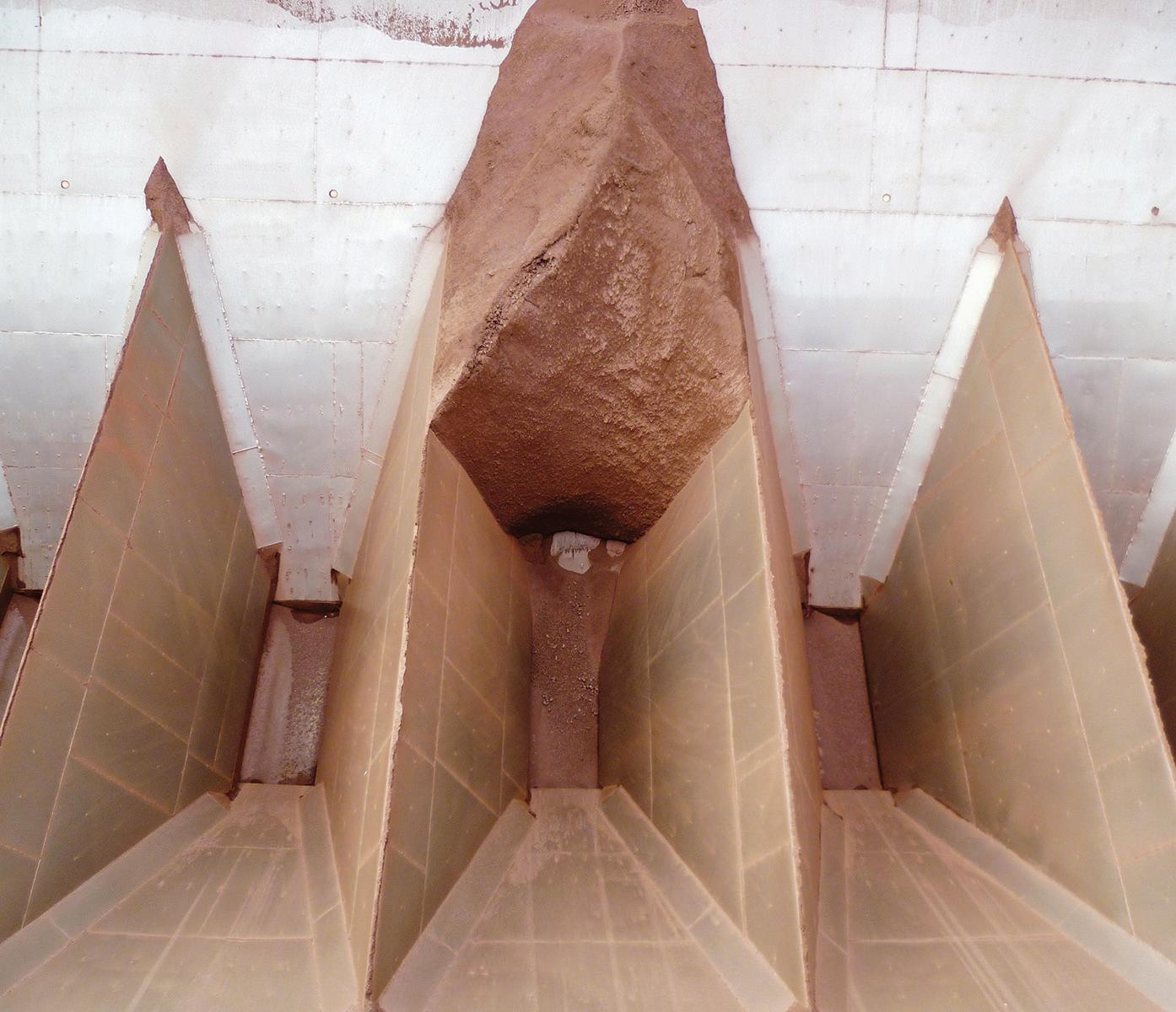
4 minute read
Oli Vibrators bust transfer chute buildup
Buildup in a transfer chute can lead to expensive complications. Removing it manually can be slow and unsafe, which is why Oli Vibrators helps remove it with the touch of a button.
WHENEVER CERTAIN MATERIALS
move through a transfer chute and hit a wear plate, they can begin to build up.
It can happen to any product that becomes glutinous or homogenises with moisture. Mark Thompson, Director at Oli Vibrators, says coal can be one of the worst offenders.
“It could be material like clay, or if you’re working on a tunnelling project and hit a water vein, that mud and hard rock could start creating problems,” he says.
Material buildup in a transfer chute will start to reduce the capacity of the transfer chute and can stifle or even block the conveyor, completely stopping the process. The resultant mess would then need to be manually dug out.
Buildup can also lead to spillage,
Buildup can also lead to spillage, is expensive and can cause damage to components. is expensive and can cause damage to components.
Thompson says an easy fix to this problem is to install industrial vibrators on the transfer chute.
“Oli Vibrators performs a detailed analysis of the chute, looking at the points where a vibrator can be fitted and where it will have the least amount of fatigue impact,” he says.
“We want to avoid any fatigue on the structure itself while also finding the best area of influence in the buildup zone. After we’ve done that, we can provide clients with advice on installations and analyse resources they have available.”
By installing a vibrator on the chute, the company can get rid of the buildup with the touch of a button. Depending on the duty cycle, the vibrators can be turned on at specific points or run through a programmable logic controller.
Internet of Things-enabled technologies can be integrated into the system, with level indicators and capacitance sensors able to detect a buildup and turn on the vibrator to automatically remove it.
This removes the need for operators to place themselves in precarious positions, often at height and in enclosed, dusty, and wet areas, to remove buildups themselves.
Thompson says, fitting a vibrator also protects the assets themselves, as often the buildup is removed by striking the chute with a sledgehammer or heavy object.
“Every time you hit a chute with a hammer, it creates a potential hang-up point for the material. I’ve seen chutes with ‘hammer rash’ where people have been constantly belting it. Seeing a bin or hopper with hammer rash is a sure sign there is an area in the process that needs addressing,” he says.
“Not only is using a hammer dangerous because you’re swinging around a large hammer at heights, but it is also bad for your bones and hearing. Using vibrators helps preserve both the structure and the person.”
Thompson adds that most designers aim to build chutes that don’t need vibration, and it is often a method of last resort or frustration. However, he adds that once they’re installed, the buildup problems disappear quick with very little effort.
Oli Vibrators can install the systems on almost any transfer point. The company has installed vibrators on chutes for cocoa in a chocolate factory and at quarries handling 500 tonnes of limestone per hour. Chutes that use ceramic lining are often unsuitable, as it could damage the
bond between the chute and lining so our flow aid range may be more appropriate.
The company has operated in Australia for more than two decades and has built up expertise in providing the right tools for the job. Thompson says Oli Vibrators’ staff are knowledgeable about its products and know how to apply them to all kinds of situations.
“Our staff have worked with materials handling for years and we have enough case studies under our belt where we can use previous experiences to find new solutions,” he says.
“What sets us apart are the high-quality materials and precision engineering that goes into making each of the vibrators. The company is based in Italy and imports its products from overseas where they must meet rigorous Australian and International quality assurance standards.
“They’re also virtually maintenance free and easily replaced. Once fitted, they go about their business based on the operation. They can be programmed to
Striking a chute with a hammer to remove a blockage can make the problem worse.
work in conjunction with the process and are energy efficient.”
Oli Vibrator’s mission statement is ‘when you need it, where you need it’. To deliver on that, the Australian business keeps plenty of spares on hand if required and can call upon all 22 of the global company’s trading subsidiaries.
Each product also comes with a two-year warranty, which includes full replacement or repair of the product.
Thompson says fast support is critical to many of its customers, who have a limited timeframe to work in.
“That’s why we offer around the clock support. If a process fails in a food manufacturer’s production line in the middle of the night, we can get a solution sent over to get everything working again by morning,” he says.
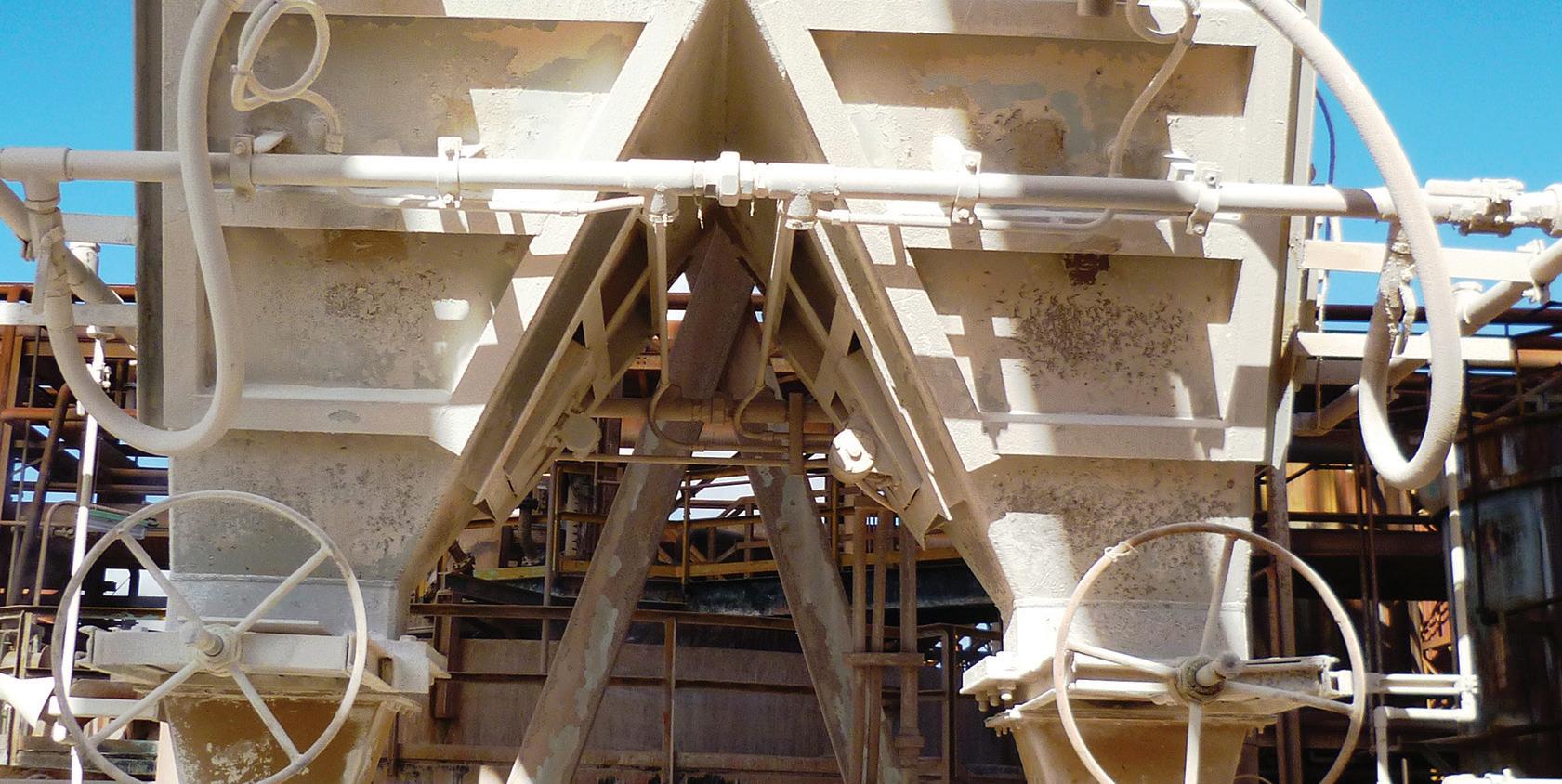
• materials handling • asset life extension • infrastructure
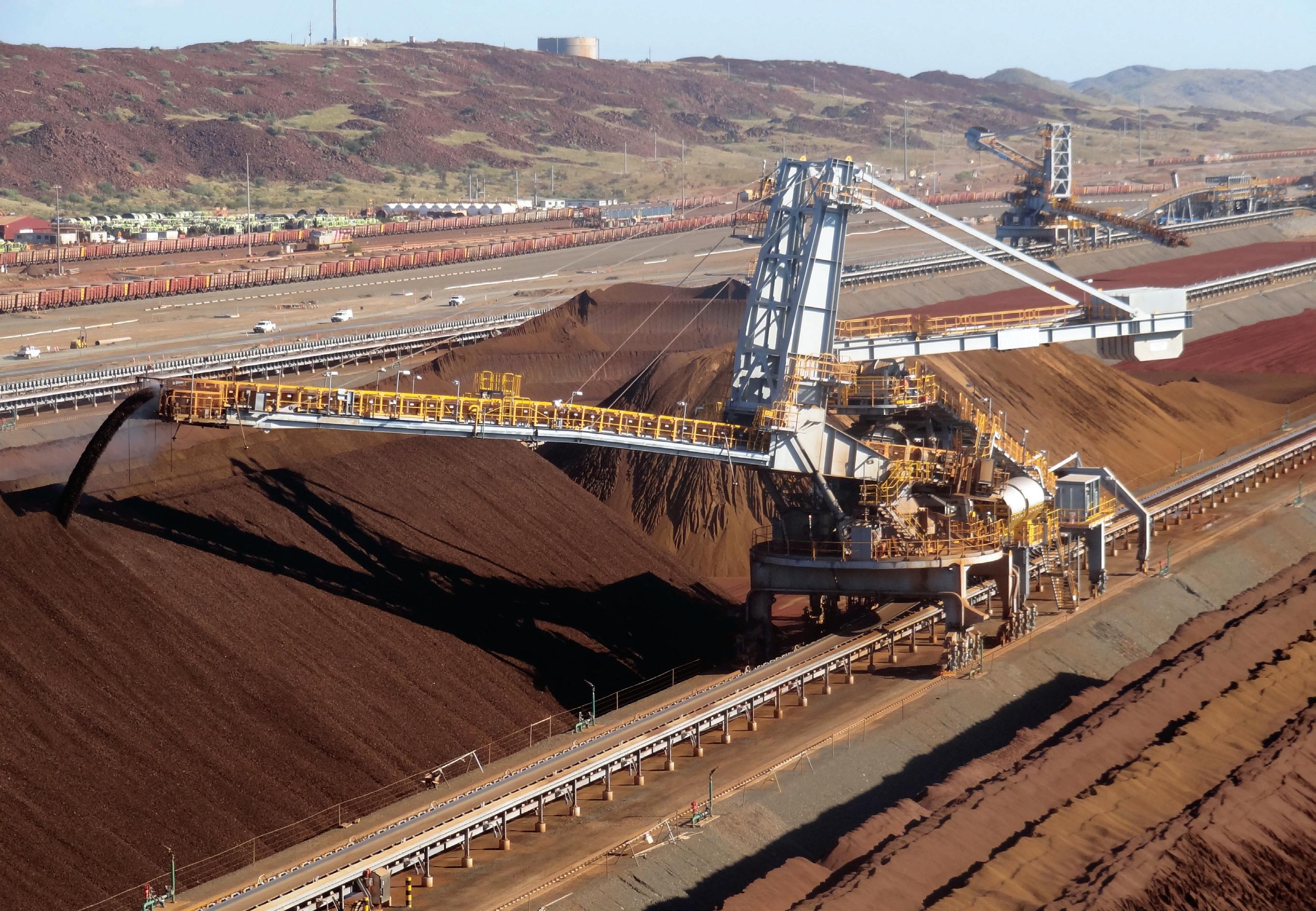