
11 minute read
MINING SERVICES
BEST-KEPT SECRET GALVANISES INTO ACTION
ARMORGALV AUSTRALIA IS THE ONLY COMPANY IN THE COUNTRY THAT USES THE THERMAL ZINC DIFFUSION GALVANISING PROCESS – A STRONGER, LONGER-LASTING, MORE AFFORDABLE ALTERNATIVE TO TRADITIONAL GALVANISING METHODS.
ArmorGalv is a superior galvanising process that uses thermal diffusion to protect ferrous and non-ferrous metals.
This cost-effective, environmentally friendly, and durable galvanising technique was designed in Israel in 1993. However, it did not find its way to Australian shores until 2010, when ArmorGalv Australia was born.
The process is unique and exclusive to ArmorGalv Australia, as it is the only plant of its kind in the country.
Based in Thornton, New South Wales, approximately 20 minutes outside of Newcastle, the Australian site is recognised as the largest ArmorGalv plant in the Southern Hemisphere.
ArmorGalv Australia general manager Clive Jones says that ArmorGalv is leading the Australian industry and has done so for more than 10 years.
“ArmorGalv is the new age of galvanising. It lasts three times longer than hot-dip galvanising, as proven by many salt spray and real life tests,” he said.
The advanced ArmorGalv coating technology is called Thermal Zinc Diffusion galvanising.
A uniform, sacrificial zinc-iron coating is applied to any ferrous item using a metallurgical vapour diffusion process.
It is a corrosion-resistant and abrasion-resistant coating solution that helps increase the life of the

ARMORGALV PRODUCTS ARE GUARANTEED TO BE FREE OF HYDROGEN EMBRITTLEMENT.
CORROSION PROTECTION FOR MINING EQUIPMENT IS ESSENTIAL.

ARMORGALV IS CORROSION- AND ABRASION-RESISTANT, AND HAS ANTI-GALLING PROPERTIES.
part, even in the harshest mining environments.
“Any components that sit in a corrosive area ArmorGalv will protect, making the metal components last longer so they are safe, and also reduce maintenance costs substantially,” Jones told Australian Mining.
Corrosion protection for mining equipment is essential due to the extreme environmental factors at play on a mine site.
High ambient temperatures, extremely high humidity, acid, and dust are combined, which results in high demands being placed on the need for corrosion-resistant machines and materials.
In contrast to other galvanising methods, Thermal Zinc Diffusion galvanising does not leave any areas of the product ungalvanised.
This is because the formation of a zinc coating by means of diffusion is not hampered by the product’s geometry.
The ArmorGalv coating is a standard finish option for all ferrous metal products, known as galvanising 2.0.
“It’s highly corrosion- and abrasionresistant, it’s controllable and precise, non-magnetic, weldable, spark-free and chip-proof,” Jones said.
ArmorGalv is used to coat millions of roof support bolts in hard rock and other mines for corrosion protection.
Thermal diffusion galvanised components have been used in the mining industry worldwide for decades due to the reliable and multifunctional zinc-iron alloy.
Important factors in the corrosion of steel in coal mines is the mine water and the coal itself.
Factors such as coal particle size, moisture content and sulphur content have a significant influence on the corrosion of steel.
“ArmorGalv is used in hard rock mining, especially. Coal mining is local to us in Newcastle, but we’re strongest where there is corrosion and where there are acidic soils,” Jones said.
“Hard rock mining is really our forte.”
ArmorGalv went through a series of salt spray tests that showed the lifespan of ArmorGalv can be up to 3000 hours, compared to hotdip galvanising that would last around 500 hours.
“Hot-dip galvanisers think they are our competitors, but we are in a different league,” Jones said.
“We both have our strengths in different products.”
Not only is ArmorGalv corrosion- and abrasion-resistant, it also has antigalling properties.
Galling is defined as when two surfaces in contact seize up, and the materials gain their corrosion resistance from a passive oxide layer over their surface. Under high contact-force sliding, this oxide can be deformed, broken and removed from parts of the component, exposing the bare reactive metal.
When the two surfaces are the same materials, these exposed surfaces can easily fuse together, causing seizure or galling.
Due to increased hardness and wear-resistant properties, Thermal Zinc Diffusion provides good anti-galling properties, predominantly facilitated by the absence of free zinc at the outer surface.
In addition, a specific point of interest is that all ArmorGalv products are guaranteed to be free of hydrogen embrittlement.
This is a particularly important component in the case of safety and products made from spring, hardened or high-strength steel.
Hydrogen embrittlement is caused by the diffusion of atomic hydrogen in the steel. Thermal diffusion galvanising is a dry galvanising process, which means hydrogen embrittlement is technically impossible.
Any hydrogen present in products will disappear during the process of heating to 300°C, before the zinc-iron alloy layers are formed, and would even relieve any residual stresses that might already be present in the fastener due to other factors.
“It is guaranteed to have no hydrogen embrittlement, it is heatresistant up to 650°C, and it’s totally heavy-metal-free and non-toxic, environmentally friendly,” Jones said.
The ArmorGalv coating becomes part of the surface of the ferrous metal and fastener through this process – it not only coats, but it also diffuses into the surface.
The result is a hard super-abrasionresistant coating that cannot easily be removed by mechanical means.
Hot-dip galvanising, on the other hand, involves the products being pretreated by acid dipping, throughout which there is a chance the products will absorb atomic hydrogen.
In 2022, ArmorGalv Australia is introducing a new product called ArmorThread, aimed at high-tensile fasteners and critical components for companies to better maintain fasteners.
Traditionally, fasteners were coated to provide them with corrosion resistance and proper torque tension characteristics, while trying to avoid inducing them with the catastrophic effects of hydrogen embrittlement.
Today, there is the added requirement – and challenge – that the process of coating the fasteners be environmentally-friendly, and that the resulting coating itself be non-toxic and chrome-free.
“Making sure things are environmentally-friendly and thinking about the future is a core part of the business. We are green, we use solar power and we’re using non-toxic heavy-metal-free components,” Jones said.
“Any of the wear components, critical components, and high-tensile products, we can actually make it corrosion protected because we don’t adversely affect high-tensile fixings.”
ArmorGalv is on the home stretch of receiving an ISO certification for quality, environment and safety, which is on the cards for this year.
The company has also recently moved into a new larger premises, has more capacity and is ready to take on 2022 headfirst.
“We’ve been the world’s bestkept secret, but now we are ready to let people know about it,” Jones concluded. AM
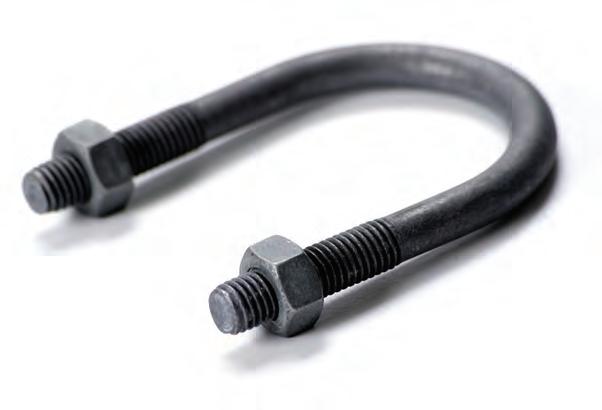
THE LIFESPAN OF ARMORGALV CAN BE UP TO 3000 HOURS.
VIBRATION MONITORING BEATS DOWNTIME
Vibration monitoring has become essential for plant and equipment predictive maintenance in mining and quarrying. Not only is it a valuable tool for preventing unscheduled downtime, but it can also extend machine operating life beyond recommended maintenance intervals. The ifm battery-operated vibration sensor, in combination with the ifm gateway, sends simple real-time monitoring and alerts to your smart device, PC or industrial computer. Powered from an internal battery with a life of at least four years, wireless vibration sensors in ifm’s vibrating-wire (VW) range are fast and easy to install, even in difficult-to-access locations. There are two versions of the VW sensor available: VWV001 and VWV002. Both have an IP68 ingress protection rating and an operating temperature range of -40°C to +85°C, allowing them to be used in the most demanding industrial applications.
• ifm.com
METSO OUTOTEC’S LARGEST SLURRY PUMP
Metso Outotec has revealed the latest addition to its mill discharge (MD) pump series, the MDM900, for use in heavy-duty concentrator plants. The MDM900 is now the largest pump manufactured by Metso Outotec and has raised the benchmark for MD pumps around the world. With heavy-duty use in mind, the pump is designed with thick all-metal walls to resist the harshest concrete mill duties. This cutting-edge pump comes with an inlet size of 900mm and is fitted with an FR2100 frame and an impeller diameter of 2100mm. The MDM900 is designed for flows of up to 3500 cubic metres per hour and heads up to 40m.
• mogroup.com
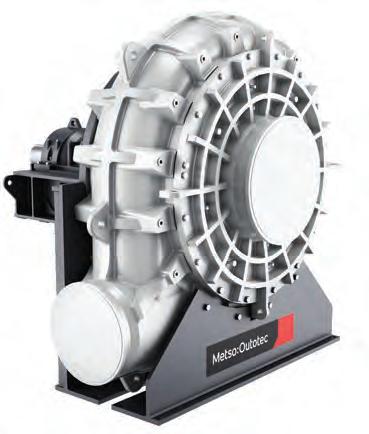
THEJO: BEST IN CLASS CONNECTING MINES WITH AI
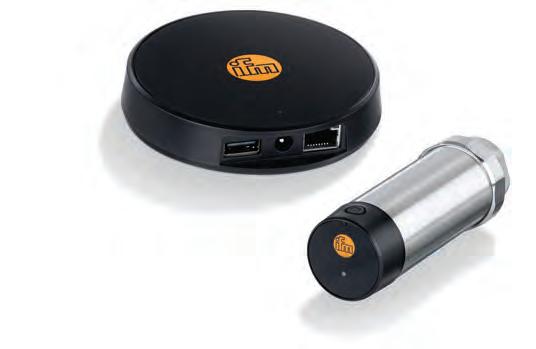
Thejo Australia strives to be the best in class, a one-stop shop for all your conveyor belt service parts. This includes steel cord and fabric conveyor belting, splice kits, on- and off-site pulley lagging, skirt rubber and skirt systems, belt cleaners and transfer point solutions (chute lining, air cannons and impact beds). The company’s extensive range of maintenance and installation equipment, including recently delivered 30T, 50T and 90T winders and multiple vulcanising presses, are capable of managing the largest of belt installations and are available 24 hours, 7 days a week for wet or dry hire. Expert service technicians take care of all your conveyor belts’ inspection, repair, maintenance and installation requirements. All Thejo Australia products and equipment are supplied under the reassurance of triple ISO certification awarded by Bureau Veritas in September 2021.
• thejoaustralia.com
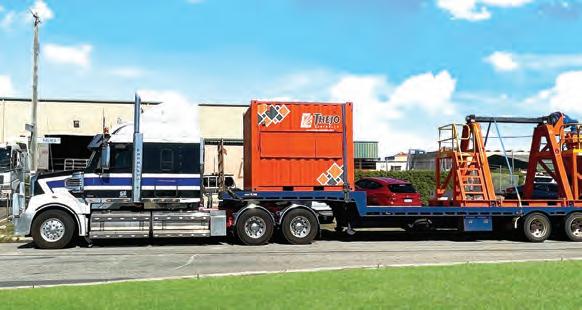
Epiroc has released a new user-friendly system with embedded artificial intelligence (AI) that enables multi-vehicle command, control and monitoring to maximise productivity and safety on mine sites. In partnership with ASI Mining, Epiroc created Mobius for Drills, a new platform to convert data into useful, actionable information that will lead mines toward automation and connectivity. Mobius for Drills displays data in an easy-to-use layout to map drill usage, evaluate statistics, track consumables, and compare planned outcomes against actual results. By providing a single platform for all stakeholders within the drilling operation, users can quickly navigate the information, filter it to their needs and streamline the decision-making process, day-to-day or over time. An added value to Mobius for Drills is its ability to work across fleets with drills from multiple manufacturers, condensing all sources of information.
• epiroc.com
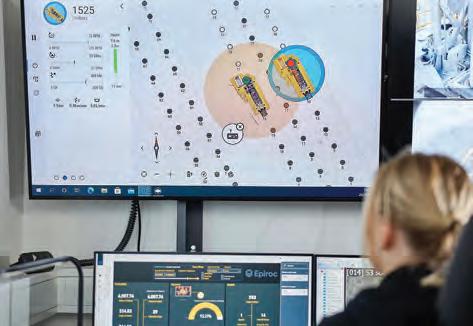
LIEBHERR WHEELS OUT NEW LOADERS SANDVIK TAKES TORO BY THE HORNS
Liebherr has launched three new wheel loaders that will increase performance, productivity and safety during daily use in the resources sector. Liebherr is modernising the three largest wheel loaders in its series with the new L 550, L 566 and L 580 models by adopting new technology that forms the basis for various intelligent features. Increasing the tip load, bucket sizes and engine power are some of the most important innovations, and the wheel loaders also feature a new electrohydraulic pilot control. The new wheel loaders feature the proven hydrostatic Liebherr travel drive, which is renowned for its great efficiency, and thanks to increases in engine power – approximately 17 per cent for the L 550 – the travel drive is even more powerful while maintaining the same low fuel consumption.
• liebherr.com
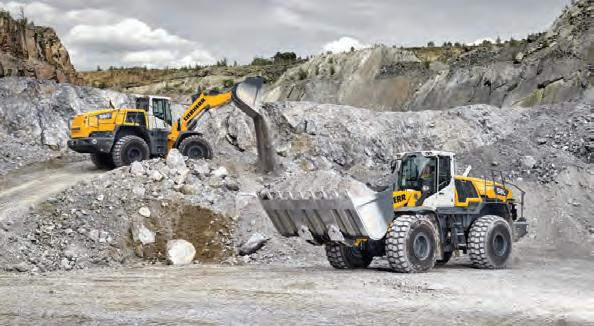
WEIR REDEFINES MINING MILL OPERATIONS
Sandvik has upgraded its Toro LH209L low-profile loader to enhance its performance, reduce downtime and control emissions. The upgraded Toro LH209L loader features a multitude of design improvements while simultaneously adding it to the Toro loader and truck family as the first low-profile model. The rear of the 10-tonne class low-profile loader has been redesigned and reinforced to better withstand ground and roof impacts that are typical in low-profile operations. For improved serviceability, extremely flat covers contribute to easy access to the service and maintenance area on top of the loader. Toro LH209L is equipped with a new operator interface with a seven-inch display, providing access to the simple and purpose-designed control system. The interface offers basic information about the loader condition and warns the operator before failures occur, preventing severe damage or potential downtime.
• rocktechnology.sandvik
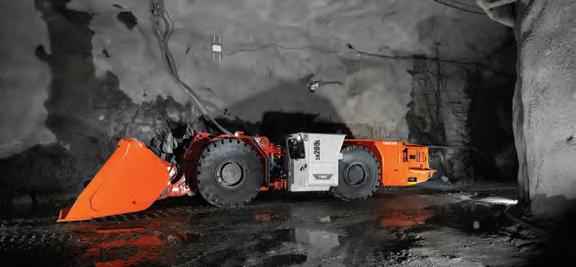
ABB STEPS UP PREDICTIVE MAINTENANCE
Vulco rubber is renowned throughout the mining industry for its exceptional wear life and reliability in mill lining systems. Having identified a need for higher-wearing rubbers for mill lining systems, Weir Minerals commenced developing an industry-leading, premium-grade rubber compound with superior wear life and performance in mill lining applications. The result was the Vulco R67 rubber – an optimum material that is manufactured with proprietary new compounds and innovative methods of processing to deliver outstanding wear life and longer uptime. Extensive field research, compound testing and site trials were conducted to ensure that it was not only able to withstand severe abrasion in typical mill system applications, but that it is best in class. In fact, it has been the most wear-resistant rubber compound that Weir has ever developed for mill lining applications.
• global.weir
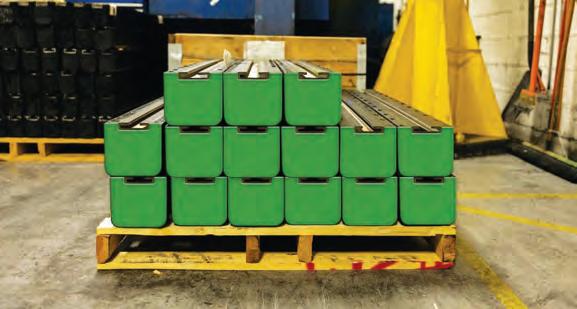
ABB has released a new version of ABB Ability Predictive Maintenance for grinding which is a unique advanced digital service to maintain, assess and analyse gearless mill drive (GMD) systems. The upgrade means that ABB Ability Predictive Maintenance for grinding is now cloud-based instead of sited on premises and includes a brand-new mobile application that allows real-time notifications on fleet status. The Grinding Connect mobile app, available for iOS and Android, means mine operators can monitor performance at any time and from any place. ABB Ability Predictive Maintenance for grinding provides easy access to GMD system parameters and allows visualisation of performance considering past activity and real-time data, and assesses future maintenance requirements. It aims to extend the lifetime of grinding assets through better use of resources and to support non-stop operation and to avoid unforeseen downtime.
• new.abb.com
