Melt Flow Direction
Extensional Flow Device
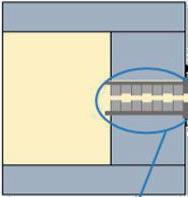
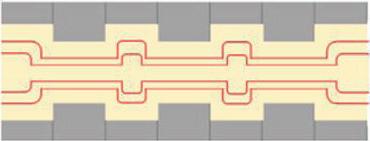
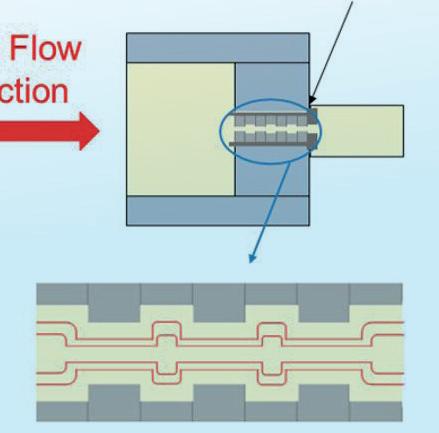
With multiple restrictions the extensional flow is enhanced
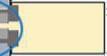
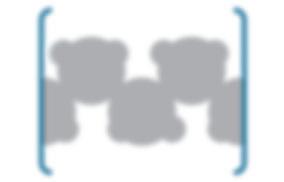
e d I tor I al C ou NCI l
Antonio Aprigio S. Curvelo (USP/IQSC) - President m ember S
Ailton S. Gomes (UFRJ/IMA), Rio de Janeiro, RJ (in memoriam)
Alain Dufresne (Grenoble INP/Pagora)
Bluma G. Soares (UFRJ/IMA)
César Liberato Petzhold (UFRGS/IQ)
Cristina T. Andrade (UFRJ/IQ)
Edson R. Simielli (Simielli - Soluções em Polímeros)
Edvani Curti Muniz (UEM/DQI)
Elias Hage Jr. (UFSCar/DEMa)
José Alexandrino de Sousa (UFSCar/DEMa)
José António C. Gomes Covas (UMinho/IPC)
José Carlos C. S. Pinto (UFRJ/COPPE)
Júlio Harada (Harada Hajime Machado Consutoria Ltda)
Luiz Antonio Pessan (UFSCar/DEMa)
Luiz Henrique C. Mattoso (EMBRAPA)
Marcelo Silveira Rabello (UFCG/UAEMa)
Marco Aurelio De Paoli (UNICAMP/IQ)
Osvaldo N. Oliveira Jr. (USP/IFSC)
Paula Moldenaers (KU Leuven/CIT)
Raquel S. Mauler (UFRGS/IQ)
Regina Célia R. Nunes (UFRJ/IMA)
Richard G. Weiss (GU/DeptChemistry)
Rodrigo Lambert Oréfice (UFMG/DEMET)
Sebastião V. Canevarolo Jr. (UFSCar/DEMa)
Silvio Manrich (UFSCar/DEMa)
Financial support:
Alain Dufresne Bluma G. Soares
César Liberato Petzhold José António C. Gomes Covas José Carlos C. S. Pinto Paula Moldenaers Richard G. Weiss Rodrigo Lambert Oréfice
d e S kto P P ubl IS h IN g www.editoracubo.com.br
“Polímeros” is a publication of the Associação Brasileira de Polímeros São Paulo 994 St. São Carlos, SP, Brazil, 13560-340 Phone: +55 16 3374-3949 emails: abpol@abpol.org.br / revista@abpol.org.br http://www.abpol.org.br
Date of publication: April 2022
Available
Polímeros / Associação Brasileira de Polímeros. vol. 1, nº 1 (1991) -.- São Carlos: ABPol, 1991Quarterly v. 32, nº 2 (Apr./June 2022) ISSN 0104-1428
ISSN 1678-5169 (electronic version)
1. Polímeros. l. Associação Brasileira de Polímeros.
Website of the “Polímeros”: www.revistapolimeros.org.br
Latex and natural rubber: recent advances for biomedical applications
Karina Luzia Andrade, Heloisa Ramlow, Juliana Ferreira Floriano, Emanoelle Diz Acosta, Fabrício Luiz Faita and Ricardo Antonio Francisco Machado
1/12
Marcel Yuzo Kondo, Larissa Stieven Montagna, Guilherme Ferreira de Melo Morgado, André Luiz Guimarães de Castilho, Larissa Anne Pereira dos Santos Batista, Edson Cocchieri Botelho, Michelle Leali Costa, Fabio Roberto Passador, Mirabel Cerqueira Rezende and Marcos Valério Ribeiro 1/14
Torsion modulus with CaCO3 fillers in unsaturated polyester resin - mechanical spectroscopy
Carlos Alberto Fonzar Pintão, Airton Baggio, Lucas Pereira Piedade, Luiz Eduardo de Angelo Sanchez and Gilberto de Magalhães Bento Gonçalves 1/10
Classification of natural rubber foam grades by optimising the azodicarbonamide content
Fateehah Baru, Sitisaiyidah Saiwari and Nabil Hayeemasae 1/8
Development and optimization by factorial design of polymeric nanoparticles for simvastatin delivery
Dalila Pinto Malaquias, Lays Fernanda Nunes Dourado, Ângela Maria Quintão Lana, Fernando Souza, José Vilela, Margareth Andrade, Juan Pedro Bretas Roa, Álvaro Dutra de Carvalho-Junior and Elaine Amaral Leite 1/10
A hybrid green composite for automotive industry
Gabriella Neto Chagas, Maiccon Martins Barros, Ariadne Gonçalves de Leão, Neyda de La Caridad Om Tapanes, Roberto Carlos da Conceição Ribeiro and Daniele Cruz Bastos 1/8
Evaluation of magnetic poly(methyl methacrylate) microspheres as catalysts in heterogeneous Fenton processes
Alan Kardec da Silva, Ezaine Cristina Corrêa Torquato, Jacira Aparecida Castanharo, Marcos Antonio da Silva Costa, Mônica Regina da Costa Marques and Luciana da Cunha Costa
1/10
Impact of controlled extensional flow during extrusion of PP, PVDF and LDPE
Marcel Andrey de Goes, João Paulo Ferreira Santos and Benjamim de Melo Carvalho 1/8
Improving the dispersion of multiwalled carbon nanotube in polypropylene using controlled extensional flow
Marcel Andrey de Goes, João Paulo Ferreira Santos and Benjamim de Melo Carvalho 1/7
Physical-mechanical behavior of nitrile rubber-synthetic mica nanocomposites
Janis Schutte Nunes, Edson Noriyuki Ito, Cléverson Fernandes Senra Gabriel, Thiago Castro Lopes and Regina Célia Reis Nunes 1/10
Development and characterization of green polyethylene/clay/antimicrobial additive nanocomposites
Priscylla Jordânia Pereira de Mesquita, Tatianny Soares Alves and Renata Barbosa
Development and evaluation of nitrile rubbers seals for power transformer application
1/8
Mauro Cesar de Avila, Ana Paula Munaro and Marilda Munaro 1/8
Scientists at the University of Birmingham have invented a new method to encourage bacteria to form growth-promoting ecosystems that could be used to coat the roots of plant seedlings, which is expected to result in stronger, healthier plants, and higher crop yields in agriculture.
In nature, the roots of seedlings form mutually beneficial relationships with communities of microbes (fungi, bacteria, viruses) in soil, and exchange nutrients, allowing both the plant and the microbes to flourish. This is particularly critical in the early stages of a plant’s life when the seedling is in a race against time to reach self-sufficient growth before the nutrients and energy stores in the seed run out.
Dr Tim Overton, an applied microbiologist from the University’s School of Chemical Engineering, and Dr Francisco Fernandez-Trillo from the School of Chemistry led a team to develop novel synthetic polymers that stimulate the formation of these bacterial communities, in a way that mirrors a natural process known as biofilm formation. A biofilm is a finely orchestrated community of microbes, supported by matrix of biological polymers that forms a protective micro-environment and holds the community together. The researchers worked jointly on a four-year project on how polymers interact with bacteria, which resulted in the synthesis of a group of acylhydrazonebased polymers.
These new polymers were designed to act as an adhesive scaffold, “seeding” the formation of a microorganism-polymer complex to initiate and expedite biofilm formation. Once the biofilm is formed, the bacteria become a self-sufficient and self-organizing community, and produce their own matrix to allow the transmission of nutrients and water, and the discharge of waste products.
The project was funded by Biotechnology and Biological Sciences Research Council (BBSRC) through their Midlands Integrative Biosciences Training Partnership. It involved PhD students Pavan Adoni and Omar Huneidi, who subsequently progressed research showing the polymers aggregate bacteria, and improve biofilm formation. Critically, they also showed the process is fully reversible, and the biofilm can be dispersed by changing the environmental conditions. The results of these experiments and further studies will be published in 2022.
Pavan Adoni commented: “We anticipate that the polymer will ultimately be used as a seed coating, perhaps in conjunction with bacteria such as B. Subtilis, which is naturally present in soil, increases the stress tolerance of plants, and is currently used as a soil inoculant. We envisage a more targeted approach that only treats the seed, so that when it germinates the bacteria are ready to grow in the safe harbour environment provided by a micro-organism polymer complex. Ultimately this should result in stronger plants, which grow more quickly, and have greater resilience to disease.”
University of Birmingham Enterprise filed a broad-based patent application covering the novel polymers, the method of forming the biofilm and the method of polymer cleaving, and its use to promote growth of a biofilm with any microorganism including those that can produce or deliver chemical or biological molecules. The patent has now been licensed to specialist life science company PBL Technology, which invests in, protects and promotes emerging innovations from public research sources worldwide. In agriculture, PBL’s technologies include crop genetics, crop treatments, precision agriculture and promoters and R&D tools.
Source: University of Birmingham – birmingham.ac.uk
Specialty chemicals company LANXESS has developed a non-halogen flame retardant that will soon be offered under the brand name Emerald Innovation NH 500. The phosphorus-based additive is designed primarily for use in glass fiber-reinforced plastics used to manufacture products for the electrical and electronics (E&E) industry.
The new polymer additive from LANXESS exhibits very good flame retardant properties in combination with other additives and easily meets the relevant fire safety tests. A glass-fiber-filled PA66 formulated with Emerald Innovation NH 500 passed the UL 94 fire test of the U.S. testing company Underwriters Laboratories Inc. with an outstanding V-0 classification at 0.8 mm test specimen thickness. In glow-wire testing, the highest intended glow-wire flammability Index (GWFI) of 960 °C is achieved without difficulty by a specimen of 3 mm thickness. The glow-wire ignition temperature (GWIT) was measured up to 875 °C which is significantly higher than that of the reference (775 °C).
LANXESS has developed versatile formulations for its new flame retardant. They ensure that the mechanical properties and other functional characteristics of the end products are maintained. In addition, the product can boast excellent thermal stability and a unique morphology. The combination of very good flame retardant properties and high dimensional stability in engineering thermoplastics, such as polyamide 6 and 66 (PA6, PA66), offers compounders and processors promising applications.
More information on LANXESS’ polymer additives is available at https://pla.lanxess.com.
Source: LANXESS – lanxess.com
5th International Conference on Academic Research in Science, Technology and Engineering
Date: November 3-5, 2022
Location: Vienna, Austria Website: www.icarste.org/
Polymer Testing World Expo North America – 2022
Date: November 9-10, 2022
Location: Cleveland, Ohio, United State of America Website: na.polymertestingexpo.com/
7th International Conference and Exhibition on Polymer Chemistry
Date: November 21-22, 2022
Location: London, United Kingdom Website: polymerchemistry.euroscicon.com/
13th World Congress on Biopolymers and Biomaterials
Date: November 21-22, 2022
Location: London, United Kingdom Website: biopolymerscongress.conferenceseries.com/
Polymers in Footwear Virtual Summit – 2022
Date: November 29 – December 1, 2022
Location: Germany (on-line only) Website: www.ami-events.com/YdPQ35?RefId=AMI+website
17th European Bioplastics Conference
Date: December 6-7, 2022
Location: Berlin, Germany (hybrid) Website: www.european-bioplastics.org/events/eubp-conference/
Third International Conference on Advances in Material Science 2022
Date: December 8-9, 2022
Location: India (on-line only) Website: icams.in
POLY-CHAR 2023
Date: January 22-27, 2023
Location: Auckland, New Zealand Website: www.poly-char2023.org/
Polyethylene Films North America – 2023
Date: January 31 - February 2, 2023
Location: Orlando, United State of America Website: www.ami-events.com/o7ezmL?RefId=AMI+Website
4th International Conference on Polymers and Plastics, Artificial Intelligence. Robotics, Smart Materials, Engineering & Information Technology (ICPPAI-FEB-2023)
Date: February 18-19, 2023
Location: Shanghai, China Website: irnest.org/icppai-feb-2023/
4th World Expo on Biopolymers and Bioplastics
Date: March 6-7, 2023
Location: Berlin, Germany Website: biopolymers.materialsconferences.com/
18th International Plastics and Petrochemicals Trade Exhibitions
Date: March 21-24, 2023
Location: Riyadh, Saudi Arabia
Website: saudi-pppp.com/saudi-plastics-petrochem Plástico Brasil — International Plastic Exhibition
Date: March 27-31, 2023
Location: São Paulo, São Paulo, Brazil Website: www.plasticobrasil.com.br/en
24th International Conference on Wear of Materials
Date: April 16-20, 2023
Location: Banff, Alberta, Canada. Website: www.wearofmaterialsconference.com/ Polymers in Flooring Europe – 2023
Date: April 18-19, 2023
Location: Berlin, Germany Website: www.ami-events.com/N3NmxB?RefId=AMI_Website
38th International Conference of the Polymer Processing Society
Date: May 22-26, 2023
Location: St. Gallen, Switzerland Website: www.pps-38.org/
Polymer Sourcing & Distribution – 2023 Date: May 23-25, 2023
Location: Hamburg, Germany Website: www.ami-events.com/event/7e7d5b18-b87b-4167bbbe-ed4142955f44/summary
Frontiers in Polymer Science 2023 — Seventh International Symposium Frontiers in Polymer Science Date: May 30 – June 1, 2023
Location: Gothenburg, Sweden Website: www.elsevier.com/events/conferences/frontiers-inpolymer-science
Gordon Research Seminar — Polymers
Date: June 3-4, 2023
Location: South Hadley, Massachusetts, United State of America Website: www.grc.org/polymers-grs-conference/2023/ Gordon Research Conference — Polymers
Date: June 4-9, 2023
Location: South Hadley, Massachusetts, United State of America Website: www.grc.org/polymers-conference/2023/
Polymer Testing World Expo Europe – 2023 Date: June 14-15, 2023
Location: Messe Essen, Germany Website: eu.polymertestingexpo.com/
Fluoropolymer 2023
Date: June 18-21, 2023
Location: Denver, Colorado, United State of America Website: www.polyacs.net/23fluoropolymer
MACRO2024 — 50th World Polymer Congress
Date: June 30 – July 4, 2023
Location: Coventry, United Kingdom Website: iupac.org/event/50th-world-polymer-congressmacro2024/
Sustainable Polymers
Date: October 15-18, 2023
Location: Safety Harbor, Florida, United State of America Website: www.polyacs.net/23sustainablepolymers
17th Brazilian Polymer Congress Date: October 29 - November 2, 2023
Location: Joinville, Brazil Website: www.cbpol.com.br/
Karina Luzia Andrade1 , Heloisa Ramlow1 , Juliana Ferreira Floriano2,3 , Emanoelle Diz Acosta1 , Fabrício Luiz Faita4 and Ricardo Antonio Francisco Machado1*
1Laboratório de Processos e Controle de Polimerização, Departamento de Engenharia Química e Engenharia de Alimentos, Universidade Federal de Santa Catarina, Florianópolis, SC, Brasil
2Laboratório Innova, Unidade de Pesquisa Experimental, Faculdade de Medicina de Botucatu, Universidade Estadual Paulista, Botucatu, SP, Brasil
3Imperial Centre for Translational and Experimental Medicine (ICTEM), National Heart and Lung Institute, Imperial College London, London, UK
4Laboratório de Altas Pressões e Materiais Avançados, Instituto de Física, Universidade Federal do Rio Grande do Sul, Porto Alegre, RS, Brasil *ricardo.machado@ufsc.br
Recently, latex (NRL) and natural rubber (NR) from Hevea brasiliensis have emerged as promising biomaterials from renewable sources for biomedical applications. Although some attempts at commercial applications have been made, there is a need to comprehensively document the state-of-the-art of these biopolymers for biomedical applications and regenerative medicine. Here we present the recent advances in the development of NRL and NR as biomedical materials with potential properties including biocompatibility and biodegradability. Due to the angiogenic properties of NRL and NR, well-defined functional materials can be used for drug delivery systems (oral/transdermal), scaffolds for skin and bone regeneration, and dressings for wound healing. The incorporation of drugs, nanoparticles, cells, and others into NRL and NR polymer chains offers a wide range of applications such as dressings with antimicrobial activity and sustained release systems. Concluding remarks on the growth of these biomaterials for biomedical applications and regenerative medicine were discussed.
Keywords: drug delivery system, Hevea brasiliensis, scaffolds, tissue repair, wound dressing.
How to cite: Andrade, K. L., Ramlow, H., Floriano, J. F., Acosta, E. D., Faita, F. L., & Machado, R. A. F. (2022). Latex and natural rubber: recent advances for biomedical applications. Polímeros: Ciência e Tecnologia, 32(2), e2022015. https://doi.org/10.1590/0104-1428.20210114
Natural Rubber Latex (NRL), produced by the Brazilian rubber tree Hevea brasiliensis, is a colloidal system containing approximately 50 wt.% water, 30-45 wt.% rubber particles (mainly cis-1,4-polyisoprene), and 4-5 wt.% nonrubber constituents, including proteins, lipids, and carbohydrates[1-4] Natural Rubber (NR), obtained from NRL, is a polymeric substance of high molecular weight and has viscoelastic properties, which makes it ideal for various applications, in which biomedical applications stand out[3-8]
Recent work has shown that NRL and NR are bioactive materials that promote cell adhesion, extracellular matrix formation, and accelerating tissue repair due to increased angiogenesis at the site of injury[9,10]. NRL and NR polymers present biocompatibility, and angiogenic properties that induce tissue healing, high elasticity, flexibility, and mechanical strength[6,7,11-14]. A range of biomedical devices based on NRL and NR have been recently developed to accelerate
tissue repair, including wound dressings, cellular scaffolds, as well as components of sustained drug delivery systems and transdermal drug delivery patches[8,11,12] (Figure 1).
Although significant progress has been made in utilizing NRL and NR as functional biomaterials, there is a need to comprehensively document these developments for biomedical applications and regenerative medicine. This review aims to study and discuss the advances in the field of NR and NRL biopolymers and to foster a better conception of how these polymers have evolved as a field of significance in biomedicine. A summary of the biodegradability and biocompatibility of NRL and NR is first presented. Next, the application as a biomedical device and the incorporation of additives are discussed. Finally, the review presents the conclusions and remarks for the future growth of NRL and NR biomaterials for biomedical applications and regenerative medicine.
The most important characteristics of biopolymers with potential application in the biomedical field refer to their biocompatibility and biodegradability, making them promising alternative eco-friendly resources to non-degradable synthetic polymers, which are common in short-term applications in biomedicine[15,16].
Biocompatibility describes the ability of a biomaterial to perform its intended purpose in medical therapy without causing harmful effects on the body[17]. The material is usually analyzed by in vitro cell culture studies, including cytotoxicity tests, biochemical measurements of cell activity, and evaluation of cell proliferation, growth, and morphology[18]. In vitro cytotoxicity analysis is standardized and regulated by a series of standards e.g. ‘ISO 10993: Biological Evaluation of Medical Devices’ that evaluate the materials intended for the manufacture of devices for biomedical applications. The in vitro evaluation has the advantage of limiting the experimental variables, and it is easy and fast to obtain meaningful data. When the nontoxicity of the material is proven, animal studies must be performed[19-21]
Several studies have already been performed regarding the biocompatibility of NRL and NR. According to the literature, the biocompatibility of NRL is well established[3,7,13,22,23].
However, there are still some aspects to be considered for this property to become even more satisfactory, such as a safer collection method and adequate processing[8]. Both factors can directly influence the biocompatibility of NRL and NR, interfering in their application. Floriano et al. observed that latex membranes in contact with ammonia during collection showed cytotoxic and genotoxic effects on cultures of NIH3T3 fibroblasts. All clones showed increased cell viability compared to the sample without ammonia[22].
Twelve types of commercial NRL gloves were analyzed and showed that residual chemicals are the main cause of poor biocompatibility. Experiments indicated that solvent washing can effectively remove residues from medical devices[24]. In return, NRL membranes showed no cytotoxicity and
allowed adhesion, proliferation, and extracellular matrix deposition for MC3T3-E1 osteoblasts[3,23]
Besides biocompatibility, biodegradability is another fundamental material property for biomedical materials. Biodegradable polymers are characterized by being broken down into biologically acceptable molecules through enzyme catalysis, involving hydrolysis or oxidation[25]. The biodegradability of NR has been widely studied due to the growing indiscriminate use of its by-products e.g. thousands of units of disposable gloves and NRL condoms that are discarded in nature, as well as the difficulties encountered in the reuse of these materials. For instance, the demand for personal protective equipment related to the circulation of the SARS-CoV-2 virus has increased since 2020. Given the limited space in landfills, the high cost of incineration, and the high potential risk to health and the environment, the studies on the biodegradability of NR become fundamental[26-28]
The first studies developed on the degradation of NR by microorganisms started more than 100 years ago, but currently there is still a shortage of biotechnological applications[26]. Some studies reporting the use of microorganisms, enzymes, and composting in the biodegradation of NR are reported in the Supplementary Material (Table S1). When evaluating the degradation of NR in the presence of Penicillium and Aspergillus, Tsuchii et al. verified a 32% weight loss in 30 days[29]. Most NRL and NR biomedical materials are still not degradable or do not present absorption by the body due to slow microbiological biodegradation, making it necessary to remove the material after implantation[8]
The blending with other compounds provides higher levels of degradation of NR, for instance, NR blended with cellulose and sodium alginate showed a mass loss of 50% after 56 days[30]. The association of NR and crosslinked nanocellulose also showed more promising degradation results by using Eudrilus eugeniae, in which about 60% weight loss was observed after 120 days[16]
Even when NRL and NR are combined with other biodegradable compounds, the problem remains. A possible solution to this fact would be deproteinization of the NRL
Polímeros, 32(2), e2022015, 2022
Andrade, K. L., Ramlow, H., Floriano, J. F., Acosta, E. D., Faita, F. L., & Machado, R. A. F.which makes the material safe to remain inside the body for long periods without the need of removal[22]. In addition, most of the studies concerning the biodegradation of NR are conducted on a laboratory scale. Another fact that deserves to be highlighted is the scarcity of studies involving the biodegradation of NR in biomedicine. There is still a need for the development of materials based on NRL and NR with a higher level of biodegradation with biomimetic characteristics, thus maintaining their structure and function for a longer time.
Among the various techniques used to produce biomedical materials from NRL and NR, the casting technique stands out for its simplicity of handling. Another technique that deserves to be highlighted, but has been little explored, is electrospinning, which can produce fibers with diameters ranging from micro- to nanoscale by controlling the process parameters. Other techniques show potential for processing NRL and NR, such as NRL protein extraction and blow spinning. Processing techniques including casting, spraying, dipping, electrospinning, among others (more information is found in the Supporting Material), result in different NRL and NR biomedical devices, which have been applied mostly as drug delivery systems and scaffolds for skin and bone regeneration, while the application for wound healing dressing and transdermal drug delivery system has been less investigated. Some in vivo tests were conducted, however, commercial application of NRL and NR as biomedical devices is very limited. The biomedical applications of NRL and NR are described below.
Drug delivery systems are responsible for the body internally delivering a drug or active compound in the desired dose to a particular region of the human body, which can improve efficacy and safety by controlling release rate, time, and location[31,32]. This system development allows a more selective and precise release to a specific site and requires a lower dosage because the delivery is in situ, with more consistent absorption and a decrease in toxic metabolites[33]
Networks’ formation by the isoprene chains works as a reservoir that allows the gradual release of compounds, highlighting its potential for drug delivery[11,34,35]. Using NR as a solid matrix for drug delivery systems is reported in several studies involving wound dressings[12,36,37]. Some studies have reported sustained-release provided by NRL and NR occurring through diffusion, which can be facilitated through fractures and pores on their surface with the ‘burst release’[34,38,39]. Drug release kinetics can be altered by structure modifications of NRL and NR devices, such as porosity increase/decrease, increased drug incorporation into the bulk material or its surface, or into the shell[4]. Combining NRL or NR with drugs or bioactive compounds promotes the incorporation of new properties to the material, which can provide even more satisfactory results in biomedical applications ‘optimization’. This incorporation is preferably done with NRL because it is a liquid suspension and provides
greater miscibility of the compound when compared to incorporation in NR, which is a solid material.
Table 1 mentions some drugs and bioactive compounds that have been used in formulations with NRL and NR, including ciprofloxacin, propolis, and Casearia sylvestris Swartz. Ciprofloxacin is an antimicrobial agent that has antioxidant potential when incorporated into any dressing, promoting the acceleration of the healing process[43]. It has long been known that silver is highly toxic to microorganisms, showing strong biocidal effects on bacteria and fungi[57]. Propolis is also an antibacterial with relevant pro-activating characteristics[58], which presents great advantages over the most common antibacterial agents, standing out due to its high biocompatibility, antimicrobial power, and natural source origin[59,60]. Propolis is widely used in biomedical dressings, representing a strategy that goes beyond the prevention of injury infections, because it still has pro-healing characteristics, triggering the acceleration of the injury healing process. Casearia sylvestris Swartz is a Central and South American tree from which its leaves are used in the treatment of gastric diseases and also for antiophidic, antiinflammatory, anti thermal, and wound healing purposes[61].
Extract of Casearia sylvestris Sw. and ciprofloxacin was incorporated into NR films preserving the properties of the substances since no chemical interaction between materials was observed[40]. The release rate of the extract was higher (~94%) than that of ciprofloxacin (~54%), both substances being adhered to the surface of porous NR films. With ciprofloxacin loading, the release of the drug was observed to be linearly proportional to the manufactured pore density[31]
Serjania marginata extract was incorporated into NR matrix, and 27% of the extract was released after 67 h preserving its antioxidant activity[39]. A sustained delivery system for metronidazole was developed from NRL, with control of metronidazole according to the polymerization temperature of the NRL matrix. Polymerization at -100 °C showed the best potential for metronidazole release, with approximately 77% of metronidazole being released after 310 h, i.e., release rate was slow[49].
These combinations provide the development of materials with antimicrobial, anti-fungal, and antioxidant activities, among other properties, that when associated with the biocompatibility of NRL and NR, demonstrate the great potential of these materials in biomedical applications. These materials reduce the cost of therapy, provide greater treatment efficacy, and improve the patient’s quality of life. It is also worth highlighting the benefits of using NRL and NR in drug delivery systems due to their versatility and easy handling, being possible to modify their release kinetics according to the type of application.
Transdermal Drug Delivery System (TDDS) is a painless, non-invasive drug delivery technique, where the drug is simply made available from a skin patch or other transdermal method/device, running through the skin layers until it reaches the systemic circulation, reaching the specific organs for the treatment. Even with the advances in TDDS and the discovery of delivery devices for drugs of
Table 1. Overview of drugs and active compounds added to NRL and NR applied to biomedicine, with respective concentrations and solvents. Drug/active compound; concentration (mg·mL-1)
Solvent for drug/active compound impregnation Reference Bovine serum albumin; 2; 10 N/A; Deionized water
Casearia sylvestris; 0.25; 0.1; 1; N/A; 0.25
Ciprofloxacin; 3; 0.1; 10; 5; 0.01
Ethanol; Ethanol; Ethanol; Ethanol and water; Ethanol [12,36,40-42]
N/A; Water; Water; Water; N/A [31,40,43-45]
Diclofenac; 3 N/A [11,38]
Fluconazole; 10 N/A [46]
Hydroxyapatite; 1, 2 and 3 THF [47]
Ketoprofen; 10 Ethanol and water [34]
Metronidazole; 10 N/A [48,49]
Propolis; 0.05; N/A; 0.05; 1, 2 and 3
Ethanol and water; Ethanol and water; Absolute ethyl alcohol and water; Absolute ethyl alcohol [35,50-52]
Serjania marginata; 30 Ethanol and water [39] Silver; 0.1; 0.1; 679.5
Sodium borohydride; Deionized water; NRL diluted in water Mili Q [53-55]
[56]
Stryphnodendron obovatum; 0.1 and 5 Ethanol and water
various origins (lipophilic, hydrophilic, and amphiphilic), dosage levels are still not competitive when compared to traditional delivery options[62,63]. This type of system can be developed using both synthetic and natural polymers as matrices including NR.
To minimize common events triggered by this type of drug delivery, a TDDS of ketoprofen was developed by its incorporation in NR biomembranes. In this study, the chemical interaction of the drug with the membrane was not verified and a drug release of 60% was observed due to the portion of ketoprofen present on membrane surface. The researchers concluded that this system is promising for drug administration, minimizing adverse effects caused by high dosages[34]. TDDS composed of a deproteinized NR matrix, hydroxypropyl methylcellulose, and dibutyl phthalate, was developed aiming nicotine release. The experiments were conducted with and without the inclusion of a protective layer to prevent volatilization of highly volatile nicotine[64]
The authors identified a slower release and permeation of nicotine transdermal patches in the absence of support, while nicotine transdermal patches with a support layer were released and permeated more rapidly, indicating that the matrix is adequate as a TDDS system.
TDDS provides several advantages such as bioavailability and local drug concentration, which avoid difficulties caused by pH changes in intestinal gastric tract and possible
interactions with other drugs. TDDS can replace oral intake in cases of vomiting or diarrhea and, in cases of emergency (unconscious patient), a quick interruption can be done by removing the patch. Although some studies have already been carried out with NR involving this type of application, this subject is still not widespread and demands further investigation.
Regeneration of skin, bone, cartilage, and organ tissues has been studied using patient cells cultivated on natural or synthetic substrates, followed by reinsertion, to regenerate damaged or lost body parts, restoring their function, the basis of regenerative medicine and tissue engineering[65]. Such substrates, known as scaffolding, are responsible for providing cellular fixation structure with cell proliferation/colonization, and stable environment, helping tissue remodeling i.e. tissue regeneration. Scaffolding for regenerative medicine and tissue engineering should mimic the functions of the native extracellular matrix[66]. Scaffolds can be produced by conventional molding methods such as casting, electrospinning, 3D printing, or by combining these techniques[67]
Studies involving NRL or NR in scaffolds’ processing have been developed to investigate potential applications in the regeneration of skin and bone tissue[3,65,68]. An example of
Polímeros, 32(2), e2022015,
Andrade, K. L., Ramlow, H., Floriano, J. F., Acosta, E. D., Faita, F. L., & Machado, R. A. F.the application of NRL and NR scaffolds with low cost is the treatment of thermal burns, a serious public health problem causing deaths and considerable psychological trauma.
Biomembranes developed from NRL for bone regeneration have shown promising results[6,22,69]. NRL biomembrane represents an alternative possibility of stimulation and potentiation of osteoconduction and guided bone regeneration, besides being biocompatible, potentially angiogenic, flexible, having mechanical properties, porosity, and permeability[3,6,70]. Additionally, Nascimento et al. showed that calcium/phosphorus compound is surrounded by NR particles due to electrostatic interactions, which can be easily changed in an ionic medium like body fluid, assisting in bone regeneration[71]
It is also worth mentioning the use of dressings commonly used in tissue engineering to improve natural skin healing. Dressings’ composition should facilitate epidermal barrier restoration adhered to the lesion, absorbing exudates, preventing infection, dehydration, promoting tissue regeneration, and limiting formation of granulation tissue[43,72]. Several investigations have been carried out regarding the use of NRL as a dressing for skin lesions[4,52,73,74]. Moreover, NRL can be associated with other types of materials, improving their existing properties, or promoting new healing properties.
In vivo models aims to characterize the process and evolution of tissue response after implantation of a given biomaterial, that is, to evaluate the tissue-material interface[75] Few works reported in the literature performed in vivo tests using NRL and NR, which include dogs[76], rabbits[6,22,77,78], rats[50,79-83], and humans[73,84,85]. Frade et al. applied an NR biomembrane on alternate days to treat chronic necrotic ulcers on the leg and foot of a 64-year-old patient[86]. The authors observed the effects of granulation stimulation after 15 days of treatment, in addition to pain reduction. After 60 days, granulation tissue reached the edges of the ulcers, so the use of the biomembrane was discontinued, followed by the use of chloramphenicol ointment. After 120 days of treatment, the ulcers were closed before clinical and histopathological reduction. The results were highly satisfactory, providing the patient with greater comfort at dressing changes. Similar data were found by Frade et al. when they evaluated this biomembrane in the treatment of skin ulcers and compared it with a treatment based on fibrinolysin and chloramphenicol. Lesions’ healing was induced by intense vascular formation with subsequent re-epithelialization[73]
NR insole was prepared by using a negative alginate personalized mold, which was further applied to diabetic foot treatment to reduce the excessive pressure in the injured regions, significantly reducing the plantar pressures on the patient’s feet by attenuating the total maximum force applied to them[84]. The most significant decrease in plantar pressure occurred in the region of ante foot. In the middle region of the foot, the reduction of maximum force was observed. This customized insole was also used in association with a device having a red LED matrix to provide mechanical support and accelerate the healing of diabetic foot ulcers, providing comfort to patients. Patients were satisfied with
the results, stating that the system was easy and simple to use contributing to the process of lesions’ healing[85]
NRL serum was evaluated as a wound healer by in vivo tests in rats undergoing dermabrasion, treated with saline, antiseptic, or latex. The antiseptic solution was compared with a commercial saline solution in vitro tests and the effects of cell migration and proliferation were analyzed. The serum of NRL showed viability in concentrations of 1% and 0.1% and migration and proliferation activity with 0.01% of serum[83]. Results showed that the serum did not present toxicity and, compared to other treatments, it was able to stimulate and accelerate the healing of lesions from abrasion.
The effects of applying P-1 (protein extracted from NRL) and Low-level Laser Therapy (LG) to the sciatic nerve of rats after crush injury were evaluated using hyaluronic acid as a carrier agent (1 wt%) with the incorporation of P-1 (0.1 wt%). The animals were anesthetized and the injury site was standardized: the upper and lower ventral spine. A ~2 cm skin incision was made perpendicularly and towards the middle region between the two mentioned points. After this, the muscle fascia was broken over the anterior femoral belly region of the biceps and gluteus maximus, and these muscles were divulsed, not requiring an incision. Finally, the nerve was exposed to the lesion by applying weight with a constant force of 15 kgf for 10 min, which caused the crushing of a circular area of approximately 0.6 cm in diameter. After finishing the lesion, the nerve was replaced and the skin was sutured, followed by medication to prevent possible complications. After 4 weeks, improvements in lesion morphology and morphometry were observed in the LG, P-1 treated, and P-1 + LG groups[87]. The researchers found that this improvement increased with treatment time.
Research on NRL began in 1994 in Brazil at the Department of Biochemistry of the University of São Paulo by Professors Dr. Joaquim Coutinho Netto and Dr. Fatima Mrue[13,88]. In 2002, a patent was filed by the University and the company PeleNova Biotecnologia S/A was created, which registered in 2004 the product Biocure®, a biomembrane derived from NRL responsible for inducing the formation of new blood vessels to induce angiogenesis. According to Rosa, its application was recommended for chronic diabetic, vascular, pressure ulcers, post-surgical or traumatic, being applied directly to the surface of the lesion. The first change was recommended 24 h after application[88]. The membrane was discontinued, due to the difficulty of application and maintenance of the product in the patient, and replaced by an ointment called Regederm®, a NR-derived compound in gelcream form (isolated angiogenic fractions free of compounds that could cause allergy), being registered in Anvisa (Agência Nacional de Vigilância Sanitária) in 2012. During this same period, PeleNova partnered with a Canadian dermatological company, Valeant. In 2017, PeleNova was taken over by the former Brazilian administrators and two years later, the company returns with its market operations, providing bioactive products to licensed companies. The following year, it restructured its operations and became part of Biocure Pharma Biotechnology, a Brazilian group that projects strong
Table 2. Comparison of electrospun fibers’ diameter from different biopolymers.
Tetrahydrofuran; Chloroform; Di-chloromethane; Toluene
water
~2.0-6.0; ~3.0-6.0; ~2.0-5.0; ~3.0-5.0
development in the markets of therapeutics, cosmetics, and actives for various segments[89]. Currently, Regederm® is not being marketed, possibly due to the company’s product reformulation after its restructuring.
Another commercially available membrane is Cellprene®, composed of poly(lactic-co-glycolic acid) and polyisoprene, the main component of NR. Cellprene® was developed and patented by the Federal University of Rio Grande do Sul (Brazil) in 2013 for application in tissue engineering[65,90].
According to the literature, Cellprene® has been used in recent studies demonstrating that this biomaterial can act in the maintenance of epithelial cells[65,91,92]
Recently, matrices obtained from electrospun fibers have gained much prominence and have been widely studied as wound dressing and scaffolds in biomedicine due to the ability to modulate cell behavior. Wound dressing and scaffolds are the main devices manufactured from NRL and NR for biomedical applications, thus, a brief discussion is made hereafter to compare the use of different biopolymers in the development of these devices. It is worth noting that, a direct comparison between the studies is difficult due to the different characteristics evaluated in each research.
A high degree of porosity and appropriate pore size are the main characteristics required for wound dressings and scaffolds to provide adequate space for cell propagation and migration, allowing for the proper exchange of nutrients and waste between the scaffold and the environment[93]
Pores smaller than bacteria help prevent infections through the sieve effect and therefore, these devices should have high porosity, preferably at the micro-and nanoscale[94,95].
The porosity and pore sizes of electrospun scaffolds depend mainly on the fiber diameter. Larger fiber diameters provide lower porosity and larger pore size[93,96] Table 2 lists some data regarding the diameters of electrospun fibers from different biopolymers.
The literature shows that poly(vinyl alcohol) and polycaprolactone electrospun fibers present diameters thinner than ~2 µm, while NR fibers have larger diameters, ranging from ~2 to 6 µm. This fact may hinder the production of NRL and NR devices suitable for biomedical purposes since the polymer chains limit the manufacturing of high-porous
biomaterials. Although NRL is inherently hydrophilic, after the drying process, it becomes predominantly hydrophobic[101] For biomedical applications, a surface with hydrophilic property is needed for adhesion, dissemination, and cell proliferation[102]
NRL fibers can be manufactured by solubilizing in water, but this procedure is little reported in the literature. Most studies involve the production of fibers from NR, which is obtained after drying centrifuged NRL. Thus, another factor that deserves attention is the use of solvents during the production of NR fibers that can cause damage to the cells due to their toxicity. It is also worth mentioning that the studies involving the use of NR in the production of fibers for the development of scaffolds and wound dressing suggest certain applications, i.e., there is still a gap of scientific evidence proving satisfactory results of clinical applications of these devices.
This review described and discussed the advances of NRL and NR biopolymers in biomedical applications and regenerative medicine, highlighting the development of drug delivery systems, scaffolds, wound dressing, and transdermal drug delivery systems. The research on these biomaterials is in full development, referring to applications in skin lesions in the form of dressings, cellular supports, bone regeneration, and release of bioactive molecules, among others. Studies show the high potential of NRL and NR due to the promotion of interesting biological properties and satisfactory biocompatible characteristics. The recent advances in biomedical applications of NRL and NR have demonstrated the multidisciplinarity required for future research that includes the study of the biopolymer (engineering and chemistry), the manufacture of the biomaterial (engineering), and the final application (biology). Current results show that these materials can considerably contribute to medical advancement through the treatment of individuals that requires less time for the cure in an accessible way. The literature lists many suggestions for NRL and NR applications, but in vivo tests are still little mentioned, and therefore represent an important gap to be filled. It is necessary to show and prove the real potentiality of these materials, thus, more studies should be developed focusing on the application. With the application of these
Polímeros, 32(2), e2022015, 2022
Andrade, K. L., Ramlow, H., Floriano, J. F., Acosta, E. D., Faita, F. L., & Machado, R. A. F.materials proven through satisfactory results, the products derived from NRL and NR will present greater chances of being commercialized, exempting the possibility of being discontinued. The simple addition of information on the packaging of the product and scientific communication is indispensable for the popular acceptance of NRL and NR biomedical devices, which present high commercial potential for products focused on tissue engineering and regenerative medicine.
• Conceptualization – Karina Luzia Andrade; Emanoelle Diz Acosta; Fabrício Faita; Ricardo Antonio Francisco Machado.
• Data curation – Karina Luzia Andrade; Fabrício Luiz Faita; Ricardo Antonio Francisco Machado.
• Formal analysis – Karina Luzia Andrade; Heloisa Ramlow; Juliana Ferreira Floriano; Emanoelle Diz Acosta; Fabrício Luiz Faita; Ricardo Antonio Francisco Machado.
• Investigation – Karia Luzia Andrade. Heloisa Ramlow; Juliana Ferreira Floriano; Emanoelle Diz Acosta.
• Methodology – Karina Luzia Andrade; Heloisa Ramlow; Emanoelle Diz Acosta; Fabrício Luiz Faita; Ricardo Antonio Francisco Machado.
• Project administration –Fabricio Luiz Faita; Ricardo Antonio Francisco Machado.
• Resources – CNPq; CAPES; LINDEN; FAPESP.
• Software –MS Word; MS Excel.
• Supervision – Fabricio Luiz Faita; Ricardo Antonio Francisco Machado.
• Validation – Karina Luzia Andrade; Heloisa Ramlow; Karina Luzia Andrade.
• Visualization – Fabricio Luiz Faita. Ricardo Anotnio Francisco Machado.
• Writing – original draft – Karina Luzia Andrade; Heloisa Ramlow.
• Writing – review & editing – Heloisa Ramlow; Emanoelle Diz Acosto; Fabricio Luiz Faita; Ricardo Antonio Francisco Machado.
The authors gratefully acknowledge Conselho Nacional de Desenvolvimento Científico e Tecnológico (CNPQ – project: #432520/2018-0) and Coordenação de Aperfeiçoamento de Pessoal de Nível Superior (CAPES) for providing financial support. EDA acknowledge LINDEN (Laboratório Interdisciplinar para o Desenvolvimento de Nanoestruturas) for the technical assistence. This study was financed in part by the Coordenação de Aperfeiçoamento de Pessoal de Nível Superior – Brazil (CAPES) – Finance code 001 and São Paulo Research Foundation (FAPESP) (postdoctoral fellowship 2017/21783-4).
1 Neves-Junior, W. F. P., Ferreira, M., Alves, M. C. O., Graeff, C. F. O., Mulato, M., Coutinho-Netto, J., & Bernardes, M. S. (2006). Influence of fabrication process on the final properties of natural-rubber latex tubes for vascular prosthesis. Brazilian Journal of Physics, 36(2b), 586 591 http://dx.doi.org/10.1590/ S0103-97332006000400021
2. Ferreira, M., Mendonça, R. J., Coutinho-Netto, J., & Mulato, M. (2009). Angiogenic properties of natural rubber latex biomembranes and the serum fraction of Hevea brasiliensis. Brazilian Journal of Physics, 39(3), 564 569 http://dx.doi. org/10.1590/S0103-97332009000500010
3. Borges, F. A., Barros, N. R., Garms, B. C., Miranda, M. C. R., Gemeinder, J. L. P., Ribeiro-Paes, J. T., Silva, R. F., Toledo, K. A., & Herculano, R. D. (2017). Application of natural rubber latex as scaffold for osteoblast to guided bone regeneration. Journal of Applied Polymer Science, 134(39), 45321 http:// dx.doi.org/10.1002/app.45321
4. Miranda, M. C. R., Prezotti, F. G., Borges, F. A., Barros, N. R., Cury, B. S. F., Herculano, R. D., & Cilli, E. M. (2017). Porosity effects of natural latex (Hevea brasiliensis) on release of compounds for biomedical applications. Journal of Biomaterials Science. Polymer Edition, 28(18), 2117 2130 http://dx.doi.or g/10.1080/09205063.2017.1377024 PMid:28875763.
5 Rosa, S. S. R. F., Rosa, M. F. F., Fonseca, M. A. M., Luz, G. V. S., Avila, C. F. D., Domínguez, A. G. D., Dantas, A. G. D., & Richter, V. B. (2019). Evidence in practice of tissue healing with latex biomembrane: integrative review. Journal of Diabetes Research, 2019, 7457295 http://dx.doi. org/10.1155/2019/7457295. PMid:30944828.
6 Floriano, J. F., Capuano, F., No., Mota, L. S. L. S., Furtado, E. L., Ferreira, R. S., Barraviera, B., Gonçalves, P. J., Almeida, L. M., Borges, F. A., Herculano, R. D., & Graeff, C. F. O. (2016).
Comparative study of bone tissue accelerated regeneration by latex membranes from Hevea brasiliensis and Hancornia speciosa. Biomedical Physics & Engineering Express, 2(4), 045007 http://dx.doi.org/10.1088/2057-1976/2/4/045007
7 Zimmermann, M., Raiser, A. G., Barbosa, A. L. T., Novosad, D., Steffen, R. P. B., Lukarsewsk, R., Silva, M. S., Lindinger, R., & Pastore, F., Jr. (2007). Biocompatibility and resistance test of latex membranes in dogs. Ciência Rural, 37(6), 1719 1723 http://dx.doi.org/10.1590/S0103-84782007000600033
8 Guerra, N. B., Pegorin, G. S., Boratto, M. H., Barros, N. R., Graeff, C. F. O., & Herculano, R. D. (2021). Biomedical applications of natural rubber latex from the rubber tree Hevea brasiliensis. Materials Science and Engineering C, 126, 112126 http://dx.doi.org/10.1016/j.msec.2021.112126 PMid:34082943.
9 Rahimi, A., & Mashak, A. (2013). Review on rubbers in medicine: natural, silicone and polyurethane rubbers. Plastics, Rubber and Composites, 42(6), 223 230 http://dx.doi.org/10. 1179/1743289811Y.0000000063.
10 Kotake, B. G. S., Gonzaga, M. G., Coutinho-Netto, J., Ervolino, E., Figueiredo, F. A. T., & Issa, J. P. M. (2018). Bone repair of critical-sized defects in Wistar rats treated with autogenic, allogenic or xenogenic bone grafts alone or in combination with natural latex fraction F1. Biomedical Materials, 13(2), 025022. http://dx.doi.org/10.1088/1748-605X/aa9504 PMid:29053112.
11 Barros, N. R., Chagas, P. A. M., Borges, F. A., Gemeinder, J. L. P., Miranda, M. C. R., Garms, B. C., & Herculano, R. D. (2015). Diclofenac potassium transdermal patches using natural rubber latex biomembranes as carrier. Journal of Materials, 2015, 807948 http://dx.doi.org/10.1155/2015/807948
12 Carvalho, F. A., Uchina, H. S., Borges, F. A., Oyafuso, M. H., Herculano, R. D., Gremião, M. P. D., & Santos, A. G. (2018).
Andrade, K. L., Ramlow, H., Floriano, J. F., Acosta, E. D., Faita, F. L., & Machado, R. A. F.
Natural membranes of Hevea brasiliensis latex as delivery system for Casearia sylvestris leaf components. Revista Brasileira de Farmacognosia, 28(1), 102 110 http://dx.doi. org/10.1016/j.bjp.2017.10.007
13. Mrue, F., Coutinho-Netto, J., Ceneviva, R., Lachat, J. J., Thomazini, J. A., & Tambelini, H. (2004). Evaluation of the biocompatibility of a new biomembrane. Materials Research, 7(2), 277 283 http://dx.doi.org/10.1590/S151614392004000200010
14. Ribeiro, J. A., Rosa, S. R. F., Leite, C. R. M., Vasconcelos, C. L., & Soares, J. M. (2017). Development assessment of natural latex membranes: a new proposal for the treatment of amblyopia. Materials Research, 20(3), 653 660. http://dx.doi. org/10.1590/1980-5373-mr-2016-0355
15 Soares, R. M. D., Siqueira, N. M., Prabhakaram, M. P., & Ramakrishna, S. (2018). Electrospinning and electrospray of bio-based and natural polymers for biomaterials development. Materials Science and Engineering C, 92, 969 982 http:// dx.doi.org/10.1016/j.msec.2018.08.004 PMid:30184827.
16 Abraham, E., Elbi, P. A., Deepa, B., Jyotishkumar, P., Pothen, L. A., Narine, S. S., & Thomas, S. (2012). X-ray diffraction and biodegradation analysis of green composites of natural rubber/ nanocellulose. Polymer Degradation & Stability, 97(11), 2378 2387 http://dx.doi.org/10.1016/j.polymdegradstab.2012.07.028
17 George, A. M., Peddireddy, S. P. R., Thakur, G., & Rodrigues, F. C. (2020). Biopolymer-based scaffolds: development and biomedical applications. In K. Pal, I. Banerjee, P. Sarkar, D. Kim, W. Deng, N. K. Dubey & K. Majumder (Eds.), Biopolymerbased formulations: biomedical and food applications (pp. 717 749). UK: Elsevier http://dx.doi.org/10.1016/B978-012-816897-4.00029-1
18 Schmalz, G., & Galler, K. M. (2017). Biocompatibility of biomaterials: lessons learned and considerations for the design of novel materials. Dental Materials, 33(4), 382 393 http:// dx.doi.org/10.1016/j.dental.2017.01.011 PMid:28236437.
19 Rogero, S. O., Lugão, A. B., Ikeda, T. I., & Cruz, Á. S. (2003). Teste in vitro de citotoxicidade: estudo comparativo entre duas metodologias. Materials Research, 6(3), 317 320 http://dx.doi. org/10.1590/S1516-14392003000300003
20 International Standard Organization – ISO. (2003). ISO 109931: biological evaluation of medical devices, part 1: evaluation and testing. Silver Spring: ISO.
21 International Standard Organization – ISO. (2009). ISO 109935: biological evaluation of medical devices, part 5: tests for in vitro cytotoxicity Silver Spring: ISO
22 Floriano, J. F., Mota, L. S. L. S., Furtado, E. L., Rossetto, V. J. V., & Graeff, C. F. O. (2014). Biocompatibility studies of natural rubber latex from different tree clones and collection methods. Journal of Materials Science. Materials in Medicine, 25(2), 461 470. http://dx.doi.org/10.1007/s10856-013-5089-9. PMid:24202915.
23 Furuya, M., Shimono, N., & Okamoto, M. (2017). Fabrication of biocomposites composed of natural rubber latex and bone tissue derived from MC3T3-E1 mouse preosteoblastic cells. Nanocomposites, 3(2), 76 83 http://dx.doi.org/10.1080/2055 0324.2017.1352111
24 Qamarina, M. S. N., Mok, K. L., Tajul, A. Y., & Fadilah, R. N. (2010). Minimising chemical hazards to improve biocompatibility of natural rubber latex products. Journal of Rubber Research, 13(4), 240 256. Retrieved in 2022, January 13, from https:// www.researchgate.net/publication/287462426_Minimising_ chemical_hazards_to_improve_biocompatibility_of_natural_ rubber_latex_products
25 Balaji, A. B., Pakalapati, H., Khalid, M., Walvekar, R., & Siddiqui, H. (2017). Natural and synthetic biocompatible and biodegradable polymers. In N. G. Shimpi (Ed.), Biodegradable
and biocompatible polymer composites processing, properties and applications (pp. 3 32). UK: Woodhead Publishing
26 Andler, R. (2020). Bacterial and enzymatic degradation of poly(cis-1,4-isoprene) rubber: novel biotechnological applications. Biotechnology Advances, 44, 107606. http://dx.doi. org/10.1016/j.biotechadv.2020.107606 PMid:32758514.
27 Nanthini, J., & Sudesh, K. (2017). Biodegradation of natural rubber and natural rubber products by Streptomyces Sp. Strain CFMR 7. Journal of Polymers and the Environment, 25(3), 606 616. http://dx.doi.org/10.1007/s10924-016-0840-1.
28 Nowakowski, P., Kuśnierz, S., Sosna, P., Mauer, J., & Maj, D. (2020). Disposal of personal protective equipment during the covid-19 pandemic is a challenge for waste collection companies and society: a case study in poland. Resources, 9(10), 1196 http://dx.doi.org/10.3390/resources9100116
29 Tsuchii, A. (1995). Microbial degradation of natural rubber. Progress in Industrial Microbiology, 32, 177 187 http://dx.doi. org/10.1016/S0079-6352(06)80032-9.
30 Supanakorn , G. , Varatkowpairote , N. , Taokaew, S. , & Phisalaphong, M. (2021). Alginate as dispersing agent for compounding natural rubber with high loading microfibrillated cellulose. Polymers, 13(3), 468 http://dx.doi.org/10.3390/ polym13030468 PMid:33535720.
31 Almeida, G. F. B., Cardoso, M. R., Zancanela, D. C., Bernardes, L. L., Norberto, A. M. Q., Barros, N. R., Paulino, C. G., Chagas, A. L. D., Herculano, R. D., & Mendonça, C. R. (2020). Controlled drug delivery system by fs-laser micromachined biocompatible rubber latex membranes. Applied Surface Science, 506, 144762 http://dx.doi.org/10.1016/j.apsusc.2019.144762
32 Bruschi, M. L. (2015). Modification of drug release. In M. L. Bruschi (Ed.), Strategies to modify the drug release from pharmaceutical systems (pp. 15 28). UK:Woodhead Publishing
33 Robinson, D. H., & Mauger, J. W. (1991). Drug delivery systems. American Journal of Hospital Pharmacy, 48(10, Suppl. 1), S14 S23 PMid:1772110.
34 Floriano, J. F., Barros, N. R., Cinman, J. L. F., Silva, R. G., Loffredo, A. V., Borges, F. A., Norberto, A. M. Q., Chagas, A. L. D., Garms, B. C., Graeff, C. F. O., & Herculano, R. D. (2018). Ketoprofen loaded in natural rubber latex transdermal patch for tendinitis treatment. Journal of Polymers and the Environment, 26(6), 2281 2289 http://dx.doi.org/10.1007/ s10924-017-1127-x.
35 Zancanela, D. C., Funari, C. S., Herculano, R. D., Mello, V. M., Rodrigues, C. M., Borges, F. A., Barros, N. R., Marcos, C. M., Almeida, A. M. F., & Guastaldi, A. C. (2019). Natural rubber latex membranes incorporated with three different types of propolis: physical-chemistry and antimicrobial behaviours. Materials Science and Engineering C, 97, 576 582 http:// dx.doi.org/10.1016/j.msec.2018.12.042 PMid:30678944.
36 Borges, F. A., Bolognesi, L. F. C., Trecco, A., Drago, B. C., Arruda, L. B., Lisboa, P. N. Fo., Pierri, E. G., Graeff, C. F. O., Santos, A. G., Miranda, M. C. R., & Herculano, R. D. (2014). Natural rubber latex: study of a novel carrier for Casearia Sylvestris swartz delivery. International Scholarly Research Notices, 2014, 241297
37 Miranda, M. C. R., Borges, F. A., Barros, N. R., Santos, N. A. Fo., Mendonça, R. J., Herculano, R. D., & Cilli, E. M. (2018). Evaluation of peptides release using a natural rubber latex biomembrane as a carrier. Amino Acids, 50(5), 503 511 http:// dx.doi.org/10.1007/s00726-017-2534-y PMid:29305745.
38 Aielo, P. B., Borges, F. A., Romeira, K. M., Miranda, M. C. R., Arruda, L. B., Lisboa, P. N. Fo., Drago, B. C., & Herculano, R. D. (2014). Evaluation of sodium diclofenac release using natural rubber latex as carrier. Materials Research, 17(Suppl. 1), 146 152 http://dx.doi.org/10.1590/S1516-14392014005000010
Polímeros, 32(2), e2022015, 2022
39 Barros, N. R., Heredia-Vieira, S. C., Borges, F. A., Benites, N. M., Reis, C. E., Miranda, M. C. R., Cardoso, C. A. L., & Herculano, R. D. (2018). Natural rubber latex biodevice as controlled release system for chronic wounds healing. Biomedical Physics & Engineering Express, 4(3), 035026. http://dx.doi.org/10.1088/2057-1976/aab33a
40 Bolognesi, L. F. C., Borges, F. A., Cinman, J. L. F., Silva, R. G., Santos, A. G., & Herculano, R. D. (2015). Natural latex films as carrier for Casearia Sylvestris swartz extract associated with ciprofloxacin. American Chemical Science Journal, 5(1), 17 25 http://dx.doi.org/10.9734/ACSJ/2015/12263
41 Borges, F. A., Trecco, A., Barros, N. R., Miranda, M. C. R., Pierri, E. G., Santos, A. G., & Herculano, R. D. (2014). Casearia sylvestris swartz extract release using natural rubber latex biomembranes as carrier. European Journal of Medicinal Plants, 4(12), 1420 1430. http://dx.doi.org/10.9734/EJMP/2014/12039.
42 Trecco, A., Borges, F. A., Pierri, E. G., Santos, A. G., Chin, C. M., & Herculano, R. D. (2014). Liberação de componentes do extrato de Casearia Sylvestris Swartz empregando membranas de látex natural como suporte. Revista de Ciências Farmacêuticas Básica e Aplicada, 35(1), 89 95. Retrieved in 2022, January 13, from https://repositorio.unesp.br/bitstream/ handle/11449/180910/ISSN1808-4532-2014-35-01-89-95. pdf?sequence=1&isAllowed=y
43 Wattanakaroon, W., Akanitkul, P., Kaowkanya, W., & Phoudee, W. (2017). Albumin-natural rubber latex composite as a dermal wound dressing. Materials Today: Proceedings, 4(5), 6633 6640
44. Garms, B. C., Borges, F. A., Santos, R. E., Nigoghossian, K., Miranda, M. C. R., Miranda, I. U., Daltro, P., Scarpari, S. L., Giagio, R. J., Barros, N. R., Alarcon, K. M., Drago, B. C., Gemeinder, J. L. P., Oliveira, B. H., Nascimento, V. M. G., Loffredo, A. V., & Herculano, R. D. (2017). Characterization and microbiological application of ciprofloxacin loaded in natural rubber latex membranes. Journal of Pharmaceutical Research International, 15(1), 1 10
45. Murbach, H. D., Ogawa, G. J., Borges, F. A., Miranda, M. C. R., Lopes, R., Barros, N. R., Mazalli, A. V. G., Silva, R. G., Cinman, J. L. F., Drago, B. C., & Herculano, R. D. (2014). Ciprofloxacin release using natural rubber latex membranes as carrier. International Journal of Biomaterials, 2014, 157952 http://dx.doi.org/10.1155/2014/157952 PMid:25587278.
46 Marcelino, M. Y., Borges, F. A., Costa, A. F. M., Singulani, J. L., Ribeiro, N. V., Costa-Orlandi, C. B., Garms, B. C., MendesGiannini, M. J. S., Herculano, R. D., & Fusco-Almeida, A. M. (2018). Antifungal Activity of fluconazole-loaded natural rubber latex against Candida albicans. Future Microbiology, 13(3), 359 367. http://dx.doi.org/10.2217/fmb-2017-0154. PMid:29464962.
47 Dick, T. A., & Santos, L. A. (2017). In situ synthesis and characterization of hydroxyapatite/natural rubber composites for biomedical applications. Materials Science and Engineering C, 77, 874 882 http://dx.doi.org/10.1016/j.msec.2017.03.301 PMid:28532104.
48 Herculano, R. D., Queiroz, A. A. A., Kinoshita, A., Oliveira, O. N. Jr., & Graeff, C. F. O. (2011). On the release of metronidazole from natural rubber latex membranes. Materials Science and Engineering C, 31(2), 272 275 http://dx.doi.org/10.1016/j. msec.2010.09.007.
49 Herculano, R. D., Guimarães, S. A. C., Belmonte, G. C., Duarte, M. A. H., Oliveira, O. N. Jr., Kinoshita, A., & Graeff, C. F. O. (2010). Metronidazole release using natural rubber latex as matrix. Materials Research, 13(1), 57 61 http://dx.doi. org/10.1590/S1516-14392010000100013.
50 Krupp, T., Santos, B. D., Gama, L. A., Silva, J. R., ArraisSilva, W. W., Souza, N. C., Américo, M. F., & Souto, P. C. S.
32(2), e2022015, 2022
(2019). Natural rubber - propolis membrane improves wound healing in second-degree burning model. International Journal of Biological Macromolecules, 131, 980 988 http://dx.doi. org/10.1016/j.ijbiomac.2019.03.147 PMid:30910673.
51. Zancanela, D. C., Herculano, R. D., Funari, C. S., Marcos, C. M., Almeida, A. M. F., & Guastaldi, A. C. (2017). Physical, chemical and antimicrobial implications of the association of propolis with a natural rubber latex membrane. Materials Letters, 209, 39 42 http://dx.doi.org/10.1016/j.matlet.2017.07.093
52. Silva, A. J., Silva, J. R., Souza, N. C., & Souto, P. C. S. (2014). Membranes from latex with propolis for biomedical applications. Materials Letters, 116, 235 238 http://dx.doi. org/10.1016/j.matlet.2013.11.045.
53
Guidelli, E. J., Ramos, A. P., Zaniquelli, M. E. D., & Baffa, O. (2011). Green synthesis of colloidal silver nanoparticles using natural rubber latex extracted from Hevea brasiliensis. Spectrochimica Acta. Part A: Molecular and Biomolecular Spectroscopy, 82(1), 140 145 http://dx.doi.org/10.1016/j. saa.2011.07.024 PMid:21803643.
54 Guidelli, É. J., Kinoshita, A., Ramos, A. P., & Baffa, O. (2013). Silver nanoparticles delivery system based on natural rubber latex membranes. Journal of Nanoparticle Research, 15(4), 1536 http://dx.doi.org/10.1007/s11051-013-1536-2
55 Suteewong, T., Wongpreecha, J., Polpanich, D., Jangpatarapongsa, K., Kaewsaneha, C., & Tangboriboonrat, P. (2019). PMMA particles coated with chitosan-silver nanoparticles as a dual antibacterial modifier for natural rubber latex films. Colloids and Surfaces. B, Biointerfaces, 174, 544 552 http://dx.doi. org/10.1016/j.colsurfb.2018.11.037. PMid:30500743.
56 Borges, F. A., Siguematsu, P. R., Herculano, R. D., & Santos, C. (2015). Novel sustained-release of Stryphnodendron obovatum leaves extract using natural rubber latex as carrier. Revista de Ciências Farmacêuticas Básica e Aplicada, 36(3), 379 384 Retrieved in 2022, January 13, from https://rcfba.fcfar.unesp. br/index.php/ojs/article/view/25
57 Liau, S. Y., Read, D. C., Pugh, W. J., Furr, J. R., & Russell, A. D. (1997). Interaction of silver nitrate with readily identifiable groups: relationship to the antibacterial action of silver ions. Letters in Applied Microbiology, 25(4), 279 283 http://dx.doi. org/10.1046/j.1472-765X.1997.00219.x PMid:9351278.
58 Roy, N., Mondal, S., Laskar, R. A., Basu, S., Mandal, D., & Begum, N. A. (2010). Biogenic synthesis of Au and Ag nanoparticles by Indian propolis and its constituents. Colloids and Surfaces. B, Biointerfaces, 76(1), 317 325 http://dx.doi. org/10.1016/j.colsurfb.2009.11.011. PMid:20015622.
59 Martinotti, S., & Ranzato, E. (2015). Propolis: a new frontier for wound healing? Burns and Trauma, 3, 9 http://dx.doi. org/10.1186/s41038-015-0010-z PMid:27574655.
60 Torlak, E., & Sert, D. (2013). Antibacterial effectiveness of chitosan–propolis coated polypropylene films against foodborne pathogens. International Journal of Biological Macromolecules, 60, 52 55 http://dx.doi.org/10.1016/j.ijbiomac.2013.05.013 PMid:23707735.
61 Ferreira, P. M. P., Costa-Lotufo, L. V., Moraes, M. O., Barros, F. W. A., Martins, A. M. A., Cavalheiro, A. J., Bolzani, V. S., Santos, A. G., & Pessoa, C. (2011). Folk uses and pharmacological properties of Casearia Sylvestris: a medicinal review. Anais da Academia Brasileira de Ciências, 83(4), 1373 1384. http://dx.doi. org/10.1590/S0001-37652011005000040 PMid:22159347.
62 Akhtar, N., Singh, V., Yusuf, M., & Khan, R. A. (2020). Noninvasive drug delivery technology: development and current status of transdermal drug delivery devices, techniques and biomedical applications. Biomedical Engineering, 65(3), 243 272 PMid:31926064.
63 Suksaeree, J., Pichayakorn, W., Monton, C., Sakunpak, A., Chusut, T., & Saingam, W. (2014). Rubber polymers for
Andrade, K. L., Ramlow, H., Floriano, J. F., Acosta, E. D., Faita, F. L., & Machado, R. A. F.
transdermal drug delivery systems. Industrial & Engineering Chemistry Research, 53(2), 507 513 http://dx.doi.org/10.1021/ ie403619b
64. Suksaeree, J., Boonme, P., Taweepreda, W., Ritthidej, G. C., & Pichayakorn, W. (2012). Characterization, in vitro release and permeation studies of nicotine transdermal patches prepared from deproteinized natural rubber latex blends. Chemical Engineering Research & Design, 90(7), 906 914 http://dx.doi. org/10.1016/j.cherd.2011.11.002.
65 Guerra, N. B., Cassel, J. B., Henckes, N. A. C., Oliveira, F. S., Cirne-Lima, E. O., & Santos, L. A. L. (2018). Chemical and in vitro characterization of epoxidized natural rubber blends for biomedical applications. Journal of Polymer Research, 25(8), 172. http://dx.doi.org/10.1007/s10965-018-1542-2.
66. Chan, B. P., & Leong, K. W. (2008). Scaffolding in tissue engineering : general approaches and tissue-specific considerations. European Spine Journal, 17(Suppl. 4), 467 479 http://dx.doi. org/10.1007/s00586-008-0745-3 PMid:19005702.
67 Zhao, P., Gu, H., Mi, H., Rao, C., Fu, J., & Turng, L. (2018). Fabrication of scaffolds in tissue engineering: a review. Frontiers of Mechanical Engineering, 13(1), 107 119 http:// dx.doi.org/10.1007/s11465-018-0496-8
68 Machado, E. G., Issa, J. P. M., Figueiredo, F. A. T., Santos, G. R., Galdeano, E. A., Alves, M. C., Chacon, E. L., Ferreira, R. S., Jr., Barraviera, B., & Cunha, M. R. (2015). A new heterologous fibrin sealant as scaffold to recombinant human bone morphogenetic protein-2 (rhBMP-2) and natural latex proteins for the repair of tibial bone defects. Acta Histochemica, 117(3), 288 296 http://dx.doi.org/10.1016/j.acthis.2015.03.006 PMid:25825118.
69 Araujo, M. M., Massuda, E. T., & Hyppolito, M. A. (2012). Anatomical and functional evaluation of tympanoplasty using a transitory natural latex biomembrane implant from the rubber tree Hevea brasiliensis. Acta Cirurgica Brasileira, 27(8), 566 571 http://dx.doi.org/10.1590/S0102-86502012000800009 PMid:22850709.
70 Carlos, B. L., Yamanaka, J. S., Yanagihara, G. R., Macedo, A. P., Watanabe, P. C. A., Issa, J. P. M., Herculano, R. D., & Shimano, A. C. (2019). Effects of latex membrane on guided regeneration of long bones. Journal of Biomaterials Science. Polymer Edition, 30(14), 1291 1307. http://dx.doi.org/10.10 80/09205063.2019.1627653 PMid:31177925.
71 Nascimento, R. M., Faita, F. L., Agostini, D. L. S., Job, A. E., Guimarães, F. E. G., & Bechtold, I. H. (2014). Production and characterization of natural rubber-Ca/P blends for biomedical purposes. Materials Science and Engineering C, 39, 29 34. http://dx.doi.org/10.1016/j.msec.2014.02.019 PMid:24863193.
72 Mayet, N., Choonara, Y. E., Kumar, P., Tomar, L. K., Tyagi, C., Du Toit, L. C., & Pillay, V. (2014). A comprehensive review of advanced biopolymeric wound healing systems. Journal of Pharmaceutical Sciences, 103(8), 2211 2230. http://dx.doi. org/10.1002/jps.24068 PMid:24985412.
73 Frade, M. A. C., Assis, R. V. C., Coutinho-Netto, J., Andrade, T. A. M., & Foss, N. T. (2012). The vegetal biomembrane in the healing of chronic venous ulcers. Anais Brasileiros de Dermatologia, 87(1), 45 51 http://dx.doi.org/10.1590/S036505962012000100005 PMid:22481650.
74 Garms, B. C., Borges, F. A., Barros, N. R., Marcelino, M. Y., Leite, M. N., Del Arco, M. C., Salvador, S. L. S., Pegorin, G. S., Oliveira, K. S. M., Frade, M. A. C., & Herculano, R. D. (2019). Novel polymeric dressing to the treatment of infected chronic wound. Applied Microbiology and Biotechnology, 103(12), 4767 4778 http://dx.doi.org/10.1007/s00253-01909699-x PMid:31065753.
75 International Standard Organization – ISO. (2007). ISO 109936: biological evaluation of medical devices. Part 6: test for local effects after implantation. Silver Spring: ISO
76 Sousa, L. H., Ceneviva, R., Coutinho-Netto, J., Mrué, F., Sousa, L. H. Fo., & Silva, O. C. (2011). Morphologic evaluation of the use of a latex prosthesis in videolaparoscopic inguinoplasty: an experimental study in dogs. Acta Cirurgica Brasileira, 26(Suppl. 2), 84 91 http://dx.doi.org/10.1590/S0102-86502011000800016 PMid:22030821.
77 Mendonça, R. J., Maurício, V. B., Teixeira, L. B., Lachat, J. J., & Coutinho-Netto, J. (2010). Increased vascular permeability, angiogenesis and wound healing induced by the serum of natural latex of the rubber tree Hevea brasiliensis. Phytotherapy Research, 24(5), 764 768. http://dx.doi.org/10.1002/ptr.3043. PMid:19943314.
78 Moura, J. M. L., Ferreira, J. F., Marques, L., Holgado, L., Graeff, C. F. O., & Kinoshita, A. (2014). Comparison of the performance of natural latex membranes prepared with different procedures and PTFE membrane in guided bone regeneration (GBR) in rabbits. Journal of Materials Science. Materials in Medicine, 25(9), 2111 2120 http://dx.doi.org/10.1007/s10856014-5241-1 PMid:24849612.
79 Cury, D. P., Schäfer, B. T., Almeida, S. R. Y., Righetti, M. M. S., & Watanabe, I.-S. (2019). Application of a purified protein from natural latex and the influence of suture type on achilles tendon repair in rats. The American Journal of Sports Medicine, 47(4), 901 914 http://dx.doi.org/10.1177/0363546518822836 PMid:30759353.
80 Brandão, M. L., Reis, P. R. M., Araújo, L. A., Araújo, A. C. V., Santos, M. H. A. S., & Miguel, M. P. (2016). Evaluation of wound healing treated with latex derived from rubber trees and Aloe Vera extract in rats. Acta Cirurgica Brasileira, 31(9), 570 577 http://dx.doi.org/10.1590/S0102-865020160090000001 PMid:27737341.
81 Dias, F. J., Fazan, V. P. S., Cury, D. P., Almeida, S. R. Y., Borie, E., Fuentes, R., Coutinho-Netto, J., & Watanabe, I. (2019). Growth factors expression and ultrastructural morphology after application of low-level laser and natural latex protein on a sciatic nerve crush-type injury. PLoS One, 14(1), e0210211 http://dx.doi.org/10.1371/journal.pone.0210211 PMid:30625210.
82. Dias, F. J., Issa, J. P. M., Coutinho-Netto, J., Fazan, V. P. S., Sousa, L. G., Iyomasa, M. M., Papa, P. C., & Watanabe, I. (2015). Morphometric and high resolution scanning electron microscopy analysis of low-level laser therapy and latex protein (Hevea brasiliensis) administration following a crush injury of the sciatic nerve in rats. Journal of the Neurological Sciences, 349(1-2), 129 137. http://dx.doi.org/10.1016/j.jns.2014.12.043. PMid:25619570.
83 Leite, M. N., Leite, S. N., Caetano, G. F., Andrade, T. A. M., Fronza, M., & Frade, M. A. C. (2020). Healing effects of natural latex serum 1% from Hevea brasiliensis in an experimental skin abrasion wound model. Anais Brasileiros de Dermatologia, 95(4), 418 427 http://dx.doi.org/10.1016/j.abd.2019.12.003 PMid:32473773.
84 Nunes, G. A. M. A., Rosa, S. S. R. F., Rocha, A. F., Cólon, D., & Balthazar, J. M. (2015). Comparative analysis of the use of natural latex custom insole in diabetic foot treatment through biomechanical evaluation in static examination. In 23rd ABCM International Congress of Mechanical Engineering. Rio de Janeiro: Associação Brasileira de Engenheria e Ciências Mecânicas
85 Nunes, G. A. M. A., Reis, M. C., Rosa, M. F. F., Peixoto, L. R. T., Rocha, A. F., & Rosa, S. S. R. F. (2016). A system for treatment of diabetic foot ulcers using led irradiation and natural latex. Research on Biomedical Engineering, 32(1), 3 13 http:// dx.doi.org/10.1590/2446-4740.0744 PMid:25992510.
Polímeros, 32(2), e2022015, 2022
86 Frade, M. A. C., Valverde, R. V., Assis, R. V. C., Coutinho-Netto, J., & Foss, N. T. (2001). Chronic phlebopathic cutaneous ulcer: a therapeutic proposal. International Journal of Dermatology, 40(3), 238 240 http://dx.doi.org/10.1046/j.1365-4362.2001.009772.x. PMid:11422535.
87. Dias, F. J., Issa, J. P. M., Iyomasa, M. M., Coutinho-Netto, J., Calzzani, R. A. J., Iyomasa, D. M., Sousa, L. G., Almeida, S. R. Y., Cury, D. P., & Watanabe, I.-S. (2013). Application of a low-level laser therapy and the purified protein from natural latex (Hevea Brasiliensis) in the controlled crush injury of the sciatic nerve of rats : a morphological, quantitative, and ultrastructural study. BioMed Research International, 2013, 597863. http://dx.doi.org/10.1155/2013/597863. PMid:23936823.
88. Rosa, J. P. P. (2016). Effects of rubber latex membrane in wound healing in rabbits experimental. Revista da Universidade Vale do Rio Verde, 14(2), 821 840 http://dx.doi.org/10.5892/ruvrd. v14i2.3344
89 Biocure Pharma Biotechnology. (2021, April 12). Retrieved in 2022, January 13, from https://biocure.com.br/pelenova/
90 Santos, L. A., Marques, D. R., Fraga, J. C. S., Schopf, L. F., & Sousa, V. C. (2011). Br PI1100522-0 A2 Rio Grande do Sul: UFRGS. Retrieved in 2022, January 13, from https://lume. ufrgs.br/handle/10183/85546
91. Henckes, N. A. C., Festa, J. C. D., Faleiro, D., Medeiros, H. R., Guerra, N. B., Santos, L. A. L., Terraciano, P. B., Passos, E. P., Oliveira, F. S., & Cirne-Lima, E. O. (2019). Tissueengineered solution containing cells and biomaterials—an in vitro study: A perspective as a novel therapeutic application. The International Journal of Artificial Organs, 42(6), 307 314 http://dx.doi.org/10.1177/0391398819833383 PMid:30838938.
92 Santos, I. F., Santos, L. A. L., Scardueli, C. R., Spolidorio, L. C., Marcantonio-Junior, E., Marcantonio, C. C., & Marcantonio, R. A. C. (2019). Evaluation of the combination of poly (LacticCo-Glycolic Acid) and polyisoprene (Cellprene®) materials: histological study in rats. Revista de Odontologia da UNESP, 48, e20190108 http://dx.doi.org/10.1590/1807-2577.10819
93 Soliman, S., Sant, S., Nichol, J. W., Khabiry, M., Traversa, E., & Khademhosseini, A. (2011). Controlling the porosity of fibrous scaffolds by modulating the fiber diameter and packing density. Journal of Biomedical Materials Research. Part A, 96(3), 566 574 http://dx.doi.org/10.1002/jbm.a.33010 PMid:21254388.
94 Murugan, R., & Ramakrishna, S. (2006). Nano-featured scaffolds for tissue engineering: a review of spinning methodologies.
Tissue Engineering, 12(3), 435 447 http://dx.doi.org/10.1089/ ten.2006.12.435 PMid:16579677.
95. Dwivedi, C., Pandey, I., Pandey, H., Ramteke, P. W., Pandey, A. C., Mishra, S. B., & Patil, S. (2017). Electrospun nanofibrous scaffold as a potential carrier of antimicrobial therapeutics for diabetic wound healing and tissue regeneration. In A. M. Grumezescu (Ed.), Nano- and microscale drug delivery systems, design and fabrication (pp. 147 164). UK: Elsevier http://dx.doi.org/10.1016/B978-0-323-52727-9.00009-1
96 Nelson, M. T., Keith, J. P., Li, B., Stocum, D. L., & Li, J. (2012). Electrospun composite polycaprolactone scaffolds for optimized tissue regeneration. Proceedings of the Institution of Mechanical Engineers. Part N, Journal of Nanoengineering and Nanosystems, 226(3), 111 121 http://dx.doi.org/10.1177/1740349912450828
97 Li, Y., Wang, X., Peng, Z., Li, P., Li, C., & Kong, L. (2019). Fabrication and properties of elastic fibers from electrospinning natural rubber. Journal of Applied Polymer Science, 136(43), 48153 http://dx.doi.org/10.1002/app.48153
98 Panichpakdee, J., Larpkiattaworn, S., Nuchchapong, S., Naruepai, B., Leekrajang, M., & Somwongsa, P. (2019). Electrospinning of natural rubber latex-blended polyvinyl alcohol. Materials Today: Proceedings, 17(4), 2020 2027
99 Costa, L. M. M., Mattoso, L. H. C., & Ferreira, M. (2013). Electrospinning of PCL/natural rubber blends. Journal of Materials Science, 48(24), 8501 8508 http://dx.doi.org/10.1007/ s10853-013-7667-0
100.Wutticharoenmongkol, P., Sanchavanakit, N., Pavasant, P., & Supaphol, P. (2006). Preparation & characterization of novel bone scaffolds based on electrospun polycaprolactone fibers filled with nanoparticles. Macromolecular Bioscience, 6(1), 70 77 http://dx.doi.org/10.1002/mabi.200500150 PMid:16374772.
101 Ambegoda, V. T., Egodage, S. M., Blum, F. D., & Maddumaarachchi, M. (2021). Enhancement of hydrophobicity of natural rubber latex films using diatomaceous earth. Journal of Applied Polymer Science, 138(12), 50047 http://dx.doi.org/10.1002/app.50047
102.Liu, Y., Zhou, S., Gao, Y., & Zhai, Y. (2019). Electrospun nanofibers as a wound dressing for treating diabetic foot ulcer. Asian Journal of Pharmaceutical Sciences, 14(2), 130 143 http://dx.doi.org/10.1016/j.ajps.2018.04.004. PMid:32104445.
Received: Jan. 13, 2022
Revised: June 23, 2022
Accepted: July 07, 2022
32(2), e2022015, 2022
Andrade, K. L., Ramlow, H., Floriano, J. F., Acosta, E. D., Faita, F. L., & Machado, R. A. F.
Supplementary material accompanies this paper.
Table S1. Biodegradability of NR.
This material is available as part of the online article from https://www.scielo.br/j/po
Polímeros, 32(2), e2022015, 2022
Marcel Yuzo Kondo1* , Larissa Stieven Montagna2 , Guilherme Ferreira de Melo Morgado2 , André Luiz Guimarães de Castilho1 , Larissa Anne Pereira dos Santos Batista2 , Edson Cocchieri Botelho1 , Michelle Leali Costa1,3 , Fabio Roberto Passador2 , Mirabel Cerqueira Rezende2 and Marcos Valério Ribeiro1
1Departamento de Materiais e Tecnologia – DMT, Universidade Estadual Paulista “Júlio de Mesquita Filho” – UNESP, Guaratinguetá, SP, Brasil
2Laboratório de Tecnologia de Polímeros e Biopolímeros – TecPBio, Universidade Federal de São Paulo –UNIFESP, São José dos Campos, SP, Brasil
3Laboratório de Estruturas Leves – LEL, Instituto de Pesquisas Tecnológicas – IPT, São José dos Campos, SP, Brasil *marcel.kondo@unesp.br
Polyamide (PA) is a well-known and researched thermoplastic due to its excellent mechanical and physical properties, making it developed in the automotive sector, suitable for lighter vehicles, and, consequently, lower fuel consumption. This review manuscript presents the applications of PA-based materials in the manufacture of vehicle parts, with a description of their processing, a discussion about their thermal properties and the crystallization of polymer structure, the challenges of machining PA-based composite materials, and the feasibility of recyclability. This work aims to revise literature about the use of polyamide 6 (PA6), polyamide 66 (PA66), and polyamide 12 (PA12) and their composites reinforced with fiberglass (FG) and carbon fiber (CF) focused on the potential that these materials have as alternative materials for the automotive industry.
Keywords: automotive industry, carbon fiber, composites, polyamide.
How to cite: Kondo, M. Y., Montagna, L. S., Morgado, G. F. M., Castilho, A. L. G., Batista, L. A. P. S., Botelho, E. C., Costa, M. L., Passador, F. R., Rezende, M. C., & Ribeiro, M. V. (2022). Recent advances in the use of Polyamide-based materials for the automotive industry. Polímeros: Ciência e Tecnologia, 32(2), e2022023. https://doi.org/10.1590/01041428.20220042
Polyamide (PA) is a semi-crystalline thermoplastic widely used in the automotive and aerospace sectors due to its excellent thermal and mechanical properties. However, PA is a highly hygroscopic polymer due to the presence of oxygenated groups (carbonyl and hydroxyl) in its polymer chain, that favors the permeation of water molecules between the chains, favoring good moisture absorption[1]. In addition, PA-based composites can be degraded by hydrolysis, and therefore PA must be subjected to the drying process before any processing[2]. However, even with the inclusion of this step before processing, PA has been standing out from other high-performance polymers, such as poly(phenylene sulfide) (PPS), poly(ether-ether-ketone) (PEEK), poly(aryl ether ketone) (PAEK) and poly(ether imide) (PEI), in use in the automotive and aerospace industries. This is because PA requires lower processing temperatures, making it possible to use the same equipment as conventional polymers, such as polypropylene (PP) and polyethylene (PE), lower raw material cost, good abrasion resistance, good chemical temperature (40-50 ºC) compatible with a different application.
In addition to being able to be recycled by mechanical, thermal, and chemical processes.
The wide use of PA in the automotive industry is justified by its numerous characteristics, such as its extreme durability, mechanical strength, good stability at high temperatures (< 130 ºC), good abrasion resistance, good chemical stability, and resistance to fuel, grease, and oils. In addition, it has an excellent oxygen barrier, provides excellent cost/benefit, and can be recycled[3,4]
However, the mechanical properties of PAs vary a lot with the level of absorbed water and the working temperature. Dry PAs are fragile at room temperature and have a glass transition temperature (Tg) above 50 °C; if applied at temperatures below 50 °C, the PAs have a high elastic modulus of maximum stress and low deformation at the break. Stress and elastic modulus values decrease with increasing temperature while straining increases[5] Furthermore, another attractive mechanical property for the automotive industry is the high friction coefficient of PA, leading to high abrasion of the parts. This characteristic
makes PAs an excellent choice for replacing other materials in components such as gears, shafts, bushings, bearings, screws, and nuts[6]. For the application of these parts, manufacturers often use further processing to force water absorption, preventing the region from becoming brittle or from water absorption during the product’s life cycle leading to part swelling[7]. The presence of moisture can have some advantages, as the absorption of water in finished parts can be the desired effect by manufacturers because the water can act as a plasticizing agent in the polymer; that is, the absorption of water tends to leave the toughest end product[8].
In the automotive industry, PA has already been widely used in airbags, car engine protections, car bodies and internal components, fastening elements (bolts, bushings, threads), and also in the manufacture of high-performance components, and in this way, it contributes with the reduction in the weight of vehicles and, consequently, in the decrease in fuel consumption[9] Figure 1 shows the main applications of PA in the automotive sector.
PA-based materials can be processed using injection molding, extrusion, compression, and additive manufacturing. The choice of the most suitable PA-based materials processing method depends mainly on the final shape of the product and the type of reinforcing agent (particles, short fibers, or continuous fibers). However, due to the hygroscopic nature of PA, a key step in PA processing is the drying step before processing, as parts may form with various defects caused by the presence of water in the material[10]
The family of PAs is quite broad, as they have different structures that enable them to have other characteristics and properties, according to the number of carbons between the amide groups present in the macromolecules (Table 1). PA6 and PA66 are the most used due to their durability and strength. PA6 and PA66 have excellent mechanical properties, good chemical and oil resistance, but low chemical resistance to strong acids and bases, low gasoline permeability and excellent gas barrier properties, wear and abrasion resistance, good resistance to long-term heat, flame-resistant, feature the highest moisture absorption rate when reinforced with fiberglass (FG) or other materials can provide superior modulus of elasticity and strength, and PA6 and PA66 parts feature excellent surface finish. The main difference between them is the monomers (Table 1). PA 6 is more flexible while the PA66 is highly rigid, in addition to the PA6 being resistant to a temperature of 180°C and the PA6 notwithstanding working temperatures above 130°C[3]
However, by modifying chemical structures, such as chain length and chemical organization, it is possible to obtain other PA family members, such as the PA12. Among all commercially available PAs, PA12 has the lowest concentration of amide group, promoting its characteristics, such as lower moisture absorption, excellent impact resistance (even at temperatures below freezing point), excellent resistance to chemicals, good abrasion resistance, and high processability. Still, it has a high cost[4]
Understanding the kinetics of crystallization, degree of crystallinity (Xc), and thermal properties, such as melting temperature (Tm) and glass transition (Tg), are essential in choosing the processing parameters of polymers and their composites. Different degree of crystallization affects their chemical and mechanical properties. Higher degrees result in higher stiffness and tension strengths, while lower crystallization results in higher impact energy absorption[1]
Although there are several attractive properties to the industry, such as excellent strength and low specific weight properties, machining presents a current challenge. One of the main attention points related to the manufacture and processing of carbon fiber reinforced polymers (CFRP) and fiberglass reinforced polymers (FGRP) composite materials
Polímeros, 32(2), e2022023, 2022
are the difficulty of performing the cutting process during the machining[11,12]
Most due to the anisotropic and heterogeneous structure of thermoplastic composite laminates and the highly abrasive nature of the FG and CF, several critical damages are observed during the machining, along with high tool wear rates[13]. According to Meinhard et al.[14], CFRP machining can lead to different types of damage patterns that can be divided into two main types: permanent damages (i.e., delamination, chipping, fiber pullouts) and defects passible of reworking (i.e., irregular shape of holes and burr formation). The majority of machining focused research that studied FG and CF reinforced PAs highlighted the highly abrasive impact of fibers during machining, leading to poor surface finish, rapid progression of tool wear, and damages such as delamination in the machined surface[11,15-17]
This review study aims to present the latest research (2018-2022) related to the PA family, in particular PA6, PA66, and PA12, from the numerous applications in the automotive industry, thermal and mechanical properties, the most suitable means of processing and feasible, facts that influence machining, in addition to the possibility of recycling.
The European Commission regulation EU 2019/631[18] motivated the search for lighter materials in automotive vehicles. By the regulation, between 2020 and 2024, all manufactured passenger cars must have emissions of less than 95 g/km of CO2. This emission is strongly related to vehicle mass, and the weight reduction strategy is cited by Nguyen-Tran et al.[19] to control the emission of CO2
However, regardless of the energy source, powered by a combustion engine, electric motor, or any alternative, the reduction in the vehicle’s total weight impacts its energy performance in transport in general, showing the importance of the search for low-weight materials by the automotive industry. Grätzl et al.[20] showed that 37% of the total vehicle weight is related to body weight. Continuous fiber-reinforced plastics are a good alternative due to their high mechanical resistance/weight rate. Besides that, the European Union[21] has the legal requirement that 95% of the vehicle’s total weight must be recyclable by 2025, which leads to a preference for thermoplastics over thermosetting polymer matrices.
According to Amasawa et al.[22], high-performance polymer materials can potentially change cars production. Nowadays, an average vehicle is made of 1163 kg of iron and steel and 150 kg of plastic. The use of polymers can affect car designs, enhance design flexibility and reduce vehicle weight. The authors cited the Japanese government initiative, with Japan ImPACT program, launched in 2014, that developed a prototype car composed of 47% of polymers and polymer composites that weighed 850 kg versus 1333 kg of a comparable vehicle using steel and glass. The main goal of the research was to analyze the life cycle greenhouse gas emission of the prototyped vehicle. The authors found that polymers and composites have
significant potential in reducing the life cycle greenhouse gas emissions of a battery-powered electric vehicle. Still, some innovations in fabrication, design, and powertrain resizing must be developed.
One of the alternatives used as a lightweight material is the PA and fiber-reinforced PA-based composites, such as FG and CF. Among the engineering thermoplastic alternatives, PAs are easy to process, are among the cheapest, and have the necessary mechanical properties, having strong fracture toughness if compared with thermoset like epoxy resin. PA-based composites are used in the automotive industry, where they are submitted to mechanical stress and high temperatures. The Polyamides are used in tires, seat belts, fan blades, car upholstery, air-intake manifold, fuel system, cooling systems, switch housing, and oil pans. The automotive sector is responsible for 35% of PA consumption, the largest PA consumer[23]. Polyamide 6 and PA66 are also prominent in the manufacture of gears for automotive use[24-28], while the use of nylon 66 can also be seen in the manufacture of leaf springs[29]
PA-based composites can be used in plain bearing, body coils, guide and coupling parts, nuts, and slides[8] According to Singh et al.[30], PA6 is used in automotive industries to fabric gear, bearing, and fitting via extrusion, compression, or injection molding and machining. By its good thermo-mechanical properties, Chen et al.[31] reported that PA6-based composites could be applied where are required creep and fatigues resistance, substituting traditional metal materials in manufacturing structural parts and components in the engine compartments, bearing, and gears for the automotive industry. Spronk et al.[32] tested CF/epoxy and FG/PA6 composites used in the automotive industry with the concern of understanding the damage caused to the material in an eventual crash, demonstrating how energy is absorbed during an impact. Murray et al.[33] have also studied the impact strength of the FG reinforced PA6 composite for structural automotive parts.
Ishikawa et al.[34] mention the use of CF-reinforced PA6 matrix composite to manufacture a complete chassis of “Lotus Elise”, originally made of aluminum alloy, to reduce the vehicle’s weight. It is essential to ensure that a material used in the automotive industry can pass through most of the automotive process chain. For these reasons, Grätzl et al.[20] tested the effect of the painting process of PA6 or PA66 based long CF composites on the mechanical properties. These materials can be used in the vehicle body to reduce the total weight. The authors described a painting process that exposed the automotive piece to a temperature above 190 °C for 20 min. They concluded that the painting process does not deteriorate the mechanical properties of the composites. The study of Caltagirone et al.[35] showed no difference in strength and stiffness in using recycled or virgin CF in manufacturing PA66 composite-based material for automotive uses.
Caputo et al.[36] investigated the use of PA6/FG composite in manufacturing an innovative engine encapsulation system for the automobile, aiming at acoustic and thermal insulation. Volpe et al.[37] studied the microcellular injection molding of FG-reinforced PA6. PA66 has a higher cost than PA6, and their fiber-reinforced composites can be
used to produce under-the-hood automotive components. FG-reinforced PA66 is used in manufacturing automotive engine bay components and its production by injection molding was simulated by Moisey et al.[38]. Wei et al.[39] researched the aging properties of PA12 exposed to biodiesel at high temperatures, citing that PA6 and PA12 can be used in vehicle fuel systems because of their excellent balance of mechanical properties and barriers properties against hydrocarbons. Hıdıroğlu et al.[40] studied the reduction of daily rate hydrocarbons evaporation from PA12 automobile fuel transfer pipes prepared by radiation crosslinking. In Table 2 is presented a summary of the important uses of polyamides in automotive industry.
PA are polymers with a high tendency to absorb water, and for this reason, special care is needed to ensure the quality of processing. As with all thermoplastics, one must pay attention to processing parameters such as viscosity, Tm, the possibility of oxidation at high temperatures or in the presence of oxygen, and the behavior of the polymer when undergoing cooling[1].
Due to the tendency to absorb water, PA pellets must be very well dried before use in any processing. This drying step is crucial for the rest of the polymer cycle, as the use of wrong temperatures and times can result in a much shorter useful life of the parts that will be manufactured. Most literature recommends drying between 70 and 90 ºC, not exceeding 12 h in an oven. A more extended temperature or exposure time can lead to pellet surface oxidation, resulting in a defective final product. PA12 has a much lower water absorption than the rest of PAs and can be processed as a common thermoplastic; the pellets can be dried much shorter[31]. In addition to water absorption, there is a widespread phenomenon of PAs after processing, called post-processing shrinkage. This phenomenon must be considered, especially when using injection molding, since the mold must be produced considering the material shrinkage rate. This shrinkage leads to higher process costs, as a mold is needed just to process the PA[41-43].
PA-based materials can be processed by extrusion, injection molding, compression molding, and selective laser sintering (SLS). Determining the proper processing technique will depend on the shape of the product. Parts with structural applications are usually processed by injection molding, replacing metallic elements. Teixeira et al.[44]
prepared PA66/FG (60/40) composites by injection molding using a mold with the ability to simulate controlled flow restriction. From mathematical models, the authors verified that controlled flow restriction affects the fiber length and fiber orientation, influencing the final mechanical properties of the composite. However, the most considerable difficulty encountered in processing is the addition of fillers in the PA matrix, which increases the melt viscosity, generating greater shear in the equipment[45]. Specific equipment must be used to degrade the parts and avoid loss of properties[46]
Another type of processing widely used by the automotive industry for PA is compression molding, where polymer plates, usually with long fibers as filler, are pressed in positive molds, generating the desired parts[47-49]. In the study carried out by Murray et al.[33], resin transfer molding was used to manufacture PA6/FG composites. The impact strength results proved promising for manufacturing parts to be applied in the automotive sector. When processed by extrusion, PAs must be dried, or an extruder with a degassing system must be used. Furthermore, an extruder with a slight compression zone is more suitable for processing due to PAs’ relatively low molar mass. These factors again lead to an increase in the production cost, as a specific extruder must be used or more time must be spent drying the material[50,51]
Hıdıroğlu et al.[40] prepared oil and fuel transfer ducts through direct extrusion in a layer extruder, where there are different dosing zones to insert different phases into the final product. According to the authors, it was proven that the degree of crosslink is directly linked to the final properties of the product, such as mechanical properties and permeability to gases. On the other hand, SLS is a relatively new process that is very promising for manufacturing high-performance PA parts, but it has not been widely investigated. However, some studies indicate good results[31,41,42].
Borrelli et al.[52] studied the performance of automotive PA components with basalt as load printed in 3D in collision tests performed by the finite element method (FEM). According to the authors, it was verified that the 3D printed parts do not present any type of deficit in properties compared to the features currently used, which consist of polypropylene (PP) and talc plates welded by vibration. This result is significant because printed pieces are relatively lighter than contemporary pieces. Lupone et al.[53] researched a new methodology to process composites and PA/CF by joining FDM and laser writing. This new additive manufacturing methodology proved ideal for achieving an alignment of
Table 2. Summary of the important information and uses of polyamides in the automotive industry.
Regulations about CO2 automobile emission and recyclability of the used materials in automobile fabrication.
Use of polymers and reinforced polymers composites as a strategy to reduce weight and improve cars energy efficiency.
Use of polyamide in tires, seat belts, fan blades, car upholstery, air-intake manifold, fuel system, cooling systems, switch housing, and oil pans.
Use of polyamide for plain bearing, body coils, guide and coupling parts, nuts and slides.
Use of PA6 for gears and bearing.
Use of Carbon Fiber Reinforced PA6 for structural car parts.
Use of PA66 for gears or leaf springs.
Use of PA6 and PA66 for under-the hood components, engine encapsulations system and engine bay components.
Use of PA6 and PA12 in vehicle fuel system parts and fuel transfer parts.
Polímeros, 32(2), e2022023, 2022
short CF, which guarantees good electrical and mechanical properties when the effort is towards the fibers.
Thermal analyzes of a polymer and its composites provide essential information for choosing processing parameters, such as temperature, time, heating, and cooling rates. The crystallization rate of semicrystalline polymers, such as PA, is strongly influenced by temperature and occurs between the T g and the T m of the material, making knowledge of these temperatures essential. The crystallinity degree (Xc) for high-performance thermoplastics directly impacts the chemical and mechanical properties of the polymer. The crystalline phase increases the stiffness and tensile strength, while the amorphous phase affects energy absorption[54]
Searching for the best understanding of the parameters that influence the properties of PA6, Liu et al.[55] evaluated the non-isothermal crystallization of PA6. The samples were heated in the temperature range of 25 ºC to 250 ºC, with a heating rate of 50 ºC/min to remove the previous heating history. It was noted that a lower crystallization temperature and a more excellent temperature range are obtained with an increasing cooling rate. As the cooling rate increases, the initial crystallization temperature decreases, indicating that the molecular chain does not have enough time to form nucleation at high temperatures. Through Avrami crystallization kinetics, it was possible to conclude that the non-isothermal crystallization of PA6 comprises a nucleation mode with one-dimensional and two-dimensional growth. Furthermore, Liu et al.[55] also apply the Liu and Mo kinetic equation[56] to provide a more accurate description of the non-isothermal crystallization process. The analysis carried out by POM shows the formation of spherulites in PA6 under the experimental conditions.
Zaldua et al.[57] evaluated thermoplastics produced by thermoplastic matrix transfer molding (T-RTM) with PA6/CF (53/47) and PA6/FG (40/60). Since the residual monomers from the polymerization effect have a plasticizing effect on the mechanical properties, TGA (thermogravimetry) analysis was conducted to determine the residual amount and the degree of conversion of the monomers into longer chains. The incorporation of fibers makes the improvement in thermal stability evident compared to neat PA6. Composites reinforced with CF had better mechanical properties, such as modulus and tensile strength, compared to composites with FG reinforcement. The influence of X c on the mechanical properties is also evaluated by Taketa et al.[58] using different cooling temperatures in PA6/CF, PPS/CF, and PP/CF composites with unidirectional reinforcement. The results obtained attest to the decrease in crystallization temperature with the increase in cooling rates. Tensile strength tests showed increased strength due to the Xc. Interfacial shear was also evaluated, showing a reduction with decreasing cooling rates.
PA6/CF composites manufactured via vacuum-assisted resin transfer molding (VARTM) were analyzed by Li et al. [59] with different molding temperatures. As preliminary results, it is observed that the satisfactory temperature for impregnation of the material is 140ºC. At this temperature,
less water absorption by the material is observed. The authors concluded that the ideal temperature range for polymerization is 140 to 160ºC, and the molding process must be conducted within 20 seconds, regardless of the size and shape of the sample.
Yaghini and Peters[60] addressed the primary and secondary isothermal crystallization kinetics of PA6 with a more robust and complete model, considering structural characteristics, such as lamellar thickness, and a rigid amorphous fraction (RAF), and a mobile amorphous fraction (MAF). The results are satisfactory for predicting properties based on the processing conditions, converging with the experimental data. Uematsu et al.[61] determined the relationship between the crystalline structure of PA6 and CF with the mechanical properties of unidirectional PA6/CF composites using Raman spectroscopy. The analysis of crystallinity and interfacial properties shows that the increase and decrease in the proportion of crystalline phases of the material influence the final strength of the composite. Handwerker et al.[62] used a new way of producing reinforced materials, both with chopped CF and continuous FG, using fused filament fabrication (FFF) or also called fused deposition melting (FDM). The heat application increases strength and stiffness, especially when annealed at a temperature of 200ºC for 6h. Although heat treatment increases Young’s modulus, microscopic analysis shows a concentration of air voids.
One of the biggest concerns when working with PA matrix composites is the influence of water absorption influence on the properties of the material. Hagihara et al.[63] used chemical and structural analysis to study the degradation mechanisms of thermoplastic composites with a PA6 matrix reinforced with CF exposed to hot steam. With crystallization, there is a decrease in the density of the amorphous phase, increasing the free volume and allowing water molecules to occupy this space, thus causing the hydrolysis of PA6 in the composite. Resistance analyzes showed that, after 28 days of aging under hot steam at 140 ºC, there was a decrease in the mechanical properties. Ma et al.[64] studied the water absorption behavior and its influence on the mechanical properties of PA6 boards and PA6 laminates reinforced with CF with different fiber orientations. Half of the absorbed water remained in the spacings between the polymeric chains, and the other half permeated in the fibers gaps and between the matrix/fiber interface. The decrease in water absorption upon reaching equilibrium results from the rejection of water from the crystalline phase and hydrolytic degradation of the matrix. Decreased mechanical properties are observed in both materials due to matrix plasticization and deterioration of the matrix/fiber interface. Chabaud et al.[65] evaluated the hydromechanical and mechanical behavior in relation to the processing of PA6/CF and PA6/FG composites by 3D printing. In addition, although the 3D printing process allows for the fabrication of more complex geometries, an increase in the porosity of the material and fiber twist was evidenced, which may result in a greater concentration of stresses. A summary of thermal properties, methods, parameters used and values, found in literature, can be seen in Table S1, for PA6 and PA6 based materials, and in Table S2, for PA66 and PA66 based materials, of the Supplementary Material.
The effects of post-condensation on PA12 crystallization kinetics have been studied by Paolucci et al.[66]. The samples were subjected to thermal annealing at different temperatures for different time intervals. It was evident that the molecular weight increases with annealing time and temperature. Although the crystallization rate is similar for samples annealed at different temperatures, it was observed that the lower the crystallization kinetics for longer annealing time. Ma et al [67] researched the thermal properties and crystal structure of neat PA12. The analysis showed that the different crystal shapes influenced the tensile properties. Thus, it is possible to obtain PA12 with an advanced mechanical performance from the adaptation of crystalline forms with the correct preparation. A summary of the thermal properties for PA12, found in the literature, can be seen in Table S3 of the Supplementary Material.
Most components made from CF and GF reinforced polymers can be manufactured to dimensions close to the final shape. However, the excess material is removed using machining to meet assembly requirements[16,68]. Furthermore, the machining process can present more economic advantages than molding processes when it demands lower production volumes[69]. Moreover, most automotive PA reinforced composites are generally manufactured by extrusion process requiring additional machining operations[70].
Nonetheless, with the increase of additive manufacturing techniques applied in the industry, the need for further machining processes is increasing. Since the lack of geometrical accuracy is one of the critical disadvantages of melted filament fabrication of reinforced thermoplastic polymers (PA12) parts, a strong need for developing hybrid manufacturing technologies was generated by combining additive manufacturing techniques and machining to improve surface roughness[71]. However, even with the accuracy provided by the machining of printed parts, the necessity of specific hardware and pre-machining routines still demands the in-deep study of the influence factors of the process.
Conventional machining methods are used to machine CFRP and FGRP composite material[11]. The drilling, milling, and grinding processes represent a significant part of machining these materials in the automotive industry[72,73]. The drilling process has an essential role in the final assembly of large and structural parts, as well as for lightweight and automotive components[13], since considering the higher loads applied to structural applications and due to safety reasons, there is still the necessity of classical mechanical joining involving machining of correlated screws holes[14].
Literature analysis revealed that the machining investigation of fiber-reinforced polymer machinability was usually realized through comparative studies to the non-reinforced polymer machinability. The machining processes of CFRP are related to abrasive solid tool wear and represent a significant process challenge due to their anisotropic structure and brittle fracture behavior. According to Meinhard et al.[14], burr formation is the dominant type of damage in the machining of CF-reinforced PA12 laminates, in contrast to delamination in the case of machining CFRP. Recent studies showed that surface roughness is highly
regarded when machining PA. Most studies try to avoid delamination and, at the same time to, achieve good surface finish results. There are several difficulties to the drilling machining process due to the vast number of influencing factors that can change the quality of drill holes and alter the damage dynamics.
Several factors can impact the machining of fiber-reinforced thermoplastic polymers for automotive applications[74]. Among others, the temperature during cutting[75], the cutting tool material and geometry[76], material composition, preparation of the machined material, and their properties also play an essential role[11]. Regarding the influence of temperature in machining, Yan et al.[73] concluded that the excellent machinability of fiber-reinforced polymer composites is due to the viscoelastic behavior of the thermoplastic matrix as temperature increases. Results show that the viscoelastic behavior also leads to a better surface finish. Bertolini, Ghiotti, and Bruschi[15] observed that the size and surface defects density increased when machining PA6 at lower temperatures.
Since the thermoplastic matrix consists of mostly linear and high molar mass entangled chains, the temperature of the process is essential for machining. Its increase can lead to changes in mechanical properties. According to Meinhard et al.[14], the machining process must be executed due to the particular thermoplastic polymeric chemical bonds and the risk of matrix melting or depolymerization at low temperatures.
Meinhard et al.[14] stated that the cutting tool geometry is critical in drilling reinforced composites since the drilling process evaluates the drill‐hole quality. The diamond-coated tool, deposed by the chemical vapor deposition (CVD) method, is indicated for thermoplastic machining[77]. However, Gaugel et al.[13] alert that the advantages of using diamond coating as cutting tools to machine CF reinforced polymers are only valid for high-quality laminates.
According to Kataras et al.[78], the tribological properties, corrosion resistance, and good mechanical and fatigue strength of PA6 components can favor minimum roughness results. An excellent surface finish can also lead to uniform distribution of stresses on the workpiece.
According to Kießling et al.[79], the extensive mechanical properties of PA would be the basis for investigating its machinability and manufacturing behavior. Even though thermoplastic composites laminates exhibit very high inplane strength, delamination is a common challenge during machining due to poor transverse strength and low delamination fracture toughness. The heterogeneity and anisotropic properties of the fiber-reinforced polymer composites allow these materials not to exhibit plastic deformation, allowing several applications in the automotive industry[11]. However, in the automotive industry, PA reinforced joints are also necessary to consider the interfacial strength on the polymer moisture content and the impact of interfacial crystallinity on the temperature of machining[79]. Another important consideration is the final porosity of the material. According to Gauge et al.[13], the residual porosity has a high impact on machining CFRP composites laminates.
It is also essential to consider the failure mechanisms and fibers orientation to assess the machinability of CFRP
Polímeros, 32(2), e2022023, 2022
and FGRP materials to both conventional and modern manufacturing and machining methods[11]. Ferreira et al.[71] observed that the addition of short CF in the PA12 matrix decreased the cutting load’s levels and tool wear, thus indicating improvement in machinability. However, parameters such as building orientation did not influence the final surface roughness. As considering the micromachining of reinforced PA, Kuram[16] investigated the micro-machinability of PA6 and FG-reinforced PA6 manufactured by injection molding, concluding that forces increased with feed rate and spindle speed. The principal observed damages were protrusion of fibers, fiber failure/fracture, and fiber/matrix debonding.
About the drilling machining process of CFRP, Gaugel et al. [13] observed that diamond-coated tools presented minor coating rounding of the coating until chipping occurrence and being the coating fracture and excessive substrate wear the most predominant mechanisms wear. Meinhard et al.[14] investigated the drilling of quasi‐isotropic CFRTP laminates made of 24 unidirectional carbon/PA12‐plies, at 100 m/min and a feed rate of 0.6 mm/rev using a carbide cutting tool. The authors observed that the decrease in cutting speed and feed rate caused damage to fraying, burring, plasticization, and fiber deflection, which was also associated with increased tool wear.
FG and CF reinforced thermoplastic polymers’ tuning process was also studied. Davim et al.[70] investigated the precision turning process of PA66 with 30 wt% of FG applying four different cutting tools. The authors observed the formation of continuous coiled microchips in all testing conditions. Bertolini et al.[15] investigated the turning of PA6 using cutting speeds from 50 to 200 m/ min and deep-of-cut from 0.25 to 1 mm in cryogenic and abundant lubrication. The authors observed the change of chip morphology during turning of PA6 with the decrease of temperature, from continuous to serrated until the Tg
region and after that from serrated to dust form. The dust form was correlated with poor surface finish.
Considering the association between additive manufacturing and machining processes of CFRP and FGRP, the contribution of machining is usually related to surface quality improvement, boosting the development of hybrid equipment to allow the fast transition of processing to machining components. Ferreira et al.[71] investigated the milling of short CF reinforced PA12 printed parts. The authors also highlight that with hybrid equipment and techniques that associate machining and additive manufacturing, a reduction of 50% in building time was observed, proving its potential application in several industrial processes.
Disposing of polymeric waste in landfills or incineration is becoming increasingly disadvantageous for industries. The development of new guidelines and environmental legislation that regulate the recyclability of these materials, which have high costs due to the high technology involved in the production process, are being led to new projects in the sector[80]. In Figure 2, it could be the possible PA recycling processes.
The automotive industry is committed to developing projects that solve environmental problems resulting from the waste generated during manufacturing components. The recycling of thermoplastics is a setback within the automotive sector and the feasibility of recycling end-of-life automotive parts. According to European Union guidelines[81], this regulation establishes that as of 2020, new car fleets must release an average of about 95 g of CO2/km. Directive 200/53/EC of the European Parliament & Council of the European Union[82] aims to end the incorrect disposal of end-of-life vehicles (EVL) and their waste. The long-term
perspective is to change the way cars are designed and produced, so the directive targets the recovery and recycling of EVL and waste. To reduce the waste generated, vehicle manufacturers must develop and manufacture vehicles that have easy disassembly, reuse, and recycling of EVLs, increase the use of recycled materials in vehicle manufacturing and reduce the use of hazardous substances in the design of new vehicles[82]
The recycling of thermoplastics can be subdivided into four processes: mechanical, thermal, chemical, and energy[83]. However, it is clear that there is a need to develop sustainable production, and mechanical recycling has been gaining prominence among methodologies as it combines technical feasibility, moderate costs, and environmental benefits[84]. This approach is more suitable for short fiber reinforced polymers, as milling induces fiber breakage. Reprocessing has decreased the material’s mechanical properties compared to chemical and thermal recycling that allowed the recovery of fibers and matrix in organic substances; however, the high energy consumption of these methods makes them less sustainable for composites with high commercial value fibers[84].
PA-based materials are feasible to be recycled, and in this way, it has been drawing the attention of PA consumer industries due to the high recycling potential resulting in suitable quality materials that can be reinserted into the production process of the generating industry or even incorporated as a material raw in another sector. It can be used in the automotive, electrical, and electronics sectors for packaging; consequently, there was a significant evolution in increasing the volume of PA residues. To remedy this problem, Chanda[85] discusses PA recycling methods; mechanical recycling is considered the easiest way to recycle PA, but as it is difficult to separate and clean the waste and be careful with repetitive melt processing, it can cause degradation of the PA properties.
Different processes can perform chemical recycling of PA. Lee et al.[86] address the chemical recycling route via catalytic pathways to recover caprolactam from PA6 with a high conversion rate. Chanda[85] discusses studies carried out with the types of decomposition of PA through hydrolysis, glycolysis, alcoholysis, ammonolysis, and mediation of ionic liquids, explaining the particularities of each technique and the parameters used in the studies. The studies by Nemade and Zope[87] carry out dissolution processes with different solvents such as dimethyl sulfoxide, dimethylformamide, formic acid, and p-cresol to degrade PA residues, with formic acid being excellent for the degradation of PA.
Alberti et al.[88] performed the depolymerization of PA6 through ring closure reactions to produce N-acetyl caprolactam, using 4-(dimethylamino)pyridine (DMAP) as an organocatalyst and acetic anhydride as a cheap and abundant depolymerization reagent. Kamimura et al.[89] studied the depolymerization of PA6 in hydrophilic ionic liquids under microwave irradiation at 300 ºC, separating caprolactam under simple extraction, and the ionic liquid, in turn, can be reused several times. Furthermore, the authors verified an improved procedure that avoids direct distillation (DD), contributing to an energetically more economical technique.
Kumar et al.[90] used a green and sustainable approach to hydrogenative PA depolymerization. The monomers obtained by this process can be dehydrogenated to return in the form of poly(oligo)amide, establishing closed-loop recycling of PA. Thus, the development of these strategies should allow better recognition of the PA residual value for the industry. The study performed by Tapper et al.[80] also presented the closed-loop recycling methodology to recover the high-quality constituents, the PA6 matrix, and the CF. The matrix was recovered by dissolving it completely in benzyl alcohol followed by precipitation, and the fibers were filtered from the PA6 solution. The authors found that even with the decrease in the mechanical properties of the recycled composite, these values were higher for any recycled thermoplastic composite and any discontinuous CF composite with thermoplastic or thermoset matrices. Mondragon et al.[91] carried out an interesting study on the recycling of PA6 fishing nets recovered from the ocean by fishermen. According to the authors, the thermomechanical processing did not affect the final properties of PA6. The PA6 residues could be reused in other applications since the analyzed properties are similar to the commercialized material.
Kunchimon et al.[92] prepared polymer blends from PA6 and polyurethane (PU) from textile waste, using the double screw melt spinning technique. According to the authors, it was possible to verify the feasibility of recycling end-of-life multi-material polymeric products to replace neat polymers such as PU. The study by Souza et al.[93] used vacuum bags of PA6 discarded after the curing process in an autoclave in the aerospace sector to produce PA6/LLDPE (linear low-density polyethylene) blends. According to the authors, this process demonstrated a new strategy for PA6 recycling, contributing to the reduction of waste from the aerospace industry.
The work of Moreno and Saron[94] was also based on recycling PA6 and low-density polyethylene (LDPE) components from multilayer polymeric packaging films. The presence of PE-g-MA proved to be economically viable due to its relatively low value compared to other additives used in polymers and its use boosting the potential application of the recycled blend. Pietroluongo et al.[95] investigated the mechanical recycling of parts of vehicle end-of-life radiators composed of PA66 reinforced with 35.7 wt% short FG to be applied in new structural or semi-structural components. The authors verified a reduction in mechanical properties is also related to different lengths of medium fibers and increasingly shorter fibers, making them less effective in resisting matrix movement. According to the study, recycled material can be used in the automotive sector to replace components made from unreinforced PA66 or with a low percentage of FG reinforcement. It may contribute to enforcing strict EU regulations on reuse and recyclability of at least 85% by weight per vehicle and reuse and recovery of at least 95% by weight per vehicle[21]
Češarek et al.[96] studied the degradation of PA66 through hydrolysis at different temperatures (170°C and 200°C) and molar ratios of 0.5, 1.0, and 1.25 HCl/amide in times ranging from 3.5 to 40 min under microwave irradiation. This methodology proved profitable for the recovery of PA precursor monomers and allowed the recovery of
Polímeros, 32(2), e2022023, 2022
the reinforcement present in the composite, making it promising. Another method of chemical recycling is the chemical decomposition of PA66 carried out by glycolysis processes with an excess mass of ethylene glycol (EG) as a decomposition agent in the presence of a catalyst, resulting in liquid samples and amino glucose with a mixture of EG with triethylenetetramine (TETA) as a decomposition agent that resulted in solid samples, proposed by Datta et al. [97]. The products obtained had the presence of molecules with hydroxyl groups and amines. The attractiveness of this technique is that it was possible to apply the chemical decomposition products to synthesize new PU with glycolysis intermediates originating from recycled PA66, replacing the commercially used polyol in the amount of 10 or 15 wt% in a satisfactory application of the process.
After an in-depth discussion of the most recent PA recycling techniques currently used, it is possible to see the extent of the viability of this process within industries. Each type of processing focuses on producing different products from recycling and demonstrates potential application in other materials and sectors. From the analyzed studies, the range of recycling techniques used for PA6, PA66, and PA12 is noticeable. Furthermore, the increased use of this material is indicative of its excellent properties and application versatility. It has great potential to close the production cycle and fit into the circular economy, benefiting the automotive sector to comply with EU laws and guidelines.
Concerns about environmental issues have led governments to establish increasingly strict rules for the automotive industry. PAs are among the most widely used thermoplastics in engineering polymers due to their excellent balance between performance and cost. In the automotive sector, they are widely used, resulting in lighter vehicles and lower fuel consumption. The keys finding regards to PA (Nylon) 6, 66 and 12 in this review research was:
• PA6-based materials are an alternative for automotive production, used inclusively in structural parts such as chassis where good mechanical performance is required;
• PA6-based materials and PA66-based are used in automotive industry in the fabrication of gears, bearing, leaf springs, under-the hood components, such as engine encapsulation and engine bay parts;
• PA12 is most used in the fuel transfer system, the fuel systems pipes;
• Due to the tendency to absorb moisture, PA must be dried before processing, which can be by injection molding, extrusion, compression molding, and additive manufacturing;
• Higher cooling rates result in lower crystallization temperatures and a more comprehensive temperature range. The incorporation of fibers increased the thermal stability of neat PA6. Higher mechanical strength was achieved with a higher degree of crystallinity. A decrease in interfacial shear resistance was obtained with a reduction of cooling rates;
• The mainly machining problems when processing PAbased composites are delamination and burr occurrence. The described relevant factors that affect machining were cutting tool temperature, cutting tool material and geometry, machined material composition, and thermal properties;
• PA-based materials can be recycled mechanically, thermally, and chemically and have been drawing the attention of companies generated from PA-based waste due to the excellent quality of the resulting recycled material.
According to the information gathered, the use of PA 6,66 and 12, and PA-based materials has the potential to assist the automotive industry in complying with increasingly stringent regulations for emission of gases and use of recyclable materials, also helping the energy efficiency of the vehicle by reducing its total weight.
• Conceptualization – Marcel Yuzo Kondo; Larissa Stieven Montagna ; Mirabel Cerqueira Rezende.
• Data curation – Marcel Yuzo Kondo; Larissa Stieven Montagna; Guilherme Ferreira de Melo Morgado; André Luiz Guimarães de Castilho ; Larissa Anne Pereira dos Santos Batista.
• Formal analysis – Marcel Yuzo Kondo.
• Investigation – Marcel Yuzo Kondo ; Larissa Stieven Montagna.
• Methodology – Marcel Yuzo Kondo ; Larissa Stieven Montagna.
• Project administration – Edson Cocchieri Botelho.
• Resources – Edson Cocchieri Botelho; Michelle Leali Costa; Fabio Roberto Passador; Mirabel Cerqueira Rezende; Marcos Valério Ribeiro.
• Software – Larissa Anne Pereira dos Santos Batista.
• Supervision – Mirabel Cerqueira Rezende; Marcos Valério Ribeiro.
• Validation – Marcel Yuzo Kondo ; Larissa Stieven Montagna.
• Visualization – Marcel Yuzo Kondo ; Larissa Stieven Montagna.
• Writing – original draft Marcel Yuzo Kondo; Larissa Stieven Montagna; Guilherme Ferreira de Melo Morgado; André Luiz Guimarães de Castilho; Larissa Anne Pereira dos Santos Batista.
• Writing – review & editing – Marcel Yuzo Kondo; Larissa Stieven Montagna; Edson Cocchieri Botelho; Michelle Leali Costa; Fabio Roberto Passador; Mirabel Cerqueira Rezende; Marcos Valério Ribeiro.
The authors would like to thank the Federal Government Program ‘Rota 2030’ linked to the “Development of Skills for Design and Manufacturing of Tooling for Composite Parts” n° 27194.03.03/2020.01-00 for the financial support; the Lightweight Structures Laboratory from IPT (Instituto
Kondo, M. Y., Montagna L. S., Morgado, G. F. M., Castilho, A. L. G., Batista, L. A. P. S., Botelho, E. C., Costa, M. L., Passador, F. R., Rezende, M. C., & Ribeiro, M. V.
de Pesquisas Tecnológicas do Estado de São Paulo) for the coordination, and also the Brazilian Funding Institutions FIPT (Fundação de Apoio do IPT), FUNDEP (Fundação de Desenvolvimento da Pesquisa) for the administrative support. The authors are grateful to the National Council for Scientific and Technological Development (CNPq) (303024/2016-8, 305123/2018-1, 306576/2020-1, and 304876/2020-8), and this study was financed in part by the Coordenação de Aperfeiçoamento de Pessoal de Nível Superior – Brasil (CAPES) – Finance Code 001. The authors are also grateful for the free figure development programs: Biorender and Canva.
1 Venoor, V., Park, J. H., Kazmer, D. O., & Sobkowicz, M. J. (2021). Understanding the effect of water in polyamides: a review. Polymer Reviews (Philadelphia, Pa.), 61(3), 598 645 http://dx.doi.org/10.1080/15583724.2020.1855196
2 Deshoulles, Q., Le Gall, M., Dreanno, C., Arhant, M., Priour, D., & Le Gac, P. Y. (2021). Modelling pure polyamide 6 hydrolysis: influence of water content in the amorphous phase. Polymer Degradation & Stability, 183, 109435 http://dx.doi. org/10.1016/j.polymdegradstab.2020.109435
3 Troughton, M. J. (2009). Polyamides. In M. J. Troughton (Ed.), Handbook of plastics joining: a practical guide (pp. 251 281). USA: William Andrew Inc. http://dx.doi.org/10.1016/B9780-8155-1581-4.50027-5
4 McKeen, L. W. (2019). Polyamides (nylons). In L. W. McKeen The effect of UV light and weather on plastics and elastomers (Chap. 7, pp. 185 222). USA: William Andrew Inc http:// dx.doi.org/10.1016/B978-0-12-816457-0.00007-1
5 Silva, T. F., Melo Morgado, G. F., Amaral Montanheiro, T. L., Montagna, L. S., Albers, A. P. F., & Passador, F. R. (2020). A simple mixing method for polyamide 12/attapulgite nanocomposites: structural and mechanical characterization. SN Applied Sciences, 2(3), 369 http://dx.doi.org/10.1007/ s42452-020-2153-1
6 Kiziltas, A., Liu, W., Tamrakar, S., & Mielewski, D. (2021). Graphene nanoplatelet reinforcement for thermal and mechanical properties enhancement of bio-based polyamide 6, 10 nanocomposites for automotive applications. Composites Part C: Open Access, 6, 100177 http://dx.doi.org/10.1016/j. jcomc.2021.100177
7. Kurokawa, M., Uchiyama, Y., Iwai, T., & Nagai, S. (2003). Performance of plastic gear made of carbon fiber reinforced polyamide 12. Wear , 254 (5–6 ), 468 473 . http://dx.doi. org/10.1016/S0043-1648(03)00020-6.
8 Obeid, H., Clément, A., Fréour, S., Jacquemin, F., & Casari, P. (2018). On the identification of the coefficient of moisture expansion of polyamide-6: accounting differential swelling strains and plasticization. Mechanics of Materials, 118, 1 10 http://dx.doi.org/10.1016/j.mechmat.2017.12.002
9 Wiese, M., Thiede, S., & Herrmann, C. (2020). Rapid manufacturing of automotive polymer series parts: A systematic review of processes, materials and challenges. Additive Manufacturing, 36, 101582 http://dx.doi.org/10.1016/j.addma.2020.101582
10 Stan, D. V. (2020). Considerations on the drying of the raw material and consequences on the quality of the injected products. Materiale Plastice, 57(1), 46 56 http://dx.doi. org/10.37358/MP.20.1.5311
11 Karataş, M. A., & Gökkaya, H. (2018). A review on machinability of carbon fiber reinforced polymer (CFRP) and glass fiber reinforced polymer (GFRP) composite materials. Defence
Technology, 14(4), 318 326 http://dx.doi.org/10.1016/j. dt.2018.02.001
12 Caggiano, A., Improta, I., & Nele, L. (2018). Characterization of a new dry drill-milling process of carbon fibre reinforced polymer laminates. Materials (Basel), 11(8), 1470 http:// dx.doi.org/10.3390/ma11081470 PMid:30126200.
13 Gaugel, S., Sripathy, P., Haeger, A., Meinhard, D., Bernthaler, T., Lissek, F., Kaufeld, M., Knoblauch, V., & Schneider, G. (2016). A comparative study on tool wear and laminate damage in drilling of carbon-fiber reinforced polymers (CFRP). Composite Structures, 155, 173 183. http://dx.doi. org/10.1016/j.compstruct.2016.08.004.
14 Meinhard, D., Haeger, A., & Knoblauch, V. (2021). Drilling induced defects on carbon fiber-reinforced thermoplastic polyamide and their effect on mechanical properties. Composite Structures, 256, 113138 http://dx.doi.org/10.1016/j. compstruct.2020.113138
15 Bertolini, R., Ghiotti, A., & Bruschi, S. (2020). Machinability Of Polyamide 6 Under Cryogenic Cooling Conditions. Procedia Manufacturing, 48, 419 427 http://dx.doi.org/10.1016/j. promfg.2020.05.064
16 Kuram, E. (2016). Micro-machinability of injection molded polyamide 6 polymer and glass-fiber reinforced polyamide 6 composite. Composites. Part B, Engineering, 88, 85 100 http://dx.doi.org/10.1016/j.compositesb.2015.11.004
17 Ramezani-Dana, H., Gomina, M., Bréard, J., & Orange, G. (2021). Experimental investigation of the mechanical behavior of glass fiber/high fluidity polyamide-based composites for automotive market. Journal of Reinforced Plastics and Composites, 40(2122), 827 844. http://dx.doi.org/10.1177/07316844211014006.
18 European Commission Regulation (EU) 2019/631 of the European Parliament and of the Council of 17 April 2019 (2019). Setting CO2 emission performance standards for new passenger cars and for new light commercial vehicles and repealing Regulations (EC) No 443/2009 and (EU) No 510/2011 Official Journal of the European Union, France Retrieved in 2022, May 17, from https://eur-lex.europa.eu/ legal-content/EN/TXT/?uri=CELEX%3A32019R0631&q id=1638814026735
19 Nguyen-Tran, H.-D., Hoang, V.-T., Do, V.-T., Chun, D.-M., & Yum, Y.-J. (2018). Effect of multiwalled carbon nanotubes on the mechanical properties of carbon fiber-reinforced polyamide-6/polypropylene composites for lightweight automotive parts. Materials (Basel), 11(3), 429 http://dx.doi. org/10.3390/ma11030429 PMid:29543754.
20 Grätzl, T., van Dijk, Y., Schramm, N., & Kroll, L. (2019). Influence of the automotive paint shop on mechanical properties of continuous fibre-reinforced thermoplastics. Composite Structures, 208, 557 565 http://dx.doi.org/10.1016/j. compstruct.2018.10.052
21. European Parliament. Directive 2000/53/EC of The European Parliament and of The Council. (2000, 18 de setembro). On end-of life vehicles. Official Journal of the European Union, France. Retrieved in 2022, May 17, from https://eur-lex.europa. eu/legal-content/EN/ALL/?uri=celex%3A32000L0053
22 Amasawa, E., Hasegawa, M., Yokokawa, N., Sugiyama, H., & Hirao, M. (2020). Environmental performance of an electric vehicle composed of 47% polymers and polymer composites. Sustainable Materials and Technologies, 25, e00189 http:// dx.doi.org/10.1016/j.susmat.2020.e00189
23 Chauhan, V., Kärki, T., & Varis, J. (2019). Review of natural fiber-reinforced engineering plastic composites, their applications in the transportation sector and processing techniques. Journal of Thermoplastic Composite Materials, 35(8), 1169 1209 http://dx.doi.org/10.1177/0892705719889095
Polímeros, 32(2), e2022023, 2022
24 Boopathy, G., Prakash, J. U., Gurusami, K., & Kumar, J. V. S. P. (2022). Investigation on process parameters for injection moulding of nylon 6/SiC and nylon 6/B4C composites. Materials Today: Proceedings, 52(Pt 3), 1676 1681 http:// dx.doi.org/10.1016/j.matpr.2021.11.316
25 Muminovic, A. J., Pervan, N., Delic, M., Muratovic, E., Mesic, E., & Braut, S. (2022). Failure analysis of nylon gears made by additive manufacturing. Engineering Failure Analysis, 137, 106272 http://dx.doi.org/10.1016/j.engfailanal.2022.106272
26 Dhaduti, S. C., Sarganachari, S. G., Patil, A. Y., & Yunus Khan, T. M. (2020). Prediction of injection molding parameters for symmetric spur gear. Journal of Molecular Modeling, 26(11), 302 http://dx.doi.org/10.1007/s00894-020-04560-9 PMid:33057961.
27. Zhang, Y., Mao, K., Leigh, S., Shah, A., Chao, Z., & Ma, G. (2020). A parametric study of 3D printed polymer gears. International Journal of Advanced Manufacturing Technology, 107(11), 4481 4492 http://dx.doi.org/10.1007/s00170-02005270-5.
28 SriMurugan, R., Ramnath, B. V., Ramanan, N., & Elanchezhian, C. (2019). Study on mechanical and metallurgical properties of glass fibre reinforced PMC gear materials. Materials Today: Proceedings, 16(Pt 2), 524 531. http://dx.doi.org/10.1016/j. matpr.2019.05.124
29 Karthikeyan , R., Rajkumar, S., Bensingh, R. J., Kader, M. A., & Nayak, S. K. (2020). Finite element analysis of elastomer used in automotive suspension systems. Journal of Elastomers and Plastics, 52(6), 521 536 http://dx.doi. org/10.1177/0095244319875774
30 Singh, R., Kumar, R., Ranjan, N., Penna, R., & Fraternali, F. (2018). On the recyclability of polyamide for sustainable composite structures in civil engineering. Composite Structures, 184, 704 713 http://dx.doi.org/10.1016/j.compstruct.2017.10.036
31 Chen, P., Wu, H., Zhu, W., Yang, L., Li, Z., Yan, C., Wen, S., & Shi, Y. (2018). Investigation into the processability, recyclability and crystalline structure of selective laser sintered Polyamide 6 in comparison with Polyamide 12. Polymer Testing, 69, 366 374 http://dx.doi.org/10.1016/j.polymertesting.2018.05.045
32. Spronk, S. W. F., Kersemans, M., De Baerdemaeker, J. C. A., Gilabert, F. A., Sevenois, R. D. B., Garoz, D., Kassapoglou, C. , & Van Paepegem , W. ( 2017 ). Comparing damage from low-velocity impact and quasi-static indentation in automotive carbon/epoxy and glass/polyamide-6 laminates. Polymer Testing, 65, 231 241 http://dx.doi.org/10.1016/j. polymertesting.2017.11.023
33 Murray, J. J., Allen, T., Bickerton, S., Bajpai, A., Gleich, K., McCarthy, E. D., & Brádaigh, C. M. Ó. (2021). Thermoplastic RTM: impact properties of anionically polymerised polyamide 6 composites for structural automotive parts. Energies, 14(18), 5790 http://dx.doi.org/10.3390/en14185790
34. Ishikawa, T., Amaoka, K., Masubuchi, Y., Yamamoto, T., Yamanaka, A., Arai, M., & Takahashi, J. (2018). Overview of automotive structural composites technology developments in Japan. Composites Science and Technology, 155, 221 246 http://dx.doi.org/10.1016/j.compscitech.2017.09.015
35 Caltagirone, P. E., Ginder, R. S., Ozcan, S., Li, K., Gay, A. M., Stonecash, J., Steirer, K. X., Cousins, D., Kline, S. P., Maxey, A. T., & Stebner, A. P. (2021). Substitution of virgin carbon fiber with low-cost recycled fiber in automotive grade injection molding polyamide 66 for equivalent composite mechanical performance with improved sustainability. Composites. Part B, Engineering, 221, 109007 http://dx.doi.org/10.1016/j. compositesb.2021.109007
36 Caputo, F., Lamanna, G., De Luca, A., & Armentani, E. (2020). Thermo-mechanical investigation on an automotive engine encapsulation system made of fiberglass reinforced
polyamide PA6 GF30 material. Macromolecular Symposia, 389(1), 1900100 http://dx.doi.org/10.1002/masy.201900100
37 Volpe, V., Lanzillo, S., Affinita, G., Villacci, B., Macchiarolo, I., & Pantani, R. (2019). Lightweight high-performance polymer composite for automotive applications. Polymers, 11(2), 326 http://dx.doi.org/10.3390/polym11020326. PMid:30960310.
38 Mosey, S., Korkees, F., Rees, A., & Llewelyn, G. (2020). Investigation into fibre orientation and weldline reduction of injection moulded short glass-fibre/polyamide 6-6 automotive components. Journal of Thermoplastic Composite Materials, 33(12), 1603 1628 http://dx.doi.org/10.1177/0892705719833098
39 Wei, X.-F., Kallio, K. J., Bruder, S., Bellander, M., Olsson, R. T., & Hedenqvist, M. S. (2020). High-performance glass-fibre reinforced biobased aromatic polyamide in automotive biofuel supply systems. Journal of Cleaner Production, 263, 121453 http://dx.doi.org/10.1016/j.jclepro.2020.121453
40 Hıdıroğlu, M., Aksüt, D., Serçe, O., Karabulut, H., & Şen, M. (2019). Reducing the hydrocarbon gas diffusion and increasing the pressure-impact strength of fuel transfer pipelines for use in the automotive industry using radiation crosslinked polyamide 12. Radiation Physics and Chemistry, 159, 118 123 http:// dx.doi.org/10.1016/j.radphyschem.2019.02.039
41 Özbay, B., & Serhatlı, E. (2020). Processing and characterization of hollow glass-filled polyamide 12 composites by selective laser sintering method. Materials Technology, 37(4), 213 223 http://dx.doi.org/10.1080/10667857.2020.1824149
42 Santonocito, D. (2020). Evaluation of fatigue properties of 3D-printed Polyamide-12 by means of energy approach during tensile tests. Procedia Structural Integrity, 25, 355 363 http:// dx.doi.org/10.1016/j.prostr.2020.04.040
43. Shinzawa, H., & Mizukado, J. (2020). Water absorption by polyamide (PA) 6 studied with two-trace two-dimensional (2T2D) near-infrared (NIR) correlation spectroscopy. Journal of Molecular Structure, 1217, 128389 http://dx.doi.org/10.1016/j. molstruc.2020.128389
44 Teixeira, D., Giovanela, M., Gonella, L. B., & Crespo, J. S. (2013). Influence of flow restriction on the microstructure and mechanical properties of long glass fiber-reinforced polyamide 6.6 composites for automotive applications. Materials & Design, 47, 287 294 http://dx.doi.org/10.1016/j.matdes.2012.12.030
45 Marset, D., Dolza, C., Boronat, T., Montanes, N., Balart, R., Sanchez-Nacher, L., & Quiles-Carrillo, L. (2020). InjectionMolded parts of partially biobased polyamide 610 and biobased halloysite nanotubes. Polymers, 12(7), 1503. http://dx.doi. org/10.3390/polym12071503. PMid:32640632.
46 Abdelwahab, M., Codou, A., Anstey, A., Mohanty, A. K., & Misra, M. (2020). Studies on the dimensional stability and mechanical properties of nanobiocomposites from polyamide 6-filled with biocarbon and nanoclay hybrid systems. Composites. Part A, Applied Science and Manufacturing, 129, 105695 http://dx.doi.org/10.1016/j.compositesa.2019.105695
47 Venkatraman, P., Trotto, E., Burgoyne, I., & Foster, E. J. (2020). Premixed cellulose nanocrystal reinforcement of polyamide 6 for melt processing. Polymer Composites, 41(10), 4353 4361 http://dx.doi.org/10.1002/pc.25717
48. Sabiston, T., Li, B., Kang, J., Wilkinson, D., & Engler-Pinto, C. (2021). Accounting for the microstructure in the prediction of the fatigue life of injection moulded composites for automotive applications. Composite Structures, 255, 112898 http://dx.doi. org/10.1016/j.compstruct.2020.112898
49 Kawai, M., Funaki, S., Taketa, I., & Hirano, N. (2019). Temperature-dependent constant fatigue life diagram for pressformed short carbon fiber reinforced polyamide composite. Advanced Composite Materials, 28(suppl 2), 1 28 http:// dx.doi.org/10.1080/09243046.2018.1434915
Kondo, M. Y., Montagna L. S., Morgado, G. F. M., Castilho, A. L. G., Batista, L. A. P. S., Botelho, E. C., Costa, M. L., Passador, F. R., Rezende, M. C., & Ribeiro, M. V.
50 Ozmen, S. C., Ozkoc, G., & Serhatli, E. (2019). Thermal, mechanical and physical properties of chain extended recycled polyamide 6 via reactive extrusion: effect of chain extender types. Polymer Degradation & Stability, 162, 76 84 http:// dx.doi.org/10.1016/j.polymdegradstab.2019.01.026
51 Ogunsona, E. O., Codou, A., Misra, M., & Mohanty, A. K. (2019). A critical review on the fabrication processes and performance of polyamide biocomposites from a biofiller perspective. Materials Today Sustainability, 5, 100014 http:// dx.doi.org/10.1016/j.mtsust.2019.100014
52. Borrelli, A., D’Errico, G., Borrelli, C., & Citarella, R. (2020). Assessment of crash performance of an automotive component made through additive manufacturing. Applied Sciences (Basel, Switzerland), 10(24), 9106 http://dx.doi.org/10.3390/ app10249106.
53 Lupone, F., Padovano, E., Veca, A., Franceschetti, L., & Badini, C. (2020). Innovative processing route combining fused deposition modelling and laser writing for the manufacturing of multifunctional polyamide/carbon fiber composites. Materials & Design, 193, 108869 http://dx.doi.org/10.1016/j. matdes.2020.108869
54 Batista, N. L., Olivier, P., Bernhart, G., Rezende, M. C., & Botelho, E. C. (2016). Correlation between degree of crystallinity, morphology and mechanical properties of PPS/carbon fiber laminates. Materials Research, 19(1), 195 201 http://dx.doi. org/10.1590/1980-5373-MR-2015-0453
55. Liu, B., Hu, G., Zhang, J., & Wang, Z. (2019). The non-isothermal crystallization behavior of polyamide 6 and polyamide 6/HDPE/ MAH/L-101 composites. Journal of Polymer Engineering, 39(2), 124 133 http://dx.doi.org/10.1515/polyeng-2018-0170
56. Liu, T., Mo, Z., Wang, S., & Zhang, H. (1997). Isothermal melt and cold crystallization kinetics of poly(aryl ether ether ketone ketone) (PEEKK). Polymer Engineering and Science, 33(9), 1405 1414 http://dx.doi.org/10.1016/S0014-3057(97)00016-5
57. Zaldua, N., Maiz, J., de la Calle, A., García-Arrieta, S., Elizetxea, C., Harismendy, I., Tercjak, A., & Müller, A. J. (2019). Nucleation and crystallization of PA6 composites prepared by T-RTM: effects of carbon and glass fiber loading. Polymers, 11(10), 1680 http://dx.doi.org/10.3390/polym11101680 PMid:31615165.
58 Taketa, I., Kalinka, G., Gorbatikh, L., Lomov, S. V., & Verpoest, I. (2020). Influence of cooling rate on the properties of carbon fiber unidirectional composites with polypropylene, polyamide 6, and polyphenylene sulfide matrices. Advanced Composite Materials, 29(1), 101 113 http://dx.doi.org/10.1080/092430 46.2019.1651083
59. Li, M.-X., Lee, D., Lee, G. H., Kim, S. M., Ben, G., Lee, W. I., & Choi, S. W. (2020). Effect of temperature on the mechanical properties and polymerization kinetics of polyamide-6 composites. Polymers, 12(5), 1133 http://dx.doi.org/10.3390/ polym12051133 PMid:32429100.
60 Yaghini , N. , & Peters , G. W. M. ( 2021 ). Modeling Crystallization Kinetics and Resulting Properties of Polyamide 6. Macromolecules, 54(4), 1894 1904 http://dx.doi.org/10.1021/ acs.macromol.0c02588
61 Uematsu, H., Kawasaki, T., Koizumi, K., Yamaguchi, A., Sugihara, S., Yamane, M., Kawabe, K., Ozaki, Y., & Tanoue, S. (2021). Relationship between crystalline structure of polyamide 6 within carbon fibers and their mechanical properties studied using Micro-Raman spectroscopy. Polymer, 223, 123711 http://dx.doi.org/10.1016/j.polymer.2021.123711
62 Handwerker, M., Wellnitz, J., Marzbani, H., & Tetzlaff, U. (2021). Annealing of chopped and continuous fibre reinforced polyamide 6 produced by fused filament fabrication. Composites. Part B, Engineering, 223, 109119 http://dx.doi.org/10.1016/j. compositesb.2021.109119
63 Hagihara, H., Watanabe, R., Shimada, T., Funabashi, M., Kunioka, M., & Sato, H. (2018). Degradation mechanism of carbon fiber-reinforced thermoplastics exposed to hot steam studied by chemical and structural analyses of nylon 6 matrix. Composites. Part A, Applied Science and Manufacturing, 112, 126 133 http://dx.doi.org/10.1016/j.compositesa.2018.05.034
64 Ma, Y., Jin, S., Yokozeki, T., Ueda, M., Yang, Y., Elbadry, E. A., Hamada, H., & Sugahara, T. (2020). Effect of hot water on the mechanical performance of unidirectional carbon fiber-reinforced nylon 6 composites. Composites Science and Technology, 200, 108426 http://dx.doi.org/10.1016/j. compscitech.2020.108426
65 Chabaud, G., Castro, M., Denoual, C., & Le Duigou, A. (2019). Hygromechanical properties of 3D printed continuous carbon and glass fibre reinforced polyamide composite for outdoor structural applications. Additive Manufacturing, 26, 94 105 http://dx.doi.org/10.1016/j.addma.2019.01.005
66 Paolucci, F., van Mook, M. J. H., Govaert, L. E., & Peters, G. W. M. (2019). Influence of post-condensation on the crystallization kinetics of PA12: from virgin to reused powder. Polymer, 175, 161 170. http://dx.doi.org/10.1016/j.polymer.2019.05.009.
67 Ma, N., Liu, W., Ma, L., He, S., Liu, H., Zhang, Z., Sun, A., Huang, M., & Zhu, C. (2020). Crystal transition and thermal behavior of Nylon 12. e-Polymers, 20(1), 346 352 http:// dx.doi.org/10.1515/epoly-2020-0039
68 Su, Y., Jia, Z., Niu, B., & Bi, G. (2017). Size effect of depth of cut on chip formation mechanism in machining of CFRP. Composite Structures, 164, 316 327. http://dx.doi.org/10.1016/j. compstruct.2016.11.044
69 Ervine, P., O’Donnell, G. E., & Walsh, B. (2015). Fundamental investigations into burr formation and damage mechanisms in the micro-milling of a biomedical grade polymer. Machining Science and Technology, 19(1), 112 133 http://dx.doi.org/10 .1080/10910344.2014.991028
70. Davim, J. P., Silva, L. R., Festas, A., & Abrão, A. M. (2009). Machinability study on precision turning of PA66 polyamide with and without glass fiber reinforcing. Materials & Design, 30(2), 228 234 http://dx.doi.org/10.1016/j.matdes.2008.05.003
71 Ferreira, I., Madureira, R., Villa, S., de Jesus, A., Machado, M., & Alves, J. L. (2020). Machinability of PA12 and short fibre–reinforced PA12 materials produced by fused filament fabrication. International Journal of Advanced Manufacturing Technology, 107(1), 885 903 http://dx.doi.org/10.1007/s00170019-04839-z
72 Chang, D.-Y., Lin, C.-H., Wu, X.-Y., Yang, C.-C., & Chou, S.-C. (2021). Cutting force, vibration, and temperature in drilling on a thermoplastic material of PEEK. Journal of Thermoplastic Composite Materials, 089270572110523 http:// dx.doi.org/10.1177/08927057211052325
73 Yan, Y., Mao, Y., Li, B., & Zhou, P. (2021). Machinability of the thermoplastic polymers: PEEK, PI, and PMMA. Polymers, 13(1), 69 http://dx.doi.org/10.3390/polym13010069 PMid:33375347.
74 Mohankumar, P., Ajayan, J., Yasodharan, R., Devendran, P., & Sambasivam, R. (2019). A review of micromachined sensors for automotive applications. Measurement: Journal of the International Measurement Confederation, 140, 305 322. http://dx.doi.org/10.1016/j.measurement.2019.03.064
75 Hiwale, S., & Rajiv, B. (2020). Experimental investigations of laser machining process parameters using response surface methodology. Materials Today: Proceedings, 44(Pt 6), 3939 3945 http://dx.doi.org/10.1016/j.matpr.2020.09.295
76 Bañon, F., Sambruno, A., Batista, M., Simonet, B., & Salguero, J. (2020). Study of the surface quality of carbon fiber–reinforced thermoplastic matrix composite (CFRTP) machined by abrasive water jet (AWJM). International Journal of Advanced
Polímeros, 32(2), e2022023, 2022
Manufacturing Technology, 107(7), 3299 3313 http://dx.doi. org/10.1007/s00170-020-05215-y
77 Li, M., Soo, S. L., Aspinwall, D. K., Pearson, D., & Leahy, W. (2018). Study on tool wear and workpiece surface integrity following drilling of CFRP laminates with variable feed rate strategy. Procedia CIRP, 71, 407 412 http://dx.doi.org/10.1016/j. procir.2018.05.055.
78 Karatas, E., Gul, O., Karsli, N. G., & Yilmaz, T. (2019). Synergetic effect of graphene nanoplatelet, carbon fiber and coupling agent addition on the tribological, mechanical and thermal properties of polyamide 6,6 composites. Composites. Part B, Engineering, 163, 730 739 http://dx.doi.org/10.1016/j. compositesb.2019.01.014
79 Kießling, R., Dittes, A., Lampke, T., & Ihlemann, J. (2021). Coupled experimental and simulative investigation of the influence of polymer moisture content on the strength of aminosilane-mediated aluminum polyamide 6 joints. International Journal of Adhesion and Adhesives, 109, 102906 http://dx.doi. org/10.1016/j.ijadhadh.2021.102906
80 Tapper, R. J., Longana, M. L., Hamerton, I., & Potter, K. D. (2019). A closed-loop recycling process for discontinuous carbon fibre polyamide 6 composites. Composites. Part B, Engineering, 179, 107418 http://dx.doi.org/10.1016/j. compositesb.2019.107418.
81 European Parliament and Council of the European Union Regulation (EC) No 443/2009 of The European Parliament and of The Council of 23 April 2009. (2009). Setting emission performance standards for new passenger cars as part of the Community’s integrated approach to reduce CO2 emissions from light-duty vehicles Official Journal of the European Union, France. Retrieved in 2022, May 17, from https://eur-lex. europa.eu/legal-content/EN/ALL/?uri=celex%3A32009R0443
82 European Parliament and Council of European Union Directive 2008/98/EC of The European Parliament nnd of The Council of 19 November 2008. (2008). On waste and repealing certain Directives Official Journal of the European Union, France Retrieved in 2022, May 17, from https://eur-lex.europa.eu/ legal-content/EN/TXT/PDF/?uri=CELEX:32008L0098&fr om=EN
83 Chohan, J. S., & Singh, R. (2022). Thermosetting polymers: a review on primary, secondary, tertiary and quaternary recycling. Encyclopedia of Materials: Plastics and Polymers, 1, 603 610 http://dx.doi.org/10.1016/b978-0-12-820352-1.00116-4
84 Howarth, J., Mareddy, S. S. R., & Mativenga, P. T. (2014). Energy intensity and environmental analysis of mechanical recycling of carbon fibre composite. Journal of Cleaner Production, 81, 46 50 http://dx.doi.org/10.1016/j.jclepro.2014.06.023
85 Chanda, M. (2021). Chemical aspects of polymer recycling. Advanced Industrial and Engineering Polymer Research, 4(3), 133 150 http://dx.doi.org/10.1016/j.aiepr.2021.06.002
86 Lee, J., Kwon, E. E., Lam, S. S., Chen, W.-H., Rinklebe, J., & Park, Y.-K. (2021). Chemical recycling of plastic waste via thermocatalytic routes. Journal of Cleaner Production, 321, 128989 http://dx.doi.org/10.1016/j.jclepro.2021.128989
87 Nemade, A. M., & Zope, V. S. (2020). Chemical recycling of polyamide waste. Journal of Engineering Sciences, 11(4), 1235 1238
88 Alberti, C., Figueira, R., Hofmann, M., Koschke, S., & Enthaler, S. (2019). Chemical recycling of end-of-life polyamide 6 via ring closing depolymerization. ChemistrySelect, 4(43), 12638 12642 http://dx.doi.org/10.1002/slct.201903970
89 Kamimura, A., Shiramatsu, Y., & Kawamoto, T. (2019). Depolymerization of polyamide 6 in hydrophilic ionic liquids. Green Energy and Environment, 4(2), 166 170 http://dx.doi. org/10.1016/j.gee.2019.01.002
90 Kumar, A., von Wolff, N., Rauch, M., Zou, Y.-Q., Shmul, G., Ben-David, Y., Leitus, G., Avram, L., & Milstein, D. (2020). Hydrogenative depolymerization of nylons. Journal of the American Chemical Society, 142(33), 14267 14275 http:// dx.doi.org/10.1021/jacs.0c05675 PMid:32706584.
91 Mondragon, G., Kortaberria, G., Mendiburu, E., González, N., Arbelaiz, A., & Peña-Rodriguez, C. (2020). Thermomechanical recycling of polyamide 6 from fishing nets waste. Journal of Applied Polymer Science, 137(10), 48442 http://dx.doi. org/10.1002/app.48442
92 Kunchimon, S. Z., Tausif, M., Goswami, P., & Cheung, V. (2019). Polyamide 6 and thermoplastic polyurethane recycled hybrid Fibres via twin-screw melt extrusion. Journal of Polymer Research, 26(7), 162 http://dx.doi.org/10.1007/s10965-0191827-0
93 Souza, G. P. M., Anjos, E. G. R., Montagna, L. S., Ferro, O., & Passador, F. R. (2019). A new strategy for the use of postprocessing vacuum bags from aerospace supplies: nucleating agent to LLDPE phase in PA6/LLDPE blends. Recycling, 4(2), 18 http://dx.doi.org/10.3390/recycling4020018
94 Moreno, D. D. P., & Saron, C. (2018). Influence of compatibilizer on the properties of low-density polyethylene/polyamide 6 blends obtained by mechanical recycling of multilayer film waste. Waste Management & Research, 36(8), 729 736 http:// dx.doi.org/10.1177/0734242X18777795. PMid:29871552.
95 Pietroluongo, M., Padovano, E., Frache, A., & Badini, C. (2019). Mechanical recycling of an end-of-life automotive composite component. Sustainable Materials and Technologies, 23, e00143 http://dx.doi.org/10.1016/j.susmat.2019.e00143
96 Češarek, U., Pahovnik, D., & Žagar, E. (2020). Chemical recycling of aliphatic polyamides by microwave-assisted hydrolysis for efficient monomer recovery. ACS Sustainable Chemistry & Engineering, 8(43), 16274 16282 http://dx.doi. org/10.1021/acssuschemeng.0c05706. PMid:33194457.
97 Datta, J., Błażek, K., Włoch, M., & Bukowski, R. (2018). A New approach to chemical recycling of polyamide 6.6 and synthesis of polyurethanes with recovered intermediates. Journal of Polymers and the Environment, 26(12), 4415 4429 http://dx.doi.org/10.1007/s10924-018-1314-4
Received: May 17, 2022
Revised: Sep. 15, 2022
Accepted: Sep. 16, 2022
Kondo, M. Y., Montagna L. S., Morgado, G. F. M., Castilho, A. L. G., Batista, L. A. P. S., Botelho, E. C., Costa, M. L., Passador, F. R., Rezende, M. C., & Ribeiro, M. V.
Supplementary material accompanies this paper.
Table S1 – Summary of the investigation of thermal properties of PA6.
Table S2 – Summary of the investigation of thermal properties of PA66.
Table S3 - Summary of the investigation of thermal properties of PA12.
This material is available as part of the online article from 10.1590/0104-1428.20220042
Polímeros, 32(2), e2022023, 2022
Carlos Alberto Fonzar Pintão1*
, Airton Baggio2
, Lucas Pereira Piedade2
, Luiz Eduardo de Angelo Sanchez2
and Gilberto de Magalhães Bento Gonçalves2
1Departamento de Física, Faculdade de Ciências, Universidade Estadual Paulista – UNESP, Bauru, SP, Brasil
2Departamento de Engenharia Mecânica, Universidade Estadual Paulista – UNESP, Bauru, SP, Brasil *carlos.fonzar@unesp.br
This work presents an alternative to studying and determining the torsion modulus, G, in composites. For this purpose, we use a measuring system with a rotation motion sensor coupled with a torsion pendulum that allows for determining the angular position as a function of the time. Then, through an equation derived from mechanical spectroscopy studies that permits the calculation of G’s value, the experiments focus on samples of different quantities of calcium carbonate (CaCO3) in unsaturated polyester resins. The results show that CaCO3 (33.33%W) fillers increase G’s value by 88% compared with unsaturated resin (100%W). Furthermore, there is a density increase of approximately 21% with the addition of CaCO3, considering the same two samples, which makes these composites the most massive. The relationship between G and composite density shows that it is possible to change the amount of CaCO3 to increase torsion resistance values in a controlled way.
Keywords: calcium carbonate, mechanical spectroscopy, polyester resin, torsion modulus.
How to cite: Pintão, C. A. F., Baggio, A., Piedade, L. P., Sanchez, L. E. A., & Gonçalves, G. M. B. (2022). Torsion modulus with CaCO3 fillers in unsaturated polyester resin - mechanical spectroscopy. Polímeros: Ciência e Tecnologia, 32(2), e2022013. https://doi.org/10.1590/0104-1428.20210105
It is necessary to know material behavior when subjected to stresses or loads to determine the most appropriate application. Therefore, the elastic modulus, which measures a material’s rigidity, must always be considered. It represents an essential property in the behavior of materials used in various applications such as aerospace[1,2], automotive[3], naval[4], civil[5], electrical[6,7], biomedical[8], implants[9], and structures[10-12] subjected to torsion and traction (compression). The elastic modulus, reported for metals and their alloys, depends on the atomic bonds and the distances between atoms in the crystalline lattice. Therefore, it is sensitive to the addition of elements, thermomechanical treatments, and deformation processing. However, composites have amorphous and crystalline parts and form with different additives or fillers. Thus, it is not simple to establish a general pattern of the influence of these same factors that consider metals and their impact on the elastic modulus.
Polymer additives are auxiliary added components. Their inclusion in polymer formulations or compositions is intended for specific applications[13-15], such as modifying and improving properties, reducing cost, or facilitating processing. Essential polymer additives include mineral inorganic fillers, plasticizers, dyes, antioxidants, ultraviolet absorbers, flame retardants, thermal stabilizers, blowing agents, flavoring agents, antifungals, and impact modifiers.
In composites, adding mineral fillers can weaken polymers, although their stiffness increases. The efforts of several authors have improved the properties of materials with the addition of inorganic fillers such as silicon dioxide[16], zinc oxide[17], calcium carbonate (CaCO3)[18], and carbon fibers[19]. Calcium carbonate is the second most used mineral material after talc. The use of CaCO3 with adequate hardness (Mohs ~3 hardness) does not cause short-term machine processing failures[20]. Calcium carbonate reduces some of the cost without affecting properties. For polymer composites, adhesion between the filler and matrix is essential. Suppose adherence is active at the interface, the modulus, stiffness, and strength of a particulate composite increase. Some authors[21-23] have directed attention to investigating CaCO3 nanofiller polypropylene compounds. However, they have yet to advance the creep-limiting properties of CaCO3 nanofiller polypropylene compounds.
Although Young’s modulus is low for plastics and never constant compared with that of metals, deflection resistance (stiffness) is often a concern with the use of plastics. The rigidity of a structure depends on the values from the elastic modulus and the geometry of the materials. Thus, there are no data on the torsion modulus in composites. This work aims to study the influence of additives such as CaCO3 in unsaturated polyester resins. Then, we want to
establish a relationship between the torsion modulus and the quantity of CaCO3
Traditionally, the static (stress-strain curves) or dynamic (ultrasound or vibration) methods[24,25] determine the elastic modulus. In this paper, the modulus of elasticity’s behavior to torsion G by an alternative technique to the traditional that is nondestructive and using mechanical spectroscopy allows for studying the effects of CaCO3 additives. Furthermore, to apply the technique, it is unnecessary to know the Poisson’s ratio of the sample.
Ashland manufactured the resin used to manufacture the specimens and classified it as unsaturated polyester resin under trade reference Arazyn 13.0. Calcium carbonate, known as calcite, is one of the most abundant minerals in nature. It is a chemical of formula CaCO3 and the main component of rocks such as limestone. The particle size is 325 mesh, and its density is between 2.70 and 2.85 g/cm3. For better use of torsion test equipment, the specimens are formed in round bars with a 5.0 mm diameter and a length of 130 mm.
The device for creating the samples constructed from a glass fiber-reinforced polyester resin mold with an isophthalic gel coat surface provides a smooth surface on the specimens and ensures the samples’ dimensional standardization. The mold has dimensions of 120 mm x 220 mm x 80 mm, a hole diameter of 5.0 mm, and guides for opening in two parts, as shown in Figure 1
We adopted the following terminology in our mix of resin and additives for the specimens: CP-00 represents a reference specimen. Samples with 100% resin and their values serve as parameters for the other combinations’ results. Calcium carbonate was added to different models (CP-11 to CP-20), ranging from 5 in 5 parts by weight to every 100 pieces by weight of the resin. Due to its high density, a composition of over 50 elements by weight represents a pasty mixture
with little use in composite parts manufacturing processes. Table 1 summarizes the composition of resin with additive characteristics of these specimens.
The mechanical spectroscopy technique to determine G’s value has been studied in our laboratories and can be used to investigate changes in these materials’ mechanical properties. Therefore, the method for determining G is brief here. It consists of one torsion pendulum that can be adjusted to set its inertia to different values (in our case, four different values were used) and register its angular position
concerning an axis of rotation as a function of time t. For this purpose, we used a rotational movement sensor (RMS; see Figure 2).
Mechanical spectroscopy[25] (i.e., the torsion motion of the pendulum) is described by the
The symbols I, G0, and i represent the rotational inertia, the torsion constant of the sample fixed to the pendulum, and the imaginary number, respectively. In this case, we assume that air resistance and the friction of the RMS and rotational system (RS) bearings are negligible because they should not significantly influence movement[26]. The solution to Equation 1 takes the form *i t 0 e θθω = , where
We express G0 as
This equation suggests that the moment of inertia of the pendulum I, the angular velocity ω0, and the term 2 δ
permit G0. It is possible to alter the masses or their position on the pendulum’s torsion rod, which changes I and modifies the
Polímeros, 32(2), e2022013,
Pintão, C. A. F., Baggio, A., Piedade, L. P., Sanchez, L. E. A., & Gonçalves, G. M. B.
1. Composition of resin with additive.
Samples Contraction linear post-cure (mm/m) Resin Part by weight
After catalysis
26.1 100 100.00 1.10 1.18 CP-11 26.2 100 95.24
4.76 1.13 1.23 CP-12 25.1 100 90.91
9.09 1.17 1.26 CP-13 24.4 100 86.96 15 13.04 1.22 1.28 CP-14 21.6 100 83.33 20 16.67 1.26 1.30 CP-15 24.7 100 80.00 25 20.00 1.31 1.32 CP-16 18.6 100 76.92 30 23.08 1.34 1.34 CP-17 21.7 100 74.07 35 25.93 1.36 1.38 CP-18 20.4 100 71.43 40 28.57 1.38 1.40 CP-19 18.9 100 68.97
31.03 1.40 1.41 CP-20 17.2 100 66.67
Figure 2. Measurement system: (a) Complete view of the system without electromagnets; (b) complete drawing of the artistic design of the system in 2D; (c) electromagnets setup; (d) detailed view of the RMS; (e) sample fixation.
value of ω0. Then, G0 depends on the oscillation system’s frequency, and we can obtain a dynamic measurement. For small angles of oscillation, in which the measuring system has a linear behavior, we can express G0 as
applied torque
because the main objective is to determine the torsion modulus G. We used a solid sample with a uniform circular transversal section of diameter d and length L.
Therefore, we can calculate the resistive torque when considering material problems[27]. The sample is submitted when it undergoes torsion through a torque applied by a pendulum (see Figure 1). The following equation calculates this torque:
Where JC is the polar moment of inertia of the cross-section. Then, the equation is
33.33 1.42 1.43
Thus, the magnitude of G results by substituting Equation 2 into (6). As a result,
If there is static equilibrium (i.e., the applied torque is the same as the resistive torque), we can combine Equations 3 and 4 to give
Equation 7 is validated in the article[28], where we show that G can change with the length (L) and diameter (d) of the sample. However, the experimental values found for CP-Ti are practically the same as those in the literature[27,29].
Authors[28,30] have validated Equation 7; now, it is applied to a composite material, which is a different situation than that of a homogeneous material (CP-Ti). Therefore, it is necessary to validate it for this case. If we replace
the solution
, relative to the differential equation that describes the motion of the free pendulum as given above, then
In Equation 8, taking the real number part gives the following equation:
The parameters
and
obtained from the experimental
versus t curve were determined using the RMS software and the Pasco interface for given L, d, and I values. A fit function similar to Equation 9 was used with Origin 7.0 software by selecting a “waveform” function such as the following:
By comparing this equation with Equation 9, we can consider the parameters
and W, as obtained by fitting Equation 10 to the experimental values, and we are then able to get the
Then, using Equation 7, we determined G and the total internal friction of the system
Our research laboratory’s method determined the torsion pendulum’s rotational inertia[26,31]. First, we determined the torsion pendulum’s inertia moment (I) by removing the sample and the electromagnetic system (see Figure 1). The literature describes several techniques to determine the momentum of inertia of a body; however, the one closest to the measurements performed stands out in this work[32] Then, we adopted the same procedure as the cited authors. The resulting torque (τ) responsible for the rotational movement of the measured pendulum system is
Here, τF is the torque of the friction force acting on the rotating shaft, whereas I and 0α are the inertia moment and the pendulum’s angular acceleration, respectively. It must be remembered that the torque of the traction force is
Tm(gr)r 0 , where r = (18.75 ± 0.03)10-3 m and g = (9.79 ± 0.01) m/s2. With Equation 12, we can show that the inclination equals I.
We realized SEM on a Zeiss model EVO LS1. Samples were coated with gold for visualization using the sputtering technique[33]. We made measurements in a high vacuum (10-3 Pa) with a magnification of 500 X and 5.0 kX of a transversal section of the sample bar’s internal region. The aim was to visualize the CaCo3 incorporated into the samples: CP-00 reference with 100%W in resin. CP-11 to CP-20 had CaCO3 added, ranging from 5 in 5 parts by weight to every 100 parts by weight of the resin.
The TG-DTA curves were obtained in an STA 449 F3 (Netzsch), using a 200 μL α-alumina crucible with samples of about 33.5 mg. The analyses were developed at a heating rate of 10 °C min-1 in a dry air atmosphere (70 mL min-1) and a temperature range of 30-650 °C. Therefore, we used the first derivative of the TG curve (DTG) to analyze it better. Furthermore, only three samples were analyzed (CP-00, CP-11, and CP-20).
Initially, the values of I, which previous authors cited, are presented because the measurement system and the four configurations are the same in this work. Then, G values for different concentrations of CaCO3, the use of Equation 7 is validated for this composite case. Finally, using the same G, the samples’ behavior as a function of different concentrations of CaCO3 and the response of their oscillation frequency as a function of the moment of inertia is analyzed.
As mentioned in section 2.2.2, we measured the moment of inertia following the same procedure described, which resulted in the values expressed in Table 2
We found these values using a method independent of that to determine G (section 2.2.1.)
Tables A1 and A2 provide G, f0, δ and Q-1 for the I’s values from Table 2. At the end of the article, we find the results of this section in an Appendix A.
We determined G for different concentrations of CaCO3 in resin. An essential question arose: If the samples used are different from those of metals considered homogeneous[28], is it valid to use Equation 7 when the internal structure of each of the specimens changed? Figure 3 was constructed based on the experimental results of Table A1, considering only diameters of 4.70 mm. Due to a possible linear postcure shrinkage in manufactured samples (see Table 1), slight variations in diameter are critical in the calculation of G. Equation 7 shows that G’s value is inversely proportional to d4.
Note that in Equation 7, G is directly proportional to Lf02, and the sample diameter, d, and length, L, remain constant, maintaining an L/d ratio close to 11.32. Thus, when
Table 2. Experimental results of the rotational inertia of the pendulum.
Mass set on the pendulum rod Rotational inertia, I (10-4 kg m2)
Set 1 98.1 ± 0.5
Set 2 207 ± 1 Set 3 398 ± 1 Set 4 526 ± 4
Figure 3. G versus Lf02 curves validated Equation 7. We used the samples CP-00 and CP-11 to CP-20. First, we set four inertia values (I1, I2, I3, and I4; see Table 2), resulting in four curves that employ a linear adjustment. Next, we determined their angular coefficients (B1 = 8.3 ± 0.9, B2 = 18 ± 2, B3 = 35 ± 4 and B4 = 46 ± 5).
Polímeros, 32(2), e2022013,
I changes the oscillation frequency value, f0, it also changes Lf02. For each sample, If02 is practically constant. As the material changes internally, it is possible that the physical parameter δ changes as the amount of CaCO3 increases. The parameter δ reflects the energy lost to each sample oscillation cycle[25,26]. Therefore, it could invalidate the use of Equation 7. We determine the relationships used in Figure 3 between moments of inertia (Ii) and Bi coefficients, where i = 1, 2, 3, and 4. Deviations are less than 4%. Thus, Equation 7 is valid for composites.
The values of the maximum shear stress or angle-specific deformation, according to[34,35], are
Therefore, we express the value of G as
Figures 4 and 5 show that G values increase with CaCO3, TR increases when d and L/θ are fixed. Then, from Equation 13, it is possible to observe that the value of the maximum shear stress τMAX also increases, which alters the oscillation frequency.
Concerning G’s value for a sample with the same internal structure, in Equation 15, we observe that if we fix L and θ (as we did during the experiment), for each selected d, JC’s value does not change, and, consequently, the amount of TR will not either. That means that TR (resistive torque) remains the same in this situation and that G must have the same value for different inertias (see Figure 5).
The results show that the frequency values increase as the quantity of CaCO3 increases for the equal moment of inertia, which means that τMAX rises. From the experimental results of Tables A1 and A2, we also observe that for each sample analyzed, If02 is practically constant when the quantity of CaCO3 is the same. Thus, if the torsion pendulum inertia increases, the value of f0 must decrease. Then, if I falls, an increase of f0 is expected. Therefore, when the quantity of CaCO3 increases, the If02 product increases (considering only samples with a diameter of 4.70 mm), corresponding to an increase in kinetic energy (1/2 I ω02) of oscillation and an increasingly more prominent τMAX. As shown in Figures 4 and 5, d and L/θ are fixed, and G increases with an increasing amount of CaCO3, so it is clear from Equation 15 that TR increases. This change in the internal structure of the composite provides an increase in G values. However, the value of G was determined using Equation 7. Then, we changed the rotational inertia I using the same experimental conditions described above (i.e., with a fixed d and L/θ). We observed that product If02 is constant for each sample. It increases with an increasing concentration of CaCO3 in the resin (see Tables A1 and A2). For this technique applied within the elastic range’s interval, we fixed a torsion angle
Figure 4. Curves of shear modulus G versus a percentage of CaCO3, %W. G = 1.33 + 0.030 (%W), valid for 0 ≤ %W ≤ 33.33.
Figure 5. Curves of shear modulus G versus I. Samples: CP-00, CP-11 to CP-20.
of 1.78 degrees in the sample (corresponding to 8 degrees in the rotation sensor).
We calculated the ratio between the torsion modulus and the density after sample catalysis (G/ρ) and the respective percentages of CaCO3. We note that G/ρ has a linear and increasing behavior, that is, G/ρ = 1.13 + 0.03 (%W CaCO3).
3.5 The quantity of CaCO3 and its influence on the structures of composites (MEV)
As the percentage by weight (%W) of CaCO3 increases, it fills a more substantial sample space, decreasing the resin amount. Because CaCO3 adheres more actively to the resin, it can most effectively influence the shear modulus G. This can be seen from section 3.2.1 when analyzing Figures 4 and 5, where the value of G increases. The photos in Figure 6 show that at magnification scales of 500 X and 5.0 kX, CaCO3 reduces resin volume and exhibits better adhesion, changing the G value. Because G values were more prominent than with a less significant quantity of CaCO3, it means that CP-00, which has 100%W resin, is less
Figure 6. Photos show that CaCO3 filler significantly reduces resin volume and improves its adhesion, which can change the G value. (a) and (b) CP-00: 100%W resin reference; (c) and (d) CP-13: 13.04%W CaCO3; (e) and (f) CP-15: 20.00%W CaCO3; (g) and (h) CP-16: 23.08%W CaCO3; (i) and (j) CP-18: 28.57%W CaCO3; (k) and (l) CP-19: 31.03%W CaCO3. Scales at magnification are of 500 X and 5.0 kX.
torsion-resistant than other samples. Another fact observed in CP-00 is higher total internal friction (Q-1) than in the other specimens. Then, pieces that have CaCO3 interfere with the material resistance so that the higher their %W, the higher the G value.
After an experimental study of the curves of the shear modulus G versus a percentage of calcium carbonate, %W, the TG/DTG-DTA curves showed the thermal stability and thermal degradation steps for CP-00, CP-11, and CP-20 (Figure 7).
In the TG curve for CP-00 (Figure 7a), we observed the thermal stability to be up to 286.4 °C; however, before reaching this value, the first step mass followed was 137.3-286.4 °C, which could be related to the evaporation of residual monomers (Δm = 3.34%). The second step of mass loss observed is related to polymer matrix degradation, from 286.7 °C (thermal stability) to 470.4 °C (Δm = 82.91%). This degradation step is associated with an endothermic event at 368.2 °C followed by an exotherm (369.4-433.0 °C) in the DTA curve. Moreover, the respective step exhibits a simple degradation profile by TG; however, by DTG, a complex degradation with overlapped and consecutive steps is observed. Furthermore, by DTG, the maximum degradation rate (MDR) was calculated, obtaining a value of 11.20% min-1; the MDR indicates how fast a material decomposes. Finally, the third mass loss step occurs between 433.0 °C and 607.6 °C (Δm = 13.75%), connected with an exothermic peak at 551.4 °C in the DTA curve, which is related to oxidation and degradation of carbonaceous matter[36]
Figure 7. TG/DTG-DTA curves for (a) CP-00, (b) CP-11, and (c) CP-20.
Polímeros, 32(2), e2022013,
Pintão, C. A. F., Baggio, A., Piedade, L. P., Sanchez, L. E. A., & Gonçalves, G. M. B.Table 3. Thermal events result in each TG/DTG-DTA curve.
Samples 1st step (residual monomer releasing) 2nd step 3rd step
MDR (%min-1)** Residual mass (%)
CP-00 θ °C 137.3-286.4 286.4-470.4 470.4-607.6 11.20 0 Δm/% 3.34 82.91 13.75
TP/°C 368.2 ↓; 369.4-433.0* 551.4 ↑ CP-11 θ °C 138.0-268.2 268.3-464.7 464.7-612.5 10.20 3.34 Δm/% 3.23 78.69 14.74
TP/°C 366.5-419.1* 544.5 ↑ CP-20 θ °C 137.0-286.0 286.0-440.3 440.3-569.5 7.13 23.72 Δm/% 3.12 63.86 15.97
TP/°C 346.2↓; 373.4-456.0* 546.7 ↑ θ = temperature range; Δm = mass loss; TP = temperature peak; ↑ = exothermic peak; * = exotherm; ↓ = endothermic peak; **maximum degradation rate for the degradation step after thermal stability.
The TG curve for CP-11 also exhibits three mass loss steps, the first of which occurs between 138.0 °C and 268.3 °C with a mass loss equal to 3.23%. CP-11 has thermal stability (268.3 °C) lower than CP-00 (286.7 °C), indicating that adding CaCO3 to the polymeric matrix can reduce its thermal stability. The second thermal loss related to polymer degradation occurs in the range of 268.3 °C to 464.7 °C (Δm = 78.69%), which is associated with an exotherm (366.5-419.1 °C) in the DTA curve. The MDR for the respective step is 10.20% min-1, confirming that CaCO3 addition can reduce thermal stability and MDR. The third step of mass loss (464.7-612.5 °C) is related to oxidation and degradation of remaining carbonaceous matter (Δm = 14.74%), with an exothermic peak at 544.5 °C in the DTA curve. A residue of 3.34% was present at the end of the analysis.
The TG curve for CP-20 (Figure 7c) also exhibits the first step of mass loss associated with residual monomer (1.08%), occurring between 120.3 °C and 219.6 °C. The thermal stability for the polymer was highly reduced in CP-20, indicating that high CaCO3 concentration can spoil the thermal proprieties of the polymer. Therefore, the second mass loss step relates to polymeric matrix degradation, starting at 219.6 °C and ending at 454.6 °C (Δm = 61.48%). Moreover, CaCO3 also reduces the MDR (7.13% min-1). The third mass loss step occurs at 454.6-597.8 °C and is related to carbonaceous matter degradation, as observed previously. A residue of 23.72% was present at the end of the analysis.
Although adding CaCO3 to the polymer matrix spoils the thermal stability of the polymer, the MDR value is improved. Furthermore, the addition of CaCO3 improves the mechanical properties. These findings regarding all samples are presented in Table 3
This study found that the torsion modulus obtained for a 100%W unsaturated polyester sample has a value of G = (1.33 ± 0.05) GPa. Different quantities of added CaCO3 increase the G values. The highest value found was for the sample with filler of 33.33%W, at G = (2.5 ± 0.1) GPa. The dependence of G and the percentage by weight of CaCO3 is linear, considering the studied range from 0 to
33.33%W. Finally, we can conclude this material’s 21% weight gain and an 88% increase in torsion resistance. Thus, we used an equation to calculate G that does not require Poisson’s ratio composites.
• Conceptualization – Carlos Alberto Fonzar Pintão; Airton Baggio; Lucas Pereira Piedade; Luiz Eduardo de Angelo Sanchez; Gilberto de Magalhães Bento Gonçalves.
• Data curation – 2019-2021; Carlos Alberto Fonzar Pintão.
• Formal analysis – Carlos Alberto Fonzar Pintão; Airton Baggio.
• Investigation – Carlos Alberto Fonzar Pintão; Lucas Pereira Piedade; Airton Baggio.
• Methodology – Carlos Alberto Fonzar Pintão.
• Project administration – Carlos Alberto Fonzar Pintão; Luiz Eduardo de Angelo Sanchez; Gilberto de Magalhães Bento Gonçalves.
• Resources – Carlos Alberto Fonzar Pintão; Airton Baggio; Luiz Eduardo de Angelo Sanchez; Gilberto de Magalhães Bento Gonçalves.
• Software – Carlos Alberto Fonzar Pintão.
• Supervision – Carlos Alberto Fonzar Pintão.
• Validation – Carlos Alberto Fonzar Pintão.
• Visualization – Carlos Alberto Fonzar Pintão.
• Writing – original draft – Carlos Alberto Fonzar Pintão.
• Writing – review & editing – Carlos Alberto Fonzar Pintão; Lucas Pereira Piedade; Airton Baggio; Luiz Eduardo de Angelo Sanchez; Gilberto de Magalhães Bento Gonçalves.
The authors acknowledge the Brazilian funding agencies FAPESP that the project was based on equipment
Pintão, C. A. F., Baggio, A., Piedade, L. P., Sanchez, L. E. A., & Gonçalves, G. M. B.
granted by FAPESP to Carlos Alberto Fonzar Pintão in 2007. #2007/04094-9; And Prof. Gilbert Bannach to perform the Thermal analysis in 2015, grant #2015/008516; and Capes for the postdoctoral fellowship in 2016, process number: BEX 6571/14-0. In addition, the authors thank the laboratory of polymer and thermal analysis at UNESP/Bauru for TG-DTA curves.
1 Costa, A. P., Botelho, E. C., Costa, M. L., Narita, N. E., & Tarpani, J. R. (2012). A review of welding technologies for thermoplastic composites in aerospace applications. Journal of Aerospace Technology and Management, 4(3), 255 265 http://dx.doi.org/10.5028/jatm.2012.040303912
2 Bochenek, K., & Basista, M. (2015). Advances in processing of NiAl intermetallic alloys and composites for high temperature aerospace applications. Progress in Aerospace Sciences, 79, 136 146 http://dx.doi.org/10.1016/j.paerosci.2015.09.003
3 Delogu, M., Zanchi, L., Maltese, S., Bonoli, A., & Pierini, M. (2016). Environmental and economic life cycle assessment of a lightweight solution for an automotive component: A comparison between talc-filled and hollow glass microspheres-reinforced polymer composites. Journal of Cleaner Production, 139, 548 560 http://dx.doi.org/10.1016/j.jclepro.2016.08.079
4 Mouritz, A. P., Gellert, E., Burchill, P., & Challis, K. (2001). Review of advanced composite structures for naval ships and submarines. Composite Structures, 53(1), 21 42 http://dx.doi. org/10.1016/S0263-8223(00)00175-6.
5 Francklin, H. M., Motta, L. A. C., Cunha, J., Santos, A. C., & Landim, M. V. (2019). Study of epoxy composites and sisal fibers as reinforcement of reinforced concrete structure. IBRACON Structures and Materials Journal, 12(2), 255 287 http://dx.doi.org/10.1590/s1983-41952019000200004
6 Araque, L. M., Morais, A. C. L., Alves, T. S., Azevedo, J. B., Carvalho, L. H., & Barbosa, R. (2019). Preparation and characterization of poly(hydroxybutyrate) and hollow glass microspheres composite films: Morphological, thermal, and mechanical properties. Journal of Materials Research and Technology, 8(1), 935 943. http://dx.doi.org/10.1016/j. jmrt.2018.07.005
7 Yang, H., Jiang, Y., Liu, H., Xie, D., Wan, C., Pan, H., & Jiang, S. (2018). Mechanical, thermal, and fire performance of an inorganic-organic insulation material composed of hollow glass microspheres and phenolic resin. Journal of Colloid and Interface Science, 530, 163 170 http://dx.doi.org/10.1016/j. jcis.2018.06.075 PMid:29982007.
8 Shrivastava, P., Dalai, S., Sudera, P., Vijayalakshmi, S., & Sharma, P. (2014). Hollow glass microspheres as potential adjunct with orthopaedic metal implants. Microelectronic Engineering, 126, 103 106. http://dx.doi.org/10.1016/j. mee.2014.06.031
9 Kaur, M., & Singh, K. (2019). Review on titanium and titaniumbased alloys as biomaterials for orthopaedic applications. Materials Science and Engineering C, 102, 844 862 http:// dx.doi.org/10.1016/j.msec.2019.04.064 PMid:31147056.
10 Ku, H., Wang, H., Pattarachaiyakoop, N., & Trada, M. (2011). A review on the tensile properties of natural fiber reinforced polymer composites. Composites. Part B, Engineering, 42(4), 856 873 http://dx.doi.org/10.1016/j.compositesb.2011.01.010
11 Dhand, V., Mittal, G., Rhee, K. Y., Park, S.-J., & Hui, D. (2015). A short review on basalt fiber reinforced polymer composites. Composites. Part B, Engineering, 73, 166 180 http://dx.doi. org/10.1016/j.compositesb.2014.12.011
12 Sarikaya, E., Çallioğlu, H., & Demirel, H. (2019). Production of epoxy composites reinforced by different natural fibers and their
mechanical properties. Composites. Part B, Engineering, 167, 461 466 http://dx.doi.org/10.1016/j.compositesb.2019.03.020
13 Yang, H., Wang, X., Yu, B., Yuan, H., Song, L., Hu, Y., Yuen, R. K. K., & Yeoh, G. H. (2013). A novel polyurethane prepolymer as toughening agent: Preparation, characterization, and its influence on mechanical and flame retardant properties of phenolic foam. Journal of Applied Polymer Science, 128(5), 2720 2728 http://dx.doi.org/10.1002/app.38399
14 Kumar, N., Mireja, S., Khandelwal, V., Arun, B., & Manik, G. (2017). Lightweight high-strength hollow glass microspheres and bamboo fiber based hybrid polypropylene composite: A strength analysis and morphological study. Composites. Part B, Engineering, 109, 277 285 http://dx.doi.org/10.1016/j. compositesb.2016.10.052
15 Bartczak, Z., Argon, A. S., Cohen, R. E., & Weinberg, M. (1999). Toughness mechanism in semi-crystalline polymer blends: II. High-density polyethylene toughened with calcium carbonate filler particles. Polymer, 40(9), 2347 2365 http:// dx.doi.org/10.1016/S0032-3861(98)00444-3
16. Sun, S., Li, C., Zhang, L., Du, H. L., & Burnell-Gray, J. S. (2006). Effects of surface modification of fumed silica on interfacial structures and mechanical properties of poly(vinyl chloride) composites. European Polymer Journal, 42(7), 1643 1652 http://dx.doi.org/10.1016/j.eurpolymj.2006.01.012
17 Zheng, J., Ozisik, R., & Siegel, R. W. (2005). Disruption of self-assembly and altered mechanical behavior in polyurethane/ zinc oxide nanocomposites. Polymer, 46(24), 10873 10882 http://dx.doi.org/10.1016/j.polymer.2005.08.082
18. Zuiderduin, W. C. J., Westzaan, C., Huétink, J., & Gaymans, R. J. (2003). Toughening of polypropylene with calcium carbonate particles. Polymer, 44(1), 261 275 http://dx.doi. org/10.1016/S0032-3861(02)00769-3
19 He, P., Gao, Y., Lian, J., Wang, L., Qian, D., Zhao, J., Wang, W., Schulz, M. J., Zhou, X. P., & Shi, D. (2006). Surface modification and ultrasonication effect on the mechanical properties of carbon nanofiber/polycarbonate composites. Composites. Part A, Applied Science and Manufacturing, 37(9), 1270 1275 http://dx.doi.org/10.1016/j.compositesa.2005.08.008
20 Morales, E., & White, J. R. (1988). Residual stresses and molecular orientation in particulate-filled polypropylene. Journal of Materials Science, 23(10), 3612 3622. http://dx.doi. org/10.1007/BF00540503
21 Herrera-Ramírez, L. C., Cano, M., & Guzman de Villoria, R. (2017). Low thermal and high electrical conductivity in hollow glass microspheres covered with carbon nanofiber–polymer composites. Composites Science and Technology, 151, 211 218. http://dx.doi.org/10.1016/j.compscitech.2017.08.020.
22 Zhang, Q.-X., Yu, Z.-Z., Xie, X. L., & Mai, Y.-W. (2004). Crystallization and impact energy of polypropylene/CaCO3 nanocomposites with nonionic modifier. Polymer, 45(17), 5985 5994 http://dx.doi.org/10.1016/j.polymer.2004.06.044
23 Xie, X.-L., Liu, Q.-X., Li, R. K.-Y., Zhou, X.-P., Zhang, Q.-X., Yu, Z.-Z., & Mai, Y.-W. (2004). Rheological and mechanical properties of PVC/CaCO3 nanocomposites prepared by in situ polymerization. Polymer, 45(19), 6665 6673 http://dx.doi. org/10.1016/j.polymer.2004.07.045.
24 Truell, R., Elbaum, C., & Chic, B. B. (1969). Ultrasonic methods in solid-state physics New York: Academic Press
25 Nowick, A. S., & Berry, B. S., editors (1972). Anelastic relaxation in crystalline solids New York: Academic Press
26 Pintão, C. A. F. (2014). Measurement of the rotational inertia of bodies by using mechanical spectroscopy. Journal of Mechanical Science and Technology, 28(10), 4011 4020 http:// dx.doi.org/10.1007/s12206-014-0914-8
27 Timoshenko, S. P., & Gere, J. M. (1972). Mechanics of materials New York: Van Nostrand Reinhold Co.
Polímeros, 32(2), e2022013, 2022
28 Pintão, C. A. F., Correa, D. R. N., & Grandini, C. R. (2017). Torsion modulus using the technique of mechanical spectroscopy in biomaterials. Journal of Mechanical Science and Technology, 31(5), 2203 2211 http://dx.doi.org/10.1007/s12206-017-0416-6
29 Majumdar, P., Singh, S. B., & Chakraborty, M. (2008). Elastic modulus of biomedical titanium alloys by nano-indentation and ultrasonic techniques-A comparative study. Materials Science and Engineering A, 489(1-2), 419 425 http://dx.doi. org/10.1016/j.msea.2007.12.029
30 Piedade, L. P., Pintão, C. A. F., Foschini, C. R., Silva, M. R., & Azevedo, N. F., No. (2020). Alternative dynamic torsion test to evaluate the elastic modulus of polymers. Materials Research Express, 7(9), 095306 http://dx.doi.org/10.1088/2053-1591/ abb560
31 Pintão, C. A. F., Souza, M. P., Fo., Grandini, C. R., & Hessel, R. (2004). Experimental study of the conventional equation to determine a plate’s moment of inertia. European Journal of Physics, 25(3), 409 417 http://dx.doi.org/10.1088/0143-0807/25/3/008
32 Amrani, D. (2006). Computerized rotational system to study the moment of inertia of different objects. European Journal of Physics, 27(5), 1063 1069 http://dx.doi.org/10.1088/01430807/27/5/005
33 Dedavid, B. A., Gomes, C. I., & Machado, G. (2007). Microscopia eletrônica de varredura : aplicações e preparação de amostras : materiais poliméricos, metálicos e semicondutores Porto Alegre: EDIPUCRS
34 Hibbeler, R. C. (2010). Resistência dos materiais São Paulo: Pearson Prentice Hal.
35 Pintão, C. A. F., Correa, D. R. N., & Grandini, C. R. (2019). Torsion modulus as a tool to evaluate the role of thermomechanical treatment and composition of dental Ti-Zr alloys. Journal of Materials Research and Technology, 8(5), 4631 4641 http://dx.doi.org/10.1016/j.jmrt.2019.08.007
36 Alarcon, R. T., Gaglieri, C., Santos, G. C., Roldao, J. C., Magdalena, A. G., Silva-Filho, L. C., & Bannach, G. (2021). A deep investigation into the thermal degradation of urethane dimethacrylate polymer. Journal of Thermal Analysis and Calorimetry, 147(4), 3083 3097. http://dx.doi.org/10.1007/ s10973-021-10610-y
Received: Mar. 15, 2022
Revised: May 27, 2022
Accepted: June 04, 2022
Polímeros, 32(2), e2022013, 2022
Table A1. Experimental result: CP-12; CP-13; CP-14; CP-15; CP-18; CP-19; CP-20. d=4.70±0.05 mm; L=53.20±0.05 mm. I (kgm2 x10-4) G(Gpa) f0(Hz)
Q-1 I f02 (kgm2) 98.1±0.5 1.69±0.07 1.98 0.171±0.005 0.00464 0.0385 207±1 1.67±0.06 1.36 0.167±0.003 0.00442 0.0383 398±1 1.68±0.07 0,982 0.168±0.002 0.00449 0.0384 526±4 1.68±0.07 0.853 0.168±0.003 0.00445 0.0383
Average I f02 value for sample CP-12: 0.0384±0.0001 98.1±0.5 1.83±0.07 2.06 0.150±0.002 0.00360 0.0416 207±1 1.81±0.07 1.41 0.152±0.004 0.00368 0.0412 398±1 1.77±0.07 1.01 0.172±0.004 0.00473 0.0406 526±4 1.78±0.08 0.880 0.173±0.002 0.00476 0.0407
Average I f02 value for sample CP-13: 0.0410±0.0005 98.1±0.5 1.87±0.08 2.09 0.188±0.007 0.00565 0.0429 207±1 1.85±0.08 1.43 0.186±0.003 0.00552 0.0423 398±1 1.86±0.08 1.03 0.200±0.001 0.00639 0.0422 526±4 1.87±0.08 0.900 0.198±0.005 0.00627 0.0426
Average I f02 value for sample CP-14: 0.0425±0.0003 98.1±0.5 1.96±0.08 2.14 0.148±0.004 0.00348 0.0449 207±1 1.93±0.08 1.46 0.145±0.002 0.00335 0.0441 398±1 1.94±0.08 1.05 0.152±0.001 0.00368 0.0439 526±4 1.93±0.08 0.915 0.150±0.002 0.00356 0.0440
Average I f02 value for sample CP-15: 0.0442±0.0005 98.1±0.5 2.4±0.1 2.34 0.151±0.006 0.00362 0.0537 207±1 2.3±0.1 1.60 0.141±0.003 0.00314 0.0530 398±1 2.3±0.1 1.16 0.139±0.001 0.00308 0.0532 526±4 2.3±0.1 1.00 0.137±0.002 0.00300 0.0530
Average I f02 value for sample CP-18: 0.0532±0.0003 98.1±0.5 2.4±0.1 2,36 0.149±0.005 0.00352 0.0548 207±1 2.4±0.1 1,62 0.145±0.001 0.00337 0.0544 398±1 2.4±0.1 1,17 0.143±0.001 0.00327 0.0549 526±4 2.4±0.1 1,02 0.140±0.003 0.00313 0.0549
Average I f02 value for sample CP-19: 0.0547±0.0002 98.1±0.5 2.5±0.1 2.40 0.17±0.01 0.0045 0.0565 207±1 2.5±0.1 1.64 0.147±0.001 0.00346 0.0560 398±1 2.5±0.1 1.19 0.155±0.001 0.00384 0.0562 526±4 2.5±0.1 1.03 0.149±0.001 0.00355 0.0558
Average I f02 value for sample CP-20: 0.0561±0.0003
Table A2. Experimental result: CP-00(d=5.00±0.05 mm); CP-11(d=4.80±0.05 mm); CP-16(d=4.80±0.05 mm); CP-17(d=4.80±0.05 mm); L=53.20±0.05 mm. I (kgm2 x10-4) G(Gpa) f0(Hz) δ Q-1 I f02 (kgm2) 98.1±0.5 1.34±0.05 2.00 0.199±0.003 0.00634 0.0392 207±1 1.32±0.05 1.37 0.183±0.002 0.00530 0.0389 398±1 1.34±0.05 0.992 0.195±0.003 0.00605 0.0392 526±4 1.33±0.05 0.861 0.196±0.002 0.00611 0.0390
Average I f02 value for sample CP-00: 0.0391±0.0002 98.1±0.5 1.49±0.06 1.94 0.163±0.003 0.00423 0.0369 207±1 1.47±0.06 1.33 0.16±0.01 0.0043 0.0366 398±1 1.49±0.06 0,963 0.167±0.003 0.00443 0.0369 526±4 1.51±0.06 0.843 0.162±0.001 0.00418 0.0374
Average I f02 value for sample CP-11: 0.0370±0.0003
98.1±0.5 2.00±0.09 2.25 0.167±0.004 0.00444 0.0498 207±1 2.01±0.08 1.55 0.165±0.001 0.00433 0.0498 398±1 2.04±0.09 1.13 0.167±0.005 0.00442 0.0507 526±4 2.05±0.09 0.984 0.161±0.003 0.00410 0.0509
Average I f02 value for sample CP-16: 0.0503±0.0006
98.1±0.5 2.05±0.09 2.28 0.165±0.004 0.00433 0.0510 207±1 2.05±0.09 1.57 0.155±0.004 0.00382 0.0510 398±1 2.10±0.09 1.15 0.166±0.001 0.00441 0.0522 526±4 2.08±0.09 0.990 0.163±0.005 0.00421 0.0516
Average I f02 value for sample CP-17: 0.0514±0.0006
Polímeros, 32(2), e2022013, 2022
Pintão, C. A. F., Baggio, A., Piedade, L. P., Sanchez, L. E. A., & Gonçalves, G. M. B.
https://doi.org/10.1590/0104-1428.20210111
This study aimed to focus on classifying rubber foam grades according to ASTM D1056. The natural rubber foams were prepared by varying the Azodicarbonamide (ADC) content from 2 - 10 phr. The results were evaluated on their physical and mechanical properties. The relative foam density of the foams decreased, and the expansion ratio increased with the addition of ADC. This was due to the increase in the gas phase raised by ADC. In addition, adding ADC also decreased hardness and compression-deflection of the foams, whereby the values obtained were higher after oven aging due to the radical recombination caused by chain breaking. According to ASTM D1056, the compression-deflection values of the foams were 2A2 and 2A3 grades, where the ADC content at 6 – 10 phr met the basic properties required by the same standard. Furthermore, the ADC content at 6 phr is strongly suggested when considering the foam morphology.
Keywords: azodicarbonamide, compression-deflection, foam, natural rubber.
How to cite: Baru, F., Saiwari, S., & Hayeemasae, N. (2022). Classification of natural rubber foam grades by optimising the azodicarbonamide content. Polímeros: Ciência e Tecnologia, 32(2), e2022014. https://doi.org/10.1590/01041428.20210111
Natural rubber (NR) has been primarily used as a raw material in the production of tyres. Tyre manufacturing consumes 75% of the total global production of NR[1,2]. The remaining uses of NR vary, and it is utilised in many applications, such as automotive parts, latex gloves, condoms and so forth. Therefore, particular attention is being given to expanding the usage of NR to other industrial products. Natural rubber foam (NRF) is an interesting rubber product that consists of rubber and gas phases in one item. NRF has been used in many applications because of its lightweight, good thermal insulation and sound absorption[3,4]. There are several methods for producing NRF. Generally, it is produced by the NR latex process, which is in liquid form. The colloidal nature of the latex requires chemical stabilisation (usually obtained with the addition of ammonia). This stabilisation mechanism and the quality of the latex can be affected by the storage time and environment[5,6]. Alternatively, rubber foams can be produced using the dried rubber process. In this research, dry rubber was used to produce foam because the processing of rubber foam from dry rubber is easier than the process involving latex.
Making NRF from dry rubber is achieved by using an additive called a blowing agent. The foam structure can be controlled by the proper selection of blowing agents and curatives, which achieves the correct balance between the gas generated and the degree of curing. There are many types of chemical blowing agents, such as sodium bicarbonate, p-toluenesulphonyl semicarbazide, 5-phenyl tetrazole, 4,4-oxydibenzenesulphonyl hydrazide (OBSH), dinitroso
pentamethylene tetramine (DPT) and azodicarbonamide (ADC). Several authors have studied how the content and type of a chemical blowing agent affects elastomers[7-10]. For example, Pechurai et al.[8] studied the effect of the foaming agent content on the cell morphology and mechanical properties of NR foams. They observed that increased foaming agent content decreased foam density and hardness due to an increase in cell size. Charoeythornkhajhornchai et al.[9] reported that the bulk density of NRF significantly decreases and the volumetric expansion ratio of NRF increases when the chemical blowing agent content is high. Coalescence between bubbles was observed in the specimens with 5 and 6 phr of ADC, owing to the high gas content in the rubber matrix. Lee and Choi[10] studied the effects of foaming temperature and carbon black content on NRF. Their results showed that higher carbon black content increased the density and mechanical properties of the foam, including its tensile strength, tear strength, hardness, modulus and stiffness. Among these, ADC is interesting as a chemical blowing agent because it leads to closed-cell foam and decomposes at low temperatures[9]
When examining the related documents, it was clear that few studies have addressed the basic properties required by a certain standard, ASTM D1056. Table 1 shows the basic properties required by ASTM D1056. This standard refers to specific properties in order to classify foam grades; for example, it refers to the compression-deflection before and after thermal ageing, as well as the foam’s water absorption capacity. This enables a distinction to
Fateehah Baru1 , Sitisaiyidah Saiwari1 and Nabil Hayeemasae1*
1Department of Rubber Technology and Polymer Science, Faculty of Science and Technology, Prince of Songkla University, Pattani Campus, Pattani, Thailand *nabil.h@psu.ac.th
Baru, F., Saiwari, S., & Hayeemasae, N.
Table 1. Basic requirement of cellular rubber (Closed-cell Sponge) according to ASTM D1056.
Change in compressiondeflection after aging at 70oC for 168 h (%)
2A0 Less than 15 ± 30
2A1 15 – 35 ± 30
2A2 35 – 65 ± 30
2A3 65 – 90 ± 30
2A4 90 – 120 ± 30
120 – 170 ± 30
Water absorption (%) Density over 160 kg/m3 Density of 160 kg/m3 or less
Remark: Type 2 is for Closed-cell rubber and Class A is for cellular rubber made from synthetic rubber, natural rubber, reclaimed rubber, or rubber-like materials where a number from 0 – 5 is based on a specific range of firmness as expressed by compression-deflection.
be made between open and closed-cell foams and would help rubber compounders to classify foam grades based on a recognised standard. In this study, NR foams were prepared by varying the concentration of ADC (2, 4, 6, 8 and 10 phr), which was used as the blowing agent, at a fixed processing time and temperature. The impacts of the ADC content on the physical and impact properties of the foams were analysed. The aim of this study was to prepare NRF that meets the basic requirements of the standard specification for flexible cellular materials like sponge or expanded rubber (ASTM D1056). These physical properties include the curing characteristics, relative foam density, compression-deflection before and after ageing and morphology. So far, no reports have focused extensively on the correlations between the basic properties of foams and the ASTM D1056. Besides, this study also introduces a new formulation for preparing the foam. In particular, the use of processing oil and calcium carbonate to promote an even distribution of cellular structure. Processing oil can help to reduce the viscosity to assist the diffusion of gas while the calcium carbonate is widely known to act as a nucleating agent in the production of foam[11]. The results obtained from this work will be useful for rubber foam manufacturers as a predetermined observation of the preparation of NRF.
The NR used in this study was STR 5L, purchased from Suansom Kanyang, Yala, Thailand. ADC was used as the blowing agent and was purchased from A.F. Supercell Co., Ltd., Rayong, Thailand. Treated distillate aromatics extract (TDAE oil) was used as processing oil which was purchased from H&R ChemPharm (Thailand) Co., Ltd. Calcium carbonate (CaCO3) was obtained from Krungthepchemi Co., Ltd, Bangkok, Thailand. Stearic acid was purchased from Imperial Chemical Co., Ltd., Bangkok, Thailand. ZnO was obtained from Global Chemical Co., Ltd., Samut Prakan, Thailand. Stearic acid and ZnO were used as activator. 2,2,4-trimethyl-1,2-dihydroquinoline (TMQ) and N-cyclohexyl-2-benzo thiazole sulphenamide (CBS) were used as antioxidant and accelerator respectively. These were purchased from Flexsys America L.P., West Virginia, USA and sulfur was purchased from Siam Chemical Co., Ltd., Samut Prakan, Thailand.
Table 2 lists the materials used at the start of the process for compounding the NRF. The full amounts of the NR, ADC, TDAE oil and other additives were prepared using a two-roll mill. The compounds were free-blown into specific shapes (12.5 mm in thickness) inside the compression-moulded at the temperature of 150 °C. The time consumed was based on the curing times determined by a moving-die rheometer (MDR), as described in the following section.
The curing characteristics of the NRF were obtained using an MDR (Rheoline, Mini MDR Lite) at the temperature of 150 °C. This was used to determine the torque, scorch time (tS1) and curing time (tC90), according to ASTM D5289.
The viscosity of the NRF was investigated by means of a Mooney viscometer, MV 3000 Basic (MonTech, Germany). The tests were performed at 100 °C using the large rotor, according to ASTM D1646.
D
Relativefoamdensity D = (1)
The physical properties were investigated, including the relative foam density and expansion ratio. The relative foam density was measured according to ASTM D3575, using Equation 1 as given below: f c
Where Df is foam density (g/cm3) and Dc (g/cm3) is compound density.
D
Expansionratio D = (2)
The expansion ratio was calculated as the density of the NR compound specimen compared to the density of the natural rubber foam, as shown in Equation 2: c f
The hardness of the NRF was measured in accordance with ASTM D2240 by using an indentation durometer
Polímeros, 32(2), e2022014,
t0 is the original thickness, t1 is the thickness of the specimens after the specified recovery period and ts is the thickness of the spacer bar used.
Swelling uptake was measured according to ASTM D471. Samples with dimensions of 25 × 50 × 6 mm3 were cut and weighed before and after immersion in toluene for 72 h under dark environment. It was preferable that the specimens were cut with clean, square edges. The swelling uptake was calculated as follows:
shore OO, and the readings were taken after a 10-second indentation. The compression-deflection of the NRF was determined according to ASTM D1056.
Compression-deflection test was done according to ASTM D575. A sample with specimens approximately 12.5 mm thick and with a minimum area of 161 cm2, was used for testing. The specimens were compressed between the parallel metal plates of the universal testing machine (Tinius Olsen, H10KS, Tinius Olsen Ltd., Surrey, UK) until the thickness reduced by 25%. The reading of the load was taken immediately. The test was repeated with the same specimen until the load readings did not change by more than 5%. For the compression-deflection change after oven ageing, similar test specimens were cut and placed in an oven for 168 h at a temperature of 70 °C. They were allowed to cool for at least 24 h and then the compression-deflection was determined. The percentage change in compressiondeflection was calculated using Equation 3.
W is the change in mass, A is the final mass of the specimen and B is the initial mass of the specimen.
Test specimens approximately 12.5 mm in thickness and 2500 mm2 in area were used for this test. Round specimens were preferable. The specimens were submerged in distilled water below the water surface at room temperature for 3 min. The specimens were removed and blot dried. Then, the percentage change in mass was calculated based on the Equation 5.
The physical appearance of NRF was captured using mobile phone camera through a default setting. While, the morphology was screened using a FEI Quanta™ 400 FEG scanning electron microscope (SEM; Thermo Fisher Scientific, Waltham, Massachusetts, USA). Each specimen was coated with a layer of gold/palladium to remove the charges that had built up during imaging.
Where P is the change in compression-deflection (%), O is the original compression-deflection and A is the final compression-deflection after oven ageing.
Compression set was measured according to ASTM D395. A representative sample, approximately 12.5 mm thick and with a minimum area of 161 cm2, was used for testing. The test specimens were compressed to 50% of their original thicknesses. The load was released after 22 h and the thickness was measured after 24 h at room temperature. The compression set calculation was as follows;
Figure 1 shows the Mooney viscosity of the NRF prepared using various levels of ADC content. The Mooney viscosity is a measure of the flow properties of the rubber[12,13]. This correlates well with the processability of rubber foam, since lower viscosity enables the easy diffusion of the gas phase while foaming during vulcanisation. It can be seen that the Mooney viscosity of the rubber compounds increased with the addition of ADC. ADC is rigid in nature, so it may reduce deformable parts and restrict the movement of rubber molecules. It was noted that the tested temperature was 100 oC, which is lower than the decomposition temperature of ADC (approximately 150 oC). Therefore, no bubbles occurred while measuring the Mooney viscosity.
The rheometric curves of the NRF produced by varied levels of blowing agent content are shown in Figure 2, while the data extracted from the curves are summarised in Table 3. It was found that the maximum torque (MH) increased after adding the ADC, showing that the material
Baru, F., Saiwari, S., & Hayeemasae, N.
is stiffer over the addition of ADC. This can be explained from the increase in delta torque (MH – ML) as the torque difference is an indirect indication of extent of cross-link[14] The scorch time (tS1) and curing time (tC90) increased with
Table
Content (phr)
characteristics of
prepared by various ADC content.
the addition of ADC. tS1 is the induction time experienced by a rubber compound before vulcanisation is initiated, while tC90 is the time rubber takes to become 90% vulcanised. The increase in these two values indicated that ADC can prolong the vulcanisation time of rubber due to its action as a blowing agent. It tended to generate the gas phase while heating and delay the action of the vulcanising accelerator while curing. Another possible reason may be the action of the ADC after chemical decomposition[15]
According to Harpell et al.[16] and Bhatti et al.[17], the decomposition of ADC goes through competitive and exothermic reaction pathways, as shown in Figure 2, producing hydraazodicarbonamide, urazol and a gaseous mixture of nitrogen (N2), carbon monoxide (CO), cyanic acid (HNCO) and ammonia (NH3). N2 is the main source of gas that make the foam free flowing. Different paths may be favored over other depending on the process conditions and the state of the product. The focal point here is the production of cyanic acid, which is acidic in nature. An increase in cyanic acid is particle size-dependent. As reported by Reyes-Labarta and Marcilla[15], when the ADC particle size increases, the reaction rate of this heterogeneous reaction may increase due to the longer contact time between the cyanic acid gas (produced from reactions i and ii) and the ADC particles. Consequently, there may be a probability that the cyanic acid gas will react with the unreacted ADC, through reaction iii, thus accelerating the degradation process. Any chemical substance that makes a rubber compound more acidic will cause the adsorption of accelerators[18] and retard their reactivity. This makes the vulcanising process longer when ADC is added to the rubber compounds.
Figure 1. Mooney viscosity of NRF prepared by various ADC content.
Table 4 lists the relative foam densities and expansion ratios of the NRF with different levels of ADC content.
Figure
Chemical
adapted from
of
Marcilla[15)
and
of
prepared by
Polímeros, 32(2), e2022014, 2022
As greater concentrations of the blowing agent were used, more gas was subsequently generated. This reduced the relative foam density, which significantly decreased from 0.78 g/cm3 to 0.46 g/cm3. Higher ADC concentrations shortened the growth time of the foam, thus restricting the escape of gas through the foam surface. This allowed the foam to expand more and, consequently, produce foam with a lower relative density[19]. The relative foam density was directly related to the porosity values and expansion ratio because the high amount of gas trapped in the matrix occurred due to the large size of the NRF specimens. For this reason, the low relative foam density when high amounts of ADC were used revealed the considerable expansion of these NRF specimens. The porosity values and expansion ratios are shown in Table 4. The decrease in relative foam density also played a role by increasing the number of cells per unit volume. Figure 3 shows that as the blowing agent concentration increased, the number of cells per unit volume also increased. This was the case except for the sample at 10 phr of ADC. As more gas was produced due to the higher ADC content, this indicated more efficient gas production. The cell sizes grew due to the destruction of the cell walls.
Table
Relative
Table 4 also lists the hardness and compression set of the NRF prepared using various levels of ADC content. The hardness decreased with an increase in the ADC content. This was due to the higher foam porosity in the NR matrix during the formation of the gas phase. The compression set of the foams was also studied to determine the recovery properties of a sample after it had been subjected to a constant deflection for a specified time/temperature/deflection by measuring its gauge before and after the test period. The compression set of the specimens was higher with the addition of ADC content. A lower compression set indicates better recovery after constant deflection. The compression set correlated well with the elastic response of the rubber in association with the crosslink density of the sample[20]. Increasing levels of ADC caused more porosity in the foam. This happened with the increment in the cell size and the reduction of the cell wall per surface area. Cell walls mainly control the elastic response due to their elastic phase. Different cell sizes and cell numbers appeared to critically affect the compression set values.
Further evidence can be identified from the SEM images shown in Figure 3. The SEM images show that a systematic correlation between the number of cells per unit volume
compression set of NRF prepared by various ADC content.
ADC Content (phr) Relative Foam Density (RFD) Expansion Ratio Porosity (1
RFD)
Hardness (Shore OO)
0.29 1.29
0.45
0.43
and the average cell size. An increase in the blowing agent concentration resulted in smaller, finer and more uniform cells. The decomposition of high concentrations of nitrogen gas occurred simultaneously for a given time, so more cells formed at that particular time. Consequently, the number of cells per unit volume increased, resulting in a smaller average cell size in the foam[9]. This phenomenon was found in reverse for the ADC sample at 10 phr. This was because of the weakness of the cell walls due to the diffusion of gas from one cell to another, which broke the cell walls and led to larger cell sizes at this amount. The SEM images are in good agreement with the porosity values and expansion ratios reported in the previous section.
The swelling uptake values of the NRF were also measured in this study (see Figure 4a). The swelling percentage was investigated by toluene uptake until equilibrium swelling was reached at room temperature. Adding more ADC caused the swelling uptake of the rubber foam to increase. As mentioned previously, the number of cells increased and the thickness of cell walls reduced when higher amounts of ADC were used. As the number of cells and the cell size increased, the porosity increased (see Table 4), the solvent could penetrate more easily from one cell to another, leading
eventually to an increase in the swelling uptake. This would increase the swelling uptake.
As highlighted in the introduction, the main focus of this study was to classify the rubber foam grade that met the basic requirements, according to ASTM D1056. From this section onwards, the required properties are presented and discussed. Firstly, the water absorption of the rubber foam will be discussed (see Figure 4b). The water absorption was used to distinguish the cell structure of the prepared foam[21]. Higher absorption of water in the sample indicated the foam had a more open-cell structure. As for the closedcell structure of the foam, the classification of foam depends on the relative foam density of the rubber foam. Referring to Table 1 and the relative foam densities listed in Table 3, the water absorption of rubber foam should be less or equal to 5%. Hence, it was concluded that the water absorption of the rubber foam met the standard requirements, regardless of ADC content. The next steps were to consider other factors in order to classify the grade number of the rubber foam.
Figure 5a shows the compression-deflection values of the NRF prepared with various levels of ADC content. It was observed that the compression-deflection decreased
Polímeros, 32(2), e2022014, 2022
with the inclusion of ADC. Low compression-deflection values indicated the poor ability of the NRF to take on external forces[22]. Increasing the ADC content caused a high amount of gas to be produced in the rubber matrix. It also definitely increased the number of cells, resulting in weaker cell walls and reductions in foam stress. The compressiondeflection values agreed well with the SEM images shown in the previous section. The compression-deflection values before thermal ageing were implemented to further classify the foam grades. Each grade is based on a specific firmness range, which is expressed by compression-deflection. The grades are designated by digit, the softer grades being identified with lower numbers and the higher grades being identified with higher numbers. Here, it was observed that the compression-deflection values were grouped as 2A3, except for the sample containing 10 phr of ADC, which was 2A2. When these samples were placed under severe thermal treatment, the values were higher than those of the unaged samples. This was due to the hardened characteristics of the foam due to the increase in modulus caused by the radical recombination of chain scission.
The values before and after ageing were then calculated for the changes in property, which can be seen in Figure 5b The property changes were reduced with the addition of ADC. Lower values indicate the higher thermal stability of rubber vulcanisate[23,24]. Increasing the amount of ADC reduced the cell wall thickness due to the increased porosity. The rubber phase was then reduced, which led to a reduction in the crosslinking site in the rubber. The thermal stability finally increased with the addition of ADC. In addition to this, property changes were also used to classify foam grades. As shown in Table 1, the ASTM D1056 requirement is that this value should not exceed 30%. The results indicated that the ADC content from 6 – 10 phr met the standard requirements. Based on the overall findings, the addition of this level of ADC content was suitable for the preparation of NRF. However, the cell morphology should also be considered because rubber foams depend greatly on this. From the optical images, together with the SEM images (see Figure 3), it was clear that the ADC content at 6 phr produced a homogeneous cell size and cell wall distribution.
This study focused on the classification of NRF grades by varying the content of a blowing agent. The foams were classified based on the basic properties required by ASTM D1056. In this study, different blowing agent concentrations (2, 4, 6, 8, and 10 phr) were shown to influence the curing properties of NRF. Increased ADC content resulted in a lower relative foam density and larger porosity value and expansion ratio. It was also found that the hardness and compressiondeflection of the NRF decreased noticeably with increased ADC content. This was due to the increase in the gas phase raised by the ADC. The addition of ADC lengthened the scorch (ts1) and curing times (tc90) of the foam. Furthermore, the hardness and compression-deflection decreased with the inclusion of ADC, since these values were higher after oven ageing due to the radical recombination caused by chain breaking. According to ASTM D1056, the compressiondeflection values of the prepared foams were the 2A2 and
2A3 grades, while the ADC content at 6 – 10 phr met the basic properties required by the same standard. Furthermore, the ADC content at 6 phr was strongly suggested, in terms of the morphology of the foam. This showed the homogeneous cell size and cell wall distribution. The results obtained from this study will provide useful information when preparing NRF that meets the basic properties stated in ASTM D1056.
• Conceptualization – Fateehah Baru; Sitisaiyidah Saiwari; Nabil Hayeemasae.
• Data curation – Fateehah Baru; Nabil Hayeemasae.
• Formal analysis – Fateehah Baru; Nabil Hayeemasae.
• Investigation – Fateehah Baru.
• Methodology – Sitisaiyidah Saiwari; Nabil Hayeemasae.
• Project administration – Nabil Hayeemasae.
• Resources – Nabil Hayeemasae.
• Software – Nabil Hayeemasae.
• Supervision – Sitisaiyidah Saiwari; Nabil Hayeemasae.
• Validation – Nabil Hayeemasae.
• Visualization – Nabil Hayeemasae.
• Writing – original draft – Nabil Hayeemasae.
• Writing – review & editing – Sitisaiyidah Saiwari; Nabil Hayeemasae.
We gratefully acknowledge the financial support by Natural Rubber Innovation Research Institute, Prince of Songkla University through the Grant No. SAT6201175S. The first author wishes to thank the Faculty of Science and Technology, Prince of Songkla University, Pattani Campus for providing a personal scholarship through the Grant No. 005/2562.
1 Toncheva, A., Brison, L., Dubois, P., & Laoutid, F. (2021). Recycled tire rubber in additive manufacturing: selective laser sintering for polymer-ground rubber composites. Applied Sciences (Basel, Switzerland), 11(18), 8778 http://dx.doi. org/10.3390/app11188778
2 Mutlu, İ., Sugözü, İ., & Keskin, A. (2015). The effects of porosity in friction performance of brake pad using waste tire dust. Polímeros: Ciência e Tecnologia, 25(5), 440 446 http:// dx.doi.org/10.1590/0104-1428.1860
3. Suethao, S., Phongphanphanee, S., Wong-ekkabut, J., & Smitthipong, W. (2021). The relationship between the morphology and elasticity of natural rubber foam based on the concentration of the chemical blowing agent. Polymers, 13(7), 1091 http:// dx.doi.org/10.3390/polym13071091 PMid:33808133.
4 Najib, N. N., Ariff, Z. M., Bakar, A. A., & Sipaut, C. S. (2011). Correlation between the acoustic and dynamic mechanical properties of natural rubber foam: effect of foaming temperature. Materials & Design, 32(2), 505 511 http://dx.doi.org/10.1016/j. matdes.2010.08.030
5 Ramasamy, S., Ismail, H., & Munusamy, Y. (2013). Effect of rice husk powder on compression behavior and thermal
Baru, F., Saiwari, S., & Hayeemasae, N.
stability of natural rubber latex foam. BioResources, 8(3), 4258 4269 http://dx.doi.org/10.15376/biores.8.3.4258-4269
6 Panploo, K., Chalermsinsuwan, B., & Poompradub, S. (2019). Natural rubber latex foam with particulate fillers for carbon dioxide adsorption and regeneration. RSC Advances, 9(50), 28916 28923 . http://dx.doi.org/10.1039/C9RA06000F. PMid:35528441.
7 Ariff, Z. M., Zakaria, Z., Tay, L. H., & Lee, S. Y. (2007). Effect of foaming temperature and rubber grades on properties of natural rubber foams. Journal of Applied Polymer Science, 107(4), 2531 2538 http://dx.doi.org/10.1002/app.27375
8. Pechurai, W., Muansupan, T., & Seawlee, P. (2014). Effect of foaming temperature and blowing agent content on cure characteristics, mechanical and morphological properties of natural rubber foams. Advanced Materials Research, 844, 454 457 https://doi.org/10.4028/www.scientific.net/AMR.844.454
9 Charoeythornkhajhornchai, P., Samthong, C., Boonkerd, K., & Somwangthanaroj, A. (2016). Effect of azodicarbonamide on microstructure, cure kinetics and physical properties of natural rubber foam. Journal of Cellular Plastics, 53(3), 287 303 http://dx.doi.org/10.1177/0021955X16652101
10 . Lee, E.-K., & Choi, S.-Y. (2007). Preparation and characterization of natural rubber foams: effects of foaming temperature and carbon black content. Korean Journal of Chemical Engineering, 24(6), 1070 1075 http://dx.doi.org/10.1007/s11814-007-01236
11 Yang, H.-H., & Han, C. D. (1984). The effect of nucleating agents on the foam extrusion characteristics. Journal of Applied Polymer Science, 29(12), 4465 4470 http://dx.doi.org/10.1002/ app.1984.070291281
12 Ehabé, E., Bonfils, F., Aymard, C., Akinlabi, A. K., & Sainte Beuve, J. (2005). Modelling of Mooney viscosity relaxation in natural rubber. Polymer Testing, 24(5), 620 627 http://dx.doi. org/10.1016/j.polymertesting.2005.03.006
13. Kramer, O., & Good, W. R. (1972). Correlating Mooney viscosity to average molecular weight. Journal of Applied Polymer Science, 16(10), 2677 2684 http://dx.doi.org/10.1002/ app.1972.070161020
14 Ismail, H., & Anuar, H. (2000). Palm oil fatty acid as an activator in carbon black filled natural rubber compounds: dynamic proper- ties, curing characteristics, reversion and fatigue studies. Polymer Testing, 19(3), 349 359 http://dx.doi. org/10.1016/S0142-9418(98)00102-0
15 Reyes-Labarta, J. A., & Marcilla, A. (2007). Kinetic study of the decompositions involved in the thermal degradation of commercial azodicarbonamide. Journal of Applied Polymer Science, 107(1), 339 346 http://dx.doi.org/10.1002/app.26922
16 Harpell, G. A., Gallagher, R. B., & Novits, M. F. (1977). Use of azo foaming agents to produce reinforced elastomeric foams. Rubber Chemistry and Technology, 50(4), 678 687 http://dx.doi.org/10.5254/1.3535165
17 Bhatti, A. S., Dollimore, D., Goddard, R. J., & O’Donnell, G. (1984). The thermal decomposition of azodicarbonamide. Thermochimica Acta, 76(1-2), 63 77 http://dx.doi.org/10.1016/00406031(84)87004-5
18 Ballard, D. G. H., Myatt, J., & Richter, J. F. P. Some observations on the mechanism of action of retarders in rubber vulcanization. A new class of retarder. Journal of Applied Polymer Science, 16(10), 2647 2655 http://dx.doi.org/10.1002/app.1972.070161017
19. Guan, L. T., Du, F. G., Wang, G. Z., Chen, Y. K., Xiao, M., Wang, S. J., & Meng, Y. Z. (2007). Foaming and chain extension of completely biodegradable poly(propylene carbonate) using DPT as blowing agent. Journal of Polymer Research, 14(3), 245 251 http://dx.doi.org/10.1007/s10965-007-9103-0
20 Yamsaengsung, W., & Sombatsompop, N. (2009). Effect of chemical blowing agent on cell structure and mechanical properties of EPDM foam, and peel strength and thermal conductivity of wood/NR composite–EPDM foam laminates. Composites. Part B, Engineering, 40(7), 594 600 http://dx.doi. org/10.1016/j.compositesb.2009.04.003
21 Zhang, G., Wu, Y., Chen, W., Han, D., Lin, X., Xu, G., & Zhang, Q. (2019). Open-cell rigid polyurethane foams from peanut shell-derived polyols prepared under different postprocessing conditions. Polymers, 11(9), 1392 http://dx.doi. org/10.3390/polym11091392 PMid:31450807.
22 Azevedo, J. B., Chávez, M. A., & Rabello, M. S. (2011). Efeito de reticulante na morfologia e propriedades físicomecânicas de espumas poliméricas obtidas com EVA e EPDM. Polímeros, 20(5), 407 414 http://dx.doi.org/10.1590/S010414282011005000002
23 Motiee, F., & Bigdeli, T. (2020). Prediction of mechanical and functional features of aged rubber composites based on BR/ SBR; structure-properties correlation. Materials Research, 22(6), e20190226 http://dx.doi.org/10.1590/1980-5373mr-2019-0226
24 Hayeemasae, N., & Masa, A. (2020). Relationship between stress relaxation behavior and thermal stability of natural rubber vulcanizates. Polímeros: Ciência e Tecnologia, 30(2), e2020016. http://dx.doi.org/10.1590/0104-1428.03120.
Received: Jan. 01, 2022
Revised: Apr. 10, 2022
Accepted: May 19, 2022
Polímeros, 32(2), e2022014,
Dalila Pinto Malaquias1, Lays Fernanda Nunes Dourado1* , Ângela Maria Quintão Lana2 , Fernando Souza2, José Vilela3, Margareth Andrade3 , Juan Pedro Bretas Roa4 , Álvaro Dutra de Carvalho-Junior1 and Elaine Amaral Leite5
1Departamento de Farmácia, Faculdade de Ciências Biológicas e da Saúde, Universidade Federal dos Vales do Jequitinhonha e Mucuri – UFVJM, Diamantina, MG, Brasil
2Departamento de Zootecnia, Escola de Veterinária, Universidade Federal de Minas Gerais – UFMG, Belo Horizonte, MG, Brasil
3Centro de Tecnologia, SENAI-CETEC, Belo Horizonte, MG, Brasil
4Departamento de Engenharia Química, Instituto de Ciências e Tecnologia, Universidade Federal dos Vales do Jequitinhonha e Mucuri – UFVJM, Diamantina, MG, Brasil
5Departamento de Produtos Farmacêuticos, Faculdade de Farmácia, Universidade Federal de Minas Gerais – UFMG, Belo Horizonte, MG, Brasil *laysndourado@gmail.com
Controlled release systems can modify the release rate of drugs and direct them to specific sites of action, making them more effective and/or reducing the adverse effects. The objective of this study was investigated, poly(β-hydroxybutyrate) (PHB) and poly(ε-caprolactone) (PCL) nanospheres to improve the delivery of Simvastatin (SIM). Nanospheres were prepared by the emulsion/evaporation technique of the solvent, varying the amount of SIM added. The SIM quantification was performed using a validated high-performance liquid chromatography method. The average diameter and PDI of formulations without SIM were lower 250 nm and 0.3, respectively. Nanospheres containing 30% of SIM showed values of 265 nm and 0.09, respectively. The average zeta potential was -31.8 mV, suggesting the predominance of repulsive forces that prevent aggregation. In vitro release suggest transport occurs by diffusion. Morphological analysis demonstrated spherical particles and rough surfaces. In conclusion, data suggest that PHB/PCL nanospheres are promising delivery systems to SIM.
Keywords: drug delivery, nanoparticles, PHB, PHB/PCL blend, simvastatin.
How to cite: Malaquias, D. P., Dourado, L. F. N., Lana, Â. M. Q., Souza, F., Vilela, J. Andrade, M., Roa, J. P. B., CarvalhoJunior, Á. D., & Leite, E. A. (2022). Development and optimization by factorial design of polymeric nanoparticles for simvastatin delivery. Polímeros: Ciência e Tecnologia, 32(2), e2022016. https://doi.org/10.1590/0104-1428.20220016
Among the statins, simvastatin (SIM) is a well-known potent competitive inhibitor of 3-hydroxy-3-methylglutaryl coenzyme A (HMG-CoA) reductase, which is the ratelimiting enzyme in cholesterol biosynthesis[1]. Recent studies have shown that the statins induce osteogenesis and inhibit osteoclastic activity by bone morphogenetic protein 2 (BMP-2)-mediated action; thus, they present an essential role in the development of bone and cartilage[2,3].
Based on this, SIM would have great potential for fractures and osteoporosis treatment if it reached selectively target to bone[4-6]. As a Biopharmaceutical Classification System Class II drug, SIM shows low aqueous solubility (0.765 μg/ mL in water at 25oC) and high lipophilicity (log P = 4.68)[7,8].
Besides extensive hepatic metabolism, studies reported that less than 5% of SIM achieve blood circulation[9]. To attain the minimum concentration required for the beneficial effects
on bone, high doses of SIM are needed, which might cause toxic effects. Thus, the association of SIM with a new drug delivery system is able to act as a controlled drug delivery system representing a promising alternative for use of SIM in the treatment of many diseases.
Polymeric nanocarriers obtained by processing biodegradable polymers have demonstrated a potential for improving the bioavailability of lipophilic drugs. Among the polymers often used in the pharmaceutical field, poly(βhydroxybutyrate) (PHB), a linear polyester produced in nature by bacterial fermentation of sugar or lipids, has received special attention due to its biodegradation and biocompatibility properties[10,11]. However, PHB presents high crystallinity (60 to 90%), which hinders the attack of degrading enzymes; therefore, its degradation occurs slowly[12,13]. Strategies to alter this property included the development of copolymers
or the blending with another polymer[14]. Previous studies showed that PHB blends with poly(ε-caprolactone) (PCL) were immiscible and incompatible[15], but PCL reduced the stiffness and improved the processing capacity of the blend as well as increased the biodegradability[16-18]
Therefore, in this study, the aim was the characterization of nanoparticles of PHB and PCL blends loading SIM in order to obtain a prolonged delivery system capable of improving the biopharmaceutical properties of SIM. Firstly, were prepared nanoparticles unloaded (without drug) and statistical tools were used to evaluate their parameters, like diameter, distribution, and surface charge. After, SIM was added to the nanoparticles (SIM-NP) and the influence of the drug incorporation on the physicochemical properties and nanoparticle stability was observed. Lastly, the drug release behavior from the polymer matrix was studied.
SIM (>99%) was purchased from Fagron (São Paulo, Brazil). PHB (Mw = 600 kDa) was supplied by PHB Industrial S.A. (São Paulo, Brazil). PCL (Mw = 80 kDa) was purchased from Sigma-Aldrich (St. Louis, USA). Chloroform and ethanol were obtained from Labsynth (São Paulo, Brazil). Water was purified using a Milli-Q apparatus (Millipore, Billerica, USA). HPLC grade solvents were purchased from J.T.Baker (Philipsburg, USA). All other chemicals were of analytical grade and were used as received.
A 22 full factorial design was used in unloaded nanoparticles to determine the influence of two factors: PHB/PCL ratios (A) and the presence or absence of copolymer (B) as well as interactions between them on the following responses: mean diameter, polydispersion index, and zeta potential. Thus, four formulations were prepared in triplicate and named according to the factors employed: PHB/PCL 20/80 and presence copolymer, PHB/PCL 20/80 and absence copolymer, PHB/PCL 80/20 and presence copolymer, and PHB/PCL 80/20 and absence copolymer. Analysis of the effect of each variable on the designated response and possible interactions between the factors was performed using the software SAEG software (Sistema para Análises Estatísticas e Genéticas, version 8.0: Fundação Arthur Bernardes, Viçosa, Brazil).
The copolymer poly(3-hydroxybutyrate-co-ε-caprolactone) (PHB-co-CL, Mw = 2kDa) was obtained by transesterification reaction from PHB and PCL and was kindly supplied by Professor Dr. Juan Pedro Bretas Roa according to previous studies[14]
Firstly, PHB was solubilized in chloroform at 40oC through constant stirring until complete dissolution of the polymer. For the PCL solubilization in chloroform, only magnetic stirring was used. The polymer solutions were added in different concentrations to obtain PHB/PCL ratios of 20/80 or 80/20. Then, the preparations were diluted in
chloroform at a final concentration of 0.1% (w/w) and were stirred for 2 h and transferred to appropriate glass bottles to avoid solvent evaporation[14]
All formulations were prepared by the oil-in-water (o/w) emulsion-solvent evaporation method previously described by Suave et al.[19], but with some modifications.
Briefly, 5 mL of PBH/PCL blend (equivalent to 5 mg of polymer) was added in 45 mL of ethanol in ice bath, and the resulting solution was slowly emulsified in 50 mL of water Milli-Q under constant agitation (9500 rpm, 5 min) with an Ultra Turrax T-25 homogenizer (Ika Labortechnik, Staufen, Germany). Subsequently, the organic solvent was removed by evaporation under reduced pressure at 40°C.
SIM loaded nanoparticles were also prepared as described above using only PHB/PCL blend at ratio 20/80 and named SIM-NP. Briefly, SIM dissolved in chloroform was added simultaneously to blend solution, in different concentrations (10, 15, 20, 25, and 30% of the drug relative to the polymer mass). Non-entrapped SIM was eliminated by centrifugation (HeraeusTM MultifugeTM X1 Centrifuge Series, Thermo Fisher Scientific, Bremen, Germany) at 10,000 rpm at 4°C for 10 min.
The average diameter of the particles was determined by unimodal analysis through dynamic light scattering (DLS) at 25oC and a fixed angle of 90º. Samples without prior dilution were transferred to a DTS0012 cell and analyzed in Zetasizer NanoZS90 equipment (Malvern Instruments, Malvern, England). The data reported were particle diameter, and polydispersity index (PDI). Data were expressed as the mean ± standard deviation (SD) of at least three batches of each formulation.
The zeta potential was evaluated by the electrophoretic mobility determination at the angle of 90º at 25oC. Samples without prior dilution were transferred to a DTS1060C cell and the measurements were performed in triplicate using Zetasizer NanoZS90 equipment (Instruments, Malvern, England). Data were expressed as the mean ± SD of at least three batches of each formulation.
The quantification of SIM was assessed by high-performance liquid chromatography (HPLC) using previously validated conditions by our group. The chromatographic apparatus of the HPLC analysis consisted of a Model 515 pump, a Model 717 Plus auto-injector, and a Model 2996 variable wavelength UV detector (Waters Instruments, Milford, USA) connected to Empower software. Separations were performed using a 25 cm × 4 mm, 5 μm Lichrospher® 100 RP-18 column (Merck Millipore, Darmstadt, Germany). The mobile phase consisted of methanol-phosphoric acid 0.1% (90:10 v/v) mixture, filtered and degassed by suction-filtration through a nylon membrane. The flow rate was 1.2 mL min-1, in isocratic flow, and the injection volume was 20 μL. The eluate absorbance was monitored at 238 nm. The standard calibration curve was linear over a concentration range of 6.0 - 48.0 µg/ml and resulted in
Polímeros, 32(2), e2022016, 2022
Malaquias, D. P., Dourado, L. F. N., Lana, A. M. Q., Souza, F., Vilela, J., Andrade, M., Roa, J. P. B., Carvalho-Junior, A. D., & Leite, E. A.the linear equation: y = 26680x + 42500, with a correlation coefficient of 0.9992 under our experimental conditions. The quantification of SIM in the nanoparticles was determined before (non-purified SIM-NP) and after (purified SIM-NP) centrifugation. Briefly, the SIM-NP formulations were disrupted using acetonitrile in a volume ratio of 1:2 and later diluted in the mobile phase for HPLC analysis. Data were expressed as the mean ± SD of at least three batches of each formulation. The encapsulation percentage (EP) was calculated using the following equation: EP (%) = [purified SIM-NP]/[non purified SIM-NP]*100.
Differential scanning calorimetry (DSC) analyses were performed using a DSC 2910 (TA Instruments, New Castle, USA). For DSC measurements, a scan rate of 10°C/ min was used at a temperature range of 25-380°C, under nitrogen purge (50 ml/min). For temperature and enthalpy calibration, we used Indium. The lyophilized samples were used for DSC study. Lyophilized SIM-NP4 was obtained using a freeze-drier (Liofilizador LS300, Terroni®, São Paulo, Brazil), after rapid freezing of the formulations into liquid nitrogen. The samples were lyophilized for 24 h at a temperature of -45°C. After freeze-drying, the lyophilized samples were placed directly in aluminum pans and all measurements were made using sealed aluminum pans, and an empty pan was used as a reference. Data acquisition and analysis were performed on a microcomputer using an Isothermal Software Kit provided by TA Instruments (New Castle, USA).
Initially, the nanoparticles were purified. Membrane (cut-off de 14 kDa, Sigma-Aldrich, EUA) filled with 1 ml of solution, and transferred for a bequer containing Milli Q water at 80°C under agitation. After 30 min, the water was removed, and fresh Milli Q water was introduced once again into the flask and stirred (four wash cycles were performed). To ensure the sink conditions (10% of the saturation concentration) SIM solubility in phosphate-buffered saline (PBS) with 0.1% Tween 80 (w/v) at pH 7.4 was previously determined (5.33 μg/mL). The dissolution/release kinetic study of SIM was investigated by the dialysis method. Briefly, aliquots of 1.0 mL of SIM-NP were enclosed in dialysis bags (cellulose membrane, Mw cut-off of 14,000 kDa, Sigma-Aldrich, St. Louis, USA), incubated in 30.0 mL of PBS buffer (pH 7.4) containing 0.1% Tween 80® at 37°C and maintained under mechanical agitation at 100 rpm. At predetermined time intervals (0, 15, 30, 60, 180, 360, 720, and 1440 min), dialysis bags were removed (n=3 for each time) and the SIM concentration was analyzed by HPLC, as described above. The drug release was calculated by the difference between the initial concentration added and the concentration retained in the dialysis bag. The mechanism of SIM release and dissolution was evaluated by mathematical models.
Atomic Force Microscopy (AFM) was applied to evaluate the morphology and diameter analysis of unloaded nanoparticle composed by PHB/PCL blend at ratio 20/80 without copolymer and SIM-NP. A sample droplet (~10 µL) was deposited on a freshly cleaved mica surface,
spread, and dried with argon flow. The measurements were performed at room temperature, in the air, on a Dimension 3000 and with Multimode Equipment, both monitored by a NanoScope IIIa controller, from Digital Instruments (Santa Barbara, USA). The images were obtained in tapping mode using commercial silicon probes from Nanosensors with cantilevers of 288 µm length, resonance frequencies of 75-98 kHz, and spring constants of 3-7 N/m. The “scan rate” used was 1 Hz. Dimensional analyses were carried out using the “section of analysis” applicative on the system. A minimum of 10 images from each sample was analyzed to assure reproducible results. The values represent the mean ± SD of at least 40 nanoparticles measurements.
The determination of the storage stability of SIM-NP containing 20% of SIM was performed by storing the formulation at 4ºC. Sampling aliquots were taken at 7, 15, and 30 days after preparation to evaluate the following parameters: mean diameter, zeta potential, pH, and drug entrapment. The mean values of these parameters were compared with those obtained at time zero.
The normality and homogeneity of the variance analysis were performed using the Lilliefors’ and Bartlett’s tests, respectively. Unloaded and SIM nanoparticles data were evaluated by the factorial design and linear or multiple regression. The difference among averages was tested using the one-way analysis of variance (ANOVA), followed by the Tukey’s test and was considered significant when P values were lower than 0.05. The statistical software used was SAEG software 8.0.
The results of the physicochemical characteristics of the unloaded nanoparticles are shown in Table 1.
In the absence of copolymer, the mean diameter was similar regardless of the polymer ratio used. However, after adding the copolymer, mean diameter values significantly increased were obtained at the highest concentration of PHB (PHB/PCL 80:20). Concerning the PDI values, a significant increase (PDI higher than 0.3) was observed at highest PHB concentration in the presence or absence
Table 1. Physicochemical characteristics of unloaded nanoparticles. Parameter PHB/ PCL Copolymer Absence Presence
Diameter ± SD (nm)
20/80 267 ± 20 Aa 240 ± 13 Ba 80/20 252 ± 23 Ab 46188 ± 8632 Aa PDI ± SD 20/80 0.20 ± 0.06 Ba 0.15 ± 0.08 Ba 80/20 0.45 ± 0.23 Ab 1.0 Aa
Zeta Potential ± SD (mV) 20/80 -32.7 ± 4.1 Ba -28.9 ± 0.9 Ba 80/20 -24.7 ± 5.2 Aa -21.9 ± 4.6 Aa
Data expressed as the mean ± SD. Mean followed by distinct letters, being small letters on the lines and capital letters in the columns differ within the Tukey’s test (p < 0.05). Abbreviations: SD, standard deviation; PDI, polydispersity index.
of copolymer. All formulations showed negative zeta potential values, ranging from -22 to -33 mV. The increase of PHB concentration led to a significant reduction of the zeta potential in the absence or presence of the copolymer.
The interaction effect can be observed in Figure 1. The great slope of lines demonstrates the larger influence of the variable on the system, and the lack of parallelism of lines suggests the interaction between the factors. Thus, there was an interaction between the factors for mean diameter and PDI (Figures 1A, B) values while this effect was not observed for the zeta potential values (Figure 1C).
Taking into account the physicochemical characterization, the formulation containing the lowest ratio of PHB and the absence of copolymer was chosen by subsequent studies to clarify the role of SIM in these parameters.
Then, the influence of different SIM concentrations on the physicochemical parameters: mean diameter, PDI,
zeta potential, and EP of the nanoparticles was evaluated. There was no significant alteration in the mean diameter after increasing SIM concentration, except at 25% of SIM. In addition, PDI values less than 0.3 were obtained for all formulations, characteristic of homogeneous preparations (Figure 2). Besides, no significant change in zeta potential values could be observed after increasing SIM concentration. Values varying from -25 to -38mV were found (data not shown).
The data of EP are shown in Figure 3. The increase in SIM concentration up to 20% gradually increases the EP, and a significant difference could be detected between formulations containing 20 and 10% of the drug.
On the other hand, after adding 30% of SIM, the EP significantly decreased compared to 20% of the SIM. Thus, the highest EP was obtained after adding 20% of SIM. These data were further evaluated by regression analysis, and the third-order polynomial model was the best fit obtained (r = 0.95). The maximum point of the parabola obtained at a concentration of 20.25% shows that the developed model describes a behavior close to that obtained experimentally.
Figure 1. Evaluation of the interaction effect between the polymer proportion and presence (circle) or absence (square) of copolymer on particle diameter (A), PDI (B), and zeta potential (C) values.
Figure 2. Effect of different concentrations of SIM on the mean diameter (bars) and PDI (blue symbols) of nanoparticles. Asterisk indicates a significant difference compared to formulations 0, 10, and 20%. Data were expressed as the mean ± SD (n = 3), and the level of significance was considered for a p-value <0.05.
Figure 3. SIM quantity associated with nanoparticles as function of the theoretical SIM concentration. Data were expressed as the mean ± SD (n = 3) and are presented as the continuous line. The dashed line represents the best mathematical model fit.
Polímeros, 32(2), e2022016, 2022
Malaquias, D. P., Dourado, L. F. N., Lana, A. M. Q., Souza, F., Vilela, J., Andrade, M., Roa, J. P. B., Carvalho-Junior, A. D., & Leite, E. A.Due to the highest EP obtained, the formulation containing 20% of SIM was evaluated by the AFM technique. For comparison, unloaded NP was also studied. Both formulations were prepared with PHB/PCL 20/80 without copolymer. The images obtained by AFM demonstrated similar morphology for unloaded NP and SIM-NP, with spherical particles, nanometric size, and large diameter (Figures 4A, B). Both formulations showed spheres with an irregular surface; however, this finding was more pronounced in SIM-NP (Figure 4C), suggesting the presence of SIM on the surface. A heterogeneous distribution in diameter and height of the nanostructures can also be observed. The 40 particles count in 10 different fields showed a mean diameter of 354 ± 96 nm and a height of 80 ± 39 nm for unloaded NP, while for SIM-NP the values were 244 ± 80 nm and 22 ± 4 nm, respectively. The ratio diameter/height obtained was 4.4 and11.1 for unloaded and SIM-NP, respectively.
Crystallinity affects several properties of the polymer material, including mechanical, physical, thermodynamic and optical properties. The rate degradation, the affinity and location of the drug in the particle, as well as the mechanism of release, can be influenced by the crystallinity of the polymer used in its preparation[20]. In view of this, DSC analysis was used to investigate the thermal behavior of the SIM-NP compared to pure components, blend, and physical mixture.
The DSC curve obtained for SIM (Figure 5A) shows an endothermic event at 140 °C (Tonset = 136.5 °C), which corresponds to the melting point of the drug, which shows its crystalline nature and agrees with previous data described in the literature[21,22]. For the PHB/PCL blend curve, two peaks at 56 ° C (Tonset = 43.6 °C) and 171 ° C (Tonset = 161.5 °C) were ascribed to the melting point of the PCL and PHB, respectively (Figure 5B).
Figure 5. DSC curves obtained under a nitrogen atmosphere and heating ratio of 10 °C/min after analysis of SIM (A), PHB/ PCL 20/80 blend (B), physical mixture of the blend and the drug (2:1) (C), and SIM-NP prepared with PHB/PCL 20/80 and 20% of SIM (D).
Similar melting points were observed in other studies that involves PHB/PCL blends[17,23]. At the physical mixture curve, peaks at 51.5, 127.3, and 166.5° C near values mentioned before were observed (Fig. 5C). On the other hand, in the SIM-NP curve, only a sharp endothermic event at 53.8 ºC (Tonset = 42.5 °C) characteristic of PCL melting point, could be verified. It was possible to observe a meaningful change in the melting event of the SIM, suggesting an interaction between drug and polymers (Figure 5D). The addition of simvastatin provided a reduction in the melting temperature of the polymers, which according to Suave et al.[19] suggests an affinity of the drug for the polymers. Similar results were described by Kouhi et al.[23], in PCL nanofibers containing simvastatin. The results obtained showed that the peak referring to the drug disappeared in the DSC curves of the nanofibers containing simvastatin, suggesting that the drug was molecularly dispersed or present in its amorphous form.
The in vitro release profiles of SIM and SIM-NP are shown in Figure 6. Initially, SIM-NP showed an initial burst release of 70%, followed by sustained release of more 10% within 12 h. After the period of the test, remains in the systems around 20% of the drug inside the nanosystems.
On the other hand, SIM has a low solubility, which can interfere in their in vitro release. However, after 750 min approximately 90% of drug could be recovered.
The SIM release kinetics from NP was fitted using zero-order, first-order, and Higuchi mathematical models. Regression coefficients are shown in Table 2. Based on these data, the SIM release from the nanoparticles followed the Higuchi mathematical model which predicts that the release
Figure 6. In vitro release profile of free SIM (circle) and SIM-NP (square) at 37ºC in PBS containing 0.1% Tween 80® pH 7.4. The insert shows the first 180 minutes of release of SIM. Data were expressed as the mean ± SD (n = 3).
Table 2. Regression coefficients of dissolution/release data of free SIM and SIM loaded NP composed of PHB/PCL 20/80.
Free SIM SIM-NP
Zero-order 0.5843 0.3396 First-order 0.4247 0.2819 Higuchi 0.7447 0.5136
occurs by diffusion of the drug through the polymer matrix and/or matrix erosion.
SIM-NP stability was evaluated for a period of 30 days, and the data are presented in Figure 7. As can be seen, there was no significant difference in mean diameter (Figure 7A). Besides, PDI values were lower than 0.2 in all timeframes, suggesting that pharmaceutical preparation did not agglomerate during this period. On the other hand, the amount of SIM-associated with NP was significantly reduced (around 55%) on the seventh day after preparing and keeping on stable after that. The regression analysis of these data showed a significant correlation (r2 = 0.99) in the concentration reduction over time.
The zeta potential values showed a variation of -27 mV to -19mV (Figure 7B), which also showed r2 higher than 0.9. However, it is noteworthy that the values still were high (near -20mV) suggesting the predominance of repulsive forces that prevent aggregation. Concerning the pH, the values ranging from 5.23 to 5.55, which allows us to suggest that there is no polymeric degradation (Table 3).
It is well-described that the success of SIM on bone health in vivo depends on the local concentration. Finding an appropriate delivery system capable to reduce the drug accumulation in the liver and to deliver to the peripheral tissue has been a great challenge. Polymeric nanoparticles have been employed for carrying insoluble drugs, such as SIM, since their easy production process and application
Polímeros, 32(2), e2022016, 2022
Malaquias, D. P., Dourado, L. F. N., Lana, A. M. Q., Souza, F., Vilela, J., Andrade, M., Roa, J. P. B., Carvalho-Junior, A. D., & Leite, E. A.Table 3. Regression analysis of the data of storage stability.
Zeta Potential -26.21 (±1.24) + 0.243 (±0.072) days 0.94 pH 5.27 (±0.07) + 0.011 (±0.004) days 0.80
SIM retention 99.03 (±0.58) – 10.42 (±0.25) days + 0.68 (±0.025) days2 – 0.013 (±0.0005) days3 0.99 NS: no significant effect.
Figure 7. Storage stability evaluation through (A) average diameter (white bars) and retention percentage (blue bars), and (B) pH (white bars) and zeta potential (blue bars) of SIM-NP. Results expressed as the mean ± SD (n = 3). Asterisk indicates a significant difference compared to day 0. The level of significance was considered for a p-value < 0.05.
for several classes of pharmaceutical drugs[24]. It is known that the formation of the nanoparticles can be influenced by numerous factors, such as the ratio of organic/aqueous phase, solvents, and especially by the polymer used[25]
Biocompatible and biodegradable polymers are promising for the development of controlled-release formulations[26-28]. PHB and PCL are some of them, and their degradation leads to the formation of inert, nontoxic, and biocompatible degradation products. Despite being biodegradable, the high crystallinity of PHB provokes a slow degradation, and the polymer might accumulate in the body. Thus, polymer blends have been used as a promising strategy to modify the physicochemical properties and control the drug release profile[29]
In this study, the effects of the composition (polymer ratio and presence or absence of copolymer) on the physicochemical properties of nanoparticles aiming to optimize a formulation for carrying SIM was evaluated. The data were analyzed using a 22 full factorial design which allowed us to predict possible interactions between variables. This finding has a
significant role in the definition of optimal conditions for formulation development.
The analysis of the influence of polymeric ratio in nanosphere diameter showed particle diameter was similar (p> 0.05) in the absence of copolymer regardless of the polymeric ratio used, as previously described[30,31]. On the other hand, the increase in PHB concentration led to PDI values higher than 0.3 suggesting heterogeneous samples (Table 1). Although studies have shown that the addition of copolymer may promote higher integration of the phases and increase the interaction between the polymer blend components[32], in this study, this effect was not observed.
For the highest ratio of PHB even after the addition of copolymer, great and polydisperse particles were formed. In study development by Leimann et al.[33] similar results were observed in the preparation of Poly(3-hydroxybutyrateco-3-hydroxyvalerate) (LPHBV) nanoparticles prepared by a miniemulsion/solvent evaporation technique. The increase of the concentration of LPHBV leads to increases in the average particle diameters and polydispersity indexes. According to the literature, this effect can be explained because of increase of the viscosity of the organic phase when higher polymer concentrations are used. Moreover, nanoparticles prepared with higher LPHBV concentrations could coalesced due to the higher viscosity of the organic phase[34]. Moreover, a great amount of SIM (25%) also can influence the nanoparticles sizes. In a recently published study by our grup[35], the presence of 25% of SIM in PHB/ PPG films leaded to instability of the PHB/PPG films which, in a way, corroborates the results of this research.
In this sense, the formulation containing PHB/PC 20/80 without copolymer was selected for incorporating SIM. Different concentrations of SIM were evaluated, and the highest EP obtained was 63% when 20% of the drug in relation to polymer mass was used (Figure 3). The low encapsulation efficiency can be explained because of the small superficial area of nanoparticles and the highly insoluble of SIM. An example of this, in a study published by Terukina et al. [36], PLGA nanospheres showed encapsulation SIM rate of 14.72 ± 0.11%. On the order hand, the encapsulation efficiencies of PLGA microspheres were 89.82 ± 0.78%.
Small and spherical particles with a rough surface were obtained (Figures 2 and 4). It is known that these parameters are strongly influenced by the drug characteristic as well as the technique used in preparing nanoparticles[37,38]. Previous study has demonstrated that the presence of the roughness on the particle’s surface can be associated with the high crystallinity and fast precipitation of PHB, after removing the solvent from the internal phase of the emulsion[12] In addition, AFM analysis showed a heterogeneous distribution
of diameter and height. A diameter/height ratio of more than 4 was detected, suggesting that nanoparticles flatten on contact with surfaces[39]
It’s also well-described that the crystallinity may affect the mechanical, physical, thermodynamic, and optical properties of the polymeric material[40]. According to the literature, many factors can influence the crystallinity of polymers, such as blend polymer and the amount of inorganic component. In study by Ding et al.[41], the authors observed that silica and calcium additions were both able to decrease the crystallinity of the PHB and PCL blend polymer. This effect was justified by the formation of hydrogen bonding or network formation between the inorganic components phase and polymer matrix.
Thus, DSC analyses were performed in order to evaluate the drug-polymer interactions in the formulation. The addition of SIM reduced the melting temperature of the polymers, suggesting an affinity between the drug and the polymers. The absence of the drug crystallization peak in the SIM-NP curve can suggest that the drug is molecularly dispersed or present in its amorphous form[42]. Similar results were described in PCL nanofibers containing SIM[23]
The in vitro release study provides essential information about the physicochemical processes as well as the mechanisms that influence the release rate of the drug. Thus, depending on the release data obtained, changes in preparation conditions, polymer ratio, or drug amount are required to achieve a release profile with desirable characteristics[43]. Drug release from nanoparticulate systems is dependent on factors like its adsorption on the surface, its diffusion through the polymeric structure, besides the degradation of the polymer[44]. Drug absorbed on the surface is released faster (burst effect), followed by a slower release of the drug inside the particle. Studies also show slow biodegradation of PCL, and for encapsulating hydrophobic drugs, diffusion is the predominant release form[45].
The percentage of drug release from SIM-NP was higher in the early hours compared to free drug. The faster release is probably due to decreased polymer crystallinity caused by the association of a small portion of the drug with the matrix. In addition, high release rates have been reported when fatty acid esters are employed in the preparation of microspheres in PLA or PHB blends[46]. Another important parameter is the drug/polymer ratio. The formation of irregular and porous particles besides phase separation between the drug and polymer due to a large amount of encapsulated drugs often results in a faster release[47]. The investigation of the release of an insecticide from PHB/PCL microspheres showed that the release rate was favored by the addition of PCL to the blend suggesting the possibility of modulating the release rate by formulating blend[19]. Therefore, in the present study, it can be proposed that both the release from the nanospheres and SIM occur predominantly by diffusion, but also by erosion of the polymer matrix[35].
Finally, an acceptable shelf-life is a prerequisite for the successful introduction of this system in therapy. To be considered stable over the period of storage, nanospheres cannot undergo physical or chemical degradation[48]. In our preliminary storage study, no significant changes were observed in diameter, PDI, and zeta potential.
The maintenance of these parameters may be explained by the electrical repulsion favored by negative zeta values, which could prevent aggregation, improving the stability of the formulations. However, SIM-loaded NP showed a significant reduction (p < 0.05) after 7 days of storage. This finding is in accordance with the hypothesis of the absorbed drug on the surface which could be released early.
SIM-loaded PHB/PCL nanospheres were successfully manufactured by emulsion/evaporation technique. The results obtained indicate that nanoparticle prepared exhibited a great potential due to high efficiency of encapsulation and stability. Thus, this novel nanostructured carrier system may serve as an encapsulation carrier system for SIM application in bone alterations.
• Conceptualization – Juan Pedro Bretas Roa; Álvaro Dutra de Carvalho-Junior; Elaine Amaral Leite.
• Data curation – Álvaro Dutra de Carvalho-Junior.
• Formal analysis – Juan Pedro Bretas Roa; Álvaro Dutra de Carvalho-Junior; Elaine Amaral Leite.
• Investigation – Dalila Pinto Malaquias; Lays Fernanda Nunes Dourado; Ângela Maria Quintão Lana; Fernando Souza; José Vilela; Margareth Andrade; Juan Pedro Bretas Roa; Álvaro Dutra de Carvalho-Junior; Elaine Amaral Leite.
• Methodology – Dalila Pinto Malaquias; Juan Pedro Bretas Roa; Álvaro Dutra de Carvalho-Junior; Elaine Amaral Leite.
• Project administration – Álvaro Dutra de CarvalhoJunior.
• Resources – Álvaro Dutra de Carvalho-Junior; Elaine Amaral Leite.
• Software – NA.
• Supervision – Álvaro Dutra de Carvalho-Junior.
• Validation – NA.
• Visualization – NA.
• Writing – original draft – Lays Fernanda Nunes Dourado; Álvaro Dutra de Carvalho-Junior; Elaine Amaral Leite.
• Writing – review & editing –Lays Fernanda Nunes Dourado; Álvaro Dutra de Carvalho-Junior; Elaine Amaral Leite.
Financial supports are provided by Conselho Nacional de Desenvolvimento Científico e Tecnológico (CNPq) and Fundação de Amparo a Pesquisa do Estado de Minas Gerais (FAPEMIG).
1. Endo, A. (2010). A historical perspective on the discovery of statins. Proceedings of the Japan Academy. Series B, Physical and Biological Sciences, 86(5), 484 493 http://dx.doi.org/10.2183/ pjab.86.484 PMid:20467214.
Polímeros, 32(2), e2022016, 2022
Malaquias, D. P., Dourado, L. F. N., Lana, A. M. Q., Souza, F., Vilela, J., Andrade, M., Roa, J. P. B., Carvalho-Junior, A. D., & Leite, E. A.2 Liu, Y. S., Ou, M. E., Liu, H., Gu, M., Lv, L. W., Fan, C., Chen, T., Zhao, X. H., Jin, C. Y., Zhang, X., Ding, Y., & Zhou, Y. S. (2014). The effect of simvastatin on chemotactic capability of SDF-1α and the promotion of bone regeneration. Biomaterials, 35(15), 4489 4498 http://dx.doi.org/10.1016/j. biomaterials.2014.02.025 PMid:24589359.
3 Yue, X., Niu, M., Zhang, T., Wang, C., Wang, Z., Wu, W., Zhang, Q., Lai, C., & Zhou, L. (2016). In vivo evaluation of a simvastatin-loaded nanostructured lipid carrier for bone tissue regeneration. Nanotechnology, 27(11), 115708 http://dx.doi. org/10.1088/0957-4484/27/11/115708 PMid:26881419.
4. Liu, X., Li, X., Zhou, L., Li, S., Sun, J., Wang, Z., Gao, Y., Jiang, Y., Lu, H., Wang, Q., & Dai, J. (2013). Effects of simvastatin-loaded polymeric micelles on human osteoblastlike MG-63 cells. Colloids and Surfaces. B, Biointerfaces, 102, 420 427 http://dx.doi.org/10.1016/j.colsurfb.2012.06.037 PMid:23006576.
5 Basniwal, P. K., & Jain, D. (2012). Simvastatin: review of updates on recent trends in pharmacokinetics, pharmacodynamics, drug-drug interaction, impurities and analytical methods. Current Pharmaceutical Analysis, 8(2), 135 156 http://dx.doi. org/10.2174/1573412911208020135.
6 Yin, H., Shi, Z.-G., Yu, Y.-S., Hu, J., Wang, R., Luan, Z.-P., & Guo, D.-H. (2012). Protection against osteoporosis by statins is linked to a reduction of oxidative stress and restoration of nitric oxide formation in aged and ovariectomized rats. European Journal of Pharmacology, 674(2-3), 200 206 http://dx.doi. org/10.1016/j.ejphar.2011.11.024 PMid:22130356.
7 Lindenberg , M. , Kopp , S. , & Dressman , J. B. (2004 ). Classification of orally administered drugs on the World Health Organization Model list of Essential Medicines according to the biopharmaceutics classification system. European Journal of Pharmaceutics and Biopharmaceutics, 58(2), 265 278 http:// dx.doi.org/10.1016/j.ejpb.2004.03.001 PMid:15296954.
8 Jiang, T., Han, N., Zhao, B., Xie, Y., & Wang, S. (2012). Enhanced dissolution rate and oral bioavailability of simvastatin nanocrystal prepared by sonoprecipitation. Drug Development and Industrial Pharmacy, 38(10), 1230 1239 http://dx.doi.or g/10.3109/03639045.2011.645830 PMid:22229827.
9. García, M. J., Reinoso, R. F., Sánchez Navarro, A., & Prous, J. R. (2003). Clinical pharmacokinetics of statins. Methods and Findings in Experimental and Clinical Pharmacology, 25(6), 457 481 http://dx.doi.org/10.1358/mf.2003.25.6.769652 PMid:12949632.
10 Paulraj, P., Vnootheni, N., Chandramohan, M., & Thevarkattil, M. J. P. (2018). Exploration of Global Trend on Biomedical Application of Polyhydroxyalkanoate (PHA): a patent survey. Recent Patents on Biotechnology, 12(3), 186 199 http://dx.doi. org/10.2174/1872208312666180131114125 PMid:29384069.
11 Bokrova, J., Marova, I., Matouskova, P., & Pavelkova, R. (2019). Fabrication of novel PHB-liposome nanoparticles and study of their toxicity in vitro. Journal of Nanoparticle Research, 21(3), 49 http://dx.doi.org/10.1007/s11051-019-4484-7
12 Bidone, J., Melo, A. P. P., Bazzo, G. C., Carmignan, F., Soldi, M. S., Pires, A. T. N., & Lemos-Senna, E. (2009). Preparation and characterization of ibuprofen-loaded microspheres consisting of poly(3-hydroxybutyrate) and methoxy poly (ethylene glycol)-b-poly (D,L-lactide) blends or poly(3-hydroxybutyrate) and gelatin composites for controlled drug release. Materials Science and Engineering C, 29(2), 588 593 http://dx.doi. org/10.1016/j.msec.2008.10.016
13 Bugnicourt, E., Cinelli, P., Lazzeri, A., & Alvarez, V. (2014). Polyhydroxyalkanoate (PHA): review of synthesis, characteristics, processing and potential applications in packaging. Express Polymer Letters, 8(11), 791 808 http://dx.doi.org/10.3144/ expresspolymlett.2014.82
14 Roa, J. P. B., Mano, V., Faustino, P. B., Felix, E. B., Silva, M. E. S. R., & Souza Filho, J. D. (2010). Síntese e Caracterização do Copolímero Poli(3 Hidroxibutirato co ε Caprolactona) a Partir de Poli(3 Hidroxibutirato) e Poli(ε Caprolactona). Polímeros: Ciência e Tecnologia, 20(3), 221 226 http://dx.doi. org/10.1590/S0104-14282010005000038
15 Gassner, F., & Owen, A. J. (1994). Physical properties of poly(βhydroxybutyrate)-poly(ε-caprolactone) blends. Polymer, 35(10), 2233 2236 http://dx.doi.org/10.1016/0032-3861(94)90258-5
16. Huang, M.-H., Li, S., Hutmacher, D. W., Coudane, J., & Vert, M. (2006). Degradation characteristics of poly(ε-caprolactone)-based copolymers and blends. Journal of Applied Polymer Science, 102(2), 1681 1687 http://dx.doi.org/10.1002/app.24196
17 Lovera, D., Márquez, L., Balsamo, V., Taddei, A., Castelli, C., & Müller, A. J. (2007). Crystallization, morphology, and enzymatic degradation of polyhydroxybutyrate/ polycaprolactone (PHB/PCL) blends. Macromolecular Chemistry and Physics, 208(9), 924 937 http://dx.doi.org/10.1002/macp.200700011
18 Chee, M. J. K., Ismail, J., Kummerlöwe, C., & Kammer, H. W. (2002). Study on miscibility of PEO and PCL in blends with PHB by solution viscometry. Polymer, 43(4), 1235 1239 http://dx.doi.org/10.1016/S0032-3861(01)00725-X
19 Suave, J., Dall’Agnol, E. C., Pezzin, A. P. T., Meier, M. M., & Silva, D. A. K. (2010). Biodegradable microspheres of poly(3hydroxybutyrate)/poly(ε-caprolactone) loaded with malathion pesticide: Preparation, characterization, and in vitro controlled release testing. Journal of Applied Polymer Science, 117(6), 3419 3427 http://dx.doi.org/10.1002/app.32082
20. Huang, J., Wigent, R. J., & Schwartz, J. B. (2006). Nifedipine molecular dispersion in microparticles of ammonio methacrylate copolymer and ethylcellulose binary blends for controlled drug delivery: effect of matrix composition. Drug Development and Industrial Pharmacy, 32(10), 1185 1197. http://dx.doi. org/10.1080/03639040600832827 PMid:17090441.
21 Oliveira, M. A., Yoshida, M. I., Gomes, E. C. L., Mussel, W. N., Vianna-Soares, C. D., & Pianetti, G. A. (2010). Análise térmica aplicada à caracterização da sinvastatina em formulações farmacêuticas. Quimica Nova, 33(8), 1653 1657 http://dx.doi. org/10.1590/S0100-40422010000800007
22 Zhang, Y., Zhang, J., Jiang, T., & Wang, S. (2011). Inclusion of the poorly water-soluble drug simvastatin in mesocellular foam nanoparticles: drug loading and release properties. International Journal of Pharmaceutics, 410(1-2), 118 124 http://dx.doi. org/10.1016/j.ijpharm.2010.07.040 PMid:20674729.
23 Kouhi, M., Morshed, M., Varshosaz, J., & Fathi, M. H. (2013). Poly (ε-caprolactone) incorporated bioactive glass nanoparticles and simvastatin nanocomposite nanofibers: Preparation, characterization and in vitro drug release for bone regeneration applications. Chemical Engineering Journal, 228, 1057 1068 http://dx.doi.org/10.1016/j.cej.2013.05.091
24. Liechty, W. B., Kryscio, D. R., Slaughter, B. V., & Peppas, N. A. (2010). Polymers for drug delivery systems. Annual Review of Chemical and Biomolecular Engineering, 1(1), 149 173. http://dx.doi.org/10.1146/annurev-chembioeng-073009-100847. PMid:22432577.
25 Farrag, Y., Montero, B., Rico, M., Barral, L., & Bouza, R. (2018). Preparation and characterization of nano and micro particles of poly(3-hydroxybutyrate-co-3-hydroxyvalerate) (PHBV) via emulsification/solvent evaporation and nanoprecipitation techniques. Journal of Nanoparticle Research, 20(3), 71 http:// dx.doi.org/10.1007/s11051-018-4177-7
26 Makadia, H. K., & Siegel, S. J. (2011). Poly Lactic-co-Glycolic Acid (PLGA) as biodegradable controlled drug delivery carrier. Polymers, 3(3), 1377 1397 http://dx.doi.org/10.3390/ polym3031377 PMid:22577513.
Malaquias, D. P., Dourado, L. F. N., Lana, A. M. Q., Souza, F., Vilela, J., Andrade, M., Roa, J. P. B., Carvalho-Junior, A. D., & Leite, E. A.
27 Deng, C., Jiang, Y., Cheng, R., Meng, F., & Zhong, Z. (2012). Biodegradable polymeric micelles for targeted and controlled anticancer drug delivery: promises, progress and prospects. Nano Today, 7(5), 467 480 http://dx.doi.org/10.1016/j. nantod.2012.08.005
28. Kumari, A., Yadav, S. K., & Yadav, S. C. (2010). Biodegradable polymeric nanoparticles based drug delivery systems. Colloids and Surfaces. B, Biointerfaces, 75(1), 1 18 http://dx.doi. org/10.1016/j.colsurfb.2009.09.001 PMid:19782542.
29 Yu, L., Dean, K., & Li, L. (2006). Polymer blends and composites from renewable resources. Progress in Polymer Science, 31(6), 576 602 http://dx.doi.org/10.1016/j.progpolymsci.2006.03.002
30. Enrrico, C., Bartoli, C., Chiellini, F., & Chiellini, E. (2009). Poly(hydroxyalkanoates)-based polymeric nanoparticles for drug delivery. Journal of Biomedicine & Biotechnology, 2009, 571702 http://dx.doi.org/10.1155/2009/571702 PMid:19789653.
31 Shakeri, F., Shakeri, S., & Hojjatoleslami, M. (2014). Preparation and characterization of carvacrol loaded polyhydroxybutyrate nanoparticles by nanoprecipitation and dialysis methods. Journal of Food Science, 79(4), N697 N705. http://dx.doi. org/10.1111/1750-3841.12406 PMid:24621231.
32 Kim, B. O., & Woo, S. I. (1998). Compatibilizing capability of poly(β-hydroxybutyrate-co-ε-caprolactone) in the blend of poly(β-hydroxybutyrate) and poly(ε-caprolactone). Polymer Bulletin, 41(6), 707 712 http://dx.doi.org/10.1007/ s002890050422
33 Leimann, F. V., Cardozo Filho, L., Sayer, C., & Araújo, P. H. H. (2013). Poly(3-hydroxybutyrate-co-3- hydroxyvalerate) nanoparticles prepared by a miniemulsion/solvent evaporation technique: effect of phbv molar mass and concentration. Brazilian Journal of Chemical Engineering, 30(2), 369 377 http://dx.doi.org/10.1590/S0104-66322013000200014
34 Musyanovych, A., Schmitz-Wienke, J., Mailänder, V., Walther, P., & Landfester, K. (2008). Preparation of Biodegradable Polymer Nanoparticles by Miniemulsion Technique and Their Cell Interactions. Macromolecular Bioscience, 8(2), 127 139 http://dx.doi.org/10.1002/mabi.200700241 PMid:18213594.
35 Dourado, L. F. N., Pierucci, A., Roa, J. P. B., & Carvalho Júnior, Á. D. (2021). Assessment of implantable drug delivery technology: poly (3-hydroxybutyrate) / polypropylene glycol films containing simvastatin. Matéria (Rio de Janeiro), 26(04), 1 14 http://dx.doi.org/10.1590/s1517-707620210004.1389
36 Terukina, T., Naito, Y., Tagami, T., Morikawa, Y., Henmi, Y., Prananingrum, W., Ichikawa, T., & Ozeki, T. (2016). The effect of the release behavior of simvastatin from different PLGA particles on bone regeneration in vitro and in vivo : comparison of simvastatin-loaded PLGA microspheres and nanospheres. Journal of Drug Delivery Science and Technology, 33, 136 142 http://dx.doi.org/10.1016/j.jddst.2016.03.005
37 Sinha, V. R., Bansal, K., Kaushik, R., Kumria, R., & Trehan, A. (2004). Poly-ε-caprolactone microspheres and nanospheres: an overview. International Journal of Pharmaceutics, 278(1), 1 23 http://dx.doi.org/10.1016/j.ijpharm.2004.01.044 PMid:15158945.
38 Souto, E. B., Severino, P., & Santana, M. H. A. (2012). Preparação de nanopartículas poliméricas a partir de polímeros pré-formados: parte II. Polimeros: Ciência e Tecnologia, 22(1), 101 106 http://dx.doi.org/10.1590/S0104-14282012005000005
39. Montasser, I., Fessi, H., & Coleman, A. W. (2002). Atomic force microscopy imaging of novel type of polymeric colloidal nanostructures. European Journal of Pharmaceutics and Biopharmaceutics, 54(3), 281 284 http://dx.doi.org/10.1016/ S0939-6411(02)00087-5 PMid:12445557.
40. Auras, R. A., Harte, B., Selke, S., & Hernandez, R. (2003). Mechanical, physical, and barrier properties of poly(lactide) films. Journal of Plastic Film & Sheeting, 19(2), 123 135 http://dx.doi.org/10.1177/8756087903039702.
41 Ding, Y., Roether, J. A., Boccaccini, A. R., & Schubert, D. W. (2014). Fabrication of electrospun poly (3-hydroxybutyrate)/ poly (ε-caprolactone)/silica hybrid fibermats with and without calcium addition. European Polymer Journal, 55, 222 234 http://dx.doi.org/10.1016/j.eurpolymj.2014.03.020
42 Calvo, P., Vila-Jato, J. L., & Alonso, M. J. (1996). Comparative in vitro evaluation of several colloidal systems, nanoparticles, nanocapsules, and nanoemulsions, as ocular drug carriers. Journal of Pharmaceutical Sciences, 85(5), 530 536 http:// dx.doi.org/10.1021/js950474+ PMid:8742946.
43 D’Souza, S. S., & DeLuca, P. P. (2005). Development of a dialysis in vitro release method for biodegradable microspheres. AAPS PharmSciTech, 6(2), E323 E328. http://dx.doi.org/10.1208/ pt060242 PMid:16353991.
44 Schaffazick, S. R., Guterres, S. S., Freitas, L. L., & Pohlmann, A. R. (2003). Caracterização e estabilidade físico-química de sistemas poliméricos nanoparticulados para administração de fármacos. Quimica Nova, 26(5), 726 737 http://dx.doi. org/10.1590/S0100-40422003000500017
45 Dash, T. K., & Konkimalla, V. B. (2012). Poly-ε-caprolactone based formulations for drug delivery and tissue engineering: a review. Journal of Controlled Release, 158(1), 15 33 http:// dx.doi.org/10.1016/j.jconrel.2011.09.064 PMid:21963774.
46 Schaefer, M. J., & Singh, J. (2002). Effect of tricaprin on the physical characteristics and in vitro release of etoposide from PLGA microspheres. Biomaterials, 23(16), 3465 3471 http:// dx.doi.org/10.1016/S0142-9612(02)00053-4 PMid:12099290.
47 Wischke, C., & Schwendeman, S. P. (2008). Principles of encapsulating hydrophobic drugs in PLA/PLGA microparticles. International Journal of Pharmaceutics, 364(2), 298 327 http:// dx.doi.org/10.1016/j.ijpharm.2008.04.042 PMid:18621492.
48 Schaffazick, S. R., Pohlmann, A. R., Freitas, L. L., & Guterres, S. S. (2002). Caracterização e estudo de estabilidade de suspensões de nanocápsulas e de nanoesferas poliméricas contendo diclofenaco. Latin American Journal of Pharmacy, 21(2), 99 106 Retrieved in 2022, February 21, from http://www.latamjpharm. org/trabajos/21/2/LAJOP_21_2_1_4_740TAXZEY7.pdf
Received: Feb. 21, 2022
Revised: June 18, 2022
Accepted: July 07, 2022
Polímeros, 32(2), e2022016, 2022
https://doi.org/10.1590/0104-1428.20220027
Gabriella Neto Chagas1 , Maiccon Martins Barros2 , Ariadne Gonçalves de Leão3 , Neyda de La Caridad Om Tapanes4 , Roberto Carlos da Conceição Ribeiro1 and Daniele Cruz Bastos3*
1Coordenação de Rochas Ornamentais, Centro de Tecnologia Mineral – CETEM, Rio de Janeiro, RJ, Brasil
2Engenharia Civil, Força Aérea Brasileira, Rio de Janeiro, RJ, Brasil
3Departamento de Materiais, Universidade do Estado do Rio de Janeiro – UERJ-ZO, Rio de Janeiro, RJ, Brasil
4Departamento de Metalurgia, Universidade do Estado do Rio de Janeiro – UERJ-ZO, Rio de Janeiro, RJ, Brasil *daniele.bastos@uerj.br
Hybrid composites were prepared using recycled polypropylene (rPP), dimension stone waste (Bege Bahia, BB) and coconut fiber (CF). Post-consumer the formulations of rPP/BB/CF and virgin PP, were processed in a Haake mixer. The films were characterized according to chemical, physical and mechanical properties. Multiple linear regression tests were used to develop mathematical models, which allow simulating the behavior of the composition of composite on mechanical properties. Density variations were associated with differences in particle packing and particle wall roughness. The impact resistance of rPP/BB/CF was slightly higher in the 70/10/20 wt% composite. SEM micrographs of the ternary (70/20/10 wt%) showed stronger traces of decohesion, allowing higher water absorption and reducing impact resistance. The response surface methodology suggest that the increase in the variable “coconut fiber content” is responsible for improving the mechanical properties of the composite. The ternary composite (70/10/20 wt%) was best for replacement of virgin PP.
Keywords: Bege Bahia, recycling, waste, statistic analysis.
How to cite: Chagas, G. N., Barros, M. M., Leão, A. G., Tapanes, N. L. C. O., Ribeiro, R. C. C., & Bastos, D. C. (2022). A hybrid green composite for automotive industry. Polímeros: Ciência e Tecnologia, 32(2), e2022017. https:// doi.org/10.1590/0104-1428.20220027
Enormous amounts of plastic waste are generated on a global scale, the majority of which is landfilled or incinerated, in both cases causing negative environmental impacts, with only a minor fraction being recycled. During dimensioning, each stone industry unit generates both solid waste and stone slurry. They either end up in landfills or other disposal sites where they degrade the environment. Coconut is an important agricultural product in Brazil. After its use, the majority ofthe coconut weightis discarded, creating a large amount of waste that is slow to degrade in nature[1-4]
Over the last decade, innovation in the automotive industry increasingly focuses on strategies directed towards meeting environmental goals and a imingat sustainability. A keycomponent of this strategyis the focuson the overall light weighing and sustainability of materials of construction. To this aim, metal-based components used in non-structural parts of the vehicle can be replaced with thermoplastic composites without compromising performance while delivering the desired reduction in weight[5-8]
According to Chandgude and Salunkhe[5] roughly 10% reduction in vehicle weight can potentially save 6%–7% of fuel. Hybrid fibers have recently be come immensely popular with polymer composite reinforcements for various automotive parts. Hybrid composites are developed by
blending natural, synthetic, or a combination of natural or synthetic fibers in a single matrix. Hybridization allows enhancements in physical, mechanical, and thermal properties of the composites.
Polypropylene (PP) is extremely chemically resistant and almost completely hydrophobic. Black PP has the best UV resistance and isincreasing lyused in the construction industry for applications as automotive bumpers, chemical tanks, cable insulation, battery boxes, bottles, Petrolcans, indoor and outdoor carpets, carpetfibers[7]
The goal of the present work was to study the impact resistance, chemical and physical performance of the hybridization of fibrous reinforcement with particulate filler, using a recycled matrix (recycled polypropylene, rPP), Bege Bahia dimension stone waste (BB) and coconut fiber (CF). Multiple linear regression tests were used to develop mathematical models, which allow simulating the behavior of the composition of composite on mechanical properties (hardness and impact resistence). The reason for using wastes and recycled material is to reduce environmental impact of these materials, contributing to sustainability. The use of BB in ternary composites has not been reported previously in the literature.
Post-consumer polypropylene was collected through selective collection after the start of the Covid-19 pandemic. The material was submitted to separation, cutting and washing to remove possible contaminants. The rPP was analyzed by FTIR in a previous work[7] and presented absorption peaks characteristic of virgin PP along with other peaks attributed to additives. Pellets of virgin PP (Braskem, Brazil),), with density of 0.905 g/cm3 and Melt Index Flow (MFI) of 3.5 g.cm-3 (230 oC / 2.16 Kg) were used as received. Coconut fibers (Cocus Nucifera) from Volta Redonda (Rio de Janeiro) were provided in the natural form of fibrous mesocarp and processed, without chemical treatment in a knife shredder. The Bege Bahia dimension stone waste (BB) comes from the processing of Bege Bahia marble in the region of Ourolândia (Bahia, Brazil). This sample was analyzed by X-ray fluorescence in a previous work[7] and contained the principal components calcium (calcite) and magnesium carbonate (dolomite). The mineral was milled to obtain particle size less than 0.037 mm.
Post-consumer PP was pressed for better homogenization, heated to 200 ° C, for 5 min at 6 tons, and cooled in a cold press for 2 min at a pressure also of 6 tons. The pressed post-consumer PP was then chopped with the aid of manual scissors. Post-consumer PP was then fed into a twinscrew extruder (Teck Tril, DCT model) equipped with ten temperatures zones, ranging from 165 to 215 oC from the feed to die, and rotation of 150 rpm. After processing, the extruded PP (recycled PP or rPP) was pressed into pellets by an accessory of the device itself, and finally packed in plastic bags.
The virgin PP and the composites were prepared in the following rPP/BB/CF proportions (weight percentage): 100/0/0, 70/30/0, 70/20/10, 70/10/20, 90/10/0, 90/0/10, and 70/0/30, in a Haake internal mixer with rollers at a temperature of 200 °C for 7 minutes and roller speed of 60 rpm. The coarse and deformed particles of each of the formulations produced were then ground in a knife mill, generating smaller particles. Subsequently, the samples were pressed at 200 ºC in a hydraulic press to prepare the test specimens for the characterization tests.
The samples were characterized according to density (ASTM D792-13), water absorption test (ASTM D-570), hardness (ASTMD2240-13) and Izod impact strength test (ASTM D-256). Morphology of the fractured materials after Izod impact testing was studied by scanning electron microscopy (SEM), with a tabletop microscope (Hitachi TM3030Plus), to observe specimens coated with silver. The images were obtained at 500x magnification and 15 kV.
The samples: PP; rPP; rPP/BB (90/10); rPP/CF (90/10)) and rPP/BB/CF (70/20/10) were characterized by Fouriertransforming infrared spectra (FTIR), with a Nicolet 6700 FTIR spectrometer (ThermoScientific). The samples were mounted on an attenuated total reflectance (ATR)
accessory equipped with ZnSe crystal prior to scanning. The spectra were obtained with an accumulation of 120 scans.
Regression is a statistical procedure for calculating the value of a dependent variable from independent variables. Helping to estimate important risk factors that affect the dependent variable. This research uses multiple linear regression to obtain mathematical models that relate the properties of the recycled polypropylene based composite with the composition, aiming to optimize the mechanical performance of composite. Análise de Variância (ANOVA) was accomplished to evaluating such models and Response Surface Methodology (RSM) for optimization. The contents of recycled polypropylene (rPP), dimension stone waste (Bege Bahia, BB) and coconut fiber (CF) in the composite were used as independent variables, also called factors. The information about each factors and corresponding levels are shown in Table 1.
The dependent variables, usually called response variables, used to optimize the mechanical performance of composite were impact resistance (IR), density (D) and hardness (H). A second-degree polynomial model was established for each response variable. In order to obtain the model, 21 experiments were carried out, each one of them was perform at random to reduce systematic errors.
Table 2 shows the results of density, hardness and impact resistance of PP, rPP and composites. Similar results of density were found by Bakshi et al.[9], who studied calciumrich marble waste particulates as inexpensive reinforcement for recyclable PP. They found density results ranging from 0.96 to 1.27 g.cm-3 (20% to 80% particulate material). Density variations come from the differences in particle packing and particle wall roughness[9,10]. All composites showed density close to that of virgin PP. Paiva and Morales[11] achieved impact resistance for virgin PP of 26.5±4.3, similar to our finding (Table 2). The rPP sample had higher impact resistance than virgin PP and higher standard deviation, attributed to the recycling of the material.
For rPP/BB composites, the increase in filler content (10 to 30 wt%) reduced the impact resistance. According to the literature, with the same hybrid reinforcement concentration, the mechanical strength properties usually decline by a greater or lesser extent with increasing particulate filler content, depending on the particles’ aspect ratio.
The rPP/CF showed a slight decrease in impact resistance with the increase in CF proportion. The factors that contributed to this decrease were filler debonding, filler fracture, matrix shearing and filler pull-out. This was
rPP Recycled polypropylene content, %m/m 70, 90, 100
BB Dimension stone waste content, %m/m 0, 10, 20, 30
CF Coconut fiber content, %m/m 0, 10, 20, 30
Polímeros, 32(2), e2022017, 2022
Chagas, G. N., Barros, M. M., Leão, A. G., Tapanes, N. L. C. O., Ribeiro, R. C. C., & Bastos, D. C.Table 2. Density, Hardness and Impact resistance values of the samples.
Sample Density (g.cm-3)
PP
Hardness (Shore D) Impact resistance (J/m)
0.829±0.011 88.97±0.03 22.77 ± 4.00
rPP 0.869±0.033 83.24±0.07 33.82 ± 4.07 rPP/BB (90/10)
0.838±0.031 83.00±0.00 33.62 ± 3.59 rPP/BB (70/30)
1.146±0.003 85.27±0.03 17.16 ± 2.76 rPP/CF (90/10)
0.845±0.096 83.55±0.05 27.05 ± 3.75 rPP/CF (70/30) 0.838±0.062 90.90±0.01 21.83 ± 2.35 rPP/BB/CF (70/10/20) 1.043±0.005 83.32±0.03 20.75 ± 2.52 rPP/BB/CF (70/20/10) 1.096±0.028 81.68±0.08 13.99 ± 3.14
confirmed by the slight increase in density values for rPP/ CF 30 wt% in comparison with 10 wt%.
Among the ternary hybrid composites, the impact resistance of rPP/BB/CF (70/10/20 wt%) was slightly higher than of rPP/BB/CF (70/20/10 wt%). This was probably due to the equilibrium between chain scission and self-reinforcement mechanisms in rPP/BB/CF (70/10/20 wt%)[11]. Taking into consideration the average error range the impact resistance of rPP/BB/CF (70/10/20) was closer to the virgin PP, indicating the potential to replace virgin PP with 100% recycled material.
A slight decrease in the hardness (Table 2) of the hybrid composites in relation to the virgin matrix was observed. According to Borsoi et al. [13] and Coelho et al.[14], this occurs due to the possible non-uniformity in the distribution of the components in the matrix.
Figure 1 shows the micrographs obtained by scanning electron microscopy (SEM). Ductile fractures are observed in the PP and rPP matrix. For binary composites rPP/BB (90/10 and 70/30), the compatibility between the two components can be achieved by physical means, due to the melting and consequent interaction of the polymer matrix subjected to high temperatures during the processing. In addition, this can be influenced by the presence of chemical additives in recycled matrix material. However, the increase in proportion (10 to 30 wt%) was associated with some traces of decohesion (fault zones), which is in accordance with the lower impact resistance and higher water uptake achieved by the 70/30 wt% composite.
For the binary composites rPP/CF (90/10 and 70/30 wt%), filler did not cause significant morphological alterations. The micrographs show that the CF filler was dispersed evenly in the thermoplastic matrix. This can be attributed to the greater proportions of thermoplastic (50 wt%), allowing more encapsulation of the CF filler and consequently better impact resistance[11]. This behavior can be attributed to the presence of additives in the recycled matrix[14].
The ternary composite rPP/BB/CF (70/10/20 wt%) showed higher traces of decohesion than the ternary composite 70/20/10 wt%, allowing higher water absorption and reducing impact resistance. The ternary composite rPP/BB/CF (70/20/10 wt%) is most suitable to substitute virgin PP, reducing the impact on the environment while maintaining good properties.
The evaluation of water absorption of the extruded samples is shown in Figure 2. The highest absorption of all the composites was found after 24 h. The water absorption
capacity was lowest of the virgin PP, followed by the rPP sample.
There was an increase in water absorption values for reinforced composites. The PP and rPP samples, without filler, are more homogeneous, avoiding presence of microcracks.
All binary rPP/CF composites (90/10 and 70/30) showed higher absorption due to the hydrophilic character of natural fibers, fibers, in comparison to rPP/BB/CF (70/10/20). This occurs due to the partial or total collapse of thermoplastics with the lumens of the vegetable fibers produced during the processing of the compound, together with the higher density of their cell walls[10].
For the binary composite rPP/BB, incorporation of 10 wt% BB particles in the rPP matrix decreased the equilibrium moisture content significantly in comparison to 30 wt% BB. The high amount of BB in the composite was associated with high uptake of water, probably due to the porosity of the surface. Moreover, the decrease in water absorption capacity of ternary composites was observed for rPP/BB/CF (70/10/20 wt%) in comparison with rPP/ BB/CF (70/20/10 wt%). Water absorption values closest to those of PP and rPP were found for the composites rPP/BB (90/10 wt%) and rPP/BB/CF (70/10/20 wt%).
In the FTIR spectrum of PP (Figure 3), peaks near 2950, 2916 and 2836cm−1 (CH2, CH3) were observed. The symmetric bending vibration of CH3 was observed near 1455 and 1375 cm−1. The stretching vibrations of CH–CH2 and CH–CH3 were observed around 1168 and 974cm−1 with medium intensity peaks around 841cm−1 (C–H)[15]. Some other bands in rPP could be attributed to the additives used to improve the flow of post-consumer polymer during reprocessing. In rPP/BB/CF (70/20/10) composite, intense vibrations exist around 728 and 843cm−1 which confirms the presence of MgO. Absorption peaks obtained around 1375 and 1452cm−1 corresponds to CH3. Peaks near 1711, 1820cm−1 were due to the presence of carbonate (CO3 2−). In the composites, the interface is physical, since there were no changes in the infrared peaks[15] .
Response measured for the impact resistance (IR), density (D) and hardness (H) were represented in Table 3. ANOVA Tables (Table 4 - 6) were used to detect the factors and their insteractions that significantly influencing on mechanical performance of composite. The second-degree interactions considered in the study were rPP-BB, rPP-CF and BB-CF.
The P-values for the factors (rPP, BB, CF) and interactions (rPP-BB, rPP-CF and BB-CF) show in the Tables 4, 5 and 6 define the influence on the response
variables (IR, D and H). As the level of confidence was considering as 95%, them if P-value of the factor or the interaction is lower or equal to the risk degree (0.05 or 5%) there is a significant correlation between the responde variables and the factor, while P- values higher than 0.05, show the ausence of correlation.
The results illustrated in Tables 4, 5 and 6 show that the BB and CF factors do not have a significant influence on the mechanical properties evaluated, contrasting, their interactions with rPP reveal high significance. For impact resistance (IR) and hardness (H) it is possible to verify statistical significance for the rPP-BB and rPP-CF. For the Density (D) only rPP-BB interaction proved to be relevant. The BB-CF interaction was also significant for the hardness and density responses.
Logically, the rPP variable represents the most significant factor in all analyses, result that is corroborated in the Pareto diagram (Figures 4 and 5).
The influence of the composition of the composite on the impact resistance and hardness can be graphically verified through Figure 4 and 5 respectivelly. The figures show the Pareto charts, that relating the effects of factors and interactions with response variables. The reference line on the chart indicates which effects are significant, in this study was used Lenth’s method to draw the reference line. The terms with effects to the right of the line represent significant parameters.
The adjusted R-Sq (adj) values for the regression models of the IR, H and D responses are 81.41%, 93.23%
32(2),
Chagas, G. N., Barros, M. M., Leão, A. G., Tapanes, N. L. C. O., Ribeiro, R. C. C., & Bastos, D. C.0.841 21.83 90.92
0.775 21.28 90.890
0.898 21.83 90.9
1.038 20.83 83.3
1.048 20.66 83.3
1.044 22.12 83.35
1.078 17.78 81.75
1.128 14.08 81.6
1.082 13.89 81.7
1.148 16.13 85.26
1.142 20 85.3
1.147 18.18 85.250
0.875 25.53 83.600
0.922 28.57 83.55
0.738 24.19 83.5
0.854 38.63 83
0.802 33.33 83
0.857 33.9 83
0.863 37.21 83.2
0.839 30.43 83.2
0.904 37.21 83.32
These coefficients present high levels (above 70%), which implies that the models have good predictability.
analysis was performed to check for the assumptions of ANOVA and validate the regressions models.
equations for the IR, H and D responses are shown in Equations 1, 2 and 3.
surfaces were illustated in Figures 6 and 7 showing the variation of Impact Resistant (IR) and hardness (H) as a function of dimension stone waste content (BB) and coconut fiber content (CF).
Figures 6 and 7, it can be seen that the dimension stone waste content variable does not influence on the IR and H results, and the increase in coconut fiber content is responsible for improving the mechanical properties of the composite. In this sense, it can suggest that an ideal composite to replace o virgin PP could have a rPP/BB/CF composition of 70/10/30 or 70/0/30 wt%.
Chagas, G. N., Barros, M. M., Leão, A. G., Tapanes, N. L. C. O., Ribeiro, R. C. C., & Bastos, D. C.
Table 4. ANOVA of factorial design for the impact resistance (IR).
Source of variation
Degree of freedom (D.F)
Sum of squares (SQ) Means squares (MQ) F-test Significance of F Regression 6 1089.575 181.5958 30.55254 2.87E-07 Residue 15 106.987 7.132465 Total 21 1196.562
Term Coeficients Standart Error Stat t Value-P intercept -240.2708 66.8512 -3.5941 0.0027 rPP 2.7522 0.6612 4.1626 0.0008
BB 0.0000 0.0000 65535.0000 >> 0.1 CF 3.9628 0.8239 4.8099 >> 0.1 rPP-BB 0.0310 0.0096 3.2250 0.0057 rPP-CF -0.0233 0.0096 -2.4262 0.0283 BB-CF -0.0082 0.0077 -1.0690 0.3020
S = 2.67; R-sq= 91.06%; R-sq (adj) = 81.41%.
Table 5. ANOVA of factorial design for the hardness (H).
Source of variation Degree of freedom (D.F)
Sum of squares (SQ) Means squares (MQ) F-test Significance of F
Regression 6 166.8046 27.8008 4529.9980 3.45E-22 Residue 15 0.1105 0.0074 Total 21 166.9151
Term Coeficients Standart Error Stat t Value-P intercept 122.6400 2.1481 57.0917 5.82E-19 rPP -0.3940 0.0212 -18.5449 9.4E-12 BB 0.0000 0.0000 65535 >> 0.1 CF 0.6415 0.0265 24.2317 >> 0.1
rPP-BB -0.0046 0.0003 -15.0587 1.84E-10 rPP-CF -0.0112 0.0003 -36.1878 5.18E-16 BB-CF -0.0279 0.0002 -112.7570 2.2E-23 S = 0.086; R-sq= 99.93%; R-sq (adj) = 93.24%.
Table 6. ANOVA of factorial design for the density (D).
Source of variation Degree of freedom (D.F) Sum of squares (SQ) Means squares (MQ) F-test Significance of F Regression 6 0.3297 0.0549 28.3399 4.62E-07 Residue 15 0.0349 0.0023 Total 21 0.3646
Term Coeficients Standart Error Stat t Value-P intercept 5.9964 1.2075 4.9660 0.0002 rPP -0.0513 0.0119 -4.2937 0.0006 BB 0.0000 0.0000 65535.0000 >> 0.1 CF -0.0465 0.0149 -3.1228 >> 0.1 rPP-BB -0.0006 0.0002 -3.4850 0.0033 rPP-CF -0.0001 0.0002 -0.4597 0.6523 BB-CF 0.0004 0.0001 2.7947 0.0136
S = 0.048; R-sq= 90.43%; R-sq (adj) = 80.57%.
Polímeros, 32(2), e2022017, 2022
All composites showed density close to virgin PP. Density variations (0.829 to 1.096 g.cm-3) came from the differences in particle packing and particle wall roughness. There was an increase in water absorption of the reinforced composites in comparison with PP and rPP.
A slight decrease in the hardness of the hybrid composites in relation to the virgin matrix was observed due to the possible non-uniformity in the distribution of the components in the matrix. Water absorption values closest to those of PP and rPP were found in rPP/BB (90/10 wt%) and rPP/BB/CF (70/10/20 wt%). Among the ternary hybrid composites, the impact resistance of rPP/BB/CF was slightly increased in the 70/10/20 wt% composite, attributed to the equilibrium between chain scission and self-reinforcement mechanisms. Moreover, the impact resistance of rPP/BB/CF (70/10/20 wt%) was closest to that of virgin PP. SEM micrographs of the ternary composite rPP/BB/CF (70/20/10 wt%) showed higher traces of decohesion than the ternary composite 70/10/20 wt%, allowing greater water absorption and reducing impact resistance. In the composites, the interface is physical, since there were no changes in the infrared peaks. The experimental results obtained in this research were corroborated through a statistical analysis. Multiple linear regression tests were used to develop mathematical models, which allow simulating the behavior of the composition of composite on mechanical properties (impact resistent and hardness). The ANOVA tests demonstrated that the second-order regression models were the best fit. The response surface methodology reveal that the dimension stone residue content does not significantly influence the RI and H results and suggest that the increase in the variable “coconut fiber content” is responsible for improving the mechanical properties of the composite. The developed hybrid composite should be used improving fuel economy of the vehicle and reducing the related harmful emission.
• Conceptualization – Daniele Cruz Bastos; Roberto Carlos da Conceição Ribeiro.
• Data curation – Neyda de La Caridad Om Tapanes.
• Formal analysis – Neyda de La Caridad Om Tapanes.
• Investigation – Ariadne Gonçalves de Leão; Gabriella Neto Chagas; Maiccon Martins Barros.
• Methodology – Daniele Cruz Bastos; Roberto Carlos da Conceição Ribeiro.
• Project administration – Daniele Cruz Bastos; Roberto Carlos da Conceição Ribeiro.
• Resources – Ariadne Gonçalves de Leão; Gabriella Neto Chagas; Maiccon Martins Barros.
• Software – Neyda de La Caridad Om Tapanes.
• Supervision – Daniele Cruz Bastos; Roberto Carlos da Conceição Ribeiro.
• Validation – Daniele Cruz Bastos; Roberto Carlos da Conceição Ribeiro.
Chagas, G. N., Barros, M. M., Leão, A. G., Tapanes, N. L. C. O., Ribeiro, R. C. C., & Bastos, D. C.
• Visualization – Daniele Cruz Bastos; Gabriella Neto Chagas; Maiccon Martins Barros.
• Writing – original draft – Gabriella Neto Chagas; Maiccon Martins Barros.
• Writing – review & editing – Daniele Cruz Bastos; Neyda de La Caridad Om Tapanes; Roberto Carlos da Conceição Ribeiro.
The authors acknowledge to CNPq – National Council for Research and Development (Processo no. 138827/20192) and Faperj – Research Support Foundation of Rio de Janeiro (Processo E-26/010.002390/2019), for financial support for such research to take place.
1 Patrício Silva, A. L., Prata, J. C., Walker, T. R., Duarte, A. C., Ouyang, W., Barcelò, D., & Rocha-Santos, T. (2021). Increased plastic pollution due to COVID-19 pandemic: challenges and recommendations. Chemical Engineering Journal, 405, 126683 http://dx.doi.org/10.1016/j.cej.2020.126683. PMid:32834764.
2 Barros, M. M., de Oliveira, M. F. L., da Conceição Ribeiro, R. C., Bastos, D. C., & de Oliveira, M. G. (2020). Ecological bricks from dimension stone waste and polyester resin. Construction & Building Materials, 232, 117252 http://dx.doi.org/10.1016/j. conbuildmat.2019.117252
3 Kumar, R., Lakhani, R., & Tomar, P. (2018). A simple novel mix design method and properties assessment of foamed concretes with limestone slurry waste. Journal of Cleaner Production, 171, 1650 1663 http://dx.doi.org/10.1016/j. jclepro.2017.10.073
4 de Farias, J. G., Cavalcante, R. C., Canabarro, B. R., Viana, H. M., Scholz, S., & Simão, R. A. (2017). Surface lignin removal on coir fibers by plasma treatment for improved adhesion in thermoplastic starch composites. Carbohydrate Polymers, 165(1), 429 436 http://dx.doi.org/10.1016/j.carbpol.2017.02.042 PMid:28363569.
5 Chandgude, S., & Salunkhe, S. (2021). In state of art: mechanical behavior of natural fiber-based hybrid polymeric composites for application of automobile components. Polymer Composites, 42(6), 2678 2703 http://dx.doi.org/10.1002/pc.26045
6. Ganesarajan, D., Simon, L., Tamrakar, S., Kiziltas, A., Mielewski, D., Behabtu, N., & Lenges, C. (2022). Hybrid composites with engineered polysaccharides for automotive lightweight. Composites Part C: Open Access, 7, 100222. http://dx.doi.org/10.1016/j.jcomc.2021.100222
7 Patil, A., Patel, A., & Purohit, R. (2017). An overview of polymeric materials for automotive applications. Materials Today: Proceedings, 4(Suppl. 2, Pt A), 3807 3815 http:// dx.doi.org/10.1016/j.matpr.2017.02.278
8 Chagas, G. N., Barros, M. M., Leao, A. G., Ribeiro, R. C. C., & Bastos, D. C. (2021). Sustainable composite from polypropylene post-consumer and dimension stone waste. Brazilian Journal of Development, 7(3), 22298 222309 https://doi.org/10.34117/ bjdv7n3-103
9 Bakshi, P., Pappu, A., Patidar, R., Gupta, M. K., & Thakur, V. K. (2020). Transforming marble waste into high-performance, waterresistant, and thermally insulative hybrid polymer composites for environmental sustainability. Polymers, 12(8), 1781 http:// dx.doi.org/10.3390/polym12081781 PMid:32784940.
10. Ou, R., Xie, Y., Wolcott, M. P., Sui, S., & Wang, Q. (2014). Morphology, mechanical properties, and dimensional stability of wood particle/high density polyethylene composites: effect of removal of wood cell wall composition. Materials & Design, 58, 339 345. http://dx.doi.org/10.1016/j.matdes.2014.02.018.
11 Paiva, L. B., Morales, A. R., & Guimarães, T. R. (2006). Mechanical properties of polypropylene and organophilic montmorillonite nanocomposites. Polímeros: Ciência e Tecnologia, 16(2), 136 140 http://dx.doi.org/10.1590/S010414282006000200014
12 Wang, K., Addiego, F., Bahlouli, N., Ahzi, S., Rémond, Y., & Toniazzo, V. (2014). Impact response of recycled polypropylenebased composites undera wide range of temperature: effect of filler content and recycling. Composites Science and Technology, 95, 89 99 http://dx.doi.org/10.1016/j.compscitech.2014.02.014
13 Borsoi, C., Berwig, K. H., Scienza, L. C., Zoppas, B. C. D. A., Brandalise, R. N., & Zattera, A. J. (2014). Behavior in simulated soil of recycled expanded polystyrene/waste cotton composites. Materials Research, 17(1), 275 283 http://dx.doi. org/10.1590/S1516-14392013005000167
14 Coelho, K. V. S., Líbano, E. V. D. G., Ramos Filho, F. G., Santos, S. F., Pereira, P. S. C., & Bastos, D. C. (2021). Develpoment of wood plastic composite with reduced water absorption. International Journal of Development Research, 11(2), 44547 44551 http://dx.doi.org/10.37118/ijdr.21116.02.2021
15 Bakshi, P., Pappu, A., Bharti, D. K., & Patidar, R. (2021). Accelerated weathering performance of injection moulded PP and LDPE composites reinforced with calcium rich waste resources. Polymer Degradation & Stability, 192, 109694 http://dx.doi.org/10.1016/j.polymdegradstab.2021.109694
Received: Apr. 26, 2022
Revised: July 05, 2022
Accepted: July 21, 2022
Polímeros, 32(2), e2022017, 2022
Alan Kardec da Silva1
, Ezaine Cristina Corrêa Torquato1
Marcos Antonio da Silva Costa2
, Jacira Aparecida Castanharo2
Mônica Regina da Costa Marques3
and Luciana da Cunha Costa1*
1Departamento de Farmácia, Faculdade de Ciências Biológicas e da Saúde, Campus Zona Oeste, Univer sidade do Estado do Rio de Janeiro – UERJ, Rio de Janeiro, RJ, Brasil
2Departamento de Processos Químicos, Instituto de Química, Universidade do Estado do Rio de Janeiro –UERJ, Rio de Janeiro, RJ, Brasil
3Departamento de Química Orgânica, Instituto de Química, Universidade do Estado do Rio de Janeiro –UERJ, Rio de Janeiro, RJ, Brasil *luciana.cunha.costa@gmail.com
This work reports the preparation of magnetic polymeric microspheres based on poly(methyl methacrylate) and the investigation of these materials as catalysts in heterogeneous Fenton processes for the decolorization of methyl orange (MO). The microspheres were prepared by polymerization of the magnetic material together with the monomers by aqueous suspension polymerization. The microspheres had specific surface area of 48.2 m2 g-1. Mossbauer data indicated that the magnetic material was a mixture of magnetite (31%), maghemite (21%), and goethite (48%). Fenton reactions were performed by varying the concentration of H2O2, pH, composite mass, and contact time. The highest color removal rates (around 80%) were reached at pH 3.0, 20% w/v of composite, 20 minutes contact time, and 10 ppm of H2O2 The composite could be reused during four cycles with removal efficiency above 50%. The results indicated that the adsorption and oxidation mechanisms act together determining the variation of the MO dye removal.
Keywords: heterogeneous Fenton reactions, magnetic materials, methyl orange, poly(methyl methacrylate) microspheres.
How to cite: Silva, A. K., Torquato, E. C. C., Castanharo, J. A., Costa, M. A. S., Marques, M. R. C., & Costa, L. C. (2022). Evaluation of magnetic poly(methyl methacrylate) microspheres as catalysts in heterogeneous Fenton processes. Polímeros: Ciência e Tecnologia, 32(2), e2022018. https://doi.org/10.1590/0104-1428.20220029
Synthetic organic dyes, especially azo dyes, are employed in various industrial processes where byproducts are these contaminants; consequently, these dyes are released in the wastewater of these industries[1,2]. According to Tunç et al.[3], “these pollutants absorb and reflect the sunlight entering the water and hence hinder the photosynthesis in aquatic plants.” These pollutants are toxic to the environment, especially aquatic lives, and conventional treatment processes for their removal are often inefficient due to their high stability and complex nature[1-4]
The Fenton process is highlighted among several advanced oxidation processes (AOPs) due to its simple operation, low cost, low toxicity of the reactants, and ability to treat many hazardous organic contaminants. Fenton’s reagent is a mixture of H2O2 and Fe2+ or Fe3+ ions (in stoichiometric amounts), generating OH and OOH radicals, at acid pH[3]
The replacement of homogenous Fenton catalysts by heterogeneous approaches has been motived by considering the straightforward recovery, possible recycling, or reuse of these heterogeneous materials, and reduction of the amount
of Fe leached into the medium, besides the possibility of expanding the pH range of using these materials[5].
Magnetic composites have received considerable attention due to their easy separation from the medium. These composites can be used in many areas, such as catalysis, environmental remediation, and biomedical processes[6-8]
A search of a scientific research platform employing the keywords “magnetic composites and heterogeneous Fenton” showed an increase in the number of publications over the years (Figure S1 – Supplementary Material).
Several magnetic composites based on polymers have been studied as heterogeneous Fenton and Fenton-like catalysts and evaluated for dye degradation. The polymers used in the preparation of these composites can be carbon-based polymers such as carbon nanotubes[1,9], carbon nanofibers[9], graphene and graphene oxide[2,9,10] and biopolymer matrices such as alginate[11].
According to Gao et al.[12], polymeric microspheres based on poly (methyl methacrylate) (PMMA) stand out among other types of microspheres (polystyrene, poly (ethylene glycol),
poly (glycidyl methacrylate), etc), due to the properties of PMMA, such as high impact strength, light transmissivity, good processability, and biocompatibility. These microspheres can be prepared by various polymerization techniques and functionalized through different strategies. The preparation of composites from PMMA microspheres can contribute to increasing the “chemical stability, mechanical strength, catalytic performance” of these materials. The synergism between the properties of these polymers and magnetic materials can enable the preparation of materials with superior properties[8]. However, no studies reported the evaluation of these microspheres as catalysts in heterogeneous Fenton processes. Shan et al.[13] report the preparation of magnetic porous Fe3O4/poly(methyl methacrylate-co-divinylbenzene) microspheres and their use as adsorbent of Rhodamine B dye. However, the authors did not study the employment of this material as a catalyst in a Fenton process and the relationship between the reaction conditions and the efficiency of this catalyst.
Because magnetic polymeric microspheres based on PMMA have not been sufficiently studied as catalysts of heterogeneous Fenton processes, this work describes the preparation of magnetic polymeric microspheres based on PMMA and the investigation of these materials as catalysts in heterogeneous Fenton processes for the decolorization of methyl orange (MO). The influence of the experimental conditions (pH, contact time, mass of composite, H2O2 concentration) on the discoloration rate of the dye solutions was investigated. The lifetime of the catalysts was also analyzed in ten cycles of reuse. The azo dye methyl orange (MO) was chosen as the target organic pollutant due to its low cost, wide application, and stability[1,4,11,14]
The synthesis of magnetic material was performed by the co-precipitation technique. Initially, 27 g of FeCl3 and 14 g of FeSO4·7H2O were solubilized in deionized water (50 mL).
These solutions were transferred to 250 mL three-necked round-bottomed reactor flask equipped with a mechanical stirrer and maintained under stirring (150 rpm) in a nitrogen atmosphere until complete dissolution of the reactants. Then 130 mL of NH4OH (28% NH3 in H2O) was slowly added to the reactor. The solution was maintained under stirring at 70 ºC for 1 h. The result of this step was a black residue. It was washed several times with deionized water until the supernatant pH was around 7. Subsequently, under gentle stirring at a temperature of 80 ºC, 10 mL of oleic acid was added. The reaction lasted 30 minutes. The final mixture was washed with ethanol several times to remove excess oleic acid and was transferred to a desiccator. The air was evacuated and replaced by nitrogen for each use[6,7]. Inorganic reactants were acquired from Vetec Química Ltda. Oleic acid was acquired from B. Herzog Varejo de Produtos Químicos Ltda. All reactants were used as received.
Magnetic polymeric microspheres were prepared by aqueous suspension polymerization in a 1 L reactor flask
equipped with a mechanical stirrer and a reflux condenser containing a silicon oil seal at the top. The organic phase was composed of 90 wt. % of methyl methacrylate (MMA), 10 wt.% of divinylbenzene (DVB), n-heptane (100% to the volume of monomers), 2,2-azobisisobutyronitrile (AIBN) (2% wt.% to monomers), and of magnetic material (5 wt. % to monomers). This mixture was left in a thermostatic bath at 50 ºC for 30 min under stirring (150 rpm). The aqueous phase consisted of 1 wt.% of poly(vinyl alcohol) (PVA) to water volume, 1 wt.% of NaCl to water volume, and distilled water. The volumetric ratio between the aqueous and organic phases was 4:1. The aqueous phase was transferred to the reactor flask, and the stirring was set to 700 rpm. Then the organic phase was dropwise transferred to the reactor. The reaction was maintained under stirring at 80 ºC for 4 h[6]. The final product was washed extensively with heated deionized water and dried at 60 ºC. AIBN was acquired from Mig Quimica and used after recrystallization with methanol. The monomers were donated by Lanxess Ltda and Nitriflex Ltda respectively. PVA was donated by Kurary Inc. Other reactants were acquired from Vetec Química Fina. These reactants were used as received.
The magnetic microspheres were characterized by optical microscopy (Olympus BX51M), scanning electron microscopy together with energy-dispersive X-ray spectroscopy (SEMEDS) (Fei Inspect 550), vibrating sample magnetometry (VSM) (Lake Shore 7400), Mössbauer spectroscopy (Fast Comtech, Germany), particle size distribution (Malvern Mastersizer 2000), specific surface area, pore volume, and pore diameter by employing nitrogen physisorption (Micromeritics ASAP 2020 apparatus). The sample’s crystalline structure was verified by X-ray diffractometry (Shimadzu, model XRD 6000). Scans were performed between 7-70º (2θ) with a goniometer speed of 2º per minute. The JADE program was used to identify mineralogical phases present in the samples. For SEM-EDS analysis, the samples were metalized with gold, and an acceleration voltage of 15 kV and magnification of 250 x was used. Specific surface area, pore volume and pore diameter were determined by employing BET and BJH Equations. Mossbauer spectroscopy was used to identify the magnetic material according to the method described by Castanharo et al.[6,7]. The FT-IR spectra of all polymers were recorded with a Perkin-Elmer Spectrum One spectrometer, (4000-400 cm-1, 4 scans, and 4 cm-1 resolution) in the form of KBr discs. The content of iron incorporated in the particles was determined by AAS spectroscopy after digestion of the microspheres by employing HNO3:HCl 1:3 v/v according to the method previously published[6]
Decomposition tests of methyl orange were conducted using a batch system in Erlenmeyer flasks (250 mL) on stirring plates under slow agitation. The tests were performed by varying the mass of magnetic microspheres (1-20% w/v), the concentration of H2O2 (0.1-50 ppm), pH of the medium, adjusted with acetic acid/acetate buffer 0.5 mol L-1 (3.0-7.5), and contact time between the solution and microspheres (0 – 30 min). The final volume of the medium was maintained
Polímeros, 32(2), e2022018,
Silva, A. K., Torquato, E. C. C., Castanharo, J. A., Costa, M. A. S., Marques, M. R. C., & Costa, L. C.100 mL, while the dye concentration was 5 ppm, and the reaction temperature was 25 ºC. Considering the possibility of dye adsorption by the composite, we also performed tests in the absence of H2O2, employing composite concentrations of 5, 10, or 20% w.t% (in relation to the total volume of the medium), pH 3.0, and 10 minutes of contact between the microspheres and dye solution. Aliquots of 5 mL of the supernatant collected after the reaction were transferred to a quartz cuvette and read at 500 nm. All experiments were conducted in duplicate, and the results are presented as average. Efficiency in removing MO was calculated by using Equation 1[15]
The studies of reuse of the microspheres as catalysts were conducted in ten batch cycles employing 5% w/v of catalyst, 5 ppm of H2O2, 5 ppm of dye, pH 3.0, and a final medium volume of 10 mL. After each reuse cycle, the microspheres were separated from the reaction medium by filtration, rinsed with distilled water, and placed in another Erlenmeyer for a new experiment. After each cycle, the dye decomposition was evaluated by collecting 5 mL samples of the supernatant and analyzing them at 500 nm with a spectrophotometer (Shimadzu, model UV-VIS – 1240).
R (%) is removal efficiency (%), C0 is initial MO concentration (mg/L), and Ct is MO concentration at time t (mg/L).
Magnetic polymeric particles were prepared by polymerizing magnetic material with the monomers MMA and DVB by aqueous suspension polymerization. SEM images shows showed these particles’ spherical shapes (Figure 1a). Malvern data showed that these particles had large size distribution (Table 1). EDS spectra indicated the presence of Au metal (used in the coating of particles for
Figure 1. (a) EDS spectrum and iron distribution map of the magnetic material, SEM image of magnetic microsphere; (b) FT-IR spectrum of the magnetic microspheres; (c) XRD spectra of the magnetic material and magnetic microspheres; (d) Transmission Mossbauer spectra of the magnetic microspheres.
Table
nitrogen
pore
(determined by nitrogen physisorption,
(determined by Malvern Mastersizer), MS: saturation magnetization (determined by employing vibrating sample magnetometry),
employing the BJH
R.: remaining magnetization (determined by employing vibrating sample magnetometry),
in the
(determined by AAS after acid digestion of the
SEM analysis); besides Fe, confirming the incorporation of the magnetic material on microspheres, along with carbon and oxygen, due to polymeric matrix composed of DVB and MMA (Figure 1a). The Fe distribution map of magnetic material (obtained through the EDS accessory) (Figure 1a) showed small yellow dots (Fe domains) distributed over the entire surface of the polymeric microspheres, along with yellow clusters, indicating that magnetic material was heterogeneously incorporated in the polymeric matrix. FT-IR spectrum of magnetic microspheres (Figure 1b) showed bands at 1724 cm-1 due to stretching of the C=O bond of the ester group, 1605 cm-1 due to C=C stretching of the aromatic ring, 1461 cm-1, and 1388 cm-1 due to asymmetric and symmetric stretching of the O-CH3 bond of the ester group, 1261 cm 1, and 1107 cm-1 related to coupled asymmetric stretching C(=O)-O and O-C-C, besides a band at 3438 cm-1 due to hydrogen bonding between carbonyl and oxygen of the (moist) MMA ester and water[16]
Peaks related to iron oxides were identified in the positions 22.9º, 38.0º, 45º, 54.9º, and 68.7º (2θ plane), 472º, 270º, 333º, 175º, and 90º (crystalline plane), in the diffractograms produced by XRD analysis of magnetic material and magnetic microspheres (Figure 1c). It was also possible to observe peaks due to goethite at 28º and 41º. XRD spectra of the magnetic material and magnetic microspheres showed the same peaks related to iron oxides, indicating that the structure of the magnetic material was preserved during polymerization[6,7]. However, it was also possible to observe the presence of an amorphous halo in the diffractogram of the magnetic microspheres, related to the polymeric matrix of this material. Magnetic microspheres presented saturation magnetization (MS) of 4.76 emu g-1 and remnant magnetization (MR) of 0.21 emu g-1, indicating a good response to the magnetic field and superparamagnetic behavior (Table 1). The magnetization curve did not have a hysteresis loop (Figure 1c), confirming this superparamagnetic behavior.
Mössbauer spectra of these magnetic polymers (Figure 1d) showed a contribution from a doublet, indicating the presence of superparamagnetic particles, and an asymmetric sextet, added to the pure magnetic material, but with a slight loss of intensity of the magnetic transmission. This result also indicates that the polymerization did not change the properties of the magnetic particles. However, the polymerization may cause a change in the inter-particle interaction parameters, making qualitative interpretation and theoretical calculation of these polymer composites’ spectra difficult[17]. The interparticle interactions were mainly: (i) dipole-dipole interaction and (ii) exchange interaction through the surface of the particles. In the case of magnetic polymers, the second interaction can be neglected because the dipolar interaction dominates the interparticle interaction[18]. This interparticle interaction can explain the difference between magnetic transmission on pure magnetic material and magnetic polymers. Mössbauer results also indicated that the magnetic material is a mixture of magnetite (Fe3O4, 31%) and maghemite (γ-Fe2O3, 21%), minerals with magnetic behavior, agreeing with the data on MS and MR, and goethite (α-FeOOH, 48%). Part of the magnetite was converted into maghemite by partial oxidation of Fe2+ to Fe3+ and magnetic particles containing a low concentration of Fe2+ ions.
The microspheres had large specific surface area and pore volume, even though containing magnetic material in their structure (Table 1). The content of iron incorporated in the polymer (determined by AAS before acid digestion of the particles) was 4.76 wt.%, indicating a high degree of incorporation of magnetic material during synthesis of the composite.
Magnetite has O2 ions coordinated with Fe2+ and Fe3+ ions in octahedral interstices and Fe3+ in tetrahedral interstices. Considering that Fe3+ ions are present in both interstices, these ions do not have a resulting magnetic moment, and the saturation magnetization is provoked by Fe2+ ions at octahedral interfaces (Figure 1c). The presence of Fe2+ ions in the spinel of octahedral sites makes these oxides promising catalysts of the Fenton process. Maghemite has a structure like a magnetite but only contains Fe3+. Goethite has an orthorhombic structure, with Fe3+ ions coordinated with O2- and OH ions[19,20]. This magnetic material can act in two ways in Fenton catalysis: (i) Fe2+ ions in magnetite domains can act directly on the decomposition of H2O2; or (ii) Fe3+ ions in maghemite and goethite domains can coordinate with H2O2 molecules, generating [Fe(III)OOH]2+ ions, which undergo decomposition, generating OH and OOH radicals (Figure 2)[8,21].
Thus, considering that the Fe2+ and Fe3+ ions present in magnetic material can act as catalysts of Fenton reactions, we conducted studies of MO degradation in the presence of magnetic microspheres by varying the pH of the medium, the mass of this composite, and concentration of H2O2.
The following reaction conditions were employed to study the effect of H2O2 concentration on MO degradation: 5 ppm dye, 1% composite, 10 minutes of contact, pH 3, and varying concentrations of hydrogen peroxide (1.0, 5.0, 20, and 50 ppm). The first results are shown in Figure 3a. We expected the increase in H2O2 concentration to be associated with a higher content of reactive radicals, consequently increasing the dye degradation rate. The color removal rate varied little with alteration of the H2O2 concentration, indicating that the reaction equilibrium was achieved. To confirm this observation, a second experiment was carried out using peroxide concentrations of 10 and 20 ppm, 5% composite, and varying the contact time between the composite and solution. The data are shown in Figure 3b. Similar removal rates were found employing 10 ppm or 20 ppm of H2O2 in the reaction time range of 0 to 30 minutes. The increase of H2O2 resulted from scavenging excess hydroxyl radicals, generating water and other byproducts with lower oxidation potential (•HO2 and •-O2), which did not contribute to reducing the dye removal[1,11]. Quadrado et al.[11] studied the influence of peroxide concentration on the action of the heterogeneous Fenton process for the decomposition of OM dye. When the peroxide concentration was increased from 5 mmol L-1 to 20 mmol L-1, the dye removal speed was slower, i.e., in 20 minutes, the removal rate reached 90% with 5 mmol L-1 H2O2 and only 40% with 20 mmol L-1 H2O2 in the same period. According to these authors, at high concentrations of H2O2, the generation of radicals (• OH) is not selective, and the H2O2 molecules can be
Polímeros, 32(2), e2022018,
Silva, A. K., Torquato, E. C. C., Castanharo, J. A., Costa, M. A. S., Marques, M. R. C., & Costa, L. C.Figure 3. (a) Effect of H2O2 content on degradation of MO (a: H2O2 content: 1-50 ppm, pH: 3, MO: 5 ppm, composite: 1%, time: 10 minutes), (b: H2O2 content: 10 or 20 ppm, pH: 3, MO: 5 ppm, composite: 5%, time: 1-30 minutes).
decomposed into water and oxygen. In addition, the radical (• OH) generated can be consumed by the H2O2 itself, resulting in hydroperoxyl radicals (• OOH). These radicals (• OOH) have less oxidizing power and can also eliminate radicals (• OH), decreasing the dye removal efficiency. Shi et al.[22] reported similar observations. They studied the influence of H2O2 concentration in a heterogeneous Fenton process for dye decomposition. Their results showed that the dye removal rate increased with the increase of H2O2 concentration, limited to an optimal concentration value, from which there was an excess of H2O2 and consequently decreased formation of radicals (•OH).
Dye removal was investigated by employing a pH range between 3 and 7 and keeping constant all other parameters: 5 ppm of MO, 5 ppm of H2O2, 5% composite, and 10 minutes of reaction (Figure 4a). The highest color removal (63%) was achieved at pH 3.0, and there was a decrease in dye decomposition with rising pH (above pH 5.0, the dye removal rate was only 30%).
The increasing dye discoloration at lower pH suggests that Fe2+ and Fe3+ ions are released in the medium from the composite, i.e., magnetic microspheres may act as
“demand-release homogeneous Fenton catalysts”. Chu and colleagues[23] observed dependence between the removal rate of dyes in a Fenton process catalyzed by magnetic biochar and the pH level, which was related to the reaction conditions. According to these authors, the increase of the dye removal with decreasing pH can be explained by the decreasing iron solubility and oxidation potential of peroxide radicals, in contrast to the self-decomposition of H2O2 to H2O and O2 at higher pH. On the other hand, Vu and colleagues[24] reported that at pH lower than 2.5, the efficiency of the Fenton reaction decreases significantly due to the formation of H3O2+ ions and complexes such as [Fe(H2O)6]2+ and Fe(H2O)6]3+, along with the “scavenging effect” of hydroxyl radicals by excessive content of H+ ions (OH + H+ + e → H2O).
The evaluation of the supernatant containing the reagents H2O2, dye, and 5 or 20% of composite by Inductively Coupled Plasma Optical Emission Spectrometry (ICP-OES) (Thermo-Scientific, Model ICAP 6300 DUO) revealed concentrations of 0.23±0.01 and 0.33±0.01 mg L-1 of Fe metal in this medium. Considering that the content of Fe metal introduced during the polymerization was 83 mg g-1 of polymer, we can affirm that the magnetic microspheres did not act as “demand-release homogeneous Fenton catalysts”.
Figure 4. (a) Effect of pH on MO degradation. Experimental conditions: pH 3-7.3, 5 ppm of MO, 5 ppm of H2O2, 5% of composite, and 10 minutes of reaction; (b) Effect of catalyst on the degradation of MO in the function of time. Experimental conditions: pH 3, 5 ppm of MO, 20 ppm of H2O2, 5% of composite, contact time range from 0-30 minutes.
It is also possible to suppose that some of the dye molecules were adsorbed by magnetic microspheres, and this adsorption was more favorable in acid media. The acid dissociation constant (pKa) for methyl orange is 3.46. Thus, at pH 3 the dye molecules are in neutral form, while above this pH, these molecules are in salt form, presenting SO3 Na+ groups[1]. Probably the adsorption of these molecules was favored in their neutral form due to the formation of hydrogen bonds involving the SO3H groups (not dissociated) of the dye and iron oxide domains of the magnetic material.
Here we used 10 ppm of hydrogen peroxide, 5 ppm of MO, different composite contents (1%, 5% and 10% (w/v)) and contact times (1, 2, 3, 4, 5, 10 and 15 minutes). The data shown in Figure 4b indicate that increasing composite mass resulted in rinsing dye removal efficiency. The highest removal rate (close to 90%) was achieved using 10% w/v of the composite material. This can be explained considering that the increase of composite contributed to increasing the concentration of Fe2+ and Fe3+ ions (consequently favoring the Fenton process) and increasing the absorbance of this dye from the medium. Arshadi and colleagues[1] reported that a large excess of catalyst could have two consequences: self-scavenging of OH radicals by ferrous ions, resulting in a reduction of dye decomposition; or aggregation of the particles due to increased collision between them, resulting in lower total surface area and greater diffusion path length, in turn reducing the adsorption capacity.
The dye removal was most significant in the first minute of the reaction, achieving a reduction of more than 80% by using 10% composite because equilibrium was reached after one minute. This result also can indicate that MO degradation is related not only to the generation of reactive radicals involving Fe2+ and Fe3+ ions present in the magnetic material, but also to release of these ions from the composite. It is possible to suppose that some of the dye molecules are adsorbed by magnetic polymeric particles. In the first stage of adsorption, many active sites are available to dye molecules, so the reduction of available sites combined with repulsion between these dye molecules surrounding the particles and the molecules on the surface of the particles
might have resulted in more negligible adsorption after the first minute of contact[25]
For these experiments, 10 mL of MO solution (5 ppm) was put in contact with the different concentrations of composite (5%, 10% or 20% (w/v)) for 10 minutes. After this period, the absorbance in each flask was analyzed. Then, 10 ppm of H2O2 was added to each flask, and after 10 minutes of contact, the absorbance was reread. The results obtained are shown in Figure 5
According to Figure 5, there was a significant increase in the dye removal rate with more extended contact of the dye with the composite, in the absence of H2O2. The variation in composite mass was accompanied by increasing color removal. It can be inferred that the composite had high MO adsorption capacity and that this characteristic strongly influenced the color removal rate in all stages of this study. After the addition of H2O2 in the medium, there was a further increase in the removal rate. The “total color removals,” as identified in the legend of Figure 5, were 55%, 66%, and 56% for composite concentrations of 5%, 10%, and 20%, respectively. Based on these results, it is possible to suppose that the total removal data represent the sum of the adsorption effect and the color removal due to oxidation of the MO by the Fe2+ and Fe3+ ions present in the magnetic material of the polymer matrix. In other words, the analysis of these data allows us to assume that the adsorption and oxidation mechanisms act together for the variation of MO removal in a heterogeneous Fenton process with the composite as a catalyst. The dye removal rate obtained via the oxidative process accompanied the dye removal by adsorption when employing 5 and 10% particles. Still, when 15% composite was used, the removal rate due to the Fenton reaction was lower than the removal due to adsorption, probably because of self-scavenging of OH radicals by ferrous ions, resulting in a reduction of dye decomposition.
Xu et al. (2018)[10] studied the degradation of MO by applying a heterogeneous Fenton process using magnetite and a composite of reduced graphene oxide as catalysts for dye decomposition. The results showed that the composite used had high dye adsorption capacity, reaching 57% removal (by adsorption) after 30 minutes of contact. A synergistic effect
Polímeros, 32(2), e2022018,
Silva, A. K., Torquato, E. C. C., Castanharo, J. A., Costa, M. A. S., Marques, M. R. C., & Costa, L. C.Figure 5. Color removal of MO due to adsorption and oxidation by Fenton processes. Experimental conditions: pH 3, 5 ppm of MO, 20 ppm of H2O2, 5%-20% wt.% of composite, contact time range from 0-20 minutes.
with slight variation until the third cycle. Quadrado and Fajardo[11] evaluated the reuse of the catalyst in the Fenton process for the decomposition of dyes. They observed that the catalyst-maintained color removal efficiency above 98% during five reuse cycles.
Figure 6. Study of reuse of composite particles for MO removal. Experimental conditions: pH 3, 5 ppm of MO, 10 ppm of H2O2, 5% of composite, contact time of 5 minutes.
was observed in the Fenton-type reaction and adsorption governing the degradation of the dye in the studied system. Because of this synergistic effect, the removal achieved was 94%.
To evaluate the possibility of reusing the composite for degradation of MO, decomposition tests were carried out by using 5% (w/v) of composite, 10 ppm of H2O2, 5 ppm of dye, pH 3.0, and 5 minutes of contact until there was no significant variation in the absorbance readings. This study determined the decomposition after each cycle by analyzing the absorbance at 500 nm. The efficiency of the composite was evaluated in a sequence of 11 reuse cycles (Figure 6). As shown in Figure 6, the initial removal rate was 63%. During the catalyst reuse cycles, there was a gradual decline in this value until the fifth cycle, from 63% to 10%, clearly indicating a loss of functionality of the composite as a catalyst and its adsorption capacity. From the fifth reuse cycle onward, the removal rate was close to 10%, and no significant variations were observed until the 11th cycle, indicating that the maximum number of economically feasible cycles is four. The reuse of catalysts has been investigated by several researchers[10,11,23,26]. Shao and Chen[26] studied the reuse of the catalyst and obtained high removal rates
In the present study, magnetic PMMA microspheres prepared by aqueous suspension polymerization were evaluated as catalysts for the decomposition of MO through a heterogeneous Fenton process. These microspheres showed a larger size distribution of the particles (20-104 µm), specific surface area of 48 m2 g-1, and pore volume of 0.35 m2 g-1 Data from XRD showed the presence of iron oxides in this material and that the magnetic material was preserved during polymerization. These data along with data of FT-IR showed that both monomers (MMA and crosslinking agent DVB) were also included in microspheres. Mossbauer data showed that these microspheres contained a mixture of minerals with magnetic behavior (31% magnetite and 21% maghemite). The observation of saturation magnetization and remaining magnetization of 4.76 and 0.21, respectively, showed that this material had superparamagnetic behavior. There was no significant variation in the color removal rate with variation in the concentration of H2O2 (1-50 ppm), around 30% by employing 1% of composite and around 60% by employing 5% composite. Still, color removal increased with a higher composite mass and was most pronounced in the first minute of contact between MO and composite, around 80% by employing 10% microspheres. The need for pH control in this system proved to be a very restrictive condition since the rates of color removal were much lower with pH above 3. The adsorption studies of the dye by the composite, carried out in the absence of H2O2, confirmed the adsorption of the MO dye by this material. This characteristic strongly influenced the color removal rate at all stages of this study. The reuse of the composite was evaluated for color removal in 11 reuse cycles, and the results indicated that from the first to the fifth reuse cycle, the color removal rate declined to about 50%.
Silva, A. K., Torquato, E. C. C., Castanharo, J. A., Costa, M. A. S., Marques, M. R. C., & Costa, L. C.
The results also indicated that the adsorption and oxidation mechanisms vary the MO dye removal rate in this heterogeneous Fenton process, with the composite as a catalyst. The results in this work suggest that the composite acts both in the dye adsorption and in the decomposition of H2O2. We achieved a maximum color removal rate of 90% using 10% (w/v) of composite, 10 ppm of peroxide, pH 3.0, 5 ppm of dye, and a contact time of 10 minutes. The composite can be applied to aid in treating effluents contaminated with dyes. However, further studies are necessary to overcome the restriction related to the pH of this material and to extend useful life.
• Conceptualization – Luciana da Cunha Costa; Mônica Regina da Costa Marques.
• Data curation – NA.
• Formal analysis – NA.
• Funding acquisition – Luciana da Cunha Costa; Mônica Regina da Costa Marques.
• Investigation – Alan Kardec Silva; Jacira Aparecida Castanharo.
• Methodology – Alan Kardec Silva; Jacira Aparecida Castanharo.
• Project administration – NA.
• Resources – NA.
• Software – NA.
• Supervision – Luciana da Cunha Costa; Mônica Regina da Costa Marques.
• Validation – NA.
• Visualization – NA.
• Writing – original draft – Alan Kardec Silva; Ezaine Cristina Corrêa Torquato.
• Writing – review & editing – Luciana da Cunha Costa; Jacira Aparecida Castanharo; Marcos Antonio da Silva Costa; Mônica Regina da Costa Marques.
We thank the Rio de Janeiro State Research Foundation (FAPERJ) for financial support.
1. Arshadi, M., Abdolmaleki, M. K., Mousavinia, F., KhalafiNezhad, A., Firouzabadi, H., & Gil, A. (2016). Degradation of methyl orange by heterogeneous Fenton-like oxidation on a nano-organometallic compound in the presence of multi-walled carbon nanotubes. Chemical Engineering Research & Design, 112, 113 121 http://dx.doi.org/10.1016/j.cherd.2016.05.028
2 Alansi, A. M., Al-Qunaibit, M., Alade, I. O., Qahtan, T. F., & Saleh, T. A. (2018). Visible–light responsive BiOBr nanoparticles loaded on reduced graphene oxide for the photocatalytic
degradation of dye. Journal of Molecular Liquids, 253, 297 304 http://dx.doi.org/10.1016/j.molliq.2018.01.034
3 Tunç , S. , Gürkan , T. , & Duman , O. ( 2012 ). On-line spectrophotometric method for the determination of optimum operation parameters on the decolorization of Acid Red 66 and Direct Blue 71 from aqueous solution by Fenton process. Chemical Engineering Journal, 181-182, 431 442 http://dx.doi. org/10.1016/j.cej.2011.11.109
4. Liu, Y., Zhang, G., Chong, S., Zhang, N., Chang, H., Huang, T., & Fang, S. (2017). NiFe(C2O4)x as a heterogeneous Fenton catalyst for the removal of methyl orange. Journal of Environmental Management, 192, 150 155. http://dx.doi. org/10.1016/j.jenvman.2017.01.064 PMid:28160642.
5 Ferroudj, N., Beaunier, P., Davidson, A., & Abramson, S. (2021). Fe3+ -doped ordered mesoporous γ-Fe2O3/SiO2 microspheres as a highly efficient magnetically separable heterogeneous Fenton catalyst. Microporous and Mesoporous Materials, 326, 111373 http://dx.doi.org/10.1016/j.micromeso.2021.111373
6 Castanharo, J. A., Ferreira, I. L. M., Costa, M. A. S., Silva, M. R., Costa, G. M., & Oliveira, M. G. (2015). Magnetic microspheres based on poly(divinylbenzene-co-methyl methacrylate) obtained by suspension polymerization. Polímeros: Ciência e Tecnologia, 25(2), 192 199 http://dx.doi.org/10.1590/0104-1428.1666
7 Castanharo, J. A., Ferreira, I. L. M., Silva, M. R., & Costa, M. A. S. (2018). Core-shell magnetic particles obtained by seeded suspension polymerization of acrylic monomers. Polímeros: Ciência e Tecnologia, 28(5), 460 467 http://dx.doi. org/10.1590/0104-1428.10517
8. Jaiswal, K. K., Manikandan, D., Murugan, R., & Ramaswamy, A. P. (2018). Microwave-assisted rapid synthesis of Fe3O4/ Poly(styrene-divinylbenzene-acrylic acid) polymeric magnetic composites and investigation of their structural and magnetic properties. European Polymer Journal, 98, 177 190. http:// dx.doi.org/10.1016/j.eurpolymj.2017.11.005.
9 Abdullah, N., Tajuddin, M. H., & Yusof, N. (2018). Carbonbased polymer nanocomposites for dye and pigment removal. In A. F. Ismail & P. S. Goh (Eds.), Carbon-based polymer nanocomposites for environmental and energy applications (pp. 305 329). India: Elsevier http://dx.doi.org/10.1016/ B978-0-12-813574-7.00013-7
10 Xu, H., Li, B., Shi, T., Wang, Y., & Komarneni, S. (2018). Nanoparticles of magnetite anchored onto few-layer graphene: a highly efficient Fenton-like nanocomposite catalyst. Journal of Colloid and Interface Science, 532, 161 170 http://dx.doi. org/10.1016/j.jcis.2018.07.128 PMid:30081262.
11 Quadrado, R. F. N., & Fajardo, A. R. (2017). Fast decolorization of azo methyl orange via heterogeneous Fenton and Fentonlike reactions using alginate-Fe2+/Fe3+ films as catalysts. Carbohydrate Polymers, 177, 443 450 http://dx.doi.org/10.1016/j. carbpol.2017.08.083 PMid:28962790.
12. Gao, Y., Zhang, J., Liang, J., Yuan, D., & Zhao, W. (2022). Research progress of poly(methyl methacrylate) microspheres: preparation, functionalization and application. European Polymer Journal, 175, 111379. http://dx.doi.org/10.1016/j. eurpolymj.2022.111379.
13 Shan, J., Wang, L., Yu, H.-J., Tai, Y. & Akram, M. (2015). Synthesis and characterization of magnetic porous Fe3O4/ poly(methylmethacrylate-co-divinylbenzene) microspheres and their use in removal of Rhodamine B. Journal of Zhejiang University. Science A, 16(8), 669 679 http://dx.doi.org/10.1631/ jzus.A1500096
14 Panda, N., Sahoo, H., & Mohapatra, S. (2011). Decolorization of methyl orange using Fenton-like mesoporous Fe2O3–SiO2 composite. Journal of Hazardous Materials, 185(1), 359 365 http://dx.doi.org/10.1016/j.jhazmat.2010.09.042 PMid:20934248.
Polímeros, 32(2), e2022018,
15 Chen, Z., Jin, X., Chen, Z., Megharaj, M., & Naidu, R. (2011). Removal of methyl orange from aqueous solution using bentonite-supported nanoscale zero-valent iron. Journal of Colloid and Interface Science, 363(2), 601 607 http://dx.doi. org/10.1016/j.jcis.2011.07.057. PMid:21864843.
16 Silvertein, R. M., Webster, F. X., & Kiemle, D. J. (2005). Spectrometric identification of organic compounds. New York: Jonhn Wiley & Sons
17 Polikarpov, M., Cherepanov, V., Chuev, M., Shishkov, S., & Yakimov, S. (2010). Mössbauer spectra of hematite and magnetite nanoparticles in polymer composites. Journal of Physics: Conference Series, 217, 012114 http://dx.doi. org/10.1088/1742-6596/217/1/012114.
18 Thakur, M., De, K., Giri, S., Si, S., Kotal, A., & Mandal, T. K. (2006). Interparticle interaction and size effect in polymer coated magnetite nanoparticles. Journal of Physics Condensed Matter, 18(39), 9093 9104 http://dx.doi.org/10.1088/09538984/18/39/035
19 Oliveira, L. C. A., Fabris, J. D., & Pereira, M. C. (2013). Iron oxides and their applications in catalytic processes: a review. Quimica Nova, 36(1), 123 130. http://dx.doi.org/10.1590/ S0100-40422013000100022
20 Freitas, N. S., Alzamora, M., Sanchez, D. R., Licea, Y. E., Senra, J. D., & Carvalho, N. M. F. (2021). Green palladium nanoparticles prepared with glycerol and supported on maghemite for dye removal application. Journal of Environmental Chemical Engineering, 9 (1), 104856 http://dx.doi.org/10.1016/j. jece.2020.104856
21 Wan, D., Li, W., Wang, G., Lu, L., & Wei, X. (2017). Degradation of p-Nitrophenol using magnetic Fe0/Fe3O4/Coke composite as a heterogeneous Fenton-like catalyst. The Science of the
Total Environment, 574, 1326 1334 http://dx.doi.org/10.1016/j. scitotenv.2016.08.042 PMid:27519319.
22 Shi, X., Tian, A., You, J., Yang, H., Wang, Y., & Xue, X. (2018). Degradation of organic dyes by a new heterogeneous Fenton reagent - Fe2GeS4 nanoparticle. Journal of Hazardous Materials, 353, 182 189 http://dx.doi.org/10.1016/j.jhazmat.2018.04.018 PMid:29674093.
23 Chu, J., Kang, J., Park, S., & Lee, C. (2020). Application of magnetic biocharderived from food waste in heterogeneous sono-Fenton-like process for removal of organic dyes from aqueous solution. Journal of Water Process Engineering, 37, 101455 http://dx.doi.org/10.1016/j.jwpe.2020.101455
24 Vu, A.-T., Xuan, T. N., & Lee, C.-H. (2019). Preparation of mesoporous Fe2O3·SiO2 composite from rice husk as an efficient heterogeneous Fenton-like catalyst for degradation of organic dyes. Journal of Water Process Engineering, 28, 169 180. http://dx.doi.org/10.1016/j.jwpe.2019.01.019.
25. Wołowicz, A., & Hubicki, Z. (2010). Effect of matrix and structure types of ion exchangers on palladium(II) sorption from acidic medium. Chemical Engineering Journal, 160(2), 660 670. http://dx.doi.org/10.1016/j.cej.2010.04.009.
26 Shao, Y., & Chen, H. (2018). Heterogeneous Fenton oxidation of phenol in fixed-bed reactor using Fe nanoparticles embedded within ordered mesoporous carbons. Chemical Engineering Research & Design, 132, 57 68 http://dx.doi.org/10.1016/j. cherd.2017.12.039
Received: Apr. 13, 2022
Revised: July 19, 2022
Accepted: July 22, 2022
32(2),
Silva, A. K., Torquato, E. C. C., Castanharo, J. A., Costa, M. A. S., Marques, M. R. C., & Costa, L. C.
Supplementary material accompanies this paper.
Figure S1: Publications on heterogeneous Fenton and magnetic composites over the years. (Database ScienceDirect, accessed in July 2022, keywords: heterogeneous Fenton and magnetic composites)
This material is available as part of the online article from https://doi.org/10.1590/0104-1428.20220029
Polímeros, 32(2), e2022018, 2022
1Departamento de Engenharia de Materiais, Universidade Estadual de Ponta Grossa – UEPG, Ponta Grossa, PR, Brasil
2Departamento de Engenharia de Materiais, Centro Federal de Educação Tecnológica de Minas Gerais, Belo Horizonte, MG, Brasil *benjamim@uepg.br
The structure and properties of semi-crystalline polymers can be drastically tailored by extensional flows. In this work, polypropylene (PP), Polyvinylidene fluoride (PVDF) and Low Density Polyethylene (LDPE) were melt extruded through a sequence of rings designed to apply controlled extensional flows in the polymer melts. The effects of extensional flow on the structure and properties of the extruded filaments were then evaluated by mechanical tensile tests, dynamicmechanical analysis (DMA) and Differential Scanning Calorimetry (DSC). The DMA and tensile tests revealed a significant increase in terms of static and dynamic moduli for the polymers extruded through the extensional flow device. PP, PVDF and LDPE had their dynamic moduli enhanced 19%, 40% and 77%, respectively. These results were ascribed to the enhancement in crystallinity and orientation degree of the polymer chains induced by the extensional flow. The crystallinity was increased around 9% for PP, PVDF and LDPE extruded under extensional conditions.
Keywords: extensional flow, extrusion, semi-crystalline polymers, crystallinity increase.
How to cite: Goes, M. A., Santos, J. P. F., & Carvalho, B. M. (2022). Impact of controlled extensional flow during extrusion of PP, PVDF and LDPE. Polímeros: Ciência e Tecnologia, 32(2), e2022019. https://doi.org/10.1590/01041428.20210085
The extensional flow is a type of pressure flow in which the speed of material undergoes increases or decreases in the flow direction. This type of flow occurs in many thermoplastics processing methods, such as extrusion, film blowing and fiber spinning[1]. Although it is relatively common in the polymer industry, the study of effects of extensional flow on properties of polymer materials is not so trivial. Several studies have been dedicated to evaluating the effects of dispersion enhancement provided by extensional flow when applied to nanocomposite processing through the construction of laboratory-scale devices[2-5]. A more recent approach in this field seeks to evaluate components to enhance the extensional flow in twin-extrusion processing, which provides gains in dispersive power in the production of immiscible blends[6,7], for example. In a previous work of our group[8] an extensional flow device was employed during single-screw extrusion to enhance the degree of dispersion of montmorillonite nanoclay (MMT) and multiwalled carbon nanotubes (MWCNT) through the melted PVDF. The improvement in terms of dispersive mixing was demonstrated by reductions in mean cluster sizes of 44% and 55%, respectively, for the MWCNT and MMT. However, the effect of extensional flow on the structure and properties of the polymer matrix was not studied.
It is known that over 50% of industrially applied polymers in the world are semi-crystalline. Among these, polyolefins are the most representative class, with Polypropylene (PP) and Polyethylene (PE) standing out[9]. PP is a thermoplastic polymer that has characteristics such as low density, low cost, chemical resistance and can be processed by several methods[10,11]. LDPE is a semi-semi-crystalline polymer that has an opaque appearance, tensile strength, rigidity and chemical resistance, flexibility even at a low temperatures[12] Poly (vinylidene fluoride) (PVDF) is a semi-crystalline polymer that presents piezoelectric properties that make it attractive for applications such as energy conversion applications involving microelectric-mechanical devices, electromechanical actuators and energy harvesters[13,14]
Due to the commercial importance of semi-crystalline polymers, over the decades studies have been dedicated to understanding their kinetics and the influence on other properties and much progress has been made since the works of the pioneers Boon et al.[15,16] and Agar et al.[17]. Processing conditions like pressure[18,19], cooling rate[20,21], and flow conditions[22,23] may cause impacts on the crystallinity of the polymeric material and can cause changes in the kinetics, final microstructure or crystallinity content. The application of fluxes during or after the crystallization of the melt polymer can result in molecular orientation, that is, alignment
Marcel Andrey de Goes1 , João Paulo Ferreira Santos2 and Benjamim de Melo Carvalho1*
of chains which in turn brings significant changes in the crystallization process[24]. This phenomenon is known as “Flow-Induced Crystallization” (FIC) and can significantly reduce the induction time for crystallization[25], increase the number of nucleation points for crystals to originate and also provide gains in terms of mechanical properties[1]
The crystallinity can be increased by the use of extensional flows that can be applied during crystallization of the polymer melt and produce molecular orientation, which can dramatically affect the crystallization process. In the work’s of Chellamuthu et al.[24] and Bischoff White et al.[26], an extensional filament stretching rheometer was used with a custom-built oven to investigate the effect of uniaxial flow on the crystallization of isotactic poly-1-butene and isotactic polypropylene, respectively. The authors demonstrated that it is possible to increase crystallinity up to 25% with the controlled use of stretching rates during crystallization. In the work of Chellamuthu et al.[24], this increase in crystallinity was associated with the increasing orientation and alignment of the polymer chains in extensional flows, which enhances the thread-like precursors responsible for the formation of the crystals in the shish-kebab morphology. However, shishkebab morphology is not always formed in crystallization by introducing an extensional rate, as pointed out in the study of Bischoff White et al.[26].
Processing methods for thermoplastics typically involves the application of heat and stress, thus inducing the plastic to assume the desired shape[25]. The flow type used during the processing can significantly change the final properties of the products[27,28]. In this context, in the current work, we studied the impact of increase the extensional flow during the extrusion process on the thermal and mechanical properties of semi-crystalline polymers. Although the effects are known, their quantification is not something so easily found in the literature. Three polymers were selected for this work: Polypropylene (PP), Polyvinylidene fluoride (PVDF) and Low Density Polyethylene (LDPE), three of
the most common semi-crystalline thermoplastics employed in the current industry.
Polypropylene (PP), H301, was acquired from Braskem. According to the manufacturer, the density and melt flow index (MFI) were 0.905 g/cm3 and 10 g/10 min (at 230 ºC/2.16 kgf), respectively. The PVDF, Kynar 1000HD, was purchased from Arkema Inc, density and melt flow index (MFI) were 1.78 g/cm3 and 1.1 g/10 min (at 230 ºC/5.0 kgf), respectively. Low Density Polyethylene (LDPE) also acquired from Braskem, SPB681, presents a density of 0.922 g/cm3 and MFI of 3.8 g/10 min (at 190 ºC/2.16 kgf).
Sample preparation was carried out in a single screw mini-extruder (Filmaq3d STD) with a die of 4 mm in diameter for filament production. For processing with the aid of the extensional flow, a device was used in place of the die, which consists of a series of 7 rings alternating their internal diameters between 2 and 4 mm. The die acted as “eighth ring”, with a diameter equal to 4 mm, a schematic of this device is shown in Figure 1. The use of the total number of 8 rings is based on the work of Jamali et al.[29] , where it was proven that this number of rings is sufficient to promote the most significant effects of the application of extensional flow in the processing of nanocomposites. The extruded filaments were collected using a filament winder that has a water-cooling system. To determine the extensional deformation rate (έ) provided with the use of the extensional flow device, we used Equation 1 presented in the work of Feigl et al.[30]:
Polímeros, 32(2), e2022019,
Goes, M. A., Santos, J. P. F., & Carvalho, B. M.refers to the true strain known as logarithmic or Hencky
and
can determine it
the equation:
is the flow rate which, considering the constant axial speed (vz) is given by:
spacing between claws used was 50 mm, a tensile strain rate of 5 mm/min and a maximum deformation (ε) value of 0.21 mm/mm. The maximum tensile strength (σmáx.) was measured by the equipment and Young Moduli (E) for the crystalline polymers were determined by the tangent method (ASTM D638).
The value of v z was considered to be the minimum tangential speed for the filament winder which was kept constant and was used in this estimate due to the water cooling system (approx. 25ºC) forcing the filament to pass under the water after leaving the matrix, preventing the winding system from contributing with a significant stretch rate. Ro and Re correspond, respectively, to the largest and smallest internal radius in the extensional flow channel; L is the length of the rings. With the values for the constructed extensional flow device, we find an extensional strain rate of 33.19 s-1. To ensure this elongation rate for all processed polymers, temperature adjustment was performed, according to Table 1, in order to provide the same flow rate (Q), providing the same value of έ, since the other parameters are geometry dependent.
The samples were processed by extrusion without the extensional flow device and with this device. For each polymer, two separate extrusions were performed the first in a conventional manner and the second using the extensional flow device. Samples processed with the aid of extensional flow will present the sulfix “-el”. All materials were processed in neat form.
PVDF was dried in an oven (70 ºC) for 24 hours before extrusion. The other semi-crystalline polymers did not go through this process. Subsequently, about 25 g of material was used to formulate each sample. The formulations were prepared twice each, aiming to carry out two processes for each, the first in a conventional manner and the second using the extensional flow device. The processing temperature was used as shown in Table 1 and screw rotation was 30 rpm for all samples.
The filaments were evaluated mechanically at room temperature (25ºC) using a universal testing machine (Shimadzu Autograph AGS - 10 kN) without an extensometer. Ten samples were tested for each one of the six compositions shown in Table 1 with a length of 100 mm being that the
Using the Discovery Hybrid Rheometer (DH-2) equipment from TA Instruments, measurements were made with the Linear Dynamic Mechanical Analysis (DMA) accessory for films and filaments. Filaments with a length of 50 mm were used with spacing between the claws of 35 mm. With the equipment operating in traction the system was adjusted to an axial load of 1 N, dynamic force at 30% of the axial load, frequency of 1 Hz, axial displacement 20 µm and a temperature of 30ºC. In this analysis, the storage moduli (E’) and loss moduli (E”) were measured. The analysis was performed for two samples of each composition shown in Table 1, with eight measurements collected in each test.
Thermal properties of the samples were evaluated by differential scanning calorimetry (DSC). DSC was performed using an equipment from Shimadzu, DSC60. Two heating cycles were carried from 25 ºC up to 200ºC (PP and LDPE) and from 25ºC to 220 ºC (PVDF). The heating and cooling rates were 10 ºC/min for PP LDPE and 20 ºC/min for PVDF. All measurements were carried out under nitrogen (N2) atmosphere using flow rate of 50 ml/min were used. The melting temperature (Tm) was determined according to the methodology of the standard ASTM D3418-15. The crystallinity was estimated from the heat of fusion, and using the value for 100% crystallinity of PP (138 J/g[31]), PVDF (105 J/g[32]) and LDPE (288 J/g[33]).
Figure 2 shows stress strain curves obtained from mechanical tensile tests. Table 2 summarizes the Maximum tensile strength (σmáx.) and Young Moduli (E). It can be seen that there is a significant difference caused by the presence of the extensional flow on the mechanical tensile properties. When extruded under extensional flow, the stress strain curves exhibited an increase in stiffness of the polymers reflected in the slope of the curve in the region of elastic deformation. Münstedt[34] and Tabatabaei et al.[35] demonstrated that extensional rates increase can result in an increase in the mechanical properties for semi-semi-crystalline polymers in the flow direction, this effect being dependent on process parameters such as cooling rate and stretching. This type of effect is usually associated as a result of the ability of the extensional flow to stretch and align the macromolecules in the direction of the flow[36], or it may also be associated with the Flow-Induced Crystallization (FIC)[24-26]
In addition to the behavior displayed on the elastic moduli, there was also an increase in maximum tensile strength (σmáx.) values found for processing with extensional flow device. The increases were 18.51, 28.90, and 7.85% for PP-el, PVDF-el and LDPE-el, respectively. Such an increase can be an interesting effect to be applied in the production of filaments with improved mechanical properties.
Table
strength (σmáx.) and Young Moduli (E) for the semi-crystalline polymers. Compositions σmáx.
Maximum
Standard deviation E (GPa) Standard deviation
0.017
0.043
0.002
Dynamic mechanical analysis is an indispensable tool when evaluating the viscoelastic properties of semicrystalline polymers[37]. The properties measured by DMA for polymers processed with and without extensional flow are summarized in Table 3.
Young’s moduli is typically associated with the storage moduli (E’), or also called the dynamic moduli, this property is commonly associated with the stiffness of the evaluated material[38,39]. Based on this and the behavior displayed in tensile curves (Figure 2), we can say that the semi-crystalline polymers evaluated in this work showed greater stiffness when processed using the extensional flow device in the extrusion processing, according to the values presented in Table 3 and Figure 3. The observed increases in E’ were 18.9%, 40.4%, 77.5%, respectively, for PP-el,
PVDF-el, and LDPE-el. Such results corroborate with the measures made in mechanical tensile tests that also pointed out an increase due to the accentuated extensional flow in the extrusion process. Regarding the differences between the E value (Table 2) and the E’ (Table 3) values, they are possibly related to the lack of use of extensometer in the tensile test and to the loss of grip of the filaments during this analysis, which must have affected the measurements of deformation. The values obtained in this analysis for E’, the PP in the study of Das and Satapathy[40] reports a similar value around 1.5 GPa also using extrusion processing. For the PVDF and LDPE, studies were found that indicate values around 3 GPa[41,42] and 1 GPa[43,44], respectively.
The loss moduli (E”) or also called dynamic loss moduli is usually associated with the viscous response of
Polímeros, 32(2), e2022019,
the material and is related to its tendency to dissipate energy that has been applied to it[38,39]. Concerning this property, the measured values (Table 3) demonstrate that the extensional flow contributes to its increase by 18.2%, 37.5% and 77.8% for PP-el, PVDF-el and LDPE-el, respectively. The dynamic loss moduli are often associated with “internal friction” and is a property sensitive to morphological changes and structural heterogeneities[39,42]. From this perspective, we can interpret that the presence of the extensional flow resulted in some morphological change in the way the chains are organized, increasing the “internal friction” or, otherwise, increase the viscous response of the material associated with the values of E”. This modification can be associated with the changes in the crystallinity of the polymers that may have been provided by the FIC phenomenon.
The complex moduli (E*) also increase for semicrystalline polymers processed with the extensional flow. The value of E* can be visualized as the hypotenuse of a right triangle where its sides are the values of E’ and E”[39] thus the increase in the values of these components, due to
the presence of elongational flow, also reflects an increase in the values of E*. The increase in the calculated values of E* were 18.9%, 42.6%, and 76.9% for PP-el, PVDF-el, and LDPE-el, respectively.
Figure 4 exhibits DSC curves of first fusion peak to semi-crystalline polymers and the main thermal properties are summarized in Table 4. For PP, a peak was observed around ≈166 ºC, which is in line with values already available in other studies [10,45,46] for α phase crystals. For PP-el, it is possible to notice a very smooth lateral shoulder at a temperature around 160 ºC that may be associated with another phase induced by extensional flow, but this was not considered in our analysis, which may cause a slight variation in the measured values of crystallinity. The melting temperature (Tm) of PVDF and LDPE were, respectively, ≈170 ºC and ≈112 ºC which was ascribed to the melting of α phase crystals[47] in PVDF and for LDPE the value is in agreement with the range of values in other works[48,49]. Therefore, as shown in Table 4, no significant difference, at the melting temperature, was observed due to the presence of extensional flow devise in processing, as shown in Table 4
Figure 3. Storage moduli (E’) measured at 1Hz and 30ºC for the crystalline polymers.
Table 4 shows an increase in crystallinity of polymers processed with the extensional flow device. The crystallinity increases were 9.1%, 8.5% and 9.3% respectively for PP-el, PVDF-el and LDPE-el. An increase in crystallinity reflects on the stiffness of the polymeric material[50], which can partially justifies the effect on the values of E’ (Table 3). It can also be related to the increase in the maximum tensile strength (σmáx.) for the crystalline polymers (Table 2). It is worthy of note that in the second heating cycle performed in the DSC, the crystallinities (Table 4) of the samples processed with and without the extensional flow device are the same, showing differences of less than 1.3%. Another indication that this increase in crystallinity is associated with the processing history with the extensional flow device.
0.09 1.84
1.04 LDPE-el 1.81
Table 4. Melting temperature and
Compositions T
PP 166.09
PP-el
PVDF 169.6
PVDF-el
LDPE 112.02
LDPE-el 112.04
-
properties for the
heating/cooling
for
Tm
163.55
163.47
169.46
ΔHm
(J/g) Crystallinity2
111.37 119.24
111.93 119.06
heating/cooling
Flow
(ºC)
Flow (a.u.)
Figure 4. First Fusion peak for polymers processed with and without the extensional device for: (a) PP; (b) PVDF and (c) LDPE.
In this work, we demonstrated that it is possible to increase the crystallinity around 9%, for the polymers evaluated here, with the use of an extensional flow device coupled to a conventional extrusion process. This effect is probably associated with the FIC phenomenon, in which stress enhances the number of nuclei for crystals to grow, which in turn increases crystallinity. In addition, the use of controlled extension flows can also contribute to an increase in the mechanical properties as demonstrated by tensile tests and DMA, bringing an increase in Young’s moduli (Figure 3) and in the maximum tensile strength (Table 2).
In brief, it was possible to produce filaments processed by extrusion with and without the extensional flow device. The association of the extensional flow in the processing of semi-crystalline polymers enhanced its crystallinity degree in 9.1%, 8.5% and 9.3%, respectively, for PP-el, PVDF-el, and LDPE-el, and this increase is probably related to FIC.
The effects of the extensional flow both in the crystallinity and in the alignment of the chains also brought reflections on the mechanical properties. The storage moduli (E’) increased by 18.9%, 40.4%, 77.5%, for PP-el, PVDF-el, and LDPE-el, respectively. This result was reaffirmed by the measurements made in the tensile test since the E’ value is often related to the Young’s moduli. The reflexes of this increase can be seen by the higher slopes for the samples
processed with the extensional flow device, indicating an increase in crystalline polymer stiffness.
The use of the elongational flow device increased the value of E” by 18.2%, 37.5% and 77.8% for PP-el, PVDF-el, and LDPE-el, respectively. This effect can be associated with the morphological modification generated by the increase in the degree crystallinity and/or increased level of chain entanglement, that contribute to an increase in the degree of “internal friction” associated with the value of E”.
• Conceptualization – Marcel Andrey de Goes; João Paulo Ferreira Santos; Benjamim de Melo Carvalho.
Data curation – Marcel Andrey de Goes.
Formal analysis – Marcel Andrey de Goes; João Paulo Ferreira Santos.
Investigation – Marcel Andrey de Goes.
Methodology – Marcel Andrey de Goes.
Project administration – Benjamim de Melo Carvalho.
Resources – Benjamim de Melo Carvalho.
Software – Marcel Andrey de Goes.
Supervision – NA.
Validation – Marcel Andrey de Goes.
Visualization – NA.
Polímeros, 32(2), e2022019,
• Writing – original draft – Marcel Andrey de Goes.
• Writing – review & editing – Marcel Andrey de Goes; João Paulo Ferreira Santos.
The authors are grateful to Coordination for the Improvement of Higher Education Personnel (CAPES) and National Council for Scientific and Technological Development (CNPQ) for the financial support.
1 Keller, A. , & Kolnaar, H. W. H. (2006 ). Flow-induced orientation and structure formation. In R. W. Cahn, P. Haasen & E. J. Kramer (Eds.), Materials science and technology (pp. 187 268). Germany: John Wiley & Sons, Ltda http://dx.doi. org/10.1002/9783527603978.mst0210
2. Covas , J. A. , Novais , R. M. , & Paiva, M. C. (2011). A comparative study of the dispersion of carbon nanofibres in polymer melts. In Proceedings of the 27th World Congress of the Polymer Processing Society (pp. 1 5). Marocco: Polymer Processing Society. Retrieved in 2021, November 24, from https://repositorium.sdum.uminho.pt/bitstream/1822/14695/1/ full_paper_dispersion_JAC_MCP.pdf
3 Vilaverde, C., Santos, R. M., Paiva, M. C., & Covas, J. A. (2015). Dispersion and re-agglomeration of graphite nanoplates in polypropylene melts under controlled flow conditions. Composites. Part A, Applied Science and Manufacturing, 78, 143 151 http://dx.doi.org/10.1016/j.compositesa.2015.08.010
4 Santos, R. M., Mould, S. T., Formánek, P., Paiva, M. C., & Covas, J. A. (2018). Effects of particle size and surface chemistry on the dispersion of graphite nanoplates in polypropylene composites. Polymers, 10(2), 222 http://dx.doi.org/10.3390/ polym10020222 PMid:30966257.
5 Matsumoto, K., Nakade, Y., Sugimoto, K., & Tanaka, T. (2017). An investigation on dispersion state of graphene in polypropylene/graphite nanocomposite with extensional flow mixing. AIP Conference Proceedings, 1914(1), 150005 http:// dx.doi.org/10.1063/1.5016782
6. Carson, S. O., Maia, J. M., & Covas, J. A. (2016). A New extensional mixing element for improved dispersive mixing in twin-screw extrusion, Part 2: experimental validation for immiscible polymer blends. Advances in Polymer Technology, 37(1), 167 175 http://dx.doi.org/10.1002/adv.21653
7 Chen, H., & Maia, J. M. (2021). Improving dispersive mixing in compatibilized polystyrene/polyamide-6 blends via extensiondominated reactive single-screw extrusion. Journal of Polymer Engineering, 41(5), 397 403 http://dx.doi. org/10.1515/polyeng-2020-0230.
8 Goes, M. A., Woicichowski, L. A., Rosa, R. V. V., Santos, J. P. F., & Carvalho, B. M. (2021). Improving the dispersion of MWCNT and MMT in PVDF melts employing controlled extensional flows. Journal of Applied Polymer Science, 138(17), 50274 http://dx.doi.org/10.1002/app.50274
9 Mileva, D., Tranchida, D., & Gahleitner, M. (2018). Designing polymer crystallinity: an industrial perspective. Polymer Crystallization, 1(2), e10009 http://dx.doi.org/10.1002/ pcr2.10009
10 Maddah, H. A. (2016). Polypropylene as a promising plastic: a review. American Journal of Political Science, 6(1), 1 11 http://dx.doi.org/10.5923/j.ajps.20160601.01
11 Santos, J. P. F., Arjmand, M., Melo, G. H. F., Chizari, K., Bretas, R. E. S., & Sundararaj, U. (2018). Electrical conductivity of electrospun nanofiber mats of polyamide 6/polyaniline coated
e2022019,
with nitrogen-doped carbon nanotubes. Materials & Design, 141, 333 341 http://dx.doi.org/10.1016/j.matdes.2017.12.052
12 Kumar Sen, S., & Raut, S. (2015). Microbial degradation of low density polyethylene (LDPE): a review. Journal of Environmental Chemical Engineering, 3(1), 462 473 http:// dx.doi.org/10.1016/j.jece.2015.01.003
13 Liu, Z. H., Pan, C. T., Lin, L. W., & Lai, H. W. (2013). Piezoelectric properties of PVDF/MWCNT nanofiber using near-field electrospinning. Sensors and Actuators. A, Physical, 193, 13 24 http://dx.doi.org/10.1016/j.sna.2013.01.007
14. Chen, X., Xu, S., Yao, N., & Shi, Y. (2010). 1.6 v nanogenerator for mechanical energy harvesting using PZT nanofibers. Nano Letters, 10(6), 2133 2137 http://dx.doi.org/10.1021/nl100812k PMid:20499906.
15 Boon, J., Challa, G., & Van Krevelen, D. W. (1968). Crystallization kinetics of isotactic polystyrene. I. Spherulitic growth rate. Journal of Polymer Science. Part A-2, Polymer Physics, 6(10), 1791 1801. http://dx.doi.org/10.1002/pol.1968.160061009.
16 Boon, J., Challa, G., & Van Krevelen, D. W. (1968). Crystallization kinetics of isotactic polystyrene. II. Influence of thermal history on number of nuclei. Journal of Polymer Science. Part A-2, Polymer Physics, 6(11), 1835 1851 http://dx.doi.org/10.1002/ pol.1968.160061102
17 Agar, A. W., Prank, F. C., & Keller, A. (1959). Crystallinity effects in the electron microscopy of polyethylene. The Philosophical Magazine: A Journal of Theoretical Experimental and Applied Physics, 4(37), 32 55 http://dx.doi. org/10.1080/14786435908238226
18 Angelloz, C., Fulchiron, R., Douillard, A., Chabert, B., Fillit, R., Vautrin, A., & David, L. (2000). Crystallization of isotactic polypropylene under high pressure (γ phase). Macromolecules, 33(11), 4138 4145 http://dx.doi.org/10.1021/ma991813e
19 Steiger, M. (2005). Crystal growth in porous materials - II: influence of crystal size on the crystallization pressure. Journal of Crystal Growth, 282(3-4), 470 481 http://dx.doi. org/10.1016/j.jcrysgro.2005.05.008
20 Boyer, S. A. E., & Haudin, J.-M. (2010). Crystallization of polymers at constant and high cooling rates: A new hot-stage microscopy set-up. Polymer Testing, 29(4), 445 452 http:// dx.doi.org/10.1016/j.polymertesting.2010.02.003.
21 Kong, W., Zhu, B., Su, F., Wang, Z., Shao, C., Wang, Y., Liu, C., & Shen, C. (2019). Melting temperature, concentration and cooling rate-dependent nucleating ability of a self-assembly aryl amide nucleator on poly(lactic acid) crystallization. Polymer, 168, 77 85 http://dx.doi.org/10.1016/j.polymer.2019.02.019
22. Lagasse, R. R., & Maxwell, B. (1976). An experimental study of the kinetics of polymer crystallization during shear flow. Polymer Engineering and Science, 16(3), 189 199 http:// dx.doi.org/10.1002/pen.760160312
23 Amirdine, J., Htira, T., Lefevre, N., Fulchiron, R., Mathieu, N., Zinet, M., Sinturel, C., Burghelea, T., & Boyard, N. (2021). A novel approach to the study of extensional flow-induced crystallization. Polymer Testing, 96, 107060 http://dx.doi. org/10.1016/j.polymertesting.2021.107060.
24 Chellamuthu, M., Arora, D., Winter, H. H., & Rothstein, J. P. (2011). Extensional flow-induced crystallization of isotactic poly-1-butene using a filament stretching rheometer. Journal of Rheology (New York, N.Y.), 55(4), 901 920 http://dx.doi. org/10.1122/1.3593471
25 Haas, T. W., & Maxwell, B. (1969). Effects of shear stress on the crystallization of linear polyethylene and polybutene‐1. Polymer Engineering and Science, 9(4), 225 241 http://dx.doi. org/10.1002/pen.760090402
26 Bischoff White, E. E., Henning Winter, H., & Rothstein, J. P. (2012). Extensional-flow-induced crystallization of isotactic
Goes, M. A., Santos, J. P. F., & Carvalho, B. M.
polypropylene. Rheologica Acta, 51(4), 303 314 http://dx.doi. org/10.1007/s00397-011-0595-5
27 Harris, A. M., & Lee, E. C. (2008). Improving mechanical performance of injection molded PLA by controlling crystallinity. Journal of Applied Polymer Science, 107(4), 2246 2255 http:// dx.doi.org/10.1002/app.27261
28 Feast, W. J., Tsibouklis, J., Pouwer, K. L., Groenendaal, L., & Meijer, E. W. (1996). Synthesis, processing and material properties of conjugated polymers. Polymer, 37(22), 5017 5047 http://dx.doi.org/10.1016/0032-3861(96)00439-9
29 Jamali, S., Paiva, M. C., & Covas, J. A. (2013). Dispersion and re-agglomeration phenomena during melt mixing of polypropylene with multi-wall carbon nanotubes. Polymer Testing, 32(4), 701 707 http://dx.doi.org/10.1016/j.polymertesting.2013.03.005
30 Feigl, K., Tanner, F. X., Edwards, B. J., & Collier, J. R. (2003). A numerical study of the measurement of elongational viscosity of polymeric fluids in a semihyperbolically converging die. Journal of Non-Newtonian Fluid Mechanics, 115(2-3), 191 215 http://dx.doi.org/10.1016/j.jnnfm.2003.08.002
31 Líbano, E. V. D. G., Visconte, L. L. Y., & Pacheco, É. B. A. V. (2012). Thermal properties of polypropylene and organophilic bentonite. Polímeros: Ciência e Tecnologia, 22(5), 430 435 http://dx.doi.org/10.1590/S0104-14282012005000063
32 Peng, Q.-Y., Cong, P.-H., Liu, X.-J., Liu, T.-X., Huang, S., & Li, T.-S. (2009). The preparation of PVDF/clay nanocomposites and the investigation of their tribological properties. Wear, 266(7-8), 713 720. http://dx.doi.org/10.1016/j.wear.2008.08.010.
33 Borhani zarandi, M., Bioki, H. A., Mirbagheri, Z.-a., Tabbakh, F., & Mirjalili, G. (2012). Effect of crystallinity and irradiation on thermal properties and specific heat capacity of LDPE & LDPE/EVA. Applied Radiation and Isotopes, 70(1), 1 5 http:// dx.doi.org/10.1016/j.apradiso.2011.09.001
34 Münstedt, H. (2018). Extensional rheology and processing of polymeric materials. International Polymer Processing, 33(5), 594 618 http://dx.doi.org/10.3139/217.3532
35 Tabatabaei, S. H., Carreau, P. J., & Ajji, A. (2009). Effect of processing on the crystalline orientation, morphology, and mechanical properties of polypropylene cast films and microporous membrane formation. Polymer, 50(17), 4228 4240 http://dx.doi.org/10.1016/j.polymer.2009.06.071
36 Petrie, C. J. S. (2006). One hundred years of extensional flow. Journal of Non-Newtonian Fluid Mechanics, 137(1–3), 1 14. http://dx.doi.org/10.1016/j.jnnfm.2006.01.010
37 Pistor, V., Ornaghi, F. G., Ornaghi, H. L., & Zattera, A. J. (2012). Dynamic mechanical characterization of epoxy/ epoxycyclohexyl-POSS nanocomposites. Materials Science and Engineering A, 532, 339 345 http://dx.doi.org/10.1016/j. msea.2011.10.100.
38 Jawaid, M., Abdul Khalil, H. P. S., Hassan, A., Dungani, R., & Hadiyane, A. (2013). Effect of jute fibre loading on tensile and dynamic mechanical properties of oil palm epoxy composites. Composites. Part B, Engineering, 45(1), 619 624 http://dx.doi. org/10.1016/j.compositesb.2012.04.068
39. Saba, N., Jawaid, M., Alothman, O. Y., & Paridah, M. T. (2016). A review on dynamic mechanical properties of natural fibre reinforced polymer composites. Construction & Building Materials, 106, 149 159 http://dx.doi.org/10.1016/j. conbuildmat.2015.12.075
40 Das, A., & Satapathy, B. K. (2011). Structural, thermal, mechanical and dynamic mechanical properties of cenosphere
filled polypropylene composites. Materials & Design, 32(3), 1477 1484 http://dx.doi.org/10.1016/j.matdes.2010.08.041
41 Correia, D. M., Costa, C. M., Lizundia, E., Sabater i Serra, R., Gómez-Tejedor, J. A., Biosca, L. T., Meseguer-Dueñas, J. M., Gomez Ribelles, J. L., & Lanceros-Méndez, S. (2019). Influence of Cation and anion type on the formation of the electroactive β-phase and thermal and dynamic mechanical properties of poly(vinylidene fluoride)/ionic liquids blends. The Journal of Physical Chemistry C, 123(45), 27917 27926 http://dx.doi.org/10.1021/acs.jpcc.9b07986
42 Sencadas, V., Lanceros-Méndez, S., Sabater i Serra, R., Andrio Balado, A., & Gómez Ribelles, J. L. (2012). Relaxation dynamics of poly(vinylidene fluoride) studied by dynamical mechanical measurements and dielectric spectroscopy. The European Physical Journal. E, Soft Matter, 35(5), 41 http:// dx.doi.org/10.1140/epje/i2012-12041-x PMid:22644136.
43 Therese Pick, L., Harkin-Jones, E., Jovita Oliveira, M., & Clara Cramez, M. (2006). The effect of cooling rate on the impact performance and dynamic mechanical properties of rotationally molded metallocene catalyzed linear low density polyethylene. Journal of Applied Polymer Science, 101(3), 1963 1971 http://dx.doi.org/10.1002/app.23709
44 Joseph, K., Thomas, S., & Pavithran, C. (1993). Dynamic mechanical properties of short sisal fiber reinforced low density polyethylene composites. Journal of Reinforced Plastics and Composites, 12 (2), 139 155 http://dx.doi. org/10.1177/073168449301200202
45 Majewsky, M., Bitter, H., Eiche, E., & Horn, H. (2016). Determination of microplastic polyethylene (PE) and polypropylene (PP) in environmental samples using thermal analysis (TGA-DSC). The Science of the Total Environment, 568, 507 511 http://dx.doi.org/10.1016/j.scitotenv.2016.06.017 PMid:27333470.
46 Sližová, M., Stašek, M., & Raab, M. (2020). Polypropylene after thirty years of storage: mechanical proof of heterogeneous aging. Polymer Journal, 52(7), 775 781. http://dx.doi.org/10.1038/ s41428-020-0327-8
47 Santos, J. P. F., da Silva, A. B., Arjmand, M., Sundararaj, U., & Bretas, R. E. S. (2018). Nanofibers of poly(vinylidene fluoride)/copper nanowire: microstructural analysis and dielectric behavior. European Polymer Journal, 101, 46 55 http://dx.doi.org/10.1016/j.eurpolymj.2018.02.017
48. Li, D., Zhou, L., Wang, X., He, L., & Yang, X. (2019). Effect of crystallinity of polyethylene with different densities on breakdown strength and conductance property. Materials (Basel), 12(11), 1746 http://dx.doi.org/10.3390/ma12111746 PMid:31146397.
49 Wu, W., & Wang, Y. (2020). Physical and thermal properties of high-density polyethylene film modified with polypropylene and linear low-density polyethylene. Journal of Macromolecular Science, Part B: Physics, 59(4), 213 222 http://dx.doi.org/10 .1080/00222348.2019.1709710
50 Dusunceli, N., & Colak, O. U. (2008). Modelling effects of degree of crystallinity on mechanical behavior of semicrystalline polymers. International Journal of Plasticity, 24(7), 1224 1242 http://dx.doi.org/10.1016/j.ijplas.2007.09.003
Received: Nov. 24, 2021
Revised: June 23, 2022
Accepted: July 01, 2022
Polímeros, 32(2), e2022019,
https://doi.org/10.1590/0104-1428.20210116
1Departamento de Engenharia de Materiais, Universidade Estadual de Ponta Grossa – UEPG, Ponta Grossa, PR, Brasil
2Departamento de Engenharia de Materiais, Centro Federal de Educação Tecnológica de Minas Gerais, Belo Horizonte, MG, Brasil aThis paper has been partially presented at the 16th Brazilian Polymer Congress, held on-line, 24-28/Oct/2021.
*benjamim@uepg.br
The use of controlled extension flows associated with processing with predominant shear flows can bring gains in the dispersive capacity of nanofillers during the processing of nanocomposites. In this work, we use a controlled flow device coupled to the matrix of a single-screw extruder to process PP matrix composites containing 0.5% and 2.5% (v/v) of MWCNT. The nanocomposites were evaluated by optical microscopy and oscillatory rheological analysis. The clusters size analysis showed that in PP/0.5MWCNT-el, 70.5% of all its clusters were below 1µm2 while its analog processed without the extensional flow showed 59.8% of its clusters below this value. The rheological analysis allowed to verify that the compositions processed with the presence of the extensional flow have their crossover frequencies shifted to lower values, that is, longer relaxation times corroborating that improved degrees of dispersion were achieved.
How to cite: Goes, M. A., Santos, J. P. F., & Carvalho, B. M. (2022). Improving the dispersion of MWCNT in PP using controlled extensional flow. Polímeros: Ciência e Tecnologia, 32(2), e2022020.https://doi.org/10.1590/01041428.20210116
Several theoretical models elaborated show that there is a large difference between the measured values and the theoretical values of properties for composites containing multiwalled carbon nanotubes (MWCNT) nanofillers[1-3] For the vast majority of these cases, these differences are mainly due to the poor dispersion level of the MWCNT in the polymer matrix and its tendency to agglomerate associated to the high surface area[3]. Due to the geometry of the carbon nanotubes that are long and twisted, they tend to entangle themselves making it even more difficult to break and redistribute the agglomerates inside polymer matrices[4]. Many different strategies have been studied to improve the dispersion level of the MWCNT and to reduce the difference between the theoretical values for the properties and those obtained, such as chemical functionalization[5], use of ultrasonic waves[6], polymer wrapping[7], shearing and extensional flows[8,9].
The use of controlled flows to increase the degree of particle dispersion is already a known method due to the possibility of allowing greater applications in terms of production scale[10-12]. It is known that the extensional flow is more efficient, when compared to the shear flow, with regard to the ability to break agglomerates and also in their redistribution throughout the polymer matrix[11]. Several studies have been carried out to evaluate the dispersive
effect of the extensional flow by developing small-scale processing devices or using small mixers which are applicable to small scales of processing[11-17]. To nanofiller such as MWCNT[18-21] and graphene[8] in polypropylene (PP) matrixes was found that the dispersion of both fillers were highly improved due extensional forces. For example, in Son’s[22] study, composites containing 0.5% w. of MWCNT in PP comparing the dispersion of the processing via twin screw extrusion and an extensional batch mixer (EBM), developed by the author’s; their results shown an increase of up to 30% in the dispersion for processing with EBM, measured by the area of the agglomerates. A more recent approach in this field seeks to evaluate components to enhance the extensional flow in twin-extrusion processing, which provides gains in dispersive power in the production of immiscible blends[23,24], for example, the validation of this approach showed that in the processing of immiscible polypropylene/polystyrene blends it was possible to provide an increase in dispersion of up to 30% for processing with extensional mixing element (EME).
In general, shear flows are commonly applied in typical melt processing devices, such as extruders and mixers[14,21]. Increase the extensional flow component present in melt processing, adding to the shear component commonly present in extrusion, can significantly increase the erosion
Marcel Andrey de Goes1 , João Paulo Ferreira Santos2 and Benjamim de Melo Carvalho1*
and the kinetics of breakup of agglomerates. For composites containing montmorillonite (MMT) and MWCNT in PVDF matrix, this approach has demonstrated its effectiveness in reducing the particle size of MWCNT agglomerates by up to 55%[25]
This study proposes to evaluate the effect of improving the dispersion of MWCNT particles in PP matrix, by associating a controlled extensional flow during extrusion processing. This approach is an innovative methodology to contribute to the improvement of fillers dispersion in the molten state processing of thermoplastic polymer matrix composites. In a previous work by this research group[25] , we described in greater detail the device developed to be coupled to an extruder die.
Polypropylene (PP), H301, supplied by Braskem. The density and melt flow index (MFI) were 0.905 g/ cm3 and 10 g/10 min (at 230 ºC/2.16 kgf), respectively. PP was submitted to the micronization process in a mill (Micron Powder Systems, model CF Bantam) at 100 rpm with liquid nitrogen in order to obtain a micronized powder. After grinding the material was sieved (80 mesh). The micronization process was carried out to improve the premix (before extrusion) of the components. Multilayer Carbon Nanotubes (NTCMC) supplied by the company Nanocyl under the trade name NC7000 were used as supplied. The average diameter and length of the MWCNTs are 9.5 nm and 1.5 µm, respectively; transition metal oxide less than 1% and surface area between 250-300 m2/g.
The nanocomposites were processed in the form of filaments by extrusion using a single-screw mini-extruder Filmaq3d STD (22 mm screw diameter and L/D = 9.1) adjusted to 30 rpm and at a temperature of 200 ºC. For processing by accentuating the extensional flow component, a flowcontrolled device consisting of a sequence of 7 rings with internal diameters alternating between 2 and 4 mm was developed. The matrix acted as a support for the assembly of the 7 rings and also as an “eighth ring”, with an internal diameter of 4 mm, this device has already been described in a previous work by this research group[25]. The device associated with the extruder die is capable of adding an estimated[26] extensional flow rate of 33.19 s-1. Extruded filaments were collected using a filament winder that has a water-cooling system.
All different compositions shown in Table 1 were prepared twice each, aiming to carry out two processes for each, the first in a conventional manner and the second using the extensional flow device. In the nomenclature the suffix -el was added for those processed using the device coupled to the extruder die.
The samples used in this analysis were prepared from the microtomy of the extruded filaments. The cuts, with a
Compositions PP (%v.) MWCNT (%v.)
thickness of 10 µm, were made with an American Optical 820 manual rotating microtome. The images were captured with the Olympus BX51 polarized light optical microscope operating in transmitted light mode, equipped with an Olympus QColor 3 camera. Using 5 images from different regions, an evaluation was made regarding the distribution of the average particle size with the ImageJ software. The automatic particle size analysis tool was used to count and measure (in area) the particles present in each image.
The rheological behavior of the nanocomposites was evaluated using an oscillatory rheometer, Discovery Hybrid Rheometer (DHR-2) from TA Instruments, using parallel plates of 25 mm diameter, working distance between the plates of 1 mm (gap), temperature 200 ºC, mode: stress-controlled force, angular frequency (ꞷ) from 0.1 to 100 hz at 0.3% shear strain. The samples were obtained from the extruded filaments, which were cut into pieces of around 3 mm and then added between the rheometer plates. The measurements were done in the linear viscoelastic regime. The following properties were measured as a function of frequency: storage moduli (G’), loss moduli (G”), complex viscosity (η*), real viscosity (η’) and imaginary viscosity (η”). The short relaxation time (tr) was calculated for all nanocomposites as a function of the value of ꞷ c which corresponds to the frequency at which G’= G”, according to Equation 1[27]:
Figure 1 shows the image of the morphology of the nanocomposites processed with (Figure 1b and d) and without the presence of the extensional flow device (Figure 1a and c). For the composition PP/0.5MWCNT-el and PP/2.5MWCNT-el it is noted that the size of the clusters are smaller, which points to a greater efficiency in reducing the size of the clusters with the processing occurring with the aid of extensional flow.
With the collected data in the clusters size analysis made with ImageJ software, the size distribution curves shown in Figure 2 and Table 2 were constructed. The PP/0.5NTCMCel composition presented 70.5% of all its clusters below 1µm2 while its analog processed without the extensional flow device showed 59.8% of its clusters below this value. For the composition PP/2.5MWCNT-el, a value of 58.7% of the clusters below 1 µm2 and 4.2% above 10 µm2 was found, on the other hand, its corresponding processed without the extensional flow presented 54.3% of the clusters below 1 µm2 and 7.5% above 10 µm2. The size reduction effect of the clusters was more significant for the composition containing 0.5%v. of MWCNT. It is known
Polímeros, 32(2), e2022020, 2022
Goes, M. A., Santos, J. P. F., & Carvalho B. M.range
Size range (
m2)
0.1-0.250.25-0.50.5-0.750.75-1.01.0-1.51.5-2.02.0-3.03.0-4.04.0-5.05.0-6.06.0-8.08.0-10.0
range (
m2)
0.1-0.250.25-0.50.5-1.01.0-1.51.5-2.02.0-2.52.5-3.03.0-3.53.5-4.04.0-5.05.0-6.06.0-7.07.0-10.010.0-15.015.0-20.020.0-30.0
Size range (
that carbon nanotubes can easily entangle themselves and with polymers chains[3,6]. Also, Jamali[18] demonstrated that a higher extensional rate represents a greater breaking force for MWCNT clusters, when processing nanocomposites containing 4% w. of MWCNT, in a device coupled to a capillary rheometer.
This clusters size reduction behavior is associated with greater efficiency of the extensional flow in generating higher levels of dispersive and distributive mixture[12,18,22,24,28,29].
The results shown in Figure 2 and Table 2 also corroborates with the effect observed in our previous work[25], that is, the reduction in the size of the MWCNT agglomerates when processing with the extensional flow device coupled to the extrusion matrix. Here we have more significant results in terms of cluster size, due to the large number of clusters analyzed (Table 2) in this measure. We can say with greater reliability that when we accentuate the elongational flow in the extruder die, we contribute to achieving higher levels of dispersion for MWCNT aggregates in PP matrix.
Rheological measurements in oscillatory regime, allow to assess the internal interaction between macromolecules and nanofillers in polymer matrix nanocomposites[20,29,30]
Figure 3 shows storage moduli (G’), loss moduli (G”) and complex viscosity (η*) versus oscillatory frequency (ꞷ) of the MWCNT nanocomposites. As expected, both G’ and G” increased remarkably with frequency, while η* presented a decrease.
The morphology of MWCNT contributes for this material to become entangled themselves and with polymers chains[3,6]. This structure presents both, high modulus and high viscosities[2,31,32], this behavior was exhibited by the
nanocomposites processed, as shown in Figure 3, and is more evident for the composition containing 2.5%v.. With regard to the effects of adding the extensional flow in processing, it was noted that MWCNT nanocomposites obtained under extensional flow had remarkable higher G’, G” and η* than the others. For example, at 0.1rad/s, PVDF/MWCNT presented G’=1616.2 Pa, G”= 4176.1 Pa and η *=4496.8 Pa.s, while PP/2.5MWCNT-el presented G’=2562,8 Pa, G”= 5387.1 Pa and η*=5990.7 Pa.s. From a rheological point of view, this result shows that improved degrees of dispersion of MWCNT were achieved for MWCNT nanocomposites extruded under extensional flow compared to their counterparts extruded without extensional flow. Similar results were obtained in other works[33-37], for example in the study of Ke et al.[33], were compared the effects of melt and solution mixing on the dispersion and on rheological properties of MWCNT/ PVDF nanocomposites. They found higher G’ for solution mixed samples than for their counterparts obtained by melt mixing. This result was attributed to the better dispersion of MWCNT achieved in the solution mixed samples than in the melt mixed ones, for MWCNT loadings lower than 5 wt.%.
In order to more clearly assess the effects of extensional flow on the rheological properties, the values of the crossover frequency (ꞷc) and also the short relaxation time (tr) were determined, which are shown in Table 3. The relaxation process referred to in the measurement is associated with relaxation of the PP chains, probably by the reptation mechanism[38-40]. We can verify that when processed with the flow-through device, the compositions have their crossover frequencies shifted to lower values, that is, longer relaxation times, which are involved with higher degrees of interaction between MWCNT and PP chains, corroborating that improved degrees of dispersion were
Polímeros, 32(2), e2022020,
Goes, M. A., Santos, J. P. F., & Carvalho B. M.PP/2.5MWCNT-el
for
with
Table 3. Frequency of cross over (ꞷc) and short relaxation time (tr) for the nanocomposites.
PP/0.5MWCNT 75.41 0.083
63.08 0.100
47.92 0.131 PP/2.5MWCNT-el 34.97 0.180
achieved for these compositions due to the finer dispersion of MWCNT through the PP matrix. This possibly occurs because the polymer chain relaxations are more restricted by the nanotubes when there is a better dispersion in the nanocomposites. A similar phenomenon was reported by Rostami et al.[41], for PC/ABS/MWCNT composites; and in the study by Poothanari et al.[42] for PC/PP/MWCNT composites; in addition, we also reported this behavior in a previous study for PVDF/MWCNT nanocomposites[25]
The influence of extensional flow on relaxation times can also be seen in the Cole-Cole plots, shown in Figure 4.
The presence of extensional flow induced smoother curves (red dots) which is related to longer relaxation times, reaffirming what was calculated and shown in Table 3. This effect was much more pronounced for the composition containing 2.5%v. of MWCNT (approximately 4.6%w.). It is known that rheological percolation is a phenomenon that can be easily noticed by the significant increase in rheological properties[43-46] and in Banerjee’s[47] work this phenomenon was observed between 3-4%w. for processing with a meltstate mixer with twin-screw components, however in our study we have no evidence of this phenomenon. Possibly, due to the proximity to the rheological percolation range for this type of nanocomposite, the effects of greater dispersion promote more significant gains contributing to the growth of PP/MWCNT and MWCN/MWCNT interactions, making the interconnected network more consistent, thus leading to longer relaxation times, for processing with accentuated extensional flow.
It was possible to process all the proposed compositions with and without the extensional flow device during
device:
PP/0.5MWCNT and (b) PP/2.5MWCNT.
extrusion. Clusters size analysis demonstrated that there was a reduction in MWCNT clusters size when processing the nanocomposites with the addition of the extensional flow rate (33.19 s-1) in the processing. The most significant effect was observed for the composition PP/0.5NTCMC-el that presented 70.5% of all its clusters below 1µm2 while its analog processed without the extensional flow device showed 59.8% of its clusters below this value.
Furthermore, the rheological analysis allowed to verify that the compositions processed with the presence of the extensional flow have their G’, G” and η* values higher compared to their homologous compositions processed without the addition of the extensional flow. In addition, the crossover frequencies shifted to lower values, that is, longer relaxation times, which are involved with higher degrees of interaction between MWCNT and PP, corroborating that improved degrees of dispersion were achieved.
• Conceptualization – Marcel Andrey de Goes; João Paulo Ferreira Santos; Benjamim de Melo Carvalho.
• Data curation – Marcel Andrey de Goes.
• Formal analysis – Marcel Andrey de Goes; João Paulo Ferreira Santos.
• Investigation – Marcel Andrey de Goes.
• Methodology – Marcel Andrey de Goes.
• Project administration – Benjamim de Melo Carvalho.
• Resources – Benjamim de Melo Carvalho.
Software – Marcel Andrey de Goes.
Supervision – NA.
• Validation – Marcel Andrey de Goes.
Visualization – NA.
Writing – original draft – Marcel Andrey de Goes.
• Writing – review & editing – Marcel Andrey de Goes; João Paulo Ferreira Santos.
The authors are grateful
Coordination for the Improvement of Higher Education Personnel (CAPES)
Improving the dispersion of multiwalled carbon nanotube in polypropylene using controlled extensional flowGoes, M. A., Santos, J. P. F., & Carvalho B. M.
and National Council for Scientific and Technological Development (CNPQ) for the financial support.
1 Bauhofer, W., & Kovacs, J. Z. (2009). A review and analysis of electrical percolation in carbon nanotube polymer composites. Composites Science and Technology, 69(10), 1486 1498 http:// dx.doi.org/10.1016/j.compscitech.2008.06.018
2 Kaseem, M., Hamad, K., & Ko, Y. G. (2016). Fabrication and materials properties of polystyrene/carbon nanotube (PS/CNT) composites: A review. European Polymer Journal, 79, 36 62. http://dx.doi.org/10.1016/j.eurpolymj.2016.04.011.
3 Ma, P.-C., Siddiqui, N. A., Marom, G., & Kim, J.-K. (2010). Dispersion and functionalization of carbon nanotubes for polymer-based nanocomposites: A review. Composites. Part A, Applied Science and Manufacturing, 41(10), 1345 1367 http://dx.doi.org/10.1016/j.compositesa.2010.07.003
4 Du, F., Scogna, R. C., Zhou, W., Brand, S., Fischer, J. E., & Winey, K. I. (2004). Nanotube networks in polymer nanocomposites: rheology and electrical conductivity. Macromolecules, 37(24), 9048 9055 http://dx.doi.org/10.1021/ma049164g
5. Zhu, B., Bai, T., Wang, P., Wang, Y., Liu, C., & Shen, C. (2020). Selective dispersion of carbon nanotubes and nanoclay in biodegradable poly(ε-caprolactone)/poly(lactic acid) blends with improved toughness, strength and thermal stability. International Journal of Biological Macromolecules , 153, 1272 1280 http://dx.doi.org/10.1016/j.ijbiomac.2019.10.262 PMid:31758994.
6 Santos, J. P. F., Arjmand, M., Melo, G. H. F., Chizari, K., Bretas, R. E. S., & Sundararaj, U. (2018). Electrical conductivity of electrospun nanofiber mats of polyamide 6/polyaniline coated with nitrogen-doped carbon nanotubes. Materials & Design, 141, 333 341 http://dx.doi.org/10.1016/j.matdes.2017.12.052
7. Voge, C. M., Johns, J., Raghavan, M., Morris, M. D., & Stegemann, J. P. (2013). Wrapping and dispersion of multiwalled carbon nanotubes improves electrical conductivity of proteinnanotube composite biomaterials. Journal of Biomedical Materials Research. Part A, 101(1), 231 238 http://dx.doi. org/10.1002/jbm.a.34310 PMid:22865813.
8 Vilaverde, C., Santos, R. M., Paiva, M. C., & Covas, J. A. (2015). Dispersion and re-agglomeration of graphite nanoplates in polypropylene melts under controlled flow conditions. Composites. Part A, Applied Science and Manufacturing, 78, 143 151 http://dx.doi.org/10.1016/j.compositesa.2015.08.010
9 Harris, A. M., & Lee, E. C. (2008). Improving mechanical performance of injection molded PLA by controlling crystallinity. Journal of Applied Polymer Science, 107(4), 2246 2255. http:// dx.doi.org/10.1002/app.27261
10 Feast, W. J., Tsibouklis, J., Pouwer, K. L., Groenendaal, L., & Meijer, E. W. (1996). Synthesis, processing and material properties of conjugated polymers. Polymer, 37(22), 5017 5047 http://dx.doi.org/10.1016/0032-3861(96)00439-9
11 Tokihisa, M., Yakemoto, K., Sakai, T., Utracki, L. A., Sepehr, M., Li, J., & Simard, Y. (2006). Extensional flow mixer for polymer nanocomposites. Polymer Engineering and Science, 46(8), 1040 1050 http://dx.doi.org/10.1002/pen.20542
12 . Covas, J. A., Novais, R. M., & Paiva, M. C. (2011). A comparative study of the dispersion of carbon nanofibres in polymer melts. In Proceedings of the 27th World Congress of the Polymer Processing Society (pp. 1 5). Morocco: International Polymer Processing
13 Oxfall, H., Rondin, J., Bouquey, M., Muller, R., Rigdahl, M., & Rychwalski, R. W. (2013). Elongational flow mixing for manufacturing of graphite nanoplatelet/ polystyrene composites.
Journal of Applied Polymer Science, 128(5), 2679 2686 http:// dx.doi.org/10.1002/app.38439
14 Pierson, H. O. (1993). Handbook of carbon, graphite, diamond and fullerenes: properties, processing and applications USA: Noyes Publications
15 Ibarra-Gómez, R., Muller, R., Bouquey, M., Rondin, J., Serra, C. A., Hassouna, F., Mouedden, Y. E., Toniazzo, V., & Ruch, D. (2015). Processing of nanocomposites PLA/graphite using a novel elongational mixing device. Polymer Engineering and Science, 55(1), 214 222 http://dx.doi.org/10.1002/pen.23869
16 Chellamuthu, M., Arora, D., Winter, H. H., & Rothstein, J. P. (2011). Extensional flow-induced crystallization of isotactic poly-1-butene using a filament stretching rheometer. Journal of Rheology (New York, N.Y.), 55(4), 901 920 http://dx.doi. org/10.1122/1.3593471
17 Bischoff White, E. E., Henning Winter, H., & Rothstein, J. P. (2012). Extensional-flow-induced crystallization of isotactic polypropylene. Rheologica Acta, 51(4), 303 314 http://dx.doi. org/10.1007/s00397-011-0595-5
18 Jamali, S., Paiva, M. C., & Covas, J. A. (2013). Dispersion and re-agglomeration phenomena during melt mixing of polypropylene with multi-wall carbon nanotubes. Polymer Testing, 32(4), 701 707 http://dx.doi.org/10.1016/j.polymertesting.2013.03.005
19 Yuan, D., Wu, T., Chen, R.-Y., Zhang, G.-Z., & Qu, J.-P. (2018). Investigation on properties of polypropylene/multiwalled carbon nanotubes nanocomposites prepared by a novel eccentric rotor extruder based on elongational rheology. Journal of Macromolecular Science, Part B: Physics, 57(5), 348 363 http://dx.doi.org/10.1080/00222348.2018.1462648
20 Silvano, J. R., Rodrigues, S. A., Marini, J., Bretas, R. E. S., Canevarolo, S. V., Carvalho, B. M., & Pinheiro, L. A. (2013). Effect of reprocessing and clay concentration on the degradation of polypropylene/montmorillonite nanocomposites during twin screw extrusion. Polymer Degradation & Stability, 98(3), 801 808. http://dx.doi.org/10.1016/j.polymdegradstab.2012.12.009.
21 Graf, A., Zakharko, Y., Schießl, S. P., Backes, C., Pfohl, M., Flavel, B. S., & Zaumseil, J. (2016). Large scale, selective dispersion of long single-walled carbon nanotubes with high photoluminescence quantum yield by shear force mixing. Carbon, 105, 593 599 http://dx.doi.org/10.1016/j.carbon.2016.05.002
22 Duc, B. N., & Son, Y. (2020). Enhanced dispersion of multi walled carbon nanotubes by an extensional batch mixer in polymer/MWCNT nanocomposites. Composites Communications, 21, 100420 http://dx.doi.org/10.1016/j.coco.2020.100420
23 Carson, S. O., Maia, J. M., & Covas, J. A. (2016). A new extensional mixing element for improved dispersive mixing in twin-screw extrusion, Part 2: experimental validation for immiscible polymer blends. Advances in Polymer Technology, 37(1), 21653 http://dx.doi.org/10.1002/adv.21653
24 Carson, S. O., Covas, J. A., & Maia, J. M. (2015). A new extensional mixing element for improved dispersive mixing in twin-screw extrusion, Part 1: design and computational validation. Advances in Polymer Technology, 36(4), 21627 http://dx.doi.org/10.1002/adv.21627
25 Goes, M. A., Woicichowski, L. A., Rosa, R. V. V., Santos, J. P. F., & Carvalho, B. M. (2021). Improving the dispersion of MWCNT and MMT in PVDF melts employing controlled extensional flows. Journal of Applied Polymer Science, 138(17), 50274 http://dx.doi.org/10.1002/app.50274
26 Feigl, K., Tanner, F. X., Edwards, B. J., & Collier, J. R. (2003). A numerical study of the measurement of elongational viscosity of polymeric fluids in a semihyperbolically converging die. Journal of Non-Newtonian Fluid Mechanics, 115(2–3), 191 215 http://dx.doi.org/10.1016/j.jnnfm.2003.08.002
27 Beatrice, C. A. G., Branciforti, M. C., Alves, R. M. V., & Bretas, R. E. S. (2010). Rheological, mechanical, optical, and
Polímeros, 32(2), e2022020,
transport properties of blown films of polyamide 6/residual monomer/montmorillonite nanocomposites. Journal of Applied Polymer Science, 116(6), 3581 3592 http://dx.doi.org/10.1002/ app.31898
28. Khajehpour, M., Arjmand, M., & Sundararaj, U. (2016). Dielectric properties of multiwalled carbon nanotube/clay/ polyvinylidene fluoride nanocomposites: effect of clay incorporation. Polymer Composites, 37(1), 161 167 http:// dx.doi.org/10.1002/pc.23167
29. Hsissou, R., Bekhta, A., Dagdag, O., El Bachiri, A., Rafik, M., & Elharfi, A. (2020). Rheological properties of composite polymers and hybrid nanocomposites. Heliyon, 6(6), e04187 http://dx.doi.org/10.1016/j.heliyon.2020.e04187. PMid:32566792.
30 Demarquette, N. R., & Carastan, D. J. (2016). Rheological behavior of nanocomposites. In J. Parameswaranpillai, N. Hameed, T. Kurian, & Y. Yu (Eds.), Nanocomposite materials: synthesis, properties and applications (pp. 233 264 ). USA: CRC Press, Taylor & Francis Group http://dx.doi. org/10.1201/9781315372310
31 Behera, K., & Chiu, F. C. (2020). Evident improvements in the rigidity, toughness, and electrical conductivity of PVDF/ HDPE blend with selectively localized carbon nanotube. Polymer Testing, 90, 106736 http://dx.doi.org/10.1016/j. polymertesting.2020.106736
32 Zhang, Q., Fang, F., Zhao, X., Li, Y., Zhu, M., & Chen, D. (2008). Use of dynamic rheological behavior to estimate the dispersion of carbon nanotubes in carbon nanotube/polymer composites. The Journal of Physical Chemistry B, 112(40), 12606 12611 http://dx.doi.org/10.1021/jp802708j. PMid:18785703.
33 Ke, K., Wang, Y., Liu, X.-Q., Cao, J., Luo, Y., Yang, W., Xie, B.-H., & Yang, M.-B. (2012). Composites : part B A comparison of melt and solution mixing on the dispersion of carbon nanotubes in a poly (vinylidene fluoride) matrix. Composites. Part B, Engineering, 43(3), 1425 1432 http:// dx.doi.org/10.1016/j.compositesb.2011.09.007
34 Vermogen, A., Masenelli-Varlot, K., Séguéla, R., DuchetRumeau, J., Boucard, S., & Prele, P. (2005). Evaluation of the structure and dispersion in polymer-layered silicate nanocomposites. Macromolecules, 38(23), 9661 9669 http:// dx.doi.org/10.1021/ma051249+
35 Durmus, A., Kasgoz, A., & Macosko, C. W. (2007). Linear low density polyethylene (LLDPE)/clay nanocomposites. Part I: structural characterization and quantifying clay dispersion by melt rheology. Polymer, 48(15), 4492 4502 http://dx.doi. org/10.1016/j.polymer.2007.05.074.
36 Franchini, E., Galy, J., & Gérard, J.-F. (2009). Sepiolite-based epoxy nanocomposites: relation between processing, rheology, and morphology. Journal of Colloid and Interface Science, 329(1), 38 47 http://dx.doi.org/10.1016/j.jcis.2008.09.020 PMid:18848336.
37 Carastan, D. J., Vermogen, A., Masenelli-Varlot, K., & Demarquette, N. R. (2010). Quantification of clay dispersion in nanocomposites of styrenic polymers. Polymer Engineering and Science, 50(2), 257 267 http://dx.doi.org/10.1002/pen.21527
38 Gaspar, H., Santos, R., Teixeira, P., Hilliou, L., Weir, M. P., Duif, C. P., Bouwman, W. G., Parnell, S. R., King, S. M., Covas, J. A., & Bernardo, G. (2019). Evolution of dispersion in the melt compounding of a model polymer nanocomposite system: A multi-scale study. Polymer Testing, 76, 109 118 http://dx.doi.org/10.1016/j.polymertesting.2019.03.013
39 Fernandez, M., Huegun, A., & Santamaria, A. (2019). Relevance of rheology on the properties of PP/MWCNT nanocomposites elaborated with different irradiation/mixing protocols. Fluids, 4(1), 7 http://dx.doi.org/10.3390/fluids4010007
40 Hassanabadi, H. M., Wilhelm, M., & Rodrigue, D. (2014). A rheological criterion to determine the percolation threshold in polymer nano-composites. Rheologica Acta, 53(10), 869 882 http://dx.doi.org/10.1007/s00397-014-0804-0
41 Rostami, A., Masoomi, M., Fayazi, M. J., & Vahdati, M. (2015). Role of multiwalled carbon nanotubes (MWCNTs) on rheological, thermal and electrical properties of PC/ABS blend. RSC Advances, 5(41), 32880 32890 http://dx.doi. org/10.1039/C5RA04043D
42. Poothanari, M. A., Xavier, P., Bose, S., Kalarikkal, N., Komalan, C., & Thomas, S. (2019). Compatibilising action of multiwalled carbon nanotubes in polycarbonate/polypropylene (PC/PP) blends: phase morphology, viscoelastic phase separation, rheology and percolation. Journal of Polymer Research, 26(8), 178 http://dx.doi.org/10.1007/s10965-019-1833-2
43 Pötschke, P., Fornes, T. D., & Paul, D. R. (2002). Rheological behavior of multiwalled carbon nanotube/polycarbonate composites. Polymer , 43 (11), 3247 3255 http://dx.doi. org/10.1016/S0032-3861(02)00151-9
44 Kota, A. K., Cipriano, B. H., Duesterberg, M. K., Gershon, A. L., Powell, D., Raghavan, S. R., & Bruck, H. A. (2007). Electrical and rheological percolation in polystyrene / MWCNT nanocomposites. Macromolecules, 40(20), 7400 7406 http:// dx.doi.org/10.1021/ma0711792
45 Wu, G., Lin, J., Zheng, Q., & Zhang, M. (2006). Correlation between percolation behavior of electricity and viscoelasticity for graphite filled high density polyethylene. Polymer, 47(7), 2442 2447 http://dx.doi.org/10.1016/j.polymer.2006.02.017
46 Huang, A., Wang, H., Ellingham, T., Peng, X., & Turng, L.-S. (2019). An improved technique for dispersion of natural graphite particles in thermoplastic polyurethane by sub-critical gasassisted processing. Composites Science and Technology, 182, 107783 http://dx.doi.org/10.1016/j.compscitech.2019.107783
47 Banerjee, J., Kummara, S., Panwar, A. S., Mukhopadhyay, K., Saxena, A. K., & Bhattacharyya, A. R. (2021). Influence of carbon nanotube type and novel modification on dispersion, melt-rheology and electrical conductivity of polypropylene/ carbon nanotube composites. Polymer Composites, 42(1), 236 252 http://dx.doi.org/10.1002/pc.25821
Received: Jan. 10, 2022
Revised: June 03, 2022
Accepted: July 06, 2022
32(2), e2022020, 2022
https://doi.org/10.1590/0104-1428.20210102
Janis Schutte Nunes1* , Edson Noriyuki Ito2 , Cléverson Fernandes Senra Gabriel1,3 , Thiago Castro Lopes1 and Regina Célia Reis Nunes1
1Instituto de Macromoléculas – IMA, Universidade Federal do Rio de Janeiro – UFRJ, Rio de Janeiro, RJ, Brasil
2Centro de Tecnologia, Departamento de Engenharia de Materiais, Universidade Federal do Rio Grande do Norte – UFRN, Natal, RN, Brasil
3Laboratório de Tecnologia de Materiais Poliméricos – LAMAP, Instituto Nacional de Tecnologia – INT, Rio de Janeiro, RJ, Brasil *janis_schutte@yahoo.com.br
Nitrile rubber (NBR) nanocomposites with different contents of synthetic Somasif ME-100 mica (sodium-fluorohectorite) were obtained by melt compounding using a Semi Efficient curing system. The effect of curing on the nanocomposties was evaluated through rheometric properties, crosslink density (CLD) and mechanical properties. The ME-100 mica dispersion in NBR was assessed by transmission electron microscopy (TEM), the Payne effect and thermodynamic properties (ΔS and ΔG). Both the curing parameters and CLD pointd out that the addition of ME-100 directly affects crosslinks formation. It could also be observed that the nanofiller dispersion state is complex, exhibiting exfoliated and agglomerated structures (TEM); besides, agglomerations rose linearly as the nanofiller was added (the Payne effect). Notwithstanding these findings, and on the basis of unfilled formulations, NBR20 nanocomposite showed improvement in mechanical properties (tensile and tear strengths) which suggests that ME-100 might be considered a semi-reinforcing filler.
Keywords: crosslink density, fluoromica, mechanical properties, nitrile rubber, synthetic mica.
How to cite: Nunes, J. S., Ito, E. N., Gabriel, C. F. S., Lopes, T. C., & Nunes, R. C. R. (2022). Physical-mechanical behavior of nitrile rubber-synthetic mica nanocomposites. Polímeros: Ciência e Tecnologia, 32(2), e2022021. https:// doi.org/10.1590/0104-1428.20210102
The high polarity of nitrile rubber (NBR), a copolymer of butadiene and acrylonitrile, makes it highly resistant to oils and organic solvents, while having low gas permeability and temperature degradation higher than natural rubber. These features enable its use in automotive products, oil seals, fuel hoses, among others[1,2]
In order to provide technological application, depending on the application of the final product, the formulation of an elastomeric composition usually contain a filler, a curing system, processing and protecting agents such as antioxidants[3]. These components alter the compound viscosity with direct impact on processing as well as on the final product physical mechanical properties[4,5]
Carbon black and silica are the most widely used reinforcement fillers for elastomeric formulations, besides, other fillers, functionalized or not, have been widely employed as an alternative to the conventional systems[6]. A significant amount of research papers has been directed to the development and use of different fillers with dimensions in the nanometric scale, clays being highlighted[6-11].
Among the group of clays being employed as nanofillers of elastomeric compositions, the synthetic micas should be highlighted. Their main advantages, as compared to
natural mica, are better control of variables such as purity and composition, besides the possibility of altering their structure for fitting in with the matrix into which they will be incorporated[12-20]
The synthetic mica marketed as Somasif ME-100 (sodiumfluorohectorite) is prepared from talc by introducing an alkaline metal in the interlamellar galleries[21]. Somasif ME-100, as well as montmorillonite, exhibits a layered silicate structure but differs from the latter by the absence of catalytically active Al ions as substitutes at the octahedral sites. A further difference is the partial replacement of silicate layers hydroxyl groups by fluorine[22]
Because of the high viscosity of the elastomeric matrix, the dispersion of any inorganic material is a challenging task, chiefly when it is related to a nanofiller. In order to reach the desired dispersion degree, various methods are proposed in the literature[6,7].
In the last seven years, few works have been published with Somasif ME-100 synthetic mica[23,24]. The amount of articles is even smaller when it comes to the use of Somasif ME-100 with polymers[15,25-34]. This fluoromic was little explored in NBR, which is a very important rubber for the industry, and only one article was found in the literature
that correlates Somasif ME-100 with NBR[16]. Justifying the work’s importance and novelty.
This work shows the continuity of Linhares et al.[16] work where ME-100 synthetic mica nanocomposites with NBR were prepared by melt compounding. This method being chosen by the versatility as concerns temperature, roller shear rate, and show practical relevance. The content of the ME-100 synthetic mica in this work varied from 0 to 20 phr. The 20phr ME-100 nanocomposite showed improvement in mechanical properties which suggests that ME-100 might be considered a semi-reinforcing filler.
The received nitrile rubber had the following features: Mooney viscosity 48 ML1+4 (100°C) and acrylonitrile content 33%. The synthetic mica for the compositions was sodium fluorohectorite (Somasif ME-100), with cation exchange capacity of 100 meq/100 g and an intergallery distance of 0.95 nm[20] and in this work will be referred to as ME-100. The characterization of this synthetic mica has already been carried out by our working group and can be found in Linhares et al.[16]. According to the manufacturer (COOP ChemicalCo. Ltd, Japan), Somasif mica ME-100 have the general chemical composition (Na)2x(Mg)3-x(Si4O10)(FyOH1-y)2·nH2O, where 0.15 < x < 0.5; 0.8 < y < 1.0.
The information on the prepared formulations is listed in Table 1, and an unfilled composition (NBR0) stands for comparison with the properties of the nanocomposites.
The preparation of the mixes was done in an open roller mill, at 50±5°C. At first mica was added to the rubber for 10 minutes at a roller shear rate of 24/40 aiming at favoring the distribution and dispersion of mica into NBR [13,16]. This procedure was carried out in all formulations in order to maintain a mixing pattern.
After this period of time, the vulcanization system was incorporated into the formulation at a shear rate of 24/34 in accordance with the ASTM D3187 Method.
The samples’ vulcanization process was performed by compression molding at the temperature of 160°C.
The period of time used for molding was the optimum curing time (t90), determined with the aid of the Rubber Process Analyzer (RPA) instrument.
The curing characteristics for the prepared mixtures were obtained using the Rubber Process Analyzer (RPA 2000 from the Monsanto Company) instrument, in accordance with the ASTM D5289 Method under the following experimental conditions: 160°C (constant temperature), 30 minutes, deformation arc 1 degree and 1.7 Hz of frequency. The RPA instrument enables the determination of the following rheometric parameters: pre-curing time (ts 1); optimum curing time (t90) related to 90% cure; minimum torque (ML); maximum torque (MH); cure rate index (CRI) the formula of which is given by Equation 1[35]
The dependence of the dynamic properties on the deformation amplitude for all of the compositions was studied by the Payne Effect as measured by the RPA 2000 instrument at 60 ºC, test frequency of 1 Hz and strain from 0.7 to 100%[36,37]. The same procedure was adopted before and after curing. According to Payne, such dependence is essentially determined by the level of agglomeration and deglomeration of the filler tridimensional network in the elastomeric matrix[37]
The Payne effect can be calculated by the difference between the complex moduli in the region of low strains and high strains, see Equation 2, based on a specific strain value, temperature and frequency being kept constant[36-40]
ΔG* will be treated as the absolute value of the Payne Effect; besides, in this work the value of G*0 will be considered at 10% deformation while the value of G*
will be considered at 100% deformation.
The crosslink density was measured with the aid of two different methods, the RPA Method and the swelling method.
In the RPA method the crosslink density (CD) is determined with the aid of the rubber processing analyzer RPA 2000. To this end the elastic modulus (G’) of the uncured compounds (G’uncured) was determined at a frequency of 5 Hz, the elastic modulus of the cured compouds (G’cured)
Polímeros, 32(2), e2022021,
Nunes, J. S., Ito, E. N., Gabriel, C. F. S., Lopes, T. C., & Nunes, R. C. R.determined at a frequency of 0.5 Hz at the temperature of 60°C and 0.25o deformation[41-43].
On the basis of the obtained results it is possible to estimate the total crosslinks (Xtotal) content in the sample, as well as the two types of crosslinks of the vulcanized rubbers: the physical links (Xphysical), related to the physical entanglements of the polymer chains; the chemical links (Xchemical), generated in the vulcanization process, crosslinks[42] Equation 3, Equation 4 and Equation 5 are used for the calculations.
The value of V r obtained in Equation 8 enables the calculation of the thermodynamic parameters. Based on the assumption that the internal energy of the tested materials has not been altered by swelling, the Gibbs free energy (ΔG) and the entropy variation (ΔS) can be determined by the Flory–Huggins equation and the statistical theory of the rubber elasticity (Equation 9 and Equation 10)[19,47-52]
The parameters of Equation 9 have the same meaning as those of Equation 7, R being the gas constant and T the absolute temperature.
Where R = gas constant (8.314 L·kPa·K−1·mol
); T = absolute temperature (333.15 K). In order to discount the presence of filler, Equation 6, the Guth-Gold[42] Equation, was used.
Where, ø is the filler volume fraction (filler volume / total volume).
The crosslink density (ν) was also determined with the aid of the solvent swelling principle, in this case acetone at 27°C, for the Flory-Rehner[44,45] solvent swelling equilibrium Equation 7:
X-Ray Diffraction (XRD) was used for the characterization and identification of Mica ME-100 and generated composites. The XRD analysis was performed in a Rigaku equipment, model MiniFlex, with 2θ scanning from 2 to 10°, CuK α radiation (λ =1.5418 Å), 30 kV and 15 mA. The interplanar distances of mica were determined by the Bragg Equation (Equation 11), based on results obtained by X-ray scattering at high angles of incidence (WAXS).
ν is the value for the crosslink density; χ corresponds to the NBR-solvent interaction parameter, (0.345 for acetone), V0 is the solvent molar volume (73.40 mL.mol-1 for acetone), the solubility parameter for NBR (acrylonitrile content 33%) is δ = 9.36 (cal/cm)2 [44] and Vr is the volume fraction of rubber in the swollen vulcanizate calculated by Equation 8 which discounts, when applicable, the volume of filler used[45,46]
Where: d is the interplanar distance, n is the diffraction order; θ is the diffraction angle (Bragg angle), n= 1 and λ=1.54 Å.
Elongation at break, tensile strength, modulus and tear strength tests were performed with the aid of a EMIC, model DL3000 universal testing machine operating with a 1 kN load cell in accordance with the ASTM D412 and ASTM D624 Methods, respectively. Hardness was determined with the Shore A durometer in accordance with the ASTM D2240 Method.
The morphology of the nanocomposites was studied by transmission electron microscopy (TEM). Samples were sectioned in a Power Tome Ultramicrotome RMC model X by using a Diatome Diamond Knife type Cryo 45°, cutting temperature -70°C cooled with liquid nitrogen, cutting speed 0.3 mm/s and cutting thickness 30 nm. After separation of the samples, samples-containing grids were taken to a Phillips transmission electronic microscope (TEM) model CM120 at an operation tension of 120 kV.
Where M1 is the sample mass before swelling; ρ2 is the sample density; Mf is the filler mass in the sample; ρf is the filler density; M2 is the swollen sample mass; M3 is the dry sample mass after swelling and ρ1 is the solvent density.
Samples were cut from vulcanized, square 20x20 mm 2 mm-thick plates, tested in duplicate and kept in a tightly closed, protected from light acetone-containing flask, for a period of 7 days at ambient temperature (27ºC).
The rheological parameters of the developed formulations are listed in Table 2
The minimum torque (ML) values, related to the viscosity of compositions prior to cure, were kept practically constant
Parameter
NBR0
Minimum Torque (ML) (dN.m) 0.7 0.7
Maximum Torque (MH) (dN.m)
ΔM (MH - ML) (dN.m)
0.7 0.7 0.8
9.0
8.3
Scorch time (ts1) (min) 0.4 0.5 0.5 0.5 0.5 0.5
Optimum cure time (t90) (min)
Cure rate index (CRI) (min)
with the filler content. It was expected that at 20 phr ME100 the increase in ML would be significant, however the ME-100 lamellar structure provided a rheological ease for accommodation of the filler in the polymer matrix, indicating that the nanofiller acted as a processing aid.
The maximum torque (MH) represents post-cure molecular rigidity of the composites and it was only at 20phr ME-100 (NBR20) that the MH value outperformed that of the unfilled composition (NBR0). Data reflected on the torque (ΔM) development, generally used to characterize filler reinforcement and formation of an elastomeric network confined within the interlayer spaces[48,52,53]. These results point out that the ME-100 offers a certain resistance to crosslink formation, reducing the amount of curing agents available for the reaction. This behavior was also observed by Kader and Nah[53] and by Pojanavaraphan et al.[50] when evaluating other nanocomposites.
As regards the vulcanization pre-time (ts1) there are no differences among the tested compositions, however, as for the period for 90% cure (t90), it was observed that for compositions with 5 and 7 phr filler, curing occurs more rapidly as compared to the remaining formulations (< t90), reflecting in this way on the increased cure rate index (> CRI). For the remaining studied compositions these parameters are similar to those of the unfilled composition. Values suggest that for amounts of mica higher than 7 phr the filler is slightly interfering on the curing system, corroborating the effects on the tested ΔM.
For elastomers with load exceeding Tg the Payne effect refers to the dependence of strain on the dynamic viscoelastic properties, For a constant frequency, the complex modulus (G*) is reduced with the increase in strain from a linear plateau value towards a lower plateau of high strain amplitude, as demonstrated in Figure 1A (before cure) and Figure 1B (after cure).
The value of the complex modulus (G*) for the NBR5 and NBR7 compositions was lower than that of the unfilled composition, NBR0, indicating that at low concentrations mica seems to aid the rubber chains to slip easier therefore reducing the energy required for strain to occur.
The filler network is destroyed under high strain and as a result, the complex modulus (G*) is quickly lowered. In this way, the modulus reduction consequent to augmented strain is also due to the rubber macromolecules entanglement and the break of the filler-filler and rubber-filler interactions. The lesser the attenuation of the dynamic modulus, the lower is the network structure formed by the filler, and the lower is the Payne effect. This indicates that the filler is
4.9
Figure 1. Variation of the Complex Modulus (G* - kPa) with strain (%) for unvulcanized (A) and vulcanized (B) NBR containing various amounts of ME-100 Mica.
better dispersed within the polymer matrix. As expected, for filled compositions, the increase in elastic modulus at low strains is attributed to the filler-filler interactions[26].
The values for the Payne effect calculated by the RPA Method for all of the compositions before and after cure are listed in Table 3
The Payne effect analysis for pure gum before and after cure refers to the chain entanglement break that is more accentuated for the cured materials due to the higher viscosity of these solutions. As for the filled compositions, the influence of the rise in ME-100 content is observed by the increase in the Payne effect potentialized in the after cure compositions. These results illustrate the strong filler-filler interaction, which is equivalent to the agglomeration and deglomeration of the filler network.
Polímeros, 32(2), e2022021,
Nunes, J. S., Ito, E. N., Gabriel, C. F. S., Lopes, T. C., & Nunes, R. C. R.The results for crosslink density as determined by the RPA Method and solvent (acetone) swelling can be found in Table 4
The RPA Method enables the calculation of two kinds of crosslinks: physical (Xphysical) and chemical (Xchemical), and as a result the total crosslink density (XTotal)[35,41,42,54]. Data acquisition is quick and does not require the use of solvents. The physical content means the initial crosslink density resulting from entanglements and other effects. Data (Table 4) indicate that the physical content was not modified by nanofillers to NBR. As for the chemical content, which results from the curing reaction, nanocomposites exhibited equivalent values and did not show any influence of the amount of filler, being lower than those for the unfilled compositions. The total crosslink density by RPA suggests that the slower curing reaction with the ME-100 content might probably due to cure retardation of ME-100 by adsorbing a part of the curing agents and blocking the movement of rubber chains as showed by the result of the chemical content. (Kader and Nah, 2004[53] and Pojanavaraphan, et al., 2010[50]). An alternative for future work would be to increase the content of the curing system, as was successfully done by Kader and Nah[53]. The swelling values corroborate the results obtained for maximum torque (TM) and ΔM (Table 2) and crosslink density by RPA.
Results for crosslink density obtained by the swelling method (ν) and those for the volume fraction of rubber in the swollen vulcanizate (Vr), both determined by the Flory and Rhener theory for all the compositions can also be found in Table 4. Data obtained from the swelling test show reduced nanocomposites crosslink when compared with the unfilled compositions as a result from lower Vr values caused by the presence of ME-100 (Table 4). As compared
with the values measured by RPA for the crosslink density, data for crosslink density by swelling are lower than those obtained by RPA, although more sensitive to the nanofiller behavior in the NBR.
The swelling behavior is in agreement with the data obtained by the rheometer and the value of the crosslink density by RPA suggest that the curing process has been restricted by ME-100 addition.
Thermodynamic effects, including entropy (ΔS) and Gibbs free energy (ΔG), that occur by swelling of the developed compositions were also determined and may provide the basis for understanding the nanofillers addition to NBR. The expansion of rubber in the presence of solvent will significantly modify the conformational entropy (ΔS) and the Gibbs free energy (ΔG)[19,47-52]
According to Table 5 the Gibbs free energy is negative for all samples. (ΔG) is correlated to the elastic behavior of the swollen compositions, influenced by the solvent, kind and ME-100 content in NBR.
It can be seen that in the presence of ME-100, ΔG falls (in absolute values) that is, the elasticity of the nanocomposites is lower than that of the pure gum in the swollen state. These results can be attributed to the low compatibility between NBR/ME-100, and are also responsible for the entropy loss as compared with the unfilled composition. The rubber molecules do not succeed in easily penetrating the galleries, hindering the process of ME-100 intercalation.
The Mica ME-100 diffractogram, which is represented in Figure 2, exhibited two peaks, one located at 7.05° and the other at 9.20°. These peaks correspond, respectively, to the interlamellar space (d001) of 1.25 nm and 0.96 nm (Table 6). According to Cattaneo et al.[55], the interlamellar space equal to 0.96 nm is related to the unhydrated silicate layer, while 1.25 nm corresponds to the hydrated form of the silicate layer.
NBR0
The intercalation of polymeric chains in the silicate layers can be characterized by an increase in the interplanar spacing[56], however this was not observed. Based on the 2θ values of the XRD (Figure 2) and the stability of the interplanar distance (Table 6) of the formed composites, there is no evidence that there are NBR chains intercalated
Table 4. Crosslink density of the NBR composites with and without ME-100 Synthetic Mica.
NBR0
NBR5
NBR7
NBR10
NBR14
NBR20
2.7±0.1
70.5±0.9 0.306±0.001
46.6±1.4 0.258±0.002
52.7±0.6 0.271±0.009
52.2±0.6 0.270±0.001
51.9±0.2 0,269±0.001
55.3±0.1 0.277±0.001
between the Mica layers. In addition, when we observe the increase in the intensity of the peaks of the composites formed, in relation to mica ME100, it is possible to affirm that the formed system predominantly presents agglomerations of filler, which increased with higher Mica ME100 content. This result is in agreement with that observed in the payne effect.
The mechanical properties of the nanocomposites are summarized in Table 7
Data of Table 7 might suggest ME-100 is acting as a semi-reinforcing filler in view of a 92% rise in tensile strength and 52% in elongation at break when data for the unfilled composition (NBR0) are compared with those for the highest filler-containing composition (NBR20), while values for hardness and minimum torque are unchanged. The mechanical results of the NBR7 sample, with the exception of the elongation, are within the experimental error. The elongation of NBR7 is an unexpected result and can be statistically compared to the value of this property with the unloaded composition (NBR0). However, it is the NBR7 composition that has the highest modulus at 100%, even higher than the composition with 20phr, and this result may be related to the low elongation value found. Therefore it is possible to state that the movement and accommodation
Table 5. Thermodynamic characteristics of the studied compositions. Composition ΔG (J.mol-1) ΔS (J.mol-1.K-1)
NBR0 -67.26 0.2241
NBR5 -43.34 0.1444
NBR7 -49.27 0.1641
NBR10 -48.91 0.1630
NBR14 -48.58 0.1618
NBR20 -51.97 0.1731
Table 6. Peak positions (2θ), interplanar spacing (d) of the Mica ME 100 peaks and their composites with NBRL, obtained by XRD.
Composition 2θ (Degrees) Interplanar spacing, d(nm)
Mica ME100
NBR0
NBR5
NBR7
NBR10
NBR14
NBR20
Elongation at break (%)
Tensile strength (MPa)
Modulus at 50% Elongation (MPa)
of the rubber chains among the Mica lamellae was favored, this in turn increasing the chain fluidity, a fact that impacted the mechanical performance.
Concerning the tear strength, the compositions with higher-than 5 phr mica contents exhibited better performance as compared to the unfilled composition, and for the nanocomposite with 20 phr ME-100 a 42% increase was observed. As the cracks of the tear test propagate through the chains, they are restricted by the crosslinks which deform up to a certain point to hinder crack propagation. Since crosslinks values were very similar for all filled compositions and lower relative to the unfilled composition, it is possible to state that in this case the tear strength is directly related to the filler ability to dissipate crack propagation.
The lamellar nature, the plasticizing effect and a certain reluctance of the nanofiller for forming crosslinks can be understood in the light of the mechanical results related to molecular stiffness such as tensile strength at 50% elongation and 100% elongation, and hardness. These results did not exhibit significant increase with the filler content, corroborating the values for maximum torque determined by rheometry. These behaviors are interesting chiefly those for the 20 phr filler composition, since as compared with the unfilled composition it has better performance as regards tensile, elongation at break and tear strength values, hardness values being kept constant.
The TEM images of the NBR/ME-100 nanocomposites containing 5 phr (NBR5), 10 phr (NBR10) and 20 phr (NBR20) are illustrated in Figure 3, Figure 4 and Figure 5 respectively.
NBR0
Figure 2. XRD pattern of NBR/Mica ME100 composites, unfilled NBR (NBR0), and Mica ME100 powder.
0.9±0.0
Modulus at 100% Elongation (MPa) 1.1±0.0
Tear strength (N/mm)
Hardness (Shore A)
Polímeros, 32(2), e2022021,
Nunes, J. S., Ito, E. N., Gabriel, C. F. S., Lopes, T. C., & Nunes, R. C. R.As the filler content rises, evidences of exfoliated platelets and large aggregates are observed, corroborating the results for the Payne effect. Dark spots on the micrographs are related to the additives employed while the dark lines (Figure 3) show the nanofiller dispersion in the NBR matrix.
Taking into consideration that there is an optimum amount of ME-100 related to the intercalation/exfoliation phenomena, TEM results indicate that the rise in nanofiller content resulted in the morphology showing predominance of aggregates (Figure 4), fact that is in agreement with what was observed in the XRD, although without prejudice to the mechanical properties, as observed in this work. As for the case with the NBR composition containing 20 phr ME100 (Figure 5) it is apparent that the layers and aggregates of the nanofiller created a morphology that resulted in improved mechanical properties[20], as shown in Table 7
NBR nanocomposites of different contents of ME100 synthetic mica were prepared by a mill mixing process and characterized.
The curing parameters indicated that the ME-100 offers a certain resistance to crosslink formation, reducing the amount of curing agents available for the reaction. This reluctance was ascertained by the analysis of the crosslink density, on the basis of the Flory and Rhener theory and RPA, both methods indicating the the crosslink density was always lower for the filled nanocomposites than for the unfilled nanocomposite. This phenomenon may have been caused by the formation of Mica ME100 clusters observed in both XRD and TEM results. These agglomerates may have made it difficult for sulfur to find the polymer chains and carry out the vulcanization reaction.
The values obtained for the Gibbs free energy can be attributed to the low compatibility between NBR and ME-100, and are also responsible for the entropy loss as compared to the unfilled composition. Besides, the dispersion state of ME-100 in NBR studied by the Payne effect indicated that the value of the modulus attenuation increased with increase in shear and with the filler content meaning low ME-100 dispersion in NBR. These results were corroborated by Transmission Electronic Microscopy (TEM) and XRD.
The TEM image and XRD of the 20 phr ME100 nanocomposite demonstrated that the layers and aggregates of the nanofiller created a kind of morphology which might have been responsible for the improvement in mechanical properties, which suggests that ME-100 mica might be considered a semi-reinforcing filler.
Since NBR is an important, widely utilized rubber, the use of a light-colored nanofiller such as ME-100 can be of huge technological interest before the results obtained.
• Conceptualization – Janis Schutte Nunes; Edson Noriyuki Ito; Cléverson Fernandes Senra Gabriel; Thiago Castro Lopes; Regina Célia Reis Nunes.
• Data curation – Janis Schutte Nunes; Cléverson Fernandes Senra Gabriel; Thiago Castro Lopes.
• Formal analysis – Janis Schutte Nunes; Cléverson Fernandes Senra Gabriel; Regina Célia Reis Nunes.
• Investigation – Janis Schutte Nunes; Edson Noriyuki Ito; Cléverson Fernandes Senra Gabriel; Thiago Castro Lopes; Regina Célia Reis Nunes.
Physical-mechanical behavior of nitrile rubber-synthetic mica nanocompositesNunes, J. S., Ito, E. N., Gabriel, C. F. S., Lopes, T. C., & Nunes, R. C. R.
• Methodology – Janis Schutte Nunes; Edson Noriyuki Ito; Cléverson Fernandes Senra Gabriel; Thiago Castro Lopes; Regina Célia Reis Nunes.
• Project administration – Regina Célia Reis Nunes.
• Resources – Edson Noriyuki Ito; Cléverson Fernandes Senra Gabriel; Regina Célia Reis Nunes.
• Software – Janis Schutte Nunes; Cléverson Fernandes Senra Gabriel; Thiago Castro Lopes.
• Supervision – Cléverson Fernandes Senra Gabriel; Regina Célia Reis Nunes.
• Validation – Regina Célia Reis Nunes; Cléverson Fernandes Senra Gabriel.
• Visualization – Regina Célia Reis Nunes; Edson Noriyuki Ito.
• Writing – original draft – Janis Schutte Nunes; Edson Noriyuki Ito; Cléverson Fernandes Senra Gabriel; Thiago Castro Lopes; Regina Célia Reis Nunes.
• Writing – review & editing – Janis Schutte Nunes; Edson Noriyuki Ito; Cléverson Fernandes Senra Gabriel; Thiago Castro Lopes; Regina Célia Reis Nunes.
Authors are indebted to CNPq, CAPES and FAPERJ for financial support and to Nitriflex S/A Indústria e Comércio for donation of the nitrile rubber, Co-Op Chemical Co. Ltda (Tokyo, Japan) for donation of the sodium fluorohectorite (Somasif ME-100) and Teadit Indústria e Comércio Ltda for donation of the additives utilized in the compositions.
1 Palaty, S., & Joseph, R. (2006). Low temperature curing of NBR for property improvement. Journal of Elastomers and Plastics, 38(3), 199 209. http://dx.doi.org/10.1177/0095244306063479.
2 Schuster, H. R. (2019). Dispersión de cargas y reforzamiento: ciencia y aplicación. Buenos Aires: Sociedad Latinoamericana de Tecnologia del Caucho - SLTC
3 Sisanth, K. S., Thomas, M. G., Abraham, J., & Thomas, S. (2017). General introduction to rubber compounding. In S. Thomas & H. J. Maria (Eds.), Progress in rubber nanocomposites (pp. 1 39). United Kingdom: Woodhead Publishing http://dx.doi. org/10.1016/B978-0-08-100409-8.00001-2
4 Sousa, A. M. F., Peres, A. C. C., Furtado, C. R. G., & Visconte, L. L. Y. (2017). Mixing process influence on thermal and rheological properties of NBR/SiO2 from rice husk ash. Polímeros: Ciência e Tecnologia, 27(2), 93 99 http://dx.doi. org/10.1590/0104-1428.1959.
5 Morrill, J. P. (1968). Nitrile Elastomers. In G. G. Winspear (Ed.), The vanderbilt rubber handbook (pp. 169 188). USA: R. T. Vanderbilt Company, Inc.
6 Galimberti, M., Cipolletti, V., Musto, S., Cioppa, S., Peli, G., Mauro, M., Gaetano, G., Agnelli, S., Theonis, R., & Kumar, V. (2014). Recent advancements in rubber nanocomposites. Rubber Chemistry and Technology, 87(3), 417 442 http:// dx.doi.org/10.5254/rct.14.86919
7 Das, A., Wang, D.-Y., Stockelhuber, K. W., Jurk, R., Fritzsche, J., Klüppel, M., & Heinrich, G. (2011). Rubber–clay nanocomposites: some recent results. In G. Heinrich (Ed.), Advanced polymer science (pp. 85 166) Germany: Springer Berlin Heidelberg.
8 Kumar, V., & Lee, D.-J. (2016). Studies of nanocomposites based on carbon nanomaterials and RTV silicone rubber. Journal of Applied Polymer Science, 134(4), 44407
9 Monfared, A., & Jalali-Arani, A. (2015). Morphology and rheology of (styrene-butadiene rubber/acrylonitrile-butadiene rubber) blends filled with organoclay: the effect of nanoparticle localization. Applied Clay Science, 108, 1 11 http://dx.doi. org/10.1016/j.clay.2015.02.012
10. Pavlidou, S., & Papaspyrides, C. D. (2008). A review on polymer–layered silicate nanocomposites. Progress in Polymer Science, 33(12), 1119 1198. http://dx.doi.org/10.1016/j. progpolymsci.2008.07.008
11 Wang, Y.-Q., Wu, Y.-P., Zhang, H.-F., Zhao, W., Wang, C.-X., & Zhang, L.-Q. (2005). Preparation, structure, and properties of a Novel Rectorite/Nitrile Butadiene Rubber (NBR) nanocomposites. Polymer Journal, 37(3), 154 161 http://dx.doi.org/10.1295/polymj.37.154
12 Carrado, K. A. (2000). Synthetic organo- and polymer–clays: preparation, characterization, and materials applications. Applied Clay Science, 17(1-2), 1 23 http://dx.doi.org/10.1016/ S0169-1317(00)00005-3
13. Gabriel, C. F. S. (2018). Desenvolvimento e caracterização de composições de NBR em fardo e em látex com mica Somasif ME100TM (Dissertação de mestrado). Instituto de Macromoléculas Professora Eloisa Mano, Universidade Federal do Rio de Janeiro, Rio de Janeiro, Brasil
14 Gatos, K. G., Thomann, R., & Karger-Kocsis, J. (2004). Characteristics of ethylene propylene diene monomer rubber/ organoclay nanocomposites resulting from different processing conditions and formulations. Polymer International, 53(8), 1191 1197 http://dx.doi.org/10.1002/pi.1556
15 Honorato, L., Dias, M. L., Azuma, C., & Nunes, R. C. R. (2016). Rheological properties and curing features of natural rubber compositions filled with fluoromica ME 100. Polímeros: Ciência e Tecnologia, 26(3), 249 253. http://dx.doi.org/10.1590/01041428.2352.
16 Linhares, F. N., Gabriel, C. F. S., Sousa, A. M. F., & Nunes, R. C. R. (2018). Mechanical and rheological properties of nitrile rubber/fluoromica composites. Applied Clay Science, 162, 165 174 http://dx.doi.org/10.1016/j.clay.2018.06.004
17 Psarras, G. C., Gatos, K. G., Karahaliou, P. K., Georga, S. N., Krontiras, C. A., & Karger-Kocsis, J. (2007). Relaxation phenomena in rubber/layered silicate nanocomposites. Express Polymer Letters, 1(12), 837 845 http://dx.doi.org/10.3144/ expresspolymlett.2007.116
18 Varghese, S., & Karger-Kocsis, J. (2003). Natural rubber-based nanocomposites by latex compounding with layered silicates. Polymer, 44(17), 4921 4927. http://dx.doi.org/10.1016/S00323861(03)00480-4.
19 Varghese, S., Karger-Kocsis, J., & Gatos, K. G. (2003). Melt compounded epoxidized natural rubber/layered silicate nanocomposites: structure-properties relationships. Polymer, 44 ( 14 ), 3977 3983 http://dx.doi.org/10.1016/S00323861(03)00358-6
20 Varghese, S., Gatos, K. G., Apostolov, A. A., & Karger-Kocsis, J. (2004). Morphology and mechanical properties of layered silicate reinforced natural and polyurethane rubber blends produced by latex compounding. Journal of Applied Polymer Science, 92(1), 543 551 http://dx.doi.org/10.1002/app.20036
21. Tateyama, H., Tsunematsu, K., Kimura, K., Hirosue, H., Jinnai, K., & Furusawa, T. (2010). US 5204078A. Retrieved in 2021, December 2, from https://patentimages.storage.googleapis. com/93/21/18/e0caa019ef57dd/US5204078.pdf
22 Gelfer, M. Y., Burger, C., Nawani, P., Hsiao, B. S., Chu, B., Si, M., Rafailovich, M., Panek, G., Jeschke, G., Fadeev, A. Y., & Gilman, J. W. (2007). Lamellar nanostructure in “Somasif”based organoclays. Clays and Clay Minerals, 55(2), 140 150 http://dx.doi.org/10.1346/CCMN.2007.0550203
Polímeros, 32(2), e2022021, 2022
23 Klabunde, S., Doerenkamp, C., Oliveira, M., Zeng, Z., & Eckert, H. (2021). Inorganic-organic hybrid materials based on the intercalation of radical cations: 2-(4-N-methylpyridinium)-4, 4, 5, 5-tetramethyl-4, 5-dihydro-1H-imidazol-1-oxyl-3-N-oxide in fluoromica clay. Zeitschrift für Physikalische Chemie, 236(68), 961 978 http://dx.doi.org/10.1515/zpch-2021-3133
24 Sugiura, M., Sueyoshi, M., Seike, R., Hayashi, T., & Okada, T. (2020). Hydrated silicate layer formation on mica-type crystals. Langmuir, 36(18), 4933 4941 http://dx.doi.org/10.1021/acs. langmuir.0c00358. PMid:32330044.
25 Alosime, E. M., Edwards, G. A., & Martin, D. J. (2015). Structure-property relationships in copolyester elastomerlayered silicate nanocomposites. Journal of Applied Polymer Science, 132(13), 41742 http://dx.doi.org/10.1002/app.41742
26 Balcerzak, M., Pietralik, Z., Domka, L., Skrzypczak, A., & Kozak, M. (2015). Adsorption of dimeric surfactants in lamellar silicates. Nuclear Instruments & Methods in Physics Research. Section B, Beam Interactions with Materials and Atoms, 364, 108 115 http://dx.doi.org/10.1016/j.nimb.2015.07.135
27 Fukushima, Y., Yamada, T., Tamura, K., & Shibata, K. (2018). Dynamic of organic species in organo-clay/polypropyrene composite by quesi-elastic neutron scattering. Applied Clay Science, 155, 15 19 http://dx.doi.org/10.1016/j.clay.2017.12.041
28. Huth, M., Chen, C.-W., & Wagner, V. (2018). Measurement of Hansen solubility parameters for organophilic fluoromica and evaluation of potential solvents for exfoliation. Applied Clay Science, 155, 120 125 http://dx.doi.org/10.1016/j. clay.2018.01.012.
29 Huth, M., Chen, C.-W., Köhling, J., & Wagner, V. (2018). Influence of Hansen solubility parameters on exfoliation of organophilic fluoromica. Applied Clay Science, 161, 412 418 http://dx.doi.org/10.1016/j.clay.2018.04.036
30 Kiersnowski, A., Chrissopoulou, K., Selter, P., Chlebosz, D., Hou, B., Lieberwirth, I., Honkimäki, V., Mezger, M., Anastasiadis, S. H., & Hansen, M. R. (2018). Formation of oriented polar crystals in bulk poly (vinylidene fluoride)/highaspect-ratio organoclay nanocomposites. Langmuir, 34(44), 13375 13386 http://dx.doi.org/10.1021/acs.langmuir.8b02412 PMid:30350703.
31 Leone, G., Giovanella, U., Galeotti, F., Barba, L., Arrighetti, G., Scavia, G., Rapallo, A., & Porzio, W. (2016). Conjugated dye-intercalated fluoromica hybrids displaying tunability of optical properties through packing variation. Dyes and Pigments, 124, 53 62 http://dx.doi.org/10.1016/j.dyepig.2015.09.003
32 Mohamadi, M., Garmabi, H., & Keshavarzi, F. (2016). An investigation of the effects of organomodified-fluoromica on mechanical and barrier properties of compatibilized high density polyethylene nanocomposite films. Journal of Plastic Film & Sheeting , 32 (1), 10 33 http://dx.doi. org/10.1177/8756087915569097.
33 Tee, N., Zhu, Y., Mortimer, G. M., Martin, D. J., & Minchin, R. F. (2015). Fluoromica nanoparticle cytotoxicity in macrophages decreases with size and extent of uptake. International Journal of Nanomedicine, 10(1), 2363 2375 PMid:25848256.
34 Zhu, Y., Edwards, G. A., & Martin, D. J. (2015). Reduction of aspect ratio of fluoromica using high-energy milling. Applied Clay Science, 114, 315 320. http://dx.doi.org/10.1016/j. clay.2015.06.020
35 Dick, J. S., & Pawlowski, H. (1996). Applications for the curemeter maximum cure rate in rubber compound development process control and cure kinetic studies. Polymer Testing, 15(3), 207 243 http://dx.doi.org/10.1016/0142-9418(95)00033-X
36 Payne, A. R. (1962). The dynamic properties of carbon blackloaded natural rubber vulcanizates. Part I. Journal of Applied Polymer Science, 6(19), 57 63 http://dx.doi.org/10.1002/ app.1962.070061906
37 Payne, A. R. (1962). The dynamic properties of carbon black loaded natural rubber vulcanizates. Part II. Journal of Applied Polymer Science, 6(21), 368 372 http://dx.doi.org/10.1002/ app.1962.070062115
38. Niedermeier, W., Fröhlich, J., & Luginsland, H. D. (2002). Reinforcement mechanism in the rubber matrix by active fillers. Kautschuk und Gummi, Kunststoffe, 55(7-8), 356 366
39 Payne, A. R. (1963). Dynamic properties of heat-treated butyl vulcanizates. Journal of Applied Polymer Science, 7(3), 873 885 http://dx.doi.org/10.1002/app.1963.070070307
40 Payne, A. R., & Whittaker, R. E. (1971). Low strain dynamic properties of filled rubbers. Rubber Chemistry and Technology, 44(2), 440 478. http://dx.doi.org/10.5254/1.3547375.
41 Chattaraj, P. P., Mukhopadhyay, R., & Tripathy, D. K. (1997). Effect of trans-polyoctenylene on crosslink structure of NBR and SBR using solid state 13C NMR Spectroscopy and RPA 2000. Rubber Chemistry and Technology, 70(1), 90 105 http:// dx.doi.org/10.5254/1.3538421
42 Lee, S., Pawlowski, H., & Coran, A. Y. (1994). Method for estimating the chemical crosslink densities of cured natural rubber and styrene-butadiene rubber. Rubber Chemistry and Technology, 67(5), 854 864 http://dx.doi.org/10.5254/1.3538716
43 Pechurai, W., Sahakaro, K., & Nakason, C. (2009). Influence of phenolic curative on crosslink density and other related properties of dynamically cured NBR/HDPE blends. Journal of Applied Polymer Science, 113(2), 1232 1240 http://dx.doi. org/10.1002/app.30036
44 Lapa, V. L. C., Oliveira, P. D., Visconte, L. L. Y., & Nunes, R. C. R. (2008). Investigation of NBR-cellulose II nanocomposites by rheometric and equilibrium swelling properties. Polymer Bulletin, 60(2), 281 290 http://dx.doi.org/10.1007/s00289007-0848-8.
45 Flory, P. J. (1953). Principles of polymer chemistry USA: Cornell University Press
46 Flory, P. J., & Rehner, J., Jr (1943). Statistical mechanics of crosslinked polymer networks I. Rubberlike elasticity. The Journal of Chemical Physics, 11(11), 512 520 http://dx.doi. org/10.1063/1.1723791
47 Hwang, W.-G., Wei, K.-H., & Wu, C.-M. (2005). Synergistic effect of compatibilizer in organo-modified layered silicate reinforced butadiene rubber nanocomposites. Polymer Engineering and Science, 46(1), 80 88 http://dx.doi.org/10.1002/pen.20450
48 López-Manchado, M. A., Herrero, B., & Arroyo, M. (2003). Preparation and characterization of organoclay nanocomposites based on natural rubber. Polymer International, 52(7), 1070 1077 http://dx.doi.org/10.1002/pi.1161
49 Mousa, A., & Karger-Kocsis, J. (2001). Rheological and thermodynamical behavior of styrene/butadiene rubberorganoclay nanocomposites. Macromolecular Materials and Engineering, 286(4), 260 266 http://dx.doi.org/10.1002/14392054(20010401)286:4<260::AID-MAME260>3.0.CO;2-X.
50 Pojanavaraphan, T., Schiraldi, D. A., & Magaraphan, R. (2010). Mechanical, rheological, and swelling behavior of natural rubber/montmorillonite aerogels prepared by freezedrying. Applied Clay Science, 50(2), 271 279 http://dx.doi. org/10.1016/j.clay.2010.08.020
51 Ghari, H. S., & Jalali-Arani, A. (2016). Nanocomposites based on natural rubber, organoclay and nano-calcium carbonate: study on the structure, cure behavior, static and dynamic-mechanical properties. Applied Clay Science, 119(Part 2), 348 357 http:// dx.doi.org/10.1016/j.clay.2015.11.001
52 Tager, A. (1953). Physical chemistry of polymers New York: Cornell University Press
53 Kader, M. A., & Nah, C. (2004). Influence of clay on the vulcanization kinetics of fluoroelastomer nanocomposites. Polymer, 45(7), 2237 2247 http://dx.doi.org/10.1016/j.polymer.2004.01.052
Nunes, J. S., Ito, E. N., Gabriel, C. F. S., Lopes, T. C., & Nunes, R. C. R.
54 Zhao, F., Shi, X., Chen, X., & Zhao, S. (2010). Interaction of vulcanization and reinforcement of CB on dynamic property of NBR characterized by RPA2000. Journal of Applied Polymer Science, 117(2), 1168 1172 http://dx.doi.org/10.1002/app.31918
55. Cattaneo, A. S., Bracco, S., Comotti, A., Galimberti, M., Sozzani, P., & Eckert, H. (2011). Structural characterization of pristine and modified fluoromica using multinuclear solid-state NMR. The Journal of Physical Chemistry C, 115(25), 12517 12529 http://dx.doi.org/10.1021/jp2020676
56 Khederlou, K., Bagheri, R., & Shojaei, A. (2014). A mathematical method for XRD pattern interpretation in clay containing nano composites. Applied Surface Science, 318, 90 94 http://dx.doi. org/10.1016/j.apsusc.2014.01.044
Received: Dec. 02, 2021
Revised: July 07, 2022
Accepted: July 21, 2022
Polímeros, 32(2), e2022021, 2022
https://doi.org/10.1590/0104-1428.20210097
Priscylla Jordânia Pereira de Mesquita1 , Tatianny Soares Alves2 and Renata Barbosa2*
1Laboratório de Polímeros e Materiais Conjugados, Pós-graduação em Ciência e Engenharia dos Materiais, Centro de Tecnologia, Universidade Federal do Piauí – UFPI, Teresina, PI, Brasil
2Laboratório de Polímeros e Materiais Conjugados, Curso de Engenharia de Materiais, Centro de Tecnologia, Universidade Federal do Piauí – UFPI, Teresina, PI, Brasil aThis paper has been partially presented at the 16th Brazilian Polymer Congress, held on-line, 24-28/Oct/2021 *rrenatabarbosa@yahoo.com
In this work, nanocomposites were developed and evaluated using high-density bio polyethylene (BPEAD)/Cloisite 20A (3 and 6%)/commercial antimicrobial additive (0,5 and 1%) containing 1% of zinc pyrithione dispersed in vinyl acetate (EVA). The samples were prepared in a single screw extruder using the melt intercalation technique and then by flat extrusion to obtain the films. X-ray diffraction (XRD) showed an increase in basal spacing and exfoliation of the structure of some films. The Fourier Transform Infrared Spectroscopy (FTIR) analysis illustrated the main functional groups for BHDPE and EVA. Thermal analysis indicated that BHDPE degradation did not change with organoclay addition, but crystallinity increased. The mechanical properties showed an increase in the elastic modulus and a decrease in maximum tensile strength. This work contributes to the development and improvement of the natural properties of BHDPE in order to enlarge its applications.
Keywords: bio polyethylene, clay, flat films, nanocomposites.
How to cite: Mesquita, P. J. P., Alves, T. S., & Barbosa, R. (2022). Development and characterization of green polyethylene/clay/antimicrobial additive nanocomposites. Polímeros: Ciência e Tecnologia, 32(2), e2022022. https:// doi.org/10.1590/0104-1428.20210097
Biopolymers and their innovative technological processes have been studied in several applications. As known, primarily for their environmental benefits, biopolymers are considered promising alternatives to petroleum-based polymers, as most can help reduce environmental pollution and greenhouse gas emissions[1,2]
Although the term “biopolymer” has several different definitions depending on the area involved, the most widely accepted one relates biopolymers to biobased and biodegradable materials. According to the IUPAC (International Union of Pure and Applied Chemistry), biologically-based polymers are derived from biomass or produced from monomers from its derivation. Hence, green polyethylene is an example of bio-based polymers[3,4]
Green polyethylene or bio polyethylene is produced from sugarcane ethanol, converted to ethylene via dehydration. According to life cycle assessment studies, bio polyethylene has a smaller carbon footprint than petroleumbased polyethylene. Furthermore, it has the differential of capturing carbon dioxide during its production, contributing to reducing greenhouse gas emissions, and maintaining the same properties, performance, and versatility of the
conventional resin, which facilitates its application in the chains of existing production and recycling[5-7].
Biopolymers have a lot of potentials. Despite increasing production capacity, they are still quite expensive, arousing interest in modification processes such as blending with other polymers and adding plasticizers or fillers[8]
The use of polymer/clay nanocomposites has been intensively studied in recent years, mainly due to improvements in mechanical, thermal, and barrier properties[9-12]. In this work, montmorillonite organophilic clay is used to produce nanocomposites. The packaging sector has invested in developing these nanocomposites, as the nanoclay, when dispersed in the polymer matrix, results in a homogeneous layer, creating tortuous paths, making it difficult for molecules to diffuse throughout the matrix[13,14]
The homogeneous dispersion of nanoclay in an organic polymer is not easily achieved due to the hydrophilicity of the clay, so the clays are organically modified to increase the affinity between the clay and the polymer, also growing the interlayer distance and lipophilicity of the nanoclay[15]. This behavior was reported in studies with nanometric clay to polyethylene. In this case, the authors used montmorillonite
in proportions of 3 to 5% in the polyethylene matrix to form nanocomposites and obtained improvements in mechanical and thermal properties[16]. In another study, the researchers added montmorillonite clay in 0.5 to 2.5% fractions and acquired better mechanical properties when incorporating it into the blend composed of polyethylene and polyamide[17]
Compatibilizing agents are also used to improve the intercalation of nanocomposites by increasing the interlayer distance of the nanoclays[18]; they may also contain biocidal groups incorporated in the polymer structure, thus conferring an antimicrobial character[19]. Chemically, antimicrobial additives can be classified by their active components. In this work, zinc pyrithione dispersed in a Vinyl Acetate (EVA) matrix was used. In addition to having antimicrobial activity against fungi, bacteria, and algae, this coordination compound has a melting point at 240 °C and can be processed with most thermoplastics and elastomers[20]
In this context, packaging has reinvented itself with more attractive features, the so-called smart or active packaging. Active packaging is a system that combines the benefits of measuring, estimating, or predicting different aspects of food quality or safety with the release of an active substance that extends the shelf life of the product[21]
Among active packaging, antimicrobial packaging becomes an up-and-coming type as it provides for the addition of an extra barrier (microbiological) to physical barriers (oxygen and moisture)[22]
Many studies with PE and its composites have been dedicated to the development of antimicrobial packaging, as in studies[23] that incorporated zinc oxide nanoparticles (ZnO-NPs) in low-density polyethylene and in studies[24] that incorporated ZnO-NPs in high-density polyethylene.
Faced with many opportunities, this study aimed to produce nanocomposites of high-density bio polyethylene (BHDPE), organophilic clay, and a commercial additive containing 1% of zinc pyrithione dispersed in vinyl acetate (EVA), which was used in the ratios of 0.5 and 1%. The films were produced in an extruder by the intercalation technique in the molten state with coupling to a matrix for flat films. The films were characterized by X-ray diffraction (XRD), Fourier Transform Infrared Spectroscopy (FTIR), Thermogravimetry (TG), Differential Scanning Calorimetry (DSC), and Tensile Strength Testing.
High-Density Bio polyethylene (BHDPE, SGM9450F), MFI = 9.3 g/10min, ASTM 1238 at 190 ºC, was supplied by BRASKEM’s Petrochemical Complex in Triunfo (Brazil) and used as received. The filler incorporated into the BHDPE matrix was Cloisite 20A supplied by Southern Clay Products. The antimicrobial additive used was Sanitized MB E 2270 provided by Clariant. The active compound used was zinc pyrionate dispersed in a vinyl acetate matrix.
The samples were prepared using EVA BHDPE/Clay/ Masterbatch containing zinc pyrithione, according to the proportions described in Table 1
The mixtures of BHDPE, organophilic clay, and the antimicrobial additive were extruded in a single screw extruder (L/D = 26), model AX-16 from AX Plásticos, operating with temperatures ranging from the first to the third zone, respectively, between 200 ºC, 205 ºC, and 210 °C and screw speed at 50 rpm, conditions established in the laboratory.
After incorporating the additives into the polymer matrix, the films were prepared in a single-screw extruder with a flat die of 220 mm width and cylindrical cooling rollers, model Lab 16 from AX Plásticos, with a temperature profile of 205 °C, 210°C, and 180 °C and screw speed of 60 rpm. The thickness of the films was determined using a thickness gauge, and the averages found for five (5) samples were: 0.06 mm (BHDPE), 0.12 mm (N31), 0.11 mm (N32), 0.22 mm (N61), and 0.15 mm (N62).
The nanocomposites were analyzed by the X-ray diffraction (XRD) method in a Shimadzu model XRD 6000 diffractometer operating in the angular range (2θ) of 1.5 ° to 30° using CuKα as incident radiation was used to determine the crystalline parameters of the films.
Fourier transform infrared spectroscopy (FTIR) analyses were performed on a Perkin Elmer SPECTRUM 400 (FT-IR/FT-NIR) spectrometer scanning from 4000 to 650 cm-1.
The thermal properties of the samples were analyzed by thermogravimetry (TG), and differential scanning calorimetry (DSC) techniques in a TA Instrument a TA Instrument SDT Q600 V20.9 Build 20, operating at a heating rate of 10 °C/min, from ambient temperature to 600 °C, under 100 mL/min nitrogen gas flow. The degree of crystallinity (Xc) was calculated according to Equation 1, where ΔH°f is the melt enthalpy of an ideal polyethylene with 100% crystalline HDPE (289 J/g[24]) and ΔHf is the melt enthalpy of the nanocomposites. The (x) values were adequate for the matrix weight fraction in the nanocomposites.
Polímeros, 32(2), e2022022,
Mesquita, P. J. P., Alves, T. S., & Barbosa, R.
Tensile properties of the nancomposites e films were determined according to ASTM D882-02[25] in a Shimadzu brand AGS-X mechanical testing machine with a speed of 20 mm/min and a load cell of 5 kN. Five test specimens were used for each composition with dimensions of 120 mm in length and 25 mm in width.
The diffractograms illustrated in Figure 1 show the peaks of Cloisite 20A, BHDPE, and nanocomposites containing the antimicrobial additive and clay. For the BHDPE, a noncrystalline halo and a very intense peak between the 15° and 25° angles and other less severe peaks between the 26° and 40° angles were observed. As well, three crystalline peaks at 2θ = 21.55°, 23.89°, and 36.36° which are characteristic of the (110), (200) and (020) planes, respectively, in a crystalline region of polyethylene[25]
The diffractograms of BHDPE and nanocomposites illustrate similar behavior and sharpness in the characteristic peaks of BHDPE. It is observed the peaks of the clay Cloisite 20A at 2θ correspond to the (001) plane and basal interplanar distance of 3,4 nm[26]. It can be seen that the nanocomposites showed an increase in the basal interplanar distance of the peak corresponding to organophilic clay for the nanocomposite with the highest content of clay and antimicrobial agent.
This same behavior was reported[27] in studies using HDPE/montmorillonite/zinc oxide nanocomposite, observing an increase in the spacing between the clay layers with the addition of zinc oxide and HDPE.
Figure 2 illustrates the infrared spectra for nanocomposite films with clay and the antimicrobial additive additions. The characteristic bands of polyethylene, 2918, 2849, 1469, 1463, 731 and 720 cm-1 (CH2 angular deformations) appear in all spectra[28,29]. Studies[30] with nanocomposites using
modified vermiculite with Zn2+ particles in the HDPE matrix also observed the same characteristic bands of pure HDPE.
The bands of the antimicrobial additive, composed of EVA[28,31], were not detected, suggesting an overlapping of the BHDPE bands due to the low concentration. However, the presence of bands in the range of 3620 cm-1 indicates the presence of O-H vibrations for Al-OH and Si-OH, and in approximately 1042 cm-1 the absorption of the Si-O from to Cloisite 20A[32]. In studies with nanocomposites using modified vermiculite with Zn2+ particles in HDPE matrix, bands ranging from 1007 to 1041 cm-1 were observed, corresponding to the stretching of Si-O of vermiculite, as well as an increase in the intensity of these bands with an increasing amount (3, 6 and 10% by weight) of the modified clay[30].
Figure 3 illustrates the TG and DTG curves for BHDPE, Cloisite 20A, and nanocomposites. The BHDPE showed a single stage degradation, starting at 454°C and losing up to 50% of its mass at 482°C, having a degradation peak at 489°C, as shown in Table 2. Similar results were found by authors who analyzed the thermal behavior of polyethylene[33,34].
Cloisite 20A shows three degradation phases: first, dehydration before 150°C; then, decomposition of organic molecules between 200 and 500°C; and finally, dehydroxylation of aluminosilicate groups between 500 and 700°C[35,36].
For nanocomposites N32, N61, and N62, minor variations were observed in the degradation temperature with 10% and 50% mass loss. However, for N31, a 10ºC decrease in degradation temperature was observed at 50% mass loss as shown in the data reported in Table 2. Studies[37] with EVA and silicates showed that the degree of clay dispersion affects matrix degradation and deacetylation of EVA, promoting an acceleration of degradation.
Organophilic clay has two opposite functions in the thermal stability of polymer/clay nanocomposites: barrier and catalysis effects. The first improves thermal stability while the second accelerates degradation[33]. Another factor that leads to faster thermal degradation of the matrix is related
Table 2. TG and DTG(derived thermogravimetry), BHDPE, Cloisite 20A and nanocomposites.
Samples Temperature (°C) for mass loss Tp (°C) Residue at 500 °C/% 10%
BHDPE
Cloisite 20A
Source: Personal archive.
0.0
72.23
0.65
2.74
2.99
4.93
Figure 3. TG and DTG curves of BHDPE, Cloisite 20A and nanocomposites.
to the alkylammonium cations present in the organoclay that can undergo decomposition by Hoffmann reaction. Their decomposition products catalyze polymeric degradation. Therefore, when a low fraction of organoclay is added to the polymer matrix, the clay must be well dispersed for the barrier effect to be predominant[38,39]. For N62, better clay dispersion was observed, as shown by the XRD analysis, and consequently, better thermal stability than the others in which the catalytic effect prevailed. The observed residues may also be due to other fillers and carbonaceous products.
DSC curves illustrate two essential parameters for the study of thermal stability: crystallinity and melting point. Figure 4 illustrates the DSC curves for BHDPE and its nanocomposites. BHDPE showed an endothermic peak at 139 °C related to its melting temperature, enthalpy of melting of 134.75 J/g, and crystallinity of 46.3%, according to Table 3. Similar results were found by authors who analyzed polyethylene by DSC[2,27]
The N32, N61, and N62 nanocomposites did not undergo significant variation in the melting temperature. However, N31 showed a 12 ºC decrease in this parameter compared to BHDPE, as shown in Table 3. Similar behavior was displayed by LDPE/Cloisite15A/EVA nanocomposites, where a decrease in melting temperature and crystallinity was observed[40]
Figure 4. DSC curves for BHDPE, N31, N32, N61, N62.
In the analysis of Table 3, there is a slight decrease in the melting temperature for the nanocomposites. The addition of clay in N31 and N32 made nucleation difficult and decreased the degree of crystallinity. On the other hand, increasing the amount of clay led to increased crystallinity. The increase in the EVA content also led to higher degrees of crystallinity in the nanocomposites.
This effect corroborates the results presented in the literature[41-43], which indicate that nanofiller help accelerate the crystal growth, which leads to crystallization at higher
Polímeros, 32(2), e2022022, 2022
Mesquita, P. J. P., Alves, T. S., & Barbosa, R.
temperatures, but can also, as in this case, generate a structure with a lower degree of crystallinity, so that a more significant number of smaller crystals are obtained.
The tensile strength of BHDPE and nanocomposites are illustrated in Figure 5, in which BHDPE had a maximum tensile strength of 58.77 MPa and nanocomposites N31, N32 and N62 showed a decrease in strength, while N61 had an increase of 21%, these values are dependent on film thickness, load direction, and processing conditions. Among the nanocomposites, it is observed that the increase in clay and EVA favored the increase in strength.
In general, the addition of Cloisite 20A and the antimicrobial agent was expected to increase the tensile strength, as occurred in N61. However, the formation of agglomerates in the matrix can occur, causing defects that concentrate mechanical stress[42,43,44] and weak interaction between EVA/Clay as reported in studies based on PE, EVA, and zinc oxide nanoparticles[20]
Figure 6 illustrates the elastic modulus values for BHDPE and nanocomposites. BHDPE had a modulus of 1384.85 MPa, an increase in this property is observed for all nanocomposites compared to HDPE. N31 had a lower modulus compared to N32, although with similar thicknesses (0.12 and 0.11 mm, respectively). N61 had the highest modulus of elasticity and the most significant thickness (0.22 mm) compared to N62 (0.15 mm). In this case, it was not possible to observe a relationship between the increase in clay and antimicrobial with the increase in the modulus of elasticity.
The decrease in mechanical properties would be associated with the high mobility of the EVA phases, which accentuates the defects around the interfaces formed between the polymers and the nanoparticles agglomerates. This effect is accentuated due to the immiscibility between the nanoparticles and the polymer matrix. Because the polymers (PE and EVA) are hydrophobic and the inorganic nanoparticles are hydrophilic and, when mixed, form agglomerates that
prevent the transfer of mechanical loads throughout the polymer matrix of the mixture[20]
The mechanical properties are listed in Table 4, noting that the yield strength follows the same behavior as the ultimate tensile strength, showing a decrease for N31, N32, and N62, while for N61, there was an increase. It is possible to observe that nanocomposites did not present great deformation compared to BHDPE, considering the applied stress and modulus of elasticity, confirming the behavior of increasing stiffness.
properties of BHDPE
Stress
Strain at
The interest in the production of polymeric nanocomposites comes from the wide range of resulting properties and the possibility of varying additives and production processes. In this work, BHDPE/Cloisite20A/EVA nanocomposites were studied. Through XRD analysis, it can be verified that the nanocomposites showed an increase in the interplanar basal distance due to the incorporation of polymer chains in the clay lamellae. By FTIR, it was possible to observe the presence of clay in the spectra of the nanocomposites, not being possible to observe the characteristic bands of EVA, since the bands may have overlapped and also due to the very small amount of EVA in the system. The thermal behavior of nanocomposites was similar to that of BHDPE, with a reduction in degradation temperature and melting temperature only observed for N31, in which clay had a catalytic action. Thus, compared to BHDPE, nanocomposites did not have their thermal stability compromised. The inclusion of clay and EVA in the BHDPE matrix resulted in a decrease in yield stress and tensile strength limit for N31, N32, N62 and an increase for N61. As for the modulus of elasticity, there was an increase compared to BHDPE, but it was not possible to establish a relationship between an increase in clay and EVA and the increase in modulus. Therefore, it can be seen that BHDPE/Cloisite20A/EVA nanocomposites are promising since it is possible to maintain or improve some properties, conferring antimicrobial properties, it is necessary to deepen the study of the proportions of additives and interaction mechanisms between Clay/EVA.
• Conceptualization – Renata Barbosa; Tatianny Soares Alves.
• Data curation – Priscylla Jordânia Pereira de Mesquita.
• Formal analysis – Priscylla Jordânia Pereira de Mesquita.
• Investigation – Renata Barbosa; Tatianny Soares Alves; Priscylla Jordânia Pereira de Mesquita.
• Methodology – Priscylla Jordânia Pereira de Mesquita.
• Project administration – Renata Barbosa.
• Resources – Renata Barbosa; Tatianny Soares Alves.
• Software – Priscylla Jordânia Pereira de Mesquita.
• Supervision – Renata Barbosa; Tatianny Soares Alves.
• Validation – NA.
• Visualization – NA.
• Writing – original draft – Priscylla Jordânia Pereira de Mesquita.
• Writing – review & editing – Renata Barbosa; Tatianny Soares Alves.
The authors acknowledge the support from the Federal University of Piauí (UFPI), Piauí State Research Support Foundation (FAPEPI), National Council for Scientific and Technological Development (CNPq), and Funding: This work was supported by the CNPq [process number: 308446/2018-6].
1 Mehta, N., Cunningham, E., Roy, D., Cathcart, A., Dempster, M., Berry, E., & Smyth, B. M. (2021). Exploring perceptions of environmental professionals, plastic processors, students and consumers of bio-based plastics: informing the development of the sector. Sustainable Production and Consumption, 26, 574 587 http://dx.doi.org/10.1016/j.spc.2020.12.015
2. Mazur, K., Jakubowska, P., Romanska, P., & Kuciel, S. (2020). Green high-density polyethylene (HDPE) reinforced with basalt fiber and agricultural fillers for technical applications. Composites. Part B, Engineering, 202, 108399 http://dx.doi. org/10.1016/j.compositesb.2020.108399
3 Vert, M., Doi, Y., Hellwich, K.-H., Hess, M., Hodge, P., Kubisa, P., Rinaudo, M., & Schué, F. (2012). Terminology for biorelated polymers and applications (IUPAC Recommendations 2012). Pure and Applied Chemistry, 84(2), 377 410 http://dx.doi. org/10.1351/PAC-REC-10-12-04
4 Brodin, M., Vallejos, M., Opedal, M. T., Area, M. C., & Chinga-Carrasco, G. (2017). Lignocellulosics as sustainable resources for production of bioplastics – a review. Journal of Cleaner Production, 162, 646 664. http://dx.doi.org/10.1016/j. jclepro.2017.05.209
5 Dilkes-Hoffman, L., Ashworth, P., Laycock, B., Pratt, S., & Lant, P. (2019). Public attitudes towards bioplastics – knowledge, perception and end-of-life management. Resources, Conservation and Recycling, 151, 104479 http://dx.doi.org/10.1016/j. resconrec.2019.104479
6 Nagakawa, Y., Yunoki, S., & Saito, M. (2014). Liquid scintillation counting of solid-state plastic pellets to distinguish bio-based polyethylene. Polymer Testing, 33, 13 15 http://dx.doi. org/10.1016/j.polymertesting.2013.10.018
7 Santos, L. A. Jr., Thiré, R. M. S. M., Lima, E. M. B., Racca, L. M., & Silva, A. L. N. (2018). Mechanical and thermal properties of environment friendly composite based on mango’s seed shell and high-density polyethylene. Macromolecular Symposia, 381(1), 1800125 http://dx.doi.org/10.1002/masy.201800125
8. Sionkowska, A. (2011). Current research on the blends of natural and synthetic polymers as new biomaterials. Progress in Polymer Science, 36(9), 1254 1276 http://dx.doi.org/10.1016/j. progpolymsci.2011.05.003
9 Chen, L., Rende, D., Schadler, L. S., & Ozisik, R. (2013). Polymer nanocomposite foams. Journal of Materials Chemistry. A, Materials for Energy and Sustainability, 1(12), 3837 3850 http://dx.doi.org/10.1039/c2ta00086e
10. Seraji, S. M., Aghjeh, M. K. R., Davari, M., Hosseini, M. S., & Khelgati, S. (2011). Effect of clay dispersion on the cell structure of LDPE/clay nanocomposite foams. Polymer Composites, 32(7), 1095 1105 http://dx.doi.org/10.1002/ pc.21127
11. Anadao, P. (2014). The use of montmorillonite clay in polymer nanocomposite foams. In V. Mittal (Ed.), Polymer nanocomposite foams (pp. 149 168). Boca Raton: CRC Press
12. Cui, Y., Kumar, S., Kona, B. R., & van Houcke, D. (2015). Gas barrier properties of polymer/clay nanocomposites. RSC Advances, 5(78), 63669 63690 http://dx.doi.org/10.1039/ C5RA10333A
13 Azeredo, H. M. C. (2009). Nanocomposites for food packaging applications. Food Research International, 42(9), 1240 1253. http://dx.doi.org/10.1016/j.foodres.2009.03.019
14 Paul, D. R., & Robeson, L. M. (2008). Polymer nanotechnology: nanocomposites. Polymer, 49(15), 3187 3204. http://dx.doi. org/10.1016/j.polymer.2008.04.017
Polímeros, 32(2), e2022022, 2022
Mesquita, P. J. P., Alves, T. S., & Barbosa, R.15 Majeed, K., Jawaid, M., Hassan, A., Bakar, A. A., Khalil, H. P. S. A., Salema, A. A., & Inuwa, I. (2013). Potential materials for food packaging from nanoclay/natural fibres filled hybrid composites. Materials & Design, 46, 391 410 http://dx.doi. org/10.1016/j.matdes.2012.10.044.
16 Laguna-Gutierrez, E., Escudero, J., & Rodriguez-Perez, M. A. (2018). Analysis of the mechanical properties and effective diffusion coeficiente under static creep loading of low-density foams based on polyethylene/clays nanocomposites. Composites. Part B, Engineering, 148, 156 165 http://dx.doi.org/10.1016/j. compositesb.2018.04.057
17 Huitric , J. , Ville , J. , Mederic , P. , & Aubry, T. ( 2017 ). Solid-state morphology, structure, and tensile properties of polyethylene/polyamide/nanoclay blends: effect of clay fraction. Polymer Testing, 58, 96 103 http://dx.doi.org/10.1016/j. polymertesting.2016.12.020
18 Liang, G., Xu, J., Bao, S., & Xu, W. (2004). Polyethylene/ maleic anhydride grafted polyethylene/organic-montmorillonite nanocomposites. I. Preparation, microstructure, and mechanical properties. Journal of Applied Polymer Science, 91(6), 3974 3980 http://dx.doi.org/10.1002/app.13612
19 Siedenbiedel, F., & Tiller, J. C. (2012). Antimicrobial polymers in solution and on surfaces: overview and functional principles. Polymers, 4(1), 46 71 http://dx.doi.org/10.3390/polym4010046
20 Galli, R., Hall, M. C., Breitenbach, E. R., Colpani, G. L., Zanetti, M., Mello, J. M. M., Silva, L. L., & Fiori, M. A. (2020). Antibacterial polyethylene - ethylene vinyl acetate polymeric blend by incorporation of zinc oxide nanoparticles. Polymer Testing, 89, 106554 http://dx.doi.org/10.1016/j. polymertesting.2020.106554
21 Vilas, C., Mauricio-Iglesias , M., & García, M. (2020). Model-based design of smart active packaging systems with antimicrobial activity. Food Packaging and Shelf Life, 24, 100446 http://dx.doi.org/10.1016/j.fpsl.2019.100446
22 Zhong, Y., Godwin, P., Jin, Y., & Xiao, H. (2020). Biodegradable polymers and green based antimicrobial packaging materials: a mini-review. Advanced Industrial and Engineering Polymer Research, 3(1), 27 35 http://dx.doi.org/10.1016/j.aiepr.2019.11.002
23 Rojas, K., Canales, D., Amigo, N., Montoille, L., Cament, A., Rivas, L. M., Gil-Castell, O., Reyes, P., Ulloa, M. T., Ribes-Greus, A., & Zapata, P. A. (2019). Effective antimicrobial materials based on low-density polyethylene (LDPE) with zinc oxide (ZnO) nanoparticles. Composites. Part B, Engineering, 172, 173 178. http://dx.doi.org/10.1016/j.compositesb.2019.05.054.
24. Li, S.-C., & Li, Y.-N. (2010). Mechanical and antibacterial properties of modified nano-ZnO/high density polyethylene composite films with a low doped content of nano-ZnO. Journal of Applied Polymer Science, 116(5), 2965 2969 http://dx.doi. org/10.1002/app.31802
25 Das-Gupta, D. K. (1994). Polyethylene: structure, morphology, molecular motion and dieletric behavior. IEEE Electrical Insulation Magazine, 10(3), 5 15. http://dx.doi.org/10.1109/57.285418.
26 . Paiva, L. B., Morales, A. R., & Días, F. R. V. (2008). Organoclays: properties, preparation and applications. Applied Clay Science, 42(1-2), 8 24 http://dx.doi.org/10.1016/j.clay.2008.02.006
27 Roy, A., Joshi, M., & Butola, B. S. (2019). Preparation and antimicrobial assessment of zinc-montmorillonite intercalates based HDPE nanocomposites: a cost-effective and safe bioactive plastic. Journal of Cleaner Production, 212, 1518 1525 http:// dx.doi.org/10.1016/j.jclepro.2018.11.235.
28. Coleman, M. M., Moskala, E. J., Painter, P. C., Walsh, D. J., & Rostami, S. (1983). A Fourier transform infra-red study of the phase behaviour of polymer blends. Ethylene-vinyl acetate copolymer blends with poly(vinyl chloride) and chlorinated
polyethylene. Polymer, 24(11), 1410 1414 http://dx.doi. org/10.1016/0032-3861(83)90221-5
29 Gulmine, J. V., Janissek, P. R., Heise, H. M., & Akcelrud, L. (2002). Polyethylene characterization by FTIR. Polymer Testing, 21(5), 557 563. http://dx.doi.org/10.1016/S01429418(01)00124-6
30 Holešová, S., Samlíková, M., Ritz, M., & Pazdziora, E. (2015). Antibacterial polyethylene/clay nanocomposites using chlorhexidine as organic modifier. Materials Today: Proceedings, 2(1), 246 252
31 Terui, Y., & Hirokawa, K. (1994). Fourier transform infrared emission spectra of poly(vinyl acetate) enhanced by the island structure of gold. Vibrational Spectroscopy, 6(3), 309 314 http://dx.doi.org/10.1016/0924-2031(93)E0065-A.
32 Yang, D., Yuan, P., Zhu, J. X., & He, H.-P. (2007). Synthesis and characterization of antibacterial compounds using montmorillonite and chlorhexidine acetate. Journal of Thermal Analysisand Calorimery, 89(3), 847 852 http://dx.doi.org/10.1007/s10973006-8318-3
33 Zhao, C., Qin, H., Gong, F., Feng, M., Zhang, S., & Yang, M. (2005). Mechanical, thermal and flammability properties of polyethylene/clay nanocomposites. Polymer Degradation & Stability, 87(1), 183 189 http://dx.doi.org/10.1016/j. polymdegradstab.2004.08.005
34 Boronat, T., Fombuena, V., Garcia-Sanoguera, D., SanchezNacher, L., & Balart, R. (2015). Development of a biocomposite based on green polyethylene biopolymer and eggshell. Materials & Design, 68, 177 185 http://dx.doi.org/10.1016/j. matdes.2014.12.027.
35. Zhang, Q., Naito, K., Qi, B., & Kagawa, Y. (2009). Epoxy nanocomposites based on high temperature pyridinium-modified clays. Journal of Nanoscience and Nanotechnology, 9(1), 209 215 http://dx.doi.org/10.1166/jnn.2009.J057 PMid:19441298.
36 Muñoz-Shugulí, C., Rodríguez, F. J., Bruna, J. E., Galotto, M. J., Sarantópoulos, C., Perez, M. A. F., & Padula, M. (2019). Cetylpyridinium bromide-modified montmorillonite as filler in low density polyethylene nanocomposite films. Applied Clay Science, 168, 203 210 http://dx.doi.org/10.1016/j. clay.2018.10.020
37 Lujan-Acosta, R., Sánchez-Valdes, S., Ramírez-Vargas, E., Ramos-DeValle, L. F., Espinoza-Martinez, A. B., RodriguezFernandez, O. S., Lozano-Ramirez, T., & Lafleur, P. G. (2014). Effect of amino alcohol functionalized polyethylene as compatibilizer for LDPE/EVA/clay/flame-retardant nanocomposites. Materials Chemistry and Physics, 146(3), 437 445 http://dx.doi.org/10.1016/j.matchemphys.2014.03.050
38 Durmuş, A., Woo, M., Kaşgöz, A., Macosko, C. W., & Tsapatsis, M. (2007). Intercalated linear low density polyethylene (LLDPE)/ clay nanocomposites prepared with oxidized polyethylene as a new type compatibilizer: structural, mechanical and barrier properties. European Polymer Journal, 43(9), 3737 3749 http://dx.doi.org/10.1016/j.eurpolymj.2007.06.019.
39. Olewnik, E., Garman, K., & Czerwiński, W. (2010). Thermal properties of new composites based on nanoclay, polyethylene and polypropylene. Journal of Thermal Analysis and Calorimetry, 101(1), 323 329 http://dx.doi.org/10.1007/s10973-010-0690-3
40 Dadfar, S. M. A., Alemzadeh, I., Dadfar, S. M. R., & Vosoughi, M. (2011). Studies on the oxygen barrier and mechanical properties of low density polyethylene/organoclay nanocomposite films in the presence of ethylene vinyl acetate copolymer as a new type of compatibilizer. Materials & Design, 32(4), 1806 1813 http://dx.doi.org/10.1016/j.matdes.2010.12.028
41 Passador, F. R., Travain, D. R., Backes, E. H., Ruvolo, A. Fo., & Pessan, L. A. (2013). HDPE/LLDPE blend-based
nanocomposites – part II: evaluation of thermal, optical and transport properties. Polímeros: Ciência e Tecnologia, 23(6), 748 757 http://dx.doi.org/10.4322/polimeros.2013.065
42. Conceição, I. D., Silva, L. R. C., Carvalho, L. H., Costa, T. H. C., Silva, H. S., Alves, T. S., Barbosa, R., & Sousa, R. R. M. (2019). Evaluation of the effect of plasma treatment on the surface of green polyethylene and vermiculite clay films. Matéria, 24(4), e-12492
43. Almansoori, A., Majewski, C., & Rodenburg, C. (2017). Nanoclay/polymer composite powders for use in laser sintering applications: effects of nanoclay plasma treatment. JOM,
69(11), 2278 2285 http://dx.doi.org/10.1007/s11837-0172408-5 PMid:31983865.
44 Min, K. D., Kim, M. Y., Choi, K.-Y., Lee, J. H., & Lee, S.-G. (2006). Effect of layered silicates on the crystallinity and mechanical properties of HDPE/MMT nanocomposite blown films. Polymer Bulletin, 57(1), 101 108 http://dx.doi. org/10.1007/s00289-006-0537-z.
Received: June 08, 2021
Revised: Apr. 14, 2022
Accepted: Aug. 18, 2022
Polímeros, 32(2), e2022022, 2022
https://doi.org/10.1590/0104-1428.20210040
Mauro Cesar de Avila1 , Ana Paula Munaro2 and Marilda Munaro1,3*
1Programa de Pós-graduação em Engenharia e Ciência dos Materiais – PIPE, Universidade Federal do Paraná – UFPR, Curitiba, PR, Brasil
2Solução Adesivos e Selantes, Fazenda Rio Grande, PR, Brasil
3Centro Universitário Curitiba, Curitiba, PR, Brasil *marilda.munaro94@gmail.com
Mineral insulating oil (MIO) and natural ester insulating (NEI) oil are used in power transformers as an insulating fluid, while elastomeric seals are usually composed of nitrile rubber (NBR). The proprieties of these seals can change in contact with insulating oil. Variation in sealant properties is undesirable in power transformers. In this work, the variation of some elastomer properties was evaluated before and after accelerated aging in MIO and NEI. The developed elastomeric compositions showed variation in the stress and strain at break after the aging test. It also appeared that MIO penetrated the samples and that dioctylphthalate (DOP) migrated or was extracted into MIO and NEI. The samples vulcanized with peroxide showed better results than those vulcanized with sulfur.
Keywords: compatibility, mineral insulating oil, natural ester insulating, nitrile rubber, power transformers.
How to cite: Avila, M. C., Munaro, A. P., & Munaro, M. (2022). Development and evaluation of nitrile rubbers seals for power transformer application. Polímeros: Ciência e Tecnologia, 32(2), e2022024. https://doi.org/10.1590/01041428.20210040
Electricity is one of the most widely used forms of energy throughout the world. In order for this energy to reach the consumer, it passes through a complex system of generation, transmission, and distribution. The distribution stage is performed using power transformers that raise or lower the voltage to enable distribution over long distances. Electrical power transformers immersed in insulating oil are fundamental for the generation, transmission and distribution of electricity, but they are also very expensive. Cooling and insulation of the electrical system in transformers is achieved by using insulating paper and insulating oils, with mineral insulating oil (MIO) most commonly used. The system is sealed with rings or gaskets composed of elastomers, especially nitrile rubber (NBR)[1-3]. Another insulating fluid used is natural ester insulator (NEI) obtained from oilseeds such as soya, canola, sunflower seeds, etc. Natural ester insulators have excellent electrical properties such as flash points greater than 300 °C, which significantly improves the safety level of the power grid, biodegradation rates of more than 95%-97%, and relative dielectric constants about 1.5 times that of mineral insulating oils[4]. NEI oils are less flammable compared with MIO oils and they do not contain corrosive sulfur. These oils also offer adequate dielectric strength, making them a feasible alternative for MIO oils in power transformers[5,6]. Another important aspect to consider in the use of natural ester as a substitute for mineral oil as a dielectric fluid in transformers is the aging of cellulose
insulating paper. When in contact with fluids of plant origin, this paper normally has a lower speed of aging than that which occurs on the same paper when immersed in MIO under the same experimental conditions[7].
NBR formulated elastomeric materials were first used in the automotive industry because of their resistance to fuels and a variety of oils and other fluids. Currently, NBR is used in a large number of applications, mainly in seals where the material is in permanent contact with the lubricants necessary for the vehicle’s moving parts[8,9]
The elastomeric seal allows complete contact between the seal and the joint and settles with slight pressure[10] Rubber products are available in different types of hardness and textures. Harder material can be used in cases of greater stress, where increased sealing power is needed. Most elastomeric seals have excellent flow and compressibility characteristics. The lateral flow increases when the stresses in the seal are high during use. Different fillers and fibers can be used in the fabrication of elastomeric seals in order to improve mechanical strength and maintain seal stability and control[11]. Nitrile rubber (NBR) is a copolymer of acrylonitrile and butadiene. The polar acrylonitrile group present in NBR imparts excellent fuel and oil resistance, and hence it is widely used in many important industrial applications like fuel and oil supply hoses, rollers, drive belts, seals, and so on[12]
Material compatibility is a vital element for transformer design. All the materials that are typically used in the manufacturing of mineral oil-immersed transformers have to be compatible with natural ester liquids[13]. Incompatibility between the seal material and the insulating oil can result in degradation of the elastomer and contamination of the oil, causing loss of the dielectric properties of the fluid, reduced useful life of the transformer, and environmental contamination due to fluid leakages. Power transformer failures lead to power supply disruption, fines paid by energy utility companies, maintenance costs, and sometimes the loss of the transformer.
Previous studies have investigated the compatibility of elastomers with lubricating oils and fuels such as gasoline, and diesel[14]. Studies have been conducted on the compatibility of nitrile rubber (NBR) with different biodiesel compositions[15]. A recent review pointed out aspects of using NEI in transformers. However, there have been no evaluations of the rubber seal[6].
The authors are not aware of studies evaluating sealing elastomers aged in insulating fluid, especially NEI. Much less is known concerning the performance of elastomers in contact with MIO and NEI[16-19]
The aim of this work is to evaluate different compositions of nitrile rubber submitted to aging in insulating oil, MIO and NEI. The samples were characterized by determination of Shore A hardness, tensile strength, and elongation, as well as by thermogravimetry analysis (TGA) and dynamic mechanical thermal analysis (DMTA) before and after the aging tests. Only the elastomer samples were evaluated. Possible changes in MIO and NEI are outside the scope of this study and have not been evaluated.
The compounds were produced using NBR containing 34% acrylonitrile 35 LM® supplied by KUMRO, dioctyl phthalate plasticizer (DOP) supplied by CYA Rubber, Nipol 1312 LV® polymeric plasticizer (low viscosity liquid NBR with 28% acrylonitrile) supplied by Zeon; and carbon black (types N762 and N339) supplied by Cabot.
The other additives used were as follows: antioxidant (quinolone type) and antiozonant (paraphenylenediamine type) from Lanxess; zinc oxide from Brasóxidos; stearic acid from SIM Stearin; ventilated sulfur, benzothiazole vulcanization accelerator (MBTS), and tetramethylthiuram disulfide vulcanization accelerator (TMTD) from Auriquímica; 40% dicumyl peroxide in calcium carbonate from Retilox, and hydrocarbon resin from Parabor.
Mineral insulating oil type AV-66 IN® supplied by Petrobras and natural ester insulating soy oil type ENVIROTEMP FR3® supplied by Cargil, both were used in the aging and compatibility assays. Some properties of the MIO and NEI are shown in Tables 1 and 2.
Preparation of the Mixtures: the formulations were prepared in a laboratory cylinder (Model Lab mil 350,
COPÉ brand), as shown in Figure 1, according to the ASTM D3182 standard method 8[20]. First, the elastomers were added to the cylinder with internal cooling water circulation, followed by fillers and plasticizer until complete mixing. Then, the other additives were added and mixed for a period of 4 minutes, except for the accelerators and sulfur. Finally, accelerators and sulfur were added and mixed for a time of 3 minutes. The compost discharge temperature was 80 °C and the total mixing time was approximately 15 minutes.
As shown in Figure 2, the samples were vulcanized for 4 minutes (for the formulations with sulfur) and 7 minutes (in the presence of peroxide), in a mold (150 mm x 150 mm x 2 mm) at a temperature of 160 °C. For the aging test in MIO and NEI , shore A hardness and tensile strength tests were performed on 5 specimens. Thermogravimetry and
Neutralization Index 0.01 mg KOH/g oil Water 20 ppm Density at 20 °C 0.887 g/cm3
Power factor at 90 °C 0.04%
Flash point 150 °C Viscosity at 40 °C 9.32 cSt Viscosity at 100 °C 2.31 cSt Pour point -60 °C
Neutralization Index 0.02 mg KOH/g oil Water 54 ppm Density at 20 °C 0.9192 g/cm3
Dielectric losses at 20 °C 0.13%
Dielectric losses at 100 °C 3.9%
Flash point 308 °C Viscosity at 40 °C 35.99 cSt Viscosity at 100 °C 8.57 cSt
Pour point -7 °C Flash point 342 °C
Avila, M. C., Munaro, A. P., & Munaro, M.
dynamic mechanical thermal analysis were performed on 3 specimens.
Four different compositions were prepared, as shown in Table 3
Aging in MIO and NEI: the aging of the vulcanized samples was performed according to the ABNT NBR 14274 standard method[21]. The test specimens were conditioned for 16 hours in an oven at 100 ± 1 °C, followed by aging in direct contact with MIO and NEI, also at 100 ± 1 °C, for 7, and 14 days. The samples were aged as shown in Figure 3
All samples were placed in the oven for the aging test at the same time and under the same conditions, as indicated in Figure 4. The first samples were removed from the oven and tested after 7 days and the others after 14 days.
Shore A Hardness: measurements were made before and after aging, according to the ASTM D2240[22], procedure 10 using an Asker Model DD2 A durometer with a load application time of 5 seconds.
Tensile Strength Test: measurements were made according to ASTM D412[23], before and after aging of the samples, with 5 test specimens being submitted to traction using a universal testing machine (Model 4467, Instron) operated with a 1 kN load cell and a crosshead speed of 100 mm/min.
Thermogravimetry: thermogravimetric measurements were performed according to the ASTM D6370 standard[24], using a Netzsch Model TG-209 instrument. An approximately 20 mg portion of the sample was heated from 20 °C to 550 °C, at a rate of 20 °C/min, in an inert nitrogen atmosphere. In the next step, an oxygen atmosphere was introduced with heating at the same rate up to 800 °C. Measurements were made using samples before and after aging for 7 days.
Dynamic mechanical thermal analysis: DMTA: measurements were performed according to the ASTM E1640[25],using a Netzsh model 242 instrument, in penetration mode. 10 mm x 10 mm plates with a thickness of 3.15 mm were used. The test was carried out in a nitrogen atmosphere in the temperature range of -60 °C to 30 °C, with 1 Hz frequency of dynamic force, and a heating rate of 3 °C/min, and nitrogen flow of 50 mL/min. The measurements were made using samples before and after aging for 7 days. MIO and ENI samples were not evaluated.
Development and evaluation of nitrile rubbers seals for power transformer applicationAfter being prepared and vulcanized, the nitrile rubber samples showed the following properties, as shown in Table 4. The samples vulcanized with sulfur showed greater hardness than those vulcanized with peroxide, indicating greater crosslinking, and therefore the tensile strength was higher for samples A and B.
Figure 5 shows the results of the Shore A hardness test applied to the compounds before and after aging in MIO and NEI.
Compounds A and B, which were vulcanized with sulfur, showed a higher initial hardness than that of compounds C and D, which were vulcanized with peroxide. This is probably due to the lower degree of reticulation in samples vulcanized with peroxide.
For samples aged in MIO, a small increase in hardness was observed in the first 7 days, stabilizing for compositions A and C, which were formulated with polymeric plasticizer. This variation, due to being small, makes it impossible to state whether any component was extracted from the formula, even though low molecular weight compounds such as stearic acid and A-80 hydrocarbon resin may have been extracted. It is also impossible to tell whether MIO permeation occurred with consequent breakage of the chain and formation of some free radicals, crosslinking and stiffening. Compounds B and D, formulated with dioctyl phthalate ester plasticizer (DOP) showed a significant increase in hardness after 7 days. This is possibly due to the extraction of the DOP from the sample, stiffening the material. After the first 7 days, there is a reduction in hardness values up to 14 days of aging. It is possible that the MIO permeated
the sample and by repulsion expelled the DOP and, after 7 days, started to act as a plasticizer, resulting in a decrease in hardness as observed in 14 days of aging. In samples B and D, with plasticizer DOP the content of acrylonitrile was lower. The polymeric plasticizer adds acrylonitrile to the formula because it is a nitrile rubber of low viscosity. Thus, the MIO finds a greater non-polar fraction in compounds B and D, which favors the permeation of the MIO in these samples. The best results were observed in sample C, where the hardness variations were smaller throughout the test, indicating less degradation.
In compositions aged in NEI, an increase in hardness was observed in the first 7 days and, afterwards, the hardness practically stabilized until the end of the test. In samples B and D, the increase in hardness was greater compared to samples A and C. It is likely that the NEI in samples A and C, due to having polar groups and a certain affinity with the acrylonitrile fraction of the NBR and with the formation of free radicals due to the degeneration of the elastomer segments, crosslinked and stiffened the compositions with a consequent increase in shore A hardness. In compositions B and D, in addition to what was described for compositions A and C, the DOP must have migrated to the NEI, which resulted in increased hardness. It was also observed that the increase in hardness was lower in samples vulcanized with peroxide than those vulcanized with sulfur after aging. The changes in these properties were smaller for samples C and D, as expected, since peroxide-vulcanized compounds possess C-C crosslinks that are more stable than the C-S bonds obtained in vulcanization using sulfur, and are therefore less susceptible to thermal degradation[26]
Figures 6a and 6b show the results of stress and strain at break for compounds A, B, C and D as a function of aging time in MIO and NEI. The values recorded in the tensile strength test in the compounds before aging showed variation, mainly in the elongation values. Sample C (polymeric plasticizer) and sample D (DOP) have the same curing system (peroxide) and the results are: stress at break of C= 18.8 MPa and of D = 16.8 MPa (C>D). Samples B and D, formulated with DOP, presented values of greater tensile strength and less elongation.
Compounds A and C exhibit similar behavior. In MIO aging, the values of maximum tension and strain at break decreased in the first 7 days and, afterwards, practically stabilized until the end of the test. MIO aging decreases the maximum stress and strain at break values. The maximum stress value is reduced, probably, due to the permeation of the MIO in the sample, which starts to act as a plasticizer and favors the movement of the segments. The reduction in the strain at break measurement value suggests that the degradation processes had started, with a consequent break in bonds. It is likely that MIO permeation accentuates the degradation processes and decreases the maximum stress and strain. The NEI sample did not significantly change the maximum stress values, but it did decrease strain at break. This behavior shows that the permeation of NEI in the samples was lower compared to that of MIO and, therefore, it did not act as a plasticizer, maintaining a maximum tension close to that of the material without aging. However, even with little permeation of NEI in the sample, some
Polímeros, 32(2), e2022024, 2022
Avila, M. C., Munaro, A. P., & Munaro, M.
processes must have started, with a consequent chain break and decrease in strain.
Compounds B and D showed similar behavior to A and C, respectively, when aged in MIO, but with higher values in the original material without aging. With aging in NEI, this reduction was more accentuated, which was expected due to the tendency of DOP to migrate to the oil.
Figure 7 shows the thermogravimetric curves obtained for compounds A, B, C and D, before and after 7 days of aging in MIO and NEI, at 100 °C.
For compounds A and C, similar behavior was observed in the thermogravimetric analysis. Before aging, an initial loss of mass was observed at a temperature of approximately 235 °C, which must be lower molecular weight and noninorganic components of the formulation that have been volatilized in this temperature range. For the formulations aged in MIO, a loss of mass was observed at temperatures below 200 °C, which can be attributed, in addition to the volatilization of low molecular weight and non-inorganic compounds as in the original sample, to the volatilization of the MIO which may have permeated between chains of the compound, in some quantity, causing some degradation, corroborating with the results obtained in the mechanical
tests. Table 5 shows mass loss of samples before and after aging in MIO and NEI up to 300 °C obtained in termogravimetric analisis
Figure 6. Results of the tensile test as a function of the aging time in MIO and NEI in 7 and 14 days of aging at 100ºC: (a) Stress at break; (b) Strain at break.
Figure 7. Thermogravimetric curves of samples (a) A; (b) B; (c) C; (d) D before and after 7 days of aging in MIO and NEI.
Table 5. Mass loss of samples A, B, C and D before and after 7 days of aging in MIO and NEI up to 300 °C. SAMPLES
A A MIO A NEI B B MIO B NEI C C MIO C NEI D D MIO D ENI Loss mass (%)
It is possible to observe that mass loss up to the 300 °C was greater after agin in MIO (A < A MIO and C < C MIO) showing MIO penetration into a sample. The mass loss curves for formulations A and C, when aged in NEI, showed small loss of mass until 300 °C compared to the original sample (A NEI <A and C NEI < C). This may be an indication that low molecular mass and non-inorganic components were extracted by the NEI during aging. Compositions A and C were formulated with polymeric plasticizer which is an elastomer, and therefore the initial mass variations that preceded NBR-related mass loss should not be attributed to the extraction of the plasticizer by NEI. The reverse is expected for B and D, formulated with DOP.
In the thermogravimetric analysis of samples B and D, a greater loss of mass was observed before aging between 230 °C and 300 °C, when compared to samples A and C. This is attributed to the volatilization of the DOP plasticizer and other components of low molecular weight. The curves for samples aged in MIO show that while part of the DOP was extracted from the formulation, part of the MIO permeated the sample, evidenced by the fact that the loss of mass started at a lower temperature and the fraction above 230 °C was lower than in the polymer without aging. For samples aged in NEI, mass loss was observed at the expected temperature range for the elastomer (above 300 °C), which may also indicate that DOP, low molecular and non-inorganic components were extracted by the NEI during the aging test (B > B NEI and D > D NEI).
The DMTA test was performed in a penetration modulus and the results are expressed in a mechanical damping modulus tan δ, as a function of temperature.
Figure 8 shows the tan δ curves obtained by the DMTA for compounds A, B, C and D before and after 7 days of aging in MIO and NEI, at 100 °C.
The behavior observed in the tan δ curves of samples A and C are similar and show that the glass transition of the material when aged in MIO shifted to lower temperatures when compared to samples without aging. This can be attributed to the permeation of the MIO in the sample, which starts to act as a plasticizer, thus shifting the glass transition. The intensity of tan δ increased in relation to the sample without aging; that is, the energy loss or viscous modulus increased, and thus it is likely that the material presents greater deformation. The material aged in NEI slightly changed the characteristics of glass transition and tan δ, suggesting that NEI did not permeate in sufficient quantity to affect the mobility of the elastomer chain segments and thus affect its viscous modulus.
For compounds B and D, the variation in the glass transition temperature of the compounds aged in MIO and NEI was shown to be close and shifted in higher temperatures. This can be attributed to the extraction of the sample’s DOP during aging. In this case, it was expected that for the material aged in MIO the temperature would be shifted to lower temperatures than when aged in NEI due to its permeation in the sample and the MIO acting as a plasticizer. However, the amount of oil that
Figure 8. DMTA curves (tan δ) of samples (a) A; (b) B; (c) C; (d) D before and after 7 days of aging in MIO and NEI.
permeated was probably not sufficient to change the glass transition temperature of the material, and as the efficiency
Polímeros, 32(2), e2022024,
Avila, M. C., Munaro, A. P., & Munaro, M.of the oil as a plasticizer was lower than that of DOP, the glass transition shifted to a higher temperature. The tan δ intensity of the material decreased in both cases, suggesting degradation processes and cross-linking, thus increasing the elastic modulus of the material aged in MIO and NEI.
All compositions evaluated showed degradation when aged in MIO and NEI. The compounds formulated with DOP plasticizer showed significant mass loss in TGA analysis indicating their migration of the composition. The NEI extracted the DOP from the samples more intensively during the compatibility test compared to MIO. Some low molecular and non-inorganic compounds were extracted from the elastomer when aged in NEI and MIO. The samples vulcanized with peroxide showed less increase in the hardness values and less variation of the tensile strength and elongation after aging in MIO and NEI when compared to the variations in the sulfur vulcanized compounds, except for compositions formulated with DOP. Based on the variation of the evaluated properties, the 35% acrylonitrile content did not guarantee the integrity of the elastomeric compositions when aged in MIO and NEI.
• Conceptualization – Mauro César de Avila; Marilda Munaro; Ana Paula Munaro.
• Data curation – Mauro César de Avila; Marilda Munaro; Ana Paula Munaro.
• Formal analysis – Mauro César de Avila; Marilda Munaro; Ana Paula Munaro.
• Investigation – Mauro César de Avila; Marilda Munaro.
• Methodology – Mauro César de Avila; Marilda Munaro; Ana Paula Munaro.
• Project administration – Marilda Munaro.
• Resources – Mauro César de Avila; Marilda Munaro; Ana Paula Munaro..
• Software – Mauro César de Avila; Marilda Munaro; Ana Paula Munaro.
• Supervision – Mauro César de Avila.
• Validation – Marilda Munaro.
• Visualization – Mauro César de Avila
• Writing – original draft – Mauro César de Avila; Marilda Munaro.
• Writing – review & editing – Mauro César de Avila; Marilda Munaro; Ana Paula Munaro.
This study was fi nanced in part by COPEL. The authors wish to acknowledge Lactec, the Postgraduate Program in Engineering and Materials Science – PIPE, Federal University of Parana - UFPR and University UNICURITIBA for the support and fellowships.
1. Bandara, K., Ekanayake, C., & Saha, T. K. (2015). Modelling the dielectric response measurements of transformer oil. IEEE Transactions on Dielectrics and Electrical Insulation, 22(2), 1283 1291 http://dx.doi.org/10.1109/TDEI.2015.7076832
2 Soares, V. R. (2015). Requisitos e restrições do uso do óleo vegetal de tungue como líquido isolante para transformadores elétricos de distribuição de média tensão (Dissertação de mestrado). Universidade Tecnológica Federal do Paraná, Cornélio Procópio
3 Grison, É. C., Becker, E. J., & Sartori, A. (2010). Borrachas e seus aditivos: componentes, influências e segredos. Brazil: Letra & Vida
4 Wang, Y. C., Wang, F. P., Li, J., Liang, S. N., & Zhou, J. H. (2018). Electronic properties of typical molecules and the discharge mechanism of vegetable and mineral insulating oils. Energies, 11(3), 523 http://dx.doi.org/10.3390/en11030523
5. Ghani, S. A., Muhamad, N. A., Noorden, Z. A., Zainuddin, H., Bakar, N. A., & Talib, M. A. (2018). Methods for improving the workability of natural ester insulating oils in power transformer applications: a review. Electric Power Systems Research, 163(Pt B), 655 667 http://dx.doi.org/10.1016/j. epsr.2017.10.008
6 Mehta, D. M., Kundu, P., Chowdhury, A., Lakhiani, V. K., & Jhala, A. S. (2016). A review of critical evaluation of natural ester vis-a-vis mineral oil insulating liquid for use in transformers: part I. IEEE Transactions on Dielectrics and Electrical Insulation, 23(2), 873 880. http://dx.doi.org/10.1109/ TDEI.2015.005370
7 Martins, M. A. G. (2015). Óleo vegetal – um substituto do óleo mineral para uso em transformadores: revisão do estado da arte. Ciência e Tecnologia dos Materiais, 27(2), 136 142 http://dx.doi.org/10.1016/j.ctmat.2015.10.002
8 Duin, N. M. V. (2020). Handbook of synthetic rubber Germany: Optimal Media GmbH.
9 Garbim, V. J. (2013). Copolímeros Butadieno Acrilonitrila (NBR): características, compostos e aplicações Sorocaba: Elastotec
10 Clark, F. M. (1962). Insulating materials for design and engeneering practice USA: John Wiley and Sons Ltd.
11 Eklund, M., Jarman, P., & Newesely, G. (2004). Transformer oil handbook Sweden: Linderoths in Vingåker
12 Kapgate, B. P., Das, C., Basu, D., Das, A., & Heinrich, G. (2015). Rubber composites based on silane-treated stober silica and nitrile rubber: interaction of treated silica with rubber matrix. Journal of Elastomers and Plastics, 47(3), 248 261 http://dx.doi.org/10.1177/0095244313507807.
13 Mehta, D. M., Kundu, P., Chowdhury, A., Lakhiani, V. K., & Jhala, A. S. (2016). A review of critical evaluation of natural ester vis-a-vis mineral oil insulating liquid for use in transformers: part II. IEEE Transactions on Dielectrics and Electrical Insulation, 23(3), 1705 1712 http://dx.doi. org/10.1109/TDEI.2016.005371
14 Zhu, L., Cheung, C. S., Zhang, W. G., & Huang, Z. (2015). Compatibility of different biodiesel composition with acrylonitrile butadiene rubber (NBR). Fuel, 158, 288 292 http://dx.doi. org/10.1016/j.fuel.2015.05.054.
15 Liu, Y., Wang, W. Y., Zhang, Z. X., Deng, T., & Xin, Z. X. (2011). Effects of blend ratio on rheology, morphology, mechanical and oil-resistant properties in chlorinated polyethylene rubber and copolyamide blends. Journal of Macromolecular Science, Part B: Physics, 50(9), 1659 1672 http://dx.doi.org/10.1080/ 00222348.2010.541852
16 An, Y., Ding, Y., Tan, J., & Yang, W. (2011). Influences of polyester plasticizers on the properties of oil resistance flexible
Avila, M. C., Munaro, A. P., & Munaro, M.
poly(vinyl chloride) and powder nitrile butadiene rubber blends. Advanced Science Letters, 4(3), 875 879 http://dx.doi. org/10.1166/asl.2011.1590.
17 An, Y., Yang, W. M., Ding, Y. M., Liu,Y., & Tan, J. (2010). Study on oil resistance properties of flexible PVC/PNBR blends. Advanced Materials Research, 87-88, 134 136 http:// dx.doi.org/10.4028/www.scientific.net/AMR.87-88.134
18 Wu, W., Wan, C., & Zhang, Y. (2013). Morphology and mechanical properties of ethylene‐vinyl acetate rubber/polyamide thermoplastic elastomers. Journal of Applied Polymer Science, 130(1), 338 344 http://dx.doi.org/10.1002/app.39046
19 Abdelmalik, A. A. (2014). Chemically modified palm kernel oil ester: a possible sustainable alternative insulating fluid. Sustainable Materials and Technologies, 1-2, 42 51 http:// dx.doi.org/10.1016/j.susmat.2014.06.001
20 American Society for Testing and Materials – ASTM. (2016). ASTM D3182-16 - Standard Practice for Rubber—Materials, Equipment, and Procedures for Mixing Standard Compounds and Preparing Standard Vulcanized Sheets USA: ASTM International
21 Associação Brasileira de Normas Técnicas – ABNT. (2013). NBR 14274- 2013 - Óleo mineral isolante – determinação da compatibilidade de materiais empregados em equipamentos elétricos Rio de Janeiro: ABNT
22 American Society for Testing and Materials – ASTM. (2005). ASTM D2240-05 - Standard test methods for rubber property: durometer hardness West Conshohocken: ASTM International
23 American Society for Testing and Materials – ASTM. (2006). ASTM D412-06 - Standard methods for vulcanized rubber and thermoplastic rubbers and thermoplastic elastomers: tension West Conshohocken: ASTM International
24 American Society for Testing and Materials – ASTM. (1999). ASTM D6370-99 - Standard Test Method for Rubber— Compositional Analysis by Thermogravimetry (TGA) West Conshohocken: ASTM International
25 American Society for Testing and Materials – ASTM. (2018). ASTM E1640-18 - Standard Test Method for Assigment of thr glass transition temperature by dynamic mechanical análisis West Conshohocken: ASTM International
26 Dluzneski, P. R. (2001). Peroxide vulcanization of elastomers. Rubber Chemistry and Technology, 74(3), 451 492 http:// dx.doi.org/10.5254/1.3547647
Received: June 08, 2021
Revised: Apr. 14, 2022
Accepted: Aug. 18, 2022
Polímeros, 32(2), e2022024, 2022
São Paulo 994 St. São Carlos, SP, Brazil, 13560 340 Phone: +55 16 3374 3949 Email: abpol@abpol.org.br