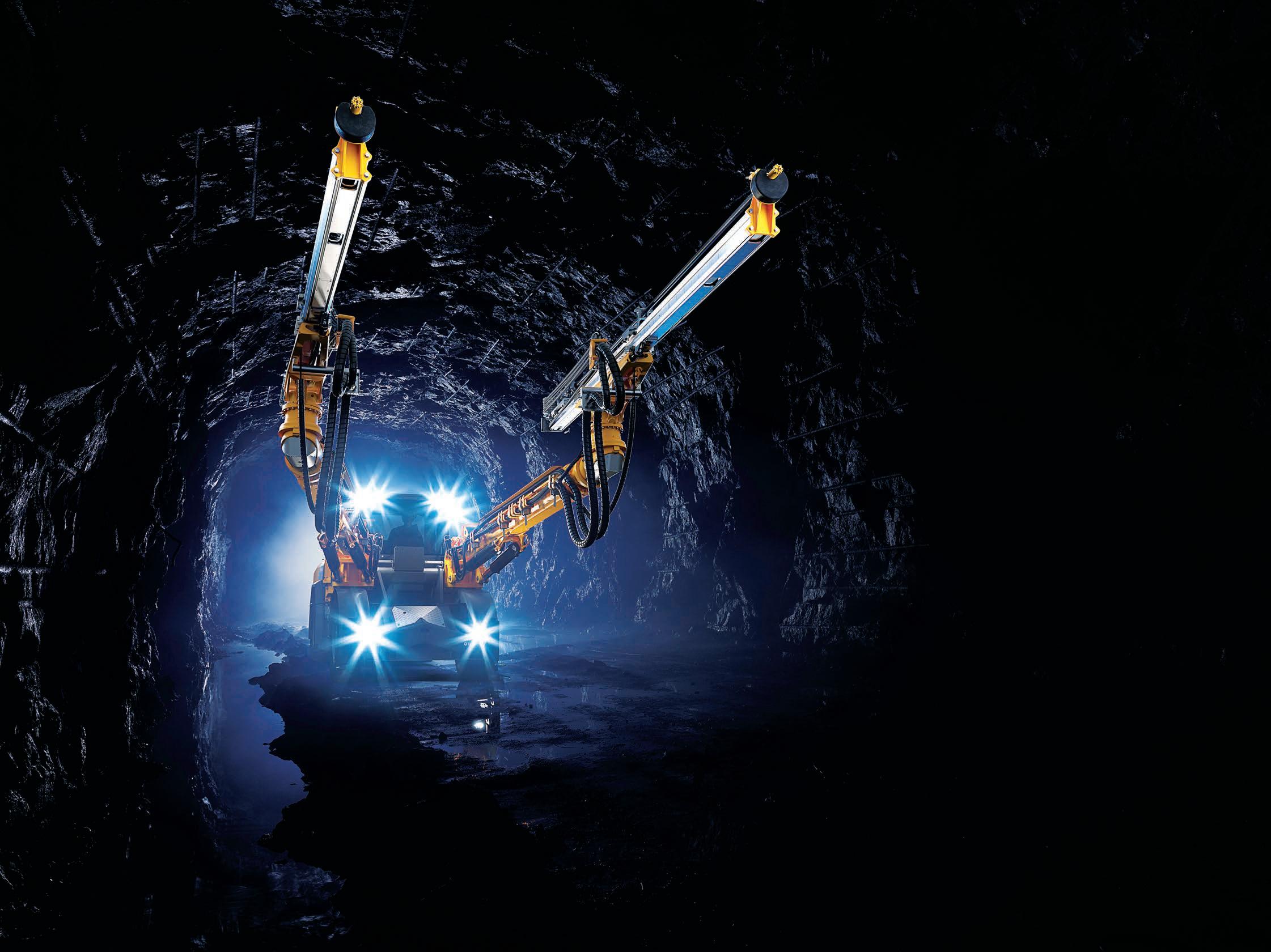
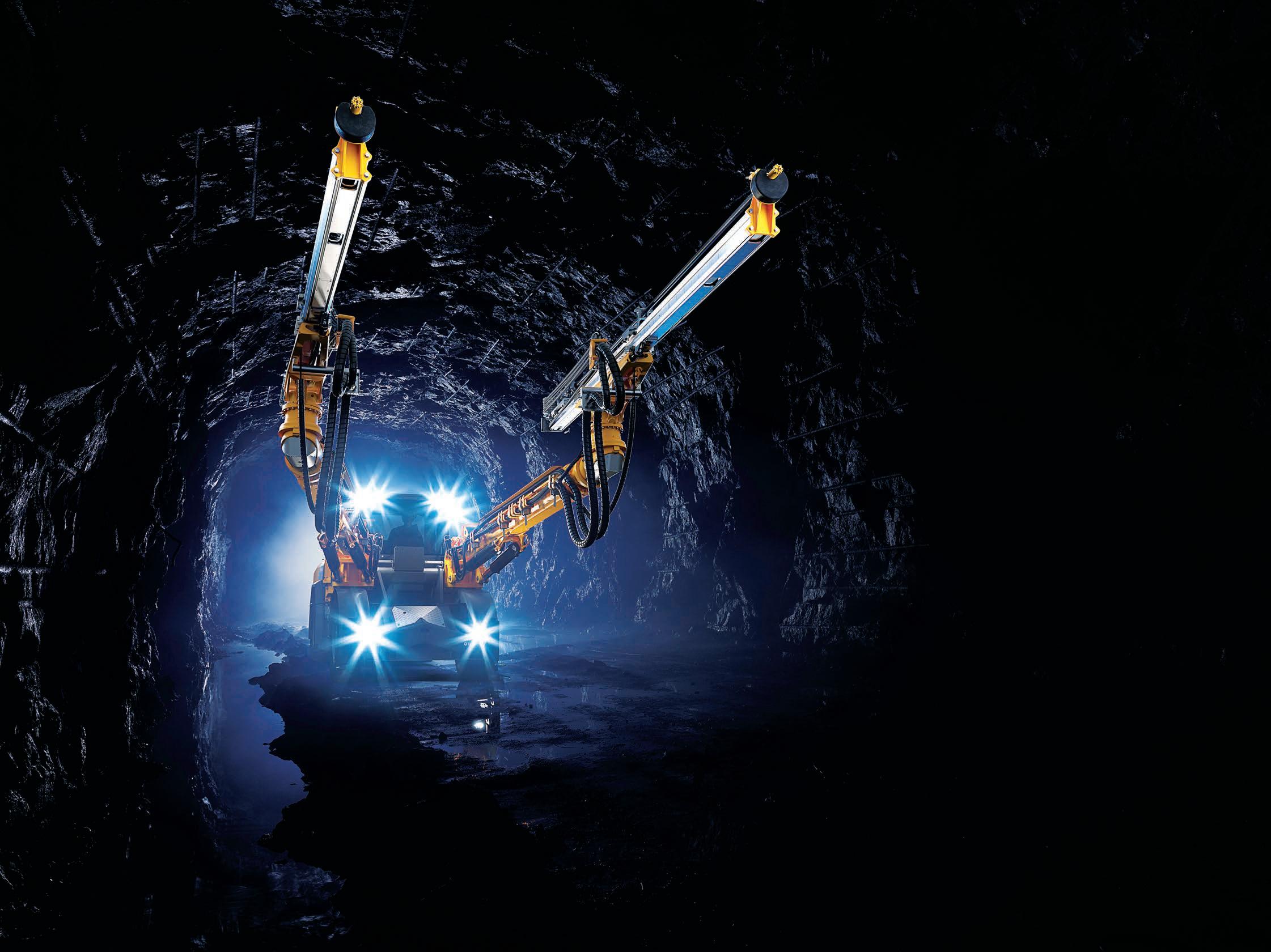
Zero-emission High productivity

United. Inspired.
Scooptram ST18 SG
Built for demanding underground operations, the battery-electric, automation-ready Scooptram ST18 SG gives you the ability to work in the toughest conditions without exposure to diesel particulates and toxic gases. This underground loader boasts a strong electrical drivetrain that is unmatched by any diesel engine, and when coupled with the traction control function, offers power and agility when entering the pile. Why compromise productivity for sustainability when the ST 18 SG offers it all?
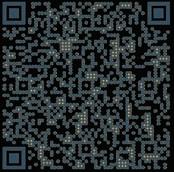

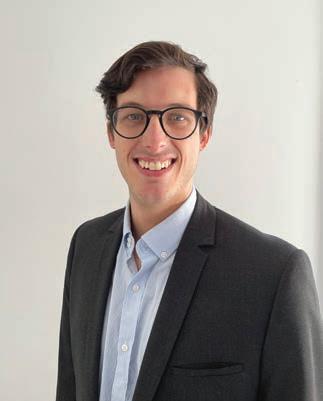
A FUNDAMENTAL PRACTICE
NO
MINE CAN OPERATE TO THE BEST OF ITS ABILITY WITHOUT HAVING PROACTIVE MAINTENANCE MEASURES IN PLACE.
As the Australian resources industry strives to keep up with growing productivity and safety expectations, machinery is placed under increasing pressure to perform.
This can place stress on an asset; it is therefore critical that mining companies and contractors consider implementing preventive maintenance measures to ensure pain points or stressors are identified before they become an acute problem.
With the importance of the maintenance industry in mind, the March edition of Australian Mining celebrates the maintenance technologies, approaches and methodologies that keeps the mining sector on two feet.
Whether it’s Epiroc and its mission to create a more sustainable mining industry through zerohour rebuilds, where a machine is remanufactured so its clock returns to zero, or the engineering ingenuity of MASPRO, a company that employs novel approaches to solving the mining industry’s most pressing issues, the Australian resources sector is in safe hands.
Other maintenance proponents featured in this issue include Dredge Robotics and its linersafe robot that can safely dredge ponds without damaging the liner, and Brennan, which is turning heads for its technology offerings that optimise the convergence of information technology (IT) and operational technology (OT).
Elsewhere, Australian Mining shines a light on the emerging vanadium industry, including
interviews with Yadlamalka Energy, which launched Australia’s first commercial vanadium flow battery in July 2023, and Australian Vanadium, which opened a vanadium electrolyte processing facility in Perth at the start of 2024.
When the Allkem–Livent merger was completed in January, it created one of the biggest multinational lithium players in the world.
The resulting Arcadium Lithium strides forth with a consolidated business model that aims to deliver more lithium, more reliably and more quickly. The enlarged company boasts a footprint spanning Australia, the US, Canada and Argentina. We break down the merger timeline and consider what Arcadium Lithium’s future looks like.
Rounding out the March edition are interviews with the likes of Atlas Copco, Kal Tire and Decoda, along with a feature on Xylem’s acquisition of Evoqua Water Technologies, creating an enlarged water technology company capable of delivering end-to-end solutions to the Australia mining industry.

no introduction, the multinational OEM always seems to be reinventing itself.
This year sees Epiroc focused on delivering zero-hour rebuilds for its customers, not only returning used equipment to its original state but also considering ways of making the machinery better. This could involve converting machines to a hybrid operation or making them entirely battery powered. First port of call is delivering hybrid machines, simultaneously powered by diesel and an electric drive system. This is the electrification offering the mining industry is crying out for.
Tom Parker EditorWith every zero-hour rebuild, Epiroc is generating the data and smarts to underscore its hybrid engineering efforts, with a goal to facilitate a “soft landing” for mining companies looking to deploy hybrid technologies.
Cover image: Epiroc
THIS ISSUE
10 COMMODITY SPOTLIGHT
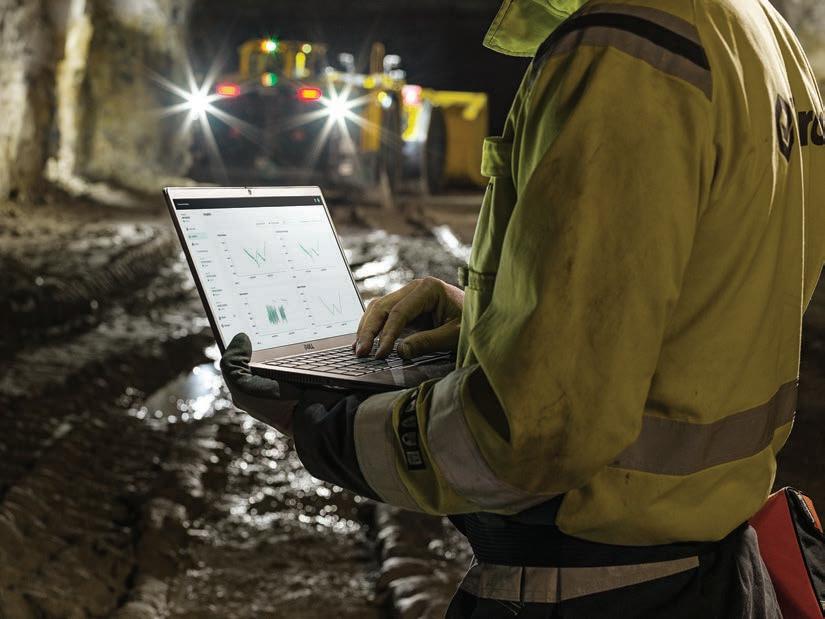
Australia’s next mining frontier Vanadium is set to take off as a new industry hits Australian shores.
14 INDUSTRY INSIGHT
Closing 2023 on a high Australian Mining showcases production highlights and project developments from the industry’s major miners.
16 MAINTENANCE
As good as new
Epiroc is working with an esteemed mining services company to complete a zero-hour rebuild, opening up significant opportunities for electrification.
18 MAINTENANCE
Solutions for the harshest conditions Australian Mining sat down with MASPRO to discuss the engineering company’s rapid growth and future objectives for the Australian resources industry.
32 MAINTENANCE
Simplifying the technology convergence Brennan believes that in a data-driven era, the synergy between information technology and operational technology can underpin a miner’s success.
44 MAINTENANCE
Rebuilding better
Hastings Deering has simplified its repair services to help customers choose the right option to suit their needs.
50 INDUSTRY INSIGHT
A lithium behemoth
After a months-long process, Allkem has finally merged with US chemicals giant Livent, creating Arcadium Lithium.
56 WATER MANAGEMENT
A match made in heaven
Xylem and Evoqua have combined to create an enlarged water technology company set to deliver significant benefits to the Australian resources industry.
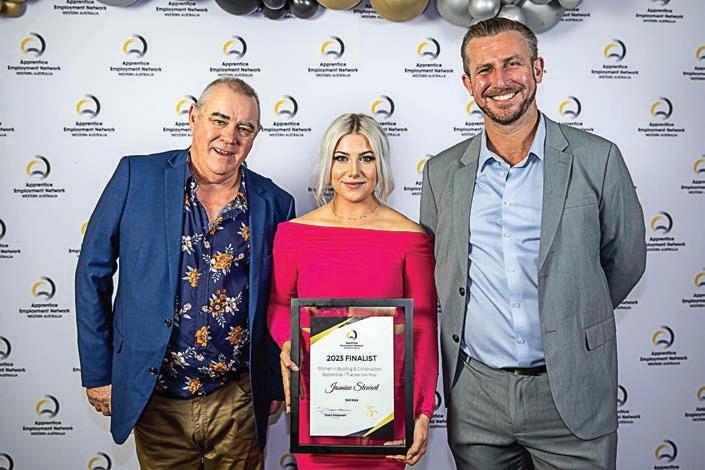

December 2023. Australian
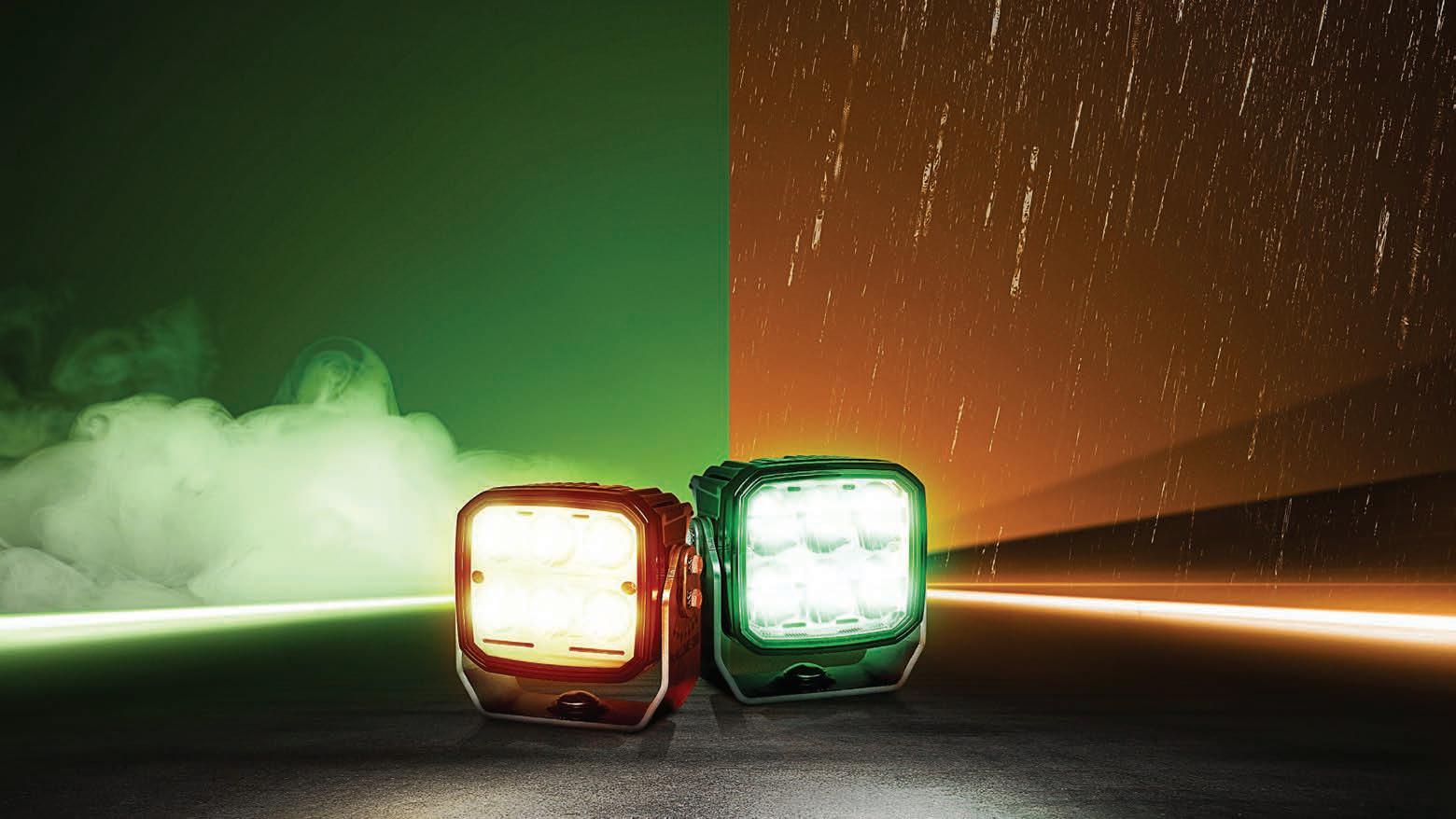
3
8
86
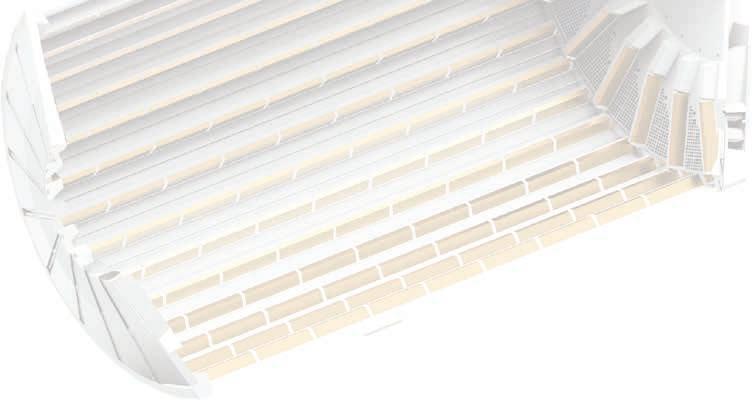


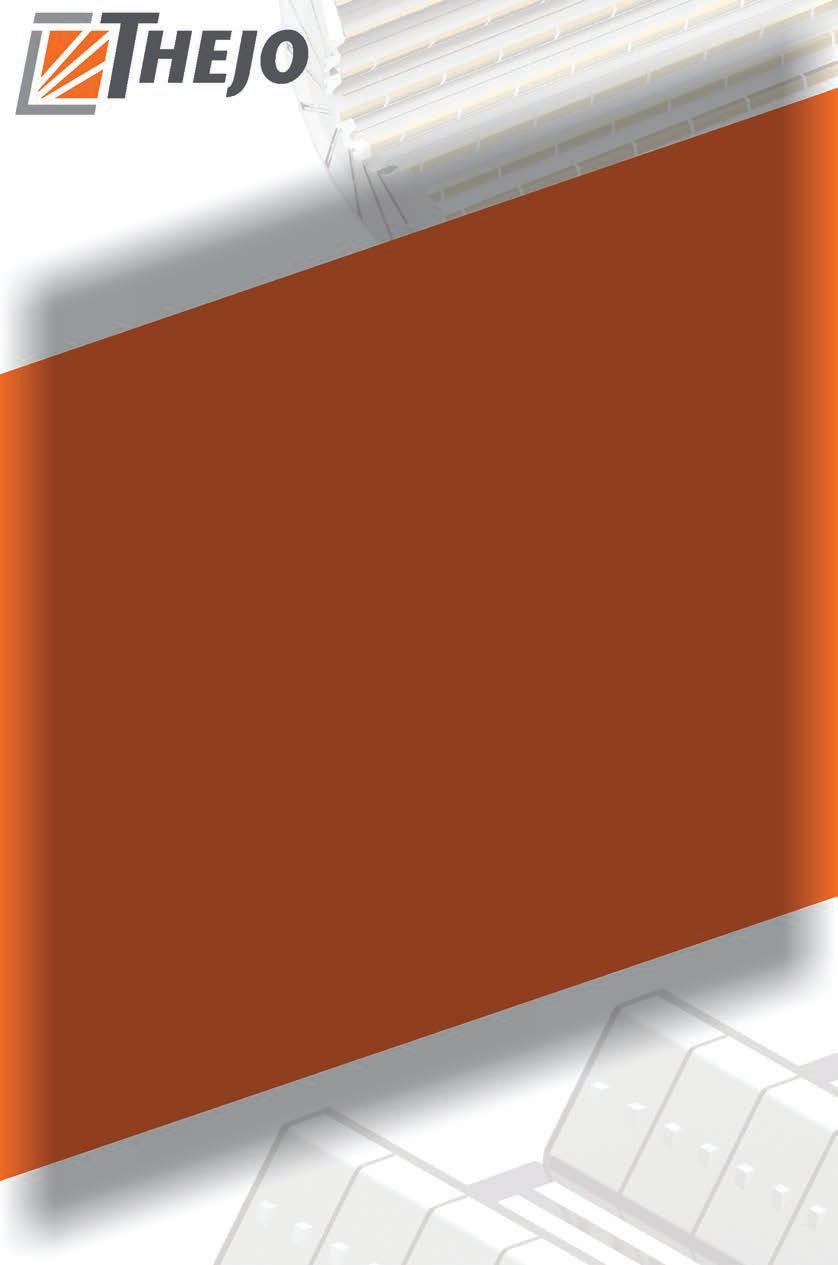
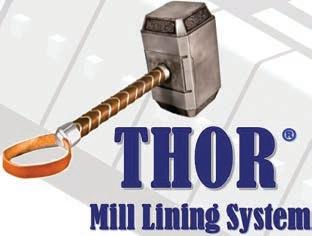
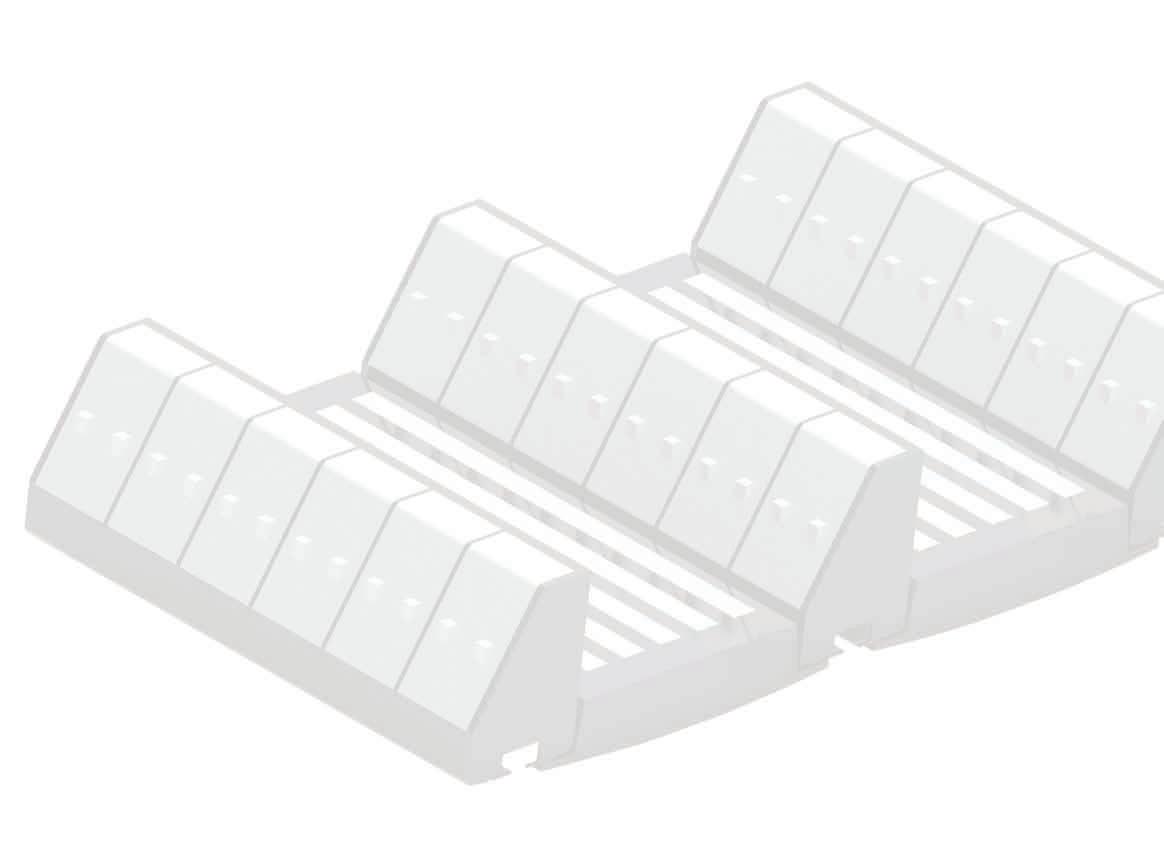
The innovative truck-mounted sensor technology helping mine sites overcome the safety & productivity risks of non-compliant bund walls.
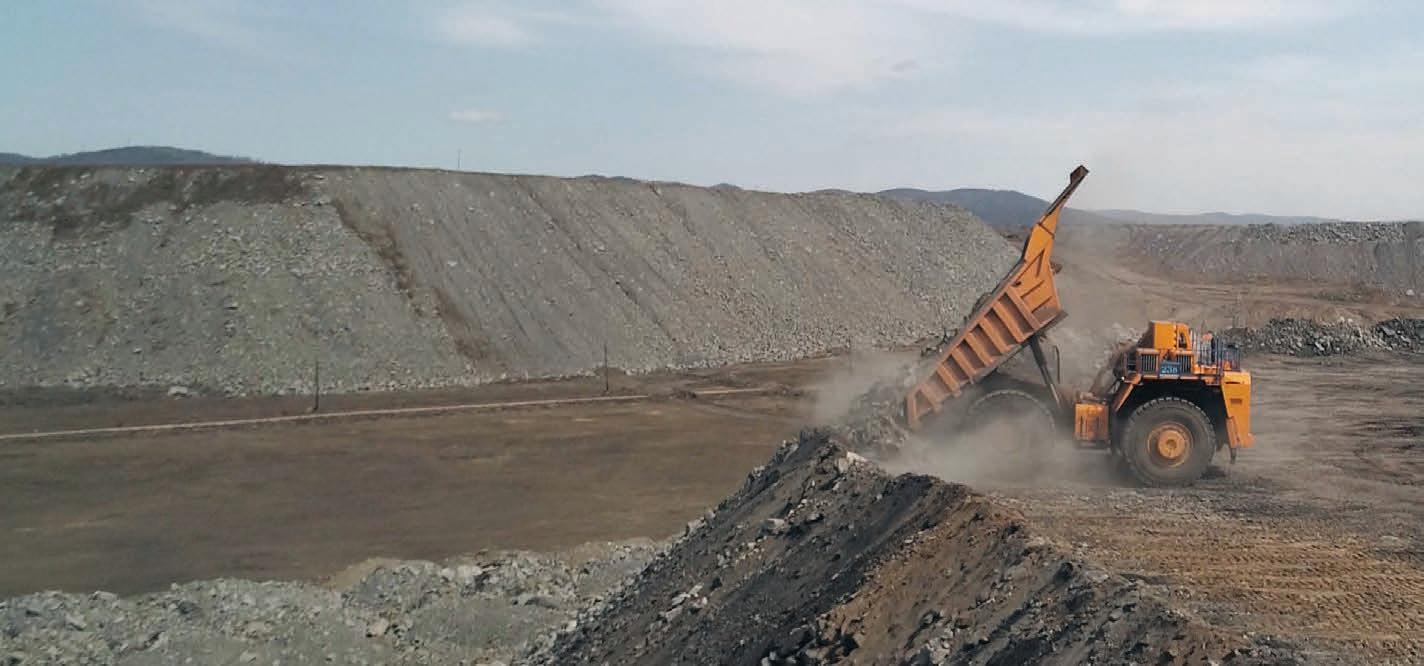
BundAware™ complete bund wall safety and compliance
In mining, the pursuit of profitability amid everchanging operational complexities requires an unwavering commitment to safety and operational efficiency. Stringent safety regulations, particularly concerning machine utilisation, mining infrastructure, and equipment operators, underscore the imperative for compliance and operational safety.
Tip heads, in particular, pose significant safety risks due to their elevation and the potential for truck breaches. Incidents caused by trucks breaching safety bunds are not uncommon and represent a considerable safety concern within mine sites. Additionally, the presence of non-compliant or critically low bund walls, essential for averting truck rollovers, heightens the risk of these incidents.
Forward-thinking mine sites are proactively adopting innovative technologies to identify gaps in bund wall compliance and enhance driver behaviour.
BundAware™ was specifically designed to prevent operators from backing up to unsafe bunds at tip heads that have deteriorated significantly; not been maintained in a straight edge; or have reduced in height and width.
Through truck-mounted LiDAR technology, BundAware™ scans every bund being reversed up to and alerts operators when the bund fails to meet site safety requirements. An incab alert instructs operators to dump short or move to another location – greatly reducing the chance of trucks breaching tip heads and rollovers occurring.
Site personnel are notified in real-time through the platform of the exact location and reason the bund does not meet the safety requirements of the site. All incidents are recorded in the platform and videos are available for inspection and auditing of detected safety concerns.
BundAware™’s advanced technology allows drivers and mine sites to take a truly proactive and preventative approach to bund management and compliance, improving overall site safety and productivity.
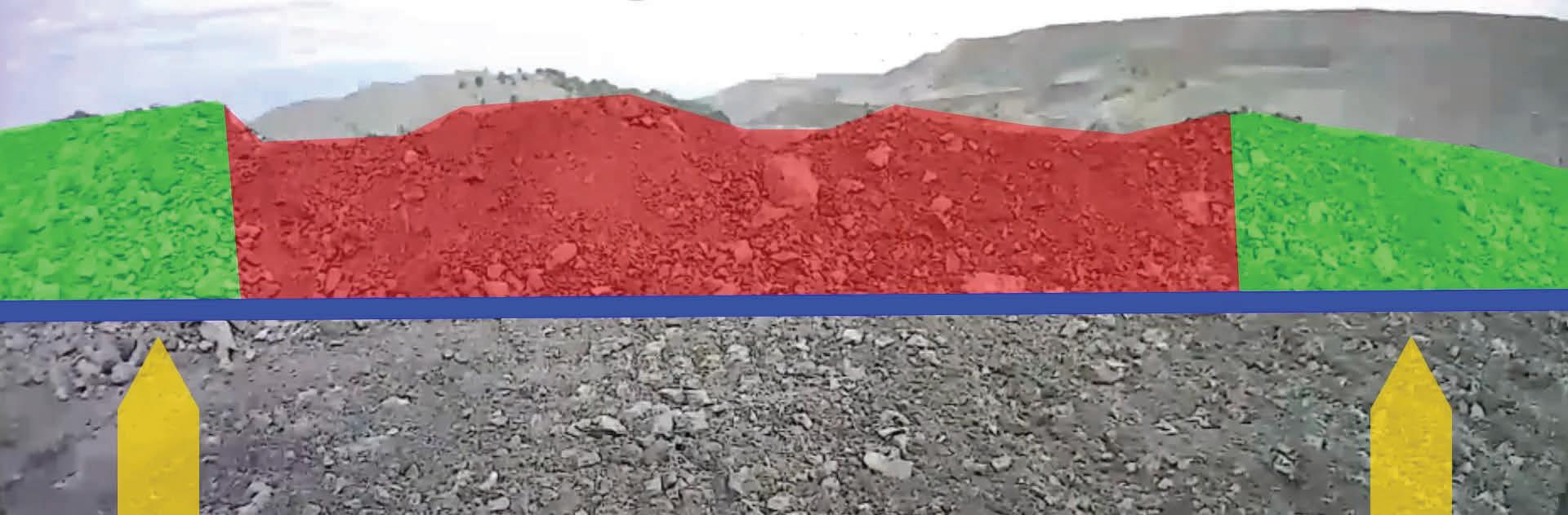
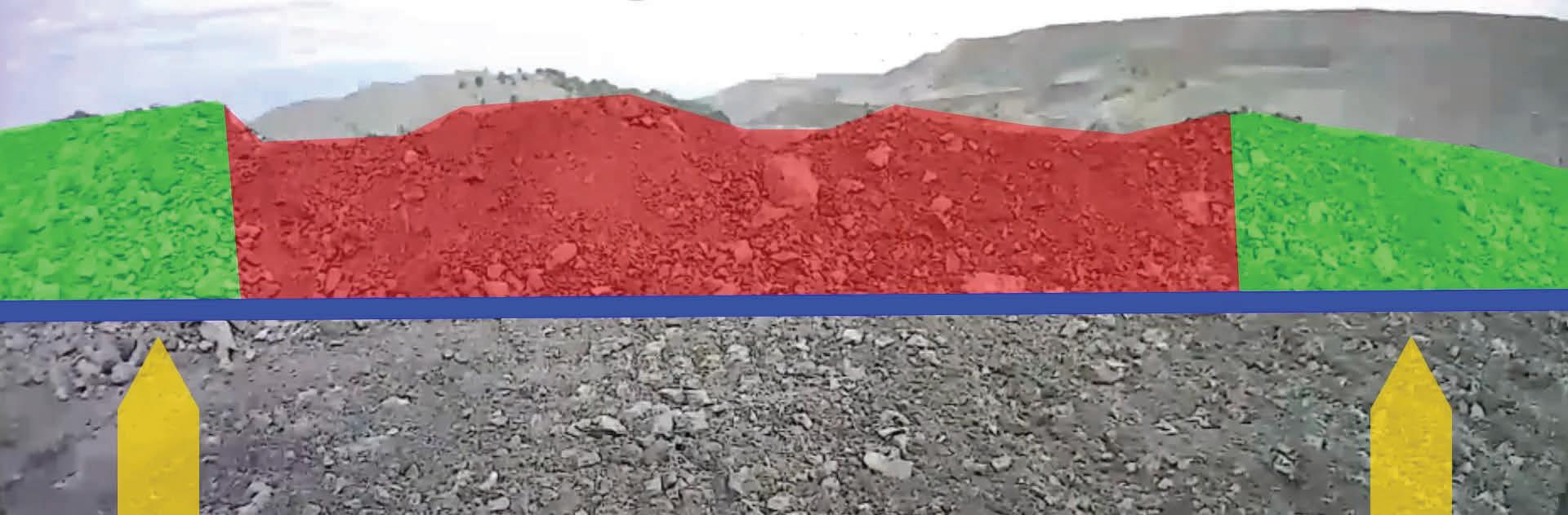
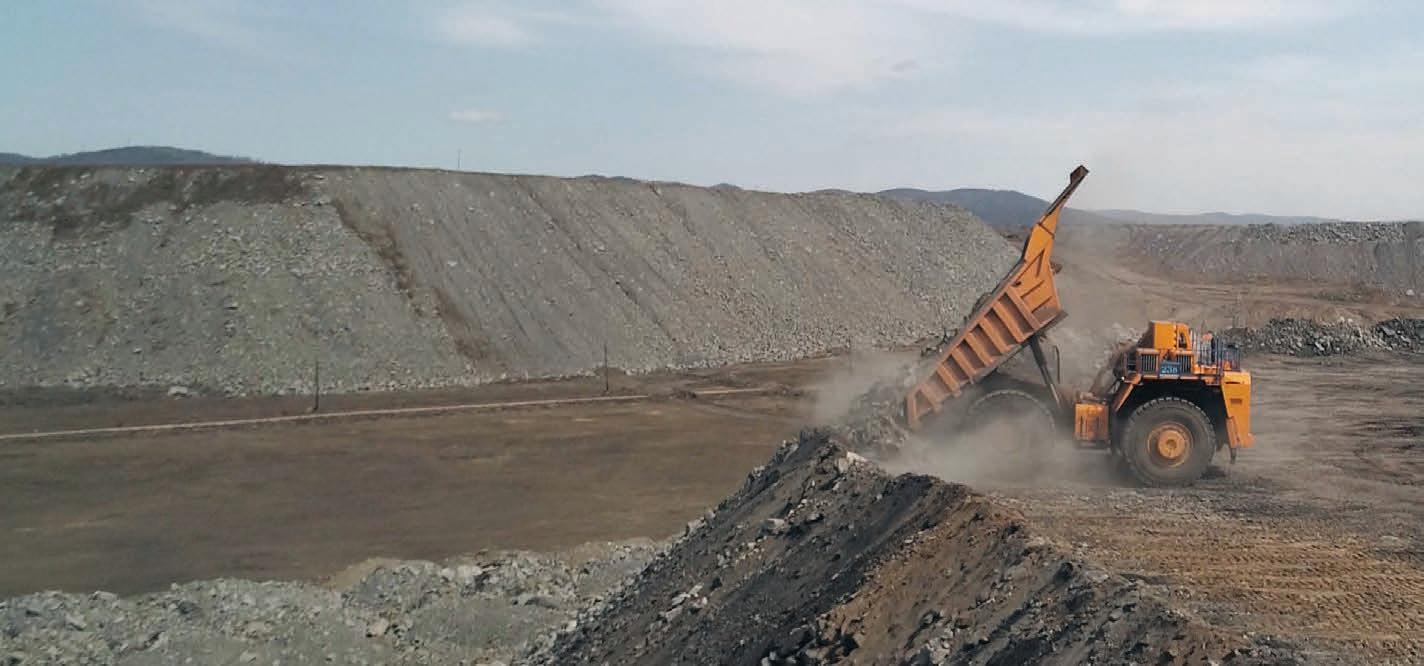
BundAware™ proactive operator bund wall awareness
Reduces the chances of accidents caused by deteriorated bunds
Ensures adherence to site safety requirements
Provides in-cab alerts to operators regarding unsafe bund conditions
Notifies site personnel instantly about non-compliant bunds
Revolutionary LiDAR technology
Brought to you by industry experts
Decoda is recognised as a technology leader at the forefront of innovation, transforming the mining industry’s adoption of data analytics and digital technology solutions to optimise mining performance.
Scans every bund during truck reversing manoeuvres
Records all incidents with available video inspection for audits
Cloud platform for data storage
Heat mapping and analytics for proactive reporting
Allows proactive and preventative bund management

Ready to start taking a proactive approach to bund wall safety management and improve the overall productivity, performance and safety of your site?
www.decoda.cominfo@decoda.com
FOLLOW THE LEADERS:
THE LATEST EXECUTIVE APPOINTMENTS
KEEP UP WITH THE LATEST EXECUTIVE MOVEMENTS ACROSS THE MINING SECTOR, FEATURING FORTESCUE, BHP AND NEWMONT.
Fortescue ended January with a corporate restructure, farewelling Deborah Caudle from her role as chief financial officer (CFO) of Fortescue’s energy division.
Caudle joined the team in August 2023 after Felicity Gooding resigned from the role.
As reported in The Australian Financial Review, a spokesperson for Fortescue confirmed that the company conducted a restructure at the top.
“As part of our transition to a One Fortescue model there has been consolidation of Fortescue’s finance functions,” the spokesperson said.
“We thank Deborah Caudle for her fantastic contribution to Fortescue and wish her the very best. In the interim, Apple Paget, acting metals CFO, will take on additional responsibilities. We thank and congratulate her.”
There are some new heads at BHP, with the major miner revealing a new iron ore and copper boss.
The Australian Financial Review reported that Tim Day will step into Brandon Craig’s role of asset president of
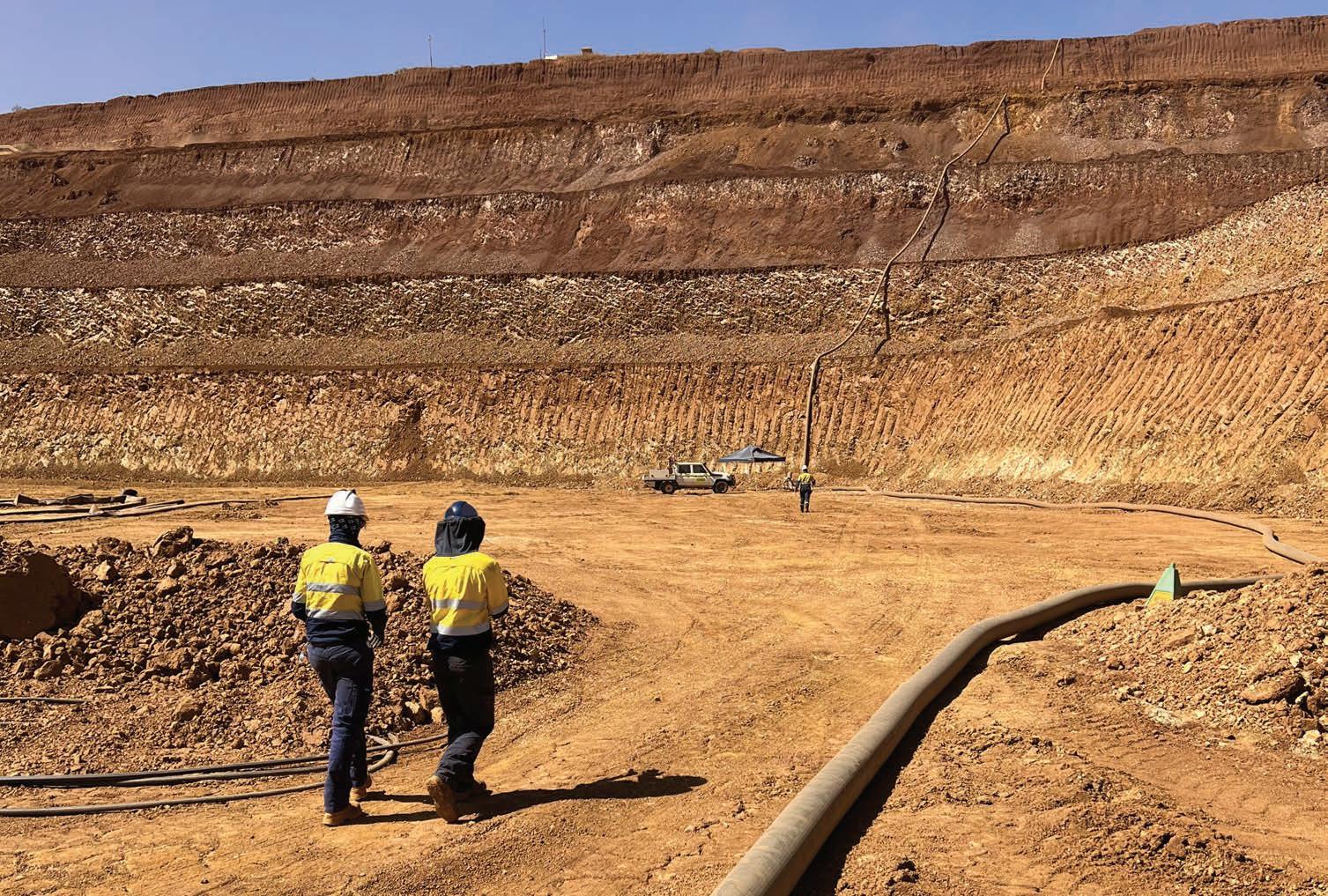
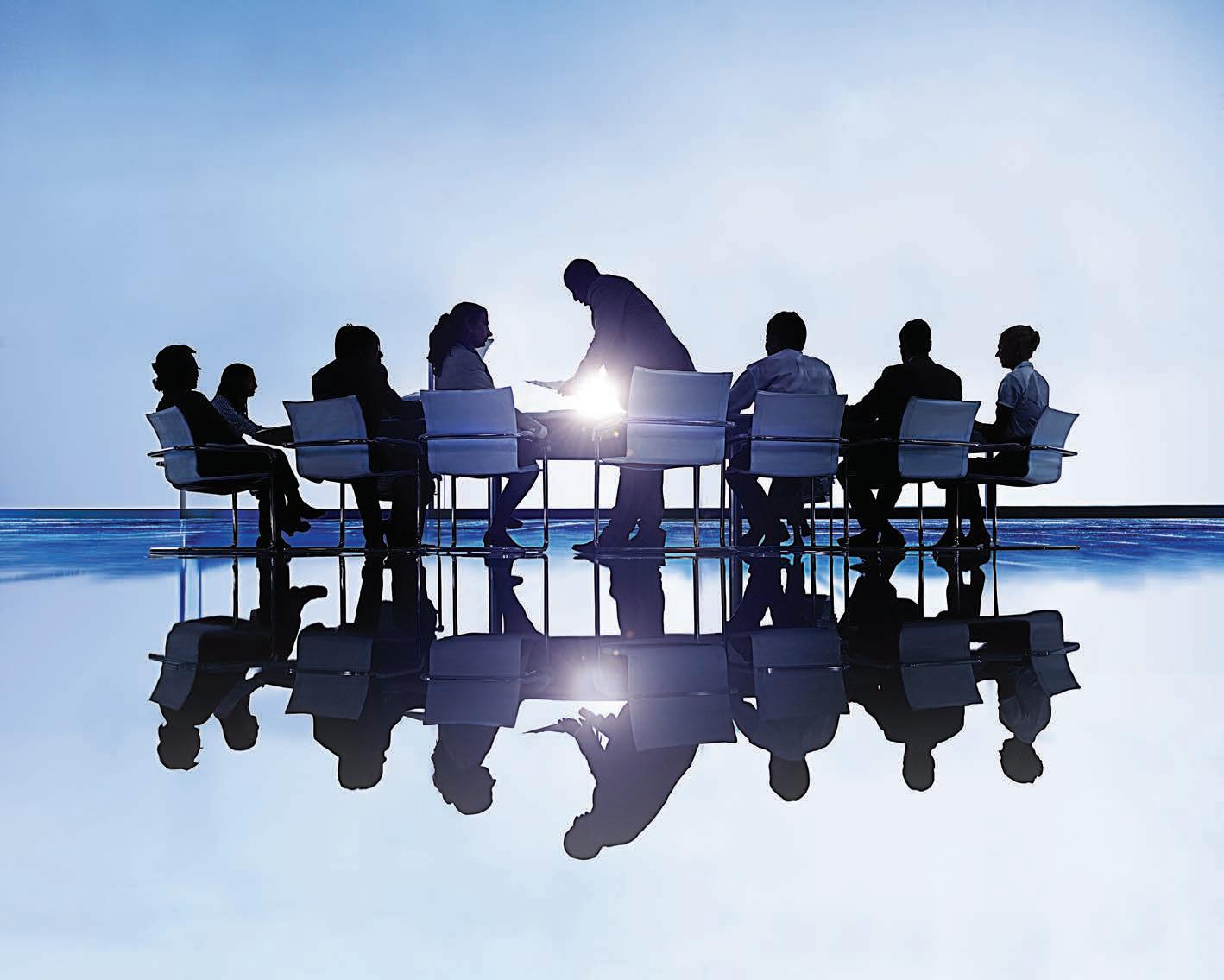
Western Australian Iron Ore (WAIO), with Anna Wiley to become BHP’s copper boss in Australia.
Day was previously acting asset president of BHP iron ore between November 2019 and November 2020, having worked his way up the company ranks since joining the major miner in 2008. He was most recently acting asset president of BHP’s BMA coal assets.
Wiley established her career at Rio Tinto, working in management positions in coal, copper and iron ore.
She has been at BHP since 2017, and was most recently the company’s vice president planning and technical.
Wiley will be tasked with growing BHP’s South Australian copper business, centred around the Olympic Dam, Prominent Hill and Carrapateena mines, along with the Oak Dam exploration project.
In December, BHP announced Craig’s promotion from WAIO president to president of Americas, which puts him at the helm of the company’s vast operations across both North and South America, spanning everything from potash to copper.
Craig’s appointment coincided with president of Americas Rag Udd taking on a new position as chief commercial officer (CCO), with Vandita Pant transitioning from CCO to CFO.
Newmont has appointed a new chief legal officer to lead the company’s legal, compliance and regulatory affairs.
Peter Wexler will join the company towards the end of the first quarter of 2024, and will be based at Newmont’s headquarters in Denver.
“Peter’s appointment further strengthens Newmont’s executive leadership team,” Newmont president and CEO Tom Palmer said.
“Peter brings decades of world-class legal and risk management experience at global organisations, which will be invaluable as Newmont continues to grow, building on its position as the world’s leading gold mining company and robust copper producer.”
Wexler is an experienced legal and risk management leader with more than three decades of experience. His expertise spans managing legal, risk, compliance, M&A (mergers and acquisitions), antitrust, litigation and corporate governance affairs.
Arafura Rare Earths has appointed a new managing director and chief executive officer following the departure of Gavin Lockyer, who has been with Arafura for over 17 years.
“On behalf of the board, I express sincere thanks to Gavin for his many and varied contributions to Arafura and the development of the Nolans project over many years,” Arafura chair Mark Southey said.
“Gavin was instrumental in driving the company forward and the many important steps taken, and agreements secured, by his team to commercially position us for the delivery phase of the Nolans project.”
Replacing Lockyer is Darryl Cuzzubbo, who has immediately assumed both roles of managing director and chief executive officer. He has been a non-executive director on the Arafura board since November 2021.
Cuzzubbo has more than 30 years of experience across global senior executive and executive directorial roles in multicommodity, services and manufacturing businesses, with 24 years being spent at BHP. AM
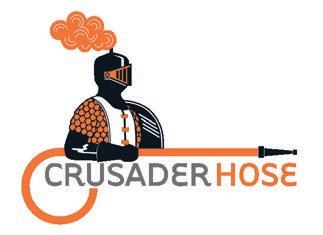
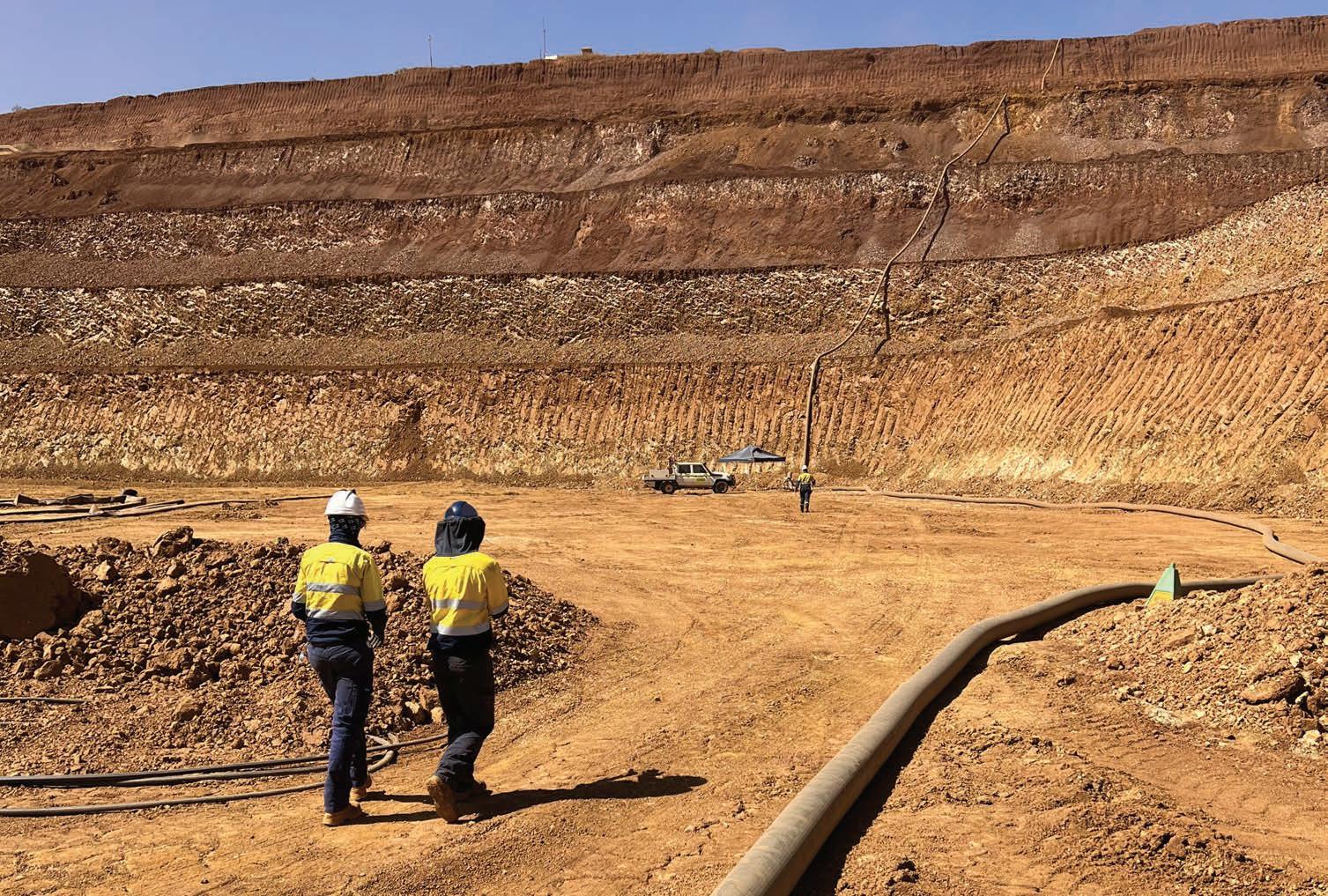
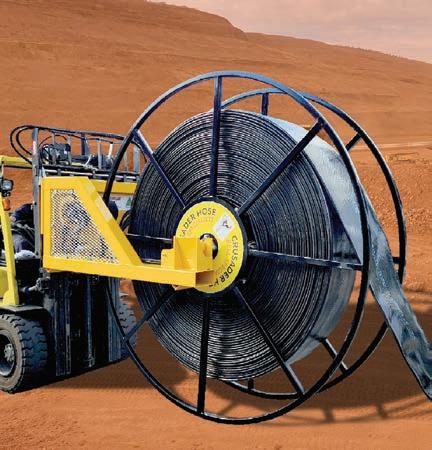
VANADIUM: AUSTRALIA’S NEXT MINING FRONTIER
THE STEELMAKING STAPLE IS SET TO TAKE OFF AS A NEW INDUSTRY HITS AUSTRALIA’S SHORES.
Vanadium has a long history in steelmaking.
The silver-grey metal is commonly alloyed with iron to make highstrength steel, and its slag by-products have typically acted as a cost-offset for producers.
But the vanadium tide may be turning in a different direction.
As the mining industry gears up to support Australia’s goal of netzero by 2050, vanadium may offer a unique solution in a future powered by renewables.
China is by far the largest global producer of the metal, with more than 60 per cent of the world’s vanadium produced and consumed on the country’s mainland. The majority of the world’s remaining supply is produced between Russia and South Africa.
But a downturn in China’s construction industry and the resulting slump in demand has seen vanadium quickly becoming known for another reason: batteries.
Vanadium flow batteries (VFBs), sometimes known as vanadium redox flow batteries, are electrolyte baths capable of immediate-release power
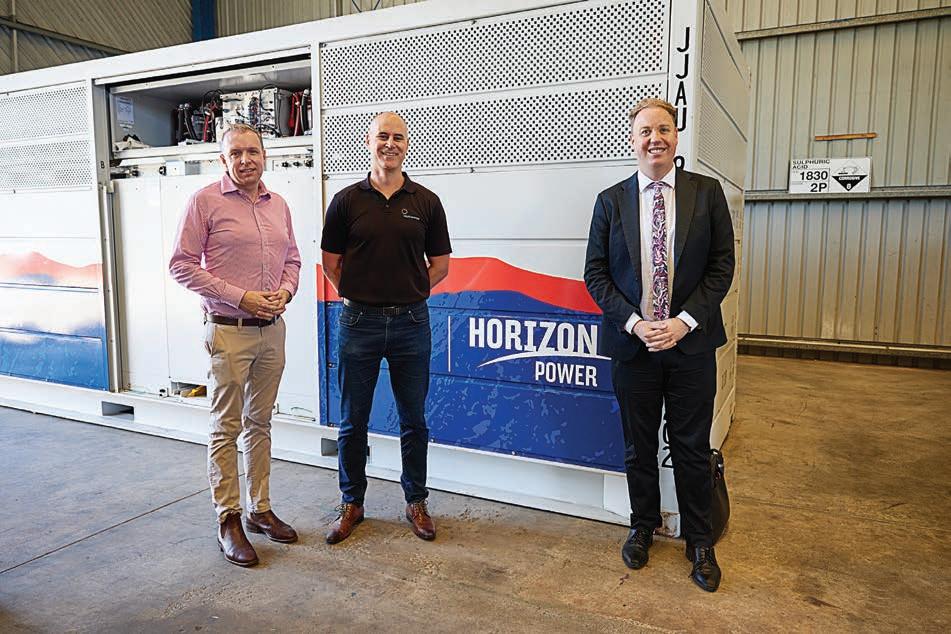

supply on a large scale. Unlike lithium batteries, VFBs are non-flammable and can be recycled indefinitely. checked in with two emerging players in Australia’s vanadium landscape: Yadlamalka Energy, which launched the first commercial VFB in Australia in July 2023; and Australian Vanadium, which opened a vanadium electrolyte processing facility in Perth at the start of 2024 and has plans to begin mining vanadium in Western Australia.
Australian Vanadium kicked off with the delivery of a VFB destined for regional service utility provider Horizon Power’s solar power site in
“We’ve been seeing a lot of interest in vanadium ramping up across Australia,” Australian Vanadium chief operating officer Todd Richardson told
“Vanadium batteries offer an alternative to lithium batteries suited to take on large-scale energy grid storage.” Shortly after the battery landed, Australian Vanadium opened the
doors to its new vanadium electrolyte manufacturing facility in Perth, which is set to produce up to 33 megawatt hours of high-purity electrolyte for VFBs per year.
The up-and-comer has now set its sights on the next step in its dream of becoming a vanadium player: mining.
There are currently no active mines for the commodity in the country, but Australian Vanadium plans to become the nation’s first and largest supplier of vanadium electrolyte from its project in the Murchison region of WA.
The goal is to produce five per cent of the world’s current vanadium supply from the site.
“You can take vanadium from ore all the way through to manufacturing VFBs in Australia fairly easily,” Richardson said. “It’s not as complex as the lithium supply chain, where you have other elements involved like nickel and cobalt.”
Australian Vanadium foresees over half of the world’s vanadium being used in VFBs by the end of the decade.
At the completion of its merger with Technology Metals Australia, Australian

“The next step for us is looking at the best parts of both orebodies and the best parts of the engineering from both sides and combining that into an integrated project,” Richardson said.
“This merger allows us to increase our project life from 25 years to 50 years, which gives us a long runway to be able to supply vanadium both domestically and internationally. Our goal is to start from the pit and produce vanadium

oxides at our processing facility which can be sold into steel and vanadium electrolyte for batteries.”
While there are no vanadium producers currently operating on Australian soil, Richardson said there are several companies in various stages of development poised to take off in the sector.
“There’s about one billion tonnes of JORC (joint ore reserve committee) compliant reserve and resource in the mid-west of WA alone,” he said. “Australia is second only to China in vanadium resources.”
Australia’s history of mining vanadium for steelmaking petered out by the turn of the century, but Richardson sees a strong future in batteries.
“I think the reason mining vanadium wasn’t successful in the past was because it was dependent upon steel production around the world, which means the commodity price for vanadium fluctuated quite a bit,” he said.
“And there were a lot of times when the production prices for vanadium were below the cost to produce vanadium here in Australia.
“Vanadium batteries are not tied to the steel industry, they’re tied to energy storage, which means that the vanadium prices should not fluctuate as they did in the past. That’s where the future of vanadium is.”
Another company with an eye on the needs on the growing sector is Yadlamalka Energy. The renewable technology solutions manufacturer launched Australia’s first commercial VFB in July last year.
The breakthrough battery was established as part of the company’s Spencer Energy project at the

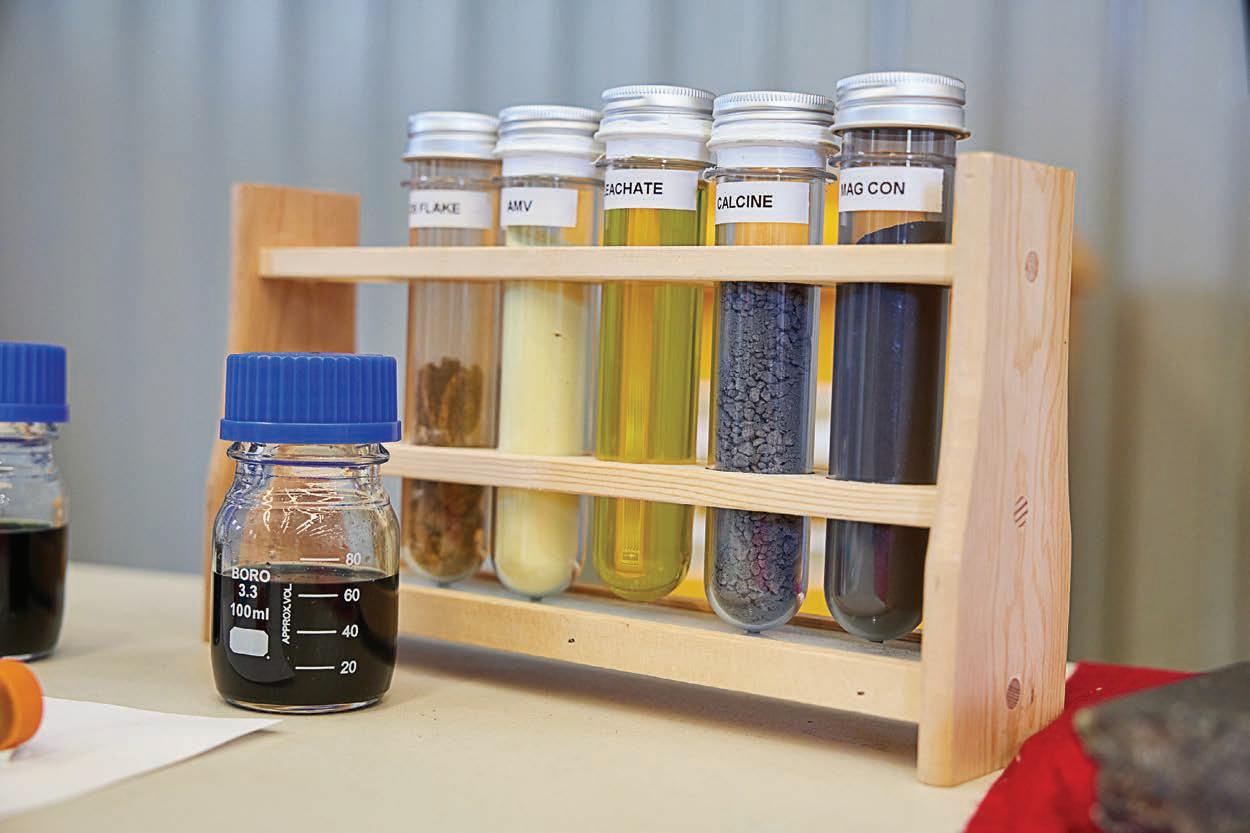
Bungama sub-station in Port Pirie, South Australia.
The project saw the battery connected to a grid of solar panels and charged with the excess electricity they produce. Under cloud cover or when the sun goes down, Yadlamalka’s VFBs power up.
“VFBs offer a number of important advantages,” Yadlamalka Energy founder and managing director Andrew Doman told Australian Mining
“Most importantly, the amount of power that you can produce from them does not deteriorate significantly over time. Over 25 years later, you can expect the batteries to be just as effective as they were on day one.”
Doman suggested the current needs of Australia’s energy grid are primed for the kind of coverage VFBs have to offer. When energy sources like solar and wind are less effective, vanadium can fill in the gaps in electricity coverage.
“We have identified in our modelling a four-hour time slot in the evenings when the sun has gone down and there’s a high demand for support to the grid,” Doman said. “That’s where VFBs come into their own.”
When demand dips during the day and supply outstrips the needs for the grid, energy prices enter the negative. That’s when Doman said Yadlamalka can strike.
“When electricity prices are negative, we’ll be buying the electricity and that will help stabilise the grid. And when prices are high, we’ll be selling power into the grid,” he said.
“That margin will have the effect of reducing prices.”
Stability is key as Australia’s energy consumption increases. Doman is confident VFBs are up to the task of keeping the lights on should Australia’s power needs change.
footprints while ensuring operations continue around the clock.
Yadlamalka worked with UK-based energy systems company Invinity to establish its Spencer project in SA, sourcing its vanadium from overseas suppliers.
VANADIUM OVERCOMES A MEDIUM-DURATION STORAGE PROBLEM. THESE ARE THE IDEAL BATTERIES FOR THOSE SORTS OF APPLICATIONS WHERE YOU’VE GOT FAIRLY RELIABLE SUN AND WIND BUT YOU NEED BACK-UP IN THE HOURS WHEN THE SUN GOES DOWN AND THE WIND DIES OUT.”
“Adding duration is quite easy with vanadium batteries,” he said. “The batteries are basically two bathtubs with vanadium electrolyte in them, and if you want to increase the duration of the battery, all you do is just add more electrolyte.”
Doman said Yadlamalka is looking to the future of mining in Australia, where reliable power is needed in some of the most remote areas of the country.
“Vanadium overcomes a mediumduration storage problem,” he said.
“These are the ideal batteries for those sorts of applications, where you’ve got fairly reliable sun and wind but you need back-up in the hours when the sun goes down and the wind dies out.”
Vanadium offers a reliable solution to sites looking to decrease their carbon
Yadlamalka is now breaking ground on a new project north of Port Augusta, SA, as it turns to sourcing vanadium on home soil – an area where Australian Vanadium is leading the charge.
“Australia is set to become a major producer of vanadium,” Doman said. “It’s worth reminding ourselves that this technology was invented in Australia in the 1970s – it’s homegrown technology. We will be using Australian vanadium.”
Not only suitable to supply energy to the grid and to remote mining projects, VFBs show promise after the battery completes its lifecycle.
“Vanadium electrolyte is a fluid which is 100 per cent recyclable,” Doman said. “At the end of the life of the battery, you simply suck out the vanadium electrolyte and resell it or it can be converted back into vanadium.”
It’s that ability to fill in the gaps in renewable power that makes VFBs attractive for investment. Australian Vanadium welcomed a $49 million Modern Manufacturing Initiative grant from the Australian Government last year for its vanadium projects.
In addition, the Queensland Government invested $75 million in the Queensland Resources Common User Facility in Townsville in early 2023 for the development of VFBs.
“These batteries will be made in Queensland, right here in Townsville, and will change the game for renewable energy storage,” then Queensland Premier Annastacia Palaszczuk said.
Critical minerals developer Vecco Group produces nine megalitres of vanadium electrolyte at the facility per year, with plans to expand as demand increases.
Other states are offering millions to companies developing energy generation and storage projects. SA, where Yadlamalka has seen such success, has taken up the challenge with more than $20 billion in large-scale energy storage projects in the investment pipeline.
With such a swell of support rising behind a home-grown vanadium boom, more and more companies are taking up the mantle.
Now, more than ever, Australia is relying on the mining industry to supply essential minerals and metals to achieve its decarbonisation goals.
Vanadium is poised to establish itself as a strong foundation in that future. AM
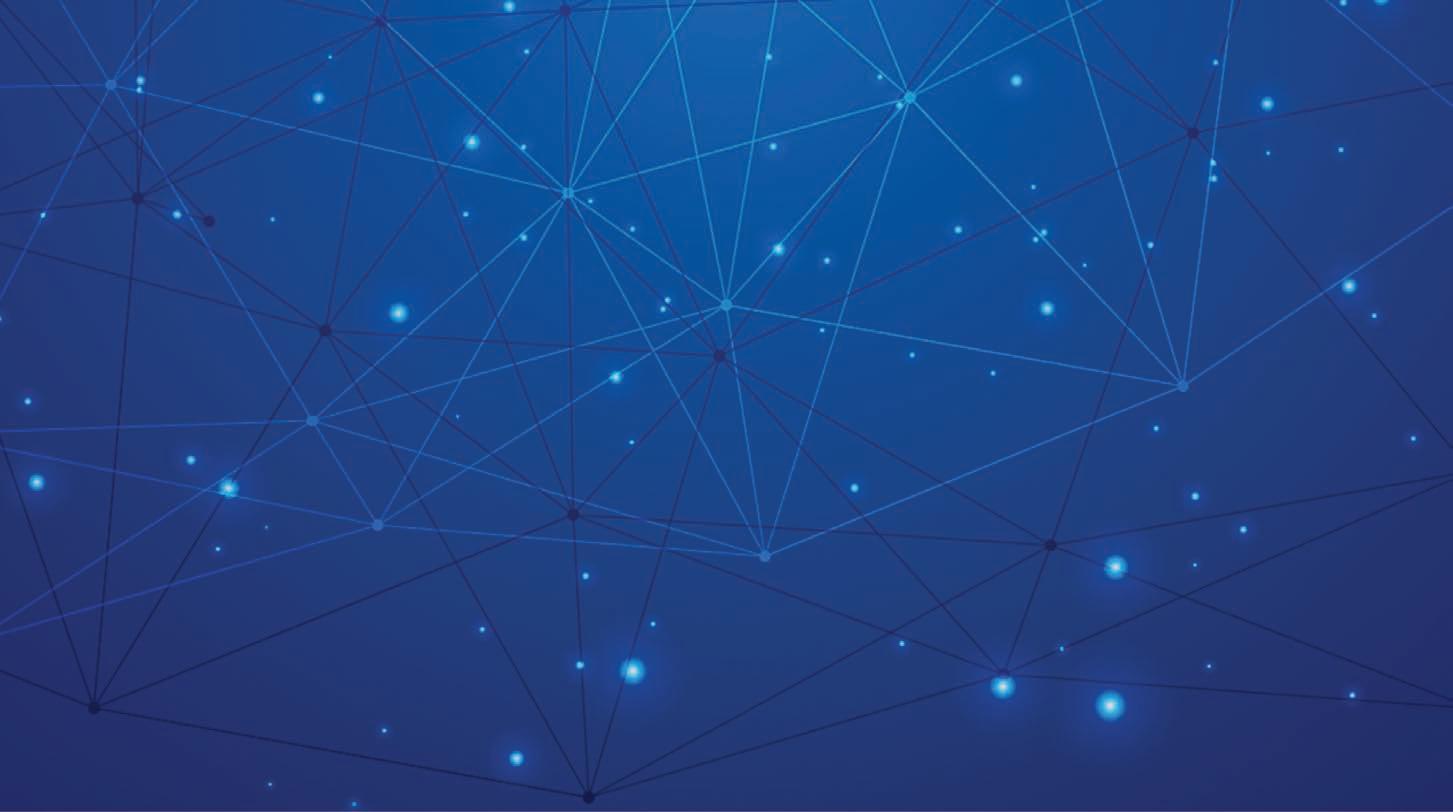
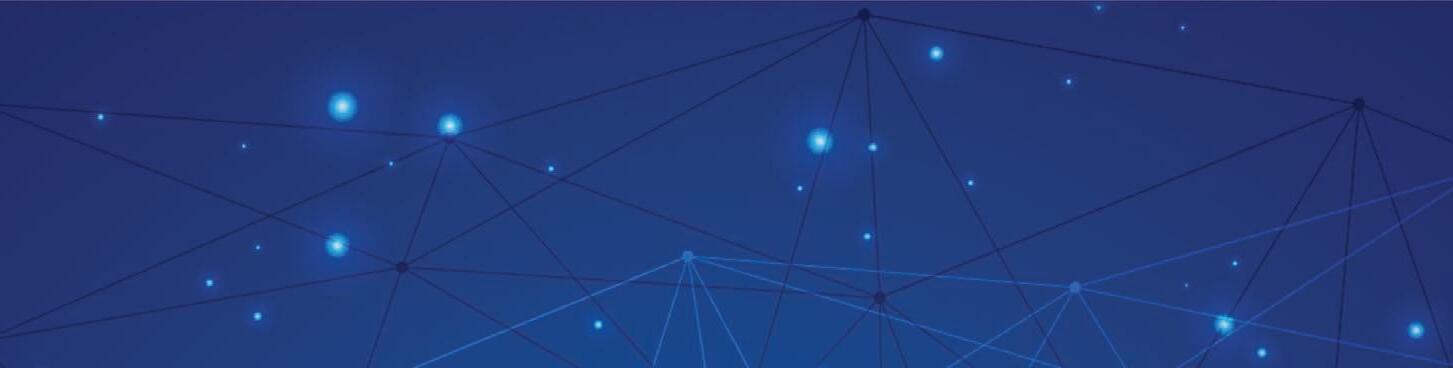
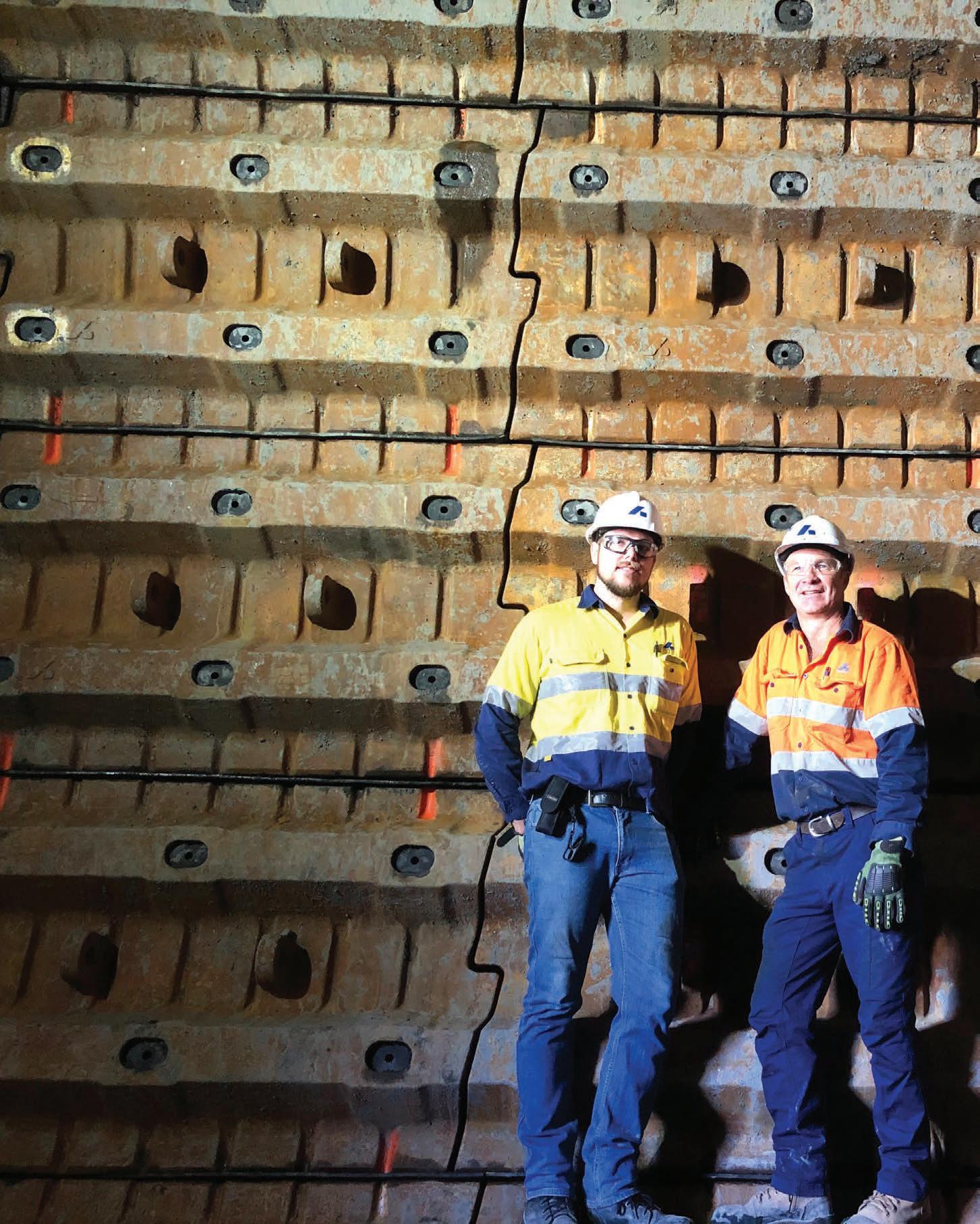
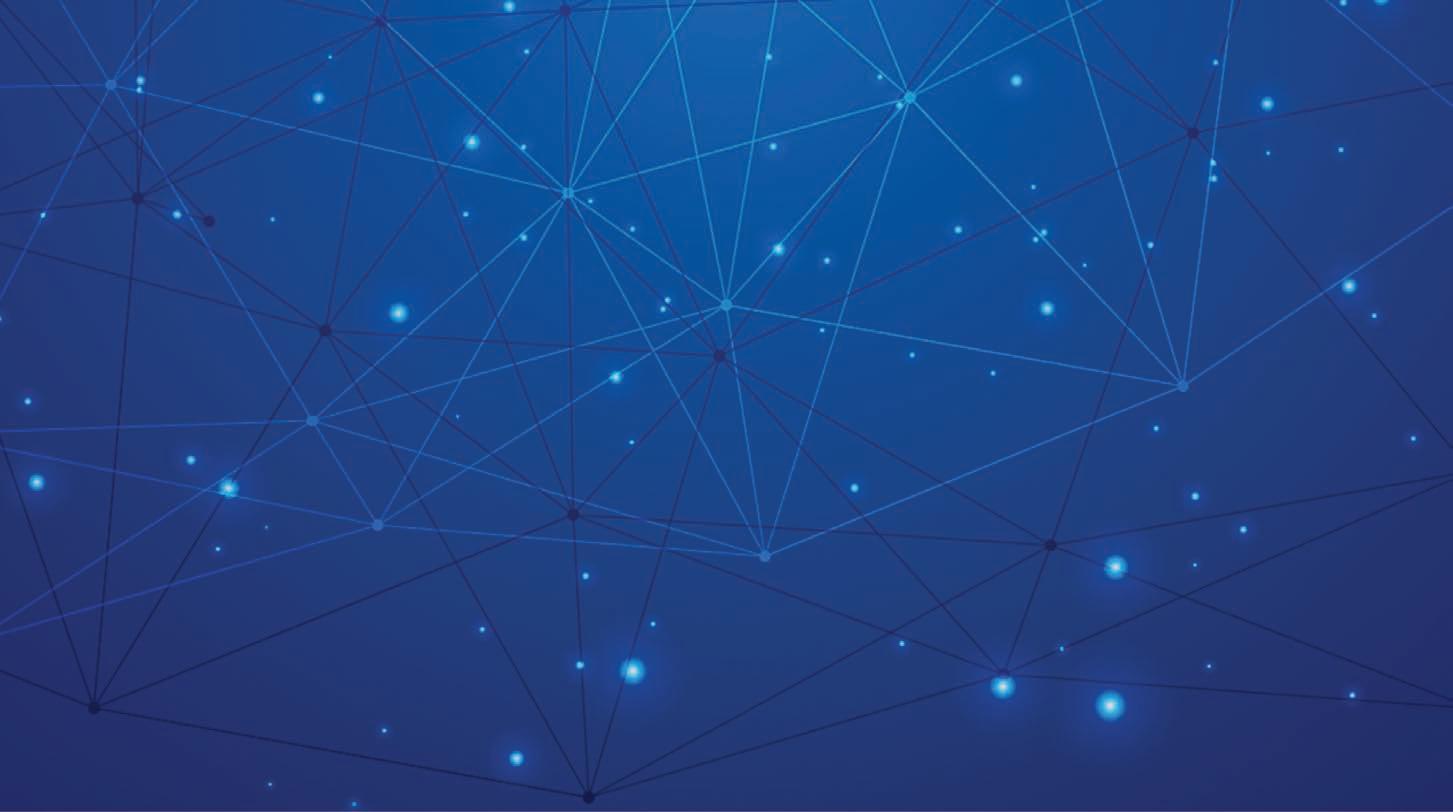
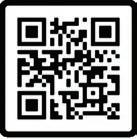
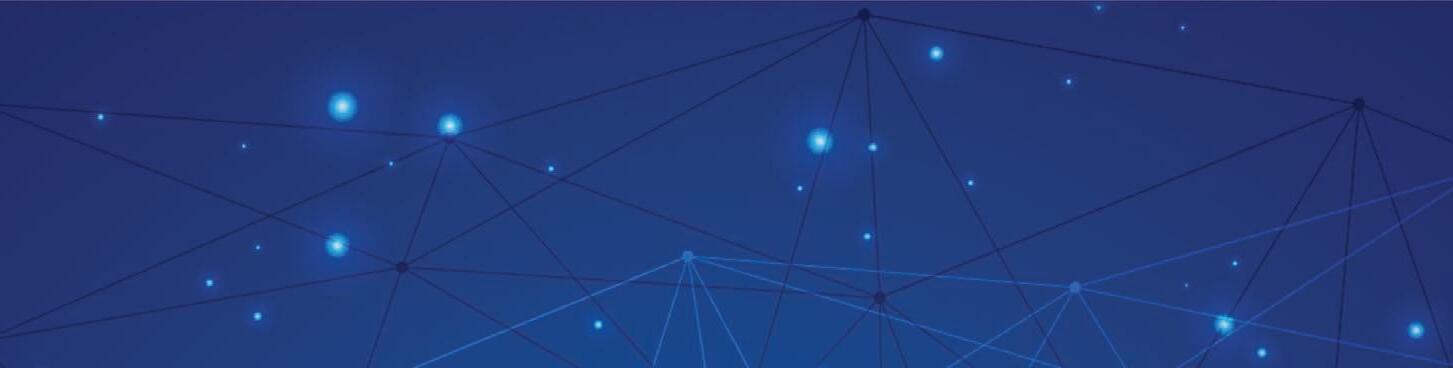
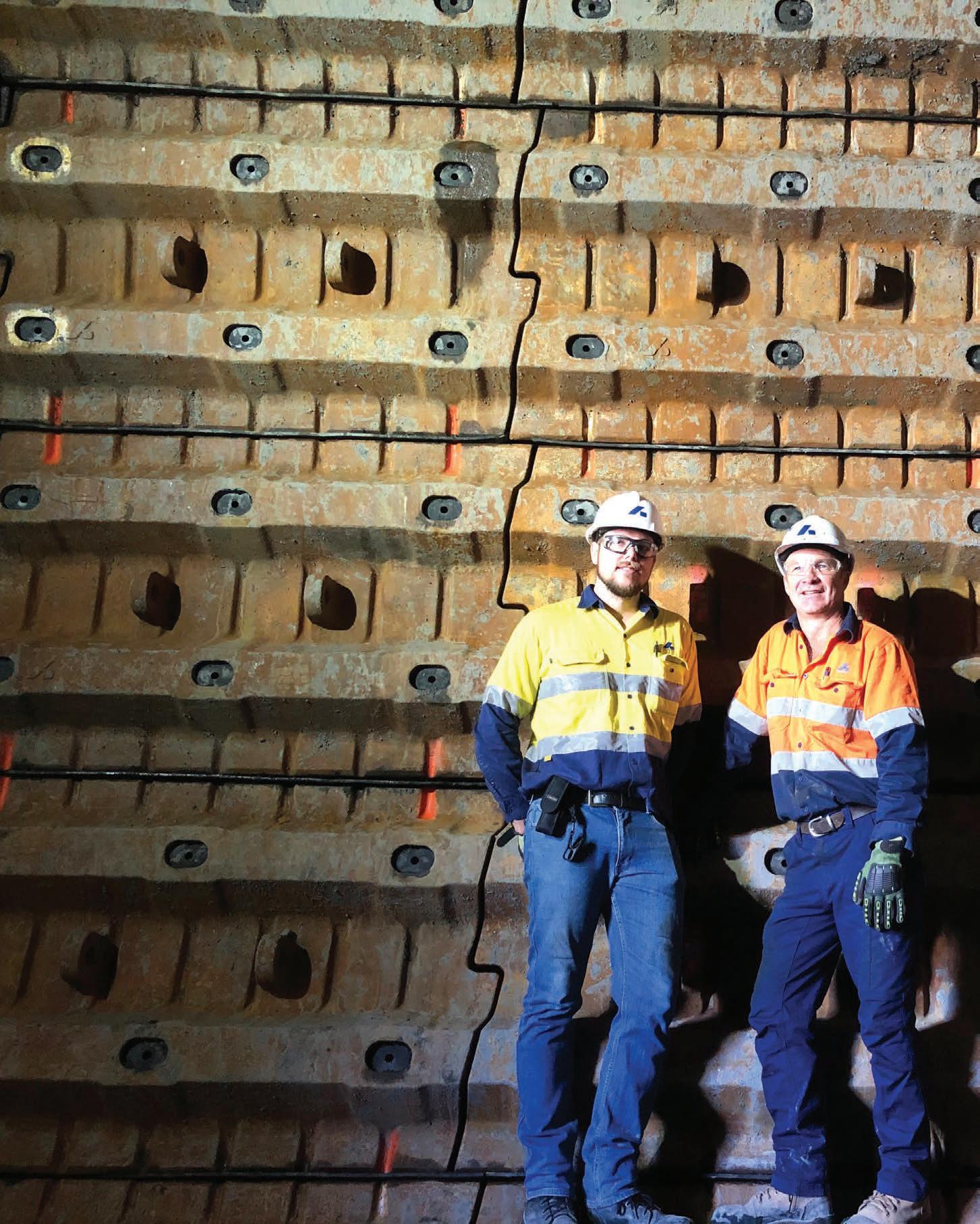
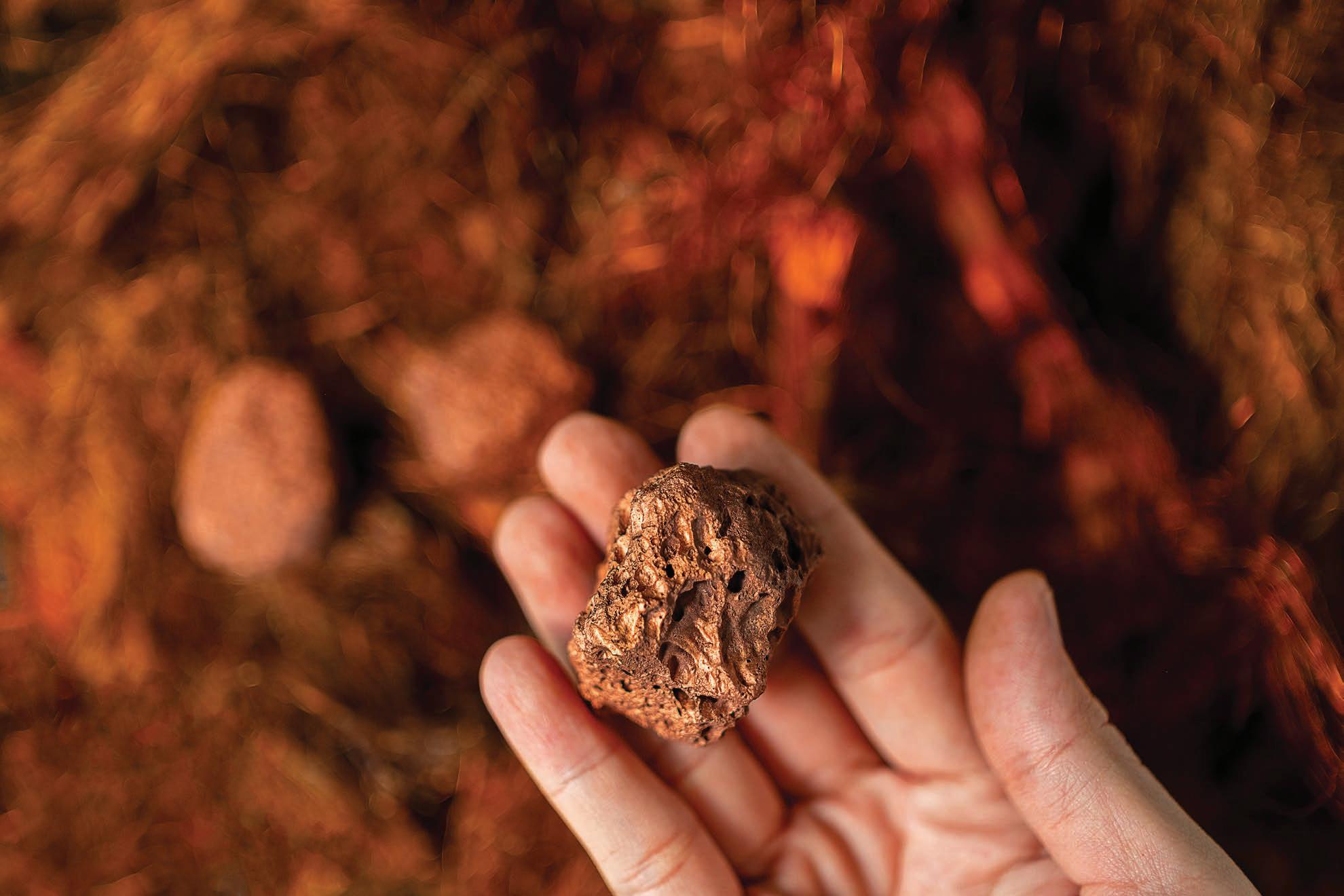
CLOSING 2023 ON A HIGH
PRODUCTION WAS ON THE UP FOR VARIOUS MINERS THROUGHOUT THE YEAR, WITH PROJECT CONSTRUCTION ALSO ADVANCING AT PACE.
The December quarter of 2023 delivered some strong results for Australia’s major miners.
While many saw production increases across commodities such as copper and iron ore, decreases in coal production were also recorded.
Australian Mining takes a look at some of the results reported by the majors.
BHP
Despite pausing part of its Kambalda nickel processing operations in January, BHP reported strong operational performances across a range of commodities for the half year ending December 31, 2023.
Copper proved to be a consistent winner, with the Big Australian reporting a seven per cent production increase in the half-year.
“Operationally, BHP has had a solid first half,” BHP chief executive officer (CEO) Mike Henry said.
“Western Australia Iron Ore production was up five per cent quarteron-quarter, while first half copper production rose seven per cent.
“We (have) successfully integrated our Copper SA business and significant exploration drilling beneath Olympic Dam has identified attractive copper mineralisation above (a) one per cent grade along a 2km strike, with areas above two per cent.”
BHP’s half-year energy coal production increased by 36 per cent, with its 2023–24 financial year (FY24) production expected to be in the upper end of the guidance range.
“NSW Energy Coal had its best first half in five years, while BMA (BHP Mitsubishi Alliance) had a tough six months following significant planned maintenance and low starting inventories,” Henry said.
Rio Tinto
Copper emerged as the winner for Rio Tinto, bringing in production of 620,000 tonnes in 2023: a two per cent increase on 2022 copper production.
The results reflect the major miner’s first sustainable production from its Oyu Tolgoi underground copper mine in Mongolia, which offset challenges faced at Kennecott in Utah due to a conveyor failure.
“We benefited from our increased ownership in Oyu Tolgoi as the underground ramps up,” Rio Tinto CEO Jakob Stausholm said.
“We have one of the most exciting exploration pipelines in years, including our new copper joint venture with Codelco, launched in December.”
Iron ore production also continued Rio’s strong delivery, with the Pilbara operations producing 331.5 million tonnes (Mt) in 2023, another two per cent increase from 2022 production.
Rio Tinto also shipped 331.8Mt of iron ore in 2023, a three per cent increase from 2022 and the second highest on record.
“There is good demand for the materials we produce, and our purpose and long-term strategy make more sense than ever,” Stausholm said.
South32
A 50 per cent drop in coal output contributed to what South32 CEO Graham Kerr described as a “mixed” quarter.
Metallurgical coal production at the Illawarra mine in NSW decreased by 39 per cent during the December 2023
half year, as two planned longwall moves were completed.
Manganese production also decreased by five per cent, despite being the standout from the previous quarter.
“With some of our commodities facing headwinds in the half, we continued to focus on delivering cost efficiencies and expect first half operating unit costs to be below or in line with guidance for the majority of our operations,” Kerr said.
Despite the declines, South32 did report some production highs.
Record half-year aluminium production was achieved at Hillside in South Africa, with the mine delivering an eight per cent increase in quarterly production.
Despite payable copper equivalent production at Sierra Gorda in Chile falling by 14 per cent, Kerr is optimistic about the mine’s future.
“Sierra Gorda also continued work on the fourth grinding line expansion project, which has the potential to sustainably increase copper production,” he said.
Whitehaven Coal
The Australian coal miner’s run-of-mine (ROM) production for the December quarter equalled 5Mt, about 300,000 tonnes less than the September quarter.
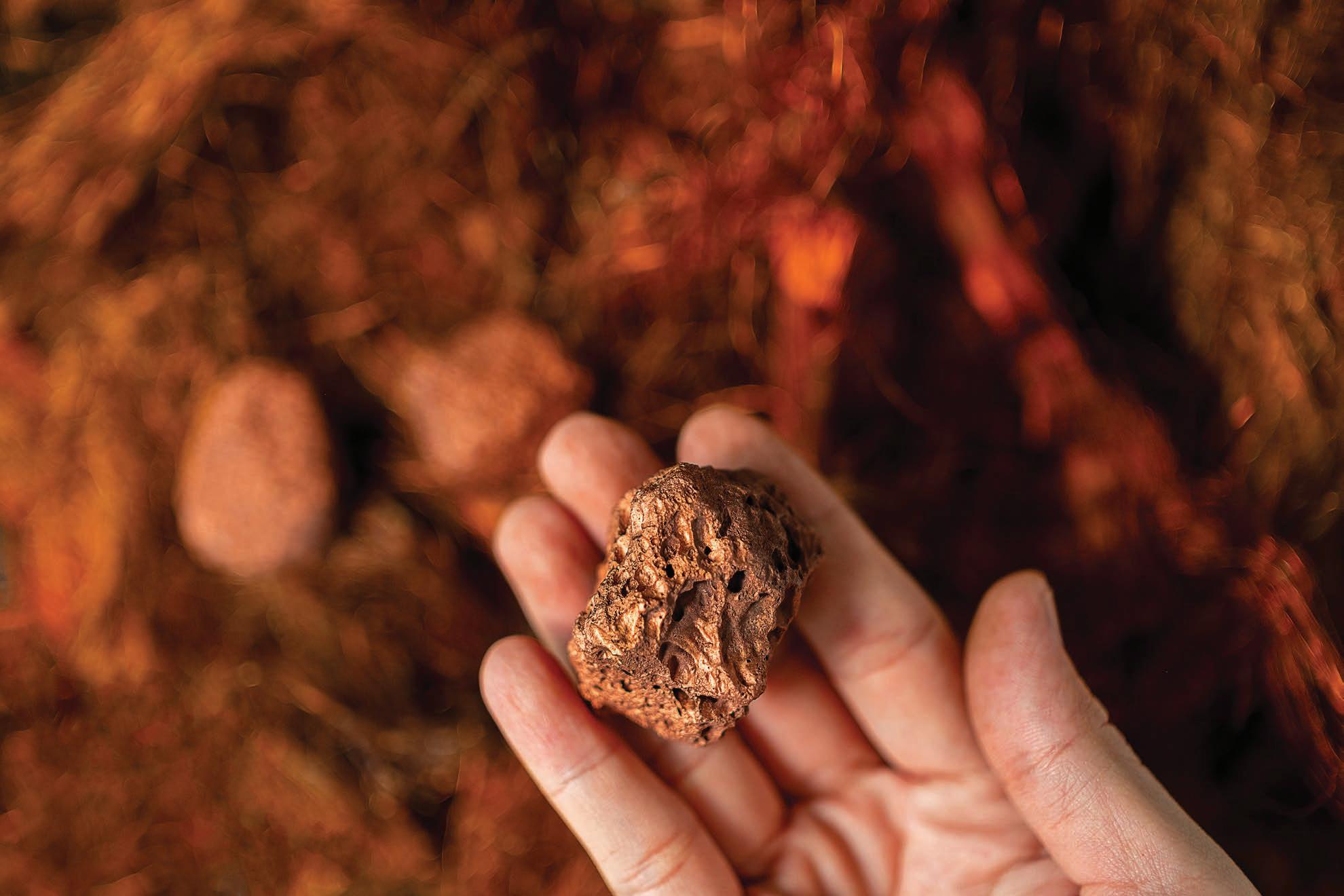
Fortescue
The iron ore giant shipped 48.7Mt of iron ore in the December quarter, a six per cent increase from the previous quarter.
This contributed to 94.6Mt of shipments being dispatched in the first half of FY24, which is the second highest first half shipments recorded in Fortescue’s history.
“We achieved this while continuing to grow our green technology, energy and metals businesses, keeping costs low and maintaining our safety performance,” Fortescue Metals CEO Dino Otranto said.
Guidance for FY24 iron ore shipments remains unchanged at 192–197Mt, inclusive of 2–4Mt for the Iron Bridge magnetite project.
“Demand for Fortescue’s suite of iron ore products remains strong and our entry into the higher-grade segment of the market through Iron Bridge has been well received, with our second magnetite shipment during the quarter,” Otranto said.
“This is further supported by the Belinga project in Gabon where we shipped our first product in December.”
The company shifted coal at an average of $216/t across the three months, which was four per cent below the previous quarter.
Despite these declines, Whitehaven’s total equity sales equalled 3.7Mt, a 21 per cent increase from the previous quarter. Whitehaven also saw a 20 per cent increase in managed coal sales.
“Maules Creek and the Gunnedah open cut mines delivered solid
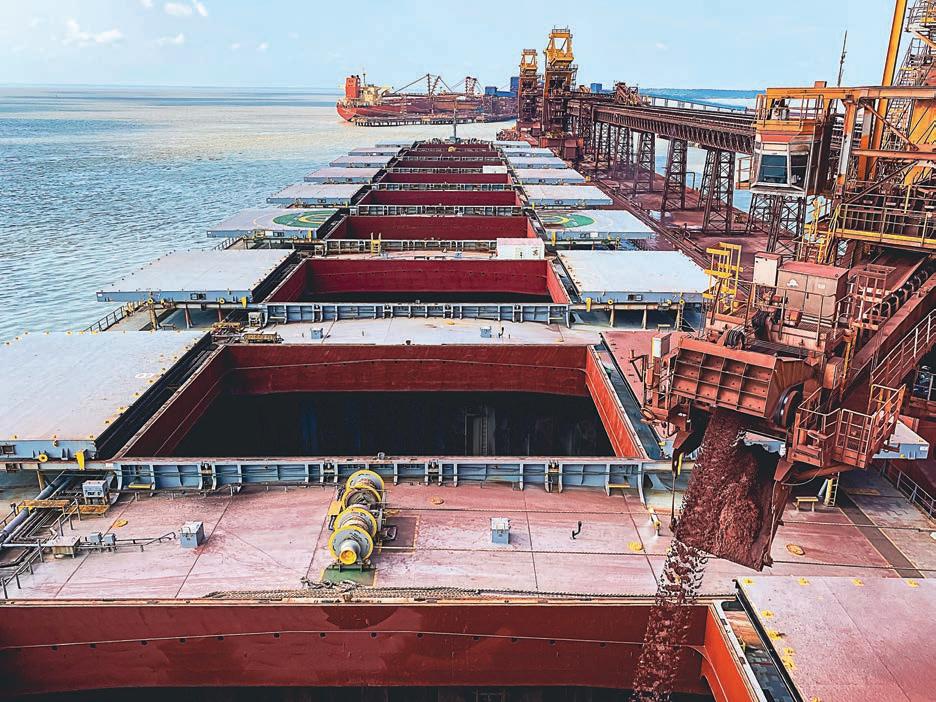
operational performances while ROM production at Narrabri was impacted by geological challenges in the current longwall and equipment reliability,” Whitehaven Coal managing director and CEO Paul Flynn said.
“Overall ROM production and sales guidance for FY24 remains unchanged. However, production and sales mix are expected to reflect the stronger
performance at the open cut mines and lower volumes from Narrabri.”
Whitehaven is expected to complete its $US4.1 billion acquisition of BHP’s Daunia and Blackwater metallurgical coal mines in early April 2024.
MinRes
Mineral Resources’ (MinRes) iron ore shipments were a winner for the company, increasing by 23 per cent during the quarter, equalling 4.8 million wet metric tonnes.
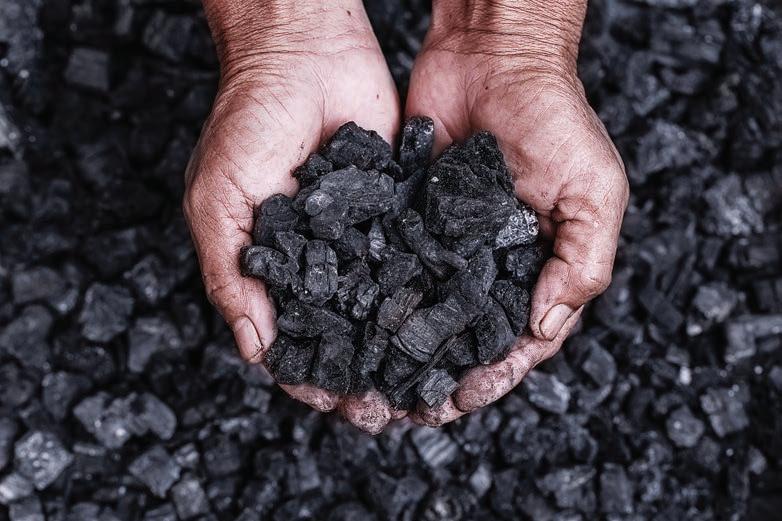
This number is expected to be boosted by the Onslow iron project in June 2024 when the site ships first ore. The project’s construction is also expected to be delivered well within budget.
“The Ken’s Bore construction camp is at full capacity, with 200 resort rooms delivered and progressively occupied,” MinRes said.
“The procurement of the autonomous road train fleet and associated systems continued (in the December quarter). The construction of the truck maintenance facility is well advanced.”
Another highlight was MinRes increasing its stake in the Wodgina lithium mine in Western Australia.
“MinRes’ share of the Wodgina mine increased from 40 per cent to 50 per cent and Albemarle took full ownership of Kemerton lithium hydroxide processing plant,” the company said.
“Wodgina achieved attributable quarterly spodumene concentrate production of 55,000 dry metric tonnes (dmt), with improved plant recoveries. Spodumene concentrate shipments increased significantly to 65,000dmt.”
Lynas Rare Earths
Described by the company as an “exciting period”, Lynas Rare Earths saw many successes during the quarter.
Construction of the Kalgoorlie rare earths processing facility in WA was largely completed, alongside full plant commissioning.
Following completion of the kiln heating and other commissioning activities, the first feed of material from Mount Weld was introduced into the Kalgoorlie facility in December 2023.
“Mixed rare earth carbonate from the Kalgoorlie facility is expected to be progressively introduced to the Lynas Malaysia plant commencing late in the March 2024 quarter,” the company said.
The Mount Weld expansion project also remains on track, with early works progressing as planned.
The WA Environmental Protection Authority also recommended that the Mount Weld life-of-mine proposal be environmentally approved.
With strong production figures across a wide range of commodities essential for the global energy transition, Australia’s major miners are well equipped to tackle what 2024 has in store for them. AM
AS GOOD AS NEW
EPIROC IS WORKING WITH AN ESTEEMED MINING SERVICES COMPANY TO COMPLETE A ZERO-HOUR REBUILD, OPENING UP SIGNIFICANT OPPORTUNITIES FOR ELECTRIFICATION.
As one of the mining industry’s most ambitious and accomplished original equipment manufacturers (OEMs), Epiroc never seems to sit still, with a constant desire for growth and innovation.
In recent years, Epiroc has met the evolving needs of its mining customers by designing and engineering novel ways to automate, digitalise and electrify operations, enabling miners to not only unlock improved productivity and safety outcomes but also become better environmental stewards.
A recent project has seen Epiroc work with an esteemed mining services company to complete a zero-hour rebuild on one of its underground trucks.
A zero-hour rebuild involves remanufacturing a piece of equipment so its clock returns to zero hours. In other words, so it’s as good as new.
“This was an opportunity for us to look at something that’s socially and environmentally responsible that picks up on Epiroc’s core visions,” Epiroc Australia regional sales manager WA Clinton Williams told Australian Mining.
“We’ve taken what would have been a discarded asset at the end of its life and we’ve refurbished the machine to give it a new life.”
Zero-hour rebuilds have been done before in the mining industry, but they are still in their infancy. This means Epiroc has the opportunity to establish a new offering for mining companies and contractors eager to reduce their environmental footprint.
A zero-hour rebuild doesn’t just mean returning the asset to its original condition; it can also involve appending it with new technologies and advancements. This could involve converting machines to a hybrid operation or making them entirely battery powered.
For a mining industry still coming to terms with what decarbonisation means for operations, there must be stepping stones for miners to commence the electrification process. This is particularly the case for underground operations, which is why the new hybrid offering is attractive and important.
“For mining companies, adopting electrification is centred around the feasibility of the technology – it’s 100 per cent about the cost,” Williams said.
“When considering a hybrid truck, for example, you’ve got a diesel generator powering an electric drive system, which doesn’t demand high revolutions and therefore as much fuel burn. That’s the attractiveness of it.”
With every zero-hour rebuild, Epiroc is generating the data and smarts to underscore its hybrid engineering efforts, with a goal to facilitate a “soft landing” for mining companies looking to deploy hybrid and battery technologies.
“We want to assist miners make that jump into electrification,” Williams said.
“Until battery technologies are proven enough that miners can fully electrify their underground and surface operations, a hybrid option enables operators to enter the battery space while maintaining the diesel engine.
“We also have to consider the mine profile. An underground mine is a unique ecosystem that requires engineers to carefully consider the mine design and infrastructure needed for battery technologies to work.
“If they’re going to do underground servicing then they’ll need to build an underground service shop. Then you need to consider whether you need a charging station – these are the bits and pieces that require additional capital and construction.”
Williams understands that many
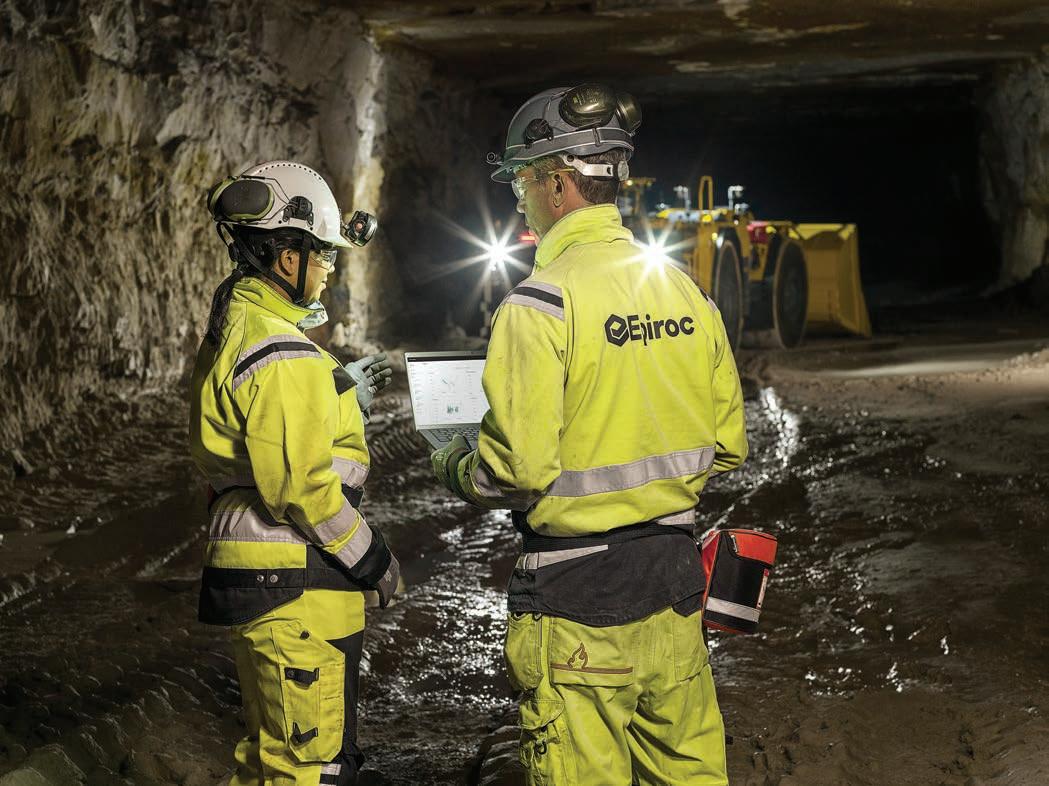
This is where hybrid machines will be key, driving down emissions in carbon-intensive applications while maintaining output.
Once this balance is proven, the sky’s the limit for Epiroc and the broader mining industry, with the potential to
And if there’s a suitable partner to facilitate this transition, it’s Epiroc, one of the mining industry’s premier innovators of battery technologies, with electric options available in its drill, loader and truck ranges.
To further support battery adoption in the mining industry, Epiroc offers its Batteries as a Service (BaaS) business model to remove the obstacles that come
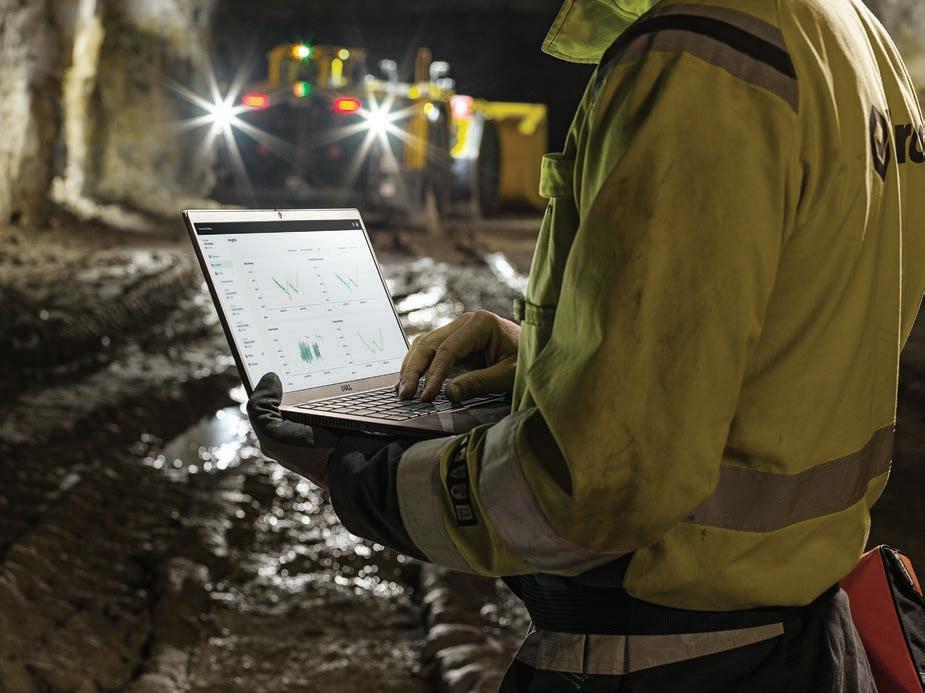
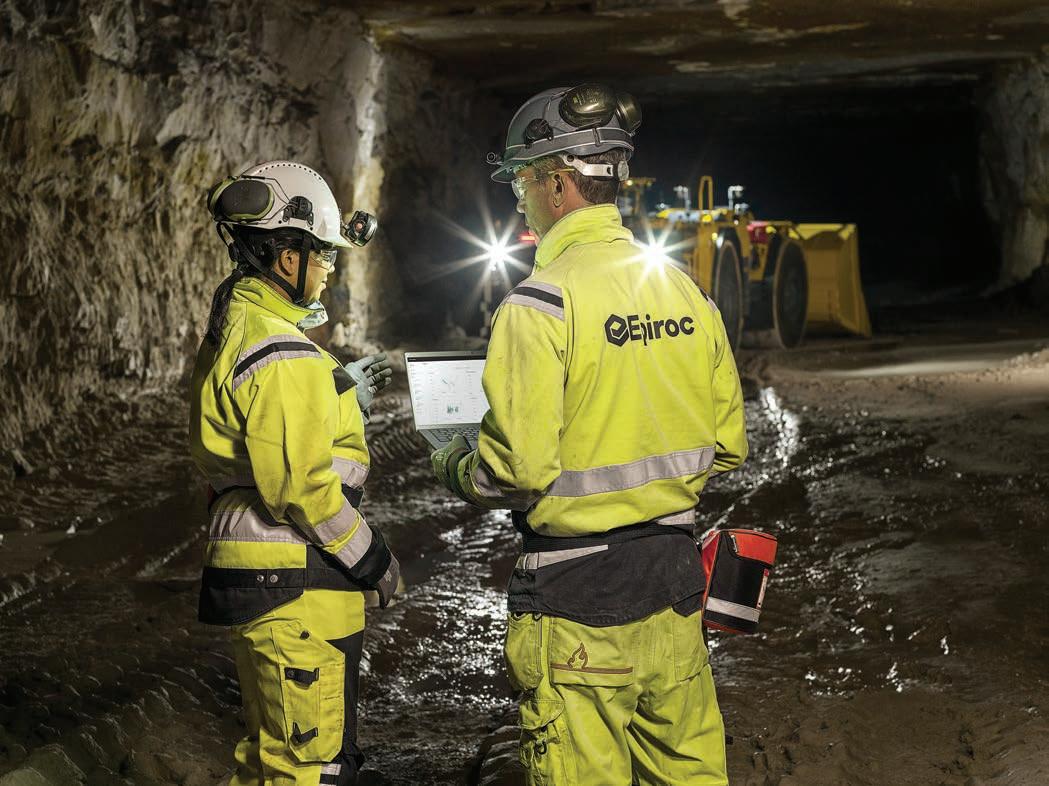
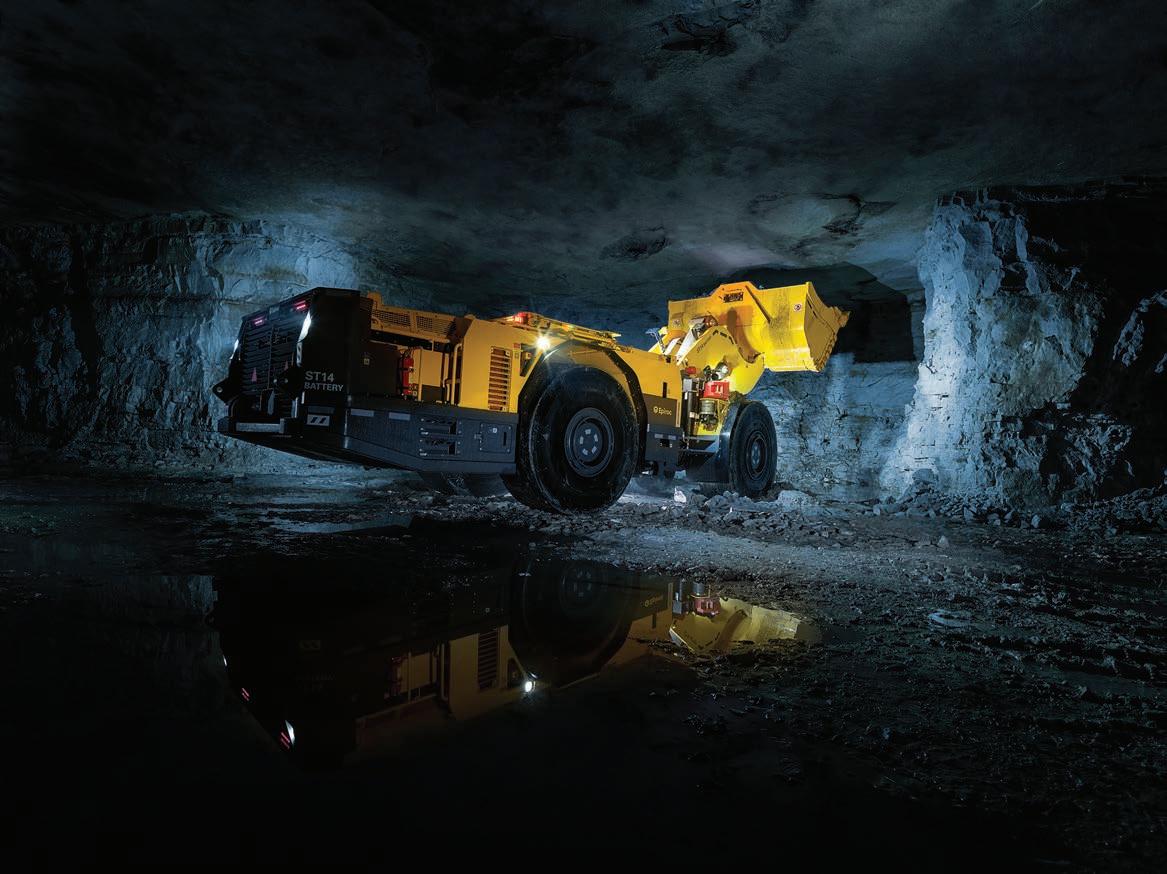
with a transition to the technology. BaaS moves the upfront costs of batteries from capital expenditure to operational expenditure, with the responsibility of this function assumed by the OEM.
BaaS is complemented by Epiroc’s recently announced Batteries with Service offering, enabling miners to own the complete equipment (machine and battery) while still benefiting from Epiroc’s service capability, with extended warranty.
Epiroc customers can benefit from insights such as battery telematics and
equipment audits, something Epiroc global product manager – battery Daniel Jonsson said were valuable tools.
“With battery telematics we can predict the battery health (and) improve and adapt based on the insights we get,” Jonsson said. “We also have all battery data available … in order to always be informed of the health.”
Batteries with Service – developed in response to market demands – can be applied to Epiroc battery-powered equipment, as well as other brands using Epiroc batteries.
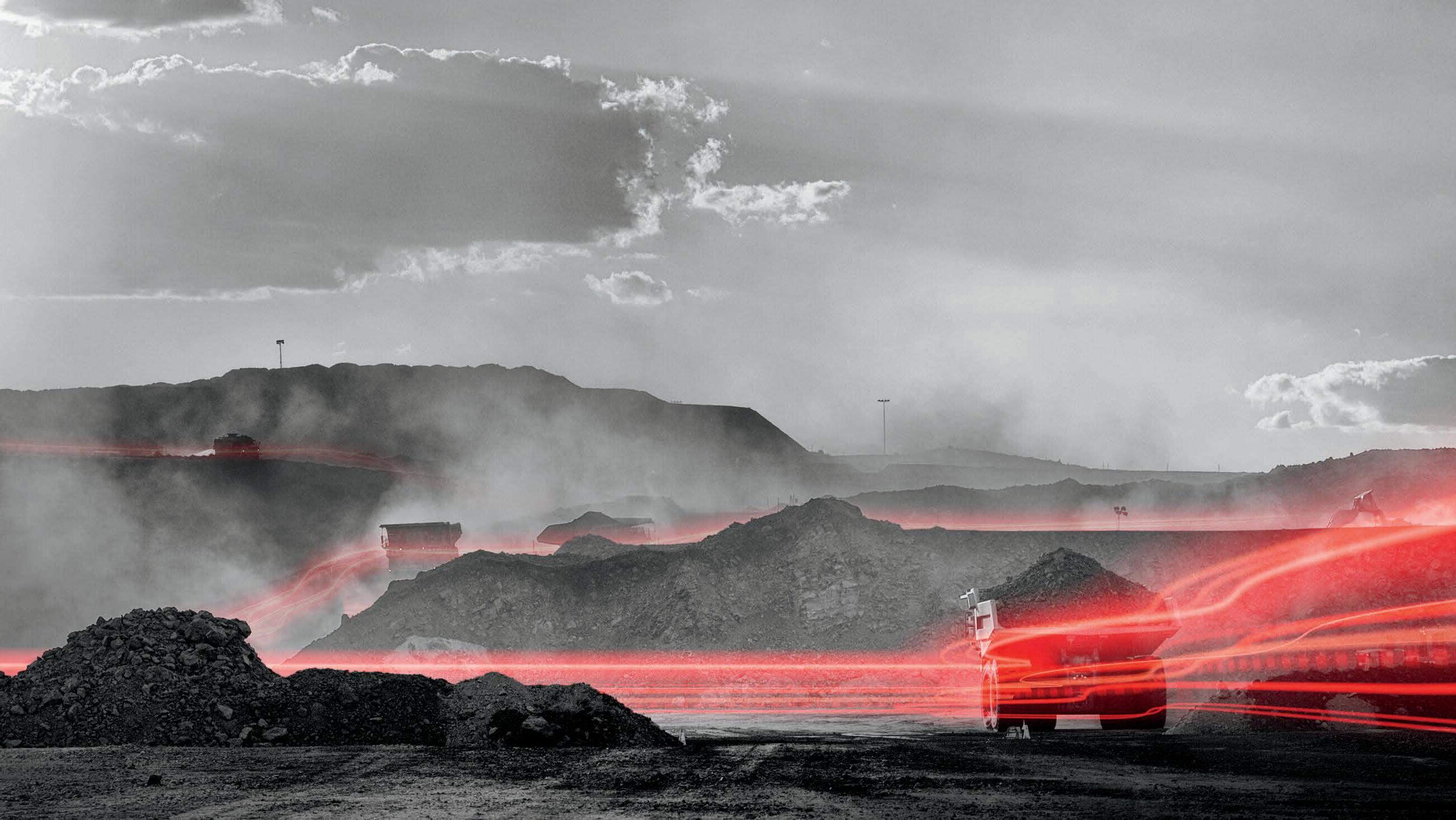
The inevitability of decarbonisation brings a lot of opportunity, but remaining patient is critical to ensure the mining industry is ready to adopt the battery technologies on offer.
The transition must be considered holistically, and the most cogent offerings from the mining equipment, technology and services (METS) sector will consider the precise operational profiles and needs of customers – something Epiroc is proactively implementing. AM
SOLUTIONS FOR THE HARSHEST CONDITIONS
AUSTRALIAN MINING SAT DOWN WITH MASPRO TO DISCUSS THE ENGINEERING COMPANY’S RAPID GROWTH AND FUTURE OBJECTIVES FOR THE RESOURCES INDUSTRY.
For almost two decades, MASPRO has been a savvy problem-solver in the Australian resources industry, innovating solutions to not only extend product life but also drive greater operational efficiency.
“We design, engineer and manufacture industry-leading solutions for mobile mining equipment to withstand the harshest mining conditions,” MASPRO sales director Martin Kennard told Australian Mining.
“We pride ourselves in partnering with customers to innovate and redesign high-quality components, parts and assemblies for the world’s best
an ill-performing component, reverse engineer it to identify the root cause, and design a novel solution that solves the issue, extending asset life in the process.
This is the MASPRO way, something that has enabled the technology company to partner with and design new products for many of Australia’s Tier 1 miners and contractors Kennard explained a MASPRO case study in the Pilbara region of Western Australia.
“We had a situation where a Tier 1 mining client came to us with a reoccurring problem where a rotation unit for a drill was failing after very low hours,” he said. “The maximum they were getting was 800 hours, and as low
due to the conditions and the situations that they were drilling in.
“So we pulled our engineering team together, came up with a proposal for the client which they were happy with and went ahead with engineering something new. And from design to manufacturing we had it on site in about six weeks.
“They ran that unit to 3000 hours – their scheduled change-out time –and were very happy with the product. MASPRO has now become this client’s preferred supplier for this component across all their sites.”
The Tier 1 mining client was not only impressed by the quality of MASPRO’s solution but also by the quick turnaround, which is something Kennard believes separates the company from similar services offered by original equipment manufacturers (OEMs).
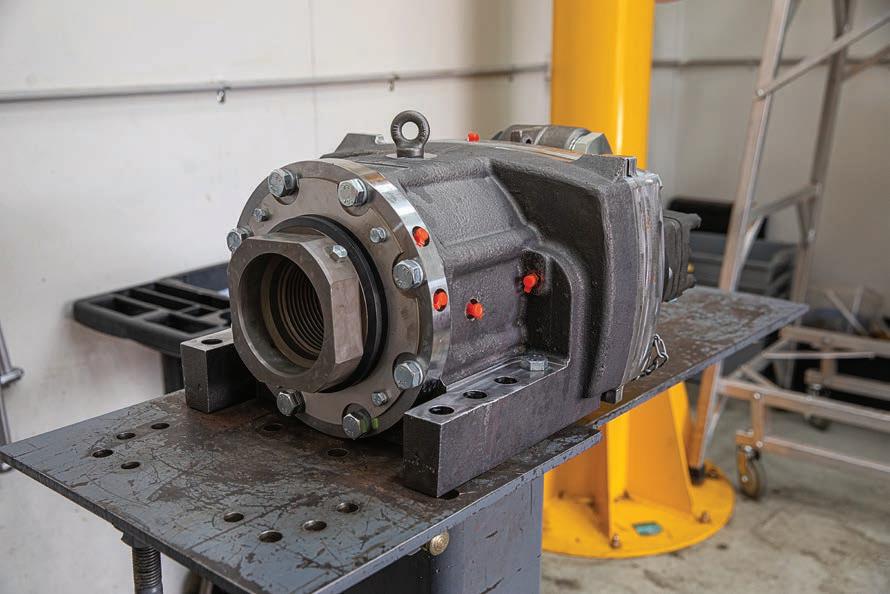
“The advantages of coming to us is that we’re an agile engineering company that can implement a change, redesign or modification to serve the customer quickly,” he said.
“Whereas for OEMs, if it’s only one site or a small portion of the customers seeing this issue, they’re not likely to start a whole change management process just to suit one customer’s need.”
Kennard said MASPRO also has the advantage of understanding local conditions.
“Many OEMs are global companies that might not have the same local engineering presence as us and may rely on their expertise overseas; but mining conditions are vastly different from country to country,” he said.
“We intimately understand the environment in which our customers are operating, leading to engineered
solutions tailored to the harsh conditions of the Australian mining industry.”
As MASPRO continues its expansion to serve Australian and international customers, the company has tripled the size of its engineering facility in Condobolin, New South Wales, in the last two years.
MASPRO has also recently established a similar-sized facility in Sydney to go alongside its existing distribution centres in Perth and Mount Isa. The company also has a new customer hub team based in Perth to better support its WA customers.
Kennard said with MASPRO’s operational capacity set up for growth, the company is now focused on expanding its customer base and broadening its product offerings.
With an expansive suite of solutions available for surface and underground drilling applications, MASPRO is now lending its expertise to load and haul, with engineered components and support available for machines such as Sandvik’s LH621 loader.
Above all, MASPRO is committed to driving greater machine uptime and availability to ensure mining companies can keep their machines on the park, meeting operational and production KPIs more of the time. AM
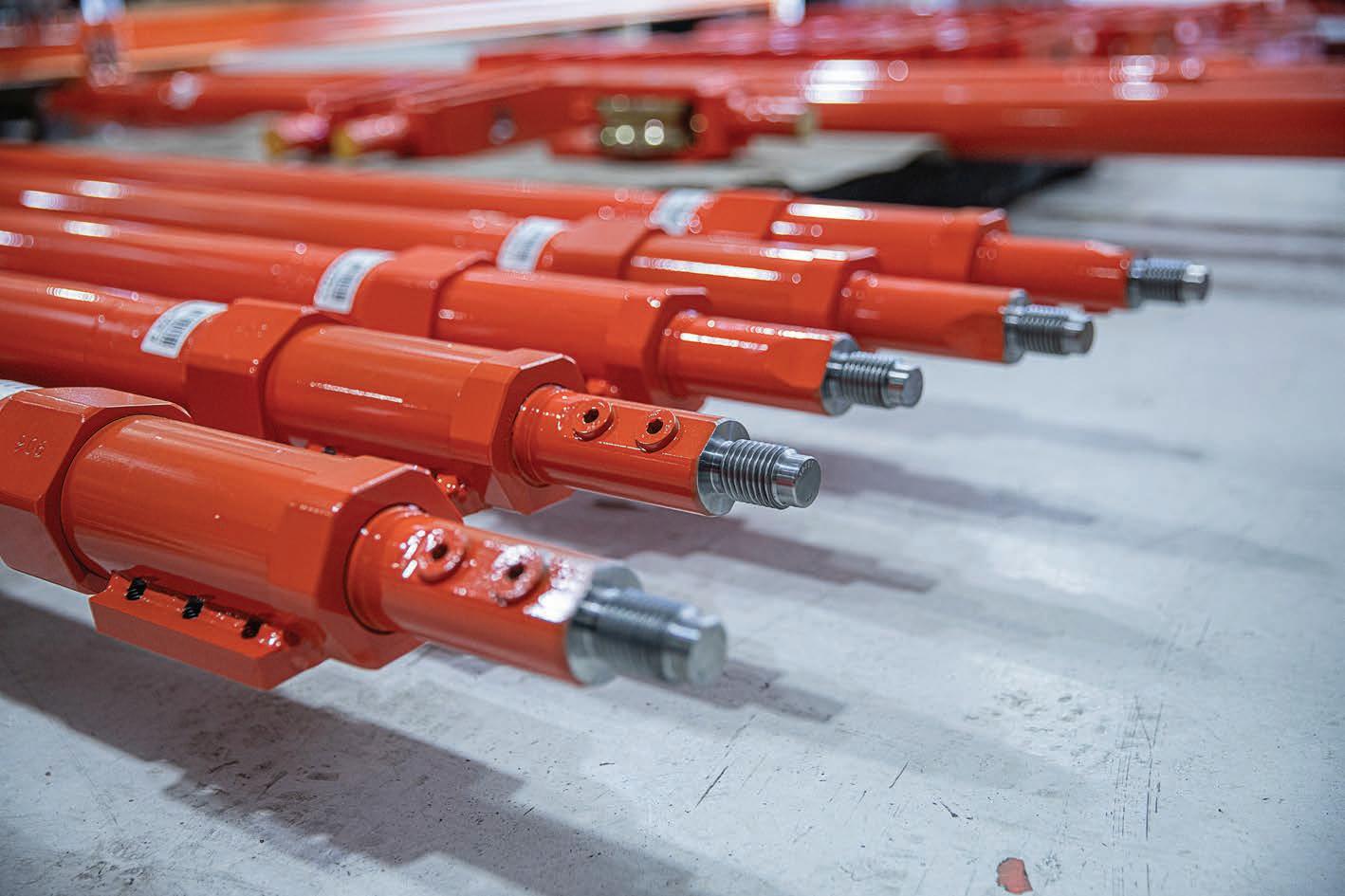
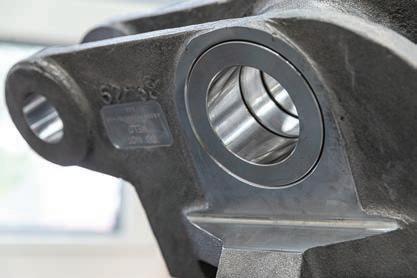
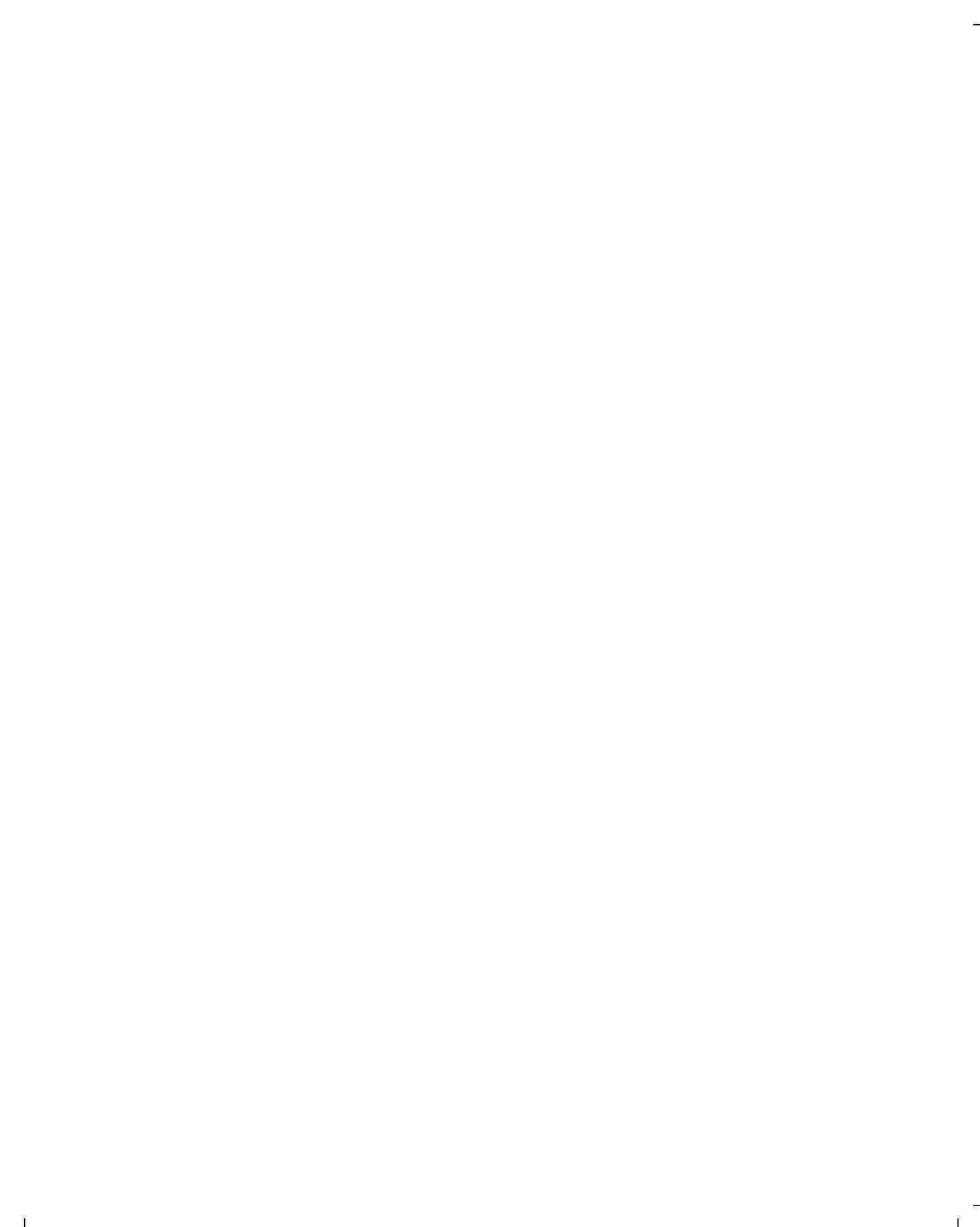
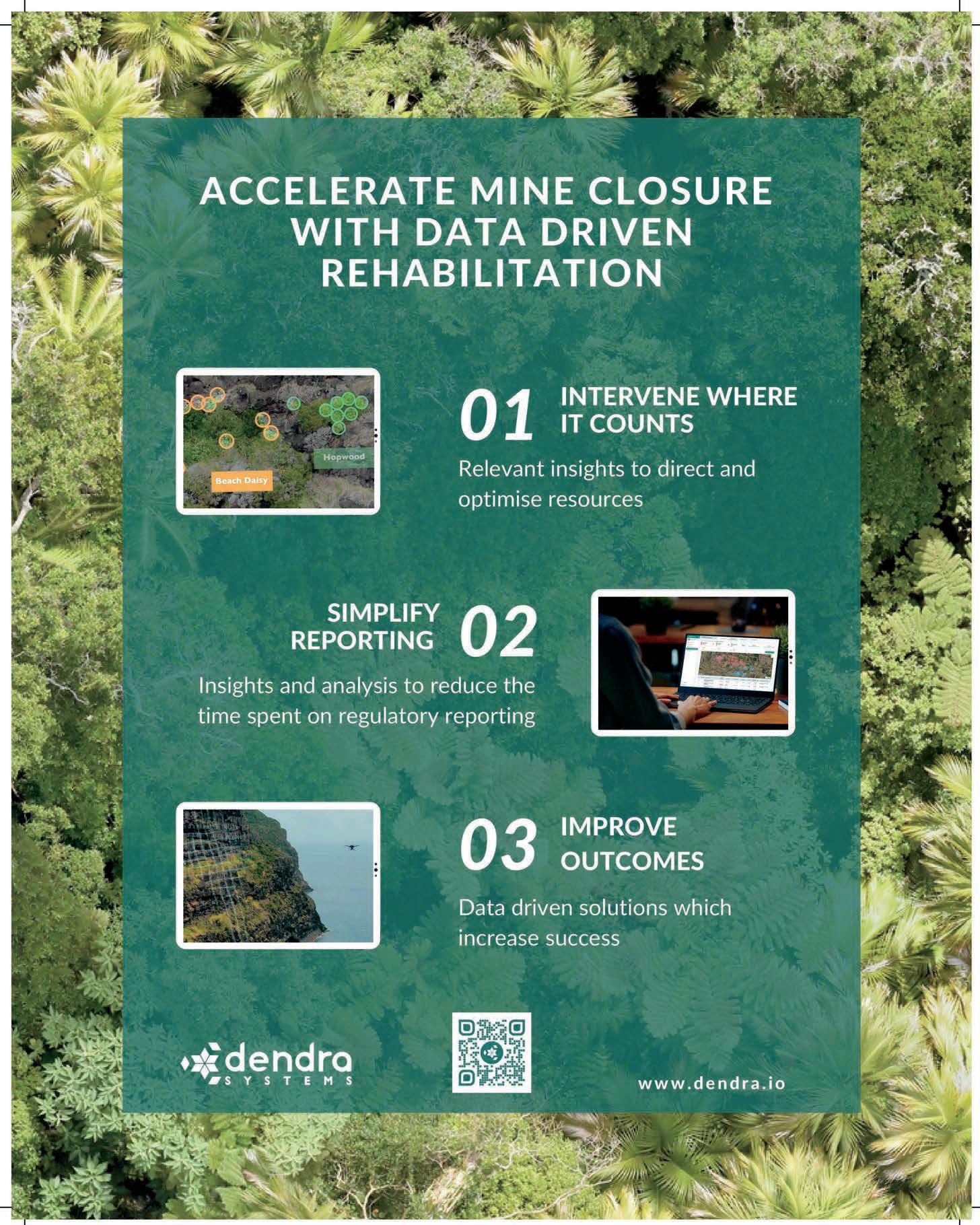
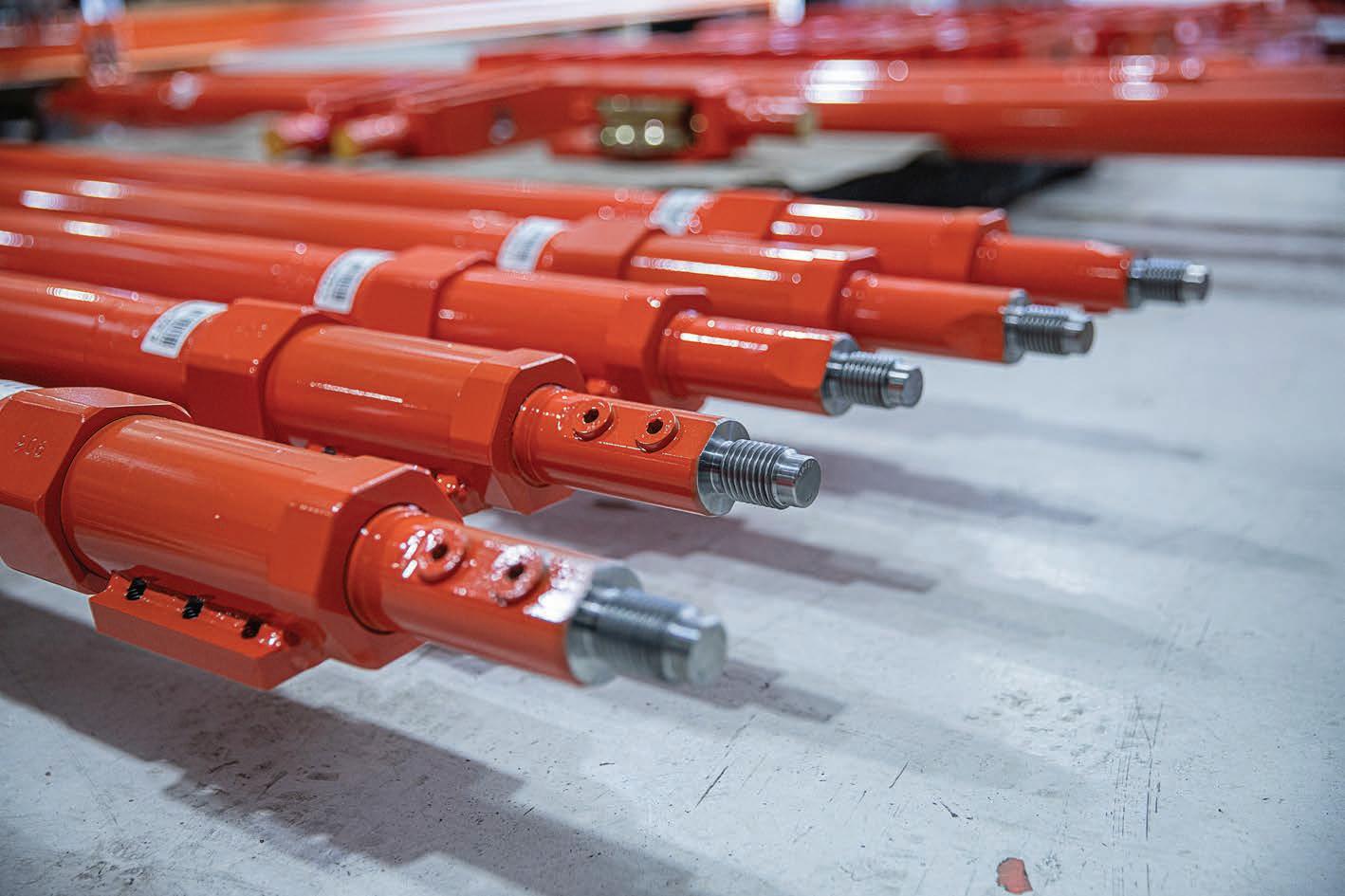
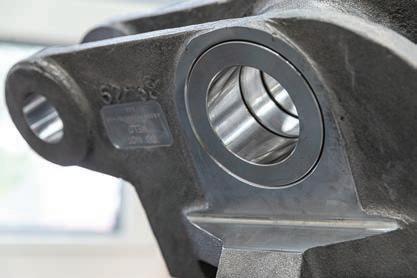
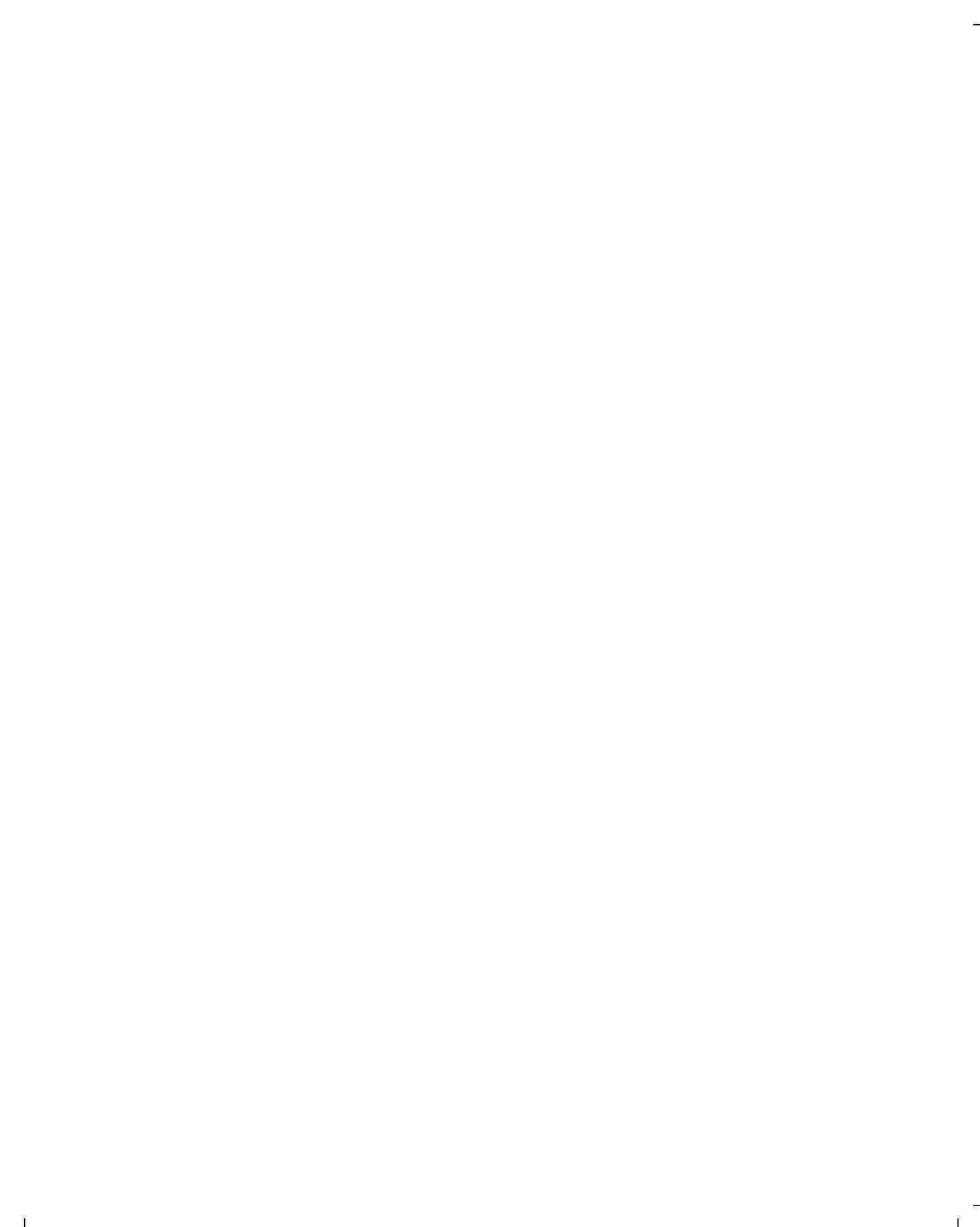
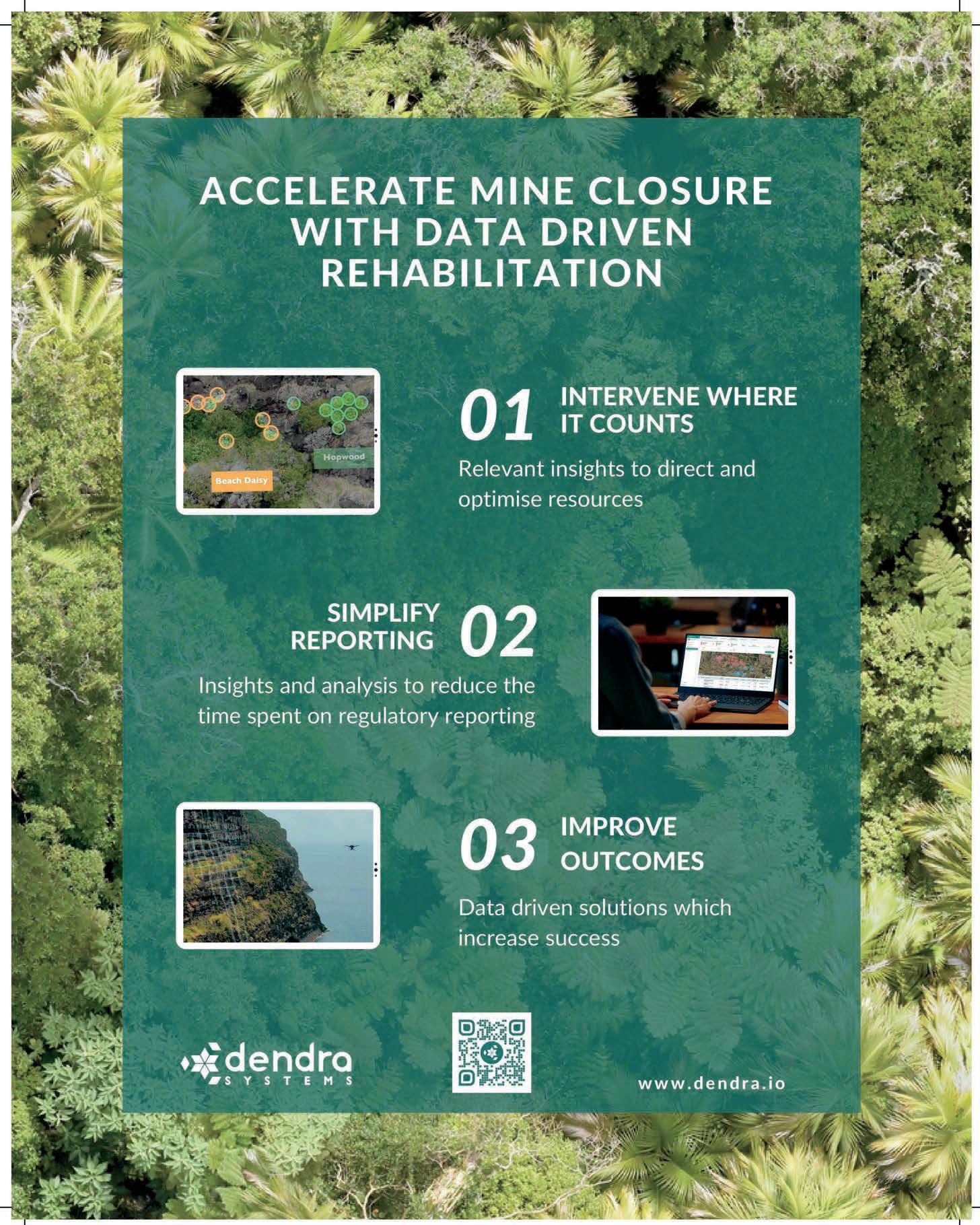
TYRE TIME IS MONEY
MINERS KNOW IT PAYS TO BE STRATEGIC WHEN IT COMES TO SERVICING THEIR EQUIPMENT, AND HAUL TRUCK TYRES ARE NO EXCEPTION.
The humble mining tyre could be called the unsung hero of a mining operation.
No truck could run without them, and without trucks, no ore would be moved and the entire mining cycle would grind to a halt.
But like all pieces of equipment, mining tyres need regular maintenance to function well and this can mean removing them from operation, leading to the burden of unplanned downtime.
“Tyre service work is a maintenance activity, and it should be treated and optimised in the same way as any other maintenance activity on-site,” Kal Tire director of business insights Mark Goode said.
“Mining companies always have one eye on improving their operational efficiency, and tyre maintenance can be optimised relatively quickly and easily using the tools that are available today.”
One of these tools is the Tire and Operations Management System (TOMS) from Kal Tire.
A maintenance planning system designed to power uptime, performance and safety, TOMS allows miners to make informed decisions on servicing their tyres, leading to an uptick in productivity and safety.
“Most tyre-related management systems are optimised to measure how long tyres last given the operating conditions,” Goode said.
“The introduction of TOMS in 2016 means that we can now tell mines how much it costs them in availability every year to service their tyres. That information is powerful in identifying opportunities for improvements.”
While tyre maintenance, whether planned and unplanned, inevitably leads to some downtime, a strong tyre management strategy means mines can make the best of these events.
“The most important thing in tyre strategy is to choose one,” Goode said. “For some mines, tyre performance may be the priority, while for others, fleet productivity will be king.”
One way to minimise downtime when maintaining tyres, while also reducing safety hazards on-site, is to schedule servicing at the same time as other mechanical work on the truck.
“A site that’s bringing trucks down more often will be placing greater stress on its tyre crew than one that’s able to aggregate its service work and have fewer downtime events,” Goode said.
“Unplanned work could also mean that service crews must be dispatched into the pit. This places them at greater risk of harm and should be avoided wherever possible.”
Through aggregated and anonymised datasets from TOMS, Kal Tire has been able to work with several of its customers to prove how effective tyre service optimisation can be.
“When mines agree on a tyre management strategy, it’s important
that they consider what success will look like,” Goode said. “They should determine whether they would like to maximise performance or productivity.
“Most operations want both, but that’s difficult to achieve.”
And while it’s not usually possible to maximise tyre performance and utilisation, Kal Tire and TOMS can help miners’ strike a suitable balance between the two, allowing them to meet their safety and financial goals.
“The ability to review the impact of a tyre service strategy on tyre performance and operational safety allows mines to quantify the impacts of their choices,” Goode said.
“There’s no right or wrong answer because, either way, the tools we have today ensure that once a decision is made, we can monitor and adjust the strategy to drive the most amount of value for each site, whatever the circumstances.” AM
SCHEDULING TYRE SERVICING WITH TRUCK MAINTENANCE CAN INCREASE PRODUCTIVITY AND SAFETY.
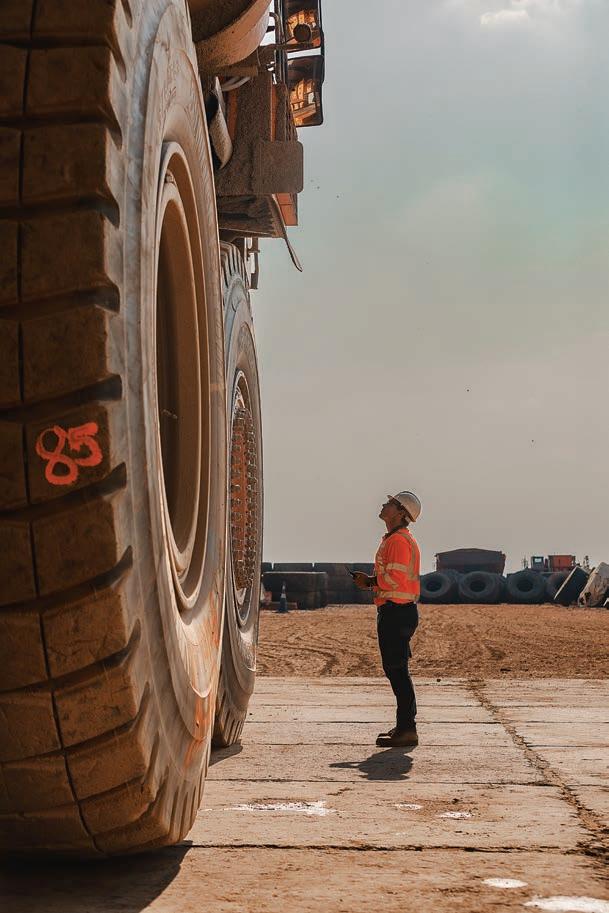
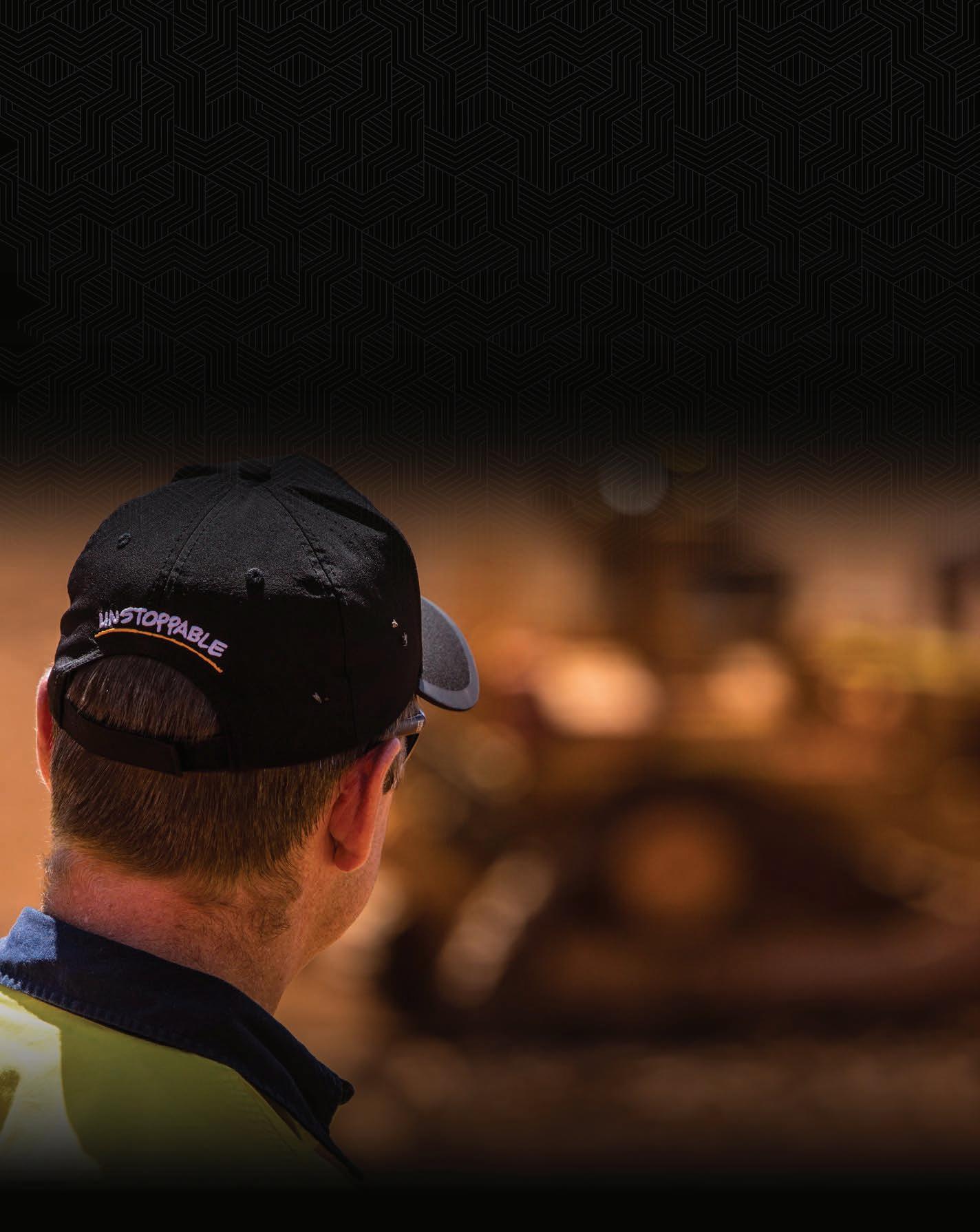
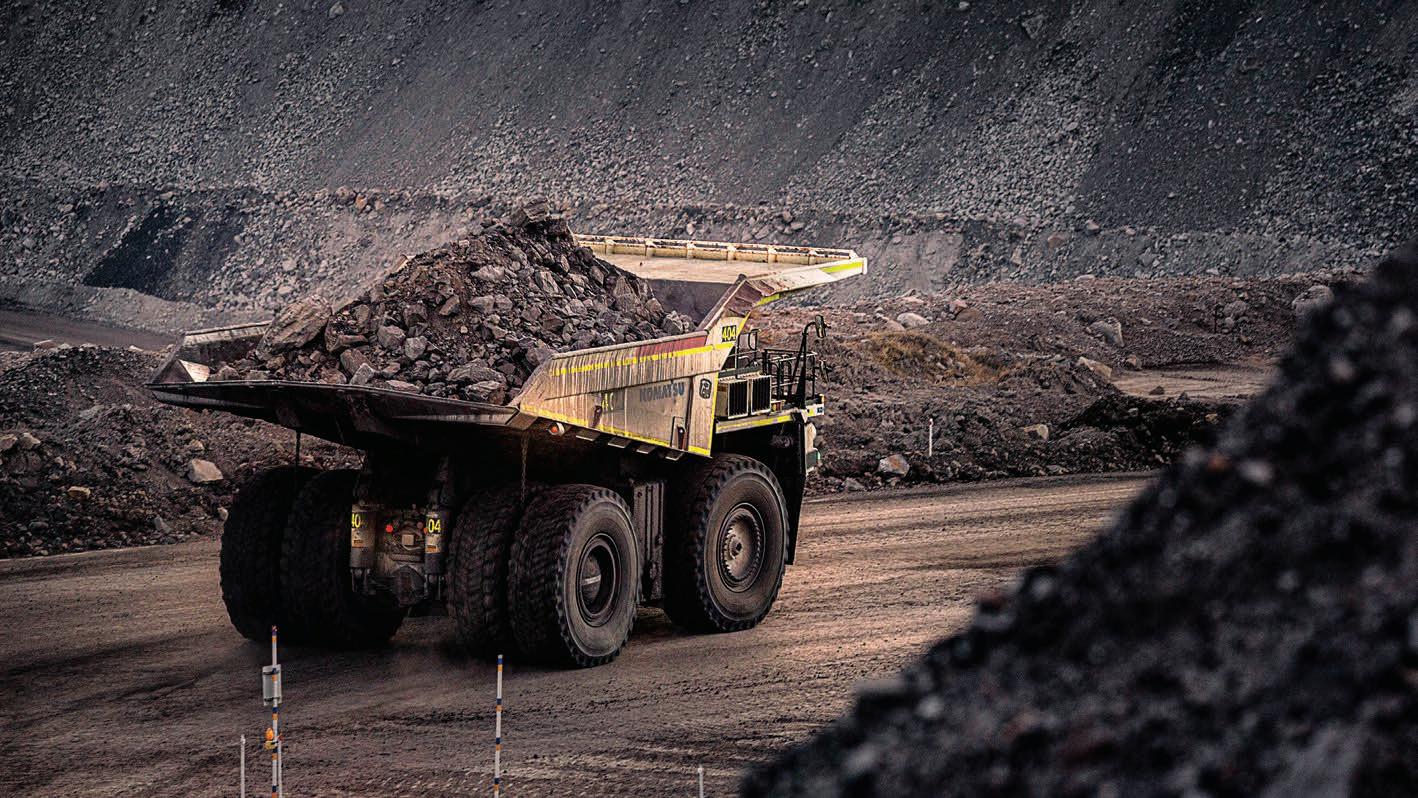
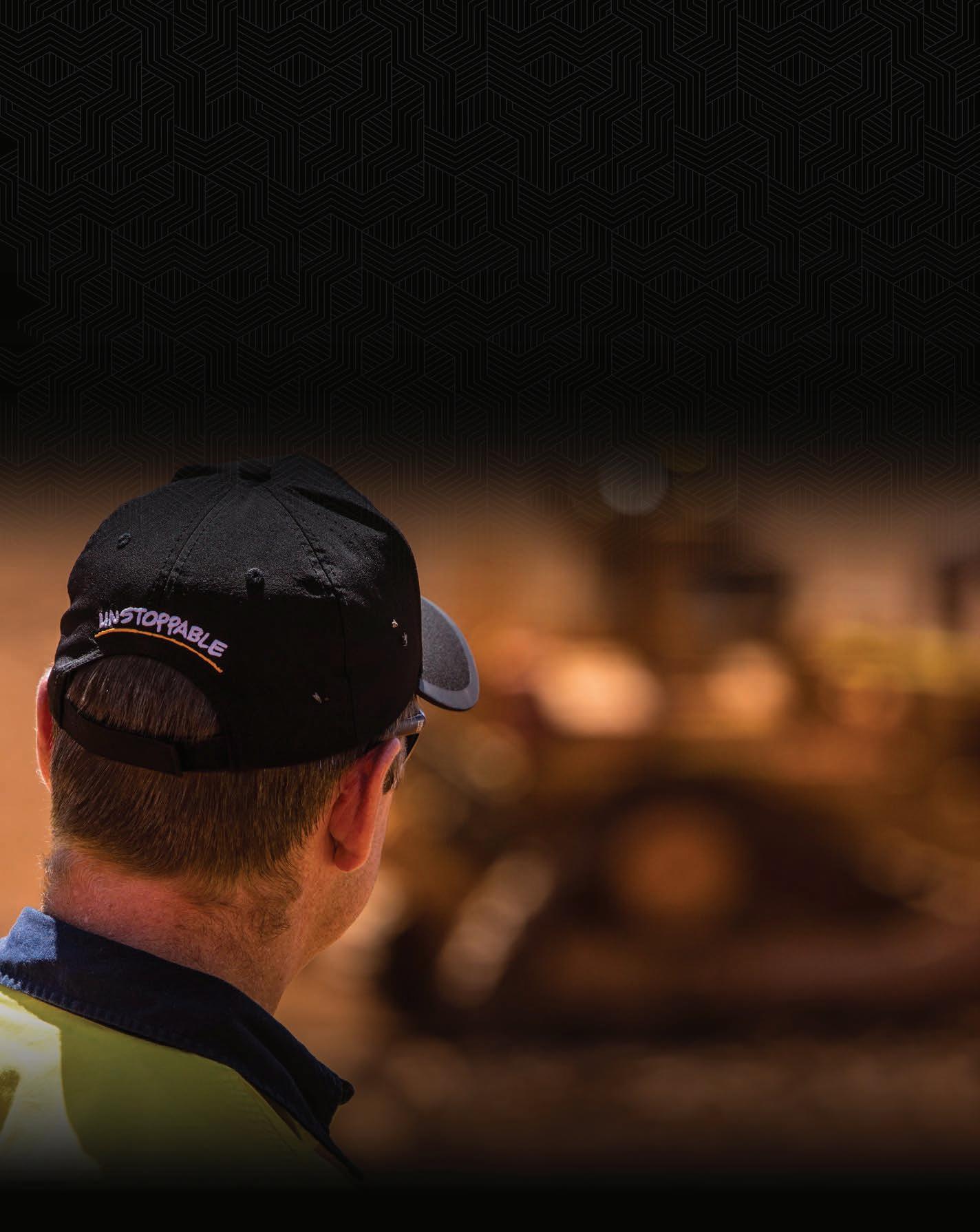
BOOSTING PRODUCTIVITY WITH ULTRA-FINE FILTERS
MICFIL AUSTRALIA SPOKE TO AUSTRALIAN MINING ABOUT ITS ULTRA-FINE FILTERS AND THEIR BENEFITS.
When engine oil is replaced, as much as 12 per cent of the older oil remains inside the engine, polluting the new replacement oil with contaminants such as wear particles and debris.
This can reduce the oil’s life and lead to premature component and vehicle failures, limiting machine availability and uptime.
Operating engines on ultra-clean oil extends the oil’s life as well as the life of the machinery’s internal components.
“With laboratory analysis, our systems allow oils to be changed based on oil condition rather than time,” Micfil Australia founder Filip de Ruwe told Australian Mining.
This is where Micfil’s bypass filtration systems for oil can help. By removing impurities, the engine oil is maintained at superior cleanliness levels, thus increasing the life of the engine and internal components.
ROAD TRANSPORT, BUS OPERATORS AND LOCAL COUNCILS HAVE REPORTED 4–6 PER CENT SAVINGS IN FUEL USE AFTER INSTALLING MICFIL ULTRA-FINE FILTERS IN THEIR VEHICLES.”
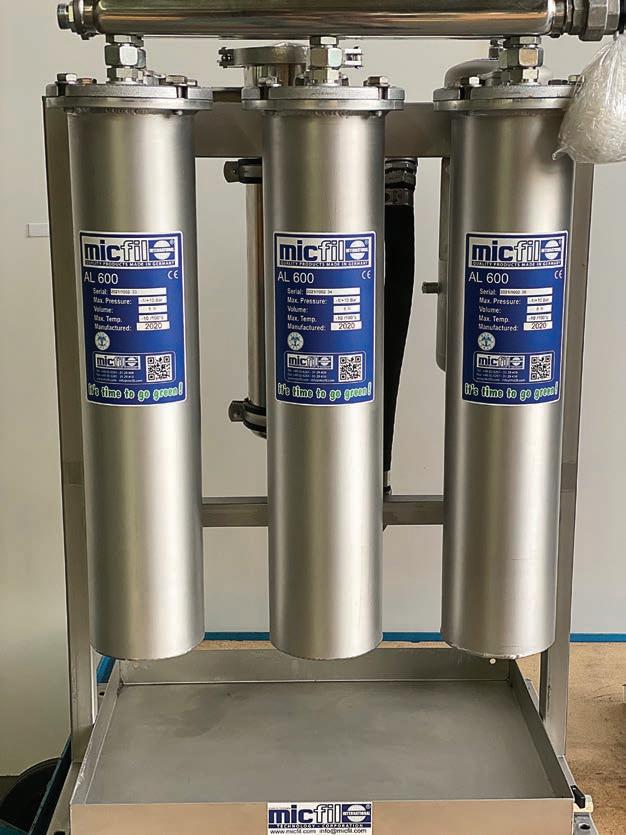
Micfil Australia is the Australian distributor of Micfil’s ultra-fine filters, which are being used worldwide in a variety of industries and applications, notably for filtering liquids such as engine oil, transmission oil, turbine oil, transformer oil, hydraulic oil, gearbox oil, fuel and biodiesel.
“Micfil Australia came to fruition after the initial Asian and Australian Micfil distributors established a market in Asia,” de Ruwe said.
“The company’s ultra-fine filters initially concentrated on the marine industry for the first few years
fuel, all while positively impacting the environment.
Water – a known fuel contaminate that causes rust, bacterial infestation and cavitation damage at the injectors – is absorbed by Micfil ultra-fine filters from diesel and biodiesel while delivering filtration of up to 0.5 µm, even at high flow rates.
The ultra-fine filter will also eliminate 98 per cent of all bacteria, fungi and mould present in diesel fuel by trapping water molecules and contaminants in just one pass.
When fuel is delivered to the injection
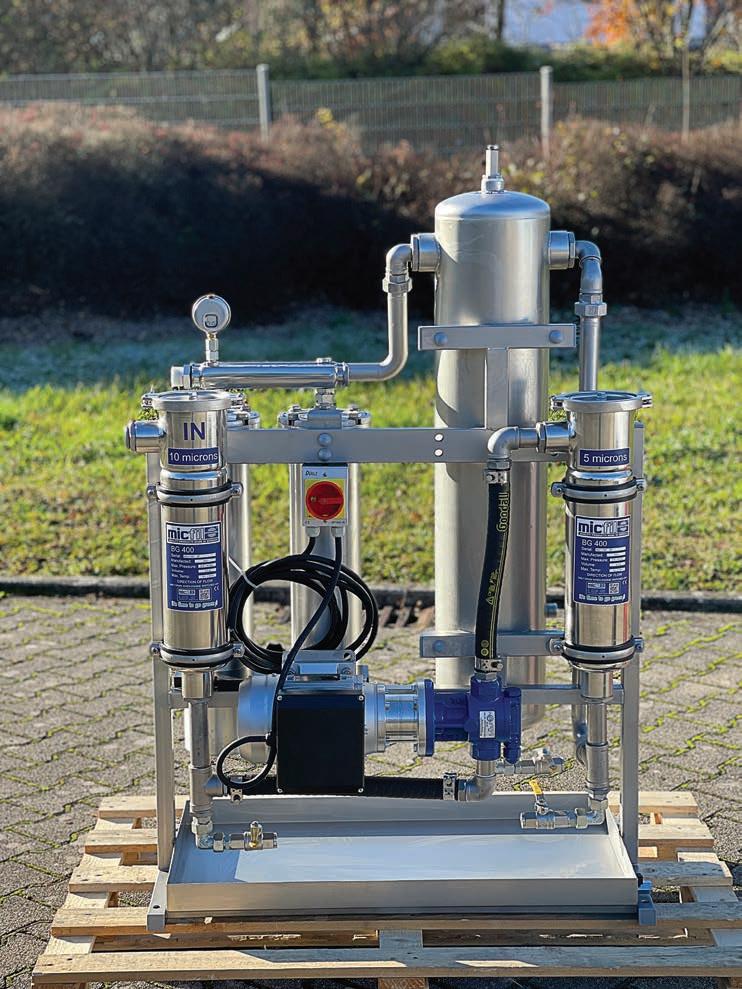
MICFIL’S FILTRATION PRODUCTS HAVE BEEN USED ON VARIOUS DIESEL ENGINES GLOBALLY.

The ultra-fine filters improve the fuel burn spray pattern, enabling improved fuel efficiency.
“Road transport, bus operators and local councils have reported 4–6 per cent savings in fuel use after installing Micfil ultra-fine filters in their vehicles,” de Ruwe said.
“Increased oil hours equals less wasted oil, boosting clean oil life, reducing fuel consumption, extending service intervals and lowering downtime, increasing productivity as a result.”
By removing contamination, Micfil’s ultra-fine filters reduce component wear and prevent damage to expensive components, increasing overhaul intervals by as many as 50,000 hours.
“This is made possible through the ultra-fine filter’s unique design,” de Ruwe said. “While it looks simple, it hides some remarkable properties.
“The water and contaminate blocking filters have a diameter of 110mm, built so any fluid filtered travels through 93 layers of material (tortuous filtration) made up of a mixture of fibreglass, polymers, high-quality cellulose and some proprietary materials.
“Think of them as an ultra-fine fluid maintenance system boasting 0.5-micron filtration with a beta ratio of 200 at two microns.”
WE HAVE RECEIVED POSITIVE FEEDBACK FROM THOUSANDS OF CLIENTS FROM ALL OVER THE WORLD, WITH MANY RAVING ABOUT HOW THEY’RE ABLE TO SAVE MASSIVE AMOUNTS OF MONEY ON OIL AND FUEL.”
According to de Ruwe, Micfil Australia and most original equipment manufacturers (OEMs) agree that quality by-pass filtration for oil and ultrafine filtration for fuel dramatically assists with the performance of your equipment.
“However, engine manufacturers have realised that ultra-fine particles below five microns at higher pressures are causing premature failures, but they are doing very little to improve the filtration of the fluids in the engine,” he said.
“This allows OEMs to increase their revenue for spare parts across the lifetime of the machinery.
“By using Micfil, components such as bearings, crankshafts, oil pumps,
rings, cylinder liners, and all components lubricated by oil or fluids have significantly reduced wear and tear.”
Micfil’s mantra – “It’s time to go green” – aligns with the company’s mission to deliver unrivalled deep filtration.
“The ultra-fine filters lower fuel consumption by 4–6 per cent on average, directly correlating with reduced carbon emissions and extended oil drain hours,” de Ruwe said.
“The filters reduce PM10 and PM2.5 (particulate matter), while NOx (nitrogen oxides), carbon monoxide and hydrocarbon tests meet Euro 6 standards.”
Equipped with various benefits, it’s little wonder Micfil’s ultra-fine filters have enjoyed great success.
“We have received positive feedback from thousands of clients from all over the world, with many raving about how they’re able to save massive amounts of money on oil and fuel,” de Ruwe said.
“Some clients installed our filters on one unit as part of a three-month trial. Upon completion, they ordered Micfil ultra-fine filters for their entire fleet after facing challenges with off-theshelf filters.
“After installing the Micfil Ultrafine filters, they told us how well the
filters work. One Micfil client with several 400-tonne dump trucks has shown savings of some 15 litres per hour per truck.”
Customers can also combine Micfil’s ultra-fine filter systems with the company’s bag filters and water separators, which prevent fuel and waterrelated failures, remove solid/semi-firm impurities such as dirt, rust and sludge, extend engine overhaul time and service life while meeting emission standards.
“Our water separators and bag filters are all manufactured with high grade marine stainless steel and are ideal for fuel farms,” de Ruwe said.
“Our range of filter canisters are made with either aluminium or high-grade marine stainless steel.
“We have installed Micfil bunkering filter systems for mining and oil companies with flow rates of over 240,000 litres per hour. We also have fuel circulation or polishing systems on fuel tanks ranging from 10,000 to 10 million litres.
“By combining Micfil’s stainless steel bag filter and water separator with the Micfil ultra-fine filter system, customers will utilise a quality circulation system that produces cleanliness to ISO 15/14/10 levels or lower, making it ideal for today’s diesel engines.” AM
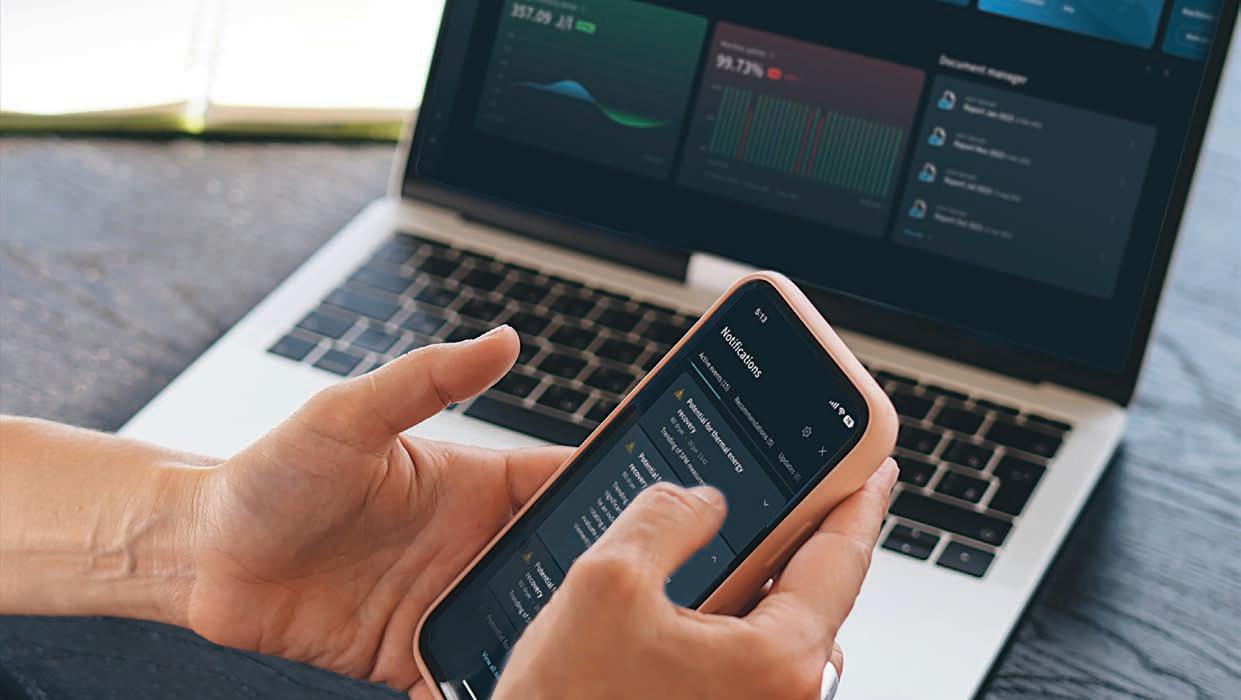
MAINTENANCE MADE EASY
ATLAS COPCO AIMS TO KEEP AUSTRALIAN MINES ON TRACK BY ELIMINATING ISSUES BEFORE THEY ARISE.
Gone are the days of carrying a canary into a mine shaft. At a modern mine site, sophisticated air compressors are tasked with keeping miners breathing easy with a reliable supply of fresh air.
When choosing the right air compressor, great care needs to be taken to ensure the machine is the right fit for the mine.
“It all comes down to quality.
Quality products, quality service,” Atlas Copco field service technician Eddie Thompson told Australian Mining. “At Atlas Copco, we’re known for setting the industry standard.”
Thompson said customers know what they’re in for when they choose an Atlas Copco air compressor.
“The quality of our materials sets us apart from the competition,” he said. “Our products are engineered in Belgium with the highest-grade steel on offer.”
When you’re sending out equipment engineered to the highest standard, making sure that equipment keeps operating to that standard is key.
Atlas Copco can provide an air compressor for any situation, but it’s the ongoing preventive maintenance of compressors that has become a cornerstone of the company’s commitment to its customers.
“Some of our customers are 1000km away in remote, hard-to-access areas,” Thompson said. “If a lack of preparation leads to a breakdown, it could mean hundreds of thousands of dollars down the drain until the equipment is back up and running.”
Thompson said skipping preventive maintenance is a costly mistake he’s seen too many times.
“If an air compressor’s filters aren’t cleaned, for example, it can’t suck in air and the strain on the machine will double electricity bills and halve its lifespan,” he said. “If you don’t take steps to effectively maintain a compressor, you’re setting yourself up for inefficiency and expensive breakdowns.”
Under Atlas Copco’s service contract plan, technicians are on hand to keep machines running as they should with genuine company-certified parts.
The company’s highly trained and experienced technicians work behind the scenes of a mine site to eliminate potential issues before they even need to be called out.
“We’re always thinking six months ahead,” Thompson said. “By identifying what parts are going to need replacing soon we can swap them out before they become a problem.
“We have technicians all over Australia maintaining air compressors so mines can get on with the work of extracting resources efficiently.”
Thompson emphasised every customer is different, so Atlas Copco works with each site to execute a maintenance plan based on the needs of an individual operation.
“Our customers can’t afford breakdowns when they’re running highturnover operations 24–7,” he said. “It’s our ability to adapt and think ahead that separates us from the competition.”
Working alongside Atlas Copco technicians is the company’s integrated SMARTLINK software solution.
By monitoring equipment and sending data directly to Atlas Copco, SMARTLINK enables technicians to
“We can see if there’s anything wrong with the machine and run diagnostics based on real-time data,” Thompson said. “We can even use the data to enable customers to quickly solve the problem before a technician even needs to be called out, saving them costly downtime.”
Thompson said Atlas Copco’s preventive maintenance offering makes it an obvious choice for a complete air compressor package.
“Our customers keep coming back because we prevent breakdowns, keep operations running, and save them time and money,” he said.
“Reliability is key. That’s where we
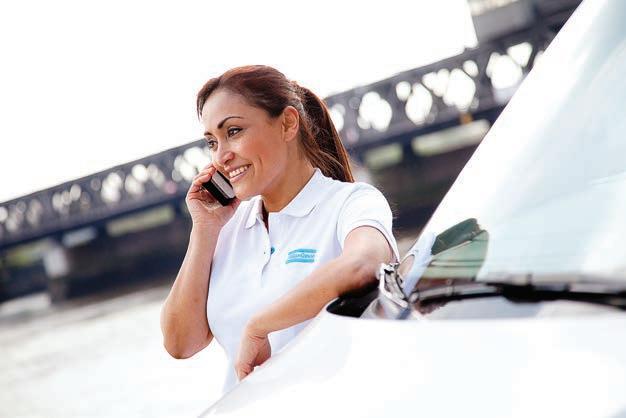
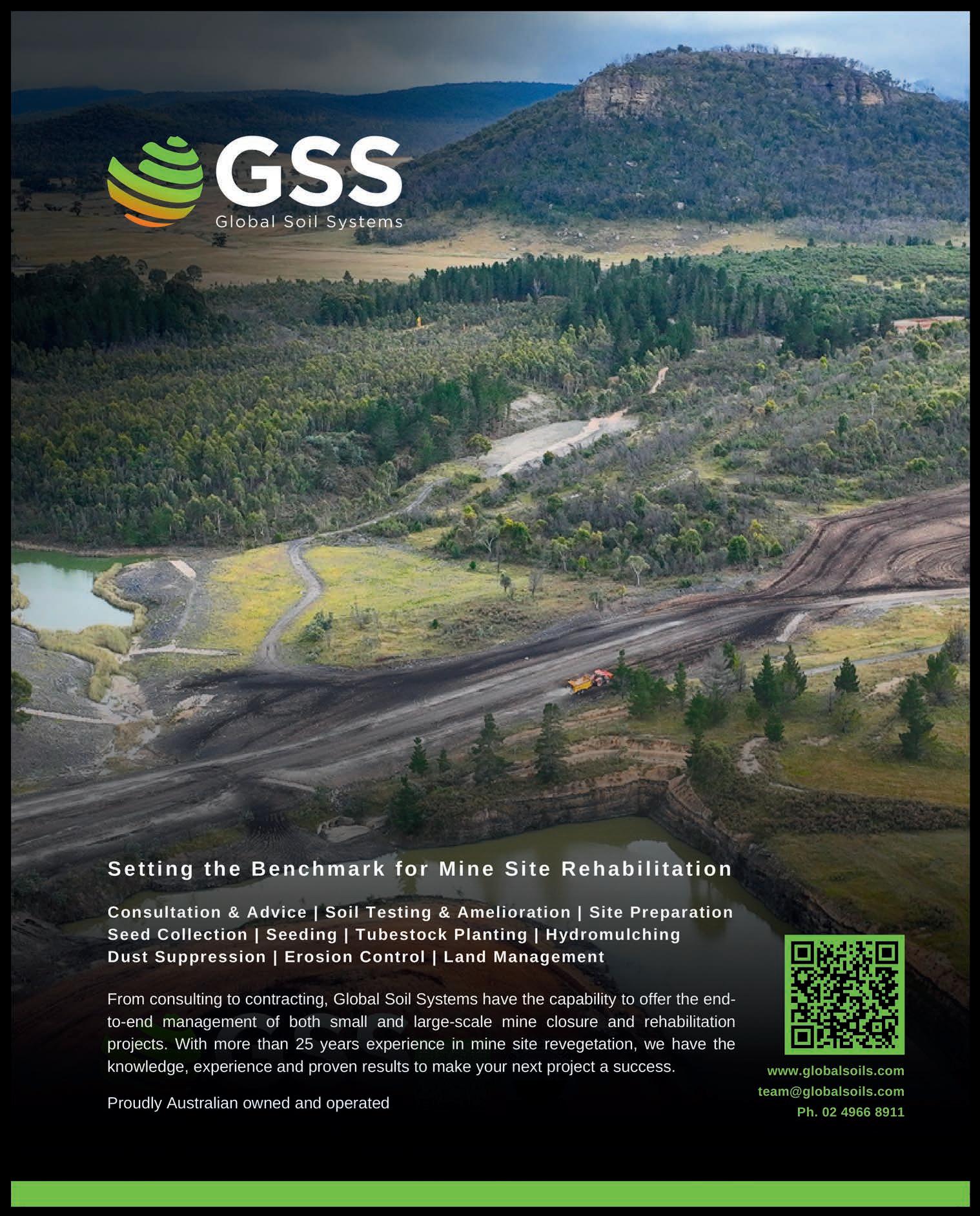
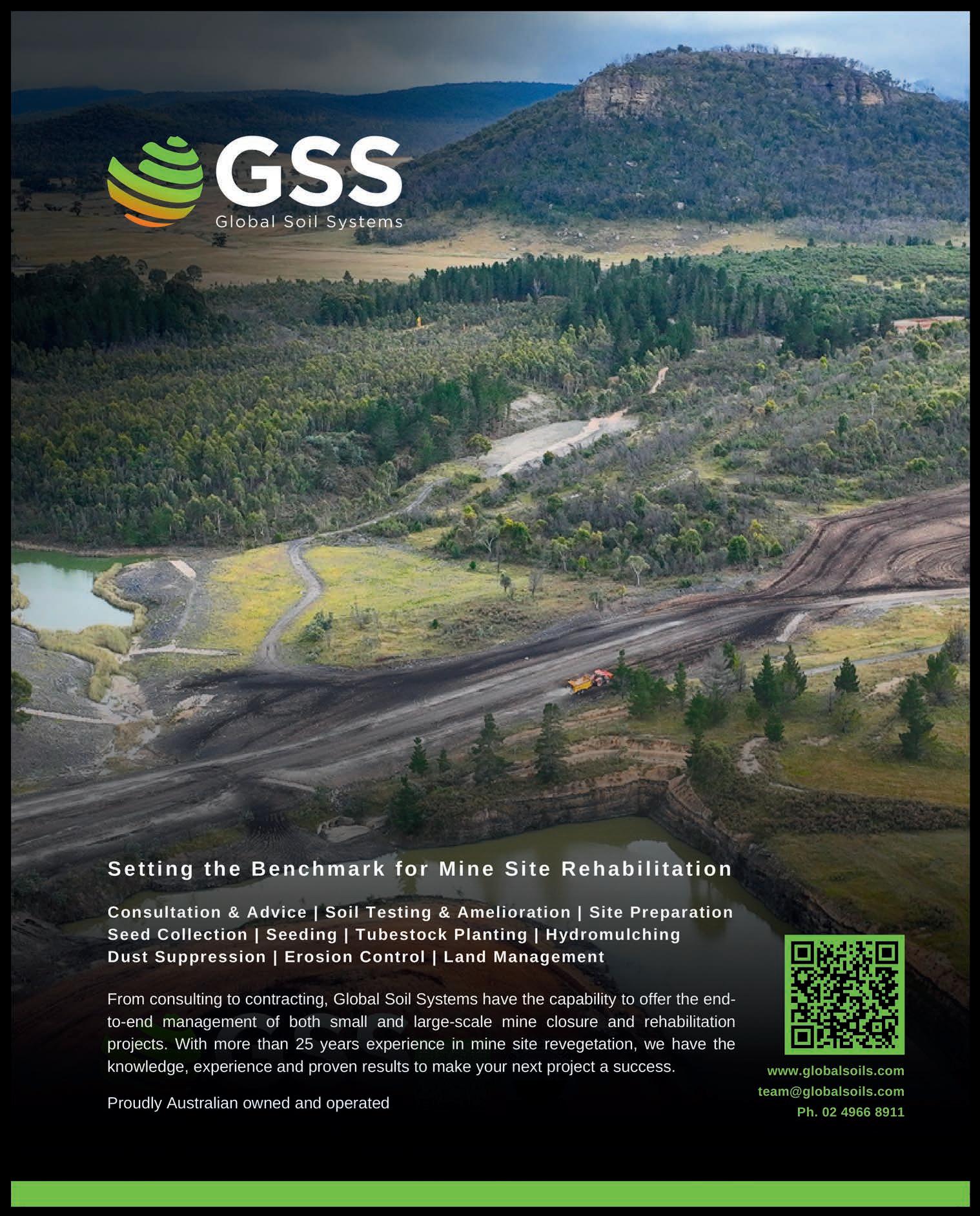
REVOLUTIONISING MILL RELINING SAFETY
BRADKEN’S SUITE OF MILLSAFE SOLUTIONS HAS BEEN DESCRIBED AS A GAME-CHANGER IN MILL RELINING SAFETY.
Agrinding mill is a hazardous environment to work within.
Having identified tasks in the relining process that require the mill team to access the interior of the mill, Bradken has developed solutions to remove personnel from these hazardous locations.
Enter Bradken’s MillSafe Solutions.
Relining a grinding mill can take in excess of 100 hours to complete.
The grinding mill needs to be isolated and safe for people to enter a confined space. The worn liners are removed, and the mill shell is cleaned in preparation for new liner installation. The new steel liners are installed, and these can weigh up to five tonnes each.
Traditionally, steel liners are bolted in manually from inside the mill, a process that involves workers operating near heavy machinery and suspended loads for hours at a time.
“The nature of grinding mills means they are classified as a confined space,” Bradken principal product manager Craig Faulkner told Australian Mining
“During a reline, the mill requires good lighting and ventilation to create a safe working environment. Furthermore, the use of heavy equipment during the relining process contributes to a highly hazardous area of work for the reline crew.”
Bradken’s MillSafe Solutions offering helps to reduce the exposure to potential hazards by improving the mill relining process, making it safer
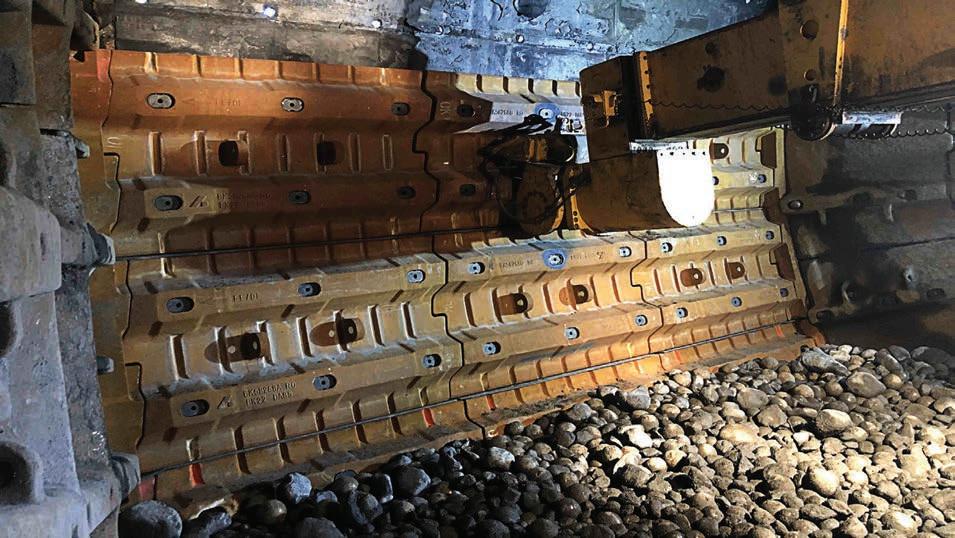
The suite comprises the following products: MillSafe Bolting System, MillSafe Backing, MillSafe Liner Location Stripes and MillSafe Combined Corner Liners. These are all compatible with autogenous (AG), semi-autogenous (SAG) and ball mills.
The Bradken MillSafe Bolting System allows liners to be bolted on from outside of the mill.
“By installing the bolts from outside, there is no need for maintenance personnel to be in the vicinity of the reline machine during liner positioning, making it a much safer practice,” Faulkner said.
Typically, the internal mill shell is lined with a 6mm rubber sheet to protect the mill shell and create a consistent seating area for the steel
liners, with workers required to clean the mill shell and repair damaged rubber sections during relining. With Bradken’s MillSafe Backing that’s no longer the case.
“MillSafe Backing is an integral coating on the fit face of our liners, eliminating the need for rubber sheet repairs and reducing customer maintenance costs,” Faulkner said.
“In addition, MillSafe Backing wraps around the side of the liners to eliminate the need for rubber filler strips, removing another process where personnel have to enter the mill.”
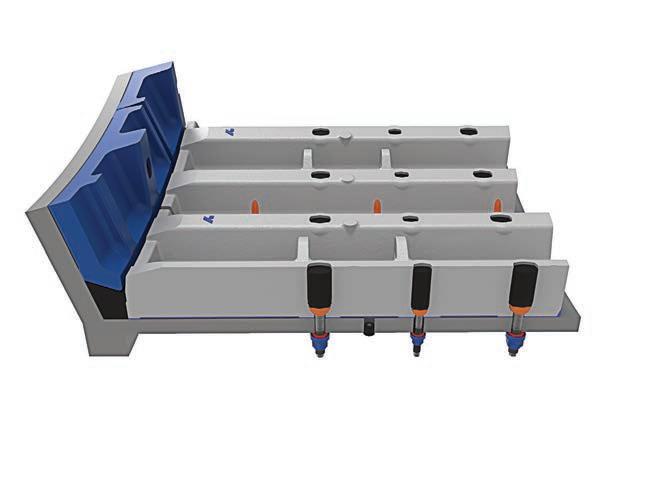
Bradken’s innovative MillSafe Combined Corner Liners are cast as part of the liner, therefore eliminating loose corner liners, and eliminating risks posed by traditional products. This also has the benefit of reducing overall liner mass.
Finally, Bradken’s MillSafe Liner Location Stripes provide visual guidance to position the liners and deliver a safer and more efficient liner install.
“Bradken’s focus is to innovate and provide our customers with a high level of engineered solutions that improve mill safety, minimise downtime and optimise performance,” Faulkner said.
“Our suite of MillSafe Solutions is a testament to that.”
Bradken analysed the benefit of the MillSafe Combined Corner Liners on a 40-foot SAG mill.
This resulted in the reduction of 60 liners, saving an estimated 12 hours in relining time, amounting to an entire shift. It also supported an increase in mill availability, improving the operation’s profitability.
Faulkner said the MillSafe suite really came into its own two years ago when one of Bradken’s customers was looking to fully automate the relining process for a grinding mill.
“This aligned with our vision and the opportunity to improve mine site safety standards and reline efficiency across the global mining industry,” Faulkner said.
“The project reached its goal last year by partnering with our customer and relining equipment suppliers to successfully achieve the world’s first partially automated installation of grinding mill liners.”
Bradken’s success with the project sets the company up to flourish in a future geared towards automation. Such solutions save customers time and money and ensure workers get home safely every day.
“Miners are always looking for ways to reduce risk to their personnel and the MillSafe suite of products presents that opportunity,” Faulkner said.
Bradken continues to look for partnership opportunities with its customers to deliver solutions that are not only sustainable, but also optimise safety and performance. AM
•
•
•
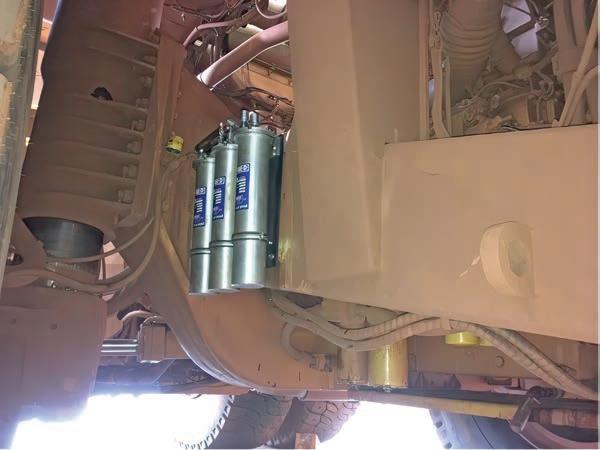
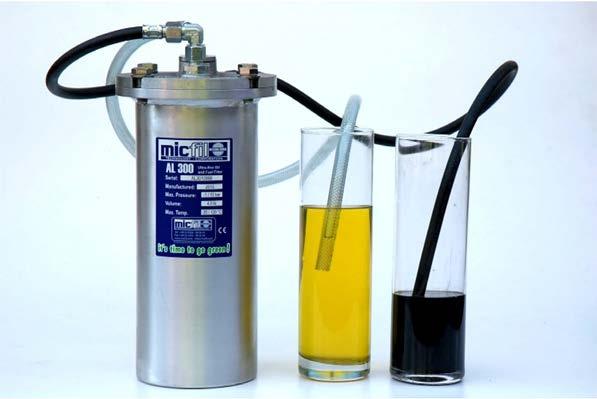
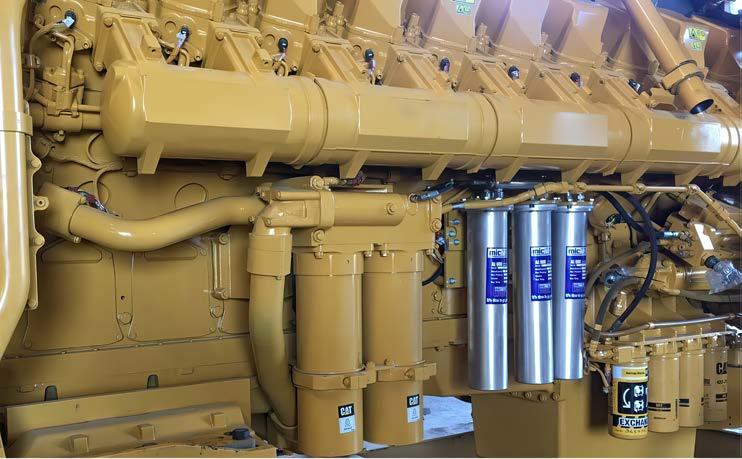
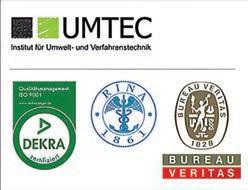
ROLL ON WITH PULFORD
PULFORD AIR AND GAS’ NITROGEN TYRE INFLATION SYSTEM IS HELPING TO ELIMINATE TYRE EXPLOSIONS ON MINE SITES ACROSS AUSTRALIA.
Most people likely don’t think about the fact their tyres could explode. For miners, however, that kind of risk is just another day.
Vehicle fires are some of the more obvious ways for tyres to explode. But, in certain circumstances, combustion can also take place inside the tyre with no visible signs.
“Whenever excess heat is developed in or applied to a tyre, it can initiate a process within the tyre known as pyrolysis – the decomposition of a substance by heat,” Resources Safety and Health Queensland said in a safety bulletin on tyre explosions.
“This can cause a build-up of flammable gases and pressure within the tyre, which may ultimately rupture or explode.”
Welding on wheel rims, overheating brakes, oxyheating wheel nuts, wheel motor fires, and high-voltage electrical incidents are all common causes of tyre pyrolysis.
And when tyres do explode, debris can be projected hundreds of metres and carry enough force to cause severe injury or even death.
Fortunately for the mining industry, Pulford Air and Gas, a leading Australian air compressor and gas company, has a solution.
Having been in the compressed air and gas system industry for almost century, Pulford has learned a few things along the way – like the fact that by
filling tyres with nitrogen, the company can drive down the content of oxygen, which has a much lower ignition point than nitrogen, within the tyre. This helps to eliminate the risks of a tyre explosion from heat.
Pulford uses its bespoke nitrogen tyre inflation system, built for harsh Australian conditions, to deliver this solution. The system can inflate even the largest haul truck tyres rapidly and with ease.
“With our nitrogen tyre inflation system, which drives down oxygen within the tyre to just 5.5 per cent, site operators can be confident that their workers and assets will be much safer during hot tyre events,” Pulford told Australian Mining.
Each Pulford nitrogen tyre inflation system is custom designed to meet a site’s specific needs.
“The system can be designed for any range or application from one to 3000 cubic metres per hour, with air purity ranging over 99 per cent,” Pulford said.
“Our nitrogen systems can also be fully containerised for ease of installation. This provides the freedom to easily move the system to a new location, should the need arise.”
In a confirmed or suspected hot tyre event, vehicles are typically required to be parked well away from workers and equipment and allowed to cool for 24 hours.
But Pulford believes that by eliminating the risks of a tyre explosion with nitrogen inflation, downtime from hot tyre events could be
reduced. For a mine site, this translates to increased productivity.
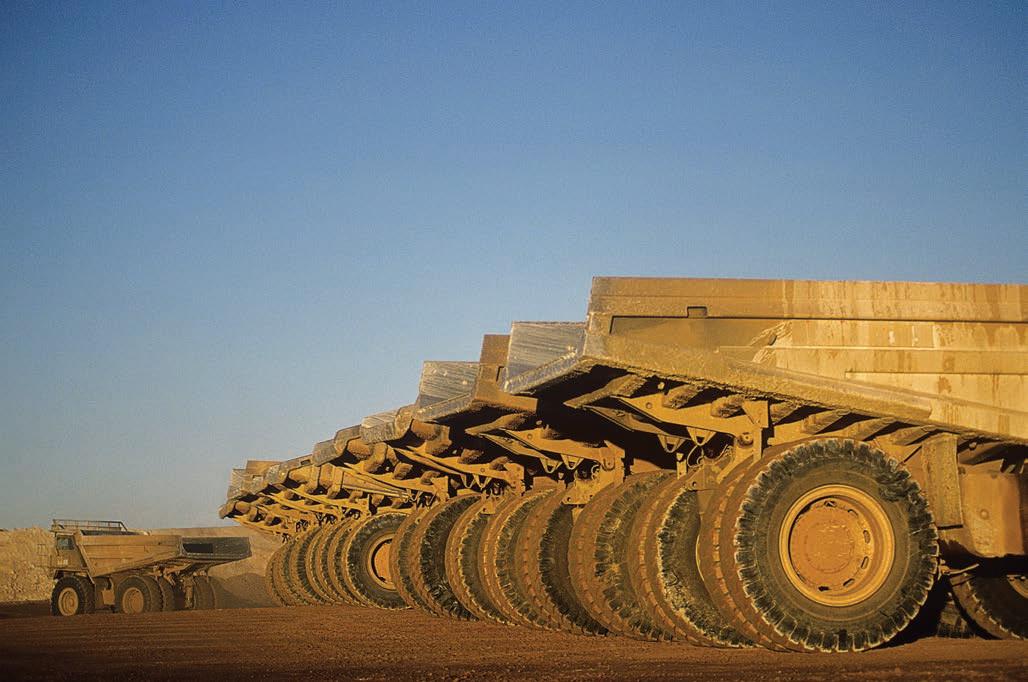
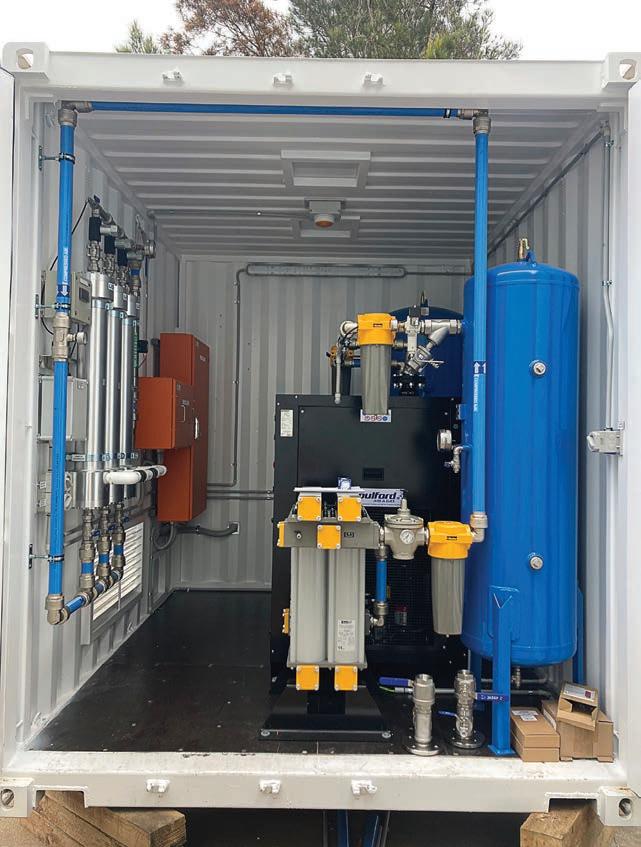
Beyond tyre inflation, the nitrogen system can also be used for the degasification of coal seems in underground mining.
Pulford currently has more than 600 nitrogen systems in operation throughout Australia.
The company does all of this work with the backing of air compressor
manufacturer and international powerhouse ELGi, which acquired the company in 2018. ELGi’s extensive range of diesel-powered air compressors has been the company’s hallmark over the years, providing a solution for compressed air requirements for drilling and exploration, while supporting temporary air requirements at mine sites across Australia.
Considering both companies’ similar approach to quality, and Pulford’s established presence in Australia, the acquisition was a logical one.
“We understand the mining industry has complex requirements,” ELGi Equipment’s executive director – OSEA (Oceania and South East Asia) Ramesh Ponnuswami said.
“Most of our competitors tend to predominantly anchor their design to European and North American conditions, whereas our designs are a lot more suited to the tropical and hot weather conditions you would find in Australia.”
ELGi and Pulford’s extensive Australian footprint is supported by distributors across the country who are not only able to supply the equipment but provide additional services such as installation support and ongoing maintenance. AM


CONTAMINATION-FREE LUBRICATION STATION
RETRA FLUID HANDLING SYSTEMS’ LUBESTATIONS HOUSE OILS, GREASES AND COOLANTS IN ONE CONTAMINATION-FREE UNIT.
Everywhere you look on a mine site, there’s equipment that needs fluids to operate at peak performance levels.
Machinery from 400-tonne haul trucks through to forklifts and even large fixed-plant facilities require engine and gearbox oils, greases and coolants.
Without these fluids, machinery will at best soon stop performing at the level required. At worst, it will break down and require significant out-of-schedule rebuilds, costing time and money.
RETRA Fluid Handling System’s Lubestation houses all of these vital fluids in one contamination-free fit-forpurpose unit.
“Statistically, over 70 per cent of lubrication-related failures are caused by contamination,” RETRA national sales manager Jay McEwen told Australian Mining.
“The primary source of revenue loss due to machine downtime is closely linked to an excess of lubricant contamination, be it dust, water, contaminants from the process itself, the use of an incorrect lubricant, or a mixture of all these elements.”
Common in industrial processes, lubricant contamination can appear at any stage in the oil’s lifecycle.
“With the Lubestation’s modular design and quick-connect fittings, contamination is all but eliminated,” McEwen said.
“Built to incorporate seamlessly with existing infrastructure, the Lubestation
is easily transportable and requires minimal maintenance, with a long design life ensuring the safe extraction and handling of fluids for years to come.”
Traditionally, mine sites have used service trucks and fixed facilities to meet their lubrication needs.
“From a cost perspective, a Lubestation has a lower cost of ownership than a service truck or a fixed facility,” McEwen said.
“There will always be a need for service trucks; however, a Lubestation will free service trucks up so that they can perform emergency maintenance rather than a quick top up. That’s why Lubestations are often used in tandem with service trucks.”
McEwen said a fixed facility is the costliest lubrication solution and could become a burden once a project is complete.
“The problem with a fixed facility is that it’s a bricks-and-mortar solution which creates an issue when the mine reaches its end of life, being a liability that costs money to disassemble when it’s time to pack up,” he said.
“A Lubestation can be relocated to various areas of the same mine or a whole new mine altogether, making it an asset rather than a hindrance.”
Lubestations are customisable to meet a range of needs. While they may not look all that different from the outside, each Lubestation has unique features that differentiate them from one another.
“Mobile Equipment Lubestations play a pivotal role in executing scheduled
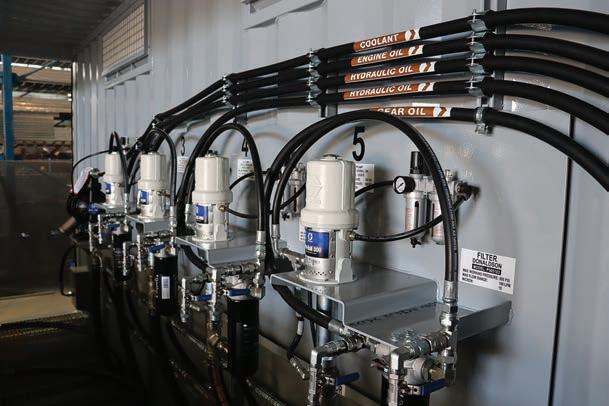
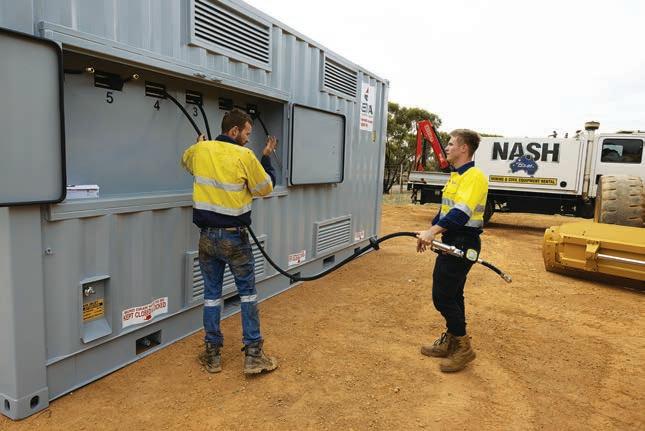
machinery, including trucks, excavators, and tractors,” McEwen said.
“Maintenance operators top up mobile machinery with userfriendly handpieces and hoses, easily accessible via a hatch on the side of the Lubestation.”
With the added advantage of being relocatable and requiring only a connection to a compressor, Mobile Equipment Lubestations are commonly deployed in field locations, such as fuel bays.
“This strategic placement ensures seamless mobile equipment operations without the need for timeconsuming diversions, ultimately boosting overall productivity and efficiency,” McEwen said.
Fixed Plant Lubestations strategically complement large machinery like conveyors and crushers, maintaining their relentless operations.
EASILY CUSTOMISABLE TO THE NEEDS OF ANY SITE, THE LUBESTATION HAS MINING MAINTENANCE COVERED.
Featuring a dedicated decanting room, maintenance experts transfer vital fluids from sizeable containers to more manageable vessels using a streamlined lube bar.
“As its name suggests, Workshop Lubestations sit in and around equipment workshops storing essential fluids,” McEwen said.
“What sets a Workshop Lubestation apart is that all the hoses originating from the unit are systematically linked to a stationary bulkhead or gantry positioned inside the workshop.”
These are attached to hose reels, allowing people to quickly top up oils and other fluids without needing to set foot inside the storage area, saving time and increasing safety.
No matter the lubrication demands of the site, RETRA Fluid Handling has the Lubestation to meet its needs, keeping operations running with well-oiled ease. AM
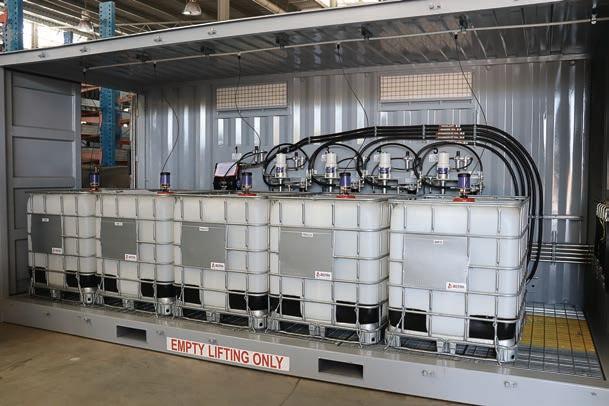
INVEST IN RESILIENCE TODAY TO MINIMISE DOWNTIME.
With over 50 years of experience in the mining sector, FM Global Australia has industry-trained risk engineers and underwriters with access to a wealth of global data to help protect your mining operation so you can minimise losses and maximise output.
Our tailored risk assessments will identify exposures so we can provide valuable insights and recommend mitigation strategies to help reduce risk in your operation for the long term.
With broad insurance coverage, up to US$2 billion capacity and swift claims resolution, we are your dedicated partner in preventing loss so your mining community can prosper.


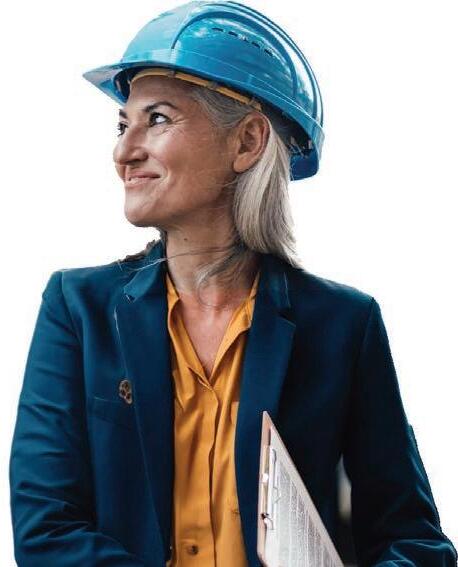
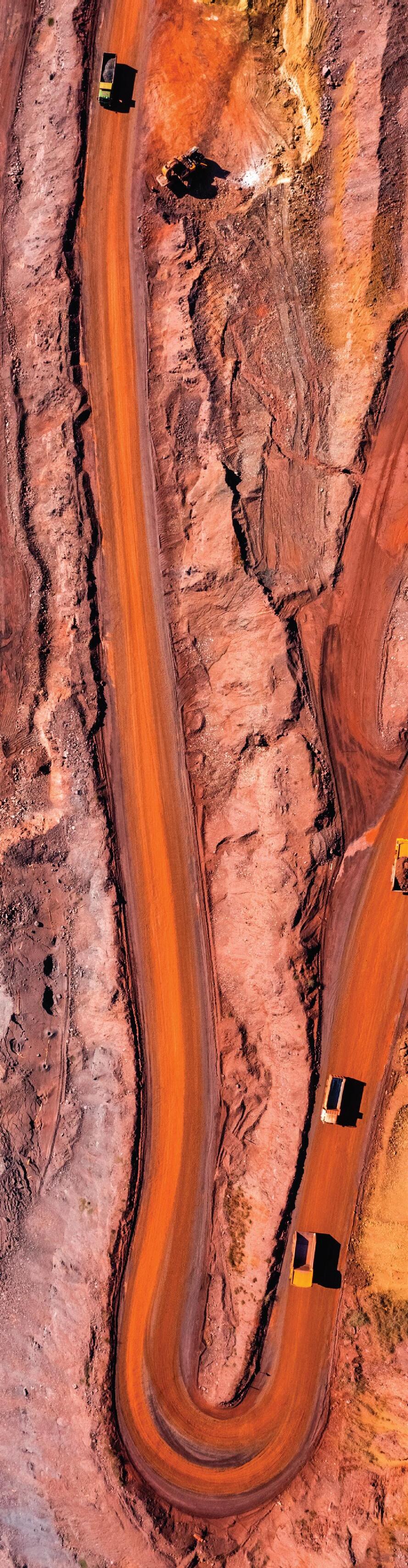
SIMPLIFYING THE TECHNOLOGY CONVERGENCE FOR MINERS
BRENNAN BELIEVES THAT IN A DATA-DRIVEN ERA, THE SYNERGY BETWEEN INFORMATION TECHNOLOGY AND OPERATIONAL TECHNOLOGY CAN UNDERPIN A MINER’S SUCCESS.
In recent years, enterprise-scale mining companies have invested significant capital in data and technological innovations to drive production efficiencies, safety, and improved decision-making at an operational and business level.
Solutions such as automation and artificial intelligence (AI) have reduced equipment and production downtime, while improving safety and environmental outcomes.
These benefits are poised to have a trickle-down effect for operators of all sizes. Due to the capitally intensive nature these investments require, offset against somewhat volatile commodity markets, some are understandably reluctant to invest in these technology types.
This is where Brennan can help.
With tried-and-true experience across the mining sector, over 25 years of deep IT experience, and trusted by more than 1400 companies, Brennan has grown to become Australia’s largest privatelyowned and trusted systems integrator.
“We have an established presence across all the major cities in Australia, along with extensive support in India and Sri Lanka,” Brennan’s mining industry advocate and Western Australia state manager, Chris Holmes, told Australian Mining.
Through its team of certified experts, Brennan removes the complexity of technology, with a specific focus in the mining industry on operational technology (OT) and its convergence with IT.
Due to the shifting nature of mining, where technology synergies are growing in importance, Brennan is continuing to evolve the links between IT and OT.
“We are IT experts with deep understanding and knowledge of the IT elements that comprise OT environments,” Holmes said. “This is of real importance because, historically speaking, IT and OT have been treated independently of each other.”
Given OT environments are key to production, their resilience and redundancy are of principle priority; however, as businesses mature their IT and OT environments, IT is helping augment and supplement operational outcomes.
“IT and OT are increasingly diffused with the convergence of data, especially at the edge, which is where Brennan can
help,” Holmes said. “Leveraging hyperconverged, multi-cloud and public cloud platforms, we assist clients by unlocking the value within their data.”
Brennan is conscious that a client’s focus is on their core business of mining and mineral processing, and don’t often see value in self-managed IT investments from a scalability, breadthof-competency, or retention perspective.
But by leveraging outsourced IT expertise, Brennan can help mining companies extract deeper operational efficiencies, lighten infrastructure management load, establish resilient public/private cloud environments, secure organisational intellectual property (IP), and forge productivity through connectivity, all while maintaining flexibility.
And miners don’t need to start from scratch. Brennan can quickly leverage reference architecture to support a new operation or application.
“The upside for miners is they get to reap the benefits of our approach and
experience without going through the learning curve, as they often don’t have the research and development capital,” Holmes said.
“We look at ways to approach reference architecture so they can be orchestrated to suit individual requirements and objectives, without starting from scratch.
“This ensures miners are getting maximum value from their existing investments in the delivery of new and ‘continuous improvement’ projects.”
Holmes said Brennan can manage a mining company’s environment across the entire IT and data landscape, but in ways that are relevant, secure and scalable.
“That’s how we’ve built upon our long-term relationships and continue to deliver tangible value for mining companies, no matter their size,” he said.
Brennan’s IT and OT capabilities have helped miners solve challenges such as risk mitigation, security enhancement, proactive maintenance, and automationbased solutions.
This had led to other benefits, such as customers freeing up their IT teams, reducing operational costs, future-proofing infrastructure, and strengthening their digital capabilities.
Alongside its IT and OT offerings, Brennan is guiding customers to strengthen their IT fundamentals and build strong foundations that can accommodate the growing adoption of AI.
“With the rise of independent, mining-specific AI engines, we’re finding that defining the use-cases where AI is most relevant to their business is a prerequisite,” Holmes said.
“AI has become a buzzword. Some people are utilising AI for AI’s sake, and it’s not necessarily providing the value they want. We’re helping customers define what that outcome must look like, and manage expectations around the investment timeframes to attain sought value.
“That’s where we’re able to add genuine value.” AM

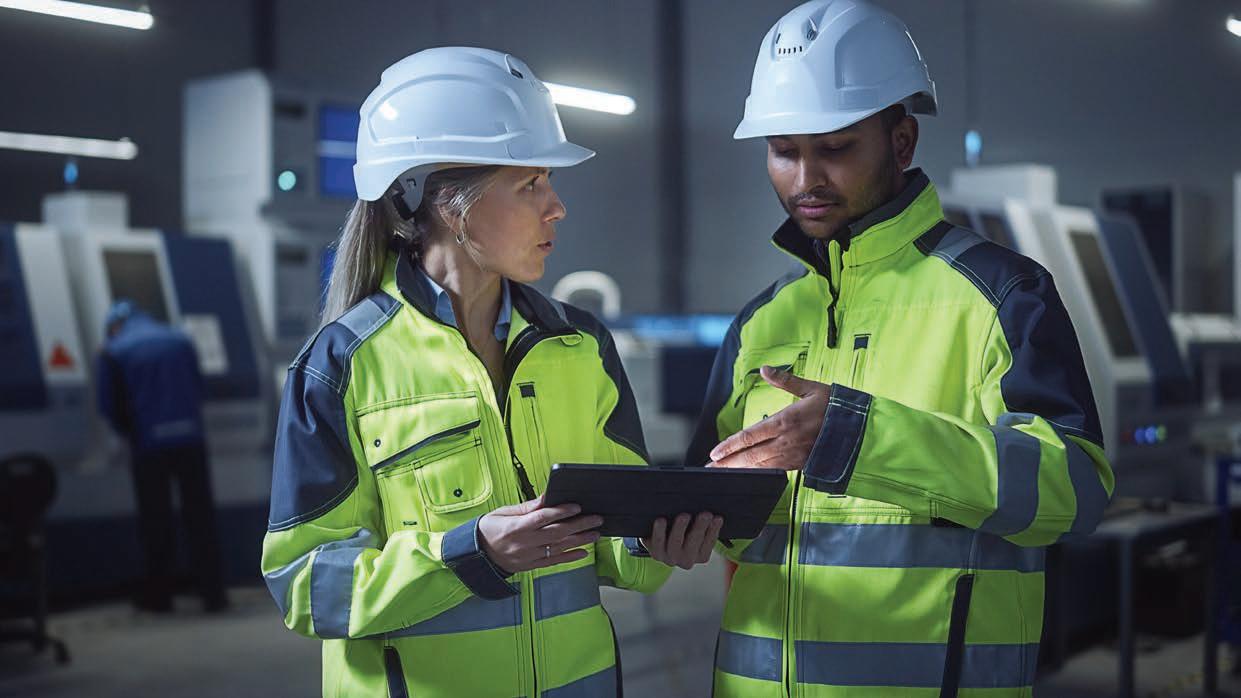

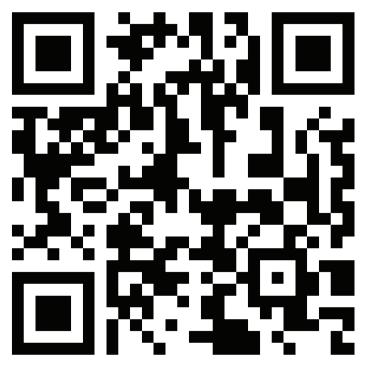
THE DIGITAL AGE OF WEAR MANAGEMENT
4D DELTA PROVIDES REMOTE ASSET INSPECTION SERVICES FOR ORE-PROCESSING ASSETS, LEADING TO AN ARRAY OF SAFETY AND OPERATIONAL BENEFITS.
Apicture is worth a thousand words.
It’s a saying as old as time, but in the case of 4D Delta and the company’s advanced 3D wear monitoring technology, it rings true.
Founded in 2014, 4D Delta inspects critical ore processing assets in mining and related industries, including transfer chutes, surge bins, impact plates, grinding mills, crushers, and more.
The company conducts wear monitoring through a unique combination of cutting-edge remote sensing technologies and its own purpose-built software to inspect sacrificial wearing parts of oreprocessing plant.
“3D laser scanning is typically an instrument for surveyors or engineers that creates a 3D digital copy of the surrounding environment,” 4D Delta chief executive officer Garth Johnson told Australian Mining
“They set up a 3D laser scanner inside an environment such as a building and several scans are taken inside and outside. When all the scans are combined you get a point cloud, which is an accurate and highly detailed digital representation of that building.”
4D Delta carries out a “very niche application” of 3D laser scanning.
“Generally, a mine site is where bearing ore is drilled and blasted, put onto a truck and taken to a processing plant where it is crushed down to a certain size. That processed ore is then transferred by train to the port and then shipped for further processing where it is turned into the end product,” Johnson said.
“But the rock is so hard that everything it touches in this process will slowly, and sometimes rapidly, wear away over time. The problem with this is you can’t have these multi-million-dollar ore processing assets being exposed to the ore and wearing away to absolutely nothing, otherwise the operator will have to replace the whole asset, which is very costly.
“This is why miners put a protective liner inside the asset, so it’s the lining system that wears away rather than the machine itself. Where 4D Delta comes
in is the inspection of those protective lining systems.”
Traditionally, carrying out wear-liner inspections can be an extended and dangerous process for maintenance personnel.
This is why 4D Delta carries out inspections remotely by using 3D sensing technologies such as 3D laser scanners. This way human risk and error is eliminated, safety is optimised, and time is saved.
“When we put these 3D sensors inside the asset, the sensors can accurately scan every surface of the protective liners in high detail, generating rich amounts of data.”
4D Delta’s core capability isn’t the 3D sensing technology itself, but the processing, display and analysis of the 3D data gathered by the sensors. The company does this through its software platform, 4D Delta Cloud.
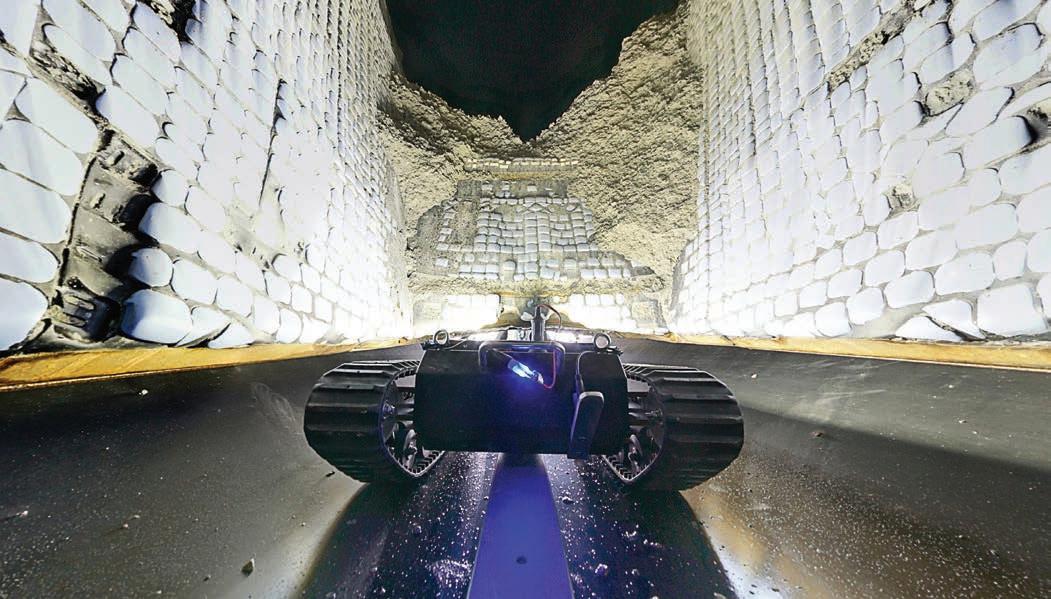
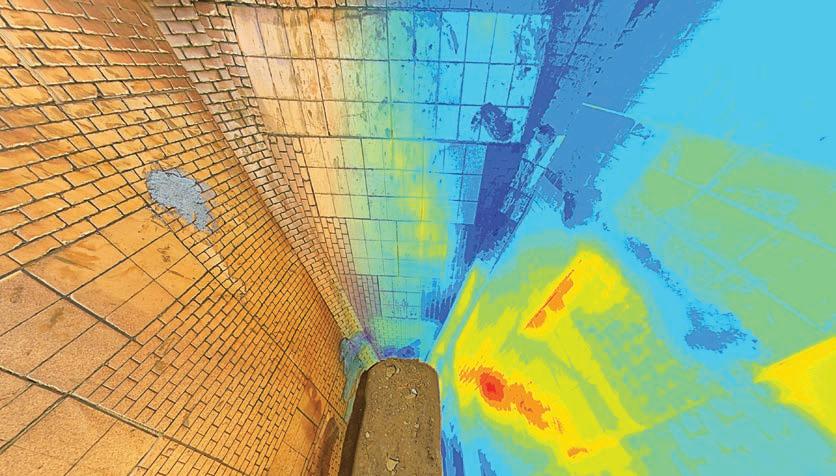
4D Delta Cloud provides a highly organised and interactive platform for engineers and planners to view and interrogate wear liner inspections. With advanced predictive algorithms, this information can help prevent liner failure while optimising maintenance schedules and asset performance.
“The analysis of that information makes decision-making more objective,” Johnson said.
“When the user clicks on the asset in 4D Delta Cloud, they can access hi-definition 360° images with precise wear map overlays to make reliable
assessments of wear liner condition.”
These visuals and scans can be accessed anywhere at any time through any computer, tablet or phone with an internet connection.
4D Delta Cloud also generates interactive reports that detail how the asset will wear and look over time. This will assist maintenance planners in detailing instructions including when to repair or replace the protective lining and what new stock to order.
Having such specific instructions eliminates unnecessary costs and waste.
“The information is continuous,” Johnson said. “If anybody questions the decisions made, the 4D Delta Cloud user can quickly backtrack to any inspection, report or maintenance plan and say, ‘This is why we made this decision’.”
4D Delta’s mission in the mining industry is in its name, literally.
“4D is space and time,” Johnson said. “And delta means change, so our name means ‘the change in space over time’. And that’s what we do, measure the change in wear liner condition over time.” AM
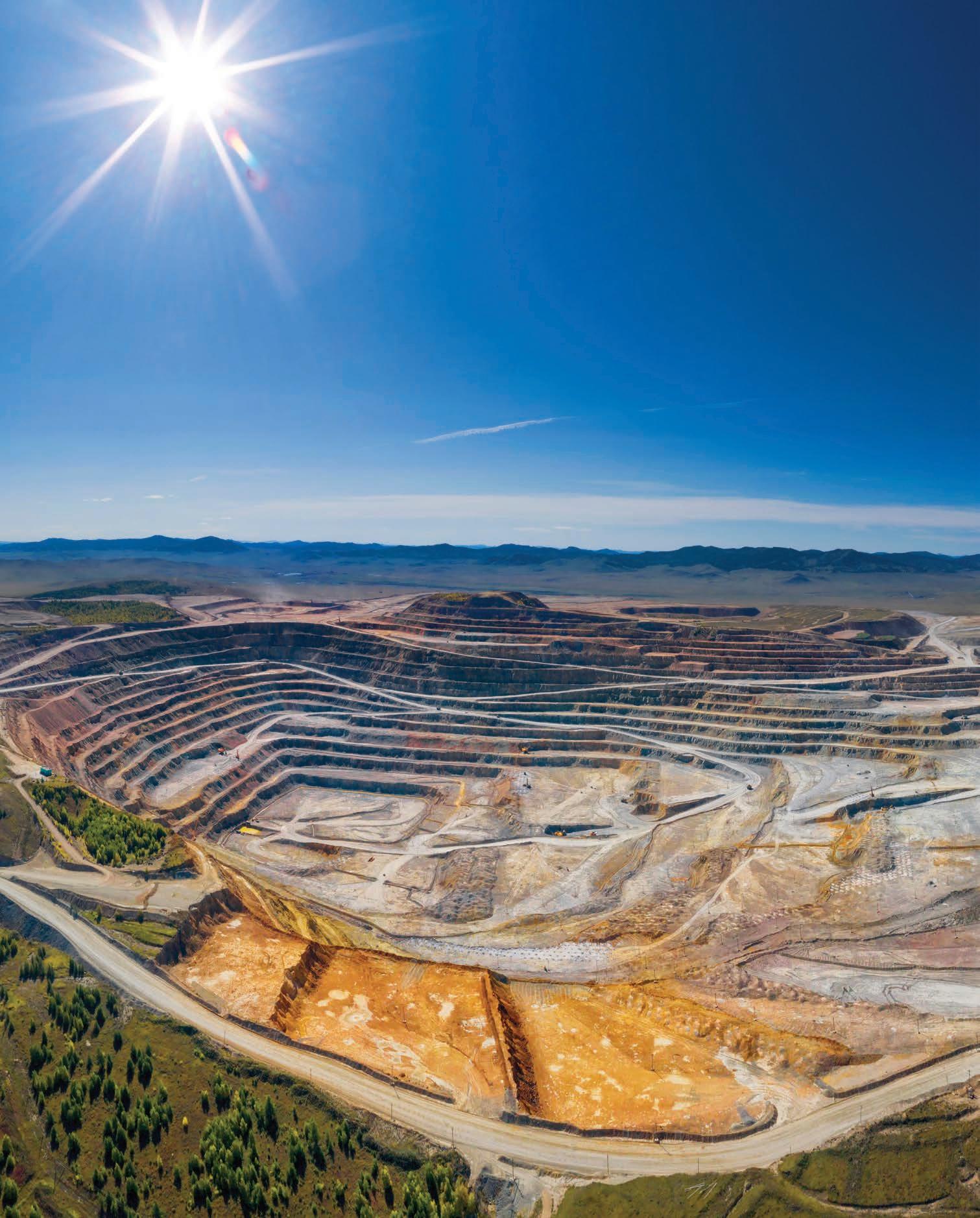
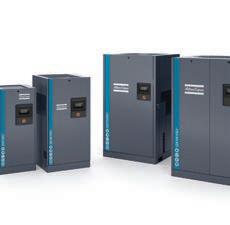
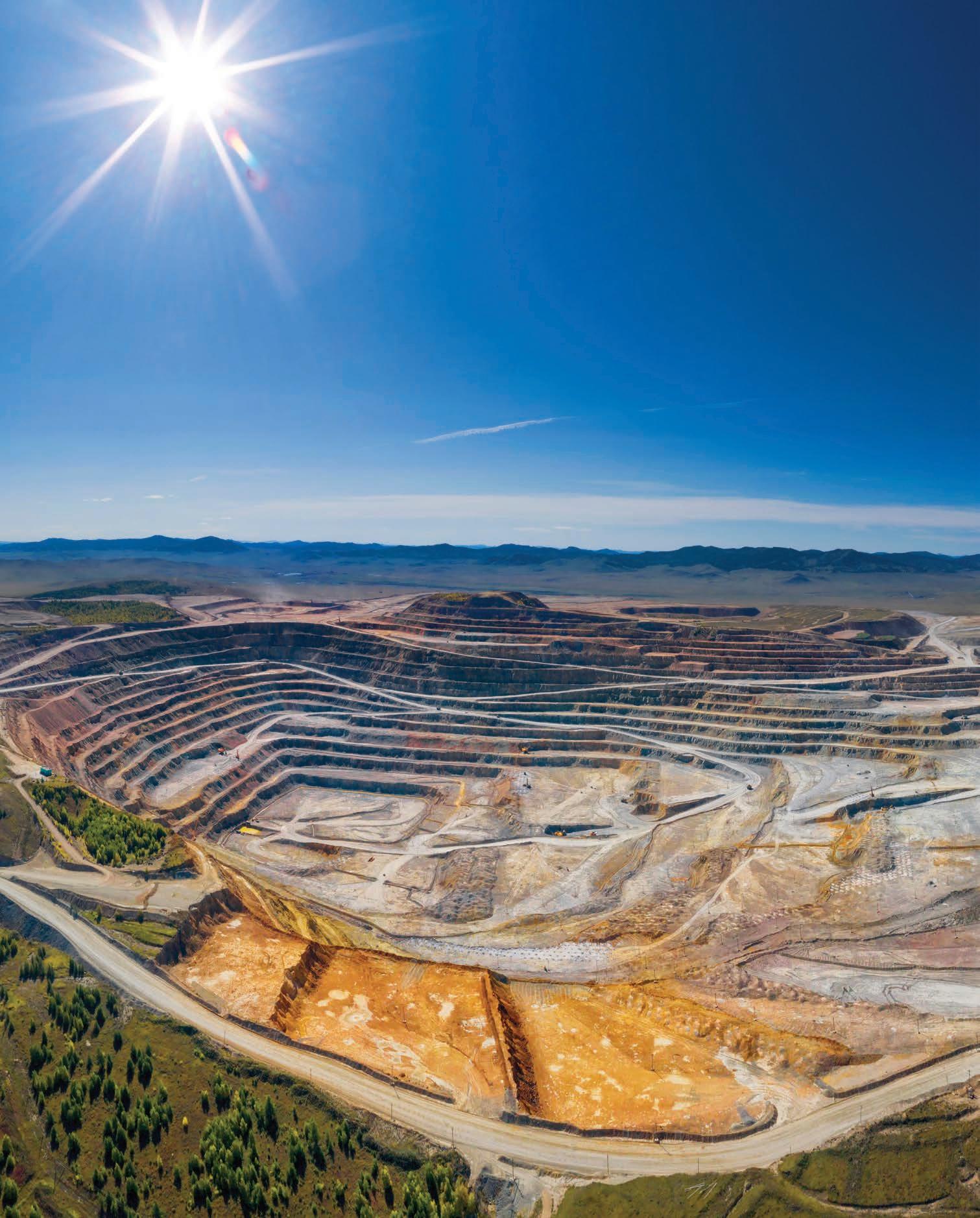
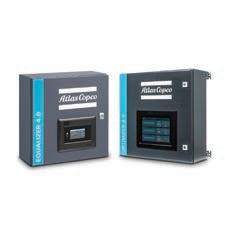
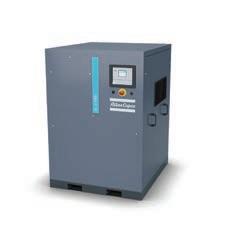

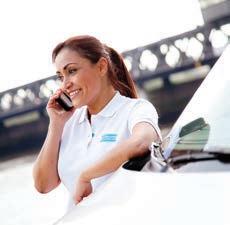
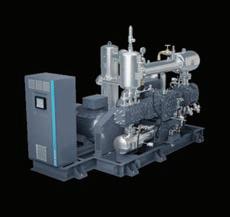

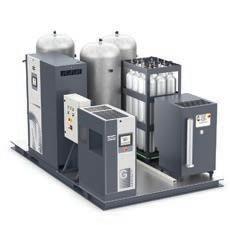
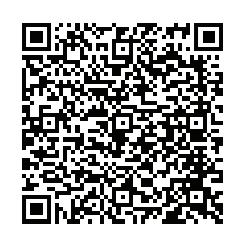
PREVENTING LOSS IN MINING
AUSTRALIAN MINING WHITEPAPER HIGHLIGHTING THE IMPORTANCE OF LOSS PREVENTION IN THE MINING INDUSTRY.
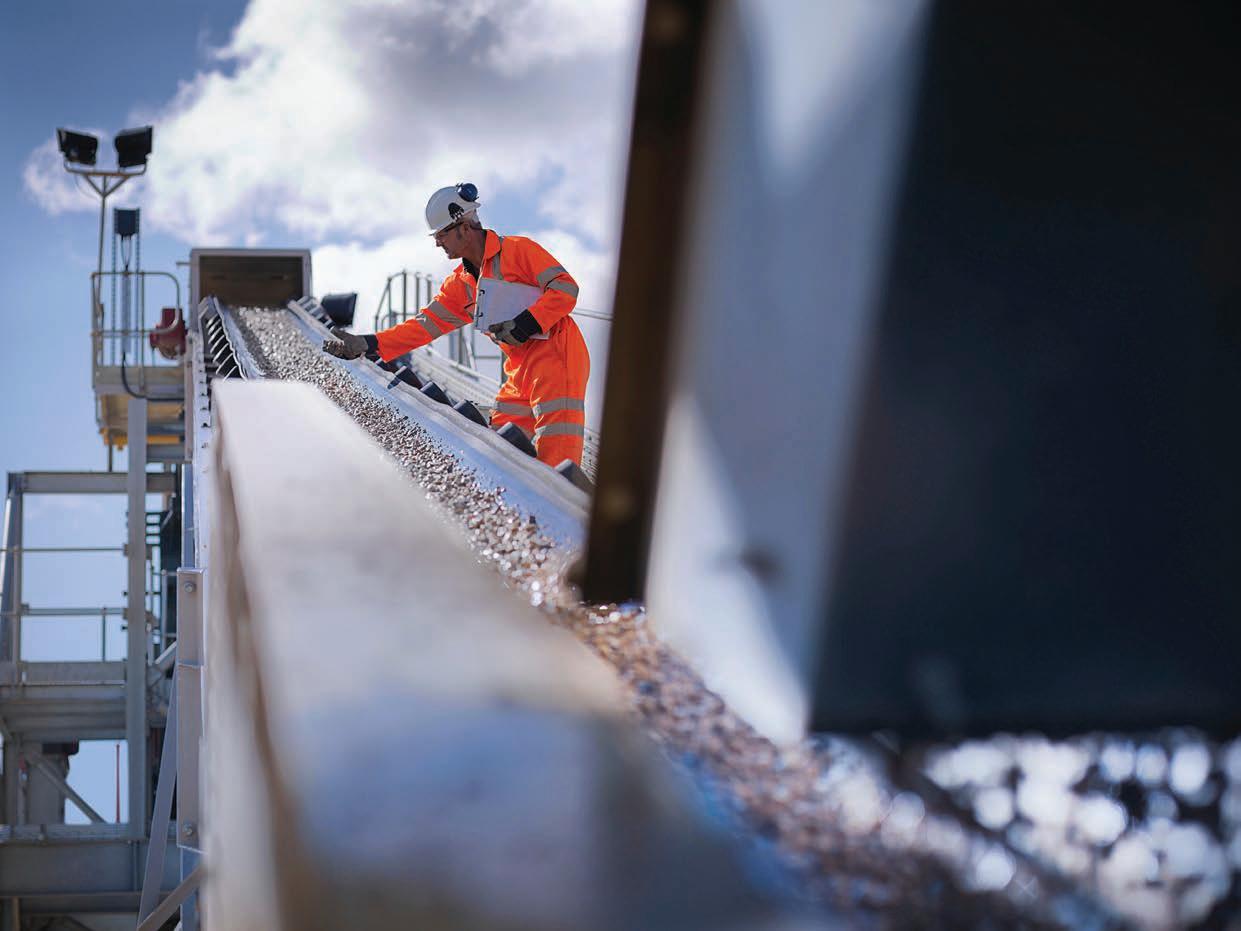
For FM Global account engineering group manager Mike Beaumont, working in the mining industry is part of his lineage.
His uncle was on the board of directors for several large Canadian mining companies and his father was born in Kirkland Lake, a gold mining town in northern Ontario.
It’s fitting that Beaumont ended up conducting risk engineering visits at gold mines when he first arrived in Australia about 30 years ago.
Throughout his career, Beaumont has specialised in the mining industry with a particular interest in the metallurgical refining field, writing papers and articles about risks and loss in the industry.
Beaumont’s latest whitepaper, ‘Understanding Mining Industry Loss Trends and Predictive Analytics’, provides valuable insights into the drivers of loss and ways to prevent and reduce it.
“FM Global has been investing in predictive analytics, machine learning and artificial intelligence to develop several risk prediction models and help our clients conduct risk improvement and build resilience,” Beaumont said.
“My desire with this whitepaper was to tie the analytics and supporting loss
history back to the mining industry and make it more relevant to the sector to then be used to help identify areas where losses could be prevented.”
As a multinational commercial property insurer, FM Global currently covers more than 300 mine sites around the world.
Beaumont’s whitepaper analyses loss history trends across the global mining industry, showing more than 400 recorded losses at mine sites over the past two decades.
Fire incidents and equipment breakdowns were the top two loss drivers, with fire accounting for 21 per cent of losses over the past 20 years and 27 per cent of all losses on mine sites over the past five years.
According to Beaumont, the increased use of plastics in the construction of buildings and equipment is driving higher fire incidents.
“Once a fire is out of control, the outcomes can be catastrophic,” he said. “When you have a bank of plastic separating spirals or similar equipment and it burns down, that can affect all the product streams and the impacts can be huge.
“If you manage change and control human factors and maintenance, you will stop many of these events.”
FM Global recommends focusing on equipment factors such as maintenance, contingency planning, operating conditions, age and history, environment, operators and safety devices to minimise losses.
“Predictive maintenance enables you to identify where you’re most likely to have a breakdown or incident and where to focus your resources, whether it’s time or capital,” Beaumont said.
“You can’t have a spare of everything. Using insights from loss history and predictive analytics can allow people to better make capital decisions.
“Contingency planning helps you make more informed decisions on where best to invest capital, whether it’s in sparring, additional protection systems, interlocking different approaches or where you need to devote more people resources. You’ll know what you need, where to get it and how to get it to the site. If miners think about those things ahead of time, they’re going to be way ahead of the game.”
Beaumont has seen the appetite for risk management methods such as predictive maintenance and contingency planning evolve and grow over the past 15–20 years.
“What I’ve seen is middle-market miners come to the realisation that they
cannot afford to be out of business,” Beaumont said.
“Risk management is more widely embraced in the sector. This has seen a few of our clients evolve from having a roguish attitude to being a well riskmanaged company.”
FM Global is interested in partnering with companies that want to go above and beyond the risk management basics.
“We’re trying to get our whitepaper out there because we think it will shed some light on important loss trends and give organisations another risk management tool,” Beaumont. “Hopefully down the road we can partner with these companies as well.” AM
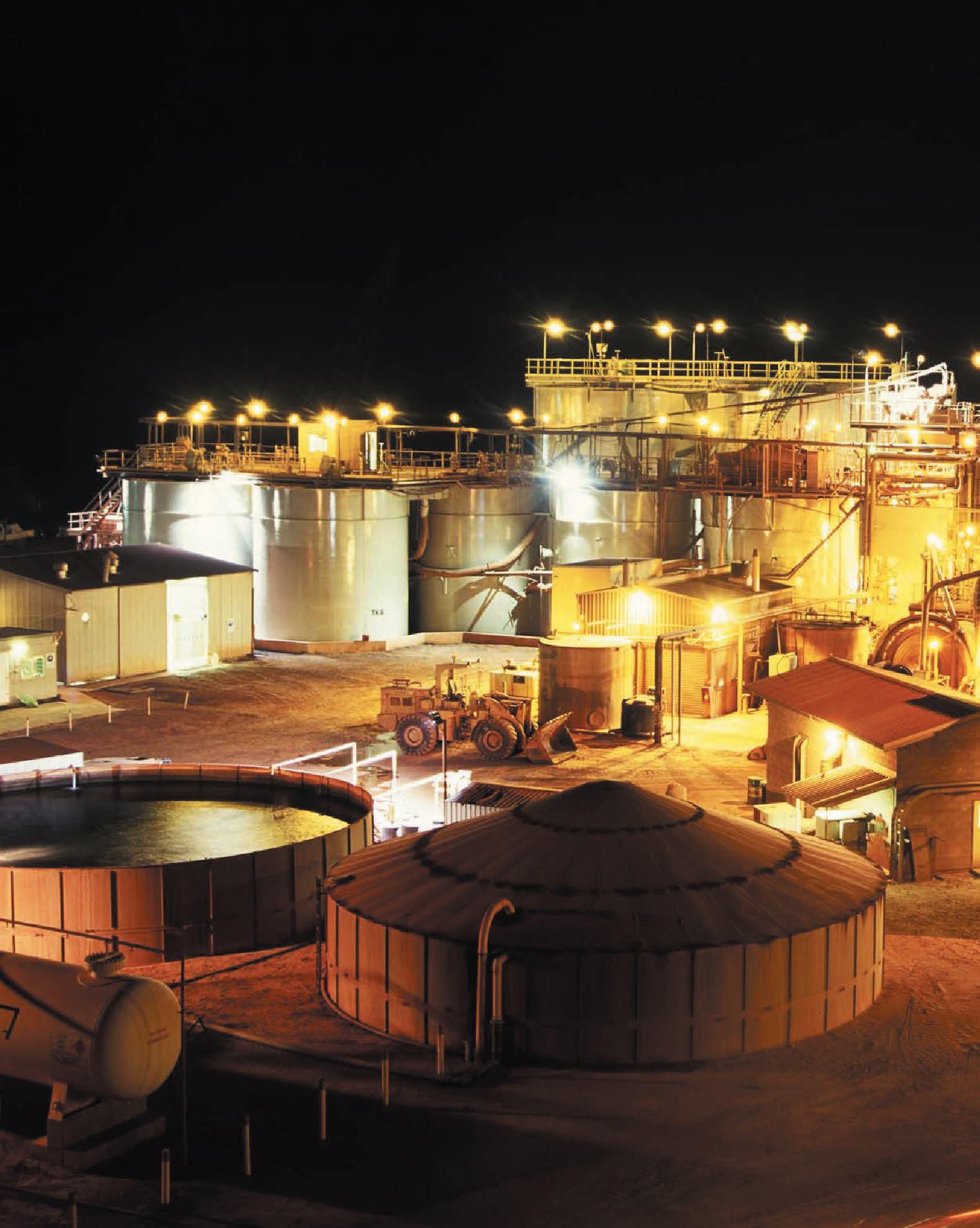
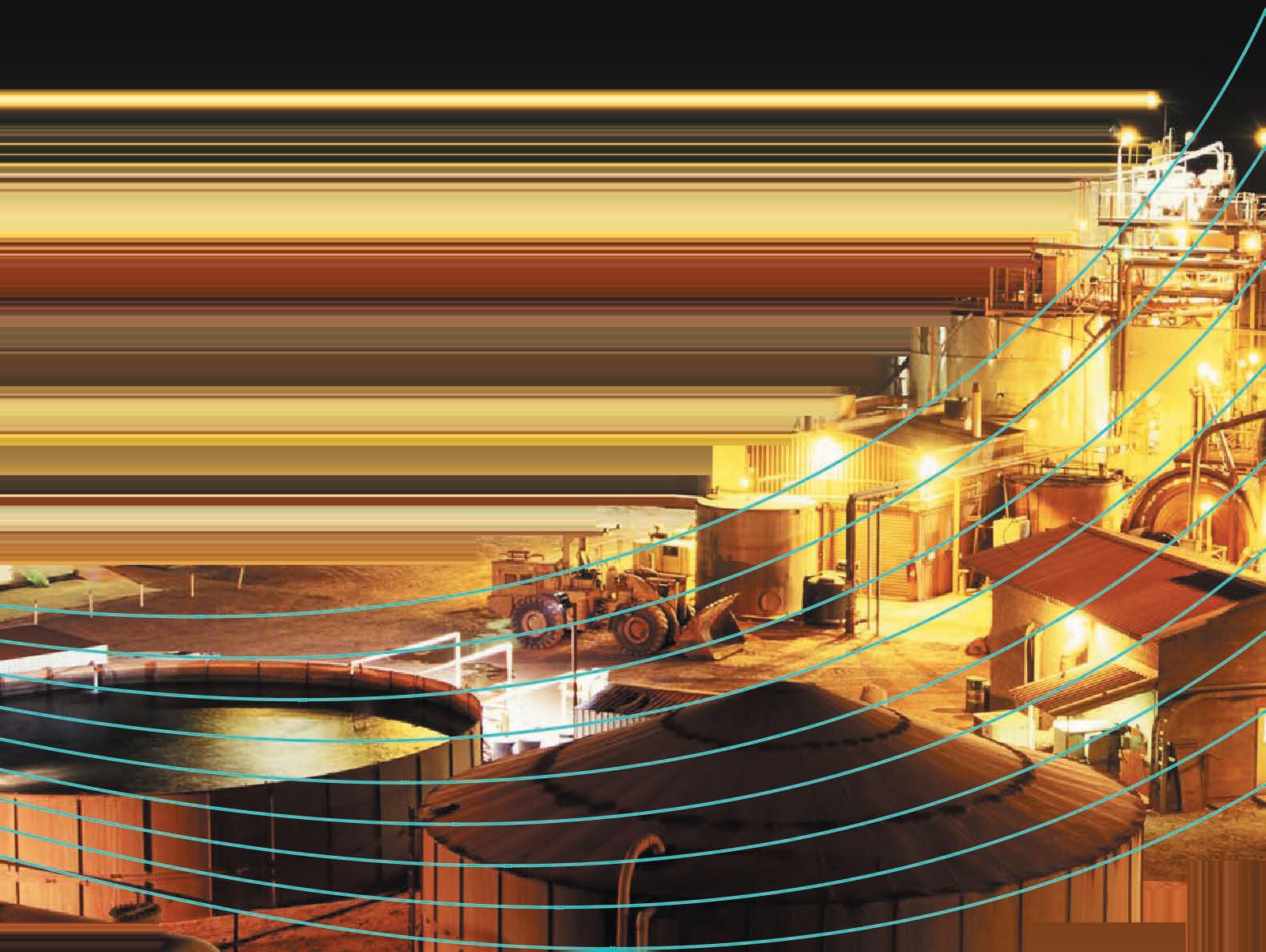

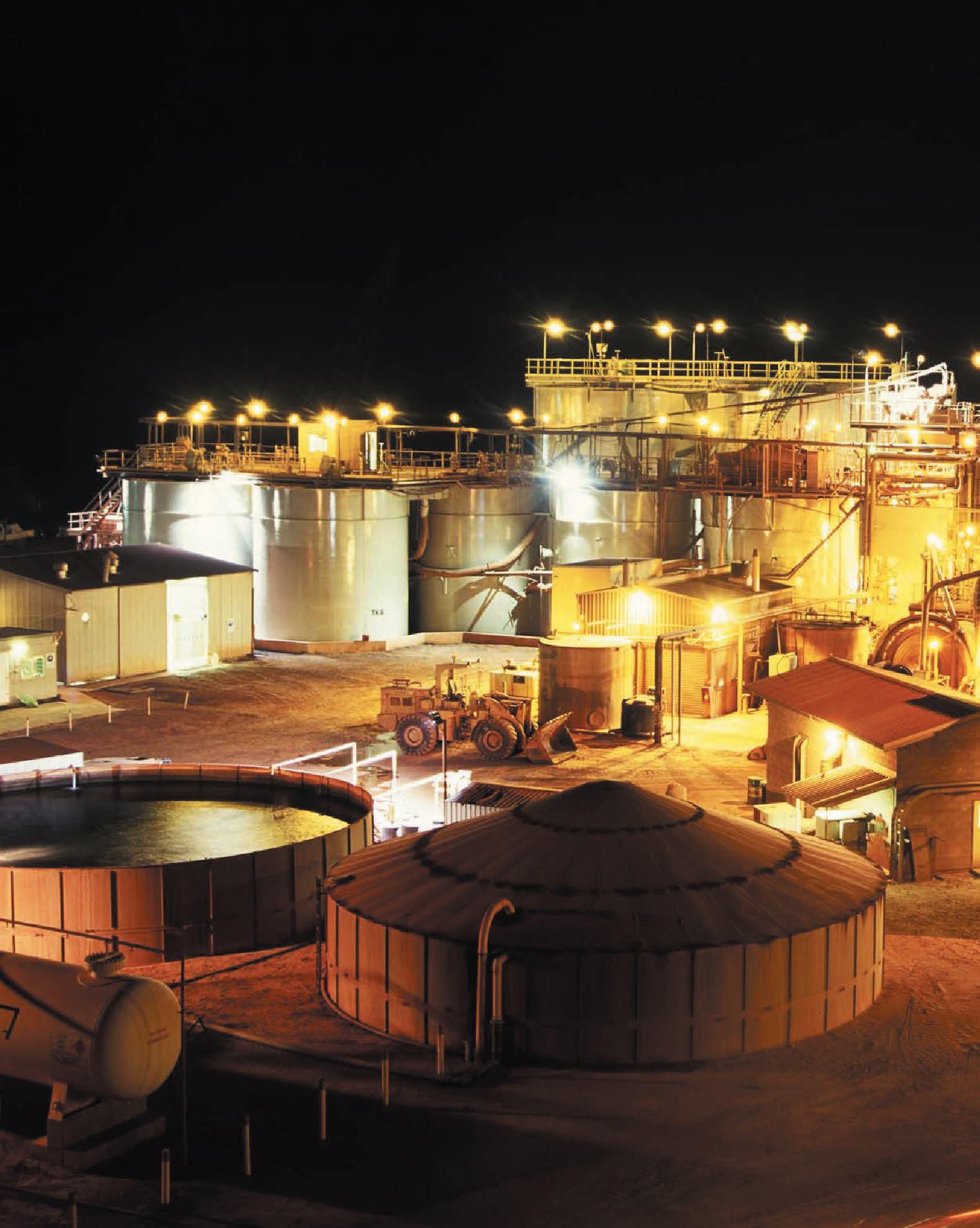
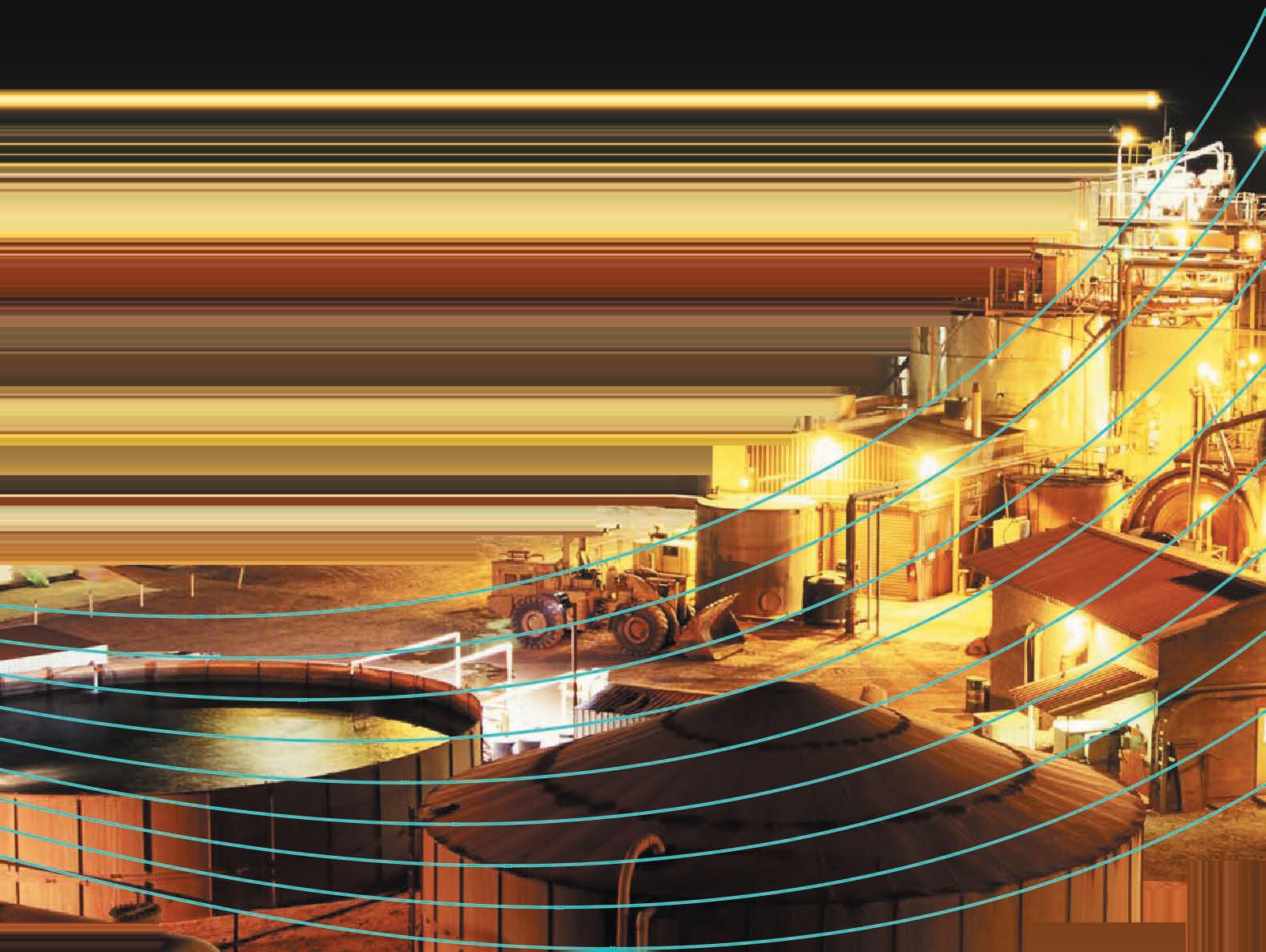
A ROBOTIC REVOLUTION
DREDGE ROBOTICS’ LINER-SAFE DREDGING ROBOTS ARE PROVING TO BE A GAME-CHANGER IN THE MINING INDUSTRY. AUSTRALIAN MINING EXPLORES THE TECHNOLOGY IN MORE DETAIL.
Mining companies need to complete regular dredging to remove sediment and vegetation from their lined ponds, a practice which, up until the emergence of Dredge Robotics, has posed challenges in both efficiency and safety.
Dredge Robotics has developed patented robotic technology that can safely dredge ponds without damaging the liner – an important protective layer that prevents water and toxins from seeping into the soil.
Other dredging practices involve tracked machinery or traditional floating barges, which can place liner integrity at risk and is widely acknowledged as unsuitable for lined pond dredging.
The liner-safe robots – capable of operating on high density polyethylene, linear low-density polyethylene, and polyvinyl chloride liners – can return a lined pond to its original state, while the pond remains in full service, and also complete additional tasks such as removing settled mud, reeds and bulrushes.
According to Dredge Robotics chief executive officer Antony Old, a key advantage of the liner-safe robot is improving health and safety outcomes, which is a critical area of focus for all major mining companies.
“After clearly demonstrating the safety advantages of this technology, we are pleased to now be regularly delivering this service to most major mining companies in Australia on an ongoing basis,” he told Australian Mining
“The technology is highly scalable, tackling anything from very small assets up to large wastewater lagoons or tailings dams. Robots can also be deployed into confined spaces through tight hatches or doorways and even navigate around internal walls and obstacles.”
According to Old, the speed of the liner-safe robot is typically equal to or better than other dredging options, due in part to the sophisticated sonar arrays and obstacle modelling capabilities of the equipment.
The robots can be fitted with an array of tooling which can be adapted to different environments, enabling the sludge to be removed efficiently from the asset.
“The sludge can then either go back into the process of the mine, into another pond, or into a geobag, which filters the water out of the sludge, leaving dewatered material which can then be efficiently removed from site,” Old said.
Many miners have implemented or are considering the potential of tailings reprocessing at their sites, where sludge
is reprocessed to recover profitable ore and create a more environmentally friendly operation. Liner-safe robots have already been proven in several case studies as a cost-positive solution for tailings reprocessing applications.
According to Old, the liner-safe robots offer a solution that many mining operations never thought possible, with operators instead typically opting for time-intensive and costly exercises such as completely relining their ponds.
In a mining industry that’s more environmentally conscious than ever, and with mining companies putting more processes in place to ensure they abide by their environmental, social and governance obligations, Dredge Robotics’ liner-safe robots have an important role to play.
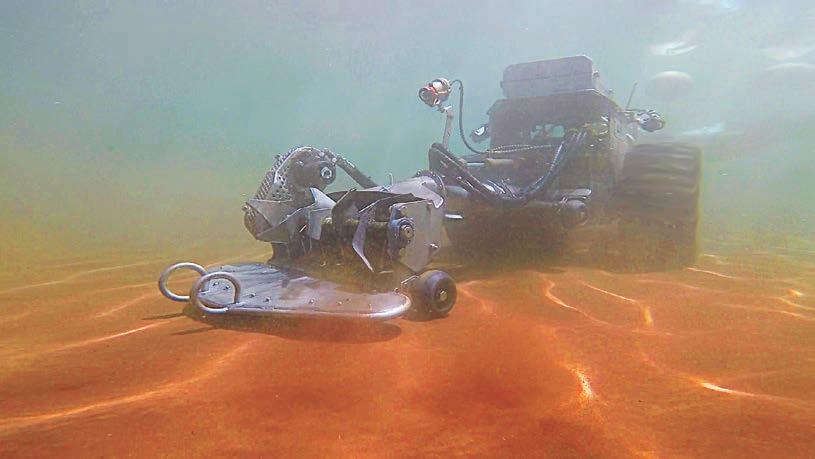
“In other dredging processes, you typically have a person on a barge, a person in an excavator or people in the pond digging with equipment. You’re exposing your staff to whatever’s in the pond, but with the robotic dredging system, those risks are totally eliminated.”
Old said the liner-safe robot can dredge “corrosive and toxic liquids” and can operate at the extremes of the pH scale, a technology made possible by Dredge Robotics’ targeted research and development (R&D) efforts.
“Assets that were previously difficult to clean due to access challenges, deep water, turbidity constraints, obstacles in the asset, or concerns around impact to liners or clay bases, can now be cleaned safely and cost effectively while they remain in service,” Old said.
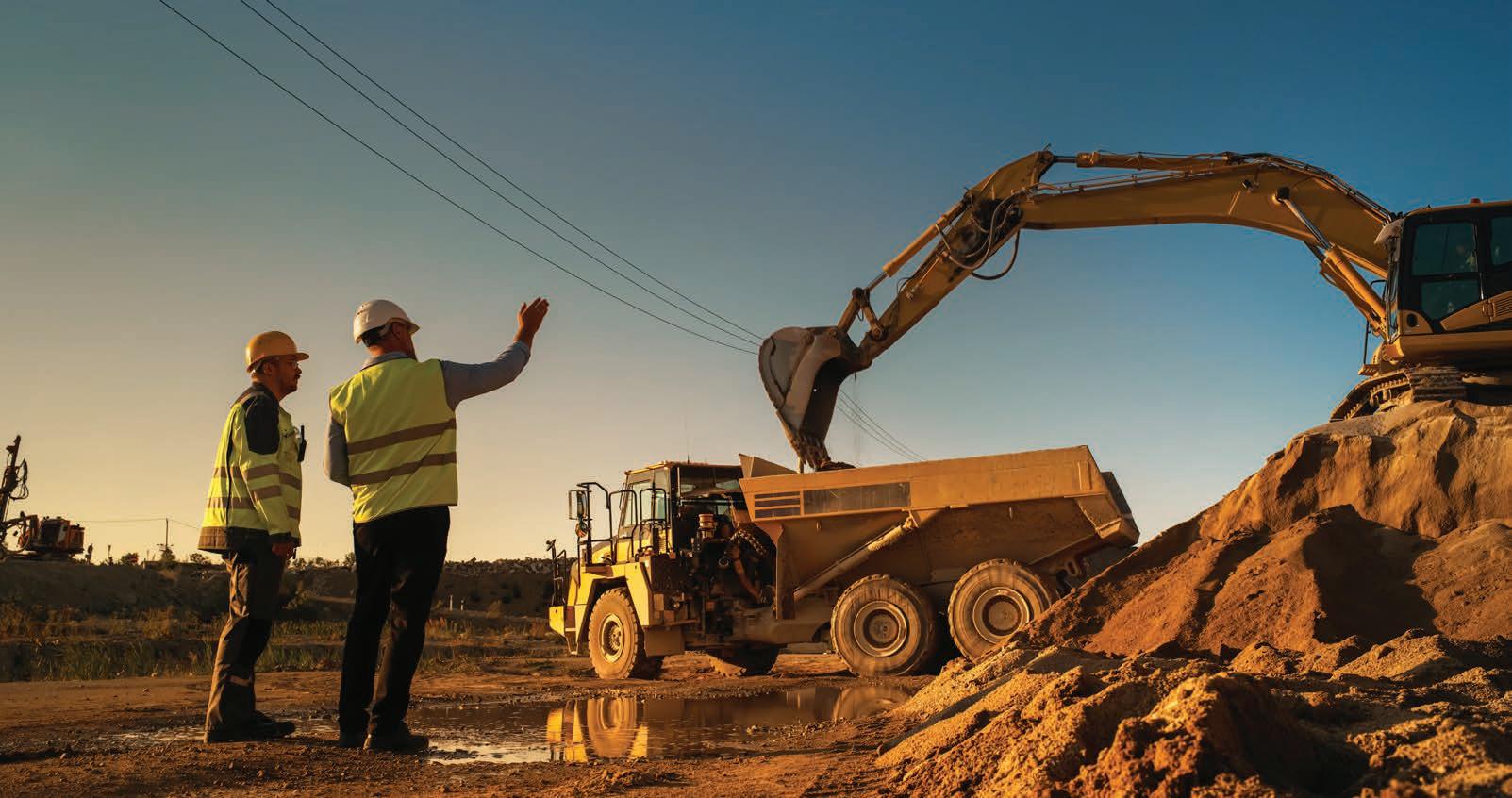
And what starts with dredging lined ponds can extend to cleaning process tanks and cooling towers.
“We have also developed a specialised robot that we can drop into a process tank and remove all accumulated sediment,” Old said. “As long as the tank doesn’t have an agitator, we can complete the cleaning process while the tank is in full operation.”
As a rapidly developing technology company with an impressive R&D division, Dredge Robotics looks set to continue delivering the mining industry world-first robotic solutions for water management and setting new standards for best practice in this field. AM
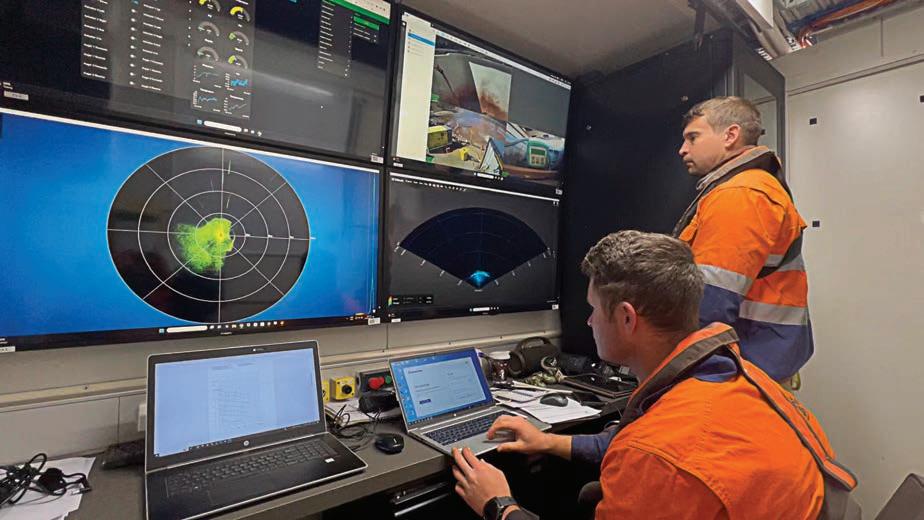
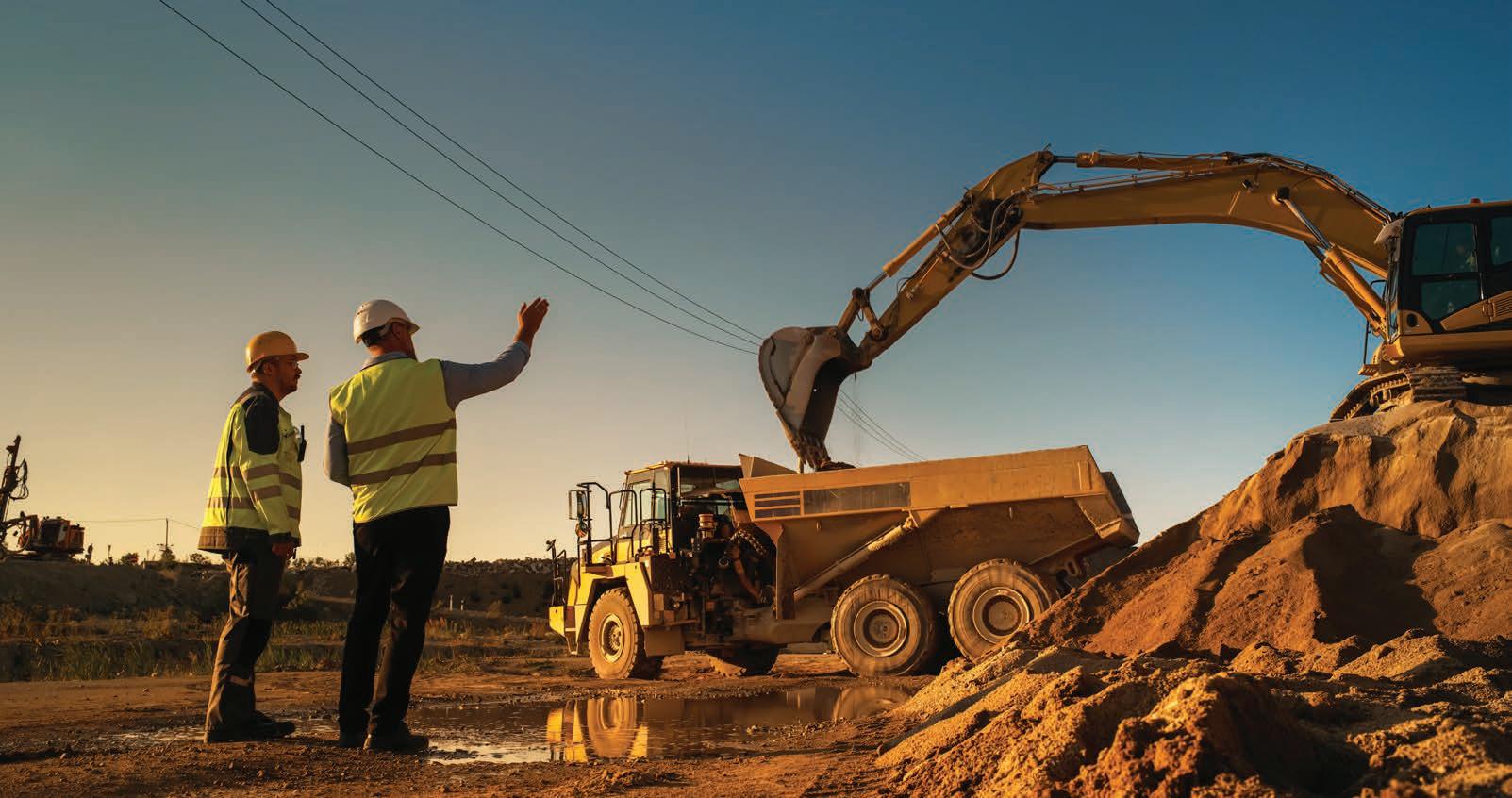
EXTRACTING VALUE, REFINING GROWTH
Full-spectrum IT solutions that unlock IT and OT value.
As mine operators continue investing in technology to drive efficiencies, lift safety, build stability, and extract savings across a widening field of operational facets, it pays to invest in partners that consistently unearth value at every level.
With an established national presence, over twenty-five years of IT experience, and pressure-tested exposure across the mining sector, our strategic thinking, proven know-how, and full-spectrum solutions work hand-in-glove across IT and OT footprints.
If you’re looking to unlock new levels of productivity and profitability, including in commonly overlooked fields such as networks, infrastructure, applications, telecommunication, and procurement, let’s talk.
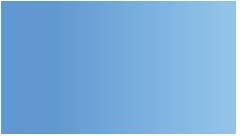
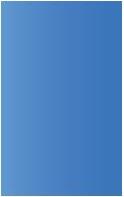
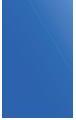



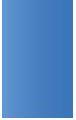
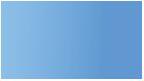

Ready to dig a little deeper? www.brennanit.com.au 1300

A PRACTICAL PARTNERSHIP
TREOTHAM HAS BEEN INTEGRATING IGUS PRODUCTS TO KEEP AUSTRALIA’S MINES RUNNING SMOOTHLY FOR MORE THAN THREE DECADES.
The mining sector is no stranger to massive equipment processing millions of tonnes of rock every day. In fact, it’s exactly what the industry does.
But in the events things go awry, operators need a quick and effective solution. Treotham offers a one-stop shop for industrial cable management solutions on which mines can rely.
Treotham supplies over 10,000 high-quality components and systems to industries across the country, with a keen eye on mining.
Treotham has partnered with German-based manufacturer igus to deliver solutions to mine sites for more than 30 years. The companies have fostered a relationship built on knowledge-sharing and staying on the cutting edge of technology solutions.
According to Treotham’s igus product manager John Sharp, igus products recently achieved $1 billion in sales, a feat made possible through collaboration and expertise in what is a niche field. The partnership has set Treotham up with a method for success.
“We understand our product applications on a deeper level, and we can identify potential problems at
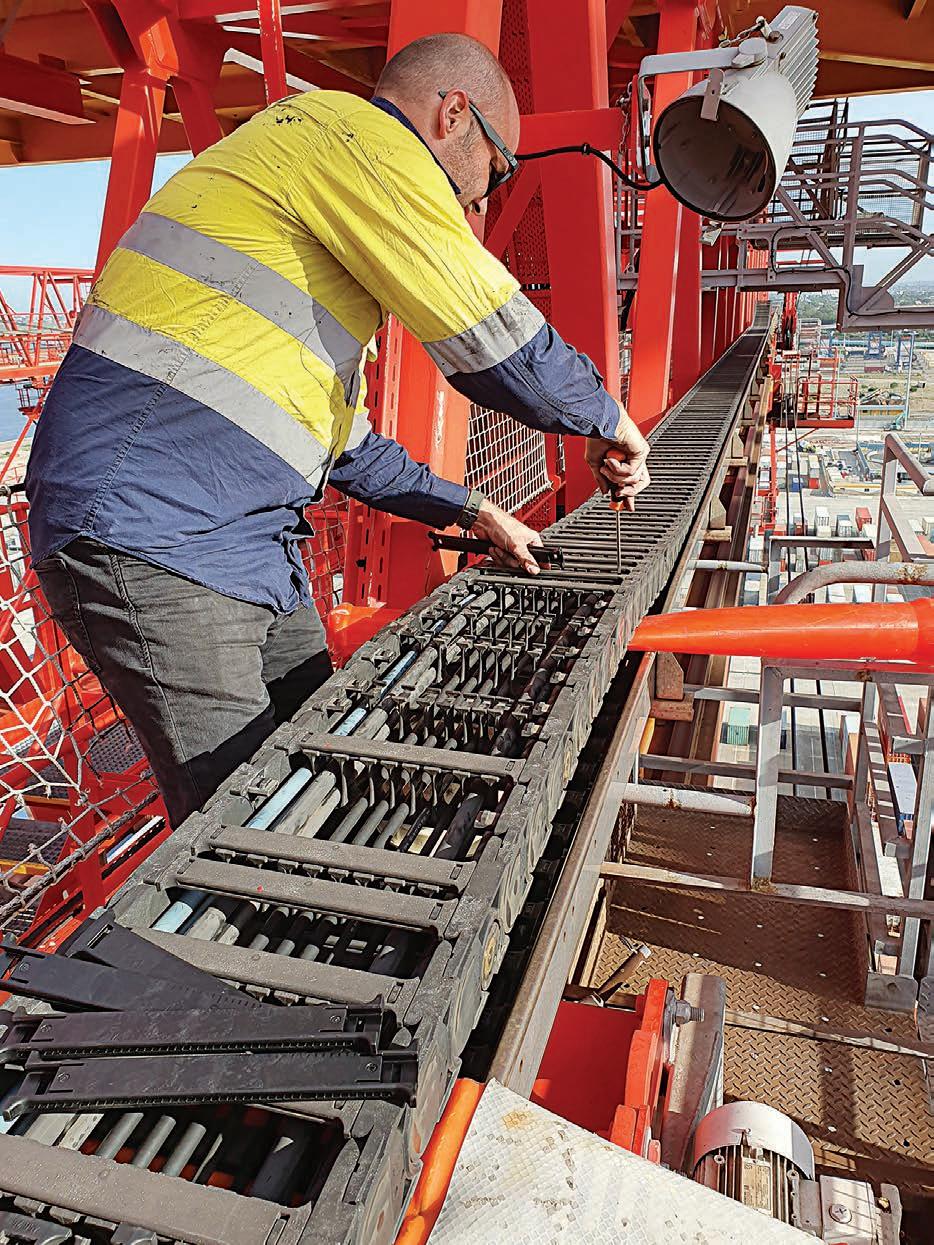
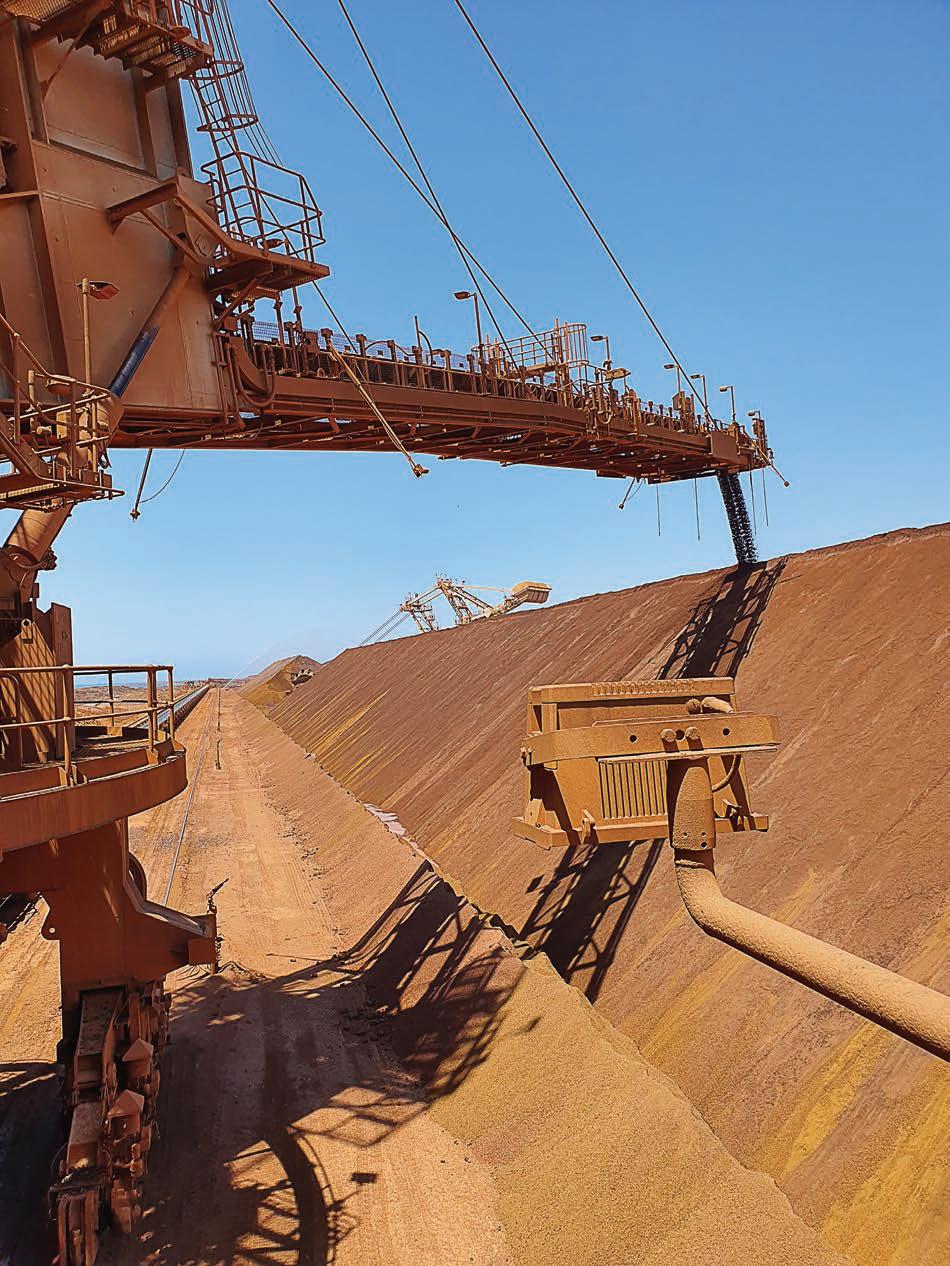
Treotham boasts a workforce of engineering experts who harness the creativity required to customise a unique solution for each project.
“Typically, a client comes to us with a concern or problem they are unable to solve,” Sharp said. “We find the quickest way to analyse the issue is to arrange a site visit to fully understand the problem and come up with a proposal to replace the failing equipment with an igus system.
“For clients who are seeing the efficiency of igus systems for the first time, it can mean change. So moving away from the ‘old’ to the ‘new’ can seem like making a big decision, but once the designs have been produced to the specifications and efficiencies realised, a new level of understanding and appreciation is achieved.
“We recently supported a mining customer who was having a problem with a car dumper. They weren’t able to provide much information, and they weren’t able to stop the machine for any length of time.
“The dumper is a critical piece of equipment, and they were having to
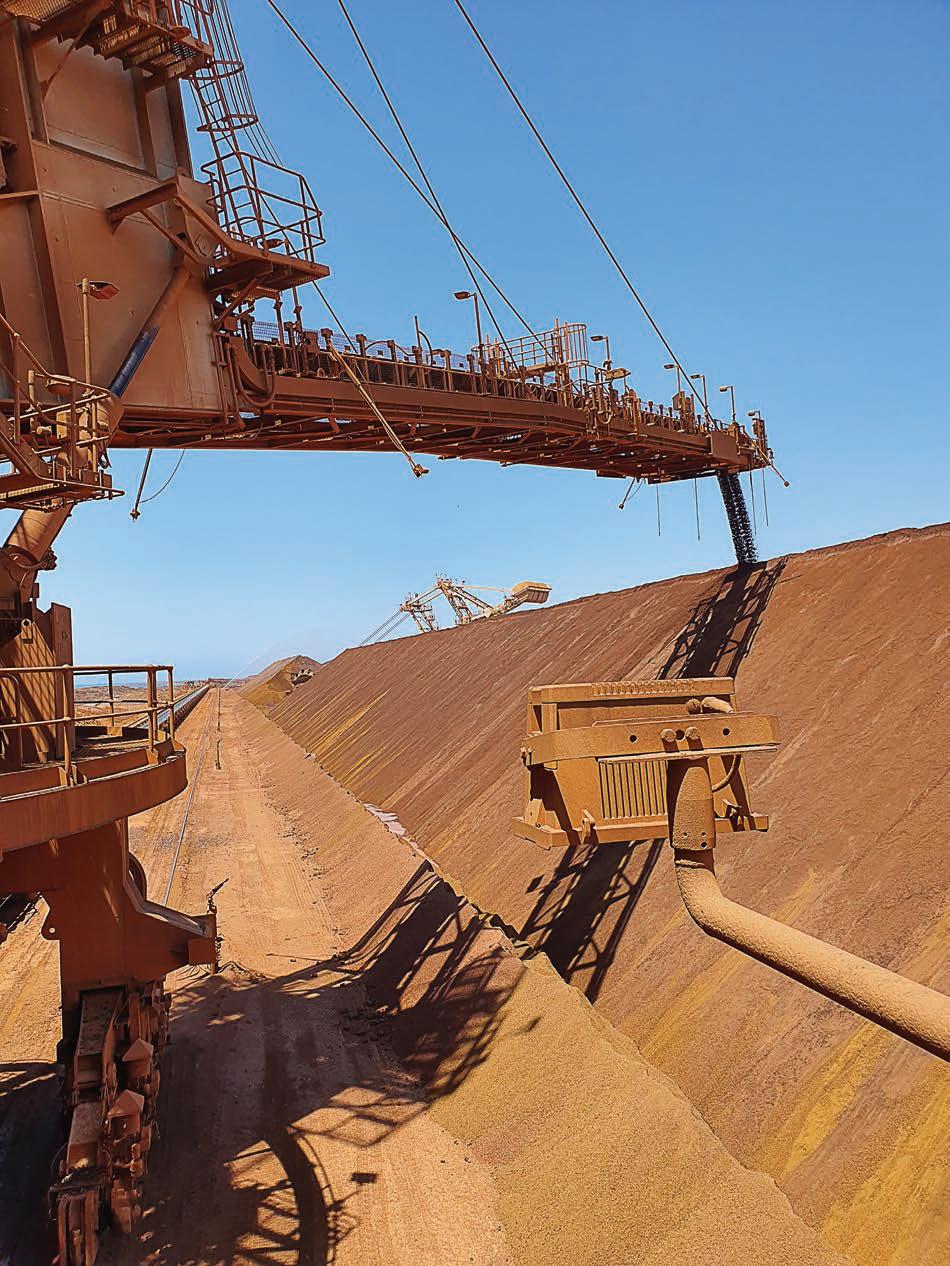
intermittently shut down to change out the cables and hydraulic swivels.”
Sharp emphasised the fact mine operators don’t have time to deal with avoidable shutdowns when they have ships waiting to be loaded with ore.
“We flew to the site to establish what the issue was and what a solution might look like,” he said. “I worked with some of their fitters to build a scale model of what we were intending to do to give them an idea of how to implement the installation.
“The solution has been in service ever since with zero issues.”
igus’ E4.1 energy chains protected the car dumper’s cables from dust, rocks and other debris that go hand in hand with mining. The chains come with the advantage of an easily maintainable modular structure comprising an inner–outer link design that provides a tough solution with a small footprint.
Treotham was able to get operations back up and running smoothly, leveraging igus products to limit potential downtime and boost operational efficiency for the site.
“It’s all about creating the best result for the customer,” Sharp said.
“By collaborating with partners like igus, we often find they have insight into similar applications and can work with us to deliver the best solutions.”
BEAT THE HEAT HYDRATION STATION
by TradesalesPrepare your team for the scorching Australian summer and ensure their safety with the Hydration Station from Tradesales. This 20-foot relocatable site solution is fully insulated and is equipped with powerful air-conditioning, high-quality fridge, chest freezer, ice machine, and a hydrating water dispenser that keeps your workforce cool and refreshed with a bulk supply of pure Australian spring water.
Trusted by industry leaders like Rio Tinto and BHP, the Hydration Station meets the highest safety standards and is fully customisable. Plus, it’s an eco-friendly choice, reducing single-use plastic waste.
Stay cool, stay safe, and stay productive with the Hydration Station.
Finding the best solution to a problem comes from having the best data. Across its centres in Sydney, Melbourne, Brisbane and Perth, Treotham is in a position to work with mine operators in Australia to determine their needs as issues arise.
“Our customers can be rest assured we have people on hand to get to the site if needed,” Sharp said. “You have to go that extra mile because so often we’re applying an alternative technology they haven’t used before.
“Operators can be a bit hesitant to overhaul a system, and understandably so. We ensure our solutions bring measurable improvements to a site that our customers will remember, so they know they can trust us, take the leap of faith, and see a huge payoff in the form of less maintenance and more productivity.”
Once a solution is in place, Treotham prioritises providing quality after-market support to help ensure customers’ continued success.
“Servicing and inspecting our solutions is highly important to us,” Sharp said.
“Customers want equipment that runs efficiently without them having to think about it. We’re more than happy to step in and make sure things keep running as they should.
“Once our customers see what we have to offer, they keep coming back.” AM

RAIL-MOUNTED GANTRY USING IGUS E4 ENERGY CHAIN.
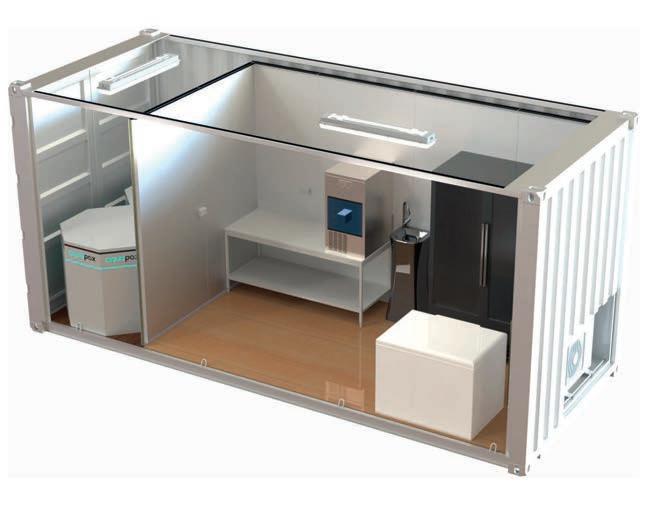
THE NITTY-GRITTY OF MACHINE STORAGE
A NEW EQUIPMENT STORAGE AND MAINTENANCE BUSINESS IS SET TO TAKE THE MINING WORLD BY STORM.

LJack Coyle, director of Gritty Contracting, a heavy diesel mechanical and storage company, has come up with another option.
“Anyone who’s in the maintenance industry knows that machinery doesn’t like to sit still,” Coyle told Australian Mining. “The longer they sit, the more problems build up.
“At Gritty, miners can store their machines locally and we’ll maintain them and keep them in good shape for when they’re needed again. We can do short- or long-term storage and can take all types of machinery, including exploration, surface and underground equipment”
Some of Australia’s largest mines are located in the Pilbara and Goldfields regions of Western Australia. But, as Coyle explained, that doesn’t mean the companies are actually based there.
“If an east coast company gets a contract to come work out west, they might have to float their machines back to headquarters when not in use,” he said.
THERE CAN BE HUNDREDS OF PIECES OF EQUIPMENT AT A MINE SITE, BUT THEY ARE NOT ALL USED AT ONCE.

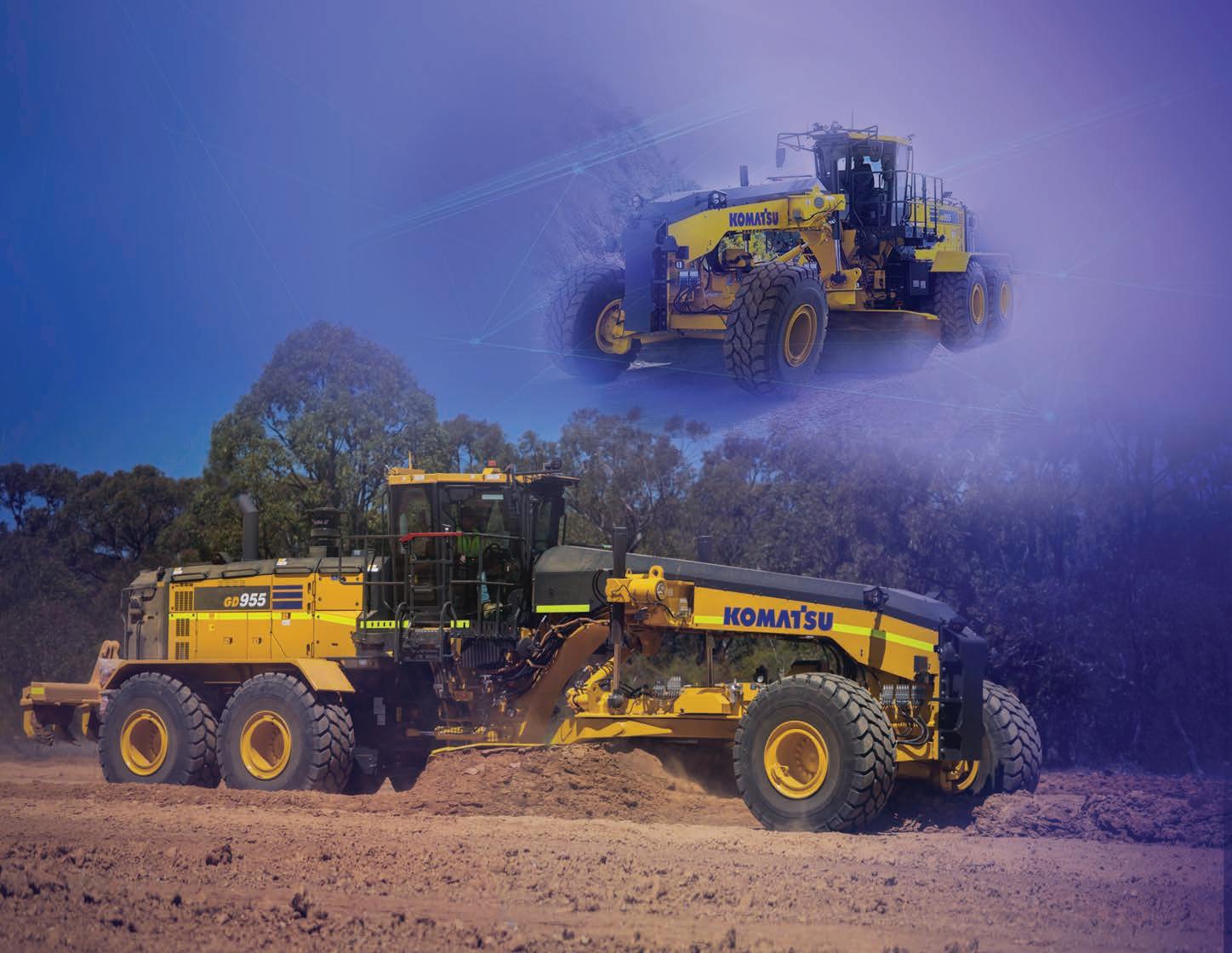
the GD955 Grader
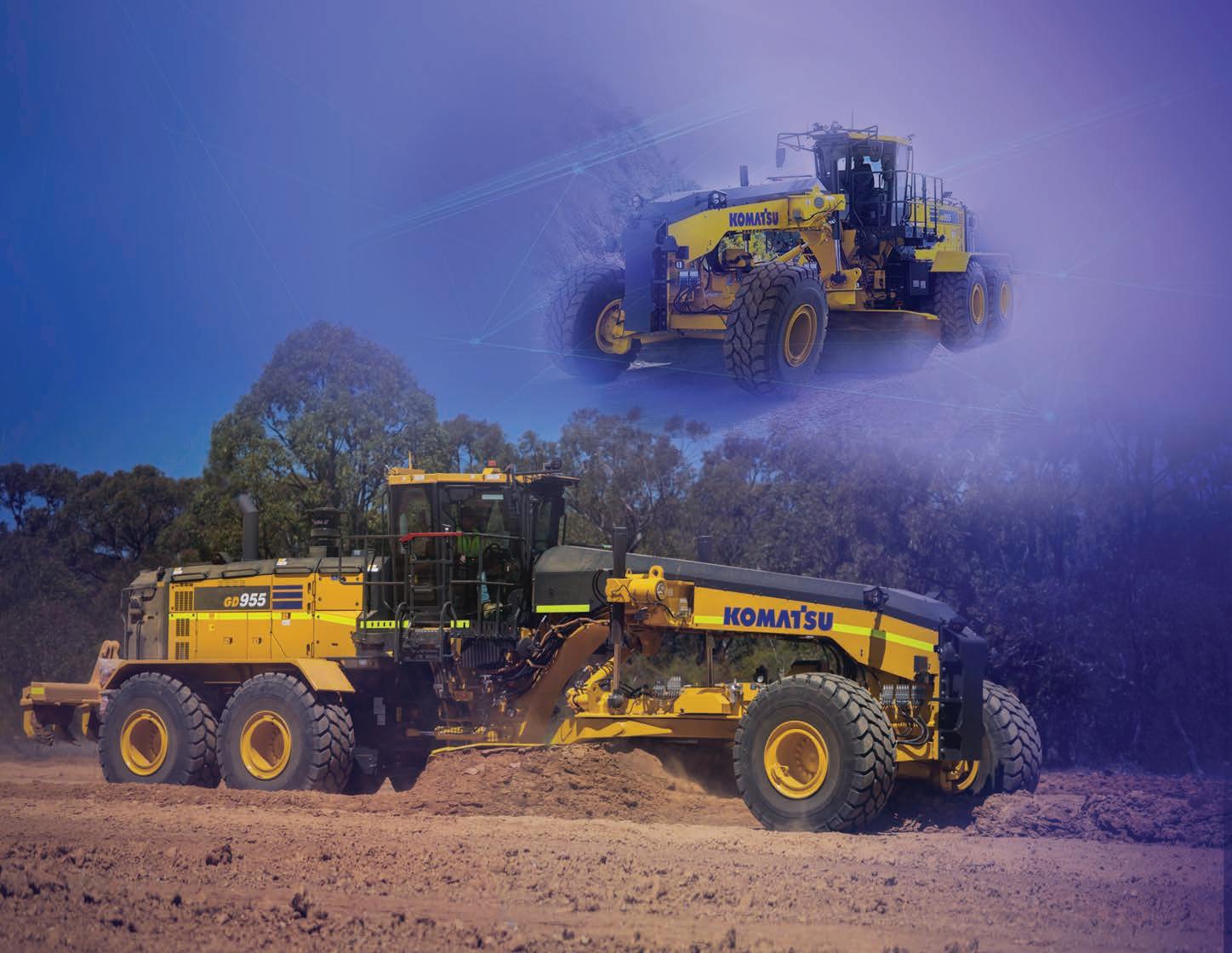
Built from the blade up
Designed to be a highly productive unit, achieved through its market leading blade down force, a 426 horsepower engine and weighing in at nearly 47 tonnes, Komatsu’s new GD955 really is built from the blade up.
REBUILDING BETTER
HASTINGS DEERING HAS SIMPLIFIED ITS REPAIR SERVICES TO HELP CUSTOMERS CHOOSE THE RIGHT OPTION TO SUIT THEIR NEEDS.
With every repair comes a different set of circumstances, including working conditions, weather, and the required materials.
This is a situation Queensland Caterpillar (Cat) dealer Hastings Deering understands, which is why the original equipment manufacturer (OEM) has simplified its repair services to help customers choose the most appropriate option for them.
Hastings Deering can rebuild and service customer needs, whether performed on-site or in one of Hastings’ Cat-certified workshops. If a customer wants to balance cost and downtime or extend component life, for example, Hastings Deering has a repair option that will suit.
“Whether you are facing a planned or unplanned component overhaul or replacement, having a more diverse range of repair options helps to lower operating costs and meet your production demands,” the company said on its website.
As part of its repair options, Hastings Deering provides complete replacements that are new and fresh out of the factory.
eco-friendly and allow for minimal downtime. The Cat and Hastings Deering remanufacturing divisions ensure all exchange component options meet Cat standards.
“Where downtime is critical and you want fast return to work, exchange your end-of-life component for an off-theshelf one for fast turnaround, as-new life, and lower-than-new component cost,” Hastings Deering said.
Each Cat component is “built to be rebuilt”, which means longer-term reusability and cost benefits beyond the initial purchase of the new component.
“(Our) Cat certified rebuild programs help you benefit from the multiple lives designed into Cat machines, power trains and major components,” Hastings Deering said.
“They are ‘built to be rebuilt’ for maximum value and longer life.
(Customers can) maximise the investment in their asset with full utilisation of a second life, at a fraction of the cost of buying new.”
In addition to machine rebuilds, Hastings Deering offers options where it will extend component life or will repair the component according to the customer’s specifications.
Hastings Deering’s exchange, rebuild
“Remanufacturing and returning end-of-life components to same-as-new condition reduces waste,” the OEM said.
“In minimising the raw material consumption needed for producing new parts, you contribute towards more sustainable development, keeping nonrenewable resources in circulation for multiple lifetimes.”
Customers who partner with Hastings Deering for a Cat certified rebuild on their machine and components will also benefit from up to 24 months and 10,000 hours in warranty coverage on parts and service for any new, exchange, or rebuild
customers with greater peace of mind, Hastings Deering’s equipment specialists work to understand the individual circumstances of the customer to help ensure the best repair option is chosen for their business and operational needs.
“They might be our people, but they really work for you,” the company said.
“Hastings Deering understands the mining industry, we know what keeps it moving and our expert teams know everything about the equipment we sell.
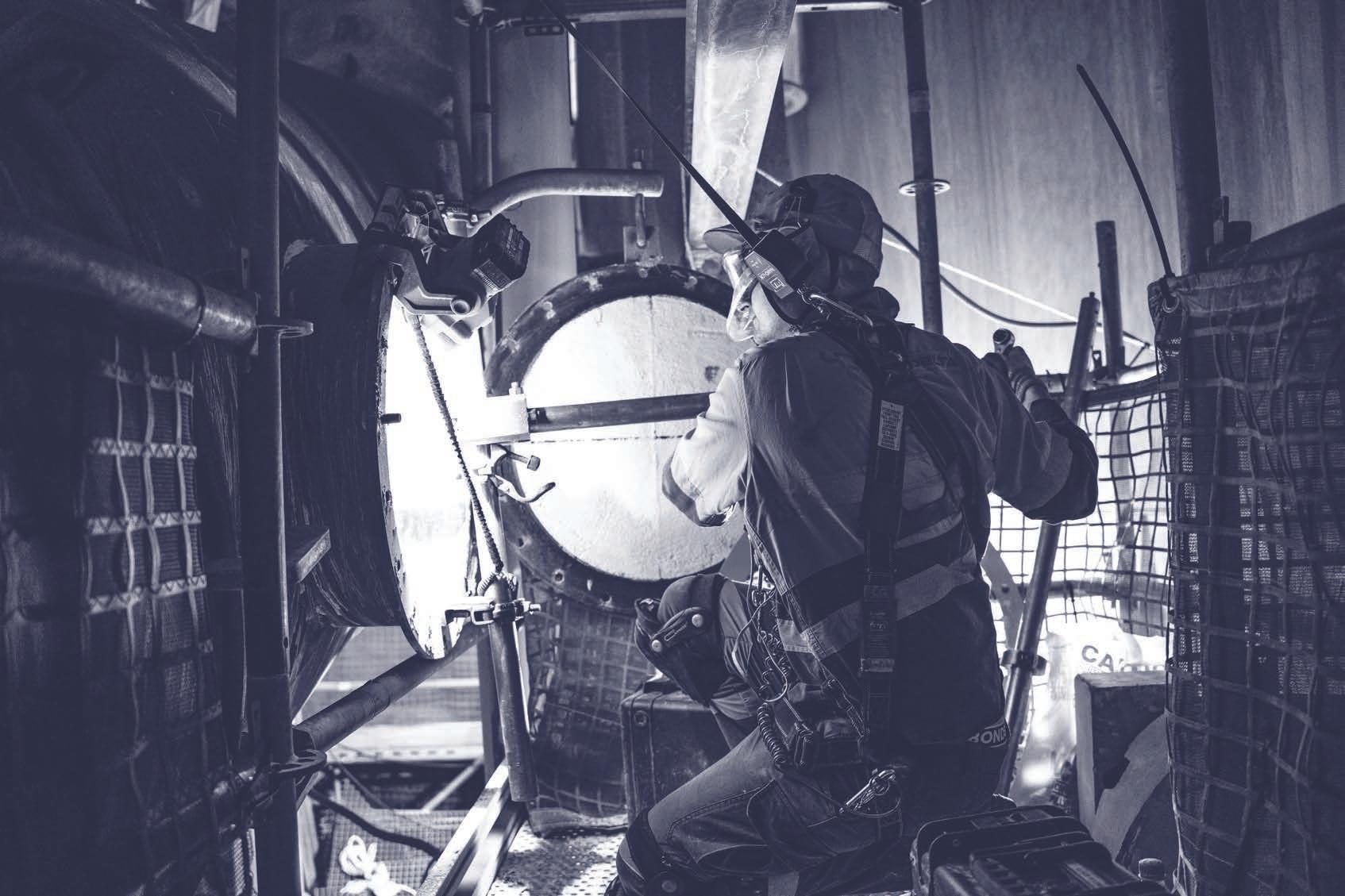
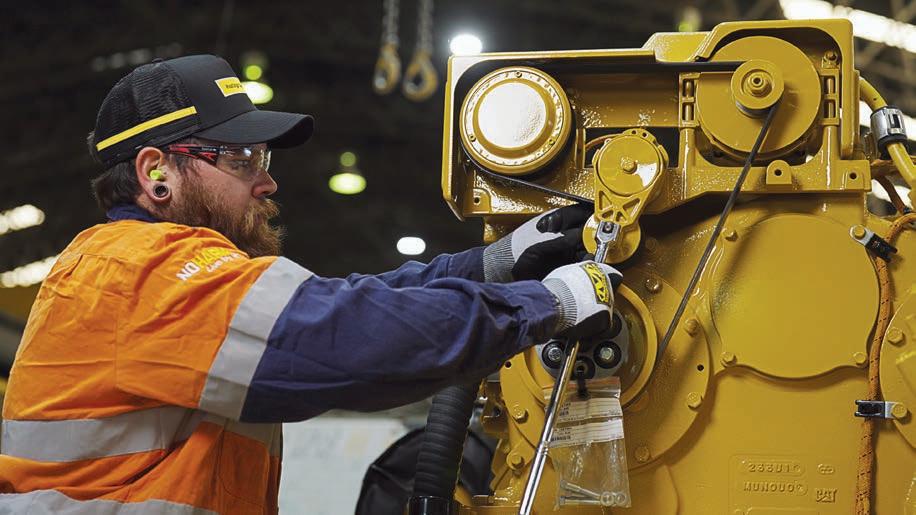
“Whether you are balancing cost versus downtime, looking to extend component life or wanting to keep your own iron,
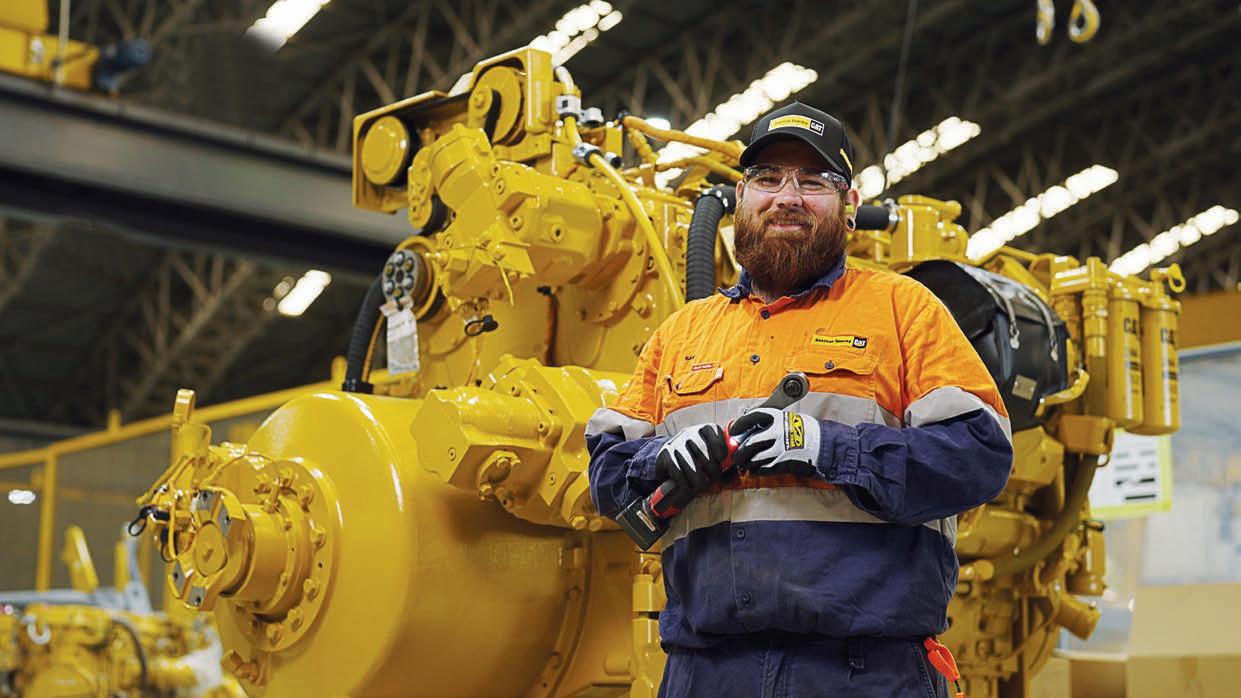
REMOTE ASSET INSPECTION
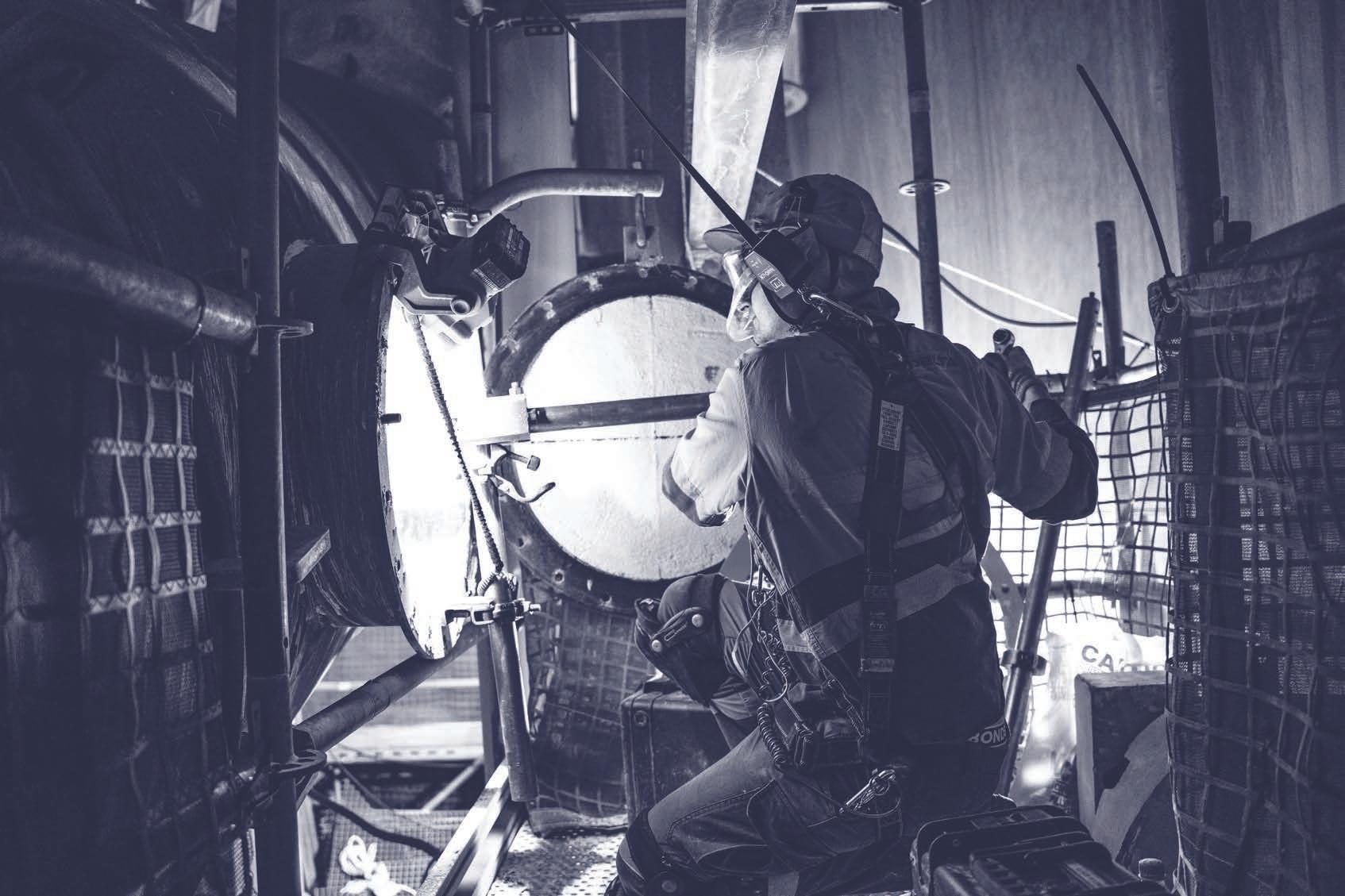
Eliminate high-risk work for your people.
Optimise performance and extend the life of your assets.
Support your decision-making with cutting edge technology & innovation.
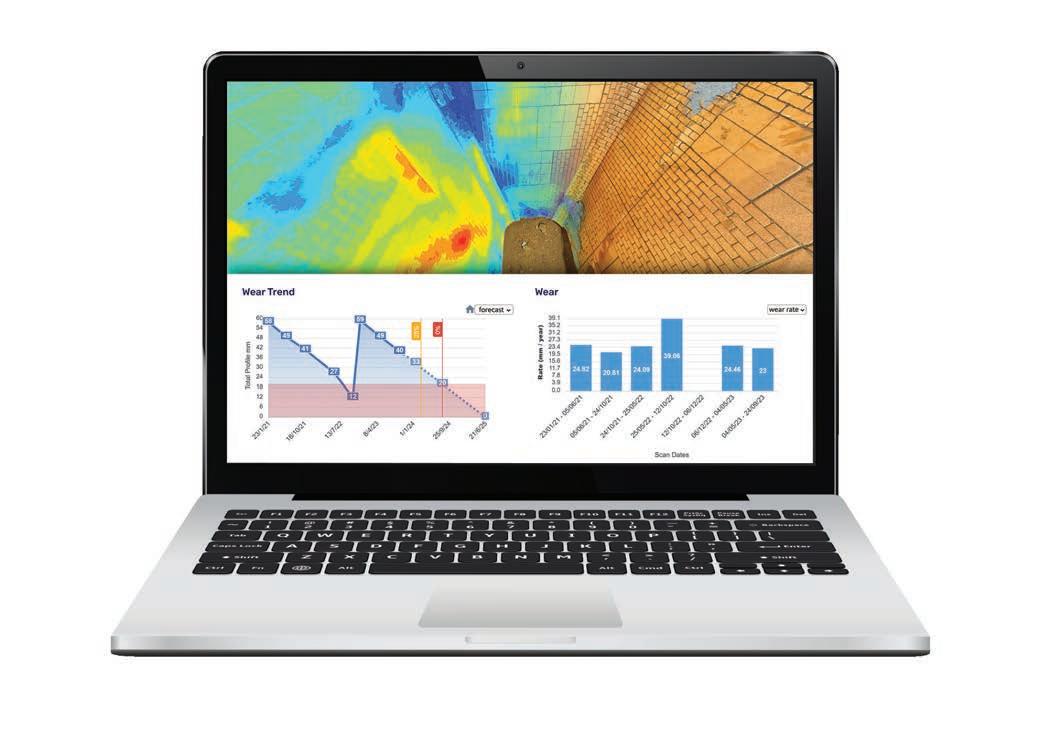

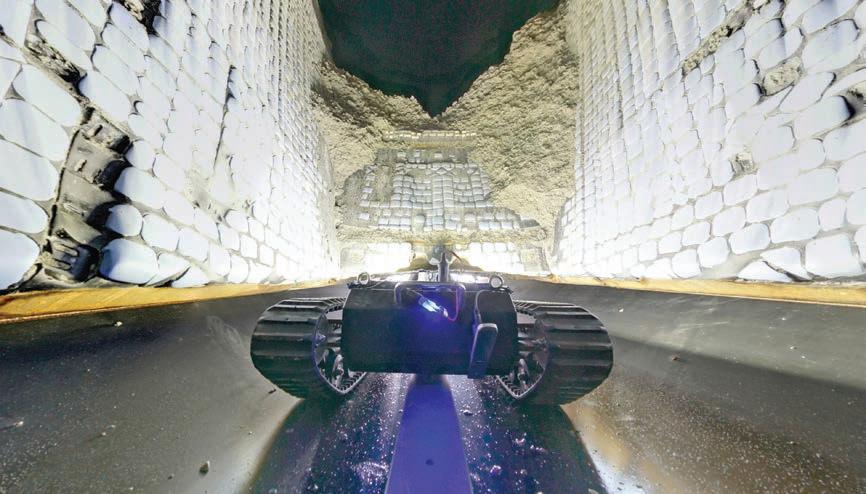
www.4ddelta.com
KEYS TO A SUCCESSFUL MAINTENANCE PROGRAM
MCLANAHAN HAS A PLAN IN HAND TO MAXIMISE SITE MAINTENANCE AND KEEP OPERATIONS ON TRACK.

Global processing solutions provider McLanahan knows maintenance is key to ensuring the longevity and optimal performance of any mineral processing equipment.
According to McLanahan director of global sales – mining Lee Hillyer, to get the best operation and lifespan from your equipment, it is vital to establish and follow a preventive maintenance schedule.
“A maintenance strategy should be determined based on the needs of each specific site, using the maintenance guidelines in the equipment manual as a baseline for the minimum requirements,” Hillyer told Australian Mining.
“A successful maintenance program will help maximise efficiency and minimise downtime.”
A mining company or contractor should ensure their maintenance plan covers all aspects of their equipment, including routine inspections, preventive maintenance tasks and scheduled
downtime for repairs, replacements and upgrades.
To help make a maintenance program a success, Hillyer recommended the following tips:
Safety first
The first rule of any successful preventive maintenance program is safety.
“First and foremost, safety protects employees and minimises the risk of accidents, but safety has other important benefits too,” Hillyer said. “It ensures compliance with mine safety standards, preserves equipment integrity and reduces downtime associated with accidents.”
The key is to provide appropriate safety training and personal protective equipment (PPE) to all personnel and ensure all personnel are familiar with and adhere to safety protocols.
All machine safety tags should be visible and legible, and machine guards should be in place where applicable.
It is important to practice good housekeeping on site to avoid slips, trips
and falls hazards. It is also important to keep up to date with safety regulations and best practice procedures.
Be consistent
Consistency is essential in a maintenance program for several reasons, all of which contribute to the overall effectiveness and success of the program.
“Consistent preventive maintenance helps to ensure the equipment is regularly inspected and serviced so that it operates at optimal performance,” Hillyer said. “It helps identify and address potential problems before they lead to failure, minimising the risk of unplanned downtime and expensive repairs or replacements.”
Consistency can increase efficiency as well as the lifespan of the equipment.
Consider OEM specialists or OEM maintenance contracts
When carrying out routine maintenance or emergency repairs, consider consulting trained specialists from the original equipment manufacturer
(OEM) to preserve the long-term integrity of the equipment.
“OEM equipment has been specifically designed for the application, and there are often parts and designs that may differ from other or similar equipment,” Hillyer said.
“Having the OEM specialist service engineers who are specially trained with many years of experience on the equipment will ensure that the equipment is back up and running quickly with trouble-free maintenance until the next shutdown interval.”
Another option to consider is an OEM maintenance contract.
“Having a maintenance contract in place allows OEMs to suitably plan and staff customers’ requirements enabling the OEM to always have labour available for planned and unplanned maintenance,” Hillyer said.
“This also allows the OEM to manage internal and external stock inventory to ensure that availability of the equipment is maintained to the highest level and unplanned maintenance is kept to a minimum.”
Don’t forget the basics
Every maintenance program should include visual inspections of components for wear or damage. This includes checking for excessive heat or noise, leaks and loose parts. Emergency stop switches should also be tested to ensure correct functionality.
Lubrication is also important for continual trouble-free operation. Contaminated lubricant, improper lubricant type and/or quantity, and incorrect lubrication frequencies can lead to component failure.
These failures are often preventable through good housekeeping and proper lubrication practices, such as:
• sealing all grease and oil containers to prevent dust, grit and moisture contamination
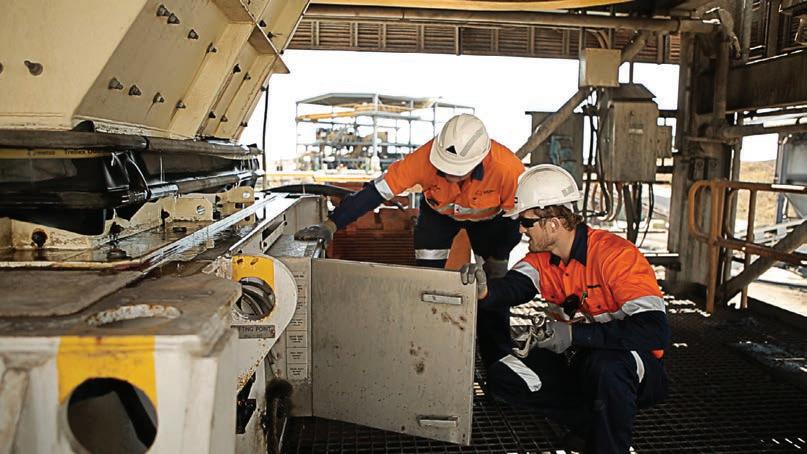
• thoroughly cleaning all grease and oil lines before installation
• w iping all fittings with a clean rag before lubrication to prevent forcing contaminants into the component
• k nowing the volume per stroke of your grease gun to appropriately lubricate the components.
Keep spares in stock
Keeping critical spares in stock is beneficial for two reasons. First, it reduces downtime in the event of a breakdown. Mine operators don’t have to rush to find a replacement or wait for one to arrive if they already have that component in their inventory.
Second, if a routine maintenance inspection reveals a damaged or worn component, a repair or replacement can be scheduled immediately.
“Rotable spares are a great way to ensure trouble-free operation of the equipment by always having a spare on site that can be quickly used in an unplanned breakdown or as a routine maintenance changeout part,” Hillyer said.

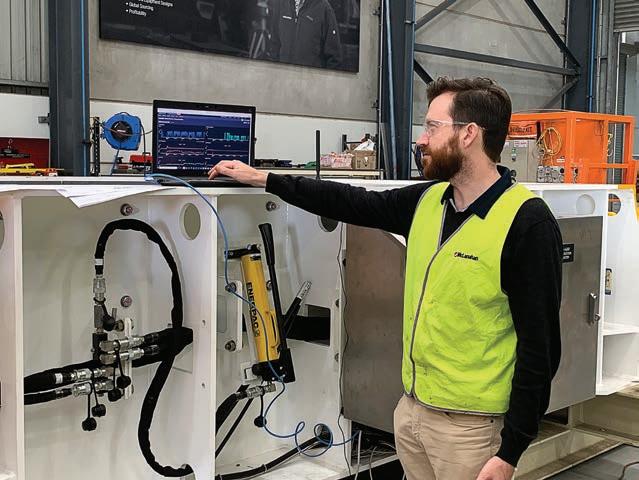
guarantee labour and parts availability.”
Once a spare part is used, it’s best practice to get another on order to replace it. Use OEM spare parts for the added benefit of warranties, quality, durability, machine compatibility and overall value.
“It’s advisable to use OEM parts on OEM equipment to maintain the warranty of the equipment but also

“OEM parts are specifically designed for the applications using knowledge gained over decades spanning hundreds of different mine sites, commodities and duties around the world.”
Consider condition monitoring
To help facilitate maintenance strategies, consider adding a condition-monitoring package to your equipment to provide a
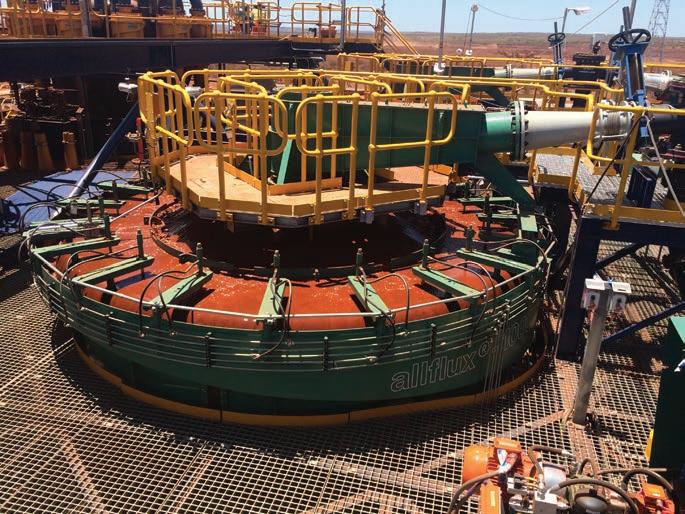
more comprehensive picture of machine health. These tailored packages use a variety of sensors to analyse conditions such as temperature, vibration, motor current and more.
Condition monitoring can help detect the potential for component failures, which will reduce unexpected downtime and predict maintenance to improve maintenance programs beyond just being a calendar event.
Invest in training
Ensure maintenance personnel are well-trained on the operation of the equipment in addition to troubleshooting and repair.
“Hosting OEMs to conduct presentations on their machines and sending personnel to industry conferences and educational sessions is a good way to invest in staff for the future,” Hillyer said. “Staying informed will keep maintenance personnel up to date on the latest technologies and maintenance best practices.”
Continuous improvement
Continuous improvement is vital for any successful preventive maintenance program. Once a program is in place, regularly review and update the plan based on performance data and feedback.
“By reviewing and updating the plan, you can ensure continued success for your maintenance program,” Hillyer said. “Nothing is worse than unexpected downtime caused by a breakdown or failure that results in loss of production and profits.”
By establishing a consistent preventive maintenance program that prioritises safety, keeping spare parts in stock, ensuring personnel are properly trained on the equipment and striving for continuous improvement, unexpected breakdowns can be effectively handled or avoided altogether. AM


STICKING TO QUALITY
AKZONOBEL HAS THE AUSTRALIAN MINING INDUSTRY COVERED INSIDE AND OUT.
Unplanned downtime is the enemy of the resources industry. It’s more expensive than ever to run a mine site, so operators need repair solutions that limit the time an operation spends out of action.
AkzoNobel is a global paints and coatings powerhouse specialising in major mining projects across Australia and around the world. But the company is concerned with more than just the usual lick of paint.
“Our leading international brand is renowned for anti-corrosive protection, passive fire protection and aesthetic solutions that are used to coat some of the world’s largest projects in impossibly remote areas,” AkzoNobel South Asia mining key account manager Amit Mehta told Australian Mining
No stranger to providing painting and coating solutions to suit tough conditions, AkzoNobel has the mining industry covered – literally.
“We have been protecting highvalue assets required for processing metals and minerals against the harsh, corrosive mining environment in
mining processing plants, smelters, and refineries all over the world for over 50 years,” Mehta said.
“Our tough durable coatings are developed to withstand the damage that results from transporting and processing corrosive, abrasive materials from location to location within the mining facility and shipping them to the global market.”
AkzoNobel is using its years of experience providing quality coating solutions to look past the paint and into the heart of Australia’s largest structures. The team is determined to keep mine sites running safely and efficiently when things go wrong.
With its high-performance epoxy coating Interzone 954, AkzoNobel is stepping up to hold the mining sector together like never before.
“Interzone 954 is a high-film-build, high-solids, abrasion-resistant epoxy that provides long-term performance in harsh environments that combine a high potential for mechanical damage, chemical attack, atmospheric corrosion, and immersion conditions,” Mehta said.
“This versatility makes Interzone 954 an all-round heavy-duty coating to watch
in the Australian mining industry.”
Versatility is the name of the game in an industry extracting minerals and metals of every shape, hardness and texture. Repairs come often and pose a threat to production if issues are left unchecked.
Not just a stop-gap solution, Interzone 954 supports sites from pit to production.
“Interzone 954 is suitable for any construction and maintenance application in mining and mineral processing operations,” Mehta said.
“Coal wash plant maintenance, wharf and jetty maintenance, thickener tanks and other highly corrosive areas where surface preparation can be difficult and costly where repairs need to be completed in a short time frame.
“Interzone 954 provides a fast and cost-effective way for repairs in mining operations and assists contractors to improve productivity and reduce costs on-site.”
AkzoNobel has been using Interzone 954 at Australia’s largest mines for years. The Interzone 954 was used to coat the internal walls of a thickener tank at a major New South Wales coal mine.
“Our track record of successful performance is second to none,” Mehta said. “Interzone 954 was selected for its well-documented performance in immersed conditions and the product’s ability to withstand highly abrasive conditions.”
Throughout its six years of operation, the tank always passed inspections with no sign of corrosion.
“What makes Interzone 954 a true all-round solution is its ability to provide high build protection in a single coat,” Mehta said.
“Combined with its surface tolerance, dampness tolerance and early water resistance, the impact of the painting process can be minimised and allow a rapid return to service with significantly reduced downtime and labour costs compared to a standard two-coat epoxy system.”
Reliability, versatility and efficiency are what has kept AkzoNobel customers coming back for over half a century.
“Australia’s mine operators can have peace of mind knowing they have the most reliable and trusted highperformance epoxy coating protecting their assets,” Mehta said. AM


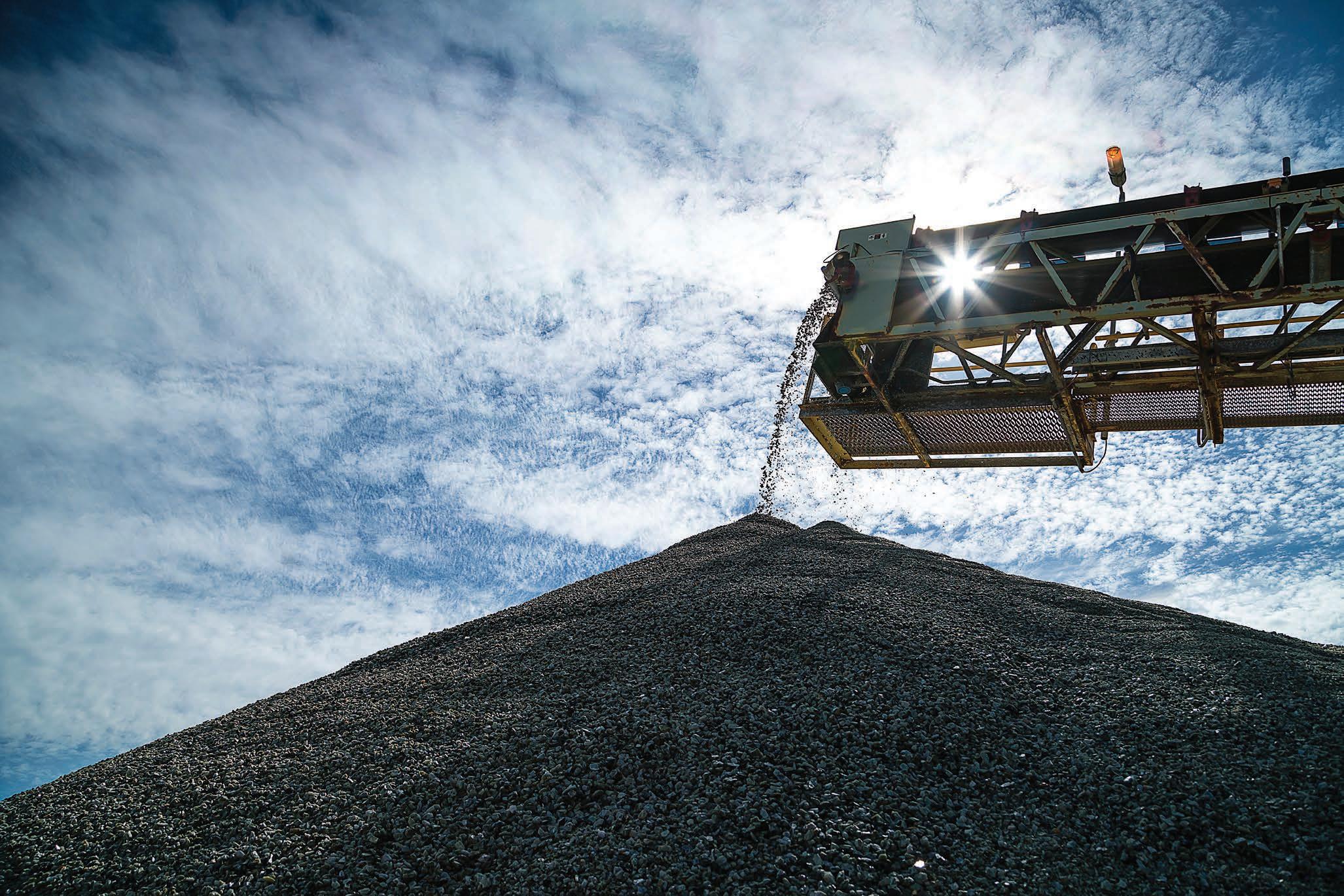
A LITHIUM BEHEMOTH
AFTER A MONTHS-LONG PROCESS, GLOBAL LITHIUM MINER ALLKEM HAS FINALLY MERGED WITH US CHEMICALS GIANT LIVENT, CREATING ARCADIUM LITHIUM.
Allkem and Livent made a cracking start to 2024, finalising their highly anticipated $US9.7 billion merger.
The new company, Arcadium Lithium, has been dubbed a “merger of equals” as it combines Allkem’s multinational upstream lithium capabilities with Livent’s downstream processing offerings.
With the merged entity set to become a leading global lithium chemicals producer, Australian Mining takes a closer look at how the multi-billion deal came to be, and what Arcadium Lithium’s future might look like.
The acquisition
In May 2023, it was announced that Allkem and Livent had signed a definitive agreement to merge the two companies, creating a $US10.6 billion global lithium major.
The merger was announced less than two years after Allkem itself was created from the merger of Galaxy Resources and Orocobre.
The goal of the combination was to create a leading global lithium chemicals
producer under a new name, which was just known as ‘NewCo’ at the time.
Under the agreement, Allkem shareholders would own 56 per cent of the entity and Livent shareholder would own the remaining 44 per cent.
“I am excited for what lies ahead as Livent and Allkem combine forces to help power the transition to electric vehicles, cleaner energy and a more sustainable future,” Livent chief executive officer (CEO) Paul Graves said of the merger’s potential in May 2023.
“As a combined company, we will have the enhanced scale, product range, geographic coverage, and execution capabilities to meet our customers’ rapidly growing demand for lithium chemicals.
“Together we can accelerate our growth plans and deliver more lithium, more reliably, and more quickly, than either of us can do alone.”
Allkem CEO Martín Pérez de Solay echoed a similar sentiment.
“The combination of Allkem and Livent is transformational with compelling strategic logic and marks a significant milestone in our efforts to grow the company,” he said at the time.
“We are bringing together two
highly complementary businesses to create a leading global lithium chemicals company, building on Allkem’s demonstrated track record of integration.”
Over the next few months, Allkem and Livent worked to ensure the merger met regulatory compliance in the jurisdictions it planned to operate, including Australia, Canada and Argentina.
It was during this time that the combined company received its new name: Arcadium Lithium.
By November 2023, Allkem and Livent had received antitrust and competition approvals from Canada, China, Japan, South Korea, and the US.
The two companies also received foreign investment approvals from Australia, the UK and the US in the same month, meaning all competition and foreign investment approvals needed before the merger’s completion were granted.
Allkem held its scheme meeting to vote on the acquisition in December 2023. Of the 72 per cent of Allkem shareholders present, 89.3 per cent voted in favour of the merger.
Livent shareholders followed suit, with the majority also voting their approval.
“Arcadium Lithium will have the scale and expertise to meet the rapidly growing demand for lithium chemical products and the product flexibility required by customers while remaining committed to the delivery and execution of a significant growth pipeline,” Pérez de Solay said.
Graves said that the strong shareholder support from both companies demonstrated the compelling value proposition of Arcadium Lithium.
“We look forward to closing the merger and pursuing the opportunities to create greater long-term, sustainable value for all of our stakeholders,” he said after the meeting.
Arcadium Lithium began trading on the Australian Securities Exchange (ASX) on December 21 2023, with Allkem ceasing ASX trading on January 4 2024, following the transaction successfully closing.
And as the dust settled on the agreement, the true power of Arcadium Lithium came to be known.
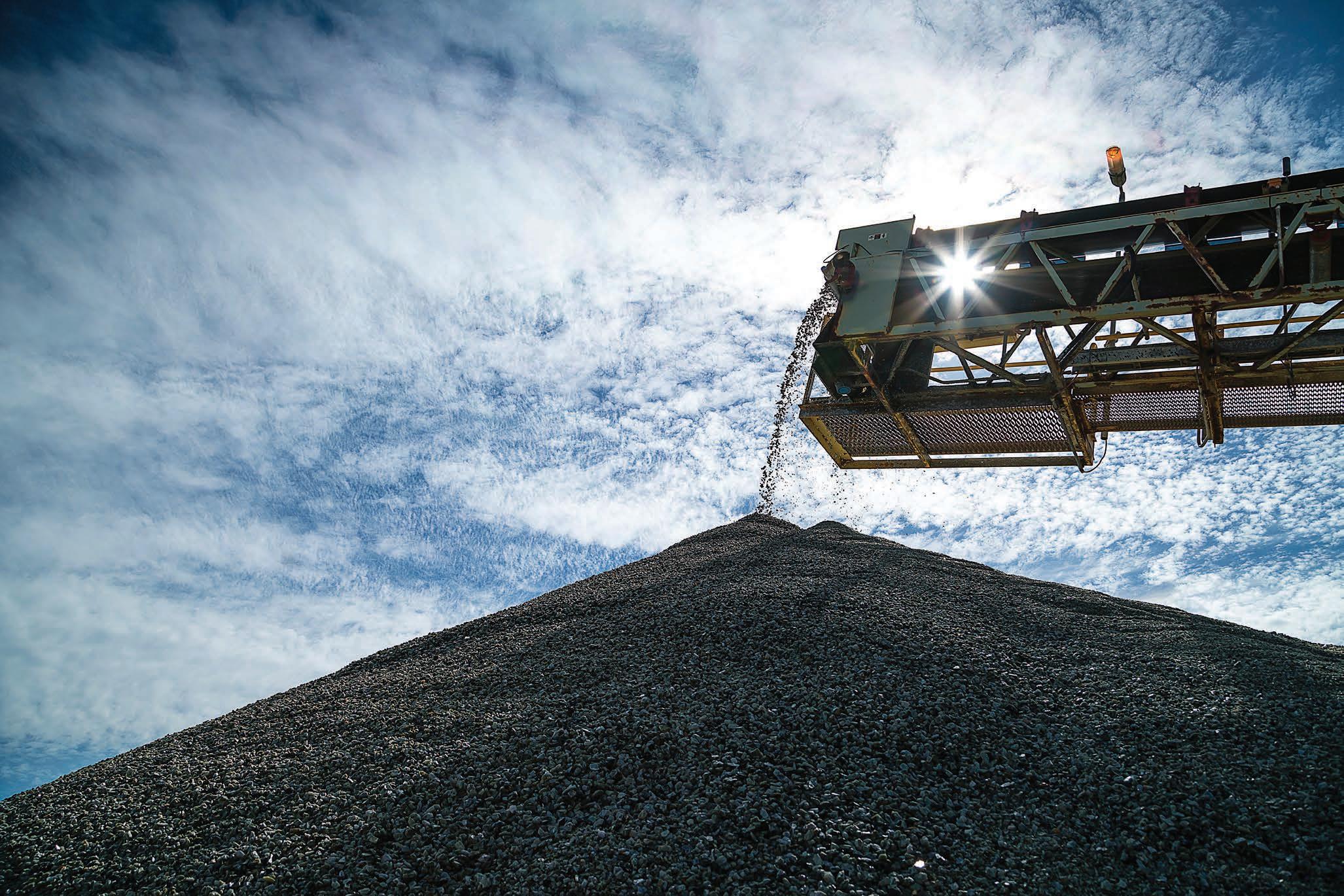

ARCADIUM LITHIUM WILL HAVE THE SCALE AND EXPERTISE TO MEET THE RAPIDLY GROWING DEMAND FOR LITHIUM CHEMICAL PRODUCTS AND THE PRODUCT FLEXIBILITY REQUIRED BY CUSTOMERS WHILE REMAINING COMMITTED TO THE DELIVERY AND EXECUTION OF A SIGNIFICANT GROWTH PIPELINE.”
With about $US1.9 billion of combined total revenue in 2022 and a global team of more than 2600 employees, Arcadium Lithium is now one of the largest integrated producers of lithium chemicals in the world.
“Arcadium Lithium has the resources, scale and expertise to meet the growing
needs of our rapidly changing industry,” Graves, now Arcadium Lithium’s CEO, said.
“We are a leader in every major lithium extraction process– from hard rock mining to conventional pond and direct lithium extractionbased brine processing– and vertically integrated, from resource to chemical manufacturing, in strategic locations around the world.
“This will open doors to new opportunities and strengthen our ability to deliver value to our customers, investors, employees and communities … We look forward to building on this strong foundation and leading our industry forward.”
Mount Cattlin
Arcadium Lithium inherited Mount Cattlin, a hard rock lithium mine originally owned by Allkem.
The open pit mine and concentrator is located approximately 2km north of Ravensthorpe in WA. It is considered to be one of the largest lithium mines globally, producing 130,984 tonnes of spodumene concentrate in the 2022–23 financial year.
“We produce high quality spodumene concentrate at Mount Cattlin that is qualified in the lithium supply chain globally,” Arcadium Lithium said on its website. “It is a mature and stable operation located in a world-class mining jurisdiction.”
During the September 2023 quarter, the mine produced a record 72,549 dry metric tonnes of spodumene concentrate at a grade of 5.3 per cent lithium oxide.
“Recovery of 68 per cent demonstrates favourable grade and favourable mineralisation as mining has moved into the central zones of the main ore body,” Allkem said in its September 2023 quarterly report.
The future of the mine is yet to be seen, but it looks set up for further success under Arcadium Lithium’s care.
Next moves
While major players like Mineral Resources, Hancock Prospecting and SQM threw themselves into a WA lithium buying frenzy last October and November, Graves – who is based in the US – believes it’s still early days for the Australian lithium sector.
As a result, he said the company is willing to wait until the dust settles on current valuations before diving in. However, the company is willing to be “aggressive” once it better understands the situation.
“There’s a massive disconnect today between the value someone’s ascribing to a very, very, very early stage, or technically challenging, projects in Australia with only a maiden resource (and) without full ownership,” Graves said in November, as reported by The Australian Financial Review
“There’s a lot of value being assigned to those by various people down there in Australia and so (it’s) a little challenging for me to know where the Australian M&A (mergers and acquisitions) market plays out.”
While it may initially seem strange that a new lithium miner doesn’t want to make big moves in the space, Graves’ strategy may pay off if the lithium assets don’t return as high a profit as originally anticipated.
While nothing is certain when it comes to commodity prices, one thing is known for sure: Arcadium Lithium has a bright future ahead of it. AM
BLASTING THROUGH BARRIERS
INDUSTRIAL SPRAY PAINTER AND BLASTING APPRENTICE JASMINE STEWART KNOWS FIRST-HAND WHAT IT’S LIKE TO BE ONE OF THE ONLY WOMEN WORKING IN HER FIELD. NOW SHE WANTS TO SEE MORE WOMEN ENTERING THE INDUSTRY.
Jasmine Stewart knows hard work. As an industrial spray painter and blasting apprentice, she’s worked on multiple major projects for the biggest names in Australian mining.
Stewart works 10 and a half hour shifts on her feet, blasting structural steel to prepare it for protective coatings and paints.
“Preparation of the steel prior to painting is an essential part of the job,” Stewart told Australian Mining. “You need to make sure you’re protected and switched on when you’re blasting, there’s a lot of risk with it.
“The blast lines, which are already heavy and full of pressurised air and grit, have a tendency to kick back if they get blocked so you really need to hold on.
“There’s also the risk of getting hit by the ricocheting material or even blasting yourself directly. This is why we always wear our PPE, including our blast helmet, coveralls and welding gloves.”
But Stewart doesn’t want to discourage anyone from applying.
When Stewart first started her apprenticeship she was told “most don’t last” in the industry.
The warning made Stewart all the more determined to succeed.
“That made me want to jump in and prove everyone wrong,” she said. “I wanted to prove that girls can do it, too.”
Now Stewart is two and a half years into an apprenticeship at Civmec Construction and Engineering in Henderson, Western Australia.
In that time she has gained a reputation for excelling in the field, and it’s getting her noticed beyond the factory floor.
Last year she swept up a finalist spot in the Woman in Building and Construction Industry Apprentice of the Year category at the 2023 Apprentice Employment Network Awards.
By her side at the awards was SkillHire apprentice and skills development coach, Terry Doyle.
“I take immense pride in Jasmine; she represents the future of our industry,” Doyle said.
Doyle and Stewart met when Stewart approached SkillHire, a recruitment and training agency part of the IntoWork Group. At the time, Stewart was considering an apprenticeship in panel beating or painting.
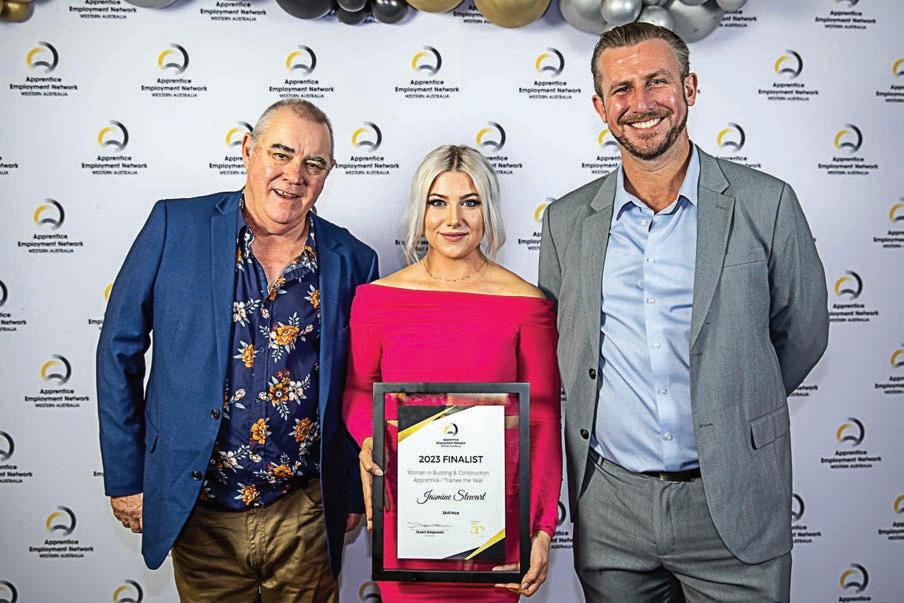
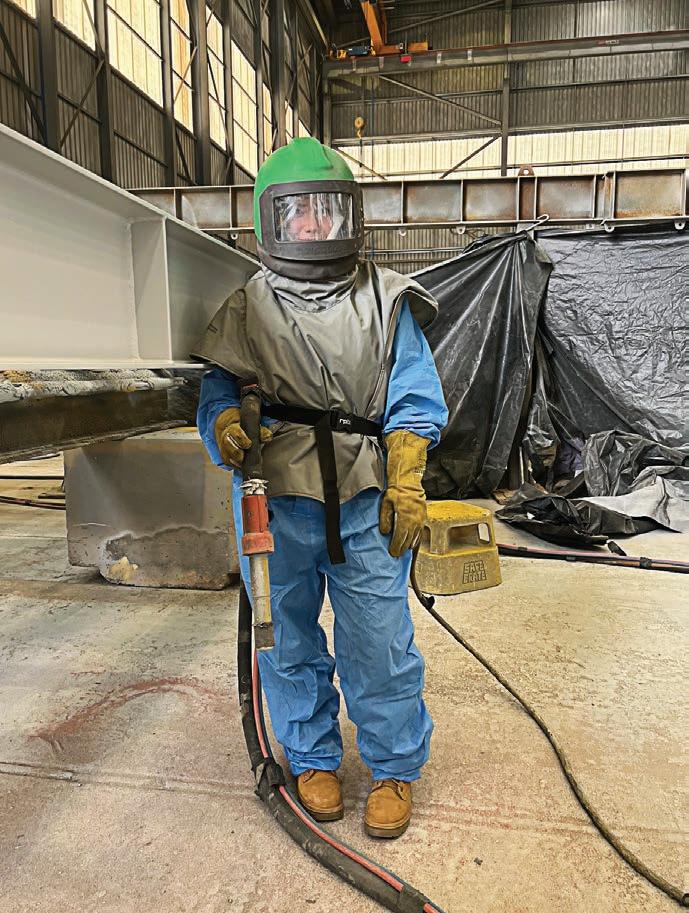
SkillHire suggested a spray painting and blasting apprenticeship
“I thought there would be more women influencing trades, especially by 2023,” Stewart said.
Stewart has taken on a mentor role for new female apprentices, offering guidance the way Doyle did for her when she first started.
“If I didn’t have the support that I had initially, I probably would have been scared off,” she said.
“Everyone at Civmec and Terry from SkillHire were there helping and making me feel comfortable and safe. It meant that I made it through those first
Stewart wants to see other women find the confidence to pursue a field they might not have considered before.
“In the trade there’s about four female spray painter and sandblasters in WA, including myself, she said. “There’s a lot
of women in the industry, but not many actually picking up this kind of trade.”
Stewart said starting at Civmec was a shock at first because the work was so physically demanding but she is glad she saw it through.
“Resilience is key,” she said. “Despite the physical shock to my body during the first two weeks, I didn’t want to give up.
“I think what holds a lot of females back is basically they’re told that they can’t or that they won’t be able to handle it. But you don’t really know that you’re capable until you do it.
“When you’re a little girl the first thing you’re handed is a Barbie doll or a toy kitchen to play with, whereas boys are given toolboxes and told to go play outside.”
Stewart said she was lucky that her farmer grandfather and plumber father encouraged her to take a hands-on approach to life.
“I already knew that I could physically do a lot of stuff and I wasn’t ever scared to,” Stewart said.
“But the reality is, male or female, it doesn’t matter. You either physically can or you physically cannot do the work.
And a lot of women would be surprised at what they can do.”
Stewart said she loves spray painting and blasting because she doesn’t have to compromise of being herself.
“On the job you can get dirty and work hard, but still go home and get to be pretty,” she said. “I like my pedicures and getting dressed up. I think a lot of women think you have to be one or the other. I love the balance this job brings.”
At Civmec, Stewart is at the forefront of construction and engineering services across the mining sector.
“We’ve worked with all the major mines blasting and painting huge structures for every step of the mining process,” Stewart said. “The scale of these operations is amazing; it’s really cool to see.”
Stewart encouraged women to take charge and pursue industrial painting and blasting if they’re thinking about it.
“There can be a stigma around
GENDER EQUALITY
Stewart and Doyle agree there needs to be more information out there around what’s involved in industrial apprenticeships so applicants can get a better idea of if it’s right for them.
“We get people applying from all ages and backgrounds and most of them have no idea what they’re getting themselves into,” Doyle said. “The people who make it through are most often the ones who have gone and gotten a certification at TAFE in the field, which gives them a taste of what the industry has to offer.
“That way when they come in, they’re more prepared for the demands of the job.”
TAFE schools offer qualifications for heavy-industry trades and are a great
ON THE JOB YOU CAN GET DIRTY AND WORK HARD, BUT STILL GO HOME AND GET TO BE PRETTY. I LIKE MY PEDICURES AND GETTING DRESSED UP. I THINK A LOT OF WOMEN THINK YOU HAVE TO BE
way for people to get a feel for what working in the industry will involve.
Mining is one of the fastest growing areas for trade education. The South and North Metropolitan TAFEs are some of the largest resources trainers in WA, offering a suite of skills in everything from fire assaying to mine management.
Doyle said the skills gained working in these heavy-industry trades sets apprentices up for more than just what’s on their certificate.
“These skills are completely transferable to anywhere in the
industry,” he said. “There’s a great future for females in this industry.
The support is there, and more and more operators are looking for female talent.”
For Stewart, that future is looking bright. She’s already had three job offers roll in before her apprenticeship has even finished.
“I’ve got a lot of opportunity,” she said. “Not just in my trade, but also if I wanted to branch off and do something completely different in my industry.
“The possibilities are endless.” AM
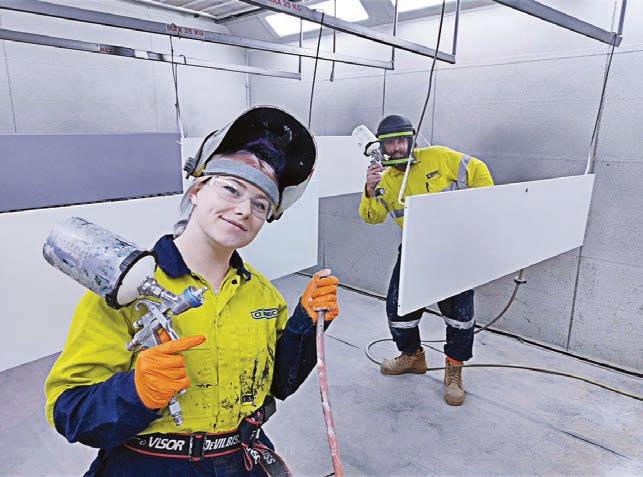
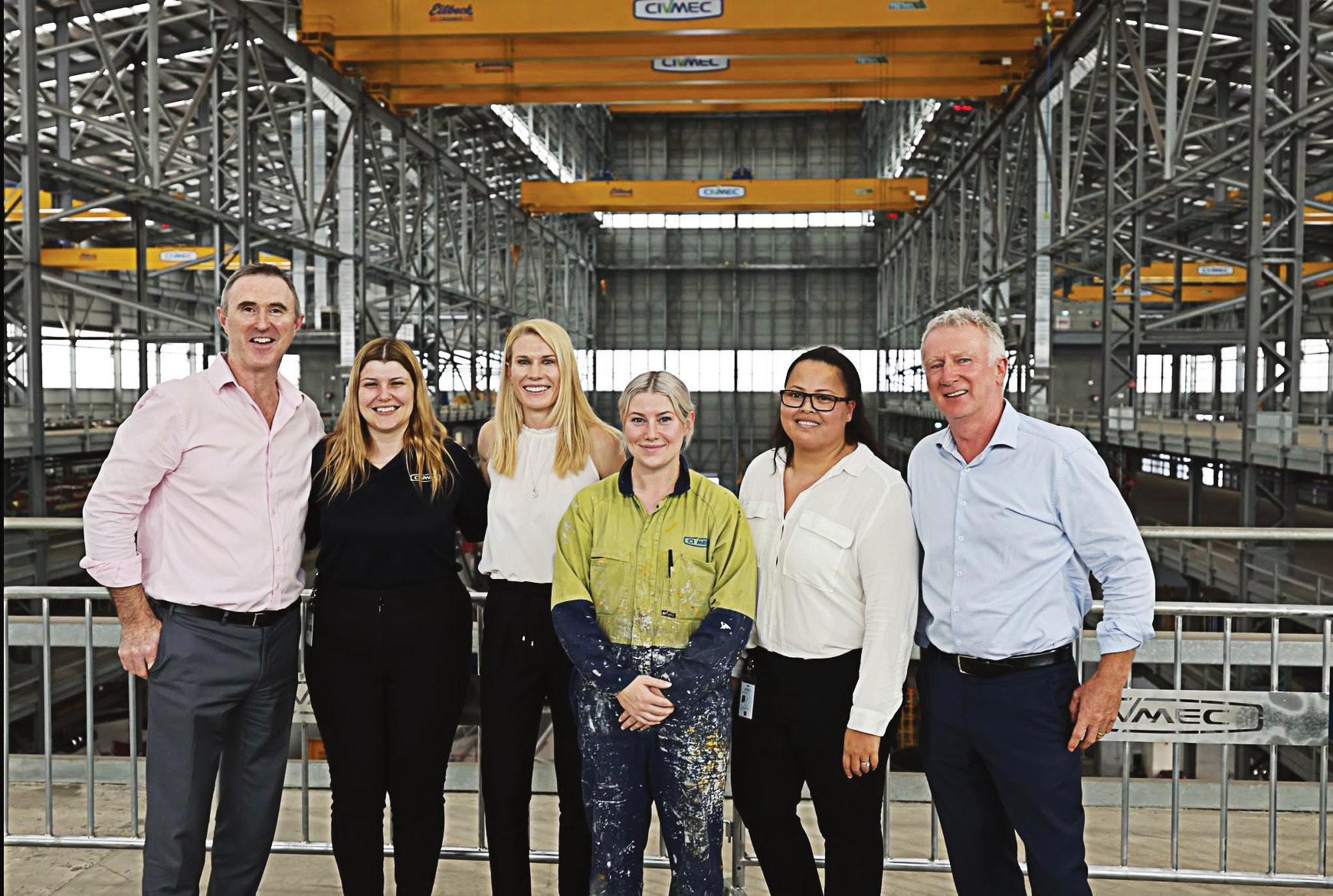
NEXT-GENERATION BROKK ROBOT
BROKK HAS LAUNCHED ITS SMARTPOWER+ GENERATION OF ROBOTS, TAKING THE VERSATILE MACHINE TO THE NEXT LEVEL.
When Brokk released its SmartPower+ range of remotely operated robots at World of Concrete 2024 in January, the Swedish heavy machinery manufacturer unveiled a suite of advancements that deliver enhanced endurance, operating experience, and intelligence.
The Brokk demolition robot’s versatility is well known, with the machine able to solve a number of mining problems through its range of attachments. The robot can, among other applications, shotcrete, drill, cut, split, and hammer oversize rocks, proving itself as a key asset in underground mines.
The SmartPower+ generation takes
“As someone who has operated Brokk robots for the last 13 years, the improvements to the control box again show Brokk’s core philosophy to improve the working conditions of operators in-field,” Brokk Australia sales manager Stefan Mace told Australian Mining
With safety a key concern on mine sites, visual status updates through incremental light indicators allow the operator to focus their attention on the demolition work at hand while simultaneously monitoring the status of the machine.
Brokk’s SmartPower+ generation is enabled for future over-the-air upgrades, so the machine can continually evolve as technologies advance.
Fast and simple settings, an increase in sensors, as well as the addition of
individual tool presets, all contribute towards a more user-friendly and efficient operator interface.
“We are thrilled to introduce Brokk SmartPower+ and a new generation of demolition robots that redefine the demolition landscape,” Krupicka said.
“This innovative advancement reflects Brokk’s dedication to pushing the limits and providing operators cutting-edge machines that surpass expectations.”
Mace said the intuitiveness of the SmartPower+ generation of robots will be a key asset to Australian mines.
“Being able to intuitively troubleshoot site challenges is going to be a huge benefit to our Australian mining customers due to the huge geographic footprint in this country,” he said.
“Not needing to travel to some of the Australia’s hardest-to-reach places, means less costs to mining companies and less downtime on-site.
“I am excited to see how Australian companies continue to use the Brokk demolition robot in non-production areas of their mine to improve safety and efficiency and minimise downtime.”
Brokk was already at the forefront of robotics, and with the SmartPower+ generation of demolition robots, the Swedish company has gone one better, delivering advancements tailored to the harsh and precise operating conditions of the Australian mining industry.
SmartPower+ will be available on the Brokk 70, 170, 200, 300 and 500 demolition robots in April, with other models to be upgraded later this year. AM

Australian mining industry.
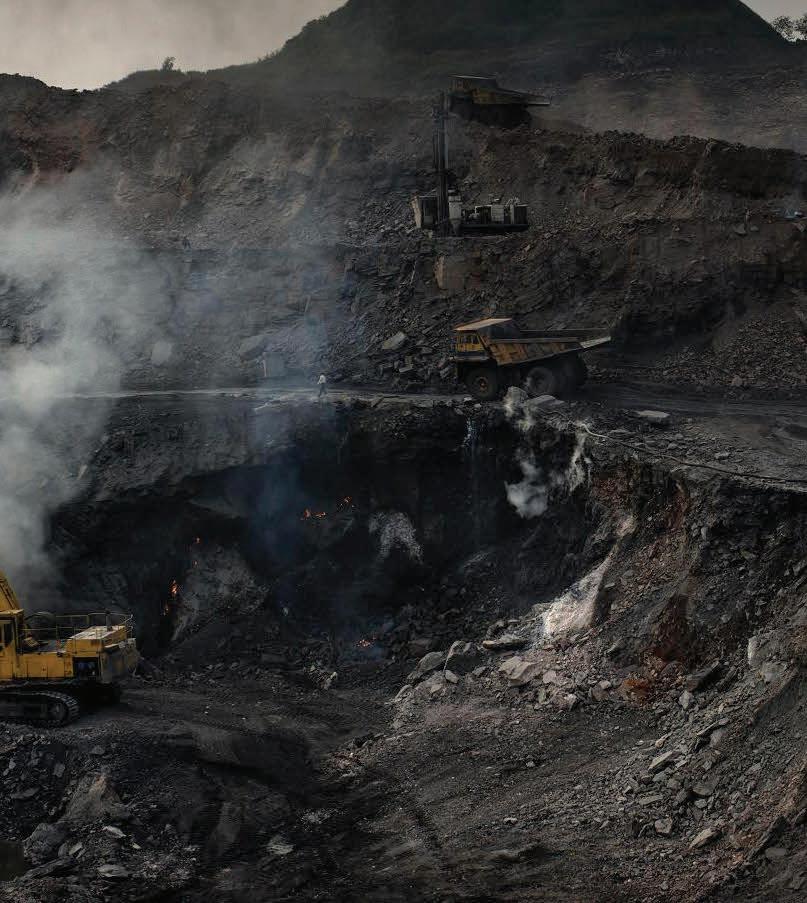
COMPLETE AIR & POWER SOLUTIONS
CAPS Australia has been supplying best-in-class air and power solutions to the mining sector for more than 44 years.
Specialising in end-to-end solutions, our in-house engineering allows us to design, supply and install bespoke, purpose-built systems to clients with specialised applications.
As an independent company with the flexibility to search globally for the best technology,
CAPS works alongside world-renowned partner brands like Ingersoll Rand, Mitsubishi, AIRMAN, and many more.
With ten branches nationwide and 24/7 service for maintenance and emergency breakdowns, CAPS Australia leads the industry in service and solutions.
AIR COMPRESSORS
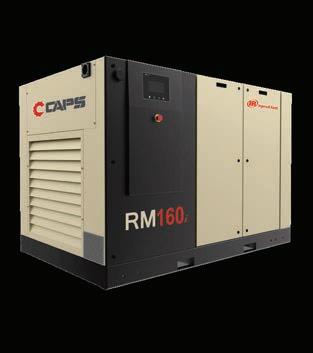
RENTAL SOLUTIONS
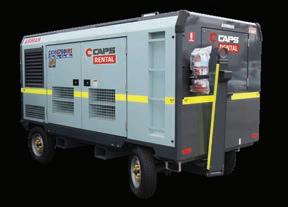
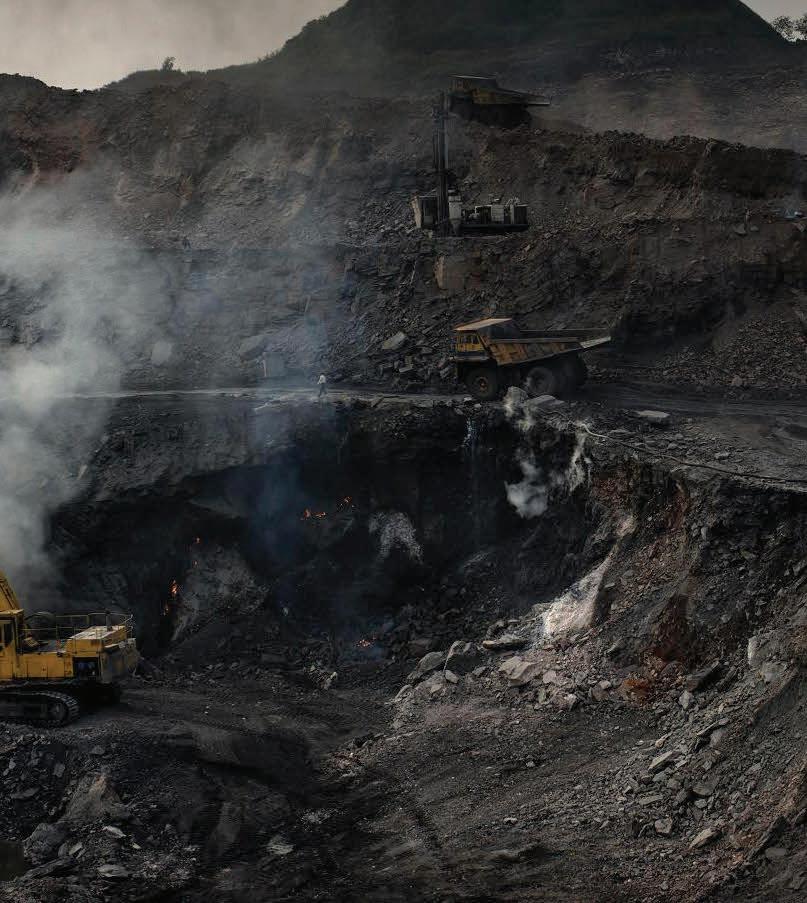
CUSTOM SKID PACKAGES
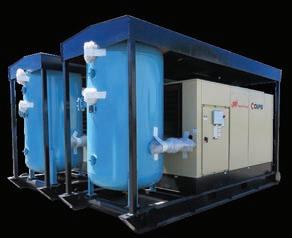
RENEWABLE ENERGY
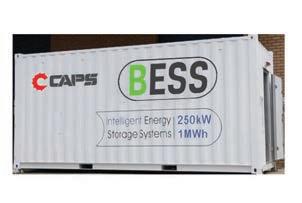

CALL 1800 800 878 OR VISIT CAPS.COM.AU
POWER GENERATORS
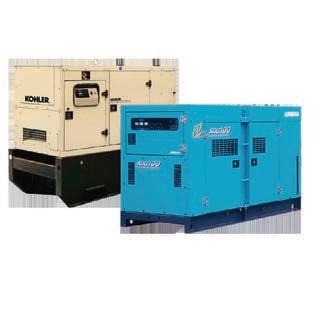
SERVICING & SPARE PARTS
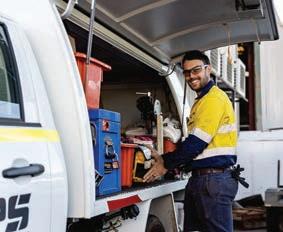
WATER MANAGEMENT
A MATCH MADE IN HEAVEN
XYLEM AND EVOQUA HAVE COMBINED TO CREATE AN ENLARGED WATER TECHNOLOGY COMPANY SET TO DELIVER SIGNIFICANT BENEFITS TO THE AUSTRALIAN RESOURCES INDUSTRY.
Last year saw Xylem acquire a leader in industrial water treatment solutions and services, bolstering the company’s offerings across the water cycle.
The addition of Evoqua Water Technologies expands Xylem’s technology platform, with new products and domain expertise capable of delivering end-to-end solutions that tackle the world’s most pressing water challenges.
In Australia and New Zealand alone, Xylem and Evoqua work in 13 locations and employ about 350 staff serving a variety of markets, including local councils, the industrial sector, the mining industry, agriculture, commercial business services, and residential communities.
solids you need to remove,” Amezquita told Australian Mining
“In those areas, we have filtration and disinfection technologies that play an important role, with these treatment offerings complementing Xylem’s renowned pumping infrastructure and technologies.
“If bore water is your starting point and you pump water from point A to point B, treatment processes are required in-between. Our technology and inhouse process experts in Australia can help in these areas.”
Some of Evoqua’s key technologies include its on-site hypochlorite generation systems (OSEC), which safely generates sodium hypochlorite on-demand, using only salt, water and power. The OSEC serves as a critical solution to many disinfection
Another established offering is Evoqua’s range of chlorine dioxide generation systems.
“Manufactured in Germany, Evoqua’s chlorine dioxide systems have been part of the company for a long time,” Evoqua business development manager – industrial Brett Creagh told Australian Mining
“These systems produce a strong oxidant for disinfection purposes. Mining companies can use chlorine dioxide to control algae growth, which can clog their systems and create costly process failures and downtime.
“Our VAF screen filtration systems – a range of automatic self-cleaning screen filters that support the removal of suspended solids from 10 to 1500 microns in size – eliminate the need for replaceable cartridge filters, while
“A coal mine would have a power station where steam is generated to produce electricity,” Creagh said. “That steam can’t come from dirty water as it will destroy the turbines. This is where ultrapure water plays an important role.”
It’s one thing, according to Creagh,

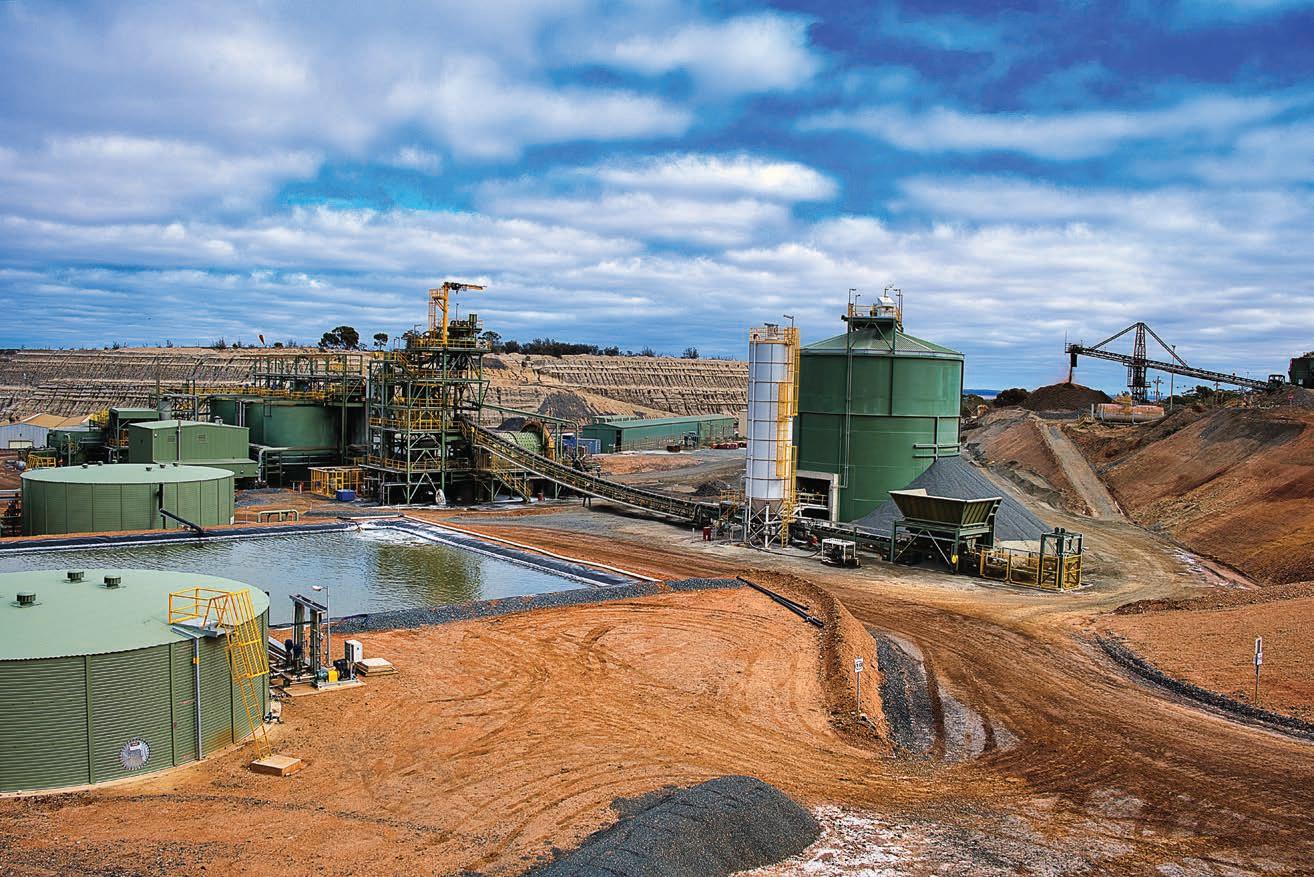
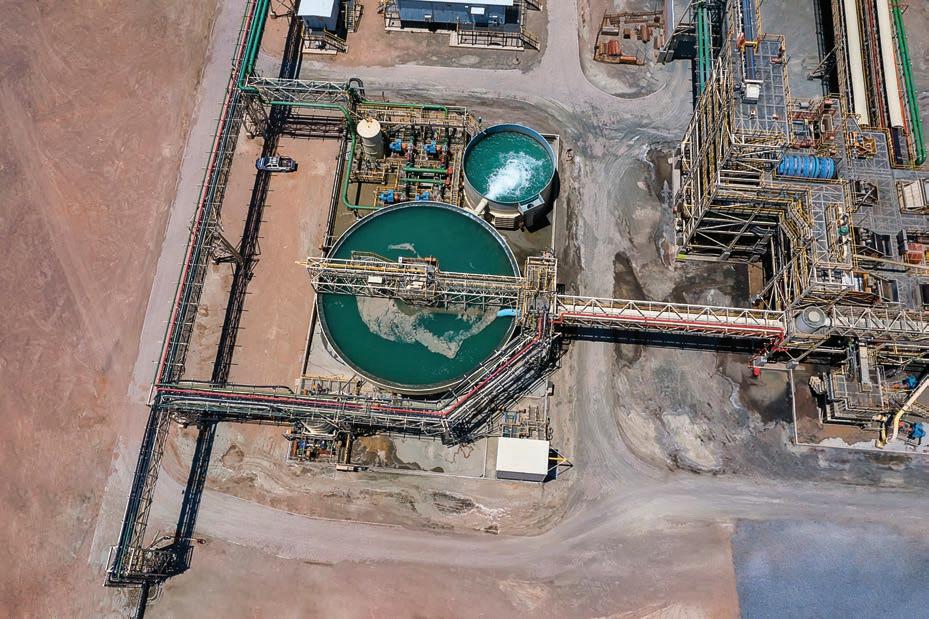
support water applications in the mining industry, but it’s another to provide them to a high level.
“ We don’t expect to run into many problems with our products, as we’ve been refining and evolving these offerings for decades,” he said.
“We have an application engineering team, a sales team and service technicians who have been with us for 20-plus years. This year we’ll be focused on visiting sites with our Xylem colleagues, talking to the mines and showcasing the Evoqua products.
“It’s just as important for us to promote our products as it is for us to understand the unique water challenges miners are currently facing, and with Xylem’s widespread presence and relationships in the Australian mining industry, we are hoping to reach new customers and mining regions.”
Creagh underlines the importance of having “boots on the ground”.
“Xylem has an office in Mount Isa (in the Gulf Country region of Queensland) that looks after that specific mining sector,” he said. “Evoqua can leverage not only a team of Xylem technicians who know Mount Isa intimately, but also tap into Xylem’s relationships and stakeholders in this region.
“This will help us build awareness, and once we have the ear of the end user, we will be able to display our solutions, show value and demonstrate the return on investment for the customer and start to see our exposure grow.”
Evoqua aims to have an immediate impact, with the company working towards one- and three-year goals to accompany its medium- and longterm aspirations in the Australian mining industry.
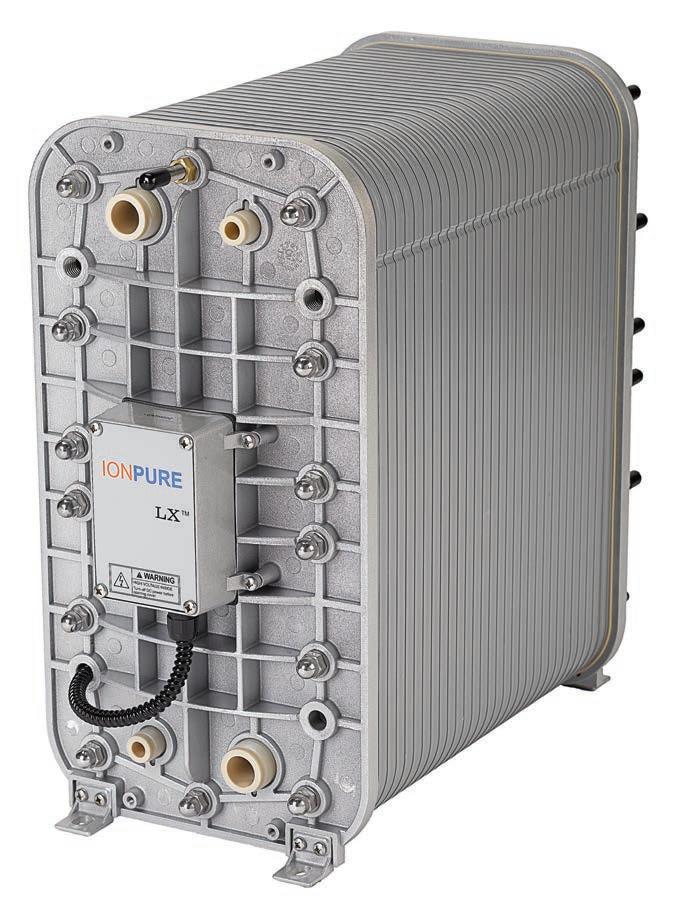
What starts with building awareness of Evoqua products and services has even greater potential once customers see the benefits of Xylem and Evoqua’s vertical integration, where the enlarged water technology company can not only deliver the pumping infrastructure critical to dewatering and other process applications, but also the treatment offerings that transport this water safely and cleanly.
“Being able to deliver an end-toend solution is something we see as a huge benefit for the end user,
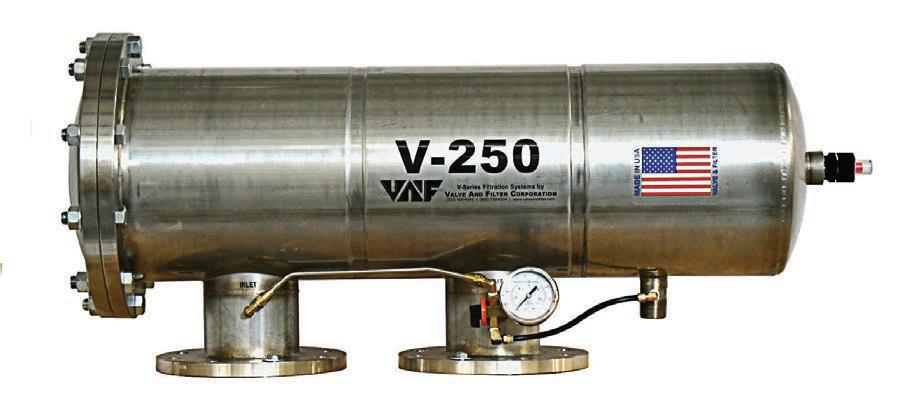
as they’ll be able to go through the different steps of the process with us,” Amezquita said.
“When we talk about disinfection, we have the electric chlorination system, but maybe the customer prefers to use chlorine gas as it might be a better fit for the process, the site, or the conditions of the customer.
“This is how I perceive an end-to-end solution. We ask the customer, ‘What’s your problem?’, and it might be water quality. Then we can not only consider the water quality of the filtration, but we can take a step back, have a look at the water source and complete a process review.”
Amezquita said process engineers could be deployed to site to review customer challenges and provide recommendations before a tailored solution is developed that harnesses the vertically integrated pumping and treatment portfolios of Evoqua and Xylem.
The partnership appears to be a match made in heaven, with Evoqua and Xylem not only able to leverage their unique ideas and offerings to support the continued evolution of global water management but also deliver solutions that can solve the mining industry’s most pressing water challenges. AM
RIGHT FIRST TIME
WHAT ‘RFT’ MEANS TO CUMMINS’ MASTER REBUILD CENTRES.
Not another acronym” may be the typical reaction to RFT, but for Cummins’ two master rebuild centres (MRCs) in Australia, it’s a key metric in proving the quality of remanufactured highhorsepower engines.
RFT stands for ‘right first time’ and, according to this metric, the MRCs in Brisbane and Perth set the global quality standard for Cummins rebuild centres.
“Last year, we remanufactured close to 350 engines at our MRCs in Brisbane and Perth and 100 per cent of those engines completed the dynamometer test without any issues,” Cummins Asia Pacific manufacturing leader David Wheatley told Australian Mining
“That was a massive achievement and a tribute to our operators, who take a lot of pride in their work.”
The two MRCs surpassed 2500 total rebuilds in 2023 after starting operations in 2008–09, and this year they are again ramping up production to meet increasing demand from mining customers.
“Reducing unscheduled downtime events for our high-horsepower engine customers is the driving force behind everything we do,” Wheatley said.
Quality engineers
The rebuild process is a 600-step procedure, covering everything from teardown to assembly.
The process adheres to the global Cummins manufacturing execution system, which provides specific electronic work instructions.
“Both of our MRCs have quality engineers who coordinate quality inspections at every phase of production – checking bolt tensioning, routing of wiring harnesses, and so on – to ensure the RFT metric is front of mind,” Wheatley said.
“Any issue that’s detected, however
Wheatley said the Australian MRCs achieve quality equal to, or better than, Cummins’ factory-built engines.
“Our remanufactured engines incorporate the latest and greatest product updates, so our customers are assured of receiving the best technology product available,” he said. “We also offer our high-horsepower-engine customers a much shorter lead time if they’re acquiring a remanufactured engine versus a new engine.”
A strategic support bank of remanufactured engines also allows Cummins to respond quickly to any unscheduled event requiring replacement
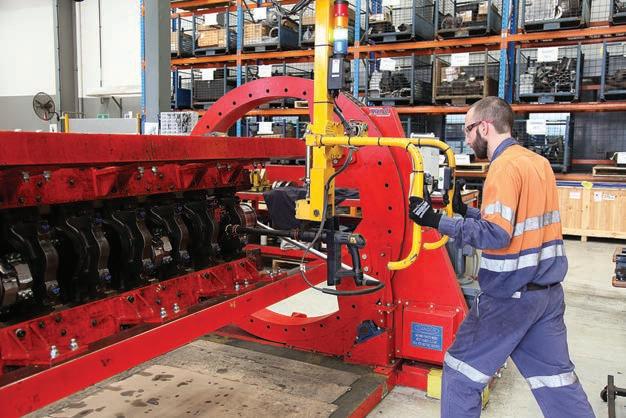
Major upgrade project
A key project currently underway at the Brisbane MRC – the first time it has been performed outside the US –involves upgrading of a fleet of 3500hp QSK78 engines with Cummins’ latest fuel system technology.
The upgrade sees Cummins’ earlygeneration high-pressure unit injection system on the 78L V18 powerhouse replaced with the high-pressure modular common rail system to achieve significantly reduced greenhouse gas and diesel particulate emissions.
The same fuel system upgrade has been carried out at both MRCs on the industry’s biggest selling mining engine, the QSK60, since 2015.
Capable of remanufacturing over 300 engines annually, the Brisbane MRC was upgraded in 2023 to incorporate four electric rollover stands, multiple production lines, numerous overhead cranes, and specialised lifting equipment.
Improved ergonomics for worker safety and ease-of-operation were an important part of the upgrades, while two new 4500hp dynamometers were also installed.
The same major upgrade program is now being undertaken at the Perth MRC.
With a proven metric for excellence under its belt, Cummins is setting a new standard for MRCs across the globe. AM
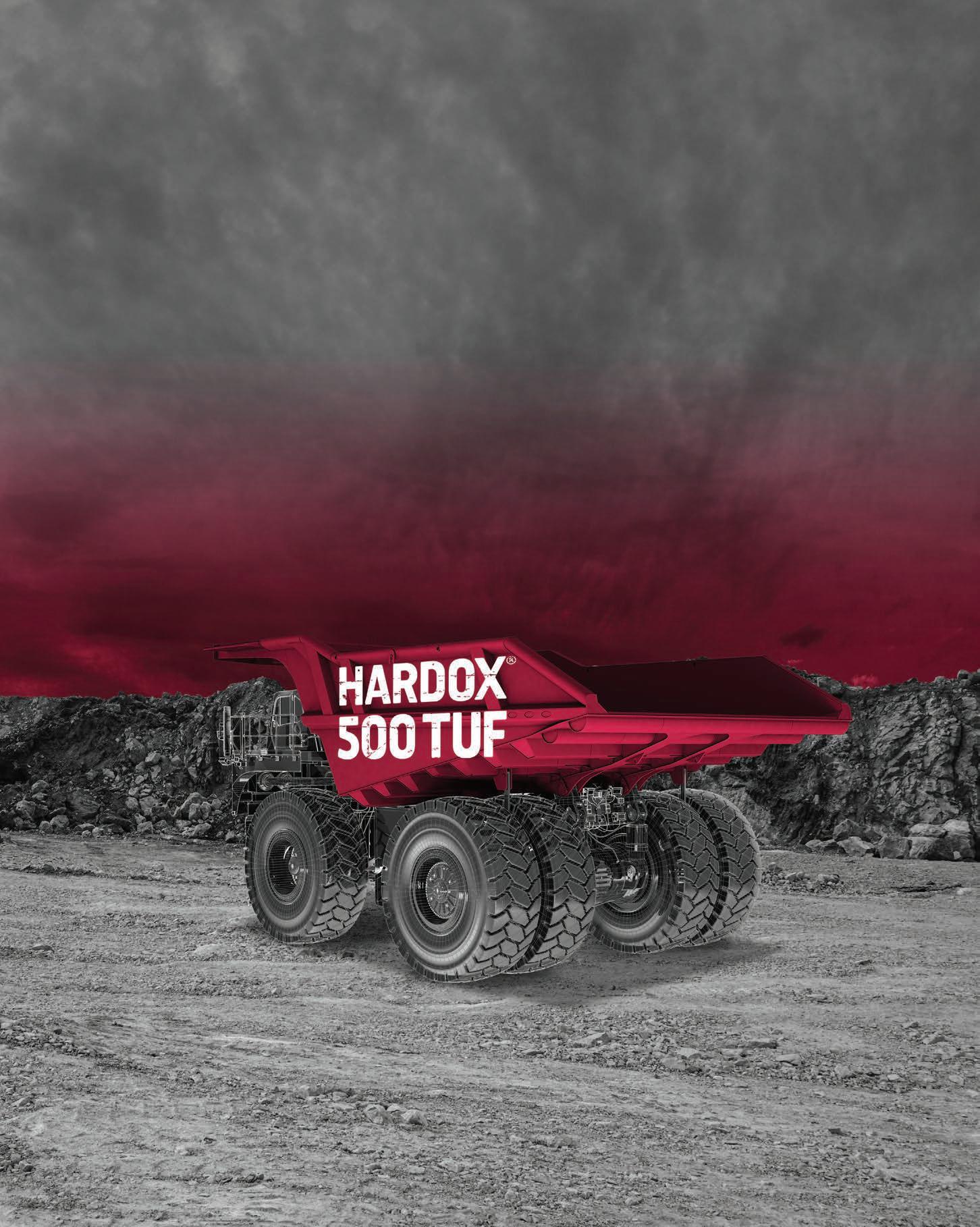
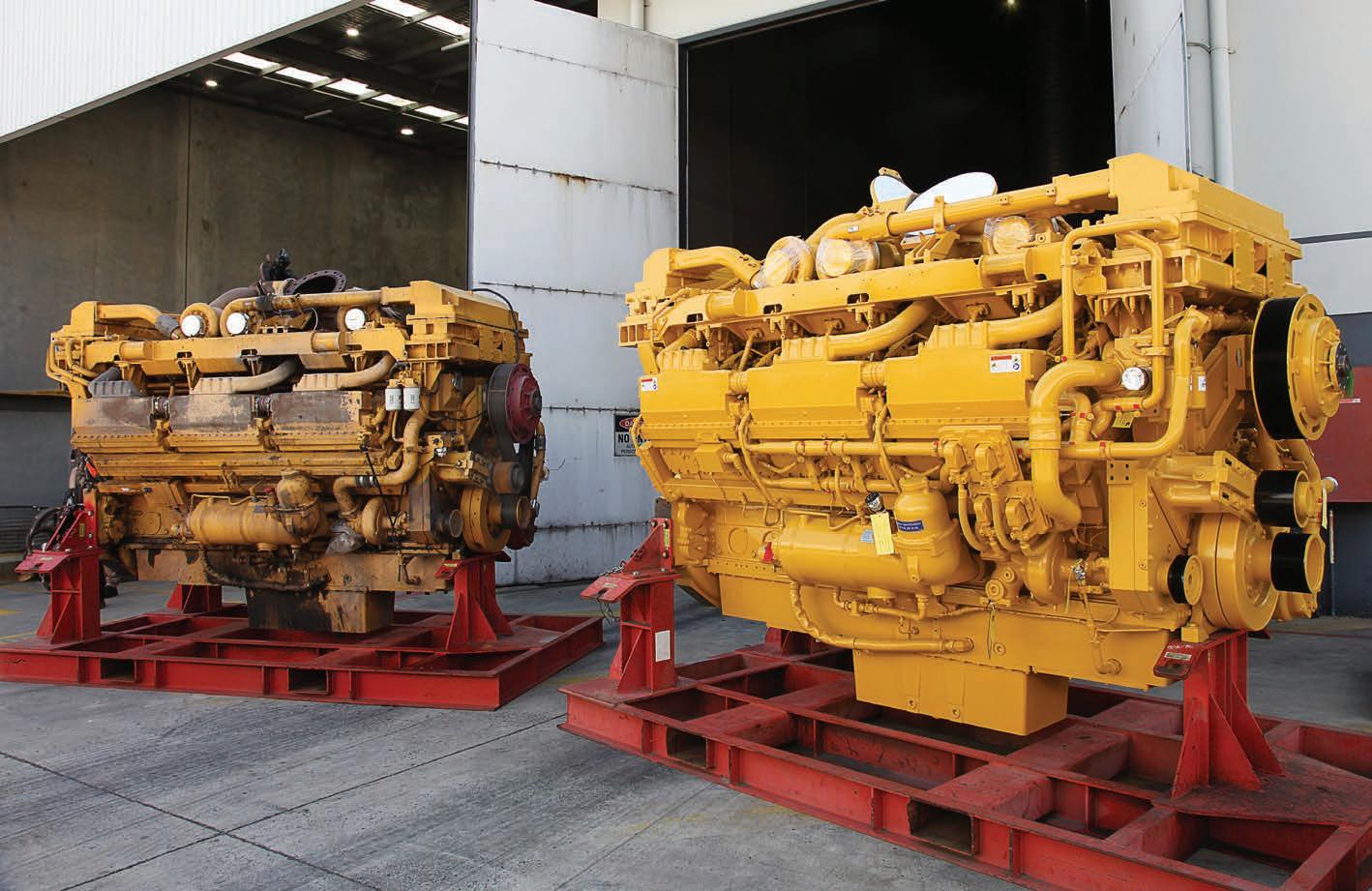
Hardox® 500 Tuf is the latest grade of Hardox® wear plate. It combines the hardness of Hardox® 500 with the toughness of Hardox® 450. The wear resistance of Hardox® 500 Tuf makes it possible to increase the load capacity by using a thinner plate and still have the same outstanding service life. Or stay with the same thickness and increase service life by 30% or more.
Hardox® 500 Tuf can also double as a structural steel. Its high yield strength and toughness allow for lighter mining bodies that are resistant to dents and can take impact loads with less supporting structures.
Get the full story of Hardox® 500 Tuf at www.hardox.com
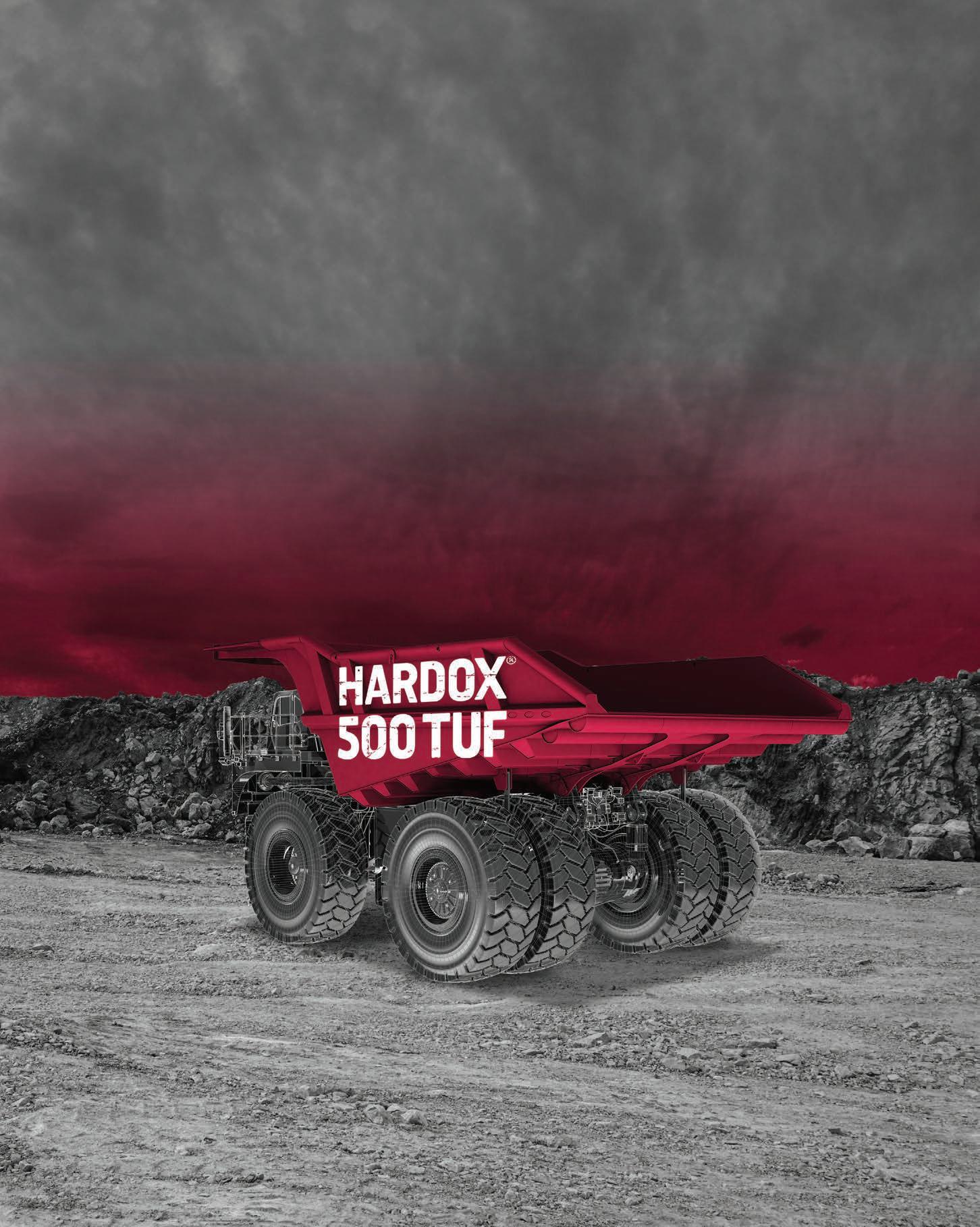
Contact SSAB
Brisbane. Melbourne. Perth
G1, 28 Balacalva Street
Woolloongabba, QLD 4102
australia@ssab.com hardox.com
LIGHTER MINING TRUCK BODY
HIGHER LOAD CAPACITY
EXTENDED SERVICE LIFE
LESS FUEL ON EMPTY RUNS
WEGSCAN: TECHNOLOGY DRIVES RESULTS
WEG HAS ADDED A NEW TECHNOLOGY TO ITS WIRELESS CONDITION-MONITORING SUITE.
WEG has introduced two wireless ‘smart’ sensors that can be used in conjunction with a smartphone interface or combined with a gateway that supports a complete monitoring and data analysis capability.
“It is well known that by monitoring the performance of your critical equipment through condition monitoring, it’s possible to detect early changes in equipment that provide you with enough time to take the necessary steps to avoid unexpected downtime,” WEG said.
“But what has changed significantly in recent times is the development of smaller, smarter, cheaper sensors and the inexpensive support systems that can provide more practical visibility to the number of machine data points with comparably little investment.”
WEG – which provides solutions for electric motors, variable frequency drives, soft starters, controls, panels, transformers and generators – outlines 10 factors necessary to ensure real outcomes for maintenance and reliability teams:
• Condition monitoring must be easy to install
• It must be easy to set up
• It must be robust and IP rated
• It must easily integrate with existing equipment
• It must be in line with site practices
• It should be suitable for use with a range of assets
• T he data must be secure and under your control
• T he collected information must be able to be dissected, allowing for the most basic monitoring to complex diagnostics
• Cost evaluations should clearly justify the outlay
• Benefits should be evident in safety, productivity and future planning
With these factors in mind, WEG is introducing an additional patented technology to its wireless conditionmonitoring suite to be used in conjunction with the WEGscan.
In a system where the sensors are already performing periodic measurements of vibration, temperature, power consumption, motor efficiency, bearing health and running hours, WEGsync technology combines the synchronous vibration measurement of multiple sensors for phase and structural deformation analysis of the asset.

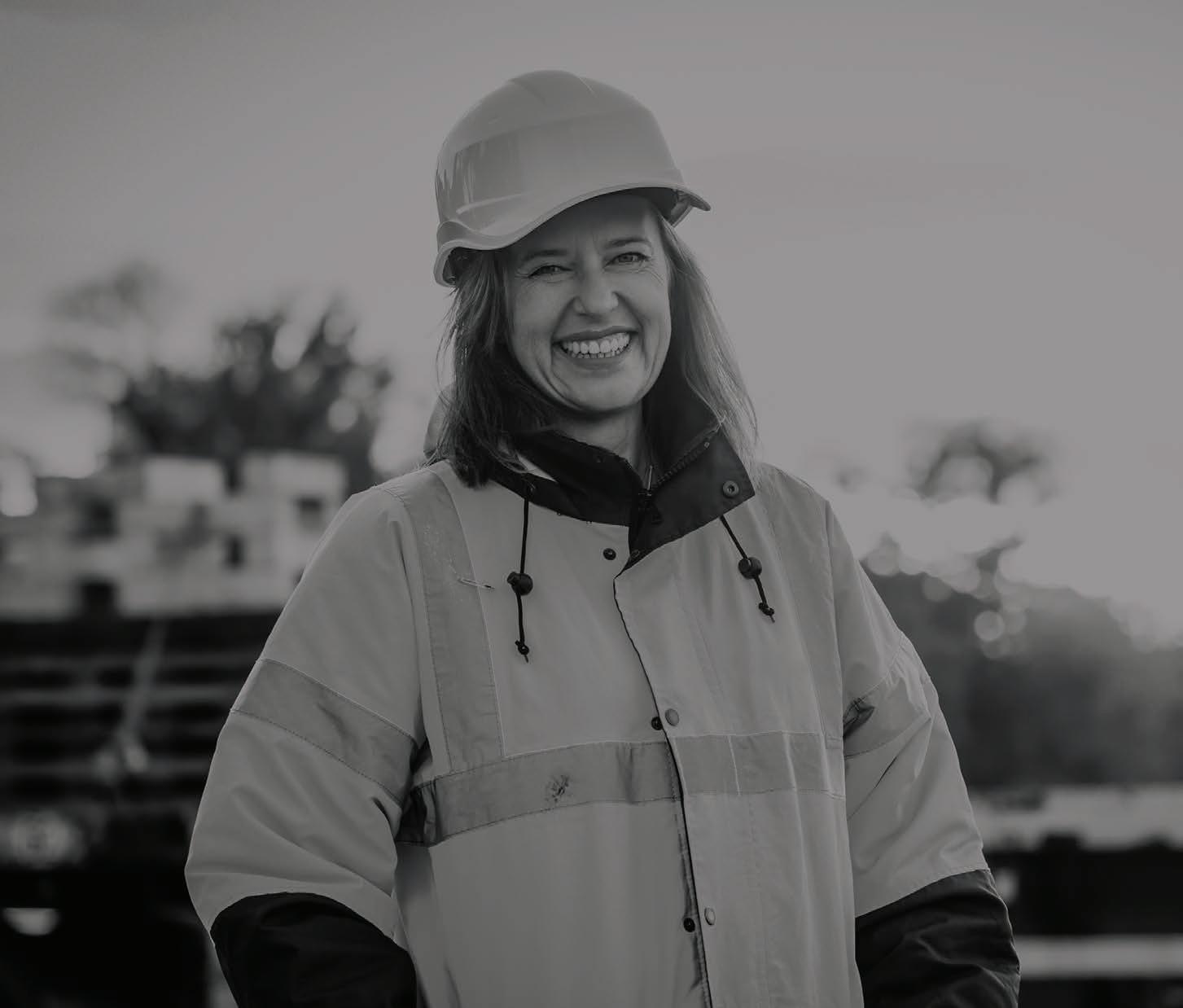


“Simply put, the data from multiple sensors is synchronised and analysed instantly at the moment of collection, allowing the specialist to concentrate on the immediate outcomes rather than the measurements themselves,” WEG said. “This saves time and the overall monitoring processes becomes less expensive.”
The sensors can be easily fitted to a variety of machines and fixed locations as required, becoming a
strategic resource for any maintenance or engineering team measuring temperature, vibration, functional hours or real-time operations, as well as for machine health trending or operational deflection shape (ODS) information.
In addition, the WEG motion fleet management platform offers access to modules such as ‘motor specialist’ and ‘exchange’, which provide access to advanced algorithms for more complex failure and energy consumption analysis
and for any data integration with the customer’s systems.
“Ultimately, plant productivity, efficiency, planning and profitability are the intended outcomes,” the company said. “And from the basics of alarms and data-viewing from your smartphone app, or analysis and datasharing through the WEG motion fleet management platform, WEGscan can be adapted to your site’s needs and practices.” AM
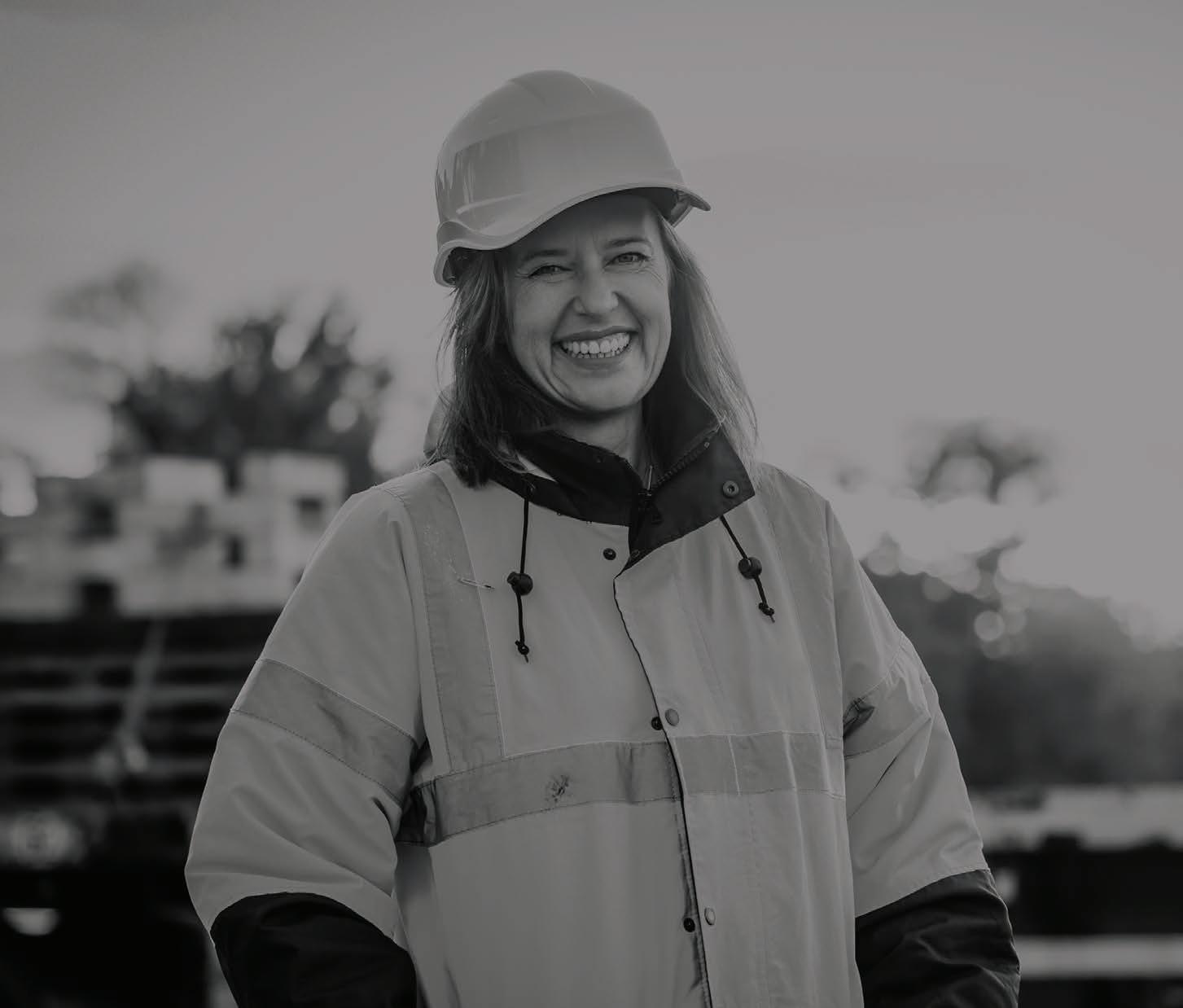

DO YOU KNOW A DRIVER OF CHANGE?
WOMEN IN INDUSTRY NOMINATIONS ARE NOW OPEN. Now is your chance to nominate an industry leader who you believe is advocating for positive change and deserves to be recognised.
PROUDLY PRESENTED BY MHD
Thurs 20 June, 2024
The Women in Industry Awards recognise outstanding women leaders from across Australia’s industrials sector.
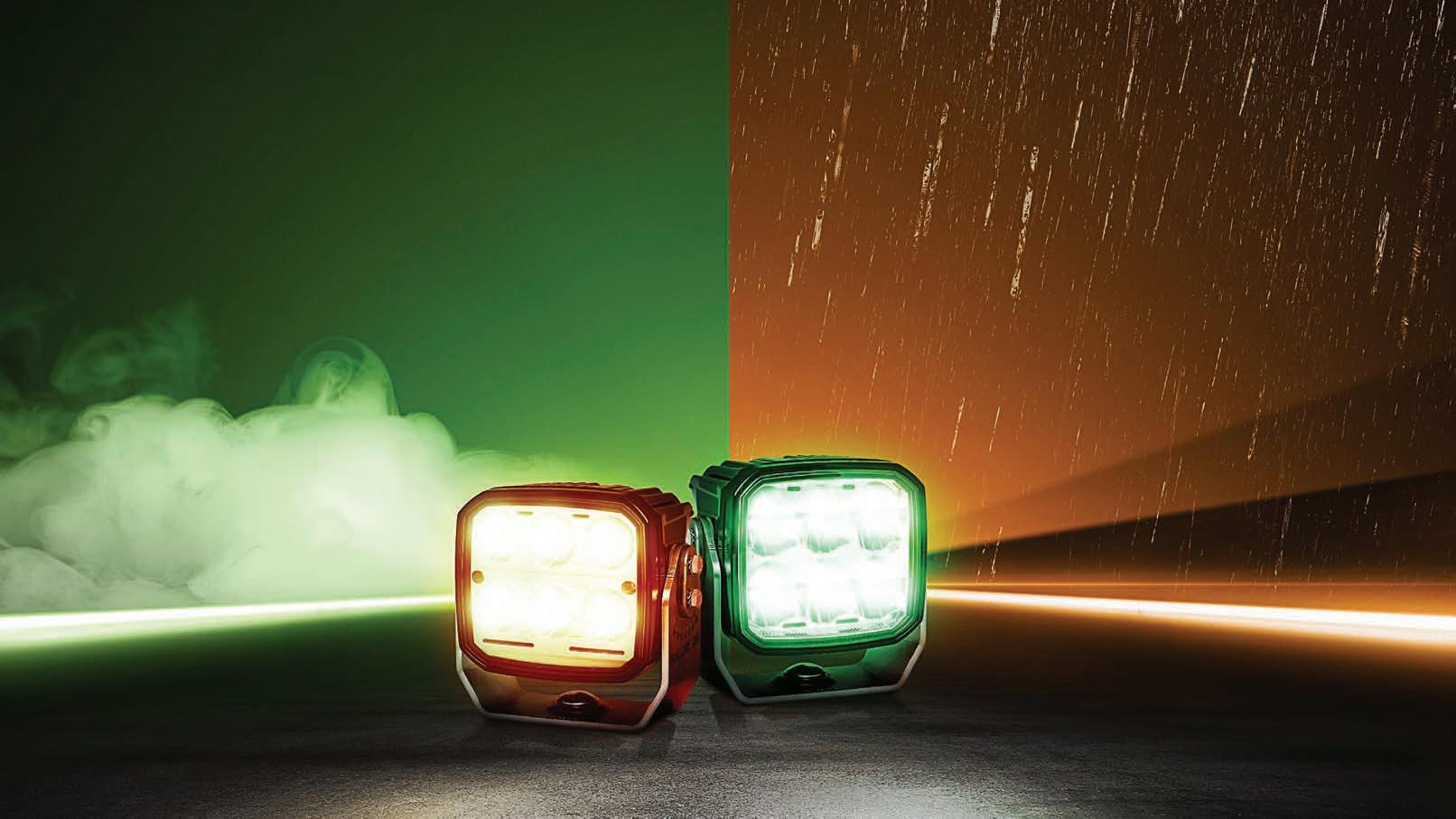
LIGHTING THE WAY WITH HELLA
ILLUMINATING MINING VEHICLES ON A DUSTY MINE IS NO WALK IN THE PARK. LUCKILY, HELLA IS HERE TO HELP.
Visibility is critical to the safety and operational success of a mine site. And although it seems simple in theory, effective illumination on mining vehicles is extremely challenging in a mining environment, where dust, round-the-clock operation, and tough conditions demand the best in quality.
The situation also demands a certain balance to be struck.
“Effective illumination doesn’t mean lighting up your mobile assets like Christmas lights. It’s about getting the most illumination for the minimum amount of wattage,” HELLA product manager Jigar Patel told Australian Mining.
Light colour, temperature, brightness and glare all also important factors that need to be considered.
With so much at stake, it’s best to leave it to the experts like those at HELLA, a supplier of lighting and electronics including premium-quality work lamps for the heavy industries.
The company’s newest product on the market, the RokLUME 280N SMART, is ideal for mobile assets in surface and underground mining.
The RokLUME 280N SMART has no shortage of intelligent features, but its most impressive one is that it can change lighting colour based on its environment in order to maximise visibility.
“Mine sites operate in a range of weather conditions like dust, rain and fog. Depending on those weather conditions, visibility can be compromised,” Patel said.
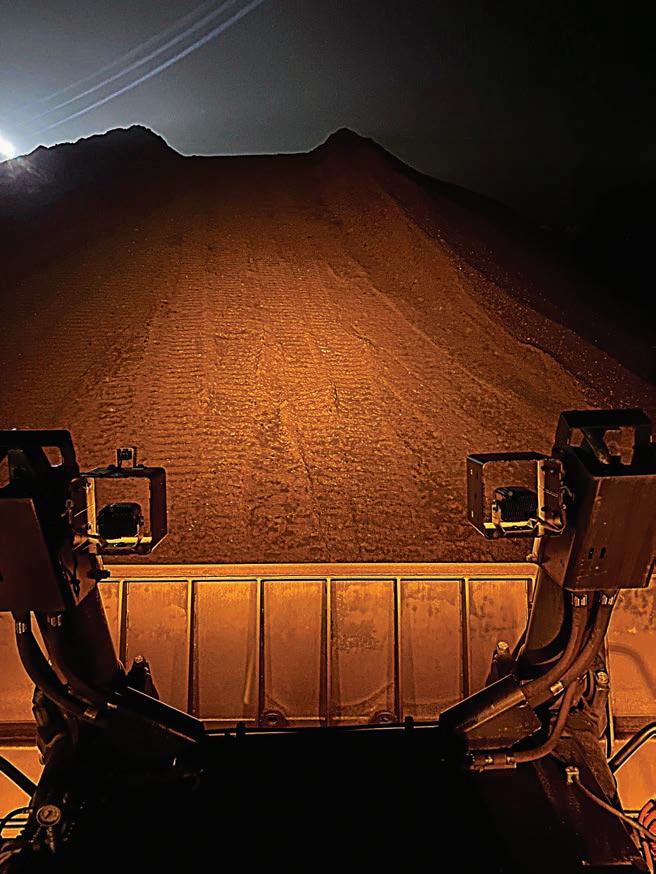
“In some harsh conditions, white light can become problematic because it is reflected more. This can make it very difficult for the operator of a mobile asset to see what they are doing, and also creates glare, which can cause eye strain and fatigue.
“Amber and green light can penetrate those harsh conditions, significantly improving visibility for an operator.”
RokLUME 280N SMART comes in three lighting variants: white to green, white to amber, and white only.
Green and amber lighting are better suited to dust, snow and fog than standard white light.
In practice, green or amber lighting will kick in in low visibility environments such as a dusty underground mine or during a morning fog. Beyond environmental conditions, the RokLUME 280N SMART can also improve many aspects of a mining operation.
The product, Patel said, has been particularly popular on excavators and haul trucks, which generate a lot of dust during operation. The special lighting penetrates the dust as the excavator loads the haul truck, allowing operators to work more efficiently.
On the safety side, the RokLUME 280N SMART makes mobile assets more visible to workers and other vehicles, reducing the risk of a collision.
And by reducing glare with green or amber light, eye strain – a significant cause of fatigue – is reduced for workers.
The lamp, which pumps out up to 3500 lumens, can also change colour temperature between cold and warm lighting. And the dimming function means the brightness level
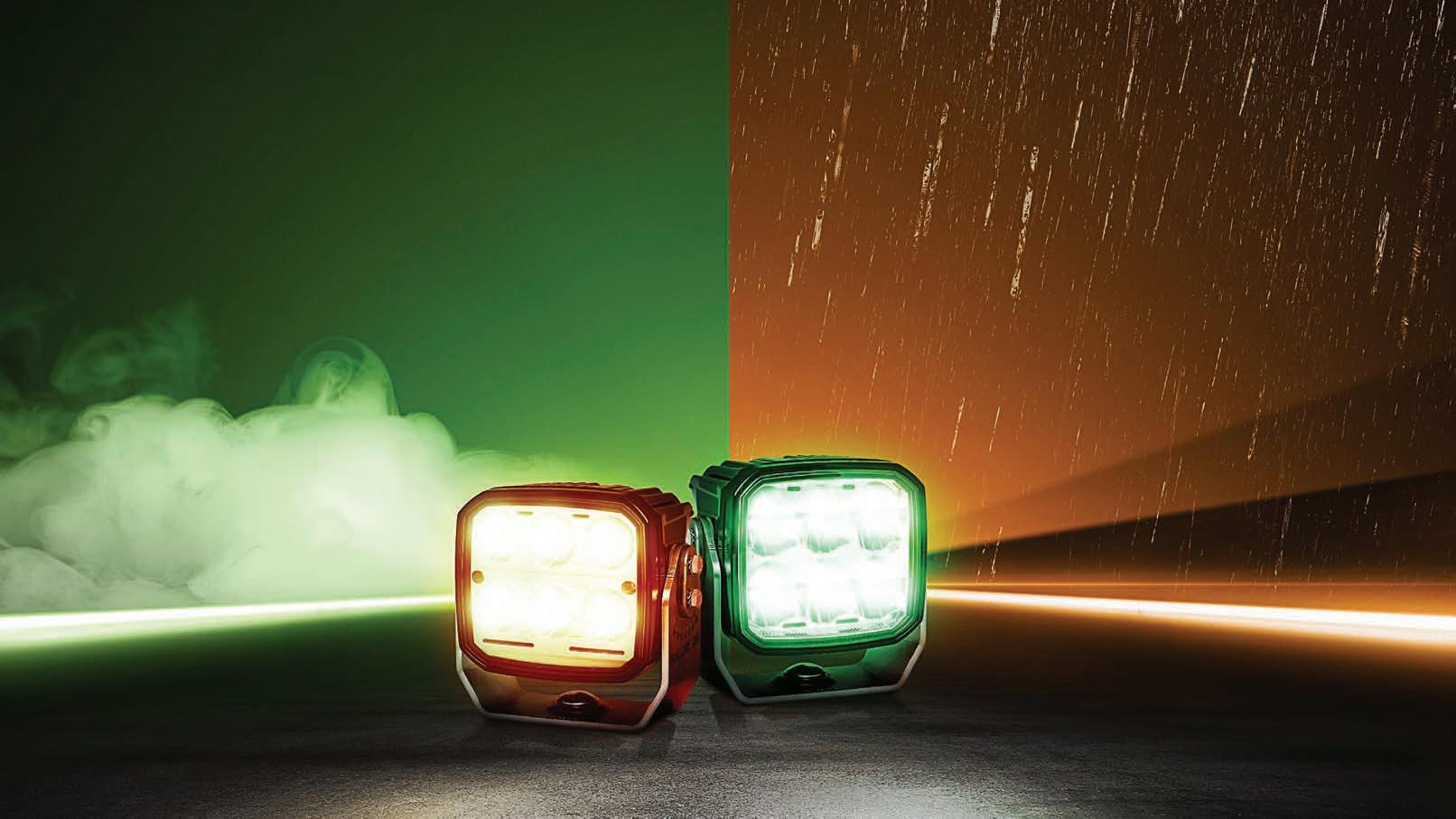
can be adjusted to the current lighting conditions, which reduces power consumption and carbon emissions.
These features can be adjusted with ease inside the vehicle using either the HELLA control panel or the machine’s native dashboard, depending on how the RokLUME 280N SMART is installed. Settings can be saved using the system’s memory function.
Installation is incredibly low impact. The control unit sends signals to the lamps via existing cables, meaning the machine’s original wiring is preserved.
Thanks to its intelligent design, RokLUME 280N SMART also generates zero-glare. A horizontal cutoff directs the light onto the ground in front of an oncoming vehicle, ensuring
Beyond a range of premium design features, the RokLUME 280N SMART is built tough for demanding mine conditions. The lamp and gateway feature ingress protection (IP) ratings IP6K8 and IP6K9K, meaning dust and liquids cannot get in, which helps with both cleaning and longevity.
Though protected on the inside
control panel also comes with a robust IP6K7 rating.
And the lamps have a work range of -40°C to 90°C, meaning they can tackle even the hottest days Australia can offer.
With its portfolio of premium quality lighting products like the RokLUME 280N SMART, HELLA is helping its mining customers shine no matter

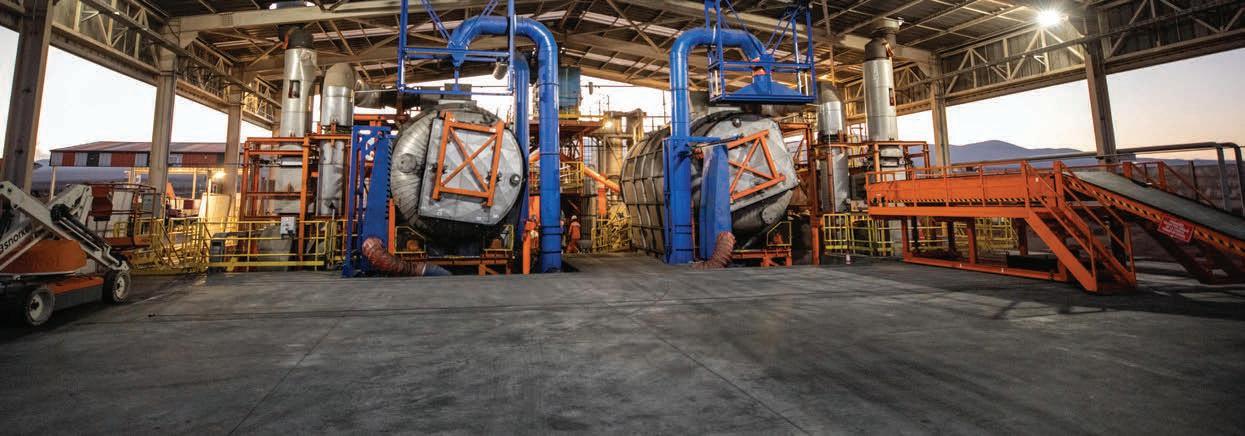
Innovative tools and offerings answer critical tyre management demands by providing solutions that improve safety, reduce downtime and advance sustainability.
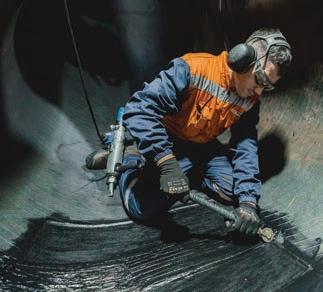
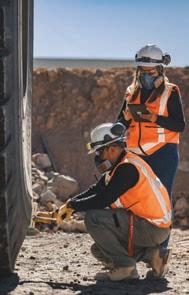
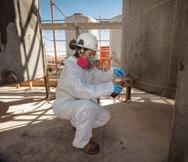




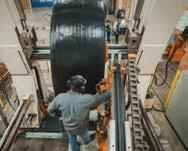
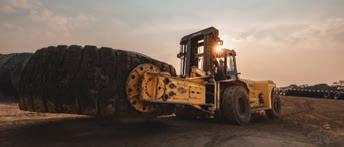
STAYING BUNDAWARE
DECODA’S LATEST TECHNOLOGY SOLUTION IS RAISING THE BAR FOR MINE SAFETY AND PRODUCTIVITY.
When you’re dealing with a high-pressure environment like a mine site, vigilance and a proactive approach to safety is paramount to reducing incidents.
But with sites often spanning hundreds of kilometres, it’s next to impossible to station someone at all points of a mine at all times. That’s where technology comes into play.
“When it comes to safety on-site, the biggest value item is being as proactive as possible,” Decoda analytics and technology manager Kurt Pidgeon told Australian Mining.
This mindset led Decoda to develop BundAware, a tool to help sites prevent accidents from an unstable or belowregulation bund wall.
Bunds are used on mines as places into which operators dump their waste ore. These large pits have walls of impervious material around them to form the perimeter, and must meet specific height requirements in accordance with recognised regulatory standards.
Reversing trucks into bund walls that are either too low, damaged, or at an
incorrect angle poses a grave risk, with the potential for significant injuries or even fatalities due to the elevated danger of encountering a substantial drop-off beyond safety bunds.
Using remote-sensing light detection and ranging (LiDAR) technology, as the operator reverses, BundAware scans the height and width of the bund, as well as the angle at which the truck is coming in.
“BundAware scans the area behind the truck to alert operators that something isn’t right,” Decoda lead systems engineer Morgan Chen told Australian Mining
“It then creates a 3D model that can be seen by operators and supervisors so they can follow up and either repair the bund or provide more training to the operator who might have come at the wall too fast or at the wrong angle.”
According to Pidgeon, training the operators not only makes an operation safer but also more efficient.
“It means you can have those one-onone conversations with the people that are making the mistakes and coach them through it,” he said.
“You can also have more constructive conversations because you have the video
of what went wrong and actually show them physically how to correct that for next time.”
While safety was Decoda’s number-one goal in developing BundAware, mines that implement the technology have the added benefit of remaining compliant.
“Certain legislation sets out the minimum height and width for a bund wall, and it varies state by state,” Pidgeon said.
“If you have an incident and the bund wall is found to not be within compliance, a site can get shut down until it’s rectified.
“The loss of productivity can sometimes be more costly than the fines that might occur.”
Decoda presented BundAware to an impressed audience at the International Mining and Resources Conference and Exhibition (IMARC) in November 2023.
“We had a lot of people come through and tell us that they had had bund wall issues but they weren’t able to find many businesses that were looking to a solution,” Pidgeon said.
“We could see how beneficial it would be to put the control back in the hands of
the operators and empower them to stop and readjust as needed.”
By measuring the speed and angle of the truck as it approaches the bund wall, BundAware helps to ensure mistakes are corrected before an incident occurs.
“There have been instances where a bund wall was used as a break, and in instances like that it’s good to have the data stored to go back to,” Chen said.
“The supervisor can match the data up with their fleet management data to figure out which driver was in control at the time and then they can educate that operator directly.”
Decoda is currently testing BundAware at some of its clients’ sites, and the feedback has been nothing but positive.
“Our clients usually don’t have visibility on what happens at a bund wall in the middle of the night or in really remote areas of their sites,” Pidgeon said.
“So to give them that visibility has been a game-changer, and we’ll continue to use their feedback in our path ahead with BundAware.
“We follow the voice of our customers when it comes to developing the right solutions for their sites.” AM
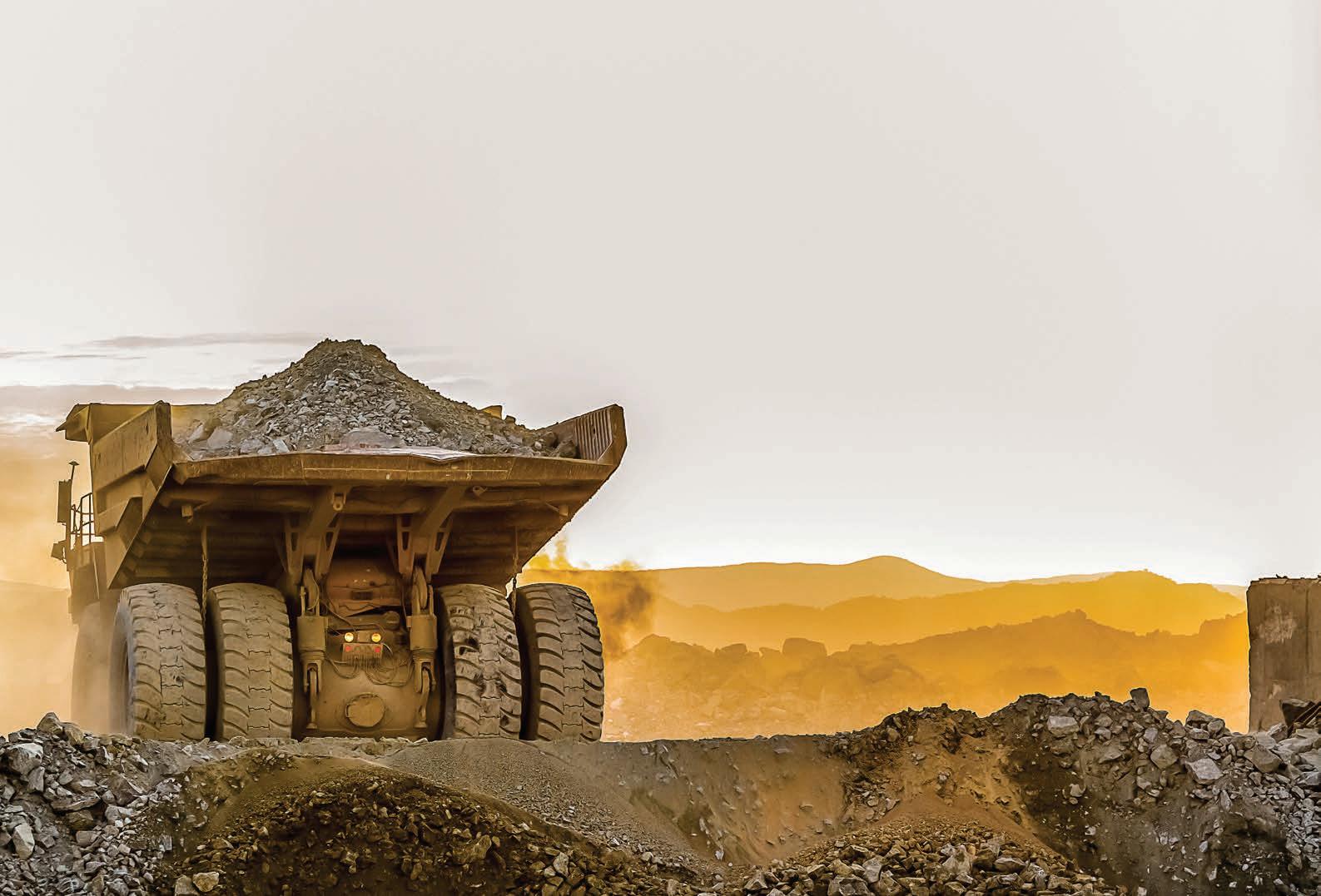
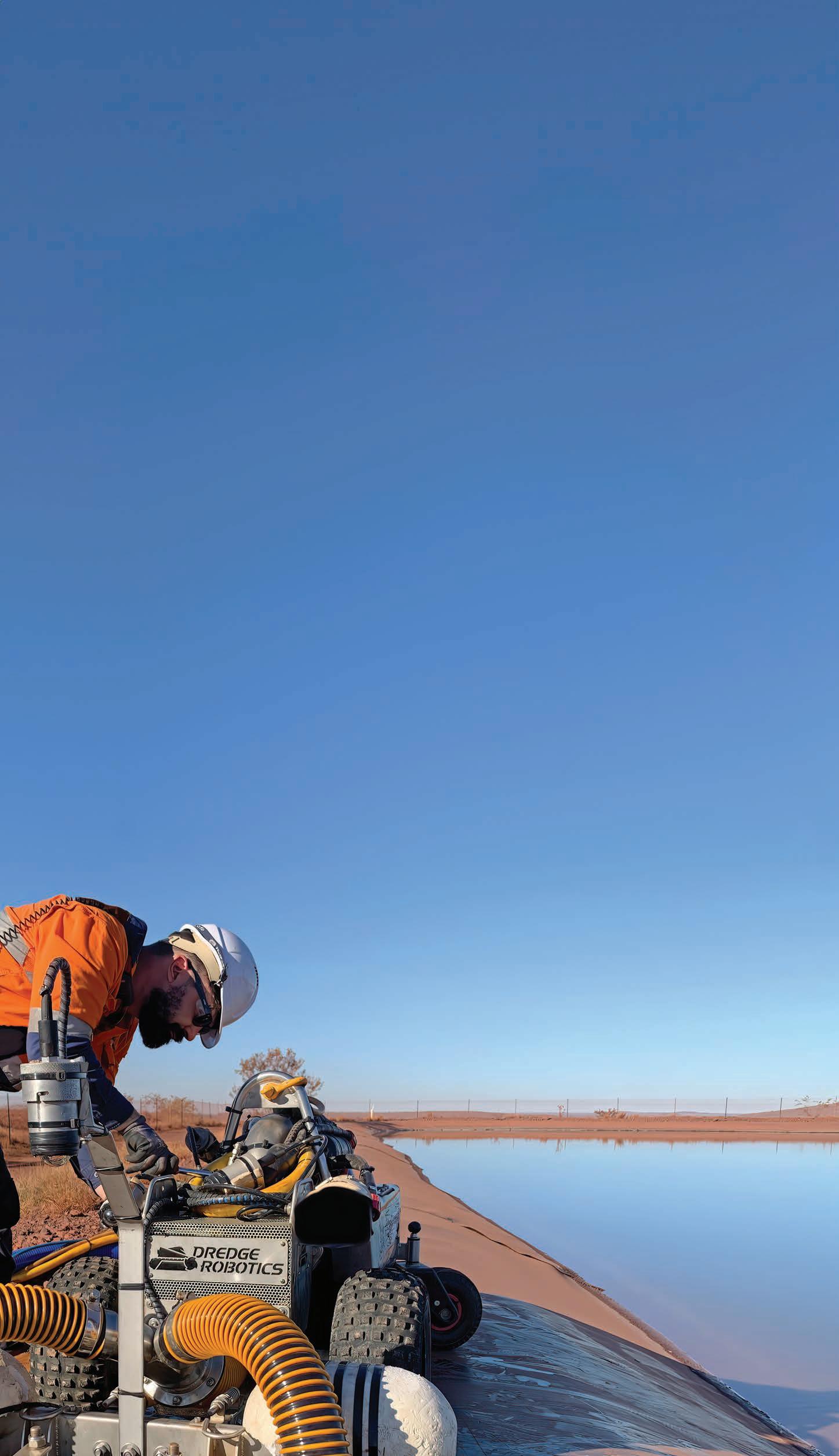
SAFELY DREDGE LINED PONDS
At Dredge Robotics we understand that downtime is costly. That’s why we’ve designed a fleet of globally unique dredging robots that can rapidly and thoroughly clean and inspect water assets while they remain in full service.
Designed and built in Australia for the harshest of conditions, our proprietary robotic dredging technology is a genuine game-changer for the mining sector.
Eliminating the need for human entry, these machines allow maintenance tasks to be performed outside of shutdown windows, delivering significant savings and reducing asset downtime.
Extensively proven in the mining industry, our capabilities include:
• Safe removal of mud, weeds and aquatic plants from lined ponds.
• Operation in corrosive and extreme pH environments (pH 1 to pH 14).
• Removal of deep compacted mud from process tanks, cooling towers and tailings dams.
If you’re looking for a smarter way to manage your water assets, contact the friendly team at Dredge Robotics today.
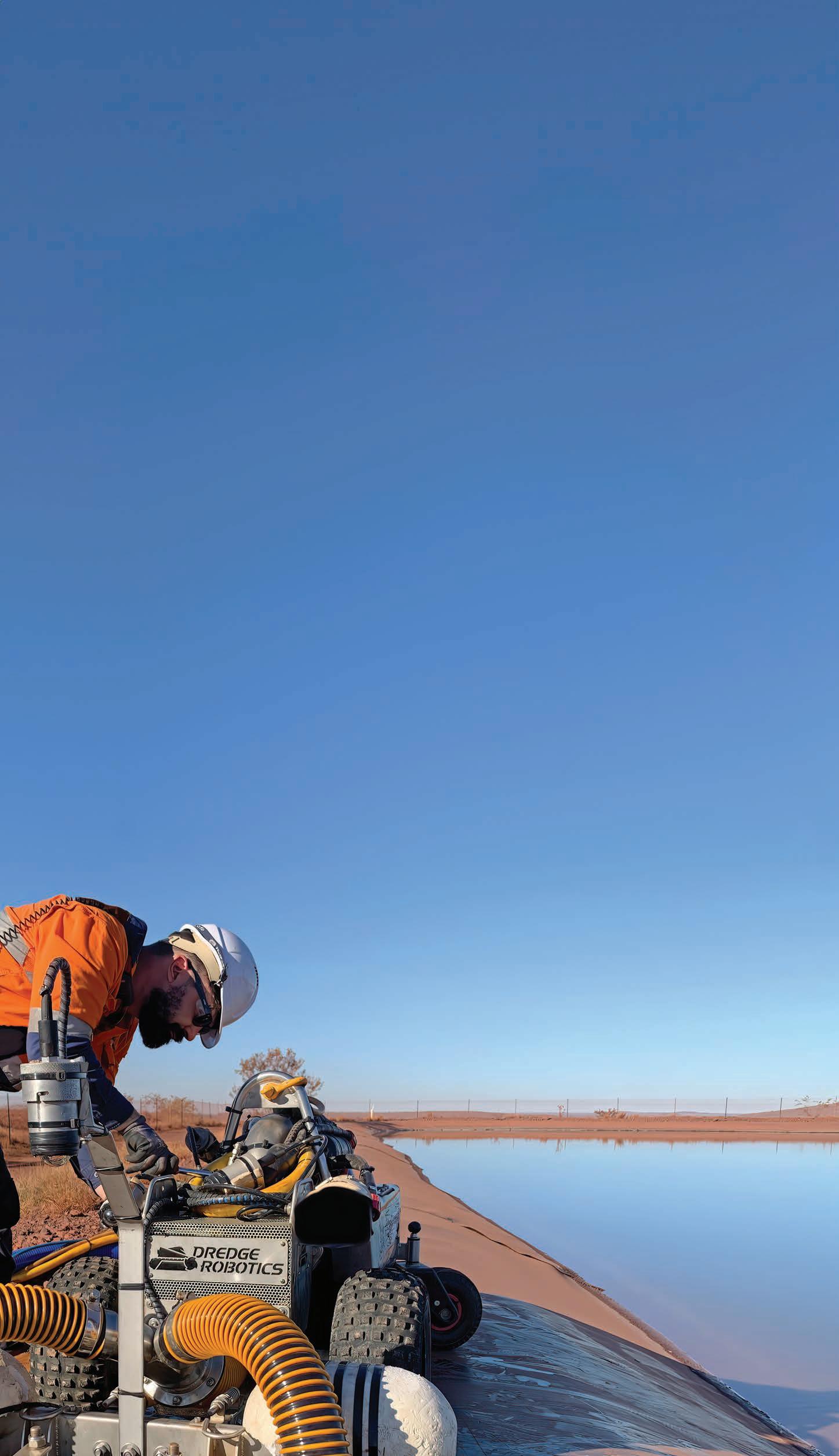
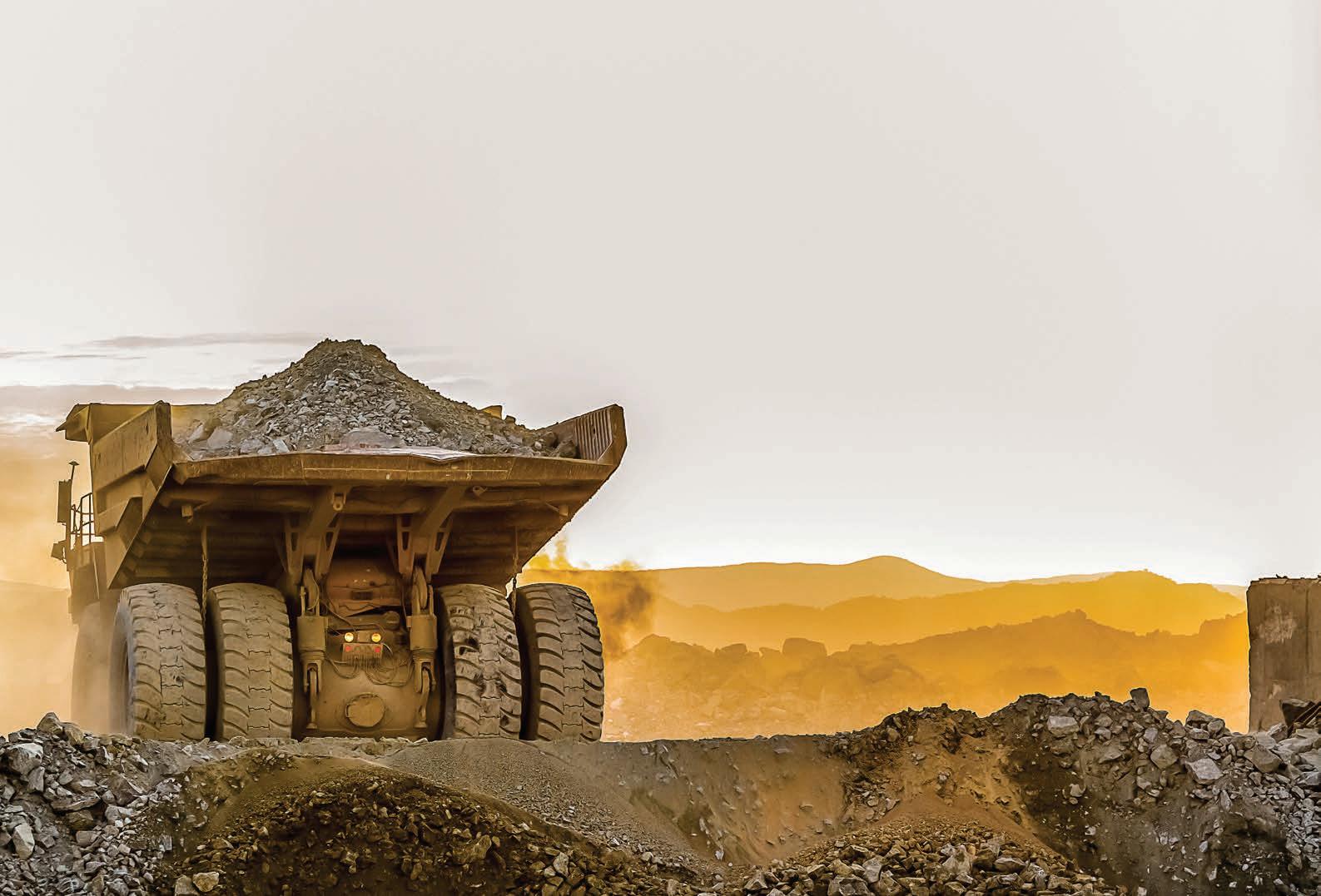
BANKING ON BOLTING
CAPS AUSTRALIA IS BRINGING THE MINING INDUSTRY’S BOLTING WOES TO HEEL WITH THE QX TORQUE MULTIPLIER.
Millions of little bolts hold Australia’s mining sector together. From the largest dump truck to the longest conveyor belt, bolted joints keep equipment running as it pulls off mining feats measured in millions of tonnes.
This means bolted joints need to be tough. But with so many bolts holding equipment together, maintenance practices can become complacent, jeopardising the integrity of the connection and the overall machine.
Mine operators are faced with the challenge of quick and accurate bolt fastening for torque-critical joints on a daily basis. These joints can be found across a site, from excavators, dump trucks, earthmovers and wheel
loaders to conveyors, tunnel-boring machines, infrastructure, pipework and upstream equipment.
It goes without saying that in a heavy-duty, high-risk environment such as a mine site, accuracy of torque applied is critical. Without a solid method for joint reliability, operators risk costly breakdowns.
CAPS offers greater accuracy, safety and accountability in bolting joint solutions with Ingersoll Rand’s range of QX torque multipliers.
Established in 1980, CAPS boasts more than 44 years of experience in compressed air and power generation. With 10 branches around Australia and 24–7 service for maintenance
Through its considerable experience, CAPS saw the potential the QX torque multiplier had to offer the Australian mining industry.
Specifically designed to replace less accurate manual fastening methods with a traceable process, OX torque multipliers aim to be a quicker and more effective alternative.
Bolt fastening has typically been a costly, labour-intensive exercise.
Technicians often use impact wrenches that can over-torque joints, and have to use two-person hydraulic wrenches that are externally powered and bulky, or air and corded electric nutrunners that change torque via a time-consuming bench torque tester.
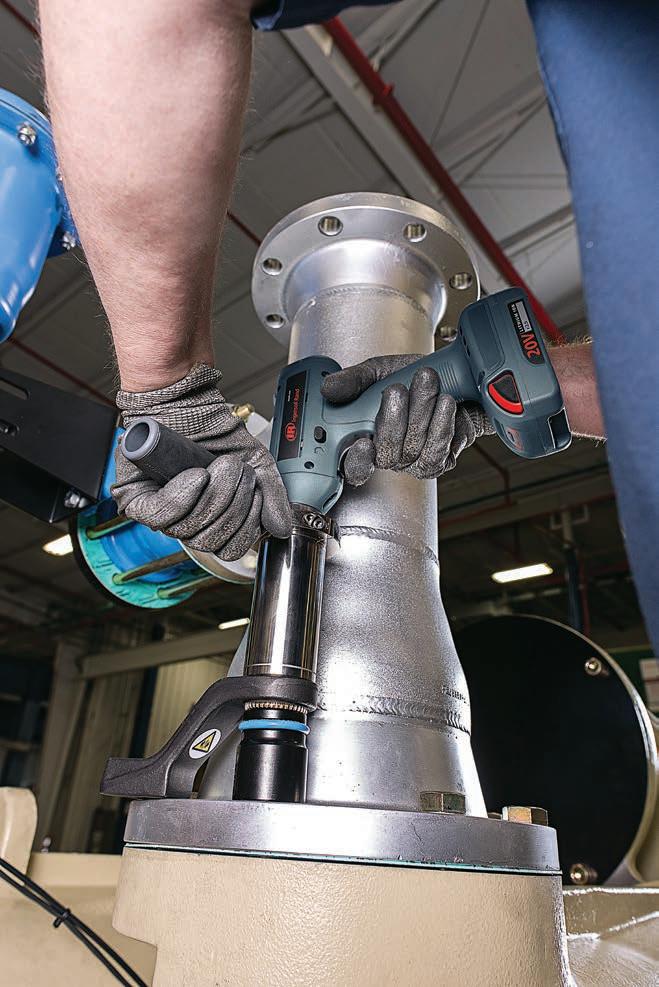
But inefficient operation is only part of the challenge. Indeterminate control and monitoring see companies manually recording torque goals with paper and pencil in the field. This is often a game of guesswork that slows down production when measurements are out of sync.
Time is certainly valuable for productivity, but it’s not the only consideration. Accuracy, consistency and traceability of performance are the cornerstones of a compliant and safe work site. Technicians need a precise auditing method to ensure the right tool is being used for the right job.
But commercial and compliance difficulties are often key drivers of innovation, and it was with these challenges in mind that Ingersoll Rand developed the QX series cordless torque multiplier. CAPS Australia now wants to optimise the mining sector with a nation-wide rollout.
Relatively new to the Australian market, the QX series torque multiplier employs advanced technology, boasts a 200–4000Nm average range, and is available in 20V and 40V options.
The multiplier features a brushless motor paired with a premium Norbar gearbox. At the heart of the torque multiplier is the Ingersoll Rand closedloop transducer, which is the key to delivering torque precision, accuracy and traceable results.
The tool operates on the Ingersoll Rand IQV20 and 40V series battery system and each 20V battery charge will rundown an average of 100 bolts.
The multi-function display module provides visual feedback via red, yellow and green lights to signal whether the bolt has met the specified torque limit or angle, or if the proper gang count was reached. This takes the guesswork out of its operation and maximises efficiency.
The only tool using a closed-loop transducer for precision, according to company, the QX torque multiplier delivers accuracy to +/- 0.1Nm without use of a test bench.
Operators are already seeing the benefit from improved efficiency and ability to hit nuts in faster sequence.
Multiple user-programmable configurations such as torque (Nm, Ftlbs, in-lbs, prevailing), angle and gang count reduce the number of tools needed for multiple applications. Up to 32 preset settings can be stored, and these functions can be navigated directly on the tool or programmed from the Insight app, a computer or data controller, or remotely online.
The quiet, cordless and compact QX torque multiplier helps to eliminate the need for a hydraulic pump or breaker bar and reduces noise and vibration levels, increasing on-site safety and reducing worker fatigue.
The risk of injury and operator strain is minimised as users move freely without the inconvenience of bulky air or hydraulic hoses or power packs, and the 360° adjustable handle provides a comfortable grip and provisions for a tethering point, allowing maximum flexibility when working on multiple joints and accessing odd angles.
Replacing potentially flawed and time-consuming manual recordkeeping practices, the multiplier tool itself can store records for up to 1200 fastenings, which can be downloaded to a computer via a USB cable or wirelessly transferred to a dedicated process communication module.
Reliable compliance data is now available for operators to review, analyse and keep record of at any time.
CAPS is the only Australian distributor of the Ingersoll Rand QX torque multiplier, which has successfully been utilised across mining, heavy equipment, rail, construction, infrastructure, military, and process automation industries around the world.
The QX series of smart tools also includes right angle wrenches, pistol wrenches and precision screwdrivers, all offering improved process control, operator comfort, and data communication while increasing productivity, lowering costs, and ensuring quality.
Bolting joints may be an essential and unavoidable part of mining in Australia, but the QX torque multiplier offers a smart solution to keeping every bolt in its place. AM
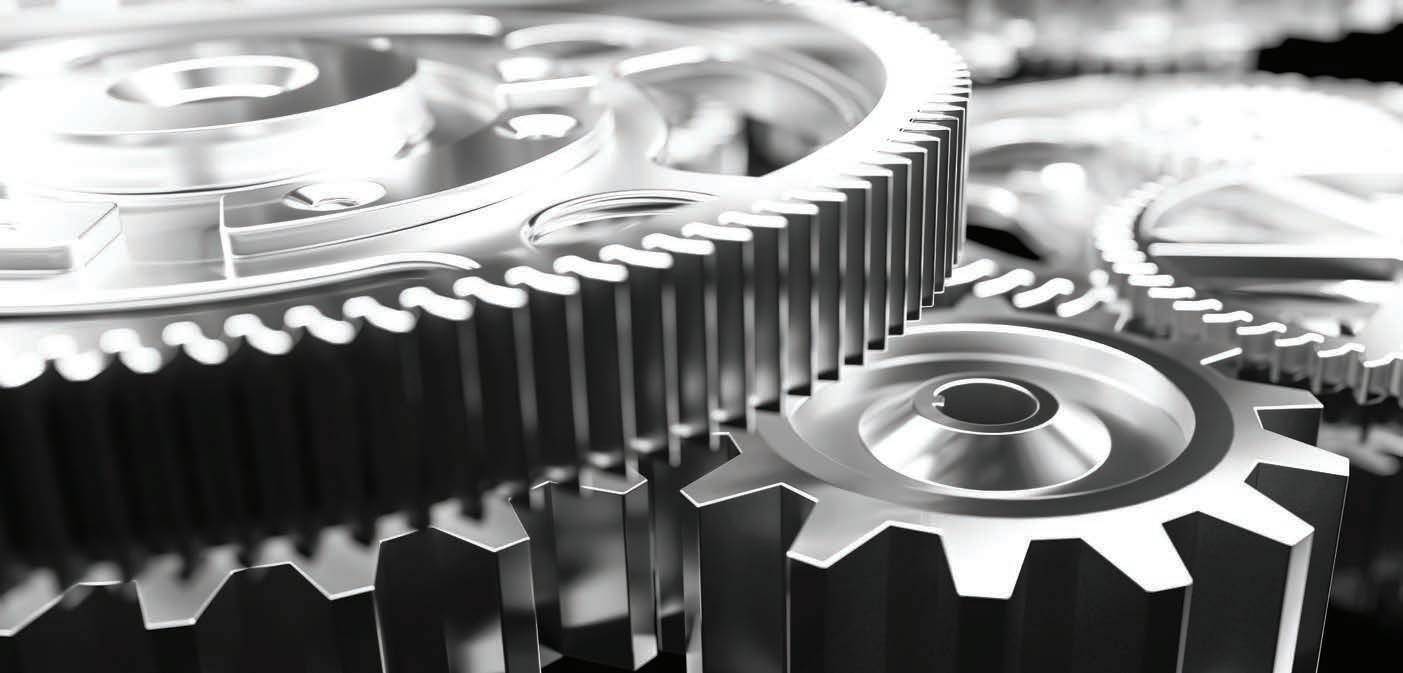
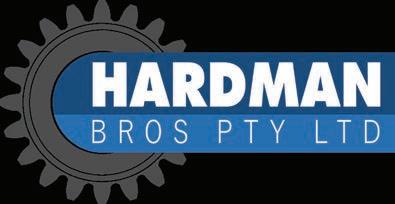
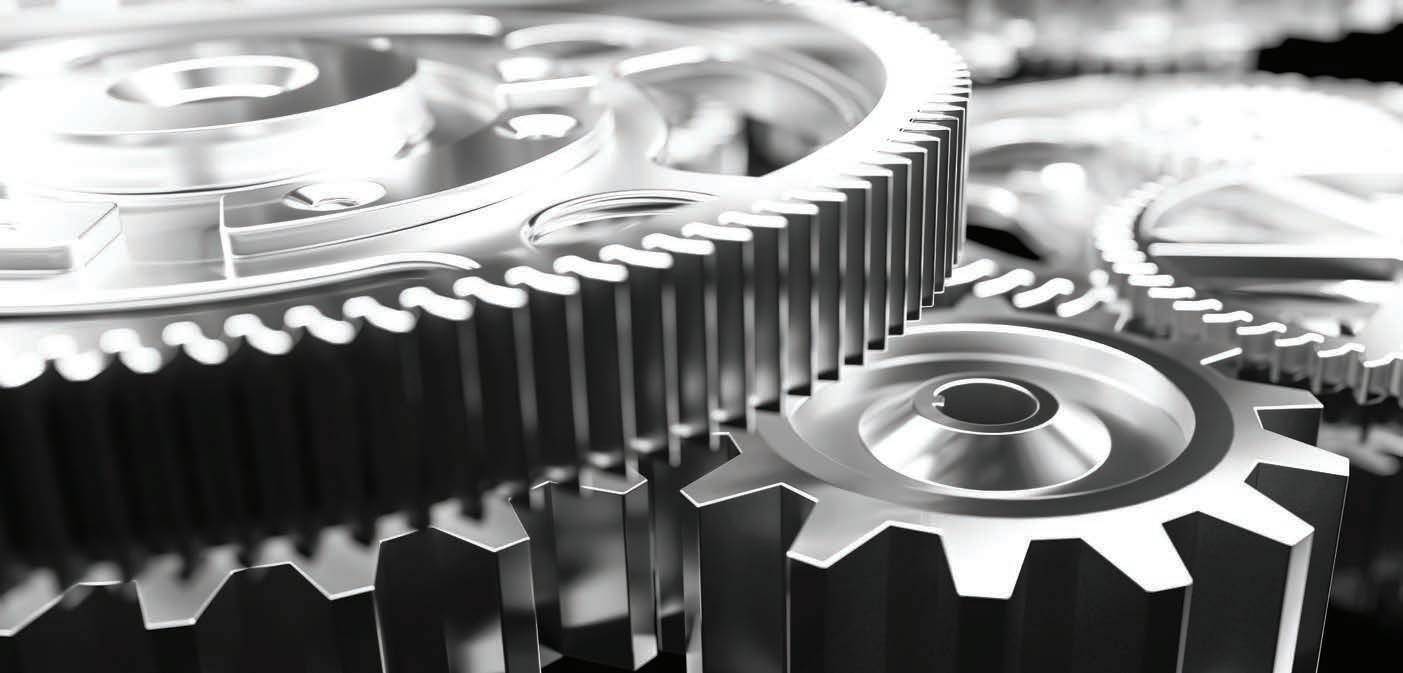
Who we are
With a history of over 70 years, Hardman Bros operates as a division within the Hardman Group of Companies – an Australian-owned enterprise of distinction. The group is renowned as a premier provider of precision machining and gear-cutting services throughout Australasia.
Having since expanded through two additional acquisitions, Hardman Group now comprises three distinct business units: Hardman Bros, R & I Instrument & Gear, and Marks 4WD.
What we do
• We operate a Quality Management System that supports the manufacture of high-precision machined components and gear cutting to leading Original Equipment Manufacturers (OEMs).
• Gear cutting and precision machining, shaping, milling and grinding, CNC machining, and general engineering.
• Assembly and sub-assembly, and on-site production with over 7,500m2 of floor space.
• Manufacture to print, maintenance, repair and overhaul capability.
• Work with customers from prototype to make to print production, including reverse engineering.
HARDOX PROTECTION
IT’S INSTRUMENTAL FOR THE MINING INDUSTRY TO HAVE ACCESS TO STATE-OF-THE-ART SERVICE NETWORKS TO CONNECT WITH THE BEST WEAR PARTS. THIS IS WHERE HARDOX WEARPARTS CAN HELP.
When Hardox Wearparts first opened its doors in Europe in 2000, momentous growth would ensue.
More than two decades later, a global network of wear service centres consists of more than 500 full-service centres in 100 countries. Over 20 of those service centres are in Australia, New Zealand and New Caledonia, supporting the
While some Hardox Wearparts centres are owned by SSAB Swedish Steel – a specialised steel company –about 80 per cent are privately owned, such as Real Steel New Zealand.
“We’ve been a member of the Hardox Wearparts network for several years. It buys us credibility with our customers,” Real Steel New Zealand managing director Luke Mathieson said.
“Flying the colours of Hardox Wearparts is a sign of quality, reliability and excellence.”
While Hardox Wearparts has expanded significantly since its inception, its values of providing customers with high productivity, flexibility and performance remain the same. This is supported by SSAB’s global organisation – a network of
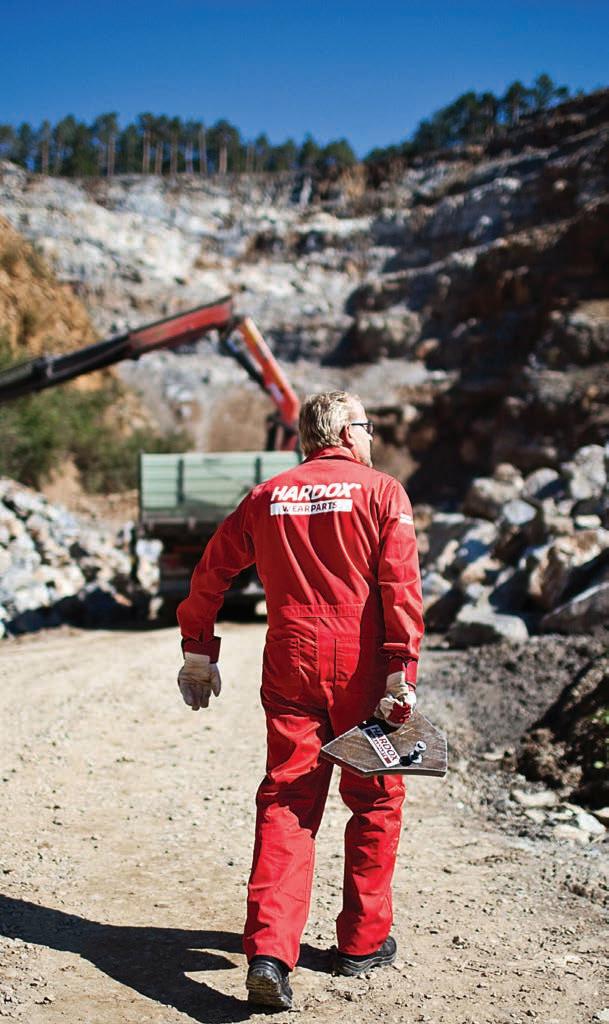
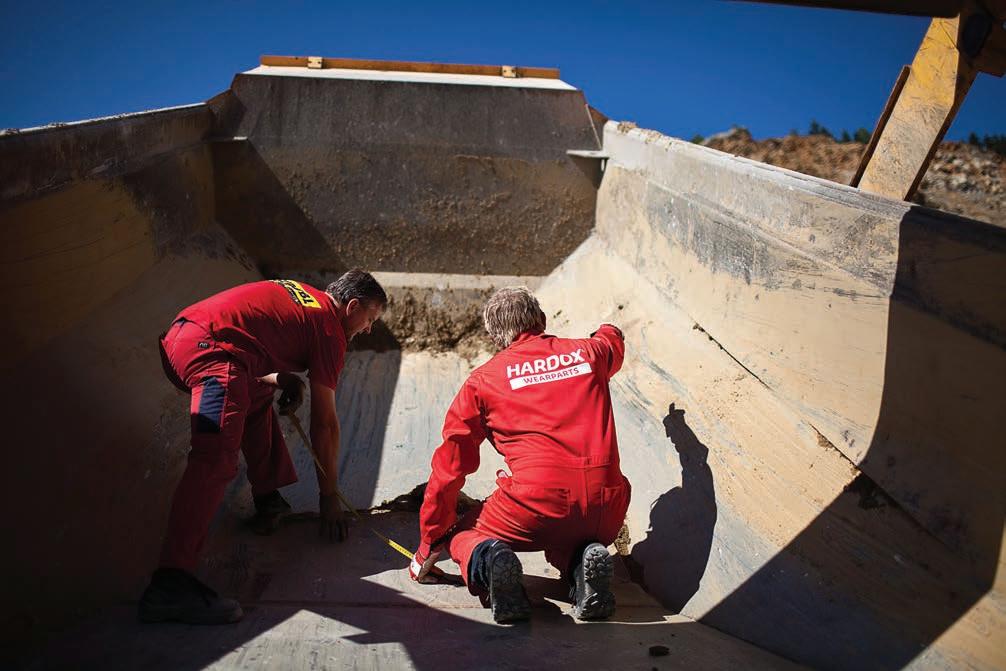
dedicated experts that, by using stateof-the-art SSAB-certified techniques and processes, can provide marketing and technical support to Hardox Wearparts centres.
SSAB manufactures a range of products, such as the Hardox wear plate, Duroxite overlay products, Strenx performance steel, and Toolox engineering tool steel.
These steel products, along with many others, are also available for purchase at a Hardox Wearparts centre.
“It was important for Hardox Wearparts centres to maintain a local focus, as this allows them to address specific customer needs more efficiently, and all wear business is local,” SSAB said.
“By partnering with local companies that supply wear services, we can provide our end customers with local and rapid access to quality wear parts and technical support.”
Hardox Wearparts members have access to one of the largest industry knowledge bases in the world. Mining companies can make use of shared experiences from other centres, and SSAB wear specialists are put to practice during equipment and installation processes.
It’s a common understanding that working in Australian mining conditions can often be unforgiving. To help mining companies work within these
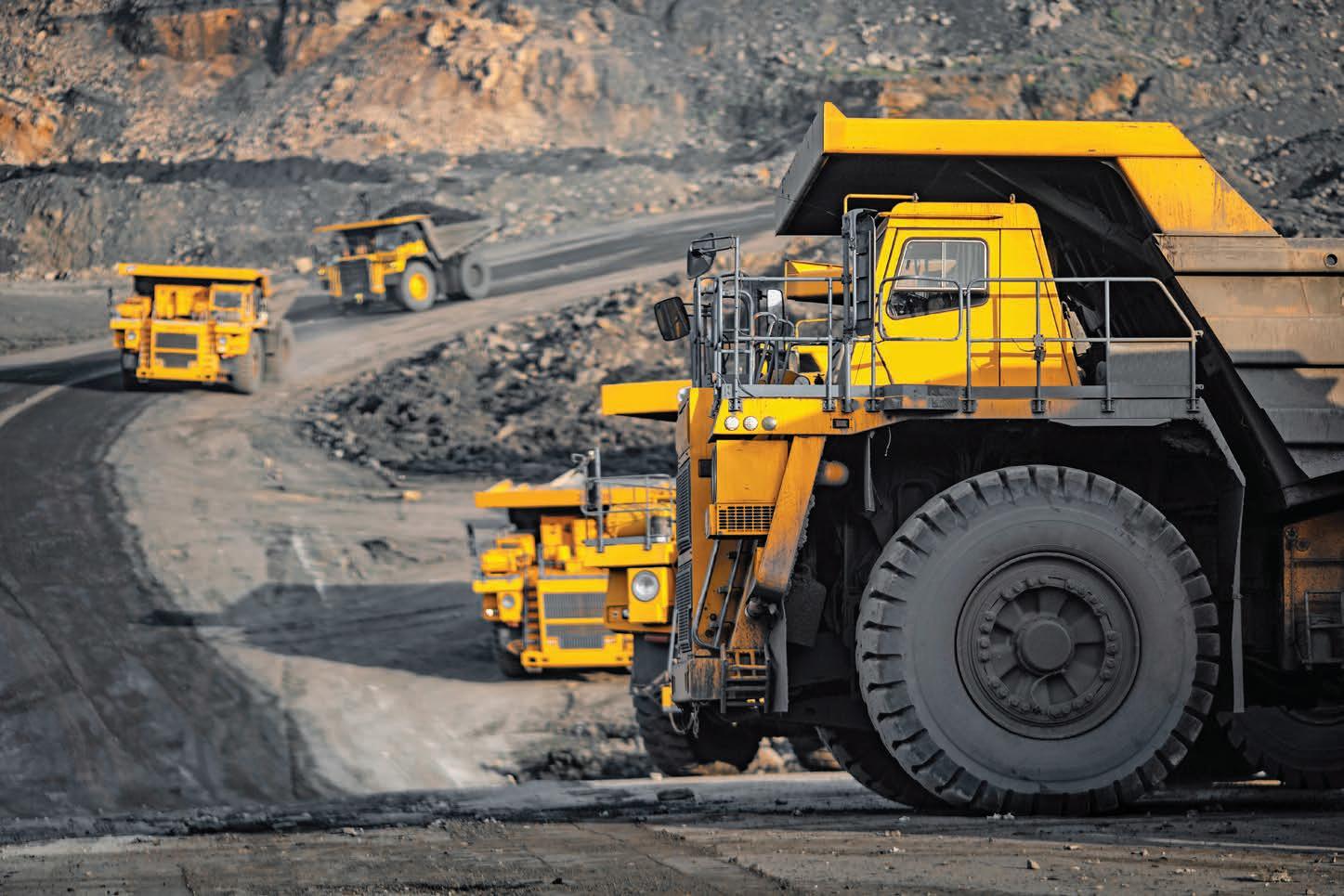
challenging environments, Hardox Wearparts supply reliable parts for underground and open-pit operations.
“Open-pit and underground mining operations rely on the performance of wear-resistant lining for loading buckets, trucks, and stationary and mobile conveyors,” SSAB said.
“Hardox Wearparts protects the mills, chutes, hydro cyclones and sorters from the particular stress conditions they are exposed to in each production process.
“In mining, buckets come in all shapes and sizes, but all can benefit from Hardox wear steel. Buckets made with Hardox last longer and keep their original shape thanks to the steel’s combination of high strength, extreme hardness, and excellent toughness.”
Selecting the right wear parts is critical to maximising uptime and finding the best performing solution at the right cost.
“When you’re doing business with a Hardox Wearparts centre, you should have high expectations,” SSAB said.
“Every centre prioritises high staff skill standards, ensuring quality, performance and safety of the centre’s parts and services.
“By growing the network of Hardox Wearparts centres, as well as growing the range of products and services they provide, we are continuously improving our service capacity.” AM
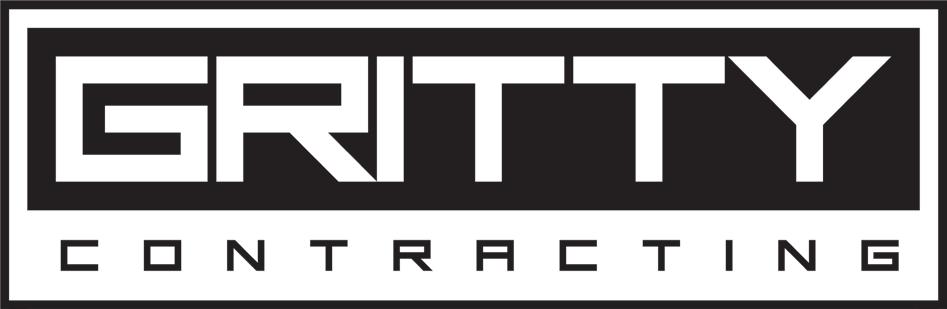
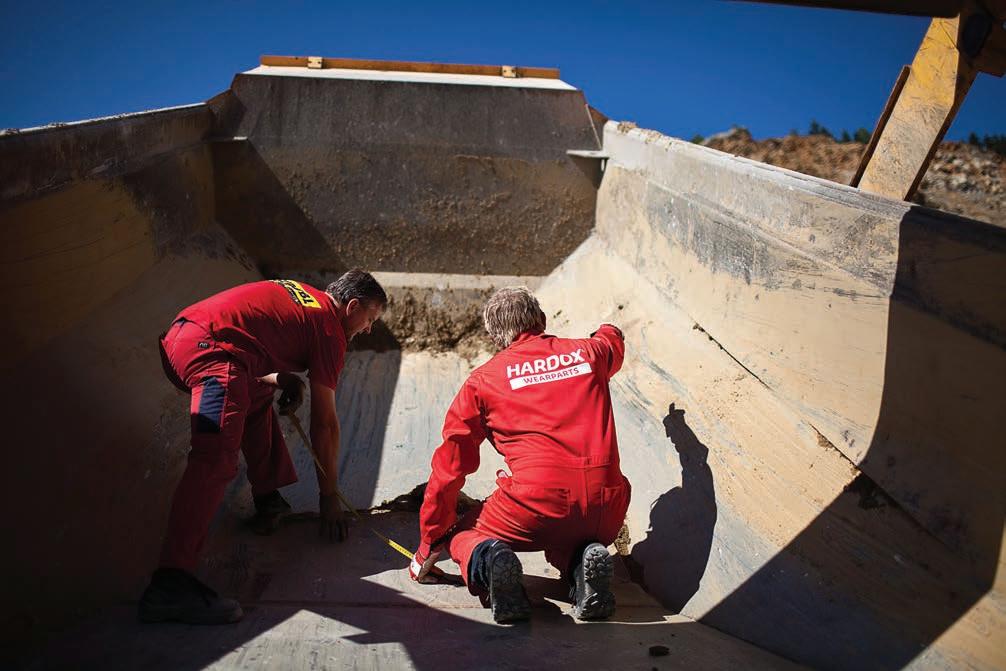
SECURE STORAGE LESS HASSLE
Say goodbye to storage-induced faults and hello to operational readiness. Discover Gritty Contracting’s unique heavy machinery storage solution.
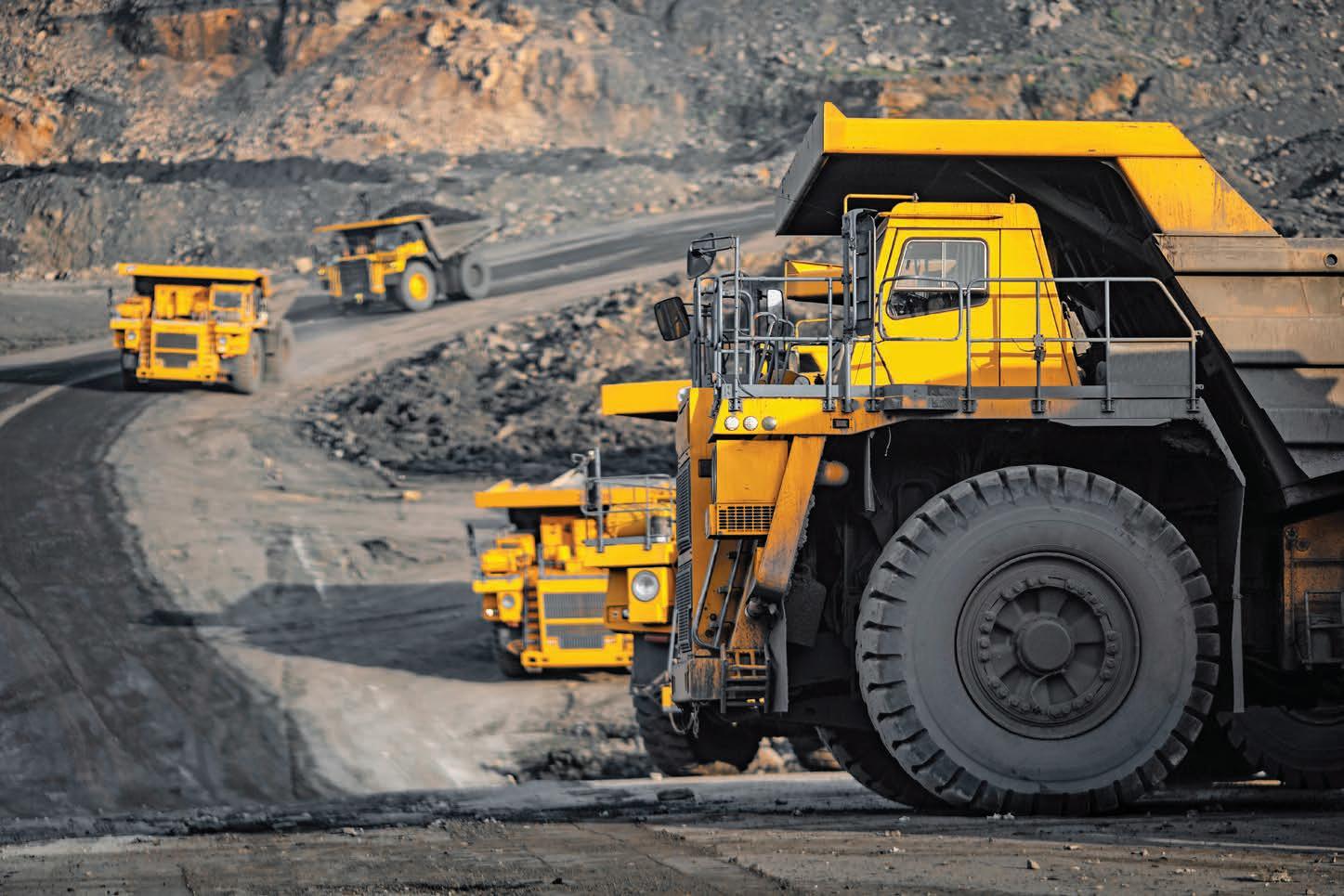
At Gritty Contracting, we understand that heavy machinery doesn’t like to sit idle. That’s why we’ve opened a specialized storage facility in the Goldfields that does more than just house your equipment. Our unique ‘care and maintenance’ package guarantees that your machines maintain their peak condition, ready to work, for a monthly fee less than a day’s labour.
Stored machinery often develops faults due to inactivity. Our proactive approach involves regular checks and maintenance, ensuring any issues are addressed immediately, keeping your equipment in ‘turn-key’ condition. This not only preserves the machinery’s health but also saves you from the unexpected surprises and delays when it’s time to deploy.
Additionally, we offer repairs and servicing while your machines are in storage. This integrated service approach reduces the need for additional logistics, streamlining your operations and taking away the headaches of equipment management. Trust us to keep your machinery ready and reliable.
GET IN CONTACT TO SEE HOW WE CAN HELP
CALL 0428 999 943 OR EMAIL ADMIN@GRITTY.NET.AU
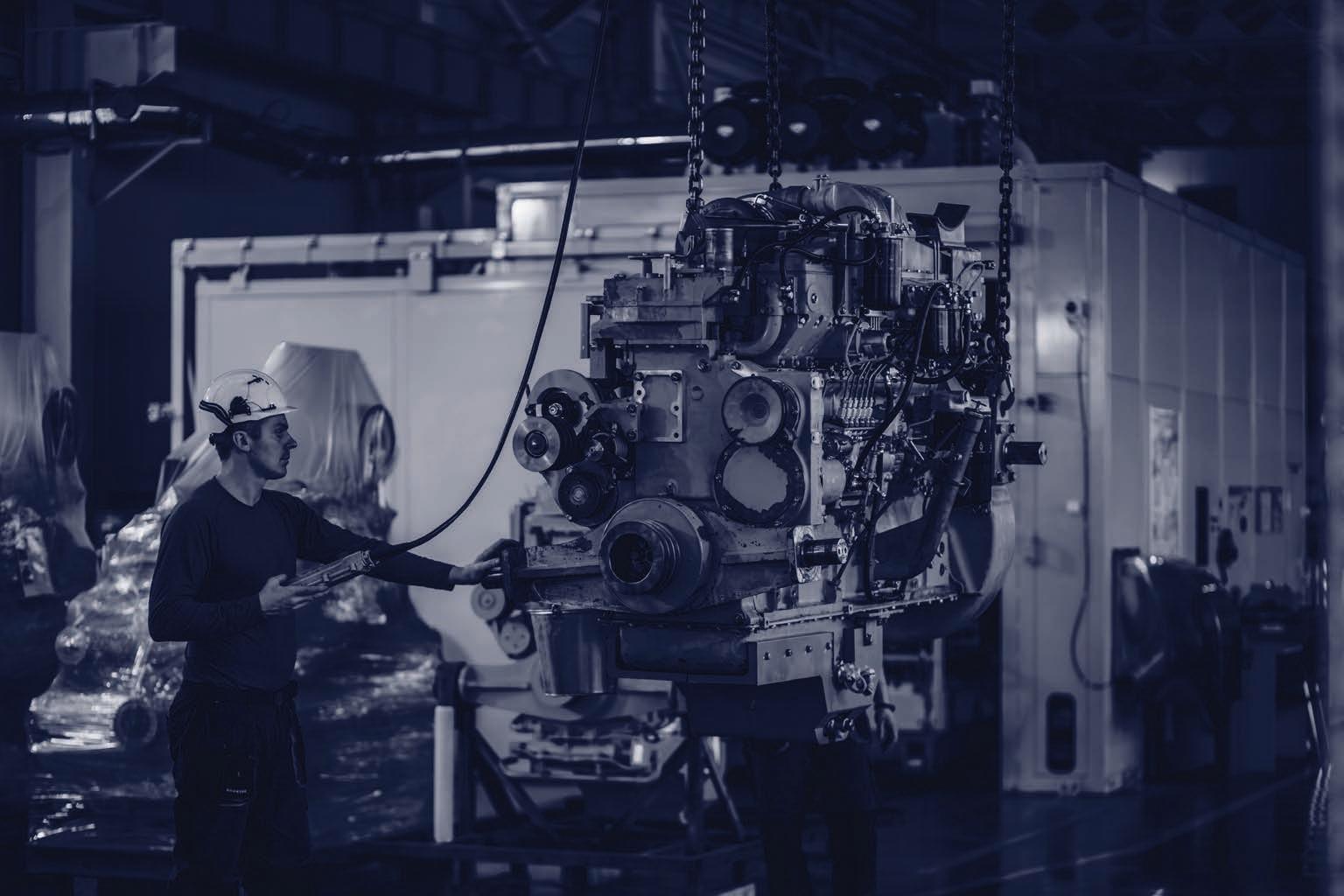
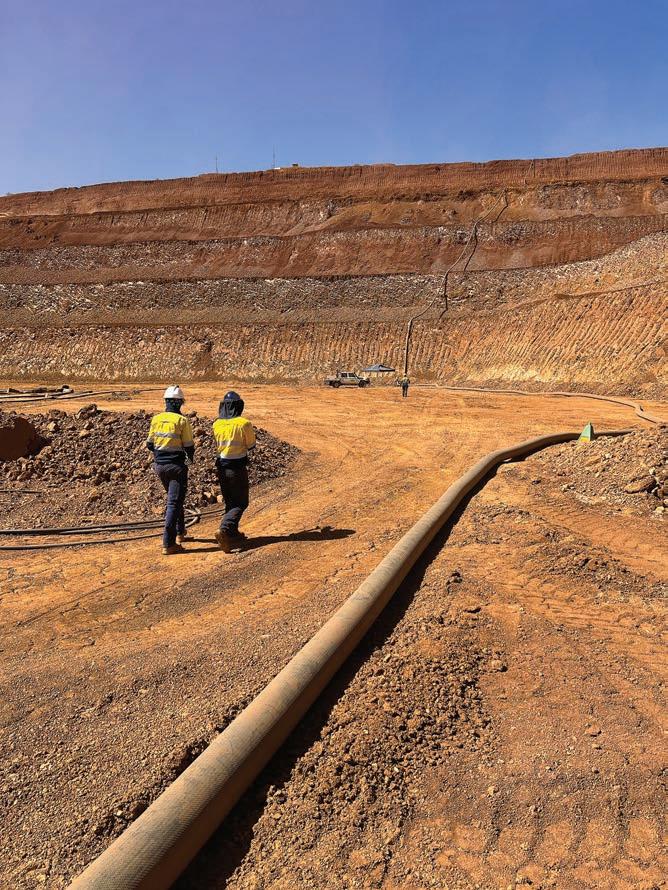
REVOLUTIONISING HOSE SOLUTIONS
CRUSADER HOSE SHOWCASED THE KEY FEATURES AND BENEFITS OF ITS INNOVATIVE LAYFLAT HOSE SYSTEM AT IMARC 2023.
The International Mining and Resources Conference and Exhibition (IMARC) brought companies from across the world to Sydney in November 2023 to showcase their latest offerings.
And Crusader Hose, an Australian leader in layflat hose and reel system manufacturing, was among them.
The company saw IMARC as a great opportunity to showcase its innovative Crusader layflat hose system.
The system reduces the time and labour considerations of installing a pipeline up a high pit wall while also lowering the safety risks.
“Imagine establishing a pipeline up a 150m high pit wall without the need for complex anchoring, building supports or recruiting welding experts,” Crusader Hose managing director Francois Steverlynck said. “Imagine replacing poly pipe with something flexible, less bulky, and easy to install.”
As well as its intrinsic safety and efficiency benefits, the layflat hose
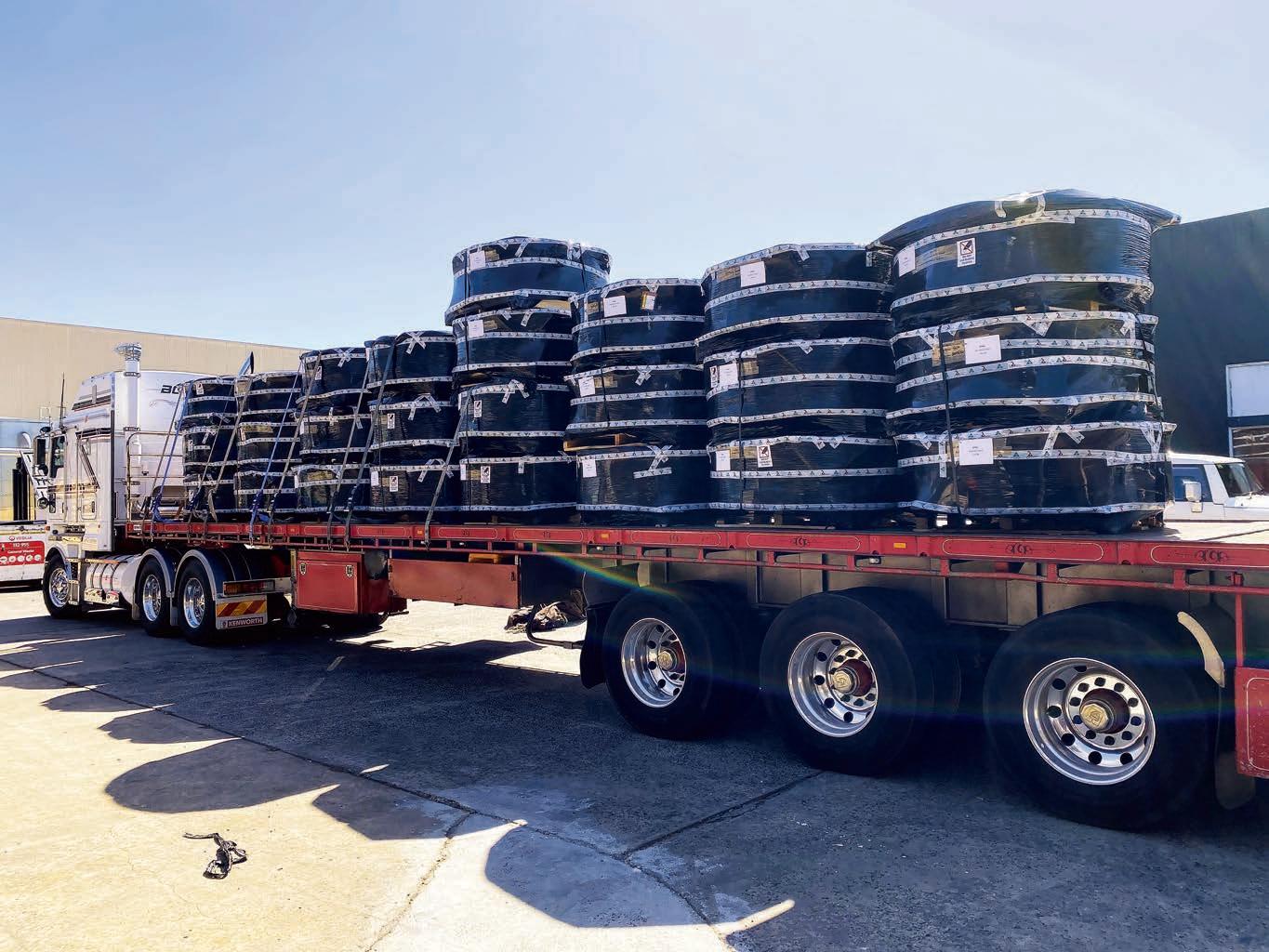
system is also easy to install, something which can be initiated by a drone slinging the rope into place.
One end of the rope is then connected to the Waterlord layflat hose sitting on a reel at the top of the pit, and the tail end is connected to a vehicle at the bottom of the pit.
As the vehicle moves forward, this rope is pulled, and the layflat hose is dragged down the slope. Because the layflat hose is flat and flexible, it follows the contours of the terrain and supports itself, meaning it does not slide down or creep.
“A major iron ore mine in the Pilbara had 15-tonne concrete blocks to anchor the poly pipe,” Steverlynck said.
“(With the layflat hose), not only do you eliminate this cumbersome handling risk, but you also do not have the risk of the rigid pipeline sliding down the wall like you do when using HDPE (high density polyethylene).”
Made up of three components, the system consists of a high-pressure woven layflat hose, secure couplings and reel handling systems.
from high-tenacity polyester yarns, the material handles all the high-pressure and tensile loads for the hose.
Thermoplastic polyurethane (PU) covers the textile reinforcement inside and out via an extrusion process, protecting it from abrasion damage. The PU cover also seals off the textile reinforcement from percolation.
“The textile reinforcement determines the burst pressure,” Steverlynck said.
“When a thicker yarn is plied by twisting more fibres together, the woven textile reinforcement results in an even higher pressure-capable hose.
“The Crusader layflat hose system is a lightweight and super-strong solution that is favoured for its ease of handling and ability to pump at high pressures.”
It’s no secret that high-pressure hoses need secure couplings. Crusader Hose has worked closely with the mining industry to design the Boa coupling clamp that stays on at 100 bar pressure.
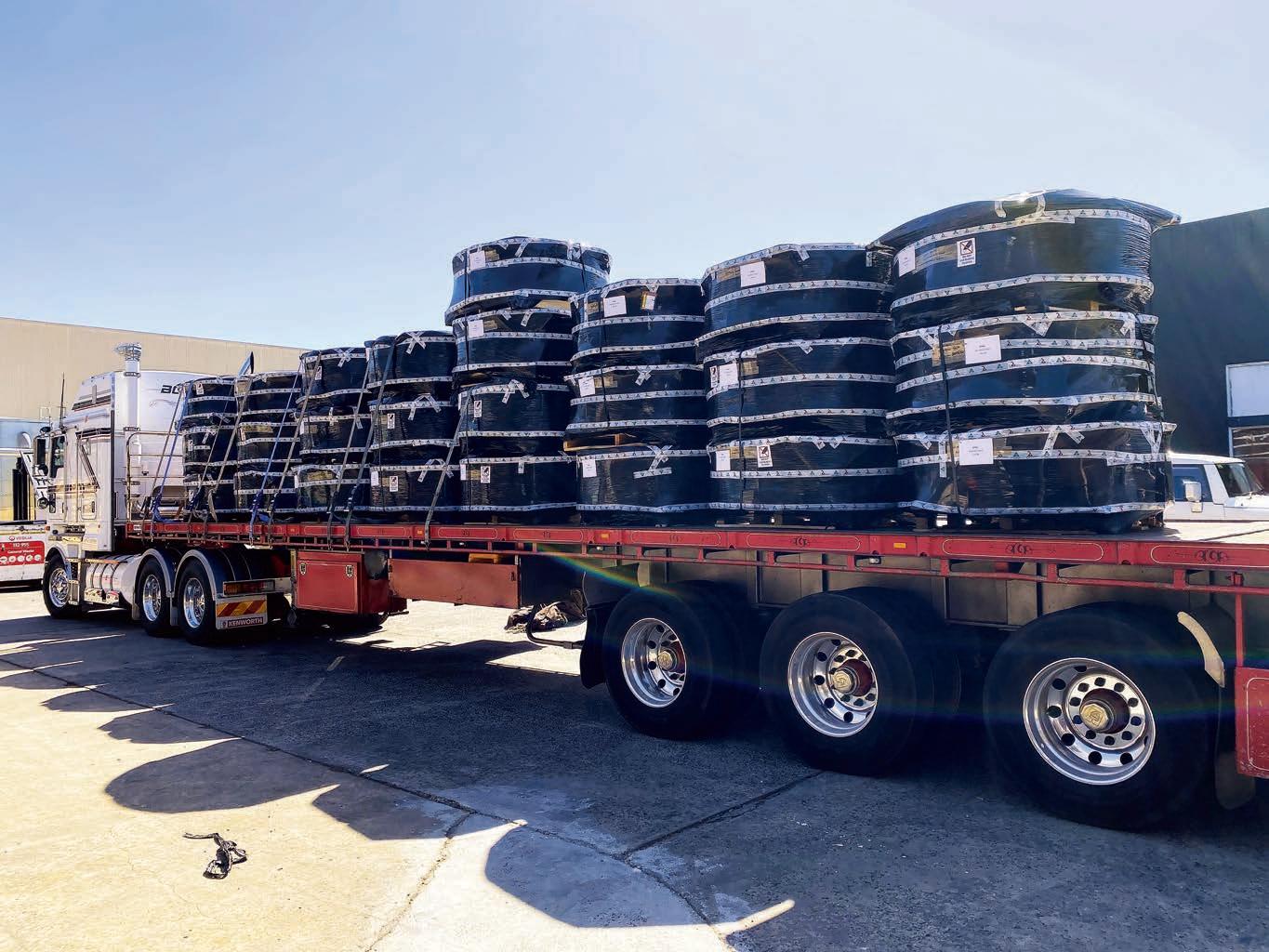
it easy to refit the couplings on-site,” Steverlynck said.
“It’s also worth noting that using Boa clamps for pumping up high pit walls at pressures ranging from 15 to 40 bar provides a high safety margin.”
Crusader’s woven layflat hose is available in continuous lengths of up to 500m and diameters of up to 300mm.
With an engineering department that designs reel systems for deploying and retrieving the layflat hose, Crusader has eliminated the need for manual handling, making pipeline deployment quick and safe, whether for temporary or permanent use.
And as Crusader Hose manufactures and tests over 1500m of layflat hose daily at its factory, the company is an expert in having the optimal reel systems for diverse site conditions.
Due to the textile reinforcement, hose pressure is unaffected by the hot sun and doesn’t need to be derated due to temperature, meaning
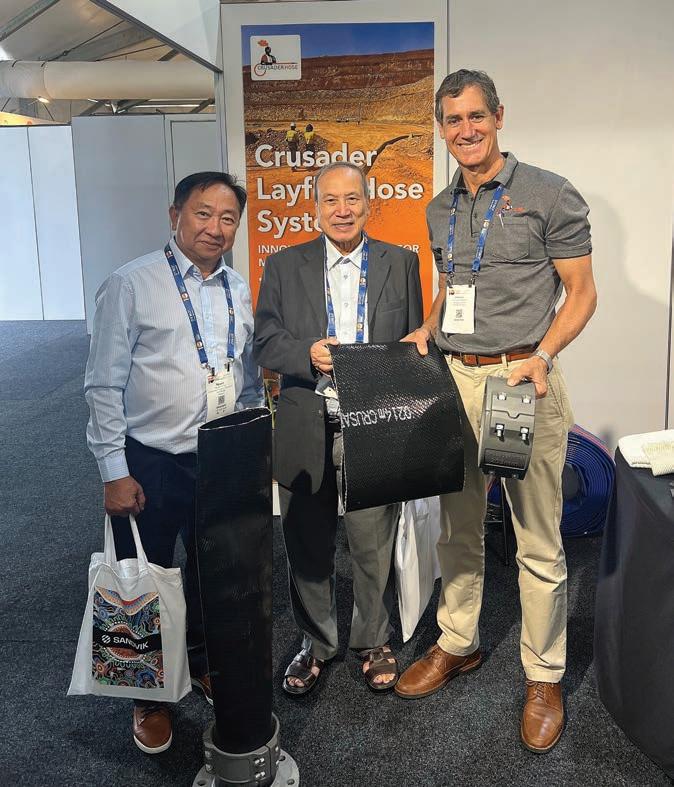
CRUSADER HOSE ATTENDED IMARC 2023 TO SHOWCASE ITS LAYFLAT HOSE SYSTEM.
CRUSADER’S LAYFLAT HOSE IS AVAILABLE IN CONTINUOUS LENGTHS OF UP TO 500M.
pack up to 4km of 300mm diameter Waterlord hose onto a single truck.
“In comparison, an equivalent amount of polypipe would require nine trucks to transport,” Steverlynck said.
“The cost savings of using layflat pipelines instead of poly can add up to significant amounts of money.”
Crusader Hose understands that mine personnel may need assistance with the installation and commissioning of pipelines, and can provide guidance on the efficient and safe handling practices of layflat hose.
“We will be assisting a large mine in the Goldfields with installing a layflat pipeline 300m up their high wall,” Steverlynck said. “We offer customer service and support across Australia.”
By creating dewatering systems that reduce risk and are easy to use, Australian-made and owned Crusader Hose is working hard to help mines improve safety and profitability, one flexible pipeline at a time. AM

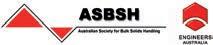
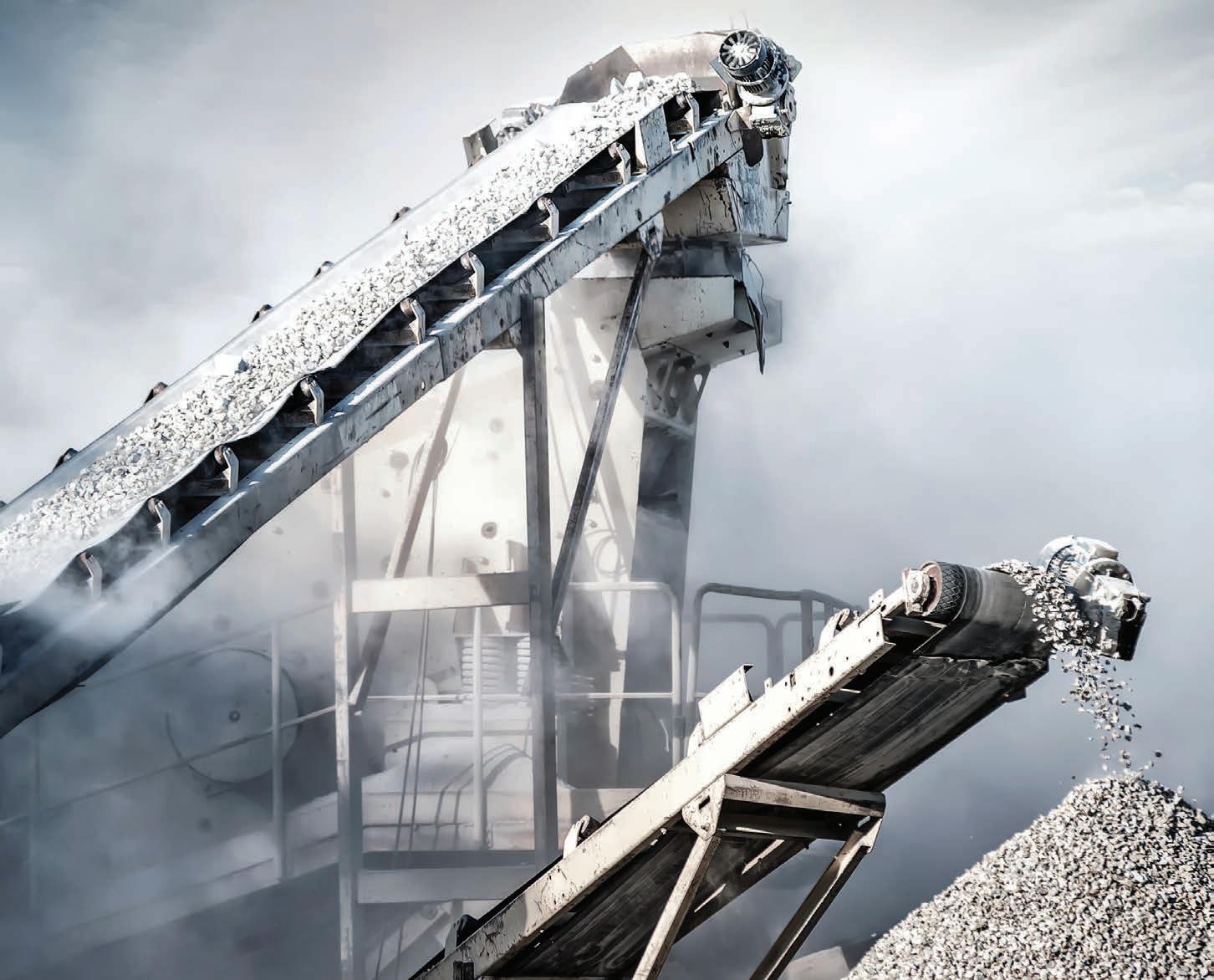
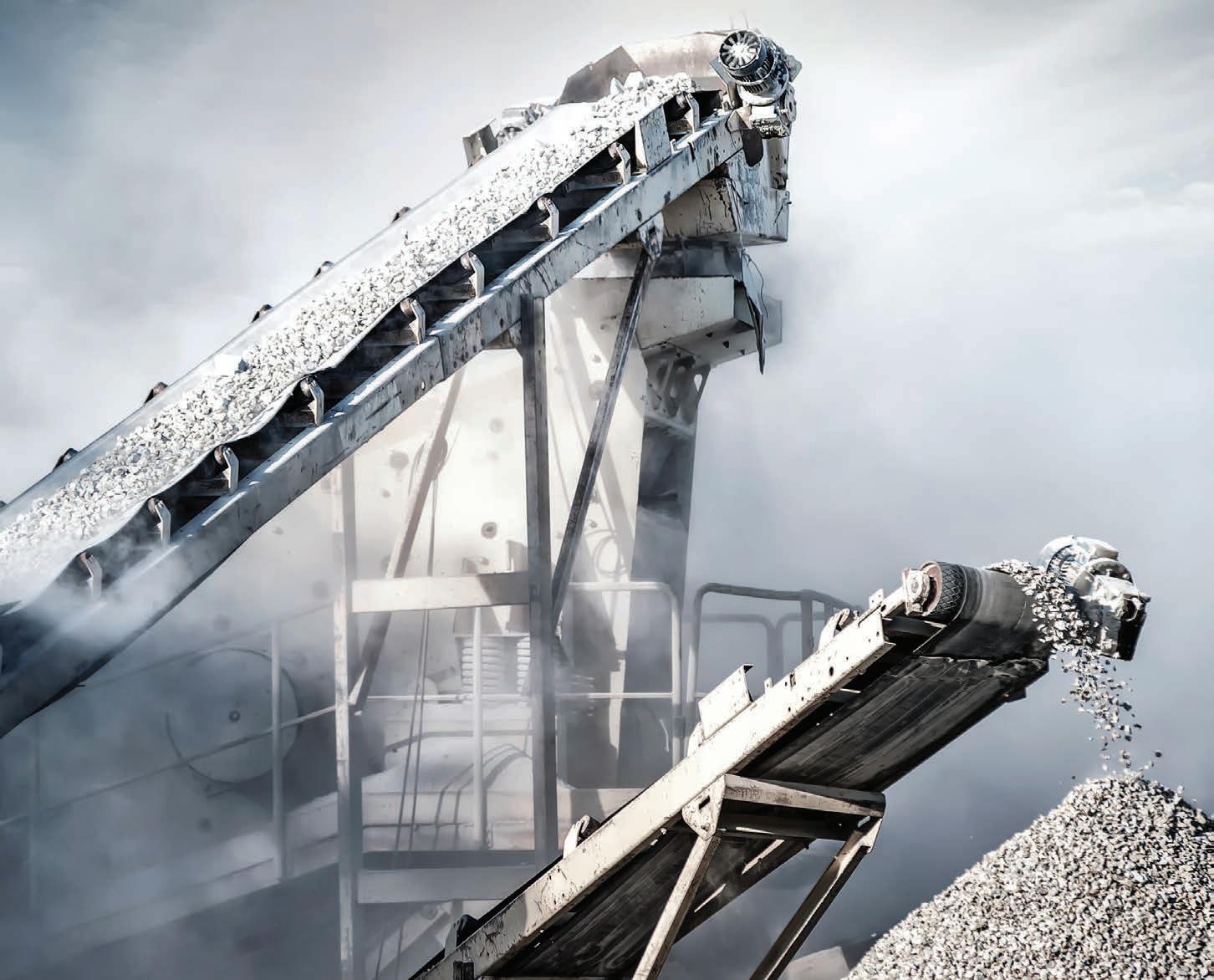
PRECISION GEAR
AUSTRALIAN MINING LOOKS AT HOW HARDMAN BROS IS LIFTING THE AUSTRALIAN MINING INDUSTRY THROUGH ITS GEARS, GEAR BOXES AND MANUFACTURING CAPABILITIES.
High temperatures, abrasive materials, constant operation.
It’s no revelation to say that the equipment used in Australian mining operations often faces harsh and demanding surroundings.
And it’s critical for machinery and parts to have the ability to withstand such conditions.
This need extends to gears and gear boxes, of which family-owned Hardman Bros is a renowned supplier.
Since its inception in Victoria in 1953, Hardman Bros has built a strong reputation in a variety of Australian industries, mining key among them.
“The Hardman group of companies is a distinguished Australian-owned enterprise that stands as a premier provider of precision machining and gear-cutting services for leading original equipment manufacturers (OEMs),” Hardman Bros chief executive officer Simon Bell told Australian Mining
“With two subsequent acquisitions, the Hardman Group now encompasses three separate business units: Hardman Bros, R&I Instrument and Gear, and Marks 4WD.”
Alongside its range of gears and gear boxes, Hardman Bros specialises in gear manufacturing, computer numerical control (CNC) machining, and general engineering.
“In a strategic collaboration, Hardman Bros and R&I Instrument and Gear have united to amplify the scope and excellence of customer services, extending our expertise from precision gear cutting to CNC machining and general engineering,” Bell said.
Hardman Bros can gear cut up to 1.5m and gear grind up to 850mm in diameter. It can also carry out CNC simultaneous five-axis milling and CNC machining, with CNC lathes up to 1.15m in height and 950mm in diameter.
“We possess the ability to fulfill any additional needs for machining, fabricating, and industrial mechanical assembly,” Hardman Bros general manager Wayne Hardman told Australian Mining. “We are also specialists in general engineering techniques such as turning, milling, grinding, honing, slotting and keyseating. We do it all.”
Hardman said providing reliable and durable components is vital in ensuring that mining equipment performs optimally with minimal downtime.
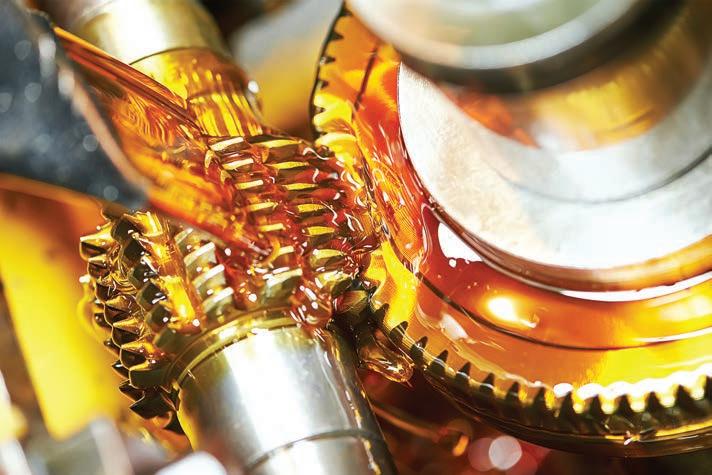
“As gears play a crucial role in the efficiency of machinery, well-designed and precisely manufactured gears can enhance the overall performance of mining equipment,” he said.
“We provide a one-stop shop with most of the broad capability requirements required for the mining industry under one roof, and an extensive well-established group of supply chain partners who complement our offering.”
Such a broad offering is seen through the company’s long-term relationship with a manufacturer client that has a presence in Australia, New Zealand and the US.
Hardman said Hardman Bros helped the client identify and manufacture
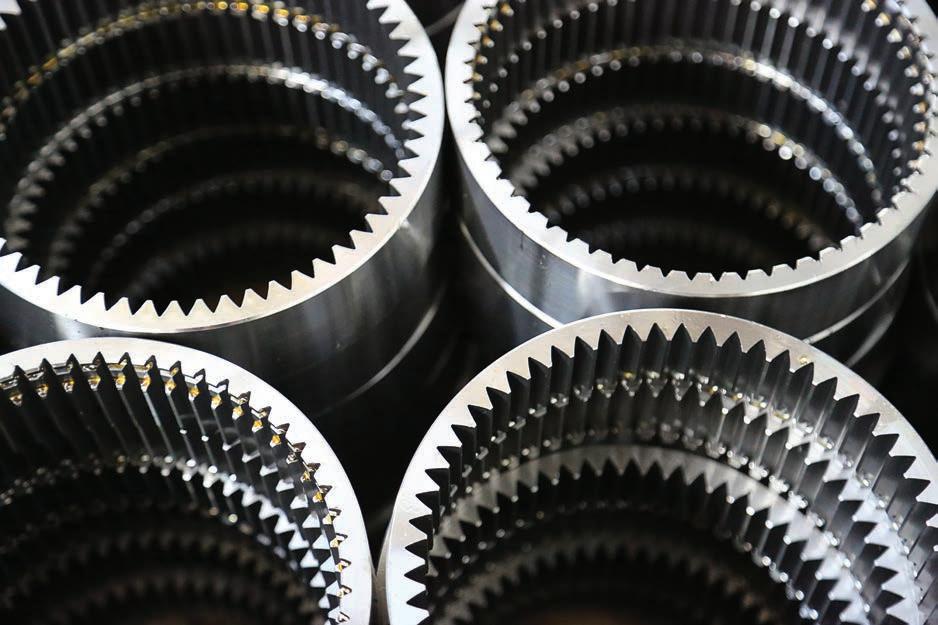
critical mining plant parts and assemblies by utilising skills such as reverse engineering and built-toprint capabilities.
“Hardman Bros, leveraging its expertise and capabilities, worked closely with the client to understand the intricacies of the problem. Through a collaborative approach, the company identified the root causes and potential challenges associated with the client’s issue,” he said.
“Hardman Bros not only provided a resolution to the immediate problem but also fostered a partnership with the client based on trust, reliability and the ability to deliver effective solutions.”
The client connected with Hardman Bros at a tradeshow in 2010.
“They (Hardman Bros) have helped us design gears and manufacture and repair spare parts,” the client said. “They have a quick response time and goodquality workmanship.”
By establishing key working relationships with fellow companies in the industries it operates, Hardman Bros has experienced significant growth, now boasting over 140 machines.
“One of the key drivers behind Hardman Bros’ success is the unwavering commitment to continuous improvement,” Hardman said.
“The company consistently reinvests in quality plant and equipment, ensuring that our manufacturing capabilities remain at the forefront of industry standards. This ongoing investment guarantees precision in products, on-time delivery, and optimum plant performance while minimising unscheduled downtime.
“Hardman Bros’ dedication to maintaining state-of-the-art machinery and equipment underscores our commitment to delivering the highest quality products and services to our valued customers.” AM
PLUG-AND-PLAY SITE SOLUTIONS
WITH TIMEFRAMES AND COSTS BECOMING MORE OF A CHALLENGE, TRADESALES IS WORKING TO ALLEVIATE THESE PARTICULAR MINE-SITE STRESSORS.
Rome wasn’t built in a day – and neither is a mining operation.
And while some sites come to fruition quicker than others, a considerable amount of time is spent on waiting for infrastructure to be built, set up and readied for use before any ore extracted from the ground, let alone shipped out.
This gap in the market led workshop designer and manufacturer Tradesales to develop a product that is helping operations get boots on the ground quicker: relocatable site solutions.
“A relocatable site solution is a containerised piece of infrastructure that
“Their modular design means they’re scalable and more locker rooms can be added and removed as the workforce changes. Being relocatable, they can also be moved to another location if the operation expands.”
Tradesales has designed, manufactured and delivered its relocatable site solutions all over the country, including to a major miner in the heart of Western Australia.
“For a large established mine, we would recommend a mix of our site solutions all stacked together to create remote workshops,” McEwen said.
“The project that we completed with a major miner involved eight 40-foot relocatable solutions outfitted with roller
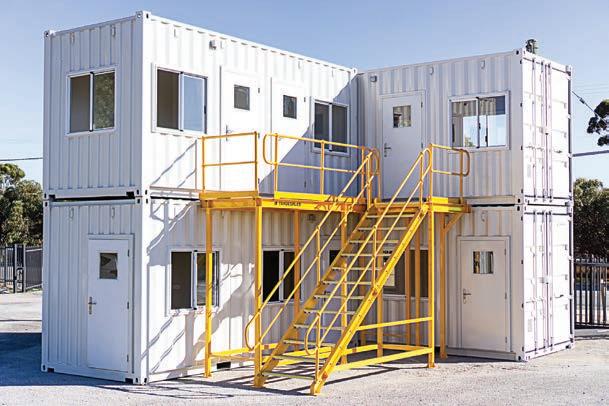
And, as McEwen explained, the relocatable site solutions last right up until the mine is ready for rehabilitation.
McEwen said. “But it generally only takes around 45 working days to manufacture a relocatable site solution once everything has been approved.
“The planning and processes that go into a relocatable site solution allow for predictable costs and precise timelines.
“Plus, they are constructed in a factory setting, meaning weather can’t delay the project, and any necessary onsite work can take place in parallel.”
With so many benefits, it’s easy to see why Tradesales’ relocatable site solutions have become staples for many sites around Australia.
“From hydration stations and on-site offices to secure tool storage and beyond, our relocatable site solutions are designed to adapt seamlessly to our customers’ evolving needs,” McEwen said.
“We would like all mines to experience the flexibility and functionality of our site solutions, tailored to enhance efficiency across their operations.” AM
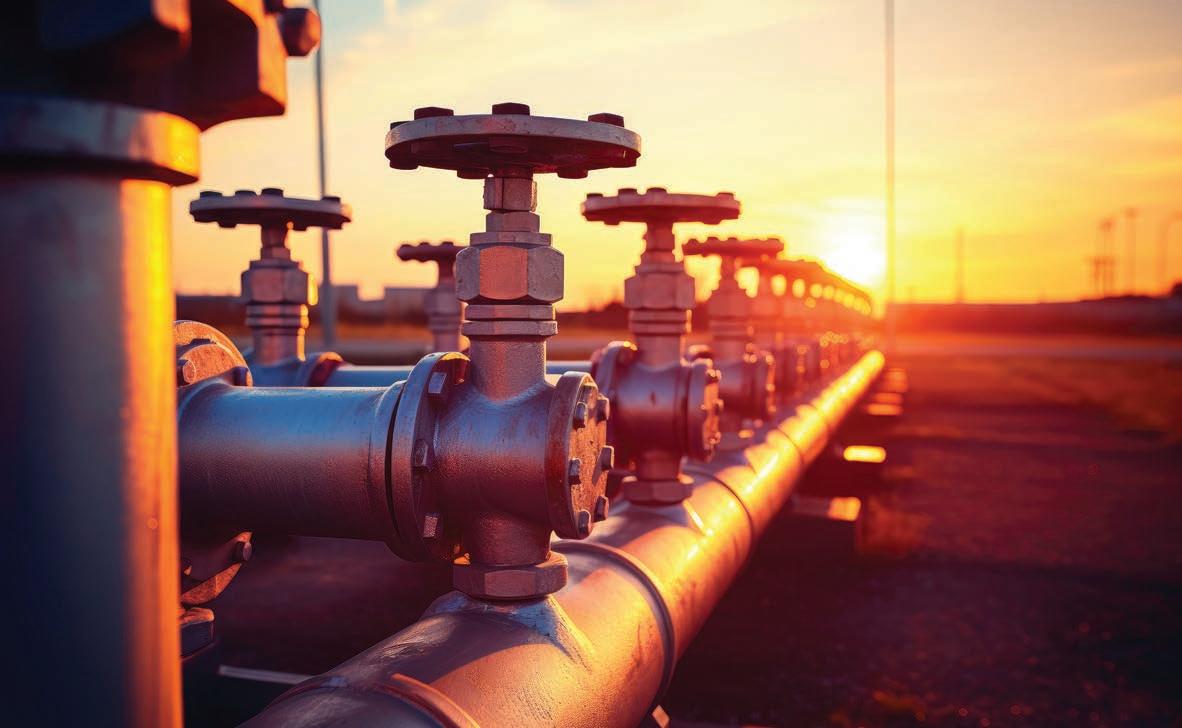
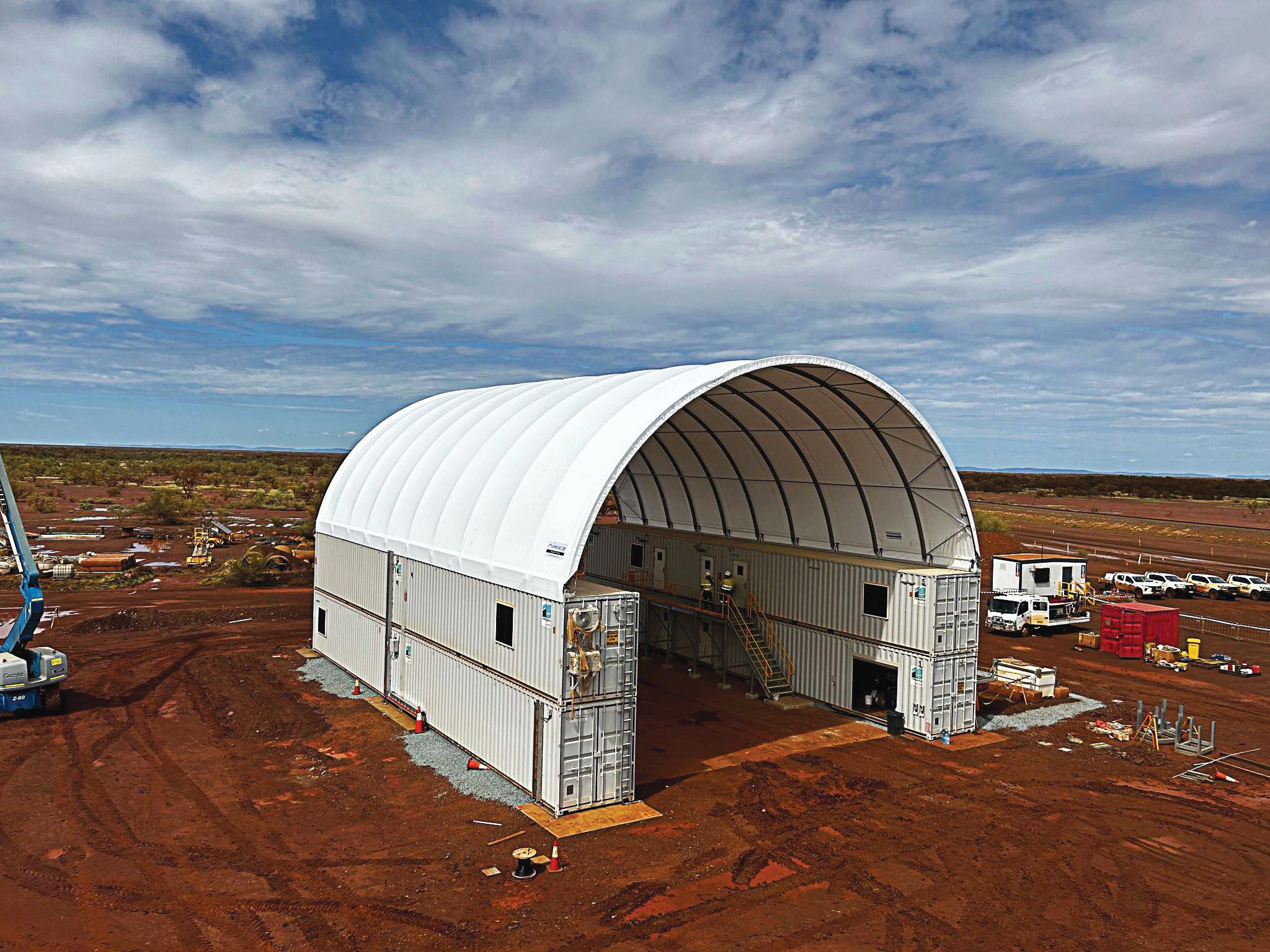
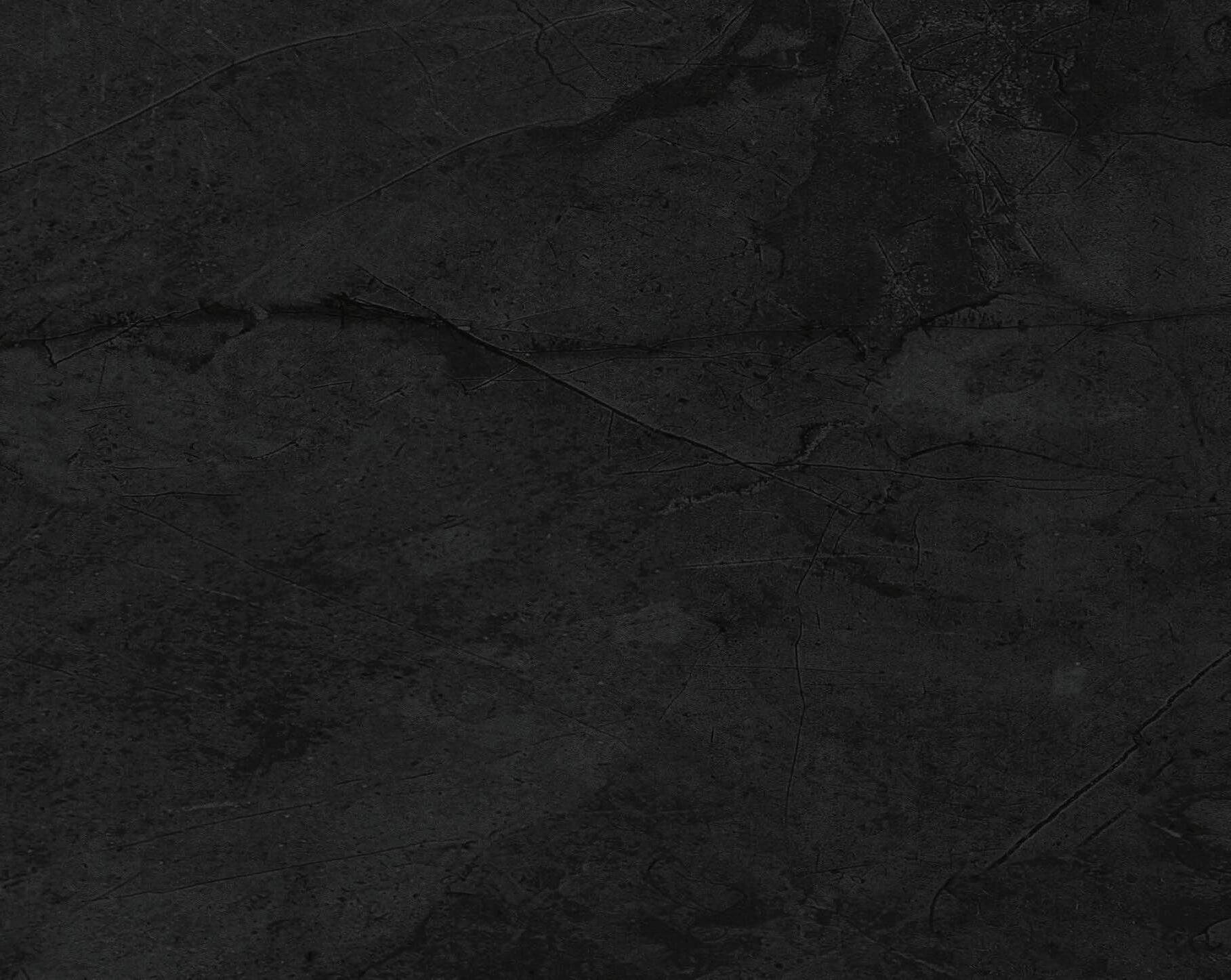
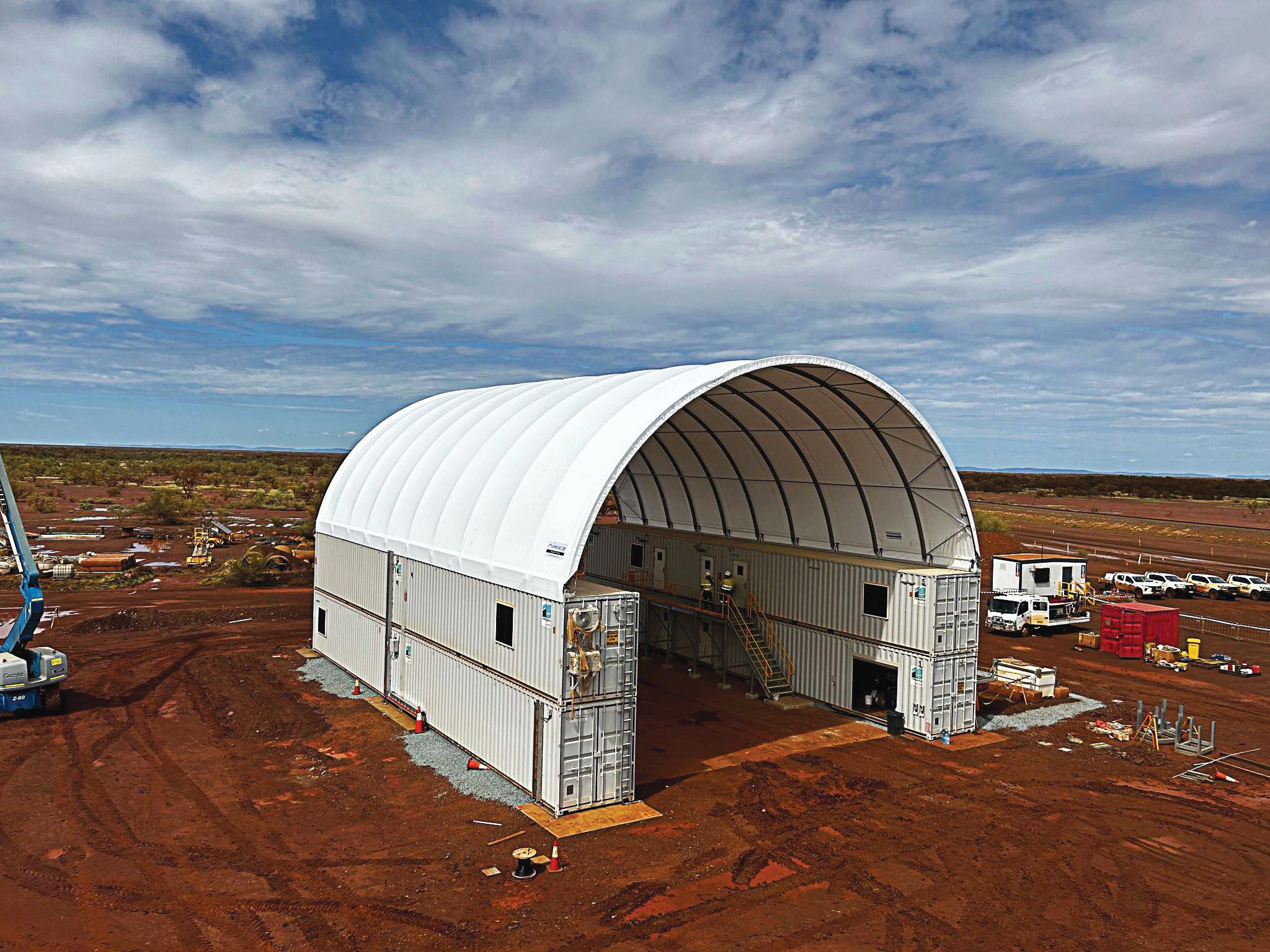

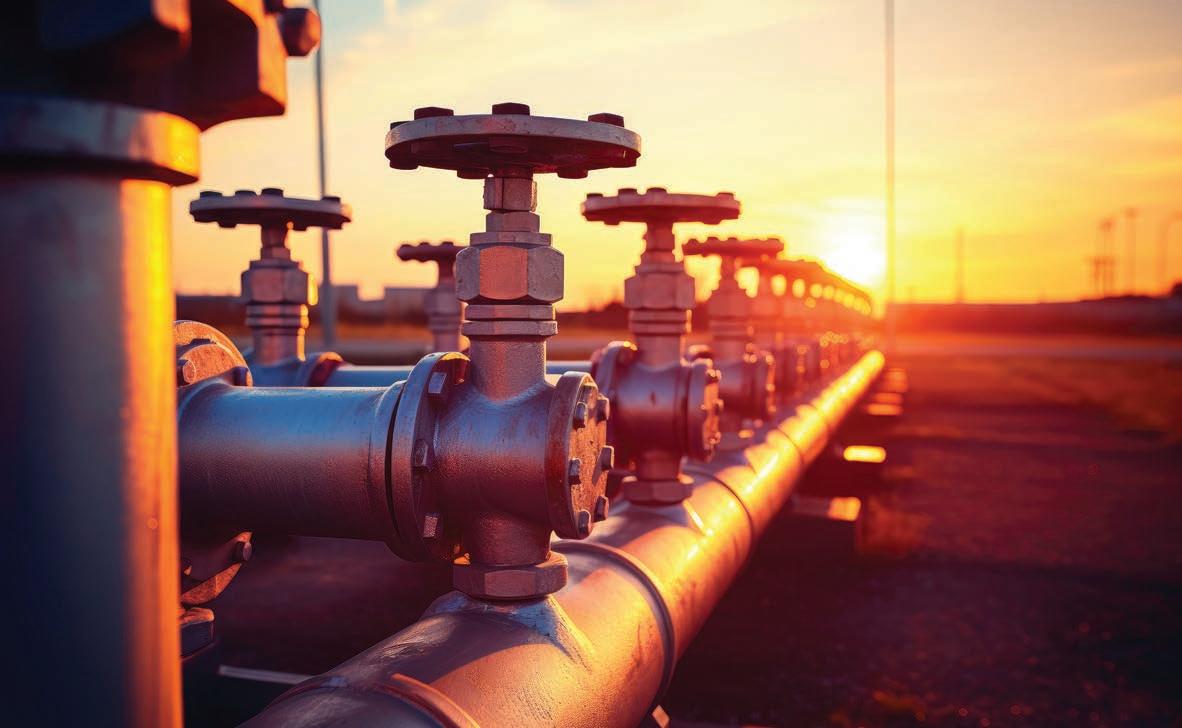
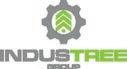
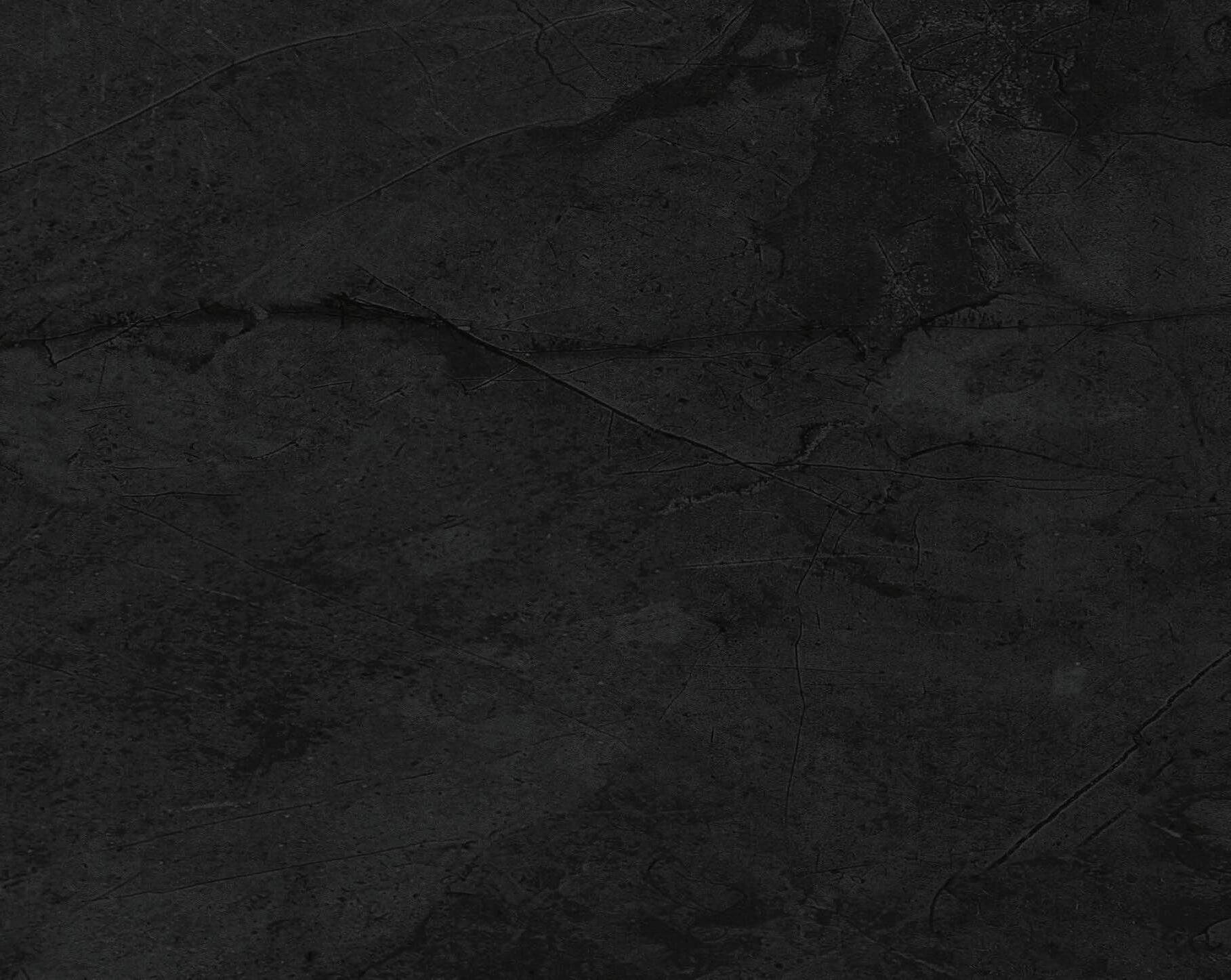
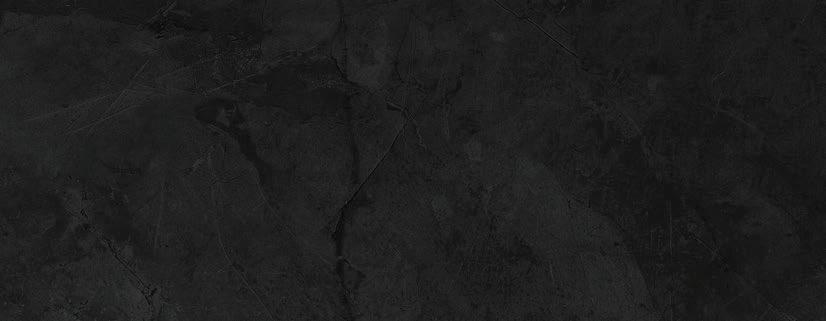
TAKING FLIGHT
THE FLY-IN, FLY-OUT INDUSTRY IN AUSTRALIA IS ONLY GETTING BETTER, WITH COMPANIES PUTTING IN TIME AND MONEY TO UPGRADE THEIR FACILITIES.
Fly-in, fly-out (FIFO) work has become a staple of the Australian mining industry, but the phenomenon is relatively new by mining standards, only becoming commonplace in the 1970s.
Since that time, companies have been working to make FIFO work more attractive to employees, offering stateof-the-art amenities and, above all, a safer workplace.
Home away from home
Because some FIFO workers are away from home for two to three weeks at a time, it’s important that their work accommodation is as welcoming and comfortable as possible.
Mineral Resources (MinRes) took this notion to a whole new level in January 2024, welcoming its first occupants to its resort-style accommodation pods at the Ken’s Bore site in Western Australia.
The pods are designed to be suitable for singles or couples, with rooms three times the size of traditional FIFO accommodation.
Some of the features include queen size beds, in-room washer-dryers, big-screen televisions with a video call function, kitchenettes, and an outdoor veranda with electric barbecues.
Additional amenities, including an Olympic-size swimming pool, bistro, lounge, indoor fitness centre, recreation building and sports courts, will also be added in the future.
MinRes general manager infrastructure Tim Clements said the Ken’s Bore accommodation at Onslow Iron sets a new industry standard.
“Everything is a first from a construction point of view and the rooms are just one part of it,” he said in January.
“The amenities are designed to improve the quality of peoples’ downtime and create a complete lifestyle experience.”
While traditional FIFO accommodation consists of a ‘donga’ – a transportable building providing accommodation for one person – these new resort style villages were made
SAFETY IS THE MOST IMPORTANT ASPECT ON A MINE SITE, AND IT MEANS MORE THAN JUST FOLLOWING REGULATIONS.
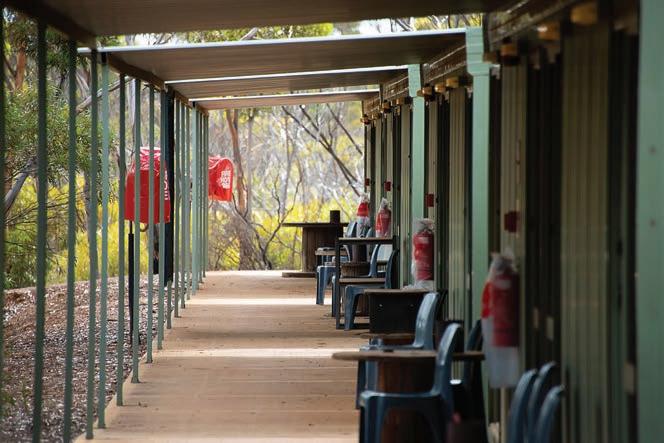
study, as it marks the first time that international experts have reached a consensus on how to optimise sleep schedules for shift workers.
“Until now, there hasn’t been consistent advice to help shift workers sleep, and that has meant a lot of them were trying to adapt standard advice to their non-standard sleep/wake patterns,” Shriane said.
The research, titled Healthy Sleep Practices for Shift Workers, offers research-informed insights, including the development of personalised sleep schedules across different shifts, utilising light effectively, and planning smooth transitions between work and rest periods.
to encourage more people to join the industry.
“Our people are the foundation of MinRes’ success and that’s why we’ll give them the best FIFO village experience in the sector,” MinRes said.
“As the race to attract and retain the best talent intensifies, we know our focus on workplace wellness will help set us apart.
“The accommodation and amenities at Onslow Iron will set a new standard, helping to change the FIFO culture and contribute to the project’s success.”
MinRes also has plans to build 10 four-bedroom homes in nearby Onslow to attract more families to the town and the workforce.
Safety
Safety is the most important aspect on a mine site, and it means more than just following regulations while working.
A CQUniversity study conducted in August 2023 found that FIFO workers who get better sleep are safer and more productive while on-site.
Published in the academic journal SLEEP, the research presents 18 clear guidelines to promote healthy sleep practices for the more than two million shift workers in Australia who work outside the conventional nine-tofive schedule.
Lead author Alexandra Shriane, a PhD candidate at CQUniversity, emphasised the significance of the
The guidelines also emphasise the benefits of strategic napping and provide insight for workers to find their ‘nap sweet spot’.
Research by Edith Cowan University found that FIFO shift workers accumulate ‘sleep debt’ over the course of their time working on-site before they then return home.
It was clear from the research that FIFO workers sleep better at home, so making FIFO accommodation more like a home and less like a temporary sleep space is one of the ways companies are combating the issue of fatigue.
As more workers join the FIFO ranks, it’s clear the industry has come a long way since its inception in the 1970s.
And with more knowledge surrounding the topic, it will only become safer. AM
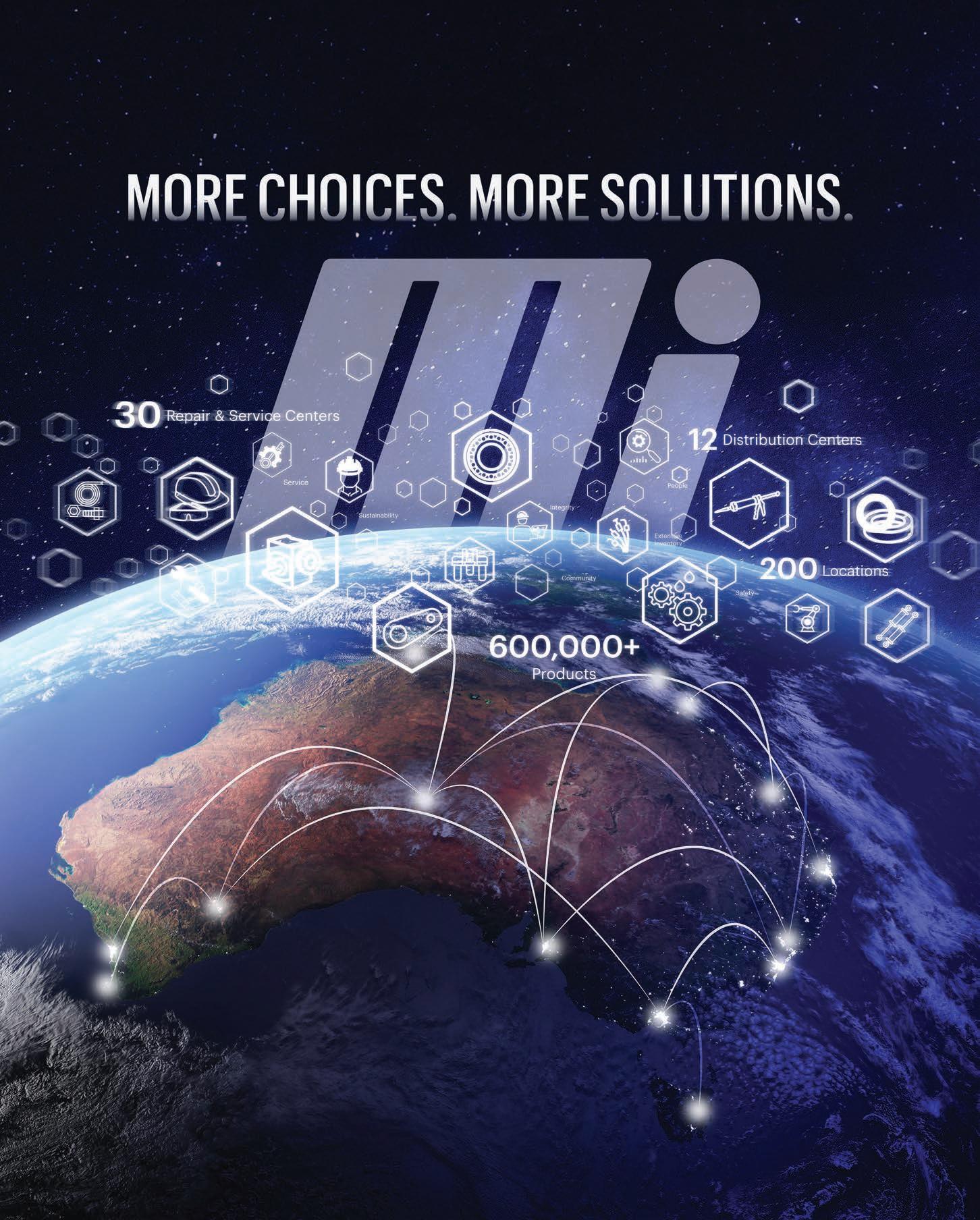
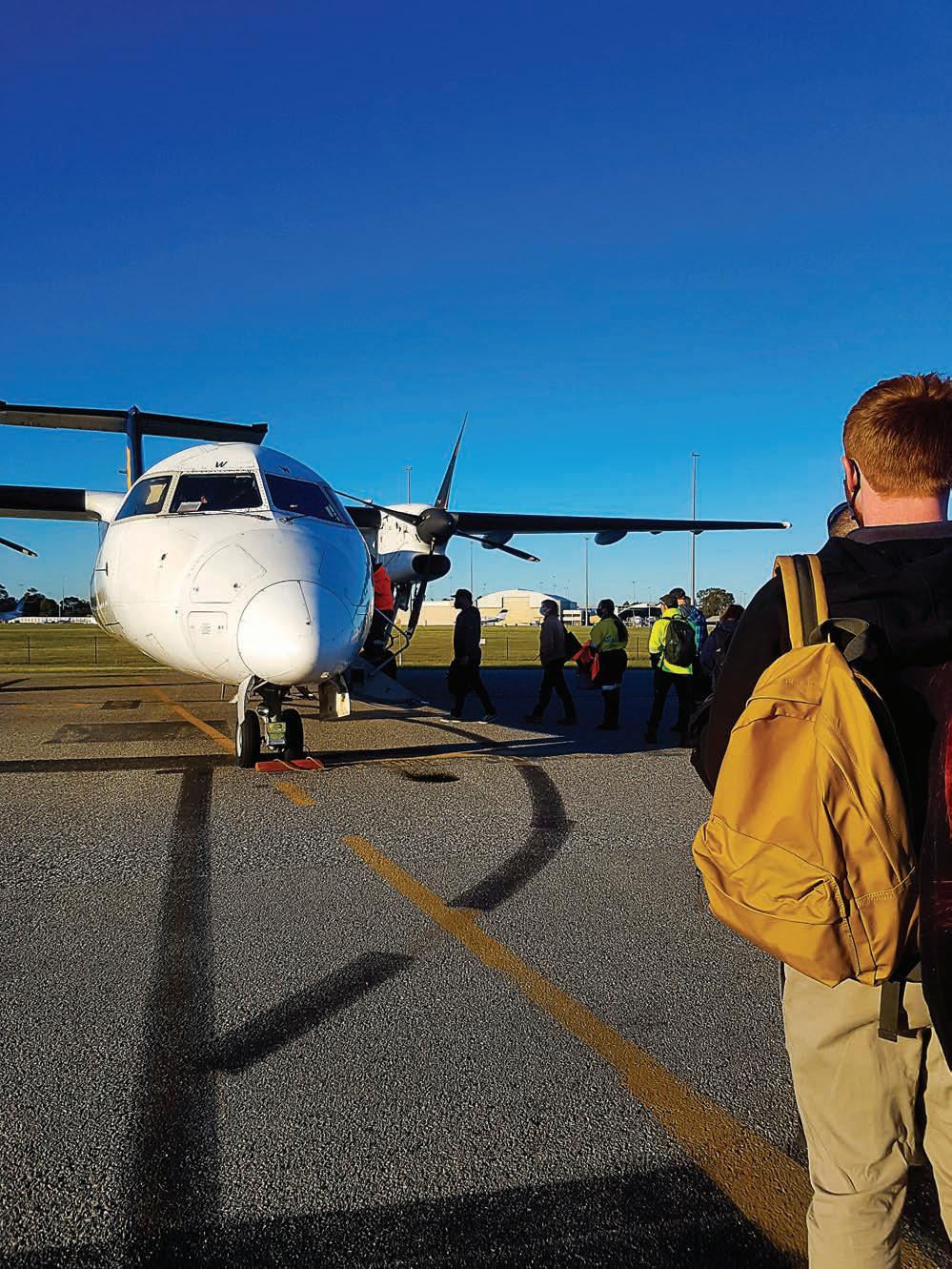
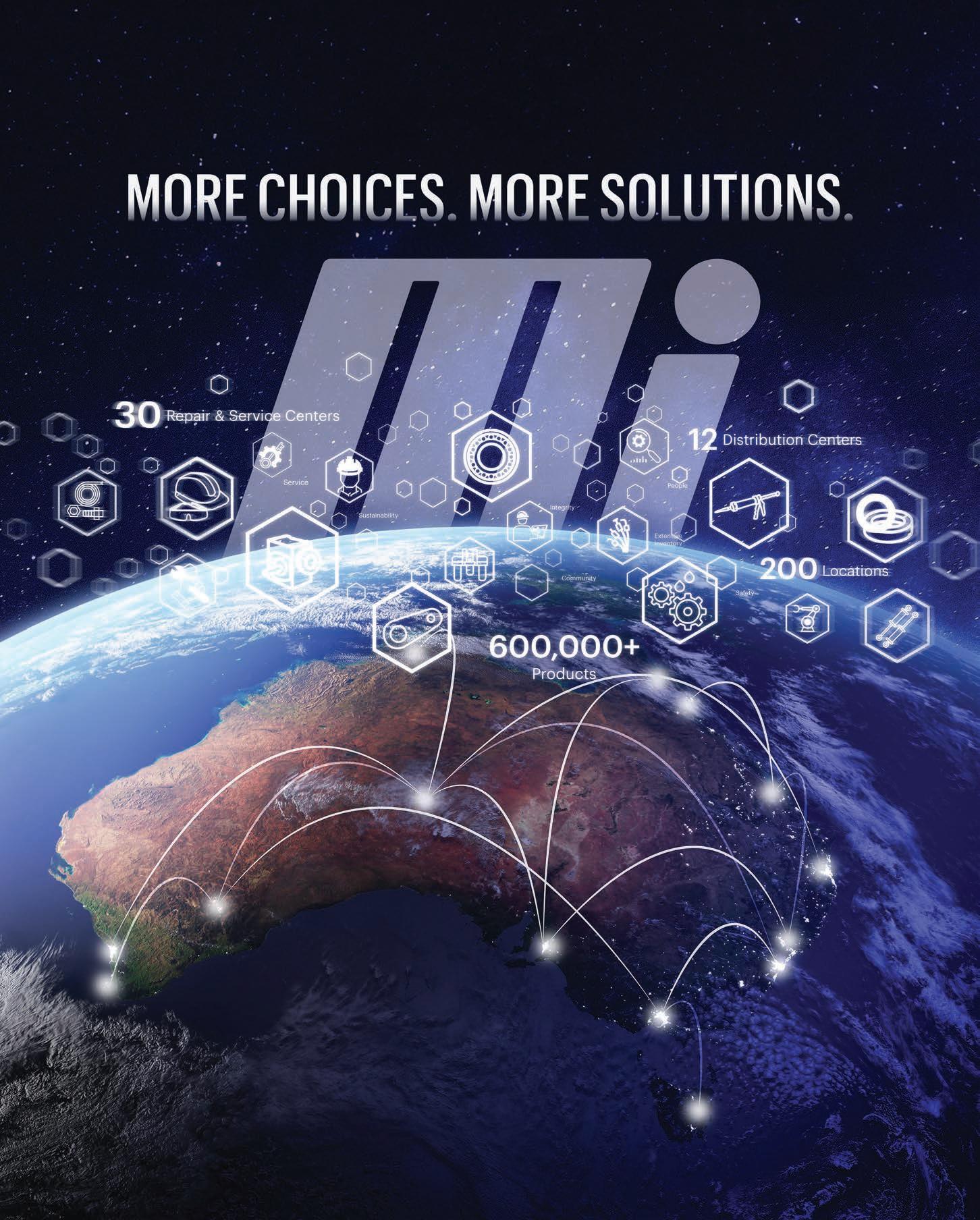
A TIMELINE DIPPED IN GOLD
THE HISTORIC PORGERA GOLD MINE IN PAPUA NEW GUINEA REOPENED ITS DOORS IN DECEMBER 2023. AUSTRALIAN MINING TAKES A LOOK AT THE TIMELINE OF THE STORIED SITE.
Few mines can boast of a history as long and varied as that of the Porgera gold mine in Papua New Guinea (PNG). Located in the country’s Enga province, Porgera’s history dates back to when alluvial gold was found in the region in 1939. No one back then could have predicted Porgera’s future importance to the PNG mining sector.
1939–1990
When government patrol officer John Black stumbled on gold while travelling through the Porgera River in 1939, he was understandably excited.
Black wrote in his diary that the find was the “best prospect I have ever seen let alone found”, but the officerturned-explorer would be waiting almost 30 years before hard rock mining at the site could begin.
The hard-to-reach area of Porgera was temporarily forgotten as World War II raged on in the early 1940s, and it wasn’t until 1964 that boots hit the ground.
The mine was then developed by an unincorporated joint venture dubbed, fittingly, the Porgera joint venture (JV).
The Porgera JV consisted of Placer (PNG), Highlands Gold Properties, Renison Consolidated Goldfields and Mineral Resources Porgera.
After negotiating with landowners and provincial and national governments, approval to mine Porgera was officially granted in May 1989.
“These negotiations included an equity component for the special mining lease landowners, Enga Provincial Government and the state, and royalties and arrangement of compensation packages to landowners,” Porgera JV said.
“(Porgera JV) was granted a temporary right to utilise the land on which it operates.”

On May 12 1989, a mining development contract was signed between the Independent State of PNG and the Porgera JV.
1990–2020
Porgera ramped up production in the late 20th century, with first gold poured on September 20 1990.
The mine was officially opened by then-PNG Prime Minister Rabbie Namaliu one month later on October 20.
“The Porgera project is of enormous importance to Papua New Guinea in
income and surpluses generated by the mining sector.”
As Porgera continued to produce gold, the coming decades would see several mergers and acquisitions shake up its ownership.
Placer Dome acquired a further 25 per cent ownership from Highlands Gold Properties in 1997 before upping its stake to 75 per cent in 2002 with its takeover of Aurion.
But it wasn’t until 2006 that things really started to change.
In a $US10.4 billion takeover deal, Barrick Gold acquired Placer Dome –and it’s 75 per cent stake in Porgera with it. Barrick acquired a further 20 per cent from Emperor Mines just one year later.
Barrick’s acquisition took Porgera to new heights. The mine produced
The following years would see the mine celebrate hitting 18 million ounces in of gold produced in 2013, 19 million in 2015 and finally 20 million in 2017. But it was only three years later that it had to shut its doors.
2020–present
Barrick had been campaigning for an extension to the special mining lease since June 2017, but by April 2020
Porgera was closed for business.
Barrick continued its discussions with the PNG Government regarding reopening Porgera throughout 2020 and early 2021 before reaching a breakthrough in April of that year.
“The Porgera gold mine is on track to resume operations later this year after the PNG Government and Barrick
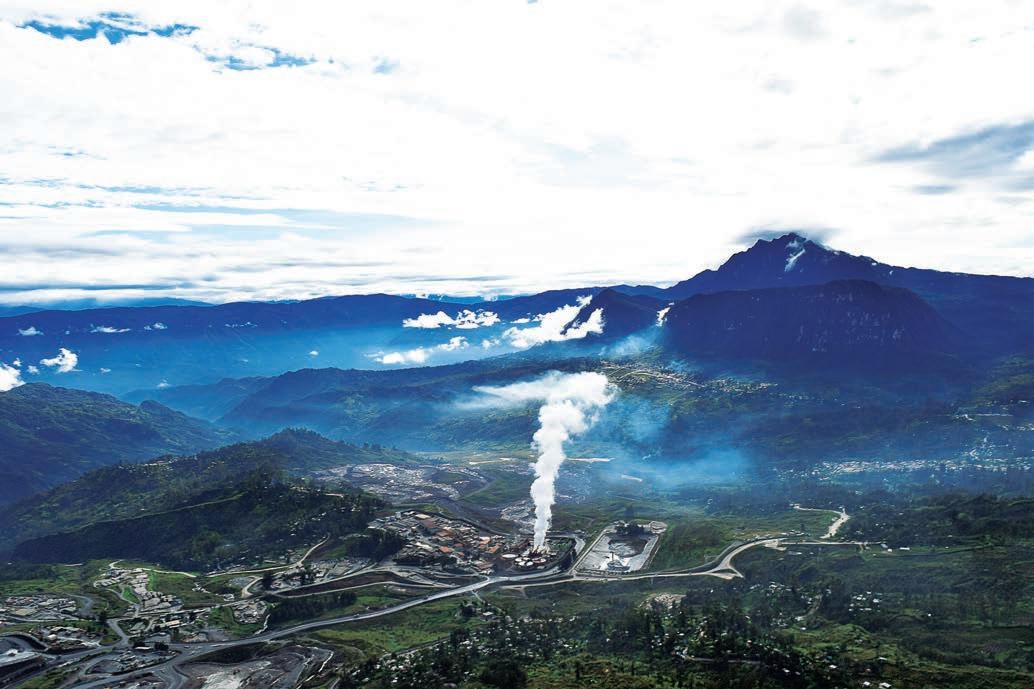
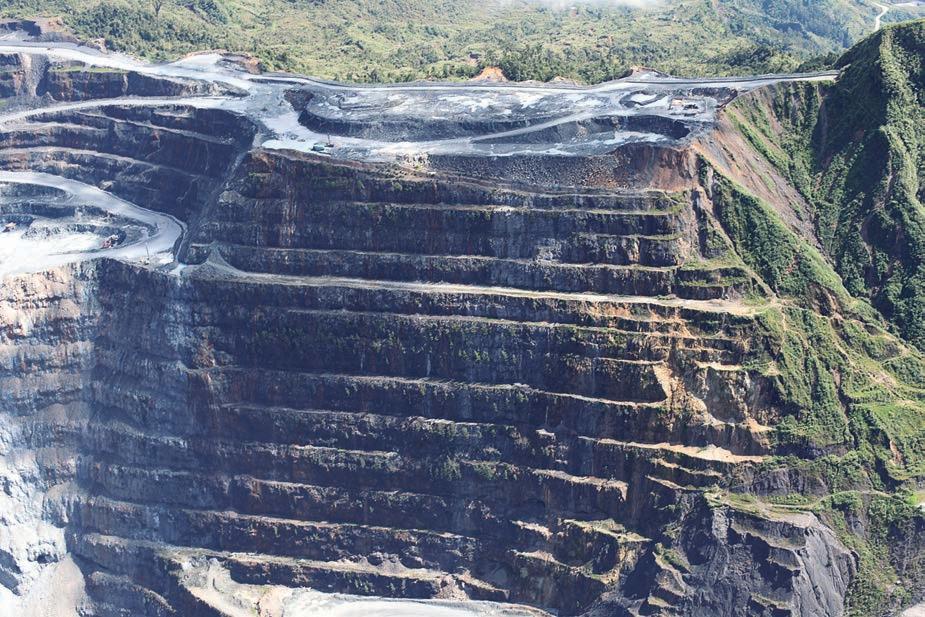
framework agreement … ownership of Porgera will be held in a new joint venture owned 51 per cent by PNG stakeholders and 49 per cent by BNL. BNL remains the operator of the mine.” But a mine as large and established as Porgera can’t restart production in a day. It wasn’t until March 2023 that
signed an agreement to progress with the resumption of operations under New Porgera Limited.
“It’s been a long journey but in the process we have secured the buyin of all the stakeholders,” Barrick president and chief executive Mark Bristow said.
our partnership philosophy so New Porgera will, whenever possible, source the goods and services it requires from businesses genuinely based and owned in Porgera, the Enga Province and PNG. “Similarly, it will give preference to locals in recruiting employees for the reopening mine.”
October 2023 saw PNG GovernorGeneral Bob Dabae grant New Porgera a special mining lease to restart production at the mine. By this time, Porgera had been sitting on care and maintenance for three years and all parties were eager to start up again.
“It’s been a long road but the end is now in sight,” Bristow said.
“Negotiations between Barrick, the government and the other stakeholders required patience and persistence, but the spirit of partnership in which they were conducted eventually led to an outcome acceptable to all.”
Just two months later, on December 22 2023, Porgera once again had boots on the ground.
“Following the formal completion of the Porgera Project Commencement Agreement, work has started on the recommissioning of the Porgera gold mine, which has been in care and maintenance since April 2020,” Barrick said. “This work is expected to be completed over the next few weeks, paving the way for mining and processing to restart in the first quarter of 2024.”
Porgera has had its share of ups and downs in its long history, but it has begun 2024 with a new positive chapter.
As operations ramp up throughout the year, Porgera is set to reclaim its place as one of the most well-known and successful mines in the world AM
BULK RETURNS FOR 2024
AFTER A SUCCESSFUL SHOWING IN 2022, THE AUSTRALIAN BULK HANDLING EXPO IS BACK. AUSTRALIAN MINING TAKES A LOOK AT WHAT THIS YEAR’S ATTENDEES CAN EXPECT.
Bulk handling is a particularly varied and diverse industry, and one that is incredibly important to the Australian mining sector.
At first glance, it might seem that a major iron ore mine, a cement plant and a grain shipping terminal have little in common. However, they each use similar equipment like conveyors, silos and hoppers to move their materials from one point to another.
The Australian Bulk Handling Expo (BULK2024) plans to bring this diverse industry together under the one roof .
To be held at the Melbourne Exhibition and Convention Centre from September 18–19, BULK2024 aims to help spread industrial knowledge, showcase the latest technologies and innovations, and provide an opportunity to network with like-minded peers.
Show director Lauren Chartes said the event is the only dedicated Australian expo for producers of bulk commodities such as grains, coal, iron ore, cement, animal feed and woodchips.
“The bulk handling industry is a vital part of Australia’s economy, with a wealth of knowledge and expertise to share,” Chartes said.
“To have all these exhibitors under one roof is not only a great place for business opportunities, but a fantastic occasion to network within this essential industry.”
The latest in equipment will be on display at the exhibition, including conveyors, silos, motors and drives, belt scrapers, container tipplers, dustcontrol systems, and weighing or level measuring products.
“Industries around the world are revolutionising as technology becomes more connected,” Chartes said. “Industry 4.0, automation and artificial intelligence have the potential to radically change the way businesses operate.
“Stakeholders from a broad range of sectors will share their insight and expertise on how to stay at the cutting edge of technology and avoid being left behind.”
Attendees will have the chance to connect with industry leaders and innovators on the show floor and at networking opportunities at the show. The event will also offer lots of opportunities to meet all new types of clients and learn about new markets.
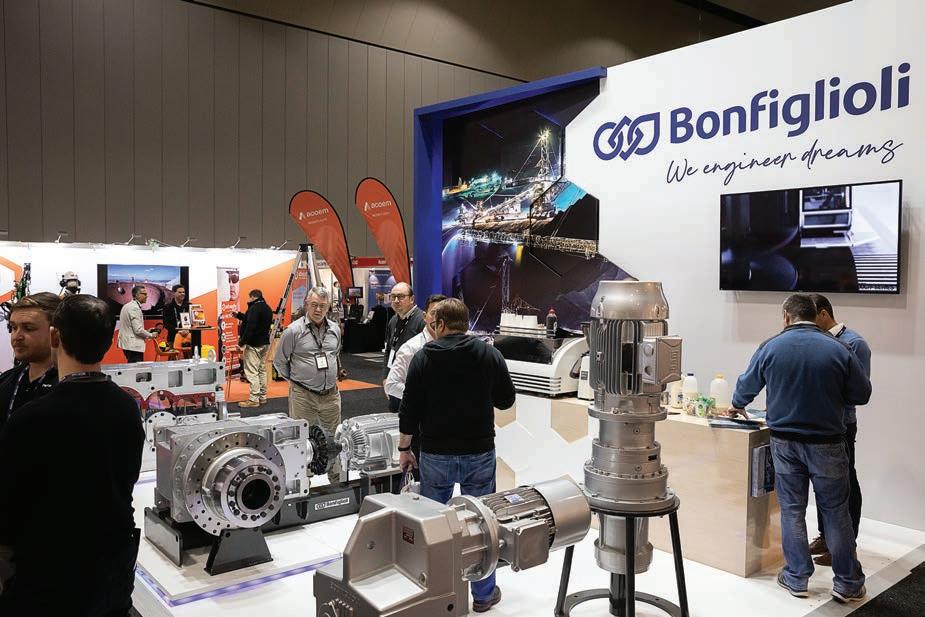
TO HAVE ALL THESE EXHIBITORS UNDER ONE ROOF IS NOT ONLY A GREAT PLACE FOR BUSINESS OPPORTUNITIES, BUT A FANTASTIC OCCASION TO NETWORK WITHIN THIS ESSENTIAL INDUSTRY.”
BULK2024 will be held in conjunction with one of Australia’s biggest transport, logistics and supply chain events, MEGATRANS. The two events will be hosted over 30,000 square metres, with one-ticket entry for access to both exhibitions.
It will also host the 2024 Australian Bulk Handling Awards, the country’s only awards program specifically for the bulk handling industry. Chartes said the awards represent an opportunity to acknowledge and celebrate the outstanding achievements and successes of companies and individuals that have demonstrated innovative practices and superior performances across the year.
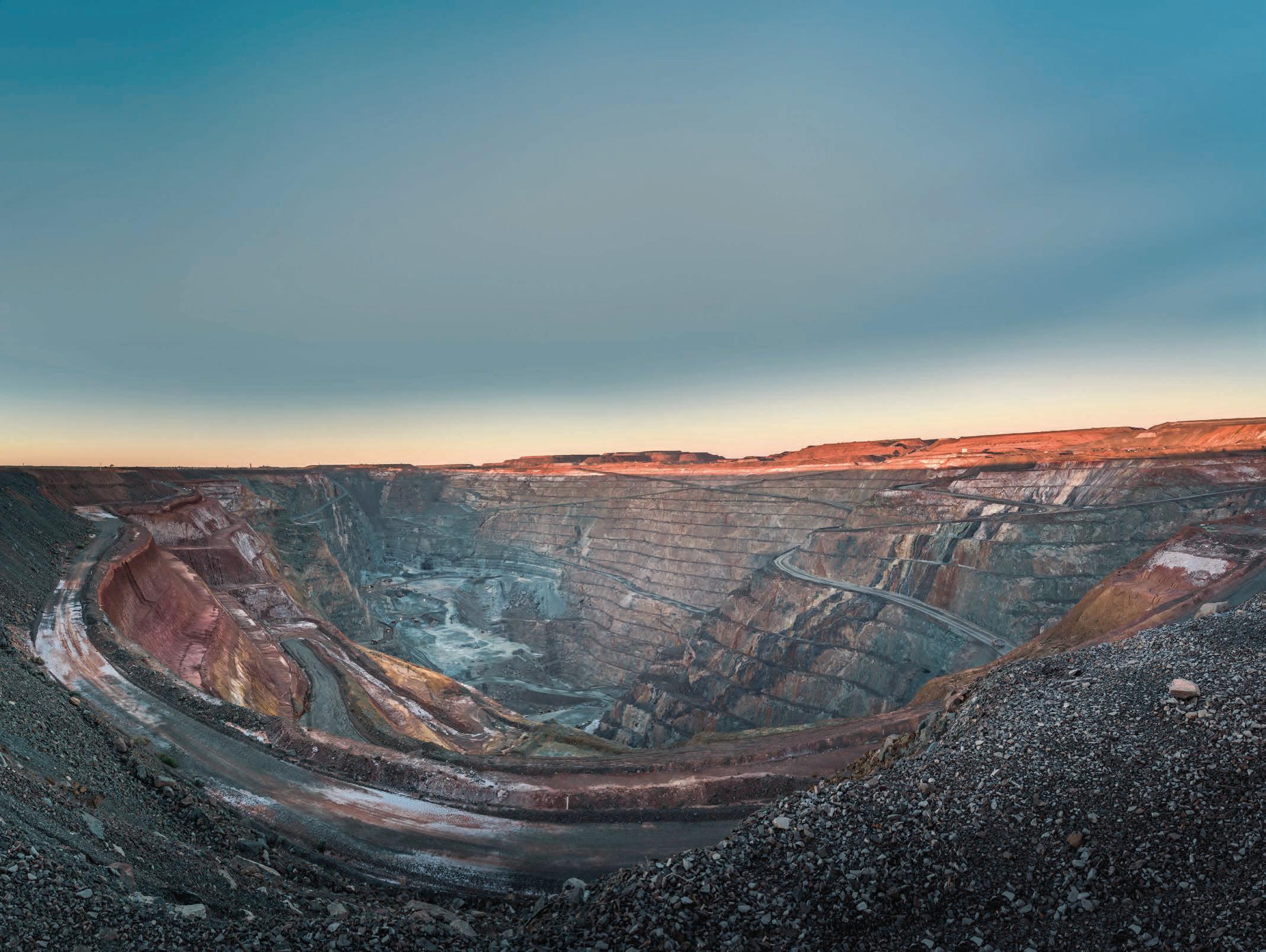
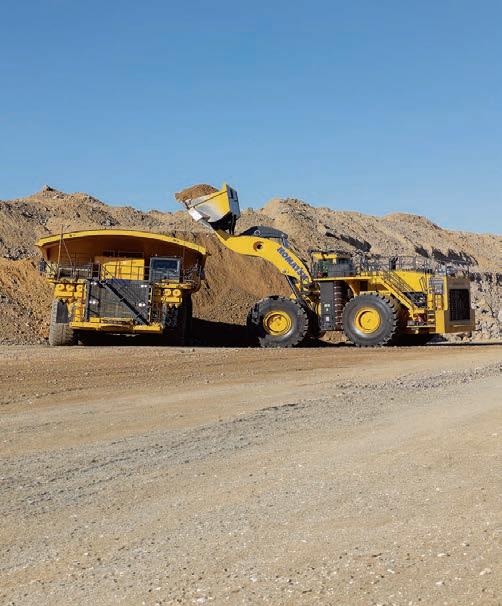
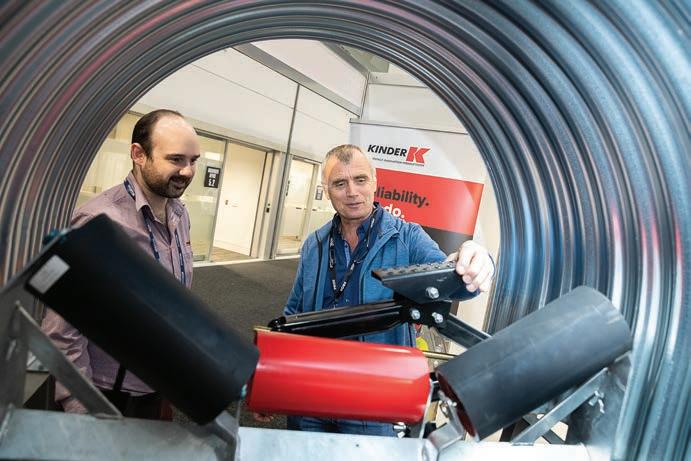
Nominations are currently open for the awards night and can be submitted online at the Bulk Handling Awards website. Winners will be announced at the gala dinner to be held on September 18.
“We’re inviting everyone to be a part of this game-changing expo – from hands-on decision makers in the bulk handling industry to CEOs, COOs,
regulatory bodies, and government at all levels,” Chartes said.
“We’ve seen how impactful bringing the industry together was at BULK2022 and are excited to see the industry continue to grow.” AM
BULK2024 will be held at the Melbourne Convention and Exhibition Centre from September 18–19.
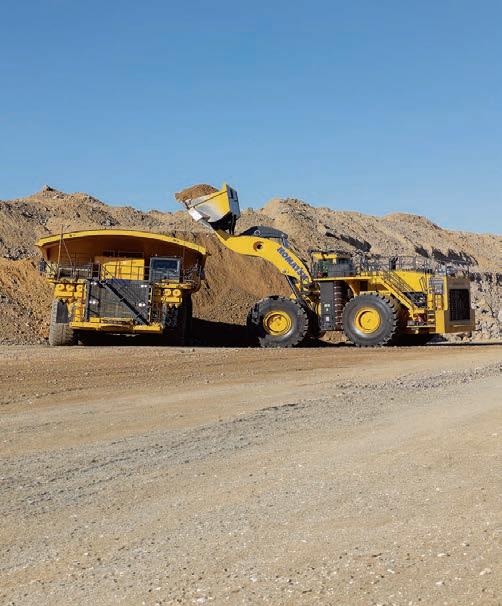
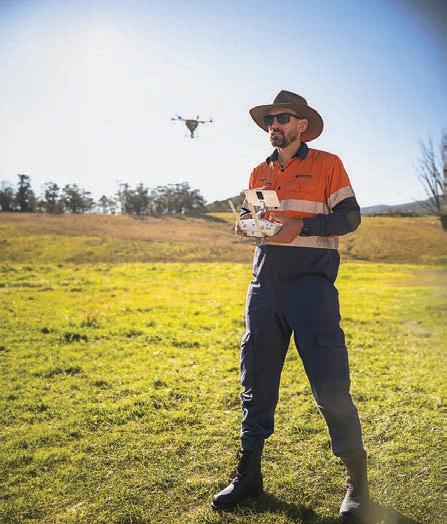
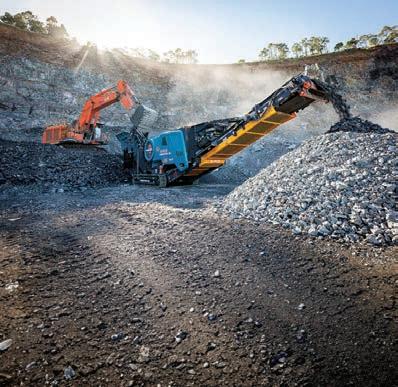
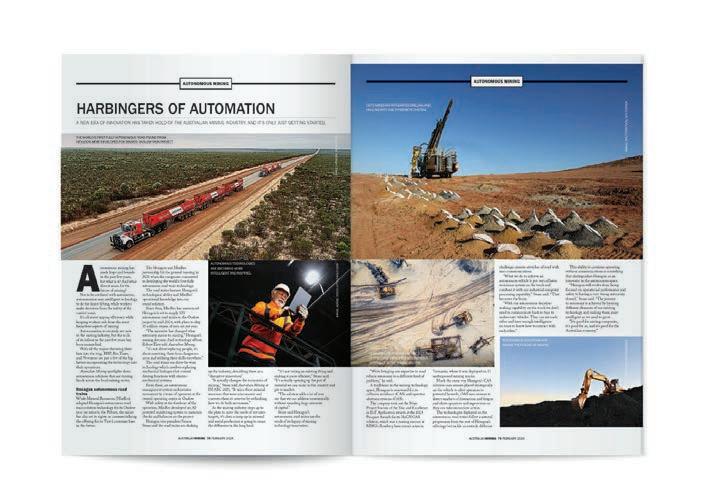


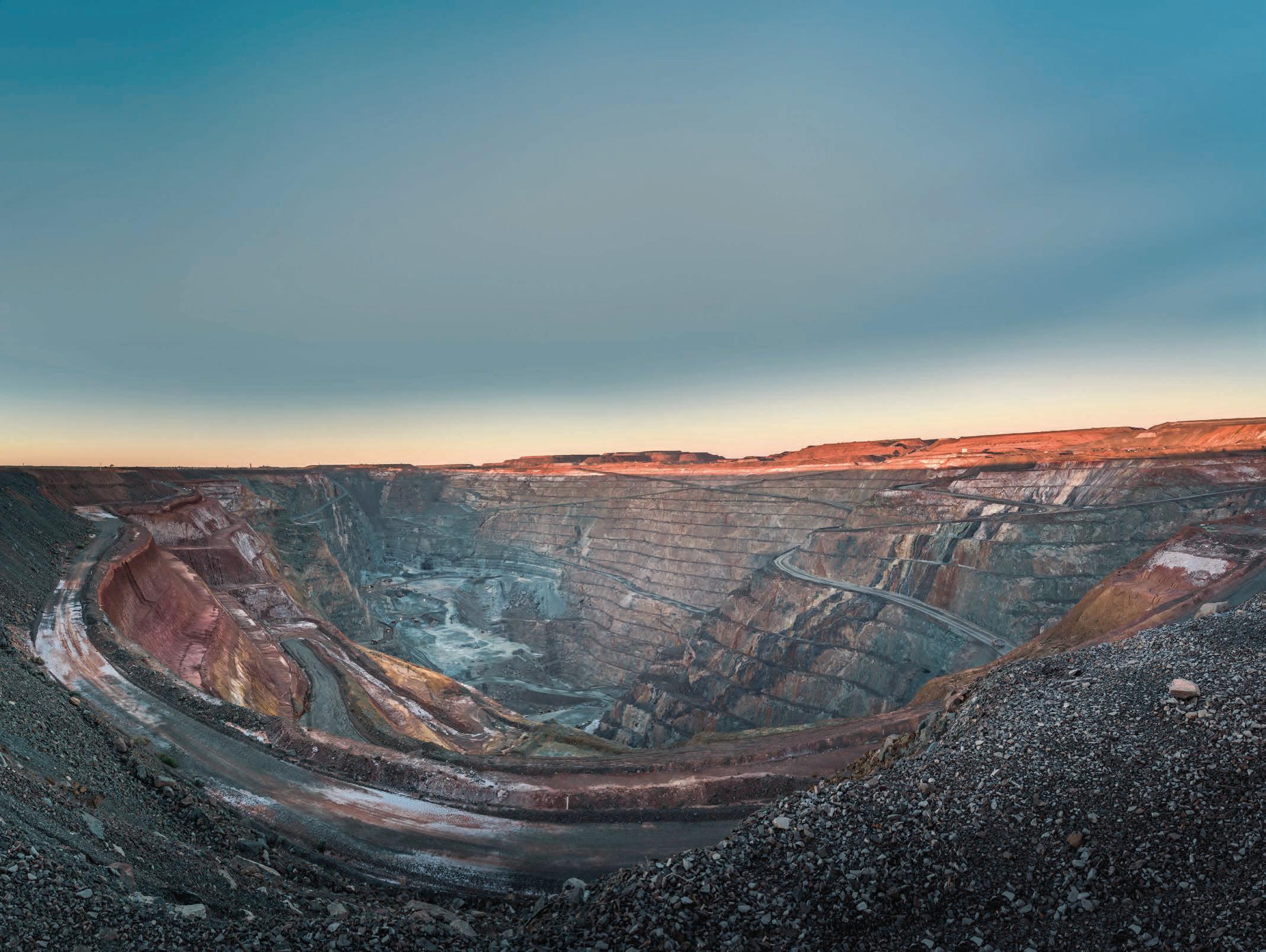
A SHIFT IN THINKING
AUSTMINE KNOWS THAT COLLABORATION IN THE MINING INDUSTRY IS THE KEY TO REACHING NEAR-TERM DECARBONISATION GOALS.
Though mining is essential to everyday life, as well as to the clean energy transition, it also has palpable effects on the environment. That’s why environmental, social and governance (ESG) considerations have become a major talking point among mining executives and stakeholders.
Deloitte’s Tracking the Trends 2023 report – which highlights 10 key trends affecting the mining industry –suggested pressure for mining companies to decarbonise is coming from both ends of the supply chain, whether it’s manufacturers wanting carbon-neutral commodities or investors prioritising environmentally proactive companies.
Mining companies who fail to decarbonise will simply be left behind, making hitting ESG targets a matter of longevity.
Recognising both the importance and scope of this challenge, many miners have committed to reducing their emissions by between 25 and 50 per cent by 2030 and 2035. And for many of these companies, one of the most logical ways to achieve such a goal is through the electrification of diesel equipment.
But Austmine innovation facilitation lead Kevin West believes while miners are looking in the right direction, in many cases the task is too complex and time-consuming for a company to achieve on its own.
West is the mind behind Austmine’s latest collaborative opportunity hosted on its mineinnovate platform.
The opportunity, named Accelerated Vehicle Acquisition and Trialling, is aimed at introducing standardised solutions to help speed up asset selection and testing for battery electric vehicles on mine sites.
“Currently the process of acquiring new assets is hampered by supply and demand issues,” West told Australian Mining.
“Lead times are long, and the trial periods are uncovering unexpected issues due to differences between traditional and new energy solutions.
“Many miners are also considering retrofitting equipment to replace
diesel as an accelerated approach to decarbonising their legacy assets.”
The problem is that mining companies – which are heavily processdriven entities – are going about the acquisition and testing of electric assets the same way as they always have with diesel assets. But market conditions and technologies have changed, which West said demands a new methodology – one driven by collaboration.
“Fundamentally, a power source has been taken out and until now miners have never had to look for alternatives,” West said.
“I remember a conversation I had with a particular company which ordered a battery electric truck,” he said.
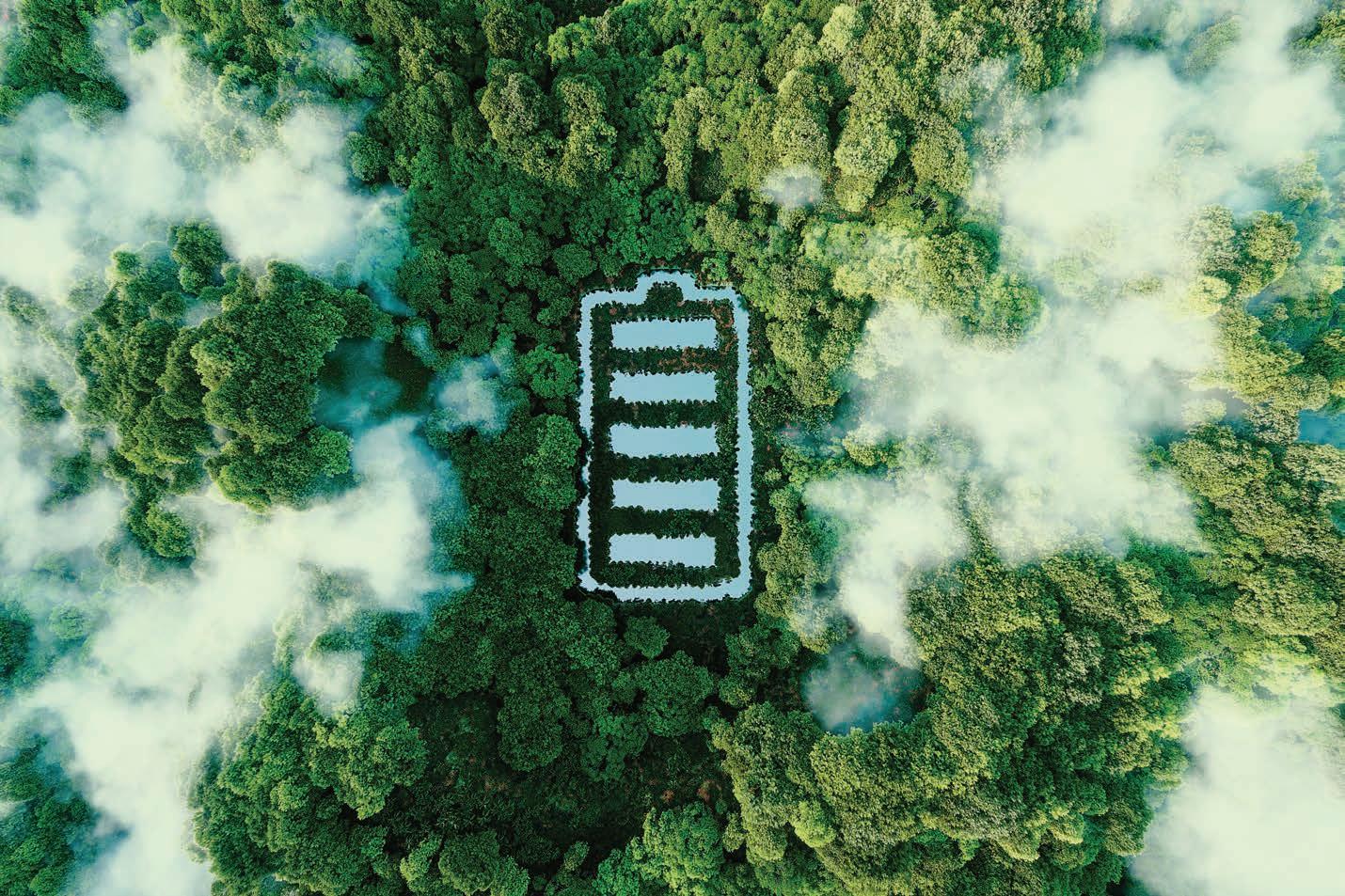

“The truck had a lead time of 15 months, which blew out by an additional 20 months. That’s almost three years just to physically get their hands on the vehicle for trialling.
“It took two months to get that truck site ready. The trials they ran were exactly the same as what they had with diesel because they didn’t know how to trial it any differently. The truck failed just six months into the trial, and the company was back to square one.”
The idea of Austmine’s latest initiative is to bring mining companies and suppliers together, with the two parties to innovate new approaches for selecting and trialling electric vehicles on mine sites.
“There are some original equipment manufacturers that are creating simulation tools for rolling out electric vehicles, but they will only guarantee that for their assets and not others,” West said.
“What we’re looking to do is create a standardised tool available to all electric vehicle manufacturers.”
Suppliers have been invited to submit proposals as part of the initiative, with selected suppliers to partner with mining companies to rapidly build:
• confirmation of the capability of their selected vehicle
• emission savings comparison data
• charging requirements for the vehicle and locations for charging equipment
• test data for vehicle trials
• a reusable template for trialling different configurations.
“The outcome of this opportunity will allow miners to run side-by-side comparisons of how different vehicles will perform in circumstances specific to each mine site,” West said.
“If a company is tossing up between five different trucks, the standardised tool can help them figure out which truck will be able to achieve their targets, taking into consideration charging requirements, carbon emissions, and whatever else. This is where the template becomes reusable.
“Instead of a year-long trial, you’re trialling against the test data. This will allow miners to compress trials down from a year to just weeks.”
West said Austmine’s Accelerated Vehicle Acquisition and Trialling opportunity will be the first in a series.
“We want to run a second challenge in the near-term that basically says: now that we understand how a single asset is going to perform, how do we upscale that if a site needs 14 of these?” he said.
“Everyone’s looking for the silver bullet that’s going to solve their ESG problems. But a bullet has a head, a shell, a charge, a primer.
“And the size of the bullet depends on whatever it is you’re trying to achieve. So in the context of the mining industry’s current challenges, that silver bullet
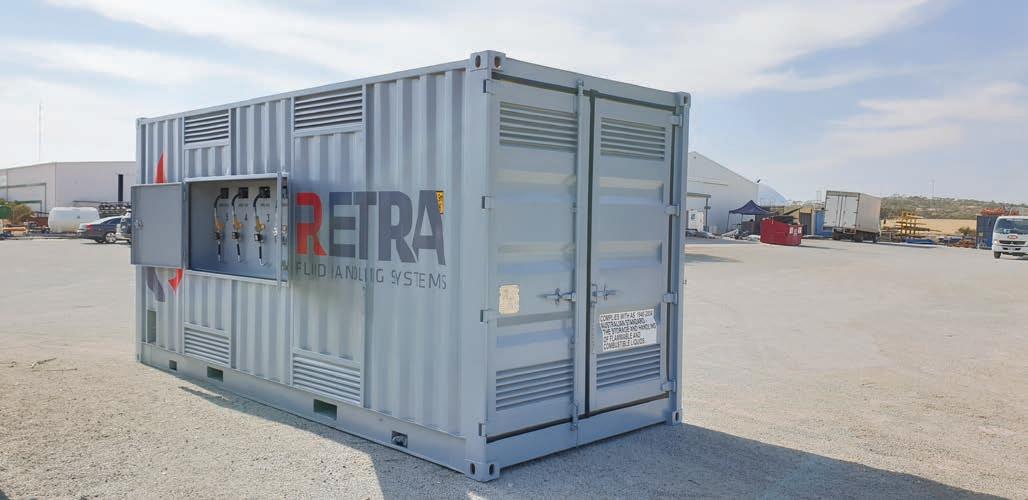



A SAFER TOMORROW
AUSIMM’S INTERNATIONAL MINE HEALTH AND SAFETY CONFERENCE WILL SHINE A LIGHT ON WHAT IS ARGUABLY THE MOST IMPORTANT ASPECT WITHIN THE WHOLE MINING CHAIN.
If you’re not aware of the risk factors on a mine site, then they won’t be dealt with.”
That’s Michael Quinlan, emeritus professor of industrial relations at the University of New South Wales and a staunch believer that mine sites can always do more to help protect their employees.
Quinlan will be delivering a keynote speech at AusIMM’s International Mine Health and Safety Conference in Perth from April 15–17, and he’s looking forward to sharing his knowledge to help prevent future incidents.
“What I often see is that latent failures that have been sitting there for years are a big cause in mine accidents,” Quinlan told Australian Mining
“There might be people who have walked past something amiss a number of times, thinking that because it’s still there it’s safe.
“But it only takes one spark for trouble
A particular topic of interest for Quinlan is that of contractors. As the mining sector diversifies, more contractors are being brought in to help the industry run, but this poses its own set of problems.
“For a site to be safe, you need people who know the workspace well,” Quinlan said. “No matter how experienced you are, if you don’t know a site like the back of your hand then you’re at greater risk.”
Quinlan’s passion for health and safety led him to write Ten pathways to death and disaster, a book now used across mine sites to educate employees about why accidents happen and what they can do to prevent them.
The book details the 10 pattern causes that repeatedly feature in mining incidents.
“I have been running safety climate surveys using Ten pathways 2017 and it’s been useful to see where management and their employees sit in relation to that,” Quinlan said.
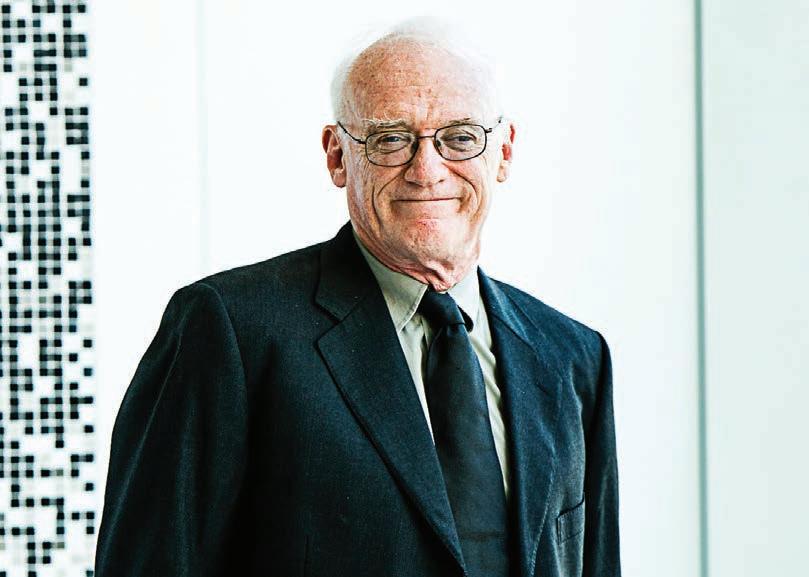
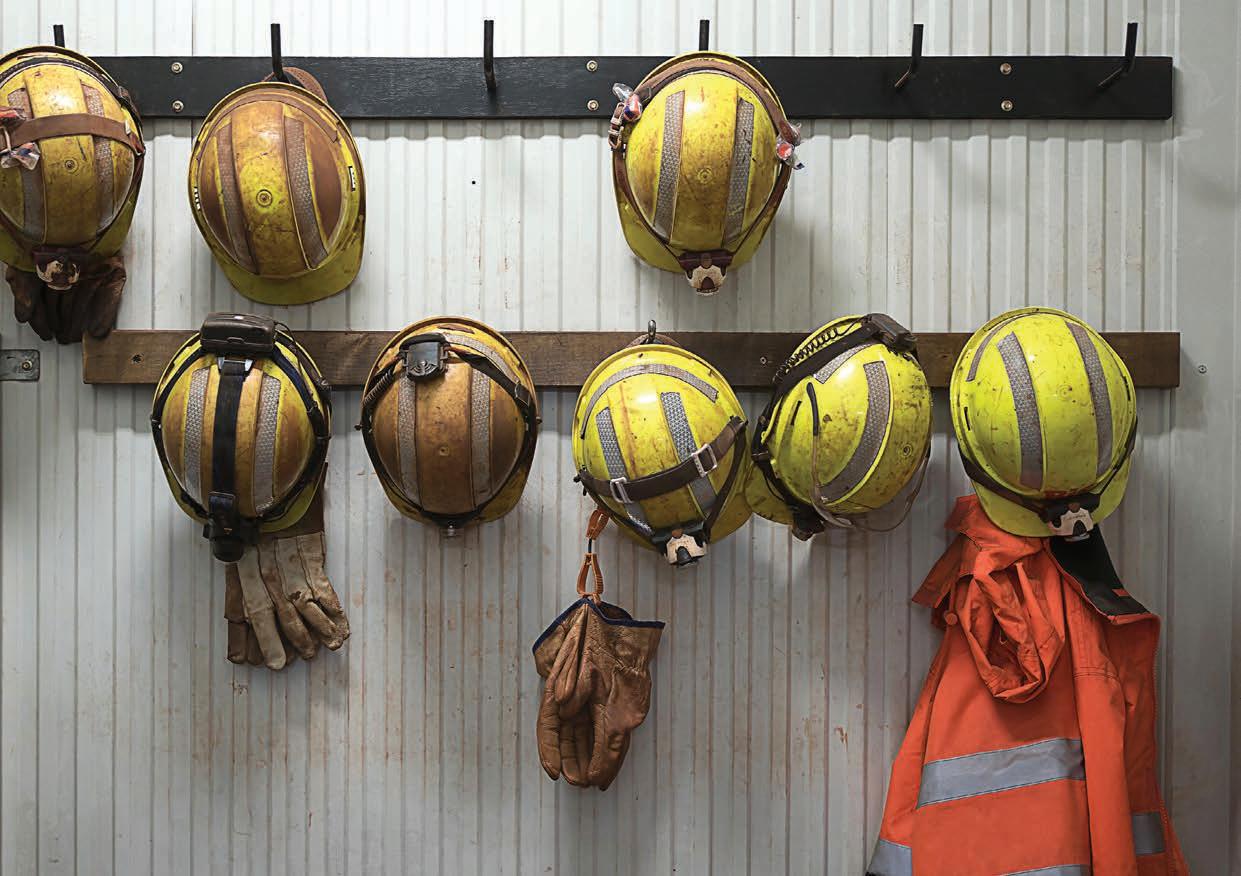
Health and Safety Conference will equip attendees with the resources they need to recognise the risk factors associated with Australia to be a model for the rest of the
RAMMER ROCKBREAKER SAFETY AND SUSTAINABILITY
CAPS MINE-SPEC COMPRESSOR SKID PACKAGE
Some studies have reported that accidents are five times more likely when working on breakdowns compared with planned and scheduled maintenance jobs.
This is where Rammer’s reputation for reliability and safety comes in – a result of over 40 years of product development, technical expertise and international maintenance programs with the company’s world-first RD3 hydraulic rockbreaker monitoring technology.
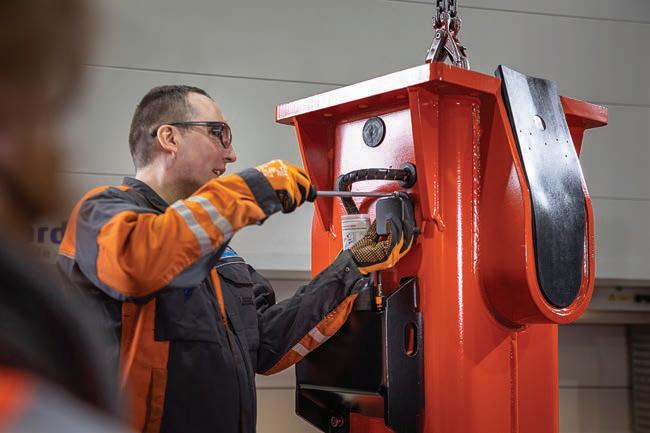
Rammer is committed to manufacturing quality products that improve safety, while minimising its environmental impact.
Adopting a sustainable approach to its manufacturing facilities and supply chains, Rammer rockbreakers are designed with the environment and responsible-sourcing practices in mind.
Helping operators work more productively and maintain their rockbreakers safely is supported by a dedicated global dealer network with readily accessible genuine Rammer parts and product expertise.
• at tachmentspecialists.com.au/rammer
WHERE AUTONOMY MEETS EFFICIENCY
The new HiLight BI+4 from Atlas Copco is an innovative and easy-to-use light tower that delivers energy-efficient light coverage to help boost operational productivity, minimise environmental impact and meet stringent safety standards.
Featuring a state of-the-art surface mount device, LED lighting technology and lithium-phosphate batteries, the HiLight BI+4 provides excellent performance and efficiency enabling operators to utilise four modes, providing them maximum flexibility while reducing their carbon footprint and operating costs.
With an innovative, fully directional, LED lens, the Highlight BI+4 also maximises light coverage while reducing lighting waste. A single BI+4 tower can cover an area of up to 4,000m2 with an average of 20 luxes of brightness ensuring a brighter, safer and more productive site.
•
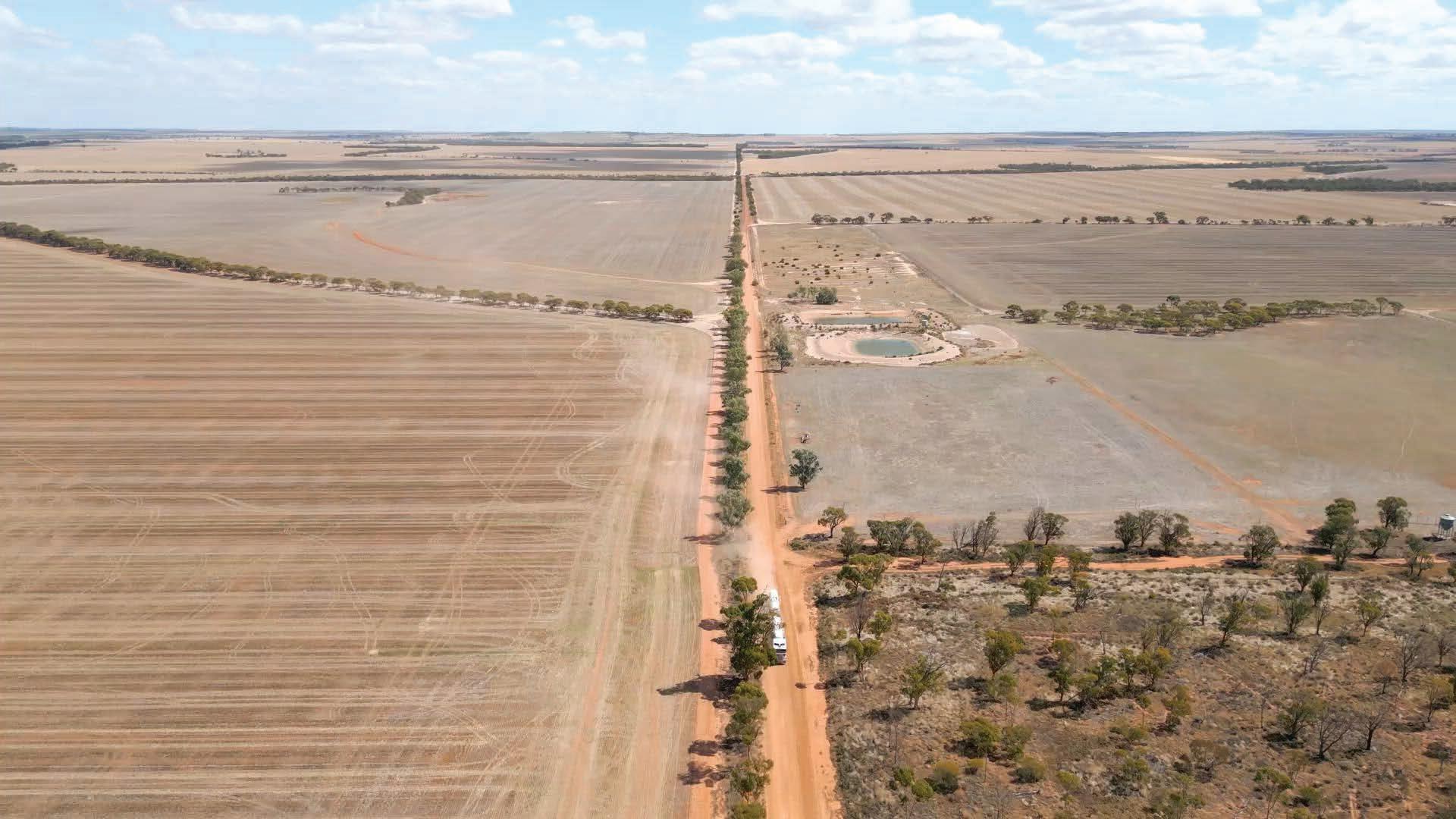
Hundreds of engineered skid packages have been designed and built by CAPS for customers in Australia and 38 countries worldwide, each fully customised to the client’s needs.

For those looking to hire for more flexibility, CAPS also offers the mine spec MM160KT Miners Pack as standard. Assembled in-house at CAPS’ Perth manufacturing and assembly plant, each package includes an Ingersoll Rand compressor modified to comply with typical mine regulations, a 3400L air receiver, and a power supply operating at either 415V or 1000V.
Mounted to a durable skid frame with a heavy-duty roof, every Miners Pack allows for easy transport and equipment protection.
Australian owned and operated, CAPS has had mining at its core for more than 44 years, offering some of the best products in compressed air and power generation, with custom engineered solutions built for any environment.
• caps.com.au
NEXT-GENERATION BELT TRACKING
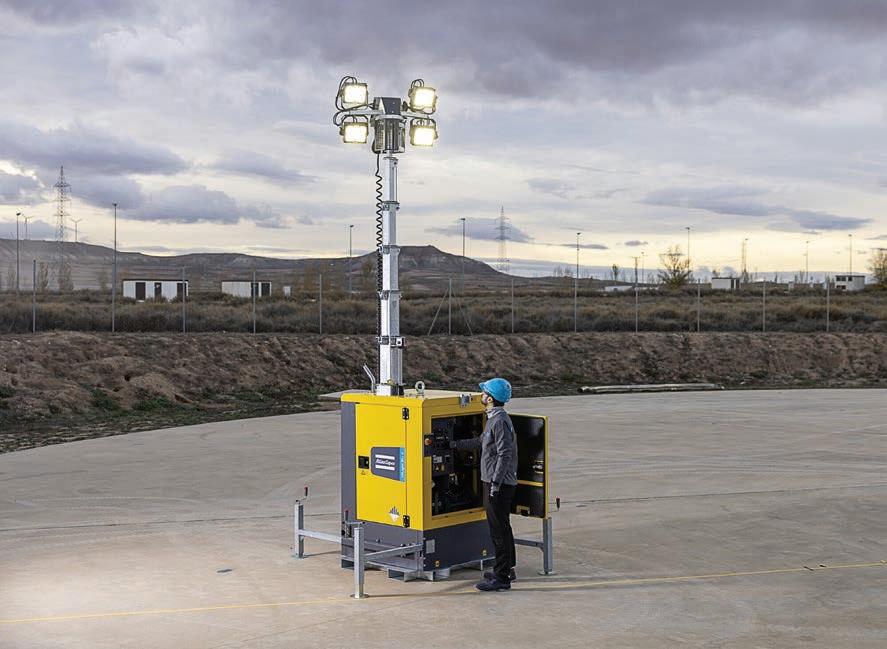
Martin Engineering has launched the next generation of conveyor belt tracking technology in a bid to eliminate belt mistracking.
The Martin Tracker HD belt conveyor alignment system provides immediate, continuous and precise adjustment of mistracking belts, using sensing rollers that ride either side of the belt and are attached to the end of an arm assembly.
As the rollers detect slight variations in the belt path, the force of the wandering belt causes the arms to automatically position a pivoting idler in the opposite direction of
The lever action requires less force to initiate the correction and only slight adjustments mean the consistent contact between the belt and idlers reduces the energy needed to bring the belt back into alignment.
The system is designed to withstand the stress associated with wider, thicker belts moving at higher speeds and carrying heavier loads.
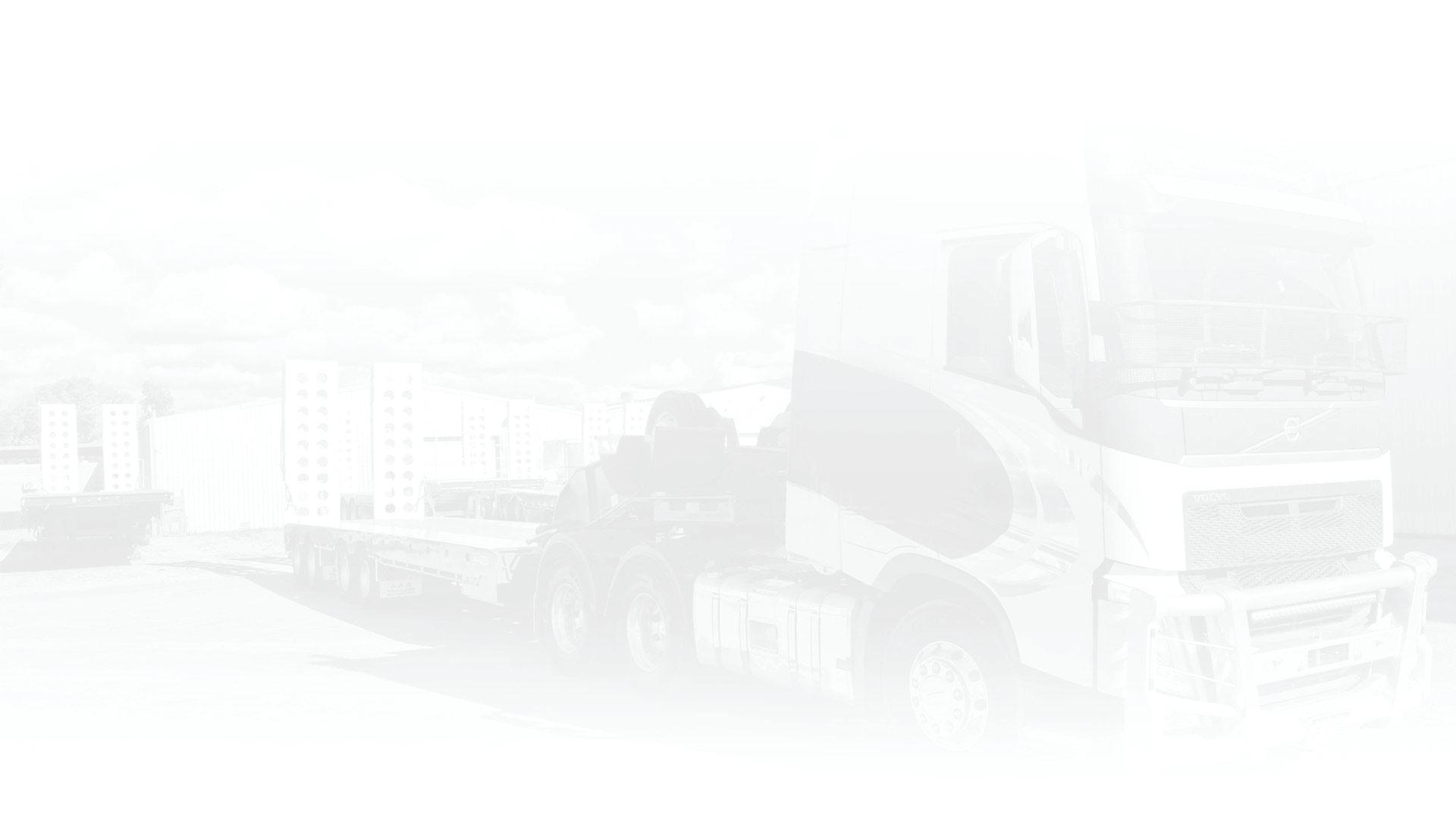
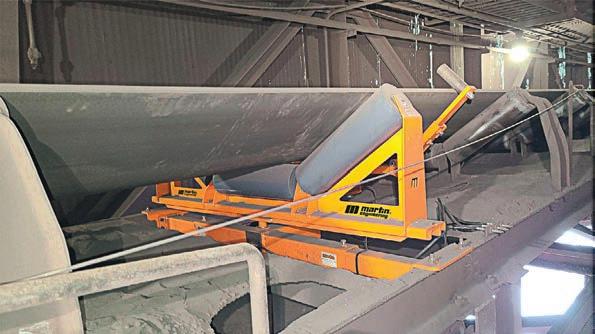

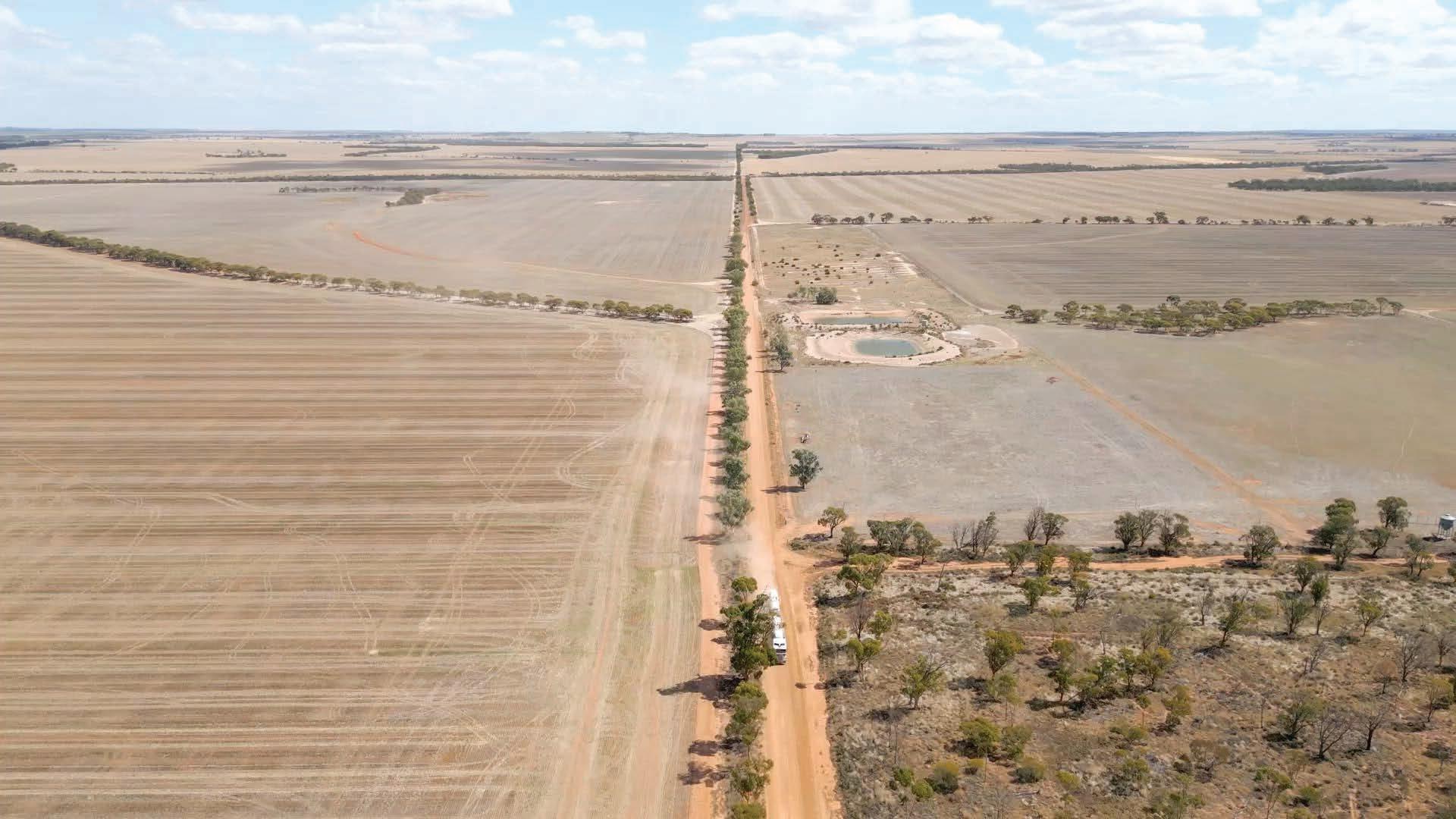

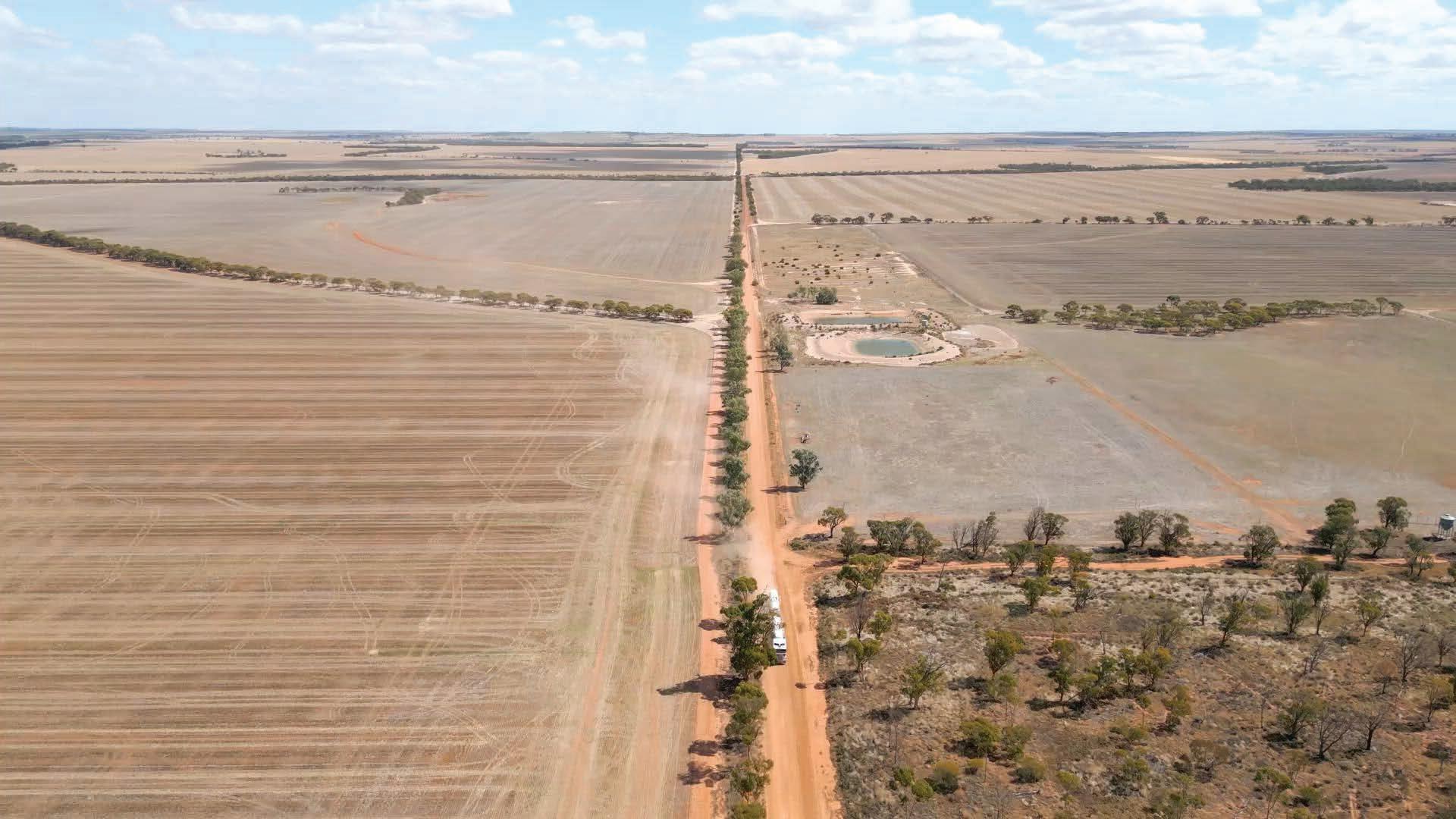

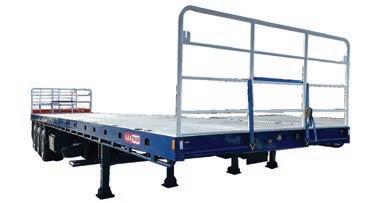
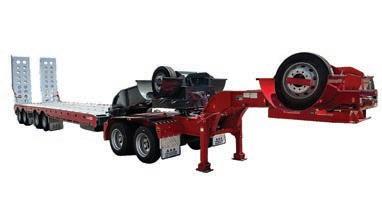
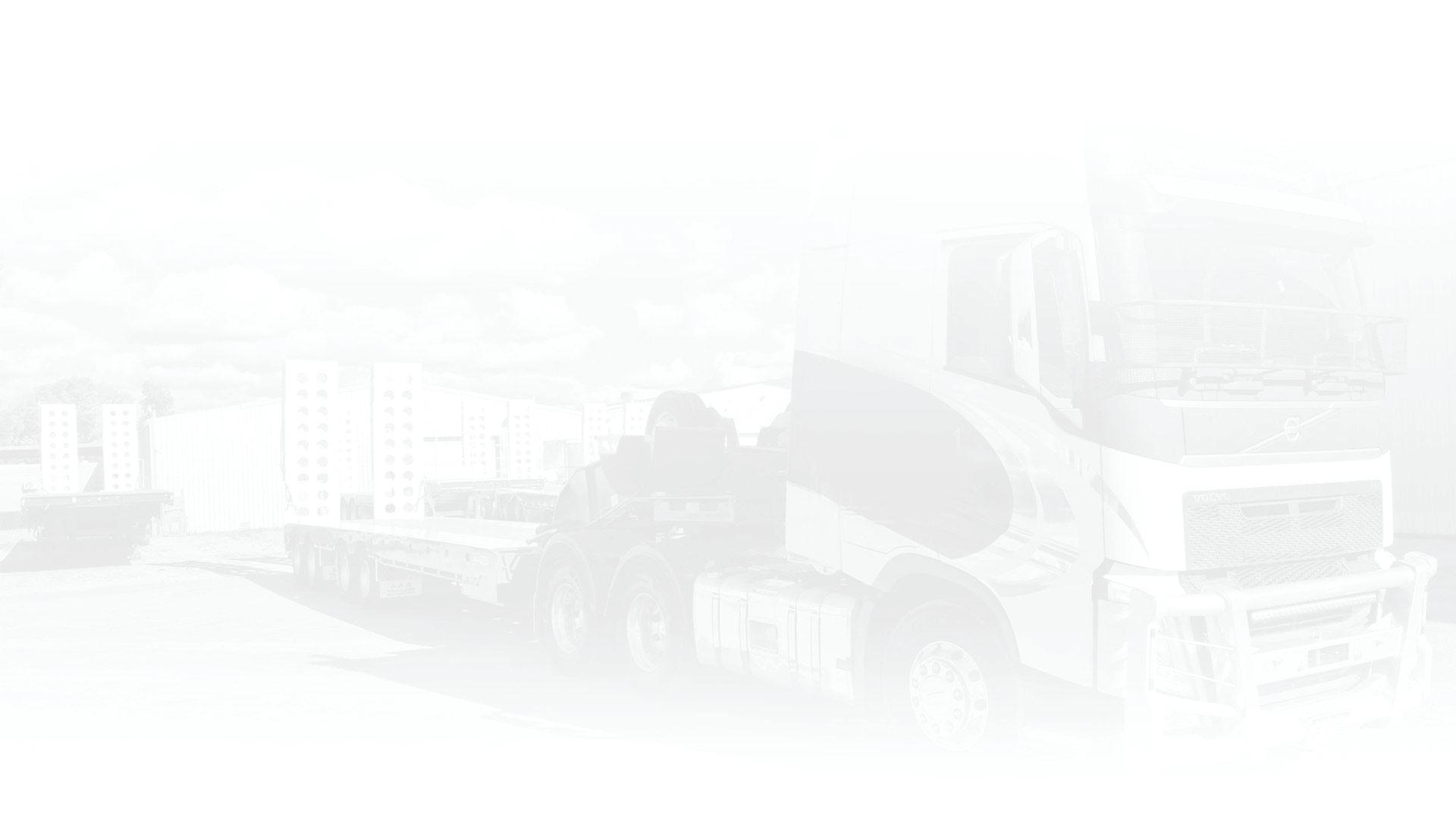
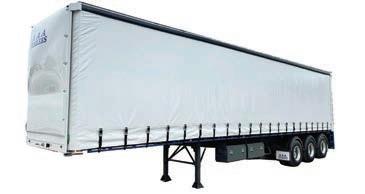
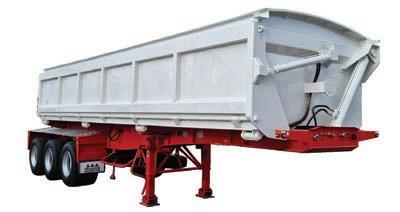
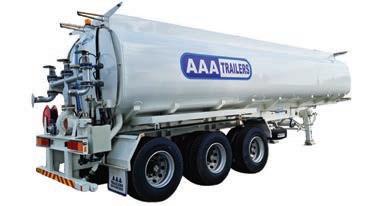
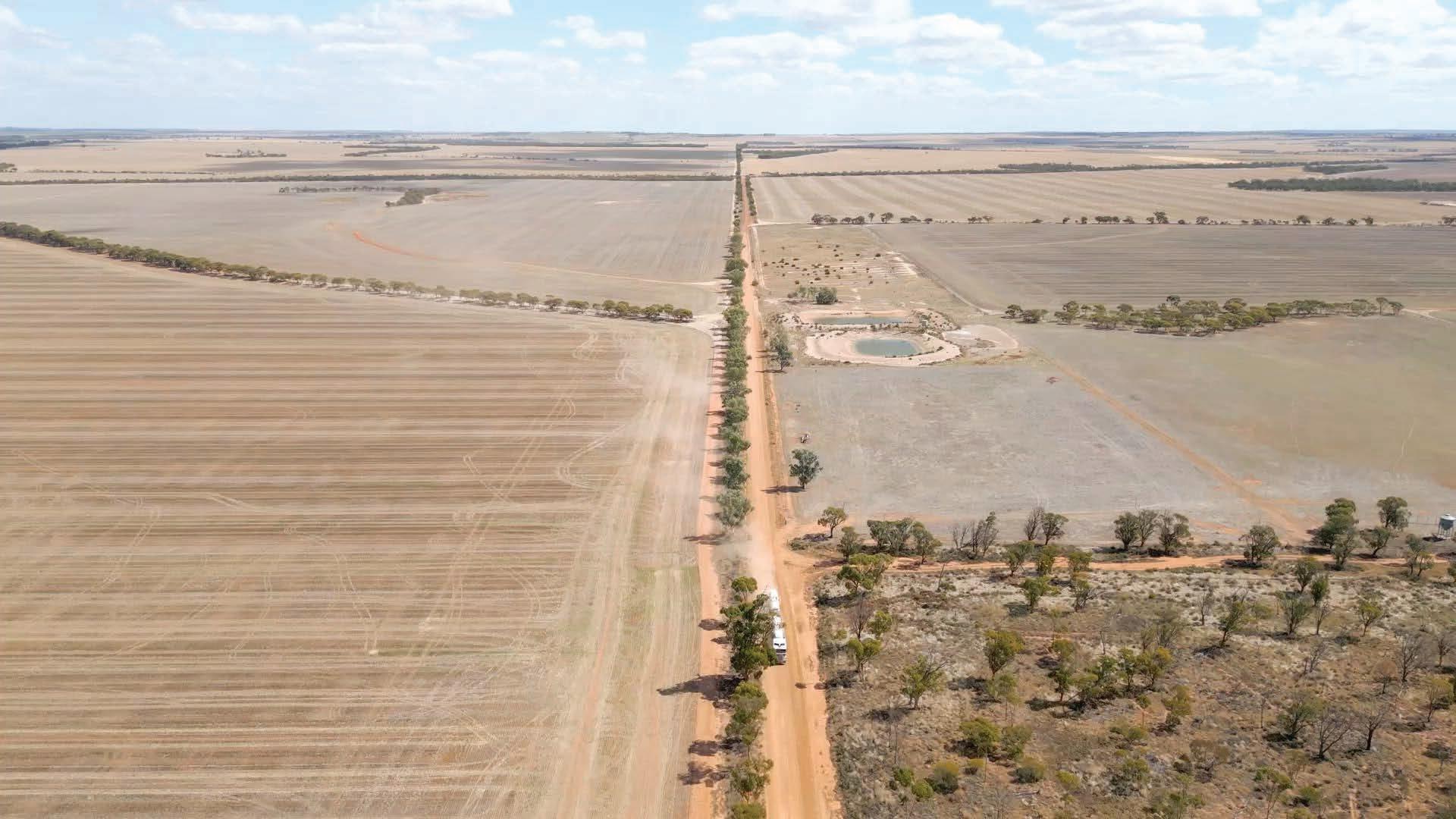


INTRODUCING THE INDUSTRY’S TOUGHEST SUBMERSIBLE PUMP
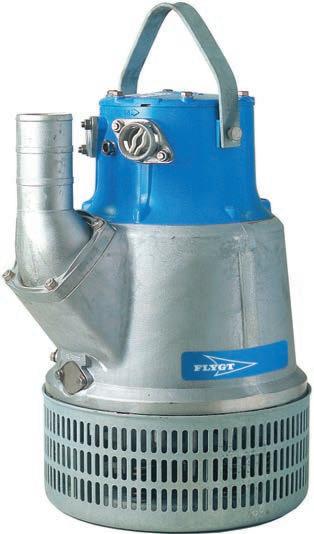
2151
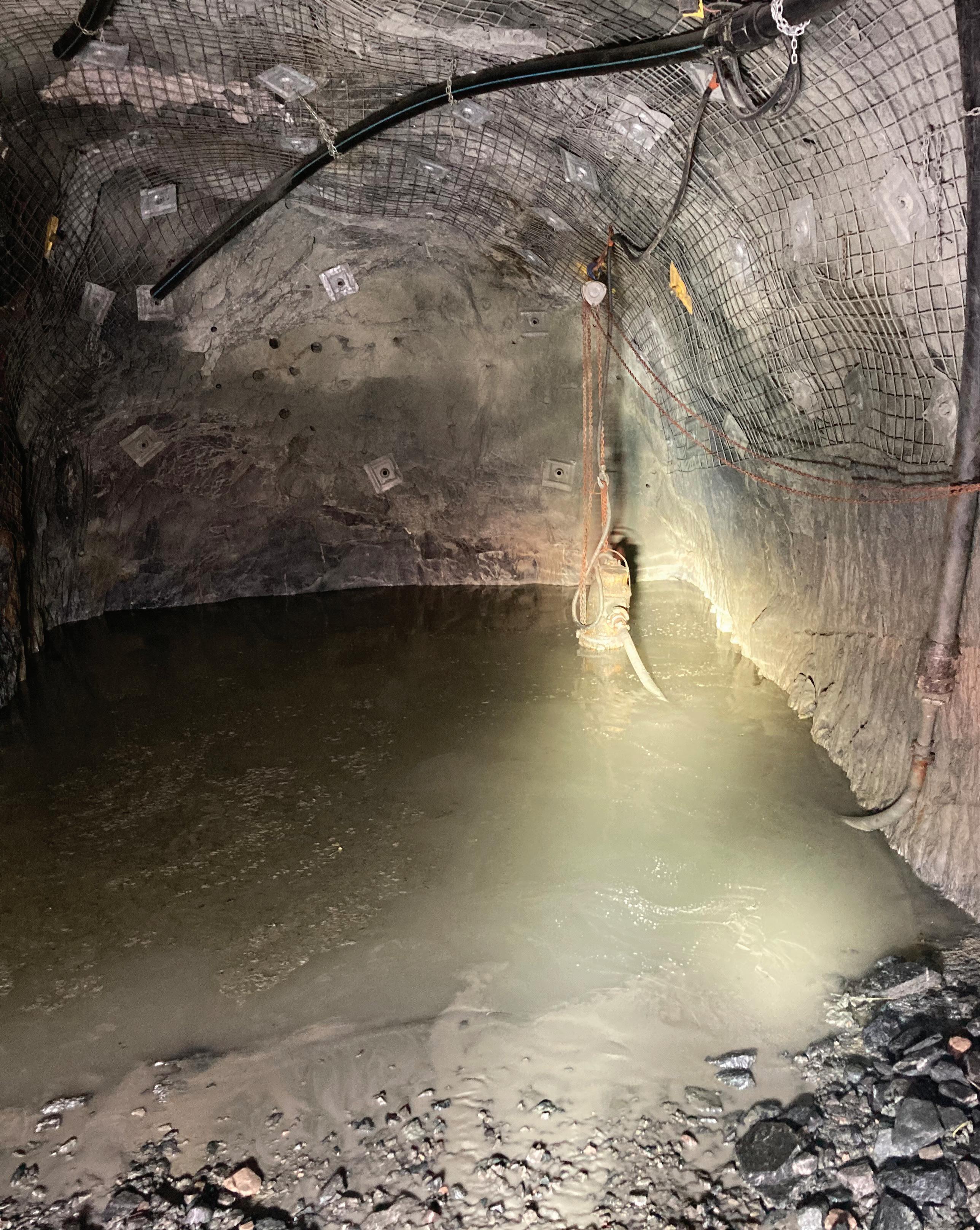
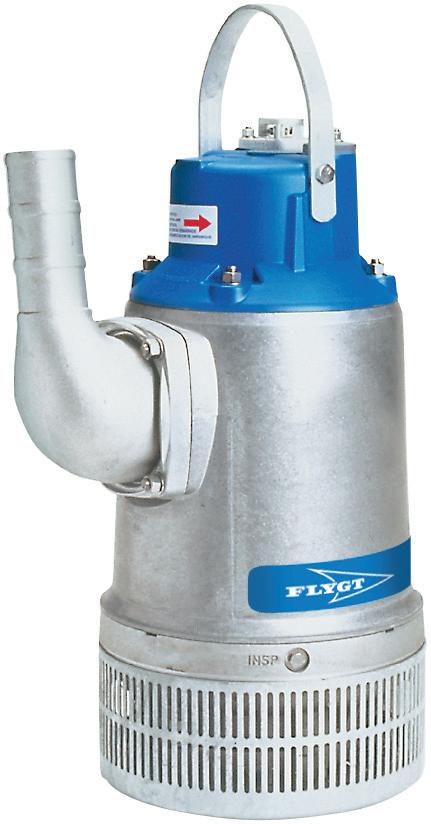
High Performance Dewatering Pumps
The Flygt Bartail 2125 (8kW) and 2151 (20kW) submersible pumps are continuing to lead the way in underground mine dewatering.
The Bartail duplex white iron and duplex stainless steel hydraulic end is engineered to best handle the highly erosive underground conditions whilst also being better suited for corrosive applications.
(8kW) 13 19 14 | solve@xylem.com | xylem.com/au @xylemanz WE SOLVE YOUR WATER CHALLENGES
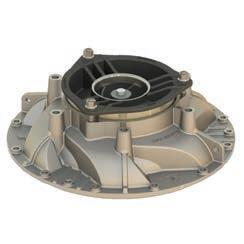
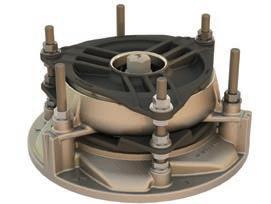