DECISION-MAKERS
PROSPECT AWARDS
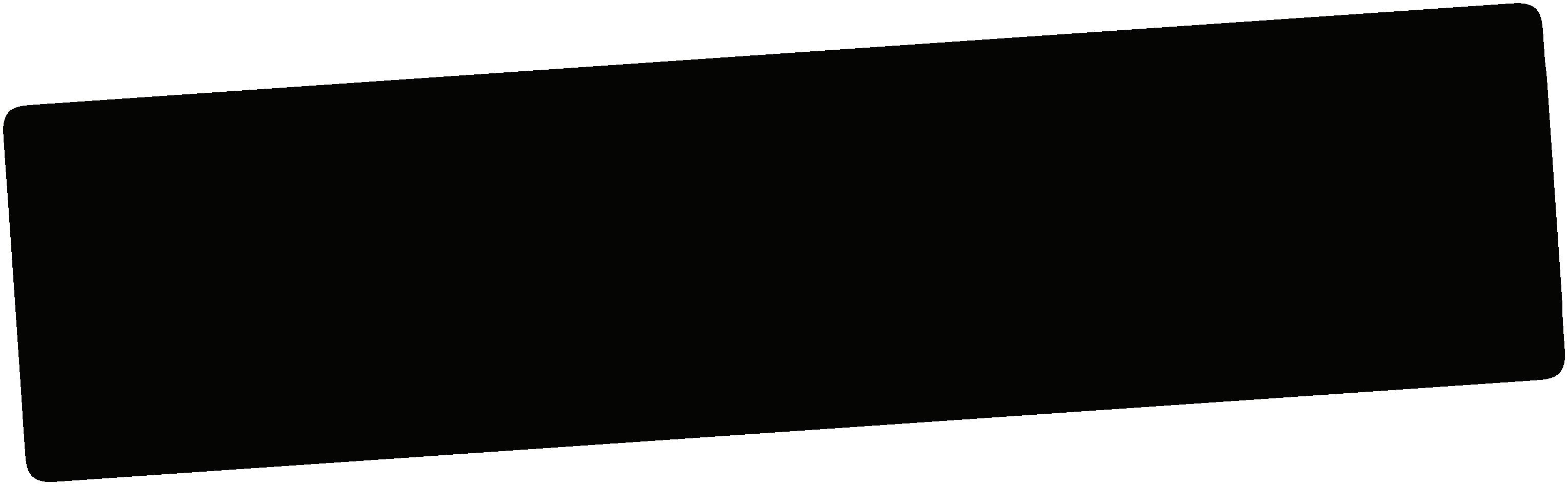
CRITICAL MINERALS


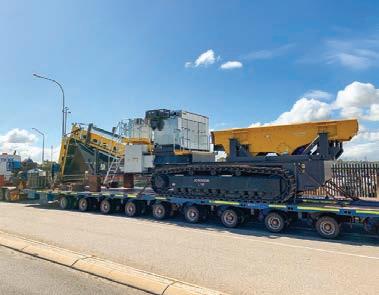


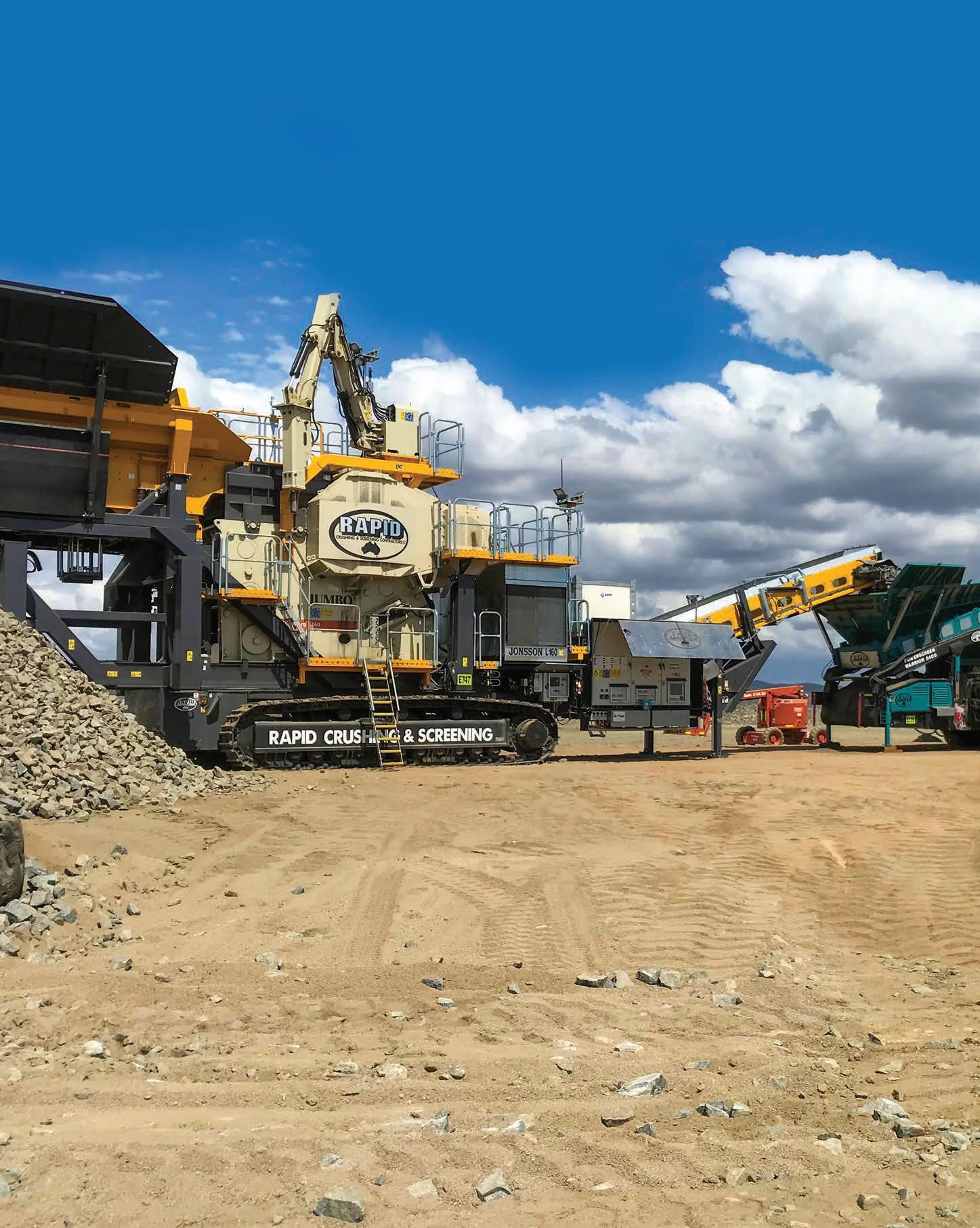
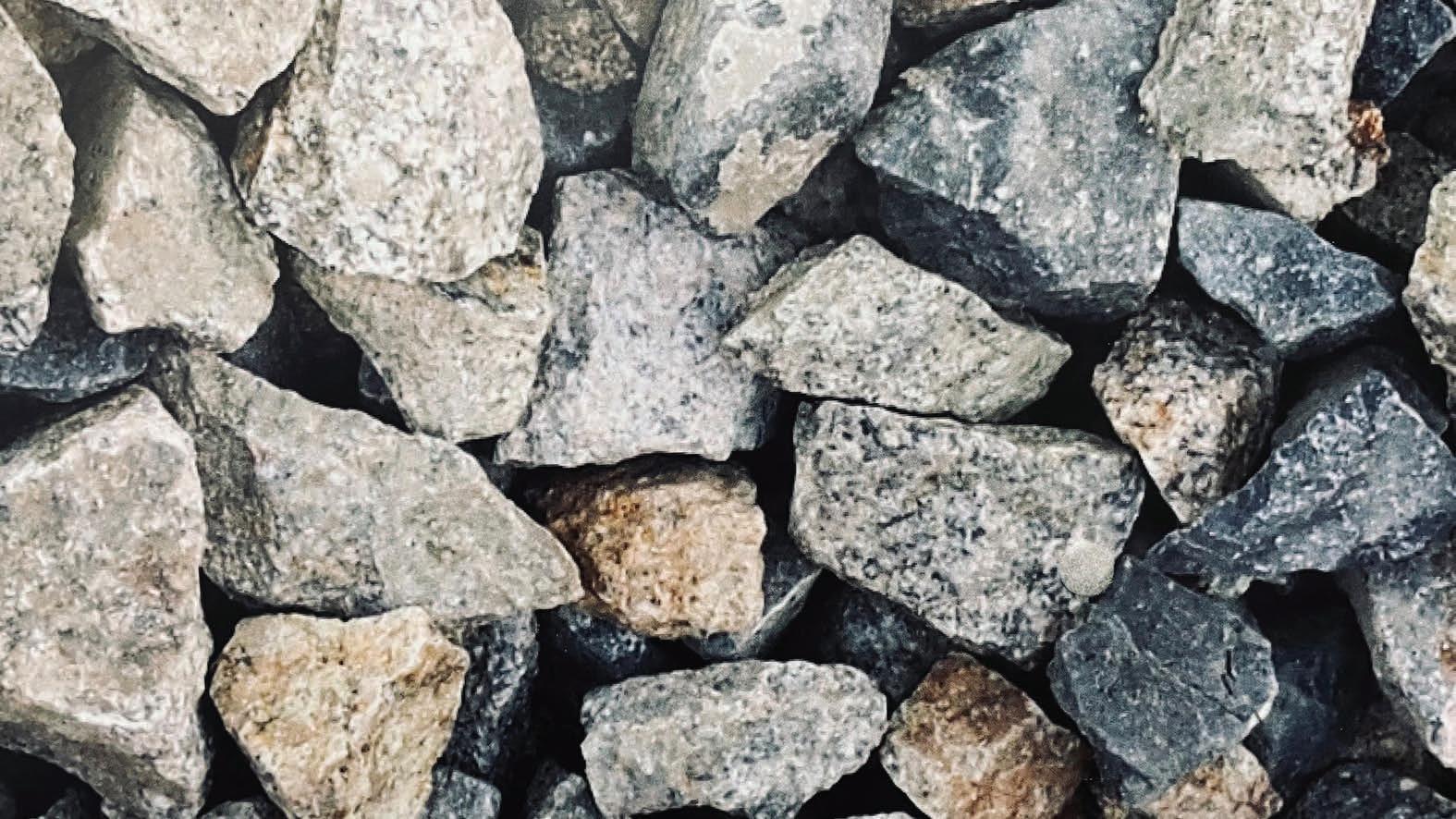
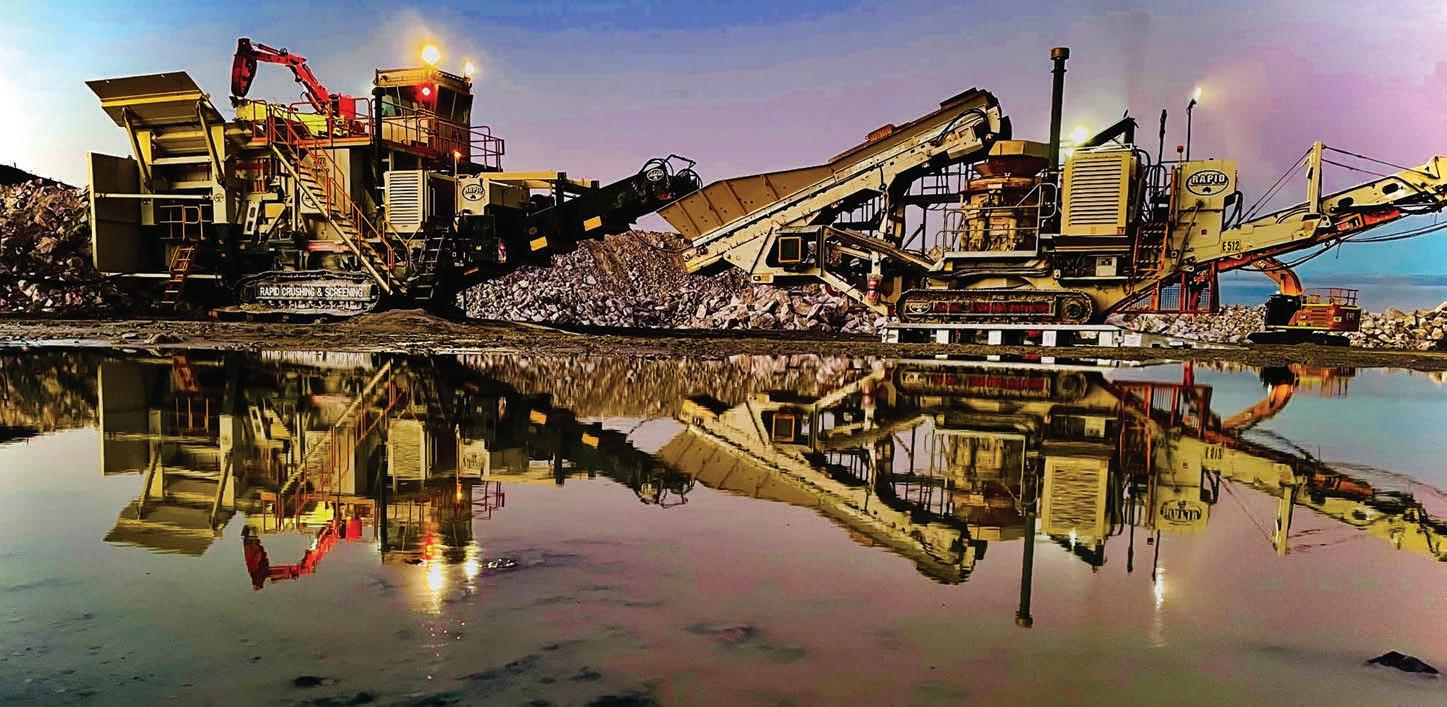
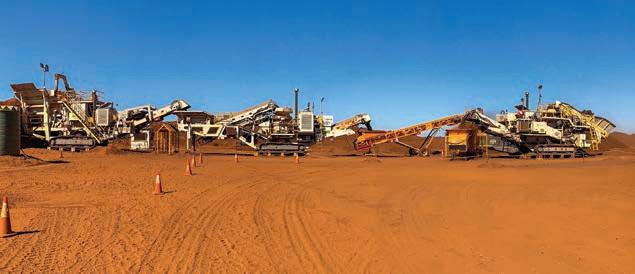
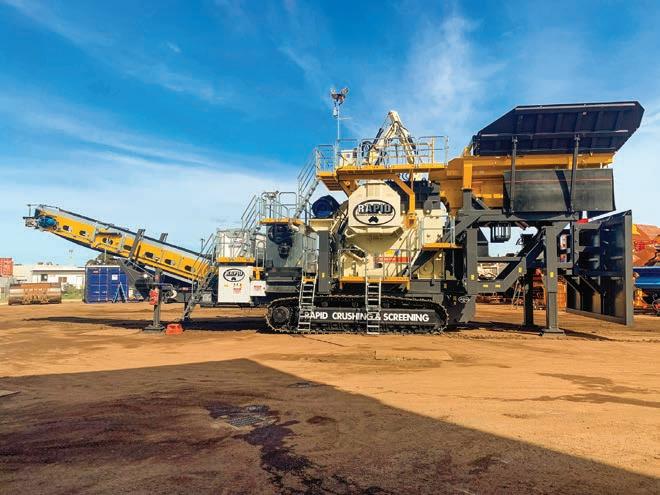


Our Pit Viper series allow fully autonomous machines with real-time data tracking that improve quality and productivity in this and the following processes in the value chain. Utilising our leading-edge control system platform, Autonomous enables Pit Vipers to productively and safely complete its mission of drilling out a drill pattern with minimal human intervention. epiroc.com/en-au
PAUL HAYES
paul.hayes@primecreative.com.au
Much of the material that is taken from the ground in the mining industry needs to be processed for use in other areas such as road, building and bridge construction, and that’s where crushing and screening comes in.
In the simplest terms, crushing equipment takes big pieces of material and uses force to turn them into smaller pieces, while screening equipment acts like a filter or sieve that separates similarly sized materials.
But that really is putting it far too simply.
Crushing and screening is a wideranging and nuanced area of the resources sector, with all kinds of machinery, processes and methods at play in creating value for mining companies.
That’s why this February edition of Australian Mining will examine the best and brightest of the innovations, products and services that go into crushing and screening – from vibration analysis to jaw crushers to modular plants to conveyor safety to various mobile crushing options.
Elsewhere in the issue we speak with all of the worthy winners of the 2022 Australian Mining Prospect Awards.
As the only national awards program to take a step back and appreciate what the mining industry is doing by rewarding those who are going above and beyond, the Prospects provide a much-deserved spotlight on some of the best people and products from across the Australian resources sector.
CHIEF EXECUTIVE OFFICER JOHN MURPHY
CHIEF OPERATING OFFICER CHRISTINE CLANCY
EDITOR
PAUL HAYES
Email: paul.hayes@primecreative.com.au
JOURNALISTS ALEXANDRA EASTWOOD
Email: alexandra.eastwood@primecreative.com.au
TOM PARKER Email: tom.parker@primecreative.com.au
LEWIS CROSS Email: lewis.cross@primecreative.com.au
In addition, we were lucky enough to sit down for exclusive interviews with some major industry decision-makers – including ABB division president – process industries Joachim Braun and First Tin CEO Thomas Buenger – to glean some industry insights at the start of what promises to be an exciting year.
Speaking of exclusive interviews, Australian Mining was also on the ground for the 2022 iteration of the International Mining and Resources Conference (IMARC), held in Sydney in November.
Offering the global resources industry the opportunity to reconnect and realign, IMARC 2022 also provided us with the chance to catch up with several major METS players to chat about their offerings and takeaways from the conference. Needless to say, we got some fascinating insights.
The February issue also shines a light on industry areas such as diversity, critical minerals, events, transportation, software solutions, and more.
And as we head into a fresh and exciting 2023, let’s hope for a great – and productive – year for the Australian resources sector.
The Tutt Bryant Group originated in 1938 and has long been known for its quality, professionalism and innovation in the construction and heavy equipment industry. The company has three principal areas – equipment sales, heavy lift and shift, and hire – and operates across Australia. It features a diverse range of capabilities, providing equipment sales and hire, spare parts, service, and engineering solutions to the national construction, mining, and trade sectors.
Paul Hayes Managing EditorASHLEY PERRY
Email: ashley.perry@primecreative.com.au
CLIENT SUCCESS MANAGER
JANINE CLEMENTS
Tel: (02) 9439 7227
Email: janine.clements@primecreative.com.au
SALES MANAGER
JONATHAN DUCKETT
Tel: (02) 9439 7227 Mob: 0498 091 027
Email: jonathan.duckett@primecreative.com.au
SALES ADMINISTRATOR EMMA JAMES Tel: (02) 9439 7227 Mob: 0414 217 190 Email: emma.james@primecreative.com.au
DESIGN PRODUCTION MANAGER MICHELLE WESTON michelle.weston@primecreative.com.au
As part of Tutt Bryant’s lineage and ethos, its people and its honest dealings reinforce how the group conducts its business, and this philosophy is expressed clearly in the ‘Tutt Bryant Way’, which is embraced by all employees and encapsulates the company’s core values of teamwork, family, integrity, versatility and enterprising.
Cover image: Tutt Bryant Group
ART DIRECTOR BLAKE STOREY blake.storey@primecreative.com.au
GRAPHIC DESIGNERS KERRY PERT, LOUIS ROMERO
SUBSCRIPTION RATES
20 I NDUSTRY AWARDS
A nnouncing the winners of the 2022 Prospect Awards
T he 2022 Australian Mining Prospect Awards gave the industry a chance to recognise and reward those who have gone above and beyond in the mining sector.
46 C RUSHING AND SCREENING
Reliable, robust and cost-effective
W ith a presence in Western Australia and Queensland, Rapid Crushing Group is not your average contractor.
50 C RUSHING AND SCREENING
M obile crushing experts
T he Tutt Bryant Group has long been known for quality, professionalism and innovation, offering leading crushing and screening solutions.
62 C RUSHING AND SCREENING
T he myth of ‘guarding by location’
M artin Engineering provides a case for global standards in conveyor safety.
66 M INERAL PROCESSING
T he A-Team of apron feeders
Apron feeders are an essential component of the mineral processing cycle – and Minprovise is now designing and manufacturing them.
68 S USTAINABILITY
M iners embracing new technologies more than ever
ABB global president – process industries Joachim Braun discusses the resource sector’s accelerated use of technology.
70 I NDUSTRY EVENTS
A milestone celebration of mining innovation
Australian Mining caught up with several major METS players at IMARC 2022.
74 DECISION-MAKER
I s this Australia’s next tin operation? Australia’s tin production pales in comparison to other commodities, but there are several companies looking to bring new mines online.
102 C OMMODITY SPOTLIGHT
L ooking to the mining horizon
A r ecent report from KPMG examines the prospects of a net-zero future for the mining industry – and lithium sits in the centre of the equation.
Thejo offers varieties of rubber & polyurethane products for filtration application in Mineral processing, Chemical, Pharma, Food & Agro industries. 'HIPO' filtration spares and solutions are marketed globally to assist our industrial clients to achieve enhanced performance by meeting the stringent technical requirements, performance life and economic objectives. HIPO products are tailored to suit and meet customer-specific needs and expectations.
► Quality & Reliability
► Easy Replacement
► Innovative Engineering
► Distinct Manufacturing Process
► In-situ Support
► Low Cost
► Standard or Customized Design of Material
AUSTRALIAN MINING PRESENTS THE LATEST NEWS FROM THE BOARDROOM TO THE MINE AND EVERYWHERE IN BETWEEN. VISIT WWW.AUSTRALIANMINING.COM. AU TO KEEP UP TO DATE WITH WHAT IS HAPPENING.
HUNDRED-MILLION-TONNE MILESTONE FOR AUTONOMOUS TRUCK FLEET
NEWMONT CORPORATION SURPASSED THE 100-MILLION-TONNE MILESTONE FOR MATERIAL HAULED BY THE FIRST AUTONOMOUS HAULAGE SYSTEM.
Newmont Corporation’s Boddington mine surpassed the 100-milliontonne milestone for material safely hauled by the gold industry’s first autonomous haulage system (AHS) fleet, using Cat MineStar Command. Command enables remote operation of load-haul-dump machines to deliver immediate productivity and efficiency gains.
Western Australia’s largest gold mine, the deep open-pit surface mine delivered 19.7 million grams (696,000 ounces) of gold and 4.6 million gold equivalent grams (163,000 oz) of other metals in 2021.
The mine’s fleet today includes 36 Cat 793F autonomous and four 793D staffed mining trucks to haul material,
and the conversion to AHS was one of the fastest in the industry, taking about seven months to roll out all 36 trucks equipped with Command.
Newmont invested $150 million in its autonomous haulage project with goals to improve safety and productivity, while extending mine life.
The first 231t Cat 793F was converted to autonomous operation in March 2021. A total of seven trucks from Newmont’s existing fleet were retrofitted with Command for hauling, while 29 trucks were new models.
The last of the 36 autonomous trucks were in operation at the mine in October 2021.
The mine reached the 100 million tonnes of material autonomously
RINEHART BIDS FOR MORE RARE EARTHS VIA ARAFURA
Gina Rinehart’s Hancock
Prospecting makes most of its money from iron ore, but appears to be diversifying, according to recent reports.
After Arafura Rare Earth in December called for $121 million for its Nolans project in the Northern Territory, Hancock is understood to have committed to investing $60 million.
The bid caused brokers Bell Potter and Canaccord Genuity to shut the books early.
The Nolans project marks a major boost for the NT, helping to secure it as one of the world’s
only sources of important critical minerals. The minerals mined from the Nolans project can be used to make technological devices like mobile phones, televisions and computer monitors.
The project includes a mine, process plant (comprising beneficiation, extraction and separation plants) and related infrastructure located 135km north of Alice Springs.
In another sign of a desire to get its hands on rare earths resources, it is understood Hancock was trying to secure a stake in VHM’s Groschen project in Victoria.
hauled benchmark by the end of October 2022.
Caterpillar technology site manager Kosie Bolton said the period between rollout of the mine’s first autonomous 793F truck to full conversion of the autonomous fleet to achieving 100 million tonnes autonomously hauled was “incredibly short”.
“This is a true testament of the great teamwork between Boddington’s talented and dedicated workforce, Cat dealer WesTrac and Caterpillar,” he said. “The supporting AHS projects will help to improve data understanding and drive operational excellence through data utilisation.”
Including the autonomous trucks, equipment featuring MineStar Terrain, and site autonomous vehicles and trucks, the mine has a total of 200 connected assets.
An entirely new AHS intelligence office, where all the autonomous trucks and connected assets can be viewed and collected data analysed, was also completed and dedicated in October 2022.
The new workspace brings together all AHS team members in a single space ,with tiered seating and screens at the front of the room.
AUSTRALIAN MINING GETS THE LATEST NEWS EVERY DAY, PROVIDING MINING PROFESSIONALS WITH UP-TO-THE-MINUTE INFORMATION ON SAFETY, NEWS AND TECHNOLOGY FOR THE AUSTRALIAN MINING AND RESOURCES INDUSTRY.
Boddington AHS control room superintendent James Earl said having everyone together in the office allowed the company to post issues on the screens in front of all workers to quickly address them together.
“We are extremely proud to deliver the gold industry’s first autonomous haul truck fleet at Boddington. This will help extend the mine’s life, reduce safety risks and lower costs. The project’s record implementation is just another example of Newmont’s trademark ability to set and achieve ambitious goals,” he said.
VHM was seeking to raise $30 million for its initial public offering and had been telling potential investors Groschen was a “globally significant Tier 1” rare earth deposit with an accompanying mineral sands resource.
Arafura’s Nolans project is the first of its kind to be built anywhere in Australia, according to Arafura managing director Gavin Lockyer.
“It will be constructed to deliver a product that is absolutely critical in the race to tackle climate change across the world,” he said.
“Because Nolans has very strong ESG (environmental, social
and governance) credentials, it will set a benchmark for new Australian resource projects and as a result is attracting a great deal of interest from international investment groups.”
Having a heavyweight like Hancock with a toehold position would potentially see the project reach new heights.
While both Hancock and Arafura declined to comment at the time, only time will tell if the mining giant continues to invest in diversifying listings, and what this will mean for the projects.
The Jonsson product range is engineered with e-Power as standard, energised by a diesel generator set onboard or connected directly to the local electric grid when available. The innovative dual power systems of the Jonsson machines make it possible for users to select the most economical power source.
The L120-330 Double Crusher features are truly unique in that it includes a pre-screen, C120 Jaw crusher, 330GP Cone crusher and a triple deck product screen built on one chassis.
Jonsson designs and manufactures some of the world’s most formidable heavy-duty, track-mounted crushing and screening plants. With crushing equipment in the 70-180 tonne range, these are the ideal mobile solution for customers with open quarries or mines in highcapacity, heavy-duty applications.
For more information, contact metso@tuttbryant.com.au
Follow us on:
Rio Tinto and Fortescue heads Jakob Stausholm and Andrew Forrest have been in talks to co-pilot a green hydrogen project.
The two Western Australian mining titans are seeking more collaborative methods to reduce their carbon emissions as they look towards facilitating large-scale solar and wind farms.
Initial talks began after Rio Tinto chief scientist Nigel Steward cast doubt on the long-term viability of implementing hydrogen. Steward spoke at Rio’s 2022 Investor Seminar in November, outlining the responsibilities surrounding the integration of hydrogen in mining operations.
“At the moment, though, hydrogen is very expensive and will require a technological breakthrough to be economically viable,” he said.
“There will be very high-power requirements to generate sufficient hydrogen to meet future demands. However, the supple chain to deliver green hydrogen is not yet well established and it will take time before it will be a material contributor to decarbonisation.
“Hydrogen will also be impacted by leakage from storage and transport facilities – an estimated one per cent per day is lost when stored in liquid form. Competitive green hydrogen requires very low-cost renewable electricity at scale. It also needs lower capital costs.
“Hydrogen has a global warming potential 5–16 times that of carbon dioxide over 100 years. Therefore, our intention is to consume hydrogen close to its point of generation.”
Forrest, for his part, wanted to address Stausholm’s concerns over transporting hydrogen.
“He was quickly reminded that green hydrogen is not a greenhouse gas,” Forrest said.
“But that is like blaming the policeman for defending a house and saying the burglar is doing a good job. The world must go to green
The mining giant believes operations like the Hillside coppergold project on the Yorke Peninsula in South Australia are key for “the future of the planet”.
Located north-west and west of Adelaide, the mine is expected to produce 42,000 tonnes of copper and 30,000 ounces of gold each year for its first 11 years.
There are also 500 jobs expected to be created during construction, with another 400 jobs up for grabs when the mine becomes operational in 2025.
“We’ve got quite a few local investors on the register, and we have a lot of interest from local suppliers and contractors,” Rex Minerals chief executive officer Richard Laufmann said.
“We’ll also be speaking to local and international banks, and with the world moving to electrification, you can’t even take the first step without copper.
“Whether you use a coalpowered station or solar, you need copper to transmit the power.
hydrogen and Rio Tinto, like every other responsible mining company around the world, knows it has to come off fossil fuels.
“We have a very collaborative relationship with Rio, and we want to make sure our chief scientists are singing off the same songbook.”
“We’re at a changing point in history where we want to clean the planet, reduce the pollution and electrify, and the first thing you’re going to need is copper.”
Laufmann said the company was preparing the site to become ready for operations, with road diversions, power upgrades and water installations.
“The site is prepped and ready to go for when we start developing,” he said. “At the same time, we’re training the people who are going to operate this mine.
“This mine just doesn’t bring jobs; it brings diversity (of industry) instead of just farmers in the Yorke Peninsula.
“This will bring in people that will support hospitals, schools, sporting clubs and all the sorts of things that make a region exciting.”
Laufmann also said the project was about “the future of the planet”.
“We’re not knocking over native forests and we’re not clearing any land that has native species living on it,” he said.
Bradken’s technology transformation is supporting the evolution of the mining industry.
•Innovative mining digital technology solutions
•Asset condition and performance monitoring solutions
•Design, engineering and manufacture
bradken.com
IGO Group and Tianqi have paid $136 million to acquire lithium explorer Essential Metals.
The two companies have partnered on lithium matters since late 2020, with the latest acquisition allowing a foothold in the WA lithium production zone between Kalgoorlie and Norseman. Under their Tianqi Lithium Energy Australia (TLEA) umbrella, the companies have signed a binding scheme implementation agreement (SIA) with Essential Metals to enact a scheme of arrangement.
The consideration for the scheme is $0.50 per share, equating to a $136 million equity value for Essential Metals.
Essential Metals has been drilling Pioneer Dome, an early-stage deposit that is currently years from development.
Pioneer Dome is located about 600km from Greenbushes, which is Australia’s biggest and best lithium mine and in which IGO and Tianqi have a 51 per cent stake.
Greenbushes is expected to run for at least another 20 years, suggesting IGO and Tianqi’s acquisition confirms their desire to push into a new lithium province rather than simply extending the existing hub.
“We believe this transaction is a great outcome for Essential shareholders and for other stakeholders, including employees, suppliers, the Ngadju people and the state of Western Australia, all of whom will benefit from the Pioneer Dome lithium project being developed
by a large, well-financed and experienced lithium sector participant as is TLEA,” Essential managing director Tim Spencer said.
IGO acting chief executive officer Matt Dusci provided some insight into the proposal.
“Both IGO and TLC are committed to progressing and growing our lithium joint venture business,” he said.
“The ESS transaction provides an opportunity to accelerate lithium exploration to bring new resources to production.”
Fortescue Metals recently announced the resignation of its chief financial officer (CFO) Ian Wells.
Wells had been with Fortescue since 2010 and held various senior executive finance roles, notably as CFO since 2018, and resigned to pursue other opportunities, the company said.
“I recall fondly back in 2010, when Ian joined our team,” Fortescue executive chairman Andrew Forrest said.
“The finance team at the time were charged with refinancing our
original project finance bonds and the successful refinancing in 2010 enabled the company to make investments to expand capacity to 155 million tonnes per annum.
“Since then, we have seen the company’s balance sheet and capital allocation change from debt repayment to reinvestment and delivering market-leading shareholder returns. We now have a strong balance sheet and a renewed focus on growth.
“Ian has made a huge contribution to Fortescue over what we will look
back on as the formative years of Fortescue. Working closely with the board, Ian and the executive team have played an important role in the development and execution of our capital allocation framework together with supporting Fortescue’s differentiating culture and values.
“Ian has been a trusted member of the executive team which has led Fortescue through a number of iron ore market cycles, more recently the impacts of COVID-19 together with global volatility.
“Despite these challenges, Fortescue has retained a reputation for consistent and predictable performance as well as operating and capital cost discipline.
“Well regarded by his colleagues through the organisation, we celebrate Ian’s contribution.
“On behalf of the board and executive, we also thank Mandy and Ian’s family for their collective contribution to Fortescue and wish them the very best for the future.”.
Our TS Gyratory Crushers are built for the toughest crushing duties while providing safety, reliability, and ease of maintenance. That means you get higher availability and throughput along with maintenance cost reductions. The TSUV Gyratory Crusher adds even more power, capacity and safety, to give miners an extra low total cost of ownership (cost per tonne) and improved availability compared to more traditionally designed crushers.
■ Ultra-heavy duty design
■ Lowest cost per tonne in operation
■ Lowest total cost of ownership (TCO)
■ Safer, simpler maintenance
■ Digitally enabled for optimal productivity
Find out more at www.flsmidth.com
The decision on the Queensland project came amid the industry’s determination to transition away from fossil fuels and towards decarbonisation.
According to Glencore, the significantly increased taxes as part of Queensland’s new coal royalties also played a role in the decision to pull the plug on Valeria.
“This decision has been made in the current context of increased global uncertainty and is consistent with Glencore’s commitment to a responsibly managed decline of our global coal business and our ambition of being a net-zero total emissions business by 2050,” the company said.
“We will continue to progress various brownfield coal extensions at existing mines in Australia but note that within the next four years our Liddell, Newlands and Integra mines will close and undergo appropriate rehabilitation.”
A Glencore spokesperson told the Australian Financial Review that Queensland’s controversial royalties program was partially to blame for the decision to withdraw.
“Abrupt decisions like the Queensland super royalty hike
Gina Rinehart’s Hancock Prospecting recently made a $60 million play for Arafura’s Rare Earths’ Nolans project. What’s driving this move?
Rinehart has set her sights on rare earths in a big way. Hancock Prospecting pledged half of Arafura’s target price of $120 million for its Northern Territory mining venture, giving Rinehart a leg up in Australia’s rare earth space.
This investment alone would be noteworthy, but Hancock shows no signs of slowing down as it swats down its competing offers for ownership of Warrego, home of the promising West Erregulla gas resource in the Perth Basin.
Hancock’s ever-expanding foray into key mining projects is nothing new, but the focus on rare earth has generated chatter regarding long-term benefits and the distinction between critical minerals.
One key reason for Rinehart’s sudden investment in rare earths is a severe lack of Australian representation in the market. Two of the largest rare earth investors in the Western Hemisphere are Australia’s Lynas Rare Earths Limited (LYC) and
have damaged investor confidence, increased uncertainty and raised a red flag with key trading partners,” the spokesperson said.
“Genuine and timely consultation with companies on the detail of the policy reforms is crucial to avoid continued uncertainty.”
Glencore’s $US1.3 billion ($2 billion) project was anticipated to
produce up to 20 million tonnes of coal per year over a 37-year lifespan.
Acquired from Rio Tinto in 2018, the Valeria project was slated to land in the Bowen Basin, 27km northwest of Emerald, and be constructed by the Blair Athol joint venture. The project was originally included in Glencore’s decarbonisation pathway, which sought to achieve a 50 per
cent reduction in carbon emissions by 2035 and achieve net-zero emissions by 2050.
Glencore listed operational employment opportunities for up to 1250 personnel, up to 1400 construction jobs and an estimated production expenditure of $1.5 billion. Construction for the mine was slated for 2025, with planned operations commencing in 2027.
The new Queensland coal royalty structure, which has netted the State Government $5.2 billion, has seen a number of companies question their future investments in the state.
BHP is among the companies that have paused investment in Queensland. Chief executive officer Mike Henry shares the sentiment that the introduction of the coal royalties was surprisingly sudden.
“It didn’t involve any engagement with industry which has been a significant increase in the sovereign risk associated with Queensland, which has caused us to say we really can’t deploy further capital into that business for the time being and we’ll go back and reassess what the plans for the business are going forward,” Henry said in August 2022.
the US’s MP Materials Corp (MP).
Rare earth elements include lanthanum, cerium, praseodymium, neodymium, promethium, samarium, europium, gadolinium, terbium, dysprosium, holmium, erbium, thulium, ytterbium, lutetium, scandium and yttrium.
Rare earth elements are primarily used in the manufacture of electric vehicles (EVs) and permanent magnets. The importance of the transition to EVs and cleaner energy is clear, and that is reflected in market prices for battery components and rare earth elements.
China owns almost 40 per cent of the world’s rare earth reserves, followed by Vietnam and Brazil, while Australia sits at sixth place with only 3.5 per cent. These smaller numbers may be the reason behind Hancock’s quiet $21 million investment in Brazilian Rare Earths.
But despite its relatively small reserves, Australia has still managed to nab a production value of 17,000 tonnes of rare earth as of 2020. As demand for rare earth elements grows, local production becomes more valuable.
Australia is looking to become a key player in the global sustainability market, but mining industry businesses lack the internal funding to fully utilise the rare earth reserves at their disposal.
Australian chief scientist Dr Cathy Foley spoke at the Rare Earth Conference in November 2022, calling on leading businesses to invest in this emerging market.
“If businesses stepped up to the plate, the government side of the equation could be properly focused on fundamental research,” Foley said. “That would put us in a much better position to solve the significant technological problems that remain.
“If you have a culture where industry is reaching into the research sector and investing in the science, the process of discovery and problem-solving becomes more integrated with real-world requirements. The demand for rare earth elements is expected to grow by up to seven times by 2040, driven by the demand boom of permanent magnets, electric vehicles and offshore turbines.
“If Australia is to reap the benefits of this boom, increase skilled employment and lift complexity in our economy, we need to move up the value chain.
“This mining opportunity is simply inseparable from the global climate ambition.”
Australia’s inclusion of critical minerals into its diet has been a healthy one. The Federal Government’s Resources and Energy Quarterly revealed the continued success of green mineral production.
Production of materials like zinc, lithium, copper and nickel place Australia high on the list of global production leaders. This sustained presence as an industry icon could be the incentive needed to expand to rare earth elements.
A combination of government backing, high market prices and business interest has finally given rare earths the attention they need. For Australia to grow its global market presence and take a bigger swing at decarbonisation, mining projects like Arafura are paramount in maintaining strides in rare earth production.
At Hastings Deering, businesses working within the mining industry can now take advantage of a new industry leading warranty with every Cat® Certified Rebuild. Get ‘as-new’ performance and benefit from the multiple lives designed into Cat machines, at a fraction of the cost of buying new.
CALL 1300 186 248 OR VISIT HASTINGSDEERING.COM.AU
The ongoing energy crisis has pushed coal prices to historical highs, with Australia’s resource exports set to hit a record $459 billion this financial year.
The revised export number, up from the $450 tipped earlier this year, was included in the Federal Government’s Resources and Energy Quarterly: December 2022.
Much of the growth in Australian resources has been driven by a global energy crisis and geopolitical instability as a result of Russia’s invasion of Ukraine and the resulting sanctions.
“Many Western nations are having to pay substantially more for energy, on the high chance that sanctions on Russia will see some Russian production – particularly gas and coal – become stranded from world markets,” the report from the Department of Industry, Science and Resources stated.
With prices having been pushed to “historically high” levels, Australia’s combined coal exports, which includes metallurgical coal and thermal coal, are now forecast to earn $132 billion in 2022–23. Such high prices and increased demand have also pushed coal to become Australia’s most valuable export, taking the top spot long held by iron ore.
Earnings from iron ore have been revised down for the financial year, with demand for the key steelmaking ingredient taking a major hit amid a slowing housing market in China, by far Australia’s biggest iron ore customer.
“Lower prices over the outlook period are expected to see Australia’s iron ore export earnings ease from $133 billion in 2021–22 to $113 billion in 2022–23, and then to $95 billion in 2023–24,” the report stated.
News of the increased earnings for coal exports came soon after the Federal Government placed a temporary cap on coal and gas prices as part of its efforts to curb runaway energy prices.
The price of coal has exceeded $US400 per tonne in 2022. It sat at around $US240 ($358.60) per tonne in late 2022.
It should be noted, however, that despite high prices and major company windfalls, the longer-term outlook for coal remains uncertain
The Federal Government is receiving pushback after its industry relations (IR) bill recently passed through parliament.
“With rising inflation, electricity costs and interest rates, the last thing businesses need is to be dragged into other companies’ IR disputes via multi-employer bargaining or have the FWC (Fair Work Commission) make their decisions for them,” Australian Resources and Energy Employer Association (AREEA) chief executive officer Steve Knott said.
The bill pricked the ears of many business owners by, among other things, introducing multi-enterprise bargaining.
The recently passed law allows unions to represent workers from similar industries and negotiate terms as a single party.
“Having a centralised employment tribunal set wages and conditions for private sector businesses, as it did in the 1970s and 1980s, put simply, is barking mad policy,” Knott said.
Knott described the move as “a recipe for lower productivity, higher inflation and less competition” and believes it would not only stifle employment growth but drive away investment and employment opportunities.
In a statement reported by 9News, Minerals Council of Australia chief executive Tania Constable said the legislation would be a “handbrake” on investment, job opportunities and wage growth.
“The reintroduction of multiemployer bargaining into the Australian workplace relations regime will have negative consequences on investment, productivity, economic growth, job security and wages for small or larger businesses across Australia,” she said.
The Federal Government’s plan for labour hire, or “same job, same pay”, has caused a stir among mining businesses. The threat of uniform wages for hire and client company employees, as well as
the reduction of casual hires, has created cause for concern due to fears of increased strikes and unfair demands by employees.
Hancock Prospecting executive chair Gina Rinehart has also argued that multi-employer bargaining has no place in the Australian resources sector.
“The mining industry does not fit the profile of an industry where employees are poorly paid,” Rinehart said. “On the contrary, if the legislation is applied to the mining industry it will have significant negative impacts on a highperforming industry.”
BHP chief executive Mike Henry also spoke out against the bill, claiming it wouldn’t apply to most workers. Like Rinehart, Henry seems to hold to the old axiom, “If it isn’t broken, don’t fix it”.
“There simply is no case for multi-employer bargaining in the mining industry,” he said. “This is an industry where the current approach has been working well.
as the world increasingly looks to renewables as a source of power generation.
“Thermal coal remains subject to challenges with finance, insurance and long-term global demand, all of which have made supply side responses slow and difficult to manage,” the Government report stated.
“These factors will likely become more forceful over time, putting the sector into a permanent higher-price phase.”
“It’s obviously a very high-paid industry; BHP’s workers would be within the top decile, the top 10 per cent of wage earners in Australia.”
The bill also makes more employee-friendly changes to topical work issues like pay secrecy, flexible hours and fixed-term contracts, much to the chagrin of large business owners.
Knott has called on the Government to cooperate should any amendments be made in the future.
“The Albanese Government will be under constant pressure to ensure adverse predictions don’t come to fruition,” he said.
“When they inevitably do, we expect the Government to engage in genuine consultation with all its constituents – not just doing the bidding of union bosses – on fixing the mess they would have created.
“We hope the Government will both consult with and properly consider the views of business for the so-called ‘second tranche’ of reforms mooted for 2023.”
Altra Industrial Motion has developed the next generation of its Twiflex dragline brakes package.
Due to how dragline bucket excavators are designed, there are few brakes that will work. Spring-applied, air-release caliper brakes are among the select few that can handle the challenging task.
Altra Industrial Motion, in conjunction with a large original equipment
manufacturer, designed a range of these brakes for use on the mining industry’s dragline excavators around 20 years ago.
More than 8000 of the resulting Twiflex brakes have since been installed in mines across the world.
The company has updated the Twiflex range to make them more environmentally friendly and even easier to maintain.
The next evolution of brake pads uses organic materials that are completely asbestos-free and have no health impacts on humans and no contaminants or oils.
“The compositions of the diaphragms in the thrusters have been upgraded to make the thrusters even more reliable, and the overall simple design makes it easy and effective to install and maintain,” Altra said.
The package includes brake callipers, thrusters, mounting frames, mounting bolts, brake discs, hubs, air-pressure regulators, local piping, and guards.
The brakes are also designed to be modular, allowing for quick changeout. The only part that needs to be changed out in its normal life cycle is the brake pad itself, which feature a wear indicator to let staff know when replacements are needed.
We’ve been maintaining, re-building and optimising Apron Feeders for years, so who better to start manufacturing?
Key Features include:
Segmented sprockets - replacement without severing chains
External Hydraulic Take-Up Adjustment
Integrated Lifting Points
Add-on Composite Customised Toolkit
Add-on maintenance platforms
Add-on incorporated dribble conveyor
Flexible Design options:
Forged solid one-piece Head Drive Shafts
Composite Shafts with keyed sprocket hubs
Electro-Mechanical Drive Units
Single or dual drives
Hydraulic or Mechanical Take-Up Adjusters
Modular Skirt options
Contact Minprovise today
Tel: 08 9359 6800 or Email: sales@minprovise.com.au
THE 2022 AUSTRALIAN MINING PROSPECT AWARDS GAVE THE INDUSTRY A CHANCE TO RECOGNISE AND REWARD THOSE WHO HAVE GONE ABOVE AND BEYOND IN THE MINING SECTOR.
Australia is the unofficial mining capital of the world and the people who work tirelessly to support it deserve to be recognised for their efforts. And since 2004, the Australian Mining Prospect Awards have been the premier event to do just that. The Prospect Awards have long been the only national awards program to take a step back and appreciate what the mining
industry is doing by rewarding those who are excelling and going above and beyond, recognising and rewarding innovation.
The 2022 iteration of the awards was held on November 17 in Perth. Western Australia played host for the first time in recognition of the vibrancy and importance of the state’s thriving recourses sector.
There was even more to celebrate in 2022, with five new or updated awards making their debut: Project Lead of the Year, Outstanding Mine
THE PROSPECT AWARDS ARE THE ONLY NATIONAL AWARDS PROGRAM TO TAKE A STEP BACK AND APPRECIATE WHAT THE MINING INDUSTRY IS DOING BY REWARDING THOSE WHO ARE GOING ABOVE AND BEYOND.”
Performance, Mine Project Success of the Year, Discovery of the Year and Sustainability Project of the Year.
Altogether, the 12 awards celebrate a wide range of achievements in
the industry, including safety, environmental and discoveries.
Keep reading to discover the winners of the 2022 Australian Mining Prospect Awards. AM
500+
FrontRunner autonomous haul trucks – worldwide
If an endless stream of driverless trucks moving across the mine site is what comes to mind, you might want to think again.
Through advances in the FrontRunner Autonomous Haulage system and the teleoperation surface mining excavator, our customers are moving toward more productive operations, while upskilling personnel to transition from the cab to the control room. Komatsu’s autonomous and semi-autonomous technology is continually evolving and redefining what it means to work for, and do business in, the mining industry.
With a tech-forward workforce and next-level equipment and solutions, we can work together to move mining toward a more innovative and sustainable future.
Develop your team. Drive efficiency. komatsu.com/autonomous
When you picture an autonomous mine, what do you see?
Arguably the most prestigious award of the night, the Australian Mine of the Year recognises a site that is not only exceptionally well-performing, but has also reached its production goals, implemented commendable safety controls, environmental and sustainability programs, and/or has shown its capacity to innovate in order to drive the industry ahead.
The award is imparted to the winner of one of the other categories, and after already taking home the 2022 Outstanding Mine Performance Award, Kestrel Coal Resources was a worthy recipient.
Kestrel underground operations manager Daniel Proffitt hailed the “special year” for the company, with significant milestones achieved across operations, culture, safety performance and community engagement.
“With purposeful investment into our safety and culture, our values drive high performance and mateship,” Proffitt said.
“We have upheld our commitment to developing our people and our frontline leaders, who are at the core of our success.
“In 2022, Kestrel Coal successfully completed the first edition of its leadership program, Unleashed. This is Kestrel’s leadership development program, developed by us, for us.
“In a nutshell, it’s a 12-month mixed-modality learning experience, meaning learning happens through a total of facilitated face-to-face workshops, developed and facilitated by our own leaders, helping to nurture in-house facilitation and presentation skills.
“Through capable and confident leaders, we’re determined to deliver our compelling vision and solid strategy to
become the mining industry’s employer of choice – the company where you can do your best work, receive support, learn and develop, and realise your true potential.”
The program also focuses on supporting and sustaining the growth of Kestrel by strengthening its people’s capabilities, transparently sharing tactics and initiatives and promising to lead the business through its people.
Kestrel is one of the world’s largest producing underground coking or metallurgical coal mines, producing around seven million tonnes of metallurgical coal a year.
Located in the Bowen Basin, 51km north-east of Emerald in central Queensland, the team at Kestrel covers the entire mining process from development to extraction and processing, environmental management and sustainable rehabilitation.
Kestrel has operated the site since 2018, with approved life of mine until 2033 and reserves to 2046, and ships 100 per cent of its coal products from Queensland’s Gladstone Port.
Kestrel has been the leading producer of underground steelmaking coal across Australia since 2019.
“As we reflect on where it all started to where we are now, there is a deep sense of pride and accomplishment,” the company said in a statement celebrating its 30-year anniversary in 2022.
“The shirts on our backs may have changed over the years, but the camaraderie and friendship has been unwavering.”
Kestrel was recognised at the awards for its hard work and highperforming teams.
“We are so proud of our team and the commitment from everyone to make Kestrel great,” the company said in a statement following the awards. AM
Recognising collaboration between Aboriginal-owned businesses and mining and mineral processing companies operating within Australia, this award was presented to Atlas Iron for its major mining contract with East West Pilbara (EWP).
Atlas Iron awarded a joint venture mining contract to EWP in August 2021, entailing load-and-haul and drilland-blast services at Miralga Creek.
The major mining contract, the first of its kind to be awarded on traditional land, is unique in that it is not a provision of a particular narrow service or activity, but is rather allencompassing.
This distinction means the contract creates employment and sustainable economic outcomes for future generations of Indigenous people to develop and operate the drill-and-blast and load-and-haul operations for an iron ore mine.
EWP managing director Troy Eaton described the contract as a watershed moment for the region and its people.
“This will be the first Indigenous business in the Pilbara to be awarded such a valuable contract to conduct these specific mining services on their own native title lands,” Eaton said.
“I know my grandfather and Nyamal man Ernest Mitchell would be so proud of what we have achieved together.
“He has always believed that mining could benefit his people and first started looking for commercial opportunities in the 1960s.”
Stacey Brown, who also took home the Project Lead of the Year award, spearheaded the Miralga Creek project to completion.
“Stacey demanded a high level of oversight and governance across all contractor and owners team scopes of work; leading to well understood and controlled cost forecasts as we moved through execution,” Atlas Iron project controls manager Scott Illingworth said.
EWP’s involvement is the culmination of generations of work and solidified the belief Eaton had in
himself, his lineage and the capabilities of the wider Nyamal community, with which the mine is based.
Eaton’s grandfather, Nyamal man and Indigenous pioneer Ernest Mitchell, was rejected and called “ illiterate” when he looked for commercial mining opportunities. But Eaton, a proud Nyamal man himself, is not resentful about the past – he just wants to set a new precedent for the future.
“It’s hard work; you have to be proactive. And if you’re true to what you need to do, hard work pays off,” Eaton said.
“I’ve got to be that beacon now. I don’t want my future generations sitting down thinking that everything comes to you.
“East West Pilbara group is built not just for my community in Nyamal, but I’ve got Elders from other groups as well, and families to be engaged with us.
“That’s how our communities up there interact – through our cultural governance and our protocols. So I’ve just got to balance it out.”
Atlas chief executive officer Sanjiv Manchanda said it’s critical the company puts the faith and investment in EWP and Ozland, a private local drilling and
blasting services business, to ensure a long-term relationship.
“From our perspective, we don’t want this to be a one-shot wonder,” he said.
“Our focus has to be, how do we sustain that and make sure that after this project? All mines have a finite life. What’s after this comes to an end?”
“Not only do EWP and Ozland have to think about that, we also have to make sure this relationship and this model is strengthened further and grows further, whether it’s some other mines sites or the same mine sites.” AM
Combining Sandvik’s expertise in crushing with the screening, feeding and loading know-how of Schenck Process, has strengthened our capacity to deliver high quality equipment and aftermarket support.
We are now better positioned than ever, to develop innovative solutions to the challenges of our industry.
The industrial internet of things (IIoT) is widely used in the mining sector as the industry continues to develop software that is designed to make operations easier.
With new applications being implemented every day, the Excellence in IIoT Application award seeks to recognise an outstanding implementation of IIoT that enhances mining and mineral processing operations.
And the Flexco Elevate by Flexco Australia was the worthy winner for 2022.
The Flexco Elevate belt cleaning monitoring system allows mining operations to remotely gather critical data and perform real-time analysis to boost conveyor efficiency.
The predictive, data-driven engine allows operations to move from traditional methods of monitoring belt cleaner performance
to a new way that empowers operations for the future.
The dashboard provides operators with immediate access to insights to easily measure internal efficiencies and monitor productivity.
The operator then has access to information such as the location of installed cleaners, belt conveyor specifications, belt and cleaner run times, and more.
“Because it has the power to turn complex data into real-world outcomes, Flexco Elevate is able to transform the way operations address pain points, allowing them to make proactive decisions that continually maximise their uptime and productivity,” Flexco director of global heavy-duty marketing Ryan Grevenstuk said.
Flexco Elevate fundamentally alters the way operations are run, and the solution’s multi-faceted benefits streamline internal processes.
“Flexco has a 110-year history of innovation, working alongside our
customers to deliver solutions that are in alignment with their operational goals,” Flexco chief marketing officer Chip Winiarski said.
“Fle xco Elevate is the first technology solution of its kind and will quickly bring increased efficiencies and improved productivity to our customers’ operations.”
Users of Flexco Elevate have reported increased productivity, improved safety and asset management, and easy installation and activation.
“With the introduction of Elevate, Flexco is reimagining the ways customers can enhance their operations through innovative solutions and added value to belt cleaners and other conveyor components,” Grevenstuk said.
The development of the system was driven by real-world challenges. The Flexco team worked with customers to identify their pain points to deliver a cutting-edge solution.
Flexco Elevate is a wireless platform that transfers data via cloud technology and provides automated collection and monitoring of data. This reduces the need for on-site inspections, including those that could compromise employee safety, freeing up working hours and reducing costs.
By enhancing the identification of specific belt cleaners in need of service, Elevate allows mining operations to predict and proactively plan for maintenance, ultimately increasing operational efficiency.
A high-production steel plant in southern New South Wales was one of the first candidates to trial the Flexco Elevate, where the monitoring device caught a puncture that would have cost the business over $35,000.
By combining first-c lass technology, innovation and real-time monitoring the Flexco Elevate has saved miners money and time and was a worthy winner of the Excellence in IIoT Application award. AM
Large material loading vehicles pose some of the biggest risks on mining sites. Drive them underground, and you’re contending with added complications such as narrow tunnels and limited vision.
Enter ifm’s infrared 3D imaging technology, capable of detecting people and objects within a wide radius of mobile equipment. This precision guidance tool pairs augmented reality with user-friendly concepts, acting as a second pair of eyes for safe navigation.
The Excellence in Environmental Management and Sustainability award recognises a mine, company or project that has developed or carried out an innovative, environmentally focused program to protect, preserve and/or rehabilitate the natural environment and improve sustainability.
The award is also designed to reward those that focus on decarbonisation and/or reducing waste and/or emissions.
IGO was a worthy winner in 2022, taking home the award for adopting internal carbon pricing (ICP), which works to increase the pace of decarbonisation
across IGO’s total carbon footprint.
According to the company, the system will be reviewed annually and will help drive emission reductions as well as generate funds for carbon offsetting projects.
“IGO was honoured to be awarded as the Australian Mining Prospect Awards – Excellence in Environmental Management and Sustainability category winner,” the company said following the awards.
“We were recognised as being an industry leader for our internal carbon price and decarbonisation fund, which is an innovative and environmentally focused initiative which improves sustainability and accelerates decarbonisation.
“This is an important step towards delivering on our commitment to be carbon-neutral across our direct operations by 2035.”
ICP allows IGO to price operational emissions and changes the decision-making behaviour of its people. The fund generated $3.7 million in the financial year 2021–22 (FY22), and is expected to allocate $7–10 million in FY23.
IGO first committed to implementing an internal price on carbon in its 2019 sustainability report, and in 2020 engaged consultants to undertake research and provide guidance on an appropriate carbon price.
ICP allows IGO to price operational emissions, allocated to
a decarbonisation fund, and drive its decision-making on low carbon investments while ensuring it targets decarbonisation projects where the most cost-effective impact can be achieved first.
“At IGO, we are committed to being carbon-neutral across our direct operations by 2035, and this initiative allows us to price our operational emissions, allocate the fee to a decarbonisation fund, and drive our decision-making on low carbon investments,” the company said.
“Thank you to Metso Outotec for sponsoring the award, and congratulations to everyone from IGO who is involved in this initiative.” AM
Our strategy identifies sustainability as a top priority. We are striving for net zero and are committed to limiting global warming to 1.5 °C. We actively support and enable our customers in their sustainability ambitions. Our Planet Positive portfolio of over 100 products and services are designed to be more energy and water efficient. They make a meaningful contribution to a circular and carbon-neutral economy.
mogroup.com
The Excellence in Mine Safety, OH&S award recognises a mine, company or project that has developed or carried out a program that increased safety, removes risk, or cuts worker issues on a project or mine.
Emerging health safety and hygiene consulting firm GCG took home this award for its Real-Time Monitoring (RTM) app.
“The team and I at GCG Health Safety and Hygiene are extremely grateful for the amazing recognition and wonderful support from Vocus,” GCG operations manager Richard Crafter said.
The RTM app is an advanced software solution developed to provide intelligent dust-exposure controls management for smarter, faster decisions.
The solution is a global first and is set to trigger a widespread adoption of real-time monitoring to the betterment of worker health.
GCG has partnered with industry to refine and optimise the innovation to ensure benefits will be realised, with Hunter Valley Operations (HVO) one company that reported benefits from using the app.
“The RTM app allowed HVO to conduct a deeper analysis of potential worker exposure to respirable dust when undertaking a specific task, allowing for task specific dust controls to be implemented and resulting in less exposure for the workforce,” HVO said in a case study.
“As an added benefit, workers are much more engaged using this task assessment approach, as they can visualise exposures and see the effect of controls in real-time.”
While conducting assessments like the one with HVO, GCG engaged workers, supervisors, health and safety personnel, return-towork coordinators, occupational hygienists, managers, corporate health managers, and general managers to gain feedback from all areas of each business.
“The feedback from these trials was overwhelmingly positive, with all clients expressing interest to continue using the app and endorsing the solution’s innovation,” GCG said in a statement.
“From the initial goals set, our trial phase was a great success.”
The RTM app creates a scientific understanding to support what is safe for workers and better enables health and safety teams to control exposures, rather than simply monitoring them.
In talking about the importance of the app, GCG highlighted the critical role that occupational hygiene plays in helping to keep workers safe from health hazards in the workplace.
Hundreds of thousands of workers in Australia are exposed to
respirable silica dust every year, so it was clear to GCG that something needed to be done to mitigate this workplace danger.
Traditional methods of dust monitoring involve a worker wearing a monitor for the duration of a shift, producing a single, overall result following laboratory analysis.
But with the RTM app, real-time monitoring can bridge the gap that is created by these traditional methods.
“Congratulations to GCG Health Safety and Hygiene for winning the Excellence in Mine Safety OH&S award at the Australian Mining Prospect Awards 2022, proudly sponsored by Vocus,” Vocus said in a statement.
“GCG won the award for developing a global first – a real-time monitoring app that enables smarter, faster dust exposure control decisions to improve the health and safety of workers.” AM
Announcing Vocus Satellite-Starlink, powered by SpaceX’s high performance constellation of broadband satellites in low earth orbit (LEO). Get on board with the world’s most advanced satellite internet.
draws on her extensive experience in strategic development, corporate leadership and communications to navigate these projects.
Atlas credits the success of the Sanjiv Ridge and Miralga mines to Brown’s hard work, determination and relationship-building.
“Stacey demanded a high level of oversight and governance across all contractor and owners team scopes of work, leading to well understood and controlled cost forecasts as we moved through execution,” Atlas Iron project controls manager Scott Illingworth said.
Hexagon Mining vice president – APAC Simon Stone similarly praised Brown in a LinkedIn post after the awards, saying she was “an incredible example of how personal commitment and energy can have a disproportionately positive impact on the world”.
The Sanjiv Ridge project didn’t just involve the design and build of the mine, but also provided support for the local Marble Bar Primary School.
Brown championed two programs while working with the school: Teach Learn Grown (TLG) and Helping Hands.
These programs produced tangible results, with 50 per cent of students demonstrating an improved positive attitude towards school, and 100 per cent of students reporting the belief that they were better at maths after the TLG program.
Brown made sure to support the community and her own teammates when working on both mine projects.
The making of great mines starts behind the scenes, and the Project Lead of the Year award seeks to recognise those individuals who work to lead site projects to a successful outcome.
The award is an update on the previous Mine Manager of the Year, having removed the requirement that nominees must hold the title of mine manager to be considered.
The deserving winner for 2022 was Stacey Brown, general manager –projects at Atlas Iron.
Brown is an experienced mining executive and oversees an expanding project team at Atlas Iron. She is responsible for a pipeline of new projects, including two new major mines, the Sanjiv Ridge and Miralga hematite iron ore mines, both of which celebrated first ore during the height of the COVID-19 pandemic.
Sanjiv Ridge (formerly Corunna Downs) is located approximately 240km from the Utah Point stockyard at Port Hedland, WA. The operation is a multipit blending operation.
Miralga mine is an extension of the completed Abydos Mine and is
located close to 100km from the Utah Point stockyard.
But these projects were not Brown’s first foray into large mine operations. She had worked as project manager on the $10 billion Roy Hill project in the Pilbara prior to joining Atlas.
“(The Roy Hill project) was a highlight of my career, and I take great satisfaction in being part of mining operations that create investment, jobs and wealth for Australia,” Brown said.
At Atlas, Brown oversees all stages of project development, from prefeasibility to site construction, and
Construction superintendent/ registered manager for the Sanjiv Ridge project Scott Fulcher said Brown provided huge support in dealing with direct reports, contractors and other Atlas staff.
“I have great respect for Stacey in the way she conducts business inhouse and with other stakeholders,” Fulcher said.
“Stacey has a very pragmatic approach. She is open to and encourages all ideas from her team and supports them to make decisions.”
Brown was also integral in establishing the joint partnership with Indigenous business East West Pilbara (EWP) for the Miralga mine. This partnership also earned Atlas Iron the Indigenous and Community Engagement award. AM
The winner of the Safety Advocate of the Year award has a very simple motto: It’s okay not to be okay. It’s okay to get help.
Nigel Gould, a Rio Tinto plant operator, has been a fierce advocate for men’s mental health since his first days as a fly-in, fly-out (FIFO) worker, and dedicates his time to different charities in order to help as many people as he can.
The Safety Advocate of the Year award recognises an individual who is committed to ensuring safety – either for an individual site or company or for the mining industry as a whole.
It’s clear that Gould makes an effort to ensure everyone’s safety, whether they are an individual or part of a larger company.
“In mining, you’re in a cab for hours and then in your donga and it can be really lonely. Men are sometimes not the best at communicating and it can get bad fast,” he told Australian Mining
“So I just try and get people to talk, and I’ve been fortunate to save a couple of lives just by talking to people.
“I’m no expert, all I do is listen and not judge. But sometimes that’s all someone needs.”
Gould has been an ambassador for Movember, a charity aimed at raising awareness for men’s mental and physical health, for over a decade.
“It’s not just men’s mental health that Movember focuses on but things like prostate and testicular cancer, too,” Gould said.
“It helps men to be aware of themselves and get those muchneeded check-ups.”
In an effort to raise more awareness for Movember, Gould sat for a portrait for the esteemed Archibald Prize.
The Archibald Prize is awarded annually to the best portrait, “preferentially of some man or woman distinguished in art, letters, science or politics, painted by any artist resident in Australasia”, by the Art Gallery of New South Wales.
The portrait captured Gould’s character, mining experience and mental health advocacy.
“The portrait is the whole story of my career involvement,” Gould said.
“You’ve got the Royal Flying Doctor Service, the Movember big mo, the big wad of money because it’s
not all about the money, even though that’s at the forefront of a lot of people’s minds.
“There’s a lot of meaning in the portrait.”
Along with operating a plant, Gould is an active peer supporter, providing a sympathetic ear to workers struggling with mental health issues, and is passionate about training and coaching new mine operators.
As a direct impact of Gould’s work on mental health advocacy, Rio has implemented new measures in its
mine sites, including peer support groups, R U OK? Day events, afterwork events at FIFO camps and psychosocial risk registers.
The result is that more people are open to discussing the issues related to mental health as Rio continues to take a proactive approach to managing the issue.
Discussing his win at the Prospect Awards, Gould said it was “an absolute honour”.
“I’m very fortunate to be known around the mine sites as someone people can go to for help,” he said.
“Sponsoring this award is extremely important to us as it is an integral part of who we are as a company,” the company said in a LinkedIn post celebrating the awards.
“Safety is our top priority here at Flexco – from ensuring the staff making our products go home safe every night, to the people who work with our products every day on hundreds of sites around the world.” AM
REAL-TIME INSIGHTS FOR BELT CLEANERS AT YOUR FINGERTIPS
Location of installed cleaners across your operation
Belt conveyor system specifications
Belt cleaner engagement
Belt and cleaner run times
Urethane and carbide
blade wear
Abnormal event notifications
Tamper detections
Detailed maintenance logs
Scan to learn more.
Recognising a mine, company or project that has developed a unique mining solution, the Innovative Mining Solution award was presented to RattleJack Innovations for its SafetySpear.
The SafetySpear was invented in response to the ever-present danger of falling drill rods in underground mining operations.
Drill assemblies are necessary to the process of underground mining but are often left abandoned in blast holes. This creates significant risks to operators and equipment within the space above.
“The SafetySpear is a proactive approach to mine safety,” SafetySpear inventor Leigh Sutton said.
“There are a lot of mines we visit that don’t realise falling drill assemblies are such a problem and, in turn, we’re able to say to them that we can effectively and safely remove that danger for them.”
Drilling assemblies have the capacity to fall down following unforeseen system failures, resulting in a heavyweight and high-speed object falling onto an area that can potentially be populated by workers.
Sutton himself was almost injured by this hazard in 2014, setting in motion the conception of the SafetySpear.
The SafetySpear works by plugging drill holes quickly and inexpensively with a lightweight, high-impactabsorbing polymer system.
It has been purpose-built to activate on impact with any downward force. Its unique two-stage design decelerates the impact by blocking the hole with its flexible upper section, conforming to the shape and size of the available space.
This stops the falling hazard with minimal backward movement, which is a new method introduced to the underground mining sector.
“The SafetySpear is made up of two components, both made of different plastics and with different functions,
to work together to stop the drill assemblies,” Sutton said.
“The strong high-impact plastic is the triggering mechanism and the polyurethane operates with a braking effect, in that it slows the descent of the drilling assembly, containing it within the blast hole.
“We’ve moved away from the traditional measures, in that everything has to be made out of durable metals, because high-density steel wasn’t able to do what we need the SafetySpear to do to prevent an accident.
“The benefits exist outside of the effectiveness of the SafetySpear in preventing the incursion of the drill assemblies, in that they are also low-weight due to being made of plastic and durable because they won’t corrode.”
RattleJack took home the award just 18 months after introducing the SafetySpear to market. The SafetySpear has been used at the Fosterville gold mine in Victoria and Byrnecut Mining Australia’s Western Australian operations.
“It takes about two-and-a-half minutes to install the SafetySpear, which is incredible when compared to set-up and drying times of previous solutions and incredibly more efficient than the reclamation process of a potentially lost drill assembly,” Sutton said. “We have experience on these sites and with these operations, so we designed the SafetySpear with these experiences in mind.”
In talking about the award win, Sutton thanked the mines that had given the SafetySpear a chance and had since achieved significant results.
“Thanks to everyone for all the support, to the true believers –Fosterville Gold Mine, Murray Engineering and Byrnecut Mining –who were willing to take the difficult road to bring such an out of the box idea to fruition,” he said.
“The SafetySpear will silently save someone’s life and they won’t even know it.
“They will go home safely to their family and that, my friends, is what we all want.” AM
Showcasing leading technologies, ground-breaking innovations and transformative solutions set to change the future of mining, Austmine 2023 Conference & Exhibition features:
100+ Exhibitors | 1200+ Delegates | Plenery Sessions & Panels
Workshops & Networking | Collaboration Laboratories | METS Tech Talks
Meet the Miners | Industry Leaders’ Awards & Dinner | Plus more!
In partnership with the South Australian Government, Copper to the World kick-starts the 3-day program, showcasing leading copper voices from Australia and globally.
For more information and to purchase your delegate pass visit: austmineconference.com.au
Principal Sponsor
The Mine Project Success of the Year award was another new category for 2022.
This award recognises a significant engineering and/or contract mining project that has been undertaken on a mine site. The project must have had a measurable improvement on the site, such as increasing safety, greater returns or a reduction in overall costs.
Roy Hill took home this award for its wet high-intensity magnetic separator (WHIMS) plant expansion project.
At Roy Hill, the use of cutting-edge technology and innovative thinking is creating a more predictable and efficient mining operation that is safe and sustainable.
The pioneering of the WHIMS plant in 2019 allowed capture of high-grade ultrafine iron ore units that would otherwise have ended up as waste.
When the original WHIMS first processed ore in December 2019, Roy
Hill was the first Australian iron ore company to use magnetic separation in a hematite mine at that size and scale, reducing waste and increasing production by approximately four million tonnes per annum.
Roy Hill has since expanded the plant to include two-stage treatment via magnetic separation and a spiral building to recover misplaced fines and high-grade ultrafines from the +125um size fraction via gravity separation.
WHIMS expansion plant (WHIMS 1.5) opened in April 2022 and is painted pink in support of breast cancer research.
As part of the contract, three new separation building units were provided, each containing stack-sizer screens, medium-intensity and wet highintensity magnetic separators and a cyclone cluster.
Capturing high-grade ultrafine material that would otherwise end up as tailings, the WHIMS plant reduces
waste and provides additional shipped ore without increasing the volume of material mined.
Construction and engineering services provider Civmec carried out the greenfield construction package at the site, saying the company was “delighted” to secure the project.
“The project combines multi-year maintenance works along with two projects within our newly formed Maintenance and Capital Works –Resources and Energy area,” Civmec chief executive officer Patrick Tallon said.
The WHIMS expansion project has had a positive impact on Roy Hill’s environmental and economic position by adding flexibility and increasing capacity.
Now fully integrated into daily operation, Roy Hill is looking at more ways to use the same technology to extract material from other waste streams, as well as the existing tailings storage facility.
“We want to further improve operational performance and reduce our environmental footprint,” the company said in a statement.
This was not the first time Roy Hill’s WHIMS expansion project has been recognised at the Prospect Awards, with the project having won the Minerals Processing of the Year award in 2020.
Speaking on the win at the 2022 awards night, Roy Hill commended not only its own team, but also fellow Hancock Prospecting Group companies that were also recognised at the awards.
“Congratulations to everyone involved in this project, and congratulations to our fellow Hancock Prospecting Group company Atlas Iron on their awards,” the company said in a statement following its win.
“The award acknowledges our integrated planning and scheduling transformation and the work done as part of our WHIMS plant expansion.” AM
Epiroc’s total focus is on helping you solve just one problem - how to move material through the value chain as quickly, cost-efficiently and safely as possible. We do this with world-class machines, aftermarket spare parts and services, and our ever-increasing digital capabilities. The growing Epiroc family offers a full suite of state-of-the-art digital solutions within telematics, situational awareness, integrated planning and system integration. Whether the task is big or, small, Epiroc provides flexible solutions to support your operation.
epiroc.com/en-au
The Outstanding Mine Performance award merged the Coal Mine of the Year and the Hard Rock Mine of the Year awards of past years into a single category.
It seeks to recognise a rock mine that is performing well and has carried out an innovative project, partnership, initiative or program.
This was Kestrel Coal’s first win of the evening, before also taking home the esteemed Australian Mine of the Year award.
For close to four years, Kestrel has steadily improved its longwall mining operation efficiencies, from longwall move to reaching first one million tonnes of coal in a new longwall block.
Kestrel believes its strong operational performance is built on confident and capable leaders and teams.
To that end, the company recently launched its Unleashed leadership program, which aims to strengthen operations by investing in the strength of its people.
The 12-month program contains nine development modules and is used as both an onboarding event and a refresher course for cemented employees.
It contains face-to-face workshops, self-paced online modules, peer-topeer virtual discussions and practical workplace assignments, all designed to invest in the company’s employees and redefine what is possible in longwall mining.
“Through capable and confident leaders, we’re determined to deliver our compelling vision and solid strategy to become the mining industry’s employer of choice,” the company said in a statement.
“The company where you can do your best work, receive support, learn and develop, and to realise your true potential.”
Along with the Unleashed program, Kestrel has invested time and coaching into its employees so they can achieve the Deputy’s Certificate of Competency for Underground Coal Mines.
“We are extremely proud of our people who have undertaken this important qualification and passed with flying colours,” the company said in a statement.
Kestrel has been the number one producer of underground steelmaking coal across Australia since 2019. The company recognised and celebrated 30 years of mining operations in 2022.
Kestrel’s safety performance continues to trend below the underground coal industry average for recordable injuries and high-potential
incidents, due in no small part to its commitment to understanding and empowering its people.
“We are quick to take action where we see a trend developing and swiftly implement our TARP (Trigger Action Response Plan) process to manage risk,” the company said in a statement.
“Not only is Kestrel committed to building a diverse and inclusive workforce; we are also committed to raising awareness of the incredible opportunities in our industry and helping to build the necessary skills to grow and succeed.”
Speaking of the award win, Kestrel said it was proud of its team’s commitment.
“Huge appreciation and thanks to everyone who has played their part in contributing to Kestrel being a highperforming mine, and a great place to work,” the company said in a LinkedIn post celebrating its wins. AM
In a world that seems to be constantly speeding up, heavy industries like mining are subject to rapid fluctuations in commodity prices. When that happens, they need to quickly ramp up production to meet the changing demand.
And that can mean acquiring new infrastructure to support their operations, just as fast. Responding to this kind of demand, SEW-EURODRIVE has introduced FleXeDrive, an industrial drive solution that sets new standards in drive technology, assembled and delivered in industry leading timeframes.
Choose success - start a conversation for your future, today:
1300 SEW AUS (1300 739 287)
For more information, scan the QR code to download the whitepaper:
The Discovery of the Year was one of the five new or updated categories making its debut at the 2022 Prospect Awards. This award celebrates a significant discovery at either a green fields or a brownfields site.
A greenfields site is an underdeveloped area within or outside of a city. It typically sits on agricultural land and offers uncomplicated and straightforward construction for mine sites.
Brownfields sites, which are classified as having been previously developed but are not currently in use, take longer to develop.
And Trigg took home the inaugural award for its Lake Throssell greenfields discovery.
Located in Western Australia, the Lake Throssell greenfields discovery is a multi-element deposit containing potassium, sulphur and magnesium –essential minerals needed for global food security and to help address climate change.
An economic scoping study on just 41 per cent of the 14.4 million tonnes of sulphate of potash (SOP) portion of the deposit indicated an initial mine life of 21 years producing 245,000 tonner per annum – making it a world-class project and a potential top-10 global producer.
Trigg founder, managing director and chief executive officer Keren Paterson said the company was “incredibly honoured” to receive the award.
“In the three years since first setting foot on Lake Throssell, it has never stopped surprising us with its grade, magnitude and potential to address global food security on a world scale,” she said.
“We would like to acknowledge the Traditional Owners, the Ngaanyatjarra Lands people, on whose traditional lands this discovery was made, and their role in this accomplishment, the technical and field crews who have worked tirelessly to make this discovery, and the award sponsor Bonfiglioli.”
Lake Throssell reported strong progress in Trigg’s June 2022 quarterly. The company said the season’s activities would include establishing new access tracks in preparation for aircore and water-bore drilling, with the results used to underpin an estimation of the project’s initial ore reserves.
Paterson said in the report that substantial progress continues to be achieved at project level.
“The brine sample program completed during the quarter paves the way for a bulk evaporation trial and production of the first SOP sample from Lake Throssell to determine processing plant design and for discussions with potential offtake partners,” she said.
“The outlook for the SOP sector has never been stronger given current geopolitical disruptions to global fertiliser supply chains.
“The opportunity for us to develop a new long-life, environment-friendly production hub in WA and play a pivotal role in helping meet the challenges of global food security has never looked more compelling.”
A heritage clearance survey was also conducted with the Ngaanyatjarra community in 2022 to clear the planned fieldwork and cover proposed geotechnical studies as part of the Lake Throssell prefeasibility study.
The project also marks a new Australian industry by extracting
minerals from brine, which can be done using the abundant solar energy. This means there is no open pit, rock waste dump or tailings storage facility.
This new industry will create 250 construction jobs, half of which are permanent, and features agreements and strong relationships with three Native Title claimant groups.
Very few of the deposits found at Lake Throssell are found globally, making the greenfields discovery especially deserving of the Discovery of the Year award. AM
The Lifetime Achievement Award is proudly sponsored by
The Lifetime Achievement Award recognises an individual who has contributed to the Australian mining and minerals processing industries throughout their life. It is the most prestigious individual recognition award of the program.
Determined through recommendations made by the judging panel, the 2022 award was presented posthumously to Ron Sayers.
Sayers passed away last year after a long battle with health issues.
Sayers founded mining services company Ausdrill with a single
drill rig back in 1987. From this humble beginning in his hometown of Kalgoorlie in Western Australia, Sayers grew his business into a billion-dollar ASX200 global mining services company, now the Perenti Group.
Accepting the award, Sayers’ nephew Mark Swiderski said his uncle was passionate about his employees and fostering an outstanding workplace culture, creating an environment where people enjoyed going to work and looked out for each other.
“Ron perfected the art of the deal, applying principles in work as he did in life,” Swiderski said.
“He respected everyone, he acknowledged others who were experts in their respective fields.”
Sayers retired in 2018 after 30 years at the helm of his business.
Speaking of his retirement, thenAusdrill chairman Ian Cochrane said Sayers had left “a great legacy that we will continue to build on in the years ahead”.
Kalgoorlie-Boulder mayor and former WA Resources Minister John Bowler led tributes for Sayers following his death, saying he left a massive legacy in the mining industry.
“I’ve known Ron Sayers all my adult life and I’ve watched him go from
being a mechanic on the Golden Mile to the head of one of the world’s biggest drilling companies,” Bowler said.
“I think Ron Sayers’ biggest legacy is the workers who worked for him. He was very loyal to them.
“He never forgot where he came from.”
In a 2018 interview with the ABC, Sayers discussed how he transitioned from working as a motor mechanic on the Great Boulder Golden Mile, now part of the Super Pit, to selling mining equipment.
“I was selling equipment to a mining contractor here in Kalgoorlie, and inside a couple of years he’s bought five or six machines but – more importantly – he had three Ferraris,” Sayers said.
“I thought to myself, ‘there’s got to be more money in using them than selling them’.
“So I hocked my house and bought a second-hand rig myself and grew the company from there.”
Sayers considered his involvement with the Super Pit to be his biggest achievement.
“We started there in 1987 with a single drill rig and we’re still there more than 30 years later, with an excellent relationship with the company and I’m very, very proud of that,” he told the ABC.
In a LinkedIn post announcing his death in 2022, Ausdrill called Sayers a “remarkable character”.
“(Ron had) unwavering focus turning Ausdrill into a global contract mining provider,” the company said in the post.
“Everyone across Ausdrill will remember him for his colourful stories and never being too busy to stop and have a chat, and of course, the world’s best potato peeler.
“Beyond Ron’s very successful life in business, he had a love for horse racing and having a good time, but most importantly for his family. His wife Lyn and his family meant the world to him.”
The WA Mining Club also expressed “deep sadness” at Sayers’ death. That sentiment was echoed by WA’s Chamber of Minerals and Energy, which said Sayers was a regular “fixture of the Goldfields mining scene for decades” and his pathway from apprentice mechanic to Ausdrill “shows what is possible” in the state’s mining sector. AM
– 305 tonnes payload capacity, four pass match loading with the R 9800
– Fast cycle times, specifically in large deep pit applications thanks to its high horsepower to weight ratio
– Backed by years of experience, structurally designed and built to last in extreme conditions
– Excellent serviceability to deliver maximum uptime with easy access to check wear components
– Enhanced operator comfort through ergonomic cab and superior front suspension system
Crushing and screening processes are highly mechanical, consume large amount of energy, and result in tremendous wear and tear on machinery.
The best gear for this arduous work must be reliable and robust, offer cost and production benefits, and be safe for operators and on-site personnel.
Rapid Crushing Group has a straightforward ethos to meet these criteria: achieve efficiency, productivity and cost savings by providing custom-made plant and equipment that is specifically tailored for project requirements.
“With operations in Maddington (WA) and Mackay (Qld), we specialise in the crushing and screening of all types of material, offering a range of custom-built fixed, modular and tracked plant and equipment,” Rapid Group’s general manager – crushing, Frazer Hayes told Australian Mining.
“The Rapid Crushing Group consists of three main businesses: Rapid Crushing and Screening Contractors, Rapid Dam Contractors and Irvine Engineering.”
Rapid Crushing and Screening Contractors, a WA privately-owned company, began operations in 1978 as Irvine Engineering. It initially serviced and repaired mining equipment before taking on the role as a crushing and screening service contractor.
“Over this period, we have built up a considerable amount of industry
experience and good faith,” Hayes said. One of the key motivators for principal Neil Irvine to enter the contracting area came when he found he could substantially modify imported machinery to make it better suited to the hot and dusty conditions of Australian mine sites, where so much crushing and screening takes place.
Rapid prides itself on the ability to crush various types of material, in sizes from 1m to less than 10mm.
“The company specialises in purchasing new plant and equipment before completing significant in-house modifications,” Hayes said.
“Our aim is to ensure the machinery meets the rigours of Australian conditions, with safety and production enhancements at the forefront of all the updates and changes we complete on our machines.”
All in-house modifications are completed by a team of highly knowledgeable staff at Irvine Engineering.
Rapid specialises in various types of crushing plant and equipment, including fixed crushing circuits, modular crushers crushing circuits and track crushers, with jaw crushers, cone crushers and impact crushers all featuring in the fleet.
“Our core business is in supplying modular, electric-powered crushing and screening plant, which we believe leads to the most cost-effective solution for our clients,” Hayes said.
“Modular plant is characterised as servicing mid-range projects in the order of five-to-seven-year duration
and is suited to campaigns of more than 500,000 tonnes, where re-location during the term of the project is not required.”
This type of plant is often configured with Metso Outotec C125 or Svedala 1208 primary jaws, with either Cedarapid MVP 450 or 550, or Metso Outotec HP300 or HP500 cones, utilising Eljay screens. In two- or threestage configurations, these machines will crush up to 800 tonnes per hour.
The modular plant is electric-powered by generator sets with switchboards. They must be placed on concrete foundations, with extensive wiring and linking up required, as they rely on conveyor systems and stacking units.
There are considerable benefits to utilising modular crushing plant, with set-up costs offset over time – ideally periods extending beyond 18 months –as higher volumes of crushed material drive the operating cost per tonne down and create cost efficiencies.
“The modular plant is inherently flexible and can be modified or changed to suit the client’s requirements,” Rapid Group’s business development manager Bernard O’Sullivan told Australian Mining.
“Often a client requires a particular solution, only for the scope of the project to shift. And we have the capacity to increase the number of conveyors or screens in use, essentially
re-arrange the plant in a short amount of time, and away we go again.”
Rapid’s purpose-built mobile track-mounted crushing circuits are best suited to smaller crushing campaigns, up to 500,000 tonnes or shorter durations.
The smaller modules in either a twoor three-stage configuration will crush 300 tonnes per hour, while the larger modules have the capacity to crush up to 600 tonnes per hour.
These self-powered mobile crushers and screens feature in-built diesel
engines and hydraulics, which means they are not reliant on generator or grid-based power. They are easily transported on low loaders and are commissioned with remote controls, enabling straightforward loading and unloading, as well as on-site positioning and set-up.
“The key benefits of the track-mount crushers are their ability to be quickly mover and repositioned,” Hayes said.
“If you have a crushing campaign where there may be multiple stockpiles of ore or feed material placed in a particular area or series of sites, it’s more cost-effective to move the crushing plant to the location of the material.
“We own two Johnsson L160 mobile tracked jaw crushers, the biggest available for hire in Australia, with availability on each side of the country.”
These machines weigh in at nearly 200 tonnes and are regarded as industry-leading equipment. They are powered by Cat 455kVA dual-power generators, perform their work with a Metso Outotec Nordberg C160 jaw crusher and have a feed opening of 1600x1200mm.
The high-capacity machines are ideal where a large amount of work is needed
in a tight timeline, giving a high level of output with cost-efficient productivity.
Mobile track crushers are suited to confined areas and where there is a need to move the plant across short distances or to nearby sites.
“Many of the modifications we make to our machines are completed with the safety of our personnel in mind, and this includes configuring access platforms, railings, guarding, upgraded pull wires for emergency stopping,” Hayes said.
“We set up our plant so that it is as low to the ground as possible, because height inherently makes machinery less safe, and we also attempt to keep componentry neat and tidy and accessible for ease of cleaning.
“All our modifications strictly adhere to all relevant safety standards.”
The company supports many Tier 1 miners, providing additional crushing capacity when their machines are offline due to scheduled maintenance or other unforeseen events.
“With an extensive fleet of screening and crushing plant and equipment, Rapid Group specialises in maintaining the capability to operate anywhere in Australia, and in some of the most remote locations and harshest operating environments,” Hayes said. AM
With its new Premiertrak 760, Powerscreen has manufactured one of the largest mobile jaw crushers on the market.
And Lincom is playing an important role in getting this big machine onto Australian mine sites.
As Powerscreen’s exclusive Australasian supplier, Lincom only recently commenced taking orders for the Premiertrak 760. But technical sales manager David McDermott said it’s already attracting plenty of interest.
“We initially ordered two Premiertrak 760s and both sold within weeks,” he told Australian Mining. “So we ordered another two.”
The Premiertrak 760 jaw crusher, fitted with the Terex Jaques JW55 single-toggle jaw, is a single toggle chamber powered via a direct drive system. This means the machine is more fuel efficient and requires less engine load to operate, unlike the less fuel efficient hydraulic-driven hydrostatic versions currently offered in the market.
As a result, the Premiertrak 760 is a cost-saver and a game-changer for crushing contractors, quarry and mining operators alike.
A 10m3 hopper with hydraulically folding sides and a wedge clamp system enables faster set-up times, while the jaw crusher features a vibrating pan feeder connected to an independent pre-screen that provides essential removal of fines material before it reaches the chamber.
McDermott said the Premiertrak 760 was developed in response to contractors and quarry operators looking for a larger mobile crusher.
“Increased feed size is one reason, increased tonnage is the other,” McDermott said as to why operators are choosing the Premiertrak 760.
“It’s the feed size the machine can handle and then it’s the throughput, the volume it’ll crush. You can open up the jaw to 225mm or you can close it in to 75mm, otherwise known as the closed side setting (CSS).”
The ability to alter the CSS enables the machine to support varied feed sizes and better align with the throughput capacity of the next mineral processing machine in the chain.
McDermott said the main objective for operators is to reduce rock size with the fewest machines possible.
“The more machines you use, the higher the cost,” he said. “So the whole idea is to try and reduce material size using as few machines as you can.
“That’s why the bigger machines come into play, because they can take
the bigger feed. You can feed them more; you can close them up tight and they’ve got bigger engines for pumping bigger throughputs.
“This does away with having to double-handle everything. So instead of having two jaws, one wide open and the second closed tighter, you’re using one machine.”
The Premiertrak 760 also comes with Powerscreen’s Pulse telemetry fleet management platform, which McDermott said is a huge bonus.
“Pulse telemetry is a remotemonitoring service,” McDermott said. “So when a machine is running, we can log in and see the time the machine started that morning, we can see what fuel it’s running at and we can monitor the engine loads.
“We can be ahead of the customer and alert them of any faults ahead of time and be proactive.”
This is not only critical for minimising failures and downtime, but also for performance optimisation.
“(Through the Pulse telemetry system) we can see whether a machine
has been working for the whole day or whether it’s been idling at all,” McDermott said.
“A contractor will have someone on the ground doing the crush and they’re supposed to try and achieve a certain volume. It could be 2000 tonnes per day, for example. If they don’t meet that, the worker might attribute it to an underperforming machine.
“Now we can see what time they started and finished and whether there were pauses throughout the day. We can now really see what’s going on on-site, and so can the customers.”
This leads to improved productivity, with employees aware that their operation is being monitored throughout the day. But this is not a ‘big brother’ scenario, with Powerscreen or Lincom only observing the Pulse telemetry system if there’s a problem.
“If the customer phones up and says the machines are only doing, for example, 800–1000 tonnes a day instead of 2500 tonnes, we can have a look and show them what the machine has done each day for the last week or month,” McDermott said.
Powerscreen or Lincom can then print them a report, providing a physical performance breakdown. The customer can also do this themselves.
McDermott said the Pulse telemetry system is “the way forward” for the mining industry, with all new Powerscreen machines fitted with the platform as standard.
The Premiertrak 760 is the next evolution in crusher productivity, with the machine’s versatility diversifying throughputs and driving down costs.
With a telemetry platform to boot, customers can manage their fleets more accurately and scrupulously, enabling better performances. AM
THE
There is much that needs to be crushed and screened on a mine site.
The process is a highly mechanical one that requires robust, reliable and safe machinery that can handle the tremendous amounts of stress that occurs through all phases.
And that’s where the Tutt Bryant Group comes in.
With an experienced and dedicated workforce in nearly 30 locations across the country, the Tutt Bryant Group provides equipment sales and hire, spare parts, service and engineering solutions to meet the challenges of Australia’s tough mining conditions.
As part of Tutt Bryant’s lineage and ethos, its people and its honest dealings reinforce how the group conducts its business, enabling continued growth and development of all stakeholders.
This philosophy is expressed clearly in the ‘Tutt Bryant Way’, which is embraced by all employees and encapsulates the company’s core values of teamwork, family, integrity, versatility and enterprising. It is upon these beliefs
that all activities associated with the group occur.
As a multi-franchise distributor of earthmoving and construction equipment, Tutt Bryant Equipment (TBE) specialises in sales and aftersales support.
“We have a plethora of fixed and mobile plant and equipment products within our portfolio, and exclusively represent a number of industry-leading global brands in Australia, including Metso Outotec and Jonsson,” TBE’s business development manager Paul Doran told Australian Mining.
Since 2012, TBE has been the official Australian distributor of Metso Outotec for mobile crushing and screening equipment, including the Lokotrack, Nordtrack and NW Rapid product lines.
TBE is one of Metso Outotec’s largest Lokotrack distributors globally, and the extensive product range includes mobile cone crushers such as the LT200HP, LT220GP, LT200HPX and the LT300HP. These are all high-capacity, powerful and versatile machines designed for reliable aggregates contracting and recycling applications.
The range also includes the LT220D and LT330D units, which feature an innovative combination of high-performance cone crusher with integrated triple-deck screens on the same chassis.
TBE distributes Metso Outotec’s mobile impact crushers, including the Lokotrack LT1110 and the LT1213S, which is a high reduction ratio crusher and screen configured on the same chassis.
As for mobile jaw crushers, TBE distributes the conventional Lokotrack LT106 and LT120 units, and the hybrid e-power solutions for use in quarry operations of varying size, including the LT120E and LT130E, along with the improved Lokotrack LT150E, the powerful industry workhorse with the largest feed opening of 1400x1200mm.
TBE distributes the Lokotrack LT7150 mobile VSI crusher, plus the Lokotrack ST2.3 and ST2.8, a highcapacity hydraulic mobile screen for scalping sticky material.
It also features a range of highcapacity and precision mobile screens designed to screen crushed rock, sand
and gravel, including the Lokotrack ST3.8 and ST4.10, and the ST4.8 that is designed for compact and closed circuit crushing in quarries and on construction sites.
“Most of the Lokotrack ST range of screens are available as e-power versions and can be operated using either a diesel engine or with built-in electrical motors,” Doran said.
“The electric motors can be powered by an external electric network or, with customisation, by a hybrid Lokotrack crusher equipped with an onboard diesel generator.
“Mining operators running screening processes with external electricity or with a single diesel engine can result in significant cost savings.”
To make the crushing and screening process as efficient and smooth as possible, Lokotracks can be monitored via Metso Outotec’s IC automation and controlled remotely with wireless Metso Outotec ICr from the cabin.
“The operator loading the machine can monitor its performance from the cabin utilising a suite of diagnostic information,” Doran said.
“There is also a powerful fleet management system which provides clients with a range of real-time data, enabling them to monitor equipment performance and fuel use, as well as consider longer-term maintenance scheduling, together ensuring productivity and cost efficiencies and enhanced safety outcomes.
“The benefits of real-time machine data flow and capture for operators is critical, as they can make safe and informed decisions while undertaking a crushing and screening campaign. And with the ability to access historical information, they have a powerful tool for developing a precise profile of costs and maintenance requirements when bidding on future projects.”
As the Lokotrack range is inherently mobile, featuring track-mounted
configuration, they are easy to move within a production site or, if required, to transport between sites on low-loaders.
With extensive expertise and a strong familiarity with the Metso Outotec portfolio, TBE recently added a new line of products from Jonsson, a Swedish subsidiary of Metso Outotec.
Jonsson only makes diesel-electric equipment and its version of metrics goes into more detail, allowing the operator to monitor the performance and the temperature of some components of the crusher via live data.
Jonsson’s mobile crushers are for the bigger end of town, from 150 tonnes and upward, so they are not going to suit every application, but they will certainly do the job for mining clients who are after a large mobile jaw crusher for their operation.
Earlier in 2022, TBE added Metso Outotec’s fixed plant crusher wears, spares and service support to its extensive and growing range in Australia.
TBE can now service the fixed plant aftermarket sector effectively and efficiently, offering large quarry producers the same level of service and support that mobile plant and equipment customers have experienced for some time.
“We provide spare parts, servicing and maintenance for Metso Outotec’s fixed and mobile plant and equipment across Australia and Papua New Guinea,” Doran said.
“There is a significant amount of construction activity occurring across Australia, with high levels of spending on major infrastructure projects, and while TBE supplies the traditional
mining states such Western Australia and Queensland with mobile plant and equipment, we are also providing solutions to assist the major road and rail projects occurring in Victoria, Tasmania and New South Wales.”
In addition to capital equipment sales, TBE supports its customers by providing technical support, wholeof-life maintenance support and breakdown repairs.
With a national reach for its genuine spare parts and consumables, TBE provides the necessary protection of important capital investments, ensuring there is no compromise on safety or performance. The company is committed to reliable service support to prolong machine life, reduce downtime and increase productivity.
TBE offers an extensive range of services, including fixed-price service, local workshop service and repairs. Its factory-trained technicians provide skilled and knowledgeable repair assistance across Australia and the Pacific.
TBE’s fixed-price service program is designed to allow the provision of budgeted and predictable maintenance costs while, at the same time, minimising downtime and creating a lower lifetime cost for machinery maintenance
It also offers flexible business finance options, either to assist with smoothing out cashflow or to prepare for future projects.
“Regardless of the type of operation, whether it is gold, coal, lithium or other rear earth minerals mining, quarrying or large-scale construction, TBE provides crushing and screening solutions that can be tailored to the client’s specific requirements,” Doran said. AM
Minerals and Primero worked together to design an improved version of the PGX1000.
It was designed to be more robust and easier to manufacture at a lower cost. Weir Minerals looked at the reliability of the equipment and the kind of maintenance processes that Primero was going to implement on-site and included several unique design solutions.
Atlas Iron general manager of projects Stacey Brown said the company was very happy with the end result.
“The project was a huge success,” she said. “It was delivered safely on budget and on time – slightly ahead of schedule.”
Primero’s operations and maintenance (O&M) performance model was developed to help break into the highly competitive crushing and screening sector.
Primero’s project manager Brett Mastaglia told Australian Mining that the team goes above and beyond to find the right plant solutions to deliver on safety, cost and reliability.
Primero’s O&M model provides project-specific operations and maintenance services to help companies navigate the transition from project inception and design through to construction and operations. It also offers operational readiness services to help clients with the development of systems and processes to take a project from design and construction to operations.
Highly trained engineering, construction, production, metallurgical, maintenance and planning staff members are available to assist with planning, implementation, rampup, turnaround and steady-state production situations.
Powering this offering is the PGX1000 crushing plant. Designed to be as modular as possible, the PGX1000 uses Weir Minerals crushing components and Primero’s own designs to meet the quality requirements of the mining industry.
“The modular plant can be tailormade to achieve efficient outcomes from 1.5 million tonnes per annum modular
beneficiation process plants through to 15 million tonnes per annum large crushing and screening facilities across a range of commodities,” Mastaglia said.
“It was born from necessity and improved upon through our knowledge of the industry and the operating requirements it would be working in.”
The company’s flagship plants can be scaled up or down depending on the client, material and throughput requirements.
Mastaglia said the company prides itself on its group’s vertical integration.
“We have teams of engineers to handle the design side of projects, a highly capable construction division to handle the installation, and our operations and maintenance team operates our own assets as well as clientowned assets,” he said.
“It means we can self-perform all aspects of the project like a true EPC (engineering, procurement and construction), which is rare in the market. We can manage the whole project process from the very inception.”
This has allowed Primero to offer a ‘build, own, operate’ package, to help its clients by increasing flexibility and derisking production. The company will often design and deliver the crushing plant to a site, have its own staff handle the operation and take the plant away when it is no longer required.
The contracting model for a crushing and screening plant is usually on a per-tonne basis, which is low risk for the client and can be scaled as needed. Primero can also offer other contracting
models depending on what suits the client’s needs.
“If there’s a production shortfall due to plant availability at a site, the mining company can call on us to deliver a fit-for-purpose and compliant crushing and screening plant to fill in the gaps,” Mastaglia said.
One example of the PGX1000 being deployed with a build, own, operate model was at Atlas Iron’s Miralga Creek Project in WA.
Primero was tasked with designing, building, commissioning and ramping up operations of a processing facility that delivered the tonnes and quality that Atlas needed. The project only had around 16 weeks of lead time, and teams from RCR Mining Technologies, Weir
Primero plans to develop its plant offering, with a PGX3000 currently in development. The system will be capable of processing up to 3000 tonnes per hour and will be modular in design, following the same principles that led to the PGX1000’s success.
Mastaglia said the company was also excited to develop processes and solutions to re-monetise potential saleable product that has already been processed as part of a mining operation.
The company plans to utilise its modular beneficiation plants and is working with other local businesses to further develop these value propositions.
“The breadth of our team’s capability is key to the delivery of these projects – there’s unlimited potential,” Mastaglia said.
“We strive to be the industry leader in the global resources industry, operating assets across the mining and processing sectors, making use of our turnkey solutions and extensive expertise.” AM
MODULAR CRUSHING PLANTS ARE HELPING PRIMERO DE-RISK THE RAMP-UP PROCESS AND DRAMATICALLY CUT DOWN ON CAPITAL EXPENDITURE.PRIMERO’S CRUSHING PLANTS CAN BE SCALED UP OR DOWN. PRIMERO OFFERS A ‘BUILD, OWN, OPERATE’ PACKAGE TO HELP ITS CLIENTS INCREASE FLEXIBILITY.
“The jaw gyratory crusher has come to us as part of our acquisition of thyssenkrupp’s mining business,” he said.
“The machine is a great offering in situations where capex (capital expenditure) or space is tight, and the customer needs to maximise crusher throughput.
“It’s a particularly good offering for underground mining applications – or potentially above-ground applications – where the customer is looking to minimise the amount of space they’re occupying.”
With a particular focus on the end user, FLSmidth designs most of its crushers in consultation with its customers, with safety also a key focus.
“All of our crushers, I can quite confidently say, are the most safety conscious of any machines in the same class,” Nicholls said.
“They’re also the most maintainable. We’ve got a lot of features specifically for those having to operate and maintain the machines to ensure they can do their job as efficiently and safely as possible.
As a leading mineral processing original equipment manufacturer (OEM), FLSmidth’s crushing and screening offerings are extensive.
The company is among the leaders of the pack with its TSUV gyratory crusher, which has redefined crushing power and efficiency.
FLSmidth APAC regional product line manager – crushing Carl Nicholls said the TSUV gyratory crusher was specifically designed based on market feedback from Australian customers.
“The TSUV is the most modern gyratory crusher on the market,” he told Australian Mining. “It’s an ideal machine for the Australian market given our focus on safety and productivity.”
Unlike other gyratory crushers, which often require workers to position themselves underneath the crusher to perform maintenance tasks, FLSmidth’s Top Service (TS) range allows service and maintenance to be carried out from above.
With parts accessible from the top of the crusher, maintenance work is expedited, boosting availability and reducing costs.
To move with an ever-evolving mining market, FLSmidth reengineered the TSUV gyratory crusher rather than adding features to its previous model. The Mark V design has been improved and strengthened to enable greater crushing efficiency.
The TSUV generates at least seven per cent more speed and 10 per cent more capacity than prior models. The machine can handle up to 1500 kilowatts (kW) of power and deliver a throughput of up to 15,000 tonnes per hour.
Nicholls said the jaw gyratory crusher was another important asset in FLSmidth’s primary crushing range.
FLSmidth has a full range of jaw crushers suitable for applications where a gyratory crusher is not required. The OEM also has a range of raptor cone crushers, which recently received a facelift.
“We’ve recently given the entire Raptor range a birthday and refreshed all of the technology, so we’re very confident in saying that it’s the most advanced crusher of its type,” Nicholls said.
“We’ve put a real focus on safety and maintainability into the refresh of those designs, so it’s a product I’m really proud of.”
“Many competitors in the field are only focused on designing a machine that will crush rock to get tonnes out. We have that same goal, but we also really value our interactions with the client and ensuring that they’re going to be safe and happy working with us and our machines for 20–25 years.”
FLSmidth is also renowned for its screening capabilities, where it offers a wide range of vibrating, rotary, wet gravity and roller screens to suit almost every application.
The OEM understands the importance of reliable and durable screening technology, meaning all of its screening products are designed with productivity and efficiency in mind.
Boasting many years of in-house design experience, the FLSmidth screen range is extremely well proven in all conditions. And, again, the end user is at the centre of the design process, meaning screening products can be designed with individual equipment, functions and operating parameters in mind.
As a premier manufacturer of stainless steel, carbon steel, polyurethane, rubber and woven wire screening systems, FLSmidth also offers a comprehensive and innovative range of screen surface media to complement its screening machines.
The company’s ultimate goal is to implement its MissionZero mine and enable its customers to achieve net-zero by 2030. This involves optimising customers’ pit-toplant flowsheet.
A pit-to-plant flowsheet can’t be optimised without efficient crushing and screening technology. Luckily enough, efficiency is FLSmidth’s cornerstone focus. AM
It’s no secret that MACA is one of the most respected mining contractors in Australia, with a particular focus on metals and mining in Western Australia. Specialising in services such as non-process infrastructure, load and haul, drill and blast, material handling, and crushing and screening, MACA prides itself on its end-to-end capability, supporting clients through all stages of the mining process.
MACA Mining general manager Jim Rayner said the crushing and screening division is a critical component of the company’s offering.
“Crushing and screening adds important value to the mining business and goes hand-in-hand with a mining project,” he told Australian Mining “We have the design, earthworks, and construction capability, and we can operate the plant and transport the feed from the pit. All these capabilities work together.”
MACA’s crushing and screening division supports plants with throughput capacity of 1–12 million tonnes per annum, with contracts primarily in WA.
“We have proven to be competitive in all types of crushing projects – smaller mobile plants producing iron ore, road base and stemming, along with larger plants producing lump and fines for Tier 1 clients in the Pilbara,” Rayner said.
“We have delivered seven-to-10million-tonne-per-annum modular plants for Tier 1 clients. Modular plants are easy to construct with lower construction costs, as minimal concrete is required.”
MACA operations manager crushing
Asmir Kursumovic said clients choose modular plants because they are more cost-effective and quicker to build than static plants. This is especially important in an Australian mining sector that has ambitious productivity standards and performance indicators.
“Modular plants can be built quickly so clients don’t experience delayed waiting periods,” Kursumovic told Australian Mining
“They don’t have that cost of extra time and a multitude of construction contractors, which is an important consideration in the Australian mining industry where everyone wants everything done quickly.
“We treat our client relationship as a partnership. Honesty is key, so we share as much as we can with the client about our processes. They can contact us at any time, request something and we will do our best to deliver.
“Once you build that partnership, you build that trust, which is the best result for our clients and MACA as a service provider.”
Since COVID-19 arrived in early 2020, the Australian mining industry has been severely affected by supplychain disruptions, meaning lead times have blown out significantly.
Despite these issues, MACA Crushing has maintained its ability to deliver equipment on time and on budget, which is testament to the contractor’s proactivity and commitment to its clients.
“The biggest driver (of our speed of service) is not only having a fleet
available but also having spare parts on hand,” Kursumovic said.
“We also have our own transport division. So we have our own floats that deliver our equipment rather than us having to rely on a third party.”
When a WA iron ore miner recently required five jaw crushers to be delivered to site on a tight deadline, MACA was the only contractor that could deliver the crushers on time.
“We fast-tracked the order and had the jaw crushers to deliver that project,” Kursumovic said.
“With a capacity of 36 million tonnes per annum, the plant had five jaw crushers in a row being fed by loaders, all delivered safely and on time by MACA.”
The company’s crushing plant can also be designed and built with remote-monitoring capabilities, which can benefit a miner’s assetmanagement outcomes.
“Through remote monitoring, you can optimise the plant and detect why problems or faults are occurring,” Kursumovic said. “Sensors can monitor the wear of the equipment and alert when a replacement part is needed, minimising unplanned stoppages.”
Remote monitoring, according to Kursumovic, is the future of crushing in the mining sector.
“If a plant can be remotely monitored, it will save worker interaction with the machine, improving safety outcomes and optimise plant efficiency,” he said.
MACA’s increased remote monitoring focus has been inspired by the company’s safety ambitions.
“We will be relying on technology more and more to help us monitor, inspect and check our crushing equipment, so that we can reduce that human interaction.”
In reducing plant downtime, remote-monitoring technologies can also uplift plant productivity, ensuring
machines exceed reliability targets.
Having recently been acquired by Thiess, MACA has long-term aspirations for growth and will work with Thiess to leverage these opportunities to build capacity.
Another priority is engagement with Traditional Owner groups.
“Crushing is a great entry point for Indigenous businesses because of the low capital requirement,” Rayner said.
“MACA brings the operational and technical skills, while Traditional Owners have the client relationship and access to minor plant and trainees. So there’s a really good opportunity for us to establish Traditional Owner relationships to not only win and do work but also build the capacity and capability of those Traditional Owner groups.”
Rayner said MACA has a strong track record in its support and development of Traditional Owner businesses, which is a central focus of the company’s crushing and screening division. AM
WE HAVE PROVEN TO BE COMPETITIVE IN ALL TYPES OF CRUSHING PROJECTS – SMALLER MOBILE PLANTS PRODUCING IRON ORE, ROAD BASE AND STEMMING, ALONG WITH LARGER PLANTS PRODUCING LUMP AND FINES FOR TIER 1 CLIENTS IN THE PILBARA.”MACA’S CRUSHING PLANT CAN ALSO BE DESIGNED AND BUILT WITH REMOTE-MONITORING CAPABILITIES.
WHEN THEJO’S FILTRATION DIVISION WAS APPROACHED TO DEVELOP AND PROVIDE REPLACEMENT OF FILTER SPARES FOR A LEADING MINERAL PRODUCER IN SOUTH INDIA, IT ANSWERED THE CALL.
Furthermore, the membrane blowouts and repairs were puncturing the expensive filter cloth. The recurring damage to the PP filter plates forced the frequent removal and weld repairing of the same, leading to increased downtimes.
Maintaining a large stock of spare plates was not economically viable, so the plant decided to limit operation to one of the two presses and scavenge parts off the other as spares to manage the pressing production requirements.
• achieve the optimum output of the plant and equipment
• maintain safety and ease of operations
• maximise filter cloth life
• ensure a high percentage of machine availability for operations
• make reliable spares at economic prices
• have a long-term sustainable solution, which could deter the client from a major capital expenditure.
With these objectives, a detailed proposal for re-engineering and retrofitting project of the two filter presses was submitted to the plant.
The south Indian mine’s prime purpose was to utilise the slime deposits generated from its existing sevenmillion-tonnes-per-annum (Mtpa) screening plant.
To achieve the specified moisture level of nine per cent, a filtration plant of 233 tonnes per hour (TPH) was installed and operated.
The 62 chamber filter presses consisted of 31 polypropylene (PP) membrane plates, 30 PP chamber plates and two PP end plates.
The frame was constructed of end cast plates bound together by two metallic side beams on which the moving filter plates were positioned. The opening and closing were operated by a moveable hydraulic unit.
A bomb door discharge at the base facilitated the onward loading of cakes onto a discharge conveyor belt.
From the plant’s inception, the filter presses were bogged down with problems such as poor performance life of the filter cloth, frequent damage to the PP membranes, leakage of slurry at the mating surface of the membrane and chamber plates, and non-availability of critical spares.
These issues hampered the effective functioning of the presses.
Unprecedented damages to the PP membranes caused frequent punctures to the filter cloth, resulting in slurry leakage into the chambers and onto the mating surface of the membrane and chamber plates.
Due to the construction of the press, the load-bearing side beams were not deflecting in tandem during the closing,
locking and pressurising operation of the plates, leading to misalignment of filter plates.
This aggravated the damage to the PP filter plates, with the slurry and compressed air under high pressure, causing them to leak through the consecutive plate interfaces and creating deep grooves on the frames of the plate.
The leakage of iron ore slurry and compressed air was causing spillage around the equipment in the plant and was a serious safety hazard.
In early 2019, Thejo’s filtration division was approached to develop and provide replacement of the filter spares.
Based on a detailed study of the presses and plant operations, the engineers from the HIPO filtration division chalked up a detailed proposal with the objective of providing a solution that would:
A new PP combination plate was designed and developed to replace the alternate chamber and membrane plates of the press.
The new plate design fitted a rubber membrane on one side and fielded a chamber on the other.
A custom-designed HIPO rubber membrane was developed for flexibility and durability, while maintaining the rigidity.
The rubber formulations provide high tear strengths, high abrasion resistance and high tensile properties, and the replaceable rubber membranes ensured better sealing and higher life of the PP plates.
HIPO rubber diaphragms drastically reduced the possibility of any damage to the filter cloth and PP plates, thereby increasing the life expectancy of both these expensive parts.
In collaboration with a global manufacturer, a fabric to meet the life expectancy without affecting the filtration was specifically designed for the operation.
The sourcing, manufacturing, inspection and disassembling of the filter presses at the client’s site, along with shipping re-engineered parts, assembling retrofit parts, commissioning the press and establishing production to meet client demands, all coincided with COVID-19 lockdowns of 2020–21 but were nevertheless executed successfully.
The project of re-engineering and retrofitting the existing non-performing filter presses with HIPO-SSS system at the client’s plant was a great success. AM
Many companies offer miners different types of vibrating screens, along with the tools and services that go with them.
Australian Mining spoke to Wilm Schulz, the parts and service manager at Haver & Boecker Niagara, a leading provider of screening, pelletising and mineral processing plants and systems, about its Pulse Vibration Analysis Service offering.
What can you tell us about the Pulse Vibration Analysis Service?
It’s used to evaluate vibrating screen performance and provide recommendations. The service helps our customers achieve production targets, prevent unscheduled downtime and demonstrate sustainable improvements through online asset management.
The service program includes a complete vibrating screen inspection by a Haver & Boecker Niagara-certified service technician. Following the inspection, customers receive a pulse diagnostic report, which provides an
analysis of their vibrating screen and detailed recommendations.
What technologies make up the Pulse diagnostics tools, and how do they work?
Haver & Boecker Niagara offers a suite of diagnostic tools strategically designed to help measure the health and performance of vibrating screens, including Pulse impact testing, Pulse vibration analysis, and Pulse condition monitoring.
Pulse impact testing, also known as the hammer test or bump test, ensures screening equipment is properly tuned to avoid operating in resonance. Operating in resonance can diminish productivity, incur damage to vibrating screens and pose safety risks.
Prior to testing, Pulse sensors are placed on the vibrating screen in key locations. From there, a certified Haver & Boecker Niagara technician strikes the machine at key points with a dead blow hammer while the machine is off.
The sensors collect data, which is analysed to identify the machine’s natural frequency. Based on the results, engineers can adjust machine parameters to avoid resonance during operation. The program’s seamless
integration into the Pulse software provides opportunities for easier on-site impact testing.
Another diagnostic offering is Pulse vibration analysis, which is designed to examine the health of any vibrating screen by detecting irregularities that could translate into diminished performance, decreased efficiency, increased operating costs and imminent breakdowns.
With Pulse vibration analysis, up to eight wireless tri-axial sensors are placed in dedicated positions on the body of the vibrating screen and send up to 24 channels of data to a dedicated industrial-grade tablet the technician then uses to complete the inspection.
A pulse diagnostics report is generated with the technician’s recommendations that can be downloaded online in two report formats: the orbit report provides a visual of orbit and wave form; the tuning report extrapolates deviations between measurement points while providing recommendations based on balance, acceleration, stroke and speed.
Finally, Pulse condition monitoring was developed within the Pulse portfolio to monitor the health of vibrating screens using modern algorithms and
artificial intelligence. Unlike Pulse vibration analysis, Pulse condition monitoring uses permanently installed sensors to monitor equipment 24–7.
The system captures real-time information on monitored equipment and provides alerts via email when it detects the first sign of potential problems. It can also provide a forecast of the equipment’s dynamic condition in intervals of 48 hours, five days and four weeks.
How do Pulse diagnostics help operations address factors like downtime and costs?
Pulse diagnostics help to measure the health of vibrating screens in an operation. The data collected throughout these diagnostic procedures measures the speed, stroke and amplitude of the machine, as well as other data points.
This data is translated into technician recommendations that fine-tune equipment for optimal performance and to maximise output, as well as locate issues that could lead to larger repair costs or machine failure and unplanned downtime if not addressed.
Can you explain the before- and after-sales support that Haver & Boecker Niagara offers?
The Pulse diagnostic tools are a critical part of our comprehensive service process, PROcheck, dedicated to keeping customers’ operations running at peak performance.
It combines our expertise in diagnostics, processing equipment, screen media, original parts, rebuilds and upgrades, services, plants and process engineering to inspect customers’ screening processes in order to recommend best practices for processing proficiency. All recommendations are available before our technician leaves the site.
Additionally, we offer a three-year warranty program called Uptime on new equipment purchases.
Uptime includes a PROcheck consultation, parts inspection, equipment assessment and a screen media evaluation, resulting in a fully optimised screening operation.
Uptime covers a three-year warranty on non-wear body, shaft and mounting components, as well as thorough machine inspections and key component evaluations to increase productivity and efficiency within a mining operation. AM
HAVER & BOECKER NIAGARA OFFERS A TECHNOLOGY THAT ALLOWS MINERS TO EVALUATE THEIR VIBRATING SCREEN PERFORMANCE.PULSE VIBRATION ANALYSIS FROM HAVER & BOECKER NIAGARA ALLOWS MINERS TO EVALUATE THEIR VIBRATING SCREEN PERFORMANCE.
Safety regulations are rarely arbitrary. They are generally based on a history of reported injuries and fatal accidents caused by a set of circumstances that regulators and insurers deem dangerous enough to require explicit rules to prevent. But rules can vary between countries (and within countries) to the extent that the definition of what is safe and unsafe can appear subjective and, in some cases, can present more design and safety issues than the regulation is attempting to remedy.
A key example is the concept of ‘guarding by location’ – ie guarding that is the result of the physical inaccessibility of a particular hazard under normal operating conditions.
Machinery may be safeguarded by location if the distance to dangerous moving parts is greater than the prescribed safety distance, which varies by jurisdiction.
Most people readily accept that conveyors and other machinery require safety guards when positioned near workers or walkways. Guarding by location is the assumption that when hazards are positioned beyond the normal reach of a worker, they don’t require a guard. Yet they can still present a serious hazard.
By not requiring a physical barrier, guarding by location creates what can be considered an exception to the general requirements for the guarding of hazards in the workplace.
There are several hazardous locations that are beyond the normal reach of a worker when working or walking under or around elevated conveyors. These hazards are considered to be guarded by location, often found in or around nip points between the belt and return rollers or drive components such as pulley shafts, couplings, drive belts, gears and chains. Additional hazards from falling components may be inadvertently ignored if considered guarded by location.
Regulations usually stipulate the distance at which conventional barrier guards must be located. Some jurisdictions specify the hazard must be at least 2.1m from the work surface
Australia 2.7m
Brazil 2.7m
Canada 2500–2700mm (depending on province)
Europe Low risk – 2500mm; high risk – 2700mm
South Africa 3.5m
United States
2.1m
Any nip or shear point is considered accessible if it is located less than 2.7m above any floor, platform, goods, or materials. (AS/NZS 4024.3610)
Exempted from guarding requirements over 2.7m provided there is no circulation nor permanency of persons in [the] hazardous areas. NR-12 (Section 12.85.1)
From the floor or working platform. (CSA Standard Z432 [R2014] Safeguarding of Machinery)
Clear height under moving parts. (DIN EN 620 – Continuous handling equipment and systems – Safety and EMC requirements for fixed belt conveyors for bulk materials)
Any pulley or idler, which is 3.5m or more in height and therefore beyond an upward reach, may be regarded as being positionally safe and need not be guarded. (CMASA: Safety Around Belt Conveyors Guideline)
Guards shall not be required where the exposed moving parts are at least seven feet (2.1m) away from walking or working surfaces. (MSHA regulations in 30 C.F.R. sections 56/57.14107)
DISTANCE REGULATIONS BY COUNTRY (FROM MARTIN ENGINEERING FOUNDATIONS FOR CONVEYOR SAFETY, 1ST EDITION, 2016)
or floor; other regulations require greater distances.
By determining a general safe height for all locations, some workers may be safeguarded while others are not.
For example, taller employees (1.82m or more) can easily suffer an injury reaching up into a moving component that is 2.13m above the ground. Working above machinery that is considered guarded by location exposes workers to increased severity of injury if they slip or fall to a lower level.
The absence of specific global standards is a fundamental problem for conveyor designers. Without such uniform standards, equipment that is manufactured in one country to be installed in a second country may not be compliant for transfer or resale in a third country. The variation on standards from 2.1–3.5m is too great to assure global compliance.
The overall conclusion is that issues which allow or even encourage risky behaviours around conveyors – usually in order to maintain production or prevent equipment damage – are generally not negated by location or position.
Most regulations do not account for the potential build-up of spillage underneath the conveyor or in walkways, which can easily change the distance between the working surface and a hazard. It is also fairly common practice to deliberately collect a pile of material or fill a bin to gain access for service or inspection of an elevated component.
Using tools and methods that extend a worker’s reach while the belt is running is a hazardous activity that can contribute to serious – possibly fatal – accidents.
Exemptions such as guarding by location do not fully address the dangers explained here. As a result, rules defining the practice become ineffective as a safety measure, especially where belt conveyors are concerned.
Despite its acceptance in various regulations, the practice of calling moving components on conveyors ‘guarded’ solely because their installation is at least a specific distance from the worker(s) is an outdated concept and ineffective in application. It should be discontinued.
The logical solution is to simply install guards and baskets to protect
workers from lateral and overhead hazards, while still offering safe and easy access.
For maximum risk reduction, all nip points, shear points and moving or rotating components should be guarded, regardless of location or access. Many vendors can fabricate and supply guards of all types to fit virtually any application needed.
However, there is also no global standard for guard mesh sizes and mounting distance from the hazard. Most standards use a gauge to measure the distance, which varies by mesh size, but these gauges were typically designed for the machine
tool industry, where a worker is placing and removing work pieces from a machine.
The use of the gauge is not necessarily appropriate for bulk material handling, where the purpose of guarding is to prevent inadvertent contact with a hazard. Most guarding standards allow alternate approaches if the reasons are documented through risk analysis.
The small mesh sizes required by the tool when a bulk material handling guard is placed relatively close to a hazard greatly reduces the ability to inspect components without removing the guard, thereby encouraging guard removal for routine inspections.
It would be far better (and safer) to standardise on a few mesh sizes and mounting distances, allowing maintenance workers to build guards to a short list of materials, using standard mounting distances and eliminating the use of the gauges.
Despite its nearly global acceptance as a concept in industrial safety, the practice of guarding by location remains a particular problem for overhead conveyor applications.
It’s time to accept that as far as conveyors are concerned, guarding by location is a myth. As such, it’s a concept that should be abandoned in order to make conveyors – and those who work on and around the equipment – safer. AM
OVERHEAD BELTS AND ROLLERS SHOULD BE GUARDED TO PREVENT NIP POINT INJURIES AND FALLING COMPONENTS.
METSO OUTOTEC IS LEADING THE WAY IN DEVELOPING SUSTAINABLE PROCESSES, PRACTICES AND TECHNOLOGIES IN A TRADITIONALLY ENERGY-INTENSIVE PROCESS.
With modern mining operations being affected by declining head grades, more material must be moved from greater depths to maintain concentrate production levels. This in turn affects productivity and energy consumption, which directly correlates to a mine’s profitability.
But now there is another factor that must be considered: the ability to complete these processes in a sustainable way.
With comminution reliant on significant energy consumption, ultimately leading to higher costs, it is vital for the provision of efficient solutions to support one of mining’s most fundamental activities.
“Comminution uses around three to five per cent of the world’s power,” Metso Outotec technology manager for crushing Amit Zadoo said.
“It’s estimated that around one per cent of the world’s power runs through Metso Outotec equipment. Given this, we have a big role in mitigating climate change through our offering.”
So how does Metso Outotec, a leading industry figure in the manufacturing of fixed and mobile crushing and screening equipment, overcome this pressing industry challenge?
“Sustainability and mining are not incompatible,” Metso Outotec vice president of crushing Guillaume Lambert said.
To better meet the challenges associated with sustainability, Metso Outotec launched its in-pit crush and convey (IPCC) solutions in 2021.
These integrated solutions consist of crushing, conveying and stacking equipment, combined with IPCC planning and life cycle services (LCS), a process designed to ensure the highest levels of productivity, energy efficiency and maintainability.
“It is a sophisticated solution that seeks to be a viable alternative to truck haulage, designed to accomplish reductions in CO2 emissions,” Lambert said.
The IPCC solutions are part of Metso Outotec’s Planet Positive portfolio, reinforced by improved energy efficiency.
Planet Positive products have considerably more energy or water efficiency than the market standards, therefore helping Metso Outotec’s customers cut their CO 2 emissions
and achieve their other sustainability priorities, such as reducing pollution.
The Planet Positive portfolio already includes more than 100 products, and Metso Outotec’s goal is to keep expanding and improving this offering by continuously innovating.
A key aspect of the IPCC solutions is the critical importance Metso Outotec places in equipment servicing
and maintenance using LCS. Such operational support helps ensure optimal availability and asset efficiency.
The IPCC offering also includes offsite and on-site assembly options.
“Our IPCC solutions differentiate Metso Outotec within the market, as our significant knowledge and experience in the development and manufacture of advanced crushing technology has led to substantial energy savings,” Lambert said.
“Whether it is our Lokotrack range of track-mounted crushers, configured as diesel or fully electric models, or a semi-mobile solution, we are leading the way with sustainable, energy and costefficient solutions.
“With our semi-mobile solution, for example, it’s installed with a conveyor system featuring patented energy saving idlers and can reduce energy consumption by up to 30 per cent.”
Key benefits of Metso Outotec’s IPCC technology include optimal processing with its patented SmartStation, up to 30 per cent higher capacity on the same crusher size and 70 per cent reduced downtime with Superior MKIII primary gyratory technology, along with better maintainability achieved
through improved crusher access and plant area isolation.
Another important area in which Metso Outotec has chosen to expand its investment is in underground crushing and conveying, as mining operations are increasingly seeing the potential benefits of using mobile crushers in underground applications.
Mobile crushers reduce the required amount of haul trucks, allowing greater dust control and reducing the overall risk for truck traffic entering and exiting a mine.
“We have developed several mobile crushing and conveying solutions for underground applications with this type of flexible and adaptable mobile solution, either on wheels or trackmounted with a compact design, allowing ease of access and movement around a mine,” Lambert said.
Metso Outotec is making great strides in reducing its energy intensity and greenhouse gas emissions from its operations. Through continued development of existing products and advances in new products and process control, as well as continuing to improve services and wear parts offering, Metso Outotec is doing its part to contribute to a more sustainable future. AM
APRON FEEDERS ARE AN ESSENTIAL COMPONENT OF THE MINERAL PROCESSING CYCLE. AFTER DECADES OF MAINTAINING, FIXING AND INSTALLING THEM, MINPROVISE HAS ALSO BEGUN DESIGNING AND MANUFACTURING THEM.
As a specialist maintenance services, products and engineering company, Minprovise provides expert support to the mining, construction, oil and gas and infrastructure industries across Australia. The company operates in key industry locations in Perth, Karratha and Port Hedland in Western Australia, and Coopers Plains in Queensland.
Minprovise offers everything from mineral processing equipment and fabrication to specialist industry products and site services.
General manager of business development John Minnaar told Australian Mining that, in the mining sector, Minprovise predominantly provides maintenance services, especially in the crushing and material-handling environment.
“Part of that is also the supply of technical specialists or subject-matter experts to maintain and optimise the equipment,” he said.
“We provide parts and services as well as products to support the mining
industry, and we assist clients to evaluate the condition of their assets to help plan and schedule maintenance.”
Minprovise was established in 2004 with a core business of reducing the risk associated with operation and maintenance of crushing equipment.
The company occasionally delved into refurbishing apron feeders, though it wasn’t a focus. But in 2017 an opportunity presented itself for Minprovise to follow apron feeders down a more permanent path.
“That’s when we decided to set up an apron feeder division and an apron feeder specialist service that I headed in 2017,” Minprovise apron feeders and materials handling technical specialist Louw Scholtz told Australian Mining
“We’ve grown from refurbishing one apron feeder a year to eleven machines this last year across the board.”
When this apron feeder specialist service was implemented, the company’s technical experts provided maintenance on any brand its customers had installed on-site.
Minprovise gained a lot of experience and knowledge, getting to know apron feeders inside and out – literally.
The specialist team managed to demonstrate the value of manufacturing Minprovise’s own brand of apron feeder based on the knowledge and experience accumulated through years of providing maintenance to other brands. Minprovise has been able to take the best design elements from each model it encountered in the field, improve on them, and incorporate the results into its own well-oiled machine.
“An apron feeder is a fairly simple piece of equipment, but our team has done a lot of innovating and research and development of safety items that we’ve designed and incorporated into our maintenance strategies and taken into account for the design of our machines,” Minnaar said.
“We were able to find out the good and bad points of all the machines out there are and bring the best of it together into our product.”
It almost goes without saying that Minprovise has an array of technical experience. Scholtz’s team is out in the field continuously working on, improving, and maintaining apron feeders.
Added to the team is Minprovise’s drawing office manager and apron feeder design and development leader Darren Brooke, who has years of experience for various market competitors.
All together, Minprovise has the A-Team of apron feeder design, maintenance and optimisation.
“We believe we’ve got a very strong technical team who take into consideration the lifecycle of apron feeders, from the design through to operation and maintenance,” Minnaar said.
Apron feeders usually have a lifespan of four to five years before replacement.
Minprovise has now developed a unique process and methodology for this replacement. This process works in partnership with the client’s own standards and procedures, as well as their needs based on the data
Minprovise has collected during the previous four to five years of maintenance.
Standards change and new ones are continually introduced; it’s a dynamic space.
“In a lot of the plants, these machines were designed before certain standards even existed,” Scholtz said.
“So we go out and assess the site for specific ways to improve that particular set-up and come up with ideas and designs to enable easier and more efficient maintenance.
“This can include building specialised platforms and devices that we can hook winches and access platforms onto or build the platforms around the machine to carry out maintenance.”
This site-specific analysis, combined with Minprovise’s more general database gleaned from years in the maintenance space, results in a comprehensive approach with unique and often subtle changes and adaptations. These can have significant impact on overall efficiency and optimisation of the circuit and, more specifically, apron feeders.
Scholtz and Minnaar agree that many of the difficulties or challenges Minprovise has come up against have forced the company to think outside the box and come up with unique
ideas, designs and safety features that mitigate some of the risks generally present in this environment.
Minprovise remains consistent with its beginnings of ‘reducing the risks’ but, as the company’s entrance into the design and manufacture of apron feeders is showing, it takes its current positioning of ‘forward-thinking partners’ very seriously.
Part of this transition and growth has been an internal overhaul in which Minprovise invested heavily in training so the revised teams are
able to improve on their knowledge development of innovative solutions.
“We have very competent people that go into the field, assess and bring the information back to us in-house, where we combine it with our greater knowledge and experience and the client’s needs and come up with innovative solutions” Minnaar said.
“The open field of development is a continuously ongoing process.
“We have our base designs and we use our subject-matter experts to invest the knowledge back into our designs.”
Minprovise values collaboration and feedback and as a company it gets involved in community activities, supporting local in all aspects of the business – manufacturing, assembly, maintenance support and operation –as much as it can throughout its home state of Western Australia.
The experienced team at Minprovise will continue to improve safety and identify efficiencies in processes where possible, staying committed to reducing costs and risks, and minimising downtime. It really is the A-team of apron feeders. AM
FEATURES:
• Over 70% load step acceptance
• Ideal for portable and intensive use
• Robust twist lock & forklift inlets
• 110% spillage free frame
• Performs in extreme temperatures & at high altitudes
• Designed with large access doors for ease of service
• Minimal maintenance and 500 hour service intervals
With two
in
LIKE TO KNOW MORE? SPEAK TO OUR TEAM TODAY
PH: 1800 733 782 www.atlascea.com.au
As the renewable energy transition gathers pace, the mining equipment, technology and services (METS) sector has a critical role to play to facilitate decarbonisation in the mining value chain.
And it’s organisations such as ABB that are leading the way, pioneering technology solutions to energise mining’s new frontier.
Australian Mining had the opportunity to sit down with ABB global president – process industries Joachim Braun during his recent visit to Australia.
Braun said that despite the global challenges of 2022, he was optimistic about the mining sector’s outlook.
“When I think specifically about mining, I’m optimistic that some of the almost centennial trends we’re now observing will probably get the upper hand over certain macroeconomic troubles we might be experiencing,” he told Australian Mining
“Commodity prices are super robust and the explanatory pattern behind that is this centennial trend of practically every industry needing to decarbonise – with great urgency –
which will require a lot of minerals and more than ever before.”
Braun highlighted the volume of minerals needed for an electric vehicle (EV) compared with a conventional car.
According to the International Energy Agency (IEA), under its sustainable development scenario (SDS)*, EV battery demand is set to grow by nearly 40 times between 2020 (160 gigawatt hours) and 2040 (6200 gigawatt hours).
Overall mineral demand from EVs under base case assumptions is set to grow 30-fold between 2020 (400,000 tonnes) and 2040 (11.8 million tonnes).
“This is, in my view, driving a very positive development for the mining industry, which is probably going to be pretty resilient against the macroeconomic ups and downs,” Braun said. “I still see a bright future for this industry and for suppliers like ABB.”
Leveraging ABB’s 130 years of experience in the mining sector, the ABB Ability eMine makes the all-electric mine possible, with fully integrated electrification and digital systems from pit to port.
The Ability eMine starts with a strong foundation, supporting mining companies with ABB’s expansive fit-forpurpose product suite.
Beyond technology, Braun spoke about the need for collaboration to build momentum and create a sense of collective action, which is necessary to drive changes at the global scale.
“No single company or organisation can solve the complex and global challenge of climate change on its own,” he said. “It requires the efforts of everyone, from miners and technology providers to OEMs, governments
and industry bodies, to work together to identify and implement the most effective solutions to reduce carbon emissions and mitigate the impacts of climate change.”
ABB formed partnerships with FLSmidth in October and Perenti in November, with decarbonisation a central focus of both agreements.
Braun said ABB and FLSmidth complement each other, as each company comes from a different angle.
“FLSmidth has a fantastic process know-how in several relevant applications for the mining industry, where ABB is coming in with great know-how on automation, electrification and digitalisation,” he said. “And it’s quite clear that these things need to go hand-in-hand.
“There are more examples like this where we have been partnering with OEMs who are manufacturing electrified mine trucks. Truck manufacturers are not familiar with the electrification of vehicles, but ABB is – we’re electrifying everything from passenger cars, public transportation, buses, trains all the way to car ferries.
“But we are not a vehicle manufacturer and in order to ensure safe operation of such vehicles, you need the manufacturer. One can’t do without the other and the sooner we realise that the better.”
Braun said collaboration may not be limited to just two parties, with
more insights needed for a cause. This ethos underpins the ABB Ability eMine solution, which interconnects stakeholders all along the mining value chain.
“Often it’s not enough if only two parties partner up because there’s also other mining equipment which needs to be electrified,” he said.
“You need to take a holistic view at this. Without these collaborations, you will end up with solutions which are not appealing to customers, because they are proprietary solutions.”
Braun used the example of a mixed fleet of electric mine trucks, where it is not viable to have a separate charging solution for each truck.
“You want to have one charging solution (for the fleet),” he said. “And none of the truck manufacturers have the interest to come up with a nonproprietary solution, but the end users have a very vested interest in this.
“ABB has the competence to develop and work on such a vendor-agnostic solution. This is how we’re being brought together – sometimes by the initiative of the end user and sometimes by our own initiative.”
The mining industry hasn’t always been accepting of new innovations and solutions, rather opting for what’s ‘tried and tested’. But Braun is noticing a shift.
“I see a massive and pervasive uptick in interest in deploying new technologies (in the mining sector),” he said. “I would almost say it’s unprecedented.
“Lots of companies who we’ve initially worked with in a transactional way, we’re now looking into a partnership. Not because they suddenly became altruistic; simply because they need to try new things. And you cannot try new things when dealing with each other in a transactional way.
“There might always be leaders and might always be laggards, but if you
look at the industry as a whole, I think it has come an incredibly long way in a very short period of time. I would say that most of this has happened probably during the past two, three years.”
The Charge On Innovation Challenge is another example of the mining industry embracing collaboration. ABB was selected as one of eight finalists in the initiative, with the company recognised for its dual-charging system solution exploring stationary and in-motion charging of haul trucks.
BHP, Rio T into and Vale were founding partners of the initiative, which invited vendors and technology innovators to collaborate with the mining industry to develop novel electric-truck-charging solutions.
As a finalist, ABB is collaborating with interested mining companies, OEMs and investors to accelerate the development of its dualcharging solution.
The ongoing energy crisis is squeezing costs worldwide, and energyintensive mining operations are being affected by soaring electricity prices.
But therein lies an opportunity to think outside the box.
“We often observe that certain electrical applications are constantly running at full throttle,” Braun said. “One example of this in the mining industry is ventilation.
“If you have an underground mine, ventilation is vital, because otherwise human beings couldn’t last underground, nor could you operate machinery, because machines use combustion engines and require oxygen.
“But many of these ventilators are running totally uncontrolled and unfettered 24–7. The least you could do is put a drive in so you can at least control how much power you’re giving to the ventilator.
“Even better, one of our solutions is called ventilation on demand (VOD), where you ventilate where required.”
An underground mine has galleries where the mining takes place; however, not all of these galleries are being used at once. This is where mining companies could gain a cost advantage.
“The standard model is letting your ventilators run at full throttle 24–7, no matter what is happening in the mine,” Braun said.
“So this is maybe one example of how in the past the energy cost might not have been such a concern for the customers, so they wouldn’t bother putting such a solution in place.
“Now that this cost does matter, there’s hope for better adoption for existing technology such as VOD to make it more efficient.”
The mining sector has come a long way in its embrace of sustainable technologies, but companies need to maintain the momentum if they are to achieve their net-zero goals.
Luckily, innovators such as ABB will be there every step of the away, ensuring every miner’s renewable energy journey is as smooth as possible. AM
*The IEA’s SDS describes an integrated pathway for the global energy sector to meet the Paris Agreement goals, while also achieving universal energy access and substantially reducing air pollution.
TrufloPumps
is an investment in superior design and quality. Manufactured in Australia to exacting standards and to your specific needs.ABB IS AT THE FOREFRONT OF AUTOMATING AND ELECTRIFYING MINING TECHNOLOGIES.
The 2022 International Mining and Resources Conference (IMARC) offered the global resources industry the opportunity to reconnect and realign. A large exhibition showcasing the latest innovations in the mining equipment, technology and services (METS) sector was accompanied by several theatres housing panel discussions and presentations exploring a variety of themes.
There was also a veritable smorgasbord of networking opportunities on offer, with dedicated lounges, events, the IMARC after dark series, and a gala dinner just a few of the social occasions that took.
To celebrate some of the companies on show, Australian Mining visited several booths to gain greater insight into the mining sector’s latest innovations.
Brokk
IMARC 2022 saw Brokk showcase its Brokk 300 demolition robot, which
is becoming a key asset in Australian underground mines, where rocks need to be broken down, excavated and removed quickly and safely.
Speaking on day one of IMARC 2022, Brokk Australia managing director Will Visser said he’d already had some productive discussions with passers-by.
“We’ve had some good conversations so far with miners looking for something new, something different to solve their problems, talking about productivity mostly but also safety,” he told Australian Mining
“I can see that is becoming more and more of an issue with a lot of these surface and underground miners – finding better solutions to support government demands to work safer but not lose productivity.”
The electric Brokk 300 is improving environmental outcomes in underground mines, while the compact modular design of the demolition robot means it can easily access confined spaces without compromising on power and safety.
With a vast array of attachments, the Brokk 300 is a machine that can complete multiple tasks.
“In doing these tasks, miners can keep people away from hazardous work zones and into a safe space,” Visser said. “This is more and more at the top of the agenda of underground miners, and we’ve got a great track record in underground spaces.
“We are now seen as an integral partner to many mining decision-makers.”
Elexon Mining showcased its underground wireless monitoring products at IMARC 2022. These solutions ensure clients can better manage their orebodies and mine at the right place at the right time.
“One of the advantages of our products is we can put them in a lowyield zone or somewhere where there may be dilution, and the markers will determine that this is an area they shouldn’t be capturing,” Elexon Mining
sales and marketing manager Sean Allen told Australian Mining
“This ensures the miner can focus on getting ore from a higher grade, and if they’re suddenly getting markers coming into their extraction, then they can go elsewhere.
“At the end of the day, if the miner doesn’t have to invest and use resources to capture low-grade ore, then they can focus on investing their resources elsewhere.”
Allen used Elexon’s Cave Tracker solution as an example.
“We can also target specific areas,” he said. “One of our systems – Cave Tracker – is used in a block caving operation; so when clients drill boreholes as part of exploration, they’ll install magnetic beacons where there are highyield areas.”
The beacons can be tracked in 3D as they move with the fragmented rock of the orebody. The ability to track beacon movement allows mine engineers to determine which parts of the cave are moving and which parts are not.
The beacons are wireless and robust, which means they can remain underground for years.
“It’s all about sustainably mining,” Allen said. “Without being blind, you can understand exactly what’s happening in a mine.”
On day two of IMARC 2022, Epiroc business line manager – digitalisation Leon Cosgrove delivered his presentation, ‘2031: A mine odyssey’, in which he spoke about the continued evolution and technologisation of the resources industry.
Cosgrove discussed the rise of automation and wireless communications underground, and the bigger role electrification is playing in mining.
“OZ Minerals has its ‘scalable and adaptable’ program where it is looking at how it can mine differently and tackle smaller orebodies,” he said. “To do this, OZ is incorporating components that are small, automated and electric.
“The Charge On Innovation Challenge is seeing a big focus on electrification in the big fleet space. Then there’s the Electric Mine Consortium, with which Epiroc is a member, and quite a few mining companies are involved in this as well.”
With BHP, Rio Tinto and Vale as its founding partners, the Charge
On Innovation Challenge invited vendors and technology innovators to collaborate with the mining industry to develop novel electric-truckcharging solutions.
Eight winning solutions have been selected from the likes of ABB, Hitachi Energy, Siemens, Shell Consortium and BluVeinXL.
70% of lubrication-related failures are caused by contamination. And the best way to manage contamination is with LUBESTATION®.
The Electric Mine Consortium (EMC) is a group of leading mining and service companies that are accelerating progress towards the fully electrified, zero-carbon and zero-particulates mine.
Alongside Epiroc, members include OZ Minerals, IGO, Barminco, Newcrest Mining, South32, Sandfire Resources and more.
Cosgrove said the EMC was considering all possibilities regarding automation, electrification and smaller fleets to achieve decarbonisation outcomes.
He highlighted the work Epiroc is doing to support the mining industry on its odyssey, where the original equipment manufacturer (OEM) has
LUBESTATION® packs all your lube, oil, and fluids under one portable roof so it can be moved to di erent areas of a mine site, saving on capital costs while protecting your pumps, reels, and hoses from the harsh Australian elements. LUBESTATION® also prevents cross-contamination of oil, grease and coolant, giving you peace of mind that you're putting fresh fluids into your expensive mobile equipment.
1300 242 504
sales@retragroup.com.au
www.retragroup.com.au
become a global leader in automation, digitalisation and electrification.
Epiroc also showcased its Scooptram ST14 battery-electric vehicle, one of the most popular underground loaders on the market.
Flanders
A global leader in drilling automation, Flanders was showcasing its full array of solutions at IMARC 2022.
Flanders strategic business development manager Owen Uebel said the company had not only had discussions around its offerings for the mining sector, but also opportunities from other sectors had also arisen.
“It’s important for us to be able to diversify,” he told Australian Mining. “Mining is still a key part of our business, but we want to do business in other industries as well.”
Uebel said IMARC gave Flanders a unique opportunity to connect with potential overseas partners.
“We’ve been having some good discussions with people from India and some other countries around the world which you would normally have to do via remote communications,” he said.
“To have these discussions face-toface has been great.”
Alongside its drilling automation system, Flanders offers control systems for shovels, draglines, haul trucks and more, as well as highperformance motors, drives and custom power systems for heavy electric mining machines.
“The key benefit for us is that we’re agnostic,” Uebel said. “It doesn’t matter which OEM brand of equipment you have; you can put the Flanders system on it.”
Attending its first Australian conference at IMARC 2022, GroundHog
showcased two digital platforms at the event – one focused on mine production planning, tracking, execution and reporting, and the other on mine safety.
GroundHog chief executive officer Satish Penmetsa said the company’s safety platform attracted plenty of interest.
“When a new person comes on-site, they need to be trained on what to look out for on a mine site,” he told Australian Mining. “If you were hired as a plant operator, you go through a classroom training and then you to do a field training where you have a secondary driver that shows you how to operate the equipment safely.
“That’s then followed by an observation or verification of competency where a safety trainer verifies that you can do the job safely. And it’s only when you finish these three steps that you’re issued a ticket to operate that plant.
“With our system, we have an app where you can do this required training, even underground when there is no network. You also need to capture
the total number of training hours and verification of that competency – all of that logic is all built into our application.”
Penmetsa said IMARC 2022 had offered GroundHog the opportunity to strategically plan meetings and connect with decision-makers – something not always offered at other conferences.
Hexagon Mining chief technology officer Rob Daw said IMARC 2022 was about demonstrating the company’s holistic capability in the mining sector.
“What we’ve done over the last 12 to 18 months has really brought together what we call the ‘Power of One’, which is all of our different solutions coming together – whether it is on the technology side or on the partnership side – to be able to serve our clients in a whole different way,” he told Australian Mining
“It’s about continuing to peddle that message, where we can be the one partner for an operation and organisation and help them from
exploration to export and all the different steps along the way.”
Power of One is made possible by a platform that connects all sensors and software with an intelligent monitoring system that can be accessed from the field to the cloud.
One example of the Power of One is HxGN MineMeasure, which is part of Hexagon’s drill-and-blast portfolio.
Drill-and-blast operations impact the entire mining process. Costs and energy usage increase throughout the comminution process. Efforts targeted at optimising the blasting process can pay huge dividends downstream, reducing costs and energy consumption.
Hexagon’s portfolio connects every individual part of that process, delivering a greater return on investment.
The DD422i dual-control drill rig and Toro LH515i underground loader were two of the products Sandvik showcased at IMARC 2022.
Sandvik product manager for underground drills (APAC) Jordan Letkeman told Australian Mining that the DD422i is focused on the country’s mining market.
“Australia does a little bit of a different mining method with the jumbo, where instead of bringing a bolter and a scaler in afterwards, Australian miners do it all with one drill,” he said.
“So that’s where this drill was really focused around the Australian mining method, where the jumbo does the boring, the bolting, the meshing and some scaling as well.”
The Sandvik DD422i is based on an intelligent control system and engineered to provide top-level performance, accuracy and reliability for underground mine development and small-scale tunnelling.
As for the LH515i, Sandvik business line manager – load and haul Andrew Dawson said the standout feature of the machine is its size-to-capacity ratio.
“The LH515i sits in the same size footprint as the LH514, which is a 14-tonne loader, but it’s 15 tonnes. So it’s got the extra tonne of capacity and it fits in the same envelope,” he told Australian Mining
“The machine is part of Sandvik’s iSeries, so it has all the smarts. It’s automation-capable and has a stage five engine as an option for Australia, which is the cleanest technology you can have right now.”
Strata Worldwide promoted two products at IMARC 2022, its StrataConnect high-speed underground communications network and the recently acquired Bright Path AI (BPAI)
platform and artificial intelligence (AI) cameras.
Strata project manager Phil Jones said BPAI separates itself in the way the hardware is implemented.
“The focus (with BPAI) is workplace behavioural change,” Jones told Australian Mining “So how we deploy the technology and integrate with an organisation’s workplace health and safety systems is where we provide value.”
Jones said BPAI is a more intelligent collision-avoidance solution that enables workers and management to have a better understanding of any incidents that take place.
“Workforce behavioural change is about providing event information to line management in a way that helps them decide whether they actually need to get involved in the operation, because of certain alerts that come from the system,” he said.
“So that encourages the organisation – from a top-down approach – to get more involved in each and every event that happens.”
Vocus
Vocus showcased a heavy lift drone, which Challenge Networks principal consultant Mal Jones said was the perfect showpiece item for passers-by.
“We’ve had a huge attraction which customers have been able to look at as
they walk by,” he told Australian Mining “This is our heavy lift drone that can provide LTE (long-term evolution) in the air in 30 minutes. So it’s a rapid deployment solution.
“The drone can deliver a complete end-to-end enterprise network solution in 30 minutes from the time it reaches the site where it needs to be deployed.
“It can then give a five-to-10kilometre coverage range of fully connected LTE services to the field operators who need to be in an area very quickly and deliver services to whatever function their responsibility is.”
Jones said the heavy lift drone was featured at Vocus’ stand to create a conversation around capability.
“Customers can see the application, and we talk about it in the context of rapid response, emergency response,” he said.
“At a mine operation where coverage doesn’t exist – it might be an exploration area – employees need to be able to report data and move files very quickly. We can provide on-the-spot coverage to enable the workforce to do so.”
This was just a small sample of what IMARC 2022 had to offer, and with the next iteration scheduled to take place in Sydney from October 31 –November 2 2023, there’s sure to be another fascinating array of innovations and advancements on show for the conference’s 10th year. AM
AUSTRALIA’S TIN PRODUCTION PALES IN COMPARISON TO OTHER COMMODITIES, BUT THERE ARE SEVERAL COMPANIES LOOKING TO BRING TIN MINES ONLINE. AUSTRALIAN MINING TAKES A CLOSER LOOK AT FIRST TIN’S TARONGA PROJECT.
First Tin is looking to bring Australia’s next tin mine online, with its Taronga project in New South Wales considered the fifth largest undeveloped tin reserve in the world. It is also developing its Tellerhäuser tin project in Germany.
Completing its acquisition of Taronga from Aus Tin in April 2022, First Tin aims to deliver a conflictfree, low capital expenditure (capex) operation that is ESG-friendly and free from geopolitical risk.
Australian Mining sat down with First Tin chief executive officer Thomas Buenger to find out more about the Taronga project and its important role in a renewable energy future.
The Taronga project has a very long history. It was explored and developed towards a pre-feasibility study in the ’60s, ’70s and ’80s by BHP and Newmont.
But in the ’80s, there was the clash of the International Tin Council, which led to a total breakdown in tin prices at the beginning of the decade. So Newmont – the owner at that time
– stopped any further development work, and then divested the asset later on.
From afar, Taronga seems to be a low-grade tin asset, but the beauty of the project is it has a very simple mineralogy, so it is possible to upgrade the initial head grade through simple mechanical processing steps from the initial low-grade to a mid-grade.
At Taronga, the cassiterite is hosted in quartz veins and if you look on top of the outcrop, you have a series of waves. There are approximately 15 to 20 per metre and they’re between 1mm and 3mm wide.
The beauty of that is the cassiterite minerals are quite large, so up to 3mm embedded in quartz veins. After mining the material, if you start the processing and crush it, you simply break off the quartz with the embedded cassiterite from the hornfels, and that already leads to an upgrade of the material.
So after the first two processing steps, we can achieve roughly a twoto-three-fold upgrade in cassiterite concentration and it brings simple mineralogy and low-grade into
something that is feasible to upgrade to a saleable cassiterite concentrate.
If you look into the previous prefeasibility study, that considers processing the whole volume from the front-end to the back-end of the processing plant.
What we consider is to discard substantial volumes early on, which leads to the option to shrink substantially the back-end of the plant, which is not only a benefit in regards to lowering the capex but also the opex (operating expenditure) as well.
After the first two steps (of processing), we will already discard 70 per cent of the volume, and a few
mechanical steps later, most probably another 20 to 30 per cent, so the backend might shrink to maybe 15 to 20 per cent of the initial volume that we start to process.
Why doesn’t Australia have more tin miners?
Australia used to be a big tin producer in the past, particularly in Tasmania. This includes Renison, with an outstanding orebody as a tin producer.
And there are more tin resources out there. There’s a lot of exploration ongoing from other companies on the market as well, so I expect there is further tin production potential.
Maybe it (having fewer Australian tin miners) is a result of the breakdown of the International Tin Council, which happened to our Taronga asset in the past.
One outstanding quality with Taronga is it’s most probably the closest to operation. Every other tin asset in Australia is not as mature as our Taronga asset and that’s one of the reasons why we are pushing very much towards it.
If everything goes according to plan, we might turn the Taronga asset into an operating mine in 2025–26, exactly when the gap in supply and demand of tin widens most.
Tin’s major use case is solar and it ends up in everything that has to do with the energy transition,
with electro mobility, with artificial intelligence and with electronics. That is the growth driver for tin demand.
What are your objectives at Taronga in 2023 and beyond?
We started at Taronga a definitive feasibility study during July last year, and we are pushing to finalise it end of next year. So that’s a mid-term target.
In parallel, we started in March last year the Four Seasons monitoring process for the environmental impact assessment, which is the input for the study.
We also have a drilling program up and running with a two-fold aim.
One aim is to increase the resource statement because if we look today, the Taronga project consists of two individual orebodies with nothing in
between as there was no exploration done by our predecessors here.
And we are doing step out drilling at the south-west end of our orebody because there is an outcrop of mineralisation at the surface which most probably will lead to the option to extend the resource.
I expect to have an update of the resource statement end of Q1, beginning of Q2 this year. AM
BATCHFIRE’S LONG TERM PARTNERSHIP WITH HASTINGS DEERING HAS SUPPORTED THE BUSINESS STRATEGY OF PHASING OUT OLDER MACHINES AND UPGRADING ITS PRE-STRIP MINING FLEET.
The 994k was customised with a 40-cubic-metre bucket, significantly increasing capacity from the old loader’s 16-metre bucket.
“There’s a huge difference in payload,” Boal said.
“It used to take us 10 buckets to load a 789 truck on the ROM. The new 994k can do that in four.”
Not only is the new Cat 994k efficient on the ground, but it also provides operators with superior levels of safety and comfort – and that is one of Batchfire’s key priorities. The model’s higher cab position, lower sound level and seat air suspension help the company to achieve maintain this goal.
“It’s a beautiful piece of machinery. The cab’s wonderfully comfortable and spacious and the machine itself delivers great performance and power,” Batchfire Resources operator/trainer and assessor Adam Burling said.
hen Batchfire Resources needed to optimise its mobile machinery to lower fuel emissions and increase operational efficiency, there was only one company that could help them out: Hastings Deering.
Batchfire, a leading Queensland producer of low-impurity, low-fugitiveemissions-energy coal, has powered the Biloela and Callide Valley in the state’s east since 1944.
Hastings Deering and Batchfire have had a fruitful partnership for many years and have committed to responsibly developing the Callide Basin’s resources through the upgrading of Batchfire’s pre-stripmining fleet.
And with nearly 100,000 hours on the clock, Batchfire’s original 994 wheel loader was one of the first to be replaced with a brand new Cat from Hastings Deering.
“This journey started in 1993, and the old 994 has pretty much been in service the whole time,” Batchfire Resources superintendent mobile –engineering and maintenance Daniel Boal said.
W“The way Caterpillar build things, they are made to last, they’re built for a long-term investment. It was an easy decision in the end to go for the new 994k loader.”
And that new Cat 994k has already achieved outstanding results for Batchfire.
Thanks to the new model’s larger and stronger design, the 994k has
generated 150 per cent more material movement without increasing carbon emissions. It has also given Batchfire higher payload and horsepower.
“On a ROM (run of mine), what you need is a reliable loader – it’s probably one of the most critical parts of the mine,” Boal said. “We’ve got 500 horsepower more in the new 994k, so we can do it quicker and more efficiently.”
Caterpillar has worked to improve the wheel loader models to provide operators with a safer work environment, including adjustments to machine access, visibility, operator comfort and a powered access system.
Seat air suspension and viscous cab mounts reduce vibrations, keeping operators comfortable and reducing fatigue throughout the day.
The higher cab position means visibility while loading has been increased in the 994k, and the Cat Detect feature enhances operator awareness around the machine.
Cat Detect uses cameras and other sensors to improve operators’ awareness of the work environment, reduce the chance of accidents, and prevent unauthorised use of equipment in an effort to increase on-site safety.
All of these features combine to give Batchfire Resources the ability to safely move material, all while reducing environmental impact and carbon footprint.
And Hastings Deering will continue to be there every step of the way.
“It’s not just the reliability that’s great with Cat machinery,” Burling said.
“What Caterpillar and Hastings Deering do especially well is the support they give. If you have an issue, Hastings is there.” AM
hen a worksite calls for a hauler that produces more uptime, guaranteed durability and outstanding productivity, one option should definitely be considered: the Volvo A60H articulated hauler from mining equipment supplier CJD Equipment.
The largest articulated hauler on the market, the A60H can shine in even the toughest terrains.
“The beauty of this machine is that it really can work anywhere,” CJD national product manager Hayden Grant told Australian Mining “Wet and muddy terrains, steep climbs, sand … the A60H can deal with it all.”
WVolvo developed the world’s first manufactured articulated hauler, known as the Gravel Charlie, back in 1966.
Since then, Volvo has continued to lead the way in pioneering technology, with the A60H being the latest example.
“The A60H will perform where others can’t,” Grant said. “If the terrain is too hard or the conditions aren’t suitable for other machines, the A60H should be your tool of choice.”
With operator comfort such a key consideration in mining machinery, the A60H has ensured it delivers this in spades. The machine is fitted with active hydraulic suspension that permits high hauling speeds in tough conditions, optimising operator comfort and stability during travel.
“We’ve been getting a lot of feedback from users that the machine is comfortable and easy to spend the day in,” Grant said.
“The operators like being positioned in the centre of the cab, and they say the steering is good at high speeds, as the wheel doesn’t fight them.
“We’ve also had reports of low noise levels in the cab and excellent suspension, climate control, space and visibility.”
The cab features a copilot option with Haul Assist – a system that
shows how much material the hauler has moved, providing operators with data and real-time insights to help achieve optimal payloads and improve productivity.
Haul Assist also has several optional features such as on-board weighing, tyre-pressure monitoring and Haul Assist map, among others.
“There are a lot of features in the A60H that are worth a mention,” Grant said.
“It has load and dump brake, hill assist, 100 per cent diff-locks in all axles and active hydraulic front suspension.”
The A60H also features the D16F, a fuel-efficient engine that is well known among Volvo equipment users. Providing one
of the best tonnes per fuel litre in the market, the D16F delivers the power and torque needed to move large payloads with ease to maximise productivity.
With the D16F, the A60H is able to deliver excellent fuel efficiency without compromising on power or performance, allowing users to meet targets faster.
And with the A60H’s dump support system, dynamic Volvo engine brake and load and dump brake, operators are able to stay in control at all times.
Servicing the A60H is also quick and easy, with excellent access as the front grill swings down, opening a service platform with anti-slip steps. The electric hood opens to 90°, allowing full and safe access to the engine compartment.
And, as always, the exclusive Volvo dealer network is available to support users whenever they need it, offering services, local knowledge and global experience.
With all of these features combined, it’s little wonder that the Volvo A60H has received such rave reviews.
“Volvo has consistently led the way when it comes to pioneering technology which delivers the ultimate in sustainable productivity, performance,” Grant said. “The A60H is living proof of this.” AM
•
•
•
•
• Complies with all relevant Australian Standards, AS1170, AS4324.1 and RPEQ requirements
The idea of outsourcing versus in-house has long been a debate. An organisation may find it necessary to outsource because it lacks the expertise or the resources to complete the process or task internally.
With mining constantly evolving, it’s becoming more important that companies have access to high-quality innovative solutions and challenge the status quo.
The argument for outsourcing revolves around the abilities of vendors, speed to market and best practices, among other benefits. Though there are risks associated with outsourcing, similar risks can come from insourcing if implications are not understood.
Rio Tinto recently announced its strategy to onboard hundreds of developers and move away from outsourcing development work to accelerate change and digital transformation. This change will no doubt provide a significant advantage and further competitive edge.
But what about smaller operators that are looking to gain a competitive edge of their own? For them, outsourcing can present a very valuable solution.
Australian Mining discussed the situation with people from two of the
country’s mining equipment, technology and services (METS)-focused software companies: CRU Software chief executive officer Jason Cameron, and Fly2Work director and chief executive officer James Kelly.
CRU Software, a leading provider of automated rostering and scheduling systems, believes technology can empower businesses to plan with confidence and function efficiently.
“One of the benefits of two-way relationships is feedback, which drives innovation, improvements, and competitive edge for the entire user base,” Cameron said. “In many cases, it solves problems that clients aren’t even aware they have.”
CRU Software’s rostering and scheduling solutions have been built to solve the specific problems related to a client’s complex workforce.
Linking solution-providers together for even greater outcomes for businesses is a further step in the outsourcing process.
CRU Software partnered with Fly2Work in 2022 to solve the complexities of mobilising large workforces by automating roster and travel integration.
Fly2Work was able to use CRU’s rostering solution to leverage seamless sharing between the two systems,
streamlining workforce and resource management for large-scale teams.
“It’s on us as organisations to deliver this value and then to listen to what customers are saying so that we can continuously evolve,” Kelly said.
“The simplification and automation of this manual process is helping our customers mobilise their workforces with fewer errors and less administrative overhead.”
A robust enterprise-grade solution requires thousands of hours of development by a team of experts. One downside of taking development inhouse is that the smaller pieces of the puzzle can often be overlooked and limit the transfer of knowledge.
An advantage of outsourcing, on the other hand, is exposure to new ideas and technology from other industries. It is the role of miner and vendor to apply the new lessons to the mining sector.
“Something that we offer is that we’ve built a product that is a true product, evolved from the input of a number of different customers and industries,” Cameron said “Our product will evolve over the next 10 years; it may not look like it did today in 10 years’ time, but clients will go on the journey with us.”
These solutions could help pave the way for more mining companies to reach the same heights as the majors.
The power of the Cru Software and Fly2Work partnership can be amplified when vendors work together, and can be an antidote to rising budget and cost pressures.
It is still possible to rapidly scale and maintain digital strategies through outsourcing, especially when they integrate and leverage the same data.
Another benefit of outsourcing vendors like CRU Software and Fly2Work is that help can be obtained quickly.
“We can use our extensive knowledge and experience to work with customers to forge a lasting relationship and add true value,” Kelly said.
Cameron agreed, saying “that was a really integral part of this partnership”.
“When something’s not working, you can call your vendor and have a conversation then and there,” he said. “We drop everything and fix the problem to make sure there is a resolution for the customer.
“With our flexibility and agility, we can get the problem fixed, so the customer isn’t losing time and productivity.”
While resources giants have the domain knowledge and ability to build their own tailored solution, companies like CRU Software can give emerging miners a leg-up to compete. AM
Martin Engineering builds an extensive array of electric, pneumatic and hydraulic vibrators for crushers, screens and shakers — including stock or custom-engineered models, as well as cost-effective, direct replacements for Derrick® shakers. Each Martin unit is backed by an industry-best three-year warranty, plus an additional three years on bearings and associated electrical parts.
Rated IP66 for dust and water tightness, our lineup of heavy-duty, low-maintenance vibrators feature high-strength cases. Explosionproof models, engineered specifically for hazardous duty, bear ETL, cETL, ATEX and IECex certification.
Don’t let your production get jammed. Get shakin’ with Martin.
VEHICLES VENTURING ONTO A MINE SITE MUST BE AS TOUGH AS THE SURROUNDING WORK ENVIRONMENT, AND AUS 4WD EQUIPMENT CAN PROVIDE THOSE VEHICLES.
The AUS Fleet Solutions (AFS) group understands that mining and vehicles go hand-in-hand.
From vehicle rental, vehicle leasing and smash repairs to mechanical servicing and vehicle sales, the AFS group can do it all – and this includes 4WD accessories.
“AUS 4WD Equipment offers its customers personal service from experienced enthusiasts,” AUS 4WD manager Stephen Gurman told Australian Mining.
“Not only do we offer quality fitment of products, but we also offer knowledge from those who use and recommend our products.”
AUS 4WD Equipment consists of a team of experts who have a long history of offroad driving.
The company understands that getting offroad can be challenging, which is why the team is there to provide and install the right protection to keep vehicles intact and moving through tough terrain.
“It’s of the upmost importance that 4WDs be equipped with the right offroad products,” Gurman said.
“It’s important not only for the safety of the people in the vehicle, but to ensure the vehicle is ready for the terrain you wish to drive on.
“A correctly built and outfitted 4WD will make the drive easier and ensure you don’t unnecessarily damage your vehicle.”
AUS 4WD Equipment can offer customers any type of necessary installation, including protection, storage, tyres, suspension, lights and more.
A key benefit in using AUS 4WD Equipment is its ability to source 4X4 products from a range of popular brands. In addition, the team can install these products on-site, so customers know they are getting quality products, service and workmanship.
If individual installations are not what the customer needs, AUS 4WD Equipment can also build a vehicle from the ground up.
“The first step our team will do is to make sure we understand everything about what you want your 4WD to look like,” the company said.
“From there, we’re able to recommend the best products and build your vehicle to take on your next adventure.
“Our team members are offroad with their 4WDs regularly and understand the importance of high-quality products that are installed correctly.”
Customers who know exactly what they want can work with the AUS 4WD Equipment team to plan out a complete custom fit. And for those who need a bit more help, their professional service staff can assist in finding the right part to fit clients needs.
While the business has a strong retail focus, its ability to source so many quality products also can benefit commercial operations like mining companies and other businesses.
“Through our many fleet partners, we offer complete fleet fit-out solutions,” Gurman said.
Each vehicle is serviced extensively and on time, with a complete checkover before it is ready for sale, helping to ensure safety at every mine site.
In addition to providing products to fit and build 4WDs, the company boasts a dedicated and experienced mechanical services team to look after each vehicle.
“We offer a full mechanical workshop service via our AUS Mechanical Services company, a part of the wider AFS Group,” Gurman said.
Factory-trained mechanics and technicians at AUS Mechanical Services are on-hand to deal with any mechanical challenge, while paint and panel repair is also available from AUS Smash repairs.
“When you are having fun offroad, things are bound to happen,” the company said on its website.
“Whether it’s for a remote mine site, travelling between warehouse locations, or weekend 4X4ing, AUS 4WD Equipment can supply the solution that suits your needs.” AM
“We are seeking to expand our capacity with everything that is required to run multiple drilling units,” Garbelini said.
The company’s equipment is maintained to the highest standards, ensuring a premium level of safety and productivity.
The main drilling rig for large-scale work is the Versa-Drill V2000, which can drill 6–24-inch hole, features an onboard 1070x350PSI compressor, and can reach depths of 1000m.
Aquatech also has a custom-built, highly manoeuvrable drill rig for intermediate work, able to complete smaller drilling projects with a smaller team of operators.
to facilitate site-specific drilling requirements.
A safety-first approach is at the heart of Aquatech’s drilling operations and all team members ensure they clearly identify and remove potential and recognised risks. Through the implementation of a rigorous health, safety and environment management system, Aquatech is committed to ensuring ongoing compliance with all relevant laws and regulations.
Additionally, the company is committed to the protection of the environment and undertakes significant consultation with clients before drilling, striving to leave the environment in its original condition.
Aprivately owned, family-run business, Aquatech has risen from humble beginnings and grown to provide costeffective water well drilling, offering clients tailored solutions and the capacity to reach significant depths.
“The company was started by the previous owner Shane Williams in his backyard in 1988,” Aquatech’s new owner Luke Garbelini told Australian Mining
“And over a period of time with machinery upgrades, a focus on operating efficiently, keeping costs under control and learning about the various types of drilling conditions, the business has kept growing and growing,”
Aquatech utilises mud rotary or air hammer techniques with its scope of work, including production bores, artesian bores, dewatering bores, monitoring bores, down hole hammer, cement grouting, water bore redevelopment and relines, as well as the installation of various types of steel and stainless-steel casings.
“Water is critically important to the mining industry; it’s utilised in every part of mining operations from processing to power generation and dust suppression,” Garbelini said.
“Every client has different requirements when it comes to water. Often there is a de-watering requirement; that is, drilling bores to stop water from entering mine workings located underground.
“Water can be used for anything, and at Aquatech we are at the forefront of providing solutions for our clients requirements, whatever they may be.”
The company is committed to being at the leading edge of drilling innovation. And while it has experienced some recent growing pains, Aquatech is focused on providing water boring and monitoring services across local, regional, and remote areas throughout Western Australia.
The company’s focus is on growth, becoming larger and stronger, and able to undertake more projects.
The company’s support truck carries a full complement of hydraulic hoses, pumps, motors and additional spare parts, enabling significant reductions in downtime.
“We want to ensure our clients feel comfortable in the knowledge that if a breakdown occurs Aquatech has another machine ready to go, and just as capable as the original unit,” Garbelini said.
“Operating multiple machines also ensures our crews gain greater exposure to different operating environments across multiple projects, driving efficiencies and improving safety outcomes.”
One of Aquatech’s inherent qualities is its flexibility, maintaining the ability to work closely with clients
Aquatech Drilling is a member of the Australia Drilling Industry Association (ADIA), and the company’s drilling teams are Class 1, Class 2, and Class 3 ADIAaccredited. Such a level of certification ensures all work is carried out to the highest of standards.
“Our approach at Aquatech is straightforward; it’s about detailed planning, it’s about reliable and robust machinery, it’s about our experienced workforce being meticulous when it comes to safety and getting the drilling done with a minimum of fuss,” Garbelini said
“We care deeply about our clients, and our reputation for undertaking quality drilling is something that we’re very proud of as a company.” AM
WITH MORE THAN 30 YEARS’ EXPERIENCE, AQUATECH HAS MAINTAINED A RECORD OF HIGH-QUALITY SERVICE TO VARIETY OF CLIENTS ACROSS MANY INDUSTRY SECTORS.AQUATECH IS COMMITTED TO BEING AT THE LEADING EDGE OF DRILLING INNOVATION. AQUATECH IS FOCUSED ON PROVIDING WATER BORING AND MONITORING SERVICES.
With 25 years under its belt, Canary Systems has established itself as a leading geo-monitoring solutions provider capable of connecting a mine site with a single data platform.
The American company can tailor its platform for any mining application, whether an operator is looking to store and analyse production or beacon data or interpret geologic mapping to understand underground or surface mining characteristics.
And that’s just the start.
“We can take all the different data types, put them into MLSuite and visualise everything that’s happening on a mine site, not just from a riskmanagement point of view but also from a production point of view,” Canary Systems founder and president Alex Neuwirt told Australian Mining
“Now there’s dimensions of understanding about data and about mining operations that weren’t possible before.”
In an underground mine, an operator would typically have a latticework of passageways that are supported by columns of rock. These columns will often feature extensometers to measure how the pillars are deforming over time.
When using Canary Systems analysis, Neuwirt said, operators have been able to gain a deeper understanding of their mine.
“An interesting correlation we’ve seen is where an operator varies the rates that rock is being drawn through a mine’s draw points, which creates more or less deformation in those pillars,” he said.
“Because you’re changing the stress, you’re changing the loading in those areas and so now you can start to understand the relationship between your production rates and the stability of your mine.
“If you destabilise that pillar and it collapses, you just lost a production area in the mine, which is very difficult to recover as it’s a collapsed area. So being able to see production data against your stability data becomes valuable.
“Maybe there’s no relationship, which is great – no matter how much you draw, you have the same stability in your pillar – but where there is a relationship, our
platform can be very useful to guide your production rates.
“So our platform becomes a tool. Having that data in one place and being able to create a simple chart of those two data types, it now becomes really useful for both production management and safety.”
It’s one thing to provide the system, but it’s another to offer the expertise to back it up. This is where Canary Systems comes to the fore.
“Typically, a pure software platform provider needs help to figure out the different data types in order to do the data integrations,” Neuwirt said.
“What we’ve seen is the provider often pushes back to the client to access what they need to get data into the platform, whereas we come to our clients with all of that domain expertise.
“Clients really want that in the mining industry. They are looking for not just a platform provider, but also a
provider that has the domain expertise to help implement the platform fully.”
Neuwirt used a specific example to explain his point.
“Say a client needs to collect more hydraulic data, and they need piezometers installed in certain locations in the mine. We can offer that as a service,” he said.
“We’ll sell them the piezometer, we’ll sell them the data collection platform, and we’ll provide the services to install and commission the system.
“That’s very different from the pure software platform providers that we’re competing with.”
To ensure its employees maintain their domain expertise as technologies and markets evolve, Canary Systems has developed its own training program: Canary University.
“Canary University has more than 200 discrete topics around what we do as a company,” Neuwirt said.
“That gives you an idea of the range of technologies and the range of data types and instrumentation that we’re having to internally train our staff about.
“It’s way beyond the platform itself; it has to do with all these different data types and data sources as well. I’m working hard to train our staff to understand how all these systems work, because when we go to the client that’s what we’re offering them.
“We’re not just providing pretty pictures for our clients – we’re figuring out how to do the full integration, we’re figuring out how to install and commission new systems for them so that all data comes into the one platform.
“This enables them to have a really clear picture of what’s happening in their mine from that risk management point of view, whether it’s an underground, open-pit or surface operation.”
Canary Systems’ Australian client base includes two Tier 1 gold mining companies operating in New South Wales and Western Australia, and 2023 will see the company looking to expand further, with a key focus to get more “boots on the ground”.
“We know that when we put people in proximity to clients or potential clients, the likelihood of securing work goes up dramatically,” Neuwirt said. “So that’s the biggest goal for us in the next year.
“For a couple of years, travel to Australia was restricted due to COVID but now that we can come to Australia – we really need to get some boots on the ground; we need to develop our Australian office and from that some fantastic opportunities will follow.” AM
The first batch of Hardox Wearparts centres was opened in Europe in 2000. And now, over two decades later, the global network of wear service centres features more than 500 full-service centres in 100 countries. But even though the centres continue to grow, the company’s core business of providing customers with high productivity and low maintenance costs haven’t changed.
“We’ve been a member of the Hardox Wearparts network for several years. It buys us credibility with our customers,” Real Steel New Zealand’s Luke Mathieson said.
“Flying the colours of Hardox Wearparts is a sign of quality, reliability and excellence.”
Real Steel New Zealand has grown rapidly since becoming a Hardox Wearparts member. The company is proud to be its country’s official Hardox Wearparts centre. Around 80 per cent of the centres are privately owned, including the one owned by Real Steel New Zealand.
SSAB is a specialised steel company that makes Hardox wear plate, Duroxite overlay products, Strenx performance steel, Toolox engineering and tool steel, and much more.
These steel products are also available at the Hardox Wearparts centre.
“It was important for Hardox Wearparts centres to maintain a local focus, as this allows them to address specific customer needs more efficiently and all wear business is local,” the company said on its website.
“By partnering with local companies that supply wear services, we can provide our end customers with local and rapid access to quality wear parts and technical support.”
Members of Hardox Wearparts have access to one of the largest industry knowledge bases in the world. Shared experiences from other centres and SSAB wear specialists are put to practice in equipment and installation.
There are over 20 Hardox Wearparts centres across Australia, New Zealand and New Caledonia, supporting
quarrying, construction, roadbuilding, recycling and mining.
Working with the understanding that Australian mining conditions can often be very unforgiving, Hardox Wearparts supplies reliable wear parts for underground and open-pit operations in some of the country’s most challenging environments.
“Open-pit and underground mining operations rely on the performance of wear-resistant lining for loading buckets, trucks and stationary and mobile conveyors,” SSAB said.
“Hardox Wearparts protects the mills, chutes, hydro cyclones and sorters from the particular stress conditions they are exposed to in each production process.
“In mining, buckets come in all shapes and sizes, but all can benefit from Hardox wear steel. The buckets made with Hardox will last longer and keep their original shape thanks to the steel’s combination of high strength, extreme hardness and excellent toughness.”
Hardox Wearparts also offer a range of customised wear-protection solutions
HARDOX WEARPARTS MEMBERS CAN ACCESS ONE OF THE LARGEST INDUSTRY KNOWLEDGE BASES IN THE WORLD, WITH SSAB SPECIALISTS ON HAND WHERE NEEDED.
for other production areas connected to mining, such as pelletising and sintering.
Selecting the right wear parts is critical in order to maximise uptime and find the best-performing solution at the right cost.
Hardox Wearparts assists in selecting the optimal solution by providing services such as wear reviews and monitoring, and by using WearCalc software that predicts wear and provides 3D scanning for perfectly fitted parts.
“When you’re doing business with a Hardox Wearparts centre, you should have high expectations,” SSAB said.
“Every centre operates according to high standards of staff skills, ensuring quality, performance and safety of the centre’s parts and services.
“By growing the network of Hardox Wearparts centres, as well as growing the range of products and services they provide, we are continuously improving our service capacity.” AM
For more information, visit www.hardoxwearparts.com
In October last year, Bauma 2022 in Germany became the centre of the mining and construction machinery industry.
The week-long event saw the Munich-based conference play host to more than 400,000 visitors and 3000 exhibitors from over 200 countries.
Liebherr was one of the premier exhibitors, and a shining star for the company’s Bauma offering was the unveiling of its new R 9300 excavator.
The R 9300, the second Generation 8 machine that Liebherr has in its mining excavator portfolio, is fitted with the most advanced Liebherr Mining technologies.
The new excavator is set to replace the R 9250 in the 250-tonne class when the model enters serial production in early 2024.
“We (were) thrilled to announce the new R 9300 at Bauma,” LiebherrAustralia executive general manager of mining Grahame Player said.
“This new machine will exceed our customers’ expectations with our advanced and industry-leading technology and capabilities.”
Another exciting Bauma unveiling by Liebherr was the SmartROC T35 E, the first ever tophammer battery-electric drill rig.
Liebherr will have a particular focus on Zero Emission Mining (ZEM) objectives in 2023 as the company pushes for complete mining solutions for dozing, loading and hauling that are free of fossil fuels by 2030.
In a nod to Liebherr’s work on its ZEM objectives, the R 9XX H2 hydrogen excavator took home the Bauma 2022 Innovation Award in the climate protection category.
The Innovation Award reflects political, social, economic, and ecological challenges. The expert jury focused on criteria such as practical orientation, economic potential, environmental protection, and resource conservation among others.
The R 9XX is Liebherr’s first hydrogen-powered crawler excavator and is powered by a H966 hydrogen combustion engine.
When used on a construction site, a hydrogen excavator emits almost no CO2, and from production to
decommissioning CO2 emissions are 70 per cent lower than those of comparable conventionally powered excavators.
But excavators aren’t the only piece of green machinery that Liebherr has to offer.
The company’s most powerful mobile construction crane, the optimised ML 140-5.1, also made an appearance at Bauma 2022. The crane’s ecological and future-oriented hybrid power concept enables all-electric operation with site power or another external power source.
“Thanks to its compact size and minimal space requirements in terms of assembly, operation and dismantling, the MK 140-5.1 is perfect for use in urban areas,” Liebherr-Werk Biberach GmbH product manager Daniel Nötzel said.
The crane can also be fuelled by hydrogenated vegetable oils (HVO), which are produced from waste, helping to reduce emissions and promoting climate neutrality on construction sites.
Finally, attendees were treated to a display of Liebherr’s T 274 haul truck with a Trolley Assist System.
The T 274 is a 305–327-tonne machine that provides fast cycle times, higher production rates, low fuel consumption, and a low cost per tonne.
The Liebherr Trolley Assist System uses an overhead pantograph to connect the electric-drive system to a mine site’s electrical network. This network can then be powered by the customer’s energy source of choice.
By integrating the Trolley Assist System, users can look forward to increased truck productivity and the potential for reduction in fleet size while maintaining yearly production.
“Liebherr is already partnering with industry experts and customers to accelerate the research, development, and integration of zero-emission solutions,” Player said.
“Combining our expertise on mining equipment with the expertise in new technologies and mining operations from our partners, we are ensuring the best industry solutions. We are making some exciting progress on achieving our goals, with Australia at the forefront of many of these technology developments and deployments.” AM
Flexco has used its considerable experience supplying belt conveyor components to the mining and bulk handling industries to develop the Flexco Elevate belt-monitoring system.
Fastened to the belt cleaners of conveyor systems, Flexco Elevate is a digital solution that transmits real-time data on belts’ health and functionality to a centralised hub, where the data can be tracked.
The system, which focuses on ensuring high levels of belt hygiene, detects whether cleaners are set effectively and that those systems are engaged at all times.
Flexco western regional manager Jayden Baker said the technology helps to prevent unplanned shutdowns.
“Ultimately, it’s another layer of protection and asset management for businesses so they can better upkeep their equipment,” he said.
“Whenever there is an abnormal event for the conveyor detected, the unit will send through an alert, which will be made accessible in the Elevate Dashboard and to the manager on-site who is responsible for delegating the upkeep of conveyors.
“This allows for businesses to be proactive and, more importantly, reactive when it comes to conveyorrelated issues. Rather than finding out about issues only at planned inspections, problems can be addressed as they arise.”
The development of Flexco Elevate was driven by the fact customers needed a method of detection and monitoring
that was automatic and connected to an easily accessible digital network.
Flexco Elevate fulfils another purpose in helping to keep “businesses accountable” by allowing operators and site management to easily track the health of conveyors.
“We have employed a traffic light system, so operators can tell at a glance what the concerns are,” Baker said.
“Green is working as intended, yellow is a minor fault and red is non-functional and indicative that the conveyor requires attention. This was designed with visibility and ease of use in mind, but also helps cut down on technicians going near to conveyors, which helps to increase positive safety outcomes.”
Flexco Elevate is able to track a variety of different issues, including tampering events, whether it’s been disengaged, and when there is wear present in the belt.
With the constant monitoring, Flexco Elevate can also help to drive down costs associated with major belt repair in that it limits the need for full replacements or unplanned downtimes.
“As businesses know, an unexpected shut down comes with two major sunk costs,” Baker said.
“The cost of the actual repair and failure, to get everything functional again. And the invisible cost of the loss of production that comes from the conveyor not functioning.
“If we can extend the need for belt maintenance by even just a week or two, that saved time adds up significantly.”
Flexco has currently developed a new function for the Elevate software that will be able to monitor carryback.
This new update, which is set to be available for trials in the second quarter of 2023, will provide information on how to optimise the belt and cleaning assets, in addition to a scorecard that provides a performance outcome of cleaning efficiency.
“Flexco is a global leader in belt conveyor solutions,” Baker said. “We work with mining companies all over the world and understand the challenges associated with keeping operations moving forward.
“Think of it as a ‘check engine’ light for your belts and the belt cleaners that can be used to keep your operation running and to get the most value out of your belts.” AM
A ROBUST AND EASILY ACCESSIBLE CONVEYOR-MONITORING SOLUTION IS CENTRAL TO INCREASING PRODUCTIVITY. ENTER FLEXCO ELEVATE.FLEXCO ELEVATE LEARNS OVER TIME AND ADJUSTS TO INDIVIDUAL OPERATIONS. INFORMATION FED BACK FROM THE FLEXCO ELEVATE UNITS HELPS TO IMPLEMENT DATA-DRIVEN DECISIONS.
AUSIMM’S
AMBASSADOR KIM SOLOMONS DISCUSSES HER ROLE IN THE SERIES.
AusIMM’s International Women’s Day (IWD) event series is a chance to celebrate women in mining across a range of networking events. Held from March 3–10 across Australian capital cities, the series is a way to bring teams together to celebrate success, network and share in industry celebration.
The series’ diversity and inclusion ambassador Kim Solomons is the face of the campaign, and she is dedicated to creating a safe space for all.
“Being an ambassador has allowed me to do a whole lot of reflection around my passion for inclusion and diversity, something that has been so embedded in the work that I do,” Solomons told Australian Mining
“I’ve always been a very curious person. I’ve also lived in different countries, so I know what it’s like to feel included and I know what it’s like to feel the opposite.
“So I have a passion for creating a space where we can celebrate all elements of diversity, no matter what it is.”
Solomons is superintendent of inclusion and talent at Newmont Australia, the principal partner of the IWD event series.
“Being asked to be an ambassador with AusIMM and Newmont is an incredible privilege,” Solomons said.
“This opportunity allows us to celebrate the partnership that AusIMM and Newmont share, and to promote the amazing work being done in both organisations.”
Along with networking opportunities, the IWD event series also features high-profile keynote speakers, diversity and inclusion workshops and empowering panel discussions.
“I walked away from the event series in 2022 feeling incredibly inspired,” Solomons said.
“Moving forward into 2023, I’m very excited to see the presentations, which
are one of the main things I’m looking forward to.”
Another exciting part of the IWD event series is the new immersive diversity and inclusion workshop that focuses on psychological safety.
AusIMM is taking a big step forward in providing a tool-based workshop alongside the celebratory side of the event series. With a Master’s degree in organisational psychology, Solomons is especially excited about the inclusion of the workshop.
“Individuals who are newer in their careers are going to get a lot out of this event series,” she said. “It will be fantastic for those coming into the resources sector to see all of the work we are doing to create meaningful change and to continue to instil that confidence in the sector.”
Newmont and AusIMM are making great strides to create safe and equitable spaces for everyone in the resources sector, including working to ensure the younger generation feels inspired to join the industry.
WOMEN IN INDUSTRY NOMINATIONS ARE NOW OPEN. Now is your chance to nominate an industry leader who you believe is advocating for positive change and deserves to be recognised.
WOMENININDUSTRY.COM.AU
The Women in Industry Awards recognise outstanding women leaders from across Australia’s industrials sector.
PROUDLY PRESENTED BY
The three Let’s Talk Diversity events covered topics ranging from environmental governance to social engagement. More than 400 people attended the events in Perth, Sydney and Melbourne to engage with ideas on
how best to attract the emerging Gen Z workforce towards the gold industry. Prevalent across each of the events was a consensus that businesses who perform strongly in the community, environment and diversity spaces will have a far better chance of not only attracting the next generation of
workers, but also retaining them for the long term.
The events were presented in a Shark Tank-like format, where ‘pitchers’ would present their ideas for workforce retention to experts in the gold industry.
The winning pitches covered a range of topics:
Perth
Bellevue Gold senior mining engineer Surja Pandit proposed an innovative five-part documentary series that would be used to “shake-up” how younger generations perceive the industry.
Sydney
ABC Bullion general manager Jordan Eliseo emphasised the importance of reframing the importance of gold to modern society.
Melbourne
Agnico Eagle Mines process operator Alia Melgin-Hill presented on how the industry can use social media and technology to showcase the best from the gold industry and market itself as a gateway to cutting-edge science and technology.
Through engagement with the gold community, the feasibility of pitches was shared and ideas challenged as presenters engaged in a friendly, open debate to refine ideas.
A common theme from each of the events was the need to understand the motivations of Gen Z and communicate with members of that workforce in a way that suits them, as well as providing a level of transparency as to how the gold industry operates.
The current skills shortage remains a concern to not just the gold industry, but the larger resources sector as significantly fewer young people are entering into mining-based roles.
Capturing the hearts and minds of these younger workers is vital for the gold industry to thrive and attract the best talent, as Gold Industry Group chair and Gold Fields Australia vice president of legal and corporate affairs Kelly Carter said during her presentation at the Perth event.
“Everyone is aware of the significant challenges around the access to labour and the importance of looking toward our workforce of the future,” Carter said.
“While these challenges are not unique to the gold industry, there is an opportunity for us to find our collective voice and position ourselves as an industry of choice among younger generations.”
The Perth event also featured insights shared by Pandit, who said the broader mining industry had a public relations problem.
The solution offered to changing a negative perception of the industry was to utilise one of the most powerful communication platforms known to this (or any other) generation: social media.
“We’ve lost Gen Z’s interest before they’ve even stepped foot in the industry,” Pandit said.
“To understand them and connect with them, we must start speaking their languages and meeting them on their platforms.”
Speaking at the Melbourne event, Melgin-Hill reiterated how the benefits of working in the gold industry can be easily shared, with minimal effort, to a market that has little idea it exists.
“There is scope for the gold industry to really attract people to working in FIFO (fly-in, fly-out) roles,” MelginHill said.
“The lifestyle of younger people aligns quite strongly with the financial freedom that comes as a part of work in gold.
“With strong marketing and showcasing what there is to be gained in both working on-site and the experiences that can be had off-site, many more young people are likely to enter into the workforce.”
Overall, the passion of those involved with the industry was a powerful tool in swaying those present on the night, and as a tool to attract interest from Gen Z in the future.
“Gold is an essential asset to human prosperity,” Eliseo said at the Sydney event.
Highlighting the necessity of gold in all its applications formed much of the ways in which Eliseo hoped to attract Gen Z to the industry.
“Let’s reinforce and explain to people all the wonderful things gold allows for in wider society,” he said.
The Gold Industry Group’s Let’s Talk Diversity events were a massive success across Australia and are set to continue in 2023, with a new topic to be announced later this year. AM
Primero is more than just your average Crushing and Screening Contractor.
• Core Values align with safety, continuous improvement, operational excellence delivering operations with capable, stable, reliable recovery and throughput.
• Industry-leading engineering teams deliver reliable, safe and cost-effective plants.
• Technical and operational experts.
• Vertically integrated mineral processing capability to provide a turnkey feasibility, condition reporting, scoping, refurbishment, recommissioning and plant ramp-up solutions.
• Flexible contracting models tailored to suit the client’s requirements.
• Full project mine-to-market solutions.
• Operational readiness packages.
• Client-owned asset operational solutions.
• Varied discipline and mineral processing capabilities.
• BOO “Build, Own & Operate” bespoke crushing and screening solutions based on field-proven designs currently in deployment.
fired power station in Boodarie allowing for this change.
Tees Valley Lithium, which plans to spend $444 million to build Europe’s largest lithium hydroxide plant in northern England, was also allocated land at Port Hedland.
Fortescue was allocated land at Port Hedland, as well as near Onslow at the 8000-hectare Ashburton North SIA.
A Fortescue spokesperson said the company was considering producing and using green hydrogen at both sites.
The iron ore miner has diversified into green hydrogen and is seeking environmental approval for a 5.4-gigawatt wind and solar farm at Uaroo cattle station south of Onslow, which could supply power to the Ashburton North site.
The Boodarie SIA is uniquely positioned to accommodate the downstream resource processing industries that are related to the iron ore and gas resources of the region.
The Western Australian Government recently earmarked land for seven renewable energy projects collectively valued at $70 billion.
The projects are mainly hydrogenrelated, with companies such as BP, South Korean steelmaker POSCO, and Fortescue Mining Group taking advantage of the allocations.
The land is located at two heavyindustrial estates near the Pilbara coastal towns of Port Hedland and Onslow.
Discussing the benefit of the strategic industrial area (SIA) allocation for the economy and health of the WA resources industry, State Development, Jobs and Trade Minister Roger Cook said the provision of these locations will help to keep mines and other operations within the state competitive in years to come.
“The approval of land allocations for the Boodarie and Ashburton North SIAs will help transform these sites into globally competitive, multi-product industrial precincts,” Cook said.
“The projects across the two SIA’ will deliver a range of projects, including ammonia, green iron ore, and hydrogen.”
BP, POSCO, Fortescue, Alinta Energy and UK firm Tees Valley Lithium were allocated land at the Boodarie SIA south of Port Hedland, where most of Australia’s iron ore exports are loaded.
BP has said it plans to progressively develop 26 gigawatts of wind and solar energy at a remote 6500-hectare site 250km from Port Hedland, securing the land to support the $53 billion Australian Renewable Energy Hub it has operated since June 2022.
The electricity would be used to produce green hydrogen.
If BP transmits the green power to Port Hedland, it could connect to the transmission system and supply the region’s vast iron ore business that the big three players – Rio Tinto, BHP and Fortescue – want to decarbonise.
POSCO works closely with Gina Rinehart’s Hancock Prospecting and plans to use hydrogen to make
high-quality pellets of iron called hot briquetted iron that, when used in electric-powered steel furnaces, removes high-polluting coal from the process.
In its sustainability report for 2020–21, Alinta Energy has given consideration to producing green hydrogen to support reducing industrial emissions generated through heavy transport and industrial processes, with infrastructure in a gas-
The proximity and service corridor connections of the SIA to Port Hedland enables it to be a key strategic area with the potential to evolve into a world-class heavy-industrial estate that specialises in multi-product, downstream resource processing and with the potential to be a leader in green hydrogen generation and use.
“From job creation to growing the local advanced manufacturing industry and servicing international markets, we will see the economic benefits of these land allocations and these projects flow through the WA economy over time,” Cook said. AM
THESTATE’S INDUSTRIAL LANDS PANEL HAS APPROVED ALLOCATIONS OF LAND FOR SEVEN PROJECTS TO DEVELOP SYNERGY BETWEEN THE MINING AND RELATED INDUSTRIES. THE LAND IS LOCATED NEAR THE PILBARA COASTAL TOWNS OF PORT HEDLAND AND ONSLOW.
“Jess (Maddren, Schneider Electric mining segment director for the Pacific region) talked about the frontend; the ability to access information and the need for the industry to have an open platform in order to achieve collaboration and innovation.
“Fazi’s (Yusafali, Stratum AI cofounder) presentation around Stratum’s methods for analysing information from the pit supports a much better understanding of the geology and block model. This in turn enables informed decisions to be made on how to mine, providing information on the feed that’s going into the processing plant, which is used to help predict and improve recovery.”
This was reinforced by the presentation from BASF’s Ken Plozza who’s talk on the ‘intelligent mine’ encapsulated the points presenters made regarding the application of data inputs – block models, sensor, operations, etc – to optimise specific process bottlenecks or expand further across the operation.
“When you know the feed going in and combine that with sensors that measure equipment performance, you can change operation parameters in real-time, control the process significantly better, and have improved throughput and/or recovery through the processing plant,” he said.
Eid used the example of FLSmidth’s LoadIQ.
LoadIQ uses smart sensor technology to accurately predict mill performance characteristics in real-time. It then combines this information with data about ore type and liner profile to determine the optimum mill performance by adjusting numerous process variables. Customers can then achieve better throughput and recovery for the same input.
In its first in-person iteration in three years, the 2022 International Mining and Resources Conference (IMARC) offered the opportunity for industry professionals to reconnect and realign, which is especially important given 2030 is only seven years away.
And what is so the significant about 2030?
Well, 2030 is the first net-zero deadline and most participants in the resources sector, whether it be a miner or a mining services company, have committed to some sort of sustainability goal by the end of the decade.
Day one of IMARC 2022 saw FLSmidth host a ‘minerals processing and refining’ panel session in the Mining Innovation Theatre, with the likes of Schneider Electric, Stratum AI, Metso Outotec, BASF, Vinca Technologies, and more joining FLSmidth APAC mining president Tamer Eid for a series of talks.
Eid said some fascinating insights came out of the session.
“There was a common theme amongst the panellists. They were all talking about the need to innovate
and collaborate with one another to achieve step change in the mining industry and help the sector towards net-zero,” he told Australian Mining
Eid said the “holy grail” for mineral processing is about knowing the geology and therefore the feed entering a processing plant’s front-end.
“It was pretty clear (from the session) that there are many really good things happening in the industry, but collaboration is needed to harness our collective brainpower to accelerate decarbonisation and reduce waste (water, energy and emissions) in the mining industry,” Eid said.
As the session chair, Eid spoke about FLSmidth’s MissionZero
mine and how change is imperative to achieve the necessary flowsheet improvements that underpin a netzero industry.
“This was an opportunity to talk about the green transition and how we all need to play a part,” he said. “Playing a part means thinking differently and using innovation to adapt to the new requirements that all mining companies will have to adhere to.
“If you think about existing flowsheet designs, if we stick to what has been traditionally done and simply electrify it, you’re only going to achieve incremental improvements in our journey towards achieving net-zero.
“To achieve real and dramatic step changes, we must do things differently – changing the flowsheet, putting things together in a different way and really challenging our conventional approach.”
Eid said that while there could be some risk involved in achieving these flowsheet step changes, those who are willing to partner and
collaborate can share the risk profile between parties.
While a ‘tried and tested’ approach is comfortable, in the context of limiting Scope 1, 2 and 3 emissions to achieve net-zero, this mindset won’t create the desired outcomes.
“When you have a new mine with a long life, decisions are being made around technology and equipment that will bind them for the next 20–30 years “Eid said.
“Companies need to be brave, and they need people with the foresight to challenge the status quo and guide people through areas of discomfort to pick technology and equipment that is going to set the mine up for success for the next 20–30 years.”
In September, FLSmidth completed its acquisition of thyssenkrupp’s mining business, tk Mining. Eid said this addition completes FLSmidth’s pit-to-plant flowsheet.
“There were a few product gaps (in our pit-to-plant flowsheet), and with this acquisition, we’ve filled those gaps,” he said.
“tk Mining has certain pieces of equipment such as the market-leading HPGR (high-pressure grinding roll), which really complements our MissionZero mine.”
“Then when you move to the pit, tk Mining has some of the best in-pit crushing and conveying solutions in the market.”
Eid said tk Mining also has a particularly strong overland conveyor offering, with some exciting and innovative technologies emerging from this space, such as the rail running conveyor.
As the Australian mining industry embarks on 2023 and takes another step forward in its net-zero pursuit, FLSmidth will continue working with its customers to leverage the company’s consolidated offering.
“With the combined FLSmidth and tk Mining teams, we are working closely with our customers, helping them improve their flowsheet for both brown and greenfield operations” Eid said. “With our combined technologies, we can apply our know-
how and technology to existing brownfield installations, help improve their NPV (net present value) and ultimately optimise the availability and reliability of their plant.”
Digitisation, automation and other process improvements can all be applied retrospectively to great effect.
“For greenfield operations, we engage early to understand what their needs are, along with their valuedrivers for success, making sure we’re working hand-in-glove with them to help get their flowsheet right for the life of the mine,” Eid said.
FLSmidth’s ultimate goal is to implement the MissionZero flowsheet and enable its customers to achieve net-zero by 2030.
The reality is clear: decarbonisation cannot be achieved without step change, and step change cannot be achieved without innovators such as FLSmidth.
With its growing presence and capability, FLSmidth is the perfect partner to help the Australian mining industry on its net-zero journey. AM
As the world moves ever closer to a decarbonised future, it’s becoming clearer than ever that the mining industry will play a vital role in helping to reduce the reliance on fossil fuels.
KPMG’s ‘Sustainability on the horizon: The prospects of a netzero future for metals and mining companies’ details the challenges and opportunities Australia’s resources sector must face in order to reduce its carbon footprint and achieve a decarbonised world.
When KPMG and Vantage Research surveyed more than 320 metals and mining leaders last year, they unearthed two key challenges many believe may inhibit plans for a sustainable future: altering production patterns in the face of shifting demand; and making substantial changes to the production footprint.
Almost 30 per cent of mining executives surveyed planned to achieve net-zero emissions by 2025.
“A further 40 per cent (would achieve net-zero emissions) by 2030,” KPMG’s global mining leader Trevor Hart said.
“A total of 87 per cent of the miners surveyed said they would have delivered net-zero emissions by 2035.”
According to KPMG Australia’s national leader of decarbonisation transformation CleAnne Gabriel, industry leaders had plans on committing to their netzero targets.
“Executives say the most effective measures that will help their companies meet net-zero targets are, first, to ensure their company communicates clearly and fully to stakeholders and, second, to see to it that net-zero objectives are incorporated into overall strategy,” she said.
KPMG said many external factors have undercut the industry’s ability to integrate greener resources into its operations, including the COVID pandemic, supply-chain disruptions, the war in Ukraine, and the surging demand for battery materials.
Creating and achieving goals that satisfy the demands of shareholders, governments and employees has been an admittedly neglected focus for major mining leaders. According to KPMG, only 30 per cent of companies have integrated environmental, social and governance (ESG) goals into enterprise strategy, while a further 48 per cent are in the process of doing so.
The report found there was no unanimous response to such a broad task, as inconsistency among government and business heads plagues options for concise ESG action. A combination of limited labour and fiscal resources and lax
strategising is also to blame for poor attempts at bring about change.
Despite this situation, KPMG Australia national mining and metals leader Nick Harridge spoke optimistically about the country’s outlook for resources as the economy shifts towards a low-carbon future.
“The Australian experience reflects the KPMG report, where more than one-third of respondents predicted they will significantly change their portfolio of products towards commodities and metals used to accelerate the transition to cleaner energy,” he said. “Locally, we continue to see critical minerals as the centrepiece for the sector in 2023.”
Australia has a wealth of key critical minerals in lithium, nickel, aluminium, cobalt and copper. As the country transitions away from fossil fuels, lithium appears to be the frontrunner in the race to replace the use of traditional resources.
As one of the main users of lithium, electric vehicles (EV) are estimated to be only roughly one per cent of the 1.4 billion vehicles in the world. KPMG estimates that more than two billion EVs would need to be made to fully satisfy global demand for internal combustion vehicles by 2050.
As the demand for EV manufacturing continues to rise, so too does the demand for production of critical minerals.
Despite its importance, lithium mining remains in its infancy.
Global production is forecast to rise to 1000 metric kilotons (kt) by 2024. If lithium was solely used for EV production, it would take 100 years to produce enough to fully alleviate demand.
“Lithium investment is really just beginning to meaningfully increase in Australia,” Harridge said. “Mining investment is increasingly turning towards it and other critical minerals.
“Given that the price of lithium has surged in the last year, the incentive to invest further in lithium production and circularity remains very high.
“We estimate lithium production would need to grow by around 12 per
cent per year every year until 2050 to produce enough to have two billion EVs on the roads. Given that lithium production is expected to grow at nearly double that pace in the near term, and that lithium investment is likely to accelerate, rather than slow, that pace of growth over time is reasonable.
“If we assume that lithium production continues to increase by 20 per cent per year until 2030, then production would need to rise by around seven per cent per year thereafter to meet EV demand – with other producers coming online, the pace of growth in Australia could slow to this and the world would still be able to meet total demand for lithium.”
While lithium procurement continues to develop, alternate technologies can supplement the demand. KPMG is hopeful that improvements in technology, while not yet commercially available, will reduce the volume of lithium required in car batteries and partially offset the global appetite.
Gabriel said demand for critical minerals to aid in decarbonisation already outweighed supply.
“The supply of minerals essential for decarbonisation, and for energy sustainability and security, is already an area of geopolitical rivalry, and will continue to be, resting unpredictability in markets,” she said.
Overall, lithium demand will remain strong in the short-term, but the required level of production is achievable with strong investment.
Harridge said Australia is producing, and will continue to produce, almost half of the world’s supply of lithium.
“The significant volume of investment that is set to take place should support supply in Australia over the next decade,” he said. “We see the incentive to increase lithium mining is set to rise and that means not just production but also refining.”
Increasing lithium production and refinement alone is not enough, however. These practices also need to be conducted through greener means.
Australia, which has historically transported unrefined lithium to China, is now investing in lithium refineries to support Australia’s projected growth in this space.
The country is expected to house 10 per cent of the world’s lithium hydroxide refining capacity, with that number said to rise to 20 per cent in 2027. This process is especially costly given the intended credentials needed to remain sustainable.
Gabriel suggested the growing interest in lithium and other critical minerals could become a catalyst for future trade ventures.
“Looking to the future, partner countries are likely to be prepared to pay a premium for ‘friend-sourcing’ their supply of minerals to ensure reliability and sustainability,” she said.
“There is potential for Australia – a country regarded internationally as a safe democracy with a stable financial market – to move into the supply of critical minerals essential for decarbonisation.” AM
THERE IS POTENTIAL FOR AUSTRALIA, REGARDED INTERNATIONALLY AS A SAFE DEMOCRACY WITH A STABLE FINANCIAL MARKET, TO MOVE INTO THE SUPPLY OF CRITICAL MINERALS ESSENTIAL FOR DECARBONISATION.”LITHIUM APPEARS TO BE A FRONTRUNNER IN THE RACE TO REPLACE THE USE OF TRADITIONAL RESOURCES.
The Atlas Copco 250 kVA Generator with 51.4L/h (100 per cent load) fuel consumption is ideal when you need an efficient solution and your application load varies. Providing power for long-term projects on remote sites, the QAS250 diesel generator is a high-quality heavy-duty industrial generator. Built tough, it can be used as a permanent source of power or moved regularly to where it’s needed. Whether that be a few metres or hundreds of kilometres, you can be assured of its easy, safe movement capabilities and guaranteed performance, even in the harshest conditions.
The QAS250 is perfect for sites requiring a semi-permanent installation that can be upgraded or downgraded. If you’re looking for an efficient solution, the QAS250 is the ideal option for you.
To find out more, contact the team at Atlas CEA.
• atlascea.com.au
When your pit needs dewatering, turn to the water logistics experts, turn to Crusader Hose.
The Rapid In-pit Dewatering System is able to pump large volumes up high pit walls requiring no anchoring at the top of the pit. This is unlike poly, which tends to slide down.
To deploy flexible pipeline down into the pit easily, look to the Crusader Hose Turntable. For relocating the pipeline, the Hamersley Reel System quickly does the job with minimal operators.
The Waterlord layflat hose in continuous lengths of up to 200m is manufactured for Australian mining conditions and handles high pressures. Additionally, the couplings and clamps from Crusader Hose are tested and guaranteed to hold securely.
Reusable and easily stored, the layflat hose dewatering system leaves no environmental footprint behind.
Crusader Hose has been manufacturing layflat hose for over 37 years and also fabricates reeling systems to keep mines profitable. The team at Crusader Hose understands the need for operational efficiency in mine dewatering and for reliable, easy-to-use equipment to support worker safety compliance. Contact the Crusader Hose team for large-diameter layflat hose and reel systems to achieve safety, profitability and sustainability objectives on-site.
• crusaderhose.com.au
EnviroSoil is a hydraulically applied topsoil alternative for when soil is unable to support revegetation. Active components include thermally refined organic fibres, high carbon, natural soil conditioners, seaweed extracts and mineral blends, including basalt and microbial inoculants.
When combined, these ingredients work symbiotically to improve the growing conditions of the rhizosphere.
The unique combination of nitrogen-fixing bacteria, in conjunction with mycorrhizae, works to stimulate the soil, mimicking the natural cycle and thereby creating a sustainable growing medium for the germination of plants.
Thermally treated fibres not only provide an interlocking matrix to minimise erosion, but act as a primary food source for microbial colonies to regenerate during initial plant strike.
Erizon’s EnviroLoc BFM (Bonded Fibre Matrix) is a premium hydromulching solution engineered for superior performance in the areas of erosion control and growth establishment.
Thermally refined wood fibres increase water retention and airflow exchange for improved seed germination. These wood fibres are engineered to withstand conditions where high levels of water velocity resistance is required. The fibres hold up to 20 times their own weight of water and provide extensive moisture retention around the seed.
The application is a two-pass process. The first pass of EnviroLoc BFM is essential to maximise the seed-to-soil contact for successful root establishment. A second pass provides thermal stabilisation, increased water retention and protection from fauna for the best chance of sustainable growth.
• erizon.com.au
Lubestation by Retra Fluid Handling Systems is a relocatable, lubrication pit stop for equipment maintenance. Built for fast, easy and contamination-free lubrication storage and dispensary on remote work sites, a lubestation can improve the lifespan and performance of equipment and machinery and ensure the success of industrial operations. Certified for cycloneprone areas and all wind regions, lubestations also feature forklift access for efficient loading and unloading, high-security ISO locking bars and dust filtration to minimise contaminants.
The multiple advantages of the lubestation include its simplicity to use and maintain, its efficient and cost-effective structures and its minimal on-site preparation requirement, among other things.
Lubestations are custom engineered to your exact requirements and supplied ready for use.
• retragroup.com.au/products
The Marland ABC Sprag backstop is the result of collaboration between Altra Motion’s brands.
The new sprag design features indexed sprags to distribute force evenly and have less internal friction between the inner and outer races. It also features lower operating temperatures when compared with similar units. The ABC series backstops are designed for installation on low-speed shafts with typical dimensional tolerances and clearances.
The components and bearings are continuously self-lubricated in a shielded oil chamber. A double lip seal is positioned adjacent to the bearings to keep oil and environmental contaminants out of the backstop chamber. In addition, a periodic check of the oil level and purity can be performed utilising the oil level indicator during operation or at rest. If the inspection reveals impurities in the oil, draining, flushing, and refilling can be easily accomplished using piping, T-connections and traps.
• altramotion.com
Hexagon Mining has introduced a significantly improved version of its collision avoidance system, consolidating powerful technology into just two hardware components: a smart antenna and a five-inch LCD display. Version 10 of the HxGN MineProtect Collision Avoidance System – known as CAS 10 – protects drivers and equipment with 360° operator awareness for vehicles, assets and operators in open-pit mines. Besides collision avoidance, MineProtect integrates systems for operator alertness, object detection, personal protection and vehicle intervention by sharing the same hardware.
The smart antenna integrates GPS, RF, Wi-Fi, LTE and ultra-wide band time of flight technology and the in-cabin, touchscreen display features modern UI/UX consistent with Hexagon’s other onboard solutions. This creates a better driving experience, reduced deployment and training time, reduced supply-chain complexity, and increased operator adoption.
• hexagonmining.com
For WesTrac, Rio Tinto and Caterpillar, this new tele-remote dozing system (TDS) at Rio’s iron ore operations in Western Australia is wholly focused on operator safety.
The solution utilises the Cat MineStar Command for Dozing technology and a dedicated operator control centre, allowing for non-line-of-site operation of dozers working in high-risk areas. There is also an over-the-shoulder console that allows operators to work within visual range, typically used for temporary or one-off movements of machines.
The remote operator control centre is similar to a simulator, with all of the incab controls replicated. Rio Tinto’s also incorporates a vision kit, making use of four cameras on board each dozer and relaying machine information and visuals in real time via a Wi-Fi network.
•westrac.com.au
Sandvik has added another low-profile loader to the Toro family, with the Toro LH208L loader designed to operate efficiently in conditions where working height is extremely limited.
The Toro LH208L loader is a strong and reliable workhorse for low-profile hard rock mining, specifically designed for the toughest and smallest of conditions, with an equipment height of only 1.6m and a payload capacity of 7.7 tonnes. With its robust reinforced structure, compact size, high payload capacity and components that are designed to perform in the mine environment, the loader is tailored to meet the productivity targets in applications where space is limited.
Toro LH208L loader frames are reinforced to resist ground and roof impacts, and the welded steel box structures used in the frame and boom provide strong resistance to shock loads.
• home.sandvik/en/products-services
EVENT SUBMISSIONS CAN BE EMAILED TO EDITOR@AUSTRALIANMINING.COM.AU
Brisbane | March 27–29
A flagship event in AusIMM’s calendar, the Underground Operators Conference will return in 2023. Bringing together mining engineers, mine operators, technical service managers and consultants, this conference sets the benchmark for sharing underground operational experiences and industry best practice.
With deposits getting deeper or lower in grade, there is increased pressure to find smarter and more cost-effective ways to extract orebodies. To address this demand, key discussion topics for 2023 centre around the evolution of digital technologies, automation and artificial intelligence and how these innovations are making it possible to mine at greater depths and lower grades.
• ausimm.com/conferences-and-events/ underground-operators/
Conference 2023
Perth | May 24–25
The inaugural Mineral Resource Estimation Conference 2023 will attract resource geologists to demonstrate Australasian excellence on resource estimation.
The conference aims to showcase best practice, case studies and research on resource estimation and the software
applications. Facilitating open exchange of information, the conference boasts interactive sessions, panel discussions and keynote presentations alongside case studies and peer-reviewed papers. Sessions topics will showcase the latest advancements and leading examples in QA/QC and sampling, 3D geological and estimation domain modelling, geostatistical analysis, estimation, validation, and risk analysis and reporting.
• ausimm.com/conferences-and-events/ mineral-resource-estimation/
Brisbane | June 26–29
Inaugurated in 1958, the World Mining Congress (WMC) is the leading international forum for the global mining and resources sectors.
The World Mining Congress 2023 (WMC) is a unique opportunity for international representatives of the world’s leading resource economies to meet, find new partners, discuss current challenges, and share the latest research, technology, and best practice.
WMC events have set the scene for international agreements and highlevel discussions that have influenced mining practices and the resource industry for decades. Join senior mining industry owners, investors, national and international government representatives, researchers, educators, regulators, suppliers and operators from
around the world in Brisbane for this genuine opportunity to demonstrate real leadership and presence on a world stage.
• wmc2023.org/
Mine Waste and Tailings Conference 2023
Brisbane | July 13–14
The 2023 Mine Waste and Tailings Conference welcomes delegates from across to globe to explore all aspects of lifecycle waste rock and tailings management, from site selection and design to post-closure care, and address current and future challenges affecting mining systems re-engineering.
Co-hosted by AusIMM and the University of Queensland, the conference will feature industry-leading keynote presentations, thought-provoking panel discussions, interactive Q&As, a suite of insightful technical presentations and exhibitors showcasing the latest innovations.
• ausimm.com/conferences-and-events/ mine-waste-and-tailings/
Life of Mine Conference 2023
Brisbane | August 2–4
AusIMM, in collaboration with the University of Queensland’s Sustainable Minerals’ Centre for Mined Land Rehabilitation (CMLR), is welcoming attendees back to the highly successful Life of Mine Conference in 2023.
In 2021, the Conference welcomed a record number of attendees from over 15 countries and is set to bring a wider global audience in 2023. Join professionals, researchers, government, and academia from a diverse range of sectors as the program explores the full lifecycle of a mine, from exploration to rehabilitation.
Delivered both in-person and online, this outstanding technical conference will address current and future challenges affecting the mining value chain and will present leading examples of sustainability in mining.
• ausimm.com/conferences-and-events/ life-of-mine/
Iron Ore Conference 2023
Perth | September 17–20
Iron Ore Conference 2023 welcomes delegates from around the globe to Perth to explore the latest developments and address challenges impacting the technical and management aspects of the iron ore industry.
Discussion across the four days will focus on genesis, geology, exploration, mining and processing of iron ores, bringing solutions to address the carbon footprint of iron and steel mining. Co-hosts AusIMM and CSIRO look forward to seeing everyone back inperson in 2023.
• ausimm.com/conferences-andevents/iron-ore/
We are a global team unified in a common purpose: creating advanced technology solutions to the world’s water challenges. Developing new technologies that will improve the way water is used, conserved, and re-used in the future is central to our work. Our products and services move, treat, analyse, monitor, and return water to the environment, in mining, quarry, public utility, industrial, residential, and commercial building services settings. We also provide a leading portfolio of smart metering, network technologies, and advanced analytics solutions.