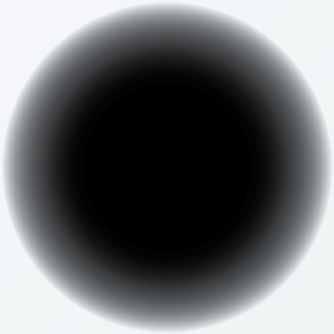
5 minute read
Good Manufacturing Environment: Key to Sustainable Business
Q. With a product portfolio which has tapped most avenues, what is next?
We are diversifying into non-woven-technical textile, filament yarns, B-2-B and renewable energy to offer more sustainable products to the society.
Advertisement
Ease of
technology transfers, R&D projects and policies for sharing the knowledge and
manpower, and exchange and training
programmes at both the
government and private levels can speed up the growth of this industry. Q. As regards your raw material availability and quality, what challenges do you face? How do you overcome the same?
Quality control at the source is important as PCR waste has a mix of polymers. Since we were facing the problem of cutting the higher IV quality part from PCR PET bottles, addition of sand / dust / moisture and intermediaries etc., we decided to set up our own collection centre to maintain the quality of input feedstock to our recycling units to provide a better quality of finished goods. So, we are setting up the waste management vertical and developing waste collection centres under it. Q. Please share your take on ‘Atmanirbhar Bharat’ and ‘vocal for local’. We find both these schemes to be useful and beneficial for the nation. The concepts are certainly beneficial for our nation’s economy. The industry needs support in terms of policies supporting R&D projects, technology transfer and infrastructure development to promote these concepts.
Q. What role has technology played this far in your success?
In our field, it is a very dynamic world. Technologies are upgrading rapidly. We always look for innovation and upcoming technologies, and continuously evaluate them and immediately adopt the suitable technologies. We have been continuously adding advanced machinery like auto sorters, segregators, grinders and many more European technology suppliers. Improved technologies and machinery have certainly helped us to expand our capacities and think of new products.
It is very important to understand the requirements of brand owners and end users to offer them sustainable products. We are open to setting up of new infrastructure and machineries to fulfill specific needs of our clients.
Q. Are you looking beyond PET waste as raw material? If yes, please elaborate. If not, tell us why?
We are already working to convert 100% PET waste content into usable products. We are going to fetch polyolefins and MLP waste from the market to convert them into sustainable products. We are also exploring converting mixed complex plastic waste, paper mills’ waste, industrial sludge etc. into energy forms.
Q. The pandemic has thrown open a lot of opportunities for many who have the grit to dive deep. What are your thoughts about this and how has the group dealt with it?
We have been working additionally during these days to keep up the pace as we were confined to our homes. All the key management people have worked hard to maintain the momentum as there were many limitations. The time spent idle was invested in pending discussions, networking and studying innovations and best practices to introduce with some concrete plans.
Q. If it was not the plastics or recycling industry, which would have been your alternate choice of business?
We have been into trading of yarns / cloth since 1979. We have also been into manufacturing of HDPE pipes and cloth, and import and sales of various commodity items; probably that could have scaled up.
Q. Where do you see the group in the next 3 years as regards the recycling business?
We should achieve the capability of recycling about 2,50,000 MT of feedstock on an annual basis by 2023. We expect our PET recycling capacities to
To know more, please subscribe to PolymErs Communiqué at subscriptions@polymerscommunique.com

The Future for Safe, Sustainable and Strong Growth
Since value creation is going to be challenging in the
VUCA world, integrating ESG scores with financial strategies and decision making will help leaders drive high-growth business performance.

Shirish V. Divgi
Managing Director, Milacron India, Plastics Machinery Asia, Ahmedabad As the pandemic continues to wreak havoc across the world, the importance of organisational responsibility towards internal and external stakeholders has come to the forefront like never before. In the present environment as well as for the future, businesses will not only need to focus on financial goals by increasing revenues and profitability, but will also be required to contribute to the larger community by integrating Environment, Social and Governance (ESG) frameworks into its business operations.
The global landscape clearly indicates that governments, investors, and even customers are now paying close attention to how a company does its business, what impact it is creating on the society and environment around it, and how robust are its governance norms. The parameters to assess companies have shifted from being merely financial to also including non-financial risk areas such as regulatory compliances, ESG issues like occupational safety, waste management, diversity, equality and inclusivity, energy efficiency and disclosures on governance factors.
While we all drive the top line and bottom line with a lot of passion and detailing, sound ESG frameworks will ensure that we are safeguarding our business against nonfinancial risks.
At present, certain companies have taken voluntary initiatives to set up ESG frameworks and reporting mechanisms within the organisation. However, given the headwinds caused by the investor community as well as financial and government institutions, ESG reporting is set to be a mandatory requirement across the world. In India, SEBI has proposed a new mandatory framework called Business Responsibility and Sustainability Report (BRSR) for the top 1,000 listed companies. Moreover, the time is not far when even non-listed companies will start following these norms - not only to attract investors, but also to create positive brand perception among customers.
Integrating ESG in Business Operations
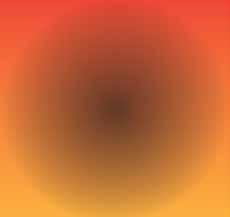
Building the foundation for a company-wide ESG framework is essential. Management teams as well as employees need to start learning and practicing aspects like business ethics and responsibility as well as sustainability practices, thereby contributing to social and environmental causes. We all have to contribute in driving greener ways of conducting business, by starting from our own offices and operations and then extending outside to our vendors, customers and society at large.
On-boarding ESG in organisations is not at all difficult. The first step is to familiarise responsible managers and employees to the basics of ESG and let them know how important it is for long-term business continuity. Enroll them for short-term courses either by CII or any other management
To know more, please subscribe to Polymers Communiqué at subscriptions@polymerscommunique.com
