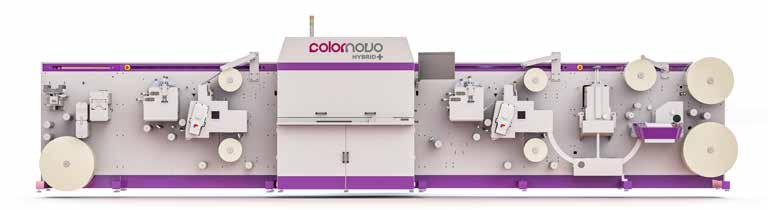
21 minute read
Monotech adds 4 new models
Monotech adds four new models to JETSCI Global brand
Covers the complete range of solutions from entry level to fully configured Hybrid version with the latest launches for Digital Label Printing.
Advertisement
Key Notes :
> A portfolio of brand new presses are developed to fit into every customer’s budget and workflow. > JETSCI KolorSmart+ - an advanced version of KolorSmart, with additional pre-inkjet
Flexo station with standard UV curing to apply primers, under white or spot colours. > JETSCI Colornovo
Hybrid - an enhanced version of the
Colornovo digital label press launched earlier. Building on the success of JETSCI Colornovo and utilising more than a decade’s inkjet expertise, Monotech Systems has launched four new models of Digital Label Presses under its renowned brand JETSCI Global. The portfolio of brand new presses are developed to fit into every customer’s budget and workflow, and also to meet the current and future market opportunities, such as time to market, the rise in substrates, shelf appeal, brand protection and sustainability. Also, they are competitively priced and a basic configured press starts from $2,25,000 without any compromise on configuration and reliability.
JETSCI KolorSmart: This is a 4 or 5 Color, 8.5 inches digital label printing press, very much suitable for the customers who want to start into digital with lower capital and/or utilise their existing converting and finishing facility.
JETSCI KolorSmart+: This is an advanced version of KolorSmart, having additional pre-inkjet Flexo station with standard UV curing to apply primers, under white or spot colours.
JETSCI Colornovo Hybrid: This is enhanced version of the Colornovo digital label press launched earlier and based on GM (Grafisk Maskinfabrik) web control system. The press can be configured with 8.5 or 13 inch, 4 to 6 Colour UV inkjet, with SPOT registered Flexo, Cold foil, and lamination before UV inkjet and all UV curing systems are with Chiller units.
JETSCI Colornovo Hybrid+: This model is suitably configured Digital Label production press having additional finishing and converting features to Colornovo Hybrid, Flexo station with Cold foil after UV
inkjet, Semi & Full Rotary Die-cut, Slitting station and Dual Rewind.
All the models utilise inkjet print head technology from Kyocera providing uncompromised quality and highly flexible UV inkjet printing at 600x 600 dpi resolutions up to 3 or 4 drop grey scale and productivity at up to speeds of 50 m/min,and UV inkjet is configured with switchable Inter Colour pinning after each Colour and provided with advanced Colour management kit for best output in Colour matching, Web Cleaner, and Corona Treater.
Strengthening the product portfolio JETSCI Global has now covered the complete range of Digital Label production solutions, and beauty is that each model is upgradable on field to next or higher model or configuration(s), so customers can start from just basic as per requirements and budget and can upgrade later on field to any other model based on the requirements thus saving them on huge capital re investments.
Jimit Mittal, President, JETSCI Global says, “We came across several potential buyers of digital label printing solutions, who want to quickly start with digital but don’t want to make heavy investment and gradually want to build the workflow around. We are on a mission to provide every Label printer the path to start with Digital printing economically, reliably & with fastest returns and maximum profits. With this launch we are now confident that our offerings from JETSCI Global will suit every label printer’s requirements. Being UV inkjet, it is the most flexible technology in terms of substrates usage, quality and adopting digital at early stage helped our customers grow faster.”
82% of employees expected to return to the office in 12-18 months, Xerox Future of Work Survey reveals
600 IT leaders across the world disclose post-COVID-19 priorities in support of a flexible work environment.
A new global business survey commissioned by Xerox Holdings Corporation shows an estimated 82% of the workforce in respondents’ organizations will have returned to the workplace in 12-18 months’ time, on average. In preparation for a return, companies are investing in new resources to support a hybrid remote / in-office workforce, with 56% increasing technology budgets and 34% planning to speed their digital transformation as a result of COVID-19.
The Xerox Future of Work Survey, conducted by the independent research firm Vanson Bourne, polled 600 IT decision makers including senior C-level professionals, whose organizations have at least 500 employees. Respondents reported challenges caused by the sudden transition to remote work, with 72% citing they were not fully prepared from a technology perspective. In addition to technology (29%), the biggest pain points during the required work from home period were communication breakdown across teams/employees (26%) and maintaining focus (25%).
“While there is no doubt the COVID-19 pandemic has changed the way we work, our research found that over time many companies plan to have most employees back in an office environment. This could be for a variety of reasons, including communication, speed of decision-making and talent development,” said Steve Bandrowczak, Xerox president and chief operations officer. “At the same time, the sudden shutdown and ongoing hybrid work environment has exposed technology gaps that require new or additional investment in the coming months.”
Key survey findings and Xerox takeaways include:
Businesses plan to return most employees to the office, though expanded remote work policies are here to stay. Prior to work from home requirements being imposed, 33% of respondents said network/ data security and privacy was their biggest concern with a remote workforce; 24% cited employee productivity followed by 16% citing technology infrastructure. These concerns, coupled with the belief held by 95% of respondents that in-person communication is important for personal development and assessing talent, indicate widespread remote work will not replace more traditional workspaces.
However, now that businesses are more comfortable with remote work, attitudes and policies of C-suite leaders and IT decision makers are shifting. Furthermore, 58% plan to change their work from home policy within the next year, highlighting the need for companies to support a hybrid workforce.
Our takeaway: Employees may not be going back to the office all at once — or even in the same capacity as before — but the need for organizations to support a hybrid workforce is here for the foreseeable future.
Sudden stay-at-home orders quickly revealed technology gaps. The rapid transition to remote work was difficult for most businesses, with only 28% saying they were fully prepared and 29% citing technology as their biggest pain point. With regards to technology specifically, respondents said their top challenges were remote IT support (35%), inadequate workflow solutions (27%), lack of communications and collaboration tools (22%) and lack of cloud-based solutions (10%). 85% of business leaders also missed the accessibility and ease of use of their office printers.
Our takeaway: To mitigate against future disruptions, such as the rapid transition to remote work resulting from COVID-19, companies will look to invest in

new technologies and seek added capability from existing tools to accelerate their processes digital transformation.
Technology purchasing priorities are shifting to better support employees. As a result of technology gaps uncovered by having a mostly remote workforce, 70% of IT decision makers globally are reevaluating their budget spend, with companies increasing investment in remote technology resources (55%) or a hybrid of remote and in-office resources (40%). The pandemic also has businesses prioritizing investments in cloud-based software (65%), remote IT (63%) support and collaboration software (52%).
Hardware such as laptops and printers were another important consideration.
Our Takeaway: COVID-19 is feeding digital transformation plans and companies are placing a renewed focus on meeting employees’ needs with both hardware and software.
Methodology The survey of 600 respondents located across the world was conducted by independent research firm Vanson Bourne in May 2020. Respondents included IT decision makers (including senior C-level professionals), all from organizations with at least 500 employees across a range of sectors, including business and professional services, retail, health care, financial services, and travel and hospitality.
The IP Journey of Pinyapel: From Creation to Going Global
As part of the global pursuit to save the earth, the packaging industry, the biggest contributor to the plastic economy, is given a tall order: do away with plastics, completely and immediately.
In each passing day, the global plastic pollution problem continues to grow more worrisome notwithstanding the widespread adoption of policies and emergence of a slew of solutions in the aims of at least cutting our current production of 300 million tonnes, as estimated by the United Nations Environment. Failing to stem this production level will only accelerate the pace of climate change, and cause our oceans to be filled with more plastics than fish come 2050, experts have warned.
The task is overwhelming but not impossible. The Design Center of the Philippines fervently believed this when it took on a yearlong research to convert pineapple leaves into a specialty paper for food packaging purposes, a product that gained global attention when it bagged last October the iconic Wood Pencil at the D&AD Impact Awards in recognition of its Pinyapel Project’s potential to have a significant impact on the environment while maintaining product sustainability.
“The ambition of the Pinyapel is to replace the take-out food containers while maximizing the use of agricultural waste to improve the livelihood of farmers. We want Pinyapel to be part of the compost bin that can be used to fertilize the soil, make it richer. So instead of continuing the traditional economic practice of taking out from the earth, we are able to give back to the earth, making as a responsible practice to preserve the earth for future generations,” Design Center Executive Director Rhea O. Matute said.
Public-private partnerships as key As early as at the ideation stage, Design Center had mapped out ways to succeed in commercialization.
The attached agency of the Department of Trade and Industry identified the supply and value chain for the project to ensure that there are ready adaptors of the Pinyapel, as well as the sustainability of its development.
To this end, the Design Center forged a tripartite memorandum of agreement with the CDO Handmade Paper Crafts Co. and Ideatechs Packaging Corp. who were identified as crucial in the materialization of Pinyapel. The agency also partnered with Nature’s Fresh Pineapples, Inc. for the supply of raw materials.
“Pinyapel development seeks to inspire and encourage government agencies and the private sectors to collaborate in order to have commercialization opportunities through adoption of developed processes and products. Partnerships could also pave the way for the implementation of circular design strategies such as choosing inputs, thinking locally, extending product’s life and closing the loop,” Matute said.
Central to the development of the Pinyapel paper is the corrugating machine of Ideatechs Packaging Corp. The machine provided the paper, which has thermoformable property, with heat and pressure to turn it into a usable material.
Amid limited resources, the agency was able to speed up its research and development, and even managed to produce three formulations for Pinyapel, thanks mostly to its partners who allowed Design Center to use their factories and equipment.
Capturing value thru utility models Following the successful experimentation, the specialty paper was ready for the market. But before its full roll out, Design Center signed up its Pinyapel for protection as a utility model.
“Pinyapel was registered as a utility model to protect the process and product generated by the collaborative effort. As a government agency and an Innovation and Technology Support Office partner of the Intellectual Property Office of the Philippines, it is important to register the development not just for protection but more importantly because disclosure of the step-by-step process in our IP document could spark innovation that would inspire anyone with technical know-how to innovate further so the cycle of innovation will be continuous,” Matute added.
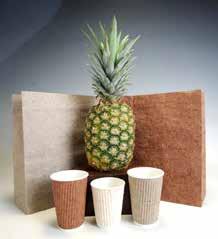
The Pinyapel project, along with the other Wood Pencil awardees, will go through D&AD’s 12-month accelerator program where they are given consultancy, mentoring, masterclasses, development grants, and access to a creative, peer-driven network for a speedier product development.
The Design Center has been part of IPOPHL’s growing ITSO network since 2012, committed to fostering a culture that thrives in design creativity, value creation, and innovation. It has filed at IPOPHL over 230 utility models and industrial designs.
Pinyapel eyes transition to patent “Although protection for a utility model is shorter, it is generally cheaper to obtain and maintain and has less stringent patentability requirements. Utility models provide micro, small, and medium entrepreneurs a low-cost and easy entry point to go global,” Matute said.
Nonetheless, the Design Center envisions further upgrading its product, with hopes of seeing it registered as a patent. This is in line with its strategy of utilizing all possible tools in the IP system. In fact, last November, days after it bagged the Wood Pencil, Design Center filed at the IPOPHL to apply protection for the “pinyapel” word mark.
“Further development is ongoing for Pinyapel and at the same time we will be launching new developments on different materials by next year,” the Matute said.
PackImpressions: The first Virtual Packaging and Printing Expo 2020
Lastmile Solutions announces the two day virtual event –scheduled for July 17th & 18th 2020.
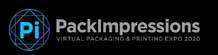
The first virtual PackImpressions for the Packaging and Printing industry will reconnect, re-group and explore the immense opportunities the world has to offer during these testing times of COVID-19. Lastmiles Solutions brings this Virtual Expo, the closest one can get in connecting, showcasing, exploring and creating opportunities to overcome the challenges and grow ones business in the new normal.
The two day event would highlight specific areas such as consumption behaviour, new marketing tools developed, policies, opportunities & growth in the current market and economy.
The PackImpressions virtual conference and knowledge will include panel discussions and knowledge exchange with the best in the industry on topics such as Packaging and Printing Industry in the post-Covid World, Covid-19 & China’s Position as Supply Base to the World, Covid-19’s Impact on CPG & Pharma Industry, The SME Perspective – Opportunities & Challenges, Innovating for Success, Safety in Packaging: The New Demands and the location challenge.
Some of the Panelists/speakers at the PackImpressions expo are as follows:
Ravi Kiran, Ex CEO South East & South Asia, CEO specialist solutions Starcom MediaVest Group, Asia; Satyaki Rastogi, General Manager, SIDBI; Naresh Khanna, Principal consultant at IPP Service, Research and Training PL (lppStar); Oran Sokol, Director and General Manager, Graphics Industrial Business, APAC, Hewlett Packard Inc, Singapore; Vivek Suchanti, Chairman & Managing Director at Concept Communication Limited; Sangam Khanna, Dy.Managing Director, Komori India, New Delhi; Michael Cunningham, Director, Co Founder Connect APAC; K. Ramakrishnan, Managing Director, South Asia – Kantar World Panel; Tim Klappe, Managing Director Asia Pacific, MPS Systems B.V; and Lloyd Mathias Board Adviser and Business Strategist Former APAC Marketing Head, HP Inc and EVP Marketing Pepsico, South Asia.
On the first ever virtual expo, Atul Maheshwari, CEO Lastmile Solutions says, “I am personally quite excited to present this virtual conference cum expo “PackImpressions” for the world’s packaging and print industry. It’s a borderless expo to a borderless world that visitors can explore freely without following routes. Just to give an idea, one will experience unlimited interactive kiosks, in an area equivalent to 10,000 sqm physical area with multiple zones. Most of
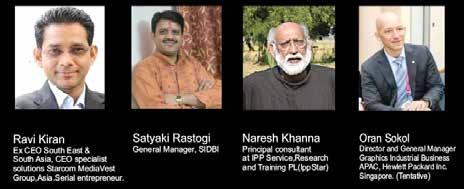
the assets of machine(s), their functioning, specific features and other solutions have been digitized and can be accessed through interactive videos, documents, websites, apps and other interactive devices within the environs of an expo very similar to the traditional one. Since there are no boundaries, visitors enter and explore the talks of experts, futuristic panel discussions and get exposed to innovative solutions from across the world, networking opportunity and experience interactions with other visitors from diverse background.”
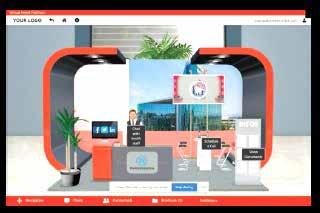
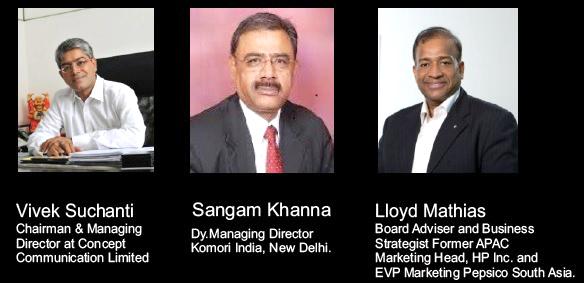

Xeikon Café TV broadcast
Xeikon’s interactive TV platform brings live updates with introduction to Xeikon CX300 digital label press.
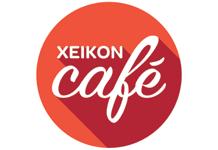
Xeikon broadcasted live on Xeikon Café TV to Australia and New Zealand. The company informed its global audience in the printing industry via its XCTV platform, an online derivative of the renowned Xeikon Café series. The sessions were live, interactive and freely accessible on devices. The dedicated session for Australia and New Zealand took place on June 16 focusing on specific subjects for the label community.
Trevor Crowley, Sales General Manager for the ANZ region adds: “We all know Drupa is postponed to 2021 but that doesn’t mean printers should lack knowledge on what is happening in the label industry and the new novelties. Xeikon is committed to keeping To provide increased service and support to Asia-Pacific customers, MPS Systems Asia hired Kane Marsh as Regional Printing Instructor. An Australian citizen, Kane is very well-versed in the label print industry from working with various printing companies throughout Asia including Indonesia, Singapore, and the Philippines. As Regional Printing Instructor, Kane will provide training on MPS’ narrow web flexo presses and specialized label applications. He will also provide customer tests and demonstrations in the MPS Asia demo center in Malaysia. Kane brings direct print experience on multiple presses in a range of printing technologies including flexo, gravure, offset, screen and a variety of applications. He has a deep understanding of various needs in food & beverage, pharmaceutical, security the printing industry up to date on its latest news and innovations. We believe it is vital that printers and converters have all the information they need right now to continue to make decisions and maintain and drive their businesses forward.”
During the broadcast, Trevor together with his colleagues from Belgium, explained the latest Xeikon views and offer advice on digital label production. There was also video footage of the new Xeikon CX300 in action and the team explained its novelties, benefits and value for Australian label converters. This is the next best thing to a live event with ample opportunity for questions and interaction with the speakers.
Label printers, industry experts and trade journalists got updated on label production with digital presses and the latest on both dry toner and inkjet technology.
Live presentations were made by Trevor Crowley, Sales General Manager ANZ and Filip Weymans, VP Marketing Xeikon based in Antwerp, Belgium printing, hair care, healthcare, tobacco products and other industries. “Throughout my career, I have had the privilege to work with flexible packaging and labels on various substrates and printing machines,” said Marsh. “This will be a great benefit to MPS customers.” “Kane comes with 18 years hands-on printing experience,” added Tim Klappe, Managing Director of MPS Asia. “He has run many different printing presses and supervised print teams in various countries and companies. We believe his in-depth printing and application knowledge of labels and flexible packaging will be a tremendous added value for our team in Asia and for MPS worldwide.” Kane officially joined MPS on June 1st and is based at MPS Asia in Kuala Lumpur,

In addition to broadcasts like the Australia/NZ edition explained above, XCTV will become a permanent communication tool offering a range of time and travel saving options for Xeikon’s current and prospective customers. For example, individualized streaming video demonstrations originating in Xeikon’s Innovation Centres can be arranged as needed, incorporating remote video from
Kane Marsh joins MPS Systems Asia as Regional Printing Instructor
multiple geographies. Malaysia. In the near future, Kane will visit MPS customers throughout Asia Pacific to provide on-site training and share knowledge to help run their presses with maximum productivity workflow and expand into new market segments.
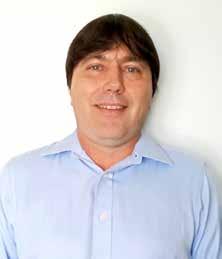
Luxury Box matches whisky’s regal roots
The packaging by Pollard Boxes conveys the luxuriousness and premium nature of the new whisky, ensuring high impact on-shelf and delivering a superior opening experience for the consumer.

A striking presentation box produced by Pollard Boxes is helping to underline the significance of the latest addition to the ‘King of Whisky’ Royal Salute’s permanent range.
The new Treasured Blend is the first 25 year old expression in the Royal Salute portfolio. Created by Master Blender Sandy Hyslop, it has been inspired by the Crown Jewels of England, bringing together precious and powerful whiskies first laid down a quarter of a century ago, and today fit for modern royalty.
The key requirement for the packaging was to convey the luxuriousness and premium nature of the new whisky, ensuring high impact on-shelf and delivering a superior opening experience for the consumer.
The box is manufactured in a book cloth material combined with intricate fine gold foil patterns and text throughout. The special double door design incorporates two highly detailed metallised labels on the front and then opens to reveal a stunning panoramic illustration from Royal Salute collaborator and fine artist Kristjana S. Williams. This depicts the animals of the Royal Menagerie attending a coronation celebration surrounded by the precious Royal Regalia at the Tower of London. The open weaves in the book cloth required complete attention to detail during the foiling process by Pollards’ expert in-house team. A similarly high level of technical skill was required in the production of the five-door design, combining traditional production methods with the latest automated equipment.
The box also incorporates Pollard’s unique FOTL (Front Opening, Top Loading) technology. This provides a faster and more efficient packing process by allowing the bottle to be placed into the box while remaining in a case of six for onward delivery. The lid is then locked into place, enabling the box to be opened from the front for effective display on the retail shelf. Vacuum formings in the lid and base hold the bottle firmly in place throughout the distribution chain.
“The 25 Year Old Treasured Blend continues Royal Salute’s legacy of distinction for elegantly crafted Scotch whisky,” commented Richard Neil, Project Manager, Chivas Brothers.
“The presentation box delivers exactly the exceptional quality of appearance and finish required to reflect the premium nature of the whisky to our global consumers.”
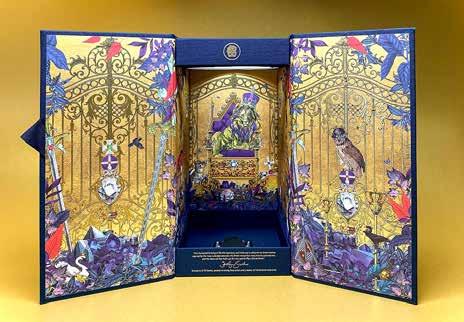
Royal Salute was first created as a gift for the coronation of Queen Elizabeth II in 1953 and has since been the official partner of all ceremonial royal gun salutes fired at the Tower of London.
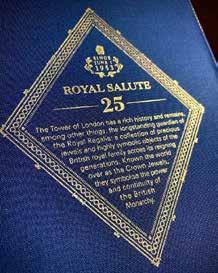
- extends capacity aiming longer runs of high quality films, such as wrap-around labels and shrink sleeves.
Birografika MB in Serbia purchased and installed their first MPS flexo press, an 8-colour EFS 430 multi-substrate press. The deal was signed at Labelexpo Europe 2019.
The newly installed MPS EFS 430 flexo press was chosen as an extension of Birografika’s current capacity, with a primary purpose for longer runs of high quality films, such as wrap-around labels and shrink sleeves. The printer is located in Subotica, Serbia.
Founded in 1920 as Birografika Subotica, the printing house transformed into Birografika MB in 2006 as a trading company to successfully secure the well-known brand and employees, which led to their success as a leading printer today.
The company’s main activity is the production of printed materials (flexible packaging and labels) with comprehensive services and equipment in flexo, digital and I have been in touch with Mr. PV Narayanan (Former Director, IIP & Chairman of SIES School of Packaging) for more than two decades now and to hear that Covid has taken its toll on one of my closest associates offset printing. Birografika takes pride in supplying large print orders, customization to meet customer needs, and boasts a number of reputable references in all sectors.
The sale was led by Aleksandar Borisavljevic, MPS representative in the region, and Sebastiaan Rakhorst, MPS Area Sales Manager. Milan Nikoletic, General Manager
As I knew him - RIP PVN ‘Saar’!
of Birografika said: “We chose MPS because leaves a painful mark, deep down in my heart.
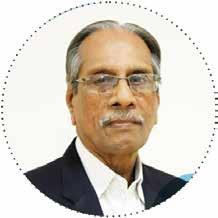
PVN ‘Saar’, as I personally used to call him, was the first editor of a packaging magazine titled ‘PLC - Packaging Labeling & Converting’ that we published under the PRESSIdeas umbrella for a few years way back in 2009. In fact, it was PVN saar who suggested us to address this particular segment of the industry through the magazine while he was working with SIES School of Packaging. He had an uncanny ability to reach to people in a deep and positive way. I remember him being closely working with the India Label Show, before it was taken over and renamed as Label Expo India by Tarsus. He was of the opinion that ‘knowledge disseminated’ is what remains
MPS EFS 430 press installed at Birografika MB

of their reputation of high quality machines and great productivity. Time is money, and service must leave an impression. These are two things we always keep in mind; MPS is the supplier that fits this vision perfectly.”
The deal between Birografika and MPS was signed at Labelexpo Europe 2019, marking one of the twelve presses sold by MPS at the show.
and so did he – live by his words and spent his entire life educating and mentoring! Students and their communities were of great importance for him and wanted corporates to generously contribute to the education system; as he passionately put up an award from PRESSIdeas at the SIES School of packaging.
An excellent speaker and eloquent personality, PVN Saar will remain close to my heart till I live. 79 years well spent sir, Salute. – (Jacob George, PRESSIdeas)