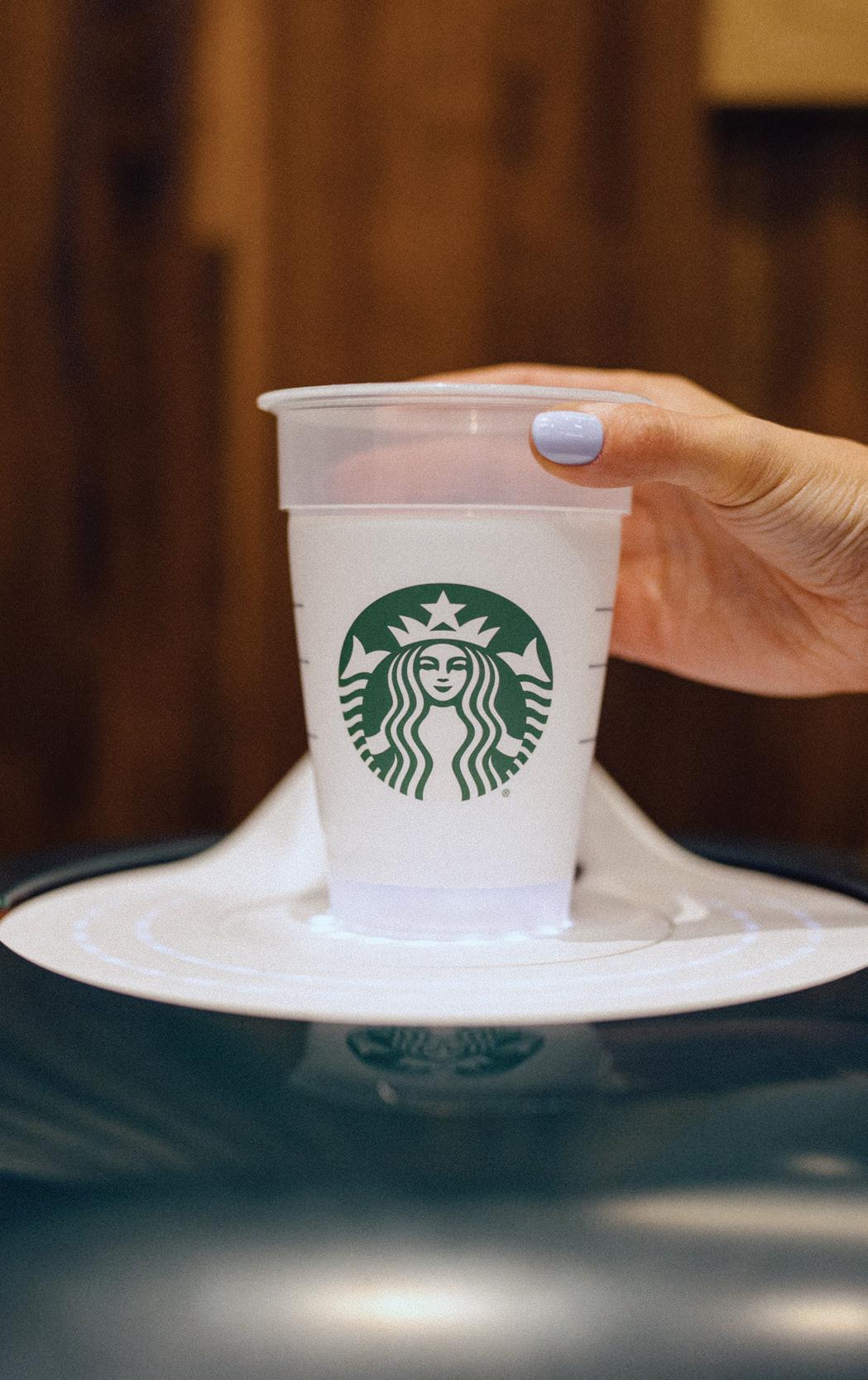

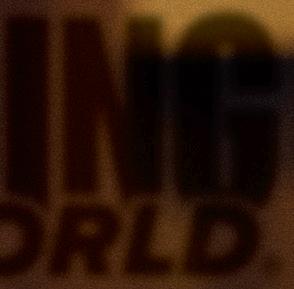
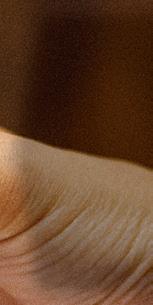



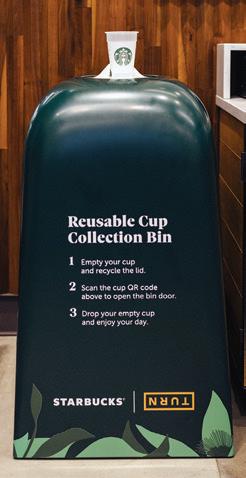

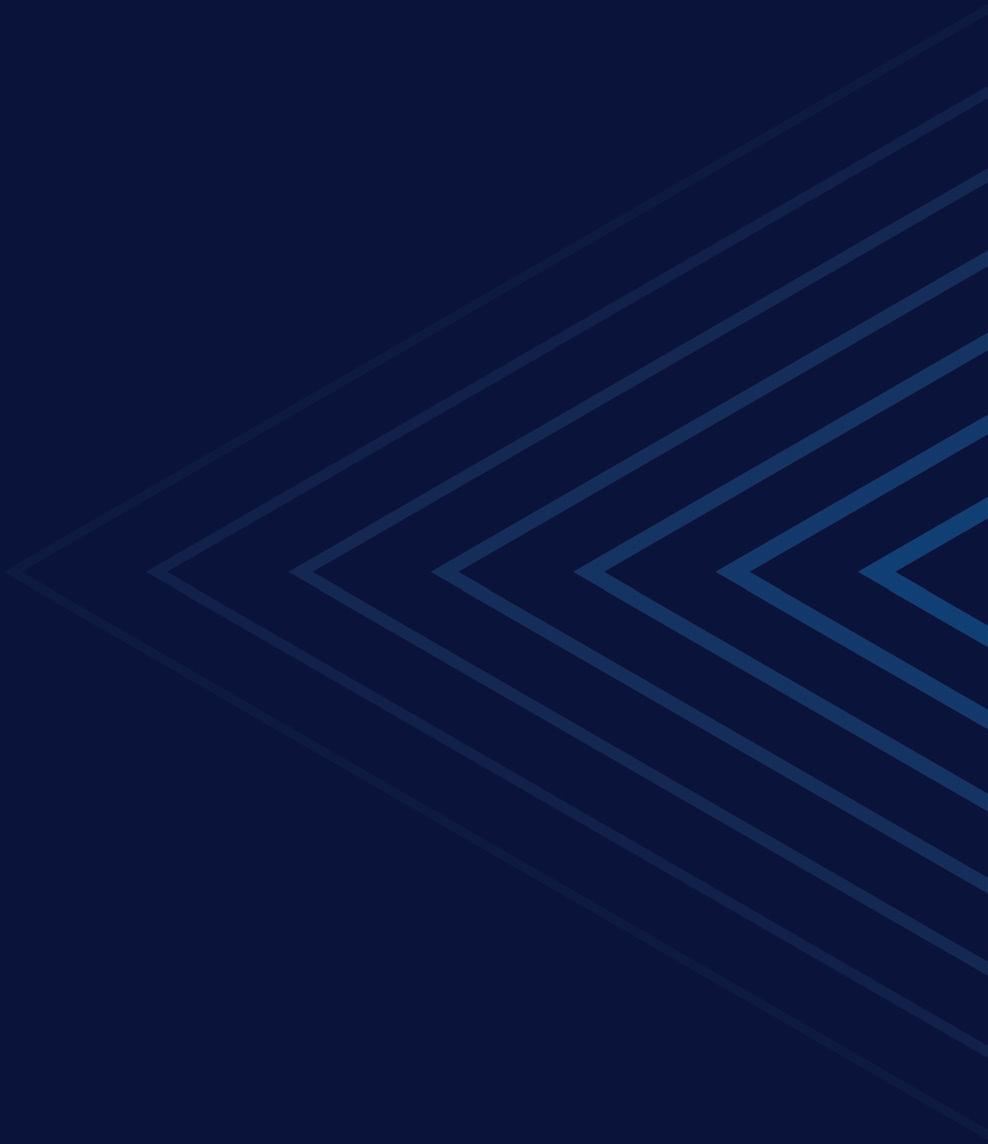

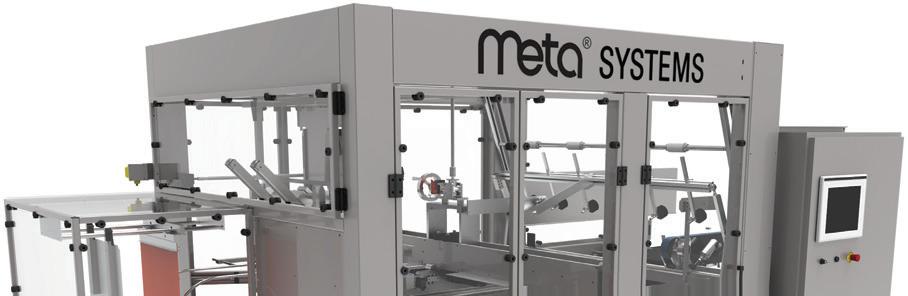
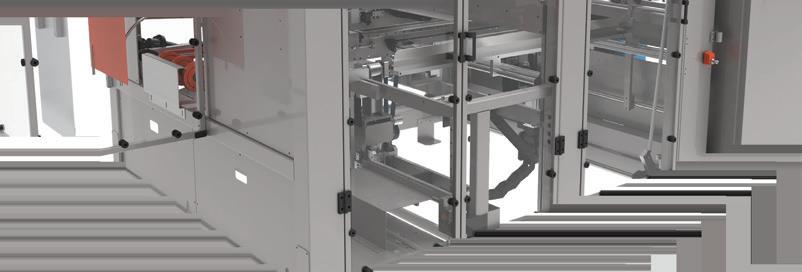








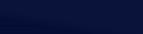

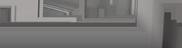

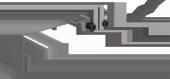

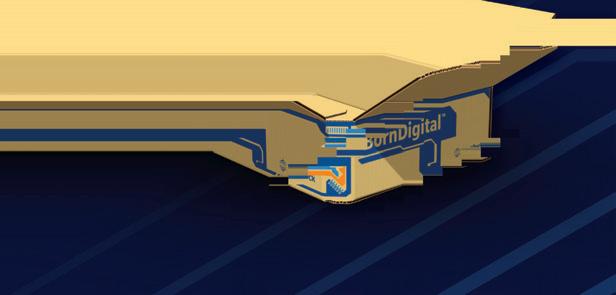


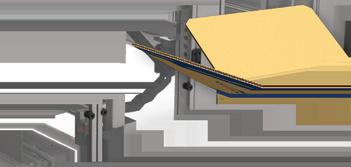
Starbucks is partnering with TURN Systems in a reusable polypropylene cup pilot. A bin that scans the cup bottoms, accepts them to be washed, and returns them to the rotation. Consumers win points and rewards for their behavior.
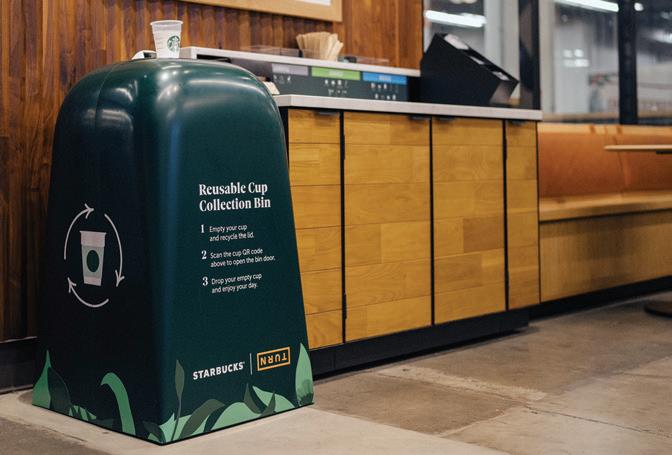
Starbucks is partnering with TURN Systems in a reusable polypropylene cup pilot. A bin that scans the cup bottoms, accepts them to be washed, and returns them to the rotation. Consumers win points and rewards for their behavior.
22
While the cornerstone of Artisan Chef Manufacturing is a passion for artisan Italian cuisine, getting such food to consumers in the supermarket requires absolute packaging mastery.
Sure, the pack redesign was an aesthetic improvement. But it also allowed the brand to consider more sustainable material options, like PCR in both the glass primary pack and the paperboard multipack carton.
While this latest batch of IoPP AmeriStar Award winners is neatly organized into categories, they all in fact are advancing and balancing multiple, sometimes competing attributes like eye-catching design, enhanced sustainability pro le, and improved functionality.
Though the leadership at PharmaMed Automation is steeped in robotics technology, robot deployment was often deemed out of scope for the integrator’s many custom, one-off, “hard automation” projects. Then a project came along in which the client had an automation request that would change the game for PharmaMed projects going forward.
COVER STORY
The Borrow A Cup pilot is built on a reusable packaging platform using an in-store bin that scans and accepts empty cups returned by a consumer, washes them, and returns them to circulation. Consumers can earn rewards based on their scanned cup data.
COLUMNS
5 Lead Off
18 The Big Picture
20 Sustainable Packaging
50 Shelf
Aladin Alkhawam Supply Chain Security Director, Endo International plc
Jan Brücklmeier Technical Application Group Packaging Technology Expert, Nestlé
M. Shawn French Director – Innovation & Packaging Engineering (Beverage), Danone North America
Patrick Keenan R&D Packaging Engineer, General Mills/Annie’s Organic Snacks
Mike Marcinkowski Global R&D Of cer, GPA Global & Hub Folding Box Co.
David Smith, PhD Principal, David S. Smith & Associates
Brian Stepowany Packaging R&D, Senior Manager, B&G Foods, Inc.
Jasmine Sutherland President, Texas Food Solutions; Vice President, Perfect Fit Meals
World®, 401 N. Michigan Avenue, Suite 1700, Chicago, IL 60611. PRINTED IN USA by Quad. The opinions expressed in articles are those of the authors and not necessarily those of PMMI. Comments, questions and letters to the editor are welcome and can be sent to: editors@packworld.com. Mailing List: We make a portion of our mailing list available to reputable rms. If you would prefer that we don’t include your name, please write us at the Chicago, IL address.
Matt Reynolds Chief Editor
Anne Marie Mohan Senior Editor
Iris Zavala Managing Editor
Sean Riley Senior News Director
Pat Reynolds, Sterling Anthony,
Eric F. Greenberg, Ben Miyares Contributing Editors
David Bacho Creative Director
David Newcorn President
Elizabeth Kachoris Vice President, Digital
Kelly Greeby Senior Director, Client Success & Media Operations
Jen Krepelka Director, Digital Media
Mike Prokopeak Senior Director, Content & Brand Growth
Trey Smith Senior Director, Events
Sharon Taylor Director, Marketing
Joseph Angel Founding Partner and Executive Vice President, Industry Outreach, PMMI
Lloyd Ferguson Founding Partner
Staff at PMMI Media Group can be contacted at info@pmmimediagroup.com
John Schrei Vice President, Sales jschrei@pmmimediagroup.com
Lara Krieger Senior Manager, Print Operations lkrieger@pmmimediagroup.com
Janet Fabiano Financial Services Manager jfabiano@pmmimediagroup.com
Questions about your subscription or wish to renew? Contact circulation@pmmimediagroup.com.
Packaging World • PMMI Media Group 401 N. Michigan Ave., Suite 1700, Chicago, IL 60611 Phone: 312/222-1010 • Fax: 312/222-1310
E-Mail: info@packworld.com • Web: www.packworld.com
PMMI The Association for Packaging and Processing Technologies 12930 Worldgate Dr., Suite 200, Herndon VA, 20170 Phone: 571/612-3200 • Fax: 703/243-8556 • Web: www.pmmi.org
Packaging innovation comes in all shapes, sizes, and materials. Sometimes it also has a way of surfacing in out-of-the-way and unexpected places. Like the Lofoten Archipelago, a remote and incredibly beautiful part of Norway that juts out into the Norwegian Sea way up in the northwest corner of the country. That’s where Angelita Eriksen and Tamara Singer co-founded Lofoten Seaweed back in 2016.
How did this small startup become a first adopter of a new packaging technology? It goes something like this. Eriksen was born in a small fishing village in Lofoten, so she knows the Arctic waters and coastline. Singer grew up in New Zealand, where, thanks to her Japanese mother, both algae and seaweed—increasingly viewed these days as “superfoods”—were everyday fixtures on the menu. The friendship between these two women and the combination of their backgrounds led to the launch of their business: wild-harvesting underwater plants by hand, drying them in a specially developed drying room, and packaging them for sale in specialty shops as well as in the Continente chain of supermarkets in Portugal. Recently this women-owned startup became the first in the world to commercialize an innovative pouch technology called Push & Dose Sprinkle Pouch system.
Push & Dose is a bottom-gusseted standup pouch with a perforated tear-off top that holds 1 to 3 oz of product depending on product density. It lets users release sprinkles or spices or fish food or just about any other flake-type product by simply inverting the pouch and squeezing the top two corners toward the center. Inside the pouch is a food-grade membrane heat sealed to the pouch material much like a roll-fed zipper reclosure feature is applied to a pouch. Laser-cut into this membrane are slits that widen into holes when you squeeze the top of the pouch, thus releasing product. The holes narrow back down to slits when the consumer stops squeezing. While this is no hermetic seal, it’s effective enough to keep the dried spices inside the package in such good shape that best-if-used-by dates are typically 18 months. (Visit pwgo.to/8073 to view a Push & Dose Sprinkling Pouch video.)
It wasn’t the Push & Dose packaging format that Lofoten Seaweed first launched with. The firm in its early days relied on a conventional paperboard canister for Smoked Seaweed Salt or a windowed folding carton for Seaweed Tagliatelle. Then at a food show in Oslo in 2019, Eriksen and Singer met Dag H. Gundersen, CEO of Fimtech AS, also a Norwegian firm. Gundersen had been working on a pouch with an integral sprinkling feature for years, and by the time he met Eriksen and Singer he’d gotten serious buy-in from HDG, the German maker of hf/f/s systems, which agreed to be the exclusive maker of machinery designed to fill Push & Dose pouches from rollstock. When Ericksen and Singer saw the Fimtech Push & Dose, recalls Singer, “We just fell in love with it because it would let us develop new products and put them in a format that was better suited to supermarket channels than the high-end gourmet channels we were in at the time. I think Fimtech gave us some pretty competitive pricing, in spite of our relatively low volumes, because they needed to have someone start using the technology on a commercial basis. They even installed a HDG machine in their facility to fill the pouches for us.”
Here, in a greatly simplified version, is how all the parts come together. The patented Push & Dose membrane that has the laser-cut slits through which product can be sprinkled is made by Fimtech. This membrane is fed from reels into the HDG hf/f/s machine in a manner similar to what we see in the application of roll-fed zipper reclosure features. Fimtech makes these reels on specialized equipment from two pieces of polyester and one piece of a special membrane material from Exxon Mobil that is an elastomeric rubber. The membrane material is married to the two pieces of polyester by way of ultrasonic welding, the slits are laser cut into the membrane material, and out comes a reel of Push & Dose “units,” enough for about 9,000 pouches. This reel is fed into the HDG hf/f/s machine that makes pouches from rollstock provided by Graphic Packaging. The rollstock is a Fibrecote 50/8/50, which is a two-layer adhesive lamination of 50g/m2 paper and a PE/EVOH/PE coextrusion. Graphic Packaging prints the paper on an HP digital press.
Singer says she’s proud to be an early adopter of this new packaging format, noting the sustainability advantages that come with just about any flexible packaging solution that replaces rigid packaging like canisters or jars. “And because they’re slimmer and less costly to ship, they’ll make it easier to ship our product around the world,” she adds. “We have a big vision.”
One final observation. As the distributor of HDG equipment in North America, Alliedflex is able to offer the Push & Dose concept in the North American market. In fact, the Push & Dose pouch was the featured technology at the Alliedflex booth at PACK EXPO Las Vegas. PW
For Rosemont, Ill.-based Lakeshore Recycling Systems (LRS), one of the fastest-growing companies in the U.S. and the nation’s fth-largest independent waste diversion, recycling, and portable services providers, the week of August 7 was brimming with news. In addition to hosting a grand opening celebration for its new, state-of-the-art material recovery facility (MRF) in Chicago on Aug. 9, LRS also announced the appointment of a new CEO, joined with the City of Chicago in launching a customerfacing website detailing its recycling services, and was selected to receive a multi-million dollar investment in new recycling equipment.
rials and opens sealed bags, an auger stream that lters out items smaller than 8 inches, a glass breaker, a cyclone separator that separates glass from paper and plastic, a paper screen, a drum magnet for ferrous materials, and the six sorters—three for ber and three for plastics (HDPE, PET, and PP). A grant from The Recycling Partnership’s Polypropylene Recycling Coalition enabled LRS to include optical sorting for PP, which used to be baled with other plastics.
The recycling system operates at 25 tons per hour, which is 10 tons more than LRS’s next most-sophisticated MRF in Forest Park, Ill., and can be expanded to 35 tons/hr. The entire facility is operated by just 11 staff members.
Present at the grand opening of The Exchange as a spectator was Matt Spencer, LRS’s newly appointed chief executive of cer, announced Aug. 7, who will have assumed the role on Sept. 12. In an exclusive interview with Packaging World, Spencer shared that he intends to leverage his expertise in M&A to continue LRS’s strategy of acquisition, which he said is “100% of our value creation.” LRS acquired 22 waste diversion and recycling companies in 2021 and 12 in 2022. “We have a really good leader of business development, Dan Goldstein,” Spencer said. “He’s very talented with process and really strong in business development. I know the partnership with him and the rest of the leadership team will be highly acquisitive, but will be thoughtful on doing it the right way.”
LRS operates more than 80 facilities in nine states across the Midwest. Its newest MRF, dubbed The Exchange, is located in Chicago’s Back of the Yards neighborhood within the company’s 25-acre eco-park. The Exchange was built in the span of six months at a cost of $50 million, with investments from Macquarie Asset Management, the Closed Loop Fund, The Recycling Partnership, and others.
Said John Sliwicki, executive vice president, Central Region, for LRS, at the grand opening, “The Exchange stands not only as a testament to our commitment to innovation, but as a beacon of the post-collection transformation and the limitless potential of technology in rede ning waste management. At LRS, we have always believed the journey of waste doesn’t end with collection. In fact, it’s where the real magic begins.
“I was once told that waste is only waste when we can’t gure out anything else to do with it. The Exchange MRF embodies this belief, as it’s equipped to handle various types of waste, including single-stream recyclables, non-hazardous and non-special municipal solid waste, and other recyclables. We’re using state-of-the-art equipment, including six optical sorters, all managed by an incredibly skilled staff that can maximize the capabilities of this equipment. ... As of now, we’re projecting that we will divert as much as 224 million pounds of recyclables annually, which will then be transformed into valuable resources that fuel industries and inspire change that will drive our circular economy.”
A media tour on the eve of the grand opening revealed a highly efcient facility equipped with sorting machinery from CP Manufacturing that includes a swing arm feeder drum that breaks up single-stream mate-
Another guest at the grand opening was Christopher Suave, deputy commissioner of Policy and Sustainability for the City of Chicago’s Department of Streets & Sanitation (DSS). Pre-celebration, Suave shared with media a new website created by DSS and LRS, ChicagoRecycles.org, that provides a story map for Chicago residents so they can see the journey their recyclables take from the point of pick-up through recycling. Since mid-2021, LRS has provided “Blue Cart” waste disposal and recycling services for four of Chicago’s six residential zones, totaling 400,000-plus households.
As part of the City of Chicago’s Climate Action Plan, DSS has committed to divert 90% of residential waste by 2040. One of the strategies to reach this goal is education and transparency. “The story map is something we’ve been working on with the LRS team for the last six to eight months,” said Suave. “It’s just a quick intro, an educational piece, for residents to see how the program works, who’s collecting in other parts of the city, and ultimately where the materials are going.”
Finishing up a week of good news, on Aug. 11, the American Beverage Assn. (ABA), a trade association representing America’s non-alcoholic beverage industry, announced that it had selected LRS to receive an investment of $3 million as part of its Every Bottle Back recycling initiative. The investment, in partnership with additional funding from Closed Loop Partners, helped support the construction and expansion of The Exchange.
“One of our industry’s highest priorities is to create a circular economy for our bottles and cans,” says Kevin Keane, interim president and chief executive of cer of ABA. “Chicago is a great and innovative American city. It is exciting to partner on a signi cant project that will serve to enhance its beauty, environment, and quality of life. America’s leading beverage companies are carefully designing our bottles to be 100% recyclable and investing in modern recycling systems to reduce our plastic footprint and keep plastic out of nature. We are excited to continue that work here in Chicago and thank everyone who made this investment a reality.”
—Anne Marie Mohan“Serving generations of meat lovers since 1902,” St. Louis-based, familyowned and operated Volpi Foods offers a large selection of dry-cured meats—salami, coppa, prosciutto, and mortadella among them—to retail stores nationwide from its location in the Italian neighborhood of The Hill. According to Volpi Foods Marketing Communications Specialist Madeline Gauch, sustainability is important to the company, as it demonstrates that Volpi has its customers and future generations in mind. “We’ve always been thinking about sustainability and improving our efforts, as we want to lead the way,” she says.
This emphasis on sustainability extends to its packaging, as well. In early summer 2023, Volpi introduced new packaging for its sliced, cured meat—a ber-based thermoform tray with a plastic layer that can be removed to allow for recycling of both the paper and plastic. The Ecocraft Shape from Südpack is constructed of 80% paper-based material and 20% polyethylene lm and uses what the supplier calls a “functional layer” to enable easy, ber-free separation of the paper and lm.
Prior to its use of the Ecocraft Shape, Volpi was a using another ber-based composite, however the layers could not be separated. The Ecocraft not only offers recyclability of both layers, but it also
retains the same 90-day shelf life as the previous packaging, provides good formability for cavities up to 15 mm deep, and is compatible with all Südpack top webs with a PE sealing layer.
The new package is printed with Volpi’s trademark blue logo on the front as well as on the back in a repeating pattern. The top web is also coated with a lacquer that enhances the package’s shelf presence and provides protection from moisture throughout the supply chain. In addition, instructions on how to separate the layers for recycling are printed on the back of the pack; Volpi also communicates this information through its digital media.
“On the new packaging, we can now highlight the fact that it is 80% recyclable,” says Gauch. This attracts customers’ attention and supports our brand promise to work for a more sustainable future, which is crucial in terms of building customer loyalty.” —Anne
Marie MohanMedium to High Speed Solution
Runs wrap around cases and trays up to 70 cases per minute utilizing continuous motion.
Ergonomic Blank Load System Conveyor fed case blank loading system accepts flat stacks of blanks for easy loading.
Private labeled and store brand food and beverage products from German retailer Netto are now digitized using Digimarc’s product digitization technology, including incorporating covert Digimarc digital watermarks into the packaging. In this system, vision hardware at various locations of a package’s journey—from packaging operations, to supply chain, to checkout, and nally at collection and recovery at a material recovery facility—can read this digital watermark and access information speci c to the package, such as its material content for sorting and recycling.
A Netto spokeperson says the move is re ective of the retailers’ extensive sustainability program, wherein responsibility for business outcomes is part of its corporate culture.
“We initially cooperated with Digimarc to optimize our checkout by digitizing our private label food and beverage products with Digimarc’s technology,” says Christina Stylianou, Netto corporate spokesperson. “Netto is now also well-positioned to adopt Digimarc Recycle by leveraging the same Digimarc digital watermarking technology that makes the checkout easier and more ef cient. We are ready and excited for Digimarc Recycle to come to Germany in the near future.”
Retailers like Netto—as well as brands, CPGs, or CM/CPs— can implement Digimarc’s digital watermarking, imperceptible to the human eye, across a package’s or label artwork’s surface area. The invisible nature of digital watermarks works well with packaging designs and branding. Netto has already enhanced thousands of food and beverage packages with digital watermarks that are now readable by certain sortation equipment.
“The fact that Digimarc digital watermarks didn’t obscure our branding and therefore enhanced packaging was another important factor in selecting Digimarc as a long-term partner,” adds Stylianou.
According Digimarc and proponents of the so-called “HolyGrail 2.0” project in Europe (more at pwgo.to/8069), Digimarc Recycle may revolutionize in the sortation of plastic waste and recycling. By linking covert digital watermarks, used to deterministically identify plastic packaging to any desired level of granularity, with an extensible cloud-based repository of product attributes, such as brand, SKU, product variant, packaging composition, food/non-food use, etc., Digimarc Recycle overcomes optical sorting technology limitations to drive a step-change improvement in the quality and quantity of recyclate. Moreover, the same information used to drive this advanced sortation in facilities can provide product-speci c and location-based disposal instructions via a brand-owned direct-to-consumer digital communication channel accessed via on-pack watermarks or QR codes.
In addition to providing the information necessary to power advanced sortation at recycling facilities, Digimarc Recycle captures and provides a holistic view of the postpurchase product journey, unlocking never-before-seen data bene tting stakeholders across the value chain, the company says.
Digimarc Recycle is expected to launch soon in France and Canada, with conversations ongoing in other countries around the globe.
“At Netto, we are committed to less plastic packaging, more recycling, and more responsibility,” concludes Stylianou. “Digimarc is a valued partner in supporting us in achieving our sustainability goals as we look to the future.” —Matt Reynolds
?
The better question is: What can’t you do with it?
Elevate your automation game with XPlanar. Developed in-house by Beckhoff, this mechatronic system makes your production literally fly with magnetically levitating movers and base tiles that you can arrange to fit your unique applications – assembly and packaging, pharma and food, entertainment and beyond.
So, what will you do with XPlanar?
Processing with up to 6 degrees of freedom
Transport and processing in one system
Wear-free, hygienic and easy to clean
Multi-mover control enables parallel and individual product handling
Fully integrated into the powerful and standardized PC-based Beckhoff control system (TwinCAT, PLC IEC 61131, Motion, Measurement, Machine Learning, Vision, Communication, HMI)
• 0DGHDW¿[HGDQJOHVRI DQGGHJUHHV
• 5HGXFHGIRRWSULQW
• (OLPLQDWHFKDQJHRYHU
DGMXVWPHQWV
• /RZPDLQWHQDQFH
• $FFHVVLELOLW\OD\RXWIRU RSHUDWRUDQGIRUNWUXFN WUDI¿F
Following on the heels of a successful collaboration with Amcor on its Instant Pot Meal Kits in 2022, Tyson Foods has introduced another new mono-material exible lm package, this one for its Jimmy Dean egg bites and frittatas, that allows for store drop-off recycling while providing functionality comparable to the multilayer, multi-laminate format it replaces.
Tyson’s Instant Pot packaging uses Amcor’s AmPrima PE Plus Recycle Ready Pouch (see pwgo. to/8068), made from a proprietary polyethylene lm that Amcor says delivers high levels of clarity, stiffness, and heat and abuse resistance while also being recyclable. In addition, it says that PE Plus does not compromise lling performance, graphics or printing, or barrier properties. The new vacuum packaging for the Jimmy Dean breakfast products—said by Amcor to be a rst-to-market solution—also uses AmPrima PE Plus, but in a forming/non-forming lm application.
According to Tyson Foods Senior Director of Packaging Jeff Czarny, in its quest to design more sustainable packaging for its products, Tyson Foods is focusing on speci c packaging formats and speci cation requirements. “The packaging format used for these products [egg bites and frittatas] is widely utilized across the Jimmy Dean product portfolio as well as other brands at Tyson,” he says. “In working with Amcor, our goal has been to develop packaging technologies that can potentially be scaled across a wide variety of products and can help support Tyson Foods’ work towards the company’s sustainability goals.”
The original packaging for the egg bites and frittatas was constructed of a polyamide-based forming web and an EZ-peel laminated non-forming lm with an oriented PET outer layer. The polyamide provided formability and toughness, while the OPET layer offered heat resistance and stiffness. With the new packaging, Tyson wanted a lm construction that would qualify for store drop-off recycling per the APR Critical Guidance test protocol for PE lms, while performing at parity to conventional lms on its existing packaging equipment, matching current speed and waste requirements.
Development and testing of the new lm was conducted by Tyson at the packaging innovation lab and pilot plant in its Downers Grove, Ill., Discovery Center. “Engineers at this facility conducted extensive integrity testing to optimize the nal package design and performance,” explains Czarny. “In addition, we leveraged the packaging testing capabilities of our strategic packaging suppliers to evaluate package integrity.”
Per data from Amcor’s Asset life-cycle assessment tool, when compared with conventional multimaterial lm constructions, Amcor’s AmPrima recycle-ready forming/non-forming lm offers a 30% reduction in non-renewable primary energy demands, a 29% reduction in carbon footprint, and a 42% reduction in water consumption, when sent to land ll. When it’s recycled through store dropoff or curbside (where available) systems, the lm reduces non-renewable primary energy demands by 80%, reduces the carbon footprint by 70%, and reduces water consumption by 68%.
The secondary cartons for Jimmy Dean’s egg bites and frittatas carry the How2Recycle label, which instructs consumers on how to recycle the components of the package. —Anne Marie Mohan
844-293-2814
4ISJOL8SBQQFST 4ISJOL#VOEMFST
3PMM8SBQQFST "VUPNBUJD'MJHIU#BS8SBQQFST
'PDVTFEPODVTUPNFSFYQFSJFODFBOEZFBSTPG FYQFSJFODF &%-IBTCFDPNFBMFBEFSJOFOEPGMJOF 7JTJU6TBU&%-QBDLBHJOHDPN
85%+
The percentage of reusable to-go foodservice items that had higher than acceptable microbial levels when tested in an independent study commissioned by the Foodservice Packaging Institute
<5 mm
The size of the plastic particles found in the heart tissue of 15 patients undergoing heart surgery; collected from team from the Beijing Anzhen Hospital in China, nine types of plastic were found in ve types of heart tissue
75K lb
The amount of plastic that Liberty Coca-Cola Beverages in Philadelphia will eliminate each year by replacing plastic rings with ber-based packaging for its canned beverages
27,100
The projected number of jobs advertised within the packaging and paper industry requiring engineering quali cations—a 127% increase since 2020, according to GlobalData
“This study from our friends at CRI [the Container Recycling Institute] and Reloop provides more evidence of what we already knew: the arguments that deposit return programs negatively impact beverage sales over time are without merit. There is ample proof that we need more bottle return programs, not fewer. It is in states’ and communities’ clear and vital interest to pass DRS [deposit return scheme] legislation, especially those legislatures that are also considering extended producer responsibility programs for packaging. Curbside pickup will remain a recycling staple, but must remain supported by proven recycling programs that create higher volumes of cleaner streams of recyclable material.”
–Scott DeFife, president of the Glass Packaging Institute, in a release from GPI, “Glass Packaging Institute Responds to Study Debunking Arguments Against Bottle Return Programs, Reiterates Calls for Adoption of DRS in States and Municipalities”
“As we think about even better serving our consumers and even better serving our retail partners, it [eliminating the bottom 25% of SKUs] is a logical part of an optimization program to nd a better, more ef cient shelf. As you can imagine, reducing SKUs in a very complex manufacturing environment frees up capacity and frees up cost, so it’s a multi-bene t space, but we’ll take our time to ensure that we do it the right way. There is no standard simple way to do this, so it requires a lot of analysis and a lot of planning with our retail partners to do it right.”
–Andre Schulten, chief nancial of cer of Procter & Gamble, in an article from Consumer Goods Technology, “P&G Trimming SKUs As Part of Collaborative Commerce Strategy”
“Beyond Meat is a signature label of the plant-based meat industry. One where too many participants and investors have overestimated demand and oversupplied the market with corresponding business failures. The complexity of alternative proteins, their price and in many cases rather poor eating quality all add up to major problems.”
–Clive Black, director at investment group Shore Capital, as quoted in an article, “A temporary blip or a sign of oversaturation? Beyond Meat’s woes and the future of plant-based meat,” from FoodNavigator.com
651-419-6050 | sales@somic.us
500 Lone Oak Road, Suite #200 Eagan, MN 55121
Website: www.somic.us
At SOMIC Packaging we provide the most compact and versatile case packer available in the world today. We don’t just focus on the machine itself; we provide a wealth of experience on selecting the best finished package format for your specific requirements. Whether you’re looking for a standard wraparound case or an eye-catching shelf ready display or a standard wraparound shipping case, SOMIC has your back!
Our latest machine generation, the SOMIC 434 offers a one machine solution for all packaging needs: Individually grouped in one-and two-piece cartons. From the array of options for grouping the products to the selection and use of all available package configurations: vertical or horizontal, single or multi-row, single or multi-layer.
SOMIC CORAS enables a freely definable 360° orientation of your products in the carton and at the same time lets you realize any mixed formats with different product types. It is ideally suited for sensitive goods, as it is very gentle on the product without the use of pickers and vacuum technology, using multi-dimensional controllable magnetic levitation technology. it offers almost unlimited possibilities for mixing, sorting, and grouping your products.
the pack size just big enough to fit the contents. For our glass jars, we source a non-plastic compostable top made from PHA [the bioplastic polyhydroxyalkanoate].
How prevalent is greenwashing in the beauty industry? Why do you think this is the case? What are some of the most egregious claims you’ve seen?
Can you tell us a bit about FLORA + BAST? What inspired you to create the company? What is your mission?
Derek Chase:
FLORA + BAST is a culmination of and interplay between my personal struggles with staying optimally healthy and my interests in helping enhance health and reduce suffering in the world. We thought, why is no one creating health-promoting cannabis products? Why is cannabis marketed like alcohol, when there are so many health-restoring bene ts when used intentionally to solve a health problem? So, we set out to create a portfolio of products that hit on segments I personally have struggled with my whole life—namely sleep, skin, sex, and stress.
Why is the environmental impact of your company and its products important to you?
When I was 10, my family moved to Massachusetts, and we would travel into Boston to hang in the Commons and walk along the Charles River. At that time, I was blown away that our rivers and streams and many other natural resources are so toxic you can’t swim in them, and then to nd out it was the direct result of known activities going on in the manufacturing world? Since this awakening, environmental degradation has always been a neurosis of mine, especially as I started my career in the CPG industry and noticed how much waste there is behind the scenes when it comes to producing packaged goods.
When it came time to design FLORA + BAST, I wanted to make sure we were being good stewards of the environment and ensuring all our packaging and processes limited waste. We started with a universal box and bottle created from agricultural waste. Knowing how much waste there is in discontinued products after having worked at Johnson & Johnson and L’Oréal, I figured this would ensure that no box or bottle would ever get trashed due to slow market movement. From there, we upgraded our approach to source a 100% post-consumer recycled bottle and have stopped using ink or metals on our boxes, making them more friendly to factory workers who are slightly poisoned every time the printers are running. Instead, we emboss and deboss only. For our pouched products, we use a compostable material and make
Greenwashing is very prevalent, but I think it’s a systemic issue not a bunch of people trying to deceive customers. I think that, when it comes to packaging, everyone worries about product stability and aesthetics rst, and the eco-nature of it is sort of a plus. I believe the problem stems from the fact that no one in a large corporation is ever measured by their ability to impact the eco-nature of their products. Brand managers are not told they need to limit waste by any amount, they are not penalized for waste, or rewarded for creating a cleaner supply chain, so the only way a large brand would consider designing something that is truly eco-friendly is if it’s part of their brand DNA. In this case, the easiest way to communicate that aspect of the brand is through primary and secondary packaging, which is a good start but falls short in terms of truly being eco-friendly, as primary and secondary packaging waste is a very small amount of the waste created.
There is no attention paid to the sturdy plastic buckets, totes, and drums used to transport raw ingredients, international shipments of ingredients and packaging that are readily available domestically, but pricier, or corrugated boxes used for transport from supplier to supplier, manufacturer to brand, and brand to retail. There are so many back-end issues with product manufacturing, and greenwashing is something that naturally occurs because people are not incentivized to do the right thing.
What are some of the challenges in educating consumers on sustainable packaging?
They don’t care a lot of the time. People are so busy and stressed nowadays, and a lot of consumers get even more stressed when they nd that something they love is killing the world, and they go into denial. I am guilty of this myself, and I experience a lot of anxiety from my purchase decisions.
Can you discuss some of the myths and misconceptions around sustainable beauty as they pertain to packaging?
The biggest myth is that packaged goods can be eco-friendly. It’s just not true, it’s more eco-friendly in some cases, though one cannot tell until they know the back end of how it was manufactured and where. So products can be less bad, but there is no such thing as a product that reduces waste.
How can the industry educate consumers? What are some of the steps you’re taking to help them better evaluate sustainability claims?
We struggle here. The only way we think the problem can be solved is through certi cation and a resulting seal on the pack. The beauty industry was fast to jump on board with Leaping Bunny, and I think that with the right incentives, and given where the consumer is now, that is to say, nally considering eco-friendliness as a major part of their purchase decision, we are at a place in time where certi cation would steer purchase decisions, and so a certifying body is needed. This agency would need to look at the whole supply chain, not just the packaging, in their certi cation process. —Anne
Marie MohanDerek Chase, founder and president of sustainable wellness brand FLORA + BAST, dispels some of the myths surrounding sustainable beauty and explains how consumers and the industry can combat greenwashing.
Customers worldwide count on Duravant’s portfolio of premium engineered automation solutions spanning the food processing, packaging and material handling segments. Backed by Duravant Integrated Solutions and SupportPro, the Duravant family of operating companies optimizes safety, productivity, efficiency and connectivity for the world’s producers and movers of high demand goods.
A project fails simply by not achieving its objective(s) within its speci ed limits of scope, cost, and time. A project can fail to the point of being abandoned, however most failures are less spectacular. Packaging projects fail for a variety of reasons, but those that I’ll discuss here have evidenced themselves time and time again.
Late start. For a new launch in particular, the start of a packaging project should coincide with that of the product. For the most part, thankfully, industry has progressed beyond sequential projects, i.e., product development completed, followed by package development. A packaged product, by definition, is composed of two components: product and package. The interdependence of the two should be acknowledged at the concept stage, which precedes project work. At that stage, references about the packaging need not be detailed, but sufficient to allow personnel to start visualizing and brainstorming.
Parallel paths. A packaging project should proceed along a path that intersects with those of other involved disciplines. It’s a requirement that’s consistent with packaging’s interdisciplinarian nature, in addition to a systems approach. There’s a dynamism and fluidity to projects, with matters in constant flux. Not only does the right hand need to know what the left hand is doing, but that knowledge might need to extend to the finger-level.
Wrong expectations. Packaging performs the overlapping functions of containment, protection, communication, convenience, and utility. Any expectations outside those functions are wrongly held. If, for example, the requisite quality, performance, and value are missing in a product, changing the package won’t solve the problem, beyond, perhaps, a temporary increase in trial purchases. Stated differently, if the packaging is not the problem, it can’t be the solution. On the other hand, for a product of requisite quality, performance, and value, the packaging can be the competitive difference.
Poor vetting. A packaging project is rarely, if ever, totally an in-house undertaking. To the contrary, it typically involves external parties, e.g., suppliers, designers, testing laboratories, contract packagers, etc. They are partners, and as go their performances, goes the performance of the partnership, and by extension, the performance of the project. It’s always an advantage when partners are of proven reliability. When, however, a project requires the recruitment of new partners, there should exist a framework for their efficient vetting.
Overinvolved stakeholders. After a packaging project is underway, stakeholders sometimes request changes. Potential problems are
two-fold. First, stakeholders are product development, production/ manufacturing, marketing, distribution, legal, and procurement, among others, so requests can be multiple and of random sequence. Secondly, no requested change can be implemented in isolation; instead, they trigger a ripple effect requiring tradeoffs. It’s essential that stakeholders establish their needs prior to the start of the project and only request changes that can be justified.
Inadequate risk management. Packaging can pose risks, in addition to being subject to risks. Project participants should not be myopic about potential hazards posed by the packaging. Being proactive and willing to engage in wide-ranging “what ifs” can prevent personal injury lawsuits or recalls. In its other capacity, packaging is a strategic asset that should be safeguarded. Some projects generate proprietary technology, intellectual property, and the like. In those instances, tight controls and sharing information on a need-to-know basis minimize the chances that the packaging will be co-opted, infringed upon, or pirated.
Wrong person at the helm. A successful packaging project requires a manager who possesses a certain skill set. The person must be adept at reconciling the dueling wants of teammates.
The person must be able to stroke egos while remaining true to project objectives. The person must be the envy of a circus juggler, maintaining balls in the air without dropping any. And yes, the person must be a master communicator. A manager can be dedicated and hard-working, yet ill-suited and over his/her head. That can happen if the manager is not the resident expert in the involved aspects.
Having discussed the seven reasons for project failure, a few concluding remarks can lend additional perspective. Industry-wide, the frequency of project failures and their severity is underreported. That’s because companies, understandably, are disinclined to such disclosures. Perfection is illusional and failure is relative. Therefore, it follows that package products can (and do) end up in the marketplace, despite operational missteps.
It comes down to potential sacrifices and potential penalties. When, for example, speed-to-market is critical, recovering from a missed launch date can take an extended period. As another example, cost overruns can force a decision between a reduced profit margin and a higher price (which might negatively impact demand). As a final example, there are the damaging effects that failure has on esprit de corps. No one craves association with failure. Team members might engage in recriminations and might be reluctant to work with certain others in the future. That’s worrisome because a corporation’s people are its most valuable assets. PW
Perfection is illusional and failure is relative. Therefore, it follows that package products can (and do) end up in the marketplace, despite operational missteps.
In the 31 years since the Federal Trade Commission (FTC) rst issued its Green Guides to regulate businesses’ environmental claims and labeling and to help eco-minded consumers make more informed product decisions, the packaging recovery, recycling, and reuse landscape has changed dramatically. Despite several revisions in 1996, 1998, and 2012 that aimed to keep pace, the Green Guides have struggled to keep up with the rapid innovations within packaging and recovery systems. One area of particular relevance is the lack of clear de nitions for popular packaging attributes like recyclable, reusable, and compostable.
Although people often portray the Green Guides as de facto law on labeling and claims, to be clear, the guides are an administrative interpretation of the law; they lack the force and effect of law. They also do not pre-empt state law, so many states have either adapted or superseded the guidelines in different ways over the years. This has put companies working across multiple states at risk of legal action due to non-compliance for products sold at a national level. It’s also created widespread consumer confusion and mistrust in the recovery and recycling processes and is impeding efforts at all levels to ensure packaging is properly handled at its end of life.
Just this year we have seen more than 30 bills within different state legislatures containing various labeling requirements. Many of these bills conflict directly with guidance set forth in the Green Guides. Perhaps the best example of such conflict and consumer confusion is in state laws pertaining to the resin identification code (RIC) and “chasing arrows” triangle symbol frequently found on consumer packaging: At least 36 states have laws mandating the use of the codes, with the vast majority of those laws requiring it in combination with the chasing arrows triangle despite the fact that the ASTM has called for a solid equilateral triangle around an RIC since 2013. A new California law that goes into full effect in 2025 will restrict the use of the chasing arrows in combination with the RIC when making recyclable claims. This means a company that sells products in California and in Indiana, for example, may have to create two different labels or packages (if the RIC is stamped) to comply with two different state laws.
Even if it did provide further definitions, the FTC Green Guides lack the legal jurisdiction to supersede state definitions/law, whereas federal definitions, enacted by Congress, could harmonize across all the states and federal agencies, including the Green Guides. AMERIPEN is urging a federal solution. Specifically, the industry and consumers need national, harmonized, and standardized definitions and marketing criteria. A federal law that clearly defines recycling, composting, and reuse to better reflect present market demands will
provide certainty for industry and consumers as well as state and local governments. This harmonization will help support the Green Guides.
The current definitional vacuum complicates product labeling and depresses packaging recovery rates. Emerging state laws, such as in California, will force companies to either develop an alternative label to accommodate individual state regulations or give up on selling in that market altogether. Codifying new, well-reasoned definitions into federal law would help industry and communities better manage the packaging lifecycle by providing easily accessible information to consumers, thereby helping to ease the flow of discarded packaging materials to the most appropriate facilities for recycling and reuse.
AMERIPEN recommends that the FTC review and update the Green Guides every five years instead of once a decade—as policy now dictates—to better keep pace with the rapid rate of change and innovation in the industry. It also recommends that the Environmental Protection Agency (EPA) become more engaged in regulating end-of-life claims made by companies. Such claims are intrinsically tied to the lifecycle management of product packaging and the U.S. solid waste system, and the EPA could play a much more proactive role given the agency’s deep expertise on these issues.
AMERIPEN believes packaging has no place in landfills, in waterways, on roadsides, or in other places that degrade our environment and lifestyles. We must recover it to recycle and reuse it, and the federal government can play a transformative role in improving recovery rates by helping provide clear definitions and updated guidance. With smart collaboration between industry and government, we can usher in a new era of recycling and reuse that will better serve consumers and the environment. To learn more about how you can engage in the process, contact AMERIPEN or your packaging trade association as well as your elected officials. PW
Join a host of big CPGs and brand owners, alongside downstream material recovery facilities, haulers, and reprocessors, as they discuss design for recyclability, recovery, and end markets among converters and materials producers supplying a circular packaging industry. Visit pwgo.to/8071 for more information.
FEEDING SYSTEMS FLOW WRAPPERS ROLL WRAPPERS
BAKERY BAGGERS
SHRINK WRAPPERS
FORMERS & CLOSERS
ROBOTICS CARTONERS
WRAP AROUND CASE PACKERS
TOP LOAD CASE PACKERS PALLETIZERS
FEEDING SYSTEMS X DISTRIBUTION SYSTEMS X FLOW WRAPPING X ROLL WRAPPING
SHRINK WRAPPING X ROBOTICS X CARTONING X CASE PACKING X STORAGE SYSTEMS
BAKERY SLICERS X BAKERY BAGGERS X PALLETIZERS XTURNKEY SOLUTIONS
Rock Hill, SC : USA + Bristol & Beccles : England + Mumbai : India + Dubai : UAE
Worldwide Representation
Autowrappers X Europack X Ibonhart Brands of the Bradman Lake Group Ltd
info@bradmanlake.com X bradmanlake.com
A Langley Holdings
While the cornerstone of Artisan Chef Manufacturing is a passion for artisan Italian cuisine, getting such food to consumers in the supermarket requires absolute packaging mastery.
By Pat Reynolds, Contributing EditorDescribed by some as a serial food entrepreneur, Joe Faro got his start at his parents’ corner bakery when he was just a child. Fresh out of the University of New Hampshire, he launched Joseph’s Gourmet Pasta and Sauces, which he sold in 2006 to the Buitoni division of Nestlé Prepared Foods. He then went on to establish numerous restaurants and catering services that now serve up Italian specialties and a whole lot more throughout the New England area.
This story is about the newest development in Faro’s Salem, N.H.based Tuscan Brands empire: Artisan Chef Manufacturing Co. The Lawrence, Mass.-based facility is producing and packaging restaurant-qual-
ity Italian style foods for distribution in much of the country through supermarket chains like Market Basket and club stores like BJ’s Wholesale Club and Costco. Two new lines currently operating in the Lawrence plant include one for ready meals and one for ravioli, those little pasta envelopes containing delicious mixtures of ground meat, cheese, or vegetables. Both lines are worth a look, beginning with the ready meals line that produces a variety of items sold refrigerated or frozen in premade trays thermoformed of crystallized PET (CPET).
“Flexibility is the key, because in addition to depositing our cooked pasta, we want to apply a variety of sauces, add different kinds of protein, add various cheeses, all those types of things—and all in-line,” says Faro. A key resource was Orics Industries and Orics president Ori Cohen. “He’s so good at entering a food manufacturing factory, recognizing the needs, and creating packaging equipment that is more or less customized just for you,” says Faro. When asked if that kind of customization comes with a hefty price tag, Faro says not really. “It’s not the least expensive machinery, but perhaps more important is that I enjoy working with Ori partly because he’ll design a piece of equipment for your process rather than having us design our process around his equipment. He’ll even modify the line after it’s in if need be, which is important because when you’re customizing equipment, things may not always be perfect the rst time around.”
It isn’t just the product going into the trays that uctuates on this ready meals line. The CPET trays, supplied by Amcor, vary as well. In addition to a single-serve meal in a tray measuring 6 x 8 in., the rm also offers a multi-serve portion in a tray measuring 12 x 8 in. The servo-driven TV 1000 tray denester from Orics handles both tray formats, dropping trays single- le onto a stainless steel lugged conveyor that indexes them forward. Also worth noting upstream from this
The servo-driven tray denester on the ready meals line handles two tray sizes, dropping trays single- le onto a stainless steel lugged conveyor that indexes them forward. Photo right shows the larger tray, which holds four servings.
screw denester is an Orics automatic denester loader that holds almost 40 minutes worth of trays.
The rst product to be deposited into the tray is pasta, which is fed by a 14-bucket combination scale from Smart Weight Packaging System Ltd., a Chinese OEM represented in the U.S. by Orics. The freshly made pasta is delivered to the overhead scale by way of an Orics incline bucket elevator. The scale selects the right combination of buckets for the weight that’s called for and those buckets drop their contents into two memory buckets. When two trays arrive in the correct position, they pause and the memory buckets open to drop their contents into the trays. Helping to cleanly guide the pasta into the trays with no chance for spillage are two funnels that stroke down into the tray just before the memory buckets open.
“Orics has a proprietary relationship with the Chinese manufacturer of the scale and actually puts the nishing touches on it, not to mention all the controls,” says Faro. “So it’s practically an Orics machine, and they’ve done an excellent job with it. We now have three of them and another one coming. We use them for everything from pasta to vegetables to grilled chicken strips to grilled shrimp to meatballs.”
Next in line is a second 14-head combination scale that deposits small pieces of cooked protein such as chicken, shrimp, or beef. It’s also fed by an Orics incline bucket elevator that takes product from a oorlevel hopper up to the overhead level.
Now it’s time for sauce, which is deposited by an Orics volumetric
the Best Defense against ALL metals… steel, aluminum, stainless steels, copper and more. Our equipment is designed for any process whether it’s wet, dry, gravity, pneumatic or conveyed. Don’t leave yourself exposed with only half of a solution.
Regardless of your objectives or the challenges with your application, Powertrain Solutions can help you achieve your unique goals. No matter what your application looks like, it relies on many components, all working together. But not ćŰŰʠĤƇŹƫƇŻIJŻǂƶʠćƮIJʠŹćīIJʠǂƇʠǣƇƮŭʠǂƇŋIJǂŒIJƮʠƮIJŰŗćģŰǩʠćŻīʠIJ ĤŗIJŻǂŰǩɡʠ¥ƇǣIJƮǂƮćŗŻʠ°ƇŰNJǂŗƇŻƶʠŒćƶʠǂŒIJʠŗŻƶŗŋŒǂ ʠIJǨƫIJƮŗIJŻĤIJʠćŻīʠ
IJǨƫIJƮǂŗƶIJʠǂƇʠIJŻŋŗŻIJIJƮʠǩƇNJƮʠĤƇŰŰIJĤǂŗƇŻʠƇŊʠĤƇŹƫƇŻIJŻǂƶʠŗŻǂƇʠćʠŊNJŰŰǩʠƇƫǂŗŹŗdzIJīʠƶǩƶǂIJŹʠʅʠŋŗǢŗŻŋʠǩƇNJʠƶƇŰNJǂŗƇŻƶʠǂŒćǂʠģƇƇƶǂʠ
ʠŗŹƫƮƇǢIJʠƮIJŰŗćģŗŰŗǂǩʠćŻīʠƫIJƮŊƇƮŹćŻĤIJ ʠŰƇǣIJƮʠĤƇƶǂƶʠćŻīʠƶŗŹƫŰŗŊǩʠƇƮīIJƮŗŻŋʠćŻīʠŰƇŋŗƶǂŗĤƶɡ WHERE OTHERS SEE PARTS, WE SEE A SYSTEM
BearingsBelt & Chain Drives Clutches & Backstops ConveyingDisc & Gear Couplings
MotorsSpeed Reducers & Gearboxes
Monitoring & Diagnostics
piston ller. The sauce is delivered from a holding tank to an overhead hopper and then down into four nozzles, two for each tray. Trays pause and sauce is deposited.
The next piece of equipment in the line, though it isn’t used for every product, is a waterfall grated cheese depositor from Quantum Topping Systems. The trays then move ahead to an Ilapak Delta 3000 shrink lm ow wrapper. The PC-controlled machine features Ilapak’s unique highspeed hermetic sealing technologies and is equipped with long-dwell technology for modi ed atmosphere packaging (MAP).
“It’s a commonly used solution for modi ed atmosphere packaging,” says Faro. “Its gas lances go all the way down the forming tube, and it creates kind of a Venturi that pushes the oxygen out and replaces it with a nitrogen/oxygen atmosphere.”
The ow wrap lm that runs on the Ilapak, supplied by Sealed Air, is Cryovac brand BDF-2060, a multilayered coextruded shrink lm formulated with anti-fog as well as both oxygen and aroma barrier properties. Says Faro, “It’s a very good solution for us for both refrigerated and frozen formats.”
Exiting the Ilapak ow wrapper, trays enter one of three Tecnopool spiral coolers. For customers who want to receive frozen product, where shelf life is nine months to a year, the spiral cooler temperatures are set accordingly. For retailers who prefer fresh refrigerated product with a shelf life of 25 days, again the cooling temperature is set accordingly. Just down-
stream from each spiral cooler is a cartoner—one is a Langen cartoner from Mpac Group, one is from Econocorp, and the third is from ADCO. Frozen trays, whether single-serve or multi-serve, go into a carton. Downstream from all three cartoners, cartons are manually placed into corrugated cases that are erected on a Lantech case erector. Both 6- and 12-count cases are done.
Unlike frozen product, the fresh refrigerated trays do not get individual cartons. Instead, they go into a corrugated case also erected on the Lantech case erector. Multi-serve trays are four per case, single serve are six. These fresh refrigerated trays get weighed and labeled by the retailer, an approach that brings with it a “fresh from our in-house deli” kind of message.
As for the cost of the prepared meals, it ranges widely depending on ingredients. But a tray of Rigatoni and Meatball holding four servings with a net weight of 24 oz is $10.99, and two trays of Italian Style Shrimp Scampi holding four servings each with a net weight of 40 oz costs $18.99.
“The prepared meal line runs either tray size somewhere around 60 trays a minute,” says Faro. “It also gives us an option for continuous motion, but we’ve realized intermittent motion works best because that way we maintain rmer control over everything. Filling two trays per cycle, it’s around 30 cycles a minute, which is an ef cient and comfortable speed. We’re pleased with the solution Orics provided. It was all a matter
of looking at the variety of items we wanted to put into these trays— whether it be meatballs or chicken or vegetables or pasta or sauce or shrimp or whatever—and then automating those processes so that we’re able to put a lot of product out the door without having too much manual labor.”
Now let’s move to the ravioli line, which substitutes a Harpak-Ulma roll-fed thermoforming system for premade trays. Why thermoforming rather than premade trays for these products? According to Faro, it’s
The upstream thermoformer on the ravioli line sends formed trays into the lling station two across. But a servo-driven shuttle system combined with a divider makes it possible to ll four memory buckets at a time, so lling is done four-up. Photo opposite shows 7-oz packs.
an established format for this style of pasta in both the retail supermarket and club store channels. “So it made sense for us to go this route,” he adds.
The multilayer roll-fed forming web fed into the thermoformer is Ecoblock from Evertis. Packages are formed two-across and depth of draw varies widely, but maximum is 3 in. After undergoing pasteurizing and drying, the ravioli is conveyed to an Orics bucket incline conveyor that takes it up to a 14-head combination scale similar to the two on the ready meals line. Thermoformed trays are indexed two-across into the lling station beneath the combination scale, but lling is done four per cycle. “We integrated a servo-driven shuttle system and a divider that lets us ll four memory buckets at a time,” says Orics’ Cohen. “So with every two cycles of the thermoformer, our machine cycles once.”
“This shuttle system is another example of the custom design solutions that we got from Orics,” says Faro. “We have very thin artisanal ravioli, and they were able to design something that operated at an
acceptable pace but didn’t break the edges and was very gentle on the product . That was very important to us.”
After ambient air is evacuated and the package is back ushed with inert gas, the trays have heat-sealed to them a Veritiv multilayer lamination offering both oxygen and aroma barrier properties. Then they pass through a Linx ink-jet coder that puts date code and use-by dates on the lidding material. Next a pressure-sensitive labeler from Diagraph applies a label to the top and bottom of the package. Then they go
through a foreign-object detector from Sesotec and nally go into a spiral cooler. Like the ready meals, the ravioli can be sent to customers either frozen or fresh. And those customers can display the product in the frozen cabinet or they can slack it out and display it in the refrigerated case. Whether it leaves Artisan Chef frozen or refrigerated, secondary packaging involves manual insertion of packs into corrugated cases erected by a Lantech case erector.
With a little more than a year’s worth of production under their belts on both the ready meals and the ravioli lines, Faro and colleagues are pleased with them from an operational standpoint. Worth noting is that they’re not done upgrading and automating yet. In the works is a system that includes an Orics delta-style robot that will pick and place sheets of lasagna dough. So it will be a matter of placing a sheet of dough in a preformed CPET tray, pumping sauce in, then placing another sheet of dough on top of the sauce, and then pumping another sauce, and so on until the tray has multiple layers of dough and multiple layers of ingredients, including shredded cheese— all done by automated systems. Key to this development is a specialized vacuum suction cup that makes it possible to pick a piece of lasagna dough from a conveyor belt. PW
The new UC18GS series combines the advantages of ultrasonic technology with powerful features to create a sensor solution that meets virtually any application challenge.
Building on experience. Driving technology. Maximizing performance.
UltrasonicSensor
Series UC18GS with IO-Link
Sure, the pack redesign was an aesthetic improvement. But it also allowed the brand to consider more sustainable material options, like PCR in both the glass primary pack and the paperboard multipack carton.
Petit Pot founder Maxime Pouvreau has been bringing classic French pot de crème desserts to the masses in the U.S. since 2014. The brand’s French desserts are thoughtfully crafted from simple, USDA organic, clean ingredients, including real vanilla from Madagascar and dairy from Clover in Sonoma, Calif. What started as a side business nine years ago is now thriving, with product available in more than 5,000 retail outlets across the country including Whole Foods Market, Sprouts, Costco, Publix, Wegmans, and Amazon Fresh.
versus throwing them away,” says Eugene Lin, chief marketing of cer at Petit Pots.
The undecorated jars are either multipacked in 2-ct packs of twoside printed paperboard overwrap, or single-packed with single-sided printed paperboard overwrap. They’re then case packed into printed e- ute corrugated cases.
Not long ago, in August 2022, Petit Pot was poised to launch a brand refresh. In doing so, Pouvreau saw an opportunity to further improve its sustainability pro le, while continuing to delight consumers with aesthetics.
“Our objective for the packaging redesign was to ensure that we kept the best elements of our beloved brand while improving on product understanding and appeal, as well as shoppability across avors and platforms,” Lin says.
The design refresh was to stretch across all its product lines, with redesigned glass jars made of 55% post-consumer recycled glass material that would be 35% lighter than the legacy jar. It would also include new, eye-catching packaging graphics on the paperboard. For instance, in a nice touch, the barcode on the label is designed to be the shape of a jar and spoon.
With this redesign, Petit Pots aimed to ensure it kept the best elements of the brand, while improving on product understanding and appeal, as well as shoppability across avors and platforms. Improved sustainability pro le was another bene t.
To replicate an authentic French pot de crème experience, Pouvreau sells his product in unlabeled, hot- lled glass jars from a France-based glass supplier that wasn’t revealed. The format is a nod to the traditional French packaging format, but the company says it also aligns with Petit Pot’s commitment to sustainability.
“Many of our consumers love to reuse our glass jars for home use,
Beyond strictly aesthetic changes, there were structural improvements to the new paperboard overwrap, too. The old design had the glass jars only “clamped” by half-enclosed paperboard. Now they are fully enclosed in a four-side wraparound.
Supply chain issues almost derailed the relaunch, as Petit Pot team’s legacy paperboard supplier and printer couldn’t meet the brand refresh deadlines. But Petit Pot reached out to JP Graphics of Santa Clara, Calif., and Monadnock Paper Mills (MPM) of New Hampshire, who together were able to deliver the printed paperboard secondary packaging and printed kraft corrugated within a week, and in time for the planned launch.
The 18-pt 100% PCW recycled ber Envi Performance board from MPM
The Velocity Series™ is the ultimate advancement in Bulk Can Depalletizing technology. Available in a variety of models, Sentry once again brings their unmatched reputation to the market to create unprecedented throughput. Contact a sales professional today for an individual consultation to learn more about the
The undecorated jars are either multipacked in two-count packs of two-side printed paperboard overwrap, or single-packed with single-sided printed paperboard overwrap. They’re then case packed into printed e- ute corrugated cases.
used in this application is FSC certi ed, produced carbon neutral, and made with 100% renewable Green-e certi ed wind-powered electricity.
Paperboard printing is done by JP Graphics in a four-color process on
YOU DESIGNED, TESTED, PRODUCED.
an HP 12000 press. An aqueous coating is added to protect the board and die cutting of the board into wraparound sleeve strips is done thereafter thereafter. According to JP Graphics’ President, Joan Escover, the converter made several cutting dies for this project, but also can ZUND cut ondemand, if the need for a specialty or short-tun size or shape should arise.
Even on this limited run Petit Pots project, using Envi Performance translated into signi cant environmental savings. According to The Environmental Paper Network’s online calculator tool, when compared to (the legacy) commodity board Petit Pots had been using, 49 pounds of solid waste were not produced, ve million BTUs of energy were not consumed, 3,700 pounds of wood was saved, 6,280 net pounds of GHG CO2 were avoided, and 2,500 gallons of water was not wasted thanks to MDM’s paper substrate.
“The consumer reaction to the look and feel refresh has been overwhelmingly positive,” Lin concludes. “As evidenced by our growing fanbase on social media like Instagram and TikTok, more people than ever are discovering our brand for the rst time while we maintain a strong core of passionate brand loyalists from before the refresh.” —Matt Reynolds
Your focus is your business. What’s ours? Solutions that get your product to your customers well protected * !ƣ%!*0(5Ł+.'%*#3%0$1/)!*//,!* %*#(!//0%)!+*0.*/%0,'#%*#* )+.!0%)!,!."!0%*#5+1.,.+ 10/Ł %/+2!.%#*+ !* !4,(+.!+1.0.*/%0,'#%*#/+(10%+*/Ł
While this latest batch of IoPP AmeriStar Award winners is neatly organized into categories, they all in fact are advancing and balancing multiple, sometimes competing attributes like eye-catching design, enhanced sustainability profile, and improved functionality.
A panel of judges from diverse packaging industry segments evaluated package entries across 17 categories for professional and student awards ( nd student award winners at pwgo.to/8040). Annie’s, a General Mills brand, came away with the program’s prestigious Best in Show for an evolving application that certainly has roots in sustainability, but not at the expense of other key elements like product protection, a nifty appearance, and user-friendly convenience and function. This multipronged approach seems to be a permeating theme among this year’s winners—sustainability might be king, but brands and their suppliers are moving the ball forward on multiple fronts, all at once. These are the winners of the 2023 Professional AmeriStar Awards.
Annie’s Certi ed Compostable Printed Shelf Stable Mac & Cheese Cup (1) from General Mills—Judges say that this cup revolutionizes singleuse packaging with technical innovation. Using wet molded ber that’s not traditionally used for shelf-stable products, it equals polypropylene thermoform in functionality. Advanced features include direct exographic printing of high-quality graphics, grease and water protection, and an improved sustainability pro le (more on that below). An enhanced consumer experience via user-friendly design includes improved convenience, comfort, and heat retention. Facebook research guided a consumer-focused communication strategy, highlighting the cup’s appealing look and emphasizing its eco-friendly bene ts. Initially launched in March 2021, the package continues to improve based on real-world feedback, earning it a Best in Show award now in 2023.
In addition to its Best in Show win, this cup also earns a nod in the Sustainable category (other winners listed on page 38) for addressing consumer demands for eco-friendly packaging. By replacing traditional thermoformed PP cups with molded ber technology, the company reduced its carbon footprint by 45%. The cup also features a renewable spray coating for grease and water resistance. The compostable nature of the cup eliminates the need for rinsing, providing an environmental-
ly friendly disposal option. Plus, the clever marketing strategy emphasizes the cup’s paper-like appearance and environmental bene ts. The pack exempli es technical advancement on several levels, from form, to function, to sustainability.
Bobbi Brown Luxe Lipstick Repack from Estée Lauder Companies (ELC)—Deserving of an AmeriStar award for its technical and ecofriendly excellence, this package’s modern design is inspired by the NYC skyline. With sleek, sharp lines and a visually elongated form, the package elevates the lipstick’s appearance. Notably, it prioritizes sustainability through a re llable, all-aluminum, and magnet-free mechanism, featuring 90% Post-Consumer Recycled (PCR) content in the outer cap and base parts. This is another instance of packaging designers working with multiple goals in mind, and more importantly, delivering on several of them at once.
Sharpie Ultimate Collection Pack from Newell Brands and WestRock—This collection pack reimagines packaging with technical brilliance, judges say. Bold, bright, and reusable, it highlights upgraded materials, hinged wings, and a striking design to enhance the user experience. Its unique shape and premium structure create a powerful shelf impact, effectively conveying the category giant Sharpie brand.
Per ex’s Grab-N-Go Shrink Bag for Bulky
Meat and Poultry (2) from Amcor Flexibles
North America—Judges say that this package’s technical prowess and market impact rede nes the industry by offering the rst-ever effective shrink bag with integral handle for heavy meat and poultry products. With a simple, strong three-hole handle and high-impact printing, it provides brand differentiation and convenience for consumers. The innovative one-piece design streamlines production, delivering signi cant savings and sustainability bene ts.
—Judges say that this lines production, delivering signi cant sav-
ELIMINATE Product Build-Up
ELIMINATE Bacterial Harborage
The new patented SSV-XP Drum Motor features an interchangeable profiled sleeve that can be removed and exchanged for another profiled sleeve to match the belt required on the conveyor without changing the drum motor.
SSV Drum Motors drive modular conveyor belts without using sprockets, eliminate gaps and crevices, and reduce washdown time and water usage by 50%.
Designed for 80,000 hours of continuous operation before maintenance, SSV Drum Motors increase throughput and reduce operational costs.
IP69K-rated Sealing System Washdown Up to 3,000 psi
Thermoformed PCR Smartphone Screen Protector Installation Tool from Plastic Ingenuity and Otter Products—The judges probably had scratched smartphones in their pockets, or maybe their hands, when they evaluated this entry. Here, an innovative redesign enhances the user experience by simplifying smartphone screen protector installation—the package itself becomes a functional aid to screen protector application. The versatile tray accommodates various phone sizes with precision, reducing SKUs and cost. The eco-friendly PCR PET material furthers the package’s appeal, aligning with Otter’s commitment to sustainability. This makes for a functional, user-friendly, and environmentally conscious packaging solution.
Sol de Janeiro Rio Deo Deodorant Stick from Viva Healthcare Packaging—This package earns an AmeriStar award for its cheerful, sustainable, and functional design that supports the circular plastic economy. Using in-mold label (IML) technology, it boasts high-de nition, bathroom- and shower-friendly decoration on 100% PCR material. The re ll cartridge system enhances usability, enabling easy re lls and reducing plastic waste by over 50%, according to the entry.
The Crystal Seal Cravings PET deli cups (3) from Placon—These EcoStar PCR PET cups offer clear product visibility and a patented tamper-evident base-to-lid closure mechanism for enhanced safety. Their
clever paperboard sleeve enables vertical standability while providing marketing space. Also, the package’s split-apart feature enhances consumer versatility and efciency in manufacturing and logistics.
QUADFLEX Recyclable Package (5) from Nestlé Purina and ProAmpac—This interesting package solution caught judges’ eyes with its transition from multi-layer to mono-material packaging, reducing virgin plastic use by one-third. The patent-pending mono-material is prequali ed for recycling programs, providing enhanced sustainability and maintaining machinability on existing equipment. The pouch offers a premium look with excellent branding opportunities and environmental bene ts, including recyclability in polyethylene streams—a win-win solution for sustainability and performance in the packaging industry.
unique design facilitates stacking, easy use, and reusability, making them perfect for on-the-go deli and prepared food products. Judges say this is cup is a game-changer in convenience and safety for both consumers and retailers.
Kirkland Signature 13% PCR Saddle Packs from TC Transcontinental Packaging—Incorporating 13.4% PCR content without compromising package performance, this innovative packaging solution diverts plastic waste from land lls. The multi-layer coextruded lm maintains product protection and freshness while supporting a circular economy, aligning with Kirkland’s commitments to sustainability.
Old El Paso Tortilla Pockets Package (4) from General Mills—Earning an AmeriStar for its advancements in protecting product integrity and extension of shelf life, this package’s U.S.-patented design combines a rigid polymer bottom with a exible top, offering eight tortilla pocket products in two cavities, each sealed with an easy-peel opening. The
Mrs. Meyer’s Clean Day Foaming Hand Soap Starter Kit (6) from SC Johnson Lifestyle Brands—With up to 99% reduced plastic use compared to single-use bottles, this durable glass hand soap bottle is in nitely recyclable and re llable. The packaging includes clear usage instructions and aesthetic details, making it user-friendly and uniquely Mrs. Meyer’s. The kit caters to both e-commerce and retail channels with a consistent unboxing experience, and minimal dunnage highlights the strong and compact design. Another instance of the wider theme, this pack represents a seamless combination of sustainability, functionality, and appealing design.
McCoy Dunnage-Free IBC Liners for Bulk Liquid Aseptic Products from Amcor—This liner changes the industry narrative and advances bulk liquid transport, making it an AmeriStar-winning entry. By eliminating the need for extra secondary packaging, it reduces waste, costs, and carbon footprint. Advanced material science and a patent-pending design make it two times stronger than typical aseptic liners, ensuring product integrity during high-abuse transport, judges say.
SEEkey Transit Tray Optimization from Integer This tray was developed for wire spools and eliminates the popping/ ying issue caused by traditional undercut snaps, providing enhanced control and security and alleviating a user pain point. Its thin, 25-mil design reduces plastic usage, achieving a 44% reduction in material and 24% cost savings. The tray’s versatility in locking and
unlocking offers ef cient product organization, while dual-nested spacing levels reduce secondary packaging and improve sustainability. Plus, its continuous stack design ensures strength and passes rigorous testing requirements.
CapSure sterile barrier packaging system (7) from Guardian Medical USA Inc.—With high marks awarded to it for performance and economy, this packaging system uses impact-resistant Tritan co-polyester to deliver superior protection with just a single barrier, reducing the package’s size and footprint. The intuitive design enhances aseptic handling and identi cation, while the pre-validated 10-year shelf life offers supply chain exibility. Eco-friendly and versatile, it is a game-changer for orthopedic device packaging judges say, providing a complete and ef cient solution.
Titan 2.0 Cord Cutter Tray, Retainer, and Triangular Stand from Prent Corp. and Standard Bariatrics, Inc.—This thermoformed solution earns an AmeriStar award for a streamlined package that reduces material usage, carton size, and overall weight, optimizing work ow and sav-
ing valuable time during operations. The complex single-part design protects the device during transportation, doubles as a stand for prepping (again, the pack itself serves an extra functional purpose), and prevents accidental activation.
Scotch Cushion Lock Protective Wrap from 3M—Engineered with a proprietary hexagonal pattern inspired by kirigami [a folded-paper art, similar to origami], this wrap transforms a at sheet of paper into a three-dimensional wrap that cushions, immobilizes, and conforms to items for proven protection during shipping, moving, or storage. Its unique design maximizes space ef ciency, reduces plastic waste, and simpli es the packing process while offering exceptional protection and sustainability, according to judges.
RIO Molded Fiber Fly Line Spooler (8) from EnviroPAK—An innovative and environmentally sustainable solution deserving of an AmeriStar award, this package is made from 100% biodegradable recycled paper. It functions awlessly, judges say, spooling all line diameters and lengths up to 120 ft. By replacing polypropylene, it reduces single-use plastic waste signi cantly, meeting RIO’s stringent quality and eco-friendly requirements while leaving no trace in the environment if it falls into the water.
GREENIS Dispenser (9) from Dermalogica and Coradin—Judges say this pack is an e-commercefriendly, consumer-friendly, and environmentally responsible solution that’s made mostly from recyclable polypropylene with minimal TPE, offering precise dosing for consumer convenience and protection for the product’s active ingredients. The lightweight design reduces shipping costs, while its environmental impact is minimized using PCR plastic and optimized packaging weight.
Liberty Coca-Cola Beverages’ Mini KeelClip from Graphic Packaging International—Made from renewable plant-based ber, the sustainable paperboard clip replaces plastic rings on mini-can multipacks. The recyclable packaging maintains can orientation, offers easy removal, and is fully recyclable in paper waste streams. This package signi cantly reduces plastic usage, aligning with Coca-Cola’s “World Without Waste” vision. Its eco-friendly design, brand impact, and efcient production earned this package an AmeriStar award. Visit pwgo. to/8041 to read Packaging World’s coverage of this pack.
Paper-based, Recyclable Chocolate Bar Wrappers from Mars Wrigley—Certi ed by the Forest Stewardship Council (FSC), this pioneering wrapper eliminates 360 tons of plastic waste and aligns with industry sustainability commitments. It incorporates a mechanical recycling loop through curbside recycling in Australia, and its extensive testing into odor, product taint, residual solvents, migration, and barriers
for water vapor and oxygen in various climates ensure its performance matches traditional materials. Visit pwgo.to/8042 to read Packaging World’s coverage of this pack.
Pentel RSVP PaperBlister Package from Sonoco Alloyd—Made entirely from paper, this package is highly sustainable from production to shelf. It is plastic-free and recyclable in curbside paper streams, and the retro t of existing equipment saved costs and prevented old machinery from going to land lls. The at-pack design allows for more ef cient shipping, reducing environmental impact. It serves as a 360deg marketing billboard while ensuring product protection, making it a deserving winner of an AmeriStar award in the sustainability category. Visit pwgo.to/8043 to read Packaging World’s coverage of this pack.
Axe Green Geranium Deodorant Stick (2.6 oz) (10) from Viva Healthcare Packaging—The eco-friendly nature of this package was a clear winner to judges in the sustainability category. It features in-mold label (IML) decoration, 100% PCR polypropylene, and is fully recyclable. With no virgin plastic, over 95% recycled material, and alignment with Unilever’s sustainability goals, it sets a new standard for eco-friendly deodorant packaging. The vivid artwork, ease of use, and environmental bene ts make them a top choice for eco-conscious consumers. —Matt Reynolds
Though the leadership at PharmaMed Automation is steeped in robotics technology, robot deployment was often deemed out of scope for the integrator’s many custom, one-off, “hard automation” projects. Then a project came along in which the client had an automation request that would change the game for PharmaMed projects going forward.
Integrator and OEM PharmaMed Automation was asked to build case labeling equipment for a manufacturer of liquid level sensors and alarm systems. The client requested a fast, full-color, on-demand label printer and a fast, exible, and precise means of af xing the labels. Answering the call, PharmaMed designed and built a self-contained labeling cell with a color inkjet label printer, a 6-axis robot, a custom label track, custom tool head, and a conveyor, with all logic residing in the robot’s built-in controller. This experience, with a speci c request to investigate Epson robotics and printers, snapped PharmaMed out of what it the integrator now considers to be an antiquated devotion to single machines accomplishing singular tasks.
“We liked to call it hard automation because it’s hard to do,” jokes Justin Mattson, Sales Engineer for PharmaMed Automation. He’s rif ng on that traditional process where factory integrators allocate machines and equipment to single, xed tasks. “Hard automation is all about rigidity, about building something that does one thing, and it’s harder because there’s no exibility.”
Dustin Hanson, PharmaMed president, agrees. “It’s frustrating because there are so many applications where a SCARA or 6-axis robot would be the way to go, but the budget doesn’t allow it.’”
Mattson’s and Hanson’s experience with Epson Robots and Epson Colorworks began just over a year ago, in 2022, when a liquid level sensor and alarm manufacturer client distinctively asked them to look at Epson’s ColorWorks CW-C6000P Color Inkjet Label Printer in combination with an Epson VT6L All-in-One 6-Axis Robot to print and apply labels. Since that introduction, the integrator has used 10 more Epson robots in projects for other clients.
“With Epson all-in-one platforms, our whole operation has opened up,” Mattson says. “Today, when we quote a project, we focus our efforts on Epson rst. Our go-to is Epson, without a doubt.”
Hanson describes PharmaMed Automation, based in Fargo, North Dakota, as a small and nimble engineering company that specializes in the most challenging factory automation projects.
He says that, when he founded PharmaMed with partner Walt Stew-
art in 2012, “the focus of the company was the manufacturing of custom, generally non-robotic, hard automation cells for pharmaceutical and medical device companies.”
Yet Hanson was intimately familiar with robotics and had worked with almost every brand of industrial robot at one time or another during his career. “Actually, at the company I was at before we started PharmaMed, we developed our own SCARA robot and the software to control it. It was the rst SCARA robot developed on the Rockwell platform.”
self-contained labeling cell. The automation solution
and applies labels to an assortment of corrugated cases.
He explains that “the job we do is very dif cult because we’re always trying to solve some new problem that no one else wants to touch. It’s a high risk, high reward type of business.”
In 2018, he and Mattson founded another company, Vektor Designs, to serve a more general manufacturing base. They merged the two rms in 2022.
With labor becoming scarer and more expensive, and production requirements always getting more strenuous, more CPGs and their integrators are turning to robotics. True robotic automation can sometimes be seen as a bridge too far for interested CPGs, but that’s very rarely the case, in reality. Find out how fast your robotic packaging automation ROI could be, and see how to justify it to management or procurement, to improve and future-proof your packaging operations.
Orange County, Calif. Sept. 27, 2023
Chicago, Oct. 3, 2023
Philadelphia, Oct. 26, 2023
Houston, Nov. 2, 2023
To learn more and register to attend, visit pwgo.to/8034 or scan the QR code.
Working under the Vektor brand, Hanson and Mattson took on this new client, the manufacturer of liquid level sensors and alarm systems. The client packages these sensors in corrugated cases of about 8 x 8 in. in length and width, and either 6 in. or 8 in. in height. It then labels these cases with a self-adhesive label that’s 6 in. wide and 4 in. tall.
Even though the switches are sold through commercial plumbing contractors, the client had been wanting to go to a full-color label to set itself apart from competitors. The company also wanted to create a more consistent look than is possible with hand-applied labels.
Most importantly, the client was facing a huge staf ng challenge, with a workforce that had dropped from about 700 prior to COVID-19 to just 400, so an automated work ow was highly desirable.
The client, Mattson says, had seen the Epson ColorWorks printer and wanted to use it in this application.
“You can buy pre-printed labels and put them onto an off-the-shelf labeling machine, but then every label on the reel is going to be the same,” he explains. “But this client might box up eight of their switches, then box up 10 more of another model, and so they need the exibility to send any print run of any quantity to the system.”
Mattson also says the CW-C6000P is fast and reliable, able to print, trim, and peel labels 8 in. wide and any height at up to 5 in. per second. Completely digital, it can switch from one label design to another without pausing. Furthermore, it comes standard with an I/O port so it can easily be integrated into an automated system.
“Beyond the label printing,” Mattson adds, “they saw that it was a better option for them to use a robotic arm to pick and place it than any sort of xed machine.”
While hard automation is traditionally less expensive than robotics, the prices of the Epson robots were attractive to the client and the Vektor/PharmaWorks design team. “Once you can buy a high-quality SCARA for under $10,000, or a 6-Axis for under $15,000, that changes things,” Hanson says.
The team designed a self-contained cell with the ColorWorks printer, a custom-built track to carry the labels, and a ceiling-mounted VT6L robot to pick up each label then apply it to the case, which is carried into position by a Dorner conveyor. The team designed and built their own pneumatic toolhead, which not only applies the label but then backs off and taps it to make sure it’s rmly applied. Then the conveyor brings up the next case.
“We have a sensor embedded into the toolhead to verify that a label is present, and then we verify that it’s been applied to the case,” Mattson says.
For now, he says, the client always applies the label onto the same position on the side of each case, but by using a robot rather than a xed labeling solution, they know they’ll be able to vary the case size and placement with just a simple software change.
The client, Mattson says, originally ordered two of these self-contained labeling machines, but when they saw how well it worked, they soon ordered a third.
Since starting on the project, PharmaMed has used Epson robots with three other clients, including two where they integrated Epson with the Siemens automation platform and one with Rockwell.
“We actually used the Epson controller to power the entire labeling cell, but it’s a small cell with a couple of air cylinders, the conveyor, and this printer. But really when you start using a robot with the major platforms, that’s where the rubber hits the road,” Hanson says. “For us that’s big, and it’s mainly because we’re putting Epson robots into projects where we would not have used any robot in the past. You get to a price point where quantities can go up and you can get volume. Volume, in turn, is how you can get your cost down. I know that’s Epson’s play, and it’s our play as well… the reason we fell in love with the product.”
There are good and bad points with every product and every business, “but we know our pain points,” Hanson says. A big source of pain is the dif cultly of designing and building xed automation solutions. “We try to get rid of pain, and so we’re willing to make a change if we nd something that works well.
“An Epson robot,” he adds, “has the features and the price point we need. It’s a good, reliable product. Programming is straightforward using the Epson RC+ environment, and it integrates well with Siemens and Rockwell, which is important for us. And it has great support.”
Would they recommend Epson for other clients’ and automation integrators’ packaging projects?
“Yes,” Hanson says. “For sure.” —Matt Reynolds
UP TO REDUCED WEIGHT VS. CONVENTIONAL ALTERNATIVES
35%
MetsäBoard Pro FBB Bright is up to 35% lighter than conventional paperboards, while retaining the same quality and rigidity.
The Borrow A Cup pilot is built on a reusable packaging platform using an in-store bin that scans and accepts empty cups returned by a consumer, washes them, and returns them to circulation. Consumers can earn rewards based on their scanned cup data.
Starbucks launched a reusable packaging beverage cup pilot program in 12 of its stores in Napa and Petaluma, Calif., just the latest example of what the company calls its “resource-positive” commitments around sustainability. Coffee connoisseurs getting their daily x in those locations will be offered the Borrow A Cup option for the 10 weeks between August 14 through October 22, so results or success metrics weren’t yet available at press time.
consumers return their borrowed cup, they will also have the option to register online with TURN to earn points for every Borrow a Cup return and prizes through TURN.
Notably, the Borrow A Cup program won’t be the only option for consumers at these Starbucks locations during this pilot. Consumers can also bring their own personal cup into the café or through drivethrough for re ll, an extension of an existing own-cup program. To help encourage folks to bring in their own, clean personal cups, they will receive the
Starbucks tapped reusable packaging pioneer TURN Systems, formerly known as Globlelet, for the pilot, using the company’s high-tech collection bins to understand cup return behavior. TURN is a reuse platform designed for scale—through a fully circular system, TURN offers integrated solutions to end single-use plastic. Starbucks developed and provided the recyclable polypropylene cup for the pilot, but it is designed to work within the TURN’s existing platform, which includes mobile washing systems, smart bins, and incentive systems. Fitted with patented digital tracking technology, the Starbucks-developed reusable cups are prominently branded with the company logo. The other elements of the TURN platform also were developed with co-branding in mind, making the whole system visually seamless.
Here’s how the California pilot model works. A consumer orders his or her drink as usual at the dozen participating Starbucks, either in the café, drive-thru, or via mobile order and pay. Their hot or cold beverage will be then served in a “borrowed” cup. When nished with their beverage, the consumer returns the cup by scanning and dropping it into a contactless return bin, designed by TURN. The cup will be professionally washed and sanitized, soon ready to be used again. And when
standard $0.10 off with an additional 25 Bonus Stars for Starbucks Rewards members. Also, consumers who opt to sit and stay in the café can choose to receive their beverages in what Starbucks calls For Here Ware—durable ceramic or glass cups.
Still, no single-use disposable cups, whether plastic or paper, will be available during the pilot—every beverage made at these 12 stores will be prepared in reusable packaging by way of a personal cup, durable table ware, or in the new, reusable Borrow A Cup that consumer
Package printing and personalization made easy
Inkjet print systems for high speed package personalization
Print on corrugate, cartons, mylar pouches, blister packs, clam shells, and other packaging materials
Personalize with variable data such as barcodes, serial #'s, lot codes, expiry dates, graphics and other compliance information.
Minimize waste with print inspection and accurate job counts
Minimize setup time with job storage and quick recall
can take with them and return in smart return bins. That is, of course, unless a consumer chooses to Borrow A Cup, but then isn’t suf ciently motivated to return it within the system.
But even if not recycled within the Borrow A Cup system, the Starbucks-designed plastic cups used in this system are made from recyclable mono-material polypropylene (PP), which can be curbside recycled in Napa and Petaluma. Should a consumer bring the Borrow A Cup home without returning it to the bin, then choose not to return to the store to return it, the cup still can be recycled. Of course, this defeats the purpose in that it eliminates the possibility of future reuse cycles. How many cycles can be expected from each cup? Given the Borrow A Cup is a prototype and Starbucks is still learning and adjusting to develop a future reusable cup, that remains to be seen.
Clearly, there are a lot of consumer behavior variables and many different potential courses of consumer action for a foodservice retailer to consider and factor into any system. Despite these challenges, the coffee giant has un aggingly shown it believes in reusable packaging. Spokespeople say that reusables tests help drive progress toward Starbucks commitment to reduce waste sent to land ll. Starbucks says it’s committed to cutting its waste footprint in half by 2030 and recently updated its target to include a commitment for all consumer packaging to be reusable, recyclable, or compostable.
“Our latest round of reusables tests around the world contribute to our goal for all customer packaging to be reusable, recyclable, or compostable in the future. We know our partners and customers care about the planet, and we’re proud to offer them ways to join us in in making sustainable choices in their everyday lives,” says Amelia Landers, VP, Business Strategy, Partner & Customer Solutions at Starbucks.
Starbucks has conducted reusables tests in more than 25 markets around the world with more planned in the year ahead. The test in California is the latest Starbucks test in U.S. with additional reusables tests completed in Colorado and ongoing in Arizona. The SODO 8 store inside Starbucks’ Seattle headquarters has been serving 100% of beverages in reusable cups since March 2022.
“These types of tests are extremely important so that the company can understand all the different ways we can make an impact and move towards goals that we have set for the future,” says Tonya Palacios, Starbucks district manager, who leads the California stores conducting the Borrow A Cup pilot. “I’m optimistic that we will execute the test at a high level and gather lots of feedback that will in uence the next step in reusable cups and our sustainability goals.”
Choosing reusables is a new habit for a growing number of consumers. Starbucks’ behavioral science-based research shows ease and convenience are foundational. Personal cup washers were developed in partnership with store partners in the Starbucks Tryer Innovation Lab and created to ensure convenience for consumers bringing their own cup. In participating stores across the Arizona State University campus, consumers can wash their personal cup or a returned Borrow A Cup right at the counter in the time it takes to complete their order.
Since May, Starbucks has been conducting this 100% reusables test at participating ASU campus stores and every consumer who brings in their own personal reusable cup or reuse a Borrow A Cup from a previous visit can receive a $1.00 discount on their beverage order. Consumers can also return their Borrow A Cup to special return bins around campus that were designed by the ASU Circular Living Lab using the equivalent of 1,350 repurposed single-use cups. PW
Emerson’s IIoT solutions and analytics software detect compressed air leaks saving manufacturers over 20% in energy costs.
Learn more at Emerson.com/Sustainable-Automation
Arti cial Intelligence (AI) has emerged as a disruptive technology in nearly every industry and sector imaginable, and graphic design is no exception. For entrepreneurs Jorge Olson and Sandro Piancone, founders of hemp-infused products company Hempacco, AI has become another valuable tool in their well-stocked packaging design toolbox. Most recently, AI assisted Hempacco in solving a formidable challenge while designing the graphics for a new gummy product for none other than rap icon Snoop Dogg.
Based in California, Hempacco develops and manufactures hemp-based products under its own brand as well as through joint ventures. Products include vapes, hemp cigarettes, hemp blunt smoking papers, gummies, capsules, pills, chocolates, shots, tinctures, and a line of beauty products and neutraceuticals, all produced at Hempacco’s three facilities—two in San Diego and one in Tijuana, Mexico. Among Hempacco’s celebrity partnerships is a joint venture company, HPSD, Inc., with Snoop Dogg, formed to create a line of hempderived products under the Dogg lbs brand name.
Since launching its first hemp cigarette product, Real Stuff Hemp Smokables, in 2017, Hempacco has produced all packaging graphics in-house, led by Olson. “For our packaging, I’m privileged to work with an incredible team of Mexican American artists from the Tijuana-San Diego border region that make me look good,” says Olson. “Hempacco has an unfair advantage here because of our location and relationship with artists. You see, my mother is an artist, her husband just retired from teaching art at the university, and he’s an art curator and artist, and both are my mentors. My cousins are artists, and I belong to a community of border artists that help us develop a unique style that can only come from a vast artistic community.”
Given this tremendous wealth of artistic resources, it may seem curious that Olson looked to AI for help when designing the packaging for the first product under the Dogg lbs brand. The most problematic part of the design, however, was the most important element: a picture of Snoop Dogg.
“We had the most challenging time finding one that Snoop liked or one we could buy the rights to use in our packaging,” explains Olson. “After six weeks of looking for photos, our project was six weeks late going into production. I generated over 200 images using AI for Snoop and the packaging idea. I thought I had some winners, but Snoop and Tiffany Chin, Snoop’s CEO of everything hemp and cannabis, shot down the concepts. That’s when I decided to go to the ‘Big Guns.’”
The Big Guns Olson refers to was his friend, Gustav Mayoral, owner of AI company Code Agents, who Olson says “has the rare combination of being a software architect and a professional photographer,” as well as an award-winning artist. He adds, “Gustavo ran his proprietary algorithm to generate Snoop images in different styles and poses. This process took a few days until, jackpot, we had the perfect image that matched the Dogg lbs brand.”
Olson shares that Mayoral’s process is the first to train AI to learn the product—everything from details of the product to imaging and design styles. Once that’s achieved, the platform is instructed to build deliverables, such as images, art design, and copy. From there, Hempacco incorporates a normal workflow for the artwork, involving its full graphic design team.
The final artwork for Snoop Dogg’s Dogg lbs Dog Treats Gummies pouch package includes the AI-generated image of Snoop Dogg, edited and enhanced by Hempacco’s graphic designers, against a deep purple background decorated with a gold paisley-style pattern. At the bottom is a band of color, either blue, purple, or red, corresponding respectively to the three flavor varieties available, Blue Raspberry, Grape, and Cherry Lemon. A QR code links to an augmented reality feature, Snoop Talk, that allows the consumer to view an AR-generated version of Snoop moving and talking. Of its use of AI, Olson says that thus far Hempacco has used technology to scale its traditional creative process to create assets, including logos, art conceptualizations, human-like and product imaging, AR, 3D rendering, and voice generation. “In the future, as we develop our toolset, we will be automating even further,” he adds. “For example, in our pipeline, we’re working towards the ability for AI to test packaging online, getting hundreds of thousands of inputs from our target market in a week, redesigning, and testing again until we get the best results, even pre-orders, from our perfect consumers.”
Answering the million-dollar question as to whether AI will ultimately negate the need for graphic designers, Olson says he doesn’t see that happening. “I see designers working differently, just like computers didn’t replace people, they made people more effective,” he explains. “Right now, Gustavo of Code Agents and I are the ones that use AI to program what we need and then give it to the designers to change, fix, enhance, brand, etc. In the future, designers will do all of that on their own. It will be part of the job to learn AI prompt programming.”
—Anne Marie MohanSelig Group’s new website consolidates its container sealing and venting technologies as well as its flexible packaging solutions.
Indorama Ventures Public Co. and Carbios signed a non-binding Memorandum of Understanding (MOU) to form a joint venture for the construction of the world’s first PET bio-recycling plant in France.
Silgan University-College of Closures’ online Learning Management System (LMS) is a learn-atyour-own-pace educational platform that allows students to complete three closure courses from their home or office.
3D[WRQȇVKLJKHɝFLHQF\GU\LQJDQGEORZR VROXWLRQVLPSURYHWKHGU\LQJRIFDQVDQG bottles for high quality labelling and coding, ZKLOHXVLQJȂOHVVHQHUJ\ȂW\SLFDOO\ JLYLQJDRQH\HDU52Ζ$QGZLWK3D[WRQȇV PowerDry™'U\LQJ6\VWHP\RXFDQVLJQL FDOO\ UHGXFHGRZQWLPHDQGTXDOLW\UHMHFWV
ABB’s new robotics packaging and logistics headquarters, located in Alpharetta, Ga., will serve as its dedicated center for robotic automation solutions in the logistics and packaging industries.
Septimatech Group celebrates its 30th year in business and appointed Eric Murray operations leader.
Nova Chemicals’ new Connersville, Ind., mechanical recycling facility will be managed by Novolex Holdings, LLC. The collaboration will increase the speed with which Nova ramps up its supply of SYNDIGO rPE.
Duravant expands its food processing solutions portfolio with the acquisition of PPM Technologies from Stonehenge Partners.
ThePackHub launched the Packaging Startup Awards, a global competition that will determine winners across six categories: alternative materials, connected packaging, increased functionality, online, refill and reuse, and waste reduction.
Weidmüller Inc., USA broke ground on a new engineering, production, and warehouse facility at its current Southlake location in Chesterfield County, Va.
3D[WRQȇVSRZHUIXODLUGHOLYHU\GHYLFHVDQG V\VWHPVUHPRYHGXVWSDUWLFXODWHVDQGGHEULV H HFWLYHO\DQGHɝFLHQWO\$QGLIVWDWLFFOLQJLV DQLVVXH3D[WRQȇVΖRQL]LQJ5LQVLQJ6\VWHPV GLVVLSDWHWKHVWDWLFFKDUJHVRQWKHWDUJHWHG VXUIDFHVDQGWKHQEODVWVWKHFRQWDPLQDQWV DZD\XVLQJD3D[WRQ3;6HULHV%ORZHU
Kasie Fairbarn, Windmoeller & Hoelscher Corp., was elected co-chair of FPA’s Emerging Leadership Council (ELC).
Brian Hutton retired as president of Columbia/Okura and Fred Robinson was appointed president.
Laurent Pierucci was named operations director of Synerlink, a BW Packaging company, and will oversee its operations in five of its six locations in France.
Ken Hundley joined Triangle Package Machinery as regional sales manager–Lower Midwest.
Waheed Chaudhry was appointed director of primary packaging for JLS Automation.
Jim McKee was named sales manager for MG America’s Processing Division.
The API Group and Accredo Packaging named Jonathan Quinn global vice president of marketing and sustainability.
Aurelio Banda was named president and chief executive officer of Turck USA.
Frank Yiannas, former FDA deputy commissioner of Food Policy & Response, joined Wiliot, an ambient IoT data platform company, as a strategic advisor.
ProMach promoted Jason Angel to global vice president of Sales and Business Development – Tray Packaging.
The PX-series of centrifugal blowers, by Paxton 3URGXFWVR HUVXQPDWFKHGEORZHUHɝFLHQFLHVDV KLJKDVȂPHDQLQJ\RXȇOOXVHOHVVHQHUJ\ RYHUDOOΖQDGGLWLRQWRWKLV3D[WRQEORZHUVFRPH ZLWKDQXQPDWFKHGWKUHH\HDUZDUUDQW\
513-891-7485
PAXTONPRODUCTS.COM
Migel Stoddard was promoted to sales coordinator for Formost Fuji.
Gerhard Schubert, founder and shareholder of packaging machine manufacturer Schubert North America, passed away on July 4, 2023.
Niverplast’s compact SpeedyPlast is designed to insert up to 25 bags/min for boxes, crates, or buckets, resulting in a faster and safer process than manual production, resulting in less downtime. It also features a left- and right-handed capability.
Niverplast pwgo.to/8059
Busch Vacuum Solutions’ COBRA DX dry vacuum pump features a plug and pump design, making it ready for immediate use. It is available in two sizes, and due to its VSD, covers a pumping speed range to 950 m3/hr and achieves an ultimate pressure of up to 0.01 hPa (mbar).
Busch Vacuum Solutions pwgo.to/8056
Integrated Packaging Machinery’s AccuTURRET cable management technology is designed to increase the agility of the end-of-arm-tool (EOAT) without increasing the demand on the robot’s wrist.
Integrated Packaging Machinery pwgo.to/8064
Continue your search for the right packaging solution. Visit prosource.org.
Multi-Conveyor’s cleated incline conveyors are designed to control product when elevating raw or packaged product in containers or individual pieces without slips and slides.
Multi-Conveyor pwgo.to/8051
CVC Technologies’ Changsung 990SR softgel capsule lling machine is designed to improve the delivery of medications and supplements while increasing operational ef ciency during the manufacturing process. The unit can run a variety of shapes and capsule sizes.
CVC Technologies pwgo.to/8046
Charter Next Generation’s GreenArrowRx exible forming lm for the healthcare market incorporates post-consumer recycled resin and can be used to create store drop-off recyclable packaging.
Charter Next Generation pwgo.to/8060
ProMach brand Ossid’s 500Li tuck and fold stretch overwrapper produces up to 60 packages/min. Ossid pwgo.to/8052
nVenia’s Ohlson rotary premade pouch lling machine has been redesigned to maximize production output for lling pre-made bags or stand-up pouches with product.
nVenia pwgo.to/8058
Eagle Product Inspection launched the MAXIMIZER RMI X-ray inspection machine designed for the poultry processing industry. It features dual lanes that can run up to 120 pieces/lane/min.
Alongside standard case and carton loading, the small-footprint Hawk robotic top-load case and tray carton loader also works well with ow wrapped or bagged products, trays, bars, clam shells, bottles, cans and other formats.
JLS Automation pwgo.to/8072
Macsa ID’s SPARK small character laser coder is designed to mark packaging substrates that include labels, corrugated cases, plastics, glass, wood, paper and board, metals, rubber, and textiles.
Macsa ID pwgo.to/8066
The WLF30T fully automatic case former from Wexxar Bel, a ProMach brand, features an integrated EPI labeler. It labels pre-formed cases at speeds to 30 cases/min.
Wexxar Bel pwgo.to/8054
Eagle Product Inspection pwgo.to/8047
Klöckner Pentaplast and Dow launch kp FlexiVac R multilayer PE vacuum lm, which is certi ed 100% recyclable by cyclos–HTP and certi ed by Interseroh. Its high tensile strength makes it suitable for bone-in cuts of fresh meat and poultry.
Klöckner Pentaplast Dow pwgo.to/8065
Aagard’s Rapid Learning innovation platform is designed to streamline processes, enhance productivity, and reduce operational complexities for new product con gurations.
Aagard Group LLC pwgo.to/8057
At
Mettler Toledo’s Version 2.6 for its ProdX inspection device management software is suitable for a range of bulk and packaged food applications.
Mettler Toledo Product Inspection pwgo.to/8050
At
Hugo Beck’s paper e-comm t packaging machine is designed to produce paper bags for e-commerce and mail order applications that require minimal material.
Hugo Beck pwgo.to/8049
Antares’ DIAMIND series of interconnected software and hardware systems provides physical products with the digital identities necessary for success in a variety of industries, including life science, food and beverage, cosmetics/personal care, and highleverage luxury goods.
Antares Vision Group pwgo.to/8045
Rennco, a ProMach brand, offers the Micro VCCL (vertical cup counter loader), which offers a reduced machine footprint of 30% without compromising throughput.
Rennco pwgo.to/8053
Wipotec’s HC-A-EX checkweigher is designed for precision checkweighing in manufacturing environments where a mix of gases or ammable substances brings moderate risk for explosion incidents and can handle more than 300 items/min.
Wipotec pwgo.to/8055
AlliedFlex’s Velteko Washdown-360 vf/f/s machine is designed to produce a range of bag styles and package size formats with quick-changeover features while accommodating strict requirements of sanitary design.
AlliedFlex pwgo.to/8044
Herma US offers an updated 132M HC wraparound labeler featuring a new HMI touchscreen and a maximum speed of 600 products/min.
Herma US pwgo.to/8048
for additional information on any of the advertisers listed or visit their website directly
Kenya’s packaging market holds immense growth potential, valued at about $585 million as of September 2021. With a projected compound annual growth rate (CAGR) of approximately 4.8% from 2021 to 2026, the industry is poised to evolve in response to shifting market dynamics. While the availability of national statistics remains a challenge, there is abundant insight into key aspects of Kenya’s packaging market, including industry trends, emerging opportunities, and strategies for success.
Kenya, being one of East Africa’s most developed countries, boasts a diverse economy where the agriculture, forestry, and fishing sectors hold a significant market share, contributing about 22% to the overall economy. The manufacturing sector, ranking second, contributes approximately 11% to the Gross Domestic Product (GDP), with packaging representing an estimated 2% of the GDP. The packaging subsector supports food and beverages, pharmaceuticals and healthcare, cosmetics, and personal care.
In response to the country’s growing population and urbanization, the packaging of Fast-Moving Consumer Goods (FMCG) has become a prominent area of focus. The mass market in Kenya, driven by the need for smaller packaging for single-use purposes known as the “kadogo” economy, presents a significant growth sector. Families, relying on daily earnings, focus on securing one meal at a time, leading to an increasing demand for packaged goods across a wide range of FMCG products.
It is important to note that Kenya banned single-use plastic carrier bags in 2017. While the ban targeted lightweight carrier bags with a thickness of less than 30 microns, exceptions were made for materials used in industrial primary packaging, bread packaging, disposable bags for handling biomedical and hazardous waste, and garbage bin liners. Plastic bag carriers remain widely accessible to traders, including food vendors, petty retailers, and wholesalers, due to their affordability, convenience, and versatility, particularly in the informal market economy. This presents an opportunity for alternative packaging solutions in Kenya.
Emerging trends and regulations in the industry focus on waste reduction, recycling, and resource conservation. Current figures and percentages show that every Kenyan generates 0.5 kg of waste daily, resulting in a total of more than 22,000 tons of waste generated in Kenya per day and 8 million tons annually. The waste composition is reported as 60% organic, 30% recyclable, and 10% other.
Regarding plastic waste, about 20% of the total waste generated
in Kenya per day is plastic. The daily plastic consumption per person is estimated at 0.03 kg. This translates to a yearly plastic waste generation of approximately 0.5 to 1.3 million tons.
However, only 8% of the plastic waste is recycled. The remainder is either landfilled, incinerated, or, in the worst-case scenario, ends up in the environment.
Figures and percentages are expected to vary over time as wastegeneration and recycling practices evolve.
To align with sustainability goals, the emerging trends and regulations include:
• Restrictions on single-use plastics; sustainable packaging initiatives outlined in the Kenya Plastics Pact (KPP) Roadmap with a national recycling target of 30% by 2030; draft regulations on Extended Producer Responsibility (EPR) that emphasize collection, recycling, and proper disposal of packaging materials; and the pursuit of a circular economy for plastics through the KPP, launched in October 2021.
• Support and collaboration are crucial in enhancing packaging knowledge and skills in Eastern Africa. The Institute of Packaging Professionals Kenya (IOPPK), as a member of the World Packaging Organization (WPO) and the African Packaging Organization, strives to improve standards, build capabilities, and promote trade. Initiatives such as IoPP’s Certified Professional Packaging (CPP) program will enhance packaging technology expertise among professionals in Kenya.
To succeed in the Kenyan packaging market, U.S. companies should undertake comprehensive market research to understand specific packaging needs and requirements across different sectors. Collaborating with local packaging professionals to provide technical support, training, and guidance on best practices and packaging technology is a smart growth strategy. Adapting to local regulations and ensuring compliance with Kenya’s sustainability goals is crucial. Additionally, offering sustainable packaging solutions that emphasize eco-friendly options using recyclable or biodegradable materials and innovative designs to reduce waste is essential.
Building local partnerships with distributors, retailers, and suppliers enhances market reach and understanding, and facilitates valuable insights, distribution networks, and customer relationships.
There is more packaging potential in Kenya than manufacturers in the U.S. might realize. With a little legwork to understand our region’s trends and emerging opportunities, and the development of the right partnerships, Kenya is a land of opportunity in the packaging industry. PW
Need more automation capability in a fraction of the space? We can help.
By engineering your EXACT SOLUTION, we make every square inch count for Case Packing, Cartoning, Palletizing, Variety Case Packing, Retail Ready, Robotics, Sleeving, and Combination machines. Our custom approach is a mix of inventive problem-solving and a willingness to take on challenges.
Aagard is a leading engineering innovator of secondary packaging automation. Check out a few of our innovative solutions:
• apid aunch- New product set-ups in minutes, no programming, no change parts, no retrofits
•Walk-Through Caser acker set up for lights-out manufacturing
• ully Automated ariety Case acking, Including etail eady ackaging
•One Case acker for Cartons and Bags, With Auto Changeover
•Telescoping Conveyor, Accessibility Without Steps Or raw Bridges
•E panded Capability with Integrated Options
TOTAL PROJECT SUCCESS happens with partnership and an iterative design process. We work together to understand the complete picture, creating the optimal solution that mitigates space, speed, and flexibility challenges to drive results.
Since 1997 we have specialized in engineering and building customized integrated combination packaging systems that fit our customers’ specific needs and spaces. Our unique packaging machines can combine many solutions into a single turn-key system with one integrated control package using our proven innovative technologies.
Whether the need is for a design solution with a small footprint or an agile system that can produce 1000s of product combinations, we will deliver
T E AA A EX E IENCE
HELPING OUR CUSTOMERS WIN
714/974-9006
American Film & Machinery is a leading manufacturer and supplier of heavy-duty shrink sleeve labeling equipment, shrink tunnels, and shrink sleeve consumables. AFM’s shrink sleeve labeling equipment includes a complete line of shrink sleeve labelers, tamper evident banding equipment, steam tunnels, electric tunnels and infrared tunnels. AFM’s labelers range in performance from 50 to 500 products per minute, offering a product and price point no matter what the application demands.
American Film & Machinery also offers a complete line of shrink sleeve consumables, including shrink labels and tamper evident bands. AFM is supported by two of the largest film converting plants – one with 7 rotogravure presses and up to 9-color stations and compatible converting equipment, and another plant with an 8-color 32” central impression flexo press.
With over 40 years of experience in the shrink labeling industry, rely on American Film & Machinery to provide the right solution to your product labeling needs. AFM products are sold through a network of authorized dealers, fully trained and capable to install, train and service our equipment. Contact us today for the name of your local reseller and find out how we can benefit your operation.
AFM, Eastey, and Squid Ink and are all divisions of Engage Technologies Corporation. American Film & Machinery (afmsleeves.com) supplies shrink labelers and tunnels, shrink sleeves, and tamper bands. Eastey (eastey. com) is a leading manufacturer of heavy-duty shrink packaging equipment and automated case sealing systems for packaging applications. Squid Ink (squidink.com) is a manufacturer of coding and marking systems for product identification and traceability, providing superior quality inks and low maintenance printing equipment.
919-772-8383
Axon, a ProMach product brand, is an industry leader in shrink sleeve, stretch sleeve, and tamper band labeling systems, offering dependable performance in key sleeving and tamper band applications including full and partial body sleeves, tamper evident bands, multipacks, and full body over-the-cap sleeves. Over 5,000 Axon systems are in operation worldwide, supported by an experienced team of engineers and service personnel.
The flexibility to run shrink sleeve labels, tamper evident bands, and multipack sleeves on a single machine makes Axon applicators and systems the ideal solution for low-to-high speed and high-performance applications in a wide range of industries including craft beer, wine and spirits, RTD beverages, food, condiments and sauces, ice cream and dairy, pharma and nutraceuticals, and more.
Axon’s systems and standalone applicators are known to deliver dependable performance and unmatched flexibility that translates into higher productivity, more savings and dollars on the bottom line.
Our success starts with listening to your needs, asking the right questions and conducting a thorough technical evaluation to deliver the rightfit solution for your business. Making use of over 50 years of shared experience in the labeling industry, our team of sales and application engineers offer guidance to ensure operational results are met, from the initial conversation through installation and day-to-day operations. Your internal teams can count on US based manufacturing of equipment and parts and local technical support provided by leading service experts that average 14 years of Axon experience.
770/772-0400
B&R Industrial Automation, a member of the ABB Group, is bringing a new level of performance and flexibility to packaging machinery in response to the needs of consumer goods manufacturers.
The B&R ecosystem offers a uniquely comprehensive portfolio of today’s most advanced automation technology – including machine vision, robotics, digital twin simulation, and mechatronic product transportation systems. Our team has the knowledge and experience to combine these technologies in a way that enables manufacturers to adapt to all types of unexpected changes without sacrificing productivity. This is the crucial ability – known as adaptive manufacturing – that CPG manufacturers can leverage to more efficiently handle the demands of direct-to-consumer and omnichannel business opportunities.
Codian Robotics became a member of the ABB Group in 2020. The integration of Codian Robotics’ delta robots into the B&R portfolio has made it much easier for customers to implement high-speed pick-andplace applications.
The mechatronic solutions have proven to be a game changer, enabling mass customization down to batch size one, changeovers on the fly, and make-to-order instead of make-to-stock. This is the essence of adaptive manufacturing, machines that adapt to the products being made and packaged, rather than forcing products to conform to a rigidly sequential process.
Adaptive manufacturing enables digital business strategies with the ability to deliver cost-effective, automated, make-to-order mass customization for the first time ever. Manufacturers can now offer personalized, even batchsize-one order fulfillment directly from the production line to the consumer.
For over 60 years, BELL-MARK has been developing innovative solutions for package and carton printing applications in the medical device, pharmaceutical, prepared foods, meat, bakery, dairy, and poultry packaging industries. BELL-MARK offers many in-line printing technologies, including piezo inkjet, thermal inkjet, thermal transfer, flexographic, and ink coder, all of which satisfy requirements to print directly onto package and carton substrates.
The accuracy of coding on your product package is crucial. Expiration dates must be clearly identifiable and easily human-readable. Bar codes must be verifiable and scannable. There are no exceptions. BELL-MARK addresses these needs with systems that provide the highest quality print available on medical paper, Tyvek, poly, and foil substrates.
BELL-MARK has successfully satisfied UDI GS1 requirements for many of our customers. We understand the UD1 rules and regulations and have experience in a wide range of applications. From retrofitting band sealers to Form, Fill, Seal packaging machines, we have the expertise to ensure your codes are verifiable and scannable and meet the necessary regulations.
Eliminate costly labeling by printing directly onto your package or replace your CIJ printer with a maintenance-free alternative. BELL-MARK offers a full line of washdown tolerant printers, including both thermal transfer and thermal inkjet technologies. Print graphics, nutritional facts, bar codes, lot/expiration dates and safe handling instructions on almost any surface. Rest easy knowing your printer is IP67 rated and can be washed down and sanitized without complicated protective procedures.
BELL-MARK’s in-line printing and coding equipment delivers industryleading reliability and durability, time and time again. High-resolution print quality that consistently affords you the peace of mind in knowing that your codes will not fail. While other companies may claim it, BELL-MARK leads the way in the lowest cost of ownership and highest return on investment.
Inc.
www.bellatrx.com
BellatRx is a leading manufacturer of packaging lines, equipment, and integration solutions and your number one source for inventive, advanced, and automated packaging and filling solutions. Our expertise lies in the engineering and manufacturing of innovative equipment designed to your specifications for a turnkey operation.
We are a global leader in the design, manufacture, distribution, and service of Complete Packaging Lines, Filling, Capping, Labeling, Inspection, and Recovery systems focusing on Rigid Containers. We serve a broad range of industries including food, beverage, pharmaceutical, diagnostics, biotech, nutraceutical, chemical, cosmetics, and personal care for solid products, liquids, and powders.
Our packaging lines are designed to meet your packaging requirements ranging from small batch runs to large high-speed operations. We design our lines with speed, efficiency, flexibility, and ease of changeover in mind. Your packaging line will be modular with expansion capabilities built to keep pace with your company’s growing demands. Our expert technical team supports customers throughout the process from kick-off to final commissioning and beyond.
At BellatRx, we live by an encompassing mindset to create a “Beyond Expectation” experience for our customers. This experience is derived from our capabilities in application analysis, innovative engineering designs, product development, project management, on-time delivery, installation, start-up support, training, and ongoing aftermarket support.
BellatRx continues to implement the latest automation technologies to manufacture packaging machines which have become the benchmark in the industry due to their intuitive operation and easy setup. We are dedicated to expanding our product lines through ongoing investments in our people, R&D, and facilities to provide our customers with the best support, lead time, and value.
QC
817/349-8555
BestCode designs and manufactures Industrial Coding and Marking Printing Systems. Systems print real-time “Best By”, “Lot Code”, “Sell By”, “Expiration Codes” and other identifying marks and codes on industrial and consumer goods to ensure product traceability.
Products are designed and manufactured in the USA; FORT WORTH, TEXAS. For more than 25 years, the BestCode group continues to produce industry-changing, forward-thinking innovative industrial printing designs. Product designs are focused on ease of use, trouble-free operation, longterm reliability, and affordable cost of ownership with an emphasis on global market requirements.
Systems print small and large character text, graphics and barcodes at high speed, non-contact, instantly dry on a wide range of substrates, including plastic, glass, paper and more - meeting the requirements for food, consumer good and industrial coding and marking applications.
BestCode offers a complete range of marking and coding solutions (50+ model configurations) - entry level affordable options through mid-range capabilities and high end, specialized engineered solutions focusing on the highest speed, most sophisticated applications.
BestCode systems minimize user interaction, limiting the hands-on time for typical coding system operations, extending the operation time between human interactions.
Systems are the most efficient CIJ printers available, lowering overall coding costs. Systems are State-of-the-Art, Current Technology, Industrial, Built-to-Last and designed for the World Market, featuring more than 20 operating/printing languages.
Bevcorp offers solutions for your filling, blending, container handling, and seamer packaging equipment, parts, and service needs. Our goal is to provide unparalleled service highlighted by our dedicated commitment to serving the food and beverage industries. We provide high speed rotary filling equipment including new and Bevcorp Certified can and bottle fillers. We manufacture both electronic volumetric and mechanical rotary filling equipment. Our Microblend Division manufactures the Micro2 Advantage Series Blender, in-line carbonator, CSD, hot fill and non-carbonated blenders, replacement parts, and provides 24-hour service and support. Our FCI Handling Division provides quick-change handling, conversions for all brands of equipment, parts carts & storage solutions, vent tubes/ ball cages, base control and neck handling solutions. Our newest division, East Coast Seamers, provides rebuilds and overhaul services for Angelus, Continental and Canco can seamers, 24-hour emergency service, parts, oil and lubrication analysis, installations and training.
BluePrint Automation (BPA) is a world leader in end of line packaging automation. With a diverse and innovative team of experts in consumer goods packaging, BPA designs, develops and manufactures packaging solutions for flexible and other tough-to-handle packages. You make it, They’ll pack it!
• rimary ackaging ision guided robots picking individual packaged and unpackaged items for loading into your containers, wrappers or hffs machines; including Carton, Case and Tray Packing, Stacking and Loading, ariety acks into Sack or Case, inner Tray oading and it Assembly
• Secondary ackaging ori ontal and vertical pack solutions for fle ible and other packages; including wrap around case packing and end-load cartoning acking shelf ready Their Easy- case is a retail-ready case that allows for easy top loading and ensures a good-looking product appearance on the shelf.
• Turnkey ackaging Systems Taking total control of your packaging line from the end of processing through palleti ing
id you know ongerius anco, a leading supplier of multipack bag-in-bag systems is now powered by BluePrint Automation? With their wide range of bag-in-bag and sealchecking solutions, ongerius anco is the perfect complement to BPA’s end of line packaging solutions.
Backed by thousands of successful installations in over 60 countries, BPA has three full-service manufacturing facilities in the USA and Europe, an additional facility in ang hou China and ten additional subsidiaries throughout the world for sales and service. BPA has clearly emerged as a global leader in the design and manufacturing of fully integrated turnkey packaging systems. The systems are constructed for around the clock operation and known worldwide for their quick change over, flexibility, speed and simple design.
Brenton is a global leader in designing and manufacturing integrated end of line case packaging systems and machines, specializing in case packing and palletizing using both robotics and other automation. With expertise in conventional, hard automation as well as robotics, Brenton has the solution to fit the customer’s specific application requirements.
Brenton’s case packers are reliable, efficient and easy to operate. With over 850 traditional case packers and robotic case packing installations, Brenton continues to be a leader in the case packing industry. These systems are designed for maximum flexibility, to accommodate diverse product requirements. Brenton’s Case packing solutions offer a wide range of options to easily accommodate our customer’s applications.
The Brenton full line of palletizing and depalletizing solutions uses rugged designs which help maximize the reliability and value of your machinery. Brenton’s systems range from single pick palletizers to bulk robotic palletizers and depalletizers as well as conventional machinery. By offering both conventional and robotic palletizing and depalletizing products, the Brenton line meets virtually every automation challenge. As a FANUC ASI and FANUC Certified Servicing Integrator and Strategic Market Specialist, Brenton’s extensive knowledge in robotics continues to grow and drive additional robotic automation solutions to their portfolio.
Brenton Integrated System Solutions offer customers a single source for all end-of-line packaging needs, from standalone applications to complex packaging systems. Brenton solutions integrate not only Brenton machines but also the entire ProMach family of brands as well as other customer specified equipment. Integrating systems streamlines the production process, allowing for maximum efficiency and increased productivity.
Brenton’s partnership does not end after installation. With one of the longest running aftermarket programs in the industry, Brenton has a team of in-house aftermarket parts, service and machine retrofit experts providing 24/7 support, keeping customers up and running at peak capacity. Retrofit upgrades also available on the competition’s solutions.
757-463-7800
www.buschusa.com
Busch Vacuum Solutions combines the precision of German engineering with American-made know-how to offer an extensive range of vacuum pumps, blowers, and compressors tailored for your unique application.
Busch is proud to offer high quality, reliable solutions crafted in the US. Our key products for packaging are proudly constructed with a combination of US-made components and international materials - giving customers both reliability and value.
At Busch, quality and innovation come first. Our expert engineering team is committed to creating vacuum systems that meet the unique requirements of our customers. With such dedication to excellence, it’s no wonder we are a leader in system building!
Keeping your production running smoothly is our top priority. Our nationwide network of service centers or on-site Field Service Specialists provides expert maintenance and repair solutions, including 24/7 support for unexpected breakdowns. Invest in peace of mind knowing that with Busch you can maximize uptime, optimize safety, and improve efficiency.
OUR PRODUCTS:
• acuum umps
• Blowers Compressors
• acuum Systems
• Spare arts Accessories
• Measurement Equipment
OUR SERVICES
• Nationwide ield Service
• Nationwide Service Centers
• acuum ump E change
• Overhaul
• epairs
• Maintenance
Founded in 1976, Buskro is an industry leader in the design and manufacture of print and personalization equipment to meet a broad range of customer applications in the commercial print and packaging markets. Buskro’s approach of incorporating the latest personalization technologies and providing an upgrade path for existing equipment allows our products to meet your current needs and gives you the ability to evolve with your future needs.
Buskro equipment features heavy duty construction with the option for 3rd party integration, a design that promotes years of trouble-free operation, and powerful Compose IQ software that has all the tools to deploy simple to complex personalization systems. Buskro offers a full suite of transport modules, inkjet printers, labelers, inspection devices and personalization elements that allow you to tailor a system that’s just right to meet the specific requirements of your jobs. Choose a printer or array of printers best suited to satisfy your print resolution, coverage, and ink needs and then define the image with Compose IQ & Workflow software, control the output, track progress, and inspect the result to confirm full job compliance.
Buskro’s Package Personalization System (PPS) has been designed to apply inkjet print, brand labels, and other personalization features such as RFID variably onto a wide variety of packaging products for jobs of any size. Employing Buskro’s configurable Modular Transport System as its foundation, personalization elements are added and placed where you need them to meet your specific package personalization requirements. Layered with Workflow Software that assists with rapid product setup and job preparation plus a camera inspection device that monitors and ensures completion and right amount of each and everyone of your products, the PPS provides all the tools to reduce waste and production costs.
Buskro research and development is constantly searching for new products, processes and systems. This commitment to innovation has produced industry leading operating systems, print technologies & transports.
BW Integrated Systems is an industry leader in the design and manufacture of end-of-line packaging equipment and robotic automation solutions, as well as the execution of integrated packaging systems. Our company attributes its decades of success to three simple principles: “People, Products, Performance.”
PEOPLE:
Striking the appropriate balance between a people-centric culture where everybody matters and industry-leading performance is core to our business. As a member of the Barry-Wehmiller family, we strive to be a company that enables its associates to return home daily with a true sense of fulfillment. Our mission is to be a company that people enjoy working for, doing business with, investing in, and having as part of their communities.
PRODUCTS:
Our diverse portfolio comprises trusted legacy products (Ambec, Fleetwood, Goldco, Nigrelli, SWF, Tisma), innovative solutions like our Maximus Case Palletizer and Fortis Bulk Depalletizer, and integrated packaging systems. In addition, our service network provides global technical support and offers peace of mind for a diverse client base that operates in a variety of market segments, including Automotive, Beer, Beverage & Craft Beverage, Wine & Spirits, Container Manufacturing, Food, Household, Personal Care, Dairy, Paper, Pharmaceutical, and Industrial.
PERFORMANCE:
BW Integrated Systems has decades of application experience in packaging line design and integration, robotic automation, and the design and manufacture of innovative packaging equipment. We have packaging equipment and systems integration installations in over 50 countries worldwide. With six manufacturing facilities and over 650 team members worldwide, BW Integrated Systems is a trusted global partner for our clients, ranging from mid-size to multi-national corporations.
Contact us to learn more.
BW Packaging is Barry-Wehmiller’s global team of packaging professionals who genuinely care about people. We show our customers that they matter by learning about their challenges and embracing them as our own. Through these partnerships, we develop purposeful packaging solutions to optimize our customers’ processes and back them with a lifetime of customer support.
Comprised of five divisions - Accraply, BW Flexible Systems, BW Integrated Systems, Pneumatic Scale Angelus and Synerlink - BW Packaging offers comprehensive packaging machinery and solutions including complete packaging lines, filling and closing, flexible packaging, labeling, end-of-line solutions, and systems integration.
Whether you need a single piece of equipment or a fully integrated line, BW Packaging provides reliable packaging solutions for food, beverage, personal care, household products and pharmaceuticals.
With 11,000+ installations around the world, BW Packaging brings a global perspective to solving the industry’s greatest challenges. Through innovation, application of our broad packaging expertise, and collaboration with our customers, we optimize packaging solutions for:
• Sustainability Infusing sustainable thinking into our business culture and practices.
• Integration Building robust connections through e pertise and IIoT solutions.
• Automation rioriti ing people and safety while streamlining production
• erformance Improving OEE with reliable solutions and lifetime customer support.
Looking to improve production and efficiency? Cama has 40 years’ experience designing and building innovative, automated secondary packaging solutions that are easy to operate, improve production and OEE, and run multiple products with quick and easy changeovers. A subsidiary of Cama Group, Cama North America is vertically integrated, providing complete sales, manufacturing and aftermarket support to North American customers, including engineering, parts and technical service.
Cama’s expertise spans a wide range of applications, including various food markets, as well as Pet Food, Personal, Health, and Home Care. Our product line includes:
• Case packers and case packing systems for SC, wrap-around, and retail-ready /display ready cases C , as well as forming, closing and lidding machines for bo es, trays and SC cases
• Intermittent and continuous motion cartoners and carton sleevers
• Integrated decoupled and monoblock robotic loading units
Check out our new BreakThrough Generation of case packers, cartoners, and sleevers BT models feature high sanitation levels quick and easy, tool-less changeovers fle ible configurations and ease of maintenance and accessibility. They offer a monoblock design, no hollow body structure, and C-less, cabinet-free technology with non-proprietary electronics In addition, they are T M-compliant and ready for the future with Industry features such as our Augmented eality A Machine Assistant.
Offering flexibility and quick changeover in a compact footprint, our integrated, turnkey systems can accept flexible or rigid products in an oriented or random configuration, orient packages as needed, end load or top load products into a carton, and case pack into a display ready and/or conventional SC or wraparound case In addition, the Cama ackaging epartment offers more than years of e perience in the design and testing of packaging cardboard, and can often help design more sustainable solutions that help our customers save material costs and reduce their impact on the environment.
Partner with Clysar for packaging with a positive impact.
Clysar is a leading U.S. shrink film manufacturer with sustainable solutions for virtually every packaging application: offering today’s most extensive portfolio of recyclable, recycled-content and right-gauged polyolefin films. Gain industry-leading expertise, 24/7 technical service and the developmental support of a knowledgeable sustainability team. Recyclable Films – Find a high-performance recycled film for every product, prequalified for Store Drop-Off by How2Recycle®. Solutions include Clysar® EVO™ all-purpose film, EVOX™ high-speed film, EVO-C™ Confidential e-commerce/privacy film, EVO™ ShrinkBox® high-abuse film and ULTRA LEG™ low-energy film.
Certified Recycled Content – Meet your goals with shrink packaging made with pre- or post-consumer recycled content. EVO-C™ Confidential film, an opaque shipping film, features Post-Consumer Recycled (PCR) content. Other clear films incorporate Clysar® ReClaim™ pre-consumer resin certified by SCS Global Services.
PVC Replacement – Improve material health and eliminate toxins with advanced polyolefin films that replace PVC shrink film (polyvinyl chloride), including our gentle new recyclable ULTRA LEG™ low-energy film.
Right-Gauging/Source Reduction – Explore options to reduce packaging, eliminate components and deliver improved performance at lower gauges. Solutions range from printed shrink film to thin films to corrugate replacement films that save up to 80% in package volume.
Reduced Energy Use/Cost – Lower impacts with films that run reliably at lower temperatures in sealers and tunnels, achieve improved speed/ throughput and eliminate rewraps.
Responsible U.S. Manufacturing – With 60+ years of shrink packaging expertise, Clysar is a responsible resource that meets rigorous qualifications for environmental, social and ethical performance. We are committed to environmental collaboration, education and improved packaging performance.
Make your next package more sustainable and successful. Visit clysar.com or talk with us to explore the advantages of full-circle shrink packaging.
Flexible Product Handling
Columbia’s conventional palletizers are the most flexible palletizing solutions available and handle virtually every package type, including shrink bundles with and without a pad, plastic totes, high CG, unwrapped trays, and more.
Industry Leading Standard Safety Features
Columbia’s standard safety package contains Category 3 electrical safety components, including dual circuit safety interlocks & full height light curtains. This safety package provides a fully guarded, Performance Level D palletizer to keep your employees safe while enhancing OEE and production demands.
Complete System Integration
Columbia Machine manufactures conventional high-speed, high-level, floor-level & robotic palletizers, load transfer stations and provides complete system design and integration. With the most flexible and modern palletizing solutions available, Columbia is the leading palletizer solutions provider in North America.
High Performance AND Sustainability
Columbia has a palletizing solution for virtually any application, each equipped with standard features designed to safely maximize OEE, throughput and uptime.
1.877.204.7444
Columbia/Okura LLC is a leading robotic palletizing integrator. Our team applies expert knowledge, gained through 26 years of business, with the right tools to solve customers’ “End of Line” production challenges for a diverse range of businesses, products, and applications. The historical success of our company can be attributed to an exclusive focus on end-ofline palletizing systems and applications.
We provide design, integration, and commission of end-of-line robotic palletizing systems including industrial robots, cobots, automated bagging machines, and integrated equipment. Through our partnerships, we procure and integrate top-of-the-line valve packers, pallet and sheet dispensers, conveyors, and any additional end-of-line equipment your line might need. By providing custom-engineered solutions, we develop robotic palletizing systems to meet demanding customer requirements.
Our team is well versed in providing solutions for most major manufacturing industries including:
• Animal Nutrition
• Beans, entils, ulses
• Building Materials
• Chemical roducts
• ood Beverage
• Milled roducts
• Medical / harmaceutical
After a system is shipped and installed, ourdedicated service team continues to support our customers with 24/7 remote support, troubleshooting, and maintenance services. We maintain a team of experienced field service technicians and engineers that are available to travel to our customer sites, offering services customized to a client’s specific needs Additionally, our team is trainedtrainers, conducting onsight training for system operators, ensuring they know how to operate the system safely.
CTM Labeling Systems
330/332-1800
www.ctmlabelingsystems.com
From design and engineering through final system set-up and quality control, exceptional expertise and craftsmanship is built in at every level to create the finest labeling machines available on the market. Setting high standards is difficult, maintaining those standards is even tougher. The highest standard, that we consider our benchmark, is unsurpassed support “after the sale.”
At CTM, supporting our customers before, during and after the sale is paramount. Our management team and dedicated support staffs are driven by some of the most experienced and well-respected professionals in the industry. From semi-automatic applications to the most demanding highspeed, high-accuracy labeling solutions, we understand your needs. More importantly, we understand how to convert your needs into successful production.
To maintain unparalleled quality standards, every phase of our company is housed under one roof. When raw material leaves the rack, it travels through the most automated manufacturing facility in the industry. Stateof-the-art equipment incorporating precise tolerances, coupled with true craftsmen at the controls, results in an impeccable product. Our promise to you — “You won’t find better quality, better service or better delivery anywhere else in the industry.”
We welcome you to tour our facility and experience the “CTM Commitment to Excellence” firsthand.
Products:
• Tabletop Wrap Systems
• Custom abeling Systems
• a abel Applicators
• a rinter Applicator
• ST Servo Tamp rinter Applicator
• T-Base, -Base Stands
Dekka is one of the only companies where the primary focus is on tape heads. Because of our dedication and focus, our team is not only more experienced and knowledgeable, but we care about every tape head that goes out the door. Our pride and passion lies in providing a consistent and reliable solution for every application for seamless integration and easy operation. We support every product because we put our customer’s reputation first.
A key to Dekka’s success was our ability to grow and develop a wide distribution network across North America. With our own experienced technicians as well as knowledgeable distributors and packaging suppliers, Dekka and our partners compose of the strongest tape head support network in the industry that will listen, understand and solve your tape head issues.
Dekka offers over 400 unique tape heads which fit on almost every case sealer, case erector and case former in the market. This versatility extends to the types of packaging tape and cases that our tape heads are able to handle as well including hot melt, acrylic, rubber, and other types of tapes for cases, boxes, recycled cartons and more. The wide range of products has been driven by the overwhelming demand for Dekka tape heads. Dekka customers understand the importance of the quality, reliability and service that comes with each Dekka tape head. Along with these tape heads, we also offer options and accessories on our tape heads such as the Tape Monitor Alert System and other retrofit packages.
Dekka also offers a line of entry level machinery, bringing the same level of quality and reliability from tape heads to case sealing and erecting machinery. These machines have been designed and built to synergize with Dekka tape heads to bring the highest level of performance and reliability to our customers. Contact us if you are having trouble with your current tape head or if you are looking for some new equipment- we are happy to help.
We are a leading manufacturer of advanced case packing and cartoning machinery. Our talented 350 employees have proven to be one of the most inventive teams in the packaging industry. Delkor has changed the landscape of retail ready packaging and is now widely recognized for creating a new generation of cutting-edge machinery and fresh package concepts.
Our team can help you comply with the latest retail-ready packaging (RRP) guidelines for major retailers including Walmart, Aldi, Kroger and others. All of Delkor’s case packers stand-alone by offering both retail ready case styles as well as the full range of club store display trays with only 8 minute full line change-over. Delkor’s popular patented Cabrio Case design is provided free of charge with the purchase of a case packer, which enables customers to source the Cabrio Case from any corrugated manufacturer. Currently over 1 billion Cabrio Cases are in use across many product categories in 2023! To see your product in a Cabrio Case, our in-house package lab can provide you with a physical sample with graphics within 48 hours.
Delkor’s robotic case packers and cartoning machines were designed for today’s diverse packaging environment.
From package design to finished pallet, we’ll help you with everything you need. We’ll handle the hassle of upstream and downstream add-ons, purchases, and recommendations for your project.
Diagraph provides identification solutions that make it easy for manufacturers to make the perfect mark – print after print after print. Diagraph focuses on partnering with customers in every aspect of their coding and labeling operations, including warehouse automation and eCommerce – providing a holistic approach that maximizes efficiencies for customers and drives tangible value throughout a long-term partnership.
Diagraph is the longest established business in the product identification industry and has been a trusted leading manufacturer and distributor of product identification solutions for 130 years.
Our solutions include:
• in small character continuous inkjet printers lead the industry in durability and reliability with the longest intervals between printhead cleanings (up to 3 months). The simple user interface allows for quick message setup and intuitive daily operation. The sealed industrial printhead provides maximum print quality protection over longer periods of time.
• The new esMark is the ne t generation standard for case coding
Utilizing its extensive industry knowledge, Diagraph engineered this intelligent system to deliver simplicity, reliability, flexibility and a lower cost of ownership over the life of the system. This high-resolution industrial inkjet printer system offers the industry s largest print area and greatest throw distance and sets the standard for durability and the lowest cost per mark. Innovative and patented rapid replace printheads can be brought online quicker, reducing production line disturbances and repairs while minimizing downtime.
• iagraph s all-electric labeling print apply systems and label applicators are simply the smartest, most efficient and reliable automated labeling systems in the industry. Industry-leading smart technology uses sensors to reduce label application complications and ensure a one-to-one label to product match for secondary packaging and pallet labeling.
469-885-5722
www.doosanrobotics.com
Founded in 1896, Doosan Group has achieved an incredible reputation as one of the most advanced industrial machinery innovators in the world. Doosan Robotics Americas continues this tradition of technological excellence with a complete lineup of cutting-edge industrial optimization and automation tools, perfect for applications of packaging, palletizing, pick-and-place, and beyond.
Doosan cobots easily integrate and interface with a wide range of equipment and systems. Having partnered with industry-leading manufacturers of tools, grippers, sensors, and software, Doosan cobots install quickly for immediate operation – they also arrive within four weeks of ordering. With intuitive one-touch programming and automatic axis alignment, these products are incredibly easy to use for dynamic processes and precision movements.
Doosan’s cobot lineup consists of three tiers and ten models with payload capacities ranging from 5kg to 25kg and reach capabilities ranging from 900mm to 1,700mm. Whether you’re looking to tackle precision palletizing tasks or heavy-duty package conveyance, Doosan Robotics has the perfect products to get the job done.
Duravant is a global engineered equipment company with manufacturing, sales and service facilities throughout North America, Europe and Asia. Through their portfolio of operating companies, Duravant delivers trusted end-to-end process solutions for customers and partners through engineering and integration expertise, project management and operational excellence. Duravant’s market-leading brands are synonymous with innovation, durability and reliability. The Duravant family of operating companies serve the food processing, packaging and material handling segments.
Duravant’s packaging families include:
Fischbein International, a global leader in sewing and sealing systems, designs and manufactures bag packaging equipment and complete systems.
Mespack is an international manufacturer of flexible packaging solutions that engineers and builds high speed machinery for the world’s leading consumer packaged goods companies.
nVenia designs, builds and integrates primary, secondary and end-of-line packaging solutions for producers of consumer packaged goods and industrial products with longstanding brands Arpac, Fischbein, Hamer, and Ohlson.
Wulftec is the world’s leading manufacturer of highly complex, fully customizable load containment solutions for end-of-line packaging applications.
Duravant’s food processing companies consist of Foodmate, Key Technology, Marelec, Marlen, Multiscan and WECO.
FMH Conveyors and QC Conveyors make up Duravant’s material handling segment.
763/428-4846
Eastey is a leading manufacturer and supplier of heavy-duty shrink packaging equipment, case erectors, case tapers, and other packaging equipment. Eastey’s shrink packaging products include a complete line of L-sealers, sleeve wrappers, shrink tunnels, and bundling equipment.
Eastey also supplies a complete line of case erectors and case tapers, from entry-level bottom and side-belt tapers to fully automatic and random-size case tapers. Eastey has been in business for over 30 years and has an installed base of over 15,000 packaging systems.
Eastey products are sold through a global network of authorized dealers, fully trained and capable of installing, training, and servicing our equipment. At our manufacturing facility in Big Lake, Minnesota, we take pride in manufacturing equipment that is First in Quality – Built to Last. We maintain an extensive inventory of replacement parts and offer prompt technical support when needed.
Today, Eastey continues to focus on its core purpose to “help companies deliver products to the world.” An expanding line of integrated products and services reflects Eastey’s commitment to meeting new needs and new challenges and ensuring that customers have reliable solutions for their packaging application.
Eastey, Squid Ink, and American Film & Machinery (AFM) are all divisions of Engage Technologies Corporation. Eastey (eastey.com) is a leading manufacturer of heavy-duty shrink packaging equipment and automated case sealing systems for packaging applications. Squid Ink (squidink.com) is a manufacturer of coding and marking systems for product identification and traceability, providing superior quality inks and low-maintenance printing equipment. American Film & Machinery (afmsleeves.com) supplies shrink labelers and tunnels, shrink sleeves, and tamper bands.
Engage Technologies Corporation is headquartered in Brooklyn Park, MN with facilities in Big Lake, MN, Spring Lake Park, MN, The Hague, Netherlands, and Shanghai, China.
(360) 673-0018
Make Crating Your Easiest Task
Revolutionary and patented Ecorrcrate® is a standalone, all-corrugated shipping crate solution. Presented in a convenient, easy-to-use format, Ecorrcrate is designed to better protect your product at a lower cost.
Do you struggle with:
• igh freight costs due to shipping heavy wood crates
• roduct damage in transit
• igh cost of packaging labor
• E port quarantine delays
The Bottom Line
We know determining ROI for your company’s bottom line is top priority. Take this opportunity to evaluate both your front end and back end costs, including product replacement rates as well as the associated cost of poor customer e periences before finali ing a decision on your shipping solution.
• Starting cost is lower than common wood crates
• ight weight Ecorrcrates will lower your freight in most situations
• Setup is easy and safe, saving you time and money on labor
• euse and repeat due to our durable and straightforward design
Wait…It’s sustainable and durable?
Finding a reliable, highly durable shipping solution that is also sustainable is often quite challenging Wood is a renewable resource but typical disposal is in the dumpster headed for the landfill.
This is where Ecorrcrate stands alone in the crated goods industry. Ecorrcrate is built from paper-based corrugate lumber. Our proprietary cross-laminated material gives the Ecorrcrate superior multi-directional strength and durability to better protect your products.
Strong, highly Water esistant, Shatterproof, Easy to assemble, enewable, Easily recycled, and IS M compliant, we are confident that Ecorrcrate will improve your processes and lower your Carbon footprint.
At Encoder Products Company, we strive to serve you with expert service, quality products, and fast delivery. EPC specializes in encoders for motion feedback in industrial automation applications such as packaging, printing, labeling, vision systems, food and beverage, motor feedback, and more.
We understand that each industrial automation application is different, and you need encoders that fit the requirements of your applications. That’s why our encoders are highly configurable, offering a wide array of shaft or bore sizes, output types, connector types, mounting options, and resolutions up to 65,536 CPR. You’ll also get an industry-leading warranty, and fast delivery from Idaho, USA.
EPC offers:
• Tru-Trac linear measurement solutions – an integrated encoder, measuring wheel, and pivot arm in one compact unit
• raw wire units with wire lengths up to 2 meters
• Accu-Coder ro programmable encoders
• Magnetic multi-turn absolute encoders that operate in the absence of power without gear trains or batteries
• obust mechanical housings for harsh operating environments, with stainless steel and corrosion-resistant options
• Magnetic encoder modules with sealing to I
• Temperature ranges from - C to 2 C
• Competitor cross referencing and drop-in ready irect eplacement encoders
• Engineering services for your custom motion feedback needs
E C is ISO 2 certified, and we design, manufacture, and assemble most of our encoders and accessories at our corporate headquarters in Idaho, USA. When you call EPC, you’ll talk to engineers and encoder experts who can help you find the right motion feedback for your application. Contact us today.
Enercon’s induction cap sealing technology reliably creates hermetic seals to prevent leaks, provide tamper evidence, extend shelf life, deter pilferage and preserve product freshness.
With industry leading application expertise, equipment design, and support, Enercon makes implementing induction sealing simple. Our application engineers will recommend the best power supply and sealing head for your specific product, cap and container to ensure you will always Achieve a Perfect Seal.
Our highly efficient power supplies & innovative sealing heads optimize induction fields for reliable sealing. Whether you package pharmaceuticals, chemicals, food, beverage, cosmetics or personal care products, Enercon has a system solution for you. Seal containers one at a time with the industry workhorse the Super Seal™ Jr. For continuous production line sealing, choose the Super Seal™ Touch & Super Seal™ Max with intuitive touchscreen control with remarkable features such as recipe control, operator lockout and integrated troubleshooting information.
For moderate & low line speeds, our NEW Super Seal™ brilliantly seals containers while offering advanced features. Integrated stalled container detection, container rejection control, fault information, and a menu-driven interface provides operators with all the tools they need for successful sealing.
Whether you are new to induction sealing or a packaging industry veteran, you will appreciate the application expertise provided to Enercon customers around the world. We offer quick start guides, application infographics, free webinars, training, and of course 24/7 service.
Eriez’ equipment for the packaging industry includes metal detectors and magnetic separators for metal contaminant removal, as well as a full line of vibratory feeders, conveyors and screeners.
Eriez’ compact Vibratory Feeders handle high-speed packaging, difficult products like flour, leafy and gummy products, and high material flow applications. These electromagnetic drives are energy efficient, low maintenance with no moving parts, and can be mated with a range of sanitary and non-sanitary trays.
Eriez Xtreme Metal Detectors offer best-in-class performance to safeguard against both ferrous and nonferrous metal contaminants. This equipment is very effective for identifying and removing stainless steel fragments in conveyed, gravity flow and liquid line sanitary processing applications. Detectors are positioned at different locations throughout the process from bulk and raw material through final package inspection. There is no better solution to ensure your product is metal-free than using Eriez magnets for steel removal and using Eriez Xtreme® metal detectors to reject nonferrous metals like aluminum, brass, stainless steel and more.
Visit Eriez.com for FREE downloadable guides packed with information to help you choose the equipment you need to fit your unique application. Eriez.com features more than 250 packaging solutions, from our best-inclass vibratory feeders, conveyors, screeners, and metal detectors, to our wide selection of magnetic plates, grates and traps. Many of Eriez’ most popular magnetic separators, vibratory feeders and controls are available for next day shipment.
FANUC America is the leading supplier of CNCs, robotics and ROBOMACHINEs with over 40 million products installed globally. We have the largest variety of easy-to-use robot and cobot models available to pick, pack, fulfill or palletize any product.
FANUC’s robots and cobots are reliable, flexible and can handle virtually any size product - from 0.5 kg. to 2,300 kg., including:
- Our CRX collaborative robots are reliable, flexible, and easy-to-use solutions for kitting, palletizing, packing and much more.
- The new DR-3iB/6 STAINLESS is FANUC’s stainless-steel food-grade delta robot for picking and packing primary food products. Rated IP69K, the robot meets USDA and FDA food safety standards.
- Expanded SCARA robot family has six models including environmental options rated IP65 to withstand dust and liquids.
- The popular LR Mate series of tabletop robots has ten models including ISO Class 4 cleanroom and food-grade variants.
- The M-20iB/25C robot with an enclosed design and IP67 rating to withstand harsh environments.
- Established M-410iC series of high-speed palletizing robots.
FANUC offers application software for packaging and palletizing, integrated iRVision® and tracking features, ROBOGUIDE simulation, Dual Check Safety (DCS), and Zero Down Time (ZDT) to help customers monitor and manage their automation.
When you’re ready to automate, FANUC and our team of Authorized System Integrators are here to provide an efficient and cost-effective solution for your plant or fulfillment center. Let’s discuss how we can help you overcome production, supply chain and labor challenges by improving your OEE, flexibility, sanitation and safety. Also, we are committed to “Service First,” providing our customers parts and support for the life of their FANUC products.
Read more about FANUC America’s innovations in Packaging World.
Factory automation solutions from FlexLink, a Coesia company, increase the overall efficiency of production by minimizing throughput time. Our standardized solutions have a strong impact on factory performance and capability to meet the labor challenges of today. Our solutions are reconfigurable, reusable and requires minimal maintenance with low power consumption.
FlexLink’s team of experienced experts can propose customized solutions according to your needs. We deliver all sizes of projects – from simple part deliveries to large and complex turn-key solutions. Our approach is based on streamlining the material and information flows in a production process to maximize the value of the process and minimize all potential losses.
Automated palletizing with FlexLink palletizers (RC10, RC12 and RI20) helps reduce the workload of your employees. Using robotic palletizing solutions enables you to achieve effective and sustainable benefits by fully automating physically demanding and time-consuming tasks.
FlexLink serves a wide customer base, from local producers to global corporations, and from end-users to machine manufacturers. Our customers are lead players within the food, beverage, personal care, pharmaceuticals, automotive, and electronics industries.
Global support is provided by our operating units in 30 countries and a network of Strategic Partners. Our partner network is an important strategic element for FlexLink’s business model since our start in 1980, enabling us to enhance efficiency at factories in more than 60 countries.
FlexLink is part of Coesia, a group of innovation-based industrial and packaging solutions companies operating globally, headquartered in Bologna, Italy. www.coesia.com
FOCKE & CO is an international leading engineering company for packaging machines within the tobacco, food, savoury snacks, and hygiene industry. With more than 60+ years in business, we are proud to offer high-level machinery with top technology. FOCKE & CO is well recognized for providing turnkey engineering solutions for primary packaging, end–of–line packaging, and palletizing.
Due to the delicate nature of snack products, FOCKE & CO’s case packers offer careful handling alongside the flexibility to accommodate tray, traywith-lid, and case (RSC) packaging. In fact, our machines - such as the HFP Base (Highly Flexible Packer) - provide multiple pack configurations that normally cannot be achieved with a typical case packer. With a clean machine concept and a compact footprint, our HFP Base is designed to fit perfectly into typical snack food production lines.
The modular machinery design of the FOCKE stacker and bagger equipment offers economic solutions for various applications for the hygiene industry. Increased efficiency and an open design enable easy operations and maintenance. Neither various bag styles nor sustainable materials affect the operation planning with this packaging line. The stacker module itself stands for high flexibility to combine multiple modules such as one or more bagger and / or cartoner, flow wrapper, case packer as well as further packaging solutions.
With sales and service centers worldwide, FOCKE & CO has the capabilities to deliver local technical support, training, and spare parts. FOCKE & CO has repeatedly set new benchmarks in terms of output and product quality. Our ground-breaking technologies in the field of motion control combined with components featuring extreme dimensional accuracy are highly acclaimed in the industry. This is why we are the leader in Packaging Solutions.
We are here to help you design a packaging solution that is EFFICIENT, RELIABLE, and SUSTAINABLE.
Equipment EFFICIENCY is the result of many different options. The features of a Formost Fuji standard wrapper include a vision system that controls registration and makes for a faster film change and an operation panel with a tablet-like, intuitive user interface that helps reduce labor hours. The ALPHA 8 flow wrapper center seals are designed with induction heat technology that provides fast and consistent sealing, which in turn increases output and saves energy. These are just a few standard features to improve your packaging line’s efficiency.
RELIABILITY has been proven time and time again with our bagging and wrapping machines. Formost Fuji equipment is designed and built for years of dependable operation. In-house dedication to the design and manufacturing of our equipment has positioned Formost Fuji as a leader in quality horizontal flow wrapping and bagging machines as well as automation systems that remain the most reliable in the industry.
Formost Fuji is a leader in providing SUSTAINABLE packaging lines for our customers. With eco-friendly and recyclable materials continually improving and becoming more readily available, we provide free testing in our lab with your product and new films. This allows you to determine if the materials you are considering will align with your product, package integrity, and marketing efforts. Other innovative solutions, such as eliminating foam trays within flow wrap packaging, help meet consumer demand for better sustainability.
You can count on your partnership with Formost Fuji to provide you with excellent customer service from the beginning of the sales cycle, through the build and delivery, and continuing with support, training, and onsite service for years to come.
From sealers and cartoners to cappers, labelers to wrappers, Frain has a wide range of packaging equipment ready to ship to your facility within 2 weeks! Each Frain machine that ships out from our facility arrives to yours completely dialed into your product so when it arrives to your facility, you’re ready to begin production. It’s the closest thing to plug and play you’ll get in the packaging industry. Read on to learn more about how Frain adds value to every equipment purchase or rental.
Equipment Rentals:
Invest only in what you need when you need it with packaging equipment rentals from Frain. Ideal for seasonal items, special edition products and new product development, Frain’s program allows firms to conserve capital and maximize profit. All rentals come dialed into your product, allowing your firm to begin production faster. Best of all, there’s no long-term commitment necessary.
Why pay in full for something before you even use it? With Frain’s Pay As You Go flexible capital program, you’ll only pay for packaging equipment as you use it. There’s no leasing and no large capital investment. Instead, you’ll have the financial flexibility to invest in more projects, take more chances and get products to market faster – and on your schedule.
Consulting and Technical Support: Setup. Inspection. Repair. Training. It’s all part of the Frain difference. All Frain rentals and purchases come with up to 8 hours of technical support from Frain engineers to get you started – and we’re standing by to help with other maintenance and service too.
Contact Frain Today:
For more information on Frain and to inquire about the next piece of equipment for your packaging line, contact us today at 630-629-9900 or visit www.frain.com.
1-800-257-8581
Founded in 1926 in Hammonton, New Jersey, Garvey is recognized as a leader in designing and manufacturing low-impact, multi-functional, pressure-less loop accumulation systems, and conveyor systems. Highly regarded for its engineering expertise in developing equipment that can handle a large variety of product shapes and sizes, Garvey’s solutions convey, accumulate, orient, single file, combine, and lane products rapidly without back pressure or operator interference. It is a leader in bottling operations ranging from small vaccine vials to wine bottles. Garvey offers a broad product offering across both modular standard and highly engineered accumulation solutions. Garvey has approximately 100 employees, including a highly technical sales and engineering organization with a proven track record of innovation within the accumulation market.
Garvey’s flagship product is the Infinity Accumulator, designed to provide efficient and rapid accumulation of products without back pressure or operator interference.
The Infinity is a modular, standard accumulation solution, highly regarded for its ability to handle an extensive range of product shapes and sizes. It can handle it all, from small vaccine vials to wine bottles. Its unique design allows for products to be conveyed, accumulated, oriented, single-filed, combined, and laned rapidly and efficiently, ensuring maximum production output.
One of the critical features of the Infinity Accumulator is its pressureless loop accumulation system. This system eliminates the need for back pressure and reduces the risk of product damage, making it a reliable and safe solution for handling products. The accumulator is also equipped with the latest in engineering expertise, ensuring that it is highly functional and efficient.
Garvey’s Infinity is a perfect solution for companies looking to improve their operational efficiency. Its modular design makes it easy to install and integrate into existing systems, and its efficient accumulation technology maximizes production output.
Looking for the lowest total cost of ownership and highest quality packaging automation solutions available for food, medical devices, and other non-food products? We can help you navigate today’s complex, rapidly changing packaging landscape. We help balance costs and functionality with innovative and emerging processes, materials, and advanced technologies; enhance your profitability and improve the performance of your primary and secondary packaging operations. Our full-service solutions address installation, training, spare parts, service and customer support.
Our capabilities span robotics and automation, thermoforming, tray sealing, filling, flow-wrapping, stretch, blister, skin pack, and vacuum. Every smart, connected G. Mondini and ULMA packaging platform utilizes Rockwell Automation’s Integrated Architecture to reduce solution complexity and maintenance costs, while realizing better quality, capacity, and throughput. We also partner with PTC to incorporate Augmented Reality tools. It all lets us leverage data to enhance your operation and realize greater productivity and efficiency.
We are focused on the environment, aiming to help you meet demand while meeting your sustainability initiatives. Our sustainable packaging options include less plastic use, thinner gauge films, optimized package sizes, reduced film scrap, and alternative packaging materials. Our customers rely on us to help them optimize their overall packaging investment, from start to finish. We offer package design and prototyping services, and can help solve production concerns with comprehensive flexible and efficient systems. We help strategize how to tackle today’s most complex packaging challenges, such as sustainability, eCommerce, robotics and digital transformation.
We focus on lowering your TCO and offering the most reliable systems available. With consistent, professional and timely customer and technical service, our partnership extends well beyond your purchase.
Heat and Control®, a world-leading equipment manufacturer, offers the latest technology and the highest quality equipment for processing, coating and seasoning, conveying, weighing, packaging, inspection, and controls and information systems, and develops innovative solutions for production challenges.
Established in 1950, Heat and Control is a privately-owned company and has 12 manufacturing, warehouse, and associated facilities, 10 testing centers, and more than 30 offices globally. Heat and Control has partnered with other global manufacturing leaders, including Ishida (weighing packaging and inspection) and CEIA® (metal detection), and their brands include FastBack® (horizontal motion conveyors and on machine seasoning), Mastermatic (fryers), and Spray Dynamics® (coating and seasoning application systems). Heat and Control can offer a single machine or can integrate several components into a complete system and assume single-source responsibility.
Heat and Control is also able to assist manufacturers with equipment for all types of food, pharmaceutical, and non-food products, as well as provide pre- and post-sale technical support, including applications assistance, engineering, installation, parts, service, and training to maintain peak efficiency.
Heat and Control has built an extensive knowledge bank and developed a wealth of experience and expertise with access to production and technical support from a network of engineers, food technicians, field service technicians, skilled tradespeople, and support teams to provide food and non-food manufacturers with the ability to achieve their production goals.
Contact us to visit one of our demonstration centers to test products on the latest equipment.
High Tek USA, Inc.
www.hightekusa.com
High Tek USA has been a major player in the food weighing and packaging industry for almost 20 years. Founder and CEO, Jason Sigman started High Tek when he noticed that companies weren’t getting a quick turnaround on either the purchase or the repair of their machines. “When a weighing packaging machine goes down, the customer doesn’t have the ability to fulfill orders, which could mean loss of revenue, loss of the food product, and sometimes the loss of their business,” says Sigman. “We make sure that doesn’t happen.”
High Tek’s machines are durable, dependable, and long-lasting, with the star being their Premium Combination Weigher. High Tek’s machines have been created with the customer’s actual needs in mind. Customers want a machine that performs the essential speed and accuracy requirements but is also easy to operate, clean, and repair. This one has so many standard features and options for customers, it delivers everything for those who need it.
High Tek’s 24-hour technical and emergency services just can’t be beaten in this industry. “We have structured our business like firefighters, meaning we have the tools and experience to quickly identify an issue and provide solutions,” says Sigman. “We can schedule emergency services and get a technician on a plane with parts usually within 24 hours.”
Rancho Cordova
847-956-6600
www.hitachi-iesa.com/industrial-marking-and-coding
Hitachi Industrial Equipment & Solutions America, LLC is a pioneering developer of marking and coding solutions. We offer a wide range of Continuous Inkjet Printers and other solutions that are aimed at increasing efficiency and reducing maintenance costs associated with package printing. Since 1975, Hitachi has provided solutions to food & beverage, consumer goods, pharmaceuticals, automotive, and industrial packaging.
The new Hitachi UX2 printer combines innovation with the reliability customers have come to expect from Hitachi. This UX2 continuous inkjet printer has several new features to enhance the coding process:
• Enhanced code quality at higher speeds – The improved dot control algorithms create more legible codes. Even at increased speeds, code quality does not degrade.
• Added convenience and safety – With a sealed Safe-Clean Station, multiple cleaning modes, and self-guided troubleshooting videos available, the UX2 puts control in the hands of the operator.
• Quick line changeovers – Move inkjet printers from production line to line with ease using preconfigured I/O connectors, eliminating timeconsuming mistakes.
• Newly designed print head – Because of the print head modification to catch inkjet build-up, the UX2 printer can run for three times longer by reducing print quality issues and electronic faults.
A vision system is developed specifically able to isolate each character in the dot matrix inkjet printing while most vision systems on the market today are limited in their ability to read dot matrix printing found on primary packaging. This provides some key benefits to manufacturing companies:
• Specifically developed to accurately read inkjet codes regardless of the printer brand being used
• Isolation of each character to detect code degradation
Intertape Polymer Group Inc. (IPG) is a recognized leader in the packaging industry. Leveraging its advanced manufacturing technologies, extensive research and development capabilities and a comprehensive strategic acquisition program, IPG has assembled the broadest and deepest range of products in the industry.
IPG’s product offering includes carton sealing and industrial tapes (masking, filament, duct/cloth, double coated, flatback, foil and electrical), stretch and shrink film, protective packaging products and complementary packaging systems for industrial and retail use. IPG also specializes in high performance tape products engineered for demanding aerospace, marine, automotive and industrial applications. The comprehensive product offering and market specialization uniquely positions IPG as the supplier of choice for leading packaging and industrial distributors and large end users across a diverse cross section of industries.
IPG employs approximately 4,200 employees with operations in 35 locations, including 21 manufacturing facilities in North America, five in Asia and three in Europe.
888-419-2358
Intralox is the leading conveyance solutions provider helping move the world’s most critical products. Our extensive portfolio of technologies and services enhances food safety, powers e-commerce, and solves challenges for industries ranging from food processing to industrial manufacturing to logistics and material handling. Our business model relies on direct collaborative partnerships rather than distributors. Serving and supplying directly provides you with distinct advantages, including:
• E traordinary customer service
• Industry-specific e pertise
• aster innovation and implementation cycles
We partner with leading companies across the packaging industry to deliver innovative technology, reliable operations, and optimized line layouts. Whether you’re an equipment manufacturer or end user, you can benefit from our innovative products, comprehensive services, and unparalleled expertise.
Intralox’s belt and equipment solutions for the packaging industry help you:
• Optimi eline layouts for throughput and fle ibility
• uture-proof lines for fle ibility and sustainability
• Standardi e belts, equipment, and components
• educe product loss, operating costs, and downtime
Our acker to alleti er consists of three core facets E pertise,Service, and Technology. Our approach helps you fully integrate these areas in order to realize the best possible results, both now and in the future. By working with Intralox early in your project, you can achieve this and more with the right components and the right services before, during, and after installation— delivered on time, every time.
(864) 297-1200
ITW Hartness, a division of Illinois Tool Works (ITW), is the first choice in secondary packaging solutions. Our product portfolio includes highquality accumulation, packing and palletizing equipment that deliver unprecedented OEE, and lead the industry in using IIoT technology to maximize customer value.
ACCUMULATION—Recognized as the global leader in first-in, first-out, pressure-free accumulation, our proprietary DYNAC portfolio includes single-file, mass flow and floor level models to fit any application. With a small footprint flexible enough to handle a wide variety of packaging types, our products are relied on by leading consumer goods companies to prevent micro stops and increase uptime – saving you money.
PACKING—No matter how complex the package, our innovative packing solutions deliver speed, flexibility, and cost savings. Top load drop packing, shrink, tray, wraparound, and robotic case packing solutions make up our diverse portfolio. We work with customers to provide the solution best equipped to meet the unique needs of your product mix and operation.
PALLETIZING/DEPALLETIZING—With more than 500 robots installed and long-tenured experience on our team, ITW Hartness leads the industry with our proven palletizing and depalletizing equipment. Built to handle a wide range of products and packaging formats with no expensive change parts and fully automated changeover, customers see ROI in as little as 18 months or less.
AFTERMARKET—Downtime is expensive. That’s why our experienced customer support team is available 24/7. From onsite service and machine rebuilds to training and equipment updates, customers rely on ITW Hartness to provide unmatched expertise and support.
SYSTEMS INTEGRATION—Using a DYNAC-centric line design philosophy and best-in-class approach to machine center selection, our expert integration team helps select customers maximize end-of-line efficiency. Projects are validated using simulation software to assess performance, allowing customers to understand their investment and ROI even before the install. With proven experience helping customers increase throughout and lower cost of ownership, our equipment portfolio adds reliability and flexibility to any line.
908/362-9266
Located in northern New Jersey, James Alexander Corporation (JAC) is a leading contract manufacturer and custom filler of single-use crushable glass and plastic ampoules. Its manufacturing facility features unique, company-designed equipment and produces its patented plastic ampoules, among other product offerings.
James Alexander Corp. has expanded its operations floorspace, adding 18,000 square feet to its warehousing capacity and 2,000 feet apiece to manufacturing and office space. The expansion provides additional capacity for servicing key markets including pharmaceutical (OTC & Rx), medical devices, health & beauty products, first aid and diagnostics.
JAC’s patented single-use plastic ampoules, which have undergone various enhancements since their initial market introduction, are available in a variety of colors and with an array of applicators, offering singlehanded activation in a customizable format. Meanwhile, the company’s glass ampoules can be filled and assembled in single-use swab or dropper packages. JAC also recently introduced a winged device, THE ACTIVATOR™, which provides easier activation for these glass formats. Other services include autoclave sterilization for glass ampoules, blister packaging and formula compounding.
James Alexander Corp.’s revolutionary plastic ampoule combines style and ease of use through single-handed activation. With just a gentle squeeze, the inner membrane ruptures, allowing the contents to be dispensed by the user. The plastic ampoule is available in sizes up to 5ml, as well as a range of colors and applicators.
James Alexander Corp.’s unit-dose swabs offer the stability of glass in one- or two-part systems allowing for convenient application of pharmaceuticals and health aids. JAC also produces single-use glass ampoules for inhalation and dropper tip assemblies for the dispensing of liquids.
JLS Automation supplies hygienic robotic packaging solutions for the food industry that solve complex packaging challenges. Designed for even the strictest sanitary environments, our custom vision-guided primary & secondary robotic packaging systems are user-friendly, fast to start-up, & ensure both worker & food safety.
Several patents have been awarded for our proprietary robotic tooling & high-speed leak detection systems. Our hygienic, vision-guided robotic packaging systems are made to get wet, simple to integrate into your packaging line & never get tired!
Talon® Primary Loading Systems – Hygienic pick-and-place systems for loading thermoformers, flow-wrappers, vacuum skin packs, trays & more.
Osprey® Case Packers - Accurate & gentle loading of thermoformed packs, bags, SUPs, trays, chubs & other primary packs into standard RSC or retail-ready cases in horizontal or vertical orientation.
Peregrine® Vision-Guided Cartoning Solution - Load tri-seal & other cartons easily & efficiently. Elimination of conveyor transfers. Robotic loading & closing. All within a small footprint.
Harrier Bacon Draft Loading System - Automatically load bacon drafts into thermoformers, save floor space, solve labor gaps & increase productivity.
Sandwich Assembly System - Automatically build various sandwiches, accurately stacking each component from the bun/bread to meat, cheese & other ingredients. Lines can include up-and downstream equipment.
Integrated Systems - We take system responsibility for your entire line from concept to design, integration, FAT & installation.
JLS View - Reduce downtime spent on service & maintenance. Virtual service calls utilizing Microsoft HoloLens 2 technology provide easy access to technicians. Save time & get your line back running quickly.
941/493-5502
King Plastic Corporation is the leading manufacturer of quality polymer sheets, slabs, and massive shapes. With over 20 product brands to choose from and applications for every industry you can imagine. The Polymer sheets are made in the U.S.A.
King Hy-Pact®, the super tough polymer sheet is the smart choice for many high abuse applications in the food service, food processing and packaging markets.
The industrial polymer sheet is environmentally stabilized with excellent physical properties. It is the product of a proprietary process called K-Stran™, the most advanced manufacturing process of quality sheets with tight tolerances and custom widths up to 60”. King Hy-Pact® has a clean white color with a smooth, non-skived finish on both sides of sheet for better material flow. It is also available in black. Tests have shown for outdoor applications after 2,000 hours of UV exposure, King Hy-Pact® outperforms both HDPE and UHMW with superior toughness in wear resistance, flexibility and high-impact strength. King Hy-Pact® is the smart choice for many high abuse applications requiring superior properties, outstanding flatness and a smooth surface while providing significant cost savings compared to UHMW. Applications include, but are not limited to, food processing chutes, star wheels, fabricated parts, snowplow blades and dock fenders. The material is easy to machine and fabricate. King Hy-Pact® polymer sheet is NSF listed to meet requirements of commercial food processing operations for direct and indirect food contact.
Applications
Bin and Mixer Linings
Chain and Belt Guides
Conveyor and Guide Rails
Food Processing Components
Machine Parts
Material Handling
Sprockets
Star Wheels
In the kp Food Packaging division, the sustainable protection of everyday needs is very important to us. Our aim is to ensure you get the most sustainable total food packaging solutions that not only protect your food products while extending shelf-life and reducing food waste, but that can also be recycled. We operate across a vast range of fresh food categories, supplying thermoformed trays, rigid films for form, fill and seal applications as well as flexible barrier and stretch films to protect your products.
With 20 manufacturing and distribution facilities across 14 countries worldwide, we maximise the value we deliver to our customers while understanding and meeting local needs.
Supplying solutions for the food packaging starts by understanding market and consumer trends and anticipating their needs. kp works with top brands and retailers to understand and develop unique solutions to make them innovators in their markets.
Our inhouse PET flake cleaning process allows us to use up to 100% postconsumer recycled PET to further support your sustainability goals and optimize the carbon footprint throughout the entire value chain.
With over half a century of experience supporting the food market, kp is uniquely positioned to offer market knowledge, in-house design capabilities and a complete solution to support our customers’ growth opportunities.
Focused on delivering its vision: The Sustainable Protection of Everyday Needs, kp is a global leader in rigid and flexible packaging, and specialty film solutions, serving the pharmaceutical, medical device, label film, consumer packaging, cards/graphics, and home building and construction markets. With a broad and innovative portfolio of packaging and product films and services, kp plays an integral role in the customer value chain by safeguarding product integrity, protecting brand reputation and improving sustainability. kp’s “Investing in Better” sustainability strategy solidifies its commitment to achieving ten clear targets for long-term improvement by increasing recycling and recyclability of products, cutting carbon emissions and continuous improvement in employee engagement, safety, and diversity, equity and inclusion. kp has earned a gold rating from EcoVadis, the leading platform for environmental, social, and ethical performance ratings, putting kp in the top 3% of companies rated in the manufacturing of plastics products sector. Founded in 1965 kp has 31 plants in 18 countries and employs over 5,900 people committed to serving customers worldwide in over 60 locations.
Collaboration is integral with each opportunity. With a cooperative approach, kp’s expert technicians visit you on-site to consult, troubleshoot, train, and provide all the necessary solutions to help optimize film performance.
You can also work together with a designated team at the kp i.center, designed specifically, to serve the pharmaceutical, nutritional supplement and thermoforming industries. Equipped with state-of-the-art machinery and expert staff, kp is dedicated to help you improve current packaging and create new sustainable solutions.
Every day, millions of bottles, cans, and PET containers run through a Krones line. As a supplier for complete systems, Krones provides beverage bottlers, food producers, breweries and CPG companies all over the world with both individual machines and complete turnkey production lines. Our technology offerings are comprehensive and ever-expanding, with solutions from process technology, filling, and packaging…all the way through material flow, IT, automation, and container recycling.
With our comprehensive Lifecycle Service (LCS) aftermarket support program, Krones also provides full engineering and manufacturing support for implemented production solutions – up to 24 hours, 7 days-a-week. The robust online platform at Krones.shop offers a user-friendly experience to not only order spare parts, but also manage substitution lists, maintain customized stockkeeping, track upgrades, plan overhauls, and more. You can even access Krones Academy training courses for your on-site teams, allowing you to fully maximize your equipment investment.
Multiple Krones subsidiaries throughout North and Central America provide enhanced expertise and horsepower to meet your total packaging, production and processing needs. Serving the beverage, food, dairy, HPC and pharmaceutical industries, Krones Process Group North America provides sanitary process system expertise backed by the global depth and experience of KRONES. Leveraging over 165 years of combined experience, Krones North American subsidiaries Javlyn Process Systems, W.M. Sprinkman Corp. and Trans-Market have aligned, combining resources and knowledge to afford customers the highest level of quality.
Krones Inc. is headquartered in Franklin, Wis. and is the North and Central American subsidiary of Krones AG based in Neutraubling, Germany.
Label-Aire is the worldwide leading manufacturer of pressure-sensitive labeling machinery.
Over 50 years ago, Label-Aire introduced a revolutionary new method for applying pressure-sensitive labels. The patented “air-blow” concept provided the packaging industry with labeling machines. This new preferred method of label application eliminated the need for additional product handling. Our pioneering technique has gained complete acceptance. The widespread growth of pressure-sensitive labels in existing and new markets worldwide resulted.
When our customers asked for a labeling machine that was easy-to-use and production-tough, we took plenty of notes. Our advanced Primary Applicator line of labeling equipment delivers top-notch performance on even the most difficult applications. Our labeling systems and labeling equipment are loaded with features: Making operating labeling systems simple and virtually maintenance-free, automatic setup, user-friendly control panel & display, stepper motor technology, and Zero Downtime labeling capabilities. And it’s all backed by the industry’s most experienced and responsive labeling systems distributor network.
Since our inception, Label-Aire’s focus has always been on providing customers with the most inventive, intelligent, and reliable pressuresensitive labeling machines. The result? Over 50 years of satisfied customers with lower operating costs and higher productivity than our competitors.
At Mamata, we understand your needs and provide solutions to increase your productivity and reduce changeover times and footprint.
Our machines are based on conventional servo technology. They are designed to offer the best OEE in the simplex pouch packaging segment.
The key features address the crucial areas in terms of efficiency, hygiene, product quality and flexibility.
HFFS Rollstock machines: Our Simplex HFFS machines allows brands to produce and package pouches at upto 120 ppm and are to a Duplex machine. It’s ideal for lay-flat pouches, stand-up pouches with and without zippers, and single-serve sample packs in the range of 80 to 300 mm. Its ability to produce pouches from recyclable mono-material films makes it unique in the industry.
Premade Pouch filling systems: These machines are designed for highspeed premade pouch-filling applications, allowing you to trade old semi-automatic or manual operations for a highly efficient packaging machine. At 65 ppm, it delivers comparable speeds to a Duplex premade pouch system or a Simplex roll stock HFFS. An ideal machine to package trail mixes and nuts, fresh and frozen produce, snack foods, powders, Pet foods, etc. It’s designed to package both PE/PE recyclable mono-material pouches & laminated pouches.
VFFS baggers: Our Vertical Form Fill Sealing (VFFS) system achieves exceptional seal integrity and optimal precision across a large range of films at up to 220 ppm, making it the fastest system in the industry for single lane pouch filling.
All above and many more that will ease your packaging process and rise above getting competition.
For your pre-sales and after-sales support, our Florida location is equipped with spare-parts, local technical support, and sales consulting.
To help you define which technology offers the best price and performance ratio for your application, Markem-Imaje offers a full range of end-of-line solutions:
High-resolution Large Character Inkjet (LCIJ piezo)
Print and Apply Labeling
Thermal Inkjet (TIJ)
Low-resolution Large Character Valve Jet
The 5000 Series LCIJ piezo coders with Intelli’Wax printheads rapidly fill and jet Touch Dry® hot melt inks which are solvent-free, safe to handle and environmentally friendly. Codes never bleed or fade, dry on contact and are 100% scannable. The Intelli’Wax printheads combined with our exclusive Intelli’Dark Touch Dry ink produce the industry’s darkest, consistently scannable, direct print codes.
The 2200 Series print and apply solutions build on a proven concept that provides reliability, efficiency and ease of use. It gives you a wide range of interchangeable applicators, optimized operational intervention and an unparalleled application rate.
The innovative eTouch-S® applicator is built with artificial intelligence (AI) to ensure that labels are applied to your exacting standards on every pack, at the highest production speeds and in the safest manner possible. Thanks to its unique SoftTouch technology, the eTouch-S® applicator offers full movement control and application monitoring. An optional Advanced Trigger Sensor can fully automate labeling operations on variable-speed production lines with no operator intervention required.
End-of-line case coding is most effective when it gets the right product to its proper destination with high uptime in your factory. Regardless of which option you choose from us, you can take advantage of the data management capabilities of our CoLOS® platform and services to get the most out of your investment.
813/889-9500
METTLER TOLEDO is the world’s largest manufacturer of metal detectors, checkweighers, X-ray and vision inspection equipment, delivering a wide range of solutions for foreign body protection, regulatory compliance, and improved profits. Systems range from economical to state-of-the-art with customized material handling solutions.
Safeline metal detectors automatically reject all types of metal contaminants, including the most difficult to detect stainless steel. Systems are offered for dry, bulk, packaged, liquid or frozen products for gravity feed, conveyorized, pumped and throat applications.
Safeline x-ray inspection systems use high-performance image processing to detect and reject all types of dense physical contaminants, as well as measure mass, check for missing or broken product, and confirm fill levels to guarantee product and package integrity.
CI-Vision machine vision systems verify label content and integrity to prevent recalls. The use of these systems in your food safety program can help you prove due diligence, pass regulatory audits, and protect your brand.
Hi-Speed checkweighers deliver productivity and profits. A wide range of sizes and configurations are available to handle nearly any container type or package design even at high production rates to ensure accurate product delivery, reduced giveaway, and optimized production processes. Patented weighing technology and over 50 years of package handling expertise ensures repeatable performance from the first to the last package weighed maintaining tight production tolerances.
As a member of OMAC, METTLER TOLEDO is committed to connectivity and data storage and retrieval to help meet regulatory requirements. Inspection systems can be connected using a variety of methods, including our own ProdX data collection and management software.
mk North America is a full-service conveyor company, offering mechanical solutions for all of your packaging and automation needs.
Since 1988, mk has been manufacturing a wide variety of conveyor systems including: belt conveyors, flat top chain conveyors, plastic modular belt conveyors, timing belt conveyors, roller conveyors, and more.
All of our conveyor models are available with our standard t-slot aluminum frames, and many models are also available in stainless steel.
mk’s conveyor line is backed by the mk line of t-slot aluminum extrusionsideal for guards, workstations, carts, and so much more. This ensures that any accessories you buy from mk will be compatible, resulting in seamless integration on the factory floor; all while saving time and money.
mk North America believes in offering not only a better product, but also a better solution. Our dedicated team of conveyor and automation experts will work with you to understand your unique application and related challenges. This partnership results in mk being able to deliver a topquality conveyor solution when you need it.
All of our conveyors are built and tested in our Bloomfield, CT facility and shipped directly to you as completely assembled as possible. So, you can rest assured your conveyor system will be ready to go when it arrives.
Whether you are looking for a single, one-off, conveyor or a complete conveyor system - remember the mk promise to provide a better product AND a better solution.
We look forward to hearing from you and proving our excellence in conveyor system solutions on your next project.
Modular Conveyor Express (MCE) is the dedicated distributor network of Nercon. Selling exclusively through MCE Distributor Partners, MCE complete conveyor systems are designed by Nercon engineers and backed by Nercon quality standards. This network includes distributors located across the United States who are fully supported by an MCE team of conveyor experts able to understand and respond to the specific operational needs of the MCE distributor network on an individual basis.
Built to maximize productivity, MCE complete conveyor systems provide a significant competitive advantage to MCE distributors. Developed and designed by highly skilled Nercon engineers over countless hours of analysis and testing, MCE conveyors skip the costly start-up of a custom process and begin with a core of proven equipment making your projects more cost-effective and MCE’s turnaround time an advantage — 4 weeks!
MCE’s conveyor systems are manufactured at Nercon’s production facility in Oconto, Wis., where Lean Manufacturing practices are employed to increase quality, identify any wasteful operations, and reduce unnecessary costs. As an industry leader in manufacturing conveyor systems and equipment, we are proud of the advanced technology and unparalleled quality our distributors can count on.
Contact us at (844) 293-2816 to learn more about becoming a distributor of MCE.
www.modularconveyor.com
518-561-1812
Plastic jars, containers, CRC, continuous thread and dispensing closures manufactured in the USA.
Build your brand and deliver packaging premiumization with MRP Solutions. More than ever, consumers expect quality products packaged to deliver an unmatched user experience and connection to the brand and product. MRP Solutions combines extensive packaging expertise with a consultative approach to reliably uncover customer needs. By understanding business goals, we can tailor smarter, safer and more flexible packaging solutions that reduce cost and increase speed to market, helping businesses capitalize on opportunities. With one of the most robust, recyclable plastic closure offerings in the market, whether you need a standard continuous thread closure, disc top, push pull caps, twist open, child resistant caps or a specialized cap like our Ultra Light® or MegaFlap®, we have an option to fit your project. From fast-order shipping of a wide range of stock components to developing custom product solutions with our in-house innovation team, MRP is your trusted supplier.
MRP Solutions leads the way in sustainable manufacturing. MRP now offers PCR resin pricing in addition to virgin resin pricing on ALL quotes, where applicable. MRP makes it easier than ever to choose sustainable, choose recycled and choose circular.
MRP Solutions is an environmentally responsible manufacturer of packaging. We take pride in our on-going initiative to delight our customers by offering more sustainable solutions which reduce the amount of plastics used, provide recyclable options and promote re-use where ever possible. We have continuously invested in our manufacturing facilities to identify technology which conserves energy, uses renewable energy, and minimizes environmental impacts to our community and neighbors while we find a way to incorporate and re-use all material and recycle all scrap. Our sustainability initiatives start with our products and penetrate everything we touch from the community to our employees and the environment. Our product design and production processes consider
Increase your Productivity with MULTIVAC, your partner for single-source full-line packaging & processing solutions. Our One Line – One Control capability allows all MULTIVAC components, such as product loading, processing, packaging, conveying, printing, labeling, & inspection, to be controlled from a single HMI. With easy setup and changeover through a single interface, we provide the perfect machine for every pack.
As one of the world’s leading suppliers of packaging & processing solutions for a wide variety of foods, life science and healthcare products, and consumer and industrial goods, long-term productivity is at the heart of every machine and solution we develop. Thanks to holistically designed systems, our comprehensive line solutions help you reach your PEAQ Performance with increased Productivity, Efficiency, Availability, and Quality. MULTIVAC Smart Services enable data collection in realtime, optimizing processes and maximizing efficiency throughout your equipment lifecycle.
Our portfolio covers all packaging design, performance, and resource efficiency requirements. In addition, it encompasses an extensive range of packaging technologies, automation solutions, and labeling and quality control systems. Finally, our offering is rounded off by solutions upstream of the packaging process: in portioning and processing and baked goods technology.
Ultimately, we see ourselves as partners making a decisive contribution to your business’s success. As a worldwide group with 85 subsidiaries, we are closely linked with our customers and their markets, allowing us to identify trends and developments early. When you decide on MULTIVAC as a partner, you opt for the highest level of quality and efficiency, comprehensive customer care, and highly qualified sales and service teams.
844-293-2814
Nercon is a conveyor systems manufacturer, providing solutions to the snack, cheese, pet food and treats, beverage, health and pharmaceutical packaging industries since 1976. An essential part of any production line, Nercon’s conveyor systems are operating in nationwide consumer packaged goods manufacturing facilities, where uptime is critical in the efficiency of operations.
Designed with a Purpose®
Our ProCore® brand serves a unique purpose in the Nercon conveyor product line. Developed by highly skilled engineers over countless hours of analysis and testing, ProCore® conveyors skip the costly start-up of a custom process and begin with a core of proven equipment making your projects more cost-effective and our turnaround time faster. The ProCore® conveyor family maximizes performance and minimizes downtime. Conveyor designs range from MatTop, belt and TableTop, moving a variety of packaging.
Built to maximize productivity, HydroCore® is our sanitary and washdown conveyor systems designed to withstand rigorous sanitation practices and daily hygienic procedures. HydroCore’s® hygienic designs disassemble, washdown, sanitize, and reassemble easily. Our uniquely innovative sanitary design is known for its versatility and durability, adding value across all product operations.
Nercon’s conveyor systems are manufactured in Oconto, Wis., where Lean Manufacturing practices are employed to increase quality, identify any wasteful operations, and reduce unnecessary costs. As an industry leader in manufacturing conveyor systems and equipment, we are proud of the advanced technology and unparalleled quality our customers can count on.
Contact us at (844) 293-2814 to partner on your next project. www.nerconconveyors.com
Welcome to NITA Sentient Labeling Systems, the original 100% Servo Labeler that dramatically REDUCES OPERATOR TOUCH-TIME and increases productivity - all while integrating the latest next-gen technology, the most intuitive user experience, best-in-class responsive support, and truthfully, pure labeling joy.
We love UPTIME. We’re so driven by it we’ve designed all the features on every NITA to create it. How? By meticulously analyzing your labeling pain points – then solving them – with innovation, technology, and certifiably flawless execution.
And how do we keep you running? By building these incredible UPTIME features into every NITA:
- Parts ordering directly from the machine via built-in 3D drawings that scale down to your specific required item
- A self-diagnosing system that identifies possible issues and suggests fixes or when parts need changing or servicing before they become a problem
- Daily Preventative Maintenance schedules and video tutorials with tieredlevel tasks
- Ultra-fast & precise color-coded changeovers with in-screen 3D location maps or even our incredible Servo-driven FULLY AUTOMATIC product changeover system at the push of a button.
- NitaCare lifetime no-charge live remote tech support built right into your screen
Nita Labeling PROMISES to do anything and everything required to make your labeling life as easy and productive as it can be. It is why we exist. Experience for yourself what the best labeling company and labeler will bring to your productivity numbers. 100% money-back-guaranteed happiness.
We cannot wait to meet you. For the love of labeling! Your NITA Team
Nordson is recognized as the world leader in hot melt adhesive dispensing systems for the packaging industry, with comprehensive product lines that include tankless dispensing systems, adhesive melters, applicators, nozzles, hoses, and pattern controls as well as tracking and verification systems.
Nordson is a global solution, with direct offices in over 30 countries. Our substantial reach in global manufacturing allows for deep customer relationships, pursuing innovative solutions for customer problems and providing long-term, hands-on customer training, service, and support.
Nordson helps automate your packaging operations with products and solutions with a low total cost of ownership. Our adhesive systems help customers achieve a lower cost per package and reduce adhesive usage. Our solutions maximize package integrity and provide flexibility to meet changing market demands. Because one solution does not fit all applications, we offer a variety of systems to fit a wide range of needs.
Our ProBlue® Flex melter is advanced technology that is modular and scalable. It brings together machine integration, and precise and accurate adhesive dispensing. The ProBlue Flex melter is complemented by Nordson’s new BBconn Controls, which allows for remote operation, more visibility, real-time oversight, and the data and analytics needed for continuous improvement.
The MiniBlue II Slim with EcoBead Inspect ensures package integrity while reducing adhesive consumption. The MiniBlue® II applicator packs high performance, high speeds, and long-term reliability in a compact size. When paired with the EcoBead™ Inspect, users can verify adhesive placement to ensure the integrity of every package and can gather data for continuous improvement.
FILLING, CAPPING & CLOSING
www.novembal.com
For over 60 years, Novembal has been a leader in plastic cap design and injection. Our extensive knowledge of the markets, our experience and our commitment to continuous quality improvement, place us among the industry leaders. By offering our customers innovative solutions, we help them maintain and build their competitive position in the market. We support our customers in each step of the process, from the conceptualization of the closure designs through industrialization and beyond:
Our experts help customers turn their ideas into reality by providing innovative designs that make their products stand out on the shelves. Once the concept is validated through pilot tooling, an industrial solution will be provided.
We emphasize unique solutions that offer quality, convenience and innovation to meet any need that your business may have. If a completely new or different design is required, we can tailor a closure to the needs of our customer.
We also offer tolling options. By combining an existing customers’ mold and our resources, we can produce, finish, inspect and package your product.
The after-sales team provides reactive and proactive technical support to troubleshoot issues, minimize downtime and optimize your production equipment. Our goal is to help you achieve your goals in production and line efficiency.
AZ Peoria
nVenia leverages the strengths of the ARPAC, HAMER, FISCHBEIN, and OHLSON product brands as a leading equipment designer, manufacturer, and integrator for primary, secondary, and end-of-line packaging solutions.
ARPAC Brand equipment is renowned for integrated fit-for-purpose production lines and includes shrink wrappers, tunnels and bundlers, tray and case formers, case packers, robotic and conventional palletizers, and pallet stretch wrapper systems.
FISCHBEIN Brand equipment is the trusted name in open-mouth bag sewing and sealing systems. Sew systems encompass plain and tape sew models, with sealers for all shapes and sizes of flexible packaging.
HAMER Brand equipment leads the market in large format bagging and automation equipment in some of the harshest production environments. The new HAMER Brand VLR-B machine delivers highly accurate dosing of free-flowing powdered products. The horizontal form, fill & seal systems are ideally suited for large scale bag filling automation, open mouth bagging machines are the industry standard for filling premade bags, and robotic palletizing systems are also ideally suited for stacking large bags.
OHLSON Brand equipment is an economic solution for automating weighing and counting operations. The OHLSON Brand includes multihead weighers, linear weighers, vertical form, fill & seal (VFFS) machines, and premade pouch filling machines.
Combined, these trusted brands deliver next-level performance through the consultative design of integrated production lines to meet the needs of a variety of industries. Our expertise as an integrated packaging systems manufacturer is born from decades of building packaging equipment and answering to the diverse requirements of our clients to package products within a single production line.
Backed by more than 300 years of experience across our brands, together we have one focus: our customers and what they need to solve.
920
www.optima-packaging.com/en-us
Filling, closing, and packaging with state-of-the-art technology. Cuttingedge machine solutions for the entire packaging world – that is our commitment.
Incorporated in 1985, with one employee in Green Bay, Wisconsin, Optima Machinery Corporation was the first international subsidiary of Optima. Over the last 38 years, the business has grown to over 100 employees in the United States and the addition of a service hub located near Raleigh, North Carolina.
Originally established as the North American sales and service point for all Optima divisions, we provide OEM spare parts, service, support, calibration services, CG membrane repairs, multi-pack bagging machine solutions, and direct machine sales for all Optima machines delivered to the U.S. and Canada. We also represent Rianta Packaging Systems with sales and support for machines in the bakery industry.
Optima supports companies worldwide with flexible and customerspecific filling and packaging machines for pharmaceuticals, consumer goods, paper hygiene, and medical devices markets. As a provider of solutions and systems, Optima guides these companies from the product idea through successful production and throughout the entire machine life cycle. More than 3,000 experts around the globe and 19 international locations contribute to Optima’s success and ensure the worldwide availability of services.
833-472-9466
We’ve manufactured and installed vertical baggers, premade pouch fillers and flow wrappers for companies around the world for more than 30 years. We’re not a typical packaging machine company. We’re a single-source provider, so you get ONE point of contact for design, manufacturing, service and integration.
Operating from eight global facilities with a passionate and focused staff, we have a strong service presence, the ability to provide systems integration and an installed base of over 7,000 machines.
Manufactured through our WeighPack, EndFlex and ValTara brands and supported by Paxiom Service, our primary, secondary, and end-of-line packaging machines will increase your production rate and save you valuable time, labor and resources. Here are a few of our popular solutions:
VF
Engineered for high-speed applications, this vertical form, fill and seal machine can handle multiple package formats and produces a wide range of package sizes providing flexibility for both retail and club-size packaging, up to 150 bags per minute.
The Swifty 3600 features an easily accessible bag magazine, automatic zipper opener, bag shaker and integrated exit conveyor. Producing up to 2,700 bags per hour, this bagger will fill pouches from DOY pack, SUP and SURP to pillow, gusseted, quad and carry handle.
PKR-MS
The perfect addition to your flow wrapping line, this top load case/tray packer with delta robot will gently pick your wrapped product by either vacuum or mechanical means and place it into your case or tray at up to 80 packages per minute to be packed for shipping in your preferred pattern.
Visit us online to explore our packaging solutions and watch real-life videos. Whether you need a vertical form, fill and seal bagger for frozen food, a pick and place robot for wrapped baked goods, a premade pouch filling machine for snacks, or one of our other machines, we’re confident we have the automation solution for your business.
In 1993, Branko and Lilly Tisma founded PMI Cartoning, Inc. in Elk Grove Village, Ill. For 25 years, PMI worked to ensure its customers were satisfied with the quality of every single machine that left PMI’s doors. PMI expanded its operations as the company grew. In addition to its headquarters that houses all engineering, parts, service and support staff, PMI opened a 100,000-square-foot manufacturing, engineering and testing facility next to its offices, and a rebuild facility down the street in Arlington Heights, Illinois.
In December 2017, Kyoto Seisakusho Co., Ltd, a leading global packaging solutions provider, acquired PMI. Today, the former PMI Cartoning continues to operate from the Elk Grove location as PMI KYOTO Packaging Systems and offers the same service and high-quality vertical and horizontal cartoners, case packers, and integrated packaging systems customers have relied on for the past 25 years. In addition, new offerings will be available from the Kyoto product line, including over-wrappers and palletizers, which Kyoto has been providing for more than 70 years to the packaging industry.
Our industry and application experience includes food, beverage, cosmetic, confectionery and pharmaceutical, among others. Application and product handling experience allows us to excel with unique applications involving high speeds and difficult-to-handle products. Built to last, it’s not uncommon to find a PMI machine still running 20 years after installation.
After the successful debut of PMI KYOTO’s compact machine line at PACK EXPO 2022, the company is proud to say that three new compact machines have entered their fleet -- the KC-100F compact horizontal cartoner, the KTB-100 compact vertical case packer, and the SPC-3000 horizontal case packer are available for those who wish to maintain space in their factory without compromising on ability or quality.
Pneumatic Scale Angelus is an industry leader in the design and manufacture of packaging solutions for wet and dry filling, capping, can seaming, and labeling applications, as well as versatile container handling systems from Zepf Solutions. We design innovative equipment, using the most advanced technologies, to the unique specifications of our customers. Since 1895, our solutions have set the standard in the Food, Beverage, Craft Beverage, Pharmaceutical, Household and Personal Care industries, and are supported by a global Service and Aftermarket network with the most robust offering of change parts and pre-owned/rebuilt solutions in the industry.
As one of five Barry-Wehmiller businesses of BW Packaging and through our diverse but complementary capabilities, PSA and our sister companies provide everything from standalone machines to fully-integrated packaging lines. We serve as trusted advisors to our customers, offering products with leading-edge technology, backed by expert service technicians capable of supporting every machine manufactured since our inception.
PSA has earned its reputation as a leader in the design and manufacture of packaging machinery by leveraging the strengths of the most trusted and innovative brands: Angelus, Burt, Consolidated, Continental / Closetech, Mateer, Multi-Tech Systems, OnTrack, and Zepf Solutions.
As a member of the Barry-Wehmiller family, PSA strives to send our associates home each day with a sense of fulfillment. We strive to be a company people enjoy working for, doing business with, investing in, and having as part of their communities. As our Chairman Bob Chapman says, “We measure success by the way we touch the lives of people.”
Propack Processing & Packaging Systems Inc. is an industry leader in robotics and innovation, manufacturing and supplying high-performance processing and packaging machinery for the global market. At Propack, we pride ourselves on working collaboratively with clients to build strong relationships and ensure the best solutions are developed to meet their unique needs.
For over 25 years, Propack has been designing custom pick and place packaging systems for a variety of markets and applications. With the highest quality machinery, built in North America, Propack has earned a reputation for outstanding food-industry automation, specializing in handling snack bar, bakery/snack cake, prepared foods and frozen products, along with many more wrapped and unwrapped products.
We provide world-class sanitary design machinery including slab formers, slitters, spreaders, and ultrasonic guillotines. We understand our customers’ challenges and pride ourselves on being able to respond with flexible processing solutions.
With extensive integrated systems knowledge and experience providing turnkey solutions, our experienced team will design and deliver complete packaging line solutions and seamless integration for primary and secondary packaging operations.
Propack’s knowledgeable support team is customer focused and our engineers possess world-class technical skills. We recognize that our service and support is key to our customers’ success and our long-term partnerships.
R.A JONES offers an extensive portfolio of solutions for both primary and secondary packaging machinery for FOOD/BEVERAGE, HEALTH CARE, HOME CARE, PERSONAL CARE and other CONSUMER GOODS manufacturers that includes:
AEROSOL: Our KP-Aerofill series of machines includes low to high speed equipment for those needing aerosol and rotary liquid fill systems, rotary base crimpers, gasser/shakers, propellant and liquid fillers, bag-on-valve (BOV), air powered through-the-valve (TTV) technology, and more.
BEVERAGE/MULTIPACKING: Our Wraptor, Meridian, and Maxim series of machines provide a wide range of solutions for any mid to high speed can and/or bottle (glass or plastic) production line needs. Whether single tier or double tier, 4 pack to 48 pack, our machines can handle multiple package configurations and types including E-Flute & B-Flute cartons.
CARTONING: Our comprehensive portfolio of machinery includes end load and top load cartoners. These can range from hand load vertical end load cartoner to fully automated systems. Familiar branded cartoning technology includes: CMV, Legend, Legacy, and Criterion.
CHUB PACKAGING: Our KartridgPak chub packaging equipment established the chub package category decades ago. Features/benefits include: close-clip option, continuous motion, rollstock clips and film, PLC controls, simplified clipping head, stainless steel construction, heat, radio frequency and extruder sealing options, and more.
CUP FILLING/SEALING: Autoprod and Holmatic cup filling systems are the flagship series of cup fillers manufactured and services by R.A JONES. Fill, seal and overcap preformed cups, tubs and trays.
POUCHING: Pouch King is our high-speed pouch-filling series of horizontal form fill seal machinery with patented printed circuit heating technology for 3-sided, 4-sided, gusseted and stand-up gusseted pouch styles.
Robatech designs and manufactures sustainable solutions for industrial gluing processes that are reliable, safe, economical, straightforward, and green. Robatech’s experienced sales and service teams get gluing projects up and running and ensure smooth operation of adhesive systems all around the globe.
INNOVATIVE PRODUCTS FOR A NEW DIMENSION IN GLUING
Robatech’s innovations save resources and thus downsize your operating costs. The smart Vision melter (pictured on the bottom right) not only melts the adhesive gently and with great reliability, but it does so with the industry’s best energy efficiency. And the performance of the Performa heated hose is an excellent match. It reduces energy consumption up to 45% compared to conventional hoses. And to make the system complete, there’s the SpeedStar Compact application head that is not only fast, durable and intelligent, but it saves you up to 40% of adhesive when used for stitching.
PRECISE AND FAST GLUING OF PRIMARY PACKAGING
Primary packaging of food and medicines puts high demands on the gluing process. Robatech offers you reliable system components that allow you to glue small packages precisely and safely even at high speeds. You can expect a consistently high-precision adhesive application with a clean cutoff, safely and cleanly bonded products, high process reliability, high production speeds, and low energy consumption.
ECONOMICAL AND RELIABLE GLUING OF SECONDARY PACKAGING
Do you want to glue secondary packaging efficiently and yet sustainably?
Whether you put primarily packaged products into secondary packaging through standard top-loading or horizontal cartoning, or whether you use on-demand packaging machines, the adhesive process is essentially the same. Robatech’s adhesive application systems apply hot melt adhesives economically and still glue secondary packaging reliably. Maximum system availability increases your production by reducing downtime, while industry leading energy efficiency saves resources and reduces operating costs.
Ryson Spiral Conveyors need less floor space than conventional conveyors and are faster and more reliable than any elevator or lift.
Unit Load Spirals convey cases, totes and packaged goods smoothly on our slat style belts and come in 9 standard slat widths ranging from 6” to 30”. Available in powder coated carbon steel, stainless steel, wet environment and freezer versions.
Mass Flow Spirals handle full and empty bottles, cans and jars in mass up to 2000 units per minute. Available in 4 different slat widths ranging from 6” to 20”.
Narrow Trak Spirals are super compact and designed to handle your smaller loads. Our 6” and 9” wide nesting slats can end-transfer small cartons and packages or side-transfer small bottles and containers in a single file or in mass at speeds in excess of 200 FPM.
Ryson’s Bucket Elevators combine vertical and horizontal transportation of bulk materials in one integral unit.
Ryson Bucket Elevators are designed for gentle handling and well-suited to transport a broad range of bulk products. Our signature feature is that they are completely enclosed with overlapping pivoting buckets, that prevent spillage and helps mitigate foreign debris.
Their modular design enables us to customize with ease. They can be configured with multiple inlets or outlets that can be controlled individually. The design makes them easy to install and modify. Available in three standard bucket sizes, yielding capacities up to 300, 700 or 1,800 cubic feet per hour. They can also be delivered in powder-coated carbon-steel, stainless-steel or wet environment versions.
All Ryson equipment is modular and built to order. No matter the application, the Ryson team is up to the challenge of finding solutions for your conveying needs.
Schubert is a global leader in top-loading packaging machines (TLM). The family-owned company based in Crailsheim (Baden-Wuerttemberg, Germany) builds on an interplay of simple mechanics, intelligent control technology and high modularity. With this philosophy and a highly developed culture of innovation the company has been pursuing an entirely independent technological path for more than 50 years. The second generation of the company now employs 1,300 people. Innovations include the vision control system, the transport robot Transmodul or the flowwrapping machine Flowmodul. Schubert provides future-proof solutions that are easy to operate, flexible in terms of format conversion, high in performance and stable in function. The machines package products of all types in trays, cartons, boxes or flow-wrap bags.
With the new Schubert lightline machine series, customers can master standardized packaging tasks with great efficiency and high quality - at attractive purchase costs and short delivery times. It consists of three machine types: The lightline Cartonpacker, the lightline Pickerline and the lightline Flowpacker.
Space-saving design, unbeatable efficiency and excellent quality control are the hallmarks of the Schubert Flowpacker. It can be equipped with four different sealing technologies. The new patented technology makes it possible to program sealing to the millisecond and ensures constant sealing times. For each flow-pack, the cross-sealing unit immediately adapts to the variable speed of our upstream pick & place robots. Like all of Schubert’s sealing technologies, the flying cross-sealing unit can be integrated into every Flowmodul and combined with other sealing technologies.
With its North American headquarters in Charlotte, North Carolina, and with sites in Dallas, Texas and Toronto, Ontario, Schubert is expanding its customer support across the continent. This support encompasses high-level accessibility, preventive service as well as extensive training for customers. Schubert has installed two training machines at its training center in Charlotte.
www.serpapackaging.com
Serpa designs and manufactures a complete range of cartoning systems for the pharmaceutical, medical device, nutraceutical, food, beverage, cosmetics, industrial and personal care markets. For more than 37 years, companies across the globe have looked to us to handle their most demanding secondary packaging challenges.
We provide horizontal, vertical, and top load cartoners that can accommodate both hand load and automatic load applications, designing systems capable of nearly any speed for the desired application. We also provide a broad range of end of line packaging solutions, including case and tray packers, robotic palletizers, literature feeders, paperboard sleeve wrappers, tamper evident labelers, and robotic product handling systems. Additionally, Serpa provides line integration and validation services, designing turnkey integrated end of line packaging systems from start to finish with single source responsibility.
Serpa machines are designed to meet the needs of demanding production environments, featuring ease of maintenance, user-friendly operation, and rapid, repeatable changeover technology. Our high-performance systems can be designed to meet sanitary and FDA validation requirements and are backed by our strong customer support program to quickly resolve issues that may arise.
98% Uptime, Guaranteed
Established in North Carolina as Shurtape Technologies, LLC, we’re a privately owned, global company proudly serving a variety of markets, including packaging, building and construction, HVAC and industrial/ MRO. Our success is built on our passion: for our products, for complete customer satisfaction, and for the markets we serve. And we seek to continually remain engaged with our markets and the customers and craftsmen who use our tape so we can deliver what they need – to the absolute highest standards.
At Shurtape, we craft our packaging solutions to one simple standard. Yours. We know every sealing situation is unique. And we understand that keeping your lines running at peak production is a priority. This is what guides and inspires our team to develop purpose-built packaging solutions that address commons case sealing issues – downtime, material waste, personal injuries, product damage – and deliver the consistent, reliable seals you demand, every time.
In our Packaging Solutions portfolio, we offer a variety of hot melt and acrylic packaging tapes for manual and automated case sealing applications, including HP Series packaging tapes, which have the highest holding power to fiberboard in the industry and perform reliably down to the core, resulting in less unnecessary downtime due to changeover frequency and more efficient tape consumption. To enhance your packaging lines, we also offer a variety of manual and automated case sealing solutions, including ShurSEAL®, which combines our HP Series packaging tape with innovative tape application technology to produce secure, tamper-evident case seals, while maximizing packaging line performance.
For the efficient way you do business, we deliver Secure Seals, Every Time™
People all over the world consume products packaged by Sidel Group solutions every day.
Each of those packaging solutions is developed according to our goal to deliver the highest quality standards to consumers. We are a leading provider of equipment, services and complete solutions for packaging liquids, foods, home and personal care products in PET, can, glass, brick, carton, pouch and other materials.
There are close to 40,000 Sidel Group machines in operation in over 190 countries today. Every one of them is the result of over 170 years of proven experience and innovation.
We continually focus on providing our partners with proven expertise in blowing, filling, labelling, material-handling, end-of-line and lineengineering solutions, including an innovative focus on the factory of tomorrow.
Delivering this level of performance requires that we stay flexible. We continuously ensure we understand our customers’ changing challenges and commit to meeting their unique performance and sustainability goals. We do this through dialogue and by understanding the needs of their markets, production and value chains. In turn, we apply our solid technical knowledge and smart data analytics to ensure lifetime productivity reaches its full potential.
We call it Performance through Understanding.
1-800-323-2464
www.signode.com
With over $2B+ in revenue, 80+ manufacturing facilities across 6 continents and over 9,000 employees worldwide, Signode is a leading manufacturer of a broad spectrum of transit packaging consumables, tools, software, and equipment that optimize end-of line packaging operations and protect products in transit. Signode brings this extensive product portfolio together under 40 of trusted brands to offer complete transit packaging solutions to its customers.
We produce strap, stretch, stapling and protective packaging. We also manufacture packaging tools and equipment used to apply the bulk packaging materials. These commercial packaging products are used to pack, bundle, unitize, protect and secure goods during warehousing and transit. Our company is a pioneer in the industrial packaging sector with a long history of customer-focused innovations in materials, processes and automation technology that have revolutionized the sector.
Signode offers tailored automation solutions that allow manufacturers of all industries, scales, and needs to maximize productivity and efficiency. Among the wide spectrum of automation capabilities are StorFast® automated storage and retrieval system (ASRS), automated palletizers, a complete range of conveyors, Automatic Guided Vehicles (AGVs), Automatic Unitizing Solutions, and more.
All of these automation solutions are made possible through Signode’s intelligent logistics management systems. These systems have the power and customizable ability to provide everything from a basic Warehouse Control System for managing pallet movement all the way up to a complete Warehouse Management System that is integrated with each customer’s Enterprise Resource Planning (ERP) and order management software.
From standalone solutions to integrated systems. Signode provides the tools, consumables, and software to optimize end-of-line packaging operations and protect products in transit. We are excited to go to market as Signode and to share the portfolio of products, services and capabilities that make us the world’s premier end-of-line packaging company.
734/426-3476
For over 50 years SIKO has been developing and producing rotating and linear measuring systems, actuators and individually programmable displays for the entire field of machine construction. With its precision and innovative power, the company sets global standards in terms of quality and reliability. SIKO has been characterized by innovative ideas and quality without compromise for our customers. Our motivated and experienced staff is the cornerstone of our success. Many years of experience in distance and angle measuring technology as well as input from our customers have created a basis for solutions for both the present and the future.
SIKO is there for your Quick Size Changeover needs.
Three solutions, one supplier for effective size changeovers
1. Compact fieldbus actuators for precise fully automated positioning to shorten size changeover times. Offered with IO-Link, Ethernet/IP, Profinet, EtherCAT, PowerLINK, RS485 and CANopen interfaces.
2. Electronic indicators that monitor changeovers for verification, accuracy, safety and speed. Also, offered with the above mentioned interfaces.
3. Mechanical indicators for low cost, reliable axis positioning.
501-492-3893
The RFL Series range of roll fed labelers was born from the same need as our shrink sleeve labelers - a need for faster, more efficient, more robustly built machines with Allen Bradley controls. In a market where efficiencies and cost of ownership are everything, Sleeve Seal has a proven history of fast, precise label application with minimal maintenance costs. Our engineers have an unparalleled depth of knowledge that has been applied to a new style of label application for today’s market. Sleeve Seal is proud to present our new range of RFL Series of roll fed labelers.
Sleeve Seal is focused on a new era of repeatable labeling performance. Built-to-last American manufacturing expertise and modern engineering are combined to produce speeds from 25 to 1600 CPM on robust machines equipped with intelligent Allen Bradley controls. Heavy weight construction and the fastest, most durable drive train in the industry provide high efficiency runs for countless hours. Sleeve Seal machines are engineered to provide quality labeling performance with simple, tool-less changeovers between container formats. Other patented innovations, such as a multi blade cutter assembly with quick-change blades have been developed for ease of maintenance.
The line of Sleeve Seal shrink tunnels features a new style of tunable controls that make shrinking labels on containers both precise and repeatable. Our shrink tunnels are available in a broad range of sizes that compliment all our labelers for shrinking labels at high speeds. In addition to newly designed controls, Sleeve Seal tunnels feature 316 stainless steel interior lining and components for maximum corrosion resistance. Every shrink tunnel model features external controls that allow the adjustment of individual arrays without exposing the operator to heat.
Since 1969, Specialty Equipment Corporation has been a leading manufacturer of American-made packaging systems. Headquartered in Houston, Texas, we have built our reputation on manufacturing high-end packaging machinery and material handling systems including:
» Liquid fillers for Pails, Drums, Bottles, and Totes
» Drum and Pallet Conveyors
» Palletizers
» Solids Fillers for Pails, Drums, and Super Sacks
» IIoT software
Specialty Equipment is well known for building the most rugged drum, tote, pail and bottle filling machines for the agriculture, chemical, cleaning, coating, food, lube, and sealant industries.
Benefits of using Specialty Equipment Liquid Fillers:
» Improves Efficiencies & Accuracy
» Increase Production & Maximize Uptime
» Add Savings to Your Bottom Line
Over our 50 years in business, we have developed a full product line of automatic and semi-automatic liquid filling machines and conveyors for industries like; agriculture, chemical, cleaners, coatings, flavors, food, food additives, lubricants, and sealant manufacturers. The products we fill and convey include; drums, pails, bins, bottles, jugs, totes, pallets, and rubber bales, a customized product.
We continue to provide high-quality packaging systems to fortune 500 companies and have developed an intuitive software to improve the filling operations for companies of all sizes.
763/795-8856
Squid Ink is a manufacturer of coding and marking systems for product identification and traceability, providing superior-quality inks and lowmaintenance printing equipment.
Squid Ink began in 1991, supplying high-quality replacement inkjet fluids. Since then, the company has grown and expanded to include a complete line of hi-res piezo printing systems, CIJ (continuous ink jet) printing systems, TIJ (thermal inkjet) printing systems, DOD (drop-on-demand) printing systems, laser coders, and a full library of inks and inkjet fluids. Our printers and ink are designed to print the highest quality bar codes, batch numbers, date codes, logos, and large or small character text, directly onto corrugated cases, plastics, metals, glass, wood, and other substrates.
And Squid Ink continues to design new products that are reliable, easy to use, and cost-effective. One of our latest examples is the CoPilot Gemini, a new feature-rich printing system that offers 360 dpi print resolution, 5.6” print height, full-color touchscreen, and the option to run from a wireless tablet. The CoPilot Gemini offers users clean and reliable printing of bar codes, logos, and razor-sharp small-character text.
Today, Squid Ink continues to focus on its core purpose to “help companies deliver products to the world.” An expanding line of integrated products and services reflects Squid Ink’s commitment to meeting new needs and new challenges and ensuring that customers have reliable systems for their packaging application.
Squid Ink, Eastey, and American Film & Machinery (AFM) are all divisions of Engage Technologies Corporation. Squid Ink (squidink.com) is a manufacturer of coding and marking systems for product identification and traceability, providing superior quality inks and low-maintenance printing equipment. Eastey (eastey.com) is a leading manufacturer of heavy-duty shrink packaging equipment and automated case sealing systems for packaging applications. American Film & Machinery (afmsleeves.com) supplies shrink labelers and tunnels, shrink sleeves, and tamper bands.
Standard-Knapp, a leader in packaging equipment since 1894, specializes in the manufacture of custom, state-of-the-art case, tray and shrink packaging machinery. Standard-Knapp belongs to international group EOL Packaging Experts, GmbH, and acts as the North American distributor and servicer of equipment from sister companies A+F, BMS and NEO.
The newest addition to Standard-Knapp’s line of case packers is the Unipack 2.0, a robotic pick-and-place dynamo that can pack, unpack and repack. Designed for small to medium food and beverage plants, this packer covers a small footprint, and is easily transported with an optional mobility kit. The Unipack 2.0 shines in the 5-15 case/minute range, and features the same color-coded change part system that makes product changeover a snap on all Standard-Knapp machinery.
Standard-Knapp’s flagship machine is the 939S Versatron™ case packer. Its patented Soft Catch technology allow for the packing of lightweight glass into partitionless cases without breakage, via a servo-actuated lift table. This allows the Versatron to actually “catch” the product while it descends into the case. Even gentler packing is achieved by the robotic Pic-N-Place model. The Versatron™ Pic-N-Place uses robust, robotic arms and adjustable, heavy-duty grippers to pick up and gently place packs of product safely into the bottom of every case.
Standard-Knapp’s full line of case & drop packers includes a variety of useful options, modules and upgrades, as well as uncasers, case sealers and product laners.
Standard-Knapp also specializes in tray/shrink technology, including the exciting new TriWraptor™ line of multipackers, shrink wrappers and TSUP (Tray/Shrink/Unsupported/Pad) packer. The TriWraptor line’s flexible highspeed Robo-Wand™ wrapping module provides consistent, tight wrapping across a wide range of product shapes and sizes.
All Standard-Knapp machinery is engineered and built to provide decades of reliable service, 24/7/365.
Syntegon is a leading single-source supplier of processing, packaging, and automation technology to the food and pharma industries. Our product portfolio ranges from standalone, entry-level machines to fully integrated systems. Our mission is to support customers in creating sustainable solutions with market-leading technologies.
Syntegon’s technology is built by some of the most iconic names in packaging. Doboy, Elematic, Kliklok, Osgood, Sigpack, and Woodman are just several in the group. Their legacies of quality, reliability, service, and dedication to the customer embody Syntegon’s core philosophies. United as one team, we are all working toward the same vision — Packaging and Processing for a Better Life.
From mixing raw ingredients to end-of-line case packers, our portfolio for the food industry includes: confectionery and bar processing equipment; product distribution, collation, and loading systems; horizontal flowwrappers; vertical bagmakers; topload, endload and wraparound cartoners; case packers; filling and sealing systems for cups and bottles; thermoforming, filling, and sealing systems; bag sealers; checkweighing systems; and sustainable packaging solutions.
Fields of application in the pharmaceutical industry are the production, processing, filling, inspection and packaging of liquid and solid pharmaceuticals (e.g. syringes and capsules).
Based in Waiblingen, Germany, and employing some 6000 associates, at 30 locations in more than 15 countries worldwide, a highly-qualified workforce develops and produces complete solutions for the food, pharma, and consumer goods industries. These solutions are complemented by a comprehensive after-sales service portfolio. A global service and sales network provides customers with local points of contact, including several locations in North America.
Texwrap, a ProMach brand is centrally located in Washington, Missouri, and is the leader in the design and manufacture of fully automatic shrink wrapping, shrink bundling, and E-commerce systems.
Known as the industry innovator, we hold patents on some of the most significant breakthrough technologies in the shrink-wrapping business. Our full line of standard wrappers includes L-bar sealers, intermittent motion side sealers, continuous motion side sealers and vertical wrappers, as well as shrink tunnels, that are all made in the U.S.A.
The Tekkra & Kayat SRX lines of shrink bundlers helps round out our shrink packaging solutions with intermittent motion, continuous motion and custom bundling systems.
To complete our product offering, Texwrap’s EPS Series of machine’s provides solutions to help E-commerce operations improve profitability by increasing throughput, preventing errors with our proprietary product tracking feature, and creating right-sized packaging that reduces film waste and DIM weight shipping costs.
Texwrap partners with a nationwide network of highly trained packaging distributors in order to better serve our customers. This partnership provides a support structure to ensure the best machinery/application fit, a smooth startup, reliable local service, and long-term return on the machinery investment.
Our mission is to provide our customers with the latest technological advances while maintaining our commitment to a user-friendly machine that is efficient and easy to maintain. The quality construction, flexibility, easy changeover and low maintenance features of our systems give our machinery the Lowest Total Cost of Ownership available in the market today.
773/889-0200
For three generations, our family-owned & operated business has provided innovative sanitary packaging solutions that are built to last & supported in the USA. Triangle packaging machines offer versatility while providing solutions that maximize production. Whether you need to weigh or bag seafood, soup, mashed potatoes, protein, baking mix, put a bag of cereal in a box or a variety of other products, there’s a Triangle solution engineered to meet your application.
Our vertical form-fill-seal baggers are designed with sanitation & ease-ofuse in mind while meeting USDA/3A & FSMA standards. All models come with an open, accessible design, sanitary forming tubes, tool-less change parts & sloped surfaces for easy run-off during washdown.
Simple, automated solution for filling & sealing pre-made pouches. Run Doy bags, 3-sided seal, flat & stand-up pouches (SUP) with ease. Simple integration with multihead weighers, augers or cup fillers.
Flexibility in a small footprint. Quick, auto-changeover from single to dual or quad packs in seconds. Pairs perfectly with a Triangle bagger & weigher combination. A unique belt infeed system protects your product.
From cereal to wet proteins, & everything in between. Unmatched accuracy & speed. Even product distribution for optimal production. Mount directly on top of Triangle VFFS baggers. No mezzanines required.
Field service is available out of our Chicago headquarters & regionally throughout the US. Our 22 service technicians offer an average tenure of 18 years. Spare parts are manufactured in-house & are typically shipped the same business day.
1-866-369-4181
Unified Flex Packaging Technologies is a global manufacturer of flexible packaging systems tailor made to customer specific application requirements. Our manufacturing facility is located in the Canadian manufacturing hub of Woodstock, Ontario with service centers in the US to ensure quick and direct customer service. We have been designing and manufacturing superior quality flexible packaging systems for more than 15 years. Our engineering team alone have a combined 50 years of packaging and automation experience over a wide variety of applications. Our expertise can be measured by the depth of the product lines we offer. We have successfully manufactured systems for liquid, nutraceutical, snack food, produce, protein, industrial product, bakery, and confectionery applications for companies. Our flexible packaging systems are simple to use, reliable and robust made from premium quality non-proprietary parts.
Unified Flex has 7 unique series (Premium VFFS, Economic VFFS, Continuous motion VFFS, Stick Pack machines, Multilane Sachet, Spouted Pouch Fill and Cap, and Pre-Made Bag Packaging Machines) with a total of 17 machine models to provide customers with unique packaging systems for a wide range of products and packaging requirements. Not only will these machines significantly improve your productivity, they will greatly streamline your efficiencies. Speeds can range from 7 to 180 bags per minute and numerous bag types and sizes are achievable, bringing you more packaging options for your products. You can count on Unified Flex Packaging Technologies to deliver intelligent machines, economical solutions, and dependable systems for all your packaging needs.
Call us at 1-866-369-4181 or email sales@unifiedflex.com
727/327-2123
Welcome to Universal Labeling Systems! We are labeling machinery. Since 1984, no one has designed and built more custom, made-to-order labeling systems than Universal. Labeling is all we do and we do a lot of it. All machines are designed and built in the USA at our St. Petersburg, Florida manufacturing facility.
Everything we are goes into everything we do. Your Universal Labeling machine is sold and supported through a worldwide network of authorized distributors. And these knowledgeable distribution partners are backed by the expertise of our technical staff. Universal’s product manuals include specifications, bill of materials, set-up and operational details, and machine maintenance.
Universal Labeling Systems offers the most complete line of pressure sensitive labeling machines. From low volume table top models to high volume zero down time systems, our machines are designed, manufactured, and tested with one purpose in mind…you and your labeling needs.
And at Universal, we do more than talk as our Performance Guarantee states:
“All equipment manufactured by Universal Labeling Systems carries a 30day performance guarantee. If your labeling machinery does not perform as stated, we will take your machine back and reimburse you in full.” Since 1984, we continue to honor this pledge.
847/459-9500
U.S. Tsubaki Power Transmission, LLC is a leading manufacturer and supplier of state-of-the-art power transmission and motion control products and is a global leader in roller and conveyor chain production.
U.S. Tsubaki is the largest global subsidiary of Japan’s Tsubakimoto Chain Company which was founded in 1917. Today, U.S. Tsubaki products are marketed in over 70 countries. Its corporate headquarter and main distribution warehouse are just outside of Chicago in Wheeling, IL and it has full manufacturing facilities in Holyoke, MA, Sandusky, OH and Milwaukee, WI. In addition to this it has service centers strategically located in Los Angeles, CA; Houston, TX; Atlanta, GA; Philadelphia, PA and Anoka, MN.
The TSUBAKI name is synonymous with excellence in quality, dependability and customer service. An intense focus on research and development, along with constant modernization of its production facilities are among the key components in Tsubaki’s ability to successfully meet the ever-changing needs of the marketplace.
Tsubaki has a wide variety of standard roller chains and attachment chains that cater to the Packaging Industry applications. It also offers a multitude of specialty chains such as corrosion resistant Neptune® chain, lube-free Lambda® chain, vacuum wrapper chain, thermoforming chain, Gripper® chain and Titan® series chain for high-speed operations. Tsubaki’s Made-to-Order capabilities allow for custom engineering of chains and attachments specific to your operation to ensure optimal performance.
888/326/1476
VDG is the leader in the design and manufacturing of drum motors for belt conveyors, with a strong focus on safety, reliability, and longevity. Manufacturing in-house in USA and Canada for 37 years, using cuttingedge production technology and automation, and with continuous improvements through R&D, VDG ensures product quality, fast delivery, and after sales support.
All drive components of the VDG Drum Motor including the electric motor, gear reducer, and bearings are enclosed inside the drum, increasing energy efficiency, operator safety and optimizing space. VDG Drum Motors are designed for 80,000 hours of continuous operation before maintenance, minimizing downtime and reducing maintenance, and operational costs.
The VDG patented IronGrip™ lagging, offered for VDG Drum Motors, enhances the durability and lifespan of the conveyor belt and the lagging. It consists of steel bars welded symmetrically on the drum with hot-bond vulcanized lagging inserts between the bars. IronGrip™ lagging eliminates uneven belt wear, improves belt tracking, increases belt traction by 40%, and has a 4-5 times longer service life compared to standard lagging.
VDG’s stainless steel SSV Series Drum Motor features an IP69K rated sealing system, withstands up to 3,000 psi washdown pressure, and drives modular, wire mesh, and monolithic conveyor belts without using sprockets. The SSV Drum Motor eliminates crevices that trap food byproducts and bacterial harborage, reducing washdown time and water usage by 50% and providing the most efficient and hygienic drive solution for food processing and handling belt conveyors.
The IntelliDrive™ Drum Motor features new synchronous permanent magnet motor technology, delivering 40% increased electrical efficiency, a wider range of belt speeds without loss of torque and an increase in electric motor lifespan compared to a traditional conveyor drive. It enables onsite diagnostics, full motor indexing speed control, and communications with other automated plant equipment.
920-564-5051
Running a business can be complicated. Your packaging automation project shouldn’t be. At Viking Masek, our packaging systems help our customers do business better. Simplified, efficient, and automated. With over 20 years of packaging experience, Viking Masek Packaging Technologies has quickly grown to become an industry leader in durable, innovative packaging machinery.
We manufacture easy-to-use premade pouch packing machines, economical VFFS baggers, high-speed continuous motion vertical baggers, carton packaging, palletizing, robotics, and multilane stick packaging machines. Through Viking Masek Robotics & Automation, we offer our clients state-of-the-art robotic packaging systems. These packing solutions significantly enhance end-of-line processes, directly improving overall equipment effectiveness, customer satisfaction, and company profit.
Our stainless-steel equipment is durable and efficient. By applying the latest engineering advances to machine software, we maximize the efficiency from each machine, giving you faster production and more profitability. We also partner with top packaging film and pouch suppliers to ensure your packaging materials meet your needs for sustainability.
We offer technical service, training, and preventive maintenance plans with the purchase of every packaging machine. Not only does our team of Sales Consultants and Project Managers ensure that our clients’ needs are met from first contact to installation, but our Service Department also works tirelessly to ensure minimal downtime if training or maintenance are required.
From cheese and coffee to raw poultry and fresh vegetables, to pharmaceuticals and dietary supplements, plus much more, Viking Masek has the right packaging solution for you.
Are you ready to take your packaging to the next level? Visit us at www.VikingMasek.com
WestRock is a global leader in sustainable paper and packaging solutions. We are materials scientists, packaging designers, mechanical engineers and manufacturing experts with a shared purpose: Innovate Boldly. Package Sustainably. Guided by our values of integrity, respect, accountability and excellence, we use leading science and technology to move fiber-based packaging forward.
WestRock’s best-in-class innovation engine leverages the largest set of fiber-based substrates, a vast network of converting and distribution capabilities and an unmatched packaging machinery platform to power the next generation of renewable, recyclable packaging. Our broad portfolio is operated in four segments – Corrugated Packaging, Consumer Packaging, Global Paper and Mill Operations. A uniquely integrated Commercial, Innovation and Marketing function offers unrivaled end-to-end solutions and support to solve our customers’ greatest challenges.
Our global operations include:
– More than 50,000 employees in the Americas, Europe and Asia-Pacific
– More than 30 containerboard and paperboard mills
– More than 320 operating and business locations
– Products in a wide range of markets, including beauty and personal care, beverage, e-commerce, healthcare, home and garden, media and electronics, packaged food, pizza and retail
Sustainability and innovation are fundamental to WestRock’s vision to become the world’s best paper and packaging company. By innovating for our customers and their customers, bettering the planet and supporting people and communities, we’re imagining and delivering on the promise of a sustainable future.
Wexxar Bel is a leading manufacturer of fully and semi-automatic case and tray forming and sealing solutions. From small start-ups to Fortune 500 companies, we provide a wide array of reliable machinery focusing on advanced technologies, easy to operate equipment and a top tier service network.
Wexxar Bel’s dedication to quality means you can take pride in the quality of your purchase and peace of mind in the reliability and performance of our machines. Many Wexxar Bel customers are excited to show-off their new purchase to visitors and stakeholders while other more long-term customers still feel that pride when they show off their nearly 40 year old still running Wexxar Bel machines. You will always feel supported by the industry’s best performing and best-serviced case/tray formers and sealers in every step that your company takes
With a wide distribution and service network across North America, customers are always fully serviced and supported quickly and reliably. Whether you decide to work with our certified partners or our own experienced technicians, Wexxar Bel and our partners will listen, understand and solve your packaging problems and issues.
Wexxar Bel is also a technological leader in the field by pushing the boundaries of innovation. The company was built on the reliable patented “Pin & Dome” system and continues to incorporate new technologies in our products to create innovative and ultra-reliable packaging machinery. This obsession with reliability has also transitioned to our IPAK product line with the utilization of servo-drives to ensure complete tray blank control at all times for precision accurate forming.
Our dedication to pushing boundaries have also put a focus on providing sustainably made and efficient machines. Our manufacturing facility in Vancouver is powered 100% by renewable energy and we also implemented sustainable practices in our manufacturing facility. Furthermore, we constantly push our machines to be more energy and maintenance efficient, reducing overall energy consumption, redundant parts and increasing overall product life.
Do you have an in-motion product weighing challenge? Then Wipotec is your answer. Our checkweighers deliver precision, accuracy, and repeatability in robust product and package weighing applications. Our X-Ray scanners and vision systems ensure that foods are free of foreign body contamination while maximizing package integrity, and product labeling accuracy. Wipotec’s TQS modular serialization and aggregation machines guard against counterfeit products entering the global supply chain. Wipotec manufacturing takes place in Kaiserslautern, Germany. The Atlanta metro area is home to the company’s North American operations. The metro Atlanta facility includes training rooms, a product showroom, application engineering labs, and an expansive spare parts warehouse.
Checkweighers prevent under filling and overfilling of product, resulting in brand protection and cost reduction due to less product giveaway. Wipotec checkweighers use EMFR weigh cells to deliver the fastest and most accurate product weights possible at throughputs up to 650 ppm. The modular design of these machines enables support for a wide variety of machine options including metal detectors.
Our X-Ray scanners and vision systems prevent expensive product recalls. These machines maximize product safety and packaging integrity. X-Ray scanners are ideal for foreign body contaminant detection, package completeness, and fill-level checks. Vision systems do a great job verifying product label contents and correct placement on your packages.
These modular machines got their start in the pharmaceutical industry ensuring end-to-end tracking of medications in order to keep counterfeit products out of the supply chain. Driven by global compliance regulations, these machines employ open interfaces and software that delivers the flexibility needed to meet each country’s track and trace requirements. These machines are now finding use in various industries such as cosmetics, medical devices, cannabis, and personal care products.
Yamato is always the best way to weigh.
Yamato Corporation is the leading provider of automatic, commercial, and industrial weighing solutions in North, Central, and South America. Our industry strengths include cheese, poultry, snack foods, confectionery, prepared meals, fresh produce, and more. Whether your product is dry and free-flowing, wet and sticky, or frozen and a little difficult to run, a Yamato scale can weigh it for packaging.
Yamato scales offer supreme accuracy and support a wide variety of markets. Our combination weighers, checkweighers, and depositors can address virtually any packaging application. Our commercial scales offer convenient weighing for a range of retail markets, and our industrial solutions are ideal for very high target weights.
We promise you the Yamato Difference. As Yamato – not a distributor or agent – we’re easily accessible and available to offer you direct advice and support. We understand that you need non-stop performance. We promise you’ll get that from our scales, and from us. That’s the Yamato Difference.
Yamato Corporation is a subsidiary of Yamato Scale Co., Ltd., headquartered in Akashi, Japan. Founded in 1920, Yamato Scale Co. is celebrating over 100 years of providing innovative, high-quality weighing equipment and systems to customers around the world.
Learn more and find your scale at YamatoAmericas.com