India: Growing interest in Oerlikon
Barmag industrial yarn systems
Technical textiles on the rise
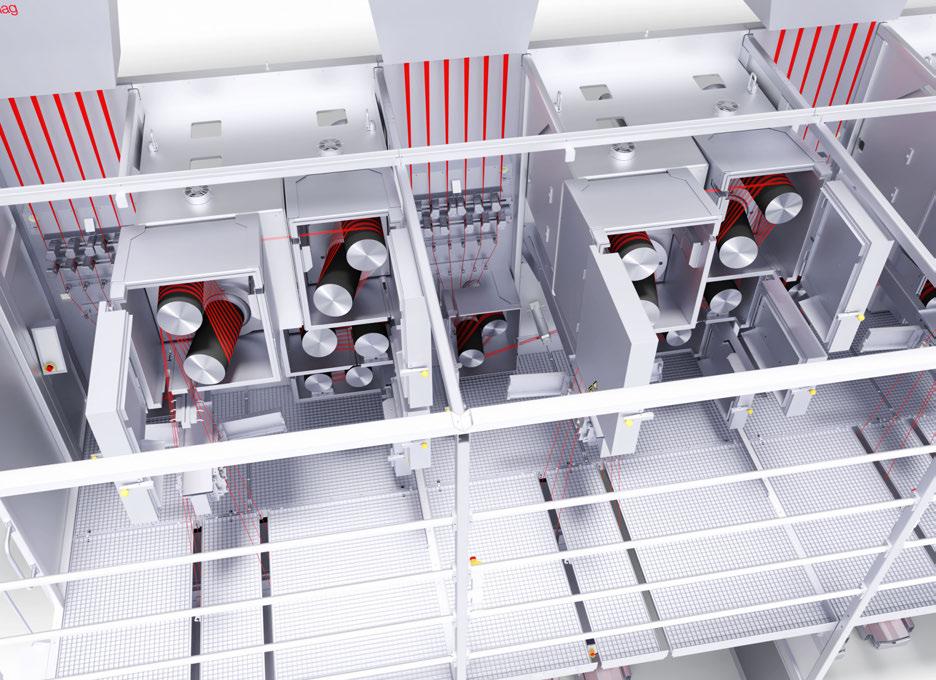
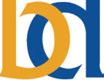
Technical textiles on the rise
(POLYESTER DIVISION)
Wadia Group is one of the oldest conglomerates in India with presence in several diversified businesses, including FMCG, real estate, aviation, textiles, chemicals, plantation and food processing. Four companies in the Wadia Group are listed on Indian Stock Exchanges, including Britannia, Bombay Burmah, Bombay Dyeing and National Peroxide.
Bombay Dyeing was established in 1879 and is a leading Indian brand in textiles, polyester and real estate.
Polyester Division was set up in 2007 and is engaged in manufacture of 100% virgin Polyester Staple Fibre (capacity 165,000 MT/p.a.) & Textile grade PET Chips (capacity 36,000 MT/p.a.) with NGSSS technology from lnvista Polyester Technologies and Chemtex International Inc., USA.
OUR PSF PRODUCTS ARE MADE FROM 100% VIRGIN POLYMER
08.JA.59644 HOHENSTEIN HTTI Testedforhamilulsubstlnoes.
WfflY.oeko-tex.comistandanllOO
Editorial
India:GrowinginterestinOerlikonBarmagindustrialyarnsystems
Technicaltextilesontherise
INDA,NWIAnnounceCollaborationAgreementtoFosterContinuingEducation oftheNonwovensIndustry
Textilemachineryforasustainabletextileindustry
Brückner,Groz-Beckert,KarlMayerandThiestoholdjointwarpknittingsymposiuminBrazil
FreudenbergPerformanceMaterialsApparelinauguratesstate-of-the-artthermalinsulation factoryinVietnam
DiloTemafasuccessfullysellslineextensiontoEco-Technilin
RelianceIndustriesUnveilsGroundbreakingFabricTechnologies atR|ElanFabricInnovationMeet
Bio-BasedSuperabsorbentPolymers: ASustainableSolutionforHygieneProducts
RevolutionizingAutomotiveInteriorswithMycelium-BasedMaterials
SpinningSuccess:India'sAscentintheGlobalMan-MadeFibresMarket
RevolutionizingTouch:emtecElectronictoShowcase Advanced
editor-in-chief
Prakashkinny contributor
ThomasChang circulation PamelaJones administration JoePereira accounts
RameshJain photography
TonyFernandes
RetailPrice:Rs.100.00 InsideIndia
Annualsubscription:Rs.400.00 OutsideIndia
AnnualSubscription:US$30.00
editorial office
TECHNICALTEXTILESINNOVATION
House No. 157, Satpala, Bhandra Lee Post:Agashi, Tal: Vasai
Dist: Palghar (401 301)
State: Maharashtra, INDIA
Mobile: +91-7798189485/09892723562
Email:info@timesinternational.in prakashkinny@yahoo.com techtexin@gmail.com
www.timesinternational.in
JAPAN
KatsuhiroIshii
MediaRepresentative ACEMEDIASERVICEINC.
12-6,4-chome,Nishiiko,Adachi-ku, Tokyo121-0824Japan
Tel:81-3-5691-3335Fax:81-3-5691-3336 amskatsu@dream.com
TAIWAN,R.O.C
Kenlychang
BUILDWELLINTERNATIONALENT.,CO.,LTD.
HeadOffice:No.120,Huludun2ndSt., FongyuanCity, TaichungCounty42086,Taiwan,R.O.C
Tel:886-4-25123015Fax:886-4-25122372
E-mailaddress:buildwel@ms23.hinet.net
India,Pakistan,Bangladesh,Srilanka,Vietnam,Indonesia,Thailand, China,HongKong,USA,Germany,Spain,Italy,U.K.&France
SignificantBoostforTechnicalTextilesin theIndianUnionBudget2024-25
The Union Budget for 2024-25 has delivered a substantialboosttothetechnicaltextilessector,with the allocation for the National Technical Textiles Missionskyrocketingby120.59%,from C175crore in2023-24toanimpressive C375crore.Thissurge in funding underscores the government's strategic focus on this high-potential segment of the textile industry.
Technicaltextilesarespecializedproductsdesigned primarily for their performance and functionality ratherthanaesthetics.Theyplayacriticalroleacross various industries, including construction, agriculture, aerospace, automotive, healthcare, protective gear, and home care. Made from both natural and synthetic fibers, these textiles offer superiorperformancecharacteristics,distinguishing themfromtraditionaltextiles.
India's technical textile sector has been growing steadily, currently exporting products worth about $2.5 billion. With the increased funding and supportivepolicies,thecountryaimstoelevatethis figure to $10 billion over the next five years. This ambitious target highlights the sector's potential to significantlycontributetothenation'seconomyand globalmarketpresence.
Bhadresh Dodhia, Chairman of MATEXIL (ManMade and Technical Textiles Export Promotion Council), hailed the budget as growth-oriented and pragmatic. He emphasized that the focus on employment generation, skill development, and investmentsiscrucialforthesector'sexpansion.The budget also introduces employment-linked incentives and skilling programs, which are expected to create substantial job opportunities withinthetechnicaltextilesindustry.
The Union Budget for 2024-25 sets a robust foundation for the technical textiles sector, promising innovation, competitiveness, and significant contributions to India's economic growth. With strategic investments and supportive policies,thetechnicaltextilesindustryispoisedfora dynamicandprosperousfuture.
India:GrowinginterestinOerlikonBarmagindustrialyarnsystems
OerlikonBarmagsuppliesitsindustrialyarnsystemsindividuallyconfigured;thesystemconceptfor HighTenacity(HT)yarnsanditsuniquepropertiesonthemarketensure theproductionofhigh-qualityyarnforthemanufactureofseatbelts.
As a traditional textile country, India has also established a strong position in the field of manmade fiber production in recent decades. The West Asian country has now become the second largest polyester yarn manufacturer in the world. The Indian textile industrycoverstheentirevaluechainfromthemelttothe finishedtextileendproduct.
The technical textiles sector in particular is regarded as a future market. With an average growth rate of 12% since 2013, this dynamic sector accounts for around 13% of the entire Indian textile and clothing market, according to the government organization Invest India.The market volume has almost doubled in the past ten years. In India, the production of industrial yarn has so far relied heavily on polyamide. Oerlikon Barmag has a strong market position here. "In recent years, we have commissioned plants for numerous customers," says Dr. Wolfgang Ernst, Head of Sales of the Oerlikon Business Unit Manmade Fibers Solutions.
Increasingdemandforindustrialpolyesteryarns
Theconstructionboomandtheincreasinguseofgeotextiles and industrial textiles in various infrastructure projects as well as in agriculture and aquaculture show enormous growth potential. This is supported by the government's 2021 industrial development program, which includes technicaltextilesasoneoftenprioritysectors.Theprogram is based on reducing dependence on imports. Until now, a largeproportionofthetechnicaltextilesandyarnsrequired inthecountryhavebeenimported.
The trend towards high-quality technical textiles for the domestic market has also been noted by the Remscheidbased machine and plant manufacturer. "We are receiving moreandmoreinquiriesfromIndiancustomersforspinning systems for industrial yarns," says Dr. Wolfgang Ernst. "Whatisnewisthegreatinterestshownbycompaniesfrom downstream processes that are looking for backward integration.Weattributethistothestricterregulationsofthe Bureau of Indian Standards. Until now, industrial yarns weremainlyimportedfromChina.Inordertoguaranteethe
quality of the processed yarns, this has been strictly regulated by the government since last year. It therefore makes sense for Indian textile producers to enter the yarn manufacturing sector." This development was also noticeable at this year's Techtextil in Frankfurt, where the experts from Oerlikon Barmag were able to hold a disproportionately high number of technical discussions withIndiancustomersandinterestedparties.
Oerlikon Barmag's industrial yarn technology offers an
extensiveprocesswindow-withoutcompromisingonyarn quality. The flexible spinning concepts enable a variety of possible yarn products for numerous applications. The portfolio includes processes for the production of polyamide and polyester yarns with the required physical properties for a wide range of end applications. Whether HMLSyarnsforcartires,yarnsforgeotextiles,safetybelts or even airbags - yarn producers will find a tailor-made concept for every end application at the Remscheid-based solutionprovider.
INDA,theAssociationoftheNonwovenFabrics Industry, and The Nonwovens Institute (NWI), areexcitedtoannounceacollaborationagreement toprovidecontinuingeducationtothenonwovens industry. This agreement expands upon the ongoing partnership between INDA and NWI, wherebythetwoorganizationshavesuccessfully presented training programs, covering the full spectrumofthenonwovensvaluechainfromraw materialstoprocessestoproducts.
Under terms of the agreement, INDA and NWI will develop and present a full roster of training courses, featuring a combination of classroom learning supported by hands-on activities in NWI's world-class nonwoven production and testing labs on the Centennial Campus of North CarolinaStateUniversity.Thetwoorganizations will also work together to explore additional educationalprogrammingtoservetheneedsofthe nonwovensindustryastheyevolveovertime.
“This collaboration agreement represents a significant next step in the partnership between INDA and NWI, as we build upon our training courseofferingtoensureitismeetingtheneedsof thenonwovensindustrynowandgoingforward,” said Matt O'Sickey, director of education and technicalaffairsatINDA.“Wearealsocommitted topursuingnewavenuestoexpandtheknowledge base of professionals working in areas related to nonwovens.”
“As we enter into this new phase of our partnership, NWI and INDA are excited to leverage our diverse perspectives and industry contacts to create an unmatched training and educationprogram,”saidTomDaugherty,deputy directoratNWI.“Thiswillensurethenonwovens industry remains competitive and is equipped with the latest skills. With the pace of change in our industry heightened due to the rapid rise of such mega trends as sustainability and machine learning, we believe continuing education in nonwovens is more important than ever – and NWI and INDAare well positioned to serve the needsofourindustryinthisregard.”
ThecurrentrosterofINDA/NWItrainingcourses include:
ElementaryNonwovens
IntermediateNonwovens
FiberandFilamentExtrusionFundamentals
MeltblownTechnology
NonwovenBondingFundamentals
Nonwoven Fabric Property Development and Characterization
NonwovenProductDevelopmentandInnovation
SpunbondTechnology
Course registration is open to INDA/NWI membersandnon-members.
For more information about upcoming INDA/NWI training courses, visit https://www.inda.org/training/.
organised in the VDMA Textile Machinery Association comment on the ambitious EU regulationsandtheirnationalimplementationfor thesustainableandcirculartransformationofthe textileandclothingindustry.
Theproductionoftextilesrequiresalargenumber ofresources,suchaswater,energyandchemicals.
“The members of VDMA Textile Machinery support customers with products worldwide to utilise great potential already at the textile production stage to thereby reduce CO2 emissions“, explained Verena Thies, Deputy ChairwomanofVDMATextileMachinery.
The position statement emphasises the importance of efficient processes, circular economy and binding rules for all market participants. Besides, the position paper summarises the status of textile-to-textile recycling processes as well as the framework conditions for reprocessing of recyclates. The companiesofVDMATextileMachinerydevelop processes and technologies for recycling and provide the technical prerequisites for the efficient reuse and recycling of textile raw materials,whethernaturalorman-madefibres.
The Executive Board of VDMA Textile Machinerystressesadditionally,thatthenewEU regulations for circular economy and their national implementation must be designed with realistic targets, measurable effects and as little bureaucracy as possible. Furthermore, market
surveillance is needed to ensure a level playing fieldforallmarketparticipants.
On behalf of the industry, the VDMA Textile Machinery Association calls for creating better location conditions in Germany and EU as a favourable environment for innovation und competitiveness for textile machinery manufacturing to significantly advance the sustainability of the textile industry: The Textile Machinery Association strongly emphasises the need for a wide range of low-cost green energy, which is essential for the implementation and sustainable use of recycling solutions in the manufacturingindustry.Theassociationalsosees the positive shaping of location conditions (the potential for skilled labour, a reduction in bureaucracy,shorterapprovalperiods,investment securityandpredictabilityaswellasareductionin thetaxburden)asadecisivefactorforsupporting sustainable business in the highly competitive textileandclothingindustry.
The complete position paper can be read and downloaded via these links: www.vdma.org/textile-machinery and www.industryarena.com/m4t.
The production programme and services of the members of VDMA Textile Machinery include equipment and technologies for recycling textile production waste, textiles, textile auxiliaries or wasteheat,andforprocessingrecycledmaterials intotextiles.
TheGermancompaniesBrückner,Groz-Beckert, the Karl Mayer Group and Thies invite representativesoftheBraziliantextileindustryto a symposium with presentations and discussion panels in Blumenau,Brazil,onAugust 21, 2024. TheeventwillbeheldatNSArmazém,Fortaleza, Blumenau and will focus on the current demand trendforwarpknittedelasticfabrics.
The demand for warp knitted elastic fabrics has increasedrapidlyinthepasttwotothreeyears.On the one hand, this offers the Brazilian textile industrynewgrowthopportunitiesandthechance to establish itself in a leading position in the growing market. On the other hand, the turnaround also holds challenges as the productionstepsinvolvedinmanufactureofwarp knittedelasticfabricsarestrikinglydifferentfrom theconventionalmethods.
In order to provide the Brazilian warp knitting industry with optimum support in this change, Brückner, Groz-Beckert, Karl Mayer and Thies areinvitingparticipantstoaspecialistsymposium on the subject of "Production of Warp Knitted Elastic Fabric". Industry experts, stakeholders and textile visionaries are invited to share their insightsandexperienceswiththeguests.
Theaimofthesymposiumistoprovideaplatform where knowledge can be exchanged and cooperation intensified. The symposium offers a
widevarietyoftechnicalpresentationsaswellas best practice examples and showcases cuttingedge technologies and innovations in warp knitting technology. Interactive sessions and discussion rounds promote exchange among participants and provide networking opportunities.TheeventlanguageisPortuguese.
This is how the German companies Brückner, Groz-Beckert,KarlMayerandThieswouldliketo provide their Brazilian customers with optimum supportinadaptingtorapidlychangingtrendsand benefiting from the current trend in warp knitted elasticfabrics.
Thoseinterestedinattendingthesymposiummay contactthesalesrepresentatives:FrankBernhard or Fabricio Rampani (Brückner, Thies & Karl Mayer),orDiomarGomesVieira(Groz-Beckert) toregister: frank.bernhard@mbrtextil.com.br fabricio.rampani@mbrtextil.com.br malharia.sudeste@ns.com.br
Venue: NS Armazém, Fortaleza, Blumenau
BR470,7109
CEP89058-020-Fortaleza
Blumenau,SC-Brasil
Date: August21,2024
FreudenbergPerformanceMaterialsApparelinaugurates state-of-the-artthermalinsulationfactoryinVietnam
Some of Freudenberg Performance Materials Apparel´s Vietnam team members with top management during the inauguration. Back row from left to right: Masahiro Nakano, VP of Finance and Controlling, Global Sourcing and Digitalization Freudenberg Performance Materials Apparel, Jonathan Oh, SVP Freudenberg Performance Materials Apparel, John McNabb,CTOFreudenbergPerformanceMaterials
Freudenberg Performance MaterialsApparel (Freudenberg Apparel) is proud to announce the production opening of its state-of-the-art thermal insulation factory located in Long Thanh District, Vietnam. This facility specializesintheproductionofcomfortemp®, Freudenberg's renowned high-performance thermal insulation material, designed to elevatefashionandsportswearapparel.
“With the opening of our first production site in Vietnamwearesettomeetthethrivingdemandin the Southeast Asian and South Asian garment manufacturing industries, reinforcing both our presenceinandcommitmenttotheregion,”stated John McNabb, Chief Technology Officer at Freudenberg Performance Materials. “By localizing the production of our thermal insulation materials in Vietnam, we are not only
reducing lead times for our customers but also streamlining the supply chain, ensuring we continue to deliver exceptional value for customers.” The Vietnamese facility is equipped to produce sustainable thermal insulations, providing customers with options that align with their sustainable garment production initiatives andgoals.
ThisadditionalnewfactoryextendsFreudenberg Apparel's thermal insulation production across key Asian markets, including the Chinese mainland and South Korea. It also significantly strengthens Freudenberg Apparel's global productioncapabilitiesandsupplynetwork.This expansionwillbolsterthecompany'scompetitive edgeinAsiaandreaffirmsitsongoingdedication to innovation and evolution within the apparel industry.
Dilo Temafa, a leading specialist in machinery and equipment for fibre preparation and natural fibre processing, is pleased to announce the successful sale of a line extension to EcoTechnilin. The machines will complement an existing flax fibre preparation plant in France to enablehigherfibrequality.
Eco-Technilin, a renowned producer of sustainable materials, has chosen Dilo Temafa machines to expand its production capacity and increase its efficiency. The plant expansion is specifically designed to efficiently clean flax
scutcher tow and meet the high demands of modern manufacturing, while increasing process stabilityandplantavailability.
DiloTemafahasbeenactiveinthefieldofnatural fibreextractionformorethanthirtyyearsandhas suppliednumeroussystemsfortheprocessingof bast fibres, e.g. flax and industrial hemp. The fibres obtained are used in various industries, including the construction, automotive, nonwovens and textile industries, and make a major contribution to minimising the ecological footprint.
TheAsiaNonwovensExhibitionandConference (ANEX2024)madeitsdebutinTaiwanfromMay 22nd to 24th at the Taipei Nangang Exhibition Center, Hall 1. The event brought together 329 exhibitorswhooccupied745booths,coveringan exhibition area of 16,000 square meters. The themes of the exhibition included nonwovenrelated raw materials, manufacturing machinery and equipment, components, and applications.
Concurrent events featured "Keynote Speech," "A-NEXTHUB:NewProductLaunch,""Global Nonwoven Summit (GNS)," and the "Asia Nonwovens Conference." Over the three days, ANEX 2024 attracted 12,187 attendees from 37 countriesandregions.
Theexhibitionshowcasedavarietyofnonwoven productsandrelatedsectors,including:
Nonwoven Roll Goods: Airlaid, Drylaid, Thermalbonded, Chemically bonded, Needled & Spunlace,Meltblown,Spunlaid(incl.SM,SMS), Wetlaid, Composite, Fibrillated or perforated
film,andotherstructures.
Applications: Abrasives, Agriculture/Horticulture, Automotive, Building, Composites/Laminates, Electrics/Electronics, Filtration, Home furnishings, Hygiene, Interlinings, Medical/Surgical, Packaging, Printing, Shoes/Leather goods, Transportation, Wiping, Upholstery, Wall coverings, Bed and tablelinen,andCoatedSubstrates.
Raw Materials: Adhesives, Hot melts, Binders, Latex, Additives, Fibers & Filaments, Films, Membranes,FluffPulp,Polymerchiporgranules, Super absorbent, Surface treatment chemicals, Tapes elastics, Mechanical fastening systems, Tissue&Papers,andWadding.
Machinery: Nonwovens production machinery, Web preparation machinery, Web forming machinery, Forming and drying equipment, Finishing equipment, Converting machinery, Wastehandlingmachinery,Onlinemonitoring& inspectionsystems,andTestingequipment.
Services: Publications, Research institutes & laboratories,andTradeassociations.
ExhibitorandVisitorProfile
Exhibitors: 329 from 18 countries and regions, occupying745boothsover16,000sqm.
Top participating countries: China (47.2%), Taiwan (23.3%), Japan (9.7%), South Korea (3.5%),India(2.5%).
Visitors:12,187from37countriesandregions.
Major visiting purposes included industry knowledge enhancement, supplier/agent search, materials and equipment purchasing, conference attendance,andindustrynetworking.
Keynote Speech: Delivered by key industry leaders and experts, attracting significant attendance.
A-NEXT HUB: New product launches with 18 sessionsand500attendees.
GlobalNonwovenSummit:Featureddiscussions by prominent figures from various nonwoven associationsandorganizations.
Asia Nonwovens Conference: Included sessions by industry experts covering various aspects of thenonwovenindustry,with167attendees.
ANEX2024successfullybroughttogetherglobal leaders in the nonwoven fabrics industry, providingaplatformforshowcasinginnovations, discussing industry trends, and fostering international collaborations.The event's debut in Taiwan marked a significant milestone, enhancing Taiwan's position in the global nonwovenfabricindustry.
As India strides forward in its journey toward industrial excellence, the technical textiles sector assumesanimportantroleinthistransformationof thistransformation.Withanincreasingdemandfor innovative solutions across industries such as healthcare, personal hygiene, packaging, and automotive, non-woven textiles are becoming the cornerstone of this industrial revolution. SOHAM Enterprises,atrustednameinthefield,isplayinga pivotal role in shaping the future of this dynamic sector.
The global shift towards sustainable and efficient manufacturing processes has sparked tremendous growthinthetechnical textileindustry.TheIndian government'sproactivemeasures,includingvarious incentives and grants, have further fueled this growth, encouraging both domestic and internationalplayerstoinvestinthesector.Notably, European manufacturers are increasingly establishingtheirpresenceinIndia,recognizingthe country's potential as a manufacturing hub for technicaltextiles.
SOHAM Enterprises: Your Gateway to EuropeanExcellence
In this rapidly evolving landscape, SOHAM Enterprises has emerged as a key enabler for businesseslookingtocapitalizeontheopportunities within the non-woven textile industry. Partnering withleadingEuropeantechnologyproviderssuchas BoninoCardingMachines,SicamSrl,andRamatex Italia,SOHAMEnterprisesoffersacomprehensive range of machinery solutions tailored to meet the diverseneedsoftheIndianmarket.
Whether it's a greenfield project or an upgrade to existing manufacturing facilities, SOHAM Enterprises delivers cutting-edge technology designed to optimize production processes for synthetic,natural,mineral,andceramicfibers.Their offeringsinclude:
Advancedfiberopeners,blenders,andmixers
High-performance carding machines with various workingwidths
Crosslappersforefficientwebconsolidation
Drum ovens and calendaring for superior compactingandconsolidation
Spunlacelinesandwetpulpformationsystems
Chemicalandthermobondinglines
Needlepunchingandspunbondlines
Textilewasterecyclingsystems
Specialized production lines for artificial leather, compositegeo-textiles,andglassfibernonwovens
What sets SOHAM Enterprises apart is their commitmenttoprovidingcustomizedsolutionsthat cater to the specific requirements of each client. Their representatives in Delhi, Mumbai, and Ahmedabad are dedicated to understanding the uniqueneedsandbudgetconstraintsoftheirclients, ensuring that they receive economic and flexible solutionsthatalignwiththeirbusinessgoals.
With a strong emphasis on innovation and sustainability, SOHAM Enterprises is wellpositioned to lead the charge in India's non-woven textile industry. Their collaboration with experienced European technology providers ensuresthatIndianmanufacturershaveaccesstothe latest advancements in textile machinery, enabling them to produce high-quality, innovative products thatmeettheevolvingdemandsofglobalmarkets.
As the technical textile sector continues to grow, SOHAMEnterprisesremainscommittedtodriving this growth by providing reliable, cost-effective solutions that empower businesses to succeed. For moreinformationonhowSOHAMEnterprisescan supportyourtechnicaltextilemanufacturingneeds, reachouttotheirteamtoday.
ContactInformation:
PrashantMandke
SOHAMEnterprises,Mumbai
Cell:9324687021
Email:prashant.mandke@sohamindia.in
Website:www.sohamenterprise.co.in
Reliance Industries Limited (RIL)’s pioneering B2B2Cbrand,R|ElanFabric2.0,recentlyhosted its highly anticipated R|Elan Fabric Innovation Meet across three major cities: Noida, Gurgaon, andBangalore.Heldonthe9th,10th,and11thof July, respectively, the events showcased cuttingedge fabric innovations powered by R|Elan speciality products, drawing an august gathering ofover250attendeesfromacrossthevaluechain, including brands, fabric and garment manufacturers,andfashiondesigners.
The R|Elan Fabric Innovation Meet provided a unique platform for attendees to explore and experiencethetransformativepotentialofR|Elan fabric technologies. The product showcases offeredaglimpseintotheadvancedcapabilitiesof R|Elan speciality fabrics, emphasizing their positive impact on value partners’product lines. From enhanced performance attributes to sustainable solutions, the innovative fabric technologieshighlightedattheeventaredesigned to meet the ever-evolving demands of modern consumers.
Key highlights of the meet included a series of
presentations and product demonstrations that captured the latest trends and inspirations across all apparel categories. Attendees had the opportunity to witness firsthand the advanced capabilities of R|Elan fabrics, which are engineered to offer superior functionality, aesthetics,andsustainability.Thesefabricsareset torevolutionizethetextileandapparelindustryby delivering exceptional quality and performance, designed to meet the ever-evolving demands of modernconsumers.
KeyHighlightsoftheEvent:
• A comprehensive showcase of R|Elan fabric innovations and their applications in various apparelcategories
• Keynote address in Noida and Gurgaon by Mr. Ajay Gupta, Head of Polyester Sector for the DelhiRegion
•KeynoteaddressinBangalorebyMr.Nagarajan Mookaiah, the Head of Polyester Sector for the SouthRegion
• Insightful presentation by Mr. David Landart, Asia Director of Carlin Group / InMouv Sports Subsidiary, discussing global trends inActive & Athleisurewear
• Product Presentation by Mr. Sanjay Gupta the headofNewProductDevelopmentPSFPolyester StapleFibre
•BrandPresentationbyMr.RiteshSharma,Head BrandandRetail–R|Elan
Mr.Ajay Gupta, in his keynote address in Noida and Gurgaon, stated, “The R|Elan Fabric Innovation Meet is a testament of our commitment to pushing the boundaries of fabric technology.Ourinnovativesolutionsaredesigned toinspireandempowerbrandsandmanufacturers tocreateinnovativegarmentsandcatertothefastevolvingapparelindustry.”
Mr.NagarajanMookaiahinhiskeynoteaddressin Bangalore emphasized on the huge opportunity for polyester to grow in India and the role of RelianceIndustriesinfuellingthisgrowth.
Mr. David Landart added, “R|Elan fabrics represent a significant advancement in textile technology. Their versatility and performance characteristicsmakethemidealforawide/range of applications, particularly in the fast-evolving Active&Athleisurewearsegment.”
Mr.SanjayGuptapresentedtheuniqueproperties of each R|Elan speciality products with special emphasis on R|Elan GreenGold and R|Elan
Kooltex,astheseproductsledtothedevelopment ofuniquefabricandgarments.
Mr. Ritesh Sharma led the brand presentation emphasizing on how R|Elan can add value to brands by empowering them with superior consumer centric innovations. He also shed light on the various marketing channels that ensure a cohesiveconsumerstoryiscreatedtohelpbrands deliverbusinesssuccess.
The event concluded with an interactive session, allowing attendees to engage with experts and exploretheshowcasedgarmentsandfabrics.The enthusiastic response from participants underscored the industry's strong interest in adoptinginnovativefabricsolutions.
R|Elansymbolizesthenextgenerationoffabrics, crafted from specially designed fibres and yarns using advanced technological expertise and Reliance Industries' robust R&D and testing systems.
TheFabricInnovationMeetactedasacatalystfor industry stakeholders to delve into the transformative potential of sustainable textiles, paving the way for a new era of environmental responsibilityinfabricmanufacturing.
Getting to the core of the matter with bio-based SAPs
Could hemp be the answer to the realisation of sustainable, bio-based superabsorbent polymers (SAPs) for absorbent hygiene products (AHPs)?
Researchers at Purdue University in the USAbelieve so and have recently patented a process for manufacturing them. If successfully industrialised, thesebio-basedSAPswouldperfectlycomplementthe ongoing commercialisation of nonwoven fabrics basedonnaturalorrecycledfibresandresins.
Bastfibres
Suchfibresincludehempitself,withcompaniessuch as INDEX™ exhibitor Bast Fibre Technologies (BFT), headquartered in Victoria, British Columbia, currently accelerating production specifically for the nonwovensindustry.
Asrenewablecrops,bastplantslikehempandflaxcan be produced in just 90 days with a high yield per acreage.Theyarealsorotational,enrichingothercrops grown after them and providing an effective carbon sink based on natural rainfall, with no need for irrigation,pesticides,orchemicalfertilizers.
Bastplantsalsotransportnutrientsthroughtheircores, which is something Bast Fibre Technologies is exploiting for superior liquid handling in terms of retentionandreleaseinnonwovens.Otheradvantages of the fibres obtained from these plants include their strength,suitabilityforthecardingprocessandnatural colorationwithouttheuseofchemicaldyes. Having completed a successful financing round in 2022, Bast Fibre Technologies is working towards buildingupanannualcapacityof50,000tonsofhemp andflaxfibresby2026.
Thecompanyhassecuredaportfolioofitsownpatents relatingtoallaspectsofprocessing,andinadditionhas anexclusivelicensingagreementonotherpatentsheld by Georgia Pacific, with whom it is working on new solutions for industrial and food service wipes, while adaptingthemforitsownfibresfordisposables.
Bast Fibre Technologies wide-ranging preparation to become a major player in the hygiene market has involvedestablishingasupplychainfromfieldtofinal product with full quality control and quality assurances, while also achieving a geographical spread enabling it to adapt to issues such as drought and floods that natural fibre crops are always susceptibleto.
With their introduction in the mid-1980s, SAPs enabled the weight of baby diapers to be reduced by around two-thirds, requiring much less fluff pulp for effective absorption. They also convincingly preventedpotentialdiaperleakage.
With a typical SAP amount of around 12 grams, today's baby diapers not only successfully prevent urine leakage, but stay dry for hours and protect the skinfrommoisture,helpingtoavoiddiaperrash.
OnegramofSAPcanabsorbupto500gramsofpure water and the liquid is not only absorbed but also locked up inside the particles even under external pressure.Theresultisasoftgelthatisstillcapableof absorbingfurtherliquid.
Today's SAPs are made by polymerizing single molecules of sodium acrylate to form long molecular chains.Thepolymerizationisactivatedbyaninitiator, and a crosslinker connects the single molecules together to form a polymer network. The crosslinker ensures that the granules remain insoluble when exposed to liquid, maintaining their absorbent properties and structure. Upon contact with aqueous liquid the sodium ions become disassociated, generating an osmotic pressure which drives more liquidintotheSAP,bindingittightlywithin.
TheSAPmarketwasestimatedtohaveavalueof$6.5 billion in 2023 with production of approaching 5 billion tons and annual growth to 2030 projected at 8.1%. Key manufacturers include BASF , Evonik, NipponShokubaiandSumitomo.
Biobasedalternatives
Overthepast20years,numerousattemptshavebeen madetodevelopreplacementsforSAPsderivedfrom oilwhicharenotrenewableorbiodegradable.
Agricultural giant Cargill, for example, attempted to make biobased acrylic acid from both 3-HP (3Hydroxypropionicacid)andlacticacidinpartnership withBASFandNovozymes.BASF,however,dropped out of the development in 2015 over concerns about the economic feasibility of the project. Undeterred, Cargill has subsequently licensed technology from Procter&Gamblethatconvertslacticacidintoacrylic acidandisworkingwithothercompaniestoscaleup thetechnology.
In 2021, Nippon Shokubai Europe also advanced its development of biobased SAPs by obtaining certification from the ISCC (International Sustainability and Carbon Certification) for a biobasedpropyleneformakingacrylicacid.
Various other natural products have also been proposed as the basis for new SAPs, including algae, bamboo, chitosan, wheat gluten protein and natto – a fermentedsoy-basedfoodthatispopularinJapan.
Purdue University researchers, however, are now proposing cellulose extracted from hemp, refined throughasequenceoftreatmentstocreatetheirpatentpendingnewSAPs.
Uniquebenefits
“Hurds and bast are two parts of the hemp plant that offer unique benefits for sustainable material development, particularly in absorption technologies,” says Senay Simsek, head of the Department of Food Science who is leading the development.“Hemphurds,foundintheinnerwoody core of the hemp stalk, are highly absorbent due to theirhighcellulosecontentandlowligninlevels.This makes them an excellent alternative for superabsorbent applications. Hemp bast, the fibrous outerlayer,whilelessabsorbent,providesstrengthand durability.”
Thecelluloseextractedfromthesepartsisparticularly effective because its molecular structure can be modified to enhance its water retention capabilities, making it ideal for products requiring high absorbency.”
“The treatments we have developed break down the naturalstructureofthecellulose,increasingitssurface areaandporositywhichallowsittoabsorbandretain more water,” Senay Simsek explains. “This a dramatically improves its ability to soak up and hold moisture,whichiscrucialforapplicationsthatdemand high absorbency. The uniqueness of our technology lies in its versatility, making it highly tuneable for diverse applications of superabsorbent materials acrossvariousindustries.”
Plans are now underway for the scaling up of production and the development team is pursuing furthercollaborationswithindustryleaderswhoshare itsvisionofreplacingtraditionalSAPswiththesenew biodegradableandsustainablealternatives.
Achangeofmindsetwithmushrooms
Microfibre-basedartificialleathersormicrosuedes are now the preferred option to natural leather for many leading car manufacturers and their customers, with benefits including breathability, softness and scuff resistance. They have also increasinglyfoundfavourwithluxurygoodsbrands andmanufacturersofhigh-endfurnishings.
Suchmaterialsaregenerallybasedon'islandsinthe sea' bicomponent fibres which are cut into staple fibres and have their 'sea' components dissolved out, before being needlepunched and dyed. They cantakeboldcoloursandprovidecarmakerswith flexibilityinseatandcomponentassembly,andasa result command premium prices – far above the squaremetrepricesofconventionalnonwovenroll goods.
Thefactremains,however,thatsuchfabricsarestill largely based on oil-based synthetic fibres and responding to the requirements of a future circular economy is leading to the development of some verydifferentbiobasedalternatives.
These are based on fungal mycelium – the vegetative stage of mushrooms – and have also recently been attracting the interest of car makers forpotentialnewinteriorfabrics.
Networks
In many ways, these new mycelium materials perfectly comply with the ISO definition of nonwovens, as being 'engineered fibrous assemblieswhichhavebeengivenadesignedlevel of structural integrity by physical and/or chemical means, excluding weaving, knitting or paper making'.
The process for their production is, however, a million miles away from the conversion of conventional nonwoven roll goods, generally involving biofabrication in huge batch systems of traysonshelves.ThisissimilartotheDutchShelf System recognised worldwide as the superior growingmethodforwhitebuttonmushrooms.
The fungal mycelium organisms grow in networkforming structures called hyphae and are mainly composedofapolysaccharidecalledchitin.
Chemically,chitin'sstructureissimilartocellulose, anditisaversatilemoleculethatcanformasemitransparentbiomaterial.Chitinisalsocharacterised by its biocompatibility, biodegradability, and nontoxicity.
A number of companies have now emerged dedicated to exploiting the useful properties of mycelium, with the major end-use application viewed as alternative leather for apparel and footwear, but also materials for automotive interiors,acousticpanelsandfloortiles.
In January this year, for example, Californiaheadquartered MycoWorks announced that its commercial-scaleplanthadsuccessfullyharvested over a thousand sheets of Fine Mycelium, its leather-alternativebiomaterial.
MycoWorks has been exploring potential automotive applications with General Motors following investment by GM Ventures in the company, as part of an over-subscribed $125 million investment round for the establishment of
the new plant. It will produce several million square feet of Fine Mycelium materials annually, onceatfullcapacity.BasedinUnionCounty,South Carolina, it is modelled after the company's semiautomated Emeryville pilot plant which has successfully demonstrated the scalability of the process.
The patented Fine Mycelium process is a proprietary biotechnology platform that engineer's mycelium to grow made-to-order and made-tospecification materials. The predictable and scalable tray-based process meanwhile offers freedomfromsupplychainconstraints.
NewYork-basedEcovative–whichhasdeveloped a process for producing full-size mycelium sheets that are up to 24 metres in length and 1.8 metres wide over the course of just nine days – has also explored the use of its materials with automotive leader Ford, as well as partnering with fashion brands including Bestseller, Pangaia, PVH Corp., Reformation,Vivobarefoot.
Ecovative's sheets can also be grown to meet specific performance in terms of tensile strength, density,andfibreorientation.
OverinSouthKorea,start-upMycelhaspartnered with car manufacturer Kia to develop another soft automotive fabric based on mycelium that can be producedinvarietyoftexturesandcanalsobedyed.
TheMycelmaterialisresistanttotearingandhasa hightensilestrength,bothofwhicharekeyforcar seats that take heavy usage. Kia has committed to eliminatingbothleatherandPVCfromallofitscars and is also exploring a bio-polyurethane derived from natural components such as corn and eucalyptusforinteriorapplications.
Car makers Volkswagen and Stellantis have meanwhile been involved in the €6.5 million EU Horizon-fundedMY-FIresearchprojecttodevelop new materials made of mycelium fibres which is nownearingitscompletion.
The project has been led by Mogu, located in Inarzo,nearMilan,inItaly,whichhassubstantially expandeditsprocessforgrowingselectedstrainsof mycelium on pre-engineered substrates made of agro-industrialresidues.
Mogu'smyceliumisgrownfromstarterspawninto thethreadlikefilamentsofthehyphaeontopofthe substrates. When harvested and dried soft, silky white nonwovens are created in sheets of between 50 to 60 square centimetres which are completely stable, safe, durable and biodegradable. The delicate material is then made stronger and more durable through the addition of bio-based chemicals.
Within the MY-FI project, Volkswagen has been assessing the materials under development for potentialuseinautomotiveinteriors.
“Customers increasingly want animal-free materials for interiors – from seat covers and door panels to dashboards and steering wheels – so adding a sustainable substitute for leather is an exciting prospect,” says Dr Martina Gottschling, a researcher at Volkswagen Group Innovation. “A fast-growing biological material that can be produced animal-free and with little effort, which alsodoesnotrequirepetroleum-basedresources,is a game-changer in interior materials and the myceliummaterialisalsolighterthanleather.”
Volkswagen's involvement in MY-FI has been drivingprojectresearchersatUtrechtUniversityin the Netherlands and ITECH (Institut textile et chimique de Lyon) in France to enhance the durability of the mycelium fabric, and samples continuetobeassessedandimprovedon.
“It's definitely a change of mindset working with mycelium in the manufacturing process,' says AnnalisaMoro,Mogu'sEUprojectleader.“You're reallycollaboratingwithnaturetogrowsomething ratherthancreatingit,soit'skindoffuturistic.”
India is a significant player in the global manmade fibres (MMF) market, being the second largest producer of both polyester and viscose globally. The domestic MMF industry predominantly consists of polyester and viscose, whichtogetheraccountforapproximately94%of the industry in volume terms. Specifically, polyestercomprisesabout77.5%ofthisvolume, withviscosemakinguptheremainingshare.
MMFsareextensivelyusedtomanufacture100% non-cottonfabricsandblendedfabrics,whichare essential in various applications such as readymade garments, home textiles, and other industrialtextiles.
The global end-use demand for textile fibres is anticipated to grow at an average annual rate of 2.80%from2015to2025,increasingfrom90.10 million tonnes to 119.20 million tonnes. Within this,thedemandforman-madefibresisexpected toriseby3.7%by2025.
Severalfactorsaredrivingthisdemand:
· Increaseduseinnon-wovenandtechnical textiles.
· Changing consumer trends, including a greateremphasisonfitnessandhygiene.
· Rising brand consciousness and rapidly changingfashiontrends.
· Increased participation of women in the workforce.
India's export of MMF textiles and apparel was valuedat$4.68billionforthefiscalyear2023-24, highlighting the sector's significant contribution totheeconomy.
GovernmentInitiativesandEconomicImpact
Traditionally,Indiahasfocusedoncottontextiles. However, with global trends shifting towards MMF,theIndiangovernmenthasrecognizedthe sector's potentialfor growth and employment.In response, the Production Linked Incentive (PLI) SchemeforTextileshasbeenintroduced,withan
approved outlay of INR 10,683 crore over five years. This scheme aims to promote the production of MMF apparel, MMF fabrics, and technicaltextileproductsinIndia.
TheobjectivesofthePLIschemeinclude:
· Enablingthetextilesectortoachievesize andscale.
· Enhancing competitiveness in the global market.
· Increasing the availability of MMF and MMF yarn to contribute to the overall growthofthetextileindustry,particularly inmixedfibre/yarnapplications.
India's position as the second largest producer of man-made fibres is reinforced by its substantial productionvolumes:
· Over 1441 million kilograms of manmadefibres.
· More than 3000 million kilograms of man-madefilaments.
The man-made fibre value chain in India is verticallyintegrated,encompassingupstreamand downstream linkages from raw materials to finished goods.This integration ensures a robust and efficient production process, contributing to theindustry'sgrowthandsustainability.
India's MMF industry is poised for significant growth, driven by global demand trends, supportive government policies, and substantial production capabilities. The focus on increasing the production and export of MMF textiles and apparel will not only enhance India's position in the global textile market but also generate substantial economic benefits and employment opportunities within the country. The initiatives like the PLI scheme will play a crucial role in achievingthesegoals,ensuringthetextilesector's competitivenessandlong-termsustainability.
The German manufacturer of specialized testing and measuring instruments, emtec Electronic, will showcase its redesigned TSA Tactile SensationAnalyzerattheCLOTECHconference inDresden,Germany,fromSeptember5-6,2024.
Taking place biennially, CLOTECH highlights globaladvancementsinprotectiveclothing,smart textiles, and related innovations. This year, Alexander Gruener, emtec's Global Business Development Manager, will deliver a special presentation highlighting the unique qualities of the TSA and emphasizing its role in enhancing quality assurance and communication within the textilesupplychain.
TheenhancedTSAprovidesobjectivedataonthe subjective phenomenon of human tactile sensation. It measures surface softness, surface smoothness,stretchandrecoverybehaviorinless than two minutes, simulating human fingertips
withitsmeasuringprinciple.Themostimportant innovationsofthedeviceinclude:
Measurement of Thermohaptics: Equipped with state-of-the-artthermohaptictechnology,theTSA evaluates thermal insulation as well as surface thermalconductivity,providingobjectivedataon howwarmorcoolamaterialfeelstothetouch.
Measuring Springback Behavior: Utilizing an improvedmethod,theTSAaccuratelymeasuresa fabric'sabilitytoreturntoitsoriginalshapeafter deformation, ensuring compliance with specific performancestandards.
Online Virtual Database: The Virtual Haptic Library, developed in collaboration with Black SwanTextiles,isalicense-basedonlinedatabase in which TSAsample data can be processed and categorized according to specific haptic characteristics.Itcanbeaccessedinreal-timeby
authorizedpersonnelfromanywhereintheworld, enabling efficient quality assurance and control regardlessoflocation.
Improved User Experience: The updated TSA device is lighter than the previous model, offers simplified assembly of parts during set-up, and features a touchscreen with smart software for user-friendlyandintuitiveoperation.
High-Resolution Camera: An advanced camera allowstheusertocaptureahigh-resolutionimage of the clamped sample, revealing the structure, texture,andvisualembellishments.
“Quantifying and digitizing haptic parameters opens up exciting new possibilities for quality assurance and product reproduction,” explains Gruener. “This innovation reduces the need to shipsamplesworldwidetotesthapticproperties, resulting in a swift and significant return on investment.”
Formoreinformation,visitAlexanderGruenerat the emtec booth during CLOTECH, and don't misshispresentation,“ObjectiveMeasurementof Haptic Quality Parameters and Digitization in a
Cloud-BasedVirtualHapticLibraryforImproved Supply Chain Communication,” on September 5 at13:15.
InJuly,KARLMAYERSalesManagerJulianSchubertspoketoStefanPassauer, ProductionManagerWarpKnittingatRÖKONA,abouthisinvolvementin thedevelopmentandoptimizationoftheEES.
EnergyEfficiencySolutionfromKARLMAYER helpssaveenergy-initialpracticalexperience
In May 2024, KARL MAYER launched its Energy Efficiency Solution (EES) for recording and analyzing energy consumption on warp knitting machines. Two months later, customers had already provided initial feedback on the innovation for greater sustainability and lower costs.
ToensurethattheycanusetheEESeasily,KARL MAYERhastranslatedtheoperatingmanualinto sixlanguagesanddevelopedatutorialwhichcan befoundontheKARLMAYERAcademyonline platform.Theexplanationsstartwithinformation on opening and configuring with customerspecific data. All display options and search functions are then presented. The final chapter focuses on analyzing energy consumption, costs andCO2emissions.
Inaddition,furtheroptimizationsfortheEESare
onthewayorhavejustbeencompleted.“Weare currently introducing a timer function feature. The complete integration of EES as a further solutioninourCustomerPortalhasalreadybeen finalised. Just like the Dashboard and CORE LITE, the EES can now also be accessed in this way.Thismakesitevenclearerandeasiertouse,” saysMarkusBahde,ProductOwnerDigitalatthe KARLMAYERGROUP.
Theinnovativemechanicalengineeringcompany is working with its customer RÖKONA on the new energy management solution. The warp knitting specialist develops and manufactures technologically sophisticated textiles for new products and applications in Germany, focusing consistently on customer requirements and relyinginparticularontechnicalinnovations.
JS: Why did you decide to work with KARL MAYERasapilotcustomerinthedevelopmentof theEES?
SP:Weareprimarilyconcernedwiththeissueof sustainability. Protecting the environment and natural resources plays a central role in our corporate policy. We have had an integrated environmental management system certified to ISO 14001 since mid-2023 and take a precautionary and planned approach to environmentalissues.Everycontributioncounts, especiallywhenitcomestoenergy.Aspecialteam at our company monitors energy consumption in all process steps of our fully integrated production.
In addition, our customers are increasingly demanding verifiable contributions to climatefriendly production. Brands in the automotive sector in particular are demanding documented data, for example on the reduction of CO2 emissionsperm²offabric.WiththeEES,wecan determine the required values, store them in a master database and compare them as proof of improvements. This also helps us with environmentalaudits.
JS: What exactly does the collaboration in the EESprojectlooklike?
SP: We were involved in the development right from the start, contributing our wishes and participating in the ideas generation process. Brainstorming started at the beginning of 2023. The following March, we installed a current measurementdeviceonthefirstmachine,anHKS 3-M ON, and began monitoring the data via the web browser. At the same time, we discussed potential improvements with the experts from KARL MAYER on an almost weekly basis. In August 2023, we connected the new HKS 4-M ONfieldtestmachine,whichisalreadyequipped with the EES, to the KM.ON cloud via the k.ey device and included it in the pilot project. Three moremachinesfollowedlater,includingadouble raschel machine. InApril of this year, we moved the system from a development server to the KM.ON infrastructure. The machines are now
integratedintonormalproductionoperationswith theEES.
JS: With four machines in the test, you can certainlyalreadygetagoodideaofhowtheEES works.Whatexperienceshaveyouhad?
SP: The solution works for us! It operates very reliably and delivers data that is easy to understand and provides valuable information. Thevariousanalysesareparticularlyimportantto us, for example comparing the costs and consumptionofamachineoveracertainperiodof time or when working with different items. It is also possible and useful to compare several machineswitheachother.Wehavefoundthatthe HKS 4-M ON produces with the highest energy efficiency. The HKS 3-M ON is the fastest machine that we have integrated and monitor in theEES.
JS:Whatfurtherdevelopmentswouldyouliketo see?WhatelseshouldtheEESbeabletodo?
SP:Westillhaveideasforfurtheroptimizationof thedisplay.Wewouldalsoliketobeabletoenter specificinputviathewebbrowserinordertolink and save article data with the corresponding operating data. Most recently, we have codevelopedafunctionforautomaticallyswitching the machine to standby mode. This is already working very well and is a huge relief for us. Previously, we only switched the machines to standby mode at the weekend using a timer, manually for each individual machine. The EES now enables automatic shutdown according to a schedule of production and heat-up times, which canbeenteredonthedisplayofanymobiledevice or computer. This means that we can also use shorter interruptions in operation, for example whenchangingarticles,tosaveenergy.
JS: This means that you are already well on the way to saving energy. I wish you continued successandthankyoufortheinterview.
OerlikonNeumagcommissionsBCFplantinChina
AutomotivesupplierSailudaintegratesbackwards inBCFyarnproduction
Thethree-endBCFS+systemimpresseswithitscost-effectiveness:highproductionspeedandcapacity andreliablecomponentscombinedwiththehighestyarnqualitymakethismodelparticularlyattractive forcarpetyarnmanufacturers.
Neumünster,15.August2024-Chineseautomotive supplierSailudaisexpandingitsprocesschainwith the commissioning of a Oerlikon Neumag BCF plant. In future, the specialist for automotive interiors will produce its own BCF yarns. The companyisthusintegratingtheentireprocessfrom the yarn to the finished carpet and can therefore better influence production and quality of its car carpets.
Sailudaisoneofthemajorsuppliersforinternational car brands such as BMW, Volvo, VW and Ford, but alsoforwell-knownChinesee-carmanufacturerssuch as NIO, Lixiang and SERES. "The quality of our products is our recipe for success," says CEO John Zhu, explaining the strategy. The company has been reporting a constant increase in turnover for years. Withitsownin-housecarpetyarnproduction,Sailuda wants to diversify its product range and create outstandingandexceptionalendproducts.Inthisway, the visionary trendsetter is creating a competitive advantageinthehighlycompetitiveautomotivesector.
Capacityexpansionalreadybeingplanned John Zhu is certain that this will not be the only investment in yarn production. "The delivery and
commissioningofthe2positionsBCFS+plantforthe production of PA6 and PET monocolor BCF yarns wentsosmoothlyandquickly;thishasencouragedus toinvestinanothersystemattheendoftheyear."John Zhu explains his decision for the proven S+ technologyofthemarketleaderforBCFyarnsystems withtheexpectedexcellentqualityofyarnsproduced onOerlikonNeumagsystems."Theyarnshaveavery uniform crimp with a high degree of coverage in the carpet."Sailudaistherebysecuringits competitiveness in the demanding market for automotivecarpets.
AutomotivesectorboostsAsianBCFmarket
While the focus of carpet yarn production has so far been in the USA and Turkey, the up-and-coming automotiveindustryinChinaisgivingtheAsiancarpet market a significant boost, among other effects. "We are registering increased demand for our BCF technologies,"agreetheresponsibleSalesDirectorsin ChinaandNeumünster,SunPengandArndLuppold. "Weattributethistotherisingproductionfiguresinthe Chineseautomotiveindustry;Chinaisaheadinterms offigures,especiallyintheelectriccarsector.Thisis boostingdemandforautomotivecarpets.”
28-31 October2025 SingaporeExpo www.itmaasiasingapore.com