Different manufacturers offer different options for linear feed pans. Feed pans can be U-shaped, V-shaped, flat or cascading. Linear feed pans also can be configured with different angles. Steeper angles help move product toward the scale’s buckets, whereas flatter feed pans will slow down round products that like to roll. All of these details are completely dependent on the product being weighed.
Bucket Size and Door Type: Choosing the bucket size of the scale is probably the easiest part when configuring a scale. The size of the buckets will be determined by the max piece size and target weight. Buckets need to be big enough to hold the product required for the specified target weight(s). They also need to be sized so that when bucket doors are open, there is enough room for the product to evacuate the bucket without catching it. Some buckets will have a single-action door, meaning only one side opens, and some will have dual-action bomb-bay style doors. Product characteristics determine which door type is best for your application. When it comes to bucket sizes, here’s a helpful hint—there is NO industry standard when it comes to quantifying bucket sizes. For example, a 3L bucket from one company could be a 5L bucket at another, and a 1L bucket at another. When talking to a scale manufacturer, especially if you’re talking to more than one, it is important to
understand how it sizes its buckets.
Collating Chutes and Funnel: A multihead weigher’s collating chutes and funnel are pretty straightforward to configure. Products that tend to stick will typically require steeper chutes and funnels, whereas free-flowing products will often have shallower, angled chutes and funnels. Some products tend to swirl. If your product swirls, depending on the severity, individual chutes and segmented funnels can be used to help guide the product more directly out of the collating funnel.
HOW MANY BUCKETS?
Once the proper scale components are selected, it is time to move on to the fun part. How fast can the scale go? What’s the most accurate it can be?
The final step is to determine the number of buckets needed to achieve the desired speed and accuracy.
Different manufacturers have different standards as to how many buckets they like to use in a combination. The more buckets a scale has, the greater the potential for speed and accuracy.
That being said, the law of diminishing returns does ring true. There is no need to spend more on additional heads if your application does not have the speeds and/or target weights to justify the additional cost. This is why the vast majority of combination scales use 14 weigh heads. Basic combination theory should also be taken into consideration.
For more info, visit yamatoamericas.com. SD
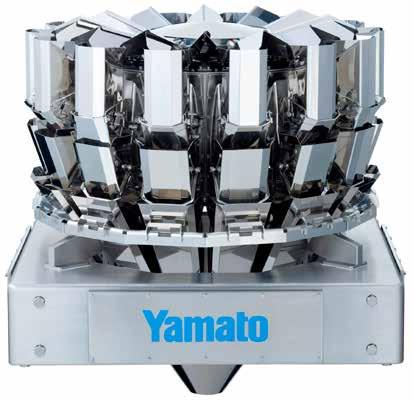
Editor’s Note: The original version of this article was written by Yamato.
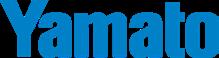
Many players, one team. www.syntegon.com
Many players, one team. www.syntegon.com
Many players working hard to ensure the productivity, safety, and sustainability of our machines are always at their best.
Many players working hard to ensure the productivity, safety, and sustainability of our machines are always at their best.
Many players, one team. www.syntegon.com
Many players working hard to ensure the productivity, safety, and sustainability of our machines are always at their best.
Many players working hard to ensure the productivity, safety, and sustainability of our machines are always at their best.
Many players working hard to ensure the productivity, safety, and sustainability of our machines are always at their best.
Many players working hard to ensure the productivity, safety, and sustainability of our machines are always at their best.
One team dedicated to providing exemplary service — every time.
Many players, one team. www.syntegon.com
Many players working hard to ensure the productivity, safety, and sustainability of our machines are always at their best.
See us in Booth C-2800!
See us in Booth C-2800!
See us in Booth C-2800!
See us in Booth C-2800!
See us in Booth C-2800!
See us in Booth C-2800!
See us in Booth C-2800!
One team dedicated to providing exemplary service — every time.
One team dedicated to providing exemplary service — every time.
Many players, one team. www.syntegon.com
One team dedicated to providing exemplary service — every time.
One team dedicated to providing exemplary service — every time.
Many players, one team. www.syntegon.com
One team dedicated to providing exemplary service — every time.
One team dedicated to providing exemplary service — every time.
Many players, one team. www.syntegon.com
Vote now for TEA winners
Recognize PACK EXPO debuts by selecting winners in four categories.
Voting closes at noon today for the 2023 Technology Excellence Awards (TEA). Votes may be cast onsite, online or on the official show mobile App, sponsored by ProMach (Booth C-3222). The winner in each category will be announced this afternoon.
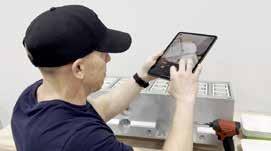

Showgoers may select winners in four categories: Food/Beverage; General Packaging & Processing; Personal Care/Pharma; and Sustainability. There are three finalists per category.
“We encourage all attendees to take part in the voting process,” says Laura Thompson, vice president, trade shows at PMMI, The Association for Packaging and Processing Technologies (Central Lobby)
FOOD/BEVERAGE FINALISTS
phragm pump from Graco (Booth N-10634)
Designed to quickly empty drums, barrels or jerricans of concentrated liquids, the Aneko Emsys system is ideal for syrup preparation rooms with sanitary construction, simple operation and an integrated weighing system. After the operator selects the product, the unit automatically detects the opening and empties the container. Once empty, the container is rinsed, and the system returns to home position for automatic cleaning in place.
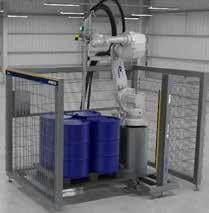
The ASD, an electro-servo pump (ESP) system from JBT, relies on electric servo motors to operate a reciprocating ball screw to move ceramic plungers, build the pressure inside an HPP pressure vessel and provide a constant flow of high-pressure media throughout the pressurization step. Recognized as green technology, benefits include 30% energy savings versus standard hydraulic systems, a 40-50% reduction in thermal load to the room, a 30% smaller footprint, an 86% reduction in oil use, quieter operation and lower spare parts and wear costs.
double diaphragm technology. It eliminates inefficiencies inherent in traditional pneumatic pumps and the cost of compressor maintenance and is up to 80% more energy efficient than air-driven technologies.

GENERAL PACKAGING & PROCESSING FINALISTS
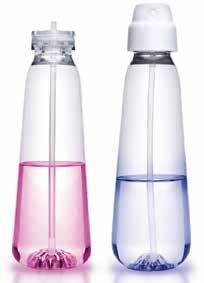
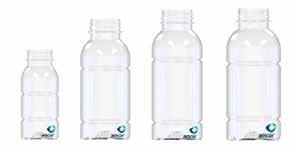
In the General Packaging & Processing Category, the finalists are an artificial intelligence (AI)-enabled augmented reality (AR) technology from Harpak-ULMA Packaging (Booth SL-6101, SL6188), DairySeal™ containers from Amcor Rigid Packaging (Booth SU-7244, SU-7254) and the SOMIC 434 next-generation case packer from Somic Packaging (Booth SL-6172)
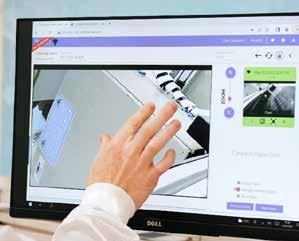
Food/Beverage finalists include the Aneko Emsys liquid evacuation system from Aneko (Booth N-10165), the Avure Servo Drive (ASD) high-pressure processing (HPP) pump from JBT (Booth SL6111, SL-6349) and the QUANTM electric dia-



Graco’s QUANTM electric diaphragm pump combines the efficiency of electric drive with the flexibility of integrated controls, plug-and-play installation, built-in diagnostics and the benefits of air-operated
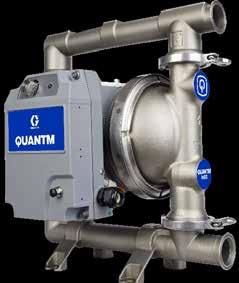
AI has become an increasingly popular tool to optimize and streamline analytics and business processes. The ability to leverage granular data sets to quickly and accurately produce recommendations can transform good solutions into great ones. This Harpak-ULMA system utilizes AI to identify patterns, predict outcomes, optimize decision-making
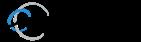
processes, and transform packaging operations.

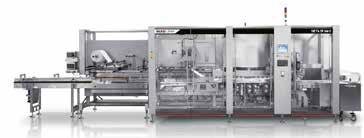
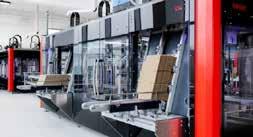
The DairySeal line for ready-to-drink products features ClearCor™, an advanced polyethylene terephthalate (PET) barrier. Along with sustainability benefits, DairySeal containers maintain physical integrity during shipment, allow customized design, meet shelf-life requirements and help improve consumer satisfaction in a highly competitive landscape.
Standardized mechatronic modules on the Somic 434 case packer maximize automation, accessibility and productivity. One of the first uses of AmorKinetics decentralized servo technology from Rockwell Automation (Booth SL-6127), the functional modules can be individually adapted to desired format ranges, thereby future-proofing the machine. A stainless-steel frame with integrated electrical provides a straightline case-packing process and ergonomic adjustment, cleaning and maintenance. Locating noise-intensive components in a cabinet reduces noise levels.

PERSONAL CARE/PHARMA FINALISTS
Healthcare Packaging serves as an alternative to rigid pill bottles for over-the-counter medications and vitamins. The pouch structure incorporates several essential features: recycle-ready, high moisture barrier, child resistance and a closure that allows pouch sizes to be miniaturized to match bottle sizes. Internal Amcor consumer testing indicates a preference for the pouch versus traditional pill bottles.
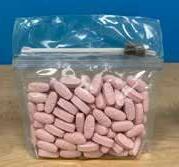
The LCA from Xyntek deploys a network of fixed-position cameras to ensure coverage of hardto-reach areas and inspects the entire line in seconds. Operators manage line clearance by exception to quickly remove any rogue product. When compared with human observation, the system reduces line inspection time by up to 85%, minimizes downtime, increases line capacity utilization by as much as 20%, and dramatically improves OEE.
Pester’s space-saving PEWO-pack 600 highspeed stretch wrapper with high-end stretching technology offers stable film packaging with sustainable packaging materials. Performance features include speeds up to 60 cycles/min., compatibility with virtually any consumer product and fast changeover. Compared to conventional shrink wrapping, the unit can cut energy consumption by 75%, material consumption by 50% and floor space needs by 30%.
SUSTAINABILITY FINALISTS
The finalists in the Personal Care/Pharma Category are a child-resistant, reclosable, high-barrier pouch from Amcor Healthcare Packaging (Booth SL6635), the SmartFactory LineClearance Assistant™ (LCA) from Xyntek, A CXV Global Company (Booth SL-6185) and the PEWO-pack 600 stretch wrapper from Pester USA (Booth SL-6726)
The reclosable, child-resistant pouch from Amcor

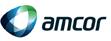
In the Sustainability category, the finalists are: the Recycle-Ready Sachet from Amcor Healthcare Packaging (Booth SL-6635), the IMA Ilapak Delta

OF-360 X flow wrapper from IMA North America (Booth C-3200, C-3400) and the SprayPET Revolution, a 100% recyclable all-polymer aerosol from Plastipak Packaging (Booth N-9357)

Designing for recyclability can be challenging for pharmaceuticals because many products rely on difficult-to-recycle foil laminations to provide a sufficient barrier to water vapor transmission. A metallized polyolefin material from Amcor Healthcare Packaging, combined with Amcor’s recycle-ready AmPrima™ film, provides an alternative, yielding a lamination that is compatible with the polyethylene film recycling stream and suitable for pharmaceutical sachets.
The IMA Ilapak Delta OF-360 X flow wrapper is considered the world’s first variable geometry flow wrapper. It is capable of running any flexible packaging material, from paper-based to complex laminates and recyclable mono-polymer films. Changeover is accomplished with the press of a button on the operator interface.
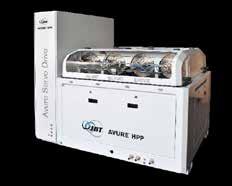
Plastipak has launched SprayPET Revolution™, a 100% polymer aerosol, which is fully recyclable. A metal-free design and all-polymer valve replaces traditional metal valves with rubber gaskets. Available in dip-tube or bag-on-valve configurations, the all-polymer aerosol offers flexible shape design for on-shelf differentiation and eliminates concerns about rusting or denting.
For more info, visit packexpolasvegas.com. SD


Confectioner switches to paperboard
Flexible automation supports transition to renewable carton.
The long-established Balocco S.p.A. confectionery company, based in Piedmont, Italy, packages its new ZeroPiù Balocco biscuits in sustainable paperboard boxes certified by the Forest Stewardship Council® (FSC). With a Multipacker from Schubert, parent company of Schubert North America (Booth SL-6820, SU-7654), the company has invested in a flexible packaging system for flowpacks and cartons that can process paper or plastic.
For three generations, Balocco has been dedicated to sweetening the lives of millions of consumers around the world. The Balocco family’s passion for sweets dates to 1927, when Francesco Antonio opened his first confectionery shop in Fossano, located in the heart of Piedmont. Today, with production and logistics facilities covering 75,000 sq. m, the company is the second largest player in the domestic market for breakfast biscuits and seasonal cakes, such as Panettone or Pandoro for Christmas and Colomba for Easter.

In 2010, the company embarked on an ambitious plan to invest in technologies to improve its environmental performance. The Fossano site and the logistics centre in Trinità are equipped with photovoltaic systems that generate some of the electricity consumed, while the rest comes from other renewable sources. Now, the company aims to significantly reduce the use of plastic in biscuit packaging by replacing plastic flowpacks with recyclable paper packaging wherever possible.
FLEXIBLE SEALING TECHNOLOGY
Since August 2021, with the Schubert Multipacker consisting of a Flowpacker and Cartonpacker, Balocco has been taking advantage of a packaging system that flexibly enables this changeover. The packaging machine’s flexibility was integrated into its design from the beginning: The sealing technology, product formats and packaging materials all can be changed over from the variants used to date to the most innovative solutions—and all with quick format changes. The rapid response time makes this packaging machine an exceptionally future-proof and cost-effective investment.
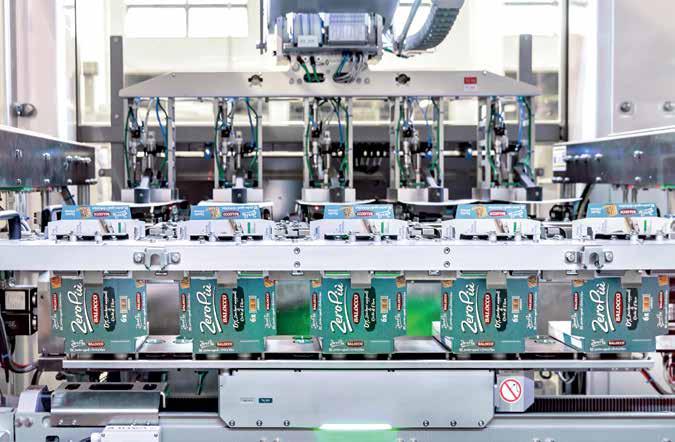
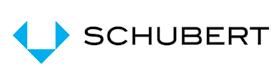
An ultrasonic longitudinal sealing unit and flying cross-sealing unit, with their constant sealing times accurate to the millisecond, seal the films quickly and reliably. They also guarantee that paper-based substrates can be processed in the future with impeccable quality.
SQUARE, ROUND OR OVAL
The Flowpacker is designed to handle different product formats with great flexibility. The fact that the biscuits are square, round or oval doesn’t pose a problem for the machine. And a program change takes only a few minutes. The integrated image recognition system, consisting of three reflected-light
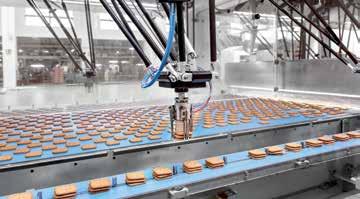
scanners, not only detects the position and orientation of the products but also ensures that only flawless products are packaged. In the event of delays on downstream equipment, the incoming biscuits can be buffered for 4 min. to ensure that the packaging process runs as smoothly and quickly as possible.
Twenty T4 robots guarantee outstanding performance and gentle picking of the products, which are then passed to the two integrated Flowmoduls. Specifically developed for Balocco’s diverse assortment of baked goods, the grippers gather the biscuits into stacks, which are then placed into the Flowmodul’s feed chains. The system also boasts Schubert’s wellknown flexibility when it comes to flowpack sizes, box formats and cartons.
and-place robots pick up the flowpacks and stack them onto the Transmodul for pre-grouping, after which they are placed into the cartons and sealed.
Alternatively, the Multipacker can erect and fill open carton trays and then pack them directly into multipack flowpacks with the aid of the integrated Flowpacker.
Downstream of the Flowpacker, a Cartonpacker loads the flowpacks into boxes. In six frames for erecting, filling and sealing, the automated process runs in sync with the upstream machines. Five pick-
In addition to its high performance, the entire system excels with an exceptionally compact design, which results in considerable space savings: The flow-wrapping machine occupies up to 70% less space compared to conventional machines. With the Multipacker, Balocco can adapt much more flexibly and sustainably to the needs of consumers and retailers, and thereby benefit from new market opportunities and competitive advantages.
For more info, visit schubert.group. SD
Bastian plans new corporate campus
HQ site includes advanced manufacturing facilities.
A162-acre site in Noblesville, IN, will serve as the future headquarters of Bastian Solutions, a Toyota Advanced Logistics company (Booth N-10343). The operation also will include advanced manufacturing facilities for the company’s supply chain automation technologies.
The new corporate campus will provide ample space for manufacturing, engineering, research and development and thoughtfully designed outdoor spaces, which will be used to engage with the larger Noblesville community. Designed to support anticipated growth over the next several decades, the facility’s groundbreaking is anticipated in the next 24 to 36 months.
“For 70 years, Bastian Solutions has experienced demonstrated success in central Indiana, and we’re proud to continue to call the region home as we embark on the next chapter in our history,” says Aaron Jones, president & CEO, Bastian Solutions.
“Our investment in the Noblesville campus will be the largest our company has made to date. This project is indicative of our commitment to Bastian employees, the material-handling industry and the state of Indiana. We’re excited to build upon the roots we’ve established here to ensure we’re successful for the next 70 years.”
To determine the optimal location for the company’s new home, Bastian conducted a thorough zip
Updated B11.0 guides use of legacy machines, remote ops

The ANSI B11.0 Machines - Safety of Machinery standard is similar to ANSI/PMMI B155.1 in content; it has a broader scope beyond packaging and processing machinery. Members who engage in business activities extending beyond packaging and processing should be certain to obtain the updated B11.0 document.

Machinery suppliers, users, modifiers, purchasers of used machinery and others can expect to be impacted by the clarified responsibilities listed. The standard includes improved and updated text involving legacy machinery, remote/tele-operations of machinery and information for use manuals.










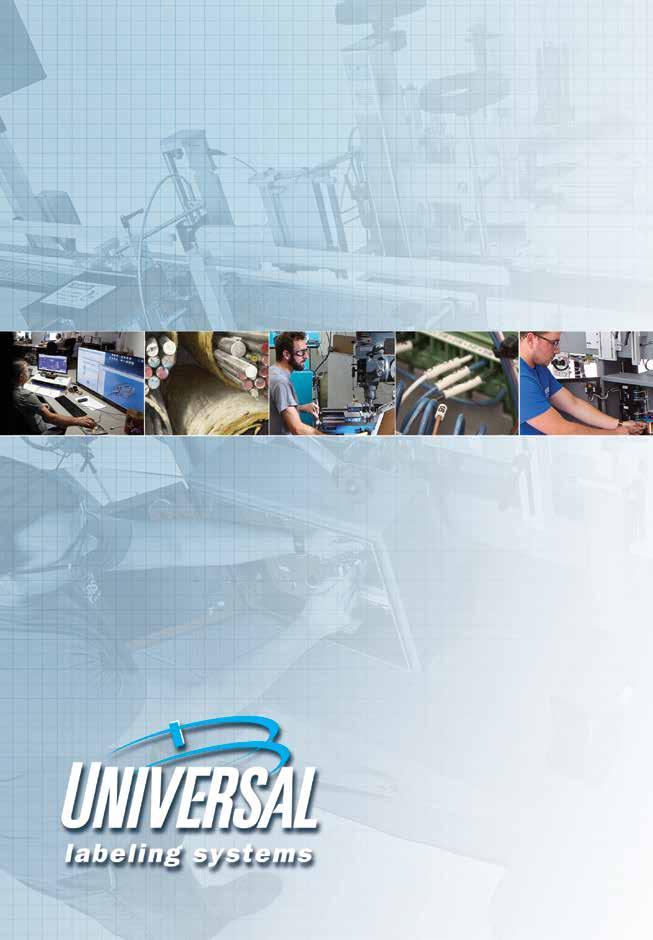
For more info, visit webstore.ansi.org/standards/amt/ansib112023?. SD
code study of its current Indiana-based employees along with housing market research and labor supply market research to support future growth objectives. The results of the study led the company to select a location in Noblesville approximately 13 miles from its current corporate headquarters in Indianapolis.
“Bastian Solutions is not only investing in their future, but also in Noblesville’s,” says Noblesville
Mayor Chris Jensen. “This project speaks to Bastian’s commitment to job growth and economic development in Noblesville, and we are excited for our upcoming successes and bright future together.”
For more info, visit bastiansolutions.com. SD
Editor’s Note: The original version of this article was posted on Jan. 26, 2023 by Packaging World.
BOOTH C-2303
X-ray inspector checks supplements
Unit handles wide array of container types and sizes.
As a leading contract manufacturer of dietary supplements, Wellington Foods is focused on producing products that help people live healthy lives. Since this includes ensuring product safety, they leverage a high-performance Safeline X37 x-ray inspection system, which can find even the hardest-to-detect foreign material such as a glass shard inside a glass bottle. The X37 x-ray system from Mettler-Toledo (Booth C-1814) offers Wellington impressive production versatility, high throughput and low energy consumption in addition to superior detection sensitivity.
“Dietary supplement manufacturing and packaging must be completed in compliance with strict regulatory oversight from government agencies,” explains Tony Harnack, CEO of Wellington. “We must also meet the high standards of our third-party cGMP certification auditors, our customer requirements and our own quality system. When we decided to invest in new inspection technology, we searched for the best system for our application.”
Steve Nering, vice president of Quality at Wellington, recalls, “We identified early on that we needed an x-ray system instead of a metal detector to help us maintain the highest product safety. For one thing, we wanted to detect all types of potential contamination, not just metal. Also, we wanted to inspect our product after the packages were sealed and many of our packaged products have a tamper-evident foil seal, which isn’t possible to inspect with a metal detector. From there, we considered the total cost of the system, equipment reliability and the supplier’s customer service. I’ve personally worked with Mettler-Toledo Safeline many times over the years, so I know firsthand that they make world-class
equipment and support it with great service.”
Juan Ortega, project manager at Wellington, agrees, noting, “Throughout our search, Mettler-Toledo was our first choice. As for selecting the exact model and options, we relied on the recommendations we got from our sales rep, Jonathon Vanderhorst of Pacific Packaging and Inspection. He helped us choose the X37, which is one of Mettler-Toledo Safeline’s most advanced detection systems. It’s able to detect a metal fragment, glass shard, dense plastic and other foreign material while also performing product integrity checks such as confirming fill level and making sure caps are applied correctly and not skewed.”
The X37 is a versatile, high-speed inspection system designed for nutraceuticals as well as pharmaceuticals, foods and other products packaged in tall, rigid containers made of metal, glass, plastic, paperboard or other materials. It’s available with a low-, medium- or high-powered generator and a choice of either a 0.4mm or 0.8mm detector. Depending on the application, it can inspect up to 1,200 packages/min.
Wellington’s X37 x-ray unit inspects liquid dietary supplements such as multivitamins, mineral products and joint health products in bottles made of high-density polyethylene, polyvinyl chloride or glass and ranging in size from 2 oz. to 1L. With a maximum throughput of 200 bottles/min. on this line, they’re able to achieve the detection sensitivity they need with Mettler-Toledo’s low-powered x-ray generator, which improves energy efficiency and reduces operating costs. The X37 unit at Wellington was installed at the end of the packaging line over an existing conveyor to minimize floor space requirements.
After the X37 x-ray system, “good” products flow downstream to Wellington’s cartoner and case packer.
Out-of-tolerance products are automatically removed from the line using a Mettler-Toledo pneumatic reject device, which pushes “bad” bottles into a lockable bin where they’re held until removed by the QA team, tested to identify the issue and ultimately destroyed.
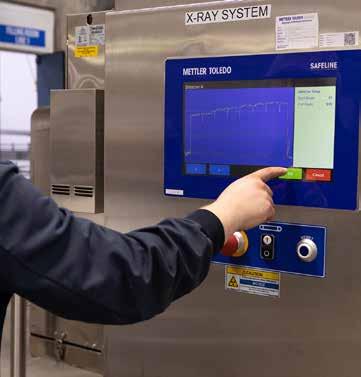

“Our X37 is the easiest system to change over on this entire packaging line. It’s programmed to know what every ‘good’ package looks like, and it will reject anything out of the ordinary,” reports Ortega. “During a changeover, we simply tap the touchscreen to select a new recipe that’s saved to memory. Then we send a couple of bottles and test rods through to verify the setup is correct. It’s very quick and easy, and it requires no adjustments.”
Nering adds, “During production, we check the x-ray system every 30 min. by sending test rods through. The X37 is extremely accurate. Even at our high level of sensitivity, we’ve had no false rejects.”
“Since we’re handling liquid products, sanitation is very important. There’s always the potential for spills and sticky surfaces,” says Chuck Sprague, vice president of Operations at Wellington. “Our X37 is actually rated for IP65 and a full washdown environment, which is more than we currently need. We typically just wipe it down, and it’s ready to go.”
Harnack concludes, “The X37 is a reliable, top-ofthe-line x-ray system. Thanks to its high level of performance, this system gives us confidence that every product we’re sending to consumers is safe. Final product inspection with our X37 is absolutely non-negotiable for both compliance and our peace of mind.”
For more info, visit: mt.com/pi-pr. SD
ProMach showcases integrated line
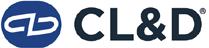
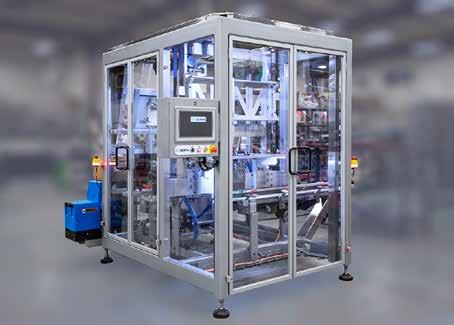
Company brands supply machines from beginning to end of line.

The ability to collaborate among brands to develop and execute fully cohesive systems and lines defines the power of ProMach (Booth C-3222). An example of this collaborative integration can be seen at Texwrap (Booth C-3625). The integrated line demo includes equipment from sister brands Quest Industrial (Booth C-3425) and Serpa Packaging Solutions (Booth C-3433, SL-6501)
On the line, filled canisters are tray packed, shrink wrapped and palletized, functions commonly performed in the nutraceutical and food industries.
Wednesday, Sept. 13
THE PARTICIPANTS

Packaging and engineering students from across the country.
THE MISSION
As the line begins, a Serpa FG1 top-load tray former forms trays from corrugated blanks. From there, trays travel to a Quest QP200-SA2 case packer, where a robot from FANUC America (Booth C-5233) orients, picks and places shrink-wrapped canisters by another ProMach brand, CL&D Graphics (Booth C-3027). Filled 12-count trays are wrapped with film on Texwrap’s Tekkra T-1030 inline shrink bundler, a continuous-motion machine with servo-driven seal bar and carriage, best suited for medium- to high-speed applications.
Tour the PACK EXPO show floor, visit participating exhibitor booths and complete challenges.
THE GOAL
Learn about new technologies and interact with industry professionals, while earning points for packaging-related challenges. Members of the winning teams will receive cash prizes, courtesy of Emerson.
Brought to you by:
Sponsored by: Booth SL-6107
Finally, Quest Industrial’s space-saving Box Bot QB320 robotic palletizer picks up wrapped trays and places them on a floor-level pallet. Every Box Bot comes standard with QBox pallet-building software, which allows operators to create new pallet patterns based on the size of the case and pallet. The Box Bot offers more than 24 standard designs to reduce complexity and lead times.
For more info, visit ProMachBuilt.com, texwrap.com, questindustrial.com, serpapackaging.com, fanucamerica.com, CLDGraphics.com. SD
CCW-AS model joins Ishida lineup
Brand marks 50th anniversary of multihead weighing.
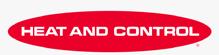
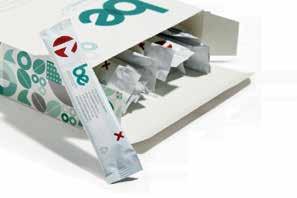
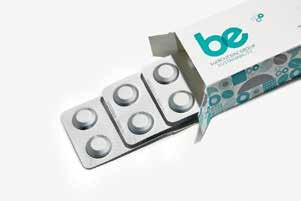
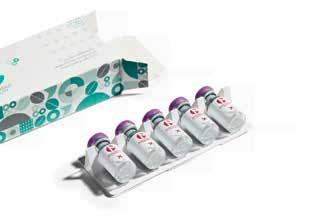
Heat and Control (Booth C-1623) celebrates its partner, Ishida, for reaching its 50th year offering multihead weighing technology. To commemorate the milestone, Ishida released a CCW-AS (Computer Combination Weighing-Advantage Series) multihead weigher.

Ishida’s long history in weighing began in 1893
when it became Japan’s first private weighing equipment manufacturer. Initally introduced for agricultural applications, multihead weighers have become essential across a wide range of markets. Due to their accuracy, Ishida’s fixed-quantity weighing systems are widely used in various sectors, including dry and frozen food, fresh meat, poultry, fish and pharmaceuticals.
marchesini.com/be
The CCW-AS Series is specifically designed to enhance productivity in high-speed weighing applications. Its advanced automation capabilities improve manufacturing and packaging efficiencies, as well as product quality and safety. This next-generation model achieves an internal calculation of 0.01g weighing accuracy.
Highly efficient operation reduces downtime and maximizes yield per hour. Smarter controls reduce operator intervention and labor reliance while enhancing robustness and reliability in harsh environments, boosting uptime.
The smart tablet touchscreen with intuitive operation reduces reliance on skilled operators. The advanced visual capabilities assist with operation, efficiency and IoT connectivity and data-handling capacity.
Reduced energy consumption and lower noise levels contribute to a more environmentally sustainable system. The hygienic design reduces chemical and water usage, improves food safety and reduces cleaning time.

Applications include snack foods, fresh produce, salad, meat, poultry, seafood, prepared foods, frozen vegetables, candy and confectionery, baked snacks, cheese, fruit, pet food and pharmaceuticals.
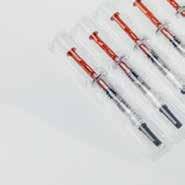
For more info, visit heatandcontrol.com. SD
Editor’s Note: The original version of this article was posted by Packaging World on June 6, 2023.
Software aids risk assessment efforts
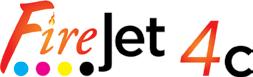

Safety in the design and operation of packaging and processing machinery is a top priority for suppliers and users of the equipment. Risk assessment tools are an effective, consistent approach for addressing risk. PMMI, The Association for Packaging and Processing Technologies (Central Lobby), provides PackSafe®, a software program that provides designers with a consistent, industry-specific method to evaluate hazards and risks through design.
The PackSafe program is updated regularly to encompass the latest safety tools. The most recent version (V9) includes improved guidance to conduct risk assessments, a new tab to better integrate func-
IoPP schedules courses this fall
Registration is open for two courses offered by the Institute of Packaging Professionals (IoPP) (Booth C-1154): Fundamentals of Packaging Technology and Packaging Machinery: Basics.
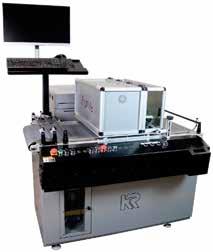
The four-semester Fundamentals of Packaging Technology is scheduled for Sept. 18-20, Sept. 2022, Oct. 9-11 and Oct. 11-13 in Oakbrook Terrace, IL. This “Packaging 101” course offers insight into packaging materials and processes, protective packaging, decorating and labeling, closures and machinery. Attendees may choose to take any number of semesters in any order.
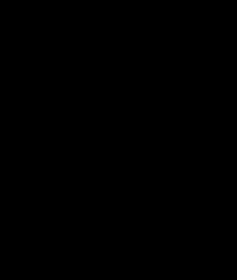
The Packaging Machinery: Basics seminar, taught by John Henry, CPP, will take place Oct. 2-4, 2023, at Frain Industries (Booth SL-5963) in Carol Stream, IL. Attendees will learn how to improve line efficiency and design packages for different types of machines.
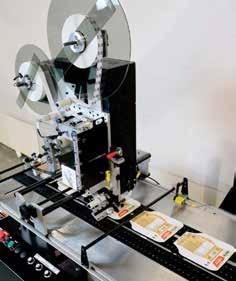
For more info, visit iopp.org, frain.com. SD
tional safety and the means to develop Alternative Methods in lieu of locking-out to control hazardous energy. PackSafe can be licensed for one or multiple seats for your engineering team.
To aid in implementing the risk assessment process and PackSafe software, PMMI offers a comprehensive training program. Bruce Main, president of design safety engineering, and his team recently led a
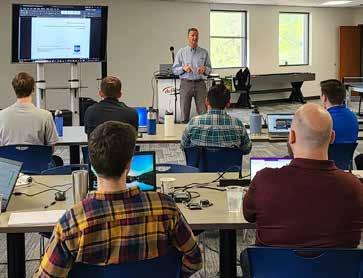
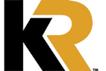
two-day course at Delkor Systems (Booth C-3840), which brought together engineers, engineering managers and project managers who interface with customers. This hands-on workshop is tailored to each company’s needs and interests and includes insights into the latest regulations and requirements.
For more info, visit pmmi.org/packsafe-software, pmmi.org/risk-assessment-workshops. SD
STAND OUT FROM THE CROWD
SEPTEMBER 12, 2023
Conveyor orients wrapped trays
Trays travel from heat tunnel to labeler to palletizer.
Aseries of four plastic belt conveyors from Multi-Conveyor (Booth C-1718) gaps, rotates, transports and right-angle transfers wrapped, corrugated trays of canned goods in a single lane.
The trays discharge wide-side leading from an existing heat tunnel onto the first conveyor, which increases the gap between trays to prepare for rotation to a narrow-side-leading orientation.
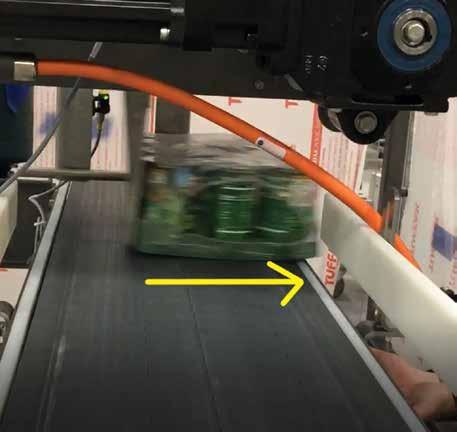
A video (youtu.be/yxDW1NV63kE) shows how the consecutive, dual-lane, product-turning conveyor rotates the trays 90 degrees. This reorientation to narrow-side leading accommodates an existing labeler (not shown), which applies labels on the wide side of the flats. Trays smoothly transfer onto the third transport belt without hesitation.
Join
Programs include:
f On the Rise Awards
f Leadership Development Program
f Quarterly e-newsletter
f One-day Young Professionals Conference
f Networking receptions at PACK EXPO trade shows For more information, visit:
pmmi.org/young-professionals
At that point, the fourth conveyor right-angle-transfers the trays using a servo-driven overhead transfer device. Each tray is conveyed to a predetermined point, where it is identified and “pushed” or “swept” at a right angle, one tray at a time, changing orientation by 90 degrees to return to a narrow-edge-leading stance.
The 60-tray/min. pusher assembly device uses logic controls, product detection and infeed sensors for the perfect transfer to feed the palletizer. Polycarbonate guarding was furnished around the pusher transfer assembly for operator safety.
Planning ahead, the overall scope-of-project also included options for two additional powered conveyors to be added at a later date.
For more info, visit multi-conveyor.com. SD
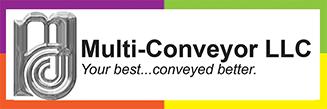
impulse heat sealing
Impulse Temperature Controllers
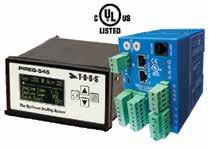
The PIREG ® heatseal temperature controllers are designed specifically for controlling the heat sealing operations performed in a wide range of applications including: vertical and horizontal form, fill, and seal; pouch filling and sealing; film wrapping, and pouch making. The PIREG ® impulse temperature controllers are cUL Listed and universally adaptable to almost any application, and do not require the use of thermocouples or RTD’s. PIREG ® temperature controllers are designed for “in cabinet” and “panel mount” uses and also available with EtherNet/IP® communication capabilities. TOSS Technology— delivering perfect impulse heat seals every time. www.tossheatseal.com
Here’s WALDO!
Booth SL-6407
Waldo Packaging Machinery is a manufacturer of fully automated vertical form-fill-seal packaging machines for packaging liquids, slurries and high viscosity products. Servicing businesses of all sizes in a range of markets that include food/beverage, cosmetics, and cleaning fluids, their complete line of machines are compact, user friendly and cost efficient. www.waldo.com.mx
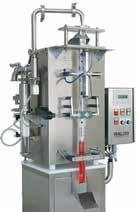
PackworldUSA Medical Sealers
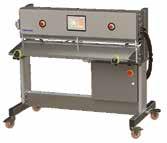
What sets PackworldUSA apart from all the rest is its use of the high response, state of-art, TOSS Technology All PackworldUSA machines come equipped with the advanced PIREG ® temperature controller. Only TOSS uses Variable Resistance Controlled (VRC) heat sealing technology to monitor and adjust temperature precisely over the full length and width of the heat sealing element, accurate up to 500°C. www.packworldusa.com
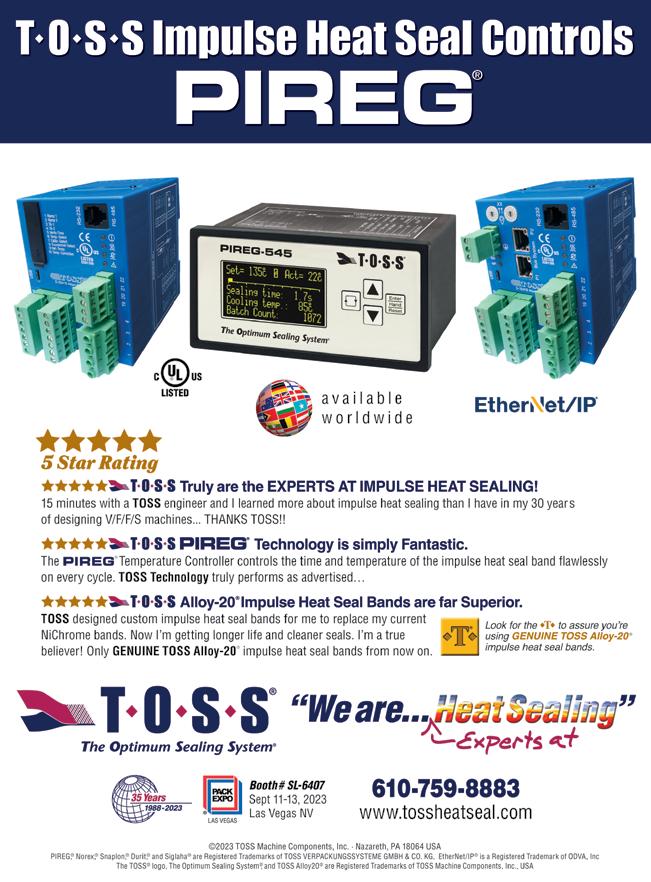
TOSS Alloy-20 ® and Norex® Heatseal Bands are available in over 350 styles, shapes and sizes. Custom designed for any application, new or existing, TOSS Alloy-20 ® Heatseal Band are longer lasting and provide for effective sealing at optimum speeds. When used in conjunction with the PIREG ® Temperature Controllers, the TOSS Alloy-20 ® heatseal bands provide instant thermostatic feedback eliminating the need for thermocouples. This instant feedback assures precise, repeatable results on each and every seal. www.tossheatseal.com
TOSS Heat Seal Cover Materials
In the optimum sealing set up, the heatseal band must be electrically and thermally insulated from the jaw bar. TOSS offers a wide selection of PTFE cover cloths and tapes that are available in standard and custom sizes. Other insulating materials available from TOSS include Silicone Rubber, Snaplon,® Durit,® and Siglaha ® www.tossheatseal.com
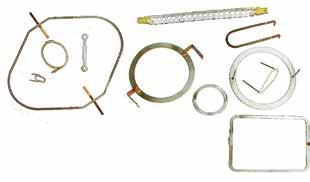

award winning packaging takes center stage
Focused interest areas
narrow search
Check out Sustainability Central, Processing Zone, Logistics and Healthcare Packaging Pavilions, other favorites.
An array of pavilions and other focused interest areas help attendees at PACK EXPO Las Vegas zero in on the products and services they need. New this year is Sustainability Central (Booth N-9455) and the accompanying Sustainability Stage (Booth N-9967) (see schedule p. 16). This interactive destination in the North Hall offers an expansive look into what sustainability means and serves as a resource for sustainable manufacturing, materials, design, recovery, logistics and data.
Another PACK EXPO Las Vegas debut, The Logistics Pavilion in the North Hall, addresses a topic that ranks in the top five searches on the PACK EXPO website. It offers targeted solutions to address the boom in eCommerce. Participating exhibitors include warehousing, fulfillment, distribution logistics and transportation service providers.
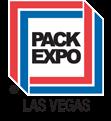
NORTH HALL Booth N–9550
Also new for the Vegas show, The Healthcare Packaging Pavilion targets attendees working in businesses devoted to life sciences. This “show within a show” in the South Lower Hall will house innovations for pharmaceuticals, biopharmaceuticals, nutraceuticals and medical devices.
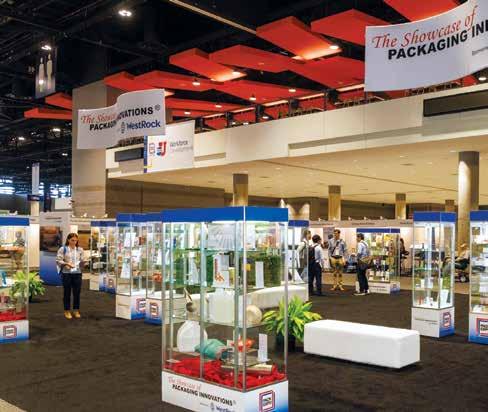
One of the largest special interest areas, The Processing Zone in the North Hall, presents products/services to help increase efficiency, achieve total system integration and ensure employee safety. Roughly 50% bigger than in 2021, this area features front-ofthe-line technologies such as homogenizing, heat treating, forming/sizing and coating. It also hosts the Processing Innovation Stage (Booth N-10511) (see schedule, p. 30).
The Confectionery Pavilion, hosted by the National Confectioners Association (Booth SU-7201), will feature the latest trends relating to aeration, batch refining, shaping, cluster production and other candy-making techniques. Located in the South Upper Hall, this pavilion also provides a spot to take a break and recharge at the Candy Bar Lounge (Booth SU-7201), sponsored by Syntegon Packaging Technology (Booth C-2800)
The Containers and Materials Pavilion will display the latest innovations in paperboard, glass, metal, plastic, flexible and resealable packaging, as well as containers and materials. Located in the North Hall, the pavilion houses The Showcase of Packaging Innovations® (Booth N-9550) (see story, p. 22). Sponsored by WestRock (Booth C-2023), this attendee favorite will display award-nominated packaging.
The PACKage Printing Pavilion in the North Hall focuses on the advantages of digital printing, showcasing the latest in cost-effective solutions for smart, short-run, on-demand, variable data and personalized packaging.
The Reusable Packaging Pavilion, sponsored by the Reusable Packaging Association (Booth SU-8000), presents sustainable packaging concepts to help reduce waste, cut costs and gain supply chain efficiency. This pavilion in the South Upper Hall also houses the Reusable Packaging Learning Center (Booth SU-8000)
The Workforce Development Pavilion (Booths N-9000–N-9026) is a one-stop shop for resources to strengthen the workforce. Learn about PMMI U offerings, including popular training workshops, and meet students interested in careers in the industry.
The Association Partner Pavilion (Booths C-1145–C-1354) houses participants in the PACK EXPO Partner Program and connects attendees to leading associations from all segments of packaging and processing. Experts from the PACK EXPO Partner Program address the latest hot topics and industry trends such as sustainability, remote access, supply chain solutions, augmented reality and operational efficiency on the Industry Speaks Stage (Booth C-1141) (see schedule, p. 24)
For more info, visit packexpolasvegas.com. SD
AI increases functionality of gripper
Artificial intelligence (AI) helps the mGripAI end-of-arm tool from Soft Robotics (Booth N-10311) pick, orient and pack items like chicken drumsticks at up to 60 units/min.
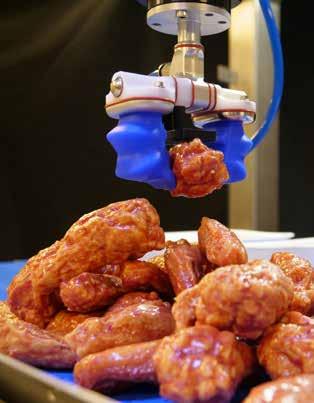
Designed specifically for the food industry, the unit combines proprietary and industry-proven 3D vision, AI and soft grasping technologies into an easy-to-integrate, IP69K-rated device, enabling automation of functions previously off-limits to robots.
Now empowered with the sensory, cognitive and dexterous abilities of human workers, the mGripAI EOAT lessens dependency on unavailable labor, saves floor space, increases throughput and reduces food waste.
A no-code interface enables any machine builder to leverage the power of AI in complex picking applications. “Ease-of-deployment is at the core of every mGripAI system,” says Austin Harvey, vice president of Product and Marketing at Soft Robotics. “It is now easier than ever for machine builders to deploy AI-enabled solutions and leverage complex object understanding for high-speed picking applications.”
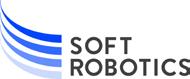
For more info, visit softroboticsinc.com. SD
Spiral conveying. Straight up!
As the market leader in spiral conveyors in the packaging industry we think of solutions for elevating and accumulating packed items. It’s what we do. At AmbaFlex it’s not just about building the right equipment, it’s about developing a special solution for you. Here’s to spiral conveying.
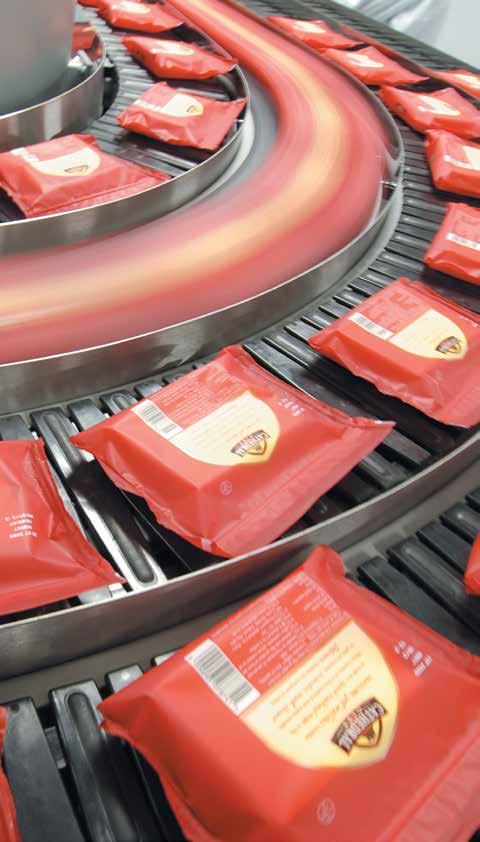
Spiral Elevators & Accumulators for primary and secondary packaging handling.

Right-sized cases spell efficiency
Right sizing cuts material/weight, boosts consumer satisfaction.
When Bill Crutchfield founded his company in the family garage in his hometown of Charlottesville, VA, in 1974, he was trying to fix a problem he’d experienced as a customer: How do you figure out which aftermarket car stereos and speakers will work in your vehicle? He realized that expert information, shared by people who really cared about problem solving, was the answer. More than 6 million customers later, those principles continue to drive the business, which now serves the entire audiovisual (AV) device and consumer elecronics technology space.
several years, and there’s a lot of trust since they’ve been strong business partners over the years. She showed me some demo videos, and I was ready to sign up for one.”
LABOR SAVINGS AND FLEXIBILITY
It wasn’t that big of a leap for Groseclose, either. The Crutchfield facility had already been running a handful of Packsize’s X4s, which Groseclose describes as the supplier’s first version of a more automated box-sizing system, and predecessor to the X5.
“And that equipment carried our business for three or four years,” Groseclose says. “But they start to age out, and repairs and upkeep are needed. When I saw that they had taken everything they learned from the X4 and put it into the X5, that was reassuring.” For instance, the X4 allows for two different corrugated tracks, or fanfold widths, on the corrugated input feed. The X5 doubles that number to four, and Crutchfield currently uses all four on the new system. The corrugated spec used in this facility is 32 ECT with standard fluting.
Crutchfield makes shift to automation early
In 2013, it became clear to Crutchfield that its own warehouse was lacking the technology it needed to keep up with demand. That’s when it first came to Packsize (Booth SU-7407) with two requests. The first was to reduce its overall carbon footprint by reducing waste from shipping boxes that were too big for their contents. It also sought to reallocate labor to more engaging, comfortable spots in the facilities.
Crutchfield has since grown to employ more than 700 people and now runs the vast majority of its business as direct-to-consumer (D2C) out of two 120,000-sq.-ft. facilities, both in Virginia. Crutchfield’s impressive offering of online sizing tools and online customer support dovetails nicely with eCommerce and D2C sales, which have grown exponentially over the past decade. Since 2013, the AV equipment and device company has been growing and evolving its D2C operations with Packsize International (Booth SU-7407) (see sidebar). But an all-new installation, the Packsize X5 model, is the next evolution of that journey.
As Packaging World recently reported, Walmart was an early adopter of Packsize’s new X5 system for right-sized packaging on-demand that the supplier says efficiently produces ready-to-pack, right-sized erected cases. The retail giant uses this system within proprietary Ultra5 machines. Now, the full Ultra5 machine equipment was designed for, and remains exclusively available to, Walmart. This equipment is being rolled out to its next generation of fulfillment centers. But the X5 system the Ultra5 is modeled after is available to any Packsize customer. Given Crutchfield’s nearly 10-year history with the eCommerce specialist, it wasn’t long before they chose to capitalize as well.
“I was a pretty early adopter, myself,” says Chris Groseclose, chief fulfillment officer, Crutchfield. “As soon as they were starting to offer them out of the beta environment, I was one of the first people that had my name on the list for one. I had a good relationship with their sales rep. She’d been with us for
“Having more fanfold width options really helps you dial in your box size and reduce your waste,” Groseclose says. “Also, they’ve simplified this model where the corrugated just runs straight through the line and just doesn’t move as much as it did in the legacy equipment. And the cutting head system on the X5 is simpler. All in all, they’ve simplified the machine, increased the fanfold widths that you can input and increased the output. And frankly, with the equipment itself being able to inject a box onto the conveyor, with a bottom that’s fully glued with the Box ID label already on it, they’ve really eliminated two- or three-people’s worth of labor. Those people were involved with getting boxes out of the previous versions of the machine, folding them, taping the bottoms and putting the labels on. Packsize has taken a big jump toward a value-added automation.”
THE NEW EQUIPMENT
The new X5 equipment provides right-sized cases for Crutchfield orders in all three dimensions: length, width and height. This equipment is capable of more than 500 cases/hr., but considering the size
“Prior to partnering with Packsize, we had manual pack stations and I had five to eight packers handling roughly between 2,500 to 3,000 orders a day,” says Chris Groseclose, chief fulfillment officer, Crutchfield. “We were kind of at the end of our rope of being able to physically fulfill the orders with manual pick carts, manual pack stations, with something like 20 or 25 different slotted corrugated boxes [RSCs] to choose from, so the packer would kind of eyeball it. Plus, the business was growing during that period, so we felt we were at a crossroads.”
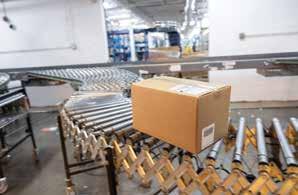
After some false starts with other suppliers, Crutchfield began its automation journey with a conveyor-based pick module from Packsize. Groseclose needed something that gave his team the right box, up front, that they could pack into.
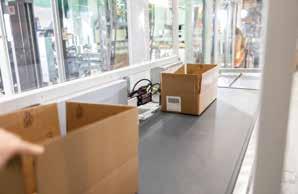
“We use a lot of the Lean Six Sigma approach to problem solving,” he says. “One of the things we want to do is reduce our product touches in the whole fulfillment process.”
That first year, Crutchfield saved about $300,000 in void fill, because box right-sizing cut overall box dimensions in half compared to where it had been in eyeballing appropriate box size. Groseclose would know, too, as the company extrudes its own water-soluble, starch ‘packing peanut’ on equipment from NewStarch Solutions.
For more info, visit packsize.com. SD

of the cases used and Crutchfield’s specific needs— it has other case-erecting equipment—the facility more commonly averages 425 to 450 cases/hr.
As Groseclose mentioned, the system uses the four corrugated fanfold infeed tracks in varying widths to optimize case sizes during erecting. The machinery operates by connecting with the consumer packaged goods or fulfillment centers’ warehouse management or enterprise resource planning systems—the X5 receives specific case size information for each order and then executes on cutting and erecting to that ∆
Helping you bring your best products to market.
Delivering Results. With Heat and Control, you have a partner with the scale to support your success, the innovation to advance your operations, and a commitment to quality that will help you offer better products for consumers.
PROCESSING AND PACKAGING SOLUTIONS

• Food processing systems
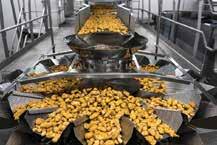
• On-machine and process area seasoning application
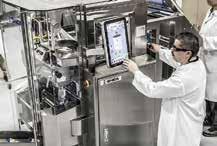
• Conveying and product handling
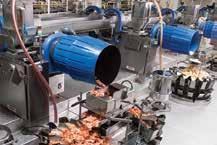
• Multihead/combination scale weighing and filling
• Snack bagmaking and case packing
• Metal detection and x-ray
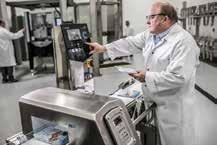
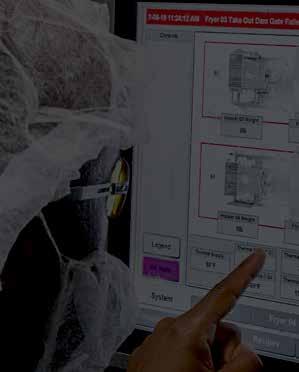

• Check weighing and seal checking
We are successful when you are successful. That’s why we apply creativity, engineering excellence, and determined perseverance to every project to help our customers get the performance their business demands—whether measured by flavor, efficiencies, sustainability, improvement, or innovation.
42 2 ~2~ ~2
107
LOOKING BACK. PRESSING FORWARD. ALWAYS INNOVATING. info@heatandcontrol.com
17 20
36 41 26
|
SEPTEMBER 12, 2023
size. Size availability ranges from 8 x 6 x 3 in., to 30 x 20 x 20 in., and the equipment can produce the largest size immediately after the smallest or vice versa without any variation in production rate, much less need for changeover equipment.
After cutting the 2D corrugated to the correct dimensions, the system then erects and closes case bottoms with adhesive. Then, pressure-sensitive printand-apply Box IDs with the item’s dimensional information—unique to every single case—are automatically tamp-applied to the erected corrugated cases.
Notably, right-sizing cases results in some scrap corrugated. This is minimized by optimizing the fanfold width, but small pieces remain. The removal of these excess scraps is also automated, with a conveyor carrying them to a gaylord that can be managed throughout the day during production and recycled with any other outgoing corrugated material.
DOWNSTREAM EQUIPMENT
At the Crutchfield facility, erected cases exit the Packsize equipment onto an IntelliROL conveyor


from TGW Conveyor Systems, which serves as the base of the whole system of pick zones that ensues. Scanners from Cognex (Booth SL-6133) read the individual Box IDs, which connect with Crutchfield’s systems and build the pick path for any given case. Once that pick path is constructed, which is almost instantaneous, that information is fed back to the conveyor’s PLC, and the conveyors “decide” into which pick zones each case needs to travel.

“Through COVID-19, I had to add extra pick zones, so now I’ve got 12 of them. We use six scanners at the induction to each zone,” Groseclose reports. “And [the system] knows whether to direct a case into each of the zones. As the case travels by the set of scanners at the front of each of the zones, the case gets scanned and the conveyors recognize ‘Yes, it needs to go in here,’ and it does. Or ‘No, it doesn’t need to go here,’ and it will pass that zone by. The cases that go through that system come to a final scan that says, ‘Yes, everything is in this order, we’re going to pass it down to shipping,’ or, ‘No something went wrong. We’re going to recirc it through the whole system and let it have another chance at getting it right.’ Sometimes, if a zone is completely full, a case will wait 10 sec., and then it’ll pass around and do a recirc of the whole system until it comes back around to the zone. Usually then, there’s an opening for it.”
Once a case is cleared to ship, it first passes manual void-fill application stations. The company uses water-soluble, peanut-style packing fill made entirely of starch.
Why would perfectly cubed and sized cases require void fill, you might wonder? That’s a good question. Crutchfield runs the Packsize equipment to an 80% fill spec. That means the cases are designed to be cut to a size that’s filled to 80% of its available space, once all the products are picked and placed to the case. But why 80% and not 100%? That’s another good question. The
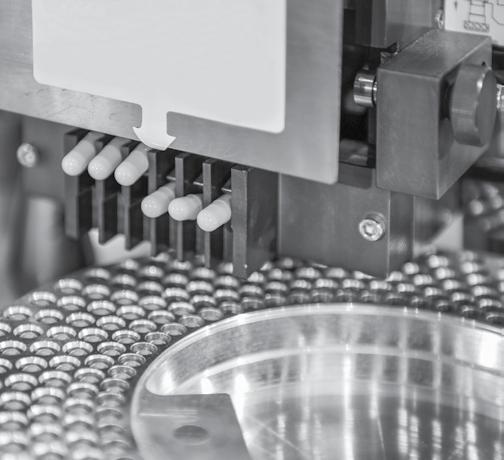
answer lies in the fact that this Crutchfield facility is a fulfillment center that receives custom orders—multiple differently sized and shaped products are often expected to fit into a single case.
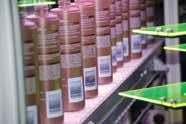

“At 100%, when there’s one single item going into the box, it will cube that box out absolutely perfectly,” Groseclose says. “But we’ve found that with two or three items, if you go with 100%, it can become too much of a game of Tetris for operators trying to figure out how to place items in the box in such a way that optimizes the use of space. So today, we run it at 20% void, I guess you’d say.”
Plus, according to Groseclose, the Packsize X5’s PackNet Cube software is smart enough to know when there is a rectangular single item, like a Sony receiver in a rectangle-shaped primary package. On those oc casions, the Packsize reverts to the 100% fill, bypassing the 80% request. The result is a perfectly cubed second ary corrugated case, and the primary package fits snug gly within, with no need for void fill.
After void fill is added as needed, the cases travel through one of two Pearson case sealers. Groseclose says these are are fully randomized, automatic case sealers ready to accommodate any case sizes that the Packsize could throw at them.
WHAT’S NEXT FOR CRUTCHFIELD?
“I think not too far over the horizon, we would add another X5 system,” he says. “Where I am right now, I have three EM7s [simpler Packsize case erectors], one X4 and one X5 in this facility. I’d like to get rid of the X4 and one or two of the EM7s and just have two X5s running the front end of it. If I had two of those in place, that puts me close to 1,000 cases an hour just with those two, and then generally that’s enough to get us through the day. I would keep some EM7s around just for supplemental volume during the holidays.”
Groseclose is also in the beginning stages of looking for an Automated Storage and Retrieval System, also called a goods-to-person system, that could potentially replace the whole conveyor piece of the existing systems.
“And I think this X5 will play in really well with that,” he says, “It’ll be a great fit.”
For more info, visit packsize.com, cognex.com. SD
Editor’s Note: The original version of this article and sidebar were posted on July 19, 2023 by Packaging World.
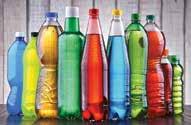
“We had manual, pneumatic sealers, but the Pearsons run three cases to every one case that ran through the manual, so we just switched over to letting two Pearsons run the case-top sealing,” Groseclose says.
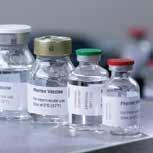
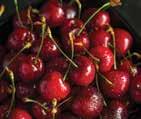
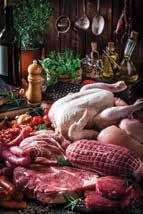
After each Pearson unit, the closed cases run across a weigh-in-motion (WIM) system, and another Cognex vision system reads both the Box ID and the weight. That begins a process of rate shopping for a carrier to get the best shipping price for a given case.
“Our system does a theoretical weight and then matches it to the actual weight,” Groseclose says. “If a certain percentage threshold of variance is met, it’ll kick it to an exception line and won’t let it ship. Once the rate shopping is complete—we do a bunch of different sorts for UPS, FedEx, postal and air shipments—they run by two print-and-apply systems that attach shipping labels, and the case then travels to a 10-lane TGW belt sorter.”
From humble beginnings growing vegetables for hungry neighbors during the Great Depression, RS Cockerill has grown to become one of the largest independent potato packers in the U.K. today. They credit much of this success to their top-quality potatoes and budget-friendly prices. These often-conflicting goals are both addressed with the help of Herbert OCULUS optical sorters from Key Technology (Booth C-4225), which automate defect removal to improve production efficiencies while ensuring final product quality of whole potatoes.
“Before Herbert OCULUS, we were sorting by hand, but that was getting increasingly difficult as the labor market got tighter and extreme weather began making incoming product quality more variable,” recalls David Elvidge, operations manager at Cockerill. “We wanted to automate sorting to take some pressure off our workforce; at the same time we wanted to improve the consistency of our final product quality when incoming defect loads would spike. We’ve been so happy with our first OCULUS,
we bought four more last year.”
Installed at Cockerill’s retail packing facility in York, U.K., five Herbert OCULUS sorters inspect whole, washed potatoes, finding and removing those with defects to ensure Cockerill achieves its final product quality specifications. The sorters recognize surface abnormalities and diseases such as bumps and notches, skin discoloration, green colors and defects like mechanical damage, scab, cracks and black dot. They also can be programmed to reject potatoes with dimensions above or below the desired length and width.
“Over the years, we’ve spoken with different optical sorter suppliers and visited sites across Europe to see a variety of technologies in action,” reports John Robinson, engineering manager at Cockerill. “For whole potatoes, it’s clear to us that OCULUS is the winner. In addition to delivering reliable results, it’s well-built and easy to operate. Among other things, we appreciate the straightforward user interface.”
Nick Larmour, technical manager at Cockerill adds, “We’ve always enjoyed working with Key. Whenever we have a question, it’s easy for us to get in touch with them. If needed, Key technicians can even access our OCULUS sorters remotely, which helps us operate continuously at peak performance.”
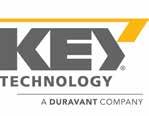
The Herbert OCULUS system conveys product over a series of rollers to present a complete 360-degree view of each tuber to the color cameras. Compared to traditional cascade bulk sorters, this unique method of sorting offers gentler handling and provides 20% more surface inspection to maximize defect removal. In addition to capturing images of all “good” and “bad” potatoes, the Herbert OCULUS system can collect detailed data about the throughput and grading results, including what percentage of the potatoes rejected had each type of defect and the size of the potatoes.
“Thanks to OCULUS, we’ve reduced our reliance on manual labor. We used to have four to eight workers dedicated to manual inspection on each line. We struggled to hire enough people, and we struggled to achieve consistent defect removal since workers get tired and tend to remove either too much or too little,” explains Larmour. “OCULUS makes objective, black-and-white sorting decisions hour after hour so we’ve got more consistent final product quality. At the same time, we’ve been able to increase our line throughput by 20–25%.”
Cockerill produces more than 1,500MT of potatoes in retail packs for supermarkets every week and even more in bulk to food processors. They selected midsize Herbert OCULUS systems from Key’s five available models to handle their line capacities of 2-8MT of product/hr.
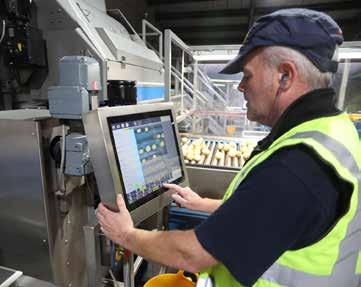
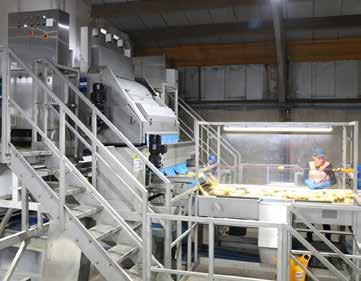
“Every customer always wants to remove all critical and major defects, but different stock keeping units (SKUs) allow for various amounts of minor defects, so
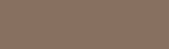
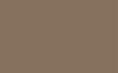
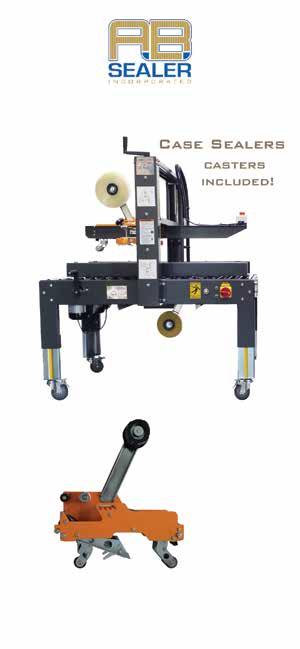
we program the sorter at the beginning of each product run to meet the exact specifications required,” says Bartosz Wozniak, production manager at Cockerill. “During a product changeover, it takes just a couple of taps on the sorter’s touchscreen to recall a recipe saved to memory. Or, when we’re running a brand-new SKU, an operator can create a new sort recipe in less than 5 min. by selecting from a list of defect types and choosing the allowable amount of each.”
“At the end of the day, our success depends on the success of our customers, so providing a reliably high-quality product on time and at an affordable price is vital,” says Elvidge. “Our Herbert OCULUS sorters achieve consistent defect removal at increased throughputs while lowering labor requirements. Plus, they’re easy to run and maintain. This technology has transformed the nature of our business—we can’t imagine having to operate without our OCULUS sorters again.”
For more info, visit key.net. SD
Optical sorters protect potato quality
Eliminating manual inspection increases throughput 20-25%.Herbert OCULUS sorters have increased line throughput by 20–25% and achieved a more consistent product quality.
Being flexible is good, being fast and flexible is even better. Schubert packaging machines are leading the way. Intelligent control and precise robotics can now replace complex mechanics to ensure maximum flexibility in all packaging processes. In fact, 80% of the leading FMCG companies count on us and our flawless packaging combined with the lowest possible consumption. In line with our Mission Blue Sustainability Initiative: A winning proposition – for our planet and for you. www.schubert.group/en/food.html
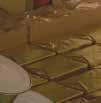
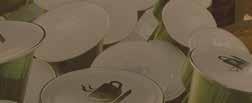



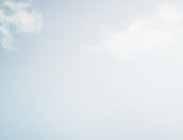

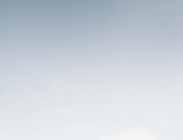
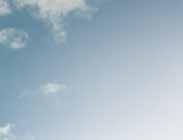
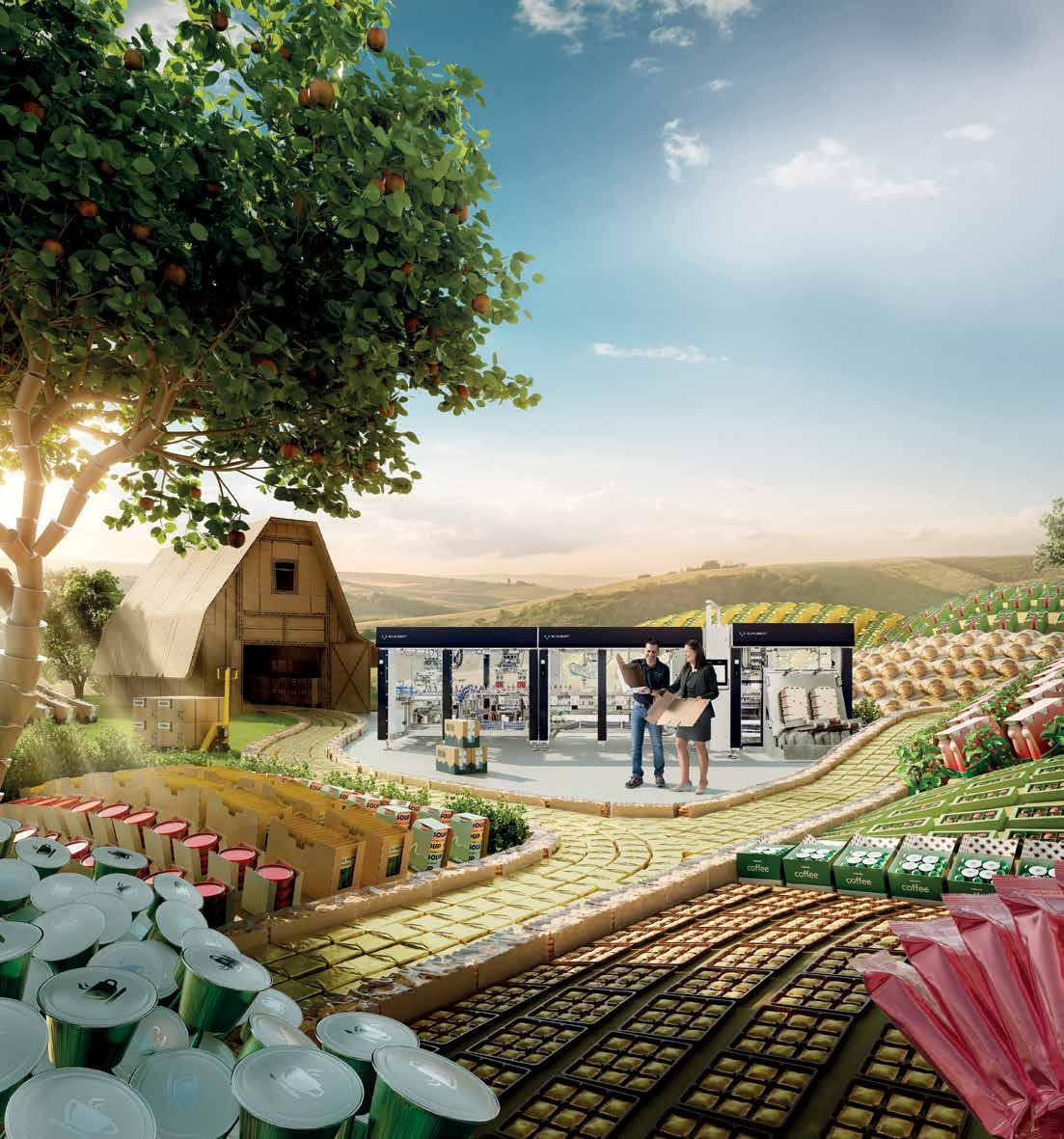
AS FAR AS YOUR EYES CAN SEE: INFINITE OPTIONS FOR PACKAGING FOOD. BROUGHT TO LIFE WITH SCHUBERT.PACK EXPO LAS VEGAS SEPTEMBER 11-13, 2023 SOUTH UPPER HALL BOOTH 7654 WELCOME
Forum sessions draw crowds
Returning to PACK EXPO Las Vegas, The Forum—An Industry Knowledge Exchange (Booth C-2158) features free, 45-min. workshops and interactive sessions on a variety of trending topics such as digitalization, cybersecurity, emerging brand development, artificial intelligence and Digitial Twins, as well as updates on courses and reports associated with the dairy industry, the cold chain, the circular economy, environmental/social/governance strategies, co-manufacturing/co-packaging trends and sustainability.
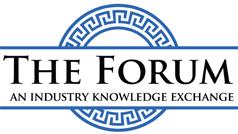
Session descriptions, times and locations are listed below. Updated schedules
EXPLORING THE POWER OF AI IN MANUFACTURING
9:30-10:15 AM
Explore different ways that manufacturers can harness the power of artificial intelligence (AI) to grow or enhance their businesses while utilizing best practices
Andy Lomasky Sr Dir, IT PMMIADD YOUR VOICE: DEVELOPING A PACKAGING SUSTAINABILITY COURSE
10:30-11:15 AM
The Institute of Packaging Professionals and its Sustainable Packaging Technical Committee are developing a curriculum on sustainable packaging. Add your input and come with your questions!
Patrick KeenanPackaging Engineer, Sustainability General Mills
Steve Carter
Packaging Engineering Mgr
Winland Foods
KEY TRENDS IN WAREHOUSE INTEGRATION AND MATERIAL HANDLING
11:30-12:15 PM
Discuss the latest PMMI research covering warehouse integration.
BEST PRACTICES OF SUCCESSFUL COMAN/COPACK RELATIONSHIPS
10:30-11:15 AM
TBD
Ron Puvak Exec Dir Contract Packaging Associationmay be found on the show website or via the show App, sponsored by ProMach (Booth C-3222)
Other free educational opportunities on the show floor include the new Sustainability Stage (Booth N-9967) (see schedule, p. 16), the new Industry Speaks Stage (Booth C-1141) (see schedule, p. 24) and the Innovation Stage (Booths C-2051, C-2058, C-2151)/Processing Innovation Stage (Booth N-10511) (see schedule, p. 30). Schedule as of August 23, 2023.
For more info, visit packexpolasvegas.com. SD
TUESDAY, SEPTEMBER 12, 2023
Jonathan Pipe Sr Consulting Analyst Interact Analysis
ESG FRAMEWORK: JOURNEY TO A SUCCESSFUL ESG PROGRAM
12:30-1:15 PM
In today’s rapidly changing business landscape, sustainability and responsible business practices have gained significant importance. To achieve a cleaner, safer, more sustainable world, all companies must realize the importance and value of managing environmental, social and governance (ESG)-related business challenges in a way that fits their pace and unique objectives. This session will look at ways to build a viable ESG program for your company.
Roy Greengrass Pres
The ESG Group APPLIED PACKAGING FOR THE COLD SUPPLY CHAIN
1:30-2:15 PM
The cold chain is a logistics management process for products that require refrigerated temperatures. Failure to keep cold-chain products cold will render them unusable, which leads to waste. A successful cold chain ensures temperature-sensitive products are kept within optimal temperature ranges and maintain the desired states from start to finish. Unpack the cold supply chain to ensure a full understanding of its
WEDNESDAY, SEPTEMBER 13, 2023
DIGITAL TWIN APPLICATIONS: PROCESSING/SUSTAINABLE PACKAGING
11:30-12:15 PM
Digital Twin technology appears to be the starting point for any operational digitization of industrial processes and the innovation of business models. Learn how digital twin supports the interoperability and sustainability of supply chains.
requirements and limitations, then piece it together again, working through how packaging can best support a good outcome.
Pierre Pienar
Packaging in the Cold Supply Chain
World Packaging Organisation
HOW TO DESIGN PLASTIC PACKAGING FOR A CIRCULAR ECONOMY
2:30-3:15 PM
The APR Design® Guide is the leading global resource for recyclable plastic package design. Technical experts from the Association of Plastics Recyclers (APR) show how this free resource can help you meet your sustainability commitments, as well as other programs like the APR Design® Recognition and APR PCR Certification.
Curt Cozert
COO
Scott Trenor, PhD Technical Dir
The Association of Plastic Recyclers
TRANSITIONING MATERIALS IN CPG OPERATIONS: WORKSHOP
3:30-4:15 PM
Interactive workshop reveals best practices for transitioning to different flexible materials in CPG operations.
Rebecca Marquez
Dir, PMMI Media Group, Custom Research PMMI
Flexible packaging checks all boxes

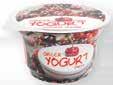
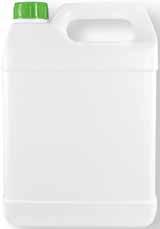
Demos of two advanced film/equipment systems from Amcor (Booth SU-7244, SU7254) fast-forward flexible packaging operations to a more efficient future.
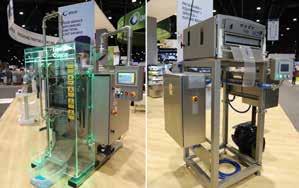
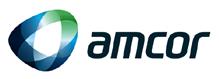
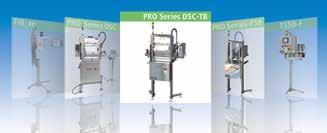
The units streamline efficiencies, lower labor costs, boost throughput and reduce the packaging elements, inventory and processes required to ship finished packages and meet quality goals.
EQUIPMENT IN ACTION
The Liquiflex® liquid pouch system showcases fast, flexible packaging technology for foodservice products, such as soups, sauces, dressing and condiments. Liquiflex pouches reduce carbon footprint by 67% compared to metal cans and provide up to 30% reduction in material thickness over competitive structures.

Liquiflex intermittent- or continuous-motion vertical form/fill/seal (V/F/F/S) machines create strong, abuse-resistant, zero-headspace pouches with superb seal integrity. Capable of handling a variety of products and pouch sizes, the machines cut costs and simplify operation. Systems feature a 200-recipe programmable memory for rapid changeover and cleanup and accurate weight control to eliminate variability and profit loss.
Strong, high-abuse rollstock options include

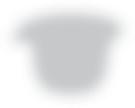

Liquiflex Advance™ films for hot-fill, ambient and cold-fill operations or AmbiLoc™ films for retort applications, with barrier structures specifically designed to enable shelf-stable distribution. Barrier properties can be customized to extend shelf life. With more film per roll, operators can produce more packages per roll, reducing changeover time and cost.
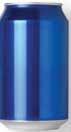
Another crowd-drawing demo is the compact, all-in-one Amcor Moda on-demand bag making and printing system for boneless or bone-in meats and cheese. This single, inline bag-making system significantly reduces material and labor costs and allows packagers to pivot quickly to meet changing stock keeping units, product sizes and labeling needs through onsite printing technology.
Part of the Amcor Moda Packaging Solutions system, the Moda Bag vacuum-packages products from rolls of Amcor shrink tubing up to 17 in. High-resolution, thermal-transfer printing delivers crisp brand graphics inline and minimizes the inventory of preprinted shrink bags or labels, eliminating the cost and waste associated with unused, obsolete packaging. The Moda Bag system is extremely change-friendly: Packaging length or printing and graphics can be changed at the touch of a button.
“Not only can the Amcor Moda Bag bring packaging material savings, but our customers are also realizing reduced labor requirements in specific applications, like export meat products,” reports Greta Shimon, marketing manager at Amcor. “The onsite printing ability of the Moda Bag eliminates the manual insertion of export placards.”
Packagers can purchase the Amcor Moda packaging system as an entire line or by individual piece. Full system demonstrations can be seen at the Amcor Innovation Center in Neenah, WI. For more info, visit amcor.com/afna. SD
•
Film/equipment duos demonstrate operational efficiencies.Amcor’s Liquiflex V/F/F/S machine (left) produces strong, abuse-resistant, zero-headspace pouches with superb seal integrity. The Amcor Moda (right) makes and prints bags on-demand for cheese and boneless or bone-in meats.
VOTE FOR BEST IN SHOW
Portfolio adds twist block technology
Automated inverting improves productivity.
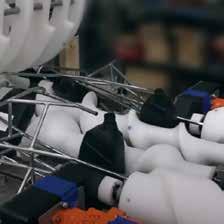
The container-inverting lineup at Morrison Container Handling Solutions (Morrison CHS) (Booth C-1651) expands with the addition of twist block technology. Twist blocks are mechanical, backlog-fed twists that require no power aside from the movement of the conveyor.
“For years, we’ve seen great success with our power twist timing screw machines, but many of our customers need to simply invert mechanically on a line with backlog present,” says Chris Wilson, president of the container handling specialist.
See Superior Innovations From the Technology Excellence Awards Finalists
Vote for the Ultimate Winner in these Categories:
FOOD/BEVERAGE
GENERAL PACKAGING & PROCESSING
PERSONAL CARE/PHARMA
SUSTAINABILITY
ACT SOON!
Vote by Tuesday at noon on the mobile app or at packexpolasvegas.com/vote.
Winners will be announced on Tuesday Afternoon!
Unlike traditional twist blocks, which sandwich together dozens of plastic pieces to create the twist, the Morrison Twist Block design consists of only a few pieces of plastic. This minimizes areas that could harbor contaminants and enables quicker disassembly, cleaning and reassembly.
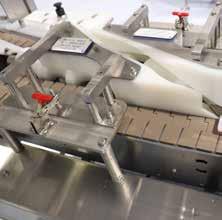
Our customers “ . . . needed a simpler design that was more sanitary and easier to clean,” explains Nancy Wilson, CEO at Morrison CHS. The Morrison Twist Block also occupies a smaller footprint. Standard models range from 12–18 in., and custom sizing is available for retrofit situations.
Featuring simple mounting, the Morrison Twist Block utilizes quick changeover clamps and a built-in handle, making it easier for operators to remove this lightweight block when performing changeovers to different container sizes.
Additional info: packexpolasvegas.com/tea
INVERTING CONTAINERS
Inverting containers manually is a labor-intensive process. With many operations shorthanded, adding equipment that automatically performs this action is one way to reduce workforce needs.
Inverting is most often used for:
• Code dating
• Sanitizing caps
• Rinsing
• Laying product down/standing it up on conveyor
• Multipacking/stacking operations.
There are multiple ways to approach inverting. Inverting blocks and power twists are most commonly used. Determining which option is best depends on:
• The shape of the container
• The rigidity of the container
• Backlogged or random-fed conditions
• Container environment (temperature and application).
Twist blocks, also known as inverting blocks, beer can invertors, container invertors, twist assemblies and can invertors, suit areas of high backlog pressure that may have tight line constraints where a longer screw-based system is not applicable or unnecessary.
When a line doesn’t have space for a larger inverting method, twist blocks can be the perfect answer. Using backlog, twist blocks are a great way to keep the line flowing correctly. Most twist blocks are compatible with rigid containers such as cans and ice cream pints.
Challenging containers or sanitary applications can be addressed with the stainless steel power twists. These twists are most commonly used for food-contact applications where the containers must be held rigidly in position. This option is preferred when food or consumables are in direct contact with the equipment and when access to the container is needed during inversion, e.g., for code dating the container.
Stainless steel power twists often are seen in multipacking operations such as stacking single-serve applesauce cups lid‐on‐lid in a cardboard sleeve. Using a power twist allows two lanes of containers to be inverted over the timing screw. Since both lanes are being controlled by the same screw, they can be stacked directly on top of each other. Once stacked, the containers would transfer to the grouping screw.
The grouping timing screw would then collate the containers to create the six-pack (three‐over‐three) configuration. If these timing screws were changed out, this could be a four-pack, making the timing screw act as a change part.
Ultra-high molecular weight (UHMW) plastic power twists are best for applications where the product is sealed. This device changes over quickly and is great for repeatability, helping cut down on wait times. They also are utilized in air rinsing.
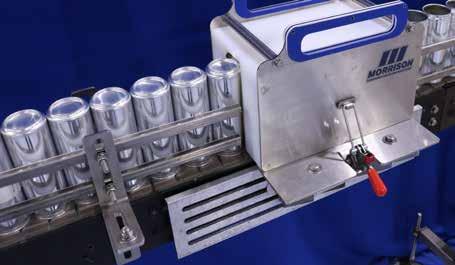
The UHMW plastic power twists are most suitable when containers need to be inverted from a backlog, indexed and inverted again in preparation for the next station on the packaging line. In one application, the UHMW plastic power twists invert the containers and then discharge groups of 12 to be presented to a packaging station downstream. This system allows for proper spacing and a consistent flow as this system required a 1 sec.-dwell time to achieve proper timing and spacing for the downstream application.
Power twist options are great for frequent changeover situations, as multiple twists can be supplied to accommodate running different containers on the same line.

Regardless of the method selected, make sure the twist manufacturer accounts for multiple transition points throughout the twist to ensure the container remains under control during the entire inversion. This will help the entire system blend together and ensure proper container placement on the conveyor.
For more info, visit morrison-chs.com/inverting. SD
Editor’s Note: A portion of this article is based on Automated Inverting Solutions to Improve Productivity in 2023, a blog posted by Morrison CHS on March 20, 2023.
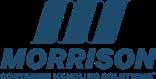
Tech integration boosts meat yield
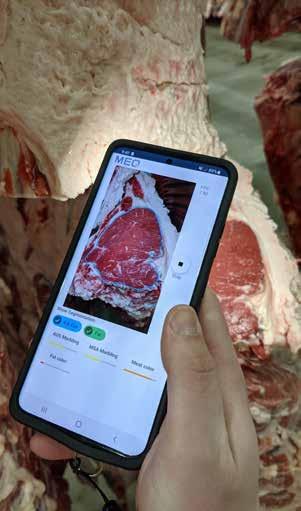
Meat harvesting and packing is a multibillion-dollar global industry, with many complex supply chain variables at play. The industry exists to serve a hierarchy of consumer needs, with consumption safety and availability laying the foundation. Because these base level needs have largely been met, today’s consumers are looking for a higher-quality and more sustainable meat product that extends across all aspects of the business, including cattle-rearing, packing, transport and consumption.
In North America, quality is divided into three categories—prime, choice and select, each based on marbling level. Demand varies by geography, consumption venue and other factors. Meat packers must attempt to harvest the available supply and efficiently use limited cold storage space to meet fluctuating market demand.
One of the greatest difficulties in harvesting, packing and subsequent delivery to market is remaining consistent in quality grading because it requires a significant degree of manual assessment. Furthermore, rising environmental concerns over greenhouse gas (GHG) emissions in the farming industry are contributing to daily challenges as well.
In response to these and other issues, Australia-based MEQ developed a series of cutting-edge products that integrate directly with the Siemens Industrial Edge technology platform from Siemens Digital Industries (Booth SL-6351). These tools provide a wealth of data and insights surrounding meat-eating quality and yield from feed to harvest with the dual impact of improving business metrics
and increasing operational sustainability. MEQ’s data analytics platform brings these metrics to life, while adding value by incorporating meat marbling measurements in the system.
GRADING AND PROCESSING ISSUES
Historically in the U.S., beef grading was an entirely manual procedure. It required visual inspection of every frozen carcass by representatives from the USDA and the meat packer, assessing numerous meat quality attributes of the carcass before assigning a meat quality grade and marking accordingly.
Inherently subjective, significant training was required to standardize the grading process. Additionally, grading the carcass in the refrigeration meat store left little time for the packer to match incoming inventory with customer orders.
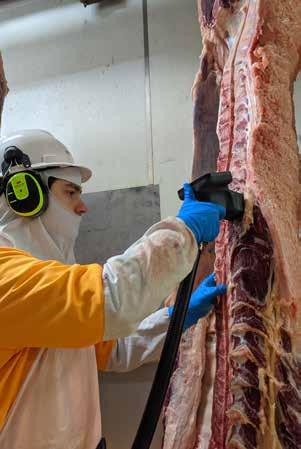
The global $700-billion red meat industry lacks timely, objective and actionable data, im-
pacting profits, customer satisfaction, nutrition and the environment.
MEQ addresses these issues with three distinct, but integrated, tools to automate meat grading, increase the quantity of data for improved decision making and generate that data and associated insights substantially earlier in the beef lifecycle. The MEQ Probe and Camera Application were developed for packers, and the MEQ LIVE sensor was created for ranchers and feedlot operators.
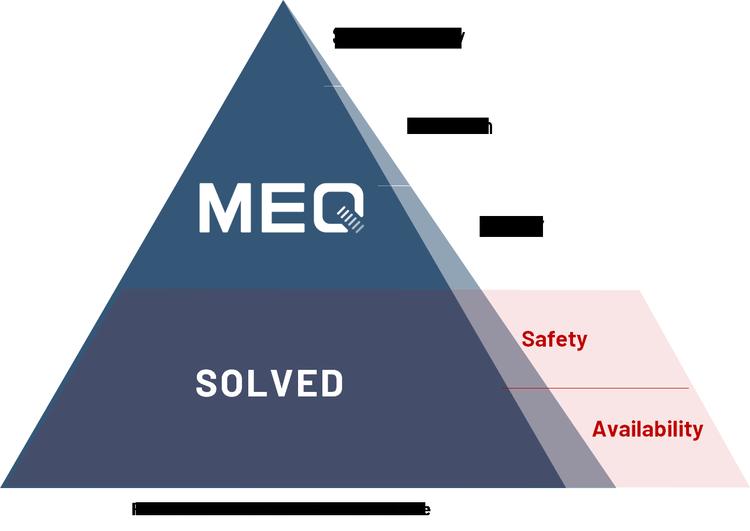
Real-time and transactional data handling from these smart AI/ML sensors are performed using the Siemens Industrial Edge, providing data capture, analytics and insights for use facility-wide and in the Cloud to enhance efficiency, quality and environmental stewardship for ranchers and meat packers.

SOLUTION COMPONENTS
A typical U.S. beef-packing facility processes 5,000 heads/day over two shifts, requiring extraordinary efficiency in moving meat among the harvest floor, refrigeration, fabrication and storage and distribution.
MEQ developed the following tools to automate meat grading aspects of the process.
MEQ Probe: The MEQ Probe is an AI-enabled spectroscopic analyzer that provides the packer with ∆
Quality, sustainability, meat-packing cycle also improve.The foundation of the meat harvesting and packing industry is assuring availability and safety for consumers, and because these aspects have largely been solved, it is possible and necessary for suppliers to turn their attention to the quality, nutrition and sustainability of their products. The MEQ Probe is a sophisticated digital device built to withstand the rigors of the processing environment. It is quickly integrated into any workflow and can grade meat at chain speed prior to chilling. The MEQ Camera mobile App enables users to capture carcass yield and eating qualities, and it can be used standalone or in conjunction with the MEQ Probe.
Leading-edge technology trusted worldwide for superior product inspection and contaminant detection.
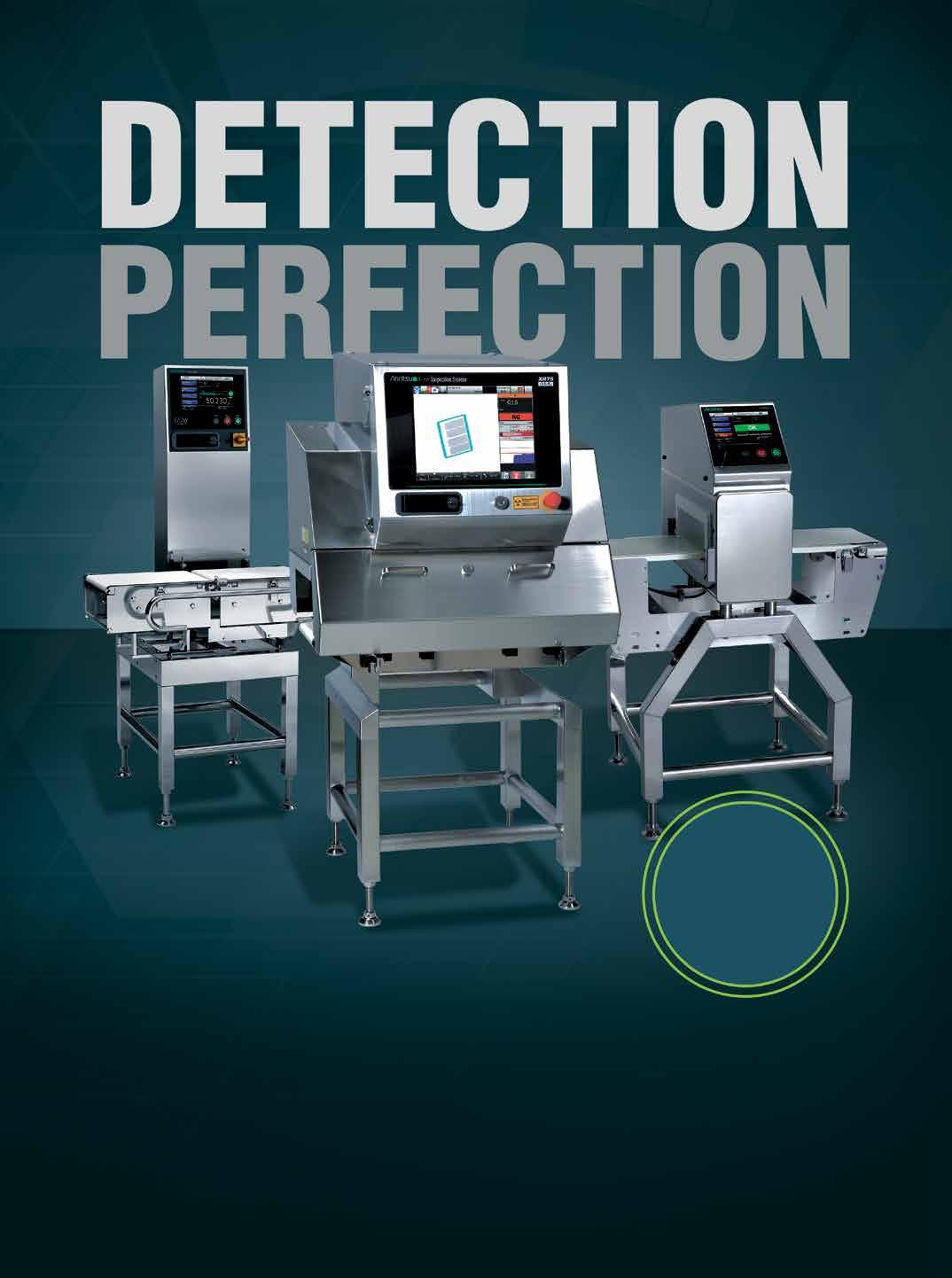
Your brand is on the line, so you need equipment that’s better than good. Anritsu systems deliver performance, reliability and low total cost of ownership Plus, we back our long-lasting equipment with unparalleled service and support.
Discover what you’ve been missing. Learn how to advance your product quality and operational efficiency at anritsu.com/infivis.
VISIT BOOTH SL-6163
M6 METAL DETECTORSEPTEMBER 12, 2023
a meat quality measurement at the harvest floor hotbox, measuring actual animal biology including meat marbling, color, brand specifications, provenance and other attributes.
This early meat quality measurement assists packers with workflow planning, providing an additional 36-hr. window to align incoming beef inventory (half sides) with customer orders, compared to the industry average of 2 hr.
It also can identify carcasses on the borderline be-
tween two grades—e.g., choice/select or select/prime— with potential for upgrade by focused refrigeration. The information is then captured and stored by the connected Siemens Industrial Edge device, and made available to local plant inventory management and other manufacturing execution system (MES) applications.
Cloud connectivity enables the plant to share details of its incoming inventory downstream throughout logistics and the supply chain. For example, if a plant receives more prime-grade carcasses than or-


ders at the local plant, this information can be used to swap orders with other plants in the packer’s network to ensure optimal order fulfillment.
The Probe keeps product intact during measurement, causing zero damage, and it can be manually or robotically operated. The objective meat quality measurement helps packers organize the refrigeration store, optimize the fabrication deboning process and minimize chain stops and product runouts. It also improves energy efficiency and dark cutter remediation efforts.
MEQ Camera: The MEQ Camera Application is used in the refrigeration store to provide a noninvasive way of assigning a USDA grade for the carcass, including cold carcass yield and various eating qualities, such as rib eye area, marbling and intramuscular fat content (IMF%).The Camera App is pending USDA certification, and it can be used on its own or as a complement to the MEQ Probe. It is used in the refrigeration store to assign the USDA meat quality grade.
The Smartphone App has advantages over current pixel/mechanical camera devices as the only solution on the market that uses video instead of still images to grade meat quality, harnessing the power of AI for continuous improvement. This method of grading also provides unparalleled yield measurement insights, in addition to ergonomic measurement flexibility for users on the harvest floor.
The data gathered by the Camera App interfaces wirelessly with the Siemens Industrial Edge, capturing the camera-measured dataset and associated half-side data to ensure 100% traceability tracking.
MEQ LIVE: The MEQ LIVE smart sensor is a scanning tool used to screen animals while alive in the field or feedlot, providing a predictive carcass value from feedlot induction onward. The LIVE sensor empowers breeders, farmers and feedlot operators to predict meat quality and yield of a live animal, while simultaneously reducing methane GHG emissions.
A report modeling emissions impacts found that MEQ LIVE could result in reducing more than 2.3 million tons of carbon dioxide-equivalent direct emissions and indirect value chain reductions across feedlot operations, equating to a 44% overall reduction.
Data captured includes marbling and other quality data, which is analyzed with AI and machine-learning technology to predict the value of each animal.
This information can be used to fine-tune feeding programs for optimizing eating quality and increasing profits, to select prime cattle for breeding programs, and to understand how animals’ genetics drive future profitability. In turn, beef processors and brand owners can harness this data to forecast sales, optimize consistency and drive greater proof points to underpin their brands.
SIEMENS XCELERATOR FOR EDGE COMPUTING AND DATA PROCESSING
The Siemens Industrial Edge platform manages all MEQ smart sensor data and integrates it with plant MES and automation systems. The MEQ
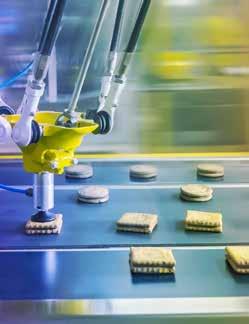
sensors are connected directly to high-performance embedded computers with proprietary AI/ML algorithms that calculate meat quality datasets. This data is stored in .jsn files, which are efficiently ingested by a Siemens Industrial Edge device using a RESTful application programming interface (RESTful API).
The MEQ Edge application collects data from the carcass radio frequency identification tag or barcode via communication connector Apps running on the edge device; speed coordination for the carcass chain is relayed to the control system from the edge device using onboard PLC Ethernet drivers.
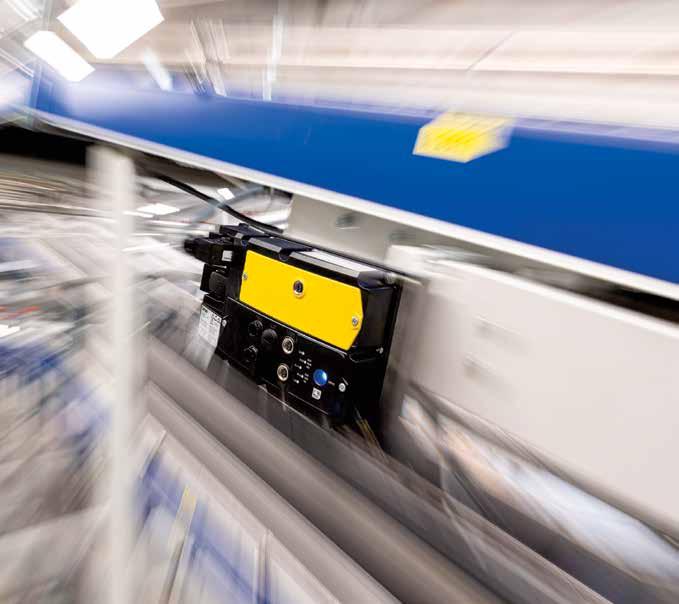
Because data processing is performed in the Siemens Industrial Edge, the data is available for use by all automation and commercial facility controllers, regardless of manufacturer. Data can be transmitted among devices, facilities and other software environments throughout the supply chain using standard interfaces, including OPC UA and the RESTful API.
Data also can be stored directly on the edge device in a SQL database format, enabling queries from higher-level systems. Using the Siemens Industrial Edge Docker Application with simple deployment of customized containers, developers can create and instantiate their own analytics applications.
This architecture allows commingling of MEQ and other facility data for inclusion in factory- and enterprise-level control systems. With the Siemens data processing engine, modern machine learning is built into data handling, producing actionable insights.
Today’s consumers demand information and transparency, and these data-processing mechanisms provide the means for suppliers to include relevant reports with their products. It also helps processors maintain compliance with nutritional and environmental regulations.
STEWARDSHIP AND DRIVING PROFITS
The MEQ Probe, MEQ Camera and MEQ LIVE devices enable meat-processing data collection to begin in the pasture as cattle feed, long before harvest. This empowers farmers to make informed cattle-raising and supply chain decisions well ahead of what was previously possible. It also provides the opportunity to proactively and dynamically adjust the way cattle are fed, preparing them for the highest meat quality possible and managing to a product specification rather than days-on-feed or other less-effective methods.
In addition, these digital tools help support and reinforce brand quality promises. This is important for specialty products, such as the Wagyu herds of California—known for their exceptional quality and rich taste—as well as for standard products. On the environmental front, these technologies and insights empower processors to:
• Increase margin per head with higher USDA meat grade.
• Improve workflow and inventory management with fewer chain stops or runouts.
• Optimize chiller use and save energy, improving processing sustainability.
• Reduce energy usage and GHG emissions while raising cattle, driven by shorter aging times.
• Enhance supply chain efficiency by placing product where required early on, reducing transport requirements. Leveraging greater data availability and earlier insights, the meat packing industry is using MEQ tools to optimize supply, better fulfill consumer demand and reduce waste throughout the entire
cattle-raising and harvesting process. As a result, processor profits are on the rise, as they deliver nutritious and high-quality product to markets with full genetics and animal traceability.
For more info, visit usa.siemens.com/packaging. SD
Editor’s Note: This article was written by Paul Bennison, regional account manager, Siemens, and Remo Carbone, CEO of MEQ.
All images are courtesy of MEQ and Siemens.
has been a
Move thousands of pounds/day
It should come as no surprise that a company with mushroom in its name knows just about everything there is to know about the little tasty fungus. And when it comes to growing them, Monterey Mushrooms has the process down to an exact science.
Everyday, thousands of pounds of mushrooms are picked and packaged from Monterey Mushroom’s Loudon, TN, facility. A new sanitary conveyor system from Dorner (Booth C-1455) plays a critical role in that process. With the help of Dorner, Monterey Mushrooms ships product daily throughout the southeastern U.S.
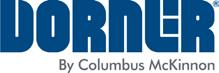
Monterey Mushrooms is a second generation, family-owned and -operated agribusiness that began in Royal Oaks, CA, in 1971. The company bills itself as the country’s largest and only national marketer of fresh mushrooms to supermarkets, foodservice and ingredient manufacturing operations. Today, the company boasts 10 growing farms throughout North America. What makes Monterey unique is that it’s vertically integrated and able to control all aspects of mushroom production from seed to customer/consumer. But before even one mushroom is packed, it needs to be grown, and that’s where the science comes in.
THE ART OF GROWING MUSHROOMS
The company grows all of its mushrooms, from white, portabella and organic to a variety of specialty mushrooms, in one of 47 indoor growing rooms. These rooms measure about 90 by 30 ft. and are filled with six levels of growing trays.
The growing process involves five steps. Phase I involves growing its own compost. Straw bedding from Kentucky horse farms, protein supplements, gypsum and water are mixed together and kept outdoors for six days to be biochemically converted by the tremendous heat naturally evolved into the preliminary food source for the mushroom.
Next, the compost is mixed with vegetable oil and more water, then moved indoors and filled into wooden trays before the next phase starts. The compost is pasteurized to free it of weed molds and insects, and then cooled to room temperature so the mushroom spawn can be added. This phase requires six days to accomplish.
After the spawn has been planted, it will grow in 13 days to completely cover the compost that now serves as a food source.
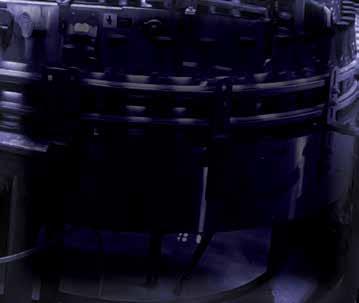
A mixture of peat moss, limestone and water is applied to the top of the tray. The spawn starts to grow
New FS2 MKII shrink labeler: Small footprint, Big performance
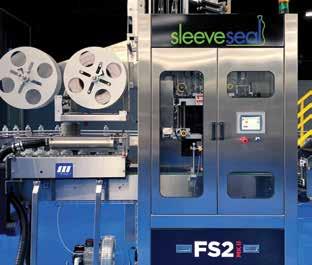
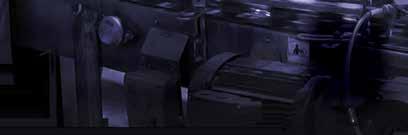

in the mixture and, in a few days, the environment is carefully controlled to encourage the mushrooms to reach maturity. The mushrooms are then picked according to size and maturity, and hand sorted into baskets. The compost is used for three growing cycles before being sold to local organizations. The entire process takes seven to eight weeks from first making compost to picking mushrooms.
MOVING MUSHROOMS
Packaging thousands of pounds of mushrooms every day is no small feat. To aid in that process, the company embarked on a renovation plan two years ago to add new dry storage space, a new cooler and additional docks. It also redesigned its packaging lines to improve efficiency.
As part of the new packaging lines, Monterey Mushrooms selected a mix of nearly 30 AquaPruf and AquaGard sanitary conveyors from Dorner.
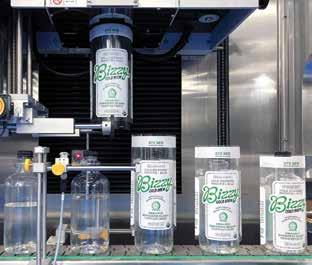
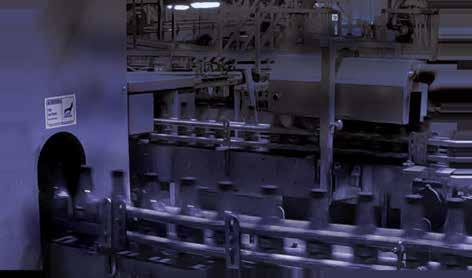
“I’ve always known Dorner was pretty top-notch, good-quality conveyors that we’ve used in the past, so choosing to continue going with them was an easy decision,” says David Redd, engineering manager, Monterey Mushrooms.

The conveyors are part of a four-lane packaging

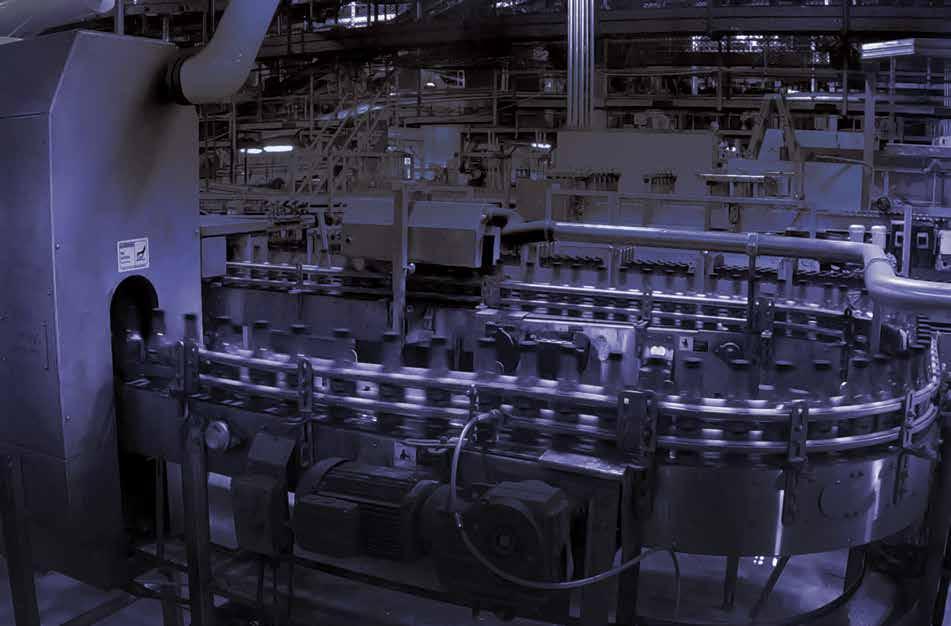
Conveyor helps mushroom producer pack faster.
line, each stretching about 50 ft. in length. Several weigh stations are positioned alongside the conveyors to allow employees to pack and weigh containers of mushrooms. Since the application called for the conveyors to be used both before and after mushrooms are wrapped and packaged, different levels of sanitary requirements were needed. On the pre-packaged side, conveyors are fully washed down and sanitized daily; conveyors used for moving wrapped mushrooms require a less stringent level of sanitation that can be accomplished through wipedowns and other techniques.
Redd worked with Steve Averdick from Belcorp, a Cincinnati, OH-based distributor of automated packaging systems, to help design the conveyor system to meet his needs.
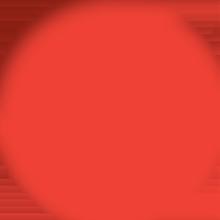


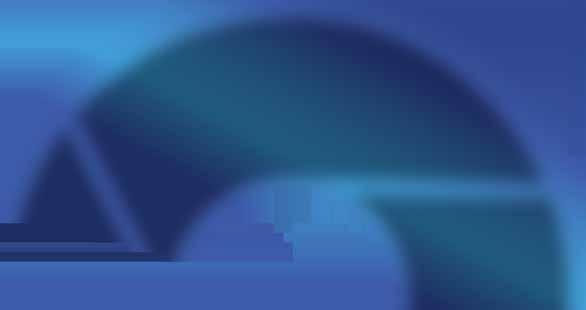

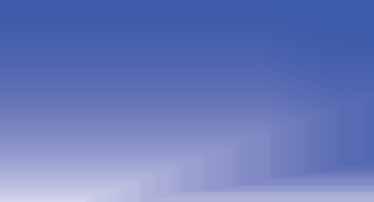
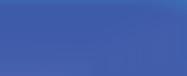
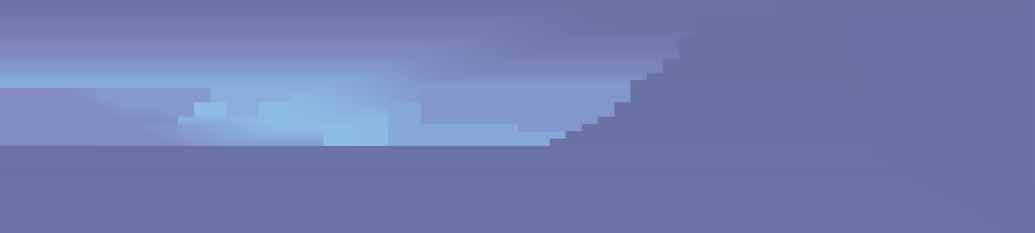
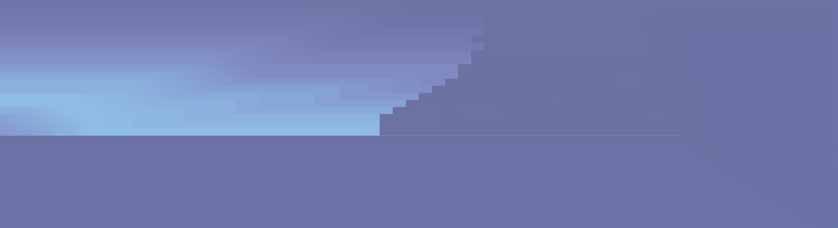

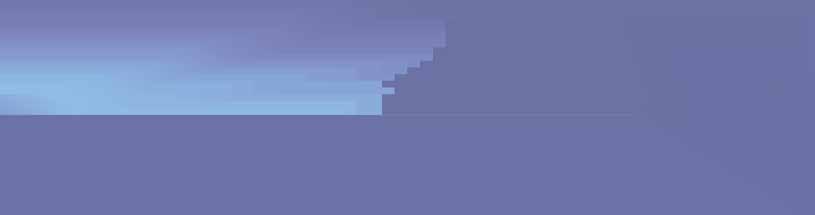
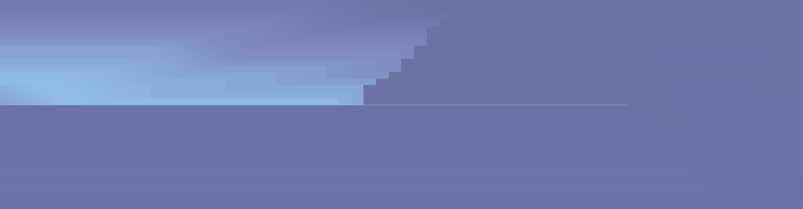

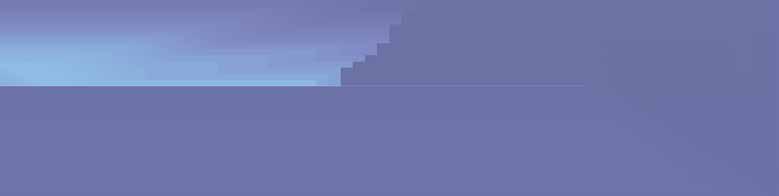
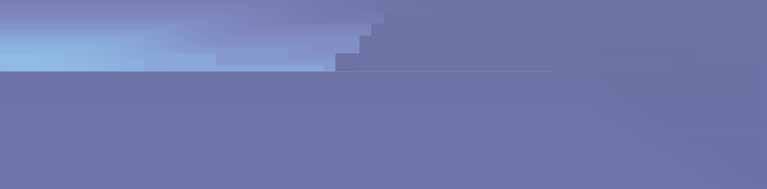


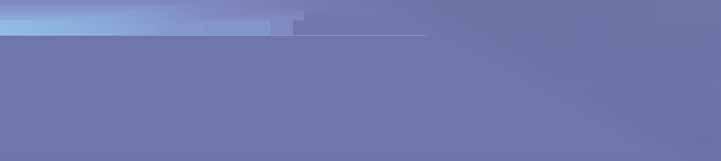


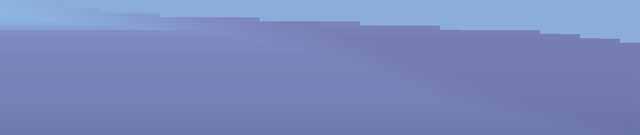
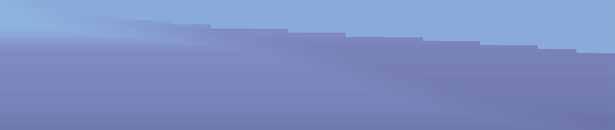




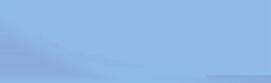
“From a sanitary standpoint, Monterey was looking for a conveyor platform that they could quickly and easily clean and sterilize,” Averdick recalls. “Dorner was the right fit for them.”




















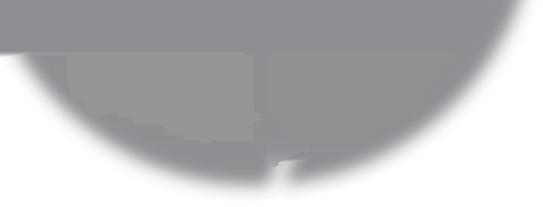
















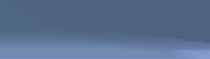






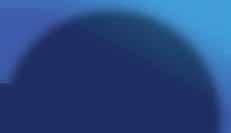



















































































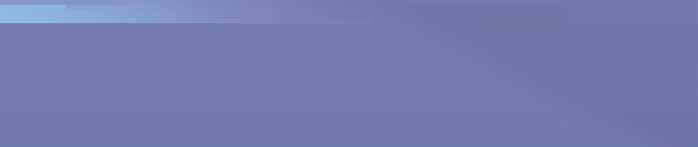
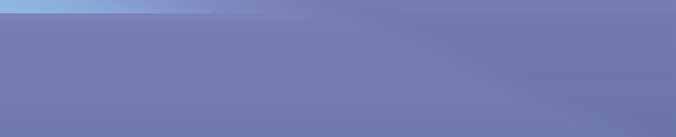
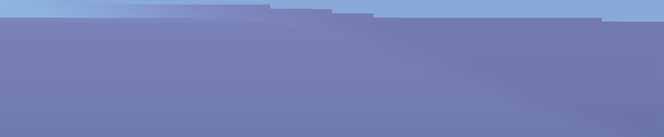
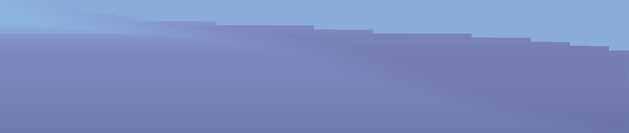

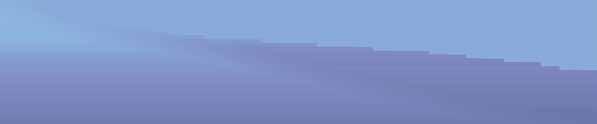
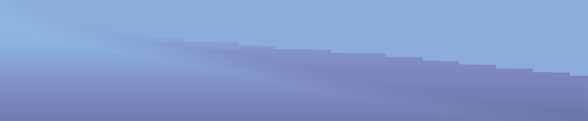
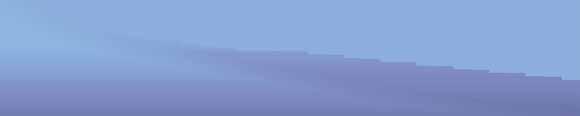



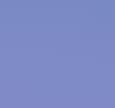

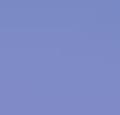
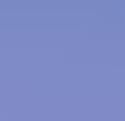

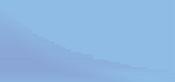
Throughout the course of a year, Averdick worked closely with Redd and Dorner in designing a system to streamline Monterey’s packaging lines. He recommended both Dorner’s AquaPruf and AquaGard conveyors, which are designed for the food and medical industries.
Dorner’s AquaPruf platform provides the highest sanitation level and the fastest cleaning times, which give Monterey more time for production and higher ROI. The AquaGard platform of stainless steel conveyors offers flexibility for a variety of products, while increasing throughput and reducing product loss.
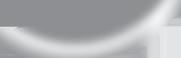
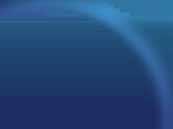
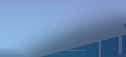

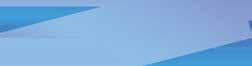
“Monterey had a plan to be able to sanitize their conveyors, and do it as painlessly as possible,” Averdick reports. “To help them achieve that goal, we installed belt lifters and tip up noses on all the AquaPruf conveyors so when it came time to clean them, they could very easily access every aspect of it.”
One person needs only 90 sec. to completely disassemble Dorner’s AquaPruf and AquaGard conveyors for cleaning. The entire cleaning process takes just a few minutes to complete.
Monterey picks and packs mushrooms up to 16 hr./day. When packing is finished for the day, a sanitation crew cleans and sterilizes every conveyor, along with the rest of the facility.
“Everyone has been very pleased with our Dorner conveyors,” says Redd. “It’s been a pretty positive experience for us, which validates that we made the right decision. Monterey Mushrooms strives to be the best in the industry, and with the addition of our
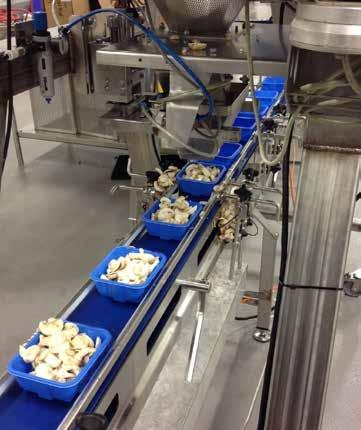
Multi-Conveyor (Booth C-1718) recently built a series of Z-shaped incline takeaway conveyors and two straight elevating incline conveyors to transport a snack-food product from the discharge of two high-speed bagmakers into several batch gates.
Although the Velocity vertical form/fill/seal
(V/F/F/S) machines from Viking Masek Packaging Technologies (Booth C-5222) are among the fastest continuous-motion V/F/F/S machines on the planet, Multi-Conveyor’s pair of nearly 14-ft. anti-slip incline conveyors and 7-ft. straight elevating inclines
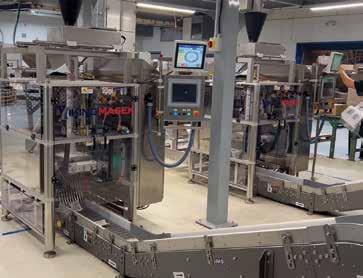
PMMI is the leading global resource for the packaging and processing supply chain. Our core purpose is to unite the industry across the manufacturing supply chain.
PMMI Business Drivers equip the makers of packaging and processing technologies to succeed in a competitive global marketplace. pmmi.org
have no problem keeping up with the 300 bag/min. pace required. The Velocity’s unique center mounted filling tube and naturally counterbalanced sealing profile, coupled with “off-the-shelf” PLC controls, ensure an industry-leading ease of use and the highest reliability.
PACK EXPO Portfolio of Trade Shows unites the world of packaging and processing to advance industries. packexpo.com
Multi-Conveyor, too, is known as an industry leader of custom (and standard) conveyors. Its design and engineering expertise was the perfect match for this high-speed line, guaranteeing the batch gates met their match-limits for extremely rapid throughput during all phases of elevated transport. Multi-Conveyor’s veteran electrical team ensures all OEM systems “talk,” which keeps them in sync throughout the entire transport process.
To aid in ultimate product control, Multi-Conveyor equipped the conveyors with Series 1100 flush-grid friction-top belting from Intralox (Booth C-1441). This belting was chosen specifically for its ability to maximize handling of the snack bags
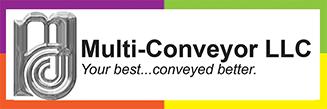
PMMI Media Group connects manufacturers year-round to the latest solutions, trends and innovations in packaging and processing. pmmimediagroup.com

during the elevation process, alleviating any backward slippage or sliding of individual bags.
For more info, visit multi-conveyor.com, vikingmasek. com, intralox.com. SD
Need guidance?
Visit us in the
How fast do you need to go? Partnering OEMs achieve desired speeed on bagging line.Conveyors from Multi-Conveyor transport bags from the discharge of side-byside V/F/F/S machines and move them up two-stage, friction-top inclines to the next operation (see video at youtu.be/bPo4YCnXivA) PROMACH (BOOTH C-3222) FOR SPONSORING THE MOBILE APP.


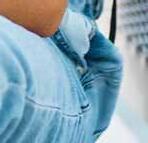

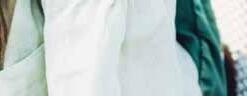

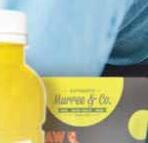
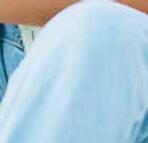
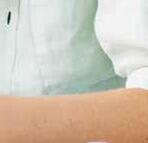
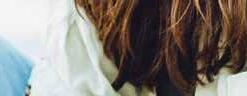
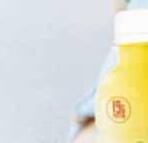
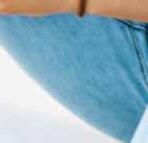
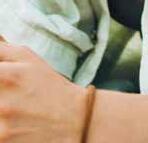

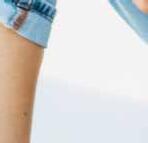
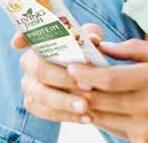
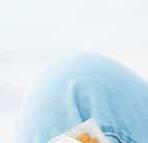
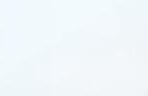

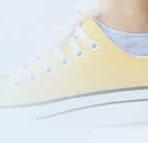
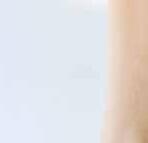
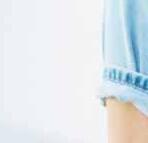
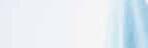
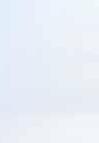









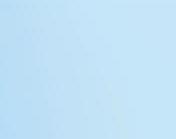
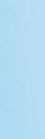


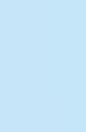

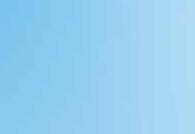
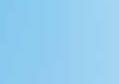
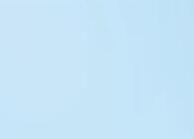
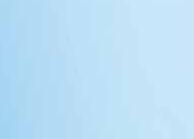


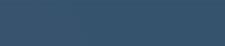

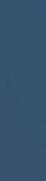
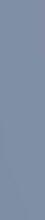


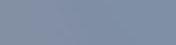
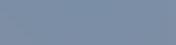



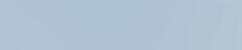
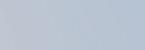


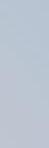


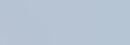



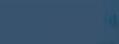
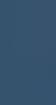


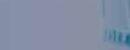



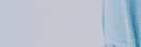

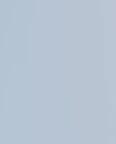
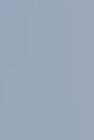

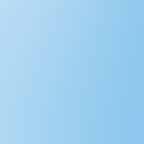
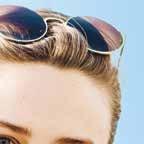
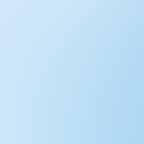

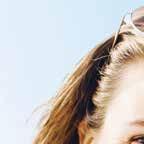
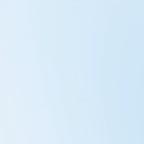



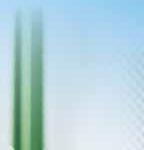
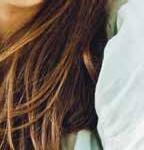
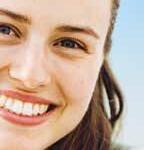





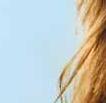

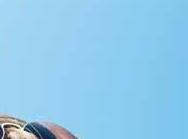
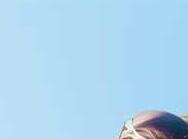
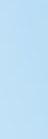

SEPTEMBER 12, 2023
PRODUCTS - PROCESSING ZONE
In the North Hall, the Processing Zone, a fixture of PACK EXPO Las Vegas, occupies 50% more space this year compared to 2021. Exhibitors specialize in the front-of-line technologies shown below. This section of the show floor also houses the Processing Innovation Stage (Booth N-10511) (see schedule, p. 30).
ROUND SPOUT SEPARATORS
Round spout magnetic separators feature a lower profile, eliminating the need for square-to-round adapters on the inlet and outlet ports. The separators are available with manual or automatic easy-to-clean functionality. The manual design provides for a push/pull operation to strip accumulated tramp metal from the grates without physically handling the magnet. The automatic version uses a set of pneumatic cylinders to clean the magnetic grates automatically at the touch of a pushbutton or timer control.
Eriez
Booth SL-5901 eriez.com
LABELING TECHNOLOGY FOR THE FUTURE
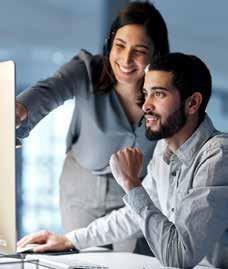
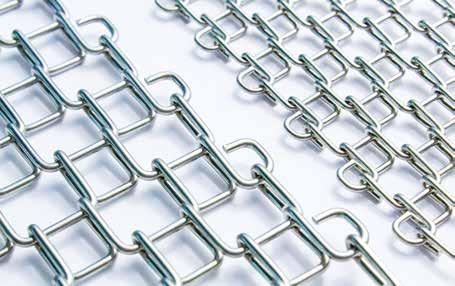
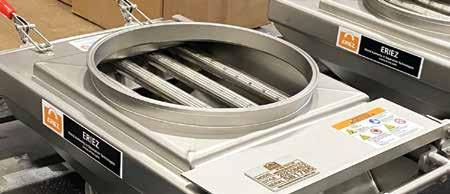
NEW at Pack Expo ‘23/Las Vegas Quadrel will introduce a system with PLC controlled, fully automatic, one button product changeover. This exciting new design reduces change overs to less than one minute. For a demonstration, stop by Booth #1655
Let Quadrel move your packaging line into the future.
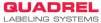
From the harshest environments to the most sophisticated Pharmaceutical applications requiring vision, validation and serialization, Quadrel is ready to partner with you. Our systems arrive Ethernet ready, with secure remote access available for monitoring, editing and trouble shooting.
In addition Quadrel systems feature Internationally compliant guarding, Allen Bradley Compact Logix PLC, Panelview color touchscreen operator interface, full servo control and redundant applicators for zero downtime non-stop operation. These systems are ideal for the most demanding pharmaceutical, food, beverage, automotive and personal care applications.
In addition, we now offer continuous motion labeling technology which dramatically increases production rates.
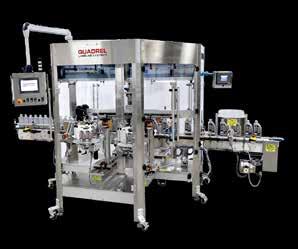
For more info, visit packexpolasvegas.com.
Editor’s Note: Product information and photos are drawn from The Processing Zone Showcase 2023, published by ProFood World
CONVEYOR BELT
The Compact-Grid CG15 conveyor belt has a 15mm mesh to handle difficult conveying challenges. USDA-accepted, the compact-grid, open-mesh stainless-steel conveyor belt offers a clean-in-place design and simple belt joining. It features a 0.082-in. wire diameter and has a 73% open surface area for increased flow-through for heating, cooling and coating applications. The thicker, larger mesh allows the belt to hold more weight per square foot.
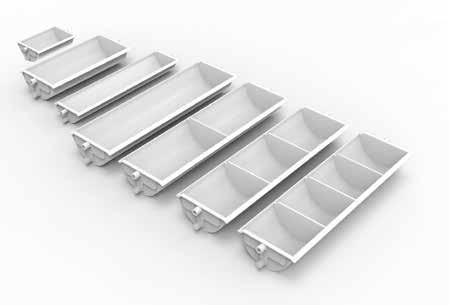
Wire Belt Company of America
Booth SU-7164 wirebelt.com
ELEVATOR SYSTEM BUCKETS
Split buckets provide the ability to fill each “split” with a different grade of nuts. The buckets, which seamlessly integrate into existing bucket elevator systems, allow nuts that have already passed through an optical sorter to be recirculated to the bucket elevator for further sorting. The nuts are refined to meet the desired grade by making another pass through the sorter.
PPM Technologies
Booth C-4800 ppmtech.com

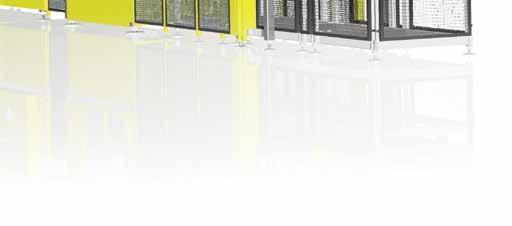

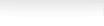
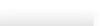








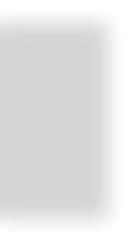



PRODUCTS - PROCESSING ZONE
CLEAN-IN-PLACE DRUM UNLOADER
A twin screw pump drum unloader with discharge pressures up to 375 psi and a 50+ gal./min. unloading capability can handle product viscosities in excess of 500,000 centipoise and transfer soft solids up to ¾ in. in size. Variable plate sizes pump out 75-, 55-, 30-, 20- and 16-gal. plastic, metal or fiber drums. Custom plates for pumping out mix kettles and pots, as well as a removable plate for pumping out totes and tanks, are available.
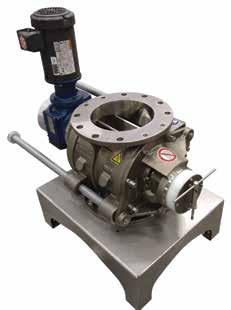
Axiflow Technologies
Booth N-10161
axiflowtechnologies.com
BULK BAG LOADER
The BFM bulk bag loader prevents material and dust from escaping during the bag-filling process, preventing contamination of the filling station. The loader is comprised of a three-layer, inflatable filling head with a stainless-steel core fully encased in flexible ether-based urethane. Standard pneumatic air inflates the sleeve in seconds, sealing it tightly on the bulk bag’s neck. After filling, the sleeve deflates to release the bag. The loader can be used with bulk bags with or without a plastic liner. It is USDA (material only), EC and ATEX compliant.
Powder-Solutions
Booth N-10855 powder-solutions.com
MEAT SUBSTITUTE EXTRUDER
A hybrid solution for meat substitute product manufacturers, the ZSK Mv Plus extruder can be used to produce texturized vegetable protein (TVP) and high-moisture meat analogues (HMMA) with a minimum of retrofitting effort. Using a Coperion adapter, the extruder’s discharge can be changed from the ZGF-centric pelletizer used for TVP to a specialized cooling die for HMMA. The pelletizer cuts product direct at the nozzle plate, while the cooling die produces a solid strand with textures similar to meat.
Coperion
Booth SU-7641 coperion.com
STAINLESS-STEEL TANKS AND VESSELS
Stainless-steel tanks and vessels are custom-engineered, built to exact process/packaging requirements and manufactured to sanitary standards. The company is accredited to manufacture ASME pressure vessels; ASME U, U/M and H-stamped vessels; and UL 142 explosion-resistant tanks. Options include mixers, heated/cooled jackets and other tank features. Sizes range from 300 to 50,000 gal. (1,100 to 190,000L).
Spokane Stainless Technologies
Booth N-10061
spokanestainless.com
USDA DAIRY-ACCEPTED AIRLOCK
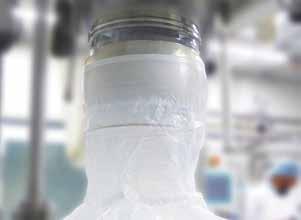
The Global USDA dairy-accepted airlock suits applications where dry raw or finished products are handled in a process and where inspection or system clean-out is required. A rail system provides access to the internal valve, cavity, rotor pockets and other product-contact areas for cleaning. A valve interference detection system protects the dismountable hygienic airlock from damage and prevents product contamination due to interference between the valve rotor and housing.
Schenck Process
Booth SU-8039 schenckprocess.com
CUSTOM PRESSURE VESSELS
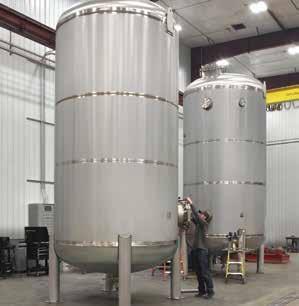
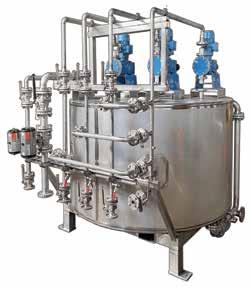
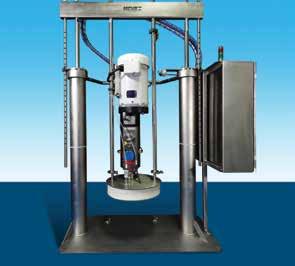
Custom ASME pressure vessels meet or exceed the standards for sanitary and other high-purity applications. The stainless-steel and higher-alloy vessels come with diameters from 2 in. to 12 ft. and thicknesses up to ½ in. The OEM holds ASME “U” and National Board “R” stamps, and its facility is 3-A certified for sanitary equipment. Atmospheric, non-code tanks; heat-transfer jackets; agitation; membrane filtration; and complete process skids also are available.
Membrane Process & Controls
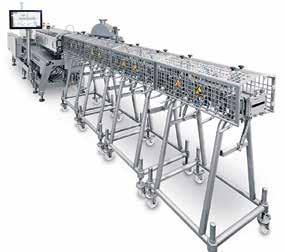
Booth N-10520
membranepc.com
PRODUCTS
VERTICAL CUP COUNTER LOADER

When limited floorspace is an issue, the Micro Vertical Cup Counter Loader can reduce footprint by 30% while maintaining speed and reliability. The system minimizes space via a shuttle tower infeed that eliminates the traditional staging area and belt infeed. The dual-lane tower can handle 330 cups/min./lane.
Rennco, a ProMach product brand Booth C-3633 rennco.com
BRIXX
BRIXX® is a new, modular, click-and-play solution based on an intuitive software to reduce the manual operations and allow quick transformations for co-packing lines. Based on advanced, mobile conveyors and robots to automate manual repetitive packing and co-packing processes.
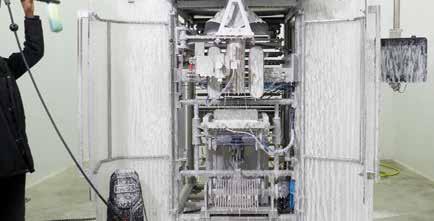
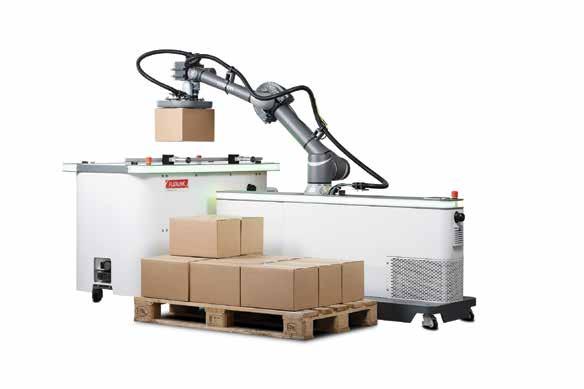
This unique design by FlexLink is a solution to automate currently manual packing operations through a flexible sytem adapting to the variability of products, packs, cartons, or trays. It is scalable according to production capacity needs, affordable and easy-to-use.

PULLNOSE DISTRIBUTION SYSTEM
Controlling product placement is essential for delicate items such as sticky bars or baked product. A DCG (distribution continuous gentle) pullnose distribution system gently discharges up to 400 products/min. onto the downstream packaging leg at 18 cycles/min.
Syntegon Booth C-2800 syntegon.com
CONTINUOUS-MOTION SANITARY VERTICAL BAGGER
Latest VF-1200 continuous-motion vertical bagger—a new stainless steel, sanitary version for high-pressure washdown applications—is suited for wet, cold and harsh environments with components that meet the highest IP standards. Continuous-motion vertical sealing bars eliminate the need to stop film for vertical seals, thereby increasing production rates.
WeighPack Systems/Paxiom
Booth C-5006 weighpack.com
Automate product transformations such as:
•Pick-and-place
•Mixing
•Handling
•Re-labeling
•Palletizing
•De-palletizing
Read more at Flexlink.com or contact us at info.us@flexlink.com
TAIL SPEND MANAGEMENT
Managing tail spend, expenditures that often fall under procurement’s radar, can help balance the budget. These purchases typically represent just 20% of volume but account for 80% of suppliers and transactions, thereby consuming a disproportionate share of time and energy. A full-service tail spend solution for indirect goods—from spare parts to IT—ensures the best pricing and terms. It also allows end users to consolidate transactions, ensure compliance and generate efficiencies.
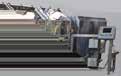

Amicus Spend Management

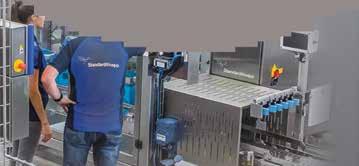
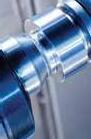
Booth SU-7699A
amicus-spend.com
SERVO DRIVE SYSTEM
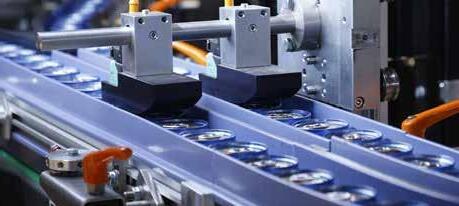
A new servo drive system offered from 50-750 watts includes a converter that enables rapid engineering via motion technology objects in connected controllers. The controller’s extended motion control functionality handles positioning functions for the connected drive axes. They are connected to higher-level controllers via Profinet and can be programmed easily by automatic motor parameterization and one-button tuning.
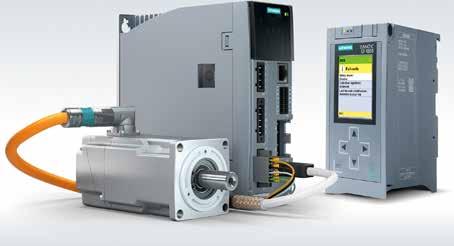
Siemens Digital Industries


Booth SL-6351

usa.siemens.com/sinamics-s210
FIBER-BASED MAP SANDWICH WEDGE

A new modified-atmosphere-packaging (MAP) sandwich wedge introduces MAP to a fiber-based format. The recyclable packaging keeps grab-and-go sandwiches and wraps fresh up to 28 days while reducing plastic packaging. A thin film lining combines with the carton board package to preserve freshness, enabling longer transit and selling time.
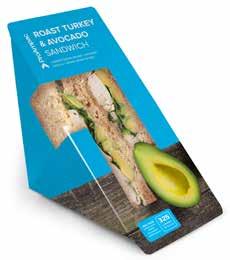
ProAmpac
Booth
ProAmpac.com

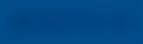

PRODUCTS
AUTOMATIC CAPSULE FILLER
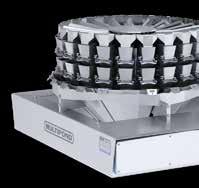
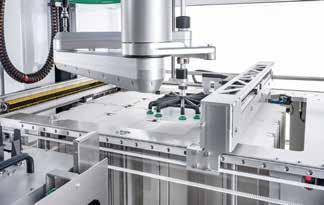
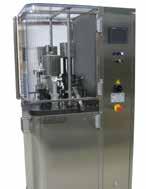
Ideal for R&D labs and clinical trials, the FlexaLAB capsule filler can fill the same capsule with different products, thanks to the machine’s modular design. At either continuous or intermittent motion, the unit can fill up to 3,000 capsules/hr with a wide product range, including powder, pellets, tablets, Micro-tablets, capsule-in-capsule, liquids and more. Optional MultiNETT or 100% weight inspector ensures accurate weights.
MG America
Booth SL-6534 mgamerica.com
CARTONER
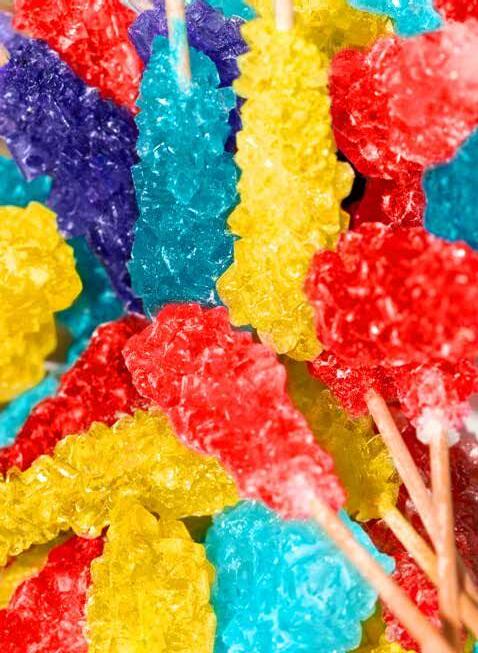
The TLM cartoner with Comfort Feeder automatically infeeds carton blanks—still in the blank sheet—into a packaging machine, direct from a pallet. An F4 robot pulls the blanks one-by-one directly from the sheet and feeds them into the erecting process at 60 cycles/min. The process saves material and labor costs.
Schubert North America
Booth SL-6820, SU-7654
schubert.group/en/schubert-north-america

THE RIGHT WEIGHING SOULTIONS FOR EVERY PRODUCT, EVERY TIME. We are your trusted partner for weighing technology, feeding and product transfer systems since 1946. www.multipond.com

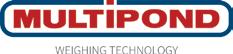
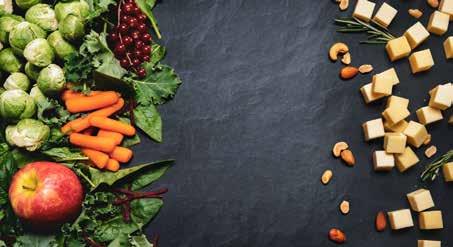
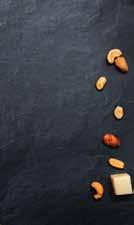
CONTINUOUSMOTION V/F/F/S
The high-speed jaw system on the MVC-300 continuous-motion vertical form/fill/seal (V/F/ F/S) machine ensures the film never stops, resulting in higher fill rates. The bagger runs a variety of films at faster rates with better accuracy.
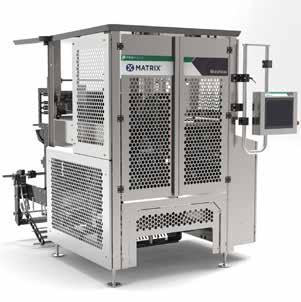
Matrix Packaging
Machinery, a ProMach product brand Booth C-2825 MatrixPM.com
Tuesday, September 12 4:00 pm – 5:30 pm Booth SU-7201
SEPTEMBER 12, 2023
PRODUCTS
X-RAY INSPECTION SYSTEM
High-resolution images generated by a new x-ray sensor enhance detection even in thick products, reducing false rejects and minimizing waste. The XR75 DualX+ x-ray inspection system can detect fine metal and bone fragments, metal, stone, glass and more with high accuracy and reliability.
Anritsu
Booth SL-6163 anritsu.com
PRE-ROLL TUBE-LOADING SYSTEM
To meet the efficiency demands of the fast-paced, high-volume cannabis industry, an automatic preroll tube-loading system receives, singulates and dispenses pre-rolled joints into rigid tubes or trays at speeds up to 3,000 units/hr. The system adapts orientation to any configuration and integrates into downstream capper and labeling machines.
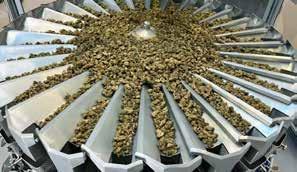
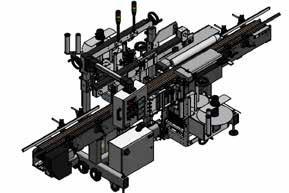
Canapa Solutions/Paxiom
Booth C-5006 canapasolutions.com
ENHANCED LABELING SYSTEM
An expansive touchscreen control package on the Contract Packager Series labelers features stepper- and servo-driven technologies along with AC drive motors. CP2000 and CP1000 front-and-back multipurpose labeling systems offer four-axis label applicator adjustments, built-in Z-axis adjustments and password protection. Other attributes include a multi-level menu system; synchronous electronic con-
trols; a wide, servo-driven overhead hold-down belt; servo-driven product positioning without change parts; extra heavy-duty welded framework; variable label dispense; and speeds up to 3,000 in./min.
Universal Labeling Systems
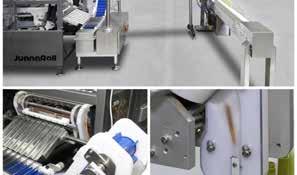
Booth C-2303
www.universal1.com
INSPECTION DEVICE SOFTWARE
ProdX inspection device management software helps monitor inspection equipment remotely and easily collects, saves, searches and shares data. Suited for a wide range of bulk and packaged food applications, the software secures digital documentation to maximize product quality and prove due diligence.
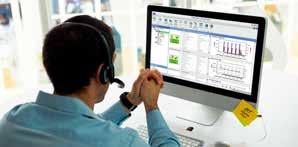
Mettler Toledo
Booth C-1814 mt.com/pi-pr
FILTER REGULATORS

Aluminum filter regulators—an alternative to stainless-steel—have flow rate capabilities up to 370.8 standard cu. ft./min. (10,500 L/min.), providing more air to the valve actuator, increasing the opening and closing speeds of process valves. Effective moisture removal keeps media dry to protect downstream devices, and sophisticated media filtration prevents downstream process contamination.
Emerson Discrete Automation
Booth SL-6107
emerson.com
PRINTER UPGRADE
New and existing FireJet printer customers can expect upgraded capabilities with the addition of the Memjet Durabolt 325C PrintEngine for CMYK sheet-fed, web-fed, simplex and duplex printing at speeds up to 450 ft./min. A digital front end streamlines interaction between the print engine and all print functions. The turnkey system prints images up
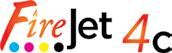
to 12.77 in. wide, using two printheads in a tandem head design.
Kirk-Rudy
Booth N-9644
www.kirkrudy.com
TAMPER-EVIDENT SALAD CONTAINER
The Fresh ‘N Clear® salad container is designed with a tamper-evident (TE) feature and made with a minimum of 25% EcoStar® post-consumer recycled (PCR) polyethylene terephthalate. Ten styles are available including a medium and a large footprint clamshell with a dome or flat lid to provide merchandising flexibility. Different depths and insert trays keep ingredients separate from the main clamshell portion until ready to mix in for consumption. The TE closure ensures the product inside stays safe until the consumer opens it, and the crystal-clear PCR material produces increased shelf visibility and helps meet sustainability goals.
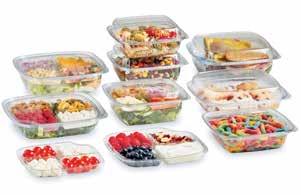
Placon
Booth N-9343
www.placon.com
WEIGHING CANNABIS
Precison meets profit when cannabis is weighed properly. With the market rapidly evolving, the high-precision weigher combines fully automatic feeding, weighing and filling in a tamper-proof system. An integrated pre- and post-weighing device continuously checks the weighed weight so giveaway is minimal. The unit also protects the product and is easy to operate.
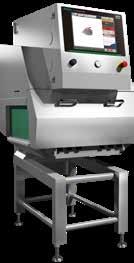
MULTIPOND America
Booth SL-6567
multipond.com/en/
WASHING CARTS
Specialized washing carts ensure product contact parts on integrated equipment are thoroughly cleaned to protect product quality. The carts—which eliminate the need for swabbing—are well suited for solid dose, aseptic liquid and non-aseptic liquid product-contact parts used by pharmaceutical, biotech and nutraceutical manufacturers and packers.
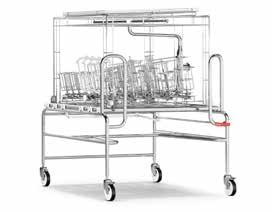
NJM, a ProMach product brand
Booth C-3225, SL-6501
NJMPackaging.com






VALIDATABLE HEAT SEALER
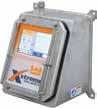
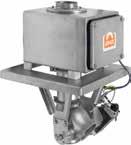
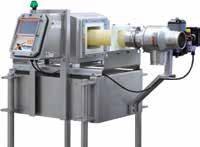
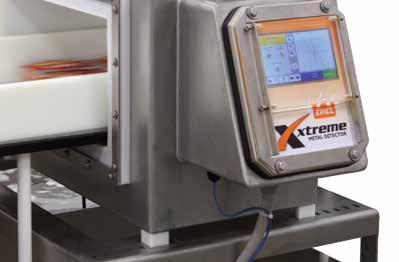
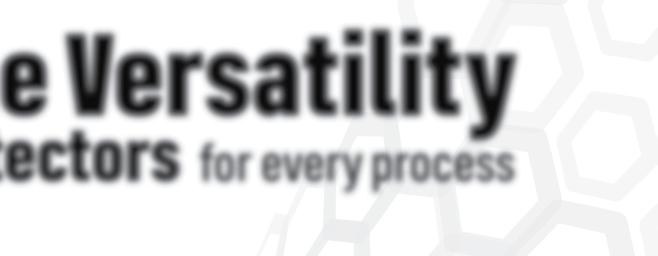
Precision-controlled medical heat sealers with the advanced Pireg® temperature controller seal any medical-grade polymeric material, meet FDA validation requirements and are ISO 11607, eGMP, CE and RoHS compliant. Visualization software tracks and records heat-sealing parameters, expediting the validation process. Variable resistance control precisely monitors and adjusts temperature across the full length and width of the heat-sealing element. Systems are available with or without programmable, multi-cycling vacuum and gas-purge capabilities.
Packworld USA
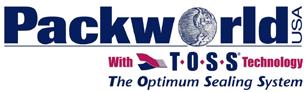
Booth SL-6407
packworldusa.com
HEIGHT-ADJUSTABLE LABELING
Adjusting conveyor height—and thus the container height—changes label height without compromising repeatability and precision. The height-adjustable labeling option—available on the VR-72 labeler—can be programmed for a new label height for a whole batch or can adjust the height of each label for individual containers. The unit applies pressure-sensitive, wraparound paper or film labels at speeds over 600 containers/min. It is particularly well suited for products with a printed fill line.

WLS, a ProMach product brand


Booth C-3225, SL-6501
WeilerLS.com
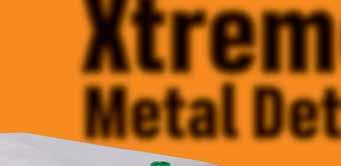
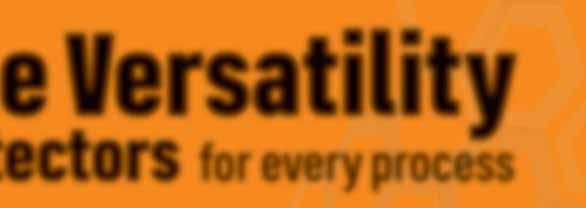
SEPTEMBER 12, 2023

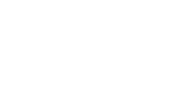
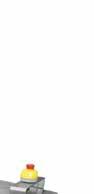
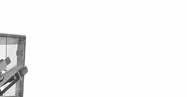
PRODUCTS
INTEGRATED PACKAGING LINE
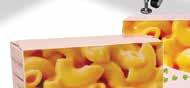
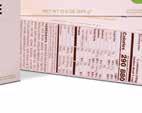
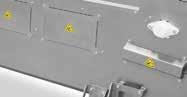
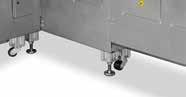
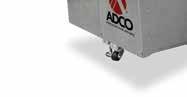
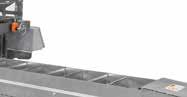
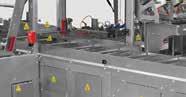

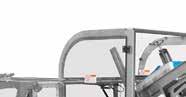

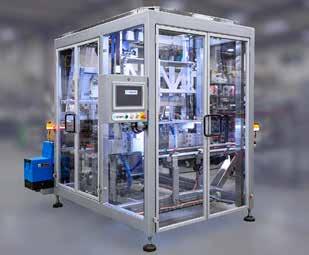
An integrated packaging line fills canisters then tray-packs, overwraps and palletizes them in a multibrand collaboration. A top-load tray former creates trays from corrugated blanks; trays continue to a case packer where a robot orients canisters before shrink wrapping and pick-and-place via an articulated robot. Finally, a robotic palletizer places wrapped trays on a floor-level pallet.
ProMach
Booth C-3425, C-3433 promachbuilt.com
AI-ENABLED, VISION-EQUIPPED SOFT GRIPPER
The commercial focus expands for the mGripAI™ artificial intelligence (AI)-enabled picking technology for consumer goods, eCommerce and logistics applications. This combination of 3D vision, AI and soft grasping gives industrial robots the dexterity and hand/ eye coordination of human workers, enabling their use in unstructured applications such as order fulfillment, sortation, decanting and kitting. The mGripAI gripper with its proven ability to reliably pick, place and sort delicate and variable products at extremely high speeds (greater than 90 parts/min.) helps warehouses and distribution centers decouple operations from the challenges of labor availability.
Soft Robotics
Booth N-5230 softroboticsinc.com
PALLETIZING WITH ROBOT

The RC10 provides easy palletizing with a collaborative robot. The standardized palletizing cell is compact, easy to install and configure. Collaborative and continuous operations are possible with no fence system needed. It is modular, easy to move and quiet. The use of a collaborative robot significantly reduces the footprint—by over 50%—compared to cells with industrial robots and provides a fast ROI and low operating cost. Four standard configurations are available.
FlexLink Systems
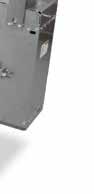
Booth C-4400 flexlink.com
Packaging Solutions That Work!
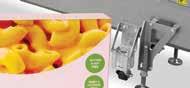
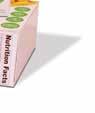
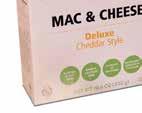
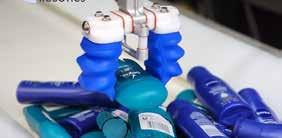
thank you to our partners!


These organizations are an integral part of PACK EXPO Las Vegas 2023 and played a pivotal role in bringing the entire packaging and processing industry together for this event.


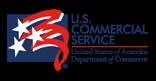
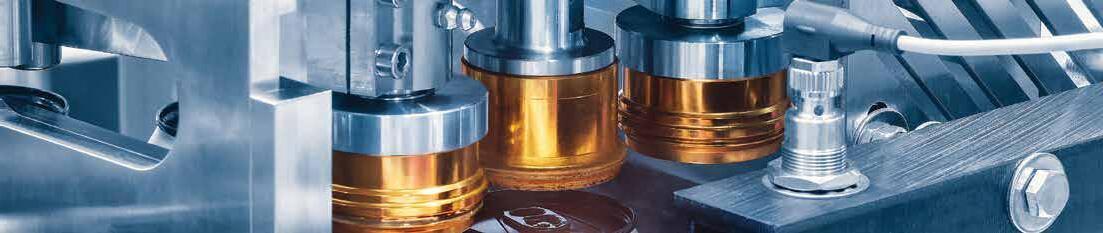
* As of July 6, 2023




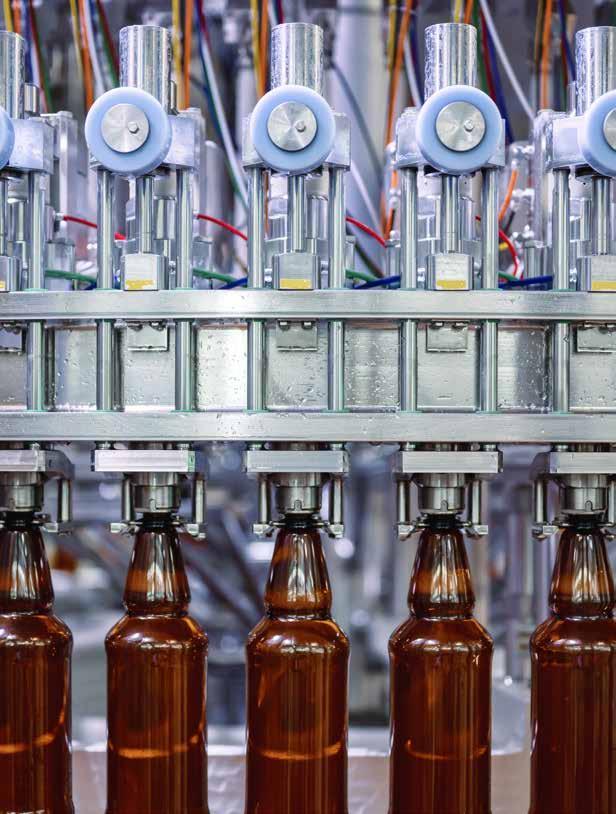
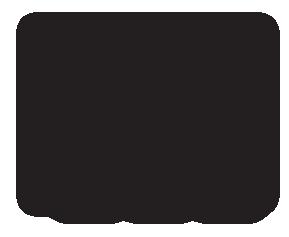












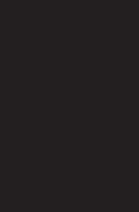



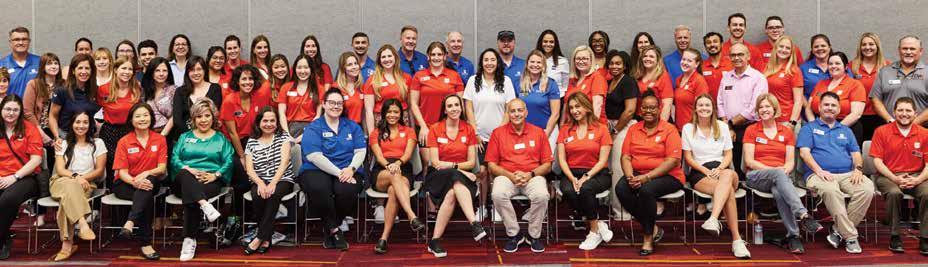
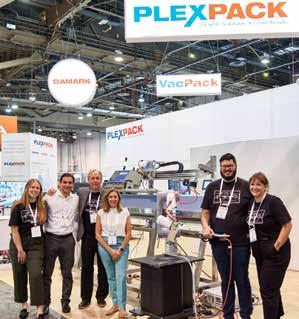
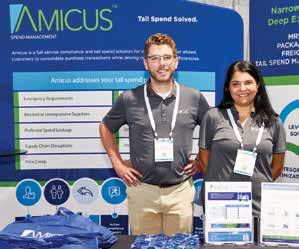
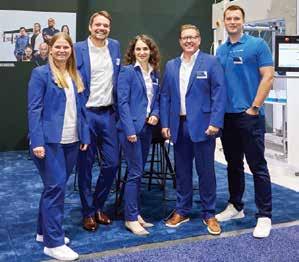
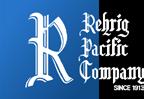


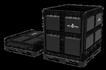
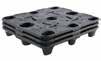
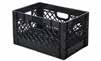

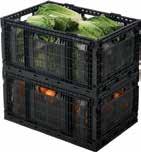
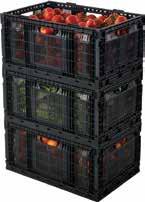
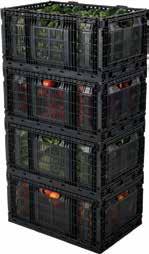

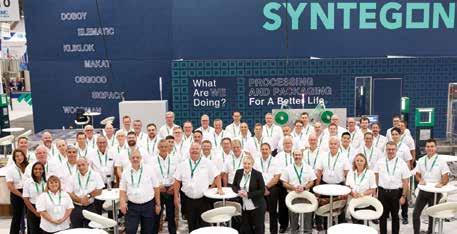
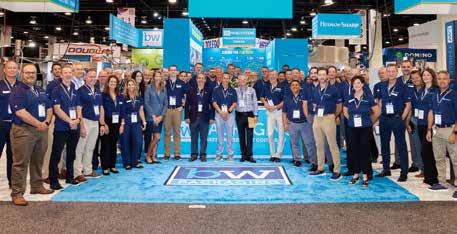

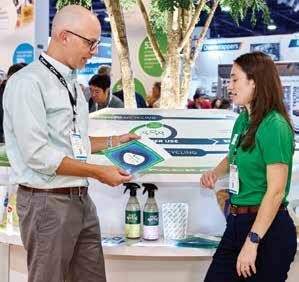
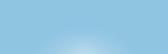

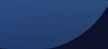

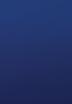

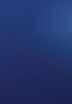

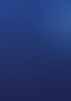





























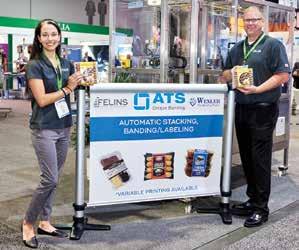


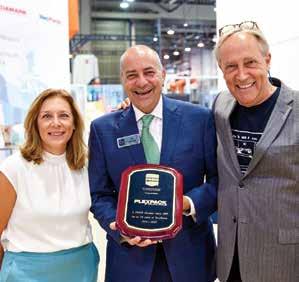



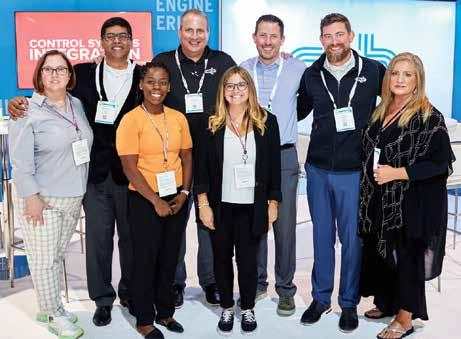
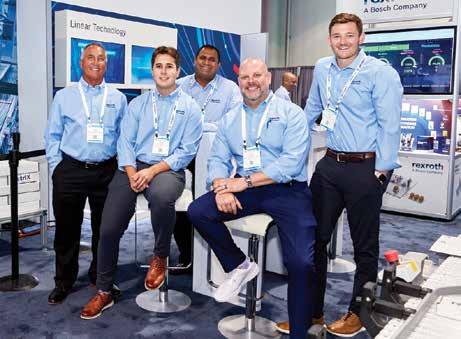
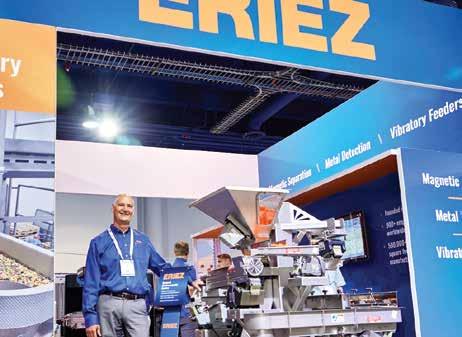
Industry Training
Elevate your talent through PMMI’s convenient training and development opportunities.
Certified Technical Sales Professional (CTSP)
Certification (for PMMI members only)
Be a trusted advisor to your customers.
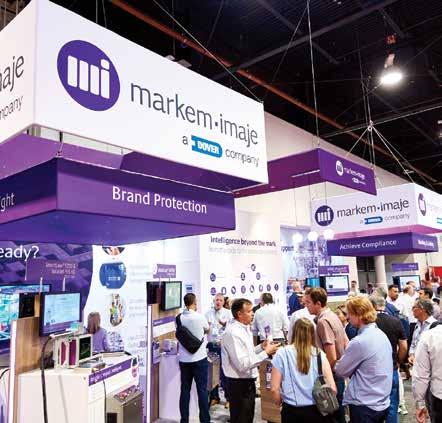
Certified Trainer Workshops
Develop your team’s training skills.
Fundamentals of Field Service (for PMMI members only)
Give your technicians the non-technical skills they need to provide great customer service.
Mechatronic Certifications
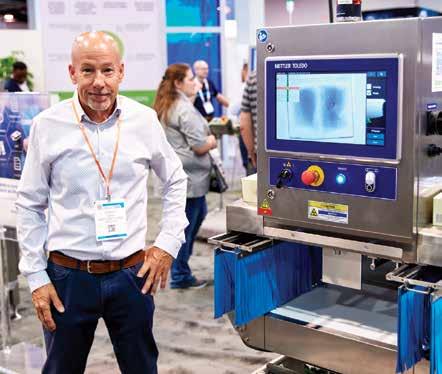
Identify multi-skilled workers to troubleshoot and repair automated equipment on the plant floor.
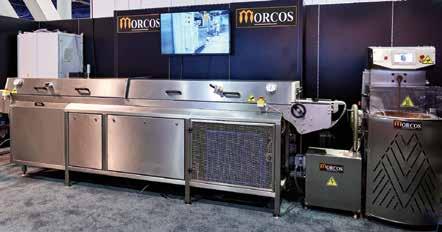
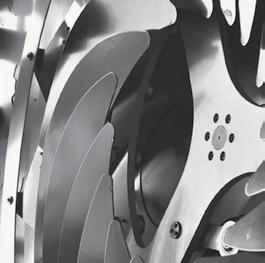

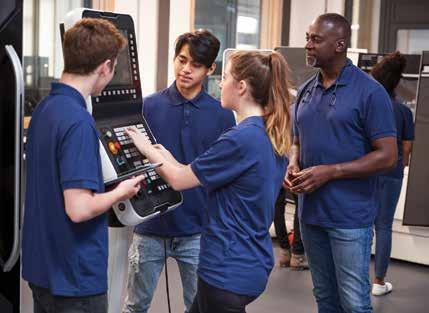
Risk Assessment Workshops
Improve productivity and ensure worker safety.
SEPTEMBER 12, 2023
Learn more at pmmi.org/industry-training
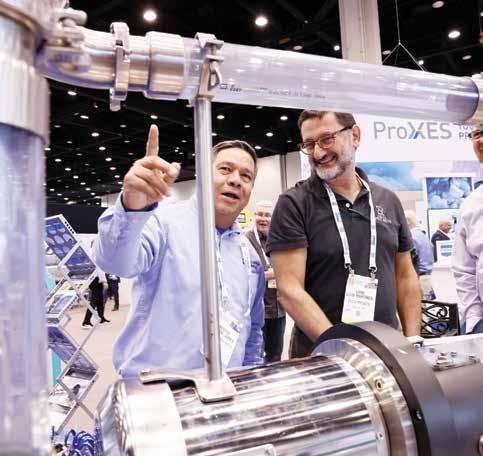
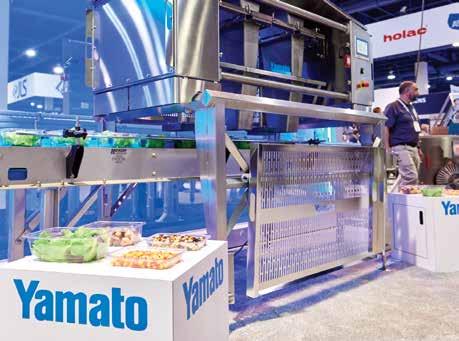


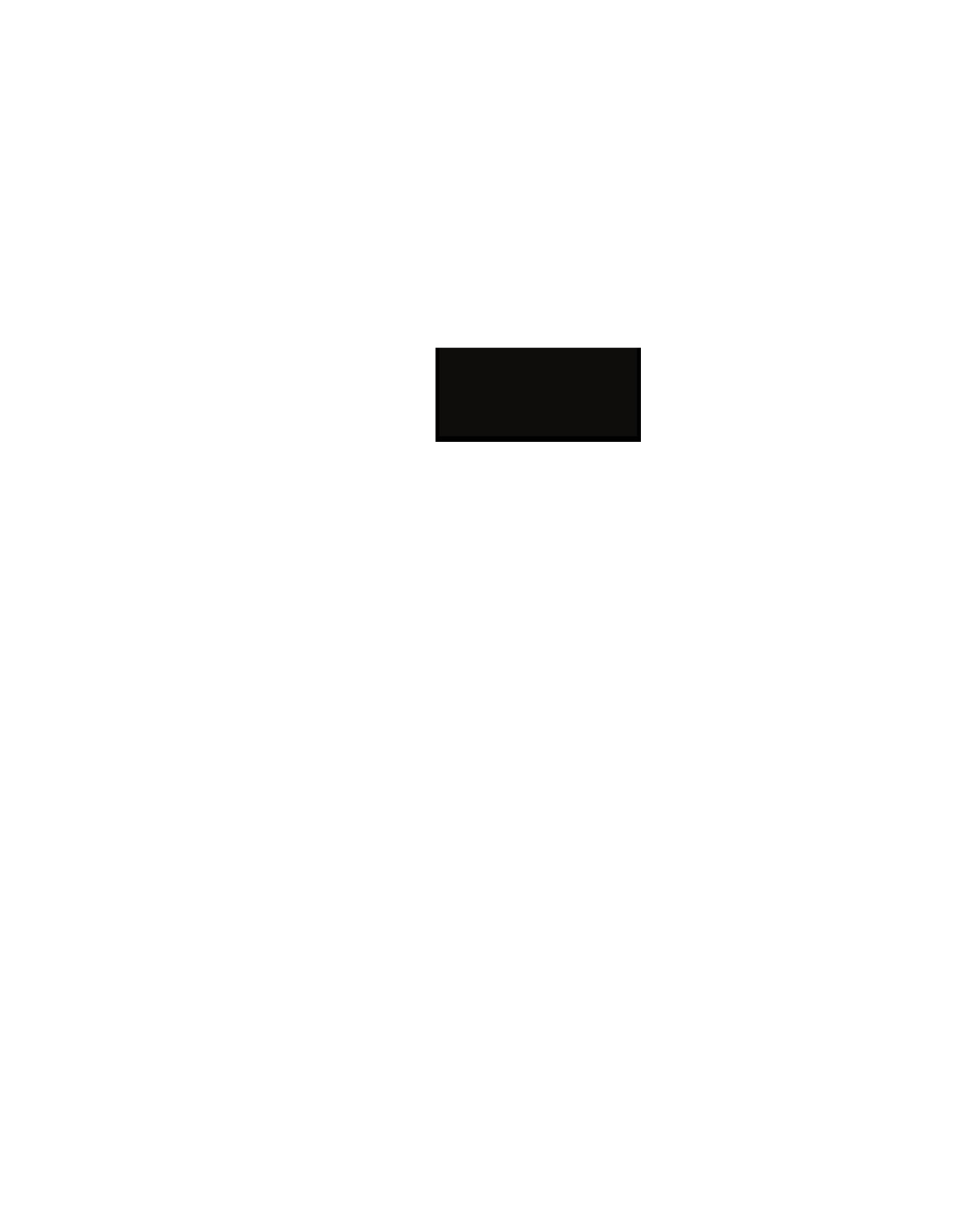
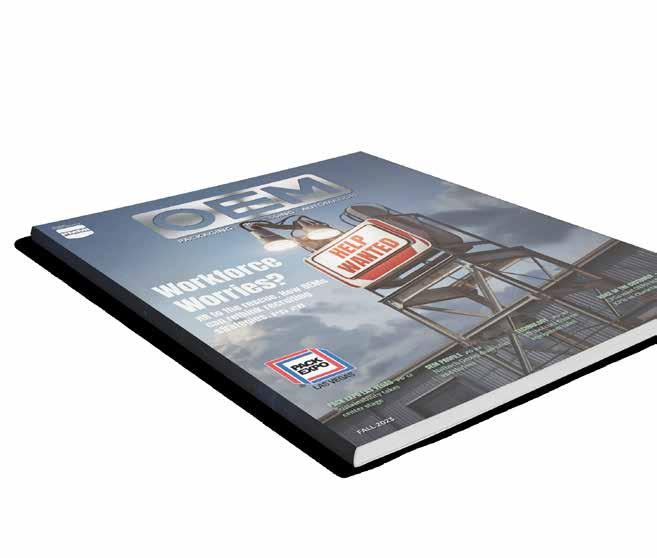

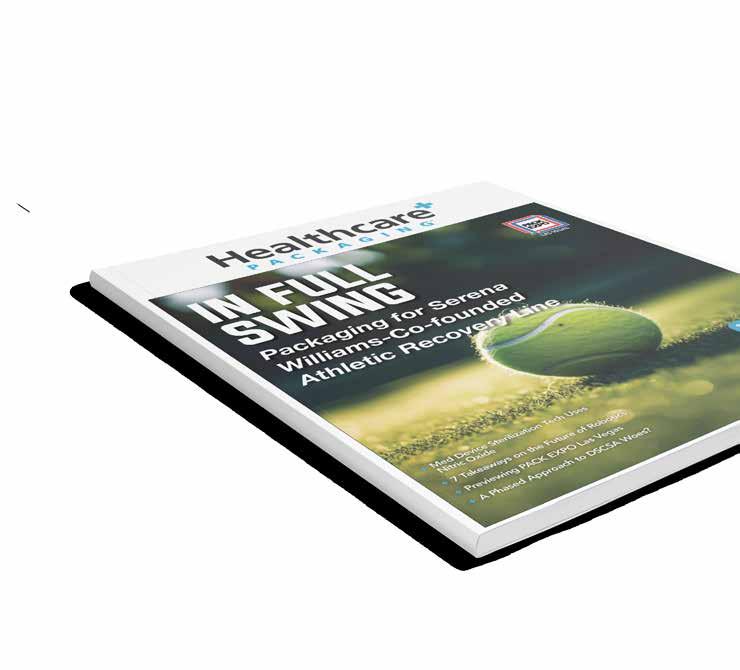
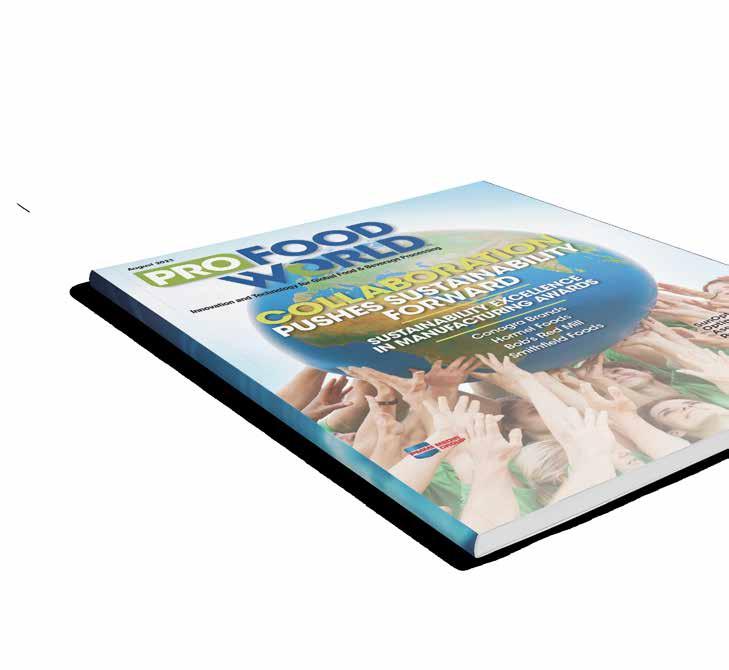
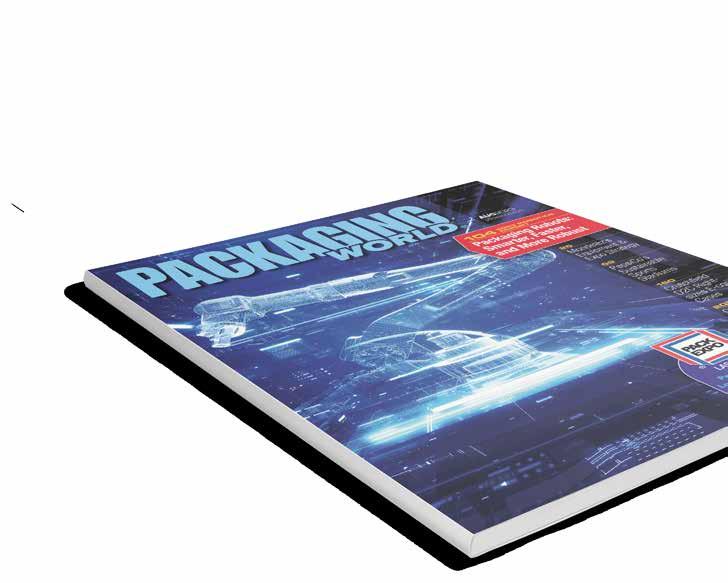
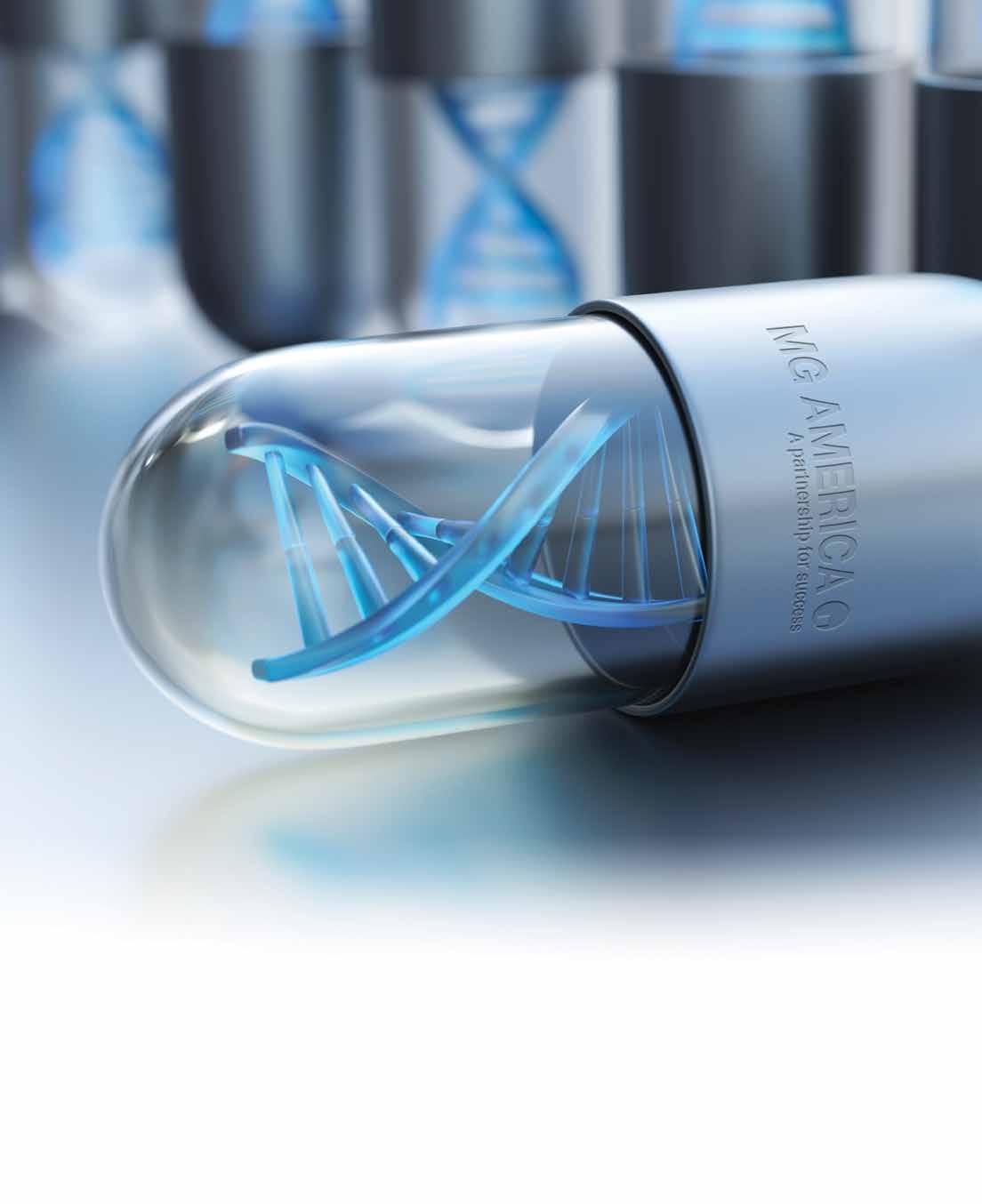
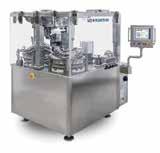

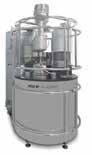
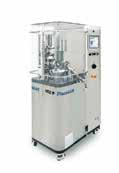