OPTIMISING THROUGH AUTOMATION
SUPPORTING OPERATIONAL PROFITS THROUGH ADDED INTELLIGENCE
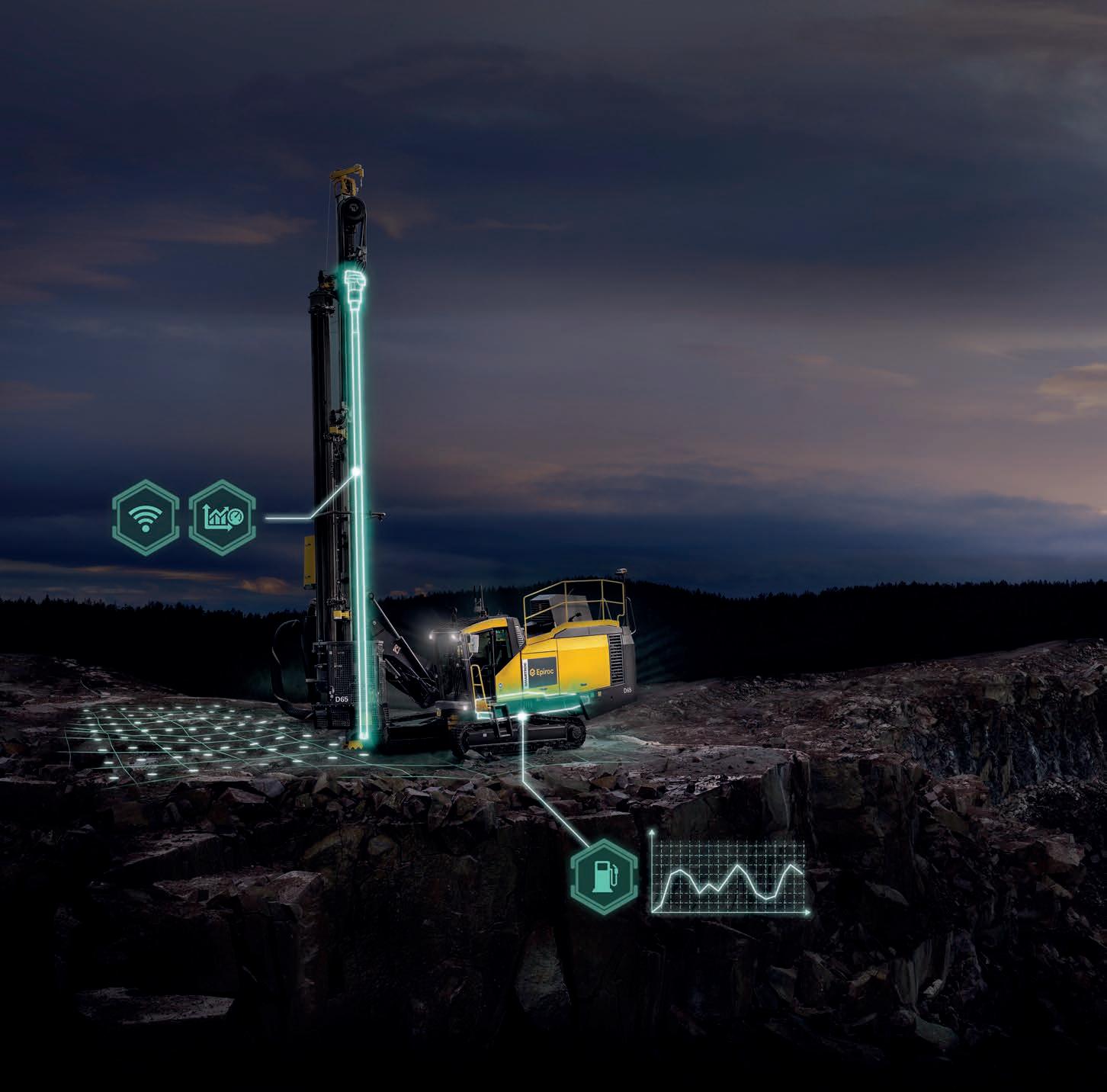
SUPPORTING OPERATIONAL PROFITS THROUGH ADDED INTELLIGENCE
The SmartROC D65 down-the-hole drill rig brings the future of mining within your reach today. It’s built to face the toughest of conditions and loaded with intelligent features that will improve your operations, increase safety and boost productivity. This rig is constantly evolving since it’s introduction in order to ensure that your investment delivers increased production and profitability shift-after-shift. Give your operation the chance to profit from the added intelligence of this market-leading drill rig. epiroc.com/en-au
CRITICAL MINERALS
MERGERS AND ACQUISITIONS
PAUL HAYES
paul.hayes@primecreative.com.au
AUSTRALIA HAS LONG RIDDEN THE BACK OF SO-CALLED TRADITIONAL COMMODITIES, BUT CRITICAL MINERALS ARE THE NEXT MINING FRONTIER AS THE WORLD CONTINUES ITS PATH TO NET-ZERO.
Iron ore, coal, gold. You don’t need to be on the frontlines of the Australian resources sector (or even work as a mining journalist) to know these are the kinds of commodities that have long driven the Australian economy.
Iron ore, in particular, has long been the workhorse of the Australian resources sector, earning an estimated $123 billion from exports in the 2022–23 financial year (FY23). Coal generated an estimated $124 billion in export earnings across the same timeframe.
These the types of ‘traditional’ commodities have long sat atop the Australian resources pyramid. And while they are admittedly likely to stay in that position for some time yet, it’s becoming increasingly clear that critical minerals will only increase in importance – for the mining industry and for the whole of Australia.
As Federal Resources and Northern Australia Minister Madeleine King said when unveiling the Australian Government’s Critical Minerals Strategy in June, the “path to net-zero runs through the resources sector”.
“The new Critical Minerals Strategy outlines the enormous opportunity to develop the sector and new downstream industries which will support Australia’s economy and global efforts to lower emissions for decades to come,” King said.
“While the potential is great, so too are the challenges.”
When BHP chief executive officer Mike Henry spoke at the recent World Mining Congress in Brisbane, he said governments around the world, including in Australia, must pursue an economywide transition to net-zero emissions, with critical minerals a key pathway on that journey.
“The Australian Government released its Critical Minerals Strategy, and we look forward to
CHIEF EXECUTIVE OFFICER
JOHN MURPHY
CHIEF OPERATING OFFICER
CHRISTINE CLANCY EDITOR
PAUL HAYES
Email: paul.hayes@primecreative.com.au
ASSISTANT EDITOR ALEXANDRA EASTWOOD
Email: alexandra.eastwood@primecreative.com.au
JOURNALISTS TOM PARKER
Email: tom.parker@primecreative.com.au
OLIVIA THOMSON Email: olivia.thomson@primecreative.com.au
working further with them on a critical minerals list that reflects the best interests of the nation,” Henry said.
“The world is on a path to what we must ensure is a better future. We will have substantially more people on this planet, seeking higher standards of living, that need to be supplied and powered by resources extracted, refined and used more sustainably.”
This thinking has been backed by the Federal Department of Industry, Science and Resources’ June 2023 edition of the Resources and Energy Quarterly report, which found rising demand for renewable energy and electric vehicles means critical mineral prices are likely to remain strong and, when combined, the minerals needed for the energy transition are expected to generate $46 billion in Australian FY23 export earnings.
“Australia is well positioned to supply long-term demand for base metals and critical minerals such as lithium, which are crucial components of cleanenergy technologies such as batteries, solar panels, and wind turbines,” King said.
With Australia home to some of the most significant recoverable critical minerals deposits on the face of the earth, the country is indeed well positioned to forge its place on the path to a greener future.
The question, however, is whether the country is ready to grab hold of this opportunity.
FRONT COVER
SMW Drilling Services is focused on the provision of safe, predictable and innovative blasthole drilling services. It has delivered more than 25 projects and forged several long-term partnerships with majors like Yancoal, Sojitz, Peabody and Thiess.
Opening its doors in 2006, the company has continued to grow. It now has a diverse fleet of more than 20 drills which the company believes, combined with the expertise of a large team, sets the standard in safe and productive drilling programs.
Cover image: SMW Drilling Services
Paul Hayes Managing EditorTIM BOND
Email: tim.bond@primecreative.com.au
CLIENT SUCCESS MANAGER
JANINE CLEMENTS Tel: (02) 9439 7227
Email: janine.clements@primecreative.com.au
SALES MANAGER
JONATHAN DUCKETT Tel: (02) 9439 7227 Mob: 0498 091 027 Email: jonathan.duckett@primecreative.com.au
DESIGN PRODUCTION MANAGER MICHELLE WESTON michelle.weston@primecreative.com.au
ART DIRECTOR BLAKE STOREY blake.storey@primecreative.com.au
SUBSCRIPTION RATES Australia (surface mail) $120.00 (incl GST) Overseas A$149.00
For subscriptions enquiries please contact (03) 9690 8766 subscriptions@primecreative.com.au
PRIME CREATIVE MEDIA Suite 303, 1-9 Chandos Street Saint Leonards NSW 2065, Australia www.primecreative.com.au
© Copyright Prime Creative Media, 2016
PRINTED BY MANARK PRINTING 28 Dingley Ave Dandenong VIC 3175 Ph: (03) 9794 8337 Published 12 issues a year
more traditional resources, but a rising demand for critical minerals.
28 COMMODITY SPOTLIGHT
Copper is key
With some of the most prolific copper resources in the world, Australia is set to be a major player in shaping a decarbonised future.
32 DECISION-MAKER
One of the global mining industry’s most legendary drill rigs has been revitalised. Australian Mining takes a closer look at Epiroc’s evolving Drill Master range.
44 DRILL AND BLAST
Drilling down to added value SMW Drilling takes pride in adding value at every stage of the drill-and-blast process.
RILL AND BLAST
Digging deeper
Aquatech has three decades of experience in water well drilling across the resources sector.
INTERNATIONAL MINING
PNG’s bright mining future
Mining is one of the major economic drivers for Australia’s closest neighbour,
which means there are plenty of opportunities to work and establish a career in the Pacific nation.
58 SUSTAINABILITY
Turning tyres into a resource
Kal Tire’s innovative method of recycling mining tyres is helping to create a more environmentally friendly resources industry.
5
8
AUSTRALIAN MINING PRESENTS THE LATEST NEWS FROM THE BOARDROOM TO THE MINE AND EVERYWHERE IN BETWEEN. VISIT WWW.AUSTRALIANMINING.COM.AU TO KEEP UP TO DATE WITH WHAT IS HAPPENING.
mineralised zone from Kaiser to Boda and then Boda Two and Three and beyond. The company looks forward to releasing results of this program as we work towards an upgraded mineral resource towards the end of the year.”
Alkane was recently awarded the NSW Minerals Council’s Explorer of the Year award for its discovery of the Kaiser gold-copper project.
Kaiser also forms part of the company’s Northern Molong porphyry project alongside Boda.
NSW Minerals Council said Alkane’s drilling program demonstrated an extensive mineralised system, and through the project the company demonstrated leading practice with its approach to exploration and its engagement with the local community.
AUSTRALIAN MINING GETS THE LATEST NEWS EVERY DAY, PROVIDING MINING PROFESSIONALS WITH UP-TO-THE-MINUTE INFORMATION ON SAFETY, NEWS AND TECHNOLOGY FOR THE AUSTRALIAN MINING AND RESOURCES INDUSTRY.
company says has the potential to make the project a large, Tier 1 goldcopper asset.
The exploration company received the favourable results from diamond core and RC drilling at its Boda Two prospect.
“We continue to see mineralisation extending to the south of Boda into
“In our recent drilling we believe we have intersected a ‘causative’ monzodiorite dyke or pencil intrusive at Boda Two. We will use these results, expected in August 2023, to assist us in locating further higher-grade areas within the mineralisation.
“There is a lot of drilling still to come to further define the full 3km
“The contribution made by all our finalists is a great example of the resilience and ingenuity shown by our world-class exploration sector in successfully overcoming a range of challenges in recent years, including floods and a global health crisis,” NSW Minerals Council chief executive officer Stephen Galilee said.
“Our exploration sector is essential to providing long-term economic security to regional communities right across NSW. It is also essential to help meet demand for the metals of the future in industries like health, defence, advanced manufacturing, renewable energy and telecommunications.”
Alkane also operates its Tomingley gold mine in NSW.
BHP chief executive officer Mike Henry took the stage at the World Mining Congress 2023, where he said mining is pivotal in preserving a better future for Australians.
Henry said mining will help improve future standards of living, job opportunities, and better access to health care and education.
“For nations, mining brings the opportunity for secure jobs, economic development and investment – as well as secure energy solutions and food supply chains that sustain lives and livelihoods,” Henry said.
“I am sure everyone in this room knows the impact that mining has had on Australia. Australia would not be the country it is today, wouldn’t have the living standards Australians enjoy today, without mining.”
Henry said that governments around the world have a responsibility to provide strong institutional and regulatory confidence to foster a dynamic, commercial and open market that encourages competition and productivity, and they must pursue an economy-wide transition to net-zero emissions – including through critical minerals.
“Last week the Australian Government released its Critical Minerals Strategy, and we look forward to working further with them on a critical minerals list that reflects the best interests of the nation,” Henry said.
“I did see some criticism that the new Strategy didn’t contain even more by way of subsidies. For what it’s worth, I think this is absolutely the right approach … What governments here
– federal and state – should focus on are those things within their control to make investment fundamentally more attractive. Not simply due to the sugar hit of a subsidy.”
Despite some positives, Henry said some recent activity in the Australian resources sector will make the country less competitive, such as the Federal Government’s ‘same job, same pay’ legislation and the Queensland Government’s decision to impose the world’s highest coal royalty taxes.
As a result of the Queensland coal royalty taxes, Henry said BHP will not be investing further money in the state.
“In this case, both the outcome and the process have meant for BHP that we have opportunities to invest for better returns and lower
risk elsewhere around the world, as well as here in Australian states like Western Australia and South Australia,” Henry said.
“And we will not be investing any further growth dollars in Queensland under the current conditions.”
Henry concluded that the resources industry is critical in enabling the future.
“The world is on a path to what we must ensure is a better future,” he said. “We will have substantially more people on this planet, seeking higher standards of living, that need to be supplied and powered by resources extracted, refined and used more sustainably.
“This industry is critical to enabling that future. And the opportunity is large. If we deliver on this opportunity, we deliver for the world.”
Major miner Rio Tinto has withdrawn its plan to mine near the town of Dwellingup in Western Australia.
The news came just days after Alcoa announced it would establish an 8344-hectare (ha) mining avoidance area around the town.
Rio planned to mine lithium and nickel in the area but will no longer move forward with this after local communities contested the plans.
“Rio Tinto is in the process of withdrawing its applications for exploration licences in the southwest of Western Australia,” a Rio spokesperson told the ABC.
“This decision has been made for a number of reasons including in response to concerns raised by local communities.”
Chief among the concerns was the protection of the nearby Northern Jarrah Forest.
Shire of Waroona President Mike Walmsley told the ABC that he was happy with the decision.
“It’s a good outcome that the companies listen to community concern and they’ve decided to withdraw,” he said.
“I’m sure there are other areas where some of these minerals might
Northern Star Resources has announced the purchase of the Millrose gold project from Strickland Resources for $67 million. The deal comprises $41 million in cash and 1.5 million fully paid shares in Northern Star.
The WA gold project has a known mineral resource of 346,000 ounces of gold at a grade of 1.8 grams per tonne.
Millrose is located 40km to the east of Northern Star’s Jundee operations. According to the company, Millrose will become a supplementary
feed source for the Jundee mill in the medium term, complementing Jundee’s underground base load.
Jundee underground operations currently source roughly 1.8 million tonnes of ore each year.
Northern Star managing director Stuart Tonkin reacted to the agreement.
“The acquisition of the Millrose gold project presents a very compelling development opportunity that is accretive to the Jundee lifeof-asset plan as it should deliver us a sizeable low-cost, high-grade
exist, but this one’s pretty special being the one and only one.
“It’s important that we protect those spots now. Going forward we need to say to some of these companies: ‘You really got to put up a pretty good case if you want to go into those spots’.”
Alcoa Australia president Matt Reed said the Alcoa’s similar decision to establish the Dwellingup no mining zone followed extensive studies and consultation, and respected feedback about the area’s growing importance.
“We hope this decision provides greater certainty about
our intentions in a prospective mineral area and demonstrates our willingness to protect important environmental and social values,” he said.
“We respect the Dwellingup area has immense lifestyle, ecotourism and forest recreational values that people want to continue to enjoy now and into the future.
“We have worked closely with the Shire of Murray and other stakeholders in reaching this decision, and we believe this commitment will provide certainty to the community for the future.”
supplementary resource feed.
“This bolt-on acquisition, which also comes with significant brownfields exploration upside, will provide us with further confidence to plan organic and profitable growth for Jundee, which already is the lowest cost asset in our Tier 1 portfolio.”
Strickland has advised its shareholders of exactly how it intends to spend its new funds.
Within the first 12 months, Strickland plans to undertake 3500m of diamond drill and 25,000m of reverse circulation drilling. The
company also intends to upgrade its portfolio of gold prospects to mineral resource status, as well as continue base metal exploration at its Iroquois zinc-lead project.
In the same announcement, Northern Star indicated it was strengthening renewable energy at its Jundee operation. The company has entered into a long-term power supply agreement with Zenith Energy, which incorporates 40 megawatts of wind and solar power generation.
Once completed, this will provide 56 per cent of the mine site’s power.
Red 5’s King of the Hills (KOTH) gold mine delivered a third consecutive month of record gold production in May.
Red 5 wholly owns the KOTH gold mine, which is located 28 kilometres north of the town of Leonora and 80 kilometres south of its Darlot satellite gold mine in the Eastern Goldfields region of Western Australia.
The KOTH gold mine produced 19,039 ounces of gold from 0.35
million tonnes (Mt) of ore processed at an average head grade of 1.8 grams per tonne (g/t) in May.
This is a notable increase from April’s recorded 18,633 ounces from 0.40Mt of ore processed at an average head grade of 1.54g/t, as well as March’s 17,550 ounces from 0.40Mt of ore processed at an average head grade of 1.49g/t.
The KOTH gold mine completed already planned mill and crusher
Glencore and Metals Acquisition Limited have officially closed the sale of the CSA copper mine in Cobar, New South Wales. The mine was sold to Metals Acquisition for $US1.1 billion ($1.64 billion).
Under the transaction, Glencore has received $US775 million in cash and $US100 million in shares, along with:
• $US75 million deferred payment to be paid within 12 months
• A $US150 million payment contingent upon future copper prices
• 1.5 per cent life of mine net smelter return royalty Glencore will offtake 100 per cent of the copper concentrate produced and Metals Acquisition will assume ownership and operation of the mine.
“The acquisition of CSA represents a strong strategic fit for Metals Acquisition. Our management team’s
maintenance shutdowns in May, which were successful and resulted in four days of zero mill production.
Work that was undertaken included replacing the crusher’s mantle and concave liners, replacing the mill’s original discharge grates with ninetimes-larger grates and replacing and bolstering heavy wear areas.
The open pit and underground mines continued to perform well
during the month, with run-ofmine stockpiles containing an estimated 560,000 of ore grading an estimated 1.2g/t at the end of the month.
The second half of the 2022–23 financial year’s production guidance is maintained at between 90,000 and 105,000 ounces at an all-in sustaining cost (AISC) of between $1750 and $1950 per ounce.
operational expertise, understanding of regional operations and relationships with local stakeholders uniquely position us to identify and realise the full potential value of the asset,” Metals Acquisition chief executive officer Mick McMullen said in 2022.
“We believe that copper has favourable fundamentals that will continue to support an elevated copper price.
“Copper is expected to play a key role in the global energy transition ‘megatrend’, with approximately one million tonnes per annum of new supply required from 2024 ... to meet the surging demand forecast.
“With few new projects globally in the pipeline, increasing permitting issues and jurisdictional risk, ... we believe that there are significant challenges ahead to close the projected supply deficit.”
We solve our mining customers’ wear challenges.
And now we’re taking on a challenge of our own.
As leading engineers and manufacturers of wear solutions, we’ve never been shy of a challenge.
That’s why we have committed to being carbon neutral by 2030, while continuing to design, manufacture and supply quality wear solutions for the resource sector.
bradken.com
vanadium flow battery was on its way to SA in December 2020.
As reported by the ABC, Yadlamalka Energy has been undertaking the
The battery will store around ten gigawatts of dispatchable solar power per annum and will be charged from excess electricity produced by the solar
Fortescue Metals has announced that Jennifer Morris has resigned as a non-executive director.
Morris’ experience with Fortescue includes being first appointed to its board as a non-executive director in November 2016, then acting as the chair of the remuneration and people committee since February 2020, and acting as a member of the audit, risk management and sustainability committee since August 2017.
Morris said it has been a privilege to work for the major miner and serve it as a non-executive director.
“This company is truly something special. I look forward to watching on as Fortescue continues to diversify and grow while setting out to become an industry leader in decarbonisation and achieve its vision to eliminate emissions across its operations,” Morris said.
Fortescue executive chairman Andrew Forrest said he was thankful for Morris’ contribution to the company.
“Jenn has made a significant contribution to the company since being appointed as a non-executive
“This is a battery that has significant advantages over lithium-ion ones; the most important one is the duration of this battery is four hours, unlike lithium
into the grid — that margin will have the effect to reduce prices,” Doman said.
“We’re on the verge of a vanadium revolution.”
director in 2016. Her experience has been valuable in guiding the board in its decision making over the past six years,” Forrest said.
“Jenn’s leadership as chair of the remuneration and people committee has been outstanding and her vitality, energy and passion will be missed. We wish her all the very best for the future.”
Fortescue non-executive director Penny Bingham-Hall will replace Morris as chair of the remuneration and people committee, and Elizabeth Gaines will transition
into a new role as a part-time executive director, both effective from July 1.
Gaines has been a global ambassador for Fortescue since August 2022, on top of acting as a non-executive director.
These leadership changes come as the company recently elected a new chief financial officer after an abrupt resignation from Ian Wells in January.
Forrest has rejected suggestions of executive dysfunction at the company.
It’s a big milestone for a piece of rubber. But Linatex® is so much more than that. It’s unlike anything else, using a unique 95% natural latex formula that has made Linatex® the strongest rubber in mining for the last century – exactly as nature intended. So, here’s to 100 Years Strong, and the next 100 to come.
Learn more at linatex100.weir
Mid-tier Australian gold producer Regis Resources has released its annual mineral resource and ore reserve update for the 2022 calendar year.
The company said its mineral resources and ore reserves show progress against its long-term strategy, as well as provides a solid platform to launch the next phase of growth.
Highlights from the report include underground reserves outpacing depletion for the second year in a row as new results highlight underground life extensions at the Duketon gold
project and the Tropicana joint venture, which Regis Resources chief executive officer Jim Beyer said was pleasing to see.
“We are extremely pleased that our underground mines at both Duketon and Tropicana have outpaced depletion for the second year in a row. We have spent the last two years investing in these mines and it is very satisfying to deliver reserve growth on these investments over this short time horizon,” Beyer said.
“It is still early days in the maturity of these undergrounds and we look
forward to the continuing growth potential as we mine deeper. Our long reserve life of eight years and (being) located wholly within Australia provides a strong platform to deliver on our long-term growth objectives and achieve superior returns for our shareholders.”
Other highlights from the report includes group ore reserves of 3.6 million ounces (Moz) and group mineral resources of 7Moz, both as of 31 December 2022.
There was an increase in new ore reserves of 210,000 ounces (koz) and an increase in new mineral
resources of 400koz, both offset by the 2022 calendar year depletion.
Long term gold price assumptions for the calculation of reserves and resources were updated but remain at moderate levels at a weighted average of $1800 per ounce for reserves and $2430 per ounce for resources.
Additionally, early results from the Garden Well exploration decline at the Duketon project has reinforced the potential for a new production front and growth in ounces per vertical metre. The underground site also established an exploration target.
Simon Trott said the major miner spends billions of dollars with local suppliers across WA every year, helping to support communities across
the State by providing local jobs for local people.
“The spending of $1 billion with WA businesses at Western Range marks a considerable milestone for both the
project and those local businesses we are partnering with,” Trott said.
“The connection between Rio Tinto and China Baowu in the Pilbara extends more than 40 years
and we are pleased to be further deepening our relationship through our joint commitment to study opportunities for the production of lowcarbon iron in WA.”
At Hastings Deering, businesses working within the construction industry can now take advantage of a new industry leading warranty with every Cat® Certified Rebuild. Get ‘as-new’ performance and benefit from the multiple lives designed into Cat machines, at a fraction of the cost of buying new.
CALL 1300 186 248 OR VISIT HASTINGSDEERING.COM.AU
Mineral Resources’ (MinRes) Mt Marion lithium operation has seen promising early results from a major exploration program.
The Mt Marion lithium operation is located in the Goldfields region of Western Australia, and is a joint venture between MinRes and Jiangxi Ganfeng Lithium – where both companies own 50 per cent. MinRes is the mine’s operator.
MinRes said the early results confirmed significant exploration potential at depth along strike
and in the surrounding region, and it demonstrates potential for open pit extensions and underground mining.
The company reported approximately 34km of drilling being completed in 2023 so far by utilising six diamond and reverse circulation drill rigs.
The first major exploration program since MinRes took control of the mine found lithium-bearing pegmatite formations approximately one kilometre below the surface.
Global investment management firm Goldman Sachs has slashed its iron ore price forecast by 18 per cent, citing weakened global demand.
The iron ore price has been downgraded to $US90 per tonne (t), down from $US110.
Goldman flagged risks of China’s oversupply in steel becoming increasingly evident, as output targets could be trimmed. A slower recovery rate in property sales saw
demand for steel fall by five per cent.
The weakened demand in China may result in a surplus of iron ore, prompting Goldman to revise the iron ore demand to “flat”.
Goldman said that 2023 was the first full year of global surplus in iron ore since 2018 and could be followed by an even larger surplus in 2024.
The Australian Financial Review (AFR) reported that the share price
MinRes said it will double exploration drilling capacity at Mt Marion by the end of the 2023 calendar year, ramping up to a 12-rig drilling campaign over the following 18 months.
MinRes managing director Chris Ellison said the Mt Marion exploration results highlight how the company is just scratching the surface of the potential lithium resource, including the possibility of underground mining.
“MinRes identified opportunities in lithium, the most important mineral
in the world’s decarbonisation, more than a decade ago and set about building a portfolio of world-class assets that could deliver long-term value,” Ellison said.
The operation produces mixed grade spodumene concentrate which is transported through the Port of Esperance for offshore conversion.
A $120 million expansion of the Mt Marion operation doubled capacity to up to 900,000 tonnes per year, with the commissioning process now underway.
for Fortescue Metals dropped 8.2 per cent on average in May, while BHP and Rio Tinto fell down 0.9 per cent and 0.2 per cent, respectively.
In April this year, Fitch Solutions increased its 2023 iron ore price forecast from an average of $US110/t to $US125/t amid improving market sentiment.
“On the demand side, we expect Chinese demand to continue with its promising momentum over the rest
of 2023,” Fitch said. “China will be the main driver of demand recovery, while other regions will struggle with lingering issues from 2022.
“However, China’s increase in demand may not translate to rallying prices due to its centralised iron ore purchaser China Mineral Resources Group (CMRG). The entity aims to exert Chinese influence over critical mineral imports like iron ore, putting limitations on price upside.”
Schenck Process Mining has become part of Sandvik Rock Processing Solutions. Combining the expertise and reach of our teams allows us to develop even better services to ensure that your equipment operates safely and at peak performance throughout its entire lifecycle.
We are now better positioned than ever, to develop innovative solutions to the challenges of our industry.
Watch this video to learn what this new parternship means to your business or visit our website:
The Northern Star Resources board has approved the expansion of the Fimiston Mill, part of the Kalgoorlie Consolidated Gold Mines’ (KCGM) Super Pit.
The expansion from 13 million tonnes per annum (Mtpa) to 37Mtpa is set to cost $1.5 billion and is due to be completed in 2026.
Located at the centre of the Kalgoorlie goldfields, the Super Pit is one of Australia’s largest open pit gold mines and includes the Mt Charlotte underground mine and the Fimiston
and Gidji processing plants.
“Today is an exciting day for Northern Star and a historic new chapter for this world-class asset,” Northern Star managing director Stuart Tonkin said.
“The board’s decision to approve the KCGM mill expansion and optimisation represents the next stage to revitalise our largest asset as well as the surrounding district for decades to come.
This project is financially compelling, and a significant enabling
step towards delivering our strategy to generate superior returns for our shareholders.”
Northern Star has had a productive start to the year at the Super Pit, increasing gold resources to 57.4 million ounces (Moz) and keeping ore reserves steady at 20.2Moz.
Tonkin said the company is confident the site will continue to produce significant value.
“Our confidence in the economics of KCGM to remain a long-life, low-cost gold mine has been further reinforced
Federal Minister for Resources
Madeleine King has released Australia’s new Critical Minerals Strategy in an effort to grow the country’s critical minerals wealth.
One of the first policy decisions under the Strategy will see the Government target $500 million of new investment into critical minerals projects through the Northern Australia Infrastructure Facility.
A process to update the critical minerals list has also been green lit and has been widely supported by the industry.
“The new Critical Minerals Strategy outlines the enormous opportunity to develop the sector and new downstream industries which will support Australia’s economy and global efforts to lower emissions for decades to come,” King said.
“While the potential is great, so too are the challenges. The Strategy makes it clear our natural minerals endowment provides a foot in the door, but we must do more to create
The Strategy will provide a framework that the Government will use to guide future policy decisions and maximise the national benefits of the country’s critical minerals and, according to the Federal Government, increasing exports of critical minerals could create upwards of 260,000 new jobs.
The Strategy highlights six focus areas:
• Developing strategically important projects, with targeted support
through the feasibility study phase,” he said.
“Expanding the processing capacity of KCGM will strengthen Northern Star’s portfolio, materially increase our free cash flow generation and progress our long-term strategy to be within the 2nd quartile of the global cost curve.
“Further, the project is important in our sustainability journey and will also sustain hundreds of local jobs, economic and social investment, and local procurement opportunities in the Goldfields region.”
optimise trade and investment settings for priority technologies
• First Nations engagement and benefit sharing, to strengthen engagement and partnership with First Nations people and communities, and to improve equity and investment opportunities for First Nations interests
• Promoting Australia as a world leader in environmental and social governance (ESG) standards
• Unlocking investment in enabling
Brokk robots are designed specifically for high-performance demolition and maintenance works and improve effectiveness, uptime, and profitability for operators.
Within a mine, Brokk robots are able to perform various tasks such as oversize rock breaking, scaling, drilling, digging, and shaft sinking.
www.brokk.com/au
KEEP UP WITH THE LATEST EXECUTIVE MOVEMENTS ACROSS THE MINING SECTOR, INCLUDING AT FORTESCUE METALS GROUP, ST BARBARA AND SANDFIRE RESOURCES.
Elizabeth Gaines – who was Fortescue Metals Group’s chief executive officer (CEO) before stepping down last year – has moved into a new role of executive director at the company.
Gaines resigned as Fortescue boss in December 2021 and officially stepped down in August 2022. Since then, she has served as a non-executive director and an ambassador of Fortescue Future Industries (FFI).
“Over the past decade since joining Fortescue, I have been honoured to serve in various roles including nonexecutive director, chief financial officer, chief executive officer and global ambassador,” Gaines said.
“I look forward to continuing to work with the executive chairman and the talented team across the business as we lead industry to decarbonise the mining operations and transition Fortescue to a global green energy and resources company.”
Gaines’ appointment coincided with the resignation of Jennifer Morris as a non-executive director. Morris’ Fortescue experience includes first being appointed to its board as a non-executive director in November 2016, then acting as the chair of the remuneration and people committee since February 2020.
St Barbara has appointed Andrew Strelein as its new managing director and CEO, after he first joined the company as chief development officer in August 2021.
During his time at St Barbara, Strelein has been influential in the acquisition of Bardoc Gold and the recent Leonora sale involving Genesis Minerals.
Before that, he was CEO of a company overseeing the development of the Nimba iron ore project in West Africa.
Strelein’s appointment coincides with Dan Lougher’s retirement from the company.
St Barbara non-executive chair Kerry Gleeson set the scene for Strelein’s new leadership while honouring Lougher’s time at the company.
“Andrew has significant global experience in business development, project advancement and permitting, and knows St Barbara well,” she said. “He is ideally suited to take over as the company enters a new phase.
“I would also like to thank Dan for his invaluable leadership at St Barbara to stabilise Gwalia performance while the company navigated a period of intense change culminating in the transaction with Genesis Minerals.”
St Barbara has also appointed Sara Prendergast as its new chief financial officer (CFO), succeeding Lucas Welsh, who has been CFO since August 2021.
Gleeson is currently overseeing a renewal of the St Barbara board and has appointed Transearch International Australia to assist with this process.
Sandfire Resources has appointed Megan Jansen as its new CFO, succeeding long-serving CFO Matthew Fitzgerald.
With more than 20 years’ experience in various finance, commercial, business integration and M&A capacities, Jansen was most recently global head of finance at Imdex. Before that, she spent 10 years at MMG.
Fitzgerald joined Sandfire in 2010 and was influential in the discovery, financing (to the tune of $380 million), development and operation of the DeGrussa copper mine in WA.
“Matthew has played a key role in the strategic and financial stewardship of Sandfire from its early days as a successful junior explorer to a company with a market capitalisation of $2.7 billion,” Sandfire managing director and CEO Brendan Harris said.
“More recently during FY23, he has been instrumental in the successful transitioning of our balance sheet to position the company well through its
next phase, including re-sculpting of the $US432 million MATSA syndicated debt facility and initial $US140M 3.2Mtpa (million tonne per annum) Motheo project finance facility.”
Russell Clark has joined Red 5 as its new non-executive chair, bringing more than 40 years’ experience to the role.
Clark served as managing director and CEO of Grange Resources for five years and was previously group executive of operations for Newmont, where he oversaw the company’s Australia and New Zealand operations, including the KCGM mine in Kalgoorlie.
The appointment comes as Red 5 continues to renew its board en route to its goal of becoming a leading mid-tier Australian gold producer.
“Russell has held board and senior management positions with major mining companies, and we look forward to his guidance and counsel as Red 5 cements its position as one of Australia’s major emerging mid-tier gold producers,” Red 5 acting chair Andrea Sutton said.
“With the ramp-up of King of the Hills well progressed and the operation now delivering solid results, this is an exciting time to welcome a new independent chair to our board as we embark on this next exciting chapter of our growth journey.” AM
THE AUSTRALIAN GOVERNMENT’S RESOURCES AND ENERGY QUARTERLY
JUNE 2023 DETAILED A SUSPECTED DECLINE AMONG MORE TRADITIONAL RESOURCES BUT INCREASING DEMAND FOR CRITICAL MINERALS.
If there is one thing the past few years have taught us, it’s that things can change at an remarkable rate.
While the Australian resources industry has enjoyed a strong year, with record earnings of $460 billion in the wake of Russian–Ukraine war and COVID-19 pandemic, a golden era of resources may be coming to an end.
The Federal Department of Industry, Science and Resources’ Resources and Energy Quarterly June 2023 has detailed a suspected decline, forecasting that earnings from iron ore and coal will begin to fall.
But the news is not all bad, with critical minerals demand set to rise.
The mining industry employed approximately 189,000 people in the
2021–22 financial year, according to the Australian Bureau of Statistics (ABS). And in a testament to the industry’s ability to grow worker numbers while also retaining existing staff members, this figure jumped to 250,000 in 2022–23.
The industry also contributed to around 13.9 per cent of Australia’s gross domestic product (GDP) and made up two-thirds of the country’s total merchandise exports.
The report forecasts Australia’s export values to be $390 billion in 2023–24, down from an estimated record of $460 billion in 2022–23.
According to the Department of Industry, Science and Resources, this drop is due to a “slowdown in the world economy and the re-organisation and improvement in energy commodity supply has generally reduced commodity prices over the past quarter”.
However, mining investments are still picking up, with the ABS Private New Capital Expenditure and Expected Expenditure survey showing a total of $11.8 billion was invested by the country’s resources industry in the March quarter of 2023.
The coal industry has had a tricky couple of years.
While job numbers were up, especially in New South Wales, which recorded 24,575 direct coal mining jobs, the controversial Queensland coal royalty taxes meant a period of uncertainty for the commodity in its traditional heartland.
Following the announcement of the increased royalties, BHP made headlines when it said it would divest the Daunia and Blackwater coal mines in Queensland in February.
The standout from Resources and Energy Quarterly June 2023 was Australia’s critical minerals.
It is almost impossible to ignore the sweeping global demand for more these minerals as the transition to net-zero ramps up. With more lithium-ion batteries for electric vehicles and solar panels needed than ever before, Australia’s vast reserves of critical minerals are enjoying their time in the sun.
Underpinning this was the release of the Federal Government’s new Critical Minerals Strategy, released in June.
One of the first policy decisions under the strategy will see the Government target $500 million of new investment into critical minerals projects through the Northern Australia Infrastructure Facility.
A process to update the critical minerals list has also been green lit and has been widely supported by the industry.
“The new Critical Minerals Strategy outlines the enormous opportunity to develop the sector and new downstream industries which will support Australia’s economy and global efforts to lower emissions for decades to come,” Federal Resources Minister Madeleine King said.
“While the potential is great, so too are the challenges. The strategy makes it clear our natural minerals endowment provides a foot in the door, but we must do more to create Australian jobs and capitalise on this unique opportunity.”
The strategy will provide a framework to guide future
Government, increasing exports of critical minerals could create upwards of 260,000 new jobs.
“The latest Resources and Energy Quarterly underlines the government’s plan to support the development of our critical minerals sector, to make Australia a clean-energy superpower, and to help Australia and our trading partners meet commitments to lower emissions,” King said.
“The road to net-zero runs through the resources sector.
“Australia is well positioned to supply long-term demand for base metals and critical minerals such as lithium, which are crucial components of clean-energy technologies such as batteries, solar panels and wind turbines.”
Resources and Energy Quarterly June 2023 found the demand for critical minerals means that Australian lithium and nickel assets are more secure as governments across the world rush to secure supplies.
“Australia has significant reserves of battery commodities critical to the global energy transition – including lithium, cobalt, manganese and nickel – and is well placed to provide raw battery materials and refined product to the world,” the report stated.
In addition, global battery demand is expected to grow to about 3041 gigawatt hours in 2030, and Australia is positioned to assist with this growth, as it holds 20 per cent of the global reserves of copper and nine per cent of magnesium ore.
King said the value of lithium exports in 2022–23 almost quadrupled from the previous financial year, increasing to
that forced coal companies to reserve 10 per cent of their output exclusively for domestic use. And the next month saw the Federal Government make its decision not to approve Clive Palmer’s central Queensland coal project.
Perhaps the biggest issue for the coal industry was China’s ban on Australian coal imports. While that decision was reversed in January, 2023 has seen lower-than-average demand for Australian coal.
fall of metallurgical coal prices.
Regardless, coal prices remain above levels seen prior to the war in Ukraine, as some Russian supply is stranded from world markets.
“Weaker demand and improved supply have recently pushed down thermal coal prices, though they are still high historically,” the report states.
“Global demand has softened due to slowing world economic growth
the outlook period, as trade flows reorganise further and supply lifts.”
Australia’s thermal coal exports are forecast to drop down from $64 billion in 2022–23 to around $38 billion in 2023–24 and $30 billion in 2024–25.
“Metallurgical coal prices remain volatile but are holding well above their pre-2019 level,” the report said.
“The Australian premium hard coking coal price is estimated to average $US273 ($408) a tonne in 2023 but
is forecast to fall to around $US200 ($299) a tonne by 2025 as supply conditions improve.”
The Australian sector is the world’s number one for iron ore resources, and it just takes a single glance at the iron-rich soil of the Pilbara to see why.
Some of the world’s largest miners have set up shop in Australia to mine iron ore, directly contributing to the $132 billion earned in exports in 2021–22. However, iron ore prices eased in the most recent quarter as global economic growth slowed.
In early June, global investment management firm Goldman Sachs slashed its iron ore price forecast by 18 per cent, downgrading it to $US90 ($134) a tonne from $US110 ($164).
A weakened appetite in China may result in a surplus of iron ore, prompting Goldman to revise the iron ore demand to “flat”.
Goldman said 2023 was the first full year of global surplus in iron ore since 2018, and that could be followed by an even larger surplus in 2024.
According to Resources and Energy Quarterly June 2023, China,
which accounts for almost 60 per cent of global iron ore demand, is projected to see a modest fall in total steel output over the outlook period to 2025. This is in turn expected to soften the rate of growth in global iron ore demand in the coming years, driving iron ore prices down.
But, more broadly, global iron ore trade is expected to grow by two per cent annually to 2025, with new supply coming from Australia, Brazil and Africa.
“Australia is projected to see continued ramp up of greenfield projects from established producers such as Rio Tinto, BHP and Fortescue, as well as emerging producers such as Mineral Resources Limited and Atlas Iron,” the report stated.
“Over the outlook period, Australia’s iron ore exports are projected to rise at an average annual rate of 2.1 per cent to reach 941 million tonnes by 2025.”
Major miners BHP and Rio Tinto had strong quarters from their iron ore operations, with Rio Tinto shipping 82.5 million tonnes of iron ore in the March quarter, a record for the period.
BHP’S iron ore output was 59.8 million tonnes, and the company
left its 2022–23 production guidance unchanged at 249–260 million tonnes.
Although the fall in earnings from coal and iron ore appears confronting, Resources and Energy Quarterly June 2023 details that falls in other resources
may be offset by the massive demand for critical minerals.
And as electric vehicles and green energy solutions become the norm, the critical minerals space will only continue to grow. AM
From majors selling copper mines for billions to chief executives touting the mineral’s fundamental importance at mining conferences across the world, it’s clear copper will play a central role as the world transitions to utilising renewable energy.
The base metal has a variety of end uses in a green economy, whether it be through electricity distribution, electrical equipment and devices, industrial machinery, wind turbines, solar panels and, of course, powering electric vehicles (EVs).
According to the Australia’s Identified Mineral Resources 2022 report, the country’s copper exploration increased by 65 per cent in 2021, with a value of $550 million up from $334 million in 2020.
This placed copper among the top three commodities in terms of exploration expenditure in 2021 – and the base metal’s rising importance has piqued the interest of major miners.
When delivering the opening address at Austmine 2023 in May, BHP chief operating officer Edgar Basto detailed the central role copper will play into the future.
“We expect global demand for copper to increase significantly as the world transitions to lower carbon sources of energy powered by more solar panels and wind turbines,” he said.
Basto also discussed the possibility of EVs accounting for nearly 60 per cent of global annual car sales by 2030 and nearly all sales by 2050.
“EVs use around three to four times more copper than petrol-based cars,” Basto said. “We often associate EV batteries with nickel and lithium, but they also require more copper – around three to four times more than an internal combustion vehicle.”
Federal Minister for Resources and Northern Australia Madeleine King echoed those sentiments in her foreword of the Australia’s Identified Mineral Resources 2022 report.
“These metals, and others, continue to play a central role in our minerals sector and provide economic growth and employment for regional communities across Australia,” King wrote.
Furthermore, the March 2023 edition of the Resources and Energy Quarterly stated that Australia’s copper exports are projected to grow from 868,000 tonnes in 2022–23 to around 970,000 tonnes in 2027–28.
“(This is) supported by additional production from new mines and mine expansions,” the report stated. “As output grows and prices strengthen, Australia’s copper export earnings are projected to grow, from $13 billion in 2022–23 to $15 billion (in real terms) in 2027–28.”
This was further supported in the June 2023 edition of the Resources and Energy Quarterly
“Growing demand from the power and EV sectors are key drivers of copper consumption over the outlook period,” the report stated.
“Australian export earnings of copper are estimated to have declined slightly in 2022–23. Higher Australian production and exports will support export earnings, which are set to grow to $13 billion in 2024–25.”
Copper’s vitality as an asset now and into the future is evident by it becoming a primary focus for many mining companies in Australian.
Chief among these examples is Glencore selling its CSA copper mine to Metals Acquisition Limited for $US1.1 billion ($1.64 billion) in June.
Located in Cobar, New South Wales, CSA is an established, high-grade, longlife underground copper mine. The site has an estimated mine life of over 15 years, and Metals Acquisition identified opportunities to further extend it, subject to exploration success.
“Our management team’s operational expertise, understanding of regional operations and relationships with local stakeholders uniquely position us to identify and realise the full potential ... of the asset,” Metals Acquisition chief executive officer Mick McMullen said.
“Copper is expected to play a key role in the global energy transition ‘megatrend’, with approximately one million tonnes per annum of new supply required from 2024 onwards in order to meet the surging demand forecast.”
Also in June, Evolution Mining extended the mine life of its Ernest Henry copper-gold operation to 2040. Located 38km north-east of Cloncurry, Queensland, the site was acquired by Evolution in January 2022.
“In under 18 months of owning 100 per cent of Ernest Henry, we have doubled copper and gold reserves and extended the mine life out to 2040,” Evolution managing director and chief executive officer Lawrie Conway said.
Copper has been essential in Ernest Henry’s growth, with the mine’s copper ore reserve increasing by almost 300,000 tonnes, to 589,000 tonnes, from December 2022 to June 2023.
South32 chief executive officer Graham Kerr listed copper as one of the commodities driving the company’s mergers and acquisitions strategy, suggesting it, along with nickel and zinc, has become “far more attractive” in a decarbonising world.
“I think the reality is that every single person in this room, and every mining company in the world, want more copper. The world needs more copper in a major way,” Kerr told the Melbourne Mining Club in April.
Copper miner Codelco signed an unprecedented collaboration agreement with BHP in May, which will focus on exchanging knowledge between the two companies in finding sustainable ways to mine.
“Our copper is part of the solution to climate change that threatens the planet and must be produced in a sustainable manner, consistent with that cause,” former Codelco chief executive André Sougarret said at the time.
“In order to imagine these new ways of doing mining, innovation is one of the main axes of our management, a focus that we can only develop in alliance with players who are equally active in this search, as is the case with BHP.”
It makes sense that Codelco would partner with BHP. After all, the Big Australian owns and operates many prominent copper mines all over the world, chief among them the Escondida mine in Chile.
“We have operated Escondida in Chile, the largest copper mine in the world, for more than 30 years,” Basto said at Austmine. “Every year, Escondida mines enough material to fill the Adelaide Oval to the roof 80 times and produces enough copper to produce around 12 million electric vehicles.”
The Escondida mine is operated and owned through a joint venture between BHP (57.5 per cent), Rio Tinto (30 per cent) and JECO Corp (12.5 per cent).
Looking locally, BHP operates the Olympic Dam mine in South Australia, which is one of the world’s most significant deposits of copper, gold and uranium. But BHP’s Australian copper assets don’t stop there.
After acquiring OZ Minerals, BHP now operates the Carrapateena and Prominent Hill copper mines, which, combined with Olympic Dam, has unlocked a new copper district in SA.
Rio Tinto is also a keen copper participator, with a 30 per cent interest in Escondida bolstered by a 66 per cent stake in the Oyu Tolgoi copper mine in Mongolia.
The major miner held an investor site visit at Oyu Tolgoi in early July, where
five years.
Other assets that will support this dream include Rio’s Kennecott copper mine in Utah, and the company’s Resolution copper project in Arizona.
Newmont chief executive officer Tom Palmer said copper demand is expected to nearly double from 25 million tonnes to about 50 million tonnes by 2035 in order to deploy the technologies needed to achieve net-zero targets by 2050.
“Based on current copper production trends, we will experience copper shortfalls of 10 million tonnes by 2035. In fact, by 2050, the world will only be producing 20 per cent of the copper needed to meet the net-zero climate goals,” Palmer said at the World Mining Congress 2023.
“Bridging this gap will require significantly more copper mines, copper recycling and enhanced copper leaching processes.”
Newmont produces copper as a secondary mineral from several of its gold mines, including the Boddington operation in WA.
A renewable future
Copper’s role in helping the world reach its future climate goals is clear, and we are beginning to see more and more collaborations to ensure this dream becomes a reality.
This includes Anglo American and Jiangxi Copper Company joining forces to create sustainable value chains in the copper industry. Under a memorandum of understanding (MoU), the companies will work together to provide greater assurance on the way copper is mined, processed and brought to market.
“We are developing a series of partnerships to shape a more sustainable and customer-centric value chain – one that meets consumer-driven demand for copper with demonstrably
“In line with our sustainable mining plan goal to establish ethical value chains for our products, this collaboration aims to support Jiangxi Copper’s efforts to contribute to the Chinese industry’s long-term decarbonisation goals and transition to a greener economy, as we work to provide materials solutions that are responsibly produced, sourced and delivered.”
Jiangxi Copper deputy general manager Chen Yunian said the company is committed to green, sustainable and high-quality development.
applications of mining, processing and smelting, and promote the development of a sustainable and responsible copper supply chain with a focus on renewable energy utilisation, energy conservation and emission reduction,” Yunian said.
Through these types of global copper partnerships and developments, it’s easy to see the base metal playing a key role in the global energy transition.
And Australia is a positioned to be a key player in that transition for years to come. AM
WE EXPECT GLOBAL DEMAND FOR COPPER TO INCREASE SIGNIFICANTLY AS THE WORLD TRANSITIONS TO LOWER CARBON SOURCES OF ENERGY POWERED BY MORE SOLAR PANELS AND WIND TURBINES.”
500+ autonomous haul trucks — worldwide
If you see an endless stream of driverless trucks on the mine site, think again.
Advances in Komatsu’s autonomous haulage system and teleoperation excavator mean transitioning upskilled personnel from cab to control room. This evolving and expanding mining technology is helping to redefine mining and boost productivity.
Let us help you embrace a more innovative and sustainable future with a tech-forward workforce and next-level equipment and solutions.
Develop your team. Drive efficiency.
Metals Acquisition Limited established itself with the
We could have bought an asset anywhere, so we looked at a lot of assets in the Americas and we ended up buying
What type of mine was the company looking for?
The beauty of a SPAC (special purpose
Listed on the New York Stock Exchange, the company had a global scope, with a desire to buy a mine in a Tier 1 jurisdiction that would produce minerals to support the renewable energy transition. This led Metals Acquisition to Glencore’s CSA copper mine near Cobar in New South Wales, which the company acquired in mid-June.
Australian Mining Metals Acquisition chief executive officer Mick McMullen to chat about what inspired the CSA acquisition and where to next for the operation.
What’s the background on Metals Acquisition Limited?
We set up Metals Acquisition a couple of years ago and we wanted a
tantalum, which is an adjacency to lithium. We looked at about 80 assets, narrowed it down to about a dozen which we did detailed due diligence on. We had four or five that we then did quite a lot of negotiating on, and then we ended up with CSA as being the one.
If you look at our background, I’d spent most of my career overseas. I spent a decade in North America, doing turnarounds on much larger businesses and, you know, we like
We also said we wanted to go where we knew the ropes, where we didn’t have to learn from scratch. I’m from Coonamble (NSW) and I built Tritton (the Tritton mine owned by Aeris Resources) 20 years ago in western New South Wales. Various members of our corporate team have also worked at Northparkes (copper-gold mine near Parkes) or Aurelia (Metals) or other assets in western New South Wales.
So we bought CSA, which is
specialists. We fix the cost base and get more out of the existing infrastructure.
We didn’t want to do a development asset in the current cost environment. We wanted to take an existing mine where the capital has been sunk and capitalise on that.
What about the CSA mine appealed to Metals Acquisition?
We see a lot of excess capacity in the infrastructure at CSA, so the processing plant will do significantly more than what the current throughput is, because it’s mine constrained.
You look for assets where you’ve got a lot of excess utilisation ability. We’ve got a phenomenal orebody and then the difference is work practices, and we can change work practices relatively cheaply.
When I ran Stillwater (Mining Company) in the US, no one’s ever heard of the mine, but it’s about five CSAs stitched together, with a smelter as well. It was the biggest company in the state of Montana, but appalling productivity. I fixed the productivity, got the cost down, got production up. That’s what that exercise was.
What are your production targets at CSA?
We think about 50,000 tonnes of copper is doable in 2024. That’s the official plan but, ultimately, we think it should do about 55,000 tonnes of copper (per year).
I’ve been using a Back to the Future anecdote: ‘This is what you did in 2017. I’m not asking or promising that this mine is going to do double the best it’s ever done. We’ve just got to get back to where we were in 2017’.
do double the best it’s ever done’, no one will believe that.
But if we say, ‘This is what you did in 2017, we want to get back to that’, and unwind some of the poor mining decisions that were made, I think we can get back to that level, but it’s probably 12 to 18 months before we get there.
Is Metals Acquisition on the lookout for any other mines?
We’re pretty busy. We had a list of assets that we looked at, so there’s a few others on that list that we could prioritise first. There are clearly some other assets in the Cobar Basin that could probably do with consolidation, but they’re a bit small. Northparkes; it’s not inside information, it’s in the newspaper. There’s sort of an (M&A) process being run, not an official process, but there’s a process. Clearly any copper asset in that part of the world is on our list. It remains to be seen where we get to on that one.
Then because our team’s split between North America and Australia, and I’ve spent a decade in North America, there’s a few assets in Canada as well that are on our list.
The last thing (Metals Acquisition chair) Nev Power ran was Fortescue. The last thing I ran was double the size of the Super Pit. And our big anchor (equity) investors, there’s six big funds, and one of them gave us $US50 million, another one $US45 million. They are backing us to recreate an OZ Mineralsstyle business because there’s a huge gap in the market.
Yeah, it’s definitely going to be bigger than that and, look, the timing of these things is not always ideal. Sometimes people kick off a process even though it’s not ideal timing for you, but, you know, decent copper assets in Australia or
CSA hasn’t been in the public domain for 25 years, and the kind of drill results we’ll be announcing very shortly definitely haven’t been seen in the public domain for a long time.
The cut-off grade has been twoand-a-half per cent, so anything under two-and-a-half per cent isn’t even in the resource. Most of our drill results are plus-five per cent and often plus 10 or 20 per cent copper, and I don’t think the market’s seen those kind of drill results since Sandfire (Resources) discovered DeGrussa (copper mine in WA).
Not only from a risk profile point of view and in investment, but you want to be able to offer ability to grow through the organisation. If you’re a single-asset company, you struggle in your ability to attract and retain talent.
If you can show that progression, the growth and the ability to grow with the company, I think we attract a higher level of candidate as well. AM
It makes sense that the World Mining Congress (WMC) 2023 would be held in Australia. After all, the country is universally known as a mining capital of the world.
And while the Australian resources sector has long ridden the wave of commodities such as coal and iron ore, it is now set to be a leading provider of the critical minerals needed for the energy transition.
Taking place in Brisbane from June 26–29, mining company executives and Australian politicians took to the WMC stage to detail the industry’s important role in supplying a greener future.
Federal Minister for Resources
Madeleine King discussed the emerging clean energy systems and how they will be mineral-dependent.
“An onshore wind power plant, for instance, requires nine times more mineral resources than a gas-fired power plant,” King told the WMC audience.
“Each new megawatt of solar power requires between 35-45 tonnes of steel. And steel needs iron ore and coal for the moment, though exciting developments may eventually see us producing green steel using renewable hydrogen.”
King urged miners to keep pace with the rising demand for clean-energy technologies.
“Recent analysis by the International Energy Agency suggests the world will need around 50 new lithium mines, 60 new nickel mines and 17 new cobalt mines to meet net carbon emissions goals by 2030,” she said.
“Right now, there are 26 lithium mines, 186 nickel mines and 89 cobalt mines operating globally. That means producing more raw materials
for renewables and clean energy technologies faster than ever.” Australia, and Queensland in particular, can play an important role in the global energy transition, particularly through vanadium – a metal that can be used to create reliable, safe and stable storage solutions for renewable energy.
“(Vanadium) batteries are large-scale battery storage systems that store excess power from the grid for use during peak demand periods,” King said.
“Unlike better-known lithium-ion batteries, vanadium redox flow batteries boast superior durability for long-term storage and charging and the technology has much greater recycling potential.
“And the technology to build them is in Australia.”
King, who emphasised the fact the road to net-zero runs through Australia’s resources sector, shone a spotlight on the Federal Government’s recently released
Critical Minerals Strategy, which she described as “a framework to grow Australia’s critical minerals sector”.
“Our strategy provides a framework for Australia to become a globally significant producer of raw and processed critical minerals,” King said.
Coinciding with the Critical Minerals Strategy discussion was Queensland Premier Annastacia Palaszczuk unveiling the Queensland Critical Minerals Strategy.
“In Queensland we have some of the world’s richest mineral-producing areas, which in north Queensland alone is estimated to be worth $500 billion,” Palaszczuk told the WMC audience.
“The Queensland Critical Mineral Strategy is about growing this industry by not just mining the raw materials but also being able to process it and manufacturing renewables right here in Queensland.
THE WORLD MINING CONGRESS WAS HELD IN AUSTRALIA FOR THE FIRST TIME IN 2023, GIVING COMPANIES FROM AROUND THE WORLD THE CHANCE TO ENGAGE WITH THE LOCAL SECTOR.MAJOR MINER RIO TINTO WAS ONE OF THE WMC’S DIAMOND SPONSORS.
“I want Queensland to be a global leader, supplier and manufacturer of critical minerals and this strategy will help us achieve that.”
Queensland Resources Minister Scott Stewart echoed these sentiments.
“Queensland has vast reserves of critical minerals, such as copper, zinc, vanadium and cobalt, that the world is demanding to produce batteries and renewable energy as part of their plans to decarbonise,” Stewart said.
As the WMC wrapped up, Federal Treasurer Jim Chalmers took the stage to discuss the integral role of mining in the Australian economy and the country’s path ahead for critical minerals.
“(The resources sector is) the largest sector of our economy,” Chalmers said. “It employs around 300,000 people, including 70,000 here in Queensland. It accounts for two thirds of our exports, bringing in around $460 billion a year.”
“And it will underpin our efforts to make the next era even more prosperous than the last, as we look to take advantage of the big opportunity that is the shift to cleaner, cheaper energy.”
It is clear that Australia’s goal to become a renewable energy superpower cannot be achieved without the mining industry.
“A strong and successful energy transformation will be built on a strong and successful resources sector,” Chalmers said. “The scale of that task is formidable, but Australia stands ready to play a big part.”
Australia will play this part via the Federal Government’s three-part approach to the green energy transition.
“One, building new resilience in supply chains. Two, making the right critical mineral investments that work for our people and our international partners. And three, linking critical minerals up properly with a broader effort to drive growth through the energy transformation,” Chalmers said.
The Federal Government has pledged billions towards building Australia to lead the way in the global energy transition.
“(The Federal Government is) allocating $23 million to ensure that Australian critical minerals have world leading environmental, social and governance credentials, and (is) making more than $2.5 billion available for government investment in critical minerals projects,” Chalmers said.
But for the mining sector to progress towards a net-zero future, sustainability needs to become a key focus.
Many mining professionals touted the importance of sustainable mining and the decarbonisation of the sector.
Emeritus Professor Mike Hood, mining and technology expert and chair of the program committee
for the WMC 2023, discussed decarbonisation efforts.
“Mining companies are actually all well engaged in using and improving existing technologies to reduce their emissions,” Hood said.
“Other players in the value chain, such as steel and cement companies, are developing, adapting and demonstrating new technologies for these downstream industries.”
RECENT ANALYSIS BY THE INTERNATIONAL ENERGY AGENCY SUGGESTS THE WORLD WILL NEED AROUND 50 NEW LITHIUM MINES, 60 NEW NICKEL MINES AND 17 NEW COBALT MINES TO MEET NET CARBON EMISSIONS GOALS BY 2030.”
University of Queensland Professor Anna Littleboy discussed the apparent clash between the need for critical minerals to make the materials, equipment and technologies to deliver net-zero emissions and the timelines required to implement responsible mining practices.
“The volume of minerals we need for this transition is absolutely massive,” Littleboy said. “It takes 25 years on
average from finding a new deposit to getting it opened. So we will be at 2050 before we know it.
“On one hand, we are working to accelerate our minerals production to meet our commitments to net-zero. On the other hand, we are tightening up our awareness of, and concerns about managing environmental, social and governance performance issues.
“We need to act fast on a global scale to meet climate change reduction commitments. But we must also ensure that at a local scale we don’t end up with worse environmental and social practices.”
It’s also clear that in order to achieve sustainability within mining practices to ensure a cleaner future for Australia and the rest of the world, the industry will need to innovate.
and related innovation will help the world move towards a sustainable future.
This included Newmont chief executive officer (CEO) Tom Palmer, who detailed key emerging global megatrends affecting the mining sector, including accelerated technology such as artificial intelligence.
“Together, these megatrends simultaneously animate, interact with, and reinforce one another in ways we cannot predict, giving rise to a growing meta-crisis, one in which we will be expected to succeed in right now and over the long-term,” Palmer said.
“The intensity and velocity of these global megatrends are so universal and disruptive that if, as an industry, we are not agile enough to adapt, align and lead, we will risk losing control of our businesses.”
Recent technology innovation has helped Newmont businesses become safer, cleaner, more efficient and productive.
“Some of the technological benefits we’ve seen at Newmont in recent years include automation and remote operations,” Palmer said.
“Automation is helping us mitigate safety risks, reduce emissions and improve efficiencies. Specifically, autonomous vehicles, automated drilling, remote operations, and asset monitoring are critical to how we mine today and, even more so, in the future.
“As part of our commitment to address the impacts of climate change, we are also challenging ourselves
and our equipment manufacturers to take risks in order to drive innovation and more rapidly develop sustainable solutions to reduce emissions.”
BHP chief technical officer Laura Tyler discussed the “transformations in mining” and how they will assist in reducing emissions.
“I believe nuclear energy will be a part of the base-load mix in the global elimination of carbon emissions-rich energy,” Tyler told the WMC audience.
“As more of our systems and decisions are automated, we will become the orchestrators of improvement and innovation – the skills we need for the future must embrace highly digital operational and project management as the way we deliver value and efficiency.
“As we stand in the future, I see an exciting, safe and automated sector, valued by society for the types of work it provides.”
Tyler said the key to this future is innovation.
“We need to expand the ecosystem of ideas that we are exposed to,” she said. “We are not in every pool of expertise, but we must be more open to conversations and ideas than ever before.”
In utilising these ecosystems, the mining industry must use data to drive solutions to make systems run better.
“Partnering on tech and innovation is making our sites safer and more sustainable as we think and act differently to deliver real results,” Tyler said.
Tyler called for all mining operations to identify, develop and implement
digital and technical innovations to meet
“Build our ecosystems, be open to new partnerships and ways of working, and be organised to move faster – driving ourselves forward with data, with people close to the opportunity finding the solution and then sharing the outcome for us all to use,” Tyler said.
“These mines of the future are vital to help deliver the world of the future and a surer pathway to net-zero – a transformation of mining to deliver a global transformation by mining.”
Fortescue CEO Fiona Hick touted the importance technology advancements will have in reducing carbon emissions. This belief led to the creation of Fortescue Future Industries, which will work to decarbonise its operations and, in time, share this technology globally.
“It is through actions like this that will deliver on that new interpretation of value into the long term,” Hick said.
Hick said the mining industry will need to work collectively and collaboratively across the value chain to drive the changes needed to lower emissions and meet net-zero goals.
“Partnerships and collaborations are pivotal to us as an industry maintaining our licence to operate, and to deliver that new kind of value-creation,” Hick said.
“The success of individual mining companies, and indeed that of the whole mining industry, creates value for local communities, for the national economy, and creates benefits around the world.
“When the mining industry is strong, there are so many direct and indirect benefits.” AM
ONE OF THE GLOBAL MINING INDUSTRY’S MOST LEGENDARY DRILL RIGS HAS BEEN REVITALISED. AUSTRALIAN MINING TAKES A CLOSER LOOK AT EPIROC’S EVOLVING DRILL MASTER RANGE.
As one of the world’s leading drilling manufacturers and suppliers, Epiroc has a knack for developing new solutions just when its clients need them most.
Whether it be the Simba, Boomer, Explorac, SmartROC or Pit Viper, Epiroc has engineered drill rigs for every application in the mining sector. And it has engineered them expertly, with Epiroc products some of the most sought-after on the global mining stage.
In the same family as the Pit Viper range is Epiroc’s Drill Master (DM) series, suitable for rotary blasthole drilling applications.
The DM range now spans seven different models, with the most recent iteration – the DM30 XC – launched in 2022, demonstrating the enduring legacy of this series of machines.
As Epiroc puts it, the DM series is “a legend in the drilling industry”.
One of the most reliable DM machines – the DML – has carved out its own reputation for being the mining industry’s go-to rotary drill rig when it needs a heavy-duty solution for the toughest of conditions.
One Epiroc customer, which has been partnered with the Swedish original equipment manufacturer (OEM) since 2012, had been a long-time user of the SmartROC D65 crawler drill. But when the miner was after a new fleet of platform drills, it turned to the DML.
Product manager – automation DS for Epiroc Australia’s surface division, Paul Skaife, told Australian Mining the customer was initially deciding between a Drill Master or Pit Viper drill rig, but they ultimately opted for the DM range as it was best suited to its operation.
The customer purchased the DML rigs in 2022, and after being transported to Perth from Epiroc’s drilling factory in Texas, the machines were modified to ensure they were compliant with Australian standards.
Skaife said the DML was going to be able to deliver the customer enhanced performance, safety and reliability compared to its existing fleet.
“The DMLs will drill production holes in low-risk areas,” Skaife said. “They’ll drill holes more accurately and efficiently not only because of the DML’s superior capacity but also because the machine has been tailored to the operation’s unique specification (spec).”
While the SmartROC D65 has been a more suitable option for the customer in high-risk locations, given it’s a smaller tele-remote rig, the DML is important for situations where drill volume is key.
The DML can also be modified to have tele-remote capabilities if and when required. This can be done by harnessing the smarts of Epiroc company Remote Control
Technologies, which the OEM acquired in December last year to boost its automation capabilities.
The DML range is one of Epiroc’s most proven drilling platforms, but the emergence of the Pit Viper, as well as the success of Epiroc’s broader drill range, has seen many customers go for alternative options in recent times. But a DML resurgence is occurring.
“The Drill Master range has a cult following,” Skaife said. “Many operators learned to drill holes on a Drill Master because they are everywhere – there are hundreds of DMLs operating globally,
“There’s a few dot points that we cover off when we first start talking to a customer,” Skaife said. “We really need to understand their resource, we need to understand their ground hardness
While the Pit Viper has turned heads across the Australian mining industry for its technological and operational excellence, the DML still has an important role to play for Epiroc
technologically advanced they might be. For many operators, the DML was the original drill rig, assisting and educating them to become the operators they are today. Its legacy is
AUSTRALIAN MINING PROFILES THE BROKK DEMOLITION ROBOT, WHICH HAS PROVEN ITS ABILITY TO COMPLETE A RANGE OF TIME-CONSUMING UNDERGROUND TASKS SAFELY AND EFFICIENTLY.
Swedish original equipment manufacturer (OEM) Brokk Global has been rapidly growing its Australian footprint, with prominence in the defence, construction, tunnelling and resources sectors.
The Brokk demolition robot is colloquially known as the “Swedish army knife” such is the electric-powered machine’s versatility to complete a range of tasks expertly.
This type of flexibility is particularly pertinent to the Australian resources industry, especially in the confines of an underground mine.
Brokk Australia managing director Will Visser explained in more detail.
“You break that mould of, ‘What can it do?’,” Visser told Australian Mining “(Someone might say), ‘It’s just a loader’. No, it’s not just a loader. It can load but it can also drill, cut, shotcrete, split and hammer oversize rocks.
“Once you have the Brokk robot working underground, you have access
to all the tools that perform these tasks. These tools are a relatively small investment compared to the safety and productivity benefit at the operator’s fingertips.
“So your big investment is in your machine,” Visser said. “Once you’ve done that, with three or four standard tools, you’re then looking at all the other possibilities. Once you combine that with an operator that endorses this new method of working, you’ve then got a winning team underground.”
And that winning team comes with reduced consumption, a reduced carbon footprint and greater capacity to complete more tasks more efficiently.
“Suddenly, you’re not using several machines,” Visser said. “You’ve got one machine with all the attachments, so your consumption underground is reduced and you have less servicing and maintenance.”
With several machines either purchased or operating in Australian mines, the local sector is beginning to recognise the Brokk name.
Visser said one Australian customer has been excavating ventilation shafts in its underground mine and wanted to further mechanise the process. The customer had previously been completing the task manually, which involved handheld pneumatic rock drills and shovels, and hand-held shotcrete spraying.
“Instead of completing these functions by hand, we can do all of this more safely and efficiently with the Brokk 200, which is a very powerful machine,” Visser said.
“We can slipe the shaft shape with a hydraulic hammer, and we can swap tools and use a bucket to move material around. These tasks usually took them two days but now we can do it in an hour.
“We’ll be drilling holes in one shift, which used to take them up to a week. We can complete concrete spraying quicker because it’s not a human holding a shotcrete hose.
“Now you’ve got a machine doing the spraying, which can lift the hose 3m high and back down again, so
you can cover larger areas and operate more efficiently.
“This brings greater safety and productivity to the underground mine.”
Another customer, Grecian Magnesite – which is mining for magnesium in the Greek archipelago – wanted to operate its underground mine fossilfree and without explosives. It needed a solution for its underground narrow vein operation, where it was mining veins that were 400m deep and 200m wide, making it one of the purest magnesite deposits in the world.
So the company turned to Brokk.
“We saw an opportunity here to extract as pure magnesite as possible with the aid of the right machine in a fossil-free way,” Grecian Magnesite engineer George Bourmas said.
“We had high ambitions and wanted to create the safest and most environmentally friendly underground mine.”
Bourmas had a theory of using a hydraulic breaker and breaking up the material to the right size, instead of using
explosives, and then loading the material out with a battery-powered loader.
“I met many sceptics who were doubtful about how effective this demolition robot would be, but I knew Brokk’s robots and … I knew how fragmented the rock looked,” Bourmas said.
“Therefore, I thought it would be possible to break the magnesite apart with a wide chisel at speed and in an environmentally friendly way.”
Grecian Magnesite commenced using the Brokk 500 in December 2021 and hasn’t looked back, with the machine delivering on sustainability, productivity and safety.
“We have large veins here and the Brokk robot is the most suitable machine to handle this type of assignment productively,” Bourmas said.
“Our only problem is that we are breaking up the rock at such a fast pace that the loader does not have time to take out all the material fast enough. But that’s a pleasant problem to have.
“The alternative would have been blasting, but this would have taken longer and created a large disturbance zone that would have required us to send the material for sorting, but this is not needed.
“Now we perform the mining with surgical precision and, in this way, we save both time and money on the project.”
Such is the Brokk’s remote capability, the Brokk 500 operator can stand 25m away from the work zone when operating the machine, which – combined with the machine’s carbon-neutral profile – has enabled Grecian Magnesite to establish a strong environmental, social and governance (ESG) reputation.
“I’ve seen all sorts of underground mines and tunnels, and this is the first where everyone feels extremely safe,” Bourmas said.
“We are the first fully electric mine in Europe and perhaps also the safest. We don’t have to be worried about anyone using explosives incorrectly, and we have no diesel fumes or rockfalls.
“That feels great and allows us all to sleep well at night.”
Brokk’s ESG attributes don’t just concern sustainability and safety, but also accessibility.
“You don’t have to be strong to operate this machine,” Visser said. “You can have female operators doing tasks they were previously not able to perform, because it was too strenuous for them to do continuously.
“So it levels the playing field for operators that maybe want to pivot into areas of mining that have typically been heavy-duty.”
Since the Brokk demolition robot became a remote-controlled unit in 1976, the operability of the machine has come a long way. This has furthered its accessibility even more.
“You don’t have to look at the controls, you look at the job, and that’s the Brokk philosophy: to be ‘one with the machine’ and not have to look down and fiddle around with the controls,” Visser said.
As more mining companies and contractors become aware of the Brokk demolition robot, the OEM has been attracting plenty of interest of late, which has not just been limited to typical Brokk machines.
“There’s a lot more enquiries coming for standard Brokk machines and special application machines,” Visser said. “Previously, customers with a unique application would have to build a whole new machine to support this, but by harnessing our experience from other industries like nuclear, defence and rescue, we’re evolving our Brokk machine to solve the previously unsolvable in underground mines.” AM
WE CAN SLIPE THE SHAFT SHAPE WITH A HYDRAULIC HAMMER, AND WE CAN SWAP TOOLS AND USE A BUCKET TO MOVE MATERIAL AROUND. THESE TASKS USUALLY TOOK THEM TWO DAYS BUT NOW WE CAN DO IT IN AN HOUR.”THE BROKK DEMOLITION ROBOT IS GAINING TRACTION IN THE AUSTRALIAN MINING INDUSTRY. THE BROKK MACHINE HAS SUPPORTED GRECIAN MAGNESITE MAINTAIN A FOSSILFREE UNDERGROUND OPERATION.
AECI MINING EXPLOSIVES IS LEADING THE WAY IN ADVANCES ACROSS THE MINING EXPLOSIVES SECTOR.
AECI’s LogShot® is a complementary software package that informs users of the blasting activity and allows operators to extract detailed post-blast activity logs.
“This is very useful for consolidating the activity of the blast itself, along with the inventory management of detonators, while highlighting typical problems users may have experienced,” Pillay said. “The DigiShot Ranger also logs user interface activity, which makes it easy to conduct operator safety audits as it can also be used to determine if there is supplementary operator training required.”
blast efficiencies irrefutably contribute to the environmental area, and the detailed blast logs that are generated help with governance by improving reporting and compliance.
“At AECI Mining Explosives, our focus is on continuous improvement along the whole value chain,” Pillay said.
“The DigiShot Ranger evolution is just one example of the company’s holistic and
Innovation and technological development are essential components of business strategy in every sector across the globe, and mining is no exception.
AECI Mining Explosives continues to invest significantly in research and development (R&D) in its quest to help the mining industry achieve better blasting outcomes.
“We pride ourselves in developing innovative solutions in the initiating systems and commercial explosives space,” AECI Mining Explosives product portfolio manager – electronic initiation systems Ashlin Pillay said. “That’s how we remain at the forefront of technology and constantly pursue sustainability and continuous improvement.”
The AECI product range is underpinned by inherently safe design principles, which includes thoroughly testing electronics before they are used in the field.
“This ensures that there is no compromise and, as a result, all of our electronic initiation systems and detonators benefit from the same intrinsically safety features,” Pillay said.
“We’ve subjected our electronics to high voltage which simulated a lightning strike. This resulted in uninitiated detonators due to the designed protective circuitry.
“We’ve ensured by design that our detonators are only initiated by our control equipment.”
AECI has announced a further development in its electronic initiation systems offering.
The DigiShot® Ranger has been specifically designed to cater for
smaller mines, quarries and civil blasting operations.
In line with inherently safe design principles, the DigiShot Ranger’s built-in long-range antenna enables the system to transmit a safe encrypted blasting signal up to 3km away when a line of sight maintained, allowing a remote blast if required.
“We’ve been working tirelessly to improve our offering for mid-tier opencast mines, civil blasting activity and quarrying operations,” Pillay said.
“The original DigiShot system is a reputable and accomplished product; however, advancement in technology allows us to better support the modernday customer and system requirements.
“The lessons we have learned from the DigiShot system have been engineered onto a technologically advanced platform concurrently integrating new technology, data and third-party requirements to create the DigiShot Ranger.”
According to Pillay, the DigiShot Ranger works with AECI’s fourthgeneration detonators, which enables storage of a wide variety of data on the detonator and tagger, including bench activity.
The last detonator check function also ensures all detonators on the string receive the blast command.
“The new system keeps the portability and ease-of-use of the original DigiShot system requiring minimal training, but the DigiShot Ranger doubles the detonator capacity (to 600 from 300), and gives the operator flexible tagging options, plus automatic detonator detection,” Pillay said.
Customers can also build their very own blast library on ViewShot® Express, detailing blast design parameters which may be used for future blasts in similar geological conditions during blasting. This is an important safety aspect, but can also help to improve operational efficiencies.
Attention has been given to the DigiShot Ranger’s ergonomics and userfriendliness. The flexibility in tagging methods defines multiple options to allow for traditional tagging and the more modern tag-by plan. The latter allows for tagging on-bench with delay and location from the pre-designed blast plan, which mitigates user input errors.
With smarter tagging methodologies, movement on the bench can be reduced and optimised. The tagger has been designed to function as an inherently safe device and cannot generate the required blast voltage or blast commands to initiate the blast – the blast command is stored in a near field communication (NFC) blast card.
Environmental, social and governance (ESG) is a fundamental element in the way that AECI Mining Explosives conducts its business.
With the DigiShot Ranger, for example, the focus on safety and operational efficiency addresses the social aspect, while the improved
Revolutionise your mining operations with autonomous mining solutions. Increase efficiency, reduce costs, and improve safety on the job with real-time monitoring and advanced analytics. Optimise production and upgrade your sites with our autonomous mining solutions.
One platform. One partner. For the life of your mine.
SMW DRILLING TAKES PRIDE IN ADDING VALUE AT EVERY STAGE OF THE DRILL-AND-BLAST PROCESS.
Safety, reliable productivity, quality and efficiency. These are the four key aspects of SMW Drilling’s business that have satisfied its drilland-blast customers for almost 20 years.
Working from its headquarters in Mount Thorley, New South Wales, the company provides responsive drilling services to mines throughout NSW and Queensland, with plans to expand to Western Australia.
“We are blasthole drilling specialists with a predominant focus on mining production drilling services,” SMW Drilling managing director Ben Chaniago told Australian Mining.
“We provide personnel and management that is highly skilled and focused on drilling-specific safety and production.”
Guided by its “adding value” approach, SMW Drilling takes pride in adding value at every stage of the drilland-blast process.
The company’s services include the ability to drill holes ranging from 57mm to 311mm in diameter utilising rotary and percussion drilling methods. It also carries out sample drilling services that includes in-pit reverse circulation drilling, and supplies drill rig and ancillary equipment for hire.
SMW Drilling partners closely with its clients to identify and implement solutions, which leads to greater productivity and efficiency.
“Where there are mismatches between planning expectations and conditions on the bench, such as geology and scheduling delays, we work closely with functional managers like client drilland-blast supervisors and tech services to give useful feedback and data-driven insights to then pass onto the planners and managers,” Chaniago said.
Focused on being nimble, reliable and responsive, SMW Drilling focuses on building a foundation of robust systems and data processes to achieve safe and efficient drilling programs.
“We pride ourselves on using technology in our systems,” Chaniago said. “This includes the ability to use data in real-time and the ability to use that data for effectiveness.
“We collect and closely analyse data. Then we share these insights with the clients as it often identifies small areas for improvement that can add up over time.”
Chaniago said that while the company’s primary focus is to provide good-quality holes that lead to good fragmentation and lower downstream
processing costs, it offers a broad range of services.
“We have the ability to supply labour hire in the form of operating capability, maintenance capability, or technical services capability, (as well as) in-house engineering – we’ve got the ability to rebuild or manufacture new parts of componentry, and complete equipment rebuilds and overhauls,” Chaniago said.
SMW Drilling’s number-one focus is the customer experience, an area in which the company has received positive feedback.
“There are other companies that drill holes and do what we do with the same sort of equipment, but our focus has always been that customer experience and being able to accommodate variances
and to be adaptable to any sort of work environment,” Chaniago said.
SMW Drilling also understands the value predictable results have in terms of customer outcomes.
“Clients want something they can plan around,” Chaniago said.
As such, the company takes a proactive approach to keeping the customers informed about what to expect and then focuses on meeting those expectations.
“We want our customers to apply useful, data-driven insights and feedback that positively impact operations and assist in developing the knowledge of client personnel,” Chaniago said.
The company’s drill-and-blast service ties in purposefully with its other mining services.
“Our in-house engineering aligns with supporting the production drilling services,” Chaniago said. “The labour hire part also supplies and supports the production drilling services.”
SMW Drilling is proud of the sustainable growth it has demonstrated in its 18 years of operation.
“We find that with smaller mines and their owners there is less understanding of drilling, and we are able to fill this knowledge gap,” Chaniago said. “We have a lot of knowledge and are happy to share it.
“Often conversations early in the planning process can lead to savings or less surprises later on. We like to engage (with our clients) early on.
“This comes in the form of helping them understand the resourcing needed to get the metres they need, especially when geology does not match what was planned for.
“Then (we) help clients gain clarity on their types of open cut mines, delays and getting alignment at different levels of their organisation through the use of better data for decision-making.”
SMW Drilling’s efficiency in mobilisation and investments in technology and data-driven production and decision-making all come together to make the company stand out from the crowd in a large Australian mining industry. AM
Derrick continues developing innovative, high-capacity screening equipment that increases our customer’s gold recovery while reducing their environmental impact. Combined with our Trilogy™ screen technology and our linear motion screens, the G-Vault® Complete Interstage Unit is a system requiring minimal maintenance to maximize efficiency and productivity. With easy installation and a small footprint, our durable higher open area screen panels allow for increased throughput.
ULTERRA’S PDC DRILL BITS ARE HIGH-TECH, DURABLE AND FIERCELY EFFICIENT.
hen it comes to equipment expenditure, it is often said you get what you pay for and it pays for itself over time, particularly when it comes to quality.
This is especially true for mining industry operators, whose safety, reputation and prosperity swing on the calibre of the equipment they use.
That is the ethos of Ulterra Drilling Technologies, a designer and builder of premium-quality PDC drill bits that focuses on operator success.
“Our competitors typically look for high volume and low cost. We’re the complete opposite,” Ulterra director Asia Pacific Joey Mos told Australian Mining
“We’re a small, specialised company offering the best drill bits on the market. We’re a Ferrari.
“The average roller cone drill bit will last around 3000m before needing to be thrown away, but our PDC drill bits often last in excess of 30,000m on a single run.”
Ulterra’s drill bits are engineered to meet sustainability targets and can be rebuilt, resulting in incredible mileage with no degradation. And the company can refurbish a customer’s bit within 48 hours at its newly commissioned facility in Mackay (Queensland).
“We’ve drilled millions of metres globally using PDC drill bits. With that history, we’ve really learned to
Wunderstand and develop our technology to create the fastest and the most durable bit,” Mos said.
Ulterra’s PDC drill bits deliver superior hole quality and reduced hole deviation, as well as significant reduction in redrill. The PDC bits also deliver an increased penetration rate, roughly 30–50 per cent faster than roller cones.
And when coupled with Ulterra’s patented SoftDrive drilling system, bit changes are further reduced to potentially every 30,000m. Each SoftDrive unit has the potential to outlast several bits prior it needing a service.
“To go alongside our PDC drill bits we use the SoftDrive system, which eliminates rod rattle while drilling,” Ulterra’s mining manager in Australia, and the original SoftDrive patent holder, Nathan Brooks told Australian Mining
“SoftDrive is filled with proprietary elastomer compound which gives a little bit of lateral movement to the drill. When the bit takes an aggressive bite of a formation and wants to stall out, rather than all of that impact being placed onto the critical cutting structure, that lateral movement soaks up the impact, preserving the bit.”
With an investment in Ulterra’s product, customers can realise true cost savings.
“Our bits drill for longer and they drill easier,” Brooks said. “Rigs are running more optimally, consuming less fuel and spending less time on bit changes, which is significantly reducing operating costs.
“You’re also saving on repair and maintenance costs because you’re not running your rigs at their limit all the time .Our end goal is overall cost reduction.”
Fewer drill bit changes mean operators spend less time in contact with heavy machinery, helping keep them safe.
And Ulterra’s control over manufacturing and design, as well as better fuel efficiency for rigs, helps mine sites cut carbon emissions.
The company also prides itself on its responsive and tailored customer experience.
“Most of our customers have similar problems which can be solved by the PDC drill bits we already offer,” Brooks said. “We can usually sort out those cases within 48 hours.”
For more unique situations, Ulterra’s engineers can deliver custom-designed drill bits, including
bits designed for philanthropic water bores in north Africa, or a range designed specifically for autonomous drilling.
In addition, all of Ulterra’s PDC manufacturing is undertaken in its North American facilities.
“If we go down the design route, we can have a prototype drill bit from North America in the ground within three weeks,” Brooks said.
Powering this rapid turnaround is the fact that Ulterra has stock points across the country, a refurbishment facility in Mackay, and offices and personnel in Mackay, Brisbane, Adelaide and Perth. This also enables Ulterra to hire the best in local talent to help support its growing footprint in the Australian mining industry.
Putting all these pieces together, it’s easy to see why Mos calls Ulterra the Ferrari of the drilling industry.
“The market in the last couple of decades has been focusing on cheaper and cheaper drill bits,” Mos said.
“You talk to a lot of the drillers that have been out in the field for a long time, and they’ll tell you they used to get higher metres with their drill bits than what they do now.
“It’s about more than just the upfront cost. It’s the cost of drilling, it’s the cost of damages, it’s the cost of maintenance, and so much more.
“We’ve proven that if you flip that on its head and pay a bit more, you get a product that’s not just a bit better, but quite simply the best that’s out there and multiple times worth it’s cost.”
ater is life. This is as true on the grand scale – for all living things on earth, in fact – as it is on the smaller scale.
Often taken for granted, water holds up many major industries, which in turn holds up everyday life. Even an industry as seemingly hot and dry as mining is utterly dependent on access to water.
Few know this better than Aquatech owner Luke Garbelini.
“Water is critically important to the mining industry. It’s utilised in every part of mining operations, from processing to power generation to dust suppression,” he told Australian Mining Aquatech Drilling is a privately owned and family-run business that provides cost-effective water well drilling. The company has been taking on drilling projects across Western Australia for more than 30 years.
“Every client has different requirements when it comes to water,” Garbelini said.
“When it comes to mining, there’s often a de-watering requirement that involves drilling bores to stop
Wwater from entering mine workings located underground.
“Water can be used for anything, and at Aquatech we are at the forefront of providing solutions for our clients’ requirements – whatever they may be.”
The company’s specialty is in water well drilling, utilising mud rotary or air hammer techniques. Using these tools, Aquatech can offer its clients tailored solutions and the capacity to drill to significant depths using powerful machinery.
Aquatech’s scope of work includes production bores, artesian bores, dewatering bores, monitoring bores, down hole hammer, cement grouting, water bore redevelopment and relines, as well as the installation of various steel and stainless-steel casings.
The company has a specialised array of drills on hand to tackle a range of tasks, all of which are maintained to the highest standards for optimal productivity and safety.
Aquatech’s primary drilling rig for large-scale work is the VersaDrill V2000. Capable of drilling 6–24-inch holes, the V2000 features an on-board 1070x350PSI compressor, and can reach depths of 1000m. It also includes an on-board
mud pump with a throughput of 40 litres per second (LPS).
Aquatech also has a custom-built, highly manoeuvrable drill rig for intermediate work that is able to complete smaller drilling projects with a smaller team of operators. This drill can deliver a 4–12-inch hole, and an eightinch-diameter hole up to 350m. It comes with a 32 LPS mud pump.
The best part is that the whole rig can be up and running in 25 minutes.
Aquatech also recently purchased a Versa-Drill NG 100 to add to the fleet,
offering the flexibility to construct medium to semi-large wells. The machine is suited primarily to hole diameters of 18 inches or smaller, effectively closing the gap between the Versa V2000 and the custom-built rig abilities.
The rig can be used for mud rotary or hammer drilling operations.
Last in the fleet is the compact trailer rig, which has just undergone a full rebuild. The drill is small in size, weighing in at only 3.5 tonnes, and is most suitable for the domestic
AQUATECH HAS THREE DECADES OF EXPERIENCE IN WATER WELL DRILLING ACROSS THE RESOURCES SECTOR.AQUATECH’S SPECIALTY IS IN WATER WELL DRILLING, UTILISING MUD ROTARY OR AIR HAMMER TECHNIQUES. AQUATECH HAS A SPECIALISED ARRAY OF DRILLS ON HAND TO TACKLE A RANGE OF TASKS.
market, in tight or environmentally sensitive areas.
Aquatech’s support truck carries a full complement of hydraulic hoses, pumps, motors and
additional spare parts, significantly reducing downtime.
The latest addition to the company’s toolkit is the underground camera, which it
can use to inspect drill holes and diagnose problems.
Progress is a common theme at Aquatech, which has been steadily growing for over three decades.
FEATURES:
• Over 70% load step acceptance
• Ideal for portable and intensive use
• Robust twist lock & forklift inlets
• 110% spillage free frame
• Performs in extreme temperatures & at high altitudes
• Designed with large access doors for ease of service
•
The company is currently looking to improve on its drilling capacity with new intermediate and large drilling machines, including the full complement of additional equipment, ensuring their units are fully self-sufficient.
“We are seeking to expand our capacity with everything that is required to run multiple highly flexible drilling units,” Garbelini said.
“We want to ensure our clients feel comfortable in the knowledge that if a breakdown occurs Aquatech has another machine ready to go – and it’s just as capable as the original unit.”
Aquatech is a member of the Australia Drilling Industry Association (ADIA), and the company’s drilling teams are Class 1, Class 2, and Class 3 ADIA-accredited.
All of Aquatech’s work is carried out to the highest of standards.
“Our approach at Aquatech is straightforward: it’s about detailed planning, it’s about reliable and robust machinery, and it’s about our experienced workforce being meticulous when it comes to safety and getting the drilling done with a minimum of fuss,” Garbelini said.
“We care deeply about our clients and our reputation for undertaking quality drilling is something that we’re very proud of as a company.” AM
With
LIKE TO KNOW MORE? SPEAK TO OUR TEAM TODAY
PH: 1800 733 782 www.atlascea.com.au
The New Leaders Summit is described as “a signature leadership event in AusIMM’s annual calendar”.
Australian Mining sat down with GMA Garnet new market and innovation manager Alex Bozward, and graduate– social performance Elyse Bosch to find out why.
Can you give us some background on your career?
AB: I have had the opportunity to work in different countries and industries. I started my career as a design engineer in England for a company delivering materials handling solutions to the automotive industry. I stayed in the automotive sector for 12 years and worked in several roles, the last being managing director of a UK operation for a multinational company.
I was given the opportunity to move to Australia in 2011. I embraced this and have thoroughly enjoyed my time in the mining sector. I recently started a new role with GMA Garnet as its new market and innovation manager at its headquarters in Perth.
GMA is different to other mining companies, as we have secured the supply chain from mine to customer. We are unique in this way, and this gives us insight into the direct customers markets.
GMA is different to other mining companies as we have secured the supply chain from mine to customer. We are unique in this way, and this gives us insight into the direct customers markets.
EB: I’m approximately six months into my graduate program at OZ Minerals/ BHP, so my working career is still well within its infancy. Throughout my experience, I’ve fostered a deep curiosity
for the resource sector. I’ve learnt how invaluable it is and how important it is for us to maintain what we do but in a far more sustainable practise.
If we count studying as part of our careers, I’ve been exceptionally busy for the last seven years. I’ve been heavily involved with AusIMM, whether be in the capacity of the AusIMM Adelaide Student Chapter or the AusIMM New Professionals Network.
I’ve attended events, I’ve facilitated events, made long lasting connections and contacts, and have furthered my pathway in the resource sector in immeasurable amounts due to AusIMM.
What does your role involve?
It involves coordination and collaboration with the GMA global sales, marketing, R&D, mining, production, customers and university research academics to identify, investigate, understand and ultimately deliver GMA products into new markets outside of existing market applications.
My role at BHP is as a graduate within the social performance team at the Carrapateena mine in South Australia. I’m doing a two-year program with the most exceptional and highly skilled team supporting me. We like to describe ourselves as highly skilled generalists, as each day, week and month we are doing something different.
Our main role in the social performance team is to empower local communities to realise their potential and to help create sustainable opportunities. This involves creating value and enabling growth within our local communities and our stakeholders.
What is currently the biggest challenge in the mining industry?
AB: I think that one of the biggest challenges is securing a talent pipeline to support future mining operations. This is why I volunteer on the AusIMM Perth branch committee in the area of student engagement and student support.
I recently joined the Get Into Resources Committee, which is a registered not-for-profit organisation that delivers a three-day careers event for Year 10 students in WA. This is supported by industry organisations that sponsor the event and volunteer technical experts’ time to showcase career opportunities through hands-on activities at the event.
EB: In my opinion the biggest challenge for the mining industry is also one of its biggest opportunities, and that is to do with the ESG (environmental, social and governance) space.
Modern mining companies have shifted focus to reaching ambitious decarbonisation goals, they are striving to elevate their mine rehabilitation procedures and to further their diversity and equity within the work environment.
The ESG term is a bit of a catch all for many important areas, but I think if we focus on just one challenge in the mining sector, you’ll find it’s interconnected to other areas and other issues.
What makes someone a good leader in the mining space?
AB: I recently attended the AusIMM New Leaders events, and the keynote speaker spoke about humanistic leaders, trusting others, being ethical, having compassion and participating as a collective whole. I believe this style, combined with embracing diversity and inclusion, makes for a good leader.
EB: A good leader in the minerals space is not afraid to think and act differently, they aren’t afraid to be agile, and they foster growth in those around them. The industry we work in is constantly evolving. Technology is always improving and therefore the way we do things changes continuously.
I think a good leader possesses the ability to adapt to updates in technology and science and to always be open to new ways of doing things.
What does the future of mining hold? What sort of leaders does it need?
AB: What I see already is a passion and a hunger. What I would like to see more of is recognising the knowledge and experience of the existing workforce –not only the leaders. There is so much that can be learnt from people who have been involved in the industry for most of their working career.
I’d love to see a future where mining is highlighted in a more positive light, and
for Infrastructure and Transport, Minister for Energy and Mining, and
in the House of Assembly; AusIMM CEO Steve Durkin; AusIMM President Nicole Brook; Steve Coughlan from Byrnecut; and Dr Paul Heithersay, chief executive of the SA Department for Energy and Mining.
The conference topics are collaboration, reconciliation, decarbonisation, future industry, new projects and innovation.
Why are events like the New Leaders Summit important?
AB: The summit provides a chance to listen to high-profile keynote speakers, industry panel sessions and case studies presented by experts. It provides an opportunity to connect with colleagues and engage with renowned mining leaders throughout the summit.
The next generation of industry leaders will be attending this event. The connections made here can last a lifetime.
EB: This summit is so important to help foster career development and growth in new professionals that want to have long and meaningful careers in mining.
If we can help to upskill our young professionals, to have them hear from renowned industry leaders, and to have them make meaningful connections, then we achieved our goal for the New Leaders Summit. These events are so important for the industry, as supporting our upcoming generations of new leaders and new professionals is essential for the mining industry to thrive in the future.
What sets this year’s New Leaders Summit apart?
AB: Attendees have been given the opportunity to deliver abstracts that, if successful, will be presented to the attending cohort. This is an excellent opportunity to use the event as a training ground or a stepping-stone to one day delivering technical presentations at major industry conferences.
EB: The New Leaders Summit for this year is particularly exciting, as we have accepted abstracts for research papers and studies. This has allowed opportunities for industry leaders of tomorrow to showcase their skills, highlight their research and, if selected, present to a wider audience. Our organising committee voted on the topics that we thought impacted our new professionals and their future careers.
We also have a jam-packed program with an exceptionally high calibre of speakers. If anyone is considering attending or has someone in mind, please suggest they attend. We can’t wait to see you there. AM
Adelaide from September 26–27.
Papua New Guinea (PNG) has a storied gold and copper mining history harking back to the early 1900s, and the likes of Ok Tedi, Lihir and Simberi are some of the active mines still producing today.
The country’s mining past has not been without its troubles, but a series of local and international companies are driving today’s sector forward, generating new opportunities for PNG communities and emerging professionals.
The IEA College of TAFE, based in the country’s capital of Port Moresby, is playing a key role in fostering PNG’s next generation of miners.
While IEA doesn’t provide education in practical trades, it does offer courses in business, accounting, IT, sales and marketing, each of which are important disciplines in the mining sector.
As PNG continues to develop and progress commercially, the country’s population is beginning to embrace the opportunities, learning the importance of professionalism and customer service.
MINING IS ONE OF THE MAJOR ECONOMIC DRIVERS FOR AUSTRALIA’S CLOSEST NEIGHBOUR, WHICH MEANS THERE ARE PLENTY OF OPPORTUNITIES TO WORK AND ESTABLISH A CAREER IN THE PACIFIC NATION.PNG’S PANGUNA MINE HAS PRODUCED THREE MILLION TONNES OF COPPER AND 306 TONNES OF GOLD IN THE PAST.
“People who get our diplomas and advanced diplomas can go on (to James Cook) after getting credit for their first year of studies at IEA,” Pedley said.
“It is noticeable whenever somebody who’s gone to Australia comes back – the professionalism they’ve absorbed from being in Australia, and the professional attitudes they’ve learned there.
“In an ideal world, you’d have all our graduates go to Australia to do one, two, three or more years’ work experience and, because they all love their country, they will probably filter back at some point anyway.
“The experience they would then bring back would have a very beneficial effect on Papua New Guinea.”
As IEA fosters PNG’s next generation of professionals, the institution’s key strategy is to get students into companies, which is often a two-way partnership.
“We also train people within companies,” Pedley said. “We’ve got links with Ok Tedi and Lihir and we’ve had a huge link with Panguna in the past, which is set to be reopen in the next year.”
Panguna – a copper-gold mine in Bougainville – has produced three million tonnes of copper and 306 tonnes of gold in the past.
Panguna’s reopening is a key objective of PNG’s Department of Mineral and Energy Resources (DoMER), with discussions between the Autonomous Bougainville Government (ABG) and the mine’s landowners continuing to advance.
It’s mines such as Panguna that not only offer career opportunities for IEA students but also enable IEA to provide career development opportunities within companies.
“We go into companies, help train their staff and give them train-thetrainer qualifications, so they know how to teach new procedures effectively to their employees,” Pedley said.
“At the same time, we look to hopefully place our students in these companies once they’ve graduated.”
Pedley said IEA has also formed ties with oil and gas companies as
the institution looks to support this growing industry. The production of liquefied natural gas (LNG), in particular, is spurring PNG’s future economic potential.
“We’ve been talking to the oil and gas industry because there are some major new projects coming online next year,” Pedley said. “Many of these companies are looking for chefs to provide catering. So we’ve got an MoU (memorandum of understanding) with a Oilmin, who are supplying catering services to many of these big projects.
“In conjunction with Oilmin, we train senior chefs who then train their students and we oversee the standard and give them a qualification at the same time.”
IEA is also working with Express Freight Management to support PNG’s next generation of logistics personnel. This is particularly important for a PNG mining sector reliant on effective sea, air and road transportation.
“These are the areas where soft skills are key,” Pedley said. “There are technical aspects to these industries, but it’s largely about sensible planning and effective training of procedures, which companies and employees typically don’ have in PNG.
“So that’s how we interlink with PNG companies and also the youth of the country.”
IEA’s mission is for its students to make an effective contribution to the companies for which they work, with a goal to train leaders who can rise up the ranks and take on management roles.
Pedley used the example of former Ok Tedi managing director and chief executive officer Musje Werror, who was the keynote speaker at IEA’s graduation ceremony earlier this year.
“Musje was born in West Papua (in Indonesia) but grew up in Papua New Guinea, and he rose right to the top of Ok Tedi,” Pedley said. “That’s the sort of goal we want for our students.”
Through its existing operations and emerging development projects, the PNG mining sector has an important role to play in not only supplying the world with important minerals but also providing career opportunities for the country’s population.
And educational institutions such as the IEA College of TAFE will key players as part of this process, enabling the next generation of miners to realise and take advantage of their professional opportunities. AM
WITH THE COMBINATION OF OPERATOR COMFORT AND INCREASED EFFICIENCY, THE VOLVO EC950E IS A GREAT CHOICE FOR A MINE SITE.
Mine sites can often be noisy and chaotic, posing a challenge to operator comfort and concentration.
Recognising the physical demands placed on operators, features like a low-noise cab, a fuelefficient machine and comfortable working conditions can make a long day fly by for an operator. Luckily, the Volvo EC950E excavator ticks all these boxes –and then some.
As the official distributor for Volvo equipment in Australia, CJD Equipment has seen thousands of vehicles come and go, but the EC950E excavator has stood the test of time.
“The EC950E was introduced to the market about six years ago, deliberately sized to be the ideal loader to the Volvo A60 articulated dump truck,” CJD Equipment national product manager for Volvo CE Hayden Grant said.
“Volvo has a strong commitment to environmental awareness and safety for
the people working around the site and those servicing the product throughout all their business interests.
“Some of Volvo’s core values are safety, sustainability and operator comfort. The company has been leaning into innovation and design and the industry is starting to adopt them as standard.
“Representing Volvo puts CJD at the forefront of manufacturing technology and machine developments.”
A standout feature of the EC950E excavator is its cycle time – the time a machine requires to complete all of its operations in one piece.
With its newly developed and fully electro-hydraulic system, combined with the high power and torque from the Volvo D16 engine, the cycle time for the EC950E excavator is cut to a minimum.
“It is important to match your equipment to the size of the job that you are working on to be cost-effective, reduce the number of cycles and eliminate unnecessary idle times,” Grant said.
“Faster cycle times can help you load significantly more tonnes per hour.”
Put simply, the quicker cycle time allows operators to do more with less, increasing efficiency across the whole operation. And the fuel savings don’t hurt, either.
which gives the EC950E outstanding fuel economy,” Grant said.
Volvo’s advanced hydraulic system delivers immense power to perform heavy-duty tasks with precision, enabling faster digging and loading cycles. By utilising Volvo’s unique ECO mode, which optimises the hydraulic system to reduce loss of flow and pressure, the EC950E allows for an increase in cycle times. Operators can select the best work mode for the task at hand in an effort to reduce fuel consumption and optimise the overall energy efficiency of the excavator.
Designed for productivity, operators can utilise Volvo’s state-of-the-art telematics system CareTrack, a GPS monitoring program that works with the EC950E’s diagnostic system to reduce fuel costs, optimise machine and operator performance, and manage service and maintenance to maximise uptime.
“Volvo’s D16 engine has Volvo’s trademark high kilowatt rating with high torque at low rotational speeds,
“Volvo’s CareTrack system keeps the customer fully aware where the machine is, its operational status,
IT IS IMPORTANT TO MATCH YOUR EQUIPMENT TO THE SIZE OF THE JOB THAT YOU ARE WORKING ON TO BE COSTEFFECTIVE, REDUCE THE NUMBER OF CYCLES AND ELIMINATE UNNECESSARY IDLE TIMES.”
fuel usage, and service requirements in real-time,” Grant said.
It might seem simple, but having reminders about servicing can make a big difference to a site’s uptime. Such reminders mean there is less chance of a machine being out of service for a longer period of time, while also allowing operators to work around scheduled service times.
All of these features are very welcome and make for a great machine, but where the EC950E really stands out is in terms of operator comfort and safety.
“It’s the little things that put Volvo apart from the competition, like the strong and efficient air-conditioning system, comfortable air suspension seat, cab layout, excellent visibility and the design strength of the machines body,” Grant said.
For operator convenience and ease of use, the EC950E cab features a comfortable, spacious and low-noise environment, with
ergonomically positioned joysticks, keypad and LCD monitor.
Viscous cab mounts support the cab and help to reduce shock and vibration levels, while sound-absorbing lining helps to further reduce noise. Air is distributed through the cab via 14 different vents, and the large windows and doors provide greater visibility.
“The air-conditioning provides positive pressurisation to the cab, eliminating dust ingression, and when fitted with the optional HEPA filters it provides the operator with a very clean and safe environment,” Grant said.
For controllability, Volvo has designed the operator seat with ergonomics in mind, featuring 12 different adjustments that can be moved independently along with the joystick console to accommodate the operator.
The seat can also be heated and cooled depending on the working climate, and can be adjusted through four levels of height.
The Volvo team is also thinking of operator comfort outside of the cab.
With boom float function, the boom is able to float following the terrain, making it easier for operators to complete grading and finish jobs.
“The EC950E stands out in terms of safety,” Grant said. “Rear vision and optional side vision cameras reduce the risk of damage when manoeuvring.
“Ground-level servicing and grouped grease banks minimise downtime and reduce the need to climb on the machine.”
The well-balanced machine also provides the opportunity to optimise bucket size to match digging conditions and material weight.
When they’re all added up, these features make the EC950E excavator a
perfect vehicle for a busy mine site. But the support doesn’t stop there.
After a Volvo machine has been purchased from CJD, customers can continue to receive after-sales support and advice.
“CJD has a very strong reputation for customer satisfaction and 24-hour after-sales service for parts and service support,” Grant said.
“CJD has been a Western Australian Volvo dealer since 1992 and we have been the national dealer and distributor since 2002.
“We have had a strong 30-year relationship with Volvo, and this has allowed us to develop our product range and our reputation with Volvo as a strong, reliable and successful dealer for the Volvo product.” AM
IN PARTNERSHIP WITH HASTINGS DEERING AND THIESS, CATERPILLAR DEMONSTRATED ITS MINESTAR COMMAND FOR DOZING AT THE RECENT WORLD MINING CONGRESS.
According to the Western Australian Department of Mines, Industry Regulation and Safety, most mine injuries in 2022 were vehicle-related.
Mines have historically been tough, and sometimes dangerous, places to work, owing in part to the heavy machinery that operates around the clock. But the industry is in the midst of a safety and sustainability revolution and companies like Caterpillar – and one of its largest Australian dealers, Hastings Deering – are leading the charge. This charge begins with getting workers off the frontlines and away from heavy machinery. It begins with autonomous mining.
The Cat MineStar Command is Caterpillar’s automation solution for the mining industry. It makes it possible for miners to automate a single process, remotely control a single machine, automate multiple types of equipment across a mixed fleet, or implement a completely autonomous fleet of haul trucks that operate continuously with no human intervention.
Command for Dozing is one of these solutions. Caterpillar showcased this technology at the World
Mining Congress (WMC) 2023 in Brisbane in June.
“The operator was set up at the congress and – in a world-first – was operating semi-autonomous tractors at a mine site 850km away,” Hastings Deering product manager Simon Zillman told Australian Mining
“This was not a practice run, but real-life bulk earth works as part of the mine’s rehabilitation program.
“It was impressive to watch multiple dozers moving full blades of dirt constantly, consistently.”
Command for Dozing affords mine operators multiple levels of control. A remote operator station enables the operator to work in a comfortable seated position with familiar controls, while a portable over-the-shoulder console works well for short-duration activities.
But the star of the show is the semiautonomous operation, which takes operators out of the machines and lets them work safely from nearby or remote locations.
“The technology allows one operator to operate up to five dozers at once,” Zillman said. “We proved at the WMC that those operators no longer need to be located on-site. Command for Dozing removes the operators from potentially hazardous environments.
“It provides a clean, vibration-free work area, it also allows multiple dozers to be operated simultaneously by a single operator, and these dozers frequently operate for more than 23 hours each day.
“Bulk dozer mining exposes operators to hazards that simply don’t exist when the operator is no longer in the cabin.”
MineStar Command is making its sites safer and more sustainable.
“With Command, there’s no time lost because of injuries relating to operating the machines,” Zillman said. “It also has the side benefit of more consistent and efficient production, which means less carbon emitted.”
Allowing a single operator to control multiple dozers at once also significantly cuts training and operating costs.
“Experienced operators are increasingly hard to find and training new operators is a never-ending task,” Zillman said.
“With Command for Dozing, the operators generally love the work and are themselves pushing the mines to use the technology more.”
And it doesn’t take long for Command to get set up and commence operating on a site.
“It takes about six months to deploy the system,” Zillman said. “Most of this is working through the site readiness
and change management tasks, such as updating safe work procedures, training, etcetera. The actual site deployment and operator training only takes about two weeks.”
There’s more to come for Command for Dozing, Zillman said, with Caterpillar looking to expand the capability of its technology.
Command for Dozing is currently active with two mining customers in Queensland, one of which is Thiess. The dozers on display at the WMC were being operated as part of a Thiess operation in Queensland’s Bowen Basin.
“This Bowen Basin site uses the semi-autonomous tractor system, which is the Command for Dozing product under the MineStar suite,” Thiess group manager Trent Smith told Australian Mining
“We use SATS (semi-autonomous tractor system) in a bulk dozer push application. Sometimes that’s in a production application uncovering coal, and sometimes in a rehabilitation application profiling to final design surface.
“They’re particularly good in rehabilitation applications because the finished profile is very accurate in terms of the design compliance. We don’t have to do any rework.”
According to Smith, the site noticed an improvement in safety after adopting MineStar Command.
“We’ve been operating with MineStar now for four years without any safety incidents, so quite a significant outcome,” he said. “We’ve also seen much higher utilisation on our assets. We’re seeing 22 to 23 hours per day of productive operation out of the dozers.”
Beyond dozing, Command is also available for drilling, hauling and in underground operations.
Command for Drilling delivers costeffective, high-precision drilling through automation. It manages everything from predrill planning to blasting.
Command for Hauling takes advantage of Cat’s most sophisticated technologies. A MineStar Command autonomous haulage fleet allows for near-continuous operations with fewer operators on-site, which improves safety, cuts costs and boosts productivity.
Thiess utilises these other MineStar technologies at its central Queensland site.
“This operation is a full MineStar site, so it has Command for Haulage and drilling, as well as fleet, terrain and health,” Smith said.
“When the site is fully ramped up, there’ll be over 100 connected assets in the MineStar system.”
Smith said the most exciting part about the MineStar Command technology is its potential to change
the landscape of employment in the mining industry.
“With Command for Dozing, we’ve potentially tapped into a whole range of new opportunities for our people with flexible work arrangements,” he said.
“Until now, there’s been a big focus on operating on-site, but the WMC demonstration allowed us to show that it can be operated safely from a remote location. So I think there’s an untapped potential there to do something longer
term in having remote operation of those machines across multiple sites in a centralised location.
“Through the collaboration of Thiess, Caterpillar and Hastings Deering, we’ve achieved something pretty incredible.” AM
KAL
Ithem a second glance – or consider what is
It turns out this question poses a number of issues regarding landfill, recycling, safety, and more.
“From a physical point of view, waste tyres are chemically inert, (but) there are still risks associated with storing them,” Kal Tire people and ESG manager Dominique Kesler told Australian Mining “Waste tyres can store water-borne pests and disease. If those waste tyres need to be moved at any point, they also pose a safety risk to employees.”
Tyres are also flammable, and tyre fires can be hard to control and extinguish if an incident were to occur.
A report published by Tyre Stewardship Australia showed that the Australian mining industry generated over 68,000 metric tonnes of waste tyres in 2019. Just one per cent of these were recycled.
There is a clear need to do something to improve this number, but there are limited sustainable solutions on offer for mining tyres, which means they can create a significant waste stream for mining operations.
Tyres don’t degrade naturally over time, but they are made from many
different products that are worth recovering, including oil, steel, carbon black and syngas.
These products can be used to replace virgin fossil fuels and reduce future resource extraction.
So what can be done to change the way in which mining tyres are disposed?
Kal Tire’s tyre recycling plant in Chile is one way the company is helping to make tyre recycling easier.
“Kal Tire has developed a unique thermal conversion process that uses heat and friction in the absence of oxygen to convert the tyres back to their base elements,” Kesler said. “One hundred per cent of the material can be repurposed.
“Chile introduced legislation several years ago that mandated that from 2023 25 per cent of mining tyres must be recycled, increasing to 75 per cent as of 2027, and to 100 per cent as of 2030.
“To enable this, Kal Tire’s Mining Tire Group opened an OTR tyre recycling facility in Antofagasta in 2021 which can now handle up to 20 tonnes of tyres per day, including ultra-class products.
“By breaking down a 63-inch OTR tyre using thermal conversion, it is
TIRE’S INNOVATIVE METHOD OF RECYCLING MINING TYRES IS HELPING TO CREATE A MORE
FRIENDLY MINING INDUSTRY.THE KAL TIRE RECYCLING PLANT IN CHILE. KAL TIRE PEOPLE AND ESG MANAGER DOMINIQUE KESLER (IMAGE: AUSTMINE)
converted back to its fundamental elements. We see this as the optimal use as it provides a substitute for new carbon products and helps to reduce the total carbon footprint.”
Kal Tire’s Chilean plant is currently the only operational and governmentauthorised recycling solution of its kind in the country.
“We need to continue the conversation and find a way for mining companies to bridge the divide between boardrooms and mine sites to raise the visibility of this issue,” Kesler said.
“Mines have remediation budgets set aside for reclamation, but the challenge is to access those funds sooner versus later when there are thousands of products awaiting disposal.
“Plans for recycling tyres throughout the life of the mine really should be developed before start-up.”
Kal Tire ensured the Antofagasta facility, located north of Santiago, was built to the highest safety and environmental standards, even proofing it to withstand a magnitude nine earthquake. And in a move toward the future, Kal Tire has ensured the facility’s recycling solution is scalable and can be replicated in other mining markets.
“We know that the desire for change in the industry is real and there is a renewed focus and the drive of ESG (environmental, social and governance) in mining organisations,” Kesler said. “This is about us already having the solution to a growing problem and offering that solution to the Australian market.”
The process of thermal conversion recovers bulk oil, carbon ash and highgrade steel from the tyre. Bulk oil can be used as is or refined and used as diesel, while carbon ash, when purified and pelletised, can be refined into highquality recovered carbon black to suit end market use.
Just one tyre conversion can recover more than 1600kg of carbon ash, 900kg of steel and 2000 litres of petroleum-based products.
“Over eight million metric tonnes
of carbon black is produced worldwide each year, and 90 per cent of that is used in rubber applications. Imagine the impact mining could have on the circular economy if it worked to turn its waste tyres into a source of value,” Kesler said. “Because carbon doesn’t degrade, OTR tyres can provide a source of carbon black which can be used to reduce pressure on primary production. Carbon ash can be upgraded and used as a replacement for new carbon black.
“The steel contained within a large OTR mining tyre is some of the highest quality bio-based products that can be refined and used to create new tyres or used as biofuel or in applications such as ANFO (ammonium nitrate and fuel oil) for blasting.
“By seeking out the highest and best use of these materials, companies can create a virtuous circle.”
Kal Tire hopes the mining industry will continue to push ahead on tyre recycling.
As a global industry, and in Australia, we need mining companies to push this agenda,” Kesler said.
“We don’t want the industry to see tyre recycling as the end of the road, but as something they can incorporate in the complete lifecycle.
“By taking a proactive approach to OTR tyre recycling, mining companies, as the end user of earth mover tyres, have the chance to better their stance as environmental stewards and boost their standing with stakeholders.
“Ultimately, a diversified and collaborative approach is required to boost uptake and accessibility in OTR tyre recycling.
“This includes government-led policy, proactive investments from mining companies, technological and product innovation from tyre manufacturers, and communication and collaboration across the complete value chain to turn these ‘waste’ products into a source of value and contribute to a circular economy.” AM
Mining companies usually implement renewable energy facilities to help decarbonise their operations, reduce energy costs, assist and support constructive obligations within communities, and aid their environmental, social and governance (ESG) ratings.
Miners typically focus on how a renewable-energy generation and/or storage facility affects project economics, and how to operate with sustainability in mind during a mine’s life.
In the past, mining companies mostly focused on production and reaching targets. But they are now seen to be working on how renewable energy assets at mines can leave a positive legacy for communities, particularly remote ones. This is a legacy that, for decades to come, improves energy security, creates jobs and opportunities, and helps the environment.
The synergies between renewablepowered mines and community development programs through the mine lifecycle and post-closure is the subject of an upcoming paper by SRK Consulting’s Ludovic Rollin, Jane Joughin and Danielle Kyan.
The paper was to be presented at an Australasian Institute of Mining and Metallurgy Life of Mine 2023 conference in Brisbane in early August.
“Thinking bigger with renewablepowered mines is also about thinking better,” Rollin, a senior environmental engineer with SRK Consulting, said.
“Mining companies should be openminded with emerging renewable
technologies and consider if they can create a positive social impact on communities long after a mine closes.”
SRK principal environmental geologist Danielle Kyan said mining companies were beginning to focus on the alignment of renewable-powered mines and community development.
“The starting point for many mining companies has been to introduce renewable energy sources and storage on-site to lower their carbon footprint,” Kyan said. “Often, the next step is to introduce electric vehicles to further reduce carbon emissions.”
The opportunity, according to Kyan, is integrating renewable energy thinking into mine planning and closure strategies – and into communityengagement programs.
“Renewable energy assets can potentially change the conversation between some mining projects and nearby communities,” she said.
“Mining companies that engage with communities to understand their longterm needs – and develop renewable assets that respond to those needs – are likely to gain greater support from stakeholders.”
Rollin believes community needs from renewable assets can be broader than energy.
“It could be about water quality, food supply or ensuring there are jobs after a mine closes,” he said.
The main issues occur when mining companies seek to introduce renewable power at existing or new mines as part of their decarbonisation strategies.
This can involve sourcing renewable energy from external sources or establishing power generation and storage facilities at the site.
Using solar panels or wind farms to generate power on-site, or establishing batteries, hydrogen facilities or pumped hydroelectricity to store energy, is complex. This often requires land access, impact assessment, planning, environmental approvals and significant community engagement over months or years.
Transitioning to renewables also raises new challenges in energy supply variabilities, land and skilled labour requirements, and in meeting mineclosure objectives.
Although renewable energy systems in mining have great potential, many Australian mines are in remote areas near sparse populations and have limited scope to leave a renewable-energy legacy. This means the likeliest outcome
“In many locations, the introduction of renewable energy is focused on the mine’s energy needs and carbon intensity during its lifetime,” Kyan said. “Potential for leaving an energy legacy when the mine closes becomes more difficult when the benefits are too low.”
Rollin said mining companies can address these and other challenges through participative stakeholder engagement.
“The goal should be to identify whether the introduction of renewable energy technology at a mine can help a nearby community and if it’s feasible for that asset to continue operating after the mine closes,” he said.
Choosing the right time is vital.
“A mining company might think 20 years ahead when factoring renewable energy into its planning and closure strategies,” Rollin said. “But with appropriate maintenance and operational support, that asset might power a
The longevity of renewable energy assets raises other issues.
“If there is an identified longterm benefit, mining companies and communities need to work together to understand how that renewables asset would be maintained, who would own it, and who is responsible for its ongoing costs and any potential liabilities, after mine closure,” Kyan said.
In some cases, this collaboration will extend beyond the mining company and communities.
“In areas where there are multiple mines and other industries, there is a potential for mining companies, industries and government to work together and form renewable-energy hubs,” Kyan said.
Rollin believes mining companies should consider a wide range of established and emerging renewable technologies – and communicate their features, benefits and risks to communities and other stakeholders.
Examples include agrivoltaics and aquavoltaics – the simultaneous use of areas for photovoltaic solar generation with agriculture or aquaculture, respectively.
Another emerging option is “solar grazing”, a method of vegetation control on a solar farm using sheep or other livestock grazing. So too are mobile water desalination plants that enhance the use of surplus power and provide isolated communities with fresh water.
“The key is to understand what the community needs and the renewable
energy technologies best placed to address that need and the mine’s goals,” Rollin said. “Then to understand the feasibility of the preferred technology and model it in mine planning and closure.”
Project economics can change when companies incorporate the longerterm social benefits of renewableenergy assets.
“In addition to financial and decarbonisation considerations, companies need to ask, ‘What are the other benefits of incorporating renewable energy and storage on-site and leaving those assets as a legacy for communities after closure, and how do we value them?’”
Rollin added some questions of his own.
“How could the implementation of renewables and the engagement that accompanies them aid project approval? How could renewables build stakeholder support in financial markets and lower the company’s cost of capital? What does leaving a positive legacy for a community through renewables do for our company’s reputation and social licence to operate?” he said.
Rollin reiterates the need to “think big” on renewables.
“When mining companies expand their thinking on renewables to a multi-decade focus, to a wider range of technologies, and to sustainable social benefit for communities, new opportunities to create value start to emerge,” he said. “That won’t be the case for every project, but mining companies should ask these questions early in the planning process.” AM
1. Follow latest developments: Trends in renewable energy – and their application to mining – are moving quickly. Understand how the mining industry is adapting to renewables and the options available. Review case studies here and overseas.
2. Seek specialist advice: Ensure your organisation has access to highquality advice. This is a highly specialised field that requires local and international expertise with renewable projects in mining.
3. Embed renewables into planning processes: The use of renewables should be an early and recurring consideration in mine planning and closure strategies.
4. Be open-minded: New renewable-power generation and storage technologies continue to emerge. These innovations are increasing the potential to leave legacy renewable assets that benefit communities long after mine closure.
5. Think longer term: Do not only focus on the impact of renewables during the mine life. Consider the full life of a renewable-energy asset and whether it could help a community for decades to come.
6. Consider non-financial value: Legacy renewable assets can strengthen community engagement, corporate reputation and social licence to operate. If these social benefits have value for your organisation, include them in project modelling.
7. Participative engagement: Renewables require a different form of engagement that is about understanding community needs, explaining the specific technology and working with stakeholders to identify mutually beneficial outcomes from renewables.
8. Collaborate widely: A renewable project could involve collaboration with other companies in the area to create a clean-energy hub; working with federal, state and local governments; or engaging with stakeholders such as institutional investors or financiers to communicate the company’s renewable strategy.
9. Identify government support: Understand funding programs available to support the development of renewables projects in your location; whether your project is a potential candidate; and the requirements to secure a grant.
10. Share lessons: Be prepared to share your organisation’s experience with renewables, its engagement processes and how communities benefited from it. The concept of leaving a legacy renewable asset for communities after mine closure has great promise, but is still in its infancy.
hen a customer in Chile reached out to Komatsu for automation solutions that were reliable, strong and advanced, the company was quick to jump at the challenge.
“The mine is a really good customer of ours,” Komatsu product manager, automation Wesley Taylor told Australian Mining.
“When they first approached us, they had a really big automation goal in mind, both at the surface mining level and on the drill-and-blast side.
“We’ve found that their business has afforded us a really interesting opportunity to trial some of our automation capabilities and they were the first to really jump into the space with us.”
Taylor has been working with the mine for about three years and said it has been great to see the site so keen on implementing the latest technology from Komatsu.
“They have a big focus on safety initiatives and operator comfort,” Taylor said. “For us, that means no operators in the cab so that they’re out of any blast patterns.
W“So we went in and offered our technology packages. You can’t just take an autonomous drill, turn it on and expect to work like you have always worked. You need to rework your processes, your handling, and there’s going to be some change management for the customer.
“But they were so keen to get their operators off board and away from that line of fire.”
Komatsu has been focusing on automating drilling services for its customers, and one of its core initiatives is to develop automation that is available for all. To achieve this goal, the company has developed remote control rooms to provide a central location from where equipment can be controlled.
Komatsu is also working to ensure its automation services fall into similar price points.
“Customers might only have one drill, but they want an autonomous solution and don’t want to see a massive investment,” Taylor said.
“But at the same time, if they have, say, 12 drills, we don’t want to see 12 times the investment, we want to see a similar price points, similar capability, no matter how big their fleet sizes.”
Komatsu is committed to ensuring customers can manage how they incorporate automation in their mines.
“Customers can add on two different levels of automation, either on machine smarts or removing that operator from the cab,” Taylor said. “We consider those two parallel technology tracks, and they are not tied to each other.
“Part of that is trying to make sure that the infrastructure costs are as small as we can make it and as light as we can make it.”
This kind of flexibility allowed operators at the copper mine in Chile to communicate what they wanted from Komatsu, which was then able to deliver.
“Automation works in a circular way for me,” Taylor said. “It’s around informing, assisting, and then automating.
“So anything that we automate, the first thing I need to know is more about it. When we look at the future of mining, the forefront is informing data, creating new data, getting data off the equipment and back into a central point for the customer to analyse.
“We can’t all automate the same way because every customer is unique. So how do we make sure that we’re adding without subtracting some of that unique
aspect of their operation, so that they don’t see automation kind of hitting their production or hitting some of their KPIs in a negative manner?”
Not only can Komatsu provide automation to mines like the one in Chile, it can also retrofit automating technologies onto older machines to provide a recycling option for the customer.
“We had a customer wanting to apply new technology to a 25-year-old electric rickshaw,” Taylor said. “They saw a large increase in productivity for that old machine, as well as the rapid reduction in damaging events and fatigue.
“So, for me, there is no barrier of only outfitting new technology on new machines; we can go as far back as possible with the customer to make sure that they’re getting extra life out of older machines.
“I really liked that because it doesn’t fit the norm. You think only the new stuff is where you get the cool new technology.
“I’ve been a champion for technology and automation and mining my entire career, and with projects like this Chilean mine, I’m going to continue to do so.” AM
Gold has been an integral part of the Australian mining environment for centuries. But as ore deposits get deeper and harder to access, processing equipment must keep up to ensure the precious metal can be mined for years to come.
Derrick Corporation has committed itself to developing new and innovative screening equipment to advance gold processing, while also contributing to a favourable investment return for its customers.
“A lot of our innovations come from providing solutions to our current customers,” Derrick general manager mining Garth Hay told Australian Mining.
“For example, the development of the G-Vault (urethane interstage screen) came from a customer complaint about their interstage screen being one of the bottlenecks of their system.”
Over a number of years, Derrick has developed screening solutions to minimise the maintenance a customer has to undertake and to reduce environmental impact.
These new designs and capabilities permit screens to replace more traditional flowsheet elements.
“A Derrick Stack Sizer can replace the hydrocyclones in a grinding circuit, resulting in greater recovery at reduced power consumption per tonne,” Hay said.
“Derrick machines provide superior performance in a smaller footprint, which can offer a huge advancement for a gold plant. By replacing old hydrocyclone technology with modern high-frequency vibrating screens, overall plant capacity can increase by 20 to 50 per cent.”
The G-Vault complete interstage unit is the latest addition to the Derrick gold processing portfolio. The G-Vault employs a modular approach, combining a screen surface with a robust and easyto-connect support structure.
“The G-Vault features tapered openings and can withstand higher temperatures, contributing to its nonblinding characteristics,” Hay said.
“These non-blinding and abrasionresistant properties result in a screen with higher throughput, increased life and less maintenance, all of which lead to a more efficient recovery of gold.”
The G-Vault, which has been installed in multiple locations around the world, has been met with wide acclaim.
“Customers are happy to report benefits from a maintenance and production standpoint,” Hay said. “From a maintenance side, we are decreasing man hours spent on maintaining a piece of equipment which in turn helps to reduce risk on-site. From a production standpoint, the G-Vault can increase
flow, help mitigate carbon loss and run a consistent CIP (carbon in pulp) or CIL (carbon in leach) system.”
One of Derrick’s primary objectives is to minimise operational costs by developing highly durable machines.
For example, the Derrick integrated vibratory motors feature maintenancefree components that eliminate the need for routine maintenance and downtime. Used in conjunction with Derrick’s longlasting Polyweb urethane panels, these motors enable clients to achieve optimal availability of their equipment.
The extensive research that goes into the development of these machines helps to ensure a high gold recovery rate and seamless user experience.
This research has evolved into the development of a range of screening solutions to address various gold-processing needs, including hydrocyclone overflow trash duty, tailings carbon safety, in-tank interstage carbon retention, degritting, loaded carbon, carbon sizing, carbon dewatering, gravity protection separation, and carbon column safety.
“Our focus has always been to reduce operation expenses by creating more robust machines,” Hay said.
“We have found our customers achieve higher availability with our machines. For example, once the G-Vault is installed, it can be operated for approximately six months before it is required to be changed.
“Other similar solutions may need weekly maintenance, which comes at extra man hours and a loss of tonnes. The G-Vault provides operational, production and safety benefits that increase profitability.”
With a new Australian office now open in Queensland, Derrick is ideally placed to help its customers make the most of its gold processing solutions, no matter the location. AM
According to a recent Mining and Energy Union audit, there have been 54 serious incidents across Queensland coal mines since the start of the year. The majority involved vehicles.
The report detailed multiple instances of collisions and unintentional movements of heavy vehicles – these are hazardous, and sometimes deadly, accidents. And it’s usually the vehicle operators who experience the worst of it.
But a tech start-up from Beijing, Eacon Mining, is looking to change that.
Eacon specialises in scalable, autonomous driving solutions for the mining and quarry industries. The company designs software and algorithms for autonomous driving and is able to retrofit its technology into a range of different truck models from different manufacturers.
In other words, Eacon takes ordinary mining trucks and transforms them into intelligent and autonomous machines. The company is looking to bring its technology to Australian shores, from the comfort of its soon-to-open Perth office.
Eacon Mining director of overseas strategy Elaine Jin sat down with
Australian Mining to explain how the company’s offering works.
“Our solution is very flexible. It fits a range of trucks and is able to adapt to various working environments,” she said.
“In China, Eacon designs the drive-by-wire system, and the original equipment manufacturers help to install all the hardware. Eacon’s autonomous technology has been fitted to mining trucks ranging from 45 to 90 tonnes.
“But for the Australian market, Eacon is looking to retrofit even larger trucks with the autonomous technology. To accomplish this, Eacon has vehicle engineering team members who have
industry experience retrofitting more than 200 mining trucks with drive-bywire technology.”
Autonomous fleets can help shoulder most – sometimes all – of the burden when it comes to mine loading, haulage and dumping. Eacon’s autonomous systems can run for many hours without the need for operator rest.
Autonomous truck technology in general is something that’s already taken off in the Australian resources sector. But it can be costly.
Eacon aims to remedy this issue by providing a more affordable autonomous solution to the Australian
mining industry. With Eacon, smalland medium-sized miners – not just the big players – can get their hands on this technology and start optimising operations.
Eacon’s latest project is the Fushan quarry in China.
“In February, 20 autonomous trucks were delivered to the site and, after only two months of commissioning, we started multi-fleet unmanned operations without safety drivers on-board,” Jin said.
“Autonomous driving has helped the mine achieve stable production during both day and night shifts.”
At Fushan, Eacon used its autonomous factory-installed battery-electric trucks, which helped the operation significantly cut its Scope 1 carbon emissions. Eacon currently offers autonomous system retrofitting to the Australian market, but it has plans to bring its ready-built electric trucks to our shores.
Eacon is also operating in two largescale open-pit coal mines in China.
“These autonomous haulage projects have been in operation for nearly three years,” Jin said.
“So far, we have deployed 14 and 39 autonomous trucks to those sites, respectively. In three years of operation, we achieved a 68 to 80 per cent labour cost reduction, a five to eight per cent increase in productivity, and zero incidents.”
So what makes Eacon’s autonomous truck solution such a success?
It’s a combination of flexibility, deep-learning algorithm and innovative safety functions.
“We use deep-learning technology to achieve accurate recognition of traffic conditions,” Jin said.
“Our system can identify hard-tospot hazards such as small falling rocks and potholes, and the vehicle can decide whether to go over or bypass them.
“And thanks to the intelligent onboard planning, the trucks are able to work in certain blind areas and during short disconnections from Wi-Fi or LTE
(long-term evolution) networks.”
The crowdsource mapping system means each truck can update the mine map in real-time without human or cloud intervention. This allows the whole fleet to run smoothly, avoiding operational delays.
“The entire process is completely automatic, eliminating the need for manual mapping and data collection, which greatly improves safety and enhances operational efficiency,” Jin said.
Also unique to Eacon is its remote driving function.
“When some failures occur on the truck side, the truck will perform a safety stop,” Jin said. “After that, the system will determine whether remote driving takeover is needed and can pass control over to an operator in the control room.”
Eacon’s autonomous solution package also includes collaborative working suites for other on-site mobile equipment such as excavators, light vehicles and water trucks, as well as dynamic dispatch technology to efficiently manage fleets.
By removing workers from the frontline, autonomous technology is playing a major role in making mining operations safer.
“Autonomous driving eliminates the risk of personal injury by reducing the on-site drivers,” Jin said.
“Human drivers have individual driving habits and skill levels – they may also suffer from fatigue. But autonomous driving strictly follows rules.
“This guarantees safety and consistency in performance. For example, our self-driving mining trucks must comply with defined right-of-way rules at crossroads, and they will not enter restricted areas.
“Our autonomous driving system also takes safety design to the highest level, ensuring safe operation through intelligent fault diagnosis and different levels of handling strategies.”
With its intelligent, scalable approach to innovation, Eacon is helping smaller miners keep pace with the industry leaders. AM
Mining will help improve future standards of living and job opportunities and help lead to better access to healthcare and education, BHP chief executive officer (CEO) told the audience at the World Mining Congress in Brisbane in June.
“For nations, mining brings the opportunity for secure jobs, economic development and investment, as well as secure energy solutions and food supply chains that sustain lives and livelihoods,” Henry said. “I am sure everyone in this room knows the impact that mining has had on Australia.
“Australia would not be the country it is today, wouldn’t have the living standards Australians enjoy today, without mining.”
Henry said governments around the world have a responsibility to provide strong institutional and regulatory confidence to foster a dynamic, commercial and open market that encourage competition and productivity, and they must pursue an economy-wide transition to net-zero emissions – with critical minerals playing a key role.
“The Australian Government released its Critical Minerals Strategy, and we look forward to working further with them on a critical minerals list that reflects the best interests of the nation,” Henry said. “I did see some criticism that the new strategy didn’t contain even more by way of subsidies. For what it’s worth, I think this is absolutely the right approach.
“What governments here – federal and state – should focus on are those things within their control to make investment fundamentally more attractive. Not simply due to the sugar hit of a subsidy.”
Despite some positives, Henry believes some recent activity in the Australian resources sector will make the country less completive, such as the Federal Government’s ‘same job, same pay’ legislation and the Queensland Government’s decision to impose the world’s highest coal royalty taxes.
As a result of the Queensland coal royalties, Henry said BHP will not be investing further in the state.
“In this case, both the outcome and the process have meant for BHP that we have opportunities to invest for better returns and lower risk elsewhere around the world, as well as here in Australian states like Western Australia and South Australia,” Henry said.
“And we will not be investing any further growth dollars in Queensland under the current conditions.”
Henry concluded that the resources industry will remain fundamental in enabling a brighter future for Australia.
“The world is on a path to what we must ensure is a better future,” he said.
“We will have substantially more people on this planet, seeking higher standards of living that need to be supplied and powered by resources extracted, refined and used more sustainably.
“This industry is critical to enabling that future, and the opportunity is large. If we deliver on this opportunity, we deliver for the world, for economies, societies and communities.” AM
CAPS Australia is an Australian owned and operated company who was born to service the mining industry with the best compressed air products and services. 43 years later, mining is still at our core with products, engineering and an expanded range.
CALL 1800 800 878 OR VISIT CAPS.COM.AU
Hydraulic wrenches, or hydraulic torque wrenches, are widely used in mining for tightening and loosening large bolts and nuts.
These tools provide high torque capability, ensuring precise and controlled tightening to enhance equipment safety and prevent failures.
They are also versatile, with various sizes and configurations to accommodate different applications across the mining industry.
Hydraulic wrenches offer efficiency, saving time and effort compared to manual methods. Built to withstand harsh mining conditions, they are a proven solution for many operations.
Despite all the advantages, hydraulic wrenches carry many safety risks, as the tools operate at high pressures, this naturally leads to significant risk to the operators.
Hydraulic torque equipment must then keep up and provide an increased focus on safety – and that’s where Atlas Copco has filled a gap in the market.
It was from this position that the Torcflex hydraulic torque wrench was developed. The Torcflex wrench features a co-axial hose system to increase operator productivity
and safety. Not only does this help to ensure a quick set-up, but also provides complete freedom of movement for the operator.
Trapped pressure and pressure intensification hazards are also eliminated in this way.
The free moving coupling provides complete range of movement and no tangled hoses, which in turn means operator fatigue is reduced.
“Using the Torcflex wrench reduces the dropping hazard, as well,” Atlas Copco global product manager –hydraulic torque Rhodri Williams said. “The new square drive retainer helps to prevent these hazards, as well as the danger of a loss of components.
“As well as the square drive, the patented retained reaction arm makes first-time positioning easy. Heavy reaction arms are also a major danger for drop hazards, so this risk has now been completely eliminated.
“In a lot of the older-style wrenches, the handles were supplied separately, so they were often forgotten in the order and secondary wrenches. And if the handle was ordered, it would be stuck in a fixed position on the wrench, so it would get in the way on certain applications.
“With the Torcflex, we’ve included the support handle as standard and
it can be indexed while still attached the tool, meaning the operator can use it in the safest and most efficient manner possible.”
Atlas Copco business manager Oceania Leo Williams has seen the Torcflex wrench used in a variety of mining applications with positive results and safety improvements.
“The mining industry in general is certainly not a new market for Atlas Copco,” he said. “But in terms of hydraulic torque wrenches, we will really be targeting the mining industry over the next couple of years.”
The Torcflex wrench works by combining the traditional mechanical wrench with innovative features for the user.
“There was little to no innovative solutions coming out of the hydraulic torque market for years,”. Rhodri Williams said
“So the engineers within Atlas Copco looked at the users’ experience and how they could innovate to solve the problems that were commonly seen from using the conventional design torque wrenches.”
It may sound complicated, but setting up and using the Torcflex wrench is a breeze, as evidenced by the positive feedback the Atlas Copco team has been receiving.
“Our customers tell us that it’s nice to see an innovative solution within the hydraulic torque market,” Rhodri Williams said.
“There will always be a need for hydraulic wrenches because of the versatility they provide.
“A lot of industries still use hydraulic wrenches, including mining, wind, and oil and gas. And now we’re coming in and helping to solve the issues people have with them, so our customers see the Torcflex wrench as a refreshing change.”
Atlas Copco has a large portfolio of bolting solutions, but it never misses the mark on its journey of continuous innovation.
“We are trying to make bolting jobs quicker, safer and smarter,” Leo Williams said. “It comes down to looking at the customer’s requirements and then developing the right tool for the job.”
Rhodri Williams said Atlas Copco will not stop developing new products as technology becomes smarter and there is increased demand for digitalisation and error-proofing within many bolting segments, specifically mining.
“And that’s really what we want to be known for,” he said. “Our focus on developing and innovating products that solve industry demands.” AM
ABB has the unique capability to design, supply, supervise the installation, commissioning and provide long-term service and support of entire mine hoist mechanical and electrical systems. With a global team of experts, 130+ years of experience and over 1,000 hoisting solutions worldwide, we manufacture Friction, Double Drum and Single Drum hoists for material handling or personnel and equipment transport solutions. Our Digital offering, ABB Ability™ Smart Hoist improves uptime, availability, performance, and productivity of your hoists.
Let’s write the future together new.abb.com/mining/underground-mining/mine-hoist-systems
In just a little more than a decade since the introduction of used oils into its various Eco bulk emulsion formulations, AECI Mining Explosives has consumed more than 80 000 000 liters of used oil. This initiative has prevented approximately 55 000 tons CO2e into the atmosphere, which equates to having to plant roughly 100 million trees. Thank you for partnering with us in our quest to drive more sustainable blasting.
As a global event that was truly unprecedented over the past century, the COVID-19 pandemic had a number of unexpected effects.
As so many people were stuck inside with little to do outside of the daily tasks associated with their job, a large proportion started to question their career or workplace. The aftermath of the pandemic saw employees resign from their jobs at an unparalleled rate.
A ‘great resignation’ or ‘big quit’, as it came to be known, descended on industries all over the world.
People left for a variety of reasons, including wages, cost of living and work–life balance. However, according to Kerry McQuillan, director of recruitment agency Randstad
was the second most attractive sector in which to work, with 47 per cent of respondents voting in its favour.
“The mining sector has long been seen as a reasonably stable job,” McQuillan told Australian Mining
“It has great career progression, long-term job security, and if you start off in the mining sector then you can generally move around and go to different places.
“There are a lot of people who moved over the last couple of years to more regional and remote areas and they find that they can still do their jobs they were doing in big cities while their partner brings home good money from the mining region.”
Survey respondents indicated that the top three things they would look for in an “ideal” employer would be work–life balance, attractive salary and benefits,
“As much as the ‘big quit’ happened, we’re now starting to see people just being a little bit more cautious about why they would move careers.
“So what we’re really seeing now is a ‘big stay’. People are only moving jobs if they really feel they need to.”
Although more people are staying in their current role, it’s no secret the mining industry needs to encourage more employees to join the sector while also retaining the employees it already has.
One way miners can encourage more and retain current employees, McQuillan said, is to focus on the bigger picture.
“A lot of the time, people have preconceived ideas about what it is like to work in a mine,” she said. “They might imagine that it’s just a big open pit and they will just be moving ore from
EVER WONDERED HOW COMPANIES BEST POSITION THEMSELVES FOR MERGERS AND ACQUISITIONS? AUSTRALIAN MINING UNPACKS THE FUNDAMENTALS.
Mergers and acquisitions (M&As) are a key driver of growth across the global resources sector, as companies look to consolidate their business or portfolio – whether harmoniously or acrimoniously.
Transactions often involve a larger company wanting to acquire a smaller peer, sometimes at the expense of the latter’s own ambitions and growth trajectory.
M&A and its influence on investment in the resources industry was recently discussed at the Mines and Money conference in Melbourne in June, where a panel discussion involved insights from investment bank Greenhill, law firm White & Case, and private equity firm Pacific Road Capital.
Partners and directors from these firms – which support mining companies through their M&A dealings – spoke
about the deals that come across their desks and what advice they give miners when they’re involved in a transaction.
Some prominent themes emerged from the discussion, including how a mining or exploration company can best position itself for M&A, and how to spot a potential M&A candidate.
Preparing for M&A
Broadly speaking, an acquirer would not start a conversation with another company unless something caught its eye. So being the target of a transaction is typically positive recognition of a counterparty’s assets and attributes.
For Matt Fifield, managing partner at Pacific Road Capital, companies looking to better position themselves for M&A must focus as much time on their business as they should on their assets.
“One of the single easiest ways to start to prepare your company to be attractive to an acquirer … is to start with things like sustainability reports, or knowing
INEVITABLY, THE BIG,
ASSETS IN QUALITY JURISDICTIONS GET PICKED OFF AT SOME POINT … THAT’S ALWAYS A GOOD PLACE TO START. THERE’S ALSO SPECIFIC SITUATIONS WHERE THERE MIGHT BE A STRANDED ASSET WHERE THERE’S A LOGICAL ACQUIRER NEXT DOOR.”
what your carbon (footprint) is, or what your water usage is,” Fifield said during the panel discussion. “As a junior mining company, you’re wrestling (with concerns such as) tonnes, grade, ‘I have no money’ (or) ‘How’s this all going to work?’.
“But if you’re actually trying to build something that somebody else wants, the acquirers are going to look at your project and they’re going to say, ‘Okay, you have a baseline’.”
Fifield said companies that can establish their business baseline –whether that means improving their reporting processes or materialising their environmental, social and governance (ESG) performance – will be more amenable to M&A as they align with the acquirer’s own business obligations.
“When you’re grooming a company or setting it up to be acquired, you need to think about what the acquirers need, and therefore what their customers need,” Fifield said.
“I have seen in a boardroom a whole bunch of people relax and say, ‘All right, let’s talk about this’, or turn their nose up and say, ‘You guys aren’t even at square one’.”
“So one of the things that I look for … is who’s doing that, who’s thinking about
SCALABLE
not only their project, but the business they’re trying to sell.”
There could be a range of reasons as to why an M&A target has attracted attention.
The company might operate in an attractive jurisdiction, be looking to mine a sought-after commodity, or hold desirable exploration tenure.
For what it’s worth, the reasons an M&A target gathers interest could be evident before a transaction is first initiated.
When Greenhill managing director Campbell Cooper considers potential M&A, he goes back to the basics.
“Long-life, low-cost orebodies is usually a good place to start,” he said. “There’s a lot of explorers and junior companies here (at the conference) , and you can tell pretty early on in the evolution of a mining asset, what it looks like.
“Is it going to be a big, scalable asset?
“Inevitably, the big, scalable assets in quality jurisdictions, if you look through history, get picked off by someone at some point. So that’s always a good place to start.
“There’s also specific situations where there might be a stranded asset where there’s a logical acquirer next door.”
Cooper said people often underestimate how difficult it can be for a single-asset company to bring a project all the way from discovery to production.
“Some people do it, but there’s a myriad of challenges there, whether it be finding the capital … (or) finding the people to help you build the project, that inevitably make management teams and major shareholders of these companies more amenable to M&A
Cooper explained this in more detail, using the example of a junior company looking to develop not only a mine but also downstream processing infrastructure.
“If you’re a junior mining company that doesn’t have a producing mine yet, (and you’re) talking about building a refinery, strategic (investors) are probably going to look straight through that to the next story,” he said.
“They prefer the smaller, simpler stores. That doesn’t necessarily mean you can’t move downstream down the track, but getting the basic building blocks first is important.”
White & Case partner John Tivey said one of the key challenges he sees is single-asset companies trying to establish a development model that’s bankable. This is especially the case for such companies looking to develop a vertically integrated business comprising mining and downstream processing infrastructure.
It might be pertinent for these businesses to contemplate potential third-party partnerships in the future.
“If you insist that you’re going to stick with a downstream processing, all-on-our-own model, it’s a real
challenge,” Tivey said. “Because a lot of host jurisdictions are requiring singleproject companies to further beneficiate their product in-country before they send it off to market, which massively adds to the capex (capital expenditure) associated with the project.
“So I think you need to come up with a model that accepts you’re inevitably going to have to have other parties in your project and work out what the profile of those parties looks like.”
Cooper provided an example to solidify Tivey’s point.
“We worked in 2017–2018 for Kidman Resources. They were in a joint venture with SQM (and) they ultimately got acquired by Wesfarmers,” Cooper said.
“They did offtake arrangements with Tesla, amongst others, and it was really important to Tesla to have a really credible party like Wesfarmers developing that asset.
“Not to say that the Kidman team couldn’t have done it, but clearly, for a junior mining company, it was going to be much more challenging to develop a really large-scale asset.
“So the point made around another driver of M&A, particularly in battery minerals, is going to be the supply chain wanting to see the right people owning and building these mines.
“At the end of the day, for the likes of Ford, Tesla and GM, they don’t want to be in the business of mining, they just want to have the security of supply.”
Avenira is another single-asset company that has prioritised third-party partnerships, having linked up with Taiwanese battery pioneer Aleees as it looks to develop one of only three LFP
(lithium iron phosphate) cathode plants outside of China.
Avenira’s Wonarah phosphate project in the Northern Territory –which is looking to commence DSO (direct shipping ore) mining in the second half of 2023 – would connect with the LFP cathode plant in Darwin, with the aim to produce battery-grade materials for global electric vehicle manufacturers.
Partnering with such an esteemed third-party means Avenira has de-risked its business model, putting itself in a better position to attract interest from acquirers or investors.
Whether a company is interested in engaging in M&A or not, the characteristics an acquirer might resonate with would likely be the same as a potential investor, so putting the work into establishing a strong, de-risked business model could prove lucrative on several fronts. AM
*When this magazine went to print in early July, Westgold’s initial takeover offer had been rejected by Musgrave, and Ramelius Resources had launched its own takeover bid, which was unanimously recommended by the Musgrave board.
IF YOU’RE A JUNIOR MINING COMPANY THAT DOESN’T HAVE A PRODUCING MINE YET, (AND YOU’RE) TALKING ABOUT BUILDING A REFINERY, STRATEGIC (INVESTORS) ARE PROBABLY GOING TO LOOK STRAIGHT THROUGH THAT TO THE NEXT STORY.”
The latest report from the Intergovernmental Panel on Climate Change confirmed that the window for transformative climate action is rapidly closing.
The Australian Government has pledged $20 billion towards decarbonising the country’s energy grid, aiming for 82 per cent renewables by 2030, in line with the greater goal of net-zero carbon emissions by 2050. Indeed, net zero by 2050 is a goal shared by many major industrial companies.
But 2050 is a long way off, and the planet isn’t getting any cooler. That’s why Bradken has set itself the ambitious goal of becoming carbon neutral by 2030.
“The most exciting part is that it’s actually going to make a difference,”
Bradken’s Carbon-Neutral 2030 project director Kirsty Morgan told Australian Mining
“Our steel foundry and fabrication operations are energy-intensive, so it’s the perfect opportunity to make significant change. Our goal is for
Bradken to be carbon-neutral for Scope 1 and 2 emissions by 2030.”
Scope 1 and 2 emissions are direct and indirect emissions generated by a company’s operations, while Scope 3 emissions come from upstream and downstream sources.
So by cutting its own carbon output, Bradken is also helping to lower its customers’ Scope 3 emissions.
“(The year) 2030 is quite close, but Bradken’s ethos is that we don’t back down from a challenge,” Morgan said.
“Taking these steps now means we’re doing our part to safeguard our planet and deliver an optimised future for our customers, ourselves and our communities.”
For Bradken, this all represents much more than just a peripheral objective.
Morgan’s role is a new one, with her team specifically dedicated to the 2030 target. The company has also pledged $US50 million ($75.6 million) in capital projects and resourcing, and has a team of sustainability business partners across the globe to support sites.
Bradken’s commitment to a carbonneutral 2030 goes right to the top. Chief
executive officer (CEO) Sean Winstone is also a sustainability champion, recognising sustainability efforts across the company’s manufacturing sites with the annual CEO Sustainability Award.
agenda,” Winstone said. “The data speaks for itself; despite increasing production by about 13 per cent in the past year, the site was able to reduce its overall energy consumption and CO2 emissions, reducing its emissions intensity by 12 per cent.”
Morgan said that senior leadership is completely on board.
“Our 2030 target is deeply embedded in the business at every level,” she said.
A veritable titan in the industry, Bradken has operations across the globe. So where does one begin with such an ambitious environmental task?
“We’ve put our sustainability roadmap in place and we have three main pillars that we’re looking at,” Morgan said.
The first of those pillars is operational efficiency.
“We melt metal – it’s really resourceintensive,” Morgan said. “So, firstly, it’s about reducing the amount of energy used so we’re not wasting any in that process.
“This year the dedicated team at Wundowie, Western Australia, has made some remarkable achievements in advancing Bradken’s sustainability
“We’re looking at the basics of how we make our products, especially energyintensive processes like metal melting and heat treatment, and finding better ways to do it.
OUR STEEL FOUNDRY AND FABRICATION OPERATIONS ARE ENERGY-INTENSIVE, SO IT’S THE PERFECT OPPORTUNITY TO MAKE SIGNIFICANT CHANGE. OUR GOAL IS FOR BRADKEN TO BE CARBON-NEUTRAL FOR SCOPE 1 AND 2 EMISSIONS BY 2030.”
Measurement and reporting has been an integral part of this initial stage, with emissions intensity and furnace efficiency being tracked at all engineering and foundry sites to monitor progress.
The sustainability business partners are looking at available technologies to make site-specific process improvements.
“When you’re making your systems more efficient, you’re using less energy – and energy prices are going up, so we’re balancing these cost impacts,” Morgan said.
The second pillar is procuring renewables.
“The first pillar is about ensuring we’re not wasting any energy, and the second is about replacing that energy with renewables,” Morgan said.
“We’re actively procuring solar, hydro and wind power to increase the renewable energy we can supply to our operations.
“Bradken is actually very good at this. Our foundry and manufacturing site in Mont-Joli, Canada, is already powered by 100 per cent hydroelectricity.
“And our Coimbatore site in India is powered by 75 per cent renewable energy, which cuts annual carbon emissions by 7700 tonnes.”
Closer to home, Bradken’s Mt Thorley mining services workshop in the NSW Hunter Valley recently installed 250 solar panels to help deliver an annual CO2 emission reduction of 19 per
cent, bringing the company closer to carbon neutrality.
The third pillar is upgrading plant and equipment.
“We’re exploring options to convert our equipment to cleaner, lower-emissions technologies,” Morgan said.
“One example of this is moving from gas-powered to renewableelectricity-powered heat treatment ovens at our sites.”
This is just the start for Bradken, which aims to similarly transform its other operations, such as its Merlimau site in Malaysia.
Achieving carbon neutrality by 2030 is an ambitious goal, but the company has the experience, knowledge, technology and people to see it through.
Morgan is expecting to be more than half-way to the goal by 2025.
“Bradken has been around for over 100 years and in that time the global population has quadrupled,” Morgan said. “We know so much more now about our impact on the planet, and we feel the urgency to do something. Climate change is a global emergency, with the planet and the people all at risk.
“The sector is aiming to be carbon-neutral by 2050. We’re more ambitious.” AM
Despite Sulzer’s REP being a new offering for the Australian mining market, the company has already reported strong uptake for the program.
“The introduction of the first wheel motors, alternators and grid blowers to suit electric drive haul trucks was launched in Queensland and Western Australia with an immediate
But Sulzer recognises that because the REP is still in its early stages, the company should not overcommit by bringing on too many clients, but rather ensure it grows the program in stages.
“We’re making a lot of big changes,” Dunk said. “Over the next six months, we’re investing significantly in our facilities, including our Brisbane workshop, where we have dedicated repair cells just for the REP.
programs. This can be done through an agreement, giving customers peace of mind regarding component availability.
Having established the REP for haul trucks, Sulzer’s sights are on expanding the offering to support rope shovels and underground flameproof equipment.
Any mining company that partners with Sulzer can open up new possibilities in operational efficiency, with the OEM able to provide 24-hour service 365 days a year through its seven service centres. This is further supported by Sulzer’s network of more than 100 service sites worldwide.
“Sulzer is your global partner with reliable and sustainable solutions for your key operations,” Dunk said. “You benefit from a local service provider with global experience in the repair and maintenance of all types of rotating equipment.”
Aoriginal equipment manufacturer (OEM) and leading rotating equipment independent service provider (ISP) for the Australian resources industry, Sulzer has a strong network of customers that depend on its products and services.
Whether it’s lightweight and robust submersible dewatering pumps or wearresistant centrifugal pumps, Sulzer’s products have supported the removal of sludge, mud, silt and water on mine sites for decades.
The expertise Sulzer has drawn from its pump offerings has fuelled the emergence and success of its services division, where the company has become a go-to rotating equipment ISP for miners across Australia.
Sulzer can conduct complete electrical servicing of haul trucks, whether that involves in-house coil manufacturing, converting DC motors to AC, or complete motor overhauls and repairs.
Sulzer Australia can also rebuild parts through its reconditioned exchange program (REP), something Warren Dunk, Sulzer Australia business development manager – services, said provides a cost-effective solution for mining companies.
“Sulzer Australia has been rebuilding the electrical components of electric drive haul trucks for most of the large
Liebherr, Hitachi, Komatsu, WesTrac and Hastings Deering,” Dunk told Australian Mining
“By offering a range of wheel motors, alternators and grid blowers, we have expanded our business offerings while helping those mining customers that do not have their own spares within their inventory.
“Our rebuilt components can be delivered to site and installed within hours. This means trucks are back operational as fast as possible, maximising productivity. We also provide specialist support for the repair and upgrade of haul truck alternators for continued reliability.”
As part of Sulzer’s REP, mines can go directly to the company for the reconditioning of electrical parts, using original components from respected OEMs. Sulzer also uses its own original parts.
“We’re the only company in Australia that manufactures commutators for DC motors,” Dunk said. “We extrude and manufacture our own high-voltage coils and slip ring assemblies in-house. There’s no other ISP in Australia that does that.”
The efficiency of Sulzer’s service is made possible by its seven Australian service centres, where mechanical engineers are enlisted to carry out REP projects to ensure the highest reconditioning standards.
“As that develops, instead of being able to recondition 25 wheel motors in a workshop per annum, realistically we’re going to be able to do 60 or 70 wheel motors in one workshop, not by going to a bigger shop, but by making investments in new equipment and people.”
Sulzer can provide components when breakdowns occur or have dedicated cores as part of scheduled rebuild
Sulzer has a dedicated Australian accounts management team tasked with directly supporting its mining customers, enabling the company to put more time into their partnerships, products and rebuilds.
This increases the mean time between failures and reduces the total cost of ownership, ensuring machines are more reliable and efficient. AM
AS RECENT TECHNOLOGY AND INNOVATION HAS CHANGED THE WAY THE SECTOR OPERATES, EMESENT IS ADVOCATING FOR MORE MINING STAGES TO BE AUTOMATED.
ith so many benefits, it’s easy to understand why autonomous operations are the key to future mining – and at the heart of Emesent.
Despite being a five-year-old company, Emesent has established itself as a leading provider of drone and robot-enhancing light detection and ranging (LiDAR) mapping and data analytics technology.
The company believes in future mines running autonomously at multiple operational stages, effectively acting as a self-managing entity.
Emesent co-founder and chief technology officer Farid Kendoul recently spoke at the World Mining Congress (WMC) in Brisbane, which was held for the first time in Australia in 2023.
Kendoul discussed how autonomous robots can reduce post-blast re-entry delays in underground mines.
“I think (the WMC) confirmed our vision for the mines of the future, and how it is aligned with what the mining company executives are thinking,” he told Australian Mining
W“They all had almost the same story: efficient extraction of minerals is critical to the decarbonisation of the planet and to sustain the industries and economy of the future. At the same time, minerals are scarce because they are a finite resource.
“If you add to that the cost pressure concerns in terms of sustainability and ESG (environmental, social and governance), then you realise that the current mining approaches are not sustainable.
“They need to find a different or new way.”
Enter mining automation, which Kendoul said is no longer a buzzword, but rather a necessity for the industry’s future.
“Many mining companies are developing 5–10-year roadmaps that show how they can transition from their current operation into a fully autonomous operation,” Kendoul said.
Autonomous mining has a number of key benefits, but the first is safety of people and equipment.
“Removing people from dangerous areas and harm is a big benefit, especially with regulations in countries like Australia,” Kendoul said.
Mining companies will also see an increase in productivity and optimisation through autonomous operations.
“Current mining operations mainly rely on manual systems and processes that are fragmented, which means it’s very hard to optimise operations when you have systems that don’t talk to each other,” Kendoul said.
“By automating a mining operation, it means that you will have one connected system. You will have a lot of data to share, which will allow you to optimise the operation, thereby increasing productivity and profitability for the mine.”
Another benefit is that automation helps to encourage sustainability.
“There is a lot of pressure placed on the mines by the government, society and other stakeholders to be sustainable towards the environment,” Kendoul said.
“When you use autonomous systems, it means that you have current and historical data, where you can then run the analytics and predictions to reduce waste and be environmentally friendly.”
Like any industry transition, going fully autonomous will take time and effort to work towards achieving shortterm and long-term goals.
“It’s not just a vision. Mining companies and original equipment manufacturers (OEMs) are already starting to develop technologies to achieve autonomy,” Kendoul said.
“It is going to take some time to fully transition because a lot of things need to happen, such as technology needs to evolve, but things are really accelerating at a high speed.”
Looking at the opportunities ahead, Emesent has a desire to grow and evolve its technology. A key example is building on the success it has found through its Hovermap solution.
Currently used by customers in underground mining environments, Hovermap is a unique LiDAR mapping and autonomy payload that combines advanced collision avoidance and autonomous flight technologies to allow drones to fly autonomously in challenging GPS-denied environments to map and explore them.
Hovermap features a sensing range of up to 300m and the ability to capture more than a million points per second. It help mining operations to rapidly capture detailed and accurate data over a wide area – accelerating a miner’s time to insight.
The system can also be used for surface mining, can be mounted onto a backpack, drone, robot or vehicle, and its technology uses innovative hardware, advanced algorithms, and machine learning to automate collection and analysis of its surroundings.
“We were the first to enable drones to fly autonomously, mapping environments without sending people into dangerous areas,” Kendoul said.
“That was just the beginning. We now want to take our solutions to the next level.
“We are focused on identifying various critical mining operations and exploring how to automate them, including the collection of data and then the processing of this data. The extraction of these insights will help mining companies make good decisions.”
Emesent is also working on autonomous solutions in an effort to avoid downtime.
For example, when rocks are being blasted at a mine site, operations will be closed down due to the resultant hazardous environment.
To help avoid this kind of issue, Emesent is proposing that post-blast operations be fully autonomous through two key systems, the first of which is an autonomous robotic system that is part of a project’s infrastructure.
“It could be a ground robot or an aerial robot that’s equipped with sensors and the autonomy that will allow it to go and inspect those areas ondemand,” Kendoul said.
This would be aided by the second system, an autonomous data system located at the surface.
“The data system would be used to deploy and operate the robots that are underground, but it would also ingest the data remotely from the robots in near real time – fusing all of that data to deliver insights and showing them to the mining operator so they can make clearer and faster decisions,” Kendoul said.
“This means we are really automating that operation and allowing mining operators to do those inspections remotely from their desk, improving safety. It will also increase productivity, as it will minimise downtime and the times you need to wait.”
Hovermap has won various industry awards, as well as acclaim from its customers, who have praised the quality of the data and the fact it can be captured in as little as 15 minutes.
Kendoul said that Hovermap also supports interoperability.
“(Customers) just want to get the information and insights as quickly and easily as possible, and to do that all these technologies and systems need to work together,” he said.
Emesent has already started working closely with several companies that are providing solutions to mining, including software companies such as Deswik, Maptek, and Pointerra.
“We started to make our systems compatible. You can take our data and then use it in their software,” Kendoul said. “Now we are looking to partner with other companies and OEMs to make sure our platform will automatically exchange data with other systems through APIs (application programming interface), which customers can access.”
As the world transitions to advanced technology to complete complex mining tasks, Emesent will be at the forefront.
“I really believe this vision will be achieved, and that in the not-so-distant future there will be more autonomy and digitalisation in mining,” Kendoul said. “The technology is evolving and Emesent will continue to develop capabilities to allow it.
“We welcome the collaboration, commitment and engagement from the mines to digitise their operations and workflows because this will drive a significant shift in value for how the mines will operate.” AM
THE HOVERMAP HELPS OPERATIONS CAPTURE DETAILED AND ACCURATE DATA, SUCH AS STOPES OVER A WIDE AREA. EMESENT’S FARID KENDOUL DISCUSSED AUTONOMOUS MINING AT THE WORLD MINING CONGRESS 2023. HOVERMAP CAN BE MOUNTED ONTO ROBOTS, DRONES OR VEHICLES.As the Australian resources industry undergoes a technology revolution, mining companies and contractors will need to institute and nurture significant organisational change.
With company boards beholden to heightened shareholder and stakeholder expectations, miners are turning to automation and digitisation to boost safety and productivity.
This is transforming what has historically been a manual, hands-on industry into one that is increasingly remotely operated.
Such a transformation is necessitating the need for renewed training and development, as workers have redefined roles or leave the field to operate machines from the office.
This is mining in the 21st century and METS (mining, equipment, technology and services) companies such as Immersive Technologies are key to ensure this transition occurs as safely and seamlessly as possible.
Immersive is one of the mining sector’s leading providers of workforce development solutions, having deployed its simulators across the world, including for many of the world’s largest mining companies, such as BHP, Rio Tinto, Vale and Glencore.
When Immersive was founded in 1993, the company’s initial focus was developing computer-based training for
mining equipment operators ,and by 1998 it demonstrated the industry’s first prototype truck simulator to Caterpillar.
Immersive launched its first haul truck simulator at the Diggers & Dealers conference in 1998, which evolved to excavator, dozer, loader and dragline simulators released in ensuing years.
Immersive now has about 550 simulators in the field in more than 50 countries, with about 50 new simulators delivered to the mining sector each year.
And while its simulators are seemingly universally used, another offering is growing just as fast.
“The advent of more complex mining technology systems has been the basis for the evolution of our digital media division,” Immersive Technologies’ regional vice president – Asia Pacific Simon Vellianitis said.
“This includes interactive content like digitised SOPs (standard operating procedures), which we call ‘missions’ delivered via virtual reality, touch screen or traditional PC devices. These are the types of procedural experiences which are complementary to new performance or automation systems going into a mining operation.
“Our digital media team went from being focused on developing the virtual environments for our equipment simulators to developing varied digital content across a much broader set of technologies. These broader technologies are what we call learning systems.”
Developing learning systems could involve the digital media team creating detailed 3D visualisations to help operators understand the terminology around machine components, or it might involve creating digitised SOPs to help operators understand how they’re meant to be interacting with mobile fleets on a mine site.
Forty per cent of Immersive’s Perthbased workforce comes from the digital media and engineering domains. These divisions are set to play an increasingly important role as the mining industry further embraces automation and electrification, with companies requiring plenty of support to understand and integrate these advancements.
Vellianitis said the safest and most efficient operators will be focused on proficiency, something with which Immersive can also help.
“Mining operations in the west are largely autonomous, while many in the east – including the Pacific Islands – are manually-operated, with the workforce development strategies being different for both,” Vellianitis said. “When it comes to automation, our methodology
and training technologies are focused on addressing high task complexity arising from the introduction of these new systems in mining operations. And that is likely to be the case with electrification, as well.”
“As new technologies, equipment and integration challenges arise, there’s going to be a change-management exercise that goes with that. And with all change management, it links back to
humans, and it links back to awareness, training and capability.
“That’s where we see our space evolving – whether it’s digital media, equipment simulators or consulting and analytics, it could be any one of those or it could be a combination of all of those.
“That’s a gap that we’re fairly certain will continue and will probably get bigger.”
A more immediate concern for the Australian resources sector is the skills shortage, where companies are finding it difficult to access experienced talent. In response, miners are thinking outside the box and recruiting workers from other industries.
This situation places increased importance on training.
“It’s been very difficult for mining companies to find operators who have a background in mining,” Vellianitis said. “As they find new people, there’s a huge learning curve for those new starters and the quality of training during their onboarding and first couple of weeks is absolutely critical.
“If they get good quality training, that generally sticks with them and serves them well. But if they get poorly structured and delivered training, it can result in a whole plethora of issues further down the track. It could be safety issues, issues related to maintenance, or the reliability of the machine.”
Vellianitis said workers who are not trained properly are more likely to use a machine outside the bounds of its operational specifications. This can cause machine downtime and lost productivity.
“Mining operations tend to look towards engineering solutions to address performance challenges not specifically linked to human performance,” he said.
“If variance in human performance is the source of a machine issue and if that can be addressed via training, then it’s often the easiest thing to do – it’s the low-hanging fruit. It’s often the least expensive thing to do as well, particularly if the mining operation already has a simulator.”
Immersive Technologies built its business before the digital age kicked into gear, and the company has now evolved to ensure it sits at the precipice of mining’s next turn.
It appears as if Immersive is always ahead of the curve, which bodes well for an Australian mining industry simultaneously facing a skills shortage, technology revolution and growing decarbonisation imperative.
As long as Australian miners have access to Immersive’s simulators, digital media and associated services, then it seems the transformation isn’t so daunting after all. AM
Immersive Technologies – a proud Austmine member – won the Craig Senger Excellence in Export award at the Austmine 2023 conference. This award celebrates companies who excel in exporting their offerings to the world.
With more than 650 members nationally, Austmine is the leading industry body for the Australian METS sector. The notfor-profit organisation exists to promote the global advancement of technology and innovation in mining.
WITH SIBANYE-STILLWATER RECENTLY SECURING NEW CENTURY RESOURCES FOLLOWING A MONTHS-LONG ACQUISITION PROCESS, AUSTRALIAN MINING REFLECTS ON WHAT LED TO THE DEAL GETTING ACROSS THE LINE.
Sibanye-Stillwater and New Century Resources have enjoyed great success as separate companies within the resources industry.
But these multinational metals players are now coming together, with Sibanye having recently acquired 100 per cent of remaining shares of New Century, which has since ceased trading on the ASX.
But after months of back and forth between the two companies, how did we get here?
February: The offer
Sibanye first made its initial off-market takeover offer to New Century on February 21.
Sibanye’s takeover offer involved acquiring up to 100 per cent of New Century’s fully paid ordinary shares at a cash price of $1.10 per share.
Sibanye, which already owned a majority 19.9 per cent stake in New Century, cited changes in strategic direction and decline in shareholder value as the reasons behind its move.
“We will continue to advocate for change in the current strategic direction of New Century,” Sibanye said in the statement announcing the bid.
“Sibanye has also recently become aware that a number of shareholders in New Century may be looking to dispose of their holdings on market.
“Sibanye has been concerned about the change in strategic direction of New Century under current management, with the building of a tailings asset management service business no longer a focus.”
Sibanye said the New Century balance sheet was “under strain” due to potential funding requirements for growth projects and could have
resulted in a raise in additional equity and a material dilution for existing shareholders.
At this time, the New Century board recommended its shareholders to take no action towards Sibanye’s bid, despite Sibanye having been its majority shareholder since 2021.
March: A deal is struck New Century remained mostly silent about Sibanye’s takeover bid until March 8, when its board urged shareholders to accept the offer.
While New Century has previously recommended its shareholders take no action towards the February bid, due to Sibanye’s increased investment percentage, and in the absence of competing bids, the company’s board changed its mind.
“Sibanye has already acquired a relevant interest in 73.41 per cent of New Century and therefore control,” the
New Century board said in the March 8 announcement.
A day prior, Sibanye-Stillwater announced it was the controlling shareholder in New Century.
“In these circumstances, the board considers it unlikely that a competing proposal will be forthcoming. The board confirms it has not received any competing proposals,” the New Century board said. “The offer delivers certain value in the form of cash consideration and, importantly, a liquidity opportunity for New Century shareholders.”
The takeover situation at the time was also affected by severe weather events in Australia.
March also saw unprecedented rainfall in Queensland, which affected the productivity and operations of many mines located in the state, including New Century’s Century mine in the north-west of Queensland. Residents in the area were forced to
evacuate earlier in the month amid the high rainfall.
The extreme rain cut off access to the Century mine by road, severely affecting deliveries to site of production consumables.
New Century said that the production and non-essential activity suspensions were likely to impact its production results for the March quarter. Regardless, Sibanye said it intended to keep its takeover offer open, providing $30 million in relief to New Century to assist in getting the Century mine back up and running.
“No safety incidents were experienced and core infrastructure remains secure; however, due to the extent of the flooding event, operations are currently estimated to remain suspended for a further 2–3 weeks,” Sibanye said regarding the suspension of the Century mine.
“Sibanye-Stillwater remains committed to working with New Century to ensure the safety of the on-site team and the safe restart of operations.
“Sibanye-Stillwater also remains committed to working with New Century to ensure that it remains in a position to meet its financial obligations while it recovers from this unforeseen event, subject to certain conditions.”
New Century announced on May 2 that Sibanye’s offer was scheduled to close on May 15, and Sibanye intended to complete the compulsory acquisition procedure in respect of New Century’s remaining shares according to the timetable set out in the Corporations Act 2001
“Accordingly, all remaining shares in New Century that have not been validly accepted into the offer by 7.00pm (AEST) on Tuesday May 2 2023 will be compulsorily acquired by Sibanye Australia,” New Century said in its announcement.
“Compulsory acquisition will be on the same terms as those offered by Sibanye Australia under the offer, which means that remaining shareholders will receive $1.10 cash per New Century share.”
New Century saw some leadership shake-ups in the wake of this news, including the resignation of nonexecutive director and chairman Kerry Gleeson.
“On behalf of the New Century team, I thank Kerry for her diligence and service as non-executive director and, more recently, as chairman of the board,” New Century managing director and chief executive officer Robert Cooper said.
“Kerry has been an unwavering source of wise counsel and leadership to the board and management team during a period of significant change for the business. We wish her well in her future endeavours.”
As Gleeson left, two non-executive directors were appointed to the New Century board: Sibanye non-executive directors Stephan Stander and Benjamin Dry. Stander was senior vice-president of mineral resource management and.
Around the same time, New Century non-executive director Peter Watson also resigned.
“I have been delighted to serve on the board of New Century with Peter, whose solid industry, technical and strategic expertise has assisted
the company during a dynamic period that has culminated in the successful acquisition by leading international mining company SibanyeStillwater,” Gleeson said. May 11 saw New Century cease trading on the ASX.
To end the months-long acquisition process, Sibanye acquired ownership of New Century’s zinc mine tailings project in Queensland.
“Australia provides a stable, robust and high-quality mining industry for us to expand our focus on metals that are crucial to renewable energy solutions,” Sibanye executive vice-president of investor relations and corporate affairs James Wellsted had told the ABC.
“We think that (tailings reprocessing) is going to become an
is becoming increasingly difficult. So the circular economy – reprocessing and recycling – is becoming of more and more value.
“Prices over the past two years have been relatively high but we have seen a pullback in most commodity prices over 2022 and going into 2023, mainly linked to global uncertainty. But I think we are starting to see some green shoots now and the outlook is more positive moving forward.
“We’re quite excited about our investment in Australia; it is a new region for us.
“We know the Australian mining industry is home to very robust, highquality operations and companies, and a lot of opportunities.” AM
The Diggers and Dealers Mining Forum aims to secure highly respected and relevant experts in the resources sector who are well-positioned to provide insightful commentary about the industry’s outlook.
It’s an opportunity for professionals to network, visit regional mining sites, engage with the media, invest in key projects, and engage with the resources sector at an executive level.
Held in Kalgoorlie, Western Australia, the unofficial gold mining capital of the country, the 2023 Diggers and Dealers Mining Forum will combine 66 corporate presentations by ASX-listed mining and exploration companies, along with an exhibition area housing over 150 exhibitors from the sector.
Coinciding with the event is the 2023 Diggers and Dealers Leadership Breakfast, hosted by the Gold Industry Group. The theme of the breakfast will be ‘Reshaping the workplace of tomorrow: Gold’s pathway forward’.
One of this year’s Diggers and Dealers presenters is Westgold Resources managing director Wayne Bramwell, who will also be part of the leadership breakfast panel discussion.
“I think the panel discussion is going to be about what gold companies are doing to build a culture of ‘everyday respect’ where everyone feels valued,” Bramwell told Australian Mining
The mining sector has always had a strong emphasis on the physical health and safety of its workers, but there is a growing need to address their psychosocial needs and motivations.
“Mental health is an area of increasing importance to all workforces, and it’s an area which companies like Westgold are spending more time on because we have to get it right,” Bramwell said.
“The Enough is Enough report and some of the other investigations done across larger mining companies have brought into clear focus workplace behaviours that have always been inappropriate.”
Culture is key and Westgold Resources has three key values driving its culture change: to choose safety, show respect and deliver value.
“In the last 12 months at Westgold, there has been a significant focus on changing our culture,” Bramwell said.
“Our culture philosophy is a simple one – leadership drives culture and culture drives performance.
“Although we are in the early stages of our culture re-set, we have started to see the benefits flow through with improvements in our safety, operational and financial performance within the last 12 months.”
Westgold’s workplace culture has taken inspiration from the saying “the standard you walk past is the standard you accept”.
“Communication is key – we encourage and help our people understand that if you see behaviour you consider inappropriate and you walk past it, you’re effectively endorsing it,” Bramwell said.
“The culture we’re trying to build is one where we look after each other and where people have the courage to raise concerns about behaviour or practices. If you have that type of workplace, it’ll not only be safer but far more productive and inclusive for everyone.”
Bramwell said a positive workplace culture is driven from the top.
“In my mind, curious leaders build better cultures. Why? Because if they’re curious enough to listen to the workforce and seek to understand, people will tell you what concerns them. If you know what the real issues are, curious and focused leadership can address those issues.”
The word ‘culture’ can sound like a fluffy buzzword, but Bramwell believes this is far from the truth.
“Culture to me is about caring enough about people to have the hard discussions,” he said. “If you care enough about people, then you will be prepared to have hard discussions around behaviour and expectations – that takes courage and real empathy.
“It also sets the tone for what we expect as we strive to create a workplace we can all be proud of.
“Changing workplace culture is a difficult thing to execute. Lots of people talk about it, but very few people do it. Building workplaces that are respectful and more inclusive will make the mining sector more attractive to more people. Showing cultural advances will change long held and many false perceptions about the mining sector.
“The mining sector has to make itself a far more attractive long-term career choice for the next generation of resource sector professionals.” AM
Diggers and Dealers 2023 will be held in Kalgoorlie from August 7–9, with the Diggers and Dealers Leadership Breakfast being held at the Kalgoorlie Town Hall on August 8 at 7.00–8.15am.
Reconditioned exchange programme. Receive rebuilt haul truck components such as wheel motor, alternator, grid blowers and more.
Electromechanical service experts. Complete overhaul and rebuild of motors, coil plus commutator production services and more. sulzer.com
Komatsu is proud to support the work of women in industry. We recognise the invaluable contributions women have made to our company and are dedicated to nurturing an inclusive environment for women across our global workforce.
Diversity and inclusion are a critical part of Komatsu’s purpose: creating value through manufacturing and technology innovation to empower a sustainable future where people, businesses and our planet thrive together. komatsu.jobs
Australia is not looking likely to step off the iron ore train any time soon, with major miners like Rio Tinto, BHP and Fortescue leading the charge from massive operations in the red soil of the Pilbara.
As reported in the Resources and Energy Quarterly: June 2023, the iron ore price is continuing to trend well above the November 2021 low, and earnings have been revised up to $110 billion for the 2023–24 financial year.
But as the mining industry looks to adopt more sophisticated automated technology and high-grade ore becomes harder to access, iron ore miners must turn their attention to how they can prepare for a greener future – while still keeping up with the demand.
This year’s Iron Ore Conference, co-hosted by AusIMM and CSIRO, is to be held in Perth on September 18–20 and aims to address the modern challenges iron ore miners face. Ralph Holmes is an honorary fellow with CSIRO and is representing organisation at this year’s Iron Ore Conference. As conference co-chair, he believes iron ore mining is at an important juncture between the way mining is currently done and the changes that need to be made.
“This year’s conference will have a lot of focus on the future,” Holmes told Australian Mining. “If we are going to move toward a greener future, then there will be more demand for highgrade iron ore. But I also expect that there will be a big focus on automation.
“We’ll be looking at what the future holds for the iron ore sector as it moves toward more machine learning and autonomous operations.”
Keith Vining, research group leader – carbon steel materials at CSIRO, said that the uniqueness of Pilbara iron ore would make for a key topic of discussion at the conference.
“Mineralogy and chemical composition of Pilbara iron ores represent a unique challenge in maintaining market share in a lowcarbon economy,” he said.
“Decarbonisation of the iron and steelmaking processes was an emerging topic of the 2021 conference and the organising committee has nominated ‘Transitioning to a Green Future’ as the theme of the 2023 conference to reflect the growing activity in this area.”
Holmes highlighted the discussion on green steel production as another avenue he is particularly excited to see discussed.
Iron ore is a key component in green steelmaking and many miners
are making changes to the way their ore is mined and upgraded to ensure it is suitable.
“We will be looking at what the future holds in terms of trying to reduce the CO2 emissions in the industry to end up with steel that doesn’t have a significant carbon footprint,” Holmes said.
“So we’ve got to enhance our efforts in exploration, geology, mining, geometallurgy and processing to meet the future requirements of the industry.”
Both Holmes and Vining are keen to hear from the line-up of speakers at the conference.
“The keynote presentations will be a highlight for me personally, with some great speakers focusing on the main theme of the conference, and I’m looking forward to hearing the views from the perspective of their different backgrounds,” Vining said.
Christiaan Heyning, director decarbonisation at Fortescue Future Industries (FFI), Darren Matthews, manager steel decarbonisation at Rio Tinto, and Kerry Turnock, global practice lead–resource at BHP, will all be on hand to deliver keynote addresses.
“We have a really good line-up of keynote speakers for this conference,” Holmes said. “Not only do we
have representation from some of the majors, but we will also have a speaker from the Department of Water and Environmental Regulation and a director from the Steel Research Hub in Newcastle.
“I’m sure all of these speakers will be tossing around many interesting ideas and asking challenging questions to the attending guests and the industry in general.”
Holmes said he would encourage anyone who is interested in the iron ore space to come and check out the conference.
“It will cover all aspects, from those just wanting a bit of an introduction into the industry to those who are really seeking the latest in technologies,” he said.
“I think those who are interested in what the future of the industry is in Australia ought to be coming along, because iron ore has been a very important export to Australia for the past 50 years or more; however, there are significant challenges ahead and we need to find economic ways of doing a lot more processing.”
“We have been running the Iron Ore Conference for over 18 years now, and they just get better and better as time goes on.” AM
THISYEAR’S AUSIMM IRON ORE CONFERENCE WILL FOCUS ON HOW THE INDUSTRY CAN TRANSITION INTO A GREENER FUTURE WHILE STILL EXPORTING THE HIGH-GRADE MATERIAL FOR WHICH AUSTRALIA IS KNOWN. THE 2023 IRON ORE CONFERENCE WILL ADDRESS THE MODERN CHALLENGES MINERS FACE. MAGE: CREDIT FORTESCUE
Inconsistent and extreme operating conditions make drilling a very demanding industry. The drill series diesel-powered skid-mounted portable compressors from ELGi have been designed and built to meet the challenges and exceed expectations when it comes to delivering superior power, performance and reliability. The new weld-free air intake system with three-stage air filtration ensures clean air enters the compressor with minimal pressure drop, enhancing operational reliability and extending the life of the compressor parts. The user-friendly control panel now features an LED light for increased ease of use. This intuitive controller integrates all main instrument controls and monitoring systems. The operational condition of the system can be easily determined, and all system warnings are clearly displayed. The unique design reduces pressure losses and increases efficiency, and the rotors ensure energy efficient compressed air supply for all demanding applications, with higher flow and better specific fuel consumption. Better maintenance intervals and best-in-class warranty further assure an overall low cost of ownership.
• elgi.com/au/
If a mining company wants to have a full vision of its on-site energy usage in order to reduce and carbon footprint, ifm has the ideal solution with its self-service industrial internet of things (IIoT) platform, moneo. moneo is used to measure voltage, current, power factor and harmonics, all of which are used to identify several mechanical faults. Having these insights readily accessible can be significantly beneficial to mining businesses; for example, the company can determine what its power factor is and if it needs to be corrected. Once the power factor is amended, moneo can be used to establish a benchmark so limits can be set to provide ongoing monitoring for the operation. moneo also acts as a predictive maintenance platform that provides information ahead of any event. The platform has been designed as an out-of-the-box, all-in-one solution that is easy to integrate with existing systems at a mining operation.
• ifm.com/au/en/shared/moneo
If you need a pit to be dewatered, Crusader Hose has the solution for you. The Hamersley Rapid In-Pit Dewatering System has been designed to be Australia’s simplest layflat hose deployment and retrieval method. It’s said to be the fastest and most compact system for delivering layflat hose in the field. Built for tough Australian mining conditions, its interchangeable spools make it quick and easy to handle multiple lengths of layflat hose up to 12 inches. The system consists of reels and a reel drive unit, which can be mounted to a variety of equipment, such as skid steers, forklifts and telehandlers. A typical operation requires one operator to drive the unit and a ground operator to help connect couplings and give verbal directions. Through the system, storage and transport is made simple. The Hamersley System is a popular choice for rapid in-pit dewatering in mines handling layflat hose.
usaderhose.com.au
Hundreds of engineered skid packages have been designed and built by CAPS for customers in Australia and 38 countries worldwide, each fully customised to clients’ needs. For those looking to hire for more flexibility, CAPS also offers the mine spec MM160KT Miners Pack as standard. Assembled in-house at the company’s Perth manufacturing and assembly plant, each package includes an ingersoll rand compressor modified to comply with typical mine regulations, a 3400L air receiver, and a power supply operating at either 415V or 1000V. Mounted to a durable skid frame with a heavy-duty roof, every Miners Pack allows for easy transport and equipment protection, ensuring continuity of production on-site.
Australian owned and operated, CAPS has had mining at its core for more than 43 years, offering some of the best in compressed air and power generation, with custom engineered solutions built for any environment.
• caps.com.au
Thejo has successfully developed the HIPO brand diaphragm for GHT 2000 filter press, considered to be one of the biggest vertical filter presses to dewater huge volumes of slurry, reaching very low values of residual moisture. Thejo’s HIPO range of filter products covers the spares required for the pressure filter presses supplied by major OEMs like Metso (Larox), Diemme, Andritz and TH Minerals. HIPO diaphragms are precisely moulded rubber membranes as replacements to major OEMs and the membranes are manufactured through an innovative process, fitment tested on jigs to ensure trouble-free fitment on existing filter frames. The compound used to make diaphragms makes them last longer with extended operational life.
• thejo-engg.com/
The Atlas Copco HiLight lighting towers were designed to offer the widest choice when it comes to finding a light tower that is right for your application.
Atlas CEA partners with a wide range of industries to provide a flexible and dynamic set of lighting options, while addressing all aspects of efficiency and safety. Users can be assured of the robust build quality and compact size for which Atlas Copco is globally recognised.
The company’s HiLight B6+ comes standard with essential features such as enhanced coverage of 6000 square metres at 20 lux, low noise levels at just 55 dBA at 7m, and improved productivity with 600-hour service intervals.
The Atlas Copco HiLight B6+ is ultra-compact for efficient transporting, is intuitive whether operated via the smart photocell or weekly timer and, according to the company, offers best-in-class performance. It’s no wonder the B6+ has been designed to be seen not heard.
• atlascea.com.au
Lubestation by Retra
Fluid Handling Systems is a relocatable, lubrication pit stop for fast and easy mining equipment maintenance.
Built for fast, easy and contamination-free lubrication storage and dispensary on remote work-sites, a lubestation can improve the lifespan and performance of equipment and machinery and ensure the success of industrial operations.
Certified for cyclone-prone areas and all wind regions, lubestations also feature forklift access for efficient loading and unloading, high-security ISO locking bars, and dust filtration to minimise contaminants.
The multiple advantages of the lubestations include their simplicity to use and maintain, their efficient and cost-effective structures, and their minimal on-site preparation requirement.
Lubestations are custom-engineered to users’ exact requirements and supplied ready for use.
• retragroup.com.au/products/
DINGO has announced the release of intelligence, the first evolution of asset health data, powered by Trakka. intelligence allows users at any level of an organisation to visualise and investigate their asset health data using a selection of out-of-the-box and easy-to-use reports. The app was born from a desire to meet client and prospect expectations.
While Trakka provides a comprehensive repository of data, this intuitive new software application allows those who are time-poor to see and report on the big picture instantly.
Interactive and up-to-date reports can be generated quickly without internal upkeep, capacity, or specialised skills. This software is uniquely positioned to analyse, interpret and translate Trakka data, including work management items, activity, KPIs and finance.
• dingo.com/solutions/intelligence/
EVENT SUBMISSIONS CAN BE EMAILED TO EDITOR@AUSTRALIANMINING.COM.AU
Iron Ore Conference 2023
Perth | September 18–20
Iron Ore Conference 2023 welcomes delegates from around the globe to Perth to explore the latest developments and address challenges affecting the technical and management aspects of the iron ore industry. Discussion will focus on genesis, geology, exploration, mining and processing of iron ores, bringing solutions to address the industry’s carbon footprint. Attendees can hear from speakers such as Rio Tinto manager steel decarbonisation
Darren Matthews, Department of Water and Environmental Regulation manager strategic airsheds Christine Hass, and BHP global practice lead – resource characterisation Kerry Turnock. • ausimm.com/conferences-and-events/ iron-ore/
WA Mining Conference & Exhibition
Perth | October 11–12
WA Mining Conference & Exhibition will integrate the innovation and research ecosystem while addressing the social and environmental standards driving a more sustainably conscious industry. The expanded exhibition will showcase the technical and digital innovation across the entire mining value chain, while the highly targeted conference will illustrate the economic importance of Western Australia and its contribution the resource technology sector, its innovation capability, its job creation, and the attraction of capital to the state.
WA Mining is the ultimate event for industry professionals, showcasing the technical and digital evolution transforming the mining industry in the state. Developed purely for the Western Australian market, WA Mining gives a blueprint to solve operational pain points while hearing from industry leading experts in the highly targeted conference.
• waminingexpo.com.au
IMARC
Sydney | October 31 – November 2
The International Mining and Resources Conference (IMARC) creates a global conversation, mobilises the industry for collaboration and attracts some of the greatest leaders in the mining, investment, and technology industries for three days of learning, deal-making and unparalleled networking.
Learn from more than 500 mining leaders and resource experts with seven concurrent conferences covering the entire mining value chain. Gain strategic insights from C-suite executives on progressing ESG and environmental resilience, accelerating mining’s energy transition and the digitisation of mines. Technical talks will delve into exploration, discovery and project developments, minerals processing, digital technology, and mining innovation.
Discover inspiration and new ideas, find practical solutions, and see demonstrations of the latest products and innovations from start-ups through to some of the biggest names in the mining industry with more than 470 exhibitors
throughout the 18,500m² expo floor all under the one roof.
• imarcglobal.com
Australian Mining Prospect Awards
Brisbane | November 9
Taking place in Brisbane in 2023, the Australian Mining Prospect Awards are a great opportunity to recognise and acknowledge the people and companies in the mining sector for their outstanding work.
Nominations are now open for 2023, with awards honouring categories such as Indigenous and Community Engagement, Mine Project Success of the Year, Outstanding Mine Performance, Sustainability Project of the Year, Discovery of the Year and more. Some of the 2022 award winners included Kestrel Coal for Australian Mine of the Year, Roy Hill for Mine Project Success of the Year, and Flexco Australia for Excellence in IIoT Application. This year, the awards will return to Brisbane in appreciation of the vibrancy and importance of the state’s thriving mining industry.
• prospectawards.com.au
Perth | November 21–23
Critical minerals are essential components in many of today’s rapidly growing clean energy technologies – from wind turbines and electricity networks to electric vehicles. The increasing appetite and rapid pace of the transition
to cleaner energy sources continues to drive demand for these minerals, and in response the supporting industries are also growing at unprecedented rates. To address this rapid growth, AusIMM will launch its inaugural Critical Minerals Conference in 2023. The event will include a multi-stream format and seek to engage with a larger audience from multiple disciplines as well as a wide range of industry.
• ausimm.com/conferences-and-events/ critical-minerals/
Sydney | June 20
The Women in Industry awards are an opportunity to celebrate the success of women who work in the mining industry.
The 2024 awards, to be held in Sydney, feature multiple categories that showcase exceptional examples of industry advocacy, mentorship and broad sector excellence.
The awards recognise outstanding women from across a range of industrials sectors; for example, those who work in mining, transport, manufacturing, engineering, logistics, bulk handling, waste management, rail and construction and infrastructure – all traditionally male-dominated sectors. This is an opportunity to recognise the women who are driving change in industry and, in doing so, breaking down barriers and creating new possibilities for the next generation.
• womeninindustry.com.au
Michael Greelish is the National Business Development Manager – Mining at Motion. His main focus is Fixed plant maintenance in the Mining and Quarry segment. With extensive experience in the mining sector, he has developed long standing partnerships with key stakeholders within this industry. Fostering strong customer relationships comes naturally to Michael, he enjoys delivering engaging value proposition presentations and contract negotiations to ensure that Motion’s customers are provided with the highest quality products and best solutions for their applications.
What’s your favourite word?
Thanks
If you could win an Olympic medal for any sport, real or fake, what would it be?
Cage Fighting
If you could change your name, what would it be?
Dusty Martin
What was your favourite subject in school?
Biology
What’s your hidden talent?
I’m still playing AFL footy in QLD
The contemporary mining and processing industry is facing a plethora of challenges, ranging from the need for increased efficiency and productivity to concerns about environmental sustainability. In this context, Michael Greelish, a National Business Development Manager with expertise in the mining and quarrying sector, emphasises the significance of Motion’s high-quality products and solutions in overcoming these challenges.
Michael highlighted skilled labour shortage as a contemporary issue the mining industry is facing.
“We have a lot of products that replace the old existing ones where you really need to be trained for it. For example, some bearings traditionally required highly skilled fitters for installation,” Michael says.
However, he notes that manufacturers have become more advanced in their production processes and can now supply fully assembled bearings that can simply be slid onto the shaft.
“Everything’s been done at the factory already prior to delivering this solution. Therefore, you don’t need to be a skilled fitter to install these bearings,” says Michael.
He elaborates on how technological advancements, such as the introduction of split bearings, have dramatically reduced the time required for bearing replacement from an average of 12 hours to a mere one hour.
Michael also highlights innovative solutions in couplings, stating, “We offer coupling solutions that you can change in situ. Just a matter of sliding
a cover back, unwrap the element, wrap a new element on, and slide the cover back on.”
These quick and easy maintenance options minimise downtime and reduce the reliance on skilled labour, allowing mining operations to get sites up and running more quickly, Michael discusses.
Michael also highlights more of Motion’s quality solutions, such as high-efficiency motors and optimised drive designs, which can make a significant difference in achieving efficiency and sustainability goals.
He explains that many belt drives on mining sites are over designed and require more power than necessary, resulting in wastage.
“We can run these drive designs on their belts to ensure that they’re efficient drives and designed for
that,” Michael says, emphasising the importance of selecting the right output for optimum efficiency.
In addition to efficiency gains, Michael acknowledges the growing focus on sustainability and environmental impact in the mining industry. He mentions that while achieving net zero emissions is a challenging goal, there are costeffective ways to reduce emissions with Motion’s products and solutions.
One example, he notes, is optimising equipment usage through proper maintenance and calibration, which can minimise energy waste and improve energy efficiency. Encouraging the adoption of energyefficient practices among employees is another effective measure. By implementing these practices, mining operations can achieve
sustainability goals without incurring substantial expenses.
However, Michael acknowledges that there may be resistance to embracing new technology and practices due to concerns about costs. “People sometimes view a high-efficiency option as costlier,” he says. “Recognising that upfront costs may be a deterrent for some in the industry.” Nevertheless, Michael points out that often customers are looking to make savings where possible, which can be a beneficial outcome.
Condition monitoring is another critical aspect of maintenance in the mining industry, as it allows for proactive identification of potential issues before they result in costly breakdowns.
“Condition monitoring tools are getting smarter - the benefits of these should not be overlooked, as identifying machinery issues will drastically reduce downtime,” Michael explains. “Motion Engineering offers several options for monitoring the condition of bearings, and we can facilitate comprehensive solutions which offer real-time monitoring.”
Motion Engineering specialises in providing advanced condition monitoring solutions for the mining industry. With their expertise in bearing technology and equipment health monitoring, they offer a range of options for proactive maintenance. These options may include vibration analysis, temperature monitoring,
oil analysis, and other advanced techniques to assess the condition of bearings and other critical components in mining equipment.
Motion is a trusted leader in providing industrial solutions for the mining industry in Australia. With a wide range of products, services, and comprehensive engineering capabilities, they offer cutting-edge solutions that set them apart and make a significant difference in this industry. As Michael states, “We have the capabilities of doing so much in-house which makes Motion really stand out.”
With extensive expertise in areas such as bearings, power transmission, automation, pneumatics, hydraulics, and safety equipment, among others, Motion is well-positioned to propel mining and processing operations into the future.
“Condition monitoring tools are getting smarter - the benefits of these tools should not be overlooked, as identifying machinery issues will drastically reduce downtime.”
According to Tony Tormey, Category Manager of Industrial Bearings at Motion, sealed bearings can provide “up to 25% longer service life”. With many sealed spherical bearings on the market, Tony says choosing a bearing appropriate for each unique industry application is important. In the mining industry, a lot of it comes down to personal preference with the
maintenance crew on site, but he says sealed spherical bearings typically provide a longer lifespan.
Sealed spherical bearings are often used in mining equipment such as conveyor systems. They play a critical role in the mining industry by helping to ensure that heavy-duty machinery operates efficiently and reliably in demanding working conditions.
“Bearings that are reliable in their applications makes a massive difference in a mine’s capability to prevent downtime from equipment breakdowns and failures,” Tony says.
These bearings are typically used in applications where the equipment is subject to heavy loads, shock loads, and vibrations. In harsh environments, such as mines, the sealed design of these bearings helps to prevent the ingress of contaminants such as dirt, dust, and moisture, which can cause premature wear and damage to the bearings.
1. Improved contamination resistance: The seals on NTN sealed spherical roller bearings help to prevent contaminants such as dirt, dust, and water from entering the bearing - reducing the risk of premature failure due to contamination.
2. Longer lubricant life: Sealed spherical roller bearings retain lubricant more effectively than unsealed bearings, which can help to extend bearing life and reduce maintenance requirements.
3. Reduced maintenance costs: By reducing the risk of premature failure and extending lubricant life, NTN sealed spherical roller bearings can help to reduce maintenance costs over the life of the bearing.
4. Enhanced safety: Sealed spherical roller bearings can improve safety by reducing the risk of contamination-related failures and reducing the need for maintenance in hazardous or hard-to-reach locations.
5. Improved environmental performance: Sealed spherical roller bearings can help to prevent lubricant leakage and reduce the risk of environmental contamination, making them a more environmentally friendly option.
“Bearings that operate in these environments need to be able to withstand all sorts of extreme working conditions, from extreme heat to increased load pressure, the bearings used need to be able to handle this,” Tony says.
A leading manufacturer for bearings, NTN has been providing products to a wide range of industries for more than 100 years since their establishment in 1918. Through the 50/50 joint venture with Motion’s CBC–which began over 50 years ago in 1971 –customers in the mining segment can benefit from this relationship.
“The benefits of the CBC-NTN joint venture relationship come down to access and consultation. Motion is the exclusive distributor of NTN bearings and has a direct line to the manufacturer,” explains Tony. “We have a network of account managers and technical experts that engage and support mines and minerals processing plants, they are always striving to improve performance and provide solutions to productivity issues.”
“The NTN sealed spherical roller bearings also come with many benefits off the shelf,” says Tony. “They can increase the service life of equipment compared with standard bearings on the market. This benefit alone makes them a desirable choice for those who work in the mining industry.”
“The NTN sealed spherical roller bearing has larger rollers and maximum number of rollers given, the industry’s highest load capacity and allowable
rotational speed, and has unique removable seals from 140mm upwards with a unique grip structure to maintain pressure under misalignment, which is a big selling point,” Tony states. “The unique lip structure along with housing grease fill and housing seal gives you three barriers to combat against ingress.
A key component of a successful mining operation is guaranteeing that heavy machinery operates efficiently and reliably under demanding conditions. By preventing the entry of contaminants, the incidence of wear and tear on the bearings in mining applications can be reduced.
“With properly matched and fitted bearings, mechanical breakdowns will be reduced, which will mean an overall reduction in equipment downtime can be seen across the board,” Tony says. “The NTN sealed spherical bearings are one of the best choices for bearings in the market, extending equipment life and reducing maintenance costs.”
As an exclusive distributor of NTN bearings, Motion offers customers highquality products and services. Their experts can assist in selecting the right product for specific needs and provide support throughout the entire product lifecycle. With an extensive network of branches across Australia, customers can easily access NTN products and services.
“Customers can have peace of mind knowing they’ll receive the best possible product matched with industry tailored advice for each product or service they need to get their operation up and running again,” Tony says.
We were able to save the coal wash plant a significant amount of cost after the second-hand gear box was sourced and fitted, which was a massive win for them,” says Michael Greelish when describing the outcome of an engineering solution for a customer.
Efficiency reigns supreme in the mining sector, where downtime is the enemy of profitability. Every moment of equipment failure is a missed opportunity to extract valuable resources and generate revenue. Consistent equipment breakdowns can take a toll on a mine’s bottom line over, eroding profit margins and jeopardising the success of the operation.
Motion’s team of engineering experts specialise in providing personalised solutions to meet the unique needs of individuals and businesses in the mining sector. As a full-service provider, the team is able to facilitate maintenance, refurbishment, repairs and overhauls through the entire life cycle of industry equipment and machinery.
“As an engineering team, we are able to do everything in house, from analysis to the repair stage of a job, we’re basically a one stop shop for all of our customer’s needs,” says Michael, who is the National Business Development Manager at Motion.
In April 2022, Michael was faced with a coal wash plant in Queensland that’s site had a failure on an old Morse worm geared drive off a conveyor. This conveyor fed directly on to the train loadout conveyor which had a gearbox that was unrepairable.
“This was the main line that feeds the conveyor that goes on to the train load out - so if you can’t load coal on to the train, you’re not making any money, so that’s how critical it was,” Michael says.
Initially, the customer explored the possibility of replacing the entire gearbox. However, with wait times of up to 30 weeks, this was not a viable option. The unfortunate consequence of such a prolonged delay would have been a significant loss of productivity due to the conveyor being out of commission for an extended period.
“It was an old English made gear
box, that they haven’t made for years, there were no replacements, no drop in ones, unless doing some major modifications.” Michael says.
Considering the circumstances, Michael and the CRAM team collaborated to devise a solution to restore the functionality of the conveyor. After much effort, the team successfully located a second-hand gearbox and promptly dispatched it to Mackay’s rebuild service centre. Bearings, seals, brake, and couplings were meticulously replaced, along with
a new motor and couplings.
Upon completion, the refurbished gearbox was promptly delivered to the coal wash plant, where the CRAM team went and skilfully fitted it to the non-functional conveyor.
“We went out and aligned all the couplings on it, fitted it all, and as a result the conveyor was back up and running in about 3 weeks,” Michael says.
Motion’s workmanship resulted in a remarkable cost-saving of a significant amount for the coal wash
plant, primarily by minimising the time required to replace the entire gearbox. It is worth noting that the conveyor is still performing exceptionally well and has planned to book in for a new gearbox replacement later in the year.
“It was a great outcome overall, the continuity we provide in our services means our customers only have to deal with the one group of people instead of out-sourcing multiple trades to do the job,” Michael says.
Motion’s engineering department is a powerhouse of expertise,
specifically geared towards delivering exceptional outcomes in assessment, review, design, and analysis for the mining industry. Their proficiency extends to repairing, refurbishing, manufacturing, and assembling new mining equipment, alongside offering on-site services for installation, commissioning, and testing. As a onestop-shop for all mining-related needs and concerns, Motion’s engineers play a pivotal role in the industry, contributing significantly to its growth and development.
“It was a great outcome overall, the continuity we provide in our services means our customers only have to deal with the one group of people instead of out-sourcing multiple trades to do the job.”
As a seasoned veteran with nearly four decades of experience in the industry, Troy Markland, the Product Manager for Power Transmission and Drive Systems at Motion, possesses a deep understanding of the dynamic world of mining. With an acute awareness of the unique needs and challenges faced by mining customers, Troy and his team at Motion are at the forefront of providing innovative solutions.
One of the key services they offer is the design of customised drive systems, specifically tailored for belt and pulley configurations used in slurry pumps.
Troy highlights the crucial role of drive systems in mining operations, particularly in powering pumps. V-belt pulley drives, which are a type of mechanical power transmission system that utilise v-belts and pulleys, are commonly employed in mining for driving pumps. Troy emphasises their criticality in various applications such as dewatering, slurry handling, and water supply.
Pumps play a vital role in numerous mining processes, including extraction, processing, and transportation of minerals and other materials, making reliable and efficient drive systems indispensable in the industry.
Troy explains, “Sometimes customers come to us with parameters, and Motion selects the appropriate drive accordingly. In other cases, customers may make their own selection, and
Motion validates their choice.”
One of the key benefits for customers in this case is Motion’s high level of technical expertise in drive systems. Troy and his team possess extensive knowledge of these systems, allowing them to provide expert guidance and recommendations to customers. This ensures that the selected drive systems are precisely tailored to meet the specific requirements of their operations, resulting in optimised performance and reliability.
Troy highlights, “Motion ensures that the selected drive system is costeffective and utilises readily available spare parts for future replacements.”
This approach helps customers save on operational costs and achieve improved overall financial performance.
Troy and his team at Motion also prioritise practicality and reliability in their drive system designs for mining operations. They aim to create drive systems that are not only effective but also durable, with a typical target service life of around 25,000 hours. This is a noteworthy accomplishment considering the harsh conditions that mining operations often face, including high loads, extreme temperatures, dust, and moisture, which can impact the performance and longevity of drive systems.
Troy recalled a customer success story where Motion worked on a major project with a tight deadline, coordinating with manufacturers to produce and ship a specialist drive
ahead of schedule.
“The customer was very pleased how quickly we got this sorted,” Troy recalls. He went on to explain that although this was an exceptional case, Motion’s ability to meet a tight deadline and deliver a month ahead of schedule was highly beneficial to the customer.
The customer faced penalties if they failed to meet their own delivery deadline, and Motion’s expedited process was greatly appreciated. Troy emphasised that this experience instilled confidence in Motion’s ability to deliver exceptional service to the customer.
Motion’s drive design services are tailored to meet the unique needs of mining customers, offering costeffective, reliable, and practical solutions to power their pumps. With a wealth of expertise, experience, and unwavering commitment to customer satisfaction, Motion has a proven track record of success in delivering timely and efficient drive designs for the mining industry.
Troy encourages mining customers to place their trust in Motion for their industrial needs, knowing they will receive exceptional service and customised solutions that meet their requirements.
For mining customers seeking dependable and effective drive designs for their slurry pumps, Motion is the trusted partner with extensive experience in the industry. Contact Motion today for expert assistance with your drive system needs and benefit from their expertise and commitment to customer satisfaction.
services outlets located in the longwall block and are attached to the longwall’s roof-mounted monorail system (which could be up to 500 metres long). The hoses then transition from the monorail to the beam stage loader (BSL) at the start of the longwall and then another 50 metres to the main gate corner.
From the BSL to the main gate corner the hoses are confined in a unique purpose-built modular channel, designed to sit on top of the longwall system and become part of the infrastructure.
The working height at this point is very low so the compact channel secures and fixes the hose system with the addition of detachable capping that protects the hoses from damage.
Our proven experience with longwalls is recognised and acknowledged throughout the underground mining sector. Motion Engineering and Services longwall specialist was recently called to a Queensland mine to finish-off a hoseup that had been left in limbo following operational changes at the longwall system OEM.
Underground mining comes with its own unique set of risks and challenges. Getting the infrastructure right – such as hosingup a new system – reduces risks to underground operatives and maintains optimal productivity. For almost 20 years the Engineering and Services division of Motion has been coordinating and installing hose-up change-outs for underground mines in New South Wales and Queensland. That’s a lot of hands-on experience. And occasionally they are called in to finish a job when things don’t go to plan.
Underground hose systems deliver hydraulic oil, process emulsion, GP water and compressed air to the diversity of equipment involved in underground longwall mining. The hoses range in size from 19mm (3/4”) to 65mm (2½”); they are rated for the different pressures required and carefully matched to the medium they are conveying and the operating environment of the equipment
that will be powering. Hoses are generally colour-coded for contents and operating pressure.
For example, roof supports are powered by a 95% water, 5% hydraulic oil emulsion, and operate at around 400 bar. The longwall shearer runs on 100% hydraulic oil and operates at around 300 bar. A typical system also includes gear oil supply hoses to fill and/or top-up all the gearboxes on a longwall system. Moreover, there are water hoses for cooling and dust suppression and hoses for the foam that is sprayed onto the coal as it comes from the face, before it goes through the crusher.
In addition, there are return hoses for the emulsion circuit and compressed air for maintenance tooling. It is possible to have up to 20 hoses run in any one system.
Installation of the hose system –the hose-up – follows well-established guidelines for safety and efficiency.
The hoses start at the pump station
The installation program was already underway; however, final supervision was required, particularly around ensuring that the hoses had been installed correctly as per the hosing diagrams. Updating the relevant Link-One drawings and ensuring the colour-coding on the hoses is in accordance with the mine’s system and the job complied with installation requirements for Queensland underground mines.
In general, the safety and mechanical regulations and requirements for hoseups in New South Wales and Queensland underground mines are substantially the same; however, there is some variance for Queensland mines.
The new hose system is now underground and working to expectations and regular inspections will ensure the system maintains its operational integrity. The longwall system is usually sent out for inspection and refurbishment at the completion of each longwall block – generally about every 12 months. The hose system will be refurbished and worn parts replaced during that scheduled overhaul program.
From enhancing site safety and productivity, to helping protect workers and the environment, 3M engineer’s innovative Personal Protective Equipment (PPE) solutions for the demands of your business.
From enhancing site safety and productivity, to helping protect workers and the environment, 3M engineer’s innovative Personal Protective
Equipment (PPE) solutions for the demands of your business.
Injuries that occur in the mining sector can be easily prevented. Mines are among the most dangerous places to work, with miners often being subjected to harsh working environments and hazardous materials. Proper implementation and use of personal protective equipment (PPE) is vital in ensuring less down-time and maintaining workplace productivity.
options, including 3M™ Anti-Fog and Anti- Scratch, and features like a removable foam gasket that combines with Pressure Diffusion Temple (PDT) Technology to create a secure and comfortable fit.
The 3M™ SecureFit™ Protective Eyewear is available for purchase in the below range:
Key Benefits & Features
3M™ TA570 Safety Helmets are Type 1 helmets that adhere to Australian standards for general mining conditions. This helmet not only protects from potential hazards but has unique cooling vents for comfort in hot and humid conditions.
Furthermore, 3M safety helmets are fully compatible with lamp brackets. 3M lamp brackets allow secure lamp attachment to the helmet. Lamp brackets are available in metal or polycarbonate material.
Metal lamp brackets are suitable where strength and robustness is required. Applications include certain mining applications where a helmetmounted lamp is required.
Polycarbonate lamp brackets provide a non-metallic solution. Polycarbonate lamp brackets are rust and corrosiveresistant and are suitable for underground mining where the use of a helmet-mounted lamp is required.
A key in all of this, is the use of high quality, durable PPE. 3M provides solutions in workplace PPE for those who work in the mining and processing sectors – offering a wide range of products specifically catering to the needs of miners who work both on ground and underground. A key component in mining safety practises is the use of hard hats. Hard hats are an essential investment for workers in this industry. 3M provides the below head, eye, face, and body protection solutions:
3M™ SecureFit™ Protective Eyewear
Miners can be exposed to flying particles, small objects, and sparks whilst on the job. These can be mechanical, thermal, or electrical in this industry.
Exposure to flying objects without sufficient eye protection can lead to serious eye injury and potential blinding. Eye injuries are extremely common in the workplace. 3M™ SecureFit™ Protective Eyewear Safety Spectacles are designed to protect workers from hazardous object contact and dangerous radiation in a stylish and comfortable way. Choosing the right spectacles for a worker’s mining job relies upon ergonomics, view, security, and coverage.
3M™ SecureFit™ Protective Eyewear Series comes with a variety of features because having options in protective eyewear can be critical. Workers can choose from several lenses coating
• 3M™ SecureFit™ Protective Eyewear 100 Series- Clear, Grey, Amber, and IndoorOutdoor Grey lens in Anti-Fog and AntiScratch coating.
• 3M™ SecureFit™ Protective Eyewear 200 Series- Clear and Grey lens in AntiFog and Anti-Scratch coating.
• 3M™ SecureFit™ Protective Eyewear 400 Series- Clear, Grey, Indoor Outdoor Mirror lens in Anti-Fog and Anti-Scratch coating.
• 3M™ SecureFit™ Protective Eyewear 500 Series- Clear Anti-Fog/AntiScratch and Clear, Grey, Amber, Indoor Outdoor lens with Scotchgard™ Anti Fog/Anti-Scratch coating.
3M™ Protective Coverall Type 3, 4, 5 and 6 coveralls can be selected to protect miners in these situations.
The key selection factors include:
• Understanding the protection level required (Type)
• Compatibility with other PPE
• Considering potential heat stress situations
There are different options such as:
• Type 5/6 coveralls: 3M 4510, 4515, 4535, 4540+
• Type 5/6/4 coveralls: 3M 4565
• Type 5/6/4/3 coveralls: 3M 4570
Motion provides expertise and knowledge to customers across the country. For more information on 3M products and their suitability to your business or individual needs, contact your local Motion branch today.
Equipment in the mining sector often works around the clock, under extreme environmental conditions. Providing appropriate lubrication is an important way in ensuring that operators receive maximum performance from their engines, hydraulic systems, transmissions, and greased components.
Reducing cost in today’s economy is essential in the mining sector. Often relying on their equipment to work harder - machines running for longer periods of time, under heavy loads can lead to increased downtime and unexpected financial costs.
With these issues in mind, Shell provides a solution. With a variety of high-performing lubricants available, Shell are utilising years of experience and knowledge in the manufacturing of lubricants – providing customers with the best possible results.
Although lubricants generally account for five per cent of total maintenance expenditure, when applied with Shell’s leading expertise in producing and managing lubricant programs, they can reduce the total maintenance budget significantly.
Choosing the best lubricant for each piece of equipment is made easy when in consultation with Shell and their comprehensive team of technical representatives. Shell’s technicians can assess equipment needs, and appropriately match the
correct product to use in each piece of equipment.
In the mining industry, hydraulic systems are used in dump trucks, diggers, and tractors. Hydraulic fluids should protect, lubricate, and help transmit power in the most effective way possible.
Shell offers a range of lubricants for hydraulic systems that are designed to improve oil life, enhance energy capabilities, and extend machine life expectancy.
From entry level to top tier lubricants, Shell has manufactured five types of products, designed to be used in various applications.
Shell’s Tellus hydraulic fluids have been offering world-class benefits to customers for more than 70 years. The company is constantly investing to create better lubrication technology for their customer base, Australia wide. Whatever the need or application, Shell can provide a full range of specifically engineered oils and lubricants for the needs of mining workers.
Motion encompasses a large distribution network, making Shell products accessible to even the most remote industrial mining and processing sites in the country. Motion is proud to be a distributor of Shell lubricant products in Australia. Viva Energy works in partnership with Motion to ensure Australian’s have access to premium lubrication products for mobile equipment.
Shell Tellus S2 MX:
• Extra protection.
• Industrial applications.
• Long life expectancy.
• Mineral and zinc based.
Shell Tellus S2 VX:
• Ultra-low temperature.
• Able to be used in varying applications.
• Special based Zinc Antiwear.
Shell Spirax S4 CX:
• Anti-wear protection.
• Low temperature characteristics.
• Oxidation stability.
Shell Tellus S3 M:
• Superior protection capabilities.
• Long life.
• Versatile in its applications.
• Mineral and zinc free.
Shell Tellus S4 ME:
• Energy saving.
• Zinc free.
• Extra-long-life expectancy.
• Synthetic and ashless.
For more information on lubricant recommendations based on application requirements, visit your local Motion branch today.
The mining and processing industry heavily relies on electric motors to power essential equipment such as mills, hoists, crushers, and pumps. However, these motors are exposed to harsh and rugged working conditions, leading to frequent mechanical breakdowns and faults that cause costly downtime for mines which can negatively impact productivity and increase maintenance costs.
To address the challenges, the mining and processing industry demands electric motors that are resilient and able to operate under rigorous working conditions. TECO, a world-renowned leader in electric motor technology, has been at the forefront of developing topquality electric motors for more than 65 years globally and this year celebrating 40 years in Australia and New Zealand.
Their expertise in this field has enabled them to create durable and reliable electric motors that can power essential equipment used in the mining and processing industry. These motors ensure maximum uptime and optimal performance, significantly reducing equipment downtime and maintenance costs, which translates to maximum uptime, increased productivity, and profitability for mining companies.
TECO Maxe3 mining motor is a durable and reliable electric motor designed to operate under the toughest mining environments.
It features a unique true grease relief system that prevents overgreasing, one of the most significant challenges faced by mining companies. This system significantly
increases the motor’s lifespan and reduces maintenance costs.
Additionally, the TECO Maxe3 mining range of motors can be modified to IECEx specification, making it suitable for use in potentially hazardous environments.
TECO’s commitment to safety is evident in their in-house modification centres certified to convert the Maxe3 motor to Ex e, Ex nA, and Ex tD, providing added flexibility and customization options.
TECO Maxe3 mining motor is an outstanding choice for the mining and processing industry, offering unparalleled durability, reliability, and efficiency. Its advanced features and benefits make it an essential investment for any mining company seeking to enhance equipment performance and reliability while reducing downtime and maintenance costs.
TECO and Motion offer customers tailored and comprehensive solutions by combining their respective strengths.
As a distributor, Motion provides TECO’s high-quality electric motors and drives to customers and offers expertise in various applications.
TECO’s exceptional solutions technology and Motion’s industry expertise combine to deliver reliable and efficient solutions, along with exceptional value and service to their customers.
Together, TECO and Motion can provide innovative solutions that help customers achieve their goals.
• Reduce power transmission losses with our MAXe3 motors high-power factor and premium high efficiency. This combination results in superior system efficiency.
• MAXe3 mining motors have a generous safety factor of 1.2 at an ambient temperature of 40 DegC
• Class H insulation system as standard.
• Oversized drive end shaft and bearings are offered on the “HX” motors for demanding applications.
• The motors also feature TECO renowned true grease relief system, preventing grease from entering the motor even when over-greased.
• All MAXe3 motors are rated IP66. Sintered bronze porous drain plugs are fitted as standard to all foot and flange motors, thereby providing excellent protection against the ingress of dust and water.
• MAXe3 motors can be modified locally to meet IECEx Ex e, Ex nA, Ex tD in TECO certified in-house modification centres around Australia.
• TECO Australia has a robust stock holding of the MAXe3 range, up to 540kW, ensuring quick and easy availability.
When it comes to bearing replacement, mining professionals require a solution that allows for swift and efficient replacement, without the need for extensive disassembly, so they can quickly get back to their critical tasks. Schaeffler’s split bearings, offers a reliable and convenient solution for in situ replacement.
Tony Tormey, Motion’s Category Manager for Industrial Bearings, and Michael Greelish, Motion’s National Business Development, explain the key advantages of using Schaeffler split bearings.
According to Michael, in many cases, traditional bearings can be challenging to replace due to being entrapped. However, Schaeffler’s split bearings are designed to be split all the way through to the shaft.
This means that when replacing a bearing, the old bearing can be blasted off and replaced with a split bearing, without needing to remove the gearbox or use cranes or other equipment. The process of changing a split bearing is quick and convenient, making it a highly efficient solution for bearing replacement in the mining industry.
He further emphasises that while traditional bearing replacements can take several hours or even days, a split bearing change can be completed in as little as an hour depending on size.
Tony highlights, “If you have a
gearbox that drives something, generally you’ll have a coupling, and bearing housing to support a shaft. Also, these things can be quite large making it much more difficult to replace.”
Therefore, the ease of installation and replacement of Schaeffler’s split bearings greatly addresses the aforementioned points, allowing mining operations to change out in situ and resume production far quicker than changing a standard configuration out.
In addition, Michael highlights the cost savings associated with avoiding the need for specialised equipment like cranes in split bearing replacements.
He explains, “If there’s a failure on a bearing, it’s a massive job because they’ve got to remove that whole gearbox. Getting cranes and scaffolding is a long process just to be able to pull off a bearing that’s probably worth a couple of hundred dollars.”
Michael and Tony collectively summarise that with split bearings, the need for cranes and the labourintensive process of removing multiple components can be eliminated, resulting in potential cost savings in terms of crane rental, labour, and equipment downtime.
One standout in Schaeffler’s split bearings range is the FAG Split Spherical Roller Bearings, which provide high load capacity and shock load resistance, making them ideal for heavy-duty applications.
These bearings generally are able to fit into existing standard plummer blocks.
Additionally, Schaeffler’s split design of these bearings reduces the risk of damaging other components during installation or removal, helping to prevent costly and time-consuming repairs, as explained by the experts at Motion.
The collaboration between Schaeffler and Motion brings together Schaeffler’s expertise in bearing technology and Motion’s extensive knowledge in industrial applications, resulting in a comprehensive offering of split bearings tailored to the unique requirements of the mining sector.
This synergy results in an enhanced customer experience, provides mining operations with reliable and efficient split bearing solutions that deliver exceptional performance and value.
Tony and Michael encourage customers to contact Motion for expert advice and access to top-quality split bearing solutions for their mining applications.
Split the difference: Mining made easy with Schaeffler
‘Virtually indestructible’ unitised bearings
Timken’s unitised bearings
SRB solid block have made a significant impact in the mining industry due to their unique design and various benefits,” says Tony Tormey, Motion’s Category Manager for Industrial Bearings. He explains why they are significantly better than conventional bearings.
“In the mining industry, equipment downtime can be both costly and time-consuming. Traditional bearings require frequent maintenance, such as
lubrication and adjustment, to ensure they function correctly.”
To address some of these industry issues, Tony proposes unitised bearings as an alternative.
“These are pre-assembled bearing units that consist of a housing, bearing, and seal. The unitised design makes installation and maintenance easy, as the entire assembly can be replaced as a single unit,” Tony discusses.
He emphasises that one of the key benefits of Timken’s unitised bearings is their “robust design for harsh and demanding applications.” According to Tony, “Strength is what this bearing type is known for. It has a virtually indestructible steel housing compared to most competitors who have cast iron alternatives.”
Firstly, steel is a stronger and more durable material, making it better equipped to handle the demanding conditions that are common in mining applications. Steel is also a more corrosion-resistant material, making it better suited to withstand exposure to water and other corrosive substances commonly found in mining environments.
In addition to their durability and ease of installation, Tony highlights that “unitised bearings can also help to improve safety in the mining industry. Traditional bearings require regular maintenance, which often involves workers accessing the equipment to perform the necessary tasks.”
This can be dangerous in a mining environment, where heavy machinery and hazardous conditions are common. Unitised bearings require less maintenance and can help reduce the need for workers to access the equipment, which can improve safety and reduce the risk of accidents.
Tony highlights, “Timken’s unitised bearings are beneficial in relation to contamination in the mining industry because they are designed with advanced sealing and protection features to prevent contamination from dirt, dust, and other harmful particles.”
He continues, “Timken’s unitised bearings are equipped with advanced sealing technology that helps to keep contaminants out, reducing the risk of premature failure and extending the
service life of the bearing.”
Timken is a renowned bearing manufacturer, known for producing high-quality unitised bearings. With over a century of experience, they have established themselves as a reliable supplier of durable, highperformance bearings that are easy to install. Timken’s unitised bearings come in various designs, such as ball bearings, tapered roller bearings, and spherical roller bearings, making them suitable for various industrial applications.
For more information about Timken’s unitised bearings and how they can benefit mining operations, customers are encouraged to contact Motion. As a trusted supplier of high-quality bearings and according to Tony, “A long-standing partner of Timken, Motion can provide expert guidance and support to help customers choose the right unitised bearings for their specific needs.”
• Simplifies installation and maintenance
• Provides reliable performance under extreme conditions
• Reduces downtime and maintenance costs
• Increases equipment uptime and productivity
• Offers long-lasting durability and resistance to wear and tear
• Offers a range of unitized bearing designs to meet different application needs
Using a Gates® Predator™ v-belt, you can reduce the number of belts you have on your drive system by up to half,” says Motion Power Transmission expert, Rob Michelson. “In addition, because of its design, the Predator belt can improve the overall longevity of the equipment.”
There’s no question as to the role that v-belts play in the mining industry, where heavy-duty equipment is used to move large amounts of materials over long distances. In this sector, belts play a critical role in ensuring that the equipment operates smoothly and efficiently. Without reliable v-belts, the machinery can break down, leading to costly downtime and lost productivity.
“Downtime in the mining sector has a huge financial burden on any operation, so having equipment that isn’t lasting or needing constant repair work is something that people in this industry really want to try and avoid,” says Rob.
The rugged terrain and harsh environmental conditions of the mining industry require belts that are built to withstand extreme loads, abrasion, and stretching, making it crucial to choose high-quality belts designed to withstand these conditions.
“The belts have to be able to cope with extreme environmental factors like heat and abrasion, many are not able to withstand this sort of pressure for long periods of time, which usually results in downtime when belts are in need to be replaced or repaired,” Rob says.
Rob, a product manager with more than 35 years of experience in power transmission products, including belts, chains, gearboxes, and couplings, explains that Gates® Predator™ v-belts offer exceptional performance compared to traditional v-belts.
“With their robust, abrasion-resistant outer layer, the cords are made out of an aramid or Kevlar cord, which is a lot stronger than traditional polyester,” Rob says.
As the inventor of v-belts back in
1917, Gates® has been at the forefront of belt technology. These belts provide excellent resistance to oil, heat, and other harsh environmental conditions, making them a perfect choice for the demanding requirements of mining applications.
“Because of the non-self-igniting feature of the belt, the belt won’t catch fire from heat build-up, even with severe slippage,” Rob says.
A significant benefit of the Predator™ belts is that they are practically maintenance free. Due to their durable construction and unique features. The belts are made using advanced materials, crafted through a unique manufacturing process that provides the belts with superior strength, flexibility, and resistance to wear and tear.
“The unique nature of the construct of the belt means that they’re virtually maintenance free,” says Rob.
As the mining industry continues to face mounting pressure to reduce its carbon footprint, finding sustainable solutions has become a top priority. The Predator™ v-belts, which offer longer equipment life, can result in positive environmental impacts. By reducing the need for new equipment production, it results in lower energy consumption and greenhouse gas emissions, making the belts an environmentally responsible choice for mining companies.
“Reducing environmental impacts in the mining sector is a challenge, but having a product that’s going to last means an overall reduction in the need for new equipment, resulting in lower energy use across the board,” Rob says.
As the largest distributor of Gates® products, Motion provides technical support to customers who need help with their drive systems.
“We have technical people like myself who are able to support the customers with the technical
• Predator™ v-belts provide superior power transmission compared to conventional belts, with the ability to transmit up to 50% more power.
• Offer higher resistance to wear and tear, allowing for higher tension and increased durability in tough mining conditions.
• Choosing Predator™ v-belts can have a positive impact on the environment, as longer equipment life leads to fewer replacements and less material waste.
• With their high strength and durability, Predator™ v-belts help to reduce downtime and maintenance costs, ensuring smooth and efficient operation of mining equipment.
• Up to 2.2 time more power than standard v-belts.
• Double layer bare back cover protects against slippage and punctures.
• No-need for constant re-tensioning.
• No increase in shaft load.
experience and help them reduce downtime in their plant and uptime in production,” Rob says.
In addition, Motion has access to Gates®’ design programs, allowing them to analyse a customer’s drive system and offer better options. This ensures that customers are using the most efficient drive system possible, promoting sustainability, and reducing environmental impact.
“It’s a real advantage that Motion offers, being able to analyse a mine’s drive system prior to offering solutions means that the best possible solution can be provided to the customer,” Rob says.
Motion’s commitment to providing exceptional customer service sets them apart from their competitors. They go above and beyond to ensure that their customers receive unparalleled expertise and support. Their dedicated team is readily available to address any inquiries or concerns from customers, ensuring a seamless experience and maximum satisfaction. With Motion and Gates®, mining companies can improve their sustainability efforts while achieving maximum productivity and efficiency.
“Customers have the best of both worlds, not only can they gain access to some of the best v-belts on the market, but through Motion’s expertise and customer support, they’re going to get the most out of their product in the long run,” Rob says.
components are essential in facilitating the seamless transmission of fluid and power, ensuring the efficient operation of hydraulic systems.
inspecting and replacing them as needed can help prevent accidents and ensure a safe working environment for mining personnel.”
Just as the heart powers the human body, in the mining industry, robust and reliable hydraulic systems are essential for the efficient operation of heavy machinery. Hydraulic hoses and fittings, purpose-built for these demanding conditions, assume a critical role.
Engineered to withstand extreme pressure and facilitate the effective transmission of power, they enable precise control over vital mining equipment, including excavators, loaders, and drilling rigs. Providing valuable insights into this process is Fellipe Ramos, a Category Manager for Motion with extensive expertise in mechanical, hydraulic, and pneumatic designs.
In order to grasp the crucial role of hoses and fittings in this process, it is essential to obtain an understanding of hydraulic systems discusses Fellipe. When providing his overview, Fellipe draws parallels between hydraulic systems and the circulatory system of a heart.
According to Fellipe, “Hydraulic systems comprise essential components, with the power pack serving as the primary power source, typically driven by an electric motor. The pump, guided by the power pack, propels fluid through a valve bank, which can be tailored to suit the specific application.”
Fellipe underscores the significance of connections between different stages, highlighting the crucial role played by hoses and fittings. These
Fellipe discusses, “Fittings and hoses ensure that the hydraulic system operates correctly and safely, especially in mining operations subjected to extreme conditions like high pressure and temperature fluctuations.”
“The diameter of the hose is also crucial to ensure that it is appropriately sized for the system’s flow rate. Otherwise, back pressure or loss of efficiency could occur, leading to increased wear and tear on the system and premature failure, causing costly downtime for the mine,” says Fellipe.
He continues to explain that worn or damaged hoses can rupture under high pressure, causing hydraulic fluid to escape which can pose a risk of fire or injury to workers.
“This is why using high-quality and correct size hoses and fittings is so important,” says Fellipe. “Regularly
• Increased risk of safety hazards for workers.
• Reduced efficiency and productivity of mining operations.
• Potential damage to equipment and machinery.
• Increased maintenance and repair costs.
• Potential downtime and delays in mining operations.
• Environmental impact and potential contamination risks.
“Motion helps customers mitigate many of these risk factors by utilising our expertise to select and design hoses and fittings that meet the unique needs of our customers,” highlights Fellipe.
Fellipe also emphasises the importance of a comprehensive maintenance plan in the mining industry. This includes regular replacement of filters, fittings, and hoses to ensure the smooth operation of hydraulic systems.
He states, “To assist with equipment maintenance, Motion offers a variety of filter kits. These kits may contain hydraulic and diesel filters, among others, tailored to meet specific equipment needs. By providing all the necessary filters in one package, the filter kits simplify the maintenance process for customers, ensuring convenience and efficiency.”
According to Fellipe, Motion’s ability to provide these kits is due to their access to different products and suppliers, enabling them to converge all the necessary filters into a single kit. These kits are available for different durations of operation, ranging from 250 to 1,000 hours, depending on the customer’s equipment requirements.
He finishes with, “Motion has an extensive network of branches strategically located across Australia, meaning that we’ve got you covered in every state. This allows Motion to offer in-house expertise and support to customers, even in remote areas. If a customer requires a specific part but is uncertain about where to find it or how to size it, Motion is just a call or email away.”
Mobile fleet and fixed plant applications play a key role in the day-to-day operation of a working mine. In the mining sector, heavy machinery often operates 24/7, under arduous working conditions. To sustain the reliability and productivity of these machines, using high quality hydraulic oil is paramount.
Hydraulic oil plays a pivotal role in the efficiency of these machines. The type of oil is also very important – lower viscosity lubricant performs better in colder conditions, and higher viscosity lubricant in hotter climates.
Gulf Western Oil established in 1988 and have been embracing the design of oil specifics and providing it to the Australian market. Using only the highest quality virgin-based oils, the company boasts some of the highest OEM approvals in today’s market.
To keep mining machinery and processing equipment in pristine condition, Gulf Western Oil provides the ideal solution:
Superdraulic Indestructible Range Available in ISO Viscosity Grades
Summary of Benefits:
Superdraulic Indestructible Range
• Offers enhanced protection even in Caterpillar hydraulic systems requiring a minimum 0.09% zinc.
• Very high oxidation stability offering extended service to 6,000 hours and beyond with regular oil testing.
• Excellent demulsification properties.
• High corrosion protection for both steel and non-ferrous metals.
• Both wet and dry filterability capabilities.
• Exceptional shear stability through ultra-shear stable viscosity modifier technology
• Excellent flow and performance even in cold starts.
46 and 68, The Superdraulic Indestructible range offers an elite level of performance and protection for hydraulic systems. The Indestructible Range of hydraulic fluids allow high class performance across varying temperature ranges and environments offering incredible performance and protection from the start to the end of operation.
Summary of Benefits:
Top Dog Indestructible 15w-40
• Superior fuel economy through reduced friction.
• Extended drain intervals.
• Improves oxidation control.
• Suitable for exhaust gas recirculation or selective catalytic reduction.
• Low SAPS formulation providing suitability for diesel particulate filters.
• Allows for a cleaner engine that offer increased service life.
• Improved shear stability resulting in decreased oil consumption.
A semi-synthetic, heavy duty diesel engine oil containing indestructible technology designed to protect high powered, turbo charged engines. The unique formulation contains performance enhancing and wear protection technology that significantly exceeds the requirements of the new API CK-4 lubricant specification and previous specifications including API CJ-4.
Black Tak Grease
Black Tak is a severe duty 5% molybdenum disulphide lithium complex mine and quarry grease. Specifically formulated for use in a wide range of quarry and mining equipment operating under heavy loads and harsh environments. The extreme pressure and anti-wear properties enable the grease to give long service life and outstanding boundary lubrication under high load and shock loading conditions from low temperature to very high temperature environments.
Gulf Western Oil have a wide variety of knowledge and expertise in helping customers choose the best product for their needs. Industry Motion is the trusted advisor to industry and provide a wealth of information on the mining segment – contact your local Motion branch today for assistance on Gulf Western Oil products and services.
Summary of Benefits:
Black Tak Grease
• Extreme pressure, boundary protection and anti-wear properties.
• Excellent resistance to water spray offs and wash outs.
• Protection against rust, oxidation, and wear.
• Contains a high level of molybdenum disulphide to protect against impact, sliding mechanisms and assist extended lubrication intervals.
V-class conveyor drives are essential to the efficient operation of materials handling in the mining, quarrying and aggregate industries. These industries rely heavily on conveyor systems to transport large volumes of material efficiently and reliably. However, common issues such as belt slippage, misalignment, overloading, and damage to the conveyor belt can cause significant downtime and unwanted costs.
To prevent these issues, it is essential to ensure proper installation, maintenance, and monitoring of the V-class conveyor drive. Regular inspections and assessments can help identify and address potential issues before they cause any significant downtime or production loss.
Regal Rexnord is a leading manufacturer of power transmission solutions for various industries, including mining. They offer a wide range of products, including gear couplings, bearings, conveyor drives, and other power transmission components, that are designed to provide reliable and efficient performance in harsh operating
Falk Lifelign Gear
Couplings:
• Offer maximum torque density and reliability.
• Designed to accommodate misalignment and axial movement.
• Minimise vibration, noise, and shock loads.
• Available in 28 sizes, including flanged, continuous sleeve, and mill motor types.
• Engineered with advanced features such as a triple-crowned tooth profile, enhanced lubrication, and sealing systems.
• Provide extended service life and reduced maintenance costs.
environments. With over 100 years of experience and a reputation for quality products and industry-relevant advice, Regal Rexnord is a trusted partner for mining companies looking to optimise their conveyor systems’ performance and reliability.
To prevent mechanical breakdown from wear and tear, Regal Rexnord provides three different solutions to keep v-class conveyor drives operational.
With the right tools, users of V-class conveyor drives can have the assurance that their equipment will have longer periods between
Falk Steelflex Grid
Couplings:
• Used in V-class conveyor drives to transmit torque.
• Designed to accommodate misalignment due to shaft deflection or thermal expansion.
• Flexible grid absorbs shock and vibration, reducing wear and tear on conveyor components.
• Easy to install and require minimal maintenance.
• Reliable and cost-effective solution for V-class conveyor drives in the mining industry.
maintenance checks and overall high rates of productivity in their use in the mining sector. Regal Rexnord’s products are both innovative and built with durability and reliability in mind.
Motion can offer mining-specific solutions that integrate Regal Rexnord products, including those for conveying drives. Their team of experts have a vast amount of experience in creating solutions that meet the unique challenges of the mining industry. By partnering with Motion, mining companies can access a wide range of Regal Rexnord products and custom solutions that are tailored to their specific needs, ensuring reliable and efficient power transmission, and conveying in mining operations. For more information contact your local Motion branch today.
Falk AirMax:
• Air-cooled disc coupling for demanding applications.
• Suitable for V-class conveyor drives in mining industry.
• Provides reliable and efficient power transmission in harsh environments.
• Easy to install and maintain.
• Air-cooling feature prevents overheating and downtime.
• Durable construction and can withstand high shock loads.
To prevent mechanical breakdown from wear and tear, Regal Rexnord provides three different solutions to keep v-class conveyor drives operational.
Conveyors play a vital role in ensuring the smooth operation of coal mines, as they are responsible for transporting large quantities of coal over big distances. They are also subject to harsh conditions including high temperatures, humidity, dust, and contaminants. These pose significant risks to componentry and equipment, resulting in costly repairs and prolonged periods of downtime.
According to Michael Greelish, National Business Development Manager at Motion, the humble bearing is a critical component that can make the difference between a conveyor running well or not.
“The role of bearings cannot be overstated and finding the right bearing for the conveyor application is of the utmost importance,” says Michael. “Often customers do not place as much importance on the type of bearings they are using, and this is where Motion can assist.”
As a leading distributor and services provider to the mining industry, Michael says that Motion is well-placed to help find the best bearing solution for their customers and can assist with installation and fitment.
“It is very important to install conveyor bearings correctly with the proper fit up, so you can get the optimal
performance and service life out of the bearing. A step-by-step fit up that includes checking and using gauges to install the bearings will ensure a prolonged bearing life in coal mining applications,” Michael says. “Our team are always available to customers to assist on fitment and installation.”
While there are a lot of different bearings on the market, Michael says Motion only partners with credible, high quality bearing manufacturers. Timken is one such supplier and sets the bar high in providing, robust and reliable bearing solutions.
For coal mining conveyor applications, Michael makes specific mention of the Timken unitised spherical bearings.
“The Timken spherical roller bearing solid block housed unit has established itself in the market as the strongest housed bearing unit of its
kind, providing exceptional resilience and strength under extreme operating conditions, and that standard remains unparalleled in the industry,” says Michael. “These are an excellent choice for conveyor applications in coal mines, providing superior performance, reliability, and durability.”
“The housing is made from solid cast steel and the bearing is fitted inside the housing at the factory level,” explains Michael. “The internal clearance is pre-set at the point of sale, and the sealing arrangement is pre-fitted to lock in grease and protect from the ingress of dust, dirt, and contaminants,” says Michael.
Timken also plays an active role together with Motion to provide knowledge and training on-site for proper installation.
“We regularly supply Timken spherical roller bearing solid block housed unit installation training to customers,” Michael says. “In conjunction with Australian Timken engineers, we teach customers how to correctly install the Timken spherical roller bearing solid block housed units. This training includes all staff on site from the apprentices to the fitters to the engineers. We encourage customers to get in touch with us about the training.”
Bearing selection critical to coal conveying
When it comes to maintenance and repair operations in the mining and processing industry, safety is key. The use of flammable products in these environments can pose significant risks, especially in areas where welding, grinding, or other potential ignition sources are present.
This is where non-flammable products, such as CRC’s Non-Flammable Brakleen and Non-Flammable Contact Cleaner, come into play.
Steve Keown, National Product Manager for Lubricants and Chemicals at Motion, highlights the importance of using non-flammable products in critical infrastructure and in enclosed areas where the risk of fire is high. In addition, CRC also has a Non-flammable water based Brakleen.
“Non-flammable products are gaining great acceptance in the marketplace,” says Steve. “They are an attractive solution to sites that need to keep going but still need to repair
• Safety: Eliminating the risk of fire and explosion associated with traditional flammable solvents
• Versatility: These are designed for use on a wide range of surfaces and components
• Compliance: Compliance with industry regulations and standards
• Performance: Highly effective in removing tough contaminants such as oil, grease, dust, and grime and leaves no residue.
something in that particular area.”
CRC is a leading manufacturer in the field of non-flammable cleaning products, revolutionising the industry with their innovative solutions. By harnessing advanced technology and research, CRC has paved the way for non-flammable cleaning products that provide a safer alternative to traditional flammable solvents.
CRC Non-Flammable Brakleen is a cleaning product specifically designed to effectively clean oil, grease, dust, brake fluid, hardened deposits and other contaminates.
One of the main advantages highlighted by Steve is the product’s convenience and effectiveness in removing contaminants without leaving any residue.
“Steve emphasises, “This is suitable for use in areas where there may be potential ignition sources, providing a safer option for maintenance and repair tasks.”
Similarly, CRC’s Non-Flammable Contact Cleaner is designed to clean electrical contacts and ensure a clean, dry, and contaminant-free surface for optimal performance.
Steve explains, “Many electrical components are shipped with a preservative on the contact area, and it is crucial to remove it before putting the component into service. The nonflammable contact cleaner eliminates the
risk of using products that could cause ignition, providing a safer alternative for electrical maintenance tasks.”
The use of non-flammable products, such as CRC’s Non-Flammable Brakleen and Non-Flammable Contact Cleaner, is crucial in the mining and processing industry to mitigate the risk of fire and ensure safety in maintenance and repair operations. These products offer convenience, effectiveness, and peace of mind in critical environments where ignition sources may be present.
As Steve states, “Using nonflammable products is a wise choice for operators who prioritise safety and need reliable solutions for their maintenance and repair tasks.”
Motion has a long-standing association with the mining and processing industry, known for its market-leading service in providing bearings, power transmission products, and now chemicals and lubricants.
“We are emerging as the trusted advisor to purchase chemicals, lubricants, lube transfer, and lube systems because the mining and processing industries are familiar with us and have experienced our marketleading service over the years,” says Steve.
To experience the advantages of Motion’s supply of CRC non-flammable solutions, customers are encouraged to contact Motion today.
Ventilation in underground mines is a vital component to upholding high standards of occupational health and safety practice. Underground mine workers are often exposed to pollutants like gas, dusts, and fumes. Exposure to these contaminants can lead to short and long-term health consequences with pro-longed exposure.
Naturally occurring gases like methane, hydrocarbons, carbon dioxide and ammonia are commonly detected in underground mines. All of which pose a potential explosive and air quality risk to workers in this industry.
The process of ventilation requires mechanical ventilation fans to circulate fresh air into an area and push stale air out. Fanmaster Australia, a leading ventilation distributor, has been providing leading solutions in ventilation systems for the mining and processing sectors since 1946.
With decades of knowledge and experience, Fanmaster provide a wide variety of products, tailored to suit a variety of underground mining conditions.
Looking at ventilation systems, the Fanmaster team have specifically designed a ventilation system for the underground mining sector, called Mancoolers. Mancoolers are a barrel style industrial fan that have the capacity to cool, ventilate, extract dust and gas –providing workers with fresh air. Made with the highest level of safety standard and are equipped with IP55 rated motors, which means they can cope in harsh environmental conditions.
Motion provides world-class advice and knowledge around Fanmaster products. For more information, contact your local Motion branch today.
• Fume extractors – IPFC range use HEPA filters to capture close to 100% of particulate matter down to 3 microns in size.
• Perfect for industrial processes like welding and grinding
• Units are often portable – can be moved as close as possible to the source of the process for local area ventilation.
• Air scrubber purifier – two-stage that removes contaminates like viruses, bacteria, and spores. Also appropriate for removal of dust and odours.
• Air blasters, coolers, purging fans and exhaust blowers.
• Perfect for confined spaces of work.
• Ideal for rugged and harsh conditions.
• Used in industrial areas where high temperatures are constant.
• Axial flow fans – come in a range of different sizes, can be bolted onto existing ducting.
• Industrial wall exhaust fans that are economic and suitable for double brick wall cavities.
• Hooded roof fans – designed for warehouses and factories.
• 4 different size ranges – 1000mm, 800mm, 600mm and 500mm
• Fitted with a standard IP55 rated motors.
• Ducting can be fitted for confined space usage.
• Available in single and 3-phase models.
• Currently used in a wide range of industries.
• Used to circulate air in a factory environment or be used to evacuate smoke, fumes or dust from a workplace.
• 2 sizes available – 300mm and 400mm
• The Fanmaster Mini Mancoolers are manufactured in our warehouse with quality parts and design.
• Units come equipped with IP55 rated motors.
• Option for ducting to be fitted for use in confined spaces.
• The Mini Mancoolers are best suited in factory environments – capable of extracting dust, fumes and smoke from these areas.
• Fans offer a flexible and compact form of air extraction and ventilation through effectively lowering the temperature, or by directing cool air over workers in hot working areas.
• Can be mounted on the wall.
IIn every industry, pumps are critical, no matter what it is. Mining, power, water, sewage treatment, wastewater, the whole lot. Everything uses pumps,” says Lance Brett, Product Manager Pumps & Mechanical Seals at Motion’s in-house sealing specialists, Seal Innovations (SiL). SiL specialises in designing advanced sealing solutions that secure and protect valuable materials in mining and ore processing applications.
With a wealth of 35 years of expertise in the field, Lance explains that mining pumps predominantly comprise of robust slurry pumps specifically designed to efficiently transport slurries with high solid content.
“These pumps are generally rubber or metal lined on the inside, and are subject to constant wear and tear, and their maintenance is crucial to maintain their performance and efficiency,” says Lance.
“In mining, the process is very abrasive, so the lifespan of the pump generally isn’t as long as it is in general industry, so the pumps need maintenance a lot more often because they wear out a lot faster,” discusses Lance.
He highlights that despite the critical role that pumps play in operations, companies may overlook or delay necessary maintenance tasks due to various reasons such as budget constraints, lack of awareness, or a focus on immediate production needs.
As a result, Lance discusses the comprehensive pump repair services offered by SiL as a solution. They provide workshops where pumps are brought in for a full strip assessment and photographic report to determine what needs to be repaired and restored to bring the pump back to its optimal performance.
“We’re a one-stop-shop because we can repair it, we have the bearings, all the parts needed, all in-house as well. Mechanical seal repair, pump repair, spares, greases, the whole lot, all available through Motion,” Lance explains. “Due to being in-house, we don’t have to rely on a lot of outside supply at all.” Keeping us competitive.
Lance explains that these pumps are often subjected to rigorous operational demands, including high flow rates, frequent use, and exposure to harsh
environmental conditions.
“As a result, they may experience wear and tear, mechanical failures, or other issues over time, which can lead to leaks, reduced performance, or even complete failure,” highlights Lance.
He explains that leaking pumps can also be a safety hazard and may result in environmental concerns or disruption of fuel supply, making prompt repair crucial to avoid downtime and potential losses.
Premature seal failures can be a major issue in slurry pumps due to the susceptibility of gland seals to malfunctioning caused by excessive friction resulting from over-tightening of the seals.
It is important to note that gland sealed pumps are designed to leak and drip so that the flushing water can cool the gland. Attempting to stop leakage by forcing too much pressure leads to increased friction in the seal, which can ultimately cause failure.
To prevent untimely seal failures in slurry pumps, a combination of measures should be taken, including selecting the appropriate seal material, ensuring proper installation, following a correct pump start-up procedure, and maintaining an optimum pressure and flow of clean flush water. Additionally, Seal Innovations provide hybrid solutions that can be effective in reducing the occurrence of seal failures.
The SiL team can also analyse problems with these types of issues on site in collaboration with the customer. The team can assess the extent of the issue, examine the problem areas such as the pump in this case and identify the root cause of the issue.
When problems like these are identified, the team can take necessary actions, which may include sourcing
• Gland Packing products
• Gland Packing installation procedures and tools
• Slurry Pump Mechanical Seals
• Water Management System to be used along with mechanical seal
• Bearing Isolators
• Rotary Seals*
• O-Rings *
• Lantern Rings*
• Shaft Sleeves*
• Gaskets (Manufactured locally and can be customised)
*Available in all sizes, profiles, design, and materials
readily available parts, and sometimes even repairing the pumps on the same day, as discussed by Lance.
“We have mechanical seals readily available on our shelf, and bearings in-house, which can sometimes result in efficient turnaround time. We are able to handle everything in-house, as long as there isn’t any significant internal damage. This is just one example of how SiL can prioritises uptime and minimise downtime for our customers,” Lance explains.
Lance explains that pumps are typically engineered to achieve specific flow rates. However, if the internal components of a pump are worn out and not functioning optimally, it can lead to a decrease in these rates. This inefficiency can result in the pump taking twice as long to complete its intended task, which can cause operational challenges.
Customers can rely on Motion’s commitment to delivering top-notch pump repair services, with a range of solutions including quality parts, spares, and greases available in-house. With a focus on reducing downtime and offering cost-effective solutions, Motion is dedicated to keeping the mining and processing industry pumping smoothly. Customers are encouraged to contact Motion for expert pump repair services and experience their exceptional commitment to excellence.
Heavy machinery in the mining sector requires frequent maintenance and lubrication to ensure equipment is efficient and reliable. In the mining sector, regular maintenance of grease pumps is not desirable, so a quality unit is desirable to prevent unexpected and unwelcomed operational issues. Faulty grease pumps can lead to significant downtime and loss of productivity – translating to increases in expenditure.
One of the most significant challenges with grease pumps in mining and processing sectors is the extreme environmental conditions they regularly endure. Pump’s must be able to withstand harsh temperatures, dusty
ratio 20kg
Grease Pump:
1. High-Pressure Output: This pump can deliver grease at a high pressure of up to 8,700 PSI.
2. Medium Capacity: Can hold up to 20kg of grease, which makes it ideal for smaller mining equipment that requires frequent lubrication.
3. Robust Construction: Made from high-quality materials that are resistant to wear and tear.
4. Easy to Use: The pump is designed for easy operation, with a simple control valve and a secure handle for easy pumping.
environments, and high humidity levels. As a result, grease pumps must be durable and reliable enough to operate in these conditions.
For operators in the industry, it’s crucial to use reliable and robust equipment. For more than 50 years, Alemlube an Australian-owned company, has been providing a range of lubrication equipment, fluid transfer, metering devices, waste oil handling systems and workshop equipment to customers in the mining industrial sectors. Alemlube pride themselves in their ability to provide customers with the highest level of standards in quality and reliability.
Alemlube stands by the high quality of these and produces three
ratio 50kg
Grease Pump:
1. High-Flow Rate: The 40:1 ratio of this pump allows it to deliver a high flow rate of grease, making it perfect for use in larger mining equipment.
2. Large Capacity: Can hold up to 50kg of grease, ensuring that there is always a sufficient supply of lubricant for the equipment.
3. Robust Construction: Made from high-quality materials that are resistant to wear and tear, ensuring that it is durable and reliable.
4. Easy to Use: Designed for easy operation, fitted with control valve and secure handle for easy pumping.
grease pumps – designed to make the process of lubrication and fluid handling more efficient, cleaner, and safer for each user.
Motion prides themselves on their excellent customer service, fast delivery, and competitive pricing. Alemlube works in partnership with Motion to ensure each customer has access to Alemlube products, no matter where they are based in Australia. To learn more about the extensive range of grease pumps on offer, visit your local Motion branch today.
55kg
Grease Pump:
1. High-Pressure Output: The 60:1 ratio of this pump allows it to deliver grease at a high pressure of up to 8,700 PSI, making it ideal for heavyduty applications.
2. Large Capacity: Can hold up to 55kg of grease, which is ideal for use in mining equipment that requires frequent lubrication.
3. Robust Construction: Made from high-quality materials that are resistant to wear and tear, making it durable and reliable.
4. Easy to Use: The pump is designed for easy operation, fitted with valve and handle.
Advanced Industrial Products (AIP), one of Australia’s leading national suppliers of industrial hoses, valves, fittings, and associated products, has been serving the mining and processing industry for over two decades,” says Troy Giggins, Category Manager for Industrial Hoses.
With a wide range of offerings and a commitment to quality and safety, AIP has become a trusted partner for mining supply companies across the country.
“One of the key uses of AIP hoses in the mining and processing industry is in fluid transfer applications, meanwhile valves are used to control the flow of materials through the hoses,” Troy highlights.
He continues, “They can be used to regulate the speed and volume of the materials, as well as to stop the flow altogether when necessary.”
“AIP offers a comprehensive range of hoses and valves for the mining industry, designed to withstand the challenging conditions and demanding requirements of this sector,” Troy highlights.
Troy highlights that AIP offers a range of valves for mining, including ball valves, gate valves, globe valves, and check valves, among others. “These valves are designed to withstand high pressure and are made from materials such as cast
iron, steel, and stainless steel,” he says.
Troy also notes that AIP provides valves suitable for various applications, such as isolation, control, and regulation of fluid flow in pipelines.
With their own swaging and crimping machines, AIP is able to manufacture hose assemblies to customer specifications, ensuring that the hoses are suitable for the demanding environments of the mining industry.
Troy discusses one of the standouts of AIP is the ability to cater individually to each customer.
“A lot of people can do the same thing, but AIP has the option of manufacturing kits to the customer’s specifications,” says Troy. “These kits can include brass or polypropylene fittings, rubber or PVC hoses of various lengths, and spray nozzles.”
By working closely with customers to develop customised solutions, Troy discusses that AIP can provide a higher level of service and support, which can help to build long-term relationships and improve customer satisfaction.
“In addition to fluid transfer applications, AIP also offers fire suppression related products for the mining industry like fire hoses, and hose reels that are ready to go,” says Troy.
These products are crucial for
ensuring the safety of mining operations, as fires can pose a significant risk in these environments.
Troy highlights that AIP conducts testing of hoses under conditions appropriate to their real-life use. After testing, AIP attaches a test plate to the hose with necessary information, demonstrating their transparent approach. This commitment to transparency helps build trust with customers and enables AIP to continuously improve their products and services based on feedback and insights gained from testing.
AIP’s hoses and valves are highly valued in the mining and processing industry, and their partnership with Motion brings added benefits to customers. “With customised solutions, rigorous testing, and high-quality components, AIP is a reliable choice for mining companies,” says Troy.
Leveraging over 20 years of experience and continuous improvement, AIP is a leading supplier of industrial hoses and valves in Australia. The seamless integration of products and services through their partnership with Motion ensures tailored solutions for enhanced customer satisfaction and operational efficiency in the mining and processing industry.
The CRC Non-Flammable Brakleen has a powerful cleaning and degreasing formula which can quickly dissolve grease, oil, and other contaminants without disassembly, saving you time and maintenance costs. It is most suitable in critical infrastructure and in enclosed areas where the risk of fire is high.
Gates® Predator™ V-belts are a highly durable and reliable solution for heavy-duty equipment. They are designed to withstand the harsh environmental conditions of the mining industry, including extreme loads, abrasion, heat and stretching. They can also reduce the number of belts required for a drive system, resulting in cost savings and a positive environmental impact.
The Timken spherical roller bearing solidblock housed units are pre-assembled bearings that operate under extreme conditions. They provide protection against contaminants, have a sealing design, and are made from solid cast steel. They are suitable for conveyor applications in coal mines, providing superior performance, reliability, and durability.
TECO Maxe3 Mining Motor is a durable and reliable electric motor designed for the mining industry. It features a true grease relief system to prevent over-greasing. This system increases motor lifespan while sustaining a low maintenance cost. It can also be modified to meet IECEx specification for hazardous environments.
Shell Tellus range offers a variety of high-performance lubricants for the mining industry, including hydraulic fluids that improve oil life, enhance energy capabilities, and extend machine life expectancy. These lubricants are designed to ensure maximum performance, reduce downtime, and lower maintenance costs.
Black Tak is a superior grease for mining and quarry equipment, offering extreme pressure and anti-wear properties. It provides excellent protection against water, rust, oxidation, and wear. With a high level of molybdenum disulphide, it ensures extended lubrication intervals and safeguards against impact and sliding mechanisms.
NTN Sealed Spherical Roller Bearings are reliable and widely used in the mining industry. They can withstand heavy loads, shock loads, heat, and vibration. The sealed design prevents contaminants such as dirt and dust from entering, ensuring longer lifespan and efficient operation of mining equipment.
Regal Rexnord Falk® Lifelign Gear Couplings are built to provide efficiency and reliability in harsh operating environments, such as mining. They are designed to accommodate misalignment and axial movement while providing exceptional torque density, noise reduction and shock load resistance.
ALEMLUBE SAMOA HEAVY DUTY 60:1 RATIO 20KG GREASE PUMP
Samoa Heavy Duty 60:1 ratio 20kg Grease Pump is a robust and easy-to-use tool that delivers grease at a high pressure of up to 8,700 PSI. With a medium capacity of 20kg, it is suitable for frequent lubrication of smaller mining equipment.
The Mancooler ventilation system is a barrel-style fan for underground mining. It cools, ventilates, extracts dust and gas, and provides fresh air. It features IP55 motors, multiple sizes, and ducting compatibility. It is also used in various industries for air circulation and dust/ fume evacuation.
Schaeffler’s Split Bearings are a convenient solution for mining operations by enabling quick installation and replacement. They are designed to be split all the way through to the shaft. They are also suitable for heavy-duty applications providing high load capacity and shock load resistance.
3M™ TA570 Safety Helmets are a Type 1 helmet specifically designed for mining conditions. They provide hazard protection, and feature cooling vents for comfort in hot and humid environments. They are compatible with metal or polycarbonate lamp brackets. Metal brackets offer strength, while polycarbonate brackets are rust and corrosive-resistant for underground mining.