
28 minute read
Heidelberg 9999th Print Unit
Heidelberg Shanghai reaches 9999th Printing Unit milestone
Heidelberg Shanghai production site successfully established in growth market of China in a remarkable fifteen years’ time.
Advertisement
Key Notes :
> Marking fifteen years in China, the 9,999th printing unit is set to be delivered to packaging printing company Xian Jun
Long. > Growth segment of packaging printing – expansion of the portfolio with special machine configurations. > Market share in China at over 50 percent – further expansion of the site planned. On 22nd June 2020, Heidelberg’s China plant in Yunguan Qingpu presented it’s an all new CD 102 - 9+L, it’s 9999th printing unit from the plant. It is from this very plant that Heidelberg has sent printing machines to over 43 countries regions around the world.
Amongst Chinese printers, the CD 102, is affectionately referred to as the “all-rounder” because of its sturdy built and flexibility, stable printing prowess, and high automation. Since its emergence at the Drupa in 1986, it has been a favoured machine for packaging printers across the world.
It was in September 2009 that the first Speedmaster CD 102 four-colour machine rolled out from Heidelberg’s Qingpu factory. Since then, Speedmaster CD 102 has firmly taken root in the Qingpu factory. With the continuous enrichment of the product line, Qingpu Speedmaster CD 102-5, 5+L, 6+L, 7+L were successively launched in the next few years. At the Print China 2019 exhibition in Dongguan, the Speedmaster CD 102-8+L model produced in Qingpu was on show. Today, the Qingpu facility has become the largest 102 format production base in the world.
Speaking remotely from Germany, Rainer Hundsdörfer, CEO of Heidelberger Printing Machinery Co., Ltd. said “Starting from 0 to 9999, 10000, Qingpu factory in just fifteen years… and it’s ‘a miracle’.” “The historic breakthrough should be congratulated, not only to boost and inspire morale, but also to highlight the importance of partnership and the Chinese market,” he added.
Timeline
2005 Construction of the first hall for the factory in China 2006 Start of production in Qingpu near Shanghai on an area of 15,000 m2, including almost 4,000 m2 for production Stahlfolder folding machines and Speedmaster SM 52 2007 Speedmaster SM 74 2009 Speedmaster CD 102 2010 Construction of the second hall 2011 Expansion of the area to 100,000 m2, including 45,000 m2 for production 2013 Delivery of the 1,000th printing press 2015 Opening of the Print Media Center Shanghai Speedmaster CS 92 2018 Speedmaster SX 74 are completely manufactured in Shanghai 2019 Switch from standard models for specially configured models 2020 Production of Speedmaster SX 74, CS 92 and CD 102 Over 10,000 printing units or close to 2,400 machines delivered to 43 countries Around 430 employees
The Speedmaster CD 102-9+L with the No. 9,999 printing unit from Heidelberg Shanghai factory with the special design featuring a painting of the Great Wall.

In his address to the gathering, Rainer mentioned that China is the single largest market for Heidelberg. Interestingly, he also added that although the Corona pandemic is unexpected, from the perspective of sales in the first half of the year, it still exceeds the level of the same period of the previous year. “The sales and production team in the Chinese market will be increased to 1,000 from the present strength,” announced Rainer.
In a festive ceremony at the production site Heidelberg Graphic Equipment Shanghai (HGES), the packaging printing company Xian Jun Long was presented with a certificate recognizing the manufacture of the 9,999th printing unit in China. In a greeting sent via video link, Rainer paid tribute to the high level of commitment and successful engagement in China. “Our factory in Shanghai has proven a real success story for Heidelberg in our core business and for our customers. China is the largest individual market for us, and we want to continue to expand our market share of over 50 percent as well as our technological leadership in what is an important market for us by continuing our program of investment.”
Packaging printing company Xian Jun Long’s success with Heidelberg machines The printing company Xian Jun Long in Shenzhen is set to take delivery of a Speedmaster CD 102-9+L featuring the 9,999th printing unit. As a special design feature, a picture of the Great Wall has been painted on all the printing units to tie in with the wall’s historical length of 10,000 li. Xian Jun Long is one of the leading packaging printing companies in China, specializing in packagings for spirits, cigarettes, and luxury goods. The partnership between Xian Jun Long and Heidelberg goes back twenty years – and the Speedmaster CD 102 with the 9999th printing unit from the Shanghai plant is also in production there. “We already have the first Speedmaster CD 102-8+L from the Heidelberg Shanghai plant and look forward to the new Speedmaster CD 102-9+L in the usual Heidelberg quality due

to be installed here in the near future. We will have another two sets of Speedmaster CD 102-8+L presses delivered to China Xian Jun Long Printing Group in August this year. Our goal is to grow successfully and to offer our customers products with more added value,” explained Kelvin Chong, Information Engineering Director of China Xian Jun Long Printing Group. The anniversary press is in operation as part of an extensive fleet of Speedmaster CD 102 and Speedmaster CX 102 systems.
Growth market China Packaging printing in China is growing with greater speed and sustainability than globally. The Speedmaster CD 102 has long been a bestseller in the Chinese market – it is highly versatile, whether for long or short runs, thin substrates or cardboard with thicknesses of up to a millimeter – the press offers outstanding productivity, quality, and value retention, and thus a high degree of investment security for customers. “The market in Asia is evolving, and we are seeing strong demand for customer-specific machines and a wealth of variants, especially for packaging printing,” explained Achim Mergenthaler, manager of the Heidelberg site in Shanghai. “We are proud of our high quality, which – thanks to the high standards of the Heidelberg production network – is equal to that of the machines from the production facility in Wiesloch-Walldorf.”
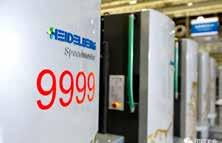
Heidelberg intends to further accelerate the expansion of its production in China. Over 30 percent of all printing units are already built in China. The Shanghai production site will further increase the manufacture of standard models for the Chinese and Asian market and add special machine configurations, especially in packaging printing, to the portfolio. This will result in a competitive offering, particularly for the up-and-coming printing companies in China, which need the best machines in terms of productivity and quality and offer comprehensive solutions.
Heidelberg is therefore the only printing press manufacturer with the flexibility to offers its customers both locally manufactured machines as well as high-end machines from Germany.
“With the extended portfolio and higher production capacity in the Shanghai plant, we have reached a new milestone for Heidelberg China in further expanding our solutions for packaging printing,” explained Benny Huang, CEO of Heidelberg Greater China at the festive presentation ceremony. “We have been producing the Speedmaster CD 102 in the Shanghai plant since 2009. It is a classic sheet-fed printing press for packaging, label, and commercial printing companies featuring increasingly innovative and optimized technologies that is widely accepted by and popular with Chinese users.”

Over 10,000 printing units have now been delivered over fifteen years from the Heidelberg Shanghai production site.
Heidelberg Shanghai: a success story The Shanghai production site has a workforce of around 430 people. Printing presses in 50 x 70 cm and 70 x 100 cm formats are produced there, mainly intended for sale in China, but also for other Asian markets and the rest of the world. Over 10,000 printing units have now been delivered over fifteen years.
The site in the industrial zone of Qingpu near Shanghai commenced operation in 2006, is built to modern standards, and now encompasses a production area of around 45,000 square meters, making it one of the biggest printing press factories in Asia based on square footage.
On-site customer events The Print Media Center Shanghai is integrated into the Heidelberg Shanghai plant and serves as a central showroom for China, other Asian Pacific markets and neighboring regions. Here, state-of-the-art technology and service solutions are presented, information events are held, and intensive tests and analyses of equipment, consumables, and workflow solutions are carried out. Customer operators are also trained here. The Print Media Center Shanghai has fully integrated workflows for commercial and packaging printers.

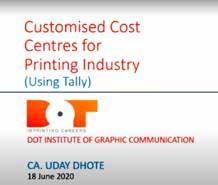
DOT Institute of Graphic Communication (DIGC), disseminating knowledge through Virtual Education, conducted three Webinars in the previous few weeks. Now shifting its focus towards an oft ignored but very criticial component of business viz., Cost Centres, DIGC conducted a Web Class on 18th June.
Cost Centres is one component of business which plays an extremely crucial role in controlling the costs. The good old Tally is capable of giving this vital MIS and one can start with this before investing in costly ERP. But there is a lack of awareness about this feature of Tally whereas, if used judiciously it provides amazing results. Another advantage is that a majority of accountants in organizations are usually familiar with Tally for their daily accounting needs, which means they need not learn anything afresh.
With an emphasis now on ‘controlling the controllable’, the ‘Cost-Centre’ feature in Tally ERP, if used sensibly, would give an edge to the organisations. It will help in identifying department/ activities which are not contributing to the bottom line while at the same time, the voucher entries relating to Cost Centres can be done simultaneously while doing an Accounting Entry and at the same time create meaningful dashboards for the management.
DOT Institute of Graphic Communication (DIGC) under the expert guidance of CA Uday Dhote, conducted this one of a kind ‘Web Class’ on ‘Creating Customised Cost Centres for Printing Industry (Using Tally)’ on 18th June, 2020. With an interactive and hands-on approach, participants were taken through the creation of Cost Centres along with live working in Tally & Excel. The audience was also taught about apportionment of overhead costs and the review & analysis of the reports of Cost Centres from Tally. The participants were a mix of business owners, accounts & finance professionals from locations like Mumbai, Thane, Pune, Ahmednagar, Jaipur, Delhi, Kottayam, Kanpur, Ahmedabad, Hyderabad and other parts of the country. The ‘Josh’ of the participants was also kept high by regular polls interspersed in between the programme which threw some very interesting results. A post event kit of templates related to the subject was also shared with the participants along with DIGC’s trademark commitment of after session support to participants.
“It was a nice Webinar on a topic to which I was seeking solutions since last 2 decades and many CAs and Cost Accountants were not able to provide solutions. It gave a scientific methodology to analyse data on Tally. I have heard and listened to Mr. Uday Dhote in many seminars earlier and liked his presentation. I would recommend Print Associations to organise trainings on topics funds from banks All India Plastics Manufacturers Association (AIPMA) has sought details of units who are facing difficulties in obtaining funds from banks. The Association has asked for details for their reference and further discussion with the Ministry of MSME, Ministry of Finance and Department of Chemicals and Petrochemicals. “In our meetings with various Ministries in Government of India, a point that was raised by many members has been regarding slow pace of liquidity flow to companies from the banking sector. Given the situation at hand and the need for funds by the industry members to restart operations and sustain the same over the coming months, Government is willing to look at more measures that can be taken to improve the comfort level of manufacturing industries
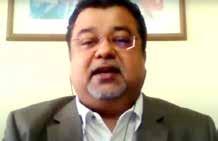
by DIGC.” - Mr. Nirmal Goyal (President, Popular Printers Secretary, ROPA, Jaipur)
“The feedback of the session given by my team was very good. It covered high value and an extremely important subject. I liked it.” Mr. Fred Poonawala (Comart Lithographers)
Similar sentiments were shared by Mr. Urvesh Umrigar, Urmegh Printers; Mr. Balakrishna Rai, Shree Pack Containers; Mrs. Kanchan Desai, Manish Printers; Mr. Biren Shah, Arun Bros; and Mr. Vibhakar Vaidya, Spectrum
AIPMA has asked details of units facing difficulties latest by 11th June.
Offset. and to enable banks to lend expeditiously,” AIPMA said in a statement.
The above information sought is only to apprise Government of the ground level difficulties faced by industry members. Interest people can send the information latest by 11th June 2020,” said Deepak Ballani, Director General, AIPMA.

Bareilly based Vardhan Printing Press installs Enthrone 429
This is the first brand new Komori Enthrone 4 colour 29 inches Printing Press for Vardhan.
37 years ago, Vardhan Printing Press began its journey in Bareilly, Uttarpradesh. Mr. Manoj, owner, Vardhan Printing Press, decided to invest in the Komori to boost his brand value and increase new business. Though the machine was ordered before the present ‘corona crisis’, it couldn’t be installed due to lockdown announced by the authorities. As soon as the lockdown conditions eased, Komori India service team got the things up and running with quick installation of the Enthrone 429 at Vardhan.
“Amid these challenging times Komori India service team has put forward their resiliency and dedication for the customer, and presented Kando Service or customer first approach,” remarks Mr.Manoj.
“The reason to invest in the new Komori Enthrone Press is continuous technological upgrades, sustaining progress and deliver quality jobs, and we are hopeful that once business opens we will be back on track,” he adds. The 72nd Annual General Meeting of DIC India was conducted through Video Conferencing / Other Audio Visual Means on Friday, June 12, 2020. The Chairman Mr. Dipak Kumar Banerjee took the chair and conducted the proceedings of the Meeting. The Chairman addressed the shareholders and spoke about financial performance of the Company, current economic situations and its impact. The Chairman thereafter declared the copies of the audited financial statements for the year ended December 31, 2019, Board’s and Auditor’s report had been emailed to the members and that the original documents along with the Statutory Registers were available for inspection electronically. The Chairman further informed the shareholders that e-voting facility has been provided to all members to vote electronically and the same was available during the meeting as well. New Enthrone accommodates sheet thicknesses of 0.04 mm to 0.6 mm. In addition, the press dramatically shortens the time required for changeover between light and heavy stocks, thanks to the elimination of transfer cylinder gripper pad adjustment step. The Enthrone is truly a futuristic press that enables working efficiencies resulting in

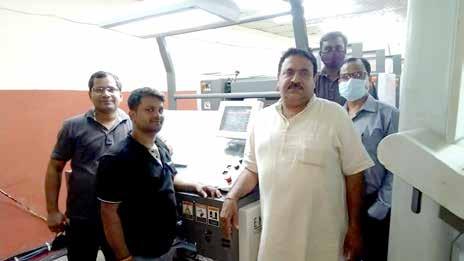
DIC conducts AGM through Video Conferencing
higher margins and business growth.
raised by the members.
The company declared dividend and appointed new Director in place of Mr. Masahiro Kikuchi who retires by rotation. Mr. Partha Mitra was re-appointment as an Independent Director of the Company for a term of three years.
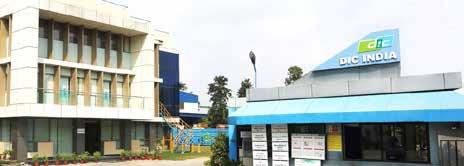
company to do a virtual AGM in India,” said Mr. Manish Bhatia, MD and CEO, DIC India. “The pandemic (COVID-19) has brought a lot of new learning and experiences and this was also new – for me; for directors and a lot of share holders. It was great to see active share holders with lot of constructive Q&A and also the cross section of share holders coming from across India. Kudos to NSDL for putting a very effective system in place,” he added.
Rajendra Kumar Anayath awarded Honorary Colonel rank in NCC
Government of India has conferred the rank of Honorary Colonel upon Dr. Rajendra Kumar Anayath, Vice Chancellor of Deenbandhu Chhotu Ram University of Scinece & Technology, Murthal. Professor (Dr.) Anayath has been appointed as Colonel Commandant in the National Cadet Corps (NCC) for the duration of his office as the VC of DCRUST.
Lt. Gen Rajeev Chopra, PVSM, AVSM, Director General NCC & Col. of The Madras Regiment, in a letter to Prof. Rajendra, conveyed the Government of India’s decision regarding the honour. “In the Armed Forces, the ‘Colonel Commandant’ is an honour conferred upon distinguished and very senior officers,” says Lt. Gen Rajeev. “We in the NCC are proud of your association with us. We look forward to your patronage and Payment of wages during lockdown has been a contentious issue especially since the order passed by the Ministry of Home Affairs under Disaster Management Act 2005 dated March 29, 2020. This order had been challenged in the Supreme Court by a number of organizations since there has been confusion regarding the responsibility of employers to pay wages of their employees during lockdown period. Though the interim order of June 04, 2020 spelt that no coercive action be taken against employers there was still a dilemma of how to pay the wages. The Supreme Court has passed an interim order on June 12, 2020 suggesting certain guidelines for resolution of this issue. However there are still many doubts regarding the order and its implementation. To decode this, DOT Institute of Graphic Communication (DIGC) has invited Advocate purposeful association for the furtherance of NCC activities. I trust that this appointment will bring you in closer contact with the NCC units in your university and enable you to interact with our officers and cadets to help and guide them to uphold the ideals of the NCC.”
“I seek your help in motivating dynamic and dedicated teachers to volunteer for selection as Associate NCC Officers, as well as in the selection of good cadets for the various NCC Units and activities,” he further states.

Prof. Rajendra Kumar Anayath will be entitled to avail the privilege of wearing the uniform and badges of rank, in keeping with the traditions of the Armed Forces during NCC
Webinar on ‘Decoding Payment of Wages during Lockdown w.r.t Supreme Court Interim Order’
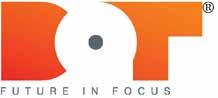
events and visits to the Corps’ Units.
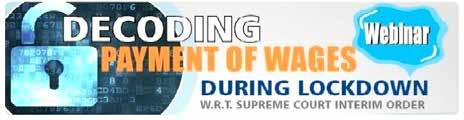
Mahesh Shukla, an expert in Labour Laws and Advisor to important government institutions and companies for a discussion to unravel the nuances of the order.
The webinar took place on June 24, 2020 between 4:30 - 6:00 pm. The event was moderated by CA Uday Dhote, Director - DOT Institute of Graphic Communication, Past President - MMS, Chairman - Education & Training - AIFMP and a print veteran.
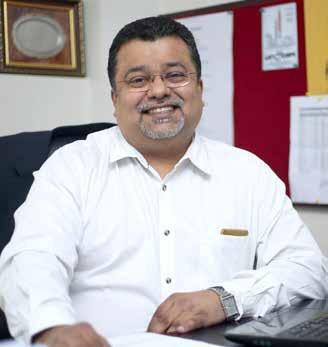

The Departments of Printing Technology in School of Engineering in Avinashilingam Institute for Home Science & Higher Education for Women, Coimbatore and PVG’s College of Engineering and Technology, Pune, have jointly organized a 5-Day online Faculty Development Program on “Online tools and techniques for Printing and Packaging” from June 22nd to 26th 2020, exclusively for the faculties of printing institutes.
With the objective to train Printing faculty and fraternity in online tools and techniques for teaching-learning process, the FDP provided the participants an opportunity of incremental learning each day. Each session had one academician and one industry person as speakers. Participants were given online assignments, the completion of which, makes the participants eligible for the FDP certificate. The entire FDP took place on the G-suite Google meet.
There were 91 registrations by faculty members in printing and packaging specialisation, from 10 Engineering Institutions, 16 Polytechnic Colleges, 2 B.Voc Institutes, 1 National skill trainer, 4 International Institutions outside India, 1 Vocational Hr. Sec School, and 4 Industry trainers. The participants were Heads of Departments, Professors, Associate Professors, Assistant Professors, Technical Assistants, School teacher and Industry Trainer.
The faculty members on the organising
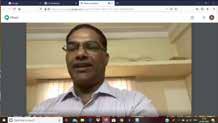
committee were the primary speakers of the FDP. An industry/media person would speak from industry perspective in each session, bridging the gap between industry and academia.
Two webinars were scheduled each day. The inaugural address was rendered by the senior management officials and senior administrators of the two Institutions.
Three well-known personalities in the printing fraternity, associated with printing education, rendered the special address: (i) Dr. Rajendra Kumar Anayath, Vice-Chancellor, DCRUST University, Haryana, (ii) Prof Kamal Chopra, Honorary Professor of many Printing Institutes, India and Abroad and (iii) Mr. Dayakar Reddy, Founder President, GIPT, Secunderabad alumni association.
Key Sessions: Day 1 – Choosing the technology, LMS or Open Web (i) Open Web platform – AGP Case Study (ii) Learning Management System (LMS) –
Google Classroom Day 2 – Teaching styles and habits needed to teach online (i) Online Teaching-Learning: Stakeholders Views – Results of a Survey (Speaker: Mr.K.Panthalaselvan, MD, Idealliance South Asia) (ii) Teaching styles and habits needed to teach online Day 2 – Problems encountered in using ICT and Making ICT work (i) Online Teaching-Learning: Stakeholders

Views – Results of a Survey (ii) Challenges in using ICT for teaching (iii) Making ICT Work Day 3 – Evaluation and Assessment in Online classes (i) Autoprint Experiences in Evaluation and Assessment (Speaker: Mr.C.N.Ashok, Autoprint Machinery Manufacturers)
Mr.C.N.Ashok shared his views on the evaluation of a candidate in service after regular interval. He explained and stressed upon criteria which should be followed for evaluation of the employee. “Employees performance on all fronts is what will help to flourish or perish”, was an important message given by him to the participants. Mr. Ashok mentioned that the evaluation of operational level employees can be done on parameters such as: Passion for Quality, Cost Prudence, Communication Skill, Customer Centric, Team Player, Taking Ownership, Willingness to Learn and Develop, etc. He added that, it is important to evaluate middle level management on the basis of the ways by getting things done and process driven problem solving. The top-level management should also be evaluated on the strategic thinking, innovation and influencing the systems. (ii) Evaluation and Assessment in Online classes Day 3 – Panel Discussion: “Tools for Planning Research &Publishing of Research Papers” Day 4 – Open Educational Resources (OER) (i) Open Educational Resources (OER) – What and Why

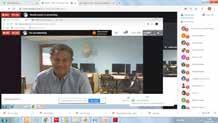

(Speaker: Mr.Jacob George, Director Pressideas Publishing) (ii) Finding, Using and Creating OERs Day 4 – Multimedia content creation and posting online (i) Creating Multimedia Content (ii) Posting Multimedia Content Day 5 – Effective use of Online resources for Labs (i) Blogging for knowledge sharing – A Sr. Label Printers Experience (Speaker: Mr. Harveer Sahni, Chairman Weldon Celloplast) (ii) Performing Practicals with V-Labs Day 5 – Panel Discussion on “Industry opinion about online Internships & Projects” Prof. Kamal Mohan Chopra, Managing Director, Foil Printers and former President of All India Federation of Master Printers has been nominated as member of the Court of Deenbandhu Chhotu Ram University of Science & Technology by the Hon’ble Governor of Haryana and Chancellor of the University. The nomination is for a term of two years and effective immediately. Court is the highest body for planning of administrative and financial activities of any university. Offset Printers Association organized a series of Webinars during the time of lockdown in the country to help out printers. Prof. Kamal Chopra, General Secretary of OPA and the former President of AIFMP, hosted the Webinars on behalf of OPA. “OPA organized 27 Webinars and 7 WebMeetings besides the regular executive and GB meetings,” says Kamal Chopra. “106 expert panelists were invited to present their views. OPA Webinars were attended by 5958 printers out of these 3270 were the first time attendees. Perhaps OPA is the only association to be able to serve the printers to this extent. The Webinars dealt with diverse topics including: printing industry after COVID-19; current scenario & scope for growth of Indian printing industry; how to be ready for Concluding Session The conveners initiated a group photo session, during which all participants turned on their videos and took screen shots. Chopra said, “It is great honour, moreover, recognition of your work and efforts always encourage for going an extra mile. I always pay my full attention to all the given responsibilities. I always try to put new things on the table and which give energy and fresh air to the body.” Kamal Chopra has been the former President of AIFMP – All India Federation of Master Printers, the largest body of printers in the overseas printing jobs; role of association during crisis; leadership challenges during and after lockdown; women entrepreneurs and post lockdown challenges; digital will grow more due to COVID-19; lockdown –
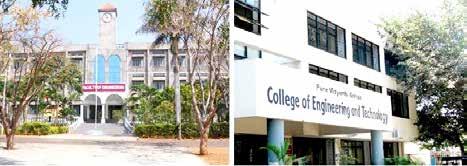
There were moments of sharing gratitude and the FDP ended with positive reviews from the participants who wished more such
Kamal Chopra nominated at the Court of DCRUST
Prof. Chopra gets nominated by Haryana Governor and Chancellor of the Deenbandhu Chhotu Ram University of Science & Technology, Murthal.
event happen in the near future.
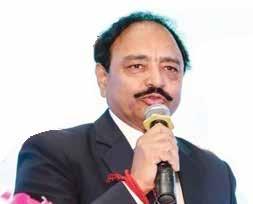
world. He has a rich experience industry experience and has been at the forefront while taking forward industry issues with the authorities as well as creating networking
OPA makes the best of lockdown with a series of Webinars
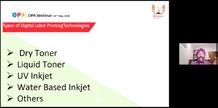

opportunities among the printing community.
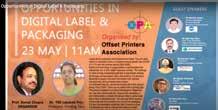
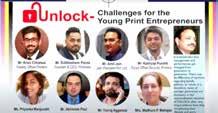
care of plant, machinery & material and many more.
The Print Show postponed to September 2021
Organisers of The Print Show have confirmed that the event will be postponed until 2021, due to the ongoing novel coronavirus (Covid-19) situation in the UK. The Print Show, and new sister event The Sign Show, had been due to run from September 27th to 29th at the NEC in Birmingham, with a number of leading brands having already committed to the show. The two events will now run from September 28th to 30th next year at the NEC.
Event director Chris Davies says that while every effort had been made to go ahead with the event, it has become clear in recent weeks that restrictions caused by Covid-19 mean that hosting the show this year would not be possible.
“Before anything else, the health and safety of our exhibitors and guests is our number one concern, and while it was a difficult decision, we believe this is the right course of action,” Davies says.
“While we hope the situation with Covid-19 will have improved by September, there is no guarantee that the event would be permitted to go ahead due to the current government restrictions.
“The government is yet to make any announcements as to when large gatherings or events can take place again, and we have to be realistic. Planning to host a large-scale event like The Print Show this year is just not feasible, given the level of uncertainty as to what situation the UK will be in come September.
“Therefore, we have decided that the best course of action would be to postpone both The Print Show and sister event The Sign Show until next year, when we hope the worst of the crisis will have subsided.”
Davies also revealed that The Print Show has reached an agreement with many of the companies that had already signed up to attend in 2020 to instead exhibit at the rearranged event next year.
“We’re finalising the details with our exhibitors and we’ll be making a number of announcements in the coming weeks and months, but it is fantastic to see this level of confidence in the show,” Davies says.
“I’ve been touched by the amount of support our exhibitors have offered and I will be delighted to welcome them to the rearranged edition of The Print Show next year. We remain fully committed to delivering a quality event that solely focuses on the UK printing industry. The Print Show is the only event dedicated to the UK market and as we emerge from lockdown and build for a brighter future, we believe our event will play a key role in this recovery process.”
The Print Show every year directly attracts the very biggest print and finishing technology manufacturers from across the UK commercial print supply chain. These companies use the show to launch brand new products that can be seen for the very first time in the UK, if not the world.
Run by the same team behind key industry titles Print Monthly and SignLink and their parent company Link Publishing, the creativity and drive behind The Print Show draws on more than 50 years of collective experience of the print industry.
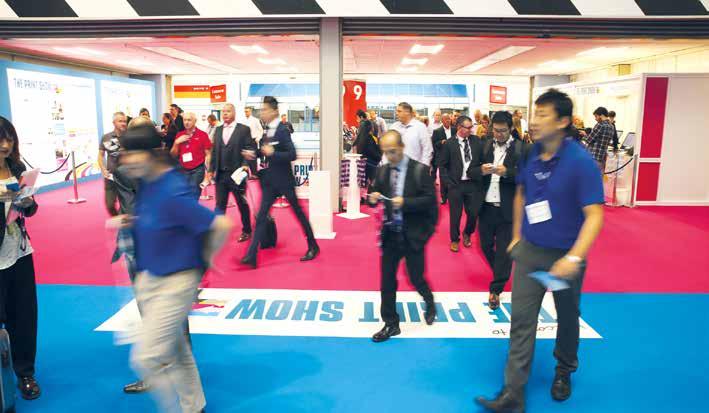
ASPA & GS1 India sign MoU
- to strengthen Anti-Counterfeiting Eco-Systems using Global Standards.
Realising the magnitude of damage caused by counterfeiting to the Indian economy, brands and consumers, Authentication Solutions Providers’ Association (ASPA) and GS1 India have joined hands to take the fight against counterfeiting to the next level in India, using global standards.
ASPA (Authentication Solutions Providers’ Association) is a self-regulated non-profit organization that represents the entire physical and digital authentication solutions industry. GS1 India, a standards body, is responsible for administering the use of global supply chain standards in India that enable businesses to implement counterfeit detection and product authentication solutions to safeguard their supply chains.
The two organisations have signed an MoU to jointly work towards mainstreaming and nurturing the anti-counterfeiting ecosystem by promoting the use of standards based solutions for the betterment of industry and consumers, at large.
Counterfeit products across various sectors in India are causing losses of over INR 1 trillion every year to the government and the number of counterfeit cases has increased by nearly 24 percent in 2019 as compared to 2018. This causes business to lose brand equity and revenues, besides putting consumer safety at risk.
According to ASPA Counterfeit Repository findings Alcohol, FMCG, Pharma, Tobacco, Agriculture and Automotive are among the top sectors with the highest number of counterfeits in 2018 and 2019. During the COVID 19 pandemic period (between January to March 2020), more than 150+
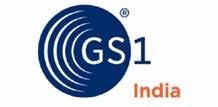
cases of counterfeit incidents had been reported in the media. In March & April 2020, more than one case per day was reported related to fake PPE’s kits, sanitizers and masks.
Jointly, the organisations will be sensitising stakeholders in this respect and will spread awareness and motivate brands and customers to use ‘Smart Consumer’ – an app launched to empower consumers with digital product information and is powered by the national repository of information on retailed products – DataKart, that is populated directly by brand owners.
Speaking about the partnership Mr. Nakul Pasricha, President, Authentication Solution Providers’ Association (ASPA) said, “We are committed to build the authentication eco-systems in the country and enhance our relationship with other bodies working in the same space. The authentication environment will support Government “make in India” initiative and its image at global level, where trust is becoming an especially important factor. We need to ensure that the “Make in India” products are genuine, safe, and secure until they are delivered to the end consumer across the globe. Involvement and active participation of all stakeholders is extremely crucial in this, as a lot of awareness is required at industry, consumer, and government level.
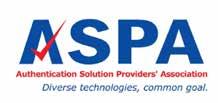
We are sure that by combining resources of GS1 India and ASPA, we will add more momentum to our endeavours in fighting the menace of counterfeiting and develop the anti-counterfeiting ecosystem.”
Sharing his views, Mr. S Swaminathan, COO, GS1 India said, “At GS1 India, we are constantly working towards overcoming the blocks in the global supply chain that prevent visibility and transparency. With this partnership with ASPA, we aim to further strengthen our endeavour to address the ever growing threats presented by counterfeit products in existing supply chains. The use of GS1 standards and solutions like traceability, Smart Consumer app, DataKart, etc., will help Indian businesses gain trust of their consumers and trading partners by seamless sharing of product information. This would also act as a foundational step in our journey and empower consumers to authenticate products using the Smart Consumer mobile app.
Together ASPA and GS1 India will jointly work together to create awareness about the counterfeiting problems and build knowledge through various tools, including trainings, publishing of articles, enriching websites, etc., to drive adoption of global standards for detecting and controlling counterfeits.
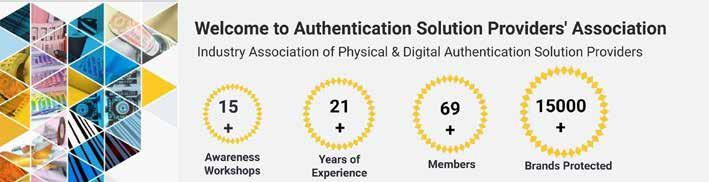