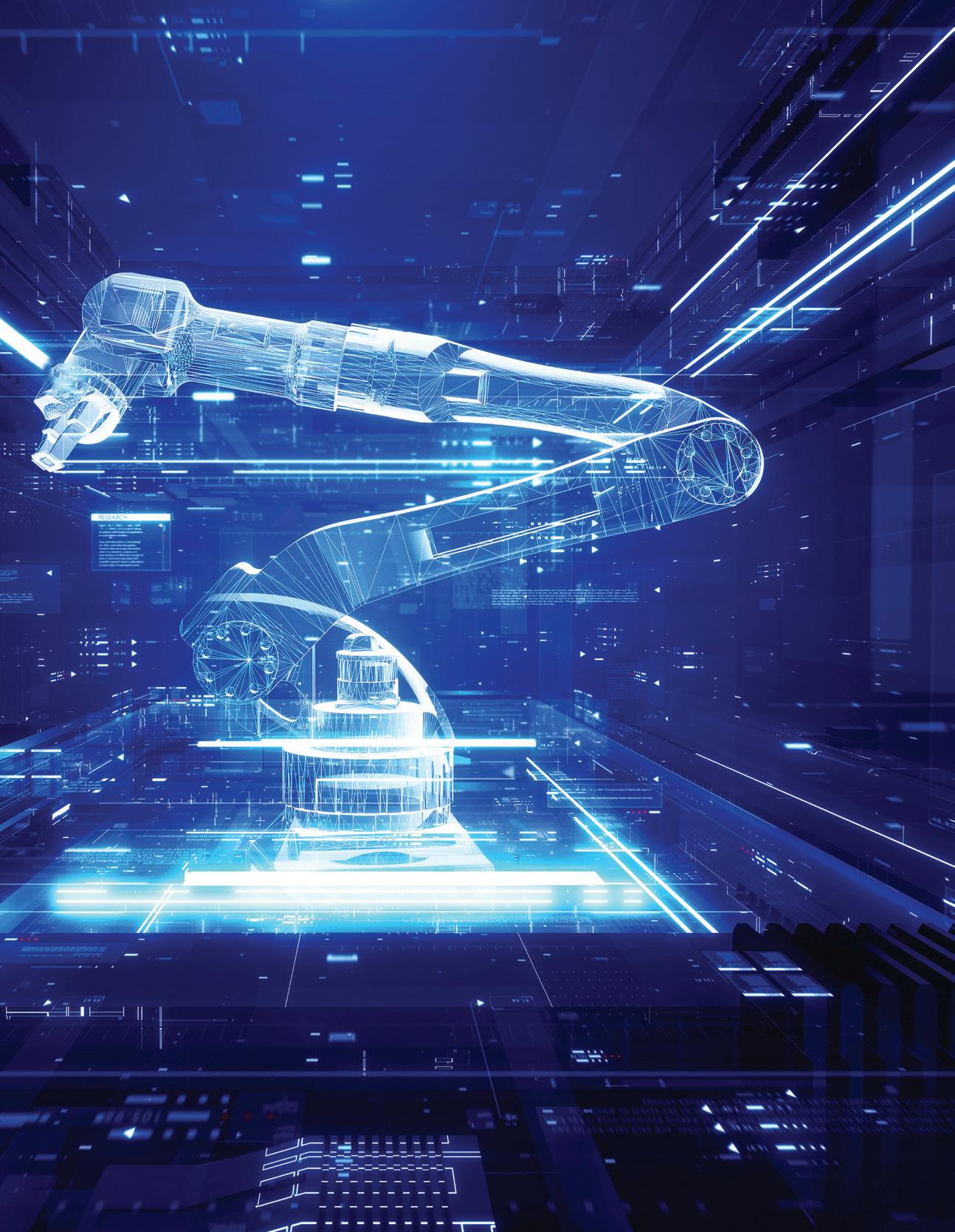
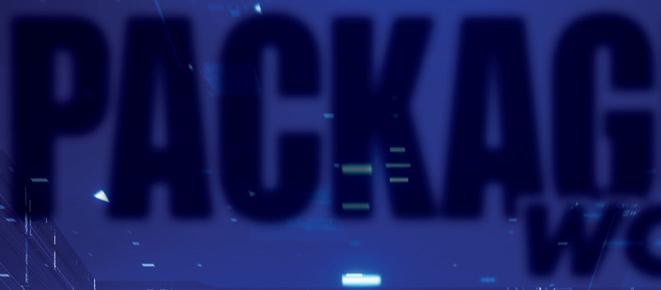


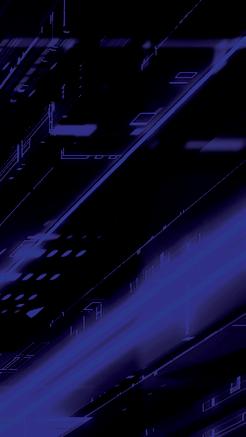
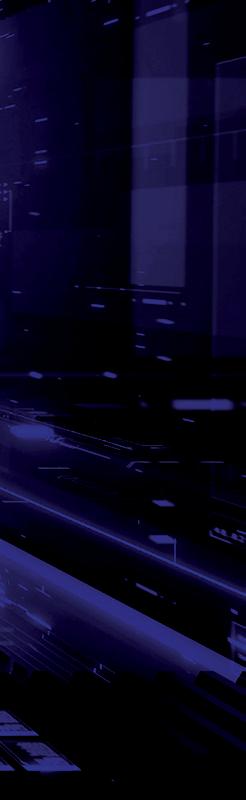
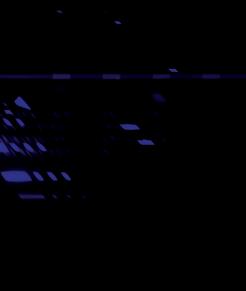
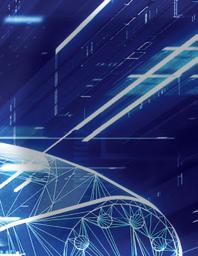
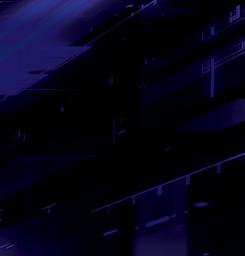
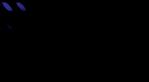
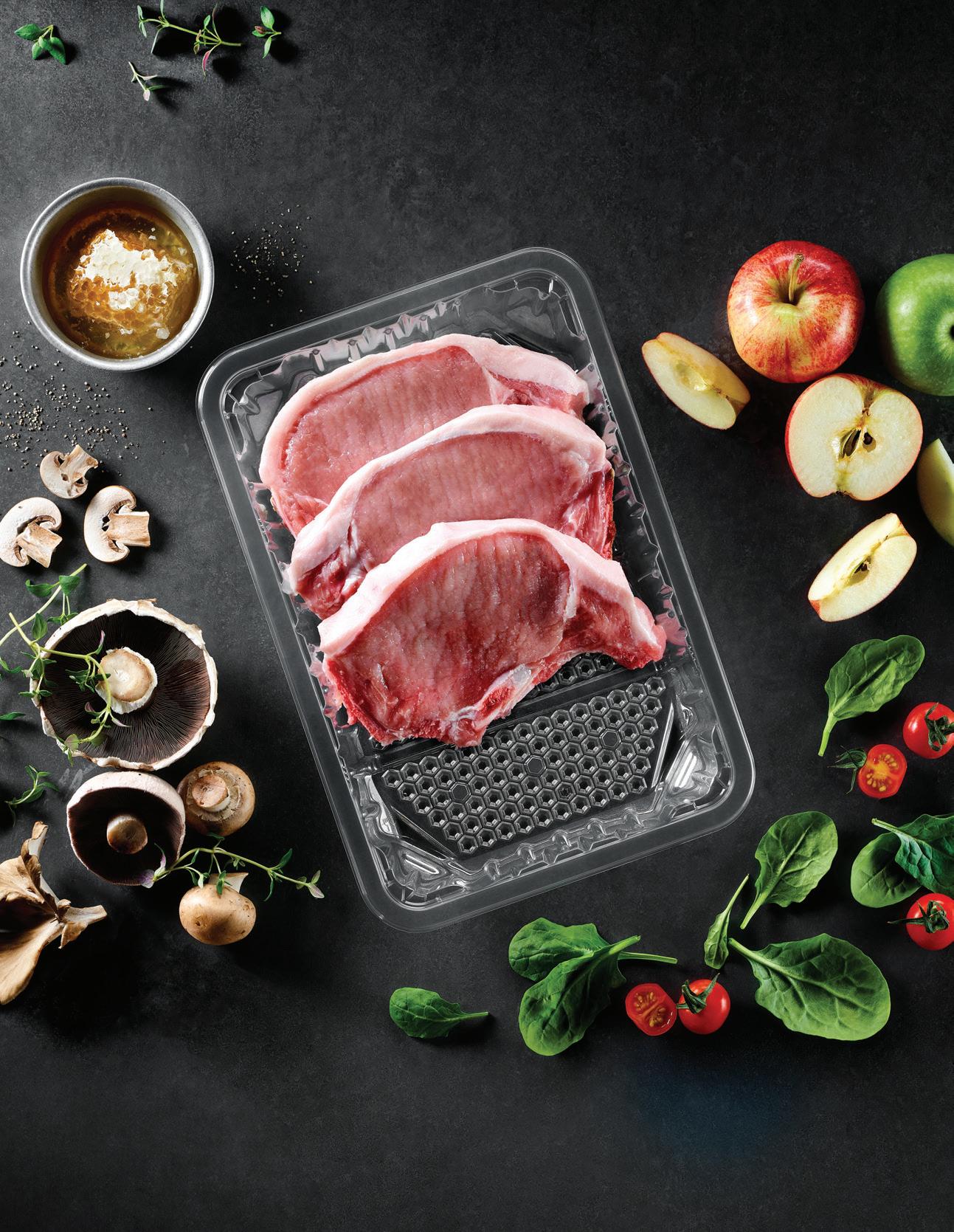
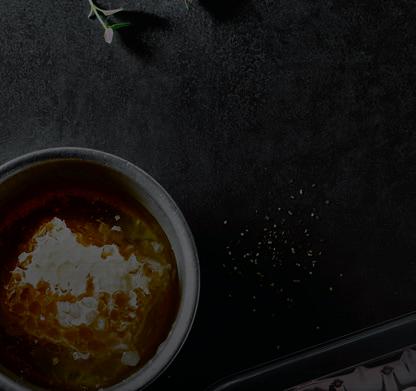
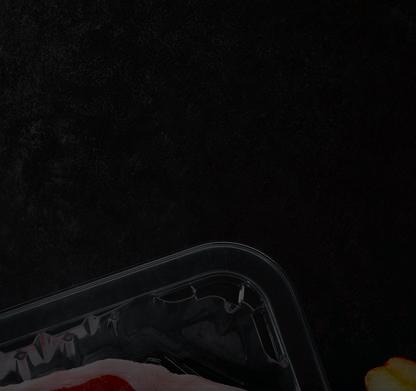

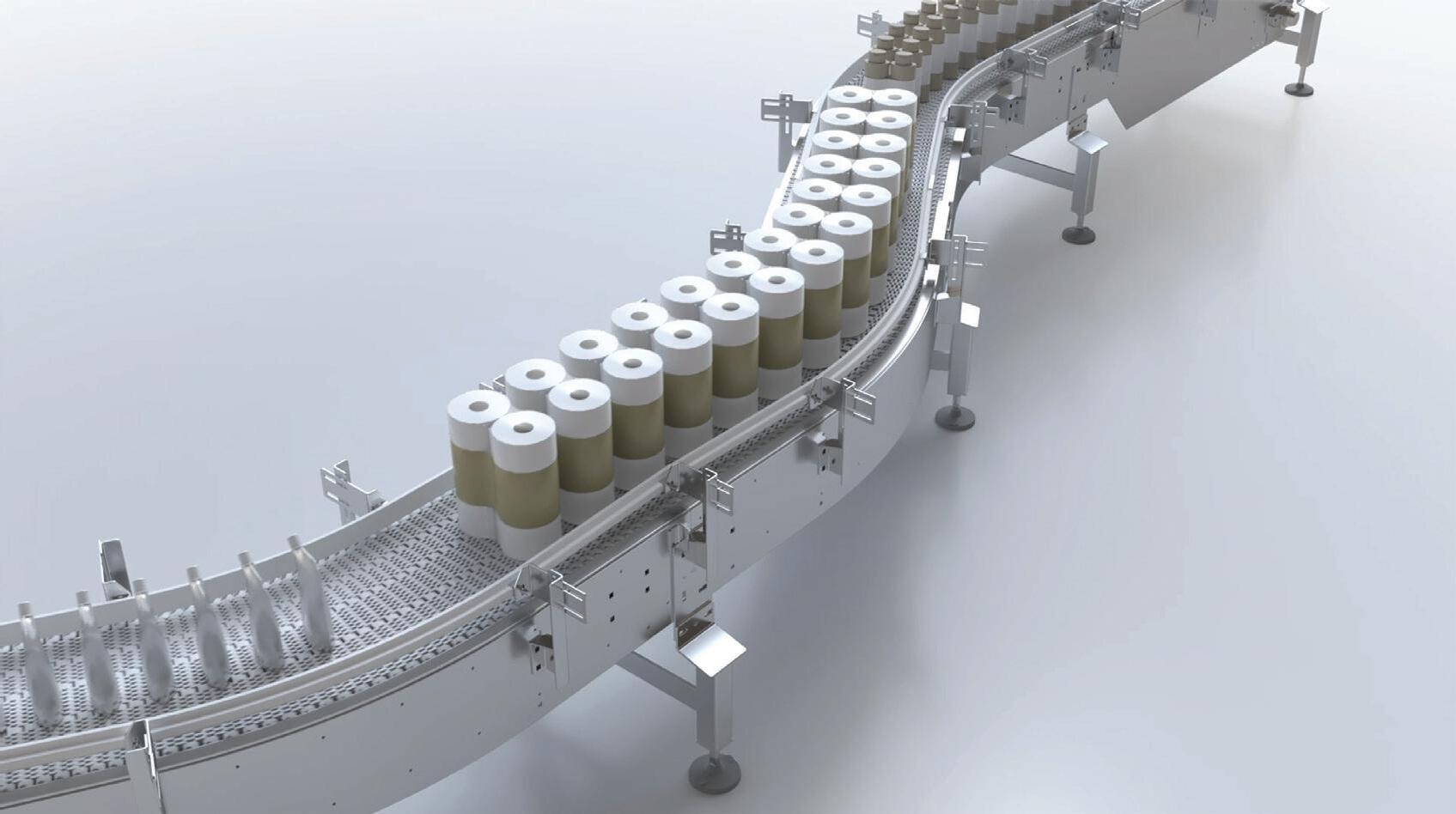
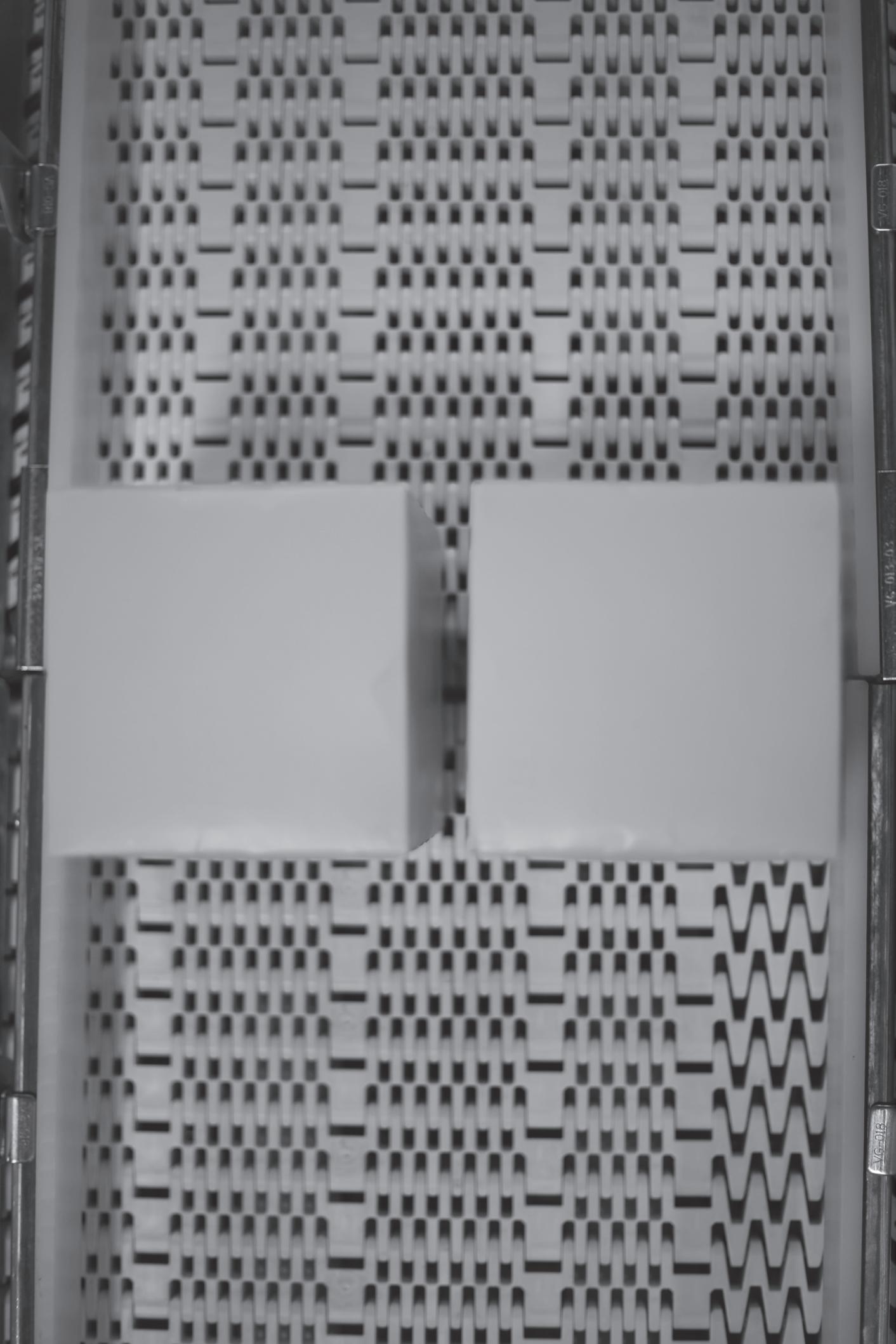
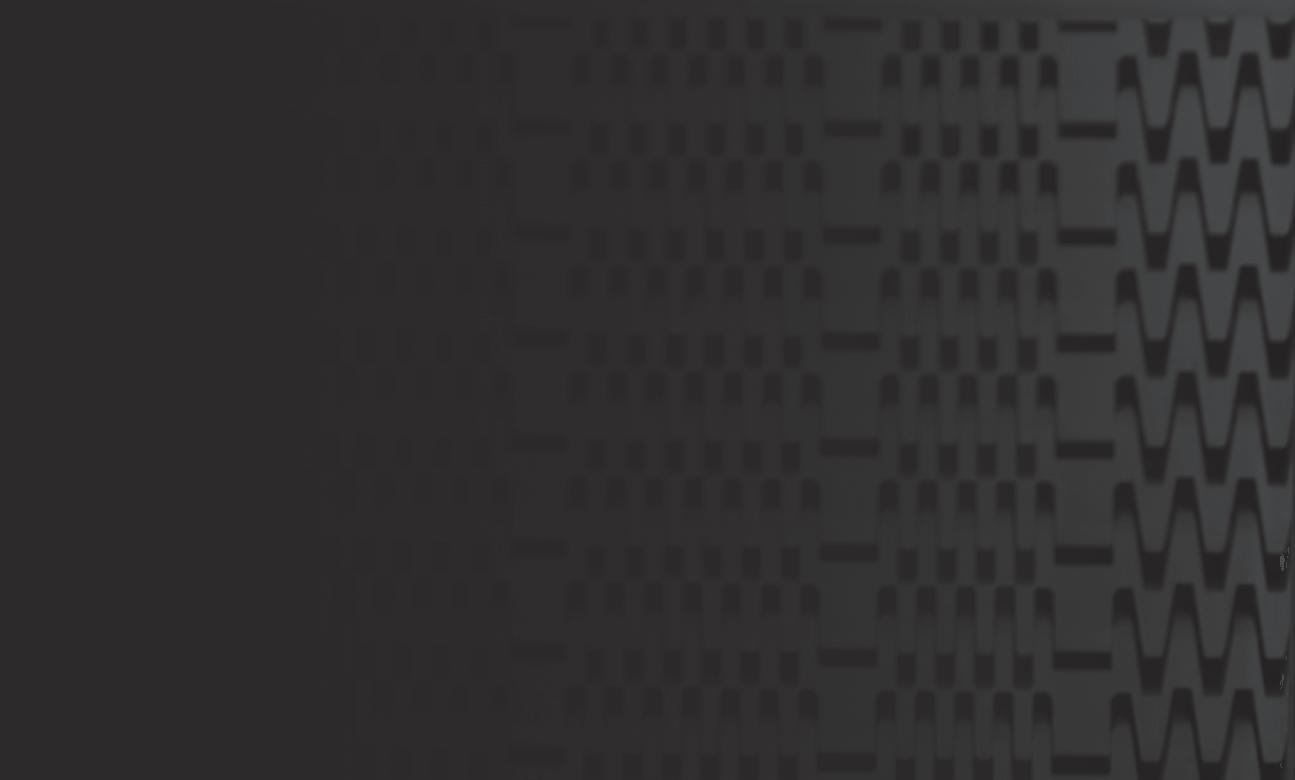
While labor is increasingly hard to nd, packaging robot technology is making strides on all fronts, from payload, accuracy, and speed to AI and machine learning. As such, packaging robot adoption is accelerating among brands and CPGs.
While labor is increasingly hard to nd, packaging robot technology is making strides on all fronts, from payload, accuracy, and speed to AI and machine learning. As such, packaging robot adoption is accelerating among brands and CPGs.
The new version broadens the scope to include co-packers and co-manufacturers and addresses cybersecurity, remote access, and more.
With big retailers becoming customers and distribution reaching 17 states, Fiesta Paci c simply had to increase capacity. They started with the case packer and worked their way back.
A collaboration between PepsiCo and the European soccer association builds upon years of progress in reducing packaging waste from sporting events with the debut of reusable packaging and biodegradable cups.
With chocolate stick demand growing and labor scarce, Sweet Candy Co. selected a robotic pick-andplace system to collate product into layers, then pick layers into cartons. Cartons are sold by weight, but stick weights vary by batch, so counts are adjusted on the y for accurate weights and limited giveaway.
According to a new study, exible plastic lms may outpace plastics overall in CAGR. And though compostables represent a small piece of the packaging pie, their pace of growth is fast. But these materials are a challenge to recycle with current infrastructure.
This year’s crop of new robotic equipment and software leans into AI technology, as well as higher payloads, greater exibility, and increased ease of programming and handling to alleviate the challenges faced by packagers as a result of the labor crisis.
For e-comm and D2C operations like Crutch eld, an audio/visual and consumer electronics specialist, right-sized cases ensure material savings, DIM weight optimization, and consumer satisfaction.
A pay-for-productivity robot model has mitigated the effects of labor shortages and provided scalability for the contract manufacturer.
172
Car wash supplier Sonny’s knew that to meet its ambitious sales goals for a quickly growing 2.5-gal detergent format, a semi-automated legacy system wouldn’t cut it. The resulting integrated robotic packaging line is the jewel of its newly opened facility.
When one of the country’s largest producers of fruit snacks boosted its candy-making capacity, primary, secondary, and tertiary packaging had to be top-notch.
The paper toilet paper packaging will eliminate approximately 500,000 pounds of plastic waste each year, the company says, and testing shows the format to be comparable to its predecessor in performance and function through rigorous supply chain, to retail, to consumers’ homes.
Powell Electronics adopts a patented new clamshell container with reclosable locking mechanism to ship delicate parts damage-free and reduce labor and packaging costs by 90%.
PACK EXPO Las Vegas 2023 will be the largest and most comprehensive edition in its history. Experience in-person an unmatched breadth of new technologies and innovations, this time with a special focus on sustainability.
A modern take on packaging signals a mindset shift for pain and athletic recovery products. Handsfree delivery, portability, and gender-inclusive shelf appeal deliver a grand slam.
FOCUS ON CRAFT BREW
Retail-friendly cans were already trending up in craft brew when pandemic-related venue closures accelerated the trend. Dust Bowl Brewing Co.’s increased, sustained reliance on this container format convinced management to double down on canning automation.
FOCUS
CRAFT BREW
Voodoo Brewing Co.’s unique franchise model promises exponential growth. Packaging operations needed an automated shot in the arm to keep up.
FOCUS ON CRAFT BREW
To contract craft brewer The Brutalist and its owner King State Beer, dissolved oxygen is four-letter word. A new ller and seamer combo keeps D.O. low and the beer quality high, while paperboard multipacks help to make an impact on the shelf.
VIDEO Robots Speed Car Wash Chemistry Line pwgo.to/8036
Aladin Alkhawam Supply Chain Security Director, Endo International plc
Jan Brücklmeier Technical Application Group Packaging Technology Expert, Nestlé
M. Shawn French Director – Innovation & Packaging Engineering (Beverage), Danone North America
Patrick Keenan R&D Packaging Engineer, General Mills/Annie’s Organic Snacks
Mike Marcinkowski Global R&D Of cer, GPA Global & Hub Folding Box Co.
David Smith, PhD Principal, David S. Smith & Associates
Brian Stepowany Packaging R&D, Senior Manager, B&G Foods, Inc.
Jasmine Sutherland President, Texas Food Solutions; Vice President, Perfect Fit Meals
VIDEO Robotic Line Uses Counter ow Principle pwgo.to/8035
VIDEO Robots Speed Fruit Snack Packaging Line pwgo.to/7992 VIDEO Filling
Matt Reynolds Chief Editor
Anne Marie Mohan Senior Editor
Iris Zavala Managing Editor
Sean Riley Senior News Director
Pat Reynolds, Sterling Anthony, Eric F. Greenberg, Ben Miyares Contributing Editors
David Bacho Creative Director
John Schrei Vice President, Sales jschrei@pmmimediagroup.com
Lara Krieger Production Manager lkrieger@pmmimediagroup.com
Janet Fabiano Financial Services Manager jfabiano@pmmimediagroup.com
David Newcorn President
Elizabeth Kachoris Vice President, Digital
Kelly Greeby Senior Director, Client Success & Media Operations
Jen Krepelka Director, Digital Media
Mike Prokopeak Senior Director, Content & Brand Growth
Trey Smith Senior Director, Events
Sharon Taylor Director, Marketing
Joseph Angel Founding Partner and Executive Vice President, Industry Outreach, PMMI
Lloyd Ferguson Founding Partner
Staff at PMMI Media Group can be contacted at info@pmmimediagroup.com
Questions about your subscription or wish to renew? Contact circulation@pmmimediagroup.com.
Editors at Packaging World have kicked around the idea of standardizing on one descriptor—among advanced, chemical, or molecular—to refer to a host of burgeoning recycling technologies that tend to revolve around (but aren’t limited to) depolymerization via pyrolysis, gasification, or solvents. My instinct was to default to “chemical” recycling, the earliest common descriptor. But “advanced” is an inclusive umbrella term that doesn’t carry the negative connotation baggage that “chemical” elicits. Meanwhile, “molecular” limits conversation to the depolymerization set of technologies, thus omitting methods like PureCycle polypropylene recovery. As PureCycle’s Matt Cripe explained to me at the recent MRP Solutions Sustainability Summit near Chicago, the tech cleans PP to virgin quality, but it doesn’t break it down to a monomer. Anyhow, PW will hold off on standardizing on a single descriptor for now.
This minor editorial conundrum is a microcosm of the public relations problem faced by advanced recycling (I guess I’m going with “advanced”). A big source of negative press has come from Senator Corey Booker (D-NJ) and other legislators who, in my opinion, have oversimplified pyrolysis and gasification (advanced recycling methods), labeling them as incineration instead of recycling to focus on CO2 byproducts. They aim to convince the Environmental Protection Agency (EPA) to keep considering these techs municipal waste combustion, and thus regulate them under the Clean Air Act. The experts tend to wear down non-expert legislators over time, so I’m hoping a course correction will occur. Or, as my buddy Eric Greenberg suggests on page 42, maybe agencies like the EPA won’t have such sharp teeth before long.
I heard advanced recycling’s PR travails laid bare in Orlando last month at the American Chemistry Council’s Innovation & Circularity Summit, in a panel discussion on the so-called mass balance approach, third-party certification for credibility, and ongoing consumer education.
Advanced recycling technologies often rely on the mass balance approach—a process of describing and accounting for the use of advanced recycled or bio-based feedstock in a final product when both recycled and virgin feedstock, or bio-based and fossil feedstock, have been used in the process. Since advanced recycling is a nascent tech, it’s not often practical for a usage figure to get even close to 100%, given chemically recycled PCR’s scarcity. So the approach is a matter of averages. Some of that chemically recycled material comes into a brand or producer facility, and some of it leaves the facility as packaging. The mass balance just accounts for how much of it is used as a part of the whole. This means the shampoo bottle with a claim that it is made from 30% advanced recycled PCR may not contain any, or perhaps more or less. But the company that produced it is indeed using that percentage of that material over a given product line.
But the mass balance approach and its traceability underpinnings require validation for credibility, said certification provider and converter panelists at the Innovation & Circularity Summit. Overcoming CPG skepticism of the tech while educating consumers is key, according to early adopter converters who were there, like Berry Global
To the uninitiated, claims based on technical-sounding terms like the mass balance approach can seem like smoke and mirrors. But other industries have gone through the same rounds of skepticism long before advanced recycling’s (and bio-based plastics’) mass balance approach. Carbon credits and carbon offsets, for instance, or even clean energy credits in powering peoples’ homes, were once seen as a means of fudging the numbers to make unrealistic claims. But as consumers and their energy, travel, and brand suppliers became more acquainted with those concepts, they largely have come around. After some education- and understanding-borne confidence, these systems enjoy widespread credibility today.
Also revealed at the Summit in Orlando, otherwise agnostic DC pollsters found high initial favorability for advanced recycling. Few Americans know what it is or how it works, of course. But when the basics are impartially explained to them, early public polling is wildly positive— upwards of 90% favorable across the political spectrum. But detractors exist, and that prior state of favorability is subject to quick erosion if proponents don’t actively control the public narrative. Visit pwgo.to/8037 to read about suggested messaging tactics to support advanced recycling’s public perception. I suppose it’s a sign of the times when the valuable science is only as good the PR campaign supporting it. PW
Long-running Maltese brewer Cisk is serving up a modernized look to solidify its popularity at home and support its growth into new audiences.
With over 90 years of brewing experience in the rear-view, the Simonds Farsons Cisk-owned brand rejuvenated its image for modern and emerging consumer groups, according to London brand design consultancy and redesign developer bluemarlin
“The modernized Cisk brand identity comprises many elements, working together to create something greater,” Susan Weenink Camilleri, head of sales and marketing at Simonds Farsons Cisk, says. “The upgraded iconic assets will work beautifully in any environment—events, points of sale, communication touchpoints, still, and animated campaigns.”
Cisk began collaboration with bluemarlin for this project in December 2021, building from a brand positioning strategy the two had rst developed in 2019, the consultancy says. It aimed to strengthen and future-proof the brand’s relevance in Malta by appealing to both loyal drinkers and upcoming generations, as well as internationally through the tourism market and Maltese expatriates.
“The new design system gives Simonds Farsons Cisk a robust and exible structure that will continue to build brand equity now and in the future,” says Andrew Eyles, bluemarlin founder and CEO. “It remains part of Maltese heritage, but with an eye rmly on the horizon.”
The brand’s stallion imagery remains above the Cisk marquee but is now freed from the con nes of a shield and has been redrawn and inverted. The hierarchy reinforces the stallion icon as a representation of the brand and “punctuates our essential claim of ‘Malta’s Finest,’” which surrounds the icon on the package, bluemarlin says.
The Cisk word marquee has been redrawn with precise cuts and angles,
a recessed drop shadow and side highlight, and without the old gradients and shading to simplify and contemporize the brandmark.
The new marquee features a few subtle nods to the brand’s heritage as well, with the ‘C’ crafted into a horseshoe and the ‘K’ resembling the now-inverted rearing stallion.
The redesign features the same red and yellow color scheme as before but drops the ornate imagery of the old design. Covering the new background is a faceted pattern based on the Maltese cross.
“It was clear we needed to harness the loud and proud spirit of the Mediterranean,” says Guy Robertson, bluemarlin lead brand designer for this project. “We wanted to add a sense of unconstrained spontaneity, so we designed a progressive fresh brand livery that speaks of Malta today.”
The brand reserved the new design treatment to its agship lager and low-carbohydrate Excel products, but the design was developed to work across all SKUs and future rollouts. The brand’s full range should be updated with the new identity by summer 2024, bluemarlin says.
Casey FlanaganZUDSSLQJQHHGV:H
VHPLDXWRPDWLFDQG
DUULYHDVLWZDVVKLSSHG
7KH6WUHWFK:UDSSLQJ([SHUWV
&RPHVHHXVDW3DFN([SR
Bottled water has been crowned America’s favorite bottled beverage, after reaching new peaks in both volume consumed and sales in 2022. That’s according to new data from the Beverage Marketing Corporation (BMC), which shows that bottled water’s total volume sold in 2022 was 15.9 billion gal, its highest volume ever, surpassing carbonated soft drinks for the seventh year in a row. In terms of retail dollars, 2022 sales approached $46 billion, up from $40.8 billion in 2021.
“Numerous qualities account for bottled water’s unceasing resonance with U.S. consumers, including its associations with healthfulness, convenience, safety, and value,” says John G. Rodwan, Jr., BMC’s editorial director. “Consumers’ thirst for beverages that offer bene ts beyond refreshment alone also contributed to the fundamental hydrating beverage’s rise in the
or additives, and it has the added bene t of packaging that is 100% recyclable,” says Jill Culora, IBWA’s vice president of communications. “Not only are bottled water containers 100% recyclable (including the cap), but they also use much less plastic than soda and other packaged beverages,”
Soda containers, on average, use 252% more PET plastic than bottled water containers—22.2 g versus 8.8 g for 16.9-oz containers, says IBWA. Soft drinks and other sugary beverages need thicker plastic containers due to their carbonation and/or bottling processes, it explains.
“Even with continuing growth and increased consumption, bottled water still has the smallest impact on the environment— thanks to the fact that it has the smallest water and energy use footprint of any packaged beverage,” says IBWA, adding that on average, only 1.39 L of water (including the 1 L of water consumed) and 0.21 mega joules of energy are used to produce 1 L of nished bottled water.
Most bottled water is packaged in 100% recyclable PET and HDPE plastic, which are the plastics most recognized by consumers as being recyclable and the most recycled plastics in the world, IBWA shares. “Consumers can be con dent about recycling bottled water containers because they are among the few consumer packaging types that are universally recyclable across the U.S.,” says the association. “Not all cities and towns recycle glass bottles or laminated paper cartons, which are most commonly comprised of multiple layers of paper, plastic, and aluminum or wax.”
beverage standings. Bottled water’s zero-calorie status and its lack of arti cial ingredients appeal to many consumers. Even where tap water may be safe and readily available, people may prefer bottled water, which they often believe tastes better.”
According to BMC data, for more than a decade, consumers have been increasingly choosing bottled water instead of lesshealthy packaged drinks. Bottled water’s volume surpassed soft drinks for the rst time in 2016 and has done so every year since.
In 2022, data shows that Americans consumed, on average, 46.5 gal of bottled water, compared to 36 gal of soda. Consumer demand for bottled water has signi cantly contributed to the industry’s growth of 30% since 2012, as people continue to switch from other less-healthy packaged drinks to bottled water. So much so, that nine out of 10 Americans (91%) want bottled water to be available wherever other drinks are sold, according to a survey conducted on behalf of the International Bottled Water Association (IBWA) by The Harris Poll
“People are choosing to drink bottled water because it is a healthy beverage choice, having zero calories and no caffeine
There is also a huge industry demand for post-consumer PET and HDPE plastics. Many bottled water companies use rPET and rHDPE plastic to create new bottles, which IBWA says helps to reduce the environmental impact of the new bottles further because they aren’t using virgin plastic.
Another positive are bottled water consumers themselves, which IBWA says recycle more often than drinkers of other beverages. Of all the PET containers recycled through curbside collections systems, bottled water containers make up approximately 49%. When not recycled, they make up just 3.3% of all drink packaging that ends up in land lls and only 0.02% of all land ll waste.
Bottled water containers are also not a major source of ocean pollution and microplastics, according to various studies. The vast majority of ocean plastic comes from sources other than the U.S. In fact, if the U.S. were to completely eliminate all plastic use, data from Oxford University’s Our World In Data website indicates that the effort would only result in a 0.25% reduction of ocean plastics. Because bottled water accounts for less than 1.58% of all plastics used in the U.S, eliminating all bottled water would only reduce ocean plastics by about 1.58% of 0.25%. —Anne
Marie MohanAfter an initial major rollout that began in Australia late last year, Mars is introducing a paper packaging pilot program to the UK, this time via the Mars Wrigley Research and Development Center in Slough, UK. This is the latest in a set of new pilot tests exploring different packaging options for the brand.
Mars is now producing the iconic Mars bars wrapped in recyclable paper packaging that are available for a limited time at Tesco stores. After extensive development work and investments, the company says the trial will achieve a signi cant reduction in plastic on the physical Mars bar—a signi cant step in its journey to innovate toward its packaging commitments.
“We are exploring different types of alternative packaging solutions for our confectionery products,” says Richard Sutherland-Moore, packaging expert at Mars Wrigley UK’s Research and Development Centre in Slough. “For Mars bar, the challenge was to nd the right paper packaging solution with an adequate level of barrier properties to protect the chocolate whilst guaranteeing the food safety, quality and integrity of the product to prevent food waste.”
More speci cally, adds Tracey Man eld, senior packaging engineer in the Global Packaging Innovations team in Slough, “We’re trialing paper packaging today to understand more about how the material performs in the factories, in terms of line speed and wastage, and also how it performs in transit from the factory to the shelf, and indeed beyond the shelf to the consumer.”
Following the trial, Mars will use the learnings from the launch with Tesco to inform other trials across the region, all in the name of the com-
panies Sustainable in a Generation plan.
“We’re delighted to partner with Mars Wrigley to trial an alternative version of their iconic Mars bar packaging—aligning to our own strategy of removing plastic and packaging in our business where we can, reducing it where we can’t, reusing more and recycling what’s left,” adds Andrew Flood, packaging development manager, Tesco.
Mars works with Amcor on the Australian paper packaging project. Packaging World asked the company about supplier partners and material specs used in this UK project, but the company declined to provide details.
A Mars Wrigley UK spokesperson did have this to say,: “The packaging consists mainly of paper, but in order to protect the chocolate bar and give us the shelf life we need, a barrier coating is necessary. The paper material can be recycled as paper and is widely recognized as a recyclable material that is suitable for curbside collection across the UK.” —Matt Reynolds
From its farming practices to its family values, California Olive Ranch holds itself to the highest standards. That’s according to the company, whose family of brands include its California Olive Ranch olive and avocado oils and sprays and olive oil-based dressings, marinades, and sauces, as well as its Lucini brand of oils and sauces. Says the company, “In partnership with more than 50 family farmers throughout the state of California and countless others across the globe, the company is committed to transparency and sustainable practices in both growing and packaging.”
Until recently, its line of edible oils was available either in glass or a bag-in-box format. But in an ongoing effort to diversify its product offerings, the company added a new and unique format for the category, an aluminum bottle, to its line of packaging options.
“At California Olive Ranch, we are dedicated to delivering a versatile product line of high-quality cooking staples that meet the needs of every consumer, and that is exempli ed by the launch of our aluminum-bottled oils,” says Mary Mori, California Olive Ranch vice president of Quality and R&D. “By creating our smallest, most lightweight bottle yet, we are able to not only continue building upon our sustainable packaging efforts, but we’re also offering consumers a more accessible price point to our bestselling line of olive and avocado oils. Additionally, the size of the bottle allows for ease-of-use for packing while traveling, which is highly appealing to our consumer base.”
The aluminum bottle, in a 335-mL size, is supplied by Trivium Packaging, which lays out the typical stats for edible oil packaging: “Olive oil, coconut oil, vegetable, and cooking oils—all unsung necessities of our daily routines—all often come in plastic bottles. In fact, in the North American market, nearly 80% of edible oil brands in packaging under 750 mL—and the majority of larger containers as well—use plastic.”
Trivium shares that California Olive Ranch is the rst of its customers to use an aluminum bottle for liquid oil. The container was custom designed to be smaller and to use a cap that helps with easy pourability and eliminates mess during use. The cap is made from high-density and low-density polyethylene. “We considered an aluminum cap to accompany the bottle, but we wanted to provide the pour-spout ability, which was not possible with the aluminum cap,” says Mori. “The consumer’s convenience in use is one of our top priorities that we did not want to lose on this packaging.”
The bottle uses a label for decoration. While Mori says this is not ideal for all recycling facilities, work is being done to make it more viable at all recycling centers. “Additionally, as we are continuously improving our products, we hope to switch to a more sustainable labeling method that would allow for even better universal recyclability.”
California Olive Ranch’s 100% California EVOO (extra virgin olive oil), Avocado EVOO Blend, and Reserve Blend in the new aluminum bottle were introduced at retail in October 2022 and direct-to-consumer via the company’s website, californiaoliveranch.com, in April 2023. Prices range from $8.99 to $10.99. Says Mori, “Competing brands offer plastic and glass bottles of the same size at upwards of $20 or higher, which puts our more eco-friendly product at a more accessible price point without compromising quality or taste.” —Anne
Marie MohanWith its new vitamin dispensing system, CVS Pharmacy is putting patient adherence and medication access front-and-center with a new countertop design that can be opened with a ngertip.
The CVS Health QuickServe Vitamin Dispensing System is composed of two components:
• A reusable dispenser base
• Individual, pre- lled vitamin and supplement QuickServe cartridges
The consumer assembles the system in simple steps with illustrations noted on the outer carton: open and remove the cap and safety seal from the cartridge and attach the base to the cartridge.
The consumer can quickly access a vitamin by opening the door with a ngertip after which a single vitamin is presented in the slot. The door features a divot for easy opening. The system is designed so that the cartridge label remains highly visible on the front, so consumers know what vitamin or supplement they’re accessing and the serving size.
“At CVS Health, we design for our customers and aim to simplify routines by innovating streamlined solutions. Through research, we learned that our consumers are looking for a better way to organize taking vitamins and want them to be visually accessible to help remember to take them. We wanted to develop a system that makes taking vitamins and supplements simple and easy to access to help consumers stick to their supplement routine,” says Heather Corkery, executive director of store brands.
A recent consumer survey conducted by CVS Pharmacy found that 75% of respondents have forgotten to take vitamins and supplements in the past year, with two out of ve people indicating they forget at least once a week. Nearly half of vitamin and supplement takers surveyed say they’d be more likely to remember to take vitamins/supplements if they were on the kitchen or bathroom counter.
“With the countertop design, consumers are more likely to remember
to take their vitamins if they are out in the open, ultimately increasing adherence and expanding on their daily regimens,” says Corkery. “The QuickServe dispenser base is currently available in one neutral color to t naturally into the aesthetic of your home.”
While speci c component material details are not available as of press time, she notes, “The QuickServe dispenser base is made of heavy plastic and is intended to be used over time with replaceable QuickServe vitamin cartridges. The vitamin cartridges are made from a lighter plastic and may be used with or without the dispenser.”
A starter kit is available which includes the QuickServe dispenser base and a 30-day QuickServe vitamin or supplement cartridge; the base dispenser and cartridges are also sold separately. “For added convenience, you may attach several bases together to create a larger set of all the vitamins and supplements you want to consume in a day,” she adds.
Design for the system was focused on ease of use for daily adherence, and Corkery says they’re excited about delivering a new way to take vitamins and supplements. “Through creative engineering, we were able to develop a system to dispense one pill at a time without jamming,” she explains. “The dispensers can be joined together through the heart connector [on the side] to create a personalized set for your countertop to help keep all the vitamins and supplements you take in a day neatly organized in one place. The dispenser base is reusable, making it easy for customers to only have to repurchase the vitamin cartridges.”
The system was launched online by CVS Pharmacy on April 14, 2023, and was of cially available in select CVS Pharmacy locations as of May 12. Currently, the QuickServe system can be purchased with Calcium, Daily Multivitamin, Daily Probiotic, Magnesium, and Turmeric + Black Pepper cartridges. Later this year, the company plans to launch additional vitamins and supplements. —Keren Sookne
Flexibility is an essential component of the MFlex™ concept. The modular design allows for one design philosophy to be utilized for a wide range of applications by simply choosing the required modules from our extensive portfolio. Composed of a label applicator and integrated product handling solution, the MFlex™ precisely labels virtually any type of packaging shapes and product types while providing an easy and flexible platform to control and maintain.
SEE HOW THE MFLEX PRESSURE-SENSITIVE LABELING SYSTEM COMES TOGETHER
SELECT AN MFLEX™ CONFIGURATION
Go from modular components to a complete configuration by selecting from one of six available pressure-sensitive MFlex™ labeling systems.
SEE MFLEX™ LABELING IN MOTION
Preview a production line in motion and see how MFlex™ pressure-sensitive systems apply labels quickly and efficiently to various product types.
ADD ADDITIONAL COMPONENTS
Needing to add variable production codes to your label or package? No problem; simply select the appropriate coding technology for a complete integrated solution.
Visit us online at: www.epilabelers.com/products/mflex-inmotion-visualizer or scan the QR code to see how MFlex™ Pressure-Sensitive Labeling Systems can accommodate primary labeling and additional coding for virtually any type of product or packaging
Specialty Equipment has a full line of bottle ĆOOLQJDQGFDSSLQJPDFKLQHVLGHDOIRUWKH OXEULFDQWVRLOVFKHPLFDOVFOHDQLQJDQG SHUVRQDOFDUHEHDXW\LQGXVWULHV8SWR ĆOOLQJKHDGVĆOOVXSWRR]WR JDOORQERWWOHVRUJDOORQ)VW\OHMXJVD PLQXWHVHUYRGULYHQLQOLQHURWDU\ĆOOLQJ ERWKćRZPHWHUDQGSLVWRQEDVHGĆOOHUV DYDLODEOH)RUPRUHLQIRUPDWLRQFRQWDFWXV DWVSHFLDOW\HTXLSPHQWFRP
%HQHĆWV
» Quick Product Changeover
» Runs 24/7 Without an Operator
» Accurate, Fast, Flexible and Silent
» Clean In-place Functionality
» Increase Production & Maximize Uptime
» Add Savings to Your Bottom Line
7\SHVRI%RWWOHV:H)LOO
Mess-free, ergonomic, and more visually cohesive, a new paperboard canister for Organic India’s Psyllium Pre & Probiotic Fiber product has replaced exible packaging for the powdered product—a move made in response to feedback from retailers and consumers. The new 10-oz canister, with a metal bottom and polypropylene lid, also aligns with packaging for the company’s number-one product, Psyllium Whole Husk Fiber.
Organic India is a Boulder, Colo.-based company offering organic products and wellness solutions for healthy, conscious living. Its Psyllium Pre & Probiotic Fiber, formulated for digestive wellness, provides a great source of ber and is combined with shelf-stable probiotics and Ayurvedic herbs for gastrointestinal detox and rejuvenation. Organic India’s products are imported from India and are USDA Certi ed Organic, NonGMO Project Veri ed, and vegan.
According to company Marketing Director Kat Wiranowski, one consumer pain point with the previous packaging was the mess it created. “For consumers, the pouches were tough to seal, creating mess and inconvenience,” she says. “The sleek, easy-seal canisters are a cleaner and mess-free upgrade.”
For retailers, the new canister offers two advantages. First, it is more consistent with the packaging for the company’s most popular product, making for a more visually cohesive presentation of the ber lineup on shelf. Second, shares Wiranowski, “the canisters take up less space on the shelf with more visual consistency and more dollars per inch, which is a huge bene t to the retailer.”
During the planning stages of the packaging redesign, Wiranowski says Organic India did look at other options for an improved sustainability pro le. But, she says, not only did the options not improve the user experience, they actually downgraded the packaging’s functionality. “Ultimately we landed on keeping the packaging consistent with our number-one SKU while we continue to nd more sustainable solutions for the entire line,” she explains.
From a sourcing and timeline perspective, the paperboard canister was also the most ef cient option for the company, as it already had a supplier in place.
Organic India’s Psyllium Pre & Probiotic Fiber product rolled out nationwide in the new canister in June in three varieties: Orange, Cinnamon Spice, and Original. The product line is available for an MSRP of $19.99 in select grocers and natural food retailers, as well as through the company’s website, organicindiausa.com, and Amazon.com.
:HDOVRSURYLGHLQVWDOODWLRQSDUWVDQGĆHOGVHUYLFH
Learn more by calling 833-467-3432 ZZZVSHFLDOW\HTXLSPHQWFRP
Regarding reception to the new packaging, Wiranowski says there has been “an overwhelmingly positive response from retailers and consumers alike, mirroring the original motivations for the change.” She adds, “It’s not much of a surprise, since it was re ective of the feedback we received, so it’s great to see it pay off.” —Anne
Marie MohanArti cial intelligence’s (AI) use in the packaging market is projected to reach a value of $2,080.8 million in 2023 and is expected to grow to $6,015.6 million by 2033. That’s according to Future Market Insights, which adds that the sales of AI in packaging are forecast to have a signi cant CAGR of 11.20% during the forecast period.
As the report explains, AI in packaging refers to the use of advanced technologies like machine learning and computer vision to improve various processes in the packaging industry. AI systems can analyze images to detect defects in packaging materials, ensuring high-quality products reach the market. It also aids in supply chain management by optimizing production and distribution processes based on historical sales data and market trends, reducing costs and stockouts. In addition, AI algorithms can generate personalized packaging designs and recommend suitable materials based on consumer preferences, market trends, and product data.
Future Market Insights adds that the demand for smart and sustainable packaging has created opportunities for AI-driven innovations such
as active monitoring systems, temperaturesensitive labels, and interactive packaging experiences, enhancing product safety and consumer engagement.
Key trends identi ed by the report include predictive maintenance, quality assurance through computer vision, supply chain optimization, voice and image recognition for hands-free operations, and data analytics for insights into consumer behavior and operational ef ciency.
The report points out, however, that there are a number of barriers to adoption of the technology, among them the high cost of implementation for smaller companies. In addition, data privacy and security concerns need to be addressed to ensure the protection of sensitive information. Integrating AI technologies with existing infrastructure also can be complex and pose a challenge for companies with established systems. The report also advises that ethical and legal considerations, such as bias in AI algorithms and the impact on human labor, also need to be carefully addressed.
—Anne Marie MohanTridyne Scale with APM Vertical Conveyorized Sealing System. Precise and dependable. Turn-key packaging for any free flowing dry material!
Horizontal Conveyorized Sealing System
A Fully Integrated Packaging System!
Supplied with verification ports for process validation of pressure, speed, and temperature. Includes crank handle for height adjustment of sealing head to position over existing variable speed conveyor.
Seals Tyvek® pouches at up to 40 feet per minute!
USDA Approved Rotary Band Sealer includes bag top trimmer and vacuum scrap removal. Superior performance and high speed production.
Tabletop Conveyorized Pouch Sealer
conveyor. Ideal for candy, confections, and snacks. The crank handle adjustment allows easy seal height changes from 2" up to 12".
52g
The weight of a new 100% rPET bottle for Blue Bin premium wine; traditional glass wine bottles weigh from 420 to 850g, with the weight accounting for 29% of the wine’s carbon footprint
882%
The percentage increase in consumer use of generative AI and ChatGPT, from 6.3 million in 2022 to 61.5 million this year—a trend that will radically change searches, the way consumers get information, and how they make purchase decisions
1B
The amount of Pringles products that will be packaged annually in a new 90% paper tube, lled on new production lines in Mechelen, Belgium
1,000
The number of items that will be launched through 2024 under Southeastern Grocers’ new clean-label private brand, Know & Love, which will include dairy products, produce, readymade food, and household goods
“In healthcare, not all plastic is bad, in many scenarios it is absolutely necessary given it’s durable, lightweight, and able to provide a sterile and safe environment for delivering extraordinary patient care. For us, the focus on plastic waste then becomes about identifying opportunities for reduction of unnecessary plastic and partnering with the recycling industry to develop the technology to recycle healthcare plastics.”
–Avery Palardy, sustainability program manager at U.S.-based Beth Israel Deaconess Medical Center, in an article from E-Magazine By Medical Expo, “Plastic Waste in Healthcare: Finding Solutions”
“What we see working with more than 33,000 brands is operational complexity. I’ve seen so many bad implementations for connected packaging, such as putting a barcode on a box and all it does is navigate the consumer to your desktop website. Please don’t do this, because you’re going to make consumers have this assumption of, ‘I did this with brand XYZ, all it does is take you to the website,’ and they’ll never scan again.”
“Less packaging material and reuse are important parts of our packaging policy. In recent years we have shown that we can successfully implement this movement, for example, by replacing the free plastic bags for fruit and vegetables with reusable fresh bags. Your own packaging is the most sustainable, and we believe that packaging-free shopping can become a routine. The improvements we are now implementing will contribute to that.”
–Anita
“This [pre lled returnable packaging] is a revolutionary approach. By collaborating on a full-system solution, brands and retailers can effectively scale-up an effective reuse model that avoids the consumer barriers. It is clear to everyone that consumers want to shop more sustainably, our climate desperately needs us to, but to date, the missing link has been the innovative solution—the future is pre ll.”
While at interpack in May, during a Nestlé Waters presentation on predictive maintenance, I noticed a CPG logo on a fellow attendee’s shirt. I took a chance on striking up a conversation with the man in the Oreo Cookies polo, and he turned out to be John Walker, senior director, Manufacturing, Supply Chain, and Infrastructure Investment at Mondele - z Europe GmbH. He said that he felt like “a child in a toy store” at these big packaging equipment trade shows, and was gracious enough to share what he’s looking for in equipment suppliers, how he prioritizes what he sees as futureleaning technologies, and areas where he sees the most innovation. His approaches and insights should be instructive to fellow brands and technology suppliers alike, especially as we embark on PACK EXPO Las Vegas.
Give us a brief overview of what you do at Mondelez.
The short answer is the machines, the nuts and bolts, and nothing to do with materials, ingredients, avors, or sugars. I’m based in Switzerland, and my team is responsible for the acquisition of those equipment assets, working with the engineers and the plants. We work with the suppliers and try to make sure that we have a good relationship, and a good asset acquisition strategy.
others have done successfully. You also get to see companies you might not know of. We have a certain set of partners, but here we get to do a bit of exploring to augment our portfolio.
So you’re always keeping an eye out for new suppliers, why is that?
It’s no secret that a big factor is risk mitigation. The past few years have been very tough, particularly in automation, with tremendous shortages of components. We’re looking to broaden our selection, our portfolio of equipment suppliers. We used to have a much more narrow portfolio of suppliers, but we’ve broadened it to limit the risk. We can’t bet on just one horse.
What are you looking for at interpack?
Anything in particular?
We’re looking for anything from a mixer all the way to the palletizer, essentially anything that produces food. The emphasis today was primarily on packaging equipment, and we’re getting more and more into the higher speeds And also, packaging solutions have to be much more exible these days, with so many more pack sizes change. E-commerce is something we deal with more and more.
Why do you come to major events like interpack or PACK EXPO?
Outside of these types of events, you can very seldom see multiple suppliers in a such a short period of time. There’s a tremendous advantage to getting around these shows. You see equipment, you see assets, you see solutions, and you see things that you wouldn’t necessarily see otherwise, because some of these technologies aren’t currently being used for your products. You see things that others have tried, you can benchmark, you can borrow ideas, and replicate what
In the old days, companies wanted to reduce the number SKUs because they wanted to reduce the complexity. But now it’s going the other way, and we’re constantly introducing new products, new pack sizes, and new varieties. It makes for an in nite combination of possibilities, so there’s a near-in nite portfolio of things we have to be prepared to make. You can’t do it all with existing equipment, so you have to you have to look what they’re showing us. The question becomes, theoretically at least, how can you make an in nitely variable portfolio, where you have an in nite number of options on your equipment? Because consumers are wanting and expecting more new product options all the time.
BULK
EQUIPMENT ENGINEERING & CONSTRUCTION ADVANTAGES.
Sanitary design is not disguising a general-purpose unit in stainless steel so it can pose in a hygienic environment. National Bulk Equipment sanitary design systems are engineered-to-application, ensuring confidence in changeovers and compliance.
Designed & Built to Hygienic Area Criteria
Fabricated and assembled to prevent liquid pooling and bacteria growth; sanitary design criteria are built-in features, not bolt-on risks.
Tool-less Cleaning & Inspection Access
Process-specific design of access points and closures aids cleaning and inspection, improves process and product safety.
Engineered to Aid CIP Cleaning Protocols
Sealed and enclosed product contact areas are thoroughly cleaned, without disassembly. CIP integration ensures efficient cleaning.
E3TM Dust-tight Bag Spout Interface Bag spout is fully enclosed during discharge; 3/4-inch thick clamp plate prevents deflection and dust release.
From raw material discharging to finished-product packaging, NBE bulk material handling equipment spans the fullstream of processing and packaging applications. Leverage the full portfolio of NBE equipment to bring optimal process performance to your production operation.
Move beyond the constraints of build-to-order and engineered-to-order equipment builders. Avoid settling for application input that falls short and project and production resources too limited to keep pace. Ensure optimal project performance from pre-RFQ feasibility testing through installation and turnover, with NBE engineered-to-application project delivery.
See for yourself. View product feature demos, watch a test of your material from your computer or mobile device, or request a rep visit. To get started, visit: nbe-inc.com or, call: 616.344.6250
Rapid or fast changeover is becoming critical. In the old days, even as recently as 10 years ago, you could run longer batches. But now you have to be able to produce a larger variety of batches. And the challenge is you want to use that equipment; you don’t want it to be sitting idle as you’re changing it over. Rapid changeover is quite interesting, I liken it to a Formula One pit crews. If you look at the crew today versus 30 years ago, and then versus 70 years ago, you can’t compare them. Today, we try to literally make changes on the y without stopping the machine. We’re not there yet, but it would be nice. Let’s say you’re making a chocolate bar and you go, let’s say, from 25 grams to 20 grams. It’d be nice to be able to do that without ever stopping the machine, right? That’s the vision right there.
Here at the show, I’m seeing lots of new materials being used, particularly in films, with monomaterials, fiber-based paper films, and compostables becoming increasingly prevalent. How is the advent of new materials affecting asset management?
It depends, but there’s always a solution. You can talk about things like sealing jaws. When you close the package, there are different temperatures, there’s different physical forces, retention forces, there’s a variety of different criteria. What us equipment people have to do when we’re dealing with the materials people is to ask, “What does my equipment need to do, to close or to seal that package, with your material?” Because the end of the day, we’re neutral on the material. I couldn’t care a millimeter less. But I have to make sure that if they say it’s a different temperature range, or a different speed, or a different
You’re seeing a lot more at the at the further end, the downstream end, when it goes into e-commerce. If someone goes into and buys from a big-box retailer, we know what they’re buying. But when it becomes an e-commerce order, the customers there want a lot more variety in what they’re actually ordering. If it’s going through an Amazon or other online product service provider, those online sellers are creating their own portfolios of product offerings. Like in the example of the chocolate bars, instead of having a standard three-and two-product [multipack] format, they will want to make a four-and one-. They’re constantly shuf ing. It puts the manufacturer a bit on edge, having to be able to provide that variety, that exibility, because we don’t have it inherently. We never had to worry about it before. If you had a 72-count package, that’s ne. But somebody says, “Hey, can you do that, but in a 58-count?” I don’t know, but I guess we have to now.
These are things that are constantly pushing to the forefront, and I don’t see any evidence they’re going away. Some people thought it was a fad, but I don’t think it’s a fad. I think it’s here to stay.
who-knows-what, we have to be able to make sure that the equipment can do these things. And that’s not always the case. Sometimes the I get the impression that the lm providers are maybe a step or two ahead of the machines. But then sometimes, I think the machines are a step or two ahead. I think it’s a constant in a leapfrogging in technology.
You and I just sat through a session from Nestlé Waters on predictive maintenance. Does that match up with some of what you’re doing at Mondele-z?
The Nestlé Waters presentation was right on the money because there’s a tremendous amount of maintenance and repair in what we do. It’s not sexy, and not a lot of people get interested in it. But there’s a tremendous amount of money to be had there, a tremendous amount of waste, and a whole lot of wasted manpower with people doing things they shouldn’t have to do. I think it’s actually a bigger opportunity than the actual asset acquisition. When I think of assets or liabilities, there’s still big-time untapped money there.
What we’re trying to push at Mondele - z is what we call AMPM, which stands for Autonomous Maintenance, Progressive Maintenance.
If it’s done right, it’s done by the operator. In the old days, you’d tell them to change all the bearings on, let’s say, a belt. Now, you don’t necessarily need to change all of them as frequently as you used to, but you may need to change two or three of them even more frequently. It depends on a lot of factors and a lot of analytics. What was interesting I thought, particularly, about the gentleman from Nestlé Waters is they’re trying to figure out exactly those data, those criteria to ask, “When do I do what I have to do?” It has been per
Interested in the latest packaging and processing trends? Don’t miss PACK EXPO Las Vegas 2023, where a multitude of cutting-edge packaging and processing innovations will be on full display. For more information, visit packexpolasvegas.com
schedule, and now it’s changing to as needed. And I think that’s the future because at the end of the day, if you do things based just on a schedule, you end up replacing things you don’t need to replace.
The analogy is that many years ago, when movie theaters use projectors with bulbs, they used to replace the bulbs every seven or eight weeks, whether they were burned out or not, because they didn’t want to burn out a bulb during a movie. But that was
With Sidel solutions to support you, going circular needn’t be a burden.
You can reduce with X-Lite, the world’s lightest PET bottle; EvoPack™ and Stryon packers, granting -15% repacking and -50% plastic. You can grow in r-PET leveraging our 20 years’ experience and our new PET recycling pilot plant. You can save up to 60% energy and water with our tunnel machines for refillable PET and returnable glass
Sidel, Empowering Sustainable Futures.
sidel.com
a tremendous waste. And to some degree, we were doing the same when we replace things like bearings that need not be replaced. Autonomous and predictive maintenance, which is driven by the operator, first off makes us more efficient because the operator knows best. And number two, we’re only we’re focusing on the things that are higher priority and the things that are critical. I think that’s really the future, and when you can do that, it means becoming more efficient at the plant floor.
What kinds of trends are you watching among your equipment suppliers?
The industry was going through consolidation some years ago, and it still is to some degree. No matter how many consolidations there are, there are always new players coming on. In fact, I’m constantly amazed that there’s always new companies out there. They may not be startups, but there’s always small and mid-sized companies that show up at these shows with a brand-new idea, a brand-new solution that you would not have expected to see before. It’s these upstarts, they’re coming out of left eld, but you see what they’re offering and say to yourself, “Well, that’s pretty clever.” They’re not in every corner of every hall, but if you have your eyes and ears open, you can see them and that makes the trip worthwhile, right there.
EPC encoders provide motion feedback designed for packaging, printing, and marking, and are manufactured in Idaho, USA. Contact us to learn more.
Can you share any examples that you’ve seen here, without giving away your specific OEM or supplier reconnaissance?
The integration of the most modern automation components in primary and secondary packaging is the biggest leap forward I’ve seen. When you get all the way down to a palletizer, let’s say, that has not fundamentally changed. You’re still wrapping lm around a pallet, and that goes into the warehouse. Where you get further upstream to where the product is being handled, and to the primary and secondary packaging, that’s where these advances are coming, in my view. They’re most evident and visible there.
It’s now faster, it’s now more exible, and it’s now lower cost, and you’re getting all three of those things. In the old days, they used to say, “cost, quality, and speed [of delivery], pick two, you can’t have all three.” What we’re nding is all three of them—it’s the speed, it’s the exibility, and it’s the cost—all three dropping, which is an interesting intersection of the three of them. Moore’s Law [of a technology’s price trending down as quality and utility trends up, over time] isn’t a bad analogy.
As for a specific example, one thing I’ve noticed is that when they’re loading products into a carton, first of all it’s faster than it used to be. And now you can actually mix different product into the cartons, you can have a variety, you can mix product into the packages in different orders or in a different sequence. You couldn’t do that before.
Depending on how you configure the equipment—or the programming I should say—you could be loading cartons with red product, and then choose one pack to be half red and half blue, then go back to all red. And that’s just based on the on the commands being applied to the automation, without disruption and without stopping. That’s something where I don’t think industry has caught up to the tech. The technology is there, but we as an industry haven’t figured out how to use it yet.
I think it’s going to continue to get better, but I think we’ve only started.
When you come to a trade show like this, it’s almost like a child going to toy store. You say, “I’d love to have that, that, and that too,” even though you might not know how all those things would t or solve a problem. So you have to prioritize, because Santa won’t give you every present. You have to determine what are the technologies that are the future. There’s going to be constant product improvement and development, and if one keeps one’s eyes and ears open, you’re going to nd good options.
—Matt Reynolds
When you come to a trade show like this, it’s almost like a child going to toy store. You say, “I’d love to have that, that, and that too,” even though you might not know how all those things would t or solve a problem.
What is your background in the produce industry?
I have a bachelor’s and a master’s degree in postharvest. I was dealing with owers to start with, and just when I was ready to go on to get my PhD, I got a position with a Canadian company called SunBlush. They came to Israel and were looking for someone to run their R&D. Israel at that time was a very big ower exporter, shipping owers to Europe, mainly to the ower auctions in Holland. The idea was to be able to pack the owers and move them to sea freight rather than air freight. So all good reasons start with the cost of shipping and the impact on the environment and the volume and so on. I joined the company as R&D director, and later on I managed the company.
We came up with a very good solution when working with the Dutch auctions. We proved that we could keep the flowers in boxes. At that time, we used boxes that were coated on the inside and created a modified atmosphere condition to preserve the freshness of the flowers and allow for the expected vase life after the flowers were unpacked. In early 2000, I moved to a flexible packaging company, StePac, when modified atmosphere packaging [MAP] was really in its infancy.
At that time, there were maybe two or three companies dealing with MAP. It was Amcor in Australia with its LifeSpan brand, and there was StePac in Israel with Xtend. These two companies primarily led the industry with the idea of reducing food waste and successfully delivering fresh produce from one area to another. For example, to export melons from Brazil to Europe, you could do it either by air, which was very pricey, or by using MAP, you would be able to deliver them by both, which made it a feasible business and also a very successful one.
When you say MAP was in its infancy, do you mean for produce packaging or overall? For produce it was never used before. At that time, SunBlush was in this business, but it was dealing with MAP packaging or gas- ushed
packaging for the fresh-cut industry. The fresh-cut industry at that time also just started. You could see some pineapple chunks from Central America shipped to the U.K., but mainly it was fresh produce. There are three major modified atmosphere solutions for produce. So there is MAP, which can be either active or passive. Active means that you gas flush the packaging with the composition of gases that you want, and the packaging will then maintain it at that level throughout the storage time. If it’s passive, a [semi-permeable] film is wrapped around the produce. It can be bulk or a box or an individual fruit. And through natural respiration, the gas composition—meaning oxygen and carbon dioxide—inside the package changes over time and basically levels at the requested or required combination optimal for the product.
In addition to that, there is controlled atmosphere, which normally deals with either very large storage rooms or containers where you create the specific atmosphere inside with a combination of oxygen and carbon dioxide. This will allow, for example, apples to be stored almost 12 months under the right conditions. That’s being done by large companies.
So, back to my experiences: I was working for StePac, and I was relocated to the States and started a business there. One experience I remember from that time is when I was visiting the market in Montreal, the Terminal Market. I was looking at the delivery of bags that weren’t under experiment yet. In talking to one of the melon shippers, I said, “We have a great solution, great packaging for melons, and we’re successfully shipping melons from Brazil to the U.K.” And he said, “I don’t want to hear about bags, and you want to know why? Come with me, and I’ll show you six or 10 pallets with rotten melons.” And I was looking at the pallets, and I said, “Okay, it all depends on which kind of packaging you’re going to use.”
So one bag is different than another bag, and there are so many characteristics within the gas-exchange rate. It’s called the oxygen vapor transmission rate, or OVTR. All of these attributes dictate the outcome of the storage in that particular packaging. So, if you use the right packaging, you could hold these melons for 25 or 30 days, and they will look just as fresh as when they were harvested. But if
In this Q&A interview, produce packaging expert Shay Zeltzer, founder of Postharvest Hub, shares his concerns over the trend toward paper packaging for produce—a trend adopted to appease consumers’ concerns about plastic, but in many cases fails to protect the product.
you put them in a bag that accumulates moisture inside and builds condensation, you’re going to end up with mold growth.
There are many stories around the selection of the right packaging for the right product. And that basically sums up the main issue— each commodity has the optimal packaging for it that will preserve the freshness and extend the shelf life. In some cases, you’re not necessarily looking at extended shelf life, you just want to keep the product fresh from the time it’s been harvested until it’s consumed, even if it’s just a couple of days. With lettuce, with green beans, we’ve shown that with the right packaging, you get exactly what you harvested. Without packaging or with the wrong packaging, you’re going to increase waste.
After working for StePac, I came back to Israel, and I started my own company working with different packing houses in Israel and abroad, developing protocols for handling fresh produce and working with companies to develop packaging in that particular area.
You have said that the produce industry is moving in the wrong direction by switching from plastic to paper packaging. Can you explain why?
One of the largest fresh produce exhibitions in the world is Fruit Logistica. I’ve been going to the show for about 15 years, and every time I attend, there are new trends, new ideas, normally you’d see new varieties [of produce], new machinery. This time the packaging section was converted, I would say almost all of it, to paper-based packaging.
So instead of PET trays there were pulp trays. Or, fiber-based packaging with or without a plastic mesh. I was at one booth, and I was looking at flat green beans, and I told the exhibitor, “The green beans are flabby, they’re not holding up.” And he said to me, “But, if you go to Europe, France, and the U.K, that’s what consumers want now.” In addition, the EU decided they want the industry to stop using plastic altogether, but it’s not protecting the product. That’s the regulation. That’s the trend. That’s where the market goes. People don’t want to see plastic.
You have said that using paper is nothing but a trend that’s leading to ecological disaster and taking a huge toll on the planet earth. Can you expand on that? What do you mean by an ecological disaster?
Yes. You live in the States, right? And when you go to the grocery store, in some cases, where they help you pack your groceries, they’ll ask if you want them in paper or plastic, right? And if you say paper, they’ll take one paper bag and then they’ll put another paper bag inside the rst one. So it’ll be a double paper bag. Then they’ll put your groceries in this double paper bag. Why do they do it? Because the paper bag is not as strong as a plastic bag. So they want to be green, but they don’t want your groceries spilling all over the oor. So the rst thing is physics. If you want to have the same strength, the same puncture resistance, you have to use much heavier, much thicker paper compared to plastic.
So that’s one thing. With that goes the volume you’re going to ship. Let’s say, in a specific-size case, you can fit 2,000 plastic bags. You can only fit one-quarter of that or even one-fifth of that of paper bags in an equivalent-size case, just because of the volume.
The other thing is that when you cut a corrugated box, there are two sheets, and then there is the fluting in the middle. The fluting is recycled paper, and the other sheets are normally virgin kraft liner. Virgin kraft means it’s the first use of this fiber. When you recycle it, you can only use it for the fluting. Why? Because it’s softer, and it absorbs moisture much, much easier. So if you want to go in the direction of packaging that will not be humidity-sucking paper, you’ll have to opt for the kraft liner. Kraft liner is a single-use paper.
So it’s misleading to say that paper is reusable. You can reuse it, but you can’t reuse it for the same purpose. You can reuse it maybe for books or for newspapers or for egg trays, but you can’t use it for the same purpose. You can’t take a paper bag that was used for fresh produce and make a paper bag again that will be as strong as the original one to be used for the same purpose.
The third issue is with the condition of the produce itself, mostly
of fresh produce. If it doesn’t have a specific peel that will resist dehydration, it tends to lose moisture. We’ve done some research on green beans grown in Mexico, shipping them to Canada, and we saw that in order to compensate for the weight loss along the journey, the growers have to pack 10% more product. Meaning that over the journey of five days from Mexico to Canada, the produce loses about 10% of its weight. So, since the retailers in Canada dictate that they want 30-pound crates, and they’re going to fine the grower if it’s underweight, the grower will overpack it with some extra in order to compensate for that loss.
The loss from moisture?
Mainly from moisture. That’s one major element. I’m calling it the silent thief that steals revenue from the store. Because even produce on the shelf gets dehydrated. And when a retailer buys say 30 pounds of cucumbers, even if they sell everything and nothing goes to waste, they’ll nd they only sold 28 pounds. Why? Because two pounds evaporated. When produce loses about 2% of its weight, it becomes soft. And people don’t like to buy soft fruit. Soft, abby vegetables are especially not wanted—not lettuce, not green beans, not cucumbers, not carrots. If it’s abby, it’s going to be left on the shelf. So that by itself increases waste because people are not going to purchase it.
We were doing research the other day on lychee [fruit] in Israel. The company wanted to switch from PET trays to pulp-based trays. What we’ve seen is that the pulp oftentimes gets pathogens in it. Fungal spores rest there and stay. Then when you pack the product, it affects the produce within. Plastic doesn’t have a porous surface. Normally the lychee comes from high-temperature production and then wrapped in a large plastic bag and put into a massive carton. The fiber-based packaging is very porous. This makes it very easy
for the fiber to absorb or make space for pathogens to rest and proliferate.
These are several reasons why moving to paper-based packaging for produce is going to be a disaster. Now also, if you look at the production of paper versus the production of plastics, the production of paper is lengthy and consumes a lot more energy. So let’s say from delivering the wood from wherever it is, to the wood processing facility, and to extract the cellulose, and then turn it into paper, a lot of water is consumed. It’s also a high-energy process versus the production of plastics. So combine all these together, and paperbased packaging is going to take a lot higher toll on planet Earth compared to plastics.
If, by using paper for produce packaging, you’re wasting product, then plastic appears to be the better choice. Yet, the perception by consumers is that paper is more environmentally friendly. Perception is horrible because we can’t argue with perception. You see it, and it looks fresh, or you see it, and it looks green, and that’s it. And you don’t have to say a word. And then you see the islands of plastic in the ocean or plastic rolling onto beaches, and say no more. Now plastics have to explain themselves and have to go through a lengthy interview and explanations. But paper, you see it and it’s green and it’s wood—it’s plants. It’s so easy to understand why it’s better for the environment
In some cases, paper actually may be the better choice, depending on the product. But in the case of produce, it seems to be defeating the purpose of using the packaging. There are some produce items that don’t need any packaging, in some cases, paper might be the right solution. But to go across the board and ban plastic and say no more plastic… . I’ve been trying to reply to posts on LinkedIn and articles over the years, but it feels like my voice hasn’t been heard. In the U.K., they were saying that
Bringing unsurpassed accuracy, efficiency, reliability & support to your packaging systems for more than 50 years. All-Fill packaging machines are engineered to excel with configurations built to outperform your production demands.
packaging was wasteful, and they were dictating to the growers to stop packaging cucumbers, but cucumbers dehydrate so fast. And I said, it’s only going to increase the waste, and it’s going to increase the waste immediately—not tomorrow, not a year from now, but immediately with the next arrival. If it’s not in the right packaging, it’s going to get dehydrated, 2% every day, and the consumer is going to leave it on the shelf.
Are you seeing other trends in produce packaging, or is the trend really just toward paper?
The change is mainly toward paper, and that was very signi cant at Fruit Logistica. With that being said, there is one particular machine by a Dutch company called BrimaPack. The owner started the company almost 20 years ago, and year after year, he had the same small booth with one machine. Over the last few years, however, it seems that growers and large shippers have begun to appreciate the bene t of his equipment. It uses a very ne lm of about 12 to 15 microns. In terms of mils, I think it’s maybe 0.6, 0.5 mil. It wraps around the product with a very minimal surface area of plastic and creates a heat-seal knot at the bottom of the produce. It’s mainly used for round vegetables, such as iceberg lettuce or cauli ower or broccoli.
It’s only this year or last year that U.S.-based companies started using it. Only with that can you reduce about 40% of plastics, and that’s the direction the market should go—to reduce plastic, but reduce it while not compromising the product itself.
What do you think about materials such as bio-based or compostable plastics for produce?
That was a trend maybe 10 years ago, when people were looking to replace plastics. One product they looked at was PLA [polylactic acid], which is derived from corn or sugarcane or sugar beet pulp or cassava. The material is clear, it looks like a bag, and it performs like bag. But there were several issues around it. First, because it’s made of a feedstock used for human consumption like corn, it drives the price of corn higher. The other thing is that its weight per volume is about 20% to 40% higher than for the equivalent polypropylene or polyethylene bag.
The other issue is that it’s very susceptible to heat and exposure to UV light, so it deforms very easily. We tried using it as a substitute for trays in Mexico, and if the trays were kept in storage exposed to the sun, not even direct sunlight, but just under the shade where the temperature rises, they deformed over time. So for that reason, and also for the price difference, people are not adopting it. People talk about PLA here and there, but it never catches on.
There is an Israeli company that is using something similar to PLA. I had some experience with this material, and normally it’s thicker, it’s cloudier, so a hazy or a milky color and a lot more pricey than alternative plastics. So again, it’s only for particular applications where people are willing to pay more for the packaging or are willing to compromise on the presentation, because it’s not as clear, and you can’t really see the produce within. But people are really keen to see what they’re buying.
That’s another reason, by the way, that paper-based packaging
is also problematic because you can’t see the product inside. That’s why some of the paper packaging includes a window with plastic mesh so you can kind of see what’s in the bag, but it’s very likely that people will either care and will check or won’t buy it.
If you were advising produce packagers or any food or beverage company that is thinking about switching from plastic to another material that consumers perceive as more sustainable, what would you say?
The rst thing is to work with professionals who specialize in this area. Find out what’s best for the product. We’re investing a lot of effort and money and energy and enthusiasm into growing the best produce. And then, by the same token, we have a post-harvest specialists who know exactly what packaging is most suitable for the product. So work with the professionals and with the companies that specialize in developing and producing packaging that is most suitable for the product. The other thing is to look for the packaging that best ts the product in terms of size and protection.
Mini, or Persian, cucumbers may be more attractive in a heavy-gauge plastic bag with graphics, but, according to Zeltzer, the large amount of plastic used isn’t necessary to keep the products fresh. In addition the use of graphics adds chemicals in the form of ink, while complex closures may hinder the recyclability of the packaging.
In many cases, if you go to, for example, Costco, you’ll see that mini cucumbers or Persian cucumbers will be packed in a high-gauge, plastic bag with a slider or zip lock. And it’s not really necessary. They also use very fancy graphics. I can’t argue with the graphics, the bag really looks beautiful. But first, there is a lot of ink, a lot of chemicals in the packaging. In addition, the high-gauge plastic bag is not necessary. The slider is nice to have, but it’s another material that makes it more complicated to recycle and increases the price of the packaging. So select the simpler, less expensive packaging solution. As conscious consumers, we should opt for packaging that protects the commodity, but not overpackaging. —Anne
Marie MohanThere’s a U.S. Supreme Court case that might soon undo one of the most basic rules-of-the-road about how our federal government works. If it does, all kinds of government regulations would be much easier for courts to overturn. And if that happens, unpredictability will be the new rule-of-the road for your business and life.
Although the past year brought many consequential Supreme Court decisions, this one, likely to emerge next year, could have perhaps the biggest effects on packagers of any decision in decades.
The case is called Loper Bright Enterprises v. Raimondo, and you can examine it for its specific details or its general themes. Specifically, it involves a challenge to regulations made by the Biden administration’s National Marine Fisheries Service that require fishing boats to pay for onboard monitors to make sure they don’t over-fish. The challengers said the law told the agency to require monitors, but didn’t say the agency could require the fishing boats to pay for them.
However, its more interesting general theme is this: The case also raises the question of whether the courts should continue to follow the doctrine from the 1984 “Chevron” case. That case, which involved EPA air pollution rules, established the concept that when courts review agency rules or other actions that involve interpretation of a law, and that law is silent on a topic or ambiguous in some way, the court will only check to make sure the agency’s interpretation was “reasonable.” If the agency’s interpretation was reasonable—that is, not nutty or clearly beyond the scope of Congress’s instructions—it would be upheld. In a word, the Chevron case says the court should “defer” to agency interpretations unless they’re not reasonable. (And by the way, if the law Congress made was clear, the court would simply check to see if the agency did what Congress instructed.)
What a judge should not do, according to the Chevron case, is substitute the judge’s own judgment for that of the agency about what should be the right interpretation of a law.
By telling courts to defer to an agency interpretation unless the interpretation is unreasonable, the Chevron doctrine meant courts almost always upheld regulations when they were challenged in court for being wrong-headed or unconstitutional in some way. Many judges and other observers say that a big reason to defer to agencies is that those agency folks have the subject matter expertise you’d want them to have if they’re going to make rules on a particular topic. Regulatory agencies have people in them, ideally, with training and education and experience that makes them appropriate folks to decide how to limit air or water pollution, or decide whether a new drug is safe and effective enough to go to market, or choose where to build an interstate highway, or where to store nuclear waste, or how to prevent over-fishing of the oceans, and so on.
The Chevron case has been cited by 19,000 other cases, according to the San Francisco Chronicle, and more importantly, it’s been a
fixture in legal doctrine for almost 40 years, relied on by industry and regulatory officials alike.
Clearly, when you defer to agency decisions most of the time, you give those agencies, rather than Congress or judges, lots more power.
(This discussion might bring to mind the recent judge’s ruling that invalidated FDA’s approval decades ago of a drug used in abortions. That ruling didn’t mention the Chevron case, oddly, and I predict the Supreme Court will find the plaintiff doctors in that case didn’t have standing—the legal right to sue—to bring the case in the first place.)
Several current Supreme Court justices have expressed displeasure with a system that allows so much power to be given to agencies, and some of the Court’s recent decisions have created workarounds from the doctrine. The most notable is the Court’s creation of a “major question doctrine” that says the Court need not defer to agency interpretations, even if they’re reasonable, if the decision implicates far-reaching matters. Their objections to it include the empowerment of agency officials who voters have no control over, as well as the fact that giving agencies so much power to decide things and fill in details about policy issues is giving them legislative power that is Constitutionally supposed to stay with Congress.
This is really just a debate over the old “three branches of government” idea that you probably learned in school. The idea is that the U.S. Constitution requires the legislative, executive and judicial branches to stay in their respective lanes, with the legislative (the House and Senate) making laws, the executive (headed by the President) implementing and enforcing laws, and the judicial (the Supreme Court and lower federal courts) interpreting laws.
If Chevron is overturned and you won’t be able to expect most regulations to be upheld, predictability for business goes way down, and the costs go up of adapting to regulations that come and go more often and more quickly.
There are echoes in this case of the kind of blind anti-expertise bias that seems to infect too many public policy issues these days— “The purpose of the regulations doesn’t matter to me, and all I know is that your alleged expertise restricts my freedom.” Well, maybe, but how else would a complex society address issues that affect everyone’s safety and fairness?
Sez me, the solution to the problem of agencies having too much discretion is that Congress should make its laws less ambiguous. The solution shouldn’t be to take discretion away from regulatory officials and give it to judges for gosh sakes, over whom voters really have no recourse (we don’t vote for them), and who may or may not have even the slightest expertise in the relevant area. Since several Supreme Court justices have already expressed exasperation about the Chevron doctrine, the good advice for all packagers is to keep an eye on this new case. But, if the common prediction is correct that the doctrine will be undone, be ready next year for a rupture in the foundation of our regulatory system, and a huge increase in unpredictability. PW
“In the South Hall, Booth #6101, Harpak-ULMA will display a complete packaging line featuring everything from an advanced G. Mondini tray sealing system to automated case packing and sophisticated collaborative robotics! Booth #6101 will also exhibit other exciting options from G. Mondini, including the Cigno (Cheen-yo) compact tray sealer and their Neural Vision Inspection system. But Pack Expo has more in store for our visitors!
In addition to these thrilling offerings, we’re presenting other exciting DSSOLFDWLRQVVXFKDVVWDWHRIDUW8/0$ÀRZZUDSSLQJVROXWLRQV today’s top vertical bagging machinery, and skin pack and medical thermoforming options to give you a full cadre of packaging choices you won’t want to miss!”
Flexibility has always been a key component of our packaging solutions. There’s no better example of that than our brand new Trave Sinfonia tray sealer from G. Mondini!
This cutting-edge system provides unparalleled control over the production line – the result of years of research and development to improve manufacturing processes’ speed and precision. With the Sinfonia, each tray is precisely controlled in position, velocity and acceleration – allowing the most accurate handling of the product.
Harpak-ULMA Packaging will prominently display the new Trave Sinfonia at our SECOND BOOTH, Booth#6188, steps down the South Hall from Booth #6101. Come join us, and discover the future of advanced tray sealing for today’s modern market.”
// Nests act as carriers for the trays, and become the complementary part of the tool during sealing
// $GDSWLYHÀH[LEOHFXVWRPL]HGSURGXFWLRQ
// Flawless position control
// High-speed transport
// Q XLFNUHFRQ¿JXUDWLRQV
Packaging is a potent, versatile, multifaceted tool that can be the source of a competitive advantage. That lofty potential most frequently is ful lled through projects. In contrast to individualized day-to-day work, a project is a team undertaking. Its purpose is to achieve a desired outcome, within speci ed constraints of scope, cost, and time. By de nition, projects are inherently complex; there is no such thing as a simple project. Project management entails all the efforts required to keep the train on the track. Ef cient project management, therefore, is indispensable. Otherwise, prospects for a successful outcome are miniscule at most.
Packaging projects run the gamut in diversity, from package research, design, and development to the installation of packaging lines—and everything in between. The justifications for undertaking packaging projects are equally diverse. The demand for packaging derives from the demand for the contained product. Changes to the product can beget changes to the packaging, thereby triggering projects. Packaging, furthermore, is among the most regulated of disciplines. Consequently, regulatory changes can trigger projects. More recently, the sustainability era continues to generate its share of projects.
Packaging professionals, perhaps more so than other team members, are suited for project work. That’s because packaging is interdisciplinary, necessitating a systems approach to manage tradeoffs among the competing and conflicting preferences of the various stakeholders, true even of day-to-day work. Such experience, carried over to project work, is valuable in operating within team dynamics.
Newly minted graduates of the various university curricula in packaging, nonetheless, don’t enter the workforce with a strong foundation in project management. Universities don’t fulfill the entire demand for packaging professionals. As such, some professionals are transfers from other disciplines, with modest backgrounds in project management. Whatever their route of arrival, it’s a near certainty that, at some point in time, if not repeatedly, the vast majority of packaging professionals will be involved in project work.
Despite the aforementioned diversity of packaging projects, each project should be conducted within the same structure—one designed for consistently acceptable results. Unfortunately, reality can be different. An example is an ad hoc approach, wherein freelancing reigns. Another example is when there is a supposed company approach to projects, but teams deviate from it under crush circumstances. It comes down to this: any structure for project work and the management of same should be built upon certain
fundamentals. No fundamental is more fundamental than the concept that a project begins, proceeds, and ends. The resulting life cycle has five stages: initiation; planning; execution; monitoring & control, and close.
• Initiation. Even the start has to be preceded by certain matters. Chief among them is authorization. The person of authority needs to be provided convincing information. The information needs to be collected, organized, and presented, which can constitute a miniproject, in itself.
• Planning. This is the roadmap, or, by a different analogy, the play book. These things must be made clear: what is to be done, how is it to be done, who is to do it, and when is it to be done. The relationship between the plans and the desired outcomes (aka the deliverables) should be readily apparent, so as to rule out conjecture.
• Execution. Here, team members are carrying out their assigned tasks and responsibilities, but not in isolation. Coordinating and communicating are vital. Unavoidably, the going is not always continuous and smooth. Members who excel at this stage are those who are agile and find ways around temporary bumps, continuing while matters are being righted.
• Monitoring & Control. “So, how is the project progressing?” That’s a question that might be asked at any time by a nonmember stakeholder. A reliable answer can be given if this stage of the project is being well-performed. The setting of milestones (established in the planning stage) is among the proven aids at this stage.
• Close. Projects are put to bed, but not to death. The company lives with the outcomes going forward. An honest and objective closeout assessment should specify what went right and what went less so. It gives useful perspectives that can be applied to other projects.
Although the five stages are logically sequential, progress does not always proceed sequentially. It is not uncommon for some stages to be repeated. Something discovered during the monitoring & control stage, for example, can justify a return to the execution stage, or even a return to the planning stage. The back-and-forth might undergo more than one iteration, also. With each iteration, there is a consequence in time and in cost.
There are various methodologies, charts, templates, and software that purport to be tools for effective, efficient project management. They don’t, however, justify giving short shrift to the human interface element of project management.
Next month’s article will address why packaging projects fail, so stay tuned. PW
Project management entails all the efforts required to keep the train on the track. Ef cient project management, therefore, is indispensable.
In every CPG category and market, efforts are underway to eliminate single-use plastic packaging when and where it makes sense. One area that has traditionally lagged behind, though, is the healthcare market, primarily OTC and pharmaceutical packaging. However, startup Cabinet Health has come up with a solution that it says has the potential to transform the industry, making it more sustainable— “from retail and pharmacy aisles to medicine cabinets and homes.”
Founded in 2018 by Achal Patel and Russell Gong, Cabinet Health: The Sustainable Healthcare Co has developed a reusable and refillable packaging system whose components include a stackable, shatterresistant and reusable glass bottle paired with refills in a compostable pouch. Its initial products, a line of OTC meds under the Cabinet brand name, first became available via D2C. In May, the portfolio, which includes allergy, pain, cold and flu, digestive, and sleep remedies, launched at retail in 700-plus CVS pharmacy stores nationwide.
Gong shares that he and Patel came up with the idea for Cabinet while they were working abroad running a social innovation program for a consulting group that focused on identifying mission-driven and sustainable startups and helping them scale as businesses. “We saw firsthand the impact of the plastic crisis and saw other industries coming up with innovative sustainable packaging solutions, but no large healthcare players were successfully tackling this issue yet,” he says. “We combined our backgrounds in sustainable startups and medicine [Patel’s grandfather built one of the first acetaminophen factories in a small town in India] to reimagine people’s medicine cabinets.”
Reflecting on the scale of the plastics crisis, Gong shares that more than 194 billion plastic medicine bottles enter landfills each year. Furthermore, studies show that humans consume nearly 5 g of microplastics each week, which is roughly the size of a credit card. “The plastic waste crisis is a public health crisis,” he says.
In developing the plastic-free reusable packaging system, Gong relates that Cabinet started from scratch, doing most of the work in-house, but did bring in some “amazing specialists and partners along the way.” The cube-shaped medicine containers, he shares, were developed with both form and function in mind. Available in a small and large size, they are made from glass, frosted to preserve the
contents, and shatter-tested for durability. They are also stackable for easy organization on consumers’ medicine shelves.
Says Gong, “With a low, square profile, the Cabinet system takes up a fraction of the space in your medicine cabinet that traditional bottles do—a dream for minimalists, aesthetes, and anyone who could use the extra storage space.”
Topping each bottle is a colorful child-resistant square plastic cap with a bayonet locking closure and integrated magnet. Nestled inside a concave area on the top of the closure is a separate, removable magnet upon which is printed directions for use of the medication, expiration date, lot number, and other required information, as well as a QR code consumers can use to order medication refills.
For the refill packaging, Cabinet chose a proprietary material that is compatible with both home compost devices and industrial composting facilities. According to Gong, the company is also currently waiting on backyard-compostable certification. Along with
the capsules or tablets, each refill pouch also holds a new snap-in magnet specific to that batch.
“Cabinet’s system uses glass, compostable flexible films, and aluminum,” Gong says. “We indexed on hyper-recyclable materials with compostable films being our path forward for earth-digestible materials. We looked into a whole host of other materials, but ultimately we needed to balance regulatory quality, cost, design, and sustainability.”
According to Cabinet, by switching to the brand’s refillable system, a consumer can eliminate up to one pound of plastic annually and hundreds of pounds of plastic in a lifetime. To arrive at that estimate, the company calculated that, on average, a single empty bottle is made of 3.75 oz of plastic and that, also on average, consumers purchase about five refills of a given medicine per year.
“Oftentimes, pills expire before they’re able to be used, or even worse, expired pills are consumed,” says the company. “Cabinet medicines come in lower pill counts than some bulk medicine offerings to minimize pill waste. With that in mind, we factored in a 0.85 to 1 ratio to account for us offering fewer pills per purchase than competitors in some cases.
“Based on the above variables, we estimate that when you buy a Cabinet medicine starter set [reusable bottle with medication
plus one refill], you are eliminating one single-use plastic medicine bottle immediately, plus four more via compostable medicine refills throughout the year. Multiply that by 0.85, and you are eliminating one pound of single-use medical plastic per year.”
The company’s products are manufactured in India, using FDAapproved active ingredients. Cabinet pays for carbon offsets to account for the transport of the product and make the supply chain less damaging for the environment.
Interested in learning more about sustainable packaging? Don’t miss PACK EXPO Las Vegas 2023, where a wide range of sustainable packaging solutions will be on full display. For more information, visit packexpolasvegas.com
The next step in Cabinet Health’s journey to “de-plastic pharmacy aisles and medicine cabinets across the country” is the use of its packaging system for prescription pharmaceuticals. This summer it began beta testing of its full-service Cabinet prescription services. For this application, the company has designed a CR pouch for refills.
In the future, Gong says Cabinet plans to offer packaging formats to accommodate other form factors, such as liquids and creams. PW
The American National Standards Institute (ANSI) requires that standards be revised and updated every ve years. As a result, for the last two years a committee at PMMI (an ANSI-accredited standards developing organization) has been working to revise the technical requirements of the ANSI/PMMI B155.1-2016 Safety Requirements for Packaging and Processing Machinery standard. The work has recently been completed and a new ANSI-approved version of the standard is expected to be published and made available soon.
risk assessment begins, and presents the basic risk assessment process in a step by step approach to assist in achieving this goal.
The outcome of completing the risk assessment process should be:
• Packaging and processing machinery ready to ship, install, or use with risks reduced to an acceptable level;
• Information for use and awareness means provided to address residual risk; and
• Documenting the results of the risk assessment process. The standard applies risk assessment, but does not replace good judgment and personal responsibility, as personnel skill, attitude, training, and experience are safety factors that should also be considered.
According to Bruce Main, president of Design Safety Engineering, Inc., and vice chair of the PMMI B155.1 Standard Committee, as well as a technical advisor to PMMI, the updated version adds some requirements for contract packers (co-packers) and co-manufacturers to address current practices and responsibilities. In addition, “we’ve updated some of the de nitions, and we’ve added some requirements for processing, remote operations, and cybersecurity,” he says.
The objective of the B155.1 standard is to eliminate injuries to personnel working with or around packaging and processing systems by establishing requirements for the design, construction, reconstruction, modi cation, installation, set-up, operation, and maintenance of packaging and processing machinery systems. Responsibilities have been assigned to the supplier, the user, and the user personnel to implement this standard.
This standard guides packaging and processing machinery suppliers and users through a risk assessment process designed to ensure that reasonably foreseeable hazards are identi ed and corresponding risks are reduced to an acceptable level. In this standard the terms “acceptable” and “tolerable” are used as synonyms. Although engineers have long applied an informal risk assessment framework, this standard introduces a formal method to conduct and document the risk assessment process.
B155.1 identi es some preparations that need to be made before a
The development committee for B155.1 includes new contributors to provide deeper insights from machine builders, consumer packaged goods (CPG) manufacturers, and technology suppliers. And the document outlines responsibilities of each role. For machine builders, speci cally, the updated standard clari es the responsibility of the OEM and the end user.
It also addresses machinery as a service (MaaS), including equipment loaned or provided by a third party and located in a user facility, as well as mobile platforms, robots used for logistics, cleaning, and more. The document states that “Machinery as a service involves machinery or equipment that is in use in the user’s facility, but not owned by the user. In some instances, the user may be prohibited from operating, maintaining, or modifying the machinery.” That puts a lot of responsibility onto the machine builder, especially as it relates to cybersecurity and remote control functions.
To that end, cybersecurity is addressed in the standard, noting it should be considered as part of the overall machine risk assessment. And the document outlines a list of requirements if a machine can be remotely controlled.
The 2023 edition of this American National Standard on the Safety of Packaging and Processing Machinery (ANSI/PMMI B155.1) includes updates in the following areas:
• Reorganization of clauses 4 and 5
• Additional and updated definitions
• Clarifications to the scope
• Updated/improved annexes
• Clarified text related to responsibilities of machinery suppliers, users, modifiers, purchasers of used machinery, and others
• Introduced concepts of co-packer/co-manufacturer and associated responsibilities
• Updated and clarified responsibilities for existing (legacy) machinery
• Included requirements for when whole body access applies
• Improved information about validation
• Improved information related to remote / tele-operations of machinery
• Expanded requirements for radiation hazards and associated risk reduction measures
represent
Modular Conveyor Express and get your conveyor systems and equipment in 3-4 weeks!
•Product Flexibility: Quickly introduce new products into inventory
•Process Flexibility: Modular conveyor systems with standard designs
•Cost Flexibility: <3;'93£<ধ329>-;,36ধ329(38'='8@683/'$;blueprint
• New requirements for heated systems and related equipment for processing of materials
• Updated requirements for information for use and manuals
• Clarified content of Table D1 on estimating severity of harm
• New annex on layout analysis
• New annexes to assist reader in applying the contents of the standard
Within the standard it lists responsibilities for components suppliers, machine builders, and machine users, so if someone were to get hurt or there is a liability claim, the standard is used to determine if the machine itself is safe.
“There are new requirements that apply to CPGs, and they need to know what those requirements are as they go about sourcing and running their machines,” Main explained. “CPGs also need to work with their suppliers as to what the end user and supplier responsibilities are. For a CPG, if you are not staying up to date with these requirements and someone gets hurt, that will be part of the discussion in a legal case.”
The latest version of B155.1 is expected to be approved in July. The rst version of the standard was approved by PMMI membership on Sept. 17, 1972 and approved as an ANSI standard on Aug. 6, 1973, and has been revised in 1979, 1986, 1994, 2000, 2006, 2011, and 2016.
The B155.1 standard can be associated with the ISO “A-B-C level” structure.
Type-A standards (basis standards) give basic concepts, principles for design, and general aspects that can be applied to machinery.
Type-B standards (generic safety standards) deal with one or more safety aspects or one or more types of safeguards that can be used across a wide range of machinery.
Type-C standards (machinery safety standards) deal with detailed safety requirements for a particular machine or group of machines.
This B155.1 standard on general safety requirements common to packaging and processing machines is primarily an “A-level” standard in that it applies to a broad array of packaging and processing machines and contains very general requirements. However, in many areas it also contains very speci c requirements typical of a type-C standard. PW
Bring your operating cost down to $0 while increasing production throughput
Say goodbye to costly consumables and downtime! The FP Series is designed as a direct replacement for Thermal Transfer Overprinters (TTO). No changes to your production machine or packaging lm are needed because of similar outer dimensions with your current TTO, as well as damage-free marking made possible by the world's rst UV laser coder.
Learn more about the FP-Series below
The MK-G Series will self-diagnose problems using KEYENCE’s proprietary sensors throughout the print head, paths, valves, and replaceable parts. After self-diagnosis, the MK-G will also run the necessary maintenance procedures automatically to ensure reliable startup or automatically recover quickly and efficiently should you run into an error during a production run.
Learn more about MK-G Series below
With big retailers becoming customers and distribution reaching 17 states, Fiesta Pacific simply had to increase capacity. They started with the case packer and worked their way back.
By Pat Reynolds, Contributing EditorIn 1980 Manuel Marruenda started a home-based business in San Diego manufacturing and distributing Horchata, Jamaica, and Tamarindo, three beverages commonly found in Mexican restaurants. The rm now supplies more than 3,000 restaurants with Fiesta beverage dispensers and bag-in-box concentrates used in those dispensers, along with sales to retailers and grocery stores.
Also made now in the manufacturing facility occupied by Fiesta Paci c since 2006 are ethnic beverage concentrates sold in 16-oz PET and 64-oz HDPE containers. Growth of this business—which has been brisk now that large retailers like Walmart have put it in their stores—is
overseen by Manuel’s son Manny Marruenda, now the president of the company. With distribution now reaching 16 states, it’s little wonder a new packaging line went into production this past January.
Considerable help in design and engineering, not to mention equipment evaluation, was provided by Russell Stone of RLS Mechanical Services, Ivoryton, Conn. A key provider of design and engineering consultation services, Stone says the line was built from the case packer back, that case packer being a 991 Unipack 2.0 from Standard-Knapp. “The case packer was really instrumental in making the line possible,” says Stone. “It has a very compact footprint considering the speeds at which
it’s running. That would be 150 bottles per minute on the 64-ounce bottles and 200 per minute on the 16-ounce.”
Standard Knapp is well known for its high-speed, soft-catch drop packers used for partitioned or partitionless cases. But this machine at Fiesta Paci c is one of the rm’s very rst gantry-style pick-and-place systems, where the picking device strokes perpendicular to the direction in which bottles are being conveyed in. With this approach, the machine footprint gets a lot smaller, says Mario Mazzotta, vice president of sales & marketing at Standard-Knapp.
“Our basic 9395 Versatron Case Packer is roughly 22.5 x 5.5 feet, or 125 square feet,” says Mazzotta. “The Unipack 2.0 running at Fiesta Paci c is 15 x 5 feet, or about 75 square feet. So it’s fair to say it represents about a 40% reduction in footprint.” Mazzotta also notes that it’s possible to add additional packing head assemblies to increase throughput if so desired.
Notable on the Unipack 2.0 is its toolless changeover feature, including self-storing changeover racks that hold the picking tool not currently in use. To go to a new bottle size, the operator presses a button on the Rockwell HMI and the servo-driven pick head automatically goes to a docking rack where the picking tool currently in use can be stored. The operator then removes a couple of
locking pins, disconnects some air hoses, and slides the tool into its docking rack. The pick head then moves to the docking rack of the tool needed for the new bottle size and the operator connects the air hoses and locking pins for that tool. With that the machine is ready for the new bottle size.
Once the case packer’s capacity was established, Stone and Marruenda moved their focus upstream machine by machine. At the very beginning of the line is a Model NEHCPCL-60 bottle unscrambler with integrated ionized air rinser from New England Machinery. An operator manually empties large bags of bottles into the unscrambler, which is also notable for its small footprint. Marruenda also likes how easy changeover from one bottle size to another is.
“It involves three areas, the rst of which is the large unscrambling bowl area,” says Marruenda. “Six acrylic parts need to be changed, and no tools are needed. Then there is an inner mold that is held in position by two butter y screws. Again, no tools needed. And nally, two screws are adjusted on an acrylic rail that stands the bottles upright. All other adjustments are dial indicators, plus one photo eye sensor adjustment. Altogether it takes about 15 to 20 minutes to change it over.”
When it came to picking a ller, one thing that was clear is that it was time to graduate from the in-line lling approach that Fiesta Paci c had always relied on and move to a rotary ller. “With the equipment we had we were lucky to ll 12 per minute on the 64-oz bottles,” says Marruenda. “Especially with the Horchata, which has a moderately viscous quality.”
Also marking a departure from past practices was the decision to go with a monoblock ller/capper. Once again it was driven partly by the need to t things into a pretty small footprint. After looking at several well-known suppliers, the machine selected by Marruenda and Stone
was a Model FSFM-246 continuous-motion monoblock from Filler Specialties. This 24-valve ller has a six-head rotary pick-and-place capper for highly ef cient capping and is able to handle speeds to 145 bottles/ min on the 16-oz size.
“Cleanliness played a big role in the purchasing decision, and Filler Specialties has a long history of producing sanitary monoblock llers and cappers,” says Stone. Also important was ll accuracy. “This ow-meter ller,” says Marruenda, “is delivering day-to-day accuracies of plus or minus .05%. That has led to huge savings, which is like icing on the cake.”
Bottles reach the ller infeed in a single le and move through a feed screw that hands them off to a starwheel infeed. Bottles are lled by way of magnetic ow meters and then move by starwheel transfer into the chuck capper for application of the injection-molded polypropylene threaded closures.
The next piece of equipment selected was a Series SL pressure-sensitive labeler from P.E. Labellers, a ProMach company. The full-wrap paper label, from DG Print Works, Inc., is printed exo in four colors plus one spot color. Just before entering the labeler, bottles get a date code printed on the shoulder by an ink-jet printer from the MK-G Series by Keyence. Keyence describes its printer as the “world’s rst self-troubleshooting inkjet designed for reliability and ease of use.”
Filled, capped, and labeled, the bottles are now ready for case packing. But rst they pass through an inspection system supplied by Tensor
FlexPak’s mission is to advance the quality, performance, and convenience of ↆH[LEOHSDFNDJLQJWKURXJKRXUDGYDQFHGODVHUWHFKQRORJ\DQGLQGXVWU\H[SHUWLVH
ID. It features two Visionscape GigE Cameras from Omron Microscan that are mounted on the conveyor along with an illumination backlight from Spectrum Illumination. A Banner Engineering laser photo sensor provides a trigger signal to the camera as a bottle passes in front of cameras and backlight. Upon each trigger signal, the cameras capture a digital image of each bottle. Pre-programmed software inspects for cap presence and ensures that each cap is completely threaded on correctly. If any bottle is missing a cap or has a cocked cap, a discrete output is sent to the inspection system’s Rockwell Micrologix PLC so that such bottles can be tracked and rejected. Worth noting is that a similar vi-
on the case packer is vacuum actuated, which means you risk sucking product up out of a bottle and into the vaccuum system of the case packer. That leads to maintenance issues that include taking things apart and cleaning them. So these inspection systems are just a huge help in eliminating unnecessary downtime.”
At this point bottles are fed in a single le toward the intermittentmotion Standard-Knapp case packer. Just ahead of it sits a CE25-ST case erector from Pearson Packaging. With a vertical case presentation and compact footprint, the case erector is a good t, notes Marruenda. It uses tape to close case bottoms.
Cases are indexed into the loading station two at a time. For the 16-oz bottles, a lane divider spreads incoming bottles into three lanes so that the vacuum gripper heads on the gantry-mounted pick-andplace tool can pick 24 of the 16-oz bottles at a time and carry them to the loading station. There the pick-and-place tool descends through a grid and gently delivers bottles 12 per case. For the 64-oz size, 12 bottles are lifted with each cycle for a format of six bottles per case.
Filled cases move next to a Standard Knapp 199 Case Tape Sealer. The continuous-motion machine uses a pneumatic tucker for trailing aps to ensure precise timing and consistent tape application. According to Standard Knapp’s Mazzotta, the taping system was kind of an afterthought.
sion inspection system was integrated upstream to ensure that bottles having defects are also rejected from the line before they get anywhere near the ller.
“These kinds of inspection systems are game changers,” says Marruenda. “It’s just not the kind of thing you can inspect for with the human eye, no matter how many people you assign to the task. And by preventing a deformed bottle from getting into the ller, let’s say a bottle that is dented, we eliminate the chance for that bottle to get over lled, which in turn causes all kinds of maintenance problems. Also optimized is the transition of the bottle from feedscrew to starwheel, because if a bottle is misshapen it’s going to cause a jam up at that transfer point.”
“Maybe even more important,” says Stone, “is the inspection for missing or cocked caps. Think about a cocked cap. When that bottle reaches a platform on the labeler, it’s not going have the precise height, which can cause jams on the labeler. Or think about a bottle that’s missing a cap. It will still likely make its way through the labeler and arrive with all the other bottles at the case packer. But the pickup tooling
“When Russ and Manny were at our facility to sign off on the case packer, I mentioned to them that we also make a case sealer that uses either glue or tape,” says Mazzotta. “We walked over to one that we had on the oor and ran it a few times and Manny pretty quickly asked me to quote him on the machine. He sent in a purchase order within a couple of weeks.”
Exiting the case taper, cases pass an ink-jet system from Matthews Marking Systems that puts best-by information and batch code on each corrugated case.
The line has now been in commercial production since January. According to Stone, by the end of the third day it was running at about 70% ef ciency, and within two months it was around 90%. Needless to say, it’s made it a whole lot easier to keep up with growing demand. Says Marruenda, “Moving to this new line was like going from a Volkswagon to a Ferrari.” PW
A collaboration between PepsiCo and the European soccer association builds upon years of progress in reducing packaging waste from sporting events with the debut of reusable packaging and biodegradable cups.
By Anne Marie Mohan, Senior EditorAccording to The Recycling Partnership, there are 9,000-plus separate local recycling systems in the U.S., with each individual program having its own speci c parameters as to which materials can be recycled, and each municipality collecting recyclables in different ways. This makes educating consumers on curbside recycling an overwhelming challenge. Now, just imagine the dif culties when it comes to capturing materials for recycling when consumers are away from home.
But food and beverage behemoth PepsiCo has found a way to turn this lemon into lemonade. For nearly two decades, the company has worked with out-of-home, closed-loop environments—particularly sports venues—to increase recycling rates and more recently, to pilot reusable packaging systems.
“The huge global scale of sports simultaneously presents environmental challenges and exciting opportunities to engage with a huge fanbase to create positive change,” explains Archana Jagannathan, chief sustainability of cer Europe at PepsiCo. “We acknowledge that food and beverage is a large contributor to the environmental footprint created at football events, but the good news is that, according to a survey by Lifetackle, 90% of fans not only share our desire to reduce waste, they are also willing to be part of the solution by collecting and recycling litter after consumption.
“An additional advantage of launching closed-loop/reuse solutions is the consumer education by creating an opportunity to test the solution at meaningful scale that serves as the reference for broader, nationwide launches of closed-loop systems.”
In its most innovative initiative to date, PepsiCo worked with the UEFA (Union of European Football Association) to implement circular economy practices for its Pepsi, Lay’s, Doritos, and Gatorade packaging at UEFA Champions League (UCL) Finals soccer games. On June 3, at the Women’s UCL Final at PSV Stadium in Eindhoven, the Netherlands, PepsiCo deployed reusable packaging and collection systems for its food and beverage products. On June 10, at the UCL (Men’s) Final at Istanbul’s Atatürk Olympic Stadium, the company supplied both reusable and recyclable options for cups, as well as recycling bins across the stadium grounds for the disposal of food and snack packaging.
Begun in 2015, PepsiCo’s partnership with UEFA across men’s and
In 2010, PepsiCo partnered with Fan Cans, a former supplier of 100% recyclable, 45-gal recycling and waste receptacles, to place the bins in high-traf c areas at select NFL, MLB, and NCAA stadiums nationwide.
Delivering Results. With Heat and Control, you have a partner with the scale to support your success, the innovation to advance your operations, and a commitment to quality that will help you offer better products for consumers.
• Food processing systems
98
17
• On-machine and process area seasoning application
• Conveying and product handling
• 1YPXMLIEHGSQFMREXMSRWGEPI[IMKLMRKERHƼPPMRK
33 32 99 36 26
• Snack bagmaking and case packing
• Metal detection and x-ray
• Check weighing and seal checking
• Controls and information systems
116
94
We are successful when you are successful. That’s why we apply creativity, engineering excellence, and determined perseverance to every project to help our customers get the performance their business
34 108
42 0842
HIQERHWƂ[LIXLIVQIEWYVIHF]ƽEZSVIƾGMIRGMIW sustainability, improvement, or innovation.
107
~2~ ~2
20
26
Sep. 11-13, 2023
Booth C-1623, Central Hall
Las Vegas Convention Center
Las Vegas, NV USA
info@heatandcontrol.com | heatandcontrol.com
LOOKING BACK. PRESSING FORWARD. ALWAYS INNOVATING.
women’s soccer is the brand’s largest global platform, with a goal of attaining zero waste to land ll at the UCL Finals by 2026 through the use of practices that focus on the 3Rs of reduce, reuse, and recycle.
PepsiCo’s history of collaboration with sports teams and venues includes a number of recycling initiatives that have become increasingly comprehensive over the years. In 2010, the company partnered with Fan Cans, LLC, a former supplier of 100% recyclable, 45-gal recycling and waste receptacles, to place the bins in high-traf c areas at select NFL, MLB, and NCAA stadiums nationwide. The Pepsi Fan Cans were produced in each team’s colors and included team logos as well as Pepsi’s “Please Recycle” logo. They were also topped with either baseball batter or football player helmet lids with special inserts with cut-outs for bottle and can recycling collection.
Another signature project, begun in June 2017, was PepsiCo’s partnership with U.S. Bank Stadium, home of the Minnesota Vikings, the NFL, Aramark, and the Minnesota Sports Facilities Authority to recover more than 90%, or 40 tons, of stadium waste at Super Bowl LII through recycling and composting. The Rush2Recycle campaign brought together all key stakeholders in the Minneapolis
For the Rush2Recycle program for Super Bowl LII, Hines Ward, Super Bowl XL MVP and Pittsburg Steelers legend, acted as ambassador.
community, including the fans, with one goal in mind: to dramati cally reduce waste on an ongoing basis leading up to and following 2018’s Super Bowl LII.
On gameday, every chef, custodian, and fan was part of the team working to recover stadium waste by recycling bottles and cans, composting organic materials like food waste and service ware, and repurposing items like discarded hand bags, signage, and construction materials through local community organizations. Rush2Recyle staff also actively encouraged stadium fans to recycle and compost. Through this process, sta dium partners introduced a tri-bin waste collection system, invested in a dedicated organics compactor, and implemented a detailed postgame waste sort to ensure each waste stream was contaminant-free. As a result of these efforts, the project surpassed its target, recovering 91% of all trash, or nearly 63 tons.
“The success inspired PepsiCo to create a playbook to guide other leagues, teams, site operators, and fans in intercepting waste in their communities,” says Jagannathan. “Years after this game ended, the work is leaving a lasting impact as the stadium’s waste diversion infrastructure is now a permanent installation at U.S. Bank Stadium, helping protect the environ ment and reduce waste hauling costs. Additionally, since June 2017, U.S. Bank Stadium partners have increased the stadium’s diversion rate by roughly 55%.”
In 2021, PepsiCo announced another partnership, this one with Seattle’s Climate Pledge Arena, the world’s rst certi ed net-zero arena
and home to the Seattle Kraken hockey team. In joining the pledge, PepsiCo committed to regularly reporting greenhouse gas emissions, implementing decarbonization strategies, and neutralizing any remaining emissions to achieve net zero annual carbon emissions by 2040.
“Our PepsiCo Beverages North America division also plans to introduce sustainable packaging within the arena, aligning with their commitment to being 100% free of single-use plastics by 2024,” Jagannathan adds.
And, earlier this year, PepsiCo announced a new program, Partners for Tomorrow, one facet of which involves a focus on the use of reusable cups to support the brand’s overarching goal to see 20% of its beverage servings delivered through reusable models by 2030. Specically, PepsiCo is conducting a pilot with global sports and entertainment company Oak View Group at its newly renovated CFG Bank Arena in Baltimore, along with scalable reuse system provider TURN to gamify the system and incentivize event attendees to return their reusable cups after use.
“We see incredible potential here as a single TURN cup can potentially displace up to 100 single-use cups and break even on environmental impact in as few as three uses,” says Jagannathan. “The upcoming UCL Champions Festival will also incorporate the TURN technology for the rst time outside of North America.”
Fans used kiosks at the nals to return their reusable cups and receive their deposit back.At the Men’s Finals, PepsiCo provided recyclable and biodegradable cups as an option for beverages.
For more than 30 years, Axon has been a leader in providing high-speed, high-performance sleeve applicators and systems. Visit Booth #C-3125 to see the latest innovations in shrink sleeve and tamper evident band application machinery in person.
NEW Aurora® 5.0 Applicator for sleeves and tamper evident bands with speeds up to 500 cpm.
NEW DL-1000 Steam Tunnel — Dual lane steam tunnel featuring modular construction for custom length and improved operator interface.
HE-500 Steam Tunnel — High-efficiency steam shrink tunnel with integrated steam generator & minimal condensation.
HydroTech™ — Tamper evident band applicator for round and non-round containers at up to 300 cpm.
EZ-100 + EZ-BR Tunnel — Find this system applying tamper bands to vitamin bottles in the NJM booth #C-3225.
Dating back nearly a decade, PepsiCo’s partnership with the UEFA Champions League came about as a result of mutual interests. “While we share a great love for football, we also share a passion for driving impact on and off the pitch [ eld],” says Jagannathan.
In 2020, the two announced an extension of the partnership through 2024 and added a multi-year premier partnership with UEFA Women’s soccer. “Throughout the partnership, we’ve worked with UEFA to support the transition to circular economy food and beverage practices,” says Jagannathan. “In 2022, we helped develop the UEFA Circular Economy Guidelines as part of a wider sustainability strategy that helps national associations, leagues, clubs, partners/sponsors, event organiz-
Pat Finlay, R&D Sr. Director, Global Beverages Packaging at PepsiCo, talks with PMMI Media Group’s Sean Riley about how to solve the packaging and processing workforce crisis. Discussed are projects like the Million-Girl Moonshot to engage one million more girls in STEM learning opportunities, and direct initiatives with SWE, Society of Women Engineers, and NSBE, the National Society of Black Engineers. Listen at pwgo.to/7906, or search for the unPACKed podcast wherever you get your podcasts. PW
ers, and other stakeholders start the journey towards the aspirational target of zero plastic waste and food waste.
“This strategy was developed by linking football to sustainability, aligned with UEFA’s principles and with the demands of global institutions and civil society. It is our goal together to attain zero waste to land ll at the UEFA Champions League Finals by 2026, starting with this year’s nal matches at Atatürk Olympic Stadium and PSV Stadium, with the operation to carry out and be regularly implemented from 2026, and eventually becoming a requirement at a selection of hosting stadiums across UEFA events in the years that follow.”
When PepsiCo announced in May the new programs it would be implementing at the nals games, UEFA Social and Environmental Sustainability Director Michele Uva said, “UEFA is delighted to continue the collaboration with PepsiCo to deploy circular economy practices across these two important nals. Our actions are focused on nding and disseminating solutions applicable to football matches taking place across national associations, leagues, and clubs in Europe to play our part in tackling environmental challenges.”
PepsiCo’s circular economy practices at the UCL nals are a culmination of its recycling and reuse innovations thus far, with each nals game having several components. According to the company, the Women’s Champion League Final was the rst UEFA nal where all concessionaire food and drink packaging was reusable.
For beverages, Germany-based company Cup Concept provided 54,000 0.4-L reusable cups made from a combination of polypropylene and polycarbonate. For PepsiCo’s Doritos Nachos snack, polypropylene trays were provided by a specialist in reusable food containers, Vytal, also based in Germany. Fans purchasing products in the reusable packaging were charged a deposit of 2 Euros.
Because the stadium requires all beverages to be served in cups, PepsiCo delivered the drinks in 100% recyclable bottles, with the bever-
Interested in learning more about sustainable packaging? Don’t miss PACK EXPO Las Vegas 2023, where a wide range of sustainable packaging solutions will be on full display. For more information, visit packexpolasvegas.com
ages poured into the reusable cups for consumption.
After use, fans returned their cups and trays to one of the return stations located throughout the stadium. Upon returning the packaging, consumers would tap their payment card to the payment terminal on the machine to get their deposit back. “We believe this method encouraged responsible actions from attendees, while not taking away from the game,” says Jagannathan.
From there, a third-party operator collected the reusable items and will put them through a rigorous cleaning process so they can be used again for other events. “We have yet to conduct a full lifecycle analysis, but we are con dent these actions at the PSV Stadium during the Women’s Final improved our carbon footprint,” Jagannathan says.
For the Men’s Final in Istanbul, PepsiCo used a combination of reusable and recyclable options. For this venue, PepsiCo worked with TURN for the reusable cup system. Fans were also offered the option of drinks in fully recyclable and biodegradable ber cups, which were used across the stadium, festival, and fan meeting points. The cups were provided by Foopak Bio Natura and were made using natural ingredients, such as ber, starch, and calcium. Unlike traditional ber-based cups that incorporate a non-biodegradable polyethylene liner that makes them dif cult to recycle, Foopak’s cups use a proprietary aqueous dispersion coating technology that allows the cups to be recycled as well as composted in 12 weeks at an industrial composting facility.
Again, in this case, PepsiCo beverages were provided to the stadium in 100% rPET bottles and the drinks poured into the returnable or recyclable cups for consumption. “There are many reasons that ber and returnable cups provide bene ts beyond bottles that are 100% recyclable,” says Jagannathan. “Both aim to eliminate single-use plastic cup waste and create opportunities for stadiums to serve beverages in sustainable containers. In Eindhoven, an added bonus is that the reusable cups will be sanitized for future events—helping to speed the lifecycle of the cups.
“The key additional bene t of utilizing the ber and returnable cups is litter prevention: reusable cups with a deposit provide a very high redemption rate at the event, and worst case, consumers take them back home to use further there. Fiber cups will biodegrade if disposed of inappropriately, so they do not harm the environment even if some will eventually end up as litter.”
Another element of the waste-reduction strategies at the Men’s Final was the use of more than 220 recycling bins across the venue into which consumers could dispose of their recyclable cups and their snack bags, along with any other paper and plastic material. Post-event, the bins were sorted by a professional waste management company that directed the materials to the
As for the non-recyclable exible lm snack bags, as part of another PepsiCo global initiative, Lay’s Replay, the brand is using the material to create soccer elds. In fact, its latest Lay’s Replay initiative involved unveiling a new soccer eld made partially from snack bags before the Istanbul nal. According to PepsiCo, from the materials to the installation, the elds are designed to minimize impact on the environment. “For example, the turf and shock pad layers are 100% recyclable at the end of their lifespan,” says the company.
Since June 2021, PepsiCo has unveiled six soccer elds in locations that include South Africa, Brazil, the U.K., the U.S., Italy, and Mexico.
In another UEFA partnership, this one with the UEFA Foundation for Children, PepsiCo is supporting community impact through Gatorade 5v5 global tournaments, which ease the barrier to entry for young amateur footballers and fuel play through grassroots programs. This year’s global 5v5 tournament nal took place ahead of the Women’s and Men’s UCL Finals.
Concludes Jagannathan, “The new improvements at both tournaments will serve as a stepping stone towards the overall goal and help make the necessary improvements in the upcoming years to ensure all future UCL/UWCL nals stadiums meet the zero waste to land ll requirement
5HO\ RQ RXU LQGXVWU\ 5HO\RQRXULQGXVWU\OHDGLQJ YDFXXPVROXWLRQV
UP TO
&HQWUDOL]H\RXUYDFXXPVXSSO\ (ɚFLHQWO\
IN ENERGY SAVINGS
'LVFRYHUKRZ%XVFKYDFXXPH[SHUWVFDQKHOS\RXUHGXFHHQHUJ\ FRQVXPSWLRQDQGFXWFRVWVE\XSWRwith our powerful vacuum solutions. Together, we’re building a brighter future for our planet. ([SORUHDQGↅQGWKHSHUIHFWVROXWLRQIRU\RXUQHHGVWRGD\
Visit us at:
With chocolate stick demand growing and labor scarce, Sweet Candy Co. selected a robotic pick-and-place system to collate product into layers, then pick layers into cartons. Cartons are sold by weight, but stick weights vary by batch, so counts are adjusted on the fly for accurate weights and limited giveaway.
By Matt Reynolds, Chief EditorSalt Lake City-based Sweet Candy Company is a 100-year-plus-old confectioner that’s on its fourth generation of family ownership and leadership, with the fth generation already coming up in the business. Founded by the Sweet family, the company distributes more than 250 high-quality candy items nationally and internationally in bulk, in bags, and in cartons. But it’s perhaps best known for a signature, chocolate enrobed stick-shaped candy that’s sold exclusively in 10.5-oz cartons. A regional favorite since it rst debuted in the 1940s, the indulgent chocolate and fruit- avored pectin treat is sold year-round. But there also had been a seasonal element to sales patterns; as a popular stocking stuffer in the intermountain region, the chocolate sticks had locally become practically synonymous with the holidays.
But these chocolate sticks are no longer a regional secret having recently acquired more of a national following via specialty candy markets that sell them as giftable, sharable gourmet treats. Sweet’s chocolate sticks can now be found nationally at retailers like Cracker Barrell Old Country Stores, Ross stores, or other candy markets that specialize in unique products outside of traditional mass merchant or grocery formats. Since the chocolate sticks are unitized as 10.5-oz with 32 to 34 chocolate sticks per carton, the price per ounce is a leader in the real chocolate category. And for a store like Cracker Barrell, this drives full margin on the product.
This recent entrance into national specialty candy markets precipitated a growth in demand over the entire year—not just during that seasonal holiday rush—forcing leadership to start thinking about making big moves in automation to keep up with increasing production
demands. These moves weren’t strictly production- or throughputbased, either. Leadership intended on increasing a level of precision in weights, sizes, and counts that it couldn’t previously maintain with a more semi-automatic packaging line. But most urgently, it needed to improve packaging operations that have, especially for this product, lagged upstream candy-making capacity. So in October of 2022, just as the seasonal rush ramped up, the company made the move with a brand-new robotic primary packaging installation. And as is usually the case, downstream secondary and end-of-line packaging automation was upgraded to keep up in a cascade of new automation.
Never shy about visiting candy manufacturers, Packaging World recently took a visit to Sweet Candy’s immaculate 180,000-sq-ft produc-
A modular design allows for many different functions within the system, including collating individual product from a loosely arranged infeed, whole-layer picking and placing into carton bottoms, wax paper application, and carton lidding.
tion facility and distribution center to check out the new fully automated, one-carton-per-second boxed chocolate stick packaging line. It centers around a Schubert robotic primary carton-packing installation with advanced, space-saving counter ow technology. Here’s what we learned about the unique project.
When installed in 1999, the legacy equipment that the new system replaces had been state-of-the-art; it was an early example of pick-andplace technology that has since become ubiquitous in packaging of arranged candy multipacks. Second-generation owner Tony Sweet was perhaps ahead of his time when, after a global equipment search in the late 1990s, he sourced the equipment from Hannover, Germany’s Haytech GmbH & Co.KG. But according to Geoff Dziuda, current VP of operations at Sweet Candy Company, the pneumatic, single-head gantry pick-and-place equipment from a now-defunct German OEM was reaching the end of its useful life 20 years later.
“The prior equipment had done a great job of getting us from the time that the Sweet family decided to move into this building, up until the present day,” he says. “But we wanted to be able to add capacity to keep up with the [chocolate stick] demand that we were seeing, and we wanted to be able to add another shift. We could see the existing
equipment just wasn’t the right machine for the future growth that we were looking at.”
In part, that’s because the case packing equipment had never been designed to pair one-to-one with the upstream processing equipment. Intentionally, right out of the gate, it was a step slow, as it had been speci ed to handle 80 to 85%, at best, of the upstream product ow. Manual picking had augmented the machine from day one, and some small percentage of rejects would simply fall off the end of the infeed belt. But in recent years, that 80 to 85% number had dwindled to 50 to 60%. That meant that until recently, nearly half of product handling and cartoning operations had been manual, done by operators working alongside the declining equipment. Since Haytech had gone out of business, replacement parts were hard to come by, and the mechanics that had been trained on the equipment in 1999 had long since retired or moved on, the situation had become untenable.
“Especially in the current labor climate, we were faced with this issue of ‘how do we increase our throughput on this line?’” Dziuda says. “Because we had this old piece of equipment that could manage about 50% of our capacity, with the support of six operators to help it along. It had a lot of defects and neither its accuracy nor ef ciency were up to modern standards.”
Exacerbating the issue, downstream case packing and palletizing op-
We are growing our recycling initiatives and offerings to meet the needs of today’s consumers and brand companies who are demanding PET products with a recycle content. We actively participate in circular economies to foster increased sustainability and reduced impact on the environment.
We are expanding our capability and capacity to offer more RPET solutions to allow for bottleto-bottle recycling applications, including the innovative Single Pellet Technology® (SPT). SPT provides an integrated recycle content (up to 25% recycle content) in virgin production operations in select PET resin offerings.
Linking innovative products to our customers’ unique requirements is what we do best.
The broad line of Laser+® PET Resins continues to be engineered to meet the changing needs of the bottling / packaging markets, while our R&D and Technical Service experts maximize XLIFIRI½XWXLEX0EWIV 4)8GERFVMRKXS your business.
At Alpek Polyester / DAK Americas we are always committed to providing environmentally conscious solutions.
Collating F4 SCARA robots near the end of the infeed belt pick product as it travels to the right. Note the amount of product has dwindled compared to the 34 x 4 format at the start of the infeed. Groups of three sticks are collated on the narrower belts that travel to the left. Finally, cartons that have been lled and lidded upstream travel to the right, and out of the system.
erations had always been completely manual. So to get more capacity and throughput out of the line, absent new equipment, it would be a function of adding as much of the already scarce labor as Sweet Candy could nd in smaller market Salt Lake City. That could be as many as 15 to 20 more people, and when considering “the variability that comes with manual labor, and their inef ciency, and just the added management for that amount of labor,” Dziuda says that automation was the obvious choice. So, he and Sweet’s fourth-generation president and CEO Rick Kay undertook yet another global search that this time landed them on Schubert robotic packaging equipment, with speed and accuracy that would precipitate a fully automated line downstream, right on down to palletizing.
While much of the equipment on the chocolate sticks packaging line is new, the primary packaging piece—placing two of layers chocolate sticks into at paperboard cartons—would set the tone for everything downstream. Delta-style robots for picking and placing were the preferred technology among the nalist vendors seeking to supply Sweet’s with this equipment. But Dziuda had been acquainted with Schubert equipment from a previous role, so he added the company to the short list. Though it offers delta-style options as well, Schubert suggested its SCARA-style F4 mulit-axis pick-and-place robots as a better t for the project. The German OEM with U.S. headquarters in Charlotte, N.C., ultimately won the contract for a host of reasons.
One primary consideration was a comparatively small footprint, “because we’re landlocked,” says Kay. “It’s a plenty big machine, but it ts.”
The machine’s footprint is able to be constrained because Schubert’s counter ow technology (patent recently expired) allows more operations to happen within a smaller space compared to a standard, mono-
infinitely flexible dramatically reduces machine size faster time to market
embed XTS directly into machines configure for any track geometry install flat, vertical or at angles repeat or stack XTS tracks 30–50% reduction in machine footprint
Manufacturers around the world need to offer increasingly customized products – with machines that deliver reduced footprint and improved productivity. 7 he eXtended Transport System (XTS) from Beckhoff answers these machine design challenges and more. In combination with PC- and EtherCATbased control technology, the XTS features a high level of design freedom for machine builders to develop game-changing concepts for product transport, handling and assembly. A stainless steel hygienic XTS version is ideal for use in the pharmaceutical and food industries. Take your next step in machine design with XTS: total freedom of installation position compact design integrates directly into machinery freely selectable track geometries few mechanical parts and system components
See XTS live in booth SL-6335!
directional downstream belt. Using the counter ow concept, individual products run past one another, in parallel but in opposite directions, akin to several multi-lane highways within a single cell composed of as many individual modules as are needed to get the job done. The F4 robots pick and place the product between ve parallel, but contra-directional belts, so neither the product nor the belts need to turn 180 deg on their own in order to continue downstream. Conceptually speaking, with counter ow, downstream doesn’t mean monodirectionally downstream. Instead, downstream product travels against the current of upstream operations, but still travels downstream. We’ll get more speci c in describing counter ow soon, but see the image on page 74, or check out the video at pwgo.to/8035, to better envision the concept.
Gentle handling was another consideration, as the enrobed chocolate product is fragile and can’t withstand too much jostling.
“That was a big topic of conversation for us,” Dziuda says. “We didn’t know how the sticks were going look after being handled by a robot at these volumes and speeds. We didn’t know what they were going to look like in the carton. Would the sticks be turned or were they going to be straight? Or could they be scuffed from a vacuum cup?”
As it turns out, all direct product handling was able to be accomplished by a custom-designed, 3D-printed vacuum end effector; no mechanical
grippers are needed to handle the enrobed chocolate sticks. The result is gentle handling that’s indistinguishable from hand labor or the legacy equipment’s single pneumatic gripper.
“Maybe the most important to us was [Schubert’s] ability to meet the supply chain challenge. This was right around the middle to the tail end of the pandemic, and it was a time where we couldn’t get anything from anybody on time; everything was delayed,” Kay says.
A complicating factor was that the installation was targeted to occur in October of 2022, so just as the seasonal holiday rush began. The entire installation, from taking delivery to SAT to production, needed to happen fast.
“We had to get an army of people [to build up inventory ahead of the installation]. And it was painful,” Kay says, able to laugh about it now. “But it wasn’t like we were going to delay until January. So we prebuilt as much as we legitimately could, and we scrambled, and we worked. And we paid for airfreight to expedite the new equipment… we learned that from another project going on with a depositor; half of the stuff got stuck in the Panama Canal for months, and then the dock strikes slowed things down. What should have typi-
Whole layers of 16- or 17-ct product are cartoned by SCARA robots with vacuumgrippers.
The lled cartons are sold by weight, not count, and product weight can be variable by batch. So the system allows for on-the- y changes from 16- to 17-ct to get a close as possible to the 10.5-oz target weight without going under, limiting giveaway of expensive chocolate.With far more precision baked into the system than the mostly manual legacy operations, Sweet Candy is asking for more rigid lids from its paper carton converter to get the most ef ciency out of its carton lidding operations.
EcoStitch is Valco Melton’s line of all-electric adhesive melters, applicators, and controls.
The EcoStitch solution eliminates the need for compressed plant air while reducing spare part consumption, required maintenance intervals, and line downtime to increase overall equipment e ciency and decrease the total cost of ownership related to the adhesive dispensing system.
cally taken three weeks for shipping, pre-pandemic, took ve months.”
This seasonal timing put the OEM under pressure to meet their deadline, and the customer-paid expense of airfreight hinged on the builder hitting the narrow time window. But Schubert builds a lot of its components—robots for instance—in-house. The company also sources many components from the region directly surrounding Schubert’s headquarters in Germany, shielding them from many more global supply chain issues.
“We pride ourselves on our manufacturing depth,” says Armin Klotz, sales account manager at Schubert North America. “Meaning 80% of what you see [in this installation] is built by Schubert. For instance, we built the vision system and the robots, and have been for 30 years. We never have had to delay a machine because we didn’t have a chip or a PLC.”
Adds Kay, “Schubert said it was going to be 38 weeks, and in exactly 38 weeks,
based on weight, not count], that was something we had to develop with them. But their technologies and their experience aligned them well with this project for us, and that became evident to us early on. It was obvious that they had the capability, the acumen, and the experience to design something that would work for us.”
the machines were delivered on time and installed ahead of schedule. They’re nimble; after all this is a product that they’ve never seen before. But since their machines are modular, with a certain range of robots able to do a certain range of tasks, they were quickly able to customize their more standard modules into running what we needed. It was so dialed in that we went from airfreight arriving to production in just two and a half weeks. That got our attention.”
“They have a menu of existing, modular options that you then customize,” adds Dziuda. “As we got into it, we had a few challenges. For instance, how were we going to add the wax paper in the middle of the two layers of chocolate sticks? Well, they just built a machine for that. Then the collation step [from loosely arranged product to layers
For the box shop, Sweet’s uses two parallel pieces of legacy equipment from the original packaging line—mold plunge-style carton erectors. One machine erects the carton bases, the other erects the carton tops.
Individual batches of the pectin-centered chocolate sticks exhibit quite a bit of variability due to how they’re produced. That’s because they undergo a long, variable hardening and curing phase. This phase occurs between liquid pectin tray depositing into imprinted forming trays, and cured pectin product being removed from the trays to be conveyed toward chocolate enrobing. The fruit pectin-based candy centers start as a hot liquid candy slurry that is pumped via stainless pipes from kitchen kettles on an upper oor to be deposited into 34- x 4-ct forming trays. Once deposited, the trays of pectin centers run through an NID starch-depositing mogul candy line that cures the llings in corn starch. These trays travel slowly through a series of connected tracks for a period of usually eight to 12 hours, rming up and cooling the hot liquid into a gummy-like candy consistency. After suf cient cooling in the mogul, and when the centers have reached the appropriate viscosity and consistency, the starch-packed centers are “bucked out” of their forming trays by inverting those trays over a belt, releasing the jelly centers to
Customers worldwide count on Duravant’s portfolio of premium engineered automation solutions spanning the food processing, packaging and material handling segments. Backed by Duravant Integrated Solutions and SupportPro, the Duravant family of operating companies optimizes safety, productivity, efficiency and connectivity for the world’s producers and movers of high demand goods.
Checkweighing and metal detection are the rst operations after cartoning (above). For any given product run, the weights of the rst handful of cartons off the line are checked, and the system calibrates for 16- or 17-ct layers to narrow in on the 10.5-oz desired carton weight.
be conveyed downstream. The result is naked, loosely arranged product centers in repeated 34 x 4 rectangular con gurations that are conveyed off the mogul line toward enrobing.
“We love pectin, but if it’s in starch eight hours versus 14 hours, the moisture loss is going to change the density and the weight of the center. So, you have a variable there,” Kay says. “And then, that machine’s 25 years old, and starch-depositing moguls are nicky. Andnally, there’s variability in the enrober which [at the time of PW ’s visit was] on the verge of being replaced. Our chocolate coverage used to be a challenge, so that could lead to some variability.”
Ultimately, the nished stick weight could be all over the board. Yet Sweet’s was selling it by weight in 10.5 oz. cartons.
“So when we were hand packing, and we were just lling the carton, a 10.5-ounce box routinely had 13 ounces of candy—that’s a lot of giveaway,” Kay says.
With the new, exible primary packaging line, operators simply weigh the rst few cartons that come off the line. Depending on how close they are to the target mark of 10.5 oz without going under, they
Laser coding provides neat, smudge-free date and batch codes without requiring ink handling or input of other consumables.
With labor becoming scarer and more expensive, and production requirements always getting more strenuous, more CPGs like Sweet Candy Co. are turning to advanced packaging automation. True robotic automation can sometimes be seen as a bridge too far for interested CPGs, but that’s very rarely the case, in reality. Find out how fast your robotic packaging automation ROI could be, and see how to justify it to management or procurement, to improve and futureproof your packaging operations.
Orange County, Calif. Sept. 27, 2023
Chicago, Oct. 3, 2023
Philadelphia, Oct. 26, 2023
Houston, Nov. 2, 2023
To learn more and register to attend, visit pwgo.to/8034 or scan the QR code.
can simply toggle back and forth between 16- and 17-ct layers, or 32- or 34-stick cartons, to dial in the correct weight and count combination, with the least giveaway while still at or over 10.5 oz.
“If the checkweigher tells the operators that the cartons are too heavy, and they’re giving away too many products, then they can use the operator interface to punch a button, and remove a chocolate stick on the y,” says Armin Klotz, Sales Account Manager at Schubert North America. “Usually you’d have to load a new program, but the software algorithm makes this possible on the y, in real time, with just one button.”
Enrobed chocolate sticks travel by belt for about 14 minutes through 180-ft of a 50°F cooling tunnel on their way to the Schubert system for primary packaging operations. At this point they’re loosely arranged in the aforementioned rectangular groupings of 34 x 4 sticks, with each grouping spaced a few inches apart. This single-belt con guration serves as the infeed, and while product isn’t randomly oriented, neither is it perfectly arranged.
Product travels most of the way through the system, counterintuitively passing through and next to parallel downstream operations, before arriving in front of one of eight F4 high-speed, collating pickand-place robots. These eight robots are arranged into two modules of four, with each module containing a 2x2 con guration of robots that pick product from the infeed belt. A vacuum-based end-of-arm
From foil sealed cups to glass beverage bottles and gallon chemical jugs, TapTone has inspection and rejection systems to handle your inspection challenges.
• Glass, plastic, metal
• Bottles, cans, jugs, tubs, cups
• Food, beverage, chemical, nutraceutical
• On-line and integrated systems
All at production line speeds.
tool on each robot picks three sticks at a time and orients them on one of two contra-directional collation belts that travel immediately to the right and left of the wide infeed belt. Pick-and-place pattern building, or collation of layers, continues by the eight robots until the desired
16- or 17-ct layers are achieved. The 2D and 3D vision systems are primarily looking for the position, orientation, and height of the sticks, to send to robots for accurate picking. But vision also looks for defects in color or out-of-spec stick dimensions. The system allows these rejected sticks to fall off the end of the belt as scrap when they’re identi ed.
The robots work from the outside in, with the rst robots picking sticks on the edges of the infeed, and later robots working toward the remaining sticks in the middle. This action funnels the product into a “V” or triangle pattern of product as it travels downstream on the infeed toward the end of the belt. Near the base of the “V,” rst sets of robots travel the fastest and complete the most movement, but also travel the shortest distance since they’re picking from the edges.
“This triangle or ‘V’ pattern means that when full 16- or 17-ct layers are close to being built—maybe there’s already 14 or 15 sticks in the layer and only one or two sticks are needed to complete it, there’s plenty of product available at the base of the triangle. The layers begin being built from the section of the infeed belt where product is most scarce and fur-
ustsubaki.com
Cartons undergo a 90-deg turn and are oriented to travel wide-side rst into case packaging operations. Once a 3 x 4 stacked format is collected, the block of cartons is pushed into postion in the wrap-around case packer. Adhesive is then applied ahead of palletizing.
thest downstream, at the peak of the triangle or ‘V,’” says Klotz. “The layer building and collation functions will never be starved for product, since the layers are closest to being completed exactly where the most product is available. Not only is there more product at the base of the triangle, that product is also nearer the edges. So product is closest to the waiting layers on the collation belt just when those layers most need a nal stick or two to complete the layer, thus the robots have the shortest distance to travel to complete a layer.”
On the other side of the coin, the robots at the very end of the infeed are tasked with essentially cleaning up the remaining in-spec sticks from the very peak of the triangle, before they fall off and are hand-cartoned or worse, become scrap. At this point, the layers on the collation belt are the least full, so there are more available spaces to place them. If the layers were already full, robots may be forced to allow product to drop off since full layers mean there’s no spot to place the sticks.
“Counter ow gives you a guarantee that you always have full, complete layers on the collation belt by the time they’re ready to be loaded into the carton,” Klotz says of this formerly proprietary system.
These layers of chocolate sticks are built on the collation belt as they travel in parallel to, but against the current of, the central product infeed belt. After the correct count is met, the entire layer is then picked up by one of four F4 layer-picking robots with larger, rectangular
vacuum end-of-arm tools. The robots place each layer in an erected carton bottom that’s traveling on a cartoning belt. Once each layer is placed, it’s traveling in the same direction as the product infeed, against the current of the collation belt, and towards the end of the machine.
Between each layer, yet another pair of robots, one on each side of the system, adds a sheet of wax paper—cut from rollstock on a specialized module—to the top of the rst layer of chocolate sticks. After that, a second layer of chocolate sticks is added by another pair of robots with the same full-layer vacuum end effectors, nishing off the 32- to 34-count carton. Another pair of robots, one on each side, nally place the carton lid onto the caron base on the two-layer cartons, and they exit the Schubert system.
Meanwhile, some sort of automation has to keep this intricate system fed with erected cartons. For box shop operations, Sweet’s uses two parallel pieces of legacy equipment from the original packaging line—mold plunge-style carton erectors by ADCO. One machine erects the carton bases, the other erects the carton tops. Operators load magazines of 2D cartons, printed by local supplier Utah Paper Box, for erecting to keep up with primary packaging operations. Cartons don’t require adhesive, and instead are held in shape by mechanical tabs. Lids and bases are laned into two, paired, lid and base conveyors, one pair for the right side of the system infeed, the other for the left.
“The lid and base carton erectors are comparatively simple pieces of equipment, but we wanted to continue using those because of the familiarity we had with them, and they still work just ne. The speeds are suf cient to keep up, and our operators all know how to use them. Schubert was willing to work with us on integrating those older, but reliable pieces of equipment,” Dziuda says.
Leaving the primary packaging system are two lanes of nished cartons that make a 90-deg to the right, then may undergo some minor accumulation behind a turnstile gate that single- les the cartons on BW Integrated Systems conveyor equipment. The now-single lane of cartons again turns 90 deg to the right, then passes through a Sentinel checkweigher and metal detector by Thermo Scienti c
Laser coding is accomplished on a Markem Imaje C150, which Dziuda says provides neat, smudge-free date and batch codes without requiring the handling of any ink or input of other consumables.
All told, this makes for seven parallel belts operating on Schubert’s counter ow principle within the system. In the center is one wide, central infeed belt. Directly to the right and left of the infeed are two product collation belts that travel back against the infeed ow to build layers of chocolate sticks. And nally, four carton infeed belts—two on each side, one for the bases, the other for the lids—enter the system parallel to the product infeed, outside of the collation belt. The carton lid infeed belt terminates as soon as lids are applied to the base. Out ow of the system occurs on three belts—some amount of rejects that were never picked exit for disposal at the terminus of the infeed belt, and the two carton belts on the right and left of the infeed travel downstream.
The system also houses a total of 16 Schubert F4 robots, grouped within modules to pick and collate product, pick layers of product and carton it, to add the wax paper, and to put the lids on the cartons.
Cartons are shrink wrapped in poly lm from Sealed Air in an Extreme (nVenia) shrink lm applicator and shrink tunnel. Dziuda notes that the heat tunnel temperatures don’t have any negative affect on the recently cooled, enrobed chocolate contents of the carton. An inline label applicator from Diagraph is next. On occasion, pressure-sensitive, sticker-style labels are added to the shrink-wrapped cartons for special product runs, but the legacy piece of equipment of unknown provenance is rarely used. Generally, cartons pass through this equipment unengaged.
Cartons then make an abrupt 90-deg turn to the right while maintaining their orientation, so the wider edge of the cartons lead for this brief interval. This is the preferred orientation for case packing operations. Cartons are accumulated and stacked into 4x3, 12-ct con gurations as they enter a wraparound corrugated case packer by BW Integrated Systems. The only current format is of 12-ct corrugated cartons, but 30-ct might be on the horizon for the company. Adhesive is applied to the cases by equipment from Nordson within the case packer, the
'LDJUDSK0DUNLQJ &RGLQJKDVEHHQSURYLGLQJSURGXFWLGHQWLÀFDWLRQVROXWLRQVIRU\HDUV WKDWPDNHLWHDV\IRUPDQXIDFWXUHUVWKURXJKRXWWKHZRUOGWRPDNHWKHSHUIHFWPDUN³SULQW DIWHUSULQWDIWHUSULQW:HIRFXVRQSDUWQHULQJZLWKFXVWRPHUVLQHYHU\DVSHFWRIWKHLUFRGLQJ DQGODEHOLQJRSHUDWLRQVWRPD[LPL]HHIÀFLHQFLHVIRURXUFXVWRPHUVDQGGULYHWDQJLEOHYDOXH WKURXJKRXWDORQJWHUPSDUWQHUVKLS
PACKAGE CODING
&RQWDFW'LDJUDSKWRGD\WRGLVFXVV WKHEHVWRSWLRQVIRU\RXURSHUDWLRQ
CASE CODING
CASE LABELING
PALLET LABELING
5HVHDUFK3DUN'ULYH
6W&KDUOHV02
GLDJUDSKFRP • VDOHV#GLDJUDSKFRP
PMMI ProSource is a free online directory with 460 categories of validated suppliers of packaging machinery, materials, and service solutions. With a powerful search engine and the ability
orientation. The company uses an interlocking column stack to stabilize the pallets, with a small amount of offset and an open chimney in the center to accommodate the offset.
Pallets are carried a short distance by forklift to a standalone Lantech turntable stretch wrapper to complete the new packaging line. Pallet rates are slow enough so as not to require an on-line pallet wrapper—not to mention other departments make use of the Lantech. Because of the conveyor layout, Sweet’s couldn’t use a traditional lift with outriggers, instead going with a counterweight lift with a heavy and high lifting capacity.
Kay and Dziuda knew going into this project that training their labor force on the advanced new equipment would be essential for success. Dziuda had worked with Schubert before and was aware of how thoroughly the OEM handles training—that’s one of the reasons he sought it out. But the Schubert training program was new to Kay.
cases are closed, and they travel downstream to the end of the contiguous line for palletization.
Case coding is done on a Markem Imaje 5940G two-head coder, and palletizing is done via a Fanuc robot arm on equipment from BW Integrated Systems. Cases on the pallet are about a half-inch out of perfect square, so they’d be fairly unstable stacked as columns in a uni ed
“Their training disciplines were something I hadn’t experienced from a supplier before,” Kay says. “Beyond the equipment itself, training certainly helped differentiate them. Just the idea that we’re going to get the support we needed was important since we’re out in the middle of nowhere. Their engagement with our maintenance team, with our operators, and with our management was remarkable. To me, that’s a differentiator in future projects; they’re at the top of the leaderboard on who we want to talk to. If you’re going to be in the food business do-
mestically and be competitive, especially confection business, you need throughput. You’ve got to run lean and mean. Downtime kills you.”
At the time of PW ’s visit, two of Sweet’s Candy Co.’s maintenance technicians have already visited Schubert’s South Carolina classroom with three more techs lined up to visit.
With increased speed and reliability in packaging operations, Sweet Candy was able to increase the speed of the upstream mogul machine by 15%. The entire line now runs at 60 cartons/min at cruising speed, 24 hours per day, ve days per week.
“On our older equipment, when we were dealing with product coming at us like it was coming out of a rehose, we couldn’t have imagined increasing speed,” Kay says. “We’ve been so thirsty for the opportunity to ne-tune things and move away from the hand-made, recipe carddriven culture, and instead take advantage of an automated, highly
engineered solution. We’ll be able to dial in and hit our spec and stop giving away chocolate. Even if that forces us to increase the size of the candy center, that’s okay. The center is a lot cheaper than the chocolate.”
The cartons themselves are getting a minor upgrade that wouldn’t have been necessary before, when hand-packaging was more common. The lids, which have been essentially using the same design for decades, have a bit of a natural bow to them. Though imperceptible to people, robots could bene t from a atter pick space. Sweet Candy is working with their supplier Utah Paper Box on a crisper, more consistent lid to dial in on some of the slop tolerances.
“The need to improve the carton really illustrates the theme of where we’re at right now. Everything got a lot more precise with this installation,” Dziuda says. Since the time of PW’s visit, the company has installed a new Aasted Master 1300 Enrober “upstream so that we have better consistency, and we’re a little bit more precise in the chocolate on average, with less tailing, and just making a more consistent product that we’re feeding into the packaging machines. We made a step change on the scrap side for sure, and like Rick said, it allows us to dial in and be a lot more precise than where we’ve been.”
With the recent upstream enrober integration is ironed out, Sweet Candy is looking into diversifying with sizes and counts. Down the road, they would consider doing a single-layer carton, or a shorter cut-off to hit different price points.
“Maybe we can upgrade box shop operations so that we can do different things, holiday sizes, bonus boxes, whatever the case may be,” Kay says. “The one-size- ts-all approach is limiting, but the basics are there with this new installation to move beyond the single carton size.” PW
According to a new study, flexible plastic films may outpace plastics overall in CAGR. And though compostables represent a small piece of the packaging pie, their pace of growth is fast. But these materials are a challenge to recycle with current infrastructure.
PMMI and the American Institute for Packaging and the Environment (AMERIPEN) recently released “2023 Packaging Compass: Evaluating Trends in U.S. Packaging Design Over the Next Decade and Implications for the Future of a Circular Packaging System,” a new study identifying key trends in packaging design and materials and the implications of these trends on legislation and the recovery systems for CPGs.
“By releasing this deep dive into the trends driving the circular packaging system, we hope to facilitate an industry dialogue that will help close the gap between design needs and recovery needs,” says Jorge Izquierdo, vice president, market development, PMMI.
PMMI’s Rebecca Marquez joins the unPACKed Podcast to discuss ndings from PMMI, AMERIPEN’s “2023 Packaging Compass.” Flexible packaging must be recycled, but how?
CAGR GROWTH PERCENTAGE
TOP THREE MATERIAL TYPES
2021 2025 -2% 1.3%
1.9% PET Bottles
1.7% Metal Beverage Cans
1.7% Flexible Plastic Pouches
Metal beverage cans, PET bottles, and exible plastic lead the overall compound annual growth rate (CAGR) in packaging materials, which has shown some uctuation since 2021, but is projected to decrease to 1.3% CAGR by 2025. Based on the report ndings, this slight slowdown re ects the movement within omnichannel commerce to design primary packaging for shipping, eliminating the need for secondary and, in some cases tertiary packaging, along with the return to retail as consumers head back to stores after COVID-19.
Looking at overall material usage, survey respondents indicate that 75% of CPG companies continue to use plastic, more than those who use paper, and signi cantly more than those who use metal or glass. When asked about shifts in packaging material usage over the next 10 years, the report indicates that CPGs are increasingly looking to sustainable materials such as compostables, certi ed SBS paperboard, certi ed Kraft paperboard, bio-based bioplastics, and post-consumer recycled
Based on extensive research and analysis conducted by AMERIPEN and PMMI, the report highlights the importance of sustainability in the packaging industry, as consumers become increasingly aware of the environmental impact of packaging materials and manufacturers strive to reduce waste and emissions. This research aims to close the gap between design needs and recovery needs by beginning a conversation on trends, presenting forecasts for the coming decade, and recognizing the role of multiple stakeholders in advancing a circular packaging system.
The results on exibles are noteworthy: exible plastic lms may outpace plastics overall in compound annual growth rate (CAGR), but these materials are a challenge to recycle with current infrastructure.
The report says exible lms are expected to grow at an annual CAGR
of 4-6%, citing a 2021 report from Mordor Intelligence. In contrast, the average CAGR for plastics overall is about 3-4%, according to a 2022 report from the Flexible Packaging Association. This makes exibles one of the fastest-growing segments within plastic packaging.
Plastic lms have signi cant advantages both in terms of operational needs and sustainability. Their tensile strength allows for greater protection with less material, they help reduce carbon emissions during trucking due to space and weight, they are highly customizable, and they run ef ciently on lling lines to reduce overall costs and time in production.
Consumers also appreciate the ease of opening, resealable capability, low weight, and small shelf space these packaging formats offer.
Electronic, bus-compatible position indicators with target /actual value comparison and intuitive operation
Automated
Mechanically compatible: SIKO positioning systems are mechanically interchangeable
4-6% CAGR
15-16% CAGR OVER TEN YEARS
GOAL OF 25-30% INCREASE BY 2025
Adopting arti cial Intelligence (AI ) technology, or developing alternative collection and sortation pathways for exibles lms may help prevent damage to existing sortation equipment and improve quality of baled materials.
Chemical recycling may help increase resin quality for reuse, permitting increased collection and reduced sortation requirements.
Only 11% of U.S. population has the ability to compost packaging. Consider closed systems for immediate impact: stadiums, food service, etc.
Current demand far exceeds available supply and US reprocessing capacity.
Quality of materials is one of biggest challenges for packaging grade PCR content.
Based on materials changes proposed by the CPG community, the report forecasts growth in lightweight materials like exible lm pouches and food wrappers that are not yet widely recoverable. Compostables are currently viewed by CPGs as seeing a signi cant increase, although like exible lms, they currently lack a signi cant recovery system to ensure they are composted after use. Lastly, recycled content in packaging is expected to grow with many CPG rms identifying plans to increase PCR content in existing packaging.
Shifting nancial and operational responsibility of end-of-life management for products to producers, instead of taxpayers and government.
Moving away from material bans to dialogues on best way to collect, sort, and reprocess materials to reduce environmental impact.
Federal investments into programs uncovering emerging science and data to drive ef ciencies across packaging design and waste management.
Providing all households with convenient and consistent access to recycling and composting services
Clear recycling, composting, and other recovery de nitions to reduce consumer confusion.
Consistent data collection to measure and benchmark performance of a circular packaging economy.
Two of the top three materials lack the necessary infrastructure in the US to support recovery needs. The third, recycled content, will also require additional stimulation to meet US demand. Two of the top three materials lack the necessary infrastructure in the U.S. to support recovery needs. The third, recycled content, will also require additional stimulation to meet U.S. demand.
Flexible plastic lms can be recycled but are typically used in downgraded applications such as plastic “lumber” or polymer asphalt. They also tend to be collected at drop-off points, which represent a drop in the overall bucket, rather than through curbside systems.
These materials are challenging as they can complicate the sortation phase of materials recovery. When exible lms are sorted at a recycling facility, their exible nature makes it easy for them to get caught in rotators, tangling, and wrapping up in the equipment.
They may also be redirected toward paper lines, increasing contamination of that stream. As a result, many community recycling programs have banned the collection of exible lm packaging formats.
Speaking of contamination, compostables, too, represent a threat to existing waste streams in existing material recovery facilities (MRFs). Many compostable materials look similar or downright identical to plastic lm, which already ends up in incorrect streams and can contaminate them. Compostables can do the same if they end up in plastic or paper streams.
Moreover, consumers still don’t seem to be clear, yet, on the differences between industrially compostable and backyard compostable materials, and they don’t always know what should be done with them. There are a lot fewer materials that are backyard compostable; most compostables are are industrially compostable only. But industrial compostability doesn’t mean that any old MRF can accept them; specialized industrial compostability centers, which aren’t as common as
MRFs, are the only appropriate destination for these materials. Compostable packaging entering traditional MRFs are a likely source of bale and material contamination.
Since exibles and compostables are expected to continue to increase in market size, the packaging industry needs to begin discussing how best to collect, sort, and either compost them, or reprocess these materials to ensure a viable end market for their reuse. PW
Download your copy of the new study, “2023 Packaging Compass: Evaluating Trends in U.S. Packaging Design Over the Next Decade and Implications for the Future of a Circular Packaging System.” Visit pwgo.to/8033 to get ahold of the executive summary, or the entire report, for free.
This year’s crop of new robotic equipment and software leans into AI technology, as well as higher payloads, greater flexibility, and increased ease of programming and handling to alleviate the challenges faced by packagers as a result of the labor crisis.
The global packaging robots market has experienced remarkable growth in recent years, and this upward trajectory is expected to continue throughout the next decade. According to Precedence Research, the market size for packaging robots reached a value of $5.6 billion in 2022 and is projected to reach approximately $15.73 billion by 2032, with a compound annual growth rate (CAGR) of 10.8% between 2023 and 2032. This growth can be attributed to various factors that have long motivated packaging companies to adopt robotics. These include labor shortages, the need for enhanced productivity, the ability to achieve consistent product handling and repeatable quality, and the paramount importance of worker safety.
However, the magnitude of some of these driving factors, particularly workforce challenges, has been ampli ed due to the impact of the COVID-19 pandemic. Prior to the pandemic, packaging operations were already facing signi cant obstacles related to labor shortages and rising wages. In the post-pandemic era, these challenges have escalated to crisis levels. Data from the U.S. Bureau of Labor & Statistics reveals that approximately 750,000 jobs in the manufacturing sector remain unlled, despite historically low unemployment rates. Moreover, Deloitte Insights predicts that by 2030, the U.S. alone will have 2.1 million unlled manufacturing jobs.
States A3 – The Association for Advanced Automation, “The syn-
ergies between the industrial automation and manufacturing sectors have always been important to both, but the current labor crisis has intensi ed the sense of urgency and is a major driver of automation adoption.”
One obstacle for packaging companies considering the implementation of robotics remains the ongoing lack of skilled staff available onsite to program and operate the machinery. In response, robot OEMs are engineering new robotics systems that are increasingly more userfriendly and intuitive to program.
According to a 2022 report from PMMI – The Association for Packaging and Processing Technologies, “Robots and Cobots – An Automated Future” (see pwgo.to/7608), “As robots have proliferated across the packaging industry, so too have AI-based applications. This rapid growth of AI-based solutions is expected to continue, with AI use in packaging predicted to grow at CAGRs of over 50% in the next ve years.”
In January, Deep Learning Robotics (DLRob) unveiled what it calls “groundbreaking robot control software,” developed for compatibility with a range of robotic platforms. “This innovative software allows users to teach robots tasks in the most natural and intuitive way possible—by simply demonstrating the task,” it explains.
Through DLRob’s advanced machine learning algorithms, robots learn by observing and mimicking human actions. Says the company, the user-friendly interface and adaptability to a wide range of robots and applications, from industrial manufacturing to home automation, makes it possible for anyone to teach robots new tasks.
DLRob’s software was introduced in January. In April, it announced its support for new hardware devices with a new software update that will enable its customers to connect and control a wider range of robotic devices, including Universal Robots’ UR series of cobots. a video of Deep Learning Robotics’ robot control software at pwgo.to/7978
In June, at the automatica 2023 trade show in Germany, Intrinsic, an Alphabet company, and Siemens announced that they have teamed up to explore integrations and interfaces between Intrinsic’s AI-based robotics software and Siemens Digital Industries’ open and interoperable portfolio for automating and operating industrial production.
Furthermore, the advancement of Industry 4.0 has emerged as another in uential force, accompanied by arti cial intelligence (AI)-driven machine learning (ML) and intelligent vision technologies. These innovations are poised to enhance robot functionality signi cantly, making them easier to deploy and expanding the possibilities for robotic applications.
In Packaging World’s 2023 Report on Robotics, we explore how these trends are shaping the development of new robotic equipment and software solutions. By highlighting a range of innovative systems that have been introduced over the past year, this report demonstrates the transformative impact of these technologies on packaging operations.
At the forefront of the fourth industrial revolution, or Industry 4.0, AI and ML are currently two of the biggest trends in robotics and automation. AI refers to software that is trained to perform a speci c task, rather than being programmed. ML uses algorithms to automatically learn insights and recognize patterns from data, applying that learning to make increasingly better decisions.
Explains Intrinsic, currently the development and runtime environments for AI-based robotics and automation components differ signicantly in their development paradigms and make integration cumbersome. “For example, deploying advanced robotic capabilities such as pose estimation, robot manipulation, or automated path planning are complex processes that typically require teams of domain experts to operationalize,” it says.
The two companies intend to investigate new methods to seamlessly bridge the gaps between robotics, automation engineering, and IT development. According to Intrinsic, bridging these worlds will speed up the development process of exible, AI-enabled robot work cells and facilitate their seamless operation. This will make industrial robotics more accessible and usable for more businesses, entrepreneurs, and developers—particularly for new market segments like small and medium-sized enterprises (SMEs).
“Intrinsic’s mission is to democratize access to robotics. However, robotics is rarely decoupled from the production environment, where the most value is created today,” says Wendy Tan White, chief executive of cer of Intrinsic. “That’s why working with Siemens Digital Industries … is an exciting opportunity to bring joint solutions to the market in the future, so many more businesses can bene t from the value that robotics and automation can offer.”
Adds Siemens CEO of Factory Automation Rainer Brehm, “Siemens is dedicated to bringing IT and OT [operational technology] closer together—the key principle of our Industrial Operations X portfolio. We are impressed by Intrinsic’s open approach to industrial robotics, and we are excited to explore with Intrinsic how coupling of AI-based robots and automation technology can be further accelerated.”
The trend toward greater customization of packaging, including pack sizes, con gurations, and packaging types, to differentiate brands and connect with consumers continues to grow and with it, packagers’ need for greater exibility. In response, packaging machinery suppliers are developing more exible and modular systems for primary packaging that incorporate robots.
Among them is BluePrint Automation. BPA’s new Spider 300v (1) case-loading system, engineered for both packaging and contract-packaging operations, combines two delta-style pattern-building robots with a 6-axis case loader. The system uses vision to allow operators to perform both vertical and horizontal case packing on the same line at the
same time. The Spider 300v also allows for random product arrival at high speeds for exibility in packaging formats. Built for quick changeover between recipes, the system can handle standard RSC cases, threesided displays, shelf-ready packaging, and a range of other secondary containers.
According to BPA, another advantage of the machine is its compact footprint. Says the company, the Spider 300v is built with a new standard modular frame that has been designed to reduce cost by minimizing wiring and decreasing the footprint of the line by eliminating bulky external electrical cabinets.
EndFlex is also using a delta robot, this one for top-load case and tray packing. The PKR Delta (2a) modular pick-and-place cell has been designed to accommodate exible pouches and is recommended for applications as varied as personal care items, vitamin gummies, vegetables, and snack foods. The modular and compact 60 x 60-in. cell incorporates the delta robot with end-of-arm tooling (EOAT) that features a Venturi vacuum system and a vision system. The PKR Delta can be customized to t into an existing production line or can be integrated as part of a complete packaging solution that includes automatic case erecting, tray forming, sealing, and robotic palletizing. Another new offering from the company is the PKR Gantry robot (2b), which can be used to pack rigid cans, bottles, jars, and cartons.
Says Jorge Perez, vice president of operations at EndFlex, “Our clients needed faster, more compact and precise modular cells to compete in their respective industries. They came to us with their wish lists and trusted us to nd a solution. Our team of engineers and technicians got to work, and their efforts led to this new generation of robotic pick-and-place cells. The gantry and delta robotic cells we developed allow us to offer unique new solutions to some of the old packaging challenges.”
4BZIFMMPUPUIF
5IFTBGFTUDPCPUPOUIF
NBSLFUQMBDF EFMJWFSFE
JOXFFLTPSMFTT
4JYBYJTBSUJDVMBUJPO
'PSDFUPSRVFTFOTPSTPO
FBDIBYJT
1-F$"54BGFUZ3BUJOH
NN3FBDI
LH1BZMPBE
EPPTBOSPCPUJDTDPN
Modularity and exibility are also the highlights of another new robotic case packer—the Proco Collaborative Robot Packer (3)—which incorporates cobot technology. According to the company, the system was created to address growing workforce issues.
“We understand that labor shortages are becoming more common in the packaging industry, and that manufacturers need solutions that can help them reduce their labor costs and increase ef ciency,” says John McCormick, president of Proco Machinery. “Our new collabora-
tive robot packer is designed to be exible, versatile, and easy to use, helping our customers stay competitive in their markets.”
The Proco Collaborative Robot Packer can perform a range of tasks, from testing containers to packing them into cases. The system is modular and on casters, making it exible and easy to use, and can be adapted to different container shapes and sizes.
R.A Jones has also recently introduced a new robotic case/carton-packing system. Shown at interpack 2023, the Intelligent Flexible Transfer System (iFTS) (4) is designed to load exible pouches into cases or trays. Explains the company, in its most typical form, the iFTS receives exible pouches in a range of sizes from upstream systems that can then be grouped, oriented, and layered for either side-load or top-load cartons or cases, drawing upon a comprehensive library of standard or custom robot tooling, various robot types and sizes, xed automation, and conveyance.
The iFTS uses 2-, 3-, or 4-axis robots from Autonox Robotics that are driven by kinematics in the same controller that runs the main machine. Says R.A Jones, the use of the same controller provides a clean and open control architecture, reduced numbers of enclosures, and simpli ed machine wiring. Standard frame mounting, guarding, and overhead enclosures can be readily and safely adapted around other machines or con gured to meet speci c manufacturing requirements.
For U.S. petfood co-packer Simmons Foods Inc., flexibility was paramount in selecting new case-packing equipment for a unique packaging application. The company—the largest private-label and contract manufacturer of wet petfood in North America—needed a system that could load varying product shapes, both cups and split cups, into plastic trays pre-inserted into cases. Making the application more challenging, Simmons required that the cups be aligned to provide uniformity of cup graphics for shelf-ready display. With varying flavors and product sizes, including small round (3.2 oz), regular round (4 oz), and a unique split-cup design, there were a multitude of moving parts that required consolidation into one solution at a rate of 600 to 700 cups/min.
Simmons found the solution with Cama North America’s IF318 monobloc loading system. The machine is equipped with Y-shaped, 2-axis native Cama robots and
is engineered to orient the cups, form cases or cartons from blanks, insert the plastic trays into the cases, load cups into trays within the cases, and close the cases, all in one compact frame. As designed for Simmons, the system features four stations: case forming, tray depositing, product loading, and case closing.
In the first station, a robotic forming unit creates four cases per cycle from a flat blank. Next, robots insert plastic trays into each of the four cases. The petfood cups then arrive pre-
oriented, single file, in two lanes. A 2-axis robot with unique end effectors then picks the cups in the required count and loads them into four cases simultaneously. To do this, robotic grippers pick the cups and place them into the plastic trays. In order to best display the product’s graphics, the trays are grooved, and cups are placed on edge. Special gripper heads ensure accurate and positive handling. In the last station, a final robot closes the cases.
“This project had some unique needs, and we were happy to provide a solution with Cama’s own robotic technology,” explains Ken Major, regional sales manager, Cama North America. “The split cups are a fairly new product, and finding a way to orient and load them was very important to our customer. With our robots, we were able to successfully orient the cups so they are all facing the same direction, with graphics aligned and in easy view on store shelves.
“Another unique challenge for this application was the tray handling,” he adds. “The plastic trays feature grooves to hold the required count of cups—between 10 to 36 cups per case— on edge. Our solution features robots to place the trays into four cases simultaneously, then place the cups into the slotted grooves in each tray.” PW a video on Cama’s IF318 at pwgo.to/7988
Interestingly, Schubert’s new robotic equipment for carton-packing operations deals not with packing, but with feeding. Typically when a carton-blank magazine runs empty in a cartoner, machine operators must react quickly to avoid unnecessary interruptions. Schubert’s TLM Comfort Feeder (5), also introduced at interpack 2023, automates the infeed of carton blanks to its snack bar packer. According to the company, the TLM Comfort Feeder is the logical extension of its signature concept of a fully integrated and controlled packaging process.
To feed the carton blanks into Schubert’s bar packer, a pallet with blank sheets is placed into the machine. The blanks are pre-cut and only connected at a few predetermined breaking points to form a sheet. For removal, a spacer xes the sheet in place, while an F4 SCARA robot pulls each blank directly from the sheet one by one and deposits it into a vertical magazine that serves as a buffer. During this process, the pallet is gradually lifted until it reaches the last sheets. A camera also monitors the corner of each top sheet so that the robot can accurately access each blank.
Next, via Schubert’s new A6 carton erector, each blank is pulled individually from the bottom of the buffer and transferred to a pusher that transports it past the gluing unit to a folding box. There, a punch sucks up the blank, pushes it through the folding box for erecting and places it onto the transport system. In spite of its streamlined single-lane design, the unit achieves an out-
put of 60 blanks/min due to its use of robotics. The feeder can also be used in Schubert machines without infeed from the pallet, but with a vertical magazine.
Flexibility and full line integration are also at the heart of Shemesh Automation’s new robotics-enhanced packaging line for cosmetics, the TKS-C60 (6). According to the company “the need to package a range of product shapes and sizes—a common challenge in the cosmetics industry—has caused manufacturers to toil with the complexities of integrating machinery from different suppliers, expensive line-changeover parts,
<285
6867$,1$%/( $'+(6,9(6 3$571(5
,QWURGXFLQJ
+%)8//(5($57+,&
+%)XOOHU§(DUWKLF SURYLGHVZDVKDELOLW\LQORZ
OHYHOVRIFDXVWLFFOHDUDSSHDUDQFHDQGQRVWDLQLQJIRRG
VDIHW\ORZWHPSHUDWXUHUHVLVWDQFHDQGJUHDWDGKHVLRQ,W
DOORZVUHF\FODELOLW\LPSURYHVEUDQGLPDJHRQWUDQVSDUHQW
SDFNDJLQJKROGVWKHODEHOGXULQJWKHSURGXFWLRQDQG
VKLSSLQJSURFHVVDQGGRHVQRWGHIRUPRUPHOWWKHSODVWLF
3$&.$*,1*62/87,216
$OORZV5HF\FODELOLW\
5HPRYHDGKHVLYHIURPERWK
VXEVWUDWHVLQDZDVKLQJSURFHVV
ZLWKRXWOHDYLQJUHVLGXH
)RRG6DIHW\
0HHWV)'$LQGLUHFW
.(<%(1(),76
&DXVWLFZDVKDEOHVROXWLRQ
/RZDSSOLFDWLRQWHPSHUDWXUH
1RVWDLQDQGORZRLOPLJUDWLRQ
)LQGXVRQVRFLDOPHGLD
,PSURYH%UDQG,PDJH
&OHDUDSSHDUDQFHZKHQDSSOLHGRQ
WUDQVSDUHQWSDFNDJLQJ
/RZ7HPSHUDWXUH
5HVLVWDQFH
0DLQWDLQVDGKHVLRQHYHQLQWKH
UHIULJHUDWRU
)RU0RUH,QIRUPDWLRQ
ZZZKEIXOOHUFRP
and changeover-related downtime, for too long.” The TKS-C60 handles the entire process, including feeding, lling, capping, labeling, case packing, and palletizing of cosmetics products in a range of shapes and sizes.
The new line is designed to provide uninterrupted bottling of products that range from creams and foundations to fragrances and nail polish at speeds to 60 bottles/min and incorporates a number of robots in different areas of the machine. ETNA, the line’s automatic bottle unscrambler, uses a delta robot supplied by ABB or Fanuc to provide precise bottle orientation, covering virtually all bottle types common to the cosmetics sector. Notes Shemesh, the robotic elements ensure no changeparts are required—except in some cases for the robot grippers—when unscrambling multiple different bottle shapes. Robots also ensure the bottles are facing the correct way for lling and capping.
Since their debut in the packaging industry more than a decade ago, collaborative robots, or cobots, have become nearly as robust and wellknown a category as traditional industrial robot styles. Lightweight, portable, and easy to program, cobots offer SMEs an affordable way to automate repetitive, low-speed tasks that were formerly done manually. For larger manufacturers, cobots enable greater exibility on production lines through modular deployments.
According to PMMI’s 2022 robotics report, the use of cobots in packaging operations stood at 27% in 2022, with usage predicted to grow to 57% by 2027. Originally designed for low-payload applications, such as pick-and-place and material handling, recent developments in technology are extending the reach (literally and guratively) of cobots all along the packaging line.
Noted PMMI in its report, in 2022, 6% of respondents were using cobots in processing; in 2027, that number is predicted to rise to 22%. For primary packaging operations, 10% of CPGs were using cobots in 2022; 22% report they expect to be using them on this part of the line in 2027. And for secondary packaging applications, 6% of CPGs said they were using cobots in 2022, with that number predicted to grow to 29% by 2027.
Spurring the growth of cobots in secondary packaging applications is the advent over the last two years of higher-payload, longerreach “industrial cobots” that can be used for palletizing. At the lower-payload range is ABB’s SWIFTI CRB 1300 (7), with a capacity of up to 11 kg. According to the company, the cobot’s high-payload capability combined with its 13-box/min palletizing speed (versus the industry standard of eight per minute) improves production ef ciency by up to 44%.
Shemesh’s continuous-motion cosmetics capping machine, the Attilus, uses a robotic sorter based on a delta robot and an advanced vision system to enable higher speeds, enhanced accuracy, and exibility in automatic screw, pump, and spray-cap sorting. The Attilus also uses a servo-controlled pick-and-place 2-axis gantry robot to track and deliver the caps to the bottles while in motion, ensuring smoother and faster production. Integrated with the Attilus and the gantry robot are a PLC and HMI from Siemens or Allen-Bradley that put the operator in control, allowing for simple programming, such as changing formats and the course of movement, at the touch of a button. The robotic enhancement of the Attilus also ensures changeover downtime is kept to a minimum of less than 20 minutes.
videos of some of the systems discussed here at pwgo.to/7979
“Our customers are looking to robotic automation to make their processes more exible, ef cient, and resilient, helping to counter labor shortages by enabling their employees to perform more value-added work,” says Andrea Cassoni, managing director for Global General Industry Robotics at ABB. “The latest addition to our SWIFTI family is a highly accurate, high-payload cobot that’s up to six times faster than other robots in its class. This means it can be used by both SMEs and large manufacturers looking for collaborative automated solutions to achieve new levels of exibility and productivity.”
The 6-axis SWIFTI CRB 1300 is powered by ABB’s OmniCore C90XT controller, which the company says allows for up to ve times greater precision than any other cobot in its class, making it suitable for tasks requiring consistent accuracy and repeatability. This precision, along with payload options ranging from 7 to 11 kg and reaches from 90 to 1,400 mm, enable the cobot to perform a range of higher-payload tasks, including screwdriving, assembly, pick-and-place, and palletizing.
To ensure operator safety, the cobot features a safety laser scanner integrated with ABB’s SafeMove collaborative safety software. If the laser scanner detects a worker within SWIFTI’s operating area, SafeMove automatically slows the robot or stops it completely. As the worker moves away, movement is restored, returning to full speed for full productivity only once the working area is completely clear. Says ABB, integrating the scanner and software is simple through the use of SafeMove’s software add-ins, enabling workers to quickly set up a safe working zone and other safety features using a hand-held FlexPendant operating unit.
The cobot is also said to be easy to program, making it accessible for non-specialists in robotics. The SWIFTI can be set up either by physically guiding it through a process (lead-through programming) or through ABB’s Wizard Easy Programming software, which is based on simple graphical blocks.
Nearly double the payload of the SWIFTI is the highest-payload cobot in Dobot’s new CRA Series (8) , which includes seven models that range in capacity from 3 to 20 kg and working envelopes from 620 to 1,700 mm. The CRA Series and Dobot’s new CRV500 Smart Camera were of cially launched at the Automate Show in May.
As Dobot explains, the series incorporates a number of new technologies that enhance performance. “Compared to its predecessor, the CRA Series has a noticeable performance boost and is more ef cient, safer, and easier to use,” says the company.
Among the new features are self-developed, highly integrated joints with high-performance harmonic drive reducers that improve cycle time by 25%, an optimized precision control algorithm that greatly reduces vibrations, a repeatability of ±0.02 mm, and a trajectory accuracy of 0.2 to 0.4 mm during complex motion. In terms of safety, the cobot features electromagnetic brakes that auto-engage in 18 milliseconds in the case of a power outage to restrict robotic arm falls less than 1 mm, effectively preventing the end tool from dropping. The CRA Series also has built-in virtual boundaries, real-time payload detection, and other features to ensure the safety of nearby workers.
According to Dobot, the series’ brand new operating software is more user-friendly as well. It supports graphical programming, scripting, and drag-to-teach for trajectory replay. It is also multiplatform and works with personal computers, tablets, smartphones, and more. The CRA Series supports Modbus, Ethernet/IP, and PROFINET communication, connecting with PLC and other automation systems seamlessly. With 24 I/O ports available and PNP/NPN switching, expansion can be carried out more easily.
The other new product from the company, the CRV 500 smart camera, employs Dobot’s 2.5D spatial compensation technology that, when used with its CRA and CR Series cobots, can accurately identify an object’s horizontal angle and inclination for accurate grabbing. The camera can be set up using Dobot’s cobot control software without further development for easy and quick deployment.
Also in the 20-kg-payload category is Elite Robots’ new , which the company says “stands out for its remarkable ease of use, safety, and expandability.” The model is a new addition to Elite’s existing CS Series of cobots, which includes 3-, 6-, and 12-kg-payload models, and offers a reach of 1,800 mm and speeds to approximately 3.9 m/sec.
The CS Series is based on an advanced software infrastructure, with an intuitive and modular graphical user interface (GUI) that supports the Python scripting language and self-developed plug-ins, offering a high level of programming customization. The series offers 24 digital I/O (8 con gurable) and 4 con gurable tool I/O, and a range of connectivity options. Safety is ensured by compliance with ISO 10218-1 and ISO 13849-1 standards.
s robotic is in or SKUs that need separate lines s to a common m can up as anes, in
A core advantage of TopTier’s robotic palletizer is in the case of multiple products or SKUs that need palletizing at the same time.
For example, if you have two separate lines and want to take the products to a common palletizing cell, one robotic arm can pick up as many as four product infeed lanes, resulting in four pallet build stations.
Our robotic palletizers are flexible because of our wide range of end of arm tool options.
These include:
xible because of our options
• a traditional vacuum head to pick up cases or bundles
• mechanical gripper style heads for bundles or cases
• tools to pick up full layers or individual products
• end of arm tools for barrels or pales (and can also be used to pick up slip sheets, pallets, and top sheets!)
Contact us today to discuss your palletizing needs!
One feature unique to the CS620, says Elite, is that it is “the world’s rst cobot to supply end effectors through a 5A tool I/O.” This ensures the cobot always has enough power to perform demanding tasks and can handle multiple devices simultaneously through its dual tool (fourpin and eight-pin) connector.
The CS620 robotic arm features an IP65-rated degree of protection, upgradable to IP68. The ISO Class 5 cleanroom designation also makes it suitable for applications that require a high level of hygiene, such as pharmaceuticals and electronics.
Boasting payload capacities of up to 30 kg and 50 kg, respectively, are Fanuc’s new CRX-25iA (10) and CR-35iB (11) cobots. The “heaviest lifter” of Fanuc’s CRX Series of cobots, the 6-axis CRX-25iA offers a reach of 1,889 mm and a maximum speed of 1,000 mm/sec, and is recommended for applications that include palletizing, material handling, machine loading and unloading, and welding, among others.
According to Fanuc, a new teach-pendant user interface makes programming easy, with lead-through teaching and simple drag-and-drop programming. For space savings, the unit is equipped with Fanuc’s compact R-30iB Mini Plus Controller. The company adds that switching out peripherals is easy with its selection of approved devices, which include an auto connector, a manual tool change, and electric and manual grippers, among other devices. Two connection ports on the J6 axis offer quick connections and interchangeability for EOAT, such as grippers and cameras. In addition, Fanuc’s intelligent features allow for easy connection to iRVision—the company’s fully integrated plug-andplay vision system, which offers machine vision in 2D and 3D—force sensors, and more.
Part of the company’s CR Series cobots, the newly revamped CR-35iC is said to be “the industry’s strongest collaborative robot.” With a payload capacity ranging from 35 to 50 kg, the cobot features a work envelope of 1,831 mm and a maximum speed of 750 mm/sec. Depending on the end-user’s needs, the CR-35iB can be equipped with a Fanuc vision sensor or a 3D area sensor, enabling it to locate or visualize products.
Also designed for ease of operation, the cobot does not require special programming or complex languages: Operators can program the CR-35iC with the Fanuc Hand Guidance option, leading the cobot through paths to teach a new task, or can use the company’s tablet TP with drag-and-drop user interface. The cobot is also compatible with Fanuc’s standard teach pendant. As with the CRX-25iA, the CR-35iB can be equipped with intelligent functions, including iRVision and force sensors.
The CR-35iB is recommended for a wide range of applications, including assembly, material removal, machine tending, load transfer, dispensing, and picking, packing, and palletizing.
With today’s workforce challenges, CPG producers need the most effective tools available to allow operators and maintenance personnel to perform at their best. GuidePoint™ does just that, quickly and clearly delivering knowledge and support resources at the point of need to maximize productivity in your operation. That’s GuidePoint, and that’s Douglas. Simplifying for success with Customer Driven innovation. Ready to ? See GuidePoint in action at PACK EXPO, Booth C-2014
Call one of our application specialists today, or visit douglas-machine.com to explore GuidePoint and our full line of Customer Driven solutions. Alexandria, MN USA • Tel: 320.763.6587 • email: info@douglas-machine.com
Weighing in with a robust 30-kg payload, the new 6-axis HC30PL (12) cobot from Yaskawa offers a maximum reach of 1,700 mm and is recommended for use in select handling, packaging, and logistical applications. Joining the company’s HC Series of cobots, the HC30PL meets the line’s established safety standards to enable safe operation with, or in close proximity to, human workers.
In order to constantly monitor force to quickly and safely react to contact, the cobot uses Power and Force Limiting (PFL) technology. Additional safety is provided by advanced pinchless geometry. With these safety standards in mind, the HC30PL offers four modes of collaborative operation and can shift between collaborative speed in PFL mode or full speed in industrial mode, optimizing cycle times based on risk assessment and process requirements.
Providing the ease of programming cobots are known for, Yaskawa’s new cobot allows operators to direct teach points with hand-guided programming without a pendant for quick implementation, and a plugand-play tool ange based on EN ISO-9409-1-80-6-MB connects a variety of EOAT for fast deployment. According to Yaskawa, installation is also quick and ef cient: “A single cable is all that is needed to connect the manipulator to the controller, resulting in easy setup and reduced expenses for maintenance and spare parts,” it explains.
Other features of the HC30PL include an IP67 rating that enables it to be used in damp or splash-prone environments, an easy-to-clean surface for use in sanitary settings where wipe or wash is required, and a compact footprint of 2 ft W x 1.6 ft H x 1.4 ft D. The cobot is controlled
YRC1000 controller and is also compatible with the YRC1000micro Controller. The HC20PL is compatible with a standard teach pendant or the company’s touchscreen Smart Pendant, designed for novice robot users.
Not a cobot, but worthy of including in this lineup of high-payload palletizing robots is Fuji Robotics-North America’s new-to-the-NorthAmerican market EC-102 (13) palletizing robot, which features a 160-kg payload. According to the company the EC-102 is the most economical and environmentally friendly robot among its offerings. Features of the four-axis articulated palletizing robot include a bag cycle time of 1,200 cycles/hr and an operating area of 2,300 mm for the Z axis (vertical), 1,500 mm for the R axis (longitudinal), and 330 deg for the Theta (rotation) and Alpha (wrist) axes. A fth axis of motion is available on the end effector.
videos of some of the cobots discussed here at pwgo.to/7980
In addition to standalone cobots that can be used for palletizing and other heavy-payload tasks, several packaging machinery OEMs have introduced new solutions this past year that incorporate cobots for a dedicated palletizing system. One such company is ONExia, with its second-generation PalletizUR, the PalletizUR 2.0 (14), which can handle case weights of approximately 20 kg using Universal Robot’s UR20 cobot arm. Emphasizes the company, the PallezUR 2.0 is not a kit. Every palletizer application is reviewed by ONExia’s engineers and is delivered with all the conveyors and grippers needed for a collaborative robot cell.
According the company, the PalletizUR 2.0 can handle virtually any size case using the company’s robotics palletizing software, with no programming required. The cobot is controlled through a single touch-
screen, which ONExia says provides a simpli ed user experience for daily operators. To add or edit pallet con gurations, boxes are positioned using the drag-and-drop interface with advanced features built-in, including conveyor control, label orientation, and slip-sheet layer placement.
Says Greg Selke, chief executive of cer of ONExia, “This is the easiest robot install our customers will ever have. Many in fact do not require any startup support from us when deploying additional palletizers to other lines in their facilities.”
As with all cobots, the PalletizUR 2.0 requires no caging or guarding to operate; it is third-party veri ed to meet the ANSI and RIA industry standards for collaborative robot safety.
Sidel’s new palletizer, the RoboAccess_Pal S (15) was designed to bring the bene ts of cobots to palletizing operations for customers in the food, home, and personal care markets. Says the company, “With the introduction of cobotics in palletizing, Sidel has been able to answer the
At over 150 lb, a half-keg of beer is strenuous to handle. That’s why more than 20 years ago, the D.G. Yuengling and Son, Inc. brewery—known as America’s oldest—made its first foray into automation when it incorporated industrial robots on its keg-filling lines.
Fast forward to the present, and Yuengling recently replaced those original robots with new state-of-the-art models. The replacements, installed in April 2023, are faster and even more robust, save time, consume less energy, provide easier maintenance and, like their predecessors, are extremely reliable, as well as reduce the risk of operator injuries.
“We basically wore out our original robots. Just their ages and the number of hours on them justified the need for updated automation,” says Bill Friedman, electrical services manager at Yuengling’s Tampa, Fla., facility. “Plus, people don’t want to handle kegs all day, and there’s always a risk of injury.”
In 2003, Yuengling installed two industrial robots from Kuka Robotics into the keg line at its Millcreek facility, located in Pottsville, Pa., not far from the company’s original brewery, founded in 1829 and still in operation. Then, in 2006, the company added a Kuka robot to the new keg line in its Tampa plant.
Yuengling is currently owned and operated by Jennifer Yuengling, vice president of Operations and a great-greatgreat-granddaughter of brewery founder D. G. Yuengling, along with her sisters and their father, Richard Yuengling Jr. According to Jennifer Yuengling, due to the brewery’s
successful relationship with Kuka over the years and the quality of the company’s robot technology, when it came time to upgrade the robots, Yuengling again opted for Kuka.
Each of Yuengling’s keg lines uses two Kuka articulated arm robots that are identical in size, reach, and payload. Within the lines, they perform depalletization and palletization. Empty kegs enter the line stacked on pallets—four half kegs (15.5-gal capacity) and eight quarter kegs (7.25-gal capacity) per pallet. The first robot removes empty kegs from the pallets and places them on a conveyor, where they travel to a cleaning process and are then refilled. Once the kegs are removed, the robot stacks the empty pallets in a holding station/table for the second robot to use. Both robots share the pallet station.
Filled half kegs weigh in at 165 lb apiece, and one robot handles two at a time during palletization. In operation, this robot removes a pallet from the holding station, places it on a conveyor, and loads it with refilled kegs. From there, the pallets are loaded into delivery trucks for shipping.
Speed and repeatability are the keys to the success of this cell, and all of its elements must be located precisely for each cycle. “The amount of work that the two Kuka robots do and the speed at which they operate is phenomenal,” says Friedman. “They can run 24/7/365, handling about 400 full kegs per hour.”
Continued on page 128
Continued from page 126
The updated robots at Yuengling’s Millcreek and Tampa facilities are Kuka KR 360 R2830 6-axis heavy-duty robots that provide the breweries with pose repeatability of 0.08 mm and an arm extension of up to 500 mm. Kuka also offers the robots in a version designed for applications that require resistance to heat, dust, and water, and with a range of mounting position options that allows for more adaptability.
Although the number one criterion for the keg line is safety, number two, according to Friedman, is reliable, continuous robot operation with minimal required maintenance. And if there is a needed repair, the fix is fast and easy to make.
“We’ve stayed with Kuka because we’ve always had extremely good support, both technical and training,” Friedman says. “The other main reason we choose Kuka robots is that they are very dependable, with a simple, practically maintenance-free design. Plus, we’ve improved our cycle times from about 250 kegs per hour to around 430.”
Friedman also noted that for six years prior to its replacement, one of the robots on the Tampa facility keg line handled both empty and full kegs. He calculates that it depalletized/palletized about 3 million kegs during its six-year working life—and over that time period, it needed only four
repairs, which involved typical wear components.
“If we had been using a traditional palletizer, the number of breakdowns in that same amount of time would have been a hundredfold,” Friedman points out. “Our original palletizer was limited to 200 kegs per hour and no faster. It was a basic over/under palletizing setup and was an extremely hazardous system that required massive safety caging.”
Yuengling’s new robots all feature the compact KRC 5 controller, which Kuka says consumes less energy compared to its predecessor and slots seamlessly into existing IT and cloud environments. Kuka adds that due to its modular cabinet system, the KR C5’s hardware is durable and futureproof, and can be expanded as required. “The highly integrated, compact control modules are easy to operate, and Yuengling can link them to various software products and digital services as needed,” Kuka explains.
The need for increased capacity was the main reason Yuengling added its Millcreek and Tampa facilities and incorporated Kuka automation. Since then, the company has increased production from 137,000 barrels to more than 2 million barrels, encompassing nine different beer types—a growth that Yuengling attributes in large part to the addition of robotic automation. PW
a video of Yuengling’s use of Kuka robots at pwgo.to/7989
for carbo closure o ers a new threa ore our tethered and non-teth
The NovaSpark™ is a plastic closure designed for carbonated products with an 1881 neck finish. Our redesigned closure o ers a new thread profile for better engagement, improved venting, and Explore our tethered and non-tethered versions for enhanced production flexibility.
growing market demand for very compact and affordable cells, which generally replace manual operations. For more demanding lines, where robotic arms could offer higher technical performances, Sidel has drawn on its 50-plus years of palletizing expertise to create an all-in-one solution that combines a small footprint, a fast return on investment, and a higher case payload and speed.”
The new palletizer operates at 12 cycles/ min and can handle case weights up to 25 kg, with an ROI of one to two years. The machine footprint measures less than 40 sq ft for two stations and has a pallet height of approximately 5.6 ft. Embedded in the machine are three new patented features: a light-weighted carbon ber and 3D-printed clamping head that helps lighten the tooling weight to increase the case/pack payload, a folding guarding system that ensures movable plug-and-play capabilities, and a mobile physical curtain that guarantees the operator’s protection during pallet supply and removal.
Recently introduced in a soon-to-be-available 25-kg-payload version, Techman Robot’s TM AI Cobot (16) series combines a precise robot arm with a native AI inferencing engine and a smart vision system in
a complete package, ready for deployment. Says Techman, “TM AI Cobot works on the principle of being smart, simple, and safe. By combining visual processing in the robot arm, the AI Cobot can perform fast and precise pick-and-place, AMR [autonomous mobile robots], palletizing, welding, semi-conductor and product manufacturing, AOI [automated optical inspections], and foodservice preparation, among many other
applications that can be accelerated by AI-Vision.”
According to Techman, the AI Cobot is the only intelligent robotic arm series on the market that comes with a comprehensive AI software suite. It includes the TM AI+ Training Server software tool, designed to help users manage image data, set up AI training parameters, and train AI models; TM AI+ AOI Edge, a smart function software that allows customers to deploy TMvision to all required areas in the plant; TM Image Manager quality tracking software; and TM 3DVision, which includes 3D vision software and a 3D camera. Together, these software programs enable users to train and tailor their system to meet their speci c application.
videos of the all of the systems mentioned here at pwgo.to/7981
Helping cobot users get up and running with their new equipment as quickly as possible is the goal of a new software product from OnRobot. Launched in January, D:PLOY (17) is said by OnRobot to be the industry’s rst automated platform for building, running, monitoring, and redeploying collaborative applications directly on the factory oor with zero programming or simulation needed, resulting in time savings of up to 90% over conventional solutions. “By automating the process of getting a robotic application up and running, D:PLOY allows complete applications to be deployed and redeployed directly on the manufacturing oor in a few simple steps, with zero programming—all within a few hours,” says the company.
At launch, the D:PLOY platform supports palletizing, CNC machine
tending, packaging, and transferring (pick-and-place) applications, with future announcements planned for additional processes.
“The D:PLOY platform and its ability to truly democratize automation has been OnRobot’s goal from the beginning, and we have been laying the groundwork for years,” said Enrico Krog Iversen, chief executive of cer of OnRobot upon the launch of the platform.
D:PLOY was developed to address the shortage of skilled robotics engineers and integrators who can help smaller, less-experienced manufacturers break through existing barriers to automation. According to Simon Potzkai, robotics sales engineer at Alexander Bürkle, an OnRobot system integrator and a D:PLOY beta tester, “D:PLOY simpli es the task of building and integrating a robotic cell with an innovative approach that doesn’t require any type of programming. With the current shortage of engineers, that’s a huge advantage for integrators. By making it easier and faster for us to deploy automation, we can serve more customers and help them more quickly realize the advantages of automation. That’s a win-win for everyone.”
D:PLOY works by automating many of the manual steps necessary today for building and running an application. D:PLOY automatically discovers most of the installed hardware and generates the robot motion based on the obstacles and cell boundaries de ned in the workspace. The program logic, signals exchange, event handling, and robot movement are automatically created for the entire application based on a few inputs such as workpiece attributes and pick position.
Demonstrating the reduction in robotic cell deployment time and complexity, OnRobot uses an example of a palletizing application, where deployment time drops from 40 hours to 4 hours, for a 90% time savings. In addition, when production requirements change, D:PLOY provides the exibility to quickly redeploy the application for new products or workpieces. Real-time monitoring improves productivity and minimizes downtime.
Says Alan Vallis, training and development manager at LG Motion Ltd., an OnRobot distributor, “D:PLOY will make automation accessible for companies who may be a bit reluctant, whether it is related to cost or in-house skills and competences. I think D:PLOY will demystify a lot of that.”
a video on OnRobot’s D:PLOY software at pwgo.to/7982
In addition to labor shortages, COVID drove another signi cant industry trend that continues to in uence the development of new robot technologies—the rise of e-commerce. Reported one article from the International Federation of Robotics, “The e-commerce revolution was driven by the pandemic and will continue to accelerate … . There are thousands of robots installed today that did not exist in this segment just ve years ago.”
E-commerce applications require the utmost in equipment exibility for products that range in size and shape and for packaging of different sizes, shapes, and materials. It also requires extreme accuracy. To deliver on these needs, Bastian Solutions, a Toyota Advanced Logistics company, has introduced its SmartPick robotic piece-picking solution (18) for fully automated order ful llment. The system combines advanced AI, machine vision, dynamic EOAT, a 6-axis robot, and seamless software integration that can turn a goods-to-person (GTP) system into a goods-to-robot (GTR) operation.
According to Bastian, the SmartPick enables 99%+ order accuracy while operating at or above manual picking speeds of 500 to 1,000 picks/hr, depending on the cell layout. The system can handle packaging that includes cuboids, cylinders, collapsible tubes, blister packs, polybags, and clamshells as well as cartons, bags, loose products, and other formats.
A fully automated order ful llment solution consists of a GTP
From the harshest environments to the most sophisticated Pharmaceutical applications requiring vision, validation and serialization, Quadrel is ready to partner with you. Systems arrive Ethernet ready, and feature secure remote access for system monitoring, editing and trouble shooting.
In addition Quadrel systems feature Internationally compliant guarding, Allen Bradley Compact Logix PLC, Panelview color touchscreen operator interface, full servo control and redundant applicators for zero downtime nonstop operation.
Quadrel
industrial robot, an AI vision system, a takeaway conveyor with automated labeling and checkweighing, and warehouse software to control the entire process.
The system works as follows:
• When an order is received, the warehouse software communicates with the GTP system to deliver the bin containing the ordered item to the robot-operated GTP workstation.
• The robot’s AI and vision platform identi es the SKU(s) needed for the order, then selects the “most pickable” product.
• The vision platform directs mechanical controls to manipulate the robotic arm and EOAT to pick an item without encroaching on other objects or the tote walls.
• The robot retracts from the bin and places the object in a secondary shipping carton, after which it’s ready for another pick-andplace sequence.
• As the robot picks different object shapes, dimensions, and surfaces, it continues to learn and improve on how to identify and pick objects in different positions. In a case where an item can’t be picked in the rst few attempts, the AI vision system determines whether the object’s orientation should be changed, and it will jostle the item to expose a different surface and try to pick it again.
• When the order is complete, the container is transported via the takeaway conveyor for further outbound processing such as checkweighing with in-line scales to ensure order accuracy and automated labeling to attach a shipping label.
Because it’s equipped with AI and machine vision, Bastian Solutions’ piece-picking robots do not require the operator to be trained or have programming skills to handle current products or new product integration. As new products are introduced, the AI software builds a library of objects it has seen and handled over time, along with optimal picking information. The AI and vision platform directly interfaces with Bastian Solutions’ Exacta intralogistics software, a scalable, modular system that acts as an interface between automation, operators, and other processes to communicate product data and order ful llment information.
Also designed to handle random bin picking is Comau’s new MI.RA (Machine Inspection Recognition Archetypes)/Picker (19), recommended for industries that include food and beverage, pharmaceuticals, and plastics, among others. The system is adaptable to any brand of commercial robot, customized bin, or customized gripper, and uses two high-resolution laser sensors and a central camera to autonomously recognize, locate, and grasp randomly placed objects at a rate of up to 40 pieces/min. According to Comau, the MI.RA/Picker guarantees optimal path management and collision-free trajectories with its virtual simulation tools and predictive algorithms.
Through the use of 3D vision technology, dual sensors, and an intuitive programming interface, the system can handle single or multiple bins containing unorganized, rigid parts whose orientation and arrangement are unpredictable. Says Comau, “Because products can be dumped in bins instead of placed in an orderly manner, the MI.RA/Picker reduces upstream process times while ensuring a simpli ed logistics
ow without singularization of the parts or rigid xtures.”
It adds, “We believe, based on internal estimates and supporting market research, that the random bin and piece-picking market could reach $1.2 billion by 2025, with a compound annual growth rate of 76% from 2019 to 2025. In this light, our novel approach to intelligent random bin picking for machine tending, pick-and-place, and kitting operations among others will undoubtedly help our customers increase both their process quality and production capacity.”
Fortna—a new company formed in November 2022 with the merger of MHS Global and Fortna—also offers a robotic order fulllment solution, the goods-to-robot system (GTR) (20), which has been designed for storage, picking, and order kitting work ows in e-commerce ful llment and other distribution settings. Shares the company, the system can result in operational ef ciency gains of up to 400% compared to manual processes and increases product storage density by enabling product picking out of double-deep storage.
The system uses Fortna integration and advanced robotic technologies, including mobile-enabled case storage and retrieval and pick-and-
place. In addition to design, installation, and validation by Fortna, the system is powered by a warehouse control system (WCS) and warehouse execution system (WES) that integrates the various automated components and robotics technology to work as a smart system.
During operation, a zero-pressure accumulation conveyor from Fortna feeds totes to and from the order ll station. Mobile robots transport totes between storage and a piece-picking robot. The robot picks each
item for the order from a source tote, packs it, and signals to the WCS/ WES that the conveyor can move the completed order to the outbound location. The robotic arm uses vision, grasp intelligence, and dynamic path planning to autonomously pick items cleanly and consistently, without colliding with the tote or being unable to pick all items in the tote.
At the 2022 AMR & Logistics Show last October, intelligent robotics provider Mujin debuted its QuickBot (QB) (21) robot cell for case handling in warehouse/e-commerce environments. The rst application using the QB is a depalletizing system for incoming cases of different shapes and sizes—a process Mujin says is “one of the most arduous tasks of the receiving process in warehouses.”
Says Mujin CEO and co-founder Ross Diankov, “In today’s day and age, a lot is demanded of robot automation systems. They need to be highly reliable, have high throughput, and—of foremost importance— they need to deploy quickly, so that businesses can enjoy the return on investment from day one.”
Among the QB’s quick-deployment features, it easily uncrates and can be transported via forklift to the installation location, everything is preinstalled on a large metal baseplate, so no drilling is required, and the safety system is preinstalled and ready to go upon arrival. In addition, a pneumatically driven, telescoping vision stand makes it easy to raise the vision system to the proper height, while the conveyor is on a rail with adjustable height and pulls out to connect to an existing
As with all of Mujin’s automation solutions, the QB is powered by the company’s intelligent robot controller, the MujinController. It allows for advanced perception and real-time motion planning, allowing for on-the- y case recognition. As a result, the QuickBot can manage real-world scenarios for both single- and mixed-SKU pallet loads without prior teaching or information from external systems. The QB arm is equipped with a universal, heavy-payload gripper to meet the physical requirements of general warehouse tasks.
As its name might suggest, one of the most de ning features of the QuickBot is that it can be deployed quickly. After forklifting the QB into place at their booth at the AMR show, Mujin claims that it took less than three hours to have the unit clearing pallets.
conveyor. Furthermore, no system-level integration is needed to operate the QB.
Also at the show, Mujin announced a partnership with Formic, a Robotics-as-a-Service (RaaS) provider, that will make the QB available through the RaaS model.
Osaro, which delivers its own robotic GTR systems, has introduced advanced machine-learning vision software for systems integrators, 3PLs, and ful llment operators that will enable them to use robots in new areas across the warehouse. Among them are applications that require precise visual perception and placement, such as depalletization, piece picking with AMR/ASRS (autonomous mobile robots/automated storage and retrieval systems), kitting, and induction.
The new SightWorks (22) software enables robots to see, perceive, grasp, and perform tasks previously done solely by humans. According to the company, the combination of its vision software and an array of associated sensor and camera technologies provides the foundation for a wide variety of systems. In depalletization, for example, Osaro’s robot can recognize and handle not only mixed cases, but also foreign objects, such as box cutters or tape dispensers, on boxes stacked on a pallet. The system knows to stop and alarm until the items are removed. The same is true for damaged boxes that might break open if lifted.
Shares Jay Dugat, CEO of automation
OEM Robotica Inc., “We needed an automated depalletizing function to complete an end-to-end offering for our decanting technology. Our DePal product, powered by Osaro, handles mixed pallets and will directly deploy our ABOT box-opening technology, providing an automated turnkey solution. Osaro was chosen after a hands-on evaluation of various solutions. We went with Osaro because of less sensitivity to variance in ambient lighting and the ability to distinguish challenging packages with high con dence.”
Osaro’s software is said to integrate reliably with other warehouse automation technologies through its modular RESTful API (application programming interface), which allows integrators to choose commands in a variety of blocks, so actions can be readily strung together in different ways. The software also tracks performance with built-in monitoring that assesses and optimizes the performance of the system. Osaro says that the use of its vision software can shorten order cycle time, speeding delivery and improving order accuracy.
videos of the some of the systems mentioned in this section at pwgo.to/7983
The Rennco ProCommerce bubble mailer system is a complete E-Commerce packaging solution.
:LWKWKH5HQQFRYHUWLFDOSDFNDJLQJPDFKLQHÀDW VWRFNEXEEOHPDWHULDORUÀDWVWRFNPDLOLQJ material is utilized to “right size” the bag around your products reducing excess material and creating cost savings.
For more information please visit our website at www.rennco.com or call us call (517) 568-4121! Don’t
Just as COVID drove the growth of e-commerce, so too did it drive a number of “essential businesses,” healthcare being primary among them. Before the pandemic, the pharmaceutical industry had been lagging in its adoption of automation and robotics, due to the highly regulated nature of the business. But the pandemic resulted in a massive acceleration in the rate of adoption of pharmaceutical robots.
a 1,418-mm reach that is equipped with sensors and force controls to immediately stop the cobot’s motion if it contacts anything solid.
According to ESS, misfeeds, incomplete loading, and empty blister feeding all represent sources of waste and line downtime for blister packaging machines. The Fanuc cobot is equipped with line tracking and vision to ensure careful blister loading, minimizing machine faults.
ESS can design a single robotic cell to handle a range of products, depending on the manufacturer’s requirements. It can then create EOAT that can pick multiple products at a time, with a spreading feature to populate multiple blisters with each cycle. By incorporating quick-release pneumatic connections and thumbscrews, a robotic end effector can be quickly removed and replaced with a new EOAT to handle a different product. Explains ESS, this has signi cant advantages in packaging lines that use shorter runs for independent SKUs.
All TaskMate Robotic Systems are designed to be compact so they can be integrated seamlessly at the blister loading station to keep required oor space to a minimum. The robotic blister loader can be integrated with new blister packaging machines, or it can be used with existing blister packaging lines to automate previously manual loading processes.
a video of the TaskMate Robotic Systems Blister Loader from ESS Technologies at pwgo.to/7984
According to A3 – The Association for Advancing Automation, orders for robots from North American life sciences companies increased by 69% in 2020 compared to 2019. And this growth shows no signs of stopping. A report from Grand View Research predicts that the global market for pharmaceutical robotics will reach $357.9 million by 2030, with the market expected to expand at a CAGR of 9.2% from 2022 to 2030. Notes the report, this growth can be attributed to several factors, including the ability of automated systems to rapidly and safely perform repetitive tasks such as moving test tubes and uids, counting pills and packaging them, and inspecting for quality control. Grand View also notes that, based on application, the picking and packaging segment dominated the market in 2021, owing to a rise in demand for personalized packaging.
Meeting this need for picking and placing of pharmaceuticals are two new robotics systems: a cobot version of the TaskMate Robotic Systems Blister Loader (23) from ESS Technologies and The Robotic 3D Control and Picking Solution (3D CPS) (24) from aseptic processing provider Steriline. ESS Technologies’ existing line of TaskMate Robotic Systems integrates Fanuc multi-axis robots and ESS-designed end effectors to create pick-and-place solutions for a variety of applications. The new blister-loading system uses a Fanuc CRX-10iA cobot, a 10-kg-payload model with
Another picking solution, this one designed for stoppering and capping primary pharmaceutical packaging, was introduced by Steriline at PACK EXPO International last year. The Robotic 3D Control and Picking Solution (3D CPS) includes both robotics and vision systems and was developed in partnership with ISS – Innovative Security Solutions, a spin-off company from technical university Politecnico di Milano in Europe. The solution is particularly suitable for capping and stoppering packaging of small batches that require an aseptic environment, such as in personalized medicine and the production of cell and gene therapies.
Some time ago, the Department of Veteran’s Affairs (VA) decided to automate its prescription fulfillment processes. The VA fulfills thousands of orders a week and millions over a year. To handle this, they entered into an agreement with an American integrator to help construct their vision.
The VA’s vision consisted of two separate facilities, each with several lines of modular cells, and each module with two halves. The first half would be for storing and retrieving pill canisters. An external carousel-style shelf would store canisters capable of holding up to 200 medications for later fulfillment. A 6-axis robot mounted to the module would oversee the movement of the canisters to and from fulfillment. On the other half of the module, four delta robots would fulfill orders. Once a canister was received, they would activate a vibration table and vacuum system to disperse capsules and remove lingering debris. Then, the robots would pick up the capsules and drop them into the bottles below, one by one. Upon completing an order, a series of conveyors and diverters would remove the bottles for further processing, such as labeling and sealing.
These modules were envisioned to work in tandem to plan and fulfill orders as they came in. However, the modules designed by the integrator were far from reliable, even after seven years of design and testing. They failed on multiple levels. The robot tool could not grip some pill types, flinging them around the module. The constant flinging and accumulation led to the rapid degradation of some of the hardware due to the trapped pills and dust. Additionally, the design made basic
repairs nightmarish because so many components were trapped behind layer after layer of bulky hardware, leaving maintenance workers with no way to remove the debris.
In short, after seven years, the integrator was never able to finish the project. Despite the VA’s initial investment in equipment and support services, a series of automation problems led to the non-renewal of their contract with the integrator, leaving the infrastructure unused and unsupported. However, with the massive sunk cost, the VA opted to retrofit the existing systems to address some issues. Universal Logic was awarded the job and has been working to bring the system online as soon as 2024.
To effectively address the VA’s immediate problems and understand their root causes, it was crucial for Universal Logic to clearly understand its pain points. Originally, the design aimed for easy production of 20 units, resulting in a modular approach where each piece was designed to perform a specific task. However, when these pieces were assembled, they lacked compatibility, causing numerous issues. This meant that not only did Universal have to mitigate the problems of the original integrator, but they also had to fundamentally change their approach.
Universal’s initial priority was pill management. To prevent pills and dust from building up on the conveyors and inside compartments, Universal needed a solution to prevent them from falling in the first place. This change meant redesigning
Continued on page 148
Continued from page 146
the robot’s end-of-arm tool (EOAT) to maintain adequate suction with each medication. Once the new tool was complete, a funnel was installed around the robot in the event of a flying capsule. If one happens to escape the funnel, it will fall into a catch pan below the robot; the catch pans act as the final defense for medications that may escape. The pan ensures that even if the tool malfunctions, dust and pills won’t accumulate on the other components.
Additionally, to prevent problems with new medications and capsule shapes in the future, Universal has designed a stateof-the-art training station that allows new pills to be trained by size and shape with Neocortex, Universal’s patented AI, for a seamless transition into production. The training station will also allow future operators to test other settings, such as robot speed and vibratory frequency, for more efficient operations and less downtime. Integrating Neocortex here and on the cell for robot picking and identification gives it more robust error handling than before. With Neocortex, the robot can identify minor differences between pills if one is in the wrong canister; it can even detect brakes or chips and avoid these pills for fulfillment.
Foundationally each change made has radically improved the process or overall efficiency. Since the improvements were made, the longevity of the system has improved. However, the system has also become more complex. One of the biggest challenges for the original design was the inability to do regular maintenance. To combat this problem, Universal removed the existing conveyor and hardware that previously handled traffic control. In doing this, they opened access to the robots, the vibratory stands, and other internal components
for maintenance. Reducing the number of vibratory stands and pick locations to just one per robot further opened space so that an operator can manually intervene in an emergency. These changes improve the system’s efficiency and make maintenance more accessible, allowing for regular upkeep and uninterrupted operations.
On the canister side, the theme of simplification persists. The original rack was designed to hold almost 200 medication types on an integrated carousel shelf. While this design certainly had more storage, the rack would often become misaligned, which prevented the robot from adding new canisters and would result in hours of downtime while the robot was recalibrated with the shelf. To negate this problem and ensure appropriate alignment, Universal designed a new canister rack with fixed shelves that provides constant alignment and zero variability in the canister locations. This solution effectively addresses the misalignment issue, ensuring seamless operations and eliminating potential downtime caused by recalibration.
Universal’s retrofitting of the existing pill fulfillment automation system exemplifies the challenges and complexities associated with upgrading and improving established infrastructure. The VA’s decision to retrofit was driven by the significant investment already made, along with the potential to salvage the existing equipment. Through a strategic redesign, Universal successfully addressed various issues that plagued the original design, including pill management, maintenance accessibility, and canister misalignment. PW
a video Universal Logic’s retro t for the VA at pwgo.to/7990
As Federico Fumagalli, chief commercial of cer at Steriline, explains, the company continues to innovate with robotics in its aseptic lling machines, developing their robotic software in-house to offer intelligent motion and activities that are often performed manually. He says that in many cases, a robotic arm will move from A to B and B to A, but this application shows how robotics can be programmed by a 3D camera that scans, nds a good trajectory to move in, picks up the stopper, and places it on the vial.
The Robotic 3D Control and Picking Solution is a mechatronic component equipped with a vision system that can detect tools within a de ned area and adapt its function based on the relative feedback. It is composed of a robotic arm, a picker, an infrared ray (IR) stereoscopic vision system, and software for planning trajectories, accessing the recipe database, and interpreting the input data coming from the sensors.
During operation, the robotic arm moves the picker throughout the working area, the dimensions of which can be modi ed based on the length of the levers. Next, sophisticated algorithms generate trajectories to allow the picker, located at the end of the arm, to reach an item, pick it up, and then move it to its nal destination. These paths are generated based on the information received by the 3D vision system, which
uses a technique in which an IR source emits an IR light pattern that is visible to visual sensors and not to the human eye. The scattering of the light is detected, acquiring a pro le of the scene. This technology allows the system to autonomously generate reliable trajectories for simpler and more linear movements and avoid any collisions with the surrounding environment.
“In the pharmaceutical industry, limiting the release of particles during sensitive processes makes the difference because it reduces the risk of contamination,” says Fumagalli. “With this in mind, we looked for different solutions on how to remove the main parts that increased the dispersion of particles during, in this case, the stoppering and capping processes. So we chose to replace the hopper, the vibrating cup, and the linear slide with robots combined with a vision system.”
The partners also sought to simplify format changes. “Flexibility is de nitely an added value of robotic solutions,” adds Alessandro Caprioli, partner at ISS – Innovative Security Solutions. “In fact, with standard solutions, the production process and the relative mechanical parts need to be recon gured in order to manage or handle a different container. With a robotic application, you generally only need to set up a different recipe via the software.”
Pack Expo
Las Vegas
Booth C-1718
Leading industry manufacturer’s choose Multi-Conveyor for custom and standard conveyor solutions. Why?
Because we are a leader in the industry for what we do ... we just can’t disclose it most of the time.
• From napkin drawing to operational equipment - we bring concepts to life
• Maximizing productivity - minimizing floor space
• OEM communications - we’ll connect the dots
• Immediate solutions - designed for future expansion
• Agency compliance built directly into the system - not an afterthought
• Satisfaction guaranteed - customer FATs approved prior to shipment
• Keep our technologically advanced capabilities a secret - ?
Multi-Conveyor ... your best, conveyed better. www.multi-conveyor.com
One of the most important—if not the most important—components of a robot is its EOAT; without it, the robot is essentially useless. The end effector plays a vital role by enabling the robot to interact with objects by gripping, grasping, and manipulating them. With recent advancements in technology, the ability of EOAT to perform different tasks based on programmed instructions has advanced signi cantly.
According to a report from MarketsandMarkets, the global robot end effector market is expected to grow from $2.3 billion in 2023 to $4.3 billion by 2028, for a CAGR of 13.5%. Reads the report, “Growing demand for modular end effectors, increasing adoption of cobots, penetration of automation in SMEs, and increasing adoption in the warehousing, pharmaceutical, and food industry are the main drivers for the growth of the robot end effector market.”
Over the past year, a number of suppliers have introduced new EOAT and tooling systems that boast advanced technology that make EOAT more exible, robust, and modular, as well as more intelligent for today’s integrated operations. Among them is Coval, which recently improved upon its range of new-generation vacuum grippers used for handling parts of various sizes, weights, and materials by adding the new CMS HD (25) series of multistage vacuum pumps.
Coval’s new generation of vacuum grippers is based on two complementary solutions: the CVGL and the MVG. The CVGL is characterized by its lightness and adaptability and is available as standard in several lengths, power ratings, and gripping interfaces. The MVG, on the other
hand, while also light, can be con gured speci cally for each application by determining the length, width, gripping interface, and vacuum generator. Says Coval, “It [the MVG] offers a tailored solution that integrates perfectly with handling robots.”
Now, the new grippers also incorporate the CMS HD series of vacuum pumps. The pumps have a heavy-duty design for high reliability even in harsh environments—they are IP65 rated—and are capable of ensuring 50 million cycles. Coval attributes the pump’s longevity to its modular design, which allows for speci c con gurations and targeted maintenance of speci c parts to optimize repairability.
The multistage CMS HD vacuum pump comes in three con gurations: non-piloted, piloted, and communicating. The communicating con guration, which makes the vacuum grippers easier to use and
parameterize, integrates the CMS HD VX multistage pump. This pump features an I/O-Link communication interface, compliant with the international IEC 61131-9 standard, for fast and cost-effective installation, continuous diagnostics, centralized parameterization, and efcient communication with higher-level protocols, including Ethernet/ IP, PROFINET, EtherCAT, and others. It can also support a Human Machine Interface (HMI) with a Near Field Communication (NFC) interface, enabling the operator to read and modify setup parameters and diagnostics from a mobile device, either Android or iOS, using the dedicated Coval Vacuum Manager app.
Destaco, a Dover Corp. company, has also introduced several new EOAT options, including a magnetic gripper and a vacuum gripper, in its new portfolio of Cobot Tooling Solutions (26), introduced in March. The tooling line was designed to simplify tool selection and eliminate integration design work for companies employing small-payload robots or cobots in their operations. Among the solutions are those designed for gripping, palletizing, machine tending, tool changing, and tool extension applications for robots/cobots with up to a 10-kg payload capacity.
“Small-payload robots are commonly found in larger industrial manufacturing facilities, but the low cost of entry into robotic automation has recently resulted
Packaging equipment for shrink bundling trayed or loose product with the option to use clear or printed film
Loose Product Shrink Bundling
Capabilities offered only by the SRX Series:
•Slide out film feed and cut assembly for easy maintenance
•Toolless adjustable wrap bar assembly
•Updated Allen-Bradley controls package with predictive maintenance flags
•Dual roll film mandrels with manual splice to minimize changeover time
•State-of-the-art airflow control
•Speeds of up to 60 cycles per minute
in signi cant growth in their use across small, light industrial, and commercial shops,” says Gary Labadie, global product director for Destaco. “Small-payload robots are now a focus and a solution for both large and small facilities coping with the economic climate.”
Destaco shares that it designed its Cobot Tooling Solutions for simplicity and ease of use, with off-the-shelf availability via kits that feature all of the end-user selected accessories, along with the hardware and tools needed for installation, reducing the need to consult an application engineer. All of the tooling solutions are compatible with cobots that have an ISO 9409-1-50-4-M6 end-of-arm mounting pattern. Blank robots and tool plates are offered for those who wish to use their own mounting patterns.
According to the company, a “standout feature” in its suite of tooling solutions is its Micro-Tool End Effectors, which enable a cobot to perform palletizing functions. Users who know the length, width, and weight of the packages to be lifted and transferred can easily select the palletizing kit type and predetermined vacuum cup size necessary for the application, eliminating tool design work with off-the-shelf kits. Other tools in the portfolio include:
• The CB-200 Quick-Move Base: Allows the cobot to be moved from one workstation to another without the need to reprogram the robot.
• The ARV-C vacuum gripper: Can pick up and move product via one air line with an auto-release vacuum generator; available in nine sizes and shapes.
• The MG magnet gripper: Allows the picking of ferrous material or components with one pneumatically actuated air line; available in two sizes.
• The Multi-Mount Tool Array: Mounts up to ve different tools to the cobot wrist through various tool mounting plates and multiple extension lengths.
• The Multi-Mount Tool Extension: Extends the reach of the cobot arm; available in a variety of tool plates and multiple extension lengths.
• The TC1 Manual Tool Changer: Allows the user to change cobot tools quickly and repeatedly and offers electric and air passthrough capabilities.
• A Tool Storage Tree: Securely stores and organizes up to six cobot tools safely and securely; fully adjustable with three different tree heights.
From Flexiv, a provider of general-purpose robotics solutions, is a new EOAT designed with exibility in mind, the new Grav Enhanced gripper (27), speci cally engineered to eliminate the necessity for EOAT changes. According to Flexiv, the Grav Enhanced can lift nearly any object it encounters—“from basketballs and boxes to letters and lollipops”—by using its two- nger adaptive-force and super-friction grasping techniques.
Shares Hao Jiang, Flexiv’s director of product development, not only is the Grav Enhanced gripper the world’s rst commercially available adaptive gripper with super-friction material, but it also eliminates the downtime related to end-of-arm tool changes. “Our customers told us that traditional grippers struggle with mixed-SKU consignments, so that’s what led us to develop the Grav Enhanced,” he explains.
Featuring industrial-grade force control and an adhesive material based on a gecko’s foot pad, the Grav Enhanced gripper can lift practically any item up to 5 kg that ts within its grasp. When manipulating objects, the gripper’s adaptive force sensing ensures an optimal grip force is maintained, while the super-friction material provides enhanced grip stability and versatile object handling. The super-friction material is said to be exceptionally strong and leaves no residue on the objects it contacts, making the gripper suitable for mixed-SKU pallet loading, where products may be sent directly to the customer.
Though speci cally designed for Flexiv’s range of adaptive robots, the Grav Enhanced is compatible with any collaborative-style robot that uses a universal mounting ange.
Lifting more with less was Piab’s goal when it developed the new piCOBOT L (28) vacuum pump unit, which can lift up to 16 kg versus the 7-kg capacity of its existing piCOBOT. Comprising a vacuum pump unit and an optional gripper unit, the piCOBOT L builds on the same technology platform as the original version. The vacuum pump unit is also scalable and can be equipped with any number of Piab’s proprietary COAX vacuum ejector cartridges.
Says Piab, “Offering a signi cantly higher vacuum performance, it [the piCOBOT L] enables fast movement when lifting heavier items for high productivity in packaging and palletizing, part assembly, or machine tending.”
The company notes that the pump’s high vacuum ow can facilitate the deployment of its large, Kenos-brand foam grippers, which can lift a wide variety of objects, from single large and heavy items to a multitude of small items simultaneously. The piCOBOT L can also use customized end effectors, either developed by Piab’s Custom Line specialists or by the customer or systems integrator. Due to a vacuum connection at the bottom of the pump, extra cabling is not required when attaching a different gripper unit.
Although the piCOBOT L allows for manual gripper changes and dissembling of the tool from the pump unit, Piab relates that the need to speed up tool changes when necessary drove the company to develop an automated process to ensure continuous operations and provide exibility for the deployment of one solution for many different tasks. The result is a new optional automatic tool changer combined with a docking station for further end effectors. The tool changer is equipped with a lever to lock or unlock the adapter plate of the end effector. The lever can be opened and closed automatically by the docking station to remove a gripping unit from the cobot and pick up and connect a different one without human intervention. Alternatively, the gripper switch at the tool changer can also take place manually.
The piCOBOT L has been designed to allow for easy access to parts for cleaning and is IP65 rated for harsh environments.
Another producer of compressed, air-driven vacuum pumps, as well as suction cups and other accessories, South Korea-based Vmeca introduced its Magic Gripper EOAT (29), for use with cartons, cases, or exible packages, at PACK EXPO International last year. The Magic Gripper can be attached to either an industrial robot or a cobot and features a decentralized vacuum that allows it to use as many or as few grippers as required by an application. Comprising a mounting bracket, vacuum generator (the Vmeca vacuum cartridge system), vacuum lter, and suction cup, the Magic Gripper eliminates the need to purchase separate ttings, connection hoses, lters, and suction cups. The pump also features a silencing technology that deadens some of the noise traditionally generated in compressed-air applications.
a video of some of the EOAT products mentioned here at pwgo.to/7985
Probably the smallest category of robots in use by packaging operations are autonomous guided vehicles (AGVs). While AGVs have been in manufacturing facilities for years, companies are increasingly turning to autonomous mobile robots (AMRs) for internal transport solutions. Says PMMI’s 2022 business intelligence report on robotics, “Eighty-two thousand AMRs shipped in 2021, with shipments predicted to reach over 600,0000 by 2025.
“More adaptable, exible, and cost ef cient than AGVs, AMRs are being used to navigate dynamic environments and transport a variety of items, from raw materials to nished products. The newest generation of sensors and AI-driven data are making AMRs exible enough to be easily redeployed and smart enough to navigate a facility without the need for guided wiring or magnets.”
For packaging operations, AMRs can be used for materials transport, including pallet loads of packaging materials, as well as machine loading. Systems that feature an industrial robot on top of a mobile platform can help with optimization of material ow and packaging processes. Mobile robots’ ability to move around the plant oor also offers
PMMI ProSource is a free online directory with 460 categories of validated suppliers of packaging machinery, materials, and service solutions. With a powerful search engine and the ability to filter solutions by machine feature and package type, ProSource brings vetted suppliers to you. Visit www.prosource.org today.
SEPTEMBER 11-13, 2023
SOUTH UPPER HALL BOOTH 7654
HEALTHCARE PAVILION BOOTH 6820
WELCOME
/V^JHUWHJRHNPUNILIV[OLU]PYVUTLU[HSS`MYPLUKS`HUKJVZ[LᄗJPLU[&>P[OV\Y ;34WHJRHNPUNTHJOPULZ;OL`LUHISL`V\[V\ZL[OL[OPUULZ[TH[LYPHSZWVZZPISL J\[[PUN[OLT[VZPaL[VYLK\JLJVUZ\TW[PVUHUKKYHTH[PJHSS`KLJYLHZL`V\Y\ZL VMYLZV\YJLZ0[»ZNYLH[MVY[OLWSHUL[HUK`V\ILULÄ[MYVTHYLHSJVTWL[P[P]LLKNL >LJHSSP[4PZZPVU)S\LHUK^LWYVTPZL!;OLTPZZPVUNVLZVU www.mission-blue.com
A WORLD OF PACKAGING SOLUTIONS DESIGNED FOR SUSTAINABILITY. BROUGHT
production exibility, as the units can travel among various packaging workstations and perform relevant work at each one.
In August 2022, Packaging World reported on one CPG and privatelabel packager, Snak King in City of Industry, Calif., that not only installed 16 robotic palletizers, but also three intelligent automated vehicles (IAVs) to transport pallets through the facility from stretch wrapping to warehousing (see pwgo.to/7986). The company selected IAVs from Quest, a product brand of ProMach, that are equipped with a lidar, or light detecting and ranging, system to move throughout the facility.
Snak King acquired the new robotic palletizers and IAVs to ease workforce shortages and to optimize its throughput capability. According to the company, the three IAVs have replaced 10 to 12 forklifts and have reduced the “chaos” that previously characterized its production oor, while at the same time being safe for workers.
To captialize on packagers’ increased interest in mobile robots, in the last couple of years, more packaging-focused robot OEMs have entered the market. In late 2022, Epson Robot introduced a 6-axis SCARA robot that can be mounted to an AMR for warehousing applications or on a mobile platform to transport materials between workstations. An expansion of the company’s VT6L Series of SCARA robots with integrated controller, the DC-powered VT6L-DC All-in-One 6-Axis Robot (30) is said to offer the same powerful features found in Epson’s high-end robots, at an “exceptional value”—$14,595, according to the company’s website.
Features of the robot include a built-in controller, a reach of up to 900 mm, and a payload of up to 6 kg in a compact footprint. It also
6ROYLQJWKH1DWLRQZLGH/DERU6KRUWDJHZLWK5RERWLFV :RUNIRUFH$XWRPDWLRQ
3DFNDJLQJ5RERWLFV/LYH /RFDOLVDQHZUHJLRQDOHYHQWVHULHVODXQFKLQJWKLVIDOOWRKHOS PDQXIDFWXUHUVRIFRQVXPHUSDFNDJHGJRRGVVROYHWKHLUODERUVKRUWDJHSUREOHP3UHVHQWHGE\
3DFNDJLQJ:RUOGWKHFLW\UHJLRQDOHYHQWVHULHVZLOOIHDWXUHLQGXVWU\H[SHUWVVKDULQJEHVWSUDFWLFHV DQGUHDOZRUOGVXFFHVVVWRULHVRIKRZURERWLFDXWRPDWLRQWHFKQRORJLHVFDQTXLFNO\LQFUHDVH RSHUDWLRQDOHIILFLHQF\DQGUHGXFH\RXUFRVWV
:HLQYLWH\RXWRMRLQXVDWDFLW\QHDU\RXWRJHWDIURQWURZVHDWWRWKHODWHVWURERWLFWHFKQRORJLHV VKRZFDVHGE\WRSVXSSOLHUVZKRVSHFLDOL]HLQDXWRPDWHGVROXWLRQVIRUSDFNDJLQJRSHUDWLRQV
)DOO6FKHGXOH
6HSWHPEHU -:0DUULRWW$QDKHLP
2FWREHU 7KH5LW]&DUOWRQ3KLODGHOSKLD 3KLODGHOSKLD3$
2FWREHU /RHZV&KLFDJR2łKDUH
1RYHPEHU -:0DUULRWW+RXVWRQ'RZQWRZQ +RXVWRQ7;
comes equipped with two development environments: Epson RC+ for full-featured, easy-to-learn programming and Epson RC+ Express for no-code programming. With the introduction of the VT6LDC, Epson unveiled a version of its Epson RC+ Express with increased functionality.
Says Epson, “Ideal for automation novices with little to no programming experience, Epson RC+ Express offers a simple, visual-based teaching environment, an easy-to-follow, block-style format, ready-to-use templates, and other time-saving features to get Epson SCARA and 6-axis robots up and running fast.”
Previously available only on select Epson robots, the intuitive software now works with hundreds of Epson SCARA and 6-axis robots. The software is equipped with time-saving features such as Epson proprietary Focus Assist technology with auto-generated elds for quick and easy setup and a built-in 3D simulator to help visualize and ne-tune applications.
“As more businesses implement automation to address workforce challenges, Epson recognizes that more users require not only easy-touse applications but also the exibility to be mobile,” says Scott Marsic, group product manager, Epson Robots. “Epson is committed to providing a simpli ed automation experience. Solutions like the VT6L-DC empower warehousing, logistics, and machine tending operators to move a traditional 6-axis robot from place to place rather than mounting it in a single, stationary location. And, with simple, visual-based programming software like RC+ Express, users can get their robotic automation solutions up and running quickly.”
At Automate 2023, dedicated mobile robot equipment supplier ROEQ debuted its ROEQ TMC130 (31), a top module and cart system for the Omron LD-90x AMR that increases its payload from 90 to 130 kg. Developed in collaboration with Omron, the TMC130 expands the options for customers to safely and reliably use the LD-90x robot for higher-payload missions, even where space is constrained.
Says ROEQ Managing Director Michael Ejstrup Hansen, “For customers looking to automate tasks such as quickly moving smaller, lighter cargo between workstations or shelves—even in narrow spaces where larger carts are challenged—this is an ideal solution.”
Like other ROEQ cart systems, the TMC130 can dock to the cart from both ends and offers the exibility of free space pick up and drop off,
enabling it to adapt to almost any workplace. The TMC130 includes mounting holes on the top module for accessories like light towers. There are also mounting holes on the cart to make it easy to adapt for crates and shelving.
The TMC130 has been designed to comply with relevant safety standards and comes with ROEQ Assist software for easy and consistent setup with the Omron mobile robot. The new cart and top module system works with Omron’s own panel and has six wheels for easy maneuverability. A side laser kit is also available for increased obstacle avoidance.
Stäubli Robotics’ new PF3 (32) AGV platform is designed to do some really heavy lifting: up to three tons, “delivering a footprint-to-payload ratio that leads the market—and paves the way for new applications across multiple industries,” the company says. Among the uses suggested for the PF3 is transport of nished pallets to shipping.
The low-pro le PF3 operates within very narrow spaces on the factory oor, easily maneuvering around obstacles and carrying out tasks with a positioning precision of ±5 mm. In addition, smart features offer future-proof production and a streamlined work ow.
The PF3 uses standard software interfaces, while an all-around LED strip and 45-deg inclined touch panel provide an ergonomic operator experience. To ensure safety, the AGV is equipped with a 360-deg human safety scanner, ve emergency stop buttons, a collision avoidance sensor, and an LED strip that communicates the AGV’s status.
Stäubli adds that the PF3 is also easy to own and maintain. It uses a “drawer” maintenance concept, which means parts are easily accessible from the sides of the AGV and can be changed in minutes. It is built on the company’s patented drive unit and constructed of industrial-proof components, which Stäubli says delivers outstanding performance in terms of productivity as well as total cost of ownership. PW a video of the solutions mentioned here at pwgo.to/7987
For e-comm and D2C operations like Crutchfield, an audio/visual and consumer electronics specialist, right-sized cases ensure material savings, DIM weight optimization, and consumer satisfaction.
By Matt Reynolds, Chief EditorWhen Bill Crutch eld founded his company in the family garage in his hometown of Charlottesville, Va., in 1974, he was trying to x a problem he’d experienced as a customer: how do you gure out which aftermarket car stereos and speakers will work in your vehicle? He realized that expert information, shared by people who really cared about problem-
solving, was the answer. More than six million customers later, those principles continue to drive the business, which now serves the entire audio/visual device and consumer elecronics technology space.
Crutch eld has since grown to employ more than 700 people, and now runs the vast majority its business as D2C out of two 120,000 sq. ft. facilities, both in Virginia. Crutch eld’s impressive offering of online sizing tools and online customer support dovetails nicely with e-commerce and D2C sales, which have grown exponentially over the past decade. Since 2013, the A/V equipment and device company has been growing and evolving its D2C operations with Packsize (see sidebar on page 164). But an all-new installation, the Packsize X5, is the next evolution of that journey. As Packaging World recently reported (pwgo.to/7993), Walmart was an early adopter of Packsize’s new X5 system for right-sized packaging on-demand that the supplier says ef ciently produces readyto-pack, right-sized erected cases. The retail giant uses this system within proprietary Ultra5 machines. Now, the full Ultra5 machine equipment was designed for, and remains exclusively available to, Walmart. This equipment is being rolled out to its next generation of ful llment centers. But the X5 system the Ultra5 is modeled after is available for any Packsize customer. Given Crutch eld’s nearly 10year history with the e-comm specialist,
it wasn’t long before they chose to capitalize as well.
“I was a pretty early adopter, myself,” says Chris Groseclose, chief ful llment of cer, Crutch eld. “As soon as they were starting to offer them out of the beta environment, I was one of the rst people that had my name on the list for one. I had a good relationship with their sales rep. She’d been with us for several years and there’s a lot of trust since they’ve been strong business partners over the years. She showed me some demo videos, and I was ready to sign up for one.”
It wasn’t that big of a leap for Groseclose, either. The Crutch eld facility had already been running a handful of Packsize’s X4s, which Groseclose describes as the supplier’s rst version of a more automated box-sizing system, and predecessor to the X5.
“And that equipment carried our business for three or four years,” Groseclose says. “But they start to age out, and repairs and upkeep are needed. When I saw that they had taken everything they learned from the X4 and put it into the X5, that was reassuring.”
For instance, the X4 allows for two different corrugated tracks, or fanfold widths, on the corrugated input feed. The X5 doubles that number to four, and Crutch eld currently uses all four of them on the new system. The corrugated spec used in this facility is 32 ECT with standard uting.
“Having more fanfold width options really helps you dial in your box size and reduce your waste,” Groseclose says. “Also, they’ve simpli ed this model where the corrugated just runs straight through the line and just doesn’t move as much as it did in the legacy equipment. And the cutting head system on the X5 is simpler. All in all, they’ve simpli ed the machine, increased the fanfold widths that you can input, and increased the output. And frankly, with the equipment itself being able to inject a box onto the conveyor, with a bottom that’s fully glued with the Box ID label already on it, they’ve really eliminated two- or threepeople’s worth of labor. Those people were involved with getting boxes out of the previous versions of the machine, folding them, taping the bottoms, and putting the labels on. Packsize has taken a big jump toward a value-added automation.”
The new X5 equipment provides rightsized cases for Crutch eld orders in all three dimensions: length, width, and height. This equipment is capable of more than 500 cases per hour, but considering the size of the cases used and Crutch eld’s speci c needs—it has other case erecting equipment—the facility more commonly averages 425 to 450 cases per hour.
As Groseclose mentioned, the system uses the four corrugated fanfold infeed tracks in varying widths to optimize case sizes during erecting. The machinery operates by connecting with the CPG or ful llment centers’ WRS or ERP systems—the X5 receives speci c case size informa-
tion for each order, and then executes on cutting and erecting to that size. Size availability ranges from 8 x 6 x 3 in., to 30 x 20 x 20 in., and the equipment can produce the largest size immediately after the smallest or vice versa without any variation in production rate, much less need for changeover equipment.
After cutting the 2D corrugated to the correct dimensions, the system then erects and closes case bottoms with adhesive. Then, pressuresensitive print-and-apply Box IDs with the item’s dimensional information—unique to every single case—are automatically tamp-applied to the erected corrugated cases.
Notably, right-sizing cases results in some scrap corrugated. This is minimized by optimizing the fanfold width, but small pieces remain. The removal of these excess scraps is also automated, with a conveyor carrying them to a gaylord that can be managed throughout the day during production and recycled with any other outgoing corrugated material.
At the Crutch eld facility, erected cases exit the Packsize equipment onto a 24-volt Intelliroll conveyor from TGW Conveyor Systems, which serves as the base of the whole system of pick zones that ensues. Scanners from Cognex read the individual Box IDs, which connect with Crutch eld’s systems and builds the pick path for any given case. Once that pick path is constructed, which is almost instantaneous, that information is fed back to the conveyor’s PLC, and the conveyors “decide” into which pick zones each case needs to travel.
“Through COVID-19, I had to add extra pick zones, so now I’ve got 12 of them. We use six scanners at the induction to each zone,” Groseclose says. “And [the system] knows whether to direct a case into each of the zones. As the case travels by the set of scanners at the front of each of the zones, the case gets scanned and the conveyors recognize ‘Yes, it needs to go in here,’ and it does. Or ‘No, it doesn’t need to go here,’ and it will pass that zone by. The cases that go through that system come to a nal scan that says, ‘Yes, everything is in this order, we’re going to pass it down to shipping,’ or, ‘No something went wrong. We’re going to recirc it through the whole system and let it have another chance at getting it right.’ Sometimes, if a zone is com-
In 2013, it became clear to Crutchfield that its own warehouse was lacking the technology it needed to keep up with demand. That’s when it first came to Packsize with two requests. The first was to reduce its overall carbon footprint by reducing waste from shipping boxes that were too big for their contents. It also sought to reallocate labor to more engaging, comfortable spots in the facilities.
“Prior to partnering with Packsize, we had manual pack stations and I had five to eight packers handling roughly between 2,500 to 3,000 orders a day,” says Chris Groseclose, chief fulfillment officer, Crutchfield. “We were kind of at the end of our rope of being able to physically fulfill the orders with manual pick carts, manual pack stations, with something like 20 or 25 different slotted corrugated boxes [RSCs] to choose from, so the packer would kind of eyeball it. Plus, the
business was growing during that period, so we felt we were at a crossroads.”
After some false starts with other suppliers, Crutchfield began its automation journey with a conveyor-based pick module from Packsize. Groseclose needed something that gave his team the right box, up front, that they could pack into.
“We use a lot of the lean, Six Sigma approach to problem solving,” he says. “One of the things we want to do is reduce our product touches in the whole fulfillment process.”
That first year, Crutchfield saved about $300,000 in void fill, because box right-sizing cut overall box dimensions in half compared to where it had been in eyeballing appropriate box size. Groseclose would know, too, as the company extrudes its own water soluble, starch ‘packing peanut’ on equipment from NewStarch Solutions PW
pletely full, a case will wait 10 seconds, and then it’ll pass around and do a recirc of the whole system until it comes back around to the zone, usually then there’s an opening for it.”
Once a case is cleared to ship, it rst passes manual void ll application stations. The company uses water-soluble, packing peanut-style ll made entirely of starch.
date any case sizes that the Packsize could throw at them.
“We had manual, pneumatic sealers, but the Pearsons run three cases to every one case that ran through the manual, so we just switched over to letting two Pearsons run the case-top sealing,” Groseclose says.
After each Pearson, the closed cases run across a weigh-in-motion (WIM) system, and another Cognex vision system reads both the Box ID
Why would perfectly cubed and sized cases require void ll, you might wonder? That’s a good question. Crutch eld runs the Packsize equipment to an 80% ll spec. That means the cases are designed to be cut to a size that’s lled to 80% of its available space, once all the products are picked and placed to the case. But why 80% and not 100%? That’s another good question. The answer lies in the fact that this Crutch eld facility is a ful llment center that receives custom orders—multiple differently sized and shaped products are often expected to t into a single case.
“At 100%, when there’s one single item going into the box, it will cube that box out absolutely perfectly,” Groseclose says. “But we’ve found that with two or three items, if you go with 100%, it can become too much of a game of Tetris for operators trying to gure out how to place items in the box in such a way that optimizes the use of space. So today, we run it at 20% void, I guess you’d say.”
Plus, according to Groseclose, the Packsize X5’s PackNet Cube software is smart enough to know when there is a rectangular single item, like a Sony receiver in a rectangle-shaped primary package. On those occasions, the Packsize reverts to the 100% ll, bypassing the 80% request. The result is a perfectly cubed secondary corrugated case, and the primary package ts snuggly within, with no need for void ll.
After void ll is added as needed, the cases travel through one of two Pearson case sealers. Groseclose says these are are fully randomized, automatic case sealers ready to accommo-
and the weight. That begins a process of rate shopping for a carrier to get the best shipping price for a given case.
“Our system does a theoretical weight, and then matches it to the actual weight,” Groseclose says. “If a certain percentage threshold of variance is met, it’ll kick it to an exception line and won’t let it ship. Once the rate shopping is complete—we do a bunch of different sorts for UPS, FedEx, postal, and air shipments—they run by two print-and-apply systems that attach shipping labels, and the case then travels to a 10-lane TGW belt sorter.”
“I think not too far over the horizon, we would add another X5 system,” he says. “Where I am right now, I have three EM7s [simpler Packsize case erectors], one X4, and one X5 in this facility. I’d like to get rid of the X4 and one or two of the EM7s, and just have two X5s running the front end of it. If I had two of those in place, that puts me close to 1,000 cases an hour just with those two, and then generally that’s enough to get us through the day. I would keep some EM7s around just for supplemental volume during the holidays.”
Groseclose is also in the beginning stages of looking for Automated Storage and Retrieval System (ASRS), also called a goods-to-person system, that could potentially replace the whole conveyor piece of the existing systems.
“And I think this X5 will play in really well with that,” he says, “It’ll be a great t.” PW
nVenia, through our legacy brands, has a long history of quality, durability and service. Whether you need primary, secondary, or end-of-line packaging equipment, nVenia will provide innovative integrated solutions.
A pay-for-productivity robot model has mitigated the effects of labor shortages and provided scalability for the contract manufacturer.
Located in Batavia, Ill., GreenSeed Contract Packaging underwent an expansion but was then challenged by the ongoing labor shortage still affecting the industry since the beginning of the pandemic. The company, which serves large and mid-sized consumer packaged goods (CPG) companies in the food industry, sought new ways to drive distribution ef ciencies while keeping costs down.
GreenSeed’s solution was to turn to automation on the line in positions which could be easily replaced and even performed more efciently by a robot or collaborative robot (cobot). Though purchasing a
robot or cobot was not what the company had in mind. They decided robots-as-a-service was the way to go.
Formic—a Robotics-as-a-Service (RaaS) provider, headquartered in San Pablo, Calif.—designed, deployed, and maintains uptime for GreenSeed’s rst palletizing systems as a rental system.
Contract manufacturers and packagers (CM/CPs) can bene t from the exibility robots, and cobots speci cally, provide. And palletizing is
0DNHFUDWLQJ\RXUHDVLHVWWDVNZLWKWKHUHYROXWLRQDU\DQGSDWHQWHG (FRUUFUDWHpDVWDQGDORQHDOOFRUUXJDWHGVKLSSLQJFUDWHVROXWLRQ 3UHVHQWHGLQDFRQYHQLHQWHDV\WRXVHIRUPDW(FRUUFUDWHLVGHVLJQHG WREHWWHUSURWHFW\RXUSURGXFWDWDORZHUFRVW
PLQXWHVHWXSWLPH
1RKDUGZDUHRUWRROV
UHTXLUHG
/LJKWHUZHLJKW ORZHU
IUHLJKW
:DWHUUHVLVWDQWFRDWLQJ
+ROGVSRXQGV
QRSUREOHP
&UHDWHGIURPUHQHZDEOH
UHVRXUFHV
(DV\WRUHF\FOH
7UXVWHGE\LQGXVWU\OHDGHUV
LQDHURVSDFHH[SRUW
WHFKQRORJ\+9$& PRUH
Ζ630&HUWLILHG
a job easily replaceable by automation, which further allows the contract packager to move its employees to more complicated positions. But considering the uidity within the contract packaging space, buying a robot may not always make sense.
Formic’s RaaS solution delivers customized robotic systems from robotic vendors such as Fanuc, Universal Robots, and Yaskawa Motoman to customers who pay by the hour for usage. The RaaS solution is designed to remove the risk, complexity, and upfront cost usually associated with the technology, and enable small and mid-size companies, such as CM/CPs, to scale their automation efforts to meet supply chain demands without relying on slow capital budgeting cycles.
“We spec the machine, we work with our builders to design the machine given the CM/CP’s available footprint and requirements in terms of speed rates and safety that they might have at their facility,” says Misa Ilkhechi, vice president of solutions and partnerships, and co-founder of Formic.
According to Ilkhechi, end-of-line palletizing and case packing are the two areas of automation most adopted by CM/CPs, followed by other secondary packaging and end-of-line packaging tasks such as shrink wrapping, labeling, and case forming.
Formic partnered with manufacturing systems integrator HCM Systems to design and deploy three robots at the GreenSeed facility. The rst two are Fanuc CRX10 cobot palletizers installed in a dual setup, allowing operators to switch out lled pallets without pausing production. The CRX10 is a 6-axis cobot with a safety scanner design and built-in safety sensors. These safety features give the cobot a smaller footprint, allowing it to be installed in areas where an industrial robot couldn’t physically t. The cobots are capable of handling a series of multiple SKUs, combined payloads of a variety of weights, and the agreed-upon cases per minute by the client.
The recently installed third robot is a 3-axis gantry system case packer from Blueprint Automation, capable of providing horizontal pack and vertical pack. The case packer is designed to pack pouches into cases and seal them.
The palletizers were installed during the rst quarter of 2022 and will be operational within GreenSeed’s facility for a period of ve years.
Formic scopes the machines during the process leading up to design and ensures the machines are serviced and maintained throughout the system’s tenure in a facility. “Once we install the cobot, we want to make sure that it does exactly what they need. And up to that point, the customer doesn’t pay us anything. So we make sure the system is performing to the metrics that we agreed on and we have a checkup every month where we go to their facility to make sure
anything that needs to be replaced on the machine is replaced,” says Ilkhechi.
Don Reed, CEO of GreenSeed Contract Packaging, explained that his operators found the cobots to be liberating because they took on repetitive and tedious labor, freeing up time for workers to focus on elevating operations.
“Our operators are excited to use the new technology because it helps them improve the process and ef ciency for our clients,” says Reed. “We’ve built a team of life-long learners and problem solvers. They look at new technology as a means for collaboration and betterment.”
Formic engineers remained on site for the rst couple of weeks to help the GreenSeed operators adapt to working alongside the palletizing cobots.
“While some in manufacturing look at automation as a threat to human workers, we look at it as a way to help expand the skills for our workers,” says Reed. “This upskilling is the reason we have been able to grow and promote internal staff into higher level and managerial positions.”
GreenSeed intends for the technology to make it more competitive and serve as an educational platform for its employees that can help them move into better roles. Following deployment, GreenSeed was able to repurpose line operators, saving approximately 35% a year in labor-related operational expenses and minimizing the company’s reliance on staf ng agencies. The use of the cobots rather than employees on those parts of the line also eliminates the amount the contract packager would otherwise pay towards bene ts and taxes.
Another signi cant bene t is the consistency and ef ciency of the palletizing cobots that could run full time if GreenSeed wished. Reed con rms the cobots have reduced downtime on the line, which further reduces cost. Additionally, Formic’s system only charges for the time the machine is actively in use.
“Our customers don’t pay us anything until we install a machine and it is operating based on the metrics we agreed on. And the only payment they have is at the end of the month for the hours that they used the machine,” said Ilkhechi.
GreenSeed plans to continue renting for the foreseeable future instead of buying its own robots and hiring the specialists necessary to maintain the machines. That partnership model will allow the company to maintain the exibility to adapt.
“In any partnership, it’s important that you evolve together. Being exible and dynamic is the key to being able to overcome obstacles now and in the future,” says Reed. PW
2VJDLMZ1MBDFPS4XJUDI%JTQMBZTVTJOHNN*OTUBMMBUJPO
Car wash supplier Sonny’s knew that to meet its ambitious sales goals for a quickly growing 2.5-gal detergent format, a semi-automated legacy system wouldn’t cut it. The resulting integrated robotic packaging line is the jewel of its newly opened facility.
In 1978, Sonny’s The Car Wash Factory started as a small parts manufacturer with a mission to “Make Car Washing Easy” for car wash owners and operators, and to become the global industry leader. Sonny’s is now the largest manufacturer of conveyorized car wash equipment, providing 12 car wash business solutions as the one-stopshop for all car wash needs. Sonny’s strategically acquired complementary businesses, including Cleveland-based Diamond Shine, the industry leader in premium quality cleaners and solvents.
Diamond Shine’s Bullseye™ line of industrial-strength commercial car wash detergents and waxes are quite a bit more potent than the buckets of suds that weekend warriors labor over as they wash their cars in the driveway. The biggest difference is that these are concentrated chemicals meant to be carefully measured and diluted in water, not used right out of the bottle. At 2.5 gallons, these F-style bottles are clearly portioned for commercial use. Once in the hands of the car wash professional, the rigid HDPE bottles with integral handle are speci cally designed to nest into the company’s Bullseye mechanical tank-based detergent delivery system, which mixes the soap solution with water and ensures proper car wash detergent dilution ratios.
Leakers are a major enemy of any liquid bottling operation, but the sentiment holds doubly true for Diamond Shine’s concentrated chemical products. Given the bottles’ industrial-strength contents, the 2.5-gal de-
tergent bottles require infrared sealing with foil as they’re capped. And secondary packaging in two-count printed cases is also about as robust as it can get, using double-walled corrugated and a Z-style corrugated partition. Two bottles per case are packed in a parallel position so they nest together in a tightly packed, partitioned packaging system. Case weights vary by product, but each one weighs somewhere around 50 lbs.
VISIT US IN BOOTH C-1800 AT PACK EXPO LAS VEGAS
Would you like to see these kinds of improvements?
One fresh produce manufacturer recently saw this improvement after installing a single Hayssen ISB.
With over 100 years of experience in flexible packaging, BW Hayssen o ers a variety of reliable VFFS and Flow Wrapping Equipment with intuitive and sanitary designs, so operators can learn to operate the equipment quickly and e ectively – with no prior training or experience – and uphold highest safety standards to ensure food safety.
In a thin labor market, growth spurs automation. Since Diamond Shine’s acquisition a few years ago by Sonny’s, it has been growing fast. This rapid growth precipitated a 2021 move from an existing location in Wickliffe, Ohio to a larger brown eld manufacturing facility in Mentor, Ohio, in a 109,000 sq. ft., 20 million-dollar renovation project to accommodate increased production. The primary impetus for the move was on the processing side of operations, in increasing mixing capacity via larger mix tanks and adding bulk storage tanks for the most-used bulk chemicals. This bulk chemical storage would obviate the need to
add many of the high-volume chemicals manually, via drums and totes, when mixing product. But as is often the case when upstream processes improve and get faster, downstream packaging operations need to come along for the ride, lest they become the bottleneck.
The 2.5-gal detergent packaging operations, known internally as the Bullseye line, landed at the top of the company’s wish list in packaging automation. This format had previously been a manual packaging process that wasn’t very labor-friendly. It was heavy in secondary packaging and created some messy situations when lling concentrated detergent.
But a lack of legacy automation meant there was little existing packaging equipment or infrastructure from the previous location that would need to be relocated or replaced. As leadership considered renovating their new facility for their needs, including a near blank-slate of a packaging line project on 2.5-gal detergents, the company reached out to packaging and processing line integrator Patrick Coakley of Plant Automation Group (PAG). He crunched the numbers on factors such as line speed requirements, the robustness of the packaging, a desire for redundancy, and a preference to be able to grow into packaging lines if speeds or demand were to increase. Coakley recommended an approach in which he and PAG would integrate the primary packaging line.
“When we started investigating the long-term requirements for automating packaging for this two-and-a-half-gallon jug, we realized it would be an interesting project,” Coakley says. “The manufacturers that we brought to the table were
Unscrambling operations at the start of the line upright and orient loose 2.5-gal HDPE bottles out of a hopper. The line is mirrored after a single unscrambling unit, but only one line is regularly in use until production ramps up to expected future volumes.
all carefully chosen to be the optimal equipment for this unique suite of wants and needs.”
Now, PAG does quite a bit of business integrating downstream secondary and end-of-line packaging applications, too. But in this case, the circumstances pointed them to a more local solution. Coakley tapped frequent project partner Hamrick Packaging Systems, an Ohio OEM that’s not too far from Diamond Shine, to integrate the box shop and secondary packaging down to the palletizing at the end of the line. The handshake between the two parallel integration efforts would occur at the case-packing function. Here’s their telling of how the collaboration came together.
“Hamrick just does a fantastic job,” Coakley says. “Jordan is growing his company, and he does the right thing for his customers. For me, part of it was that Hamrick was physically close to the manufacturer, but also has the ability for robotic placement of containers. And because of the weight of the containers, we needed a robotic placing solution.”
With a robust packaging system handling 50-lb cases being the name of the game,
Filled bottles are conveyed to a frontgated, custom designed timing screw, where one-by-one they are accelerated and metered out until they reach a stationary pocket on the screw and a chuck-style screw capper pushes a cap onto the bottle. Capping torque must be precise to accommodate an inner cap foil seal that will be infrared sealed to the bottle downstream.
Filling is done on six-head llers where lances descend on ball screws into the empty bottles. Top lling, bottom lling, or a hybrid of the two methods called tracking can be used to ll the bottles depending on product characteristics. Each bottle sits on an individual load cell, and lling is metered by weight rather than volume or ll line.
less emphasis would be placed on overall speeds—six cases per minute, per line (the line is mirrored), or 15 cases per minute for the whole system, was going to be more than enough for the foreseeable future.
“Patrick asked us, ‘Can you guys case pack these? Can you do erect, seal, palletize, and do the partition inserting?’” Jordan Hamrick recalls. “And yes, we could. We had done robotic partition inserting before, just not for a Z-style. That was a new piece of equipment that we had to come up with. The case erector we had done before, but not for a double-walled case, so we added some components to be able to run that. But we had the blueprint in place to be able to furnish the entire line in house. It just took some minor tweaks and engineering to get the job done.”
Initially, Hamrick had looked at using another vendor’s case erectors, which they frequently sell and integrate for their own customers. But Hamrick realized that, at these speeds, they might be better off taking this step in-house as well.
“This is a great partner company to us, but in this case, models start 25 cases per minute. They had a 15 case-per-minute model, but they
Fossil free energy reduces the environmental impact of fresh fiber paperboard and enables a lower footprint. At Metsä Board, 87% of our total energy consumption is fossil free, with an aim to reach 100% by 2030. metsagroup.com/metsaboard
MORE THAN YOUR AVERAGE PAPERBOARD
discontinued it, and 25 cases a minute was a little overkill for what we needed to run ve or six cases a minute per line. And we had our own 15 per minute case erector model that we redesigned a couple years ago,” Hamrick says.
Robotic con gurations and end-of-line operations were next to be discussed, and another change in plans came not long after Hamrick entered the fray. Initial designs had called for a single secondary packaging line. But Sonny’s sales team concurrently set for itself an ambitious, long-term goal to ip its mix of detergent package formats between drums and the 2.5-gal packs. This change will not happen overnight, far from it. But if and when the sales team begins to meet its sales mix goal, a single-lane secondary packaging line would become obsolete for the predicted volume very quickly. So, the new plan of attack became a mirrored two-line system with plenty of runway for the expected future growth in this package format. The plan would be able to maintain single robotic installations at the case packer and palletizer, though two mirrored partition inserting robots would still be used in the box shop.
NOP (No-Plastic Program) means we promote eco-friendly plastic substitutes for the packages manufactured on IMA machines. rough the research and testing of alternative processes and materials together with our partners we foster plastic-free and sustainable, compostable, biodegradable or recyclable packaging solutions.
According to these objectives, IMA established OPENLab: the Group’s network of technological laboratories and testing area, dedicated to the research on sustainable materials, technologies and production optimization processes.
Discover more about IMA NOP on ima.it/imazero and IMA OPENLab on ima.it/open-lab
PACK EXPO
Las Vegas 2023
September 11th-13th
Central Hall Booth 3200/3400
“The way we and Hamrick designed the line was to provide a single robotic installation supporting two lines,” Coakley remembers. “So, although redundancy isn’t there in terms of clear one-to-one ratio, we’re reducing footprint. And since Hamrick’s done such a fantastic job with Fanuc robots over the last three years, and the con dence was so high with me, we recommend Jordan also manage it to do a robotic palletizer for their needs.”
With roles and responsibilities sorted, nalized plans for the line came together fast. PW spoke to Sonny’s automation engineer Adam Harper, the brand-side counterpart to PAG and Hamrick on the installation, in late 2022. As could be expected, there were some hiccups along the way, because “not everything in 2D or 3D CAD always lines up perfectly,” Harper jokes, but the three parties worked through what’s now a pretty nifty full packaging line.
Integrated by PAG, primary packaging operations begin with empty 2.5-gal F-Style HDPE bottles coming into the Mentor facility on pallets of about 60 bottles per row, at eight rows high, with slip sheets separating each row. Operators manually depalletize by cutting through the pallet shrink and placing each row of bottles on an incline elevator belt feeding a single unscrambler assembly from Pace, a ProMach brand, which begins with a ring hopper that spins parallel to the oor on a mezzanine level. The hopper orients the bottles on their sides and places them on a series of timing belts, but the direction they face as they travel
(bottom-leading or closure-leading) remains random until the bottles pass through a mechanical turning hook assembly that orients them in the desired bottom-leading posture. After orienting, a mechanical lip on the belts catches the at surface of the leading bottoms of the bottles as they travel by, uprighting them from their sides.
“The next step is that all the nozzles have to be facing the same way, with the nozzle leading,” Harper says. “So at the very end of the bottle unscrambler assembly is a bottle orienter. It has two Allen-Bradley laser photo eyes, one viewing for the space inside the handle, and the other viewing the nozzle. If the bottle is facing the correct way, with the nozzle leading, the sensors both read the handle and orientation as true and the bottle isn’t turned. If the bottle is facing incorrectly, with the nozzle trailing, one photo eye reads the handle as true, but the other reads the nozzle as false. When that’s the case, it’s moved up the line slightly to be turned 180 degrees by a rotating arm, and all bottles leave the Pace unscrambler in the correct orientation.”
Are you asking yourself, “Wait, just one single unscrambler? I thought this was a mirrored, dual-line operation?” If so, good catch; here’s where the line splits into two.
Box shop operations include erecting a heavy, double-walled printed corrugated case, automatic taping,
partition inserting.
As the capped bottles pass underneath this equipment, an infrared sealing system suf ciently heats the precisely positioned foil lid that rests on the lip of the bottle, underneath the cap, so that the foil and bottle adhere to one another.You need automation technology that inspires you as much as you inspire your team. iCube Control scales and grows with your ever-expanding vision. The technology works as one, with one controller, and will perform impeccably over the life of your system, without fail and with total security. With iCube Control, you’re in total control.
Once oriented, a diverter conveyor from Wrabacon Inc., a PAG company, branches the single conveyor into a ‘Y’ shape with two downstream lines. A gate at the split diverts bottles downstream into whichever line needs feeding.
The two lines travel in parallel to two mirrored six-head llers from Massman’s PASE Group, where lances descend on ball screws into the empty bottles. Each of the two llers handles six bottles at once. Each bottle sits on an individual load cell, and lling is metered by weight rather than volume or ll line.
“In an ideal world, we’ll be doing 12 bottles per minute on each side, or about 30 seconds per cycle,” Harper says. “But we make soaps that are extremely concentrated, so it can be very sudsy stiff. A more realistic goal for the foamier chemicals is to ll about 10 bottles per minute, over the course of the whole run. But we’re shooting for 12.”
The six-head llers are capable of top lling, bottom lling, or tracking, depending on the viscosity and foam characteristics of the detergent being lled. Top lling is fastest, and as the name implies it lls from the top of the bottle, where the lances remain during the entire lling. Top lling is suitable for waxes and products that lack surfactants, thus can handle
some agitation without foaming. But chemical products that contain surfactants can’t be easily top lled due to their foaming characteristics, so that’s where bottom lling comes in. The lances are plunged to the bottom of the empty bottle and remain there for the ll. This is the slowest method, considering as much as 25 lbs of liquid detergent will pool above the lance as it lls, working against the ow. But it’s also gentlest on the foamier, suds-prone products. To make up some time on a bottom- ll, the tracking ll option can be used. When using this method, the lances are raised up a bit more than an inch for every ve pounds of liquid detergent that’s lled. This is sort of a best-of-both-worlds approach that’s gentle on the product and still faster than bottom lling, but it requires operator input. Ultimately, choosing between the three is a function of the product, the operator, and the desired or required ll speeds. Flexibility to change methods for different products and requirements is the important factor for Sonny’s. Filled bottles are then conveyed to a front-gated, custom designed timing screw, where one-by-one they are accelerated and metered out until they reach a stationary pocket on the screw. Despite the conveyor continuing to run beneath the temporarily stationary bottle, it is held in place under a chuck-
MAKE PRECISION YOUR BIGGEST SAVINGS
CHOOSE A WEIGHTPACK MACHINE
MAX PRECISION = ZERO WASTE
infousa@weightpack.com
style Balpack screw capper, purchased from All-Fill, until a pneumatic arm successfully pushes a cap onto the bottle. The caps themselves are fed into the screw capper via a hopper and incline elevator, then are dispensed down a chute into a cap pocket, where each cap will precisely meet the waiting lled, but uncapped bottle. The pneumatic air cylinder then drives down the positioned cap, and spins it onto the thread of the bottle’s neck. Before the capped bottle has even left the rst capping pocket, the following uncapped bottle has cleared the stop-gate at the head of the timing screw and is already traveling through the screw to be capped.
“Once it goes through that rst station where the cap has been applied, the timing screw carries it slightly further to take the bottle to a second torquing station to do a secondary torquecheck on the top of the cap just to make sure it’s at the right torque setting,” Harper says. “It’s important that it’s at the correct torque since there’s a foil lid on the inside of the cap that needs to be snug enough that, when it goes through an infrared sealer further down the line, the foil is positioned correctly to line up and seal to the top of the bottle, rather than to the cap. If it’s too tight, it will crease the foil, resulting in a bad infrared seal. And if it’s too loose, it won’t get sealed onto the bottle at all.” More on that infrared seal later.
After exiting the second torquing station, each bottle travels through two separate Keyence sensors. First, a foil detection sensor con rms that there is a foil in the cap and rejects those that don’t onto a reject tray. A cap height sensor is next; Harper explains its purpose.
“The weights are substantially different between of our chemicals, slightly distending the bottles in different ways, and each one slightly changes the height of the cap, even on the same sized bottle,” Harper explains. “The correct height range gets adjusted during each run by the operator. Using the rst six bottles that exit the six-head ller on a production run as a representative sample of what’s to follow, the operator sets the torque height limit for the remaining bottles. Then any that are out of spec, plus or minus one or one and a half millimeters, those are also rejected.”
Downstream of capping operations and related quality assurance, pressure-sensitive label application is done on a NITA labeler, a machine that Harper says is easy to use and required very little training. While this equipment is certainly capable of more complex jobs and many recipes, labeling variation on the 2.5-g liquid chemical line is fairly limited. Label positioning tweaks during changeovers are infrequent, and usually are based on minor bottle distending or deformation that may occur with heavier liquid detergents or the occasional hot- lled product.
After labeling we nd the only signi cant piece of legacy equipment that came over from the previous, mostly manual packaging line in Wickliffe. That’s an Enercon infrared sealer, which doesn’t physically touch the bottles at all. Remember how important the correct torque was in
capping operations? As the capped bottles pass underneath this equipment, the Enercon device suf ciently heats the precisely positioned foil lid that rests on the lip of the bottle, underneath the cap, so that the foil and bottle adhere to one another. This is an important step, since when a car wash attendant nally opens the cap to mix the detergent in a Bullseye device, they will nd a foil seal underneath the cap. The Bullseye dilution station then then breaks that seal to release the detergent within the equipment, meaning the car wash attendant doesn’t have to handle the concentrated liquid chemicals.
Some accumulation occurs after foil sealing, and the bottles are again oriented, this time to prepare them for robotic case packing. Using a simple but slick mechanical turning hook assembly, bottles are turned to travel downstream broadside rst, nozzles facing out. Lagrotta Packaging incline product conveyors supplies the timing belts and conveyance for this portion of the line.
“There’s a variety of methods you can use to turn these bottles,” Hamrick says. “There’s a star wheel, there’s timing screws, and other options, but the most cost-effective way for that speci c bottle on lower speed lines is to use the turning hook assembly.”
At this point, the line transitions from primary to secondary packaging, and that’s where PAG handed over the line integration keys to Hamrick. At the beginning of case packing operations, two left-handed, mechanical Hamrick case erectors with Festo pneumatics operate in tandem, with one cleverly oriented at a 45-deg angle of the other to accommodate a structural pillar in the facility. But why use two separate, independent box shops for these slower speeds and a single pack format?
“Initially, at these speeds, we looked at running one case erector, one partition inserter, and then diverting the cases to pair with either one line or the other, whichever was more starved for cases. Afterall, the pack format is dedicated on both lines, it’s all 2.5-gallon bottles,” Hamrick recalls. “But the formula of the soaps, and the artwork on the cases, could vary between the two lines. One ller could be one type of detergent, the other a different type. And if we only had one box shop, we would need to do mixed pallets or mixed magazines of cases. In the end, it was easier to do a dedicated box shop on each line. And then, we were able to use the robot to be able to synchronously pack between both, even when they’re running a different product on each line.”
The box shops are designed to handle extremely heavy, 48 ECR double-walled corrugated to
PMMI, the association for packaging and processing technologies and the producer of the PACK EXPO portfolio of trade shows, is celebrating our 90th anniversary with a focus on the resources we offer to ensure our industry’s strength for years to come.
To nd out how you can bene t, go to pmmi.org.
Interested in packaging robotics?
Don’t miss PACK EXPO Las Vegas 2023, where a wide range of packaging line integration solutions featuring robotics will be on full display. For more information, visit packexpolasvegas.com
accomodate 50-lb liquid loads. Each case erector features a 6-ft (roughly 100-ct of corrugated blanks) magazine, a squaring mechanism, and servo indexing system, with controls on the back side. A tape head from DEKKA, a ProMach company, on each of these case erectors tapes the bottoms of erected cases; a servo arm simply advances the erected case along a bottom apclosing xture, and past a tape head.
Immediately following, and in fact mated to each case erector, is a robotic partition inserter. Hamrick selected two 6-axis LR Mate 200iD/7L from Fanuc for this operation.
“You don’t need a high payload here since it’s just the partition insertion; you only need speed and reach,” Hamrick says. “The partition might only be a fraction of a kilogram. Small vacuum plates pick at 2D, pre-scored partitions off a stack, then run then through a curved mandrel to create the Z format, then plunge them into the case.”
Erected, bottom-taped cases proceed on TGW Case Conveyors-powered roller conveyor underneath the two bottle-infeed lines and turn 90 deg to align and run parallel to one another, as two paired product/case infeeds. A ve-axis M-710iC/50H robot from Fanuc resides between the two parallel lines. A sixth axis isn’t necessary there since all the work being done is on the same plane—bottles don’t require rotation or further manipulation. The end of arm tooling designed by Hamrick is a hybrid of vacuum and mechanical clamps that grabs bottles by the handle, picking two bottles at a time. As the robot picks and carries the bottles from the product infeed, a mechanical collar descends over the open aps of next case to be packed, ensuring proper placement into the partitioned cases and avoiding bottles catching on corrugated case aps.
The six ller-heads upstream on each line predicate that most downstream operations are done in groups of six, as evidenced by the cap height sensor calibration step mentioned earlier. Case packing is also done in groups of six, but with an added two-bottle buffer. The single
We’re spicing things up at PACK EXPO Las Vegas in booth #C-1614!
See what it’s all about, add us to your show plan.
End-of-line operations are accomplished by another single robot arm, but this one with roughly a 370-pound potential payload. In this operation, the arm is picking up three cases at a time, so at roughly 50-lb per case, that makes for 150-lb picks. Perhaps surprisingly, end-ofarm tooling is able to easily accomplish 150-lb-plus picks using only vacuum suction, and no mechanical clamps. Pallet conveyors include a pallet dispenser, a gantrystyle sheet inserter, and pallet conveyor/accumulation.
robot arm will case pack one line until the opposite line accumulates eight (six plus a buffer of two) bottles. It will then change from one line to the other, to do three picks of two, two, and two, leaving the last two bottles in place as the line replenishes to eight. The robot will then switch to the other line, by which time eight bottles will have accumulated, and this process is repeated for the entire run.
“It works out well because there’s eight bottles, and the robot picks up six of them,” Harper says. “That’s two bottles per case, and three cases per line being pushed downstream in each cycle, which is exactly what the palletizer grabs in each pick. There’s convenience and ef ciency baked into that design.”
Top aps of the packed cases are mechanically closed and taped on another DEKKA tape head as they’re conveyed toward palletizing. Automated case labeling also now occurs at the handshake between case packaging and palletizing. Sonny’s had been pre-labeling the corrugated blanks in the early days of this packaging line’s production, but the company has since invested in two more NITA labelers designed for corrugated cases that were integrated into the line immediately downstream from case packing, just before palletizing, to allow labeling to happen on-demand.
End-of-line operations are accomplished by another single Fanuc robot arm that serves both lines, this time an M-410/185-kilogram robot, which equates to about a 370-pound potential payload. In this operation, the arm is picking up three cases at a time, so at roughly 50-lb per case, that makes for 150-lb picks. Since each pick is six total bottles or three cases, the pace is notably slower at the end of the line, easily outpacing primary operations.
Hamrick left pallet pattern preferences up to Harper, who naturally consulted the employees who had been manually palletizing operations at the Wickliffe plant. Those employees’ selected 3x4, or 12-ct per layer pattern, at three rows in height, which remains the preferred pallet pattern today. Slip sheets are placed on top of the empty pallet via gantry after pallet dispensing–none are required between layers. The three rows are stacked without rotating the center row, thus avoiding overhang. Though the heavy weight works against going tall with pallets, it makes for sturdy, robust 36-ct unitized pallets that travel well, according to Harper. As for speeds, each line produces a pallet every six minutes at cruising speed, with room to speed up from there if necessary. Even at the end of the line, packaging operation hew to a rule of sixes. If you remember, lling operates at 10 to 12 bottles per minute per line. That equates to one 72-ct pallet of bottles, or 36-ct pallet of cases, every six minutes.
A more recent development has been training the robot to rotate picks in such a way that ensure labels are outside-facing on both sides
of the pallet, as the most natural pallet pattern would result in all the labels only being visible on one of the pallets four sides.
“It just makes shipping easier, and it’s easier for our distributors,” Harper says of the upgrade.
This palletizer’s end effector was supplied by Joulin, a Piab company, and perhaps surprisingly, is able to easily accomplish 150-lbplus picks using only vacuum suction, and no mechanical clamps.
“The original plan behind this was to go with a similar tool that we had used for a bottled water company, which was more like a fork and a clamp,” says Jeff Eckstein, director of engineering at Hamrick. “But we brought in Joulin, who we have worked with on a number of other applications. They were very con dent that we could pick these using a simple vacuum, which simpli es everything since robot can hover and make these rows very easily without interfering with anything else, and without needing to open up clamps, or anything like that.”
Prime Conveyor supplied pallet conveyors for the project, providing a pallet dispenser, a gantry-style sheet inserter, and pallet conveyor/accumulation. Stretch wrapping isn’t done in-line; pallets are manually rolled from the packaging line to a stretch wrapper. Plans for 2023 include an in-line stretch wrapper.
No project is without its hurdles, and the ones faced in the Sonny’s detergent automation project bear mentioning. As occurred with most automation projects undertaken during the pandemic, supply chain issues were a hinderance to timelines. One workaround that ended up being a surprising nd for Hamrick and Sonny’s alike was the pivot to Weintek HMIs and Mitsubishi Electric drives and drives and servos. Standard Allen-Bradley PLCs, though, were integrated on all machine centers.
“I hadn’t been that familiar with them, but they’ve been great. They’re very user friendly, and just as good as anything else we’ve seen,” Harper says of the interfaces and drives.
For its part, Hamrick had intended for this project to be the rst full line build and factory acceptance test (FAT) in its own brand new, 65,000-sq-ft facility. But that wasn’t possible because construction and supply chain issues of their own delayed the facility build. While individual machine centers were tested at the existing Hamrick facility, there wasn’t room to FAT the whole line at once, so the FAT ended up being a site acceptance test, too. Many of the kinks that Hamrick would have ironed out in his own new facility would have to happen at the customers’ site. But these types of experiences were common, possibly even typical in 2022.
“That’s just the reality we all dealt with, and there are always going to be start-up pains. We just saw more of them since we started it up here,” Harper says. “Not to mention, we were starting our own new manufacturing facility, too. Like I said, CAD plans aren’t perfect in the real world. That’s just how it is in the world of packaging.
“But I wouldn’t change a thing,” Harper concludes. “Patrick and Jordan, and really every single manufacturer and supplier that we dealt with has been great, I don’t have any concerns about anyone that we’ve gone with. And every time we bring our customers, or brother and sister companies into this plant, nobody can take their eyes off the robots. They’re basically a showpiece.” PW
Producing fruit snacks 24/7 and operating now since November 2021, Mogul Line 5 at PIM Brands requires some serious packaging equipment to cope with the volume of fruit snacks it generates. So for primary packaging the Somerset, N.J., rm lined up eight combination scales from Multipond each paired with a vertical form/ ll/seal twin bagger from GEA
“It’s a direct feed from processing to packaging,” says engineering manager Chris Greco. “That means we don’t bulk off the product and then move it to packaging. In fact we don’t touch the product at all. It comes off the mogul [the term used in the confectionery industry for the machinery that makes shaped candies] into nished product conveying and then continues straight through to packaging. So as we evaluated the equipment we wanted on the new line, speed and footprint were two priorities. That’s where the Multipond/GEA stack-ups come in. Each pair pushes out about 360 bags per minute with each bag weighing 0.8 ounces.”
Packaging begins on an overhead level, where nished product is directed onto one of two long vibratory conveyors from Layton Systems. Running perpendicular to each of these conveyors
Shown here are three of the eight twinbagger discharge stations that deposit 0.8oz bags of gummies onto the conveyor that carries them to a cartoning operation. Inset shows three of the carton sizes produced.
When one of the country’s largest producers of fruit snacks boosted its candymaking capacity, primary, secondary, and tertiary packaging had to be top-notch.
Editor
The 24-bucket combination scale mounted over PIM Brands’ Tishma cartoner is a Yamato DataWeigh ADW-0-06245. It’s notable for a piece of patented technology called the SVR Reject System. To understand the benefits it brings, it’s best to take a look at an operating problem common to many radial combination scales available today: overfilled weigh buckets.
Weigh buckets can be overfilled in a number of ways, but it’s seen most frequently when product bridges and jams up as it makes its way from the dispersal cone to the feed pans to the weigh buckets. Back pressure eventually breaks the jam, causing product to be propelled out into a weigh bucket in far greater numbers than what’s called for. The end result is that that weigh bucket ceases to operate until an operator manually removes it from its mount and empties its contents back into the top dispersal cone so that the items can be redistributed out to the weigh buckets again in a more measured manner. And with a combination scale, whenever even one weigh bucket is out of operation, both speed and accuracy of that weighing system are compromised.
Yamato’s SVR Reject System addresses this problem by introducing a rotating ring right beneath the weigh buckets. Also important is that the weigh buckets are dual-acting. On-target weigh buckets are discharged to the inside chute leading down to the bagger. But overfilled weigh buckets are discharged outside and onto the rotating ring. This brings two significant benefits. First, if a weigh bucket does get overfilled, it does not cease to operate, so productivity is not negatively affected. Second, there’s no need for an operator to climb up and empty an overfilled weigh bucket back into the central
dispersal cone. The overfilled weigh bucket simply discharges its contents onto the rotating ring. The ring then delivers its contents to a discharge chute. At PIM Brands, rejected bags drop from the rotating ring onto a conveyor that leads back up to the top dispersal cone. PW
are four smaller vibratory conveyors each leading directly to a Multipond scale. Product ows through these vibratory conveyors based on which scales are calling for it.
All of the Multipond scales are the Model MP-36400-400-J2. Product falls into 36 buckets whose load cells register how much product is in each bucket. The weights are communicated to a central processor that then picks which combination of buckets contains 0.8 oz of product. Those buckets then release product down the twin tubes leading to pouch forming and sealing, which is where the GEA Smartpacker Twintube C machines come in. All eight of them pull roll-fed metallized lm up over a forming mandrel and down into the sealing and lling station. The sealing jaws produce the top of the exiting bag and the bottom of the next bag. Why the Welch Foods graphics on bags and cartons? Because PIM Brands produces the fruit snack gummies under a licensing arrangement with Concord, Mass.-based Welch Foods, Inc.
Mounted on each of the GEA baggers is a SmartDate X30 thermal-transfer printer from Markem Imaje that imprints lot and date code information.
• Increase productivity
• Improve quality control
• Reduce waste
• Optimize oorspace
• Prevent workplace injuries
• Simplify machine changeover
• Reduce maintenance costs
Let the Schneider expert engineers solve even the most complicated case packaging challenges through FANUC robotics or traditional case packing methods.
Schneider palletizers incorporate FANUC robotics to create unique, exible, and intuitive machines to meet your facility and production requirements.
sales@schneiderequip.com
The case packer includes a pair of robots that quickly and ef ciently orient cartons into the patterns required (right). Case blanks are automatically erected, cartons are inserted, aps are closed by way of hot melt adhesive, and nished cases are ready for palletizing (below).
At this point the 0.8-oz pouches are down at oor level. But they need to return to the overhead level to reach the infeed of the combination scale that delivers them to a oor-level cartoner directly below. They make this return to the overhead level by way of a bucket incline conveyor from Wiese. “We like the Wiese equipment because it doesn’t use a chain to drive the buckets,” says Greco. “It’s a rubber-coated cable instead. By eliminating that metal-to-metal contact of chain on sprockets, you minimize wear. Also part of the Wiese system is storage capability that holds about 10 minutes of production so we can keep our baggers running if anything downstream goes down.”
The unique combination scale above the cartoner is from Yamato (for more, see sidebar on page 196). Directly beneath the Yamato scale is a TT-400 continuous-motion top-load cartoner from Tishma Technologies. A rotary picking device picks a at carton blank from a magazine and places it into one of multiple pockets that move along an elliptical track. After bottom aps are glued by a Nordson hot melt adhesive unit, the carton arrives under the Yamato scale’s dispensing bucket, which has been lled with the correct amount of pouches. Once pouches have been dropped into the carton, it advances to a station where top aps are glued shut. At that point it’s on to case packing, though each carton rst passes through a metal detector/checkweigher from Loma
“We like the exibility of this cartoner, which is the third we’ve installed from Tishma,” says Greco. “We’re able to run anywhere from a 10-count to a 160-count carton on it, though the two sizes we run on it most frequently are 22-count at 110 cartons per minute and 40-count at 70 cartons per minute. Servo motors make changeover quick, too.” The servos and overall controls package are from Rockwell
To watch a video of PIM Brands packaging line in action, scan the QR code, or visit pwgo.to/7992.
Before exiting the Tishma system, each carton runs past a laser coder from Markem-Imaje that delivers date code information. Cartons then are conveyed into end-of-line equipment from Schneider that includes case packing, palletizing, and stretch wrapping. “We installed a Schneider machine around seven years ago on a different project,”
says Greco. “We got good service, the equipment is robust, and so we stuck with them since. Of course for this project we went out and got competitive bids, but once again when we factored in footprints, delivery times, performance, and cost, everything pointed to Schneider.”
The horizontal case packer includes a pair of Fanuc SCARA robots that perform an important carton rotating function. “Some cartons coming off the cartoner aren’t in the correct orientation for placement into the RSC case,” says Greco. “So these robots use a vacuum cup grip to turn a carton 90 degrees or 180 degrees, or they do nothing if the carton is correctly oriented.”
Integrated into the case packer is a 1580 ink-jet coder from Videojet as well as a ProBlue 7 hot melt glue system from Nordson. Also notable is the inclusion of two Schneider features:
• ProAdjust automatic changeover system, which utilizes a series of electric and air-driven power packs to reposition machine components when changeover is needed. It allows changeover from one product to the next in a matter of minutes instead of
hours, and it’s done at the push of a button. Currently, two case formats predominate: either six 40-count cartons per case or six 22-count cartons per case.
• Intelligent Illumination, which proactively cues operators where attention is needed with customizable colors. Task lighting illuminates the machine where operators need good visibility to perform maintenance. This also allows operators to perform basic upkeep without even having to consult the HMI.
In addition to placing cases on a pallet (above), the end effector on the robotic palletizing arm can also pick and place an empty pallet into the case-loading station (left) or pick a corrugated slip sheet and place it on top of a nished pallet just before it’s conveyed to a stretch wrapper.
Next in line is a Schneider palletizer notable for the variety of tasks it performs. First, a ve-high stack of empty pallets is conveyed into the system, and as soon as it’s in place the palletizer’s Fanuc robot uses built-in end-of-arm tooling to pick the top pallet and place it where it needs to be. That tooling then folds up and, for all practical purposes, disappears so that vacuum suction cups that are also part of the end-of-arm tooling can pick a paperboard slip sheet and place it on the pallet. The same vacuum suction cups are used to pick corrugated cases and place them on the pallet. When a pallet load is complete, the robot picks a paperboard slip sheet and places it on top of the load. The nished load then proceeds on oormounted roller conveyors until it reaches a WCA-Smart stretch wrapper from Wulftec, a Duravant company.
“PIM Brands was a good partner in making sure we worked through all of the accumulation, safety, and shut-down considerations for the equipment,” says Schneider applications engineer Kevin Helinger. “That included such things as bypass options so that manual case packing or palletizing could be done if maintenance is needed on the equipment. It also included the placement of operator HMIs, E-stops, and disconnects in just the places where the PIM Brands operators need them.” PW
Emerson’s IIoT solutions and analytics software detect compressed air leaks saving manufacturers over 20% in energy costs.
Learn more at Emerson.com/Sustainable-Automation
Visit us at Pack Expo 2023
South Lower Hall, Booth 6107
The paper toilet paper packaging will eliminate approximately 500,000 pounds of plastic waste each year, the company says, and testing shows the format to be comparable to its predecessor in performance and function through rigorous supply chain, to retail, to consumers’ homes.
By Matt Reynolds, Chief EditorQuilted Northern, a Georgia Paci c (GP) brand, is launching paper packaging for the bestselling packs of its Ultra Soft & Strong line, making it the rst national toilet paper brand to offer recyclable paper packaging in major retailers.
The paper packaging, which will be available on the product’s 6 Mega packs and Amazon case packs, is expected to eliminate approximately 500,000 pounds of plastic waste each year, the company says.
“We are serious about our sustainability journey and decreasing our environmental impact,” says Amanda Gage-Cole, vice president and general manager of the Quilted Northern brand. “That’s why we are proud to be the rst national toilet paper brand to launch curbside recyclable paper packaging. Our product development team has worked diligently since 2020 to develop the innovative packaging to withstand manufacturing and shipping without ripping, while meeting all requirements to make recycling easier for our shoppers.”
The legacy pack format used on Quilted Northern was LDPE plastic shrink lm, which exhibits both puncture resistance and water resistance. So from a functional standpoint, any paper-based material that would replace the LDPE format would also have to suf ciently exhibit those qualities for the tissue product to make to make it through the supply chain, through retail, to consumers’ homes intact and dry.
Sure enough, the new paper format “was designed to withstand potential tears and punctures throughout the supply chain, from the manufacturing facility in Louisiana to the customers’ home,” says Jason Morgan, director of packaging, GP. “And while not ‘waterproof,’ the paper packaging was designed to provide adequate water resistance and protect the product during customary transport by the customer; for example, taking the product from the store to your car during a rainstorm.”
The paper packaging is produced using a 2.4 mil-thick virgin ber that incorporates some adhesive coatings, but those coatings do not affect the recyclability pro le. Perhaps most interesting to other brands
and CPGs interested in this project, the new paper product runs on existing equipment—with some minor retro ts, of course.
“We found that this gauge of paper provided the optimal blend of runability on our processing equipment, protection of the product throughout the supply chain, and ease of use for our customers,” Morgan says. “We formulated the paper wrap to work well with our existing packaging equipment. We did have to make some modi cations to those production lines, but the existing equipment is used.”
5V[OPUNPUZWPYLZ\ZSPRL`V\YJOHSSLUNLZVU[OLWYVK\J[PVUÅVVY
That’s why our new Power-Fill® Bulk Bag Fillers are designed to save time, reduce operator MH[PN\LHUKLUHISLZHMLYLSPHISLK\Z[MYLLÄSSPUN*\Z[VTMLH[\YLZPUJS\KL!
7V^LYLKÄSSOLHKOLPNO[HKQ\Z[TLU[ MVYIHNZPaLÅL_PIPSP[`
Easy-Load TM rotary bag hanger MVYLYNVUVTPJIHNSVHKPUN
Fill-by-weight capabilities
MVYHOPNOS`HJJ\YH[LÄSS
/LH]`K\[`KLUZPÄJH[PVU Z`Z[LTMVYPTWYV]LKÄSS]VS\TL
*OHSSLUNL\Z[VTHRLHKP LYLUJL VU`V\YWYVK\J[PVUÅVVY | 4H[LYPHS;YHUZMLYJVT
7JTJUVT!#PPUI $$FOUSBM)BMM 6HSWHPEHU /DV9HJDV1HYDGD86$
9HUWLFDO)RUP)LOO6HDO
0DFKLQHV
The new pack-format product rollout is not just a more sustainable option, it’s SKU-wide. All 6M and Amazon case packs will only be available in new recyclable paper packaging. It is available at select retailers throughout the country, in addition to via e-comm channels. Speaking of e-comm channels, how does the paper packaging perform in the rigorous, many-touch D2C environment?
“We went through extensive testing with the design and found good performance through the e-comm channel,” Morgan says. “We have also conducted audits of e-comm and retail product and found good performance from a handling and supply chain damage standpoint.”
From an aesthetic perspective, the paper is printed via exography. Morgan says the company and its suppliers optimized the number of colors to provide excellent graphics while minimizing the amount of ink used, and no issues with printability on the paper substrate have been found. Ink minimization is just a drop in the bucket when it comes to sustainability-minded perks of the new format.
While GP has not conducted a third party-reviewed life cycle analysis (LCA) of the full suite of environmental impacts on the LDPEto-paper switch, it should be noted that plastic lms are not now widely recyclable at all, much less curbside recyclable. Contrast that with paper packaging, which is 100% recyclable, and overwhelmingly curbside recyclable in most municipalities. It stands to reason that, according to Todd Wing eld, Sustainability Director, GP, “the paper packaging increases access and ease of recycling and reduces plastic waste while still providing shoppers with the same quality and comfort expected from the brand.”
The virgin paper product is not FSC certi ed, but it still can claim circularity bona des, since “two trees are planted with the Arbor Day Foundation for every tree used by our paper suppliers,” Wingeld adds.
0DFKLQHV\RXFDQ WUXVW
3HUIRUPDQFH\RXFDQ UHO\RQ
7HFKQRORJ\WKDW LQFUHDVHV\RXU SURGXFWLYLW\ HIILFLHQF\
86EDVHGVXSSRUWIRUVSDUHSDUWV
WHFKQLFDOVXSSRUWDQGVDOHVFRQVXOWLQJ
We asked Wing eld, how are these types of sustainability chops, and the newfound recyclability pro le, communicated to consumers? Afterall, they should now start recycling this Quilted Northern packaging when they haven’t been able to previously.
“Front of pack communication focuses on ‘Recyclable Paper Packaging, to clarify for the consumer what the material is made of, and to call out the most valued bene t of paper wrap packaging to the consumer: recyclability. Back-of-pack communication clari es that the packaging is curbside recyclable,” he says. On-pack communication does not include information from third parties, but Wing eld con rms that the packaging passed repulpability and recyclability testing per protocol by an independent third-party testing facility.
Packaging World asked who the supplier was of this paper packaging but Quilted Northern and GP declined to identify them.
Notably, PW also reported on the SOFIDEL own-brand Nicky being tested in the U.S. last year online (pwgo.to/7994). But the Quilted Northern pack switch appears to be a more signi cant roll out of paper since the Nicky brand is not considered a national toilet paper brand that would be distributed in the majority of retailers across the U.S. Also, the Quilted Northern brand is selling products in paper packaging to in-store retailers, not just online. PW
•Robotic Palletizers
•Integrated Bagging Lines
•Collaborative Robots
Let’s talk about your project today!
WE BELIEVE IN THE TRANSFORMATIVE POWER OF AUTOMATION
Powell Electronics adopts a patented new clamshell container with reclosable locking mechanism to ship delicate parts damage-free and reduce labor and packaging costs by 90%.
Offering more than 7 million SKUs, Swedesboro, N.J.-based Powell Electronics is among the largest distributors of custom-made electronic components and value-added services. Its products include electronic connectors, switches, sensors, and related electromechanical products—all of which are very sensitive parts with extremely delicate handling requirements.
According to company CEO Ernie Schilling Jr., for more than 20 years, Powell searched without success for a protective packaging solution for its fragile parts, experimenting with a number of different packaging materials and formats. But a chance encounter with custom plastics supplier Jamestown Plastics at a sporting goods show several years ago resulted in Schilling nding the ideal packaging solution for the company’s needs, a patented reusable and recyclable clamshell container, the Clamtainer, which he says just “clicked.” He adds, “I immediately saw that the Clamtainer solved our issue.”
Powell Electronics is a national company with global distribution and represents nearly 150 manufacturers. The company employs a staff of over 200 people at 11 U.S. locations, supplying industries that include the military/aerospace, telecommunications, transportation, medical imaging and instrumentation, and the U.S. government, among others. Products are delivered to these customers in shipping cases with the components individually packaged. According to Schilling, the parts are inspected at both shipping and receiving and are oftentimes stored for many years, as in the case of military preparedness, or are sent to third-party contract manufacturers.
For years, Powell experienced damage of its parts during shipping in the form of bent pins, or contacts, and loose parts when the packaging failed to remain closed or maintain its structure. “Parts were splashed in the larger shipping box,” says Schilling. “Because each connector is
custom, and we support over 7 million SKUs, the dimensions [of the packaging] were almost impossible to match perfectly every time. It was an enormous undertaking to match a part to a shipping container without advance forecasts or estimates. We received over 1,500 returns per year due to bent pins or failed packaging. What was so offensive is that the returns were for dollars against tens of thousands of dollars but had the effect of killing our quality rating with our customers.”
To address the damage, Powell tried multiple paperboard cartons, however there were strength issues as well as inspection issues, as operators had to open the cartons at shipping and receiving to inspect the parts. The company also tried various polypropylene lms stretched over paperboard as well as vacuum packaging and trays. “All lacked the exibility and universal ‘adaptability’ of the Clamtainer,” Schilling reports. According to Jamestown Plastics CEO and inventor of the Clamtainer Jay Baker, the patented clamshell container is the only one of its kind that is sold as a standalone product to consumers, in addition to being supplied to brand owners as a packaging solution. Part of its appeal to both is its sustainability features. “We like to say of the motto, ‘reduce, reuse, recycle,’ that there has never been a clamshell application that hits on all three of those more resoundingly than the Clamtainer,” Baker says.
The bulk of the Clamtainers produced by Jamestown are 100% recycled-content and 100% recyclable PET. The container can also be made from BioPET—a blend of bio-based and petroleum-based plastics—oceanbound rPET, recycled polyvinyl chloride (rPVC), and polylactic acid (PLA). According to Jamestown, the Clamtainer uses less plastic than traditional clamshell packaging, which means less space is needed in trucks and distribution centers and shipping costs are decreased due to reduced dimensional weight.
One of the aspects of the Clamtainer that most differentiates it from the traditional clamshell, however, is its patented Click-It Closure. As
Regardless of your objectives or the challenges with your application, Powertrain Solutions can help you achieve your unique goals. No matter what your application looks like, it relies on many components, all working together. But not ćŰŰʠĤƇŹƫƇŻIJŻǂƶʠćƮIJʠŹćīIJʠǂƇʠǣƇƮŭʠǂƇŋIJǂŒIJƮʠƮIJŰŗćģŰǩʠćŻīʠIJ ĤŗIJŻǂŰǩɡʠ¥ƇǣIJƮǂƮćŗŻʠ°ƇŰNJǂŗƇŻƶʠŒćƶʠǂŒIJʠŗŻƶŗŋŒǂ ʠIJǨƫIJƮŗIJŻĤIJʠćŻīʠ
IJǨƫIJƮǂŗƶIJʠǂƇʠIJŻŋŗŻIJIJƮʠǩƇNJƮʠĤƇŰŰIJĤǂŗƇŻʠƇŊʠĤƇŹƫƇŻIJŻǂƶʠŗŻǂƇʠćʠŊNJŰŰǩʠƇƫǂŗŹŗdzIJīʠƶǩƶǂIJŹʠʅʠŋŗǢŗŻŋʠǩƇNJʠƶƇŰNJǂŗƇŻƶʠǂŒćǂʠģƇƇƶǂʠ
ʠŗŹƫƮƇǢIJʠƮIJŰŗćģŗŰŗǂǩʠćŻīʠƫIJƮŊƇƮŹćŻĤIJ ʠŰƇǣIJƮʠĤƇƶǂƶʠćŻīʠƶŗŹƫŰŗŊǩʠƇƮīIJƮŗŻŋʠćŻīʠŰƇŋŗƶǂŗĤƶɡ WHERE OTHERS SEE PARTS, WE SEE A SYSTEM
BearingsBelt & Chain Drives Clutches & Backstops ConveyingDisc & Gear Couplings
MotorsSpeed Reducers & Gearboxes
Monitoring & Diagnostics
Baker explains, the core of the invention is a post and hole mechanism, positioned inside the Clamtainer on the vertical side. Called the “Click-it” due to the clicking sound it makes when it’s closed, the locking mechanism involves snapping the post into the hole—an action that can be done with one hand and allows for reclosure, making the container reusable.
“I’ve done a lot of demonstrations at trade shows of the Click-it Closure,” says Baker. “I use this analogy: I say, ‘Okay, so when you go to bed at night, do you close your door, get out a nail and a hammer, and drive a nail through your door into your door jamb, and then pry it back out again the next morning? Or do you use a deadbolt? Well, the Click-It Closure mechanism is the deadbolt solution in the Clamtainer space. Everything else is a version of a nail and a hammer.’
“All other clamshell closing solutions aren’t permanent, they rely upon the coef cient of friction, in some way. They use a round hole and a square peg that snap together. It’s a rim lock that snaps over. That’s why, when you drop a blueberry container, the clamshell explodes, because the forces involved overcome the friction resistance of the buttons or the rim lock. And so, when the force builds up, the clamshell opens, and the blueberries go all over.
“In order for the Clamtainer to fail, you either have to shear the pin off or you have to tear through the sidewall, where the hole is, which takes an incredible amount of force. It’s really surprising. And the other unique thing about the closing mechanism that makes it so resistant to opening when it’s dropped is that the forces that are blowing open that blueberry container are pushing that hole—
because it’s on the side of the container not on the lid—harder against the pin. So the forces are working somewhat in your favor as you compress it, because it’s pushing against the pin, it’s not pushing the pin away from the container.”
Another notable advantage with the Clamtainer, Baker adds, is that the rst step in packaging is the last. Meaning, once an operator places the product into the container and snaps it closed, the packaging process is complete. No additional tools or sealing operations are required, which he says results in “incredible efciencies.”
After being introduced to the Clamtainer, Powell Electronics began testing the packaging in 2019, expanding every year to include additional sizes and material types to accommodate parts valued over $1,000, as well as low-cost parts. “The goal was to use the Clamtainer technology on everything, we just needed to calibrate the material costs and dimensions,” says Schilling.
For Powell’s massive and varied assortment of SKUs, Jamestown custom designed a number of Clamtainers to hold the company’s highestvolume products. Powell is also using a number of stock square and rectangular containers. Explains Baker, to optimize the range of containers used by a company, Jamestown will either use the company’s actual products or its CAD les to nd commonalities in sizes and then
With the Click-it Closure, no additional sealing operations are required, and the container can be opened and closed multiple times with no degradation of the locking mechanism.
create groupings. “So that’s what we did with Powell,” he says, “and the project was relatively straightforward.”
Schilling explains that Powell’s warehouse operators use a decision tree to select the right-size container. “Before we were hybridizing and collaging the original factory packaging with tapes and cardboard to
The Click-it Closure locking mechanism is positioned inside the container on the vertical walls of the clamshell. Watch a video on the Clamtainer at pwgo.to/8021For 75 years, Lenze has been a leader in delivering automation innovations for the packaging machine industry - from the geared motor to the cloud.
We partner with you in all phases of your projects in accordance with your individual goals and requirements. When you design an innovative overall concept, we are there to help you make it a reality.
Discover new out-of-the-box automation solutions.
craft thousands of semi-unique packages, all in an attempt to preserve the parts,” he says. “Now we access the value of the part on the pack list and choose a corresponding Clamtainer to meet the part and size.”
Among the advantages of the Clamtainer is that warehouse staff can now inspect the part after the packaging process, as the container is clear, which means Powell no longer needs a more expensive Quality Control staff.
“But the real savings is in time to package and the elimination of the quality returns,” says Schilling. “The previous packaging had assembly required and other soft costs. With the Clamtainer, parts pullers are now able to pull products 10-times faster, while the personnel used to do the nal packaging are ‘exponentially less expensive.’
“The Clamtainer eliminates all the soft costs and is comparably priced to the box, plastic, and foam alternatives. The Clamtainer-ized materials can also travel through all of our automated carriers without fail.”
These advantages have translated to a 97% reduction in damaged parts as well as a 90% decrease in material and labor costs for Powell.
In terms of the package’s ability to be reused, Schilling says one of the best potential applications for the Clamtainer is its ability to be incorporated into a system for factory automation, expanded packaging, and secondary uses. “It offers our customers the ability to forward parts to third-party assemblies, contract assemblers, and end customers,” he says. “They need not repackage them.”
Since launching the new packaging, Schilling says no news has been good news. “We wanted no customer response, RMA [return merchan-
PMMI ProSource is a free online directory with 460 categories of validated suppliers of packaging machinery, materials, and service solutions. With a powerful search engine and the ability to filter solutions by machine feature and
dise authorization] reduction to zero was our goal,” he says. “What has been fantastic is the corrective action process on requested returns. It has virtually eliminated RMAs from bent pins, and when they are requested, we are able to vet the return for root cause … customer, third party, etc. We win every packaging debate, and the root cause is most often attributed to the customer’s internal handling.” PW
PACK EXPO Las Vegas 2023 will be the largest and most comprehensive edition in its history. Experience in-person an unmatched breadth of new technologies and innovations, this time with a special focus on sustainability.
SEPTEMBER 11-13, 2023
Las Vegas Convention Center Las Vegas, Nev.
Registration Pricing: Get ready to experience a show floor like you’ve never seen at PACK EXPO Las Vegas—the largest show ever. Registration is $130. You can attend the PACK gives BACK™ Cirque du Soleil event Sponsored by Rockwell Automation, for an additional fee (more on page 222). Why Register? PACK EXPO Las Vegas registration is a great value. Your badge gives you access to:
• More that 2,000 packaging and processing solutions suppliers
• Personal show planner called “My Show Planner” that lets you customize your experience
• 100-plus free educational sessions, such as at the Innovation Stages, the Processing Innovation Stage, the Sustainability Stage, The Forum, or Industry Speaks sessions, with on-demand access to sessions after the show
• Special exhibits such as Sustainability Central, an interactive exhibit examining packaging’s essential role in sustainability, recycling, and a circular economy—including forward-thinking presentations from industry thought leaders
• Networking on the show floor and select events, including the Young Professionals Networking Reception Sponsored by Beckhoff Automation, Booth SL-6335, the Packaging and Processing Women’s Leadership Network Breakfast, the FirstTime Attendee Networking Reception Sponsored by ProMach, Booth C-3222, and more
Please note: No one under the age of 14 is permitted on the show floor.
PACK EXPO Las Vegas 2023 (Sept. 11-13, Las Vegas Convention Center) will be the largest, most comprehensive edition of this trade show since its inception, with 30,000 attendees expected to explore over 2,000 exhibitor solutions spanning nearly 1,000,000 net sq ft of exhibit space.
Produced by PMMI, PACK EXPO Las Vegas is the premier destination to witness cutting-edge packaging and processing solutions, with suppliers showcasing diverse innovations for more than 40 vertical markets, making it the most inclusive packaging and processing show in North America this year.
“Our industry is stronger than ever and positioned for unprecedented growth, making the connections and innovations that come from a world-class trade show more crucial than ever,” says Jim Pittas, president and CEO, PMMI. “PACK EXPO Las Vegas offers unrivaled opportunities to explore and learn about packaging and processing solutions. It is the best place to gain market-trend insights, forge relationships, and see the latest technologies—all in one place.”
Show attendees will see machinery in action, learn about the latest materials, hear from experts, experience innovations rsthand, gain insights into critical industry trends, and discover solutions they didn’t know existed. Walking the PACK EXPO Las Vegas show oor is an eyeopening and educational experience that will expand knowledge and networks for professional growth. Attendees will gain insight from 100plus educational sessions, talk to suppliers, participate in The Forum’s roundtables, and feed off the energy of nearly 30,000 industry peers engaging and sharing ideas. There is nothing like PACK EXPO Las Vegas. Visit www.packexpolasvegas.com to learn more, search suppliers, register, and plan your visit to the show.
PACK EXPO is strengthening its sustainability commitment through all facets of the show, with support from of cial Sustainability Partner Dow. Through targeted show features, increased recycling, and improving processes on the show oor, every PACK EXPO stakeholder is working together to create a more sustainable world.
PACK EXPO Las Vegas 2023 is highlighting the importance of sustainability in the industry. As part of its commitment to sustainability, show producer PMMI, along with its partners, vendors, and exhibitors, are working together to create actionable sustainable solutions in manufac-
The Reusable Packaging Association, Booth SU-8000, will once again sponsor the Reusable Packaging Pavilion, featuring exhibitors offering reusable transport packaging to help attendees move their products ef ciently, effectively, and sustainably. Located in the South Upper Hall.
•
turing, materials, and design, as well as through improved processes on the show oor. Debuting at PACK EXPO Las Vegas this year, Sustainability Central will take an expansive look into packaging sustainability and what it means to brands, including expert speakers, interactive content, and a look at actionable sustainable solutions in manufacturing, materials, recovery, logistics, analytics, and design. Located in the North Hall, Booth N-9455.
At the Sustainability Stage, located within Sustainability Central, attendees will hear from industry experts on a range of packaging sustainability topics and learn how to make their brands more sustainable. Located in the North Hall, Booth N-9455. Scan the QR code on page 224 for the latest schedule of speakers.
The PACK EXPO Green Program and accompanying icon identi es exhibiting companies that provide sustainable solutions via new materials, technology, or strategies, such as sustainable processes and machines, renewable and biodegradable packaging, source reduction and lightweighting, recyclable and recycled-content materials, or innovations that reduce carbon footprint. Look for companies participating in the PACK EXPO Green Program by seeking out the PACK EXPO Green Icon. They also will be highlighted by the PACK EXPO Green Icon in the Exhibitor Directory at pwgo.to/8025, where you can see the growing list of sustainable solution suppliers that will help advance your company’s sustainability goals. And look for the PACK EXPO Green Icon to highlight educational sessions focused on sustainability. Visit pwgo.to/8024 to learn more about the program.
Located within the Reusable Packaging Pavilion, at the Reusable Packaging Learning Center you will hear from experts on strategies to implement a reusable packaging system that can improve materialhandling performance, reduce operating costs, create new economic values, and lower the environmental impacts of your supply chain. Located in South Upper Hall, Booth SU-8000. Scan the QR code on page 224 for the latest schedule of speakers.
PMMI Media Group has created the PACK EXPO Sustainability Solutions Finder, a targeted curated list of sustainable solutions exhibitors will be displaying at the show. Visit pwgo.to/8022 to learn more. Exhibitors can participate in a post-show donation program, bene ting local organizations in the Las Vegas area, by donating any unwanted food, electronics, or booth materials. PMMI also will donate or recycle any remaining carpet after the show.
• Industry Speaks Stage
Experts from the PACK EXPO Partner Program, covering multiple industry verticals, will address the latest hot topics and industry trends such as sustainability, remote access, supply chain solutions, augmented reality, and operational ef ciency. Located in the Central Hall, Booth C-1141. Scan the QR code on page 224 for the latest schedule of speakers.
• The Logistics Pavilion
This Pavilion is new at PACK EXPO Las Vegas. Logistics is a crucial part of the product journey from manufacturer to consumer—and among the top ve searches on the PACK EXPO website. With the boom in e-commerce, the Logistics Pavilion in the North Hall will be the place to nd targeted solutions related to the supply chain, including warehousing, ful llment, distribution logistics services, and transportation providers.
Now housed in a new format, the Healthcare Packaging Pavilion is same great destination. Life sciences is an important focus for PACK EXPO Las Vegas, and this “show within a show” on the lower level of the South Hall will houseinnovations for pharmaceuticals, biopharmaceuticals, nutraceuticals, and medical devices.
• Innovation Stages
Now tried-and-true PACK EXPO favorites, the Innovation Stages are free, 30-minute seminars on breakthrough technologies and best practices presented each day by suppliers and subject matter experts. No registration is required; stop by and discover the latest innovations. Located in Central Hall, Booths C-2051, C-2058, C-2151.
The Technology Excellence Awards are back at PACK EXPO Las Vegas 2023, and PMMI needs your help to select winners. The awards recognize innovative technology, developed by exhibitors, that has not previously been shown in the PACK EXPO family of events. Voting will take place live, starting when the show opens on Sept. 11 through Sept. 12, via the official show mobile app (more on page 220) or online. Attendees are encouraged to visit the finalists’ booths and check out the technologies for themselves, then vote for their favorite.
The Technology Excellence Awards 2023 Finalists are as follows:
• Aneko Emsys. Designed specifically for the beverage industry to simply and quickly empty all kinds of concentrated liquids contained in drums, barrels, or jerricans. Aneko, Booth N-10165
• Precision Servo Tech for HPP. System brings a smart, efficient High Pressure Processing pump system to the market via servo. JBT Corporation, Booth SL-6349
• QUANTM Electric Diaphragm Pump. A departure from air-operated double diaphragm (AODD), these new pumps are designed to provide efficiency gains over traditional pneumatic pumps. Graco, Inc., Booth N-10634
• AI-Enabled Augmented Reality. Leveraging granular data sets quickly and accurately produces recommendations and results, transforming good solutions into great ones. HarpakULMA Packaging, Booth SL-6188, SL-6101
• DairySeal featuring ClearCor. An advanced PET barrier gives dairy and similar products a new shelf presence, along with ecobenefits. Amcor Rigid Packaging, Booth SU-7244, SU-7254
• SOMIC 434 Case Packer. The modular machine concept is based on fixed-function groups consisting of proven, standardized mechatronic groups, and uses Rockwell ArmorKinetix. Somic Packaging, Inc., Booth SL-6172
• Child-Resistant, Reclosable, High-Barrier Pouch. Replace rigid containers across many categories including beverages, baby food, and shelf stable meals, with a high barrier. Amcor Healthcare Packaging, Booth SL-6635
• CXV Global SmartFactory LineClearance Assistant. Uses a network of fixed-position cameras that are deployed across the entire line, covering the risky and hard-to-reach areas of the line. Xyntek, A CXV Global Company, SL-6185
• PEWO-pack 600 Stretchwrapper. High-speed stretch bundler for sustainable films operates up to 180 bottles/min with flexible handling for most consumer products. Pester USA Inc., Booth SL-6726
• Recycle-Ready Sachet. Metallized polyolefin material for lamination gives barrier properties like multi-material foil laminations while designing for recyclability. Amcor Healthcare Packaging, Booth SL-6635
• IMA Ilapak Delta OF-360 X. Run any film—from paperbased to laminations to recyclable mono-materials—with a onebutton changeover. IMA North America, Booth C-3200, C-3400
• SprayPET Revolution. This 100% recyclable all-PET polymer aerosol is entirely metal-free, including the valve. Plastipak Packaging, Booth N-9357
SEE US ATBOOTH SL-6163
Leading-edge technology trusted worldwide for superior product inspection and contaminant detection.
<RXUEUDQGLVRQWKHOLQHVR\RXQHHGHTXLSPHQWWKDW·VEHWWHUWKDQ good. Anritsu systems deliver performance, reliability and low total cost of ownership Plus, we back our long-lasting equipment with unparalleled service and support.
'LVFRYHUZKDW\RX·YHEHHQPLVVLQJLearn how to advance your SURGXFWTXDOLW\DQGRSHUDWLRQDOHIÀFLHQF\DW DQULWVXFRPLQÀYLV
M6 METAL DETECTOR XR75 X-RAY SSV CHECKWEIGHERJoin the Packaging & Processing Women’s Leadership Network (PPWLN) for a conversation with award-winning entrepreneur and reality TV show Dragon’s Den judge Manjit Minhas. She’ll talk about what it takes to defy the odds and thrive in an industry dominated by men. A petroleum engineering student turned beer baroness, at age 19 Manjit co-founded Minhas Breweries, Distilleries and Wineries—becoming the youngest brewery owner in the world. It’s now the 10th largest brewery in North America. Manjit also is a venture capitalist and the star of Canada’s Dragon’s Den, where she coaches and often invests in entrepreneurs. In a conversation with her during PPWLN’s breakfast event, Brewing Success: How Manjit Minhas turned an idea into a Beer Empire, Minhas will share the story of how she broke into the notoriously competitive beer and spirits industry, and offer advice on ways to conquer obstacles and live the life of your dreams. This networking breakfast takes place Tuesday, Sept. 12, at 7:30 a.m. to 9:00 a.m. in room N-247. Visit pwgo.to/8028 to learn more and register.
Sponsored by BW Packaging, Emerson, ID Technology, Morrison Container Handling Solutions, Septimatech Group, SMC Corporation of America, WestRock, and PowHer, a ProMach Women’s Resource Group. PW
The Processing Innovation Stage, located at N-10511, will offer free show- oor education focusing on the latest breakthroughs in processing. No registration is required; anyone can attend when convenient and learn something new.
Scan the QR code on page 224 for the latest schedule of speakers at both the Innovation Stages and the Processing Innovation Stage.
• The Forum
A growing staple in the PACK EXPO portfolio of trade shows, The Forum will return to PACK EXPO Las Vegas with its interactive industry knowledge exchange. The Forum offers free, 45-minute learning sessions on the latest industry trends, including hands-on activities, small group discussions, and Q&A. Located in Central Hall, Booth C-2158. Leading organizations holding interactive sessions at The Forum include:
• OpX Leadership Network
• CPA, The Association for Contract Packagers and Manufacturers
• The Organization for Machine Automation and Control (OMAC)
• PMMI Business Intelligence
• The Showcase of Packaging Innovations
This attendee-favorite will display award-nominated packaging solutions. Located in The Containers and Materials Pavilion in North Hall, Booth N-9550. Sponsored by WestRock, Booth C-2023.
• The Processing Zone
In today’s manufacturing environment, processing and packaging are coming together as an integrated system, making it more important than ever to bring both packaging and processing solutions under one roof. The Processing Zone, which is double the size that is was in 2021, supports the integration of processing and packaging, a key function in the manufacturing environment. It is a great place to start your search for front-of-the-line solutions such as homogenizing, heat treating, forming/sizing, and coating. Within The Processing Zone at PACK EXPO Las Vegas, visitors will discover solutions to help increase efciency, achieve total system integration, and ensure employee safety.
• The PACKage Printing Pavilion
Located in the North Hall, the PACKage Printing Pavilion will focus on the advantages of digital printing, showcasing the latest in cost-effective solutions for smart, short-run, on-demand, variable data, and personalized packaging.
• The Containers and Materials Pavilion
Here you will nd the latest innovations in paperboard, glass, metal, plastic, exible, and resealable packaging, as well as containers and materials. Located in the North Hall.
• The Reusable Packaging Pavilion
We mentioned this earlier among the show’s sustainability features, but it bears repeating here among other pavilions. Sponsored by the Reusable Packaging Association, the Reusable Packaging Pavilion will present sustainable packaging solutions to help reduce waste, cut costs, and gain supply chain ef ciency. Explore reusable transport packaging products and services and see innovative reuse solutions. The Reusable Packaging Learning Center will be located within this pavilion at South Upper Hall, Booth SU-8000.
• The Confectionery Pavilion
Here you will learn about the latest trends relating to aeration, batch re ning, shaping, cluster production, and other candy-making technologies. Sponsored by the National Confectionery Association (NCA), this pavilion provides an opportunity for attendees to network and gain valuable insights. Come and recharge at the Candy Bar Lounge (located in South Upper Hall, Booth SU-7201), sponsored by Syntegon Packaging Technology, Booth C-2800, hosted by NCA.
Download the PACK EXPO Las Vegas Mobile App sponsored by ProMach, booth C-3222, to your smartphone in advance of the show to start developing your show plans.
• Free to download and use
• Search exhibitors, products, and sessions
• If you created a plan for the show via My Show Planner (more below), your saved information will sync to the Mobile App
PMMI is offering popular training workshops in Las Vegas to coincide with PACK EXPO Las Vegas 2023:
• Risk Assessment Workshop, Sept. 9-10
• Certified Trainer Workshop, Sept. 11-12
• Fundamentals of Field Service Workshop, Sept. 11-12
Visit pwgo.to/8026 to register for or login to PMMI U, then browse through these workshops to register. PW
• The Workforce Development Pavilion
This is a one-stop shop for resources to strengthen the workforce. Learn about PMMI U offerings, including popular training workshops, and meet students interested in careers in the industry. Located in North Hall, Booths N-9000 to N-9026.
• Association Partner Pavilion
The PACK EXPO Partner Program connects attendees to leading associations from all segments of packaging and processing. Located in Central Hall, Booths C-1145 to C-1354.
PACK EXPO Las Vegas offers programs and activities aimed at getting students excited about careers in packaging and processing.
• Future Innovators Robotics Showcase
Robotics teams from Las Vegas area high schools bring in robots they have designed and built and show them in action. Come watch these fun demonstrations and feel free to ask questions. Located at Booth N-9769. Sponsored by Bastian Solutions, Booth N-10343.
• The Amazing Packaging Race
Attendees should also visit www.packexpolasvegas.com where they can view floor plans, search exhibitors by keyword or product category, schedule meetings in advance with exhibitors, and more. To keep track of all the new additions as well as old favorites, attendees can use My Show Planner to check the schedule of booth activities, add itinerary sessions, and plan routes around the show floor. PW
The Amazing Packaging Race returns to PACK EXPO Las Vegas. This event provides rsthand experiences with several career possibilities in the packaging and processing industry. Teams from colleges, trade schools, and universities across the U.S. race around the PACK EXPO Las Vegas show oor to complete tasks or solve problems at the booths of participating exhibitors. Sponsored by Emerson Discrete Automation, Booth SL-6107.
CareerLink LIVE is an opportunity for PMMI, CPA, and IoPP members—along with CPGs—to connect with students pursuing careers in packaging at PACK EXPO Las Vegas. Visit pwgo.to/8029 to register.
Interested in getting involved or competing in the PACK Challenge in Chicago next year? Stop by booth N-9026 to meet PMMI’s 2022 PACK Challenge champions from Waterford Union High School, and see their winning ller machine. Information on the 2024 competition and the upcoming Chicago-area qualifying event where nalists will be selected will also be available.
• PACK gives BACK visits Cirque du Soleil
PACK gives BACKTM features an all-new format this year. Jumpstart the PACK EXPO Las Vegas 2023 show on Sunday evening, Sept. 10, by gathering with colleagues and customers to enjoy a private performance of “O™” by Cirque du Soleil®at the Bellagio Hotel & Casino. Rockwell Automation, Booth SL-6127, is the title sponsor and proceeds
The Emerging Brands Summit is back and will take place on Sunday, Sept, 10, prior to the start of PACK EXPO Las Vegas, at the Westgate Resort & Casino. Extend your stay in Las Vegas and experience this one-day event specifically designed for fast-growing brands in
bene t the PMMI Education Foundation. Tickets are available for single purchase for $95 each or in blocks of 10 for $855. The price includes general admission seating and drinks/snacks at the theater. Visit pwgo. to/8030 for more information and to reserve your spot.
If this is your rst time at a PACK EXPO event and you are at the show to nd products and solutions for your business, stop by the First-Time Attendee Lounge and get assistance on how to navigate the show, access product locators, talk to experienced show staff and attend beginner type sessions from industry experts. Or, simply relax and recharge here to help maximize your time at the show. Your “First-Time Attendee” badge is your access pass.
Open during show hours. Located in South Building, Room S-220. Sponsored by ProMach, Booth C-3222.
the $1M to $20M+ revenue range seeking to scale their manufacturing operations. With educational sessions, panel discussions, and networking opportunities with industry experts, contract manufacturers, and leading packaging and processing suppliers, you’ll gain valuable insights into scaling your brand. Plus, one exceptional brand will be awarded a $50,000 grant to assist with the purchase of packaging or processing machinery for their or their co-man’s facility. Maximize your time and expand your knowledge by attending both events. Visit pwgo.to/7699 to learn more. PW
The Young Professionals Network will host a networking reception at Topgolf Las Vegas, located at the MGM Grand, on Monday, Sept. 11, from 7:00 p.m to 10:00 p.m. Sponsored by Beckhoff Automation, Booth SL-6335. Visit pwgo.to/8031 for more information.
The Ask the Experts program is an additional attendee resource offered on-site at PACK EXPO Las Vegas and serves as an extension of the PACK Match Program. Ask the Experts will be located in the Central Hall and South Lower Hall Lobbies and will be staffed by experienced packaging or processing industry executives. Attendees will receive expert guidance on nding the right packaging or processing solutions to address their speci c challenges. PW
TAWI, the inventor of the vacuum lifter, designs products that enable faster, safer, and easier material handling for a variety of applications.
Vacuum Lifters for Boxes, Bags, Crates, Kegs, Buckets, Pails, and More: Vacuum lifters are perfect for pouring bags into mixers or palletizing boxes at the end of a packaging line. TAWI offers portable options for order picking as well as container loading and unloading.
Portable Electric Lifts for Roll / Reel Handling and Drum Dumping: Ideal for loading film or paper rolls on packaging machines or lifting and tilting (pouring) drums up to 550lbs.
TEL: (630) 655-2905
WEB: www.tawi.com
EMAIL: la.us.info@piab.com
IL 60440 - USA
Scan these QR codes for updated schedules on all of the show features listed below.
Innovation Stage: Get a heads up on industry developments with up-to-the-minute content. Learn about breakthroughs and discoveries, new products, and best practices during fast-paced, 30-minute seminars presented on three stages addressing dozens of topics.
Processing Innovation Stage: Find out about the latest breakthroughs in food and beverage processing, including food safety, HPP, sustainability, cleaning and more in 30-minute seminars. Content is targeted to food and beverage manufacturers.
The Forum: Enjoy a rare opportunity to discuss common issues and collaborate on solutions with peers from other companies. These 45-minute sessions kick off with a short introduction to the topic by a moderator before participants break into roundtables.
Sponsored by
Reusable Packaging Learning Center: Learn about incorporating reusable assets for the transport and handling of goods into your supply chain reusables, increasing its sustainability and efficiency. Hear directly from suppliers and users of reusable packaging systems about topics such as logistics, intelligent supply chains, value assessment and more.
Industry Speaks: Hear from those who have their pulse on the industry. Leading associations will discuss the latest hot topics affecting the packaging and processing community. Topics range from the implications of present and future packaging policies, envisioning the future of food manufacturing facilities, to the business case for SLAM solution in e-commerce fulfillment. The panel will also shed light on the factors driving interest in the contract packaging and manufacturing industry.
Sustainability Stage: Hear from industry experts on a range of packaging sustainability topics and receive actionable advice on how to make your brand more sustainable. Listen in on these sessions located in Sustainability Central, a new, must-see destination aimed to help guide you through a complete understanding on how to achieve packaging sustainability and what the means for your brand.
A modern take on packaging signals a mindset shift for pain and athletic recovery products. Hands-free delivery, portability, and gender-inclusive shelf appeal deliver a grand slam.
By Keren Sookne, Editor in Chief, Healthcare PackagingWith Serena Williams in its court as co-founder, this active recovery line’s packaging is designed for top notch performance.
Launched in December 2022, WILL PERFORM is offering a refreshing take on athletic recovery with muscle care and pain management. “Our brand is very much about the idea that recovery is bigger than just the reactive pain relief. Recovery should be something that we think about every day, especially for people like Serena, who are working incredibly hard and need to make sure that they can perform the next day,” says Alexia Lundberg, Ph.D., chief product of cer and biochemist by training.
As Lundberg explains, co-founders Eric Ryan and Serena Williams knew each other through her investments in OLLY (Ryan is co-founder of several recognizable brands including Olly, Method, and Welly). “They came together with a shared interest in rede ning the athletic recovery category. Serena wanted to create something that felt authentic to her, with products she wanted to use. That, combined with Eric’s idea that Millennials think about health and wellness as a lifestyle pursuit and want products to support that, led to the start of the brand,” she says. Ryan brought in Hank Mercier as the CEO of WILL PERFORM and its third co-founder.
The new line consists of six products with different bene ts for recovery—pain relief and muscle care—with two roll-ons, three lotions, and a spray accounting for the six formats.
• WILL Relieve, Pain Relief Roll-on and Spray both contain 4% lidocaine and botanicals in a thin, gel-like formula delivered by a triple rollerball system in a 3-oz bottle or a 4-oz aerosol, respectively.
• WILL Cool, Cooling Pain Relief Roll-on contains a blend of menthol, camphor, and botanicals in a thin, gel-like formula that is delivered by a triple rollerball system in a 3-oz bottle.
• WILL Rest, Nightly Muscle Recovery Lotion is an emollient lotion with lavender and geranium to help with calm and sleep. It also contains magnesium and Vitamin D and is delivered in a 3-oz squeezable bottle with an angled applicator for a hands-free delivery option.
• WILL Soothe, Daily Muscle Soothing Body Lotion is a lotion with a viscosity that allows for easy application and massage. It contains magnesium, ceramides, and Vitamin E to help restore skin and muscles daily and is delivered in a 6-oz squeezable bottle.
• Launched in late March, WILL Relieve, PainRelief Lotion contains 4% lidocaine and botanicals in a creamy lotion formula that is delivered by a hands-free angled applicator in a 3-oz bottle.
Entering the pain relief and muscle care categories, WILL PERFORM is combining ef cacy with modern aesthetics and ease of use. All of the formulations are intended to have a high level of ef cacy and an elevated product experience, with a focus on feel, smell, and delivery. Lundberg explains, “Recovery and rest are obviously top of mind for professional athletes, but for a lot of people they’re not. The Rest and Soothe lotions are our introduction to what we call Performance Care and is a mindset shift in thinking about recovery and performance daily, intended for day and nighttime use.”
Of course, certain bene ts help t a new product into a familiar consumer routine. With many women used to applying lotion after a shower, they added ceramides and vitamin E to the Soothe lotion for antioxidant and skin barrier protection, along with magnesium for muscles.
Reducing the stigma of pain relief and reaching women were key goals. “With traditional pain relief products there can be an association with ‘You’re older, so you hurt.’ We also talked to a lot of women as we were designing this brand, and no woman thinks that there’s a product
From left, a cooling pain relief roll-on, a muscle recovery lotion with angled applicator, and a daily muscle soothing body lotion (not to scale).
in this category that is made for them,” Lundberg says. “So that’s the other piece. We want to reach every athlete, but there is a miss with women in this category and we want to make sure we’re speaking to them. This is one of the reasons our cartons feature images of men and women.”
The product line launched online at WILL PERFORM and Target websites on December 8, and in Target stores on endcaps on December 22. After some time on endcaps, they moved in-line at the end of March via eye-catching displays with a picture of Williams and education about the products.
WILL PERFORM had a number of challenges to solve for as they iterated on the industrial design and graphics.
The three Relieve products in roll-on, lotion, and spray formats contain lidocaine. Lundberg explains, “It’s a highly effective ingredient and allows us to create elegant products, but it requires a child-resistant [CR] cap. Child-resistant closures are a highly regulated area, so we knew we
had to design something that could pass the required testing but still look unique. Not easy at all!”
They also wanted hands-free delivery options, so consumers didn’t have to touch the products if they didn’t want to. To accomplish this, they designed applicator heads to optimize the product experience they were trying to target. Maintaining a cohesive aesthetic across a range of formulations and delivery mechanisms was also top of mind.
For primary packaging of all products except the aerosol, the team selected 100% HDPE bottles because they wanted to offer consumers the ability to recycle. “Rest is a very viscous lotion—squeezability was something we had to keep in mind. At the same time, we wanted recyclability,” Lundberg says. “So we played around with blends of LDPE and HDPE. But knowing that that can pose issues with recycling, we leaned into HDPE. We worked on creating a package where we could thin out the sides in certain areas to make the sides squeezable, and then redistribute plastic in other places to create an element of squeezability that you need to get the product out, but that still lets us use HDPE.”
Since three of the products in the HDPE bottles are over the counter (OTC) drug products, the brand needed to nd a way to label them with all the required information on a small primary package. They chose a multi-panel pressure sensitive label applied to the back of the package to solve for this. All other artwork is screen printed.
“We added design elements like debossed grooves and pops of color to create an aesthetic that felt sporty and fun,” she says. “When designing the packaging, we were very conscientious about how an athlete would use the product. Hands-free application and a loop to allow the product to be clipped to a gym bag are examples of how we kept the athlete in mind during industrial design process.”
With custom packaging, designing a child-resistant cap can be risky. “We knew we wanted to do custom packaging for most of the products, because we believe that design is one of the most impactful ways to build a brand. We did look at stock to make our lives easier, but we always landed back at doing something custom,” Lundberg says.
In designing for child-resistance, WILL PERFORM opted to bring in consultants who’d forged the path with other brands and had overcome similar challenges. “It took a lot of work to be able to land an aesthetic that we really liked, while also creating functionality. There was a lot of pilot work as we were iterating, testing at the same time. That was probably one of the biggest risks we had throughout the entire development process,” she notes.
For the lidocaine products, the CR cap is a squeeze-and-turn mechanism, with a triple click. On either side is a small divot with instructions. Lundberg says, “Throughout the entire process, not a single kid was able to open it. To be honest, our biggest challenge when we were developing this was making sure adults could open it.”
For the spray, they did opt for a stock child-resistant closure (CRC) be-
The aerosol spray features a stock child-resistant closure (CRC).
cause designing a custom aerosol bottle with a CRC didn’t seem like a viable option.
While contract manufacturing or packaging suppliers couldn’t be named, Lundberg explains that they use one contract manufacturer for processing and another for packaging. They sought partners they could trust to produce topical OTC products and the ability to do CRC.
WILL PERFORM sought hands-free delivery for a few reasons. “Serena brings that athlete’s perspective to say, ‘Here are things that I really like or don’t like.’ Many people don’t participate in this category, either due to strong smells or they don’t think about it because there’s nothing that feels like it’s for them. So we wanted to create something that people actually want to use,” she adds.
The application of lidocaine and menthol bene t from being as hands-free as possible. Says Lundberg. “With lidocaine and menthol there are a few reasons why you don’t want to touch them with your ngers. Not that it’s bad to touch, but it can create other issues such as when you rub your eyes or brush your teeth. So we wanted the pain relief products to be hands-free.”
With the Rest and Relieve lotions, Lundberg’s team created an angled applicator that could be applied directly to the body so people can choose whether to apply via applicator or by hand. The angled head can also be used to as a massage tool.
The roll-on Relieve and Cool products use a triple rollerball design to dispense product. “We liked the idea of a triple rollerball because not only does it look cool, but we felt it could also be a massage tool and it adds to the cooling effect of our WILL Cool Pain Relief product. With the single plastic rollerballs, there can be a lot of product that ends up coming out, and so the idea with the triple rollerball is you can use it for massage without soaking yourself in product. Also, some people feel a spray isn’t as effective for targeted products. It’s not necessarily true, but it’s just a consumer perception,” she explains.
Caps feature a loop so the product can be easily strapped to gym bags for on-the-go use.
Vial Filler & Stoppering
Optional Feature: Industrial Internet of Things (IIoT) Technology
Rotary Piston Filler
Optional Feature: Remote Support/VPN Switch with Lock & Key
For launch on D2C and endcaps at Target, the brand chose a ve-panel carton design to add space for consumer education. As they move in-line at retail, they are shifting to a four-panel carton.
A key focus for WILL PERFORM was creating a cohesive product family across the various formats and delivery mechanisms that will look good at-shelf. In this case, the inner and outer cap worked in their favor. “It’s a two-component cap and it works because it allows you to do both a CRC and non-CRC that look exactly the same from the outside,” Lundberg explains. “The spray is the outlier only in the sense that it’s not a plastic bottle, but we still have the same graphical treatment. We wanted to create an iconic look, where people are able to identify this brand by the way the package looks and create continuity across all products.”
For portability, the brand sought to bring in texture and functionality. The team created a loop on the cap made from TPE (thermoplastic elastomers), so the product could easily be strapped to gym bags for on-thego use. The cap is composed of an inner and an outer component made from polypropylene for both form and function. “The translucent outer cap allowed us to show through to a pop of color on the inner cap, which
was designed in a color that complemented the color of the TPE ‘loop.’ The two-cap system also allowed us to create visual continuity in the cap design whether or not the cap needed to be child-resistant,” she says.
Though many are incorporating QR codes for communication with the consumer, in this case, its value is geared internally. “We worked with our contract manufacturer to design a system where the QR code on the back of the screen-printed bottle helps them place the label exactly where it’s supposed to be. The code goes to our website but doesn’t have a function from a readability standpoint, it’s just for proper label placement. Our contract manufacturer said this is something that’s pretty unique,” she says.
The team initially wanted to stick to primary packaging because they loved the bottles so much, but they opted to add a carton. Along-
side other considerations, a main carton-development driver was that consumers wanted education on their products. “When we were rst thinking about it, we thought we’d be able to put all the drug facts and information on this tiny little bottle, and there was just no way to include that in addition to the educational content” she says.
The team designed their cartons to t the bottles snugly with no inserts. Per Lundberg, “We right-sized the cartons for each bottle so there were no inserts used. It wasn’t that challenging because three of our products are the exact same size, and then the aerosol and Soothe are almost the same size. So we ended up with just two carton sizes, which wasn’t overly complex from an operational standpoint.”
For launch via D2C (direct to consumer) and endcaps at Target, they chose a ve-panel carton design and placed images of Williams—who lends a lot of credibility—and everyday athletes on the extra panels. It was important for WILL PERFORM to show that these products were designed for every athlete, not just the best of the best.
As it moves in-line at Target, WILL PERFORM will start to phase-in a four-panel carton. It will continue to showcase images of all athletes on the cartons, but the front panel image will focus on the primary package. “We ended up cutting off that wing, and now we’re going to be in a four-panel. We continue to learn and optimize, and with the four-panel the key information is right in front of you and more focused. All the feedback we’ve gotten… everybody loves the bottle itself. Maybe eventually we get out of a carton altogether—there’s other things we have to solve for, related to that,” she says.
With the recent launch, Lundberg says she’s incredibly happy with the packaging: “With anything new there are opportunities to learn and improve and we will certainly do that, however, we are very proud of how of primary package turned out. A theme that runs through all of Eric Ryan’s companies is to create a package that is counter-worthy. This helps with compliance, which is important for ef cacy, and can take away the stigma that can be associated with a product.”
In the case of pain relief products, Lundberg reiterates the stigma around using these products and differentiating their industrial and graphic design from the current pain relief category. “Many consumers don’t enter this category, despite needing to, because they don’t believe the products were made for them. Our packaging design and messaging is one way we can help change that. As much as we love our primary packaging, we felt it was important to use a carton to help the consumer understand what the products do and when to use them. This is particularly important for WILL Rest and WILL Soothe, which are all about daily muscle care—something that is new for many consumers.
“We love the look. But there are always things that you want to change. Our philosophy with any new brand is that the rst year is ‘launch and learn.’ You put it out there, go with your gut, and gure out what you think is best, but quickly, you’re going to learn,” she says. “So when it comes to packaging, whether it’s messaging or the fth panel or other things, we just plan that we’re going to be iterating, iterating, iterating… listening to customers and making adjustments accordingly.” PW
Retail-friendly cans were already trending up in craft brew when pandemic-related venue closures accelerated the trend. Dust Bowl Brewing Co.’s increased, sustained reliance on this container format convinced management to double down on canning automation.
In U.S. history, the Dust Bowl describes a depression-era drought in the Midwest that forced many of its “Okie” inhabitants to migrate from their infertile farms in America’s breadbasket toward California, based on mostly unrealistic promises of employment and prosperity. In John Steinbeck’s classic novel The Grapes of Wrath, protagonist Tom Joad leaves Oklahoma on an ill-fated hero’s journey that at times is pretty dark, even by today’s standards. But it’s also a hopeful depiction of resourceful people who leaned on each other to survive hard times in search of a better life for their children.
VISIT
The latest innovation from LEIBINGER labs in Germany, the IQJET printer redefines the market standard for reliability and autonomy in marking & coding. Its unique, disruptive design will transform industry’s experience working with Continuous Ink Jet (CIJ): 100% clean, seamless start and stop, 5 years operation without scheduled maintenance, unparalleled cost of ownership, CIJ reinvented.
Changing the game.
Brett Tate is one of those Californians who traces his family’s heritage back to the Dust Bowl. When the retired teacher turned entrepreneur opened a new brewery venture in 2009 in Turlock, Calif., he named it Dust Bowl Brewing Company as an homage to this history.
Out of the gate, Tate secured a local rising star in craft brew circles to be his brewmaster. He hired Don Oliver, also from Turlock, who was the winner of the 2006 Samuel Adams Longshot Homebrew competition. By 2009, the aptly named Hops of Wrath IPA, among other brews, rst came to market in Dust Bowl’s brewery and taproom. Satellite Dust Bowl taprooms began opening over the next decade as the brewery and its portfolio of beers expanded, and before long a new 30,000-sq-ft production facility anchored the enterprise. The package format mix was bottle-intensive for most of the brewery’s early history, as the groundswell of a canned beer trend hadn’t quite landed until more recently. Cans were a growing part of the mix, but a low-speed, reliable canning line remained suf cient for some time.
Then, in early 2020, another mass migration—this time the pandemic-induced consumer shift away from restaurants, bars, and taprooms—shook the craft brew landscape. But production didn’t need to slow down if Dust Bowl could recalibrate its packaged product mix to accommodate a new reliance on retail. At that point the brewery’s increased focus on canned beer distribution was not just on-trend, but necessary for survival.
“We were able to switch gears and pump out more cans, but it took some work,” Oliver says. “We only had a small Codi canning line than ran at 50 cans a minute when we were running 12-oz cans. That was a great line and it did well for us, but it wasn’t going to keep up with the number of cans that we needed to produce after the onset of COVID-19. When you’re trying to drain 200-barrel brite tanks, 50 cans a minute is pretty slow.”
Trying to keep up with canning is what led Oliver to approach David Weller at Paci c Packaging Systems Inc., a line integrator specializing in craft brew, in search of faster can output. But footprint was an initial hurdle. A 30,000-sq-ft facility seems like plenty of space, but a lot of that was tied up in the brewing process and an existing bottling line.
“We were trying to squeeze all this new canning equipment into a small space, and I knew it was not something we were going to be able to achieve on our own, so we reached out to David [Weller] at Paci c,” Oliver says. “I think we went through around 18 or 20 design iterations to gure out how we were going to put all the equipment in. Our bottling line from CFT was taking up the entire packaging area, and we needed to canibalize some of its footprint. The bottling line had the classic horseshoe-type shape, so the idea we came up with was to chop the line at the bend, ip the horseshoe the other direction and tighten it up, and then squeeze all the new canning equipment into the space we’d freed up.”
That strategy did the trick. Armed a the new canning line that it can
grow into, the brewery hopes to nearly double its production over the coming years, from 22,000 barrels in 2022, to a goal of nearer 40,000 down the road.
For the heart of the canning line, Oliver and Weller landed on a KHS Inno ll CAN Compact 18-valve rotary monoblock ller with rotary seamer, capable of lling and seaming well over 200 cans/min. The system handles 12-, 16-, and 19.2-oz cans with minimal changeover.
“KHS seemed like a good t for us for the [low lead time] timeline, for its compact size, and for the cleanliness of the machine. We heard some nightmare stories about seamer cleanliness and other issues on some others that we’ve seen,” Oliver says. “We’ve had to make a couple of programming modi cations. Also, we got rid of the bubble breaker because we didn’t feel it was really helping us with dissolved oxygen, and it was more of a contamination risk. So, we eliminated that and then we saw some bene ts there. Now it’s running at around 210 cans per minute at max speed for 12-oz printed cans.”
Can formats that require label application, or larger 16- or 19.2-oz cans that require can handle multipack applications instead of cartoning, are slowed to between 90 to 180 cans/min to accommodate their respective downstream operations. More on that shortly.
With that much increased lling repower, an almost entirely new
packaging line would be required. However, a few accessory items from the original line still operate today, including a CODI depalletizer and triple-twist rinse conveyance at the front of the line.
“Coming off the CODI depalletizer, we have a larger, full-sweep conveyor that was supplied by Bevco. From there, it goes to a single ler that travels back into the CODI for the twist rinse, and we place an air ionizer on whichever lane we’re using to feed the KHS monoblock ller.”
After lling and seaming, cans get a quick rinse and travel single le through a Filtec machine to con rm ll-height and reject non-conforming ll levels. A block inverter then ips cans over for bottom date and batch code on a Videojet CIJ coding and marking system.
“Once it gets the date code, it goes through another inverter, and a blower to dry off the top. The conveyor then passes through the labeler, a Pack Leader USA 501. If we’re adding labels to brightstock, we’ll set it up and slow everything down for the label job. Printed cans will run right through the unengaged labeler at full speed.”
Once past the labeler, 12-oz cans are diverted toward a DMM Packaging carton erector and cartoner, which side-pushes cans into a 12pack erected carton format, applies adhesive to the aps, and closes the cartons. Dust Bowl has the change parts for a 16-oz 8-pack, but seldom uses this format. The cartoned 12-packs receive a date and batch code of their own from another Videojet CIJ.
Larger 16- and 19.2-oz cans aren’t cartoned. Instead, they receive HDPE can handles from a PakTech machine. This compact equipment can apply handles to 180 larger-format cans/min. Once can handles have been applied, the 4- or 6-can multipacks travel on a small conveyor that bypasses the DMM cartoning machine and ends up punching right into the inlet of another DMM machine, this time a tray former and packer. Most trayed can formats are of 24 cans in either 4- or 6-packs, with one exception.
“For the 19.2-ounce cans, we chose to go on a 12-pack format tray,” Oliver adds. “It’ll get two 6-packs of PakTech-applied multipacks pushed into a smaller 12-pack tray with a higher wall. We’ve got a good relationship with a local company out of Modesto, California called Paci c Southwest Container. They provide us with all our all our board, so all the cartons and all the trays come from them.”
Conveyance carries the three most common pack formats—12-pack cartons of 12-oz cans, 24-pack trays of larger or labeled brightstock cans, and on occasion, 12-pack trays of 19.2-oz cans—to palletizing and pallet wrapping. Both are done on a TopTier TT-L20 Low Level palletizer that comfortably handles four pallets per hour max lling speed of 210 cans/min.
“We had looked at a couple of other models, and we couldn’t nd anything that was going to t within our footprint and within our budgetary constraints, and then TopTier was able to take care of both of those issues,” Oliver says. “The footprint is really small. And price-wise, it’s incredibly competitive.”
The (almost entirely) new canning line at Dust Bowl “is enough to get us quite a ways down the road, as far as production goes,” Oliver says, adding there’s no current need to make further improvements to can lling operations. “I think this canning line is enough to get us up to that 40,000-barrels-a-year mark. We hit a little over 22,000 barrels last year, in 2022, so we still have plenty of room to grow into this line. And even though growth isn’t what it used to be, we grew 4.5 percent last year. Any positive makes us happy considering what we’ve seen out in the market; there’s a lot of uncertainty right now. We’ll hope for the best and plan for the worst, knowing this new canning line gives us the runway and capacity to grow cans even further.” PW
Brightstock cans are depalletized overhead on a high-trim Ska Can-i-Bus, then single- led and lowered through a twist rinser on the way to the ller and seamer.
Voodoo Brewing Co.’s unique franchise model promises exponential growth. Packaging operations needed an automated shot in the arm to keep up.
Founded in Meadville, Pa. in 2005, Voodoo Brewing Co. represents an impressive comeback story. Despite award-wining craft beer offerings, the brewery narrowly survived the Great Recession of 2008-2009. But it emerged in 2010 under new ownership with a new lease on life. After brothers Matteo (CEO) and Curtis (brewmaster) Rachocki took the reins, Voodoo quickly assumed a growth trajectory. The rst local taproom opened in 2012. A second opened in Pittsburgh in 2015, followed by another in Erie, Pa. in 2016, and yet another was soon to land in State College, Pa. During this urry of growth, the company recognized the need to produce in larger volume.
So, in early 2017, Voodoo Brewing Co. opened its production facility with practically unlimited room for expansion. The sweeping 10-acre space currently pumps out about 6,000 barrels a year. Given the newfound production capability and rapid expansion, an entirely new business model swam into view.
“During that time, we put together a model on how to build streamlined, ef cient, cost-effective [brew pub-style] restaurants,” Matteo Rachocki says. “We documented it, put together our rst operations and
Take back control of your products with our patented, durable plastic chain designs. Span Tech chain not only sets the industry standard for quality and innovation, but also provides solutions applicable to a variety of products and industries. With over 1000 di erent chain configurations paired with our custom conveyor systems, we are capable of moving a multitude of products in any direction you may need to go.
Franchise Disclosure Documentation (FDD), and decided to roll out a franchise program.”
This new direction led Voodoo to recalibrate its packaging mix. Like most breweries, Voodoo packages product in a mix of kegs, cans, and bottles. Kegs, of course, are aimed drafts at taprooms or restaurants. On the bottling front, formats include classic 12-oz bottles for volume brews, a 500-mL format for limited release beers, and a barrel aging program uses both 12- and 22-oz bottles. But if you’re following craft brew at all, you know that cans are king these days. Plus, they are quite adept at retail distribution, and are often the best bet for the volumes required of a franchise network.
“When the franchise model started to take off, it really ramped up the need for packaged product,” he says. “That’s because we don’t just service our retail locations. We’re also servicing the greater distribution territory surrounding those wholesalers. That was a major catapult for us to expand our capability on the canning line.”
Previously, the brewery had been using a mobile canning line that it transported back and forth between the original brewery and the new production facility. Speeds were low on the self-engineered canning line, maybe only two cases or 50 cans/min. To help “catapult” canning
into high gear, Rachocki rst zeroed in on a couple pieces of equipment that he knew he wanted. The rst was a ProBrew ProFill ller/seamer combo that runs up to 200 cans/min.
“We looked at a bunch of different options. Almost everybody we talked to had a reason why they didn’t like what they had. But the few people we know that have worked with the ProBrew llers love their machines,” Rachocki says. “We love the fact that was made in the U.S., near Milwaukee. Our industry friends told us that this is the only machine consistently canning at under 30 parts per billion on DO [dissolve oxygen]. It’s all solid stainless; there’s nothing plastic on the thing. It wasn’t the cheapest machine, but when you add in the [favorables
around] parts, accessibility, repairs, and downtime, it just made a lot of sense.”
Rachocki was also keen on the classic Pack Leader USA 501 labeler. With those two anchor pieces selected, the brothers then turned to Ska Fabricating for the front of the line.
“Every single friend of ours in the brewing community that has a Ska depall[etizer] says they love it. We might have shopped for another option just for a price comparison, but our minds were already made up. We didn’t even really shop elsewhere,” Rachocki says.
“We called them to buy a depalletizer but came to nd out they offer other solutions and could help with the engineering or do some of the conveyance. I think we ended up redesigning the conveyance on that about four times before we had a solution that I was comfortable with. Our facility’s footprint is substantial, but I want to use all of it. I wanted to be able to expand later and not break the bank now. Drew and KG at Ska got that. … Their design team was great to work with and didn’t try to sell us something we didn’t need. They really got a sense of what we were looking for, and then they worked backward from there.”
Finished in August 2022, the canning line at Voodoo begins with a Ska high-trim Can-i-Bus depalletizer. The Can-i-Bus is the original of a range of Ska depalletizing equipment, which includes the even higher production Magic Bus. But this high-trim, mezzanine-level Can-i-Bus model depalletizer was the center of the bullseye for Voodoo’s Rachocki, easily meeting desired production speeds with plenty of runway left for speeding up the line in the future. Ska and MCE Conveyance equipment then single le depalletized cans overhead, and they descend toward the ller via an A&E Conveyor Systems Inc. twist rinser. Cans are inverted, rinsed by an ionized air rinser, then twisted upright into a transfer plate to be presented to the ller.
At the heart of the line, cans are counter-pressure gravity lled on the continuous-motion, 24-valve, rotary ProBrew ProFill ller, then seamed on a continuous motion ProBrew seamer, all within a single monoblock enclosure. The canning line makes a 90-deg turn to the left exiting the ller and entering the seamer, then turns another 90 deg in the same direction exiting the seamer. That equates to a full 180-deg
line horseshoe, and cans continue downstream in parallel to the upstream empty cans as they approach the ller.
Filled cans then get two sets of rinses, followed by an ef cient Republic Manufacturing air knife dryer, prior to passing through a Filtec low ll-level reject system.
Coding and marking comes next, and ink is applied via a Markem Imaje CIJ 9450 date coder, the core component of Ska’s D.I.C.S. (Date Inline Coding System). Coded cans on the line make another 90-deg turn to the right this time to enter a large accumulation table by MCE.
“We added an oversized accumulation table because, especially if you’re not using printed cans, you’ve got to do label changes. Also, if we’re running two tandem pack-off lines eventually, it’ll be nice if you can have transfers between the two pack-off lines,” Rachocki says. “We did go overboard on the accumulation side, but I’m glad we did because once the machine is on, it needs to stay on. You don’t want to stop that machine for anying. Accumulation is great because it buys you a lot of time. If you have a hiccup somewhere on the line, you have a chance to
A large accumulation table ahead of labeling, can handle application, and pack-off lets the ller keep lling, even as downstream xes or changeovers happen.
Lowest Cost Solution Available
Fits new and retrofit FFS machinery
Simple drop in technology into existing machinery
Expandable design – 1 to 20 lanes
Lifetime Warranty – Guaranteed reliability
Booth 9503
The line then makes a nal 90-deg turn to the right to be once again parallel with the ller infeed and seamer outfeed, representing a second horseshoe on the line. There, cans receive a p-s label on the Pack Leader 501, which Rachocki affectionately calls “a beast.” Finally, PakTech can handles are applied on an American Canning can-handle applicator, and the contiguous line ends in a manual pack-off station, where 4- and 6-packs of 12- and 16-oz labeled brighstock cans are loaded into pop-up corrugated trays and moved of ine for palletization.
Rachocki has considered cartoning and tray-erecting equipment, but the operation hasn’t quite maxed out the 200 can/minute potential that could bene t from cartoning automation. Voodoo tends to run closer to 120 cans/min at this point, and with operators already on-hand to attend to the line, manual pack-off into trays is suf cient. Palletization is mostly manual, with pallet wrapping equipment nishing the line.
“Once we tune this thing up and we’re running at full speed, we’ll add have a second, mirrored pack-off line that will resemble the one we have now. We’ll also add a small diverter to make sure you’re diverting the cans to the appropriate station of the two,” Rachocki says. “That’s just how Voodoo has always done stuff. We bought a brew house too big for our britches, we gured we might as well buy a canning line that’s too big for our britches, make sure it will run well at 100 cans a minute, so we know it’ll also run well at 200 when we need it.”
Other than the eventual mirrored pack-off station, next up for the new packaging line will be a new can size, 19.2 oz cans for two of the brewery’s offerings. Voodoo has a new twist rinser on order that will be
After PakTech can handles are applied to labeled cans, operators pack cans into pop-up trays in a pack-off station that ends the contiguous line.
able to be swapped in and out to accommodate the larger can format. For their part, Ska say they had a blast working with Voodoo. When asked if anything made this project unique, Hudson Grigg, senior project manager at Ska, had this to say: “What stood out was working with Matteo, he was just friendly and positive. And, you know, as stuff comes up in these projects, he was just easy to work with. He’s just that kind of guy that you’d really want to go visit his brewery and drink beer with him.”
That’s high praise for the leadership of any growing craft brewery. It’s a character trait that permeates the operation, and will keep Voodoo on a continued growth path. PW
To contract craft brewer The Brutalist and its owner King State Beer, dissolved oxygen is four-letter word. A new filler and seamer combo keeps D.O. low and the beer quality high, while paperboard multipacks help to make an impact on the shelf.
The Brutalist is a 3,500-barrel/year collaborative contract brewing facility in St. Petersburg, Fla., headed by Aric Parker of King State Beer. The Brutalist has its own line of branded of brews that it sells out of its taproom, Temple of Beer. And as a contract brewer, it sells brewing and packaging capacity to high-end craft brewers looking to scale with the help of higher-volume professional equipment. Meanwhile, King
State Beer—the beer-brewing arm of a King State operation that’s also known as a coffee roaster, coffee cold-brewer, and breakfast and cocktail bar—owns The Brutalist Brewery and in a sense is its own biggest customer with its line of branded King State Beer varieties. Perhaps this unique arrangement makes for a tangled web of stakeholders, but it’s hard to complain when the result is innovative, artisanal craft brew
Depalletized brightstock cans travel through a twist rinser into a ller and seamer, prior to date coding, labeling, and paperboard multipacking.
under an evolving variety of banners, brands, and titles.
“King State’s lineup has our lagers and more traditional styles, with the occasional sour. The Brutalist tends toward on-trend brews like hazy IPAs or pastry stouts, and we have the freedom to take it wherever we want. And nally, our contractors are mostly smaller breweries or sophisticated home brewers that are willing to pay a premium to grow their footprint or up their production,” Parker says, disambiguating the three primary constituencies of King State, Brutalist, and contract work.
As he built out the brewery’s new canning line in June of 2022, Parker began with the ller/seamer, working backward from there. After some extensive comparison shopping, he landed him on a 50-can/ min CB50C integrated counter-pressure in-line ller and seamer from Pneumatic Scale Anglus (PSA), a BW Packaging company.
“I selected the PSA for the counter-pressure functionality in particular, and I think of the Angelus seamer as the industry best,” he says. “At rst, I saw some other competitors’ counter-pressure llers and I wasn’t particularly impressed. But then a friend dragged me to another brewery where I saw the PSA in action, and I met PSA at the Craft Brewers Conference soon after. By then, I de nitely knew that that’s the one I wanted—especially for the price, too. We’re in the teens for dissolved oxygen [parts per billion]—usually sub-ten. PSA has been amazing. I love that line.”
With the ller and seamer selected, Parker turned to Ska Fabricating, which PSA had recommended for depalletization. He chose a Ska Can-i-Bus overhead depalletizer for the front of the line, and that relationship grew to Ska also working on both line layout and integration. Depalletized cans travel through an integrated twist rinser to reach the PSA ller and seamer.
Parker was able to source a few used pieces of equipment that would ful ll downstream operations, namely two used Videojet date coders and a used Pack Leader USA 501 labeler. The Brutalist and King State both stock their own p-s labels for application on the labeler, and contracting brewers supply their own rollstock to the brewery’s specications.
Instead of multipacking beers into cartons, traditional plastic, or newer HDPE can handles, The Brutalist is one of an increasing number of breweries that have opted to shift to paperboard can handles. The brewery uses a WestRock system consisting of its paperboard CanCollar 6-pack can holders that are applied by a manual can multipack station, called the Chunk. This system includes a collapsible side table for compact footprint, supports multiple can sizes with one simple height adjustment (The Brutalist does 12- and 16-oz cans), and has an ergonomic, height-adjustable operator handle.
Unit Load Spirals convey cases, totes and packaged goods smoothly on our slat style belts and come in 9 standard slat widths ranging from 6” to 30”. Available in powder coated carbon steel, stainless steel, wet environment and freezer versions.
Mass Flow Spirals handle full and empty bottles, cans and jars in mass up to 2,000 units per minute. Available in 4 different slat widths ranging from 6” to 20”.
Narrow Trak Spirals are super compact and designed to handle smaller loads. Our 6” and 9” wide nesting slats can end-transfer small cartons and packages or side-transfer small ERWWOHVDQGFRQWDLQHUVLQDVLQJOH¯OHRULQPDVV at speeds in excess of 220 FPM.
Ryson’s Bucket Elevators combine vertical and horizontal transportation of bulk materials in one integral unit.
Our Bucket Elevators are designed for gentle handling and well-suited to transport a broad range of bulk products. They are completely enclosed with overlapping pivoting buckets, that prevent spillage and helps mitigate foreign debris.
7KH\FDQEHFRQ¯JXUHGZLWKPXOWLSOHLQOHWVRURXWOHWVWKDWFDQEH controlled individually. Available in three standard bucket sizes, yielding capacities up to 300, 700 or 1,800 cubic feet per hour. They can also be delivered in powder-coated carbon-steel, or stainless-steel for wet environments.
$OO5\VRQHTXLSPHQWLVPRGXODUDQGEXLOWWRRUGHU1RPDWWHUWKHDSSOLFDWLRQWKH5\VRQWHDPLVXSWRWKHFKDOOHQJHRI¯QGLQJVROXWLRQVIRU your conveying needs. For application assistance or more information, give us a call or visit www.ryson.com .
Check out our running equipment at Pack Expo | Booth C-4736
www.ryson.com
(757) 898-1530
Ryson Spiral Conveyors need less floor space than conventional conveyors and are faster and more reliable than any elevator or lift.
“We went the paperboard can handle route for a couple different reasons,” Parker says. “In particular, we did it for environmental reasons as [the system] uses 90% less plastic. Also, if we eventually decide to buy [the CanCollars] in bulk, it gives us a design advantage because we can have their tops printed any way we want. Multipacks can be branded King State, or The Brutalist, whatever we want it to be. On top of that it’s also cheaper than the high-end HDPE can handles, which is nice as well. It’s a threefold advantage for us.”
At this point, MOQs don’t allow the brewery to source printed CanCollars. Given their lay- at 2D dimensions, a typical MOQ of a pallet of can handles equates to as many as 81,000 cases of beer, which is generally out of reach for contractors. The brewery itself isn’t quite there yet, either.
“Having enough volume to justify the MOQ is the only way you can get to that printed level,” Parker says. “We even have a design for King State, we’re just waiting to pull the trigger on it until it makes sense for us.”
The 6-pack multipacks are then manually packed in a 24-ct into high-walled (4 in tall wall) corrugated trays by Romanow Container
“The taller walls are better for the 16-oz beers, and they’re really nice, with handles,” Parker adds. “For our 12-cans, we use shorter trays with the WestRock can handles—we can’t do the high-walled trays with 12-oz CanCollars.”
What’s next for the brewery? Parker is eyeing a 19.2-oz can option, among other potential developments. But between King State Beer’s twist on time-honored brews, The Brutalist’s on-trend creations, and whatever undiscovered beer varietals that smaller local breweries can
This version of WestRock’s ber-based CanCollar system uses a manual station called “the Chunk” to apply paperboard can handles to 12- and 16-oz 6-packs.
dream up, this Tampa-area craft beer operation brews and cans the whole beer gamut. The new canning line with ultra-low dissolved oxygen pickup, plus a differentiating paperboard multipack, will serve it well in coming years. PW
Craft beer has been a thorn in the side of big brand breweries for some time, with the category taking a 13.2% bite out of the market in 2022. Furthermore, the craft beer segment is attracting the younger generation—50% of millennials aged 25 to 34 versus 36% of U.S. consumers overall, according to a report in Marketing Science. So how can commercial brewers tap into this demographic?
While big beer brands may be inclined to adopt the whimsy and eccentricity of craft beer package design to attract younger consumers, it’s important to remember what attracts millennials to craft beer—authenticity, flavor, and history—and that’s something larger commercial brands offer in spades. Over the past year, a number of established beer brands have redesigned their packaging with graphics that tap into the heritage of their brews, emphasizing their long and storied histories. This strategy not only brings the authenticity sought by younger beer consumers, but it also provides familiarity to its existing base, oftentimes the baby boomers.
With Coors Banquet beer dating back to 1873, “the history of Coors Banquet is the history of American beer.” That’s according to parent company Molson Coors, which in April of last year launched a
limited-edition line of packaging to pay homage to the brand and its inextricable link with American beer history.
Coors Brewing Company was established in 1873 in Golden, Colo., by immigrant Adolph Coors, who developed a recipe using 100% natural Rocky Mountain water. For years, Coors Banquet was a favorite among local gold and silver miners. When prohibition hit Colorado in 1916, the brewer was ordered to drain 516 barrels of beer, only starting production back up again after the repeal of the law in 1933. For years after, until 1991, the beer was available only in a handful of western states, leading fans of Coors Banquet—“The Coveted Lager”—to smuggle it across state lines. And, in 1959, the brand pioneered the use of the two-piece recyclable aluminum can, a development that revolutionized the beverage industry.
With these colorful stories to draw from, Coors Banquet created a number of Heritage Collections over the years. However, the 2022 line was reimagined. “In the past, this promo would be, ‘Let’s redo a can from 10 years ago and release it into the market,’” says Aaron Funke, senior creative director for Equator, the packaging and brand design agency that worked with the Coors Banquet on the limited-edition line. “But Coors wanted it to be something different, something that appealed to longtime fans of the brand and also a new consumer target.”
Equator began the design process for the collection a year
before its launch, in spring 2021, collaborating closely with the company’s design team—in particular Candace Walters, U.S. Design & Graphics team manager, and Stephanie Clanfield, global marketing manager for Coors Banquet.
According to Funke, the Coors Banquet team writes design briefs that are “second to none.” He adds, “When we start a project with them, they give us a good background on the brand, where it’s going and why, as well as some thought starters on where we could go and positioning. So, they’re great on giving us a steer.”
For the 2022 Coors Banquet Legacy Collection, Funke shares that the brand was looking for something that appealed to millennials and would have greater stopping power when put together in-store. “It wasn’t just about the cans but also the secondary packaging; creating visual theatre, so when it’s all stacked together, it creates a greater story,” he says. “It was as much about the impact as it was about the heritage.”
An important element of the limited-edition Coors Banquet collection was the secondary packaging, which was used to create ‘visual theatre’ on-shelf.
In developing the design strategy, Equator began with how to match the Coors Banquet legacy with the millennial consumer in terms of what the brand stands for and what millennials are seeking and tried to find a link between the two. “This led to creative pathways, which eventually led to can designs,” says Funke. “We came to the idea of the outdoors and, specifically, the concept of the golden hour.”
Research for the design was done at Coors’ archives center in Golden, where Equator was given access to the brand’s past devices and cans. “They have this big warehouse where all of this stuff exists, as well as a pretty substantial archive of vector files, or usable art, that we could download and then use on the cans,” shares Funke. “So we used assets that were given to us, a lot of them historical, but then we also needed to bring impact to this as something different.”
The difference was a bold can design with a reflective gold color
Changeover Repeatability
Consistent, repeatable changeover including easy access to all critical areas of operation.
Medium to High Speed Solution
Runs wrap around cases and trays up to 70 cases per minute utilizing continuous motion.
Ergonomic Blank Load
Conveyor fed case blank loading system accepts flat stacks of blanks for easy loading.
on the top half. On the bottom were the heritage pieces: information on where the beer is made, where it’s from, the year the brewery was founded, and more. The collection included three cans, each of which harkened back to a different era of Coors Banquet’s past, one reading, “Brewed Only in Golden, Colo.,” another, “The Coveted Lager,” and the third, “Quality and Tradition Worth Keeping.”
The half-and-half aesthetic of dark gold on top and the copy against a Coors Banquet yellow on the bottom tied the collection together. Graphic elements from the standard can that were retained included the logo and Coors Banquet colors. “We wanted consumers to recognize that it’s Coors as quickly as possible when they’re in the store,” Funke says. “They know that Coors Banquet is an iconic, buffyellow color and that the brand mark is usually blue, so we tried to keep a lot of those things consistent, as well as the familiar ‘Banquet’ badge.’”
Rounding out the collection was a culminating Coors Banquet stubby bottle design, with a story on the label summarizing the stories on the cans. Says Funke, the same graphic language was used on the bottle, just adapted to the smaller space. On the opposite end of the spectrum was the secondary packaging. There, the graphic language was expanded to fit. It was also there that The Legacy Collection moniker was used.
The 2022 Coors Banquet Legacy Collection was launched on April 7 of last year, fittingly on National Beer Day, and was available through the end of June 2022. A QR code on the secondary packaging gave consumers the opportunity to win exclusive merchandise in collaboration with premium American apparel brand Huckberry.
One of Scotland’s oldest beer brands, Belhaven Best, has unveiled a new look that celebrates its 300-century-plus brewing history. The design, by specialist creative agency Thirst, showcases the authentic provenance of the beer, which has been produced in the borough of Dunbar, Scotland, since 1719.
“Belhaven’s success over the past 300 years is built on creating exceptional quality beers, but also on our ability to respond to the changing tastes of modern drinkers,” says Belhaven Brand Manager Fiona Matheson. “Best is as popular as ever and is currently gaining in market share, but we felt that it deserved better when it came to its presentation. We also wanted to challenge the old-fashioned image of ale and communicate its freshness.”
Needing to appeal to the next generation while not polarizing Belhaven Best’s existing loyal drinkers, Thirst says it identified a new target audience that appreciates “tradition, celebrates progression, and seeks real easygoing moments.” It adds, “As a beer that champions effortless moments together, we needed to inject refreshing confidence, natural simplicity, and unmissable vibrancy.”
The centerpiece of the new design is a barley sheaf with outstretched bristles doubling as sunbeams framed by the two famous chimneys of the original Belhaven brewery. Says Thirst, “The image is a nod to the ancient malting process that goes into creating the brewery’s ale, as well as a reference to its coastal home, known colloquially as ‘sunny Danny.’”
The base color is an ownable deep blue that captures the Scottish
element of the brand and was selected, Thirst says, to distinguish Best from other category competitors as well as open the door to the color becoming emblematic of the ale brand. The dark blue color is part of a three-tone palette that also includes a lighter blue and gold.
The Belhaven Best brand icon of a rampant lion also has undergone an evolution. The “rampant lion” is a design that harkens back to the reign of King Richard and comprises the profile of a lion on its hind legs. The revised Belhaven Best icon is said by Thirst to offer a bolder depth and detail visible at both large and small scale and is designed to amplify the brand’s sense of craft. In addition, the lion’s face has been reworked to reflect a prouder stature.
“Our aim was to put the heart and soul back into Belhaven Best,” explains Thirst Executive Creative Director Matt Burns. “Belhaven is determined to reach new audiences, and particularly those who appreciate tradition while celebrating progress. That’s why it was so important for the visual identity to play a role in telling the brand story—from the pride in the elevated lion brand icon to the optimistic outlook in the sunshine and heritage in the barley and brewery.
“We have created a design that is now unmistakably Belhaven, and truly brings out the best in a brand at the heart of Scotland’s brewing heritage.”
The new can designs were unveiled in May 2023 and are being backed by a launch campaign across all media types through this year.
Not all commercial beer brands have a history that spans several centuries, but many have a good story to tell nonetheless. Such is the case with Natural Light, or “Natty Light,” an American-style light lager introduced by Anheuser-Busch in 1977 that soon became a collegeparty staple due to its low price point.
Headquartered in North Carolina, Chase-Logeman Corporation has been creating monoblock style filling and finishing equipment for over 60 years. To meet your exacting production needs, Chase-Logeman can integrate an entire production line for a turnkey process package.
Whether you are using bottles with plugs and caps, or vials with stoppers, filling microliters to 125ml, Chase-Logeman has decades of experience to integrate the complete filling line.
Simple Dependable Repeatable Contact us at: Chase-Logeman Corporation
303 Friendship Drive Greensboro, NC 27409
336.665.0754
info@chaselogeman.com
https://www.chaselogeman.com
Filler, Capper, and Labeler Unscrambler Bottle Cleaner Neck Bander/Shrink Sleeve Applicator Shrink Tunnel AccumulatorIn a case of what’s old is new again, in February, the beer brand replaced the existing packaging design for its flagship All American Wheat Ale with one that conjures images of 1979. The vintage
graphics, which the company says are a permanent replacement for its previous packaging, include a throwback logo and crest, and the brand’s classic color scheme of red, gold, and blue.
Before the vintage can was rolled out nationwide, Natural Light conducted two limited-edition runs to gauge consumers’ reaction to the “old is new” design. As the brand shares, over the course of 12 months, the Natural Light vintage design improved share-of-category trends and had the best rate of sale in more than a year. In addition, the retro graphics performed very well with the brand’s 21- to 29-year-old demographic compared with the previous can design. The pilots also confirmed Natural Light’s popularity in coastal regions of the east and south, where consumers affectionately refer to the beer as “Shore Champagne.”
The vintage can design was introduced alongside a full brand refresh that includes the return of Natural Light’s Act Natural campaign, which reminds consumers to “confidently pursue a life you want and remain unabashedly true to yourself.”
Said Krystyn Stowe, head of marketing, Natural Family & Busch Family, at the time of the national launch, “Today is a historic day for Natural Light—the start of our refresh to embrace a broader fan base and introduce the entire country to a new can design. The cans are undoubtedly sleek, and will pop on shelves and make people stop in their tracks. From beach hangs to clambakes, cases of the new vintage-inspired cans will be everywhere friends gather to Act Natural and just be themselves.” PW
&RQQHFWDQG&ROODERUDWH
$FURVV(YHU\6HJPHQWRIWKH &LUFXODU6XSSO\&KDLQ
'LVFRYHUVXVWDLQDEOHSDFNDJLQJVROXWLRQV
DQGWKHPDWHULDOVDQGUHF\FOLQJSURIHVVLRQDOV
ZKRFDQDGYDQFH\RXUJRDOV
/HDUQKRZWRGRJRRGDQGSURILWIURPWKHSURPLVHRIDFLUFXODUHFRQRP\7KHQHZ
3DFNDJLQJ5HF\FOLQJ6XPPLW EULQJVWRJHWKHUDOOVWDNHKROGHUVLQWKHVXVWDLQDEOHSDFNDJLQJ DQGSDFNDJHUHF\FOLQJPDUNHWSODFH
,I\RXłUHDEUDQGRZQHUUHWDLOHU05)SURIHVVLRQDORUUHSURFHVVRUFRQYHUWHURUPDWHULDOV KDXOHURXUFRQIHUHQFHSURJUDPLVGHVLJQHGIRU\RX
$VDQDWWHQGHH\RXłOOJHWHGXFDWHGRQ
7KHHFRQRPLFVRIUHF\FOLQJLQFOXGLQJRULJLQDOUHVHDUFKWRWDNHKRPH
&XUUHQWUHF\FOLQJSROLFLHVDQGUHJXODWLRQV
7KHUDQJHRISRVWFRQVXPHUDQGYLUJLQSDFNDJLQJPDWHULDOVŋIURPSODVWLFWRSDSHU DOXPLQXPDQGJODVV
6RUWDWLRQDQGUHF\FODELOLW\
0DWHULDOVDQGGHVLJQLQQRYDWLRQVĽDQGPRUH
0HHWPDWHULDOVDQGUHF\FOLQJVXSSOLHUVDQGOLNHPLQGHGGHFLVLRQPDNHUVZLWKZKRP\RXFDQ FROODERUDWHWRDFKLHYH\RXUVXVWDLQDELOLW\REMHFWLYHV
3ODQQRZWRDWWHQGDQG
UHJLVWHUE\6HSWHPEHUWRVDYH
3DFNDJLQJ5HF\FOLQJ6XPPLW 1RYHPEHU
*UDQG+\DWW$WODQWDLQ%XFNKHDG
ProMach brand NJM’s specialized Steelco Pharma washing carts are designed to improve the cleaning of product contact packaging machinery parts, thus protect product quality. Booth C-3225 NJM pwgo.to/8018
Belden launches 4-Channel SMPTE cable and VFD cable glands designed to provide enhanced security, better performance, and seamless integration. Belden Inc. pwgo.to/8007
The XCP Series continuous motion, direct load case packer by Brenton, a ProMach brand, is designed for case packing applications up to 70 cases/min and can run wrap-around cases and trays for products in bottles, jars, canisters, cups, and other rigid packaging. Booth C-3822 Brenton pwgo.to/8027
Tamper Technologies’ tamperevident tapes and labels are designed with advanced technology ensuring they cannot be removed without leaving evidence of tampering.
Tamper Technologies pwgo.to/7923
The Volkmannn vibratory feeder dosing system can be con gured for a variety of lling and packaging line applications. Booth SU-8260
Volkmannn pwgo.to/8003
PAC Machinery’s FW 650SI
+ Labeler is a servodriven ow wrapper designed for feeding soft or delicate products at speeds to 80 packs/min. It comes standard with a belted infeed conveyor and can accommodate products up to 12 in. wide or 8 in. high. Booth C-2418 PAC Machinery pwgo.to/7999
The Rotzinger robot with an integrated buffer and a hygienic conveyor for dry cleaning addresses labor shortages, space limitations, ef ciency, and food safety concerns. Booth SU-7113 Rotzinger Group pwgo.to/8005
Pregis’ AirSpeed Hybrid Cushioning (HC) Renew PCR high-pressure air cushioning lm is made with 80% PCR content.
Pregis pwgo.to/8014
Regal Rexnord introduces the Rexnord curve system with 1540 Series MatTop chain for conveyor lines requiring a zero-tangent 180and/or 90-deg curve.
Regal Rexnord pwgo.to/7919
R.A Jones launches the Orbi-Trak TC-6 speedup kit for its Meridian XR multipack cartoners, allowing beverage and food manufacturers to run a variety of canned product con gurations at speeds to 345 cartons/min.
R.A Jones pwgo.to/7758
The FOX IV L3904E all-electric label print-and-apply system can thermally print onto continuous, direct thermal, linerless label stock, cut the stock to the label size, and automatically apply it using a fully electric application cylinder and pad. Booth SL-6301 FOX IV Technologies pwgo.to/7997
WeighPack Systems’ WeightCheQ 0-250 features electromagnetic force restoration (EMFR) weigh cell technology to achieve the highest tolerances possible while reading in three decimal points.
WeighPack Systems pwgo.to/7887
Ranpak Holdings launches the Geami MS Mini paper-based wrapping system designed for warehouse packaging stations. It is applicable for low-volume operations as well as mega-volume and omnichannel ful llment at major retailers.
Ranpak Holdings pwgo.to/7946
The Videojet 3350 and Videojet 3350 Smart Focus 30-watt CO2 laser marking systems are designed to mark sharp, complex codes at high speeds for the food, beverage, cosmetics, pharma, and packaging industries. Booth C-1935 Videojet pwgo.to/8002
Loma Systems expanded its Pipeline portfolio with the X5 Pipeline, a 4-in. option, designed for inspecting pumped and free- owing applications, including large-formed hams and gammons.
Loma Systems pwgo.to/8009
The BTS blister transport system from Pharmaworks and Serpa is designed for transferring blister packs from blister machine to cartoner. It is recommended for pharmaceutical, biotech, nutraceutical, and medical devices. Booth C-3225
Pharmaworks
Serpa pwgo.to/8000
Newtec’s laser FlowPack700 is designed to wrap tray fruits and vegetables packed in laser-sealed, ultra-thin lm at capacities up to 80 punnets/min.
Newtec pwgo.to/8010
Mondi’s 100% recyclable Hug&Hold paper-based packaging is designed to wrap and transport PET beverage bottles, replacing plastic shrink wrap. It features a kraft paper sleeve and corrugated clip to secure the bottles. Mondi pwgo.to/7935
Allpax, a ProMach brand, will introduce its suite of software applications, including retort supervisory control (AllSet), tamper resistant data capture (AllLog), and retort and retort room automation machine control (AllView). Booth C-3214 Allpax pwgo.to/7996
ProMach brand WLS’ heightadjustable labeling option for its VR-72 labeler automatically adjusts the height of the conveyor, and thus the containers, to effectively change the label height. Booth C-3225 WLS pwgo.to/8004
Schubert’s TLM cartoner with Comfort Feeder is designed to automate the infeed of carton blanks directly from the pallet to the packaging machine.
Booth SU-7654
Schubert North America pwgo.to/8001
U.S. Tsubaki’s Dura Drum sprockets, available in full-faced or A-plate drum models, are designed to reduce downtime, increase savings, and provide greater reliability for conveyor systems.
U.S. Tsubaki pwgo.to/8008
The Dynamic Conveyor DynaPro low-pro le conveyor comes in a range of lengths and widths, and includes enhanced features as standard offerings.
Dynamic Conveyor pwgo.to/7920
ABB Robotics’ AI and vision-based Robotic Item Picker can accurately detect and pick items in unstructured environments like warehouses and ful llment centers.
ABB Robotics pwgo.to/8011
Rockwell launches the Allen-Bradley ArmorBlock 5000 I/O blocks designed to operate in a wide range of temperatures and offer up to IP69K protection for high-speed applications in harsh environments.
Rockwell Automation pwgo.to/7964
Syntegon’s SVX Agile is designed for production of 300 bags/min with one lm lane. Its patent-pending cross-seal control allows for custom and accurate sealing pressure. The SVX Duplex can produce 600 bags/min, due to two accessible lm lanes, while maintaining a compact footprint for seamless production integration. Booth C-2800
Syntegon pwgo.to/8019
The TurboFil in-line dual syringe labeler offers reliable, accurate wraparound labeling of up to 30 cartridges/min.
TurboFil Packaging Machines pwgo.to/7933
Identify
Learn
SEPTEMBER 11-12, 2023
SEPTEMBER
PACK
OCTOBER 5-6, 2023
Septimatech; Waterloo, ON, Canada
SEPTEMBER 11-12, 2023
PACK EXPO Las Vegas; Las Vegas, NV
OCTOBER 3-4, 2023
Septimatech; Toronto, Canada
Continued from page 276
Rigid metal packaging, already a formidable option for foods and beverages, is readying a new cadre of reusable, re llable, recloseable, and sculpted containers for the 2030s.
In their pursuit of sustainability, can makers are being driven by regional and local government policies that are pushing to eliminate packaging waste, as well as consumer preference for containers perceived to be “sustainable.”
The phrase “sustainable packaging” is often taken to mean, “made for more than one use” and “not made of plastics.”
In their desire to satisfy their customers and comply with packaging-diminishing policy mandates without going out of business, can makers are working to refine their sustainable design and engineering technologies. The aim of these initiatives is to broaden the capabilities of metal containers beyond their traditional applications into new territories, including the challenging potable water market, the specialty realms of glamorous cosmetic applicators, and demanding pharmaceutical packaging.
The North American metal packaging field is expected to expand by a compound annual growth rate (CAGR) of about 4% into the 2030s. The growth rate for metal caps and closures is expected to rise “at a healthy CAGR of 6% between 2022 and 2032,” according to researcher Future Market Insights (FMI). The firm expects North America to account for about 12% (~$51 billion) of the global market by 2032. That would allow cans to continue enjoying the bigger (88%) slice of the 2030s metal packaging market pie.
If recent metal packaging developments are any indicator, the future of metal packaging will evolve from its linear developmentdelivery-disposal process into a far more circular developmentdelivery-reclamation-reutilization business. Some developments coming out of the circular manufacturing model could include:
• Decarbonized steel cans. Microbes prepping ore for Direct Reduced Iron (DRI) hydrogen refining into iron for packaging applications could lead to lower/no carbon-footprint steel cans. In the DRI process, microbes eat impurities in the ore to smooth its processing without the need for high-energy consumption blast furnaces. Mining company BHP Group Ltd. is working with Allonnia,
a biotech start-up, to whet the microbes’ appetite for gangue (impurities in which ore is embedded).
• Setting circularity records. Are 100% of aluminum beverage cans recycled? Not yet, but Brazil hit 98.7% in 2021, enough to let them boast about achieving 100% recyclability, according to local authorities. 100% recyclability is more than twice as high as U.S.’s best (45.2% in 2020). “If aluminum cans are to be a perfect fit for a circular economy,” says can maker Ball Corp., “then the recycling rate needs to be close to 100%. We believe that is possible by 2030.”
• Dimpled can walls. As far back as the 1960s, Toyo-Seikan Co., Ltd. developed its Diamond-Cut can dimpling process for two-piece drawn and ironed steel or aluminum cans. Diamond-Cut dimpling reduces the weight of the cans by 30% while making them three times more resistant to panel crushing. It also improves the gripability of the cans, and potentially increases their impact resistance, making them particularly wellsuited for beer and carbonated beverages.
• Lower carbon footprint. A proprietary aluminum alloy called ReAl is behind Ball Corp.’s next generation aluminum aerosol shell with a claimed carbon footprint that’s 50% smaller than a standard aluminum aerosol can. Ball relies on hydroelectric power to extract the metal from bauxite, cutting emissions of carbon dioxide equivalent (CO2e) by 75% vs. the global average for aluminum production.
• All around more colorful. Advanced metal can printing technologies lay down sidewall-to-top CMYK graphics. Ardagh Metal packaging is debuting its H!GHEND printing technique in Europe. American craft brewers were first to see Ball’s Cameo End Printing technology at 2018 Craft Brew Conference.
• Aluminum healthcare bottle options. As an alternative to plastic bottles, Chilean manufacturer Condensa offers 105mL-, 180mL-, 300mL-, and 347mL-capacity threaded or flip-top capped aluminum bottles for dry nutraceutical, OTC oral doses. Bottles incorporate BPANI internal coating.
• Refillable applicators. Replenishable “zero waste” metal sheaths and tubes for mascara and refillable metal pots for makeup are trending in the beauty market. Key to their success are designs that simplify replacing and refilling of spent containers. PW
Pack Expo Las Vegas 2023, Booth C-2423
We design & manufacture liquid filling, capping and blow molding machines
Engineered for reliability and longevity, VDG Drum Motors are designed for 80,000 hours of continuous operation before maintenance, reducing operational and maintenance costs and increasing throughput.
IronGrip™ Lagging
IMPROVES Belt Tracking
INCREASES Belt Traction by 40%
EXTENDS Lifespan of the Conveyor Belt
For food processing and handling belt conveyor applications, the SSV Series Drum Motor drives modular conveyor belts without using sprockets.
Eliminate Drive Sprockets
IP69K Sealing System
Washdown Up to 3,000 psi