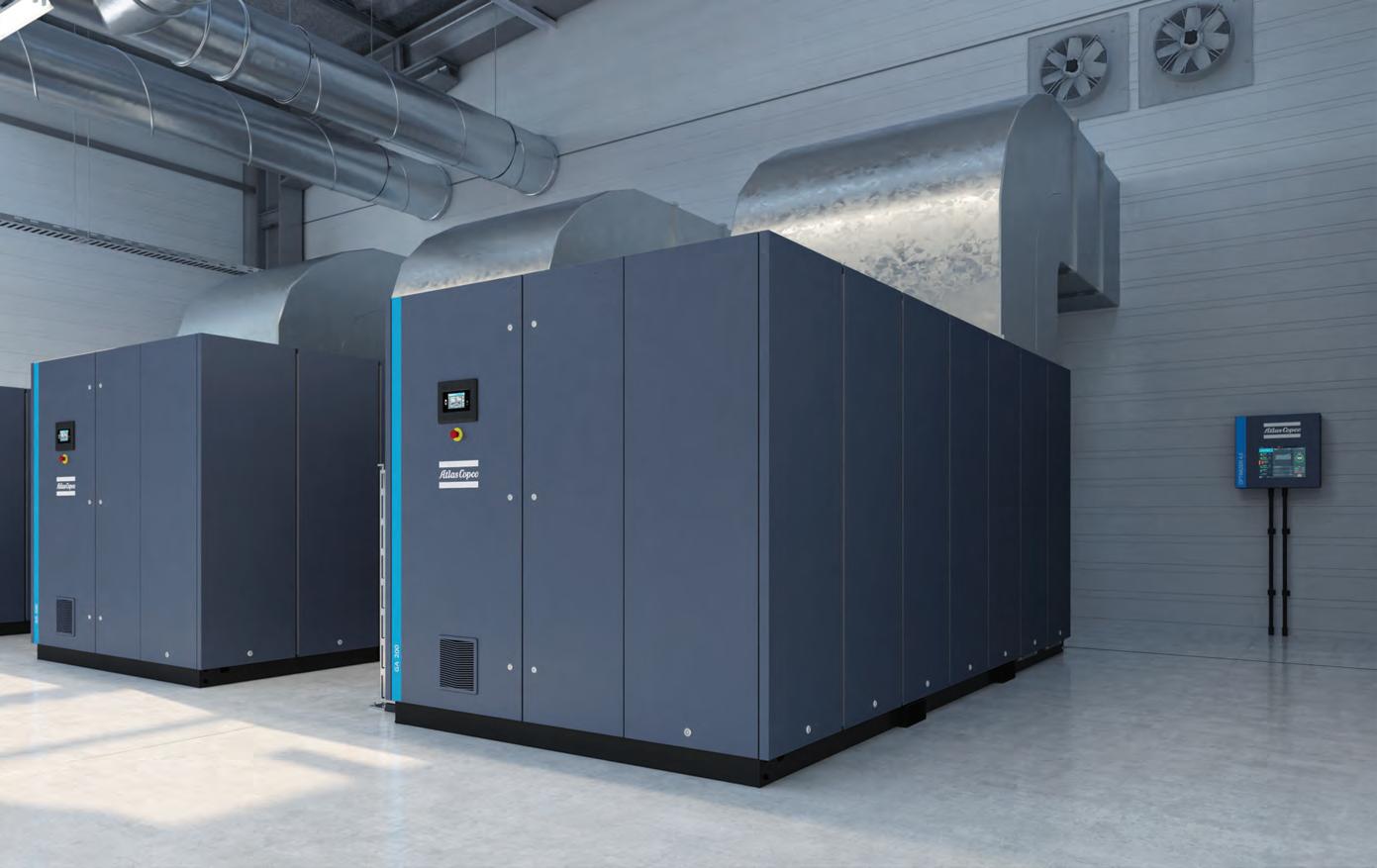
19 minute read
MAINTENANCE
THE COMPANY STRIVES FOR EFFICIENCY, PROFITABILITY AND SUSTAINABILITY FOR CUSTOMERS.
ATLAS COPCO COMPRESSES ITS FOOTPRINT
SETTING ITS SIGHTS ON REDUCING EMISSIONS IS NO EASY FEAT, BUT ATLAS COPCO COMPRESSORS MAKES IT LOOK THAT WAY. LAUNCHING MORE THAN 15 NEW PRODUCT RANGES IN THE MIDST OF A PANDEMIC, THE COMPANY IS PROVING ITSELF AS AN UNSTOPPABLE FORCE.
The Atlas Copco group is innovating for a sustainable future and has launched ambitious targets to reduce carbon emissions, corresponding to the 2015 Paris Agreement.
The targets will reduce CO2 emissions with the aim of slowing down and preventing the impacts of climate change in its own operations, as well as for its customers.
For its value chain, most emissions come from the use of its products, so by constantly innovating to reduce the climate impact of its products and solutions, the company is also supporting its customers’ own sustainability ambitions.
Atlas Copco Compressors is one of the group’s signature brands, working from the research and development of compressors, through to the production and the project planning of systems and services.
As a compressor manufacturer, the company strives for efficiency, as well as the highest possible profitability and sustainability for the customers.
“A big compressor of 500 kilowatts is going to be producing about 2800 metric tonnes of CO2. What we do is develop air compressors that are 10 to 50 per cent more efficient than the typical compressors in the market,” Atlas Copco Compressors Australia oil-injected screw compressors product manager Delfin Perozo said.
As part of the Atlas Copco group, the business has been manufacturing equipment for the mining industry for over a century, providing complete solutions for its customers, and helping to maximise operational efficiency and profitability.
Mine equipment is subjected to incredibly harsh environments and continuous operation, and any unexpected downtime from equipment failure is costly due to the lost production of minerals.
All compressed air and industrial gas solutions installed at these mining operations are required to be tough, reliable and built to last.
Atlas Copco Compressors has a proven reputation when it comes to product quality and caters to the unique needs of every mine site, with not only its products but also its inhouse engineering team.
The engineering team can design in accordance with any specifications, a turnkey installation that is exactly what is needed for the site.
The engineering team is connected with the design teams and engineers abroad at the product company, enabling them to tap into a wealth of knowledge in compressed air technology spanning decades.
“We complete the cycle, not only just supplying the equipment, but also maintaining the equipment and keeping the equipment running at the best efficiency point,” Perozo said.
“It is the complete solution that we provide to the customer, analysing what is happening with the system, and if the system is not the ideal one or if the consumption has changed on the mining side, we propose the corrective actions on how to fine-tune it to have the best energy consumption.”
The company is well-versed in ensuring its products are of the utmost efficiency. It has developed processes to make them more reliable and less stringent on the maintenance side of the business.
The company’s new generation of oil-injected screw compressors, as an example, do not require an oil change before 8000 running hours or a whole year of use.
Traditional oil-injected screw compressors need to have the oil changed every 2000 running hours or every three months.
Atlas Copco Compressors are not only making maintenance more achievable but are also contributing to less waste in its customers’ operations.
Research and development have been a major reason why the company has been able to continuously improve the efficiency and reliability of its products.
“We spend a large portion of our revenue on research and development. This gives us the ability to always have best-in-class equipment,” Atlas Copco Compressors Australia oil-free air division business line manager Pierre Matschke said.
“When we say best in class, we mean the performance of the free air delivery or the amount of air that you get compared to the power that you put in will almost always be better than an opposition machine.”
Throughout the last couple of years, as the world has struggled through lockdowns and restrictions, Atlas
Copco Compressors has been hard at work developing new products and launched more than five new product ranges during the COVID period.
By focusing its efforts on making compressed air systems more sustainable, the company can make a real change.
“We estimate that 10 per cent of the total energy used globally is for compressed air,” Matschke told Australian Mining.
“If we can optimise every compressed air system by 10 per cent, then that will have a 1 per cent net effect on global energy requirements. So we can have a major impact.”
Atlas Copco Compressors was the very first compressor manufacturer to use true variable speed drive technology and with that its compressors were saving on average 35 per cent in energy in the early ’90s.
“Today we have some ranges that can save up to 50 per cent in energy. Imagine if I can replace every compressor out there with a machine that can reduce the energy by 50 per cent. We could reduce the energy usage across the globe by five per cent. The impact is massive,” Matschke said.
Recently launched to the market at the end of 2021 is the GA 180 315 oil injected screw compressor family, including fixed speed and VSD+ versions, which brings with it a game-changing revolution in the compressor industry.
The VSD+ offers energy savings up to 50 per cent compared to fixed-speed models and is the most energy-efficient compressor range on the market.
It raises the bar in performance, reliability and connectivity to support sustainability and productivity goals.
“This is the base of the hybrid solution that we just launched at the end of the year,” Perozo says.
“They have two drivetrains, with two oil-cool models, and we have the fixed bit version and the variablespeed drive (VSD) version of that configuration.
“The new GA180-315 family is the extension of the GA90+ 160 compressors we launched in 2018. They share the same high efficiency oil cooled motors and the reliability based on the IP66 drive train,” Perozo said.
Having two drive trains and taking the best of fixed speed technology and mixing it with the best of VSD+ technology increases its efficiencies even more.
The hybrid version is the step up from what is currently the latest innovation in the market and is expected to reach the Australian market before the end of 2022.
“Selling, developing and having efficient equipment is only one part of what we do,” Matschke says.
“It’s not just about replacing a compressor; it’s about looking at the pipework: Is the pipework sufficient? Are they using the right technology for the right application? Are there air leaks?
“There is so much more to this than simply putting a machine on a site and pressing the start button. Our team is very consultative, very knowledgeable and very experienced.” AM
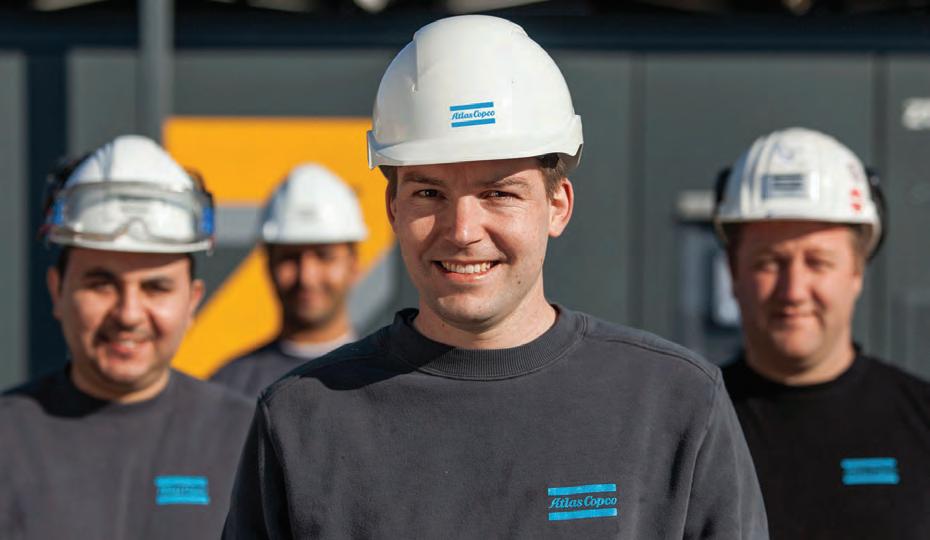
THE ENGINEERING TEAM CAN DESIGN IN ACCORDANCE WITH ANY SPECIFICATIONS.
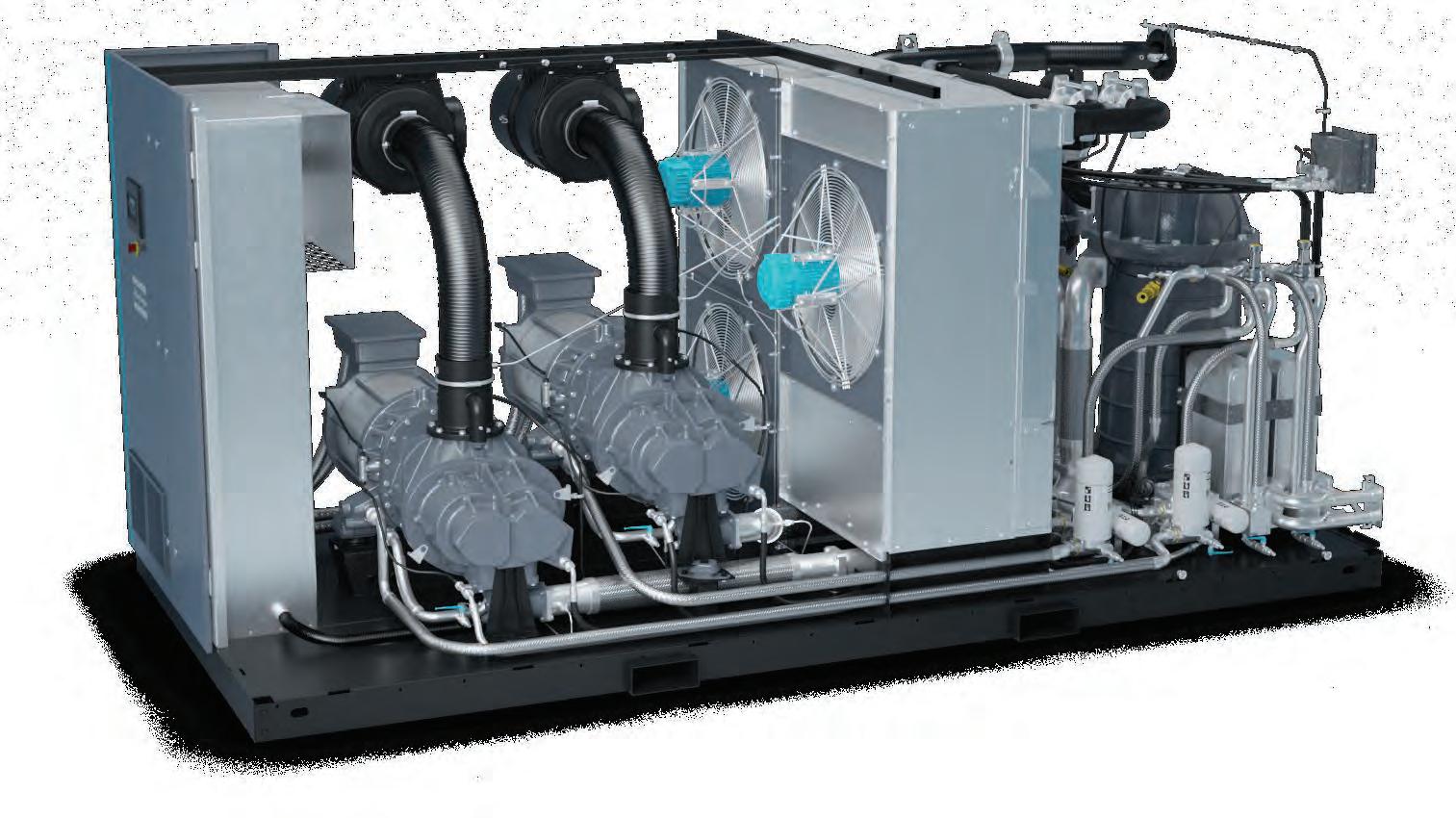
THE CULTURE BEHIND A WELL-OILED MACHINE
EFFECTIVE MAINTENANCE PRACTICES ARE BUILT ON A SUPPORTIVE TRAINING ENVIRONMENT, A DEDICATED WORKFORCE, FORWARD PLANNING, AND A GOOD UNDERSTANDING BETWEEN SUPPLIER AND CUSTOMER, ACCORDING TO THE TEAM AT NATIONAL GROUP.
To keep Australian mines running smoothly, only the best equipment and support will do. When mine owners attempt to produce thousands of tonnes of ore every day, rarely is there time for a break in play or a malfunctioning machine.
Understanding this reality, leading mining equipment supplier National Group puts many hours into improving its maintenance team so that they, in turn, can best support Australian miners.
National Group founder and managing director Mark Ackroyd said the company prioritises its maintenance team to ensure 24–7 availability for its customers.
“It’s prudent throughout most mine sites to maintain fleet availability and access to skilled workforces. These things can be quite difficult for some businesses, so having uptime in the equipment is highly important to us and our customers,” Ackroyd told Australian Mining.
“To achieve that, you need the right people doing the right maintenance and it all goes hand in hand.”
To ensure his crew can be counted on for any repair jobs that come up, Ackroyd said the company instils a culture to “train and retain” staff,
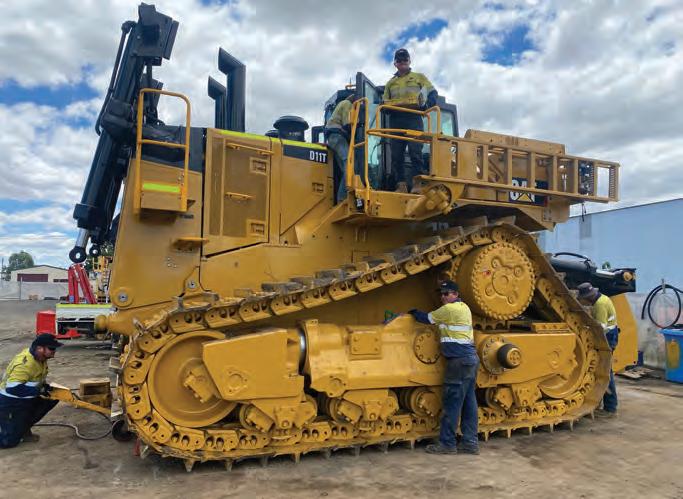
NATIONAL GROUP RETAINS ITS PEOPLE TO MAINTAIN ITS MACHINES. to ensure they know exactly what the company and its customers expect.
“We operate across a lot of mine sites these days and for many we supply fully trained superintendents and maintenance personnel to carry out those tasks whenever required,” he said.
“They work on site every day to provide 24–7 maintenance and maximise fleet availability.”
At the coalface, National Group Queensland maintenance manager Craig Weller is a testament to the culture and quality of the company.
As a qualified diesel fitter, Weller was contracted by National Group 14 years ago and has now made his way through the ranks to manage Queensland’s maintenance department.
Weller described what kept him around and why the next generation would love to take the same path.
“When I joined, National Plant & Equipment were the people to work for,” Weller said.
“These days, one point of difference for the company is we can train people, especially apprentices, in every facet of the trade.
“We’re not just parts fitters. We do a lot of repairing of our own components using our own rotatable stock. Having this system is a big bonus to us and our customers in reducing downtime.”
The variety of work is another
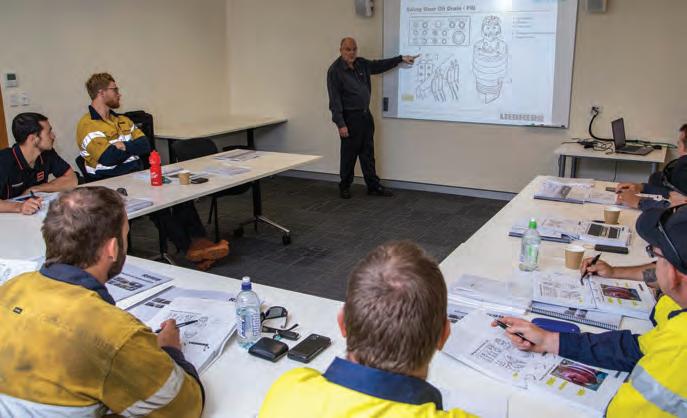
NATIONAL GROUP MAINTENANCE TEAMS TACKLE EACH JOB FROM ALL ANGLES.
plus, according to Weller, who said most people were enticed to the company by the range of equipment and projects.
He expects this will be enough to welcome a new class of apprentices in 2022 to rival the intake from 2021.
“We want to train these people our way and retain them so that in the future we can send them out to do a job knowing they have the skillset, they know what we expect and we can confidently rely on them to get it done right,” Weller said.
New apprentices will not only be walking into a comprehensive training program, but into a tightknit community among National Group customers and staff, according to Weller.
This connection is the key to effective maintenance in order to understand exactly what needs attention and an expectation it will be managed appropriately.
“There are important relationships across National Group. They’re at the sales levels to understand the top-down requirements of businesses across Australia, but they’re also at the coalface,” Weller said.
“It’s a big thing to have a relationship not only with the National Group supervisors and the managers on-site, but also with the customer’s maintenance team.
“This is because some of our jobs we do hire the equipment out and maintain it ourselves, but other jobs when we’re 100 per cent dry hire, the client maintains it.
“So relationships with everyone on-site are key to maintaining equipment and it makes everyone’s job so much easier.”
With the skills and understanding ingrained into the National Group culture, downtime can be minimised and everyone comes away happy.
“My phone is on 24–7 and then there’s a group of people who do the same in case I’m not able to be contacted,” Weller said.
“If there’s a call made and we haven’t got something on the move within two hours, I’d be pretty disappointed.”
Proud of a job well done, Weller gave an example of when this system sprang into action and satisfied one of many customers.
“Yesterday, I received a phone call from Curragh coal mine, I rang Komatsu in Emerald, the parts were in stock, so I ran straight there and took them myself,” he said. AM
ELPHINSTONE SWITCHES TO SUSTAINABLE SOLUTIONS
SINCE REFORMING AS A COMPANY IN 2016, ELPHINSTONE HAS CONTINUED TO EVOLVE ITS UNDERGROUND HARD ROCK MINING PRODUCT RANGE TO ADD VALUE TO ITS CUSTOMERS’ BUSINESSES AND TO MEET THE EVER-CHANGING REQUIREMENTS OF A GLOBAL MARKET.
ALL MACHINES FEATURE AN INTEGRATED CATERPILLAR POWERTRAIN.
Elphinstone is a worldrenowned designer and manufacturer of quality products for the global underground, surface mining and rail maintenance industries.
The brand’s legacy evolved with the underground load haul dump (LHD) loaders and trucks. While being subjected to harsh conditions, the machines aided the design and development of the company’s current range of underground hard rock mining support vehicles.
Headlining the range is the WR810, a purpose-built and highly configurable 10-tonne nominal base platform available in forward- or centre-mount cab configurations.
Designed and manufactured in Burnie, Tasmania, the WR810 range comprises a scissor-lift, an agitator (6m³), a fuel and lube truck, a delivery with crane, and an innovative water cannon.
All machines feature an integrated Caterpillar powertrain, electromagnetic retarder, and oscillating hitch, delivering optimum performance, handling and reliability in the harsh underground environment.
The WR810 machines are available in Tier 3 and Tier 4 engine arrangements, providing the customer with more sustainable alternatives.
Two Tier 4 machines were recently delivered to Toromont, an authorised Caterpillar and Elphinstone dealer located in Ontario, Canada.
Toromont has a longstanding relationship with Elphinstone, and with Canada governed by more stringent emissions standards, Toromont requested a Tier 4 machine and Elphinstone delivered.
“Canada is leading the way in the underground mining equipment market, and they’re pushing the industry towards equipment which produces fewer emissions resulting in the development of battery electric vehicle (BEV) solutions,” Elphinstone global sales and marketing manager Tim Mitchell said. “Hence why there is an increase in mining companies trialling these types of machines, not only in Canada but in Australia also.”
The Tier 3 and Tier 4 WR810 models may look the same on the outside, resplendent in yellow, large and robust, but the distinguishing feature is the engine management software.
“They utilise a different exhaust control system to manage emissions. The Tier 4 machine uses AdBlue which, when mixed with the exhaust gas, breaks down the nitrogen oxide into harmless elements,” Mitchell said.
The WR810 is designed to operate for no fewer than 20,000 hours, and up to 30,000 hours, provided the recommended maintenance schedules are followed.
“If you were to compare our machine to others in the market, the WR810 has a larger, more robust chassis, providing greater structural reliability. Engineered to outlast our rivals in the field, the WR810 provides greater value and a lower cost of ownership,” Mitchell said.
Maintenance of all mining equipment is important, and the design of the WR810 has made the serviceability of the machine simple and easy to access.
“Ground access to all major service points has reduced the need for maintenance staff to climb onto the machine”, Mitchell told Australian Mining.
“If they need to climb onto the machine, there are handrails and steps ergonomically positioned to allow access to critical components and service points.”
The flagship of the Elphinstone range, the WR810 Water Cannon, is a specialised dual application machine, operating both as a production and support vehicle.
As a production machine, the water cannon uses high-pressure water to blast and wash valuable ore fines from difficult to access areas of the mine.
Additionally, the water cannon can wash down the internal surfaces prior to the shotcrete process to recover ore fines.
As a support vehicle, the highpressure water cannon can be used to unblock open stopes by blasting the fines and smaller rocks away, as well as dislodging the remaining material.
In addition, water spray valves mounted at the rear and sides of the tank suppress dust from the haul roads, improving the operating conditions and resulting in improved health and safety.
The water cannon can also be used in the case of a fire emergency to fight the fire from a safe distance.
“The dual application reduces the need for multiple machines, reducing capital, operational and maintenance costs plus the amount of heat and emissions produced. By combining two applications into one, you gain more value from the use of one machine.” Mitchell said.
Three WR810 Water Cannons have sold within Australia, operating at mines in Western Australia, Victoria, and New South Wales.
Two units were initially on trial,
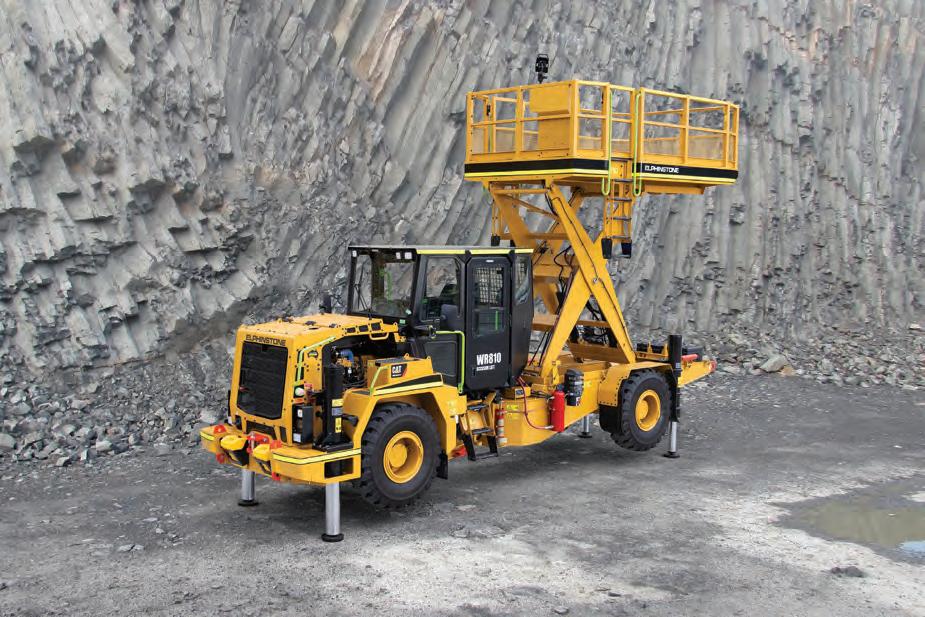
THE WR810 IS AVAILABLE IN TIER 3 AND TIER 4 ENGINE ARRANGEMENTS.
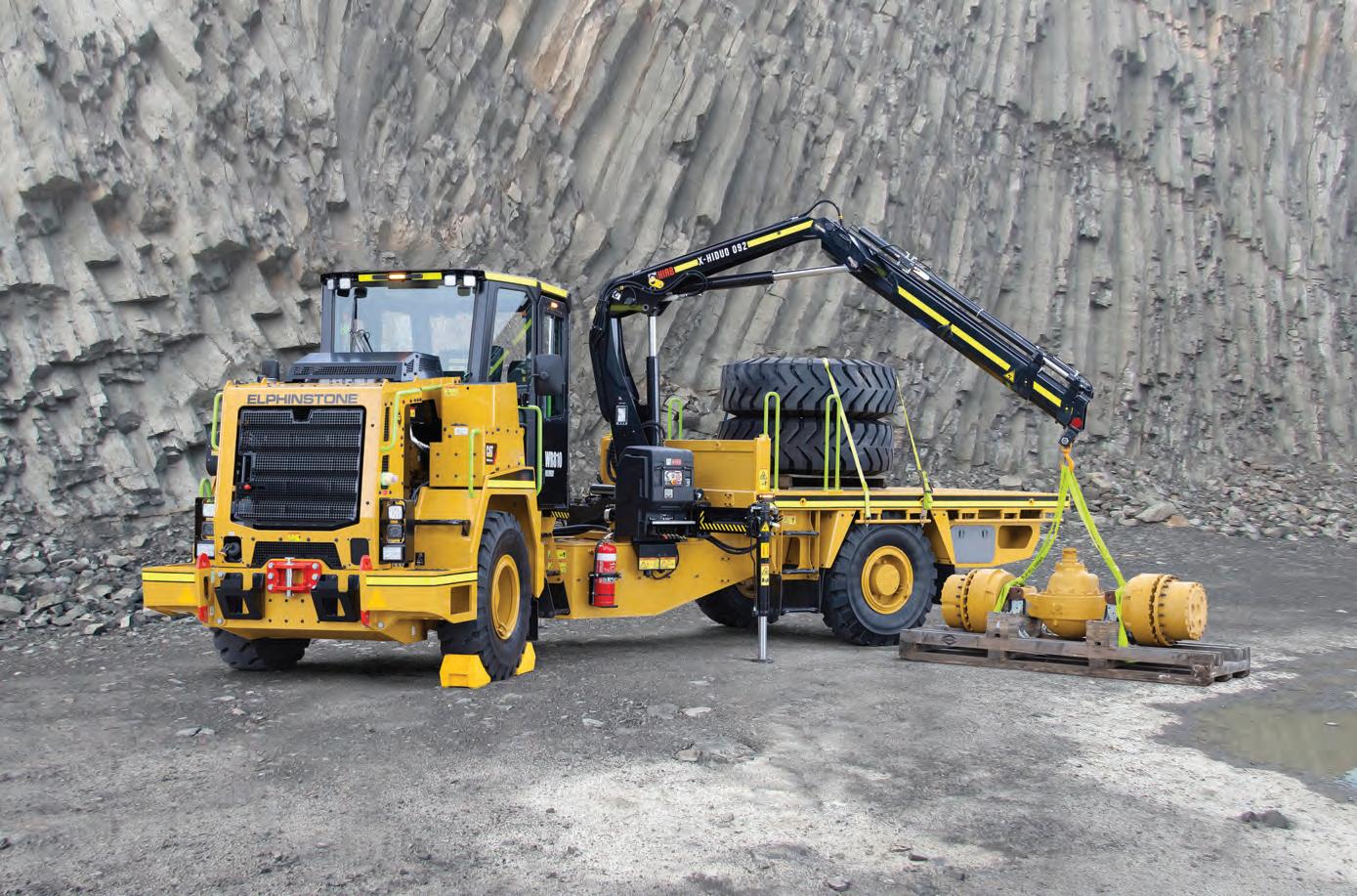
exceeding the customers’ expectations and resulting in machine sales to different mining companies.
“In both cases, the water cannons were trialled at gold mines where their primary purpose was ore recovery. The third machine was delivered to a copper mine that suffers from high temperatures so the dust suppression system will also be used for cooling” Mitchell said.
Elphinstone products have been designed and manufactured in Burnie since the business began in the 1970s.
In 2000, Elphinstone was bought by Caterpillar, which continued to operate the Burnie facility for another 16 years before moving offshore to Thailand.
A community of 20,000 people faced losing a considerable portion of its highly skilled workforce, so Dale Elphinstone took it upon himself to keep the journey going.
“Dale decided to restart Elphinstone primarily for the local community,” Mitchell said.
“If we didn’t keep those high-skilled people here in Burnie, they would have either gone to the mainland or somewhere else looking for work.
“There was a lot of talent amongst those people of which Elphinstone was able to retain here.
“It’s vitally important for the local community, and Australia as a whole, to have a manufacturer of underground hard rock mining equipment in this country.”
Elphinstone has a varied product range that it has developed in only six years from when the company reformed in 2016.
Having invested a lot of resources into product development, Elphinstone has its eyes set on the future.
“We have the Tier 3 and Tier 4 engine – our next step is to add battery electric to the WR810 and underground grader models as well,” Mitchell said.
Elphinstone envisage that the battery electric vehicle project will also create further opportunities and growth in the state and local communities, something Elphinstone has proudly supported for many years.
“We have a project team focused on battery electric, and we’re also developing other products in parallel while seeking customer feedback,” Mitchell said.
“Our ultimate aim is to add value to our customers’ businesses with our products while creating opportunities for growth.”
The battery electric products are still in development, but Elphinstone plans to have them commercially available in 2024. AM

TWO OF PERFORMANCE MINING’S VOLVO EC350D EXCAVATORS.
CJD SUPPORTS PERFORMANCE OF EMERGING MINING SERVICES
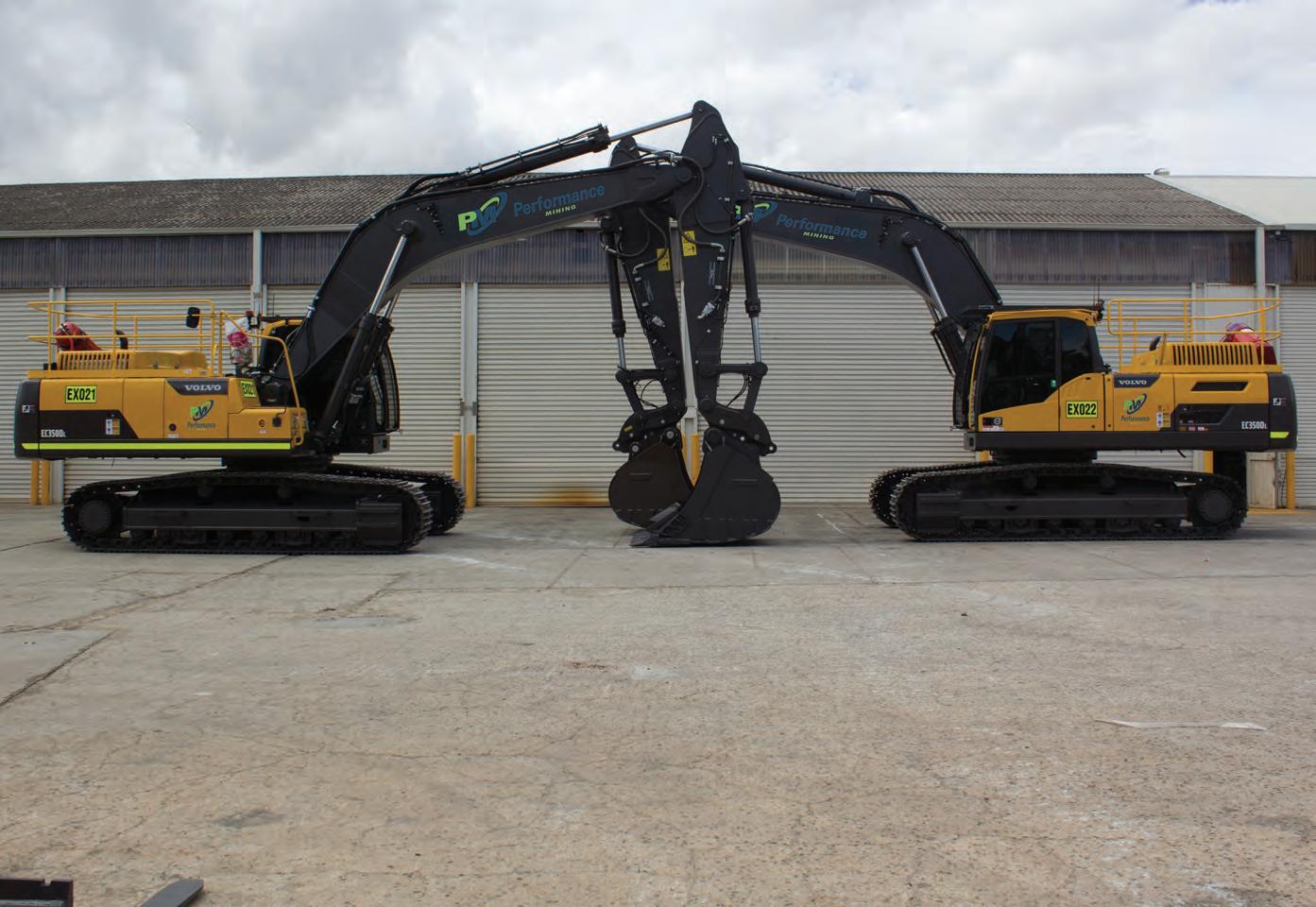
WITH EQUAL PARTS QUALITY MACHINERY AND A SUPPORTIVE SUPPLIER, THIS COMPANY HAS SEEN EXPONENTIAL GROWTH IN ITS SIX YEARS. PERFORMANCE MINING GIVES BACK TO THE COMMUNITY THAT RAISED IT THANKS TO CJD EQUIPMENT.
As a privately owned service provider to the mining and civil construction industries, it was always going to be a battle for Performance Mining to make a name for itself in Western Australia.
The company was founded in 2016 out of Pinjarra, south of Perth, offering tailored solutions in areas such as plant hire, maintenance services, rockbreaking, access road maintenance and resource development works.
Performance Mining director Jarrod Seymour said the vision for the company was always about repaying the industry for the career it had given him and business partner Ray Bushnell.
“The key motivation for us as directors at Performance Mining is to give back to the industry what we were fortunate to have learnt from our seniors over the term of our careers,” Seymour told Australian Mining.
Seymour and Bushnell have more than 60 years of experience in the mining industry between them, having worked for public and private sector companies in Australia and overseas.
Since its foundation, Performance Mining has grown to service WA’s Peel, Southwest, Goldfields, Pilbara and Kimberley regions. The team also has a plant on long-term hire in Whyalla, South Australia.
Such experience meant the team knew exactly what to look for in its equipment supplier, namely a capable company that could support Performance Mining out of its infancy.
CJD Equipment was just the ticket for Seymour and Bushnell.
“The quality of their equipment is excellent, but what’s more the team at CJD really got behind us when we were kicking off the business and provided a finance solution that allowed us to step into new equipment,” Seymour said.
“We also felt well supported by their parts and services account, which is critical for any company getting started.”
Performance Mining has made use of three Volvo EC350D excavators and one L90F wheel loader from CJD, along with two Kenworth T659 prime movers.
These 36-tonne excavators and the 15-tonne wheel loader have been a strong choice for Performance Mining, according to Seymour.
“We have had exceptional reliability and availability out of our Volvo machines, which has converted to more productive hours per shift,” he said.
“Our Volvo excavators are currently running at 93 per cent mechanical availability, whilst our loader is at 95 per cent.
“We were also fortunate enough to have the CJD team support running a larger batter bucket on one of our excavators in a frontline sand application, loading Volvo articulated trucks that reduced the loading time by a complete bucket cycle.”
This kind of availability ensures Performance Mining can live up to its name. Complimented by capable support staff, the company can branch out into some of WA’s more remote locations.
Seymour described how CJD supported his company to minimise downtime.
“We have CJD complete our valve sets to ensure that our engine health is maintained to the right standard,” he said.
“We also rely on CJD for our Matris (for fuel use) and track/tyre reports when our machines come back from hire.
“CJD has attended a couple of minor warranty matters on our excavators in the Pilbara, which resulted in very little downtime due to the team’s responsiveness.”
Most important to a sufficient maintenance service is strong communication and an understanding of what’s expected from both parties.
While Performance Mining has cemented itself in WA, plenty of growth remains ahead, with the company having doubled in size year-on-year since it began.
Seymour said CJD was a strong choice to partner through the early stages of an aspirational business.
“It’s absolutely critical to maintain a strong working relationship with your OEM (original equipment manufacturer) so you have access to the right team member – irrespective of which day of the week it is – so you can share problems if they occur,” he said.
“Both parties have put a lot of energy into maintaining the relationship so there are open communication channels on both sides through to the senior executive members as required.” AM
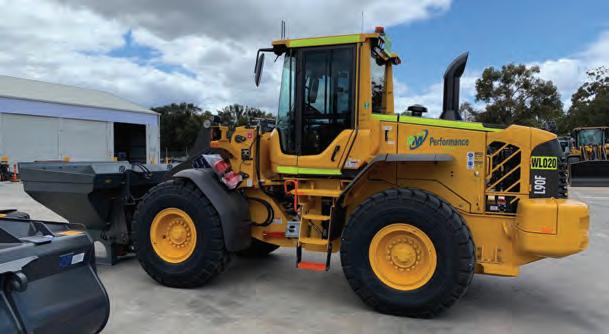