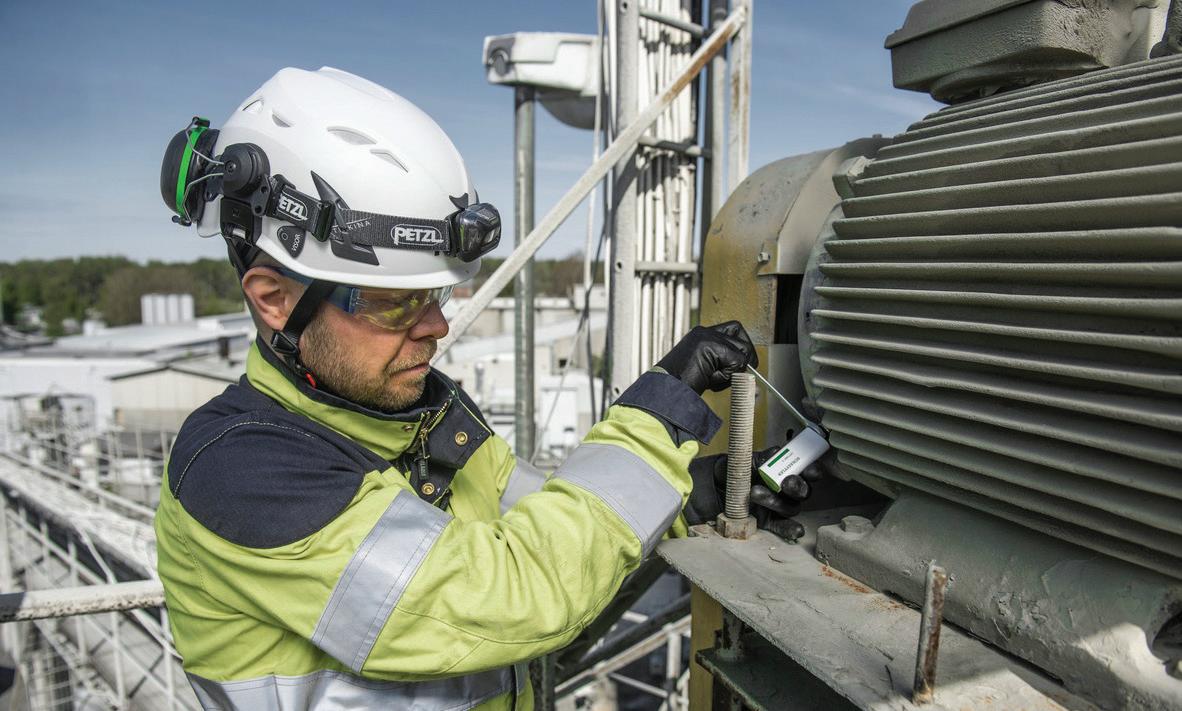
5 minute read
Optimising uptime with OPTIME
Schaeffler has designed a system that takes the guesswork out of the entire condition monitoring process – from installation to analysis with a single, out of the box solution.
CONDITION MONITORING IS KEY
to success for most modern mines. It can help prevent catastrophic machine failure, optimise maintenance, and improve machine life.
However, these systems have been historically expensive to deploy and complex to install. According to bearing manufacturer Schaeffler, up to 95 per cent of all machines inside factories are only sporadically monitored, or often not at all.
Mark Ciechanowicz, Industrial Services Manager at Schaeffler Australia says one key issue is getting the inventory or spare parts and the logistics of getting human resources –whether they are internal or subcontracted – to the site.
“A lot of Australian mine sites are remote, which poses many challenges in terms of machine maintenance,” he says.
“And obviously downtime costs are a major factor, especially when commodity prices, such as iron ore prices, are at an all-time high. In these instances – where a mining company needs to be at maximum production to meet demand – they don’t want to be caught in a situation where a critical asset such as a conveyor system is down.”
Additionally, offline condition monitoring systems – which require the manual collection of data at specific time stamps – have their own limitations and challenges.
“If you consider the footprint of a mine site, it involves a huge amount of coverage – just one division might take a week to walk around,” Ciechanowicz says. “Offline collection is not only time-consuming and impractical; it will only provide a periodic snapshot of that machine’s health.”
Online systems can be scheduled to gather data at several points in a day, however not all are made equal.
Ben Kang, Schaeffler Australia’s Industry 4.0 and Engineering Solutions Manager, says cabled systems can be complex to install when time is precious and become very expensive very quickly.
“Imagine the size of an iron ore site and the sheer amount of copper and resources required to cable those systems up. It has not been a costeffective solution for many mining operations,” he says.
This data then needs to be interpreted, which requires special expertise and comes with a host of additional expenses.
To address these challenges, Schaeffler has developed a comprehensive condition monitoring solution that is both easy to set up and highly cost efficient for bulk handling operations.
Called OPTIIME, the system is a wireless online solution that uses inbuilt algorithms for expert diagnostics of rotating equipment, without the need for a user. This lets customers know if there will be an issue far in advance, and the steps they will need to undertake to resolve them.
Ciechanowicz says this means the user spends less time on the analytics side, and more time actioning the results that come out of the system.
“What it affords the customer is time to be able to plan maintenance, inventory,
The sensors are wireless, battery operated vibration and temperature sensors that come with a stainless-steel mounting pad.
and in a proactive sense conduct maintenance on their terms rather than the machines dictating what they do in a reactive sense,” he says.
What sets the system apart is its ‘plug-and-play’ nature. OPTIME is made up of three parts, the sensors, a gateway, and the digital services. To set the system up, a user needs to download the OPTIME smartphone app and connect the gateway.
The sensors are wireless, battery operated vibration and temperature sensors that come with a stainlesssteel mounting pad that can be glued onto the surface or bearing housing of a rotating machine. They are activated via a mobile smart device using Near Field Communication (NFC) and automatically connect to the gateway and to other sensors.
Ciechanowicz says the process of setting up each sensor is exceptionally fast, taking about five minutes.
The gateway collects data from the sensors and transmits it to the cloud, using a specialised, independent, mesh network. Customers can then use the app to access the digital services, which includes the in-built algorithms that analyse data and provide diagnostic reports.
OPTIIME is a wireless online solution that uses in-built algorithms for expert diagnostics of rotating equipment.
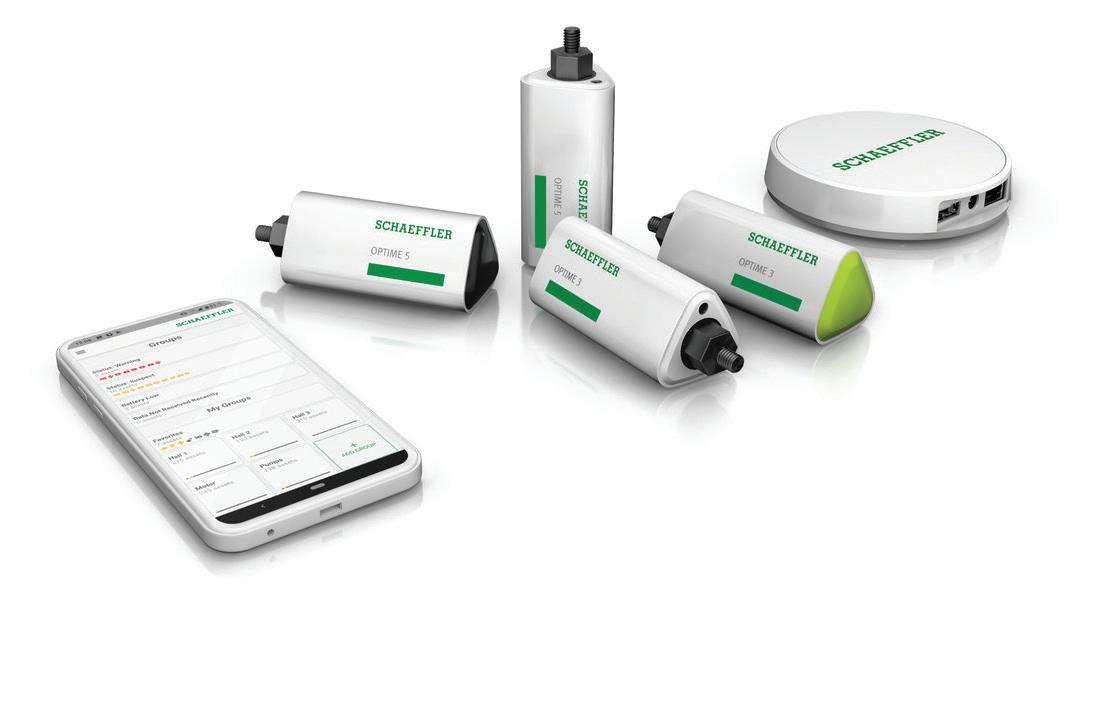
“The app has been designed so the customer can do everything on the app, from provisioning the gateway and sensors, to adding meta data,” Ciechanowicz says.
“The system algorithms work off an intrinsic library – for example, if the customer types in a bearing designation, the system can work out the kinematic frequencies or the fault frequencies and use that in the diagnosis. Essentially, the more meta data the customer puts in when they set up the sensor – and they can do this retrospectively – the more accurate that analysis is going to be.”
He adds that customers do not require any condition monitoring experience to start benefiting from the diagnostic reporting.
“This is quite unique given that most systems require some kind of condition monitoring savvy to be able to set them up and then to interpret the data,” he says.
OPTIME has also been designed from the ground up to be deployed in large volumes across a plant. Schaeffler expects the sensors to be measuring hundreds or even thousands of machines, with operations able to quickly scale up if needed.
All the sensors automatically connect with each other and can act as repeaters. This means sensors could be hundreds of metres away from the gateway, scattered across a wide area and still reach the cloud.
Kang says OPTIME and all its inbuilt smarts is the result of Schaeffler’s extensive technical expertise as a world-leading solution provider for rotating equipment.
“This is a solution that has been designed and manufactured by a technology company which has its roots in roller bearings,” he says.
“The outputs of this system will be vastly different from other wireless systems that don’t have Schaeffler’s foundation in rotating machinery. All of these algorithms have been developed on top of years of automation, analysis, machine learning and artificial intelligence. And they work seamlessly behind the scenes to give customers clear, easy-to understand insights that they can action instantaneously.”
Government incentives available now
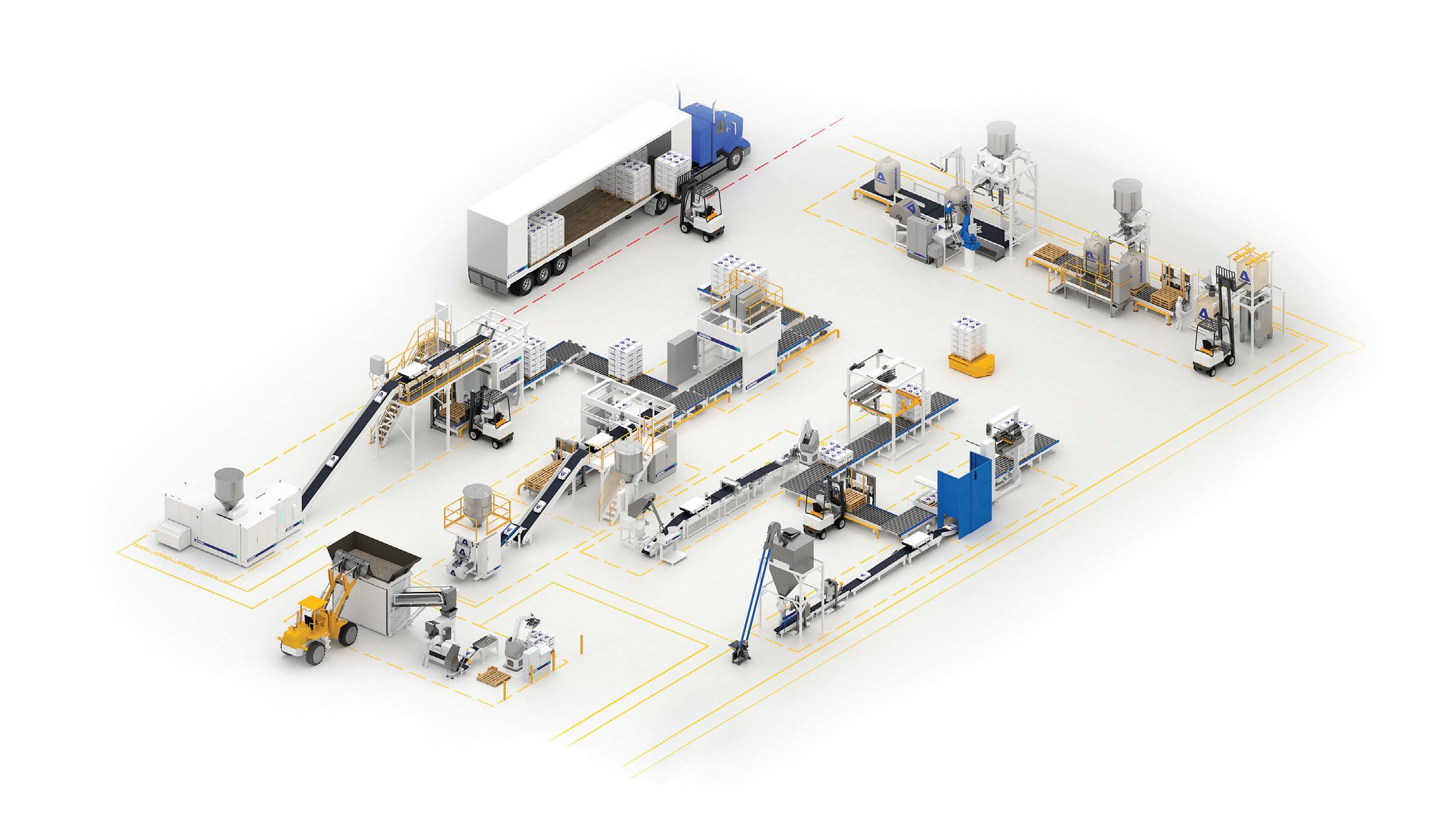
Now is the time to invest in automated packaging and get your business ahead. You could save tens of thousands through two Australian Government schemes. Learn more at aurora-process.com/incentives