
3 minute read
Tribotech develops a polymer roller that lasts longer than steel
Max Otis, Director of roller manufacturer Tribotech, tells ABHR how and why the company developed a plastic roller that can outlast steel.
WHEN MAX OTIS BEGAN
researching the Australian mining industry in 2014, he was somewhat disappointed. According to him, many rollers were still being made and used the old-fashioned way, and innovation wasn’t up to standard at the time.
This was one of the driving forces behind the creation of Tribotech. The company is named after tribology, the science of interacting surfaces in relative motion, and focuses on developing innovative conveyor roller designs.
Otis says one of the main innovations the industry had welcomed was moving from steel to plastic rollers.
“This has been under way for the past 40 years or so, but the rollers haven’t changed much since then,” he says.
“The type of plastic used is often either polyvinyl chloride (PVC) or highdensity polyethylene (HDPE), which are quite economical materials. They’ve been used heavily in the plumbing industry for the same reason.
“We wanted to bring the engineering to a higher standard and use materials that were more exotic to find a better fit for the heavy-duty mining industry.”
Tribotech began trialling several different materials to build the rollers. They were looking for one that provided optimal wear resistance, in addition to catering for maximum loads and ultimately a longer lifespan. In doing this, the company’s engineers investigated alternative industries, such as the aeronautics sector, to find a material that would make a viable roller.
After heavy research and development, Tribotech chose a particular polymer – and so Weartech was born.
Otis says Tribotech originally tested the Weartech rollers to be suitable for the iron ore industry, which experiences the most problems with rollers. He details the initial methodology that was undertaken to combat the main challenges present in this area.
“Iron ore is extremely abrasive. It has a higher density than other materials and is typically carried at a higher volume. This means that the tonnes per hour carried on the conveyor is the highest in the industry, which often leads to a higher rate of roller failure,” he says.
“Weartech offers all the benefits of plastic while also having the ability to outlast steel. The performance of the rollers that we’ve seen with this product has been unwavering.”
One example of this can be seen in a Pilbara iron ore mine, who trialled Weartech after a bad experience with PVC rollers. Due to a high failure rate caused by extremely high wear and tension on the conveyor belt, the client had previously decided to replace the steel rollers with PVC ones to reduce the risk of belt damage. This came at a cost, as the PVC rollers had a significantly lower lifespan, at around six to eight weeks.
Weartech offers all the benefits of plastic while also having the ability to outlast steel.
Tribotech manufactures the tubes in-house instead of having them externally manufactured, which reduces the long-term cost.
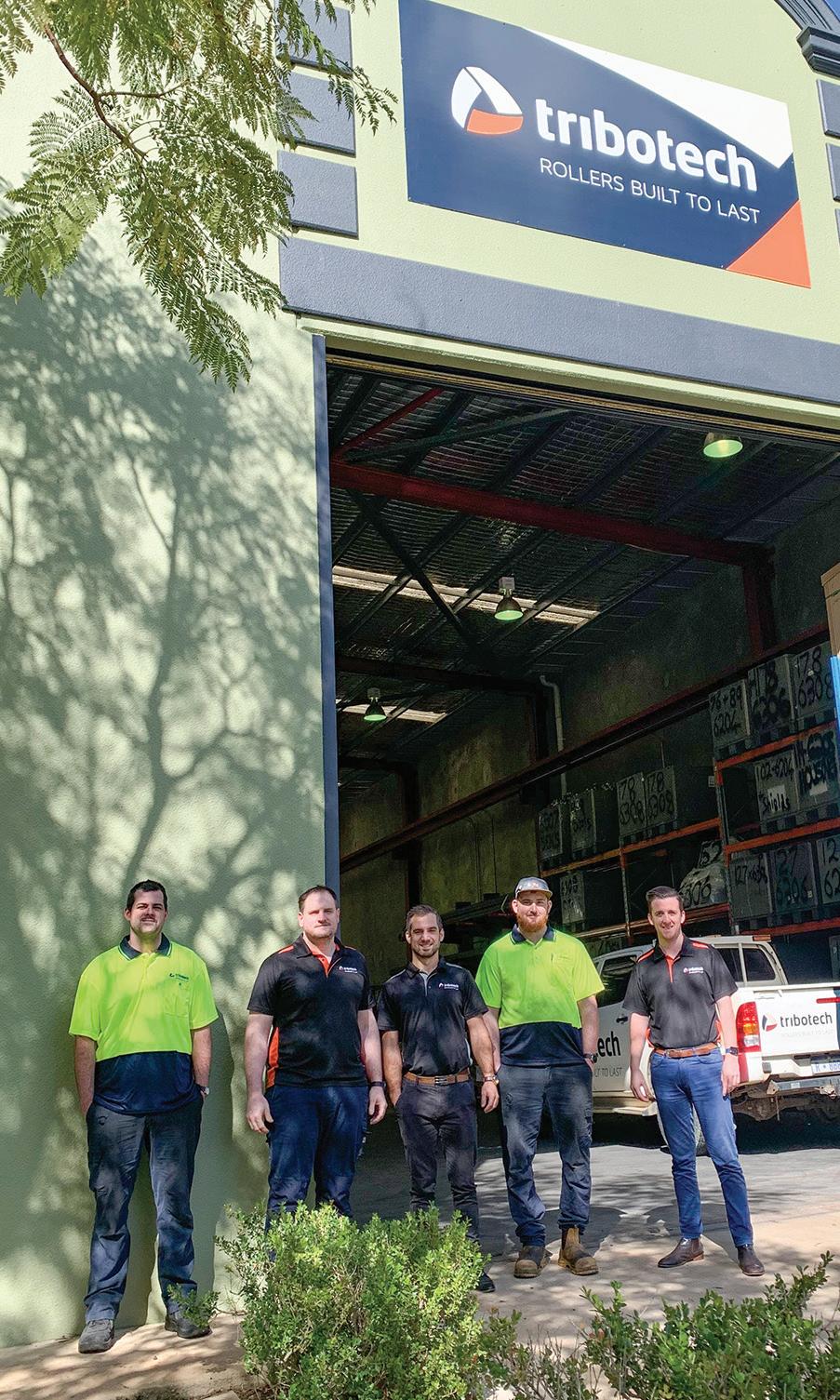
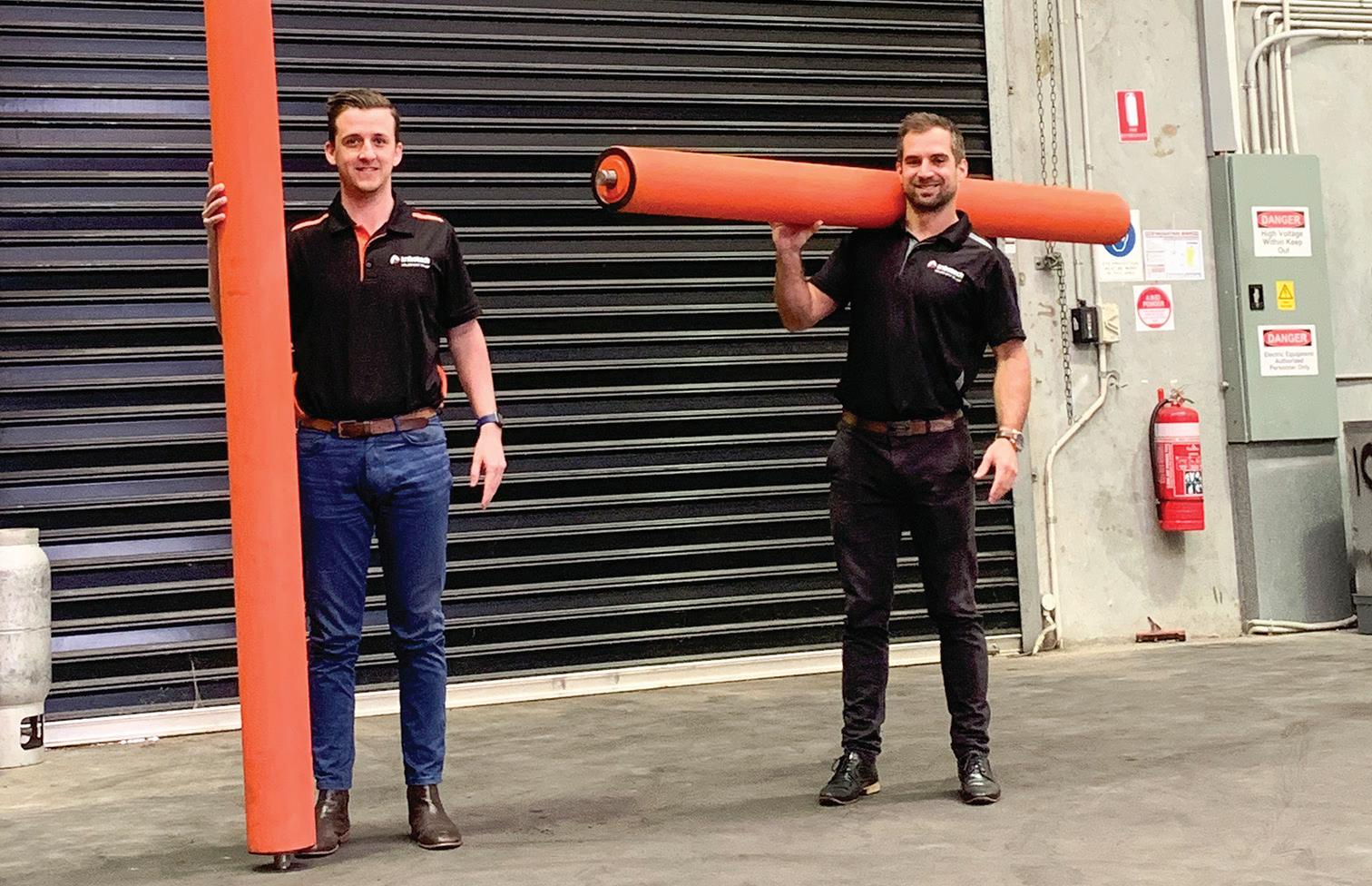
Tribotech proposed the client trial Weartech due to its weight and beltfriendly properties, and the results were immense. The rollers managed to outlast conventional steel rollers by a factor of seven.
Otis says the company decided to manufacture the tubes in-house, in

Tribotech offers trials of its products to showcase its quality and reliability.
Western Australia, instead of having them externally manufactured, which reduces the long-term cost.
“We use our experience as a chemical company and make it all here, reducing the cost significantly.” he says.
“We also organise our production to manufacture the rollers in a short lead
Tribotech’s engineers investigated alternative industries, such as the aeronautics sector, to find a material that would make a viable roller.
time, as our customers rely on a 10 day or less delivery schedule. Every year we are looking for new innovations to reduce lead time and improve our designs.”
Otis is looking forward to continuing Tribotech’s journey in revolutionising the industry. The company readily offers trials to showcase the quality and reliability of their products to any mine sites who are experiencing issues with their rollers, or who just want to see what else is out there.
Bulk solids storage and handling solutions generated in Australia for Australian Conditions
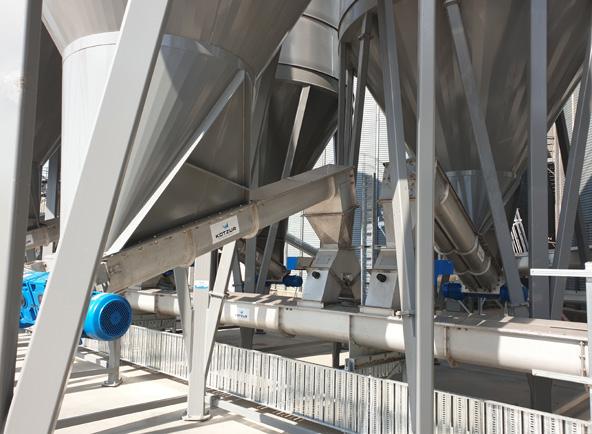


Walla Walla, NSW Toowoomba, QLD Perth, WA
(02) 6029 4700 (07) 4634 4622 (02) 6029 4700