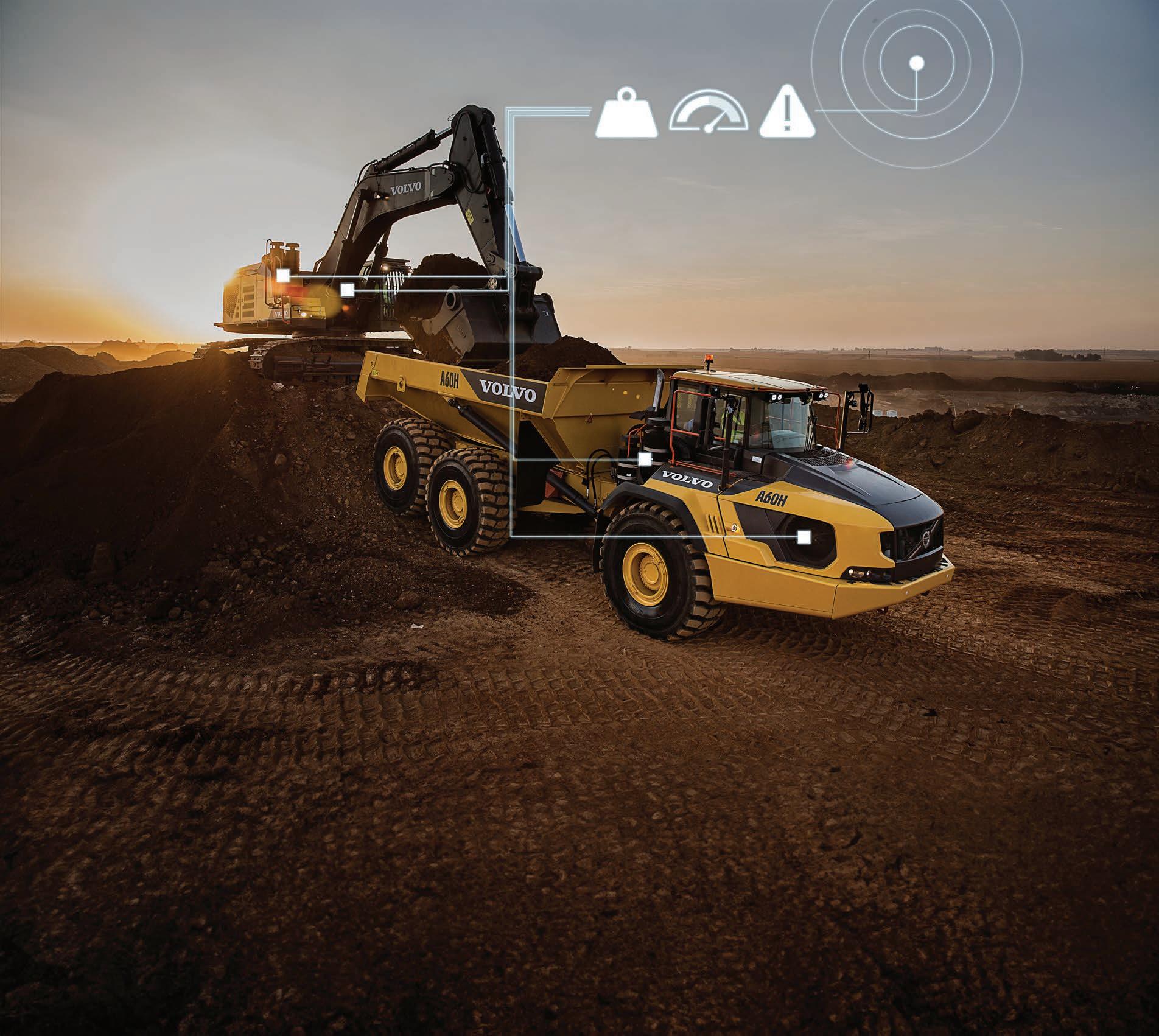
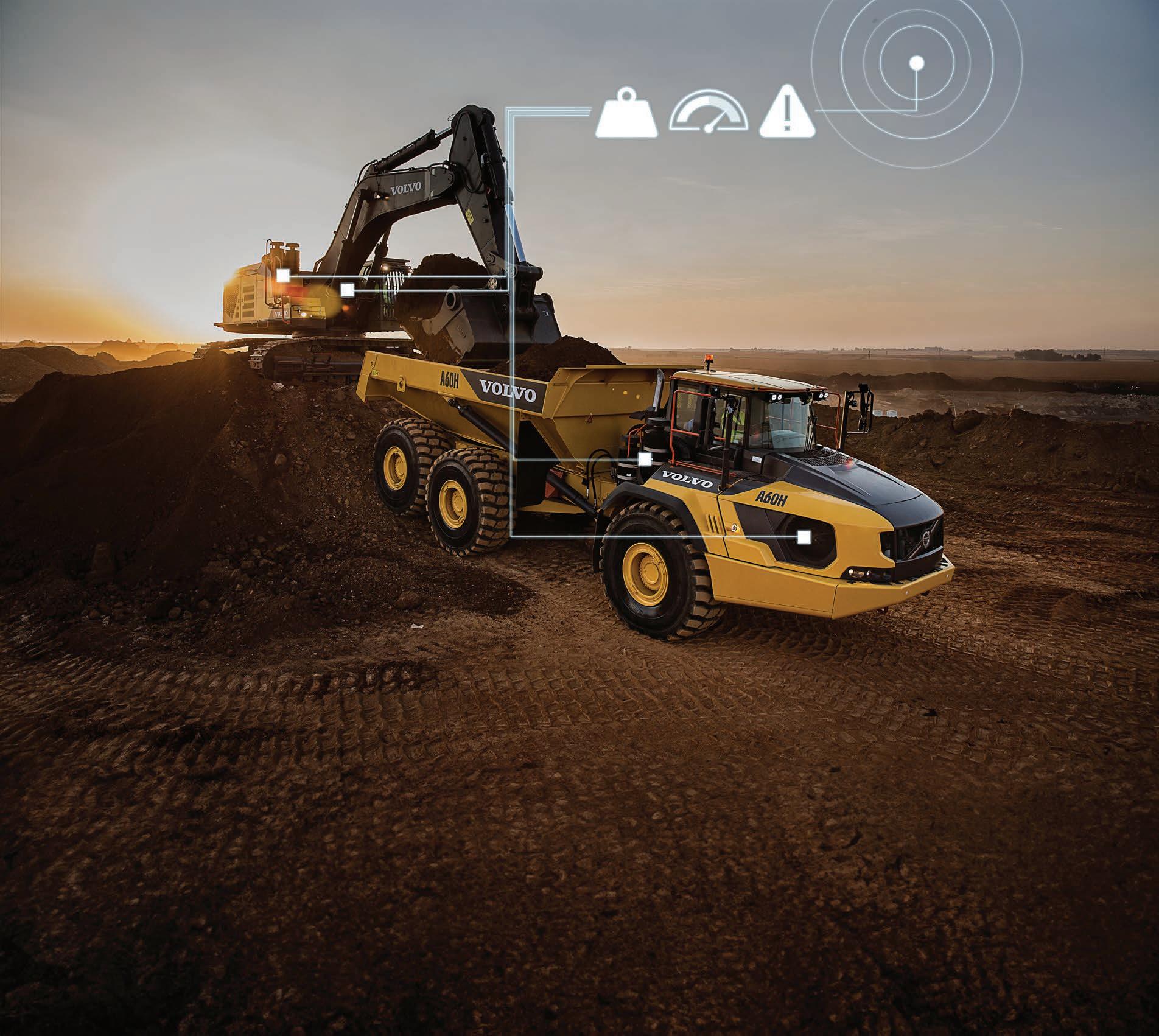
Diamond technology that makes your drill bit last longer

United. Inspired.
Powerbit X
Drill bits where the buttons are engineered with diamonds. This technology is called PCS (polycrystalline diamond), and it protects your people, your productivity, and the environment. Improve safety with fewer bit changes, boost productivity by drilling without interruption, and cut down on CO2 emissions by up to 90% since there won’t be a need for regrinding! Explore how Epiroc diamond technology can benefit your mining operations.
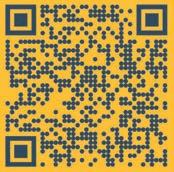

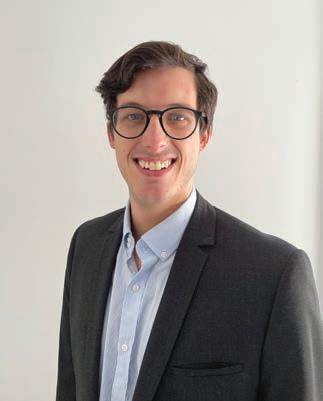
FIRING ON ALL CYLINDERS
IN A MINING SECTOR WHERE OPERATIONS ARE PRESSED TO DELIVER MORE TONNES MORE QUICKLY AND SAFELY, THE METS SECTOR HAS NEVER BEEN IMPORTANT.
The Australian resources industry couldn’t operate as it does without the mining equipment, technology and services (METS) sector delivering the innovations and continued advancements it does today.
Investors and company executives are calling on miners to deliver more tonnes to circumvent any losses incurred from rising capital and operational expenditure.
And miners can only do the best with what they’ve got, which can be difficult when deposits are simultaneously declining in grade.
This is why maximising the efficiency of an operation is so critical to a company’s bottom line, with companies and contractors who can extract more ore through a lower footprint that will be best off.
Driving greater operational efficiency is not just about meeting production KPIs and lowering costs, it’s also about limiting carbon emissions and satisfying the increasing sustainability expectations of investors, stakeholders and regulators.
In the May edition of Australian Mining, we showcase the METS companies that are enabling this new reality, with specialist engineering, tailored technology, and improved operational synergy seemingly the way of the future.
We sat down with MASPRO to discuss the company’s Bolting Series 2.0 – a series of specialist components that are boosting the machine life of Sandvik’s widely used SB60 booms.
Regal Rexnord also takes the spotlight, with its many different brands providing critical
braking technologies for the Australian mining industry. Namely, Svendborg Brakes is a key braking solutions provider for ball and semiautogenous grinding (SAG) mills, shovels, draglines and reclaimers.
Smart-VOD shines a light on its innovative ventilation on-demand solution, while Observr is ensuring mining companies can do away with paperwork for good. That’s just the beginning of our ‘efficiency and optimisation’ featured section.
Elsewhere, we tell the story of Epiroc’s commitment to electrification, and explore how the esteemed original equipment manufacturer is facilitating the electric transition.
Mineral Resources has been particularly active in growing its Australian lithium business in recent times. We unpack several of the company’s key lithium moves.
This edition also prioritises mental health, with a feature diving deep into the latest iteration of Curtin University’s Mental Awareness, Respect and Safety (MARS) study, where more than 2550 Western Australian mine workers were surveyed for their perceptions of mental health awareness in the workplace.
To round out this edition, feature stories explore what Australia’s precious metals future looks like, and how the copper industry is looking to drive down carbon emissions.

FRONT COVER
Founded in 1974, CJD Equipment is a privately owned Australian company whose core business involves the national distribution of construction equipment and trucks.
The CJD product portfolio consists of world-class brands such as Volvo, SDLG, Kenworth, DAF, Isuzu, and Fuso.
Volvo Construction Equipment (Volvo CE) offers solutions to enhance site management through optimised Volvo excavators, wheel loaders, and articulated haulers. Integrating these solutions is vital for companies aiming to stay ahead in competitive markets like quarrying and mining.
This is where Volvo CE’s Connected Map comes to the fore, providing real-time digital mapping of all of a site’s machines, vehicles and personnel, allowing for enhanced visibility and informed decision-making.
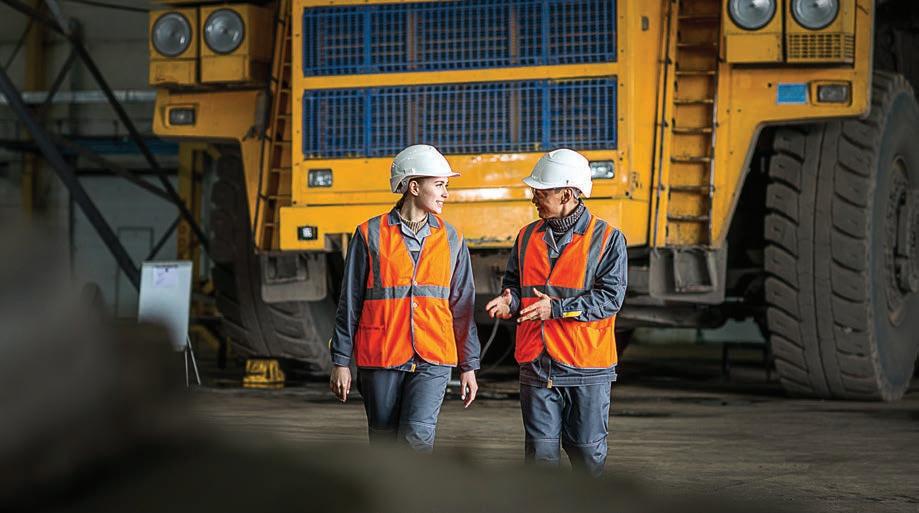
Lithium: MinRes’ proven winner
Lithium is becoming MinRes’ bread and butter. Australian Mining takes a look at the major’s latest moves.
14 INDUSTRY INSIGHT
Head in the game
The latest MARS mining mental health study revealed an era of change for the industry. So what are operators doing to prioritise mental wellbeing?
18 EFFICIENCY AND OPTIMISATION
Beyond machinery
Visibility in equipment brings insight, opportunities for growth and improvement, and ability to manage operations and enhance safety and efficiency.
36 EFFICIENCY AND OPTIMISATION
iSense comes to the rescue
Treotham is bringing igus’ iSense range to Australia’s mining industry for smarter energy chain maintenance.
Coatings to cure corrosion woes
IGS’ alloyed coating solutions keep even the most aggressive corrosive materials away from critical mining equipment.
54 SUSTAINABILITY
On the copper road to net zero
Copper is a critical enabler for a decarbonised world. But how can the industry ensure copper mining stays as sustainable as possible?
66 COMMODITY SPOTLIGHT
The future of precious metals
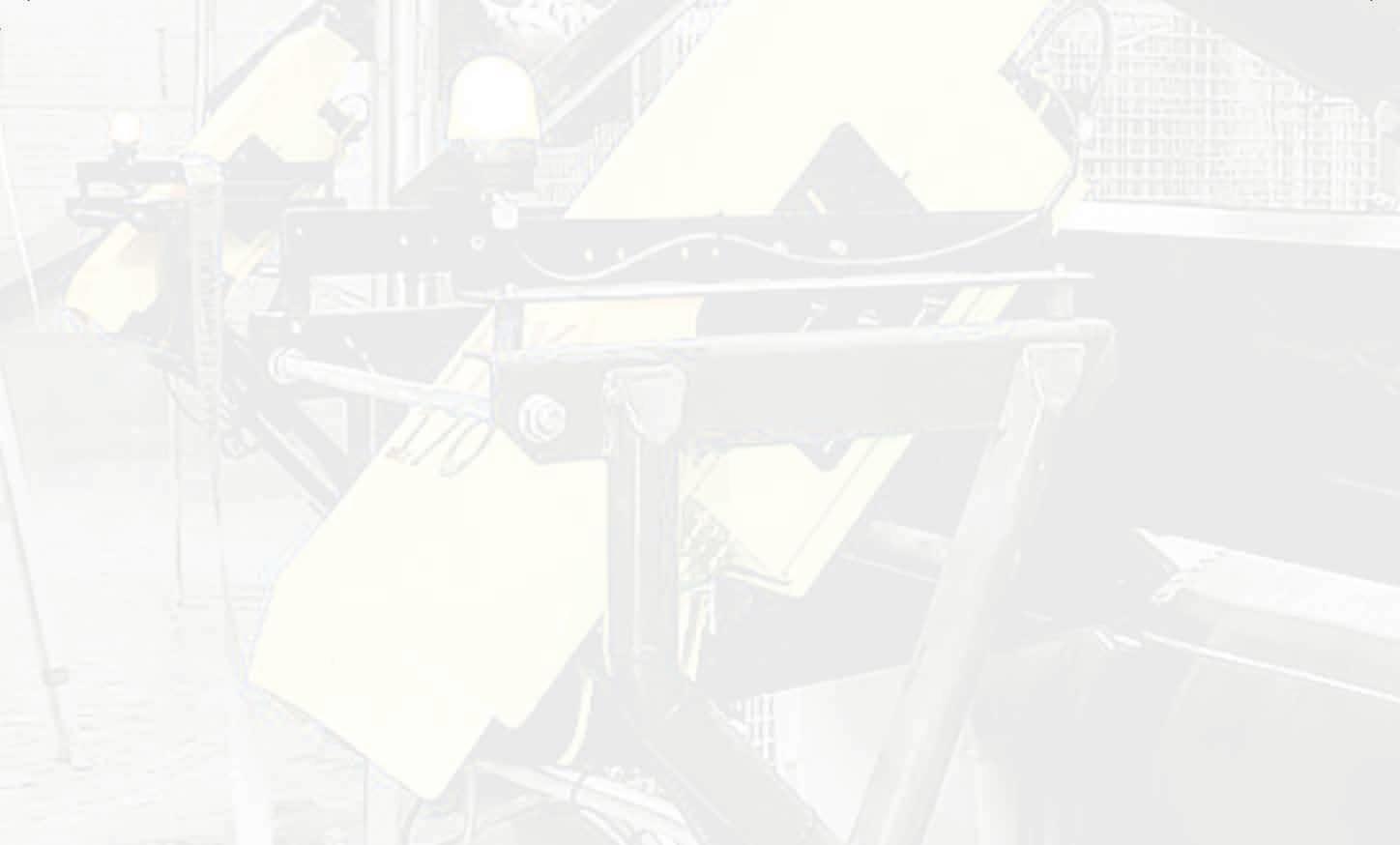
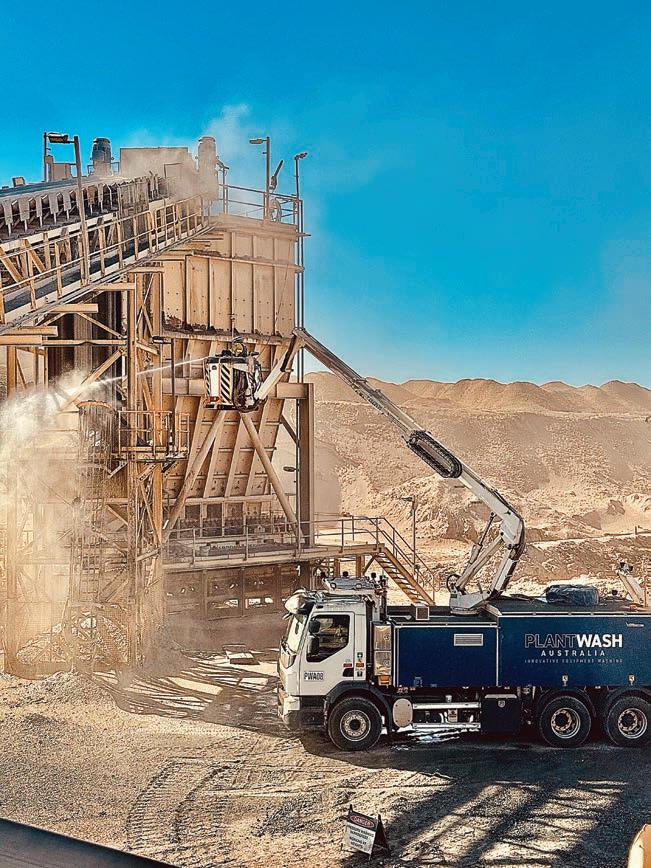
Australian Mining shines a light on Argent Minerals, Kalamazoo Resources and Falcon Metals – three companies looking to become precious metals producers.
70 EQUIPMENT
A Herculean achievement
WA mining product and services supplier Schlam reached a significant milestone with the delivery of its 2000th Hercules dump truck body.

Unveiling the future
The countdown is on for the highly anticipated 2024 Queensland Mining and Engineering Exhibition
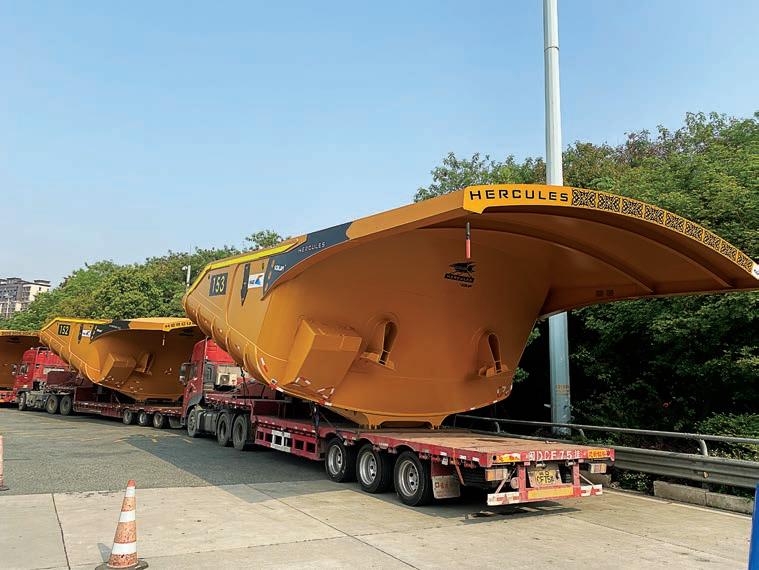
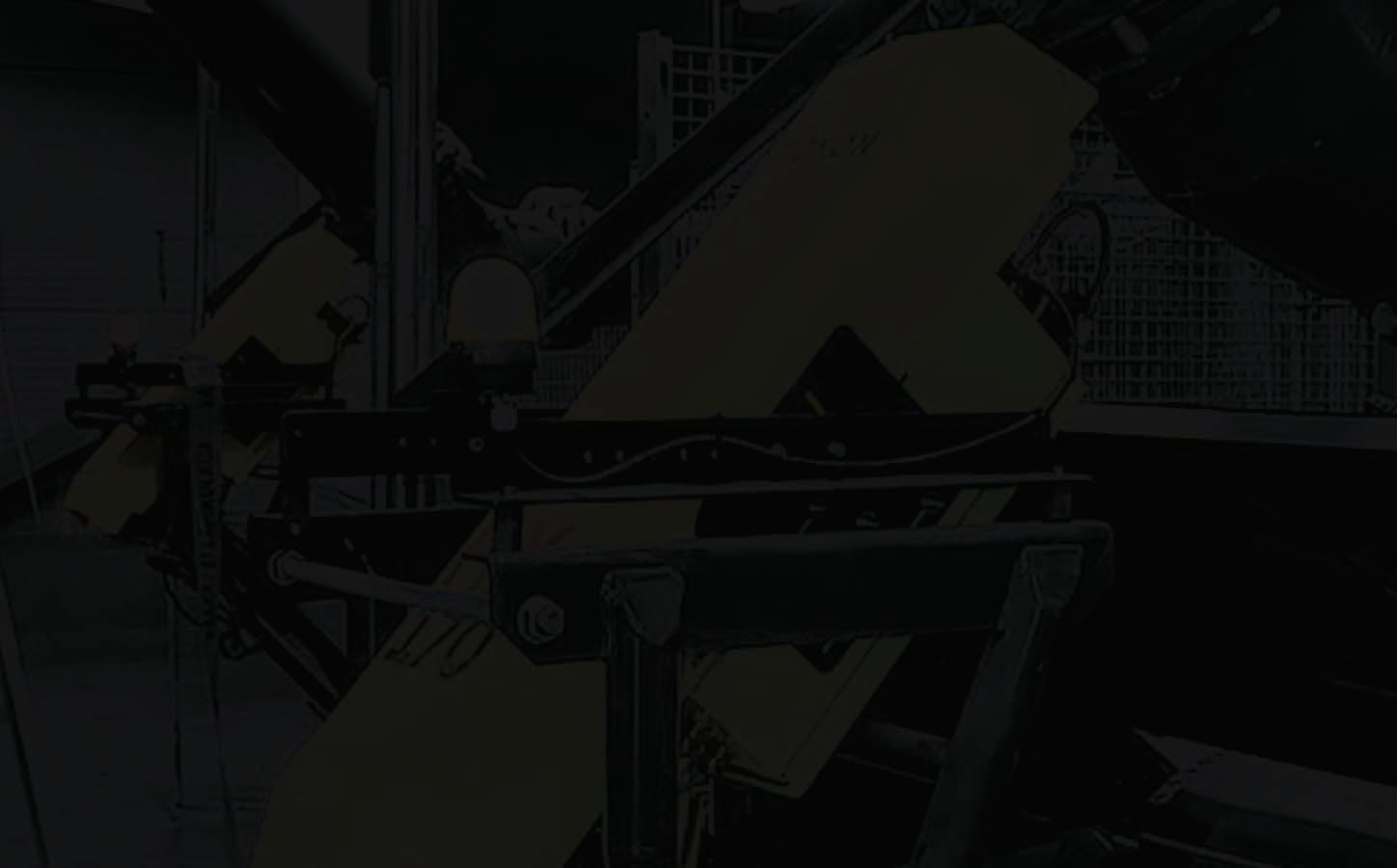
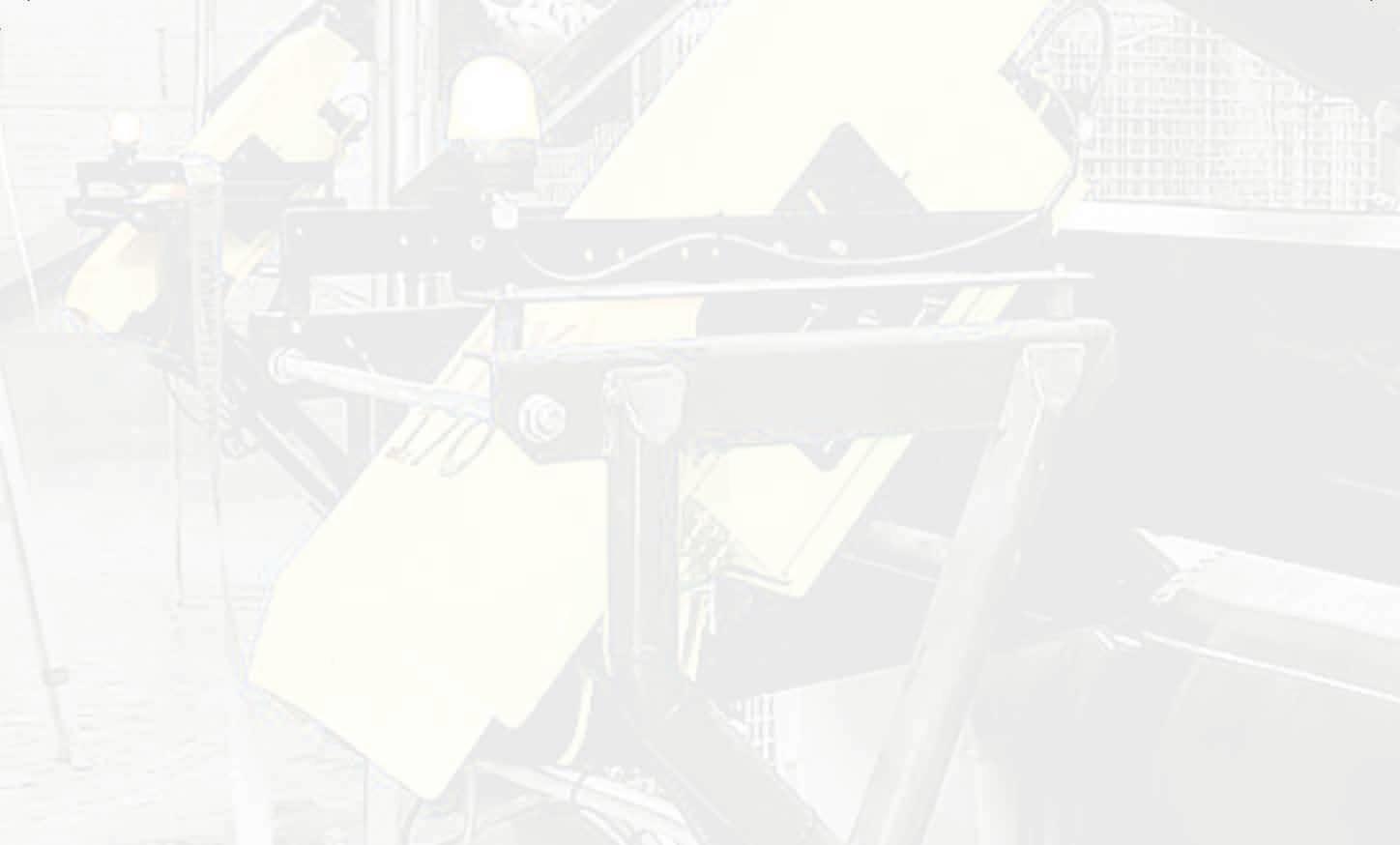
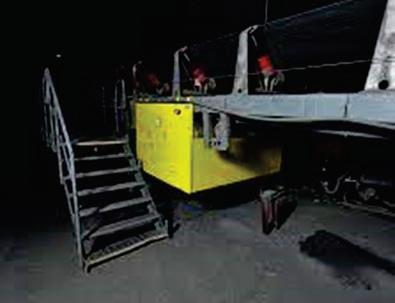
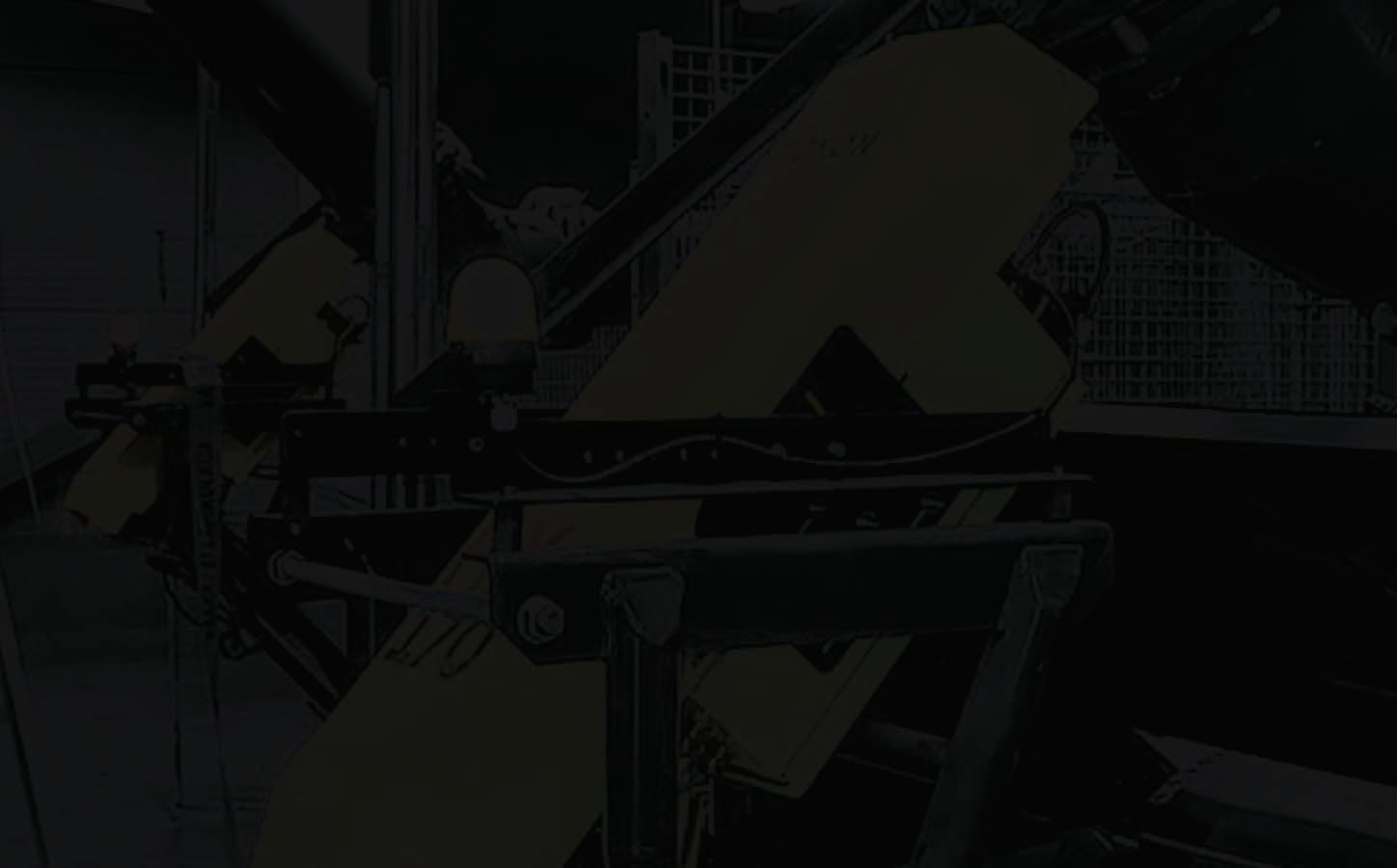

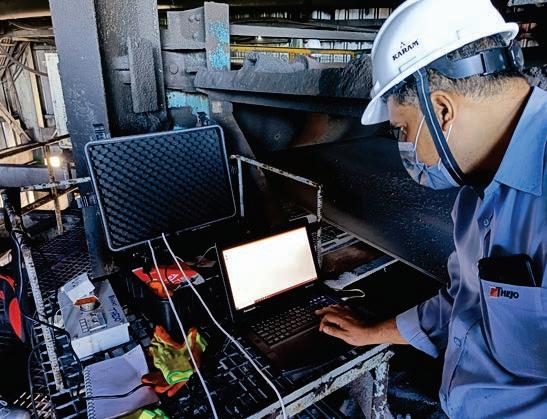
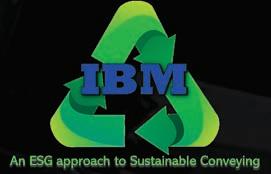
FOLLOW THE LEADERS: THE LATEST EXECUTIVE APPOINTMENTS
KEEP UP WITH THE LATEST EXECUTIVE MOVEMENTS FROM ACROSS THE MINING SECTOR, FEATURING BHP, RIO TINTO AND GLENCORE.
BHP announced changes to its board in March that saw new talent join the team, while the company said goodbye to a familiar face.
insights and perspectives through a period of significant change for BHP and he has been committed to creating shareholder value.”
MacKenzie went to on welcome Lindsay.
BHP non-executive director Ian Cockerill has confirmed his decision to retire after he was appointed chief executive officer and executive director of Endeavour Mining in January.
Cockerill joined the BHP board in April 2019 and has since been a member of the Risk and Audit Committee and Sustainability Committee.
Taking Cockerill’s place as nonexecutive director is Don Lindsay, bringing over 35 years of experience in the resources sector and investment banking.
From 2005 to 2022, Lindsay was president and chief executive officer of Canadian miner Teck Resources.
Lindsay is currently the chair of Manulife Financial Corporation and has also served as the chair of the Board of Governors for Mining and Metals for the World Economic Forum and other leading bodies.
BHP chair Ken MacKenzie farewelled Cockerill and wished him success in his next role.
“I would like to thank Ian for his considerable contribution to the board and BHP during his time as a director,” he said.
Ian’s deep global technical and operational experience across a range of commodities has provided valuable
“We are delighted to announce that Don Lindsay will join BHP,” he said. “Don has extensive experience in global mining operations, having been the CEO of Canadian diversified mining company Teck Resources for 17 years.
“Don brings a strong focus on global resource development, growth and value creation and community health safety and education.”
Rio Tinto has appointed its former copper chief executive Bold Baatar to the role of chief commercial officer (COO) following its current COO Alf Barrios’ decision to retire.
Baatar is set to take on accountability for business development immediately, and will relocate to Singapore to take up the role of COO in September.
The new appointment will see Baatar lead Rio’s commercial organisation, accountable for sales and marketing, procurement, marine, and logistics activities.
He will also take on leadership for business development and maintain his role as executive committee lead for Guinea, continuing to head Rio Tinto’s relationships with its joint venture partners on the Simandou project.
“Bold is ideally suited to help deliver our strategy of building a stronger Rio
Tinto for the future and growing with discipline, as he leads our commercial and business development activities,” Rio chief executive Jakob Stausholm said.
“The directors are very pleased to welcome John Wallington to the board,” Madhavpeddi said.

“He brings deep experience across geographies, commodities, and markets – and combines strong business development expertise with a focus on developing world class relationships.
Baatar joined Rio in 2013 and has been an executive committee member since December 2016.
Glencore has announced that Peter Coates will be retiring from his role on the board. Coates joined the board in 2011 and chaired the HSEC Committee from the beginning.
“Peter’s retirement marks the end of two long eras,” Glencore chair Kalidas Madhavpeddi said.
“First, it ends a career in mining that goes back more than half a century. Second, it completes a thirty-year association with Glencore, which started in 1994 when he was appointed to lead Glencore’s then embryonic coal industrial business.
“All of the board joins me in wishing Peter a long and happy retirement.”
John Wallington has been appointed as an independent non-executive director, effective from June 1.
Wallington brings over four decades of experience to the role, having held positions as chief executive officer of Anglo Coal, Coal of Africa and Riversdale Resources.
“We believe it is crucial that we have several non-executive directors who know the industry well and who can appraise and challenge decision making from a technical as well as a commercial perspective.
“John has spent his entire career in the mining industry and we look forward to benefiting from his skills and experience.”
Karen Lloyd joined the team at Genesis Minerals as a non-executive director on April 1.
Lloyd is an experienced mining engineer and geologist with a PhD in mining and metallurgical engineering from the WA School of Mines.
Genesis chairman Tony Kiernan said Lloyd is a welcome addition to the team.
“Karen’s knowledge and diverse range of experience across all aspects of the mining business will complement the board’s existing skill set and prove invaluable as we implement our growth strategy,” he said.
“Genesis has established the asset base to ensure we meet our 300,000-ouncesper-annum target.
“We are now focused on the operational and commercial strategies which will drive this growth and Karen’s deep technical understanding of our industry means she will play a key role in helping us achieve these objectives.” AM
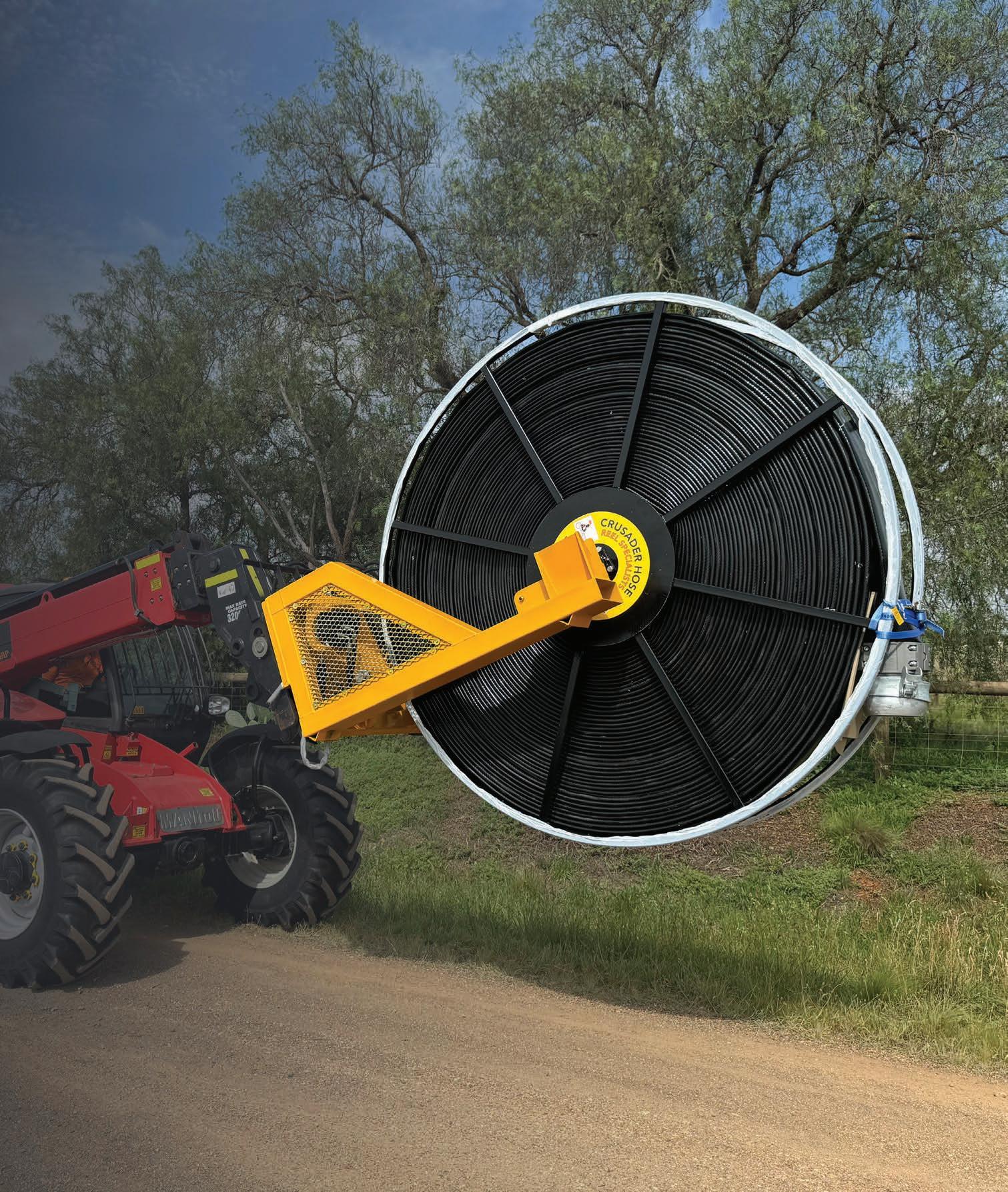
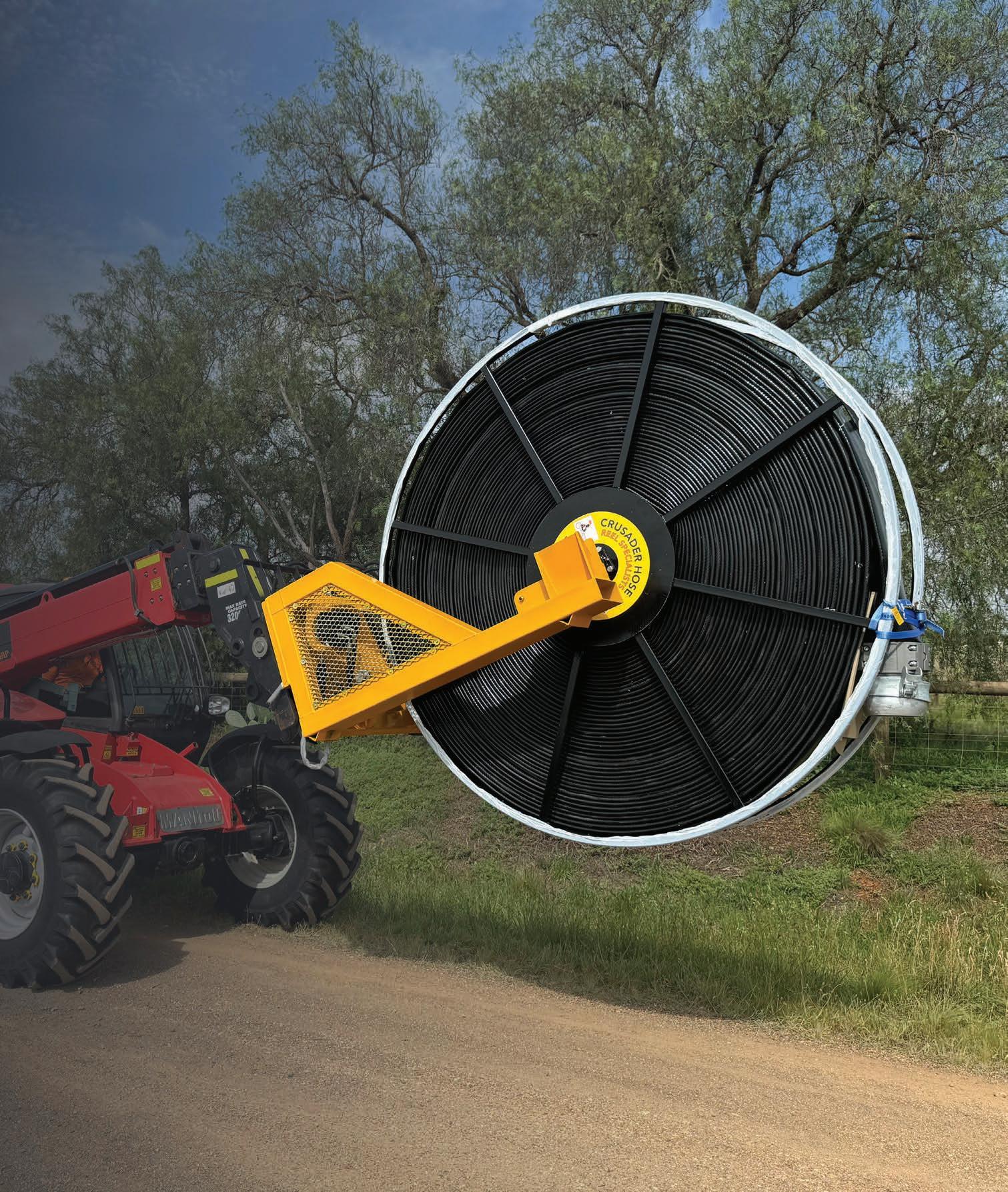
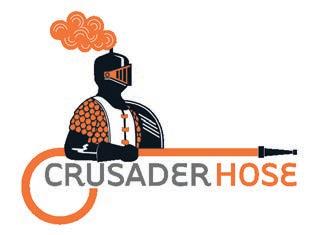
THE LATEST MINING AND SAFETY NEWS
WHAT’S NEXT FOR THE AUSTRALIAN RESOURCES SECTOR?
THE DEPARTMENT OF INDUSTRY, SCIENCE AND RESOURCES’ MARCH 2024 RESOURCES AND ENERGY QUARTERLY IS OUT, FORECASTING HIGHS AND LOWS ACROSS AUSTRALIAN COMMODITIES.
The Resources and Energy Quarterly (REQ) for March 2024 has estimated earnings from resources and energy exports may fall to $417 billion from $466 billion recorded in 2022–23 as world economic growth remains soft.
Despite the drop, the forecast is an improvement from the $408 billion estimated in the December REQ.
“While global prices are easing, the March 2024 Resources and Energy Quarterly shows demand is likely to be sustained for commodities used in low emissions technologies, including iron ore, copper, aluminium and lithium,” Federal Minister for Resources Madeleine King said.
Iron ore
Demand for Australian iron ore is set to rise over the next decade, but the overall outlook may be more complicated.
Prices hovered around $US125 per tonne (t) in January and February, a marked improvement from a previous $US98/t slump in mid-2023.
But a swift fall to seven-month lows in March reflected rising concerns about a rapid build-up of Chinese iron ore inventories amid sluggish growth in steel output in early 2024.
As additional greenfield supply comes online from established and emerging producers, Australian export volumes are forecast to increase by 1.6 per cent annually through to 2029.
Iron ore exports are tipped to rise to $136 billion in the 2023–24 financial year (FY24), before dropping to $107 billion in FY25 and $83 billion by FY29.
Lithium
While the world’s hunger for lithium is set to more than double by 2029, Australia’s export earnings for the metal are projected to fall by more than half between now and then.
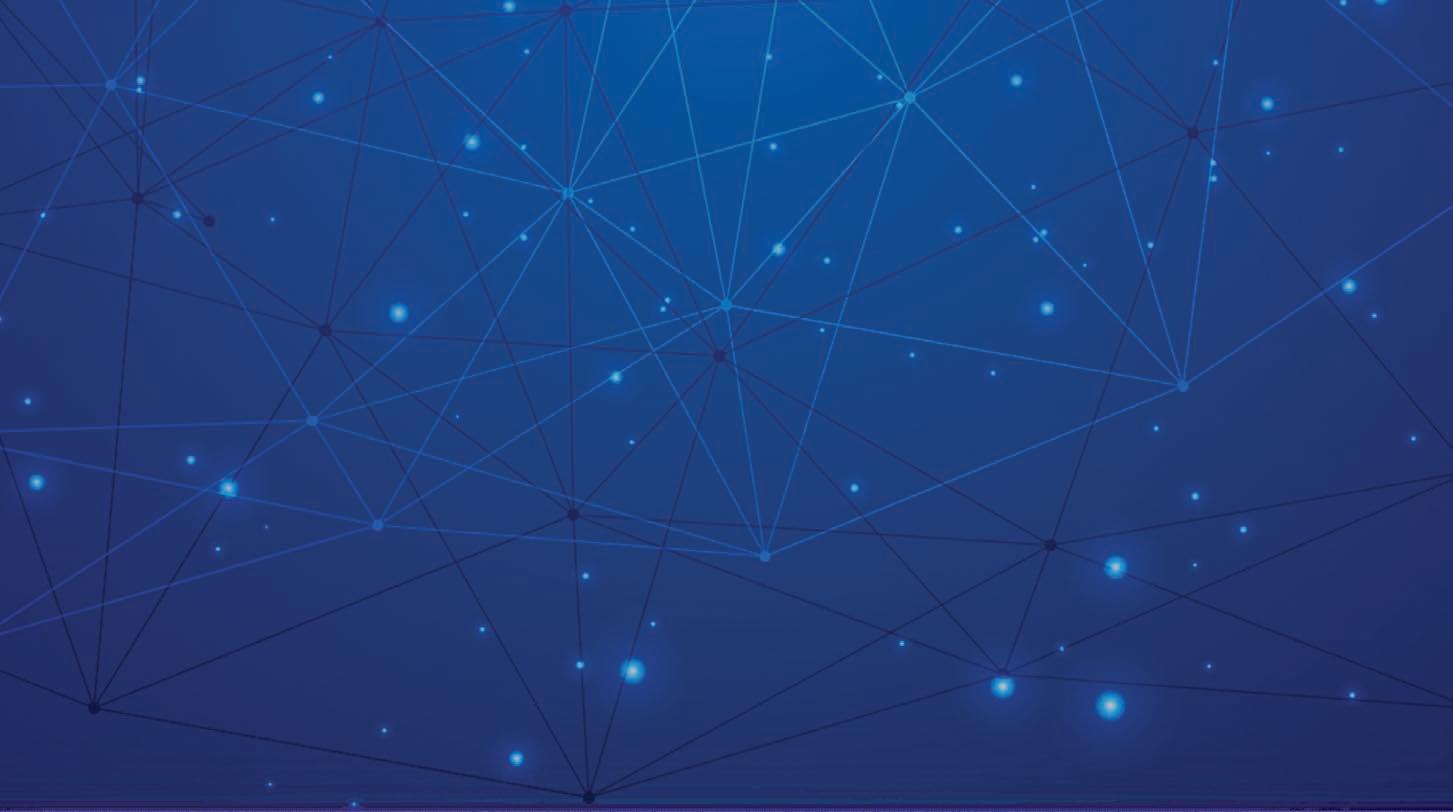
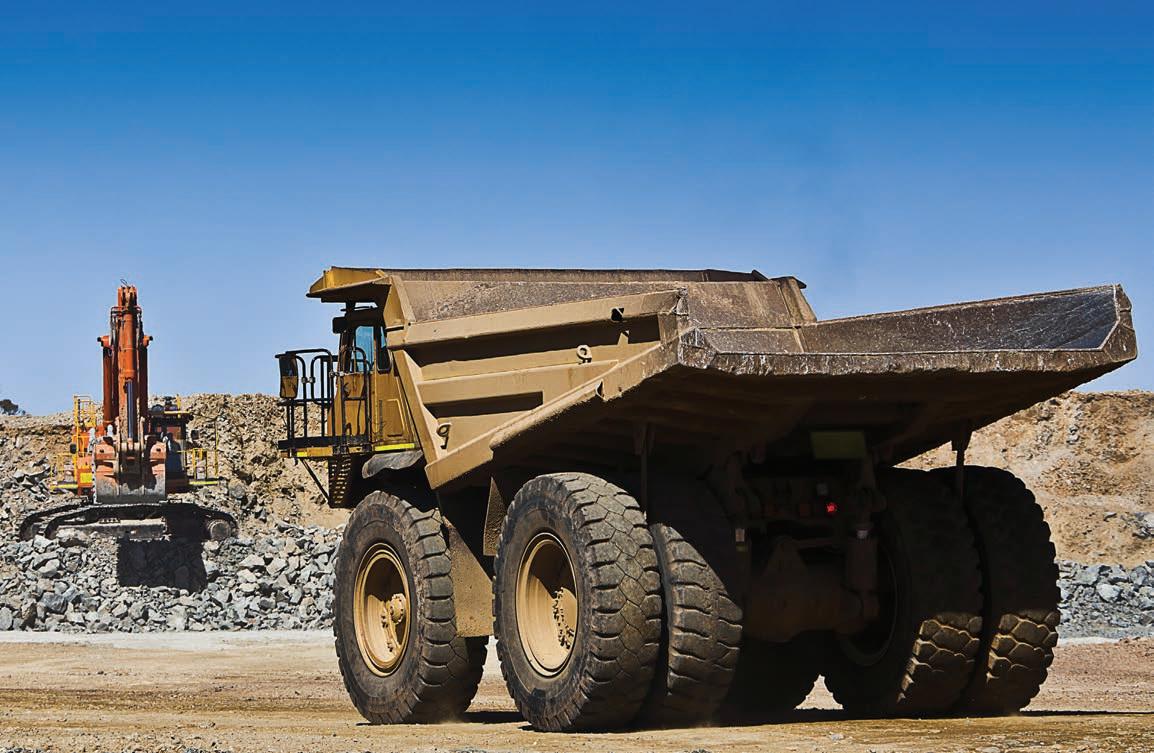
That’s a decrease of $21 billion to $9 billion over five years. But the outlook is not so grim, with the REQ emphasising that prices are extremely difficult to predict with certainty. Lithium exports are also coming off record high levels.
Encouragingly, the REQ expects lower prices to be offset by a projected 70 per cent increase in Australia’s lithium mine production to 2029.
Overall global lithium supply is projected to broadly keep pace with rising demand, with promising project pipelines among large producers such as Australia and China, supported by new and emerging producers like Argentina and Zimbabwe.
Electric vehicles are set to drive global demand, with a forecast 16 per cent rise every year, reaching 2.3 million tonnes by 2030.
In February 2024, the lithium spodumene price fell to an average of $US1000/t, while the lithium hydroxide price fell to average $US13,350/t.
But it’s important to remember commodities rise and fall in waves, and
prices have returned to similar levels as was seen prior to the 2021 rally.
Indeed, the REQ foresees a steady rise in prices to 2026 before edging back again. The spodumene price is forecast to rise to about $US1360/t, and lithium hydroxide is tipped to push $US18,000/t.
Coal
The global appetite for coal grew eight per cent in 2023, but global conditions and volatile weather patterns are setting an uncertain stage for the commodity.
The REQ revealed coal to be Australia’s largest exporter in 2023 at around 170 million tonnes.
It’s a huge boon for the country, as overall global metallurgical coal demand is projected to rise from 317 million tonnes in 2023 to 331 million tonnes by 2029.
On the price side, Australian prime hard coking coal averaged $US294/t in 2023, significantly lower than the 2022 average of $US360/t.
The REQ forecast prices to continue to experience volatility as a result
of supply side issues like logistical pressures and weather events like Cyclone Jasper.
Prices are expected to broadly trend downwards in 2024, averaging $US277/t for the year.
The volatility comes from the likelihood of a new La Niña cycle and associated disruptions. In real terms, prices are expected to fall to $US185/t by 2029.
But the REQ held an overall positive outlook as Australian coal export volumes are expected to increase from 161 million tonnes (Mt) in 2023–24 to 175Mt by 2028–29, as mines in NSW and Queensland ramp up.
These prospects include Bowen’s Bluff mine, Burton and Broadmeadow East projects, Pembroke’s Olive Downs complex, and Anglo American’s German Creek among others.
Overall, the fundamentals remain favourable, with Australia primed to continue dominating the global market for commodities in 2024 and beyond.
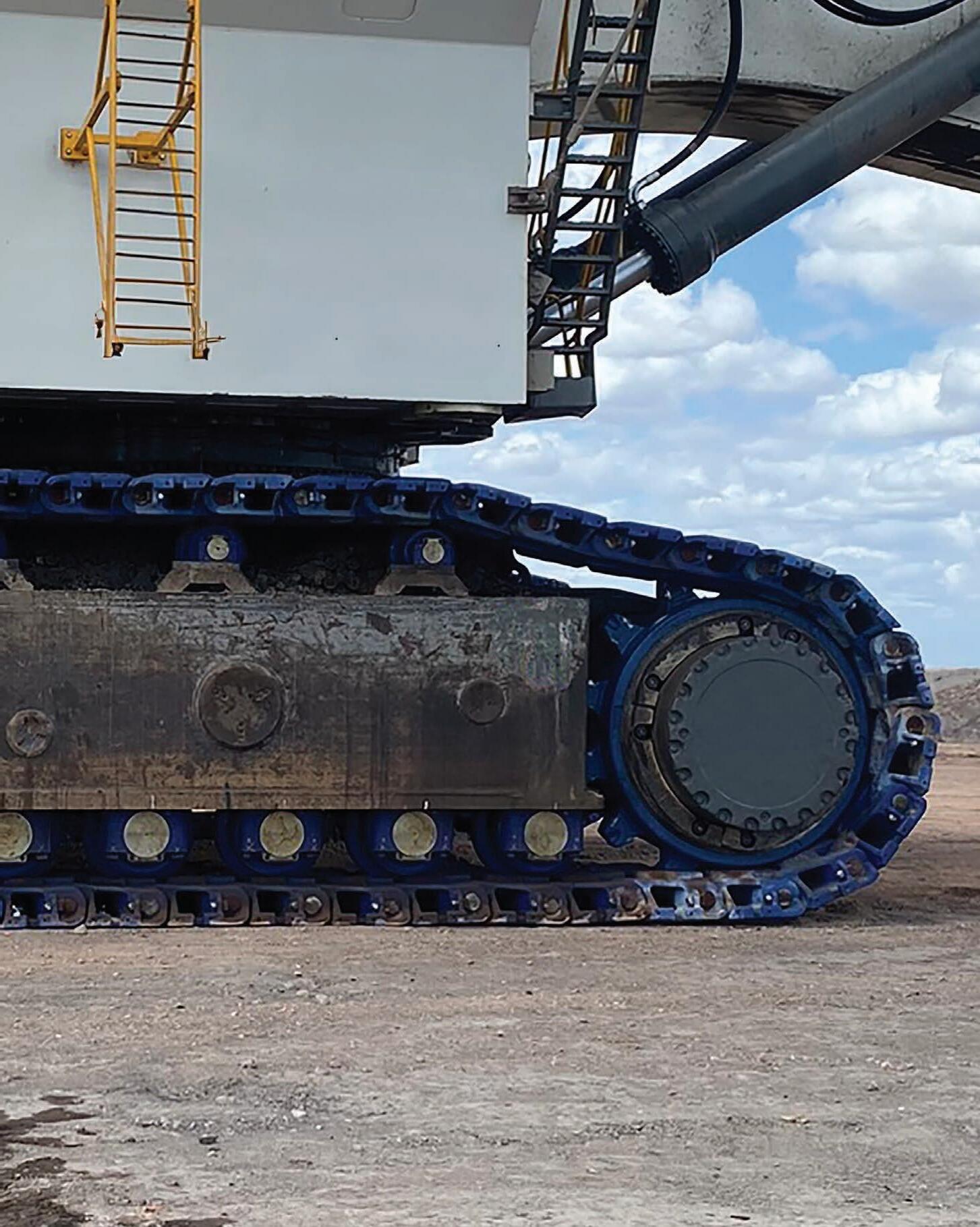
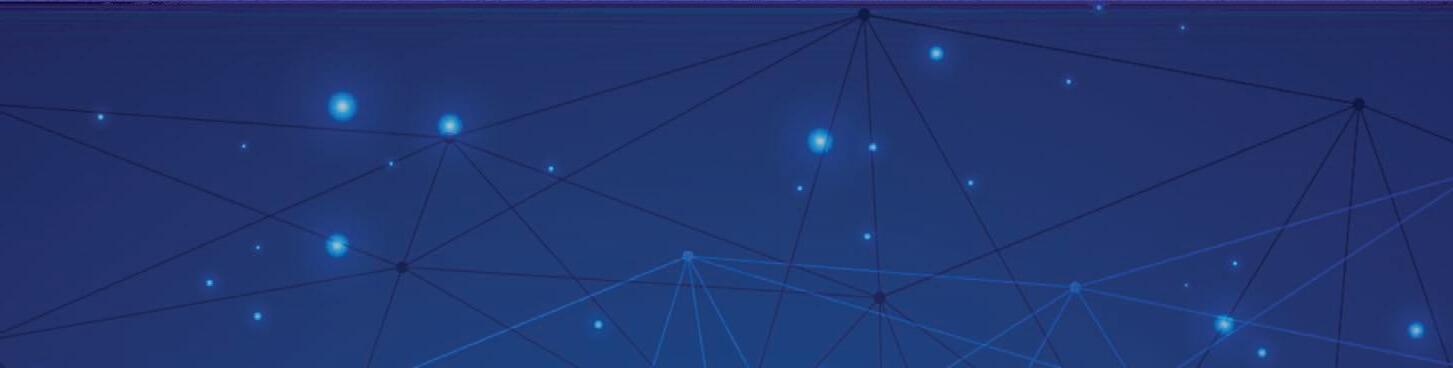
Now Selling Direct to Market. Bradken® Undercarriage for R9800 Excavators
With over four decades of expertise in delivering cutting-edge undercarriage solutions worldwide, Bradken has optimised the R9800 to improve performance.
Bradken has long been the manufacturer for the OEM. From 2007 to 2021 Bradken seamlessly designed and supplied crawler shoes to the OEM, equivalent to more than 65 full machine fitments for mining customers.
Our products include:
• Crawler Shoes
• Drive Tumblers
• Return Rollers
• Load Rollers
• Idlers
bradken.com
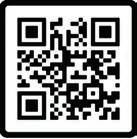
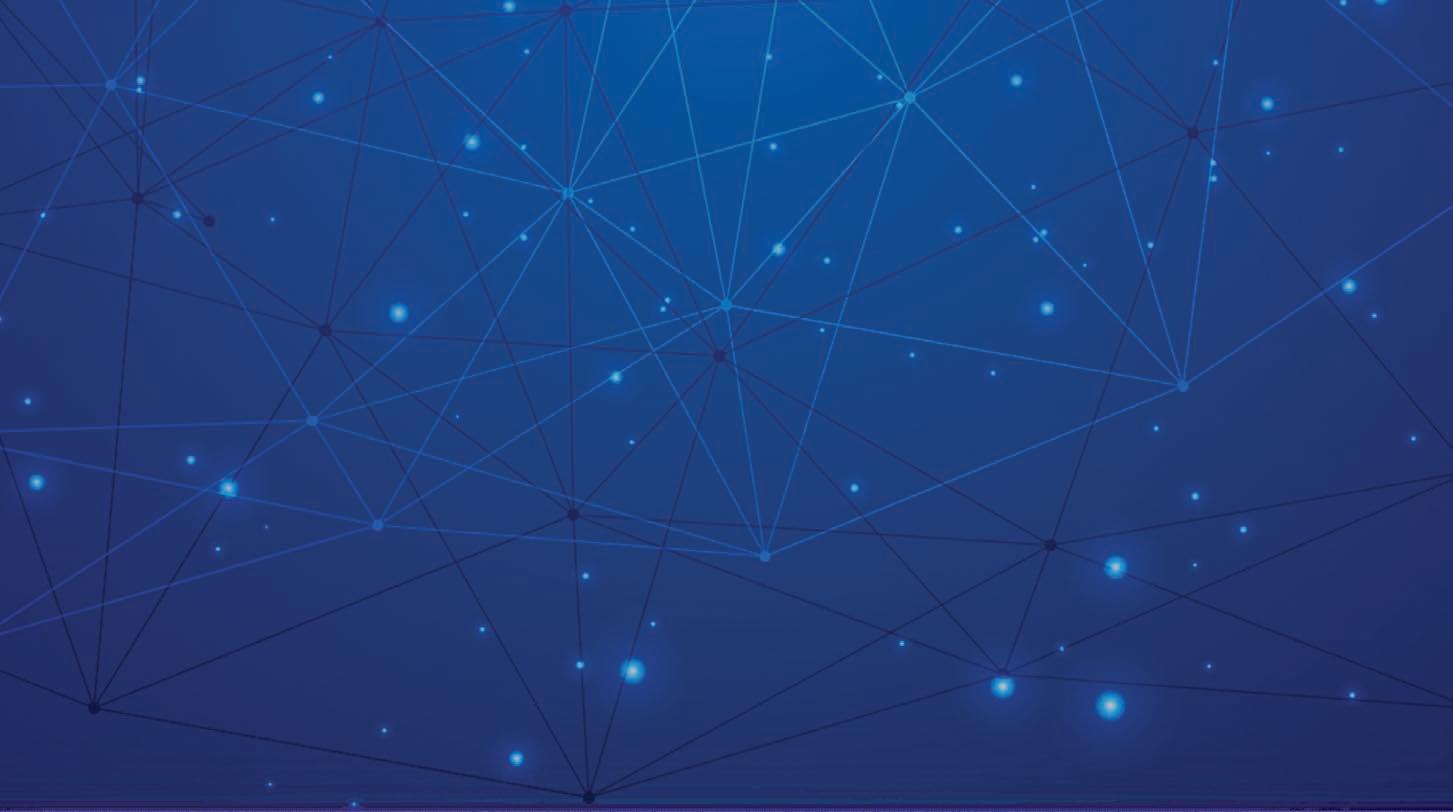
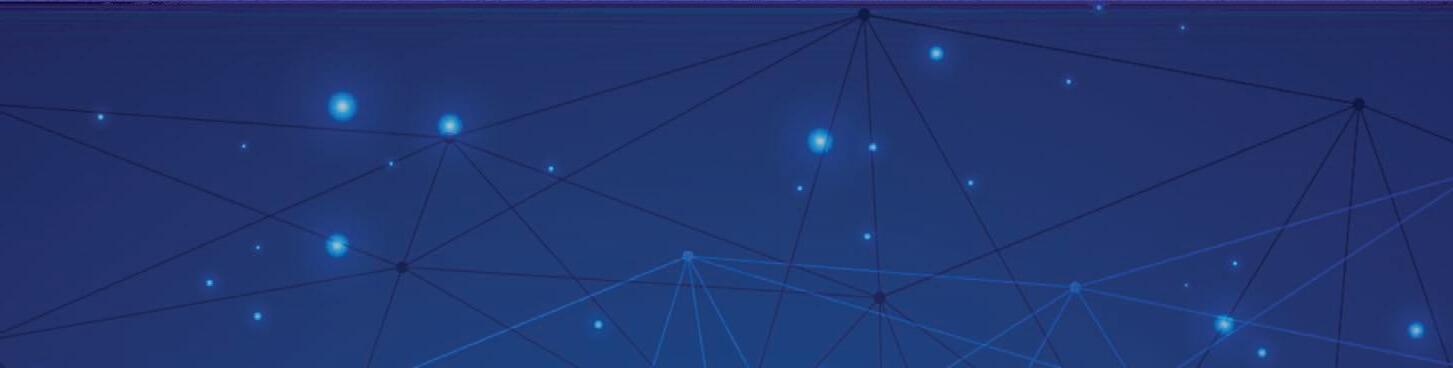
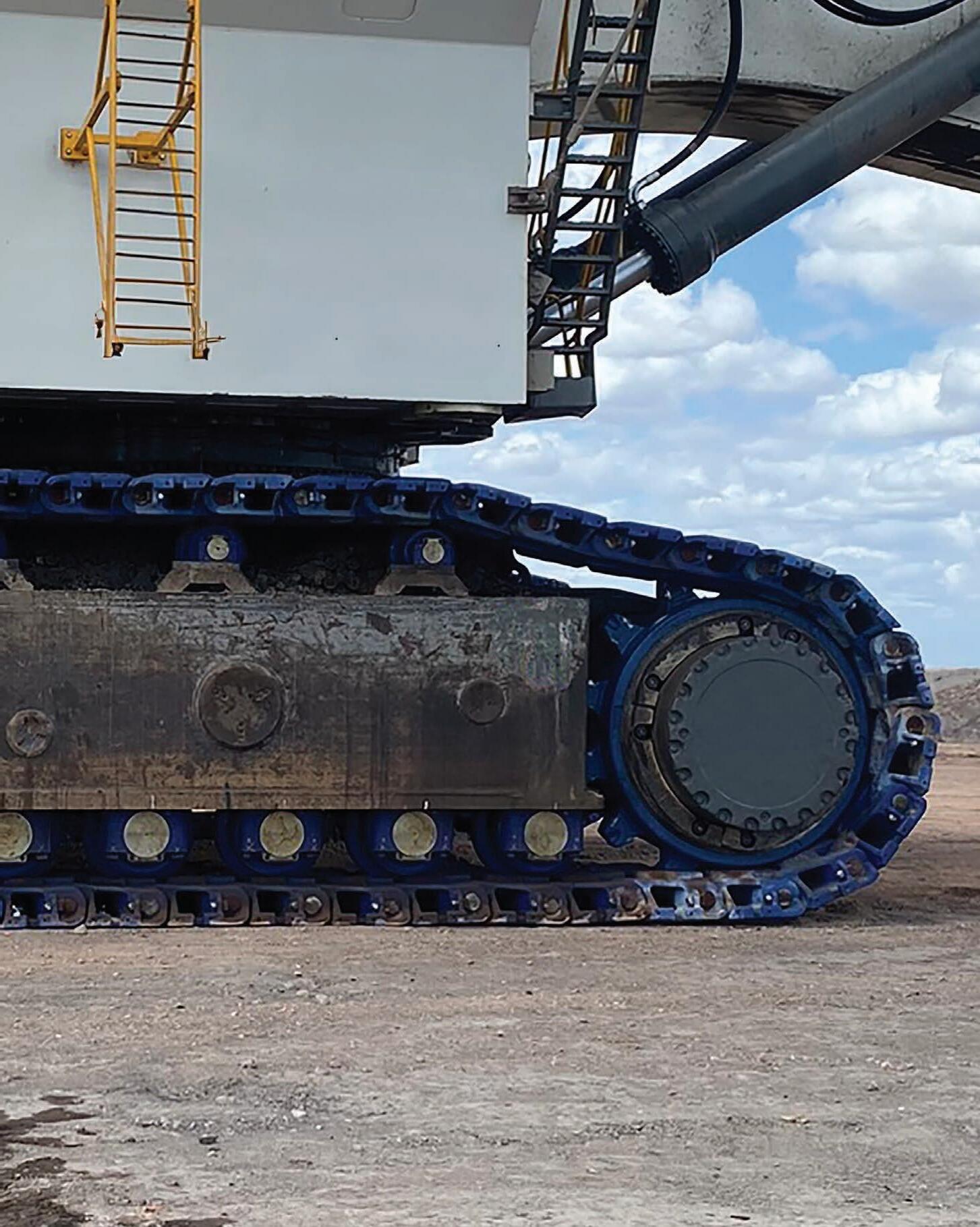
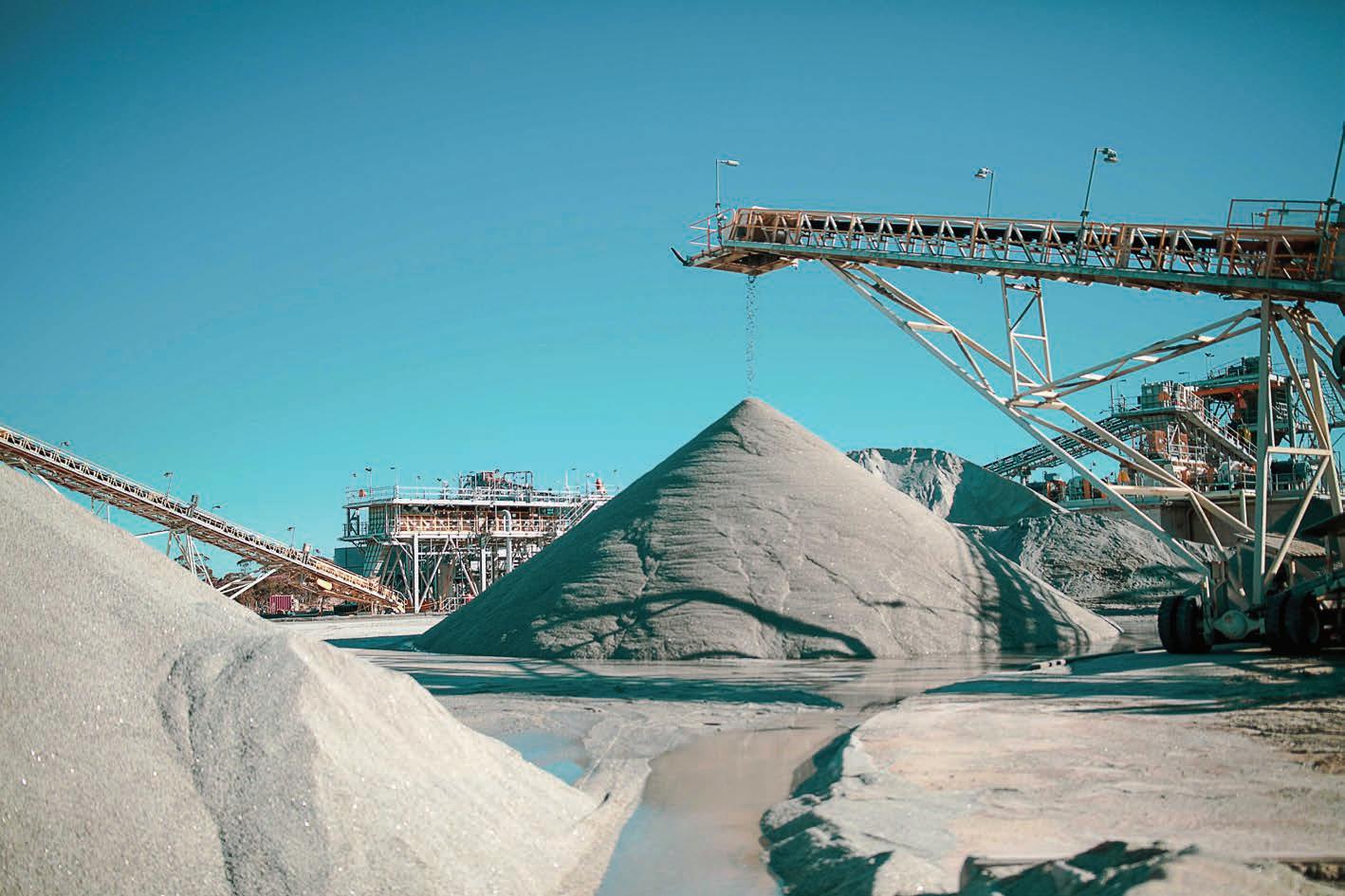
LITHIUM: MINRES’ PROVEN WINNER
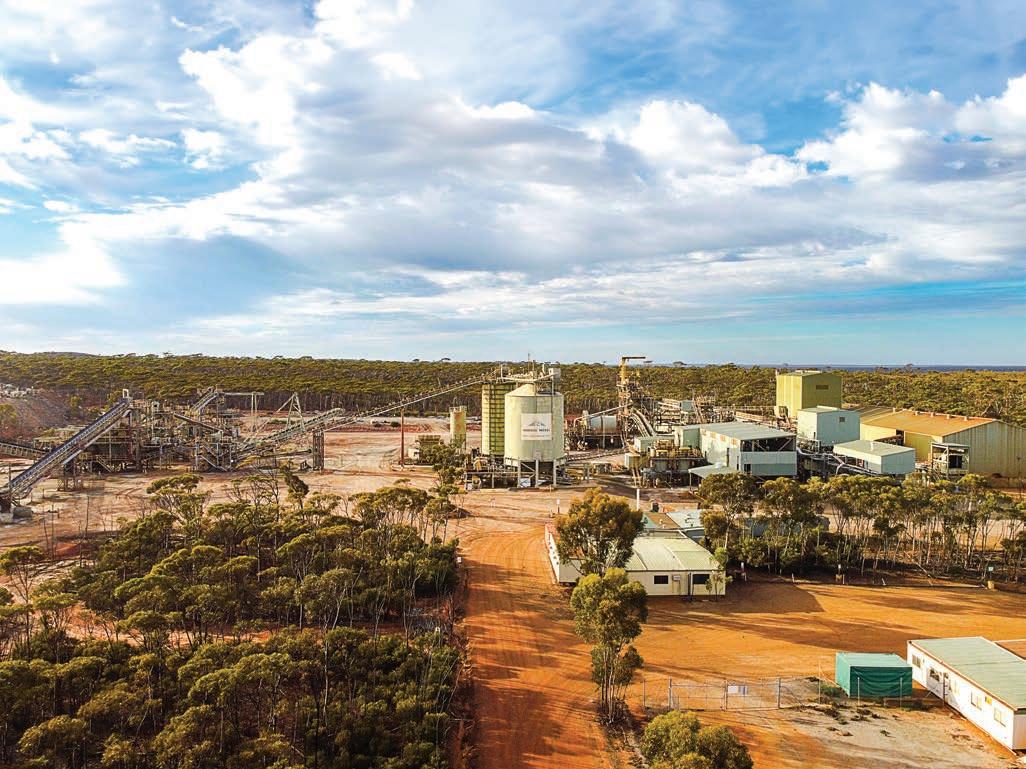
Mineral Resources (MinRes) is no stranger to lithium. From operating the Mount Marion and Wodgina mines in Western Australia to acquiring the Bald Hill mine last November for $260 million, the major miner is truly embracing the critical mineral.
Despite a recent downturn impacting various Australian lithium operations in 2024, MinRes has only upped its investment, reinforcing its place as a leading Australian lithium powerhouse.
So how is MinRes continuing to grow its lithium market share?
Dynamic Metals
Under a binding joint venture (JV), Dynamic Metals will sell 40 per cent of its lithium rights on the Widgiemooltha project in WA for $5 million.
Upon completion in the second quarter of 2024, HoldCo – a MinRes subsidiary – and Dynamic will form a 40:60 JV to advance lithium exploration at the site.
MinRes will have the option to sole fund $15 million of expenditure over four years to increase its stake to 65 per cent.

The company can also increase its stake to 80 per cent by sole funding expenditure through to a decision to mine.
If MinRes gains an 80 per cent interest, Dynamic can either remain in the JV and contribute to its expenses or convert its interest into a royalty.
“The Widgiemooltha project is a regionally significant tenement package that has yet to be fully assessed for its lithium potential,” Dynamic Metals

managing director Karen Wellman said in March.
“Although we have had some encouraging results with our first exploration activities, the sheer size of the project means that it would likely have taken Dynamic many years and considerable expenditure to assess its potential and realise value.
“We are excited by this transaction as MinRes is a leader in the lithium sector
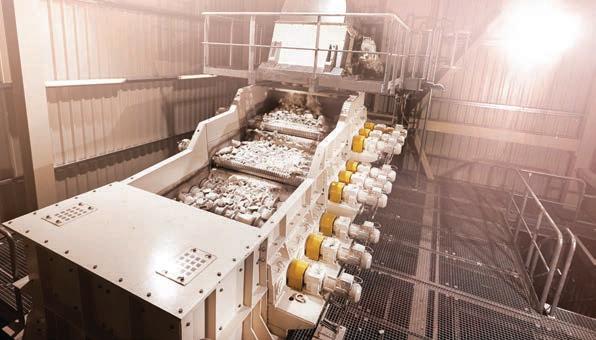
2/6 Meares Way, Canning Vale, WA 6155 info.australia@allmineral.com

For more information, contact JACO BOTHA jaco.botha@allmineral.com or +61 439549
•
in Australia, with the technical expertise and financial capabilities to do the project justice.”
Lithium Australia
In August 2023, MinRes and Lithium Australia entered into a joint development agreement to advance Lithium Australia’s LieNA technology, which has demonstrated the potential to revolutionise lithium extraction.
MinRes invested $4.5 million in Lithium Australia to fund the development and operation of a pilot plant, and an engineering study for a demonstration plant, all while supplying the raw materials.
Lithium Australia’s LieNA technology involves recovering lithium from fine and low-grade spodumene usually disposed as waste streams.

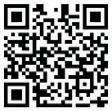


During the LieNA process, fine spodumene is fed into an autoclave, where it reacts with caustic soda to form a synthetic lithium sodalite. Lithium is then recovered from the sodalite via a simple solid–liquid separation step.
Lithium Australia believes the LieNA technology could enhance lithium extraction yields by up to 50 per cent compared to current market performance.
If the pilot plant yields successful results, both companies will form a 50:50 JV to own and commercialise the LieNA technology through a licensing model.
The potential JV intends to license the LieNA technology to third-parties at a royalty rate of eight per cent.
“Our preliminary testing with Lithium Australia has yielded promising results and warranted this investment to further develop the technology,” MinRes chief executive of lithium Joshua Thurlow said in August 2023.
“The goal is to fast track the commercialisation of LieNA to drive efficiencies and initially extract more value from our two world-class lithium operations in Western Australia.”
Jumping ahead to January, Lithium Australia managing director and chief executive officer (CEO) Simon Linge revealed that Lithium Australia and MinRes aim to complete the joint development scope.
And things stayed on track, with both companies piloting the LieNA technology two months later.
“The planned JV and licensing model with MinRes can capture a significant opportunity in the lithium market,” Linge said.
“LieNA has potential application at new and existing lithium mines, with the royalty model expected to expand the company’s addressable market by capturing a fee on all tonnage processed.”
Poseidon Nickel
MinRes is set to acquire Poseidon Nickel’s Lake Johnston nickel concentrator and tenures in WA to convert it into a lithium hub.
Located approximately 185km southwest of Kalgoorlie, the acquired tenure covers 86km2 with one exploration license and 10 mining leases. MinRes will own the tenure outright, including all mineral rights.
The Lake Johnston nickel concentrator plant has a 1.5-milliontonne-per-annum capacity and is capable of being converted to treat lithium ores.
MinRes will pay $1 million on execution of the agreement, $6.5 million on completion of the sale and purchase agreement and $7.5 million a year after the transaction is completed.
“This is an exciting opportunity to develop MinRes’ third lithium
processing hub in the Goldfields and the first to include flotation capacity to treat fines,” MinRes managing director Chris Ellison said.
“We intend to bring our expertise in spodumene production to Lake Johnston, which has the potential to service projects throughout the world’s most prospective region for lithium.”
Poseidon Nickel said the $15 million will support its exploration of highgrade nickel discoveries, and continued care and maintenance activities at its Black Swan project that was hit by the nickel downturn.
“The proposed transaction will crystallise value for shareholders through the monetisation of one of our assets and will enable the company to continue with its strategy to progress the exciting exploration targets identified at Windarra,” former Poseidon Nickel CEO Craig Jones said.
Lord Resources
In March, MinRes entered into a binding farm-in agreement with green metals explorer Lord Resources, focusing on the Horse Rocks lithium project.
The partnership will see MinRes provide Lord with non-dilutive funding and access to its expertise in lithium exploration and production.
“We are extremely excited to secure a strategic partnership with MinRes,”
Lord Resources managing director Barnaby Egerton-Warburton said.
“The agreement validates the strong work Lord has already completed at the Horse Rocks lithium project and provides the opportunity to collaborate with a world-class exploration team drawing on their knowledge and expertise of this highly prospective lithium region.”
Under the agreement, MinRes can acquire an initial 40 per cent interest in Horse Rocks by spending $1 million on exploration within 18 months.
Lord and MinRes have agreed to create a JV in Stage 2, where MinRes will have the option to earn a further 30 per cent interest by funding $5 million in expenditure within 36 months of Stage 2’s commencement.
MinRes can then earn a further 15 per cent interest in Stage 3 by funding expenditure through to a decision to mine, bringing its total potential interest in the project to 85 per cent.
Once Stage 3 is completed, Lord has the option to stay in the JV and contribute to all future costs. Alternatively, it can convert its JV interest to a 1.5 per cent royalty.
While the outcomes of these transactions are yet to be seen, MinRes has cemented its reputation as one of Australia’s leading lithium miners by investing in a myriad acquisitions, technology and exploration. AM


HEAD IN THE GAME
THE LATEST MARS MINING MENTAL HEALTH STUDY REVEALED AN ERA OF CHANGE FOR THE INDUSTRY. SO WHAT ARE OPERATORS DOING TO PRIORITISE MENTAL WELLBEING?

Physical safety has been a critical focus for mining companies for decades. But a different kind of safety concern has been rising to the fore in recent years: mental health.
Mental wellbeing is a difficult thing to quantify, but Curtin University’s Centre for Transformative Work Design aimed to do just that in the latest iteration of its Mental Awareness, Respect and Safety (MARS) study.
Over 2550 Western Australian mine workers were surveyed for their perceptions of mental health awareness, respect, and safety in the workplace, with another 60 employees interviewed one-on-one.
What emerged from the surveys and interviews was a sense of a changing tide in the mining industry, marked by operators striving to incorporate initiatives to bolster mental health. But it also found room for improvement.
Only four in 10 workers reported experiencing positive aspects of mental
health at work, and nearly four in 10 reported feeling burnt out.
But the MARS study’s lead author Cheryl Yam is optimistic the mining industry is making significant progress in improving its mental health response.
“The mining industry set itself apart as the leader in physical safety, and in more recent years that has shifted to a more holistic approach towards mental health and wellbeing,” Yam told Australian Mining.
“The industry is following a trajectory where we are starting to see the collective effort foster really positive results.”
When it comes to making real differences in the mental wellbeing of workers, Yam said the most durable changes come from a top-down approach.
“It’s what happens at an organisational level that really makes a difference for people; these are the differences that really stick above and beyond other individualised training programs,” she said.
Yam believes operators who tackle mental health in the workplace from
a ‘work design’ approach see the most benefits in the wellbeing of their staff.
“‘Work design’ is the content and organisation of a workers’ roles and responsibilities that all come together to make up a person’s job,” she said.
“When designed well, we have more resources available to deal with the demands of work.”
Simply put, well-designed work leads to better mental health outcomes and decreases the likelihood of issues like burnout and anxiety.
Yam emphasised a major highlight of the report was seeing the positive impacts an organisational mental health focus can have on worker wellbeing.
“It was very nice to hear firsthand from some of our interviewees that they can actually see the organisations are making changes for the better,” she said.
Mental health initiatives have been cropping up across mining operations for years, with a focus on areas like the wellbeing of fly-in, fly-out (FIFO) workers and recognising mental health struggles in co-workers.
Australian Mining lifted the lid on the specifics of what operators are doing to rise to the challenge of creating mentally healthy workplaces.
Mineral Resources
Mineral Resources’ (MinRes) commitment to prioritising the mental health of its workers is embedded in its health and safety strategy.
The company aims to foster an environment filled with resilient people through the “active investment in the health and wellbeing of (its) people through education and initiatives”.
“We have a clear focus on our peoples’ ‘fitness for work’ encompassing all elements of physical and mental health,” the company said.
“As we expand our business, we will continue to focus on working safely and providing our people with the necessary skills, systems and processes to perform their roles safely.”
In 2023, MinRes won the Mentally Healthy Workplace Award at the annual WA Mental Health Awards.
The awards recognise and reward the achievements of those who demonstrate excellence, innovation and initiative in supporting consumers of mental health services, as well as their families and carers.
The Mentally Healthy Workplace Award recognises a workplace that encourages excellent mental health for its staff and volunteers through initiatives, programs, procedures, policies and/or organisational culture.
MinRes was recognised for actively supporting employees facing mental health challenges by promoting psychological wellbeing and reducing stigma.
“MinRes has trained mental health champions, partnered with Mental Health First Aid Australia, and initiated the Mind Matters series to educate employees and families,” event host Western Australian Association for Mental Health said.
MinRes has been involved in a host of mental health initiatives both within the company and in the broader community.
In late 2023, MinRes launched a program in partnership with The Y WA for its fifth annual Inside Our Minds campaign, showcasing a short film series featuring young people sharing their experiences with mental health.
Speaking at the launch, MinRes psychologist and head of mental health Chris Harris said the company recognised the importance of encouraging open conversations.
“At MinRes we know that mental health is just as important as physical health and we have introduced a range of programs to encourage a workplace culture where mental health is spoken about openly and support is easily accessible,” Harris said.
BHP
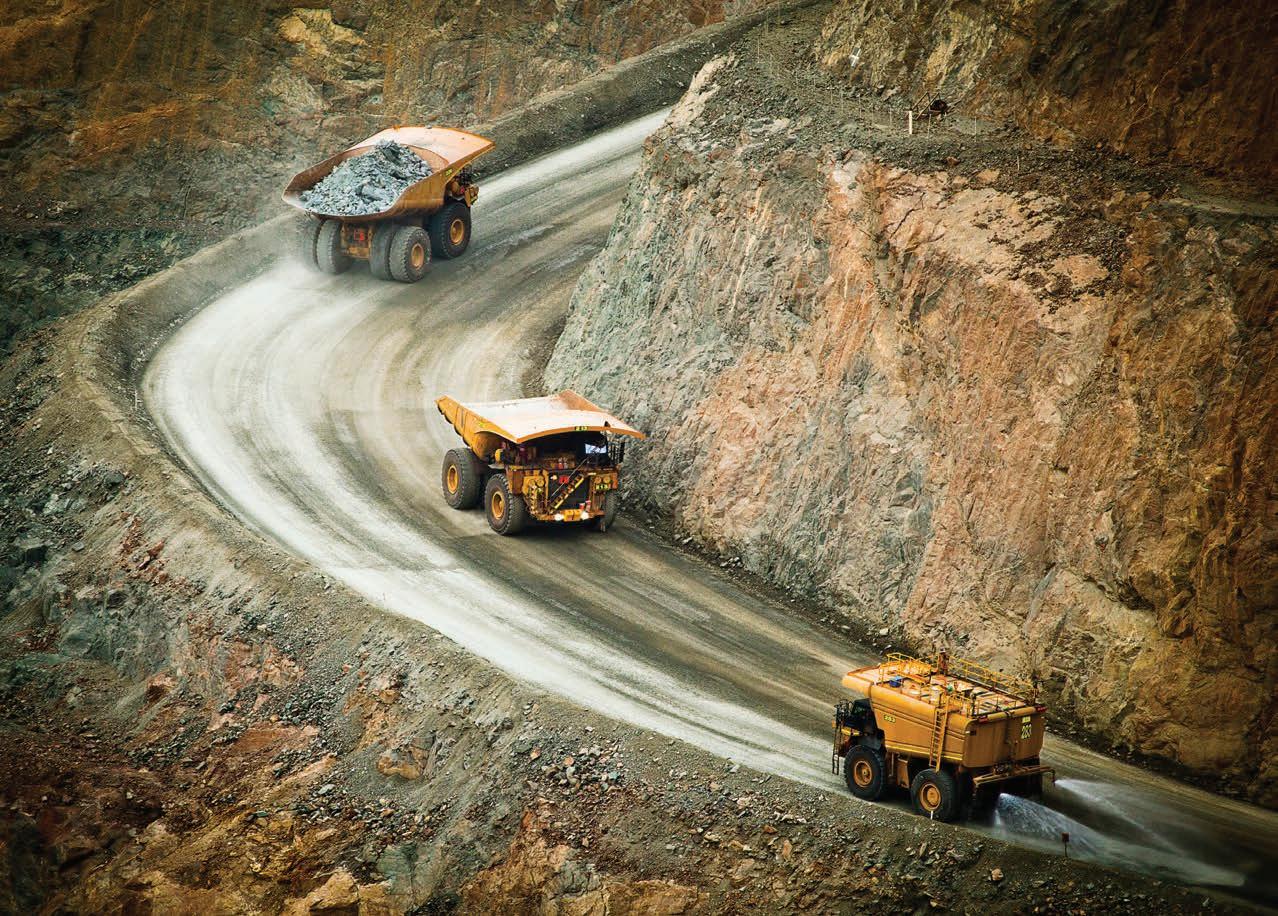
The Big Australian is a founding partner of the Global Business Collaboration for Better Workplace Mental Health.
According to the collaboration, 12 billion working days are lost across employees each year to depression and anxiety alone, with poor mental health costing the global economy $2.5 trillion every year.
Since launching its mental health standard in 2014, BHP has aimed to close the gap.
BHP chief executive officer Mike Henry said the company asked its employees and contractors directly how it can better support them in their mental health journeys.
“At BHP, we’re committed to supporting the mental wellness of our workforce and those in the communities in which we operate,” he said.
“The first priority in everything we do is keeping people safe and healthy, both physically and mentally.
“That’s not only because it’s the right thing to do, but workplaces that support better mental health have improved safety, higher productivity, and greater work satisfaction.”
Through its employee assistance program, BHP offers its workers and their immediate family members access to free and confidential support.
The aim is to give workers and families help, advice, or someone to talk to in an effort to destigmatise mental health.
Henry said this is the first step in creating the right mental health culture.
“We’ve embedded our mental health framework into our management rhythms and routines and we regularly measure progress,” he said.
“We’ve shifted BHP’s position on mental health from being largely reactive, to now being much more planned and proactive. We definitely have further yet to go, but we are making real progress.
“The imperative is clear for our businesses, our people, and our communities – together we must
continue to destigmatise mental health challenges to ensure our workplaces are conducive to mental wellness and to ensure the provision of effective mental wellness support.”
BHP also works with partners to bring awareness to mental health within the broader community.
In October 2023, BHP donated over $500,000 to Lifeline WA, a mental health service that provides 24–7 crisis support and suicide prevention services.
BHP’s funding went towards helping Lifeline WA recruit, train and deploy an additional 50 crisis supporters to provide help for those who need it.
“The work Lifeline does is aligned with BHP’s values as an organisation to keep our workforce, their families, and the communities in which we operate physically and psychologically safe and healthy,” BHP vice president of health safety and environment Australia Nektaria Zois said.
With BHP’s support, Lifeline WA is expected to have the ability to respond to more than 100,000 calls for help in 2024.
Glencore
Another major miner working to improve the mental wellbeing of its workers is Glencore.
The miner has committed to a ‘healthy lives, healthy workplaces’ strategy aiming to support physical and mental wellbeing in order to achieve a better quality of life for its workers now and into the future.
This strategy led Glencore to its longstanding partnership with the MATES in Mining program.
The MATES program has been running for nearly two decades with a goal to provide on-the-ground programs training miners to recognise the signs of mental struggle in their colleagues.
Glencore was one of the early adopters of the MATES program, as it looked for an evidence-based approach to support its employees’ mental wellbeing.
Glencore director of health, safety and training Kylie Ah Wong said Glencore values the wellbeing of its employees, who are the pillar of the company’s success.
“We know that when someone is struggling with mental health issues, they’re unlikely to seek help,” she said.
“Our employees look out for one another’s safety every shift, and that sense of camaraderie is deeply embedded in the mining industry.
“It makes sense to use that same approach when it comes to looking out for the mental health and wellbeing of our workmates.”
Since being rolled out across Glencore’s 16 sites, the MATES program has successfully trained over 9000 employees to help and support their colleagues.
Whitehaven
Whitehaven emphasises the mental health and wellbeing of its workforce as being integral to achieving an overall safe workplace.
“We strive to reduce psychological hazards in our workplace, build a culture of resilience, and equip our people with positive coping strategies to manage their health and wellbeing,” the company said.
“One way we are doing this is through ongoing education of our leaders and workforce, emphasising the importance of mental wellness and healthy lifestyle choices.”
Whitehaven’s annual Safehaven Conference aims to equip attendees with valuable insights into safety, leadership, and mental fitness.
Last year’s conference was the biggest in the event’s nine-year history, bringing together over 250 attendees.
The conference enables Whitehaven to highlight the successes and challenges it faced over the year, while reinforcing its strategic focuses of alignment and consistency, continuous improvement, and cultivating a culture of trust.
Whitehaven’s executive general manager health, safety and environment Sarah Withell praised the quality of presenters and the participation from attendees.
“The Whitehaven Safehaven Conference serves as a crucial platform to bring together leaders and experts in health, safety and environmental leadership,” she said.
“It underscores the importance of collaboration and knowledge exchange to drive positive change within our industry. We look forward to another great event in 2024.”
Attendees also provided input through SLIDO, an interactive tool that enabled Whitehaven to gather real-time feedback to inform its health, safety, and environment business plan going into the future.
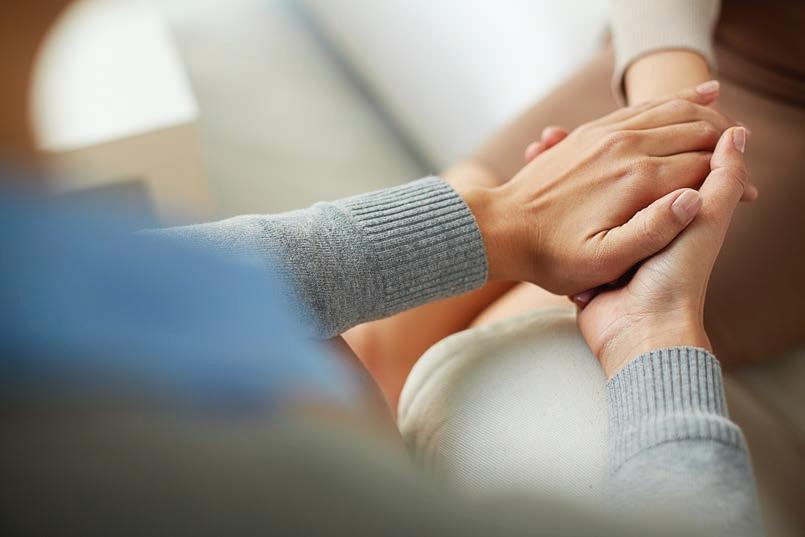
operators are making a difference in the lives of its employees.
It’s all part of a greater commitment to continually update its mental health response in partnership with its employees and the community.
The latest MARS study has shown the initiatives taken by Australia’s
And when it comes to implementing mental health initiatives, Yam had a message for operators:
“People do see the effort put in, and they appreciate the efforts that your organisation makes to support them,” she said. “I’m optimistic we will continue
to see positive change as we continue to talk about this and lower the barriers of having these conversations.
“The mining industry is a leader in physical safety. With the support and resources from the MARS program, we are confident that the mining industry is well positioned to also be a leader in mental health and wellbeing.” AM
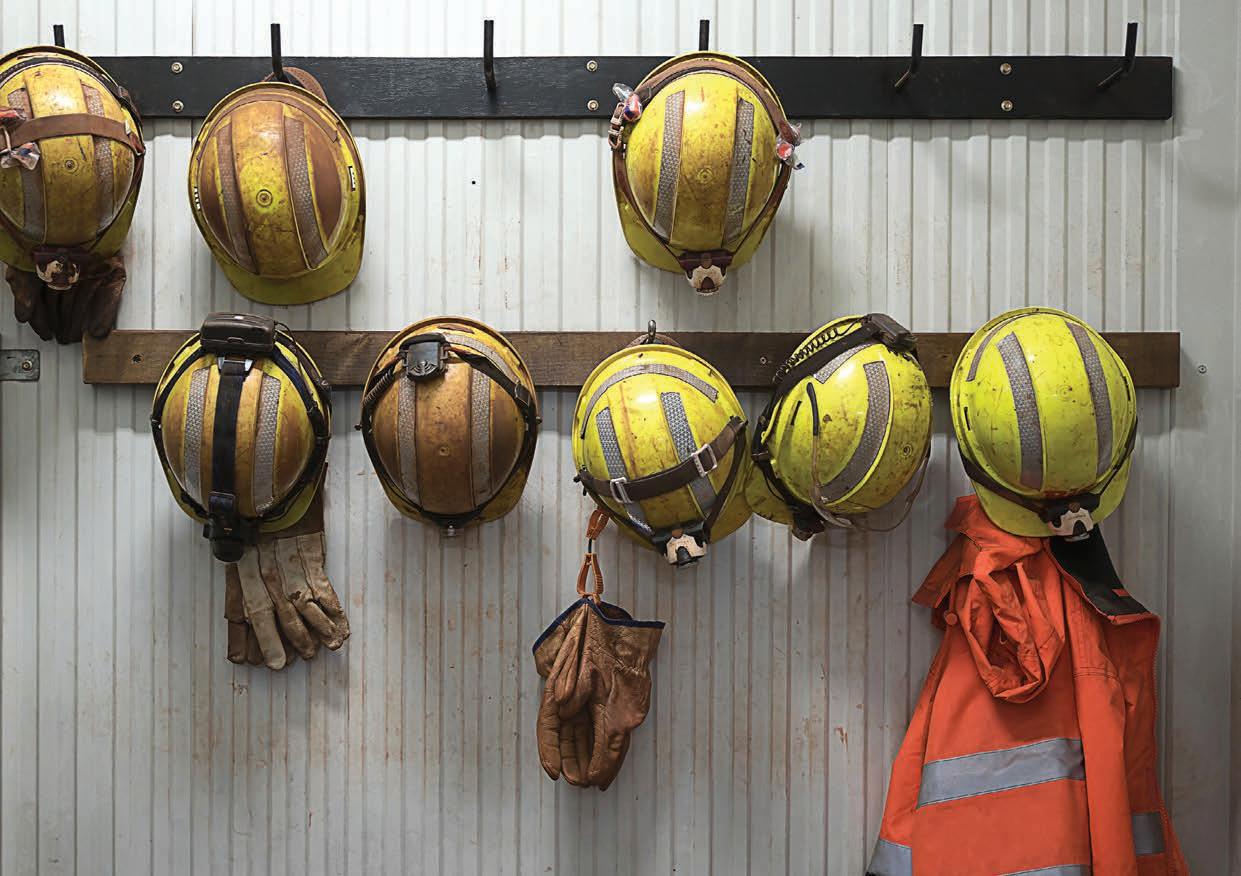
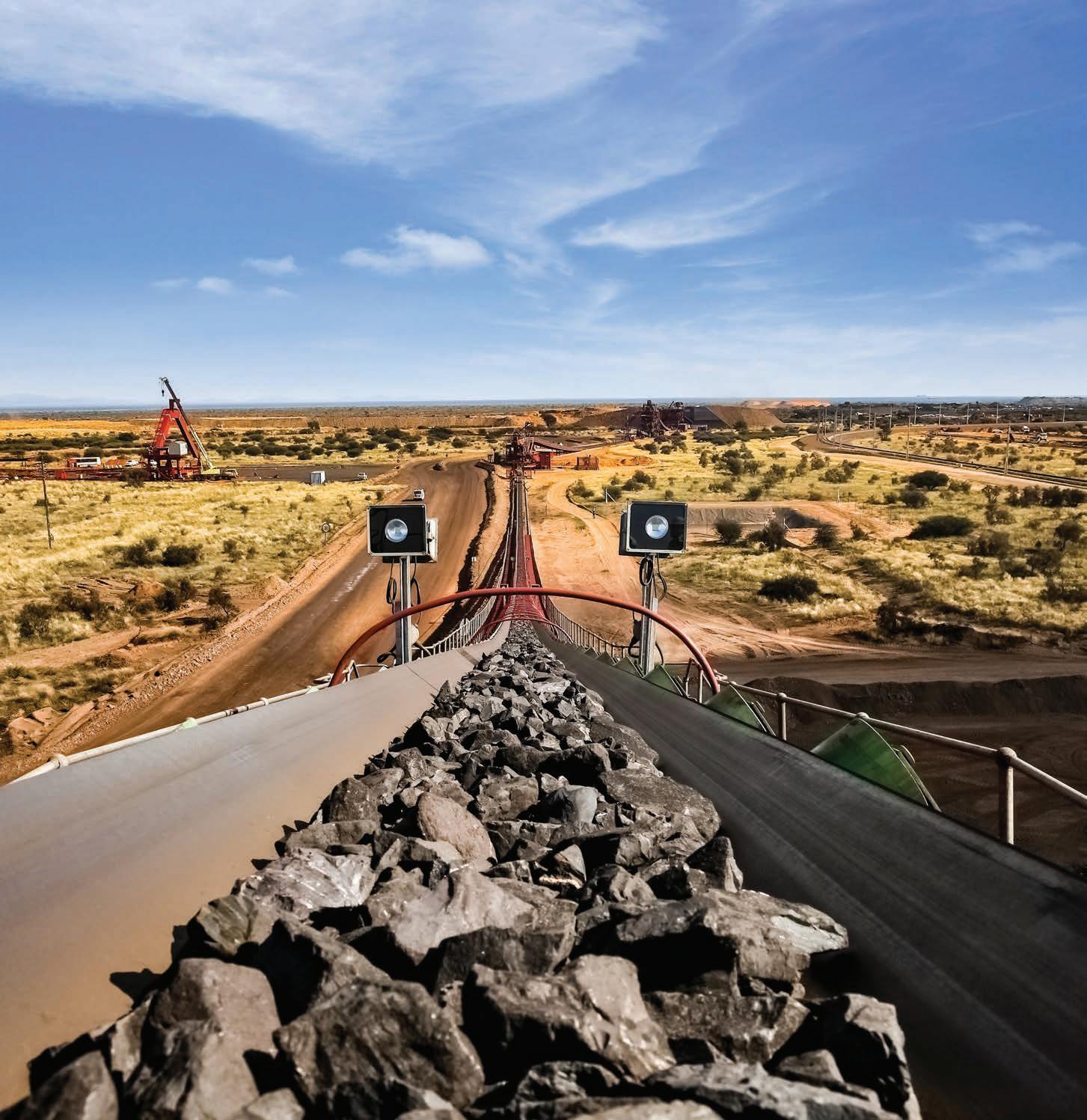
INTELLIGENT END-TO-END POWERTRAIN SOLUTIONS
With an increase in tonnages and declining conveyors with several hundred metres of drop, the installation of intelligent soft braking systems to address the starting and stopping requirements under various load conditions is an imperative.
Svendborg Brakes’ unique SOBO® soft braking control provides a range of safety and durability benefits in harsh mining applications. Decelerating and stopping heavy conveyor loads is critical, and controlled braking is essential for a significant reduction of torque peaks, preventing belt and mechanical component damage.
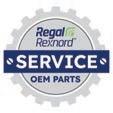
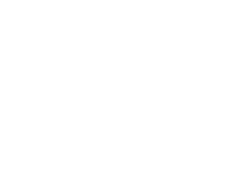
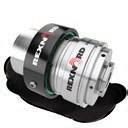
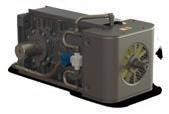

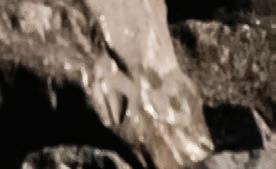
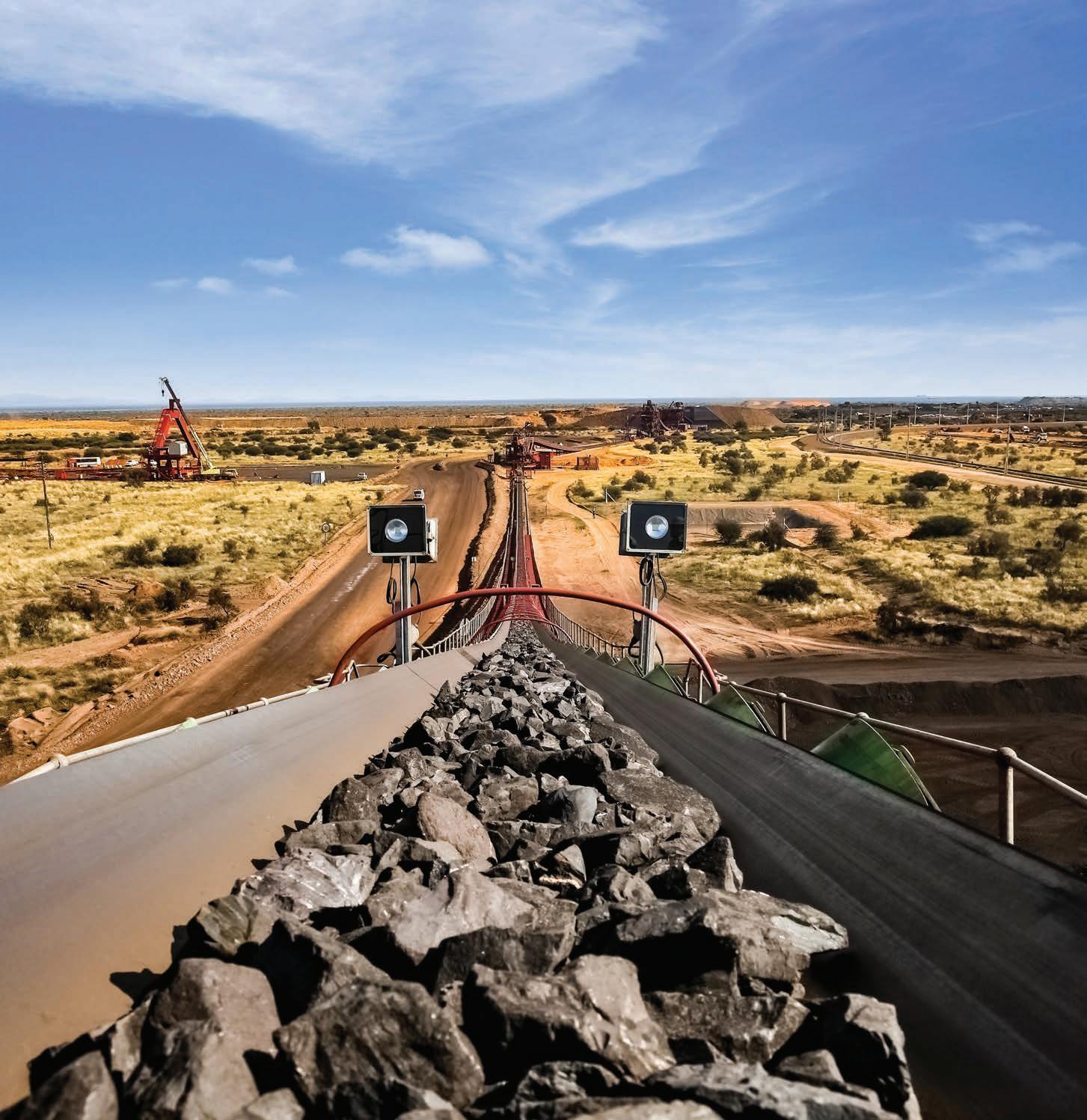


BEYOND MACHINERY
AND ABILITIES TO MANAGE OPERATIONS AND ENHANCE SAFETY AND EFFICIENCY.
Discussions between contractors and heavy equipment manufacturers often centre on cutting-edge machine technologies to enhance on-site efficiency and safety.
But amid the excitement of new machinery, the critical role of supporting services in optimising machine performance can sometimes be overlooked.
While high-quality machines lay the foundation, combining them with value-added services creates a holistic solution, giving businesses a competitive edge.
“It’s not a one-size-fits-all when it comes to productivity services,” CJD Equipment productivity services manager Andrew Minty said.
“From understanding your business, your fleet, the direction of where you want to take your business, and how to improve that, we can then assist in putting a plan in place to get your business there.
“It’s important to understand the foundation of your business and equipment, as well as its needs and benefits.”
Volvo Construction Equipment advocates the synergy of the right services with machines to deliver the best solutions. Its new services are aimed at facilitating – and accelerating – work completion, reducing costs and maximising uptime.
Connected maps
Streamlining transport operations is crucial for cutting travel times, minimising material mixing and reducing fuel consumption and emissions.
Connected maps in Volvo equipment provides a real-time digital mapping of all of a site’s machines, vehicles and personnel, allowing for enhanced visibility and informed decisionmaking. This service boosts productivity and improves safety by identifying bottlenecks and optimising traffic flow.
With connected maps, all machines and vehicles can see each other, and
managers can see what the site looks like from an office.
Volvo’s connected maps office portal provides a visual overview of all machines, operators and temporary site visitors, allowing site managers to react to the prevailing conditions.
Site managers can introduce measures such as one-way traffic or restricted zones and communicate these changes to all users instantly, helping to improve awareness, reduce accidents and increase productivity.
“Connected maps gives insight into all the machines and your overall site view,” Minty said. “It can be tailored to your overall needs, what you require that is visible on your site.
“If your focus is on reducing accidents on-site or the productivity of your equipment, Connected maps helps understand the losses and gains in your site and where to improve efficiency.”
Connected maps also has a search functionality feature, ensuring stakeholders can track the whereabouts of their machines in real-time. This not

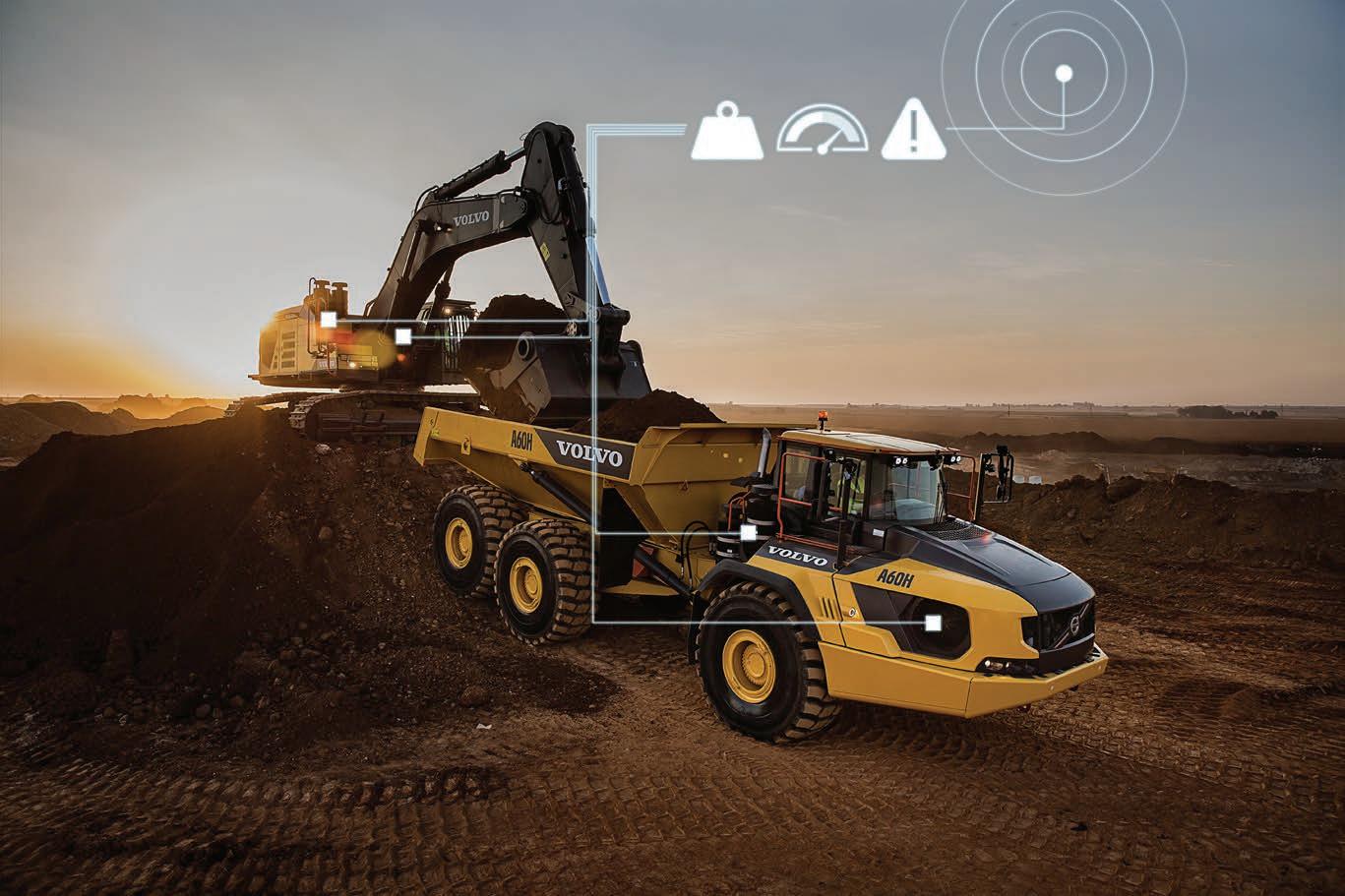
only enhances operational oversight but serves as a proactive measure in asset management and security.
Performance indicator
For detailed insights into production processes, Volvo’s performance indicator utilises on-board weighing and machine data to deliver performance metrics in real-time.
With customisable dashboards, users can monitor production, fuel efficiency and machine cycles.
“Performance indicator creates graphs, information and data to be analysed. This can be shared with operators, site managers or executives to understand where their losses and gains are,” Minty said.
“CJD Equipment can come in and help you understand what this data means and give suggestions based on the data to improve your operations.”
The performance indicator means site managers can visualise their operations with clear, easy-to-create dashboards, assess whether production is on track,
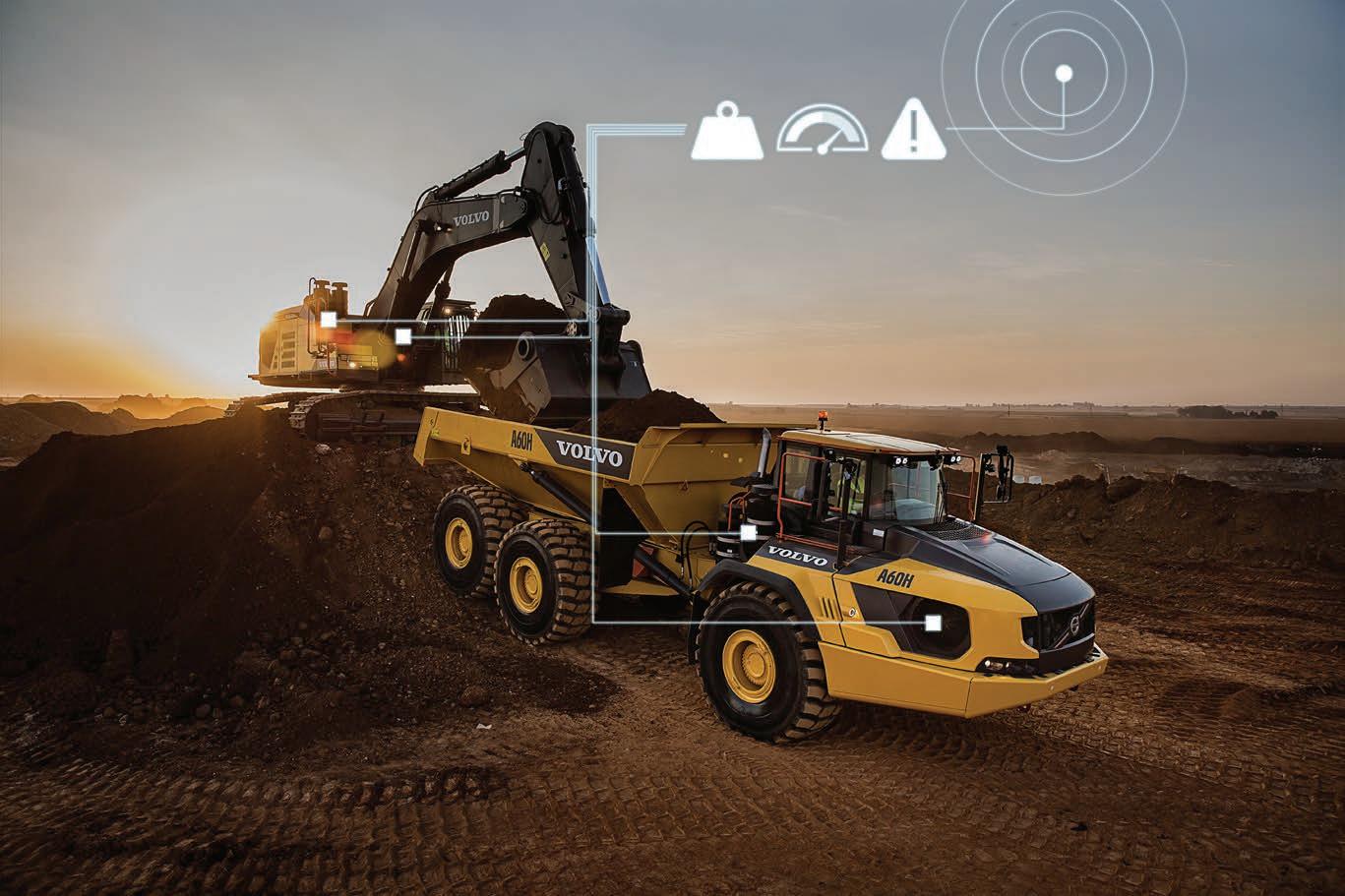
“The performance indicator can also

and be forewarned of any production or operational issues. Performance indicators take the guesswork out of observing operation performance metrics to allow for better decisions to improve efficiency and productivity.
Speed and location are also obtained from the machine’s Connected Map. Production data is captured automatically for Volvo machines with Volvo co-pilot and On-
This tool aids site managers in planning, providing foresight into project timelines to determine if they’re on schedule or facing delays.
The interdependence of tasks on a site makes effective planning paramount, especially when managing numerous
companies on the same project. Task manager can prove invaluable for this user demographic, offering compatibility with machines of any brand.
While operators using Volvo machines may benefit from a more streamlined experience, those utilising other brands can access it via mobile phones.
Connected load out
“Connected load out is tailored for road transport operations and gives insight into how you can meet targets for your customers, reduce downtimes and idling, and complement your sales techniques by capturing data you wouldn’t have previously,” Minty said.
“Both the loader and the truck on-site can be assured that the correct material and weight of the material is being moved, increasing efficiency.”
This service transforms the efficiency of material-loading processes, facilitating seamless communication between loaders, site offices and truck drivers.
By allowing truck drivers to place orders via a mobile app and coordinate loading operations, connected load out optimises workflow, reduces downtime and enhances overall site organisation.
These innovative services represent Volvo’s commitment to providing cutting-edge solutions to optimise business operations.
Complementing existing services like site simulation and active care empowers businesses to enhance productivity,
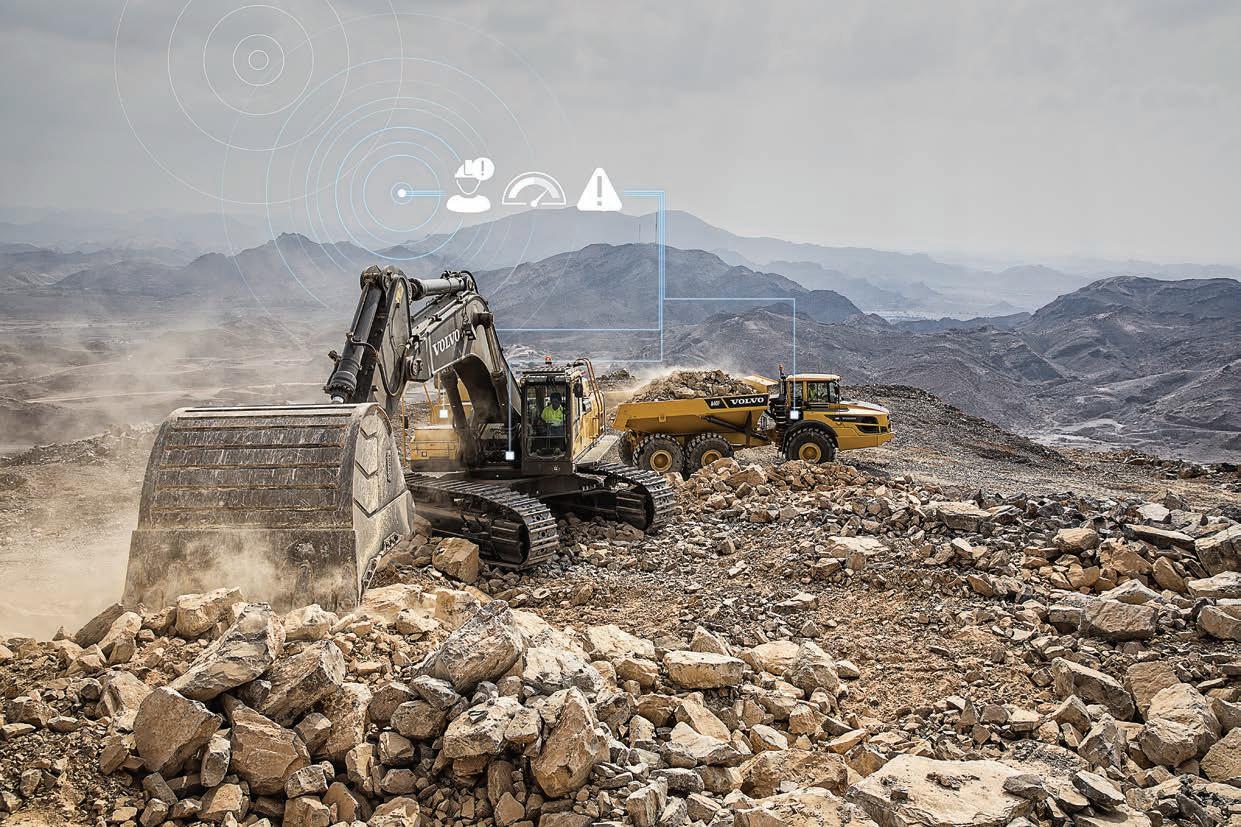
BRAKING TECHNOLOGY IN FULL FLIGHT
WITH MORE THAN 60 BRANDS TO ITS NAME, REGAL REXNORD CONTINUES TO GROW ITS PRESENCE IN THE POWER TRANSMISSION INDUSTRY.
The acquisition of Altra Industrial Motion in 2023 saw Regal Rexnord add a suite of esteemed clutch and braking brands, including the likes of Svendborg Brakes, Stromag, Twiflex and Marland Clutch.
Svendborg has long been a key player in the Australian mining industry, providing intelligent braking solutions for many of the sector’s conveyors, ball and semi-autogenous grinding (SAG) mills, shovels, draglines and reclaimers.
And Svendborg isn’t sitting still, with a constant focus on research and development (R&D) to continually improve its products.
“Svendborg is on the leading edge of development of braking systems for heavy applications,” Regal Rexnord regional marketing manager – Oceania Greg Josephson told Australian Mining
“We’ve got products like the SOBO intelligent soft braking system, which is like the ABS (anti-lock braking system) of conveyor brakes. It’s a brand that’s continually innovating and trying to look for the safest possible way to handle the massive loads you see in the mining and bulk material handling sectors.”
The SOBO braking system provides a range of safety and durability benefits in harsh mining applications by enabling conveyor systems to safely decelerate and stop heavy conveyor loads.
Regal Rexnord Australia national product manager Rex Sinclair told Australian Mining the system is based on closed loop control.
“With the SOBO technology, a speed sensor connected to the conveyor sends feedback to a controller that is programmed to a certain stopping time,” Sinclair said.
“For example, if a conveyor has a 15-second stopping time, regardless of the load on the conveyor, whether there’s zero load, half load, partial load or full load, it will always exactly stop in 15 seconds.”
The SOBO system’s consistent conveyor braking helps to ensure greater operational predictability, which provides not only safety advantages but also enables greater synergies between linked conveyor systems.
“In a mining operation where there is more than one conveyor connected to each other, if the conveyors don’t stop at the right time operators will end up
SVENDBORG BRAKES PROVIDES INTELLIGENT BRAKING SOLUTIONS FOR MANY IMPORTANT MINING APPLICATIONS.
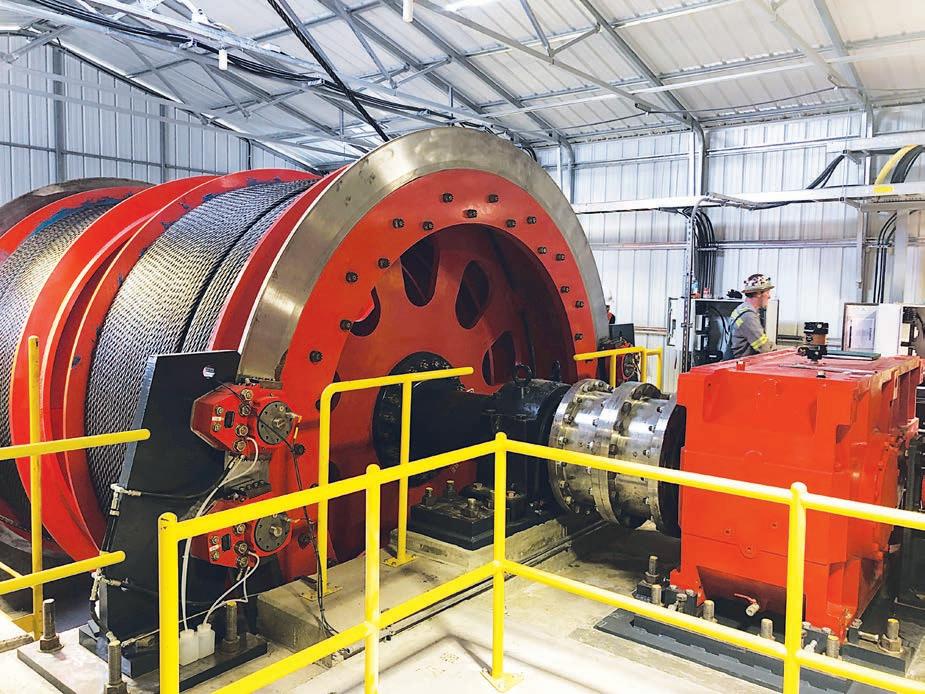
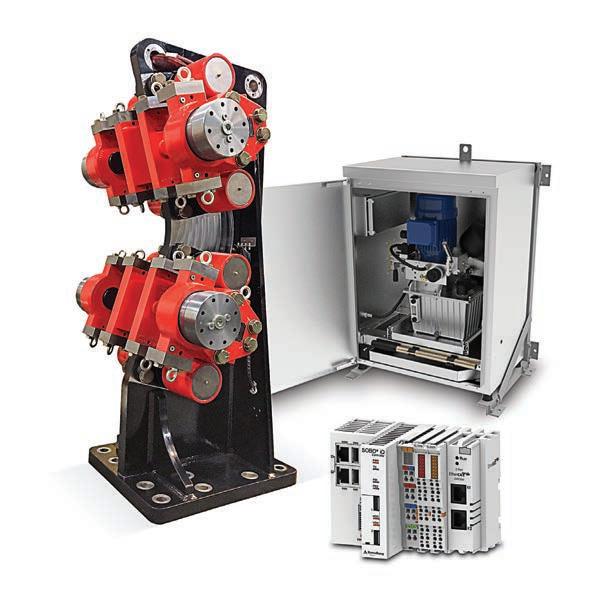
with all sorts of issues, including blocked shoots,” Sinclair said.
“But if operators can rely on a consistent conveyor stopping time, then there will naturally be more synergy in their operation, leading to improved productivity.”
Given the SOBO technology enables conveyor systems to gradually decelerate to a stop, regardless of whether the conditions are dry or wet, less strain
SVENDBORG BRAKES’ SOBO BRAKING SYSTEM ENSURES CONSISTENT CONVEYOR BRAKING TO ENSURE GREATER OPERATIONAL PREDICTABILITY.
is placed on the brakes, bearings and rubber belting, prolonging the life of the equipment.
The SOBO soft braking system is also compatible with the Svendborg Brakes IoT (Internet of Things) gateway technology, which enables operators to monitor the performance and wear of their brakes in real-time.
Regal Rexnord offers 24–7 service support for its Australian mining
customers, with OEM-trained technicians operating out of service hubs in Newcastle, Perth and Mackay, and the US company also has an engineering facility in Australia.
“Our engineering team based in Newcastle has the capacity to not only design and build customers a single gearbox but the full end-to-end drivetrain, which consists of the gearbox, coupling, brake system, backstop and electric motor,” Sinclair said.
Josephson said Regal Rexnord has turned to its engineering team in Australia to help support a rapidly growing footprint.
“Because Australia is geographically remote, we’ve set ourselves up to build end-to-end powertrain solutions ourselves,” he said.
“And we’ve now come full circle where we’re not just building for our local area, but we’re now augmenting the global supply of some of this equipment. We’re supplying into Chile, Asia, Europe and Canada, to name a few.”
While Regal Rexnord is a global company, it maintains a local presence wherever it operates, with service offerings and products tailored to the unique operating environments that each jurisdiction presents.
And with emerging technologies like Svendborg’s SOBO intelligent braking system consistently entering the fray, customers can be assured that Regal Rexnord is always innovating to ensure it finds the next cutting-edge solution. AM


CONVEYOR CLEANING MADE EASY
THE BROKK DEMOLITION ROBOT HAS A NEW ATTACHMENT, WHICH IS HELPING INDUSTRIAL CLEANING APPLICATIONS IN THE AUSTRALIAN MINING INDUSTRY.
The Brokk demolition robot was already known for its versatility, with the ability to complete a number of heavyduty tasks on a mine site.
With upward of 15 attachments and 10 different machine iterations in the range, the Brokk robot can already complete tasks that a mobile or fixed rock breaker, loader or drill rig would usually carry out independently.
And as is the case with any pioneering product, the Brokk demolition robot continues to evolve, with the company now adding vacuum excavation to the list of applications.
Brokk Australia managing director
Will Visser said vacuum excavation has several use cases on a mine site.
“Vacuum excavation is a savvy and safe way to complete industrial cleaning, whether it be under a conveyor, around busy transfer points or within a crusher,” Visser told Australian Mining.
“By utilising a vacuum system on a Brokk machine, operators can keep
workers out of hazardous areas where there are moving conveyors or moving equipment. You can put the remotely operated Brokk machine in and carry out your industrial cleaning tasks stress free.”
Given ore accumulations around conveyors can cause wear and tear, limit conveyor speed, and lead to potential breakdowns, conveyors need to be regularly cleaned. This is where the vacuum attachment comes to the fore, with operators able to suck up any excess rock as effortlessly as a vacuum would suck up dust in a family home.
And because the vacuum hose has a tapered, funnel-like design, the vacuum isn’t prone to blockages despite encountering rock fragments of all sizes.
Vacuum excavation can also be conducted without interrupting operations, ensuring there is no unnecessary equipment downtime when cleaning is carried out.
The end result is a clean conveyor or transfer point, which not only ensures operations remain safe but also
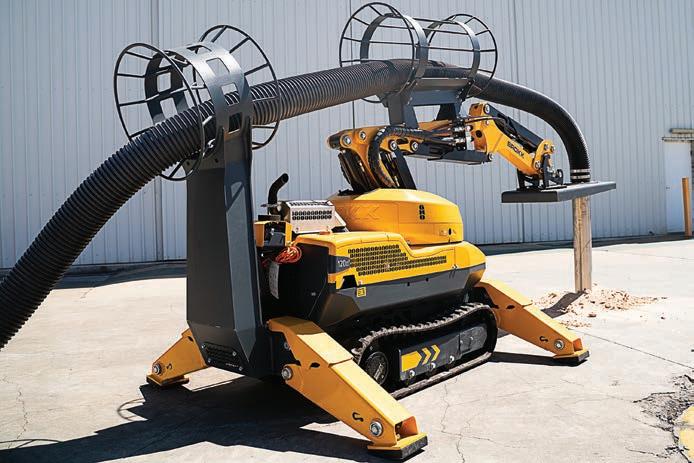
enables maintenance teams to complete regular or urgent servicing safely and without hindrance.
A case study involving a cement plant saw a Brokk vacuum increase the removal rates from six tonnes per shift to at least 60 tonnes per shift.
If the Brokk vacuum can clean around conveyors and transfer points, then it can assist in any industrial cleaning
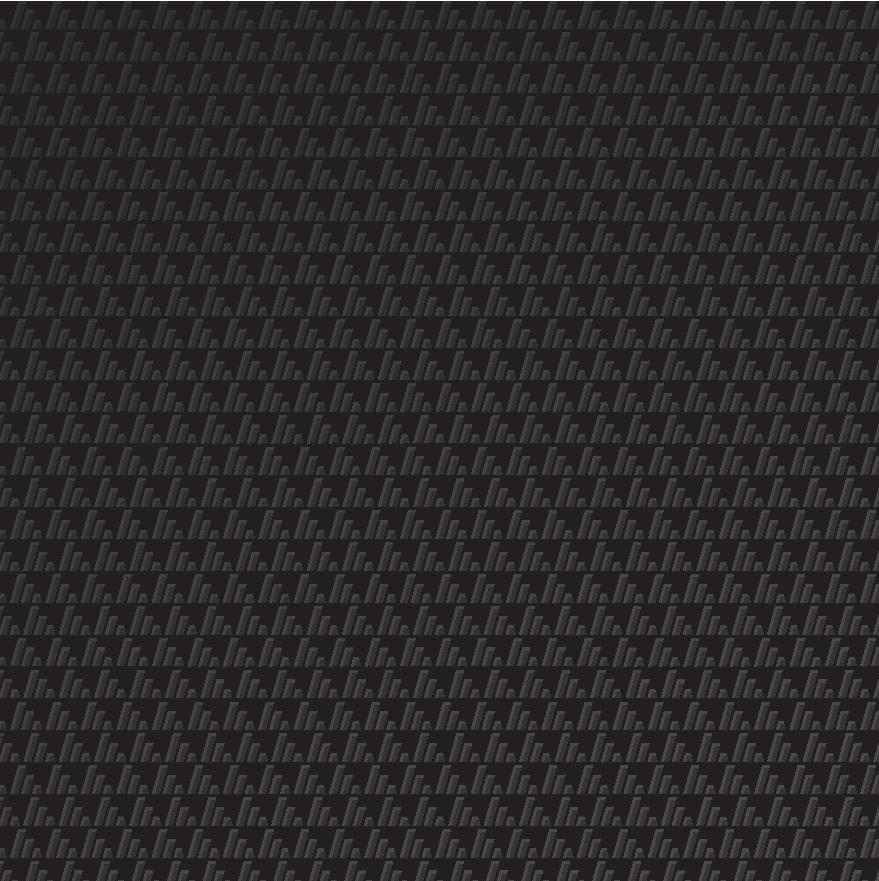
scenario where there is ore build-up or potential blockages on a mine site. This could be in and around mobile and fixed plant, within processing facilities or inside silos.
And if a customer was looking to clean a conveyor in the morning and then carry out underground drilling in the afternoon, the vacuum attachment can be replaced with a drill bit in a matter of minutes.
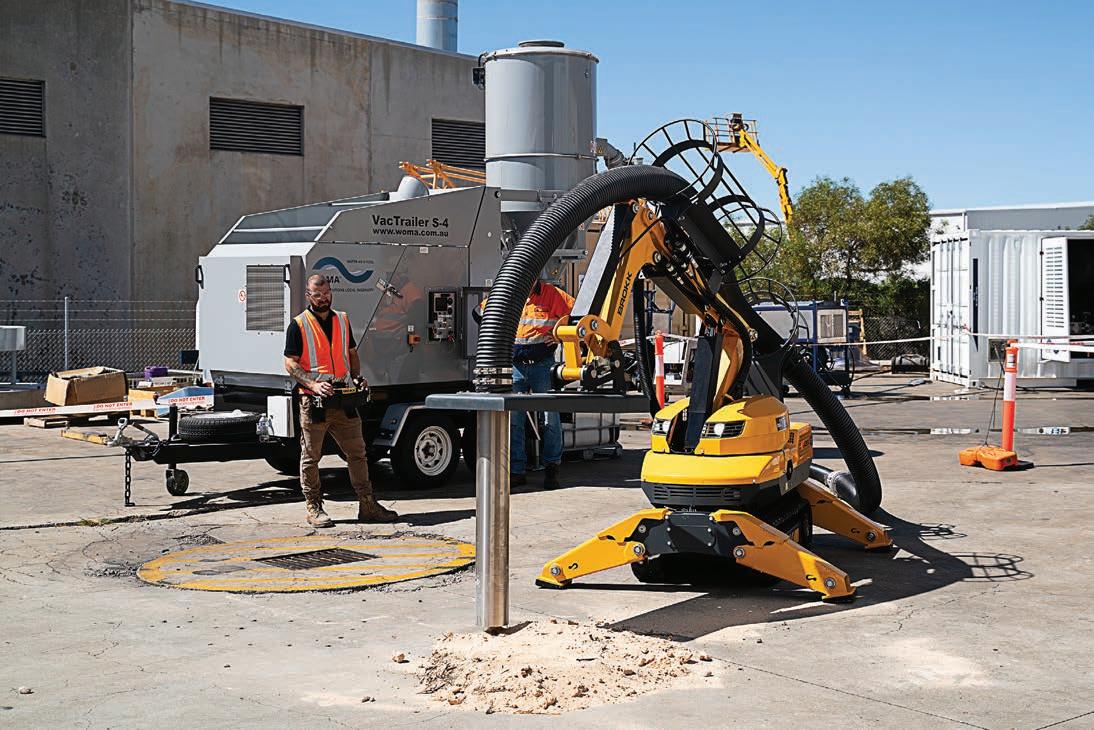

“You’ve got the versatility of this robust piece of equipment,” Visser said. “And whether you operate a small machine or a big machine – they function the same way – you don’t have to be retrained to operate a differentsized machine.
“Most importantly, the Brokk machine removes personnel from hazardous work environments, boosting the overall safety of underground or surface facilities and ensuring workers go home safe at the end of their shift.”
The demolition robot can be operated via an ergonomic remote within line of sight, with Brokk’s SmartRemote technology boasting a range capacity of up to 300m.
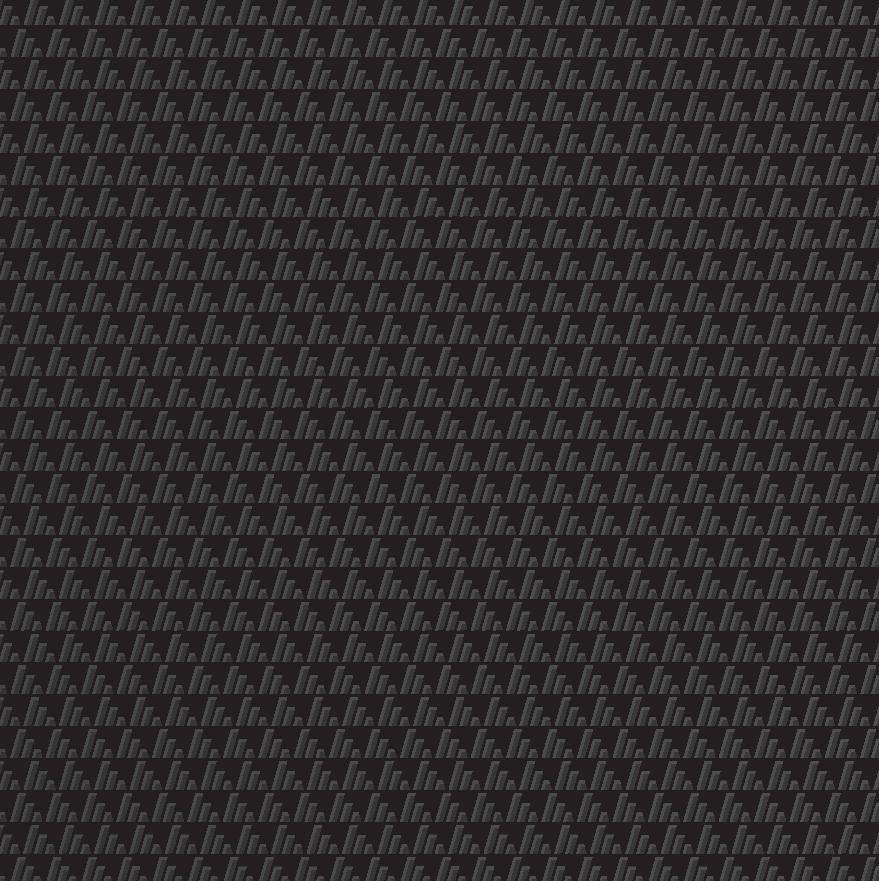
Otherwise, the machine can be operated from a control room at least 2000m away through an Ethernet or Wi-Fi connection.
The ergonomic Brokk control station contains integrated controls and video screens, enabling video and audio feedback and enhancing the overall operator experience.
Add Brokk’s recent SmartPower+ upgrade to the mix, which delivers increased endurance, intelligence and boosts the overall operating experience, and the Swedish company has many mining applications and operational desires covered. AM

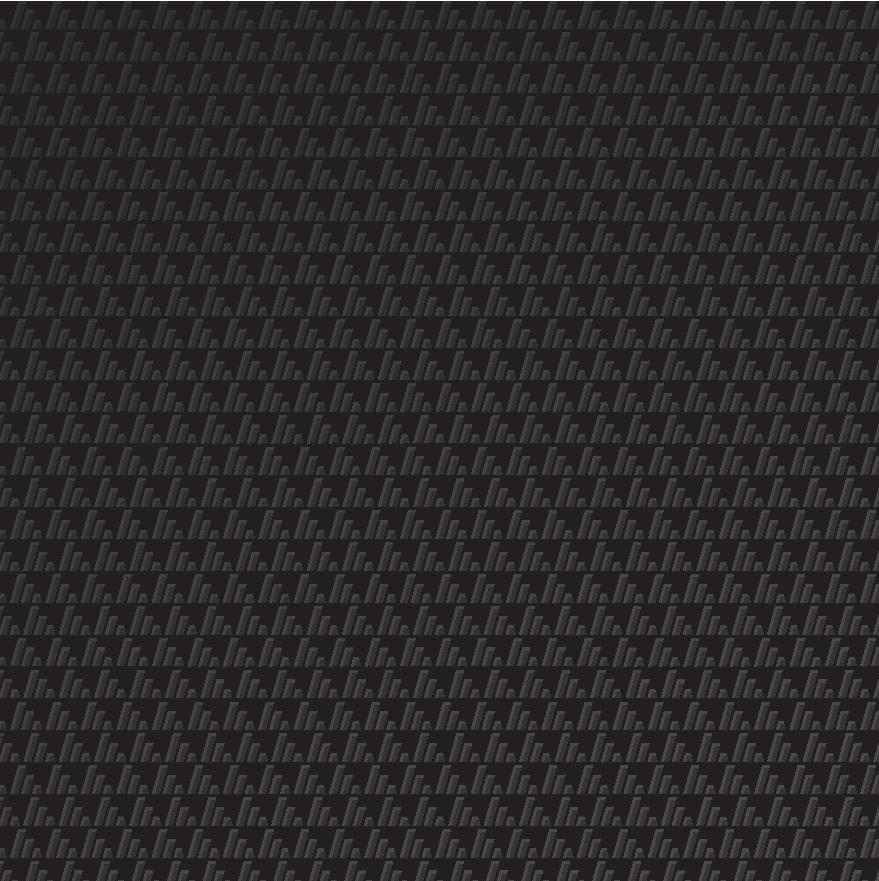

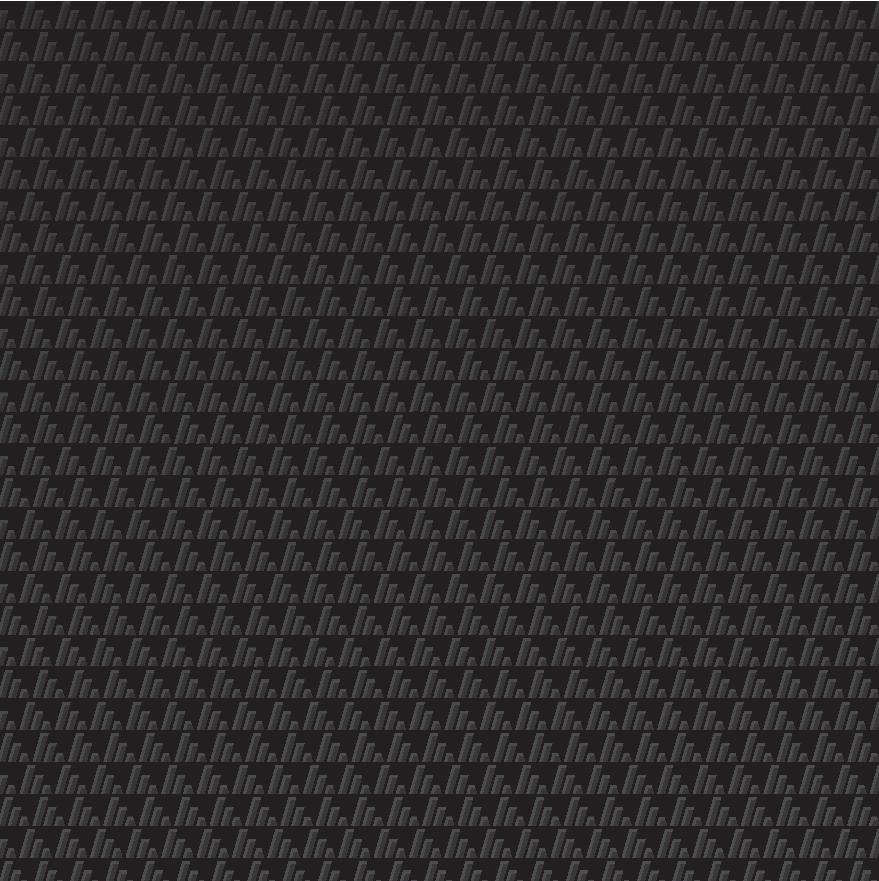
PARTS ENGINEERED TO PERFORM IN HARDROCK MINING

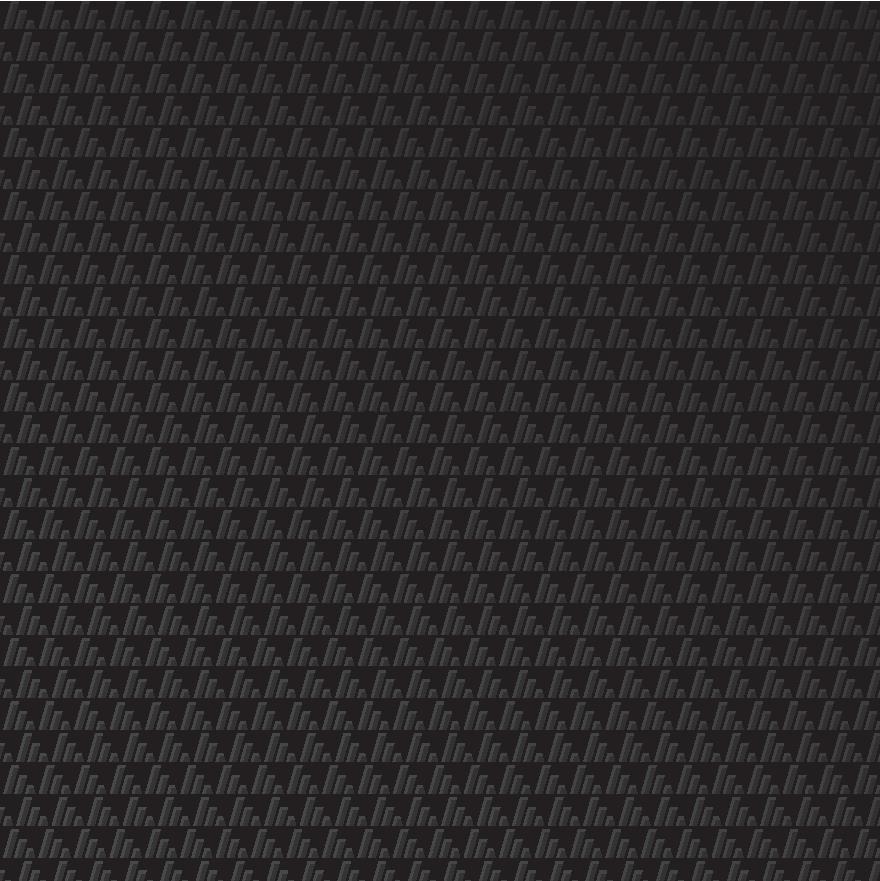
SURFACE PARTS SPOTLIGHT
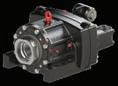
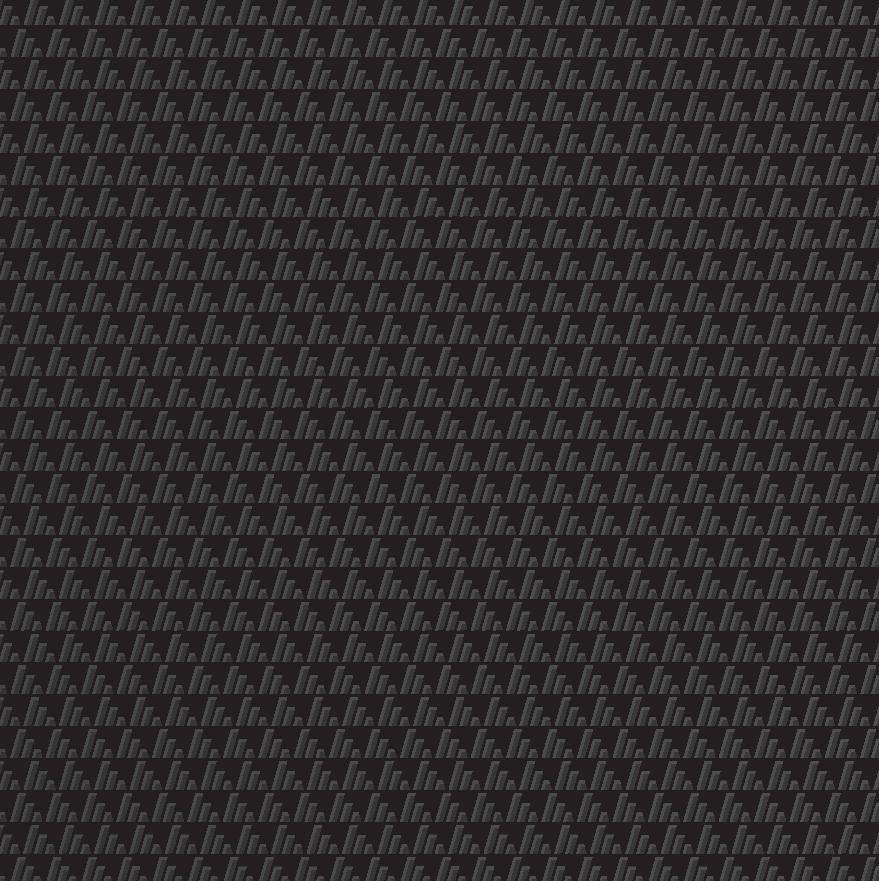
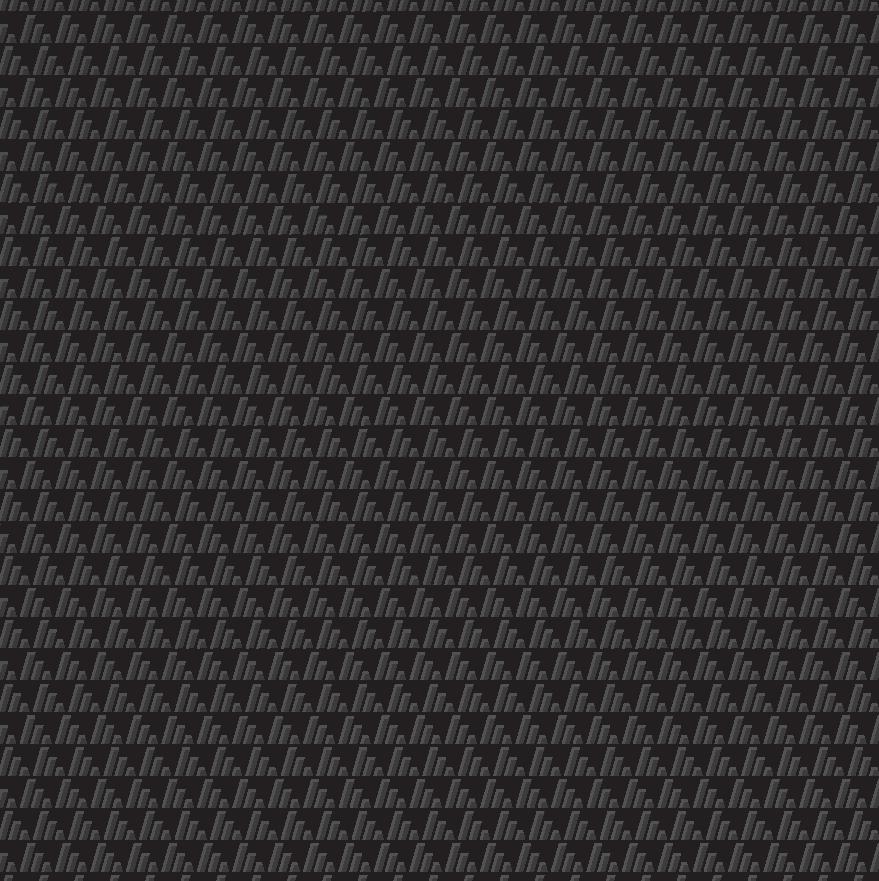
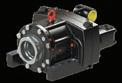
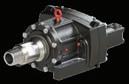
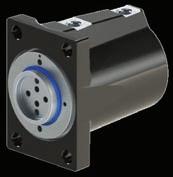
UNDERGROUND PARTS SPOTLIGHT
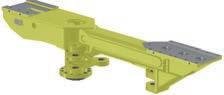

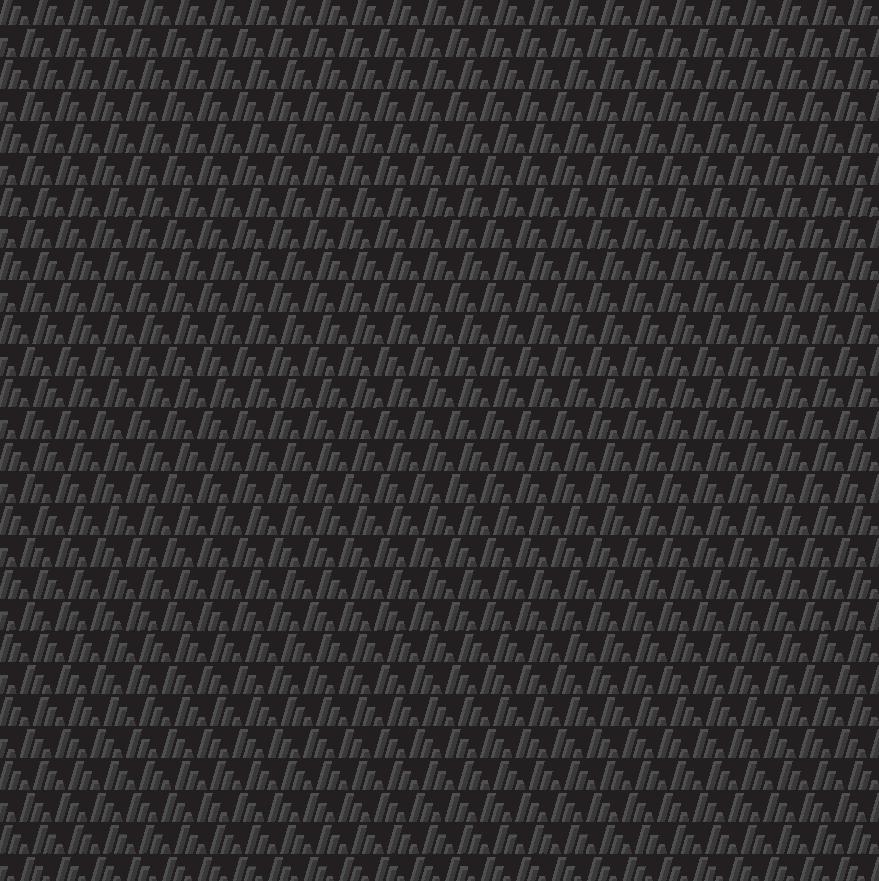
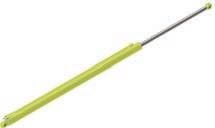
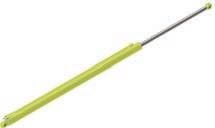
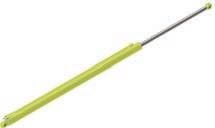
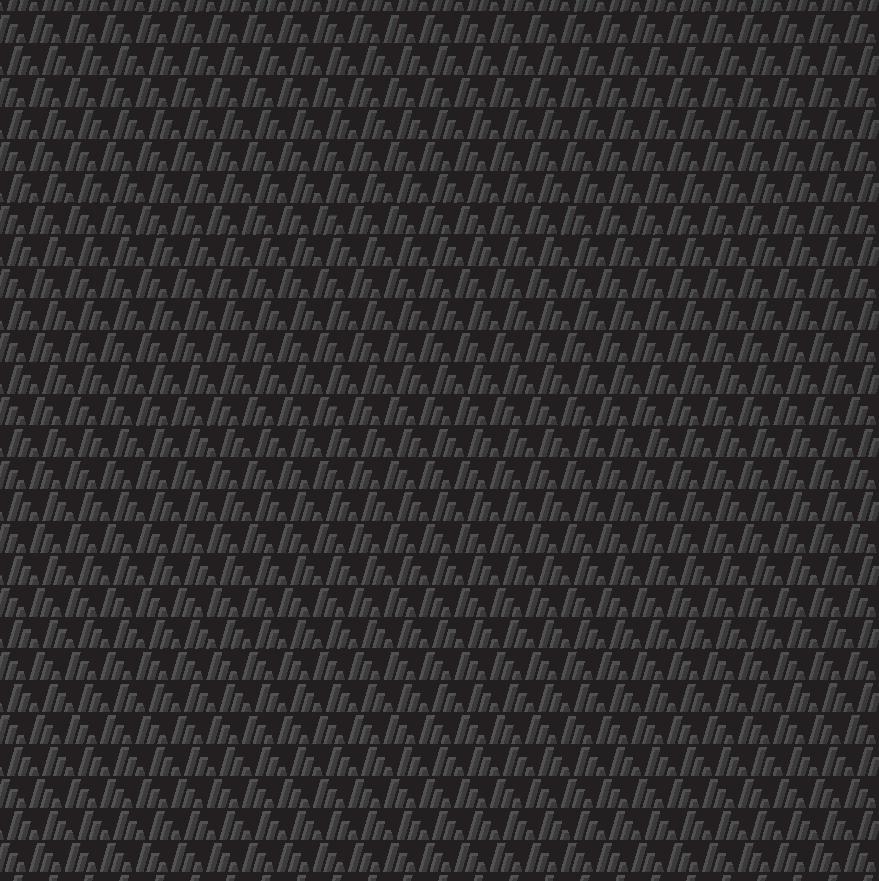
MASPRO is a leading provider of cutting-edge engineering solutions for underground and surface operations in the hard rock mining industry. What sets us apart is our unwavering commitment to optimising the parts we produce to increase safety and reliability. Our team works closely with customers to ensure that their machinery performs at its peak, even in the harshest mining conditions. If you’re looking to drill deeper, move more ore, and push your equipment to the limits while maintaining the highest standards of safety and operational reliability, talk to the MASPRO team today!
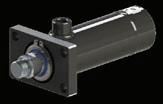
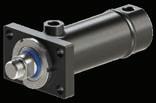
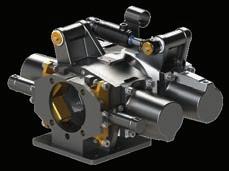


Follow us on:
maspro.com.au
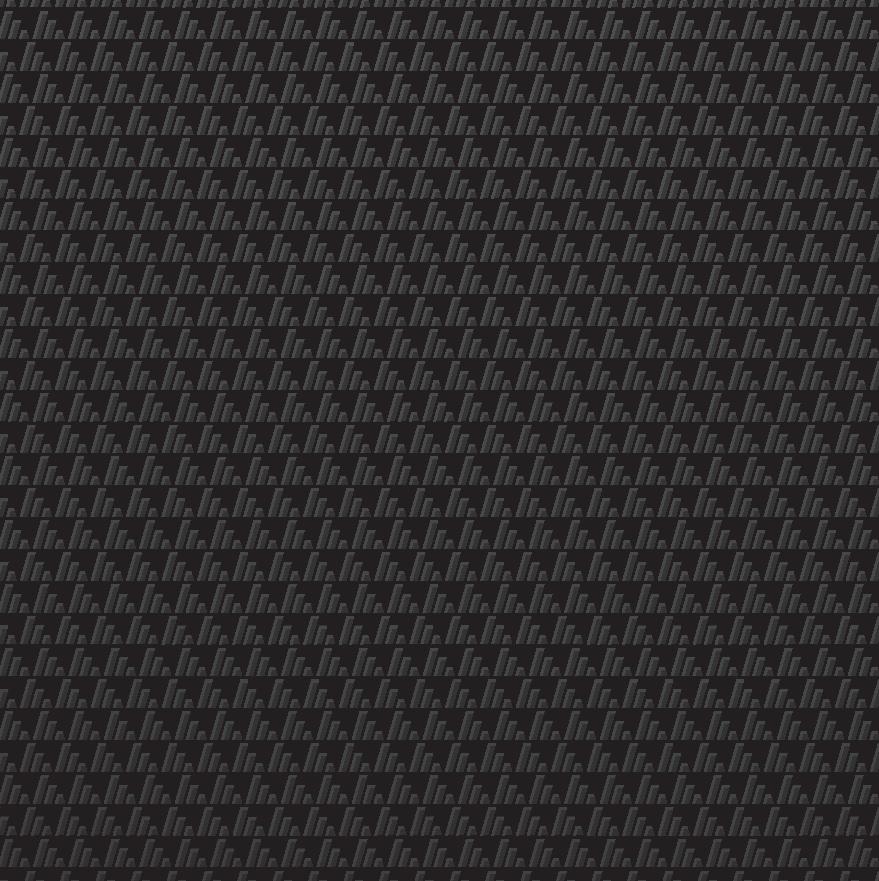

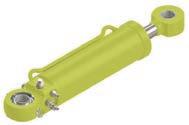
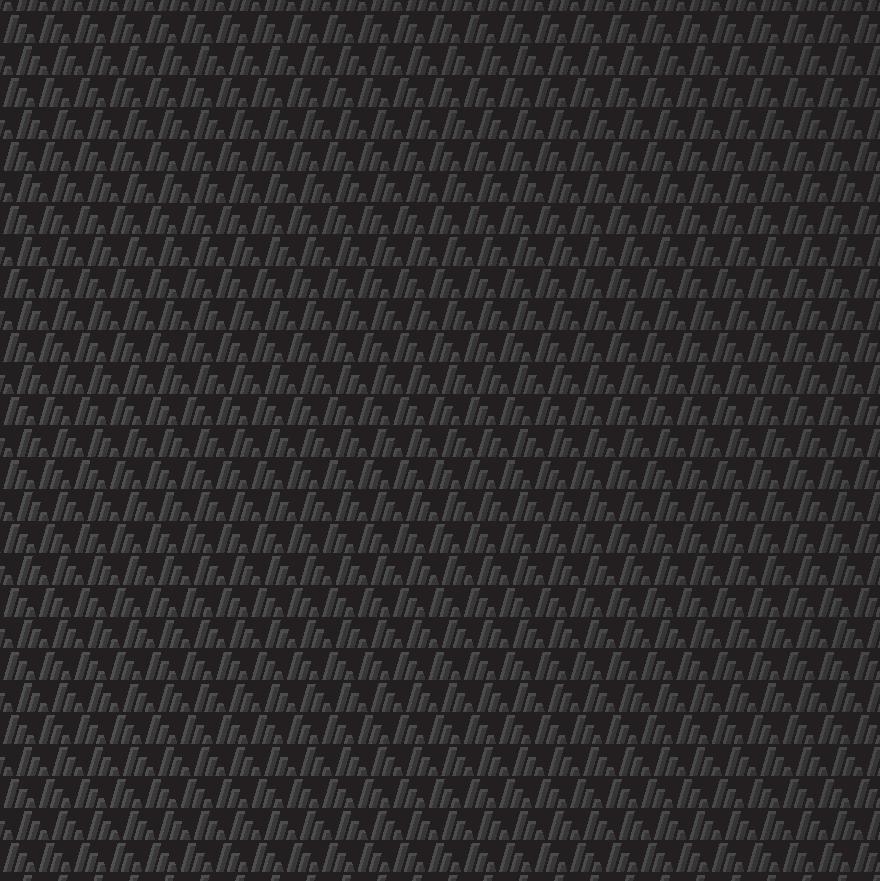
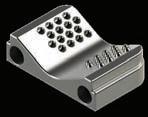



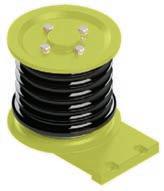
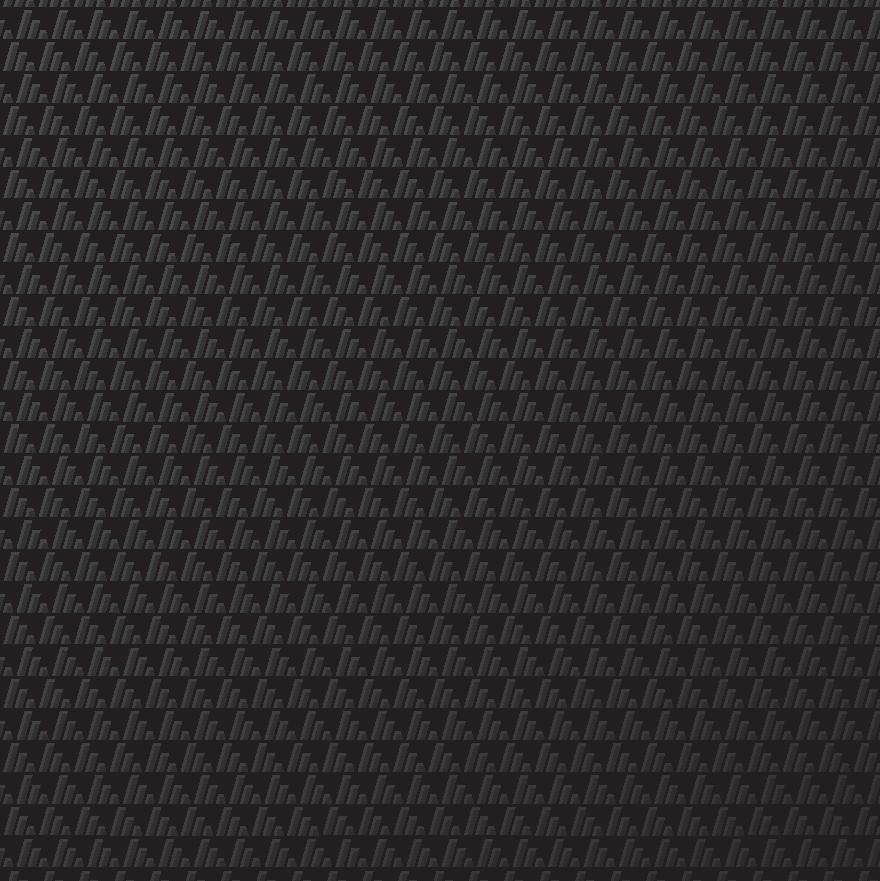
LOADING UP FOR PULLEY SUCCESS
FENNER CONVEYORS DEMONSTRATES THE VALUE OF TESTING PULLEYS AT RUN-CONDITIONS PRIOR TO SITE INSTALLATION, SAVING A BOWEN BASIN COAL MINE POTENTIALLY MILLIONS IN PART REPLACEMENT AND DOWNTIME.
Conveyor systems are a cornerstone of the mining process chain. Within a conveyor system, pulleys are critical pieces of equipment, driving the conveyor belt and enabling change of belt direction.
When equipment fails and a conveyor stops, millions of tonnes of product come to a standstill. That translates to lost productivity and an astronomical financial cost to operators.
This exact issue could have been the fate of a coal mine in Queensland’s Bowen Basin if Fenner Conveyors and its engineering division, Australian Conveyor Engineering (ACE), had not been contacted to perform load testing of pulleys prior to installation on site.
The mine wanted to ensure the quality of (non-ACE) conveyor pulleys before installing in underground operations and contacted its long-time supplier, Fenner Conveyors, for help.
With a network of manufacturing and service locations across Australia, Fenner Conveyors was well positioned to rise to the challenge quickly and efficiently.
ACE was engaged to perform pulley load-testing services, using local, inhouse equipment designed to meet the needs of any site.
“Our load-testing machine can be customised to simulate any conveyor condition, giving us a highly accurate report on the pulley performance, revealing any faults before the pulley even gets to site,” ACE engineering operations manager Dean Bazley told Australian Mining.
ACE’s load-testing machine also comes with real-time conditionmonitoring thanks to the company’s partner, SKF, allowing for instant reportage of even the slightest issue.
Bazley said that of the 16 pulleys ACE analysed with its load-testing machine, six failed to hold up against vibration due to issues such as bearing faults.
“Had the mine site’s pulleys failed on the conveyor and needed replacing, the cost per pulley would be extremely high given the difficult conditions of underground mining, not to mention substantial lost production due to downtime,” Bazley said. “That’s where our load-testing machine really proved its value.”
ACE has been bringing pulley solutions to the Australian mining industry for more than 20 years. But since joining the Fenner Conveyors Group in 2012, both businesses
combined forces to become a one-stop shop for the sector’s conveyor needs.
By doing more than completing the load testing for the customer and replacing the unfit pulleys with ACE engineered alternatives, ACE general manager Mark Wilcock emphasised Fenner Conveyors and ACE’s combined ability to deliver complete conveyor solutions to its customers.
“Since the beginning, Fenner Conveyors has developed a strong relationship with the mine site through supplying all their conveyor belting,” he said. “And today, we’re extending that relationship to include mechanical and electrical engineering and product overhaul supply that realise the benefits of our one supplier offering.”
Wilcock said the customer has been extremely satisfied with the commitment of the Fenner Conveyors Group, which has seen savings materialise beyond the site.
“We’re the only player on the east coast of Australia with this kind of pulley testing capability, meaning mines have a highly-valuable solution in their backyard, eliminating the need to ship pulleys across the country for testing where they might be out of action for weeks,” he said.
“Having pulleys travel over thousands of kilometres of road also has the potential to add bearing damage and shorten the life of the pulley, meaning more downtime and lost production.”
While the Fenner Conveyors Group offers a load-testing service for its competitors’ pulleys, Wilcock said the best way to ensure maximum
quality is to rely on Fenner Conveyors’ Australian-made pulley offering from the outset.
“Our pulley quality assurance is unmatched,” he said. “We have stringent processes in place to eliminate faults, such as building our pulleys in a cleanroom environment and wrapping the pulleys in UV-stabilised protection to guard against any conditions.
“It’s all about ensuring our customers’ operations keep running smoothly with instant access to conveyor engineering support when they need it.” AM
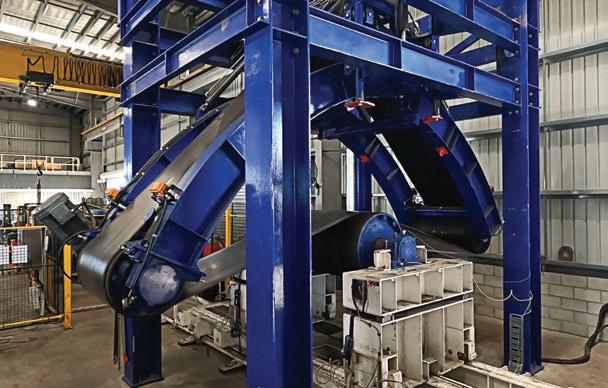

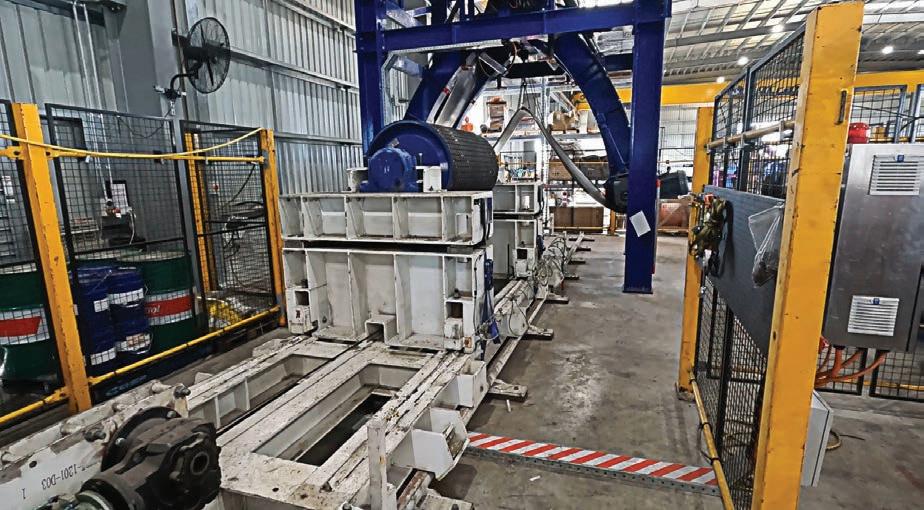
Smart crushing, adapted to you
Upgraded 800i crushers with new ACS-c 5
Even the best can always get better. Upgraded 800i crushers with new ACS-c 5 are our smartest, safest and most productive yet – designed around the needs of the people who work with them to raise the bar of what a crusher can be. Combining simple yet robust mechanical design with powerful user-friendly automation, 800i crushers are true workhorses that improve your ability to process more material, more accurately and more sustainably.
Discover the upgraded 800i crusher series with new ACS-c 5 today, and see what’s possible when a crusher is designed with you in mind.
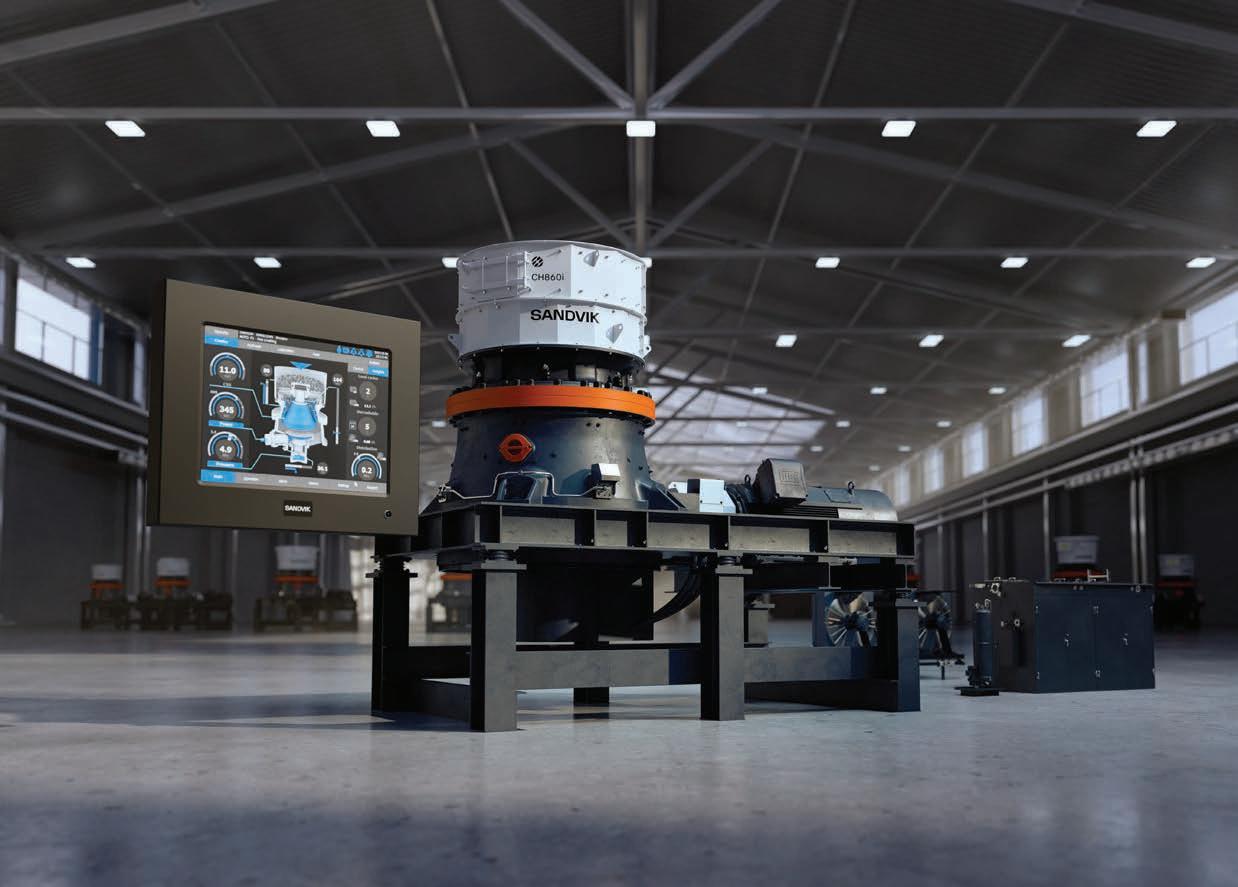
FROM PAPERWORK TO PERFORMANCE
OBZERVR HAS TAKEN THE MINING INDUSTRY BY STORM AS IT DOES AWAY WITH UNNECESSARY PAPERWORK IN THE FIELD.
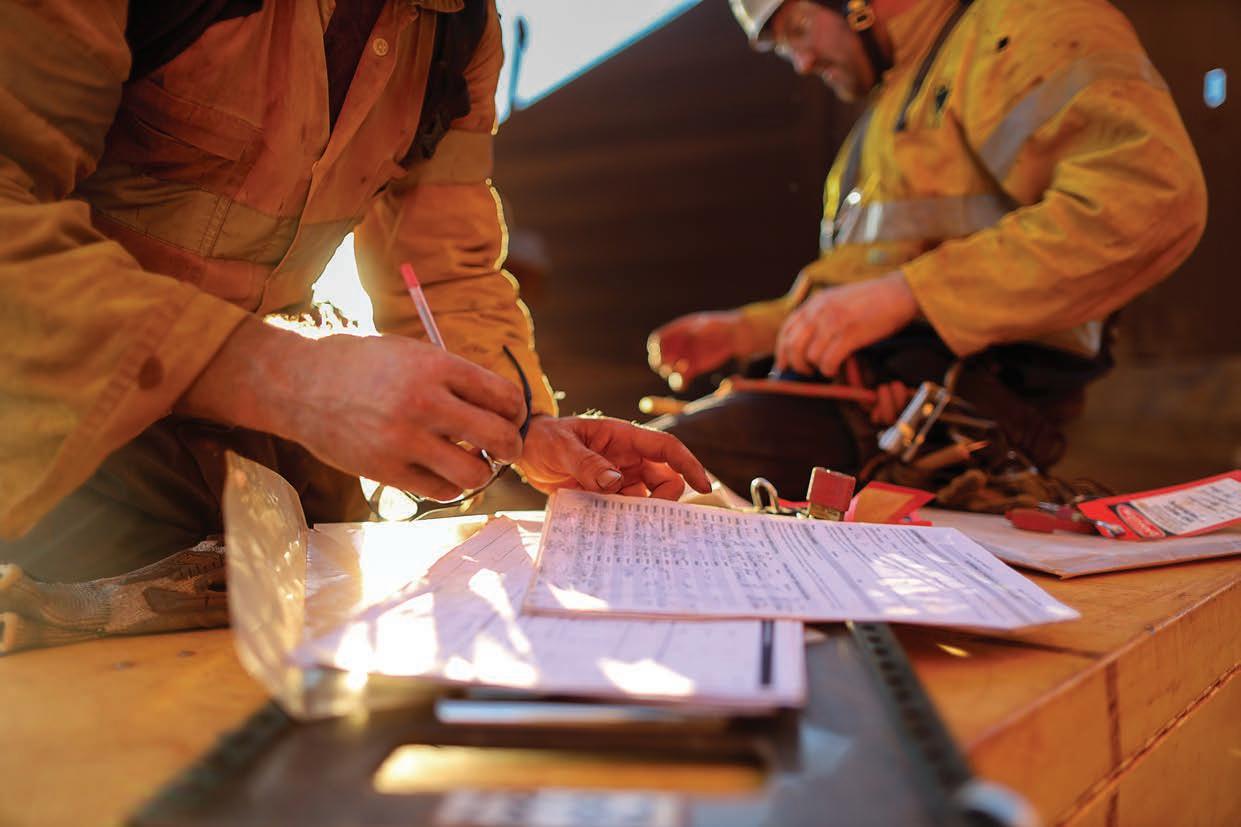
As mining companies push ahead with efficiency and optimisation projects, there can be an information disconnect between the backend systems and what is happening on the ground.
According to Obzervr, that is largely driven by the fact efficiencies are more likely to get lost when using a paperbased system to collect information.
For example, supervisors can spend hours re-keying data from manual forms in an effort to put information back into the enterprise resource planning (ERP) system rather than being in the field working with their teams.
For the past seven years, the Obzervr team has worked closely with the mining industry to solve this problem by developing an easy-to-use cloud-based platform that is designed to do away with paper for good.
Obzervr digitises the work to unlock more hours of productivity, enabling a seamless connection between ERP systems and front-end systems used in the field.
The Obzervr team found that field workers and technicians were facing
issues with paper-based processes that didn’t support standardised ways of working, leading to inefficiencies and confusion.
“This problem has gone unsolved and almost hidden for quite some time and it’s having a real impact on people’s work,” Obzervr head of growth Peter Livingstone told Australian Mining.
“With Obzervr, we’re streamlining work by going through and adding value in the way that work is done. Through easy-to-use interfaces, field workers can access important information online or offline, attach photos and comments, and even review reference materials.”
With so much work to be done in the field, it’s little wonder paper records can be lost or inputted incorrectly.
During his time on mine sites, Livingstone saw there was often a big difference between what the head office system said and what was actually happening in the field.
Obzervr changes this equation by removing the administrative burden from asset-management and minimising the errors typically caused through legibility and double-handling.
An operator can use the Obzervr system through an app on their phone

WHAT WE ACHIEVED (WITH OBZERVR) WAS A DIGITAL MINE, GAINING ACCESS TO REALTIME DATA STREAMS AND PREVENTING FAILURE IN ONE OF OUR CRUSHERS, SOMETHING THAT WOULD NOT HAVE BEEN POSSIBLE IN THE OLD PAPER PROCESS.”
to quickly identify work or log a job as complete, rather than heading back to the office to hand in their paperwork.
Not only does this allow the operator to move on to another job faster but it also means supervisors are spending less time at the desk, potentially saving hours of desk work during a typical shift.
“It gives them more time to be out in the field guiding and leading workers and fixing problems rather than be chained to a desk filling out paperwork,” Livingstone said.
It’s not only supervisors who benefit from the time-saving nature of Obzervr.
“When someone is going out to do their work, whatever that may be, they will have everything they need to do that job at their fingertips,” Livingstone said.
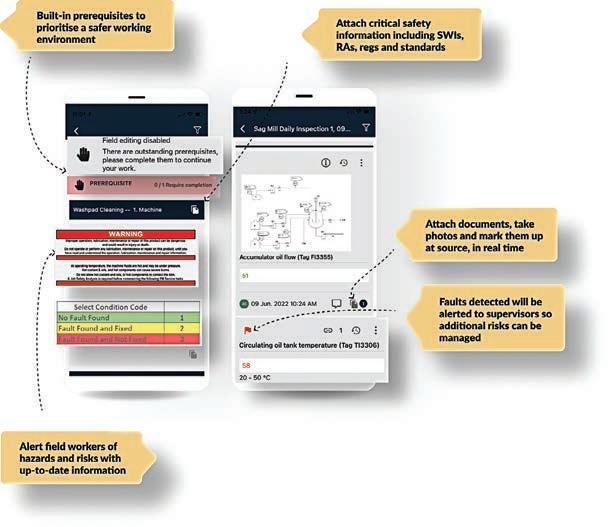
With Obzervr, employees don’t need to walk back to the office to get information about a new job or to get an extra part.
IMAGE: OBZERVR
instructions, removing the paper and improving the efficiency and productivity for our team,” a group asset maintenance team member at the gold mine said.
“What we achieved was a digital mine, gaining access to real-time data streams and preventing catastrophic failure in one of our crushers, something that would not have been possible in the old paper process.”
With a system providing flexibility across all different areas of the business, it truly can be called a ‘onepane-of-glass’ solution.
“Most of the sites that use Obzervr are expanding, and they are using the system across many different areas,” Livingstone said. “It becomes part of what they do and use on a daily basis.”
OBZERVR’S LEADING DIGITAL FIELD MOBILITY SOLUTION HELPS MAKE WORKPLACES SAFER, AND MORE COMPLIANT AND EFFICIENT.
If they do happen to get paused on a job, they can also move straight to the next one, because they have access to the next job on the list.
Obzervr’s solution has been implemented at some of the largest mines in Australia to wide acclaim.
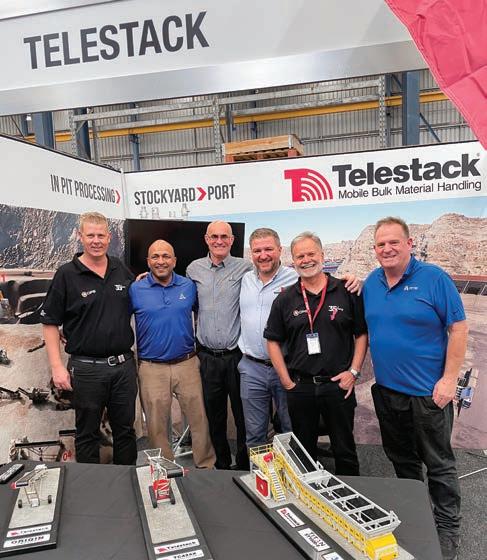
“Obzervr has become an integral cog in the machine for a large number of mines,” Livingstone said. “We’ve even had wordof-mouth instances where a supervisor will use Obzervr at one site and then move to another site and tell them that they also need to implement Obzervr.”
A gold miner, one of Obzervr’s top customers, sang the praises of the system.
“We set out to convert our paperbased work instructions to digital work
At the end of the day, the team at Obzervr is happy if customers are happy.
By freeing people up from desk work and enabling these projects to happen quickly and more efficiently, Obzervr gives teams insight into where breakdowns are happening, where things might need some extra attention.
Above all, Obzervr said, it’s putting control back into an employee’s hands. To put it most simply, Obzervr works to provide the mining sector with the optimisation and efficiency it needs to get the job done right. AM
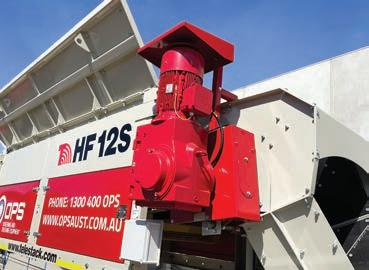
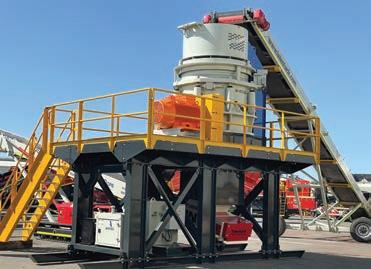
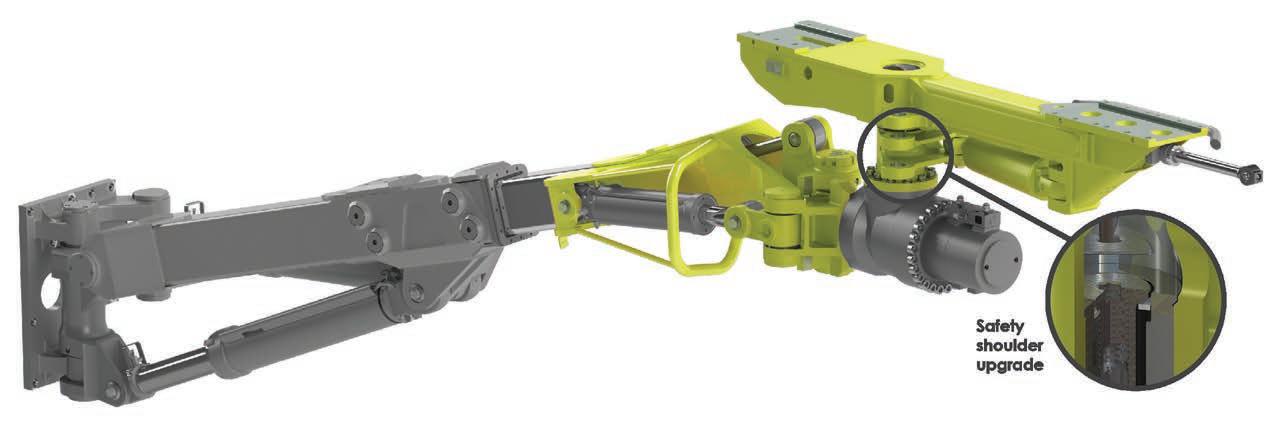
PROLONGING EQUIPMENT LIFE
MASPRO RE-ENGINEERS AGED OR ILL-PERFORMING
COMPONENTS TO AS-NEW OR BETTER CONDITION, DELIVERING LONGER EQUIPMENT LIFE FOR ITS MINING CUSTOMERS.
The Australian mining industry is known for offering some especially harsh working conditions –and sometime equipment struggles to cope.
That means local engineering and servicing, ensuring parts and attachments are manufactured and maintained with Australian conditions in mind, can be critical to the success of a mining operation.
That’s where MASPRO comes to the fore. MASPRO, which specialises in solutions “that surpass industry standards”, re-engineers aged or ill-performing original equipment manufacturer (OEM) parts to as-new or better condition, designing, engineering and manufacturing new components in a matter of weeks. This enables operators to keep their machinery on the park for
MASPRO head of engineering Tony Waterman told Australian Mining company’s approach starts with understanding a customer’s needs.
“MASPRO’s sales team gets the needs of the customer – what they wish for and expect – and then the rest of the company works together to make that happen,” Waterman said.
“The engineering department can design anything, but that doesn’t mean it can be made. So we have to work really closely together to make sure that what we make meets or exceeds the client’s expectations and is done in a way that is repeatable.”
MASPRO can complete one-off projects but the company specialises in batch solutions that are applicable to a wide range of equipment or are synonymous to a particular product. Such is the case with MASPRO’s Bolting Series 2.0, a range of engineered parts for Sandvik’s widely used SB60 booms.
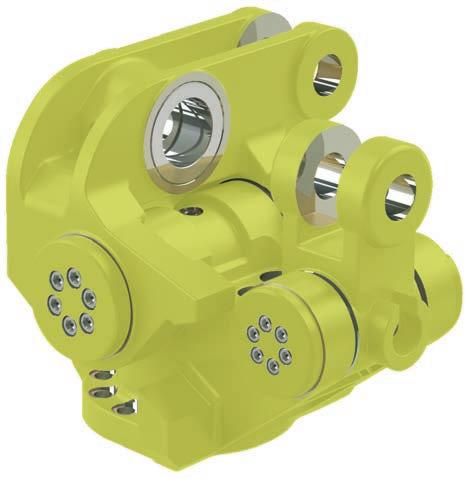
The Bolting Series 2.0 includes a bolting cradle assembly, inner zoom, cylinder and downhole power unit (DPU), with MASPRO working on an outer zoom to add to the collection.
into a range of critical parts that are enabling operators to achieve better performance and get more hours out of their bolting rigs.
“Customers were experiencing failures with their DPUs, from excessive pinwear and cracked castings happening really early,” Waterman said.
“You could expect to have a casting last several years, but in some instances fatigue cracks were occurring in eight months.
“So we redesigned the casting components with our proprietary steel, changed the design to be fatigueresistant and improved the interactive surfaces. This improved the DPU’s tensile and yield strength, and its fatigue performance to enable it to last longer.
“From that, we developed the cradle, bolting cylinder, inner zoom and the zoom cylinder, and now we’re developing the outer zoom.”
The Bolting Series 2.0 has been well received across the Australian mining market, with strong testimonials for all parts.
“We’re seeing a significant increase in life,” Waterman said. “We had one DPU, for instance, that despite being more two years old still looked in as-new condition with little wear to
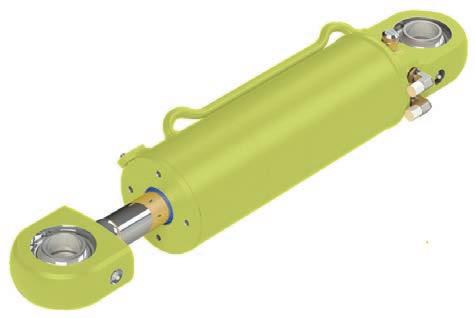
“We haven’t had any issues with the cradle. We’re currently running cradle trials with some clients to see how it performs when regimentally documented on a month-to-month basis.
“As for the inner zoom, there’s been no failures and no surprises – it just works.”
Waterman said the Bolting Series 2.0 is unique to the market, with few other designed, engineered and manufactured bolting offerings available for the Australian mining sector.
MASPRO’s commitment to specialist bolting products is allowing customers to achieve greater flexibility with their operation. This includes being able to bolt with a jumbo drill rig.
“We’re focusing on bolting because we know some customers would, in certain operations, prefer to bolt with a jumbo rather than a cable bolter. So we’re trying to meet that need in a safer way for our customers,” Waterman said.
“The focus is always on increasing the life of the product for the customer, so they can either increase their service life or know they’re going to reliably meet their scheduled service life.
“If it’s a 12-month service interval, it’s going to be a 12-month interval, not six, seven or eight months. It’s about reliability and performance and enabling customers to have continuity and trust in their operations.”
As MASPRO services the unique and precise needs of its mining customers, the company is faced with new challenges every day.
Waterman acknowledged that MASPRO is “often going back to the drawing board”, but this only fuels the company’s ingenuity and brings rise to its most inspired innovations.
For MASPRO, no conundrum cannot be solved, which means miners are always in safe hands. AM
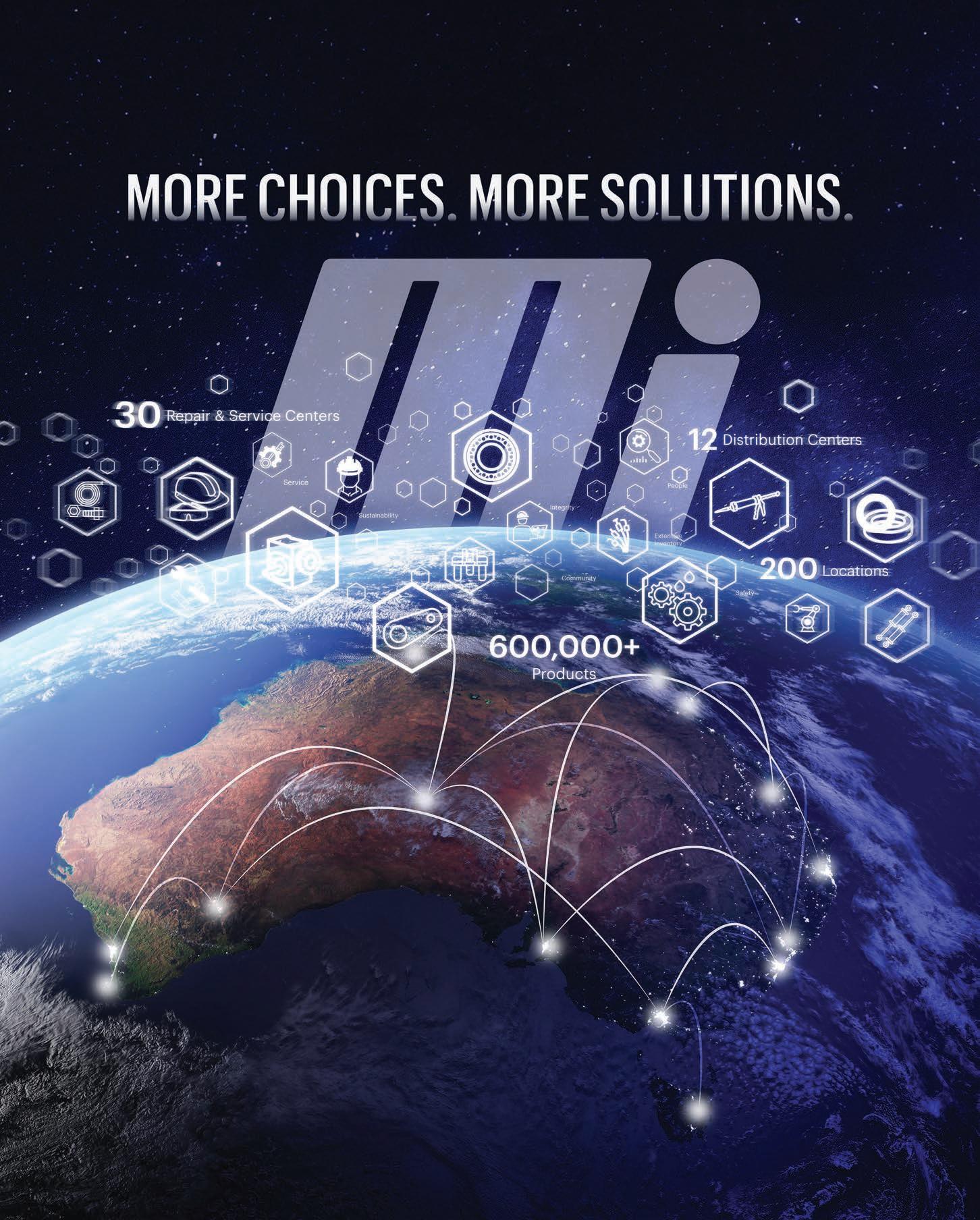
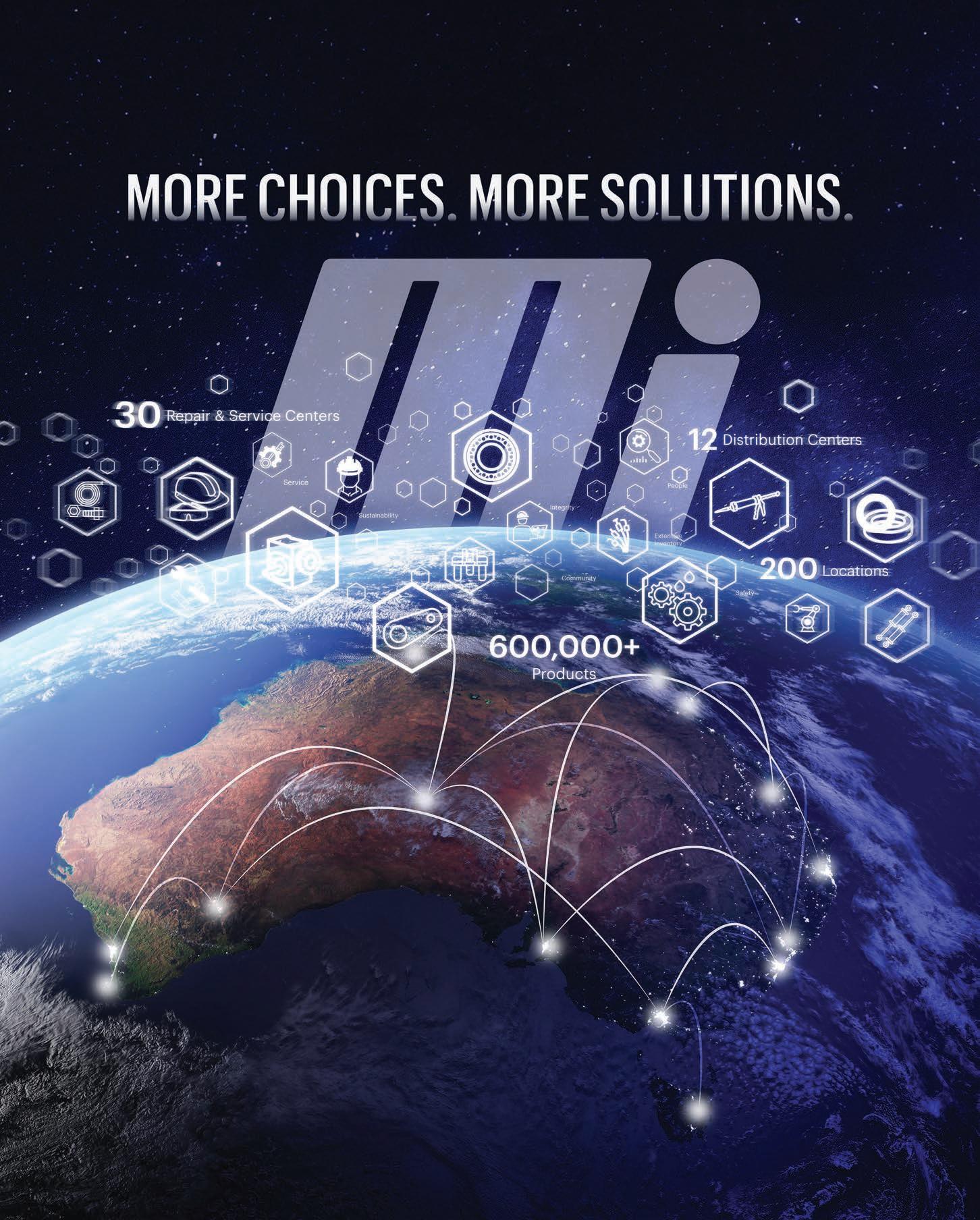
ONE-STOP WASHING SOLUTION
PLANT WASH IS BRINGING THE BENEFITS OF THE MINE EQUIPMENT WASHER TO THE AUSTRALIAN MINING INDUSTRY.
Fcompany’s inception stemmed from his encounter with the Mine Equipment Washer (MEW) truck at a prominent mining services facility in Pinjarra, WA. the MEW in passing, until a colleague highlighted its remarkable capabilities,” Marwick told then that my interest was truly ignited.” an electronic brochure showcasing the MEW truck’s innovative features,
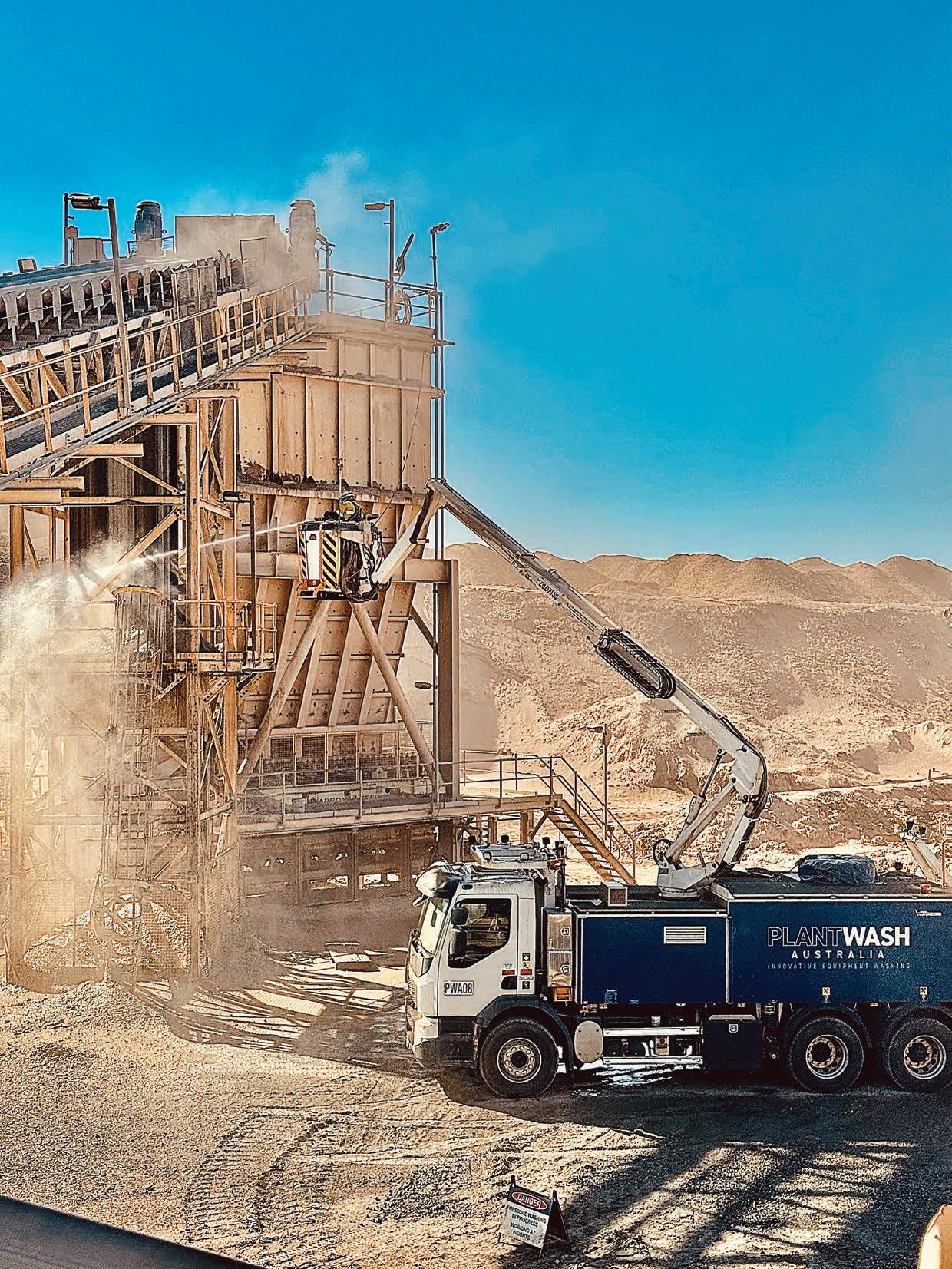
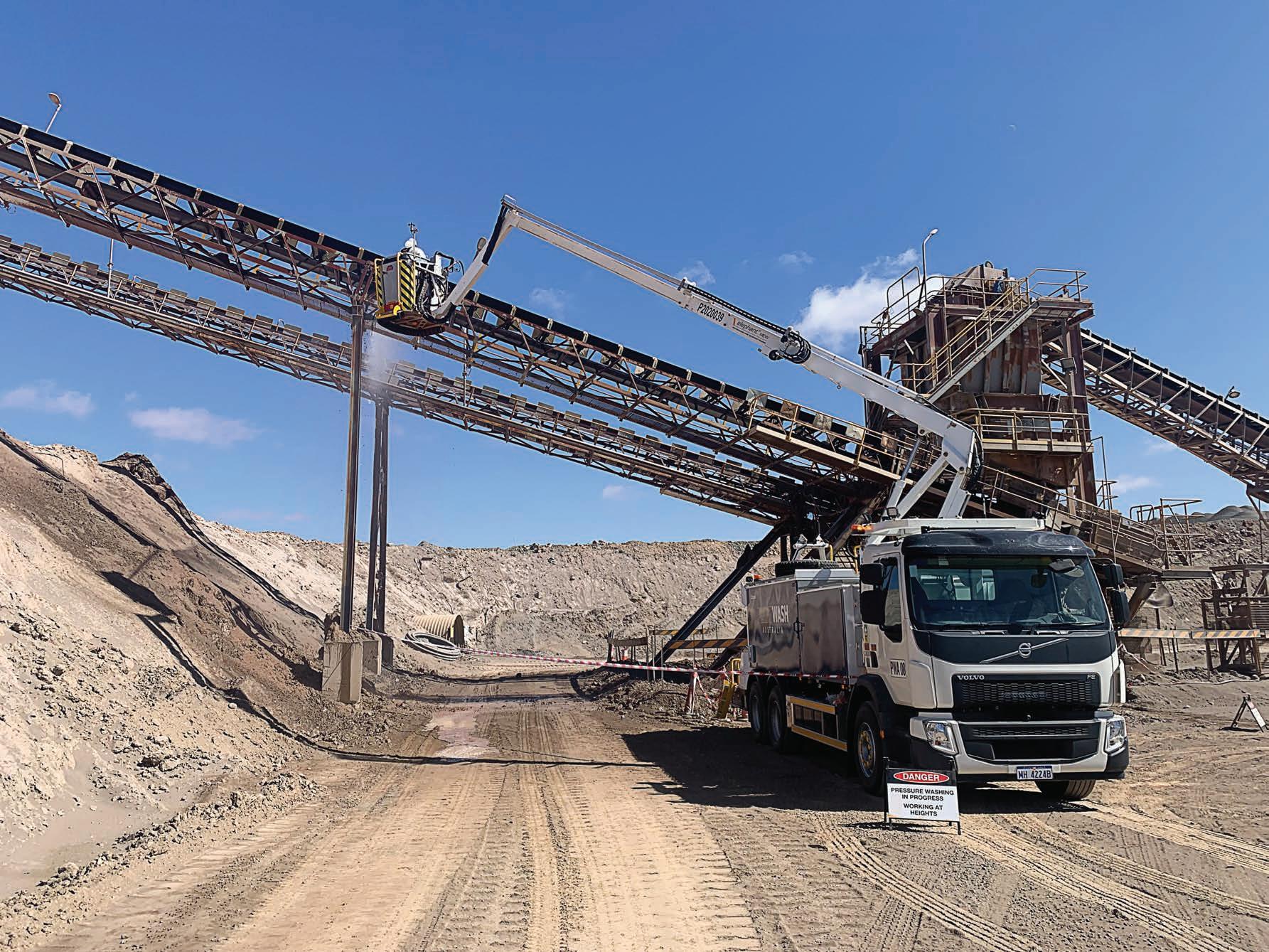
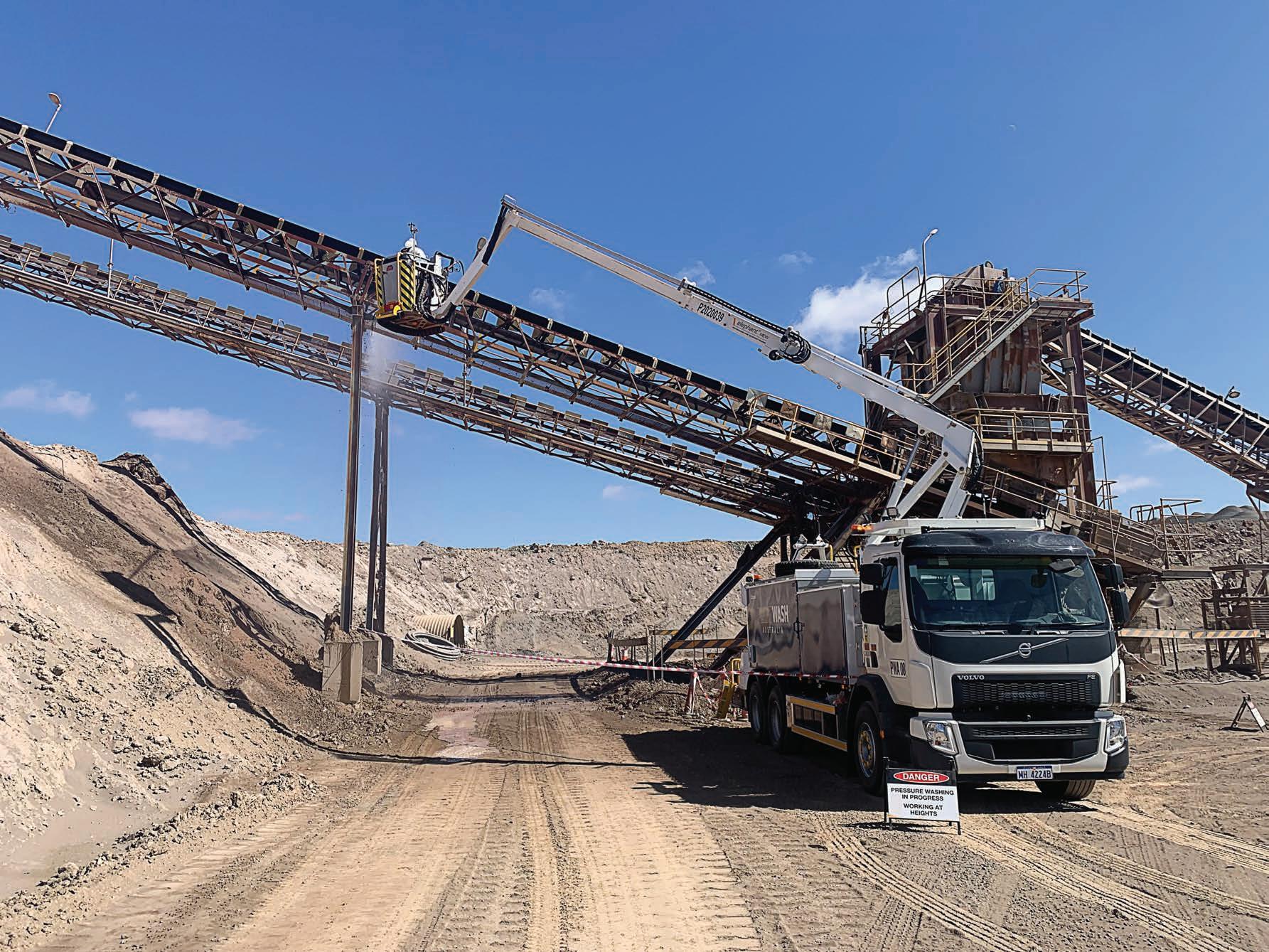
Equipped with an elevated work platform (EWP) with a 15m reach and a robust chassis engineered to withstand winds of up to 72km per hour, the MEW boasts a 7000L on-board water storage capacity and a 230kW diesel heater, ensuring water temperatures reach an optimal 95°C for peak performance.
Marwick underscores the MEW’s user-centric design and stringent safety features, including proximity sensors and anemometers, which safeguard operational integrity even in adverse conditions.
Furthermore, the unit’s versatility facilitates online washing, enabling concurrent maintenance activities without disrupting operations.
Describing the MEW as a comprehensive “all-in-one” solution for elevated work, Marwick highlights its efficiency over conventional methods.
“We can deploy directly to site without the need for supplementary equipment,” he said.
In addition to equipment washing,
Plant Wash offers vacuum loading services that utilise hydro vacuum excavation trucks, which are remotely controlled for heightened safety and efficiency.
Renowned for their prowess in nondestructive digging, high-pressure jetting and controlled waste removal, these trucks exemplify Plant Wash’s dedication to delivering holistic industrial solutions.
As a proudly family-owned and operated enterprise, Plant Wash places a premium on personalised service and rapid response times.
“Clients can depend on us for bespoke, punctual solutions,” Marwick said. “We are committed to fulfilling their requirements, whether it entails on-site assessments or troubleshooting.”
In essence, Plant Wash typifies innovation, efficiency and personalised service, catalysing a paradigm shift in industrial cleaning within WA’s esteemed mining sector. AM
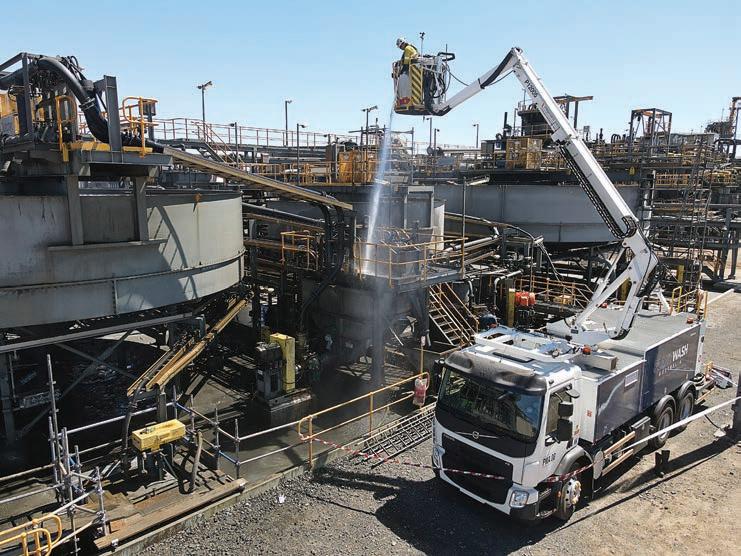
ENGINEERING EXCELLENCE EXTENDS MACHINE LIFE
AUSTRALIAN MINING SAT DOWN WITH BRADKEN TO DISCUSS THE EVOLUTION OF ITS UNDERCARRIAGE TO ENHANCE LIEBHERR R9800 MACHINES.
Across more than 40 years of undercarriage production, Bradken has sold in excess of 250,000 crawler shoes to the global mining market.
The company designs and manufactures undercarriage solutions that optimise customer operations, with a focus on critical deliverable areas, such as total cost of ownership advantage, quality assurance and reliability.
Bradken has long been the manufacturer for the OEM. From 2007 to 2021, Bradken seamlessly designed and supplied crawler shoes for Liebherr’s R9800 excavator, equivalent to more than 65 full machine fitments for mining customers.
The company can now offer its R9800 undercarriages direct to the market, providing customers with the advantages of working with the company, as designer and manufacturer of the component, first-hand.
And given Bradken’s comprehensive service offering, customers have not only been able to gain access to a quality product, but also the after-sales support that comes with it.
“We have an experienced field crew that monitors undercarriage equipment,” Bradken sales manager Stuart Hipkins told Australian Mining.
“We can predict end-of-life for undercarriage components, and we can deliver on-demand service by monitoring a customer’s platform in-field, free of charge.
“Given this is a high-capital-purchase product, customers benefit from having a Bradken representative assess their undercarriage, utilising decades of experience in varying conditions around the globe, rather than someone internally who might not have the specialist knowledge.”
Bradken provides preventive maintenance support, with customers able to accurately address pain points and schedule shutdowns, meaning greater uptime for their R9800.
“Liebherr’s R9800 excavator is often one of the most important pieces of

process, with wear-monitoring technology enabling the customer to understand the wear and performance of an undercarriage.
The ultimate goal of wear monitoring is to reduce total cost of ownership of an R9800 undercarriage, extending the life of the asset and limiting the amount of capital spent on maintenance and upkeep.
Hipkins said Bradken has seen some of its R9800 undercarriages last 5–7 years out in the field.
“We believe we’re a world leader in undercarriage solutions, and certainly a suitable component supplier
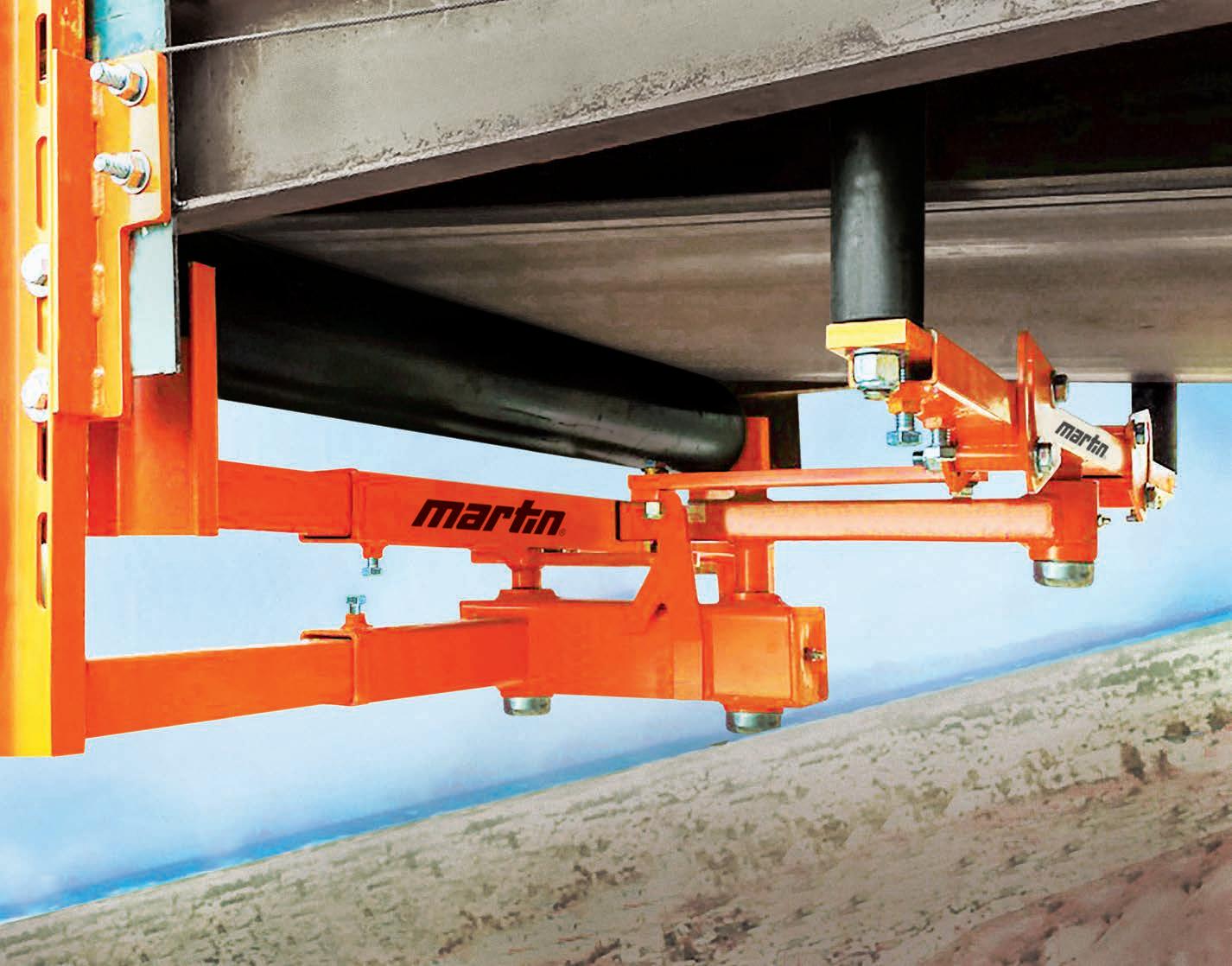
BRADKEN’S R9800 UNDERCARRIAGE HAS BEEN A FUNDAMENTAL PRODUCT FOR THE LIEBHERR
FOR
improvements in the track reliability of the R9800 shoe.
Some proven features include deep induction hardened roll path and the use of Bradken’s high-strength proprietary alloy. The rollers and idlers are also available in grease or oil-filled configurations, with multiple ports in each end block for easy lubrication flushing.
Customers who work directly with Bradken can be rest assured that they are receiving products and service support directly from the manufacturer.
“We have gained decades of product knowledge,” Bradken global
conditions and customer requirements.
“We are constantly looking at the conditions, what’s happening with the wear life and considering if there are ways to improve design or material to withstand those.”
With the R9800 undercarriage, Bradken has developed a fundamental component for a critical piece of mining machinery.
But the company is not finished innovating, with more advancements in the pipeline set to further extend the product’s wear life, ensuring customers can keep their Liebherr R9800 excavators on the park for longer. AM

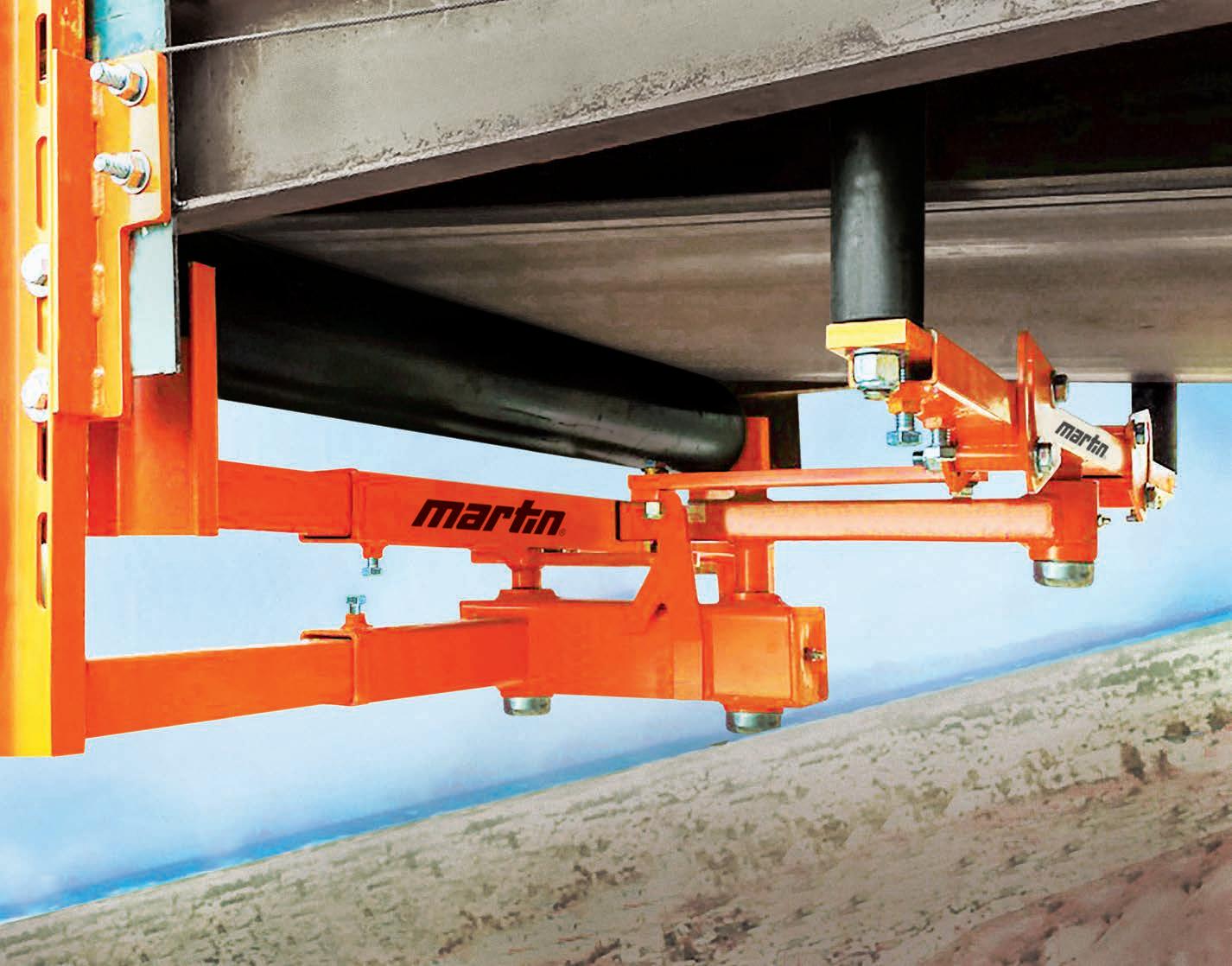
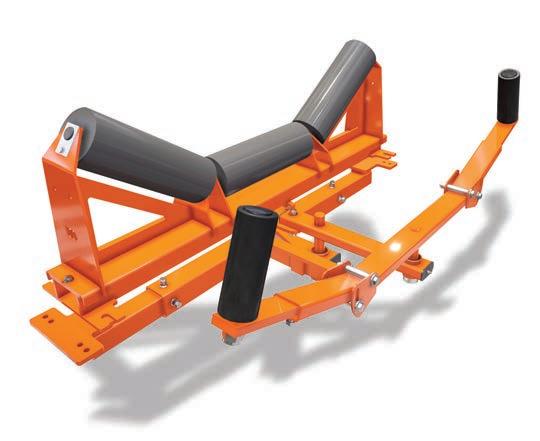
Amisaligned conveyor belt cannot properly handle the load it was meant to carry, causing product to fall off the belt. From a high-speed conveyor, this fugitive material can build up rapidly, requiring clean-up and driving up costs. More importantly, it also introduces an inherent risk to the people working around a moving conveyor.
The multi-pivot design of the Martin® tracker corrects many of the problems with other belt training systems. By continuously mitigating tracking issues rather than reacting to them, our multi-pivot design significantly reduces the risk of component failure or production stoppage.
At Martin, reducing your downtime and operating costs are always top of mind. But, as with all of our other products, safety is the primary motivation behind the design and function of our multi-pivot trackers.
Martin® Tracker™PIONEERING UNDERGROUND
MINE VENTILATION
SMART-VOD IS TAKING ITS VENTILATION ON-DEMAND SERVICE TO THE NEXT LEVEL.
Most underground mining vehicles in use today are powered by diesel motors.
That means forced air ventilation is required to remove diesel exhaust, blast gasses, and reduce the ambient temperature for underground operators.
Mining companies are after a ventilation solution that not only complies with ventilation standards but minimises power usage and associated cost. And this is precisely where SmartVOD steps in.
Since it was established in 2020, Smart-VOD has great success through its ventilation on-demand solution.
“Smart-VOD has successfully rolled out ventilation on-demand across multiple gold mines in Western Australia,” the company said.
“We have continued to develop and refine our ventilation on-demand offering so we can deliver a better solution for our clients.”
The Smart-VOD ventilation ondemand solution is comprised of three key components:
• A method of controlling the fan output
• A demand control signal
• Monitoring and reporting on the ongoing performance of the system
Fan output can be controlled with a variable speed drive (VSD) or a SmartStarter. A VSD offers continuous control over fan speed, while a Smart-Starter allows remote control of both stages of a dual fan starter.
Operating a dual-speed fan with one stage on and one stage off delivers about 80 per cent of the air volume at half the power.
Smart-VOD’s ventilation ondemand solution uses radio-frequency identification (RFID) to track vehicles entering and exiting a ventilation zone, thereby providing demand control signals based on vehicle movements.
Additionally, Smart-VOD provides a centralised mine dashboard displaying the status of the ventilation zone along with the savings performance.
To further simplify the adoption of ventilation on-demand, Smart-VOD has developed the Smart-Starter core, which can be retrofitted onto existing dual-fan direct online (DOL) starters, transforming an existing fan starter into a Smart-Starter. This enables control of the existing fan starter through Smart-VOD’s ventilation on-demand control system.
“The Smart-Starter core acts as a smart switch that’s remotely controllable, receiving demand control signals from the vehicle tracking systems,” Smart-VOD said.
While dual-motor secondary fans are very common in underground mining, some mine sites find the VSD adoption challenging. Smart-VOD recommends these sites adopt the Smart-Starter.
“The Smart-Starter core is a low-cost entry for sites looking to utilise SmartVOD’s ventilation on-demand system,” Smart-VOD said.
“The Smart-Starter core is an off-theshelf product designed to be seamless
integrated with an existing dual-fan DOL starter.
“It’s built small to allow for a simple retrofit into an existing dual-fan starter, while being durable and reliable.”
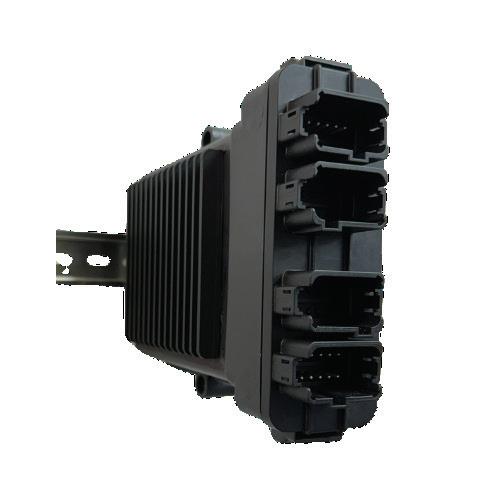
The ventilation on-demand system has delivered 54 per cent in energy savings over its last 100,000 hours of operation, Smart-VOD said, and the company believes a dual-fan DOL starter fitted with the Smart-Starter core can deliver 50 per cent in energy savings.
“This represents a significant reduction in ventilation power usage and emissions,” the company said.
“The noticeable reduction in on-site power usage has helped customers reduce their all-in sustaining costs, leading to more profitable mining.”
A Smart-Starter can be upgraded to a VSD by simply unplugging the SmartStarter and plugging the VSD in. SmartVOD’s ventilation on-demand system will recognise the type of starter being used and control it appropriately.
Smart-VOD recommends larger sites have a mix of VSDs and Smart-Starters.
“This is because the potential energy savings vary across location and time with the varying mix of mining operations,” Smart-VOD said.
“They are different technologies that provide varying degrees of adjustability.
“To maximise savings,sites can install VSDs where more intensive operations take place and have Smart-Starters located everywhere else.”

SMART-VOD HAS DEVELOPED THE SMART-STARTER CORE.
Smart-VOD’s ventilation on-demand unit has been designed to operate autonomously, which means it doesn’t require continuous network connectivity.
“Some companies use other mine control functions and technology to adjust ventilation but that requires manual input from people at the surface, whereas ours does not,” the company said.
When network connectivity is available, further features are enabled, including a centralised mine dashboard showing the status of the ventilation zone and the savings performance, as well as reports on vehicles in each ventilation zone and their ventilation flow. This helps demonstrate compliance with legislated ventilation standards.
As mine sites look for ways to be more energy-conscious, Smart-VOD’s ventilation on-demand system is proven to help customers save on energy costs and reduce their carbon footprint. AM

SMART-VOD’S VENTILATION ON-DEMAND SYSTEM USES RADIO-FREQUENCY IDENTIFICATION TO TRACK VEHICLES.
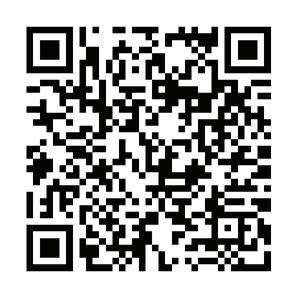
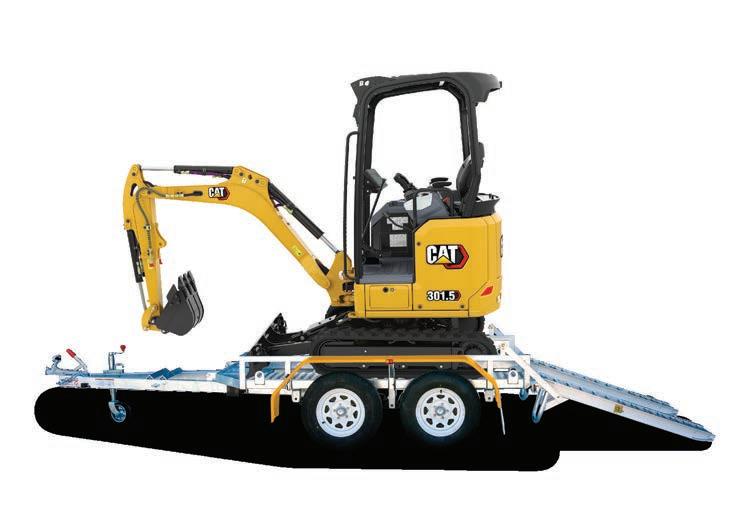
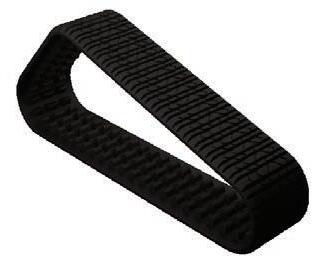
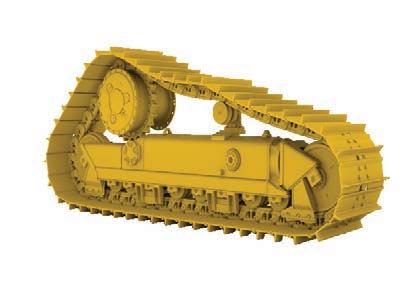
ISENSE COMES TO THE RESCUE
TREOTHAM IS BRINGING IGUS’ ISENSE RANGE TO AUSTRALIA’S MINING INDUSTRY FOR SMARTER ENERGY CHAIN MAINTENANCE.
ISENSE COMPLEMENTS IGUS ENERGY CHAINS TO CREATE A RELIABLE LOADING SOLUTION.
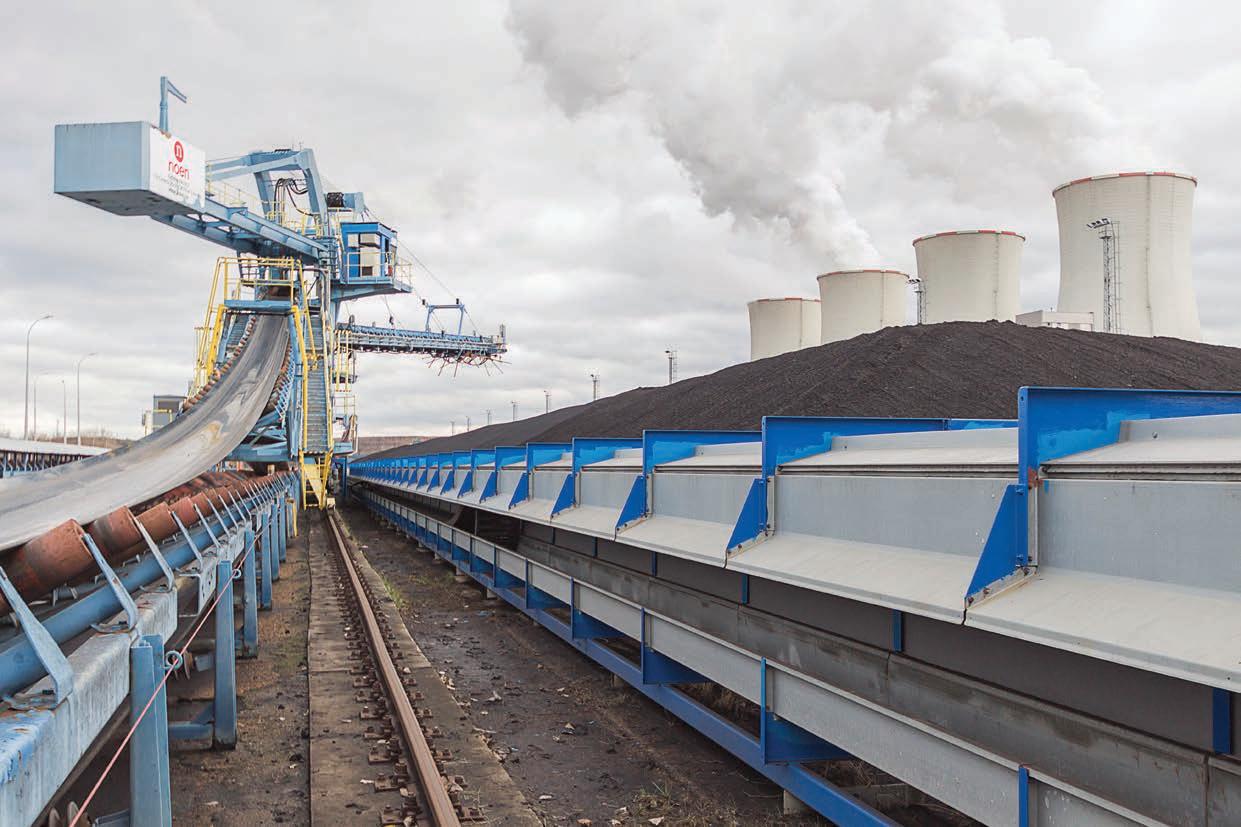
Getting Australia’s minerals from pit to port is no small feat.
With millions of tonnes of product shipped every year, operators need loading systems they can rely on.
Where ship-loaders have previously relied on outdated cable technology like reelers or festoons, Treotham is on a mission to upgrade the industry with the latest in energy chain technology.
While cable reelers and festoons are subject to issues like friction, sagging and environmental degradation, energy chains are providing the mining industry with a tough solution built to last in any condition.
Treotham is the sole distributor of its German-based partner igus’ energy chains, which use high-strength plastics to keep cables in action while keeping costs down.
This is bolstered by igus’ iSense condition monitoring system.
Links in igus energy chains are made for tough, continuous use. Paired with igus’ iSense condition monitoring offering, operators have the ability to access real-time data into the performance of their energy chain at any point in time.
“igus’ iSense condition-monitoring provides operators with an embedded reporting function that pinpoints an exact area of a chain that may be in need of maintenance,” Treotham national sales manager John Sharp told Australian Mining
“The goal is to get an overall outlook on the condition of the system and enact maintenance that prevents unplanned stoppages, boosting the overall efficiency and optimisation of an operation.”
iSense sensors constantly measure the push and pull forces along the chain. The data is then processed through a module in the switch cabinet that can make instant executive decisions when it senses trouble, like a safe shut-down.
ISENSE CONDITIONMONITORING PROVIDES OPERATORS WITH AN EMBEDDED REPORTING FUNCTION THAT PINPOINTS AN EXACT AREA OF A CHAIN THAT MAY BE IN NEED OF MAINTENANCE.”
With 50 or more metres of chain, knowing its real-time condition at the touch of a button allows operators to focus on the task of shipping essential minerals without worrying about unforeseen issues.
“The iSense system captures data that will quickly reveal any anomalies,” Sharp said. “The data can then be used to monitor how wear is progressing and extrapolate a lifespan report and
simultaneously trigger an inspection of the equipment should it need it.”
By providing in-depth data, operators are given a level of autonomy that puts them ahead of the game. Should they decide they don’t have the scope to account for such valuable information in their day-to-day, operators can choose to defer to the experts.
“If the customer decides the information iSense provides is outside of its remit, they can choose to send it back to Germany to the igus experts who monitor the system on their cloud,” Sharp said. “That way, the customer doesn’t have to interface with the control system but can still receive critical information when they need it.
“It’s just another way igus is able to adapt to the needs of its customers and develop a solution that works in collaboration with their system.”
Sharp said the iSense offering enables operators to be more proactive about their maintenance strategies, limiting
unnecessary equipment downtime and ensuring operations remain on track.
“It breaks the cycle of a purely reactive maintenance program,” he said. “Rather than waiting until equipment breaks down to fix it, operators have their finger on the pulse of what needs to be done before the situation becomes serious.”
Sharp said iSense has the potential to change the way energy chain maintenance is carried out forever.
“There’s nothing like this on the market at the moment,” he said. “We’re really changing the game with a solution that hasn’t been seen before.”
A recent Treotham customer had a close call when a ladder left leaning against a ship-loader system became lodged in the energy chain.
Luckily, the customer had just installed iSense at its operations.
“When the customer went to travel the ship-loader, it wouldn’t move,” Sharp said. “iSense found the ladder jammed in the system and triggered an immediate stop. They were able to remove the ladder and immediately commence operations with zero damage.
“Without iSense, the system would have kept running with the blockage and the damage could have been catastrophic, with repair and downtime costs through the roof.”
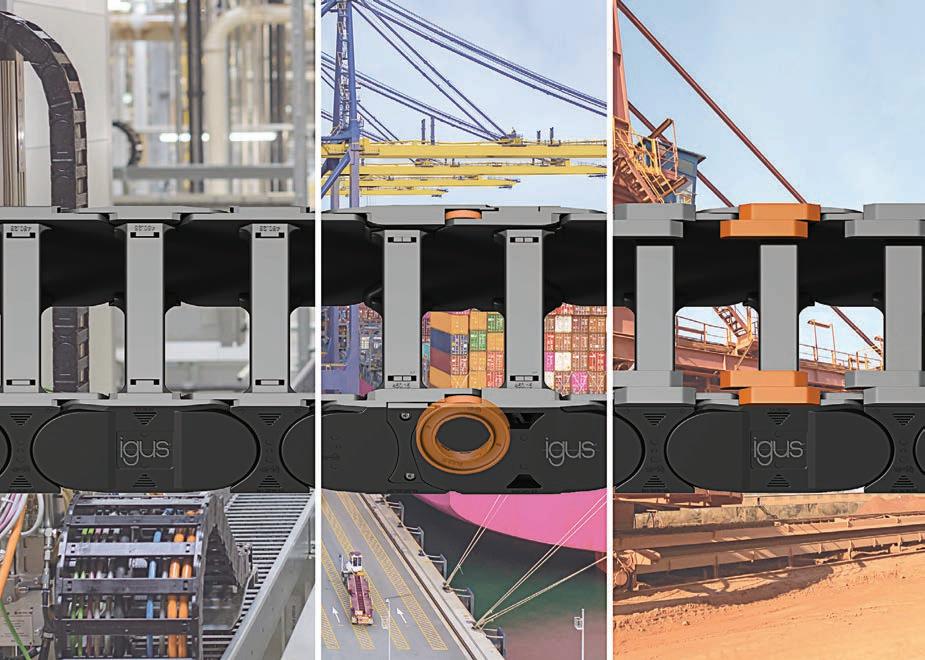
Sharp said success stories like this are why Treotham is keen to unlock the potential of igus’ iSense offering at sites across Australia.
processing,
“By growing our footprint in mineral

▲
•
•
•
▼
•
•
•
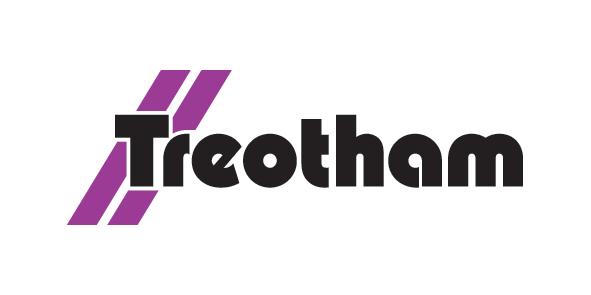
“NOBODY REBUILDS BETTER”
WITH A CUSTOMER-FIRST APPROACH, HASTINGS DEERING IS HELPING ITS MINING INDUSTRY PARTNERS UNLOCK THE MULTIPLE LIVES DESIGNED INTO CAT MACHINES.
Productivity is one of the key factors to success at any mine site globally. A key facilitator in production is having the right assets working to keep product consistently moving from mine to market.
Heavy mobile equipment is no exception. Operating for thousands of hours each year in extreme environments, the equipment and their components inevitably wear and need replacement to ensure machine uptime.
But what if there was a way to give these machines a new life?
This is the ethos behind Hastings Deering’s rebuild program.
“Cat machines, power trains and major components are not only built tough the first time but are also built to live multiple lives,” Hastings Deering executive manager site performance
Matt Small told Australian Mining “We’re partnering with our customers to deliver tailored rebuilds, allowing customers to maximise asset life and performance in accordance with
what they need from each machine.
“Rebuilding with Hastings Deering means building to your own scope, not ours.”
As one of the largest certified Cat dealers, the Hastings Deering experts know how to maximise the life of these assets for their customers.
“We can provide expert advice on the operational performance of your machine better than anyone else, to design the best rebuild for your needs,” Small said.
“State-of-art tooling, workshops and proprietary know-how ensure your Cat components can be rebuilt again and again.
“Our expertise with critical component wear limits means replacing the right parts at the right time.”
Rebuilds also come with extensive as-new warranty coverage on both parts and service for peace of mind.
Beyond maximising asset life, Hastings Deering’s tailored approach to rebuilds is also making machinery more efficient.
“Productivity declines as a machine ages and its components experience wear and tear,” Small said.
“When you go through a rebuild program with Hastings Deering, you are going to restore the efficiency of that machine, returning it to an as-new state.
“A rebuild also provides the opportunity for engineering updates that further improve performance and reliability. This could include fuel burn optimisation and other enhancements that were made available since the machine rolled off the factory floor.”
Mining operations across Australia are already reaping the benefits of choosing Hastings Deering.
Such was the case in 2023 when Hastings Deering was contracted to rebuild eight Cat 793F off-highway trucks at Stanmore Resources’ Poitrel coal mine in Queensland.
“For this project, we worked closely with the customer to develop a scope and a tailored package that suited their requirements for those eight trucks at site,” Hastings Deering resource industries support representative Daniel Edge-Williams said.
“There was an individual scope required for each truck, not

just a one-size-fits-all approach.”
Hastings Deering established a work group with Stanmore to plan, manage and execute the project, with open communication from start to finish.
“The project heavily leaned on the fact that we were able to be flexible, work with the customer, and tailor the package,” Edge-Williams said.
“We didn’t try to tell them what scope they had to use. They told us what scope they wanted, and we came back to them with the right solutions, which were unique to each asset.”


Utilising its extensive facilities, highly trained staff, and genuine Cat parts, Hastings Deering swiftly delivered all eight rebuilds.
“We had a strict timeline, a strict budget and at the end of the project we wanted to achieve reliability,” Poitrel mine senior reliability engineer Ryan Shortis said. “The project was a success.”
Cat certified rebuild
Hastings Deering is also capable of providing Cat certified rebuilds, wherein the entire reconstruction process adheres
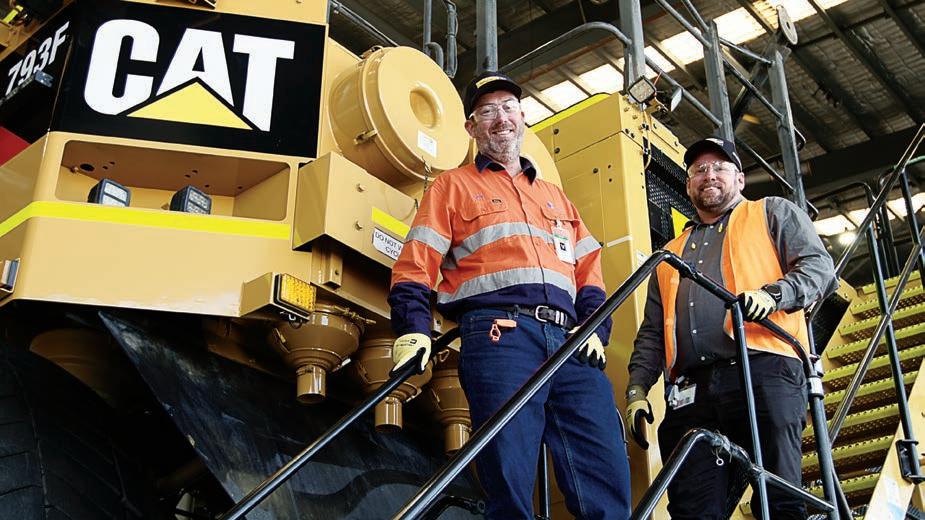
and auto replacement of parts that don’t meet guidelines. For a machine rebuild, that amounts to approximately 7000 parts and 350 tests and inspections.
“The intention of the Cat certified rebuild program is to create a globalised standard,” Hastings Deering aftermarket solutions consultant Cody Welker said.
“It enables the dealer to almost take on the role of OEM because in that instance we are taking that machine or
DESIGNED TO DELIVER ENHANCED PERFORMANCE
machine comes out with a new product identification number and can be treated as a new asset for tax purposes. Machines can be returned to as-new performance and productivity for around 65 per cent of the cost of a new asset.
And Hastings Deering backs each Cat certified rebuild with a 24-month, 10,000-hour warranty.
Whether by a flexible rebuild tailored to a customer’s needs or a rigorous Cat
machines and major components.
“Hastings Deering understands the mining industry. We know what keeps it moving and our expert teams know everything about the equipment we sell,” Welker said. “Whether you are balancing cost versus downtime, looking to extend component life or wanting to keep your own iron, you can rely on us to go the extra mile.
“Nobody rebuilds better.” AM

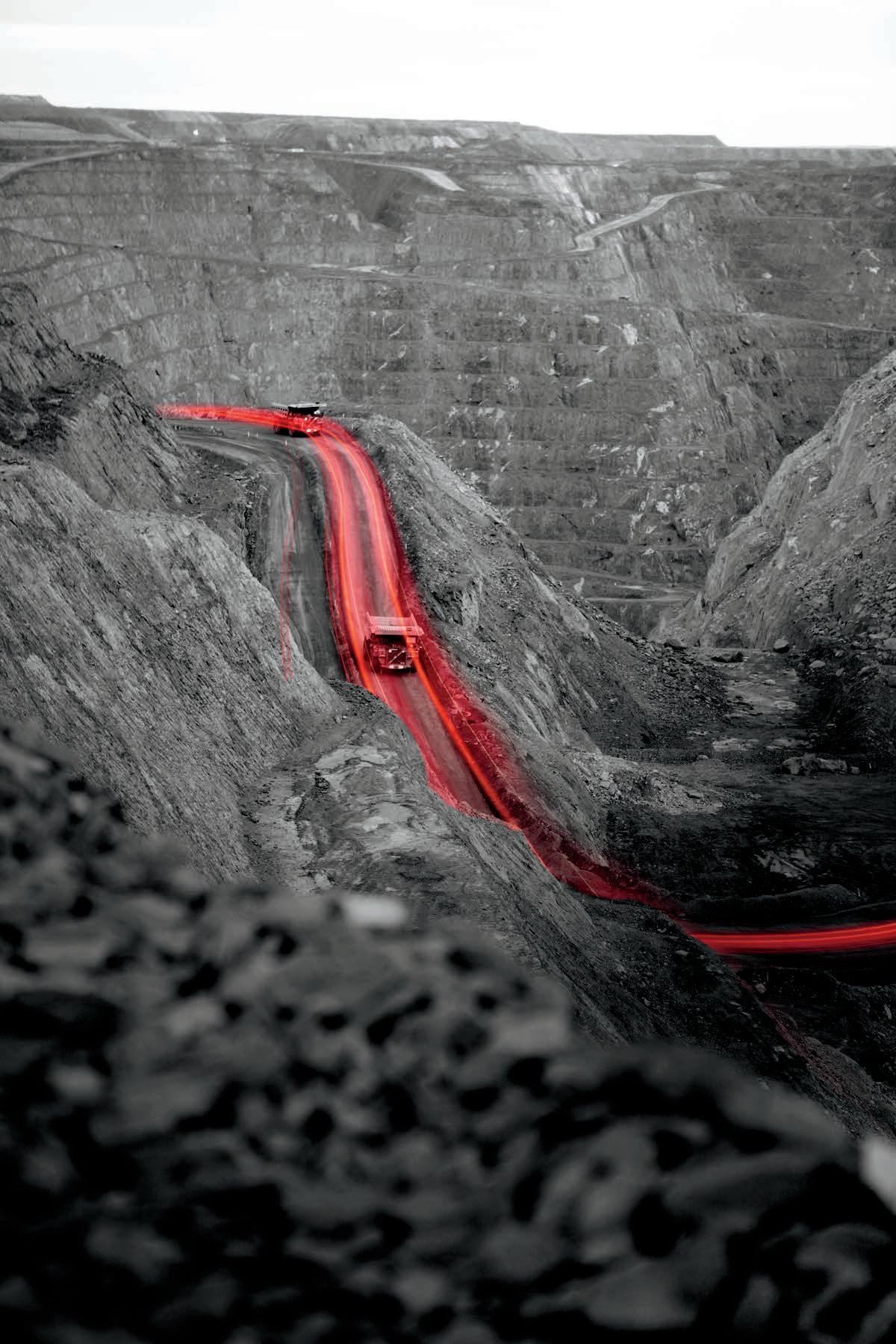
IS YOUR CONVEYOR UPGRADE
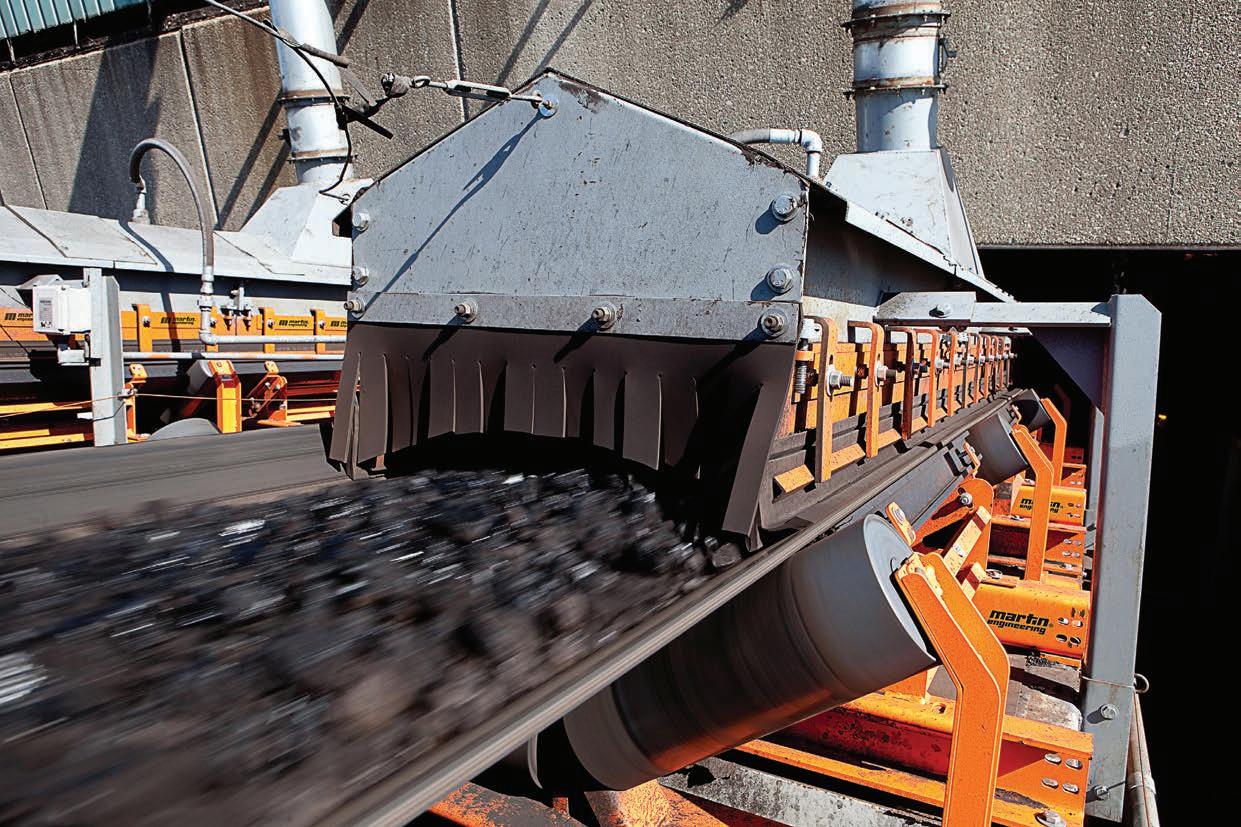
When greater production is needed to meet rising demand or lower quality raw materials
require more tonnes to be processed, many operators simply speed up the conveyor.
But rather than increasing capacity, this often results in reduced capacity, because changes in the trajectory of the discharged material can cause build-up and clogging in hoppers or chutes.
In some cases, the proper answer to the question, “Can we increase capacity to the existing conveyor?” should be, “No, we need to start over”.
Conveyor design
Conveyor design is an iterative process. When purchasing a conveyor at the lowest capital cost, the design is likely to use the maximum loading capacity on the narrowest belt travelling at the maximum speed for the raw material, while meeting only the minimum safety standards and codes.
If the goal was to design a conveyor with the lowest cost of ownership over its intended life, it was likely designed with less than maximum loading, a slightly wider belt and the capacity to run at a reasonable speed, while exceeding minimum safety standards and code requirements. The best practice is to re-

establish the original design intent and compare it to the existing conveyor. Conveyor technology changes over time, particularly in belting and calculation methods.
The most recent Conveyor Equipment Manufacturers Association (CEMA) design guide, ‘Belt conveyors for bulk solids’, requires predicting power requirements within -0 to +10 per cent of actual.
It’s vital to define the problem the conveyor upgrade plan is trying to solve.
Not understanding the primary reason for an upgrade could cause address symptoms rather than root causes. A new design might not address the primary need for a performance upgrade. For example, if the chutes are plugging or there is spillage, it might not be a conveyor issue but instead an operator or maintenance issue.
Component standardisation
It is usually desirable to try to use belting, idlers and other components that are available elsewhere at a site or are
common supplier stock items. This may not always be possible, but the capital cost alone should not force a less than optimum design solution.
Because increased tonnage might escalate idler loads, rolling components may require a higher load capacity to obtain an acceptable life. It is important to consider the lifecycle costs of design and component selections.
A process called ‘loading on the transition’ – loading the conveyor before the belt is fully troughed – is a common way to save money on installation, but it is also one of the biggest contributors to damage and the release of fugitive materials.
Loading on the transition best practices:
• If space permits, rectify the loading so it starts at the second fully troughed idler
• Vertical curves, if properly designed, are not an issue but the design calculations need to be verified if the belting or tonnage changes
• Using bend pulleys for convex curves rather than a spaced array of
troughing idlers is often a source of spillage and should be avoided
• Diverter plows and other devices, which tend to force the belt to one side or the other, should be located where the belt has enough distance for returning to running centered in the idlers
• W hen loading round particles or operating in wet environments, a belt incline of 5° or less will help create a mass that prevents rolling or fluid cargo from flowing backward toward the tail pulley; the best practice is to load horizontally and transition into the slope
• For round material, consider installing curtains along the slope to knock down bouncing particles and allow them to form into a stable profile
Belt width and trough angle
The trough angle is initially selected based on experience or the existing idlers for standardisation.
Belt width is selected by calculating the cross-sectional area of the bulk material by assuming a troughing angle, an idler with three equal roll lengths and the surcharge angle, lump size and flowability of the bulk solid being handled.
There are two important crosssectional areas to consider: CEMA 100 per cent full and full edge-to-edge.
The 100 per cent full area is based on a standard belt edge required to prevent spillover between idlers as the belt sags on the carrying run. The full edge-to-edge loading is used to calculate the maximum potential load on the structure.
area to allow for surge loads, off-centre loading or normal mistracking.
Two common techniques can be incorporated into a new or complete conveyor design to make future upgrades less costly.
The first is changing the trough angle of the idlers to raise the capacity by increasing the cross-sectional area. In new designs, consider using 20° idlers. Upgrading to 35° idlers is a 27 per cent increase in cross sectional area, and going from 20° to a 45° trough angle is a 37 per cent increase.
Although 35° idlers are fairly standard, it is important to note that for retrofit upgrades going from 35° to 45° idlers is only an eight per cent crosssectional area increase.
The second common technique for new construction is to design the structure for the next wider belt and use CEMA wide-base idlers.
The mounting dimensions of the wide-base idlers allow for a future replacement with a wider belt. For example, if the structure for the 1200mm belt and 20° surcharge angle using 35° trough idlers was designed for wide base idlers, the belt width could be increased to 1400mm, resulting in a 33 per cent capacity increase with the same trough angle and belt speed.
Changing from a 35° to 45° trough angle and the wider belt and idlers would result in a 90 per cent increase in cross-sectional area. This method is not often used because there is resistance to increasing capital cost for a wider and
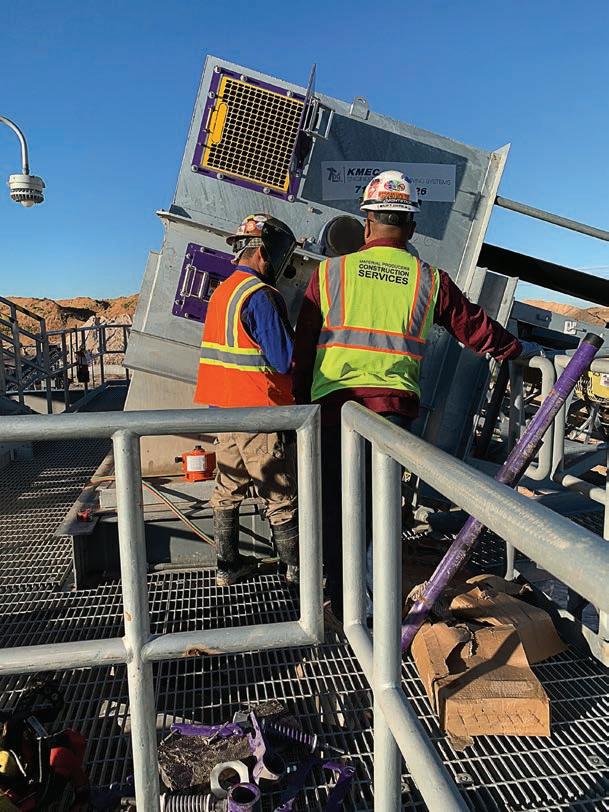
lower speed will reduce fugitive material release, given the potential for fugitive material release is directly proportional

iterations can then be tried by changing the belt width, trough angle and belt speed to arrive at a reasonable solution.
Discharge chute
The discharge chute will need close review for a capacity increase. The trajectory path should be plotted so the stream of material affecting the chute does not create a situation where there is zero or negative vertical velocity on impact with the chute.
If the material can stay suspended at the impact location, it will increase the chance of build-up and blockage of the chute. If the angle or liner is changed, it must not create a slow flow situation where material backs up and accumulates in the chute.
The discharge chute cross sectional area should be a minimum of four times the cross-sectional area of the loose bulk solid.
The design of the loading chute and skirtboards requires close attention to minimise release of fugitive material.
CEMA uses two-thirds of the belt width for the inside dimension of the loading chute skirtboards, regardless of belt width. Idler fouling and spillage can happen when uneven loading causes the belt to drift to a degree that there is an opening between the inside of the chute wall and the edge of the belt.
Best practice in design considers the amount of allowable mistracking plus the thickness of the sealing system to determine the distance from the edge of the belt to the outside of the skirtboards as the minimum dimension on each side. AM
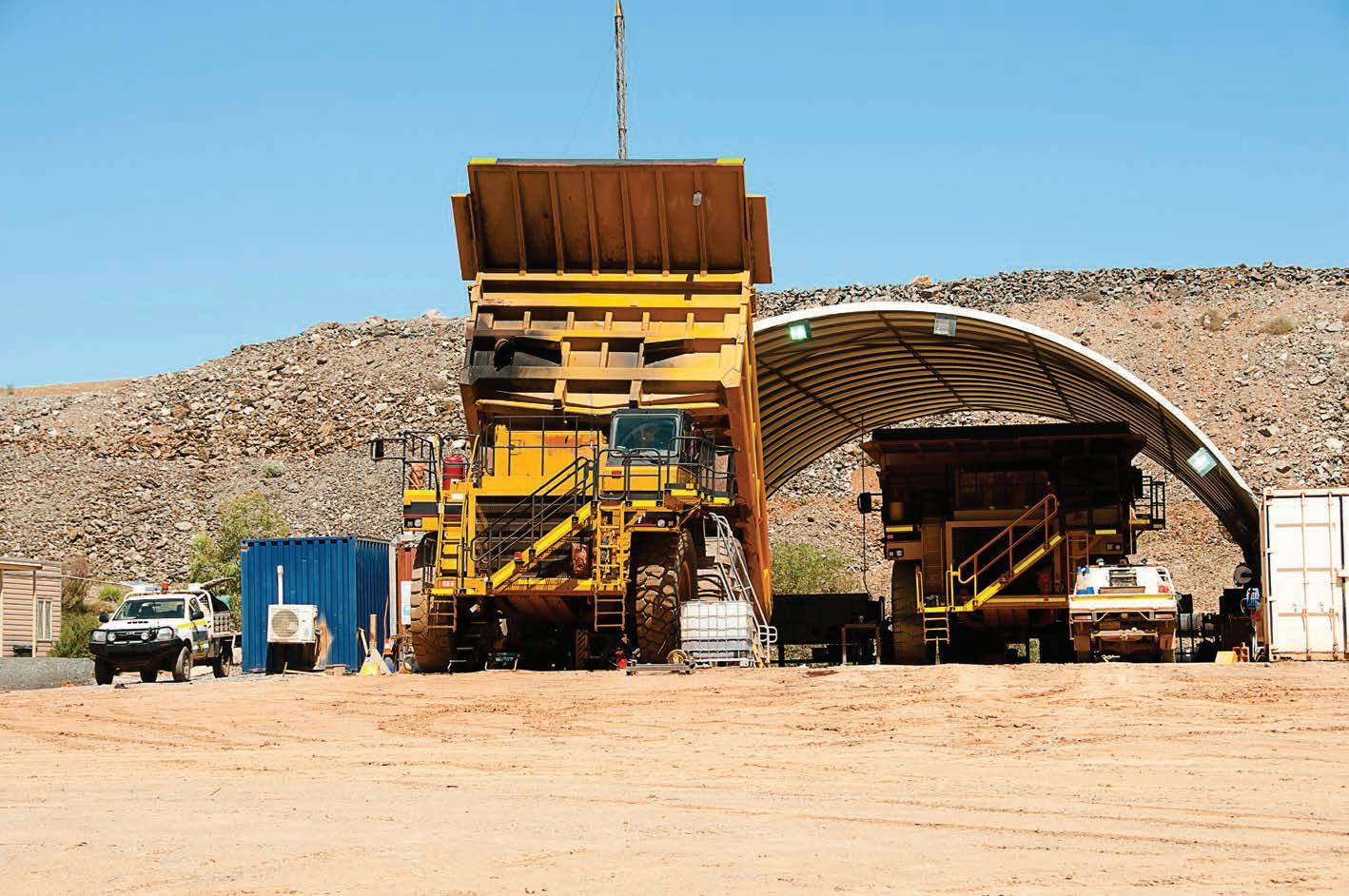
IRONING OUT FERROUS CONTAMINATION
MAGSHIELD IS BRIDGING THE GAP LEFT BY STANDARD MEDIA FILTERS TO TACKLE FERROUS CONTAMINATION IN THE AUSTRALIAN MINING INDUSTRY HEAD-ON.
Ferrous contamination is an issue that has plagued heavy industry for decades. As metal components go through regular wear and tear, microscopic iron particles leach into essential fluids that keep Australia’s most critical mining equipment running.
This contamination wreaks havoc on machinery systems and leads to significant damage, increased downtime and eventual breakdown.
While original equipment manufacturers (OEMs) fit mining machinery with standard media filters, most aren’t up to the task of handling ferrous contamination, leading to billions of dollars lost every year in downtime and replacement costs across Australia.
But MagShield has a vision to work with pre-fitted media filters to fight ferrous contamination and rid the industry of its iron plight. That’s why MagShield takes its motto ‘Best Practice for Fluid Contamination Control’ seriously.
The solution is simple: fitted ahead of the factory filter, a pre-filter acts as a magnetic shield (Mag-Shield) to attract metallic particles as fluid passes through the machine, continuously keeping it clear and on track.
MagShield is installed without any physical or mechanical adjustments to
the machine, meaning it can be removed or changed out with ease.
All it takes is one simple installation and MagShield can help reduce, or even eliminate, the build-up of slurry ferrous contamination in the system and premature wear and tear.
Seasoned industry operator and MagShield general manager Neil Cropper believes the solution can set operators up for best practice maintenance that will optimise Australian mine sites and boost efficiency to the next level.
“The filter removes 99 per cent of ferrous material from equipment circuits,” Cropper told Australian Mining “That means customers get longer oil life, better OEM filter performance, and extended component life.”
MagShield has an extensive range of innovative products to fit most equipment models and can tailor its solutions to suit the needs of any mining equipment, no matter the size or positioning of its oil reservoir.
For applications where an oil reservoir may be less accessible, Mag-Shield’s counterpart Mag-Shield X can be on hand to act as an inline solution.
Offering a dynamic approach is all part of MagShield’s mission to deliver the best possible outcomes for its customers.
“We quickly found that our products and services helped solve a number of
ongoing challenges faced by equipment owners or fleet reliability managers, and through requests from our clients, we expanded our footprint and product range,” Cropper said.
“We now service a global market across a range of equipment types and applications, all focused on reducing the impact of ferrous contaminants in fluid systems.”
MagShield’s aim, Cropper said, is to complement OEM filtration systems to offer an added layer of ferrous contamination protection.
“OEMs traditionally use paper elements to clean up fluid systems, but these filters don’t capture all contaminants and if the micron rating is too small the filter can clog prematurely. This leads to unfiltered fluid bypassing the element which creates other issues,” he said. “MagShield complements OEM filtration systems by capturing ferrous material before it can accumulate.
“There’s very little pressure differential with MagShield products, so operators can rest easy knowing there’s no adverse effect on the machinery’s circuit and no downstream implications other than cleaner oil and an extended equipment lifetime.”
MagShield has been used extensively in hydraulic circuits across mobile mining equipment from graders to wheel loaders and excavators.
Mining is known for its large equipment, but MagShield has been successfully rising to the challenge for years.
When it comes to customers seeing the benefits of MagShield, Cropper highlighted an unexpected advantage.
“Our customers recognise an added benefit following equipment failures,” he said.
“While they initially value MagShield for its proactive protection, it is during a machine breakdown when they witness the significant amount of ferrous material MagShield has prevented from entering the system. This is when they truly appreciate the effectiveness of the solution in maintaining machine productivity and minimising costly downtime.
“I’m talking up to a 15-fold reduction in downtime, repair costs and clean up thanks to the amount of contamination that has been removed from the system.”
As MagShield continues to boost operational and financial efficiencies across Australia, Cropper is confident the solution has a strong future in optimising the mining sector.
“It’s a proven solution to a pervasive problem,” he said. “We’re positioning Australia’s mine operators as the next generation with best practice for fluid contamination control.” AM
BELT SCALE SYSTEMS TOP DYNAMIC DUO
The most intelligent integrator on the market, the Rice Lake Master Enterprise 1280 and the Rice Lake Master BS14 Belt Scale Series are now available! 1280 Enterprise Integrator
Programmable digital weight indicator
150 built-in functions to simplify programming
Customisable Colour display with touchscreen
Built in Web Server for Network & Remote access
Retrofit to most other Belt Scale Brands
Handles up to 4 scales at once

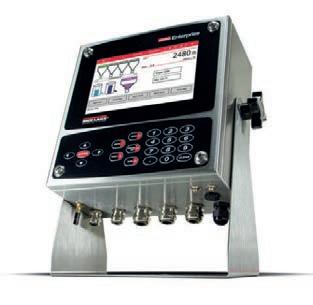
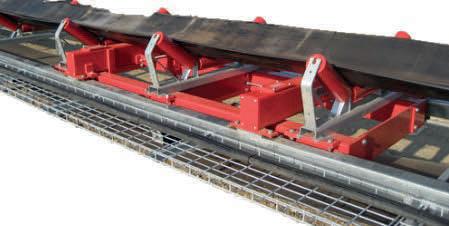
Custom made frames to suit conveyor belt specs
Highly accurate to within 0.25% or better
Industry Standard fully floating belt scale systems
Suited to a broad range of capacities and belt speeds
Suitable for all mining and process applications
Industry leading Dynamic Duo when paired with 1280 Controller
Contact Minprovise today Tel: 08 9359 6800

www.minprovise.com.au
ENGINEERING, DONE DIFFERENTLY
DAD, A SOFTWARE SOLUTION FOR THE ENGINEERING AND MANAGEMENT OF COMPLEX SYSTEMS, WAS RECENTLY PUT TO THE TEST AT A MAJOR IRON ORE MINE IN THE PILBARA.
DAD’s client in the Pilbara wanted to improve the engineering and management processes of the electrical, instrument and control, and communication (EI&C) systems on a large greenfield iron ore project.
Having successfully used DAD on other projects and sites for more than 10 years, the client understood its value, so it was an easy decision to again turn to DAD for its new iron ore project.
DAD enables complex systems to be digitally modelled and managed throughout the lifecycle.
A system model contains all current and historical hardware and software information about objects (equipment, cables, etc), their connections and their relationships. It creates a centralised database of extensive system information and is the central tool used by everyone involved with the system, from designers
client’s project were modelled in DAD by the engineering and procurement teams, which accessed and modified the model
from different locations across the world.
Given system information is centralised, this made working with different teams in different zones easily achievable. Team members were able to use the model to create, edit and find information about the system in real-time.
Revisions and approvals were also handled within the model, rather than using traditional processes that rely on drawings and documents.
DAD, however, because the design and construction teams had access to the model, which is a central database of system information.
Therefore, all design changes were coordinated using the model, and everyone accessing and viewing the same information resulted in greater accuracy.
Construction contractors were provided read-only access to view and generate work packs from the model.
BECAUSE DAD AUTOMATICALLY RECORDS
ALL CHANGES AND MAKES THIS INFORMATION INSTANTLY ACCESSIBLE, THE CLIENT WAS ABLE TO FUNDAMENTALLY IMPROVE ITS CHANGE MANAGEMENT.”
Because DAD automatically records all changes and makes this information instantly accessible, the client was able to fundamentally improve its
The as-built information was relayed to the design team using marked-up DAD PDF outputs. The information was then updated in the model using the design phase revision and


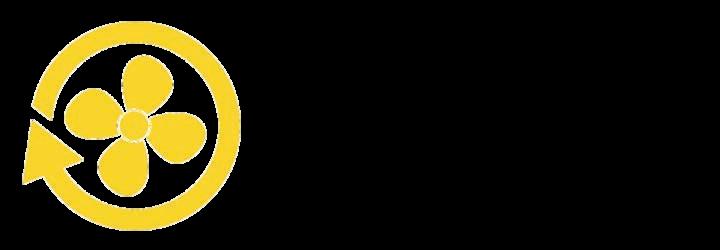
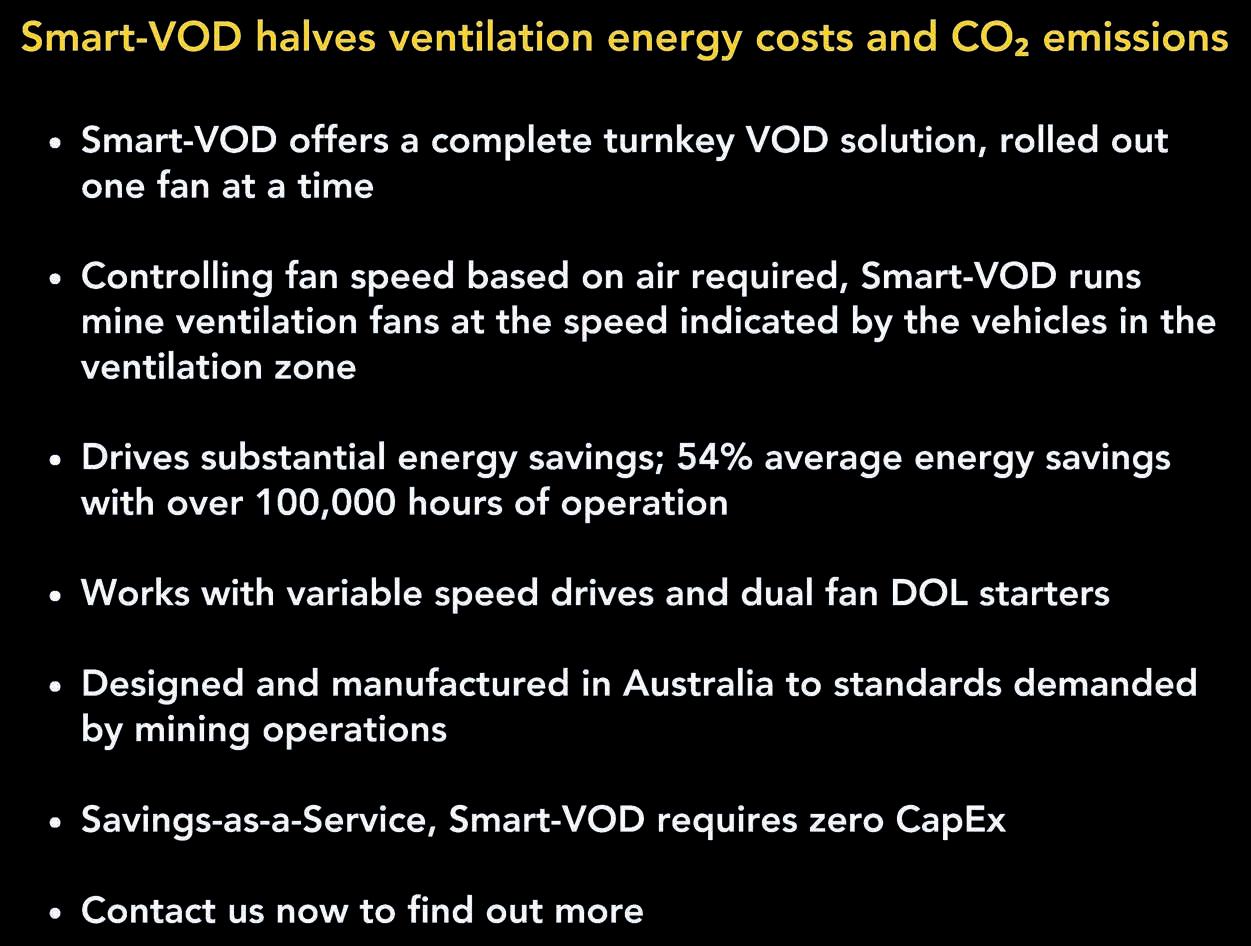

www.smartvod.com.au


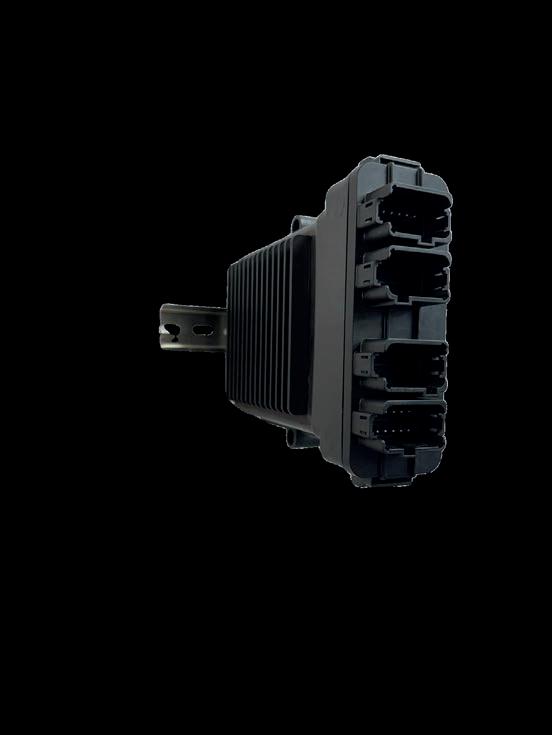
LEADING THE WAY IN A BOOMING SECTOR
FROM SHUTDOWNS TO TAILORED LOGISTICS SOLUTIONS, AUSTRALIAN-OWNED BOOM LOGISTICS HAS BEEN PROVIDING COMPREHENSIVE PROJECT SERVICES TO CUSTOMERS ACROSS A RANGE OF INDUSTRIES FOR 20-PLUS YEARS.
Ever since BOOM Logistics was founded in 2000 and listed on the ASX in 2003, the company has made its mark in a wide range of Australian industries, especially the resources sector.
“We provide services to a range of customers across the mining, oil and gas, infrastructure, defence, renewables and heavy plant sectors,” BOOM Logistics general manager – West Coast Lester Fernandez told Australian Mining “BOOM Logistics is also the only ASX-listed crane service provider in the Australian market. We are owned by Australians, we employ Australians, and we service Australian industry.”
The company currently carries out most of its mining services and capabilities in Western Australia, Queensland and New South Wales.
“In Western Australia, we have involvement in gold, lithium and nickel, and in Queensland and New South Wales, we work with coal customers to provide lifting, shifting and maintenance services for their mine sites,” Fernandez said.
“These services include the building of infrastructure, the construction and maintenance of dump trucks, mining excavators and draglines through to complete mine shutdowns.”
Over the years, the teams within BOOM Logistics have worked closely with customers to better understand the demands they face and to tailor specific packages of services for each customer.
This collaborative approach enables BOOM Logistics to provide the resources sector with complete project services involving heavy lift projects completed with fit-for-purpose assets, on-site management, specialist labour services, scheduling and facilities maintenance requirements.
Shutdowns are a critical aspect of mining operations, and BOOM Logistics understands the gravity of downtime.
“Every minute counts during a shutdown,” Fernandez said. “The costs can escalate rapidly – from lost production to equipment maintenance. That’s why we leave no stone unturned in planning and execution, ensuring minimal disruption and maximum efficiency.”
Recognising the capital-intensive nature of crane procurement for mining companies, BOOM Logistics has a diverse fleet of over 350 assets ready for deployment at a moment’s notice.
“From an assurance perspective, being a publicly listed company means BOOM
BOOM LOGISTICS IS A TRUSTED SERVICE PROVIDER TO THE AUSTRALIAN RESOURCES INDUSTRY.
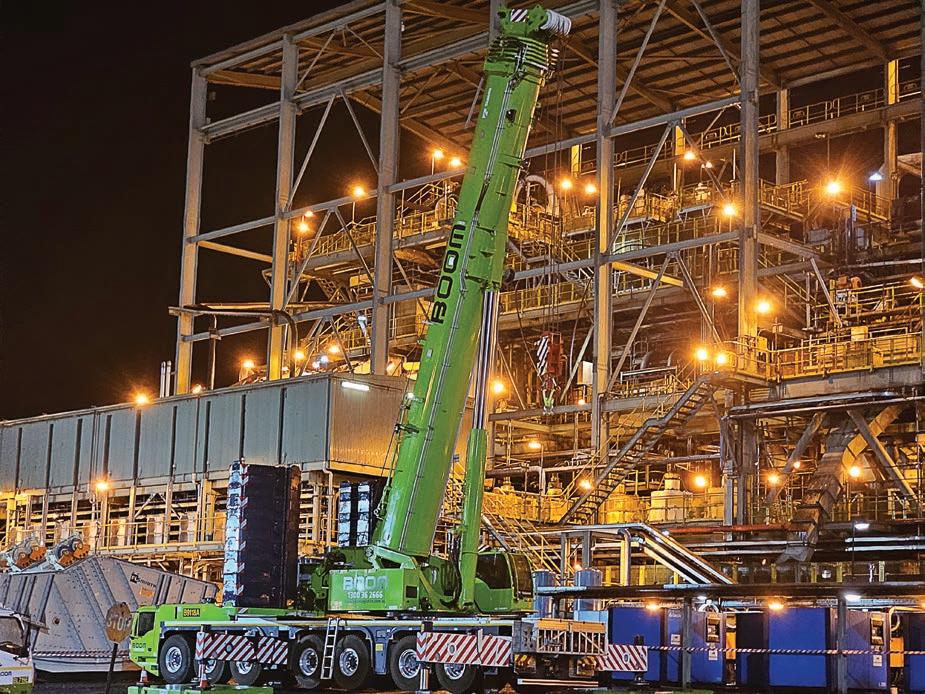
Logistics has significantly higher levels of compliance and governance we must adhere to, which automatically elevates our products and services,” Fernandez said. BOOM Logistics takes an adaptive approach to mining customer requirements, tailoring services to align seamlessly with each unique requirement. Offering turnkey solutions, the company stands as a reliable onestop-shop for service delivery, extending beyond cranes to encompass various equipment and machinery needs.
“If a particular customer doesn’t want to deal with multiple suppliers for multiple pieces of equipment, and this is often the case, BOOM Logistics has the capability to project manage or procure, service and support specialised equipment and machinery on behalf of the customer,” Fernandez said.
“We provide end-to-end turnkey solutions and we have the capability and expertise to be a one-stop-shop for service delivery, which isn’t limited to cranes.”
With the global energy transition moving ahead at full speed, BOOM Logistics is onboard the journey.
“We are fully aware of our responsibilities to provide
environmentally sustainable solutions for our customers,” Fernandez said. “Today, industries including the resources sector are examining ways of reducing carbon footprints and limiting the level of emissions from vehicles. Crane OEMs have been designing and engineering alternate fuel solutions for various industries for years.
“BOOM Logistics is very much across these developments and as part of our commitment to provide customers with lifting solutions featuring the latest technology, we are introducing these alternate fuel technologies into our fleet.
“Many mining companies are now involved in the move to renewable and sustainable energy sources which involves building and installing wind turbines, transmission line constructions and upgrades.
“We have a proven track record and significant experience in building and maintaining wind farms and working on energy interconnector projects. It’s one of our core industry sectors. It’s certainly an exciting time to be involved with and assisting the mining industry by aiding a transition towards a more sustainable future for all of us.”
From project planning to execution, BOOM Logistics collaborates closely with clients to provide tailored solutions that meet their specific requirements. This proactive approach not only enhances operational efficiency but also fosters long-term partnerships based on mutual trust and value.
BOOM Logistics is involved in clients’ projects from the early planning stages which ensures the project is allocated the right-capacity cranes and experienced crews.
“With our collaborative approach to projects, and being involved at the early planning stages, customers are able to accurately budget for the works and we are able to ensure we have the rightcapacity cranes and crews available,” Fernandez said.
“Quite often, we will provide services for a specific project and find ourselves working on another project for the same customer 12–24 months later, but on a site somewhere else in the country.
“Customers come to understand that partnering with BOOM Logistics adds value to their operations and that we are prepared to go that extra mile to ensure projects are delivered on time, in full and on budget.” AM




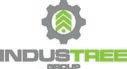

Secure your business as a leading supplier to the growing PNG mining sector GROWING
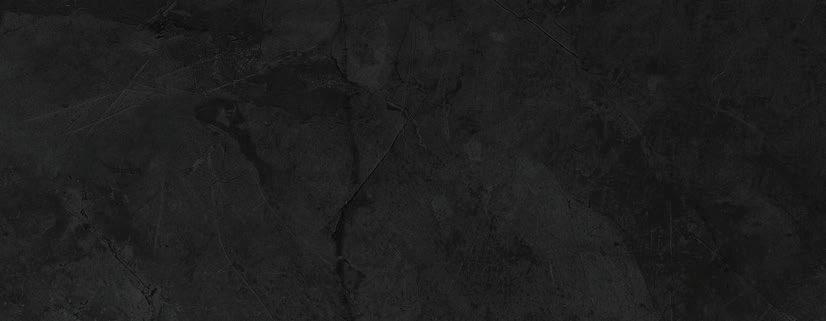
EXHIBITION SPACES ON SALE NOW
Learn more
AN END-TO-END TECHNOLOGY SOLUTION
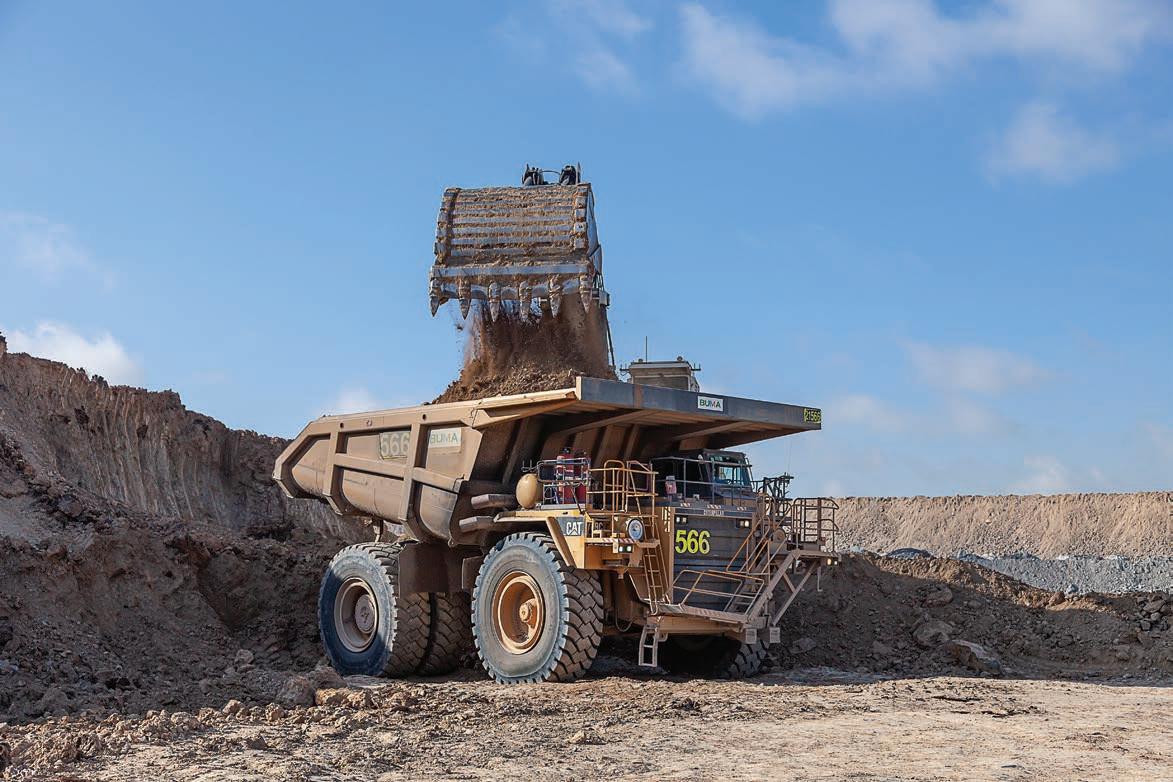
Mining services provider BUMA offers comprehensive end-to-end services to its clients throughout Queensland with ongoing support from its technology solution partner, Aptella.
With a focus on safety and collaboration, BUMA has rapidly expanded its use of operational technology in recent years, tailoring solutions to meet the requirements of each client and project.
Jack Walker leads operational technology initiatives across BUMA sites, providing solutions and offering comprehensive support for technology incorporated into the day to day running of a mine.
“As a mining services provider we partner with our clients over the long term and our commitment is to deliver on their evolving objectives,” Walker said.
BUMA’s scope and scale of operations are varied and dynamic, offering tailored mining service solutions to clients. These range from comprehensive full scope services to fulfilling specific requirements such as integration with a client’s fully autonomous fleet, rehabilitation services and asset maintenance.
“We take pride in our ability to adapt our approach and be agile, quickly mobilising to address new requirements or meet changing project demands,” Walker said.
Responsible for examining the latest advancements in technology, Walker engages with external stakeholders to seek solutions that optimise performance, asset management and rural network connectivity.
Collaboration with all major departments, particularly asset technology, allows the business to work cohesively and deliver wellrounded solutions.
BUMA’s journey into operational technology stems from a fundamental focus on taking care of its people, company assets including trucks, excavators and dozers, and the mine itself.
“Safety is the number one value at BUMA. We continuously look to integrate and utilise technology to create a secure working environment for all employees, both our own and our clients’,” Walker said.
The use of high precision machine guidance for excavators and dozers, coupled with survey solutions, machine health monitoring, and site networking, enhances the efficiency of the mine and lifespan of the machinery.
“Optimising the safety of our people, as well as the health and performance of our equipment, ultimately leads to improved pit compliance and extraction,” Walker said. “That in turn translates to higher quality outcomes for clients, both in the short- and long-term.”
As a growing company, BUMA focuses on downstream technologies that materially support strategic mine planning.
Survey, machine guidance and drone technology help to ensure accurate and safe mine designs that enhance overall efficiency. Additionally, BUMA is investing in modern network infrastructure to maintain dataflow and real-time operations.
In choosing a technology provider, Walker said it was important the company aligned with BUMA’s agile, tailored approach.
After years of successful deployment at the Commodore mine, near Toowoomba in Queensland, Aptella (formerly Position Partners) has supported BUMA’s expansion of technology across all sites, with rapid deployment within a six-month period.
“We value Aptella’s adaptability, aligning with BUMA’s commitment to client needs,” Walker said. “Aptella’s agnostic products provide us with a wide
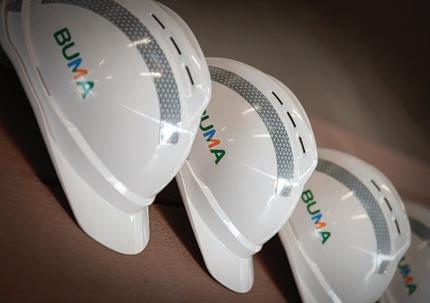
range of solutions across various mining functions, enabling us to choose and deploy the best tools for each project.”
Aptella mining business executive manager Andrew Granger said the company deeply values its collaborative working relationship with BUMA.
“As a company that lives and breathes its commitments to safety and progress, it has been a privilege to support BUMA’s growth by providing end-toend technology services to meet their evolving needs,” he said.
As a multi-solution distributor with offices throughout Australia, SouthEast Asia, and New Zealand, Aptella has a strong commitment to providing local service and support capabilities to customers.
Like BUMA, Aptella recognises that every site and client has unique requirements when it comes to both the technology, service and support that will suit them best.
“Our approach is to listen to customer challenges and understand desired outcomes, first and foremost,” Granger said. “We then innovate to source and deploy the best, fit-forpurpose technology to help deliver those outcomes and support our customers over the long-term.”
Aptella provides BUMA with 24–7 asset monitoring and support, which includes access to Aptella’s remote access platform that enables technicians to contact, troubleshoot and resolve issues remotely.
This service provides BUMA with fast, proactive support, and is backed by a local team of technicians who can deliver site maintenance and training.
“In the dynamic industry that is mining, unplanned maintenance is part of the journey,” Walker said. “Having Aptella’s readily-deployable resources make a significant difference, enabling us to address any issues quickly, minimising disruption and ensuring smooth operations.”
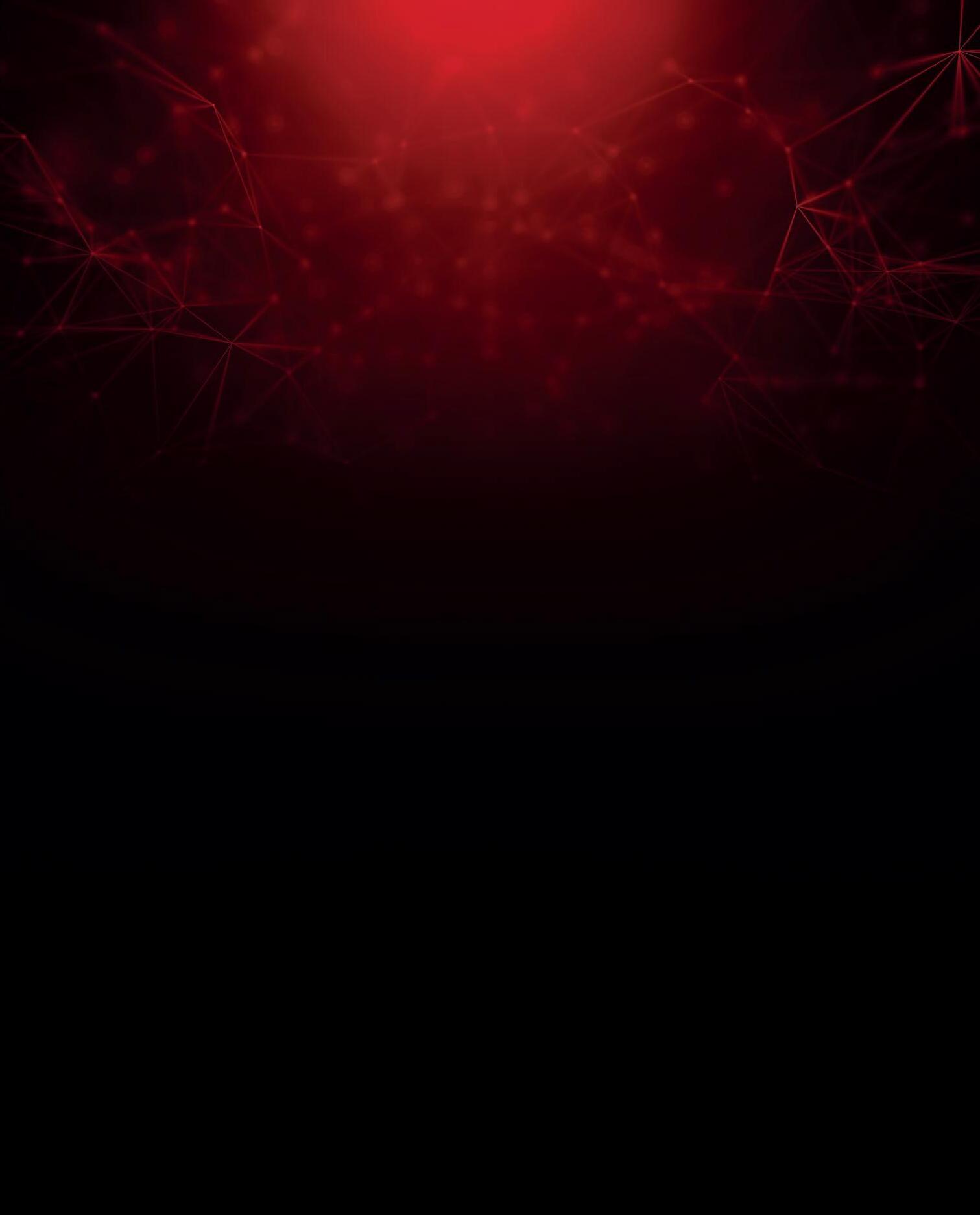
Streamline your engineering and management processes with DAD, a powerful software tool.

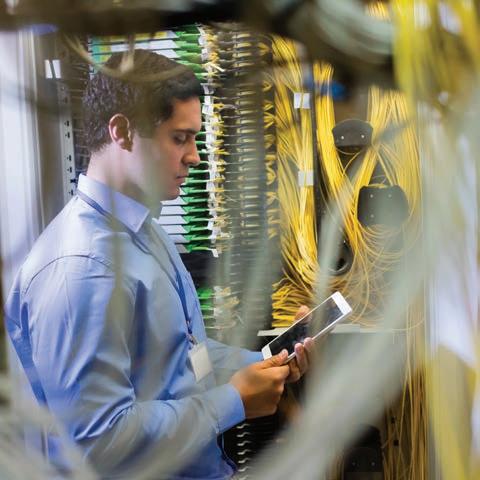
ENGINEERING, DONE DIFFERENTLY.
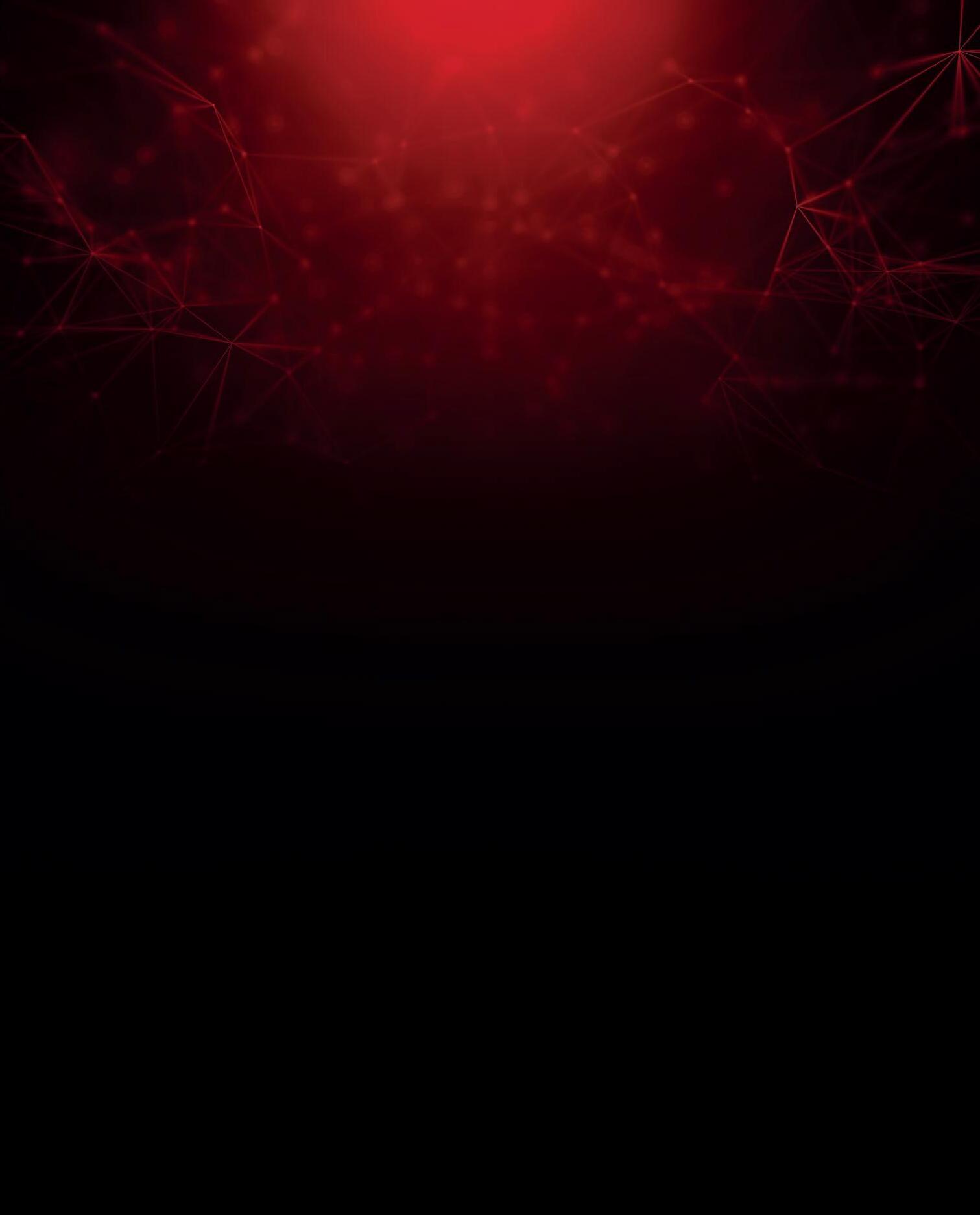
Discover how you can design and manage complex systems at half the price, guaranteed
It’s about time.
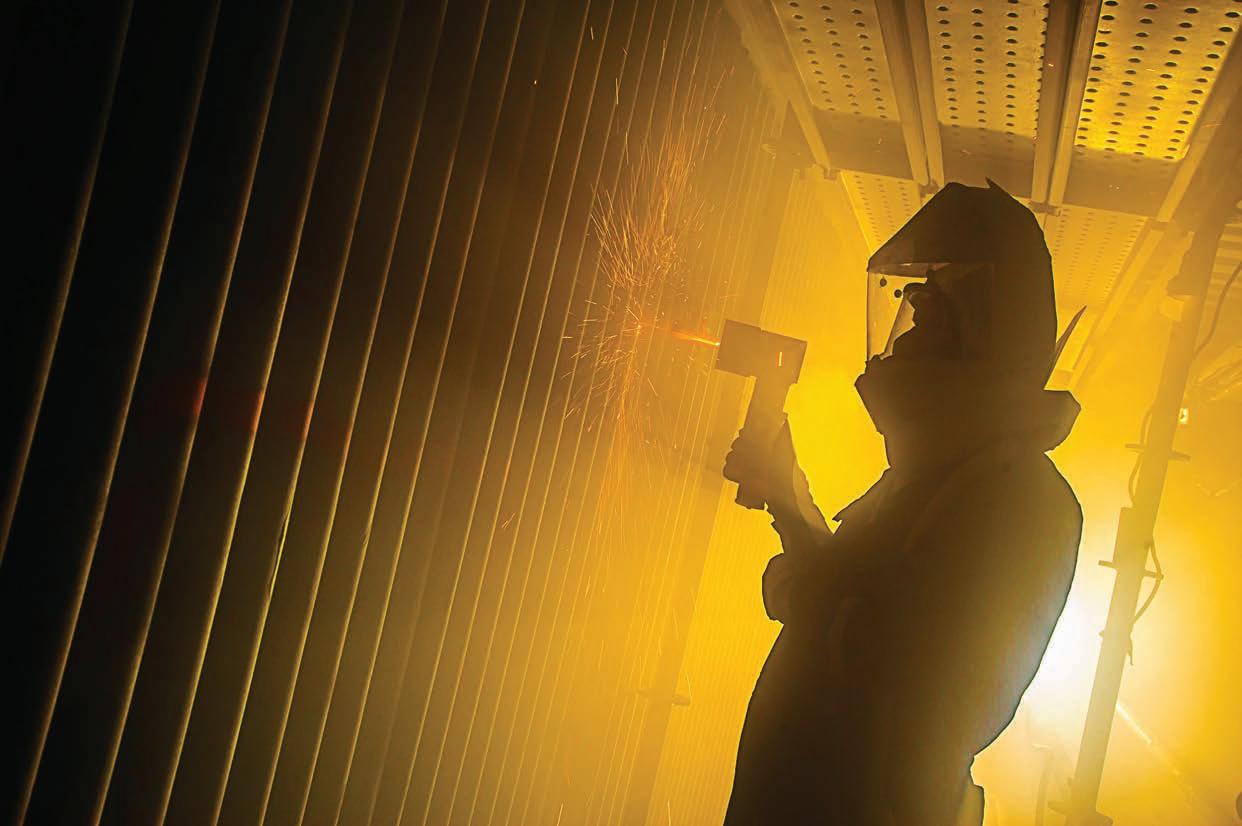
COATINGS TO CURE CORROSION WOES
IGS’ ALLOYED COATING SOLUTIONS KEEP EVEN THE MOST AGGRESSIVE CORROSIVE MATERIALS AWAY FROM CRITICAL MINING EQUIPMENT.
High-temperature chloride sulfidation and acid corrosion are just as nasty as they sound, and that’s exactly what awaits some of the most critical mining equipment when not protected.
When essential minerals like copper and platinum are refined and processed, their flow patterns release aggressively corrosive particles that can damage everything around them. This includes machinery made from carbon steel like smelters, boilers and driers – key elements of the mineral processing chain.

Once corrosion begins, machinery shutdown is inevitable, leading to lost production and potentially millions of dollars spent on replacing equipment.
Fortunately, Integrated Global Services (IGS) specialises in developing surface technologies to protect critical equipment in highly corrosive environments.
“If operators could make this kind of equipment from a more chemically durable material like gold, I’m sure they would,” IGS director of global minerals and mining Teresa Huysamen told Australian Mining
“But as that’s not exactly cost effective, we’ve come up with a highly effective solution that protects equipment and increases its lifespan by decades.”
IGS’ solution comes in the form of highly durable corrosion-resistant alloyed coatings sprayed onto machinery using high-velocity thermal spray equipment.
“This acts as a barrier between machinery and the processing environment, significantly extending its lifespan and reducing maintenance costs by employing a once-off solution,” Huysamen said.
“We can easily extend the lifespan of critical equipment from 20 to 40 years, saving operators potentially millions.”
When it comes to ensuring the best possible outcomes for the customer, Huysamen highlighted IGS’ holistic approach to getting the recipe right.
“Our coatings are completely customisable, depending on the environment and processing needs of our customers,” she said. “Our teams run extensive tests on each coating to ensure the customer is getting the best solution for their specific application.”
IGS has a technical evaluation laboratory in the US, where it carries out comparable processing environment tests and develops a solution for the needs of its customers’ sites.
Specialised technicians assess a range of factors like temperature, pressure, processing material and operating conditions.
With operations centres in the US, Canada, Japan, Kazakhstan, Saudi Arabia, Qatar, the United Arab Emirates and South Africa, as well as equipment on the ground in Australia, IGS is well positioned to service any situation the mining sector may present.
“This is what sets us apart in Australia and across the globe,” Huysamen said. “We analyse, evaluate and validate solutions for our customers with expertise from every corner of the world.”
It’s this kind of expertise that helps IGS find the right solution for its customers.
Huysamen said how long the coatings need to last is a key consideration for IGS when working with a new site.
“If a customer is currently replacing equipment every two or three years then we need to take into consideration how
heavy-duty the coating needs to be,” she said. “We don’t want to develop a Ferrari solution to a Toyota problem.”
“This helps us find the most costeffective solutions for our customers while maximising the quality of our coatings.”
Huysamen emphasised the fact IGS takes a human-focused approach when implementing its coating solutions to a mineral processing operation.
“When equipment erodes it becomes vulnerable to potentially catastrophic scenarios,” she said. “For example, if a waste heat tube breaks down over a boiler bath, it can cause an explosion and put workers at unnecessary risk.”
An overseas customer of IGS had its worst nightmare realised when a corroded furnace exploded, causing multiple fatalities. The furnace was supposed to have a seven-year life span, but the incident occurred only one year into its operation.
Following the incident, the customer contacted IGS to implement a coating solution on its equipment to ensure such an event never happened again.
The customers’ operations have been running smoothly and incident-free ever since.
“Not only are we looking to make our customers’ lives easier, but our coatings also have the potential to save lives as well,” Huysamen said. “IGS’ coating solutions are an obvious choice to keep people safe and keep operations running.” AM


BUNNINGS ACQUIRED TOOL KIT DEPOT IN 2020, WHICH WAS THEN KNOWN AS ADELAIDE TOOLS.
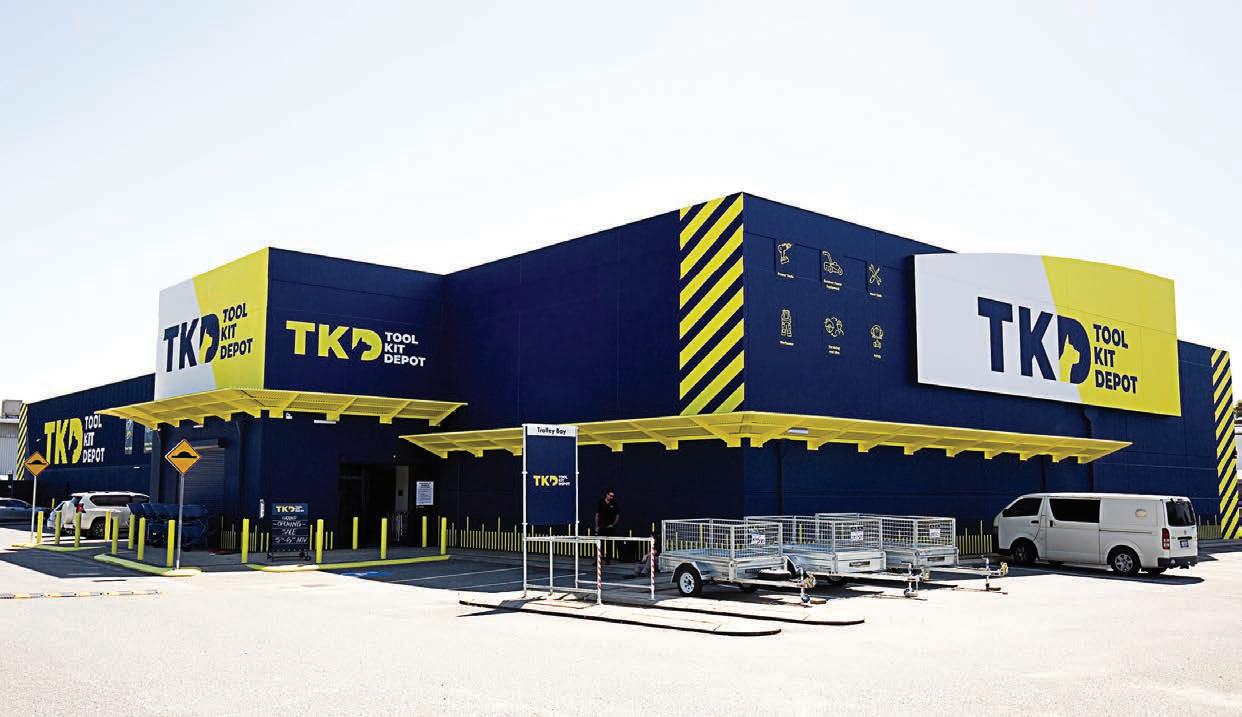
ONE-STOP TRADE SHOP
WITH OVER 200 BRANDS UNDER ITS BANNER, TOOL KIT DEPOT IS BRINGING ITS TOOLS, EQUIPMENT AND SAFETY GEAR AND WORKWEAR TO THE AUSTRALIAN MINING INDUSTRY.
When Bunnings acquired Adelaide Tools in 2020, it had a lofty ambition: to deliver the ultimate tool, equipment and safety gear and workwear offering to trade professionals across Australia.
After almost four years, it’s safe to say the business – now named Tool Kit Depot – has achieved its goal and is looking to grow further.
The company currently has five stores in South Australia, seven in Western Australia, and one each in Queensland and Victoria. It also has plans to expand into New South Wales, Tasmania and Canberra.
“We’re a tool specialist company that has over 75 years’ experience,” Tool Kit Depot commercial manager Chris James told Australian Mining.
“Our deep history in the space started around tool repairs and servicing, so that’s a key element to our business. We offer a holistic approach to tools as opposed to only selling products.”
Tool Kit Depot is now bringing its offerings to the Australian mining industry.
“Over the last 12 to 18 months, we’ve worked hard to gain access to anything and everything, so that companies working within the mining industry had everything they need,” James said.
“We’ve tailored our range and services to create efficiencies while becoming the one-stop shop for solving problems our customers face on a day-to-day basis.
“This ranges from sustainability to ease of service, all the way through to holding products and kits for particular trades.”
Tool Kit Depot is highly regarded for its ability to quickly respond to requests and deliver stock directly to customers.
“This is because we have a network to leverage and all the Tool Kit Depot stores act as one team, rather than separate entities,” James said.
“There’s no two-to-three-week waits. If we can get the right product and it’s in stock, then it’ll be on site the same day or the following day, which is appealing to customers that need a quick turnaround.
“And we work with our partners to leverage their supply chain wherever we can to get anything that isn’t in stock.”
Tool Kit Depot advocates for repairing tools instead of outright replacing them, supporting sustainability in the industry.
“We work with a Tier 1 mining company, where one of our account managers will go and pick up their tools whenever necessary and they’ll take it
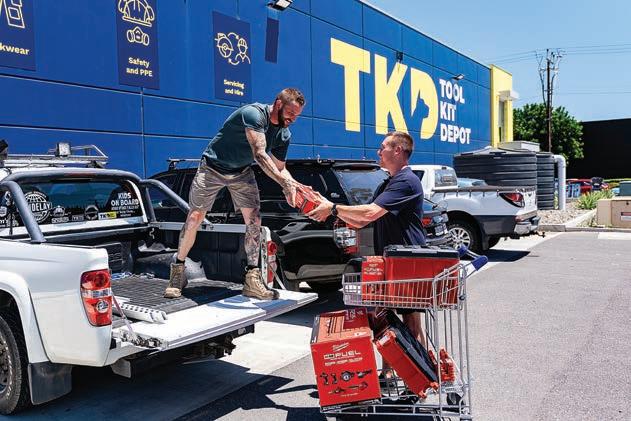
back to the local Tool Kit Depot store for repairing,” James said. “Once they’re repaired, they’re then taken back to the site.
“And it’s a constant cycle where their gear is looked after as opposed to throwing it out and starting over. Economically it makes sense and sustainably it makes sense as the lifetime of the tool is extended.”
Tool Kit Depot wouldn’t be as successful as it is without its strong relationships with suppliers.
“The most important part of what we do is finding the right tool for the job,” James said.
“We’ve got access to thousands of products, so you’re never going to be an expert in all of them. But the suppliers often are and that’s where we leverage those relationships because they know the range in depth and can provide the most relevant information and expertise.
“After we make a sale, our suppliers are available to help customers if any changes to the tool are required. We will then work with the supplier and customer to ensure the product works in the most efficient way possible.
“Our suppliers have invested significant amounts of time and money in driving that experience for the end user. And it’s the partnerships with our suppliers that really make sure the customer experience is the best it can be.” AM


ON THE COPPER ROAD TO NET ZERO
COPPER IS A CRITICAL ENABLER FOR A DECARBONISED WORLD. BUT HOW CAN THE INDUSTRY ENSURE COPPER MINING STAYS AS SUSTAINABLE AS POSSIBLE?
On the road to net zero, every speed bump counts.
In 2022, the Federal Government legislated Australia’s greenhouse gas emission reduction targets, with the whole country pushing to reach net zero by 2050. While that might sound like a long way in the future, time is flying –and the industry must keep up.
The International Copper Association Australia (ICAA) is committed to helping the Australian copper mining industry reach net zero as fast as possible. To achieve this goal, the ICAA has released a five-part ‘Roadmap to zero’, a framework drawing on the latest global innovation in sustainability and enlisting industry-wide collaboration.
The roadmap, first launched in 2020, identified key themes the industry needs to consider in reaching net zero: water, material movement, mineral processing, and ventilation and emission reporting.
Water
Water is an integral part of copper mining.
“The use of water is already significant and expensive across the copper industry, with purifying, pumping, recycling and managing it all energy intensive,” the ICAA said in its water report.
According to the ICAA, copper producers are already operating in areas of high water stress.
And as the world looks to secure more copper to use in solar panels, construction and home appliances, it faces a growing pressure.
“Water management is also highly complex and interdependent, with the capacity to enhance or derail metal production processes and their optimum economic performance,” the ICAA said.
“There is no one simple solution or ‘one-plan-fits-all’ option for every company and mine site.”
Instead, the ICAA recommends that copper miners look to a series of complimentary actions they can take to help drive down emissions: electrify, digitise, set a long-term strategy, transform industry culture, and define success and personal commitment.
“Overall, to thrive, the industry must go from ‘pilot’ to ‘this is real’,” the ICAA
said. “The challenges are large, and the transformation will not be simple, fast or cheap.
“A zero-emission copper mine of the future can be achieved and will be significantly different from the current copper production process.
“It will require fundamental changes in how energy and water are sourced and used.”
Material movement
When broken down to its most basic principles, the movement of ore from one site to another is perhaps the most fundamental part of a mining operation.
The ICAA’s material movement report explores how copper miners can reduce or eliminate emissions when moving ore.
“Material movement is a foundation process in copper mining,” the ICAA said in its report. “As copper demand continues rising, especially due to expanding renewable energy and zero-emission systems, material volumes moved at copper mine sites are increasing.
“In addition to rising metal demand, declining ore grades further increase material movement.”
Electrifying processes where possible stood out as the top recommendation from the report.
“Producers should establish plans for electrification of material movement machinery and systems,” the ICAA said. “In some applications, alternate fuels are available and net-zero cycles or carbon offsets are possible.”
Electric mining vehicles have already made a name for themselves.
Electrification has been touted as a way to reduce energy and maintenance costs by up to 70 per cent and 30 per cent, respectively. Many of Australia’s largest miners are transitioning to electric vehicles, and the ICAA is hoping copper miners will follow suit.
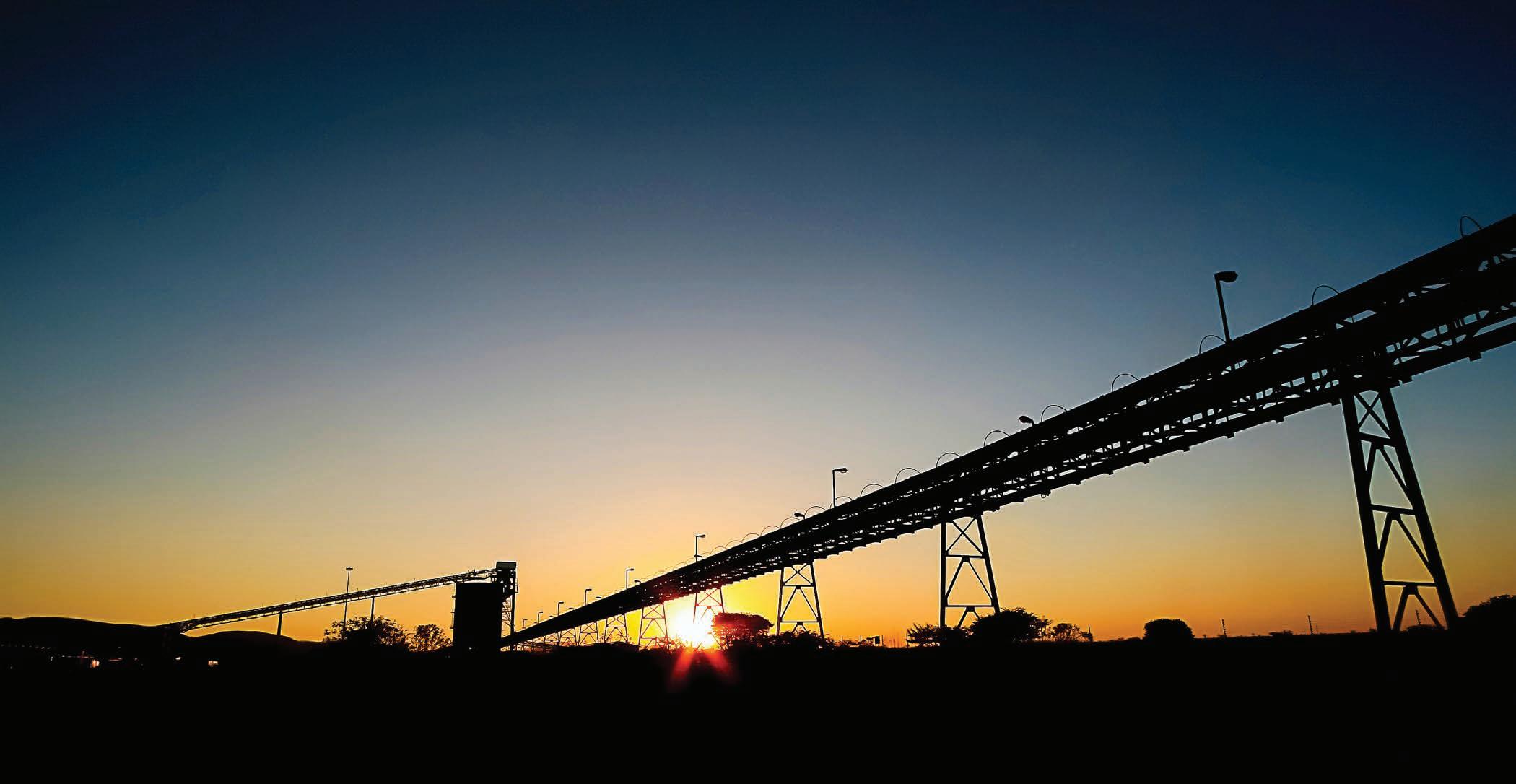
COPPER IS ESSENTIAL IN THE DECARBONISATION JOURNEY, BUT THE MINING OF COPPER MUST ALSO BE SUSTAINABLE.
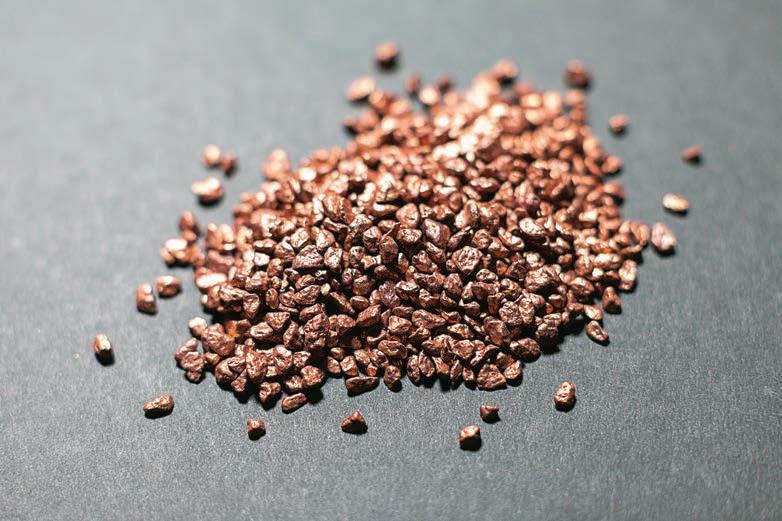
“When combined with a renewable electricity source, the electrification of mine haulage presents the opportunity to eliminate what is likely the single largest source of carbon emissions from a modern copper mine,” the report said.
“Furthermore, BEVs (battery-electric vehicles) have significantly reduced supply and logistics trains.
“By eliminating the need to bring quantities of diesel fuel on site, a significant amount of secondary vehicle transportation can be eliminated.”
Mineral processing
A process that transforms copper ore into concentrate or metal, mineral processing is one of the most critical functions in copper mining.
But it can also be made more sustainable.
“(Mineral processing) is the most energy-intensive part of upstream copper production and can contribute significantly to a site’s emission profile,” the ICAA said.
For the ICAA, collaboration is the most crucial step in decarbonising mineral processing.
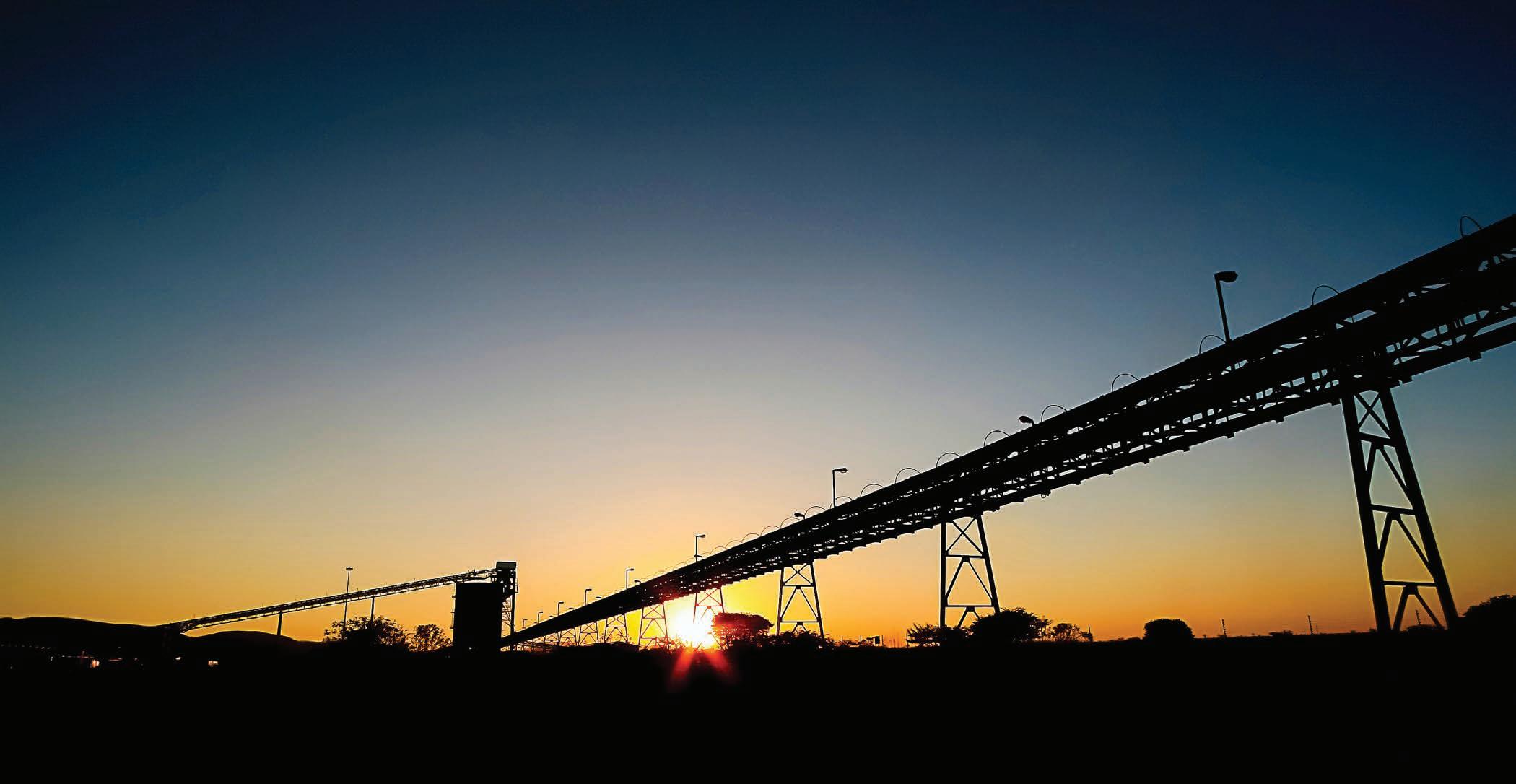
“No one company, start-up, university, peak body or government agency across the copper and mining sector holds all the answers,” the ICAA said. “But by working together, sharing knowledge, and trying innovative solutions, we are bound to get there.”
In particular, the report calls on copper project proponents to collaborate with local service providers to evaluate the composition of energy demands and availability from a local grid.
“Once the characteristics of the local grid and infrastructure are understood, copper operations must evaluate and negotiate the terms and conditions of existing power contracts,” the ICAA said.
“Copper mining facilities typically require a consistent and steady base load of electricity.
“Thorough planning across a site’s current and future assets is essential to accommodate the anticipated higher demands and to ensure uninterrupted operations.”
Ventilation and emission reporting
The latest piece of the puzzle from ICAA outlines the critical aspect of ventilation and emission reporting in copper mining and the ways companies can examine and address their carbon footprint.
“Since the inception of underground mining, the importance of adequate ventilation has been well recognised
and has evolved significantly over time to meet the demands of modern mining operations,” the ICAA said in its report.
“Each mining operation is different, and advanced ventilation systems are designed to address unique site-specific requirements and challenges.”
By nature, mine ventilation systems are capital-intensive and designed to prioritise reliability, performance, and preparedness for worstcase scenarios.
Any innovations related to ventilation can reverberate through other mining processes, highlighting the interconnected nature of these operations.
“Optimising the design and management of a ventilation system presents a complex array of challenges that need to balance safety, compliance, cost, positional and energy efficiency,” the ICAA said.
“The sector is also facing an energy conundrum, grappling with the dual challenges of high energy demands and the need for steady-state baseload power alongside the pursuit of sustainable, low-emission energy sources to power critical systems.”
Adopting a holistic approach to ventilation and emissions reporting will be crucial to reaching net-zero.
“This approach necessitates careful planning, significant investment, ongoing commitment, and specialised
skills to ensure these efforts effectively contribute to both site and corporate objectives,” the ICAA said.
“Embracing the transition to a lowcarbon economy is an opportunity for producers to innovate and become a leader in technology adoption across the ever-complex landscape of upstream copper production.”
From jewellery to cars to the roofs on people’s homes, copper is seemingly in everything.
To protect the copper mining industry and ensure this commodity is around to power our homes for years to come, there is no better time than now to start the journey to decarbonisation. AM

POWERING THE FUTURE
DELOITTE’S LATEST REPORT IS A HELPING HAND TO MINERS WONDERING ABOUT THE NEXT STAGE IN THEIR RENEWABLE JOURNEY.
Managing energy correctly and sustainably has never been more important.
As the world transitions to net-zero, industries across the globe are embracing the shift to greener power, and the mining sector is no different.
The latest report from Deloitte, ‘Energy management in mining’, sets out the compelling reasons mining companies should be looking to shift to green energy as quickly as possible.
“As the global climate crisis intensifies, the energy transition has emerged as a pivotal strategy for combating climate change,” the report stated.
“The increasing demand for mined products amidst a changing energy paradigm is driving a shift in the future of mining operations.”
According to Deloitte, there are a number of facets mining companies must consider when switching to renewable energy, including:
• how the company will organise and coordinate resources
• what talent the company needs now and in the future, and what new skills will be required in the upcoming energy landscape
• what the company’s system of energy assets, hardware and software platforms will be.
“We encourage mining operations to define a clear path forward, (and) ensure sufficient lead time to build and buy these capabilities alongside your company’s decarbonisation roadmap,” the report stated.
One of the key takeaways from the report was the suggestion for every mining company to have a transition strategy to help ensure they are not caught out when the time comes.
“The rapidly declining costs of renewable energy, increasing availability of energy storage, and a drive to meet decarbonisation goals is seeing many mining companies transition their energy arrangements,” the report stated.
“Electricity supply to mining is fundamentally changing.”
In order to successfully transition to renewable energy, mines must shift their thinking from being energy consumers to energy suppliers, Deloitte said. This could be as simple as transitioning coal- or gas-fired turbines and diesel generators to batteries, wind farms, solar or biofuel generators.
If a company is looking to decarbonise further, it could consider drawing power from a portfolio of supply and storage options.
“Mines may consider operating with or without grid connection, making the most of renewable and distributed energy resources,” the report stated.
“These are large-scale changes requiring organisational consideration. Mining operations will need to evolve from expecting supply to match their demand to optimising across supply and demand.”
But how can a mine run as productively and as safely as it always has while shifting to a completely new energy system? Deloitte has an answer.
“The electric mine’s integrated network and operational control centres create an intelligent mine able to predict and respond to intermittency and flexing capability,” the report stated. “In an electrified mine of the future, the role of electricity usage and availability changes.”
Deloitte recommends the integration of on-site generation and battery systems to capture and store excess renewable energy. This strategy would maintain connection to the power grid while acting as a back-up source of power and providing an opportunity to sell excess renewable energy.
“Under this paradigm, mining operators can mature energy management by monitoring and analysing energy-intensive processes and taking action,” the report stated.
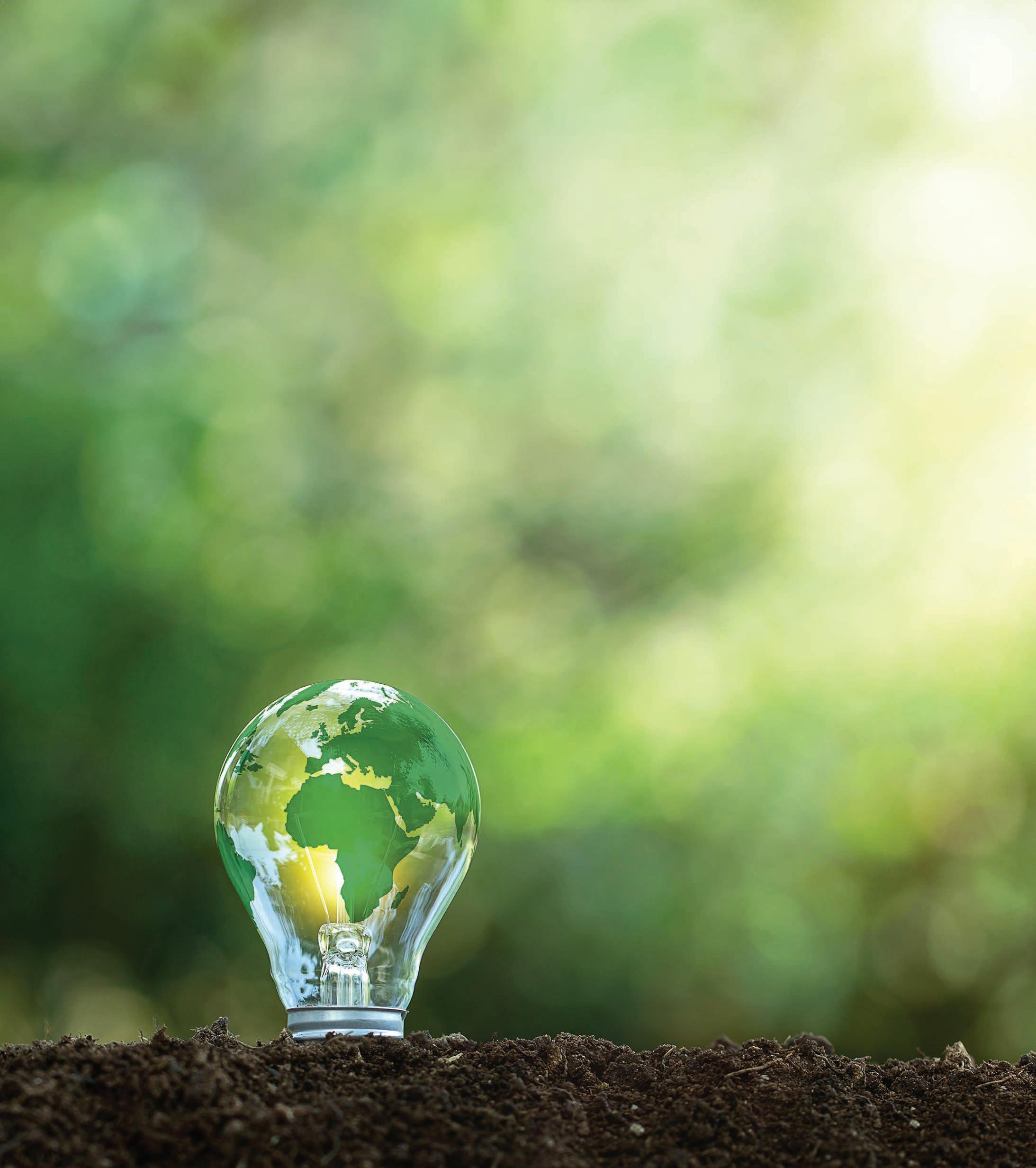
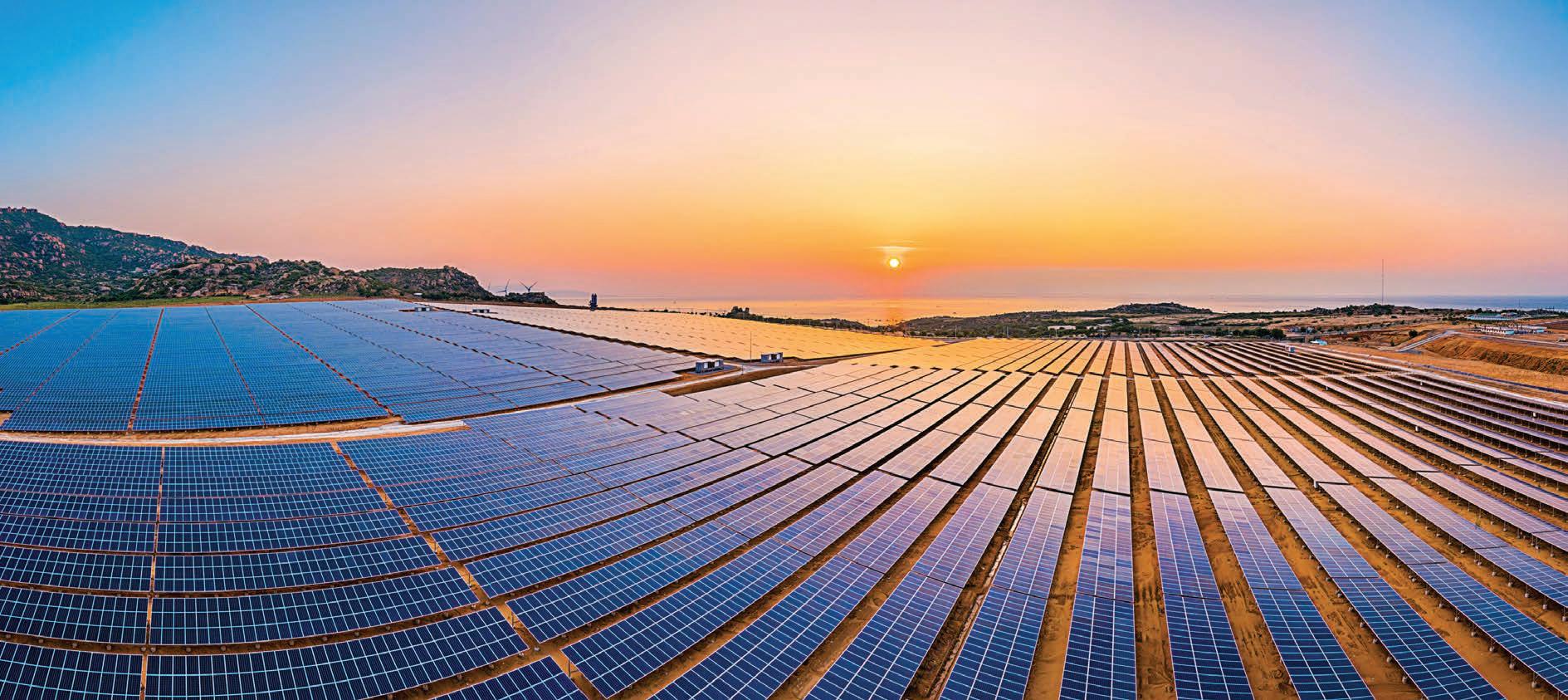
SHIFTING TO RENEWABLE ENERGY WILL ONLY BECOME MORE IMPORTANT AS THE WORLD TRANSITIONS TO NET-ZERO.
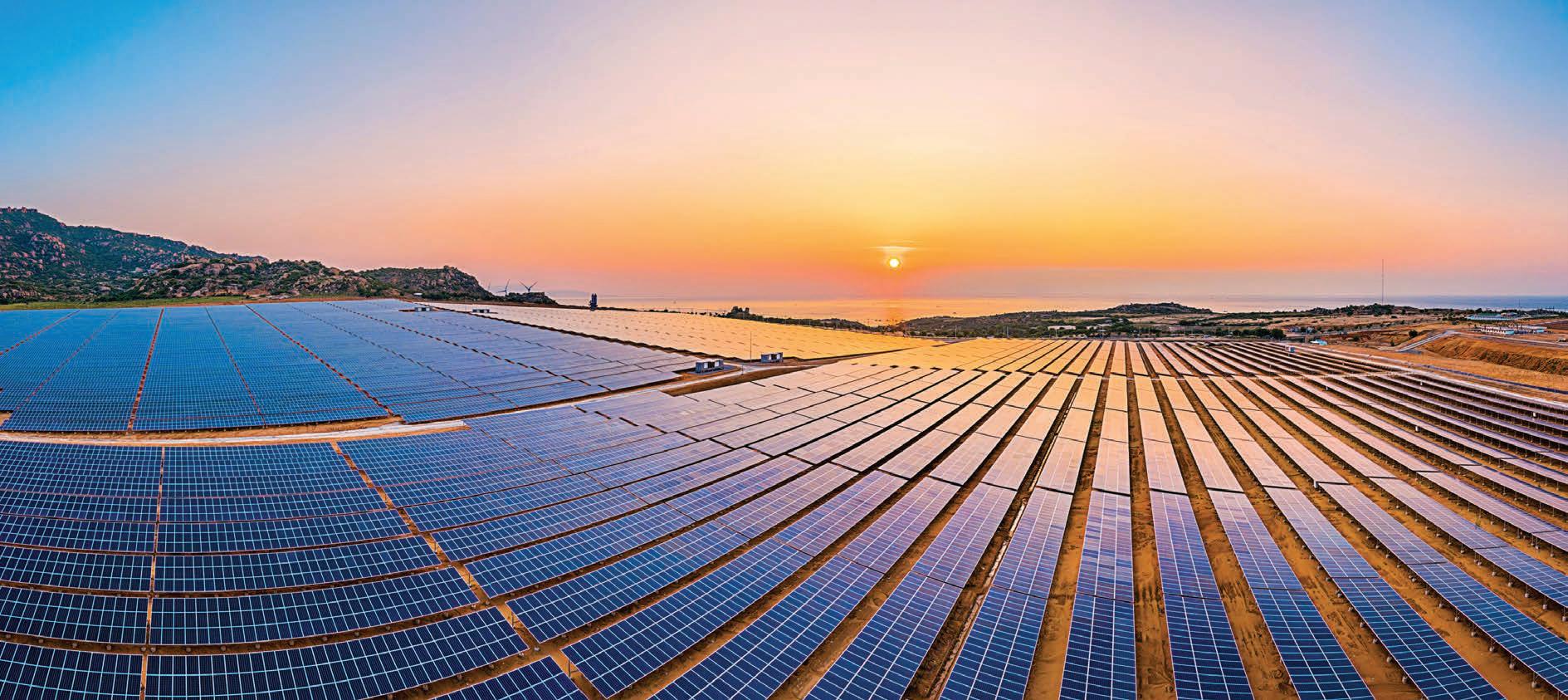
With demand for skilled workers set to rise amid the energy transition, the collaboration of interconnecting industries could be a key enabler. “Mining companies, energy companies and other major industrials will be competing in similar markets for talent, materials and equipment,” the report stated.
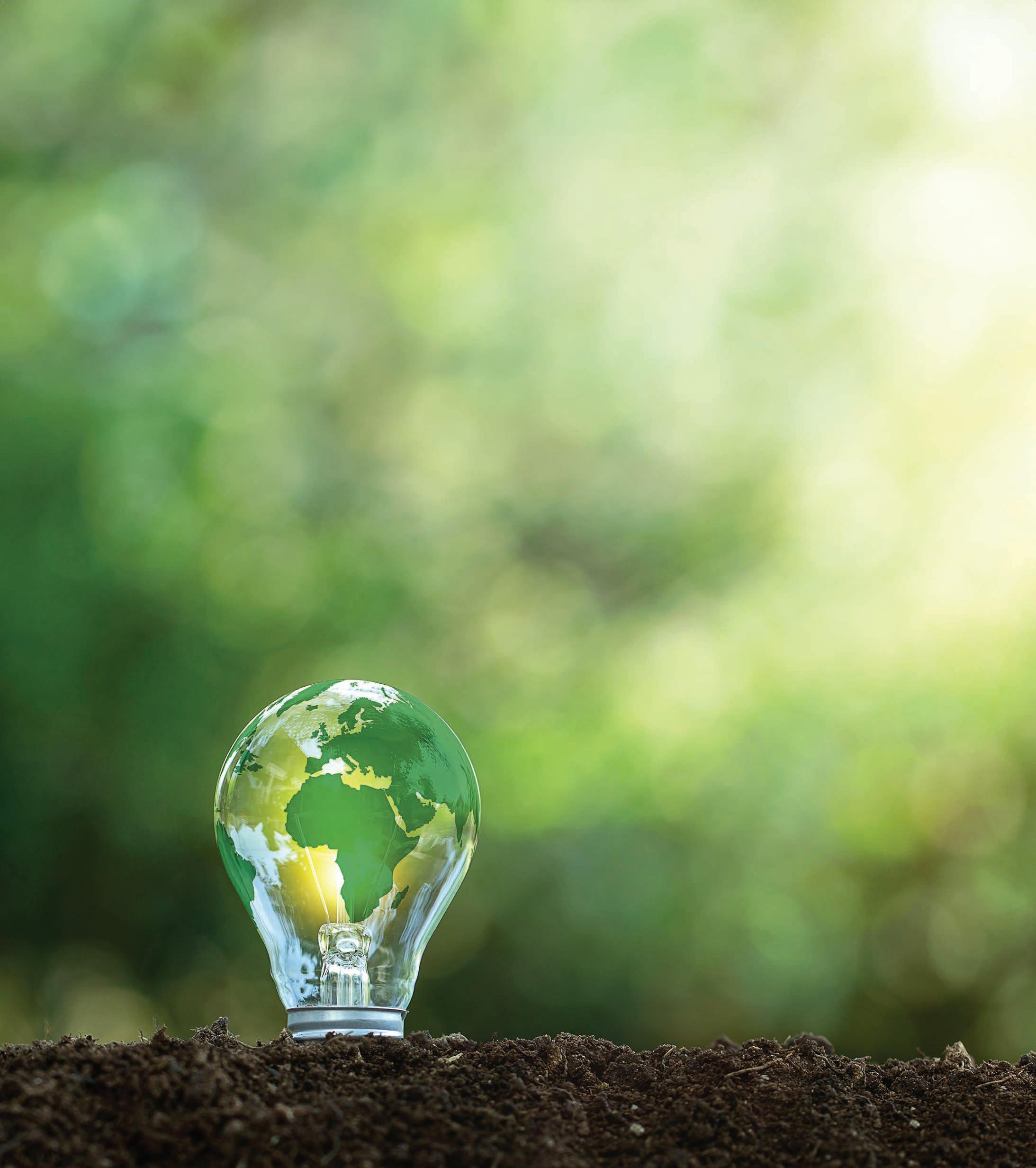
and working with – rather than against –the ecosystem will be necessary to meet major capital and production goals.”
So what can mining companies expect for the future? While there is no crystal ball, Deloitte has an educated idea of what the electrified mine will look like.
“Mining companies will require
electrified mines,” the report stated. “These will need to be part of the operational control centre for a truly integrated view of operations.”
Deloitte recommends that miners consider a wide breadth of options for their mines of the future, including digital twins and self-healing networks. It might sound a bit like a science
current behaviour of a mine, helping to optimise future performance.
Enabled by sensors in the physical mine and integrated with data and analytics from the digital world, a digital twin allows operators to test how things might perform without having to go through the trial and error in person.
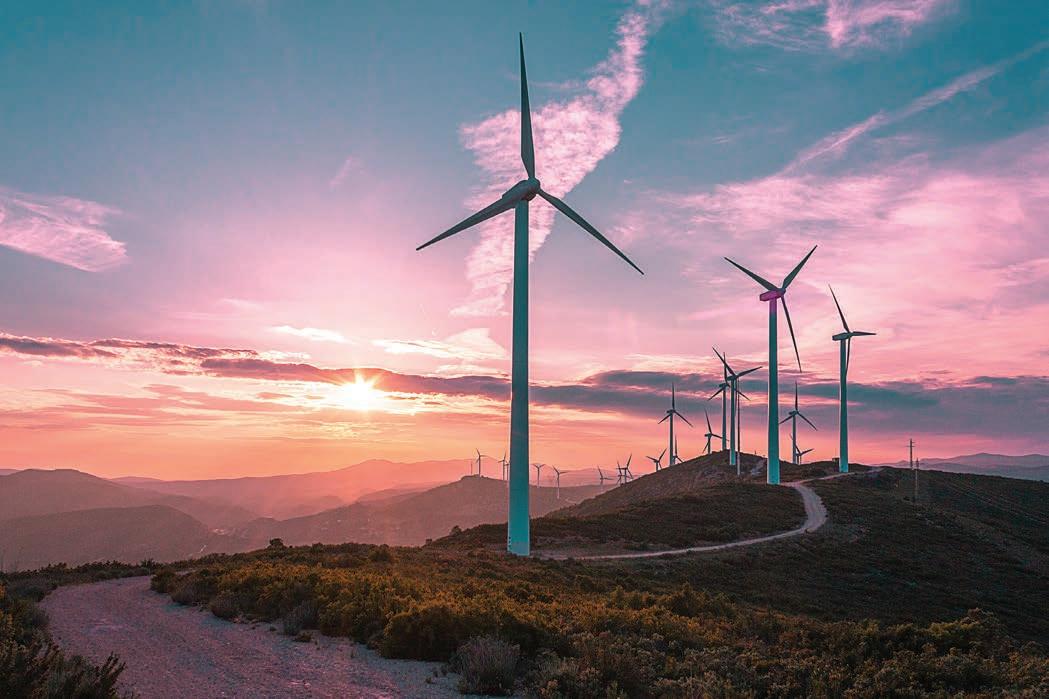
A self-healing network, on the other hand, uses combinations of physical and digital technologies to bring the system back to a steady state.
These are networks with built-in properties to protect against failures by predicting problems, providing workarounds, supporting recovery and preventing future incidents from
Regardless of how companies choose to switch to renewable energy, the important thing is that by doing so they are helping the world reach net-zero as quickly as possible.
“The integration of renewable energy into mining operations has the potential to revolutionise the industry,” the report stated. “Embracing electrification will fundamentally reshape mining operations.
“Transitioning from fossilfuel-dependent energy supply and machinery to renewable generation and storage and electric-powered equipment not only reduces emissions but is driving a wave of innovation, digitalisation and an urgency for new capabilities.” AM
BREAKING THE STATUS QUO
EPIROC UNDERSTANDS THE STEP CHANGES INVOLVED WITH GOING ELECTRIC. SO IT’S PUT MEASURES IN PLACE TO FACILITATE THE TRANSITION.
Diesel-powered equipment has long been the most cost-effective option for the sprawling and largely remote Australian mining industry.
With the convenience of the combustion engine and Australia’s traditionally affordable fuel prices, mining companies and contractors haven’t had to think twice about what equipment to buy.
But now that mining’s environmental performance is being questioned, and even reprimanded, the local sector is having to reconsider its methods and the machinery that supports them.
A generational shift is occurring, and that is bringing rise to new environmentally conscious methodologies and technologies, including electric-powered equipment.
In delivering its mission to support the digitalisation, automation and electrification of the global mining industry, Epiroc is at the cutting edge of innovation and sees Australia as a significant growth market for its electrification offerings.
Electrification is gradually becoming more commonplace in underground mines, with Epiroc already offering battery-electric truck, loader and drill options. This includes batteryelectric jumbos (Epiroc Boomer range), bolting rigs (Epiroc Boltec range) and production drills (Epiroc Simba range).
Epiroc continues to build out its electric drill range for surface mining, with the original equipment manufacturer (OEM) recently launching new electric Pit Viper blasthole drill rigs.
The Pit Viper 271 E can drill singlepass holes up to 18m with diameters of up to 311mm, while the Pit Viper 275 E can handle multi-pass holes up to 76m with diameters reaching 270mm.
Both of these drills can be configured with Epiroc’s XC (Xtra Capacity) package to provide 85,000 pounds (38.5 tonnes) of bit load capacity, ensuring operators don’t lose out on productivity.
The new models in the electric Pit Viper range are the PV231 E and PV235 E, which are suited to ‘one size smaller’ drilling operations.
These platform drills come fitted with Epiroc’s suite of automation features, as well as smart functionalities that enhance operational safety, accuracy and productivity, all the while eliminating live work.
For clients taking the electrification plunge for the first time, Epiroc can offer integrated solutions for an electric mine, incorporating infrastructure, chargers and other consulting services like electrical audits.

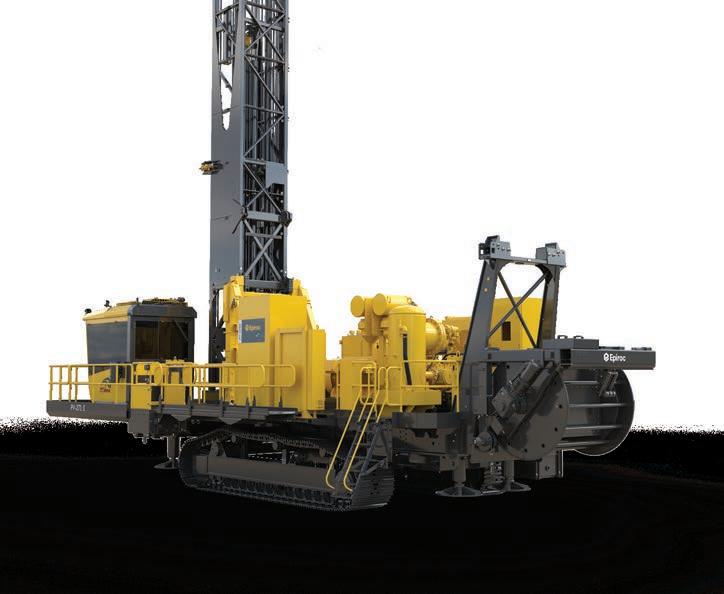
This can come in the form of a battery or electric conversion, which sees a diesel operation retrofitted with electric capability.
The OEM can also provide support through its Batteries as a Service (BaaS) offering, which removes some of the obstacles that come with making the electric transition.
BaaS moves the upfront costs of batteries from capital expenditure (capex) to operational expenditure (opex), with Epiroc taking full responsibility for the batteries, from certification to maintenance and technology upgrades.
In addition to Epiroc’s batterypowered equipment, BaaS is also available on gear from other OEMs that use Epiroc batteries.
Epiroc product manager – drilling solutions Hans Hilden said it is only logical that more and more Australian mining companies will seek out battery and electric conversions.
“Miners understand they need to get the full lifetime out of their assets,” Hilden told Australian Mining.
“And because Australian miners increasingly want to standardise their equipment, we expect more battery and electric conversions to occur as the mining sector decarbonises.”
Battery and electric conversions typically take place in a midlife rebuild, with Epiroc able to refurbish equipment to give it thousands of new hours with a zero-emission footprint.
While the Australian sector has been somewhat behind other markets in its
take many more successful case studies to spark an electric evolution.
“Once we get more proven customer cases, it can open the door for electric technologies to become more accepted in Australia and in mining,” he said.
“I’ve seen that happen in the automation field of mining equipment, and I expect it to be the same case with electrification.”
Hilden said the Australian mining sector’s Tier 1 companies and contractors have been particularly proactive in deploying electric technologies.
“The big players in the mining industry are showing great interest to start moving towards something other than diesel-powered machinery, including in the drilling space,” he said.
“Soon enough, electrification won’t be optional but mandatory, and it’s going to be a really interesting five to 10 years to see how far the mining industry actually evolves.” AM


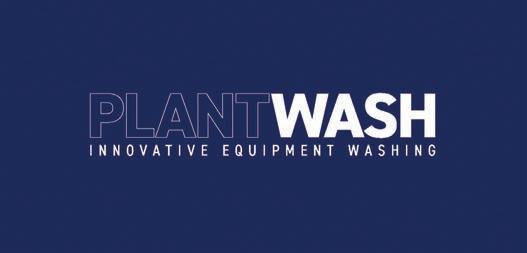
A PROCESSING PARTNERSHIP BUILT TO LAST
ASTEC AND OPS ARE COMMITTED TO GROWING EACH OTHER AND THE MINING INDUSTRY.
All hands were on deck at the OPS Screening and Crushing Equipment open days on March 21–22.
Held at OPS’s Perth facility, the expo celebrated 35 years of the company supplying critical equipment to Australia’s mining and quarrying industry.
To mark the occasion, OPS welcomed industry players from across the world to take part in two days of exhibitions, presentations and displays.
Rock-to-road solutions expert Astec was a major participant at the event. The company was also celebrating its decadelong partnership with OPS.
“Both Astec and OPS have seen excellent growth through our partnership,” Astec business line manager – material solutions Adam Gordon told Australian Mining
“A key factor in the relationship is we know we can rely on OPS to provide quality service and expert technicians ready to rise to any challenge.”
Gordon said OPS is a trusted distributer of Astec’s bulk material handling and fixed plant equipment to
equipment and ship-loading range Australia-wide.
“Astec manufactures equipment for the entire mineral processing chain, including crushing, screening, handling and washing,” he said.
“It’s big equipment for a big industry, and it requires knowledge, expertise and an extensive range of high-quality products to get the right machines to the right sites.”
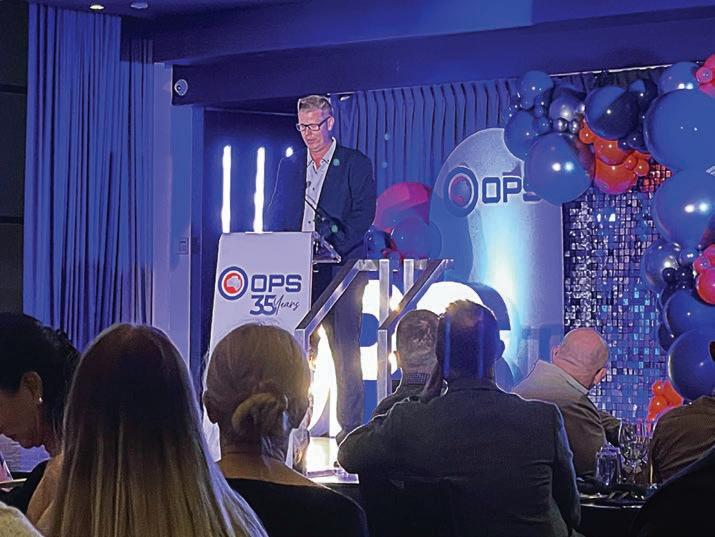
Between them, Astec and OPS teams have built hundreds of years of industry experience, including expertise drawn from the 16 respected brands under the Astec umbrella.
“While Astec and OPS are successful businesses in their own right, they’re even better working together,” Gordon said. “We each bring different strengths to the partnership – strengths that we then build on to benefit each other and our customers.
“And with our combined experience, we have the Australian mining and quarrying industries covered.”
According to Gordon, one significant advantage in working together is the companies’ ability to deliver advanced training to teams on the ground.
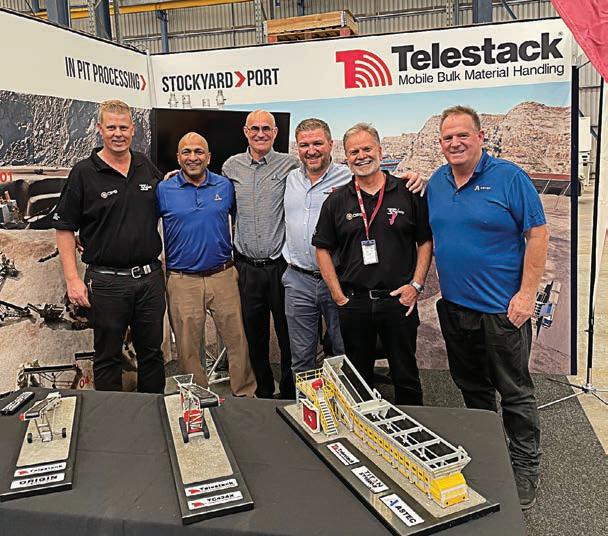
are capable of providing outstanding service to customers, Gordon credits Astec’s tailored approach in ensuring OPS staff members are well equipped to face any challenge.
“We have a lot of equipment in the thousands-of-tonnes-per-hour range and
Astec’s ship-loading and modular plant crusher facilities.
“Being able to showcase the scale of our capabilities was a major highlight of the event,” Gordon said.
one-on-one environment, to ensure these

The recent expansion of Astec’s Omagh manufacturing facility in Northern Ireland is another important factor in the company’s ability to support OPS.
“This expansion has effectively doubled our manufacturing capability, meaning we can supply more equipment more often to OPS, thereby keeping our customers up to date with the latest products and critical support when they need it,” he said.
Gordon emphasised that through Astec’s commitment to continuous improvement, the company is already designing and building equipment for the future, and it’s counting on OPS to be with them on that journey.
“We are very proud to be associated with OPS,” Gordon said, “We’re similar businesses, with the same goal of providing our customers with the best possible equipment to meet their needs.
“We work very well together, and we’re looking forward to a great future of growth.” AM

SHAPE THE FUTURE WITH POSITION PARTNERS REDEFINED

With world-class automation + positioning technologies that keep your people machines and assets safe.
Learn more and get in touch today
aptella.com
A SUPPLY CHAIN TO BE PROUD OF
SUPPLY CHAIN OPTIMISATION IS CRUCIAL IN THE MINING INDUSTRY, AND GEOGRAPHE HAS WORKED NIGHT AND DAY TO ENSURE IT CAN HELP THE INDUSTRY MEET ITS NEEDS.
For Geographe, supply chain optimisation is simple: it means finding the most effective manufacturing, procurement or transport solution while ensuring rigorous quality standards are being met. “We regularly evaluate our processes, solicit feedback from customers and stakeholders, and implement targeted improvements to enhance efficiency, reliability, and customer satisfaction,” Geographe’s Head of Supply Chain Alex Poezyn told Australian Mining.
chain, we are able to lower our lead times and service our customers’ planned and unplanned maintenance events, and remain agile and responsive in addressing parts shortages.”
major downtime for a mining operation. And that equals lost productivity.
“The opportunity cost for mining operations when they have a machine down is massive and Geographe recognises this,” Poezyn said. “Any delay in machine maintenance can lead to significant production and financial losses to the mine site.
“Ensuring a robust supply chain reduces the likelihood of not having stock, which in turn reduces the length of downtime for miners.
“We understand that a reliable supply of parts ensures our mining clients can maintain their operations
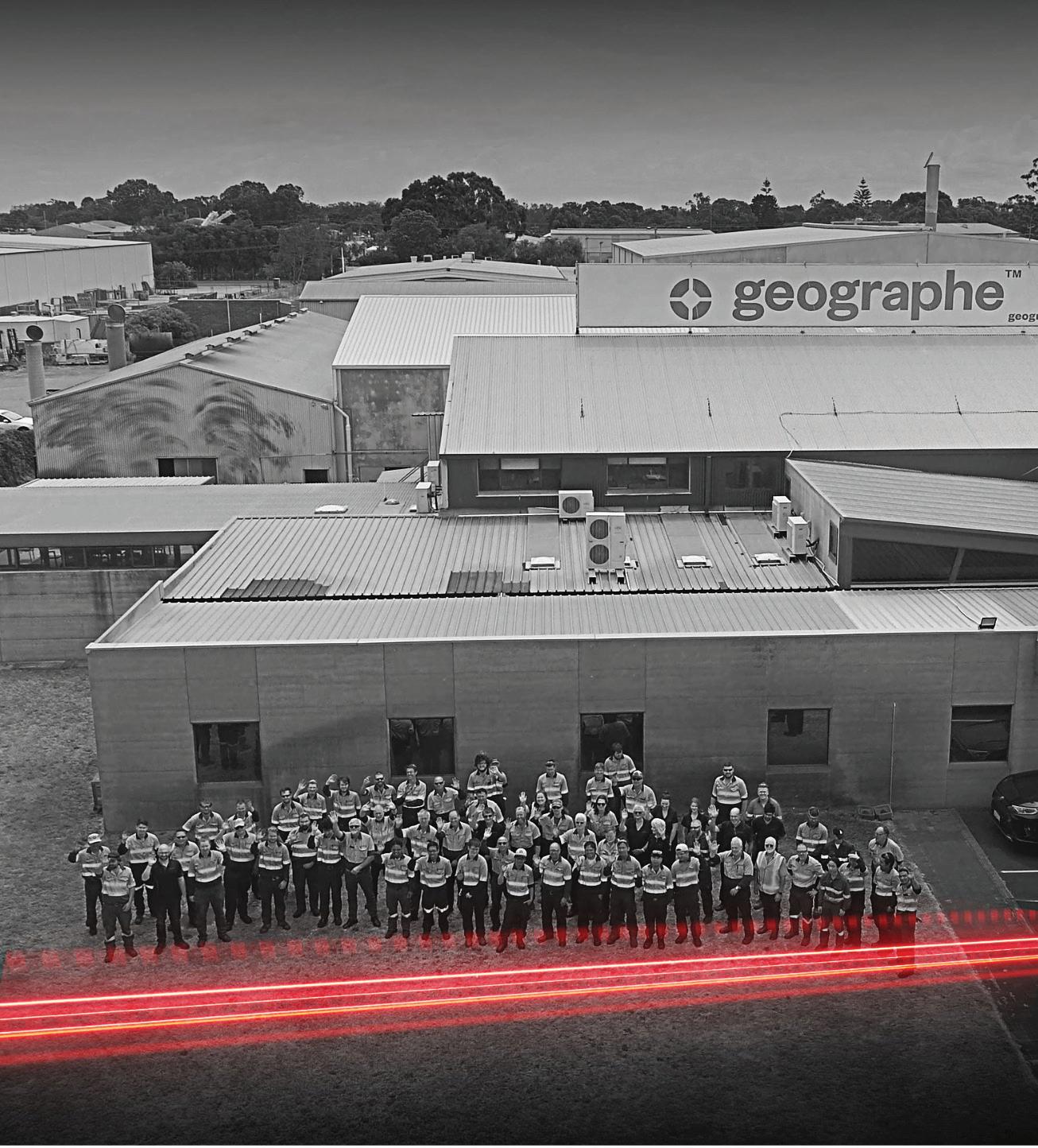
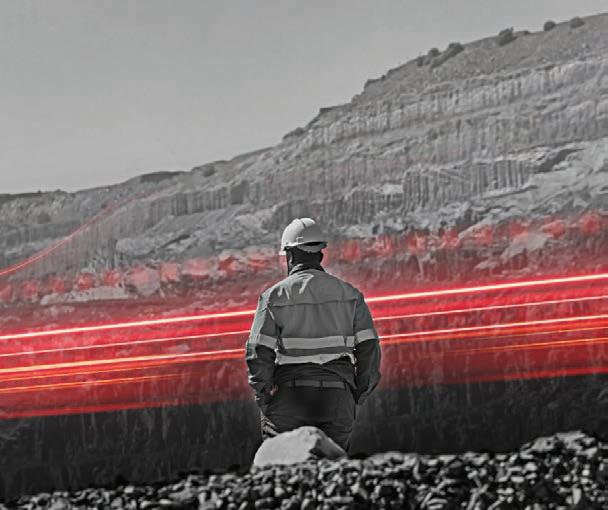
“While there are products that we source globally – such as our raw material – we manage these risks by having multiple suppliers that we work closely with to ensure ongoing availability of parts and specialised tooling solutions.
“Also, given our agility as a business, we are able to make decisions quickly and with limited red tape when we see there are potential disruptions on the horizon.”
Geographe leverages technology and innovation in order to truly optimise its supply chain, .
“Since 2002, Geographe has been using SAP (an enterprise resource planning software),” Poezyn said.
“Then in 2018, we adopted S4Hana Cloud to improve our digital infrastructure and provide further automation for our administrative roles.
“However, we have also invested in our own technical capabilities and our own software to further our automation capabilities.
“We integrate our in-house-developed software with SAP, ensuring a fully compatible digital architecture.”
And with a robust investment in robotics, Geographe is able to keep its production facilities running 24–7.
“As we’re a manufacturing business, we have full traceability on our products, from the raw material that was used and its chemical composition right the way through to the production order the item was produced on,” Poezyn said.
“Every manufactured product has the Geographe production order number engraved on it, along with the Geographe part number.”
Any amount of downtime can be detrimental to a mine. But Geographe’s commitment to innovation means the sector is one step closer to eliminating supply chain woes for good. AM

Optimising Mining Operations: Your Partner for Shutdowns, Logistics and Maintenance MINING RENEWABLES RESOURCES

Scan the QR code to find out more!
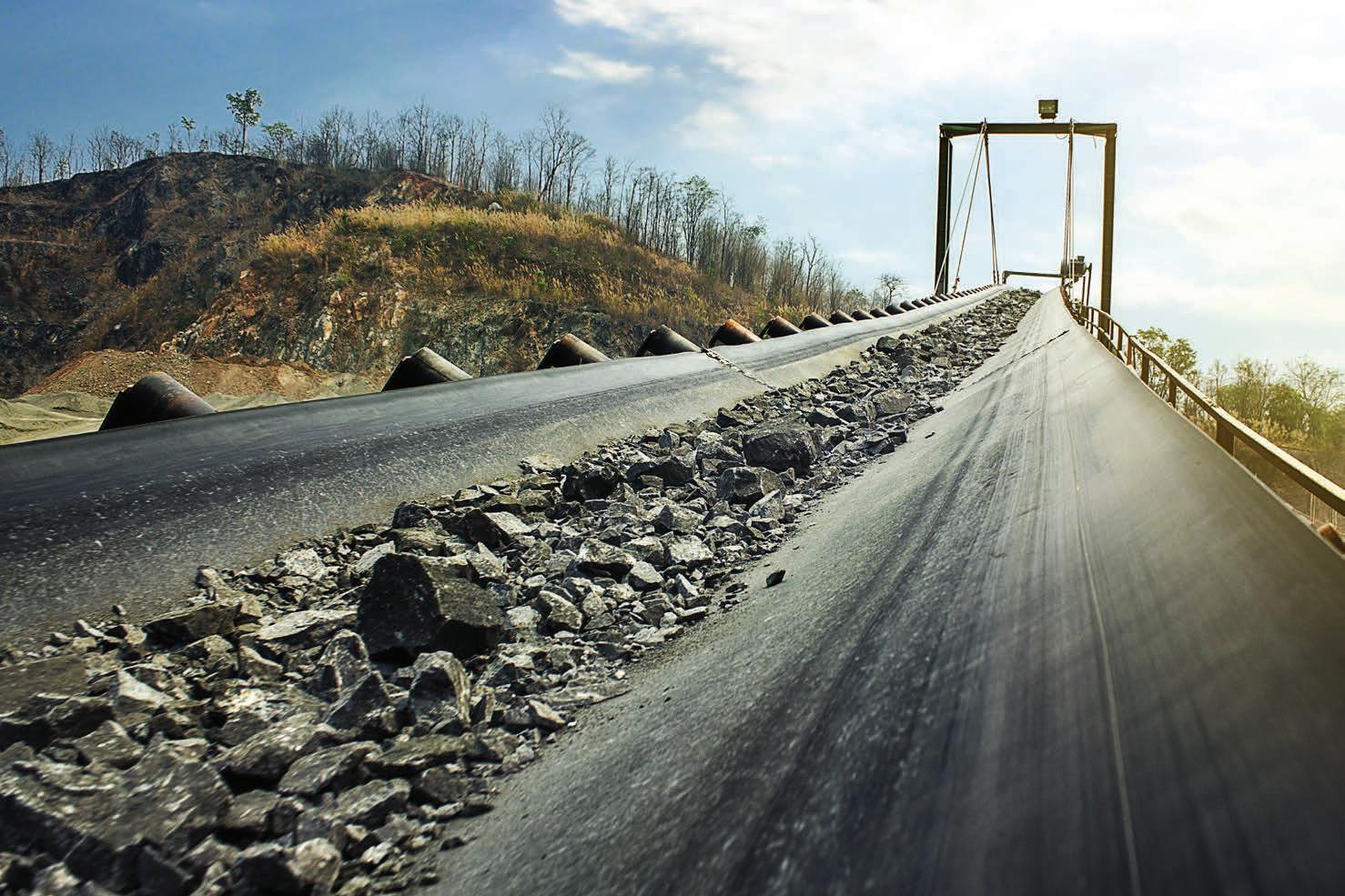
When Minprovise product specialist Robert Arezio was asked to describe the Rice Lake Master 1280 Integrator, he didn’t even pause to think.
“It’s a breeze to use,” he told Australian Mining. “It’s easy to program, and deliberately designed to be user friendly. The program layout and menu structure are highly intuitive, making the 1280 Enterprise simple to use.”
In the modern mining world, there are thousands of pieces of machinery on-site. Each has an important job to do, but the Rice Lake Master 1280 Enterprise Integrator stands out for its simplicity thanks to its design and features.
The digital weight indicator and belt scale controller allows operators to see the most important information about their weigh systems at a glance.
“The best part is the 1280 Integrator can be customised to meet the specific operational needs of a mine site,” Arezio said. “Whether it’s adjusting formulas, configuring timers, or controlling various functions within the system, the 1280 Enterprise offers unparalleled flexibility and control.

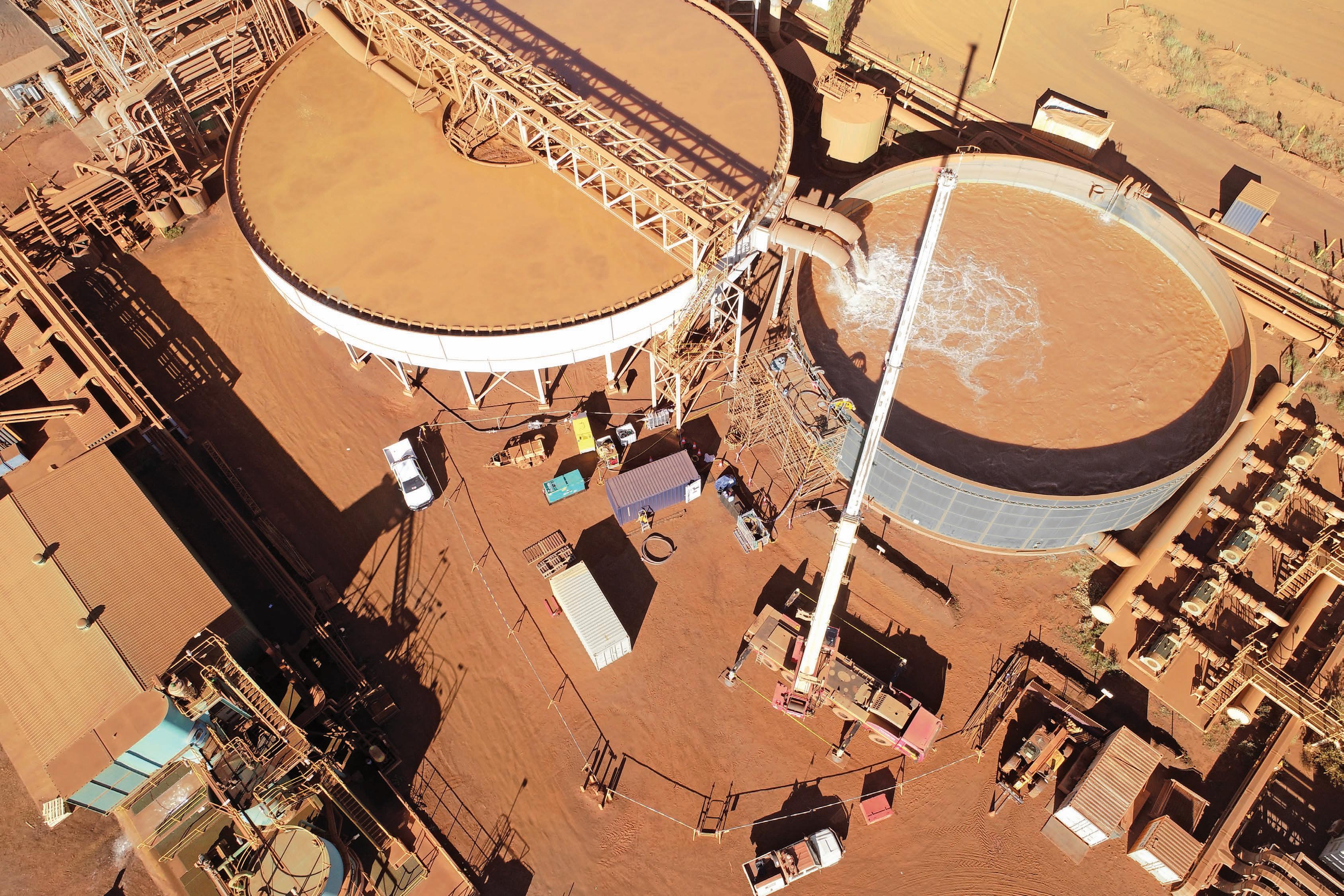
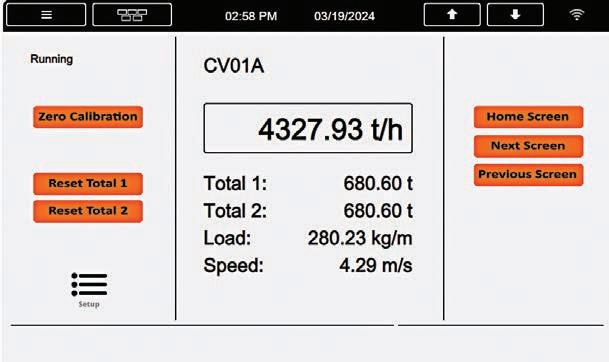

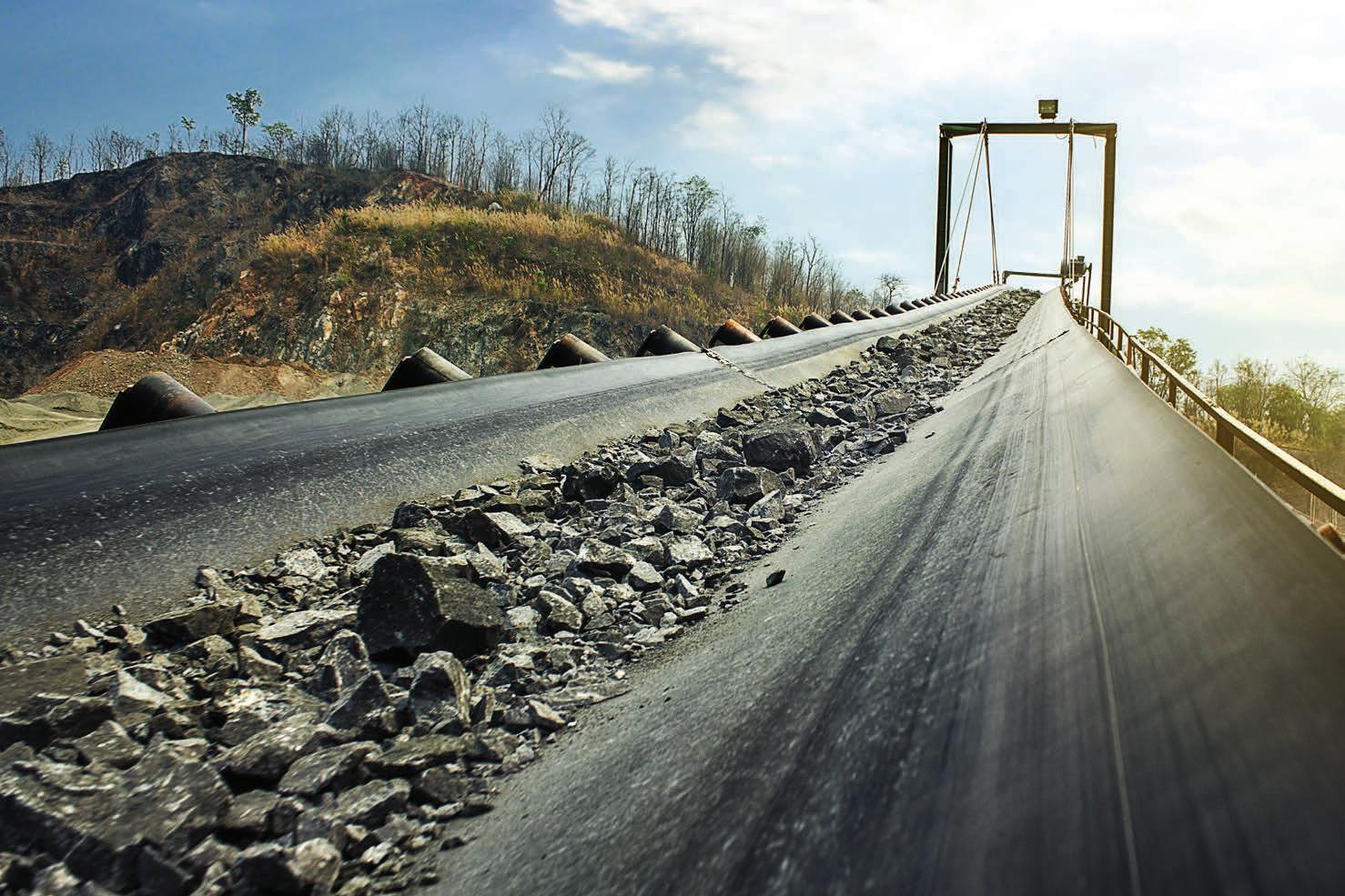
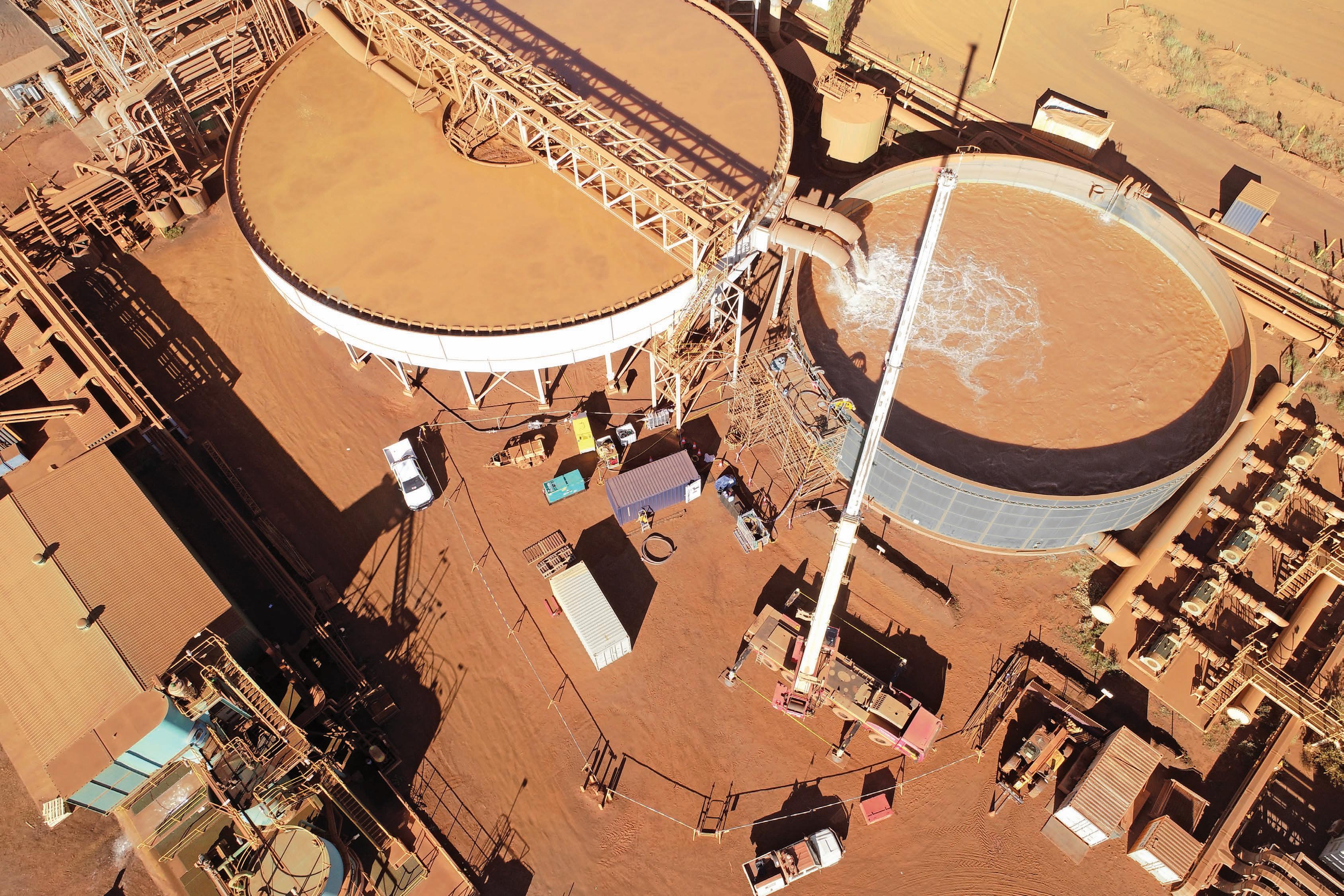
SAFELY DREDGE PROCESS TANKS, ONLINE
At Dredge Robotics we understand that downtime is costly. That’s why we’ve designed a fleet of globally unique dredging robots that can rapidly and thoroughly clean and inspect water assets while they remain in full service.
Designed and built in Australia for the harshest of conditions, our proprietary robotic dredging technology is a genuine game-changer for the mining sector.
Eliminating the need for human entry, these machines allow maintenance tasks to be performed outside of shutdown windows, delivering significant savings and reducing asset downtime.
Extensively proven in the mining industry, our capabilities include:
• Removal of deep compacted mud from process tanks.
• Safe removal of mud, weeds and aquatic plants from lined ponds.
• Operation in corrosive and extreme pH environments (pH 1 to pH 14).
If you’re looking for a smarter way to manage your water assets, contact the friendly team at Dredge Robotics today.
www.dredgerobotics.com.au
info@dredgerobotics.com.au
+61
THE FUTURE OF PRECIOUS METALS
AUSTRALIAN MINING SHINES A LIGHT ON ARGENT MINERALS, KALAMAZOO RESOURCES AND FALCON METALS – THREE COMPANIES LOOKING TO BECOME PRECIOUS METALS PRODUCERS.
Gold and silver have differing but equally robust economic outlooks.
Gold is set to continually benefit from factors such as sustained geopolitical uncertainty and growing central bank activity. The precious metal typically surges in popularity in times of global unease, a seemingly perpetual modern reality.
Silver has become a largely ubiquitous raw material, with applications including, but not limited to, electronics, soldering, chemical production, jewellery and photography.
This commodity is expected to grow in importance as the energy transition ramps up given its importance in electricity-based systems. Solar panels and electric vehicles (EVs) are expected to drive greater silver demand in the years to come.
Australian Mining spotlights three companies who, through their own strategies, are looking to become precious metals producers.
Argent Minerals
Owner of one of Australia’s most promising polymetallic projects, Argent Minerals hopes to become a key supplier of high-grade silver, gold and base metals for global markets.
The Kempfield project in the Lachlan Orogen region of NSW has a mineral resource of 38.9 million tonnes at 102 grams per tonne (g/t) silver equivalent (AgEq) for 127.5 million ounces AgEq, containing 42.8 million ounces (Moz) of silver, 149,200oz of gold, 181,016 tonnes (t) lead and 426,900t zinc.
Argent recently announced what it believes to be a major silver-base metal discovery north-east of the main Kempfield deposit, with surface sampling returning assays of up to 177g/t silver, 1.89 per cent lead and 1.21 per cent zinc.
“Surface assay results have confirmed the discovery of mineralised extension zones along strike from the main Kempfield deposit,” Argent managing director Pedro Kastellorizos said.
“These exciting new zones host the same geology and geochemical signatures as the main mineralisation over the Kempfield deposit.”
The extension known as Kempfield NW Mineralised Zone is approximately 1.72km along strike of the main Kempfield deposit with an average width of 100m. Three distinct silver-lead-zinc zones have been delineated here.
Kastellorizos said Argent will be focused on aggressive drilling programs in 2024 as the company continues to build out the Kempfield resource, along with an economic scoping study to further understand the viability of the project.
“I believe we’ve got something quite a lot more expansive than is currently known at Kempfield,” he said.
“On the basis of that, we will be continuing drilling throughout this year, and outside of the main resource area as we’re looking to potentially delineate more tonnes and grade proximal to the current orebody.”
The Kempfield project belongs to a group of Paleaozoic volcanichosted massive sulphide (VHMS) deposits in the Lachlan Orogen. Other VHMS deposits in the region include Woodlawn, McPhillamys and the recently mothballed Thalanga mine.
Eastern Australian Paleaozoic VHMS deposits have been a major source of lead, zinc, silver and gold for over a century, and Kastellorizos believes no NSW silver deposit matches Kempfield for grade.
“The average grade of a silver deposit is … 62 grams per tonne silver equivalent, whereas Kempfield is 102 grams per tonne silver equivalent,” he said. “The mineralisation also starts almost at the surface at Kempfield, which means you’re literally digging into paid dirt rather than having to strip back material.
“So when you start looking at the economics of the project, Kempfield can definitely be a very profitable operation.”
Kalamazoo Resources
Kalamazoo Resources’ ‘project generator’ model has grown the company’s liquidity on the ASX in recent years.
The explorer’s objective is to ‘identify, acquire, discover, enhance and create value’, which has been proven through the sale of a 50 per cent stake in the Queens gold project in Victoria to Novo Resources for $1.5 million, and an option agreement to sell the Ashburton gold project in WA to De Grey Mining for up to $33 million.

lithium operation and MinRes’ Wodgina operation.
“The shareholder returns from the Kali spin-out alone amounted to about $16 million,” Kalamazoo chief
has a good history of generating shareholder returns through its ‘project generator’ model.
“We find good projects, we do good work, we add value and we’ll either fund

unloved resource or project.
“Most importantly, it needs to be something where we believe we can add value.”
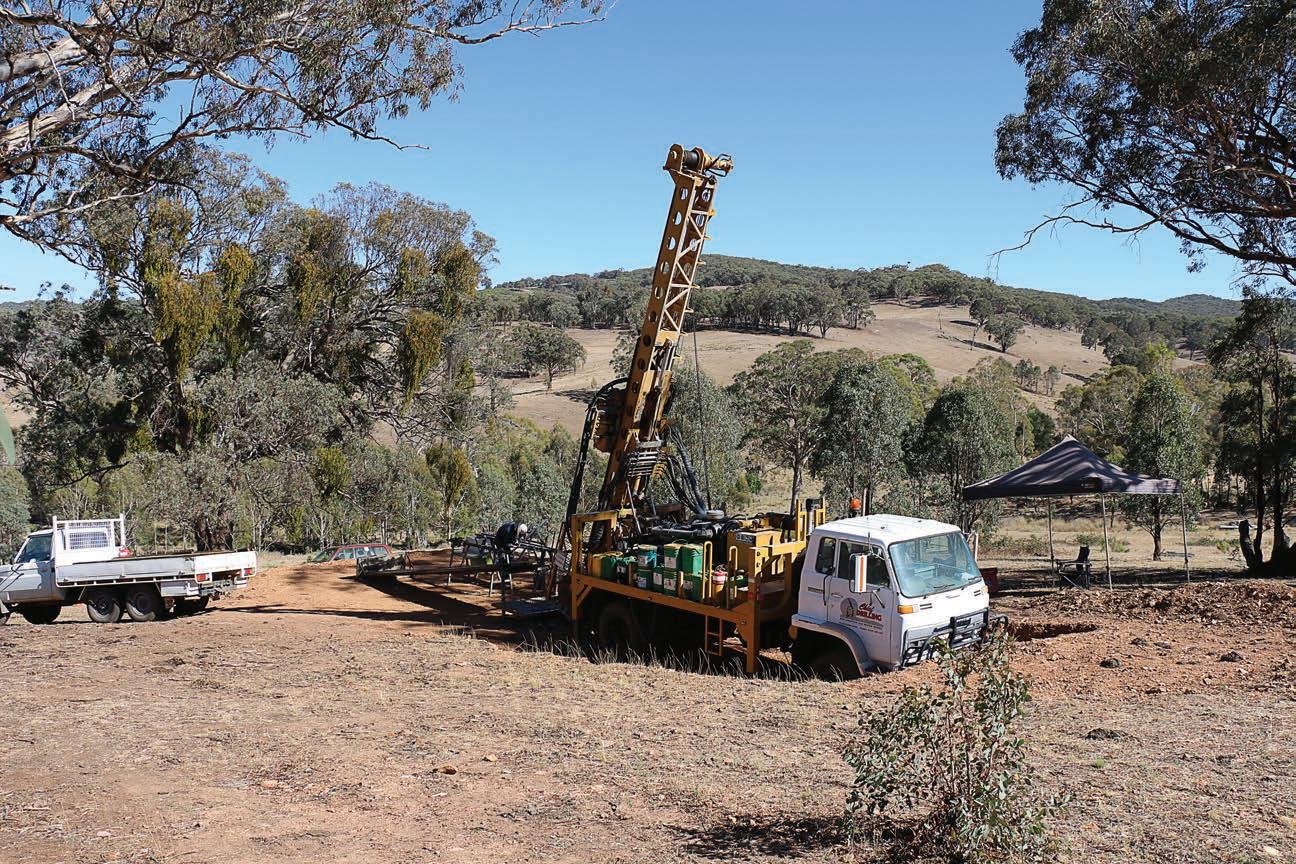

Falcon Metals
Initially spun out from Chalice Mining as a pure-play gold explorer, Falcon Metals has diversified its commodity profile, adding mineral sands and nickel to the mix.
The addition of mineral sands has come as a bonus for Falcon, with a recent 77-hole aircore (AC) drilling program returning encouraging levels of heavy minerals including zircon, rutile and ilmenite at its Pyramid Hill project in Victoria.
“We’ve got a very large ground position that targets the Murray Basin, which was primarily pegged for gold,” Falcon managing director Tim Markwell told Australian Mining.
“The Murray Basin is also known to host multiple very large mineral sands deposits, including VHM’s Goschen project, Iluka’s Wimmera project, and Astron’s Donald asset.
“We have two permits to the northwest of Bendigo that have quite a long east-west trend, and they go right across several mineral sands deposits.”
Falcon’s EL006864 block includes WIM Resource’s Wedderburn heavy mineral sands project within it, demonstrating the potential for mineral sands prospectivity across Falcon’s tenements.
With AC drilling returning hits of up to 18m in length and up to 21.6 per cent in total heavy mineral (THM) grade, Falcon plans to advance mineral sands drilling in parallel with its gold exploration.
While Pyramid Hill and the Mt Jackson gold project in WA continue to be Falcon’s priorities, the company recently discovered a 1km gold trend at its Bamganie gold prospect near Meredith in Victoria.
The Bamganie prospect is unique in that Falcon believes it is located within a forgotten goldfield.
“While Bamganie was mined in the early 1900s, it has never had any proper exploration,” Markwell said. “It’s got a decent-sized footprint – it’s not a small goldfield where you’ve only got a couple of 100m of strike.
“Because Bamganie appears to shallow in depth and covers a footprint of a couple of kilometres, it makes us think, ‘Could there be another Fosterville? Could Bamganie be an area that’s been worked previously, but if you drill deeper, maybe it will improve at depth?’”
Agnico Eagle’s Fosterville gold operation in Victoria is considered one of the lowest-cost gold mines in the world, in part due to its very highgrade mineralisation.
Falcon is advancing infill and reconnaissance AC drilling across its Pyramid Hill project, which spans more than 5000km2 predominantly in the Bendigo region of Victoria.

The company is determining continuity across a range of prospects, with infill drilling currently focused on the EL6669 block near Kerang, EL6960 near Eddington, as well as the Wandoo prospect.
Other significant Pyramid Hill prospects include Karri, Ironbark and Banksia.
Falcon Metals has also been active on other fronts including the recently announced deal where the company vended two of its applications in the Kimberley region of WA to Stavely
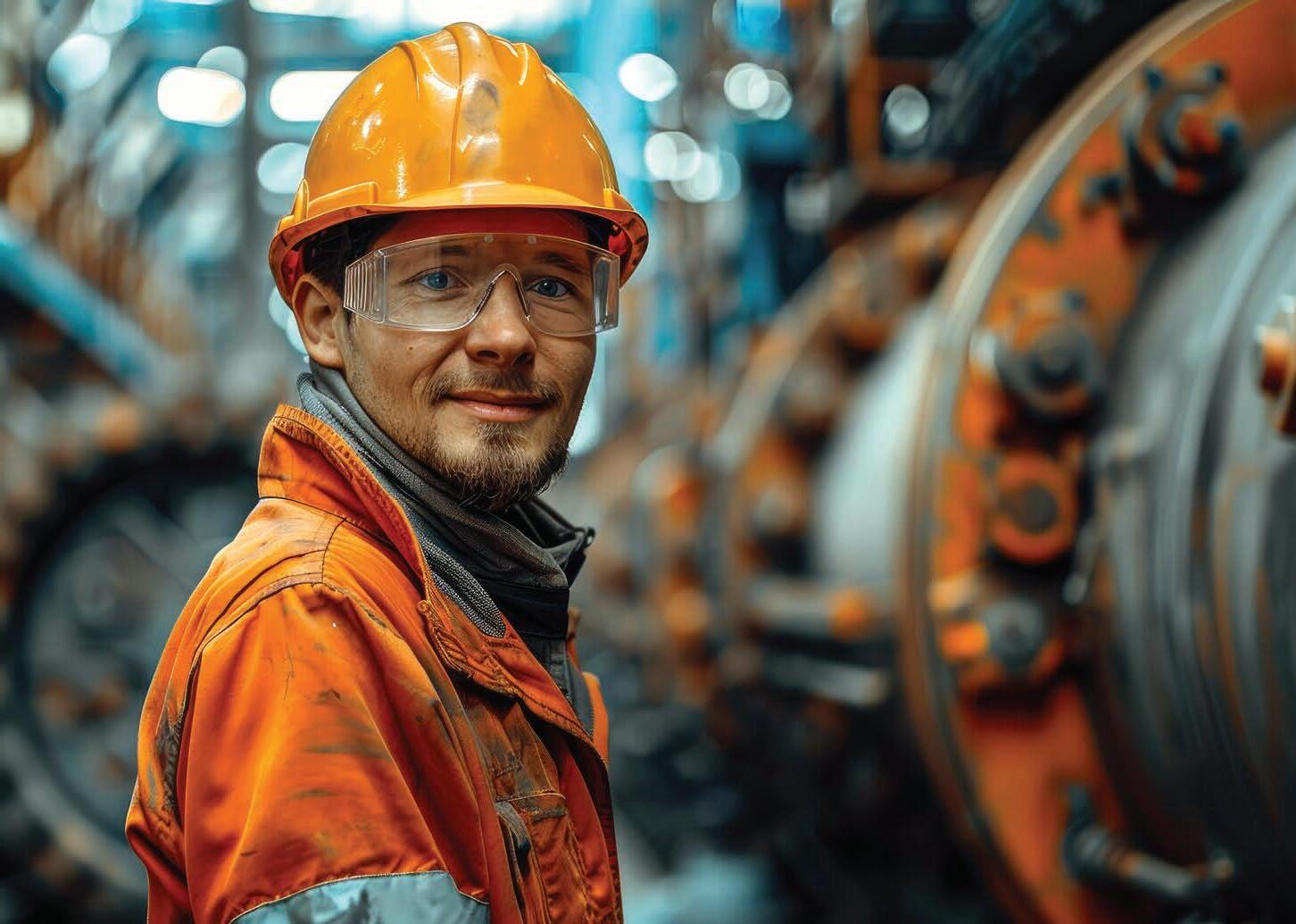
Minerals, adjacent to Stavely’s Hawkstone nickel-copper project. Stavely can spend $500,000 to earn an 80 per cent stake in the two Falcon applications.
Markwell said the earn-in enabled Falcon to secure a “strategic entry” into the emerging West Kimberley magmatic nickel province.
“The IGO/Buxton Dogleg nickel sulphide discovery demonstrates the potential for new nickel discoveries, and we believe there is outstanding potential to discover more high-tenor magmatic
nickel sulphide mineralisation across this district,” he said.
Diversification can be a critical differentiator in today’s mining industry, providing companies with more levers to attract investment and generate shareholder returns.
While Argent Minerals, Kalamazoo and Falcon Metals aim to be precious metals producers first and foremost, each company has diversified their portfolio to gain exposure to a range of commodities, some of which will be essential to the clean energy transition. AM
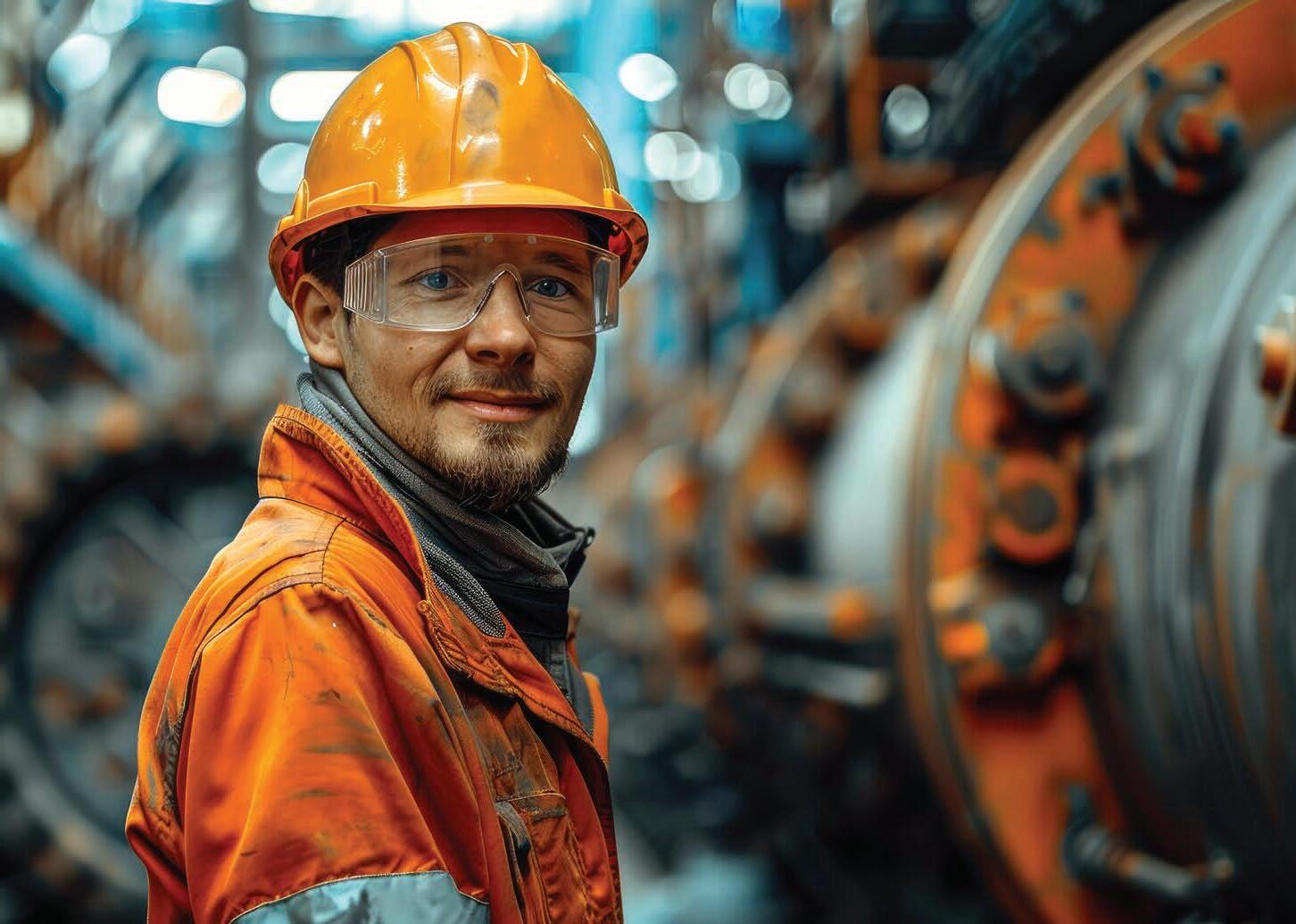


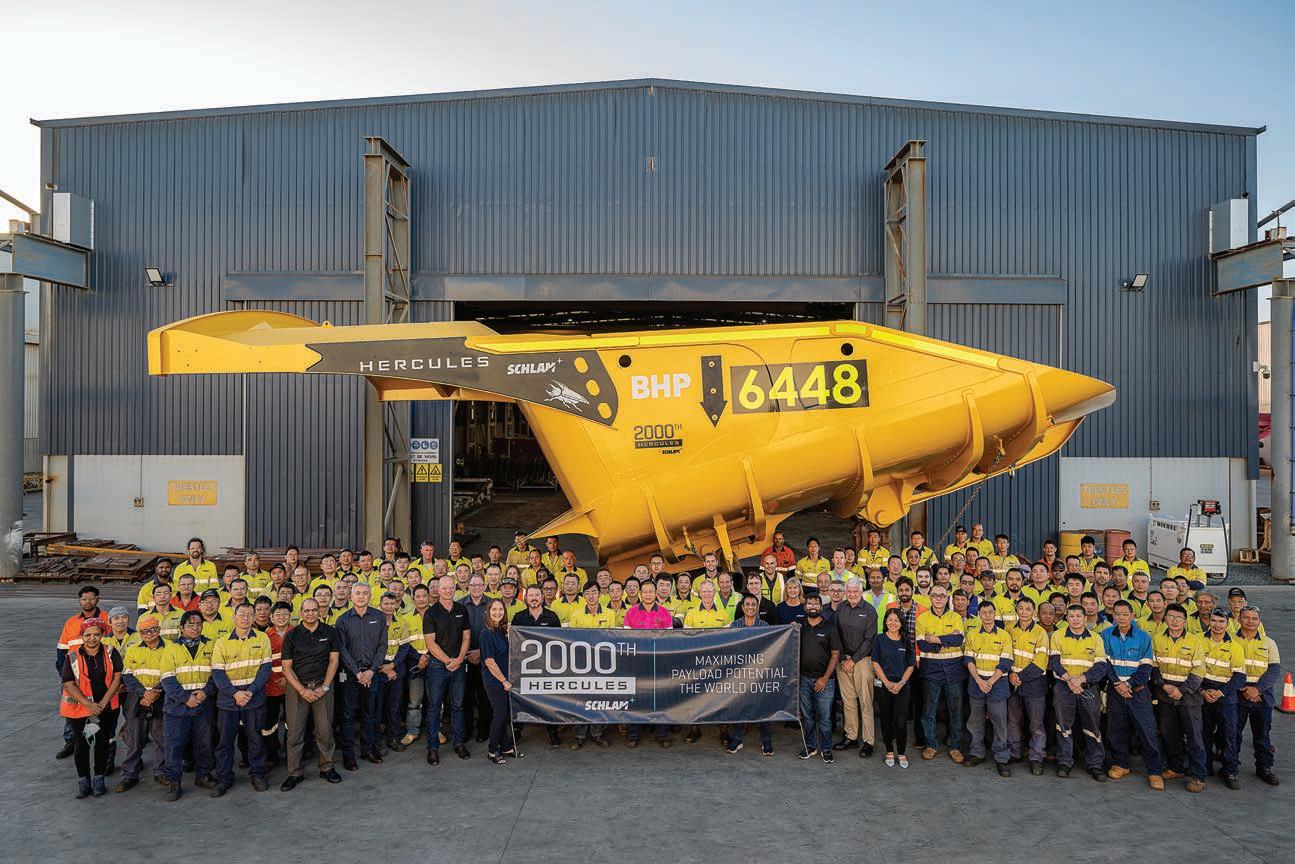
A HERCULEAN ACHIEVEMENT
WA MINING PRODUCT AND SERVICES SUPPLIER SCHLAM REACHED A SIGNIFICANT MILESTONE WITH THE DELIVERY OF ITS 2000TH HERCULES DUMP TRUCK BODY.
Schlam celebrated the recent achievement of its 2000th Hercules dump truck body with the completion of Hercules A2000, which the company called a testament to its “dedication to excellence and innovation in mining equipment”.
The body was recently transported to a BHP mine site in the Pilbara to join another 300-plus Hercules bodies in the BHP Western Australia Iron Ore (WAIO) fleet.
The commemoration of the 2000th Hercules dump truck body marks a historic moment for Schlam. Employees from various departments gathered to celebrate the milestone and reflect on the company’s continued success.
Schlam Payload Asia-Pacific managing director Hendrik Mueller expressed his pride in the team’s effort.
“It was great to see our extended team collectively celebrating an important milestone in our company history, one that they all played a part in,” he said. “The collective pride was also a testament to our principle of working ‘stronger together’.”
Maximising payload through innovation
Innovation and advanced engineering design have played a big part in Schlam’s success, particularly with its Hercules open-cut dump bodies, which continue to deliver significant payload benefits for miners around the world.
The Hercules dump truck body, first manufactured in Australia in 2003, has earned a reputation for its performance, quality and reliability. With its unique curved design and advanced use of materials, the Hercules offers miners significant advantages, including a demonstrated payload increase above 10 per cent, according to Schlam.
The Hercules is designed to reduce the weight of all non-wearing areas, utilising thicker and harder grade steel in high-wear areas and optimising lighter materials for structural components, all without sacrificing structural integrity.
“A lighter and stronger dump body enables miners to carry more ore, which not only translates into increased payload, but also savings in terms of fuel and ultimately carbon emissions,” Mueller said.
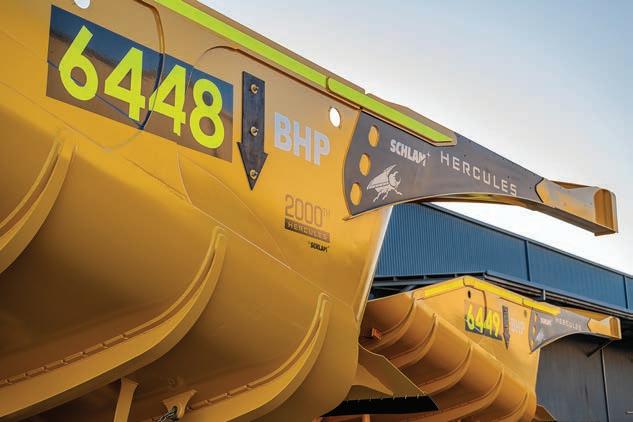
Hercules dump bodies are also regarded for their extended service life, with the company assisting its customers to mitigate the issues of wear common in hard rock mining environments.
“Hercules bodies generally have a longer service life, which can be further extended with the right wear mitigation strategy,” Mueller said. “In fact, Hercules A0071 was recently decommissioned after operating in the Western Australian goldfields for 16 years.”
Built with miners, for miners Schlam believes its success in reaching its 2000th Hercules dump body milestone can also be attributed to its commitment to delivering exceptional customer service.
“Hercules is built for miners, with miners,” Mueller said. “Our sales and technical support teams work closely with our customers to ensure that every Hercules is uniquely designed and built to meet the specific site requirements.
“We’re also growing our sales and after-sales teams, ensuring that customer
service is exceptional at every step of their experience with Schlam.”
For Schlam, innovation stems from researching and addressing the new challenges and opportunities presented in the mining industry.
“We do this by working closely with our customers, with our continual learning being the key part of our innovation,” Mueller said.
“So when we celebrate a milestone such as this, the celebration also extends to our valued customers.”
Meeting a growing global demand
Trusted by Tier 1 mining companies, contractors and original equipment manufacturer (OEM) truck suppliers worldwide, demand for Hercules dump bodies continues to increase globally.
After the first Hercules was manufactured in Australia in 2003, it took 17 years to reach the 1000th milestone, with the 2000th body built just four years later.
Hercules dump bodies are now actively engaged in mining operations across six continents. From the scorching deserts of Australia to the frigid plains of
Northern Star, Newmont, and other major miners, Hercules is set to continue along this upward growth path.
To meet the growing demand, and to continue its dedication to satisfying customer needs, Schlam has worked to improve its manufacturing capabilities.
In 2023, the company implemented LEAN manufacturing principles, similar to those used by leading automotive and aircraft manufacturers. In the same year, the company invested significantly in automation, including a manufacturing execution system to integrate and streamline its production operation.
Schlam introduced robotics into its manufacturing operation in 2024, with other innovations ready to be implemented.
These initiatives have not only improved manufacturing efficiencies and working environments but have created more jobs and brought Schlam’s manufacturing capabilities to worldclass standards.
“We have created efficiencies in our manufacturing processes through the introduction of robotics, automation, and LEAN manufacturing principles, all the while maintaining our focus on safety,
and Mexico, allowing the company to quickly respond to the demands of customers in key international markets.
Schlam opened a dedicated Americas office in Tucson, Arizona, in 2023 to better serve its customers within the region.
Last year also saw Schlam transport seven Hercules bodies across China to supply a leading miner in Kazakhstan. The 6000km project was keenly viewed by a Chinese TV audience of 36 million people.
“In a relatively short time, we’ve developed into a truly global company,” Mueller said.
The achievement of delivering the 2000th Hercules dump body underscores Schlam’s commitment to driving efficiency and productivity in the mining industry. It also reaffirms the company’s commitment to partnering with its valued customers.
As Schlam looks towards the future, the company remains steadfast in its mission to make mining equipment more productive.
With a legacy of problem-solving engineering dating back to its founding in 1996, Schlam continues to push boundaries and set new standards in the mining industry. AM
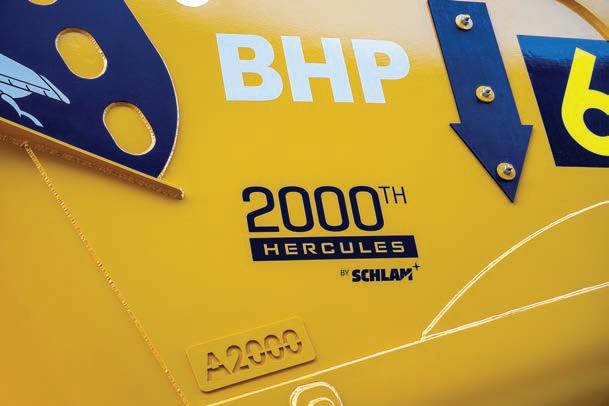
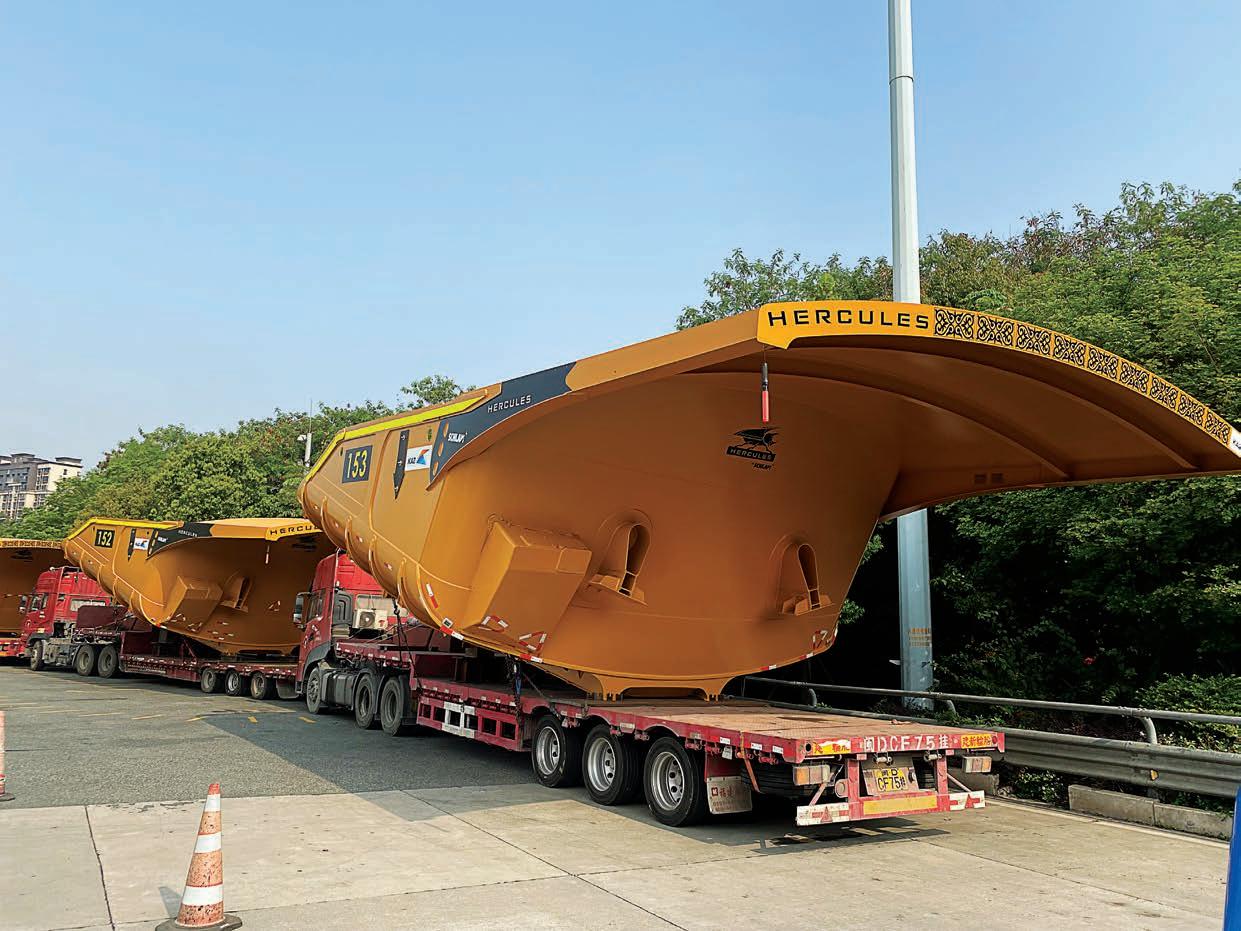
THE HERCULES DUMP BODY FEATURES A UNIQUE CURVED SHAPE.
REDEFINING THE DECARBONISATION NARRATIVE
HYDROMULCHING AND DUST SUPPRESSION ARE VITAL PARTS OF REHABILITATING A MINE. AUSTRALIAN MINING LOOKS AT HOW COMPANIES ARE MAKING THESE PRODUCTS MORE SUSTAINABLE.
Revegetation and rehabilitation are essential parts of the mining life cycle.
But in order for a mine’s rehabilitation to be truly effective, the products used in the process must be environmentally friendly.
Australian Mining sat down with Global Soil Systems, its parent company B & K Revegetation & Landscaping, and rehabilitation product manufacturer Vital Chemical to discuss the sustainability of two vital products used in mine rehabilitation: dust suppression and hydromulching.
Dust suppression
A key process in the mining industry, dust suppression is used to reduce negative environmental impacts and improve air, water and soil quality.
Miners can use a variety of methods from water spray systems to chemical suppressants to keep the air healthy.
But with so many types of dust suppression methods available, it can be hard to know where to start. Vital Chemical breaks it down.
“At our core, we are scientists,” Vital Chemical director Paul McMullen told Australian Mining. “We substantiate everything we do with science, and we make clean chemicals for the environment and for sustainable purposes.”
While many may not automatically think of sustainability when hearing the word ‘chemical’, Vital Chemical is keen to change that narrative.
“We’ve had a direct shift in the last 20 years and now 90 per cent of our raw materials are sourced in Australia,” McMullen said.
“By domestically sourcing the raw materials for dust suppression, we are automatically decreasing carbon emissions while maintaining a higher standard of quality control.”
Dust suppression methods that meet site obligations and productivity constraints while being environmentally friendly can be hard to deliver, but Vital Chemical is up for the challenge.
B & K REVEGETATION & LANDSCAPING APPLIES VITAL CHEMICAL’S VE GRO-MATT REVEGETATION SOLUTION.

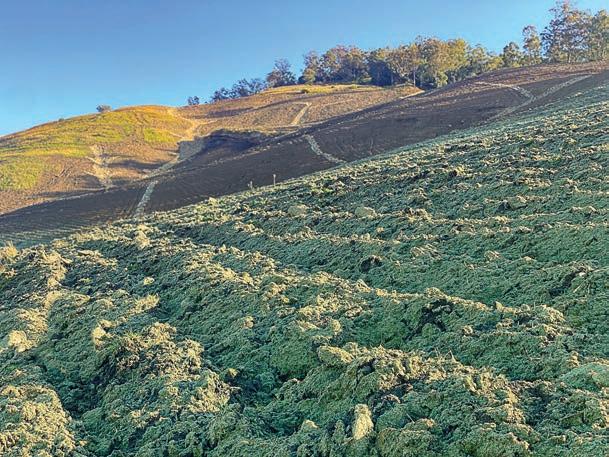
“The mines we rehabilitate cover large areas, which means the carbon farming opportunities are great. Mines are really starting to see this, and they’re turning to more sustainable dust suppression methods as a result.”
Hydromulching
Perhaps less well-known than dust suppression (but no less important), hydromulching involves spraying a mixture of water, seed, fertiliser and mulch to revegetate damaged soil.
Having specialised in hydromulching since 1983, B & K have worked hard to ensure this crucial rehabilitation process is as sustainable as possible.
“Made from a by-product of forestry materials, our hydromulch is a mix of wood fibres, fertilisers and seed which is mixed in a tank and then sprayed onto
and a bed for the new seed to grow on.”
Instead of planting and growing a whole forest just to cut it down for mulch, B & K makes hydromulch out of waste product.
“It could be timber that doesn’t meet housing or building specifications,” Nebauer said.
“Instead of that being thrown away or discarded, it’s made into a valuable resource.”
This process creates a continuous lifecycle with no end date.
“We’re growing trees from wood fibres that can then be used to produce more wood fibre that can then be used to produce more trees,” Nebauer said.
“The decarbonisation outcome from that process is really important in the effort to cut emissions.”
As the implications of climate change make themselves more known, mines
much as possible. KPMG’s ‘Mining Risk
KPMG partner risk consulting Caron Sugars said the finding represented an opportunity for the mining industry to set strong climaterelated goals.
“There is opportunity ahead for Australian miners to focus not on extraction but also processing, with Federal Government support being provided for critical minerals,” Sugars said.
“This is a key part of the response to climate change risk and reflects the positive outlook for the sector longer term in both traditional mining and critical minerals.”
McMullen and Nebauer agree.
“When you think about what the sector can do next to keep up with its decarbonisation goals, the answer is pretty simple: use more products that are sustainable,” McMullen said.
“There has been a lot of improvement in the last two to three years, but there can always be more.”
Nebauer said this can be as simple as ensuring products used in rehabilitation are sourced domestically.
“It really is that simple,” he said.
“It doesn’t make sense to source something that we can get here from the other side of the world.
“Start small, start with making sure your products are locally sourced and made, and then watch your goals fall into place.” AM
NEXT GENERATION BEST PRACTICE for fluid contamination control
MagShield is addressing the gap left by standard media filters to combat ferrous contamination in the mining industry.
Ferrous contamination has been a longstanding issue in heavy industries for decades. As metal components undergo regular wear and tear, microscopic iron particles seep into essential fluids that are vital for operating critical mining equipment.
This contamination wreaks havoc on machinery systems, leading to significant damage and eventual breakdown.
Now, there's a new, enhanced, and complementary solution for preventing ferrous contamination.
Capture contaminants as small as 0.1 micron
Hold up to 950 grams of ferrous material
Stop 99% of ferrous contamination from recirculation

0 flow rate impact and less than 2 PSI pressure drop under normal operation
Innovative Products:
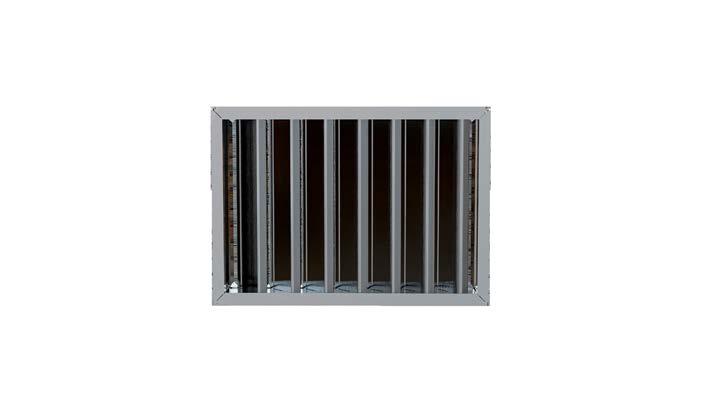
The MagShield® Difference is: Our
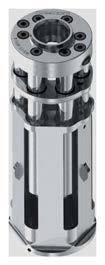
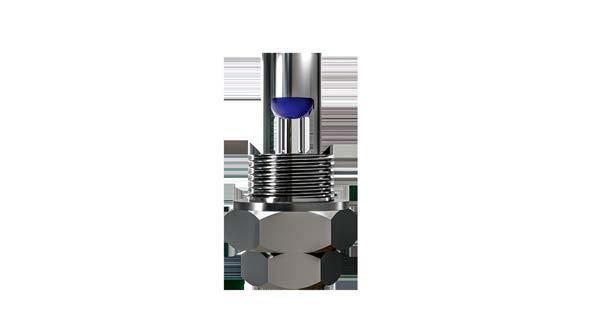
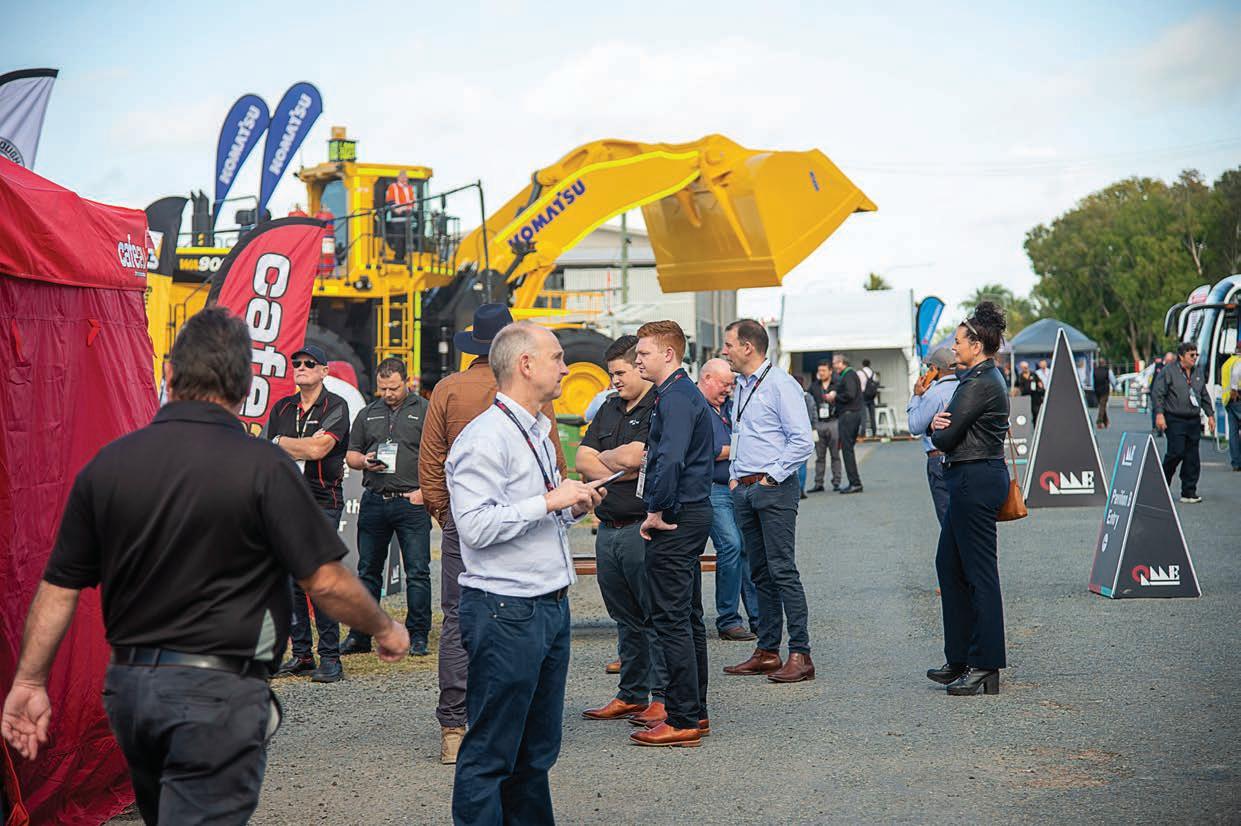
UNVEILING THE FUTURE
THE COUNTDOWN IS ON FOR THE HIGHLY ANTICIPATED 2024 QUEENSLAND MINING AND ENGINEERING EXHIBITION.
As the Australian mining industry embraces a new frontier in technology and innovation, the 2024 Queensland Mining and Engineering Exhibition (QME) is set to be more important than ever.
Held from July 23–25 in Mackay, QME has everything for mining professionals who want to strengthen their business, from finding new suppliers to making new connections and learning from experts.
QME is not your typical mining event. It’s the leading mining and engineering event in Queensland and the largest regional mining exhibition in Australia, giving QME attendees access to more than 300 mining suppliers, free-to-attend seminars, and the opportunity to connect with industry peers from across the sector.
Australian Mining caught up with QME exhibition director Samantha Martin to get a sneak preview into this year’s event.
What can attendees expect at QME this year?
This year’s QME is on track to be the largest in over a decade. Attendees will have the opportunity to see over 300 suppliers showcasing the latest in equipment –and by equipment, I mean some really big equipment –and technology, from autonomous haulage systems to augmented reality in mining operations, as well as suppliers showcasing the latest tools, safety, wear parts, consumables and so much more.
We also have a new focus on decarbonisation and renewable energy technology, where attendees can find smart and sustainable solutions that can help mining companies with their environmental, social and governance (ESG) goals.
You mentioned big equipment. Can you tell us more?
I don’t think there has ever been this much equipment at QME. It is going to be operational Tetris to get these pieces all in.
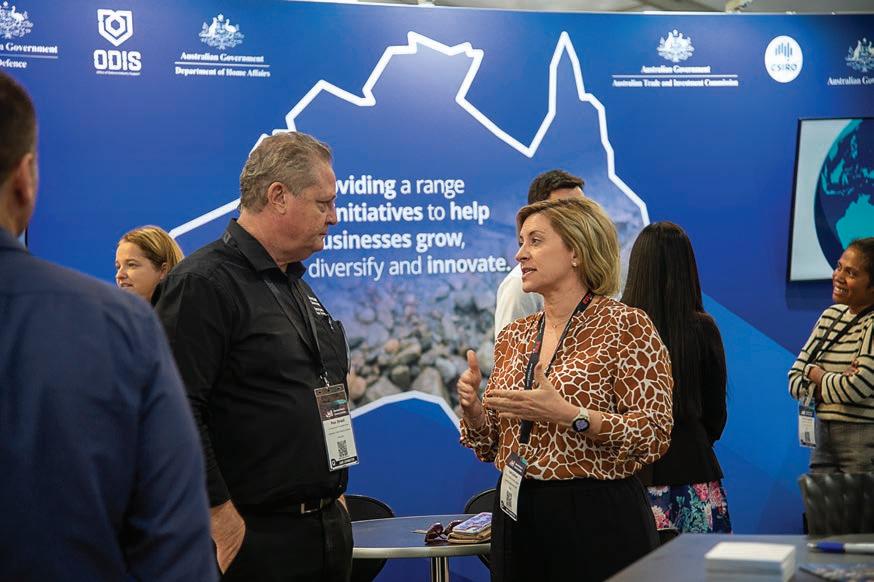

And while I would love to tell you everything we have coming; I have been sworn to secrecy for the moment as there is some new things being unveiled at QME.
What I can say is you will see some impressive things from Hastings Deering, Komatsu and Hitachi.
What networking opportunities are in store this year?
The QME opening party, which is once again sponsored by Hastings Deering, will be held on Tuesday July 23 on-site at Mackay Showgrounds from 5.00pm.
We invite all visitors and exhibitors to stick around for a drink. It’s a great way to catch up with people you know from the industry, as I am sure there has been a few shirt changes since the last event.
You also need to block out the evening of Wednesday July 24 for the Queensland Mining Awards. This amazing event is like the Oscars for the Queensland mining industry. Organised by the Bowen Basin Mining Club in partnership with the Queensland Resources Council, this is a celebration of mining excellence across Queensland.
What else can people see and do at QME?
Alongside the 300 suppliers, QME will host a seminar series that has been sponsored by Komatsu.
We will have themes covering the future of mining, diversification, critical minerals, smart technology, clean energy, occupational health and safety, and the investment outlook.
You will have the chance to hear from leaders from mining companies, consultancy groups and leading suppliers. There will also be ministerial attendance this year which, given it is an election year in Queensland, will create some interesting discussions.
Some of the big names speaking at this year’s seminar series are Federal Resources Minister and Minister
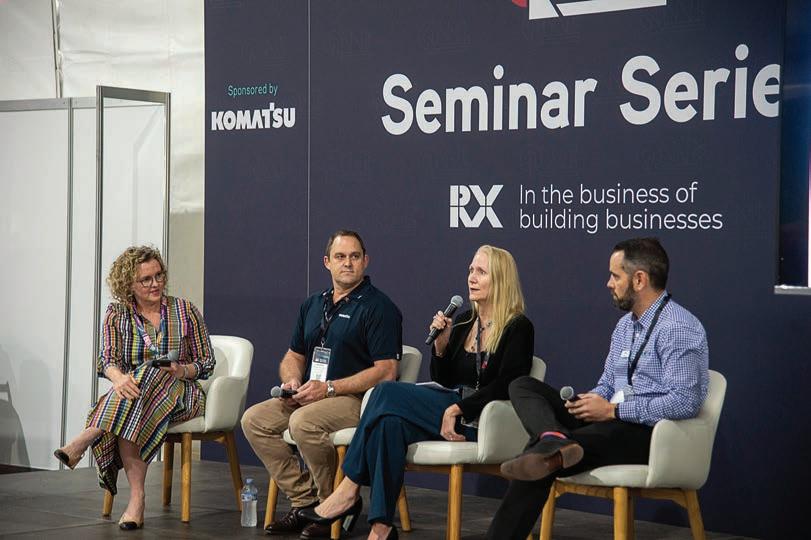
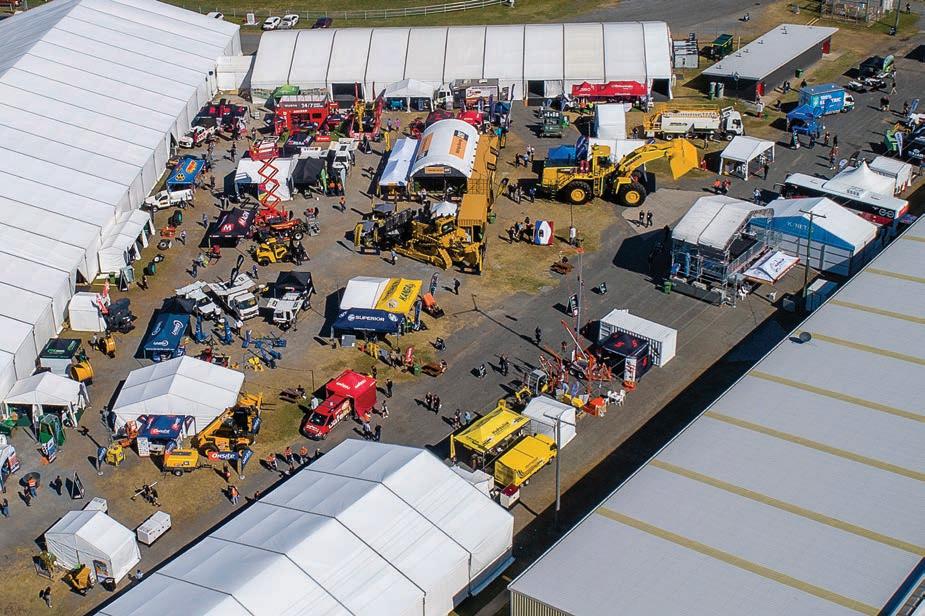
for Northern Australia Madeleine King, the Queensland Minister for Resources and Critical Minerals Scott Stewart, and the Queensland Shadow Minister for Natural Resources and Mines Dale Last.
Queensland Resources Council chief executive officer Janette Hewson and the Department of Resources directorgeneral Warwick Agnew will also speak at QME 2024.
The Decarbonisation Program will be the key focus on Wednesday July 24.
Decarbonisation Accelerated – a partnership between the Resources Centre of Excellence, Greater Whitsunday Alliance, and Local Buying Foundation – will deliver a one-day program that showcases the growing decarbonisation imperative in mining operations and associated supply chains.
We also have the largest line-up of mining companies and contractors exhibiting at QME this year. The likes of Anglo American, BHP and BMA, Bravus, BUMA, Glencore, MacKellar Group and Whitehaven Coal will appear at the expo. These companies are eager to talk about their job vacancies, engage with suppliers at the exhibition, and speak to the industry face to face.
Why should people come along to QME?
I have been running events for nearly 20 years across numerous sectors and I will be the first to admit that I might be a little biased, but QME is the best event in the country.
There is just such a great buzz around town when QME takes over Mackay and there is no other event where you
will see this much equipment next to this many suppliers.
You can reconnect with current suppliers or find new ones, you can hear directly from some of the smartest people in the industry, and better yet you can connect and build relationships with so many people over the three days.
It doesn’t matter if you are on the tools, driving the trucks, managing a site or heading operations; QME has something for everyone in the mining sector. AM
The Queensland Mining and Engineering Exhibition will be held from July 23–25 at the Mackay Showgrounds. The exhibition and seminar series are free to attend, but visitors are encouraged to register online ahead of the event at queenslandminingexpo.com.au
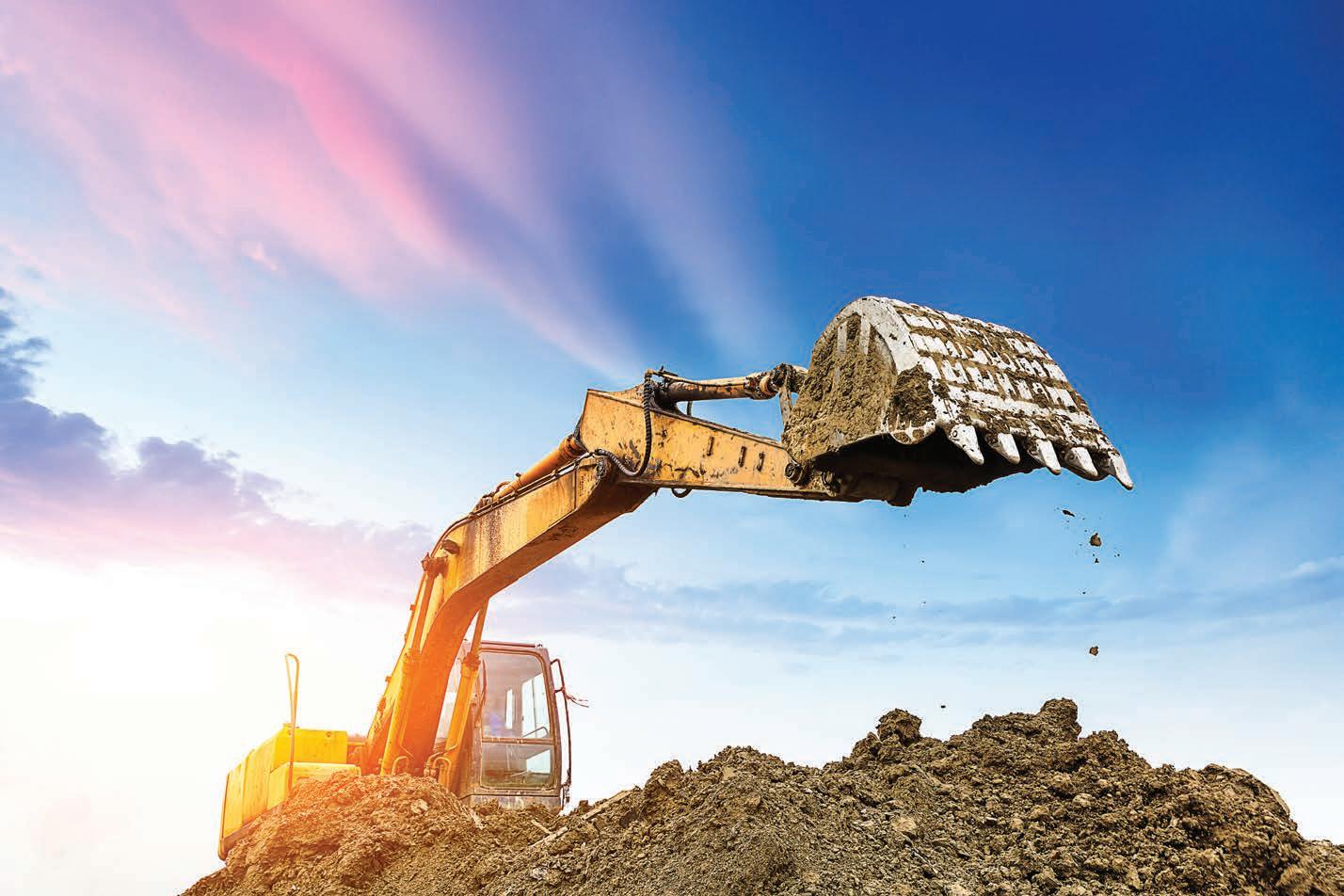
TALKING MINING IN PNG
AUSTRALIAN MINING WILL BE ON THE GROUND AT THE UPCOMING 2024 PNG INDUSTRIAL AND MINING RESOURCES EXHIBITION AND CONFERENCE IN PORT MORESBY.
From new mines to critical minerals, the Papua New Guinean resources sector is set to continue thriving well into the future.
The 2024 PNG Industrial and Mining Resources Exhibition and Conference (PNG Expo) will be the premier event for industry professionals to discuss the latest developments in the Pacific nation.
Australian Mining takes a look at some of the top talking points.
Critical minerals
With its vast reserves of copper, cobalt, nickel and mineral sands, Papua New Guinea is well-placed to help provide the critical minerals necessary for the world’s transition to net-zero.
Mayur Resources has been working to get its lime and mineral sands project up and running to help strengthen supply. The company’s Central Lime Project is located along Papua New Guinea the coast near Port Moresby and was recently bolstered by a $9.4 million funding commitment.
“This capital injection is a vote of confidence in our ability to deliver high-value, sustainable projects,” Mayur managing director Paul Mulder said.
“It enables us to continue progressing the early development works at our Central Lime Project, setting a
solid foundation for the commencement of construction.”
Mayur is aiming for the project to become Asia-Pacific’s first carbonneutral cement and lime producer.
It’s this sort of innovative planning that will be on show at the PNG Expo in Port Moresby from July 3–4.
“PNG Expo will be the platform to engage and drive transformative changes towards a sustainable future,” show director Lauren Chartres said.
“Our mission is to equip the industry with the right tools.”
Education and training
The name Ok Tedi Mining (OTML) often goes hand-in-hand with education, training and apprenticeship opportunities in Papua New Guinea.
The start of 2024 saw OTML deliver more than $121,000 in scholarships, welcome 22 new apprentices, and pledge to donate vehicles and an analytical chemistry laboratory facility at PNG University of Technology.
The scholarships, OTML’s most recent initiative, have seen 10 thirdyear university students supported with full tuition and boarding for the year, plus a book allowance and stipend, travel assistance, industrial training and an offer into the two-year graduate development program on completion of studies.
“The program aims to assist university undergraduate students with school fees and other associated costs while ensuring OTML maintains an industry–institution relationship with respective universities that provide graduates into its training programs and workforce,” OTML said.
Elsewhere in the resources sector, Kumul Petroleum’s training entity Kumul Petroleum Academy is building a new facility to expand its coaching and employment capabilities.
“We are passionate about investing in programs and projects that will upskill and develop our young Papua New Guineans so that they are ready for the projects that are coming online now,” Kumul Petroleum managing director Wapu Sonk said.
The Kumul Petroleum Academy is expected to open within two years and will have the capacity to train 350–400 trainees.
Current projects
The restart of the Porgera gold mine has been in the news a lot recently, and for good reason.
Owned by Barrick Gold, the Porgera mine is located in the Enga Province of Papua New Guinea, about 600km northwest of the capital of Port Moresby.
The Papua New Guinea Government backed the restart
throughout 2023 and the mine was able to pour first gold in February 2024, with Prime Minister James Marape on hand to witness the milestone.
“This first gold pour is the outcome of the (Papua New Guinea) Government, New Porgera Limited, Enga Provincial Government, and mine-affected communities working together,” Marape said at the time. “This is teamwork.”
Enga landowners, the Enga Provincial Government and the state will receive a combined equity share of 51 per cent from Porgera.
In the energy sector, the PNG LNG (liquefied natural gas) project is ramping up, with Santos selling its five per cent stake to Kumul Petroleum.
The $US19 billion project is an integrated development that includes gas production and processing facilities that extend from the Hela, Southern Highlands, Western and Gulf provinces to Port Moresby in Central Province.
As Papua New Guinea’s national oil and gas company, Kumul is already a partner in the PNG LNG project.
These key projects, and much more, will be among the top discussion points at the 2024 PNG Expo, the safest and best place to network, share ideas and learn more about what companies are doing in these spaces.
Tickets can be booked through the PNG Expo website. AM
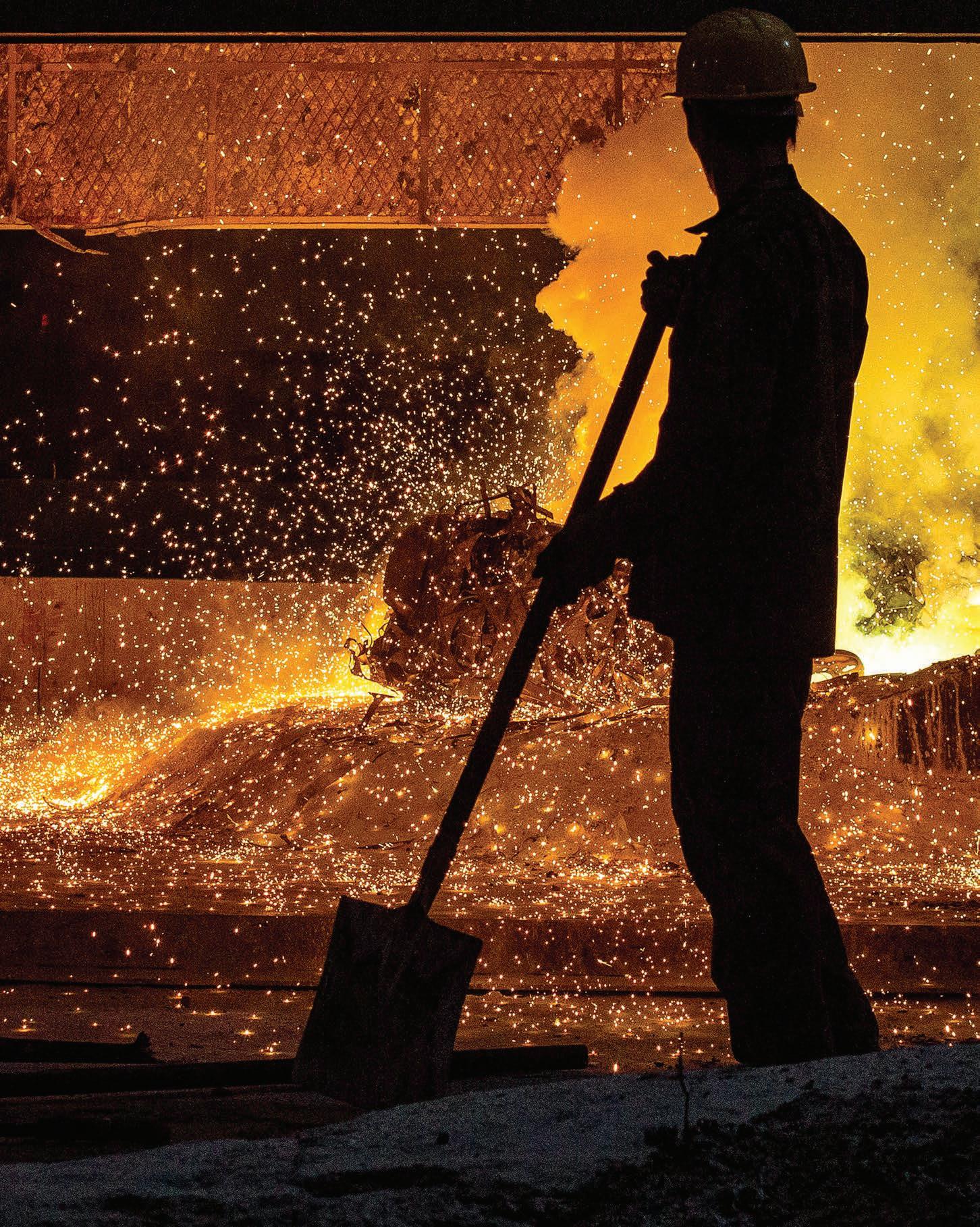
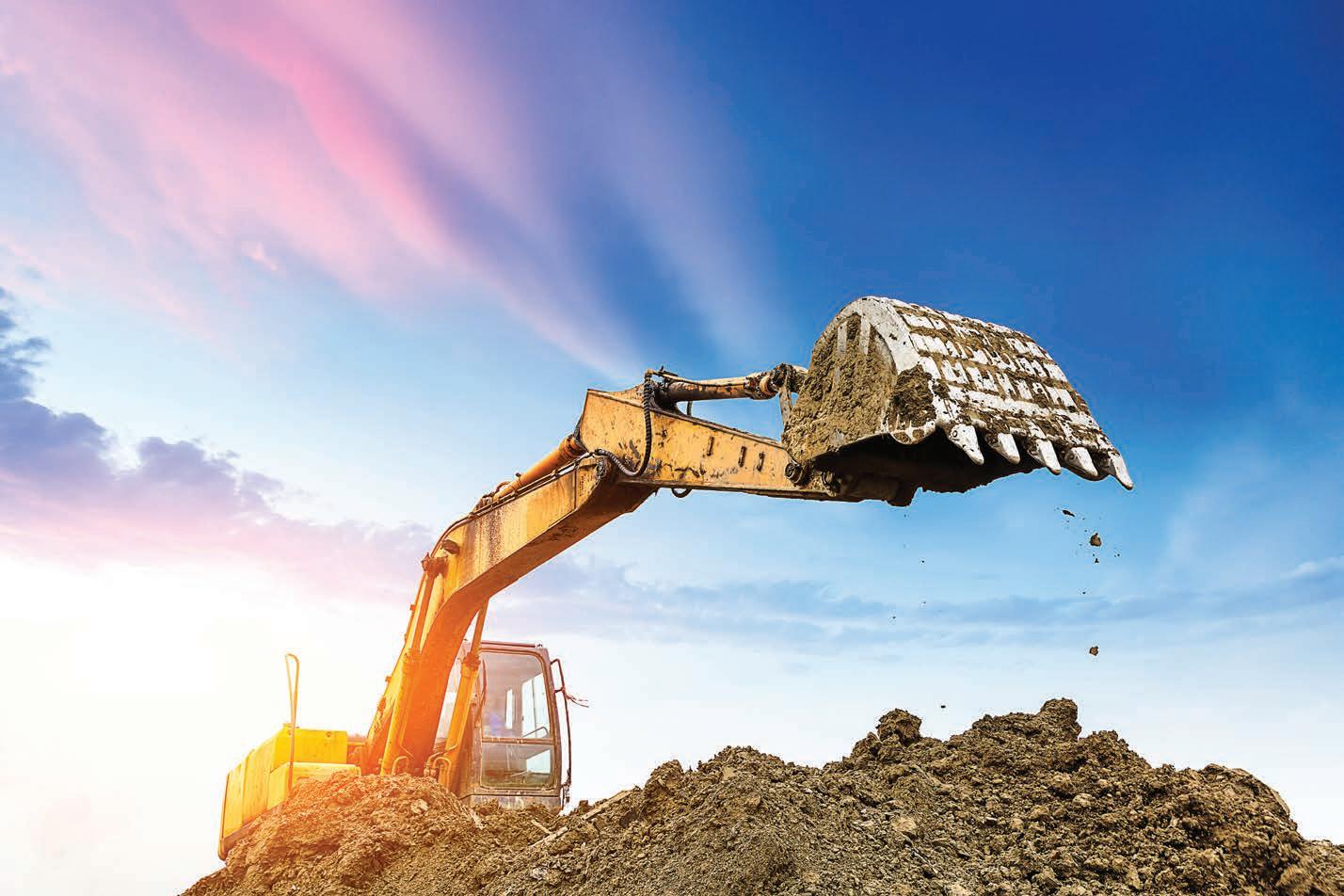
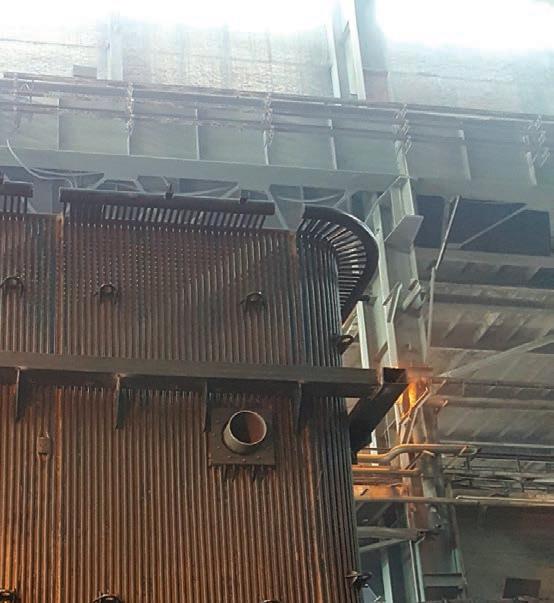
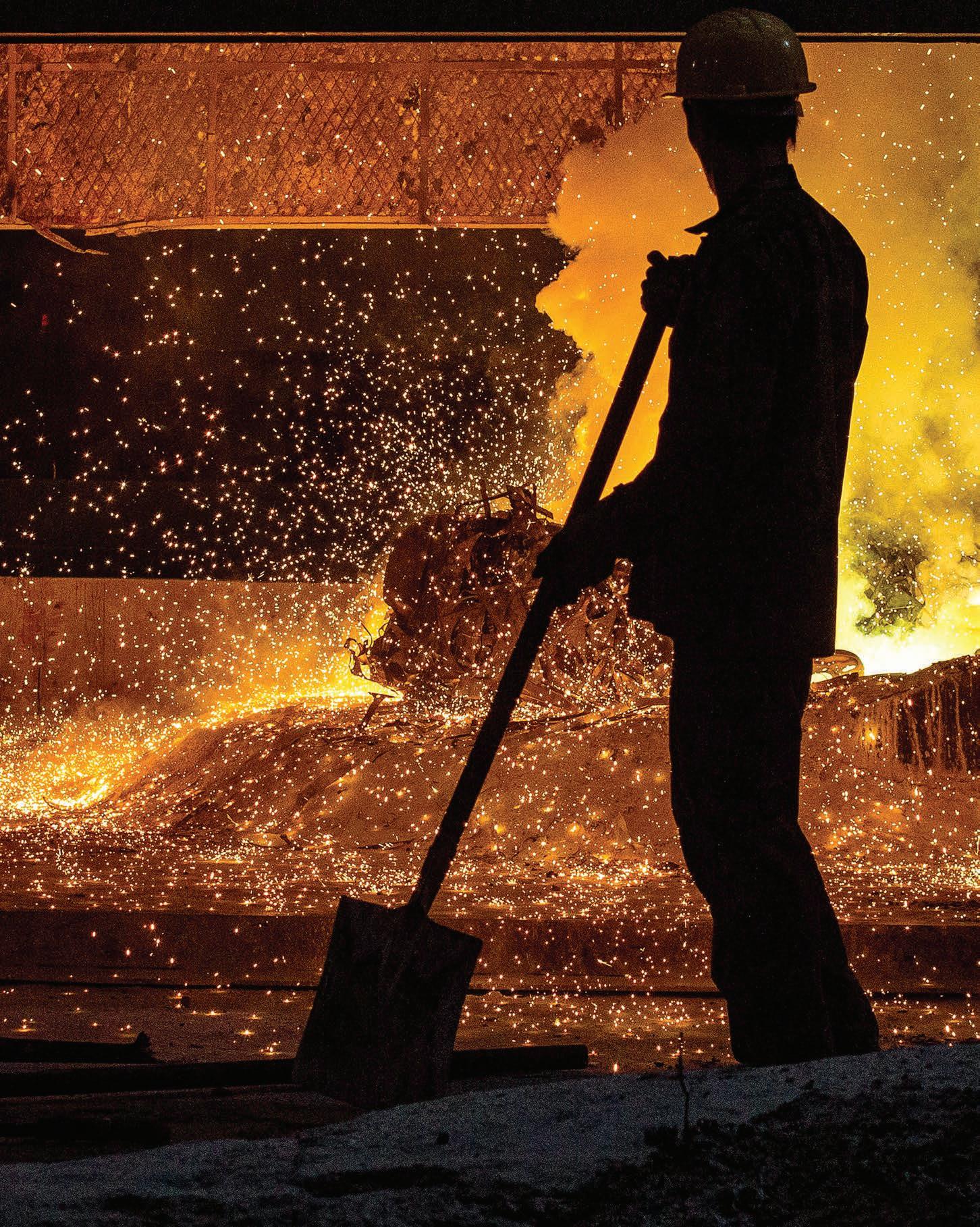
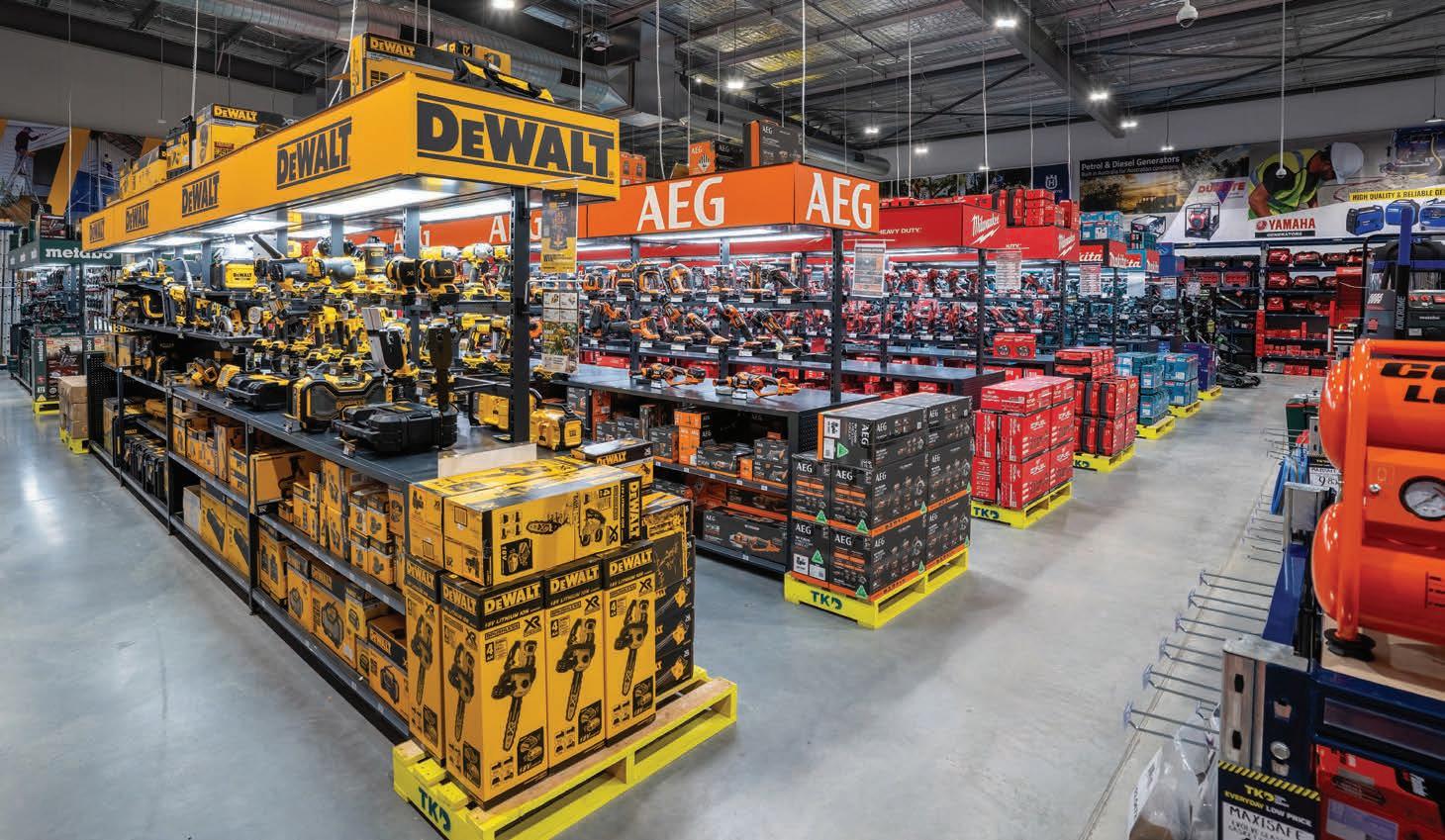
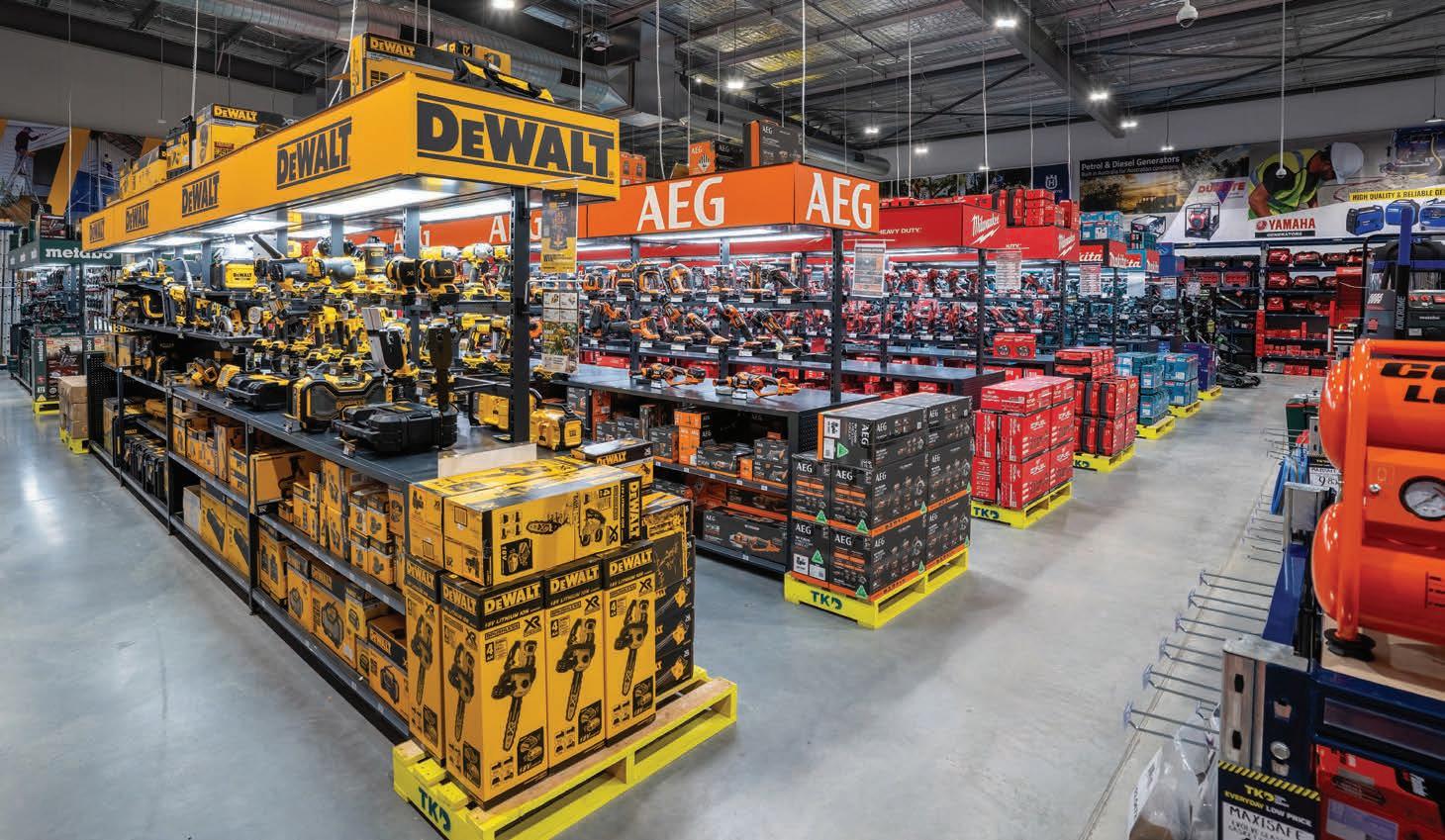
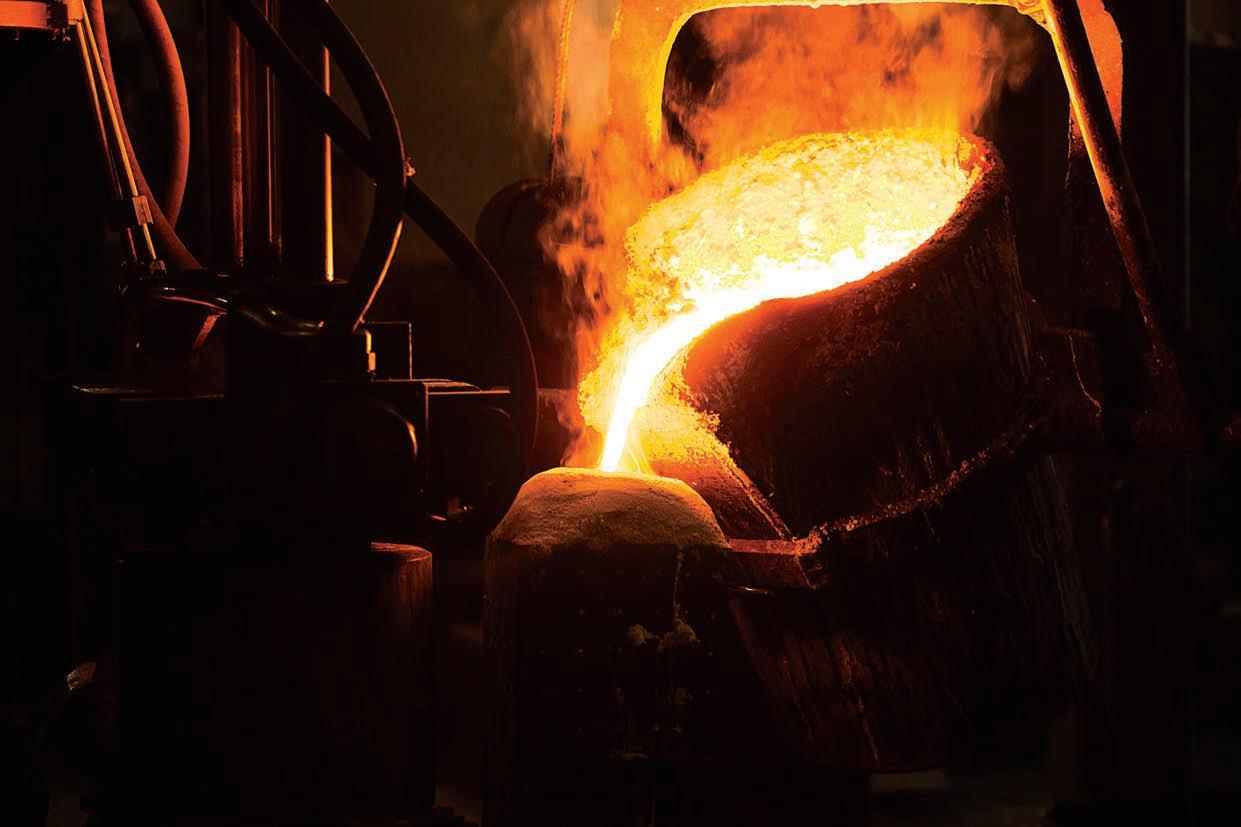
COMING IN HOT
FROM PRE-CONFERENCE WORKSHOPS AND SITE TOURS TO PLENARY SESSIONS AND A PACKED EXHIBITION, MOLTEN 2024 IS SET TO STUN.
As the world transitions to a clean-energy future, pyrometallurgy (the high-temperature processing of metals) might not be the first thing that comes to mind.
But this treatment method plays a vital role in recovering the critical minerals needed for decarbonisation.
This is what will be discussed at AusIMM’s 12th International Conference on Molten Slags, Fluxes and Salts (MOLTEN 2024) when it takes place in Brisbane from June 17–19.
“This year marks the first time since 1997 that the conference will be held in Australia,” conference co-chair and research fellow at the University of Queensland Dr Denis Shishin told Australian Mining.
“This homecoming is significant for the Australian metallurgical community and will foster a strong local presence.”
Dr Shishin has been involved in the chemistry and pyrometallurgy world since he finished high school. As a result, he is a strong advocate for its use in decarbonisation.
“Pyrometallurgical refining of metals such as copper and nickel plays a crucial role in decarbonisation and creating a circular economy,” he said.
“Countries committed to the energy transition must prioritise and promote onshore pyrometallurgical refining with advanced technologies, strict
environmental standards, and efficient recycling practices.
“Revitalising and modernising this sector will be crucial to capitalise on Australia’s natural advantages.”
Dr Shishin sees MOLTEN 2024 as a catalyst for sustainable metal production.
“MOLTEN 2024 will foster collaboration,” he said. “Bringing together industry, academia and government officials sparks innovation in clean metal production for renewable energy needs.
“It also inspires the next generation. By showcasing the importance of molten materials, the conference can attract new talent who will develop the next generation of eco-friendly metal production techniques.”
Although the molten slags, fluxes and salts field may be specialised, Dr Shishin was quick to point out the global nature of the pyrometallurgy community.
“The molten field is a vibrant global network,” he said. “MOLTEN provides a unique platform for researchers from universities around the world to connect with industry engineers, fostering a sense of belonging for a highly skilled professional family.”
MOLTEN 2024 will focus on groundbreaking advancements and practical improvements because, while breakthrough discoveries are exciting, even incremental progress is crucial for the industry.
“All improvements, no matter how small, matter,” Dr Shishin said.
“We want researchers to feel equally proud whether they develop revolutionary new technologies or optimise existing processes to achieve a 0.1 per cent improvement in metal recovery. These seemingly small gains can have a significant cumulative impact on sustainability and profitability.”
As conference co-chair, Dr Shishin expects MOLTEN 2024 to be an especially stellar conference.
“We have reviewed the selected abstracts submitted to the conference, which was followed by a rigorous
process for full research papers,” he said. “This guarantees a program featuring cutting-edge research and valuable insights.
“The design of the conference program was another key focus area. By strategically grouping researchers working on similar topics, we aim to spark dynamic discussions and facilitate collaboration.”
So who should be attending MOLTEN 2024?
“MOLTEN 2024 truly highlights Australian expertise,” Dr Shishin said. “In pyrometallurgy, passion for the field is the only prerequisite.” AM
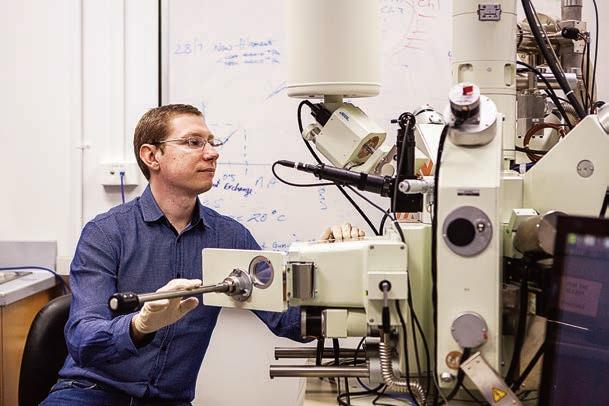
A NEW ERA OF UNDERGROUND BLASTING
Drill and blast is a critical part of mining operations. Indeed, miners have been blasting their way through hard rock to move stubborn earth and access locked orebodies since the 1600s.
But while those pioneering miners of old used gunpowder and gumption, modern drill and blast technology is a lot more sophisticated – and it’s hard to talk sophistication in drill and blast without talking about Orica.
Orica has been refining its recipe for success over the last 150 years, from its founding days supplying Victorian gold mines with explosives to the global footprint it has today.
And with the launch of its new 4D bulk explosives system, the recipe has been improved once again.
The science behind 4D is complex, but at heart it’s a delivery system that tailors explosives energy to the conditions of the hole.
Orica lead engineer – underground technology Sam Evans said that 4D
energy level from a very large selection ranging from RBS (relative bulk strength) 50 all the way to RBS 170.
“With 4D, this can happen on a hole-by-hole basis, or even within the same hole.”
In other words, Orica’s 4D bulk system enables mine sites to achieve an incredible degree of blasting precision.
Another significant accomplishment of the 4D bulk system is its ability to maintain explosive density within drill holes.
“Just like being underwater, the deeper you go, the more the pressure builds,” Evans said.
“It’s the same with standard emulsion; when you pump it into a hole, the density changes in the column of explosives.
“This can change how the energy is distributed in an explosion, which can have unintended consequences.
“But 4D has essentially eliminated this variable, effectively delivering the same energy the whole way through the hole without any changes. This gives engineers the opportunity to select the energy they need and be confident that
multiple different energy levels within the same hole,” Evans said.
“This is important in cases where you want low energy at a shallow depth to protect the hanging wall, and higher energy deeper in the hole.”
A zinc mine in north-west Queensland reaped the rewards of this technology when Orica trialled its 4D bulk system underground.
The trial compared the performance of 4D to standard products, with the aim of helping the site improve ore recovery and reduce dilution (the portion of waste material that gets mixed in with the ore).
“The mine gave us a really good set of baseline data, which showed that dilution was hovering around 11 per cent,” Evans said.
“Using 4D across the extended trial period, we got that down to an average of 3.7 per cent – quite a significant drop.
“We were then able to drive dilution down even lower to two per cent reliably.”
Evans said that going into the trial, it was important for the Orica team to make 4D’s implementation as low impact as possible. This involved substituting
cent, then subsequently stabilise that recovery at 95 per cent.
“The baseline data showed us that the site juggled increasing recovery with lowering dilution – when one was up, the other was down.
“Fortunately, 4D allowed the site to optimise both aspects at once.”
Beyond performance, the 4D bulk system is also simple to operate.
“The control system is designed to take a lot of the manual work out of the operator’s hands, making it much easier to follow their blast design,” Evans said.
“The system automates a significant amount of the process, simplifying the job for an operator.”
Orica’s 4D bulk system is delivering improved orebody recovery, reduced overall explosive consumption, and better fume, vibration and nitrate leaching control to mine sites.

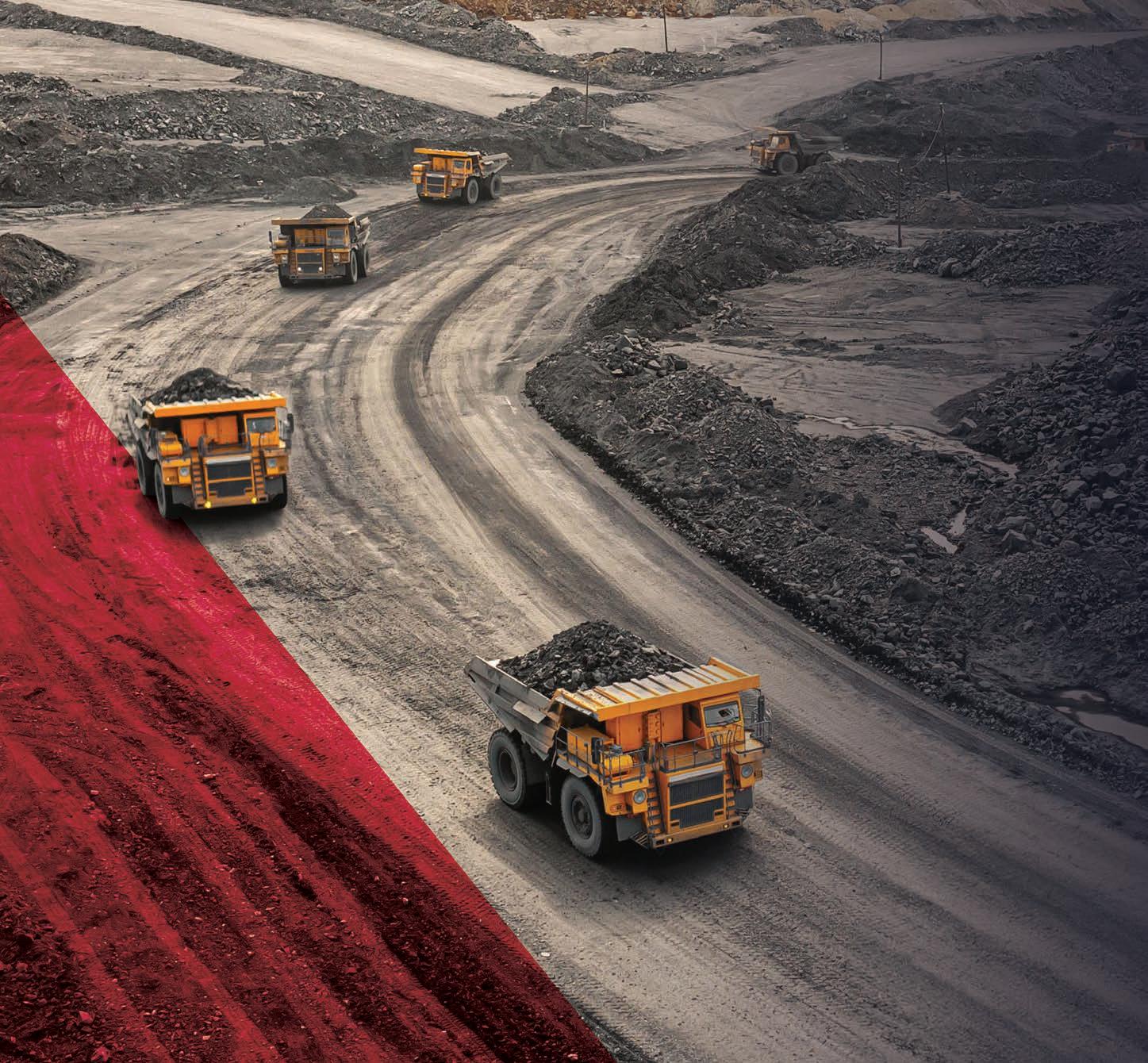
Queensland Mining & Engineering Exhibition
23-25 July 2024 | Mackay Showgrounds
AUSTRALIA’S LARGEST REGIONAL MINING EXPO & SEMINAR SERIES
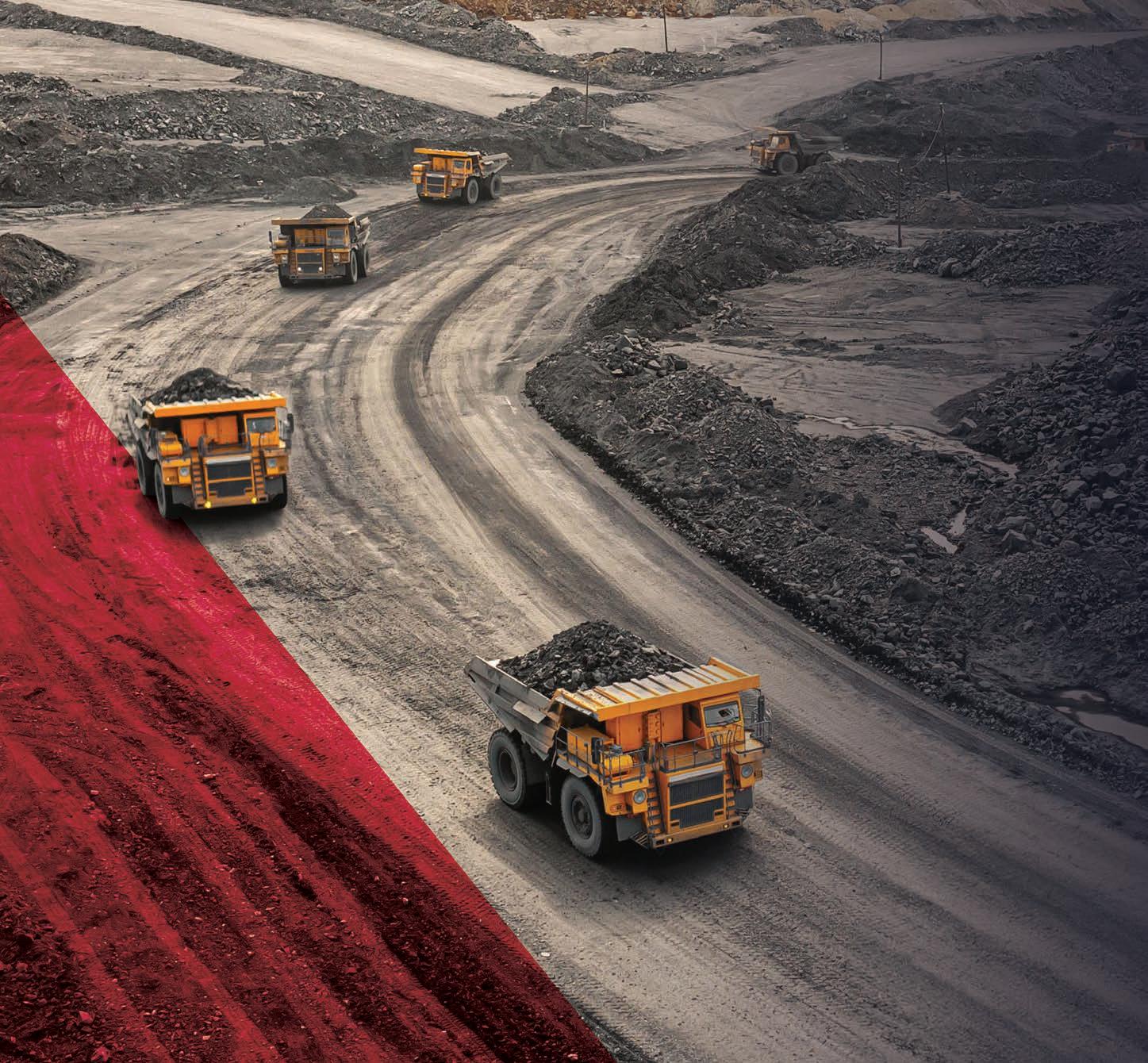
5,000+ Industry Personnel
300+ Leading Suppliers
REGISTER FOR FREE AT QMEEXPO.COM.AU
Industry Supporters:


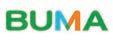
50+ Expert Speakers

ARGYLE LAYFLAT HOSE REEL – WHERE MOBILITY MEETS EFFICIENCY
Crusader Hose leads the way in advanced layflat hose and reel solutions tailored for Australia’s rigorous mining sector.
Crusader Hose’s Argyle hose reel system is an innovative hosehandling solution for layflat hose pipelines.
Made in Australia and revolutionary in its design, the Argyle alleviates the manual labour challenges associated with deploying and retrieving layflat. Engineered for portability, its trailer-mounted construction brings unmatched agility when needed most. Safe and reliable, the Argyle eliminates all heavy lifting and bending over when handling pipelines.
The Argyle features two individually operable reels, fitted inside a heavy-duty crate. Each crate is demountable and is attached onto a trailer.

The Argyle’s crate capacity is up to 200m of an 8-inch layflat hose, and is known to be compact and modular.
Custom trailers are available for heavy-duty use with 4WD-ratings.
• crusaderhose.com.au
WHERE AUTONOMY MEETS EFFICIENCY

THE IMPORTANCE OF SHELTER SOLUTIONS IN MINING OPERATIONS
Allshelter’s fabric shelters are crucial in a mining environment. These highly versatile structures can withstand tough environmental conditions while providing excellent protection. Allshelter’s fabric structures ensure critical equipment remains operational and protected from adverse weather effects.
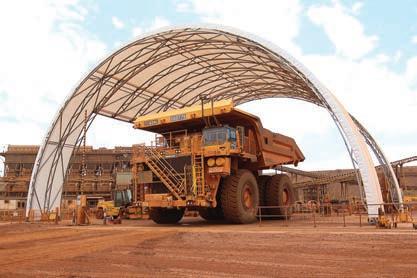
By minimising exposure to rain, UV radiation and temperature fluctuations, Allshelter’s mining shelters help extend the lifespan of assets, reduce maintenance costs, and optimise operational uptime.
With Allshelter’s expansive, flexible mounting options and customisation, its shelters can be tailored to meet specific sizes, layouts, and functional requirements. With optional add-ons, including doors and guttering, Allshelter’s fabric shelters offer a wide range of design possibilities.
The shelter’s frames are made from 100 per cent recyclable steel, and the translucent fabric tensioned cover is environmentally adaptable, energy efficient, and can let natural light in, reducing the need for artificial lighting during the day. With easy installation, dismantling and relocating, Allshelter’s shelters are a great solution to short-term and long-term projects requiring swift pack-up or relocation.
• allshelter.com.au
SANDVIK’S MOST ADVANCED HAMMER TOOL SYSTEMS
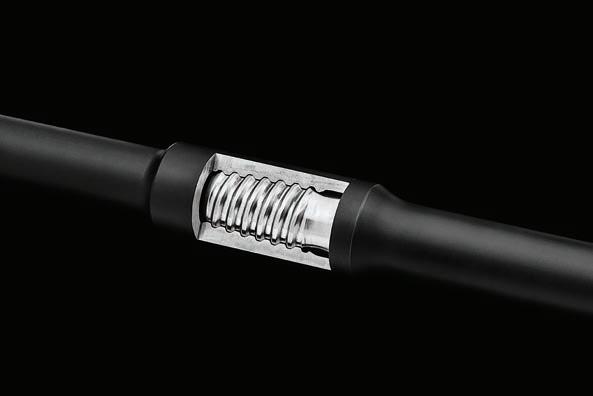
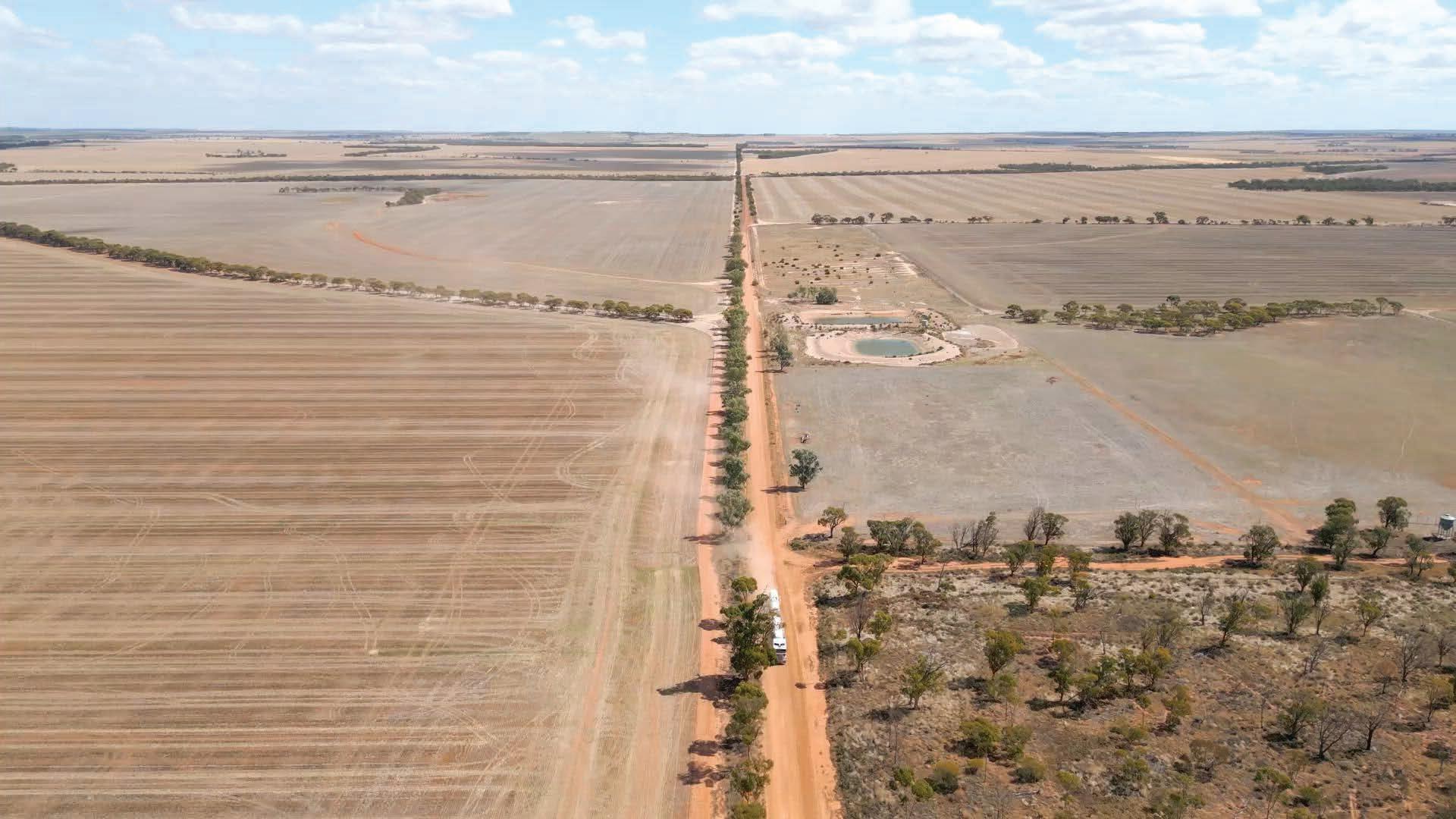
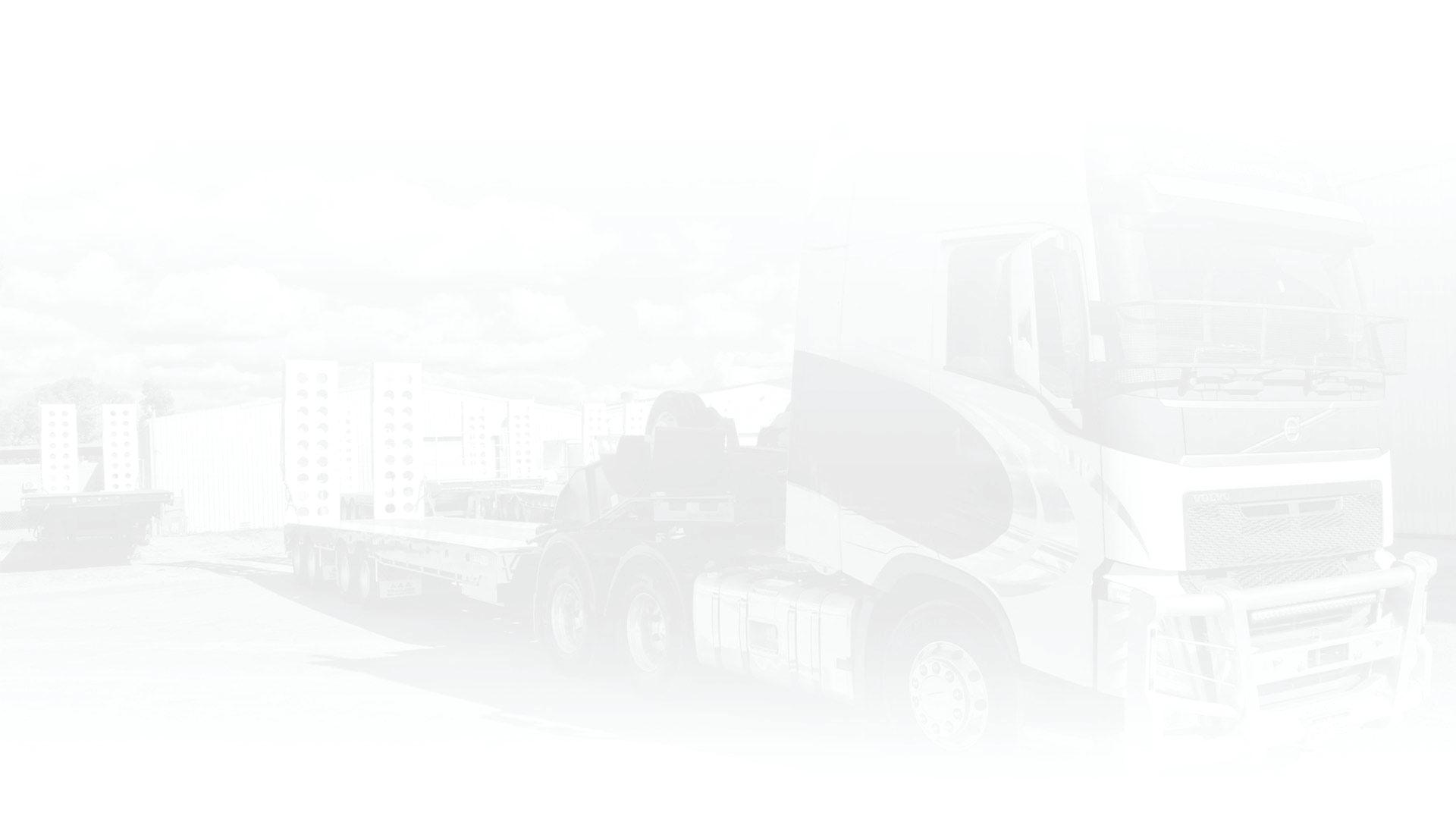
Sandvik has launched its new CT55 and CT67 top hammer tool systems – the most advanced of their kind.
Sandvik’s CT55 and CT67 curved thread systems are both suited for surface mining, while the CT67 system is also suited for underground mining. The design of the CT55 and CT67 top hammer tool systems is intended to increase efficiency and reduce costs while saving fuel and simplifying automated drilling in surface bench and underground long-hole applications.
The design is said to deliver a 15 per cent productivity increase while also reducing fuel consumption by 15 per cent, as faster drilling means less flushing time.
Sandvik’s new curved thread CT range is designed to increase drilling productivity when carrying out underground and surface mining. The stronger geometry that comes with the curved thread design is said to boost tool service life by more than 30 per cent.
• rocktechnology.sandvik/en



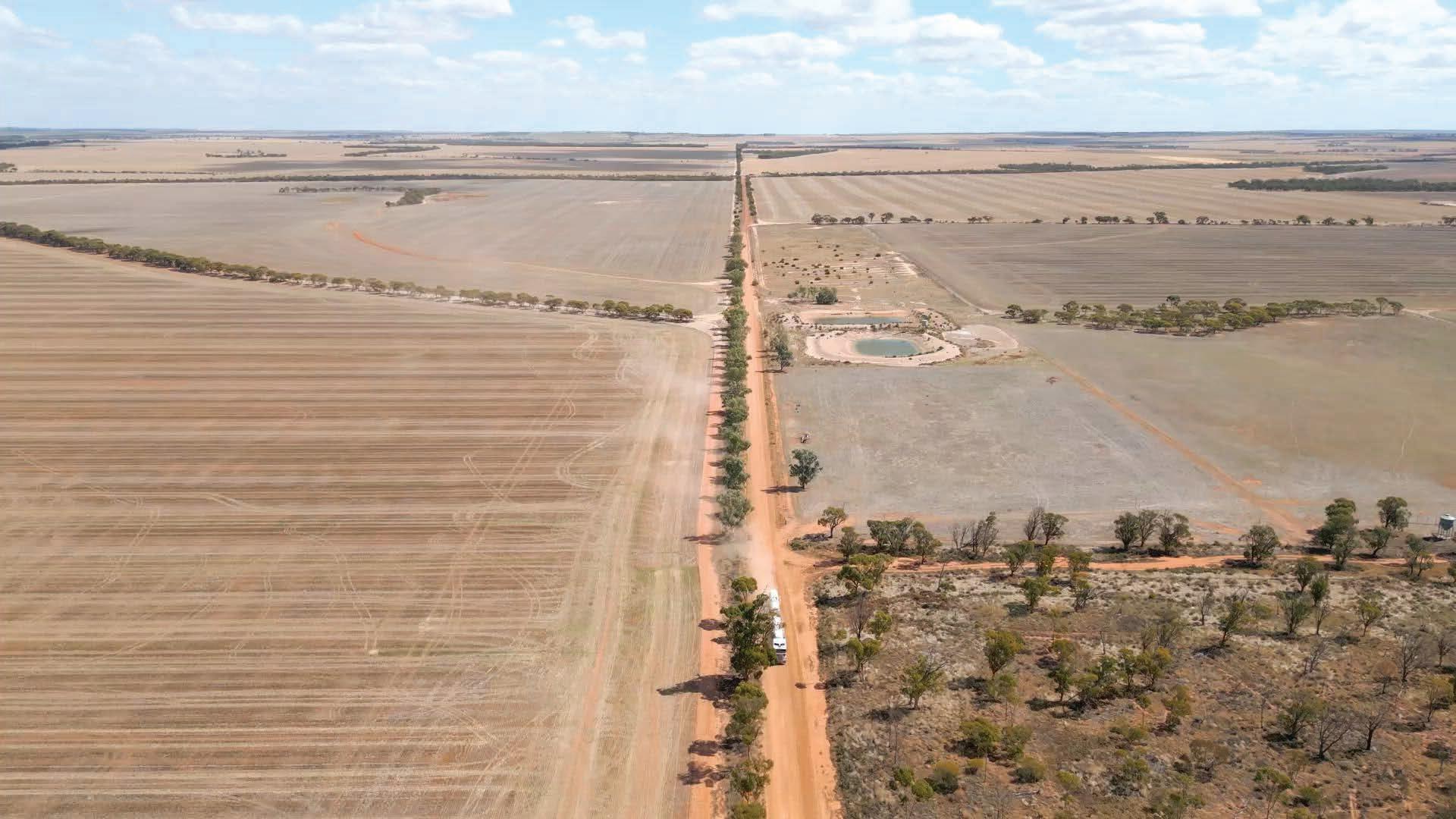

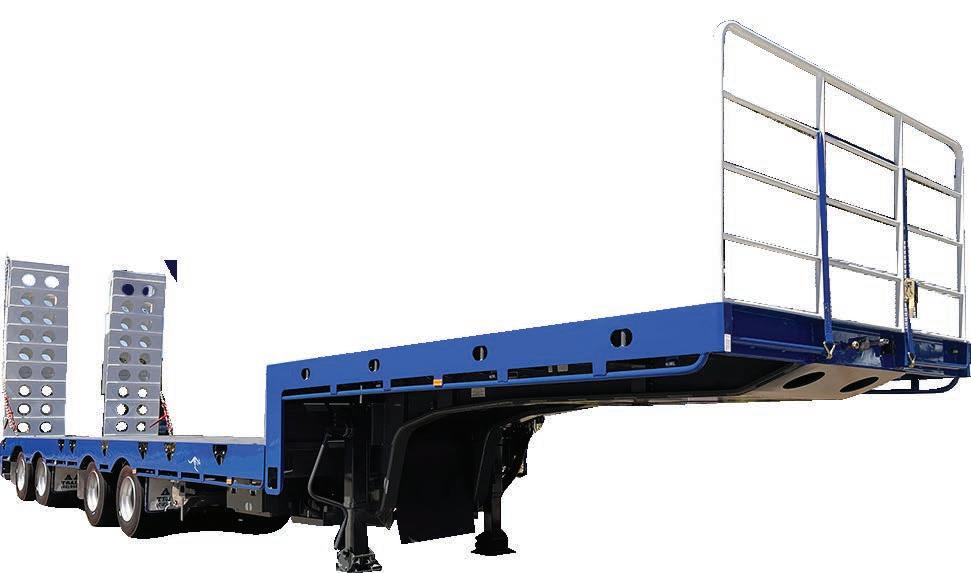
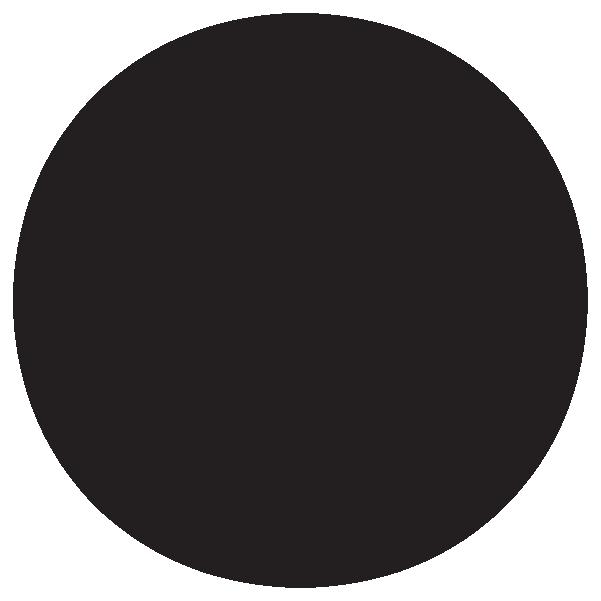
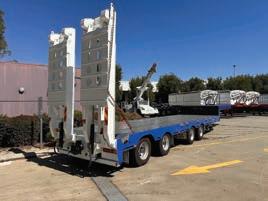

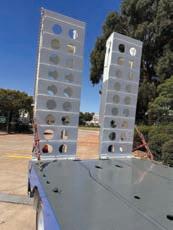
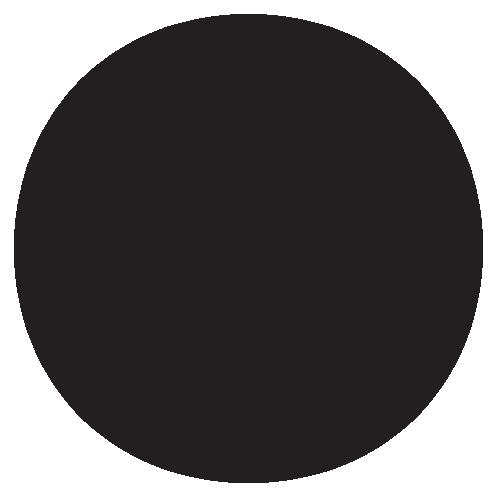
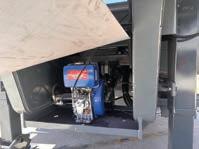
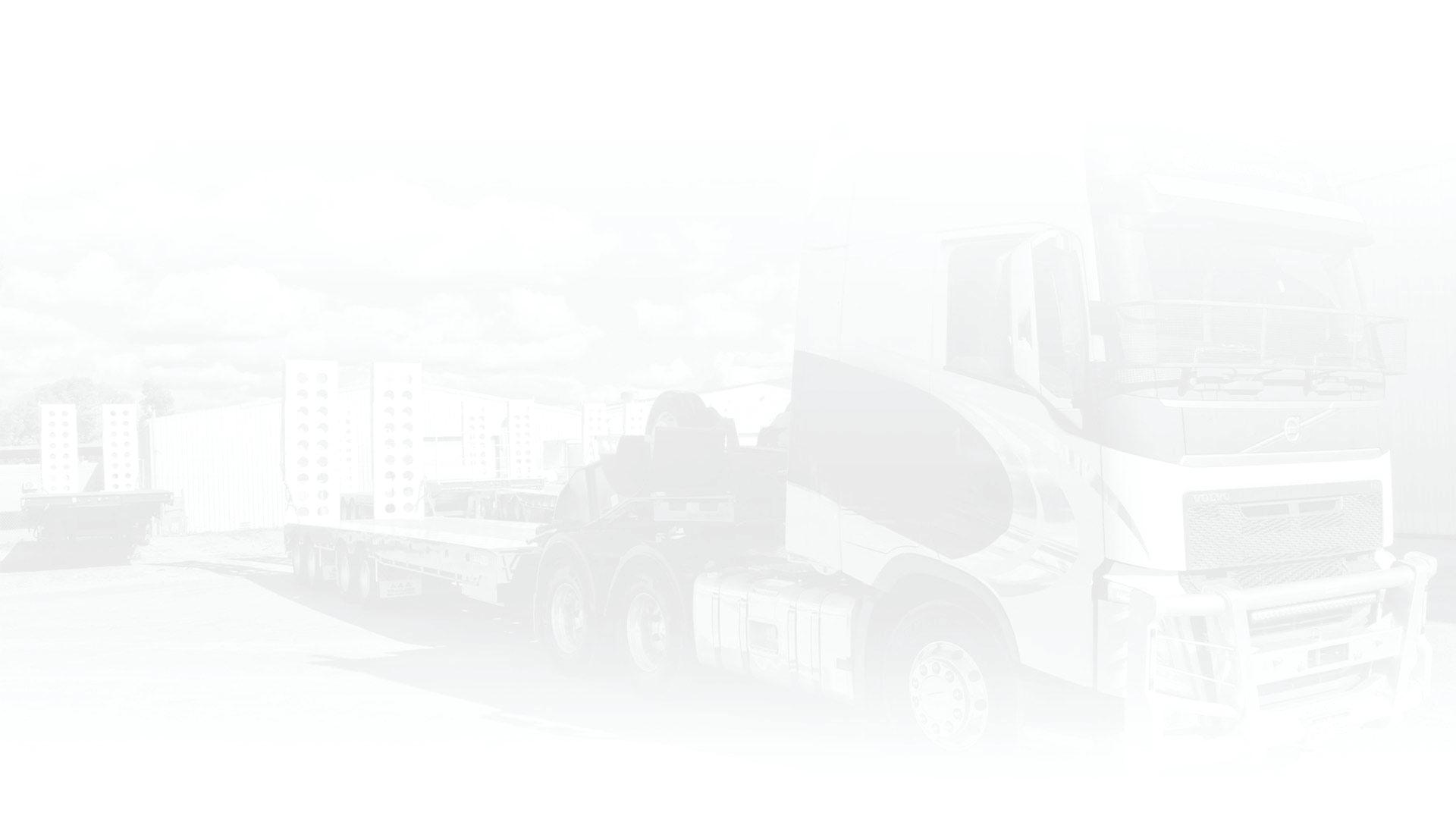
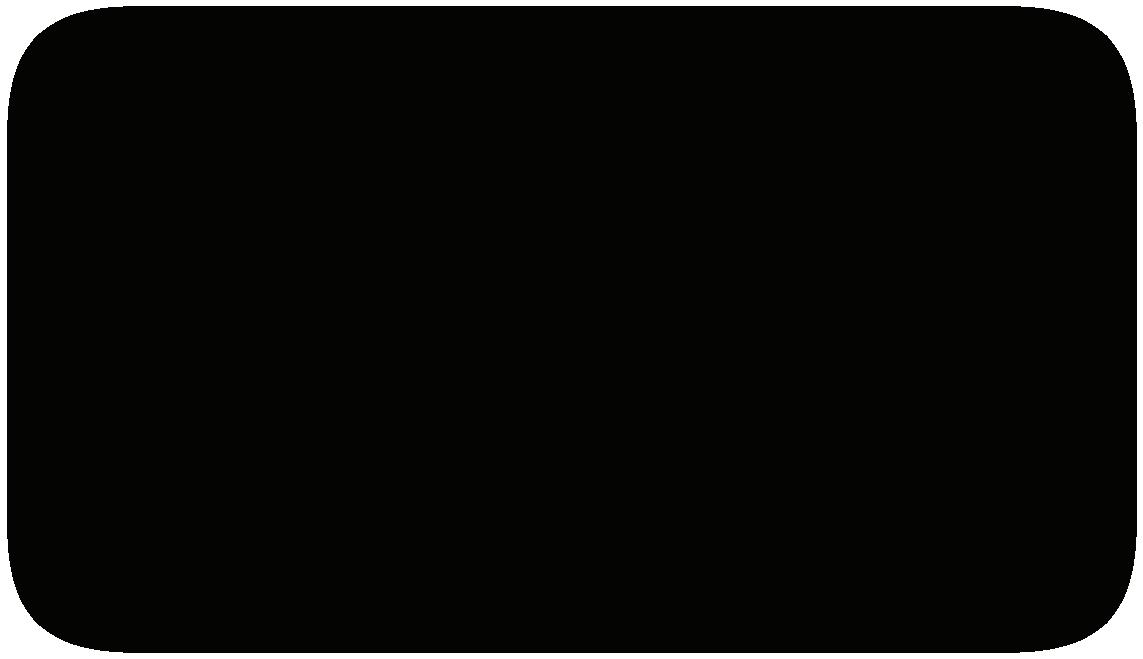



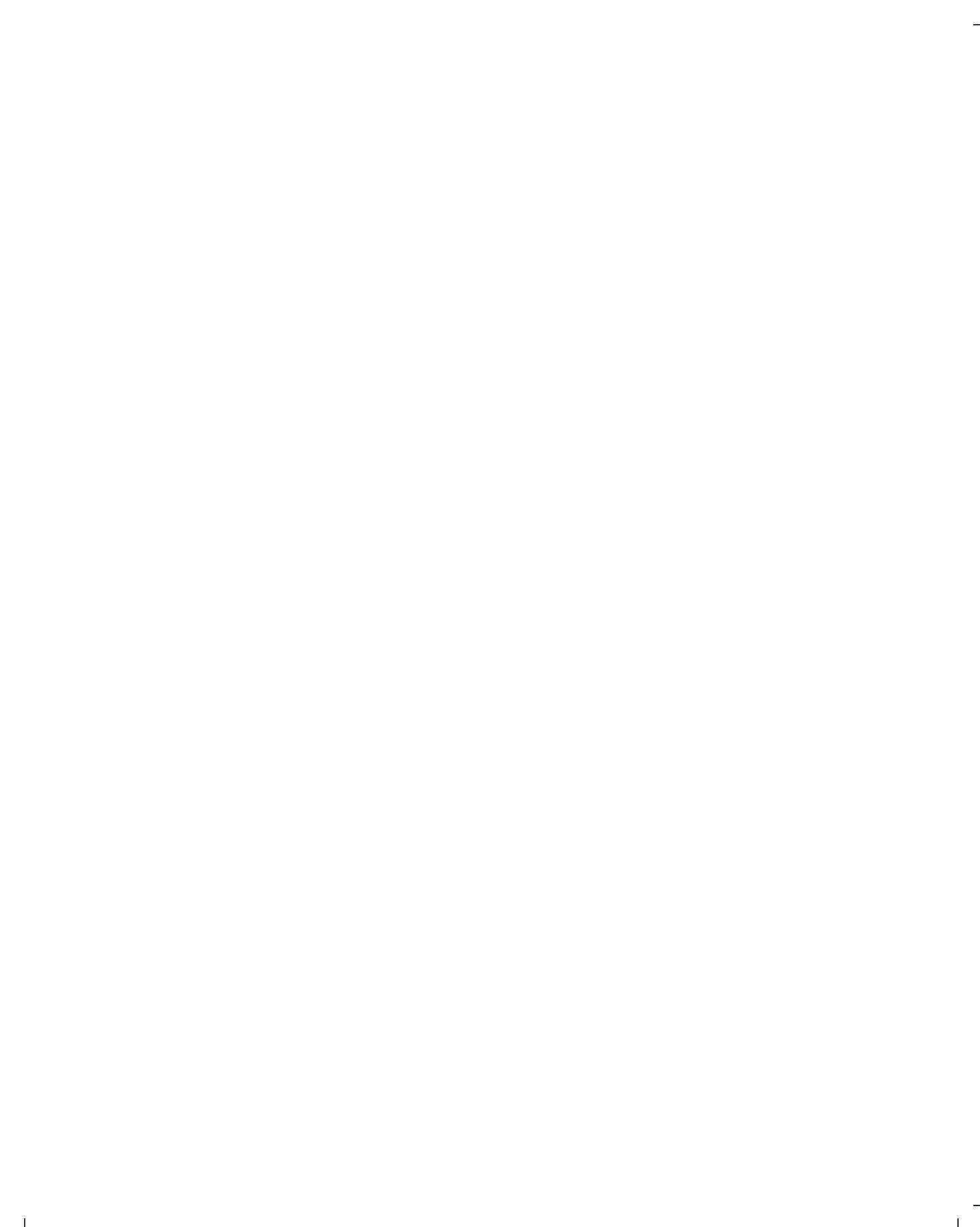
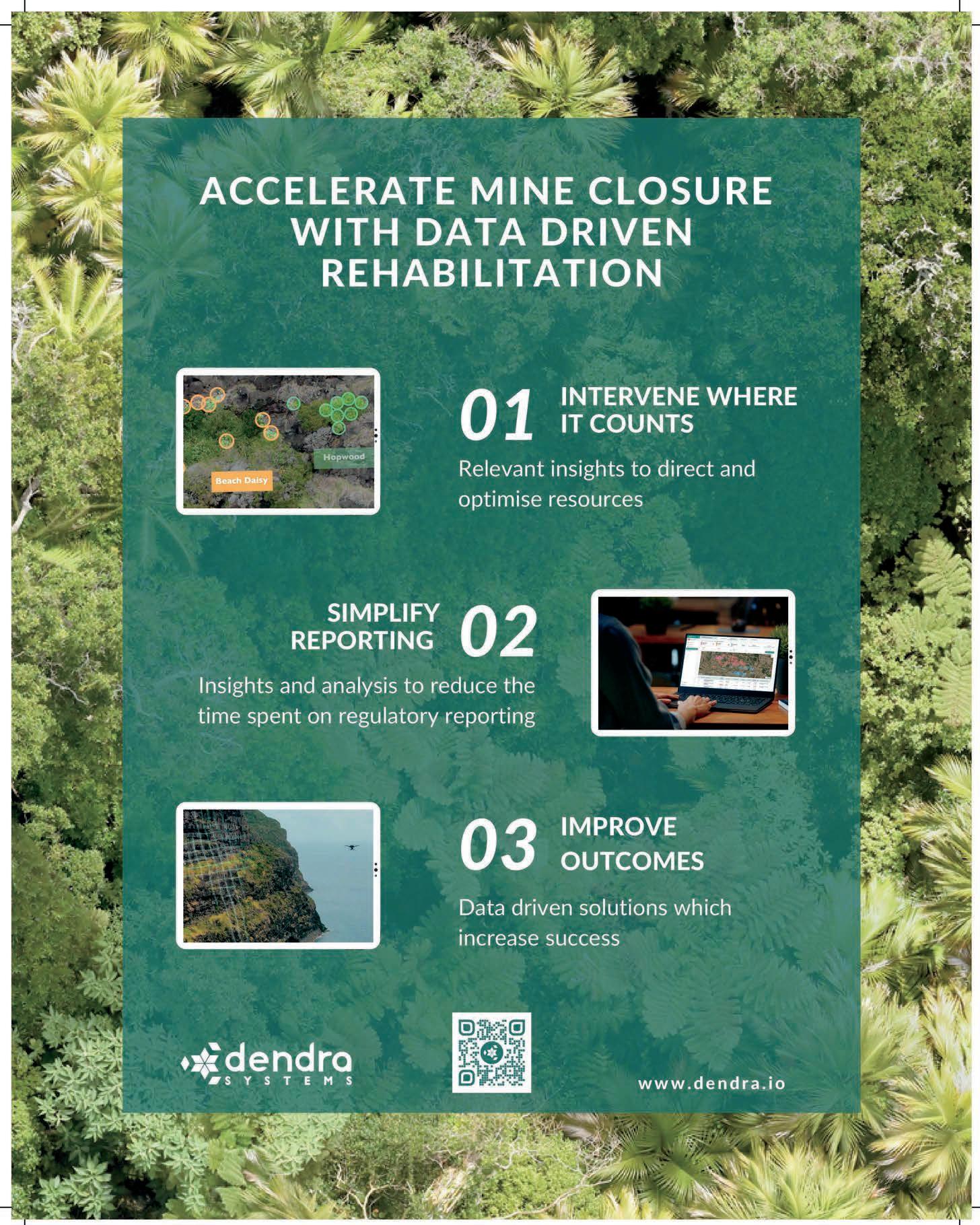