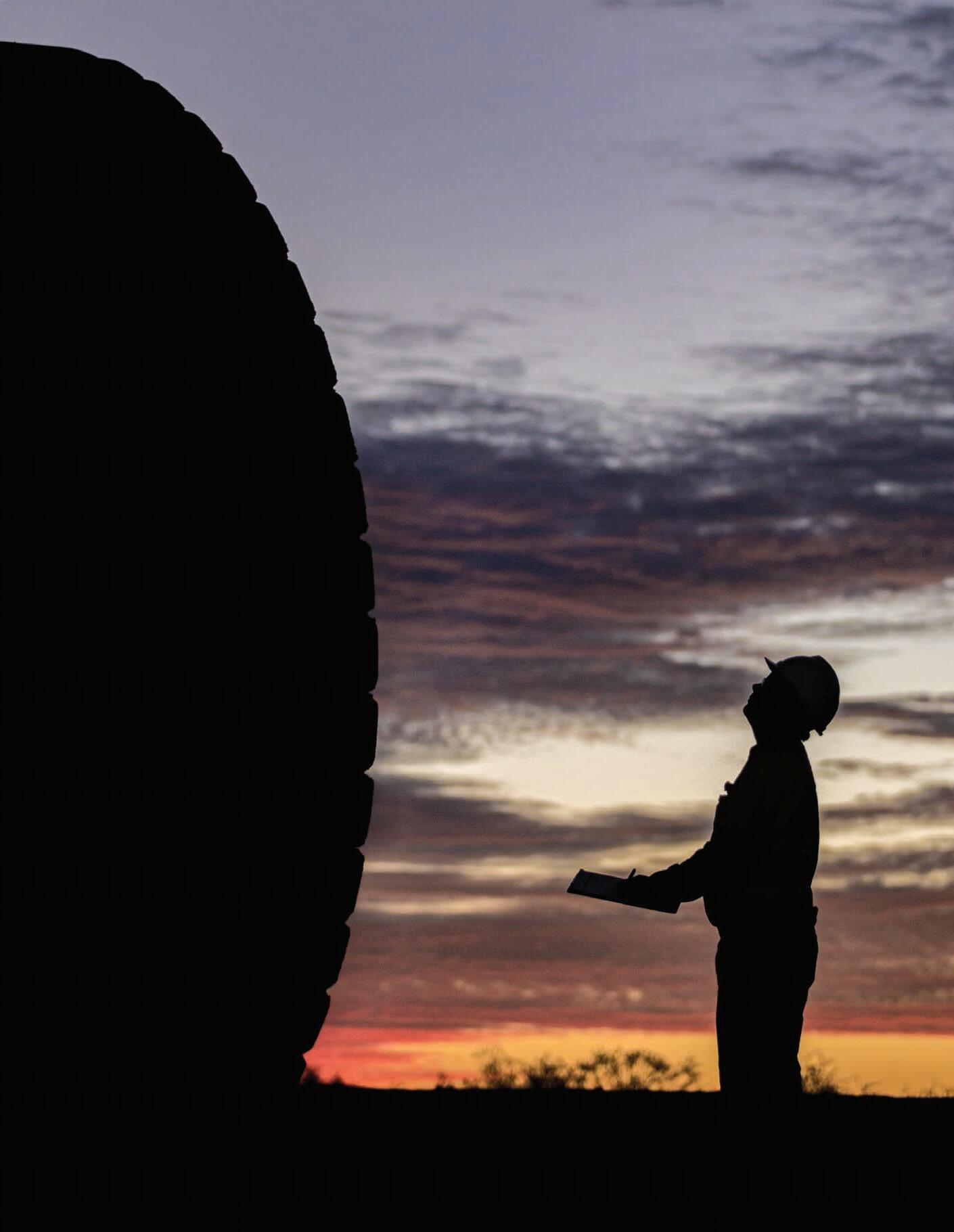
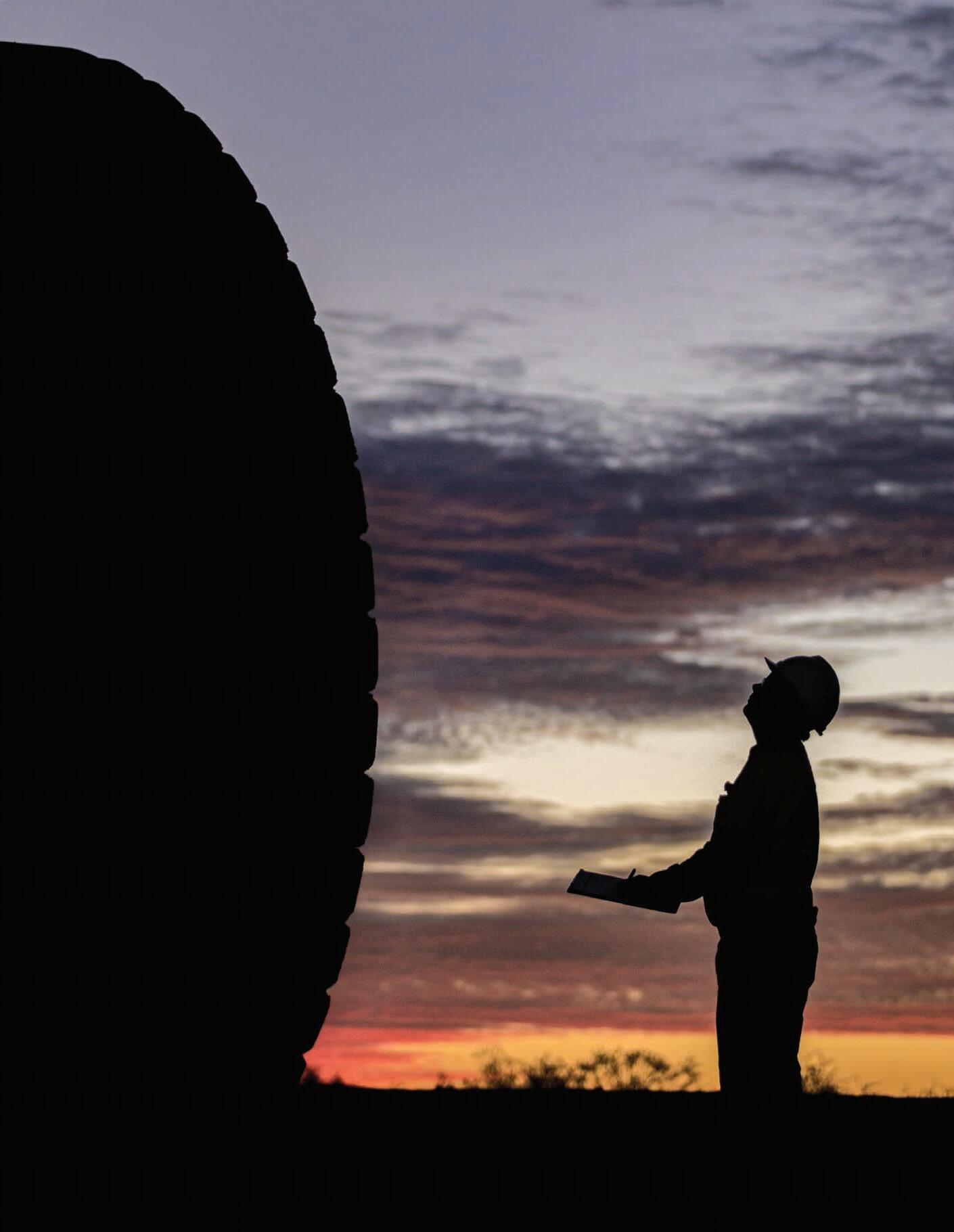
Expect more sustainability
Solving the challenge of scrap tyres in a way that’s practical and sustainable could be around the corner for Australia. After successfully opening a thermal conversion OTR tyre recycling facility in Chile that converts scrap tyres into base elements for reuse, Kal Tire is ready to bring this scalable solution to other regions.
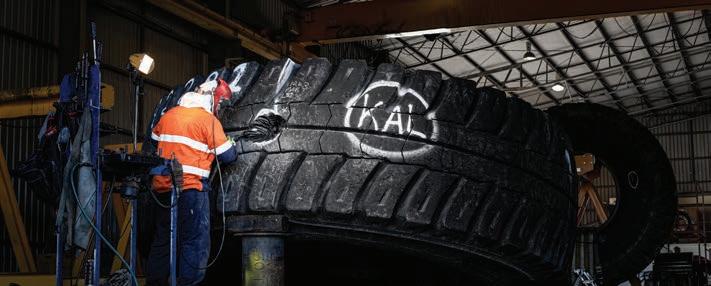
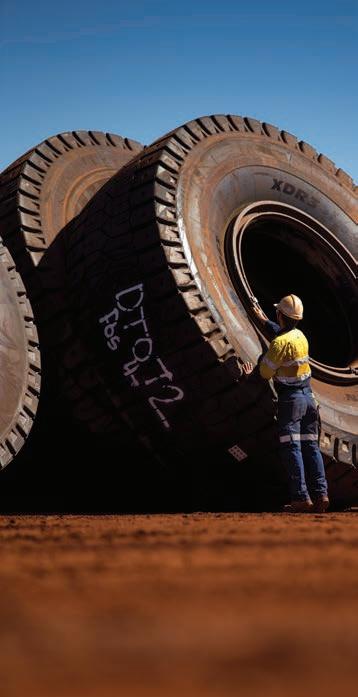
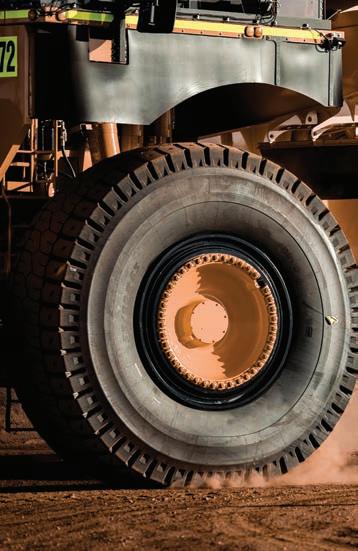
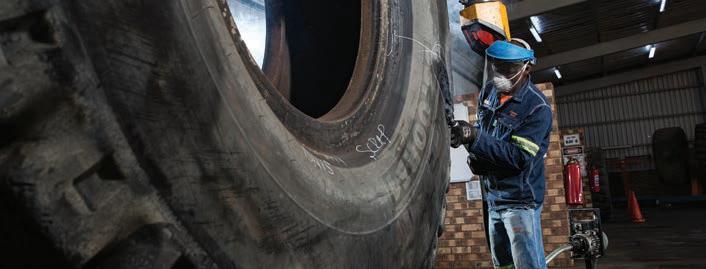
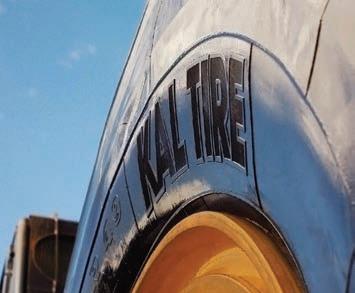


DOING MORE WITH LESS
EFFICIENCY AND OPTIMISATION ARE PILLARS OF MODERN MINING
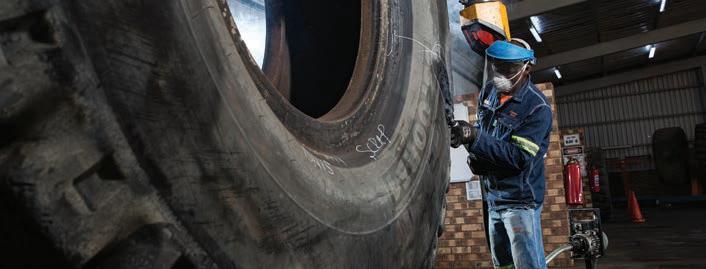
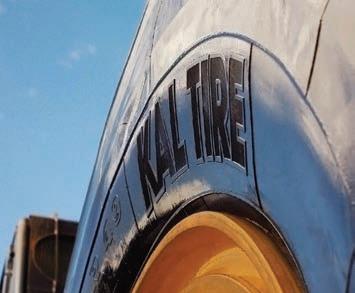


The goal The enabler
The transition to clean energy technologies places higher demands on mining companies to extract more minerals even more efficiently without compromising on safety or sustainability. An impossible equation? Not if you dare to think new. We are constantly developing new intelligent technologies that accelerate this transformation.
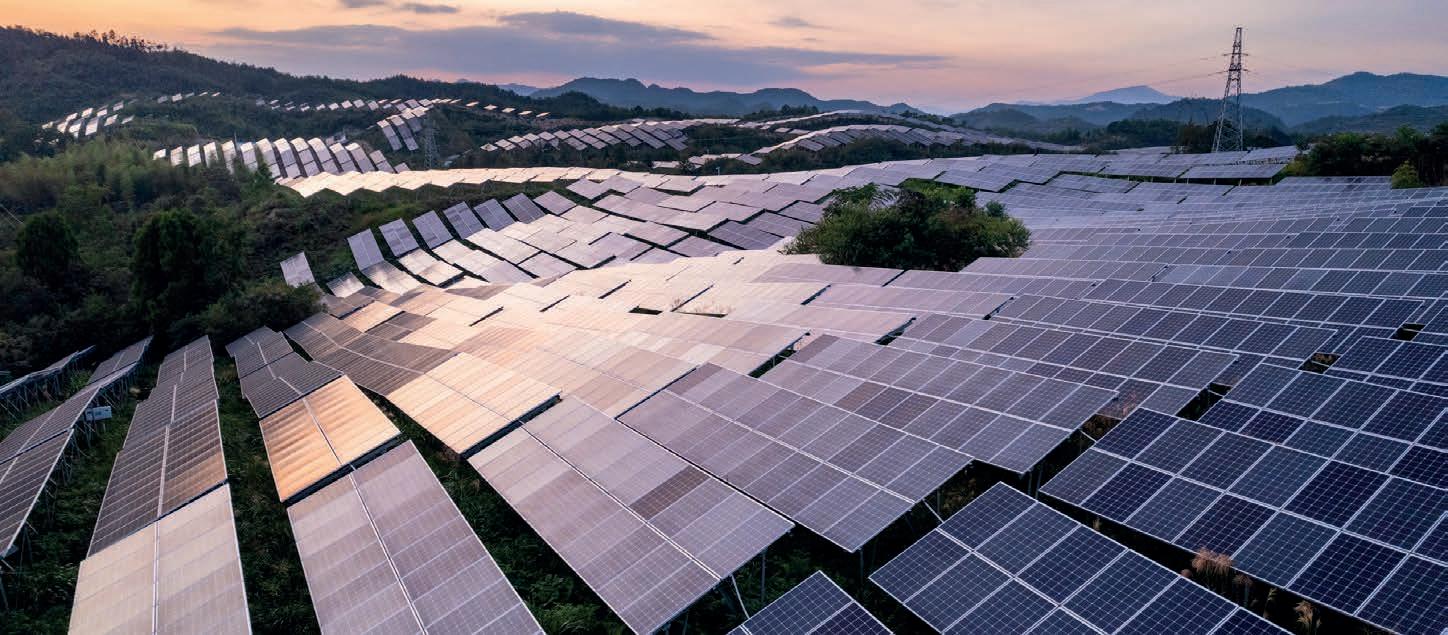
See how we accelerate the transformation

PAUL HAYES
paul.hayes@primecreative.com.au
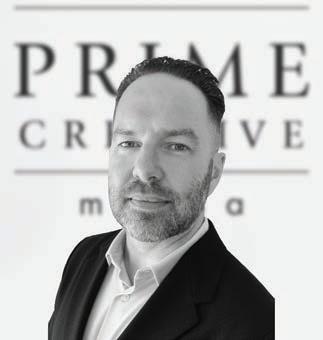
OPTIMISING PRODUCTIVITY
The sheer size and scale of the resources industry – from the moment a mineral discovery is made to the precious ore being dug from the ground to the finished product being delivered around the world –means the opportunities for increased efficiencies are practically limitless.

With so many commodity prices fluctuating, as well as the pressures that come with uncertain supply chains, increasing energy costs and an incredibly tight labour market, mining companies cannot afford any amount of lost production.
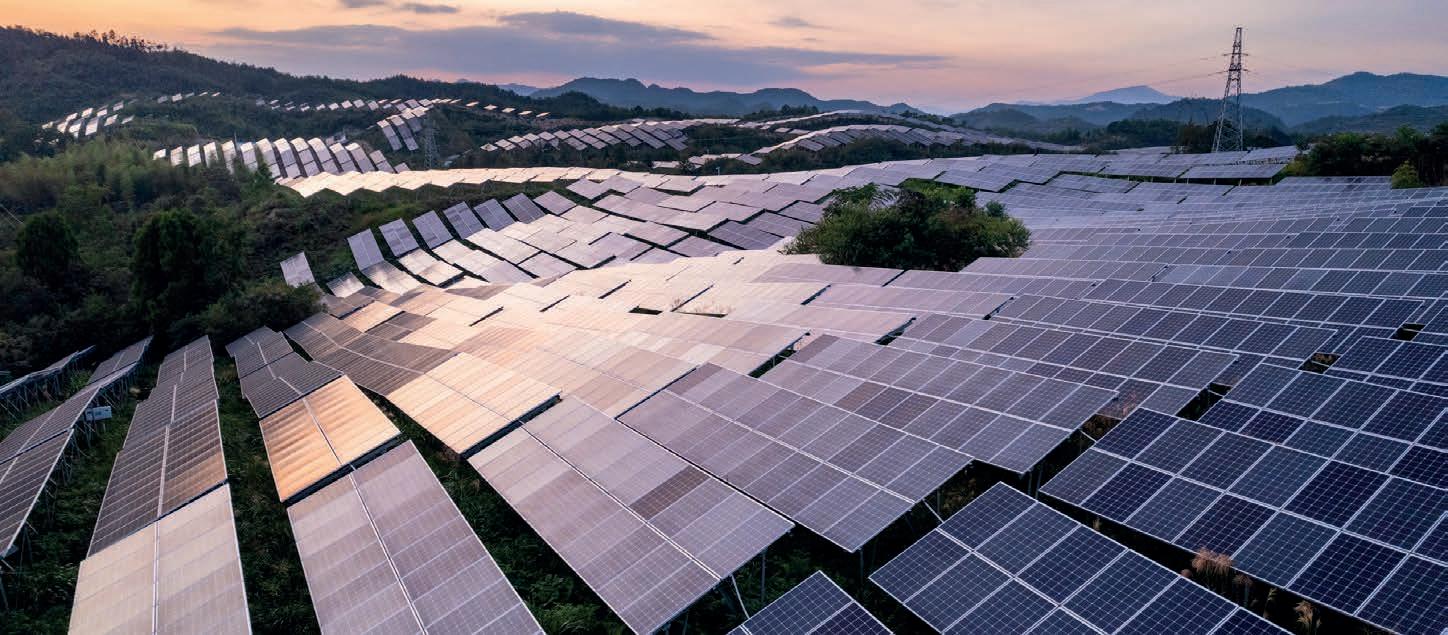
Efficiency in the mining industry can broadly be defined as the ability to achieve more desirable output with a lower environmental cost.
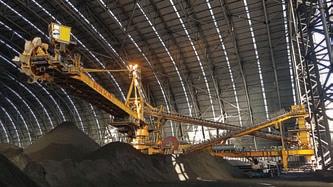
Any products, innovations or services that can speed up and/or make any part of that system run more smoothly – ie increase efficiency and optimisation – would be a welcome addition to the sector.
The May issue of Australian Mining takes a closer look at some of these products, from improved and evolving conveyor technology to waste retreatment screening to pulley lagging systems to wearable smart technology to proximity detection systems to battery energy storage.
Elsewhere in this issue, we run the second in our two-part series on Deloitte’s ‘Tracking the Trends’ report for 2023. We break down the seven remaining trends, digging into subjects such as building resilient supply chains, making genuinely holistic change, rethinking external talent pathways, safety and sustainability, and more.
Staying on the industry insights, we take a deep dive into a recent spate of takeovers across the mining sector.
CHIEF EXECUTIVE OFFICER JOHN MURPHY
CHIEF OPERATING OFFICER
CHRISTINE CLANCY EDITOR
PAUL HAYES
Email: paul.hayes@primecreative.com.au
JOURNALISTS ALEXANDRA EASTWOOD
Email: alexandra.eastwood@primecreative.com.au
TOM PARKER
Email: tom.parker@primecreative.com.au
LEWIS CROSS
Email: lewis.cross@primecreative.com.au
TIM BOND
Email: tim.bond@primecreative.com.au
ASHLEY PERRY
Email: ashley.perry@primecreative.com.au
While some of these takeovers have been larger than others (and some have certainly been more successful than others), now is a good time to examine what’s behind all of these attempted moves. The answer, it turns out, has a lot to do with how mining companies see the future and, perhaps more importantly, their place in it.
Australian Mining was also on hand for a recent Q&A with some of BHP’s most senior executives, including chief executive officer Mike Henry and president Australia Geraldine Slattery. These major decision-makers had plenty to say about their company’s present and future, including its focus on copper and nickel operations, and the decision to sell two of its coal assets in Queensland.
On something of a smaller scale, we chat with Tyler Mahoney, a fourth-generation gold prospector from WA, about her new book, Gold Digger. Mahoney, whose chosen profession has taken her all over the world and seen her on the small screen as a star of Aussie Gold Hunters, has fascinating insights into modern prospecting.
Finally, we dig into prehistoric past. As it turns out, mining has played a key role in the discovery of a number of important dinosaur fossils in Australia over the years. In fact, BHP helped to unearth a very rare, 100-million-year-old dinosaur fossil in western Queensland as recently as March, and Atlas Copco even has a dinosaur named after it. Who knew?
FRONT COVER
Bedeschi has been designing complete turn-key solutions for bulk handling, mining, and container logistics for more than 100 years.
Established in 1908, it is today one of the oldest European companies, specialising in the creation of bespoken solutions for bulk handling.
The company’s longstanding experience handling different types of materials, together with a very high level of design, engineering and manufacturing, allow Bedeschi to offer integrated solutions in order to cover every client need.
Bedeschi is experiencing constant and continuous growth, and has just opened its new branch in Australia to better serve its customers.
Cover image: Bedeschi
Paul Hayes Managing EditorCLIENT SUCCESS MANAGER
JANINE CLEMENTS Tel: (02) 9439 7227
Email: janine.clements@primecreative.com.au
SALES MANAGER JONATHAN DUCKETT Tel: (02) 9439 7227 Mob: 0498 091 027
Email: jonathan.duckett@primecreative.com.au
SALES ADMINISTRATOR EMMA JAMES Tel: (02) 9439 7227 Mob: 0414 217 190

Email: emma.james@primecreative.com.au
DESIGN PRODUCTION MANAGER
MICHELLE WESTON michelle.weston@primecreative.com.au
ART DIRECTOR BLAKE STOREY blake.storey@primecreative.com.au
SUBSCRIPTION RATES Australia (surface mail) $120.00 (incl GST)
Overseas A$149.00
For subscriptions enquiries please contact (03) 9690 8766 subscriptions@primecreative.com.au
PRIME CREATIVE MEDIA Suite 303, 1-9 Chandos Street Saint Leonards NSW 2065, Australia www.primecreative.com.au
© Copyright Prime Creative Media, 2016
EFFICIENCY AND OPTIMISATION ARE FUNDAMENTAL PILLARS OF ALMOST ANY INDUSTRY, ESPECIALLY MINING.
20 INDUSTRY INSIGHT
Tracking the trends 2023: Part two
Australian
the
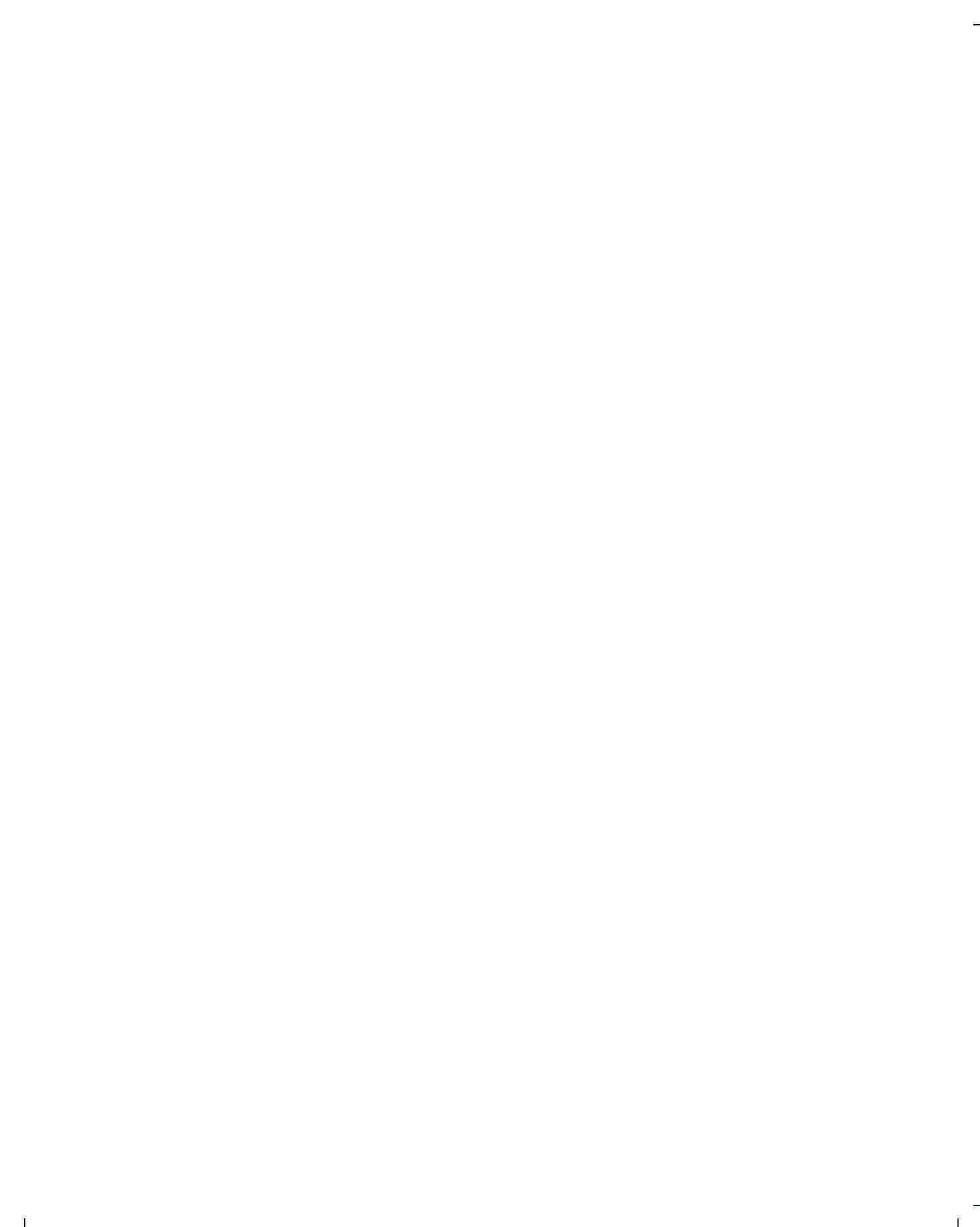
24 EFFICIENCY AND OPTIMISATION
Becoming RockAware
26 EFFICIENCY AND OPTIMISATION
An essential guide to skirtboards Martin Engineering explains how a conveyor transfer point without skirting is a major cost – and a major hazard.
30 EFFICIENCY AND OPTIMISATION
Modulaveyors ramping up the Australian mining industry
Fenner Conveyors’ easy-to-assemble modular conveyors have been a hit in the food processing and agriculture industries for years – and now demand is growing in the mining sector.
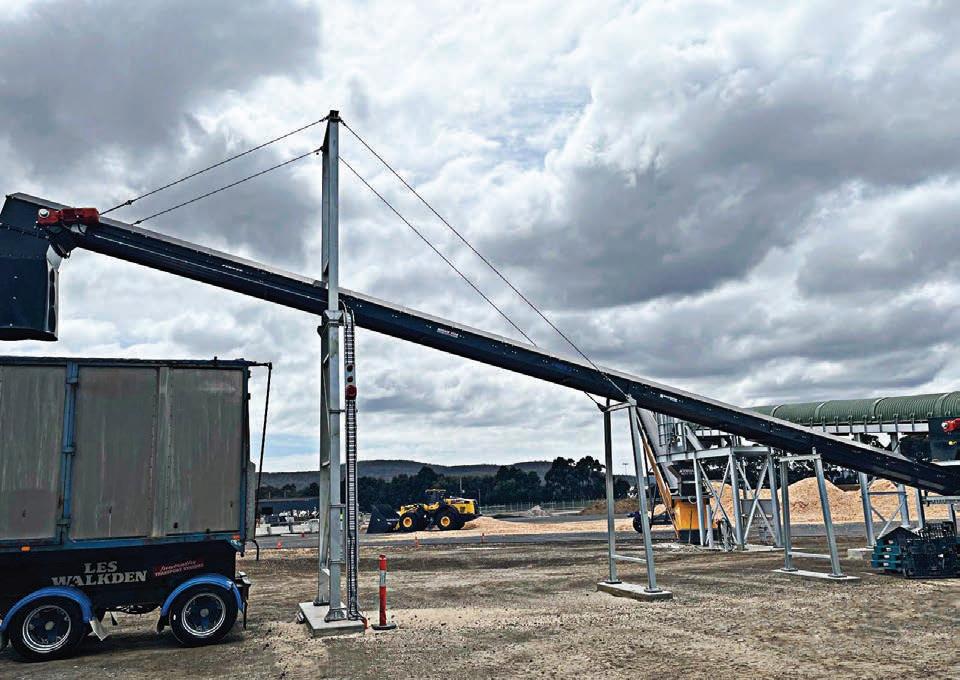
36 EFFICIENCY AND OPTIMISATION
Screening the green transformation Astec and mining contractor Salmon NC have developed a bespoke waste retreatment screening solution for a major nickel miner in New Caledonia. And Astec’s screening offerings don’t stop there.
46 E XPLORATION
All that glitters
Tyler Mahoney is a fourth-generation gold prospector, and a fierce advocate for gender equality and mental health awareness in the mining industry.
52 ORIGINAL EQUIPMENT
Unlocking the Australian market Bedeschi draws on its long and successful history to provide leading turn-key equipment solutions to the Australian mining sector.


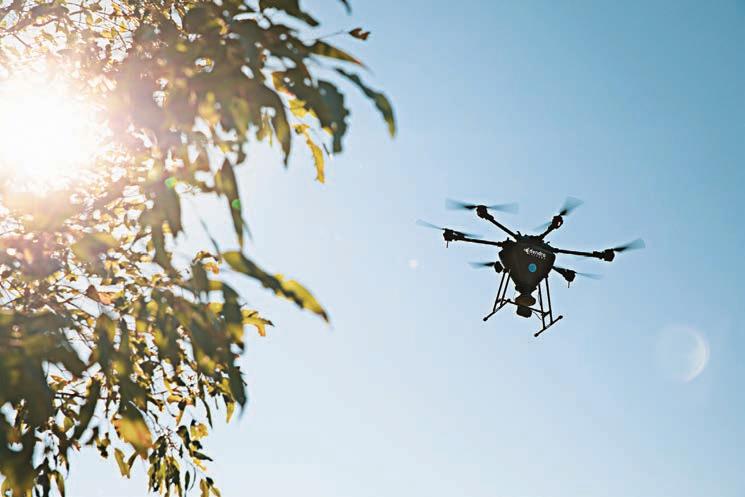
54 DECISION-MAKERS
From coal to copper to lithium Australian Mining sat in on a BHP shareholder Q&A, where the company addressed a number of hot topics for the sector.
66 INDUSTRY INSIGHT
Takeover targets
This year has seen a string of takeover offers hit the ASX as mining companies battle it out to acquire more resources. What has prompted so many bids?
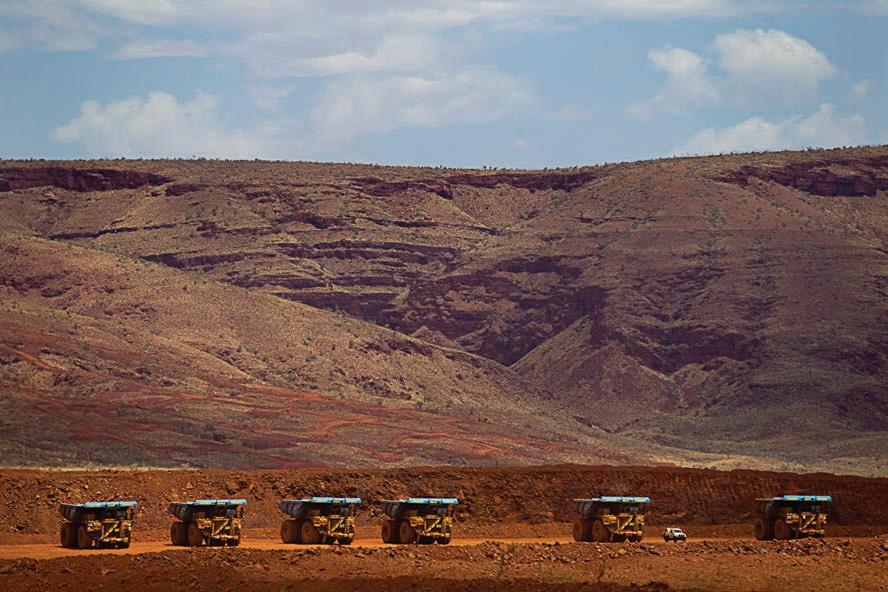
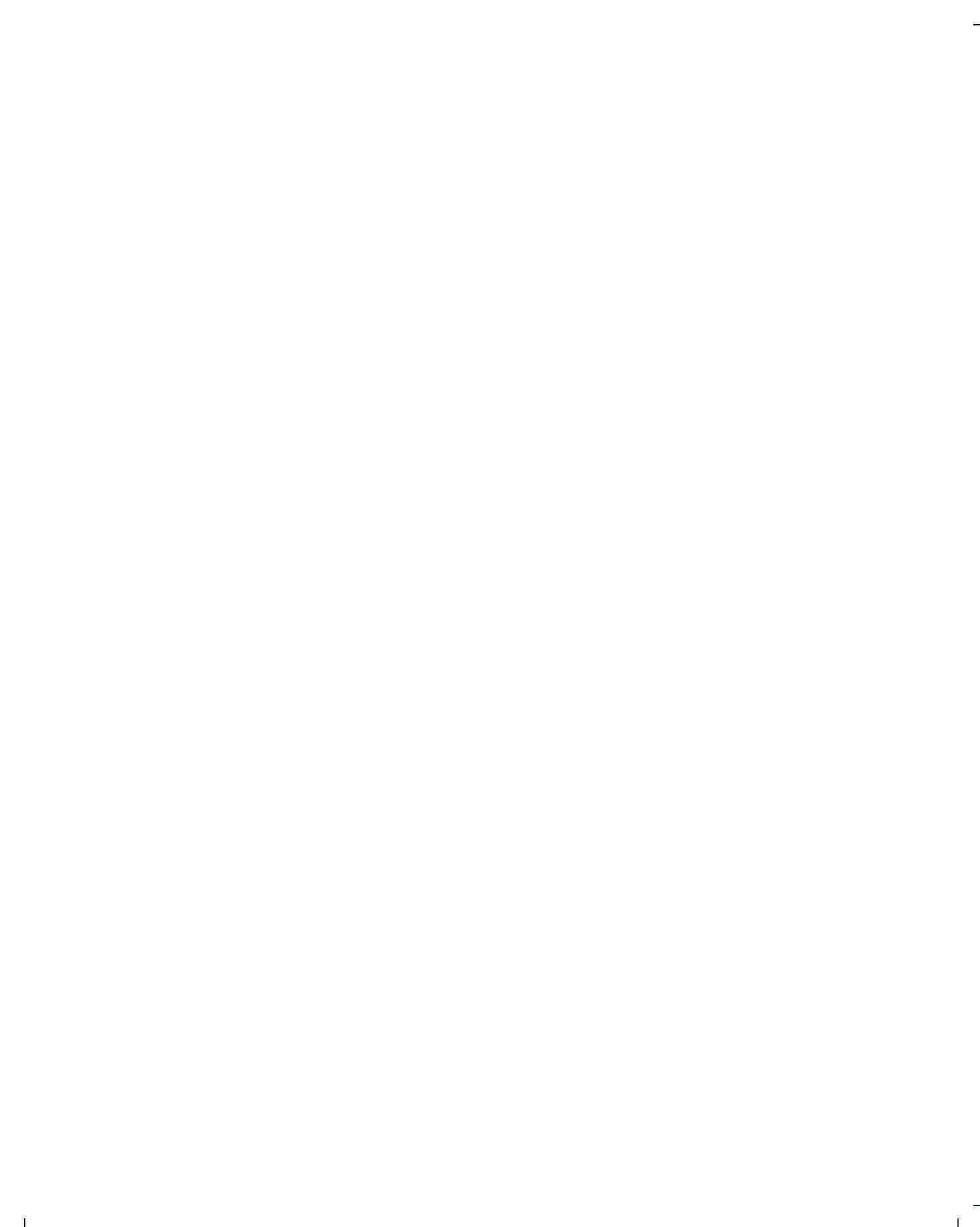

THE LATEST MINING AND SAFETY NEWS
AUSTRALIAN MINING PRESENTS THE LATEST NEWS FROM THE BOARDROOM TO THE MINE AND EVERYWHERE IN BETWEEN. VISIT WWW.AUSTRALIANMINING.COM. AU TO KEEP UP TO DATE WITH WHAT IS HAPPENING.
Western Mines Group (WMG) in April announced the “pivotal discovery” of a significant nickel system, causing a spike in the company’s share price.
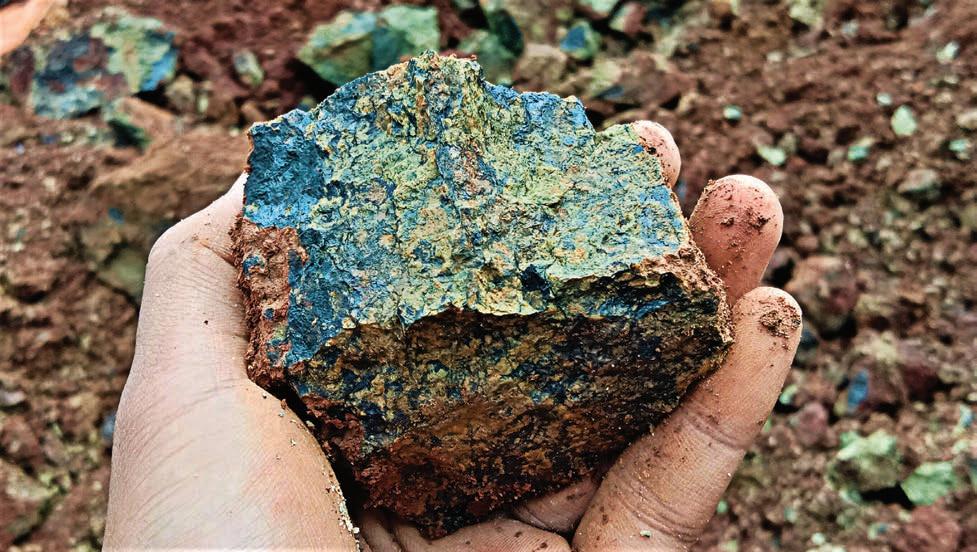
The gold and nickel exploration company aimed to test drill the deepest part of a particular grant at its flagship WA Mulga Tank project to gather geological data. The result was the discovery of an extensive nickel sulphide system.
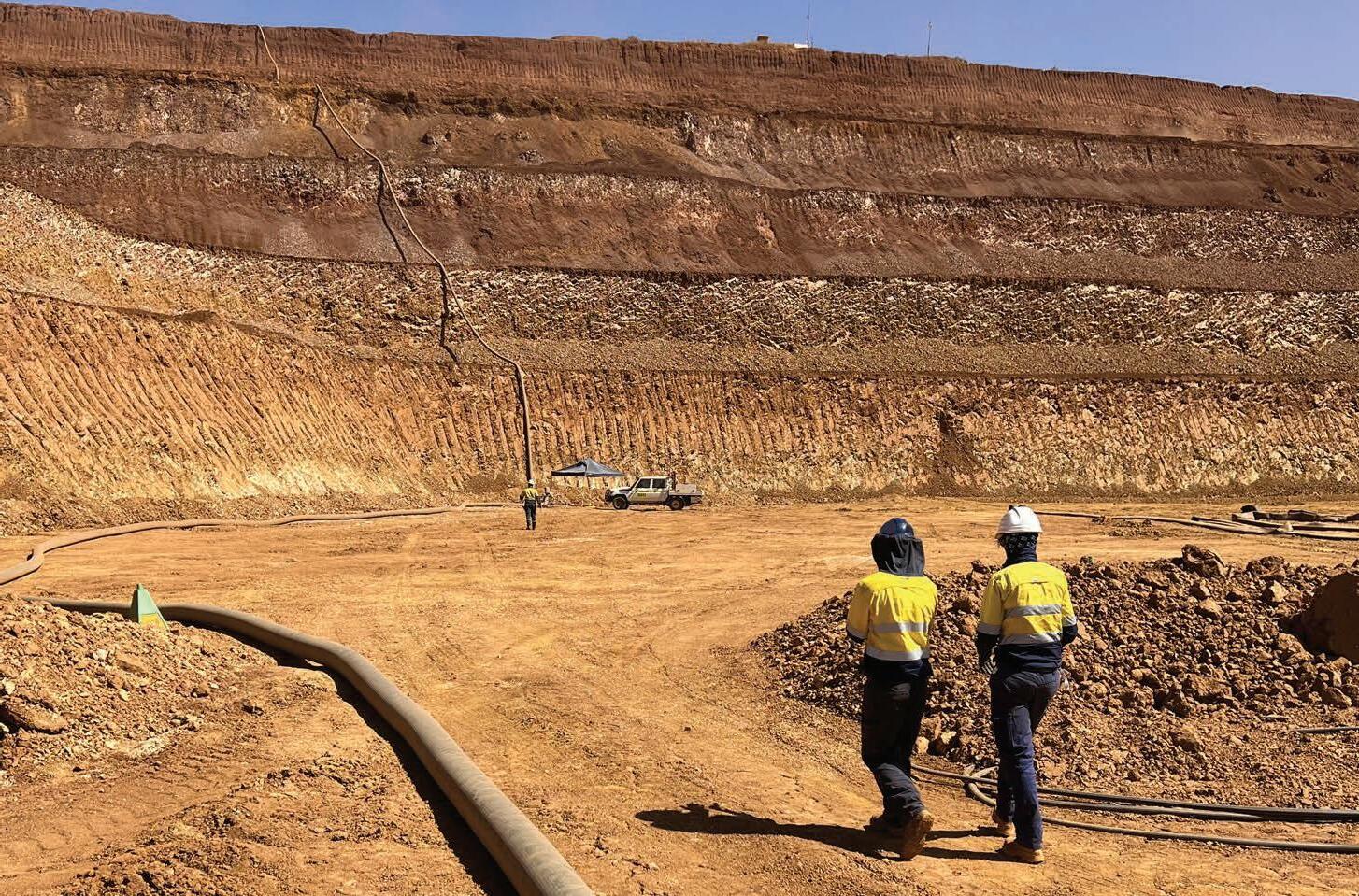
The ASX reacted in kind to the news of the discovery.
FIFO
Mineral Resources (MinRes) will begin construction on new resortstyle accommodation villages for the Pilbara’s fly-in, fly-out (FIFO) workforce.
Located at the Onslow Iron project in WA, the two new villages will feature rooms three times the size of traditional FIFO accommodation, with a queen-size bed, ensuite, laundry, kitchenette, lounge and balcony.
The rooms will be linked by walkways and workers can enjoy gathering spaces, barbecue areas
After closing Tuesday April 4 at $0.115 per share, WMG clocked in $0.315 per share the following day, a 110 per cent increase in performance for the week.
Located in the Eastern Goldfields of WA, WMG’s Mulga Tank is considered highly prospective for nickel, copper, and platinum-group elements.
“(The drill hole) MTD023 was a big hole for WMG, in more than one sense,” WMG managing director Caedmon Marriot said. “With the aid of
our EIS (Exploration Incentive Scheme) grant, we simply aimed to drill the deepest part of the complex to gather the greatest amount of geological information we could.
“It could well be a pivotal hole for the company, with these assay results confirming the visual observations of extensive disseminated nickel sulphide mineralisation.
“The hole validates our geological model of the complex and really demonstrates a significant working
AUSTRALIAN MINING GETS
THE LATEST NEWS EVERY DAY, PROVIDING MINING PROFESSIONALS WITH UP-TO-THE-MINUTE INFORMATION ON SAFETY, NEWS AND TECHNOLOGY FOR THE AUSTRALIAN MINING AND RESOURCES INDUSTRY.

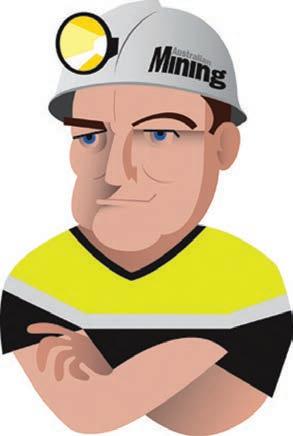
nickel sulphide mineral system with huge volumes of mineralised ultramafic magma.”
WMG technical director Ben Grguric said the geological data “bodes extremely well for the prospectivity of the project”.
“Every new drill hole in the main Mulga Tank dunite body is showing broad intersections of disseminated sulphide together with scattered intersections of high-grade remobilised nickel sulphide,” he said.
“These are clearly hallmarks of a very large mineralised system.”
The company indicated it was undertaking a diamond drilling program to test a number of followup targets.
and places for quiet reflection in the villages.
To prioritise health and wellbeing, the villages will also have an Olympicsize swimming pool, indoor fitness centre and gym, a cafe, and a recreation building with a cinema, golf simulators and pool tables.
Safety will be another priority, with enhanced security measures such as CCTV included.
There are hopes the resort-style accommodation will encourage
more women and couples to work on resources projects in the Pilbara.
“Our people are the foundation of MinRes’ success and that’s why we’ll give them the best FIFO village experience in the sector,” MinRes chief people and shared services officer Bronwyn Grieve said.
“As the race to attract and retain the best talent intensifies, we know our focus on workplace wellness will help set us apart.
“We’re rolling out resort-style accommodation villages across our long-life mine sites.
“The accommodation and amenities at Onslow Iron will set a new standard, helping to change the FIFO culture and contribute to the project’s success.”
Construction at the first village will begin in the first half of 2023, and 10 four-bedroom homes will be built in nearby Onslow in an effort to attract more families to the town and the workforce.
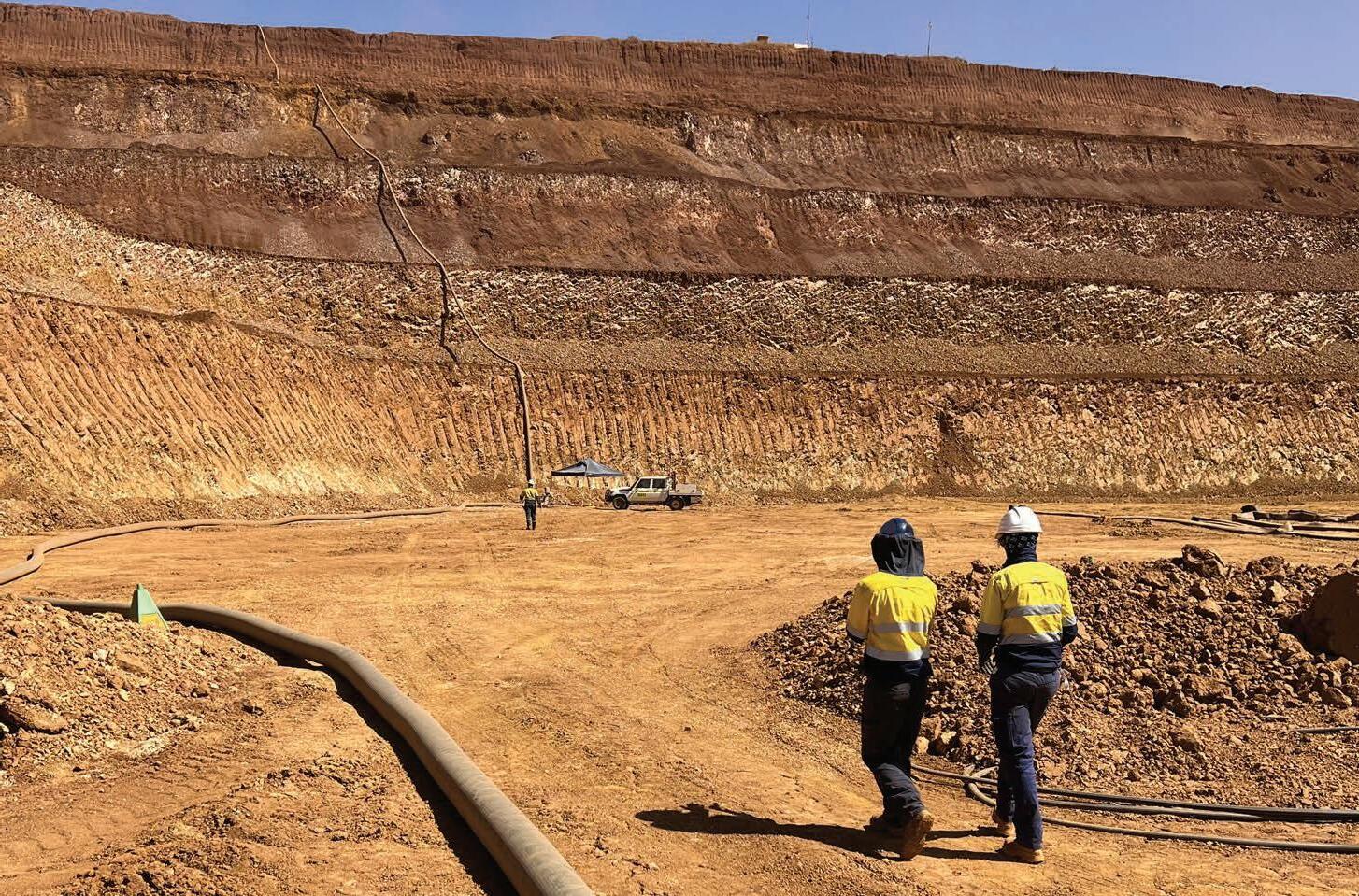
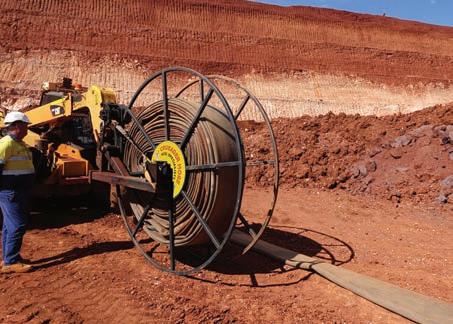
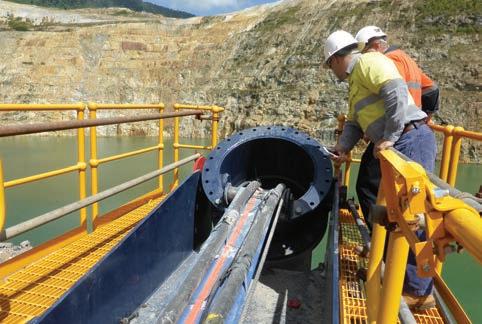

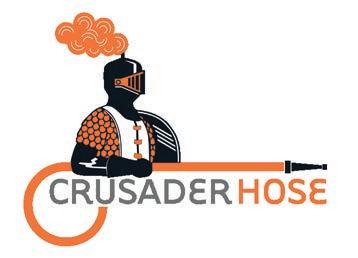
RIO TINTO SPENDS BIG DOWN UNDER
Major miner Rio Tinto injected $15.3 billion in the Australian economy in 2022 by spending more on Australian suppliers.
The company has an ongoing commitment to support the communities in which it operates, with the $15.3 billion spent across 6200 businesses, an increase of almost nine per cent on 2021.
More than $565 million of the total amount was spent with Indigenous businesses in a 40 per cent increase from 2021.
The spending spree helped support tens of thousands of Australian jobs and delivered significant economic contributions to communities across the country. This includes Australian-owned and-operated businesses and locally-ownedand-managed branches of global companies.
Rio Tinto, which engages with over 20,000 suppliers around the world, owns a variety of operations in Australia, including in the Pilbara. It
WHAT’S BEHIND THE FORTESCUE JOB CUTS?

also owns the now-shuttered Argyle diamond mine.
“Supporting local businesses in the communities where we operate is a key priority for Rio Tinto,” Rio Tinto chief executive Australia Kellie Parker said.
“We strive to employ local people, buy local products and engage local services –especially from Indigenous, small and regional businesses.
“We are working hard to improve our approach to Indigenous business
development and engagement in Australia.
“And while there is still more work to do, last year we significantly increased our spend with Indigenous suppliers.
“We couldn’t do what we do without our local supplier partners, and having good relationships with them helps us find better ways to provide the materials the world needs and innovate to decarbonise our operations.”
While the major miner didn’t comment on the number of job cuts made, one source told the Australian Financial Review that is was fewer than 100.
However, this number may not stay the same for long, with more jobs tipped to go in the coming weeks.
With the company’s profit up by $3.4 billion in the second half of 2022,
the vacant positions relate to a move to clean energy.
The company has not been quiet about its bid to push ahead with at least five clean energy projects before Christmas, including a green hydrogen production facility in Geelong, Victoria.
Other clean energy projects that Fortescue is working on will make their way to the US and Norway.
“We are always looking for opportunities for continuous business improvement to maintain our industry-leading cost position,” the spokesperson said.
“Right now we are growing globally and allocating resources swiftly to North America, responding to the Inflation Reduction Act (IRA). Projects such as Iron Bridge are coming into
With more green energy projects in the pipeline, FFI is actively recruiting for manufacturing technicians, planners and battery-test engineers at its Australian locations, including roles in its green fleet development.
It remains to be seen whether the job cuts will contribute significantly to Fortescue’s green energy push.

By utilising the latest technologies we provide an advanced combination of innovative solutions which optimise our customers mining operations performance, sustainability, availability and safety, around the globe.

We supply:
• Wear parts and solutions for mineral processing, mobile and fixed plant operations
• Digital and equipment connectivity
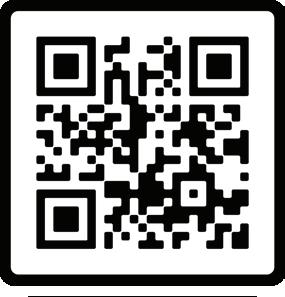
• Asset condition and performance monitoring
• Design, engineering and manufacturing solutions
bradken.com
Epiroc has secured its biggest ever automation order to convert Roy Hill’s mixed fleet of haul trucks to driverless operation, making it the world’s largest single autonomous mine.
Epiroc announced the Roy Hill project with ASI Mining in January and has now received a $70 million order for the development of an autonomous haul truck solution that is interoperable and scalable regardless of manufacturer.

The contract covers the driverless conversion of Roy Hill’s entire fleet of
96 haul trucks, including 54 Caterpillar trucks and 42 Hitachi trucks.
Additional orders will be booked in the future, with the project expected to run until 2024.
The conversion is made possible thanks to ASI Mining’s Mobius-based autonomous haulage system, with the support of Epiroc – which owns a 34 per cent share of ASI.
“We are very excited about supporting Roy Hill in the work to create the world’s largest single autonomous mine,” Epiroc
president and chief executive officer Helena Hedblom said. “The benefits for both safety and productivity will be substantial.”
Epiroc president of surface division Jose Sanchez also reacted to the news.
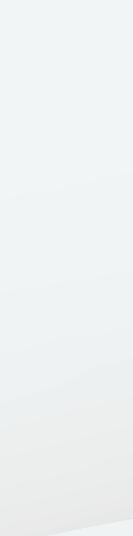
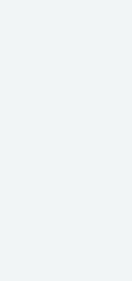
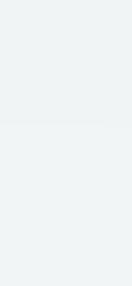

“Roy Hill, led by its executive chairman Mrs Gina Rinehart … is a true pioneer and will set a new gold standard for autonomous surface mining,” he said.
“Our team working on this is doing an excellent job.”
Roy Hill’s production verification phase is complete and autonomous haul trucks are running 24–7 in a dedicated autonomous operating zone. The fleet is meeting safety standards and achieving higher productivity than conventional haul trucks.
Located in the Pilbara, Roy Hill is one of Australia’s largest iron ore operations. The mine is majority owned by Rinehart’s Hancock Prospecting, with the remainder held by Marubeni Corporation, POSCO, and China Steel Corporation.
Federal Minister for Resources
Madeleine King has affirmed Australia’s position as a world leader in the lithium sphere.
“As the world’s largest producer of lithium, a key component in batteries for electric vehicles, our minerals sector has an enormous role to play in the success of the energy transition over the coming decades,” King said.
“Demand for battery minerals is surging with the uptake of electric vehicles and our lithium sector is going from strength to strength.
The Minister’s comments formed the foreword of Geoscience
Australia’s 2022 report on Australia’s Identified Mineral Resources (AIMR).
The report confirms Australia’s position as the world’s number-one producer of lithium, boasting almost a third of the world’s known resources.
The report – which estimates Australia’s reserves and resources as at December 31 2021 – shows that Australia produced a record 55 kilotonnes of lithium in 2021, compared to 40 in the previous year.
The report also confirms Australia’s status as the world leader in the production of four other important commodities: bauxite, iron ore, rutile and zircon.
Exploration expenditure increased 28 per cent to an impressive $3.6 billion, making it the largest such expenditure in almost a decade.
Although national lithium production is second-to-none, King said more needs to be done to keep processing operations onshore.
“As Prime Minister Anthony Albanese said at his National Press Club Address in February, Australia must not only extract more critical minerals like lithium but also look to process those materials here to protect our national sovereignty,” she said.
Mineral Resources (MinRes) recently splashed close to $1 billion
for an interest in lithium processing plants in China.
MinRes managing director Chris Ellison told the Australian Financial Review that the offshore investment would ensure the company could convert its Wodgina-sourced spodumene into battery-grade chemicals in the short term.
“Doing more here in Australia is my preference over the long term,” Ellison said. “ We need capacity today.”
Soon after, Pilbara Minerals and POSCO secured $682 million funding for the construction of a lithium processing plant in South Korea.

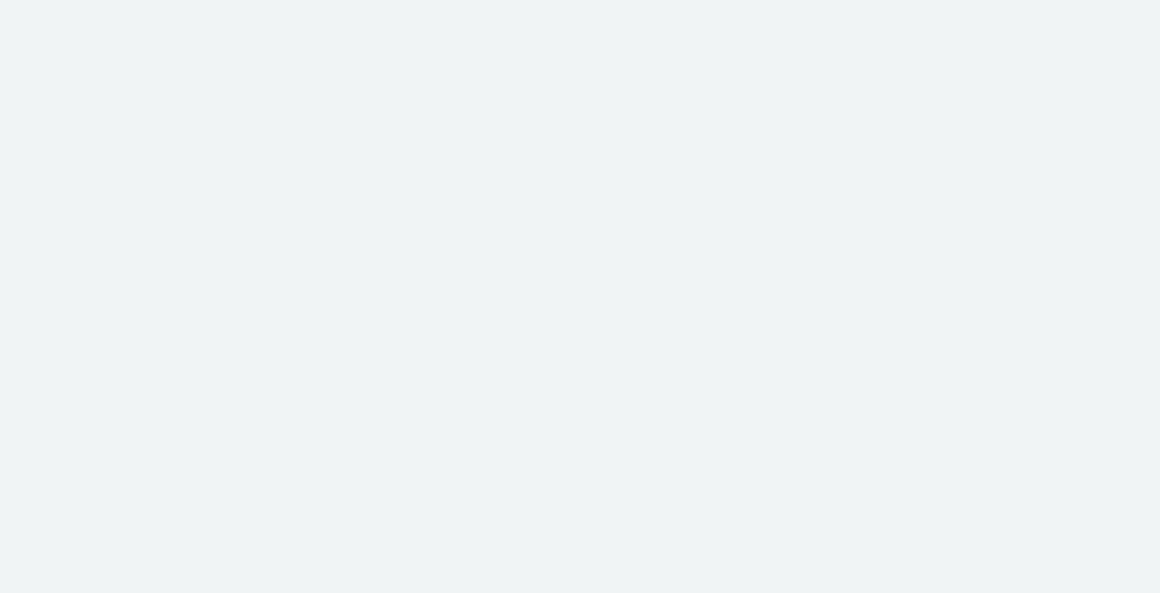
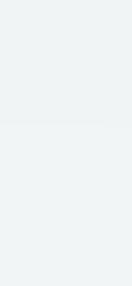
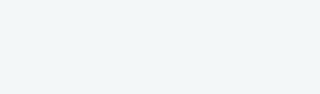

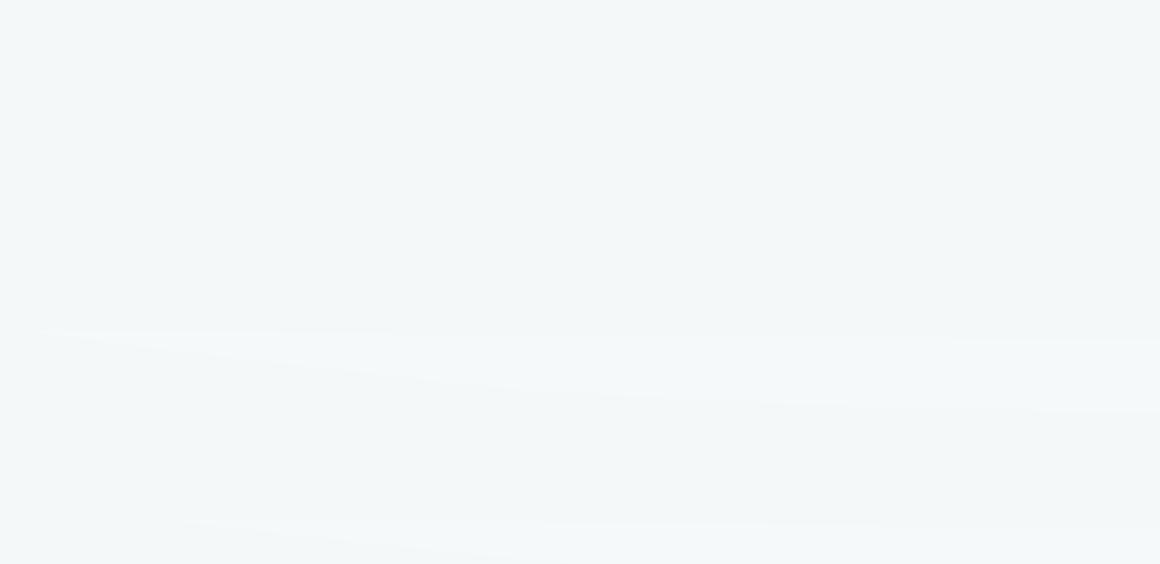





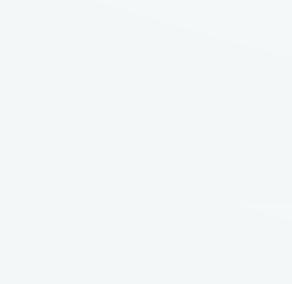
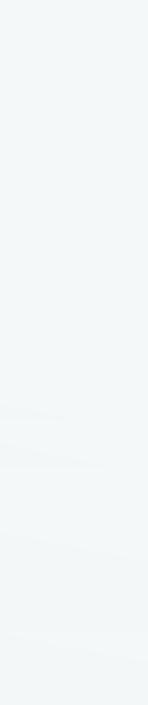
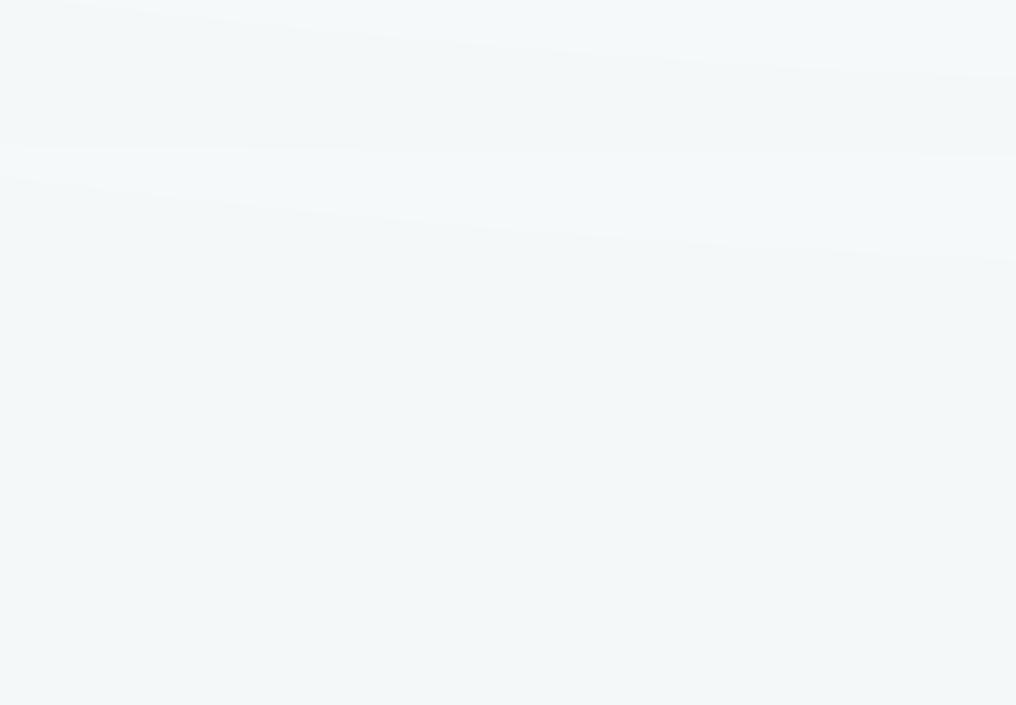
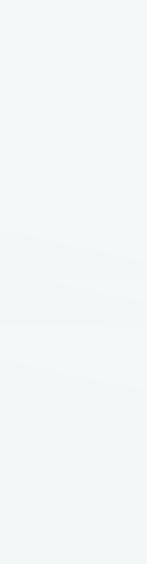

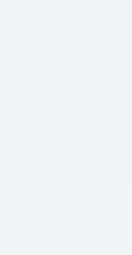
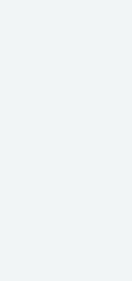
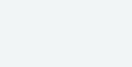
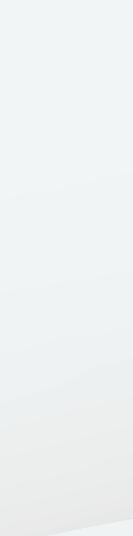
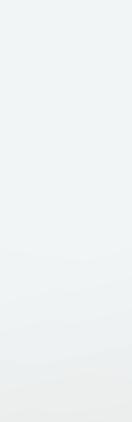
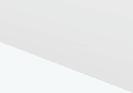
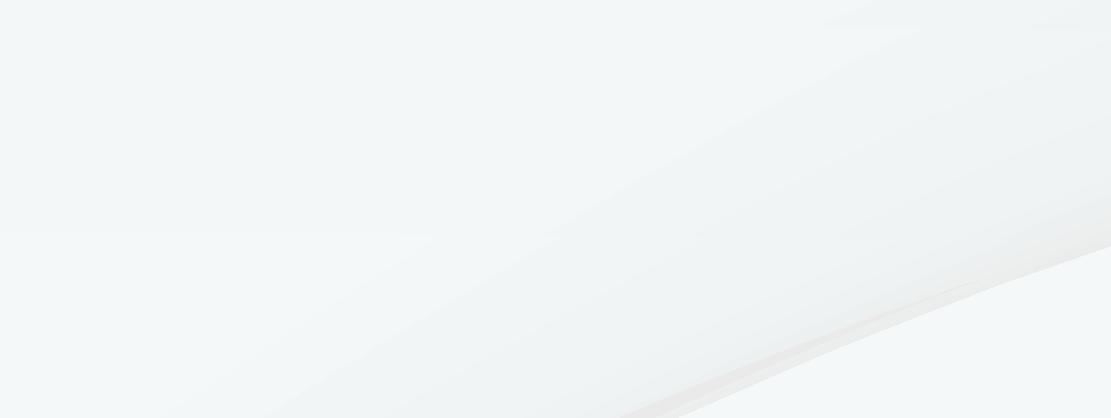


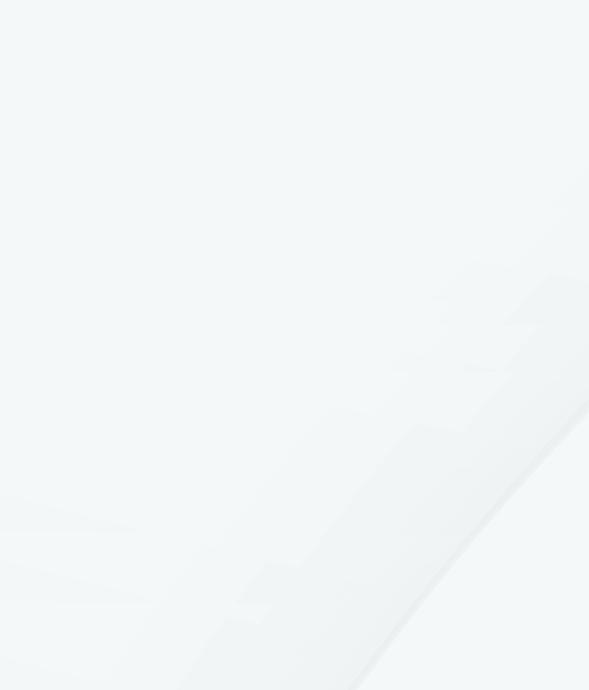
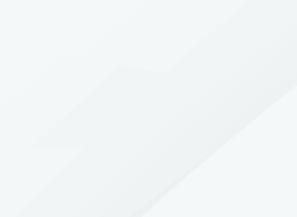
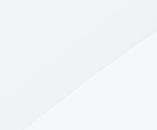

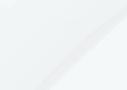
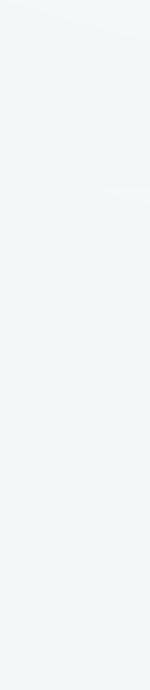
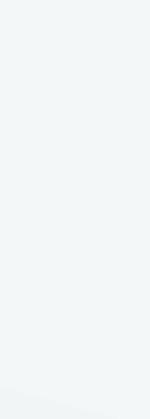


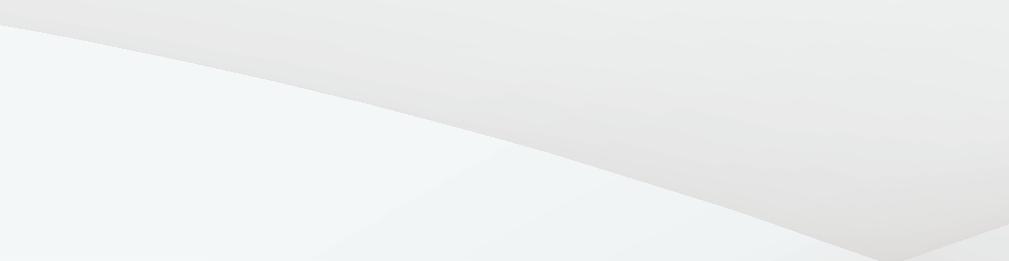
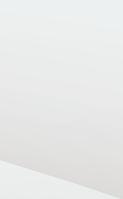
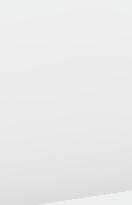









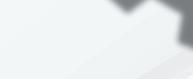
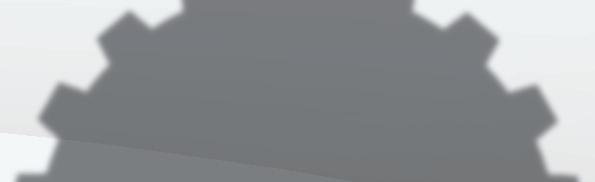

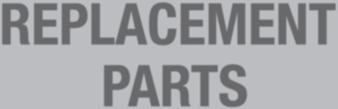


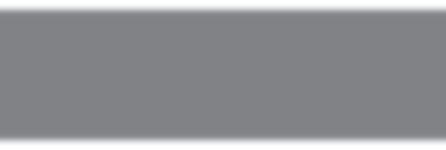





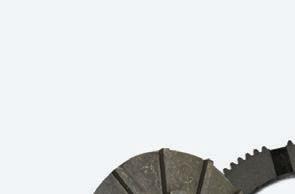

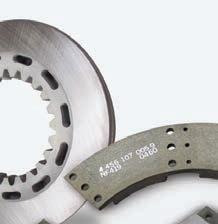

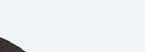
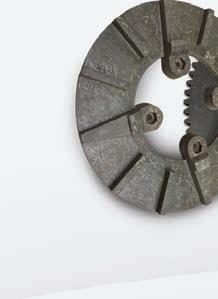
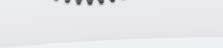
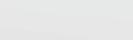
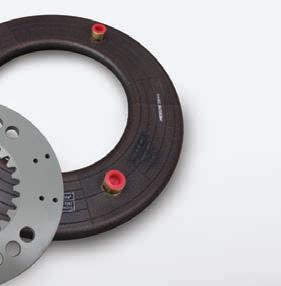
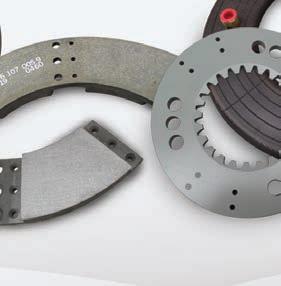
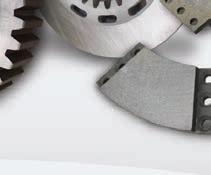

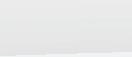
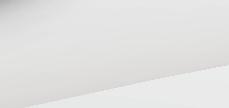
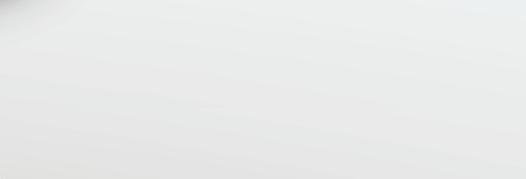
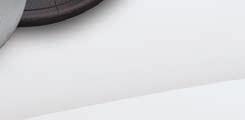

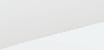
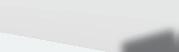


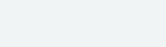

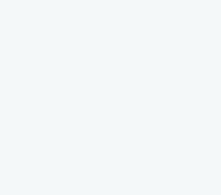
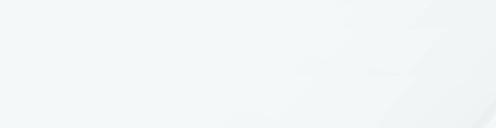
DARTBROOK COAL MINE ON TRACK FOR RESTART
The Dartbrook coal mine in New South Wales is set to restart in the second half of the year after it was closed in 2006.
Australian Pacific Coal and its joint venture partners have been working to recommission the mine.
“AQC and our joint venture partners have made good progress on all major critical path activities since the end of December, particularly the remediation operations at the mine site and efforts to secure
funding to enable production restart in H2 2023,” Australian Pacific Coal interim chief executive officer Ayten Saridas said. “The strong interest in the data room confirms the attractive investment proposition of the Dartbrook project.”
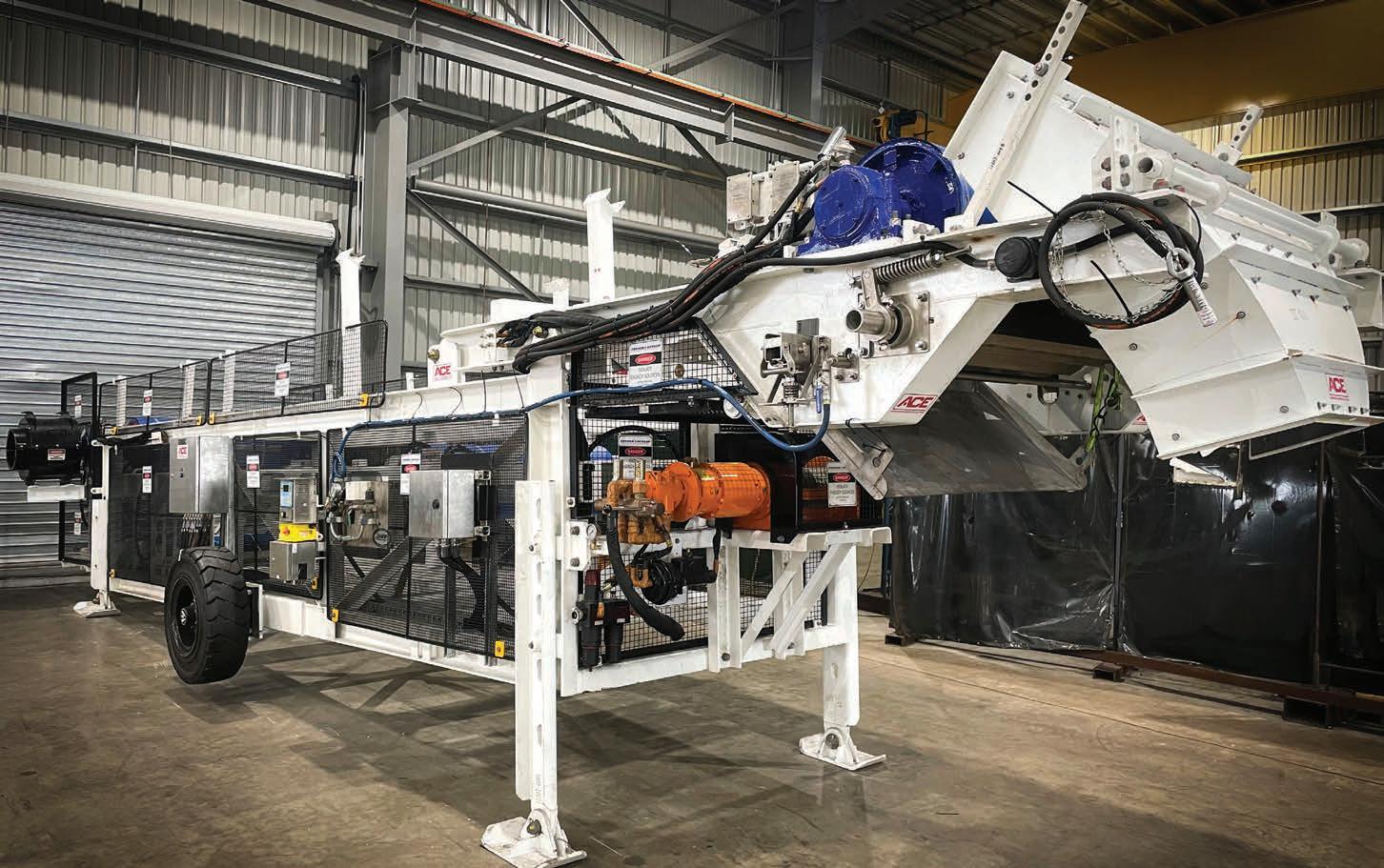
The terms for recommissioning Dartbrook were only agreed upon in September 2022, but Australian Pacific Coal has been working hard to get the project up and running since then.
GLENCORE HIGHLIGHTS CLIMATE ACTION
Glencore’s 2022 annual report and climate report detail the company’s actions towards reaching its climate strategy.
The annual report details how the company continues to support the transition to a low-carbon economy while meeting the need for universal access to reliable energy.
Glencore said it remains focused on operating responsibly and ethically by creating sustainable long-term value for all its stakeholders.
“We recognise our responsibility to contribute to the global effort to achieve the goals of the Paris Agreement by decarbonising our own operational footprint. We believe that we should take a holistic approach and have considered our commitment through the lens of our global industrial emissions,” the company said.
The Glencore climate report provides an update on progress the company has made in implementing its Climate Action Transition Plan, Pathway to Net Zero, originally published in 2020.
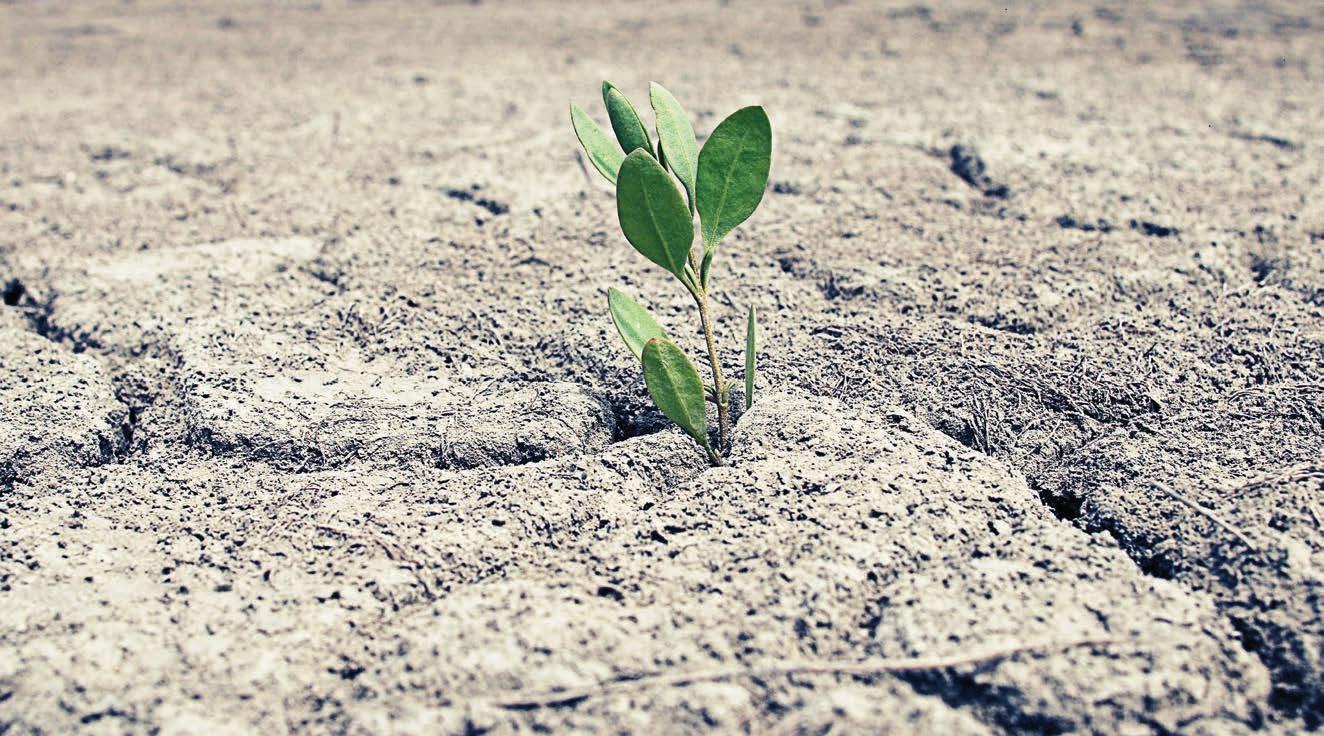
The company is currently working on dewatering the main access Hunter Tunnel in order to reestablish the ventilation circuit, a critical component that will facilitate work on supporting the roof and ribs of the mine.
The tunnel held approximately 57 megalitres of water, 45 megalitres of which approximately have been removed.
Dartbrook is ideally placed to support mining operations in
the immediate vicinity, including the Bengalla JV (a joint venture between New Hope, Wesfarmers, Mitsui and Taipower), Mt Arthur (BHP) and the adjacent Mt Pleasant approved development project (Mach Energy).
The recently completed mine plan review has resulted in superior outcomes, according to Australian Pacific Coal, and Dartbrook now has the potential to enhance coal quality when it reopens.
The report highlights the company’s increased transparency based on feedback received from extensive shareholder consultations following the 2021 climate progress report and disclosure of its direct advocacy linked to climate-related topics.
Glencore’s annual review found that 75 per cent of its capital expenditure was spent on sustaining and expanding its metals operations and 25 per cent was used in the responsible management of its energy portfolio in 2022.
Glencore chairman Kalidas Madhavpeddi said the company has continued to actively respond to the challenges of climate change and to take action to deliver its strategies.
“I am proud of the progress we are making in delivering our climate commitments and believe our holistic approach to supporting the global transition to a low-carbon economy,” Madhavpeddi said.
Glencore also announced it will hold its 2022 annual general meeting on 26 May.
INTEGRATED MOBILE CONVEYING SOLUTIONS AVAILABLE & READY FOR HIRE
Fenner Conveyors offer a range of temporary development conveyor systems, each complete with belt, mechanical and electrical components and optional PLC conveyor control operating systems. Engineered designs utilise integrated modular equipment to ensure simple, effective operation, rapid installation and relocation.
• Systems range from 75kW modular-style conveyors, up to our flagship 320kW VSD ‘Caddy’.
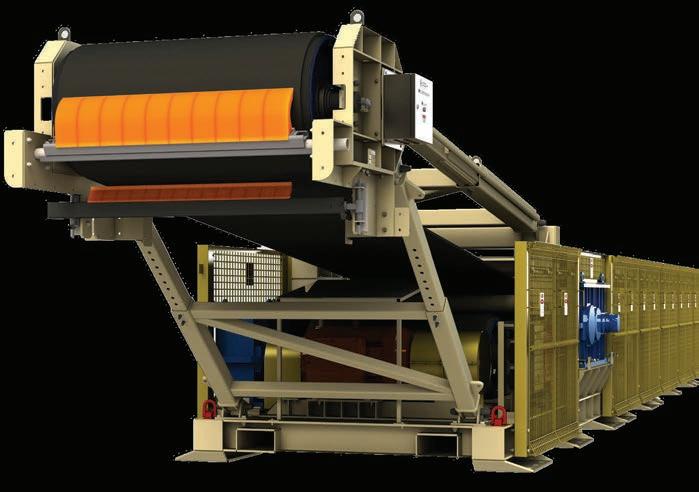
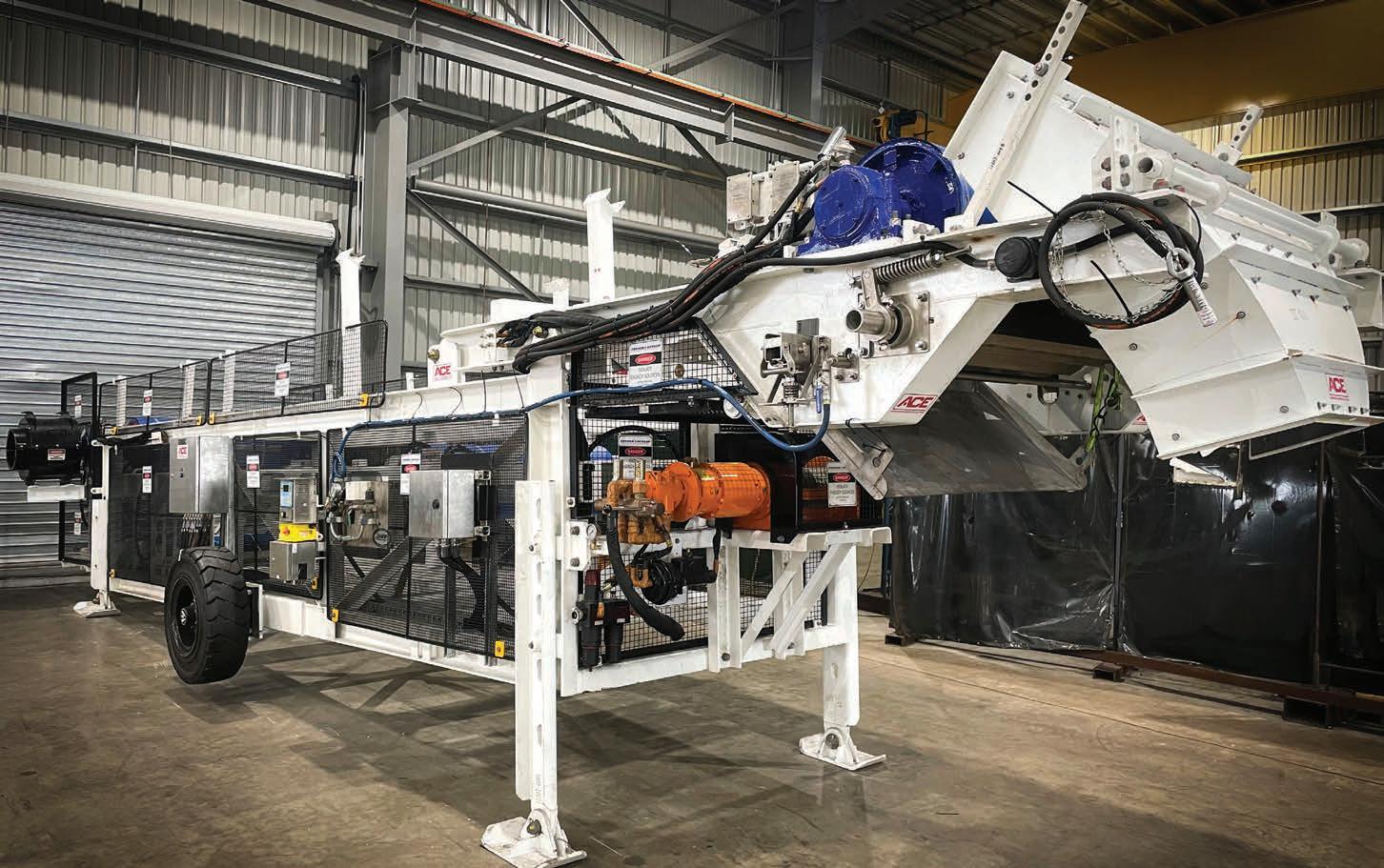
• Variety of additional accessories are available as per individual client requirements.
• Equipped with required safety devices including belt tracking, belt rip, loop take-up travel limits, belt slip switches, and can be specified for flame-proof operation.
• Compliant to Australian mining safety standards.
Phone 1800 Fenner (336 637)
fenner.com.au | sales@fenner.com.au
NEW HOPE SET TO DOUBLE COAL PRODUCTION
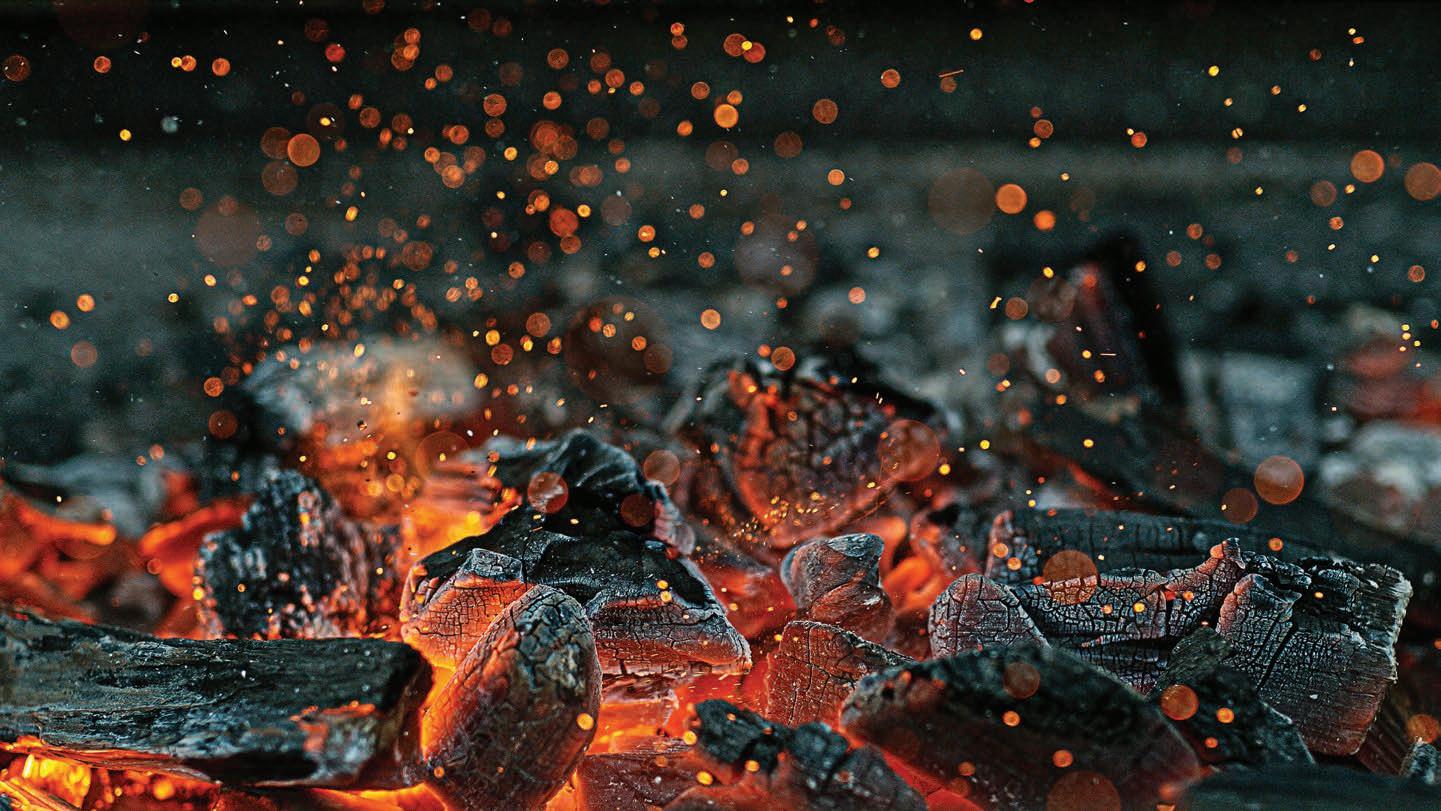
Major miner New Hope is set to significantly boost its production in the coming years as the wheels begin to turn on its coal projects.
The New Acland open-cut coal mine in Darling Downs, Queensland,
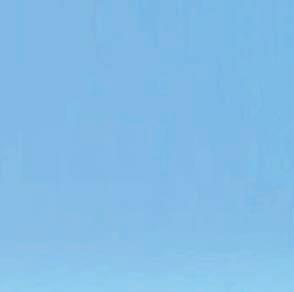
New Hope chief executive officer
Rob Bishop told the AFR the company was also interested in a bid for BHP’s Queensland coal assets, alongside rival bidder Yancoal. BHP made headlines when it announced its plan
to divest the Daunia and Blackwater coal mines in Queensland.
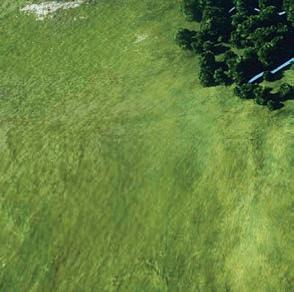

The company cited Queensland’s controversial three-tier coal royalty system as influential to its decision.
In a March shareholder Q&A, BHP
president Geraldine Slattery indicated company was choosing to focus on high-grade coal for steelmaking, and that the coal produced at its two Queensland projects was on the lower end of that quality spectrum.
MEET THE ASX’S BIGGEST DIAMOND COMPANY
Burgundy Diamond Mines is set to acquire the world-class Ekati diamond mine from Arctic Canadian Holdings for a cool $209 million.
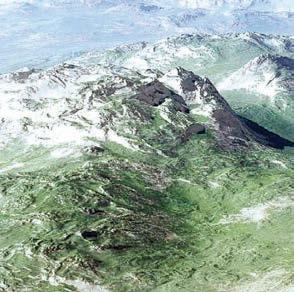
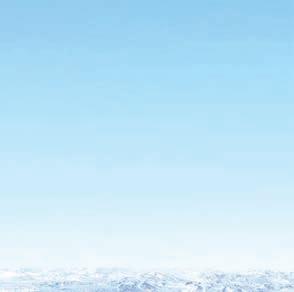
Ekati is Canada’s first surface and underground diamond mine, which sits about 200km south of the Arctic Circle.
The Canadian mine sold 4.2 million carats in 2022 alone, delivering revenue of over $742 million.
To fund the proposed acquisition, Burgundy will seek to generate $231 million in equity through a conditional placement.
The purchase amount includes $32 million in Burgundy shares and a deferred payment by Burgundy of $23 million in cash. In addition,
Burgundy will front the majority of the seller’s outstanding debt, roughly $154 million.
According to Burgundy, global demand and supply trends support a favourable long-term pricing outlook for rough diamonds.
Ekati has a current life-ofmine plan of six years, but the diamond company has said it would look at innovative mining techniques such as underwater remote mining and AI-driven exploration to extend the life and access deeper resources.
“This is an exciting and transformational acquisition for Burgundy, with potential to generate significant and growing returns for
our shareholders,” Burgundy chief executive officer, Kim Truter, said.
“The acquisition of Ekati is complementary to Burgundy; we’ve been purchasing rough fancycoloured diamonds from Ekati in recent years, then cutting and polishing them in our facilities in Perth to go into high-end jewellery designs.
“We view this acquisition as a wonderful marriage between Burgundy and the Arctic Companies, delivering immediate and meaningful production to our portfolio.
“As a result, Burgundy will become the largest ASX-listed diamond company and be well positioned for sustainable growth.”
Burgundy’s executive chairman Michael O’Keefe called the transaction a “game-changer”.
“Having been involved with Burgundy since 2017, this exciting acquisition completes Burgundy’s vertically integrated business model; bringing some of the world’s most beautiful diamonds to market,” he said.
“We are confident that both Burgundy and Ekati have a very bright future and we expect this transaction will create significant value for all stakeholders.”
In September last year, Burgundy recovered its first diamond – a fancy yellow clocking in at 1.51 carat – at its Ellendale diamond project in WA.
SUSTAINABLE BLASTING
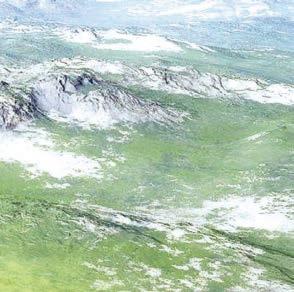
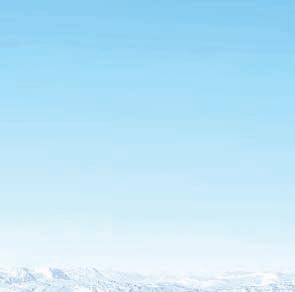
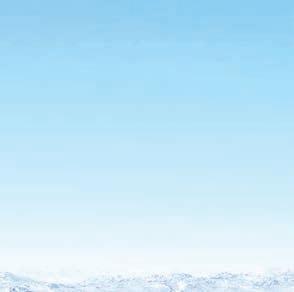
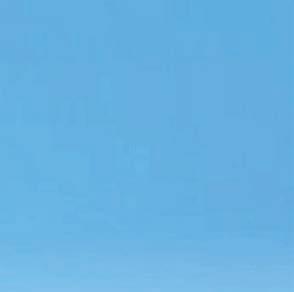
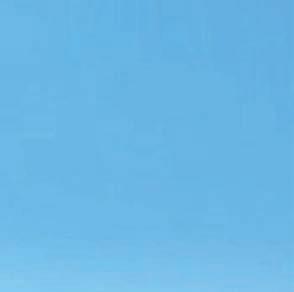
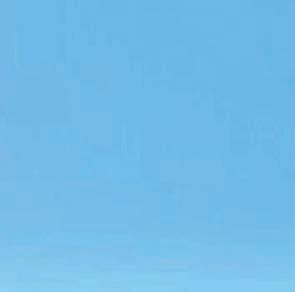
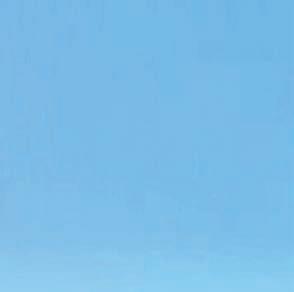
100 MILLION TREES
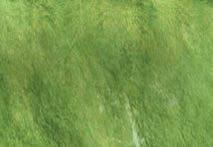

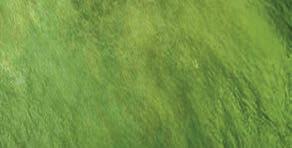
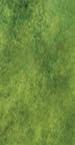
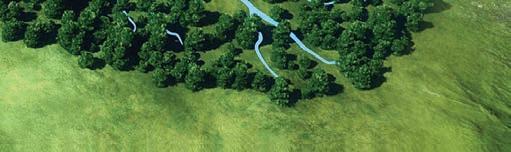
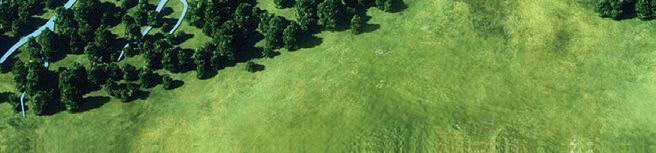
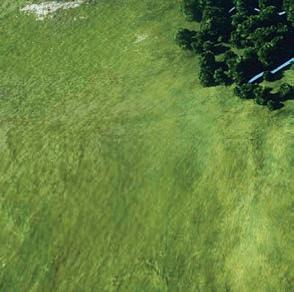
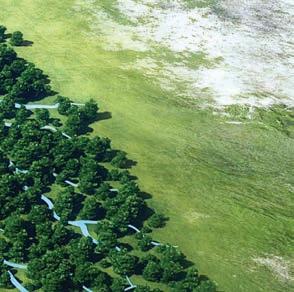
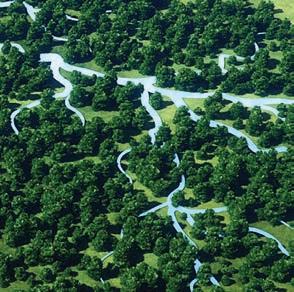

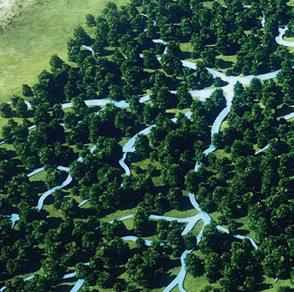


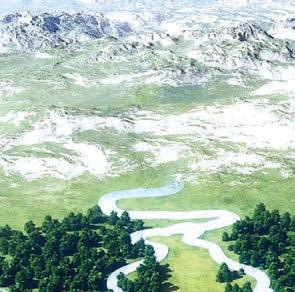
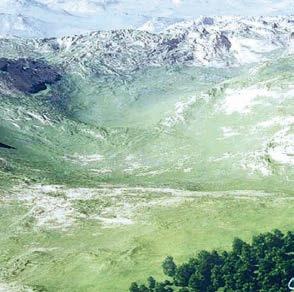
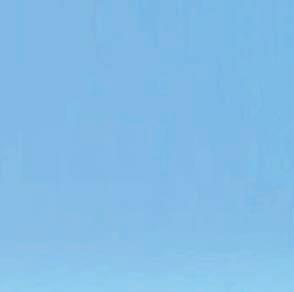
Eco-friendly explosives, for greener blasting.
In just a little more than a decade since the introduction of used oils into its various Eco bulk emulsion formulations, AECI Mining Explosives has consumed more than 80 000 000 liters of used oil. This initiative has prevented approximately 55 000 tons CO2e into the atmosphere, which equates to having to plant roughly 100 million trees. Thank you for partnering with us in our quest to drive more sustainable blasting.
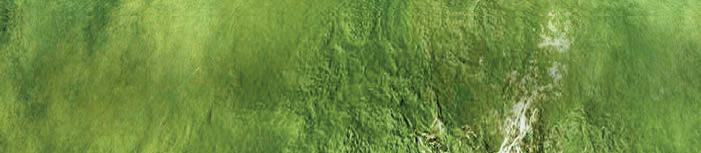
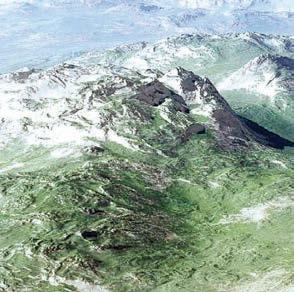

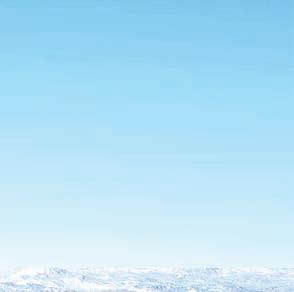
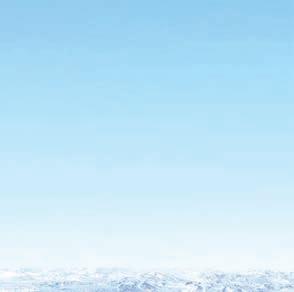
FULL STEAM AHEAD FOR COWAL
Evolution Mining’s Cowal gold operation has commenced underground production ahead of schedule.
The Cowal operation is located 350km west of Sydney and has been owned by Evolution since July 2015.
The first underground stope started being mined and processed in March, with continued ramp up of the underground area expected over the remainder of this financial year.
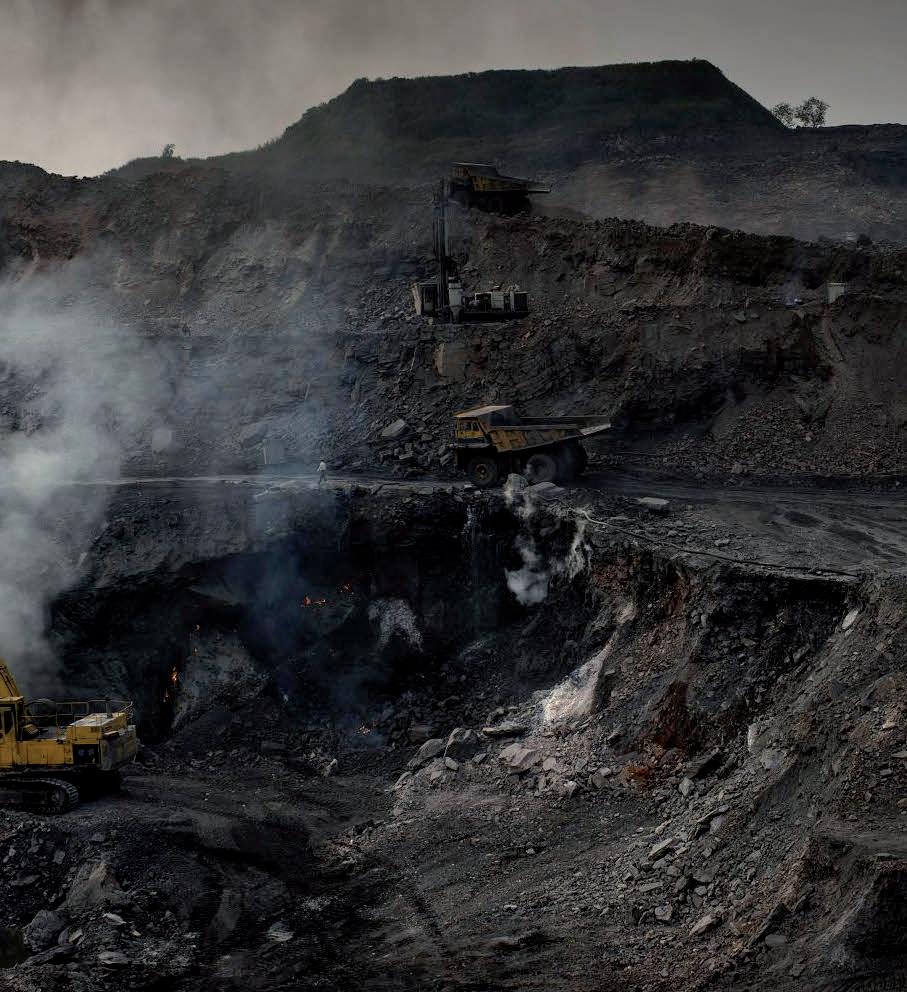
“We have achieved a major milestone at Cowal with the early commencement of production from the new underground mine,” Evolution chief executive officer and managing director Lawrie Conway said.
The production is a full three months ahead of schedule and remains within the original $380 million budget.
The completion of the accommodation village and commissioning of the paste plant
remain on track for the June 2023 quarter.
“It is a credit to the project team to be able to commence production ahead of schedule and on budget in the current inflationary market conditions,” Conway said. “We are on the pathway to increase production from the current FY23 guidance of (approximately) 275,000 ounces to FY24 outlook of (approximately) 320,000 low-cost ounces.”
Evolution also announced that its recovery plan for Ernest Henry
was still underway after heavy rainfall in north-west Queensland forced its production suspension in March.
“As the recovery plan continues, the impact on the group FY23 guidance will be fully understood and communicated,” Evolution said in a statement.
“The company’s liquidity remains strong with the cash position at the end of February ahead of plan and the $525 million revolver facility being undrawn.”
BELLEVUE’S 200,000-OUNCES-OF-GOLD-PER-ANNUM MINE
Bellevue Gold released its half-yearly financials, reporting the steady progression of its flagship project.
The WA mine is fully funded and on track for production in the second half of this year. The Bellevue mine –which boasts a mineral resource of 3.1 million ounces – is forecasted to rank among the top 20 gold mines in the country.
The Bellevue gold mine is also estimated to be a high-grade, lowcost operation with all-in sustaining costs of $1000–1100 per ounce. With
an estimated annual production of 200,000 ounces of gold per annum, the mine is expected to generate $2.1 billion in net free cashflow, with an internal rate of return of 68 per cent.
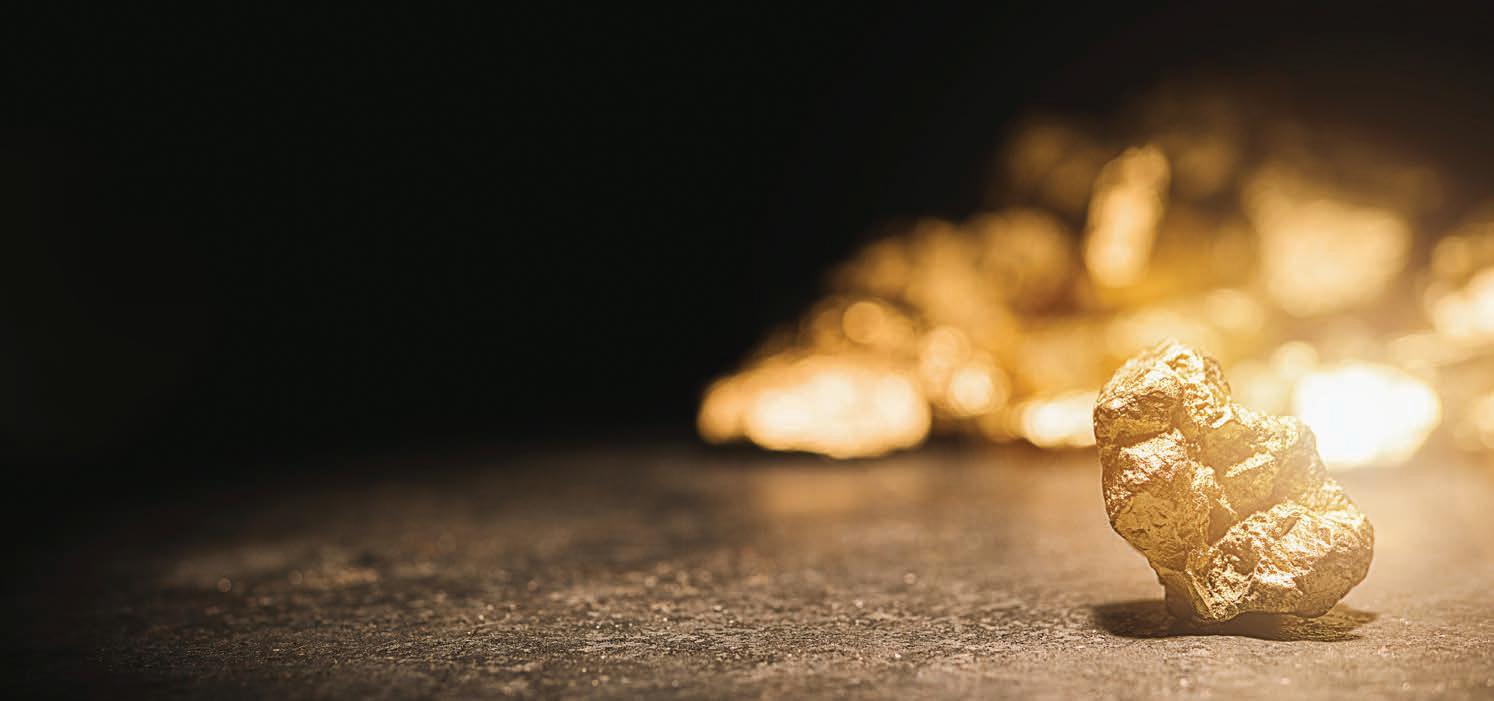
The mine has an initial lifespan of 10 years, but Bellevue is confident this will be extended by ongoing exploration activities.
Bellevue is in the final stages of constructing a one-million-tonnesper-annum (Mtpa) processing facility in support of the site. According to the company, the facility shows the
potential to increase to 1.2Mtpa with no additional capital investment.
The company also announced its net zero target for the Bellevue gold project, which it aims to meet by 2026. Underpinning this goal is a renewable energy power station with a 70–80 per cent renewable energy penetration rate.
The flagship gold project has been a long time coming for Bellevue.
In February, the company announced a major board reshuffle in preparation of start of production at the mine. Darren Starlow was
appointed managing director and chief executive officer, replacing Steve Parsons – who now settles into the role of non-executive director.
Bill Sterling was appointed chief operating officer to assist with the transition.
“Bellevue is set to start production later this year,” Bellevue chairman Kevin Tomlinson said. “With this in mind, it is the right time to appoint the team who will lead our company into the next highly rewarding phase of its growth and development.”
COMPLETE AIR & POWER SOLUTIONS FOR MINING

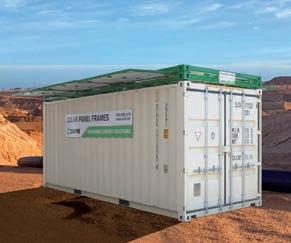
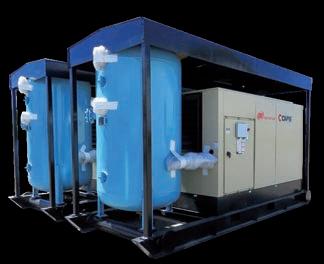
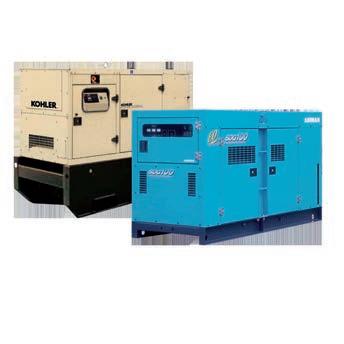
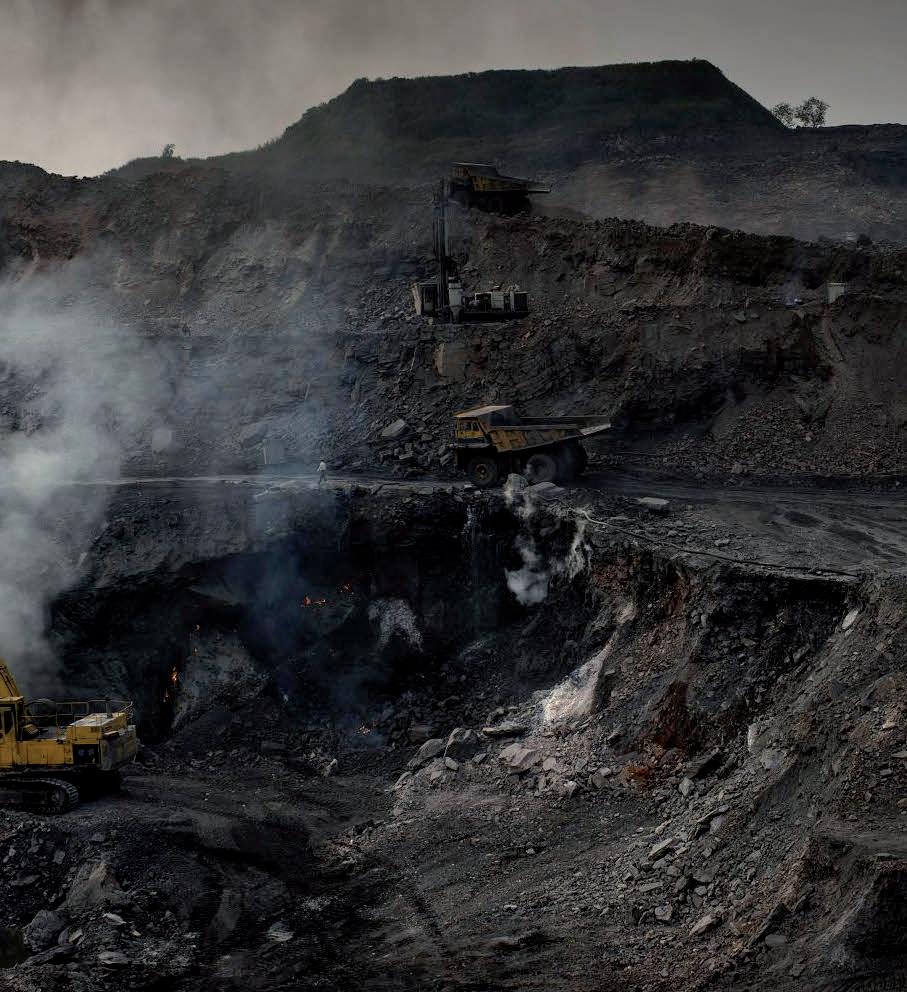
CAPS Australia is an Australian owned and operated company who was born to service the mining industry with the best compressed air products and services. 43 years later, mining is still at our core with products, engineering and an expanded range.
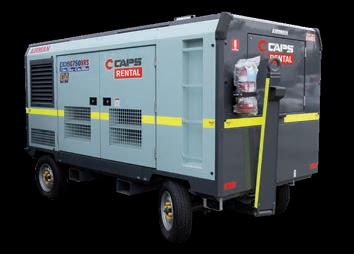
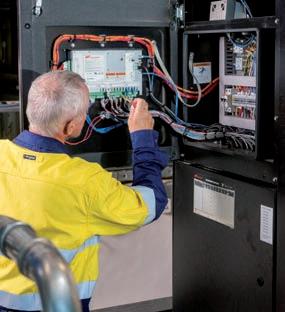
FIXED AIR INSTALLATIONS
CUSTOM SKID PACKAGES
RENEWABLE ENERGY
POWER GENERATION
RENTAL SOLUTIONS
SERVICING & SPARE PARTS
CALL 1800 800 878 OR VISIT CAPS.COM.AU
TRACKING THE TRENDS 2023: PART TWO
In its ‘Tracking the Trends’ report for 2023, Deloitte experts were very clear about labelling green energy and innovation the keys to future growth.
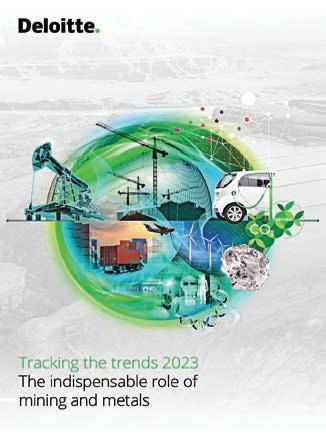
The first three trends in the report deal with environmental, social and governance (ESG) value and economic circularity, which were discussed at length in the April edition of Australian Mining
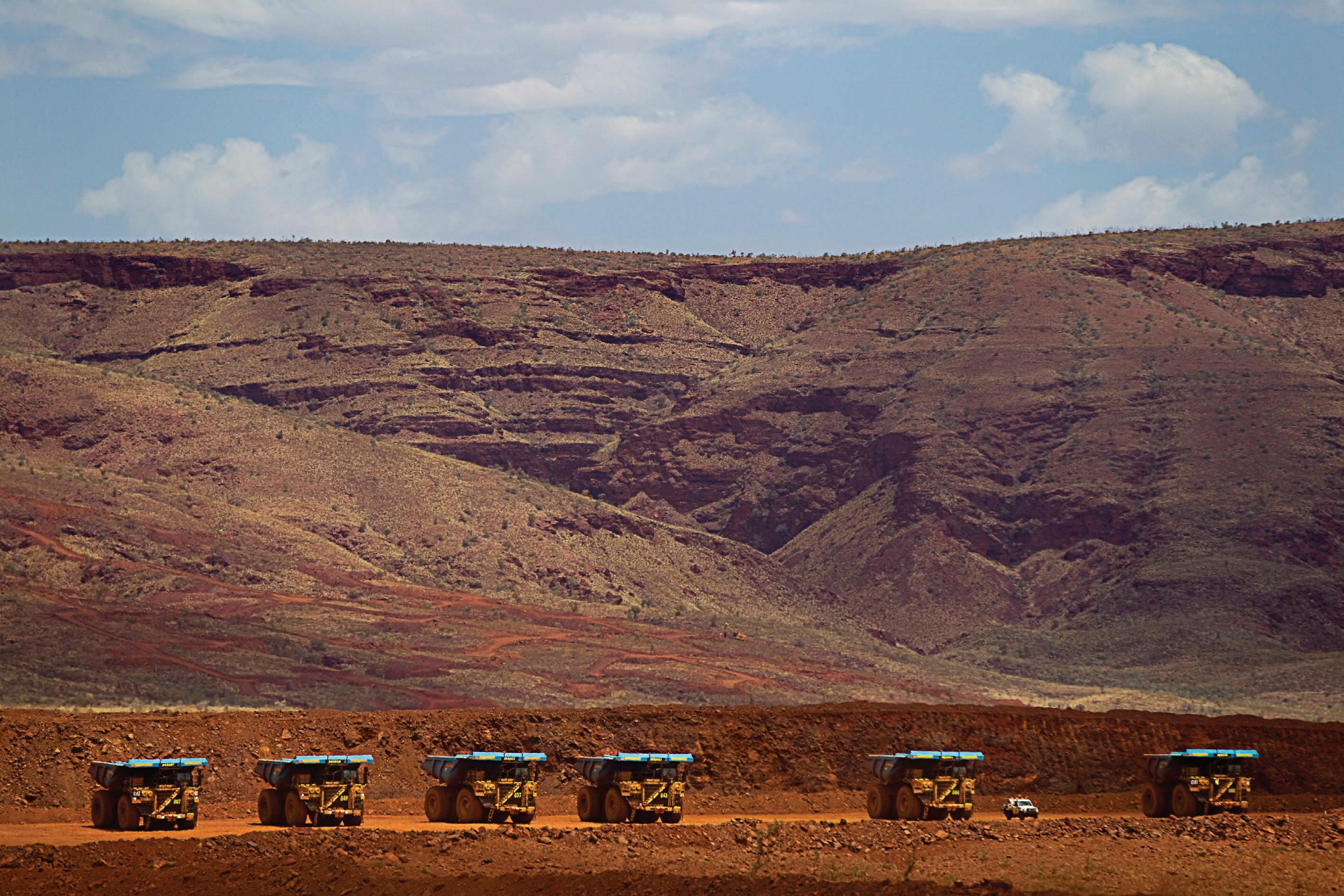
The remaining seven trends can be broadly understood as highlighting the importance of innovation in the technological, social, and cultural sense. Collaborate, incubate, accelerate
This fourth trend speaks to the importance of innovation in a general sense.
From a business perspective, technological innovation can help mining companies lower costs, reduce dangers and minimise their environmental impact. This not only helps to ensure profitability, but also promotes sustainability over time.
Social innovation through ESGrelated goals can help companies secure social license to operate. By being more socially responsible, companies can experience less public resistance and obtain smoother permitting for projects.
Finally, business model innovation allows companies to incorporate circular economic principles, maximise the value of their assets, and bolster their operations against future disruptions.
Building resilient supply chains
Labour and material shortages, as well as high costs in the wake of the COVID pandemic, have been further compounded by the ongoing Russia–Ukraine conflict.
Metal provenance is a growing concern around the world as China dominates 80 per cent of rare earth metal supply, prompting some governments – such as the US – to declare their supply chain a matter of national security.
As a consequence, many miners are diversifying their supply networks and being choosy about business partners to ensure their resilience in unstable times.
Deloitte highlights the importance of third-party risk management as a way for companies to protect themselves.
“Mining and metals companies should be looking to build AI-based predictive models that can enable them to look into the future and perform risk analysis on suppliers at different levels of the supply chain,” Deloitte global risk advisory partner René Waslo said.
“This will allow them to strategically plan for and lower their own exposure to risks, such as human rights violations, failing of debt structures, or poor reputation in the media.”
The importance of ESG targets in the mining industry has provided the sector an opportunity to work collaboratively to tackle global problems such as decarbonisation, issues beyond the capacity of one entity to solve.
One such collaborative effort is ELYSIS, a joint venture between Rio Tinto and Alcoa, with support from other brands and government bodies. ELYSIS utilises carbon-free smelting technology to produce aluminium with no greenhouse gas emissions. The process instead releases pure oxygen.
Rio signed an agreement with Japanese conglomerate Marubeni Corporation that will see ELYSIS aluminium hit supply chains in Japan.
Making change more holistic
This sixth trend advocates for systems thinking, which involves understanding
and characterising a whole system by examining the linkages and interactions between its elements.
“The mining industry tends to focus on deploying point solutions – for instance, battery-electric or hydrogen trucks – rather than fundamentally rethinking the mine design, material
movement and energy systems to create the best possible system solution,” Deloitte Canada director of consulting Adriaan Davidse said.
An example of systems thinking is simulation and modelling technology. Sibanye-Stillwater uses a digital twin of its underground Nye site in the US,
using a single intelligent system to run a variety of scenarios to compare risks and surplus.
This saves the company time and helps address potential operational issues months in advance.
Rio Tinto’s Gudai-Darri iron ore mine in WA employs a similar system, with a full digital twin of the processing plant.
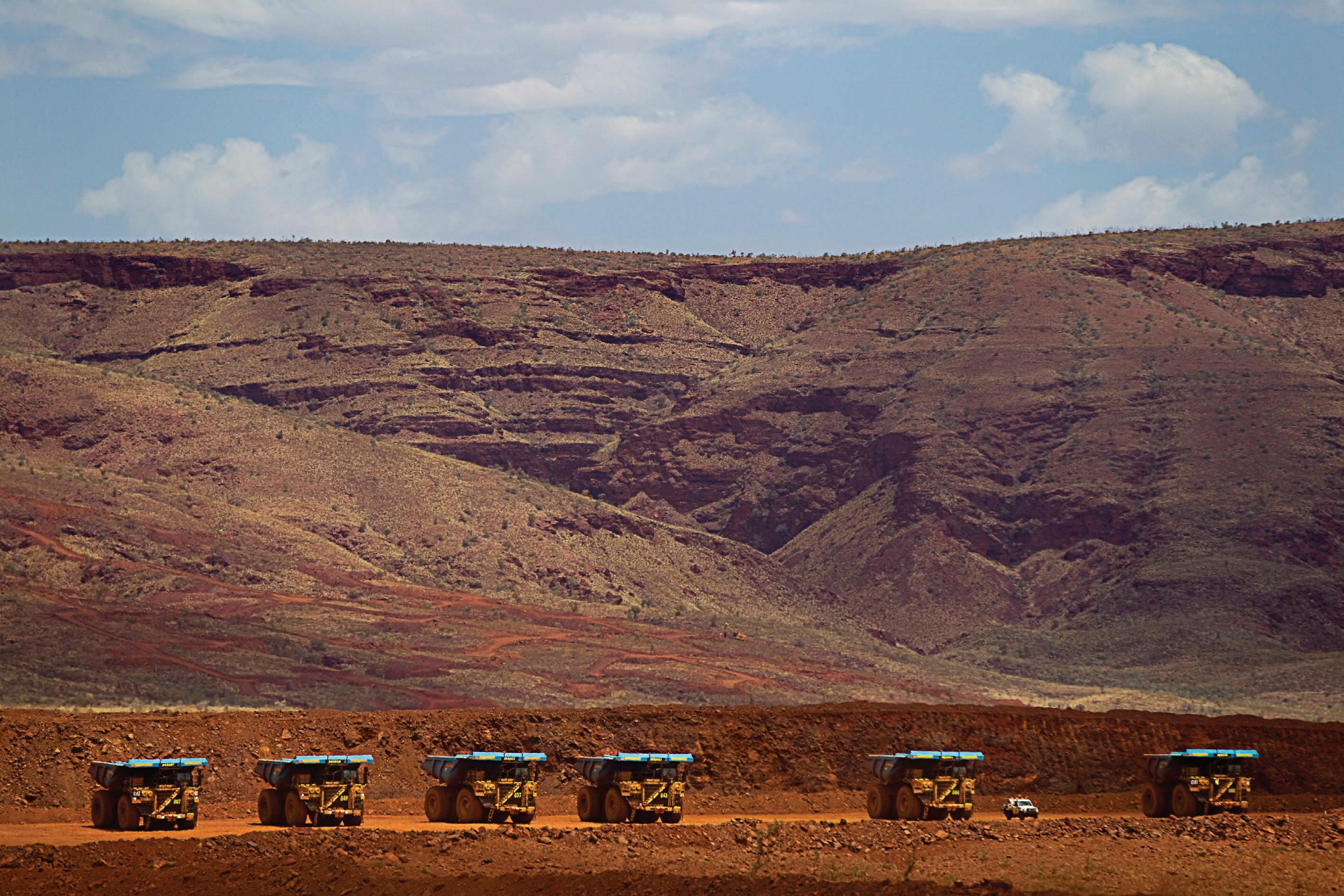
This enables the company to monitor and respond to data collected from the plant, as well as provide an interactive 3D environment for virtual training.
Rethinking external talent pathways
Deloitte highlights an evolving labour market in the seventh trend.
“We’ve been hearing a lot of commonalities in the mining and metals industries’ people challenges. Across continents and countries, we see leadership teams working to balance labour shortages with booming demands,” Deloitte partner Janine Nel said.
“There are also requirements to attract and retain the appropriate talent and skills, source diversity of talent, bring forth diversity, equity and inclusion in the workplace, and shape and embed sustainability into organisational DNA.”
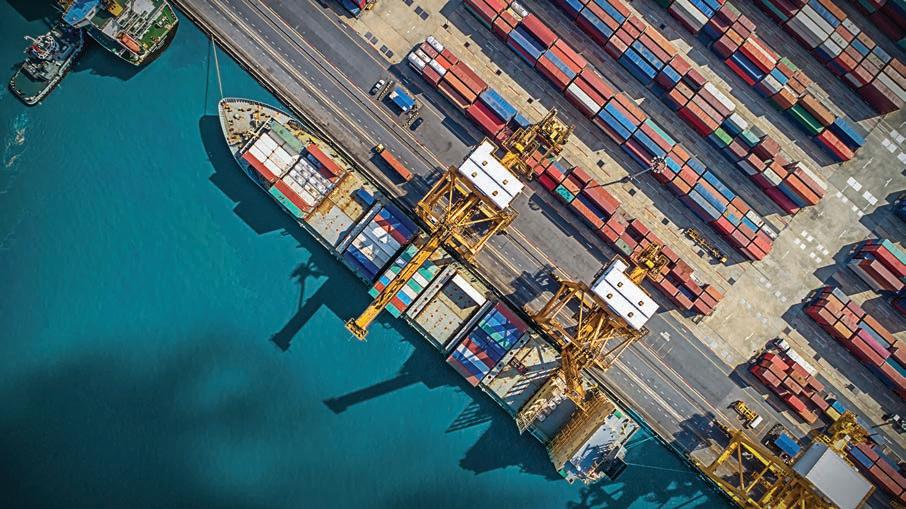
By better reflecting on social values and creating two-way relationships with the local communities in which they operate, mining companies can change the way they are perceived. A positive image will help attract the next generation of talent, whose members are increasingly interested in environmental sustainability and meaningful work.
Layering safety for greater sustainability
Generally speaking, fatality rates have been steadily declining across the industry as the mining sector places an increasing emphasis on physical safety.
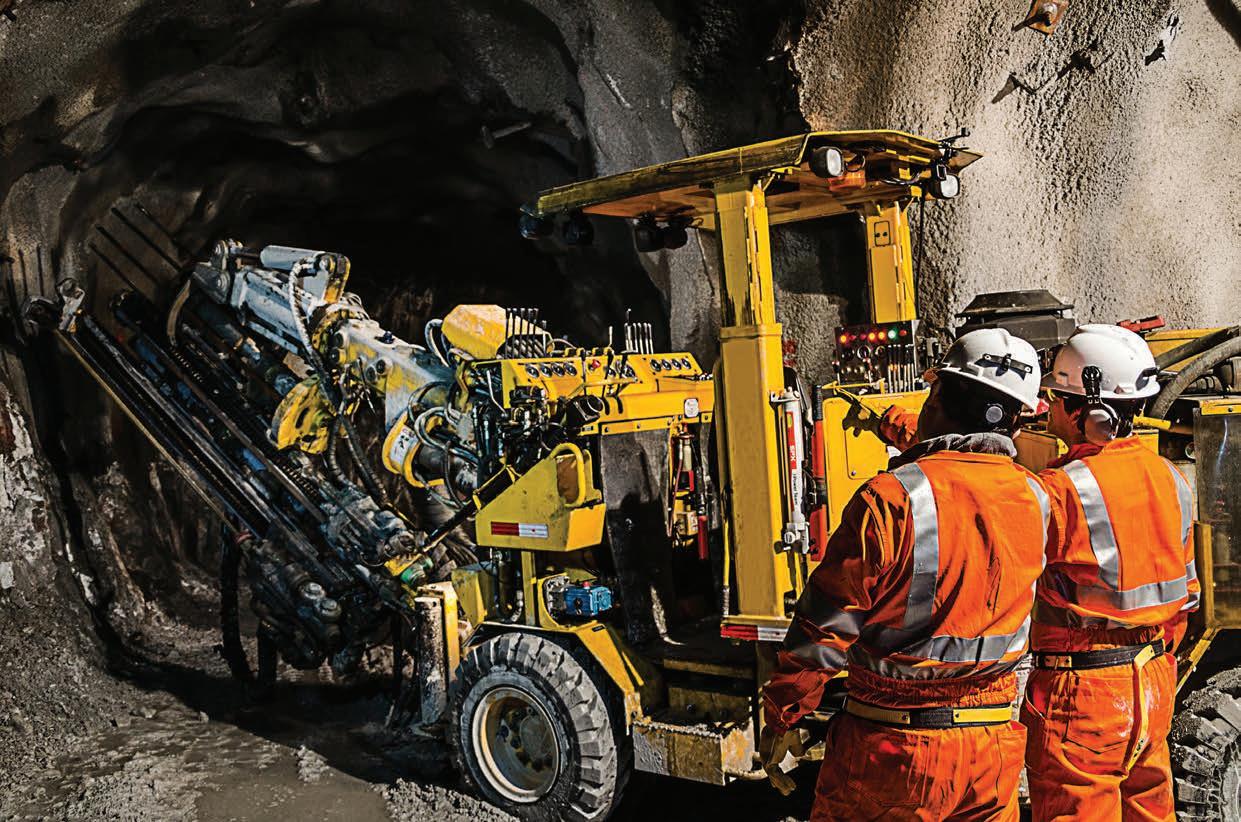
But Deloitte’s eighth trend highlights the emerging concern over safety of a different kind. Trends suggest a
growing emphasis on not only physical safety at work, but also psychological, cultural, and cyber safety.
“These four layers of safety link and build upon each other to create foundations for a secure organisation,” Waslo said.
“Mining and metals leaders who can seamlessly integrate and have genuine engagement, action, and advocacy for all aspects of safety will lead their organisation toward a more sustainable, secure, resilient, and prosperous future.”
Transparency equals trust
In the coming years, organisations can anticipate thorough examination of their economic and tax contributions by various stakeholders, including tax authorities, investors, and local communities.
In its ninth trend, Deloitte says mining and metals companies must cultivate an image of trust with their stakeholders.
And this involves more than just meeting mandatory reporting requirements.
Deloitte proposes linking tax implications with a company’s sustainability strategy, bringing transparency into focus as a matter of long-term survival, rather than a peripheral consideration.
The power of the cloud
The final trends deals with cloud data storage.
The fast, reliable and remote access to cloud servers has afforded businesses a certain stability in the past decade. Equipment failure becomes less of a headache when data is backed up and can be accessed via cloud.
Roughly 80 per cent of the organisations surveyed for Deloitte Australia’s cloud imperative report stated cloud technology helped their businesses navigate challenges and address organisational needs.

In the latter part of ‘Tracking the Trends’ report for 2023, Deloitte put forward the challenge for companies to rethink their supply chains, systems design, and social image.
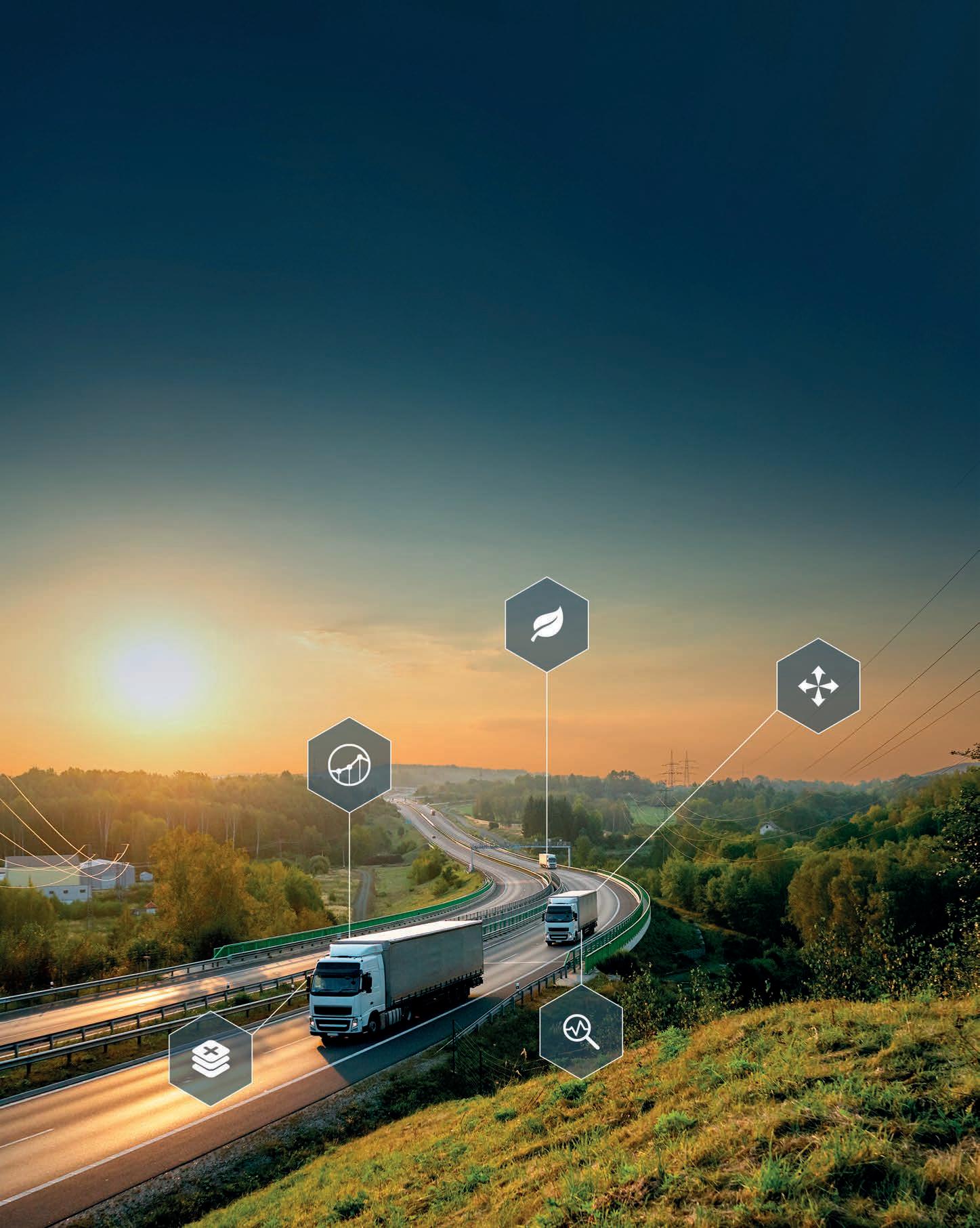
Emerging social and environmental trends are forcing companies to adapt or be left without a social license to operate. Things like supply-chain decarbonisation, holistic working environments, and corporate transparency will become increasingly important in coming years.
And supply-chain instability is demanding technological innovation for companies to remain competitive across a range of factors.
With this latest report, experts from Deloitte have thrown down a gauntlet for mining companies in 2023. AM
Optimize your fleet with data-driven insights and AI powered by the #1 global telematics provider.
One platform for connected and sustainable fleet performance.
Geotab’s AI-driven platform transforms real-time data from any source into actionable insights that provide measurable business value, help reduce fleets emissions and costs while improving operational efficiency. Optimize your fleet’s performance and stay ahead of the competition.
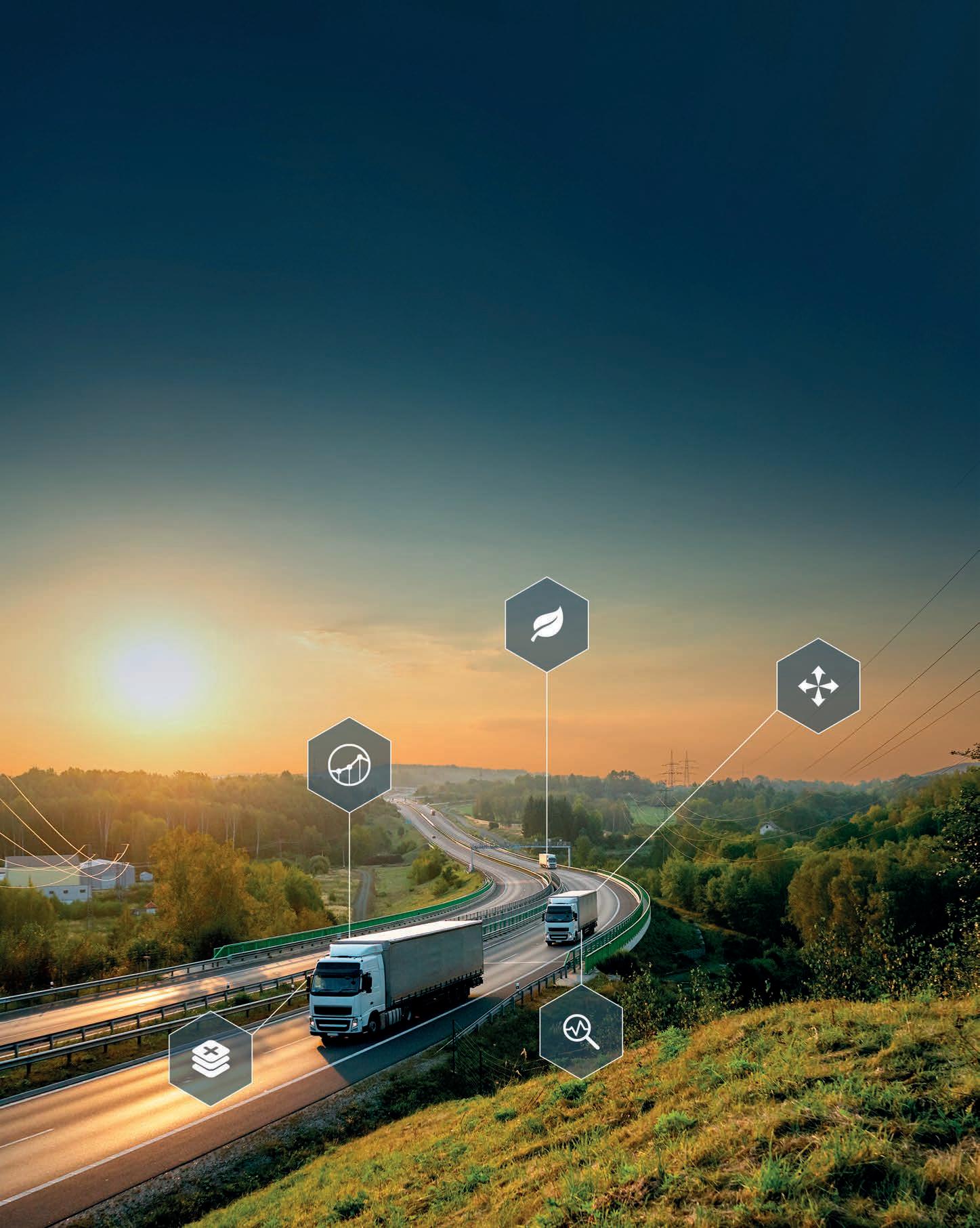
BECOMING ROCKAWARE
ROCKAWARE IS A LEADING AI DETECTION SYSTEM FROM DECODA THAT HELPS DETECT OBSTACLES BEFORE THEY CAN SHRED A HAUL TRUCK’S TYRES.
Haul truck tyres are some of the most important components on a mine site. Without them, products don’t get to where they need to go.
It is estimated that haul truck tyres regularly fail at just 40 to 60 per cent of their expected life, causing major disruptions on mine sites and leading to blown-out maintenance budgets.
Many of these tyre failures are quite straightforward – the direct results of continued run-ins with sharp rocks.
When Decoda saw these issues, the company knew it had to do something about it. And from there, RockAware was born.
“The idea for RockAware started when we went out to a customer’s site and heard about the issues they were having with tyres,” Decoda executive general manager George Spink told Australian Mining
frustration with how quickly tyres wear out and the potential safety hazards – a rock run over by a haul truck can quickly become a dangerous projectile.
“The risk of a fatality during tyre maintenance is 10 times higher than that of non-tyre related vehicle maintenance,” Spink said. “Every customer I’ve spoken to has told me how much they worry about tyre explosions and the risk that comes from them.”
But RockAware is here to help. By combining LiDAR (Light Detection and Ranging) and a camera, the technology scans the ground on which a truck is driving and alerts the operator to any damaging rocks in their path.
“The LiDAR and the camera are the two main pieces of technology that RockAware uses,” Spink said. “Then we have an edge computer that is capturing, modelling, and analysing the data that the operator sees in real-time before it is sent to the RockAware cloud platform.”
operators are using the machines and then provide a coaching session to improve this,” Spink said.
It’s not just the safety aspects that have mine operations excited about RockAware. There are environmental benefits, too.
“One of the major environmental issues concerning tyres is that old ones have to be disposed of somewhere,” Spink said.

“So if a customer is only getting 50 per cent of life out of a tyre, that’s twice as many changes they’re having to do. And these old tyres can really pile up.”
By installing RockAware on a haul truck, operators can avoid the hazards that have historically reduced tyre life and get more out of their money.
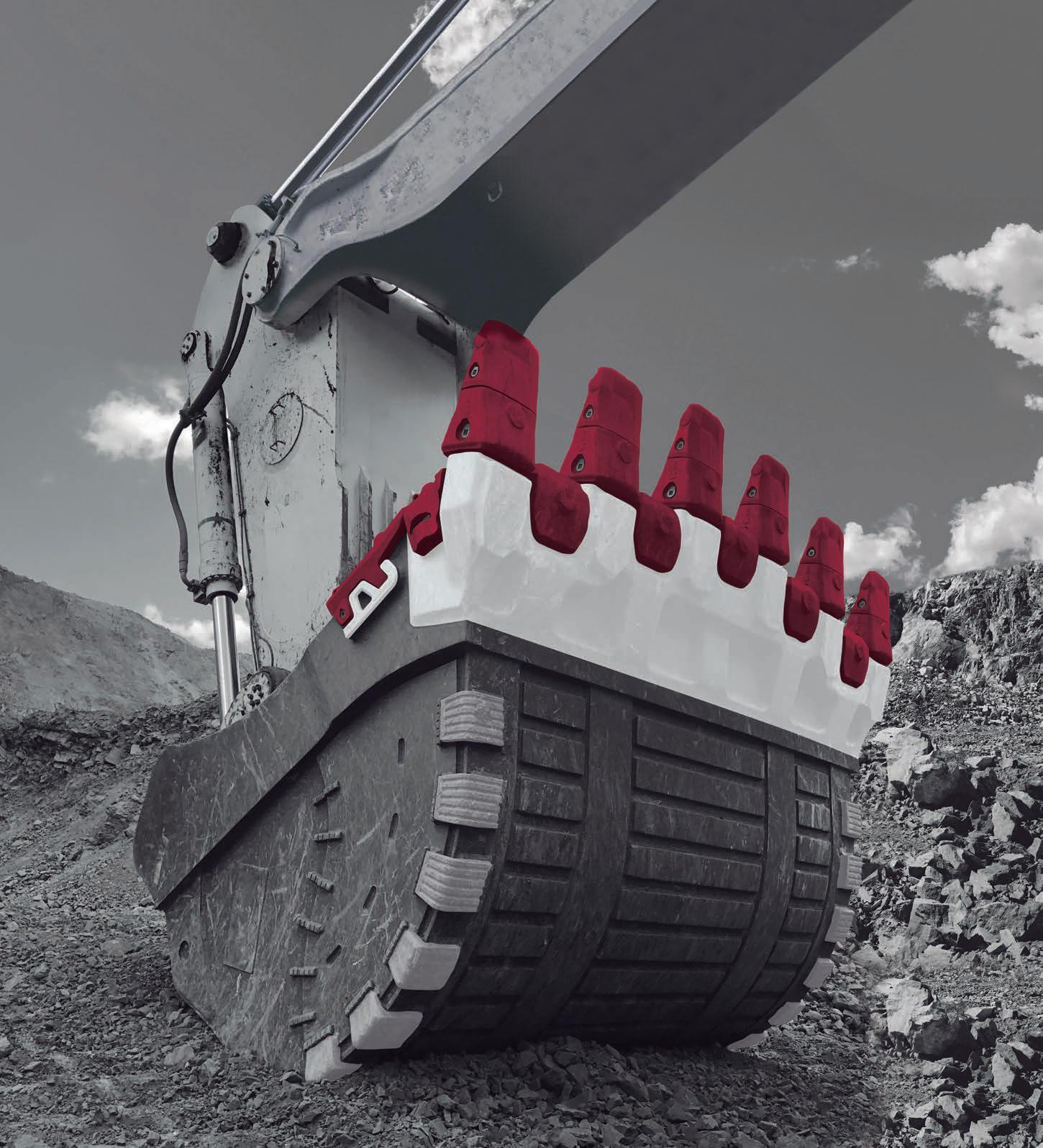
“One customer was spending more than double their tyre budget because of the continued issues,” Spink said. “And obviously that’s not sustainable.”
The production issues that can
But by linking up with other technologies that are already in the market, RockAware can ensure a mine’s production stays at its peak.
“Thermal scanning looks for hot spots of damage in tyres and identifies where the damage is most pronounced,” Spink said.
“RockAware can work with thermal scanning to prevent the impact happening in the first place but also to track how many impacts a tyre had prior to its failure through the platforms portal.”
The ability to provide RockAware to different sites has been invaluable for Decoda.
“Partnerships between Decoda and companies in the mining industry are great because we can work together to test out technologies that make the sector safer, more cost-effective and more productive,” Spink said.
“Making the industry safer is a
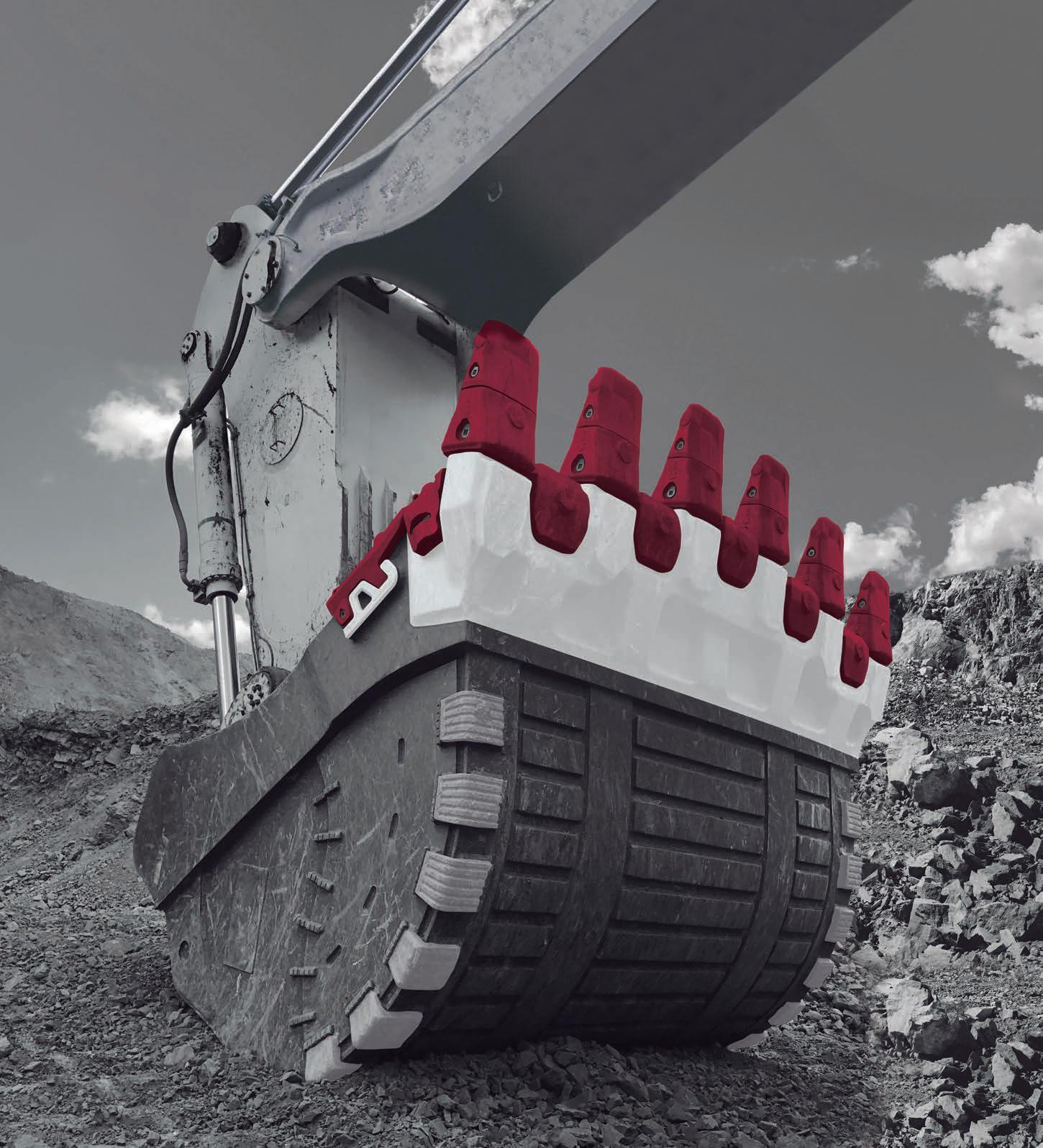
AN ESSENTIAL GUIDE TO SKIRTBOARDS
hen bulk material hits a moving conveyor belt, the landing can cause aggregate, dust and fines to splash and pelt the sides of the enclosure before settling onto the belt. Without skirting, that material escapes and piles under the structure, spills into walkways, fouls equipment, and chokes the area with dust, creating an expensive headache for operators.
When tonnes of bulk material hit a moving belt, three things happen: fines scatter in a random direction; cargo shifts as it settles to the centre of the belt; and dust becomes airborne.
According to Martin Engineering, a properly designed enclosure should manage bulk solids and contain all of the dust. Inside a settling zone enclosure, the impact can create turbulent air that seeks the easiest escape from any gap it can find, carrying dust and fines with it. These gaps generally appear on the sides of the enclosure between the chute wall and the belt. Skirting systems address the challenge of containing fugitive dust.
Cluttered walkways and blocked access to systems is an implication of spillage. Since slip and fall injuries are some of the most common, Safe Work Australia guidelines recommend regular clean-up of all debris on the walkway and providing clear access to machinery.
In addition to safety hazards, material piling in the loading area can quickly encapsulate the belt and tail pulley.
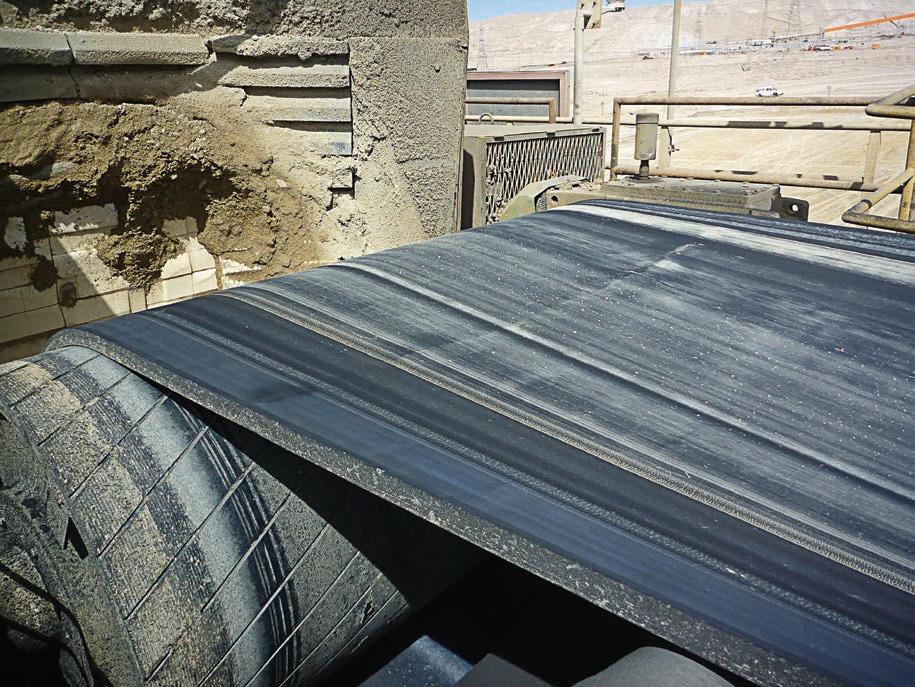
WSpillage of just 4g per hour will result in an accumulation of 680g by the end of a week. With spillage of just one shovelful per hour, the total could reach 227kg of material every day. That kind of volume can cause equipment breakdowns, foul the pulley face and promote belt alignment issues.
Installation and service of skirtboard systems can also be hazardous, with some designs welded to the inside of the chute structure, involving confined space entry with a grinder or blow torch to perform maintenance, repair or replacement.

Properly sealing the chute using modern skirting designs can help avoid equipment breakdowns, improve workplace safety and prevent excessive downtime due to dust and spillage.
Anatomy of a sealed chute
The components of a well-designed and sealed loading zone will likely consist of a combination of components, including an enclosed loading chute, a heavy-duty belt support system, closely spaced idlers to avoid belt sag, adjustable skirting to contain fine particles, easily serviced wear liners, dust curtains to control air flow, a sealed tail box to protect the tail pulley, and exit curtains to prevent release of fugitive dust.
The trough angle will change throughout the settling zone, so proper skirt design for adequate sealing is important.
Usually made from natural or styrene-butadiene rubber (SBR) rubber,
the skirting extends the length of the transition enclosure and is generally tapered at the bottom to match the trough angle of the belt. It is intended to ride the inside edges of the belt to maintain a seal on the enclosure and help trap any fine particles and dust that is not contained by the wear liners and chute wall.
Without a wear liner to protect the skirt and chute wall from serious damage by bouncing and shifting cargo, both will degrade and fail quickly.
As the skirt edge loses its seal due to wear or belt sag, gaps are created that can allow material to become trapped in a ‘pinch point’, causing abrasion that gouges or chafes the surface of the belt down its entire length.
Often blamed on pressure from the skirt, pinch points occur most often when there is inadequate belt support or loading is done before the belt is fully troughed.
Major issues that result from entrapment include scalloping, which occurs when trapped material forms a high-pressure area between the roller and the skirt; and grooves being created by trapped debris under the skirt causing friction damage.
Regardless of the belt tension provided by the take-up pulley, small amounts of belt sag will occur between the skirt and belt, creating a space for fugitive dust to escape or material to become entrapped.
This is avoided by using impact cradles or edge support rather than rollers in the loading zone for a more consistent belt plane through the settling zone.
Skirting types
The main skirt sealing configurations are vertical sealing systems, internal wear liner and skirting, internal wear liner with external skirting, and external wear liner and skirting.
Segmented vertical sealing systems use a series of interlocking sealing blocks installed outside the skirtboard on special mounting plates.
MARTIN ENGINEERING EXPLAINS HOW A CONVEYOR TRANSFER POINT WITHOUT SKIRTING IS A MAJOR COST – AND A HAZARD.
“AS THE SKIRT EDGE LOSES ITS SEAL DUE TO WEAR OR BELT SAG, GAPS ARE CREATED THAT CAN ALLOW MATERIAL TO BECOME TRAPPED IN A ‘PINCH POINT’, CAUSING ABRASION THAT GOUGES OR CHAFESSCALLOPING OF THE SKIRTBOARD. GROOVES IN THE BELT.
them prone to material entrapment and leakage of dust and fines.
Internal wear liner and skirt configurations are not usually adjustable and require significant downtime to repair, maintain and replace.
A self-adjusting interior skirt features an L-shaped system with an outside assembly – similar to the selfadjusting skirt – with an inward 38mm extension under the wear liner that rides on the belt closer to the cargo to increase the range of tolerance for belt mis-tracking.
Old belting should never be used for sealing, as the fabric will trap abrasive fines and wear grooves in the belt. Even with a deflector-style wear liner, cargo will get between the seal and belt, and the pressure of the load will create wear unless the bulk material is totally non-abrasive.
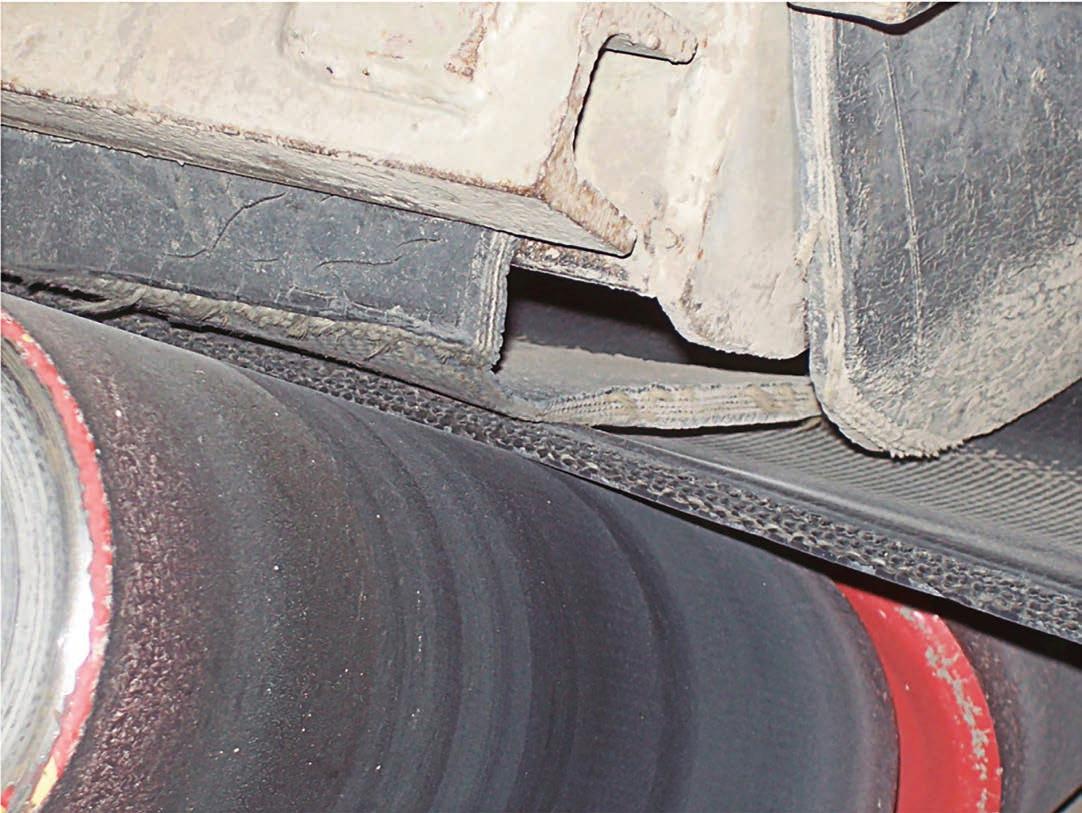
The internal wear liner and external skirt configuration has been industry standard for decades. It offers a safer and more adjustable solution, as it is typically held tightly against the skirtboard using an adjustable clamp system that can be accessed from outside the chute. However, the internal design can allow some material build-up in the gap between the wear liner and the skirtboard.
Martin Engineering’s external wear liner and skirting configurations place both pieces of equipment outside the chute wall. If not originally supplied, this may require some restructuring of the chute.
Placing the skirt seal and wear liner outside of the chute makes it easier for workers to perform adjustments safely and more frequently, resulting in a better seal on the belt and less material entrapment, while eliminating the need for confined space entry.
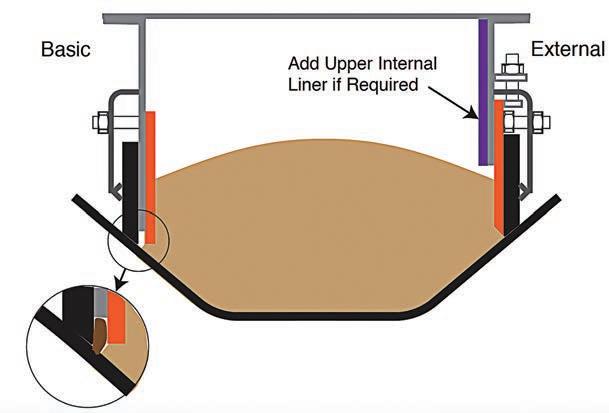
The low profile of the skirt seal assembly needs only a few inches of clearance, allowing installation and maintenance in space-restricted areas. The design of the components drastically reduces scheduled downtime and the potential workplace hazards.
Sealing by the numbers
Innovative skirt designs apply practical engineering for safer and more effective sealing for trough angles up to 45°. They are often made from improved materials to deliver chemical resistance and lowabrasion index characteristics for reduced friction on the belt and splice.
Many dusty applications may need skirts featuring a secondary ‘dual seal’ that rides further up on the belt angle behind the primary seal to offer an added layer of protection.
Once the edge is worn, some designs allow the strip to be flipped over, effectively doubling the service life.
Self-adjusting skirting maintains a seal automatically, as the belt path fluctuates due to its design, without the need for adjustment and only periodic inspection. Self-adjusting skirting is also good for tight spaces where maintenance may be difficult. A low-profile skirting assembly should need only 152mm of clearance for installation and maintenance in small spaces.

Skirting best practice
The skirt should be considered a safety device first and foremost, protecting the work environment from fugitive dust and spillage and therefore reducing the time exposed to hazards while cleaning, with the added benefit of increased efficiency.
With this in mind, any manager contemplating a capital investment in a skirting and wear liner system should consider:
• hiring an external engineer to design the best system for the application
• installing equipment that features external maintenance
• utilising a skirting strip that extends the length of the chute to avoid seams
• choosing skirting material that is free of fabrics, with a lower abrasion resistance than the belt
• installing a self-adjusting system
• choosing the option with the least worker exposure to equipment hazards.
Since skirts are wear parts, it is important that they are easily installed, adjusted, maintained and replaced to avoid dust and spillage, mitigate downtime, improve workplace safety and reduce the cost of operation. AM
A SOLUTION PROVIDER
BRADKEN COMBINES A CENTURY OF EXPERIENCE WITH INTELLIGENT MODERN TECHNOLOGY TO DELIVER SOLUTIONS TO ITS CUSTOMERS.
The global mining industry is rapidly changing, emphasising the importance of working with partners who can help operations achieve productivity improvements and optimisation.
And that’s where Bradken comes in. Bradken is a manufacturer and supplier of wear products for the resources sector. Its engineering team employs a solutions-based approach, working with customers to adapt its products to meet a range of needs and issues.
A typical situation begins with collaboration. Bradken works with a customer to identify a problem, and then pulls from its team of experts and decades of experience to discuss solutions the company has implemented elsewhere.
Such was the case when Bradken was engaged to optimise a large copper mill in North America that was seeking to improve the output and profitability.
“The client reached out to us and asked, ‘How can you help us achieve our goal?’” Bradken product lead in North America Matt Hazell told Australian Mining. “Collaborating with the site, we identified constraints in the AG
mill, impacting the efficiency of the concentrator plant which we could improve.
“We found the mill was not discharging efficiently and there was an opportunity to leverage Bradken’s global experience, analytical capabilities and modelling tools to resolve the issue.”
Bradken provided a full mill redesign to suit the site’s operation.
But suggesting a complete redesign isn’t always easy.
“Many sites are risk-averse, especially when proposing major departures from their current designs – even if the potential reward could be significant,” Hazell said.
Customers need certainty, and Bradken delivers.
“We work to be as transparent as possible in predicting the success of our proposals,” Hazell said.
“Typically, customers first want to know if proposed designs have been proven in the field. This is where Bradken’s global wealth of experience adds value.”
Bradken also adds validation through advanced numerical modelling tools and discrete element method (DEM) simulations to evaluate particle motion and collisions within the mill.
In other words, Bradken runs engineer-reviewed simulations to validate design features and potential outcomes on-site performance before ever installing a part.
This is exactly the technology Bradken employed to help secure the go-ahead at the copper mill site in North America.

“Using DEM, Bradken was able to analysis the results of several designs to ensure the optimal package was implemented to suit sites operation” Hazell said.
“Beyond that, we have made some incredible developments in our digital tools to accurately predict performance. Bradken was successfully able to forecast the mill performance over a 12-month period and guarantee a five per cent increase in production.”
The project outcome exceeded the original forecast, resulting in a further five per cent improvement over the agreed benchmark.
As valuable as it is in the moment, a big part of Bradken’s service is its aftersales support.
“We don’t really treat ourselves as a product supplier – we’re a solution provider,” Hazell said. “The products are the tools we use to craft those solutions.
“So that means the collaboration and service continues beyond those products being installed. It’s about making sure that they continue to perform as expected.”
Bradken designs and manufactures its own products, allowing the company to tailor its offerings to each customer and provide the optimal solutions.

“We challenge ourselves to continue to improve. This is seen in our development of new materials, products and digital solutions,” Hazell said.
“We choose to continually innovate.”
As a manufacturer, Bradken invests in the research and development (R&D) of its range. Its optimised products help customers hit their environmental, social and governance (ESG) goals by running more efficiently.
Bradken is incorporating circularity in its mining consumables, improving its management of emissions throughout the product’s lifecycle to provide a holistic path to zero emissions manufacture.
The company’s R&D efforts, supported by government research programs, have resulted in improved production efficiencies and reduced emissions.
The company also provides a comprehensive liner recycling program, significantly reducing waste a mine site would otherwise have to deal with. Once removed, 98 per cent of the metal liners are recycled and put back into the chain of production.
Through its broad range of experience in its teams, range of materials and products, along with intelligent simulation modelling, Bradken is helping customers optimise their operations. AM
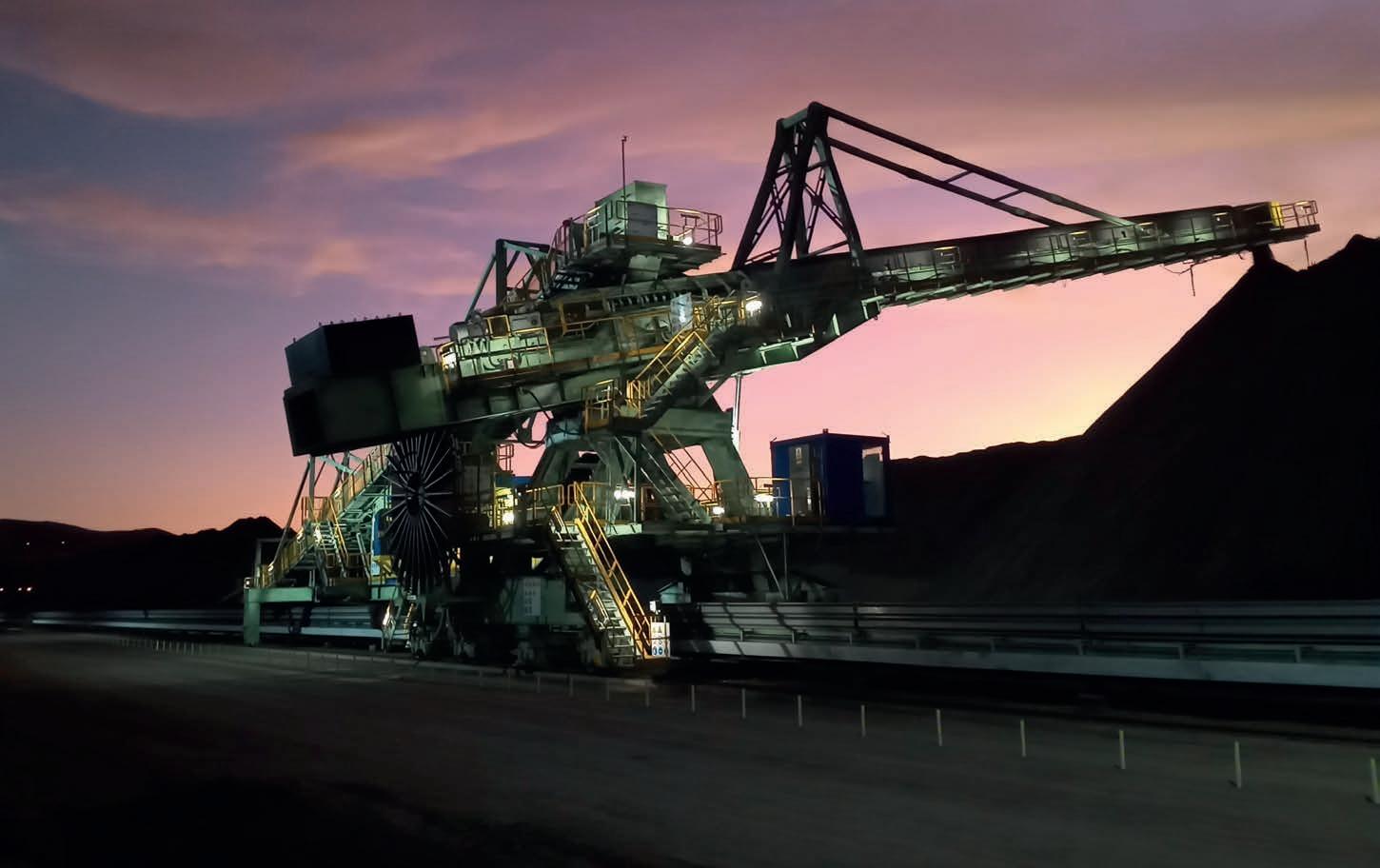
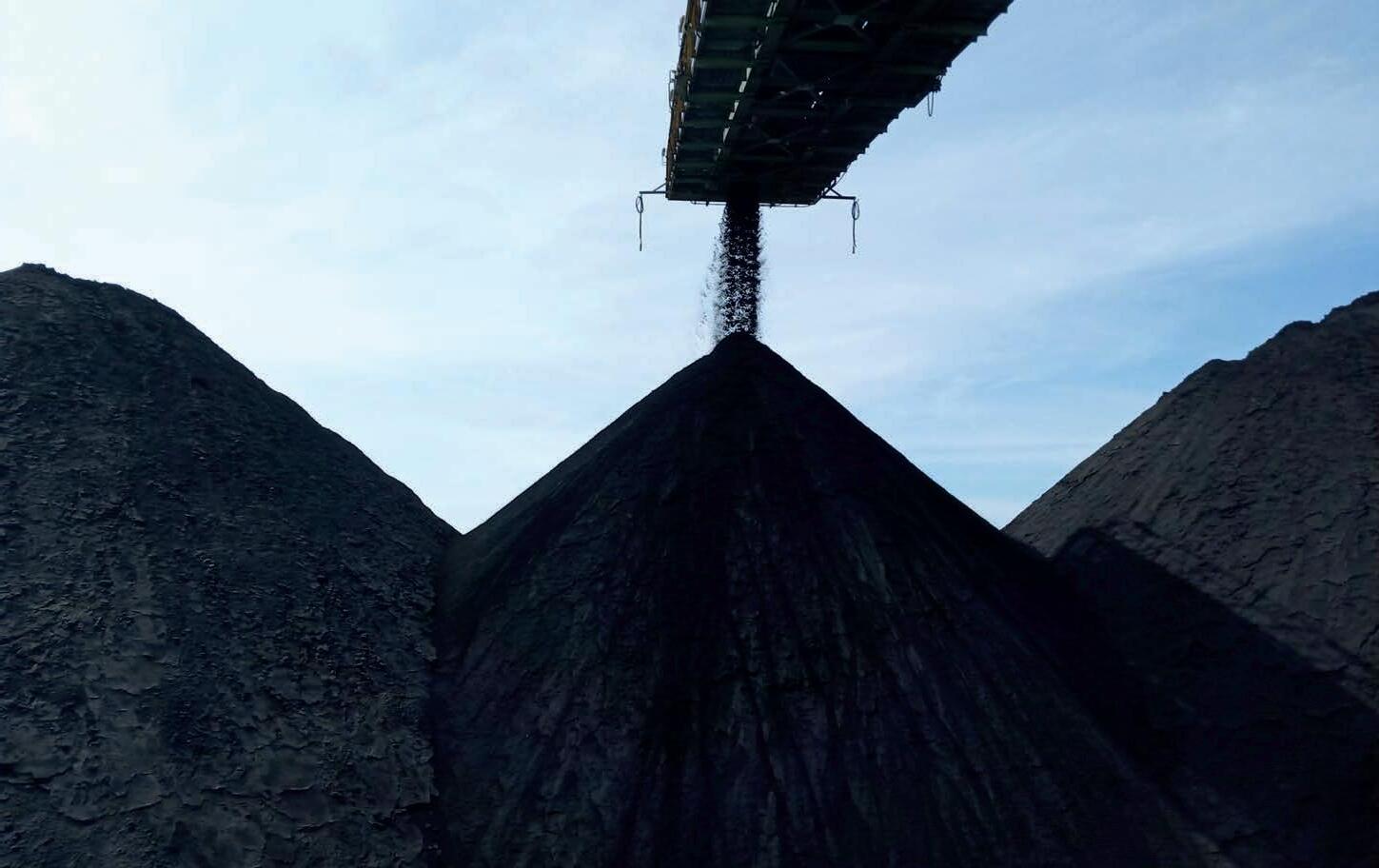
MODULAVEYORS RAMPING UP THE AUSTRALIAN MINING INDUSTRY
On the western edge of the Sahara, where the desert sands meet the Atlantic Ocean, you’ll find one end of the world’s longest conveyor belts.
Clocking in at almost 100km and regularly transporting 2000 tonnes of phosphate rock per hour, you can even see it from space.
Suffice it to say that conveyors can be enormous, with the infrastructure and price tag to match. But bigger isn’t always better, and not everyone has the luxury of working in a space as vast as a desert.
Budget constraints, infrastructure limitations and the challenges of working in small spaces can sometimes call for a more subtle tool.
That’s why Fenner Conveyors’ modulaveyor exists. The modular conveyor is a lightweight, easyto-assemble conveyor line. Think a high-quality Meccano set that can be customised to suit any game or player.
“It’s essentially a jigsaw puzzle that has a lot of extra add-ons that can be fitted reactively or proactively to suit the customer,” Belle Banne Conveyors regional manager Beau Weiss told Australian Mining.
The Belle Banne Conveyors brand is 100-per-cent-owned by the Fenner Conveyors company.
“Fenner’s modulaveyor is designed to accommodate situations where a traditional conveyor system might not be the most applicable answer due to
certain time restraints, cost, workspace or infrastructure,” Weiss said.
Fenner first bought the design around six years ago, and the machine has been making waves in the agriculture and food processing sectors. Fenner is now expanding its range and abilities due to increasing demand in the mining sector.
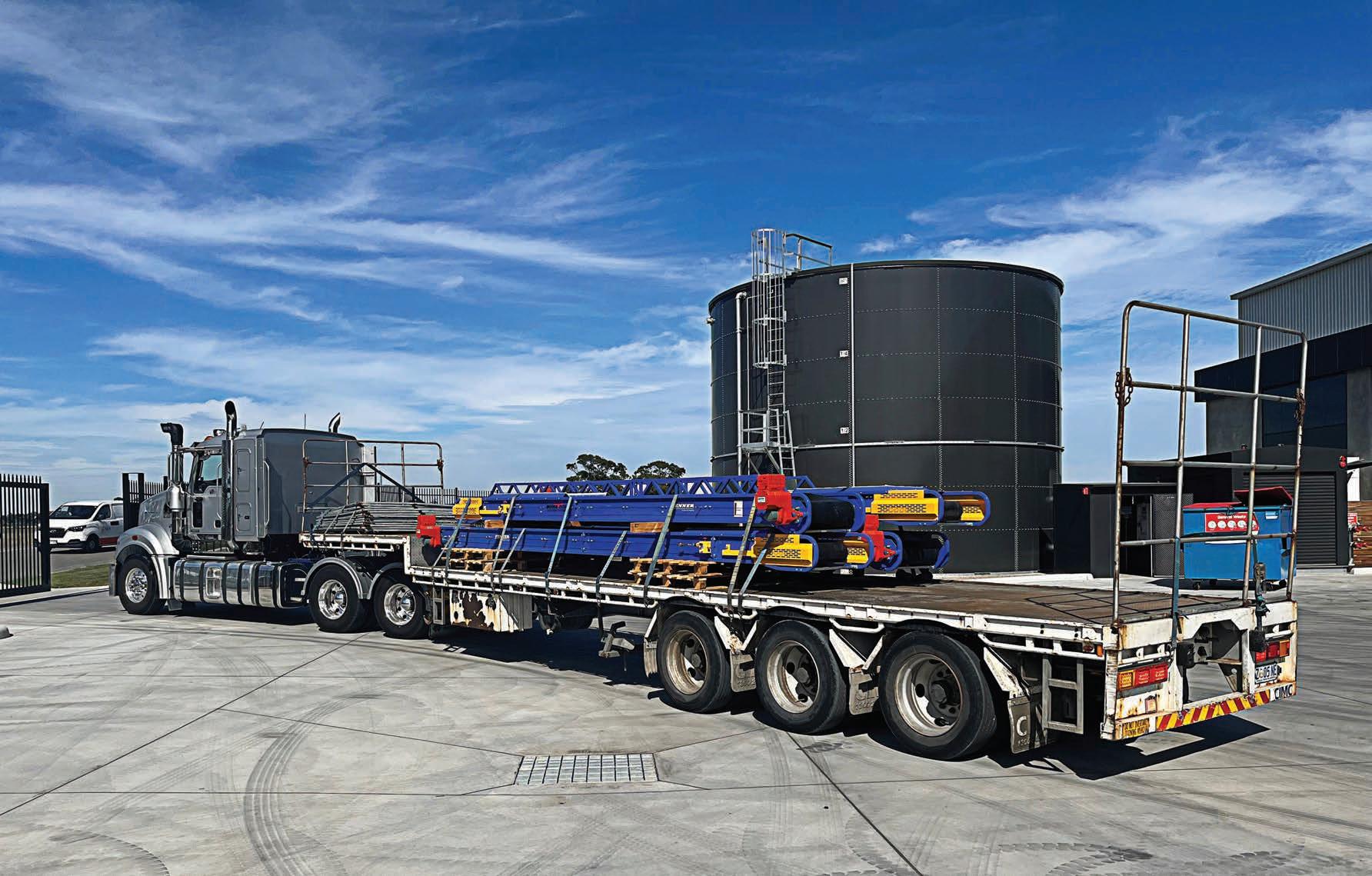
Weiss recounted some of the modulaveyor’s greatest hits, such as the time a primary conveyor broke down at a mine in Tasmania.
“The mine operators needed to get material out of their pit in a really confined space on short notice,” he said. “There was really no way to move it out because nothing could get in. So on five days’ notice, we manufactured a 65m modulaveyor that sat directly next to the existing conveyor system, and we managed to sort out their problem.” On another project, a customer at a major port used the modulaveyor to increase its grain capacity.
FENNER CONVEYORS’ EASY-TO-ASSEMBLE MODULAR CONVEYORS HAVE BEEN A HIT IN THE FOOD PROCESSING AND AGRICULTURE INDUSTRIES FOR YEARS – AND NOW DEMAND IS GROWING IN THE MINING SECTOR.
FENNER’S MODULAVEYOR IS DESIGNED TO ACCOMMODATE SITUATIONS WHERE A TRADITIONAL CONVEYOR SYSTEM MIGHT NOT BE THE MOST APPLICABLE ANSWER.”A FENNER MODULAVEYOR EN ROUTE TO A CUSTOMER FROM THE DANDENONG MANUFACTURING FACILITY.
“A traditional conveyor system was going to take several months’ worth of engineering, and longer again for design and manufacture,” Weiss said.
“We supplied them a couple of modulaveyors and increased their throughput by 10 per cent at essentially 80 less cost – and we did it in six weeks.”
The modulaveyors are on the smaller end of the scale, primarily for bulk materials or package handling applications such as ore extraction, sand, coal, gravel, woodchip, recycling or even just boxes, with a capacity of 200 tonnes per hour.
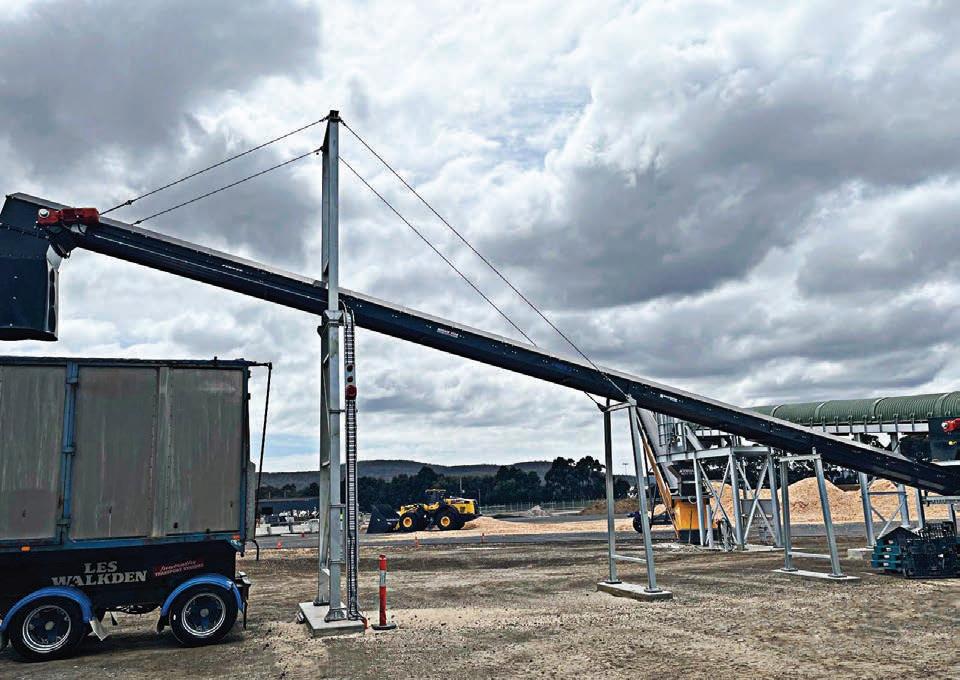
This is exactly what makes the product so handy in a pinch.
“It’s cheaper, it’s faster and it can be constantly changed,” Weiss said. “You can’t change the length of a traditional conveyor system, but the modulaveyor is fully customisable.”
The adjustable design means it can be assembled by just about anyone, if Fenner’s expert technicians don’t beat you to it.
“At the present time and historically, we’ve made and are making conveyors on short notice and planning projects for customers,” Weiss said. “We’ve got customers that have revenue of $200,000 a year and customers that have revenue of $2 billion a year. The modulaveyor can suit most applications.”
Key to the fast turnaround is the fact that all fabrication and design of the modulaveyor is handled in Victoria, with manufacturing done exclusively in Dandenong.
The conveyors are fully built and tested at the factory, then dissembled based on a customers’ site-handling requirements.
In other words, the modulaveyor will not be arriving on-site in 100 separate pieces.
Fenner has a 100 per cent domestic capability when it comes to conveyors, sourcing all of its mechanical and electrical components from other Fenner names and primary partners like SEW Eurodrive, Flexco, and many more.
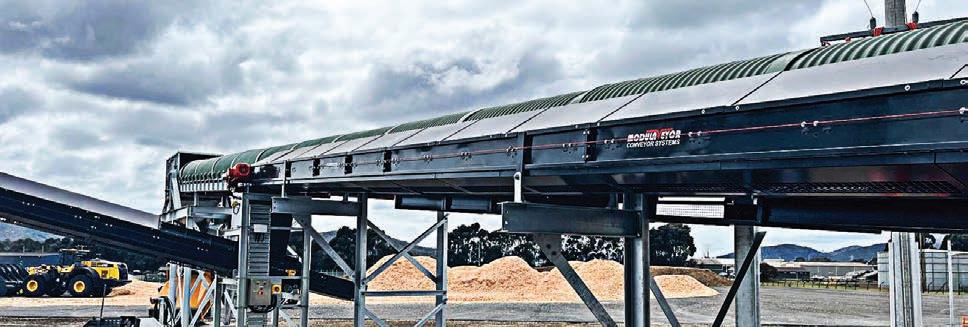
And there are benefits of working within a business as enormous as the Fenner Conveyors Group.
“Because we’re such a large, integrated specialty group, there’s essentially a resource for every and any problem,” Weiss said.
“That’s one of the benefits of having a national footprint. We have so many fantastic professionals it allows us to offer an array of expertise to our customers on short notice.”
The modulaveyor captures such a niche in the market that customers keep coming back for more.
“Around 70 per cent of our modulaveyor orders are actually repeat customers,” Weiss said.
“Normally, if we sell one to a medium or larger company, they’ll tend to come back for another modulaveyor, be it for another project or site.
“We’ve actually got 11 of these things running at a particular mineral sands project in Australia.”
With its customisable design, fast arrival, ease of assembly, and backing of vast support network, the modulaveyor is providing essential machinery to the mining industry without the usual headache.
“The modulaveyor’s got a range of applications, big and small,” Weiss said. “Major industry players, right down to small artisanal miners, they’ll all get something out of it.” AM
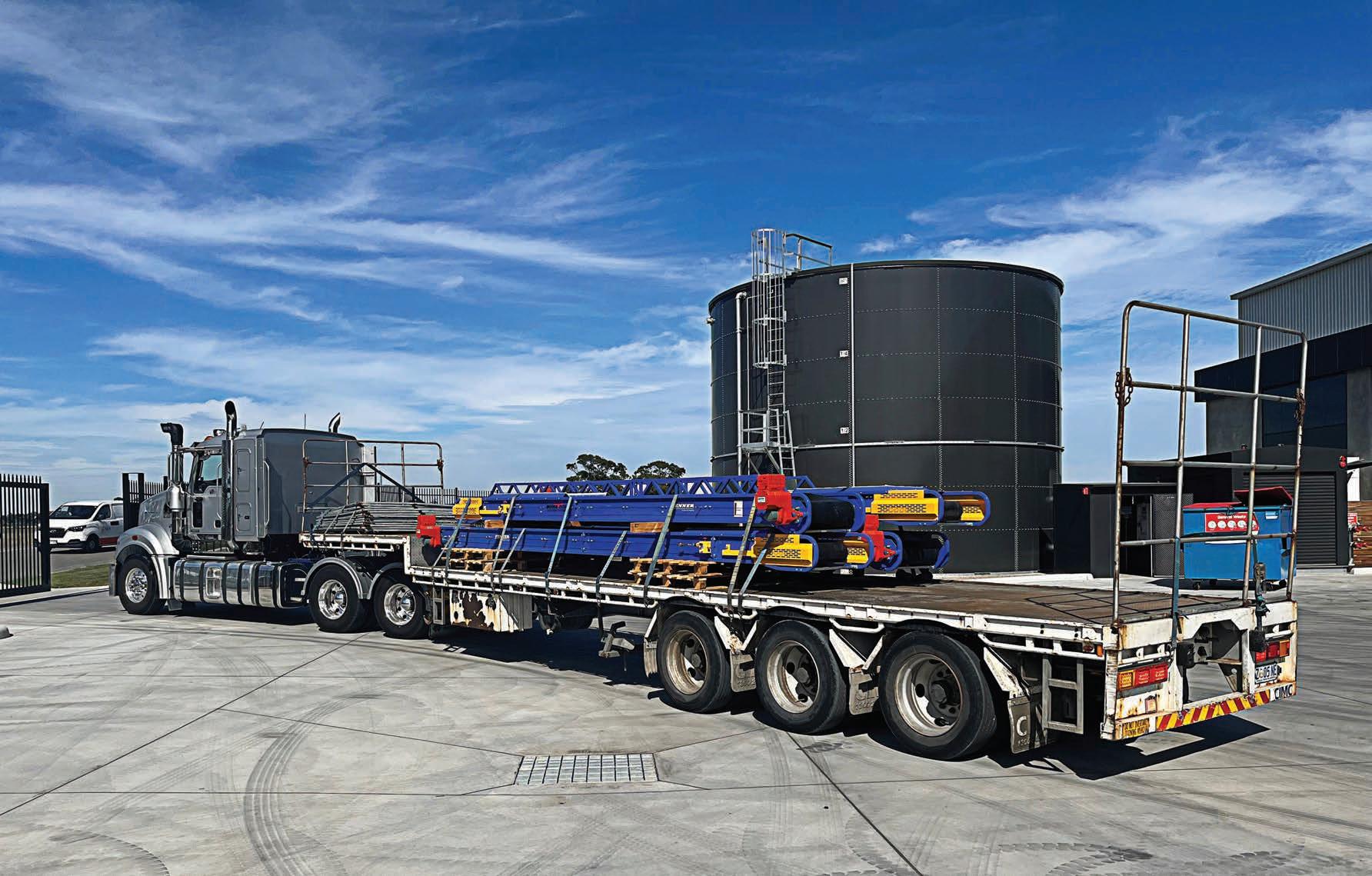
THE MODULAVEYORS ARE ON THE SMALLER END OF THE SCALE, PRIMARILY FOR BULK MATERIALS OR PACKAGE HANDLING APPLICATIONS SUCH AS ORE EXTRACTION, SAND, COAL, GRAVEL, WOODCHIP, RECYCLING OR EVEN JUST BOXES, WITH A CAPACITY OF 200 TONNES PER HOUR.”THE MODULAVEYOR IS LIGHTWEIGHT AND EASY TO ASSEMBLE. ONE OF FENNER’S MODULAVEYORS AT WORK IN TASMANIA.
PULLING AHEAD
In today’s truly global market, it’s never been easier to be choosy about the products we purchase. And in that market there’s undeniably a certain appeal to inexpensive, cookie-cutter products churned out of massproducing economies.
But what good is, say, a cheap pair of pants if they don’t fit, or if they bust a stitch when you bend over?
Expedience has a way of stacking up –but it’s quality that really lasts.
This is all the more the case for the machine components at work in the mining industry, where much more is at
stake than just embarrassment caused by a pair a dodgy pants.
Poor or ill-fitting components require constant maintenance, which in turn disrupts operations and can lead to costly downtime.
When these troublesome parts inevitably give up the ghost, they’ll need
replacing. That squeezes yet more time and money from a company, which would have been better off buying something decent in the first place.
The mining sector needs quality, tailored products to keep the gigantic wheels of industry turning.
And that’s exactly what Flexco has been providing to its customers for almost four decades with its line of pulley lagging.
Lagging is the layer of material bonded to the shell of a conveyor pulley which serves to protect the conveyor system and increase friction to drive the belt. Lagging comes in various embodiments, each with different capabilities and strengths – but not all of them are created equal.
Flexco has been manufacturing lagging in Sydney for the entire Flexco group across the globe since 1985, making it the oldest such manufacturer in Australia. The company has learned a few things in that time, not least the value of providing a high-quality, tailored product to customers in the mining industry.
“What differentiates us from our competition is that we’re flexible,” Flexco lagging specialist Phil Dreghorn told Australian Mining.
“We can manufacture lagging in different thicknesses from 10 to 30mm. We offer ceramic dimple and smooth, and rubber lagging, and we can put more or less ceramic tiles in the lagging to change the friction factors.
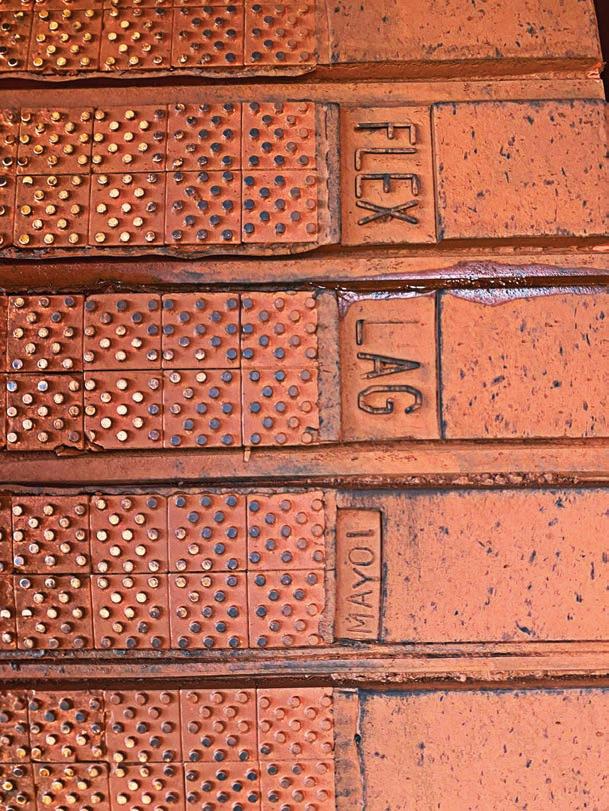
“Whether it’s continuous lengths of lagging strips to minimise wastage or making specific lengths and thicknesses of lagging, we’re able to adapt to a customer’s requirements and do it quickly.”
Flexco offers four different lagging application methods: cold bonding, CN
lining, hot vulcanising, and weld-on. The bonding depends on budget and the toughness of the conveyor’s job.
“In terms of the lagging itself, the ratio of ceramic to rubber depends on what coefficient of friction is required to drive the conveyor belt,” Dreghorn said.
“The ceramic laggings have the longest life. We’ve got one that’s been running at BHP’s Nelson Point operations since 2001 – that’s over 22 years of operation. As for the cheaper rubber option, you’ll typically get around 10 years of use from them.”
The company produces 76km of rubber and ceramic lagging every year, the approximate distance between Brisbane and the Gold Coast. Flexco can have custom pulley lagging shipped within 2–3 weeks.
Key to Flexco’s quick turnaround on customised lagging is that its manufactured here in Australia.
“Manufacturing locally gives us that agility to react to customer needs quickly,” Flexco Sydney plant

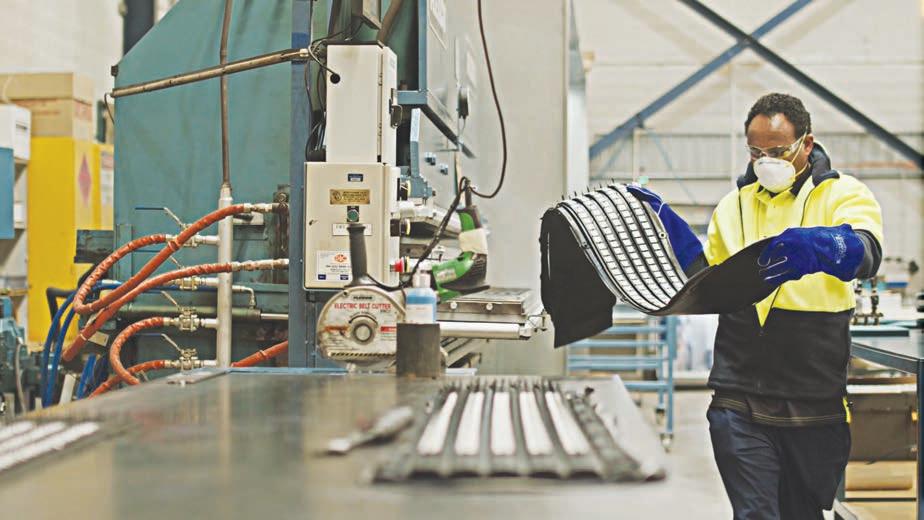
FLEXCO’S AUSTRALIAN-MADE PULLEY LAGGING ALLOWS THE COMPANY AGILITY IN RESPONDING TO THE NEEDS OF ITS CUSTOMERS IN THE MINING INDUSTRY.
MANUFACTURING LOCALLY GIVES US THAT AGILITY TO REACT TO CUSTOMER NEEDS QUICKLY. WE CAN MANUFACTURE SPECIFICALLY FOR THE CUSTOMER’S PULLEY SIZES AND CUSTOM-MAKE THE LAGGING.”FLEXCO LAGGING IS TESTED FOR TENSILE STRENGTH, ELONGATION, ABRASION RESISTANCE AND BONDING STRENGTH. A CLOSE-UP OF FLEXCO CERAMIC LAGGING INSTALLED IN 2001.
manager Phil Brodbeck said. “We can manufacture specifically for the customer’s pulley sizes and custom-make the lagging.
“We source the rubber locally and extrude it on-site. We’ve got five moulding presses here which gives up significant production capacity.”
Nationally, Flexco processes 210 tonnes of rubber every year, roughly the weight of five Boeing 737s.
Australian-made means Australianoperated, and Brodbeck said one of the best parts of keeping manufacturing onshore is creating local jobs. The lagging department in Sydney alone employs 13 people, including a full-time quality assurance employee.
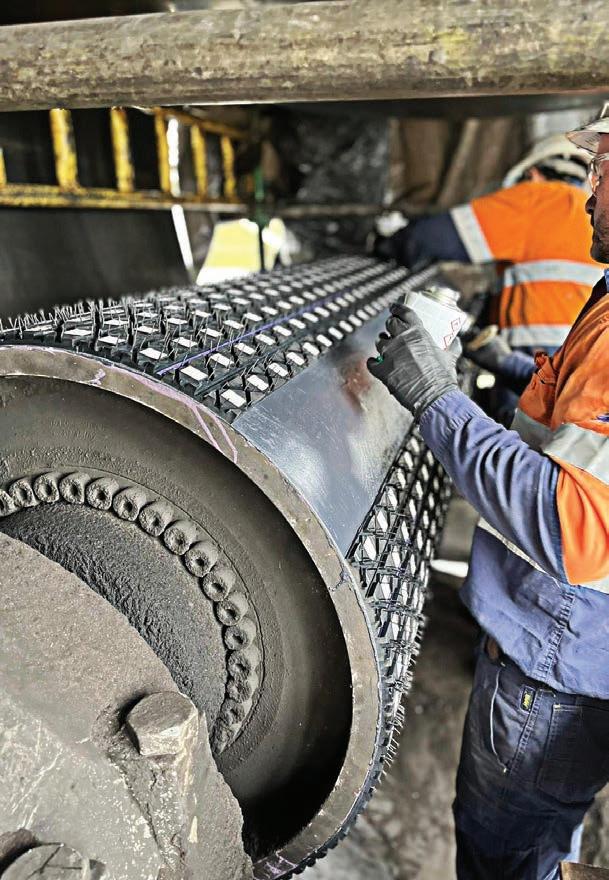
Flexco lagging is regularly tested for tensile strength, elongation, abrasion resistance and bonding strength to ensure product consistency. The company also tests the chemical composition of its ceramic tiles to ensure maximum bonding strength and wear resistance.
Another benefit of staying local is operational oversight, allowing for greater transparency.
“We can supply all the traceability data, information like where the raw materials come from, when they were made, the use-by date, when we made the lagging, who made the lagging, who tested the lagging, who did the quality assurance checks on the lagging, and so on,” Dreghorn said.
“Traceability is a big one for endusers. They want to know where their products are coming from, they want quality assurance, and they often won’t buy without it.
“We supply all of that with our lagging.”
And with locations on both sides of the country, plus salespeople in most states, there’s back-up if anything goes wrong – which it rarely will, because Flexco pours time and resources into the research and development of its lagging products.
In addition, Flexco provides training to its customers when it comes to proper pulley lagging application. After all, you don’t stay in the game for almost four decades by being complacent.
The company has an in-house lagging design expert to test the friction coefficient of its different lagging applications. In other words, Flexco can calculate the best thickness, tile coverage, composition, bonding application for the job.

It’s this kind of effort that makes Flexco’s lagging advice amount to more than just “trust me” – there’s proven science behind it.
Almost four decades in the Australian lagging manufacturing space has given Flexco an arsenal of tools. It knows what its customers need, and through its highquality, custom products with a quick turn-around in supply, the company has the agility to deliver. AM
TRUST ITM™: TRACK YOUR FUTURE
WITH ITS TRUST ITM SOLUTION, ITM MINING IS PROVIDING AN INTELLIGENT CONTRIBUTION TO PREDICTIVE MAINTENANCE AND OPERATIONAL EFFICIENCY.
Nobody likes faulty equipment.
Generally speaking, the more complex the tool, the more costly the fix when it breaks down. And when it comes to mining, it doesn’t come more complex – or expensive to repair – than machine undercarriages.
Since its foundation in Valsamoggia, Italy, in 1957, ITM Group has designed, manufactured and distributed an inclusive range of undercarriage parts and customisable solutions for several industry segments, and the company continues to be ahead of the curve.
Its latest technology is called TRUST ITM, which was recently launched in the Australian market by ITM Mining, one of Australia’s leading suppliers of undercarriage components for heavy mobile equipment and fixed plant.
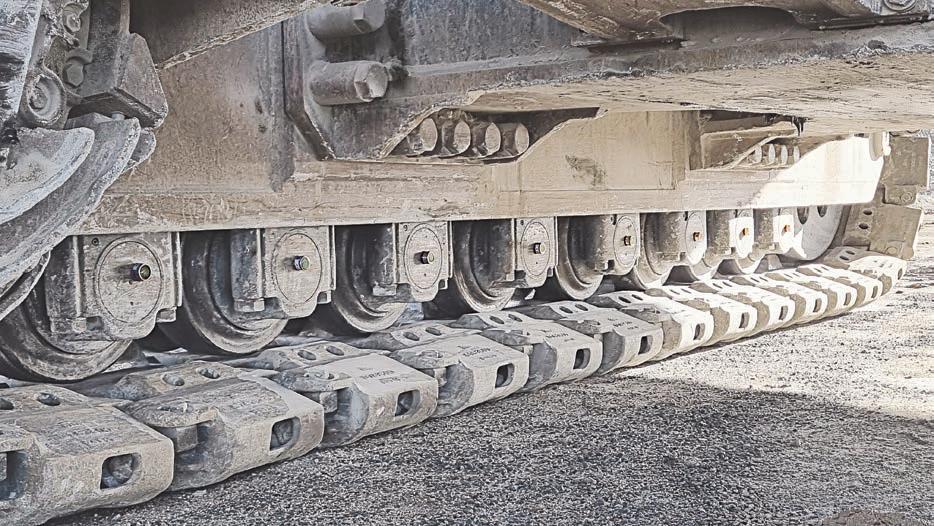
TRUST – Track Advice Undercarriage
Smart Technology – provides live data about the current state of the undercarriage, such as its temperature and predictive maintenance. The data is transmitted from a series of sensors inbuilt or magnetised to the undercarriage.
In an ordinary scenario, a mining operator would have to stop roughly every 20 minutes and wait for the undercarriage to be manually tested with a temperature gun. With TRUST ITM, an operator can monitor the state of their undercarriage while on the move.
“Thanks to real-time temperature
“We can learn how long it takes for a roller to heat up while the machine is tramming and how long it takes to cool down.
“This kind of data helps you operate your machine to its maximum performance.”
Not only does TRUST ITM make
Temperature is an indicator of a faulty part. By monitoring the state of the undercarriage in real-time, operators and mine managers can enact predictive maintenance before a breakdown occurs.
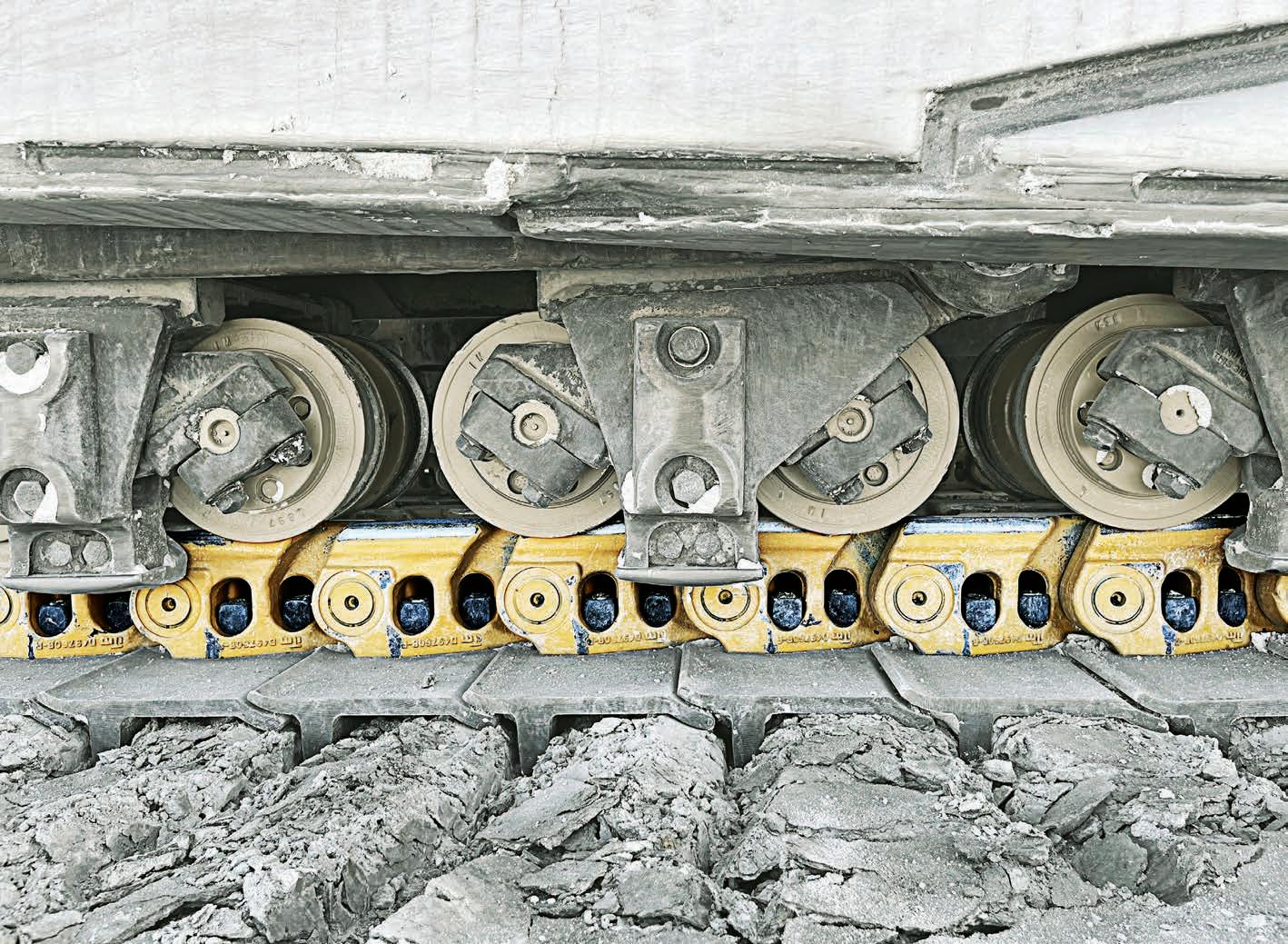
As ITM puts it, “you cannot improve what you cannot measure”.
“Safety-wise, you’re also keeping your
“There’s roughly a 100m exclusion zone when these machines are moving, so it’s hard to get a visual or take a measurement when these things are operating.
“So the safety aspect of TRUST ITM is quite enormous.”
ITM Group has provided undercarriage components for over 65 years, and now the with TRUST ITM, the company is positioning itself within a new digital era, where efficiency,
“Real-time data is the key,” ITM said. “We provide a constant monitoring of components while the machine is operating, and send an automatic warning when the temperature reaches a critical level.”
TRUST ITM data is safely stored on a cloud-based system and can be read on an operator’s dashboard, a mobile app, and a mine manager’s remote PC.

This means a mine manager is able to
According to the company, TRUST ITM can help miners cut costs and get more accurate and specific readings.
“Undercarriage maintenance is upwards of 50 per cent of your maintenance costs,” ITM said.
“A mining company could be spending millions on an undercarriage and still manually measuring things with a ruler and a temperature gun – and that’s as sophisticated as it gets.
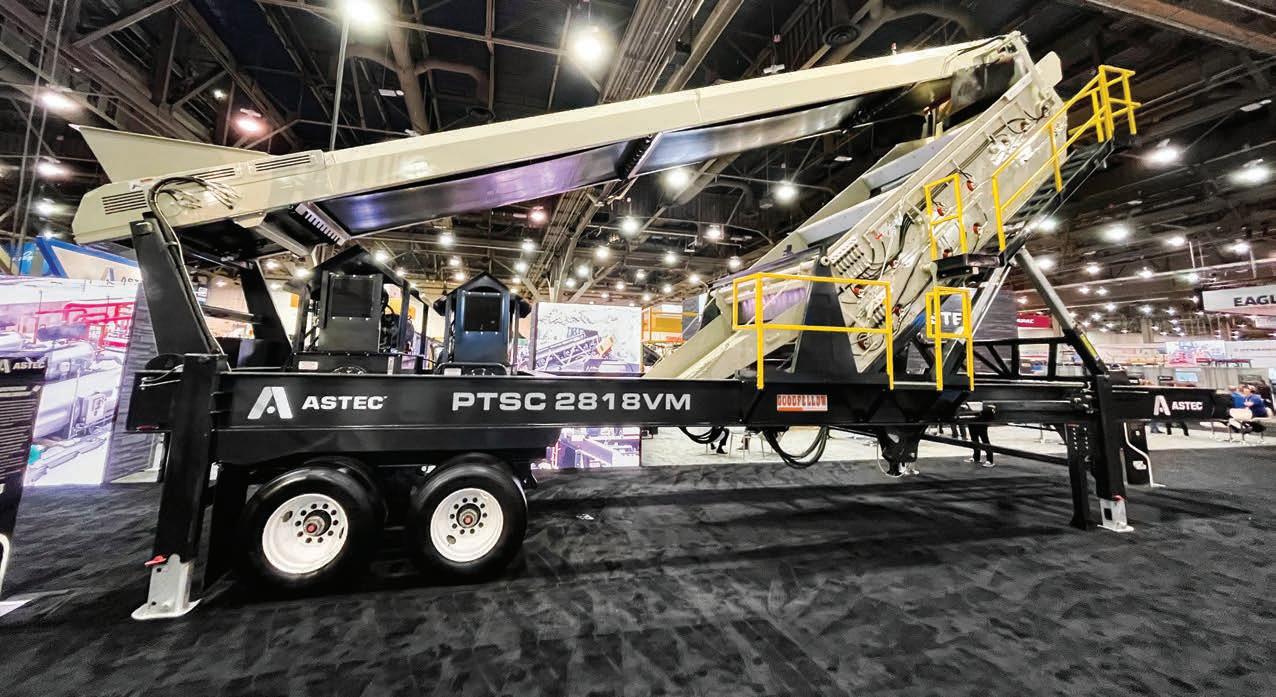
“With our product, you can see in
TRUST ITM has been tried and tested in the field.
“The technology is already at work in different mining sites around the globe,” the company said. “In WA, we have some shovels and dozers operating with TRUST ITM.”
“We got regular email alerts showing that in the case of one particular dozer at the WA site, two of its rollers had increased in temperature quite considerably.
“We were then able to tell the mine operator exactly where those two rollers were, as well as the nature of the problem, which was a failed pin that caused the rollers to overheat.”
The TRUST ITM undercarriage technology is available in two forms: built-in sensors and wearable sensors.
“The wearable kit can be plugged on to any metallic surface – such as a gearbox – to monitor temperate and other parameters,” ITM said.
This makes the wearable sensor handy to a number of industries beyond the mining sector.
TRUST ITM improves operational efficiency, cuts maintenance costs, allows for predictive maintenance, and helps to keep employees safe.
“Efficiency, predictive maintenance, and supply chain management is becoming pivotal for our clients,” ITM
• Conventional screen blinding and bottom overload.
SCREENING THE GREEN TRANSFORMATION
As we near a net-zero reality, there is an increasing need for more materials to develop the necessary green technologies.
Renewable energy sources such as wind and solar require up to five times more copper than comparable non-renewable technologies, while the World Economic Forum believes demand for lithium carbonate equivalent (LCE) could surpass three million tonnes by 2030. The world produced 540,000 tonnes of LCE in 2021.
LCE, derived from lithium raw material, spodumene concentrate, is a critical material in renewable batteries used in electric vehicles (EVs).
While primary production will remain key, as mineral demand increases into the future amid growing decarbonisation, mining companies will need to be more creative in how they commercialise their material.
A nickel mine in New Caledonia, some 1200km east of Queensland’s Sunshine Coast, is doing just that.
SLN (Société Le Nickel), which operates a nickel smelter and several mines on the island, has established a unique method for recycling nickel slag –a major by-product of the nickel refining process – with the assistance of mining contractor Salmon NC and leading mining equipment supplier Astec.
The recycled nickel slag is sold into a variety of markets, including the abrasives industry in the US, where it is used as a sandblasting medium.
While heavy equipment hire has always been Salmon NC’s bread and butter, chief executive officer Chris Salmon turned to Astec when it came to finding the specialty equipment needed to re-process nickel slag.
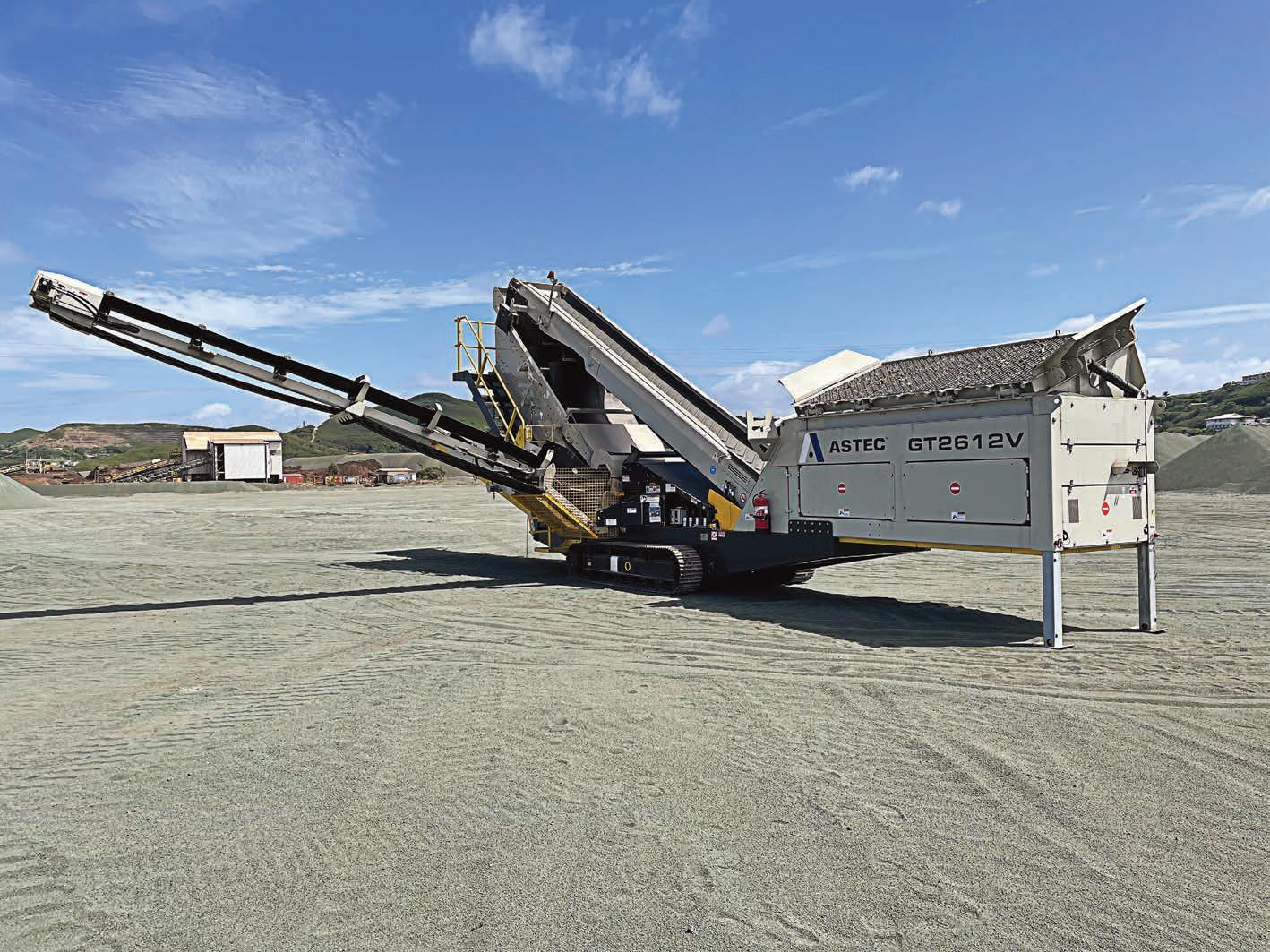
“I’d known Astec from a past life when I was involved in basalt quarrying, and they’ve always come really well referenced,” Salmon told Australian Mining. “I’d reached out to some industry contacts explaining what I was trying to achieve and Astec’s highfrequency screens were mentioned a couple of times by people I trusted.”
Salmon got in touch with Shaun Quinn, Astec’s senior account manager,
materials solutions – northern region, and before too long an Astec GT2612V high-frequency screen had made its way to New Caledonia.
“Shaun was very helpful in identifying the type of unit we wanted,” Salmon said. “We were looking at fixed and tracked solutions, but we chose the tracked machine because we needed mobility around how we were building our stockpiles.
“We’ve been impressed by Astec’s after-sales support, too. We need that support given we’re quite isolated in New Caledonia.”
The Astec GT2612V high-frequency screen has 10 vibrators that directlyinduce vibration into the bed of material at between 3600–4200 revolutions per minute (RPM), to ensure increased probability of stratification and material separation.
A unique media rotary tensioning system used on the high-frequency screens means operators of the GT2612V can quickly and efficiently change screen media when switching between applications, supporting a more efficient and productive operation.
And while the GT2612V is powerful, it’s also versatile.
“The screen itself is made up of four six-by-six-foot panels, with the first panels on each deck having three independently adjustable vibrators,” Quinn told Australian Mining. “The screen operates between 28–43° of inclination, with the vibrators running at up to 4200RPM with as much as 2mm of stroke, so you can ensure they are optimised for each application.
“On average, these machines can induce around 10g of force into the material if you’re running them flat out, but you can also de-tune individual sections accordingly to stop ‘popcorning’, or the bouncing of the raw material, from occurring.”
The GT2612V was delivered and commissioned to New Caledonia in November 2022 and has been processing large volumes of material ever since.
The process involves feeding stockpiled nickel slag through a static grid to remove larger agglomerates before it reaches the high-frequency
screen, which then refines the product into a usable material.
“Minus-50mm material is sent to the high-frequency screen, which separates anything bigger than 4mm,” Quinn said. “Anything smaller is finished product in this application.”
The GT2612V’s adjustability came in handy when the Salmon NC team discovered the nickel slag material was more abrasive than anticipated.
“This briefly caused some operational issues for us,” Salmon said.
“But the Astec support team was fantastic. They helped us make tweaks and adjustments to settings and flow rates, and alter the way we were processing the material to best deal with its abrasive nature.
“Now we’re getting the best out of the machine itself, and the best operational efficiency.”
Since the six-foot-wide GT2612V arrived in New Caledonia in November 2022, Astec has developed a larger eightfoot-wide, 18-foot-long high-frequency screen. Quinn said the new model, launched at CONEXPO in Las Vegas in mid-March, enables greater capacity.
But when finding the right screen for a customer and for a particular application, bigger is not necessarily better.
“It comes down to what customers are looking for,” Quinn said. “If they don’t have room to set up a fixed plant, and if they want something that’s mobile and able to be utilised in a tighter, confined space – as with Salmon NC and the nickel slag application – the tracked
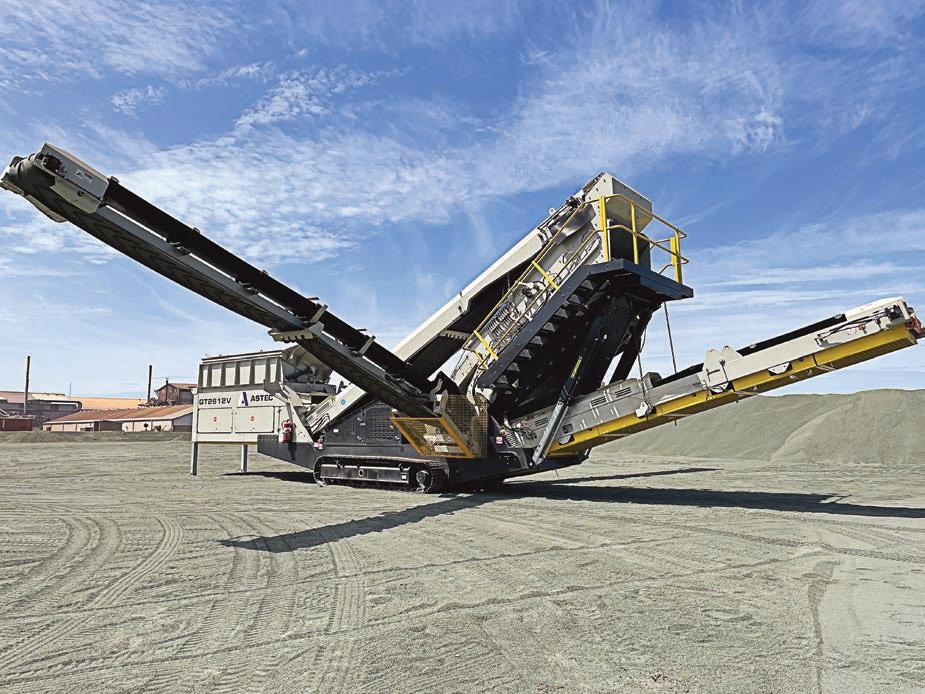
works and, with its multiple tuning options, we will ensure screens are optimised to suit any application and material.”
Quinn said that just a few weeks on from CONEXPO, Astec had already sold two of the eight-foot-wide screens
throughout the whole screen but also utilise our high-frequency technology on the bottom deck.
“The high-frequency action provides additional vibration directly into the media on the bottom deck which helps
in repurposing mine waste for a major nickel miner in New Caledonia, and many other Australian mining companies and contractors can attest to the supplier’s capability.
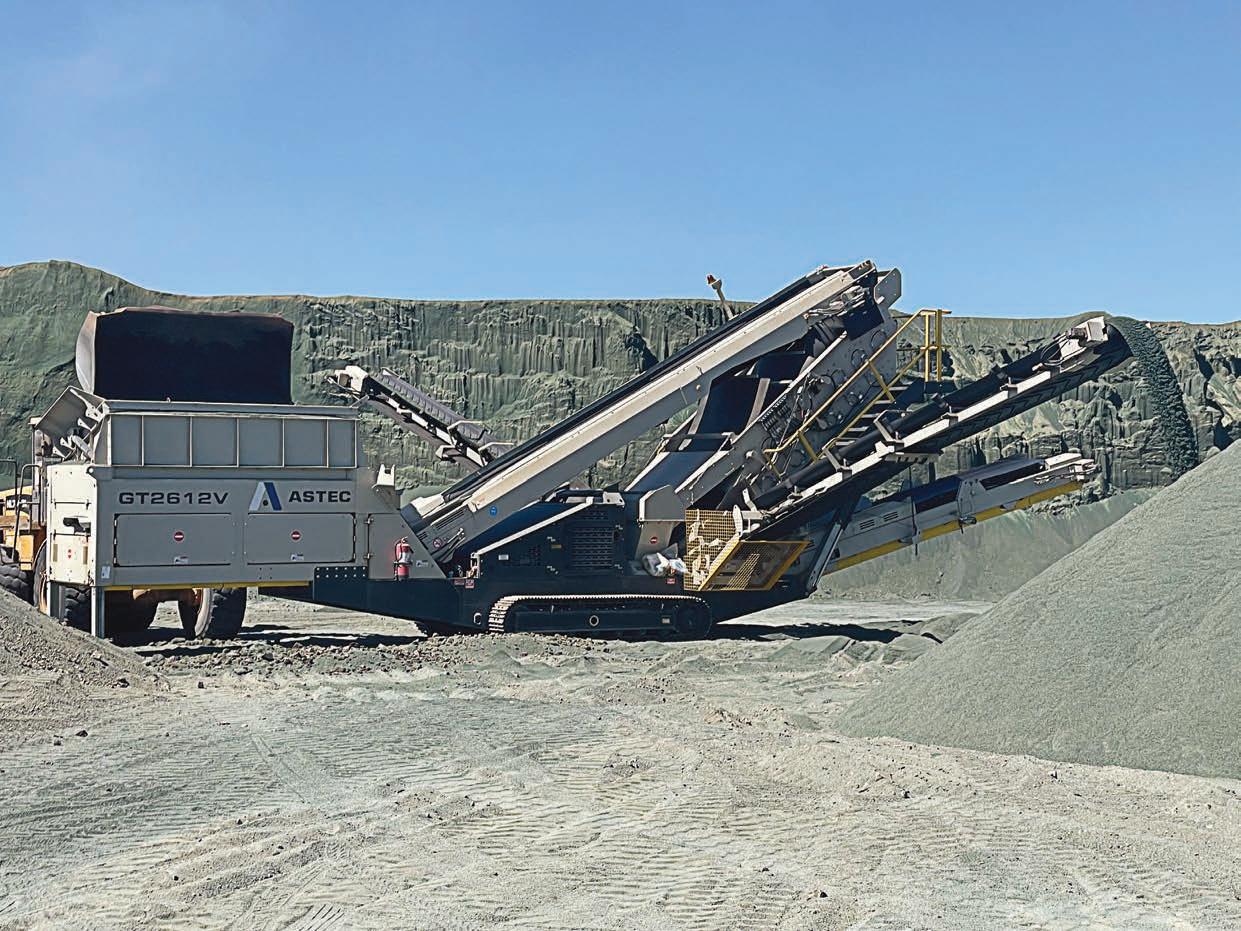
And as demand for minerals increases
transformation, Astec’s ongoing role as a
AI DRIVES THE FUTURE OF EXPLORATION
SRK CONSULTING IS TACKLING THE AGE-OLD PRACTICE OF MINERAL EXPLORATION THROUGH A NEW LENS, WHERE MACHINE LEARNING UNDERPINS NEW WAYS OF PROSPECTIVITY MODELLING.
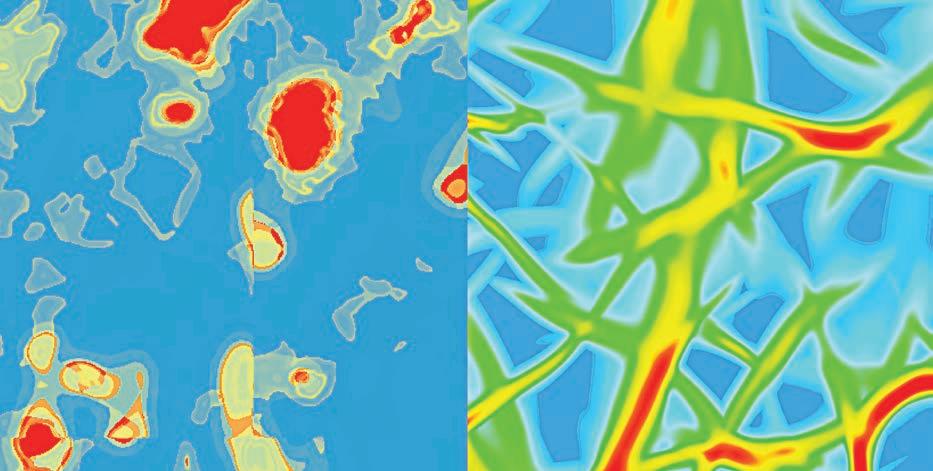
As artificial intelligence (AI) changes the way the world operates, machine learning is becoming an increasingly prominent methodology and practice in mining and industrial sectors.
Machine learning is being embraced by major mining companies as they look to gain an operational edge, but it is also supporting greenfields and brownfields projects as a way of improving prospectivity modelling in mineral exploration.
As a data-diverse industry, mineral exploration offers significant opportunities for machine learning to not only accelerate data analysis of assay results but also remove human bias from the practice.

Data is ingested into a computing platform and machine learning applies algorithms to establish, or ‘learn’, patterns in the data, enabling it to make predictions to support future drill programs and exploration. It does this in a fraction of the time it would take a geologist to investigate the data and make their own estimations.
Leading international mining consultancy firm SRK has been an early adopter of machine learning when it is applied to mineral exploration, having established a keen interest in the emerging technology through SRK senior structural geologist Antoine Caté.
Caté participated in a series of crowdsourcing exploration competitions, including the Integra Gold Rush Challenge in 2016 which invited geologists and data scientists to crunch decades’ worth of exploration data and produce targets at Integra’s Lamaque project in Val-d’Or, Québec. A $C1 million prize pool was on offer.
OZ Minerals launched its own Explorer Challenge in 2019 involving a $1 million prize pool for those who could develop novel exploration approaches at a site near the Prominent Hill coppergold mine in South Australia.
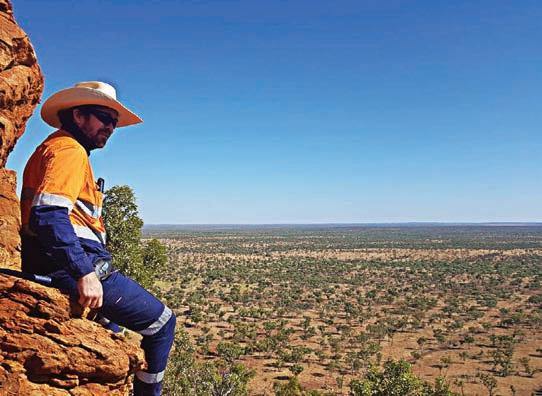
The common theme between these competitions was the provision of data. Each of the participating companies had immense catalogues of data at their disposal to allow for new exploration approaches and innovations.
Enter geologists and data scientists from across the world, and soon enough
the concept of machine learning in exploration was taking hold.
SRK principal geologist Mark Rieuwers said the company’s Canada and Australia offices came together when OZ Minerals’ Explorer Challenge took place, with Rieuwers and his team complementing Caté’s team’s machine learning expertise with local geological knowledge.
“OZ Minerals put up most of their data on public domain. People would go register and come up with new datadriven targets using various approaches,” Rieuwers told Australian Mining
“Antoine was crunching the machine learning side of things, and we found this particular exercise involved an
iron oxide copper-gold (IOCG) style of exploration, which myself and some others in the Australia offices had quite a bit of experience in, particularly with
“From that, we developed an integrated workflow (between Canada and Australia) which we’ve adopted for quite a few different projects since.
“We’ve combined the data-driven machine learning-based approaches with knowledge-driven geological reinterpretation to be incorporated into a
SRK’s approach is unique in that it attempts to create feedback loops by pairing the smarts of machine learning with the domain expertise of its geologists.
“Knowledge-driven prospectivity modelling is quite a different philosophy,” Rieuwers said.
“Here, you don’t need any known deposits or training sites for the machine learning algorithm to do its thing, you simply need some concepts and combine these with traditional algorithms and formulas.
“That’s one advantage (of knowledgedriven interpretations); you can be in a greenfields environment where there aren’t many known deposit types of the ones you’re looking for and still be able to make an assessment.
“Machine learning requires training sites, which are known deposits of a
particular type preferably in your area of exploration interest.
“If you’ve got a lot of training sites in a very data-rich environment, it’s well suited to machine learning. If you don’t, having that feedback between knowledge-driven methods and machine learning is quite powerful.”
Between 2020 and 2021, SRK partnered with BHP and DeepIQ to conduct a machine learning pilot study investigating new ways of delineating large porphyry copper deposits in the northern Chilean Andes. This initial study has since been followed by a new one in 2022, which applied lessons and workflow developments from the pilot study to a greenfields area in another part of the Andes.
Rieuwers said the companies were working on what was thought to be well-understood and relatively wellexplored terrain, but the pilot study unearthed some new exploration ideas in the region.
The mining industry is facing steep demand forecasts in the years to come, and in order to unlock more deposits, it is going to be increasingly important for future exploration programs to be more accurate and more precise.
Machine learning can help to speed up the process, pointing mining and exploration companies in the right direction when it comes to find that next discovery. AM
IntelliZone® is a user-friendly proximity detection system that creates shaped and dynamic shutdown/caution/operator zones to enhance miner safety while maintaining productivity.

• IECEx-certified for underground coal in Australia and Queensland since 2018 and EMESRT Level 7 & 9 compliant.
• Shaped-zone technology minimises nuisance alerts - works on standard or articulating equipment.
• Continuous miner operator can stand close to the machine and remain in a safe area.
• Purpose-built for underground mining and can be installed on all mobile equipment.
• 2021 U.S. National Institute for Occupational Health & Safety’s Mine Safety and Health Technology Innovation Award winner.
THE NEWEST CAB OFF THE RANK
Elphinstone unveiled its WR810 cab at the 2023 Underground Operators Conference in Brisbane, where the company showcased the latest in its underground application portfolio.
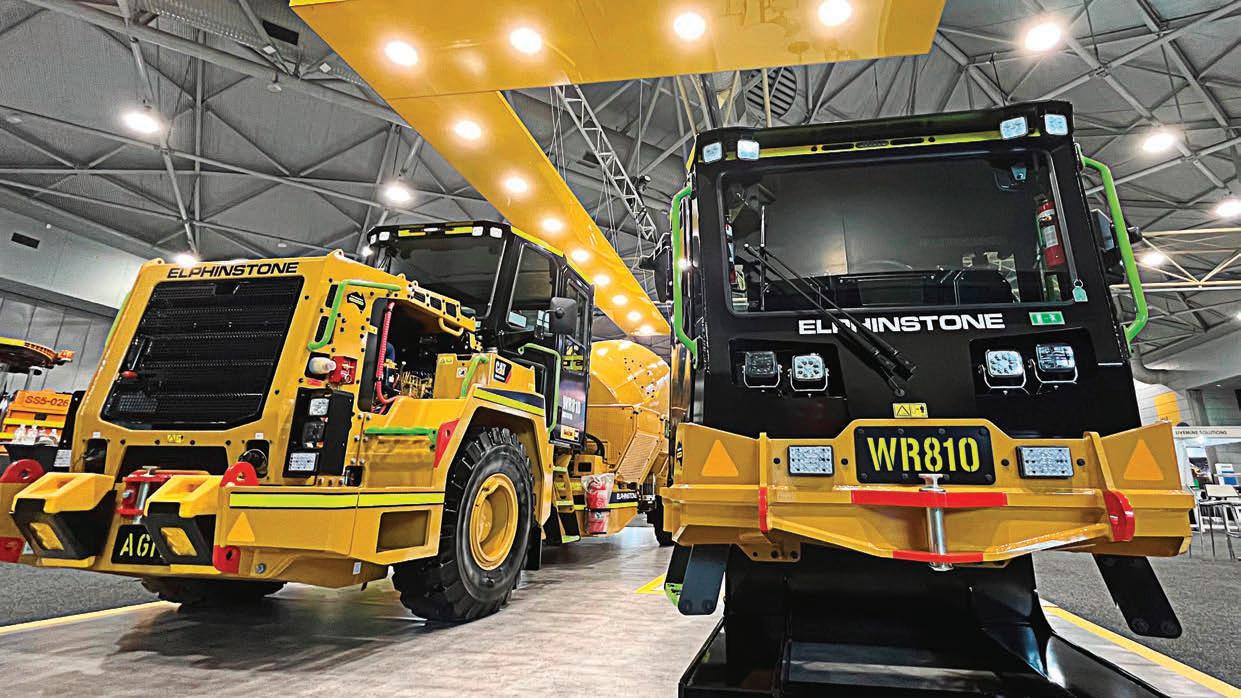
The front cab was quick to draw the attention of onlookers as they made their way into the exhibition – and it’s not hard to see why.
The WR810 series is a modular and highly configurable 10-tonne nominal base platform with a high level of interchangeability of parts and components between machines, from scissor lifts to water cannons and almost anything in between.
All WR810 models can be optioned with either a centre-mounted 3m cabin or a low-profile front-mounted 2.4m cabin.
Both operator stations feature a three-seat configuration which is suited to training or transporting work crews, eliminating the need for additional light vehicles.
A central driving position with occupant seats displaced behind the operator provides 180° visibility and equal judgement of distance to both sides of the machine.
The seats can be configured with airride or optional active-ride cushioning and feature ergonomic and position adjustable controls.
A 12-inch LCD touchscreen displays machine information, on-board fault register, machine health and diagnostic functions, while air temperature and quality are maintained with optional HEPA filter, climate-controlled air conditioning and cabin pressuriser.
Models in the WR810 series all share a common engine front frame featuring the Cat C7.1 with Caterpillar’s breakthrough ACERT technology to meet exhaust emission reduction standards.
The engine can be optioned as a Tier 3 with optional diesel particulate filter or Tier 4 final with standard clean emissions module.
“With such a high number of common configurable parts and components readily available, partstocking is reduced, simplifying machine maintenance and operation”, Elphinstone global sales and marketing manager Tim Mitchell said.
An oscillating hitch provides operator comfort, four-wheel ground contact and reduced wear on the hitch and steering components. The hitch incorporates a heavy duty 600mm frame section with +/- 42.5° steering articulation and +/- 10° oscillation.
Nitrogen-charged hydraulic suspension cylinders provide strong front axle ride quality over rough terrain. The combination of the front axle suspension,
oscillating hitch and suspended seats deliver a high level of machine comfort to the operator and passengers.
The front-mounted cab’s improved weight distribution and machine stability increase maneuverability in smaller, more confined mine site applications.
For strong braking performance on grade, the WR810 features an electromagnetic retarder and electronic speed control.
The innovative electronic design helps to significantly reduce the retarder’s energy consumption, preserving electric circuits. The retarder is controlled via an integrated multi-function joystick controller located on the operator’s rightside armrest.
The electronic speed control function permits the operator to set a speed and the machine will use the engine speed, transmission and retarder to maintain that speed.
“The operator can increase machine speed on level ground using the accelerator, but as soon as they remove their foot from the accelerator pedal the machine will return to the set speed,” Mitchell said.
All engine and machine isolation functions are located on a single panel accessible from ground level on the lefthand side.
The front cab design provides improved service and maintenance
accessibility, with all service points such as tanks, filters, lubrication points and compartment drains located at ground level.
The monitoring system and alarm strategy provides a three-tier warning and shutdown functionality, alerting the operator of any abnormalities and automatically limiting the machine’s functions.
To simplify machine servicing, onboard machine diagnostics provide the operator and maintenance staff with valuable information.
In January 2022, Elphinstone announced its intention to develop a suite of battery-electric vehicles for underground hard-rock mining to address the increasing decarbonisation efforts and expectations of its global customer base.
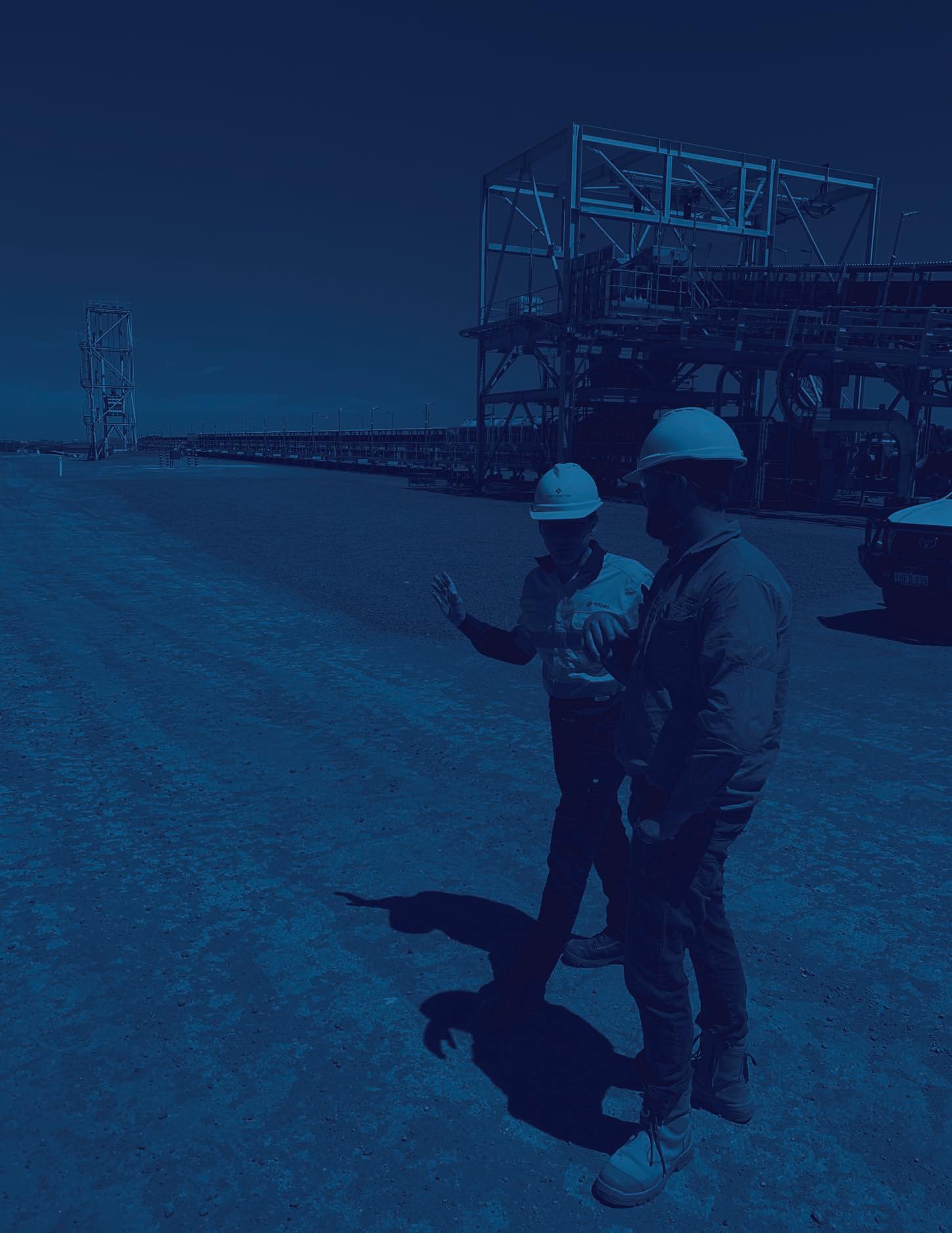
Once further development is completed, the battery-electric version of the powertrain will be available in a similar low-profile platform.
Elphinstone continues to build an experienced and capable development team with a vision to provide a batteryelectric vehicle solution at the forefront of technology.
With an increased domestic footprint, new models soon to be released, and a progressive battery-electric vehicle program, the future is looking bright for this industry leader. AM
A global leader in operational technology, control systems and engineering services across the mining value chain beyond the solution
No two projects or clients are the same.
At Mipac, our global team of technology specialists have real-world experience across the entire mining life cycle as well as every layer of the automation pyramid.
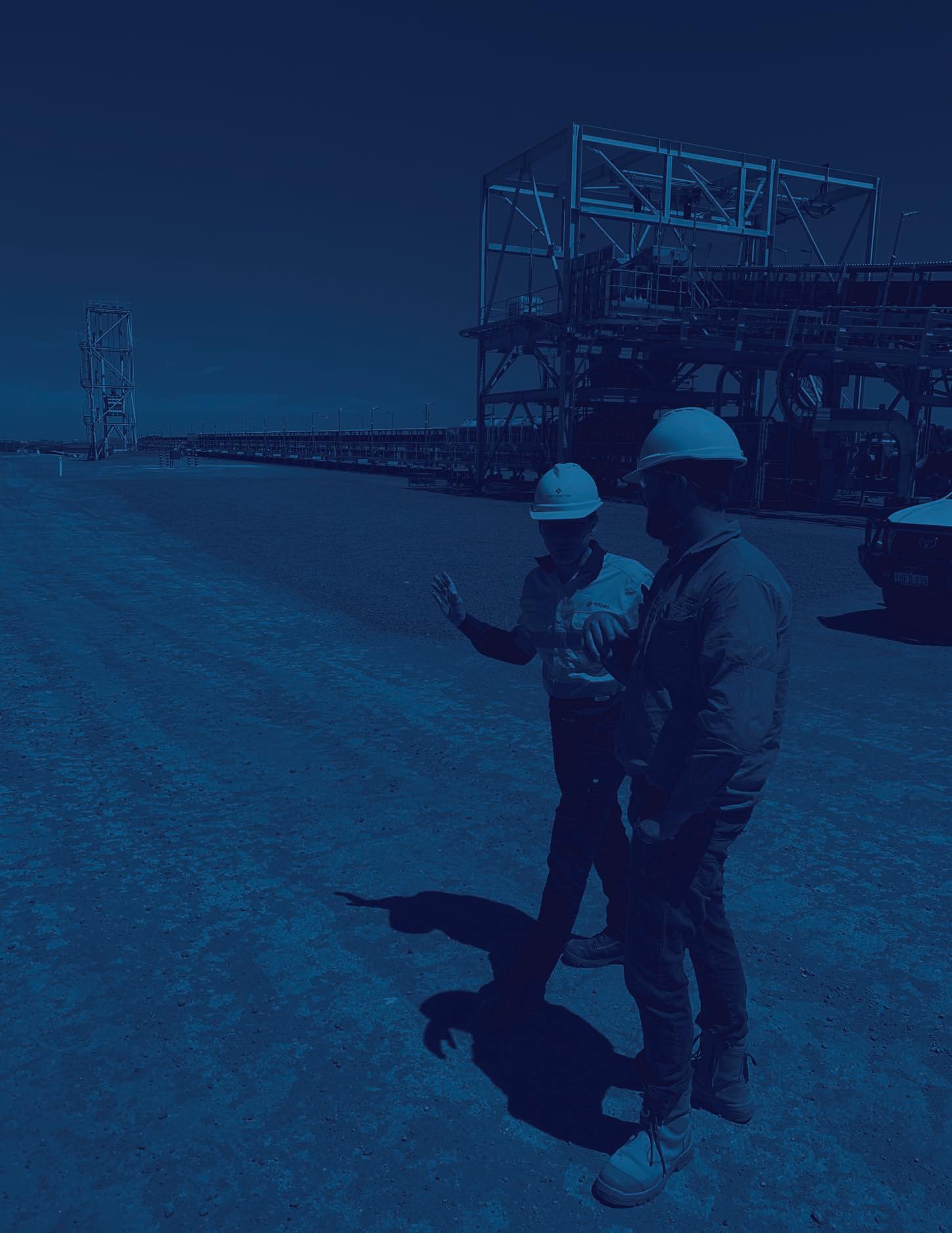
Whether you’re a greenfield or brownfield operation, our team has the know-how to design, build, operate and optimise your site, delivering tangible benefits including cost savings, productivity and efficiency gains.
If you’re facing a complex problem, let Mipac be your trusted partner in finding the best solution.
Mipac Services
Industrial Automation
Industrial Software Solutions
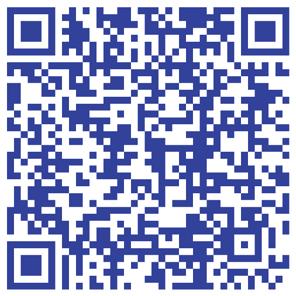
Advanced Process Control
Cyber Security
Mining 4.0 Consulting
Process Optimisation
Data Visualisation & Analytics
Electrical & Instrumentation Operations Support

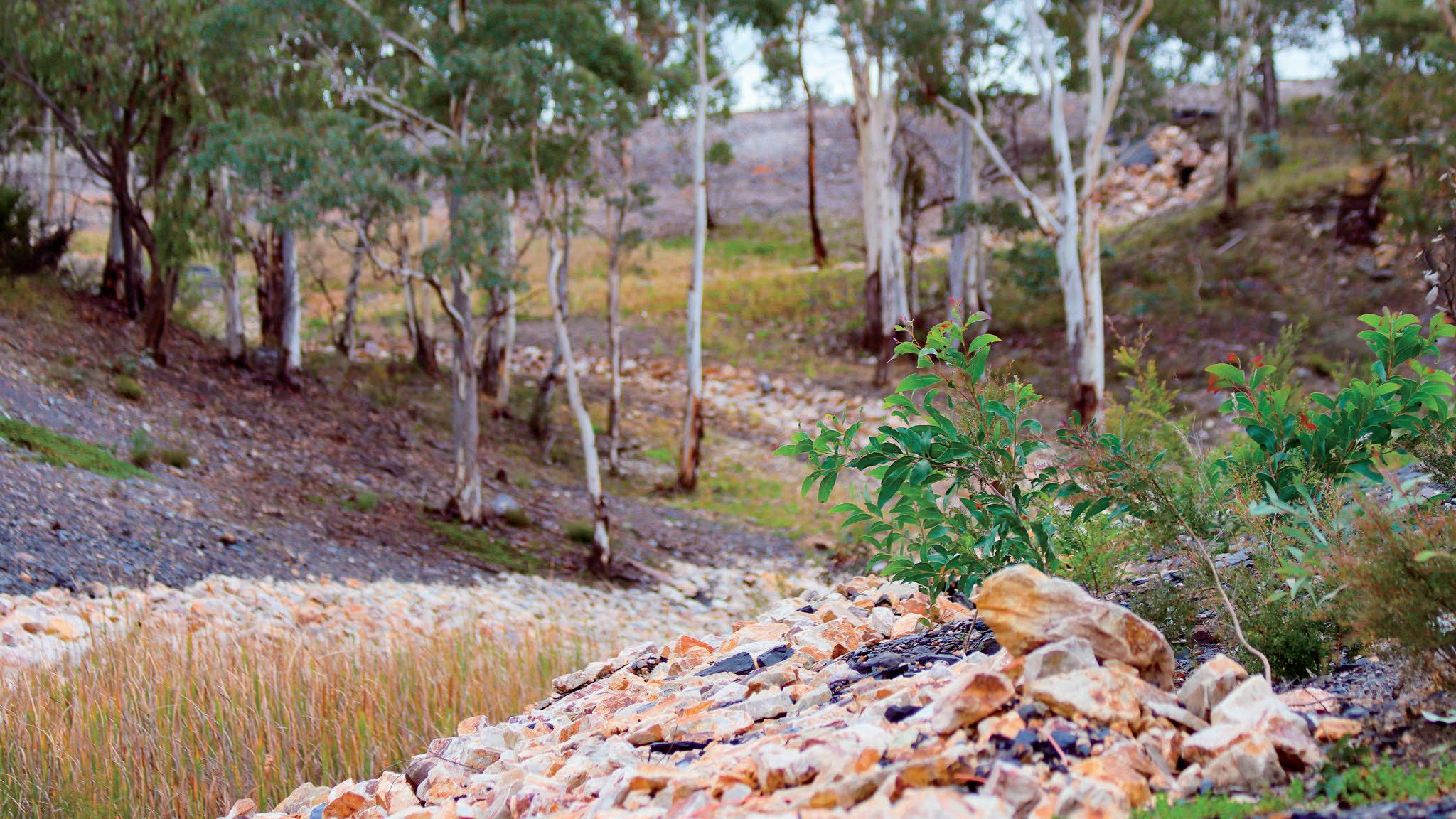

Setting the Benchmark for Mine Site Rehabilitation
Consultation & Advice | Soil Testing & Amelioration | Site Preparation | Seed Collection
Direct Seeding | Tubestock Planting | Hydromulching | Dust Suppression | Erosion Control

For over 25 years, Global Soil Systems has delivered world class mine site rehabilitation, pioneering many of the techniques used in mine site rehabilitation today. Offering end-to-end management of projects of all sizes and complexities, we continue to develop innovative techniques and processes to restore and enhance native vegetation and ecosystems.
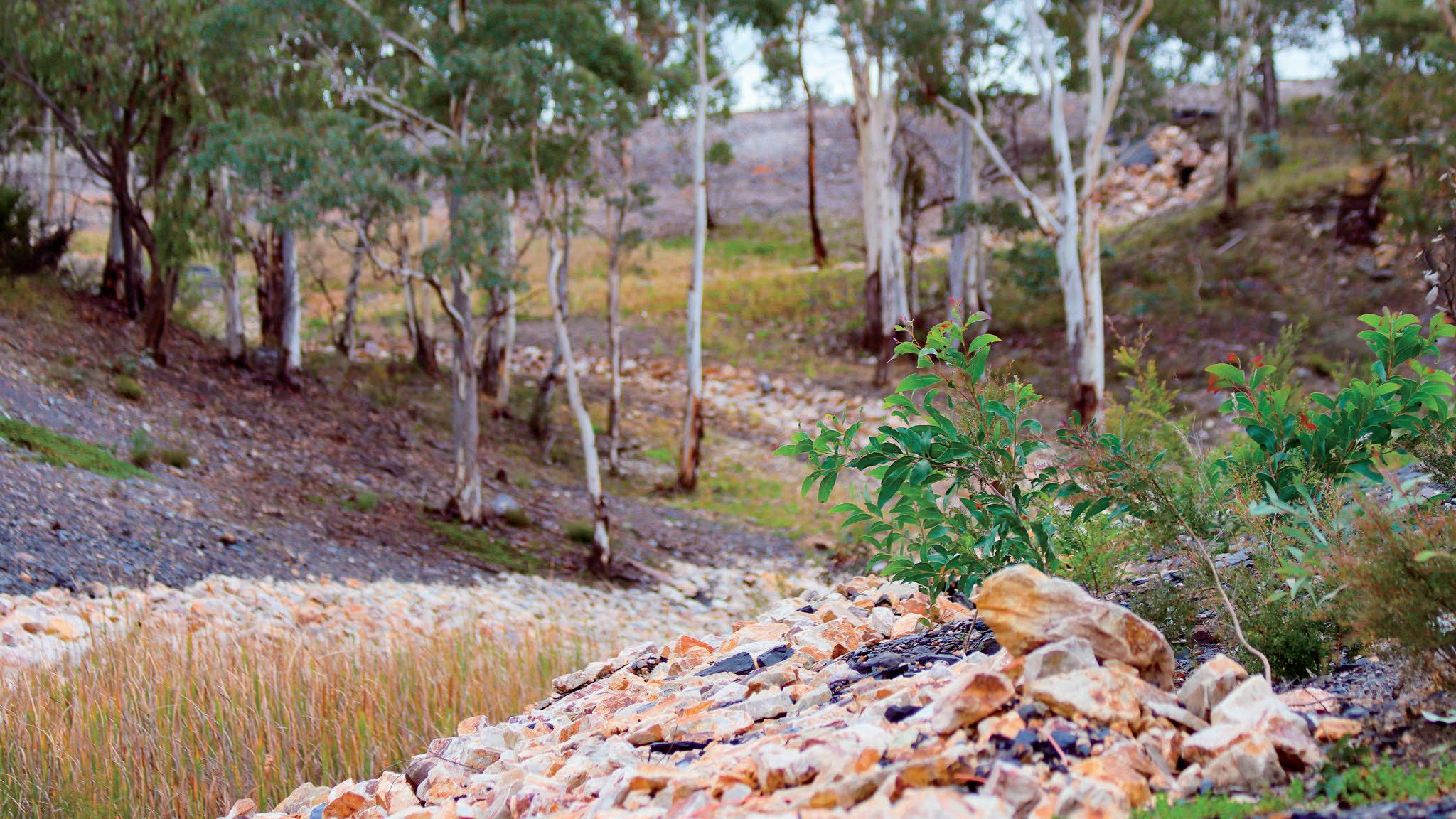
Proudly Australian owned and operated. www.globalsoils.com
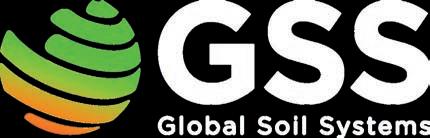
BATTERY ENERGY STORAGE: TACKLING SUSTAINABILITY HEAD ON

AUSTRALIAN MINING SHINES A LIGHT ON ATLAS COPCO’S ZENERGIZE BATTERY ENERGY STORAGE RANGE, WHICH DELIVERS ZERO-CARBON POWER GENERATION WITHOUT
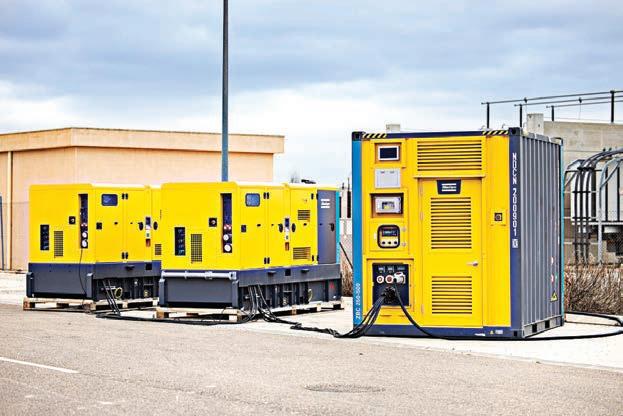
The BESS is also durable, delivering 40,000 hours of power across their life, equating to more than 5000 cycles or over 1600 days of continuous operation. This leads to a low total cost of ownership, with the system potentially paying itself back within approximately three years.
Perhaps most significantly, the Zenergize system generates zero greenhouse gas (GHG) emissions when operated alone. And when operated in hybrid mode alongside a generator, the Zenergize system can reduce GHG emissions by up to 50 per cent.
Atlas Copco estimates this can lead to savings of 100 tonnes of carbon dioxide

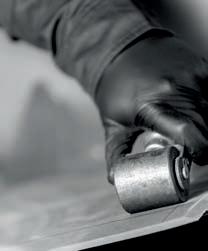
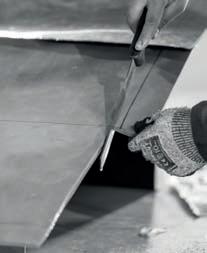
emissions across the machine’s lifecycle, or the equivalent of planting 450 trees.
The Zenergize medium-range BESS, the ZBP, has a compact footprint of 1.4 square metres, while the large-range solution, the ZBC, has a footprint of 7.3 square metres and is seen as an ideal solution for demanding applications requiring a constant and significant flow of power.
The ZBC is also scalable, with the potential for 30 ZBCs to be working in parallel on any power node, and it can even act as the ‘brain’ of a microgrid, managing the power supply of entire areas such as small towns, university campuses, and neighbourhoods.
The global energy crisis and rising inflation have seen fuel prices in Australia rise to new highs in recent times.
And with many of the heavy machines that underpin today’s Australian mining industry running on petrol and diesel, miners and contractors are facing cost pressures like never before.
In parallel, the Australian mining sector is facing new challenges environmentally, with net-zero obligations and goals necessitating action on emissions reduction.
This is where battery energy storage can help.
As much as electric vehicles are becoming more and more prominent, battery energy storage is also growing in popularity.
Atlas Copco has developed a battery energy storage solution (BESS) that can deliver more than 12 hours of power with a single charge, which can be charged from empty to full in 90 minutes.

The leading original equipment manufacturer’s Zenergize system can serve as a primary source of power, replacing a generator when noise sensitivity is a concern or when fuel fumes are not permitted, or where large generators are low loaded which can damage the engine or burn fuel unnecessarily.
Through Zenergize, mining customers can be smarter with how they manage their power.
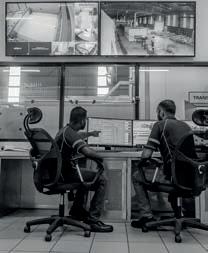
“By incorporating smart load management with the Zenergize
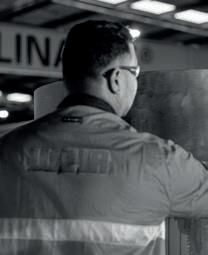
to significantly reduce their fuel consumption by running generators less,” Atlas CEA power specialist Greg Conrad told Australian Mining
“This is because the Zenergize system can supply power during peak periods and during the night when loads are much lower and noise pollution is unsuitable for construction and camp sites.
“Customers are also able to reduce the size of the generator required and possibly go down an engine size which means lower upfront capital equipment cost, lower fuel usage, less maintenance, and less-expensive spare-parts cost that a larger generator requires.”
And these aren’t the only benefits.
“The Zenergize system has also been able to reduce generator run hours and associated servicing costs,” Conrad said. “And by adding more renewable energy, such as solar panels, straight into the power system or directly into the batteries, the customer proportionally reduces the amount of fossil fuels used.”
Built with high-density lithium-ion batteries, the Zenergize system is lighter than traditional alternatives, making transportation easier, while the machine is also 70 per cent more compact, enabling greater versatility, usability and scalability.
And operators can be assured they’re not losing out on power quality, with medium 10kVA (kilovolt-ampere) to 90kVA and large 100kVA and 1000kVA Zenergize ranges designed to deliver optimum performance across their 12 hours of operation.
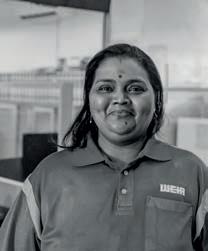
To support the Zenergize battery energy storage range, Atlas CEA –Atlas Copco’s Australian distributor – has a comprehensive service team across its branches in Brisbane, Sydney, Melbourne and Perth, with technicians at the ready for servicing or if a customer runs into any difficulties.
Through the Zenergize system, Atlas Copco has innovated an inspired new way of delivering improved environmental outcomes on mine sites without compromising on performance.
Operators can reduce fuel costs and limit their carbon footprint, satisfying two rising industry missions with one solution.
As the need to decarbonise becomes more pressing in a power-dependent Australian mining industry, the Zenergize battery energy storage range has an important role to play in the years
CUSTOMERS ARE ALSO ABLE TO REDUCE THE SIZE OF THE GENERATOR REQUIRED AND POSSIBLY GO DOWN AN ENGINE SIZE, WHICH MEANS LOWER UPFRONT CAPITAL EQUIPMENT COST, LOWER FUEL USAGE, LESS MAINTENANCE, AND LESS-EXPENSIVE SPARE-PARTS COST THAT A LARGER GENERATOR REQUIRES.”THE ZENERGIZE SYSTEM GENERATES ZERO GREENHOUSE GAS EMISSIONS WHEN OPERATED ALONE. BUILT WITH LITHIUM-ION BATTERIES, THE ZENERGIZE SYSTEM IS 70 PER CENT MORE COMPACT THAN TRADITIONAL TECHNOLOGIES.
It’s a big milestone for a piece of rubber. But Linatex® is so much more than that. It’s unlike anything else, using a unique 95% natural latex formula that has made Linatex® the strongest rubber in mining for the last century – exactly as nature intended. So, here’s to 100 Years Strong, and the next 100 to come.


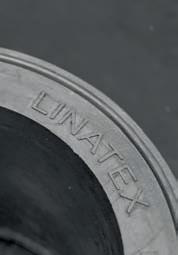

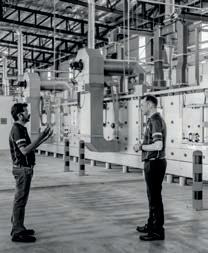
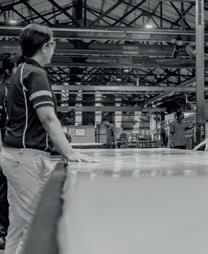

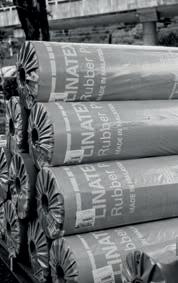
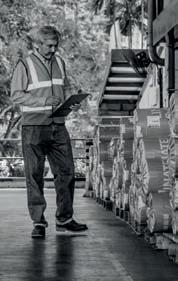
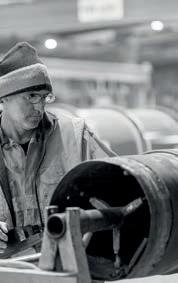
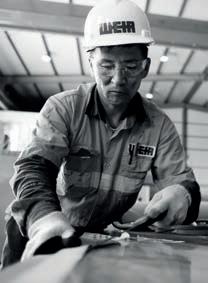

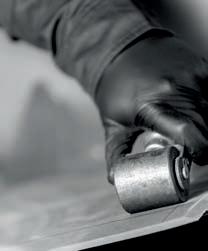
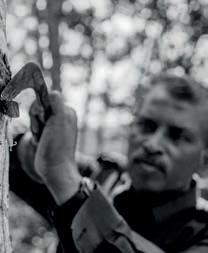
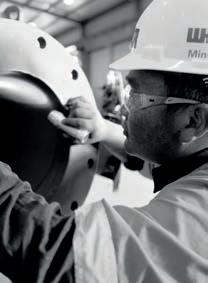
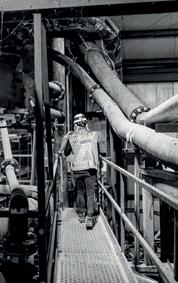
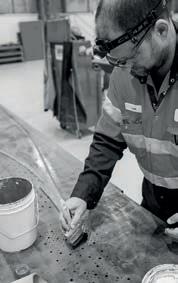
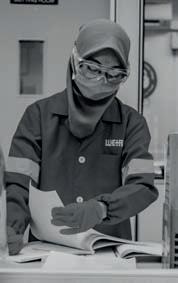


Learn more at linatex100.weir
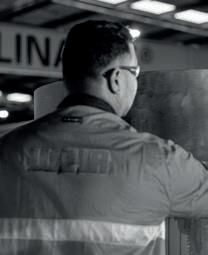
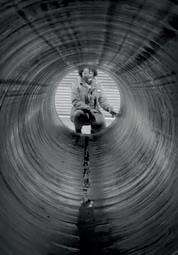

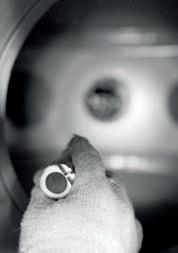
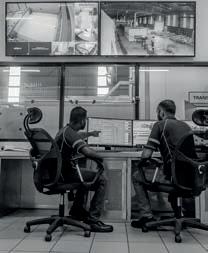
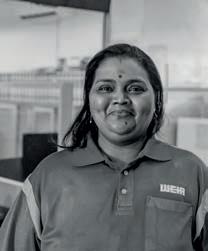
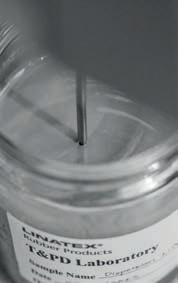

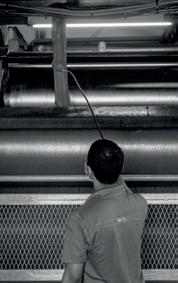
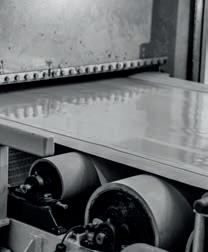
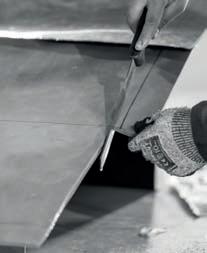

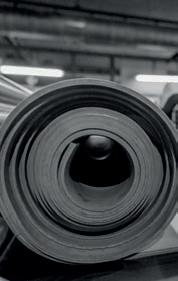
ALL THAT GLITTERS
hen Tyler Mahoney’s greatgrandfather began prospecting for gold in Western Australia, metals detectors were considered something of a novel introduction.
But now, many years later, his greatgranddaughter regularly uses state-ofthe-art detectors to scan the ground for the very commodity he sought to find.
WMahoney credits her greatgrandfather and her grandmother for getting the family into gold.
“My grandmother loved prospecting, and she was a prospector at a time when there wasn’t a lot of women doing it,” Mahoney told Australian Mining she really helped pave the way for me.”
Mahoney’s parents and brother are also full-time gold prospectors. And while she’s no stranger to digging with them, she has also taken on some big side projects of her own.
As a star of the Discovery Channel’s Gold Rush, Mahoney has travelled across the globe in search of that glittery payday, and has recorded a podcast and written a book in the process.
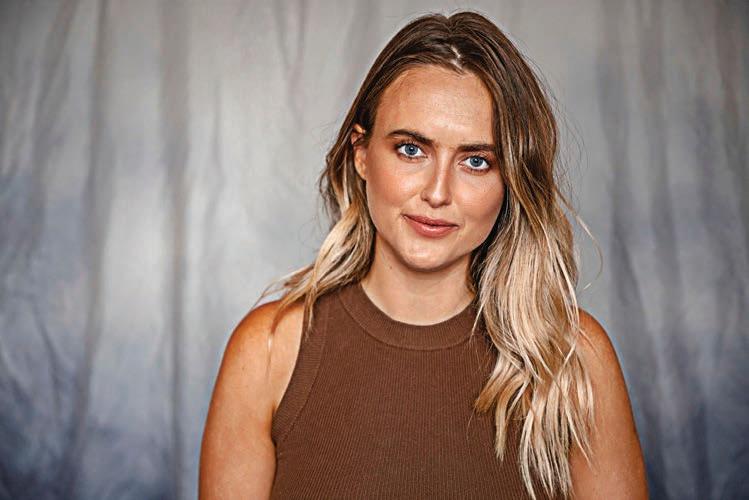
Despite her adventures, Mahoney is happiest in the red soil of outback WA.
“I truly love gold prospecting,” she said. “I love the thrill of finding gold nuggets, I love being outside, I love that every day is different.
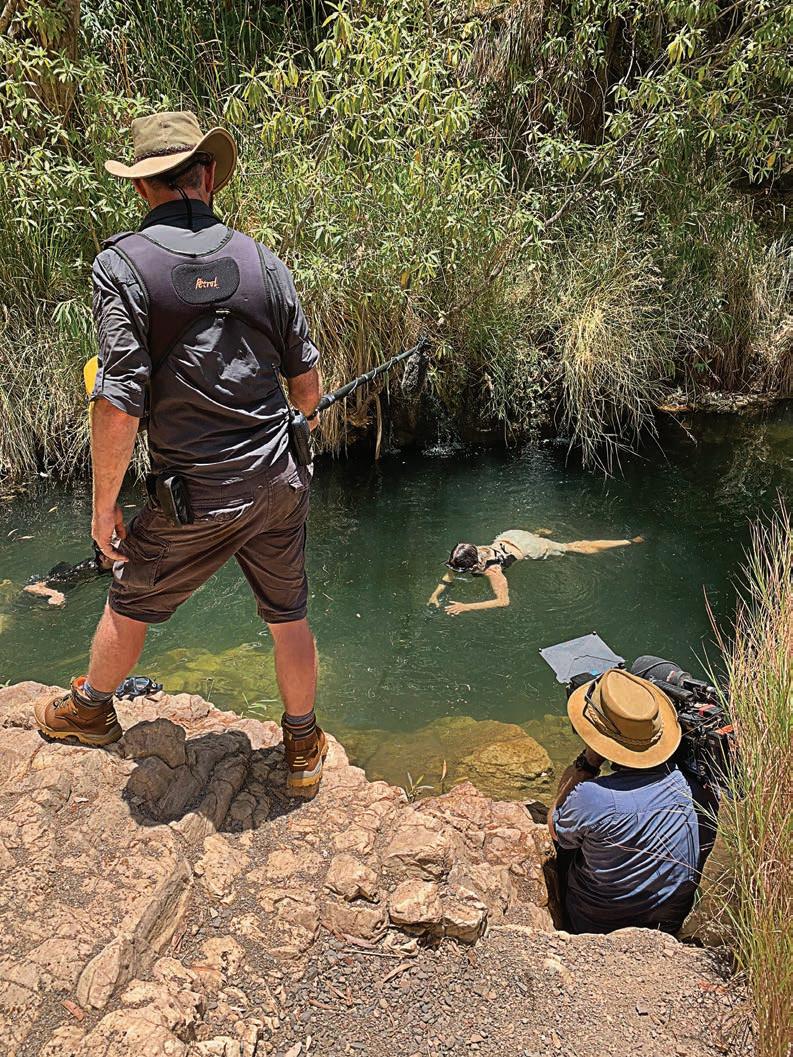
“I couldn’t imagine myself doing anything else.”
Gender equality
Mahoney is no stranger to the so-called “man’s world” of gold prospecting, or of the wider recourses sector in general.
Mining is the most disproportionately male industry in the country, toting a ratio of 80 per cent men to 20 per cent women, according to Australia’s Workplace Gender Equality Agency (WGEA).
“When I walk into a room with any of my male peers, they are given respect automatically, but I am constantly proving myself and trying to earn that respect,” Mahoney said.
“I believe a woman should be able to step into any part of the mining industry and feel as though it is a safe space for her.”
Mahoney is dedicated to using her voice to get more women into the sector, but said that she would like to see everyone get involved in the fight, regardless of gender.
“You can’t be what you can’t see,” she said. “But I also think that a lot of responsibility lies in men calling out their mates when they hear or see something wrong.
“We have some great allies out there, and it’s time to amplify our voices more so we can get a spot at the table.”
Mental health advocacy
In addition to advocating for gender equality, Mahoney is also a fierce supporter of mental health awareness in the mining industry.
“I was diagnosed with bipolar when I was in my early 20s,” she said. “It was a long road of denying the diagnosis and not actively wanting to get better.
“As a result, my mental health deteriorated a lot.”
Throughout her journey to acceptance, Mahoney found that bipolar, and mental health in general, was not talked about enough in the industry. She decided that if no one else was going to talk about, she would be the change she wanted to see.
“Once I started talking about it, others opened up about their stories,” Mahoney said.
“It makes you feel safer, and it made me want to help other people to know that they aren’t alone and that there is light at the end of the tunnel.”
In one study, ‘Psychological distress in remote mining and construction workers in Australia’, it was found that 40 per cent of respondents rated the stigma surrounding mental health as the source of their stress, highlighting the importance of early intervention and discussion. The study also found that a working model of four weeks on and one week off was the most detrimental to mental wellbeing.
“So many of my friends who do FIFO (fly-in, fly-out) work in Kalgoorlie struggle with their mental health,” Mahoney said. “Men’s mental health especially is very stigmatised, because in the mining industry there’s a notion that men have to be big and tough.
“I would encourage everyone to remember that just because something isn’t hard for them doesn’t mean that it’s not hard for others.
“And for anyone struggling with mental illness, I want them to know that their experience is valid, and I urge them to take it seriously and seek professional help, or even just talk to a mate and get it out there.”
On paper and on screen
When Mahoney isn’t prospecting for gold in the remote WA outback, she’s keeping herself busy with some big projects.
One of these is Gold Rush: Parker’s Trail, a television show developed by the Discovery Channel that follows Parker Schnabel, owner of the Big Nugget mine in Alaska, as he mines for gold in Victoria, Queensland and WA.
Mahoney joined Schnabel for two seasons of the show, with a third season scheduled for 2023, and she was presented with the opportunity to mine in Bolivia, Peru, Alaska and Canada as part of the program.
Mahoney also starred on Aussie Gold Hunters, a show that follows gold miners across WA, Victoria and Queensland as they strive to reach their set season targets.
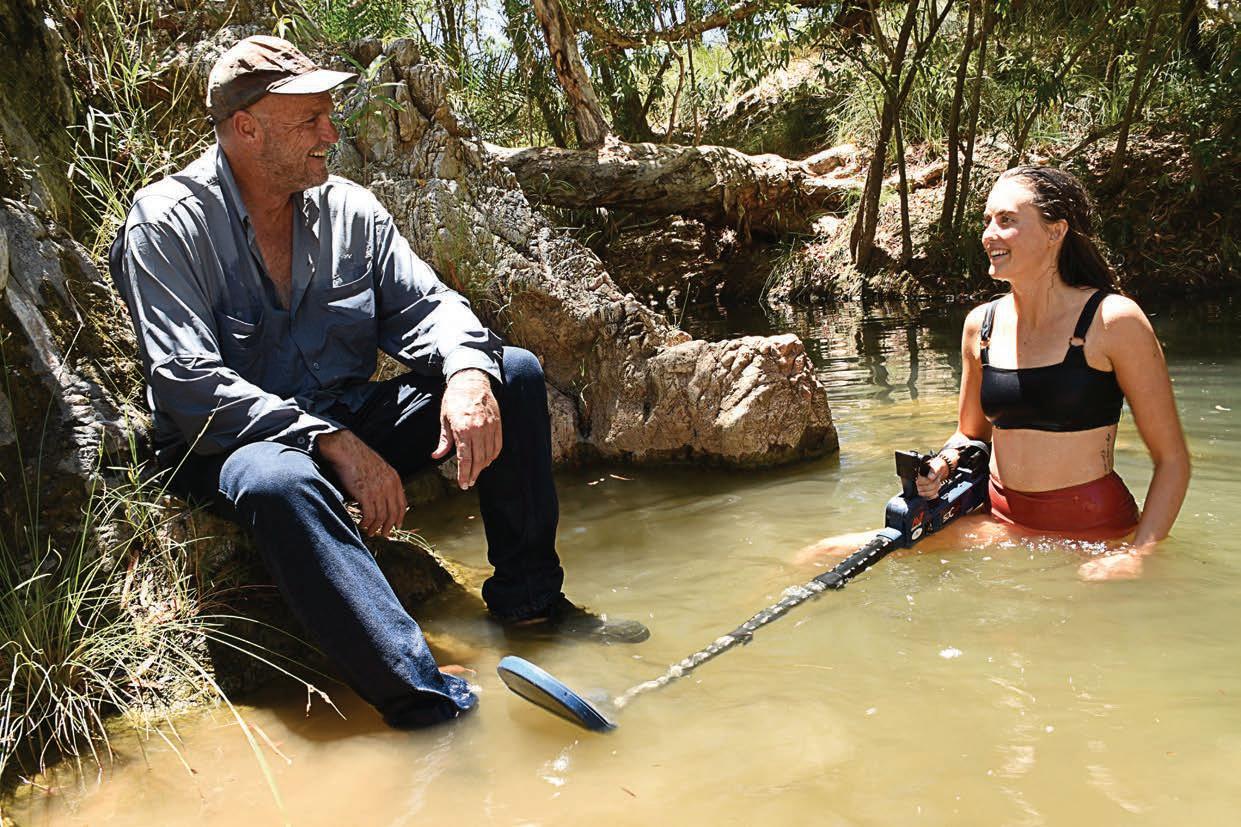
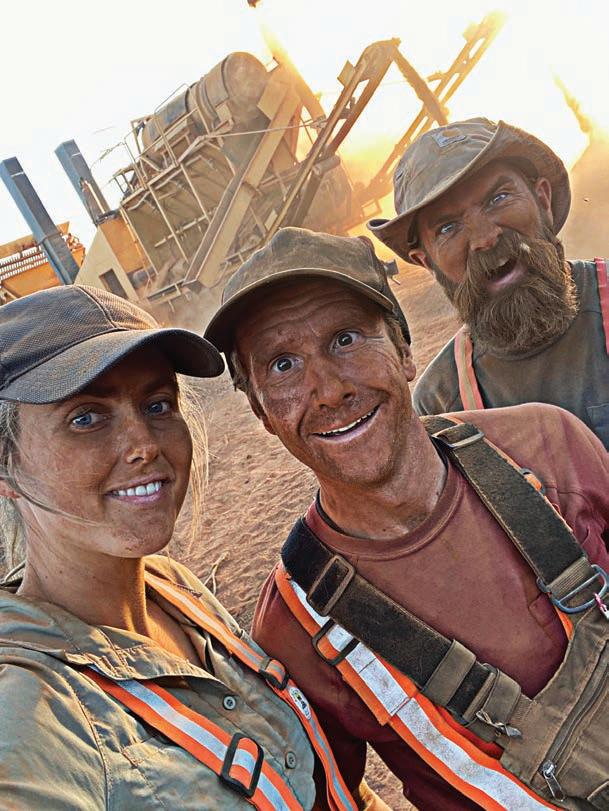
In between all her travels, Mahoney has also written a book of her own: Gold Digger
“The book follows my journey through gold mining, from leaving the gold world for a bit in my early-20s to travelling the world for the television show and detailing all of the stories that come with gold mining,” Mahoney said.
Despite these whirlwind adventures, Mahoney’s favourite gold mining story happened right in her own backyard.
“My parents were prospecting and came across a massive gold ring,” she said. “It ended up being 22 karats, so really solid.
“It was in perfect condition, and it had some numbers stamped right on top, which was weird.
“We couldn’t wrap our heads around why these numbers were on the ring but then it clicked: it was an old GML (gold mining lease) from the gold rush, so around the late-1800s.
“So what we think had happened was that a prospector had some good luck at a particular GML and used some of the gold to get a ring made. But when he went back out into the bush to search for more gold, he lost it.
“I just think, if that ring could talk, it could tell us so many stories from the last 100 years.
“I love finding gold, obviously, but sometimes the treasures are their own special find.” AM
SCIENTIFIC AI MEETS CHEMISTRY
ith innovative products, global field support and leading technical expertise, BASF is providing advanced technological solutions aimed at improving margins by increasing throughput and recovery across the hydrometallurgical mining process.
This extends throughout operations, from stockpile and the ore that feeds the plant to leaching to solvent extraction to grinding to flotation to solid–liquid separation to tailings management.
“We are involved in the provision of mining chemistry and mining solutions globally,” BASF regional head of digitalisation Ken Plozza told Australian Mining
“A significant aspect of our value proposition to the market is not just the chemistry itself, but how the chemistry interacts with the operational process.
“Or, more specifically, how the process actually responds to the chemistry – as a two-way street –with all the challenges associated in providing both a chemical and a valueadd solution.”
WBASF and IntelliSense.io partnered to create a synergy that brings together mining process knowledge with chemistry, software, and scientific AI (artificial intelligence) dedicated to the mining industry.
“Together we deliver what mining professionals need. From the real-world on-ground experience to operational excellence, we have eyes and ears on the needs of the industry,” Plozza said.
“Our collaboration became stronger with BASF Venture Capital leading a strategic investment round in IntelliSense.io, which increased its applications portfolio and supports its distribution capacity across the world.”
Announced in mid-2020, the exclusive partnership – known as the ‘BASF Intelligent Mine powered by IntelliSense.io’ – effectively combines BASF’s expertise in mineral processing and ore beneficiation chemistry with IntelliSense.io’s data analytics and Scientific AI technology.
“IntelliSense.io are able to produce real-time recommendations derived from our chemical processes,” Plozza said.
BASF’s Intelligent Mine brings smart technologies and smart people
together. It is designed to support across architecture design and implementation, project management, configuration, training, process optimisation, data integration and migration according to each operation’s specific needs.
The company’s mine and metals experts deliver answers to help customers, and BASF said its chemistry expertise – now enhanced by IntelliSense.io’s mining AI – has saved $4 billion across 200 operations.
“In essence, it’s a product-based approach where our first principals’ knowledge of how chemical interactions work combines with industrial AI, together referred to as Scientific AI, leading to far more successful optimisation outcomes,” Plozza said.
Process optimisation is underpinned by brains.app, a real-time decisionmaking software platform that collects, cleans, interpolates, and assimilates a federated data lake ready for AI.
“As the mining industry collects a significant amount of data, the key is to produce value from this almost limitless resource,” Plozza said.
The platform incorporates a material handling model that tracks material
flows and geometallurgical and physical properties with associated uncertainty from the pit throughout each of the unit operations in the processing plant, providing real-time information and predictions on when material will arrive at a particular point.
It also tracks and predicts the effect of incoming material on processes in realtime, known as material influence.
Another platform technology is the dual modelling approach that combines machine learning and first principal models to create Scientific AI that powers the BASF Intelligent Mine outof-the-box optimisation applications.

These applications have been proven at Tier 1 mining operations and have established the BASF Intelligent Mine approach as a unique solution that delivers proven results.
Virtual sensors are a further platform technology. These provide the output of a digital asset, as well as a realtime model output based on dynamic and static inputs that can be used in operational and financial decisionmaking, automated control, and machine learning and empirical simulation-based prediction models.
MANAGEMENT
The data is organised into a connected virtual asset or metric structure. In this structure, data of varying resolution is filtered practically and statistically through the BASF Intelligent Mine data quality model, which ensures only quality data is used in process simulation.
The Scientific AI solutions are based on a hybrid cloud architecture, enabling on-site and cloud deployments, to help mining industry partners accelerate their digitalisation programs in their operations.
The BASF Intelligent Mine is driving efficiency gains throughout mining operations across the globe, including in places such as Chile, Brazil, South Africa, Australia and in other locations.
“Our scientific AI generates a significant amount of value connecting the chemistry with the operational processes in realtime. As such, the information that’s generated is far more precise,” Plozza said.
from ‘soft sensors’ as they are processed in the cloud, with the benefit of constant retraining and re-calibration. The accuracy and robustness of the outputs is cross verified using equivalent outputs of parallel models, and their deployment within a mine site is non-intrusive.
soft sensors can be used to reconcile production metrics, creating a single source of truth for the mining operation. This reconciliation decreases the total uncertainty of data along the value chain to produce a coherent data set that can confidently be used in reporting
ATLAS COPCO
mine planning.
The BASF Intelligent Mine value model accurately calculates and, when paired with the digital process model, predicts asset-based operating unit costs using dynamic financial variables.
QAC 1450 TWIN POWER GENERATOR
FEATURES:
• Over 70% load step acceptance
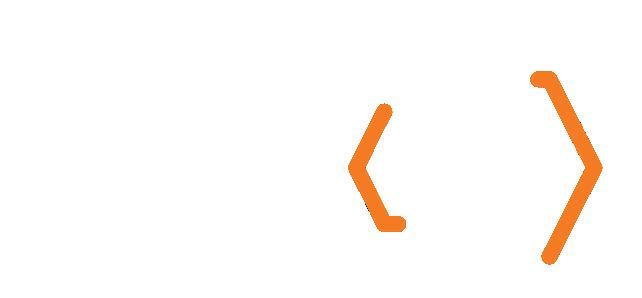
• Ideal for portable and intensive use
• Robust twist lock & forklift inlets
• 110% spillage free frame
• Performs in extreme temperatures & at high altitudes
• Designed with large access doors for ease of service
• Minimal maintenance and 500 hour service intervals
BASF is a proud member of Austmine, the leading not-for-profit industry association for the Australian mining equipment, technology and services (METS) sector.
For over 30 years Austmine has advocated for Australia’s METS sector to be recognised as a world leader in mining innovation and technology. AM
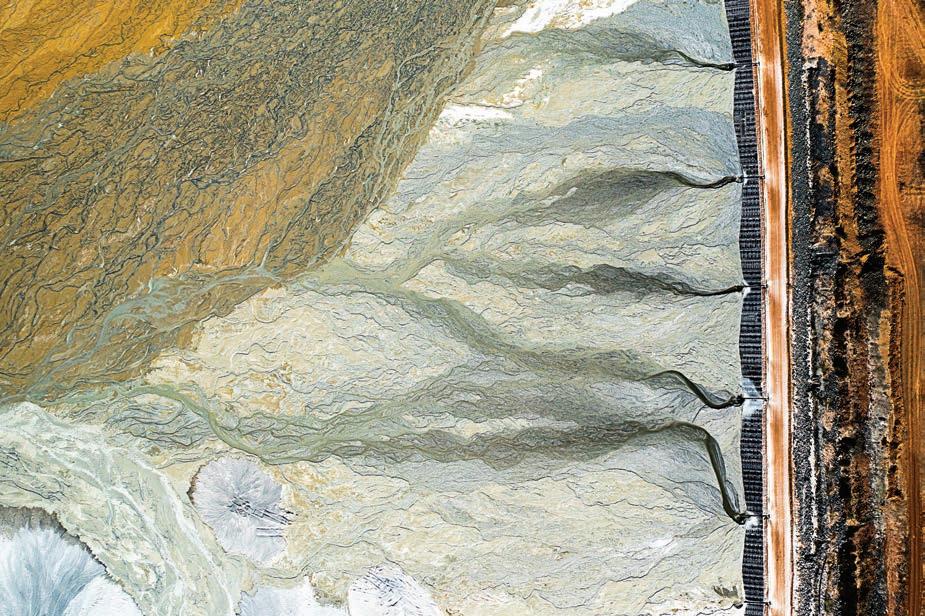
With two generators in one platform, the QAC 1450 TwinPower™ provides the flexibility you need to run at 100% power load or low power loads in the most efficient way. What’s more, every feature you need comes as standard.

LIKE TO KNOW MORE? SPEAK TO OUR TEAM TODAY
PH: 1800 733 782 www.atlascea.com.au
The QAC 1450 TwinPower™ is the ideal generator for applications requiring variable power needs that can be set to suit the time of day or specific usage requirements. Featuring 2 x 725 kVA generators inside the 20 foot containerised unit the QAC 1450 TwinPower™ allows you to run on one engine while servicing the other, providing a built-in backup as standard.
TAILINGS
IS ONE OF THE AREAS IN WHICH BASF IS PROVIDING INNOVATIVE SOLUTIONS.
PLANTING THE SEEDS OF REHABILITATION
WHEN GLENCORE’S BAAL BONE COLLIERY MOVED INTO MINE CLOSURE WORK, IT TURNED TO GLOBAL SOIL SYSTEMS TO ASSIST WITH REHABILITATION AND REVEGETATION ACROSS THE SITE.
Located 130km from Sydney in the western coalfields of New South Wales, Glencore’s Baal Bone site has played host to a number of different projects throughout the years.
First established in 1983, the site operated as an underground and opencut coal mine before transitioning into a Glencore employee training facility from 2012–18.
But 2019 saw the site go through what all mining operations will eventually face: mine closure.
A mine’s closure planning is guided by its regulatory approvals, the site’s regional context, long term post-mining land uses, and by consultation with all relevant stakeholders.
For Baal Bone, mine closure process involved the dismantling and removal of infrastructure and extensive rehabilitation work across the site.
When it came to rehabilitation, Global Soil Systems was the company’s preferred supplier.
“We’ve worked on Glencore sites for many years now, so we’ve really cultivated our working relationship,” Global Soil Systems project manager Craig Outridge said. “We were one of the first revegetation specialists in the Hunter Valley and we’ve worked on pretty much every coal mine in New South Wales at some point in time.”
The 25 years of experience that Global Soil Systems has under its belt has allowed the company to hone its skills in returning sites to agreed postmining land use options. In fact, it was its reputation as a safe operator that was another important consideration.
“Safety is our number-one focus, and it’s also a primary focus for Global Soil Systems,” Baal Bone mine manager Mark Bulkeley said. “Having worked with them in the past, we know their work is always to a high standard.”
At Baal Bone, Global Soil Systems revegetated over 100 hectares of land, including direct-seeding over 55 hectares of native woodland and hydromulching more than eight hectares of steep slopes and batters.
The company also propagated, planted and maintained 12,000 tubestock across the site, including 1300 endangered capertee stringybark trees.
“The mining process involves disturbance of native vegetation” Outridge said.
“Rehabilitating and reforesting the land helps to mitigate any impacts and support the restoration of functional, self-supporting ecosystems.”
Among the other rehabilitation efforts, Global Soil Systems also cultivated and deep ripped all areas prior to seeding.
Deep ripping is a technique that involves breaking up compacted soil layers to improve soil structure and water infiltration, and to reduce the
risk of erosion from water run-off ahead of seeding.
“After mining and associated activities have finished at a site, the soil can be hard and compact, which makes it difficult for plant roots to penetrate and access water and nutrients,” Outridge said.
“By deep ripping the soil, the texture becomes finer, making it easier for seeds to germinate and establish.”
Choosing the right vegetation for a site is a matter of researching what plants traditionally grew in the area before mining commenced.
While the research is undertaken by ecologists, Global Soil Systems can tap into its extensive knowledge base and advise which plants will thrive in the conditions.
“We have an insight into how things will actually grow given different site conditions, or if something might be more suited to a particular method of revegetation,” Outridge said.

This knowledge is invaluable, as the soil goes through a lot of changes during the mining process, and what once might have grown well in one spot may not necessarily be suitable anymore.
“We can also provide advice on species selection, sowing rates needed to provide specific cover, and what plant species may need a bit of extra help because they are harder to establish on mine sites,” Outridge said.
Expertise and the willingness to see the job done from start to finish was another reason Glencore was so eager to employ Global Soil Systems’ services at Baal Bone.
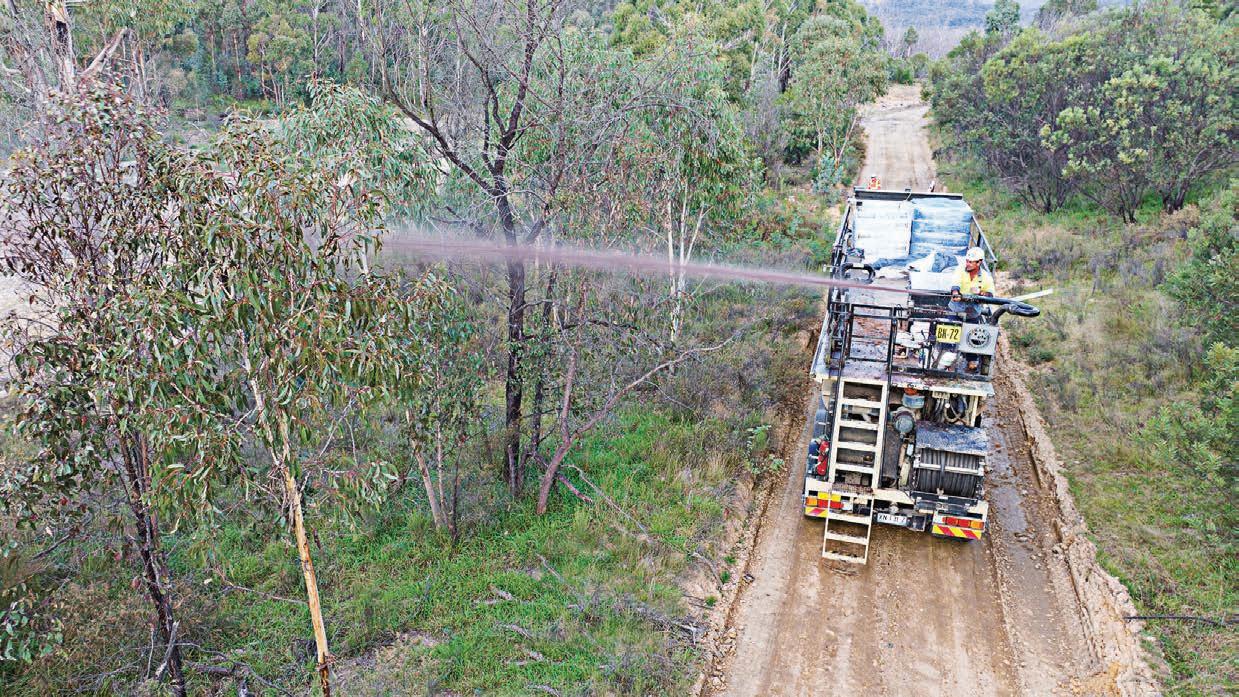
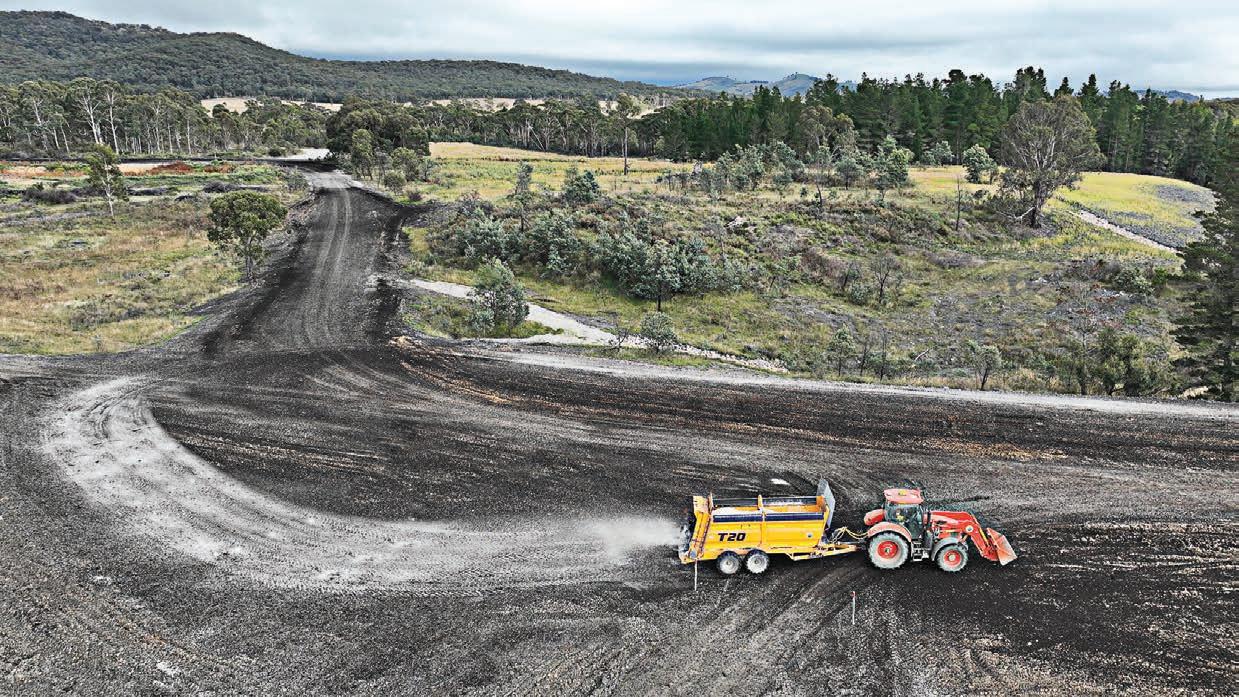
“They kept in contact with us from the get-go and are more than happy to come back and deal with any problems if they arise,” Bulkeley said.
Outridge is also proud of the legacy the company has built throughout the past 25 years.
“We have pioneered quite a few different methods and techniques over the years,” he said. “The relationships that we have built over time have also
been special to us. We really take the time to make sure each job is done correctly, and we ensure everyone in our team is across every aspect of the project.
“Our attention to detail and passion for our work is what enables us to consistently deliver positive environmental outcomes.” AM
REHABILITATING AND REFORESTING THE LAND HELPS TO MITIGATE ANY IMPACTS AND SUPPORT THE RESTORATION OF FUNCTIONAL, SELF-SUPPORTING ECOSYSTEMS.”GLOBAL SOIL SYSTEMS HAS AN EXTENSIVE KNOWLEDGE BASE AND CAN ADVISE WHICH PLANTS WILL THRIVE IN DIFFERENT CONDITIONS. GLOBAL SOIL SYSTEMS CULTIVATED AND DEEP RIPPED ALL AREAS PRIOR TO SEEDING.
UNLOCKING THE AUSTRALIAN MARKET
BEDESCHI DRAWS ON ITS LONG AND SUCCESSFUL HISTORY TO PROVIDE LEADING TURN-KEY EQUIPMENT SOLUTIONS TO THE AUSTRALIAN
Like so many companies, Bedeschi was born out of a labour of love and a dedication to quality products.
Its founder, Guglielmo Bedeschi, wanted to build a company that provided turn-key solutions to a variety of industries, including bulk handling, bricks and mining.
Bedeschi (the company, that is) was established in 1908 and, only one year later, its latest extruder was awarded the certificate of honour and the first-degree gold medal at the 1909 International Expo in Turin, Italy.
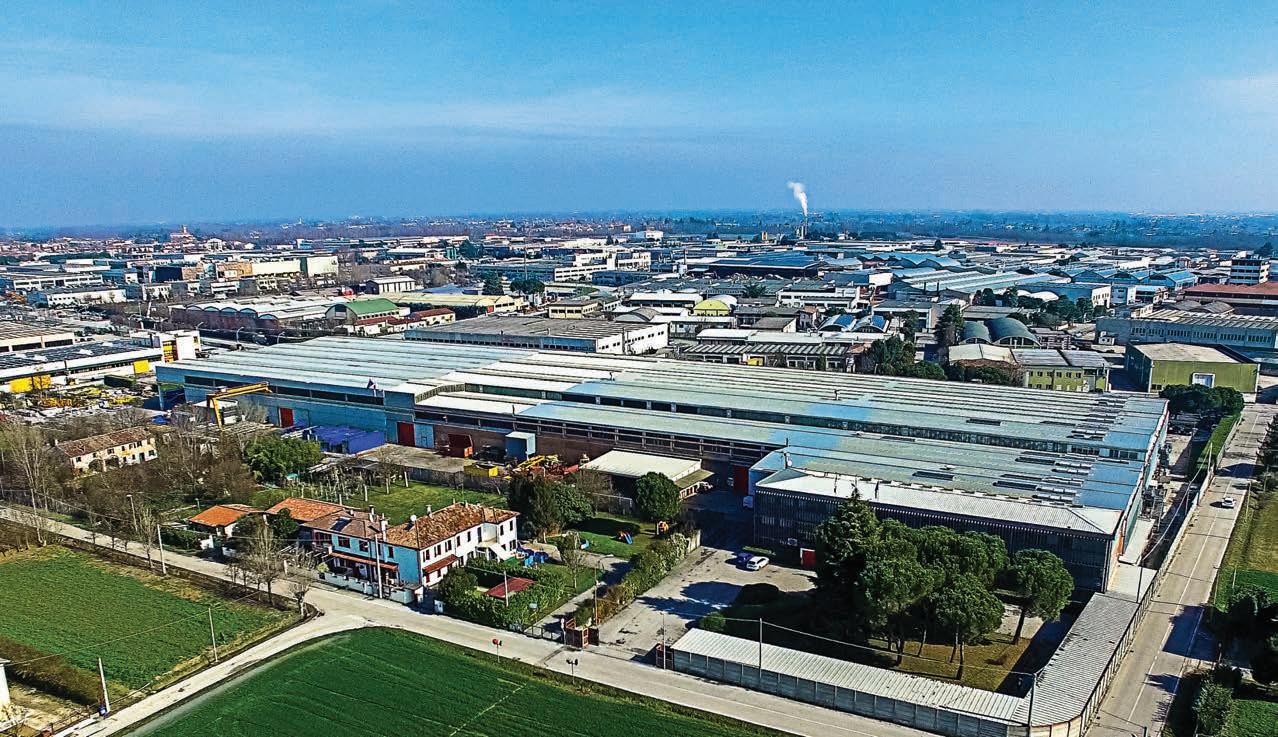
And the business’ success has continued at a steady rate ever since.
“Diversification is one of Bedeschi’s major assets,” managing director and owner Rino Bedeschi told Australian Mining.
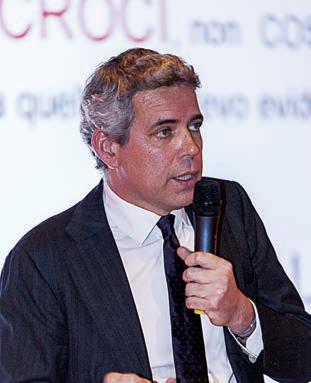
“We provide the best tailor-made solutions to meet our customers’ needs.
“Since its inception, the company has only gotten bigger under the direction of the Bedeschi family.
“We are an industry leader in the design, engineering, manufacturing and technical assistance of solutions as a direct result of our long history.”
A key aspect to Bedeschi’s growth has been the extension of its offices into other parts of the world. The company announced its new Australian
subsidiary in February 2023, with a Perth head office and satellite offices in Port Hedland and Brisbane. Uwe Zulehner was also announced as the new Australian chief executive officer.
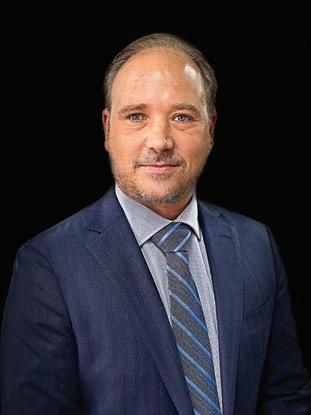
“Bedeschi believes that the executions of capital projects and service support can only be completed efficiently and
effectively if project and operational requirements from our customers are clearly understood and support is given without delay,” Zulehner told Australian Mining.
“In order for us to understand the changing requirements of our customers, a regular presence on mine sites and an active communication with the specialists at our clients’ sites are fundamental to fuel our development programs and to provide the OEM (original equipment manufacturer) support our customers want.
“Our new office locations enable us to act quickly to customer requests and mobilise services for capital and aftermarket inquiries immediately.”
Bedeschi has a strong after-market portfolio, including spare parts supply and warehousing, shutdown and maintenance support for mine and port operations, and off-site repair work for parts.
Having offices close to the major mining hubs in Australia means these after-market services can be completed quickly and efficiently.
“Bedeschi has a long history of executing complex projects and stands behind each product with its name and heritage,” Zulehner said.
The company already has one workshop location established in Welshpool, Western Australia, with a second one planned.
“We understand the requirement of the Australian mining industry for an established OEM,” Bedeschi said. “Before the development of our
Australian locations, we had already completed a number of projects in Australia on an ad-hoc basis.
“The close proximity to our customers and the daily communication and support to projects and operations is paramount for strong future partnerships.
“Bedeschi also prides itself on the continuous development of our machines and equipment.
“Bedeschi has a clear strategy to cement its position as a leading global
OEM for balanced machines in all mineral commodities and Australia is an absolute key market for mining.”
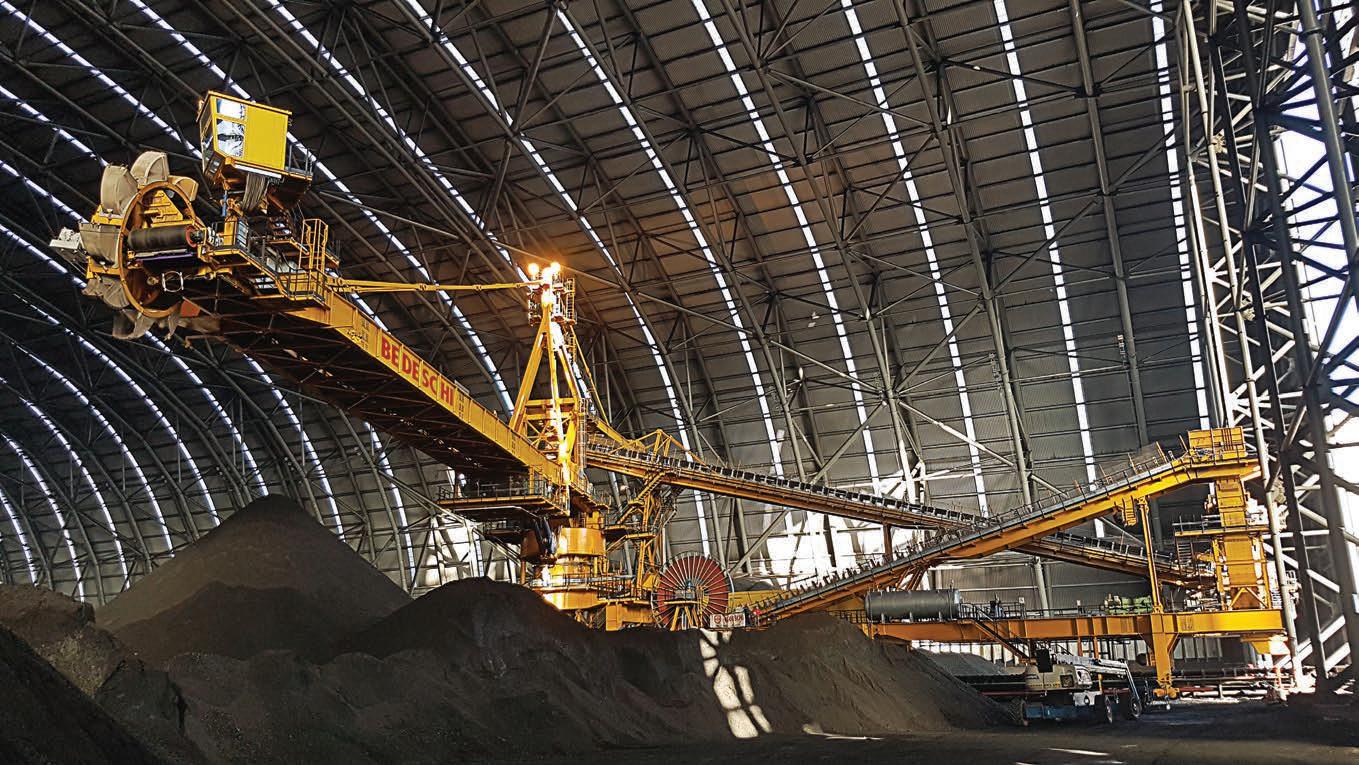
With a strong backing from its European branches, Bedeschi is in a strong position to meet the demands of the Australian mining sector.
“Apart from potential external fabrication partners in Australia, we operate several large workshops within the Bedeschi group under our ownership,” Zulehner said.
“Those workshops enable us to fabricate machine steel- and mechanical structure efficiently, pre-assemble machines in modules in our lay down yard and ship from our workshops through direct port access to anywhere in the world.
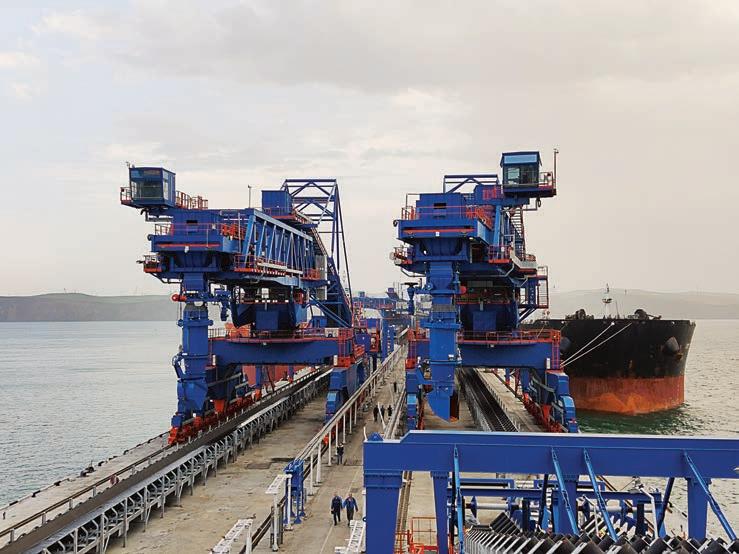
“Through these facilities, we can manage our quality control and inspections as well as the required labour and cost base better, rather than going through a third party for fabrication.
“The result is evident in a higher standard quality product delivered on cost and in time.”
With a robust history in Europe and new offices in Australia, Bedeschi is well placed to take the mining industry by storm.
“Our European manufacturing facilities have made us one of the fastest growing companies in our industry,” Bedeschi said.
“And with our full commitment to our customers, Bedeschi is on the path to establishing ourselves as a global number one in balanced machines.
“We need to keep developing and deepening our customer relationships, stay on the pulse and understand our customers’ requirements in an everchanging environment.
“Bedeschi will continue to grow as we continue to hire, retain and grow the best talents in the industry.”
And for Zulehner, the future of Bedeschi lies in the values established in the past.
“An important aspect of the Bedeschi business is that is privately owned and operated,” he said.
“The fourth-generation owner, Rino Bedeschi, is actively involved in the business and knows the majority of our customer base personally.
“Decisions are made fast, bureaucracy is kept to a minimum and customer satisfaction is an absolute priority. For our customers, Rino is only a phone call away.
“A presence in the market at different locations and a strong engineering, execution and service team with decades of experience is what we offer to our customers in order to minimise response times and to deliver the highest quality of service at the time when it is required.” AM
FROM COAL TO COPPER TO LITHIUM
From the divestment of its Queensland coal assets to its snapping up of OZ Minerals, there’s a lot on the go for mining giant BHP. Fortunately, Australian Mining was on hand for the latest BHP shareholder Q&A in March and was able to peer through some of the fog of war.
Are they still attractive places to invest?
In January, former NSW Treasurer Matt Kean unveiled what has become known as the coal reservation scheme, which requires coal companies in the state to reserve 10 per cent of their output exclusively for domestic use. These requirements, designed to ensure the state has enough coal to fire its power stations, left many unhappy.
“The NSW directive on supplying coal into the domestic market for
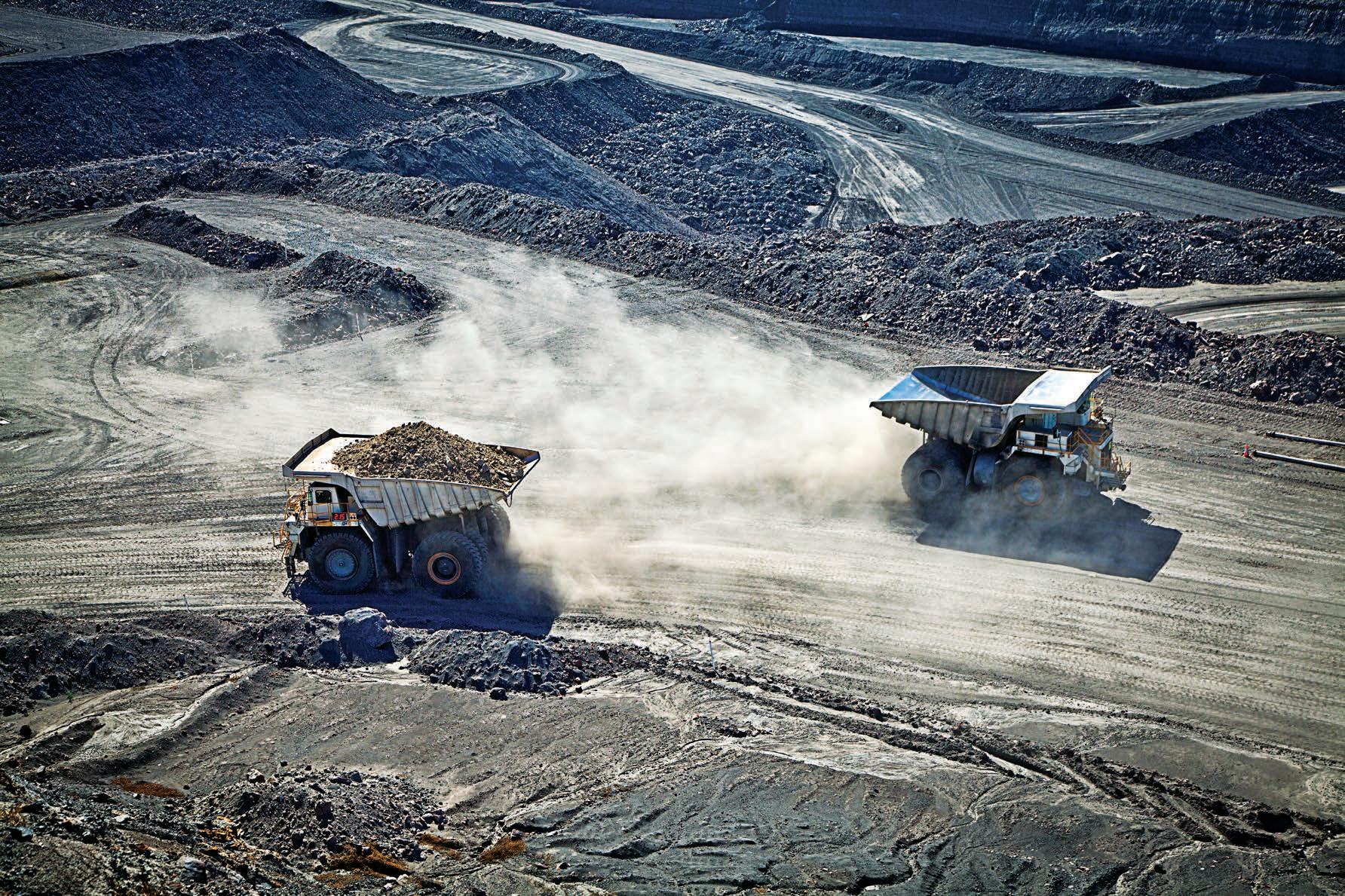
capped price is quite disruptive to our operations,” BHP president Australia Geraldine Slattery said at the Q&A.
“Our NSW operations provide exclusively to the export market, so there are some logistical and commercial matters that we’re working through to comply with those directives.
“But the broader issue I’d like to call out is the concern we have about market interventions such as what we’ve seen in NSW, but also in Queensland, where the State Government increased royalties to the maximum highest globally.”
Queensland’s controversial threetiered coal royalties system started on July 1 2022, hitting producers with a 40 per cent tax on all coal prices of more than $300 a tonne.
The two accompanying tiers enforce a 20 per cent tax on coal above $175 and a 30 per cent tax on coal above $225, a reality that has left many majors pushing back on the proposal.
The Queensland mid-year budget revealed the State Government had earned a surplus of $5.18 billion, due in large part to higher coal and petroleum royalties.
The costly royalties also formed part of Glencore’s decision to pull the plug on its $2 billion Valeria coal project in Queensland.
“So what you have then is a market intervention that’s both quite suddenly applied and equally calls into question for the stability of investing in Queensland,” Slattery said.
“Why does this matter? Ultimately, the competitiveness of Australia’s mining sector relative to our global peers is incredibly important.
“The returns that come from those investments go right back into the Australian economy, to communities, to governments, to employees, to partners and to shareholders.”
AUSTRALIAN MINING SAT IN ON A BHP SHAREHOLDER Q&A, WHERE THE COMPANY ADDRESSED A NUMBER OF HOT TOPICS FOR THE SECTOR.BHP SAID QUEENSLAND COAL ROYALTY RATES ARE HURTING THE STATE’S ATTRACTIVENESS TO INVESTORS
Echoing Slattery’s message, BHP chief executive officer Mike Henry called the Queensland royalties system “particularly egregious”.
“The other thing that I think the public doesn’t understand is that about 70 per cent of Australians actually hold shares in BHP, either directly or through superannuation funds,” he said.

“BHP also makes up roughly 10 per cent of the ASX.”
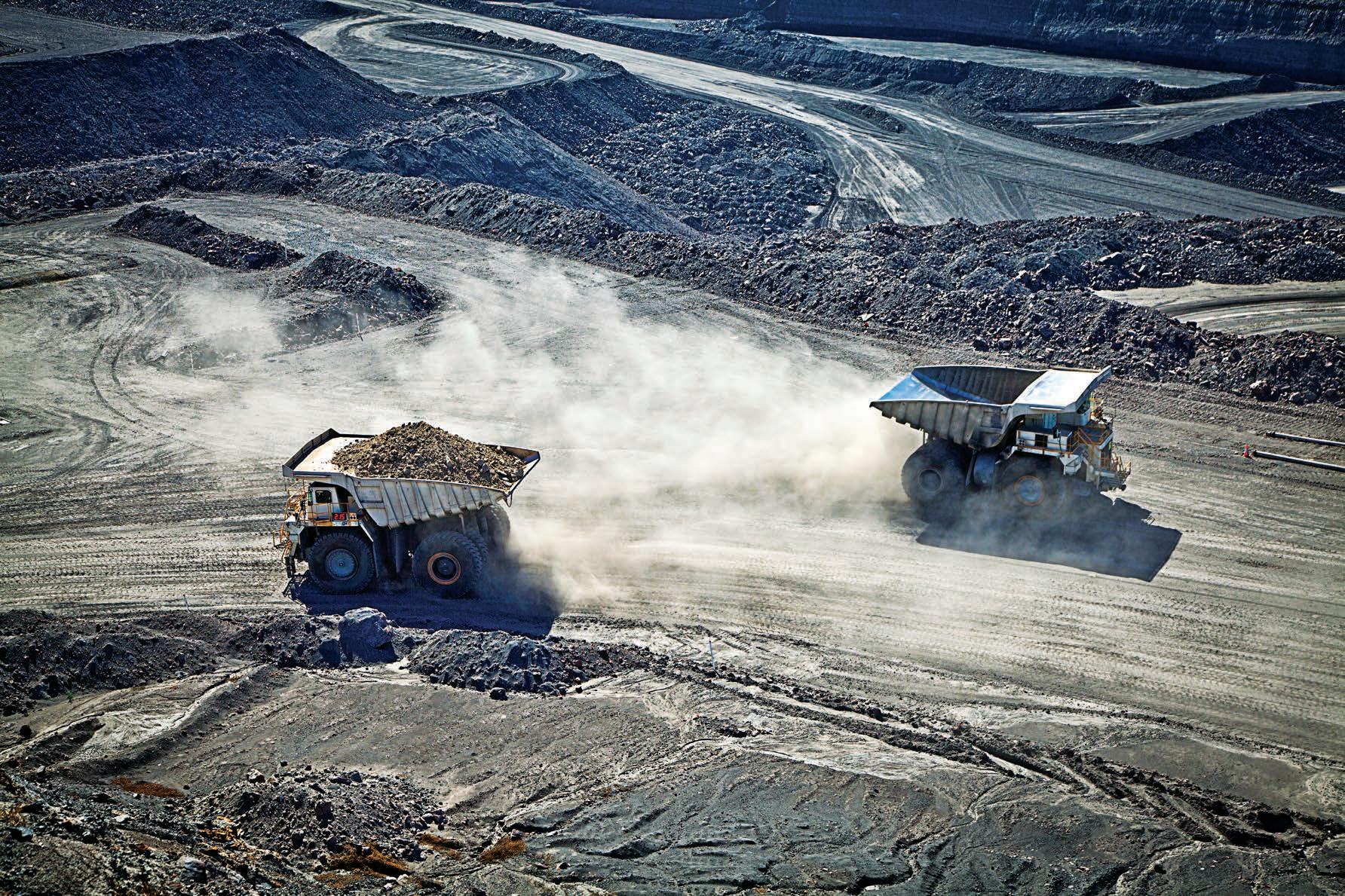
“That goes to show the importance of the health of a company like BHP and the broader mining sector, because not only is it contributing to the economy today, it’s contributing to the wellbeing income of 17 million Australians in the future. It’s in all of our best interests that the sector remains globally competitive.”
Queensland’s coal royalties system was also partly the cause of BHP’s decision to part with its Daunia and Blackwater
“While not the direct driver of the decision, it (the royalty tax) was another overlay on the competitiveness of those
BHP first announced in its half-yearly report that it was looking for buyers for the Bowen Basin coking coal operations, both of which are jointly owned by BHP and Mitsubishi as part of the BHP
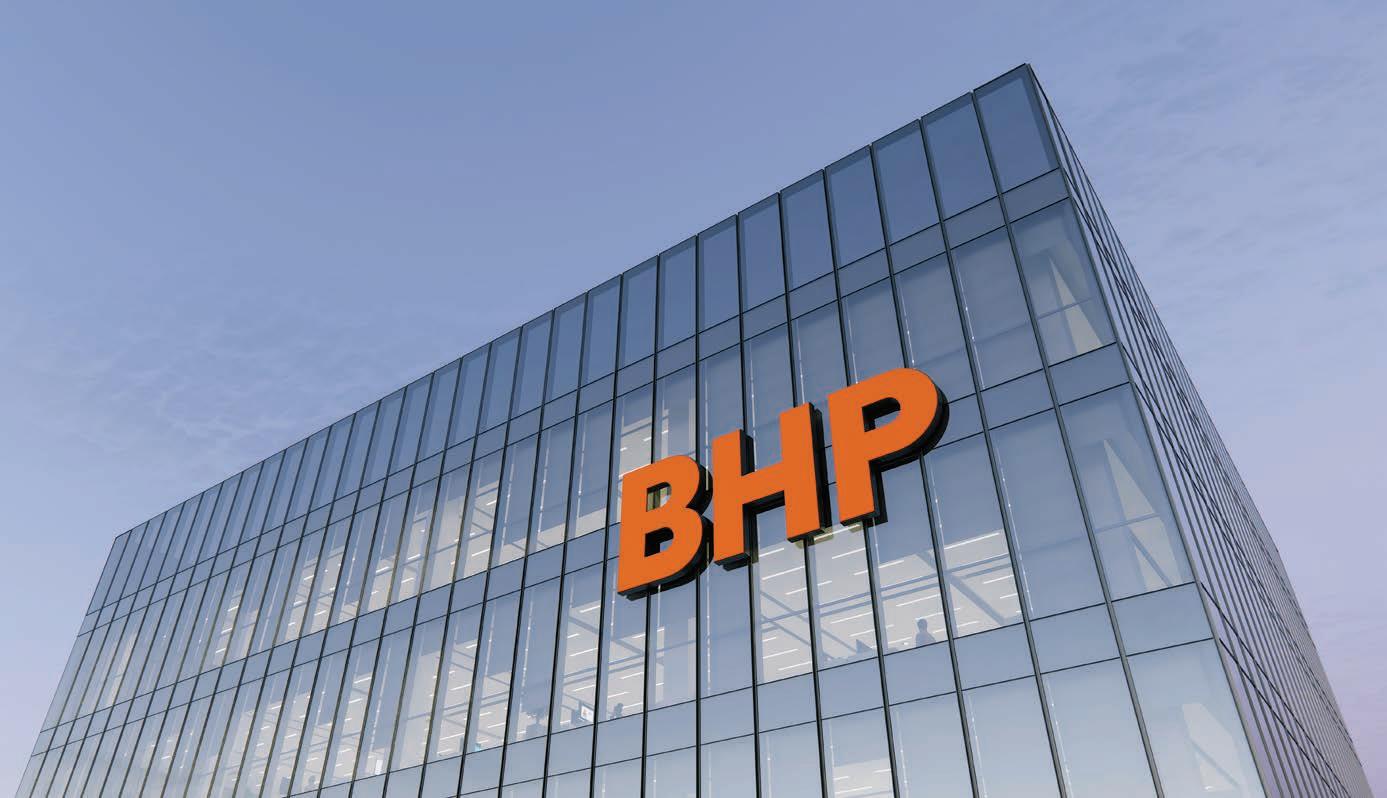
But Slattery told shareholders there was more to the decision than costs.
“Our decision is fundamentally based on seeking to high-grade our metallurgical coal portfolio to those assets that we believe are best positioned in terms of what the steel market will be looking for,” Slattery explained.
Slattery said the steel industry is after higher quality coking coal to relative to its carbon dioxide potential, which helps to optimise and decarbonise operations.
“Daunia and Blackwater are at the lower end of the quality spectrum for coal,” Slattery said. “Now they’re still great assets, but they’re not competitive within BHP’s portfolio.”
Copper – not lithium
Lithium is a future-facing mineral needed for batteries in electric vehicles, among other things. Demand for lithium is immense, and as the world leader in lithium production, miners operating in Australia are wellpositioned to capitalise on their country’s vast resources.
But, according to Henry, lithium isn’t for BHP.
“There has to be sufficient scale in the industry for it to be to be a needle-mover for us,” he said.
“There’s a number of dimensions for lithium that don’t quite match up with those requirements from a BHP perspective.”
Instead, the company is choosing to prioritise copper, another minerals the world needs to meet electrification and power-supply needs.
“Copper’s a bigger industry, both now and in the in the future. The underlying assets can be quite large scale, which is wholly aligned with BHP’s capabilities,” Henry said. “We believe that it’s going to afford better margin potential for the company over time.”
Henry said the company was also choosing to focus on nickel, another future-facing commodity.
“Electric vehicles actually use a lot more nickel than lithium, and we believe that nickel demand for batteries is going to be pretty durable,” he said.
“We have the world’s second largest nickel sulphide resource, we’ve got the world’s largest copper resource, we already have a great set of infrastructure in place.”
It’s the same story for hydrogen, according to Slattery.
“We don’t think that hydrogen is a commodity that best matches our capabilities,” she said.
“We don’t have a competitive advantage there, so likely we’ll look to others in the advancement of the hydrogen industry.
“We do think that hydrogen as a decarbonising technology … is some decades off at scale, and so we’re convinced on metallurgical coal having a very commanding presence in steelmaking for decades to come.”

The OZ acquisition
BHP announced its desire to acquire OZ Minerals late last year. After BHP made an increased $9.6 billion takeover offer, which followed a months-long back and forth between the two companies, the OZ board unanimously recommended that shareholders accept the deal.
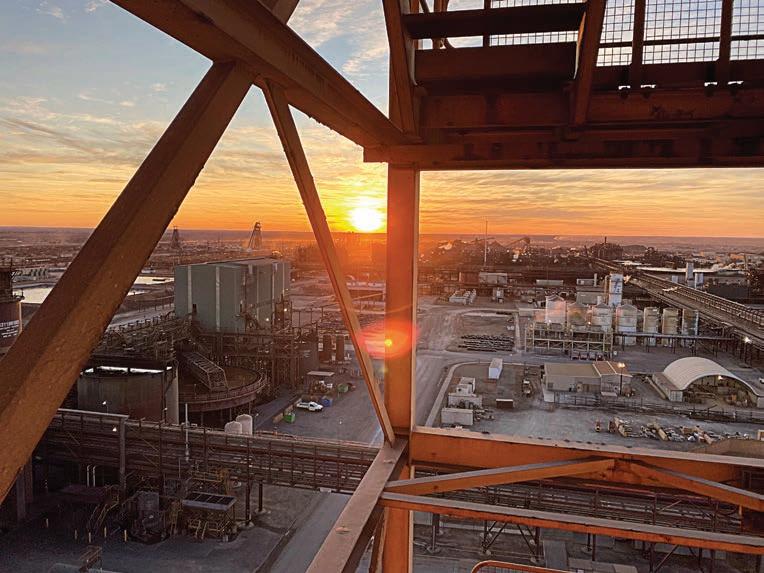
The takeover will allow BHP to consolidate its copper holdings in South Australia and nickel deposits in Western Australia.
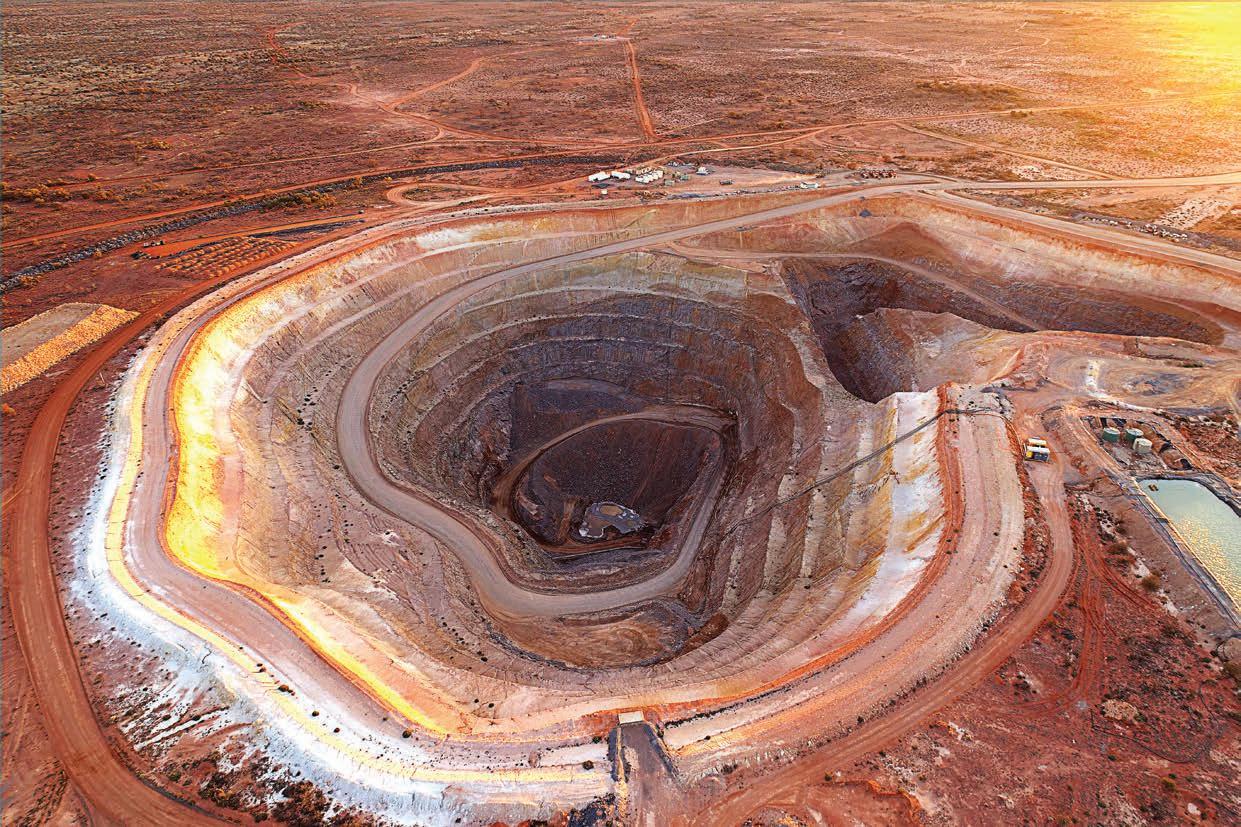
BHP chief financial officer David Lamont said OZ Minerals assets were complementary to BHP’s portfolio.
“There are synergies between our assets, particularly in copper and nickel, two of the commodities that we’ve
indicated are important for BHP’s future,” he said.
Same job, same pay Slattery took the opportunity at the Q&A to call out the Australian Government’s proposed job reforms, dubbed the ‘same job, same pay’ reforms.
The expected reforms will require employers to pay labour hire workers the same rate as direct employees doing the same job.
In December 2022, the Australian Bureau of Statistics revealed that the nation’s mining sector has a significant proportion of vacant positions compared to previous years. With a labour and skills shortage across the industry, it’s not clear exactly what effect the proposed reforms will have on the labour hire market.
“The mining sector enjoys that some of the highest wages in Australia,” Slattery said.
“While we certainly support the Government’s objective in seeking to protect low-paid workers, we don’t think that it’s relevant to the mining sector.
“And back to maybe a point I made earlier, it’s incredibly important for the resources sector in Australia to stay competitive in regard to labour costs
“We’re working to influence that piece of policy to minimise its effect on the mining sector.”
The shareholder Q&A shed light on
plans for the future. It’s not clear how recent and proposed policies will affect the company moving forward, but with its vast arsenal of assets and acquisitions,

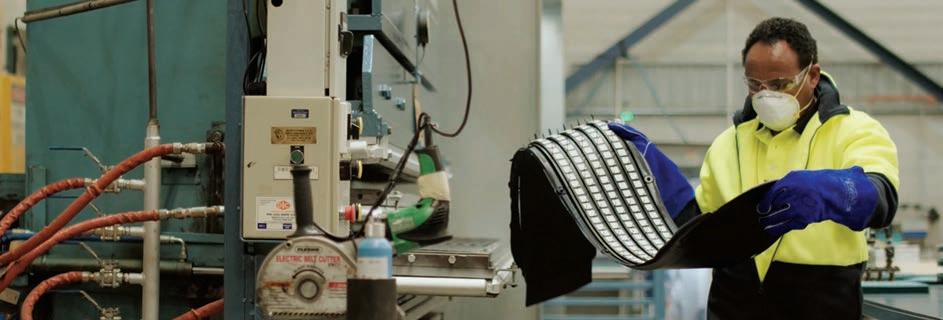
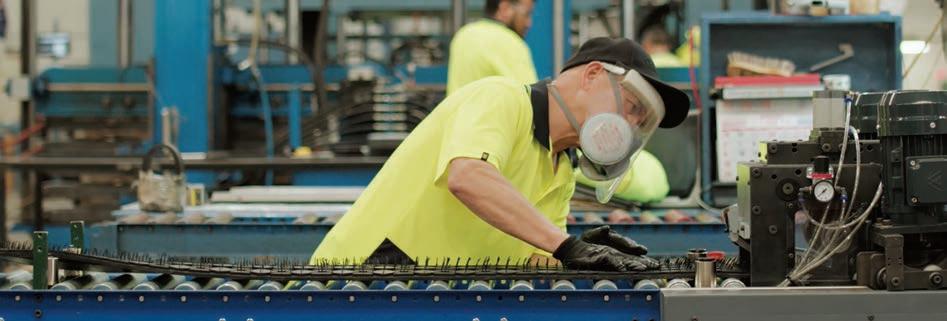
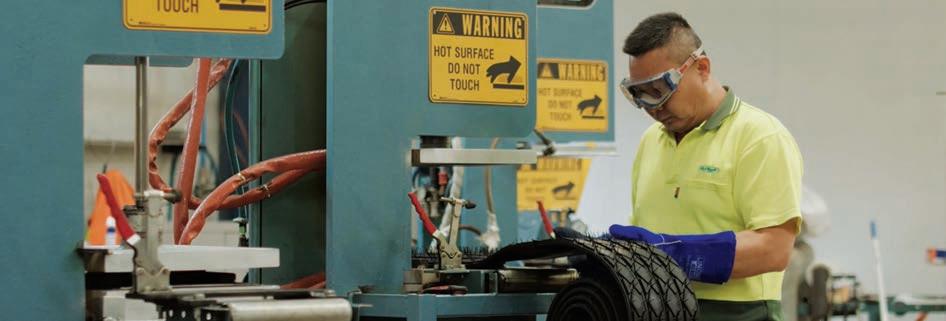
CONQUERING MINE REHABILITATION HOLISTICALLY
PROACTIVE ECOSYSTEM RESTORATION ENABLES POSITIVE SOCIAL, ENVIRONMENTAL AND ECONOMIC OUTCOMES FOR A MINING OPERATION. IT COULD BE CRITICAL TO A COMPANY’S BOTTOM LINE.
hile it’s always been a critical practice, ecosystem restoration feels like an emerging theme in the Australian mining industry.
It’s becoming more and more important in the environmental, social and governance (ESG) era for mining companies to be ‘responsible’ miners and stewards of the land with which they operate.
Dendra Systems ecology manager Guy Smith described ecosystem restoration as “a holistic and ongoing, multi-year process”.
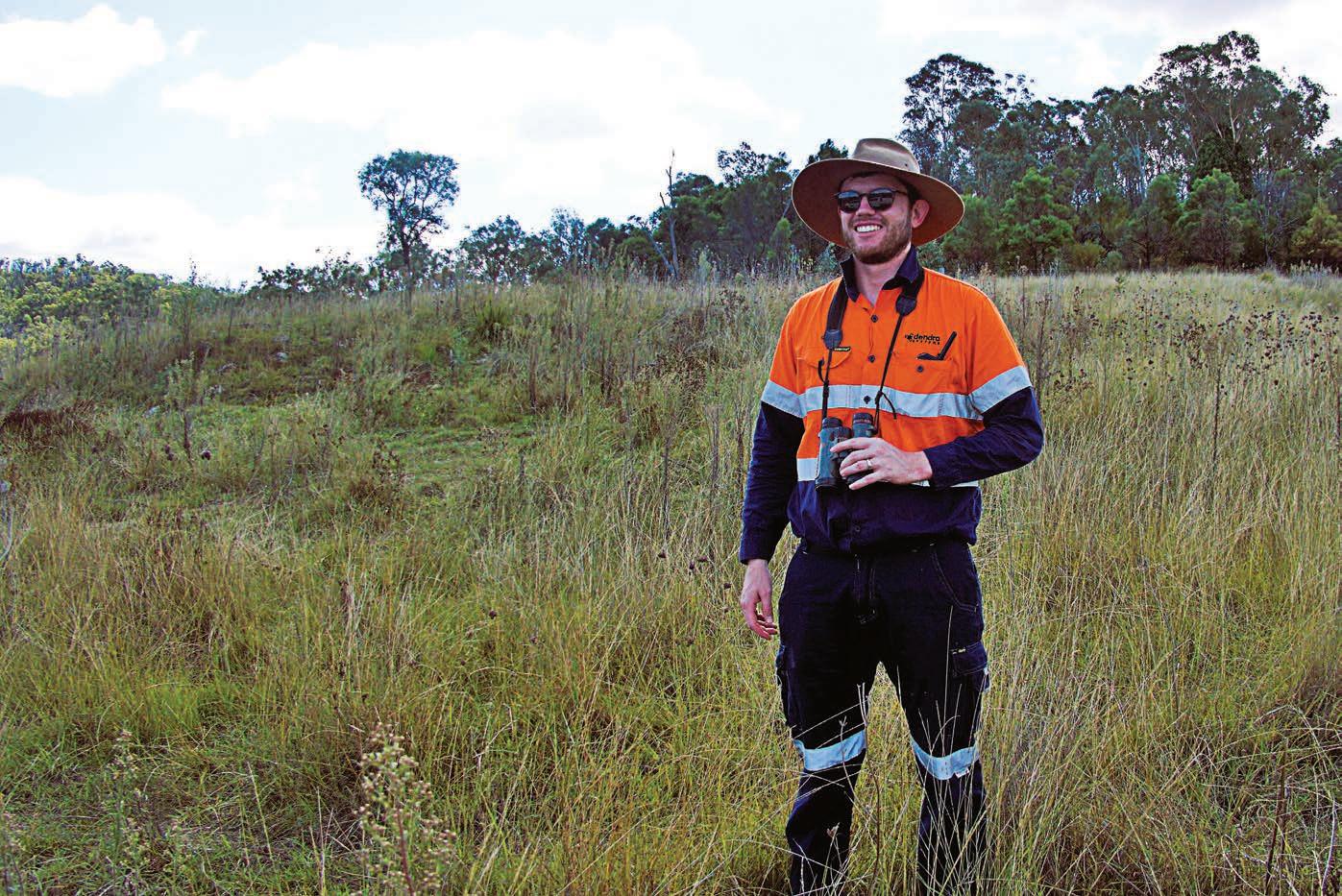
“Ecosystem restoration (in the Australian mining industry) is essential, probably now more than ever,” he told Australian Mining.
“It’s a holistic and ongoing, multi-year process that looks to restore, as closely as possible, the ecosystem that was removed or modified to allow the extractive mining process to be undertaken.
W“At a higher level, ecosystem restoration represents a sense of trust and assurance in the mining process, such that ecosystems are permitted to be cleared or modified under the condition that they and their unique features are re-established and restored post-mining.
“If done well, ecosystem restoration at a mine site can represent a level of ‘healing’ at both local and landscape levels and have tangible benefits for both communities and the natural environment.
“If done poorly, or not at all, it can have detrimental impacts on the local community and natural environment for an extended period of time and reflect poorly on all involved.”
The world is industrialising at pace, and more man-made structures are occupying the global landscape. But this doesn’t lessen the importance of ecosystems and biodiversity. With precise environmental planning and implementation, both can happily and healthily co-exist.
enabling fast, effective, transparent and scalable ecosystem restoration. It foresees the impact of infrastructure and industrial practices before structures are built and operations even commence.
The environmental technology company supports its mining clients with high-resolution full-site data capture and seeding solutions – through a fleet of custom drones – alongside its Dendra
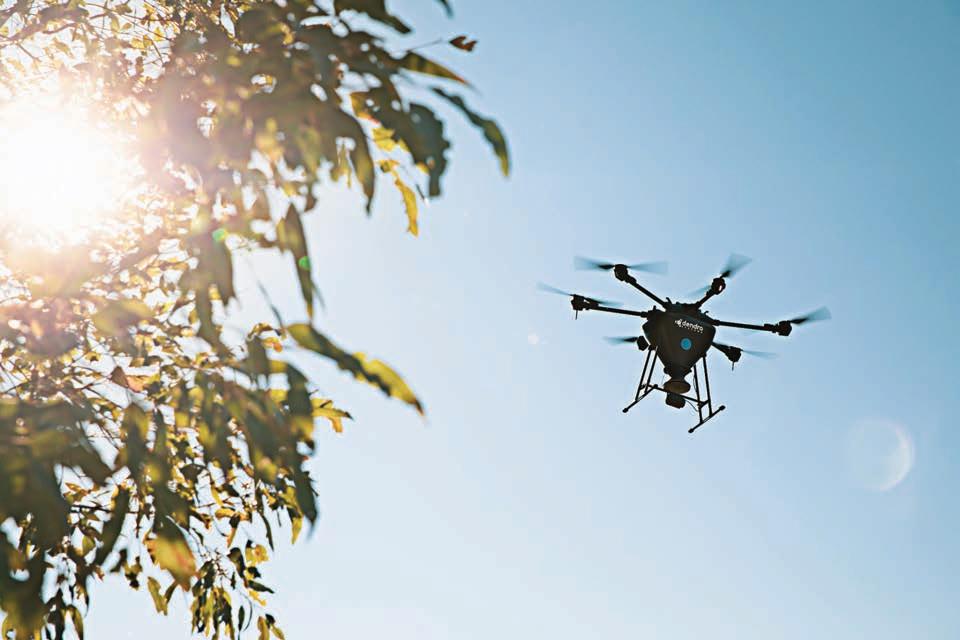
machine learning to provide a wide range of accurate, timely and actionable ecosystem insights at scale.
When it comes to mining, Dendra assures that ecosystem restoration is a process and methodology that encompasses the whole life of mine.
“The most representative and recognised part of mine rehabilitation –being the post-mining phase – is the tip
of the iceberg in terms of a restoration journey, and a lot of the work will have already happened in the planning and preparation stages of that restoration work,” Smith said.
“The restoration of a functioning ecosystem is a significant undertaking and requires experience and expertise at all stages.”
A mining company that is proactive about ecosystem restoration would commence the process well before they have even built their mining operation.
“The ecosystem rehabilitation process should start well before ground is broken,” Smith said. “A plan will identify high-level details such as the total areas to be first removed and then restored, and the specific vegetation communities that comprise this area should all be fully recorded.
“From this, seeds of key species can be first identified, then collected and prioritised for collection locally, if not, from the very vegetation being removed.”
Proactive seed identification and implementation establishes “genetic provenance” for the ecosystem in question, which promotes resilience and provides the seeds, and ultimately the restored vegetation communities, with the best chance of success.
This is particularly important given the mining industry is often subject to harsh conditions and nutrientdeficient soils.
“The message there is to plan well and be guided by evidence from both site-specific examples and relevant cases where they are available,” Smith said.
“Proactive ecosystem restoration steps I’ve witnessed include a series of rehabilitation trials, including different planting into different soil and substrate treatments.”
This includes the application of composts and other organic matter, along with retained topsoil at different application rates. Results are then compared and contrasted, with the best outcomes applied to the next rehabilitation areas.
Smith said ecosystem restoration “is a constant multi-year learning journey”.
“Alongside planting, proactive ecosystem restoration can involve habitat replacement trials to install permanent habitat features within rehabilitated ecosystems,” he said.
“This could include installing hollowbearing trees and nesting boxes, rock piles and logs to the ground layer. This is all part of a holistic process rather than just planting trees and hoping for the best.
“The addition and monitoring of fauna habitat features encourages native fauna recolonisation, reintroduces the ecosystem services they provide, and promotes a self-sustaining system.”
Proactive restoration enables positive social, environmental, and economic
outcomes. What begins with truth, transparency and environmental safety can evolve into a positive legacy and future financing gains.
“Ecosystem restoration builds trust in the community, with successful restoration works enabling ecosystems to persist long after mining operations have ceased,” Smith said. “It leaves a positive legacy for all to see and for all involved.
“The flip side is a tainted legacy. The repercussions of not implementing and maintaining successful ecosystem restoration has a lasting impact and leaves a tainted reputation for the parties responsible.
“If you’re looking for new project financing and you’ve got poor legacies or are battling legal claims over mismanaged rehabilitation, that affects you commercially and financially.”
In supporting its clients across the whole life of mine, Dendra harnesses the latest technologies and innovations to ensure it can capture and analyse an entire mine area in high resolution, including difficult-to-access locations.
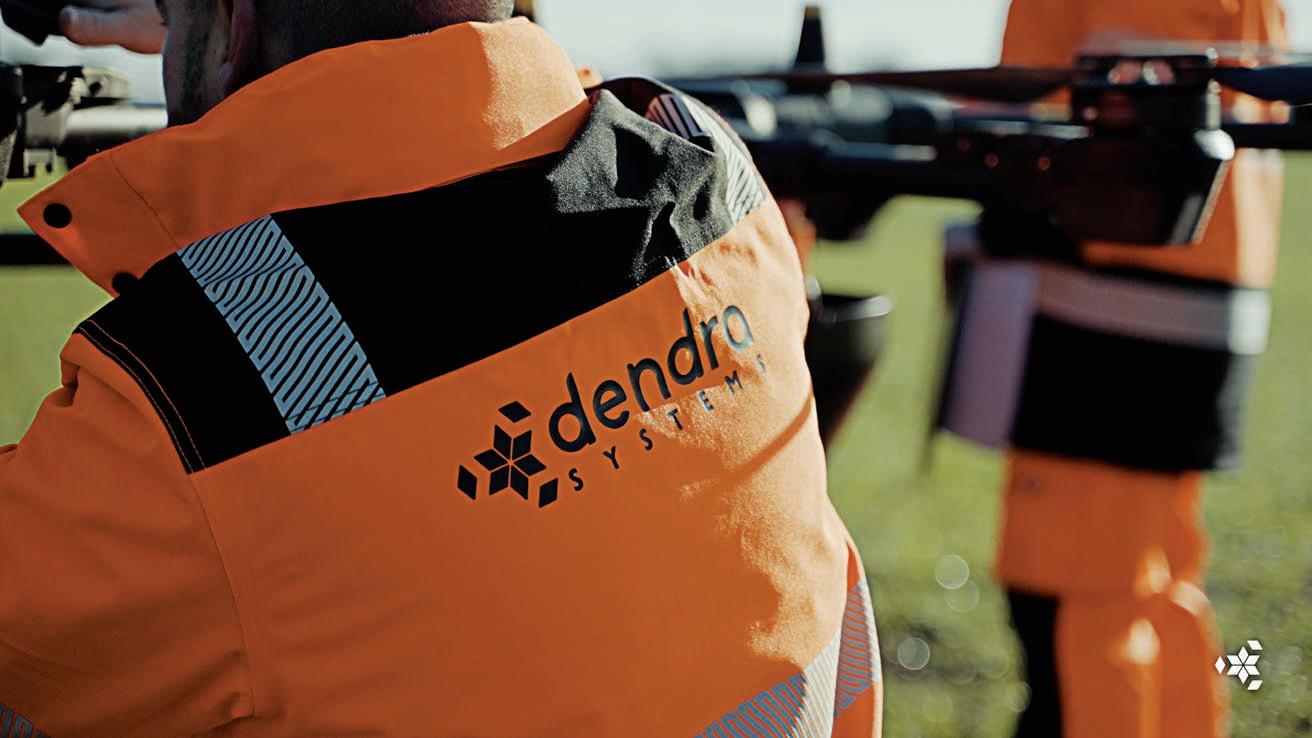
A regular monitoring cycle ensures issues like erosion and weed infestation can be identified and managed before they develop into more costly challenges.
“Dendra operates a fleet of custom seeding drones that spread a biodiverse mix of native species (specifically selected for a site) over difficult-tonavigate terrain,” Smith said.
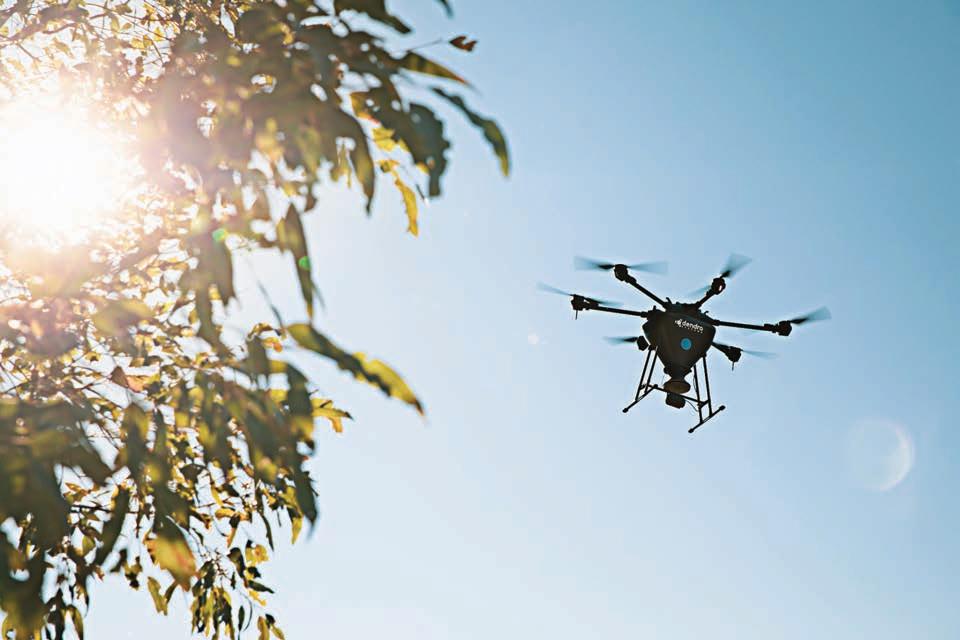
This is where insights from the Dendra platform come to the fore.
“Once established, these ecosystem restoration efforts and the resulting yearon-year trends are monitored within the Dendra platform using data collected from our custom drone-based set-up that flies over the entire area in question and captures the environment in high-res and multispectral imagery,” Smith said.
“The data obtained is then analysed by a unique combination of ecologyaware machine learning supported by a team of experienced ecologists.
“Analysing a rehabilitation site using Dendra’s platform allows land managers to see the full picture literally and have complete transparency across their entire ecosystem rehabilitation area.
“This is in contrast to traditional methods, where small sub-sets of the area would typically be surveyed and the rest extrapolated based on those results.”
Smith said having complete transparency and vision throughout an entire mine site enables clear evidencebased decisions to be made across all aspects of restoration to ultimately achieve the best results.
The ability to combine deep domain expertise with the latest technology means Dendra is strongly placed to support the mining industry’s growing environmental quandaries. It’s a reality only likely to snowball as the ESG revolution further intensifies. AM
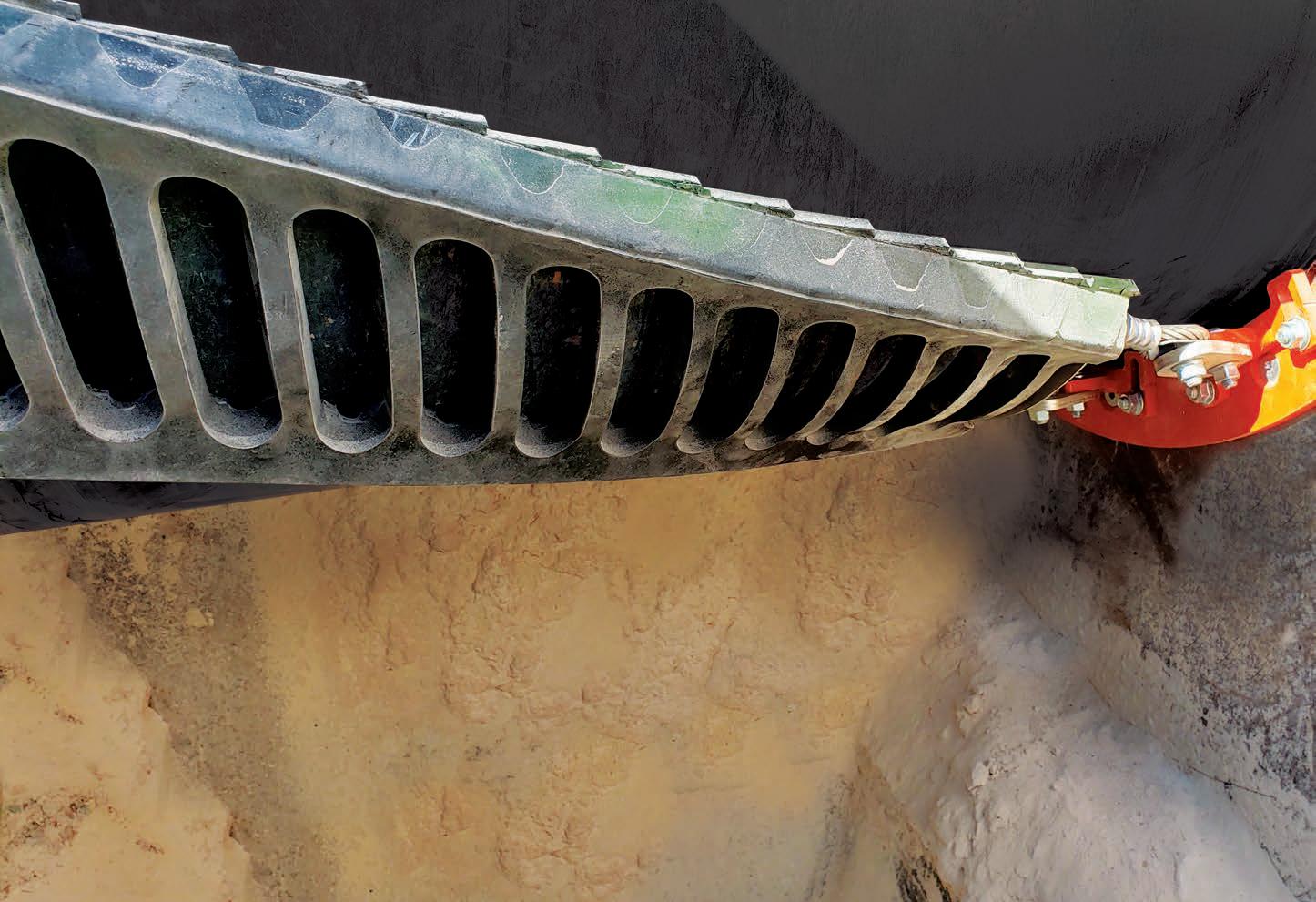
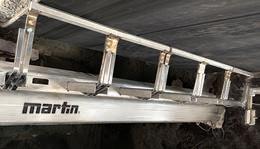

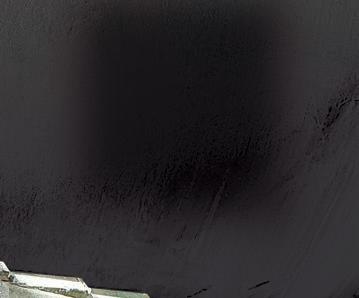
EMBRACING THE UNKNOWN
Change is as rapid as it is constant. The push toward digitalisation and automation – the focus on Mining 4.0 – puts pressure on industry players to keep up and not be left behind.
But with so much information and so many solutions on the market, which is the best one for your specific problem?
How can you ensure any changes you make deliver significant benefits not just to your operation, but to your shareholders and stakeholders more broadly?
And how can you position yourself to attract new, diverse talent that is future-oriented and looking for purposeful employment?
The only way to be is bold Mipac is among the global leaders in operational technology, control systems and engineering services.
From industrial automation and software solutions to advanced process control, process optimisation, electrical and instrumentation engineering and consulting, Mipac works with clients around the world to design, build, operate and optimise all stages of their mining operation.
Since its inception 26 years ago, the company has been characterised by its boldness and willingness to tackle complex challenges head on. It’s something managing director Eddie De Rivera says is in the team’s blood.
“From the very beginning, our engineers have been passionate about working in close collaboration with our clients to deeply understand the challenges they’re facing,” he said.
“We’re not afraid of venturing into the unknown to find the best solutions for our customers, and innovation is a value we bring to everything we do.
“Because our team comes from a range of industries and has both extensive onground experience and technical knowhow, we can help our clients see the bigger picture and can work with them to provide solutions that not only deliver increased revenue but also safety and productivity gains, positioning them for sustainable success for the long-term.”
A global approach
With over 100 clients around the world, including many of the industry’s biggest players, Mipac is proud of its longstanding relationships and the difference it has made across the globe.
“Some of our biggest projects from the last few years have included First Quantum’s Kansanshi copper smelter
and the Cobre Panama mega project, which included a 300MW power station and a large copper concentrator,” De Rivera said.
“These are exciting projects in which we get to leverage technology, come up with sophisticated and out-of-thebox solutions, and go beyond what is expected of us to deliver the best solutions for our clients’ needs.”
Over its history, Mipac has worked on over 650 projects worldwide, from Australia to the Americas to Europe to Asia. It’s a legacy that De Rivera is proud of, and one he attributes to the team’s genuine care for its clients and its people.
“Mipac has always been a close group of engineers that’s very passionate about its clients and its clients’ solutions,” he said. “Our team truly cares and I believe that’s what sets us apart.
“We have a can-do attitude and go above and beyond to develop solutions for our customers, even if that means developing something new internally.”
Software developed collaboratively to meet challenges
One of the ways Mipac has provided innovative solutions to its clients’ needs is by developing a suite of software solutions that address common industry challenges. In most cases, this software
has been developed in close collaboration with a client, ensuring the end product is fit-for-purpose and adaptable to further developments.
One of these is TCard, an operations management tool to enhance plant stability through teamwork, structure and insight. Another is MPA, a suite of apps that manage variability and enable predictive operations.
But growing its software offerings is only one of Mipac’s many ambitious goals for the future.
“My vision for Mipac is to grow into new regions and to utilise the advancement in technology to provide new information system solutions for our clients,” De Rivera said.
“The advancement in technology is opening up new opportunities for Mipac to turn data into information and allow our customers to understand how their plants are operating and what they need to do to improve the performance of their plants.”
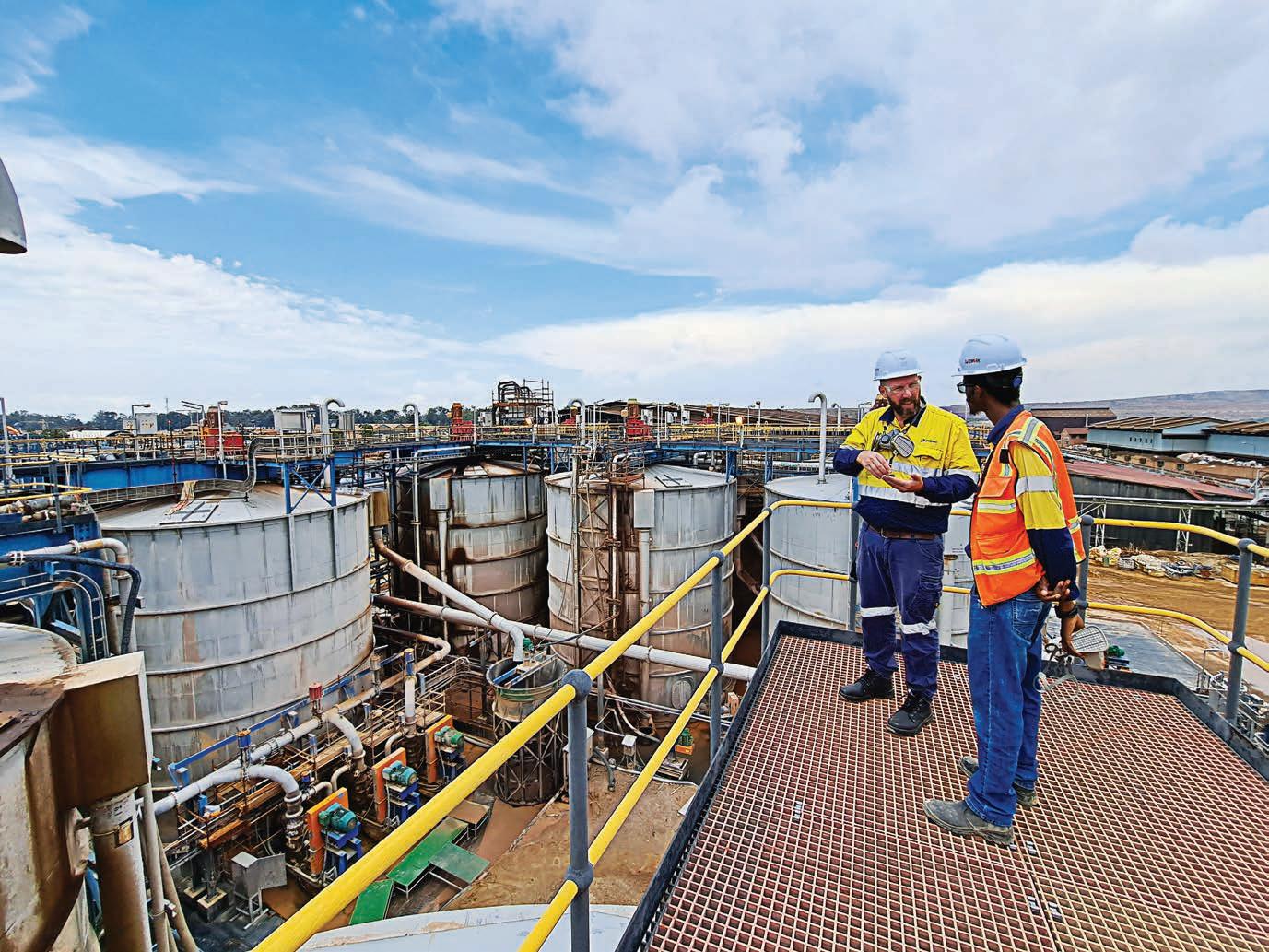
Digital transformation in the mining industry is no longer optional – it is happening whether people are ready for it or not.
Mipac is committed to not only riding the waves of change, but to taking its clients with it to make the most of the many new possibilities and opportunities that exist. AM
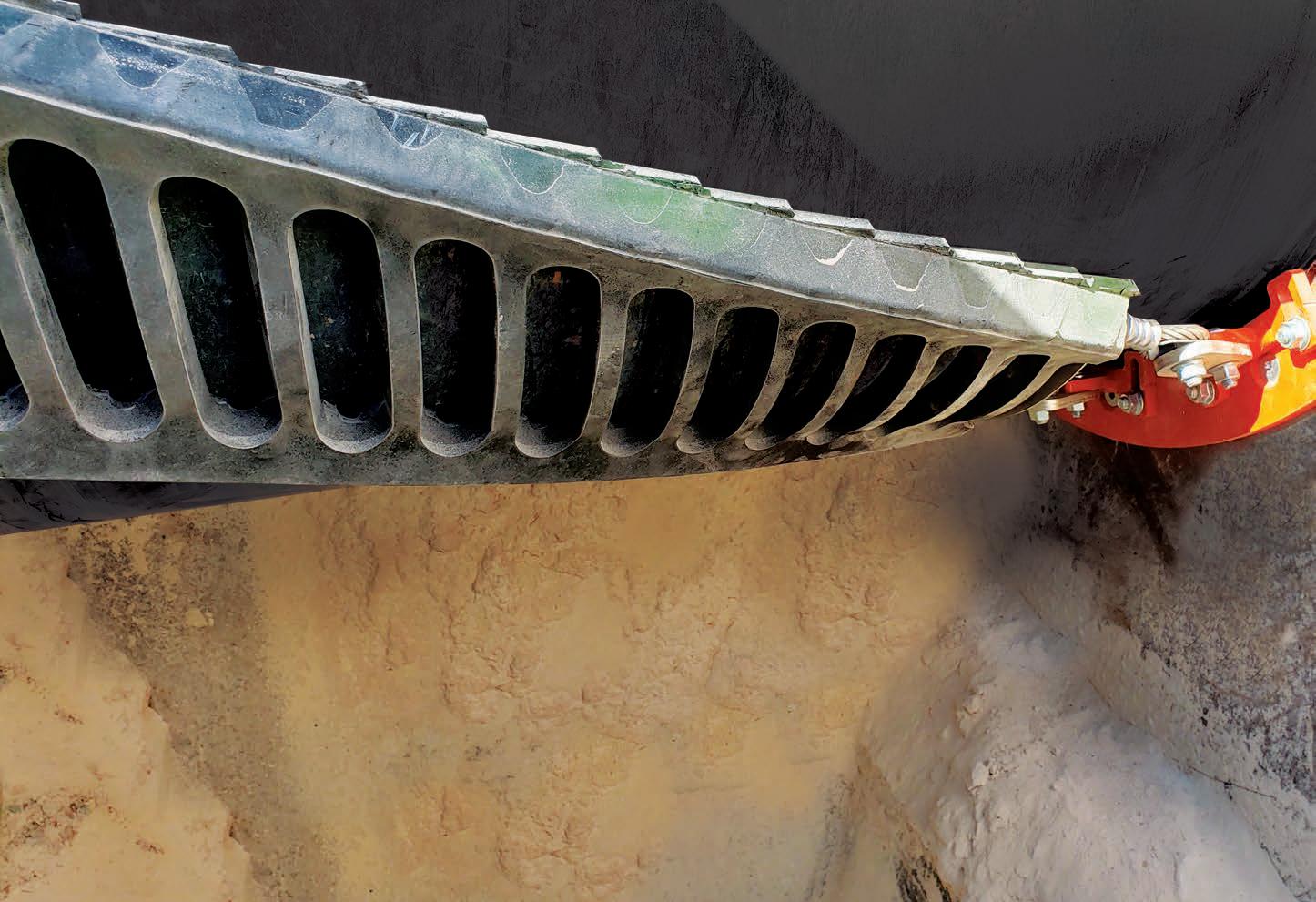
DYNAMIC UNDERGROUND SAFETY
MATRIX DESIGN GROUP PROVIDES CUSTOMISED SAFETY SOLUTIONS WITH ITS SOPHISTICATED IECEX-CERTIFIED INTELLIZONE PROXIMITY DETECTION SYSTEM.
As underground mining continues to evolve, with the ever-present emphasis on efficient, productive and sustainable operations, innovative safety solutions have never been more important.
Headquartered in the US, with offices in Queensland and New South Wales, Matrix Design Group provides its underground mining customers with sophisticated safety solutions that include the award-winning IntelliZone proximity detection system (PDS).
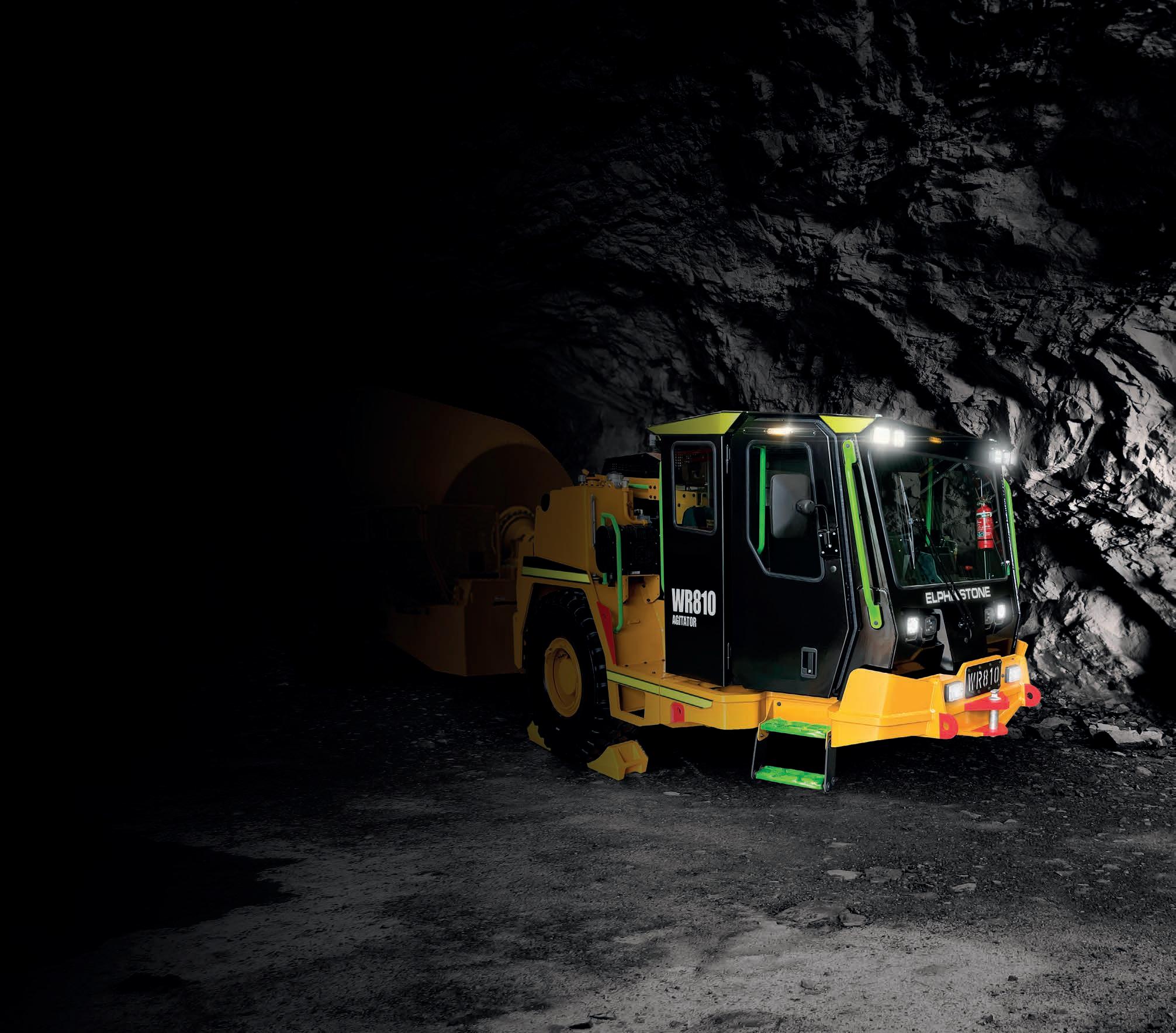
“Matrix develops, distributes and supports innovative and operator-friendly technology solutions that enhance productivity and improve safety in underground mining environments across the world,” Matrix vice president of international operations Wes Chitwood told Australian Mining
“We formed Matrix Design Australia in March 2022 to service and support the Australian and New Zealand markets with our industryleading PDS technologies, which we continue to innovate.”
IntelliZone is the most implemented PDS solution in the US and is rapidly expanding globally, with a strong and growing position in South Africa and entry into emerging markets in Europe, Asia and South America.
“As we expand into new markets, we learn, and as we learn, we innovate and improve, which is benefit to all of our customers globally,” Chitwood said.
“With their incredible achievements and innovations in mining, we are very excited to partner with Australian mining companies to help enhance safety and continue the advancement of PDS technologies.”
IntelliZone, which features patented SharpZone technology, is designed for use on various types of underground mobile equipment, allowing users to create customisable caution, shutdown and operator zones. It has been fully IECExcertified (International Electrotechnical Commission explosive atmospheres) for underground coal in Australia and Queensland since 2018.
IntelliZone technology detects workers in low-visibility or obscured lineof-sight locations and zones, automatically extending or contracting based on mobile equipment speed.

Significantly, unlike bubble-zone systems, IntelliZone’s shaped-zone technology minimises nuisance alerts without affecting production.
“For the Australian market, it is clear that IntelliZone represents an ideal third-party PDS technology solution for use on underground mobile equipment regardless of the OEM (original equipment manufacturer),” Matrix Design
Group Australia and New Zealand general manager Pieter De Klerk told Australian Mining
“Mine regulators are recommending that PDS technology be fitted on underground mining equipment, and we believe IntelliZone is the best choice for mine operators given not only its advanced capabilities, but also due to its lowest-in-industry downtime, ease of maintenance and repair, and data-rich log files and reporting.
“In essence, we can create a safe zone off the machine, ensuring an operator working under difficult conditions can control, for example, a continuous miner positioned beside the machine yet remain out harm’s way.
“The ability for a continuous miner operator to stand close to the machine and remain in a safe area while undertaking work is a huge advantage of the IntelliZone PDS technology.”
In 2021 Matrix won the US National Institute for Occupational Health and Safety’s Mine Safety and Health Technology Innovation Award for its enhanced IntelliZone system, which is now standard on the PDS.
All components of the IntelliZone system are purpose-built for the underground mining environment and are extremely durable and simple to operate.
The IntelliZone system ships with a range of key components, including a
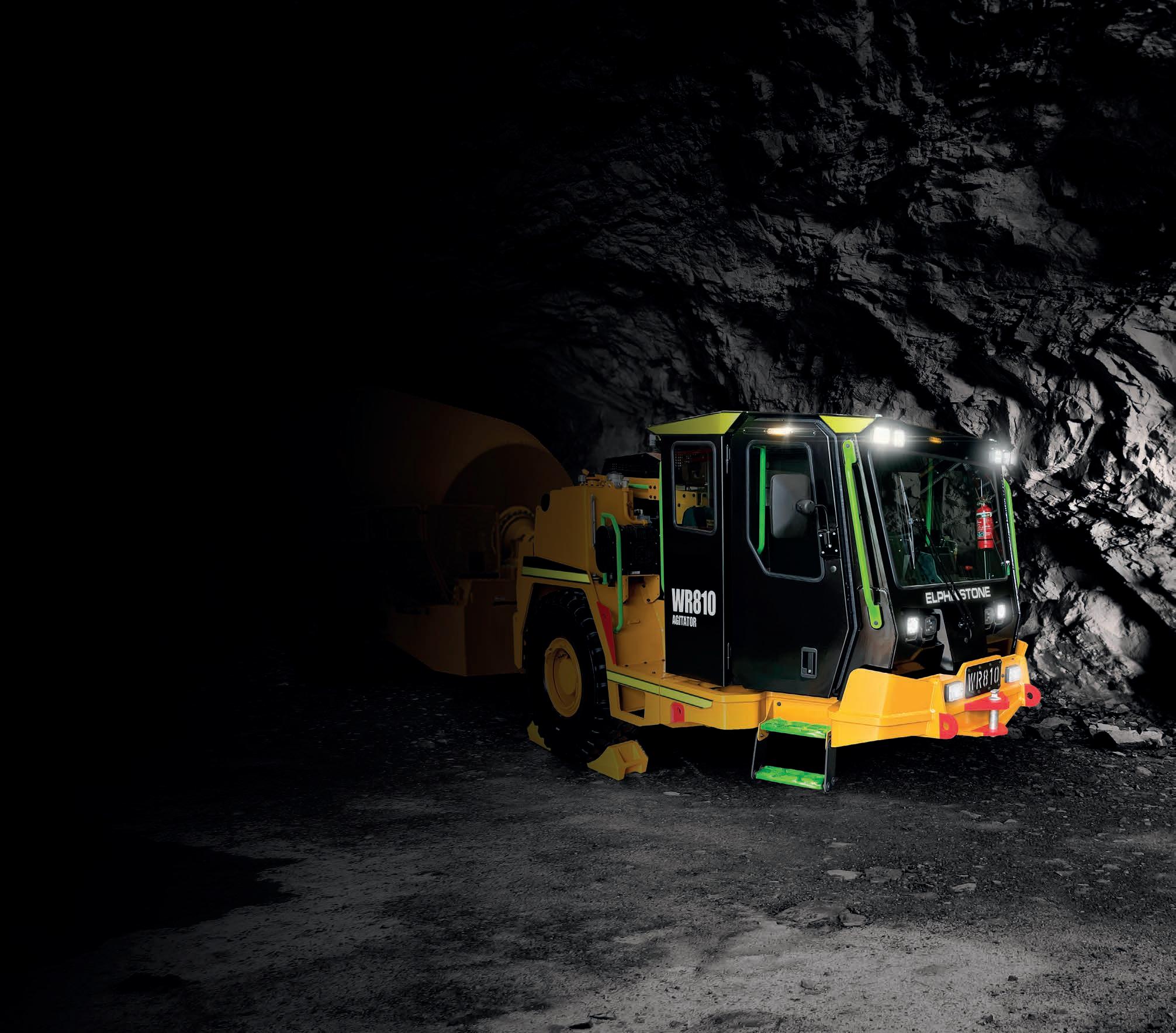
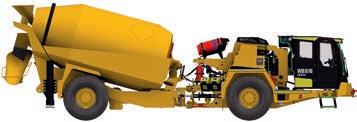
WEIR WORLDWIDE WOMEN
Starting a new job in the midst of a pandemic was a daunting prospect for anyone, let alone if that job opportunity came when your state was closed off from the rest of the world. But when Kristen Walsh was offered the position of regional managing director, Asia Pacific at Weir Minerals, she took it all in her stride.
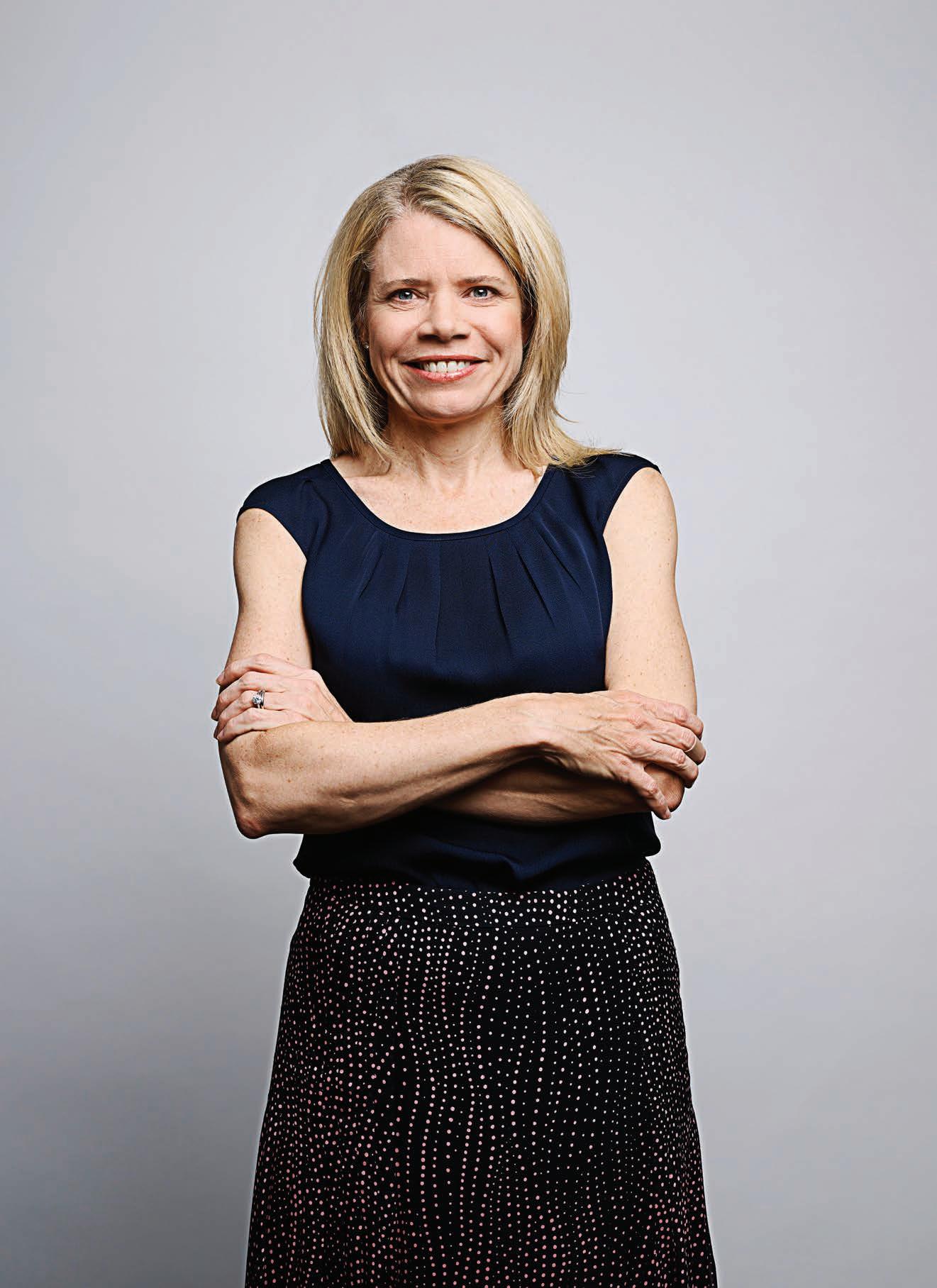
“For the first three or four months of my role, the borders were closed in Western Australia,” she told Australian Mining. “So I took that as an opportunity to visit customer sites to listen and learn about customer challenges.”
These early days at customer sites set the tone of Walsh’s leadership at Weir Minerals.
“I learnt a lot about the challenges that each customer faces, and then I got to observe how our team interacts with our customers to solve problems,” Walsh said.
“Seeing that, and also observing the Weir culture of high performance, inclusive and wellbeing that matches our brand promise, was really exciting.
“Even when I was first applying for the role, I found the Weir values strongly resonated with me and that has only strengthened since coming aboard.
“Weir Minerals is focused on providing an inclusive employee environment that is fundamental to delivering our strong customer value proposition.
“I’m an engineer at heart and I have a strong interest in innovation, and I really feel as though that is what we do at Weir Minerals every day. We ask ourselves how we can add value to our customers and create a workplace
culture that is inspiring for employees.”
A key initiative for Walsh has been to champion regional participation in the global Weir Women’s Network (WWN).
An affinity group dedicated to the attraction, retention and continued development of women in Weir, the WWN is open to all women at the company, and their allies, who are devoted to championing the work of the network.
First launched in the US, the WWN has since expanded to chapters all over the world.
“When I joined Weir Minerals, we didn’t have an active Australian chapter of the WWN,” Walsh said.
“A strong focus on gender equity is really important to me, so I was keen to figure out how best to drive visible leadership at Weir.
“One of the things we do at Weir Minerals is we set targets to increase our female representation, and in 2022 we increased our representation from 14 per cent to 16 per cent and we’re on a journey to increase that further.
“The WWN is one of our formal initiatives we have undertaken to increase our representation. Today we have established chapters in Australia, India and Malaysia.”
An important aspect of the WWN is ensuring that men are involved as allies.
“Men attending WWN meetings and hearing the stories and experiences of women is incredibly important,” Walsh said.
“It’s also important that men are encouraged and supported to model a good work–life balance so that we can all equally share the responsibilities of work and life.”
Walsh said that she was proud of the success of the WWN expansion.
“When you’re working in an organisation that has a low representation of females, you’re often the only female in the room,” she said. “And sometimes you may not necessarily feel very welcome at the table.
“For me, it’s important to ensure there are visible women leaders and allies in the workforce that are proactively creating networks of support.
“If there is a career path that someone is interested in, they’re more likely to
FOSTERING A SAFE AND INCLUSIVE WORKPLACE ENVIRONMENT IS IMPORTANT IN ANY COMPANY, BUT WEIR MINERALS HAS TAKEN ON THE TASK WITH PARTICULAR GUSTO.
GENDER EQUALITY
go into it if they can see people like themselves succeeding in it.”
Weir Minerals is also a strong supporter of the Women in Industry awards and is sponsoring the Excellence in Mining award at this year’s ceremony.
The Women in Industry Awards recognise outstanding women from across a range of industrials sectors; for example, those who work in mining, transport, manufacturing, engineering, logistics, bulk handling, waste management, rail and construction and infrastructure – all sectors that are traditionally maledominated.
The awards are an opportunity to recognise the women who are driving change in industry, and in doing so breaking down barriers and creating new
The Excellence in Mining award recognises an individual who has made a positive contribution to one of the many facets of the mining industry, and Weir Minerals couldn’t be happier to sponsor it.
“I feel really proud of the company being a sponsor,” Walsh said. “And I think that the Women in Industry Awards is such a great opportunity to tell stories that are inspiring to future generations.
“I always feel inspired hearing the stories of how women have got to be where they are and achieved what they have.
“It’s for that very reason that I believe that awards like the Women in Industry are so important, to acknowledge and celebrate the journey that people have been on to get where
One of Weir Minerals’ primary goals is to be an inclusive workplace, and the company is well on its way.
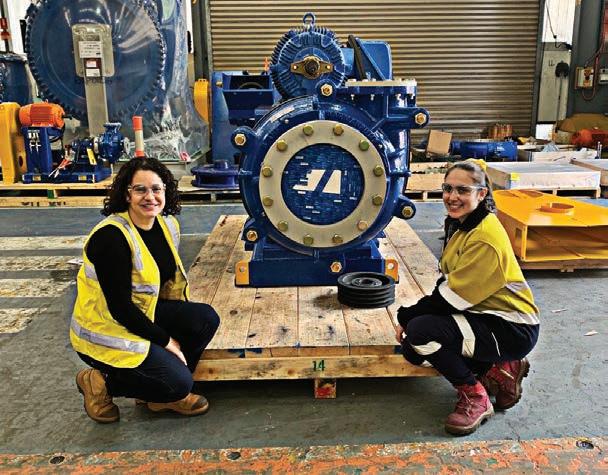
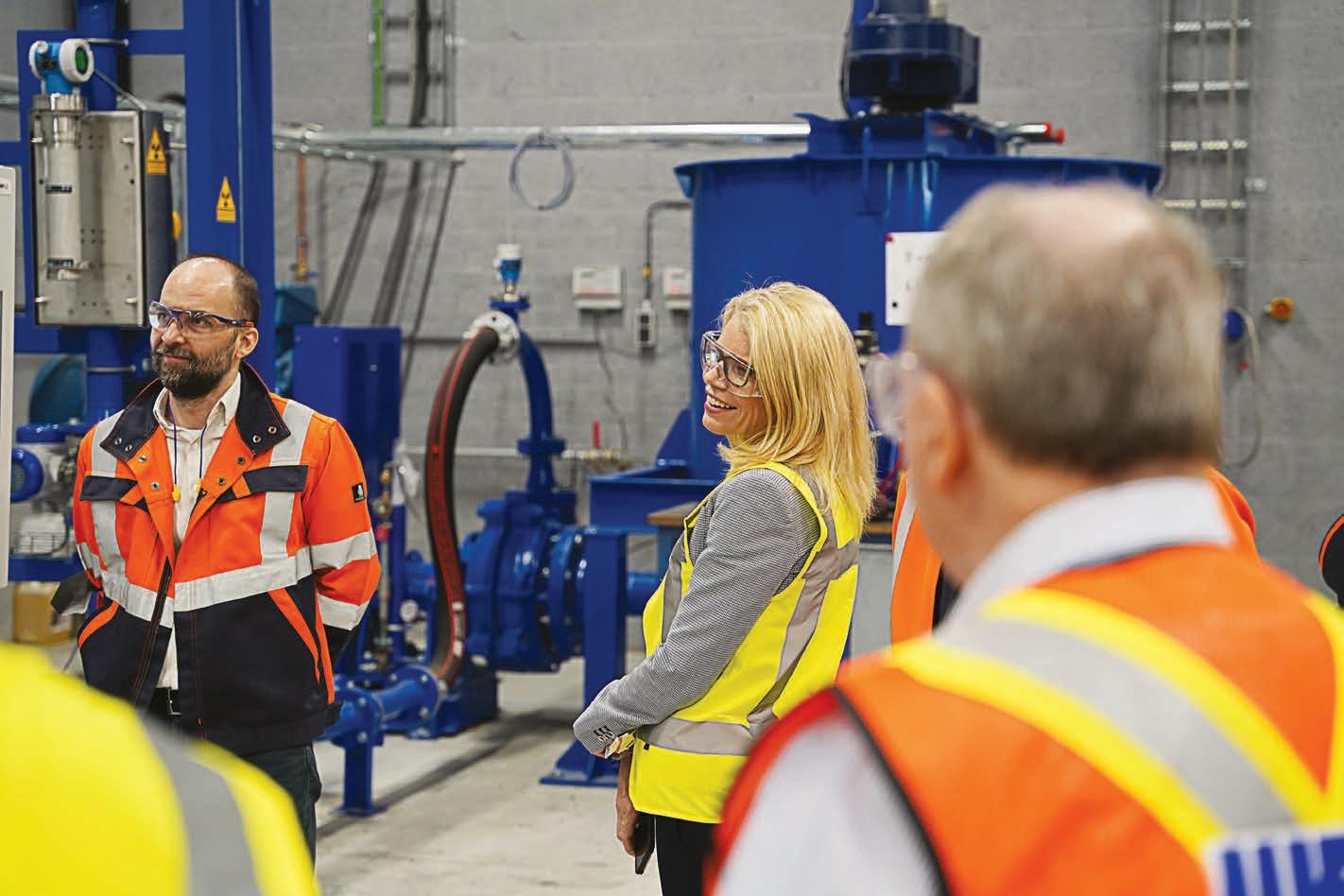
“We want our workforce to represent the community in which we live,” Walsh
amount of work to do around education and understanding.
“What we must keep in mind is that we’re on this journey together to try to build a common set of expectations of
WEIR MINERALS IS FOCUSED ON PROVIDING AN INCLUSIVE EMPLOYEE ENVIRONMENT THAT IS FUNDAMENTAL TO DELIVERING OUR STRONG CUSTOMER VALUE PROPOSITION.”KRISTEN WALSH (RIGHT) AT WEIR’S TEST CENTRE FACILITY IN VENLO, NETHERLANDS. WEIR MINERALS GRADUATES FRANCESCA DE LUCA (LEFT) AND JASMINE SCLOSA (RIGHT) AT WEIR MINERALS’ FACILITY IN ARTARMON, SYDNEY.
TAKEOVER TARGETS
THIS YEAR HAS SEEN A STRING OF TAKEOVER OFFERS HIT THE ASX AS MINING COMPANIES BATTLE IT OUT TO ACQUIRE MORE RESOURCES. WHAT HAS PROMPTED SO MANY BIDS?
The word ‘takeover’ has been flung around the resources sector all year, so much so that a new announcement each week has seemingly become par for the course.
But there has to be a reason for this uptick of bids. Australian Mining takes a closer look.
What is a takeover bid?
Put simply, a takeover bid is the most common way for one company to gain control of another company.
There are two types of bids: offmarket, whereby a bidder makes individual offers directly to target shareholders to acquire their shares; and on-market, whereby the bidder places a buy-order on the ASX trading platform to buy all shares.
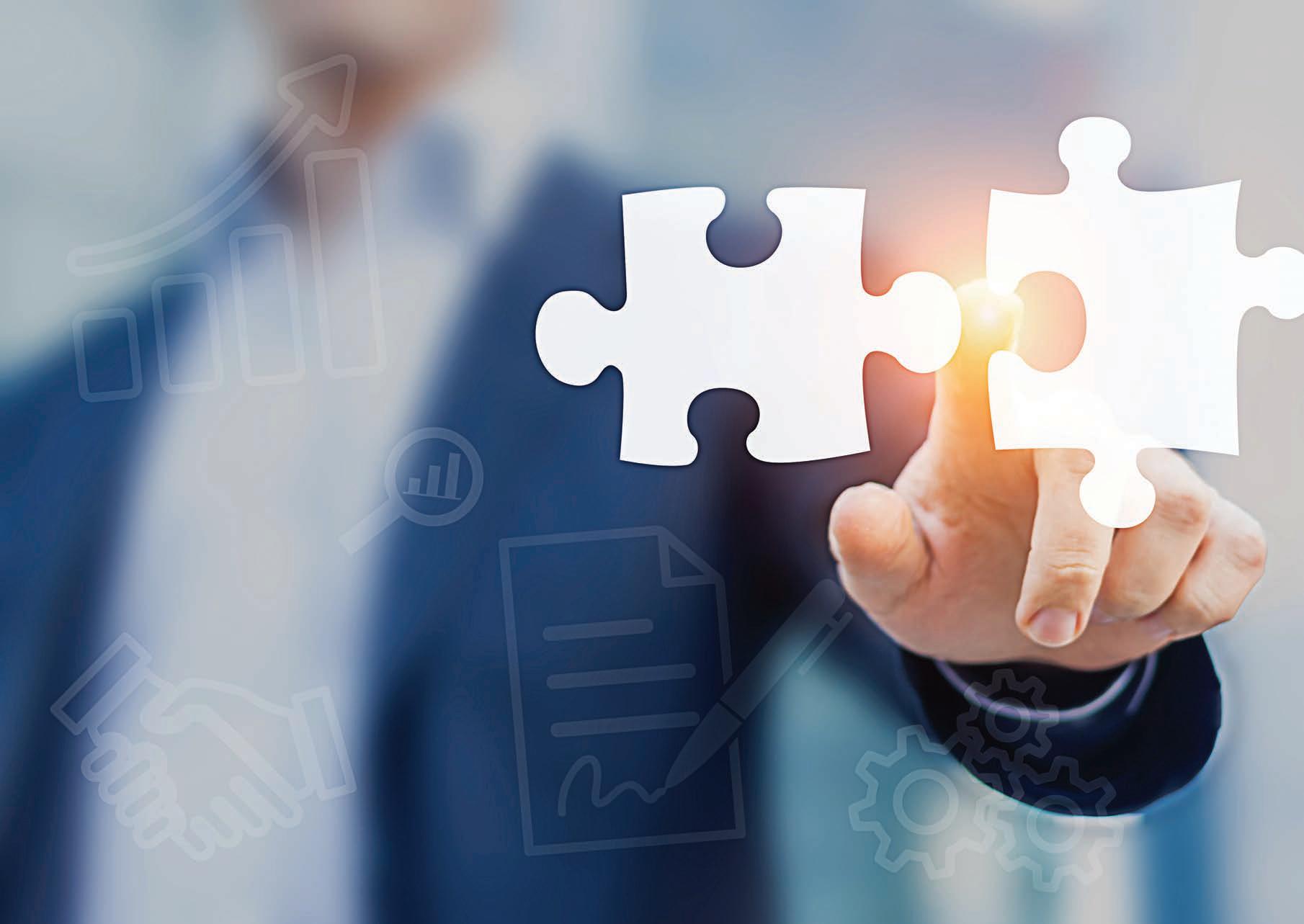
There are many reasons one company may want to purchase another – the target may have assets that would expand the bidder’s portfolio, or perhaps a majority shareholder is dissatisfied with the way the company is being run.
Lately, takeover bids in the mining sector have focused on assets from critical minerals to gas, as companies battle to control more assets that will put them closer to the forefront of the green energy transition.

TAKEOVER BIDS IN THE MINING SECTOR HAVE RECENTLY FOCUSED ON ASSETS FROM CRITICAL MINERALS TO GAS.
Critical minerals
When Wyloo Metals made its $760 million bid for Mincor Resources in March, the company had one thing on its mind: nickel.
A critical mineral, nickel is widely used in rechargeable batteries and nickel–metal batteries used in hybrid vehicles.
It is also a useful mineral for Wyloo to mine, in accordance with its actively green policy.
Wyloo is owned by Andrew Forrest, who founded Fortescue Metals Group and its subsidiary, Fortescue Future Industries (FFI).
Like Wyloo, Fortescue and FFI have ambitious environmental targets, including supplying green electricity to the entirety of Kenya’s grid and a green hydrogen production facility in Geelong, Victoria.
According to the International Energy Agency (IEA), the demand for critical minerals hit a peak in the mid2010s and has kept climbing, owing to the world’s shift towards clean energy.
“Electric vehicles (EVs) and battery storage have already displaced consumer electronics to become the largest consumer of lithium and are set to take over from stainless steel as the

For Wyloo Metals, new nickel assets will allow the company to “discover the metals needed to build our future”.
“Our commodity focus reflects changing consumption habits associated with rising global standards of living and the transition to a low-carbon future,” Wyloo said on its website.
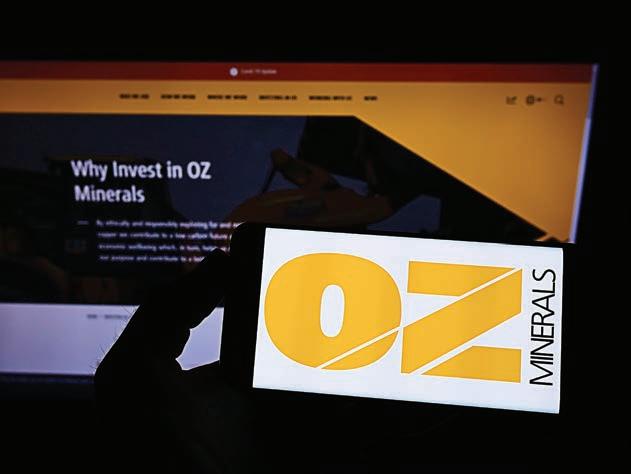
BHP has also been looking to get its hands on more nickel. In November 2022, a $9.6 billion takeover deal allowed the Big Australian access to OZ Minerals’ nickel deposits in Western Australia.
Arguably the most well-known takeover deal from the past year, the OZ Minerals board unanimously recommended the bid (after it was increased from its original $8.4 billion) and allowed BHP to consolidate plans for major nickel operations.
The acquisition also allowed BHP to link its Nickel West mine in WA with OZ’s nearby West Musgrave copper-nickel operation.
With the push for a net-zero mining industry only growing stronger, this probably won’t be the end of the takeover deals in the critical minerals sector.
CRITICAL MINERALS ARE USED TO MAKE BATTERIES IN ELECTRIC VEHICLES AND HAVE BECOME THE SOURCE OF MANY TAKEOVER BIDS.
The mining and energy sectors have always worked side-by-side, with the mining industry supplying the resources the energy industry needs to operate. But this year, it has been the mining companies that are after something from the energy sector – and that something is the companies themselves.
2023, four companies fought it out for ownership of Warrego Energy, based in WA’s Perth Basin, and two of them were mining companies.
And while Gina Rinehart’s Hancock Prospecting emerged as the winner, Mineral Resources (MinRes) put up a good fight.
north of Perth.
The site is said to be a source of inexpensive gas for power generation and mineral processing, which will prove especially important as the resources sector faces a more difficult fossil-fuel market in coming years.
With the war in Ukraine exacerbating the energy crisis, control of and access to gas assets has become all the more important, which is why MinRes didn’t stop its takeover efforts when it was knocked back by Warrego.
The company instead turned its attention to Norwest Energy, which initially rejected the $403 million bid from MinRes.
“MinRes is seeking to secure control of Norwest and its Perth Basin assets without paying an appropriate premium,” Norwest said in a statement.
“Accepting the offer would reduce shareholder exposure to the Lockyer project … while increasing their exposure to the risks associated with MinRes’ other businesses and commodities.”
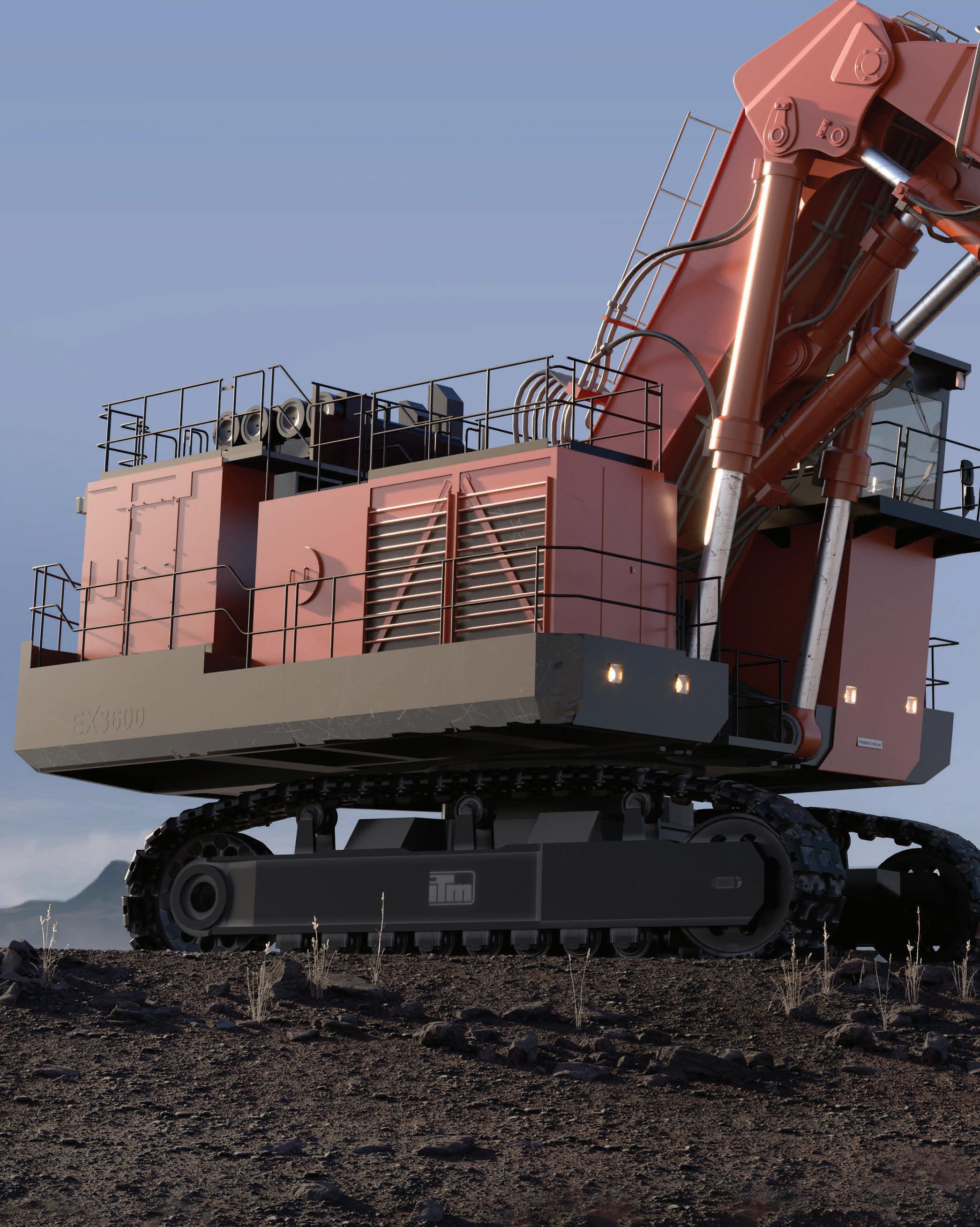
Norwest board.
“The Norwest board is satisfied that MinRes’ improved offer is now a good deal for shareholders, and in the absence of a superior offer, unanimously recommends shareholders should accept the revised offer before it closes,” Norwest chair Ernie Myers said at the time.
Gold
Gold fever might be a cliché, but it seems to have hit many in the mining sector with force.
The first quarter of the year saw a total of three takeover offers for gold companies, and several acquisitions for new exploration tenements.
Most recently, Catalyst Metals finalised its takeover of Vango Mining for $66 million in late March.
But what is so special about gold?
Unlike critical minerals and gas, it plays no part in the movement toward net-zero.
As it turns out, defining the purpose of gold has been a key concern in the industry.
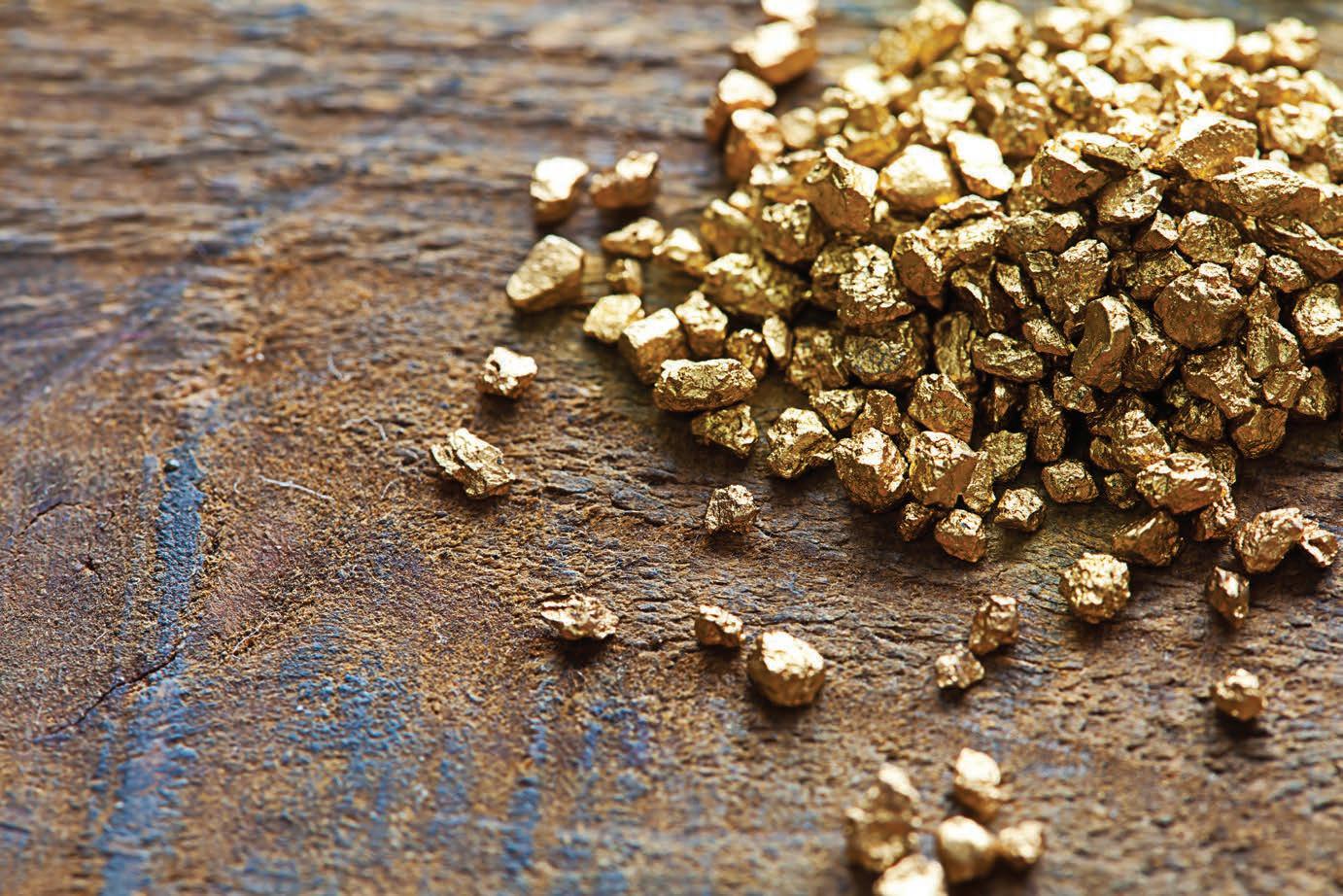
“People still struggle with the purpose of gold,” Northern Star managing director and chief executive officer Stuart Tonkin said at a Melbourne Mining Club luncheon in October 2022.
“To me, it’s very simple: it is their currency, and it underpins all the fiat currencies around the world that governments use as that physical asset.”
The majority of gold mined in Australia is sent overseas to companies that buy it as investments, as the precious metal remains volatile than other investment avenues.
Additionally, gold mines are relatively easy to develop when compared to other commodities, meaning the supply and demand is more balanced.
When Ramelius Resources lodged an all-script takeover offer for the Lake Roe
gold project from Breaker Resources in March, it cited the project’s potential for further development.
“Lake Roe is an outstanding opportunity for Ramelius to consolidate its (Lake Rebecca Gold Project) acquisition from 2022 with almost three million ounces in combined resources, underpinning a likely future production centre for the company,” Ramelius managing director Mark Zeptner said.
“The Breaker team has done an excellent job advancing Lake Roe … and have clearly demonstrated its potential for development into … what we believe is a Tier one gold mining region.”
The nature of the mining industry means new takeovers and acquisitions are constantly in the pipeline. The sector have to wait and see what comes next. AM
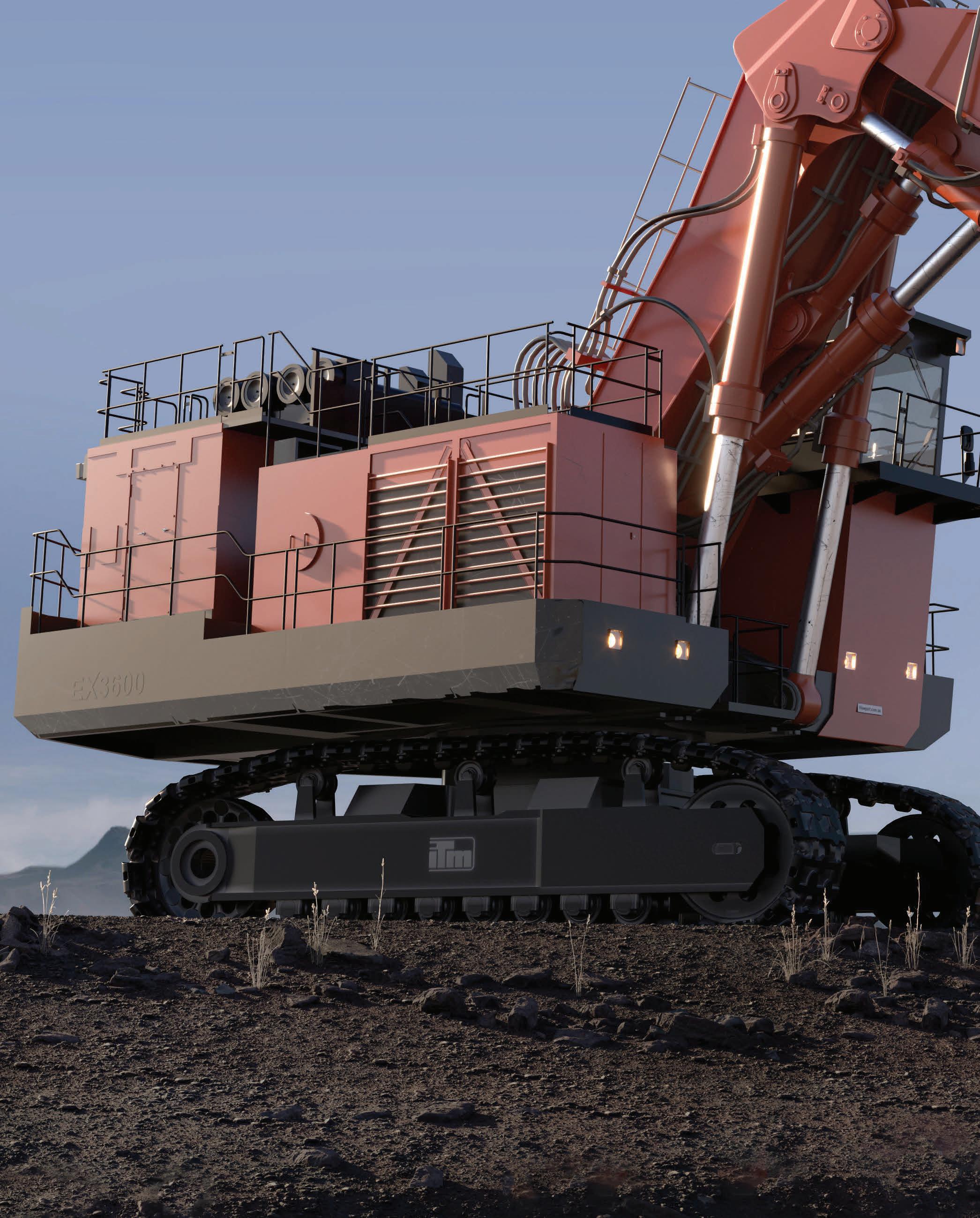
THE (TAKEOVER) TARGET MAY HAVE ASSETS THAT WOULD EXPAND THE BIDDER’S PORTFOLIO, OR PERHAPS A MAJORITY
SHAREHOLDER IS DISSATISFIED WITH THE WAY THE COMPANY IS BEING RUN.”GOLD IS ENJOYING ITS MOMENT IN THE SUN AFTER SEVERAL TAKEOVERS AND ACQUISITIONS THIS YEAR.
TRACK YOUR FUTURE
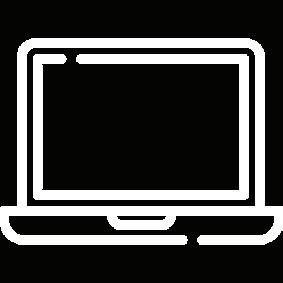
ALWAYS BY YOUR SIDE, EVEN FROM AFAR
TRUST ITM™ technology optimises machine performance and undercarriage maintenance across the power of data. Through wireless sensors and cloud based app technology it has never been easier to empower your mine with on hand real time visibility.
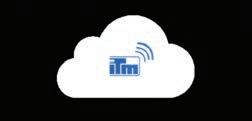
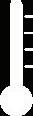
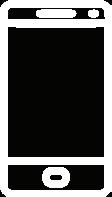
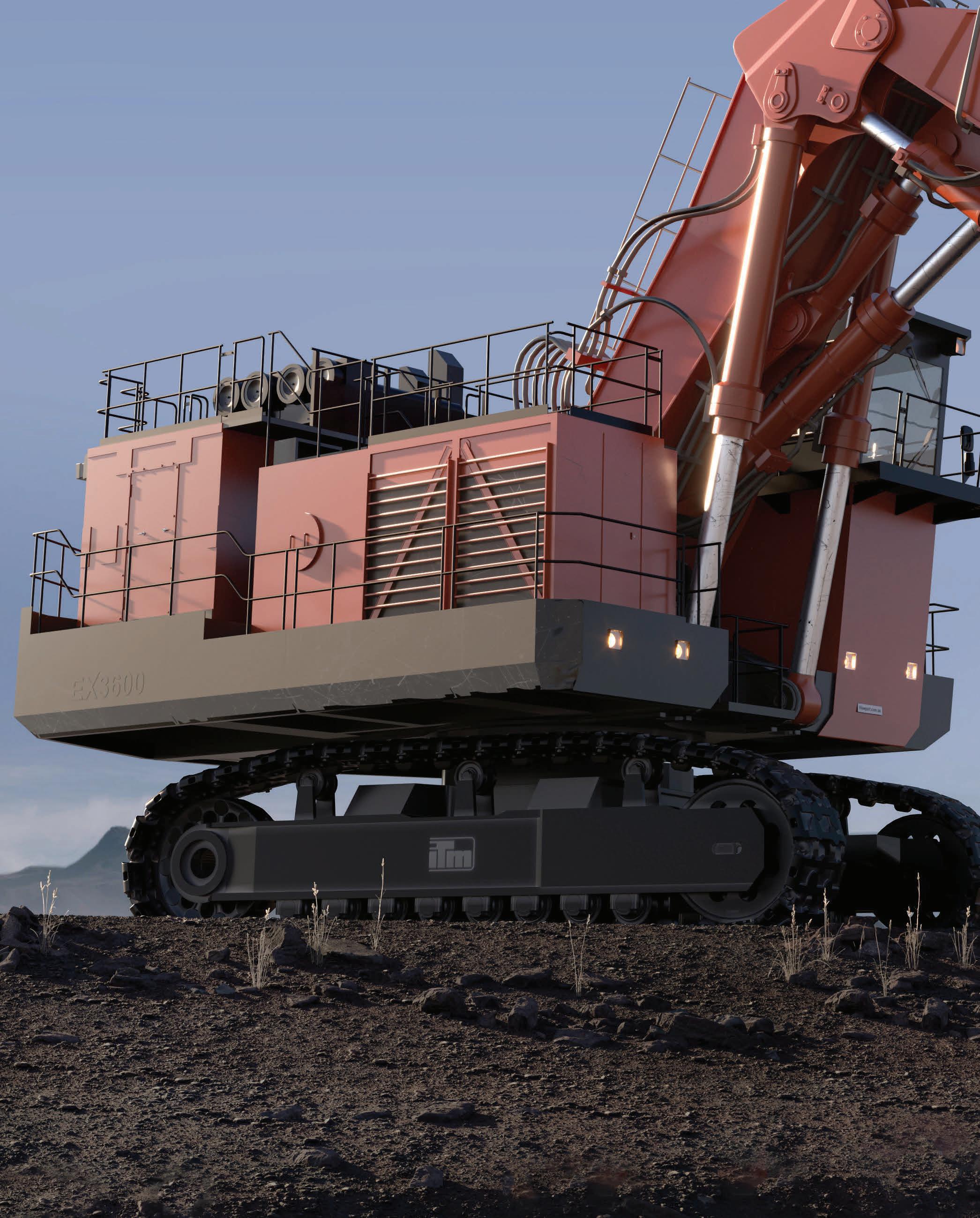
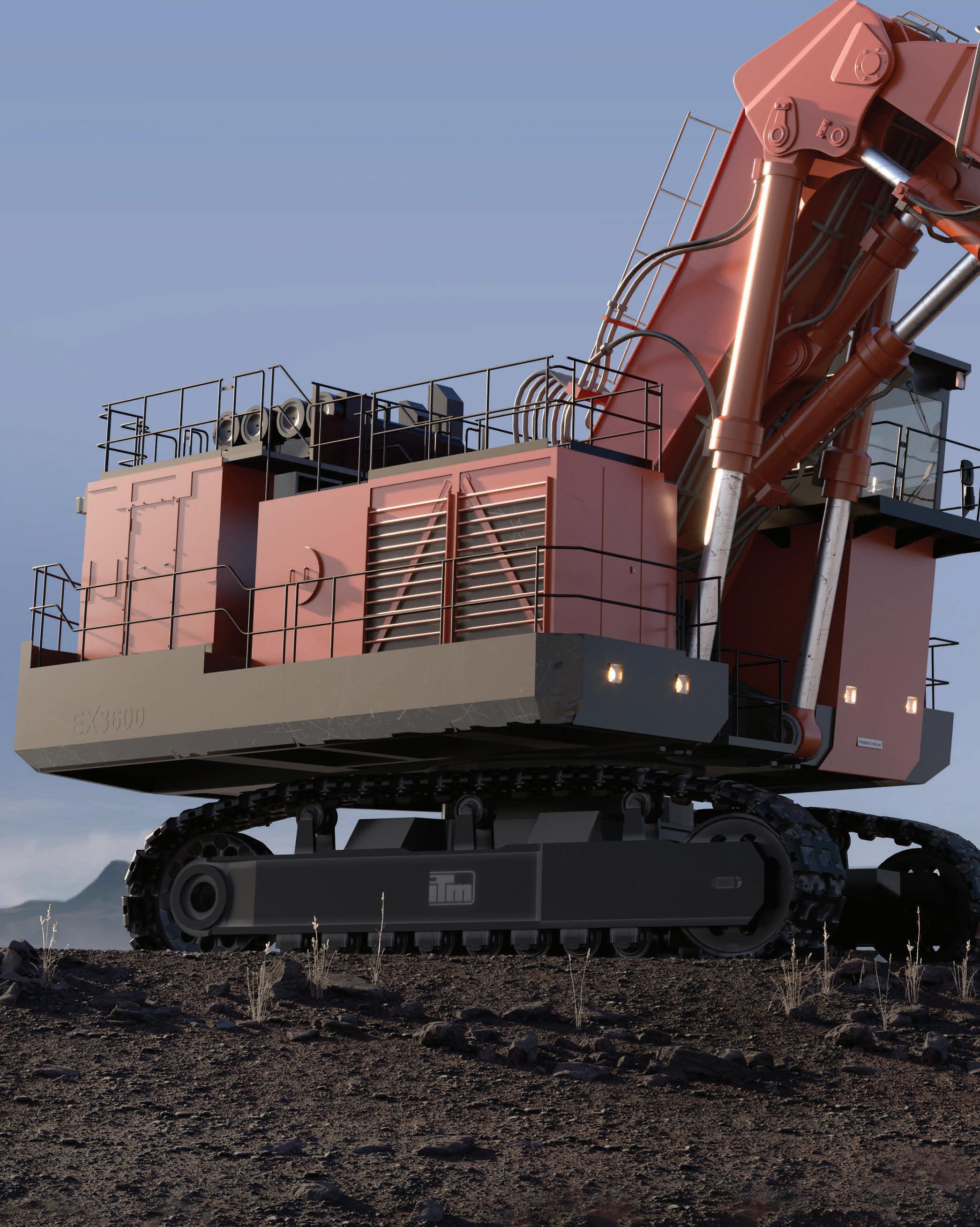
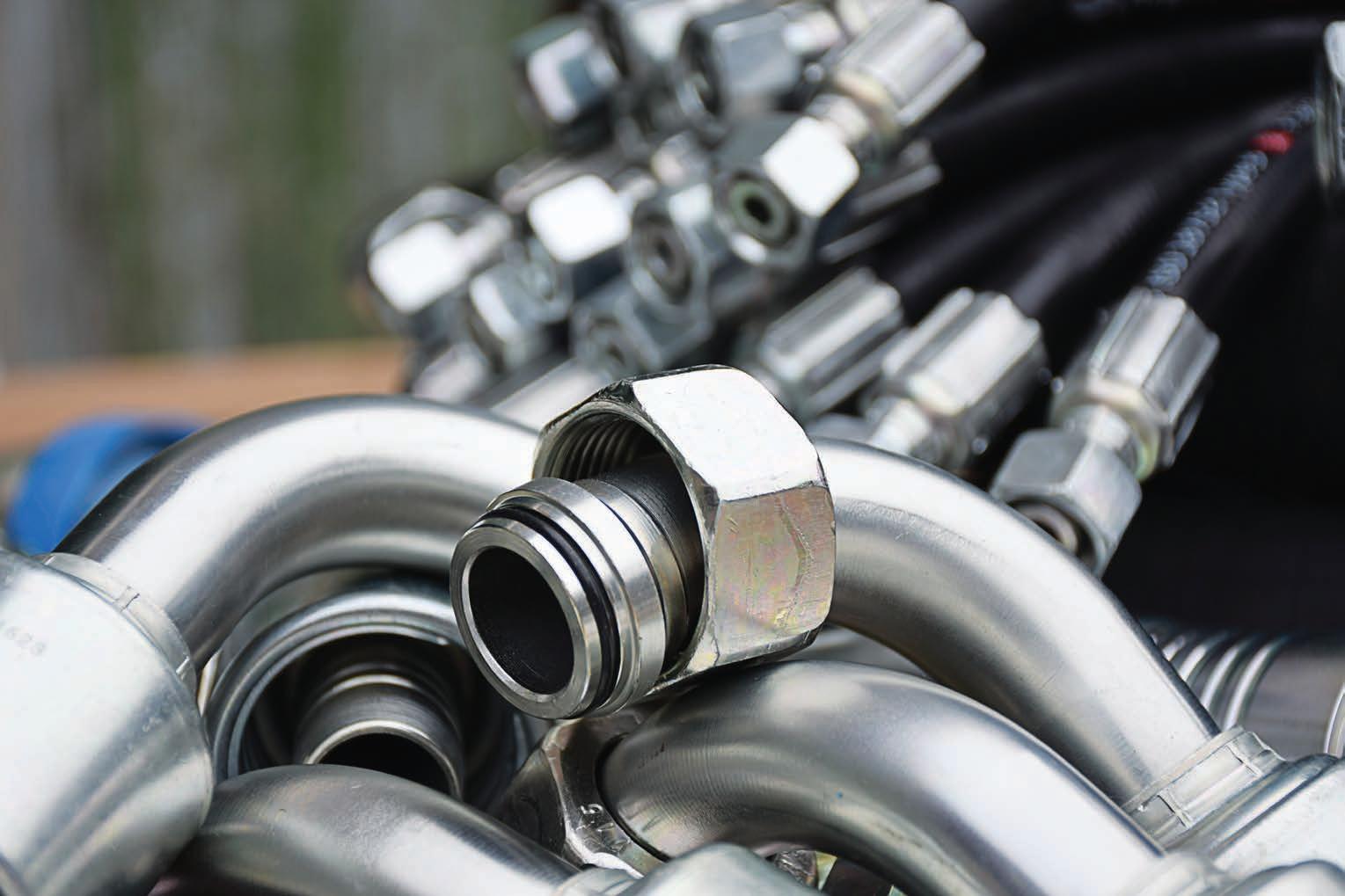
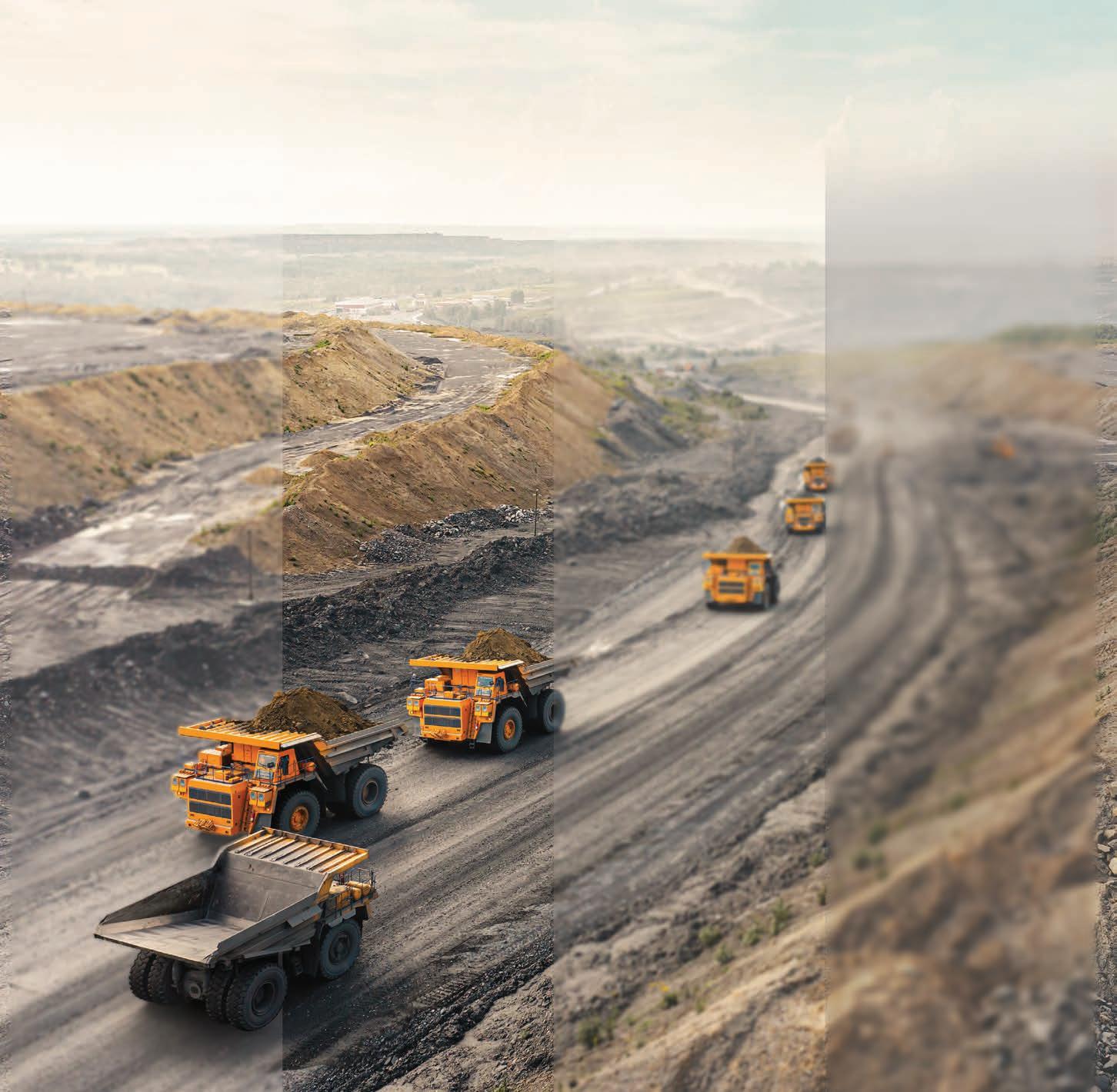


THE FUTURE OF FLUID TRANSFER TECHNOLOGY
hether it’s a scraper, a loader, a bulldozer or a drill rig, most mining equipment requires a hydraulic hose to operate the machinery correctly, according to Motion Australia’s Aaron Bryer.
“Hydraulic hose fittings, adaptors and accessories are really important for mining equipment,” Bryer said.
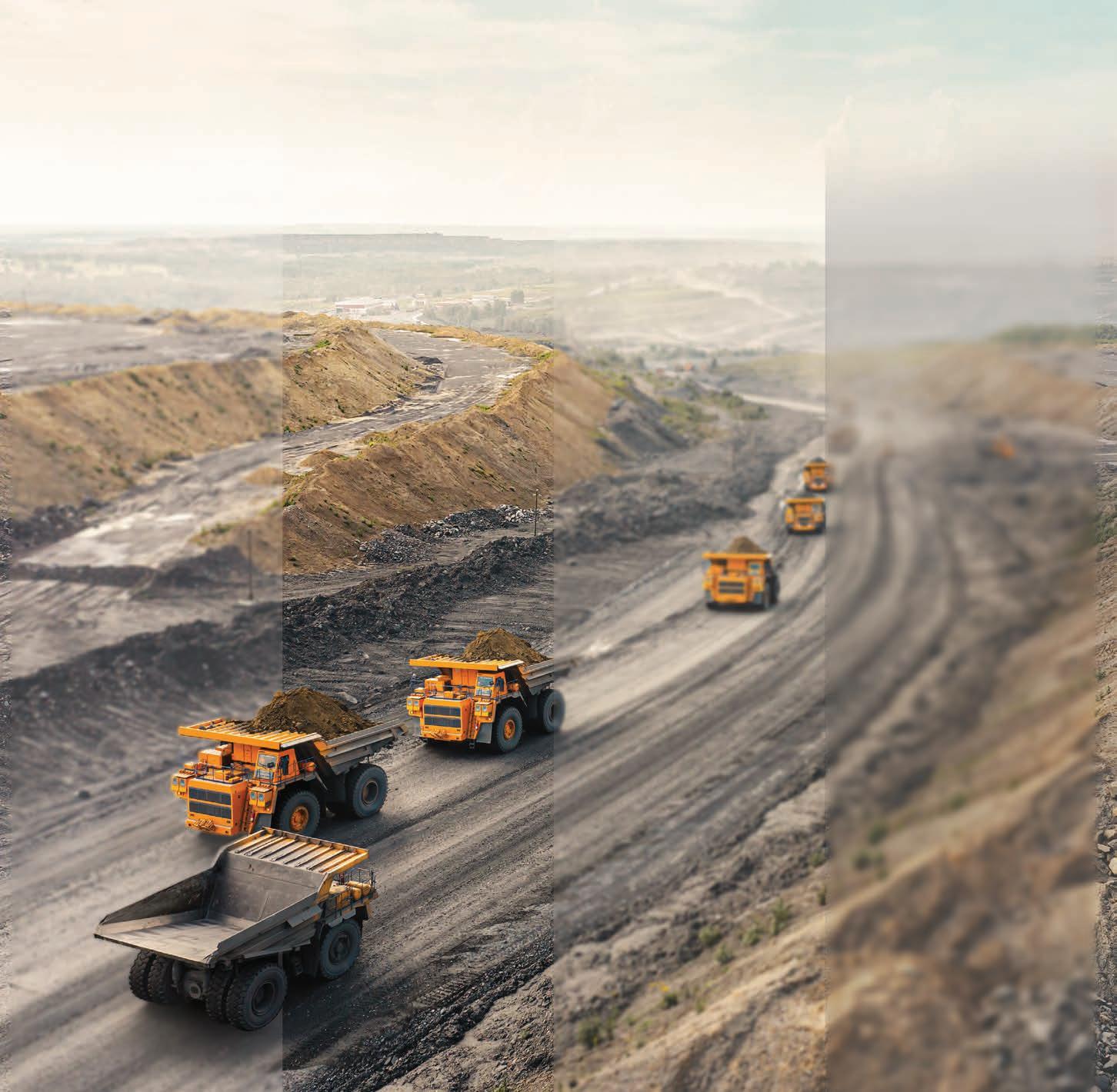
“The hose is the critical transfer item on pumps to extract a particular fluid or medium from a charged area. Hydraulic hose and pumps are the key components in any mining extraction method, essentially.
“If you look at a loader or a digger which articulates up and down, there will be a pump that is forcing the liquid or medium, which will later discharge through a hose.
“To put things in perspective, the pressure rate in one of these hoses is going to be up to 6000psi (pounds per square inch) going through a halfinch hose. So the quality of the hose is
Wimperative for the functionality of the equipment, but also the safety of the set-up, because obviously that level of pressure needs to be handled with care.
“In particular, jumbo drill rigs in underground mining have strands of hose that twist around a rail pulsating backwards and forwards and can be subject to failure that will happen very quickly.”
As Motion Australia’s hydraulic hose and fittings category manager, Bryer looks after the business side of strategies and market channels within the hydraulic hose portfolio, under the business group department of flow technologies.
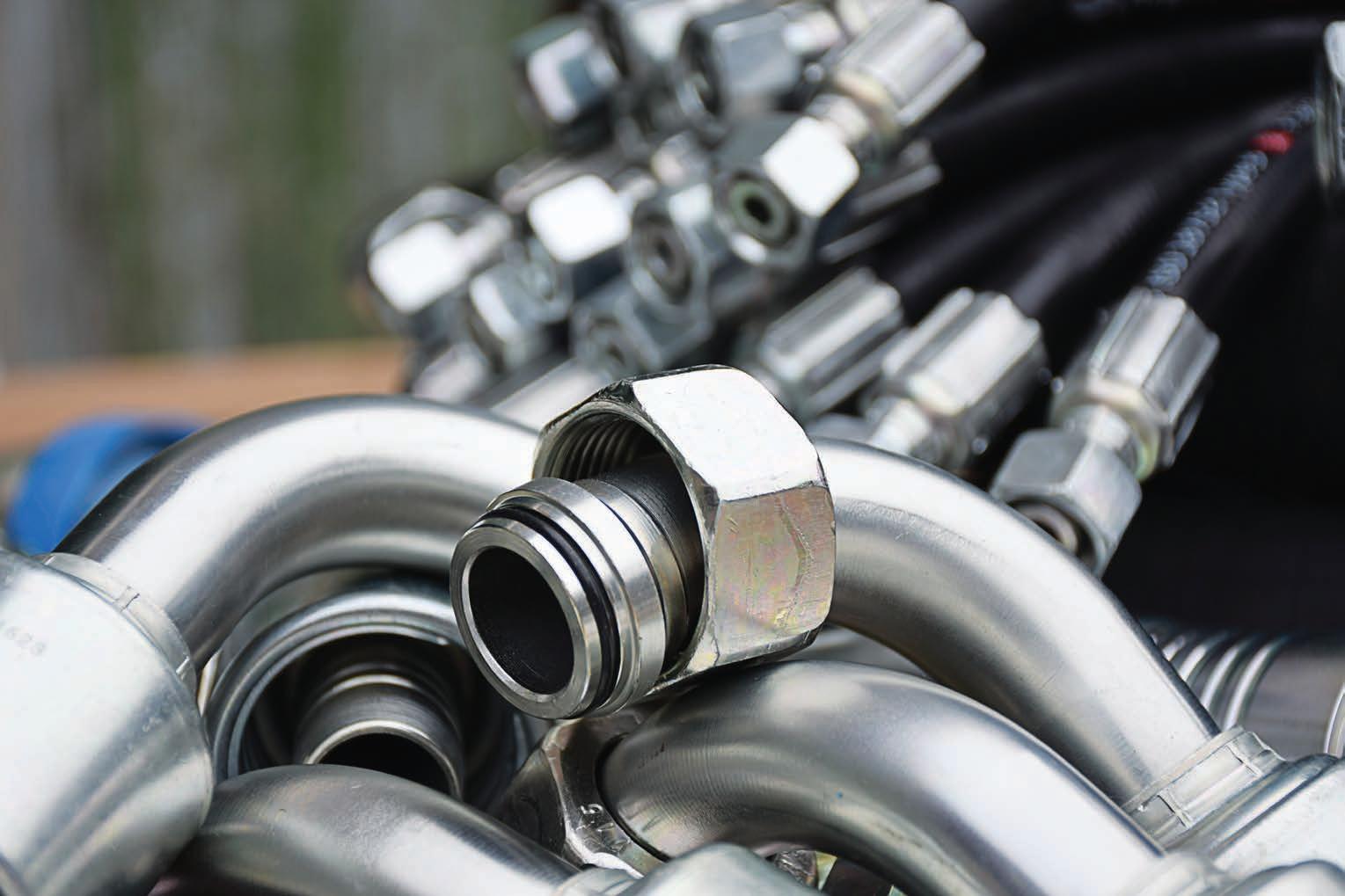
Having been in the industry for 15 years, Bryer knows his way around fluid transfers and connection products for the heavy industrial sector.
Over the past 12 months, Motion Australia, in partnership with original equipment manufacturer (OEM) Gates, has introduced new hydraulic hose capabilities and fluid transfer services to customers within the mining and quarrying sectors.
At the same time, Gates has introduced an entirely new standard range of hydraulic hose products: the Gates MegaSys MXT and MegaSys MXG 4K and 5K hydraulic hose range styles.
A significant benefit of the new hose design, according to Bryer, is that it is formulated around Gates’ invention of an outer-cover compound that enhances abrasion and ozone resistance.
“Combine this with the new Gates XtraTuff Plus wire braid reinforcement technology and the construction offers more wire than a conventional twowire hose,” Bryer said. “This new range of hydraulic hose products is really challenging the traditional style of hydraulic hose by offering more freedom around the flexibility, with about 40 per cent more flexible force event ratio.
“The flexible, durable and lighter cover in a new standard range has given us less products to deal with but at a superior level of performance.
“It’s a very economical solution all around, for both Motion Australia as a distributor and our customers on their applications. Because of the construction
of this new hose, we are seeing double the service life.”
Gates and Motion Australia have been working hard to collaborate on joint calls to various sites to educate customers and end users on the efficiencies of these products, including reduction in assembly times and waste and increase in fuel efficiency.
In addition, Motion offers an efficient vendor-managed system in these mining workshops that has seen customers reduce their dead inventory rationalisation, reduce administration account costs, obtain instant stock reports, and better manage their assets and traceability.
“We also have our 1800 HOSEVAN business arm that has been playing a pivotal role in maintenance overhauls for mining equipment, keeping fleets and equipment operating with scheduled maintenance, and providing hose auditing and breakdown service,” Bryer said.
“All the while, we’re remaining fully stocked with all of the new Gates MegaSys MXT and MegaSys MXG products.” AM
DIGGING UP THE PREHISTORIC PAST
THE AUSTRALIAN LANDSCAPE PLAYS HOST TO A WIDE VARIETY OF COMMODITIES, FROM NICKEL AND LITHIUM TO GOLD AND COAL. BUT THERE ARE LARGER THINGS LURKING UNDERGROUND, TOO.
The word ‘mining’ brings to mind images of open pits, large machinery and glittering golden veins tracking through rocks. But the underground environment can also offer up secrets of a very different nature, and that is exactly what happened in March when BHP helped to unearth a rare, 100-million-year-old dinosaur fossil.
Project DIG, a partnership between BHP, BHP Mitsubishi Alliance and Queensland Museum Network, worked to uncover the head and associated body of an Elasmosaurus, a long-necked plesiosaur that coexisted with dinosaurs in the early Cretaceous period.
The fossil was found in western Queensland, which was covered in a vast, shallow sea during the early Cretaceous period.
It was the first time a preserved head and body
of an Elasmosaurus has ever been found together in Australia.
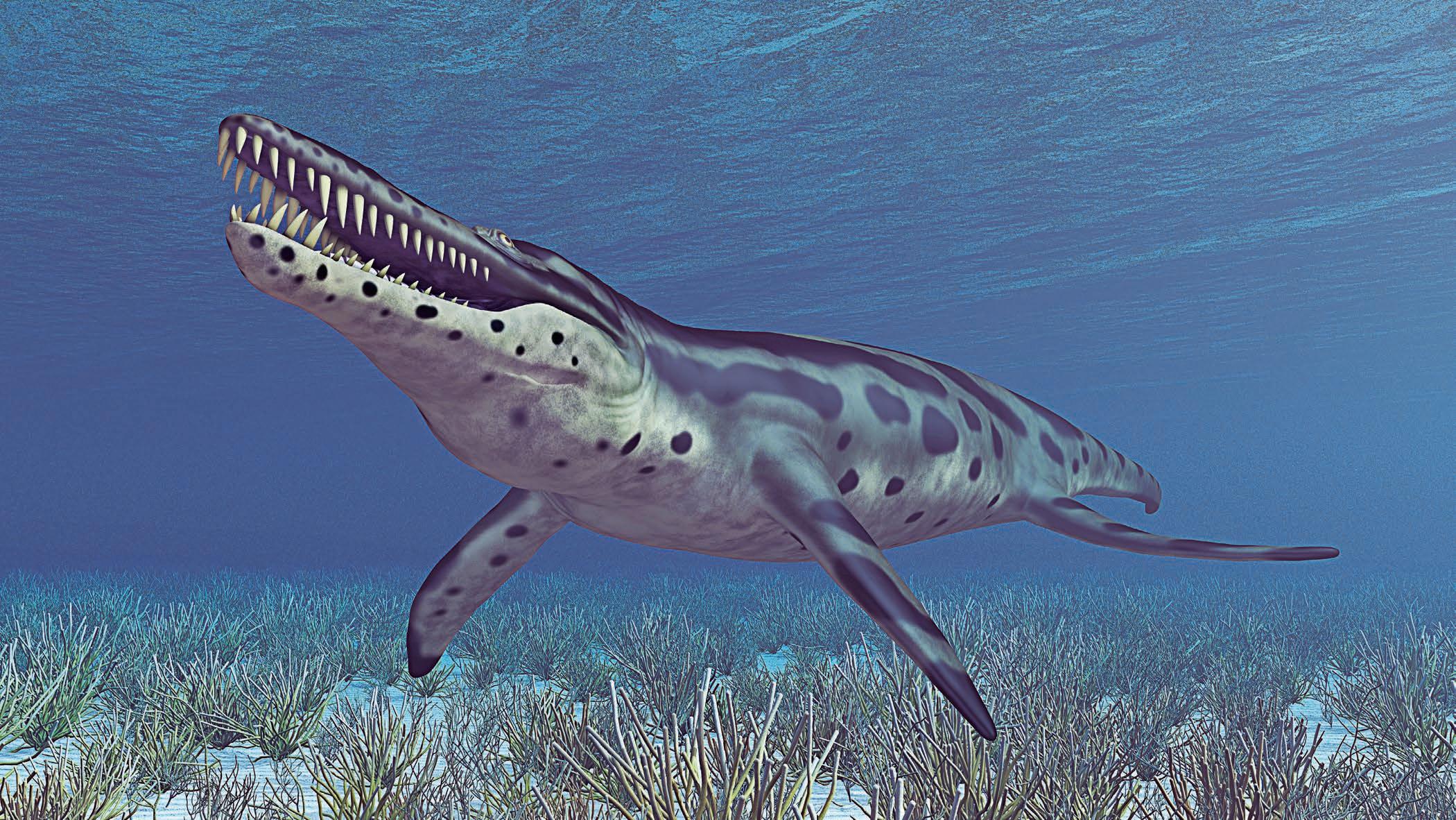
One of the largest ever marine reptiles, the Elasmosaurus was first discovered in 1868 and, when alive, reached up to 46 feet in length. Much of that length was taken up by its neck, which was believed to be an incredibly long tail when first discovered.
Fewer than 15 different specimens have ever been found by palaeontologists around the world, making the Australian find an exceedingly rare one.
The Elasmosaurus lived in the Eromanga Sea, which covered large parts of inland Australia between 140–100 million years ago.
“We were extremely excited when we saw this fossil – it is like the Rosetta Stone of marine palaeontology as it may hold the key to unravelling the diversity and evolution of long-necked
plesiosaurs in Cretaceous Australia,” Queensland Museum’s Dr Espen Knutsen told 7 news.
“We have never found a body and a head together, and this could hold the key to future research in this field.”
Several other specimens, including fragments from an Ichthyosaur, were collected from the site in western Queensland and will be transported to the Museum of Tropical Queensland in Townsville for research.
Project DIG is designed to transform how the museum stores, explores and shares the state collection.
“The fossils teach us much more about the history of this ancient inland sea (in which they lived),” Knutsen said in a Queensland Museum Network video.
Finding the head and the body together, according to Knutsen, was a very rare thing and something that would allow the researchers to gather data on the diversity of the species and the ecology of the dinosaur.
As it happens, this is only the latest example of a mining company playing a role in digging up the prehistoric past in Australia.
The Elasmosaurus discovery was reminiscent of a 1984 find which took place in Victoria.
At that time, palaeontologist Thomas H. Rich was leading a 10-year research project in Dinosaur Cove near the Otway Ranges when he discovered the fossil of a small ornithopod.
Using equipment from Atlas Copco, Rich dug up the fragments of an upper jaw with teeth, plus several jawbones, leading the palaeontologist to name the dinosaur the Atlascopcosaurus loadsi.
The dinosaur was named for the company and also for William Loads, the then-Victorian state manager of Atlas Copco who decided to support the dig and periodically volunteered in the search.
A herbivore, the Atlascopcosaurus loadsi is estimated to have been 2–3m metres long, weighing approximately 125kg.
Dinosaur Cove, as the name suggests, is a fossil-rich area located on the south-east cost of Victoria, but uncovering the fossils there is no easy task.
“The fossils were embedded in layers of sand, mud and clay, which over a period of more than 100 million years
had been pressed together into hard rock,” Atlas Copco said on its website.
“To free 1kg of dinosaur bone, approximately 30kg of hard rock had to be removed. The scientists often worked in dark and narrow tunnels, which at times were muddy and slippery.
“Work was also complicated by the excavation site being close to a steep cliff that dropped down to the sea. In conducting excavations, the research group had, among other things,
compressors, rock drills of various sizes and pneumatic tools.”
In 2009, Rich also discovered the bones of a type of tyrannosaurus in the area. The creature would have been about 3m long, weighing in at 80kg.
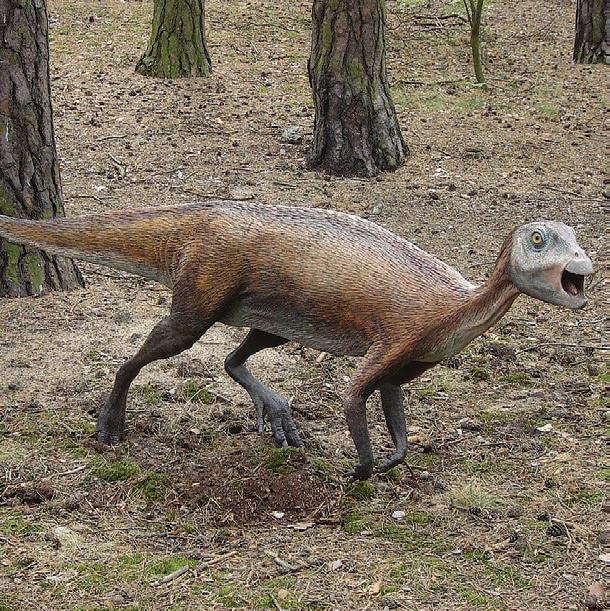
“This discovery filled a gap in the tyrannosaurus’ evolutionary history, and disproved previous theories about this type of dinosaur having only existed in the Northern Hemisphere,” Atlas Copco said.
“The new discovery showed that the tyrannosaurus had been a global species, but that it only developed into an enormous flesh-eater north of the equator.”
With the fossils residing alongside precious commodities, it is not unusual for miners to stumble upon the remains.
This is exactly what happened in 1987, when an opal miner came across the opalised remains of a Pliosaur in Coober Pedy, South Australia.
Like the Elasmosaurus, the Pliosaur was a sea dweller, but it had a larger skull and a shorter neck than its Queensland counterpart.
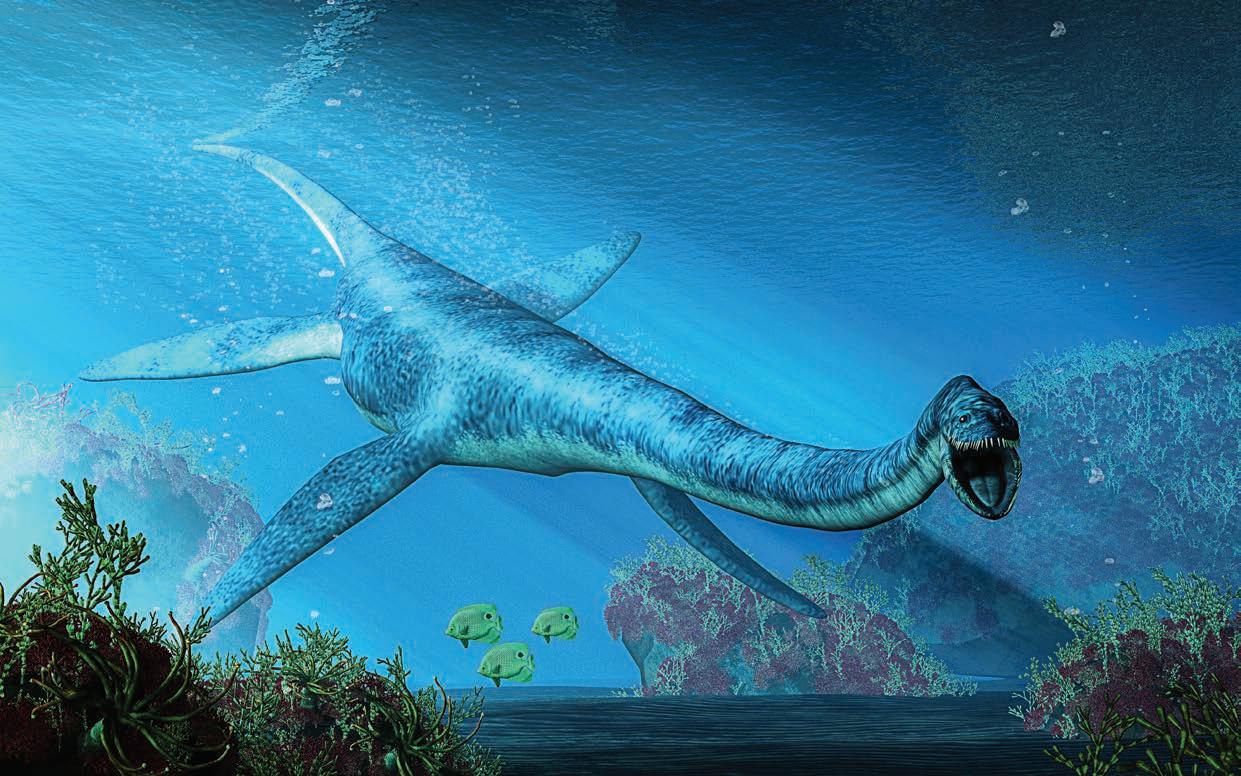
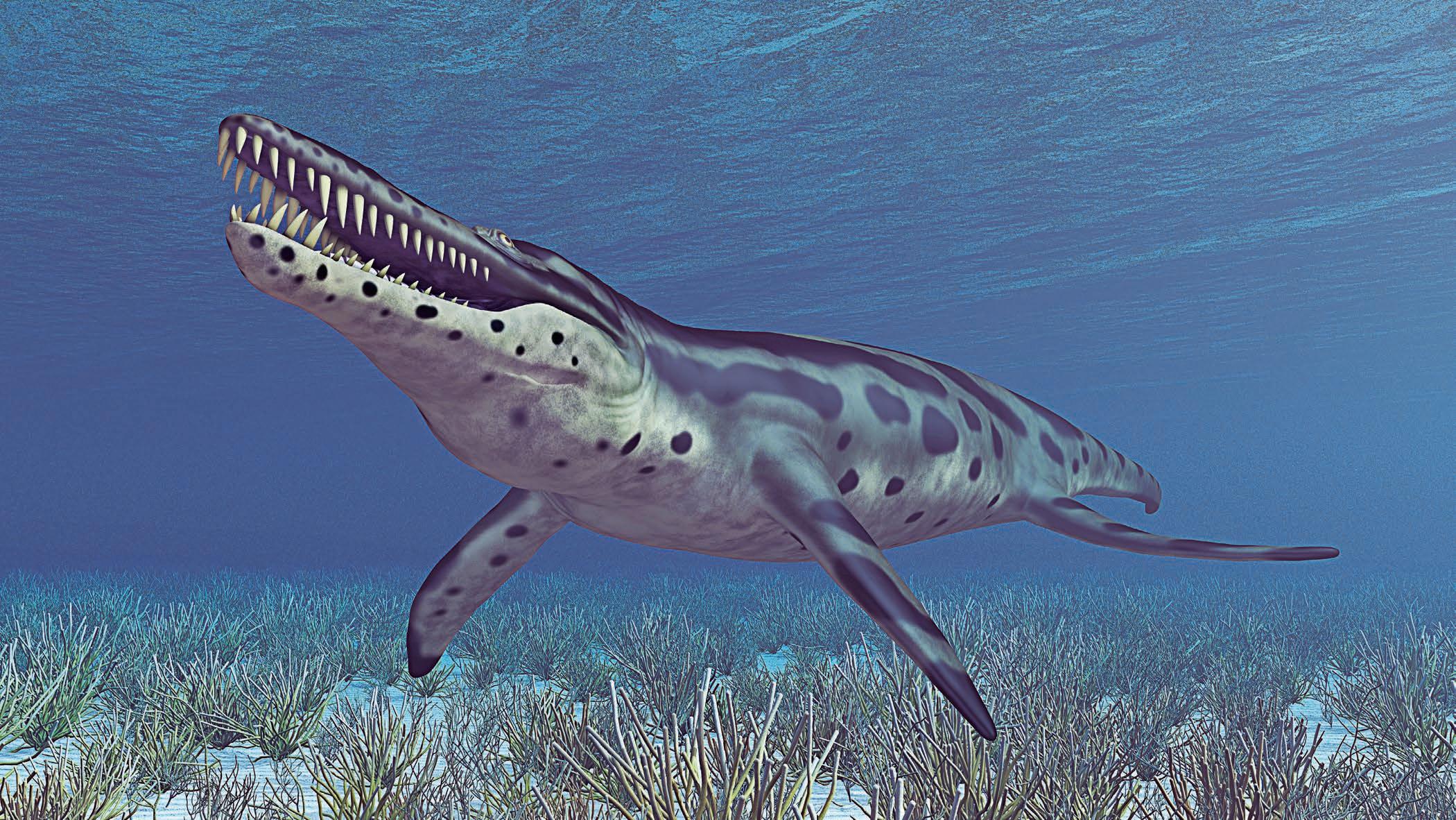
When conditions are right, opals can merge with the bones, forming an opalised fossil. Almost all of the Coober Pedy fossil’s 2.1m body was covered in opals, which the miner tried (and failed) to extract.
Named Eric the Pliosaur, the fossil now resides in the Australian Museum in Sydney and is a shiny beacon for anyone visiting the exhibit.
The opal content in Eric was said to have a value of about $25,000; however, the fossil itself was worth significantly more and the miner sold it to Australian businessman Sid Londonish for $125,000.
Londonish then hired archaeologist Pail Willis to help preserve the fossil and, upon inspection, an opalised fish bone was found inside the stomach. The fish bone was named Wanda.
Lucky miners have continued to uncover dinosaur bones throughout the last several years and with mining equipment only getting smarter, there seems little doubt the trend will continue. Only one question remains: what will be discovered next? AM
MT MORGANS: A GOLDEN TIMELINE
RECENTLY SUSPENDED
Located in Laverton, Western Australia, the Mt Morgans site enjoyed wide acclaim as the only large processing plant in the Laverton gold fields not in the hands of a major miner.
1896–1911
The story of Mt Morgans begins in the late 1800s, when gold was first discovered in the area by a prospecting party led by Harry Lilley.
Lilley sold the lease a year later to Alfred Edward Morgans, a representative of a British syndicate who renamed the operation the Westralia Morgans Mine.
In 1903, the town of Mt Morgans had reached a population of 1250, with Westralia Morgans Mine being the town’s largest employer.
However, by 1911 Westralia had gone into liquidation, leaving a new company to take on the lease and operation.
1914–1952
With the re-opening of the mine in 1914, the township of Mt Morgans was able to survive for another few decades.
But the isolated nature of the mining town meant residents struggled, and by 1937 the town’s police station, hospitals
and shops had closed, and people began to move out of the area.
The Mt Morgans mine remained in operation until 1928, but by 1952 the operation had shuttered and the town was declared abandoned.
1988–2012
The Mt Morgans mine passed through many hands in the years between 1988 and 2012, opening for nine years in 1988 and then, after another long closure, opening again in 2009.
Dacian Gold purchased the site in 2012.
2012–2018
Dacian ramped up towards an average steady-state ore production target of 8000 tonnes per day.
In 2018, Dacian executive chairman Rohan Williams said it was a strong start to production that enabled the company to make its first debt repayment of $16.5 million.
In December of that same year, Dacian announced it was on track to establish a 10-year mine life.
2019
This year was a big one for Dacian, which realised its goal of achieving a December start to commercial production.
The company had high hopes for the $200 million project, having declared itself “Australia’s next 200,000-ouncesper-annum gold producer”. But the good times didn’t last, as Dacian lowered production guidance in June 2019, blaming the return of underground performance issues.
During July 2019, Dacian downgraded its mine plan to eight years.
2020–2021
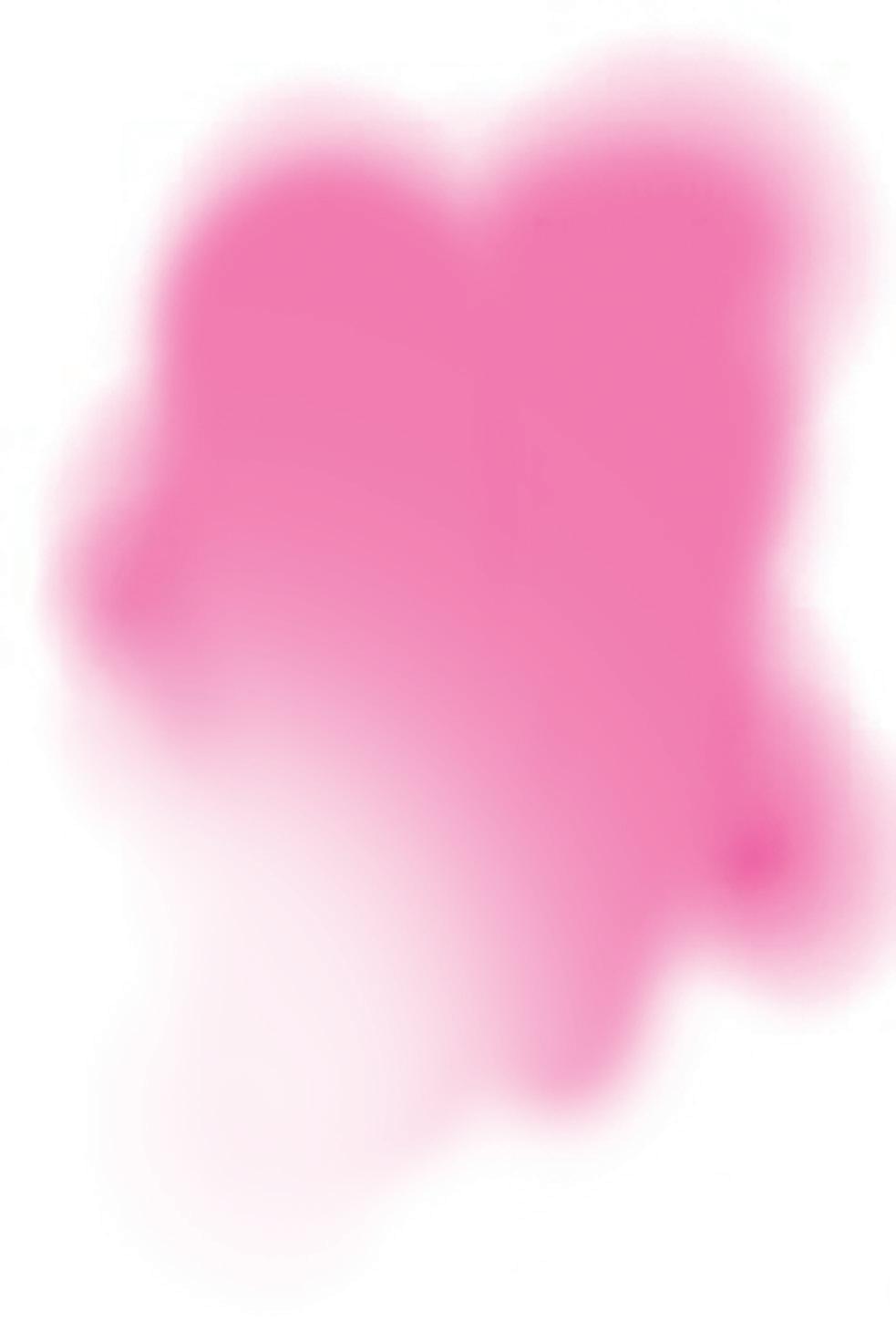
As the world plunged into the COVID-19 pandemic in the early months of 2020, Dacian announced that Mt Morgans had hit output guidance of 30,000–33,000 ounces of gold for the March quarter, despite the global impacts of the pandemic.
In January 2021, Dacian said it was on track to hit its financial year production target thanks to Mt Morgans.
Dacian’s then-managing director Leigh Junk said the company was looking forward to incorporating the Redcliffe gold project, located within 100km of Mt Morgans, into the site to extend mine life and to diversify and bolster production.
2022
This marked the beginning of the end for Mt Morgans. Junk stepped down as Dacian managing director in June,
triggering a suspension of operations at the mine. The company announced gold production in the December quarter was 12,039 ounces, down from 21,525 in the September quarter of 2022.
2023
January hailed the announcement that many had seen coming: Mt Morgans would close at the end of March.
“The decision to place Mt Morgans on care and maintenance was not taken lightly, especially given the impact on our loyal employees and contractors, and the community in which we operate,” Dacian non-executive and independent chairperson Craig McGown said.
“However, a period of care and maintenance will ultimately benefit all stakeholders by providing time to develop a robust, low risk, sustainable plan, necessary to underpin the future resumption of operations.”
In April, it was announced that operations had been suspended indefinitely.
The Mt Morgans mine enjoyed over 100 years of on-and-off operation before the historic site was shut down, leaving many to wonder if this really is the end for one of WA’s most famous gold producers. AM
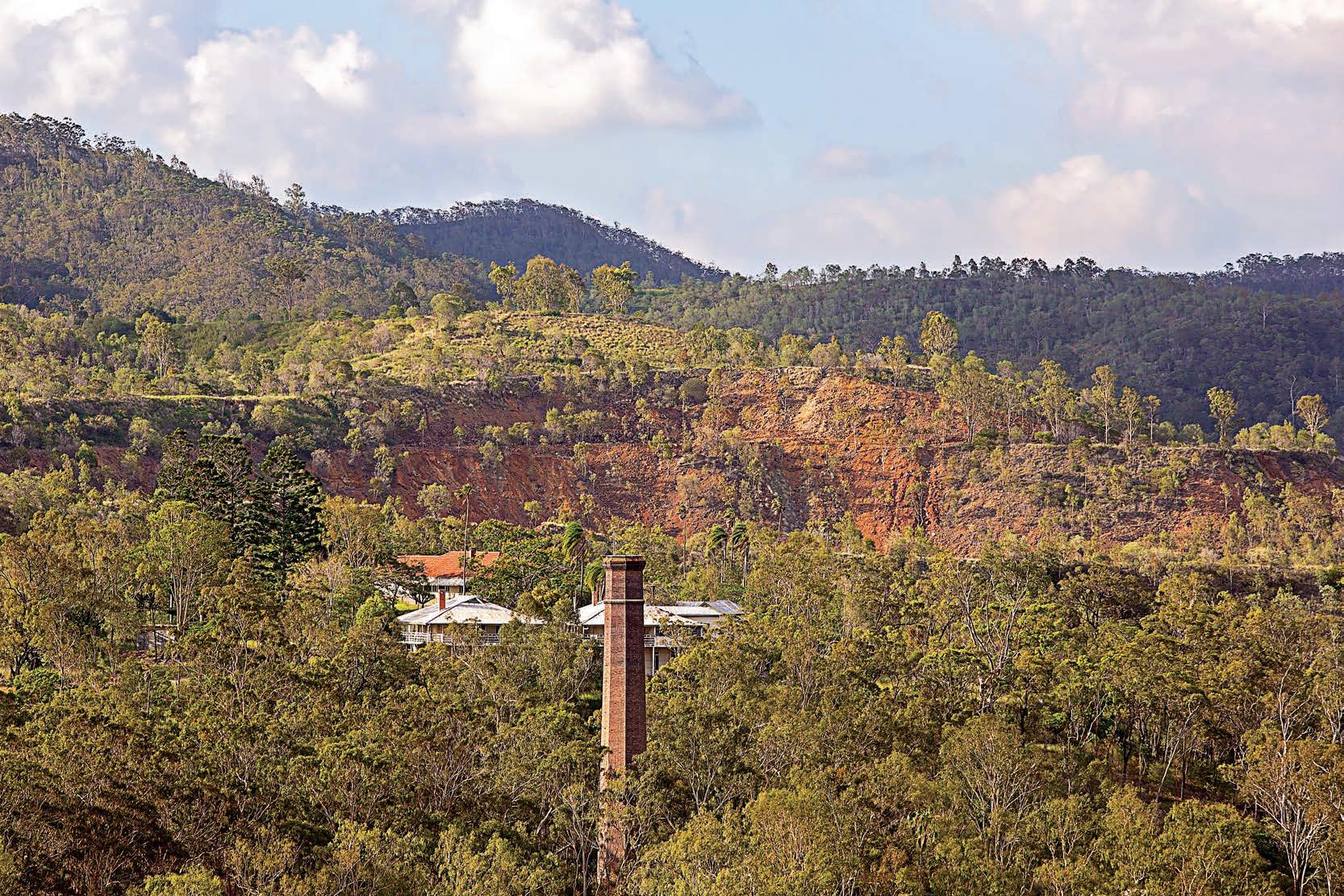
DACIAN GOLD’S MT MORGANS MINE HAS HAD A LONG AND WINDING HISTORY, AND WITH OPERATIONS
INDEFINITELY, AUSTRALIAN MINING TAKES A LOOK AT THE HIGHS AND LOWS OF THE SITE.THE MT MORGANS MINE ENJOYED ONAND-OFF SUCCESS FROM 1896 TO 2023.
JOIN US TO CELEBRATE THE BEST OF THE BEST
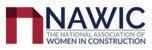
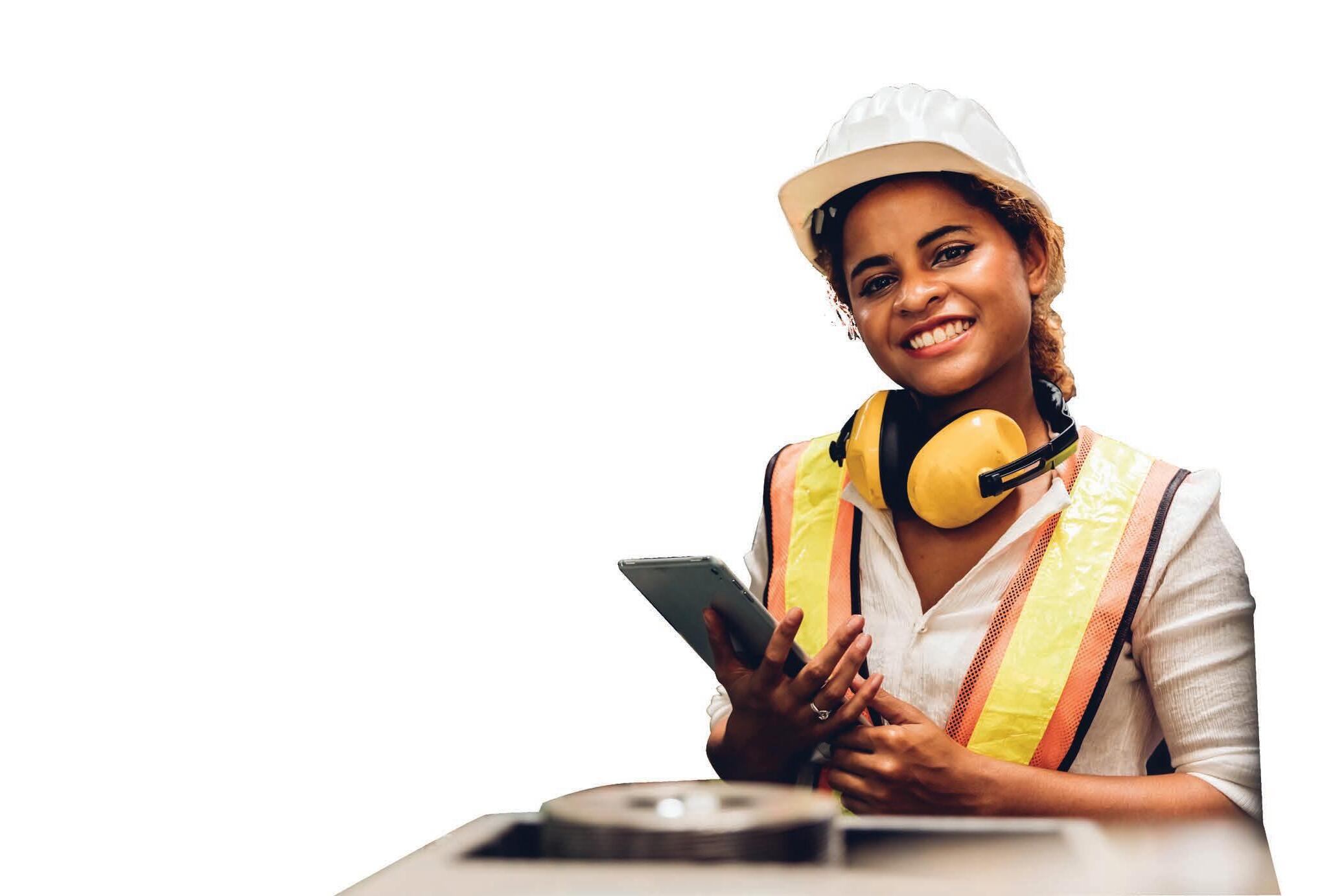
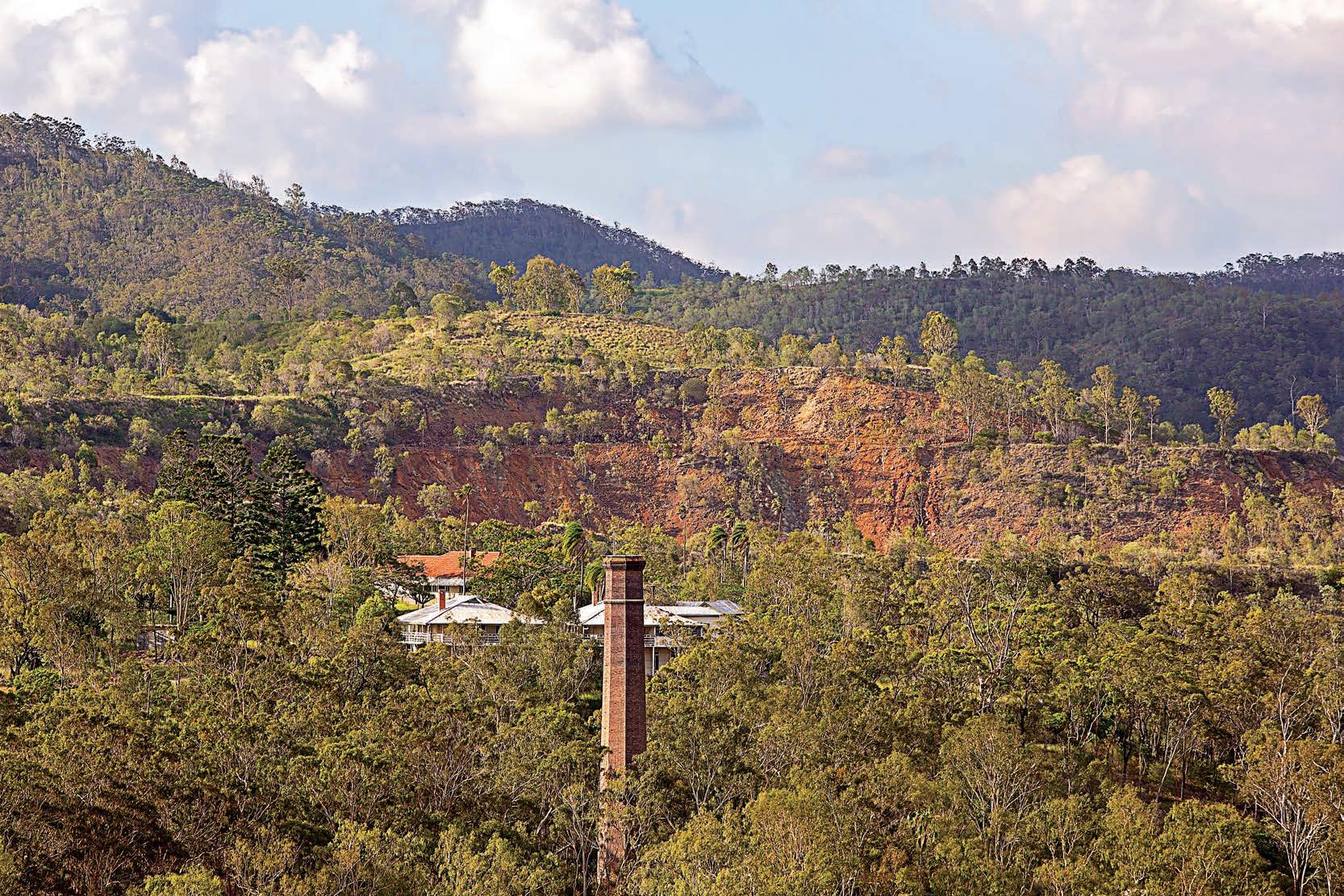
TICKETS ARE NOW ON SALE


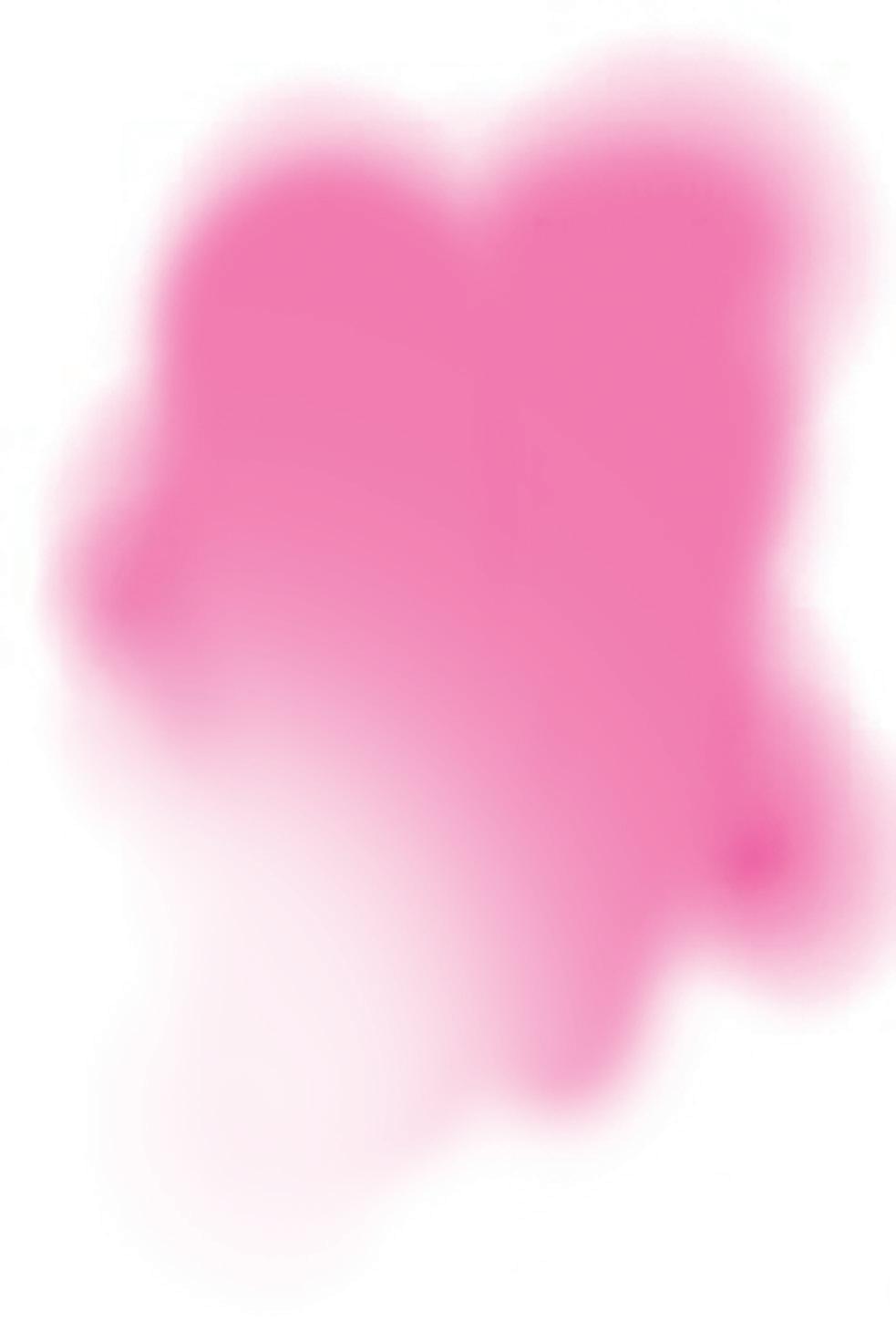
THE FLEXITRUFF IMPACT CRADLE
Thejo has introduced its latest innovation in the FLEXITRUFF Impact Cradle, which features a patented garland-form bed integrated with a rugged steel frame that provides uniform support across the impact area.
The unique garland form maintains the natural trough, which helps the belt remain stress-free. The flexible arrangement eliminates misalignment in the loading area and helps the belt run in its true line.
The cradle is mounted on multiple shock dampeners that are specially designed to absorb heavy loads that reduces the impact load by up to 90 per cent. Flexibility of the bed allows multi-axis motion of the bed to disperse the impact load quickly and efficiently.
FLEXITRUFF maximises the advantage of modular construction, making installation and maintenance very easy. Interchangeable modular parts help in cutting down inventory costs.
FLEXITRUFF impact cradles are available for belt widths from 650mm to 2400mm. Customised sizes are also available.
• thejoaustralia.com
FLEXIBORE 250 – LAYFLAT SOLUTION FOR SUBMERSIBLE PUMPS
The Flexibore 250 bore water pipeline is compact and easy to handle. Its modern, flexible technology allows operators to install submersible pumps in a fraction of the time compared to conventional fibreglass risers.

Constructed by integrating thermoplastic polyurethane into a high-tenacity polyester woven textile reinforcement, the hose has exceptional tensile strength in one continuous length.
Similar to a 16-tonne-rated lifting sling, Flexibore can support the submersible pump and the water column without a safety cable.
With its inherent swelling feature, Flexibore is resistant to corrosion and microbiological damage. This preserves its excellent hydraulic efficiency for the life of the hose. As fibreglass pipe can often create a rigid surface for encrustation, the associated pumping costs due to increased energy needs often go unnoticed. In contrast, Flexibore will never succumb to iron bacteria build-up, according to the company. Flexibore is reusable, easily relocated and can be left out in the sun without damage.
Crusader Hose designs and manufactures Flexibore in a range of diameters up to 10 inches and with deep bore pumping capabilities to depths of 400m. Crusader Hose is here to support your mine in achieving its profitability and sustainability objectives.
• crusaderhose.com.au
NORD DRIVESYSTEMS HAS A MOTOR FOR EVERY NEED
NORD Drivesystems is renowned for providing innovative and intelligent drive technology for water, wastewater, waste, and raw materials management. Among the company’s newest products are the DuoDrive geared motor and the SAFOMI-IEC adapter, which build on the company’s reputation. DuoDrive is an integrated gear unit/motor concept in a hygienic wash-down design, combining the efficiency of the IE5+ motor and a single-stage helical gear unit. DuoDrive is optimised for high system efficiency, high power density and low noise emissions. It features plug-and-play commissioning, meaning the total cost of ownership is significantly reduced.
The SAFOMI-IEC adapter is optimally suited for mixers. The adapter provides an integrated oil expansion volume, reducing wearing parts and attached components, and resulting in greater operational reliability and less maintenance. Conversion features six easy steps and, accordnig to NORD Drivesystems, results in excellent operating reliability in a compact and simple design.
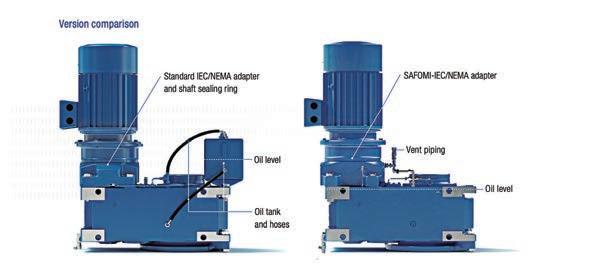
• nord.com
RETRA FLUID’S LUBESTATIONS FOR EASY MAINTENANCE

Lubestation by Retra Fluid Handling Systems is a relocatable, lubrication pit stop for fast and easy mining equipment maintenance. Built for fast, easy and contaminationfree lubrication storage and dispensary on remote worksites, a lubestation can improve the lifespan and performance of equipment and machinery and ensure the success of industrial operations.
Certified for cyclone-prone areas and all wind regions, lubestations also feature forklift access for efficient loading and unloading, high-security ISO locking bars and dust filtration to minimise contaminants.

The multiple advantages of the lubestation include their simplicity to use and maintain, their efficient and cost-effective structures, and their minimal on-site preparation requirement, among other things.
Lubestations are custom-engineered to your exact requirements and supplied ready for use.
• retragroup.com.au/products
ENVIROSOIL: A HYDRAULICALLY APPLIED TOPSOIL OFFERING SUPERIOR PERFORMANCE
EnviroSoil is a hydraulically applied topsoil alternative for when your soil is unable to support revegetation. Active components include thermally refined organic fibres, high carbon, natural soil conditioners, seaweed extracts and mineral blends, including basalt and microbial inoculants. The unique combination of nitrogen-fixing bacteria, in conjunction with mycorrhizae, works to stimulate the soil, mimicking the natural cycle and thereby creating a sustainable growing medium for the germination of plants.
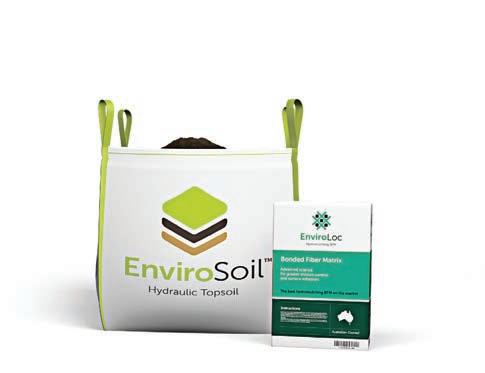
Thermally treated fibres provide an interlocking matrix to minimise erosion, and act as a food source for microbial colonies to regenerate during initial plant strike.
Erizon’s EnviroLoc BFM (bonded fibre matrix) is a premium hydromulching solution engineered for superior performance in the areas of erosion control and growth establishment. Thermally refined wood fibres increase water retention and airflow exchange for improved seed germination. These fibres are engineered to withstand conditions where high levels of water velocity resistance is required. The fibres hold up to 20 times their own weight of water and provide extensive moisture retention around the seed.
The application is a two-pass process. The first pass of EnviroLoc BFM maximises the seed-to-soil contact required for successful root establishment. A second pass provides thermal stabilisation, increased water retention and protection.
• erizon.com.au
WORKWEAR THAT GETS THE JOB DONE
LASE INTRODUCES NEW TWIXBEAM
The supplementary component TwixBeam consists of two mm-high perforated aluminium U-sections bolted to one another. The component lengths range from 0.8–6.6m.
Lightweight components made of aluminium, plus the option of dismantling them, speed up assembly and facilitate their use in cramped conditions; for example, when passing the material through narrow manholes. Depending on the task, matching expansion parts are also available, such as a beam connector, an insertion beam, a spindle strut for stiffening and bracing, and a swivelling spindle for every required angle.
Combination with the Layher construction kit is also an important factor: standard and suspended structures can be built, with Allround standards passed through with the standard connection or with the swivelling spindle. Geometry adjustments, plus solutions for side protection, can also be achieved using standard Allround parts. A combination with the aluminium FlexBeam is also possible.
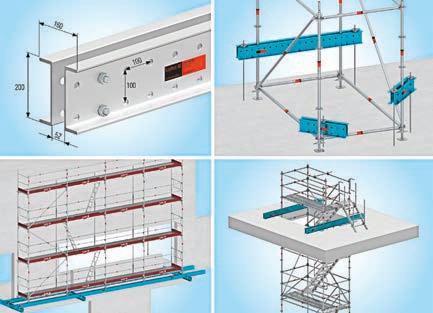
• layher.com
CEA STOCKS TWINPOWER GENERATOR
The Atlas Copco QAC 1450 TwinPower generator is ideal for applications requiring variable power needs that can be set to suit the time of day or specific usage requirements. Featuring two 725 kVA generators inside the 20-foot containerised unit, the QAC 1450 TwinPower allows you to run on one engine while servicing the other, providing a built-in backup as standard.
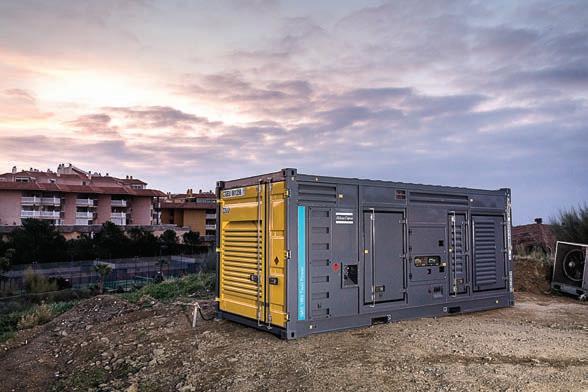
With two generators in one platform, the QAC 1450 TwinPower provides the flexibility you need to run at 100 per cent power load or low power loads in the most efficient way. What’s more, every feature you need comes as standard.
If you’re in the market for a new generator, get in touch with the team at Atlas CEA’s Brisbane, Sydney, Melbourne, Adelaide or Perth branch.
• atlascea.com.au
Jobs that require hard work need workwear that is up to the job in keeping workers safe and designed to last. Heavy industrial workwear has the added condition of being able to withstand industrial laundering.

Blackwoods has access to one of the largest ranges of heavyweight workwear options to keep workers safe on those tougher jobs.
Along with the foundations that 145 years of experience delivers, Blackwoods has a team of technical specialists and dedicated account managers who can conduct on-site visits to deliver in-depth fit-for-purpose product assessments, in-field technical support, product profile reviews and recommended stock profiles that are aligned directly to the needs of your business.
• blackwoods.com.au
CONFERENCES, SEMINARS AND WORKSHOPS
EVENT SUBMISSIONS CAN BE EMAILED TO EDITOR@AUSTRALIANMINING.COM.AU
Mineral Resource Estimation
Conference 2023
Perth | May 24–25
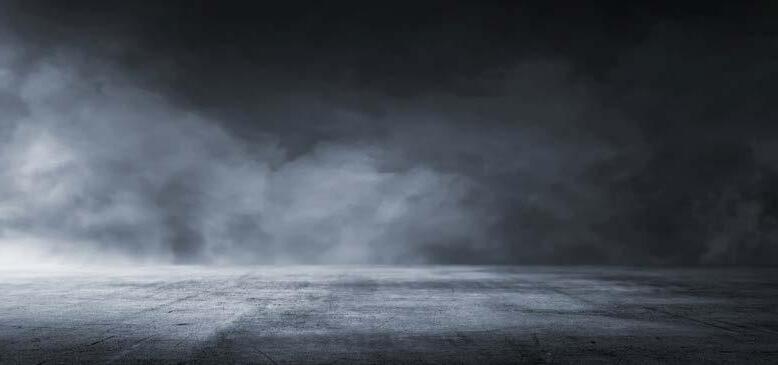
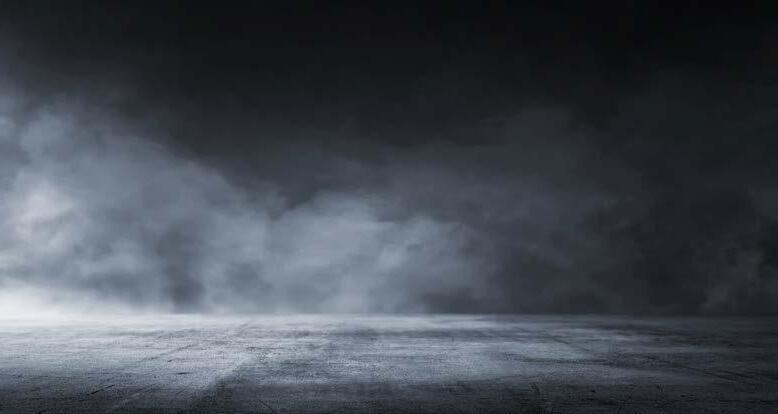
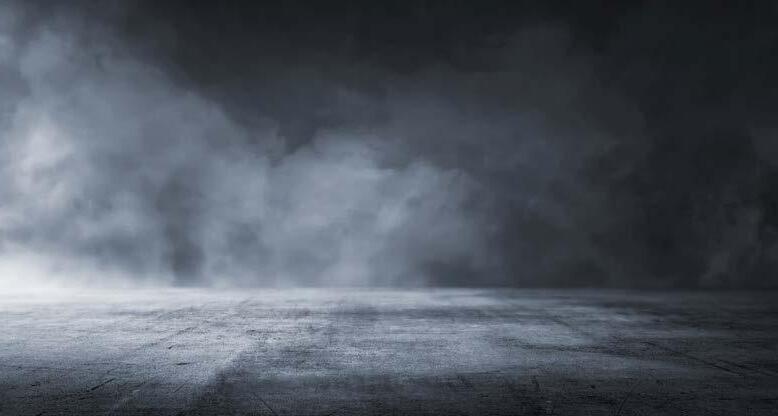
The inaugural Mineral Resource Estimation Conference 2023 will attract resource geologists to demonstrate Australasian excellence on resource estimation. The conference aims to showcase best practice, case studies and research on mineral resource estimation and the software applications required. Facilitating open exchange of information, it will include interactive sessions, panel discussions and keynote presentations alongside case studies and peer-reviewed papers.
Sessions topics will showcase the latest advancements and leading examples in QA/QC and sampling, 3D geological and estimation domain modelling, geostatistical analysis, estimation, validation and risk analysis and reporting.
•ausimm.com/conferences-and-events/ mineral-resource-estimation
World Mining Congress
Brisbane | June 26–29
Inaugurated in 1958, the World Mining Congress (WMC) is the leading international forum for the global mining and resources sectors.
The WMC 2023 is a unique opportunity for international representatives of the world’s leading resource economies to meet, find new partners, discuss current challenges, and share the latest
research, technology and best practice. WMC events have set the scene for international agreements and highlevel discussions that have influenced mining practices and the resource industry for decades.
Join senior mining industry owners, investors, national and international government representatives, researchers, educators, regulators, suppliers and operators from around the world in Brisbane for this genuine opportunity to demonstrate real leadership and presence on a world stage.
•wmc2023.org
Mine Waste and Tailings Conference 2023
Brisbane | July 13–14
The 2023 Mine Waste and Tailings Conference welcomes delegates from across to globe to explore all aspects of lifecycle waste rock and tailings management, from site selection and design to post-closure care, and will address current and future challenges affecting mining systems re-engineering. Co-hosted by AusIMM and the University of Queensland, the conference will feature industry-leading keynote presentations, thought-provoking panel discussions, interactive Q&As, a suite of insightful technical presentations and exhibitors showcasing the latest innovations.
•ausimm.com/conferences-and-events/ mine-waste-and-tailings
Life of Mine Conference 2023
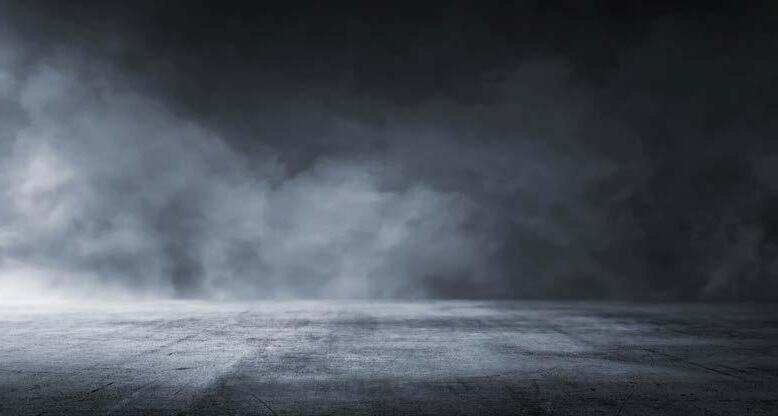
Brisbane | August 2–4
AusIMM and the University of Queensland’s Sustainable Minerals’ Centre for Mined Land Rehabilitation (CMLR) are welcoming attendees to the Life of Mine Conference 2023.
In 2021, the conference welcomed a record number of attendees from over 15 countries and is set to bring a wider, global audience in 2023. Join professionals, researchers, government, and academia from a diverse range of sectors as the program explores the full lifecycle of a mine, from exploration to rehabilitation.
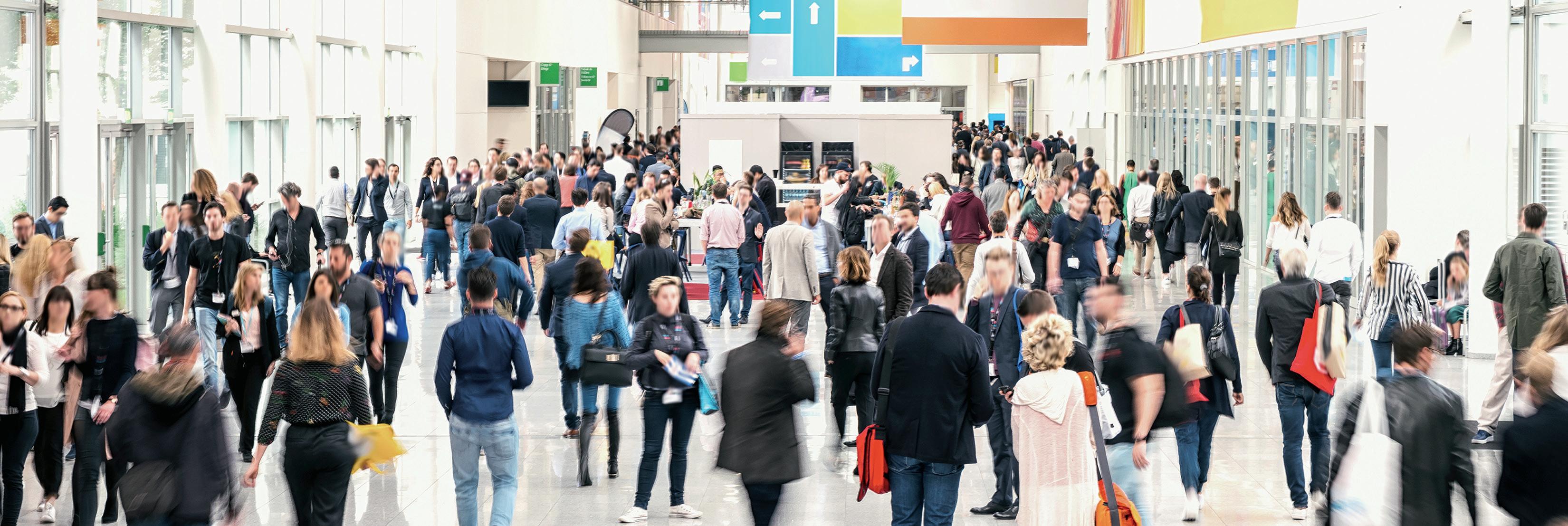
Delivered in-person and online, this outstanding technical conference addresses current and future challenges affecting the mining value chain and will present leading examples of sustainability in mining.
•ausimm.com/conferences-and-events/ life-of-mine
Australian Mining Prospect Awards
Brisbane | November 9
Taking place in Brisbane, the 2023 Australian Mining Prospect Awards are a great opportunity to recognise and acknowledge the people and companies in the mining sector for their outstanding work.
Having recently celebrated the 2022 Prospect Awards winners, nominations are now open for 2023, with awards honouring categories
such as Indigenous and Community Engagement, Mine Project Success of the Year, Outstanding Mine Performance, Sustainability Project of the Year, Discovery of the Year and more.
Some of the 2022 award winners included Kestrel Coal for Australian Mine of the Year, Roy Hill for Mine Project Success of the Year, and Flexco Australia for Excellence in IIoT Application. This year, the awards will return to Brisbane in appreciation of the vibrancy and importance of the state’s thriving mining industry.
•prospectawards.com.au
Critical Minerals Conference 2023 Perth | November 21–23
Critical minerals are essential components in many of today’s rapidly growing clean energy technologies – from wind turbines and electricity networks to electric vehicles.
The increasing appetite and rapid pace of the transition to cleaner energy sources continues to drive the growth in demand for these minerals, and in response the supporting industries are also growing at unprecedented rates.
To address this rapid growth, AusIMM will launch its inaugural Critical Minerals Conference in 2023. The event will include a multi-stream format and seek to engage with a larger audience from multiple disciplines, as well as a wide range of industries.
•ausimm.com/conferences-and-events/ critical-minerals
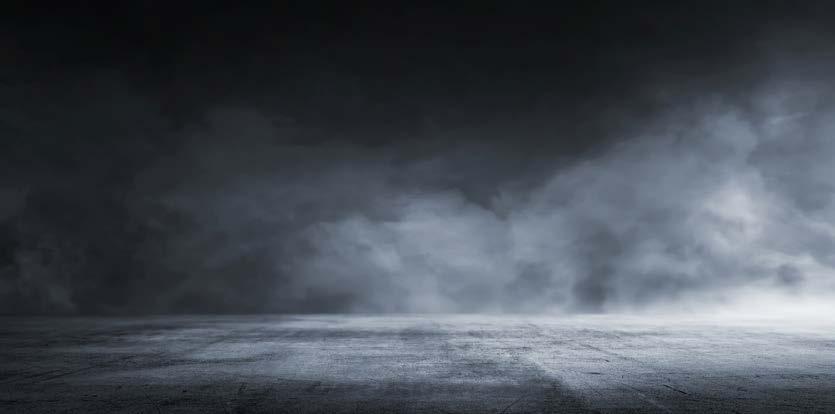
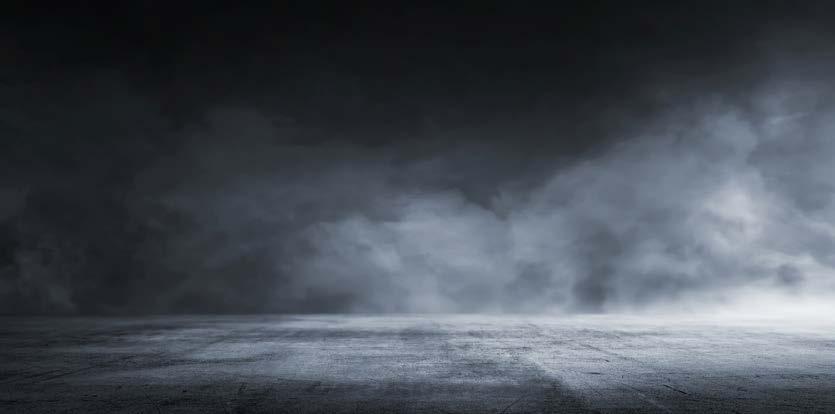
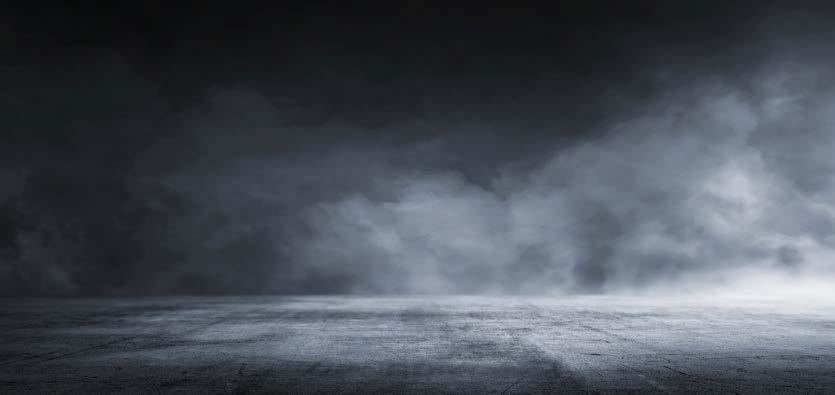

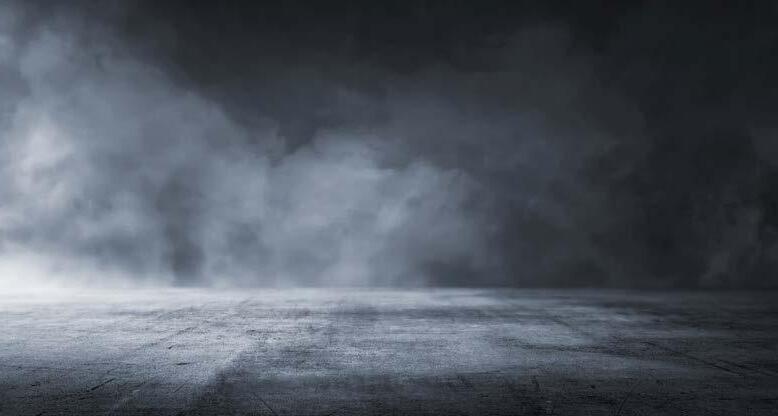
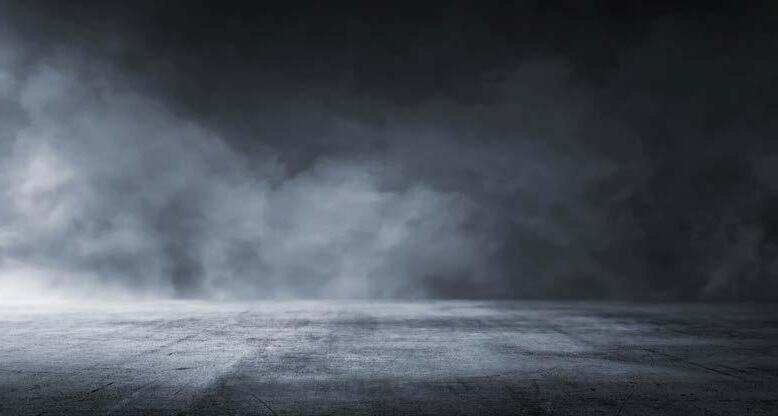
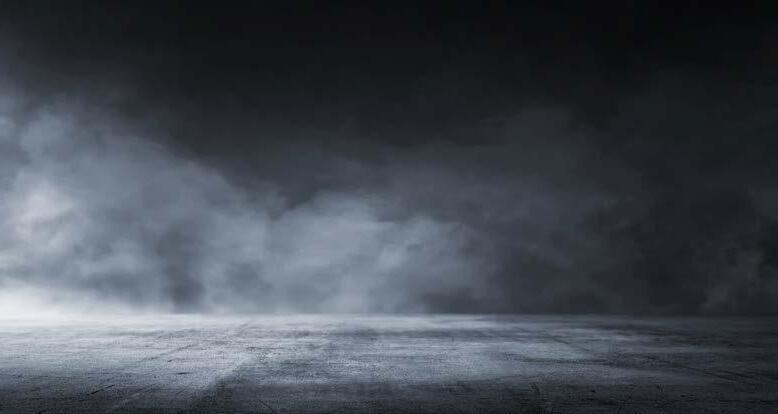
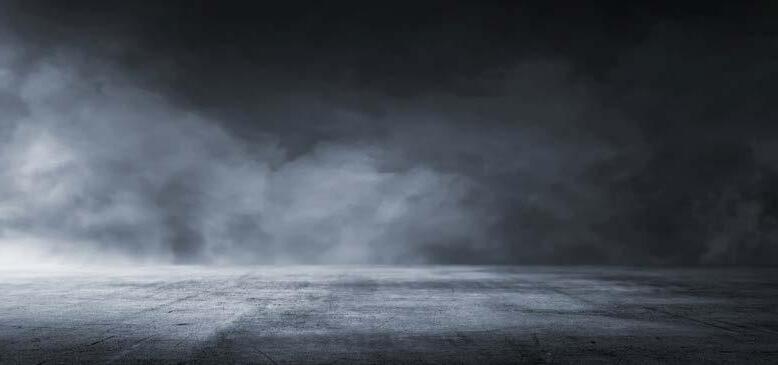

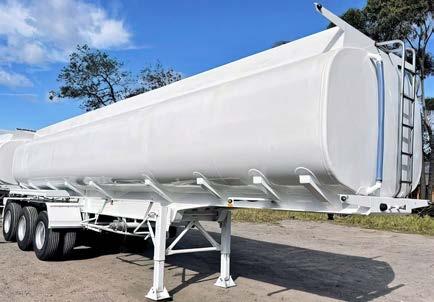
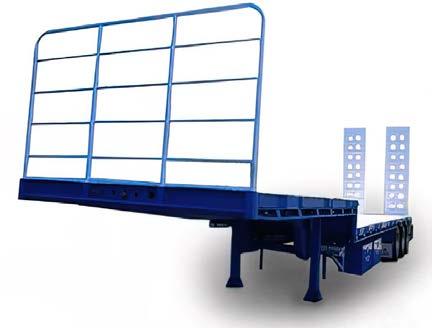


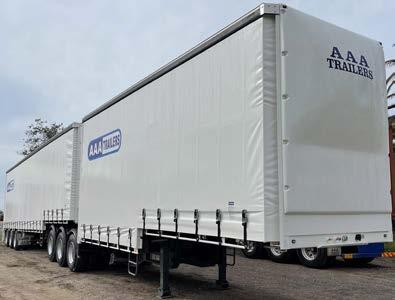

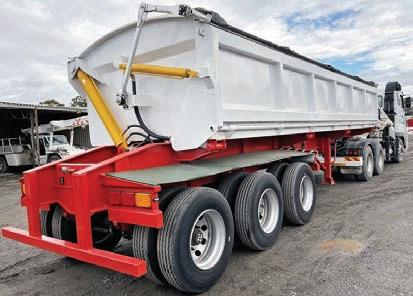
WE SOLVE YOUR WATER CHALLENGES
SUBMERSIBLE SLURRY PUMPS FOR HEADACHE SUMPS
Less sediment, less downtime, less trouble.
Slurry sumps can be a constant hassle. Pumps wear hard and fast, and the sumps fill up with sediment. Cantilever pumps are often not up to the task. We know, because that’s when we are called in.
The advanced CFD design of Flygt slurry pumps ensures exceptional levels of abrasion resistance. In addition, we provide an array of measures that keeps sumps clean, even with the heaviest slurries.
SALES - SERVICE - RENTAL
