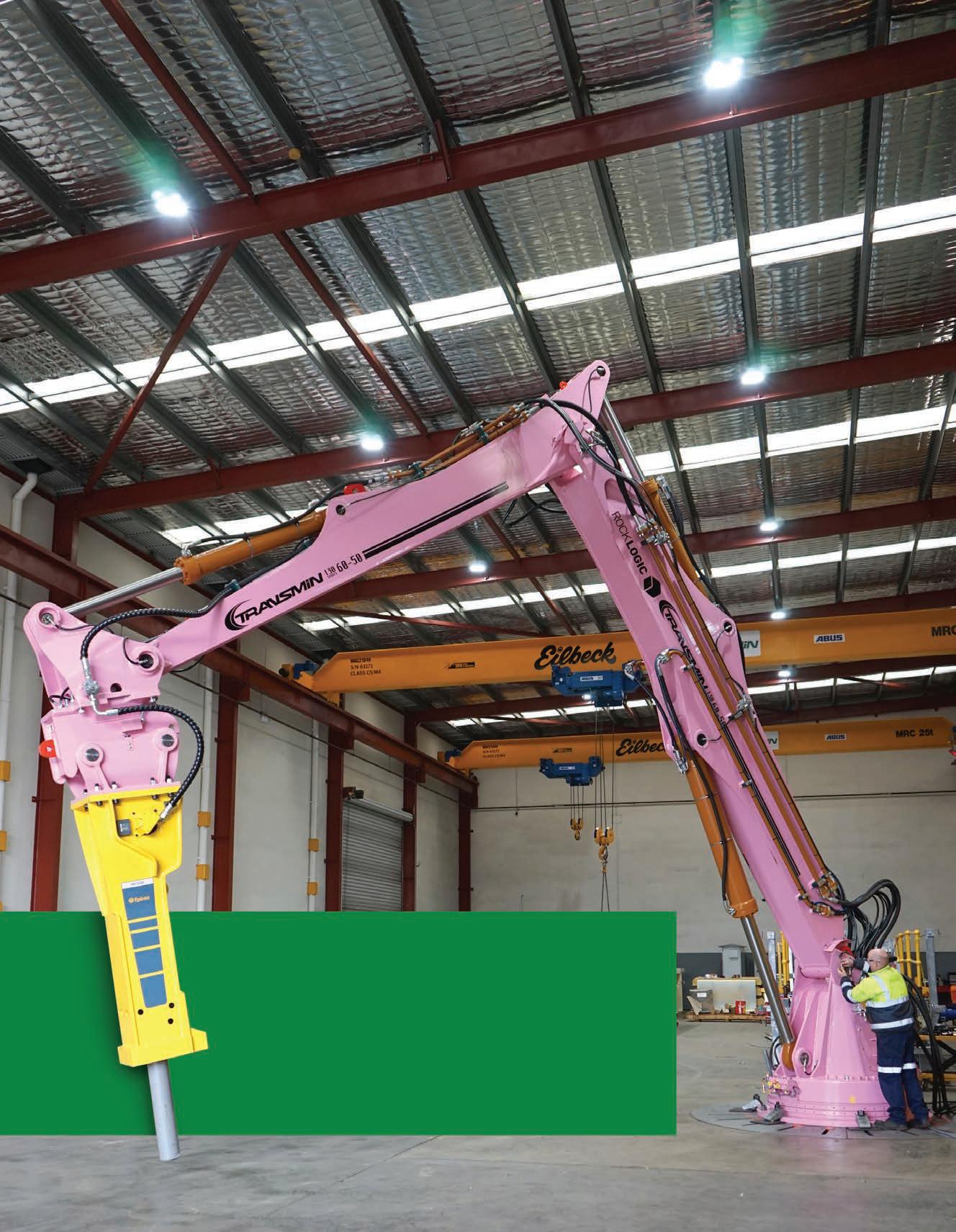
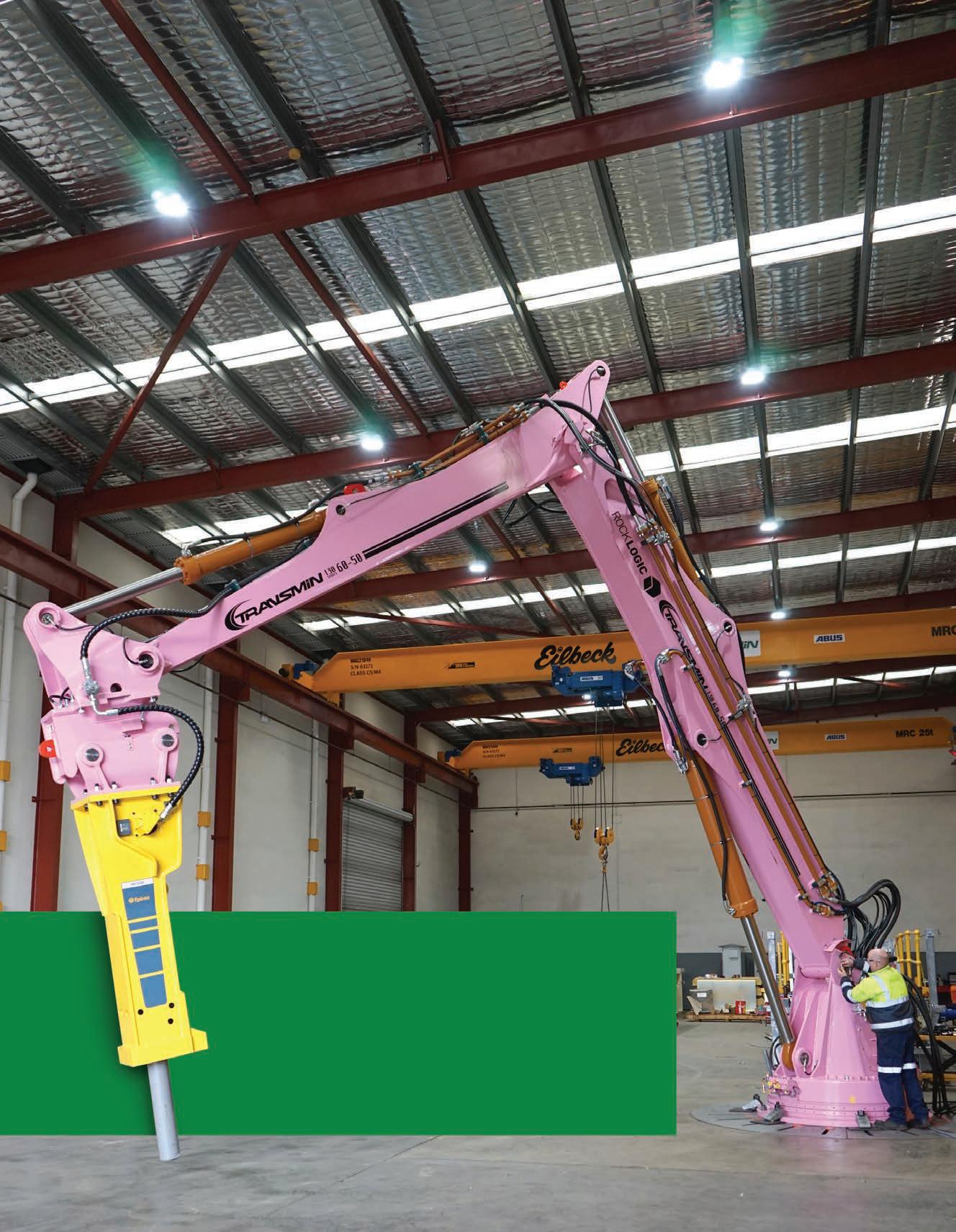
READY-MADE
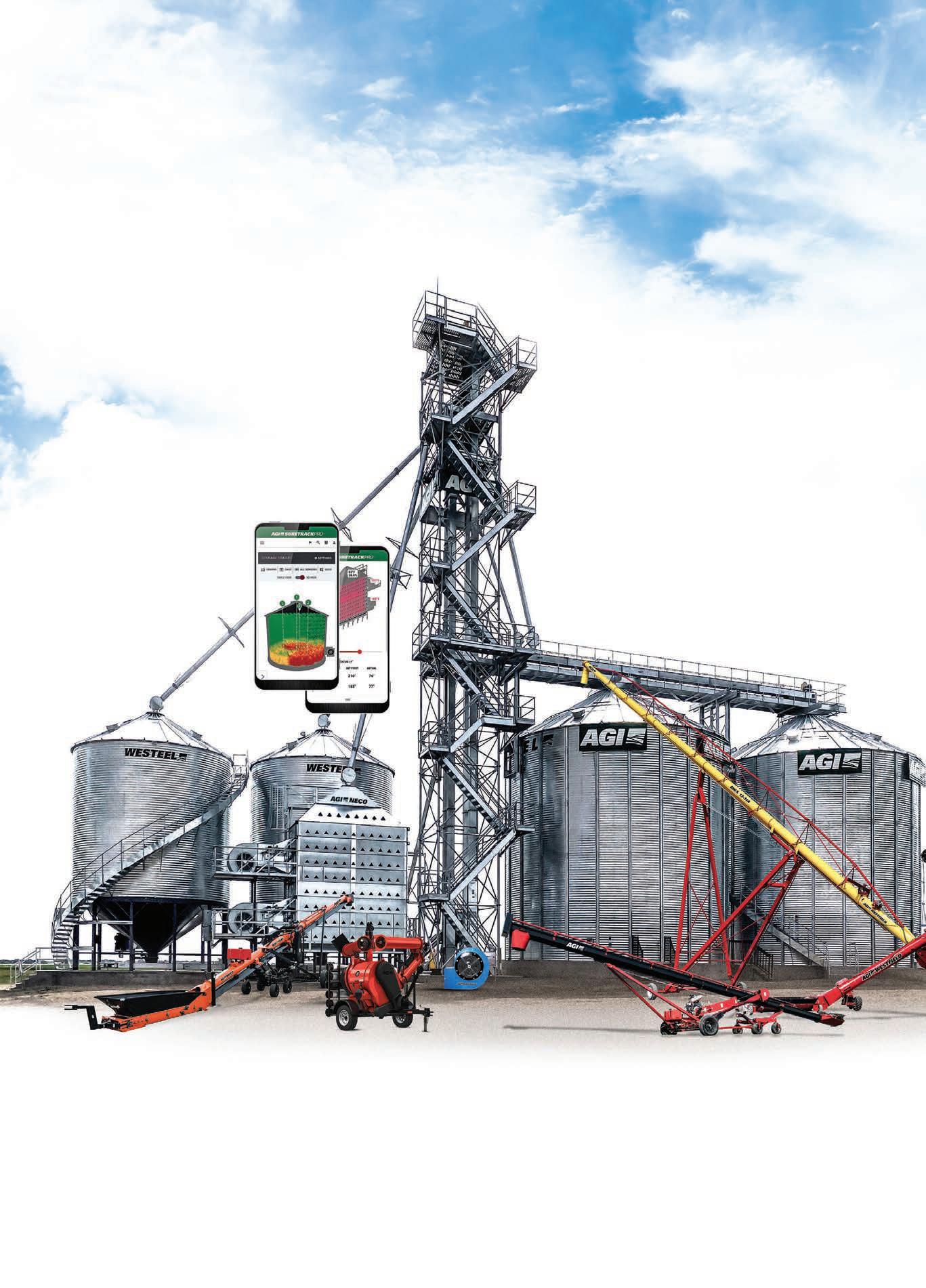
Conveyors
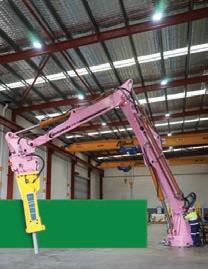
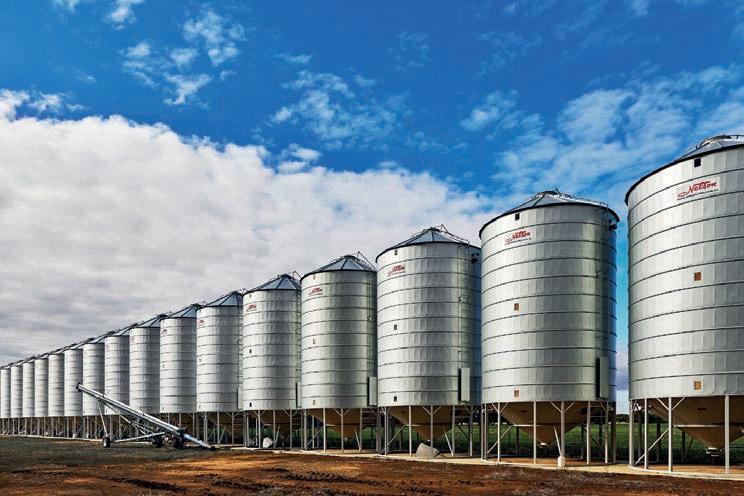
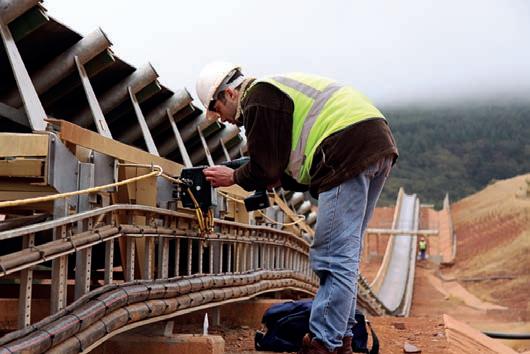
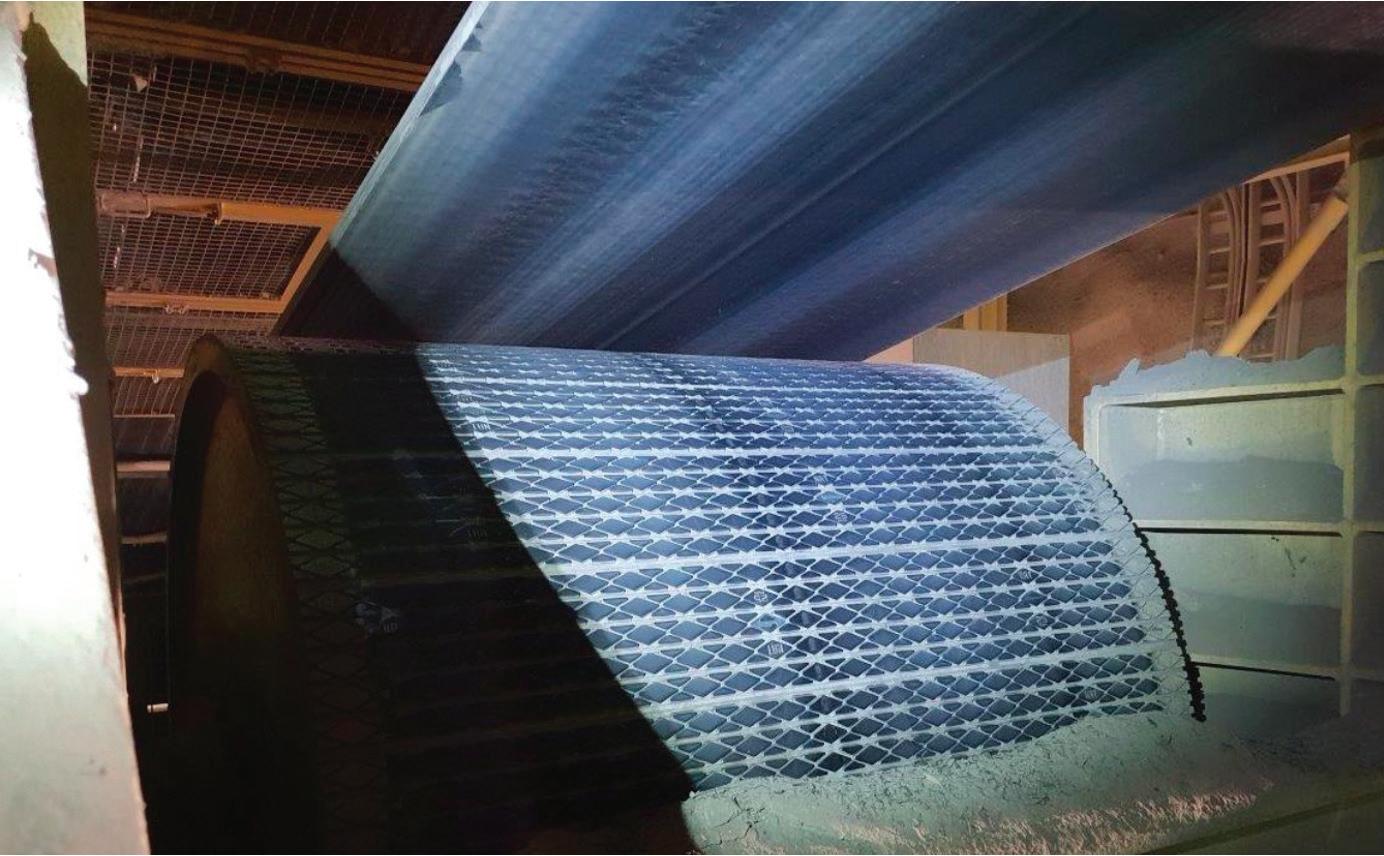
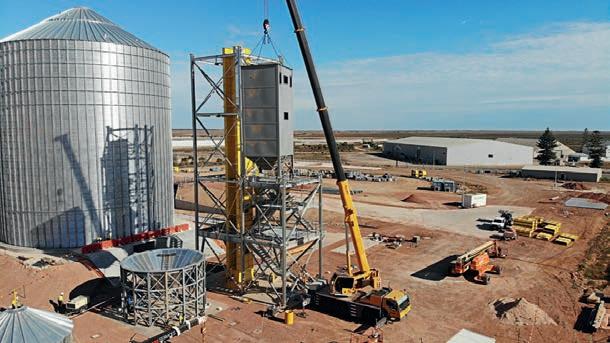
Published
11-15
South
T:
www.primecreativemedia.com.au
COO
Christine Clancy
E: christine.clancy@primecreative.com.au
Editor
William Arnott
E: william.arnott@primecreative.com.au
Business Development Manager
Rob O’Bryan
E: rob.obryan@primecreative.com.au
Client Success Manager
Janine Clements
E: janine.clements@primecreative.com.au
Design Production Manager
Michelle Weston
E: michelle.weston@primecreative.com.au
Art Director
Blake Storey
Design Louis Romero, Kerry Pert
Subscriptions
T:
E: subscriptions@primecreative.com.au
www.bulkhandlingreview.com
The Publisher reserves the right to alter or omit any article or advertisement submitted and requires indemnity from the advertisers and contributors against damages or liabilities that may arise from material published.
© Copyright – No part of this publication may be reproduced, stored in a retrieval system or transmitted in any means electronic, mechanical, photocopying, recording or otherwise without the permission of the publisher.
Connecting industries
If there is one thing the past couple of years have proved, it’s that bulk handling is a critical industry.
Mines needed to keep producing ore, energy producers needed to keep the lights on, and people working from home needed flour for their sourdough starters.
The industry adapted to a changing work environment. Automation and remote operation technologies boomed, along with plenty of online meetings.
Cloud computing and massive amounts of data help manage inventories, production, and spot components in need of replacing before they even begin to fail.
One day, hopefully soon, we might even be able to automate the dull, dirty, and dangerous jobs completely, freeing up workers for more important tasks.
While it might sound futuristic, we’re already seeing organisations develop ways of making it a reality.
The Australian Bulk Handling Awards were an opportunity to celebrate the organisations and individuals that have pushed the industry forward.
The winners, which were announced at a gala dinner, have showcased their engineering expertise, helped overcome challenges, developed new products, and have improved the overall safety in the industry.
The event took place at BULK2022, which brought together an industry under the one roof, after years of isolation. Local and international decision makers came together to share their newest innovations and products.
A two-day conference, hosted by the Australian Society for Bulk Solids Handling, helped encourage knowledge sharing, with presentations discussing a wide range of topics.
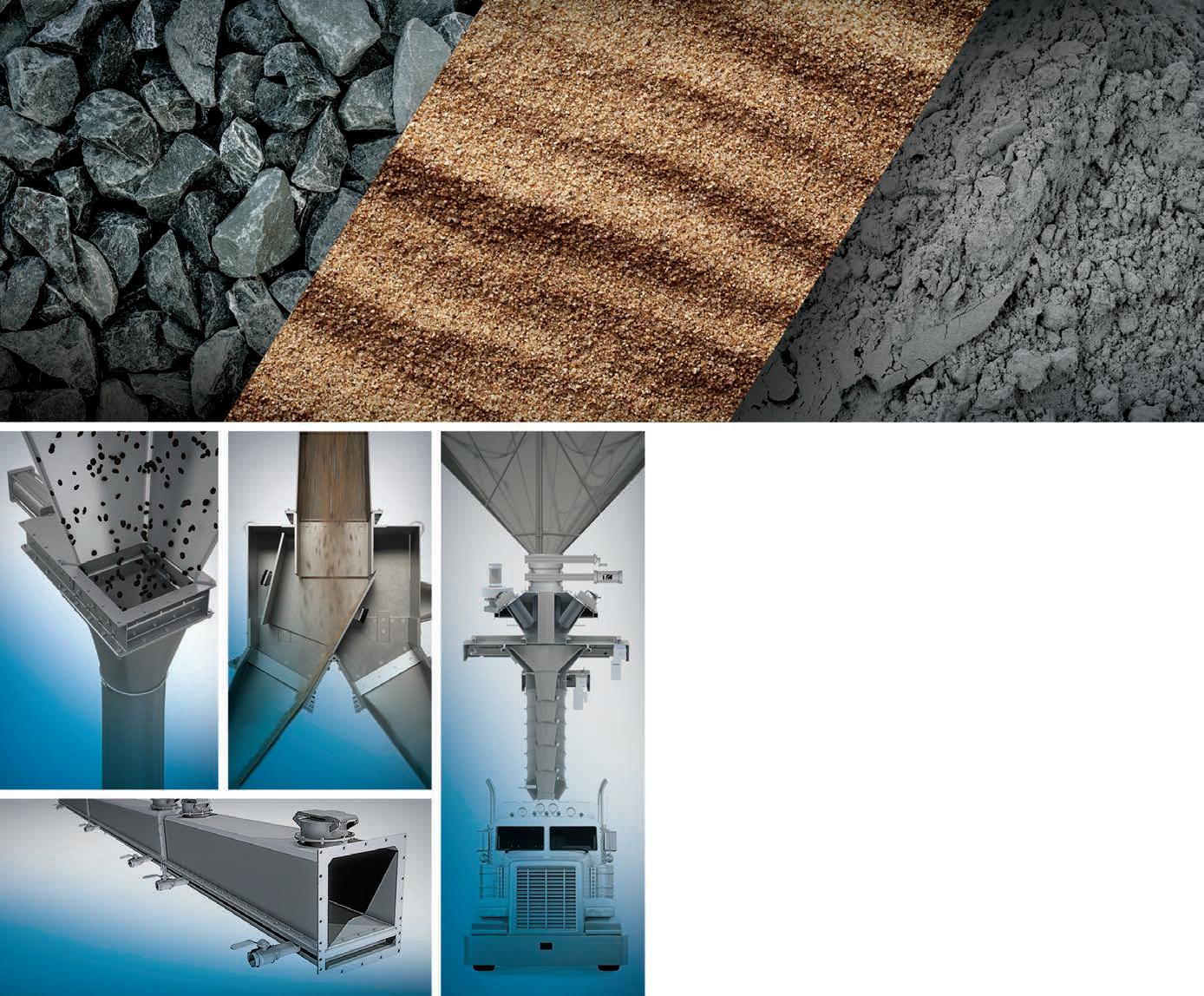
The Australian Bulk Handling Review team would like to thank the event’s sponsors – VEGA Australia, PROK, Premier Tech, and LEAP Australia – along with the talented event coordinators.
William Arnott Editor - ABHR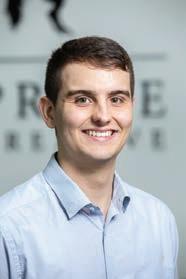
There’s no time for down time.
PROVIDING SOLUTIONS
For over 45 years, Vortex has supplied dry material handling components to a global network of Original Equipment Manufacturers, Fortune 500 companies, and process engineering firms. Throughout the world, over 15,000 companies have utilized Vortex’s innovative slide gates, diverters, iris valves, loading solutions and custom engineered products to improve process efficiency.
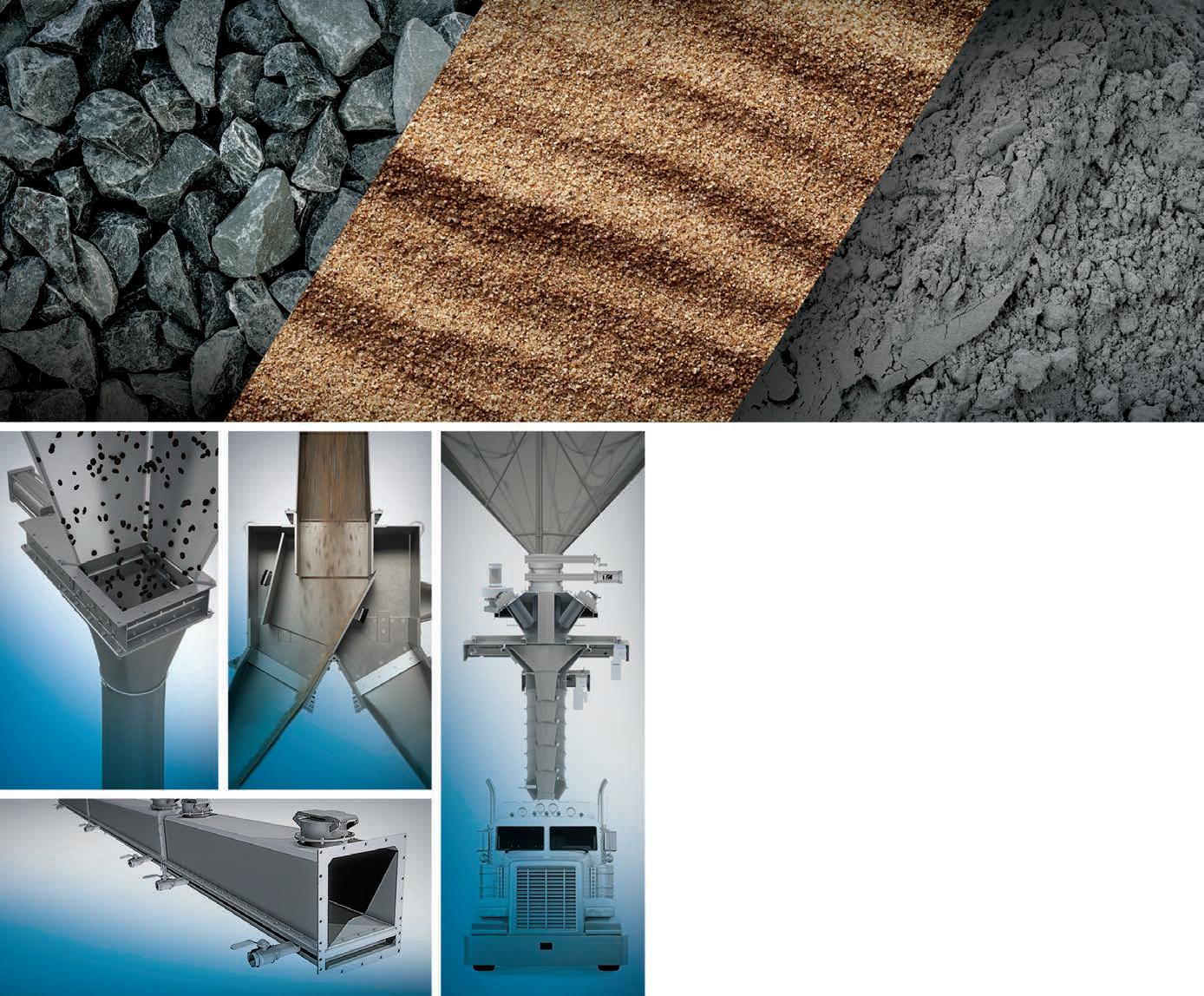
With sales and service offices located in North America, Europe, Asia and Latin America, Vortex’s success comes from a philosophy, which includes focus on quality, timely customer service and dedication to adding value to our clients’ processes.
PROVIDING SOLUTIONS
Each Vortex component is appropriately selected to meet the demands in every application. With an in-house team of engineers, Vortex product designs can be completely customized for individual applications or special installations. Vortex understands the value of your process. Our team of application engineers have more than 150 years of combined dry material handling experience. Vortex’s knowledge of handling dry material characteristics in pneumatic, vacuum and gravity flow applications is unsurpassed. Vortex delivers intelligent, cost effective solutions for all dry bulk materials. No application is too large, too small or too difficult to handle.
INDUSTRIES
Fenner finalises CPS acquisition
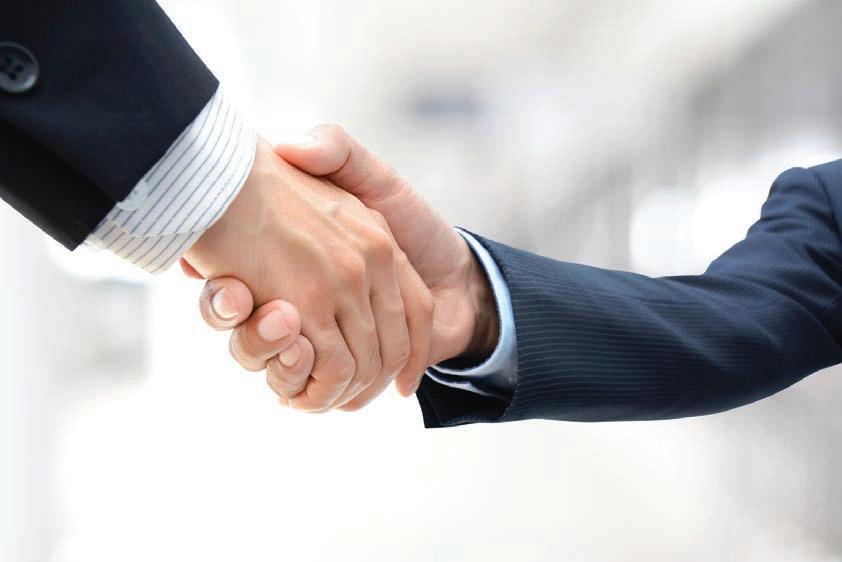
FENNER AUSTRALIA HAS Fenner Australia has completed the total acquisition of Conveyor Products & Solutions Pty Ltd (CPS).
CPS is an Australian manufacturer of high-quality conveyor rollers, idlers, and pulleys for the mining and bulk materials handling markets.
Fenner, a manufacturer of conveyor belting for industrial application, aims to strengthen its capability to provide customers with a comprehensive, end to end, one stop shop for all conveyor related needs.
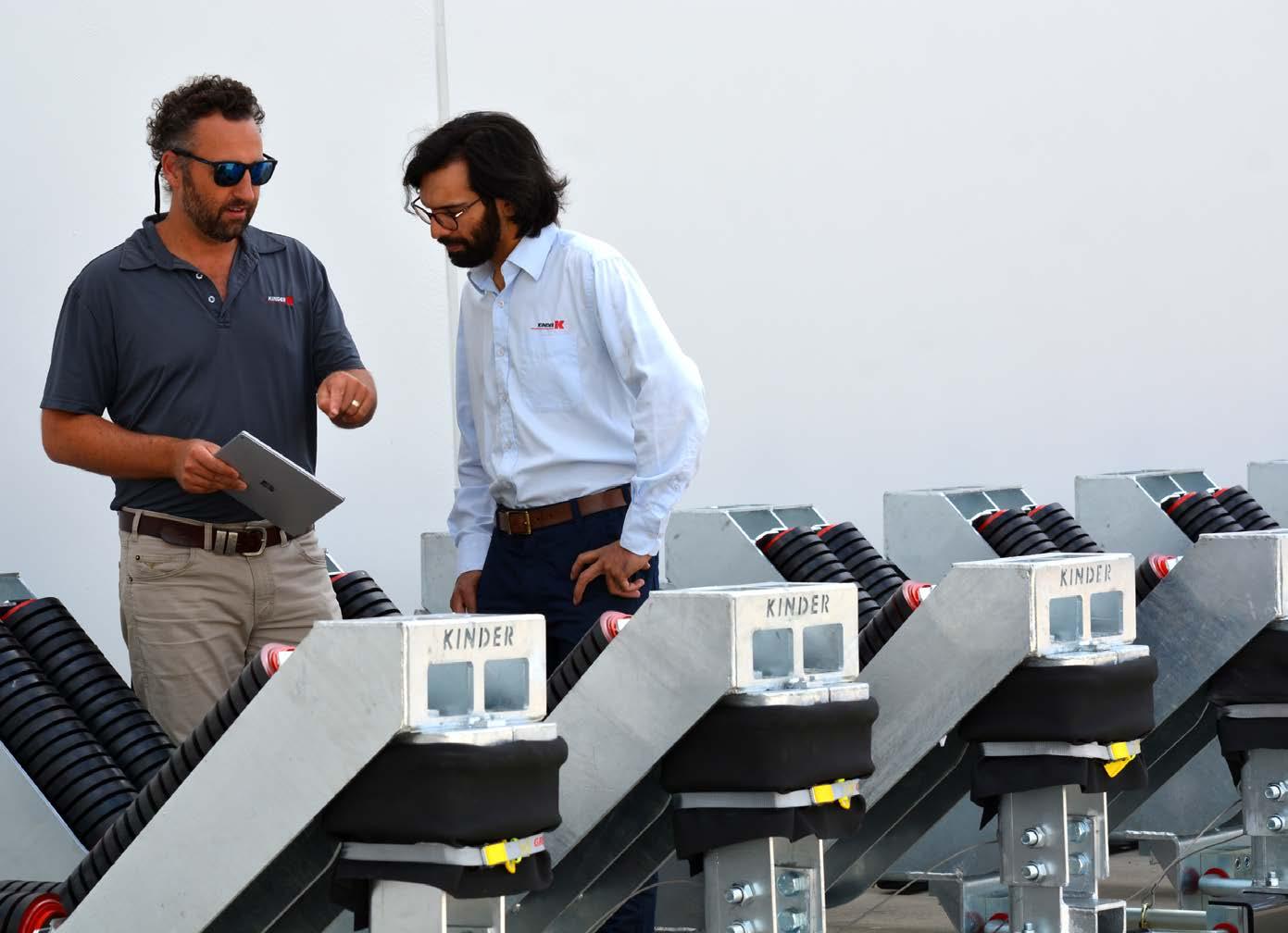
“We are delighted that CPS has joined Fenner and the One Michelin Group Australia, as it provides great opportunities for our collective customers and our combined team of talented people,” Fenner Executive Director, David Landgren said.
Combining the two business in Australia, which have similar values regarding quality local manufacturing and support, aims to support ongoing commitments to people and the environment.
CPS’s WA-based manufacturing
capabilities are equipped with automation, digital and robotic production tools and are expected to add significant value when combined with Fenner’s existing Australia–wide conveyor footprint.
The customer support offices of both companies also provide further synergy and strength to a national and international capability.
“Joining Fenner represents an
exciting time for CPS, which has established itself as the industry leader in composite conveyor rollers, idlers, and pulleys,” CPS Managing Director and CEO Michael Einhorn said.
“Integration with Fenner allows CPS’ successful growth strategy to continue on the next phase of ensuring we deliver maximum, sustainable value to our customers and provide opportunity to our people.”
Contractors chosen for Port of Bundaberg bulk conveyor
KEY CONTRACTORS HAVE been selected to build the Common User Infrastructure at the Port of Bundaberg, Queensland.
Loftus Contracting and engineering firm e2o, a wholly owned subsidiary of Clough, have secured the construction contracts for the project.
The contractors will deliver a new bulk goods conveyor facility at the port that will provide efficient loading facilities for a wide range of bulk minerals and agricultural products.
Gladstone-based Loftus Contracting
has been engaged to conduct the civil works, which have already commenced. e2o will complete the construction of the new conveyor infrastructure including modifications to the existing ship loading facilities and the structural, mechanical, and electrical works.
Local fabrication company, BME Australia, will work closely with e2o on the fabrication of the main structural components, all of which will be fabricated in Bundaberg.
Once complete, the Common User Infrastructure will provide an opportunity
to increase exports of bulk commodities including minerals, timber products (wood pellets and woodchip) and agricultural products.
“This project is great news for the people of Bundaberg but also the broader Burnett region, creating jobs and opportunities for businesses in the region,” Federal Assistant Minister for Regional Development, Senator Anthony Chisholm said.
“The Federal Government understands how important it is to create jobs and opportunities across regional Queensland,
and projects like this show our continuing
The Federal Government has committed up to $17.7 million in funding for the project, with additional funding committed by Sugar Terminals Limited (STL) and Gladstone Ports Corporation (GPC), provided on behalf of the Queensland Government.
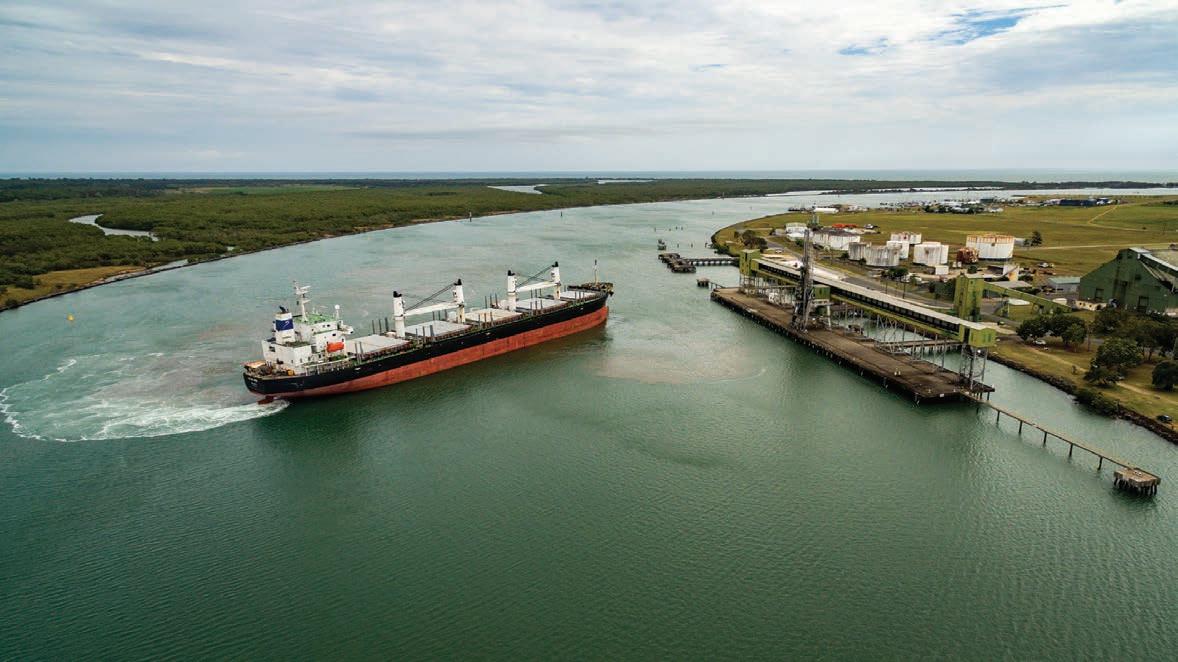
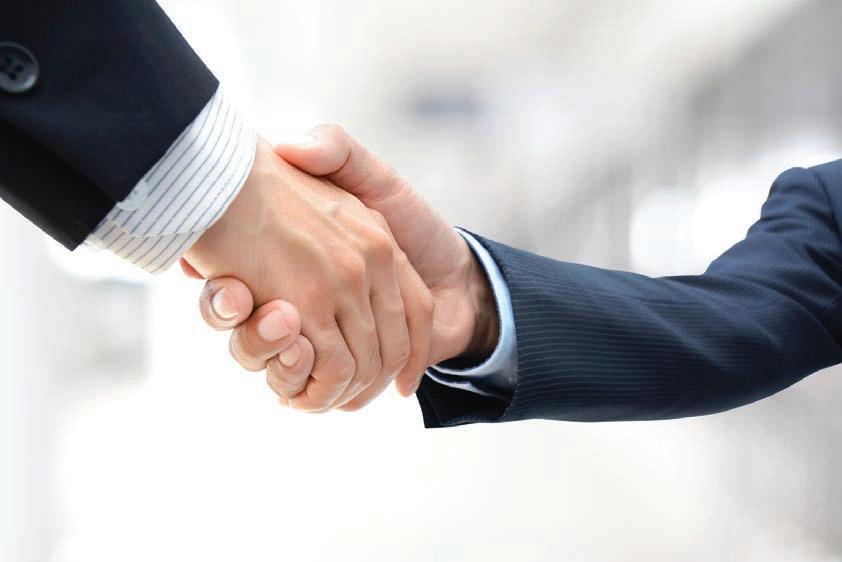
The project is part of the Hinkler Regional Deal and is expected to be commissioned by April 2023.
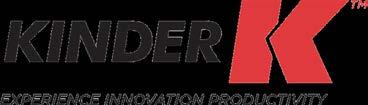
“This is an important project not just for the Hinkler, but for Queensland, as it will ensure this vital port can expand its export capabilities and is ready for the future, Federal Infrastructure, Transport, Regional Development and Local Government Minister Catherine King said.
“Constructing this new conveyor facility will unlock opportunities for local producers to compete in world markets, supporting businesses and the regional economy into the future.”
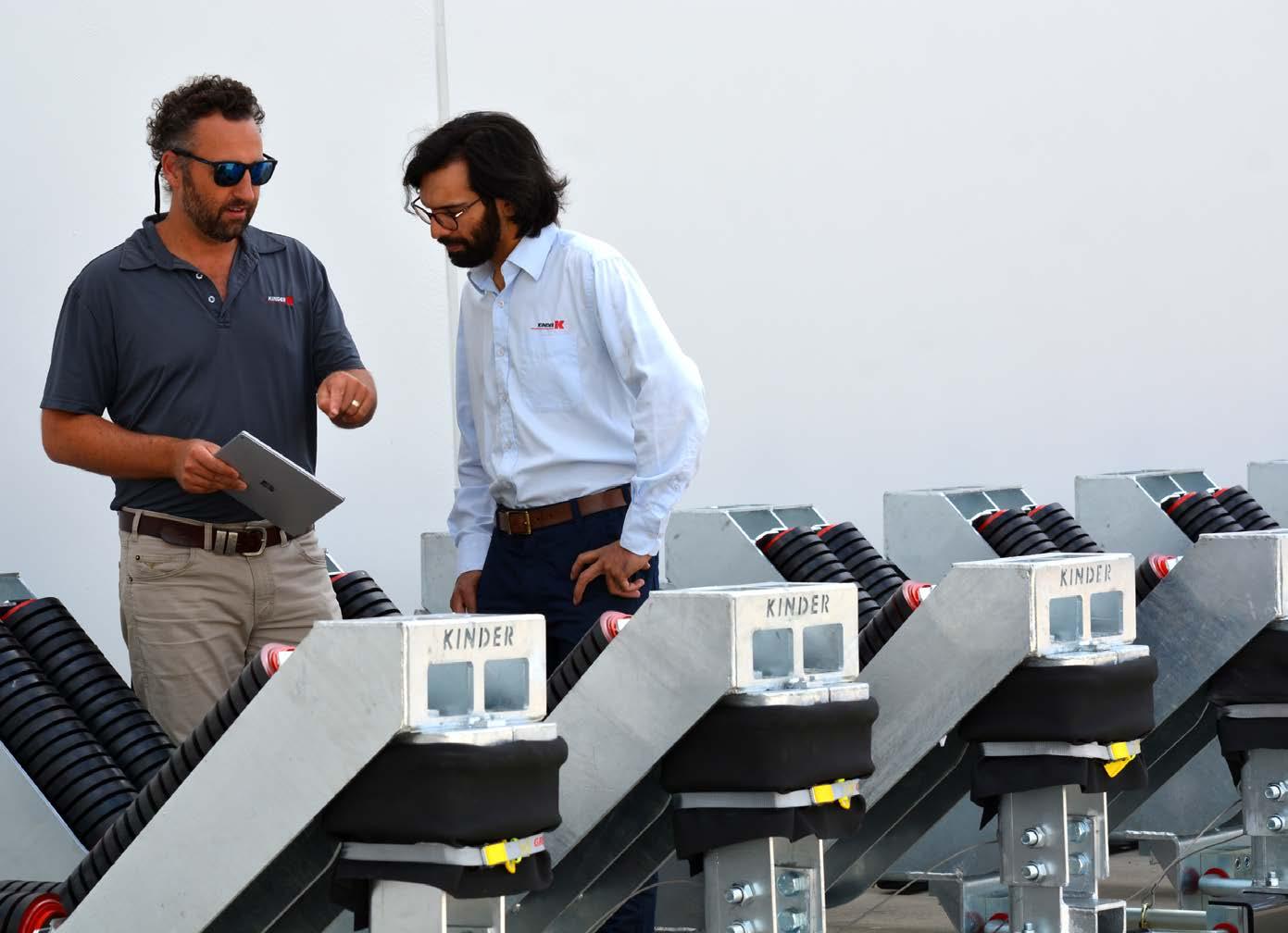
Innovation
our Motivation...
Solidifying safer systems for smashing rocks
Equipment manufacturer Transmin has changed up its strategy to develop safer, more productive rockbreaker systems.
FEW OTHER INDUSTRIES
operate machinery in conditions as harsh as a mine site, which is why mining companies want equipment they can trust.
Equipment is put to the test in dusty, hot environments, often working around the clock to meet high standards of productivity.
If a machine breaks down, that creates expensive headaches for the site. Mines are usually in remote areas, so if something goes wrong, it could affect productivity for hours, if not days. And that downtime comes with a significant price tag.
However, equipment robustness is not the be all and end all. There has been a push for machinery that meets increasing safety requirements and takes advantage of new technology.
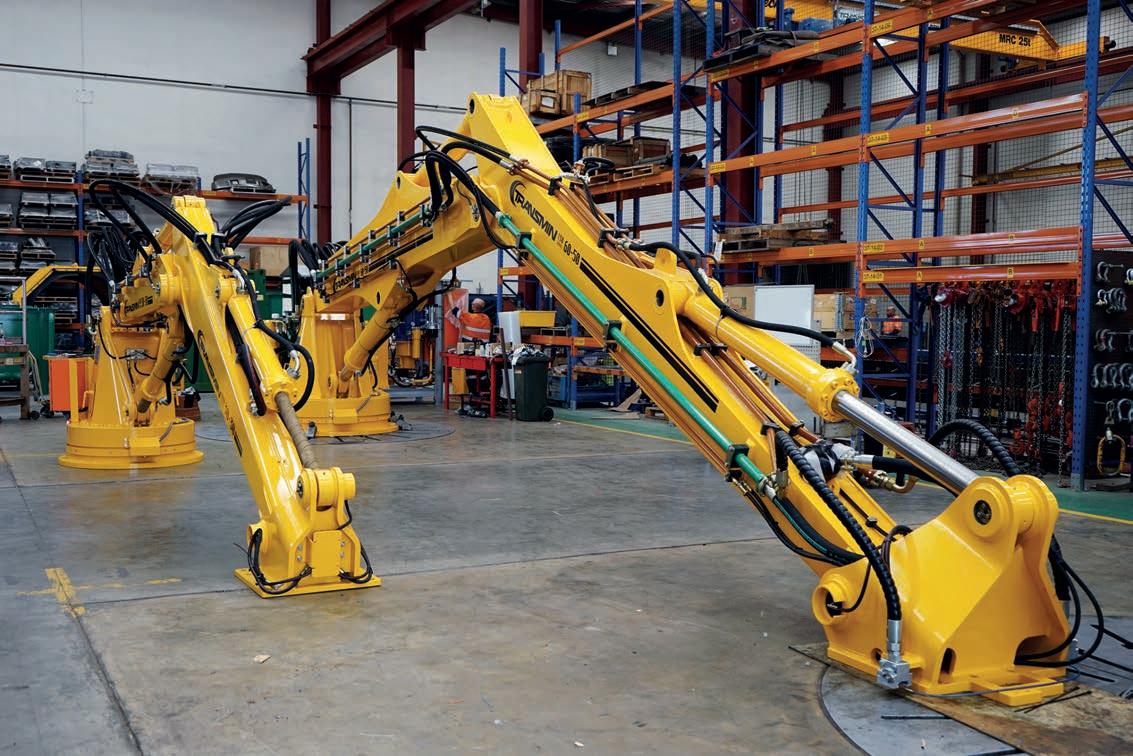
had been a big focal point for the development of the company’s range of rockbreakers.
“The technology is moving forward very quickly,” he told ABHR. “Innovation is massively important, because if you’re not innovating, your competitors are.
“We aim to optimise our equipment as much as we can, but we resist the urge to include new technology for novelty’s sake.
“We want to add value to our customer’s operation, not gimmicks.”
Transmin’s BoomerHD rockbreakers have undergone years of design evolution and development. The machinery is engineered for large-scale mining and mineral processing plants located in some of the toughest conditions on the
In addition, Transmin has created the RockLogic System, which provides anti collision and automated movements to optimise operator efficiency and minimise potential damage to the rockbreaker units and the surrounding plant structures.
The first step is to create a digital twin of the operating area in 3D, this provides all of the critical elements that need to be identified for collision avoidance. Military spec inertial sensors are mounted to the rockbreaker boom system which provide the exact position of the rockbreaker. The control system using this data to position the rockbreaker in the 3D environment. In the event the system detects the potential for a collision it will override the operator and bring the rockbreaker to a controlled
stop before collision occurs.
“The system has proven to be effective for some time now, but it is beginning to show its age,” Carter said.
“That’s why we are making improvements to the system to improve useability and installation. We want to make it even easier for our clients to install, set up and calibrate the rockbreakers.”
Reliability and safety are the two key aspects that Transmin is looking to improve, particularly when it comes to functional safety in control systems.
In addition to the RockLogic system, Transmin has been developing a functional safety framework to ensure safety of people in the vicinity of the rockbreaker operating.
Carter said that while the ability to remotely operate rockbreakers can be helpful, there is still a lot of demand for people to work nearby the machines.

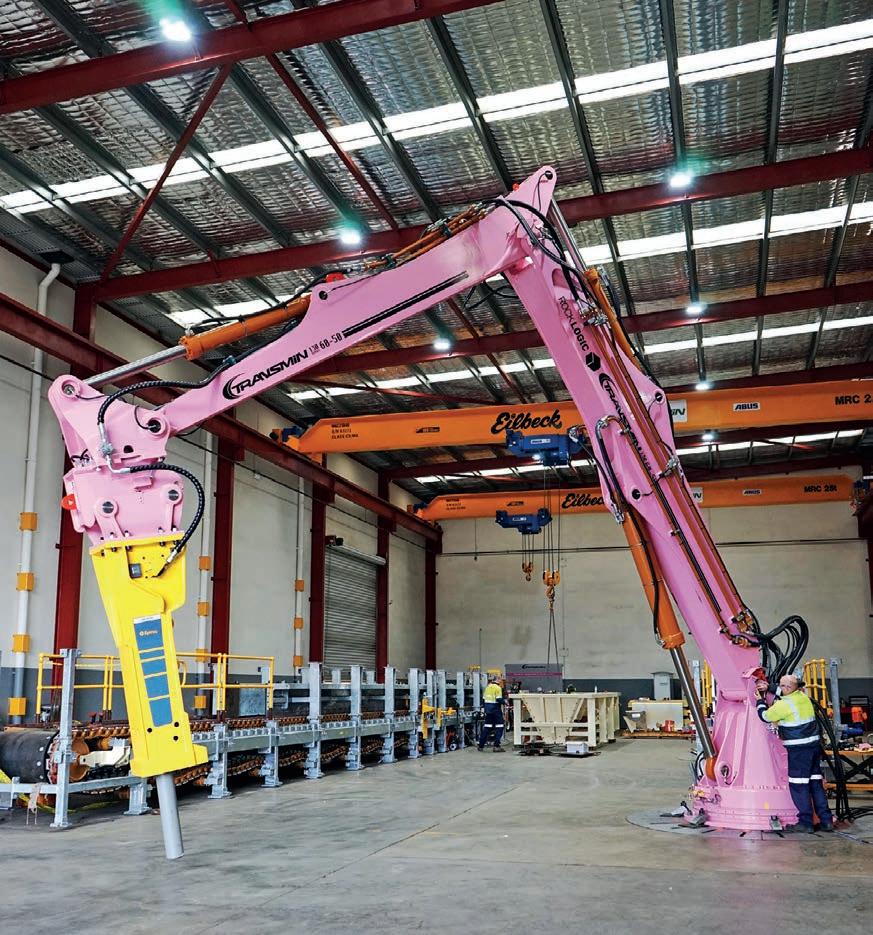
“Any interaction with a person and a rockbreaker has risks,” he said. “On top of that, every site is different, so we go work with the client to identify all the potential risks that operators are exposed to, then go through a process of risk mitigation.”
Functional safety starts when the risk mitigation strategy employs electrical and electronic programmable systems. This requires a higher requirement for quality management, documentation, verification, and compliance. Transmin’s rockbreakers use a safety gate system to
create a perimeter around themselves, similar to how other robotic arms work.
Carter said the best way of keeping people safe is to remove them from the area and use a safety gate system to create a perimeter similar to how robotic arms are made safe. When that can’t happen, Transmin introduces movement limits to ensure the machinery can’t physically reach the operator. This is by using safety rated sensors to monitor the position of the boom system to prevent the hammer from raising above the ROM bin or primary crusher walls, therefore using the wall as a guard. The system is controlled using a Safety PLC. In the event the hammer is raised above the wall, the system will trigger a safe stop. The entire process needs to be planned, documented, and reviewed at each stage.
Unfortunately, the technology employed by current collision avoidance systems, including Rocklogic, cannot comply with functional safety standards. Transmin has recognised this and taken steps to ensure they can comply with this important safety requirement.
Transmin is looking to improve the reliability and safety of its rockbreakers.
the machine to them.
“The challenging part is for the machine to know what has been fully broken and what hasn’t.
“We’re looking to continue developing the technology and rolling it out across several years, before packaging it into the next generation of machinery.”
The company has been developing rockbreakers for more than 20 years and has developed a strong aftermarket support segment. Its account managers work closely with key customers to troubleshoot any problems they may encounter.
Transmin considers the rockbreaker as a complete system and are continually looking to optimise the mechanical, hydraulic and lubrication systems to ensure its customers have robust and reliable systems that are easy to maintain.
“Transmin has a robust research and development process. As we progress from product testing to simulation to prototyping and beyond, we make sure everything undergoes rigorous testing,” Carter said.
A functional safety framework is in development to help improve safety around the rockbreakers.
“We are looking at developing autonomous rockbreakers to increase safety and productivity significantly,” he said. “We’re currently looking at sensor technologies and potential partnerships to further our research.
“The easy part is identifying which rocks need to be broken, then deploying
“We’ve moved into a product vertical process to better understand the areas we need to be targeting across our three core technologies – feeders, plant systems, and rockbreakers and gates.
“Our customers have given us great feedback, they like the technology and the direction its going in.”
TAKRAF stacker ready for duty at key bulk terminal
TAKRAF Australia has designed, fabricated, supplied, and erected a unique stacker to the Dalrymple Bay Terminal. ABHR speaks with Gavin Smith, project manager, to learn more.
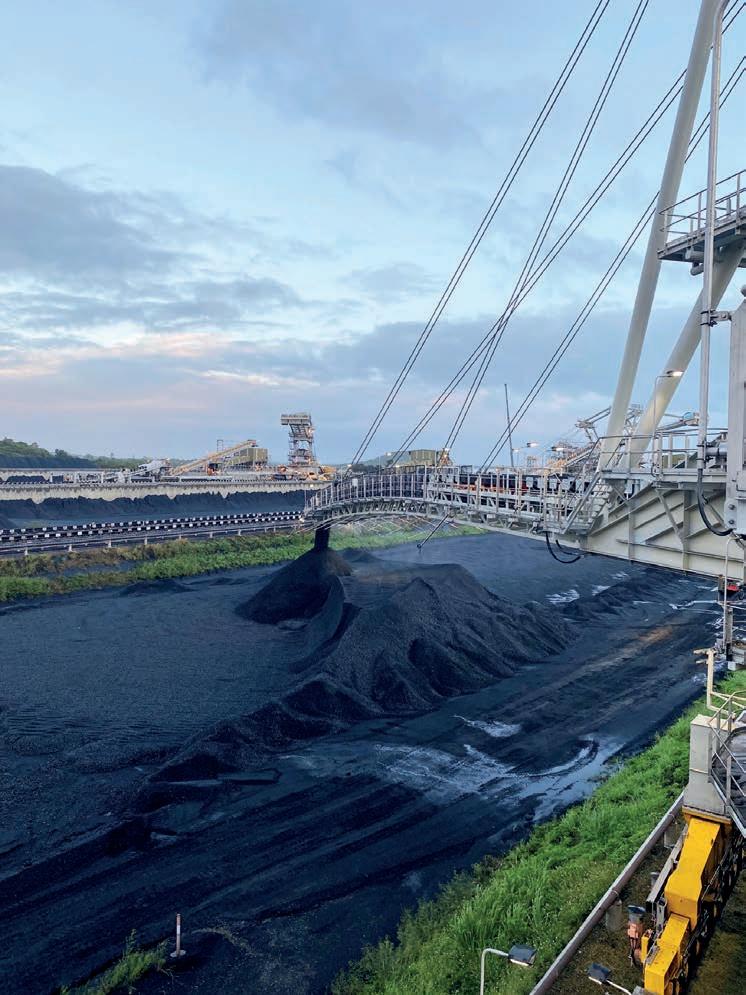
ONE OF THE EXISTING STACKERS at the Dalrymple Bay Terminal (DBT), on Queensland’s Central Coast, needed replacing.
Originally installed as part of the initial development of the terminal in the early 1980s, the stacker was reaching the end of its life.
Dalrymple Bay Infrastructure Management (DBIM) signed a contract for the design, fabrication, supply, installation and commissioning of the new machine with balance machine specialist, TAKRAF after a comprehensive tender process.
Gavin Smith, the project manager at TAKRAF, said the project was complex and involved many local stakeholders.
“The client wanted to ensure the stacker was fabricated in Mackay, so that it would support local businesses and be ‘close to home’,” he said.
“The DBT is located next to the ocean, in an environment with high humidity, so they wanted to make sure everything was manufactured to their specifications.”
The stacker’s structures were built to a stage where it was feasible to transport them by road, minimising the time spent on site to dress the structure out before installation.
Scheduling of the site erection of the machine needed to take into account North-East Queensland’s challenging climatic conditions, with the possibility of cyclones and heavy rains in the wet season.
To help deliver the project, TAKRAF, DBIM and other stakeholders formed an integrated management team. This team helped solve any issues that arose and was designed to foster collaboration across he project.
Smith said one of the unique aspects of the machine is its curved boom geometry.
“The machine is designed for some of the highest volumetric stacking rates ever
bottom of the pile as possible – reducing the potential for dust emissions.”
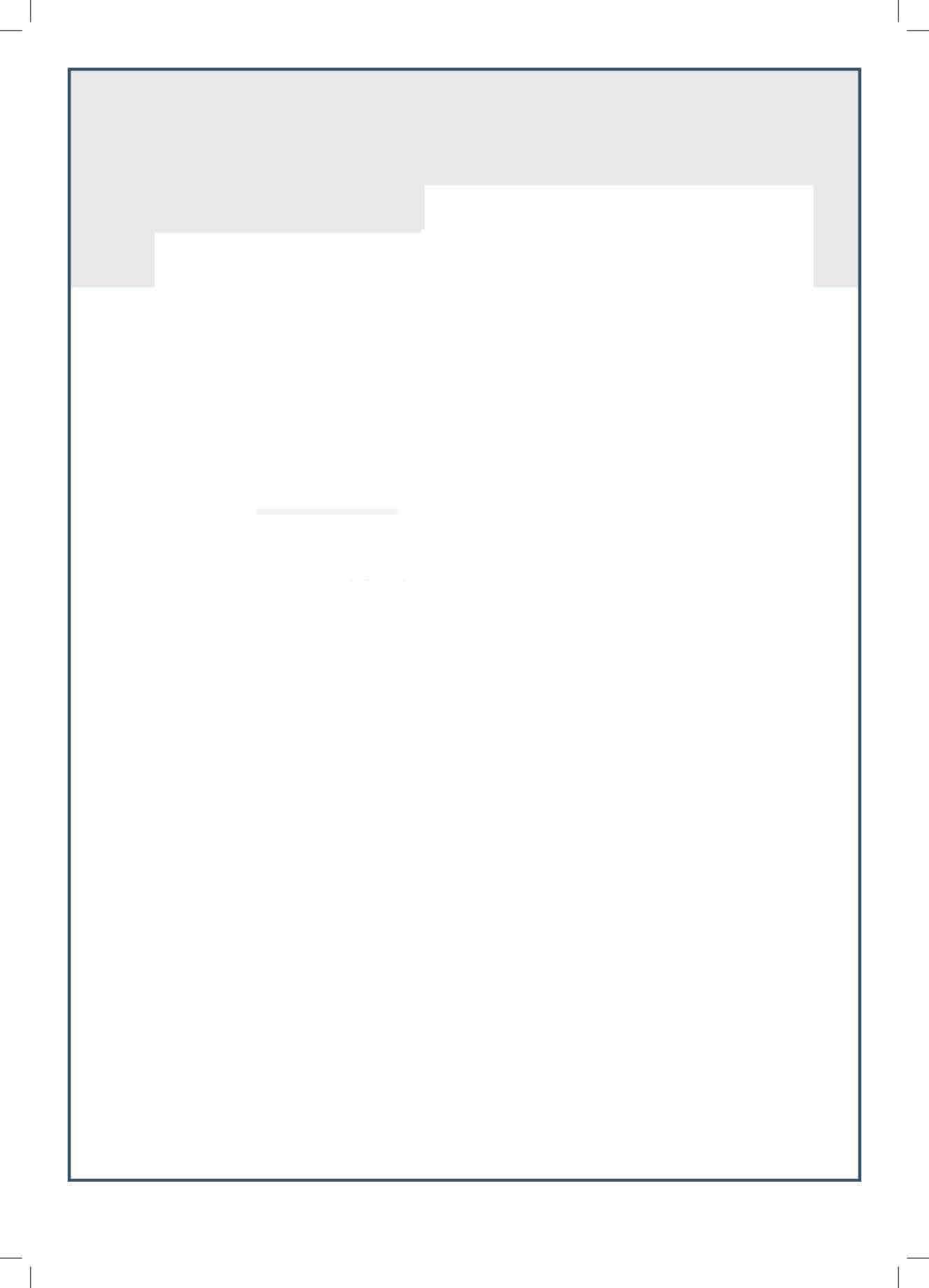
The stacker also boasts an initial peak stacking capacity of 6560 tonnes per hour. It was designed to accommodate a peak volumetric rate of up to 10,700 cubic metres an hour – or about 9600 tonnes per hour – for a proposed future upgrade.
Commissioning and installation of the machine are complete, with the first train being successfully stacked during April and handover to Operations achieved in May this year.
Smith said TAKRAF will continue to support DBIM with after sales
needed,” he said.
“The TAKRAF Australia team, led by Frank Hahn, deserves to be commended on the quality and performance of the finished machine, despite the project being executed throughout the global pandemic and encountering several challenges along the way.
“The commitment and extensive collective experience in the materials handling team has undoubtedly played a large part in meeting the client’s rigorous specifications and inspection routine. We look forward to the machine delivering on its design promise.”
PneuCalc
Design software for pneumatic conveying systems
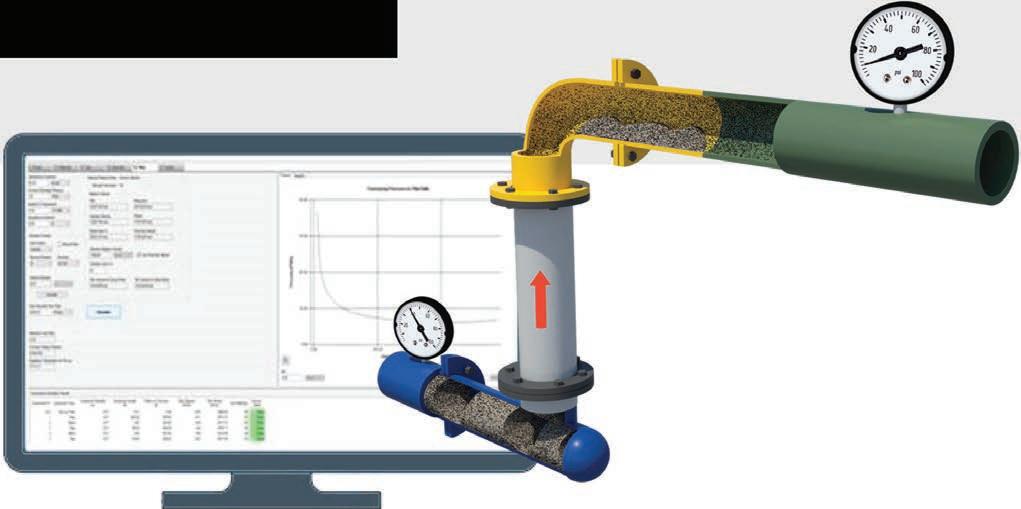
Need help with designing or troubleshooting pneumatic conveying systems?
PneuCalc is the only software application that can optimize your design while avoiding pitfalls. Better design systems in a fraction of the time!
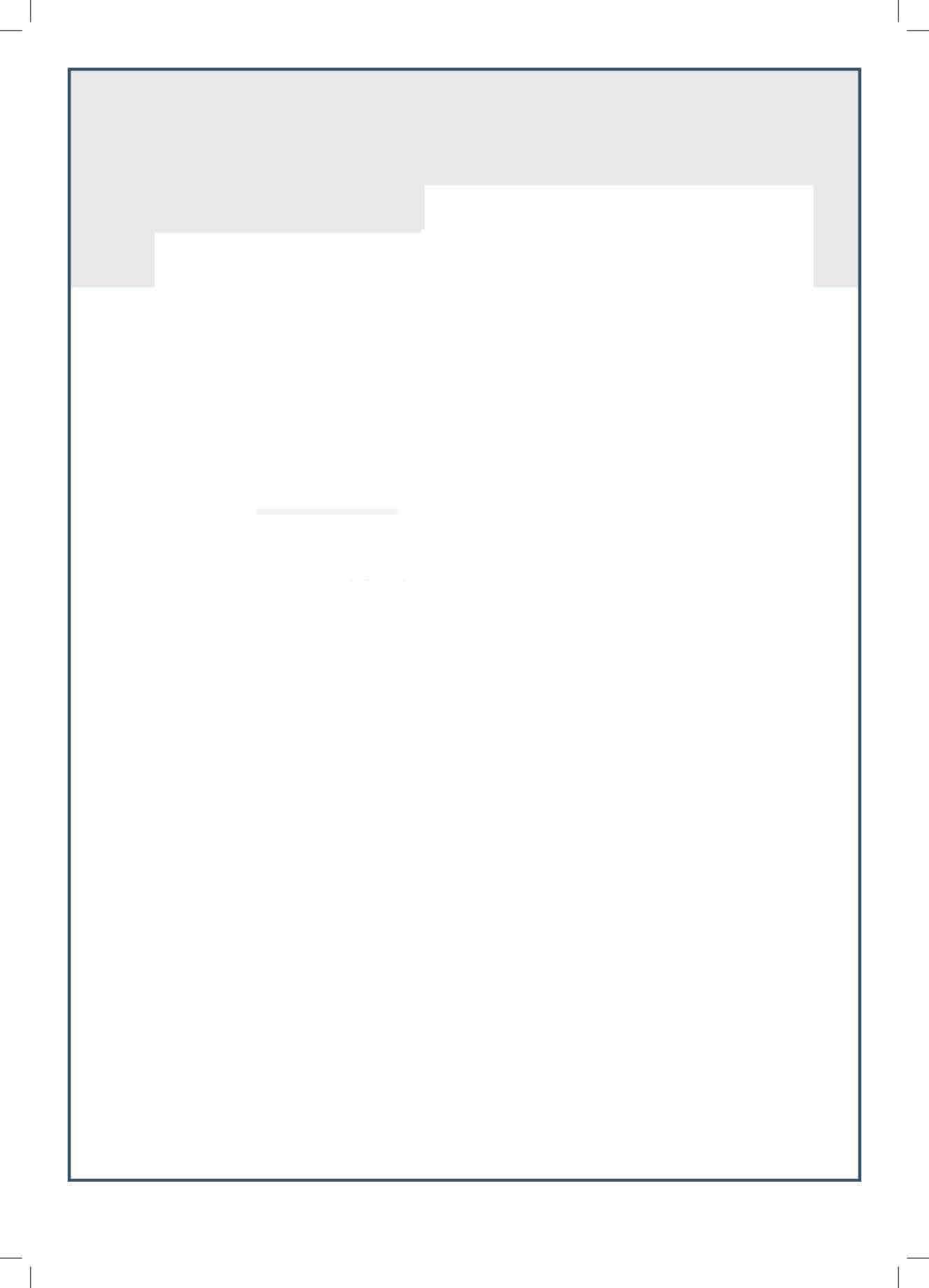
Improperly designed conveying systems or process changes can wreak havoc on production lines with blockages in the system, irregular feed rates, or premature equipment wear. Understanding how the system parameters influence the behavior of conveyed material is key to efficient and reliable pneumatic handling of bulk materials.
Make smart design choices!
Let PneuCalc help you reach production capacity and improve your bottom line!
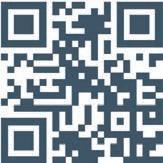
time and download
free demo today.
DYNA over the decades
Graeme Greaves has been the managing director of DYNA Engineering for more than 17 years. ABHR sat down with him to learn more about how the industry has changed.
WHEN GRAEME GREAVES LEFT his engineering job in Sydney in 2000, he was making a move into a whole new industry.
Greaves had previously worked in the food, automotive and aerospace sectors, but decided to move across the country to Perth to go into business for himself. He soon purchased DYNA Engineering, a small manufacturer of scrapers and impact beds.
“When I bought DYNA, the team was about five people – including myself,” Greaves told ABHR
“The mining industry was smaller in those days, it was a lot easier for a startup to get jobs with the major miners.
“The technology used in the mining industry really took off. Computerisation made processes bigger, more efficient, and more professional.
“Reliability and proven downtimereduction also became more important as the mining industry grew.”
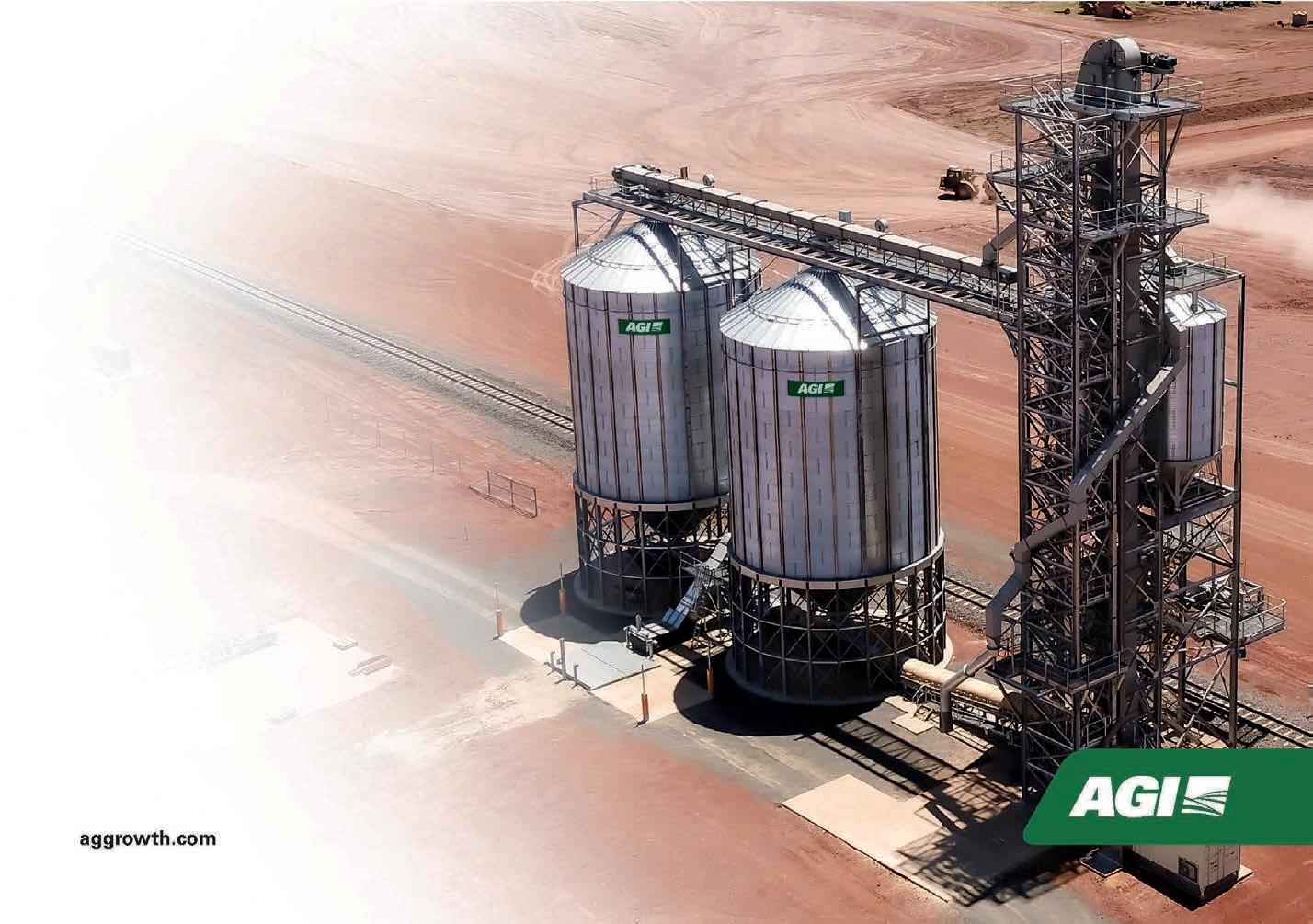
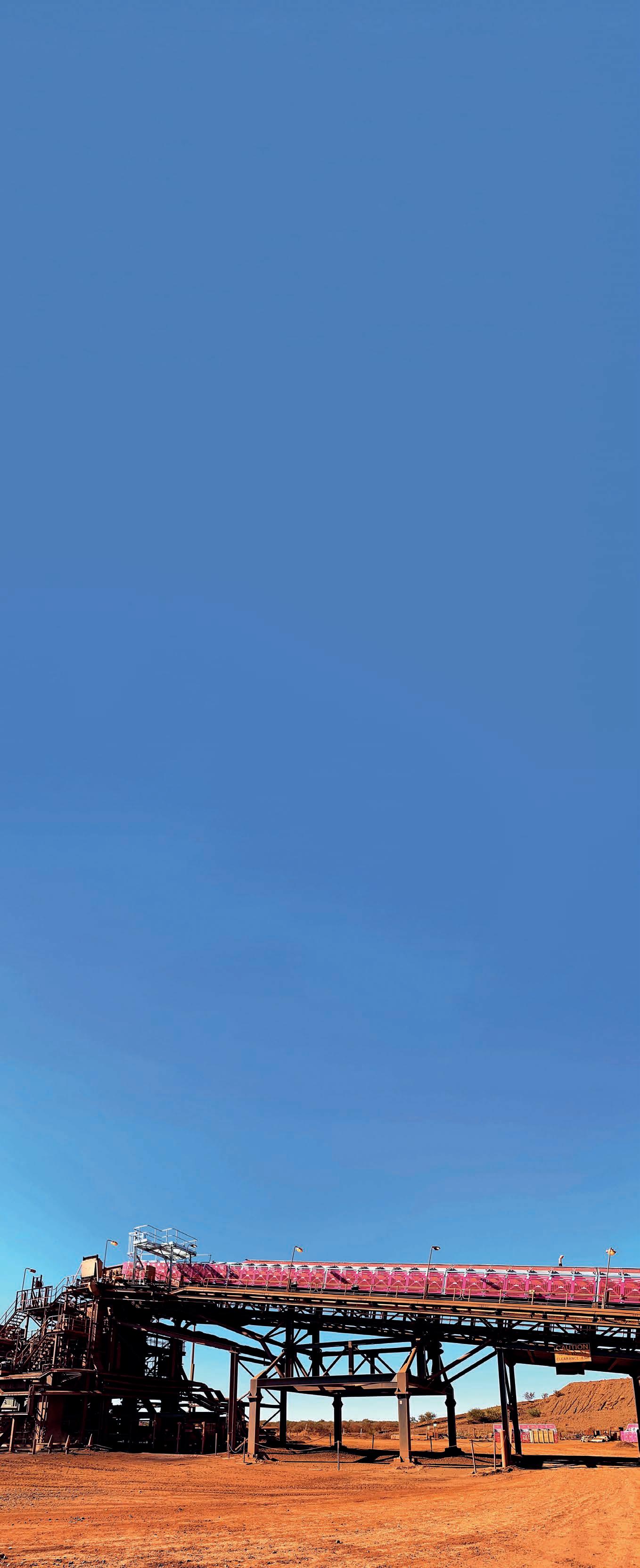
Continuous development was key to DYNA’s survival. Every few years would see the company change how it did business, introducing new products, services and systems to ensure it stayed competitive. The company redesigned its cleaners and impact beds so they would
work better and be easier to manufacture.
Finding ways to improve on price was also critical, which is why the DYNA began using computer numerical control (CNC) machining. This not only made the manufacturing process cheaper, but it also made it more reliable and less reliant on manual labour.
Greaves said one of the key challenges facing the industry today is the skills shortage.
“There’s a labour shortage affecting everyone at the moment. Skills that used to be common are becoming harder to find,” he said. “For the mining industry, technology and new developments will help address this.
“The real challenge for us is to bring these new products to market.”
One of the new developments the company has created is its line of high-density polyethylene (HDPE) conveyor guards.
Mine sites traditionally used steel to manufacture conveyor guards, which meant they were often heavy and awkward to move. Site staff will often need to remove and re-install guards to maintain the conveyor, which can add repetitive stress and safety risks.
HDPE conveyor guards can be up
to 40 per cent lighter than their steel counterparts and can be removed in a matter of minutes, all without the need for special tooling. The guards simply slide into place and are fastened with two bolts, requiring no special skills.
During maintenance shutdowns, HDPE guards can be safely and easily secured on the conveyor handrail. This conveniently ensures they are out of harm’s way and reduces the likelihood of them being misplaced, which sometimes occurs amid the pressures of a maintenance shutdown.
Conventional steel guards also require a considerable amount of painting to maintain the safety yellow colour. The size of the mesh makes this a costly and often wasteful process – a lot of paint is used and a significant amount is lost in the process. Operators often resort to hand painting, which is time-consuming and expensive.
HDPE conveyor guards, on the other hand, are made from safety yellowcoloured material, so no painting is required, which greatly reduces conveying system maintenance hours and cost.
The plastic guards cannot rust and are recyclable, which Greaves said is a major benefit to an industry that is looking to continue building its environmental, social
and governance (ESG) credentials.
“The mining industry wants to become cleaner and greener,” he said. “The mines know how important their reputations are, and how important sustainability is.
“In 20 years’ time, there might not be any diesel trucks left operating in Australian mines.”
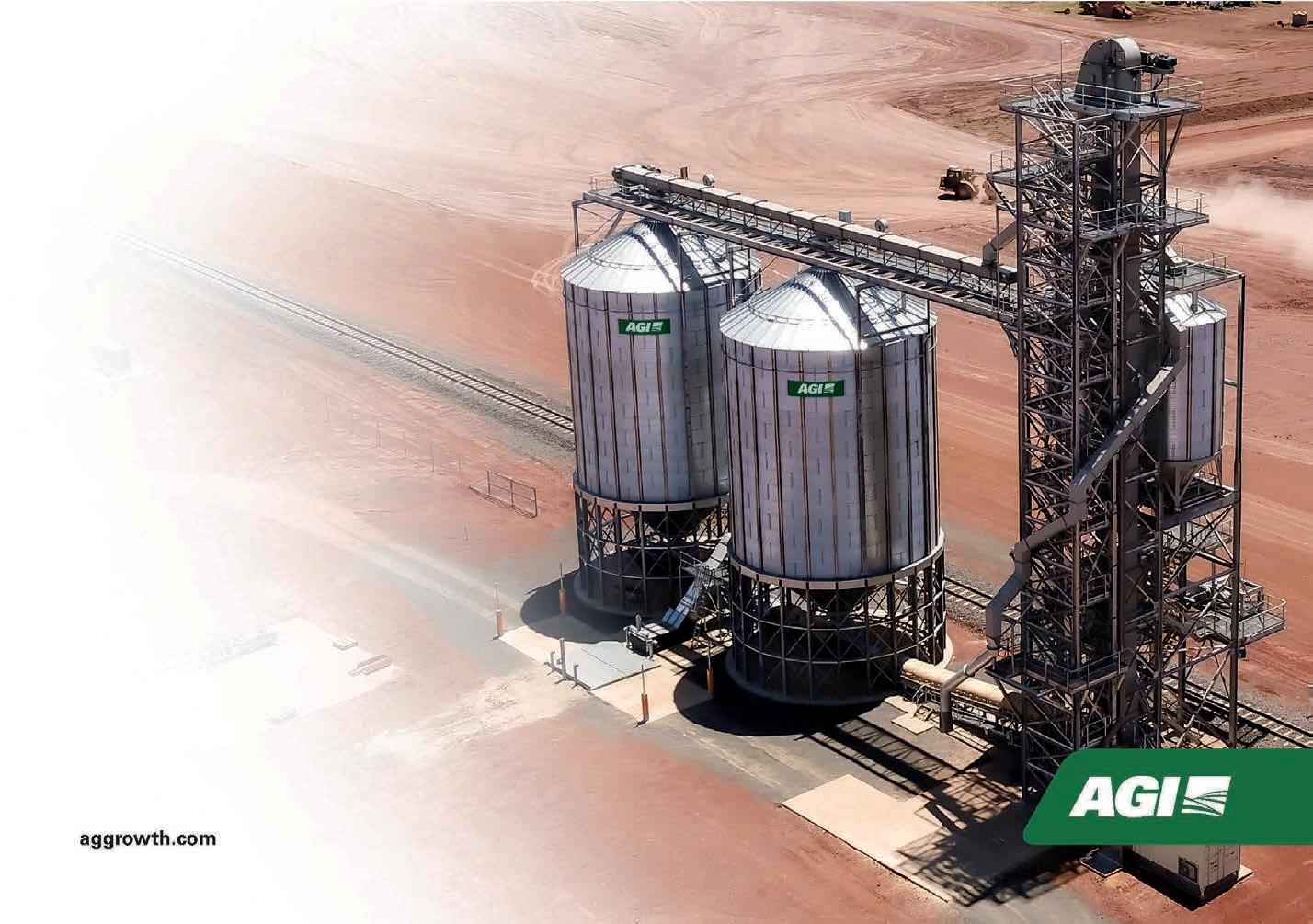
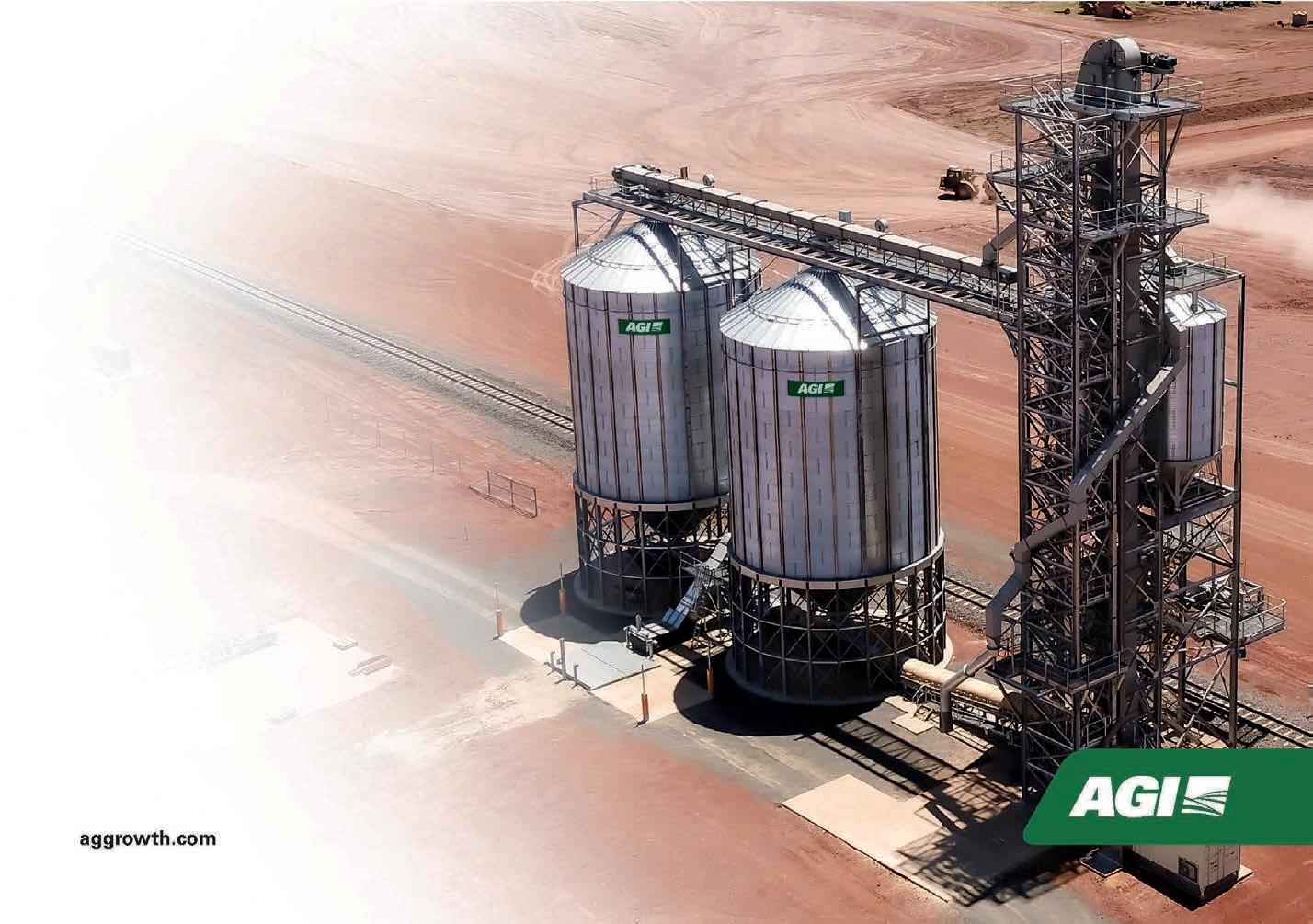
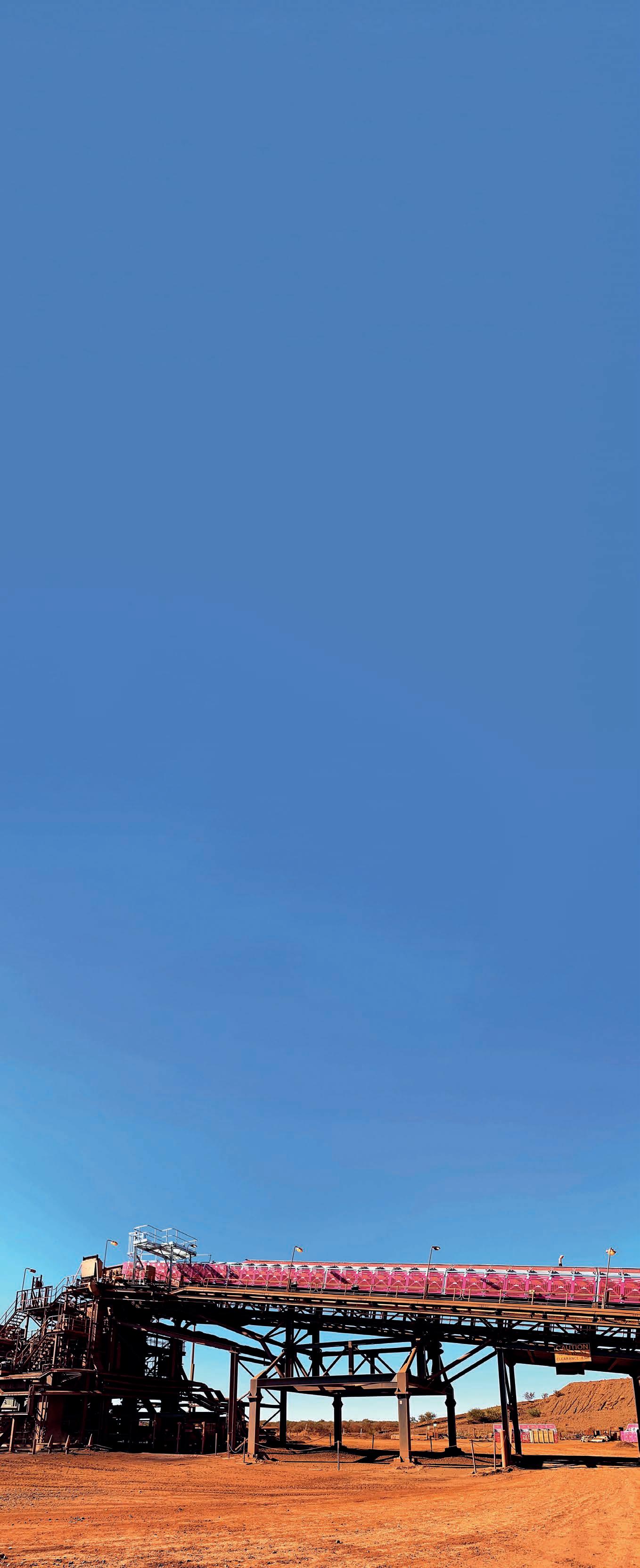
Because the HDPE guards are easier to manufacture, DYNA can scale their production at its Perth-based facility based on the needs of the client. Replacement guards can be built in a couple of days and delivered directly to the customer, providing faster turnarounds when compared with international markets.
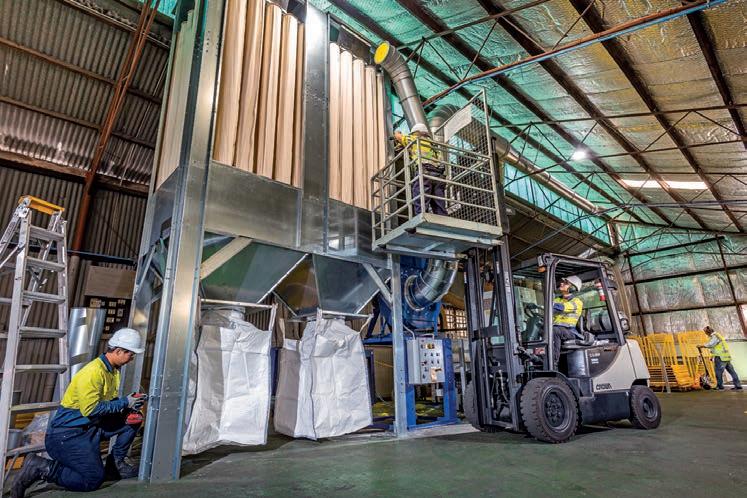
Supply-chain shortages have highlighted the benefit of staying local, as these manufacturers are far more insulated from major interruptions.
Greaves said a strong Australian industry benefits everyone, which is why DYNA is committed to supporting its local customers.
“If you manufacture in Australia, it builds local jobs, expertise and experience,” he said.
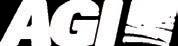
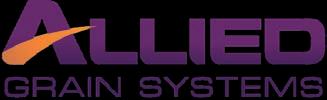
“Stakeholders from industry and government need to recognise this and support that side of the industry – and we’re already seeing this happen.”
The most important lesson Greaves has learned throughout his career is to focus on delivering good engineering.
“If you can build something that is well designed, meets the client criteria and operates effectively, you will always be successful,” he said.
“Good engineering sets us apart, which is why we are always looking at new inventions and ways of doing things.”
NetterVibration Australia is getting things moving
ABHR speaks to NetterVibration Australia managing director John Isherwood to learn why the German manufacturer established a dedicated local branch.
JOHN ISHERWOOD HAS WORKED with NetterVibration products for more than 20 years as the general manager of the original import agent and with vibration generally for over 35.
The German company had supplied its products to Australia through the agent since the 1970s but decided to change its strategy in 2019.
NetterVibration approached Isherwood with a proposition: lead the company through a joint venture called NetterVibration Australia.
“The branch is a part of NetterVibration, but now we sell directly to the customer,” he said.
“We set up an office and a warehouse in Mandurah, south of Perth, and have more than doubled our turnover over the past three years.”
NetterVibration Australia’s range includes electric, pneumatic, and hydraulic vibrators, with force outputs from 14N to in excess of 170,000N.
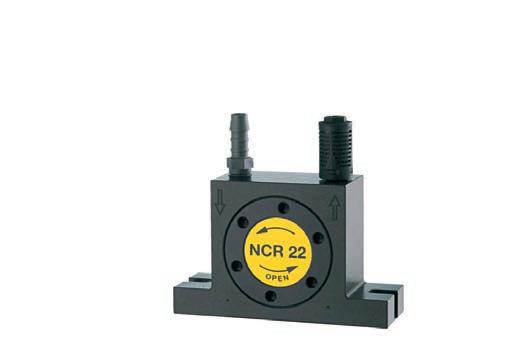
One size does not fit all, however, which is why the business works with the customer to find the most efficient and economical model for the specific application.
Whether it’s to help product
The vibrators are manufactured to extremely high quality in Europe.
move from hoppers or chutes, or to act as drives for vibrating feeders and compaction tables, Isherwood said NetterVibration can help choose the right model from their range of 4000 models.
“Anybody who has a storage bin –whether its flour, uranium or iron ore – will have to deal with hang-ups and blockages,” he said.
“The material properties can also change if there’s a change in moisture, or particle size.
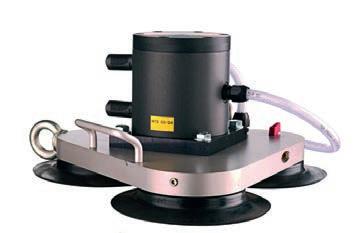
“If something doesn’t come out the bottom of the bin when it should, you could bang it with a stick, but that’s not safe or effective.”
The self-contained vibrators require only suitable lubrication, with many available as lubrication free, to ensure they continue working properly.
The vibrators are manufactured to extremely high quality in Europe, with ATEX rating as standard on most electric models, and rating 1 and 2 available to order on all models. Stainless steel versions are available for food industries and for aggressive atmospheres.
“NetterVibration has a very good reputation around the world. It has been manufacturing vibrators
for almost 70 years, and you can rely on the European standards of quality,” he said.
“Over that time, the business has only focused on vibration and improving its products. It’s developed specialist expertise and understands what works and what doesn’t.
“It’s a global company, with seven branches and about 40 agents located around the world that share knowledge and support.”
The vibrators are also often found in trucks, as the vibration during
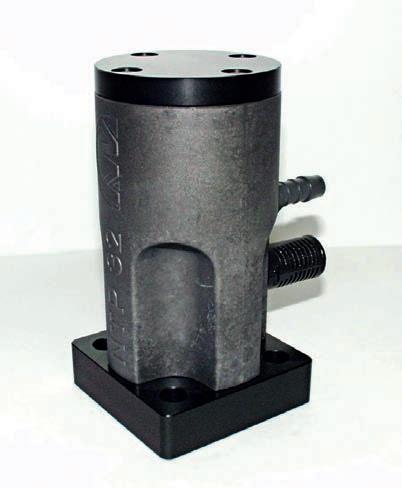
transport can cause bulk materials to compact.
Isherwood said the company is continuing to grow in the Australian market, with Australian manufacture of vibrating feeders and compaction tables, specifically designed to meet the needs of each client.
“We’re working close with clients to help them achieve optimum outcomes in their processes.
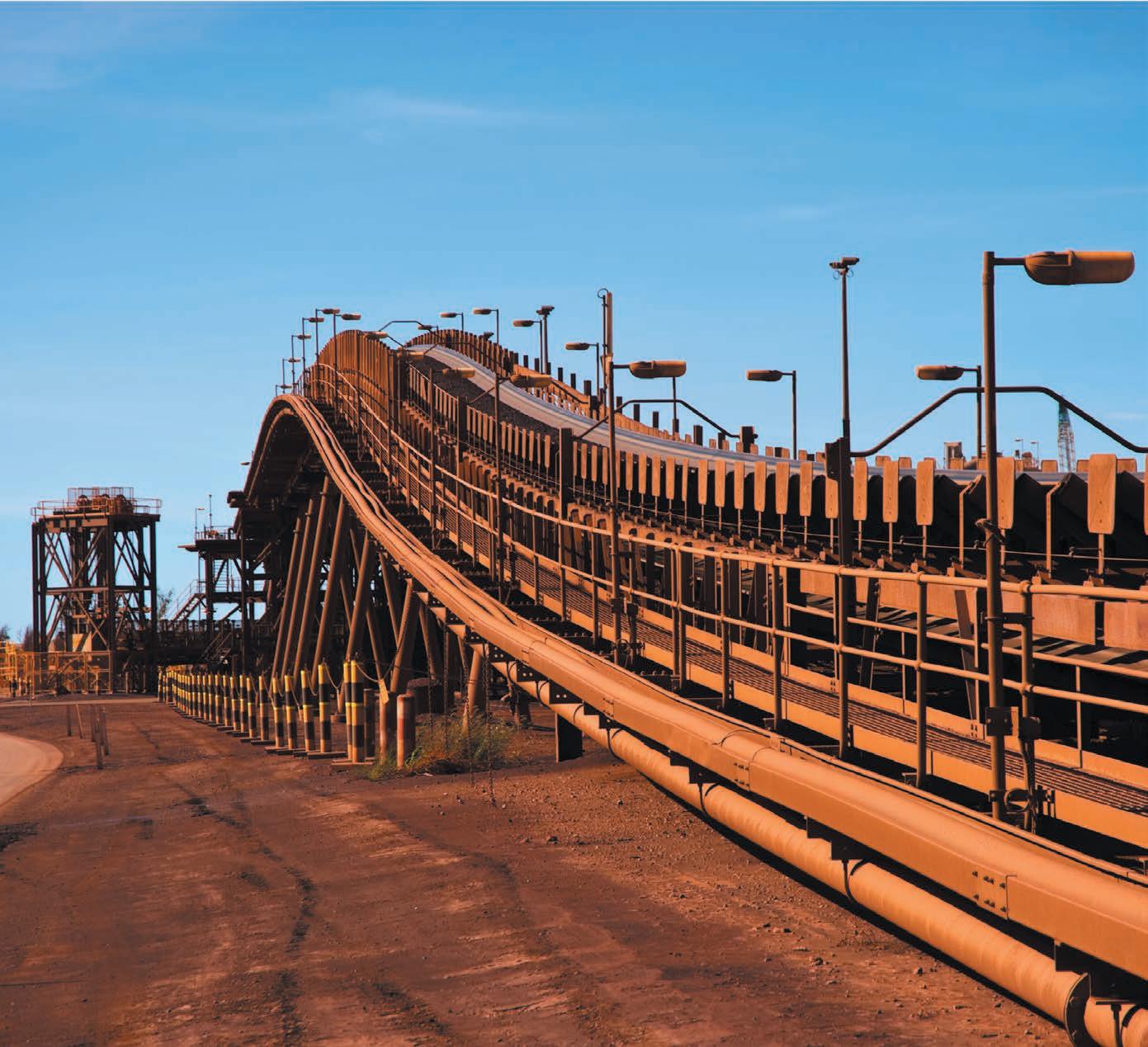
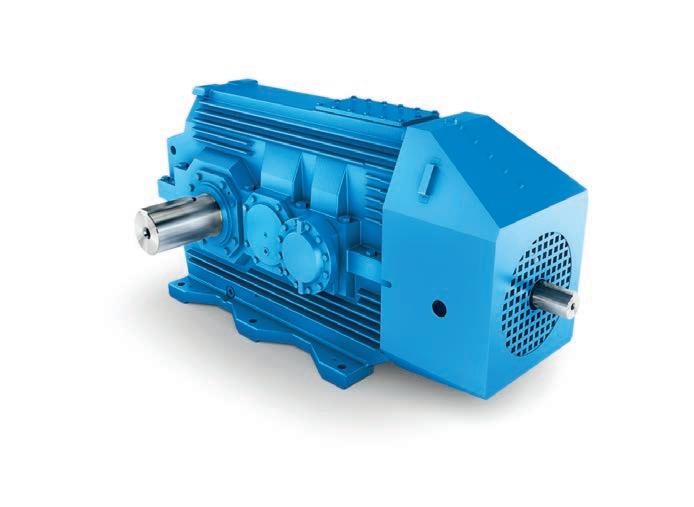
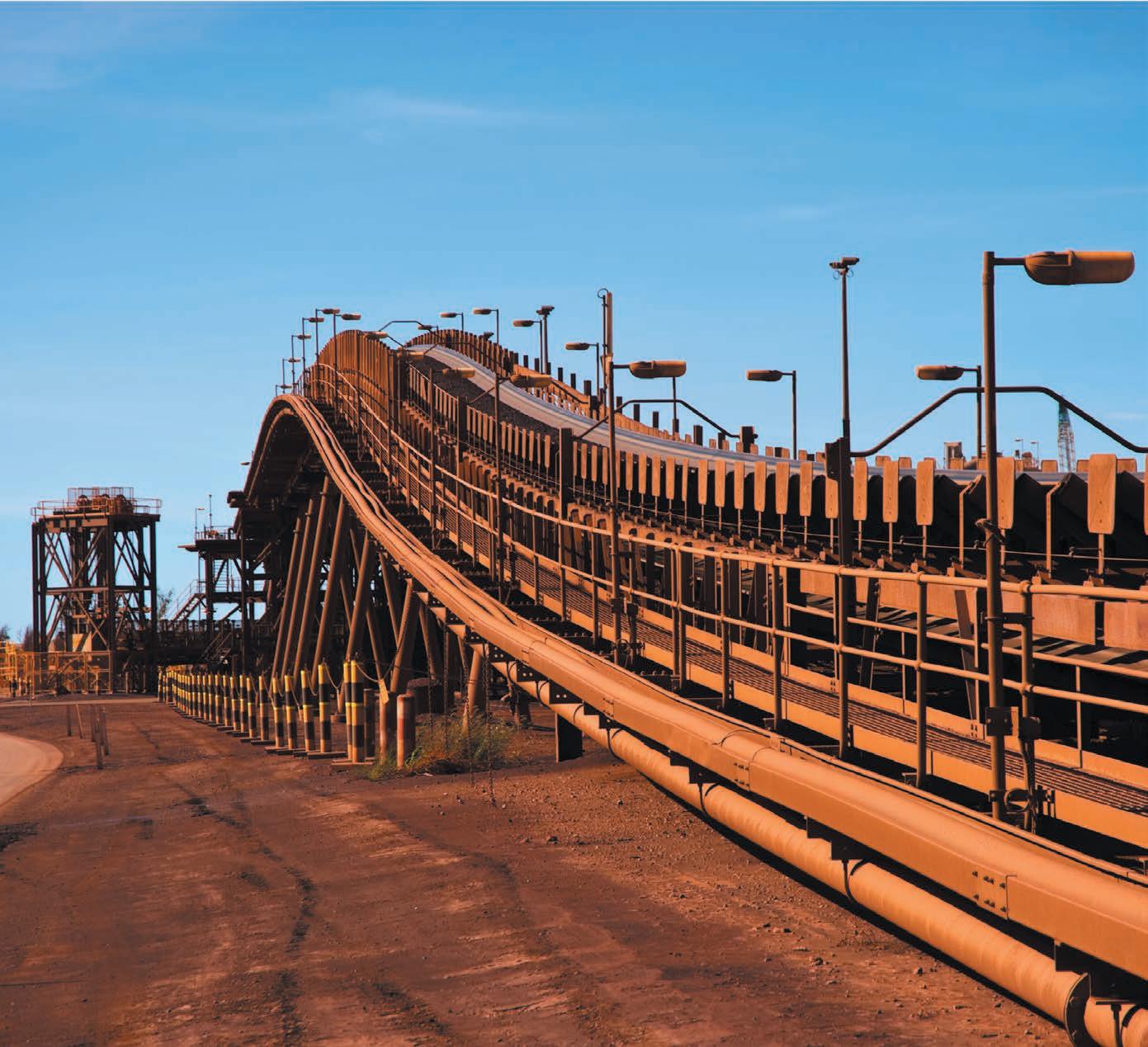
Capacity up and labour down with bulk bag weigh batch discharging
To meet growing demand and raise quality standards, an Indonesian drink manufacturer installed twin Bulk-Out bulk bag weigh batch dischargers from Flexicon (Singapore).
bulk bags, Flow-Flexer bag activators raise and lower opposite bottom edges of the bag with increasingly longer strokes as the bag lightens, eventually raising the bag bottom into a steep ‘V’ shape.
The hoppers include a bag dump hood for manually adding sugar from 25 kg bags, providing Singabera the flexibility to use material from bags of multiple sizes.
“Most factories in Indonesia still use the smaller bags and sometimes we have to use them because of supply shortages,” Na said.
INDONESIAN DRINK manufacturer Singabera produces natural ginger mixes and other local specialties from locally sourced ingredients before they are shipped off to buyers around the world.
Michael Na, the company’s managing director, said the business is committed to creating the highest quality products derived from natural plants while managing its environmental footprint.
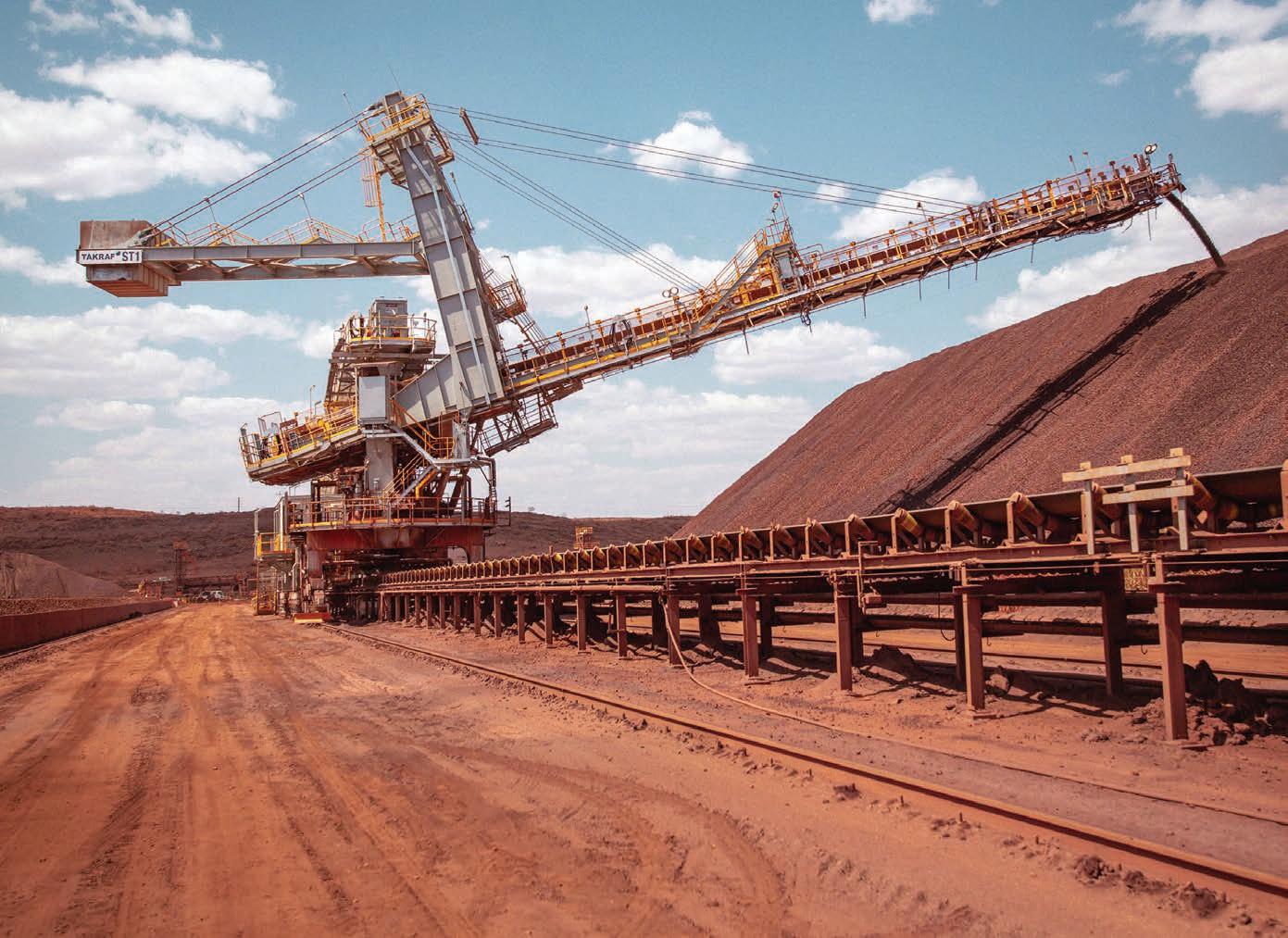
At its old factory, everything was done by hand. Workers would transport, weigh, and add coconut and cane sugar from 25 kg bags, cutting each open one at a time.
“That was a lot of work,” Na said.
Foreign objects entering the process was another concern.
“The US is our biggest market, and the standards are very strict. Any concern about quality is unacceptable,” he said. “We needed to do something differently to have fewer people at the operation and to ensure consistency.”
To meet growing demand and raise quality standards, Singabera built a new factory and installed twin Bulk-Out bulk bag weigh batch dischargers, each feeding
parallel lines of three flexible screw conveyors, from Flexicon (Singapore).
The automated system weighs and delivers fine sugar to six juice cookers at high rates while containing dust and improving safety.
System handles bulk bags and handheld bags
The twin bulk bag discharging and conveying lines are positioned side-byside and parallel to one another, each supplying sugar to three cookers on a 2m high mezzanine.
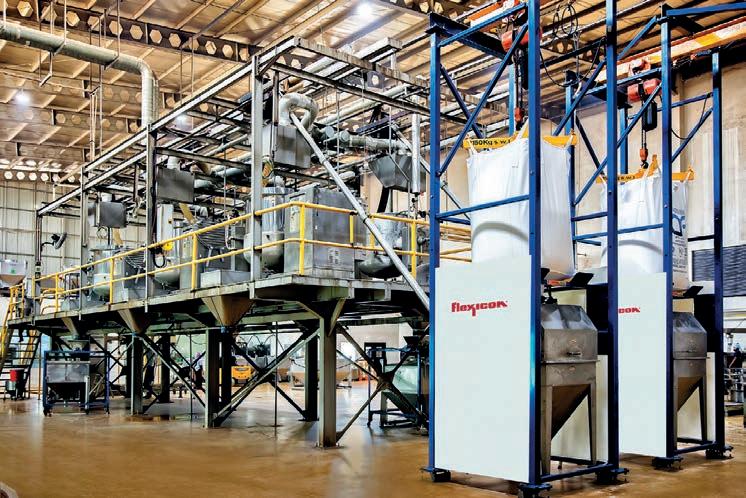
Each model BFC discharger is mounted on load cells and equipped with a cantilevered I-beam, hoist and trolley that lifts and positions a one tonne bulk bag into the discharger frame without the need for a forklift. A worker pulls the outlet spout through a 380mm diameter iris valve, which closes around the spout, preventing material flow. The spout is then untied and the valve opened slowly, preventing uncontrolled bursts of material and dust from entering the 400L floor hopper.
To promote evacuation of sugar from
Discharging smaller bags at floor level into the manual bag dumping station means that workers no longer need to carry the bags up ladders or stairs to empty the contents into the cookers. This not only reduces the risk of injury from a repetitive and potentially hazardous manual process, it also reduces the time to achieve the desired batch weights when using smaller bags. A rigid screen keeps foreign objects and packaging material out of the hopper and supports the bag to ease the strain on workers.
Conveying in multiple directions, selectively by weight The floor hopper for each station charges an inclined 7.5m long flexible screw conveyor that either feeds the first juice cooker or the charging adapter of a horizontally oriented 4.5m long flexible screw conveyor. The horizontal conveyor can, in turn, feed the second juice cooker or the charging adapter of another horizontally oriented 4.5m long flexible screw conveyor that feeds the third juice cooker.
The sugar exiting the inclined conveyor passes through a short length of downspouting into a pneumatically actuated slide gate valve. This either
opens to deposit the sugar into the cooker or closes to move the sugar through the horizontal conveyor to the next discharge point. The closed slide gate also reduces the effects of the cooker’s heat and steam on the sugar which could otherwise agglomerate and cause the convey line to shut down.
Each conveyor’s polymer outer tube encloses a flexible steel spiral that is driven beyond the point of discharge, preventing material contact with the bearings or seals.
Once an operator selects which juice cooker should receive a batch of sugar, a programmable logic controller (PLC) actuates the corresponding slide gate valves and 4 kW gear drives of one, two or three of the horizontal conveyors.
When feeding the first juice cooker, the PLC runs the inclined conveyer at full rate, and then at trickle feed rate prior to stopping the conveyor when the bulk bag discharger has lost the accurate batch weight. When feeding the second
or third juice cooker, the PLC additionally starts and stops the horizontally oriented conveyors in the same manner.
Once a batch of sugar—typically 150kg —is added to a corresponding volume of juice, the solution cooks for 45 to 60 minutes.
More capacity, accuracy, and consistency
A level switch in each bulk bag discharger’s floor hopper signals when workers need to load another bulk bag. The PLC maintains inprocess batch information to ensure that weight accuracy is maintained during changeovers.
Depending on the season, Singabera runs its drink-making process over two or three 8-hour shifts, employing three workers per shift instead of 10 workers required previously. Sugar throughput is 7 to 15 tonnes a day, twice what the old factory could handle.
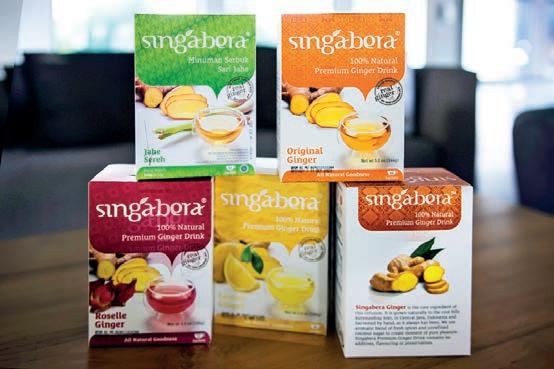
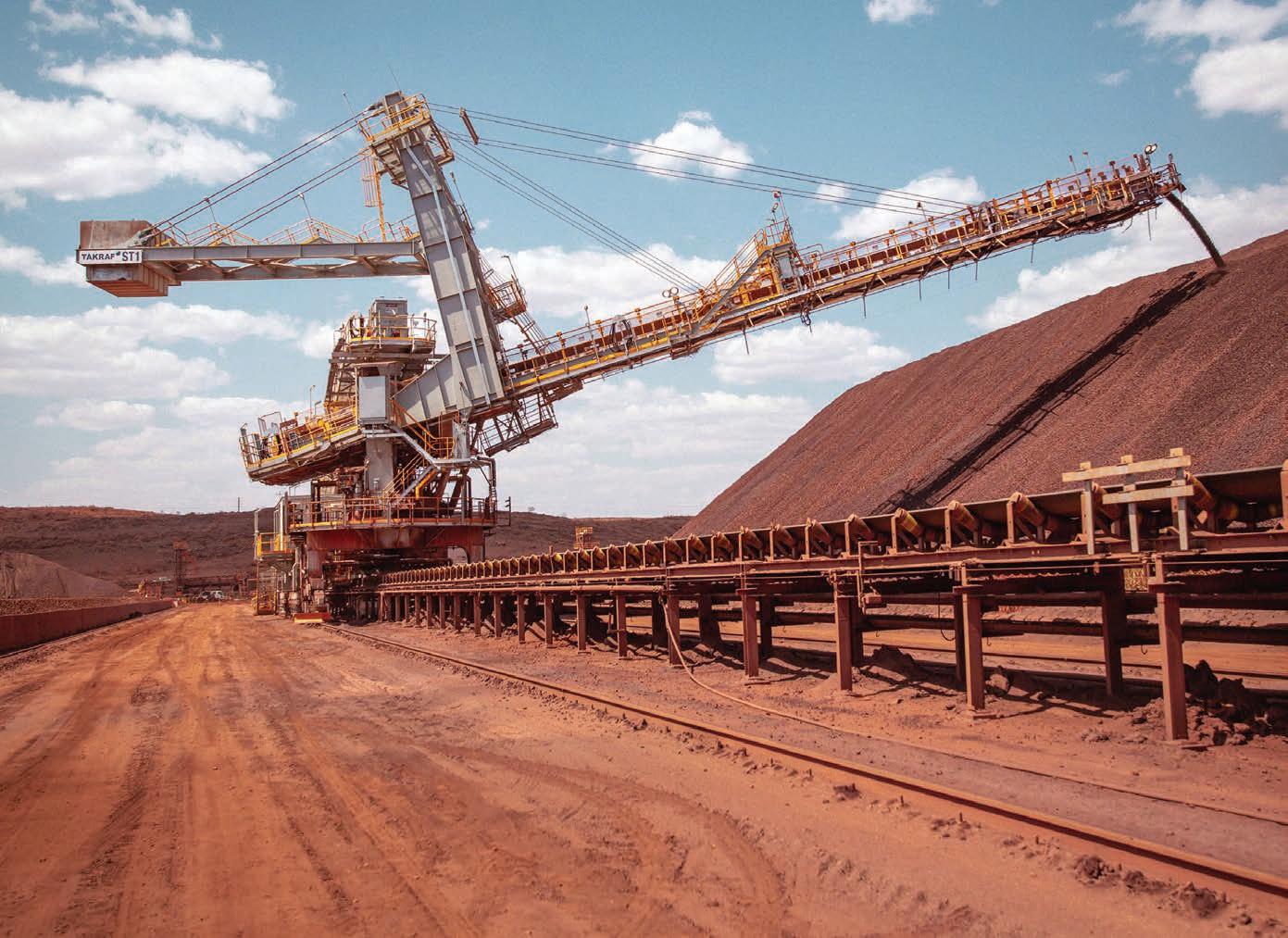
“The system eliminates heavy manual
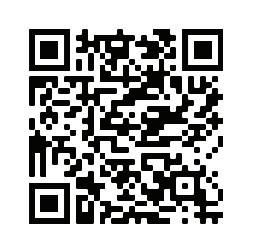
labour, helping worker well-being tremendously,” Na said.
“Other benefits are accuracy, consistency, and hygiene. We can stack the bulk bags using forklifts or put them on racks, making warehousing more efficient than with smaller bags.
“Flexicon gave us a turnkey solution, and it’s been working to its full capabilities.”
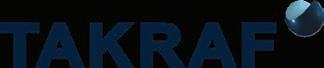
Keeping the customers close
Flender has invested in new Australian facilities to ensure it is more agile, responsive and customer-centric.
INDUSTRIAL GEARBOX Manufacturer Flender has developed a service-centric culture following its carve-out.
The company, which has been around for more than 100 years, used to work through its business partners, dabbling in service and support.
But Kareem Emara, head of Australia and New Zealand at Flender, said the original equipment manufacturer’s (OEM) new business model meant working closer to its clients.
“Flender’s gearboxes have a proven track record and are an industry benchmark,” he said.
“Our products have some of the largest install bases in Australia and are known for their reliability and quality, backed up with in-depth technical expertise.
“We have been involved with the industry for some time and knew we could further adapt our portfolio and products based on continuous improvements. Part of this was to improve our service and support offering and establishing a dedicated local presence in Australia.”
Flender invested heavily in growing its local operations, opening facilities in Rockhampton and Perth. It also acquired the Finnish wind turbine gearbox manufacturer Moventas in April, along with facilities in Melbourne.
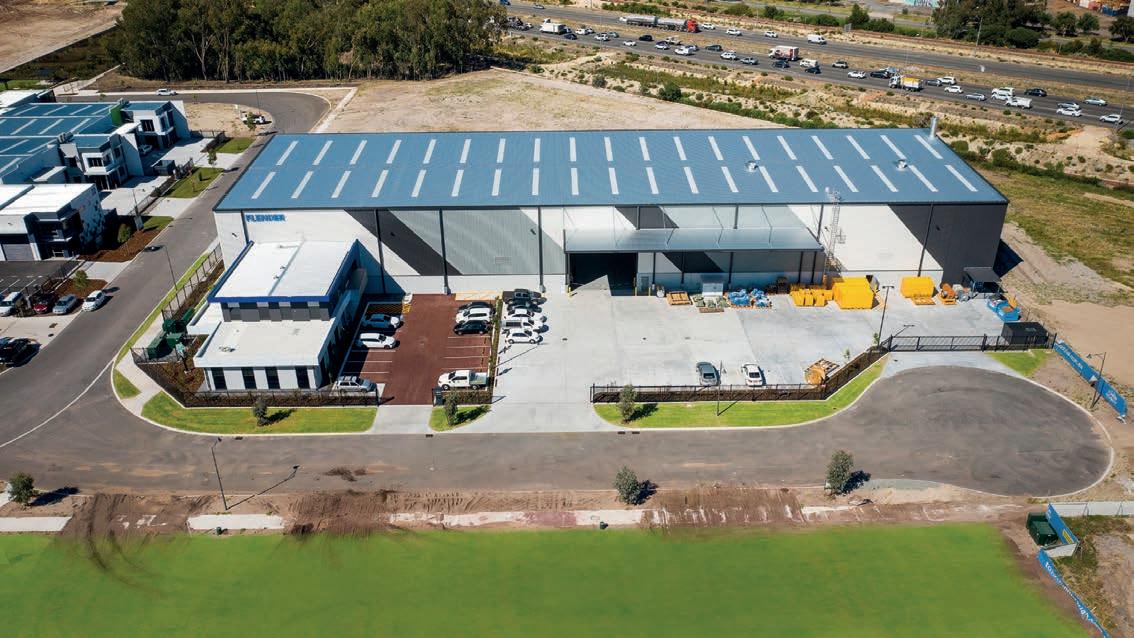
In addition, the company aims to open its new Sydney facility by the end of the year to further support its New South
Wales customers.
The facility will be just over 1800 square metres and has the structural capacity for a 50-tonne crane. Emara said the new location will have all of the equipment required to deliver an OEM standard to its customers.
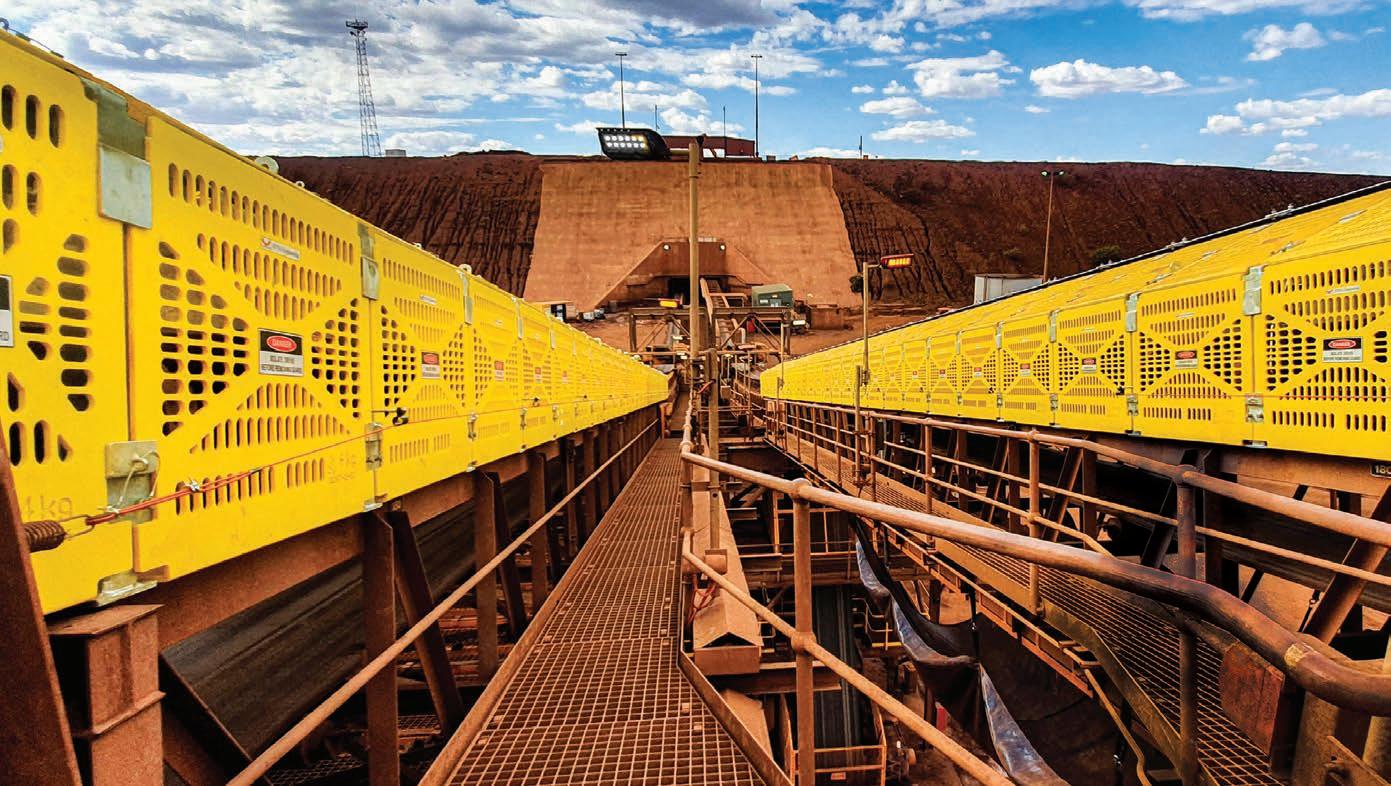
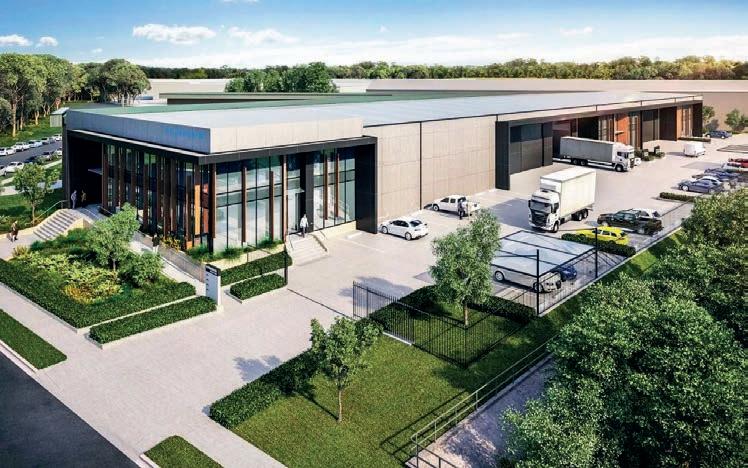
“It’s important to be close to your customers,” he said. “It allows you to be more agile and respond to their needs as quickly as possible.
“All of our facilities can operate 24 hours a day if needed, letting us turn things around quickly.
“We can also provide proactive support, using our OEM knowledge, vibration analysis and conditionmonitoring expertise to help them avoid unplanned shutdowns.”
Flender’s facilities are set up to support the entire lifecycle of a product, with teams that can provide everything
from installation to decommissioning.
It can also leverage global support from its global network. Flender has extensive research and development teams in China and Germany that provide experienced aid in even some of the most unique of cases.
Emara said there has been positive feedback from the industry, which appreciates the customer-driven focus.
“Having the right people, with the right knowledge close at hand means our customers have everything they need to thrive,” he said.
“Flender equipment is built with reliability in mind, with some of our assets still in use since they were installed in the 1970s.
“We aim to provide our customers with the latest technologies and support them with digitisation so can they get the most out of their equipment.”
Safeguard
operations
DYNA Engineering Conveyor Guards
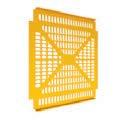
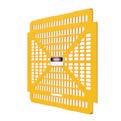
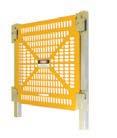
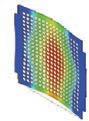
leading the way towards a more environmentally
future by being manufactured with recycled and recyclable HDPE plastic.
Robust
Our “X” design increases the guard’s strength and is simple, intuitive and robust. DYNA Engineering doesn’t compromise on your safety.
Lightweight
Reduce your material handling risks and increase safety for your personnel with our guards, which are up to 40% lighter than conventional steel guards.
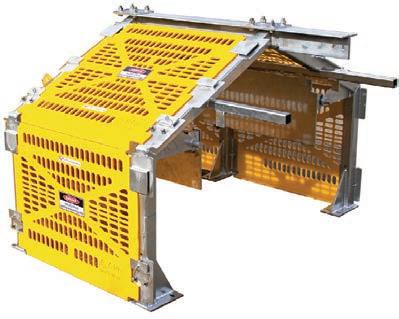
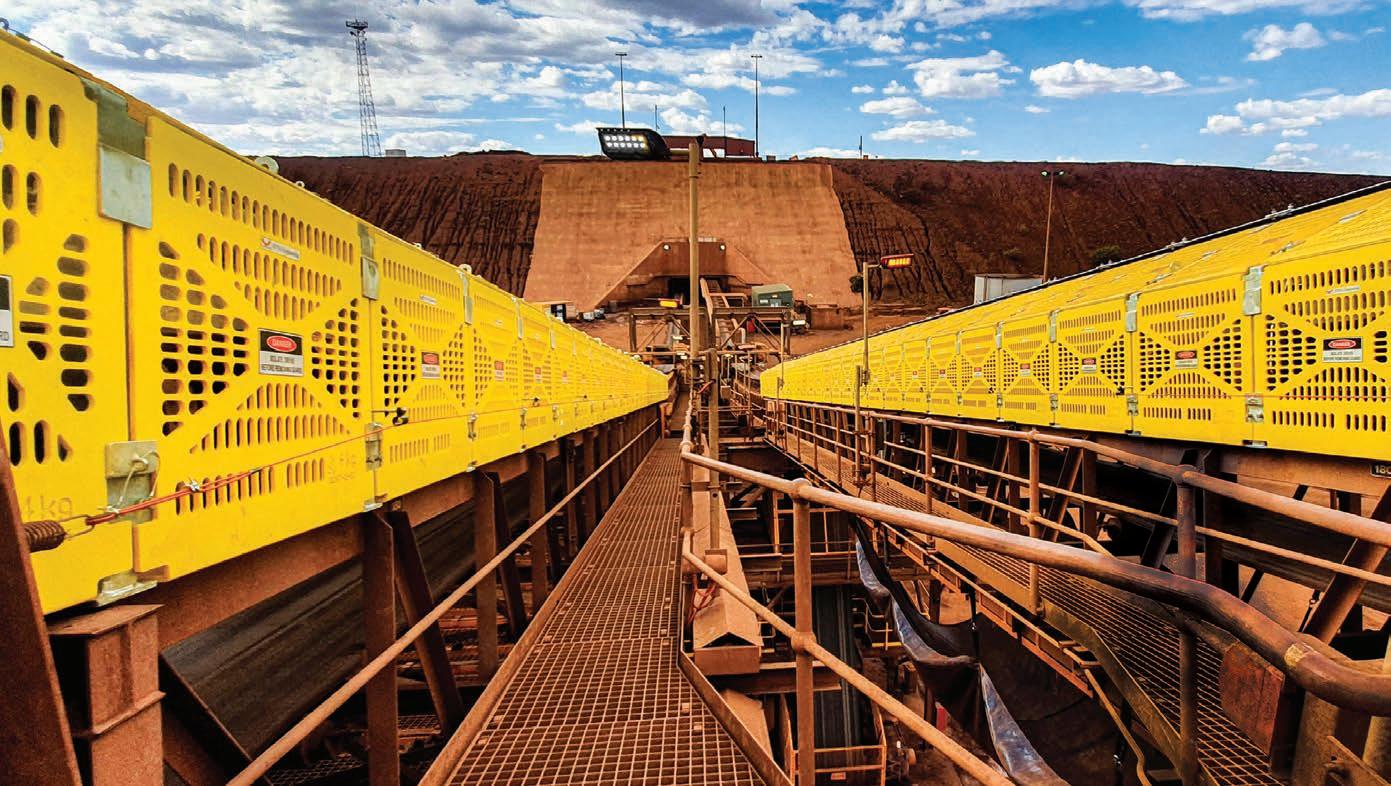
Economical
Our HDPE Conveyor Guards
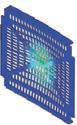
reduce your overall maintenance cost as they do not require
and will not rust or corrode.
Smart Series helps stop nuisance tripping
Pacific Automation is ready to launch its new series of conveyor accessories that aim to eliminate lengthy production breaks.
Nuisance tripping can cause mines to lose a lot of money through lost productivity.
AN AUTOMATIC SAFETY ALARM
An automatic safety alarm halts a massive, 10km overland conveyor. One of the sensors has tripped the alarm, and a response team is deployed to find the cause of the issue.
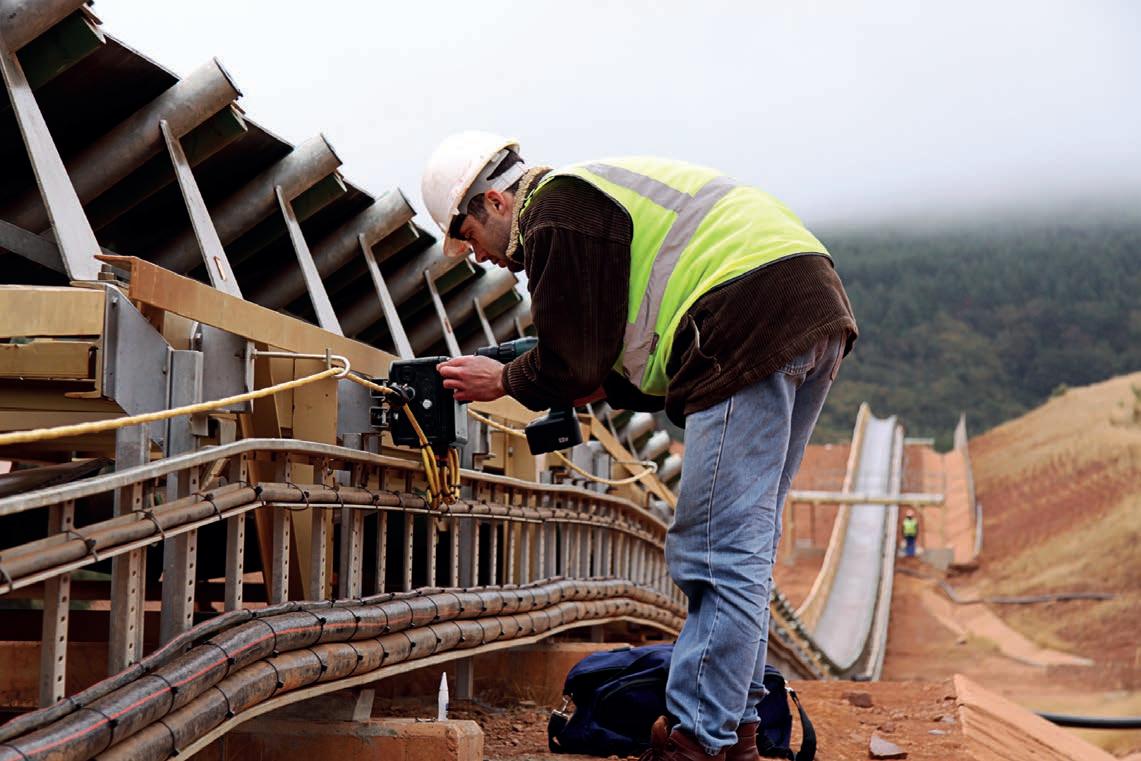
The team gets into a vehicle and drives along the conveyor to find the fault. They begin to search the nearby area and check for any faults – but can’t find anything.
It turns out the brutal heat from the Australian sun and vibration from the conveyor loosened one of the terminal screws used in a safety pull wire switch. The nearby vibrations from the conveyor cause the screw to begin moving,
loosening the control wire and activating the automatic stop.
Finding this loose wire is the tricky part. Now that the conveyor has stopped, it looks like every other wire in the nearby terminal. To make matters worse, the wire could be in one of several terminals all along the conveyor’s length.
Minutes pass as the team hunts for this mystery wire. All the while the belt lies dormant, potentially costing the site millions of dollars in lost productivity.
This is a situation Johan Blignaut, a field service engineer at Pacific Automation, has seen countless times.
“As part of my role, I’ve gone to a client’s site to help their crews with this
issue,” he told ABHR. “Nuisance tripping can happen every hour, or it can be at random intervals.
“If you add up all the time spent on dealing with it, it equates to a lot of lost money.”
Blignaut has more than 12 years’ experience in Australia working alongside these kinds of systems and has used his knowledge to help develop Pacific Automation’s new range of conveyor components.
The Smart Series brand includes a range of products for the control, safety, and monitoring of conveyor belt operations. It includes belt rip and belt tear detection systems, misalignment
sensors, a full range of conveyor monitoring devices, and safety pull wire switches.
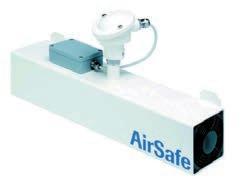
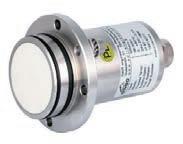
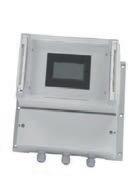
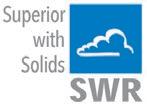
The pull wire switches, also known as pullkeys, serve as emergency-stop extension cables that can be tripped manually by operators by pulling an attached length of cable or rope.
Smart Series pull keys are highly customisable and available in a range of configurations. Options include durable polycarbonate and marine-grade LM6 aluminium housings.
Blignaut said the Smart Series range is suitable for all Australian mining conveyor belts.
“We have developed and tested the range to ensure they meet Australian and international standards,” he said.
“Smart Series components are ideal for conveyors longer than 10km in length but can alsobe used on shorter conveyor belts within minerals processing plants and bulk material handling facilities.
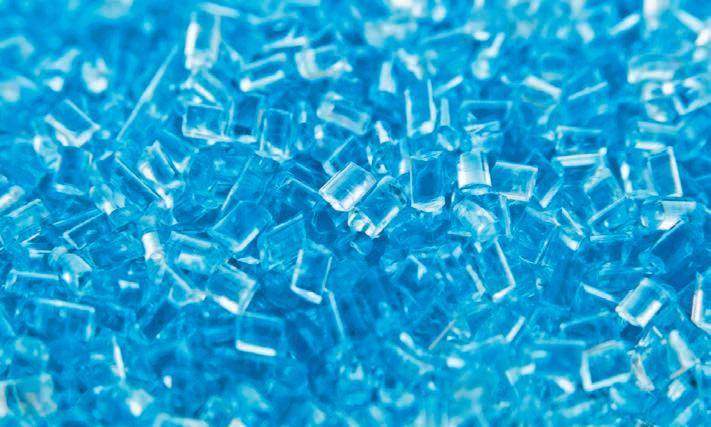
“We can now offer our customers everything required for successful conveyor beltoperation, from safety through to monitoring.”
In addition to the pullkeys, the Smart Series conveyor protection devices can help monitor for belt rips, spillage, misalignments, belt drift and blocked chutes. These devices gather feedback that is then made available to operators, who can instantly know where the faults or trips are.
Accessories have also been engineered for compatibility with all of the devices and components within the Smart Series range. These include pigtails, eye bolts, spring tensioning kits, wire rope grips and turnbuckles, pull wire and more.
Pacific Automation began developing the range several years ago. While the company had several products for conveyor safety applications, it didn’t yet have the complete package.
Stephen Armstrong, the company’s chief executive officer, said the team decided to develop the range so companies could source a complete solution for their belts and access expert technical support from a single partner.
“Previously, mine operators have had to source different pieces of a solution from multiple suppliers, purchasing electronic conveyor monitoring solutions from one supplier while sourcing physical safety devices from another,” he said.
“We wanted to be a single source for monitoring equipment, so that our customers can come to us for the essentials, the nuts and bolts, the smaller components and everything in between.”
The range is now ready for release on the market and can be incorporated into large- and small-scale projects. Pacific Automation can tailor its devices for specific sites and is able to retrofit the entire product line onto existing sites.
Armstrong said the company is confident in the quality of the Smart Series brand.
“We are excited to provide our industrial customers with the new range and hope to improve the performance of their plants or resolve any issues they may be facing,” he said.
FLOW MEASUREMENT
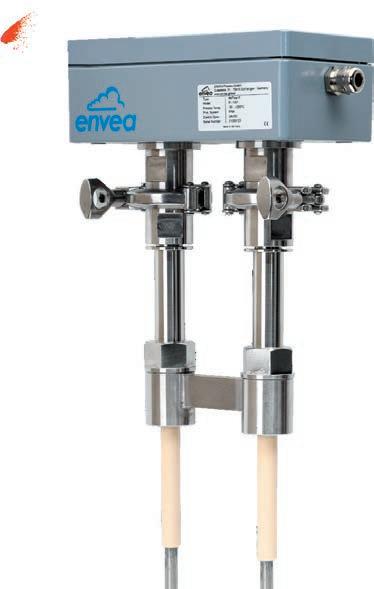
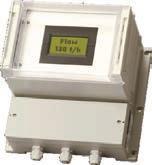
DRY BULK
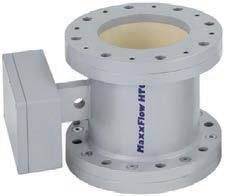
Measure twice, build once
Australian equipment manufacturer Tecweigh is partnering with bulk handling sites early in the design phase of new projects to ensure measurements remain accurate.
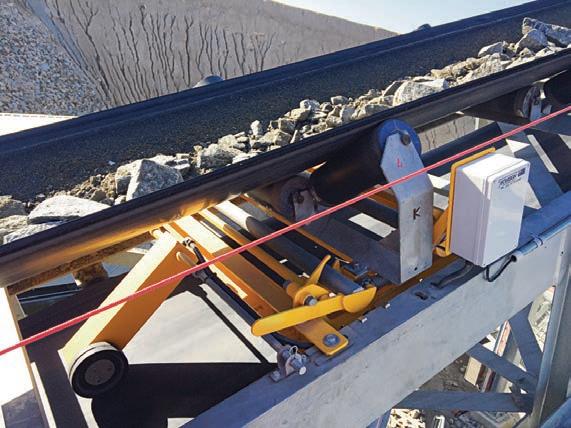
THE PLANNING PROCESS IS A crucial make-or-break period in the lifecycle of a bulk handling project. In these early stages, even some of the smallest decisions can have longterm effects on the productivity of the overall plant.
Weighing equipment is often chosen during these early stages of a project, which is why Australian equipment manufacturer Tecweigh aims to partner with bulk handlers as early as possible.
Barry Gamble, business development manager at Tecweigh, said getting involved during the planning process was crucial for process optimisation.
“Our team will work with a client to prepare a weighing solution that is custom-tailored to the site’s requirements,” he said.
“They can guide clients through our range of high-quality weighing-in-motion equipment and metering products.”
Founded in 1973, Tecweigh designs and builds equipment for bulk material handling. It can provide solutions for various industries, such as chemicals, crushed stone, sand and coal, and accurately measure sticky, low-density, or abrasive materials.
The company specialises in three product ranges – belt scales, weigh belt feeders and volumetric feeders.
Gamble said Tecweigh offers several models of weigh belt feeders that can be custom designed for almost any application.

“They have throughputs from 100kg per hour to more than 1000 tonnes per hour, with models ranging from medium to ultra-heavy duty for blending, loading or truck filling,” he said.
“We also use stainless steel, hermetically sealed IP68 load cells designed to provide accuracies of ± 0.5 or ± 0.25 per cent for our feeders and belt scales.
“The weigh idler systems have also been designed to be easy to calibrate and to provide consistent accuracy.”
Tecweigh can manufacture weigh belt feeders to specific lengths and widths from powdercoated mild steel or stainless steel to best fit the requirements of the application.
The company’s volumetric feeders feature an external agitation system that eliminates product degradation, ratholing and bridging. The single auger design allows for uniform and accurate
metering of the product. It includes minimal moving parts, and common wear parts can easily be replaced.
Available in three sizes, the volumetric feeders can accurately accommodate feed rates of up to 30,000 litres per hour. Typical applications provide around two to three per cent accuracy, given consistent material bulk density and flow characteristics.
All of Tecweigh’s manufacturing takes place at its facility in Carrum Downs, Melbourne. Gamble said this gives the company the ability to quickly respond to its customers and has insulated it from supply chain interruptions.
“We can normally deliver what the client needs within seven to 10 days for stock items,” he said. “We have built strong, long-lasting relationships with our own suppliers as well.
“Tecweigh also offers local after sales support and maintains a significant stock inventory for its conveyor belt scales, volumetric feeders, and weigh belt feeders.
“Our team has more than 100 years of combined experience in providing bespoke bulk weighing solutions, and we’re excited to continue supporting the industry with accurate and dependable equipment.”
engineering
proven 4-leg base design
on load cells. This unique Nelson design
accurate weight measurement.
grain, legumes, sugar and flour, and plastic granules, Nelson 4-leg design silos are available in pre-painted steel. For flour, sugar, plc and industrial powder, Nelson are building fully welded stainless steel silos, also with the proven 4-leg design, mounted on load-cells.
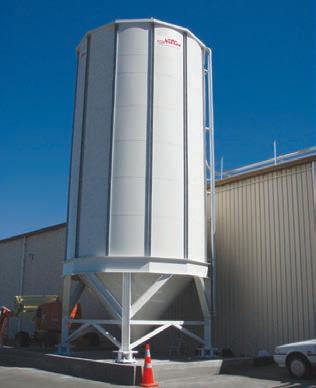
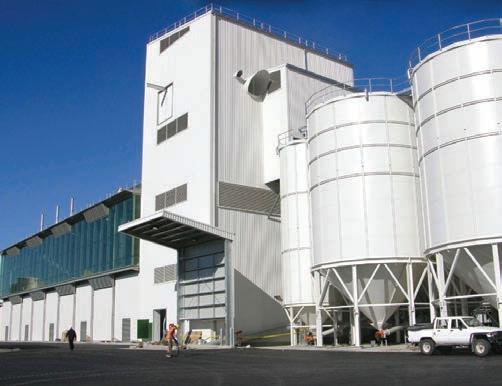
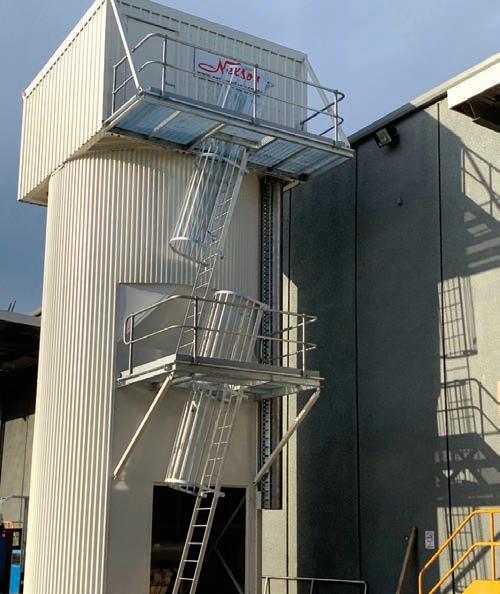
the Nelson CAD programme,
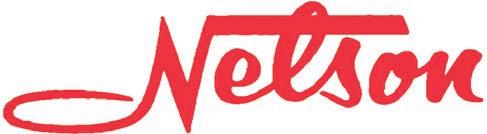
have the capacity to develop a cost effective design package to meet the needs of the industry. We can then engineer your order in our own complex - with a fixed price that will save you up to 50% of the cost of on-site construction.
And Nelson can deliver, install and commission purpose-built silos, with an absolute minimum of lead time.
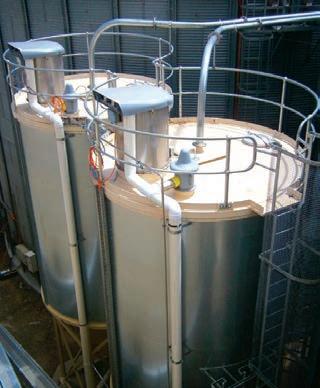
Conveyor pulley replacements are easier than ever
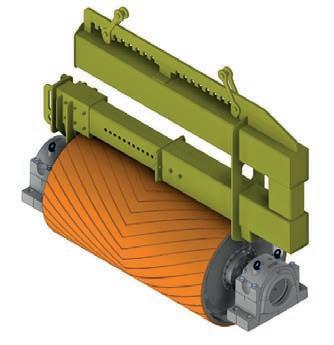
TS Global’s range of pulley lifting beams are innovative in reducing the manual handling risks associated with removing and replacing conveyor pulleys.
PULLEY REPLACEMENTS ARE A difficult maintenance task to achieve safely and efficiently, particularly when it comes to reducing human interfacing.
TS Global has heavily invested in the development of a product that uses a telescoping body to secure the beam across the face of the pulley for removal. The lifting beams are completely adjustable to suit varying face widths and include added safety features such as an adjustable front hook.
They are designed and tested in accordance with AS4991 standards and are coupled with additional safety chains to suit the applicable size beam. The design has evolved to include unique cam-style adjustable dog bones, further increasing the lifting beam’s usability and efficiency.
According to Jamie Whybrow, technical services manager at TS Global,
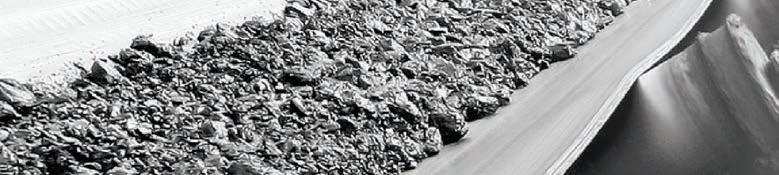
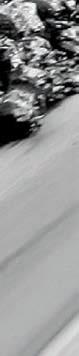

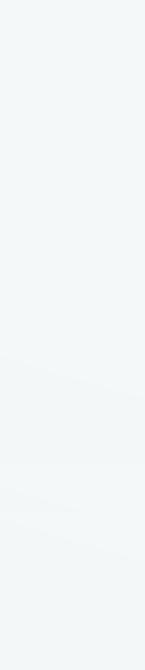
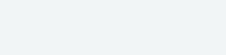
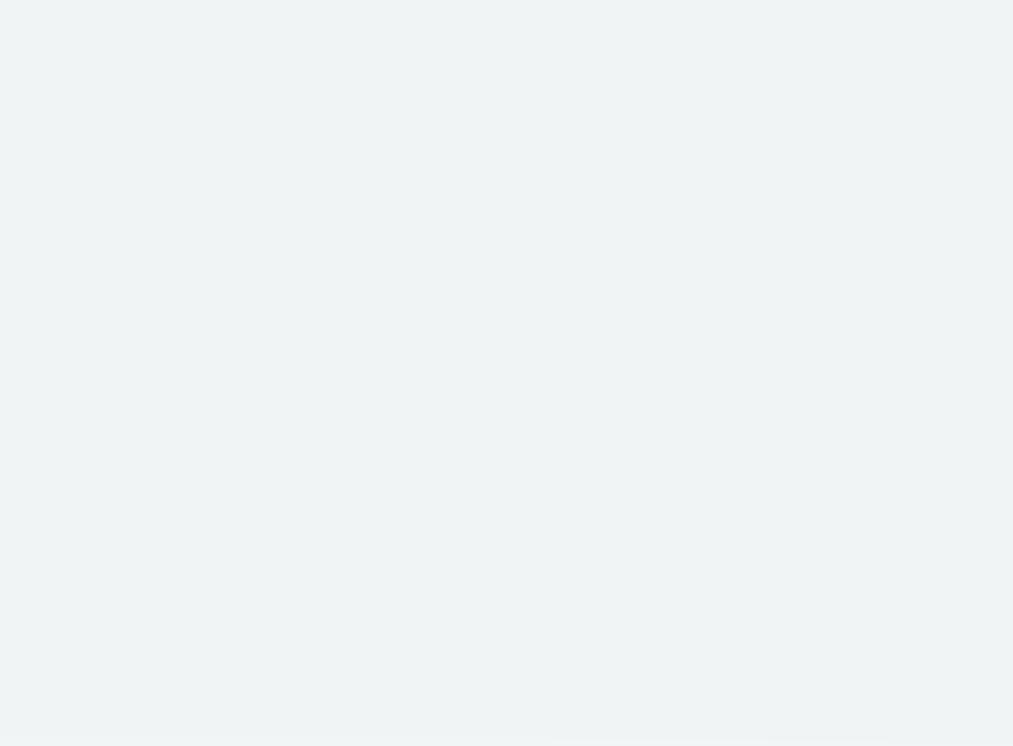
The beam can be used on all pulley variants.
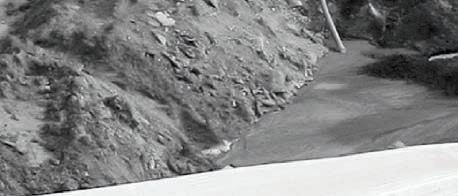
“it was very important for us to develop a product that the end user can effectively and efficiently use whilst ensuring operator safety”.
“What you need to keep in mind, is if the product is simple and quick to use whilst also assisting the end user to safely achieve their task, it’s a win/win,” he told ABHR. “That’s why we are continually pursuing product improvements.”
TS Global’s technical service department specialises in belt conveyors and can help end users minimise the manual handling risks associated with pulley replacements. This is done by eliminating the need for personnel to be in an unsafe proximity of the pulley and minimises the requirement for all the mechanical aids typically used for this task.
The TS Global Pulley Lifting Beam can be used on all pulley variants (live shaft and dead shaft) and positions. For cases with an unbalanced load, such as a drive pulley, operators can utilise the cam style dog bones to rapidly adjust the lifts’ centre of gravity.
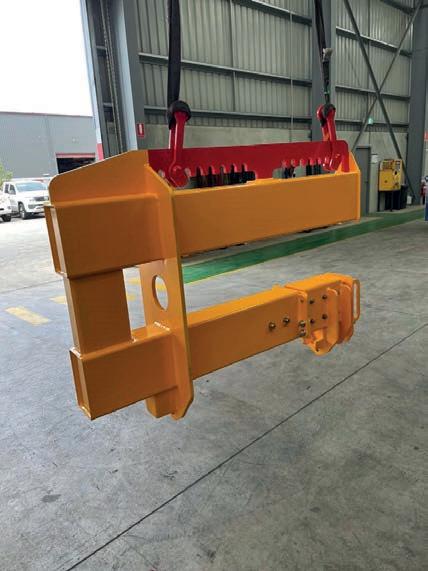
(4.5T WLL), medium (7T WLL) and large (12T WLL), we can also offer custom designs specific for the end user’s needs,” Whybrow said.
“Our products are designed to require low maintenance,” he said. “All of us at TS Global have done that job before, so we know what is and isn’t easy to maintain.
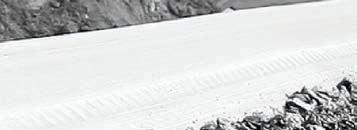
As an Australian-owned business, TS Global manufactures all its products in-house.
“TS Global offers end-to-end sales and technical support to assist with troubleshooting, design and installation support,” he said.
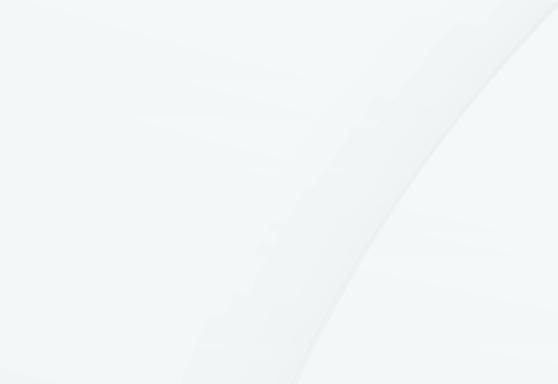
“We like to go above and beyond for after-sales support and can produce any spares, that the customer may need, at our workshop.”
The company has undergone exceptional growth over the past two years, almost tripling its workforce and expanding heavily into the Western Australian and Queensland markets.
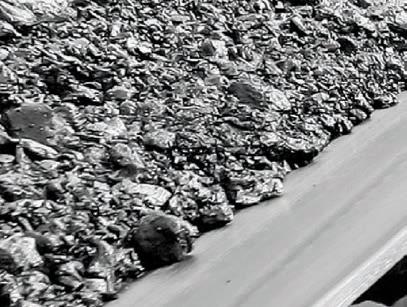
“With a full complement of technical and sales-based personnel, we can increase our market presence and keep moving forward developing innovative products that cater for the market needs,” he said.
TS Global manufactures all its products in-house.
“While we have a standard range of pulley lifting beams available in small
TS Global manufactures all its products in-house.
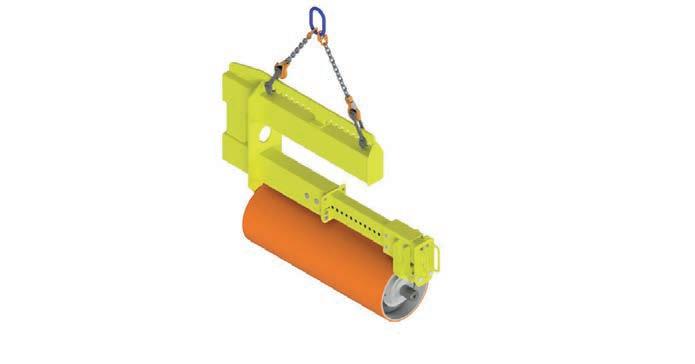
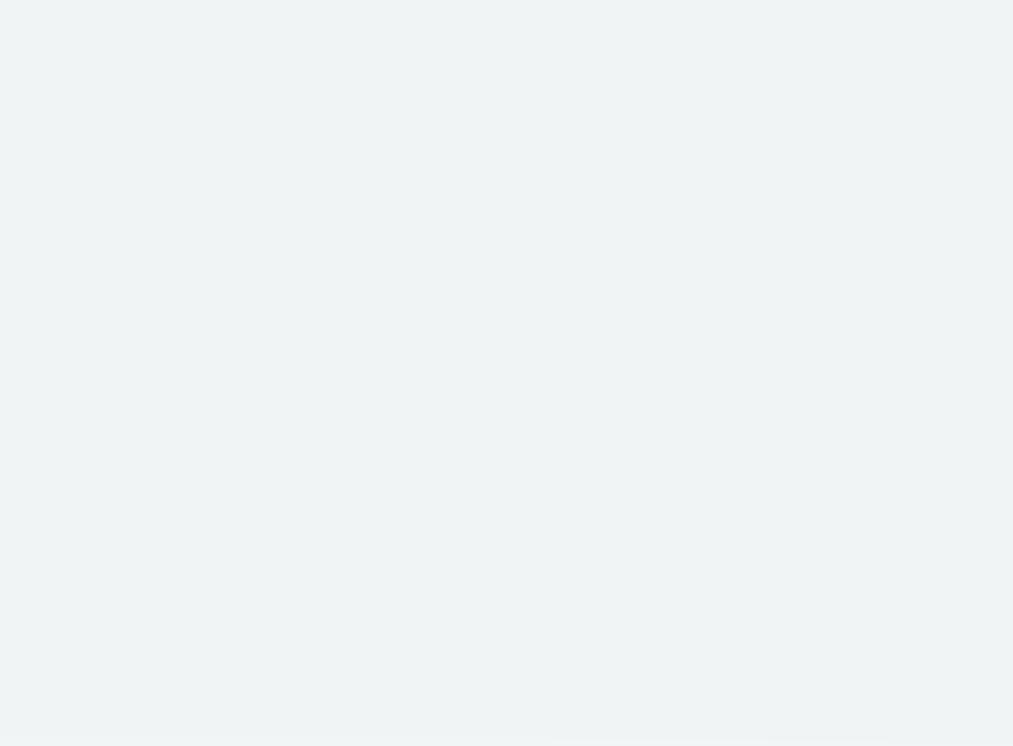
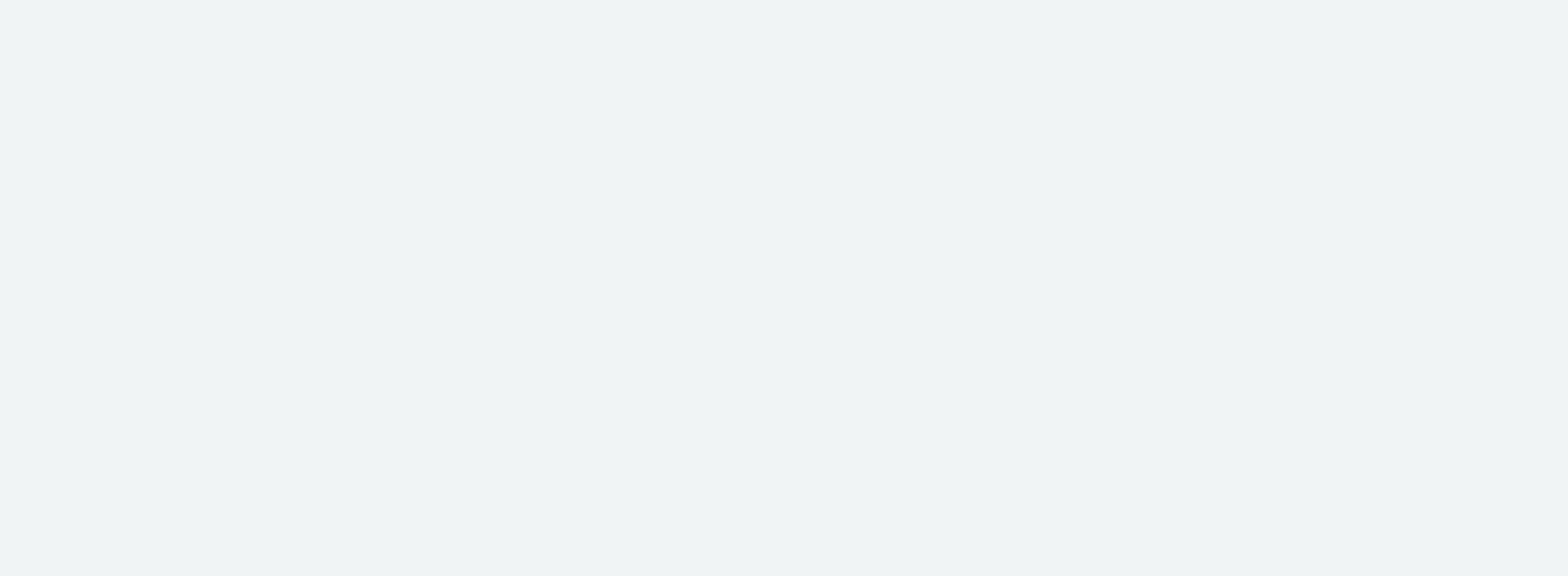
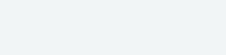
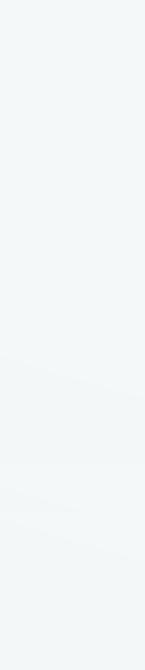
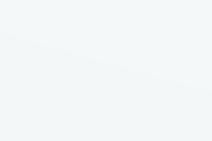

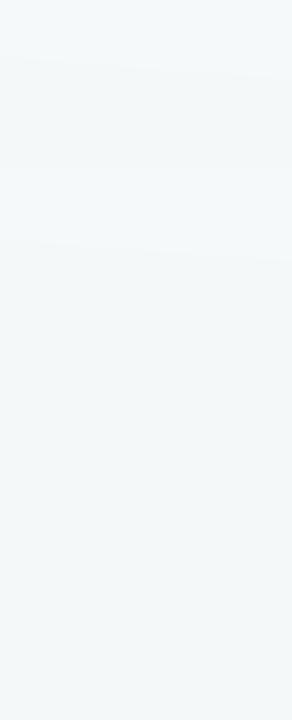
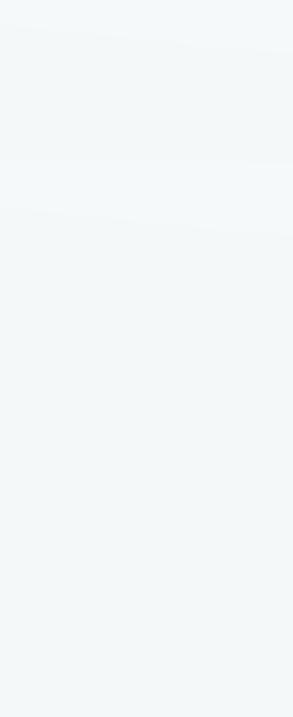
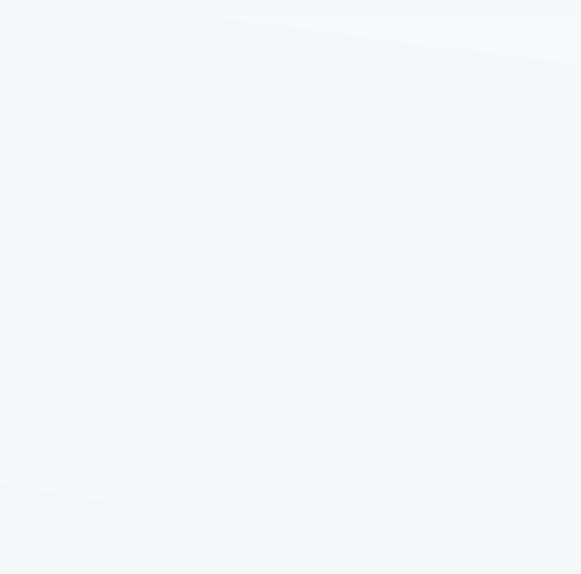
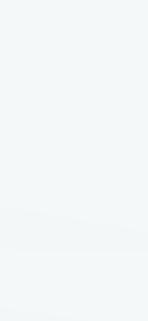

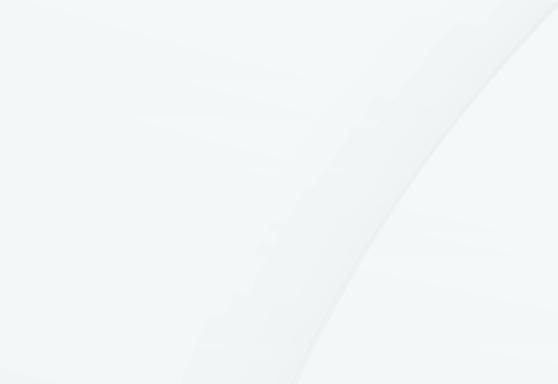

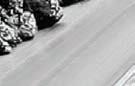
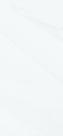
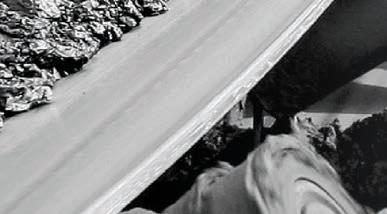

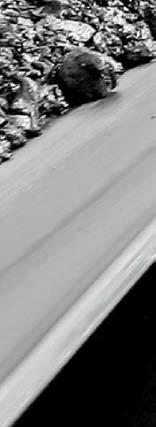
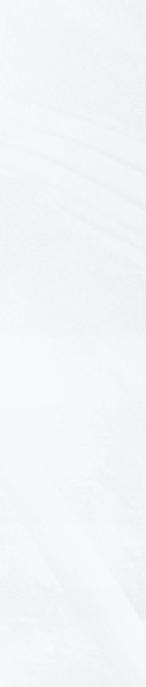
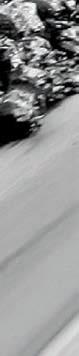
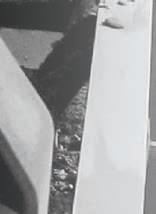
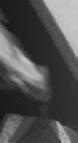
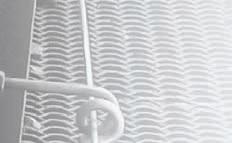
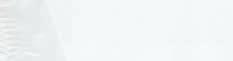

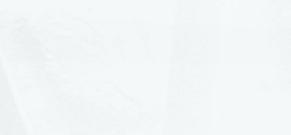
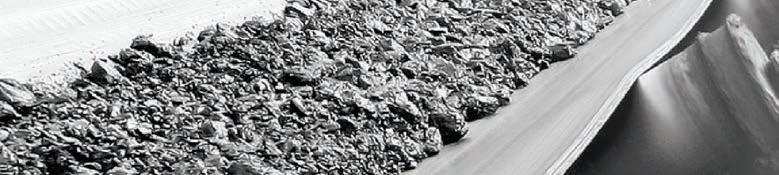
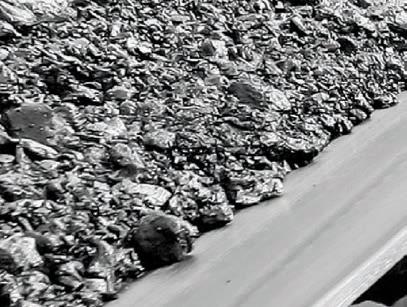
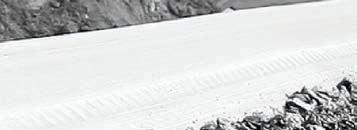

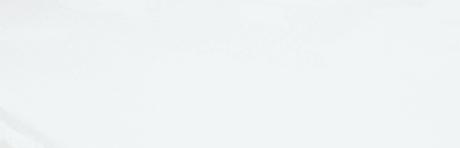
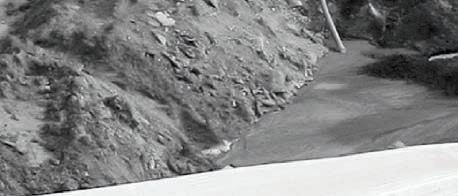
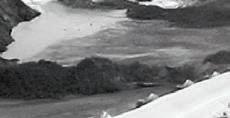

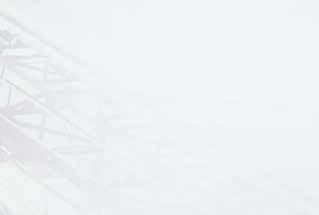
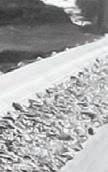
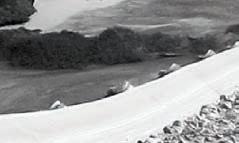
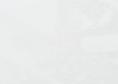


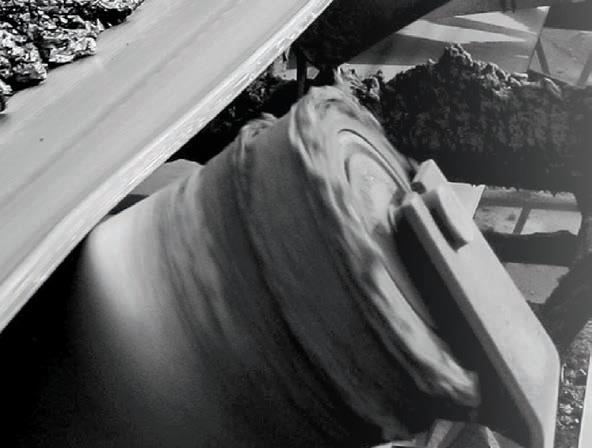
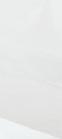
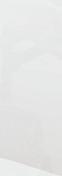

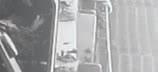
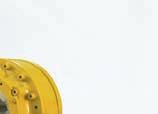

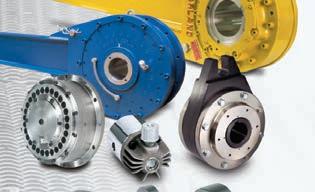
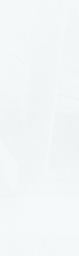
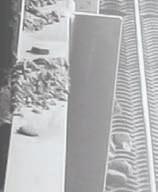
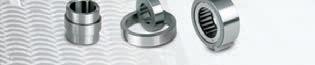
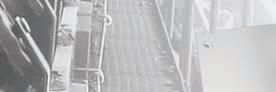

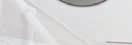
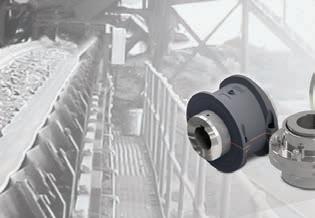
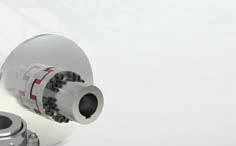
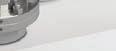
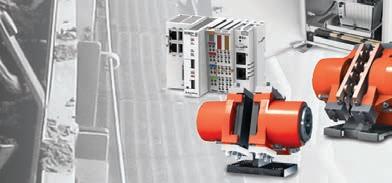
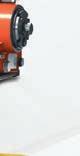
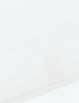

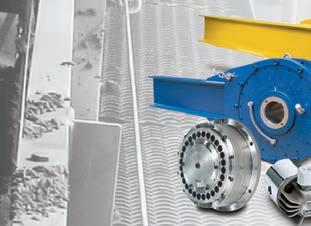
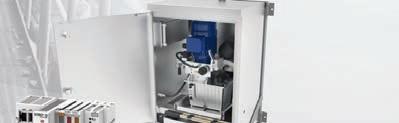
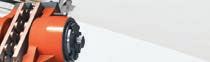
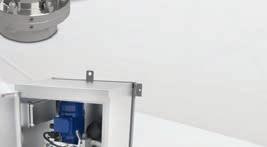
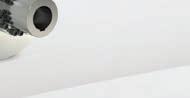
Strength of titans
ABRASION IS A KILLER WHEN IT comes to bulk handling equipment, as the flow of material wears down vital components.
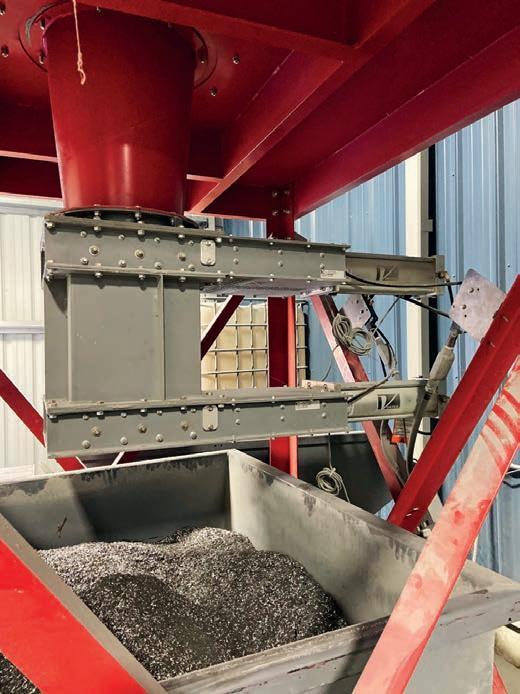
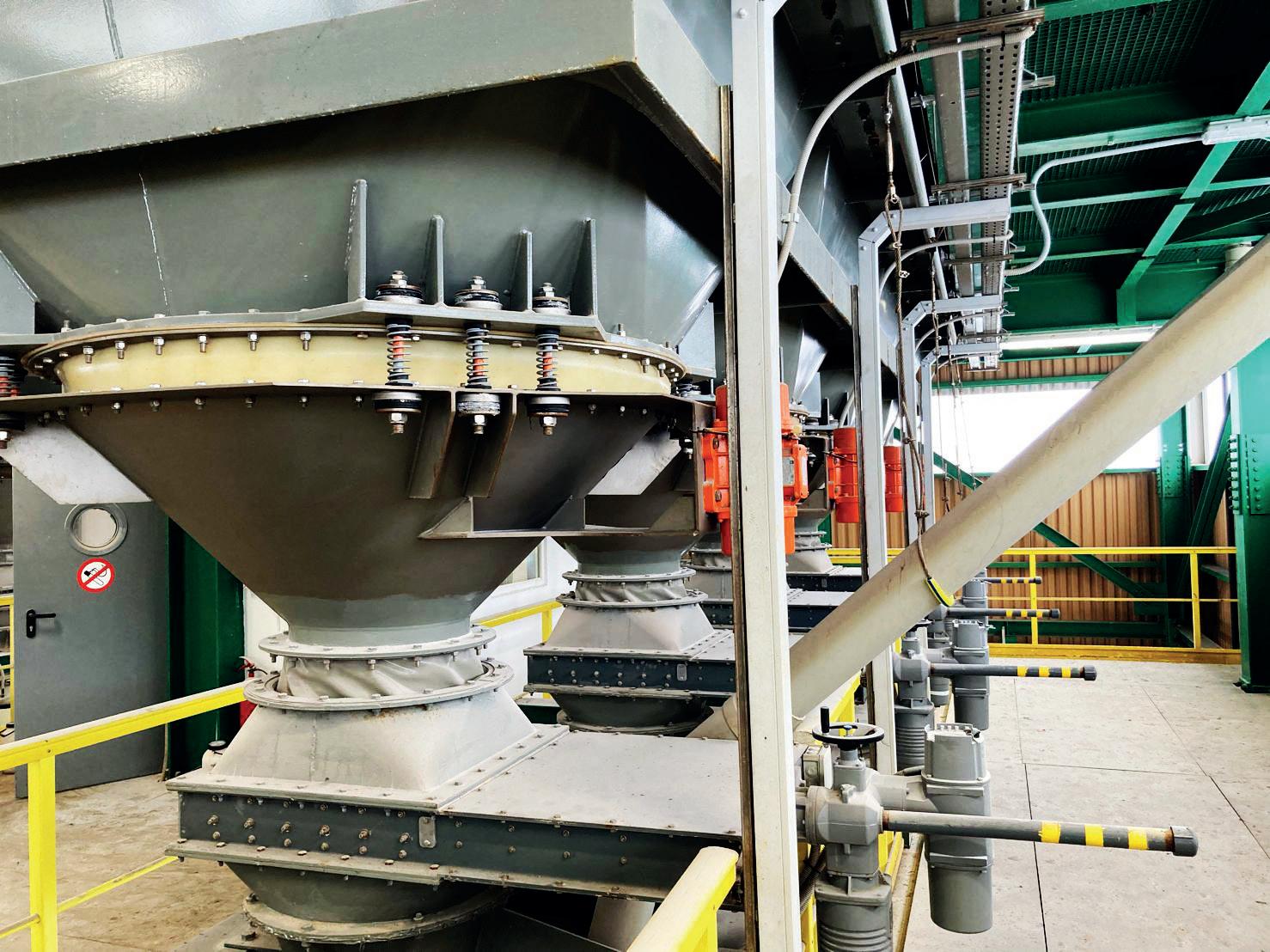
Laurence Millington, Vortex Global’s managing director, told ABHR that the company’s customers have been looking for a more heavy-duty, abrasionresistant slide gate.
“We took our standard roller gate and made it much stronger, which is how the Titan Slide Gate was created,” he said.
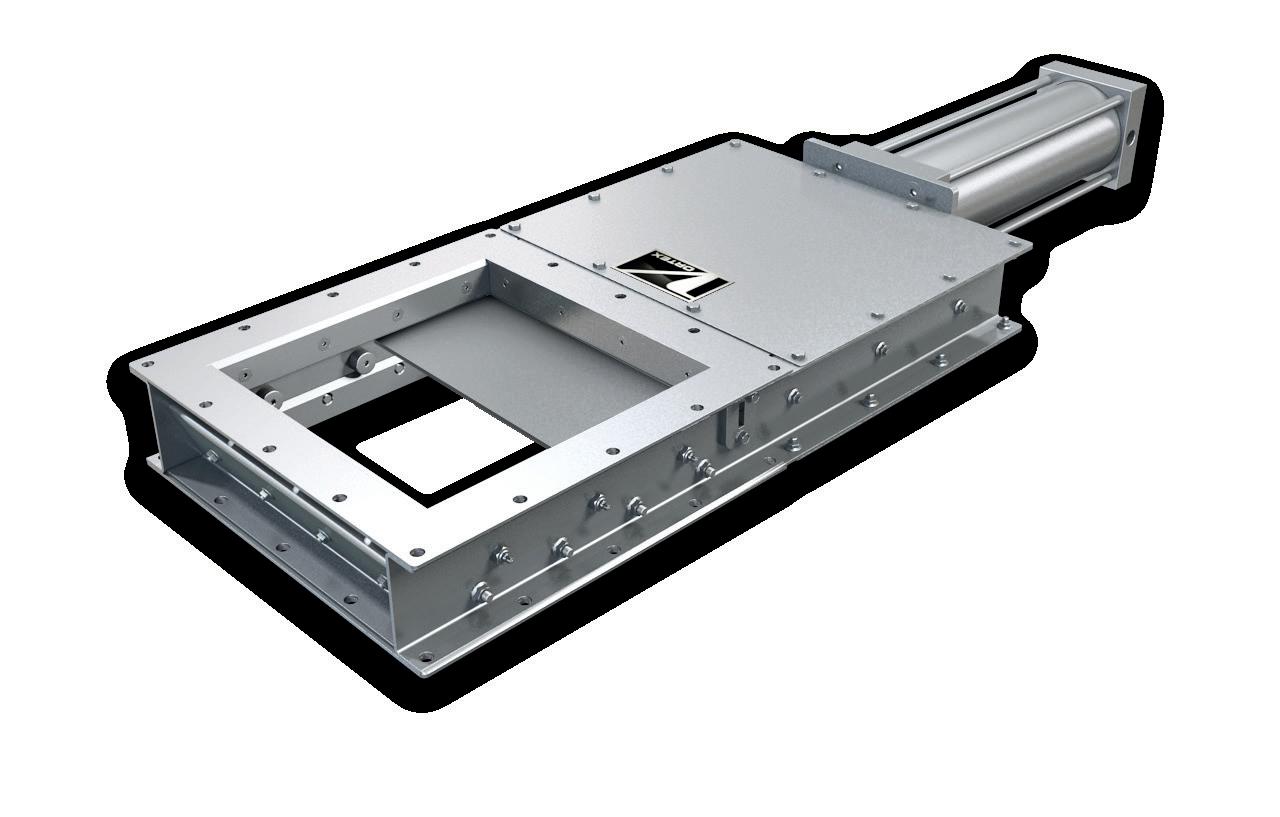
The Titan Slide Gate is designed to handle some of the most demanding applications when handling heavy-duty abrasive materials such as sand, gravel, coal, metal powders or minerals. It is used in gravity flow applications where positive material shut-off and dust-tight sealing are required.
It features a live loaded, hard polymer bonnet seals that compensate for wear and provide material seal across
The hard polymer seals have a compressed rubber backing to ensure that even as the polymer experiences
to protect them from abrasion. This design
maintains the gate’s positive seal of materials with infrequent maintenance intervention.
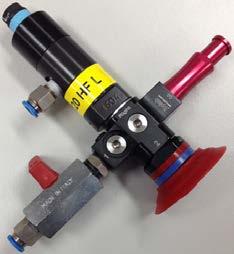
The Titan Slide Gate also includes abrasion-resistant liners that can be replaced when needed, as well as easily accessible, hardened steel cam-adjustable rollers and polymer blade guides.
Millington said a wide range of industries, from food to mining, wanted a slide gate that could handle intense use.
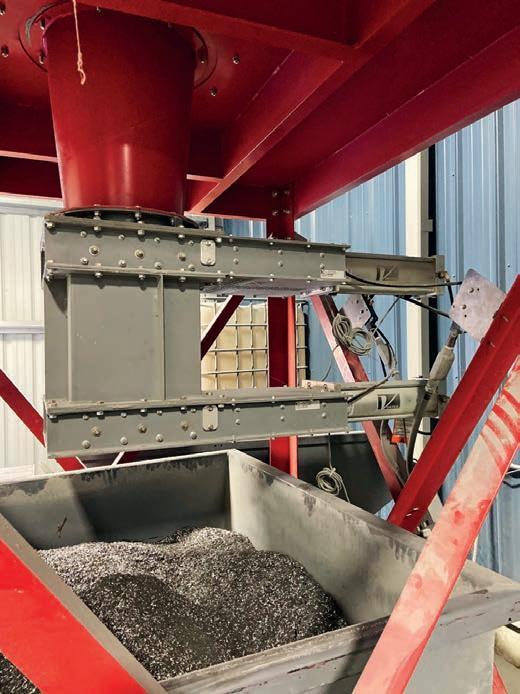
“The Titan Slide Gate comes with thicker blade assemblies and is manufactured out of carbon steel, but we can modify them to fit almost any application,” he said.
“We can change the sides or shape, provide stainless steel options, the options are almost endless.
“There have been some really unique requests, which have shown just how customisable the slide gates are.”
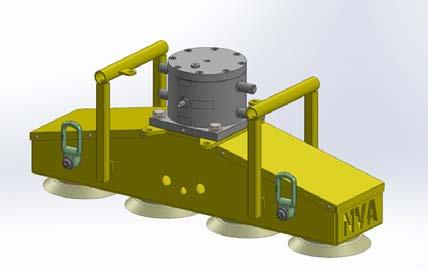
Adapting the slide gate to a system is made easy with a wide selection of gate positioning controls, position indication switches, and flanges.
The gate also offers a wide variety of modifications to accommodate a range of temperatures, corrosive, humid, and explosive environments.


Vortex slide gates offer a wide variety of actuation choices, including electric, hydraulic, pneumatic, chain wheel, and hand crank. Features include hardened steel cam-adjustable rollers, grease zerks, side mounted switches, carbon steel contact, inlet or outlet transitions, seal access ports, and removable seals.
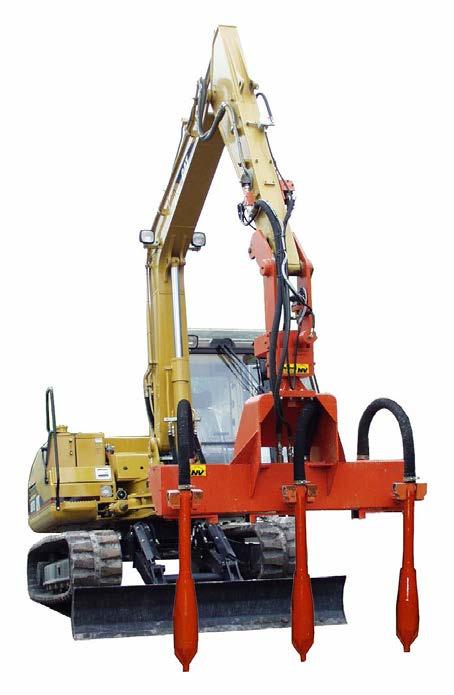
Millington said ease of maintenance was key to the slide gate’s design.
“It’s easy to strip down and all of the access points are on the side,” he said. “The cylinder mounting is standard and can be removed, along with the rollers if need be.
“When used in the correct application, the Titan Slide Gates require almost no maintenance and will last a very long time.
“If something does happen, we offer 24-hour support across the world and have local representation to ensure all of our customers have that peace of mind.”
Nelson Silos’ focus on further fabrication
The Australian-based manufacturer has expanded its factories to keep up with demand –and plans to continue growing.
AUSTRALIA’S EAST COAST is heading into another year of good rainfall, three years on from the drought.
With conditions continuing to improve, agricultural producers are looking to expand their storage capacity and grow their businesses.
Eric Nelson, managing director at Nelson Silos, said that with farmers and bulk handlers reinvesting into silos, his company needed to expand to keep up.
“Last year we saw record-breaking harvests across the country,” he said. “And with the current uncertainty in Ukraine, Australian grain prices are expected to hold at this level for another two years.
“We’re a privately-owned business, which means we can be agile and respond to the market. That’s why we’ve been quick to expand our factories.”
Major upgrades have been made to the company’s facility in Rochester, Victoria, including the installation of a new spray booth.
The spray booth is large enough to paint two fully assembled silos and can
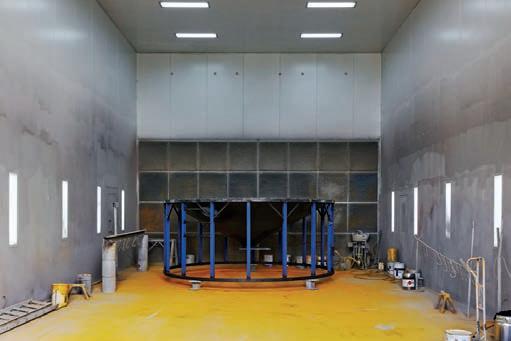
superphosphate or lime storage silos. The booth has been up and running for the past year and has improved the speed at which the manufacturer can deliver its silos.
To further improve its effectiveness, Nelson Silos is further upgrading the spray booth with a heating unit. This will ensure that the paint is applied at 22°C, which improves adhesion, finish and curing time.
The company is also planning to install a similar-sized grit-blasting booth. The booth means grit blasting can be performed indoors and better prepares the silo for the painting process.
Nelson said the company’s larger clients insist on grit blasting for industrial silos.
“They need a high-quality paint finish when working with abrasive or corrosive materials,” he said.
“Farmers are also looking to get the best possible quality from their silos, as they want their investments to last as long as possible.”
Silos produced at the company’s facilities in Rochester and Parkes, New
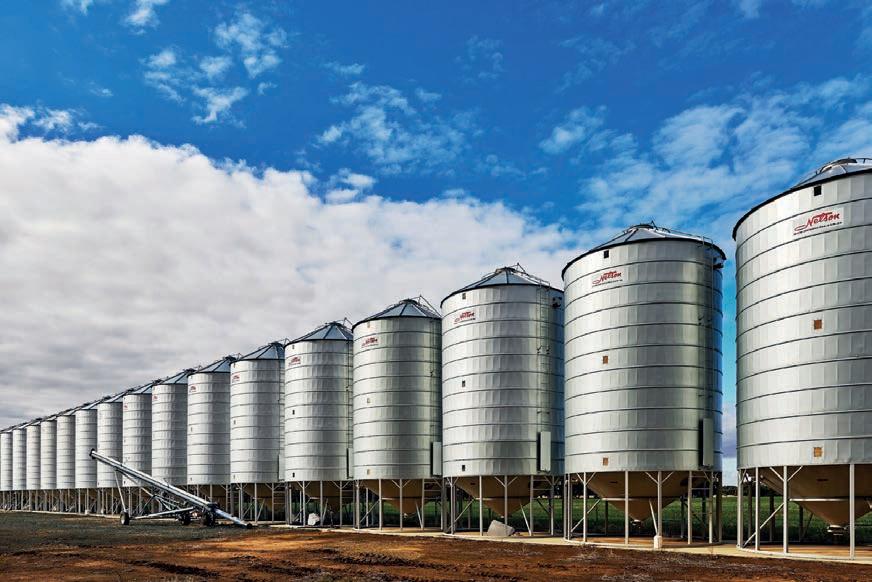
assembled while larger silos are split into two or three pieces for shipping. This is done to reduce the amount of time required for installation on-site.
These silos are shipped across the country with Nelson Silo’s fleet of heavy-duty trucks, which has also been expanded. The company has purchased three new large Mack trucks – one of which is a superliner – and has bought a new low loader to transport steel between its factories.
It has also just ordered a second A-double trailer for longer hauls from its Parkes factory to customers in northern NSW and southern Queensland.
Nelson said these regions are major growth areas for the business.
“There’s a big demand for these silos there,” he said. “Larger companies are starting to re-evaluate expansions in the future and recent issues with global supply chains have highlighted how important it is to buy local.”
He adds that the increased capacity has proved popular among existing clients.
“We’ve had many customers come back to us for repeat orders,” Nelson said.
“Our aim is to be able to build several large silos for multiple customers at the same time, which is why we’re looking to keep expanding.”
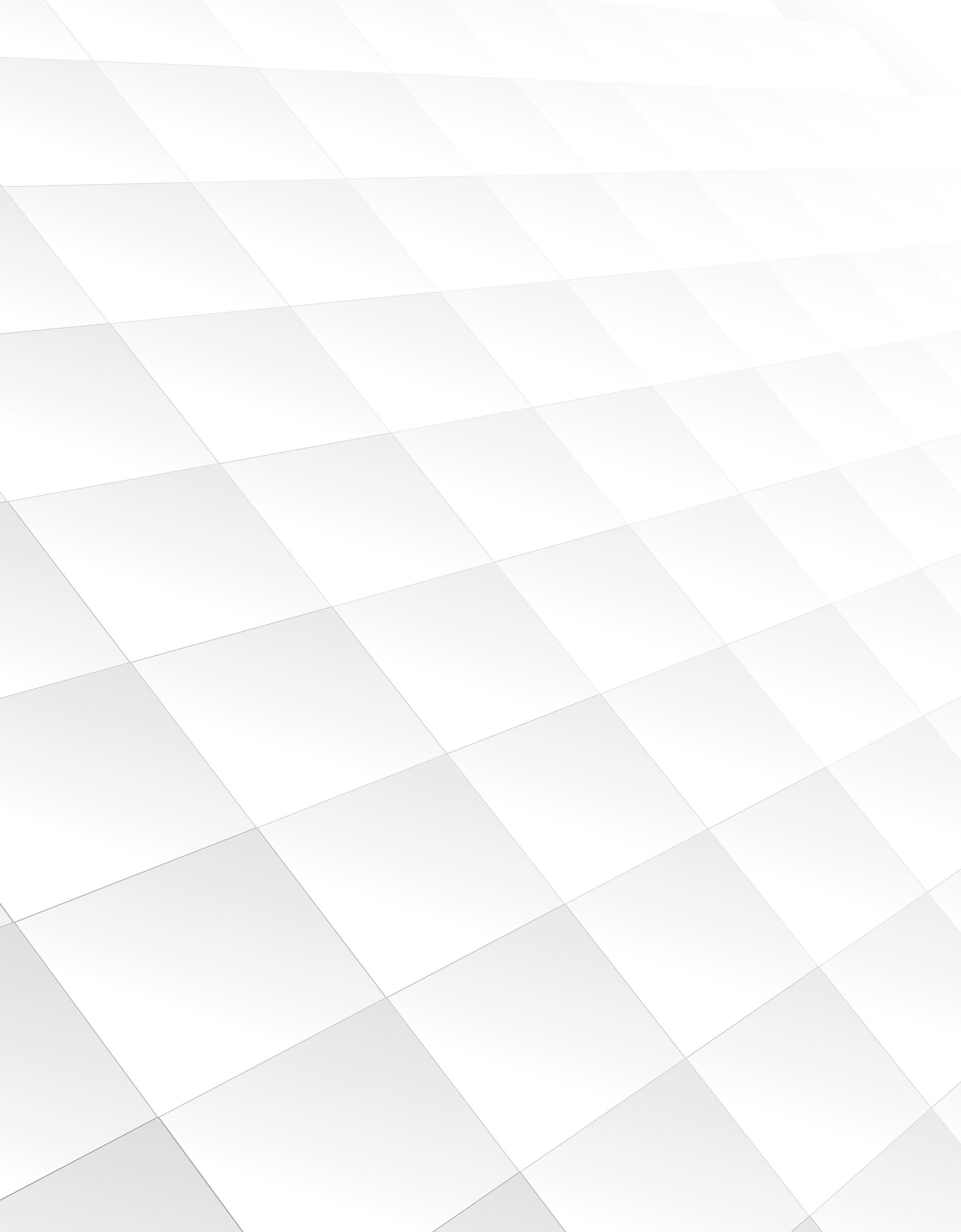
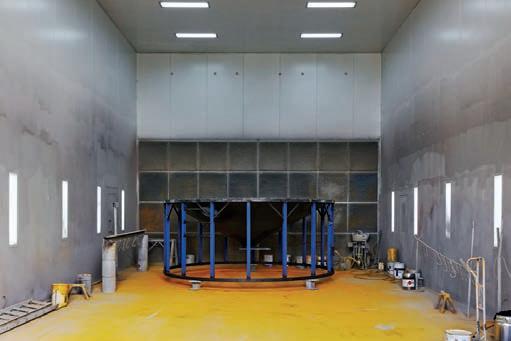
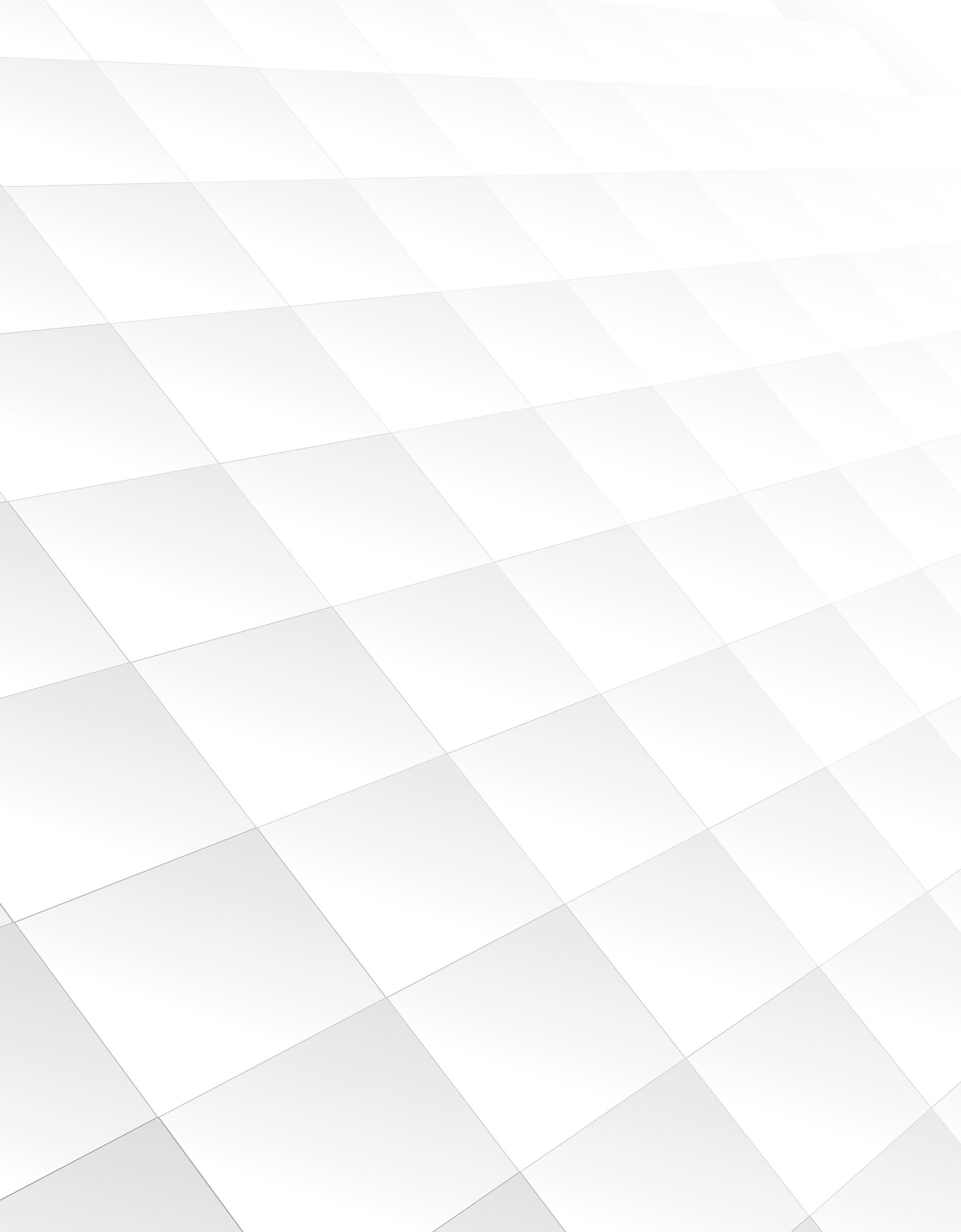
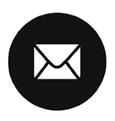
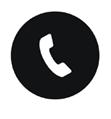

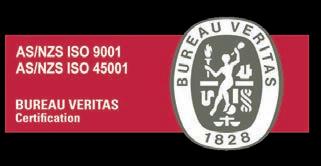
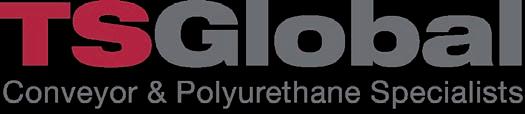
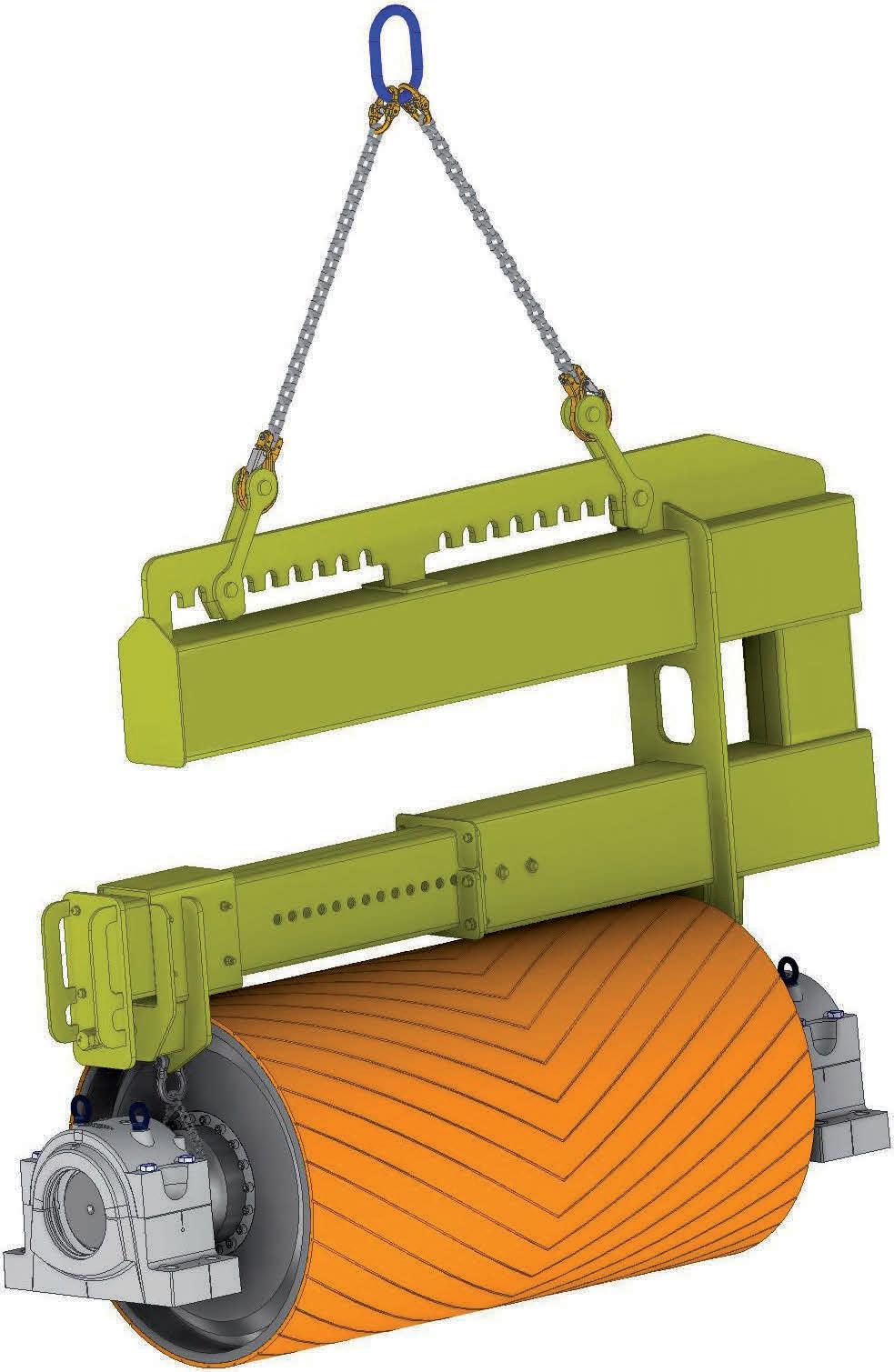



Conveying with the Hi Rollers
ABHR chats with AGI’s Peter Forster to learn how the company’s Hi Roller conveyors can help bulk handlers move grain reliably and without dust emissions.
THE HI ROLLER CONVEYOR SYSTEM
was originally designed to solve a specific problem: grain dust.
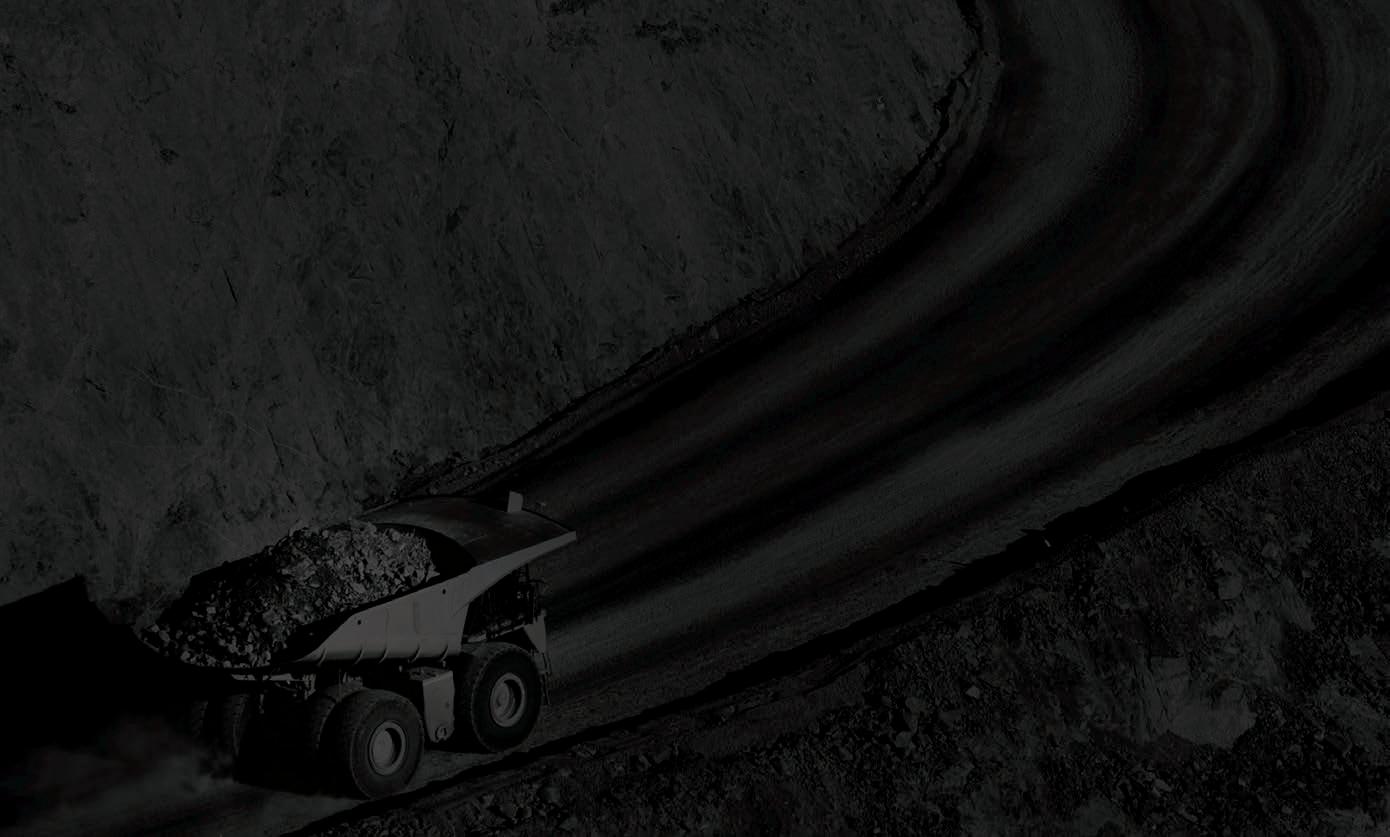
When grain is conveyed, it releases dust into the surrounding area, which poses health risks to nearby workers and requires clean-up.
And while capturing the dust in an enclosed space reduces the amount emitted into the neighbouring area, it poses an explosion risk.
Enter Ag Growth International’s (AGI) High Roller conveyor, which contains dust and spillage while also reloading material back onto the carrying surface of the belt.
All of the bearings are isolated and there are no ledges in which build-up can gather. Instead, any spilled product or dust falls onto the return belt and is brought back to the tail section, where
it is then diverted to the outer edges of the pulley that feature flippers to pass it back onto the belt.
Peter Forster, AGI’s Australia and New Zealand business manager, said the design has been refined over the decades.
“Hi Roller conveyors have been installed in more than 10,000 different applications across the world,” he said. “Around 90 per cent of grain terminals use them, as it’s a leading product that can be relied on to deliver.
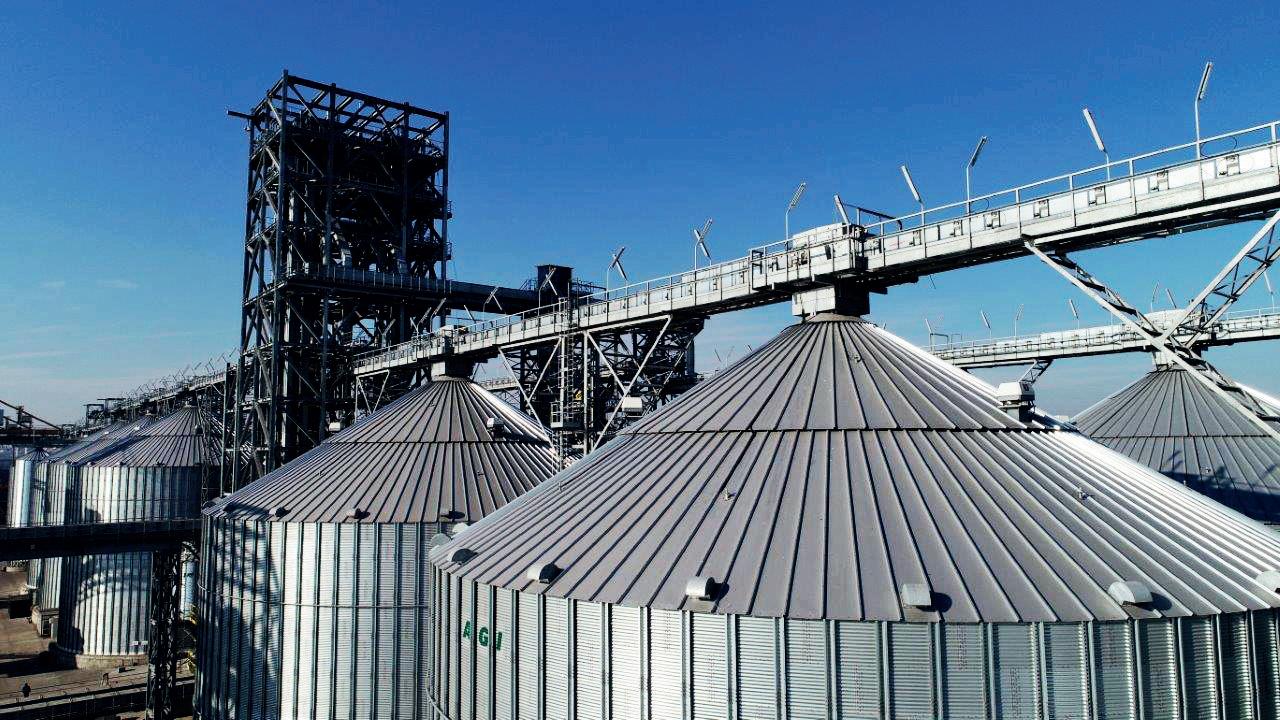
“It’s most often used in missioncritical applications for high-use facilities, like mills and ports, where it works day in, day out.”
The conveyor’s self-cleaning abilities also makes it a good fit for port and outloading facilities, which may need to move different grains or materials.
AGI acquired the Hi Roller product in December 2006, adding it to the global agricultural equipment manufacturer’s portfolio of brands.
One of these brands is CMC Industrial Electronics, which manufactures hazard-monitoring systems for industrial applications. CMC’s devices are used to perform temperature checks on bearings, and scan for belt misalignments and plugged discharge sensors.
Working in tandem with the Hi Roller conveyor, CMC’s lowvoltage digital sensing platform can help monitor the shaft speed, bearing temperature, belt misalignment and vibration in harsh industrial environments.
Forster said the sensors and monitoring systems add additional
reliability to the Hi Roller conveyors.
“CMC’s platform is often deployed alongside Hi Roller conveyors to provide automatic safety measures,” he said.
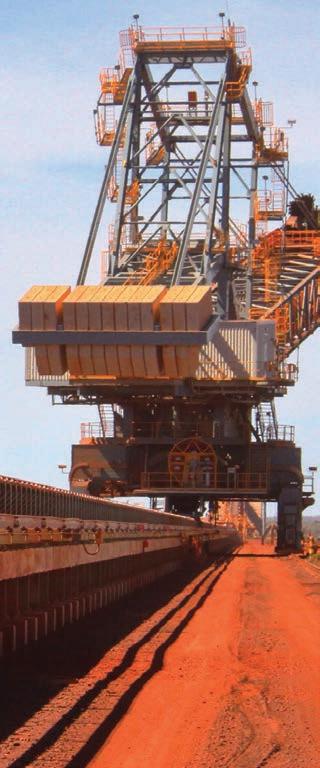
“If the belt’s take-up shaft slows by 10 per cent, an audible alarm will sound to alert operators. At 20 per cent, the feed will go into a controlled shut down, taking away the potential for human error.
“It will monitor for any blocked chutes, any increases in bearing temperature, belt slippage, and more. It connects to a programmable logic controller and can then send all that information to a phone or tablet in real time.
“If there’s a sudden failure, you will know about it straight away.”
Close collaboration between the brands means that all of AGI’s silos and support structures can easily integrate Hi Roller conveyors and monitoring systems. This attitude also applies to AGI’s dedicated support contractors, who are trained to diagnose and solve any issues across the company’s broad range of products and services.
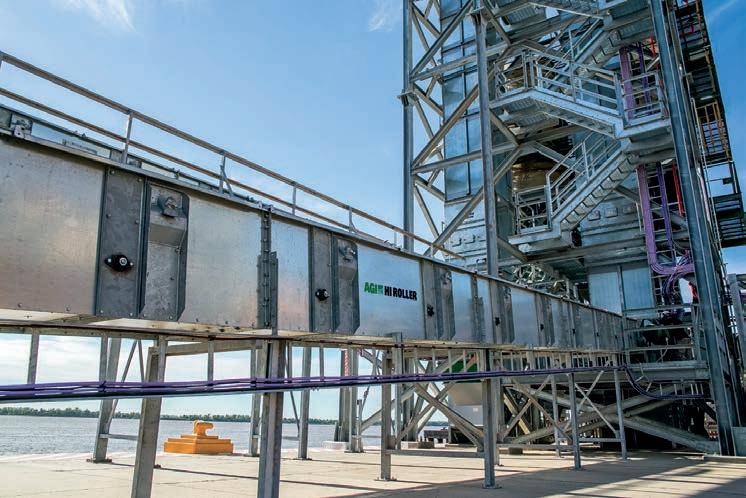
Forster said the company plans to continue improving the Hi Roller design and has plans to develop further technologies to improve reliability even further.
“We have a lot of experience working with these products and know what to expect for all kinds of
applications,” he said.
“AGI is a global company, which means our engineers have experience almost every condition around the planet.
“We can draw on that international expertise to ensure all of our equipment is fit for purpose and will last.”
West
Conveyor
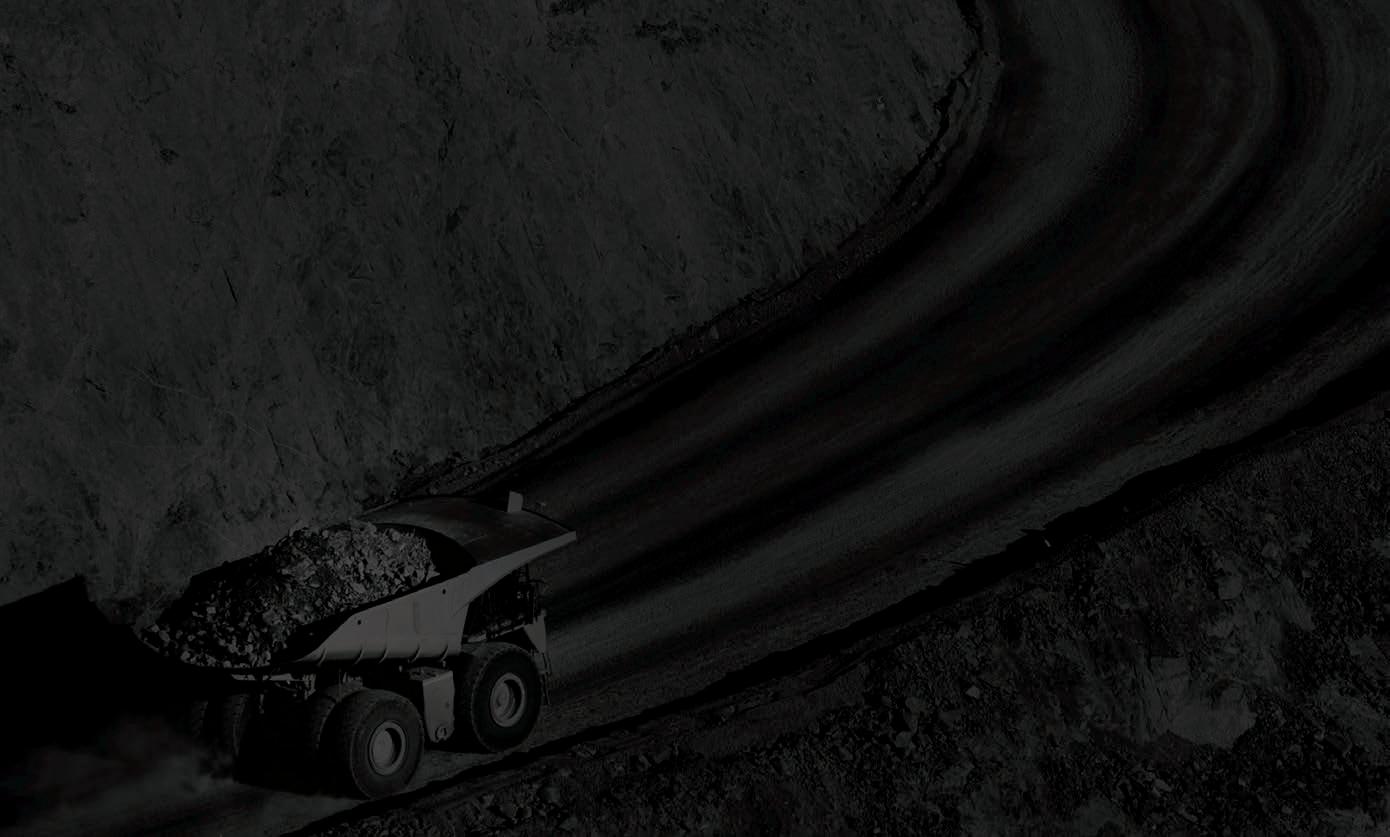
Commissioning its biggest backstop
Altra Motion Australia was tasked with manufacturing and commissioning their largest Marland backstop in its history of supply to a major gold mine.
contracts manager at Altra Motion Australia.
“The backstop unit measures 1.2 metres in length, 1.4 metres in width and 67 centimetres in depth and weighs over 5 tonnes,” Pavlou said.
Marland BCMA bearing supported backstops are designed to be mounted on the low-speed drive shaft. The selfcontained, oil lubricated units feature a grease labyrinth that prevents dust from attacking oil lip seals.
Pavlou said the backstop unit installed on the mine site is designed to have a life cycle of at least 15 to 20 years. This is based on the OEM stipulated maintenance scheduling and operating conditions.
“Altra Motions Australia is currently working with the client to formulate a maintenance plan, which would include annual inspections of the backstops and the brakes on the same conveyor,” he said.
the reverse movement of a belt on Industrial Motion, specialises in backstopping technology and has introduced several brands to the worldwide market, including Formsprag Clutch, Marland Clutch and Stieber.
While Altra’s products are widely used on inclined conveyor drives, reclaimers and stackers across a wide variety of mine sites, the company was put to the test when it was tasked with supplying its biggest Australian backstop to date.
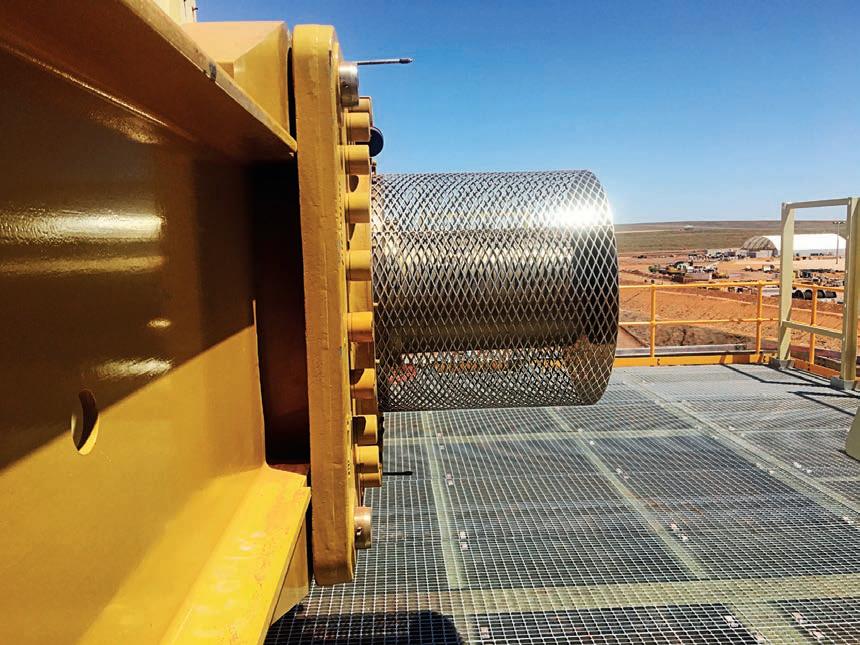
Rex Sinclair, Altra Motion Australia’s national sales manager, said a major gold producer needed a reliable robust solution on a new mining project.
Altra Motion Australia supplied a BCMA roller-type Marland backstop that could handle backstopping torques over 1.2 million Nm.
To enable the backstop to handle such a high torque load, the unit was manufactured with a shaft size of 400mm and a torque arm length of nearly four metres, measured to the bore’s centreline, according to Paul Pavlou, national
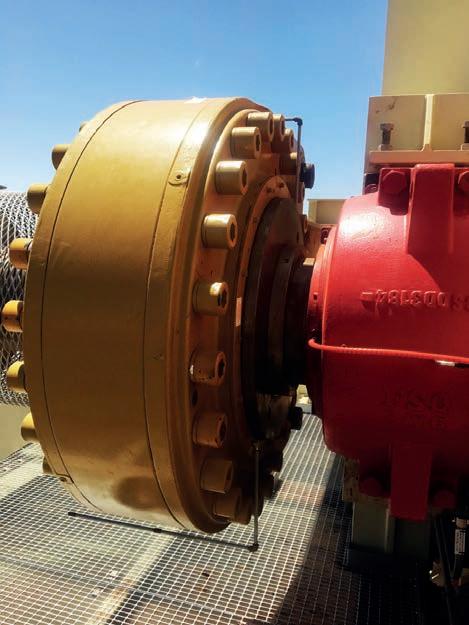
Sinclair said the company’s strength lies in providing a comprehensive portfolio of backstopping solutions and supporting customers with a complete servicing and genuine OEM spare parts package.
“The Altra Motion Australia team consists of factory-trained Service Technicians. When these service techs visit any site or interact with customers, they understand the customer’s needs and then work with the Altra brands to provide the right solution,” he says.
In addition to sales offices across Australia, Altra Motion Australia also has service workshops in Perth, Sydney, Mackay, and soon to open Newcastle, where the service technicians are trained in overhauling the backstops for repair or rebuild under the supervision of service managers. The technicians also frequently visit sites to offer on-site maintenance services.
“All our maintenance and overhaul team members are trained to handle any technical issues with backstops. When they visit the mine sites, they can cover all aspects from commissioning new
backstops to carrying out routine servicing or fault finding,” Sinclair said.
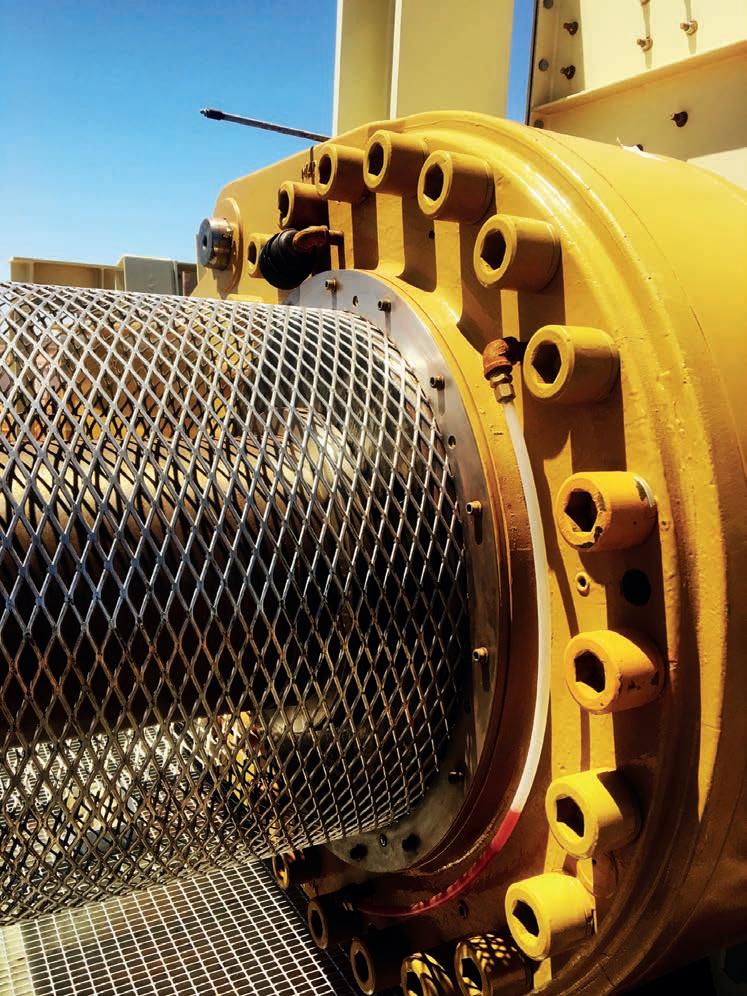
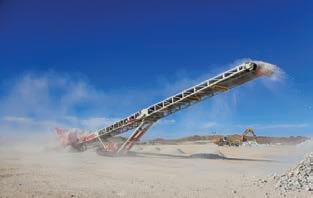
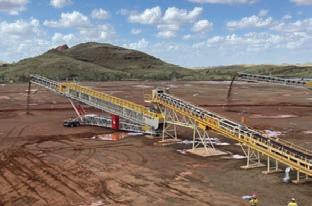

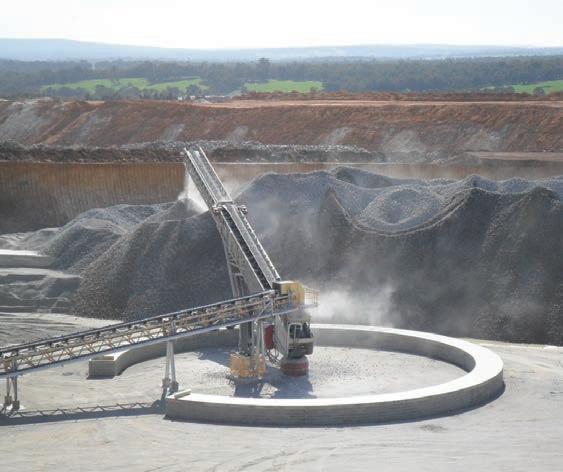
“At the workshop, they can overhaul backstops back to new condition using genuine parts covered with a factory warranty.”
Where an application requires unique backstop solutions that are not readily available, Sinclair said the team at Altra Motion Australia could go back to the design engineers at each brand’s factory to work out a custom-built solution for the customer.
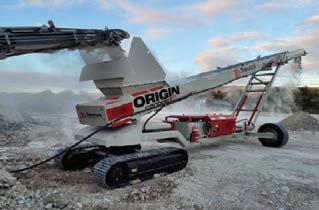
“When we sell backstops, we don’t just sell a unit. We also support our customers throughout the product’s lifespan, from the cradle to the grave. We aim to provide the best backstopping solutions in Australia, and Altra Motion undeniably has the experience to support that goal,” Sinclair concludes.
Altra Motion offers genuine OEM spare parts, servicing, and rebuilding for all our 26 world renowned brands.
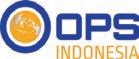
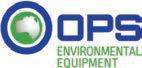
Reaping the benefits of bulk weighers
Continuous bulk weighing systems offer grain handling facilities accuracy, reduced waste and improved operational performance, which is why Allied Grain Systems has started developing bulk weighers.
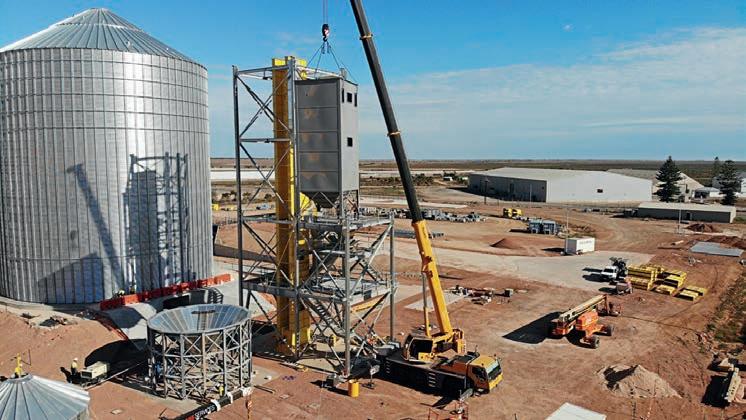
“They’re mainly used to accurately weigh the outloading of a commodity for record keeping but can also be used to deliver a preset amount of grain with incredible accuracy.
“The whole system is controlled by a programmable logic controller, which stores and saves weights automatically.”
Allied Grain Systems performs 3D modelling with AUTOCAD to ensure the design will fit the application and ensure the towers are able to handle the associated loads.
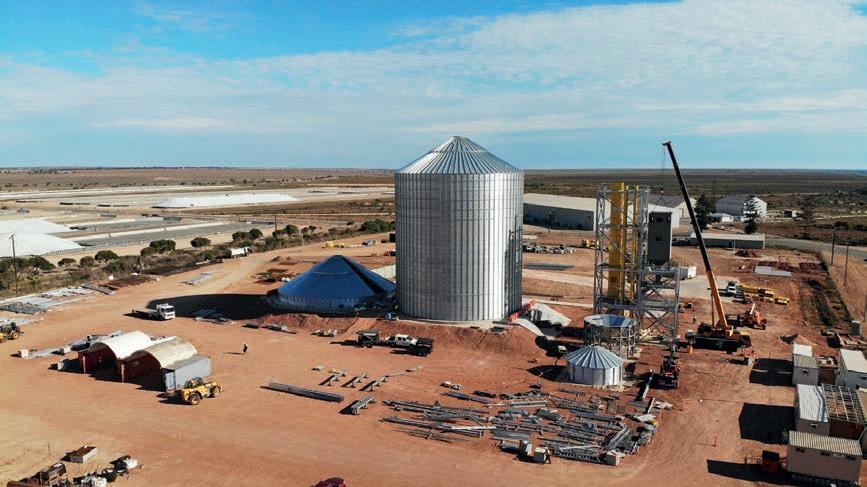
IN THE UNITED STATES, BULK weighers are a common sight on grain handling facilities.
John White, managing director at Allied Grain Systems, wants to see them become more popular in the Australian market.
“Traditionally in Australia for out loading of grain from facilities, we use a garner bin positioned above ground on weight cells,” he told ABHR
“It’s hard to get this type of system certified due to wind loading effecting on the side of the garner bin which effects the accuracy of the weigh cells.
“You have to load a truck and run it over a certified weigh bridge system to get similar levels of accuracy, which in some applications can add much more time and effort.”
Most of the bulk weighers in Australia have been imported in the past. This is an expensive process, as often they are too large to fit inside a container and need to be shipped on open deck.
Allied Grain Systems decided to design and manufacture its own range of bulk weighers in Australia. The company’s team worked closely with Mettler Toledo Australia for the weighing equipment of the bulkweigher system as Mettler Toledo components are used in
overseas models. The larger bulkweighers were designed and built in sections, to be delivered to site as a wide loads to be bolted together on site.
Ceramic tiles are installed at all of the heavy wear points to add longevity to the system, while hydraulic slide gates are selected to operate the continuous internal slide gates.
White said Allied Grain Systems can customise the design of the bulk weighers for applications between 50 to 2500 tonnes per hour.
“There are a lot of applications where bulk weighers can be installed, and we have the design skills to ensure each meets the client’s requirements,” he said.
It also provides full installation services and after sales support. While the bulkweighers themselves are reasonably low maintenance, the company can provide periodic preventative maintenance and provide test weights with the units so customers can calibrate at any time they choose.
White said the market for bulk weighers is growing fast.
“We have installed a few around the country and the feedback from customers has been very positive,” he said.
“They’ve been trouble-free and work day in, day out to provide accurate measurements that can be relied on.
“We’d really like to provide more for the local market, which is why we aim to
BULK2022 brings industry together
ABHR was on the ground when Melbourne recently played host to Australia’s largest dedicated bulk handling events.
THE 2022 AUSTRALIAN BULK Handling Expo saw local and international decision-makers come together under the one roof to showcase and share the latest in the world of bulk handling.
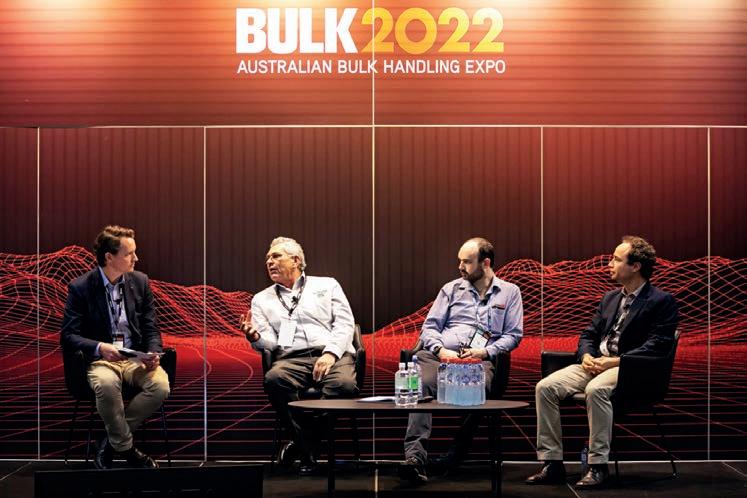
And after three years of COVIDinduced delays, the industry was happy to have one of the biggest events on the bulk handling calendar back on the agenda.
“It’s wonderful to be face-toface once again,” Mark Jones, chair of the Australian Society for Bulk Solids Handling (ASBSH) and director of TUNRA Bulk Solids, told ABHR.
“It’s been quite some time since there has been a show for the bulk handling industry.”
The event, held at the Melbourne Convention and Exhibition Centre from 24–24 August, was aimed at bulk commodity producers, manufacturers, and suppliers.
The latest equipment was on display, including a silo, rollers, conveyors, dust control systems, air cannons, and levelmeasuring products.
VEGA Australia had its newest range of advanced radar level sensors on show, with several units measuring a variety of solids and liquids.
Tony Scarborough, NSW business development manager for VEGA Australia, said the 6X range of advanced radar level sensors can reliably measure across a broad range of characteristics including hot, cold, liquid, solid, hazardous, and corrosive materials.
A live demonstration showed how the radar technology worked, highlighting the straightforward nature of its programming and set-up, and how it can be integrated into existing systems with either hard-wired or wireless connections.
Scarborough said the variety of people at the expo was especially invaluable.
“I’m learning more about the bulk solids handling industry – myself coming from more of a water and wastewater background,” he said.
“I have spoken to people in an allied industry, and it’s been quite informative to share my knowledge of what I do and their knowledge of what they do.”
To further encourage this knowledgesharing, the ASBSH hosted a two-day conference at BULK2022, sponsored by LEAP Australia. Speakers delivered presentations on a wide range of subjects, including the technology of tomorrow, the road to net-zero, and how safety can be improved on-site.
“There is a really good range of suppliers, and there’s quite a few end users that have attended,” Jones said.
“The exhibitors I’ve spoken to have all been pleased about the sort of enquiries they are getting, so there’s certainly
quality there.
“As part of the BULK2022 program, the ASBSH also hosted a networking event for prospective and current members. With around 40 participants, the event provided an informal atmosphere for meeting like-minded people in the bulk handling sector.”
Peter Poklepovich, aftermarket manager at PROK, was pleased that a large number of customers were interested in PROK’s HDPE rollers and engineered pulleys.
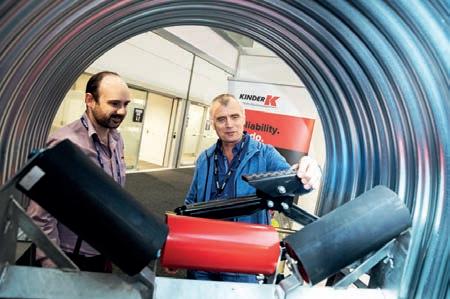
“It’s great to be able to showcase the different options available,” he said. “There’s been a lot of people who are interested that have visited the stand to talk about our quality offering.
“They want to learn about us and what we can offer them as a company.”
PROK is one of the sponsors of BULK2022, along with Premier Tech and VEGA Australia.
Commenting on the success of the expo, event coordinator Hope Potter said it had been great to hear so much positive feedback from the industry.
“We look forward to seeing the bulk handling industry again at the next expo,” she said.
Winners revealed for Australian Bulk Handling Awards
Engineering excellence was on display at the 2022 Australian Bulk Handling Awards.
THE AUSTRALIAN BULK HANDLING
Awards have returned in 2022, with finalists from across the country attending a gala dinner in Melbourne to find out who would be taking home the coveted awards.
The awards are Australia’s only dedicated event that specifically focuses on the outstanding achievements and successes in the bulk industry.
ABHR is proud to present the winners of the awards:
Innovative Technology Award Metso Outotec – FMR Pumping Application FMR invested in two Metso HH200 pumps to replace existing units that were nearing the end of their effective life. The new mill discharge pumps are equipped with Metso’s unique slide-base technology. The slide-base allows operators to open the pump without removing the suction and discharge pipework, making it extremely easy to inspect wear components and conduct routine maintenance. FMR can now ensure that their pumps operate efficiently by regularly optimising wear components. The slide bases have also reduced the time required to get a blocked pump online again.
Dust Control Technology, Application or Practice
Enviromist Pty Ltd and Action Drill&Blast Pty Ltd – Drillrig Dust Suppression System
In early 2020, Action Drill & Blast (ADB) approached EnviroMist to reduce the levels of dust emitted during blast hole drilling operations. Water used during the drilling operations is effective in suppressing dust whilst drilling, however a secondary source of dust suppression was considered important to reduce exposure for any on-bench workforces. By introducing a water mist while drilling ensured the hole collar was damp and created a crust that sustains dust
suppression for a longer period. This has benefits in terms of health and safety for shotcrew, maintenance personnel, and other mine personnel working in the open. The installed system is now fully available for the next installations.
Excellence in the Application of Gears, Motors and Drives
Kilic Engineering – Cargill stockpiling operations optimisation
When agricultural services company Cargill began to review its supply chain infrastructure, it needed to find a way to optimise its stockpiling operations. Cargill reached out to mechanical handling equipment designer Kilic Engineering to design a solution that would improve the discharge chute and allow it to be independently moved up, down and sideways to fill a bunker more efficiently. The solution came in the form of the LINAK LA36 actuator, an electric device that converts rotational motion in low voltage direct current motors into a linear push/ pull movement. The LA36 model has been designed for harsh outdoor applications. With the expanded mobility and the ability to throw gain further, Cargill can now fill certain voids within the stockpile with less movement of the stacker itself, optimising the process significantly.
Excellence in Transport and/or Conveying
OMC International – Dynamic Under Keel Clearance System
OMC International provides a suite of digital port optimisation solutions under the banner of the Dynamic Under Keel Clearance System (DUKC) and provides 24/7 unlimited support for these critical operational systems. DUKC safely facilitates the export of more than 1.5 billion tonnes of bulk commodities per annum, including 99 per cent of iron ore
exports, 90 per cent of coal, 99 per cent of alumina, and 77 per cent of bauxite. DUKC typically increases the amount of cargo that a vessel can carry by increasing available draft. Alternatively, for a given sailing draft, DUKC can increase the available sailing window allowing the vessel to depart earlier or later. Providing this operational flexibility enhances the efficiency of the ports.
Best Practice in Safety (sponsored by Bonfiglioli)
Centre for Bulk Solids and Particulate Technologies (CBSPT) – Transportable Moisture Limit (TML) Project
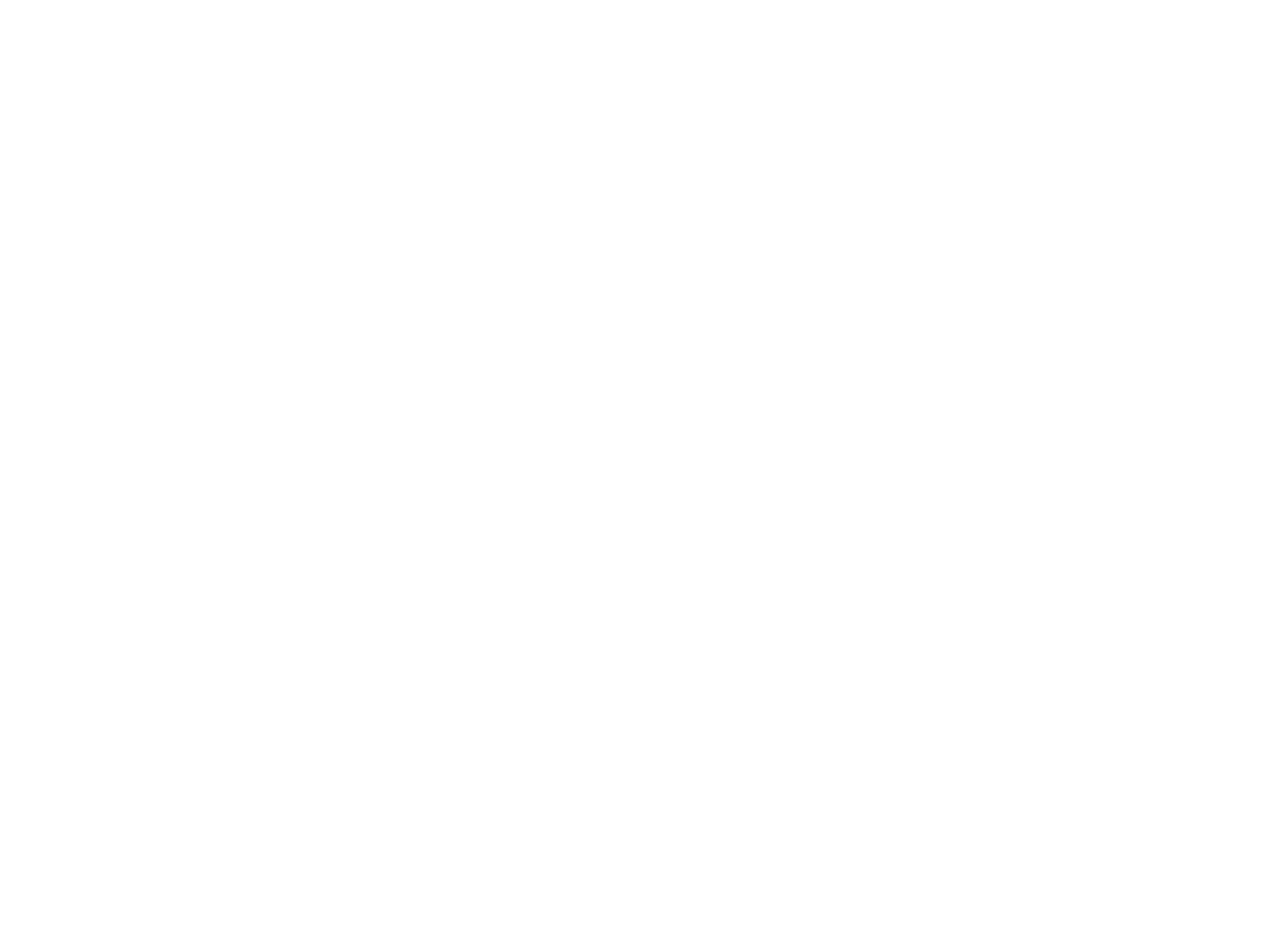
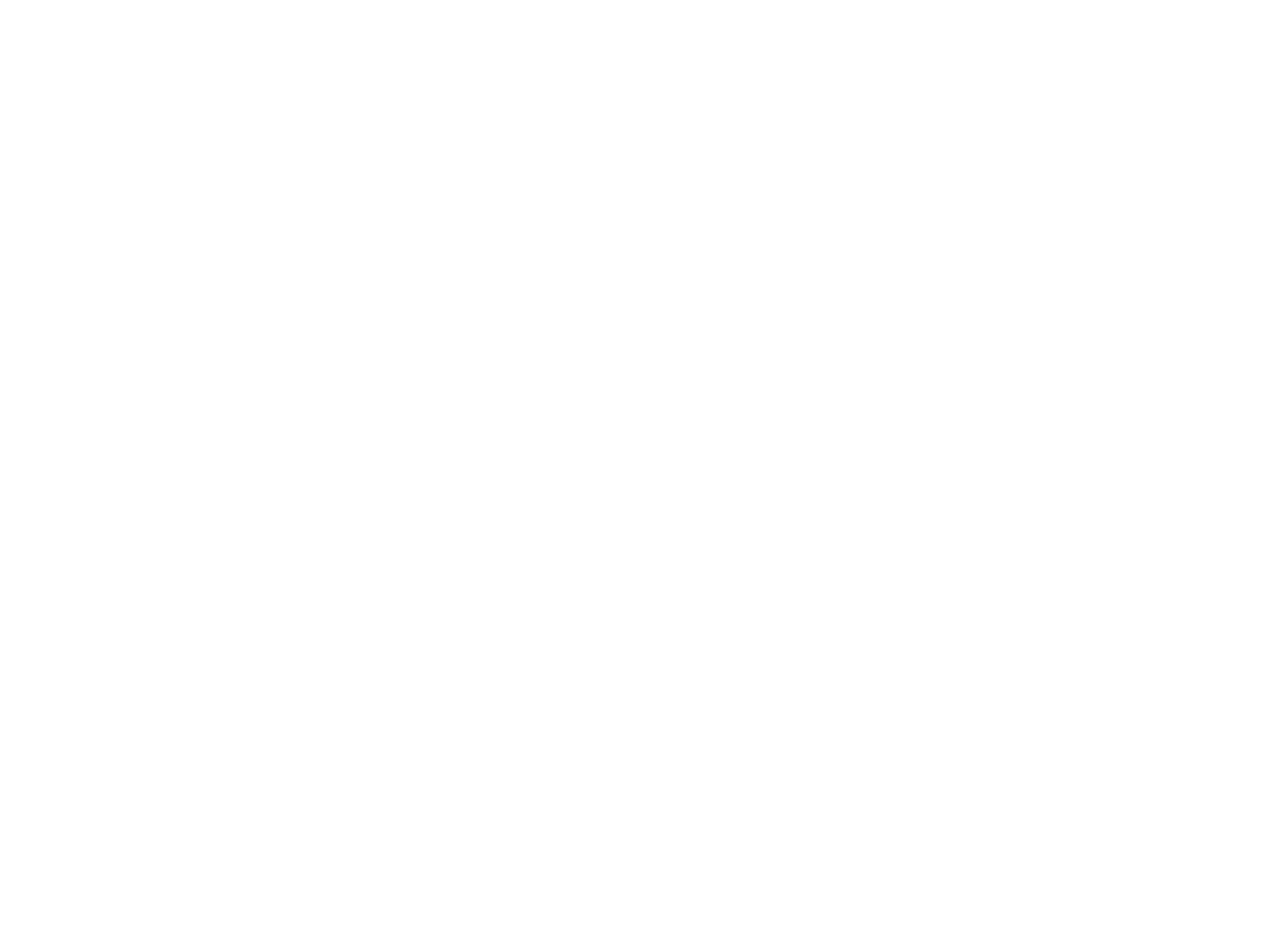
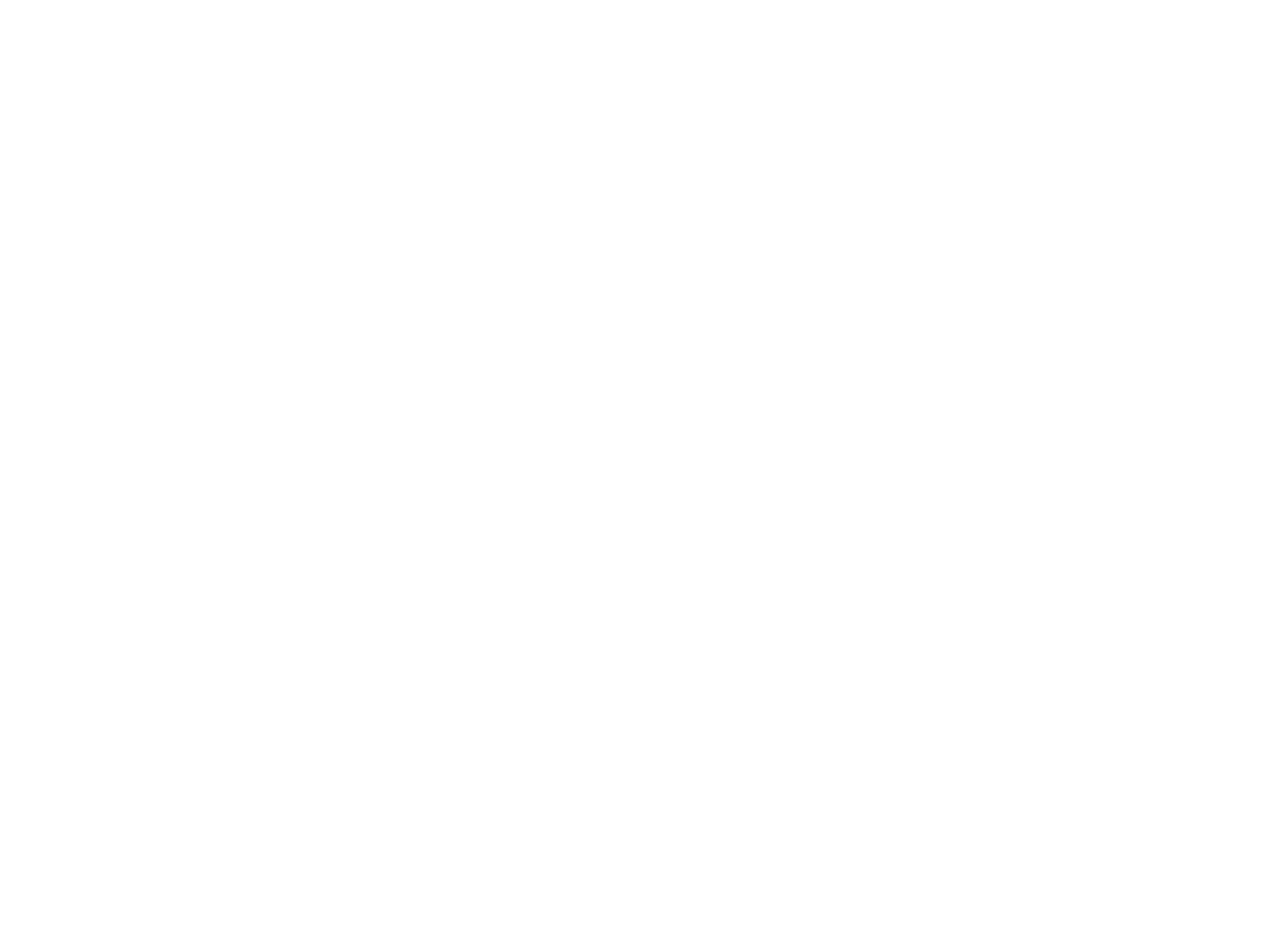
The TML project carried out by CBSPT aimed to develop a new international testing regime for cargo stability and liquefaction during seaborne transport, with an international focus.
The International Maritime Solid Bulk Cargoes (IMSBC) Code categorises solid bulk cargoes based on hazard/risk. Group A considers cargoes which may liquefy if shipped at a moisture content exceeding their TML. To control the risks of liquefaction, Group A materials are tested regularly to determine their TML and Moisture Management Plans must be in place to ensure all cargoes are shipped at or below their TML. This testing regime has now been accepted by the International Maritime Organisation as the nominated method to assess coal TML.
Supplier of the Year (sponsored by SEW-EURODRIVE)
Kinder Australia
Kinder Australia has accumulated over three decades of experience, expertise, and credibility in the bulk materials handling industry. They are recognised as a leading global independent supplier and manufacturer of innovative materials handling solutions, designed in-house, and manufactured from
high quality materials to improve conveyor productivity and efficiency to a broad range bulk materials handling industries and applications. Engineering is the driving force at Kinder, which has resulted in significant investments in conveyor engineering prediction and design software, SOLIDWORKS, Helix and AutoCAD proficiency and further training of their highly technical engineering team. This conveyor engineering design, technical knowledge base combined with on-site field exposure translates to better understanding, diagnostics, and confidence to recommend the most practical and cost-effective solution.
Bulk Handling Facility of the Year (sponsored by VEGA Australia)
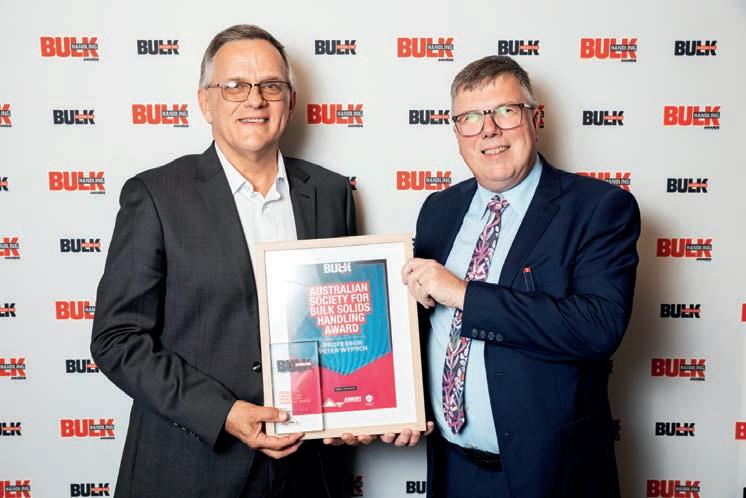
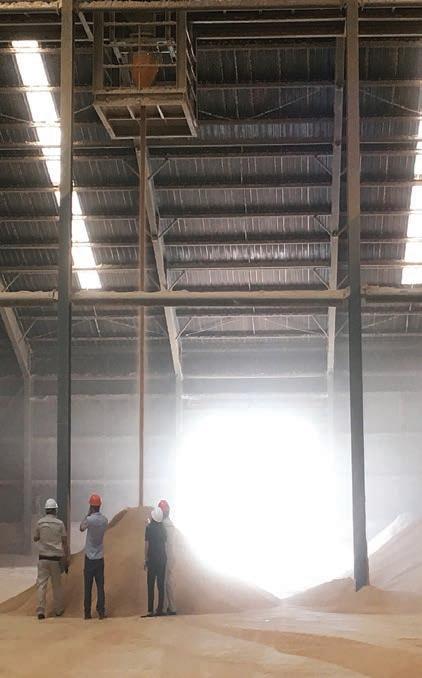
Metso Outotec – Boral Ormeau
Boral awarded Metso the contract to design, manufacture and supply a crushing and screening plant to support the increased throughput. Metso has
AW Roberts Award (presented by ASBSH)

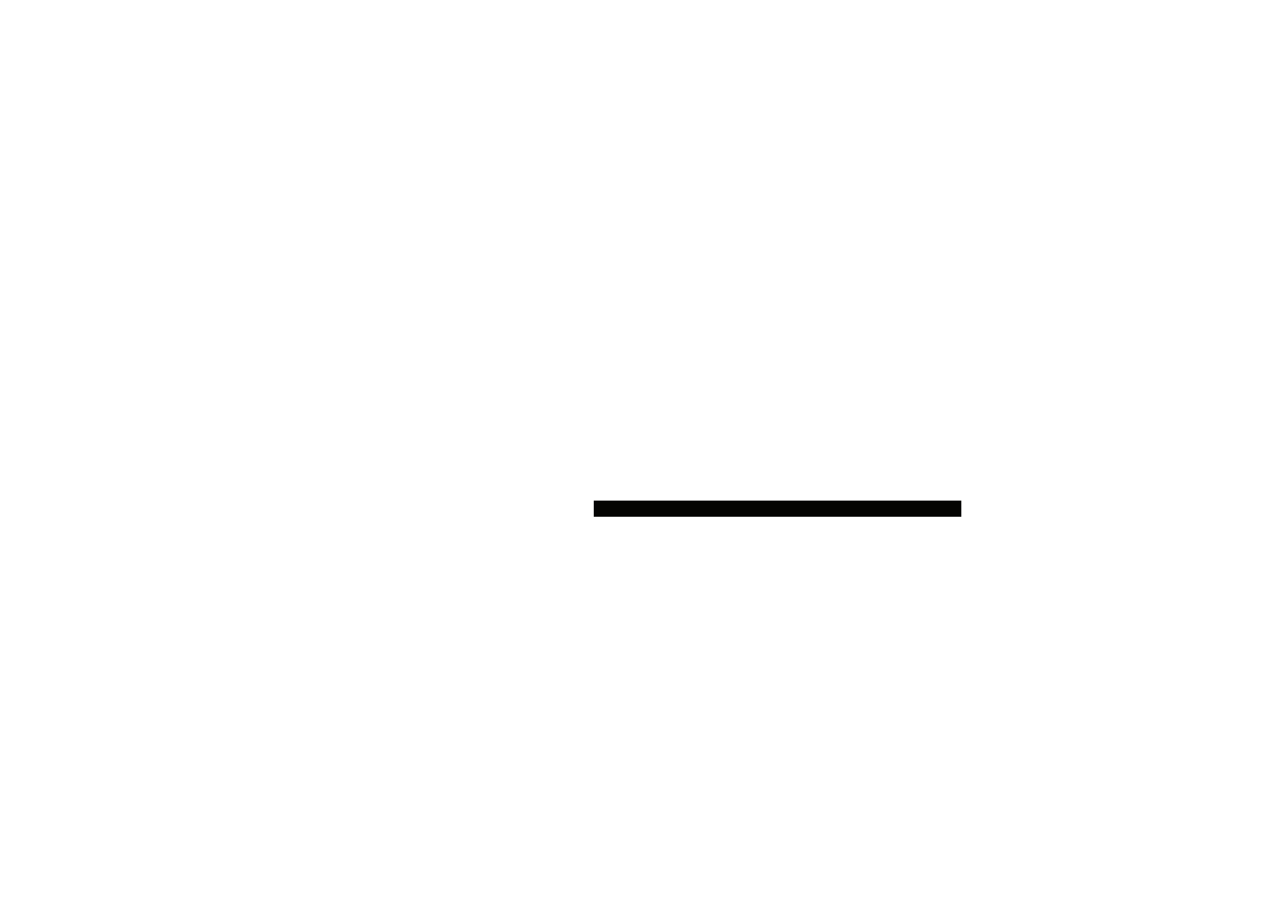
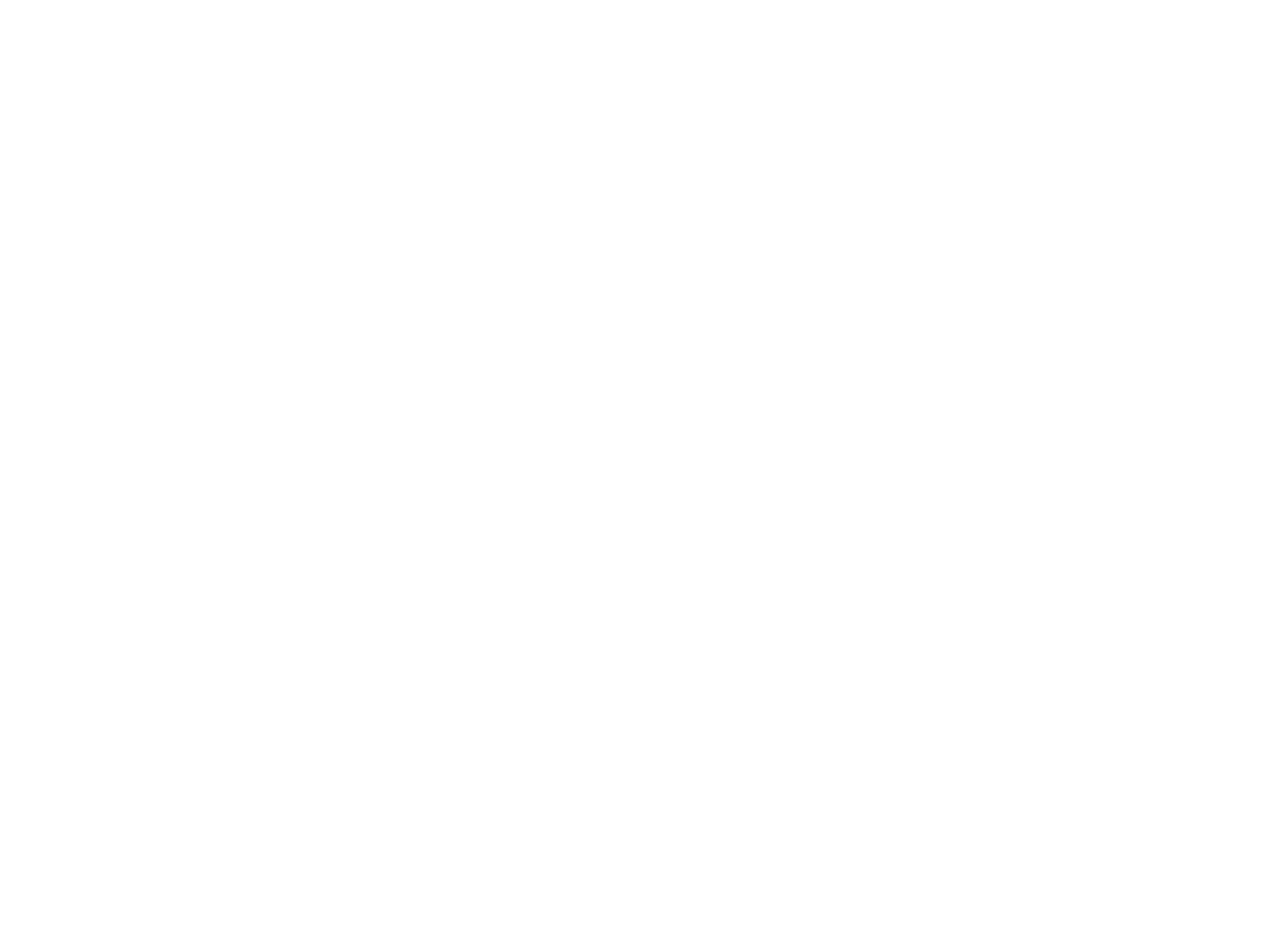
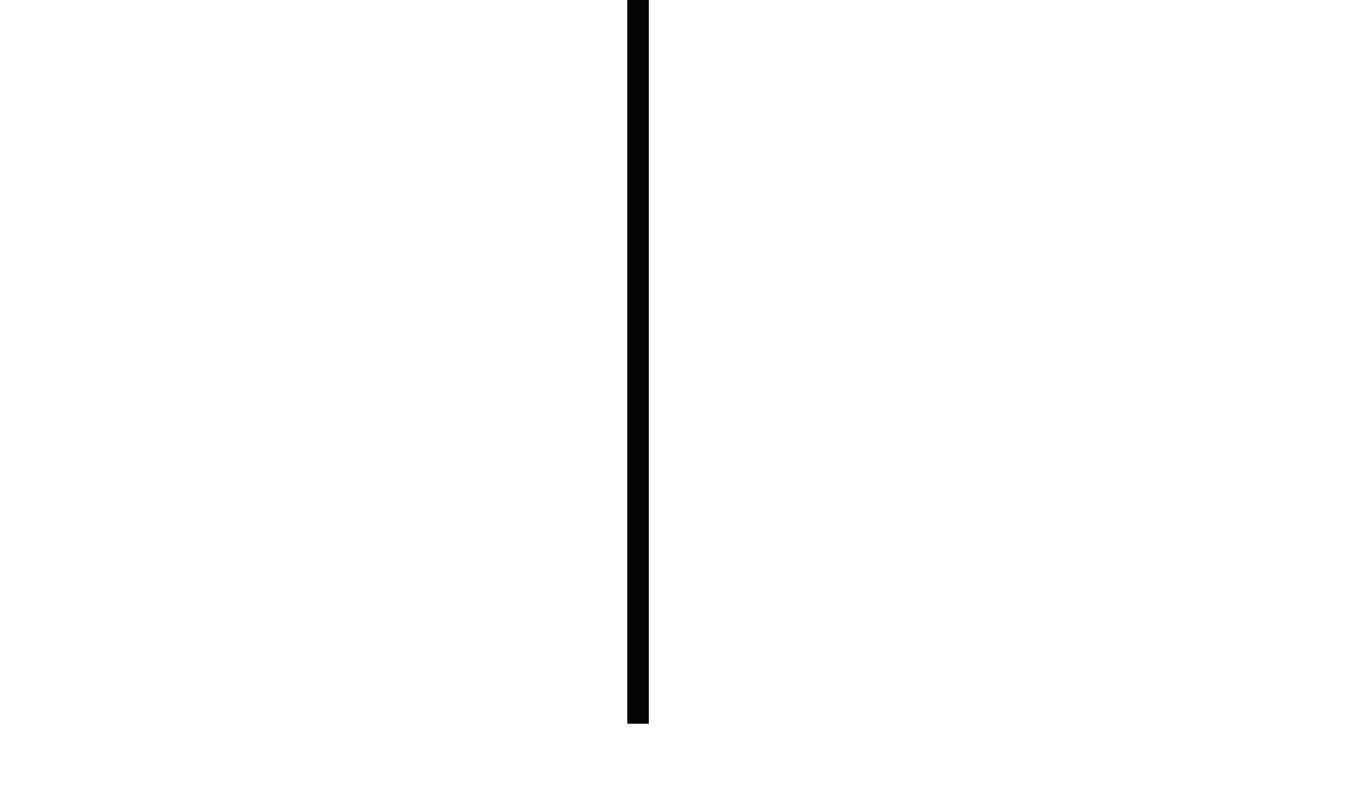
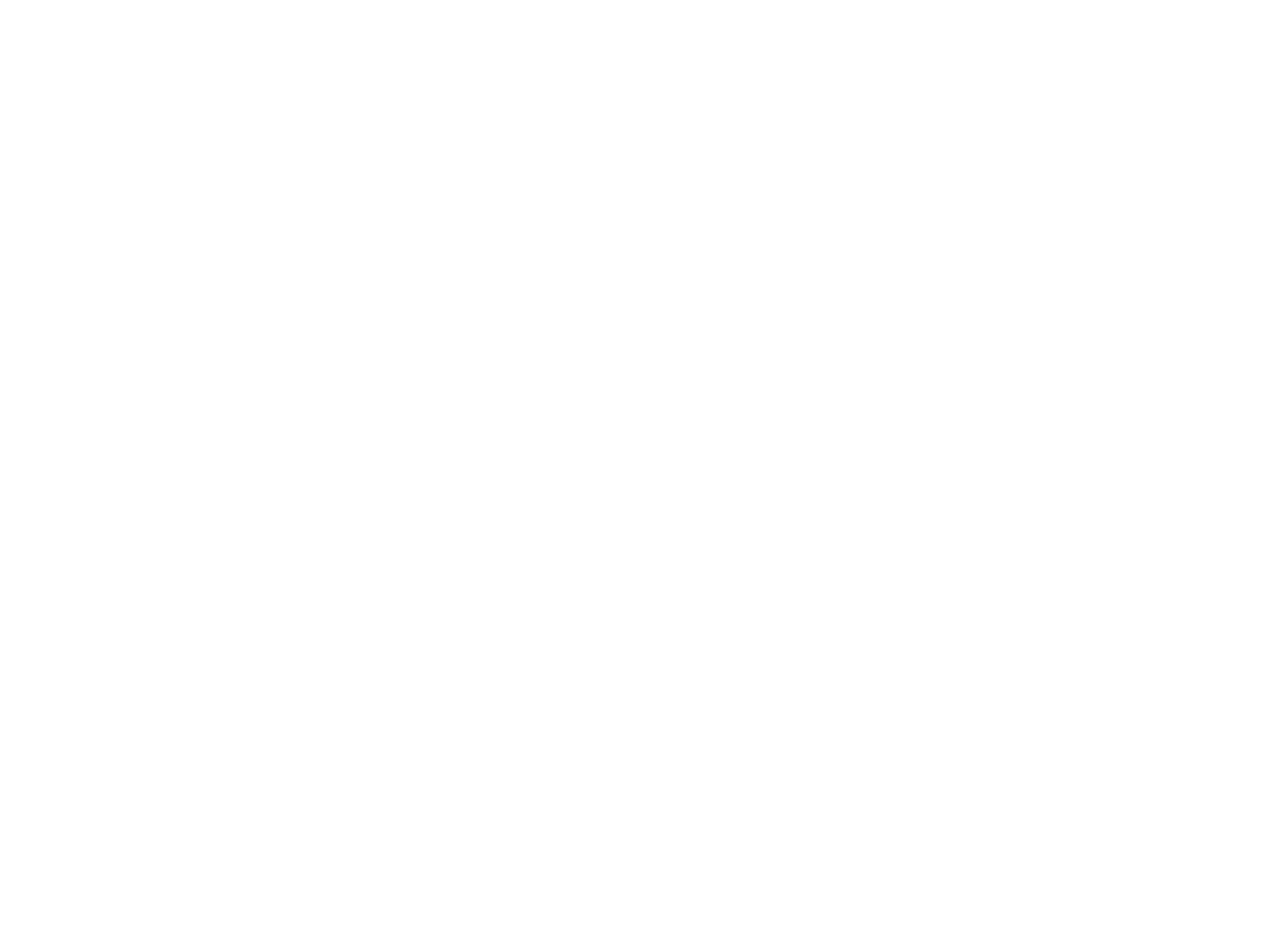
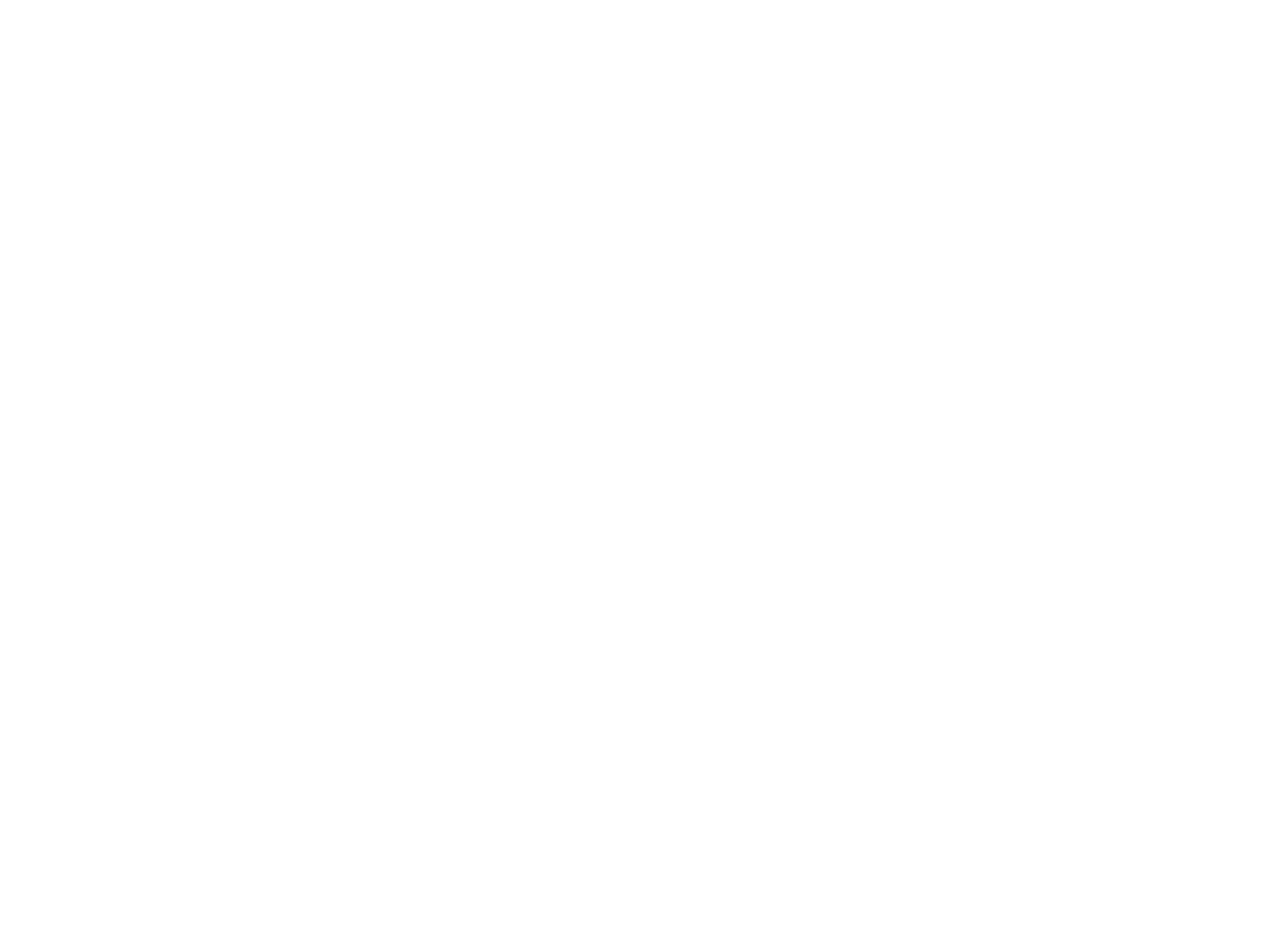
Dr Dusan Ilic
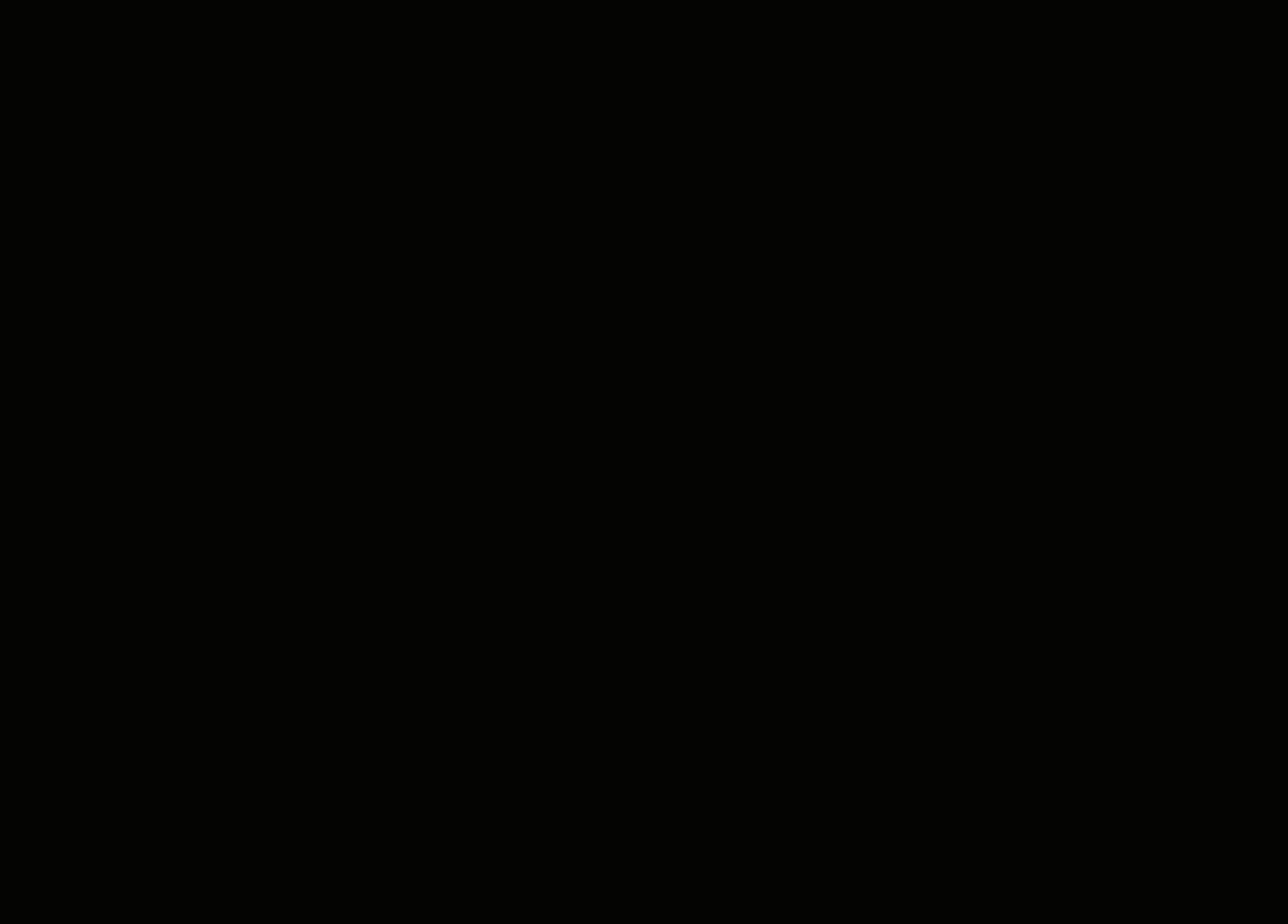
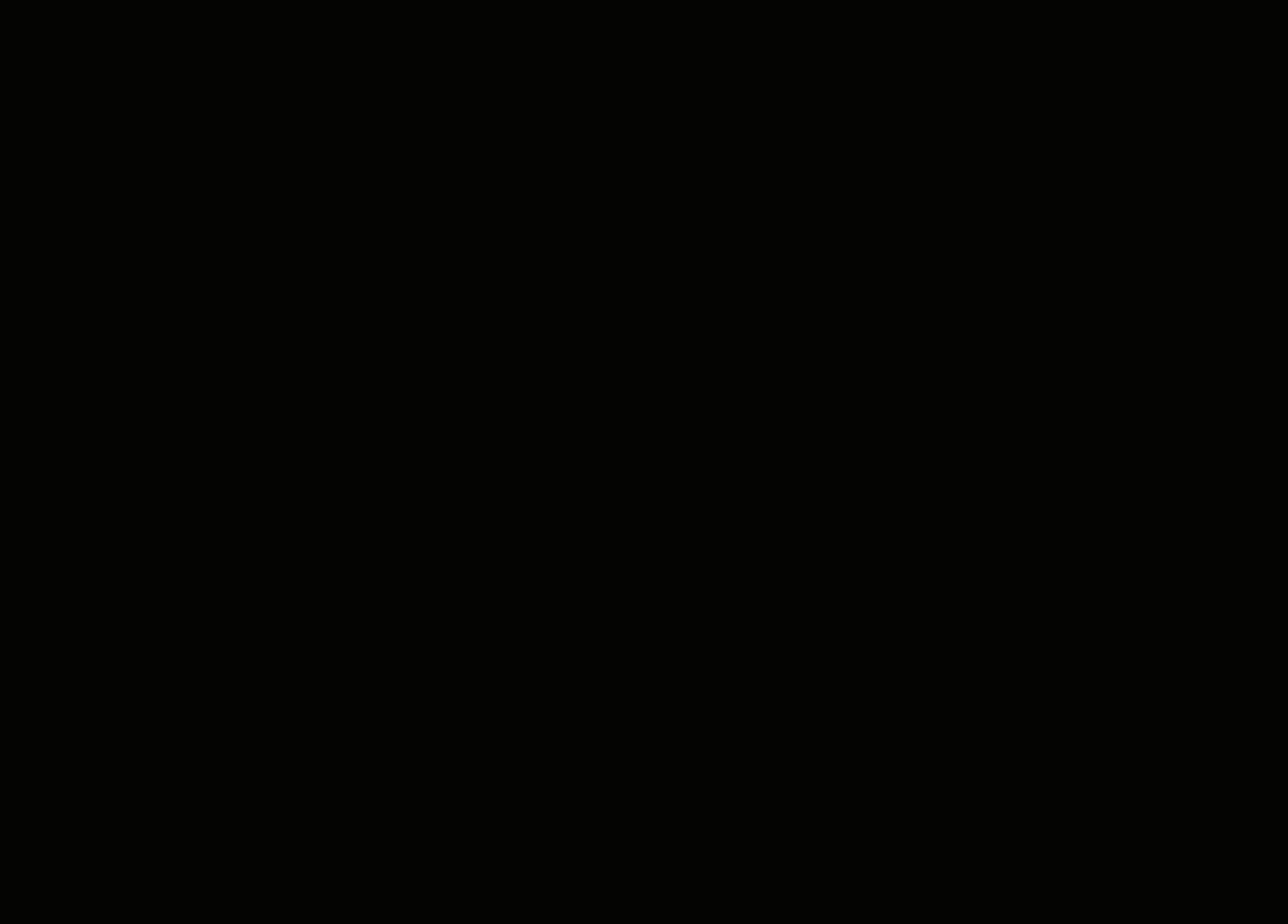
Dr Dusan Ilic is a Senior Research Associate with the Australian Research Council Centre of Excellence and has over a decade of high-level professional consultancy and R&D. He has collaborated with more than 150 different industry, academia and government partners around the world on close to 250 projects. Since 2017 he has been involved with the ARC’s Discovery on biomass pneumatic conveying, Industrial Transformation Hub advancing Australian iron ore technologies, Centre of Excellence on eco-beneficiation for minerals, MRFF’s EPCDR Initiative on bushfire particulates in addition to a number of industry, government and ACARP projects.
Australian Society for Bulk Solids Handling Award (presented by ASBSH)
Professor Peter Wypych
Peter Wypych is the founder and general manager of bulk materials engineering Australia and has completed over 500 projects for all sectors of industry, involving troubleshooting, design, feasibilities and research and development of bulk material handling plants and processes. He has published over 500 articles in these areas and is the immediate previous Chair of the Australian Society for Bulk Solids Handling, Engineers Australia. He is also the Founding Director of the newly formed International Solids Handling Research Institute at the University of Wollongong.
Professor Peter Wypych (L) and Professor Mark Jones (R).What type of conveyor
Screw Chain Pneumatic
A. R Brenya Company Ltd arbrenyacompanyltd@gmail.com 233557504815
KAUMAN kauman@kauman.com 34678754615
WAM AUSTRALIA alessandro.bini@wamgroup.com 431897954
www.promet.com.au info@promet.com.au 08 9249 8749
Transmin amerander.emmadi@transmin.com.au0438856798
Dos Santos International, LLC info@dossantosintl.com +1 770 423 9895
CRP Industries sales@crpindustries.com.au 03 9768 2228 Conveyor Manufacturers Australia ajolly@cmacv.com +61283588660
Tecweigh Pty Ltd barry@tecweigh.com.au 0430166444
JET Materials Handling Pty Ltd admin@jetmaterialshandling.com0428116368
Qetra admin@qetra.com.au 62097712
MECEBA babayigit.cevdet@yahoo.com 905323209042
OREFLOW AUSTRALIA PTY LTD chrisc@oreflow.com.au 0439993484
•
• DYNA Engineering dyna@dynaengineering.com.au 08 9473 4300
WA Belting Solutions david@wabelting.com.au 1300651320
• ProStack - A Terex Brand ProStack@terex.com 028 7122 3110
Hyer Industries Inc desmond@thayerscale.com +17818268101
•
• R BRUNONE commercial.brunone@brunone.fr +33232642020
REMA TIP TOP communications@rema-tiptop.com.au423608343
Finlay Screening & Crushing ggrigson@finlay.com.au 07 38881777
• STMalnati S.a.s. info@stmalnati.com +39 0289501730
STUDIO TECNICO MALNATI S.a.s. BMH giovanni.malnati@stmalnati.com 3487013414
•
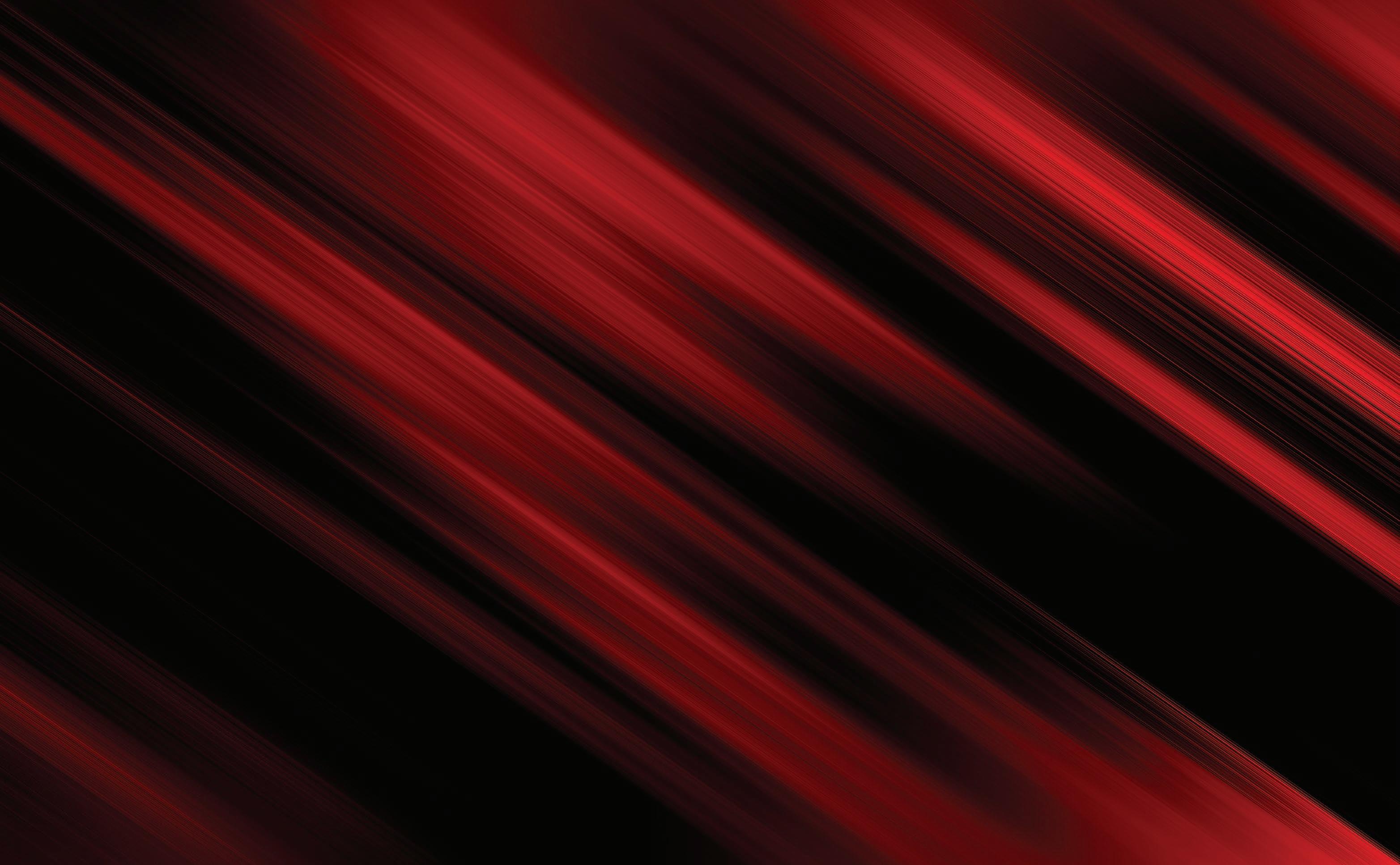
• • Floveyor enquiries@floveyor.com +61893783333
Flexicon Corporation (Australia) PTY. LTD. sales@flexicon.com.au 61 7 3879 4180
Tecnipak mineria@tecnipak.com +56 2 24965600
Nilos Australia Pty Ltd info@nilosaustralia.com 0439082080
Continental Conveying Solutions www.continental-industry.com +61 (3) 9720 9428
Bridgestone Mining Solutions Australia461 Dundas Road, Forrestfield, WA 6058 400066505
Bruks Siwertell magnus.rundqwist@bruks-siwertell.com+17708490100
STM SpA stm@stmspa.com 390513765711
Diacon Australia reception2@cpeqld.com.au 0749572472
Mitchells Equipment micmittasch@mitchells.net.cn18601149793
Premron Pty Ltd sales@premron.com.au 07 49722982
NRC Industries Limited psbhawal@nrcconveyor.com+919830250122
AGI apac@aggrowyh.vom 0477474726
TUNRA Bulk Solids enquiries@bulksolids.com.au61240339055
PRIME PRECISIONS rajulu@primeprecisions.com+919677737122
Martin Engineering info@martin-eng.com 309-852-2384
VAYERON info@vayeron.co.au 1800 404 160
Tega Industries Limited sandip.de@tegaindustries.com+919007056231
Bulk Connections sifison@bulkconnections.com27314669618
Kinder Australia Pty Ltd conveyorsolutions@kinder.com.au +61 3 8587 9111
BEUMER Group GmbH & Co. KG info@beumer.com +49252124-0
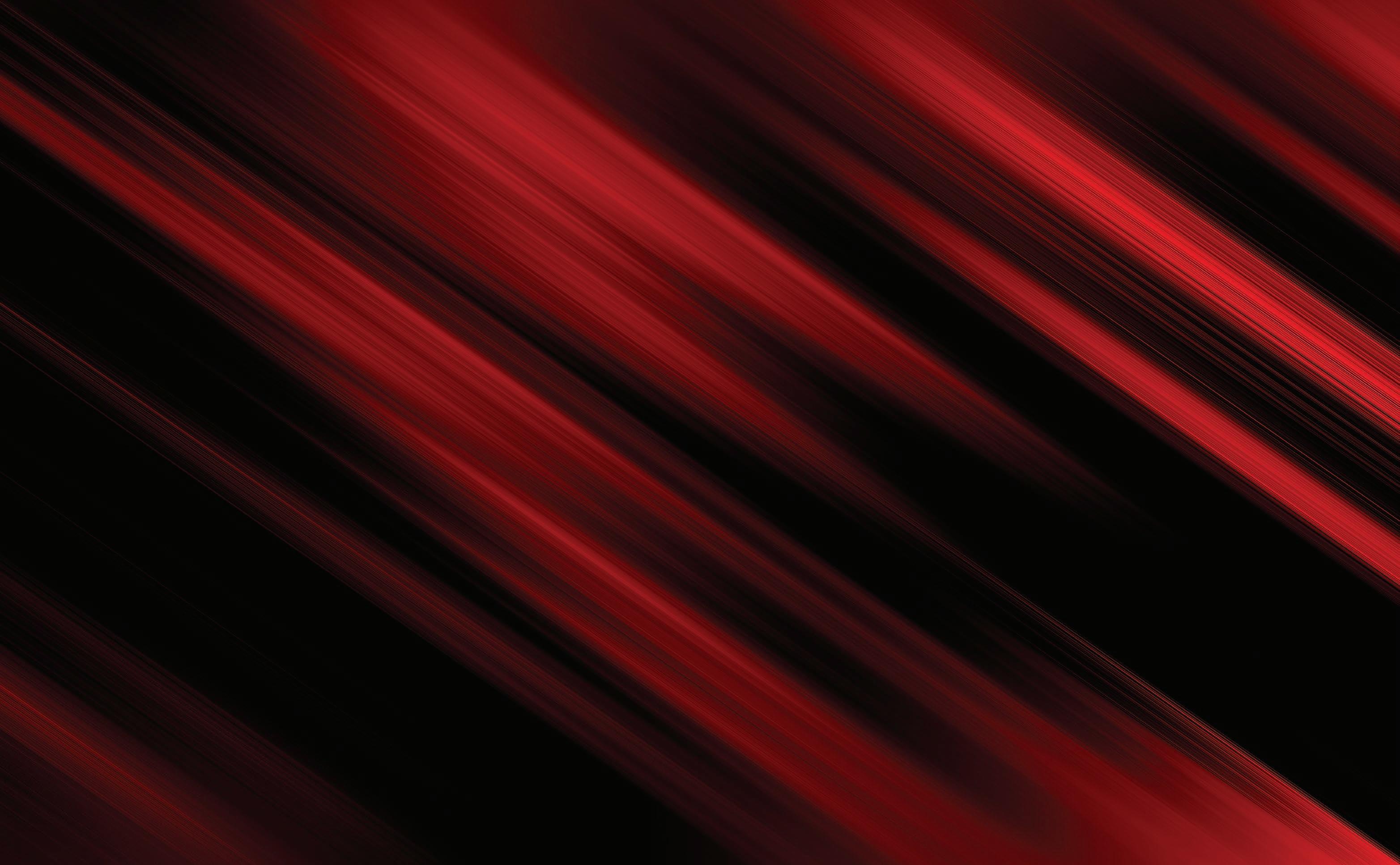
Side tipper unloader stacks up
The OPS Group is helping Australian bulk handlers get access to Telestack’s range of unloading equipment, reducing cycle times, and improving efficiencies.
MINE, PORT AND QUARRY
operators that use fleets of trucks for material handling are often on the lookout for ways to reduce costs through efficiency improvements. One way to do this is to reduce cycle times during unloading of bulk materials.
The faster a truck can deliver its load and leave, the faster the next delivery in line can be made.
Operators of haul trucks need to reverse into position – directed by a spotter – to tip their load, before then backing out before the next truck can arrive. One solution is to utilise side tipper trucks, but this is often not feasible due to limited feeding options and often expensive civil works.
Ben Suda, chief operating officer at the OPS Group said there is a better way.
Telestack, a specialist manufacturer of mobile bulk handling systems, has designed the Titan Side Tipping Truck Unloader modular system to support mine and quarry operators.
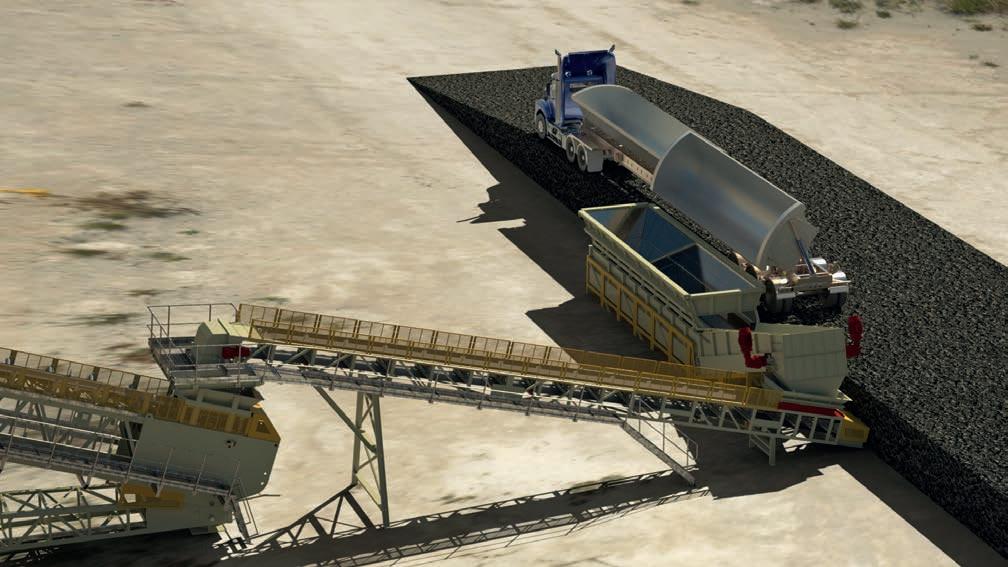
Based on a modular plug and play model, the Telestack Titan Truck Unloader enables trucks to “tip and go” based on the holding capacity of the hopper.
“Trucks can line up, unload and keep moving, drastically improving productivity,” he told ABHR

“Conventional deep pit or underground truck tipping hoppers require expensive civil works to install and cannot be moved or relocated as a plant expands. A surface feeder allows our customers the flexibility of a semi-permanent solution that has the added advantage of being fixed during operation, while also being relocatable later,” he said.
The side tipper trucks unload into a hopper featuring a heavy-duty apron belt feeder and 70° tapers along with wear resistant wear liners to enable a controlled material flow for even the
stickiest of materials.
Surges of material are handled by high torque planetary gearboxes. All units are equipped with variable speed drives to allow the operator to adjust the speed depending on the material characteristics.
Once a regulated feed is discharged from the side tipper, material is transferred at 90° to a radial telescopic stacker, which can be set up to either manually or can automatically stack the material.
Suda said all equipment is supplied by Telestack have been tried and tested in similar applications all around the world.
“The equipment is standardised and modular and can be used with a variety of materials for common side tipper bulk materials handling applications, like to feed a stacker on quarry or mine site to build up stockpiles, dumping material onto an overland conveyor, loading material at rail depots directly into rail wagons or even to feed conveyor systems into bulk storage sheds to eliminate use of pushing up with loaders,” he said.
“There’s also a massive cost advantage when compared with a customised unit, as you can move, reuse or demobilise and resell the machine if necessary.”
The OPS Group has a long-standing partnership with Telestack. As part of this partnership, The OPS Group supplies Telestack machinery to its customers, along with extensive support, through its OPS and Minerals Processing Solution (MPS) companies throughout Australia and Indonesia.
The company works closely with its clients to ensure they get the right machine for the right task and in many instances can even help reduce the amount of capital expenditure by moving costs to operational expenditures through rental and rent-to-buy arrangements –which can be vital for smaller operators.
Suda said the Telestack Titan Side Tipping Truck Unloaders are manufactured to a European quality in Northern Ireland, where they are fully assembled and tested before being
disassembled for easier shipping.
“A lot of thought has gone into modularisation so that the solution is available to sites that might otherwise be difficult to access,” he said.
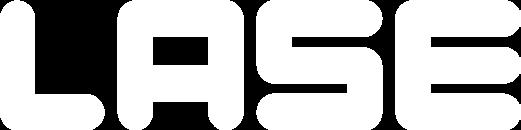
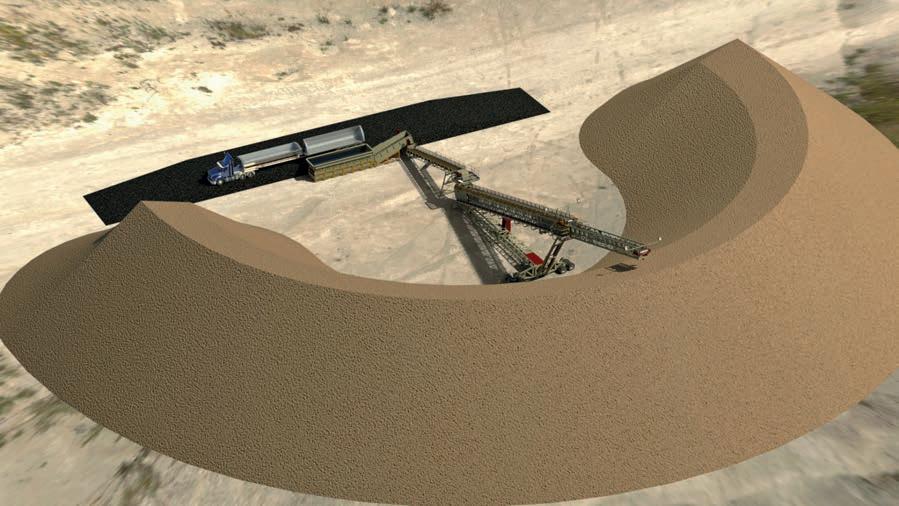
“We can package the system into
shipping containers, allowing us to transport it easily.”
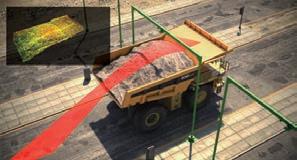
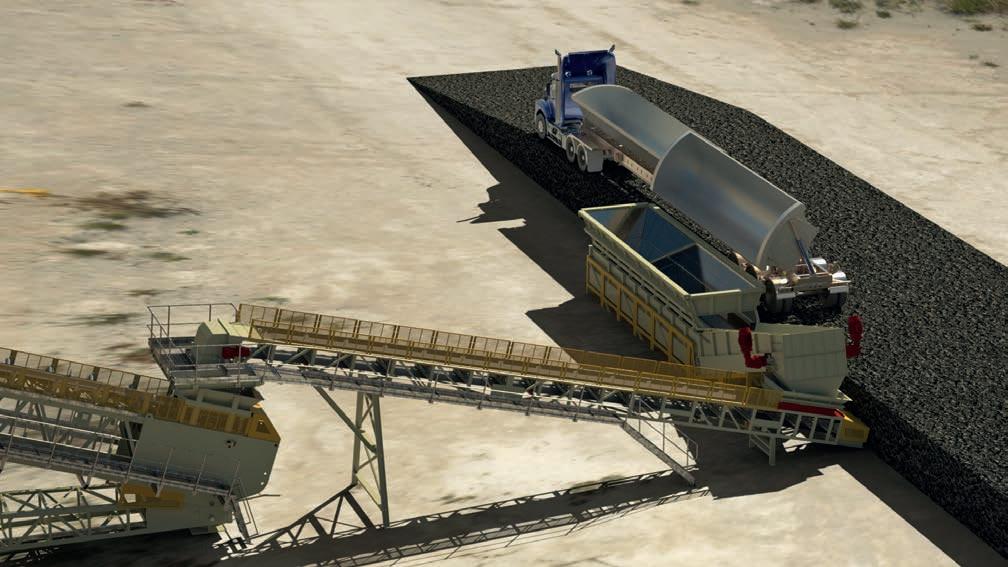
The OPS Group also offers a full suite of aftermarket support, with fully equipped workshops in Perth, Adelaide, Brisbane, and Darwin as well as sales
support in Melbourne, Jakarta, and the Hunter Valley. All maintenance team members are factory trained and attend updated training every 12 months for new and upgraded products.
The company also offers 24/7 technical support and a field service for general maintenance or breakdown situations.
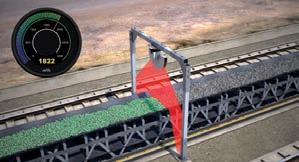
Suda said OPS Group is always looking at different avenues for growth.
“Ports are a major growth area. All around the world there are companies that are looking to improve their ship loading capacity while limiting the need to expand infrastructure,” he said.
“OPS Group offers a variety of Telestack solutions with a solid global installation base to reference.”
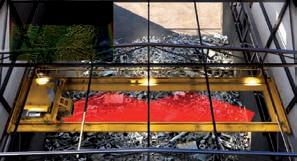
“Another area we’re looking to grow is our environmental business. The market is still in its infancy in Australia, and we are positioning ourselves to grow with the industry with a variety of processing and material handling solutions.”
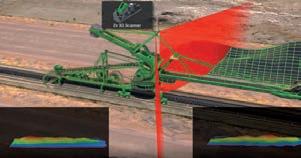

Carryback solution delivers easier maintenance
Martin Engineering has announced two new secondary conveyor belt cleaners, engineered for fast and easy maintenance.
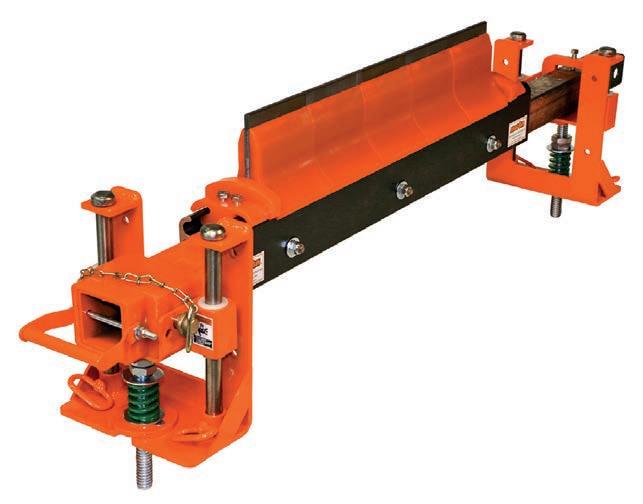
OPERATORS AT THE PUEBLO VIEJO Dominicana Corporation (PVDC) mine in the Dominican Republic had a problem. The mine’s conveyor had excessive carryback and dust, resulting in expensive equipment failures, unscheduled downtime and increased maintenance.
The mine operates every day of the year, but the weather between April and October can lead the fine clay particles to become moist and sticky. The resulting material had the consistency of thick toothpaste and would adhere small chunks of aggregate to the belt, damaging the pulleys and headers.
The operators reached out to Martin Engineering to help find a solution. In two weeks, the Martin Engineering technicians had replaced the existing belt scrapers at 16 locations with its new range of secondary belt cleaners that could endure the hot summer temperatures, high moisture and constant production scheduled.
The DT2S and DT2H reversible cleaners feature a split-track blade cartridge that slides in and out on a stainless-steel mandrel, allowing them to be serviced or replaced without stopping the belt.
conveyor products manager said even when the cleaner is encrusted with material, one-half of the split frame can be removed so the cartridge can be changed in just five minutes.
“This allows users to have a spare cartridge on hand and quickly change it out when the blades need replacement,” he said.
“Then they can take the used cartridge
the blades so it’s ready
The cleaners serve a wide variety of applications, ranging from mining, material processing and quarrying to cement production, food processing and other bulk material handling operations.
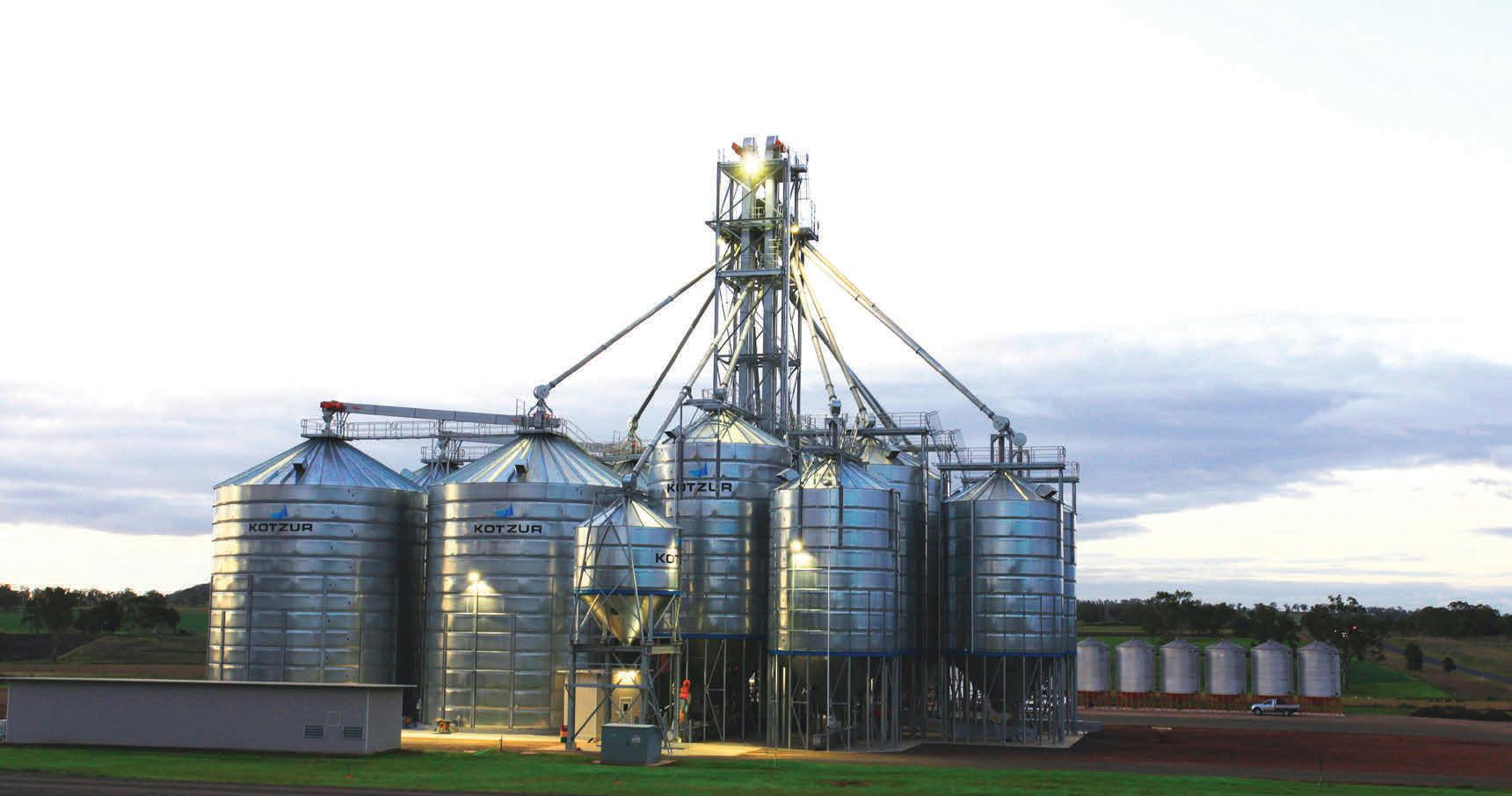
Both products significantly reduce material carryback, and they’re engineered to accommodate reversing conveyors to avoid damage to the belt or splicing. With steel blades and tungsten carbide tips set into a flexible base, the DT2 cleaners offer simple, effective solutions that can solve several carrybackrelated problems.
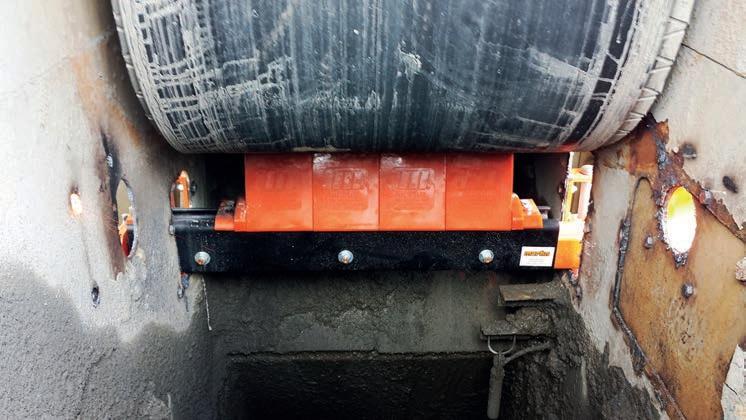
Martin DT2H Reversing Cleaner XHD
Designed for particularly demanding conditions, the DT2H Reversing Cleaner XHD is suited for heavy material loads on belts ranging from 400 to 2400 mm wide that operate at speeds up to 6.1 m/sec.
Carryback accumulations along the return run of the conveyor can occur when the cleaning systems on a conveyor fail to remove most of the material that adheres to the belt after unloading its cargo. Increased buildup results in unnecessary labor costs for cleanup, and can lead to
premature failure of conveyor components if left unchecked.
“Carryback can have an extremely sticky texture and abrasive nature, which can muck up conveyor components and contribute to premature failure,” Mueller said.
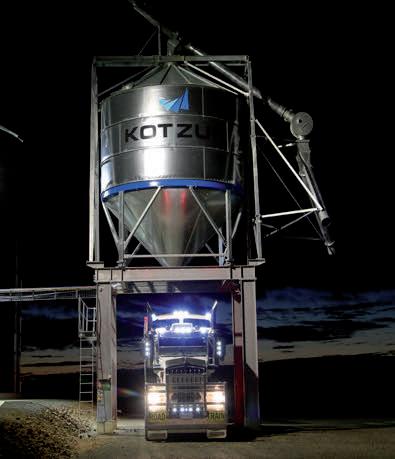
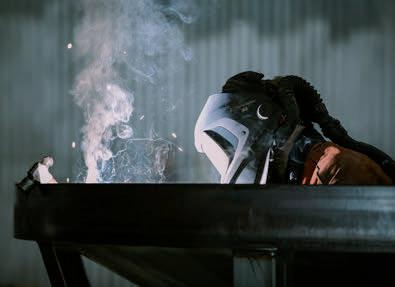



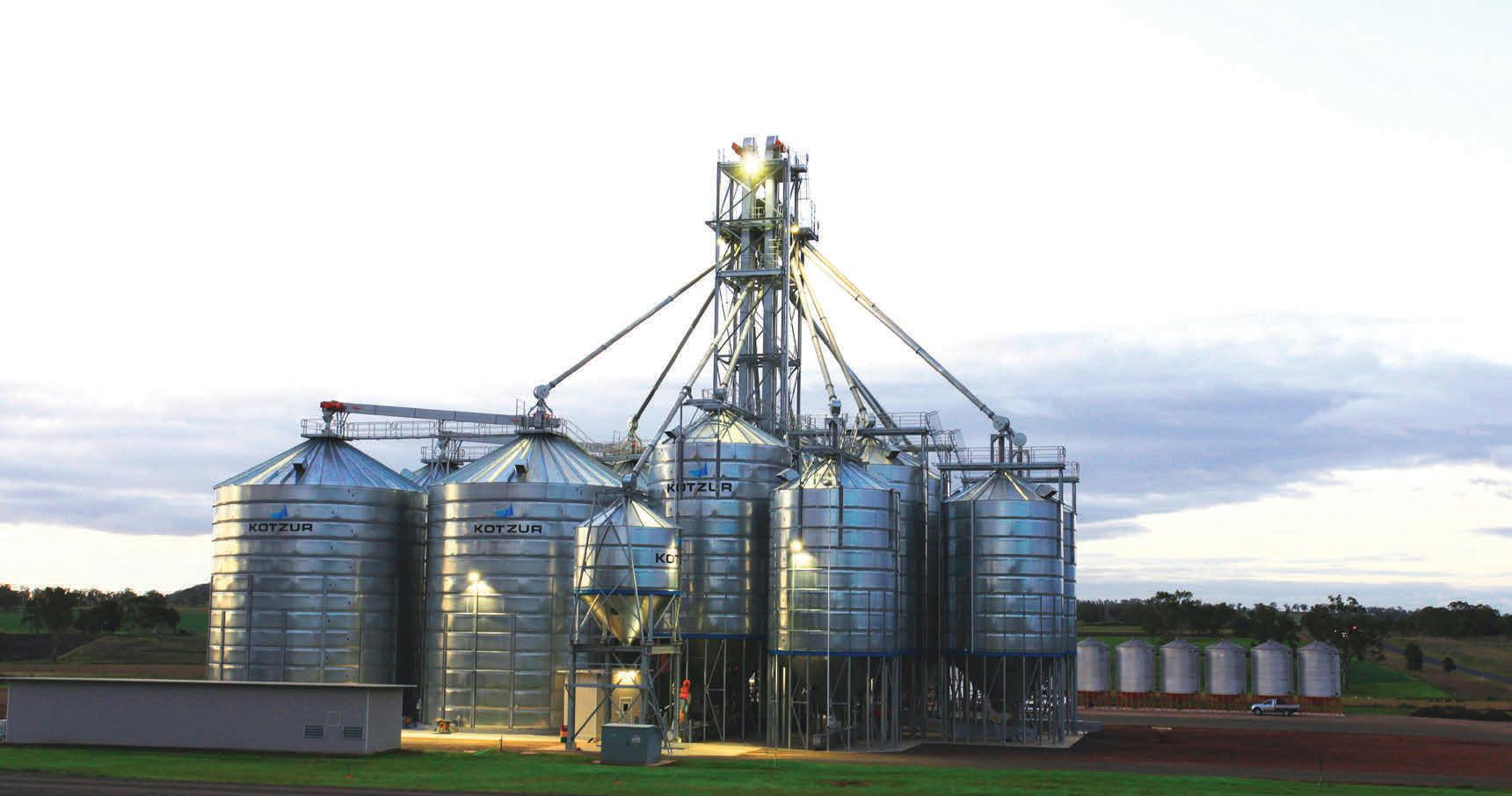
“One key to the success of these cleaners is the blade’s negative rake angle (less than 90 degrees). With a negative angle, you get a ‘scraping’ action that mitigates potential belt damage, while delivering outstanding cleaning performance.”
Martin DT2S Reversing Cleaner



Like its larger counterpart, the Martin DT2S reversing cleaner can be installed on belts ranging from 400 to 4800 mm wide.
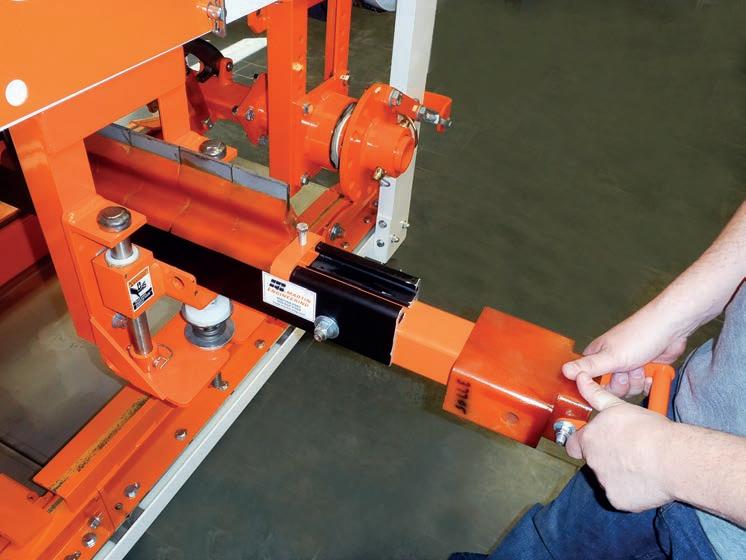
Unlike the DT2H, the DT2S is designed for a lower maximum belt speed of 4.6 m/ sec on belts with vulcanised splices.

Mueller said this is primarily due to the difference in applications.
“The DT2S has a slim frame that allows it to fit in spaces as narrow as 178 mm. As a result, the DT2S can be attached to belts that may be too small for primary cleaners,” he said.
Both of the DT2 cleaners can be used in medium to heavy duty environments, providing a lasting solution to a diverse array of complex problems that are caused by carryback and minimising fugitive material.
Following the upgrades, PVDC’s mine operations are now cleaner, safer and more productive, providing stakeholders with more confidence in the sustained operation of the mine.
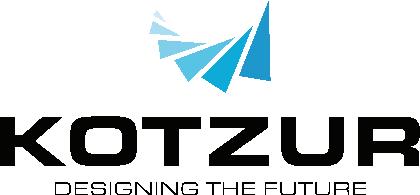
Pulley lagging performance engineering analysis
Pulley lagging has historically been treated as a consumable and replaced when there’s a failure, without much further analysis other than historical experience. Mariana Ballestrin from Elastotec explains why making solutions based on historical experience is a simple guess.
PULLEY LAGGING FAILURES ARE
one of the main causes of conveyor stoppages impacting production output.
There are recurrent pulley lagging failures in the field, mainly on drive pulleys and non-drive high tension bend pulleys. Failures are seen as lagging debonding, lagging fatigue, belt cover damage and reduced splice life.
There’s a lack of understanding on the root cause of these failures. The cyclic shear stress developed at the interface of pulleys under different operating conditions are unknown and the fatigue limit of the different pulley laggings available in the market is also undocumented.
Every other aspect of the pulley is engineered to perform, yet there’s no engineering analysis available on the lagging.
Elastotec and Conveyor Dynamics Inc. (CDI) have developed a software tool that helps the industry understand the risk of failure of pulley lagging. This software tool compares the stresses developed for a specific application, to the fatigue limit of the lagging selected indicating if the lagging is working in a safe operational envelope.
Pulley lagging to belt interface cyclic stresses developed Conveyor pulley lagging is subject to a normal pressure due to the belt tension and belt wrap around the contact face. In addition, driven pulleys develop a surface shear stress to transfer the applied drive torque.
The lagging analysis tool developed calculates the normal pressure, lagging contact shear stress, friction developed and localized slip (if present) under
Figure 1.
both dry/clean and wet/dirty conditions using a variant friction model and the specific lagging shear modulus.
Additional shear stress caused by differential contact diameters across the face of the pulley caused by belt/ lagging wear or material build-up is also accounted for in both driven and non-driven pulleys. Typical on hightension bend pulleys in contact with carry side of belt with belt cover in contact with lagging changing profile with age.
The lagging analysis tool defines the range of normal and contact shear stresses that the lagging is subject to and forms the basis for comparison against a lagging performance envelope which defines the capability of a lagging product to endure the applied stresses of the application.
Lagging performance envelope
Finite element analysis (FEA) is used to define the fatigue limit of the lagging and the lagging shear modulus over the full range of normal pressure and surface shear stress conditions. The lagging capability is expressed in the form of a lagging performance envelope which evaluate the fatigue limit at each of the critical locations including:
• Internally in the pulley lagging rubber
• At the interface with the pulley steel shell, ceramic tile interface (where applicable)
• At the contact interface with the conveyor belt.
The lagging performance envelope plot is a complex representation of the traction and shear stress fatigue limits of a lagging product. The fatigue limit is based upon the lagging rubber materials endurance limit at 1.4x10^8
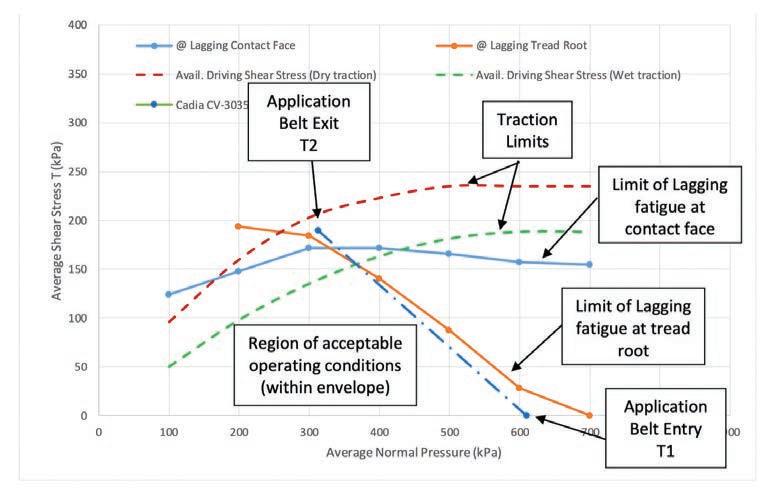
cycles which is equivalent to a typical pulley operating at 60 rpm for 5 years at 90 per cent utilisation.
The envelope lines at each of the physical locations represents the endurance limit, above which is indicative of excessive levels of fatigue shear stress developed.
The application duty line represents the range of average normal pressure and average shear stress developed along the arc of contact between the belt entry point to exit point:
From the example plot in Figure 1 it can be interpreted that the application line is within the performance envelope for the lagging type evaluated. However, the last approximate 20 degrees of contact arc before the belt exits the pulley at T2 does indicate the fatigue shear stress in the lagging rubber at both the tread root and contact face is marginally exceeded.
This would indicate a fatigue life in these locations of slightly less than 5
years. It also indicates that under less than ideal (clean dry) conditions, the last 20 degrees of contact may exhibit excessive slip which can result in an increased rate of abrasion selected
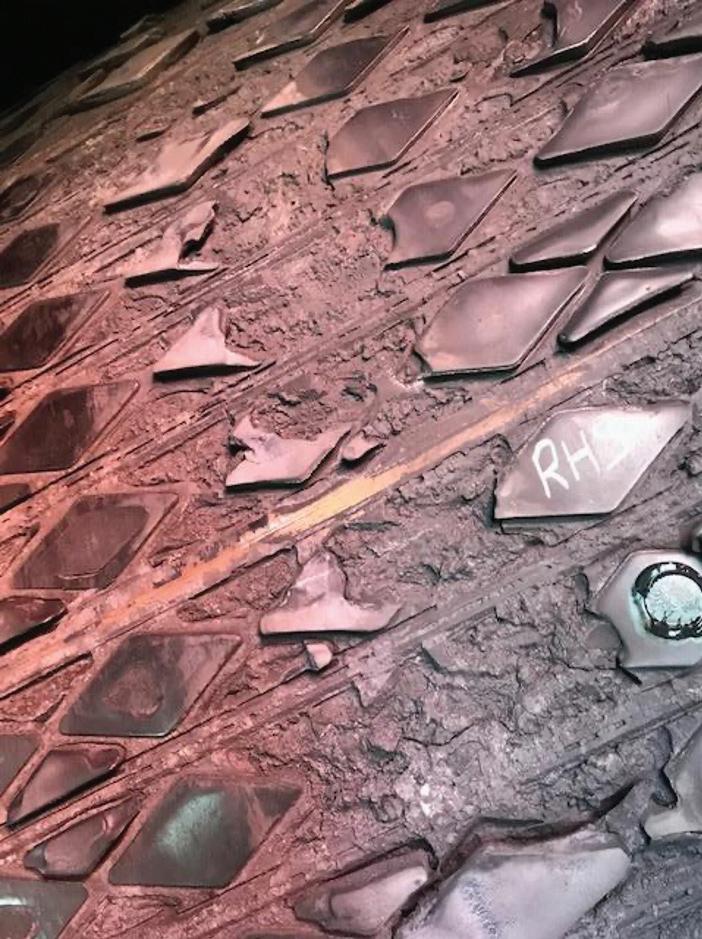
FRAS tests according
Independent belt conveyor testing, audits and reviews
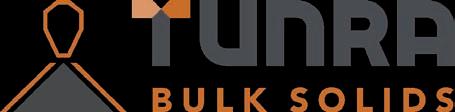
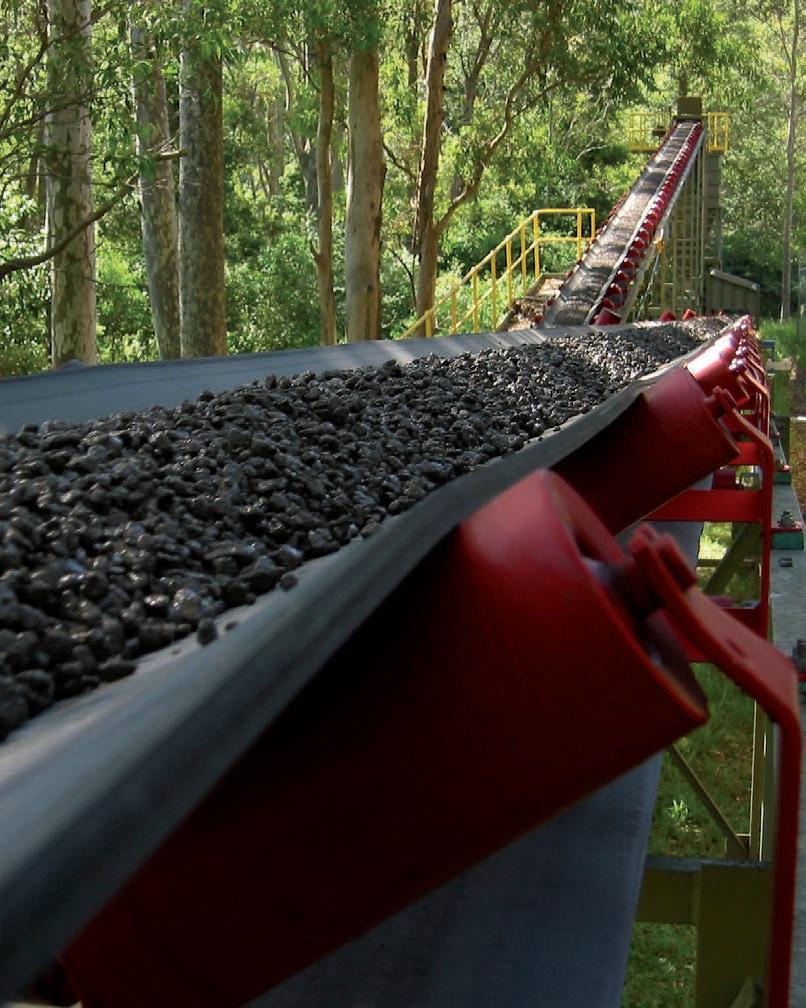
Idler roll noise testing, including self-noise and operating noise
Belt cover ply adhesion and resistance to tear propagation
Cord breaking force, static & dynamic cord pull-out strength
Small and large sample indentation rolling resistance measurement
Belt surcharge angle and maximum inclination angle
Belt scraper efficiency
Idler roll rotational resistance testing, including rim drag, break-away force and maximum start-up drag, MIS and TIR of idlers
Idler dust and water ingress
Conveyor belt tensile strength and elongation
Troughability
Abrasion testing for idler and belt components
Inspections and failure analysis, as well as site inspections
Thermal imaging
Belt
accordance
other
1313,
ISO5048,

& other
& MDG3608.
CEMA
Figure 2. Diamond pulley lagging failure.for the upgraded application given its flawless performance when installed on the drive pulleys before the upgrade.
Following 4 weeks of operation with a heavier, higher-rated belt, catastrophic failure of the lagging occurred on both drive pulleys, as shown in Figure 2. This failure resulted in 3 days of unplanned downtime and ~$21m in lost production.
An engineering review of the lagging selection using the performance envelope software tool identified the lagging was operating above its fatigue limit, a parameter not considered in current design standards. Replacement of the lagging with a rubber herringbone pattern, with theoretically an identical coefficient of friction to the diamond
Figure 4. Performance envelope tool showing application Operating +2 times over the fatigue limit of the lagging at the tread root location.
Benefits to end-users:
• Optimise the performance of existing and new conveyors.
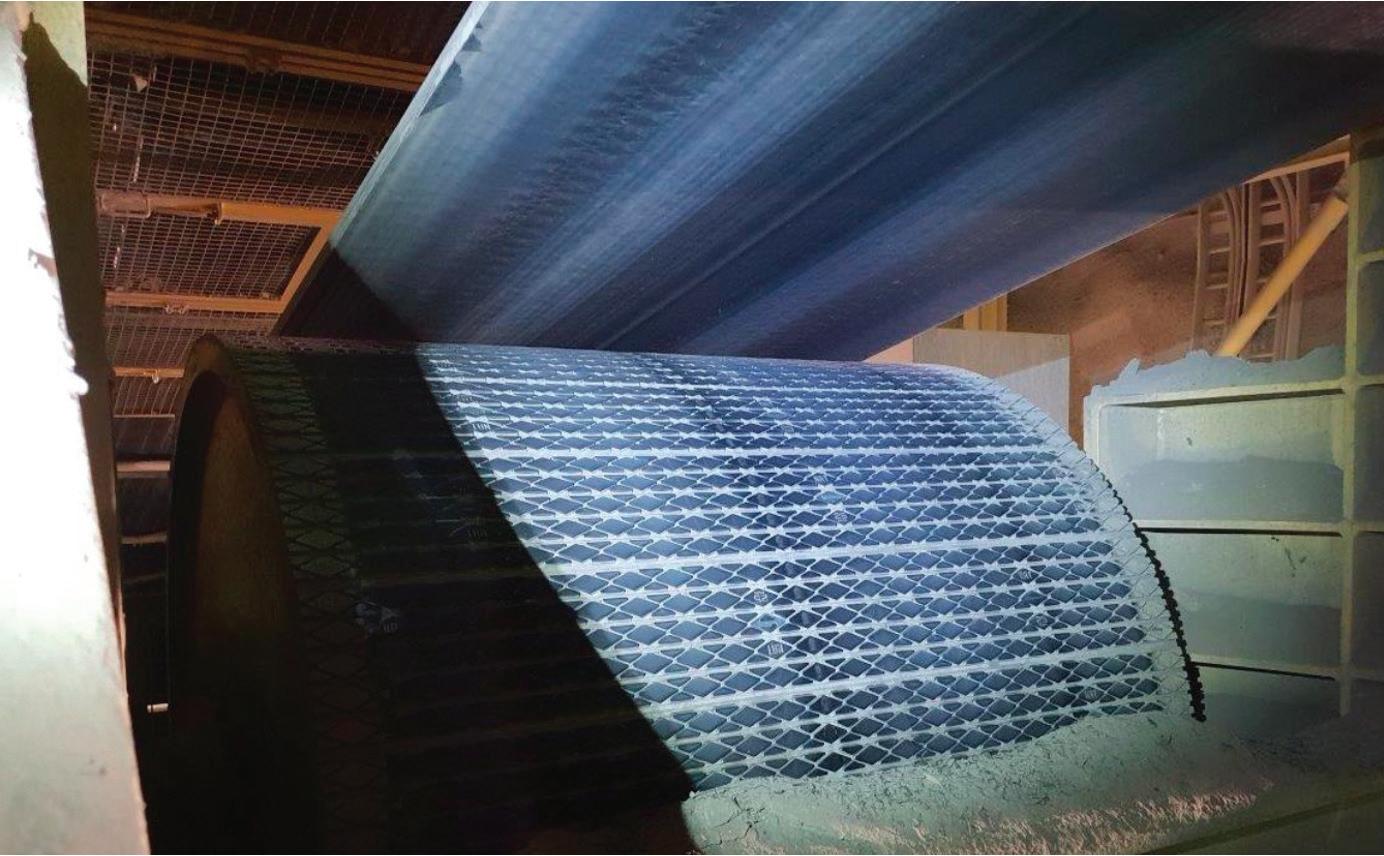
• Improve confidence in conveyor design, reducing the risk of catastrophic failures and unplanned downtime.
• Aid the selection of appropriate conveyor belt/ lagging combination to optimise performance and cost.
rubber lagging, has been in operation for nine months with no visible signs of fatigue.
Pulley lagging is a critical aspect in conveyor design, with inadequate
• Provide engineering data to support component selection and investment.
• Ensure that the conveyor belt/ lagging combination optimises belt splice service life.
• Validation of conveyor belt/ lagging selection against site/ equipment standards.

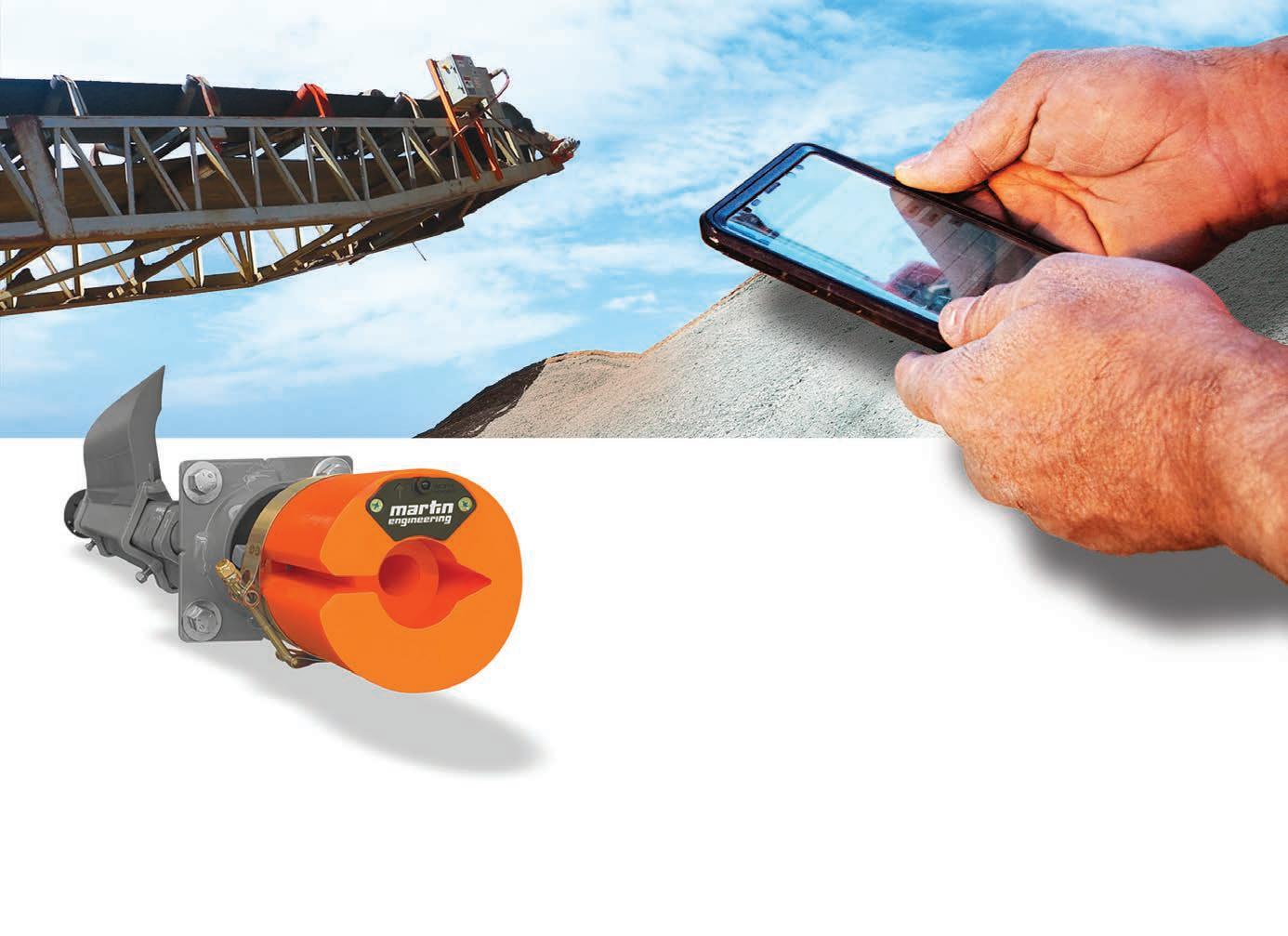
Benefits to conveyor belt manufacturers:
• A deeper understanding of the shear stress applied to the bottom cover of the belt, reducing delamination failures and downtime.
• Ensure that the conveyor belt/ lagging combination has been selected to maximise the performance of the belt and splices.
• Performance testing of new and existing splicing methods under operating conditions.
• Selection of belt/lagging combination based on engineering data and analys
Benefits to pulley manufacturers:
• Maximise the pulley service life
• Verified engineering data to aid the selection of lagging for the application for the pulley to operate as intended.
• A detailed understanding of load/stress distribution on the pulley due to belt wear.
Figure 3. Drive pulley in operation with diamond lagging.
Benefits to conveyor designers:
• Improved confidence in engineering design
• Provides the ability to evaluate different conveyor belt/ lagging combinations and compare performance limits based on a proven model
• Enable conveyor designers to identify potential system design performance problems
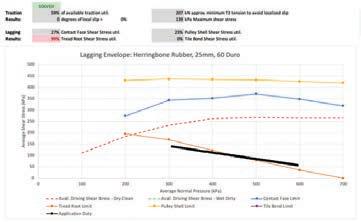
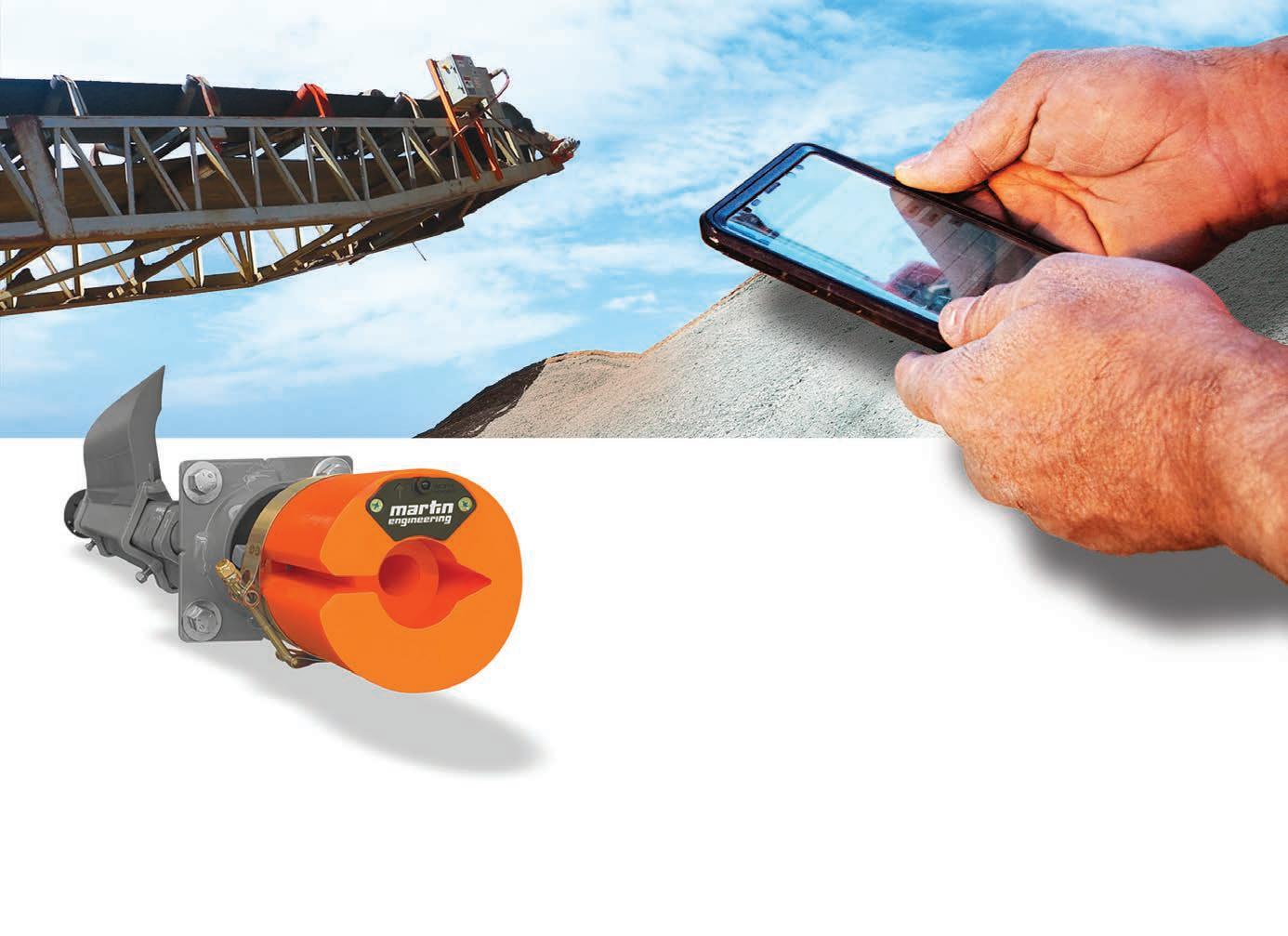
• Selection of belt/lagging combination based
• on engineering data and analysis
• Verified data to aid selection of drive pulleys, lagging, pulley infrastructure (angle of wrap and snub pulley placement) and counterweight.
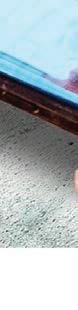
position
design or selection resulting in unplanned failure and downtime, and lost production. The rate of incidence of these failures continues to increase with larger drive power and belt tensions driven by the demand for higher throughputs.
The outcomes of this project benefit conveyor designers, pulley and conveyor belt manufacturers and end-users.
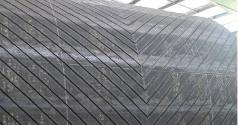
conveyor
cleaners, allow
event
real-time conditions
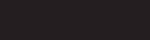

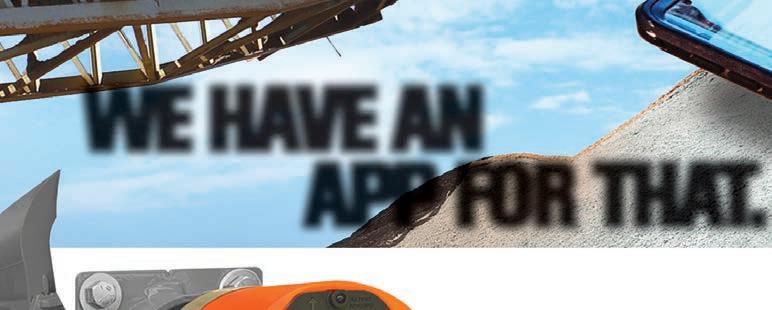
Dust – The great escape
Dust is inevitable and gets everywhere. Jack Cain, mechanical engineer, at Kinder Australia explains how dust escapes bulk handling systems and what can be done to contain it.
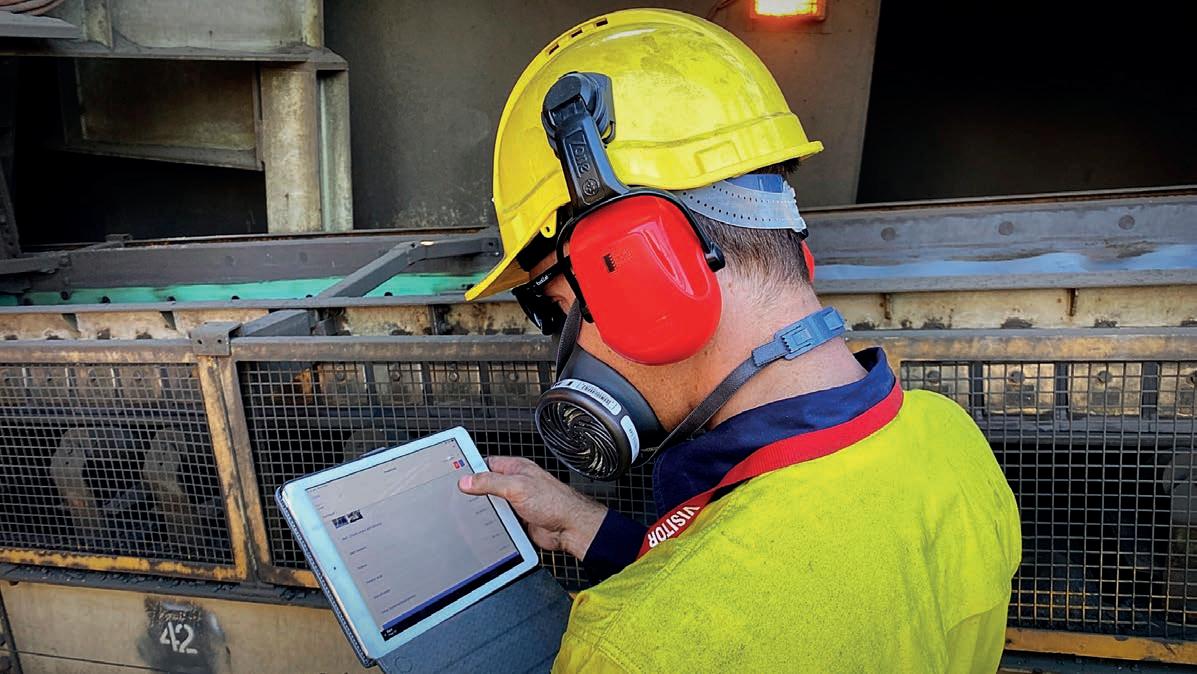
WHETHER IT’S GRINDING UP ores to extract the sweet, sweet minerals inside, or from crushing, what are essentially boulders, into tiny, little rocks that are a much more manageable size for handling and transport, or even just when handling the super fine aggregates so often used in construction, the emission of at least some amount of dust is nigh unavoidable.
And dust just gets everywhere. The formation of this dust is not entirely unwelcome, however, and in some cases, the dust is the intended product; so, efforts to negate it are rarely required, nor are they entirely plausible. Therefore, the more auspicious approach is to control the spread of this biproduct by removing any possible avenues of emission into the environment. It doesn’t matter how much dust you produce if it never gets a chance to see the light of day.
Dust tends to be most prevalent in some rather specific locations: transfer points, where the product is in its most turbulent state. At the end of the belt where the material is discharged, especially when into open air, such as onto stockpiles, rather than into sealed chutes or hoppers. In areas where product is exposed to environmental factors, primarily wind, which can whip the top layers up into a violent frenzy. In any areas where vibration is common, where this jolting movement can bounce the material around, causing unsettled particles to wander off the conveyor looking to wreak havoc. In places where carry-back or spillage are present, since these are unintentional there are usually few safeguards present to prevent these issues causing excessive dust to spread. And if the particulates are fine enough, the movement of the belt starting, stopping or even just when travelling at high speeds can be all that’s needed to disturb the top layers of material and throw dust.
The fineness of dust is categorised as particulate matter (PM), then subcategorised based on size. Fine particles (PM2.5) are smaller than 2.5 μm (1 μm = 0.001mm), coarse particles (PM10) are sized between 2.5 μm and 10 μm and “larger than PM10” is for all particles with a diameter of 10 μm or greater. Coarse and larger than PM10 particles make up the largest proportion of what is typically produced in quarrying and mining activities.
With all these different factors why even bother putting in the effort to stop the spread in the first place? Well, just listing the rampant health issues associated with fine airborne particulates from mining and industrial sites, we have the numerous respiratory diseases, such as silicosis, coal workers pneumoconiosis, chronic obstructive pulmonary disease, and the savagely increased risk of lung
cancer, which are just the result of working around coal and silicas dusts. This is without even mentioning the plethora of health risks from working with the metalliferous dusts inherent to ore mining, or the outright toxic particulates from industries such as fertiliser manufacturing, as well as the numerous cardiovascular issues, kidney disease and autoimmune diseases such as scleroderma.
On top of the copious amounts of health issues we also have numerous other hazards: including the very real risk of dust explosions, impaired visibility, damage, and accelerated wear of exposed electrical and mechanical devices, including motors- which are large fire hazards, plus a significant loss of product. There are a considerable number of plaguing issues that stem from dust exposure, so it’s best to implement a few
measures to keep the dust down.
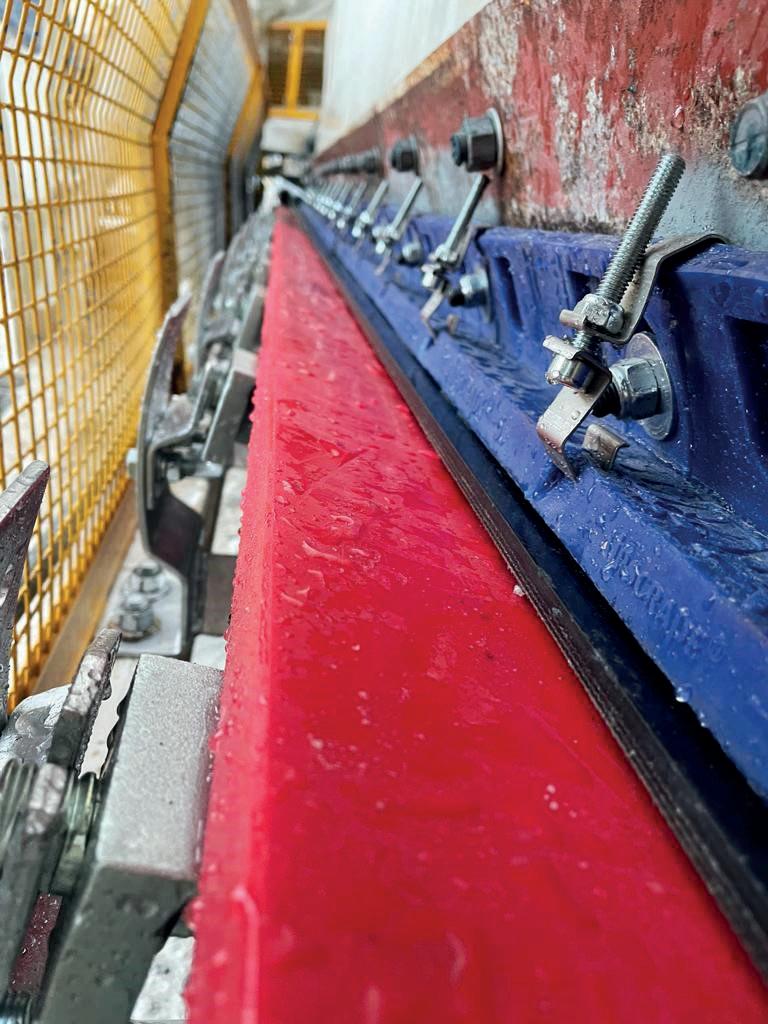
Thankfully when it comes to subduing the beast that is dust, modern conveyor solutions provide quite the arsenal. Take the transfer for example, likely the dustiest place on any conveyor. Skirting is one of the most effective methods of keeping material from just spilling out of your transfer the moment it touches the belt. Ideally you would want skirts that provide some sort of contact seal, but when the diameter of dust is measured in microns, even a 1mm gap is enough for millions of particles to escape. So, a proper seal needs this belt contact to be effective, and contact means wear, so a skirt needs a way to combat wear or it risks quickly becoming worthless.
A self-adjusting skirt, that maintains full effectiveness for its entire lifecycle without the need for direct maintenance, is incredibly cost effective. These selfadjusting skirts are typically quite soft to allow for them to conform to the
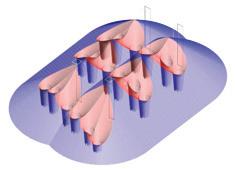
ThankYou
YOUR BULK MATERIALS SOLUTION PROVIDER
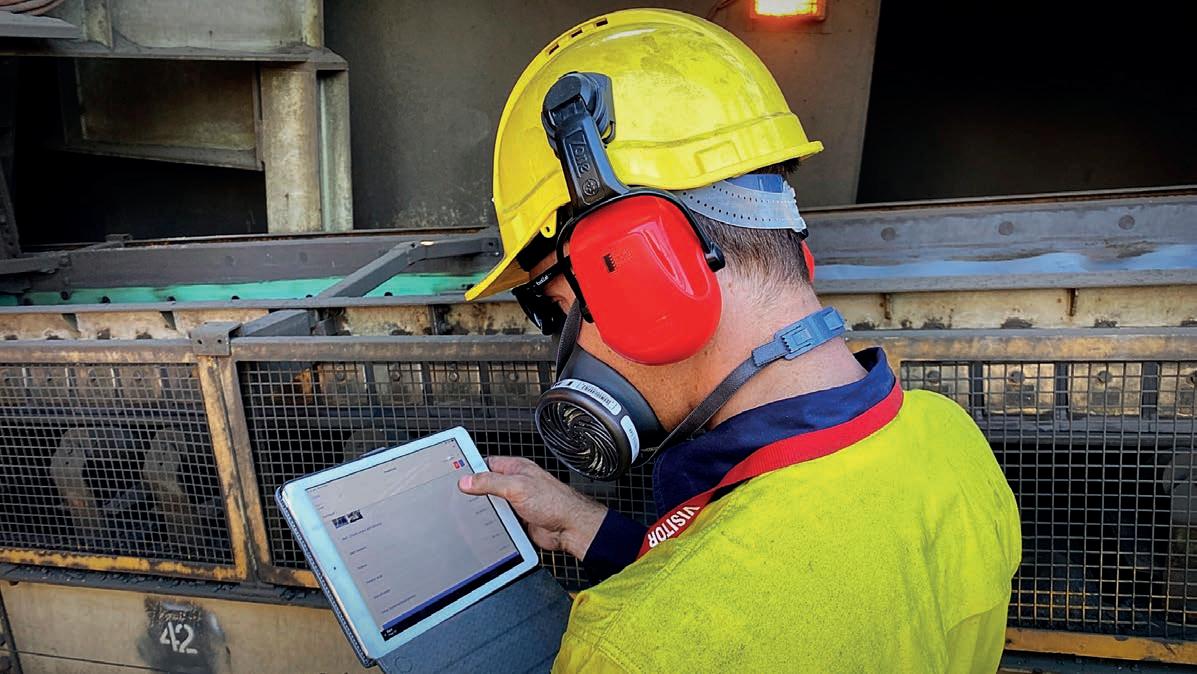
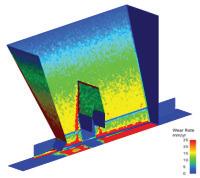
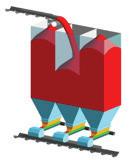
belt unhindered. This softness leaves them vulnerable to the harshness of the material stream, which can cause some serious damage as it flows by, so typically a hard internal skirt, that stops just short of the belt, is used to keep the material at bay, while the soft skirt picks up the slack and completes the contact seal in relative safety.
But if the wear and tear of contact systems rubs you the wrong way, then the innovative, contactless external skirts may be your best bet. While they do tend to hit a higher price point in the short term, these marvellous devices tend to make up for it with their almost non-existent maintenance costs. Using their unique geometry to manipulate the power of airflow; a continuous suction effect is created to keep dust in. These contactless skirts still require the support of an internal hard skirt to make sure they don’t clog up with the larger product, but their overall effectiveness is impressive.
Whatever your preference, having at
least some basic skirting is always better than having none.
Of course, with all this skirting it’s imperative that your belt profile is well supported to maintain consistency and prevent gaps, even more so with contactless skirting which requires a very particular spacing for the proper suction flow to be possible. Any sag in the belt and you can suddenly find yourself wondering where you left your shovel.
How you go about supporting your belt is usually determined by the conditions of your transfer point. Systems that experience low impact from a small fall height or light products can get away with static belt support systems, which provide little in the way of impact support, but help maintain that perfect, flat surface across the transfer.
Environments that require at least some impact support should invest in an impact bed, a large structure with flexible rubber rails that alleviate some of the impact force from the belt. For
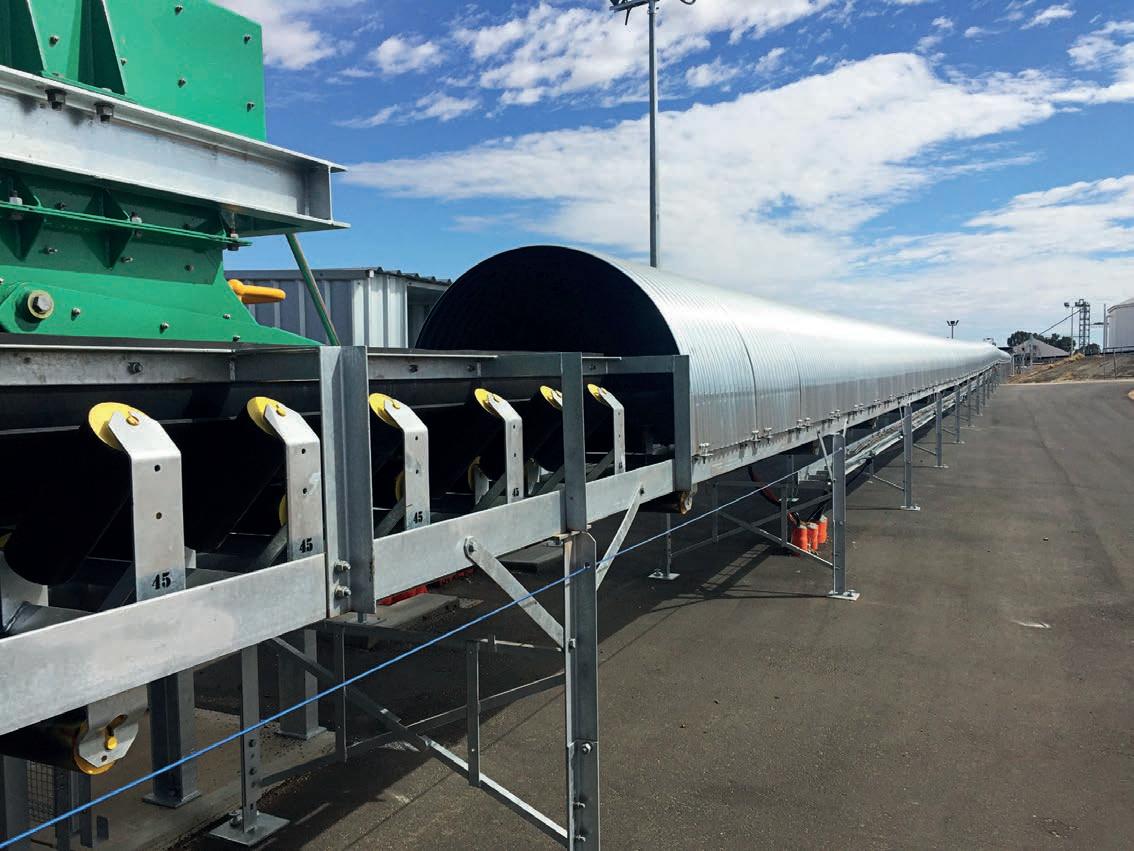
situations where severe impacts are common, a dynamic bed may be required. These utilise a trough panel suspended by spring elements to support the belt, while the static outer rails maintain the edge profile. These systems all tend to utilise low frictions rails (typically < 0.3 static coefficient of friction) on the wings to create a consistent surface for the belt to move across, however, this is still an increase in friction over most rollers. While these rails typically quite resistant to abrasion, they will eventually require replacement as well.
The problem of dust cannot be solved solely at the transfer, however, as even if the dust is controlled there and the product is settled, the dust can still present new problems across the rest of the conveyor.
Compared to the transfer point, the run of the belt typically has far less structure to encase the product and protect it from the open elements, sometimes as little as just a set of
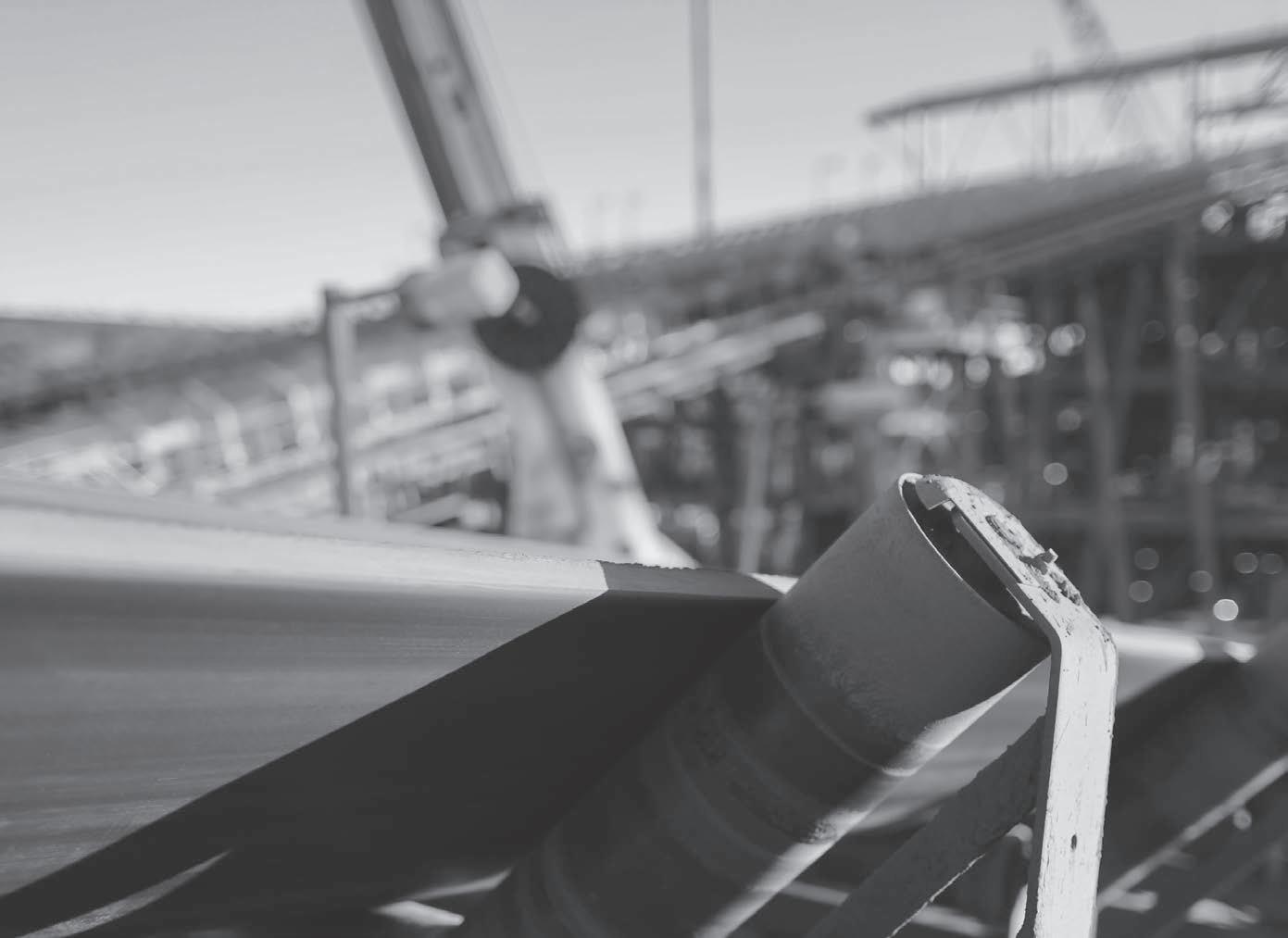
stringers are present. Therefore, special equipment adapted to these constraints must be used; belt covers are physical barriers that attach to the stringers and almost completely enclose the belt, preventing the influence of wind, and trapping dust that is disturbed by vibration and belt movement.
Belt covers typically are made from rigid materials such as steel or reinforced plastics, which are effective barriers, simple to install, and can be modified with features like inspection and maintenance windows, alternatively more flexible materials like mesh cloth can be used, which maintain airflow and a degree of visibility while preventing dust migration.
Water sprays can also be used and are very effective for dust suppression, however, the resultant water saturation is undesirable for a lot of products and the wastewater must be delt with limiting their desirability for numerous applications.
Similarly, extraction fans can be very effective when run across the belt length, but maintenance for these is high as filters must be replaced to maintain effectiveness. Unlike the belt run, discharge points can usually be encased in structure with dust curtains to prevent any wayward dust spreading, but when material is being discharged into open space say for stockpiles, an extendable loading chute is more appropriate as it can be used to guide the material down to the stockpile without excessive dust being thrown during the fall.
Belt cleaners are also essential in preventing carry back, which causes a slow loss of material on the underside of the belt which creates opportunities for dust in unprotected areas. Effective belt cleaning in an enclosed area can alleviate this risk of carry back and thus prevent the dust that results from it.
Dust is an innate biproduct of the conveying process. Preventing it outright is essentially unfeasible due to costs
and difficulty, however, controlling and containing dust is both simple and affordable with an abundance of modern products for the many aspects of dust control.
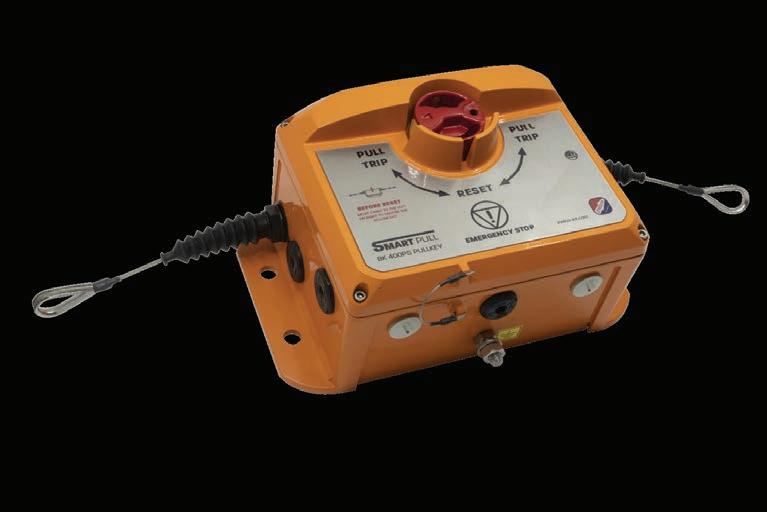
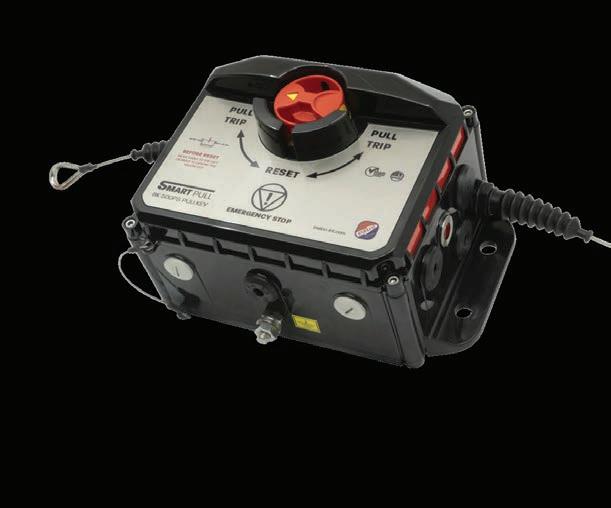
Maintaining a low level of dust is important for a plethora of reasons, including the health risks associated with airborne dust, even in small quantities, wear of mechanical and electrical systems, poor visibility, and the overall loss of product. Operators should evaluate their conveyor and determine if there are any locations that are a source of dust, so that a solution can be applied.
Operators who would prefer evaluations confirmed or would prefer professional input on the severity of issues can seek conveyor inspections from the numerous available conveyor solutions providers.
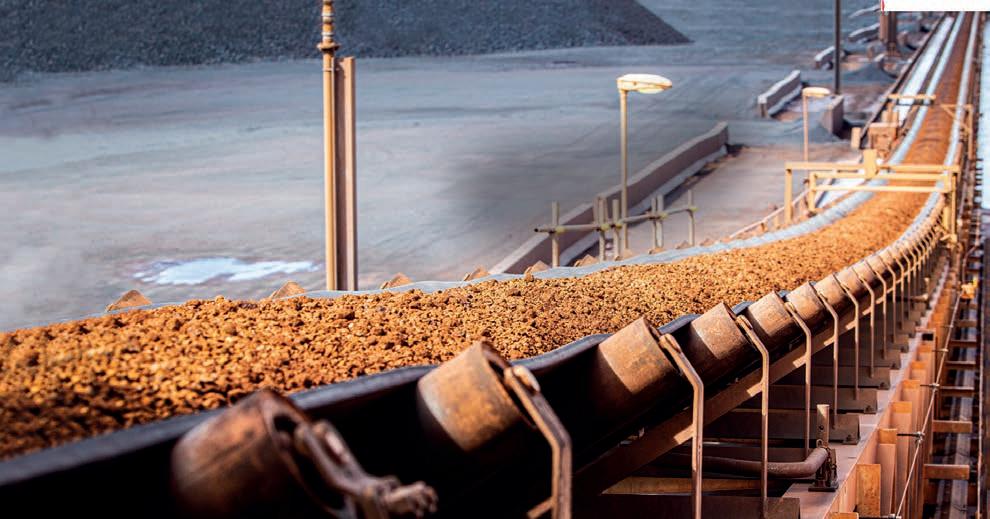
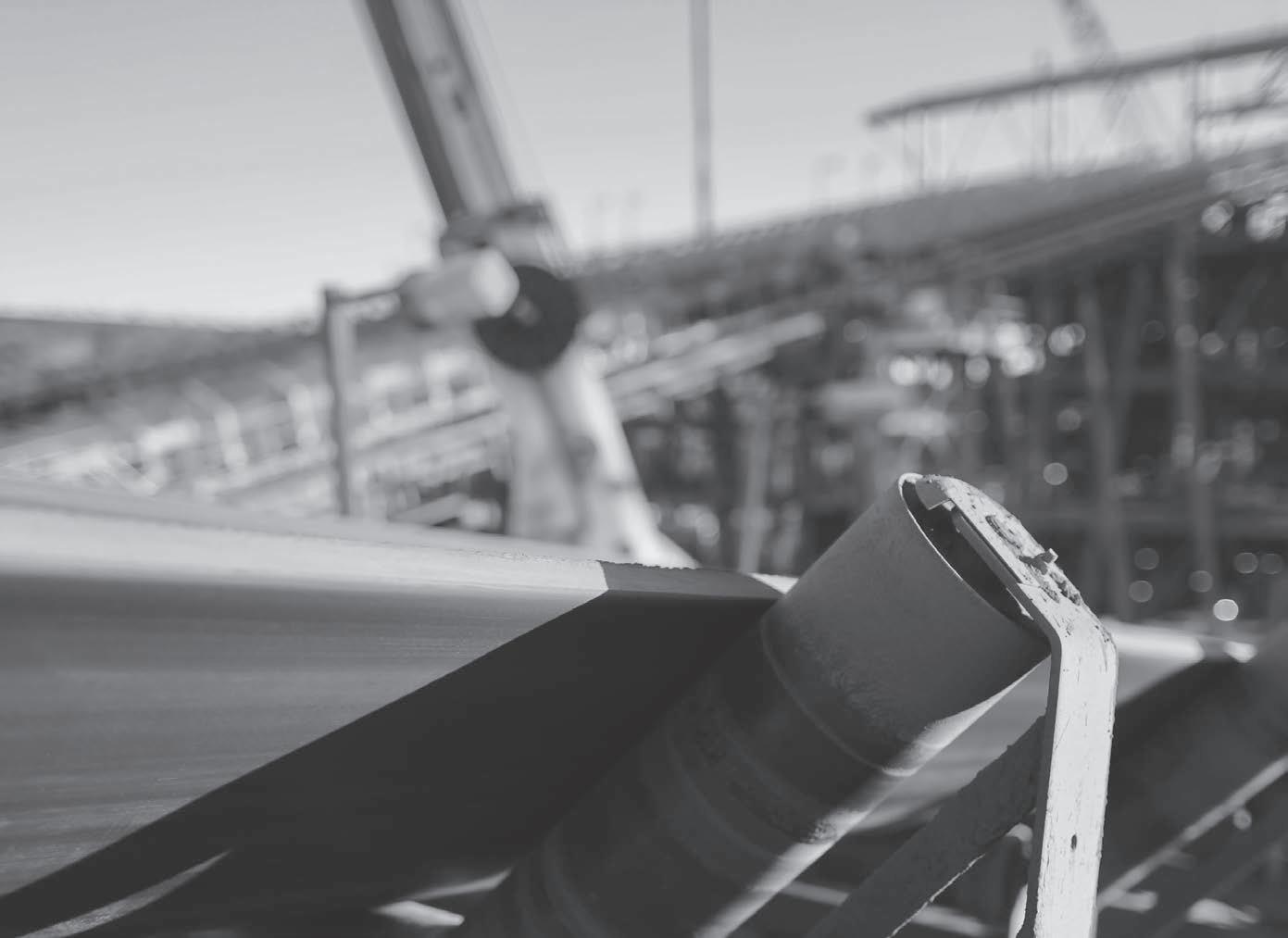
Jack Cain is a mechanical engineer at global supplier and manufacturer of bulk solids handling equipment, Kinder Australia
When reliability matters, choose Smart solutions
for conveyor safety, protection & monitoring.
See the full range of Smart Series:
pacauto.link/smart
STEVE DAVIS Steve Davis discusses Australia’s bulk handling sector, highlighting the advancements the industry has made and the organisations that are providing local innovations and expertise.
Steve has worked in bulk handling for 30 years, for both resource companies and professional engineering firms, in Australia, South Africa, the Middle East and Canada.
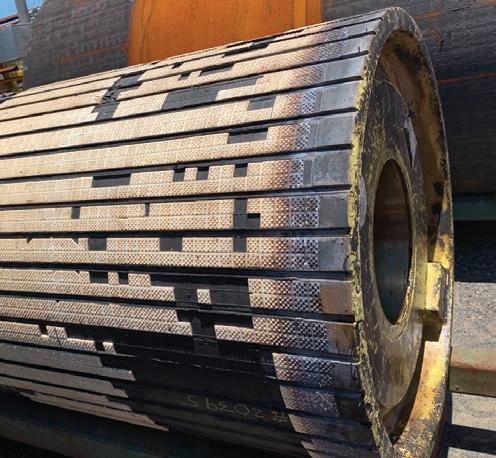
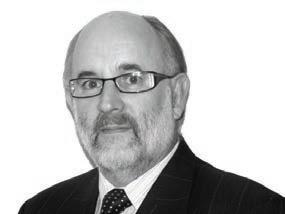
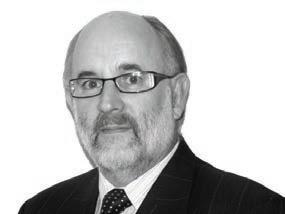
His experience encompasses such commodities as iron ore, coal, potash, phosphates, petcoke, sulphur, sands and grain.
talk
What can you do to reduce dust?
In his regular BULKtalk column, Steve Davis discusses the hazards dust emissions add to a site, and how to combat them.
SAFETY IS CRITICAL IN THE industry, and we know that dust emissions bring with them several hazards. Inhalation of fine airborne dust, particularly silica and carbonaceous materials is a well-known cause of lung damage, and we all prefer not to have to wear respirators when working near conveyors. Other dusts to be careful around include base metals, wood materials, and asbestos.
Many dusts are also potentially combustible and can create large explosions when at specific concentrations in an enclosed space such as a chute or bin. Small explosions may lead to larger ones by causing a pressure
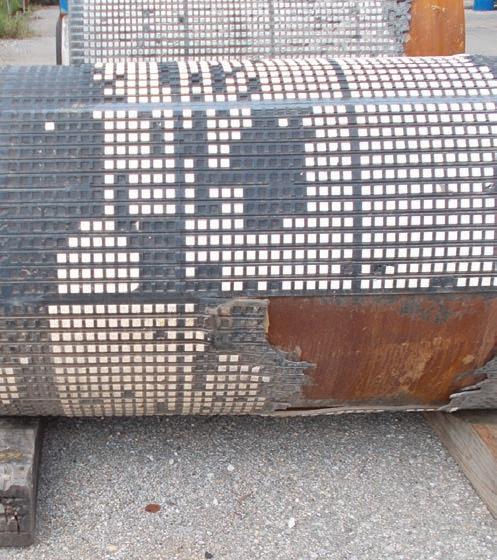
wave that releases accumulated dust, and facilities are destroyed regularly from these events. Airborne dust accumulates on structures and equipment causing failure, bringing down the roof from excess loading and with a little moisture can create accelerated corrosion.
Equal with safety is our focus on environmental impacts of our activities. Airborne dust that is harmful to people is usually harmful in the wider environment, killing fauna and flora and contaminating land. Even if not harmful we are concerned about perception and a large dust cloud or shadow is not acceptable in most situations.
An example is shown in the
Google view of a phosphate conveyor feeding from the Boucraa mine to El Marsa port in Morocco, where the white dust shadow is clearly seen over much of the 110 km route.
In the Pilbara and other locations, the dust shadow is the same colour as the landscape and is not as obvious. Dusty conveyors that are in proximity to other operations and to populated areas are liable to raise complaints.
A further problem with high dust environments is the potential for abrasive and corrosive damage to equipment. Sulphur dust for example mixes badly with electrical and electronic components. Any dust
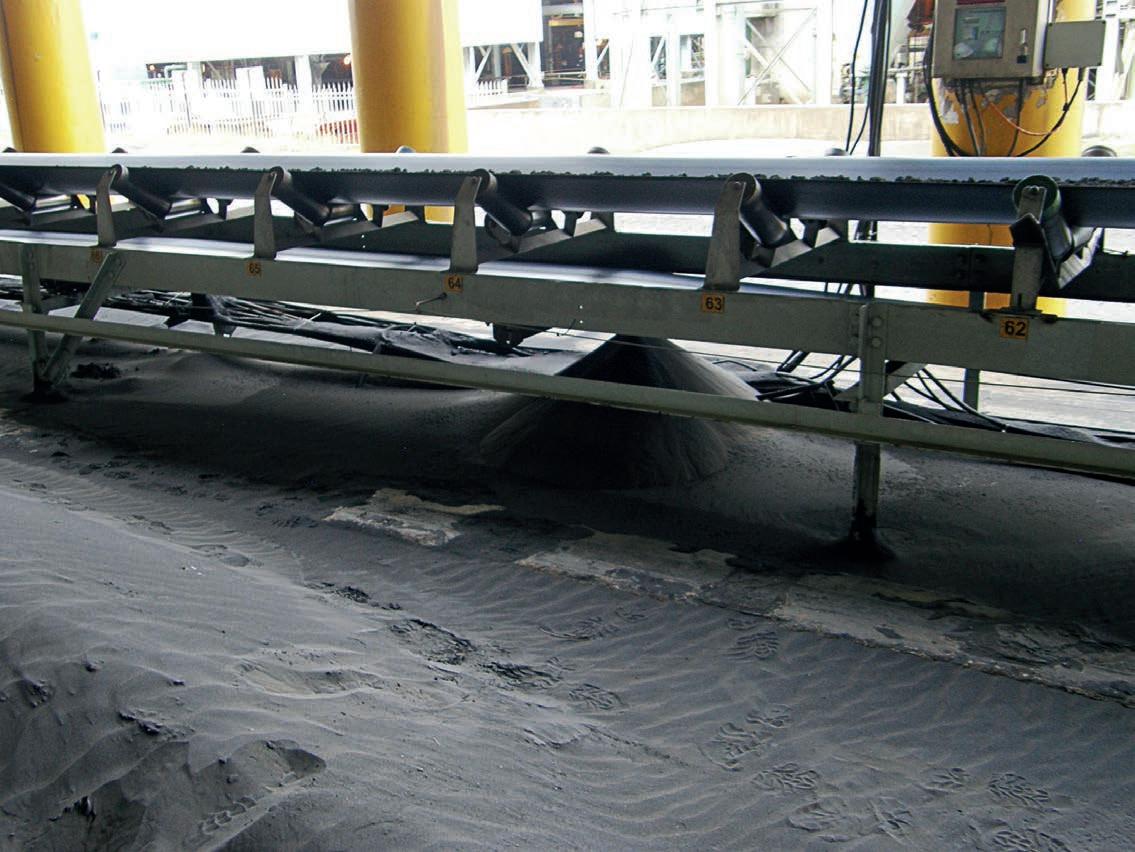
that builds up on seals will accelerate failure. Some dusts, like clinker, will solidify after a short period of time if any moisture is present. Over time this can build into a thick concrete like coating.
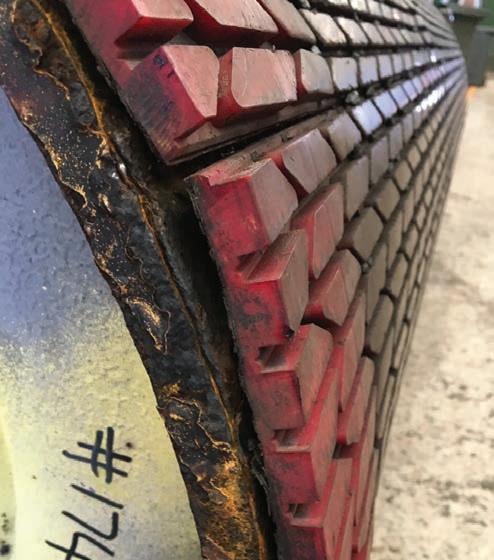
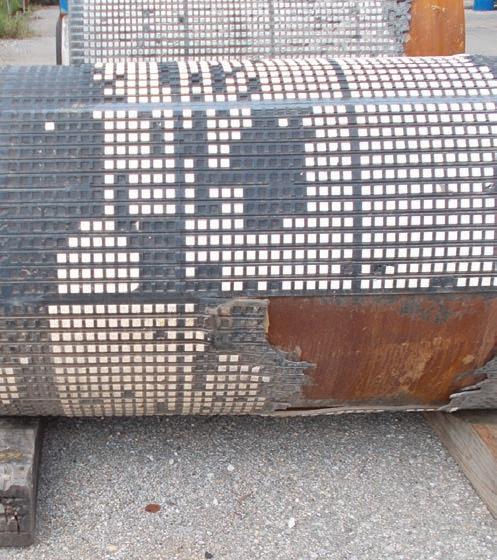
Dust occurs on conveyors when we transport many materials. Dust is the finer size fraction of the material conveyed that separates from the main body of the material when exposed to a suitable airstream. Higher velocity airstreams will carry away larger particles, so controlling airflow relative to stream flow is one method of reducing dust emissions. Dust storms and sandstorms are the ultimate example of the interface between moving air bodies and finer particles.
Dust is increased through attrition during handling. We measured particle distribution through a multiple conveyor and storage system and noted an increase in the finer fractions after each transfer, leading to a significantly
higher fines content at the delivery point.
Common locations and causes for potential dust release, and which will need some attention to meet exposure and release limits include:
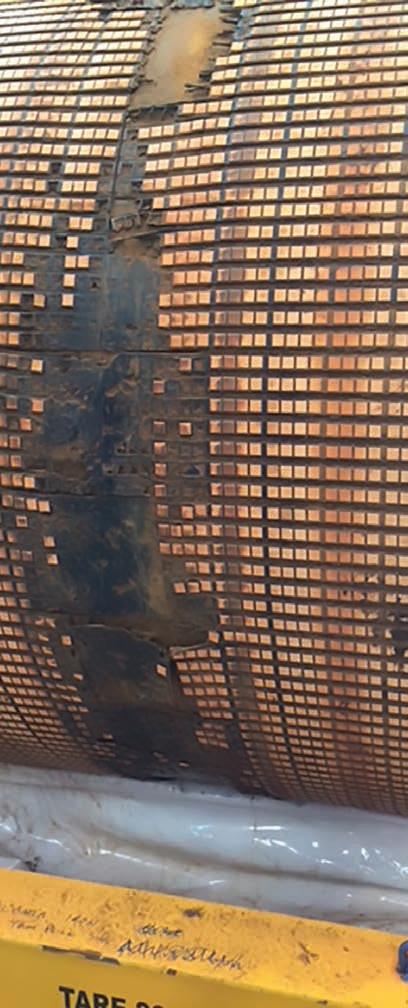
• Chute designs that do not control flow. If falling material is allowed to ricochet off chute walls with no control, or fall height is such that velocity opens the flow pattern, finer particles will form into dust clouds. Chutes of various types are available to keep material flow contained to a large extent and reduce dust separation. Some chute designs available that are designed to manage internal airflow such that dust is contained. Material drop height should be minimised as far as practical as this reduces impact forces, material spread and likelihood of dust generation. There are examples where change from a basic
drop chute to controlled flow reduces visible dust by significant amounts. We have many practitioners who can predict flow, why not use them?
• Free discharges, such as conveyors feeding stockpiles, where the fall height can be many metres and separation of fines into dust is probable need some attention. The drop height can be managed by using a luffing feed to maintain the lowest practical fall. Rill towers might be effective for fixed points. Some materials are amenable to push stacking using a scraper stacker, which takes away the fall; be wary of potential attrition during push and reclaim as this may increase dust in downstream conveying.
• Chutes with open skirt system risk dust being generated after the load point. Loading chutes where material drop occurs, such as pulsed filters, often have incorrectly selected skirt systems that blow out and generate

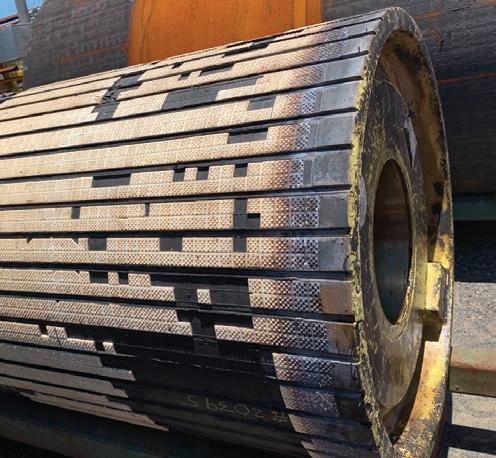
Any dust that builds up on seals will accelerate failure.
to spray out of the contact zone, which creates both spillage and dust.
• Dump hoppers are a common dust source, as the action of dumping separates the material in free fall. As material flow fills the hopper, it displaces air and carries dust out of the hopper. Closed bins and silos have similar issues, but the dust is generally easier to contain.
• Belt speed can give rise to a steady emission of dust along a conveyor. In this situation the material is moving next to a static air body. We can easily measure dust lift off speed for any material and decide whether measures should be taken to mitigate dust generation.
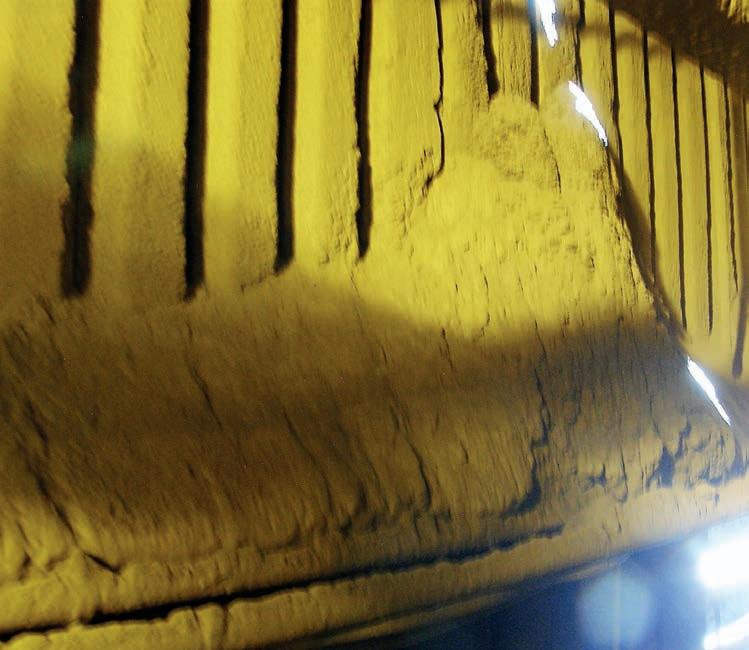
• Carry back and spillage are common sources of fugitive dust even with wet material. As the spilled material dries out, wind or other air movements will carry surface fines away as dust. Cleaning up dried spills often releases more dust as the source is removed. The cost of cleaning and the potential value loss from product that cannot be recycled and often must be treated or discarded at an additional cost should be enough to focus on carry back and spillage prevention, not to mention the benefit to personnel from having a clean facility.
• Belt cleaners by design clean off the finest material from the belt and this cleaned stream will lead to dust if not managed well. Worn, incorrect type and poorly adjusted or installed cleaners are liable to be ineffective
from belts, but design does often not consider where the cleaned material is deposited leading to a dust source.
There are many methods for managing dust, and this would start with identifying the criticality associated with the dust and the volume expected. What is to be done with the dust; return it to the system for onward carry, return it to the system elsewhere, collect and dispose? Are there any issues to consider, such as potentially flammable or explosive dust, toxic dust? Is there a limit to how much water can be added, and are additives viable?
The best way to limit dust emissions is to remove the fine particles. For most bulk materials this is not possible, and even if it were, some dust is almost certain to be generated through attrition in any multiple handling system.
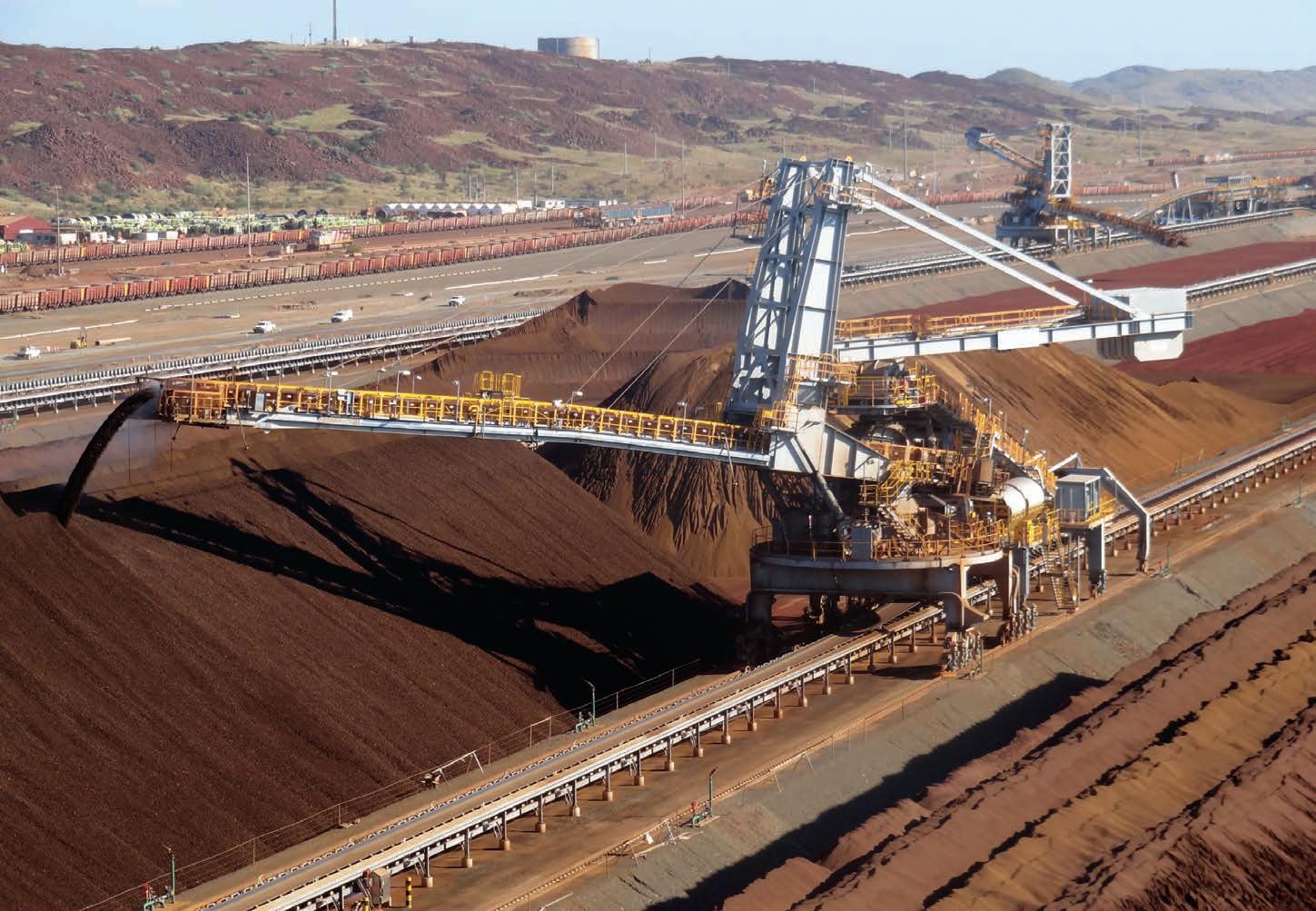
Is it reasonable to assume that a conveying system, that is built to best design practice and maintained well, will not emit any dust without suppression or collection? Probably not, however the spend on installing and operating dust management on a well-designed conveying system will be much lower .
Suppression or collection?
Suppression assumes that some form of suppressant will be added to the bulk material to keep the finer particles in the main material stream,
so they are not dislodged into an airstream. Collection assumes the dust laden airstream will be extracted and collected in a system appropriate to the dust and the chosen method of disposal.
If sprays are the format to be used, then they should be designed to add a defined amount of wetting over the width of the material using nozzles that generate droplets small enough to bind with dust particles. Should the spray be in the chute, where penetrating the body of material in freefall allows more wetting? Should the spray include a wetting agent or surfactant to extend the life impact of the sprays, if so is there a process contamination problem? Many materials have limitations on how much water can be added.
The theory of suppression assumes very small droplets will collide and adhere to dust and coalesce into sufficient size that the airstream cannot float them away. Considering this, is a fogging system more appropriate. Fog nozzles produce much smaller droplets than sprays and are very effective at controlling dust. Water quality and capital and operating costs are an issue, but water consumption is low. Effectiveness may offset significant other costs in clean up and maintenance.
Foaming agents create a sticky blanket over the body of material to prevent dust lift off by binding small particles. Consumption of foam is roughly one tenth that of spray water to get similar effects. These systems are like fog systems in size and complexity and generally use SLS or similar soap to produce foam. Residual effects may control dust for some time. Foam is not always viable due to potential for material contamination.
Dust collection generally falls into two categories for conveyors, either dry filters or wet entrapment. For any dust collection system to work, the collector and all ducting and collection points must be designed and installed to match dust loading and pressure drop needs. Dust systems that cannot be easily accessed cannot be maintained. There are many dust collection systems
for conveyor systems that are not well designed and are either turned off or assumed to be working well because no dust reaches the collector so there is no dust load in the discharge.
Filters are generally bags or cartridges and will have reverse pulse air or shakers to loosen dust and allow it to collect in a hopper. Insertable filters are the simplest and most economical and are generally installed in a covered skirt system or in the top of a transfer chute. When the bags or cartridges are cleaned dust falls back onto the conveyor or into the chute. Although the dust is captured and released at each transfer, it finds its way to the end of the system and does not become a separate return or disposal stream, and no value is lost.
The alternate, particularly if dust is explosive, is to capture dust in a wet system such as a scrubber. In a scrubber the dust laden airstream is mixed with
removed as a slurry. It may be possible to return the slurry to the conveyor, however it is usually necessary to dispose of the waste somewhere else in the process or off site.
One observation is that dust suppression and dust collection can work together for better overall control, however the two do not mix too well inside the same space. Dust collectors
cause blockage.
Dust impacts are being recognised as a conveyor problem, but good technologies to manage it well are readily available. Like many things, these technologies must be designed and installed to correct parameters and such that they can be easily and safely
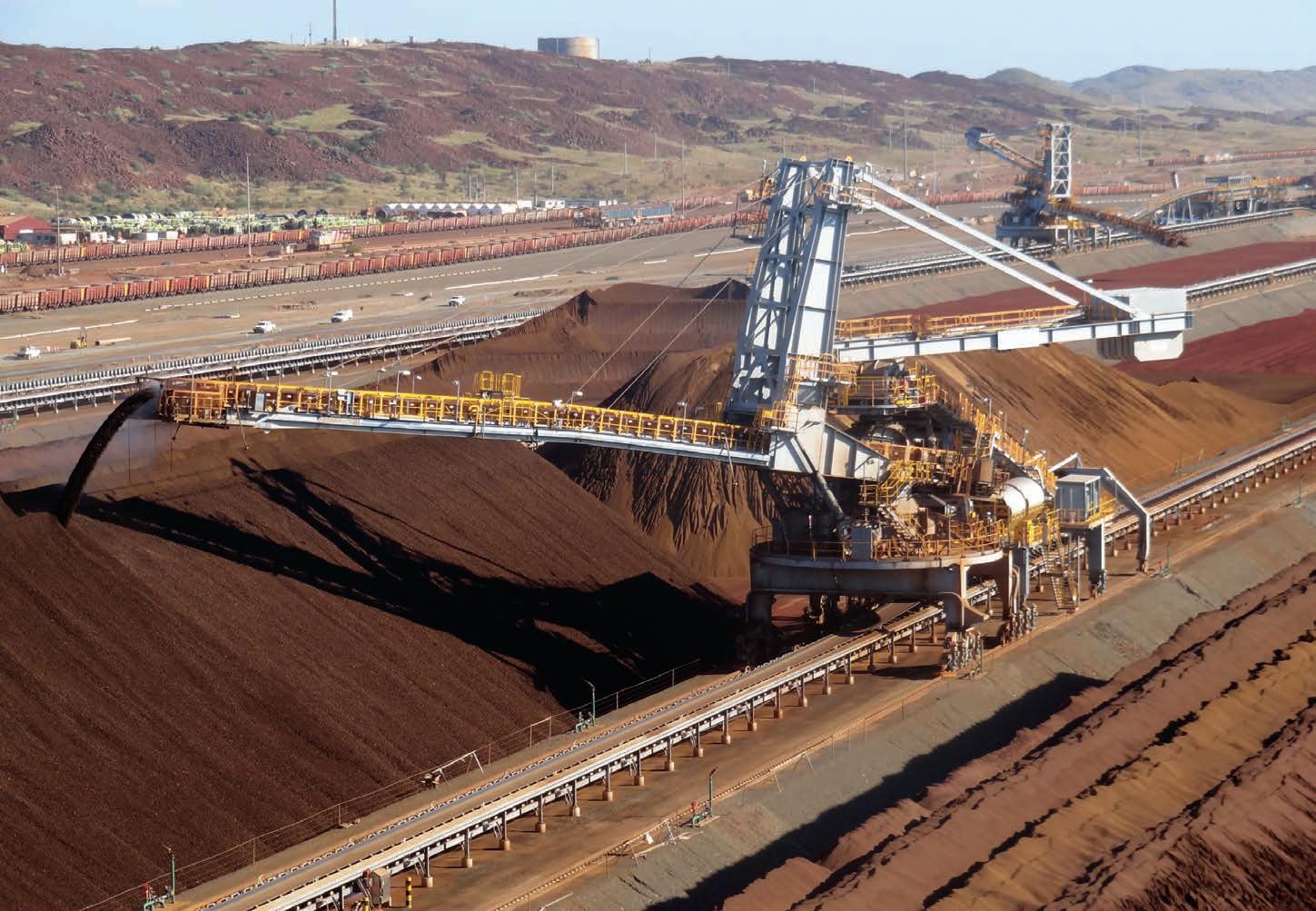
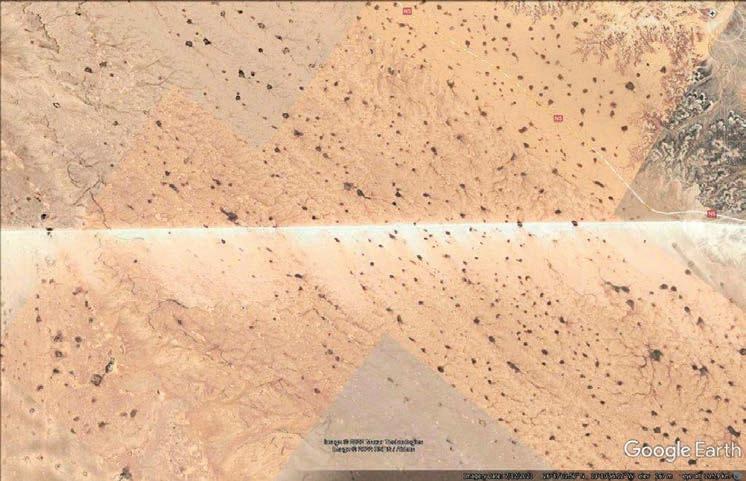
Stockpile drainage and seepage, a case study
Stockpiles are widely used but may experience different mass transport related phenomena resulting in solids flow problems and safety risks. J&J Engineers have utilised a simulation technique to model the flow of liquids within a porous media to help determine the final moisture retained in the bulk material after gravity drainage.
STOCKPILES VARY IN SHAPE
(mainly flat, conical or prismatic) and size (1000 up to 500,000 tons). They can be uncovered (exposed to the environment) or partially/fully covered. They are formed by overhead conveyors such as stackers, shuttles, or t¬¬¬rippers, or by dump trucks, frontend loaders, or bulldozers. Reclaim is usually done by gravity via various types of hoppers and feeders or gates housed in concrete tunnels beneath the pile [1], or mechanically using scrapers, bucket wheel excavators or front-end loaders. Figures 1 and 2 show typical stockpile geometries and a bucket wheel reclaimer often used in industry.
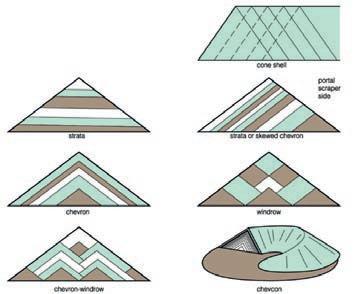
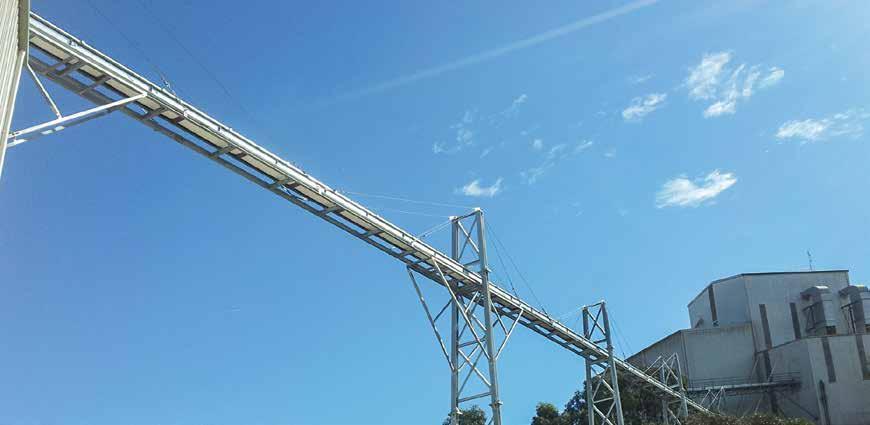
In mining, stockpiles separate the discontinuous mine operations from the plant that must operate continuously. In exporting ports, they provide surge
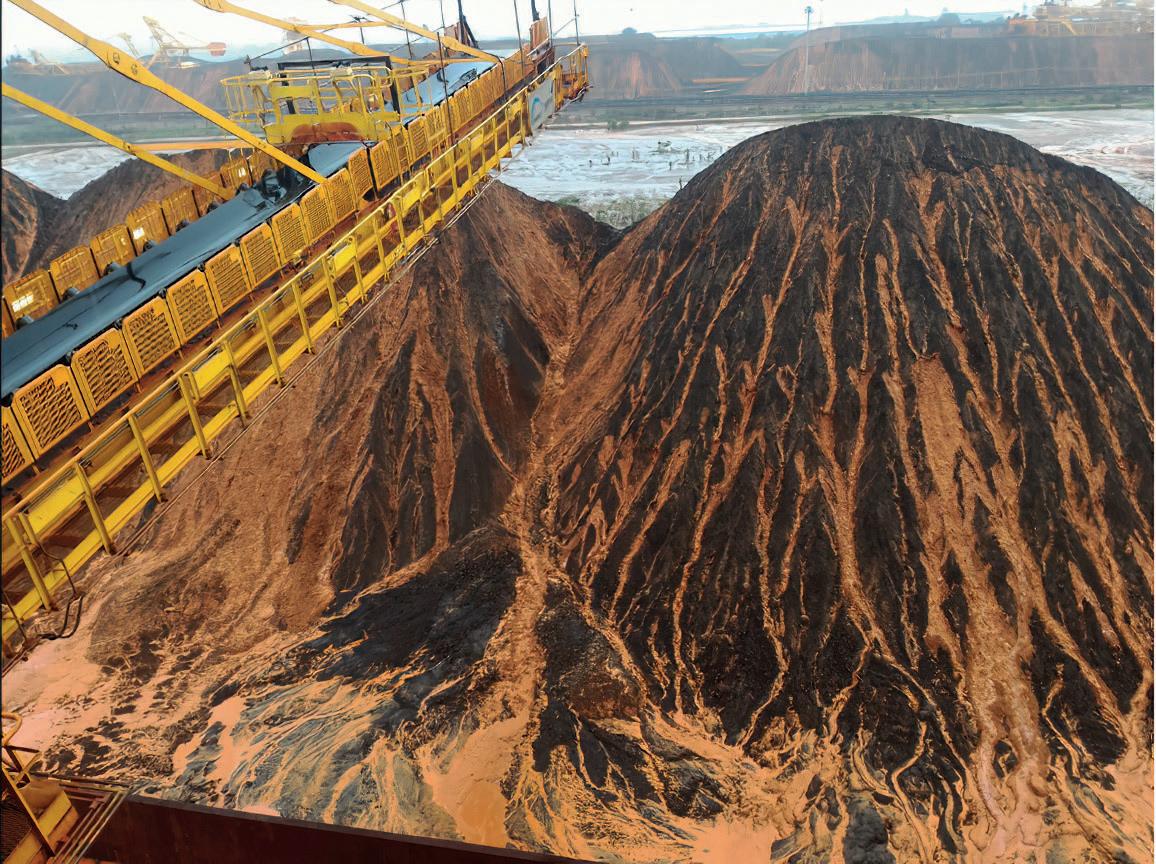
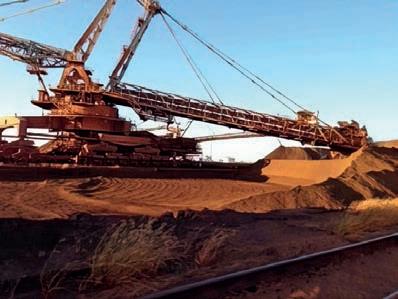
capacity while waiting for ship loading. In many quarry operations the sand is excavated, washed, classified by sizes, and then stockpiled for natural drying. This process saves energy and prevents the risk of instabilities in the base of the piles. Dewatering wet and saturated sand stockpiles by gravity drainage and solar evaporation allows for the reduction of the sand’s moisture content down to four per cent to five per cent after several days at rest depending on the permeability, particle size, shape, and pile height [2].
Issues due to excess water in the material Rainfall onto an open (uncovered) stockpile can either run off the pile surface or will seep into the pile body. The infiltrated water can evaporate,
drain naturally by gravity, or remain trapped within the material as free moisture. To minimise infiltration that may cause higher transportation costs, handling, flooding and/or flushing problems, compacting the surface of ore and coal stockpiles with bulldozers improves and increases the potential for surface runoff. The runoff water can then be collected in sumps and ponds for proper water management and/or treatment [3]. Also, the excess water usually contains a significant quantity of fine particles flowing in suspension (mudflows) that might contaminate rivers and oceans. Figure 3 shows an example of stockpile mudflows that can occur during an intense rain event.
Liquefaction problems are created by the flow of water in stored materials. It refers to the unwanted change of state
of the material when its shear strength is reduced to near zero and the material behaves like a liquid [4]. Several large bulk carriers have sunk or capsized due to the liquefaction of the cargo (mainly iron ore fines and nickel ores) when the cargo slides or shifts from side-to-side.
The rapid movement of material, resulting from flowslides failures that have occurred with stockpiled coals and other ores have also been attributed to liquefaction of saturated and relatively loose material, where shearing is accompanied by generation of excess pore water pressure with a resultant loss of strength. Investigations have revealed that some of these stockpile failures were preceded by rainfall infiltration and/or downward migration of moisture present in the material at placement [5, 6].
This liquefaction phenomenon may also occur on belt conveyors or in open
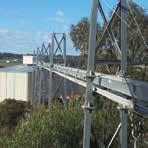
trucks and railcars, leading to unsafe operation and accidents.
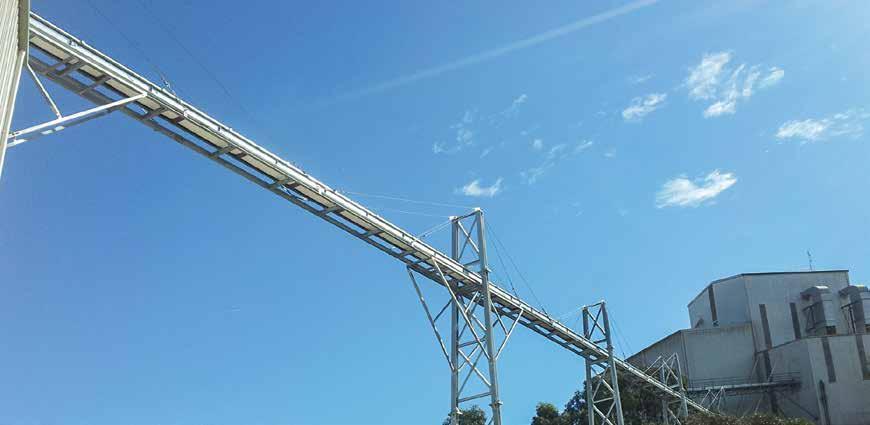
Material characterisation
It’s important that material characterisation is performed on the handled material to understand whether water will free drain or be retained. The results from the test work will inform the simulation and analysis.
Different tests are available to determine the material characteristics related with stockpile drainage and seepage. These tests are particle size and size distribution, particle density, compressibility (or bulk density as function of consolidating pressure), moisture content, bed porosity, saturation, as well as the water retention and hydraulic conductivity properties of the material.
The hydraulic conductivity depends not only on material properties such
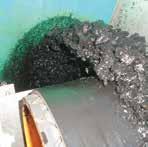
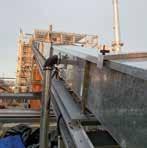
as porosity, particle size, density and shape, but also on fluid density and viscosity, and on the consolidation pressure of the sample. Many of these tests follow well-known ASTM and/ or ISO standard procedures. Others require skilled technicians to operate scale models or special equipment to “mimic” the real-life conditions as no standards have yet been developed.
Analysis of water infiltration and runoff of iron ore stockpiles
A mining company was experiencing severe stockpile stability issues of some of its prismatic-shape iron ore product stockpiles during the winter season. This was resulting in damage to multiple stockyard machines (i.e., stacker, reclaimers, conveyors, etc.), safety issues, and production limitations. An example of the slope stability issues is shown in Figure 4.
CONVEYOR
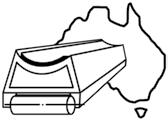
The stockpile failures were attributed to water saturation and pore pressure development in the bottom layers of the pile preceded by significant rainfall events. Contributing to the stockpile failures, the stockpile erosion and sediment transport (mudflows) to the vicinity of the stockpiles toe during the intense rainfalls was blocking the natural drainage of the stockyard, causing ponding near the stockpile toes.
J&J was contracted to investigate water drainage and seepage in the stockpiles (refer to Figure 5), considering rainfall events (i.e., intensity and duration) recorded by an onsite weather station. Similarly, to the above example, to model the flow of water or seepage within the stockpile, COMSOL Multiphysics software was
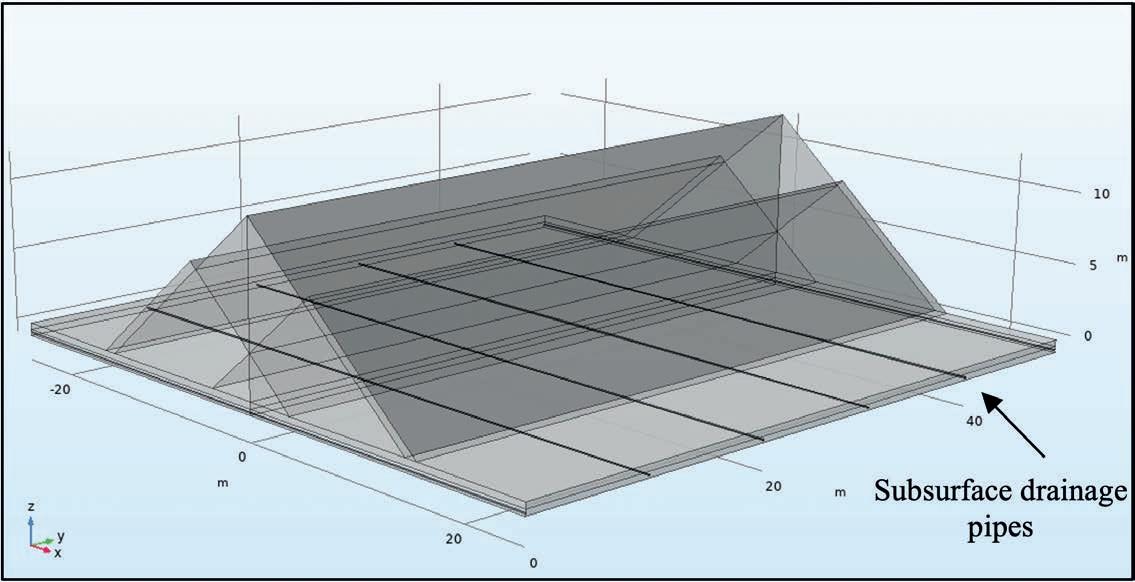
utilised using the Richard’s equation model for flow in variably saturated porous media. The hydraulic and other physical properties measured for several samples of the iron ore material were utilised in the analysis.

Rainfall can either infiltrate the stockpile or directly run off the surface of the pile. The relationship between stockpile run off and infiltration is dependent on factors such as degree of saturation at the surface, particle size, stockpile surface texture, rainfall intensity and duration, moisture content, and the degree of compaction of the surface. For this study, we considered that rainfall infiltrated the stockpile depending on the degree of saturation near the stockpile surface, the rainfall intensity and duration. No other additional resistance to water infiltration was considered. A daily rainfall was assumed for the analysis (repeated for five consecutive days), a constant rainfall intensity was also considered.
The results of the simulation conducted by J&J engineers are illustrated in Figure 6. A good drainage system was compared to a poor drainage (or impervious stock pad), taking into consideration the rainfall events from the nearby weather station. The colour legends illustrate the effective degree
of saturation.
Given the high hydraulic conductivity of the ore, for the cases of poor drainage at the base of the pile, the initial water content of the ore in addition to the infiltrating water from the heavy and consecutive rainfall events can quickly mound at the bottom of the stockpiles; a water table inside the stockpile of approximately 4 m high formed during storage. The amount of water accumulating at the bottom of the pile was significantly reduced when a good drainage system at the bottom of the pile was considered. The analysis indicated that forming the stockpile with a certain initial moisture saturation was effective in limiting excessive accumulation of water at the bottom of the pile.
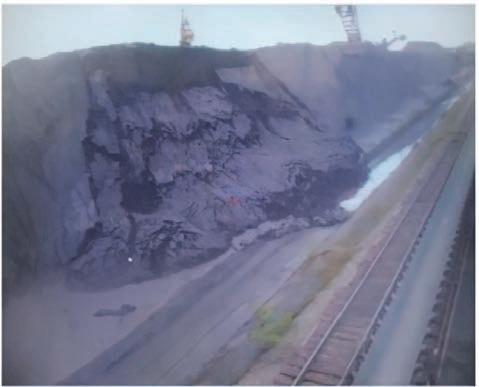
Conclusions
COMSOL Multiphysics finite element analysis was conducted to estimate the drainage and seepage in an iron ore stockpile, utilising well recognised equations to describe the flow of fluids in unsaturated porous media. The outcome of the presented example illustrates the effective use of the COMSOL simulation tool to analyse and predict drainage and seepage in stockpiles and provide the necessary inputs to a commercial installation to
corrective actions as
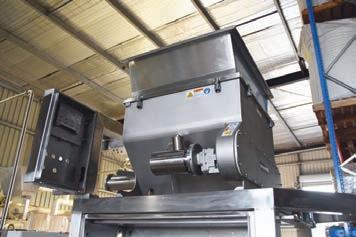
References
1. Cabrejos F. and Goodwill D., “Tunnel Reclaim from Ore Stockpiles”, Bulk Solids Handling, Vol. 16, No. 3 (July/Spt. 1996), pp. 393-400.
2. Hashemi E., “Experimental Study for Enhanced Drainage from Sand Stockpiles”, M.Eng. thesis, School of Civil, Environment and Chemical Engineering, RMIT University, Australia, August 2011.
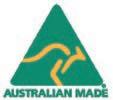
3. Campbell Q., Le Roux M. and Espag C., “Coal Product Moisture Control Using Stockpiles”, XVIII International Coal Preparation Congress, Rusia, 2016, pp.747-752.
4. DNV, Bulk Cargo Liquefaction - Guideline for Design and Operation of Vessels with Bulk Cargo that may Liquefy, Norway, 2015.

5. Eckersley J.D., “Flowslides in Stockpiled Coal”, Eng. Geology, 22 (1985) 13-22.
6. Davies P., Zargarbashi S., and McQueen L., “Flow failure in coal stockpiles – how to reduce risks”, ACG, Slope Stability proc. 2013.
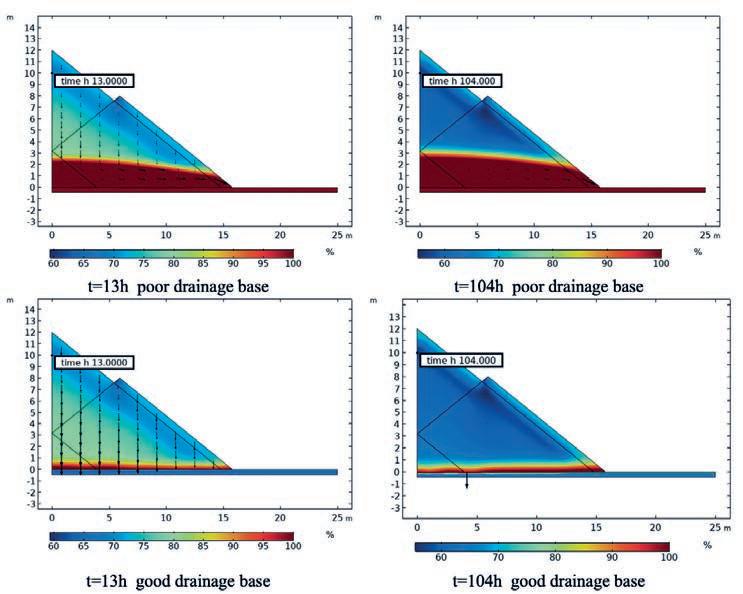
WEIGH BELT

Fatigue of bulk materials handling machines
Materials handling machines are complex structures which often rely on load limiting devices to prevent damage.
AROUND 10 PER CENT OF FAILURES in complex materials handling machinery were attributed to fatigue failure in a previous investigation in 2002. In most cases these failures were unexpected and lead to catastrophic consequences.
Figure 1 shows the number of machine failures versus the age of the machine at failure. The failures can be divided into two groups: the first group of failures occurs within the first five years after commissioning and the second group of failures occur when the machines are greater than ten years old. About ten percent of all failures or about one quarter of the failures that occurred when the machine was greater than ten years old can be attributed primarily to fatigue damage.
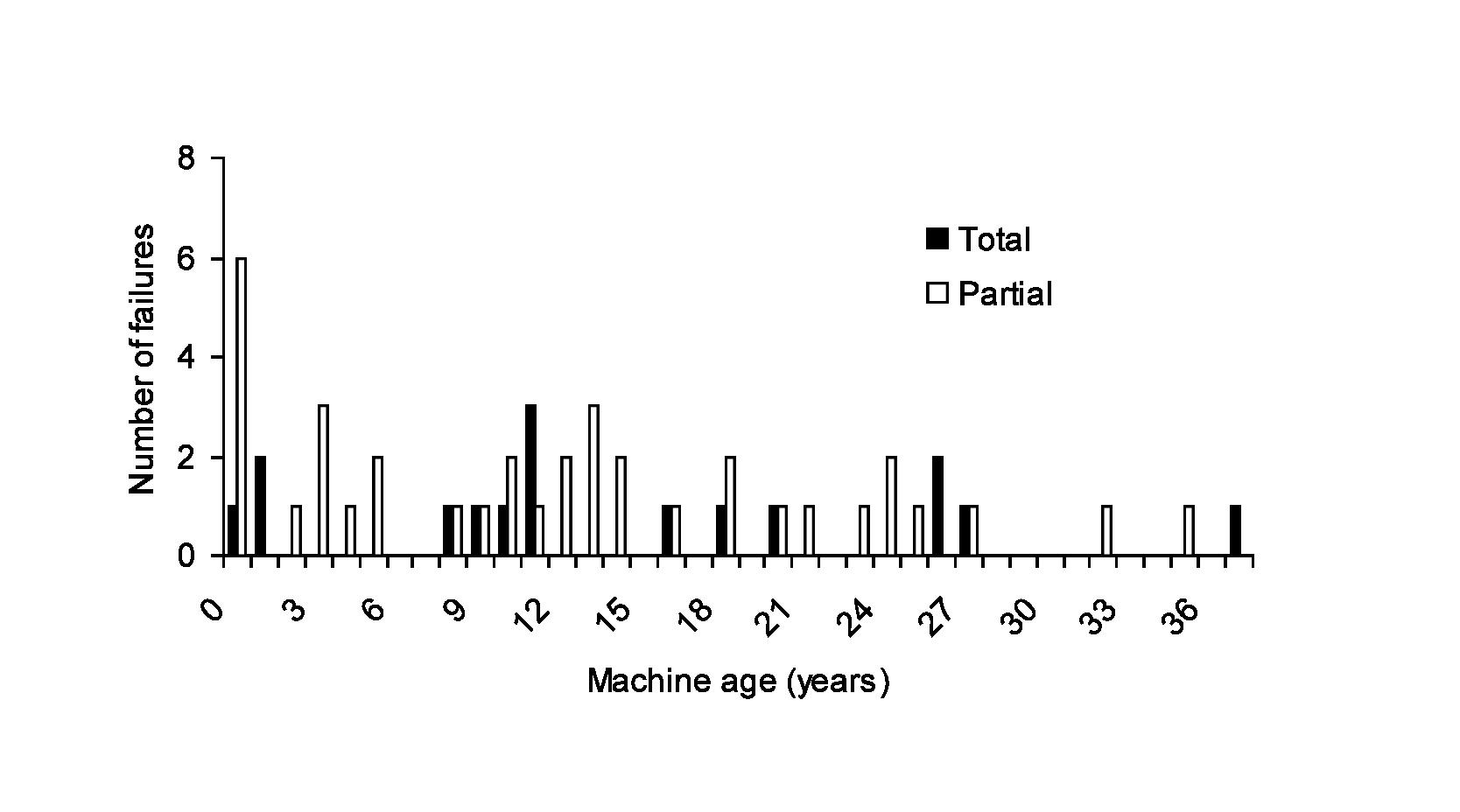
The process of fatigue means that steel strength deteriorates under the action of cyclic loads and this may ultimately lead to cracking and the unexpected failure of structures. The American Society for Testing and Materials defines fatigue as;
localised permanent structural change occurring in a material subjected to conditions which produce fluctuating stresses and strains at some point or points and which may culminate in cracks or complete failure after a sufficient number of fluctuations.”
Two key points to note in this definition are:
• Progressive implies that the fatigue process occurs over a period of time. Fatigue failure may be sudden with no warning, however the mechanisms involved have been operating since the beginning of the structure’s usage.
• Localised implies the fatigue process operated at local areas rather than throughout the entire structure. The ultimate cause of all fatigue failures is that a crack has grown to a point at which the remaining material can no longer tolerate the stresses or strains and sudden fracture occurs.
The fatigue process involves two stages:
Crack initiation involves changes to the material microstructure such that distinct crack initiation sites occur. As cycling continues, crack propagation occurs and the fatigue cracks tend to coalesce and grow along planes of maximum stress. The majority of cranes and rail mounted materials handling machines have significant welding and hence small defects (cracks) are already present. To account for this, current design standards assume that small cracks will always be present and that crack propagation is the only part of the fatigue process.
Statistical nature of fatigue
The concept of ‘remaining fatigue life’ can be simplistic and misleading especially for older, deteriorated structures. Fatigue life is a statistical quantity – design curves are based on results from test specimens and considerable deviation from the average curve determined from a few specimens occurs.
Figure 2 shows typical results for fatigue tests on a fillet welded T-joint. The tests were performed with different stress ranges and the number of cycles to failure were found. The geometry and weld procedure were the same for all the test pieces. As can be seen, the test data has considerable scatter even though the test pieces and field conditions were very similar.
The usually specified reliability factor for a detail is 0.9773, that is, two standard deviations from the mean. If the structure were subjected to the design cumulative damage, and the details were working to the allowable limit, without intervention one detail in 45 on average would fail. If you consider that a typical bucket wheel reclaimer can have between 5000 and 10,000 details, this would not be acceptable.
Design standards such as AS4100 recognise the reduced reliability for fatigue versus strength design and stipulate that dynamically loaded structures affected by fatigue must be regularly inspected for code rules to apply. Regular inspection of these structures should increase the reliability of the structure to an acceptable level.
Codes also recognise that where parts of the machine susceptible to fatigue are not accessible for inspection, then further conservatism needs to be incorporated in the design.
Issues with fatigue damage
Fatigue crack growth rates are strongly influenced by the environment. Corrosion can have a significant effect on fatigue life which can be reduced by half in corroded areas. Higher stresses can be caused by pitting or reduced plate thickness.
Also corroded structural steel has no fatigue limit, that is, a corroded component will fail regardless of the magnitude of the stress range. In general, good fatigue design and detailing is closely linked to high corrosion resistance.
Poor weld quality significantly increases the probability of fatigue damage development. For example, the fatigue life of a component can be shortened by two and a half times if a fillet is too near an edge of a member. Welding procedure affects fatigue life considerably. Occurrences such as weld spatter, accidental arc strikes, weld flaws, poor fit-up, misalignment can lead to lower performance than its classification would indicate.
Secondary Members
The fatigue analysis usually only considers the global effects on the machine and accounts for primary structural steel alone. International research shows that up to 70 per cent of fatigue damage occurs in secondary members, which are not usually checked in the design stage (eg. brackets carrying electrical cables, welded cover plates). Damage due to effects from secondary members is not necessarily detrimental to the performance of the structure provided it is found early, via regular inspections, and repaired before the damage propagates to
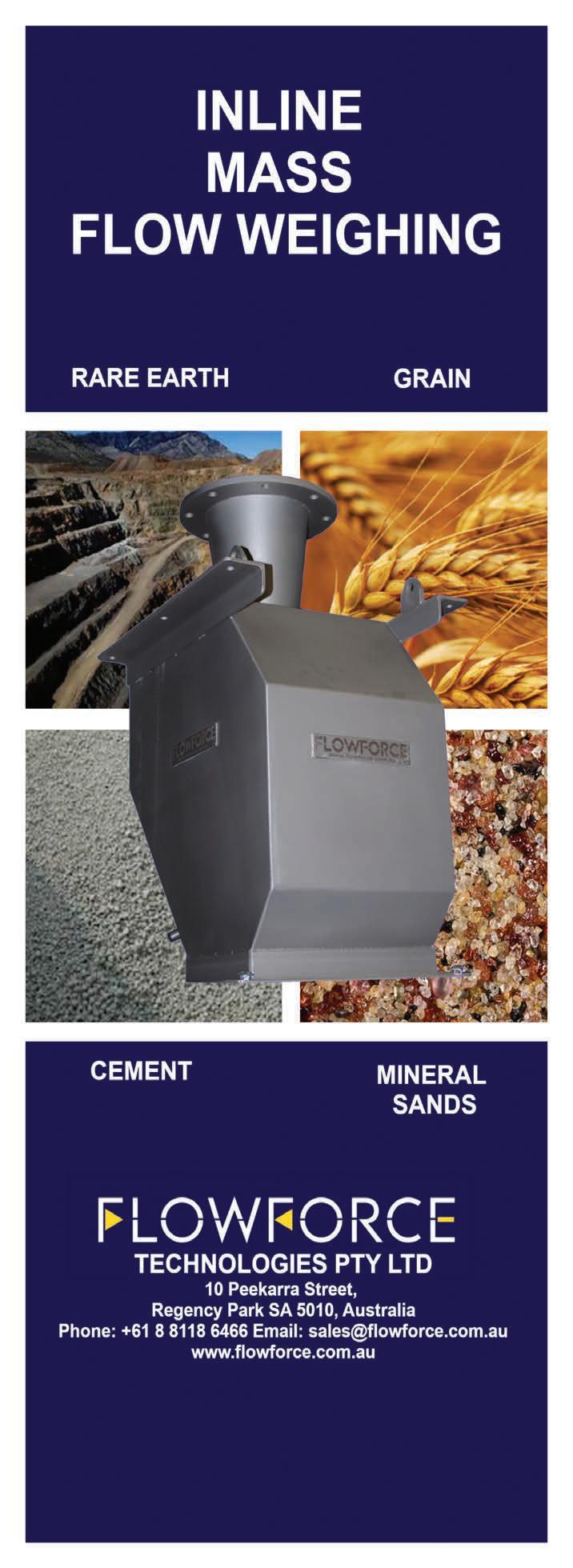
the main structural sections leading to failure of the structure.
Inspection
Dynamically loaded structures affected by fatigue must be regularly inspected for fatigue damage for design code rules regularly inspected for fatigue damage for design code rules such as Australian Standard AS4100 to apply. The limit of detectable crack size in the field is 6mm long by 2mm depth.
However, the detection of cracks above this detectable size is not a certainty. Reliable crack detection is affected by many factors:
• The skill of the inspector. Experienced inspectors should have a higher likelihood of detecting cracks compared to an inexperienced person.
• The specific area to be inspected. It is easier to detect cracks in a specific location such as a particular component compared to the total machine
• The accessibility of the detail including details that may be hidden behind other structural components. Some details may be difficult to access or may be completely hidden from view by other structural members. Corrosion products or paint that may be inside the crack.
What to do if cracks are found
Where cracks are found on a structure in service, owners need informed
advice on how long they can continue to operate before undertaking repairs, replacements or further inspection and monitoring.
A fracture mechanics assessment allows crack growth curves to be developed for particular details. Figure 3 shows a typical crack growth curve on a welded structure with the crack size given on the vertical axis and the number of cycles on the horizontal axis. The crack growth is exponential. Once a detectable crack is found on a critical detail, there may be limited time
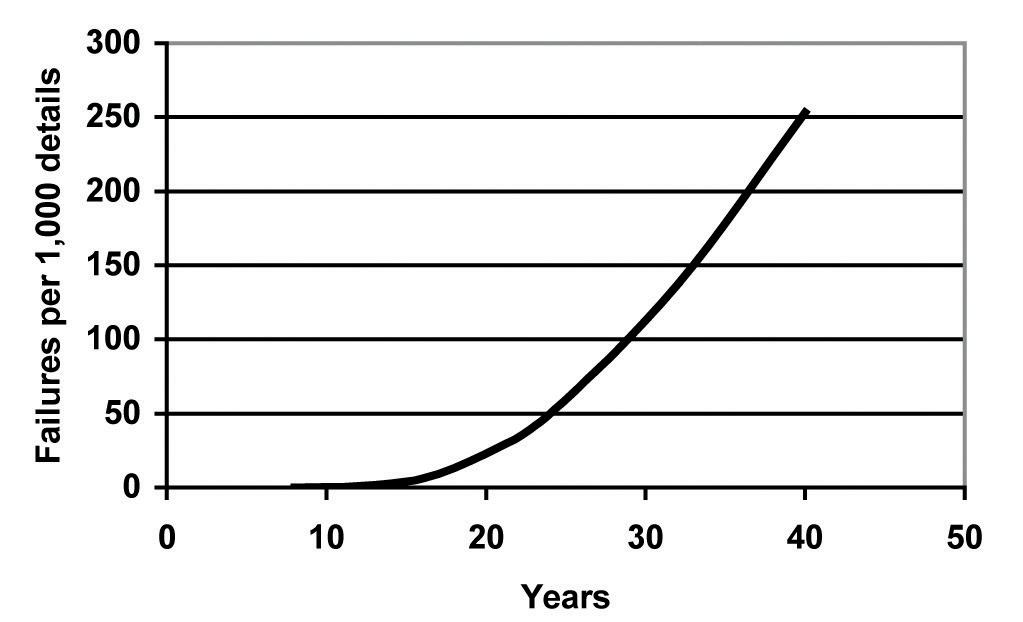
available to undertake remedial works.
It is important to note that the following points:
• Cracks are to be expected. Current fatigue design codes have details with a reliability of 0.9773 or a one in 45 probability of cracking at the end of their design life. This compares to structural strength design which has a reliability of 0.999. The reliability also decreases with age of the structure.
• Satisfactory control of fatigue damage relies on adequate methods of fatigue crack detection and the ability to repair or replace the damaged component.
An effective methodology for the structural appraisal of large structures should consider:
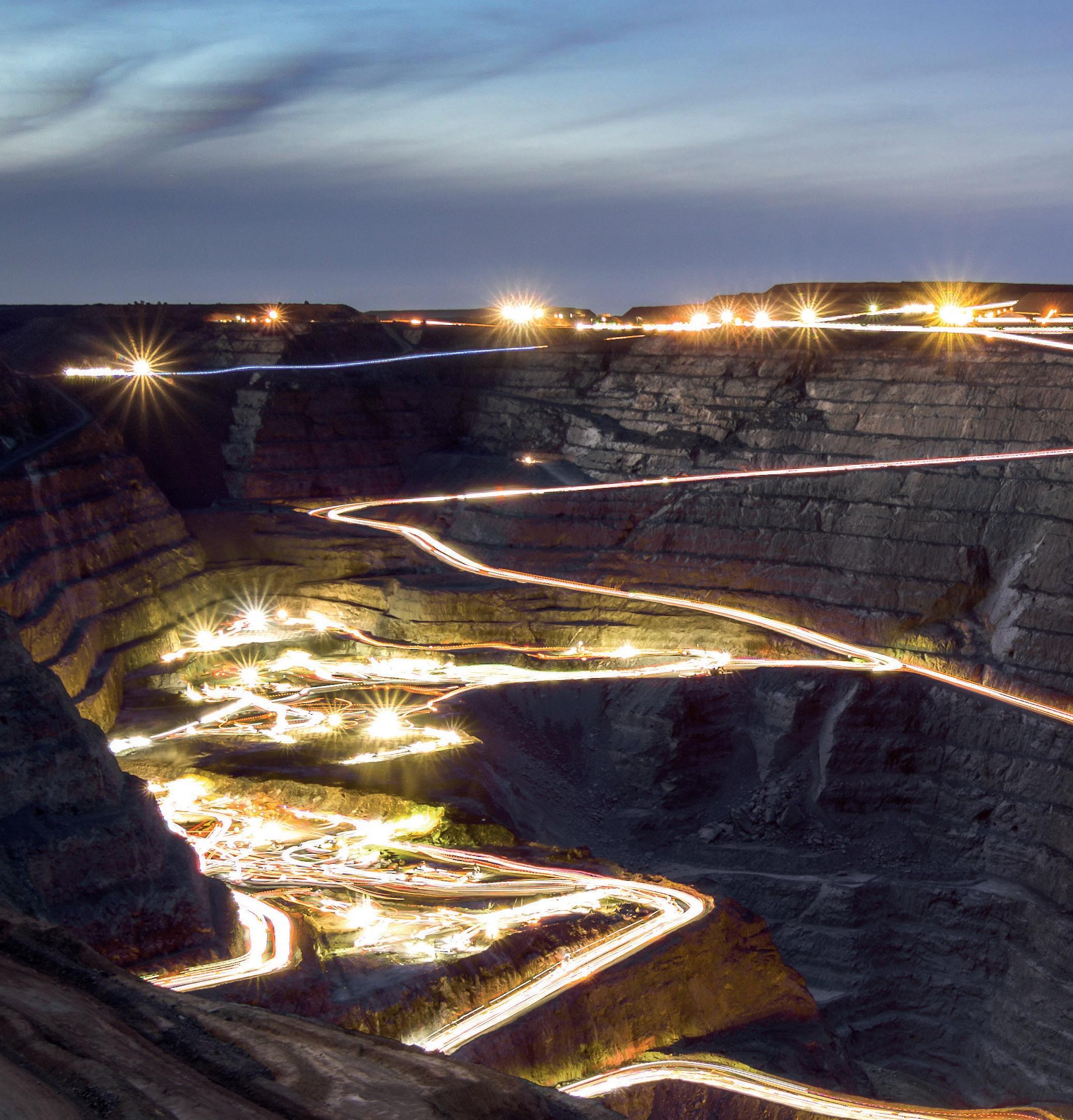
• Structural analysis. Locate high stress and investigate possible failure mechanisms.
• Fatigue analysis. Locate areas where there is a high likelihood of fatigue cracking occurring.
• Inspection. Non-destructive testing of critical areas and visual inspection of non-critical and secondary members.
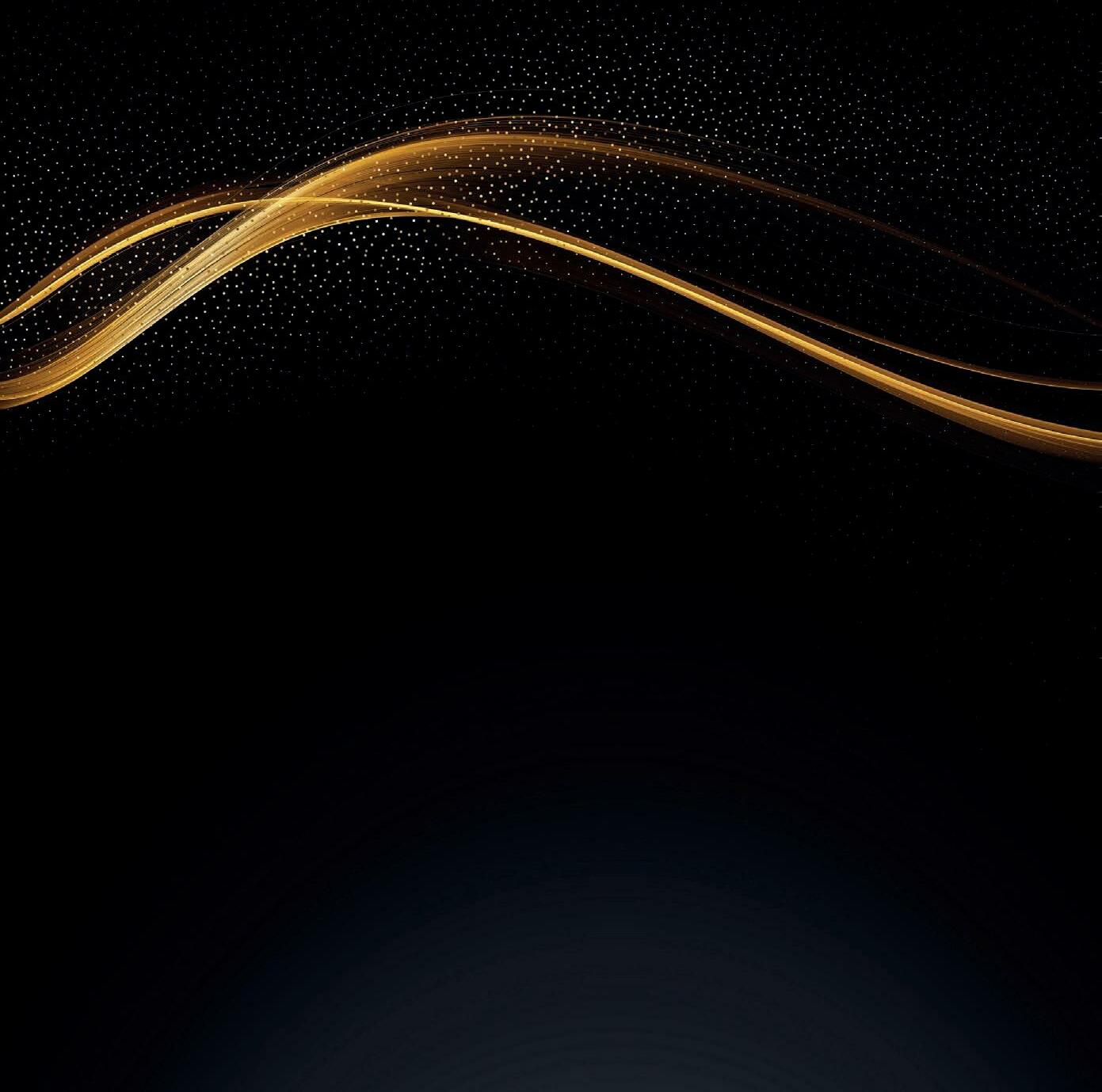
• Fracture mechanics assessment to predict crack growth rates and inspection regimes in critical areas.
Crack growth rate for single edge crack in tension.
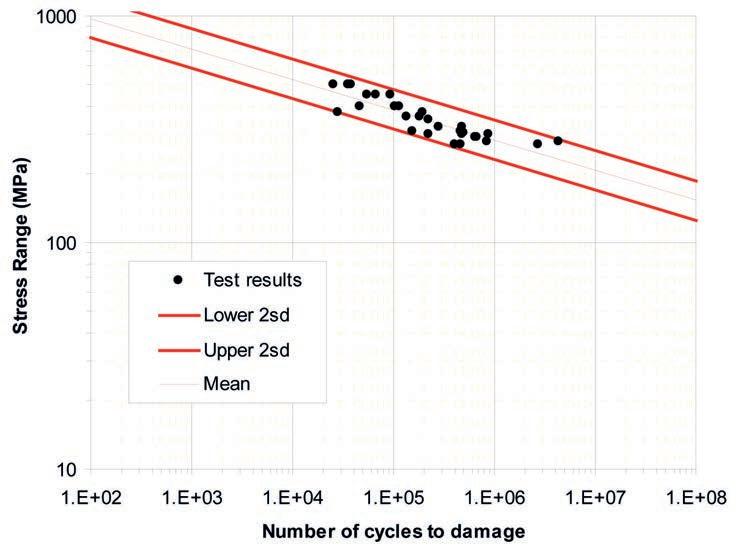
ON
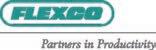
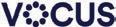

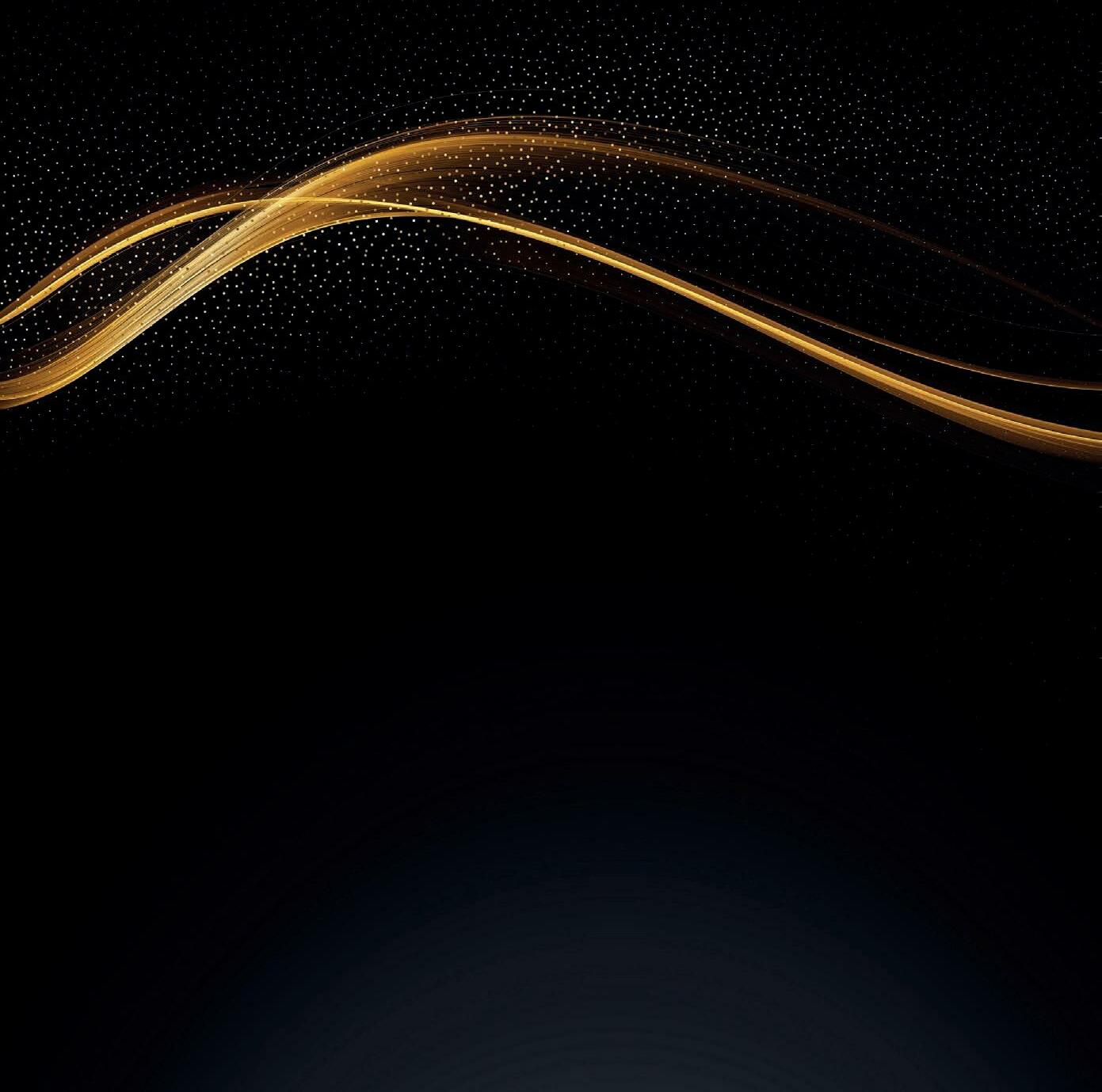
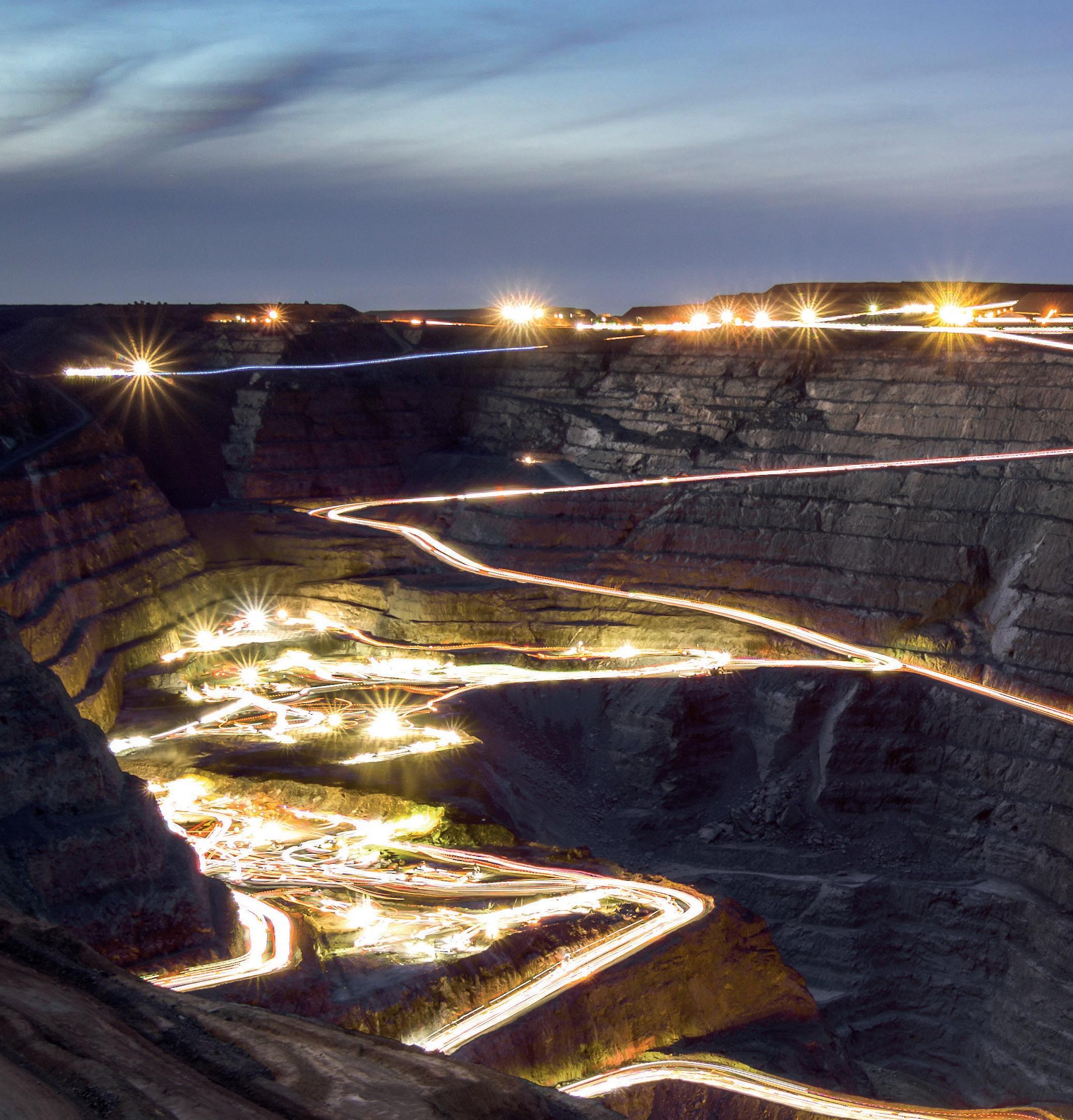
Real world example using simulations to model dynamic silo behaviour
Liam Andrews, Luke Stone and Brian Moore demonstrate how the discrete element method (DEM) can be utilised in the prediction, measurement and mitigation of silo quaking based on research and recent advancements in technology and techniques available to industry.
THE STRUCTURAL DESIGN OF BULK
material storage vessels such as silos, bins, skips, and flasks, requires careful calculation of the material loads that are exerted on the vessel and the supporting structure during filling, storage, and discharge conditions. The design of bulk material storage vessels is governed by design standards for the given location of operation. However, these standards do not include analysis techniques for predicting or capturing the impact of silo quaking on design life. Silo quaking severity can range from a minor nuisance such as noise pollution, to structural failure through fatigue, which is why the analysis of this phenomenon is crucial for the safe design of such vessels.
There has been considerable research into measuring and predicting silo quaking using both analytical and numerical methods however a gap still exists when implementing this in industry. An example of this is the analytical solutions used to estimate a pulsating load, where these
calculations are limited to low flow rates and small-scale installations.
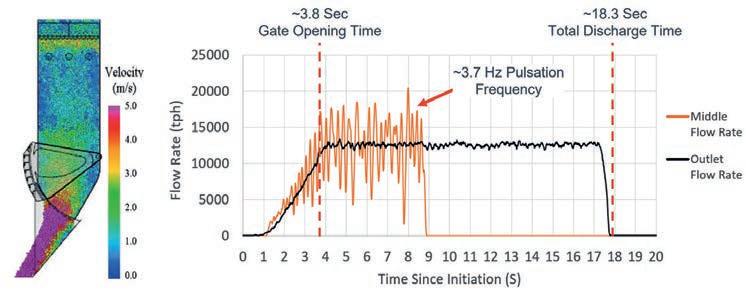
It has been highlighted in other research papers that certain geometrical features and material properties can be used to determine if a vessel will be prone to silo quaking, although no definitive prediction of the phenomenon has been made.
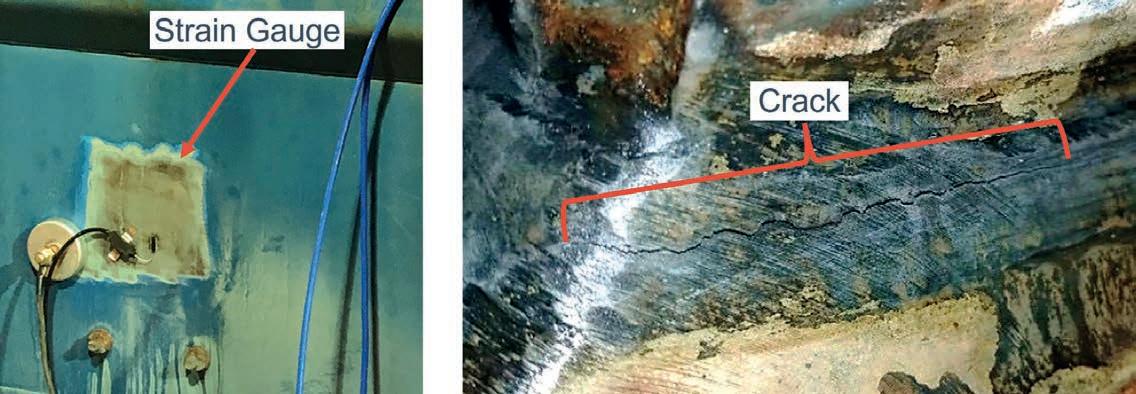
As computer processing power becomes increasingly affordable, the
practicality of modelling the complex phenomenon of silo quaking is more feasible than in the past, particularly with multiple GPU solver options available. As such, DEM has become a well-known and respected numerical technique, that leverages a calibrated model, to replicate and predict bulk flow behaviour.
Due to the complexity of silo quaking, there is added benefit in modelling the entire system’s dynamic reaction and not
just the material internal to the vessel. This can be achieved through two-way coupling of DEM which provides the bulk solid particle behaviour during discharge and multi-body dynamics (MBD) which captures the rigid body motion of the vessel and supporting structure. This allows the fidelity of the analysis to be improved by capturing the influence of the structure’s movement on the bulk flow behaviour either exacerbating (or dampening) the pulsations and capturing the loads exerted on the supporting structure from relative movement or resonance.
For the investigation of localised
Hatch has successfully utilised DEM, MBD and finite element analysis (FEA) (verified and validated by comparison to measurements taken on site) to replicate silo quaking in a typical slender storage vessel and provided a proven design solution that has since rectified the quaking issues, refer Figure 1.
Results DEM Simulation
An uncoupled DEM simulation of a skip discharging was first developed based on material flow property data and calibrated using measured variables on site. This included the gate opening time,
the bulk density and when the material ‘sticks’ the material consolidates, with the bulk density expected to increase.
DEM – MBD simulation
The uncoupled DEM simulation presented above showed good correlation to the measurable parameters of the skip during discharge, however, one parameter that could not be confirmed using this approach was the skip displacement with each pulsation event. Using a two-way DEM and MBD coupling, a simulation capturing this behaviour was possible and allowed verification of this final parameter.
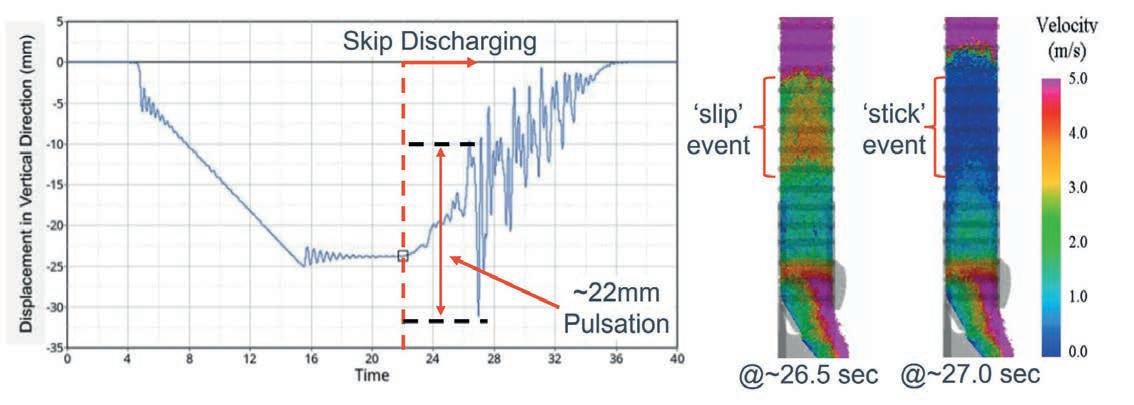
Referring to Figure 3, from five seconds to 16 seconds, the skip is filled with material. After filling, a six second delay is present before the gate is opened at 22 seconds. Pulsations start at approximately 25 seconds. The pulsations induce a displacement of 22 mm which is comparable to the measured range of approximately 20 to 30 mm recorded by site, refer Table 2-1.
stresses induced in the vessel and supporting structure, one-way coupling of DEM and FEA is recommended. The one-way coupling can provide further information on the significance of fatigue in the design of the vessel and structure, by rationalising cycle count and load reversal severity.
Hatch’s Centre of Excellence in Granular Flow Performance team leverage DEM to solve the needs of our clients.
A case study is presented in this article focusing on a skip installation that was experiencing ‘bouncing’ and fatigue cracking after only 12 months of operation.
MBD
pulsation magnitude
DEM simulation
the largest pulsation
total discharge time of material, and skip displacement magnitude and frequency. The flow rate of material was measured from the outlet of the skip (black line in plot) and approximately half-way up the skip (orange line), refer Figure 2. The orange line shows significant fluctuations to the flow rate, these fluctuations are due to the material slipping and sticking during discharge. The ‘slip’ event is characterised by an increased velocity (increase in flow rate) and the ‘stick’ event is characterised by a reduction in velocity (reduction in flow rate). It is also noted that during the ‘slip’ event the material dilates, reducing
Table 2-2 provides a basic summary of some of the parameters used in the MBD simulation. The overall mass of the system and the stiffness of the supporting structure was provided by the client. The damping of the system was determined from iterations of the skip displacement from filling and discharge, with the result shown in Figure 3 confirmed to be reasonable.
DEM and FEA simulation
To further develop the analysis, and how the pulsations are transmitted to the skip wall plate, a one-way coupling of DEM
and FEA was completed. It was observed that during discharge the pulsations created localised stress concentrations in proximity to the level of material in the skip. This relates back to the DEM simulation with the pulsations in DEM resulting in an increase in velocity ‘slip’ and a decrease in velocity ‘stick’, this
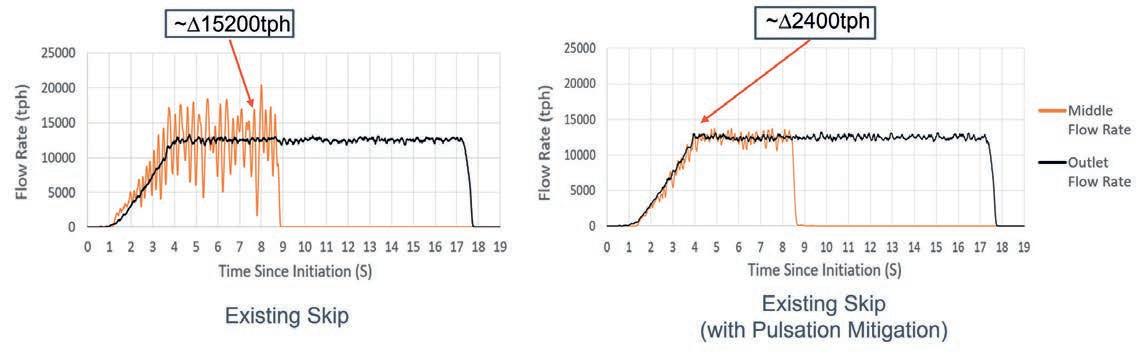
will tend downward and contributes to the displacement of the skip during discharge, refer to the pulsations in Figures 2 and 3.
Mitigation of silo quaking
Silo quaking mitigation devices were designed and assessed using the analysis techniques discusses above. The
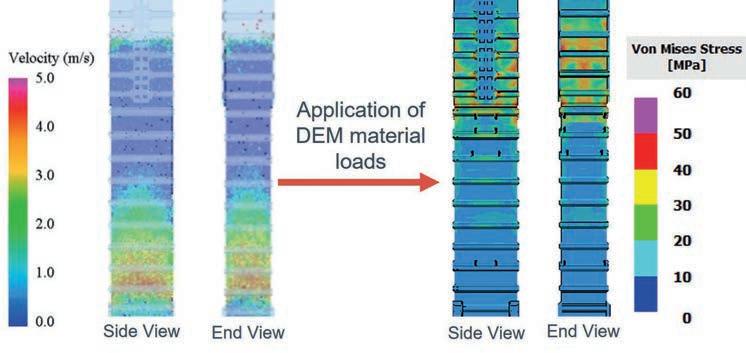
increase in weight and no significant increase in discharge time. Once installed our client reported a 60-70 per cent reduction in quaking with the devices planned to be installed in future skips.
Conclusion
In summary, silo quaking has been identified as a significant aspect of the design of any storage vessel and should be considered in parallel with the material load derivation to the governing standard.
DEM has been used for the accurate calibration, assessment, and testing of silo quaking with correlation to measurable data received from site. The assessment was advanced through coupling of DEM and MBD for the assessment of the rigid body motion of the skip and FEA was used to assess the stresses developed during pulsations. Significant localised stresses were identified in concentration areas in close proximity to the cracking shown in Figure 1. This validated the analysis behind why the skip was bouncing and the likely cause of cracking.
Gate Opening Time Total Discharge Time Pulsation Frequency Pulsation Magnitude
– 3.8 sec – 18.6 sec – 3 to 4 Hz– 20-30 mm
‘stick’ event is presented in Figure 4. At the time of the ‘stick’ event the material consolidates, and normal and shear pressure is applied to the skip walls, refer Figure 4 which shows the localised stresses. The resultant force in the normal direction will tend to zero, however the resultant force in the vertical direction
assessment showed the mitigation device reduced the pulsations significantly, refer Figure 5 which shows a 15200tph pulsation in the existing skip and a 2400tph pulsation in the upgraded skip. The installed device was custom designed to facilitate installation in the existing skip with minimal modifications, no significant
This work supported pulsation mitigation devices which were designed using DEM and installed in existing and new skips with reported reductions of 60 to 70 per cent. This was an effective solution for the client as the devices did not require significant modification to the skips and did not increase the weight or the discharge time.
Hatch’s Centre of Excellence in Granular Flow Performance team in Wollongong are continuing this work on silo quaking improving the prediction, and mitigation techniques utilised in industry.
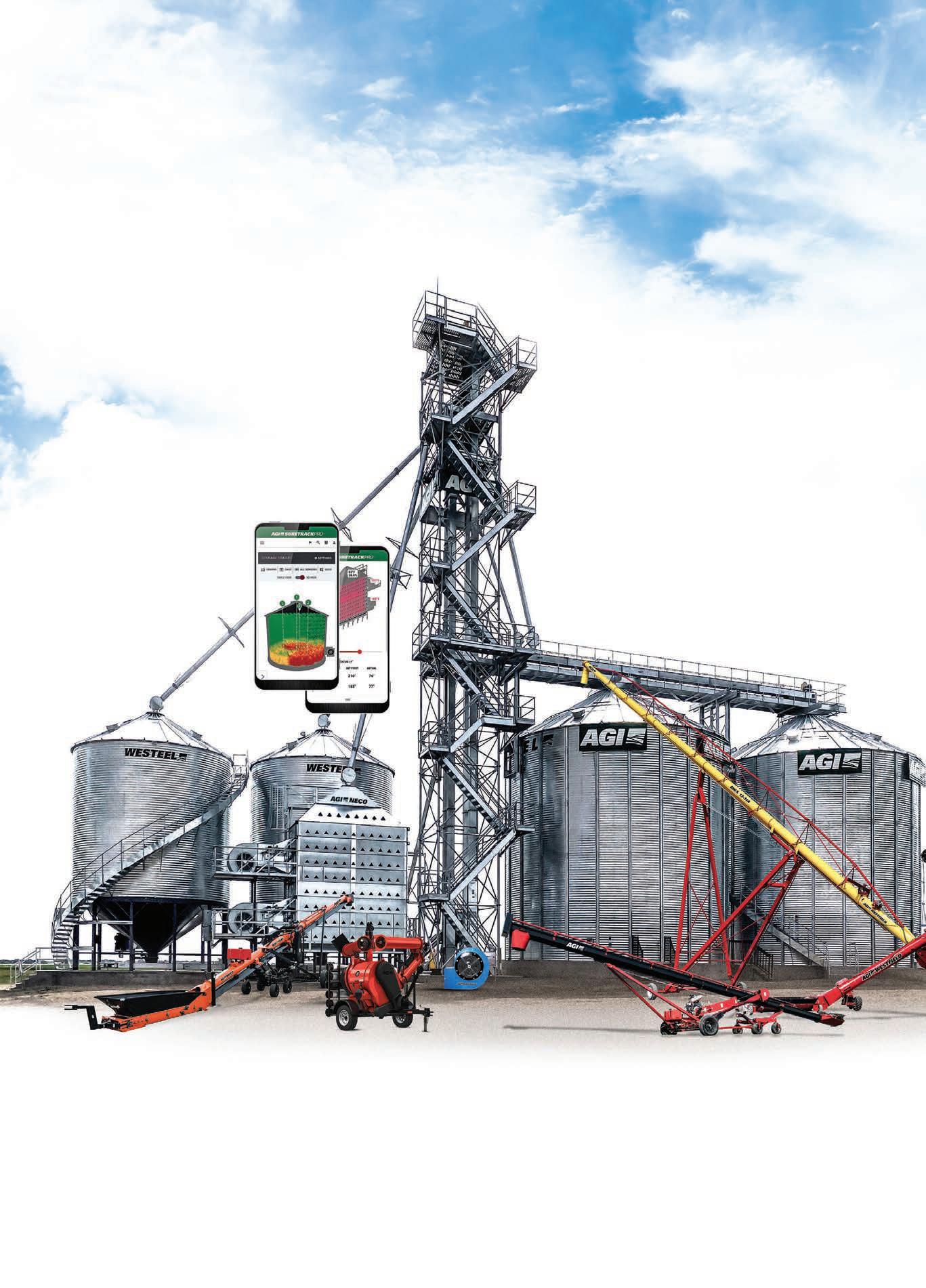
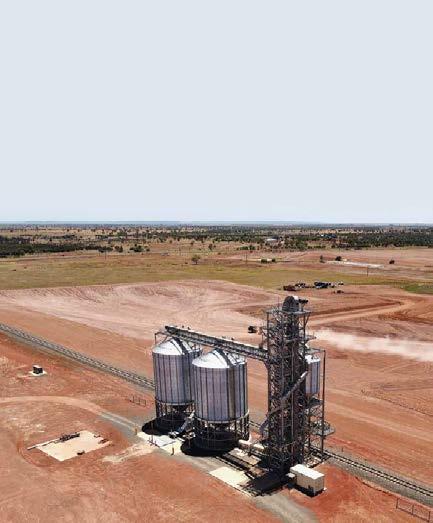
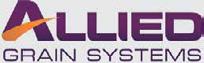
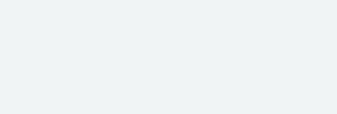

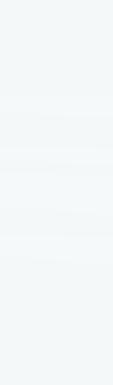
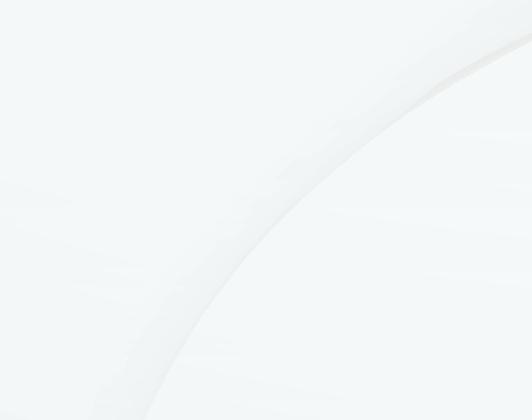
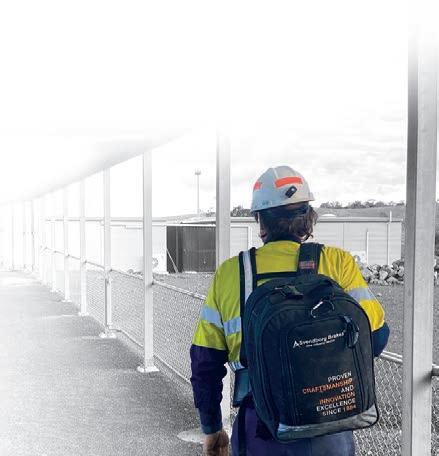

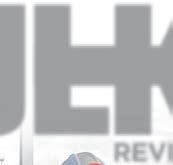
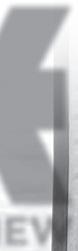
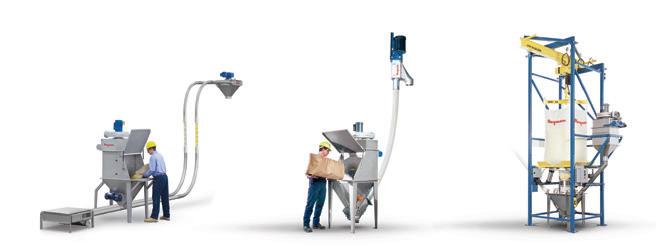
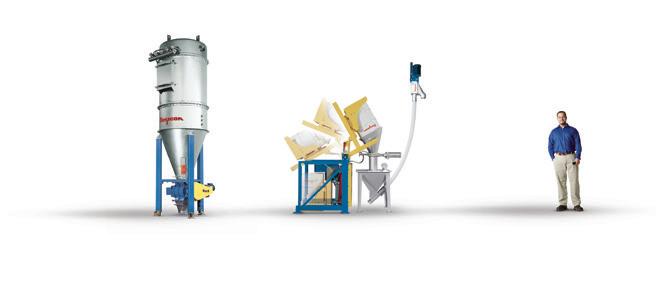
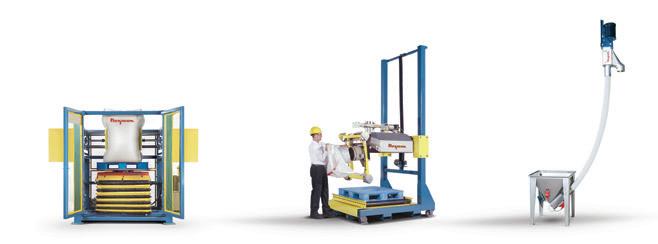
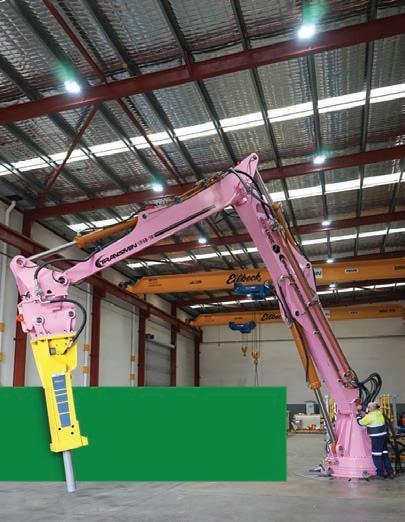
FLEXI-DISC®
Cable
Conveyors gently slide fragile foods and non-foods through smooth stainless steel tubing routed horizontally, vertically or at any angle, over short or long distances, dust-free. Single or multiple inlets and outlets.
FLEXICON® Manual Dumping Stations allow dust-free dumping of bulk material from bags and other containers. Automatic reversepulse filter cleaning allows continuous, efficient operation. Available with integral bag compactors for total dust containment.
BULK-OUT® Bulk Bag Dischargers
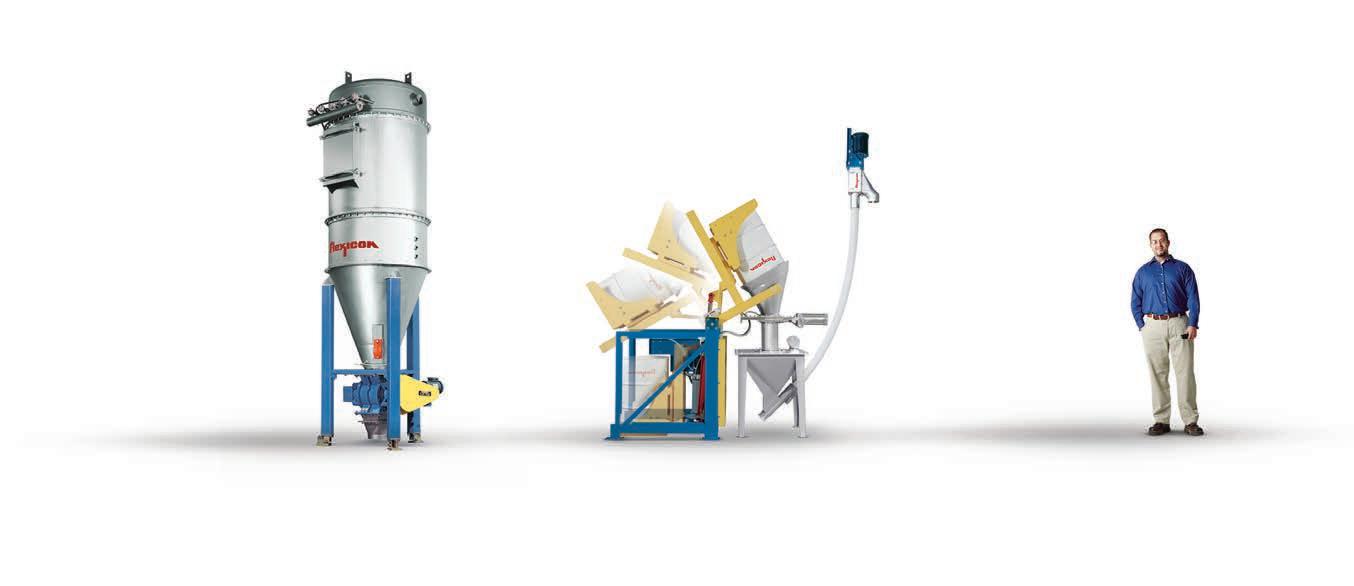
unload free- and non-free-flowing solids from bulk bags automatically. Allows untying, discharging, retying and collapsing of bulk bags—all dust-free. Available with weigh batching controls.
BLOCK-BUSTER® Bulk Bag Conditioners loosen bulk materials that have solidified during storage and shipment. Variable height turntable positions bag for hydraulic rams with contoured conditioning plates to press bag on all sides at all heights.
SWING-DOWN®, REAR-POST and TWIN-CENTREPOST™ Bulk Bag Fillers can fill one bulk bag per week or 20 per hour at the lowest cost per bag. Numerous performance options. Available to industrial or sanitary standards.
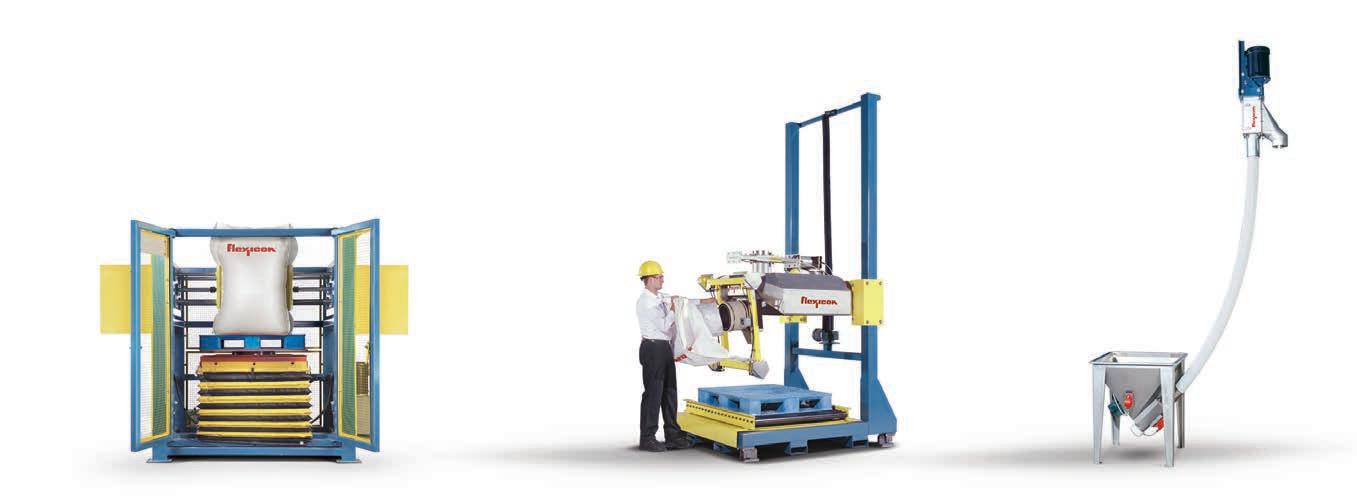
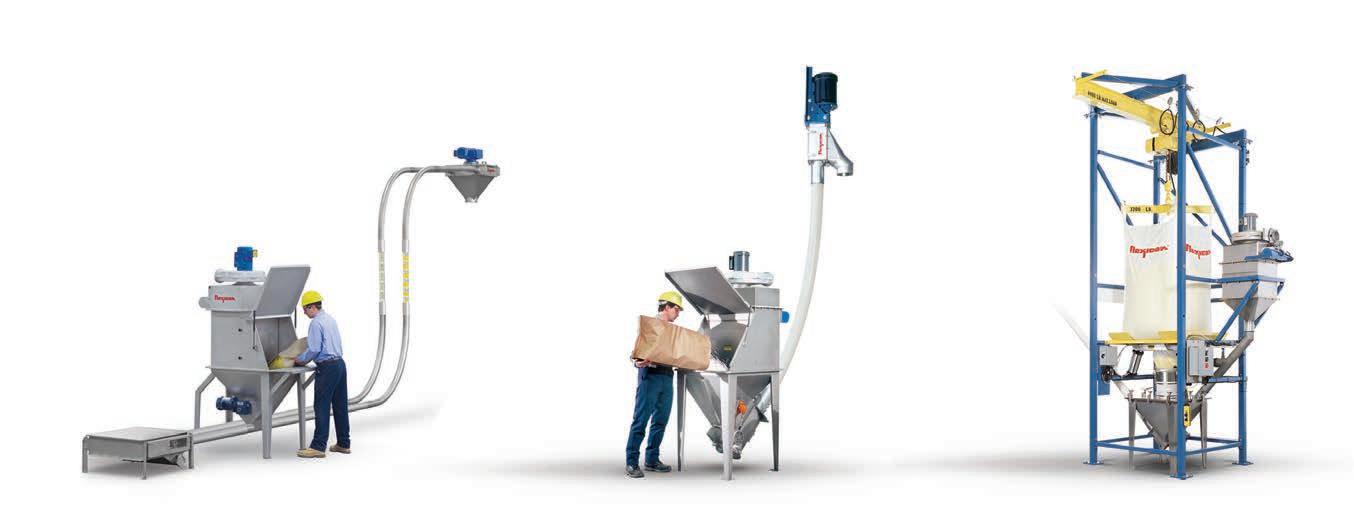
FLEXICON® Flexible Screw
Conveyors transport free- and non-free-flowing bulk solid materials from large pellets to sub-micron powders, including products that pack, cake or smear, with no separation of blends, dust-free at low cost. No bearings contact material. Easy to clean quickly, thoroughly.
PNEUMATI-CON®
Pneumatic Conveying
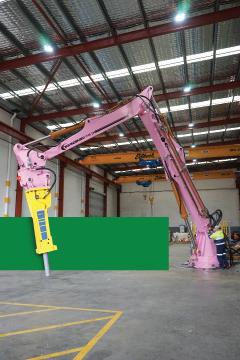
Systems move a broad range of bulk materials over short or long distances, between single or multiple inlet and discharge points in low to high capacities. Available as dilute-phase vacuum or positive pressure systems, fully integrated with your process.
TIP-TITE® Container Tippers
dump bulk material from drums (shown), boxes or other containers into vessels up to 3 metres high. Dust-tight (shown) or open chute models improve efficiency and safety of an age-old task.
The FLEXICON® Lifetime Performance
Guarantee* assures you of a successful result, whether you purchase one piece of equipment or an engineered, automated plant-wide system. From initial testing in large-scale laboratories, to single-source project management, to after-sale support by a worldwide network of factory experts, you can trust your process— and your reputation— to Flexicon.