
7 minute read
Discover the Fourth Generation
Salvagnini’s presence at EuroBLECH 2024 sets out to become a new milestone in the sheet metal working market.
Always focusing on innovation, the company will be presenting the new generation 4 (G4) of its whole range of technologies. The goal is to offer a new perspective to go beyond manufacturing and meet the market’s most urgent requirements, including labour shortages, and look for ever-more efficient solutions to maximize productivity, ensure increasingly high product quality and reduce errors and consumption.
With the new generation 4, Salvagnini presents innovative solutions for improving the simple use and repeatability of jobs, eliminating low-added value activities, reducing lead times and optimising production flows for lower product costs and increasingly high business competitiveness.
To achieve these goals, at EuroBLECH, Salvagnini will exhibit a complete range of solutions: machinery, automation, software, and services. At booth D94 Hall11, with multi-level automation, two different factory proposals will be on show, able to operate with different production strategies: in line with the possibility of standalone processing and with single technologies that, when necessary, work collaboratively.
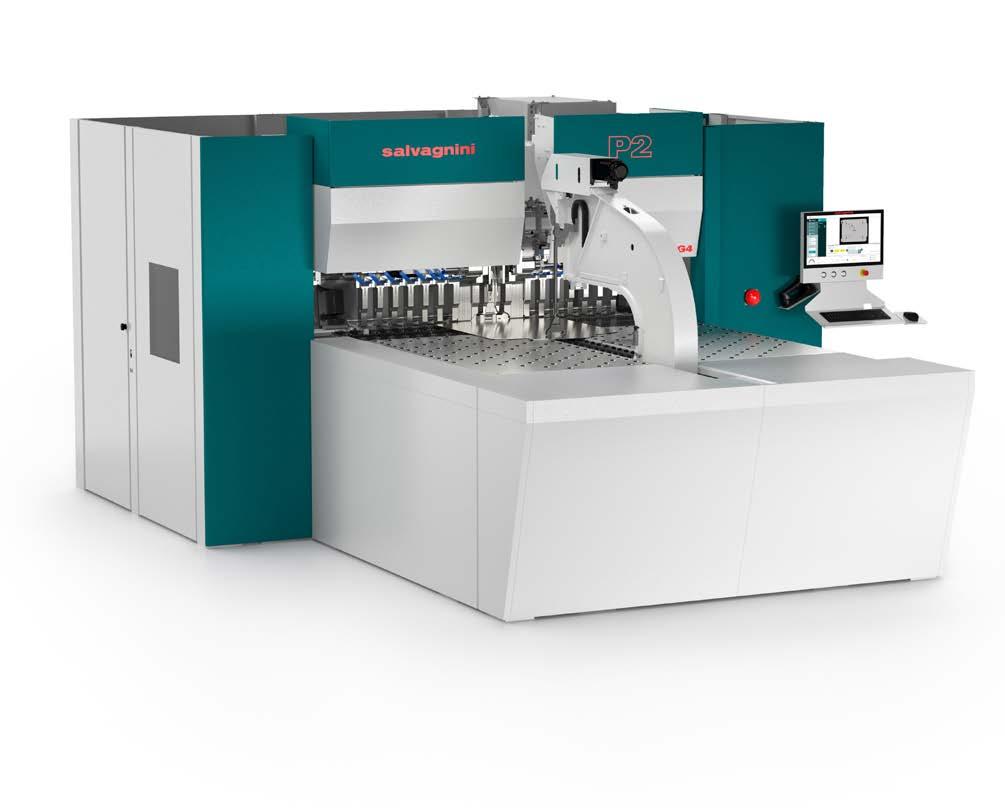
Embrace a more sustainable future and measure the difference every day, with Impacts
All Salvagnini systems are lean, their energy absorption is smart and limited to the actual job needs. Yet, in an evolving world that pays increasing attention to sustainability, we have to objectify energy efficiency with precise data. This is why at EuroBLECH the consumption of all the systems on the Salvagnini stand as well as, a new world premiere, even single machine programs, will be measured by Impacts.
Impacts measures the consumption of electricity, compressed air and assist gas in Salvagnini systems. It is the first step towards calculating volumes of CO2 equivalent of each single manufactured component. The way Impacts aggregates data depends on the services used to view them: FACE, the Salvagnini HMI interface for the whole product range, and LINKS, the Salvagnini IoT solution that monitors system performance, or an OPC UA interface. In perfect Salvagnini style, Impacts is also a flexible product that can customise data collection according to specific needs.
What are the benefits guaranteed by Impacts?
• Impacts is used to monitor and become aware of our own consumptions, to optimise and reduce them. It increases profitability because reducing consumption means reducing running costs.
• Helping to optimise and reduce consumption, Impacts ensures greater environmental sustainability and greater corporate social responsibility.
• Impacts helps to comply with the latest environmental standards.
• Impacts helps to obtain financial and tax incentives available to companies investing in high energy-efficiency machinery often linked to the update of national regulatory frameworks.
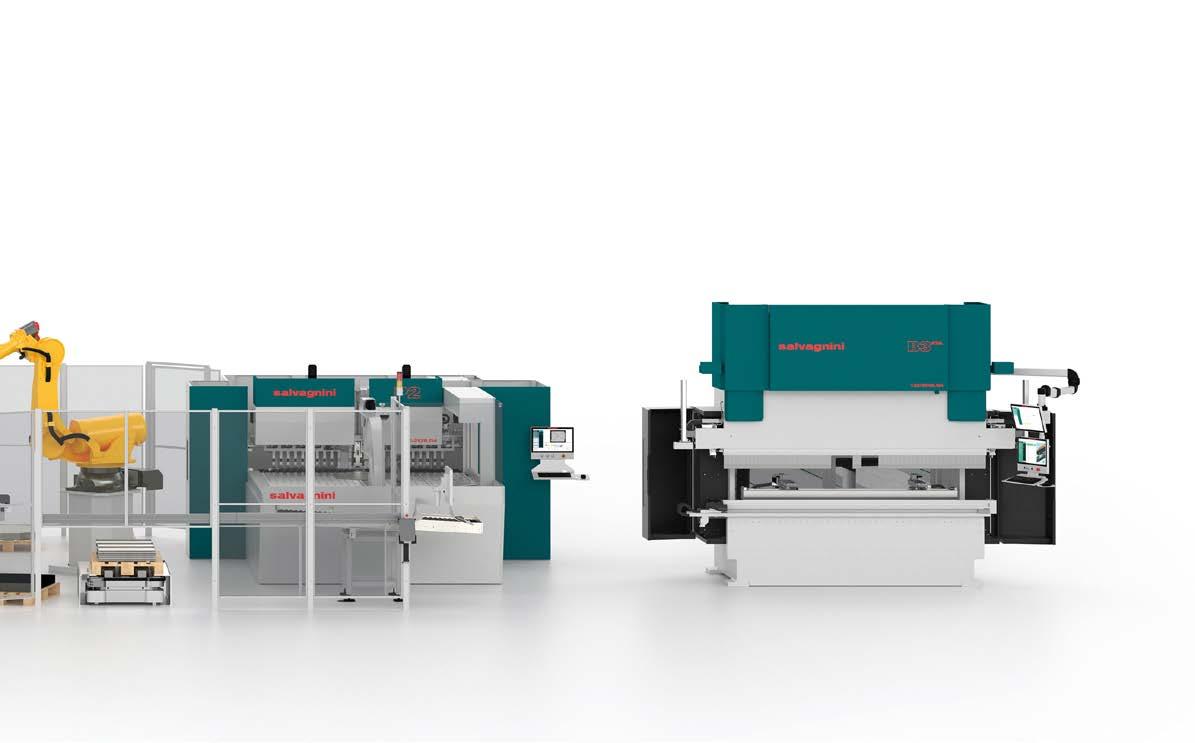
Multi-level automation: the enabling factor for factories of the future
Salvagnini’s many multi-level automation solutions are applied to both individual production steps and to eliminate low-added value activities and bottlenecks:
• the punching-shearing centre is equipped with a multipress head with tools always available; it eliminates setups while ensuring high-quality machining and reduced cycle times;
• the panel bender is equipped with universal bending tools that automatically adapt to the size and shape of the part to be produced, in cycle and without machine downtimes; it does not need re-tooling and processes the whole range of machinable thicknesses and materials;
• the laser, with single-optic cutting head to machine all workable thicknesses and materials, requires no adjustment and speeds up production changeovers.
• P-Robot, with the new artificial vision system, maximises the cell autonomy without affecting flexibility;
• with the ATA, ATA.L, MVM and AU-TO devices, the series of press brakes adapt automatically in re-tooling and in managing tools according to what has to be produced, extending its flexibility and autonomy.
In production contexts marked by low volumes and rapid production changeovers, connecting automatic loading/ unloading devices to the systems helps to recover efficiency.
Lasers, punching machines, and panel benders are extremely fast systems, and loading and unloading increasingly creates risks and creates dangerous bottlenecks.
This is why Salvagnini’s extremely wide, modular range of automation has naturally evolved over the years to configure each system differently depending on production needs and includes:
• automatic loading/unloading and sorting devices that reduce idle times for sourcing the sheet metal and the risk of error or damage to the material during stacking;
• automatic loading devices that eliminate waiting times for incoming sheet metal and improve production rates;
• robotised unloading devices that ensure the immediate availability of the machine for the next job, making the part immediately available for downstream operations, even on non-Salvagnini stations;
• intermediate automation devices – transfers, turnover units, etc. – that balance material transfer times from one station to the next;
• a wide range of simple, user-friendly software solutions that facilitate the production process by reducing errors and operator intervention times.
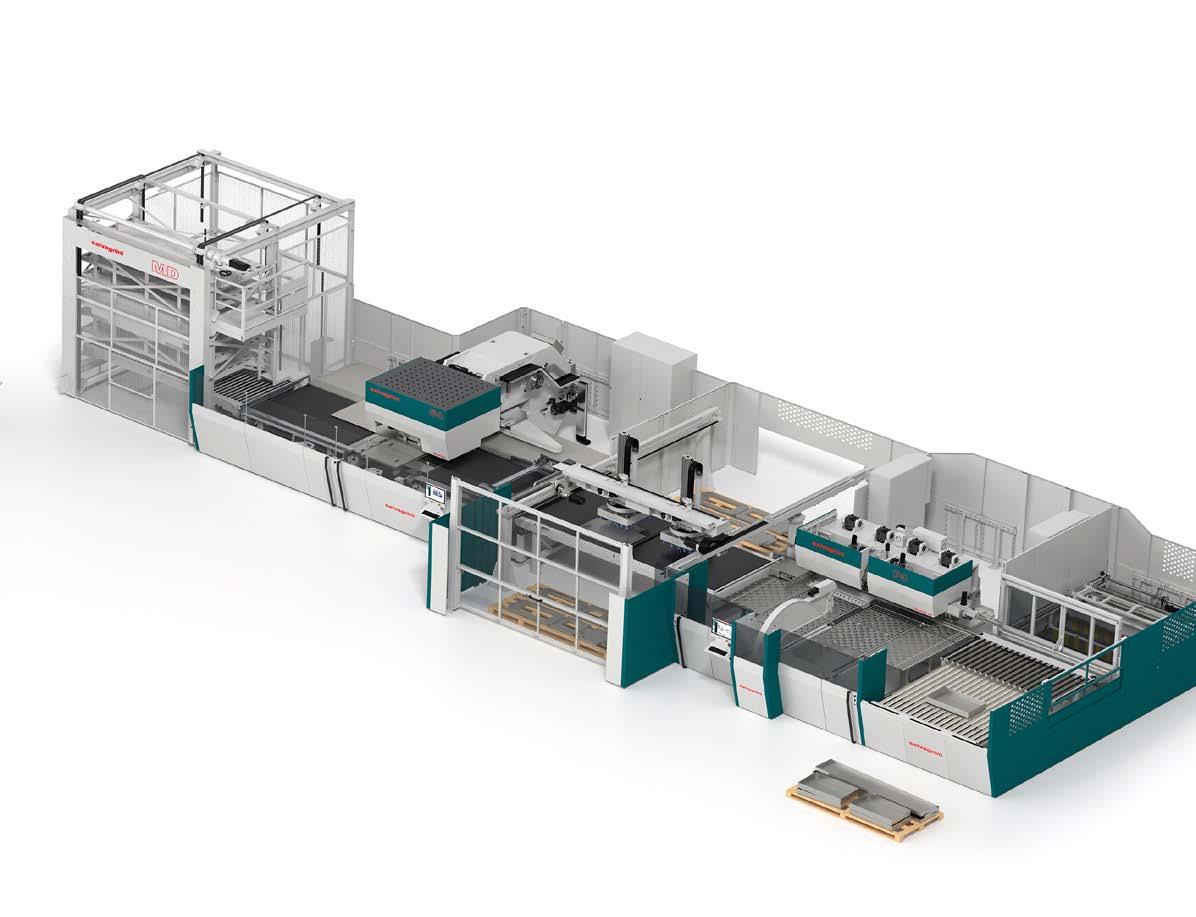
B3.G4-ATA: the press brake combining productivity and flexibility
B3 is the ideal Salvagnini press brake for dynamic production, perfectly combining productivity and flexibility. Designed to combine the features and benefits of the electric and hydraulic solutions available on the market with the in-depth business skills of automation, software, mechanics, and electronics, B3 is available in 19 models, from 2 to 6 meters long and from 80 to 400 tons.
The B3 press brake presented by Salvagnini at EuroBLECH to complete its Flexible Smart Job Shop is 3 meters long with 135 tons of force. Equipped with ATA and ATA.L devices, B3 automatically adjusts the length of the upper and lower bending tools, saving time and recovering production efficiency. Changeover is fast, taking just a few seconds, and programming is simple and intuitive. ATA is an exclusive, patented device that guarantees full flexibility in terms of the tools used to manually integrate standard WILA or special tools, such as flattening tools, on the line.
What makes the Salvagnini B3 press brake particularly interesting are the adopted technical solutions, including Direct Drive and KERS, which help to respect humans and the environment without reducing productivity. With Direct Drive technology, the ram movements are driven by two independent direct drive brushless motors, which allow to achieve both fast approach and fast return, with speeds as high as 250mm/s. On the other hand, the KERS energy recovery system is used to recover energy waste and reuse it in subsequent steps, accelerating and reaching higher speeds with the same consumption.
All the B3 press brakes are equipped with MAC3.0 – a set of integrated adaptive technologies that make the system intelligent and cancel out waste and corrections.
S-Crowning is the intelligent crowning system that ensures consistent bending angles along the entire bending length: as the parameters – material, thickness, length and therefore the required bending force – change, the effective curvature of the lower table is measured and compensated in real-time without any operator intervention. TFC2.0, Total Frame Control, prevents deviations in the bending angle using an algorithm derived from the FEM study of each model. TFC2.0 compensates for any in-cycle deformations of the press brake structure according to the variations of the characteristics of the part being processed. AMS is a laser angle measurement system that detects and corrects variations in the bending angle due to sheet metal spring back. Regardless of the length of the press brake and the part being bent, the angle is always measured in one single point: this approach helps reduce the cycle time without compromising precision.
B3 can be programmed on the machine, but programming in the office maximises its efficiency: the STREAMFORMER software automatically creates the bending sequence, setups, and bending stations, integrating perfectly with ATA devices to enhance performance. Programming in the office also increases productivity, as while the programmer deals with the programs in the office, the operator continues to bend. STREAM maximises the performance of the press brake, allowing it to communicate with the other systems in the Salvagnini Flexible Smart Job Shop.