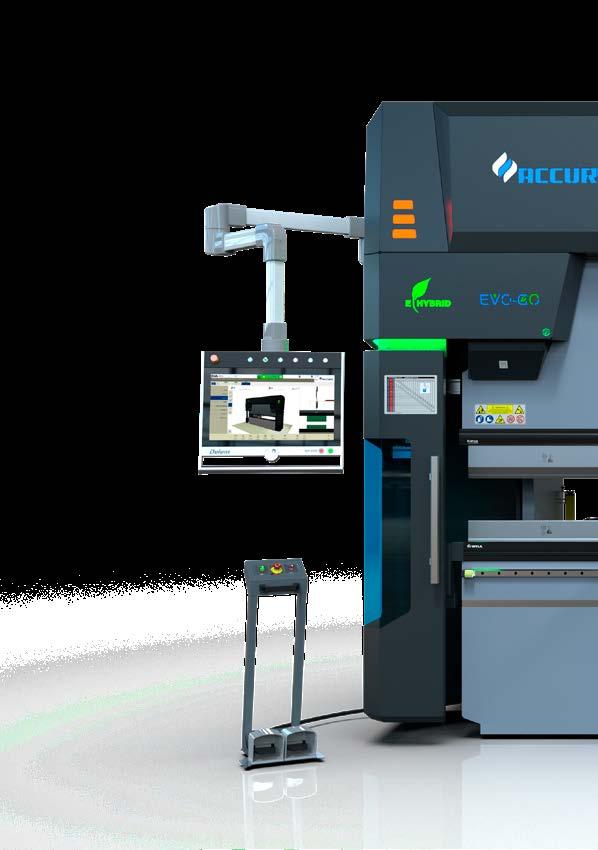
5 minute read
Powerful press brake and fully automated robotic bending cell
ACCURL and its partner MicroStep Europa will bring powerful and innovative bending systems as well as an ultra-powerful 60 kW laser system to EuroBLECH 2024.
Two press brakes, one robot and a lot of innovation: ACCURL will bring a powerful press brake from the EUROMASTER series and a fully automated, all-electric bending solution based on the eB ULTRA series to EuroBLECH 2024 (Hall 13, Stand E138). "With our innovative product solutions, we cover the entire range of different applications in the field of bending technology. At EuroBLECH, we will be showing an excerpt of this that is quite something: Anyone who wants to find out how to be able to bend particularly precisely, efficiently and reliably in the future should definitely visit us," explains Cameron Lee, CEO of ACCURL CNC Machine Tools.
The EUROMASTER series stands for top quality and maximum reliability – for the entire life of the machine. ACCURL engineers have consistently relied on 3D CAD software and the latest generation of FEM analysis tools during the development of this series, thus achieving maximum structural stability.
The EUROMASTER is an extremely reliable and highly efficient press brake, economical to purchase and offers many possibilities even in the high-quality basic equipment with Delem control technology. The series is equipped per se with a highly efficient and extremely economical electro-hydraulic press drive from HAWE Hydraulik. In addition, it has movable support arms in the basic package as well as ACCURL® quality tool clamps, type PROMECAM. Alternatively, the EUROMASTER can also be equipped with tool clamps and crowning systems from the renowned manufacturer WILA. With a press force of up to 4,000 kN and a working area of up to 4,200 mm in length, it is also equipped for larger tasks. For particularly efficient work, material handling to and from the system can be automated in combination with a robot.

At EuroBLECH, the system type will be experienced live in action with the following equipment: Four meters bending length, 3,200 kN press force, 69S flagship control from Delem including the new dual screen, 6-axis backgauge with pneumatically movable supports, hydraulic tool clamping and CNCcontrolled crowning from technology leader WILA, angle measuring system iMeasure from ACCURL, laser bending line as well as CNC-controlled bending aids, Lazer Safe safety device IRIS and much more!
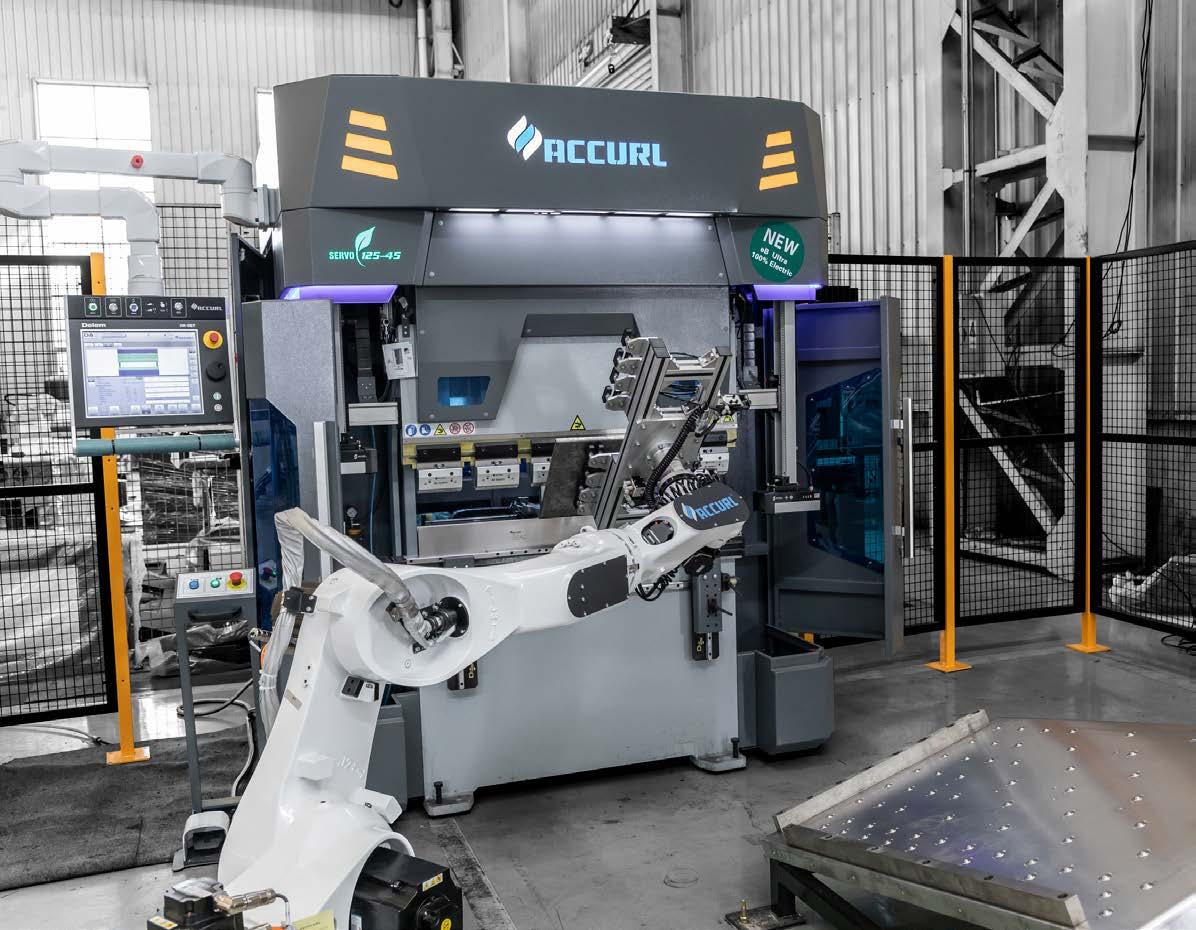
At the EuroBLECH, the homogeneous interaction of an ACCURL robot type ER35B with a press brake with a press force of 450 kN and a bending length of 1,250 mm and many other systems can be experienced.
Bending cell live in use: Robot loads and unloads all-electric press brake
A highlight of automated, dynamic bending technology can also be seen in Hall 13: a fully automated bending cell will be presented. The sheets are guided into position by a robot and precisely shaped by the all-electric press brake of the eB ULTRA series. The robot then picks the bent parts and places them on the designated storage surfaces. "This is a highly efficient system that pays for itself quickly, especially for larger batch sizes," explains Cameron Lee.
The 100 percent electric press brake is highly efficient, extremely precise and works incomparably fast due to its innovative drive system, among other things. The eB ULTRA reduces cycle time and energy consumption to a minimum compared to a system that is operated purely hydraulically and is therefore extremely economical in operation. Even in the basic version, the series has movable support arms as well as pneumatically operated ACCURL Air® quality tool clamps, type PROMECAM. Alternatively, the series can also be equipped with tool clamps and crowning systems from the renowned manufacturer WILA. The dynamic press can be configured with a press force of up to 1,250 kN and a length of up to 3,050 mm.
At the exhibition, the homogeneous interaction of an ACCURL robot type ER35B with a press brake with a press force of 450 kN and a bending length of 1,250 mm and many other systems can be experienced. Among other things, with upper and lower ACCURL tool clamping (the latter allows both WILA and PROMECAM tools to be clamped as well as multiple dies), high-precision ACCURL Ultra wedge crowning, angle measuring system from IRIS Plus from Lazer Safe, two adjustable supports and integrated tool storage.
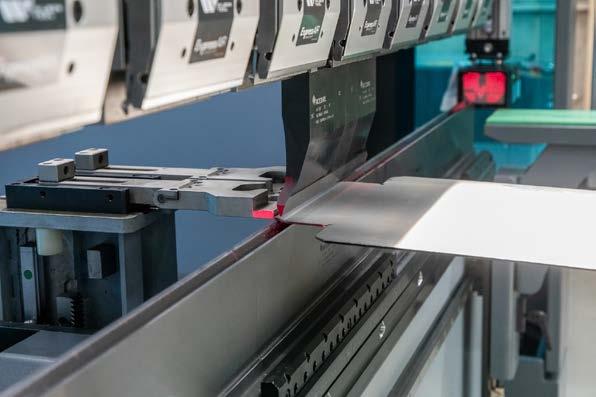
Award Participant: Laser high performer with 60 kW power
At EuroBLECH, ACCURL will present itself with its sales and service partner MicroStep Europa, which is responsible for the Germanspeaking countries and linked by a close research and development partnership. The duo will also be showing something unique in the laser cutting sector at the exhibition: With the high-power version of the MSE SmartFL laser series, the technology partners will be presenting a cutting system in action that is equipped with a 60 kW laser source.
Among other things, the system allows extremely fast processing of very high material thicknesses and was designed with further technology partners such as RAYCUS and BOCHU. Mild steel with a material thickness of 20 mm, for example, can be cut at a speed of up to 11 m/min.
Material thicknesses of up to 200mm can be processed at its peak. This combination of laser system and 60kW laser source, shown live for the first time so far, has been nominated for the EuroBLECH Award 2024 in the field of cutting technology. Innovative products and solutions are awarded.
"In 2024, we will present an excerpt of our enormous technological diversity, which we are bringing to the European market together with ACCURL, to the specialist audience in the exhibition halls in Hanover. Visitors can be sure that we will provide them with cutting-edge technologies that are precisely tailored to their applications. In combination with our digital solutions, we equip customers from a wide range of industries to be able to produce highly productively, reliably and flexibly in the long term," says Johannes Ried, Managing Director of MicroStep Europa GmbH.