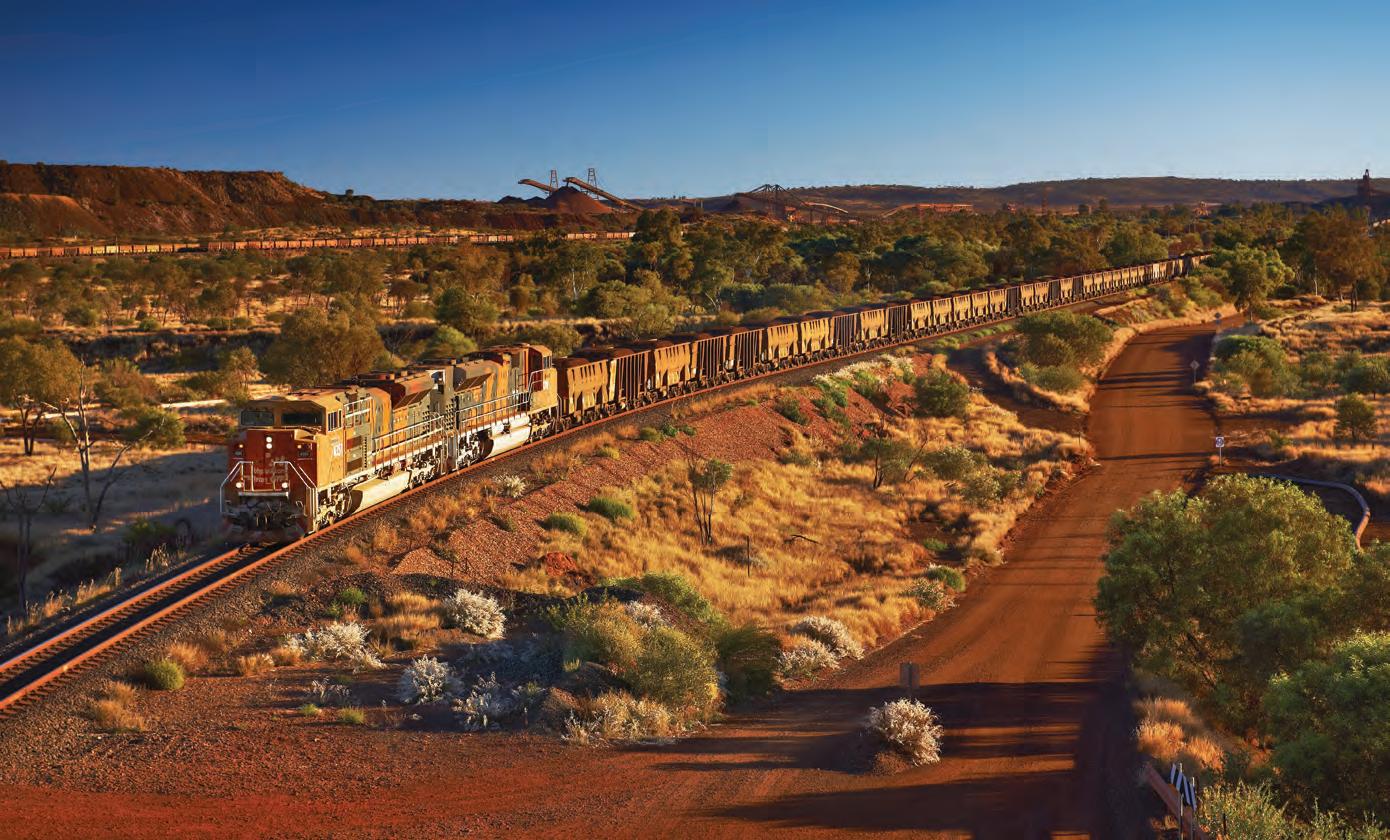
12 minute read
TECHNOLOGY
BHP’S WA IRON ORE RAIL NETWORK WILL WELCOME FOUR BATTERY-ELECTRIC LOCOMOTIVES.
MINERS MAKING INROADS TOWARDS GREEN RAIL
THE PAST SIX MONTHS HAVE SEEN A FLURRY OF MAJOR MINERS MAKING HEADLINES FOR THEIR EFFORTS IN DECARBONISING RAIL NETWORKS THAT SUPPORT THEIR SITES. AUSTRALIAN MINING EXAMINES THE VIABILITY OF THIS GREEN RAIL MOVEMENT.
A2019 report from the Australian Government and the Australasian Railway Association estimated the country’s rail network was almost 33,000km long.
Playing a significant part in the country’s mining supply chain and rail network were Western Australia’s Pilbara iron ore network (measuring 2642km), central Queensland’s coal networks (1979km) and New South Wales’ Hunter Valley coal operations (785km).
With only 10 per cent of the country’s rail network electrified in 2019, the remaining 30,000km was reliant on diesel-powered locomotives to keep Australia moving.
Along these tracks, rail operators like Aurizon and the Australian Rail Track Corporation facilitate the transport of millions of tonnes of mined material like coal and ore from pit to port.
But as mining companies and rail operators turn their focus to the elimination of Scope 1, 2 and 3 carbon emissions, hundreds of dieselpowered locomotives have come under the spotlight.
In September 2021, Roy Hill purchased the world’s first fully battery-powered, heavy-haul locomotive from Pittsburgh-based Wabtec. The FLXdrive locomotive will arrive on Australian shores in 2023, when Roy Hill will use it to haul iron ore through the heat of the Pilbara region.
In December 2021, Fortescue Metals Group welcomed two new locomotives to its research and development facility outside Perth, allowing the miner to test a new fuel system to decarbonise its rail freight.
The testing is being handled by Fortescue Future Industries (FFI), a Fortescue subsidiary, as the new trains join a two-stroke version procured earlier in 2021.
In the same month, Australia’s largest rail freight company, Aurizon, announced a strategic partnership with Anglo American to investigate hydrogen-powered bulk freight trains.
The partnership will consider the use of Anglo American’s hydrogen fuel-cell technology, already in advanced trials on its ultra-class 290-tonne haul truck fleet at the Mogalakwena platinum group metals mine in South Africa.
And now, in 2022, fellow heavy hitters BHP and Rio Tinto have each announced orders of four batteryelectric locomotives to reach their lofty carbon emission reduction targets.
Therein lie the questions: How important are these efforts in zeroemission rail freight? Will they be enough to wipe rail freight emissions from the radars of Australia’s major miners? And, if not, what more needs to be done?
Of the eight battery-electric locomotives purchased between BHP and Rio Tinto, six were ordered from Wabtec following Roy Hill’s purchase in September.
According to Wabtec senior regional vice president for southeast Asia, Australia and New Zealand Wendy McMillan, the answer to the first question – how important are these efforts in zero-emission rail freight? – is “very”.
“The mining industry is taking an aggressive approach to decarbonising its operations and setting ambitious goals to reduce emissions,” she told Australian Mining.
“The major mining companies are being proactive in addressing the emissions of their rail operations. Industry leaders such as BHP, Rio Tinto and Roy Hill are setting an example for mining companies worldwide by ordering the FLXdrive battery locomotive.”
BHP is targeting a 30 per cent cut to its operational GHG emissions (including rail) by 2030.
Conveniently, a full transition to battery-electric locomotives would reduce BHP’s WA iron ore (WAIO) diesel-related carbon emissions by the same percentage.
WAIO’s rail fleet includes more than 180 locomotives, and for each dieselpowered locomotive converted to an alternative energy source, up to 3000 tonnes of carbon dioxide is eliminated per year, according to McMillan.
Considering this and BHP’s 16.2 million tonnes of GHG emissions during the 2021 financial year, the four FLXdrives mark a key step in the company’s progress.
Anglo American is also taking steps towards its goal of carbon-neutral mining operations by 2040, with Scope 3 emissions (including rail) to be halved by that time.
Chief executive officer of Anglo American’s business in Australia Tyler Mitchelson said the hydrogen haul truck trials were a pivotal part of the company’s wider ambitions to decarbonise.
“An advanced trial of our fully functioning two-megawatt prototype truck is already underway at our Mogalakwena platinum mine in South Africa,” he said.
“Through this work, our ultimate aim is to reduce the use of the
majority of diesel at our mining operations throughout the world to help reduce emissions, and we believe this same technology could have similar applications for other heavyhaulage providers, such as heavy haul rail freight.”
As Aurizon operates the rail network Anglo American uses to transport its mined material from pit to port, the two companies have found many synergies in their partnership and are working to achieve shared emissions reduction goals.
Aurizon head of asset management James Petty said it was important for companies to work together, especially in eliminating Scope 2 and 3 emissions.
“Aurizon sees great opportunities in developing ‘green commodity supply chains’ to support Australian commodities in remaining a premium product in global markets,” Petty said.
“By forming partnerships and collaborations with our customers, suppliers and innovators, Aurizon believes we can expedite decarbonisation of our rail services.”
Aurizon has also partnered with the University of Queensland (UQ) to strengthen its credentials in zeroemission rail freight technology, investigating new-generation batteries and green hydrogen fuelcell technology.
The research will assess the energy requirements of Australia’s 33,000km rail network to understand how new technologies could replace current power systems.
Petty said the research would map out a future in green rail solutions by understanding what more needs to be done in the space.
“Ultimately the research will help us design new and future solutions to decarbonise rail freight and contribute to climate change efforts,” he said.
“We intend to publish findings to share our conclusions on the best technologies for the heavy-haul industry to adopt or pivot towards.
“We’ll also highlight where there may be knowledge, manufacturing, or performance gaps in the emerging technologies to allow future research to target and resolve.”
Petty agreed on the importance of companies working together to solve these challenges and said the company is exploring every avenue to achieve that goal.
“The decarbonisation of supply chains is a priority for companies that are committed to the collective global efforts to combat climate change,” he said.
“There are many initiatives underway across the international rail industry to reduce carbon emissions in rail operations, and Aurizon plans to tap into this wave of technology and innovation to play its part in reducing carbon emissions.”
Of course, these many hours of research and collaboration wouldn’t be necessary if there weren’t significant challenges involved with the decarbonisation of the world’s heavyhaul rail freight.
Aurizon’s 2021 Sustainability Report outlined its current standing in GHG emissions, and its devotion to net-zero Scope 1 and 2 emissions by 2050 – as well as a 10 per cent decrease from 2020 to 2030.
The report found the company released 847,312 tonnes of Scope 1 and 2 carbon emissions in the 2021 financial year. This was comprised of about 60 per cent Scope 1 emissions and about 40 per cent Scope 2 emissions.
Most of the former came from diesel locomotives and most of the latter from powering electric locomotives.
“Freight trains require a very large source of energy to be housed within the profile of the train and the railway corridor,” Petty said. “Very large power demands are required, especially when pulling heavy loads for long distances or up long gradients.
“Trains also need the infrastructure to charge and re-charge a battery, or in the case of hydrogen, to supply it at the train origin, destination and potentially
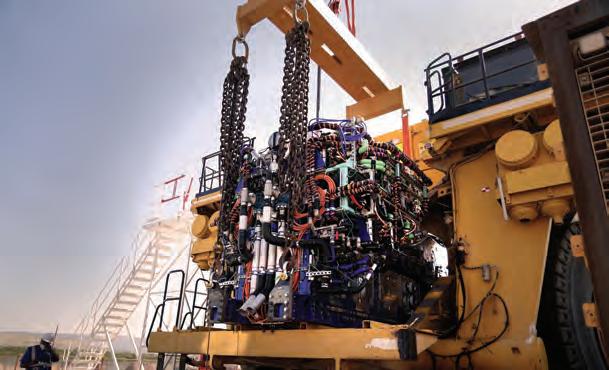
A HYDROGEN-FUELLED ENGINE BEING INSTALLED IN AN ANGLO AMERICAN MINE HAUL TRUCK.
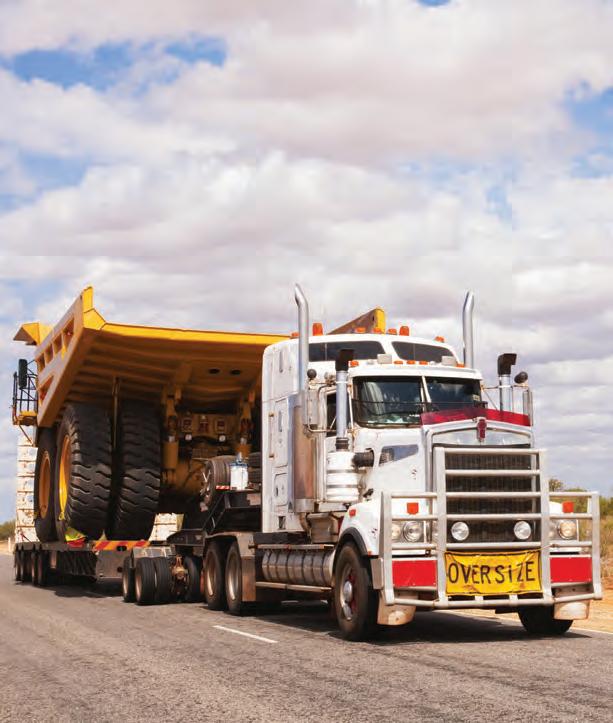
along the rail corridor.
“All these issues need to be worked through as we better understand the technology and how it can be adapted to heavy-haul rail environments. Plus, there may be a need for different solutions for different rail routes and customer needs.”
These different solutions could come in the form of hydrogen, battery power, or even ammonia, as FFI has been investigating at Fortescue.
Fortescue chief executive officer Elizabeth Gaines said FFI was considering all angles to decarbonise all corners of the iron ore producer cum “green resources company”.
“FFI’s Green Team are successfully trialling technology on hydrogen, ammonia and battery power for trains, ship engines, haul trucks and drill rigs for technology demonstration,” Gaines said.
“The Green Team have recently commenced ramping up the decarbonisation of our locomotive fleet, with the arrival of two additional locomotives at FFI’s research and development facility in Hazelmere, Perth, bringing the total to three.”
This will allow FFI’s Green Team to expand their development in green rail freight, an integral part of Fortescue’s attempts to decarbonise its 54-strong locomotive fleet.
While the obstacles to greener rail networks remain, McMillan said Wabtec was bullish about the prospects of the technology.
“Previously, there were several challenges to implementing zeroemission technologies. However, advances in battery capacity, reduced costs and improved computing capabilities make it the right time to apply battery technology to rail,” McMillan said.
“Additionally, Wabtec continues to advance and improve the capabilities of these technologies, including advances in hydrogen solutions.”
To advance these technologies, Wabtec and General Motors announced last year they were collaborating to accelerate the development and commercialisation of battery and hydrogen solutions for Wabtec locomotives.
Specifically, the technologies were GM’s Ultium battery technology and HYDROTEC hydrogen fuel cell systems.
This partnership itself represents the fact there isn’t a single perfect answer to a decarbonised rail network, but instead a plethora of options waiting to be developed for the right applications.
Petty echoed this sentiment as the company explores all avenues in the hunt for greener rail freight.
“Aurizon continues to assess a range of alternate low-carbon energy sources for its rail operations, including battery and hydrogen,” he said.
“Aurizon is not fixed on one energy solution, but rather we will examine in parallel the emerging technologies and how effectively they can operate in different situations across our national footprint.
“Battery, hydrogen or hybrid solutions may be used – we certainly believe they can have a strong future in the heavy-haul rail industry, including those services for our mining customers.”
The resounding message from these leaders in mining and rail operation is that goals have been set, and with each new battery-electric locomotive, research partnership and trial project, the industry comes another step closer to achieving those goals. AM
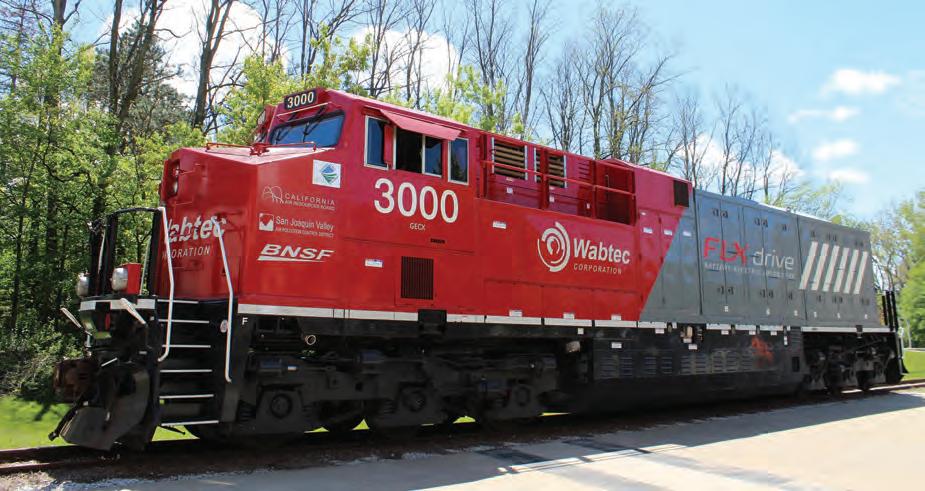
WABTEC’S FLXDRIVE LOCOMOTIVE IS THE NEWEST DEVELOPMENT IN BATTERY-ELECTRIC RAIL FREIGHT.

ALTRA MOTION: RUNNING AT FULL TILT
ONCE AN ALTRA MOTION PRODUCT IS PURCHASED, THE OEM GOES TO WORK, PROVIDING COMPREHENSIVE SERVICE THAT ALWAYS PUTS THE CUSTOMER IN THE DRIVING SEAT.
Altra Motion is a global designer and original equipment manufacturer (OEM) of 26 globally recognised and wellrespected power transmission brands, including Svendborg Brakes, Twiflex, Marland Clutch, Wichita Clutch, Industrial Clutch, and Stieber.
As Altra Motion Australia shapeshifts and expands, the company has experienced industry misconceptions about being a distributor. However, Altra Motion national marketing manager Gabriel Brooks is keen to put that to rest.
“The way we’re educating customers is by co-branding our well-recognised portfolio of brands; it’s important to us that our customers recognise we are the actual OEM, not a distributor. We carry out the R&D (research and development), design, and manufacture,” Brooks said.
“Altra Motion Australia provides our customers in mining with the engineering and application expertise of the world’s leading brands in mechanical power transmission and motion control technologies.
“Our customers can source multiple components from a single company, providing convenience while ensuring compatibility and optimised drivetrain performance.”

Expanded comprehensive service and support nationwide Altra Motion Australia also offers a well-respected service division with facilities across Australia.
“Altra Motion has three service facilities strategically located nationwide with qualified service technicians to support on-site and workshop requirements,” Altra Motion WA service manager Chris Gordon said.
“Our local service facilities in Sydney, Perth and Mackay also serve as certified rebuild centres for Svendborg Brakes, Marland Clutch, Stromag, Ameridrives, Stieber and Industrial Clutch.
“We will also open a new additional service facility in early 2022 to expand our corporate footprint and provide an even faster response to customer needs.”
All Altra service facilities are staffed with local teams of highly trained technicians that provide fast-response on-site service, including 24–7 breakdown assistance, along with installation and commissioning support.
“If a customer is unable to send their Altra product directly to one of our service facilities for testing and diagnostics, we can send a qualified service technician on-site to identify and rectify a fault,” Gordon said.
“Providing customers with the peace of mind knowing that if a component has failed but is too difficult to disassemble, Altra Motion can come to them and minimise downtime. If necessary, we can also provide a temporary (rotatable) original equipment replacement.”
While COVID-related global supply chain challenges have significantly affected some component suppliers, Altra Motion has a comprehensive supply of genuine replacement parts from various brands stocked in Australia. This allows them to complete repairs quickly without the hassle of long lead times.
“We offer preventive maintenance plans that allow our customers to pre-empt future setbacks. For example, if a product has reached the end of its service life, we recommend upgrading and retrofitting,” Gordon said.
“However, suppose the component has been in operation for a prolonged period and is beyond repair. In that case, we will offer a replacement with the latest generation of that specific product model.
“If there are any modifications in terms of mounting due to an updated product design, we would offer an entire package and assist in the retrofit installation.”
Altra Motion also offers on-site training for its mining customers in Australia, which can help improve maintenance teams’ understanding of the products and anticipate faults before they arise.
Customers are also trained on how to install replacement components. This training can be particularly beneficial for more extensive mining operations that utilise products from several Altra Motion brands.

Advanced technologies provide mine service and maintenance improvements Altra Motion has developed Industrial Internet of Things (IIoT) solutions to expedite further servicing, including Svendborg Brake’s portable IIoT Universal Control Case (UCcase).
By utilising the UCcase, Altra Motion mining customers that need assistance with commissioning, servicing, or troubleshooting of their braking systems can connect with a local or international Altra MotionSvendborg service technician in real-time. The case can even offer real-time software upgrades and be used underground. AM
ALTRA MOTION HAS A WELL-RESPECTED SERVICE DIVISION ACROSS AUSTRALIA.