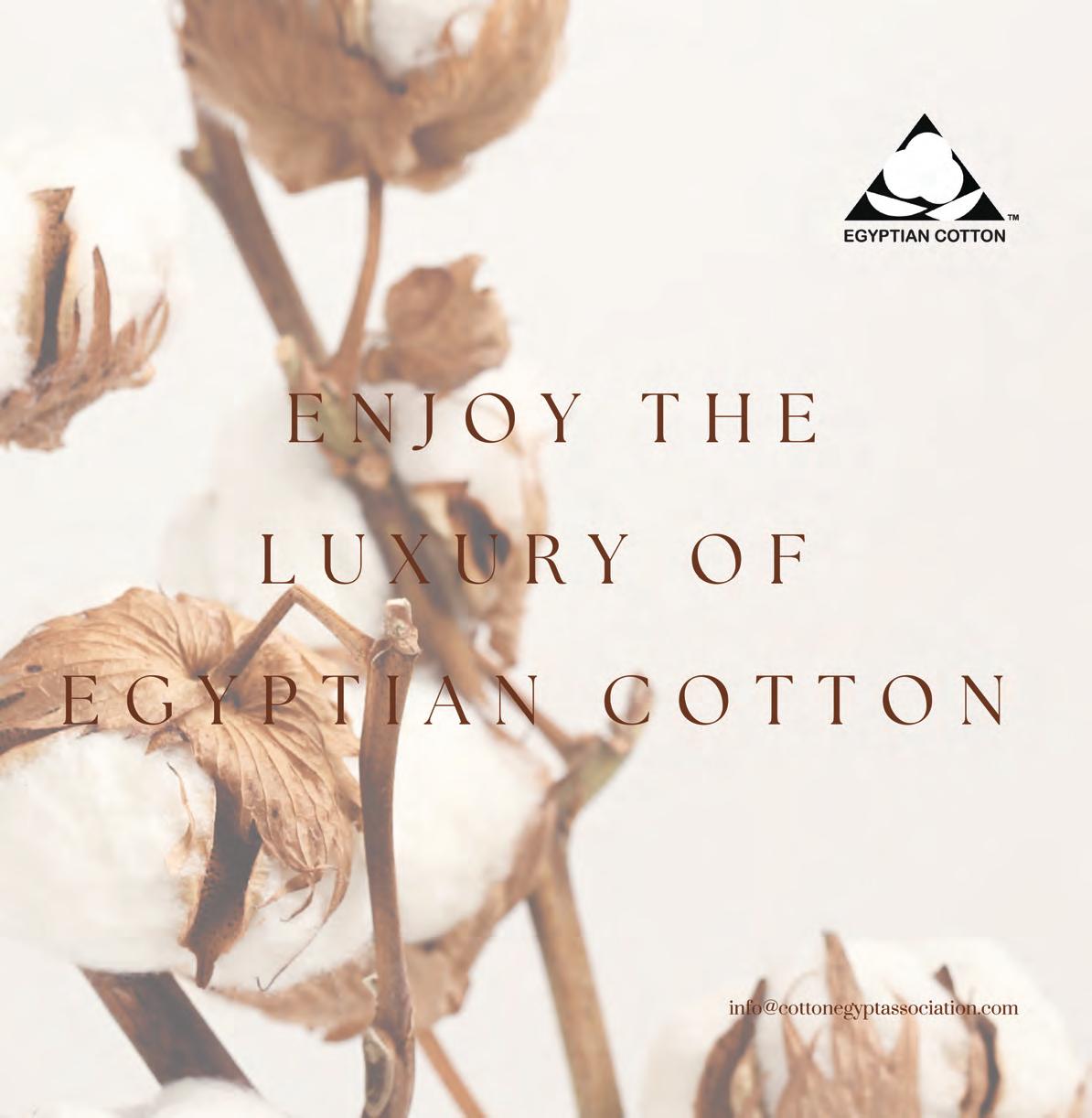
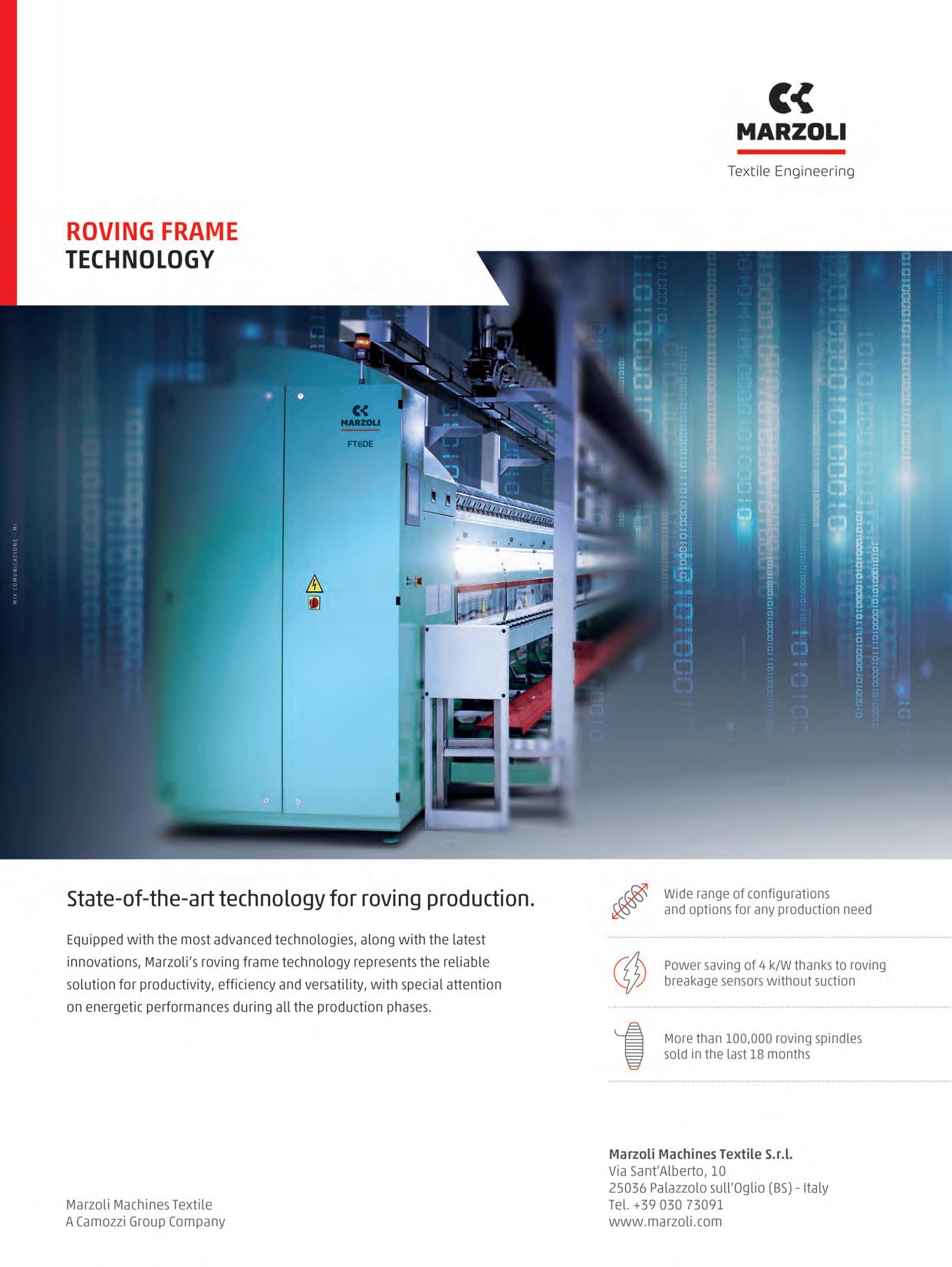

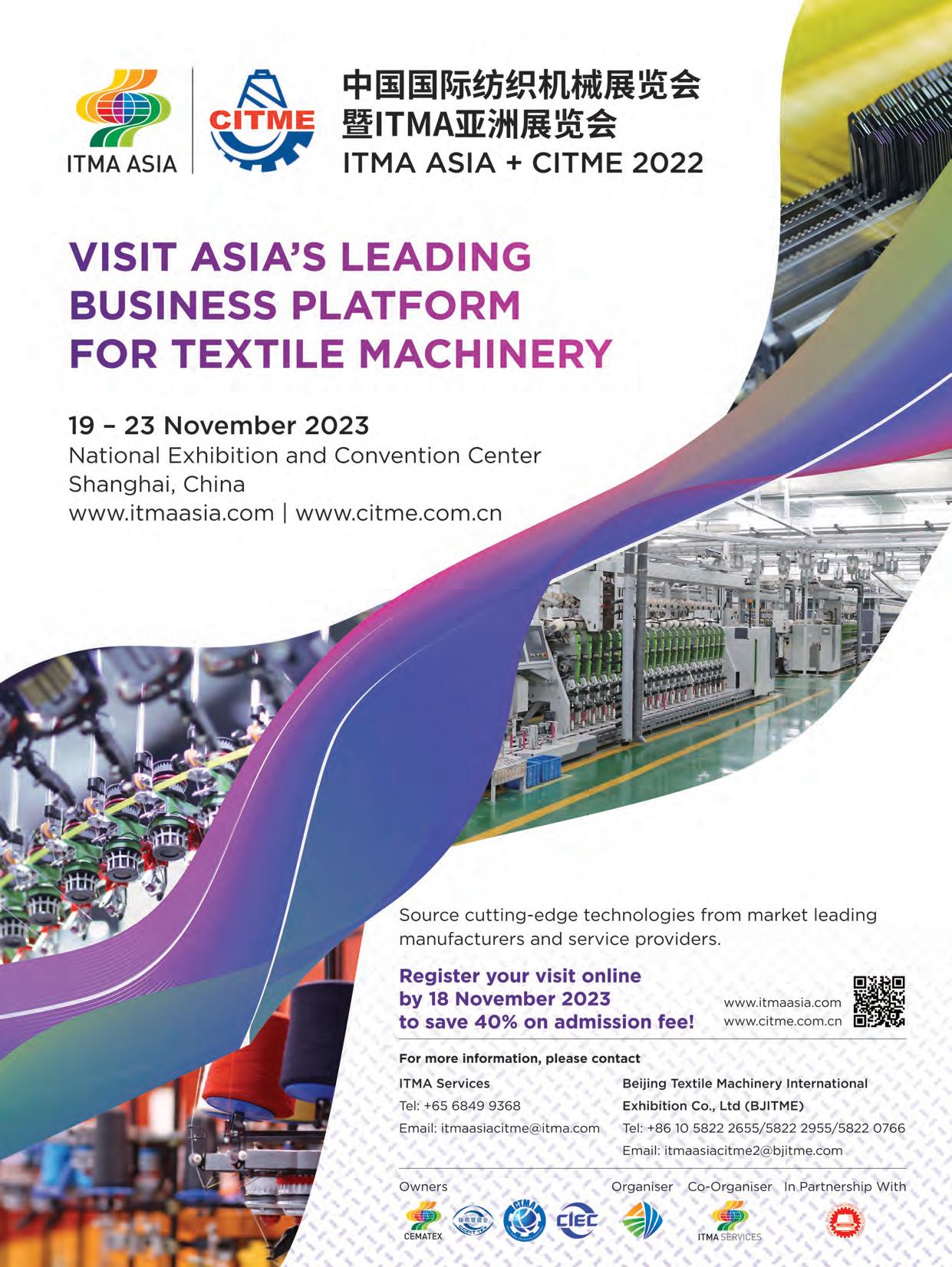
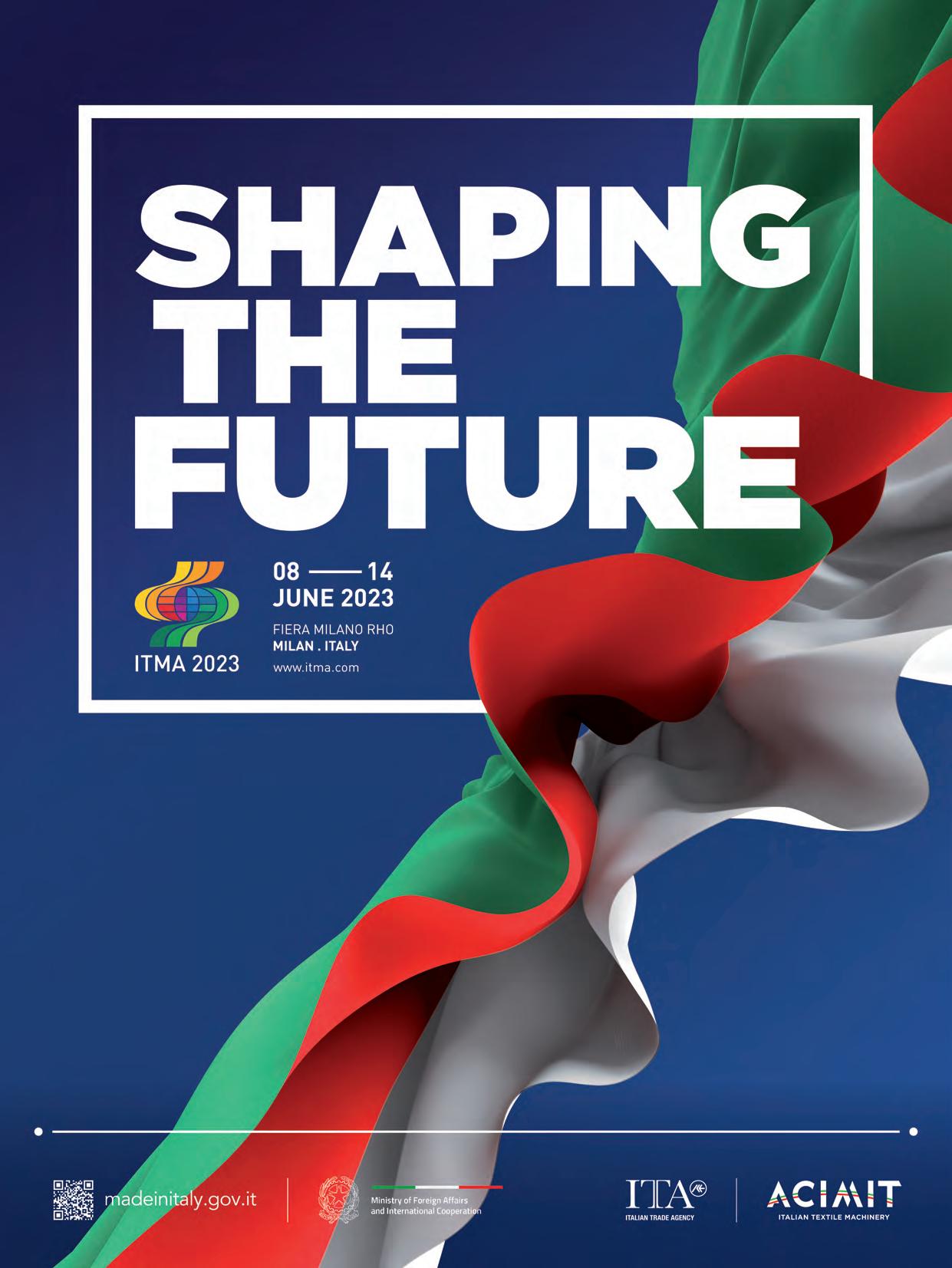
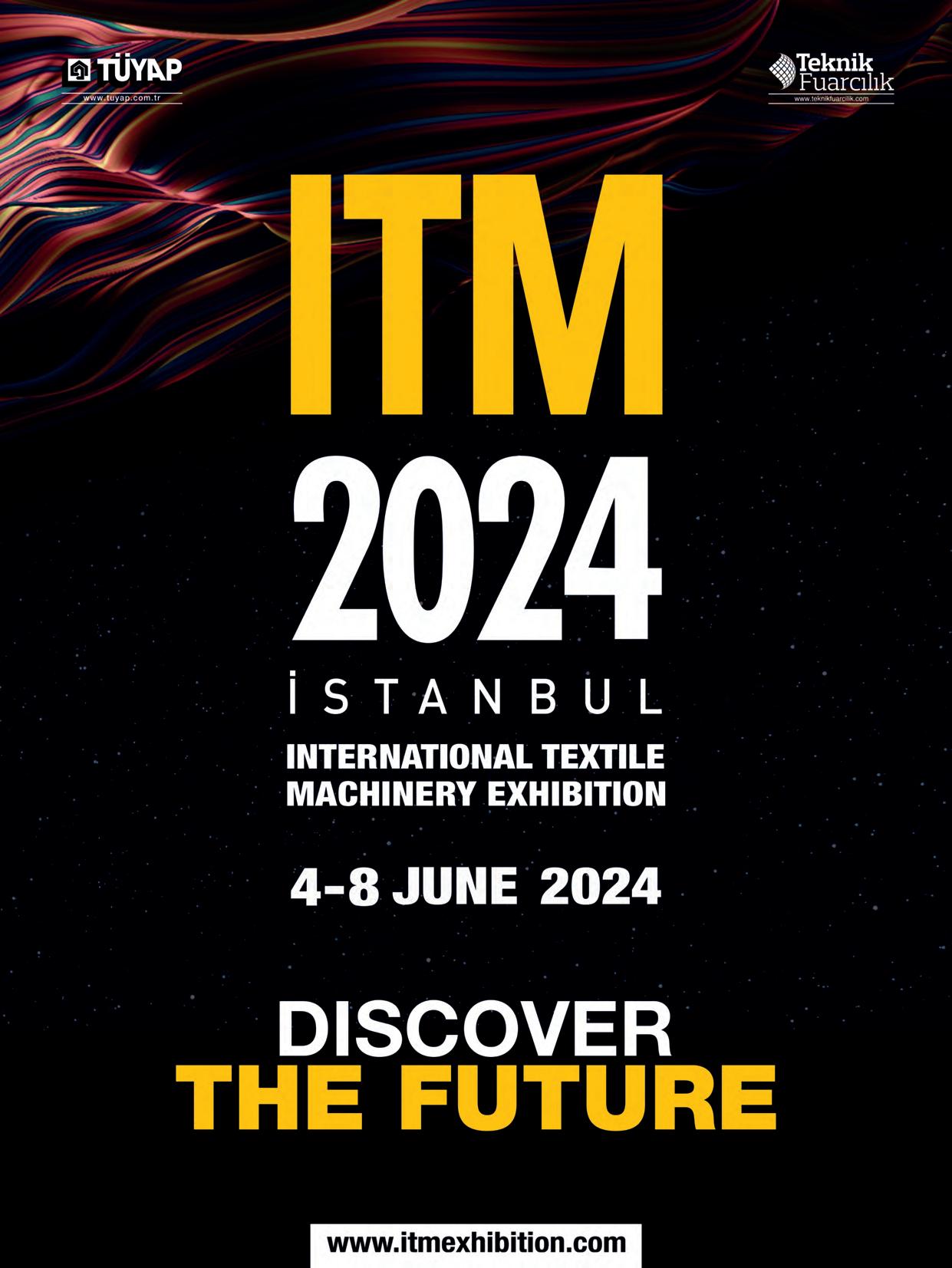
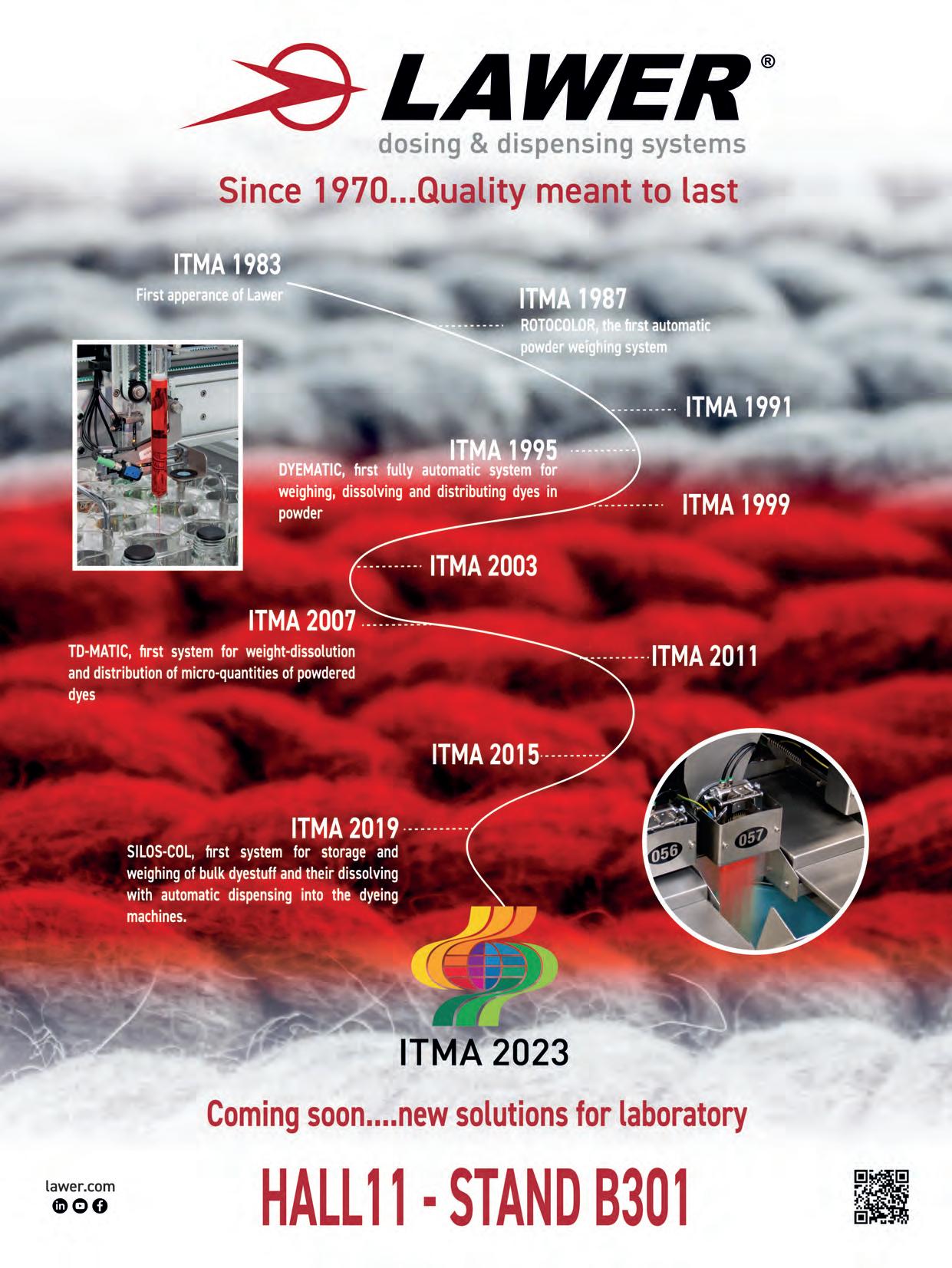
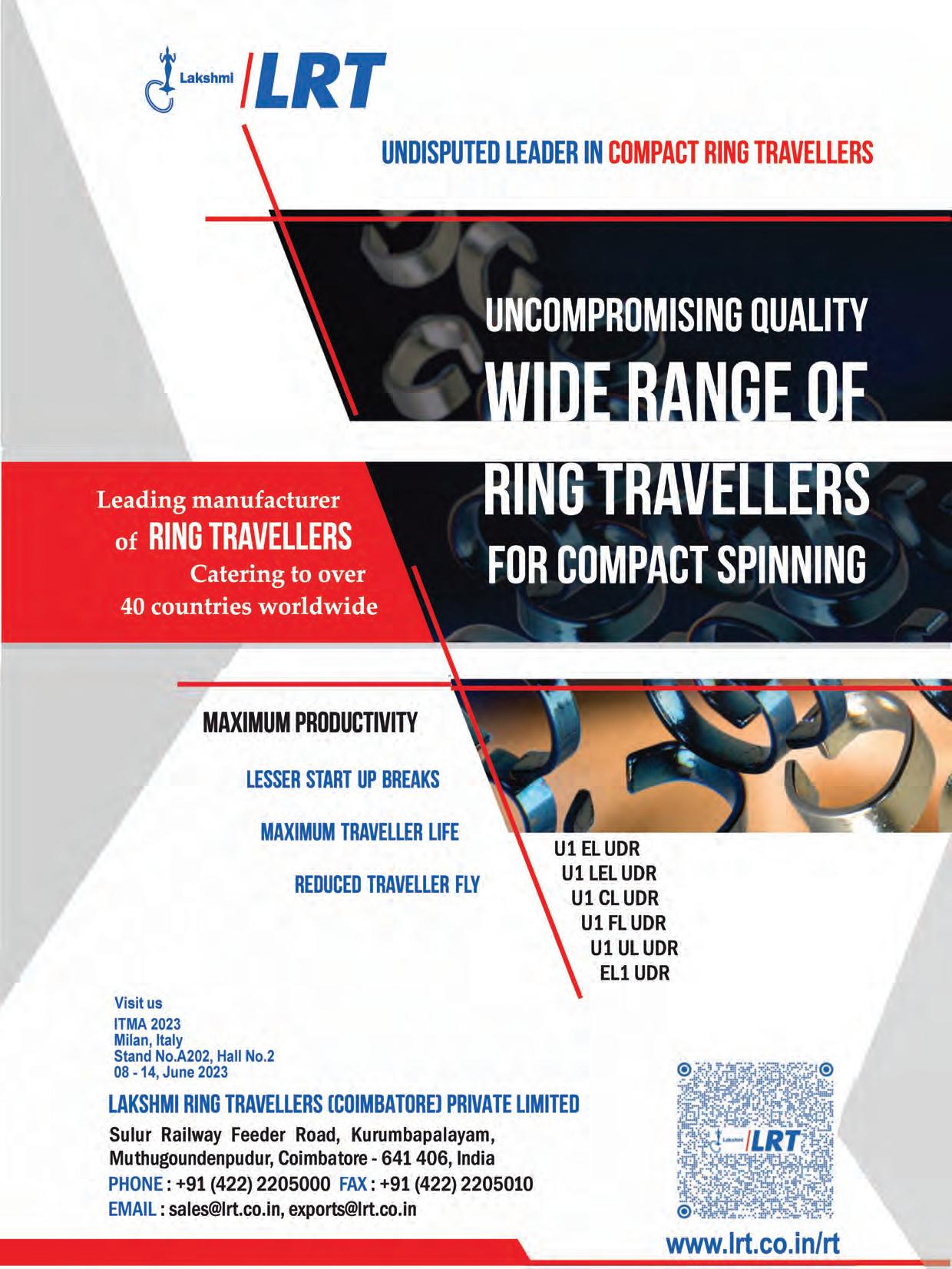

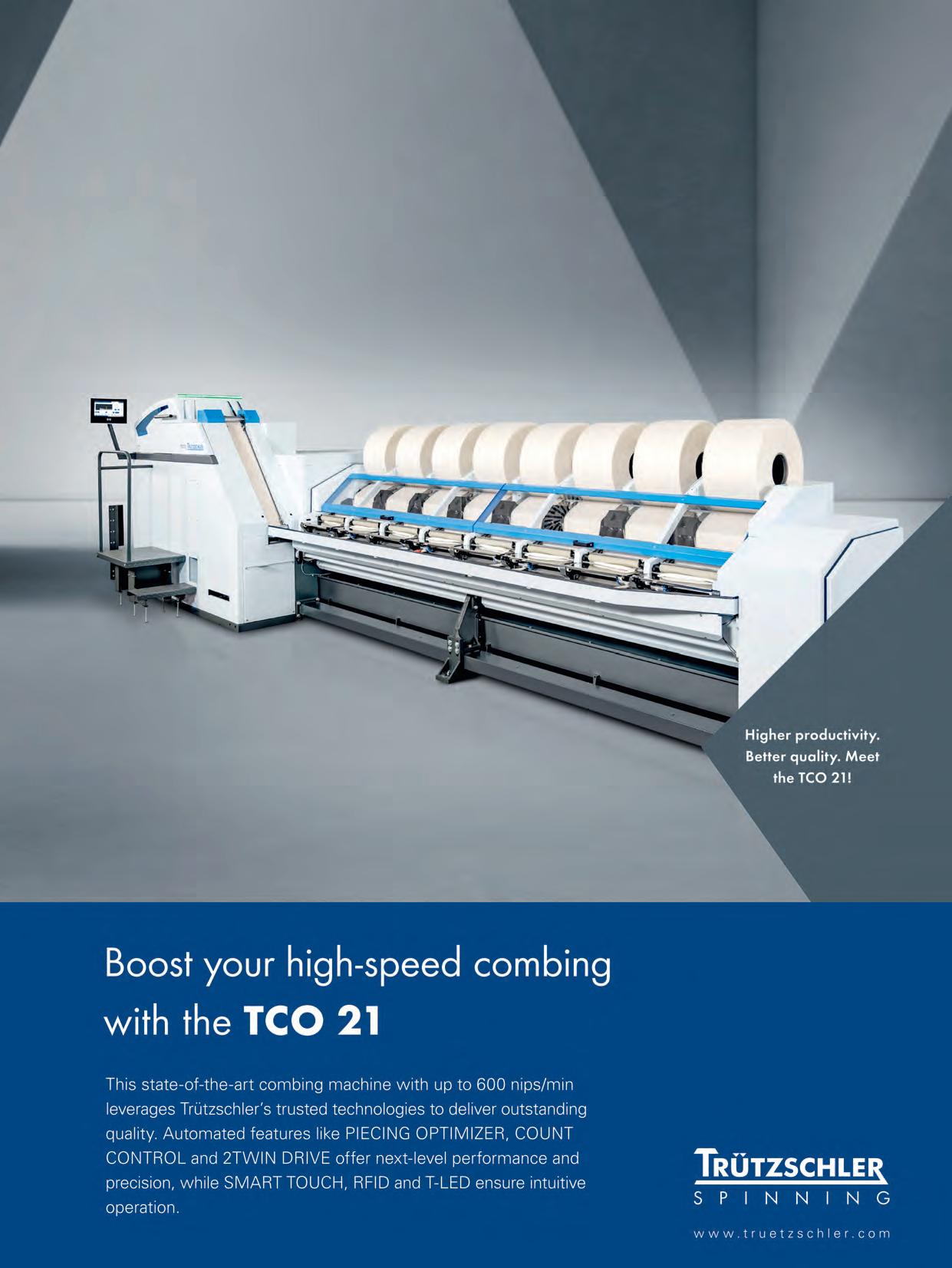
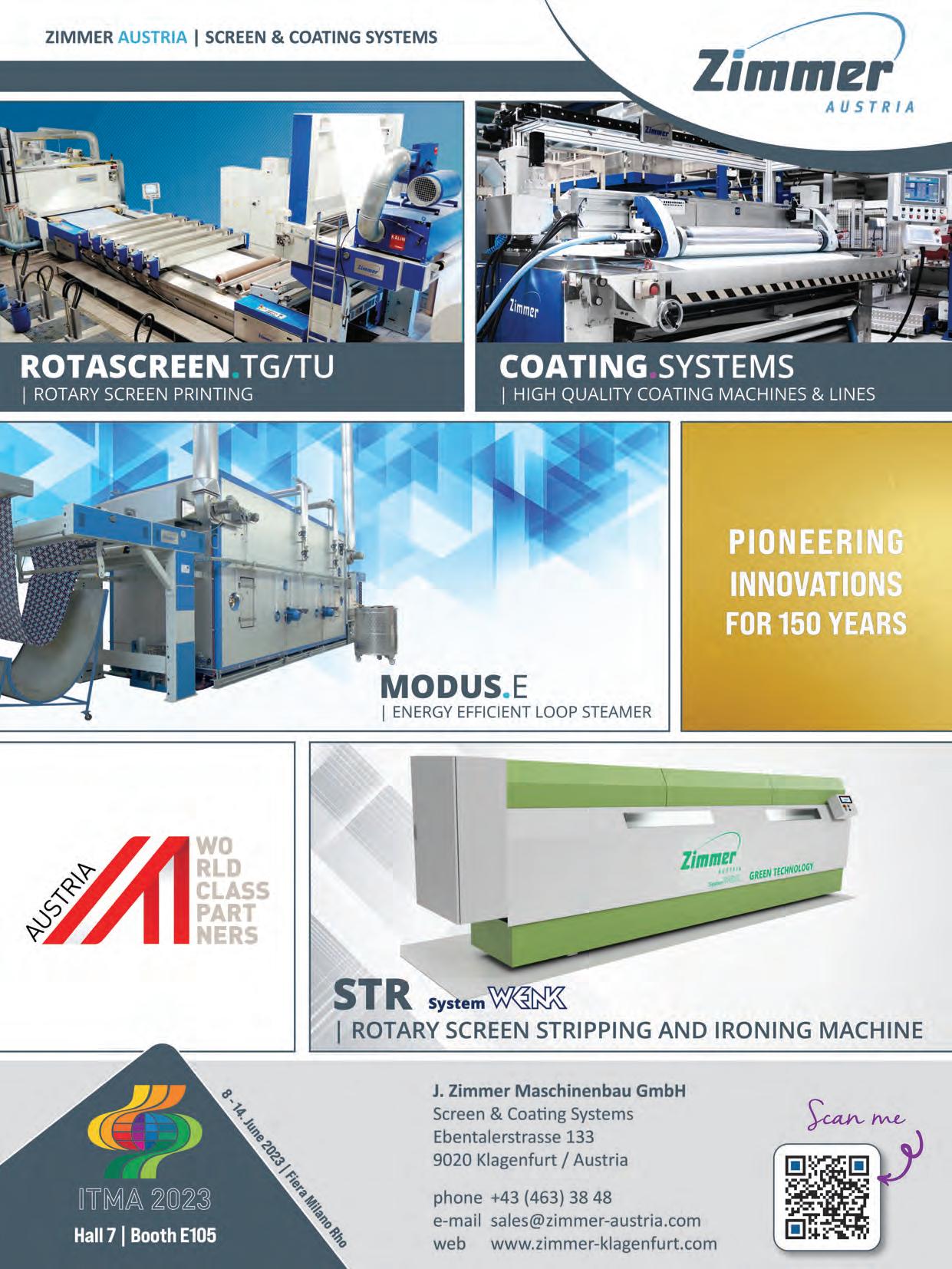

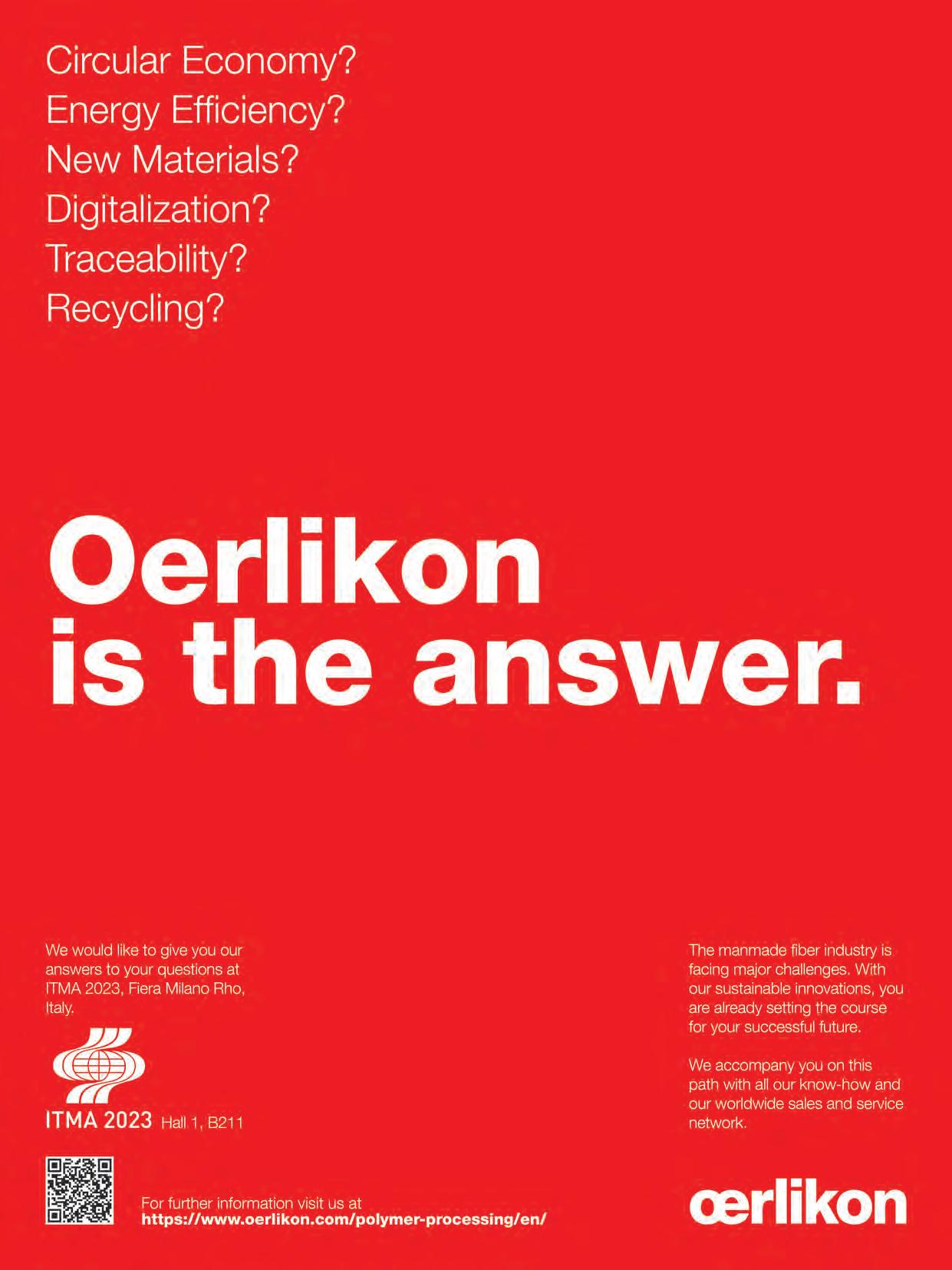
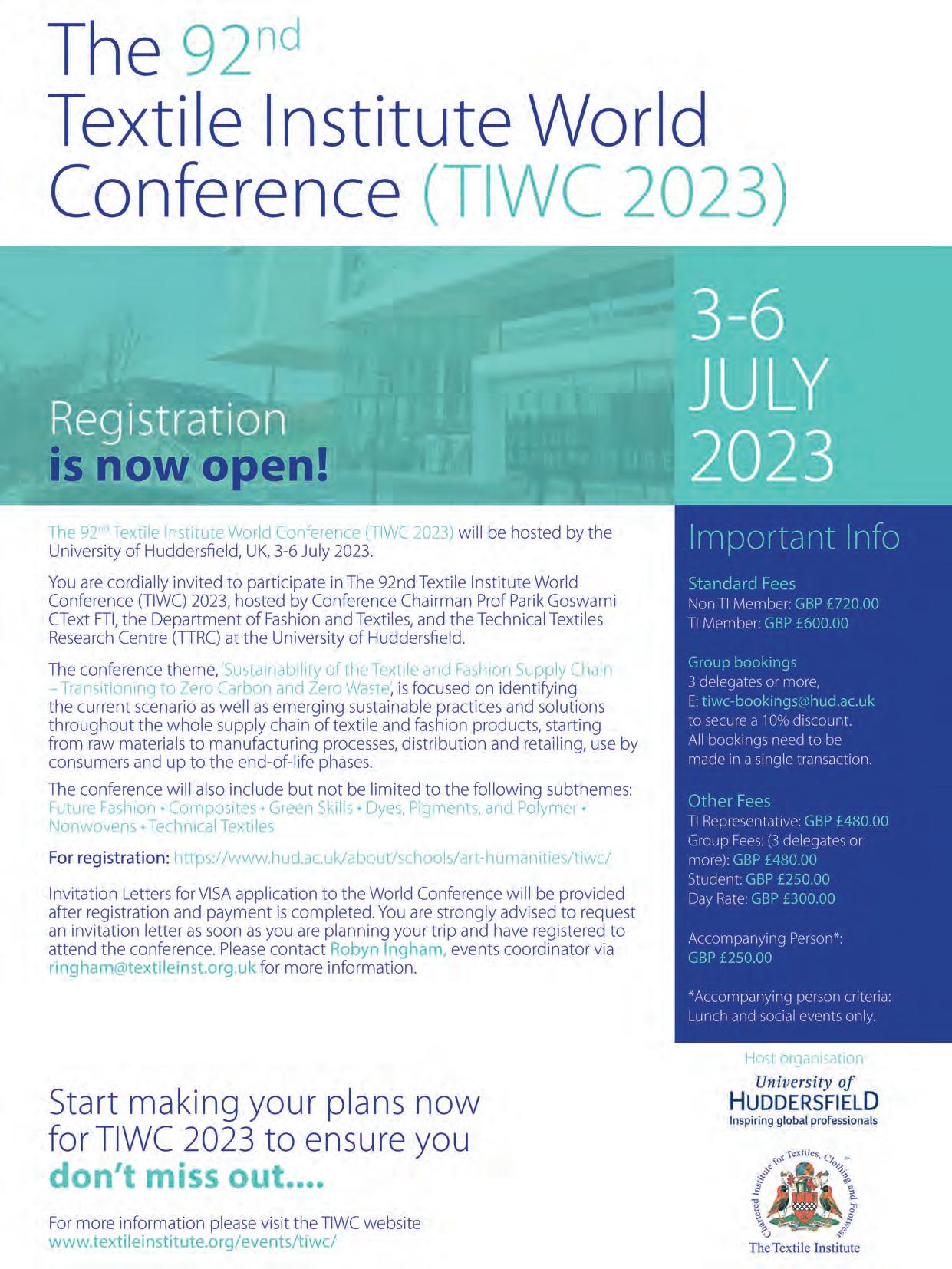
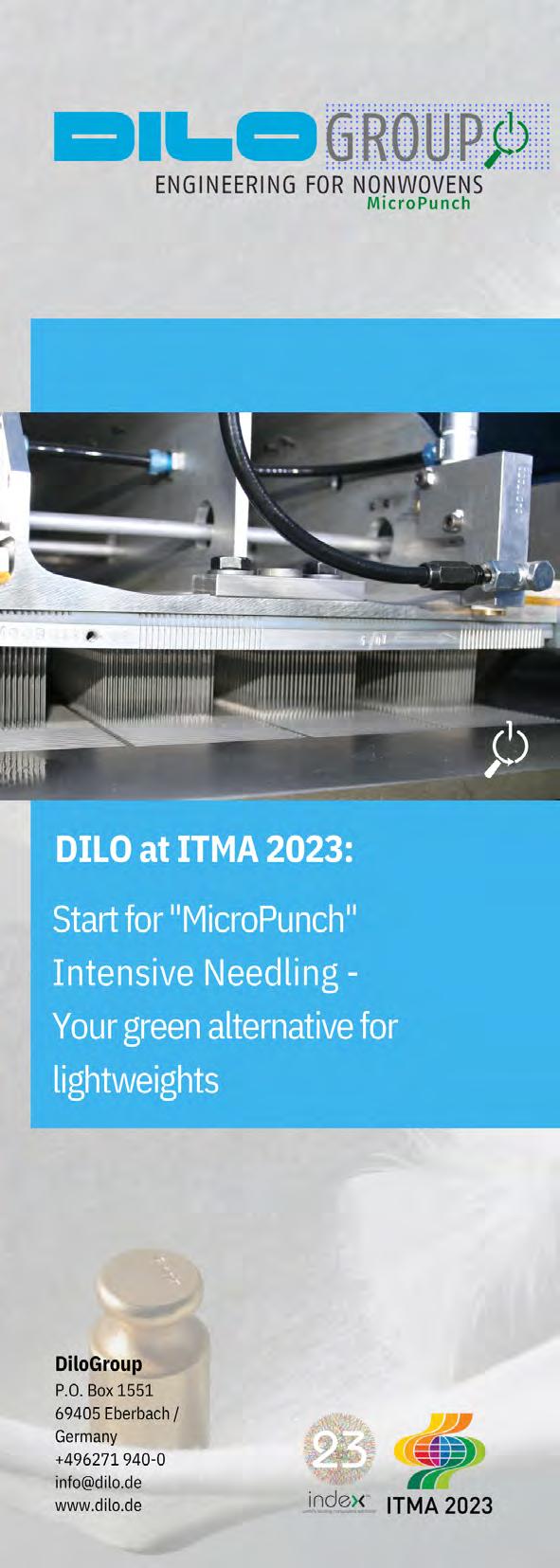
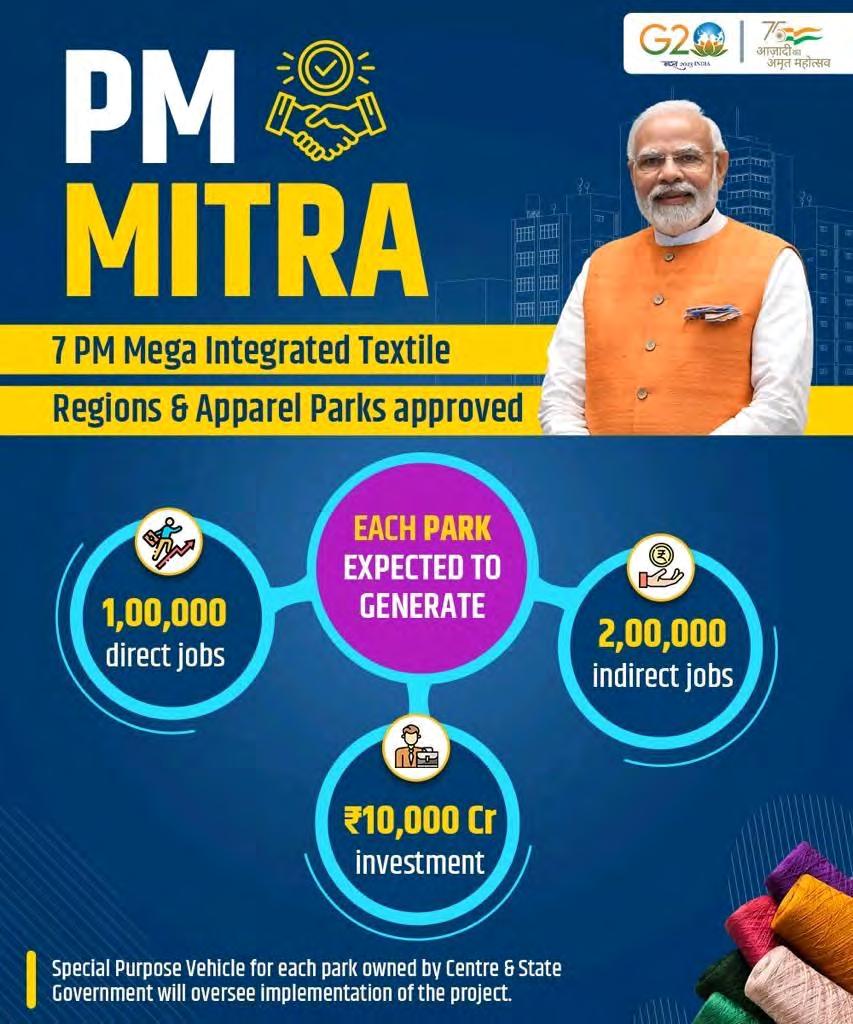
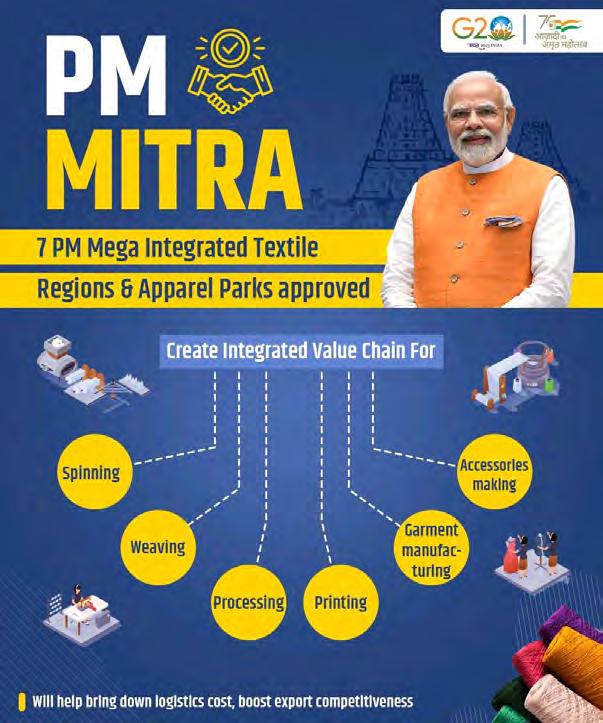
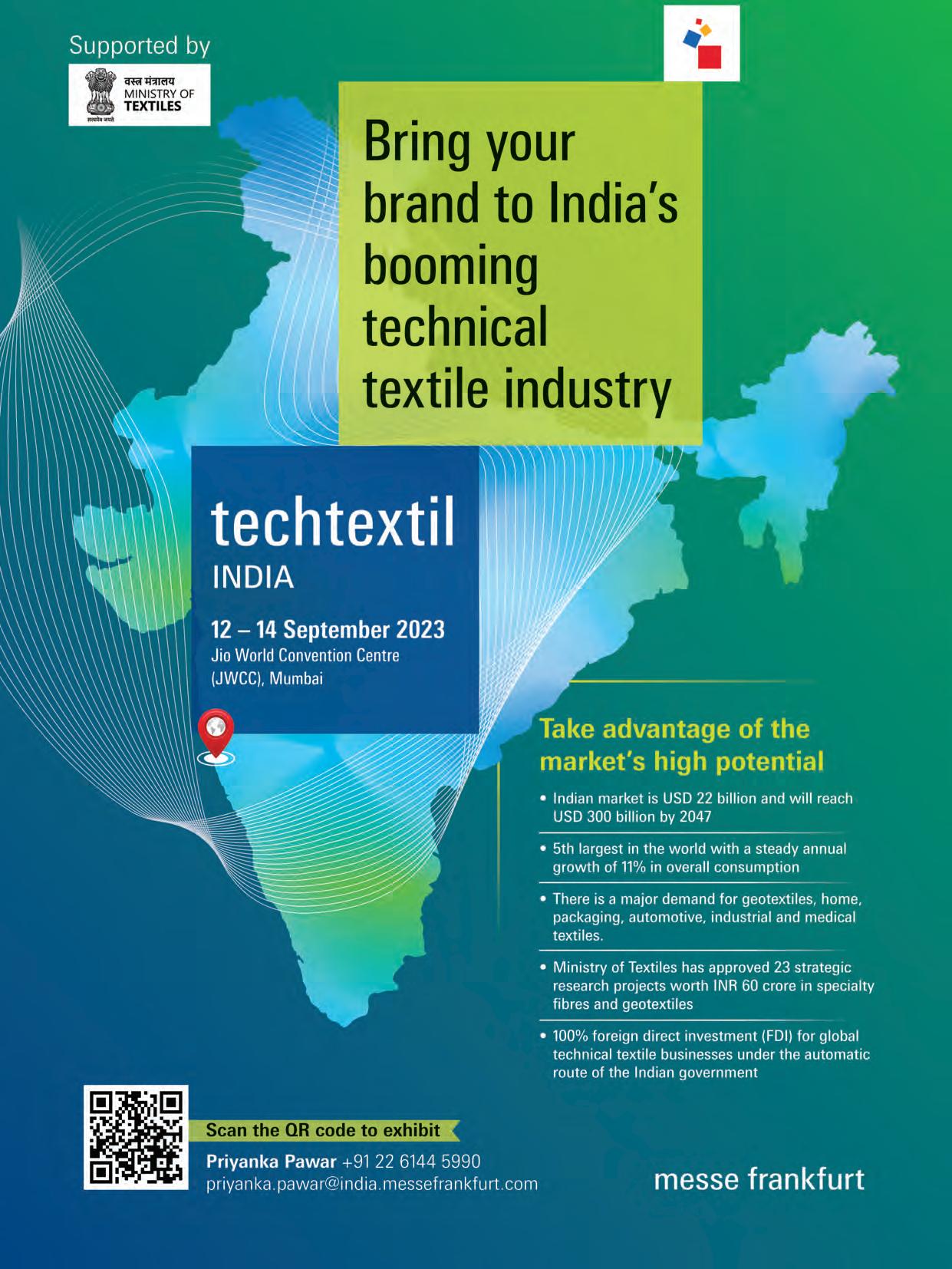
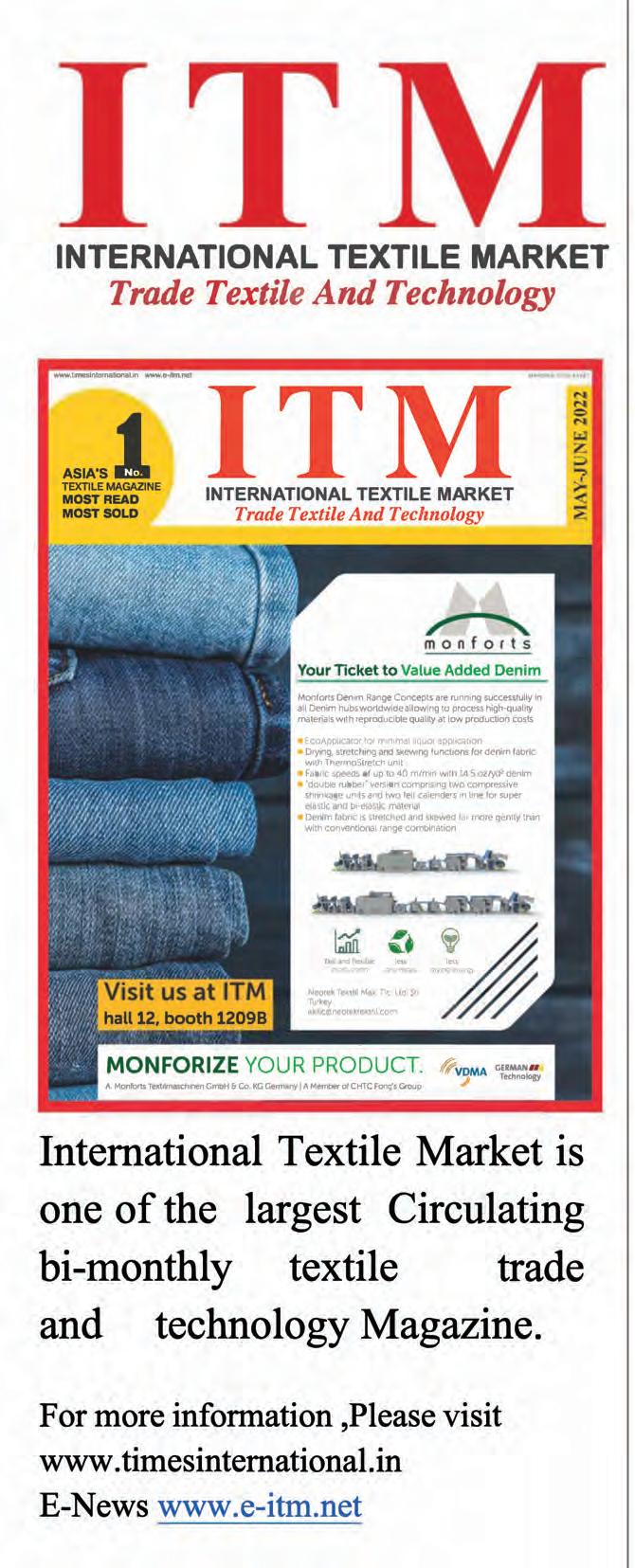

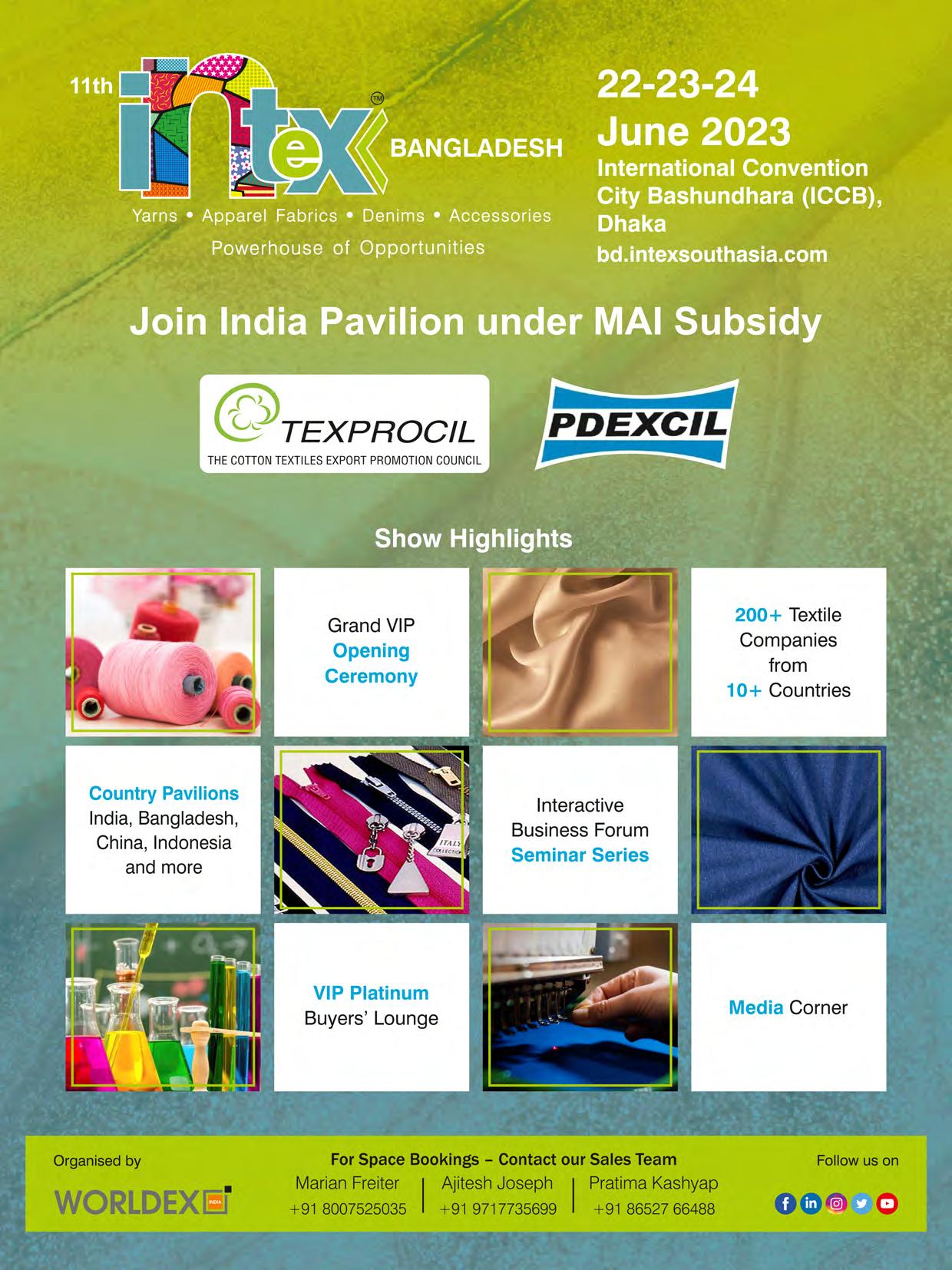
TMTMachinery,Japan
PET-NYPOV/FDY/IDY SpinningPlant.TexturizingMachine
AIKI RiotechCorporation,Japan
AirTexturising/CoveringMachine SplittingMachine
lricoGualchieraniHandling, Italy TextilePlantAutomation
ChemtexGlobalCorporation,U.S.A. ContinuousPolymerizationPlants
Slack& Parr Ltd., U.K. SpinningGearPumps/SpinFinish Pumps
AWASpindleCo.Ltd.,Japan
Interlace/OilMigrationNozzles
Binsfeld EngineeringInc., U.S.A. RotaryTemperatureTransmitters
Lawson-HemphillInc., U.S.A. TestingEquipments
TsudakomaCorp.,Japan
WaterJet/AirJetWeaving& PreparatoryMachines
BarudanCo. Ltd.,Japan
StitchingandHemmingMachines (forTowels/Sheeting)
Thema System,Italy
UnparalleledandUniqueyarn qualitycontrolsystem
CampenMachinery, A/S,Denmark Air-laid,CarpetBacking&Non-woven
SandoTech.Inc.,Japan ProcessingMachinery
Kiji ReedCo.Ltd.,Japan Reeds/UltrasonicReed CleaningMachine
NankaiIndustrial,Japan
HealdFramesforLooms
Kasen NozzleInc.,Japan Spinnerettes
MatsumotoYushi - SeiyakuCo.Ltd., Japan SpinFinishOils (forPOV/FDY/IDY/PSF)
Editorial
TrützschlerGroupatITMA2023
Sustainabilitymode
Swisstextilemachinerycompaniesfocusonwide-rangingenvironmentalpriorities
OerlikonwithworldpremieresatITMAMilan2023
Usterisbringingnewvaluepropositionstoitscustomers
Masteringthefuturewithsustainability
ITMA2023:ExploringnewroutestoefficiencywithThermexandEcontrol
RevolutionizingtheFabricIndustry: RabatexIndustries'TechnologicalSolutionsSince1962
UnfoldingatITMA2023,RimtexGroup'stransformativespinningtechnologies.Get readytobeamazed!
TheImportanceofInnovationand SustainabilityinItalianTextileMachineryManufacturing
ThestrategyforinnovationisthebasisforDiloGroup'ssuccess
StäubliInvitesCustomerstoFindSolutionsto WeavingChallengesatITMA2023
BRÜCKNERatITMA2023-sustainable,digitaland onthewaytoclimate-neutralfinishing
Howdesignsonfabricshavebeenevolved
EgyptianCotton:TheGlobalStandardofQuality, Luxury,andConsumerPreference
07798189485
The global textile industry has had to continually adapt to changeandinnovationovertheyearstoremaindynamicand competitive. Events such as ITMA have become indispensable platforms for the world's textile professionals toshowcaseproducts,equipment,andservices.
With the next edition of ITMA in 2023, textile companies across the world have a unique opportunity to capitalize on this global platform to present their latest offerings and innovations.The show is attended by leading professionals, decision-makers, and potential customers, providing companieswithatremendousopportunitytostrengthentheir brandandexpandtheirbusinessopportunities.
The COVID-19 pandemic has accelerated digital transformation, driving textile companies to adopt technological solutions to improve efficiency, streamline workflows, and offer differentiated value propositions to customers.TheupcomingITMA2023eventwillreflectthis new paradigm by showcasing cutting-edge technologies, machinery, and techniques to help companies remain competitiveinthetextileindustry.
The upcoming ITMA 2023 event promises to be a gamechanger, with a significant focus on sustainability, digital access, and automation. The event will explore sustainable textile manufacturing trends, showcasing breakthrough innovations that can help textile companies reduce their carbon footprint and improve their environmental sustainability.
Digital access is also an essential theme at the upcoming ITMA2023event,withmanycompaniesdemonstratinghow technology solutions can help textile professionals access critical insights, data, and analytics, driving informed decision-making.
AutomationisanotherkeytopicthatITMA2023anticipates exploring. The integration of artificial intelligence, automation solutions, and robotics in textile manufacturing will drive significant transformation in the textile industry, and attendees will get an exclusive opportunity to witness this.
In conclusion, the textile industry continues to evolve at an acceleratedpace,andeventslikeITMA2023havebecomean essential platform for the industry. The event will provide global textile professionals with a unique opportunity to experiencecutting-edgetechnologies,innovativemachinery, and sustainable techniques that are essential for industry transformation.
India,Pakistan,Bangladesh,Srilanka,Vietnam,Indonesia,Thailand, China,HongKong,USA,Germany,Spain,Italy,U.K.&FranceIt’sfinallythattimeagain:Trützschlerisattending theITMAinMilanfromJune8toJune14,2023at FieraMilanoRho.Atour1320-square-meterstand numberC101inHall3,wewillintroducethelatest machines and technologies from the entire Trützschler Group –including Spinning, Card Clothing,NonwovensandMan-MadeFibers.
Trützschler Spinning and Trützschler Card Clothing
Trützschler Spinning will showcase innovations for carding,drawframeandcombingwhichmeetthemost important customer requirements in fiber processing: higher efficiency, more sustainable raw material utilization and intelligent automation – while also displaying the potential of digital technologies for spinning mills. Visitors can also look forward to the introduction of our new brand TRUECYCLED for textile recycling. Our machinery expertise and technological know-how enable our customers to produce sliver with the highest possible level of qualityandmakeitpossibletoturnwasteintovalue.
Trützschler Card Clothing (TCC) will present a wide range of technologies from its clothing portfolio, whichcoversthecompletespectrumofapplicationsin thespinningandnonwovenmarkets.Thisincludesall of the service features and machinery equipment that are supported, which will be demonstrated live at the boothaspartofan“ActionPoint”presentation.TCCis also focusing on recycling applications and will showcaseitscontributiontosustainabilityinthetextile industry. These features and functions are all supplemented by “My Wires”, our digital wire performance solution that is integrated into the Trützschlerdigitalplatform.
Trützschler Nonwovens will focus on solutions that take nonwoven production processes to a new level. The story of innovations for needle-punching will be toldattwobooths:Trützschlerisgoingtoconcentrate on the holistic T-SUPREMA package of excellent machinery, tailor- made production lines, integrated digital support and global service. Our cooperation partner in needle-punching, the Italian company Texnology S.r.l., will offer details about machinery and Trützschler Group at ITMA2023 applications at boothA101inHall10,andwillalsoprovideachance tocheckoutarunningneedle-punchinglinefeaturing someoftheT-SUPREMAmachinery.
Trützschler Nonwovens will also showcase solutions fornewandenvironmentallyfriendlywipematerials, aswellasaninnovativedryingconcept.Unlockingthe potentialofdigitalizationisthekeytopicatourT-ONE corner, where our experts will demonstrate every aspect of our digital environment – from quality control and recipe management through to real-time processmonitoringandAI-basedlineoptimization.
Last but not least, Trützschler Man-Made Fibers will demonstratethepowerofOPTIMA,TrützschlerManMade Fiber’s flexible platform for all types of Bulk ContinuousFilament(BCF)carpetandIndustrialYarn (IDY).
TheITMAoffersagreatopportunityforpeoplefrom acrossthetextilesindustryaroundtheworldtotalkto ourexpertsfromeverybusinessunit.Weareexcitedto finallymeetournewandexistingcustomersinMilan.
Swisstextilemachinerycompaniesfocusonwide-rangingenvironmentalpriorities
VisitorstoITMA2023willseesignificantinnovations from members of the Swiss Textile Machinery Association – with a special focus on solutions for a moresustainablefutureinthetextileindustry.Details ofplannedexhibitsrevealhowSwisscompanieshave been acting in specific technology developments, as wellasmulti-facetedbusinessstrategiestomeettheir ownsustainabilitytargetsandthoseoftheircustomers.
Some of these actions go beyond products and applications to take in ‘behind-the-scenes’ measures such as improving internal ecosystems and streamliningmanufacturing.Activitiescoveredbythe Swiss firms’ technology embrace the concept of safeguardinga‘livableplanet’forfuturegenerations, andthispolicystartswithinthecompaniesthemselves, as they commit to careful management of their businesses to protect the environment and conserve global resources. Real outcomes are already being proudlypresentedasvisibleprogressforthebenefitof customers.
Swiss textile machinery manufacturers apply their innovativepowertomakeproductionassustainableas possible – tackling issues such as saving water, chemicals, raw material waste and energy, as well as improving hardware life-cycles. Machine developments empowering more environmental production are continually growing in importance, as producersinvestinthementhusiastically.
Sustainable solutions for cotton spinners include mechanical compacting systems by Swinsol. These unitsneednoelectricityandarethereforeCO2neutral in operation. The company also offers recycling of usedcomponents.Loepfeprovidesyarnclearerswith latest technologies enabling settings to balance the required yarn quality against contingent productivity losses. The results avoid waste of both yarn and energy. Retech develops solutions to improve the footprintofmillsspinningman-madefibres.State-ofthe-art heating godets with energy-optimized motor technologies and heating systems enable energy savingsofupto35%.
For Stäubli, sustainable investment also means ensuring its machinery is reliable enough to allow continued production over many years, even under harshest and most demanding conditions. Customers canrelyonthefirm’sequipment,servicesandsupport foranimpressivelylonglife-cycle.
The idea of a circular economy promises a massive leap forward for global sustainability goals. Using recycled fibres is a good start for the textile industry, and Swinsol systems make it possible to spin 100% recycled fibres – even without adding new fibers due to a high short fibre distribution. Jakob Müller providestechnologiesinnarrowweavingthatenables the processing of sustainable yarns and therefore the manufactureofclosed-loopproducts.
Serious rethinking of business models is clearly essential if long-term sustainability goals are to be met. In synthetic spinning, a completely new production line might not be needed when the extrusion process is still working perfectly. But it could well be the drawing and heat treatment system that is limiting the production of the yarns customers demandtoday–inwhichcaseRetechhastheanswer, with its ability to upgrade or rebuild existing lines, including providing new and energy-optimized drawingsystems.
The idea of converting or retrofitting machines and systems often develops in response to changing customer requirements. Specifications in such cases arealreadywelldefinedinadvance. Trackingfibres,andmanyotheraspectsoftraceability, are further topics of innovative developments currentlywithSwisstextilemachinerycompanies.
Mostsustainablesolutionsshowanadditionalbenefit: cost saving. Costumers’ investments therefore empower the protection of the environment and prosperous business. Machine manufacturers
committing to the various sustainability aspects are actually generating value for customers, organisations,widersociety,andtheenvironment.
Machinemanufacturersmustalsofocusonmanaging their own ecosystems in a sustainable way. Jakob Muller for example wants to be a role model in handlingitsownsystemaccordingtobestpractices.At itsheadquartersinFrick,Switzerland,variousprojects significantly reduce the consumption of gas, oil, and most of all electricity.Also, the production area was challenged for more sustainability. The space for machine manufacturing was optimized first, greatly reducing the energy consumption needed for climate control.
Stäubli installed photovoltaic systems in its premises around the world, also taking the opportunity to generatelocalandsustainableelectricityandlowerthe carbonfootprint.
The reduction of CO2 emission is one of its key focusesandidentifyingthecarbonfootprintofallmain productionunitsisamongtheprioritiesfor2023.The company is designing a sustainability roadmap to determineactions,resources,andatimeline,working on a long-term vision with tangible benefits for the environmentandsociety.
SwissTextileMachinerymemberstakecenterstageat ITMAbecause of their innovative reputation – but a closer look at latest developments will show these world-class suppliersof m achinery, components and services are themselves striving, as are their customers,tohavethebestpartnersforsustainability incomponents,rawmaterialsandservices.
The ultimate goal is the same: business success with environmental responsibility for themselves, their customersandtheworld.
This year's ITMA trade show appearance of the Oerlikon Group will focus on current challenges that the entire textile industry has to deal with: creating a circular economy within the textile value chain, providing energy-efficient technologies, using digital solutions to support a sustainable production, processing new materials, and finally the traceability ofallproductsandtherecyclingofrawmaterialsused. And there are certainly many more subject areas that the visitors of the ITMA will have questions about. Oerlikon therefore invites all trade fair visitors to engageinadialogwithallitsexpertsatitsboothinhall 1, B211. On more than 500 m², Oerlikon will give initial answers to the urgent questions of the present andthefutureandwillpresentitstechnologysolutions in an innovative way within its inspiring experience center.
“At Oerlikon, we contribute with our innovative technologies for resource-saving use in almost all
manmade fiber spinning mills in the world. Our promise for the future is to continue to expand the zero-wasteproductionapproachandthustakecareof achievingourcustomers'andourownsustainability goals”, says Georg Stausberg, CEO of the Polymer Processing Solutions Division and Chief SustainabilityOfficeroftheOerlikonGroup.
This sets out the claim of one of the world's leading suppliers of machinery and plant solutions for manmadefiberproductionnotonlyforthisshow:In the future, it will be solely a matter of sustainable innovations.
Circular Economy and recycling? Enabling customers to achieve more with less Textiles are becominganincreasinglybigpolluter.Totacklethe growing mountains of used clothing, it is above all European politicians who are developing a comprehensive strategy for a regulating circular economy.Andthetextilesindustryisalsomakingits mark with innovative technologies for recycling manmadefibers.However,thereisstillalongwayto go before we have a sustainable textile world. According to the European EnvironmentAgency, the consumption of textiles is already the fourth-largest sourceofnegativeenvironmentalandclimatechange impacts within the European Union (EU). A major reason for this is relentless textile growth: the Ellen MacArthur Foundation states that the global production of textile almost doubled between 2000 and2015.Andtheannualconsumptionofappareland shoesisexpectedtofurtherriseby63percentby2030 –fromcurrently62millionto102milliontons–adds the European EnvironmentAgency.With this market developmentinmind,Oerlikonisintensivelyinvolved in WornAgain Technologies.The British partnership is focusing on a solvent-based recycling technology, with which both end-of-life textiles comprising polyesterandpolycottonblendsandPETplasticscan be converted into circular raw materials and fibers (polyester and cellulose). For this, a large demonstration system for upcycling 1,000 tons of textiles per annum is being created in Switzerland. “We are supporting technological innovators such as Worn Again Technologies because we believe their solution is extremelypromising and because they are
“Technologyisonceagainenablingustocreateabetterworld”
OerlikonwithworldpremieresatITMAMilan2023
drivingcooperationbetweentheindividualproducers withinthevaluechain.Recyclingonlyworkswhenall players cooperate in a circular system”, emphasizes Stausberg. He is already looking to the future: “The timeforclosed-loopstrategiesandthecorresponding sustainable technologies is now – let's talk about it at ITMA.”
Intermsofsustainability,however,Oerlikonalsosets itself high goals. Stausberg: “It is no surprise that we haveappliedhighstandardsofinnovationtoourown operations and practices. For several years, Oerlikon has been creating pilot initiatives that we intend to implement company-wide to the greatest extent possible.Forexample,wearecommittedtoachieving CO2neutralityinallourlocationsby2030aswehave alreadydoneatoursiteinLiechtensteinthatprovides ourblueprintformeetingthiscommitment.Ourgoals also include obtaining 100% of our electrical energy fromrenewablesourcesandachievingthestandardof ,ZeroHarmtoPeople'”.
In addition to regulatory initiatives, technical innovationisrequiredtoconnectthebeginningandthe endofthelineartextilesindustryandtoclosetheloop. Onedecisivecirculartechnologyhereisfiber-to-fiber recycling.Onlyafewyearsago,thisprocesswasused to recycle around just one percent of used clothing worldwide into fibers for new apparel. McKinsey market researchers are now talking about 18 to 26 percent being recycled by 2030 – if the full technical
recycling potential is utilized and more textiles are collected. For this, manual processes will have to be automated, clothing waste qualitatively sorted, buttons and zips removed, and fiber compositions unambiguously identified – and all less expensively. Separatingmixedfibersstillrepresentsanobstacleas well. Finally, the recycled materials must be suitable forthespinningprocess,provideausableyarnquality andbeabletobefurtherprocessed,i.e.,dyed.Despite thesechallenges,therearepromisingsolutionsonthe horizon,eventhoughsomeprocessesarenotyetready forcommercialexploitation.
Oerlikon Barmag is offering technological solutions forrPETthatenablecustomerstosavemilliontonsof CO2peryear.In2022,OerlikonBarmagintroduced,a homogenizerrecyclinglinespecificallyforcustomers in China andAsia where bottle flakes and film waste can be agglomerated, extruded, homogenized and meltedtoproducepolymermeltorchips.Itenablesthe polymerqualityofrecycledbottlesorfilmwastetobe precisely adjusted to the requirements of different downstreamextrusionorinjectionmoldingprocesses.
AnotherrPETsolutionistheVacuFilsystemfromthe Oerlikon Barmag joint venture, BB Engineering. VacuFilisauniqueandinnovativePETrecyclingline, uniting gentle large-scale filtration and targeted intrinsic viscoscity (IV) regulation for consistently outstanding rPET melt quality. In 2022, BB Engineeringlaunchedapatentedkeycomponentofthe VacuFil system, the Visco+ filter as a separate and
easily integrable upgrade component that enables precise IV setting and pure melt with the help of vacuum.IVisthecentralqualitycharacteristicinPET recycling and rPET processing. It determines the meltingperformanceintheproductionprocessandthe properties of the end products and is thus essential in the recycling process.TheVisco+ process is reliable, verifiable and 50% faster than conventional liquidstatepolycondensationsystems.
Energy Efficiency? EvoSteam process revolutionizespolyesterstaplefiberproduction
There is a huge demand for textile fibers: population growth of around 3% per annum, fast fashion and manyotherfactorsarefuelingthisdemand.According to international studies, global demand for staple fibersmadefrompolyesterwilltotal20milliontonsin 2025 – this is approx. 33% more than the production volume recorded in 2013. In view of noticeable climate change and its impact on people and the economy, resource- and environment-friendly manufacturing methods are absolutely crucial for the future.Highproductioncostsarecurrentlyeatinginto the margins of fiber producers. Noteworthy here are above all massively increased energy and polymer prices,butwaterisalsoanimportantresourcetoday–veryfrequentlyscarceandconsequentlyexpensive.At this year's ITMAin Milan, Oerlikon Neumag will be unveilingitsnewEvoSteamprocesstointerestedtrade visitors,viewedbymanyprocessexpertsasanenabler
for more sustainable staple fiber production in the future. The objective of the new development is to lowerbothoperatingexpenses(OPEX)andthecarbon footprint with minimal consumption of energy, water andpolymer–simultaneouslywiththeexcellentfiber qualities demanded by downstream processes and highproductionvolumes.
Looking back at the regulations of the European Union,amongothers,therearealsomajorchallenges for new materials. In that regard the Green Deal can only be realized if new European Union policy frameworkscreatecertaintyforfutureinvestments.
“Inthepolymerprocessingindustry,wehavetocome to a sustainable, closed circular economy for packaging materials and textiles, for example, while simultaneouslyintensivelyexpandingtherecyclingof the materials used. Here, new materials also offer opportunities – opportunities that we as a machine manufacturer and plant engineering company will exploit. However, compared to non-biodegradable, petrochemical-based polymers such as PE, PET and PP,thepricesforbio-basedpolymerslikePA5.6.and biodegradablepolymerslikePLA,PBATandPBSare notyetcompetitive.Incontrast,thepropertiesofbiobased materials used for consumer products, especially those used in the packaging industry, are already competitive. It appears compostable textiles willremainanichemarket”,explainsStausberg.
“But one thing is certain: utilizing current Oerlikon technologiesandfutureinnovations,wewillbeableto transform virtually any raw material into an ecologically attractive end product. The economic questions will ultimately be answered by consumers. Technologyisonceagainenablingustocreateabetter world”,saysStausberg.
With its sustainable and closed loop-compatible textilesstrategy,theEUplanstobecomeapioneerfor the global circular economy as well. By 2030, textile productsmarketedwithintheEUaretobecomemore durable and recyclable, predominantly comprise recycled fibers, contain no hazardous substances and bemanufacturedincompliancewithsocialrightsand inamannerthatprotectstheenvironmental.Thisalso includestheintroductionofadigitalproductpassport andtheamendmentoftheEuropeanTextileLabeling Act:Toimplementtheclosed-loopprincipleandother important environmental requirements, players along the value chain must also fulfill new information obligations about the composition of textiles. At the show, Oerlikon will present own digital technology solutions and those that have been tested in collaboration with various partners for the use in Oerlikontechnologies.
Theterm"digitaltwin"wascoinedin2014byMichael Grieves and John Vickers (NASA) and is used and interpretedfordifferentscenarios:Thesimplestdigital twinsmapadigitalinventorylistofarealmachine,for example,inordertobeabletosupplyexactlymatching spare parts for a customer-specific plant.At the other endofthecomplexityscalearedigitaltwinsthatmap thekinematicsand/ordynamicsofamachineorplant. At ITMA, Oerlikon Barmag will present a complete WINGSPOYwindingheadasakinematicmodelasa
digital twin. For this purpose, all essential machine components were modeled as rigid bodies and connectedtoeachotherviajointsandcontactbodies. Theactuatorspresentintherealworldweresimulated by forces and moments.Analogously, the sensors are simulated by contact bodies and corresponding collisionbodies.Withthiskinematicmodel,itisnow possibletomapalltheprocessesthatoccurduringthe operation of a winding head in virtual space. Customers can thus be offered faster and more costeffectiveproductionsolutions.
MarketlaunchoftheDigitalAcademy–itsjustthe beginning
Interactive and customized, modular and flexible in terms of time – all features of a modern training concept.Adaptedtotheneedsandgeneralconditions of the respective student, training sessions should be independentoftimeandplaceandthecontentsshould betailored.Thisconceptisbeingimplementedwithin the Digital Academy at Oerlikon. The digital online trainingcenter,availablethroughthemyOerlikon.com e-commerceplatform,comprisesacollectionofrolebasede-learningmodulesonsuchtopicsasoperation, maintenance and repairs – currently for the Oerlikon Neumag BCF S+ and S8 machines. Training is targeted at operating staff, process engineers and technicians, and quality assurance officers. The Digital Academy learning contents will be available fortheOerlikonNeumagBCFS+andBCFS8systems from ITMA onwards. Further contents will be continually expanded and made available to all customers.
How can an upgrade increase Oerlikon Barmag POY yarn manufacturing process quality while simultaneously cutting energy consumption, waste, timeandpersonnel?AtITMA,Oerlikonwillshowits long-awaited upgrade:ACWWINGS drawing fields.
Established technologies can always be made better. When the Advanced Craft Winder (ACW) was launched in 1998, it was truly convincing with its sophisticated modifications for initial string-up and yarn transfer. WINGS replaced it as the new benchmarkin2007.
OerlikonBarmagWINGSPOYITMA2023
However, because Oerlikon Barmag technology last for decades, many ACW and WINGS winders are beingoperatedpracticallyside-by-sideinsomeplaces. Customers asked Oerlikon: please build a WINGS drawingfieldsoverourACWwinders!AtITMAitwill be shown for the first time at an exhibition in hybrid way – a WINGS drawing field in combination with virtualACWWinder.
OerlikonBarmagWipingRobot
Regular wiping of the spin packs is important for process stability and yarn quality. Automating the processwithOerlikonBarmag'swipingrobots,which can be retrofitted to numerous spinning plants, delivers considerable benefits, as it reduces the yarn breakratebyupto30%,improvesprocessstabilityand reduces downtime. In addition, wiping robots help to indirectlyreducewasteasaresultofa90%decreasein the use of silicone oil spray cans and a 15% to 20% decreaseintotalsiliconeoilconsumption.
Newair-texturizinglineforPOYandFDY
ThenewJeTexbyBBEngineeringisaproductionline forhigh-qualityair-texturedyarn(ATY).Itcombines an innovative texturing system developed by BB Engineering as key component with state-of-the-art components by Oerlikon Barmag to ensure fast production speed, the desired effects, and the quality oftheproduct.
Gear metering pumps in textile manufacturing are extremelypopular.Thisisaboveallduetothefactthat numerous systems are being modernized in terms of theirefficiencyandspecialization.And itisprecisely here that Oerlikon Barmag pumps are deployed, as those are the perfect solution for nearly every application.TheOerlikonBarmagspinningpumpsare high-precisiongearmeteringpumpsinroundorsquare shape for the production of continuous filaments. Possible applications are the pre-stage production of carbonfibersforreinforcedcompositematerialswith low weight and high resilience or the production of aramid fibers. The different fibers are used in quite different areas such as aviation, sports equipment or safetyproducts.Twolarge3Dmodelsforspandexand aramidwillbeondisplayatITMA.
Oerlikon Nonwoven's HycuTEC inline charging technology is used to create high-end charged meltblown filtration media. Introduced in March, it went on to win the 2022 FILTREX™ Innovation Award. One of the reasons HycuTEC won the award was that the meltblown media treated with the technologyrequires40%lesspolymer(fabricweight) to achieve the same filter efficiency than the nonwoven material that was not treated. In other words, filter specification is easier to achieve while reducing waste in production. Compared with other hydro-charging concepts, the unit significantly reduces water and energy consumption due to the elimination of an additional drying process and the lowerpressuredropinthefiltermaterial.HycuTECis the first industrially manufactured hydro-charging solution that can be easily retrofitted to existing systemsasaplug-and-producecomponent
DavideMaccabruni,CEO,UsterTechnologies
during the pandemic, Uster is bringing new value propositionstoitscustomersinthemarketinvirtually allbusinessareas.What'smore,wearecontinuingthe shift in focus from products to solutions, with a dedicatedapproachthatwillbelaunchedattheITMA 2023.
4)Howdoyouseefuturetrendsincaseoftechnology?
Davide Maccabruni: I see a clear shift from the traditional, product-driven offer to a more integrated, data-based value proposition for customers along the textile value chain. To achieve this, the necessary supporting technologies will have to be combined in smartandefficientways.
5)Whatgrowthyouhaveyouseeninthelast3years?
DavideMaccabruni:Aftertheworldwidereductionof businesslevelsin2020duetothepandemic,wesawa sharp recovery in 2021. This extended through the wholeof2022,reachingevenhigherlevelsincertain areas.
6) How do you see Uster Technologies AG in next 5 years?
DavideMaccabruni:2022wasanexcellentyearfor Uster,evenbetterthanthealreadyexcellent2021.The businesslevelisbackto–andinsomerespectsabove–pre-pandemicvalues.
2) Uster Technologies offer in case of sustainability?
Davide Maccabruni: Sustainability has multiple dimensions, all somehow affecting our lives and the way we do business. Many years ago, Uster started a dedicated initiative to support customers in their sustainability endeavors – from recycling to traceabilitytolabeling,tonameafew.Thiswillalsobe one of our focus areas at the upcoming ITMA exhibitioninMilan.
3)UsterTechnologiesinnovations?
Davide Maccabruni: Among many innovations, the launch of Uster Quantum 4.0 and its connected servicesmarksamilestoneforthetextileindustry.Its fullimpactwillbeevenmorevisibleinthenextcouple ofyears.
Thanks to significant investment in innovation, even
DavideMaccabruni:Iamconfidentthatwehavebeen investing–andinvestingintherightway.Thatisvital, notonlytomaintainourcurrentworldwideleadership in our core business areas, but also to enhance the addedvalueweofferourcustomersincompletelynew dimensions. We will also continue to play an increasinglyleadingroleinthefieldofsustainability.
7) Which are the most promising present and future marketsforUsterTechnologies?
Davide Maccabruni: In fact, we are global leaders in mostofthemajormarketsandinmostofthebusiness areasinwhichweareactive.Ingeographicalterms,we are seeing a solid development of our business in nearly any of the emerging markets, for example Uzbekistan.
8)YoursparticipationatITMA2023?
Davide Maccabruni: Uster will have two booths and our largest exhibition area at any ITMAso far in our history.Wewilldisplaymanynewproductsandvalue propositions, with a lot of 'world-first' items. But we don't want to spoil the surprise by revealing just yet exactlywhatwewillbeshowing!
Sustainability–acentralthemeoftheKARLMAYERGROUP atITMA,08-14.06.2023,FieraMilano,Hall4B119
TheKARLMAYERGROUPisafamilybusinesswith a long tradition and a strong sense of social responsibility. In its corporate strategy, it commits to act in line with social and ecological goals and to orienting itself towards the "Environmental Social Governance(ESG)"standards.
With a focus on a future worth living in, the KARL MAYER GROUPensures sustainable processes with itsproductsandservices.
Sustainability will be the overarching theme shaping the KARL MAYER GROUP's presentation at the world'smostimportanttextilemachineryexhibition.A compact sustainability gallery will feature elements including an example of the circular economy of material from the warp knitting sector, a 3D-knitted garment with extremely low-waste production, and a technical warp knitted grid fabric that offers two
environmentalbenefitsinone:notonlyisitmadefrom naturalfibres,butitisalsousedasacarriermaterialfor CO2-effective vertical urban greening. Another feature of the sustainable innovations collection revolvesaroundproductiontechnology:Forthedenim industry, a solution for indigo dyeing that has an extremelylowcarbonfootprintwillbeshown. In addition to the focused performance show, ITMA visitorswillseethethemeofsustainabilityreflectedat almost every turn around the rest of the KARL MAYER GROUP's stand. Under the motto “Master the Change – profitable, flexible, sustainable”, solutions and innovations are provided to answer our customers'keyquestions,including:“HowcanIdeal withtheincreasingpressuretobemoresustainable?”
Onepotentialwayforwardforwarpknittingisshown
byanewfallplateraschelmachine,which–thanksto specific modifications – is suitable for processing staplefibres.Theresultingwarpknittedtextilesarenot only chic but also sustainable, meeting the growing demandforclothingwithalowecologicalimpact.
Ahigh-performancetricotmachineoperatesusingan energy-efficientdirectdrive.Theenergyconsumption canbecheckedthroughnewlydevelopedmonitoring. In addition, the machine uses pattern data from the cloud rather than pattern discs, thereby reducing its material and transport intensity. A warp knitting machine with weft insertion demonstrates how an optimisedweftcarriercansavewasteintheweftyarn, andSTOLL'sADFmodelrequireslessenergythanks toarangeoftargeteddesignchanges.
Digital solutions also contribute effectively to increasedsustainabilityandeconomicefficiencyatthe sametime.Asanexample,thelatestinnovativedesign
software for flat knitted textiles – k.innovation CREATE DESIGN – can interact with any 3D software. Thanks to this connection, realistic 3D renders can be created, thereby enormously reducing the need for physical patterns and by extension, loweringmaterialconsumption.
Inadditiontotheexhibits,theambienceinwhichthey are presented will also reflect an air of sustainability. Thefocusedstandconceptreliesonminimalmaterial consumptionforthewallandfloorstructuresthrough the use of many modular and reusable components, without compromising on hospitality and clarity. Transport routes will be minimised by working togetherwithanItalianstandbuilder,whileattentionis also being paid to reducing catering-related waste, such as by using reusable crockery and avoiding packagingwherepossible.
At ITMA 2023 in Milan from June 8-14, experts from Monforts will be on hand to ouline the latest significant advances that have been made in sustainable continuous dyeing for woven fabrics and yarns with its industry-leading Thermex ®systemconfiguredfortheEcontrol process.
Over 900 Monforts Thermex hotflue dyeing systems are now operational in the main textile producing
countries like Bangladesh, Brazil, China, India, Mexico,PakistanandTurkey,witharound150ofthem already reaping the benefits of the Econtrol® and ® EcontrolT-CAprocesses.
“Thecurrentfocusoftheindustryisverymuchon cleaner processes to meet the commitments on sustainability made by the major fashion brands and with further regulations anticipated,” says
MonfortsTextileTechnologiesEngineerJonasBeisel. “This is calling for new investments that enable a significant reduction in resource consumption to be achieved, but that are easy to integrate into existing production systems. Econtrol® lines fit the bill perfectly.”
®Econtrol is a continuous process for the dyeing of wovencottonandcellulosicfabricsinwhichreactive dyestuffsarefixedintothefabricinaone-stepdyeing and drying process with a controlled combination of steam and air. The entire pad-dry process takes just two-to-threeminutesatatemperatureofbetween120130°Candarelativehumidityvolumeof25-30%.
®“Econtrol ensures excellent reproducibility of all colours,improveddyepenetrationondifficultfabrics andnoriskofthebrowningofthefibresduetothelow fixationtemperature,”Beiselexplains.“Assuch,itis the ideal process for fast change technology and operationalsavings.”
In addition, compared to other processes, no salt is usedandnosteamerisrequiredforaseparatefixation step. The process is also urea-free and no smoke or depositsaregenerated.Directfeedbackofthedyeing results eliminates batching time to guarantee good reproducibilityfromthelabtobulkproductionandan immediate wash off is also unnecessary, allowing for flexibleproductionplanning.
® The Econtrol process is suitable for pale to dark shades with very good fastness properties and has proved a particularly versatile route for denim manufacturers.
“Differentiation is the key in the highly-competitive denim fabrics industry, whether that is through the successful incorporation of new fibres, accommodatingnewfabricconstructionsorexploring themanyoptionsforhowtotreatthematthefinishing stage, to gain a market advantage,” says Monforts Head of Denim, Hans Wroblowski, who as a processing and engineering expert has travelled very widelythroughoutthekeydenim-producingcountries and worked closely with many partners to develop advancedsolutionsinthisfield.
HeaddsthattheselatestMonfortslinesallowusersto be extremely versatile and respond quickly to market demand, while also allowing very short production runs.
“We are very much looking forward to fruitful discussions in Milan about the many options for increasing productivity while making major sustainablegainsthroughresourceefficiency.”
MonfortsisinHall18atstandB106atITMA2023.
® * Econtrol is a registered mark of DyStar Colours DistributionGmbH,Germany.
RABATEX INDUSTRIES – INDIA (Since 1962) havebeenanindispensablepartoffabricindustrythe world over with new technological evolutions equivalent to any global know how in warp preparation machinery, fabric sampling machines , materialhandlingandstorageequipmentformorethan 6decades. Thus,thevacuumwhichtheIndianfabric industry has been subjected to once, could be eliminated by advanced technological import substitutemachinery.
Rabatex experts have been interacting with the technical experts in the textile industry across the world over their actual requirement with respect to value for investment as well as product output expectation. With patience and creation ability, Rabatex Team has made a detailed analysis of the future demand and customer expectations as well as global opportunity for the Indian Textile Fabric Manufacturing Industry. Rabatex decided to help the Indiantextileindustryinexploringtheopportunitiesin displaying its creativity and value addition capabilities.Rabatexispioneerinmanufacturingstate ofartWarpPreparatoryMachinery/FabricSampling Solutions/MaterialHandlingandStorageEquipment / ASRS (Vertical Lift Module) and enjoys major marketshareinIndiaaswellasglobalmarketsinmore than36countriesacrossglobe.Keymarketsinwhich Rabatex witnessed higher growth include USA, CANADA, TURKEY, RUSSIA, SOUTH AFRICA , INDONESIA , BANGLADESH , UKRAINE and INDOESIAetc.
Customersatisfactionisalwaysatthecoreforuswhile ourproducts&servicesarebuiltaroundthiscore.We always look forward to staying abreast in technology for delivering quality performance to our customers. Maintainingtheleadershippositioninallthemarkets
being our key objective, Rabatex would continue to strive for being a leading global player and capture a considerableshareinalltextile-producingcountries.
RabatexIndustriesisthelargestsupplierofweaving preparation products manufactured in India. There are already about 3200 Nos. of Sectional Warpers & Fabric Sampling Machines & about 5600 Material Handling and storage equipment working across the world.Moredetailsaboutproductscanbeviewedon www.rabatex.com
Rabatex' newly launched products developed for fabric sampling solution are installed globally includingUSA,Turkey,IndonesiaandsomeinIndiaat Nandan (Chiripal Group ) , Shahi Exports , Saam Textiles , Nitin Spinners , Sangam Group , Kanchan Group,RajapalayamMills,BirlaCenturyandmany more.
Atextilesampleisapieceofclothorfabricdesigned to represent a larger whole fabric. A small sample, usuallytakenfromexistingfabric,iscalledaswatch, whilst a larger sample, made as a trial to test print production methods, is called a strike off. For plaindyed fabrics it is called a lab-dip, and for yarn-dyed fabrics (like stripes and checks), it is called a handloomsamples
Theuseofswatcheshasformedanessentialpartofthe designprocessoftextilesthroughoutdifferentcultures across history. Samples enable designers to display differenttypesoffabric,demonstratinghowdifferent colours,materials,trimsandmethodsofweavingwill lookinrealterms—somethingthatmaynotbereadily apparent from a paper of digital design—before the entirefabricismanufactured.
A textile manufacturer may bring together several
swatchesofmaterialsintoasinglesamplebook,which may serve to enable a salesperson to display a wide selection of fabrics to potential customers in a convenient manner. A textile swatch book may also serve as an internal reference for materials that have been made previously and could be manufactured again. Rabatex experts, have been interacting with the technical experts in textile industry across the world over about their actual requirement with respect to value for investment as well as product output expectationinquickestfabricsamplingsolution.With patienceandcreationability,RabatexTeamhasmade analysisoftheneedofthefuturedemandandcustomer expectation as well as global opportunity of Indian TextileFabricManufacturingIndustry.
New trend in the fashion industry is that brand promoter or designer need to feel fabric as actual garmentaswellastotestmarketwithsmallquantityof garment, where Advanced Sample warper makes major roll to prepare a short length actual warp with minimumquantityofwarpyarnwithunlimiteddesign or pattern possibility. This process improves highest successratioofanynewproductpromotioneffectively with actual test market results. Apart from this the customisation of the fabric need is increasing day by daywhereuserneedstohavespecificdesignorpattern of fabric, which can be fulfilled with use of this technology.
RABATEX Industries have been an indispensable part of fabric industry the world over with new technological evolutions equivalent to any global know how in warp preparation machinery, fabric
sampling machinery and material handling and storageequipmentformorethan6decades. Thus,the vacuum which the Indian fabric industry has been subjected to once, could be eliminated by advanced technologicalimportsubstitutemachinery.
Embracing its legacy of innovation and excellence in manufacturing spinning cans and components, Rimtex Group is poised to unveil a remarkable array of product innovations and showcase their latest international line-up at the highly anticipated ITMA 2023 event in Milan. Committed to propelling spinning technology forward, Rimtexaimstoempowerspinningmillswithtransformative solutions that not only enhance the value of yarn but also revolutionisetheefficiencyofspinningmachines.Ifwego by the reports, the Rimtex group promises to introduce a neweraofcutting-edgeadvancementsthatwillredefinethe spinningindustry'sfuture.
Inthequestforenhancedproductionefficiencyandelevated quality standards, leading spinners worldwide are on the lookoutfornewparadigms.Recognisingtheevolvingneeds of the yarn manufacturing industry, Rimtex Group diligently monitors its development and steadfastly commits to spearheading the future of spinning. With a strong focus and research on sustainability, spinning mill agility, future-oriented sliver can transportation solutions, the optimal lifespan of spinning rings and travellers, and segment-specific castors and wheel designs, the Rimtex Group has been developing a host of technologies. The culminationoftheseeffortswillbeunveiledatITMA2023,
RABATEX has now come out with a complete range ofFabricSamplingSolutionslikeSmallWidthFabric Weaving Machine, Small Width Single End Warper, ConetoconesizingandAdvancedSampleWarperfor shortlengthpreparationwhichhasitsuniquefeatures tosubmit. Ofcourse,theaddedadvantagesorspecial features which every RABATEX brand products alwayscarryhavebeenfedintothisnewlaunchalso. Morethan6decadesoftraditioninspiresthemtocome outwithsomethingneweverytimefortheirpatrons.
whereRimtexissettoshowcasearangeofground-breaking technological innovations. The buzz surrounding these advancements is palpable, and the industry eagerly awaits advancementsfromRimtex.
For decades, Rimtex has been at the forefront of technologicalshiftsintheindustry,andthisyear'sITMAis settobebigger,better,andmorespectacularthanever.Mr. GauravParmar,jointMDofRimtexGroup,expressestheir commitment to the development of the spinning industry, stating, "The industry looks up to Rimtex Group for new solutionsthatsetthecourseforthefuture.Eachoneofusat Rimtexisdrivenbyourpassionanddedication,whichfuels our innovative ideas and pioneering technologies. This ITMAwillbetrulyspecialaswelaunchawholenewrange offuturisticspinningsolutions.Weareexcitedtowelcome youtoourstandatITMA."
With the captivating theme 'Here to Transform', Rimtex Group has set the stage for an exciting and transformative experience. The anticipation grows as we await the unveilingoftheirvisionaryspinningsolutionsattheevent. MakesuretovisitRimtexGroupinHall1,StandnoE202.
manufacturersdeclinesitscommitmentonthesideof sustainability.Acommitment thatACIMIThas made its own by developing the Sustainable Technologies project.AttheheartoftheinitiativeistheGreenLabel, the document that certifies the energy and environmental performance of the machinery and summarizes it by giving a value to the Carbon Footprint of the machine itself. Regarding the innovation textile companies need technologies that are highly interconnected with each other and with their ERPand MES systems, and machinery that can make textile production increasingly competitive. So ACIMIT developed the digital certification, named DIGITAL READY, designed to simplify the productionprocess,makinguseofastandardlanguage and unique data reading system that allows different types of machinery to dialogue with production systems.
Technological trends focus on sustainability and digitization increasingly. Indeed, textile machinery make possible a growth in the competitiveness of its users, reducing production costs and increasing production efficiency. During ITMA Milan visitors will be able to verify that the displayed innovations willgointhisdirection.
In 2022, the value of Italian machinery production exceeded 2.7 billion euros, up about 13% on the previous year. Exports account for more than 86% of thisvalue(+15%comparedto2021year).Despitethe negative factors like the inflationary pressures and political crises caused by the pandemic and RussiaUkrainewar so evenin2022 theupward trendof our industry goes on.Also thanks to ITMA, we expect a further growth in demand for Italian machinery in 2023.
Increasedawarenessofecologicalissueshasinvolved theItaliantextilemachineryindustry.Thereduceduse ofresources,foralowerenvironmentalimpact,isjust one of the topics through which the Italian
The best strategy to increase market share is to keep being innovative and offer the best and tailor-made solution to each customer. Always aware of their customers' strategies, Italian textile machinery manufacturershavewellunderstoodtheimportanceof the transition to a more sustainable fashion industry andhowtechnologiesareexpectedtomakeaconcrete connection between eco-efficiency and ecoeffectiveness. For example, some Italian textile machinery manufacturers are committed in the production of technologies for the recycling and regenerationoftextilewaste.OtherItaliancompanies are making an effort to find solutions in the field of augmentedrealityandartificialintelligenceinorderto support textile customers in optimising production using real-time data and in enabling both predictive andpreventivemaintenanceofthemachineryinuseat thecustomer'sfacility.
5. WhyInternationalTextileIndustryshould Choose Italian Textile Machinery for Manufacturing?
Creativity, reliability and flexibility characterize Italian textile machinery supply. I believe that Italian companies can reply quickly and with right solutions to the ongoing challenges that the global textile industryfaceseveryday.
6. HowdoyouseeMadeInItalyConcept?
The concept is a combination of tradition and innovation.Especiallyinthetextilesector,thosewho buyMadeinItalymachineryknowthatitistheresult of a historical legacy of know-how and passion and stronginnovativecreativity.
7. Italian Textile Machinery Participation andExpectationfromITMA2023?
Italy is the first represented Country at ITMA, with about410exhibitorscoveringaround36,000sq.mts. Fully30%ofthetotalexhibitionspaceatITMAwillbe takenupbyItalianmachinerymanufacturers.Afterthe pandemicyears,ITMAwillmarkabreakfromthelast three years. There is a willingness of the whole industrytocometogetheragain,andItalianexhibitors expect a high number of visitors and a positive businessclimate.
The Dilo machine building was founded in 1902 in Eberbach,Germany.ThegroupwithDiloSpinnbau,a cardingspecialist,DiloTemafa,specializedinopening and blending equipment, and Dilo crosslappers and needlelooms successfully formed since 1996 and 2005, is a specialist for the production of complete needlinglines.Needlingisoneofthemostprominent and important consolidation technologies for nonwovenmaterialinalmostanysectorofapplication. WiththatbasisDilohasbeensuccessfullongtermand sees a bright future for its range of machinery which are included in a comprehensive and modern leading programme. In cooperation with partner companies also the sectors through-airbonding, thermobonding, chemical bonding and water entanglement can be offered in the complete line business.
2. How is DiloGroup adding digitalization to itsproductportfolio?
It is worthwhile noting that needling lines have since decades a very high degree of automation and extremely high productivity due to the speed needled productscanbemanufactured.Thelinesrunwithvery little manpower and tie in all components through variabledriveswhicharesynchronizedandcontrolled. PLCscontrolallfunctionsintheprogrammedwayand get from the operator's control station and the graphicalscreenmonitorsthroughtheoperatorstheset values individually adapted or from a recipe library.
Digitalization today however means more than this basisofdigitalcontrolsfordrivesandlineintegration which is sometimes described as smart industry or Industry4.0.Softwareadditionsandsensorsassistthe operatorsinordertoreducethedegreeofcomplexity andprovidemeanstorunthelinesinahigherdegreeof automation for example during a startup mode where assistance particularly is needed (“Dilo smart start”). Dilooperator'sassistancemodules,forexample,offer insight,alsoremote,foralllineparameterssetandreal. And also give insight to surveillance processes of individual machine components for preventive and predictive maintenance actions by monitoring temperatures, vibration, pressure and parameters of thatsortinordertoprepareactionandincreaseuptime.
Other modules save energy by helping to adjust drivesforpneumaticallyconveyingfibreflocksin the network of ducts to various machine componentsaswellasinthepneumaticdedusting and filtering systems from DiloTemafa's Airsystemsengineering.
The status of machine components in the fibre preparation section is monitored by the “smart guide light” system to assist the operator in his surveillance job about the status of individual components.
This process of developing operator's assistance system is evolutionary and not revolutionary. All
attempts so far to provide complete digital solutions, for example in the auto industry, have not been successfulorcouldnotberealizedyet.Onthelevelof cardriverassistancesystemsmoreandmoremodules aremadeavailableasinthecasewithourlines.
Ourstrategyforinnovationisthebasisforourgroup's business. Since we are provider of machines which have in our long history in many ways contributed to improve performance of nonwoven lines through innovations, inventions including revolutionary changes and modifications in the complete range of our machinery. Always with the aim of increasing productivity by speed and efficiency as well as improvingqualityofthetextileproductandreliability of line performance in the long term.
Sustainabilityisaveryimportantmoveinoursocieties andintheindustryinmanyways.Theprotectionofthe environment and the avoiding of waste of natural resourcesisamust.
DilowithitsnewMicroPunchlineoffersawayasof ITMA 2023 to produce lightweight fine fibre nonwovens for the hygiene, medical and technical sectorbyneedlinginsteadofwaterentangling.Evenin the range of 40 to 100 g/m² needling through MicroPunchreducestheamountofenergyneededby
approximately 75 %; no water is consumed, no gas neededtodrythewateroutofthefleece.Atthesame time, less fibre is consumed. MicroPunch is consideredabreakthroughfortheneedlingtechnology to provide a green alternative for the production of lightweightnonwovens.
Energyandwatersavingsshouldnotbethesolefocus for sustainability. Fibre material savings are at least equallyimportant.Forthispurpose,Dilohasstarteda cooperation with our Italian partners Dell'Orco& Villani and Techno plants who are specialists in the provisionoftearingequipmentforhardandsofttextile wasteandforgarmentclippingsrespectivelyworking at high throughputs and alternatively for controlled tearing in order to keep the staple length as long as possible.Fortheshorterrangeoffibreandhighmass per unit area, for the manufacturing of the more voluminousandthickmaterialsappliedinacousticand thermal insulation as well as in cushioning pads the aerodynamic webforming process is offered by Techno plants, an expert in this field, which DiloSystems integrates together in their range of complete lines for nonwoven production including needling, through-airbonding, end-of-line components which include packaging. With this technology, several cycles of reusing end-of-life textiles,alargecontributiontobettersustainabilityis providedthroughDiloGroup.
4. How do you see future trends in case of technology?
In my previous answer about MicroPunch we can prescribeawayforcontinuedsuccessofDiloGroupat least for the next five years. Our main business, needling lines for a large array of applications like floor coverings, automotive, filtration, geotextiles, synthetic leather, industrial and household wipes, mattress and upholstery is now completed with a specialty technology also for the lightweight range usingveryfinefibreandthroughourRecyclo-Lineto processwastetextileforitsreuse..
5. How do you see DiloGroup in the next 5 years?
seeabove
In the light of sustainability and environmental protection, Dilo has completed its machine programme offering a huge amount of savings for electric energy, gas, water and fibre. Our Recyclo-
LinesengineeredtogetherwithourpartnersDell'Orco & Villani and Technoplants can help to transform textile waste into meaningful nonwoven quality products.Thesetechnologiesareavailablefortheuse inmanyareasofapplicationinthenonwovenssector. Dilo looks forward to engineering closely with our customerssuchlinesinordertobeenergyandmaterial efficientforabetterfuture.
Noonereallyiscapabletolookintothefuture.Many politicalinfluencesinourglobaleconomyplayalarge role also for our industry. Yet, DiloGroup is getting preparedforthisshowbyallmeans.Dilowillpresenta complete line for intensive needling in the MicroPunch mode. On a stand of 750 m² approximately25peopleofoursalesandserviceteam are ready to receive you at our booth, hall 10, booth No.A201,whereweareconfidenttolaythebasisfor futuresuccessnotonlyatDilobutevenmoresoforour customers.
Originally founded in 1892 as a small workshop in Horgen,nearZurich,todayStäubliisaninternational group headquartered in Pfäffikon, Switzerland, operating with over 6,000 employees in 29 countries on four continents and generating 1.6 billion Swiss francsinannualrevenue.Stäubliisaglobalindustrial andmechatronicsolutionproviderenablingcustomers to increase their productivity in a wide range of industrial sectors. Focusing on differentiation and growing businesses with strong potential, the Group has four Divisions: Electrical Connectors, Fluid Connectors, Robotics, and Textile. Operational excellence,clearfocus,andstrategicinvestmentshave enabledStäublitoconstantlygrowandtakealeading position in the defined businesses and markets. PassionandfamilyspiritmakeStäubliunique.Longterm business activities and independence are other keyfactorsofStäubli'ssuccess.
thefieldofdigitalization.Forone,Stäubliwillpresent its new customer portal MyStaubli.As a new contact channel to Stäubli, this platform provides personal access to online information, solutions, and Stäubli's broadrangeofservices.
WeinviteallITMAvisitorstocometoourboothand discoverStäubli'slatestdevelopmentsandofferingsin
We've been delivering premium-quality products and servicesforsustainableimprovementsinindustryand society for over 130 years. Stäubli's renowned reliability and stability are based on uninterrupted familyownership,andourtechnicalexcellenceisthe result of a consistent focus on industrial customers. This is all part of one overarching goal: to develop solutions for even safer, more efficient, and costeffective industrial processes.As a global supplier of high-qualityindustrialandmechatronicsolutions,we focus on providing tangible benefits for the environment and society, espousing a long-term vision.Sofar,wehaveidentifiedthreemainpillarsfor oursustainabilitystrategy.InterestedvisitorsatITMA in Milan can find out more about this from our
specialists there. Stäubli machinery is renowned not onlyforlongservicelifebutalsofortheavailabilityof spare parts many years after purchase, both of which are important aspects of sustainability. For a good exampleofcombininginnovationwithsustainability, have a look at our new LX PRO, LXL PRO, LXXL PRO series of Jacquard machines. These machines will serve many years under the harshest conditions and at the highest speeds while providing energy savings thanks to cutting-edge technology like our NOEMI electronics architecture that ensures optimized ventilation and operation temperatures of themachineandtheMXPROmodules.
4) Howdoyouseefuturetrendsincaseof technologyandRoboticsinTextileIndustry?
Like some other industrial sectors, the textile industry is facing challenges in terms of staff shortages.Automationisapotentialsolutionhere, especially for tasks that involve heavy loads or constantrepetition.Executingtaskshand-in-hand with cobots is an option that deserves increasing consideration – and solutions are available. Another task is the transport of warp beams, and here automatic guided vehicles (AGVs) are an interestingoption.Roboticsinthetextileindustry isagrowingtopic,andweavingmillsthataimto stay at the forefront will doubtlessly be implementing robotics solutions in the near future.
5) HowdoyouseeSTAUBLI inthenext5 years?
The Stäubli Group has clear goals for the forthcoming years and is in constant evolution. With its four divisions, the Group offers a large and innovative product portfolio including dedicated market solutions as well as custom
solutions for highly specific needs. The Stäubli Groupwillcertainlycontinueasagloballeaderin the textile machinery industry as well as many other industries. In Textiles we are leading provider for shed formation systems, including the above mentioned Jacquard machines, but we offer as well outstanding solutions for frame weaving and the so important process step of weaving preparation. Quality style changes and automated warp changes influence the downstream weaving process positively. These automation solutions support perfectly aligned warp yarns that stand for many more meters of quality fabric. This will be the increasingly important in the coming years when buyers will focusthemoreonqualityfabricsinasustainable fashion approach. Here Stäubli provides the TIEPRO, TOPMATIC and MAGMAwarp tying machinesforavastvarietyofyarntypes,andthe SAFIR automatic drawing in machines featuring new AWC 2.0 technology to be discovered and experiencedduringITMAinMilan.
6) STAUBLI Messagetocustomers?
Come to Booth A201 in Hall 6! Meet our specialists there and discover, experience, and find solutions to master your daily weaving challenges.
7) YourExpectationfromITMA2023?
WearedelightedtobebackinMilanafter8years. The Fira Milano Fairground is fully booked, which demonstrates the optimism of virtually everyone in the sector. Stäubli looks forward to meeting customers, partners, and new contacts and discovering complementary or parallel innovationsinallareasoftextileproduction.
BRÜCKNER, leading supplier of customized machinery and lines, presents innovative and trend-setting highlights fortextilefinishingandcoatingatITMAinMilan.
BRÜCKNER will show the next stenter generation POWER-FRAME SFP-4 with many new features: new electric / hydrogen-powered heating systems, intelligent software solutions for optimizing formulas, systems for heat-recovery and exhaust air purification, innovative application systems for chemicals, and newly developed machineconcepts.
The most important innovation of the BRÜCKNER dryer are without doubt the innovative heating sys-tems. Driven by the energy crisis and the constant focus on energyefficient solutions, new possibilities to combine different heating media like gas, steam, oil or electricity have been developed. In addition, BRÜCKNER also offers burners which can be operated with hydrogen in the future. These combination possibilities allow the textile finisher maximum flexibility in the choice of the energy carrier. Another exciting development are solutions for the purely electricheatingofindustrialovensbymeansofheatpumps, which BRÜCKNER offers together with a partner. In the present situation and with a view to the future, these new typesofheatingofferdecisiveadvantages:Greenhydrogen and/or electricity reduce the dependence on fossil raw materialsandcontributeconsiderablytominimizetheCO2 foot-print.
Digital products and services are another highlight. On request, new lines are equipped with various intelligent assistance systems that support the machine operator in finding the optimum machine setting for each process. A special innovation is the new simulation tool ExperTex: with the help of artificial intelligence, the desired productionprocessofdryingorheat-settingissimulatedon the computer. Different scenarios can then be compared with each other: Throughput times, energy consumption, CO2footprintandproductioncosts.Thisinnovativesystem offers customers considerable added value, as it allows accurate pre-calculation of orders, opens up productivity gains and/or energy sav-ings, and permits "right-first-time production" by means of pre-optimized formulas. Expert knowledge and years of experience in textile finishing are thus available at the push of a button. This tool and much morewillbeavailabletocustomersinthenewmyBrückner customer portal in the future. All important machine information,accesstodigitalservices,andaservicesystem willbebundledthereandcanbeaccessedatanytime.
The new generation of ECO-HEAT heat-recovery and ECO-AIR exhaust air purification systems features a new type of intelligent control. Both types of lines can also be retrofitted at any time to older lines from various manufacturers in order to realize the best possible energy savings and solve existing ex-haust air problems. All
BRÜCKNERatITMA2023-sustainable,digitaland onthewaytoclimate-neutralfinishing
exhaust air treatment systems can be tested in advance at customers'sitesbymeansoflaboratorysystemsinorderto betterassessutilizationrateandefficiency.
Of course, customers can inform themselves on the BRÜCKNER booth also about numerous further possibilitiestosaveprimaryresourcessuchasenergy,water, chemicalsandwastewater.Here,forexample,theminimum application unit ECO-COAT should be mentioned, a new type of padder with minimum preparation quantity or residualliquor,andafurtherdevelopedcoatingunitOPTICOAT 2in1, which combines the use of floating knife and knife-over-cylinderapplicationinonesystem.Withahighprecision coating cylinder and a perfectly ground coating knife,excellentresultscanbeachievedforpasteandfoam coatings.Inaddition,thespecialdesignoftheunitensures optimum accessibility for cleaning and maintenance purposes.
Another highlight is a completely new designed highperformance relaxation dryer POWER-DRYwhich can be heated CO2-free by means of a high-temperature heat pump. In order to show the variety of BRÜCKNER's productportfolioandtoillustratetechnologiesinarealistic
and "tangible" way, many machine models will also be exhibited.
The total cost of ownership (TCO) is lower for BRÜCKNER'slinesthanforothersuppliers.Thisappliesto all presented machines in the field of finishing of carpets, nonwovens and denim, migration- and crease-free continuous dyeing as well as in the versatile field of technical textiles and is supported by the technological adviceofexperiencedexperts.
With regard to sustainability and resource conservation, BRÜCKNER's After Sales team and the technology team offer numerous possibilities for modernization and technologicaleonsite.Itisnotalwaysnecessarytoinvestin a new line, often the potential of older machines can be exploitedquicklyandefficientlybymodificationsandalso by technological consulting. Noticeable improvements in productivityandenergyefficiencycanbeachievedwithout longerdowntimes.
Let yourself be inspired by these highlights! The BRÜCKNER team is looking forward to meet you personally and to talk about further innovations in hall 18, boothno.A101-thewayisworthwhile!
The textile patterns are been an inspiration from different aspects like nature, art, and more. For many decades the tradition of clothing indicates the social status of various members of society. Attire today matters on the fabric to thencreateanattractivepurchaseforthefashionista.Fabrics then have fancy names like knitted, woven, cotton, and more. What matters is how the fabric feels lightweight brings you comfort and makes you have a perfect appearance.AfabdesigncompletestheFabric,nomoreon thedesignthatcanhavemadethegenzgovogue:
Ÿ · Checkered: Most popular pattern design which suits mostIndianbodytypes.Thispattern seems to stay longer in trend, especially during summer-spring. Thebrightandeye-catchypatternis just flawless with the perfect additional vintage look from corporatetopartynights.
Ÿ Floral: One of the most preferred pattern and design people who opt for elegance and comfort over fashion. Floral prints print is going to be the defining print of the summer. Every woman graces themselveswhentheywalkoutinan Indian floral design attire. Be it for smallerorbiggeroraboldprintone can carry it with a charismatic look foreveryoccasion.
· Chevron: Chevron, in all of its zig-zagging glory, is a must-try designthissummer.Chevrongraphics have become especially popular amongst every fashion type shopper. What goes well is the demand drift towards vibrant prints that can suit both beach and more casual dressy looks.
· Harlequin:AHarlequinprintisa repeating pattern of contrasting diamonds or elongated vertical squares.Itisalsothenameofthe color between green and chartreuse. It is the most eye catchy design which is easy to attract and gives you a vintage look.
· Ikat: There's something undeniablyattractiveaboutikat.It is a dyeing technique used to create distinctive styles of textile patterns. Ikat is made by dyeing some threads before weaving the fabric.Oneshouldalwayshavean ikatdesignoutfittheirwardrobeas itfavorsalltimeoftheday.
Introduction:
In the vast landscape of the international textile industry,certainfabricsriseabovetherest,embodying excellence,luxury,andenduringappeal.Amongthem, Egyptiancottonstandsasanunrivaledgem,renowned for its exceptional quality, remarkable durability, and undeniable allure. In this editorial, we delve into the inherentcharacteristicsofEgyptiancottonthatmakeit highlydesirableforproducingtop-qualityfabricswith enhanceddurability.Weexplorehowitsluxuriousfeel and softness cater to the preferences of discerning consumers worldwide, while analyzing the growing global demand and positive consumer perception of Egyptiancottontextiles.
QualityandDurability:AStandardofExcellence
Egyptian cotton has earned its reputation as a benchmark for quality and durability in the international textile industry. Its unique characteristics, including an extended staple length and fine fibers, allow for the creation of fabrics that surpass ordinary standards. This exceptional cotton produces yarns that are stronger, resulting in textiles that resist pilling and tearing. Whether it graces a finelytailoredsuitorasumptuousbedsheet,Egyptian cotton's inherent quality ensures that the fabric maintains its integrity, standing the test of time and multipleuses.
The luxurious feel and unmatched softness of Egyptian cotton fabrics provide a sensory experience likenoother.Whendrapedagainsttheskin,itssmooth and silky touch creates a sense of opulence and refinement.Discerningconsumersintheinternational market appreciate the exquisite sensation that Egyptian cotton offers. From high-end fashion garments to lavish home textiles, this fabric lends an air of luxury and sophistication to every textile creation.Itisthisluxuriousappealthatcaptivatesthe heartsofconsumersseekingunparalleledcomfortand indulgence.
The global demand for Egyptian cotton textiles has been steadily rising, driven by a positive consumer perception of the fabric's superior quality and luxurious attributes. Consumers around the world recognizeEgyptiancottonasasymbolofprestigeand refinement. The fabric's association with top-tier craftsmanship and comfort has created a strong affinity among discerning buyers. The growing awarenessofsustainableandethicallysourcedtextiles hasfurtherboostedthedemandforEgyptiancotton,as it aligns with consumers' desire for environmentally consciousproducts.
Conclusion:
In the ever-evolving international textile industry, Egyptian cotton stands as the global standard of quality,luxury,andconsumerpreference.Itsinherent characteristicsofsuperiorqualityanddurabilityhave made it highly sought-after for producing top-quality fabricsthatsurpassordinarystandards.Theluxurious feelandsoftnessofEgyptiancottoncatertotherefined preferences of discerning consumers worldwide, creatingasenseofindulgenceandsophistication.The growing global demand for Egyptian cotton textiles and the positive consumer perception of this fabric reaffirm its status as a pinnacle of excellence in the internationalmarket.
As we navigate an era where consumers prioritize quality, luxury, and sustainability, the international textileindustrymustembracethetimelesseleganceof Egyptian cotton. By nurturing its production and availability, we can continue to meet the demands of discerning consumers while promoting sustainable practices. Let us celebrate Egyptian cotton's global reputationanditsabilitytotransformeverydaytextiles intoextraordinaryexperiencesthatdefinetheessence ofluxury.