automation

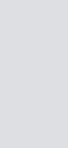
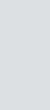






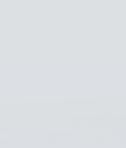
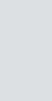




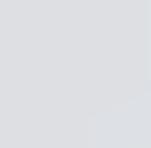



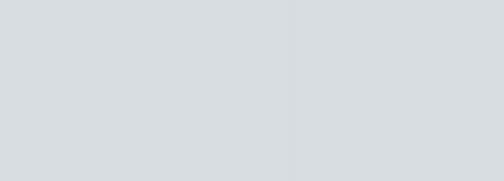



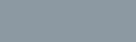



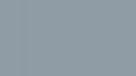
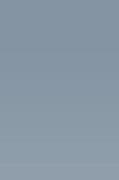

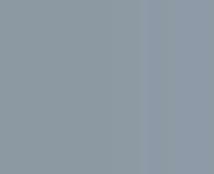


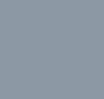
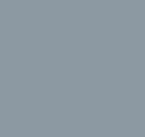
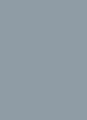









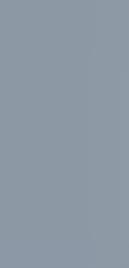
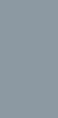





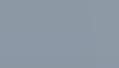
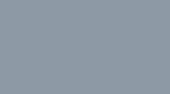



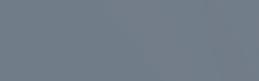




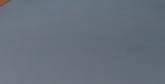







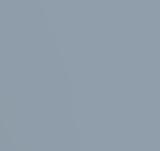





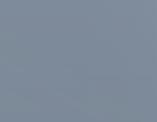

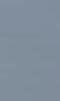


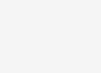
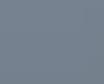
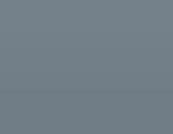

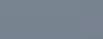







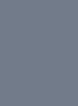

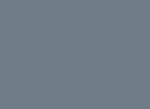
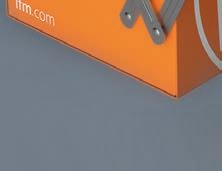
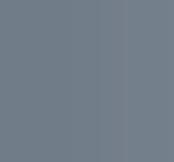
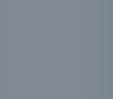

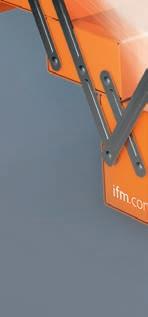
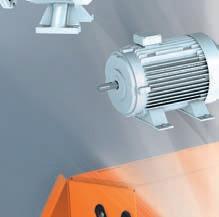


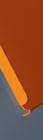
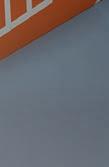

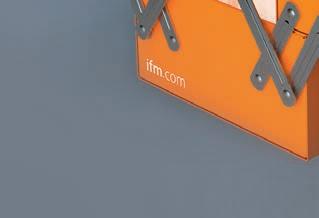
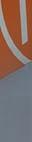


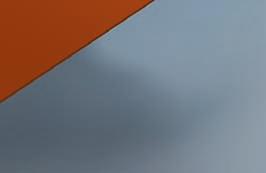
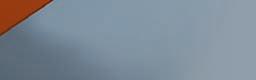
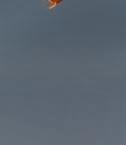

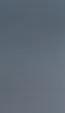


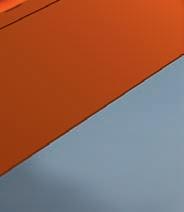



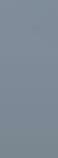



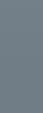
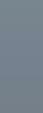
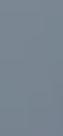



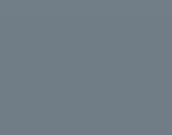



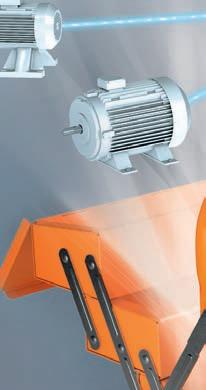



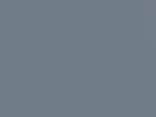
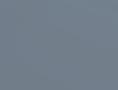


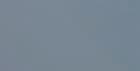
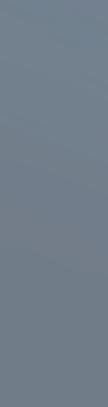
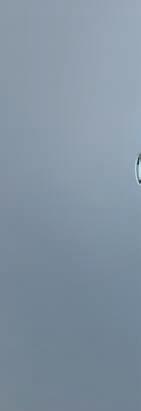
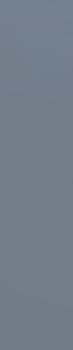
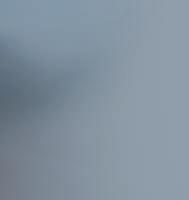
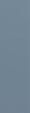
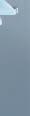
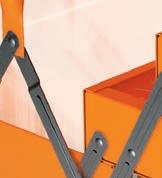

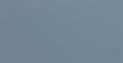
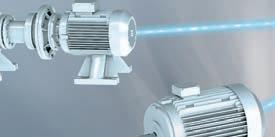

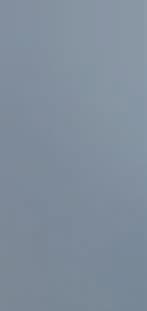
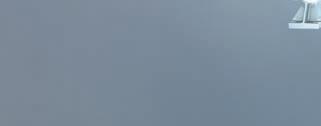
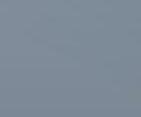







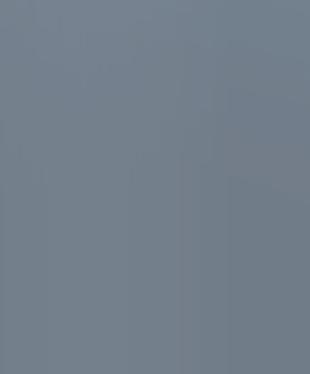


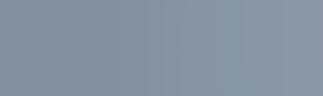
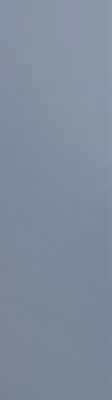


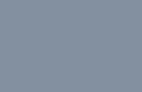



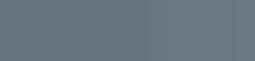
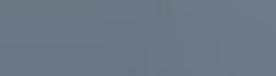

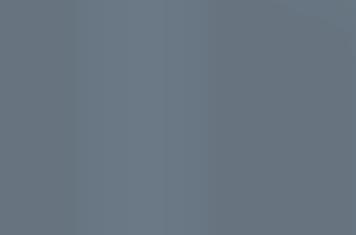
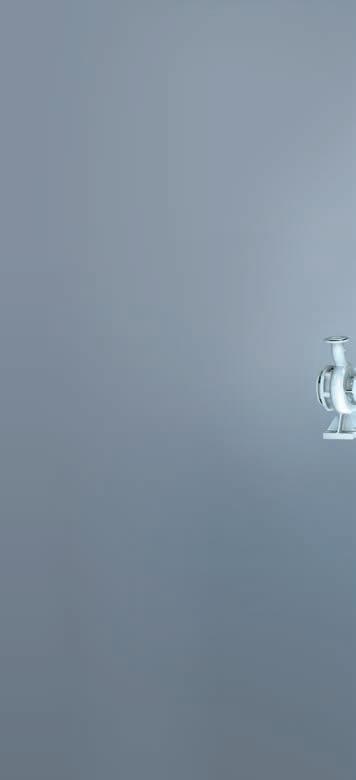
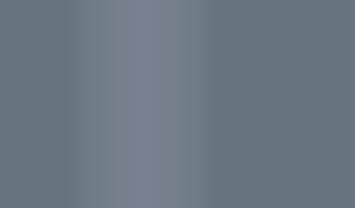
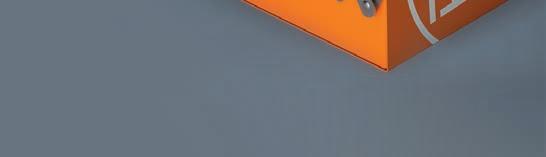

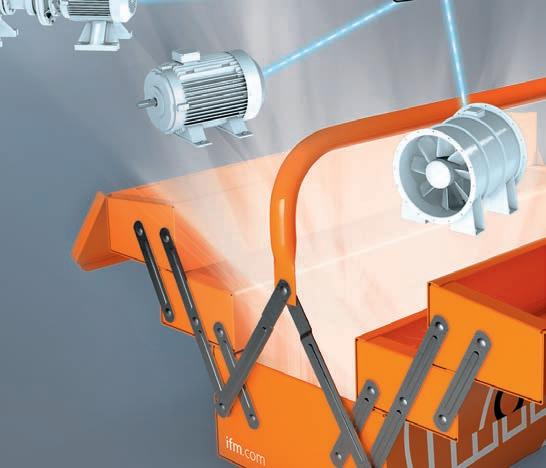
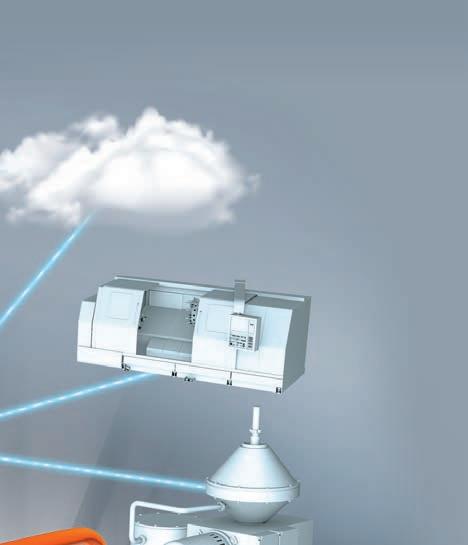
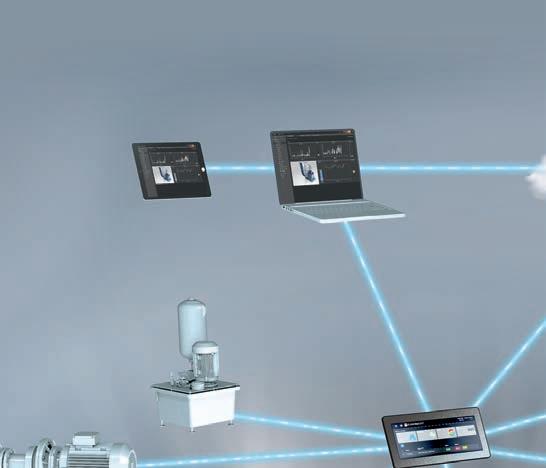
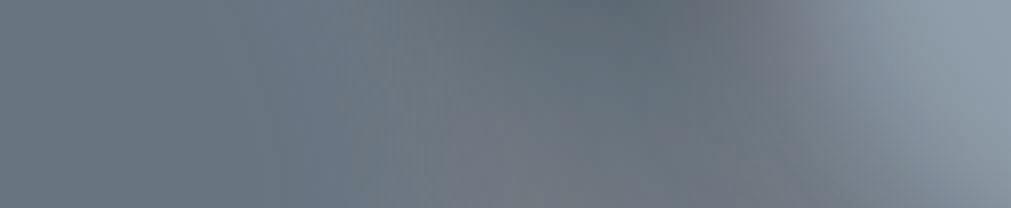






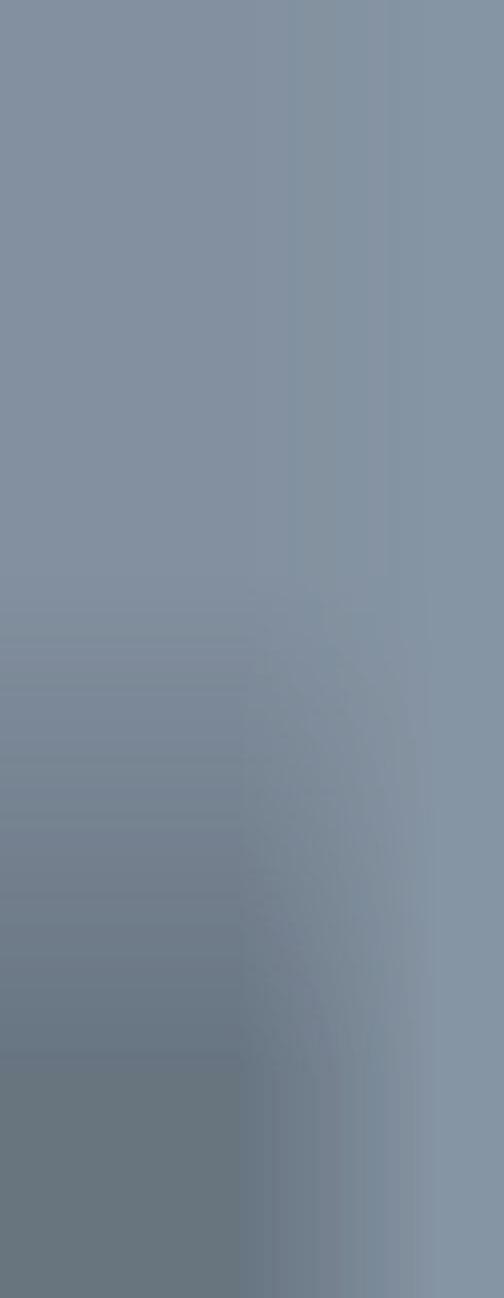
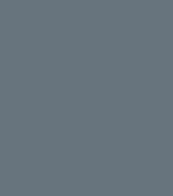
automation
United. Inspired.
Without proactive maintenance, as your equipment ages there is a risk of unplanned repairs, early replacement and costly downtime. Midlife services from Epiroc is a flexible service solution that will prolong the lifespan of your asset. Replacing old with new components, returning your equipment to maximum productivity and operating efficiency at a fraction of the cost of a new machine.
IMARC will allow global leaders and emerging gamechangers from the entire mining value chain the unique opportunity to come together under one roof.”
Those words are from IMARC director of conference content and strategy Sherene Asnasyous discussing this year’s International Mining and Resources Conference (IMARC), set to be held at the ICC Sydney November 2–4.
IMARC has always been where global mining leaders connect with technology, finance, and the future – and the 2022 iteration will be no different. That’s why this month’s issue of Australian Mining features an in-depth preview of the event.
With so many industry events having taken place in recent months, it’s especially exciting for IMARC, which has lain dormant since 2019, to be back on the calendar.
And if any further evidence was needed to confirm that events are back – and that Australian mining is as strong as ever – one need look no further that the fact this year’s IMARC has had to expand its exhibition floor by 40 per cent to accommodate an exhibitor list 85 per cent bigger than 2019.
While this year’s event will cover a huge range of topics, one of the biggest talking points is bound to be the skills shortage that continues to plague the mining industry.
This month’s Australian Mining also looks at the issue. We chat with a handful of industry
experts about how the country’s resources sector can recruit, train, and retain employees during what has been called “the worst skills crisis in a generation”.
Elsewhere, we take a deep dive into two of Australia’s most plentiful future-facing minerals – copper and nickel – looking at the current state of the market and why so many companies seem especially eager to get their hands on as much of these resources as possible.
Speaking of handling resources, this month’s issue also has a special focus on bulk material handling.
It can sometimes be easy to forget that mining is far more than digging previous ores and minerals from the ground. Those materials have to move from point A to point B (and beyond) and the process of getting them there involves a lot of technology and expertise.
We take a look at any and all aspects of bulk material handling, from conveyor guards to sustainable belts to workers’ safety and potential danger zones.
Founded in 1944, Martin Engineering has a global presence in 17 countries on six continents, with customers in dozens of industries.
The company’s engineers have been solving bulk material handling problems around the world for over 70 years and are available to provide expert advice and assistance for any issue, whether it’s material clogging the discharge port of a container or railcar, or a fugitive dust issue that can’t seem to be brought under control.
How Denmark is helping to drive sustainability in Australian mining T he likes of FLSmidth, Aalborg CSP, DHI, Advent Technologies and C.C. Jensen are among the Danish companies helping the Australian resources sector move into a more sustainable future.
E xplore, develop and invest at IMARC E xtraordinary demand has seen Australia’s largest mining and resources conference and expo significantly expand its floorplan in 2022.
D riving efficiencies in material handling A stec Telestack’s mobile systems are providing Australian mining operations with a cost-efficient, flexible and reliable material handling and processing solution.
C opper and nickel: Pillars of the future?
A s the world continues its march to net-zero, the race is on for minerals essential to decarbonisation. Copper and nickel are at the top of the mining industry’s wish list.
T he world’s first battery-electric surface drill rig E piroc has teamed up with Swedish construction company Skanska to develop the first-ever battery-electric surface drill rig.
Filling the gap: Recruitment and the future of mining
A ustralian Mining speaks with industry experts about how the country’s resources sector can recruit, train, and retain employees during what has been called “the worst skills crisis in a generation”.
M itigating the long tail of dust
W hen it comes to tailings and other excess waste, miners need dustsuppression technology that can handle the size of their operation.
58
Transforming digital communications for mining N okia is engaged in developing innovative digital communications solutions for the resources sector, seeking to enhance operations, optimise safety, expand sustainability and drive efficiencies.
Due to the size and complexity of mining operations, most miners know (and expect) that inefficiencies and performance gaps exist across their mine value chain - particularly in load and haul circuit capacity.
Suboptimal haul routes, ineffective strategies, machine downtime, poor operator behaviour and inefficient processes are all some of the common problems that result in millions in lost production value every year. And with commodity prices climbing - masking true production and cost/ tonne output - potential profit losses could be closer to tens of millions annually.
Because of this, an increasing number of mining operators are turning to data and analytics to address poor productivity once and for all, closing the gap to best potential performance.
Decoda is a leading provider of Analytics as a Service, working with mine sites globally to achieve greater efficiency, mine plan compliance, and overall productive operations through delivering insights and improvements across the entire mine value chain.
Our intelligent, integrated Mining Operating System (iiMOS) uses real-time key performance insights, dynamic operational strategies, and remote haul road condition analysis to
help you drive efficiency and remove unpredictability across your load and haul circuits.
As your digital execution partner, Decoda provides an end-to-end service that allows you to develop strong alignment between your operational teams and the digital strategy underpinning your approach to data and analytics. This helps mine operators to:
• Achieve best potential operational excellence across the value chain
• Identify gaps in operator and machine performance to improve operational productivity
• Uncover millions in lost value opportunities
• Embed improvement strategies to improve mine site profitability
• Reduce variability and improve mine plan compliance.
Decoda brings together people, technology, and analytical methods to correct declining productivity and foster continuous, sustained improvement across mining value chains.
AUSTRALIAN MINING PRESENTS THE LATEST NEWS FROM THE BOARDROOM TO THE MINE AND EVERYWHERE IN BETWEEN. VISIT WWW.AUSTRALIANMINING.COM.AU TO KEEP UP TO DATE WITH WHAT IS HAPPENING.
Australia’s critical minerals will help drive the United States’ electric vehicle program following its move to grant preferred status to free trade agreement (FTA) partners. The US Inflation Reduction Act is expected to boost the Australian Government’s manufacturing agenda and help underpin the
demand for high quality Australian battery minerals.
Under the Act, a new electric vehicle will only be eligible for tax credits when at least 40 per cent of the battery’s critical minerals came from the US, an FTA partner such as Australia, Chile or Canada, or recycling in North America.
That could increase to 80 per cent by 2027.
The new law is a major milestone in the US’ transition from an economy long driven by fossil fuels to one that will be dominated by minerals such as lithium, nickel and aluminum.
Lithium share prices shot up when the ASX opened for the first time after the bill passed the House of Representatives. Companies such as Piedmont Lithium, Core Lithium, Sayona Mining, Allkem and Global Lithium Resources all surged.
Minerals Council of Australia chief executive Tania Constable said the development would strengthen the case for investment capital into mining.
“Australian mining needs about $20 billion per year to sustain current production,” she said.
“If we are going to increase the capacity of existing mines or open new mines – including in the commodities needed for our global transition to net zero emissions – capital investment will
Mineral Resources (MinRes)’ transformational Onslow Iron project (formerly known as the Ashburton project) in Western Australia has commenced early works to support first ore on ship around December 2023.
Onslow Iron will unlock stranded deposits that would otherwise remain undeveloped in the West Pilbara region, using MinRes’ innovative and proprietary equipment designed to process and move bulk commodities at lower costs and with a reduced environmental footprint.
Following receipt of preliminary approvals, project preparations are on track and early construction activities, including bulk earthworks, have begun at the port of Ashburton, south of Onslow. At the nearby truck
maintenance facility, installation of the temporary construction village is underway, with first buildings to be installed from early September.
Mine development activities have also progressed at the Ken’s Bore Deposit, east of Onslow, with construction of the A320-capacity airport and the installation of two camps to support drilling and early construction works.
Recruitment for the construction phase of Onslow Iron is also well underway alongside a continued focus on community and stakeholder consultation.
In line with the project schedule, long-lead items have been ordered, including the first transhippers, which will be used to load capesize vessels that will be anchored offshore Ashburton port.
Each transhipper has a 20,000-tonne capacity, is fully enclosed to avoid dust pollution and has a significantly lower environmental footprint when compared to the major dredging activities that would be required to construct deepwater berths.
Onslow Iron will be one of the largest iron ore developments undertaken in WA and deliver substantial benefits to the state, including thousands of construction and operational jobs, billions of dollars of direct local investment through capital expenditure and billions of dollars of state and commonwealth royalties over the life of the project.
MinRes managing director Chris Ellison said the project would be the cornerstone of the company’s
AUSTRALIAN MINING GETS THE LATEST NEWS EVERY DAY, PROVIDING MINING PROFESSIONALS WITH UP-TOTHE-MINUTE INFORMATION ON SAFETY, NEWS AND TECHNOLOGY FOR THE AUSTRALIAN MINING AND RESOURCES INDUSTRY.
need to be increased by an order of magnitude.
“The Bank of America estimates that $US150 billion per year will be needed in global mining to produce the minerals needed to achieve the global transition to net-zero.
“Australia needs to position itself as a competitive destination for this capital in order to realise its full potential.”
iron ore strategy to deliver low-cost, long-life operations with project economics that are compelling through commodity price cycles.
“Importantly, our innovations will drive lower emissions across the project. Onslow Iron has been designed with a low environmental footprint and will be dust-free from pit to port,” he said.
“We’re also setting a new FIFO standard with our industry-first resort-style accommodation to ensure the physical and mental safety of our people, and to encourage more women and couples to live on site.
“It’s in our DNA to aim higher, push the boundaries and forge new paths, which is why Onslow Iron really represents a new paradigm for mining in WA.”
its underlying attributable profit had risen more than 40 per cent to $US23.8 billion ($33.89 billion) for the year to June 30.
“These strong results were due to safe and reliable operations, project delivery and capital discipline, which allowed us to capture the value of strong commodity prices,” BHP chief executive Mike Henry said.
bringing full-year dividends to $US3.25 a share.
The annual report also indicated an attributable profit of $US30.9 billion ($44 billion), net operating cash flow of $US29.3 billion ($1.73 billion) and record free cash flow of $US24.3 billion ($34.61 billion) for continuing operations.
Leading Australian contract miner Byrnecut is set to bring in six Sandvik battery loaders for use at OZ Minerals’ operations in South Australia.
Under a deal with Sandvik Mining and Rock Solutions, Byrnecut will take delivery of the batteryelectric units in 2023 and 2024 for use at the Prominent Hill copper, gold and silver mine, southwest of Coober Pedy, and the Carrapateena copper and gold mine, north of Port Augusta.
Byrnecut has been engaged by OZ to provide underground mining services at the mines and it currently has a fleet of Sandvik LH621i loaders with automation operating on both sites.
Byrnecut asset manager Max Woods said the company was leading the way with battery-electric vehicles in Australia by putting the Sandvik loaders into service over the next two years.
“Not only will the use of electric vehicles significantly improve the working environment underground,
but it will also help our customers to work toward their emissions reduction goals – something that is increasingly important in the mining sector,” he said.
Woods said the purchase of the loaders, which will be equipped with Sandvik’s Automine automation system technology, was part of Byrnecut’s commitment to exploring and embracing new technologies that make its operations safer, more efficient and more sustainable.
“Eliminating emissions from loaders from the underground environment helps us create a better workplace, as does AutoMine technology that enables operators to work from comfortable remote control rooms,” he said.
Another major benefit to Byrnecut is the anticipated increased performance the new loaders could provide.
The company worked closely with Sandvik prior to purchase in order to model various application scenarios, including manual and automated operation.
Amid the record numbers, Henry said geopolitical factors would continue to affect the company in the near future.
“We expect China to emerge as a source of stability for commodity demand in the year ahead with policy support progressively taking hold,” he said.
“At the same time, we expect to see a slowdown in advanced economies as monetary policy tightens as well as ongoing geopolitical uncertainty and inflationary pressures.
“The direct and indirect impacts of Europe’s energy crisis are a particular point of concern.
“Tight labour markets will remain a challenge for global and local supply chains. Waves of COVID-19 infection continue to occur in the communities where we operate, and we are planning accordingly.”
BHP said its FY22 profit increase stemmed from higher coal and copper prices and a strong underlying operational performance, including record sales at its Western Australia Iron Ore operations (WAIO) and near record concentrator throughput at its Escondida copper mine in Chile.
The miner said its result was partially offset by COVID restrictions and supply constraints, higher inflation affecting diesel, electricity and consumable prices, along with lower copper grades at Escondida and wet weather at its BHP Mitsubishi Alliance (BMA) coal operations in the Bowen Basin.
“We’re expecting the loaders to provide greater throughput in both manual and automated modes while delivering a similar total cost of ownership per tonne delivered to their predecessors,” Woods said.
The loaders are expected to bring major cost savings across their lifecycles. They are likely to require fewer replacement parts than their predecessors, and servicing is simpler and more efficient.
Sandvik 18-tonne battery loaders are among the most compact on the market. The powerful electric motors, innovative electric driveline, and the smaller tyres on the rear compared to the front result in small machine size, high payload with good visibility and impressive speeds.
Battery machines produce no underground exhaust emissions and significantly less heat than traditional diesel engines, supporting the mines to reach sustainability targets, through reduced carbon emissions.
Sandvik business line manager for load and haul Andrew Dawson said the first Sandvik battery-electric loaders began arriving in the country about a year ago, and interest has been extremely strong.
“We’re very pleased that Byrnecut and OZ Minerals see the benefits of this technology and are demonstrating it to the rest of the industry. We have always had an excellent working relationship with Byrnecut and look forward to cooperating with them throughout the roll-out and beyond,” he said.
Byrnecut is a renowned specialist underground mining contractor offering a unique range of services and depth of experience.
Sandvik’s AutoMine is an automation system for autonomous and tele-remote operation for a wide range of Sandvik loaders and trucks. The system is scaled from teleremote or autonomous operation of a single machine to multi-machine control and full fleet automation with automatic mission and traffic control capability.
idoba chief executive officer Sarah Coleman was a big winner at the recent Women in Industry Awards, taking out the Excellence in Mining award.
Fulton Hogan was also a major winner, coming out on top in multiple categories.
Fulton Hogan general manager Sarah Marshall was awarded the Excellence in Construction and Woman of the Year awards, while
Joanne Jeffs, Barbara Pitos and Nina McHardy were awarded the Social Leader of the Year award, Safety Advocacy award and Industry Advocacy award, respectively.
The Women in Industry Awards are held each year to recognise the exceptional work and dedication of the women in the industrials sector.
The awards are an invaluable opportunity to recognise not just the nominees and winners, but the hard
NRW Holdings made a higher pershare offer, but it had too many strings attached for MACA.
When MACA’s founding shareholders recently entered into written acceptance deeds allowing Thiess to secure 15.9 per cent of the mining services provider, it came after Thiess increased its off-market takeover bid from $1.025 cash per share to $1.075.
The boosted offer valued MACA at $367.3 million.
“Thiess’ increased offer is compelling and an attractive price representing a strong premium to recent trading prices prior to the
announcement of the initial Thiess offer,” MACA founding shareholder Geoff Baker said.
“My fellow founding shareholders and my fellow MACA director Rob Ryan have agreed to accept the revised offer price and have agreed not to withdraw those acceptances for the duration of the offer period.”
However, NRW, another WAbased mining contractor, had previously made a $1.085-pershare offer for MACA.
So why was the higher offer rejected?
According to the MACA board, NRW’s offer was inferior because
work and dedication of all women in industries such as mining, road transport, manufacturing, engineering, logistics, bulk handling, waste management, rail and infrastructure.
Marshall has been leading the Fulton Hogan team as general manager for over three years, while also serving as board director for the Australian Constructors Association. She has spent her career
spearheading positive change in the industry by driving sustainability, improving culture, and driving improvements in gender diversity.
The 2022 awards were sponsored by Atlas Copco, Weir Minerals, and Komatsu. Commenting on the awards, Komatsu expressed pride in its sponsorship.
“Komatsu is proud to once again be a sponsor of the Women in Industry Awards to celebrate the successes of the incredible women working in our industry,” the company said.
“All nominees and winners are making their workplaces and communities a better place for future generations, which closely aligns to our core values at Komatsu.”
The Excellence in Mining award, sponsored by Weir Minerals, went to idoba chief executive officer Sarah Coleman.
Coleman is a knowledgeable mining and management consulting executive with experience in operations, improvement, innovation, technology, and asset management. She founded leading business improvement company ImpRes in 2010, and now heads idoba as its CEO.
• S age Hahn– Business Development Success of the Year
• L ouise Adams– Excellence in Engineering
• Rebecca Healy– Excellence in Manufacturing
• Frances Ross– Excellence in Transport
• Danielle Bull– Mentor of the Year
• Helen Tower– Rising Star of the Year (sponsored by Atlas Copco)
only half of the proposal was in cash – NRW would have paid out a total of $188.6 million in cash, with the remainder to be paid in company stock.
It also came with several risks, including whether NRW could secure adequate financing.
“The NRW indicative proposal was a non-binding indicative proposal, was subject to conditions and there was no certainty that giving NRW (and its financiers) access to MACA to do due diligence would result in a binding offer or the execution of a scheme of arrangement implementation agreement,” MACA said in rejecting
the NRW offer earlier in August.
One MACA investor was more straightforward when suggesting NRW needed to make a firmer offer.
“NRW likely should put on their big boy pants and make a better offer with fewer strings attached,” the investor, who declined to be named, told the Australian Financial Review.
MACA’s boards ultimately determined the NRW offer was too great a risk and recommended shareholders accept the Thiess bid, which is waiting on approval from the Foreign Investment Review Board.
With Sandvik’s decades of experience designing mining equipment and unbeatable expertise with BEVs, we design our battery electric trucks and loaders to be the best choice for more sustainable mining. Minimum mine infrastructure needs, high payload capacity, fast and easy battery swap, purpose-built chemistry, and electric driveline with superior power; meet Sandvik battery electric trucks and loaders.
When Mineral Resources announced the second-best annual result in the company’s history, it highlighted lithium growth as one of its four key business pillars.
“MinRes began building a worldclass, long-life lithium business in Western Australia more than a decade ago,” MinRes managing director Chris Ellison said following the release of the company’s 2022 financial year report.
“Our foresight and investment are starting to bear fruit.
“Today we already are the largest ASX-listed spodumene concentrate producer and one of the first to derive earnings from lithium hydroxide.”
While MinRes’ 2022 underlying net profit of $400 million represented a 64 per cent drop on the previous year, the company said it experienced “a strong second half performance” due to record lithium prices.
Lithium carbonate and lithium hydroxide prices have held steady since April’s record high levels, with leading price reporting agency Benchmark Mineral Intelligence indicating both products are still trading more than 300 per cent higher than a year ago.
MinRes has also reported a big future in lithium growth.
“In lithium, MinRes and our JV (joint venture) partner
Ganfeng approved the next stage of expansion of Mt Marion to 900,000 tonnes per annum,” the company said. “We also delivered maiden earnings from lithium hydroxide production – a first for an ASX-listed company.
“Production resumed at Wodgina, one of the world’s largest hard-rock lithium mines, following the start-up of trains 1 and 2.
“The Kemerton lithium hydroxide plant, which like Wodgina is part of our MARBL JV with Albemarle, is in the final stages of pre-production activities.”
Paul Brown, MinRes chief executive – lithium, recently said upgrades at Mt Marion would further strengthen the company’s position as a “globally significant producer of lithium products”.
“Lithium is one of MinRes’ core commodities,” Brown said. “We’ve built a long-term business horizon that will guide us to expand and diversify our lithium portfolio in line with global demand.
“Doubling capacity at Mt Marion means this Tier 1 asset will become even more important to MinRes’ ongoing success, helping us continue making valuable contributions to the world’s renewable energy efforts.”
Global analysts like Goldman Sachs and Credit Suisse sent shockwaves through the sector in
June when they predicted a crash in lithium prices.
Goldman Sachs said there had been “a surge in investor capital into supply investment tied to the long-term EV (electronic vehicle) demand story, essentially trading a spot-driven commodity as a forwardlooking equity”.
“That fundamental mis-pricing has in turn generated an outsized supply response well ahead of the demand trend,” the company said.
That assessment was quickly rebutted, however, with Benchmark Mineral Intelligence highlighting several reasons it believed Goldman Sachs was wrong in its predictions.
More recently, a newly passed US law designed to drive EV production is likely to be a boon for Australian lithium producers.
Under the US Inflation Reduction Act, an new EV will only be eligible for tax credits when at least 40 per cent of the battery’s critical minerals came from the US, a free trade agreement partner such as Australia, Chile or Canada, or recycling in North America. That could increase to 80 per cent by 2027.
“Australian mining needs about $20 billion per year to sustain current production,” Minerals Council of Australia chief executive Tania Constable said of the new US law.
“If we are going to increase the capacity of existing mines, or open new mines – including in the commodities needed for our global transition to net-zero emissions –capital investment will need to be increased by an order of magnitude.
“The Bank of America estimates that $US150 billion per year will be needed in global mining to produce the minerals needed to achieve the global transition to net-zero.
“Australia needs to position itself as a competitive destination for this capital in order to realise its full potential.”
Goldman Sachs, for its part, may have changed its tune on the critical mineral.
Lithium – along with other futurefacing minerals such as nickel and copper – is a key ingredient in batteries and equipment needed in decarbonisation.
In a note to clients, Goldman Sachs said it expects “battery and hydrogen storage solutions to continue to receive greater attention from investors, who we believe have not yet fully appreciated their importance in mitigating market disruptions”.
“Globally, we see several regulatory initiatives that could provide tailwinds to accelerate solutions such as battery storage and hydrogen to alleviate energy reliability issues.”
Our industry has witnessed some crippling fires originating from the ignition of screening media. The source of these fires is linked to maintenance hot works and even equipment failure during normal operation. As well as posing a serious hazard to personnel, the cost of equipment damage and lost production can border on the incalculable.
Screen house fires can’t be prevented by operating procedures alone. The good news is that we can help you permanently eliminate this risk with our innovative Fire Resistant screening media.
See for yourself how easily these fires can occur and how Screenex®
Fire Resistant screening media can help to eliminate this hidden hazard
Rio is teaming up with its biggest customer – China Baowu Steel Group – to develop the Western Range iron ore project in the Pilbara.
Rio Tinto and Baowu announced in September they had agreed to enter into a joint venture on the project, with a total investment of $US2 billion ($2.96 billion).
Rio will invest $US1.3 billion ($1.92 billion) and hold a 54 per cent stake in Western Range, with Baowu paying $US700 million ($1.03 billion) for the remaining 46 per cent.
“This is a very significant milestone for both Rio Tinto and Baowu, our largest customer globally,” Rio Tinto Iron Ore chief executive
Simon Trott said. “The development of Western Range represents the commencement of the next significant phase of investment in our iron ore business, helping underpin future production of the Pilbara Blend, the market benchmark.”
Western Range’s annual production capacity of 25 million tonnes of iron ore will, according to Rio, help sustain production of its Pilbara Blend from the miner’s existing Paraburdoo hub.
The Western Range project includes construction of a primary crusher and an 18km conveyor system that will link it to the existing Paraburdoo
processing plant. Construction is expected to begin in early 2023, with first production anticipated in 2025.
Rio and Baowu also entered a sales agreement that will see Baowu buy up to 126.5 million tonnes of iron ore over approximately 13 years.
“The signing of the joint venture agreement for the Western Range project is a significant event in the history of cooperation between Baowu and Rio Tinto,” Baowu Resources chairman Shi Bing said.
“We fully appreciate the persistent efforts of both teams in accomplishing the important achievement.
South32 posted record profits of $US2.6 billion ($3.76 billion) in the 2021–22 financial year.
The windfall profits represent a 432 per cent jump from FY21 ($US489 million), along with a 156 per cent increase in underlying EBITDA (earnings before interest, taxes, depreciation, and amortisation) to $US4.76 billion ($6.87 billion).
a record $US1.3 billion ($1.88
billion) of returns in FY22, which is 10 per cent of the miner’s market capitalisation.
The Perth-based miner’s profits were driven largely by surging prices for metallurgical coal and aluminium, with South32 recording realised prices of $US1.54 billion from coal
exposure to metals critical for a lowcarbon future. Chief executive officer Graham Kerr said the company was aware of the need to move towards more future-facing minerals.
“We have repositioned our portfolio toward metals critical for a low-carbon future,” he said.
“We hope that the two parties will deepen the mutually beneficial and win–win partnership, continue to carry forward the spirit of sincere cooperation and further expand cooperation in more fields and aspects on the basis of working together to operate the project well.”
Rio’s Pilbara Blend products “are the world’s most recognised brand of iron ore and are known for their highgrade quality and consistency”.
“Our Pilbara Blend products make up approximately 70 per cent of our iron ore product portfolio. It is also the largest and most liquid iron in the market today,” the company said on its website.
an additional shareholding in the hydro-powered Mozal Aluminium smelter and the restart of our 100 per cent renewable powered Brazil Aluminium smelter.”
News of the record profits came days after South32 announced it had decided not to progress
artin provides the most innovative bulk material control com ponents in the industry. Self-adjusting skirting, wear liners and dust curtains effectively control fugitive material. Support cradles eliminate belt sagging and pinch points. Engineered chutes are designed for optimal dust containment and air flow management.
Our components reduce harmful conditions, decrease maintenance and insurance costs, and increase overall productivity. Got dirt? We’re ready to assist with all of your bulk material handling problems.
the first open-cut coal mine in Queensland to be fully rehabilitated and relinquished.
The Queensland Government has accepted surrender of New Hope Group’s environmental authority and mining leases for the site after critically assessing the project and concluding that all rehabilitation requirements had been met in full, deeming the site safe, stable, non-polluting, and able to support grazing.
Chief executive officer Rob Bishop said New Hope Group made the decision to backfill the voids, reshape and rehabilitate the area to meet community expectations.
“The extensive rehabilitation works were conducted between 2014 and 2017, with ongoing works undertaken over the past eight years,” he said.
“The Chuwar Coal Mine site demonstrates New Hope Group’s commitment to being a responsible operator and ensuring
Stanmore Resources fully acquired the former BHP Mitsui Coal, previously renamed to Stanmore SMC after the company bought BHP Minerals’ 80 per cent interest through the acquisition of all the shares in Dampier Coal.
The subsidiary entered into a definitive share sale agreement to take over the remaining 20 per cent interest in SMC held by Mitsui.
Stanmore chief executive officer Marcelo Matos said the transaction allowed the company to consolidate its position as a leading metallurgical coal miner in the Bowen Basin in Queensland.
“Having 100 per cent control of South Walker Creek and Poitrel, as well as Wards Well and other projects, allows Stanmore to
land use.”
New Hope Group has long championed one of Australia’s most ambitious and practical land management programs.
“Our progressive rehabilitation program at New Acland returns mined land to agricultural and conservation uses while contributing to the region’s agribusiness industry,” Bishop said.
“To date, more than 740ha of land has been rehabilitated at
recognised by the Queensland Government, who has formally ratified 349 hectares of progressively rehabilitated mined land.
“At the time of the Queensland Government’s announcement, it was the largest single area of certified rehabilitation for an open-cut coal mine in Queensland.
“To put the size of the area in context, the certified, rehabilitated land at New Acland covers about 300 Suncorp Stadiums.”
maximise value amongst our assets in the region” he said.
The purchase price upon completion is $US380 million, and will be reduced by any dividends paid to Mitsui by SMC prior to completion.
Based on current market conditions, Stanmore anticipates it will continue to have sufficient internal sources to meet all ongoing
cash requirements and fund the acquisition without the need to issue any new debt or raise capital.
Stanmore owns and operates the Isaac Plains Complex in the Bowen Basin region, which includes the Isaac Plains mine and processing facilities, the adjoining Isaac Plains East and Isaac Downs mining areas and the Isaac Plains underground project.
Australia’s third-largest iron ore miner reported a profit of $US6.2 billion ($9 billion) in the 2021–22 financial year (FY22), down from $US10.3 billion ($15 billion) in FY21.
While the profit was down 40 per cent year-on-year, it still represented the second-highest earnings result in Fortescue’s history.
The fact Fortescue recorded a reduced profit in the face of record shipments of 189 million tonnes or iron ore reflects a steep drop in price for the steel-making material amid an economic slowdown in China.
The price for iron ore has been hovering around $US108 per tonne after a high of almost $US160 per tonne in March 2022.
Fortescue said the 189 wet metrics million tonnes of iron ore it shipped in FY22 “exceeded the top end of guidance” and was a major contributor to the bottom line.
“Guided by our unique culture and values, the team has delivered another year of record operational performance for FY22, contributing to net profit after tax of $US6.2 billion, the second highest annual profit in Fortescue’s history,” Fortescue chief executive officer Elizabeth Gaines, who is stepping down from the role and into the company’s minerals division, said in the FY22 results announcement.
The profits also mean a windfall dividend for Fortescue shareholders, with chairman – and major shareholder – Andrew Forrest taking home $2.34 billion.
“Reflecting our ongoing commitment to delivering enhanced shareholder returns, the board has declared a fully franked final dividend of $1.21 per share, bringing total dividends declared for FY22 to $2.07 per share,” Gaines said.
“This represents a 75 per cent payout of full-year net profit after tax, consistent with our stated intent to target the upper end of our policy to payout a range of 50 to 80 per cent of NPAT (net profit after tax).”
While commodity process and mining companies have been hit a series of COVID-induced hard lockdowns in China, analysts believe Australian miners are set to benefit from the expected return of their biggest export customer.
According to a recdn t report from Ausbil Global Resources Fund, China is “likely to accelerate growth coming out of recent hard COVID lockdowns through significant stimulus”.
“Throughout 2022 … we have seen the government setting up for more aggressive stimulus, which we expect to play out during 2H 2022,” Ausbil co-portfolio managers Luke Smith and James Stewart write.
“While rolling lockdowns remain in place, the implementation of stimulus measures is likely to be somewhat constrained, but the building blocks are in place to accelerate economic activity.
“Given China represents at least 50 per cent of commodity demand, we believe commodities are likely to benefit from Chinese stimulus which is yet to hit the ground.
“Metal markets are currently tightly balanced in terms of supply and demand, with limited excess capacity available in any commodities following an extended period of underinvestment.
“Metals inventory remains low. Although demand may soften from the west, markets are tight and any acceleration from Chinese demand should underpin prices that are already stretched due to low inventories and underinvestment in supply.”
BHP has rejigged its executive leadership team, to take effect from October 1.
Edgar Basto will be appointed chief operating officer and Geraldine Slattery will assume the role of president, Australia.
In his new position, Basto will enable acceleration in safety and productivity improvement across the group. He will have accountability for the continued transformation of BHP through the embedment of the BHP operating system, and for BHP’s global performance and improvement and health, safety and environment functions.
Since May 2020, Basto has been BHP’s president minerals, Australia. He has more than 30 years of operating experience across BHP’s minerals, including overseeing the company’s two largest assets, Western Australia Iron Ore and Escondida, and leading the global health, safety and environment team.
Slattery will be responsible for BHP’s Australian operations. From March 2019 until the completion of the Woodside merger in June this year, she had been president petroleum and led BHP’s business, which included oil and gas interests and development and exploration programs in the US,
Australia, Trinidad and Tobago, Algeria, Mexico and Canada.
BHP chief executive officer Mike Henry said the appointments would enable the miner to build upon the strong performance delivered in recent years to drive even better safety and productivity outcomes.
As a result of these changes, the leadership team will comprise:
• Chief operating officer, Edgar Basto
• Chief legal, governance and external affairs officer, Caroline Cox
• Chief financial officer, David Lamont
• Chief commercial officer, Vandita Pant
• President, Australia, Geraldine Slattery
• Chief technical officer, Laura Tyler
• Pr esident, Americas, Ragnar Udd
• Chief development officer, Johan van Jaarsveld
• Chief people officer, Jad Vodopija.
Denmark has long been at the forefront of the global sustainability push –and with good reason.
“In the early 1970s, Denmark was 99 per cent dependent on fossil fuels,” Her Excellency Pernille Dahler Kardel, Denmark’s ambassador to Australia, told Australian Mining
“When the oil crisis hit, Danish citizens had difficulty heating their homes and everyone was forced to abandon their cars on Sundays.
“This crisis galvanised the nation to move away from its reliance on fossil fuels and sparked what some might say is a national obsession with becoming green – long before it became fashionable.”
Denmark’s hunger to become green permeates across the country’s policy and practice, and the nation has become a world leader in wind energy and waste, while its bike culture is certainly no joke.
So how is Denmark, a country not known for its mining, assisting the
Australian resources sector with its own sustainability objectives?
Kardel put it simply.
“While Denmark is not a mining nation, it is a nation that has long looked for solutions to reduce energy and water consumption,” she said.
“And many of those solutions can be applied across multiple industries, including the mining industry.”
Danish original equipment manufacturer (OEM) FLSmidth has been supporting the sector for decades and has become a market leader for its pit-to-plant solutions spanning everything from crushing and milling, pumping, flotation and separation through to tailings management and beyond.
With a customer base brimming with the world’s leading mining companies across commodities such as iron ore, gold, copper, nickel and lithium, FLSmidth aims to achieve “sustainable productivity through innovation”, a vision embodied by the OEM’s MissionZero strategy.
MissionZero is centred around driving a paradigm shift of zero emissions, water waste, and energy waste in mining by 2030 not only for FLSmidth’s own operations, but also for its customers.
This ambition becomes possible when multiple technologies are combined. An example of this is FLSmidth’s MissionZero Mine.
“To achieve zero emissions, it’s not simply about electrifying the mine operation; it’s also about changing the flowsheet using different technology, to reduce the energy and water needed for production,” FLSmidth APAC mining president Tamer Eid told Australian Mining
FLSmidth found that if a mining company replaced a traditional wet milling SABC (SAG mill/ ball mill/pebble crusher) circuit, standard flotation cells and a cyclone sand tailings dam with the MissionZero Mine, the operation would realise a 30–45 per cent reduction in overall energy consumption, along with an 80 per cent reduction in water consumption.
The operation would also realise increased metals recovery.
“If we put in different technology together such as coarse flotation, REFLUX flotation, our market leading high-pressure grinding rolls (HPGRs) and dry stack tailings, you can actually change the flowsheet to reduce your energy and water demands significantly,” Eid said.
Comminution (making a big rock into a small rock) is estimated to use in the vicinity of 2–3 per cent of the world’s total energy.
“So when you have different technology that can change the game of comminution and reduce that energy consumption, that is significant,” Eid said.
FLSmidth’s OK Mill can use dry grinding instead of a waterbased method, saving on water and energy usage by 10–20 per cent kWh/t (kilowatt-hour per tonne) in the process.
HPGRs also use a dry grinding process and are therefore a more sustainable alternative than SAG mills and ball mills.
Miners will not only save energy with HPGRs, but they also achieve emissions reduction indirectly from the elimination of the steel grinding media needed inside SAG and ball mills.
Coarse flotation also reduces energy consumption.
“Coarse flotation enables miners to beneficiate with larger particle sizes, meaning they can grind less to liberate the ore, using up to 45 per cent less energy per kWh/t,” Eid said.
“With coarse flotation alone, you reduce the amount of energy needed and therefore the amount of energy generation required to deliver the same throughput, and it can be applied to existing circuits.”
There are also opportunities in tailings management.
“Instead of having a tailings pond, you can have dry stack tailings, where tailings are stacked on top of one another,” Eid said.
“That means you can recover up to 95 per cent of valuable water, utilise it back in the process, and you don’t have big tailings dams and high-water usage.
“Especially in the drier places of the world, such as some of the mines in the north-west and Pilbara region of Western Australia, water is at a premium. For some new mines, companies need to have different dewatering and tailings arrangements to enable these mines to be viable.”
Eid said while each of these technologies is effective independently, they produce even greater results when combined.
“We work closely with customers to help integrate these different technologies – using our end-to-end flowsheet capability. This delivers extra value and supports not only
changing the NPV (net present value) of the mine itself, but also fulfilling their corporate social responsibility goals,” he said.
Aalborg CSP is another Danish company with sustainability solutions for the Australian mining industry.
The company’s technology – which supports solar, boilers, heat pumps and storage – replaces the energy derived from fossil fuels with energy generated from the sun, which can be stored and distributed to satisfy demand for electricity, heating and process steam production, cooling and desalination.
Via the company’s heat exchanger and heat pump solutions, excess electricity from wind and photovoltaic (PV) technology can be converted to heat or process steam to operating conditions of between 40°C and 565°C.
The thermal energy solution can be integrated with other renewable energy solutions and Aalborg CSP’s high- or low-temperature storage technologies to secure a constant supply of energy.
Andreas Zourellis, Aalborg CSP’s vice president of technical sales –international markets, said the Danish EPC’s (engineering, procurement, and construction) solutions are well suited to the dry terrains of the Australian mining landscape.
“What is intriguing and special about the Australian mining industry is some mine sites are very remote and decentralised and they are in locations where the sun is shining for most of the day,” he told Australian Mining
“By combining a solar thermal plant, whether it’s low-temperature or high-temperature, with thermal battery as grid-scale storage, we can offer a completely decentralised system generating green heat or
The 36MWth (megawatt-thermal) system generates 1700MWh (megawatt-hour) of electricity per year and 20,000MWh of heat per year, and desalinates 250,000 cubic metres of water per year.
Zourellis said that while this case study is relevant to the agriculture industry, a similar energy system could be used in the resources sector.
“The Australian mining industry uses extensive amounts of energy to desalinate water or treat water that can be used later for mining processes,” he said.
“We can power a desalination unit with solar power and then provide fresh water. This is already up and running in Port Augusta.”
With water scarcity a global issue and saline wastewater ever-present on a mine site, desalination is a costeffective way of reusing water. Other than providing emissions free heat and electricity, Aalborg CSP’s thermal energy solution gives a desalination unit the green tick.
“Our world is water.”
DHI has an expert understanding
tools that can be used to understand their water impacts and conduct forecasting. For example, DHI’s FEFLOW tool has been used for decades to model open-pit dewatering, with many Australian Tier 1 miners implementing this solution.
The company is now moving into the digital advisory space through its MIKE Mine solution, which provides real-time monitoring, forecasting, scenario-testing and reporting of water operations on a mine site.
MIKE Mine – which DHI calls a “decision-support system” – sees the company build a web-based browser for mining companies, combining operational data and planning data in the process.
DHI then brings in forecast models to understand the direction of the site’s water operations, before combining all available data to create a water action plan for the mining operation.
DHI executive vice president Stefan Szylkarski said the ultimate goal was to provide mining operations with a real-time, automated water management system.
“Instead of someone running it (water management) manually, we’ve
dewatering is progressing in real-time, how their water operations are going at any one point in time.”
Advent Technologies is becoming another vital piece of the mining industry’s renewable energy puzzle.
Holding the intellectual property for next-generation HT-PEM (high temperature-proton exchange membrane) technology, the company develops, manufactures, and assembles complete fuel cell systems and supplies customers with critical components for fuel cells in the renewable energy sector.
Advent fuel cells are multi-fuel capable, meaning they work on hydrogen as it comes in many different forms (methanol, e-methanol, e-fuels, natural gas), thus eliminating the need for complex hydrogen infrastructures.
The company was listed on NASDAQ in February 2021 and has already deployed over 1000 telecom fuel cell units worldwide.
Advent’s fuel cells can provide up to 100kW of critical power and have proven an essential back-up power source for the telecommunications
alongside renewable sources such as solar and wind.
Advent’s vice president of sales and marketing Alan Kneisz said the fuel cells are instrumental where the use of grid power is challenging or not possible, which can be the case in the remote expanses of the Australian mining industry.
Kneisz said that while Advent can’t yet compete with diesel from a price perspective, fuel cells will become increasingly important as their total cost of ownership decreases and the world nears the net-zero thresholds of 2030 and 2050.
“We are working with the mining industry on smaller applications and, as our technology develops and we have more partnerships, we aim to develop them into bigger applications such as larger scale power stations,” he told Australian Mining
A global leader in oil maintenance, C.C. Jensen’s CJC offline oil filtration solutions reduce component wear and oil consumption on a mine site, in turn delivering major efficiency improvements.
C.C. Jensen provides solutions for various pieces equipment across a mining operation, whether it be a haul truck, crushing equipment, hydraulic loading systems, flotation and grinding applications in a processing plant, or one of many other options.
The filtration solutions can support diesel fuel, hydraulic oil and gear oil, enabling unique productivity and environmental outcomes for each application.
“With diesel, we want make sure that finer particles and water are not present,” C.C. Jensen’s business manager for mining in the Asia
Pacific Nicolaj Vestergaard Sandt told Australian Mining. “Water in diesel creates bacterial growth and will create rust in the bottom of the tank.”
Sandt said if contaminants get to the injectors or the fuel pump, they can get stuck in the fine tolerances and ruin the equipment.
“These are failures that have been common in the world for many years, but there is no need for those failures,” he said. “They shouldn’t be there if we remove the core reason why.”
C.C. Jensen can extend the lifetime of hydraulic systems by up to 95 per cent through oil filtration, Sandt
said, while the company’s gear oil solutions have significantly improved the efficiency of heavier applications such as crushers and mills, leading to a 60 per cent reduction in the use of spare parts.
C.C. Jensen has demonstrated its ability to avoid three out of four shutdowns, and one copper mine in Chile was even able to reduce shutdowns by 87 per cent by using the Danish company’s oil filtration solutions.
Despite almost daily in-line filter changes, the copper mine previously had to make oil changes every two
months as dirt and contamination accumulated in the oil.
Since installing offline oil filtration, however, the Chilean mine shuts down once a year for six hours for a single oil change, not only reducing downtime but limiting oil usage and the operation’s CO2 footprint.
As the Australian mining industry races towards a decarbonised future, there is going to be greater demand for environmental innovations. And as a global sustainability trailblazer, Denmark will continue to be an important part of the net-zero narrative. AM
The International Mining and Resources Conference (IMARC) will host more than 7500 attendees from over 100 countries at Sydney’s International Convention Centre from 2–4 November.
The conference, the largest of its kind in Australia, will provide the opportunity for domestic and international industry leaders to engage, learn, network and, most importantly, do business, while addressing the energy transition,
rising costs, skills shortages, social performance, and diversity within the resources sector.
IMARC is the most significant in-person gathering of Australian and international mining and resources representatives in almost three years and will be held under the one roof across a massive 17,000 square metres.
IMARC managing director Anita Richards said the response to this year’s event has been overwhelming.
“We’re welcoming a record number of delegates this year, representing 800 mining companies, and with IMARC
exhibitors increasing by 85 per cent since 2019, we’ve had to expand the expo floor by 40 per cent,” she said.
“The program will see over 450 speakers across six concurrent conferences covering global opportunities, industry collaboration, the energy transition, investment, innovation and more.”
A major networking and investment opportunity, IMARC is also the only event of its kind that uses enhanced and accurate networking technology to match delegates, allowing them to pinpoint new
business and investment opportunities and start crucial conversations.
“This is not just a conference and exhibition; real deals are closed on the IMARC floor,” Richards said.
The mining industry is facing more challenges than ever before, including supply-chain volatility, the rising cost of business, environmental, social and governance (ESG) pressures, navigating the energy transition, and growing social and investor expectations.
IMARC is a key forum that addresses these issues by gathering a wide cross-section of the mining value chain to share lessons and insights, and help each other navigate pathways to a sustainable and prosperous future, whether in exploration and investment, operational transformation, workforce growth or community engagement.
For example, IMARC’s Balance for Better, Next Gen programs and First Nations partnership initiatives aim to set the tone for a more diverse future, encouraging attendance from Indigenous delegates, providing opportunities for young people, and championing equality, with women in leadership positions, community roles and engineering a key focus.
The Next Gen program is for students, graduates, and future leaders. It provides an opportunity for the industry’s future workforce to network, learn and be inspired by leaders in mining, resources, and technology at Australia’s largest industry event.
Developed in partnership with the Victorian Government, the program is committed to promoting STEM (science, technology, engineering, mathematics) across the mining and resources industry.
Those in attendance at IMARC
Next Gen can expect to build relationships, learn about a diverse range of careers, gain insights from current leaders, meet over 470 companies representing all aspects of the mining value chain, and connect with mining C-suite executives, human resources managers, and key advocates for the future workforce.
Global mining leaders look to IMARC as a crucial opportunity to build on the progress the sector
is making towards sustainability, diversification and addressing the skills shortage facing the industry.
Fortescue chief financial officer Ian Wells will be speaking at IMARC. He believes talent needs to be a key focus across mining and resources.
“The mining sector is a great place to work with many opportunities, and while our sector is committed to training and developing Australians to be part of the workforce of the future, current acute skills shortages means
we must look beyond our borders for additional workers,” Wells said.
“As an industry, we must and can do more to build on our commitment to developing a diverse workforce that is reflective of society and to foster a workplace culture that truly embraces diversity and inclusiveness.
“We believe that diversity has been key to our success and we remain strongly committed to increasing female and Aboriginal employment across the business.”
COMMODITIES FROM ACROSS AUSTRALIA WILL BE DISCUSSED AT THE CONFERENCE.
While looking internationally, Fortescue has also invested heavily in local talent, including through the Billion Opportunities program which has invested more than $4 billion into Aboriginal businesses since 2011.
IMARC director of conference content and strategy Sherene Asnasyous said the forum would provide a platform for conversations about the next steps towards an essential increase in recruitment and retention across the industry.
For more than 30 years, we have been the global contact for high-precision and robust laser measurement technology for industries. With our sensors and in-house developed applications, our systems stand for more safety and efficiency. Our goal is to drive the automation of industry with easily retrofittable solutions. With 30 partners worldwide, we are always at your side.
A highly accurate 3D laser measurement system for automatic and dynamic mea surement of truck-load volumes during a passage for various materials such as stones, sand, ore or wood products.
no conversion factors
exclusion of manipulation
easy and fast installation
“IMARC will allow global leaders and emerging game-changers from the entire mining value chain the unique opportunity to come together under one roof and tackle not only the skills shortage but other urgent challenges facing the industry right now,” Asnasyous said.
“This is including the energy transition, rising costs, social performance, and diversity within the resources sector.”
More than 250,000 people are employed across the Australian mining value chain, making it one of the largest employment industries in the country.
Another key theme this year is innovation and technology, with local start-ups and leading global brands showcasing their latest products and services across automation, communication, safety and sustainability to create better, faster, safer, and more profitable operations.
“This industry has seen so much change since the last in-person IMARC event, but this November global delegates will finally have the opportunity to connect face-toface in Sydney, build relationships,
forge partnerships and do business,” Richards said.
AspenTech vice president and general manager of metals and mining Jeannette McGill said it’s vital the sector comes together to discuss challenges – especially where technology is concerned.
“Industry collaboration enables critical debate to build consensus amongst movers and shakers of the industry. Hence, it is necessary to keep the conversation going and agree to disagree before the industry, as a whole, levels up,” McGill said.
Other themes at this year’s conference include:
• accelerating the energy transition
• embracing digital technology and mining innovation
• investing in exploration and project developments
• m inimising disruptions and building resilience
• progressing ESG and strengthening social value
• redesigning the mining workforce and culture.
The theme of accelerating the energy transition will be especially important as the global mining and
resources industry continues to make a serious and collaborative effort in responding to the threat of climate change.
Miners joining this conference will benefit from hearing what their peers are doing in terms of climate resilience and decarbonisation.
An array of presentations from climate change experts, as well as discussions from renewable and energy providers and technology showcases, will provide insights as to what options and capabilities are available to meet decarbonisation requirements.
The brand-new three-day conference on accelerating the energy transition will focus on:
• powering mines with renewable energy sources
• low-carbon, low-energy technologies
• electrification
• climate resilience and decarbonisation strategies
• critical and future facing minerals
• t he role of fossil fuels in the energy transition
• hydrogen production and export.
Attendees will hear from METS
Ignited national cluster development
manager Andrew Scott and Pilbara Minerals chief operating officer Dale Henderson, among others.Asnasyous added that with such a diverse cross-section of the mining and resources industry attending, the event is a unique opportunity for collaboration to address evolving challenges.
“IMARC will shine a spotlight on the role the METS (mining equipment, technology and services) sector is taking in driving the global energy transition, how it is bringing innovation to the exploration and development of new future-facing resources, and how it is helping balance the needs of the developed and the developing world, as well as local communities and environments, in the resource transition.
At its core, IMARC creates a global conversation and is all about the business of mining and resources.
It provides extensive opportunities for collaboration, knowledge-sharing and crosssector engagement to help drive a smarter, more productive industry of the future.
“We’re a company that can develop something exactly for what a customer needs for the exact purpose.
“What separates us is that total service of being able to design, engineer and fabricate a product all under the same roof.
“It’s been engineered, it’s been certified, and it’s gone through an extensive process to ensure it outperforms its use.”
Certification is critical to the design and engineering of any mining equipment, let alone material handling items, which navigate extreme weights to ensure goods are stored or transported safely and efficiently from one place to another.
“The industry’s understanding of why things need to be safe, why things need to be certified (is improving) and it also goes back to the method of use – having correct equipment that’s fit for purpose and engineered for purpose that’s being used in the correct manner,” he said.
“Yes, it’s about production, and yes, it’s about making money, but you don’t want people out there risking their lives to satisfy the bottom line.
“Sometimes it is more expensive and that’s the thing – you’ve got to think of cost and value. They’re two very different things.
As one of Australia’s leading mining services companies, Bend-tech Group offers a holistic approach to solution management, ensuring mining companies or contractors can access a product that’s been specially designed for them and their operation.
This is particularly true in the material handling sector, where Bend-tech not only has an extensive product offering but also the capacity to customise solutions to suit the intricacies of a specific operation.
“We can basically develop a material handling device or solution for almost anything,” Bend-tech marketing manager Rhys Werndly told Australian Mining
“We’ve got a team of on-site consultants, so we might get a request for a site visit that might be a material handling or equipment handling issue that is maybe being done manually or being done unsafely.”
Once Bend-tech receives the request, its team attends the site to better understand the situation, including the weight of the item, how it is lifted and where it needs to be placed, before developing a concept to make it safer and more efficient.
“Everything we do is engineered and certified to Australian Standards,” Werndly said.
“So you can be sure that if you have a two-tonne item, the material handling device or solution you’re using is designed, engineered and certified to handle six tonnes – it has to be certified to handle three times more than its loading limit.”
Once a material handling concept has been developed, it needs to be approved before progressing to engineering and into production. Bend-tech handles the process from initial consultation to manufacture, ensuring customers receive an end-to-
“If it’s not certified, then it hasn’t been proven to perform beyond its use,” Werndly said. “If someone’s just welded up some steel and is starting to lift stuff with it, who knows when it could break or fail?
“That’s why we get so much work, because our equipment is certified. It’s a requirement for Safe Work audits. Some of the engineering processes we need to go through to get one of our products on-site are extreme.
“Whether it’s an access platform or any other materials handling product, mining companies literally won’t use it if it’s not certified.”
Werndly said the Australian mining industry is moving in the right direction regarding the prioritisation
“Having something that might be more expensive on face value, the value that brings to your personnel, their peace of mind, their productivity, their efficiency in real-time because they know what they’re using is safe. That may not be measured and probably should be.”
To complement its holistic, end-toend approach to solution management, Bend-tech offers a comprehensive suite of products for the material handling sector.
This includes – but is certainly not limited to – lifting and handling equipment, maintenance tooling, storage benches, containers and racks, trestles and work stands.
Bend-tech’s emphasis on engineering and customising certified,
WHERE
MORE
Mining companies are forever seeking new ways to lower production costs for material handling and processing applications.
In partnership with OPS Group, Astec Australia is doing just that.
OPS and Astec have maintained a strong and exclusive partnership since 2014, with OPS supplying the mining industry with technologically-advanced equipment from Northern-Ireland-based Astec subsidiary, Telestack.
Telestack continues to invest heavily in its Omagh facility as part of a long-term strategy to futureproof its capacity to support the development of an extensive range of world-class, innovative and quality products.
This includes its partnership with Astec Australia and OPS.
Astec Telestack specialises in the complete design, manufacture, installation and commissioning of mobile bulk material handling systems across a range of sectors, including mining.
And with more flexible stockyard system requirements and the push for greater cost efficiencies in the stockyard equipment space, the Astec Telestack range has become an important option for operators who require innovative equipment with custom-designed features and high build quality.
The equipment is robust and built to operate under difficult mining conditions.
“The Telestack equipment has many advantages; it’s made in a quality-assured factory in Northern
Ireland, by a global OEM (original equipment manufacturer), and the products are manufactured to a high quality,” OPS Group chief operating officer Ben Suda told Australian Mining
The Astec Telestack range has also become more popular with the re-emergence of heap leaching in the Australian mining sector. Heap leaching is an industrial mining process used to recover minerals from low-grade ore through a series of chemical reactions.
Suda said heap leaching enables mining operations to avoid more intricate ways of beneficiation.
While smaller heap leach stockpiles could be stacked by excavation equipment, when an operation chooses to build a larger heap leach pile it would be more appropriate to use a stacker.
This is where the Astec Telestack range comes to the fore.
The modular configuration of the product range results in lower capital expenditure and running costs, which is a distinct departure from traditional large and sometimes cumbersome stacking machinery. It is also more affordable than bespoke engineered solutions.
“Traditionally, sites often have a system designed specifically for their requirements, which requires significant engineering hours, and they’ll typically come up with a design that’s built for that particular application,” Suda said.
“But in addition to engineering hours, there’s also contingency applied and generally a large construction component specific to that installation must be entirely amortised over the one build.
“In my experience, you will see costs much greater with a site-specific engineered solution compared to utilising an existing Telestack product.”
Suda said there’s also less risk in opting for a modular solution such as the Astec Telestack range, because the customer knows exactly what they’re getting and can have confidence that it has a proven track record.
“The performance of the Telestack range is predictable and basically everything we manufacture is pre-assembled and tested in the plant,” he said.
When working with a customer, OPS will point to a similar case study to ensure they have a reference point and can see the application in play.
“Typically, we’ll be able to find an application we’ve already installed that is similar to what we’re supplying, so the customer can see how that’s working, possibly get a reference from that site or, in some instances, even visit that application,” Suda said.
“That gives them more peace of mind that what they’re seeing is what they’re getting.”
Telestack stacking systems offer automatic stockpiling capability, eliminating material compaction and resulting in a process that reduces costs per tonne and increases the capacity and quality of the material.
The system is also designed to be easy to transport.
“Our Telestack equipment is modular, in many cases easily containerised and able to be moved by standard road-going trucks,” Suda said.
“This supports our remote clients such as remote Australian mine
sites and other remote markets such as Indonesia. Here, you sometimes don’t have the transport corridors you might have in more centralised locations.
“Because these machines can be containerised, you can break them down into assignments easily and load them into trucks, so you can get them on-site and then reassemble them in modules. So you’re not building the plan from scratch.”
With transport practicality comes build practicality and Suda said once the Telestack machine arrives to the mine, it can easily be assembled by the on-site team without the need for specialist support.
“Once you’re on-site you don’t require the contingency of a construction team completing significant site preparation or months of engineering to configure the equipment, because our products have already been pre-assembled and tested prior to being modularised for transporting.
“Our customers place an order and we start building the Telestack machinery immediately, which substantially reduces time and costs.
“In some instances, where flexibility allows, we may offer an alternative solution based on existing stock availability to reduce lead time further.”
The OPS team works very closely with end-users, ensuring the Astec Telestack equipment is tailored to specific on-site conditions.
“Customisation is an important aspect of our service delivery,” Suda said.
“Depending on the site location, there may be a requirement to meet specific safety standards, including the positioning of walkways and access points, and other key operating processes and procedures.
“Our standard mobile units can still be customised to meet certain customer requirements, including the ability to modify belt widths, install additional guarding and other key components, including roller changes, depending on the type of material being transported.”
The Astec Telestack range covers all facets of moving and processing material, capable of capacities in excess of 3000 tonnes per hour.
“Because our products are mobile, they are hugely flexible, and if the
mining operation has a relatively short life, then the equipment can easily be redeployed to another location or re-sold,” Suda said.
“Our products can possess strong residual value, which isn’t always the case with a site-specific engineered solution.”
OPS has invested in branches across Australia as the group expands and diversifies, supporting specific mining regions with capital equipment – either for sale, hire or demonstration purposes – as well as full service and parts support capability.
The company offers process engineering, on-site commissioning, training and maintenance, with a team committed to delivering quality and value through its ‘whole of life’ equipment service offering.
OPS Group and Astec Australia also have a parallel agreement through OPS subsidiary Mineral Processing Solutions (MPS), providing another pathway for Astec’s bulk material handling equipment.
MPS distributes Astec’s Kodiak cone crushers to the Australian mining sector, including sites across
Western Australia, South Australia and the Northern Territory.
MPS managing director Shane Czerkasow said reliability is a key that sets Astec equipment apart.
“The Kodiak 350+ cone crusher is fit-for-purpose. It’s been designed and built for use in the rugged Australian mining environment,” Czerkasow said. “That’s Kodiak’s competitive advantage.
“In the case of the 350+, decades of experience and innovative design have combined to produce a highlyreliable, low-maintenance, operatorfriendly crushing unit.”
The Kodiak incorporates a unique roller bearing design that, according to Astec, increases energy efficiency and reduces operating costs by up to 50 per cent. In addition, the crusher is equipped with the Kodiak control system (KCS) ,which allows for continuous monitoring and on-thefly adjustments.
Whether it’s an Astec Telestack stacker, a Kodiak cone crusher, or any other bulk material handling machinery, the Australian mining industry is better for Astec and OPS Group’s long-term partnership. AM
THE TELESTACK EQUIPMENT HAS MANY ADVANTAGES; IT’S MADE IN A QUALITYASSURED FACTORY IN NORTHERN IRELAND, BY A GLOBAL OEM, AND THE PRODUCTS ARE MANUFACTURED TO A HIGH QUALITY.”
Remote, real-time monitoring of belt cleaners from an intuitive digital dashboard, Flexco Elevate is the first-of-its-kind technology that delivers predictive data-driven insights to manage belt cleaner performance. Move from reaction to prediction and optimise belt maintenance for your operation.
Scan to learn more.
“That’s the thing about DYNA; we’re always developing new and improved versions of our HDPE guards, listening to customers when they express, as a priority, the need for greater visibility or increased spraythrough capability,” Greaves said.
“We respond to their feedback and, through iteration, go about designing, developing and manufacturing a new and improved version of the HDPE guard.”
The improved guards are versatile and able to be configured for access platforms, conveyor pull wires, retractable idler roller frames, metal detectors, and belt change stations, while maintaining strong chemical resistance.
“If you’re dealing with a product that is corrosive, HDPE guards tend to resist pretty much most common chemical products or by-products that are found on mine sites,” Greaves said.
The sustainability benefits of the HDPE plastic guards are significant, and within the mining industry DYNA Engineering is at the forefront of the circular economy by making its panel components infinitely usable.
After designing, manufacturing, and distributing a new conveyor guard system for mining operations across Australia, DYNA Engineering listened to customer feedback and has undertaken further modifications to its high-density polyethylene (HDPE) plastic guards.
“Since releasing our HDPE guards in 2019, there have been requests from customers to see greater capability for the use of high-pressure hoses in order to more easily spray water beyond the panels, as well as a need for increased visibility in the configuration of the guards,” DYNA Engineering general manager Thomas Greaves told Australian Mining.
“The mesh size for HDPE guards is a lot thicker than steel mesh, so recently we have developed a different type of mesh. It’s triangular in shape, creating increased viewing
angles, addressing our customers’ visibility requirements.
“We have also developed a solution for high-pressure hose use, which is superior to our original squareshaped guards.”
Using DYNA Engineering’s HDPE plastic conveyor guards rather than more traditional steel mesh guards comes with some significant benefits. Chief among them is the fact the lightweight HDPE guards eliminate the stress of heavy lifting, while still being robust and easy to install.
“In terms of safety, when lifting them on and off conveyor systems workers are exposed to less repetitivestrain injuries,” Greaves said.
Installing and removing the HDPE plastics guards takes only minutes, limiting the amount of time spent around the conveyor and reducing the risk of accidents occurring during periods of maintenance.
Conveyor belt systems are among a mine site’s most high-risk areas, so the ability to limit time spent around them is of significant benefit to workers.
The fact the HDPE panels can be installed or removed quickly also limits downtime, and their makeup helps limit maintenance.
“HDPE guards don’t corrode or rust, nor do they require surface treatment such as galvanising or painting,” Greaves said. “Often conveyors are not properly guarded because of corrosion. Steel mesh guards rust, they break, and then they aren’t replaced, so the HDPE guards simply stay in place longer, requiring less repairs and maintenance and, if need be, are able to be replaced quickly.
“They are very cost-efficient due to their longer life spans … with a lifespan in the range of 10 to 15 years.”
DYNA is always looking to innovate but doesn’t make any decisions about its products in a vacuum.
“We use recycled and recyclable plastics, the kind of plastics that are commonly used in bottles and containers, and once they have completed their service life they can be recycled into new HDPE plastic conveyor guards,” Greaves said.
“We firmly believe that recycled material is the future, and we are determined to see the rest of the industry embrace a greater focus on sustainability.”
DYNA’s latest HDPE plastic conveyor guards are manufactured at the company’s new workshop south of Perth.
Customers have already provided positive feedback, impressed with both the design improvements and with the product’s sustainability credentials.
“Our customers want to use a product made out of plastic that can be recycled, that isn’t going to end up in landfill,” Greaves said.
“And our HDPE guards are fundamentally sustainable, assisting the mining industry establish sound environmental outcomes.”
Improved throughput combined with lower expenditure and operating costs. These are just some ways you could benefit from working with the only OEM that provides market-leading solutions throughout your process chain.
But complete pit-to-plant coverage means more than just solutions - it means holistic knowledge, optimised practices and an integrated flowsheet approach when it comes to identifying ways to improve your operations and lower your environmental footprint.
And since we also deliver a best-in-class digital solutions, we can work with you to maximise productivity throughout your mine operations. Discover how we can take your productivity to the next level.
set on rolling idlers, wrapped around large steel drums at each end, and driven by a high-torque motor.
In most applications, a conveyor belt moves at a relatively constant speed, commonly running
focused on the race. If this athlete became tangled in a conveyor belt travelling 1.5mps, they would be carried 0.27m before even realising what has happened.
A ‘regular’ worker would likely require considerably more time to react.
For simplicity’s sake, we can assume it would be twice the athlete’s reaction time, so the worker would be pulled twice as far, introducing the potential to strike many more components or to be pulled farther and harder into the first one.
In addition, most conveyors are engineered with the ability to start remotely. The system may go from dormant to active at any time at the push of a button, and that ability can suddenly catch a worker unaware, leading to serious injury or death.
“When a conveyor belt is moving, there will usually be more tension
stored energy.”
Marshall said that a system under tension will always try to approach equilibrium; that is, it will try to release the energy. This release will likely come in the form of a pulley slip, which occurs when the belt slides around the head pulley to equalise the tension.
The distance the belt will move is proportional to the amount of tension stored and the belt’s modulus (elasticity), possibly several feet. If a worker is on the belt or close enough to be pulled in during this sudden release of energy, injuries or death can occur.
According to Marshall, there is a very simple rule of thumb when it comes to conveyors.
“If it’s moving, don’t touch it,” he said.
“The most common way to prevent inadvertent contact is with suitable guarding that renders the moving components inaccessible.”
For maintenance or repairs, procedures for lockout/tagout/ blockout/test-out should always be followed when working on a stationary conveyor, and systems should be equipped with antirollback devices (also known as backstops) on the head pulley.
Many of the moving parts on a conveyor belt system are rotating components. These include idlers, drive shafts, couplings, pulleys and speed sensors.
Items rotating at a high speed pose the risk of entanglement or entrapment.
“All moving machine parts should be guarded with adequately
constructed, properly installed, functioning and well-maintained guards,” Marshall said.
A conveyor features many pinch points – components that the belt actually touches or comes near –including the drive pulleys, snub pulleys, idlers, stringer, chute walls and deflectors.
If a worker’s limb travels with a conveyor belt, it will meet one of these components. The limb, as well as the worker to whom it’s attached, will become trapped between the belt and the obstruction.
The same thing can happen with a tool, which can pull a worker into the entrapment faster than the person can let go.
“Effective fixed guards should be absolute in their protection,” Marshall said. “Workers should not be able to reach around, under, through or over the barrier separating them from moving components.”
Many of the fatalities around conveyors have happened when a worker was cleaning fugitive material from the structure or components of a conveyor system.
The process of cleaning may put a worker in proximity to a very dangerous machine. The need to shovel, sweep or hose off accumulations puts the person within
arm’s length of the conveyor, and often closer.
Airborne dust can cause numerous health risks, ranging from material buildup in the lungs to explosions.
Categorised as either ‘respirable’ or ‘inhalable’ according to particle size, dry, solid dust particles generally range from about 1–100 microns (µm) in diameter.
According to the Environment Protection Authority (EPA), inhalable coarse particles are 2.5–10µm in size. They are typically caught by the human nose, throat or upper respiratory tract. In contrast, fine respirable particles (under 2.5µm) can penetrate beyond the body’s natural cleaning mechanisms (cilia and mucous membranes), travelling deep into the lungs and causing long-term or chronic breathing issues.
While it’s virtually impossible to prevent all fugitive material from escaping a conveyor structure, taking practical steps to minimise it as much as possible helps reduce the dangers it can introduce.
When cleanup is necessary, performing the job while the conveyor is running should not be an option.
Operators concerned with the cost of lost production from stopping a conveyor to clean need only consider the consequences of an accident to confirm the wisdom of this rule.
Until recently, the engineering of belt conveyors to carry bulk materials hadn’t changed much in the previous half-century, despite the fact that virtually every requirement for safety, regulatory compliance and production performance has been raised during that time.
Standards continue to tighten and industry best practices now often exceed government requirements.
“Using these new and emerging technologies, even poorly performing conveyors often don’t need to be replaced or rebuilt, but merely modified and reconfigured by knowledgeable and experienced technicians installing the right modern equipment,” Marshall said.
“Specialised conveyor training and trusted resources from global suppliers are helping to raise operator awareness to make conveyor systems cleaner, safer and more productive.”
Give tyres with large injuries a second life.
Send tyres with large injuries back into production and see thousands of hours of like-new performance with Ultra Repair™. Our proprietary process effectively repairs injuries on all areas of the tyre, restoring its original strength and integrity at a fraction of the cost of new tyres.
Lincom has been a trusted partner of the Australian mining industry for decades, supplying operations with some of the best screening, crushing, bulk handling and recycling equipment on the market.
The company’s support of the mining sector goes hand-in-hand with its support of the community, so it was a significant milestone when Lincom was officially certified as an Australian Owned business in July.
The well-known certification helps customers to easily identify Australian companies, providing them with greater confidence about investing in a company that benefits Australia first.
Lincom chief executive officer Stephen Watterson said that while
the company has grown significantly since it was established in 1998, it has always remained grounded and true to its roots.
“The significance of getting the Australian Owned certification is that we are a proud Australian company,” Watterson told Australian Mining
“We want the Australian mark against our name so people know and can see that we are investing in the country, we’re investing in the people and we’re giving back to community through employment and by our continued growth in all those areas.
“For our customers, who are handing over a lot of cash for the equipment we supply, it’s important for them to understand that we’re investing in them as much as they’re investing in us.”
Watterson said the ability to provide employment is one of Lincom’s biggest contributions to the community.
“First and foremost, we do as much as we can to offer employment opportunities to the local areas that we operate in,” he said.
“We run an apprentice program for young school-leavers where we supply apprentices a kittedout toolbox as soon as they sign up, which they use all the way through to getting their papers. We then hand that toolbox over to them when they become a qualified tradesperson.
“We want to give school-leavers employment and the opportunity to organically grow within Lincom because that’s another way we can support the community.”
Lincom recently supplied two radial stockpilers to Adani’s Carmichael coal mine in Queensland, which Watterson said was a significant achievement for the company.
Lincom took full responsibility for the logistical intricacies of getting the stockpilers on-site by the deadline, which was no easy task given the supply-chain disruptions currently affecting the Australian mining industry.
But Lincom delivered the machines on budget and ahead of schedule.
“There were contracts and things in play, but we formed a strong relationship with Adani and the company felt comfortable because we were the decision-maker, and we were in control of our own destiny,” Watterson said.
“What we said we would deliver, how we would deliver it and when we would deliver it – that was all on us.
“When you’re a family business like ours – where decisions can be made fast, and we can quickly act on issues that may arise – for us to be able to deliver the machinery on time gives them comfort that we certainly mean business.
“And it proves that we can deal with both big companies and small companies.”
With a strong footprint in New South Wales and Queensland, Lincom is focused on growing its presence in Western Australia. It has a stockholding facility in the Perth suburb of Henderson where it has a rental fleet, sells new and used equipment, and offers spare parts and consumables.
A WA-based service team is capable of completing on-site repairs, as well as a rebuild facility, which Watterson said can give machines a “birthday”, removing the need to invest in new equipment.
“For customers who struggle to get the capital needed for a new machine, we can refurbish their existing equipment,” he said.
“We’ve done quite a lot of rebuilds in our Henderson depot, which is fully kitted out to be able to accommodate that.”
Watterson said the sky’s the limit regarding Lincom’s WA aspirations.
“We’ve certainly got down growth plans for the west and other parts of
the country,” he said. “Anyone can sell a machine, but it’s the back-up, it’s the relationships, it’s everything that goes with the journey, rather than just the machine sale.
“We want repeat business and we get repeat business, and that philosophy is the same whether we’re servicing customers on the west coast or the east coast.”
AM
Flender has traditionally worked through business partners to provide support for its industrial gearboxes.
However, according to Flender’s of Australia and New Zealand Kareem Emara, the original equipment manufacturer (OEM) has developed a new business strategy.
“Flender’s gearboxes have a proven track record and are an industry benchmark,” he said.
“Our products have some of the largest install bases in Australia and are known for their reliability and quality, backed up with in-depth technical expertise.
“We have been involved with the industry for some time and knew we could further adapt our portfolio and products based on continuous improvements. Part of this was to improve our service and support offering and establishing a dedicated local presence in Australia.”
Flender invested heavily in growing its local operations, opening facilities in Rockhampton, Queensland, and Perth, Western Australia. It also acquired the Finnish wind turbine gearbox manufacturer Moventas in April, along with facilities in Melbourne.
In addition, the company aims to open its new Sydney facility by the end of the year to further support its New South Wales customers. The facility will be just over 1800m2 and has the structural capacity for a 50-tonne crane.
Emara said the new location will have all of the equipment required
to deliver an OEM standard to its customers.
“It’s important to be close to your customers,” he said. “It allows you to be more agile and respond to their needs as quickly as possible.
“All of our facilities can operate 24 hours a day if needed, letting us turn things around quickly.
“We can also provide proactive support, using our OEM knowledge, vibration analysis and condition-
monitoring expertise to help them avoid unplanned shutdowns.”
Flender’s facilities are set up to support the entire lifecycle of a product, with teams that can provide everything from installation to decommissioning. It can also leverage global support from its worldwide network – Flender has extensive research and development teams in China and Germany that provide experienced aid in even some of the most unique of cases.
Emara said there has been positive feedback from the industry, which appreciates the company’s customer-driven focus.
“Having the right people, with the right knowledge close at hand means our customers have everything they need to thrive,” he said.
“Flender equipment is built with reliability in mind, with some of our assets still in use since they were installed in the 1970s.
“We aim to continue serving our customers with the latest technologies and will support them with digitisation and condition monitoring to ensure they get the most out of their equipment.”
Flender offers comprehensive services for gear units and couplings across the entire lifecycle. In addition to spare parts services, repairs, maintenance and technical support, the company can also provide various retrofit and modernisation options, along with diagnostic services. The standard repair service includes all necessary measures to investigate the condition of a product and restore its functionalities through repair or replacement of the damaged parts or assembly groups.
Flender’s repair analysis service includes a complete product assessment as well as a preliminary estimation of the repair costs and duration. To help achieve an optimum balance between plant availability and capital, Flender can analyse plant inventory and available spares in stock to deliver tailored recommended actions.
The bulk handling industry has been pushing for a lighter and more durable conveyor roller as it looks to boost operational efficiency and the volume of materials being transported.
As an alternative to heavy metallic rollers, high-density polyethylene conveyor (HDPE) rollers are being used more in conveyor operations due to their low weight and ease with which they can be changed out.
Matching the needs and demands of the bulk transport industry, PROK has long provided a range of HDPE rollers to fulfil the bulk handling needs of mining operations.
Due to the number of rollers required in longer transport systems and the forces generated on them through constant movement, rollers need to be regularly replaced – a task that poses manual handling safety risks.
PROK engineering manager Ray Anderson said the HDPE rollers
are becoming increasingly popular.
“We’ve seen an increasing demand from our customers and from the market to move towards a lighter weight roller,” Anderson told Australian Mining
“This is made worse with traditional heavy steel rollers. So there’s been demand from the market and the industry to move towards a composite lightweight material to reduce potential injury risks, which is what we have been providing with the PROK HDPE.”
PROK has facilities across the world, and the company’s strong client base enables insights into what customers look for in their conveyor solutions.
“Our engineering team has done a lot of research and development on this product over many, many years,” Anderson said.
“Before we launched the product we worked with the industry on various testing processes, with different loads and conditions in place to ensure the rollers performed the way they were supposed to once they hit the market.
“We have installations across the globe and while we started with predominantly iron ore, we’re starting to see our products used across many different commodities globally.
“Traditionally, mining companies would use steel rollers, which are quite heavy. And when you’re changing out rollers consistently throughout the day, you’re confronted with a manual handling safety issue.
Understanding that conveyor rollers need to be replaced over time as they experience wear, PROK has implemented a conveyor wear indicator in the HDPE rollers to limit the amount of downtime through unexpected failures and subsequent replacements.
The PROK HDPE yellow tube combines with a green inner layer to act as a visual wear indicator for maintenance teams. The co-extruded HDPE tube changes colour after 5mm of wear, allowing maintenance and scheduling teams the ability to identify worn rollers, localised wear and, in turn, upstream conveyor issues such as excessive carry-back or burden overflow contacting the roller.
As an Austmine member for many years, PROK has benefited from the events and connections the industry association offers, as PROK marketing manager Ryan Silvester explains.
“There’s many different channels and connections we have through our partnership with Austmine. They’ve been a great support,” Silvester said.
With reliability a key focus for PROK, the HDPE roller offers a lighter, safer and more efficient roller for conveyors in Australian mining.
We know that the mining industry is under significant pressure to manage quality, safety and operational performance with a rapidly changing workforce.
We understand the need to manage the complexity of high risk work, often performed by a large contract workforce subject to dynamic challenges such as:
• The ability to rapidly onboard large and diverse cohorts
• Maintaining quality and safety in this dynamic environment
• Keeping on top of constant requests and issues raised due to unforeseen situations
• Working to ensure good on-site communication and documentation when there is a major change.
All while maintaining a safe, efficient and compliant operation.
Harry
Ask Harry is a voice-based smart assistant. Call and speak to Harry using your phone or two-way radio. Harry uses AI technology to understand requests, lookup information or even make calls to the right people.
Call Harry to:
• Send off a hazard report, converting voice-to-text. Follow-up and keep the reporting person in the loop
• Report a defect, then optionally escalate it with a call through to the right person
• Request critical information on a changed condition or unforeseen situation.
Acritical component in the conveyor system is the transfer point where the bulk material is transferred from or to a belt.
If the transfer point is not designed and maintained properly, bulk material may fall off the conveyor system, resulting in spillage.
The moment the material becomes fugitive, it instantly becomes a hazard, adding a burden to the operating costs, productivity, and efficiency of the plant. Spillage also significantly reduces equipment service life and poses great risk to safety of the employees.
Spillage from conveyor may be the result to various problems, so it is important to find out the root cause and address it at its source. A comprehensive spillage control audit helps in identifying that cause and list out practical solutions.
Common causes of spillage include off-centre loading of material, belt sway, improper sealing of the skirt zone, inadequate belt cleaning, overloading of belt, poorly designed transfer point, and more.
With implementation of proper control measures, however, efficiency and productivity of the plant can be
improved, and operating costs and safety risks reduced.
The major steps to be followed to achieve a spill-free transfer point are load zone containment, proper belt support, carry back control and control dust generation.
This is one of the key factors to be considered when implementing any spillage-control measures. Perfect alignment of a belt while in operation – without any sway – must be ensured to prevent spillage.
There are many things that can cause the belt to sway. The most common are carry-back of material,
off-centre loading, improper belt tension, mis-aligned pulleys and idlers, and faulty splice. Heavy cross winds can also cause belt sway on open conveyors.
Improvements like the provision of proper belt cleaning, replacing wornout pulley lagging, and ensuring pulley alignment helps to control the belt sway within acceptable limits.
While it is ideal to address the root cause of the sway and correct it, using a belt tracker is a quick workaround and is commonly practiced.
A belt tracker consists of the tracking roller and a sway-sensing mechanism (usually a roller).
steer the belt back to its true line.
Multiple belt trackers are typically installed on a conveyor depending upon the length of the belt and severity of the problem. Belttracking rollers are rubberised to increase the traction between the roller and the belt and improve tracking performance.
Dynamic belt tracking systems use advanced technology to provide precision-sensing and positive, multi-plane movement to track the belt continuously and ensure its true running.
Well-engineered modular transfer chutes are particularly important in order to contain materials prone to becoming fugitive.
Engineered transfer points reduce the impact force, reduce dust generation, and ensure centreloading and smooth transfer of material to the receiving conveyor, thus eliminating causes of spillage.
A properly designed skirting system combined with skirt seals and wear liners creates an effective sealing system that contains the material well.
Selecting the right type of skirt sealing is critical and must be done with the objectives and application conditions in mind.
Sufficient attention must also be given to the skirt board design. Too much gap between the skirt board and the belt results in ineffective sealing, regardless of the skirt sealing choice.
Skirt board enclosure should have adequate volume to contain
induced air. Dust curtains may be provided inside the skirt board to create dead zones that promote settlement of airborne dust.
The success of load-zone containment depends hugely on the close tolerances that can be maintained for the skirt seal. The impact of material often leads to sagging of the belt and gaping of the seals at the point of impact, thereby allowing material to become fugitive.
To overcome this issue, proper support should be provided beneath the belt at the impact zones. Impact cradles should be used below the load zone, creating a low-friction bed for the conveyor belt and preventing sagging.
By providing a firm support to the belt, the skirt sealing forms a close seal with the belt and prevents spillage and leakage of air-borne dust. A well-designed impact bed also dampens the force of material on the belt, resulting in extended service life.
New innovations such as dynamic impact beds with garland profile offer three-dimensional relief and are
highly recommended for load zones with heavy impact, spillage, and mistracking issues.
Carry-back is among the most common causes of material spillage in any plant. It often leads to a host of operational issues such as belt mis-tracking, idler seizure, uneven belt wear, and accelerated belt cover wear.
Spilt material also poses safety risk to the workers. Belt cleaners are the most effective way to combat material spillage due to carry back.
A well-engineered belt cleaning system effectively eliminates carry back, thus reducing material loss and clean-up costs. It also improves plant productivity and the service life of belt components.
A multiple-cleaner approach, varying upwards in the efficiency of cleaning, is often recommended to solve the carry-back problem. This essentially consists of at least a primary cleaner installed on the head pulley, clear off the material stream, and a secondary cleaner installed at the point where the belt leaves the discharge pulley.
Depending upon the severity of carry-back, additional cleaners may be installed. It is always recommended to refer to a belt cleaner selection chart provided by the manufacturer to select
the right type of cleaner for the given application.
A vast range of belt cleaners is available in the market; however, proper selection of the one to suit the application condition and operating parameters is key to meeting the objective.
It is equally important to properly install and maintain the belt cleaners to get the optimum results. Service and maintenance-friendly features like quick-release tensioning systems and track-mount blade cartridges make the life easier for the technicians and can cut downtime.
Properly setting up the equipment plays a major role in achieving the objectives in a sustainable manner. Due importance must also be given to regular maintenance and performance monitoring of the installed equipment.
Partnering with a manufacturer offering all the spillage-control accessories, as well as maintenance of the equipment, is the best way.
Manufacturers with well-equipped research and development facilities can make quick changes to their products to meet site requirements, which is better than using a standard product that might not be suited to the given application.
These companies provide a holistic solution, including spare management, helping to eliminate major challenges.
While plants should be wary of manufacturers that offer only standard products that cannot be customised, they should avoid switching between suppliers without acknowledging the importance of maintenance. This would result in dumping the plant with a variety of equipment from several suppliers, none of which deliver the desired results. AM
An all-compatible ABB industrial drive, offered in cabinet-built drives and with drive modules, to control applications in mining. Designed for harsh conditions, with long maintenance intervals, they have an output power up to 6000kW.
Cabinet protection IP42 as a
standard, with optional IP54 changed takes 98% of the heat losses away from the drive avoiding the need for additional ventilation the same sized air cooled drive
No air filters to be External liquid cooling system
Up to 30% more power versus Harmonic current distortion is significantly reduced to <3%
Continental is at the forefront of reducing energy costs and driving efficiencies in material handling.
“In general terms, steel cord conveyor belting on overland conveyor systems is used for large-scale materials handling applications due to the demanding nature of modern mining operations, with significant belt tensions required to transport materials at high capacities over very long distances,” Continental Conveyor Belt Group business development manager Scott Little told Australian Mining
Continental is engaged in a process of supporting carbon-neutrality targets with products that can be integrated within existing material handling systems and servicing regimes.
This ongoing development is not easy, however, as the low-carbon products must withstand the many stresses associated with operating around-the-clock and in harsh mining environments.
Continental’s Eco Series conveyor belts reduce power consumption by as much as 30 per cent, which positively impacts emission-reduction strategies as mining operators strive to meet carbon neutrality.
In conveying systems, the belt runs over idlers, with the bottom cover deforming. The resulting indentation rolling resistance is the main contributor to the power requirement of a conveyor belt.
The low rolling resistance properties comprising Continental’s Eco Series conveyor belts are designed to reduce energy loss.
The Eco Plus and Eco Extreme rubber formulations are integrated into a number of Continental longdistance overland conveyor belts, including Flexsteel and Phoenocord series steel cord belts.
These belts are utilised in tough mining applications, offering significant durability and performance reliability. They possess high dynamic efficiency, corrosion resistance and low elongation, which are critical in long-length conveyor systems in underground and surface mining environments.
“The Eco Series is designed to assist with the power draw by reducing the indentation effect of the rubber surrounding the pulley cover as the conveyor belt passes over an idler,” Little said.
“The pulley cover rubber contains special properties, specifically designed to reduce the amount of energy that’s required to pull the belt over many rollers along the length of the conveyor belt.”
Thousands of kilometres of conveyor belting on mining operations across Australia and beyond are benefitting from Eco Plus and Eco Extreme.
As the desire for carbon-neutral technologies continues to expand, Continental is positioning itself to meet this demand by supplying its customers with sustainable solutions embedded within material handling systems.
A Continental service team recently installed an Eco Series conveyor belt, measuring 7.5km, at a large iron ore mining operation in Western Australia’s Pilbara region.
“Our service teams are highly experienced and knowledgeable, and we leveraged all of our capabilities when successfully completing the recent overland conveyor system installation in the Pilbara,”
Continental Western Australian regional operations manager Wayne Sheriffs told Australian Mining
This conveyor belt is providing high performance and reliability in a harsh operating environment.
“Continental is engaged in a vertically integrated process, including our own rubber mixing and manufacturing capabilities, and this enables us to maintain rigorous quality control in the production of our worldclass conveyor belts,” Sherriffs said.
Continental offers a comprehensive approach to service, including conveyor belt installation, technical support, training and belt monitoring.
Together with advances in sustainability, Continental regards safety as a fundamental priority, striving to ensure people working on and around conveyor belt systems are in safest of conditions.
“Safety is the most important aspect of Continental’s conveyor belt maintenance practices,” Sheriffs said.
“Whether it’s related to installation, undertaking repairs, or general maintenance activities, our trained and experienced teams are actively identifying potential hazards and instigating risk-mitigation measures and process improvements.”
The company provides support across all stages of the conveyor belt lifecycle, offering a highly flexible and customer-orientated approach with experienced teams able to complete belt installation and replacement, splicing with advanced processes such as Preform splicing, and conveyor maintenance and repair.
The company supports its customers under long-term contract agreements, offering emergency call-out support with rapid response times, conveyor inspections and audits, and now offers in-house design and supply of belt-handling equipment, such as winders, left-off stands and belt pullers.
We often think of plant feed as being homogeneous, uniform and well suited for steady state operation. The reality, however, is quite different.
The normal day-to-day operations of a mineral processing circuit find plant feed to be variable in size, shape and physical properties.
These variances are caused by numerous factors, including mining in different pit areas, operating at different depths, upstream crusher performance, circuit screen efficiency and even current weather conditions. Each variance can result in the crusher’s feed material changing substantially.
Crusher performance itself is also subject to change depending on liner condition and wear rates.
It is evident that crusher performance, specifically crusher throughput and crusher product size distribution (PSD), can change rapidly and true steady-state operation is seldom achieved for continuous periods.
To optimise crusher performance in real-time, traditionally highly subjective manual crusher setting changes are made based on limited data usually gleaned from a visual observation of the product on the belt or a rough evaluation of crusher power draw and hydraulic pressure. The outcome of this approach is mixed and provides no clear cut, quantifiable data to support any scientific decisionmaking process.
The crusher’s performance tends to be sub-optimal, and the throughput not homogenised.
To resolve the issue, Minprovise has a system that automatically analyses the crusher product belt and provides documentable numerical data reflecting crusher performance based on current feed ore characteristics, enabling a real-time adjustment to ensure optimal production.
The system requires no manual intervention and accommodates not only feed material property changes but also crusher liner wear profile variances.
Minprovise has assembled a Kawasaki ZI-2100 cone crusher at its Perth-based workshop and connected it to the Active Gap Control (AGC) system for prospective clients to view without having to go to site.
This system needs to react quickly to changes in the crusher circuit and prove its worth in terms of increased production quality and rate, which is exactly why the AGC system was developed.
In-house tests using the ZI-2100 cone crusher and the AGC system lived up to expectation and were able to modify crusher operating parameters in all cases, resulting in an optimal, steady-state operation.
The system uses an advanced particle-size analysis camera to accurately assess crusher product size distribution and production rate on a continuous basis.
Changes to the crusher settings can then be made using this information. When coupled with a Kawasaki ZI Cone crusher, or any Hydro Cone style crusher on-site, these changes can be made on the fly, meaning no reduction in feed rate or stopping of the upstream circuit equipment is required in order to affect the required change in gap-setting.
The system ensures the optimal PSD is always achieved and overcomes circuit instability brought about by feed material property changes, feed material moisture content variances, crusher liner wear profile, upstream crusher performance variances, and upstream and closed-circuit downstream screen efficiency changes.
Ensuring optimal crusher size distribution has multiple benefits to the overall operation. These may vary based on the exact operating conditions and circuit layout, but there’s a number of more general benefits.
The AGC system ensures the crusher is operating within its ideal design gap setting, so crushing chamber wear profiles can be improved and problems
associated with poor crusher wear profiles avoided.
Since the performance of downstream equipment is heavily dependent on receiving the ideal feed-size distribution from the upstream crusher, improvements can be made when screens and size classification equipment run within well controlled operating parameters.
Product quality and throughput increases Given ‘design’ crusher gap settings are selected to maximise plant
performance – eg generation of lump versus fines in iron ore, or liberation of high-value minerals – monitoring and ensuring operation at the ideal crusher setting means the overall product quality is likely to increase.
Additionally, since the AGC circuit design limits recirculating loads by operating at the optimal crusher settings, material is crushed to the right size the first time, preventing multiple passes through the circuit.
This increases achievable plant capacity while reducing circuit operating costs due to recirculation inefficiencies.
SKF AUSTRALIA HAS DEVELOPED A SOLUTION FOR CONVEYOR PULLEYS THAT PROVIDES THE OPTIMAL BALANCE OF USERFRIENDLINESS, HIGH PERFORMANCE, AND VALUE. MEET THE SDVD PLUMMER BLOCK ASSEMBLY.
Such is SKF Australia’s connection with its client base that a recent solution for the Australian mining industry was initially driven by a customer request.
SKF’s SDVD plummer block assembly was developed in collaboration with one of the biggest users of conveyor pulleys in Australia, and the solution is now available for mineral processing and bulk material handling applications sector-wide.
Conveyor pulleys are a critical component of any mining conveyor, and SKF understands that a standard housing assembly doesn’t always get the job done.
“The customer recognised that generic bearing housing assemblies, even with taconite seals, could not deliver the performance and bearing reliability requirements in their operations,” SKF Australia engineering manager Darren Kenworthy told Australian Mining
“So SKF developed a highperforming concept – the ‘threebarrier solution’ – consisting of a spherical roller bearing with integral contact seals, together with a premium SNLD plummer block housing equipped with SKF’s heavy-duty TK taconite seals.
“This combination of SKF technologies has brought a step change in bearing reliability in the most arduous of operating environments – the Pilbara iron ore industry.”
Kenworthy said the customer recognised the expertise and value of the new bearing housing and wanted to extend its SKF partnership and solution to benefit the Queensland coal industry, which has its own unique operating environment and pulley applications.
Design features and manufacturing specifications for SDVD housing assemblies are tailored to provide the optimal balance of user-friendliness, high performance and value.
Kenworthy said a key advantage for pulley designers and manufacturers is the minimised
width of the assembly, which allows the bearing to be positioned closer to the pulley drum.
“This reduces bending of the pulley shaft, enabling more optimised and cost-effective pulley designs,” he said.
“The other main benefit for pulley builders and maintenance teams is the simple and robust seal design, which speeds up assembly and reduces the risk of mistakes.”
Kenworthy said the SDVD plummer block assembly is also more practical for end users.
“Along with the simplicity and ease of use, the unique design
provides the potential for simpler and faster change-out of bearings insitu,” he said.
“It also benefits pulley life-cycle costs, as there are no spring-loaded seal lips contacting the shaft, meaning re-use of pulley shafts without re-work is more likely.”
The SDVD plummer block assembly is more versatile in that it’s fully compatible with most existing conveyor pulleys, while it also meets all common market standards – which is the result of it being conceived and built from scratch.
“The SDVD solution has been conceived from the ground up as a pulley housing, whereas traditional housing solutions are adaptations of generic designs and therefore don’t incorporate all the specific design objectives and advantages,” Kenworthy said.
The installation process for the SDVD plummer block assembly is not too dissimilar from traditional plummer block housings; however, the one-piece seal components are assembled axially rather than radially, as is traditional for split taconite carriers.
Kenworthy said this simplifies the procedure and makes it easy to achieve accurate results without risk of damaging the rubber seal elements.
Alongside in-depth instructions and accompanying training videos
that take customers through the installation process step-bystep, SKF provides hands-on training sessions through either scheduled courses or dedicated onsite sessions.
SKF’s vision to deliver high performance, high reliability and long service life for conveyor pulley bearings sits at the core of the SDVD plummer block assembly, because conveyor downtime can be a killer for mining companies and contractors.
Kenworthy said the SDVD plummer block assembly is an illustration of the Australian mining sector’s proactivity in the conveyor pulley field.
“We believe Australia leads the world in conveyor pulley design,” he said. “Regarding bearing assemblies, Australia has pioneered the widespread use of taconite seals and global adoption of the sealed spherical roller bearing.
“Pulley acceptance testing (PAT) is a phenomenon which has been widely adopted in Australia within the last few years but is largely unknown overseas.
“In this respect, the SDVD is driven by Australian needs and innovation, as the housings are specified to provide the best chance of avoiding false-positives in PAT testing.”
THE SDVD SOLUTION HAS BEEN CONCEIVED FROM THE GROUND UP AS A PULLEY HOUSING, WHEREAS TRADITIONAL HOUSING SOLUTIONS ARE ADAPTATIONS OF GENERIC DESIGNS AND THEREFORE DON’T INCORPORATE ALL THE SPECIFIC DESIGN OBJECTIVES AND ADVANTAGES.”THE SDVD PLUMMER BLOCK ASSEMBLY WAS DEVELOPED IN COLLABORATION WITH ONE OF THE BIGGEST CONVEYOR PULLEY USERS IN AUSTRALIA.
CONVEYOR OUTAGES ARE OFTEN ASSOCIATED WITH POOR PULLEY BEARING RELIABILITY.
High-speed and reliable connectivity is a key part of any plan to attract skilled employees and to look after their health and wellbeing when working away from home. Vocus’ fibre network and integrated satellite services provide secure, reliable, and resilient high-speed connectivity to some of the biggest names in the resources industry.
To learn more about what our high-performance fibre network can deliver for your business, visit vocus.com.au or call 1300 88 99 88.
W hen OZ Minerals swiftly rejected BHP’s recent $8.4 billion takeover bid, the copper-nickel miner was clear in its reasoning.
OZ Minerals deemed BHP’s “highly opportunistic” $25-per-share offer insufficient given its strong portfolio of future-facing minerals that will prove increasingly important – and valuable –into the future.
“We are mining minerals that are in strong demand for global electrification and decarbonisation … and we have a long-life resource and reserve base,” OZ Minerals chief executive Andrew Cole told investors in a statement knocking back the offer.
“We do not consider the proposal from BHP sufficiently recognises these attributes.”
These attributes, to be specific, are copper and nickel, both of which are set to play a fundamental role in the world’s efforts to reduce emissions and achieve its climate goals.
“The critical role copper will play in achieving the Paris climate goals cannot be overstated,” Goldman Sachs said in a recent report, ‘Green metals: Copper is the new oil’.
“Without serious advancements in carbon-capture and storage technology in the coming years, the entire path to net-zero emissions will have to come from abatement – electrification and renewable energy.
“As the most cost-effective conductive material, copper sits at the heart of capturing, storing and transporting these new sources of energy.
“In fact, discussions of peak oil demand overlook the fact that without a surge in the use of copper and
other key metals, the substitution of renewables for oil will not happen.”
In the same vein, nickel is a critical metal in the batteries that are increasingly being used to store energy. So critical, in fact, that far more nickel than lithium is used in ‘lithium batteries’.
“The lithium is actually two per cent of the cell mass,” Tesla chief executive officer Elon Musk said in a 2016 presentation. “It is like the salt on your salad.
“It’s a very small amount of the cell mass and a fairly small amount of the cost, but it sounds like it’s big because it’s called (a) lithium-ion (battery).
“But our batteries should be called nickel-graphite, because it’s mostly nickel-graphite.”
Each Tesla battery is said to contain 50kg of nickel.
Looking back on BHP’s move on OZ Minerals, many considered it a further
sign the mining giant – and likely the entire resources sector – is pushing to secure more future-facing raw materials like copper and nickel.
“The deal would fast-track BHP’s desire to get more exposure to the metals needed for decarbonisation and electrification, specifically copper and nickel, after a whirlwind four years under chairman Ken MacKenzie that has seen BHP exit the vast majority of its oil, gas and coal assets,” the Australian Financial Review reported in August.
The Paris-based International Energy Agency (IEA) sparked a surge of interest in energy metals with its report, ‘The role of critical minerals in clean energy transitions’, warning that in order to meet climate pledges the world needs, among new lithium and cobalt mines, 60 new nickel mines over the next seven years.
The IEA didn’t specific how many copper mines will be required, but the industry estimates the need for at least 10 new major mines.
“Additional investment is needed in the short-term, particularly in mining, where lead times are much longer than for other parts of the supply chain,” the IEA said.
Copper Australia is home to the secondlargest copper reserves on the planet, behind only Chile, and is the sixth largest producer in the world at around 900,000 tonnes per year.
Government data shows Australia housed 38 operational copper mines in 2020, though that number has increased since then. Some of the top copper mines in Australia include Olympic Dam (BHP, SA), Mount Isa (Glencore, Qld), Cadia (Newcrest, NSW), DeGrussa (Sandfire, WA), and Prominent Hill (OZ Minerals, SA).
Companies have also been working to develop more copper mines across the country.
Rio Tinto has been drilling tenements in Western Australia, with first ore expected at its Winu coppergold project in 2024. Winu is home to an inferred mineral resource of 503 million tonnes of ore at 0.43 per cent copper equivalent, with Rio saying it plans a shallow open-pit mine to take advantage of the resources.
Hammer Metals is developing its Mount Isa project in Queensland, while Havilah Resources has been bullish its Kalkaroo project in South Australia, describing it as the largest undeveloped open-pit
“The future for copper production in Australia remains bright through the next few years thanks to increasing prices and large investments in exploration and development,” according to Investing
copper export over coming years, with exports expected to hit one million tonnes a year in 2026–27.
Nickel Australia was previously a major global
drops in the face of the global financial
was BHP’s then-new Ravensthorpe operation in WA, which somewhat notoriously shut its doors in January 2009 after less than a year of operation. Ravensthorpe is now owned by First Quantum Minerals and produced 14,018 payable tonnes of nickel in 2021.
Australia holds 22 per cent of the global nickel reserves and produced 170,000 tonnes of nickel in 2020.
The majority of Australia’s nickel reserves are located in WA, which is clearly reflected in the location of the country’s top nickel mines in Australia: Murrin Murrin (Glencore, WA), Nova (IGO, WA), Mount Keith (BHP, WA), Leinster (BHP, WA), and Ravensthorpe.
Armed with the knowledge more will be needed in the future, other Australian majors are looking to expand their nickel operations.
For example, when IGO purchased nickel miner Western Areas for $1.3 billion in June, it added two WA nickel mines to its portfolio – the Forrestania mine, which is already in production, and Cosmos operation, where mining is due to start by the end of 2022.
By the time BHP made its play on OZ Minerals in August, the price for copper and nickel was trending higher.
The price of nickel briefly soared to a high of $US100,000 per tonne
amid a feared shortage after Russia, one of the world’s largest nickel suppliers, invaded Ukraine, but it has since settled at around $US24,000 per tonne.
According to the IEA, nickel is expected to further increase in value as demand grows.
“By 2030, nickel is facing the largest absolute demand increase as high-nickel chemistries are the current dominate cathode for electric vehicles (EVs), and are expected to remain so,” the IEA said.
BHP, for its part, is also high on nickel.
“Longer-term, we believe nickel will be a core beneficiary of the electrification megatrend, and that nickel sulphides will be particularly attractive,” the company said.
BHP currently has deals to supply nickel to Tesla, Ford and Toyota, and while its existing reserves will cover these deals, the major miner is on the hunt for more.
“We’re actively exploring globally, and we’ve significantly increased our own exploration spend within the portfolio of land tenure that we have,” BHP Nickel West asset president Jessica Farrell told the ABC in August.
per cent increase in electric vehicles, and then out to 2040 we see that going up another 30 per cent, to 90 per cent.
“So we see an incredibly good trajectory for demand, and that’s globally. We’ll also see that transition locally, I think, a lot faster than we expect.”
Looking at copper, prices have been on the rise since last year, reaching a fresh all-time high of $US10,674 per tonne in early March 2022, partially as a result of concerns over low inventory levels.
BloombergNEF believes the drive to electrification will see its value grow by 53 per cent by 2040. Supply, on the other hand, is only expected to rise by 16 per cent, creating a shortfall of 14 million tonnes of copper by 2040.
“The world may have to rely on new recycling technologies to prevent shortages of copper as the shift toward clean energy supercharges demand for the wiring metal,” BloombergNEF said in an August report.
What is becoming increasingly clear, however, is that the world is starting to take the need to decarbonise more and more seriously and a number of specific mineral resources are needed for that ongoing transition.
Copper and nickel are at or near the top of that list, and many mining companies in Australia look set to benefit.
As a manufacturer of sensors and controls for industrial automation, ifm efector wanted to future-proof itself.
And as Industry 4.0 began to gather steam, the company found there was still a wide gap between operational technology (OT) and information technology (IT).
Following the acquisition of several software companies, ifm efector began developing a platform that could bridge that gap, using sensor data gathered in industrial applications to provide engineers with the tools they need to improve operation.
ifm’s national Internet of Things (IoT) business manager Freddie Coertze said the Industrial Internet of Things (IIoT) platform moneo was designed to be easy to use.
“moneo help engineers look after their assets and help them make better decisions,” he told Australian Mining
“The platform is middleware, which means it can collect data inside the platform, analyse it without any need for set-up or programming, and then send information to other enterprise resource planning systems.
“What helps it stand out is inbuilt machine learning. Artificial intelligence can examine previous performance to predict when maintenance will be required. This is something that usually needs a data scientist, but we have put it back into the engineer’s hands.”
moneo takes the user through a fivestep wizard. This lets the engineer choose a target variable (eg vibration, temperature, flow) and select the support variables (eg current, pressure).
The user can remove data from periods that would affect the data – like during a shutdown – before running several formulas through a neural network decision tree to provide the engineer with confidence bands for predictive maintenance and to detect anomalies.
Coertze said the information can then be automatically sent from moneo and integrated into other systems in use at the site.
“It’s not just a dashboard tool, it can integrate with other systems,” he said. “For example, if moneo detects an anomaly, it can submit a maintenance ticket automatically so that maintenance staff are dispatched as early as possible.”
The platform launched in Australia in 2021 and is already being used in the mining industry.
“Hydraulic units are the heart of mining operations,” Coertze said. “We can use sensors to help predict issues occurring at this critical point to remove the risk or a shutdown.
“moneo can also detect if a roping event occurs in a cyclone. These separators are usually hard to monitor, as everything inside moves too quickly to predict.
“Sensors can help detect if pressure inside is too high or low to ensure no precious metals are lost or production stopped.”
ifm provides consultation services as part of its offering, sitting down with mining engineers to learn more about the problems they are looking to solve.
moneo is just one tool in the ifm arsenal that can help detect and eliminate these issues. Coertze said the company has an applicationfirst mindset.
“In today’s age, there is always a new way of doing things,” he said. “When consulting with customers, they might have heard about the latest technology, but often these are still proof-ofconcepts and might not solve the problems the engineer is dealing with.”
Scalability is an important part of this process, with the first system acting as a starter kit loaded with all necessary software and hardware. From here, a mine can add other appliances and systems across the site or organisation.
Digital transformation can be a tricky process and starting small allows mines to remain agile if a change of course is needed. Data gathered from these applications may even show the engineers there is something entirely unexpected on which to focus.
ifm has offices across Australia that can help customers implement, install and operate their sensors and systems.
“Once we start on a project, we set up a project team to assist the mine and ensure everything goes smoothly,” Coertze said. “Inside the software, there is a support line that allows engineers to ask the experts for help if needed.
“We have also designed moneo in a way that we release a new version every three or so months. If a mining organisation purchases it today, that means it will still have the latest version with new features in 10 years.”
Having designed and engineered batteryelectric loaders, trucks and underground drill rigs, Epiroc is again charting new territory with the first-ever battery-electric surface drill rig.
The leading original equipment manufacturer (OEM) is trialling the drill rig in partnership with Swedish construction company Skanska, with the design based on Epiroc’s well-known SmartROC T35 surface drill rig.
Once developed, the SmartROC T35 E will enable zero-emission surface drilling, improving the sustainability profile of a mine site and its owner.
The drill rig will come with a range of smart features, options
and enhanced automation solutions for optimal safety, reliability, and performance.
“Epiroc has bold sustainability targets in place for the year 2030,” Epiroc president and chief executive officer Helena Hedblom said.
“With the SmartROC T35 E we are taking a large step towards reaching our promise to offer a full range of emissions-free products for quarries and large construction applications.”
Skanska Industrial Solutions AB project manager Johan Eliasson said an exciting opportunity awaits to continue the battery-electric revolution.
“A milestone has been reached and a new opportunity has come to reduce our climate impact,” he said.
“Both companies have set bold environmental goals – this project really takes a great step towards
Skanska’s goal of being completely climate-neutral by 2045, which is an important part of our promise to build a better society.”
After being manufactured in Orebro, Sweden, the drill rig is being tested by Skanska at a quarry near Stockholm, with Epiroc to announce the product release date in due course.
Epiroc’s battery-electric products delivered a record performance in the second quarter of 2022, with the company winning several orders for battery-electric equipment spanning greenfield projects, battery retrofits and electrical infrastructure solutions.
For Epiroc, electrification doesn’t stop at developing new equipment, with the OEM eager to be a total solutions provider that offers holistic support for the batteryelectric transition.
This includes introducing battery conversion capabilities for customers who’d prefer a retrofit over a new unit.
Epiroc turns to its Canadian subsidiary Meglab for batteryconversion expertise, with the technology integrator able to design, manufacture and install cost-effective electrification and infrastructure solutions to customers in several countries.
Epiroc acquired FVT Research to further support its battery conversion aspirations in November 2021.
“Bringing the strong team at FVT Research into the Epiroc group fits perfectly into our strategy to provide emissions-free battery-electric vehicles,” Hedblom said.
“Our customers are increasingly discovering the significant benefits that come with using battery-electric
vehicles, and FVT Research’s technical expertise and competence will be key assets for Epiroc as we continue to provide more solutions in this area.”
Epiroc has also established a partnership with Kempower, with the leading electric vehicle (EV) charging company supplying Epiroc with a range of flexible charging products for mining equipment.
Kempower uses 70 years’ experience in power-source manufacturing to support its sustainability objectives – carbon neutrality by 2035 and almost total recyclability for all charging products.
Epiroc’s underground loaders have been at the forefront of the batteryconversion story, with the company’s first-ever battery conversion taking place on a 10-tonne Scooptram ST1030 in Canada in April 2021.
In late 2021, Evolution Mining ordered the conversion of two dieselpowered ST1030 machines for use at its Red Lake gold mine in Canada.
“Converting existing diesel machines to battery-electric will be a smart and cost-efficient alternative for mining companies that want to electrify their operations,” Hedblom said.
“It will be an important part as we together continue the drive toward emissions-free operations.”
Conversion kits for other machines will follow, including the Scooptram ST14 loader and the Minetruck MT436B, which are already being tested as converted versions.
Converting to battery-electric not only provides the opportunity for mining companies and contractors to reduce their environmental footprint, but it also enables cost savings.
A battery-driven fleet saves on maintenance, ventilation and cooling expenses, as the cost of ventilation related to the use of diesel is one of the biggest expenditures in many mining operations. With electric machinery, this spend can be reduced by at least half.
comply with CE standards (European Union product safety directives) and have a built-in, multi-layer safety system, from cell design to a deformation zone.
Epiroc offers a quick turnaround time for conversions – which can be included in a midlife rebuild – returning machines back to site without unnecessary disruptions to production.
If new battery-electric equipment and conversion kits provide the infrastructure for an electrified fleet, Epiroc’s Batteries as a Service (BaaS) business model is the glue to the transition.
come with going electric, providing an ‘instant technology leap’ to batteryelectric machinery.
The holistic solution shifts the upfront costs of batteries from capital expenditure to operational expenditure, with the responsibility of this function assumed by the OEM.
Epiroc takes ownership of the battery itself and can automatically replace and update customer units as needed. Customers need not stress about battery maintenance or performance, with Epiroc taking this responsibility into its own hands.
“Batteries as a Service helps our customers benefit from the latest battery technology without having to worry about facilitating upgrades and removals – they can focus on their business and we make sure they have all the power they need,” Epiroc commercial manager – Rocvolt Fredrik Martinsson said.
With every acquisition, partnership or in-house innovation, not only does Epiroc have the opportunity to further advance its BaaS scope, but its holistic battery-electric vision receives further endorsement.
Electrification is the way of the future. Epiroc knows it, and the Australian mining industry is starting to understand it, too.
exploration activities and emergency mine teams.
“At the moment there is an exploration boom occurring for rare earth minerals, and with so many mapping, surveying and drilling programs taking place, exploration teams require agile, stable and lowlatency communications,” Boylson said.
“Gone are the days of hard drives, so in order to store large amounts of modelling information, the ability to access cloud-based internet data storage providers in remote locations is a necessity.”
Vocus’ advances in fibre and satellite networks will immeasurably benefit people living and working at remote mine sites, and further strengthen the critical services on which rural and regional communities across Australia depend.
An example of Vocus providing communications benefits to a local community is in the delivery of an upgraded private network to Minjar
Icustomers with stable, fast, lowlatency communications.
From exploration teams to mine workers and community-based organisations, Vocus is providing the vital communications infrastructure that helps to ensure the safety, health and wellbeing of people in some of the harshest environments and most remote of areas in Australia.
“Vocus operates Australia’s secondlargest long-haul fibre network, we’re supporting government, defence and enterprise across several large-scale national projects, and we have points of presence in over 150 major data centres,” Vocus account director –natural resources Benedict Boylson told Australian Mining.
The company has long been developing multiple technology solutions to service remote mining operations, developing a capable, secure and cost-effective fibre network infrastructure. It has also invested significantly in low earth orbit (LEO) satellite communications for expanded internet communications and cloudbased data storage.
The investment roadmap that Vocus is undertaking across the Pilbara region of Western Australia is substantial,
March 2023 and will form the Darwin–Jakarta–Singapore Cable (DJSC).
The DJSC will provide a unique, geographically diverse and protected wet route from the Pilbara to Perth, and a direct low-latency route to Singapore and many key cloud computing hyperscalers.
Additionally, the 1600km Project Horizon is under construction and scheduled to be completed by December 2023. The project will complete a ‘western loop’ of assets by connecting Geraldton to Port Hedland, via Meekatharra and Newman, linking natural resources hub in the Pilbara.
Vocus is currently in the process of developing options to support individual mining operations along the route of the trunk cable system.
The benefits of the DJSC include its capacity to support edge computing, LEO systems and private LTE/5G networks, while ensuring secure, reliable and high-performance internet connectivity for people working and living in remote rural and regional areas of Australia.
Stable, high-speed network capacity will support bandwidthhungry applications and provide critical connectivity for mineral
the mine site’s previous connectivity speed, boosting it from 40Mbs to nearly 500Mbps.
The solution for Minjar Gold included working with Vocus’ fixed IP wireless partner Goldnet to implement a microwave technology solution that connects the mine through line-ofsight fixed IP wireless to Vocus’ fibre point of presence located north of the Southern Cross township.
The project not only delivered improved connectivity to the Minjar Gold mine site, but also to the wider Southern Cross community, which was offered access to the private network to help ensure more reliable connectivity and faster internet speeds.
“Vocus prides itself on a superior track record of on-time and on-budget project delivery, achieved with an engineering pedigree few large carriers possess, along with highly advanced communications knowledge and partnerships, especially in the space
VOCUS’ NETWORKS WILL BENEFIT PEOPLE
AND WORKING AT REMOTE MINE SITES.MANY AUSTRALIAN MINES ARE IN SOME OF THE MOST REMOTE PLACES IN THE COUNTRY AND NEED RELIABLE CONNECTIVITY.
DYNA Engineering Conveyor Guards are leading the way towards a more environmentally sustainable future by being manufactured with recycled and recyclable HDPE plastic.
Our “X” design increases the guard’s strength and is simple, intuitive and robust. DYNA Engineering doesn’t compromise on your safety.
Reduce your material handling risks and increase safety for your personnel with our guards, which are up to 40% lighter than conventional steel guards.
Our HDPE Conveyor Guards will reduce your overall maintenance cost as they do not require painting, and will not rust or corrode.
The need to provide advanced critical communications infrastructure to support the mining industry remains a key focus for Nokia.
Digital transformation and automation are delivering significant rewards for mining companies.
Advances in the Industrial Internet of Things (IIoT), artificial intelligence, machine learning, and augmented and virtual reality, together with 5G connectivity and edge computing, make it possible to vastly improve mine productivity and safety.
Nokia is at the forefront of developing new technological innovations and digital solutions that are transforming mining operations above and below ground.
As industrial-grade 4G/5G network capability continues to grow, Nokia has sought to partner with leading Australian telecommunications companies and mining system integrators to introduce automation and virtualisation technologies enabled through the deployment of private wireless networks.
These private networks allow mining operations the ability to embrace new operational approaches, processes and opportunities without relying on legacy private mobile radio or public networks.
Mine sites utilising 4G/5G networks will be able to remotely operate autonomous vehicles, other high-speed robotic processes and drones, with the ability to connect to hundreds of thousands of IIoT sensors and industrial devices, as well as provide CCTV camera feeds and allow personto-person or group communications across the entire mine.
Mines sites will use these 4G/5G private networks to control autonomous vehicles and drones, and monitor and control high-speed hazardous robotic processes. They will also be used to connect to the thousands of IIoT sensors and CCTV cameras located throughout the mine site.
“Ten years ago, Nokia deployed its first private long-term evolution (LTE) mining network in the Pilbara. The project was success, so much
so that Rio Tinto won an Australian innovation award on the back of it,” Nokia head of mining, oil and gas for Australia and New Zealand Brendan Conroy told Australian Mining
“In 2014, a reporter wrote, ‘I’m in a very big hole in the middle of nowhere and there’s better mobile internet than in my Parliament House office’.”
“In the meantime, our mining solutions are moving to 5G in order to future-proof mining operations, ensuring low-latency and high throughput for secure voice, data and video communications, as well as many automated applications.”
Nokia provides private wireless network solutions for open-pit and underground mining operations. It works with original equipment manufacturers (OEMs) like Komatsu, Caterpillar and Sandvik, integrating Nokia’s advanced digitalisation solutions directly into these company’s products in order to enhance safety, sustainability, productivity and efficiency.
Private wireless networks are an ideal solution for handling all missioncritical applications.
Deploying a single-network
costs, while making a range of operational gains through Industry 4.0 digitalisation, automation and monitoring.
Another significant technology that Nokia is developing is edge computing.
Nokia’s proprietary private wireless solutions bring edge compute to even the most remote mine sites. This enables cloud services that provide many benefits for mining operations, as it combines plug-and-play 4.9G/ LTE and 5G connectivity with onsite data management and processing to support real-time applications, especially in remote settings.
Nokia’s private wireless solution is designed to be scalable, allowing mine operations of any size to integrate network equipment with a cloudbased operation-monitoring system that can collect, processes and host all generated data on-site.
The solution can be bundled with a series of applications, such as missioncritical push-to-talk and push-tovideo, as well as a growing range of ruggedised industrial devices, ie smart phones, work pads, handhelds, field dongles, and field routers.
air-conditioning and power units. Gone is the clunky hardware or the need for racks of physical on-site digital storage,” Conroy said.
Also in development is Nokia’s next-generation 5G edge slicing technology, which allows communications service providers to offer their customers the ability to have differentiated quality of service between services being run over their private 4G or 5G network.
“For example, a high priority network slice could be used to control the mining machinery, while a lower priority slice could be used to carry video from the CCTV cameras monitoring the perimeter of the mine,” Conroy said.
“When it comes to investment in new technology, the mining industry has often been conservative in its approach; however, the productivity and safety benefits that private wireless networks can provide, in the form of voice, video and data services, is really profound. The flexibility and reliability that today’s 4.9G/LTE and 5G networks bring is unmatched by any other network technology.
“Nokia critical communications
A flexible transport solution with
on
off capability ideal for moving parts, components, equipment, and maintenance personnel safely and securely throughout the mine site. Flat deck has the capacity to
standard size
Large flat deck provides optimal space for transport of parts, components, equipment, and maintenance personnel safely and securely throughout the mine site. Flat deck has the capacity to
standard size pallets.
down valuable ore fines, blast material hang
The dual application machine features
and fight fires.
road dust and wash
the
and rear water sprays
surfaces.
Designed for in situ top up servicing of machines and equipment within the mine. Eliminates the need for production machines to leave remote work areas for minor maintenance work, reducing servicing time and traffic on haul routes.
Specialising in the transport of small
with an
top speed
full capacity
times
increasing production.
A purpose-built underground elevated work platform with 17% levelling capability utilising hydraulic jacking legs. Ideal for the safe transportation and installation of large components and services into the ceiling of the mine.
As a leader in the field of Bluetooth technology applications, Contact Harald was a key provider of close-proximity location solutions globally during the COVID pandemic.
The Australian-born technology and design company has a significant footprint in 19 countries and employs highly experienced design and engineering teams in Sydney and Melbourne.
To maintain its global momentum, Contact Harald has unveiled a new suite of safety and productivity solutions called Ask Harry and Find Harry.
Ask Harry is an intelligent digital assistant designed to streamline mining safety procedures and increase operational productivity. Controlled by voice, Ask Harry makes the finding and lodging of reports faster, easier, and less error-prone than traditional methods.
“Ask Harry humanises technology, making filing a detailed hazard report as simple as a conversation with a co-worker,” Contact Harald head of product and technology Matt Denton told Australian Mining
“Harry breaks down barriers and increases engagement.”
Accessing Ask Harry is as simple as a phone or two-way radio call, and the system can converse in multiple languages.
Find Harry is an integrated system allowing for real-time and last-seen location tracking.
“Find Harry is the natural evolution of our work in location technologies over the past decade,” Denton said.
Find Harry allows mine operators to access a clear picture of workers’ whereabouts, as well as the precise location of tools, equipment, inventory, and assets at all times. The system is able to do this by combining multiple technologies such as Bluetooth, GPS and Wi-Fi.
“We are expanding our products to include indoor, outdoor, and proximity-based solutions,” Denton said.
“When you add Ask Harry in the mix you get location with intelligence, creating smarter ways to use your location data.”
Ask Harry and Find Harry can be combined to make the most of the technologies.
By joining the ease of use, speed, and multilingual offerings of Ask Harry with the locating capabilities of Find Harry, mining companies can enjoy an array of features.
These include enhanced communication, faster access to information, quicker and more accurate safety reporting, and inventory, equipment, asset and fleet management optimisation.
Contact Harald chief financial officer Nick O’Halloran has been happy with the number of mining companies who are already keen to implement this new technology.
“Those in the mining and allied sectors such as construction have expressed a considerable amount of interest during the development of our new products and are eagerly awaiting opportunities to trial, in view of largescale roll outs,” he said.
“It’s great to see such a high degree of interest in embracing new technologies.
“I’m certain that the sector is about to make great strides in productivity and worker safety.”
Users of the Harry systems will be able to view a digital map of their mining sites, which they can then use to find the location of people and equipment. Mining personnel can also access job information, directions, and safety updates by calling Harry and using voice commands.
Any reports that need to be made can be uploaded in real-time through a worker’s mobile phone or two-way radio. Using voice increases safety report volume and speeds up report lodgements, which in turn means the necessary steps to remove hazards can occur quicker.
Incidents are also able to be reported faster, with people nearby able to alert emergency personnel through Harry. Harry can then provide emergency services with the exact location of the incident.
Ask Harry and Find Harry will be available in the Australian and US markets by the end of 2022. O’Halloran said both markets are keen to access the technology, but added that Contact Harald has been receiving interest from all over the world.
“We’ve been getting some very interesting enquiries from abroad, such as in Africa, so we may end up moving our 2023 market entry dates forward to keep up with the demand,” he said.
Mining and construction services should find benefit in the use of Ask Harry and Find Harry, as the novel approach to location and tracking, merged with the power of artificial intelligence (AI), brings significant operational and process improvements to a site.
“Ask and Find Harry form a powerful duo to help create a safer work environment, plus increase productivity,” Denton concluded.
WA Mining is the ultimate event for mining and engineering professionals. The high-calibre conference will explore the technological advancements in mine operations and how critical minerals and sustainability will drive the WA mining industry forward. Alongside the conference will be an expanded exhibition featuring over 100 leading suppliers where you can see first-hand the latest equipment and innovation shaping the sector.
Michelle Ash Technology Executive Lead Oz MineralsHon Bill Johnston MLA WA Minister for Mines and Petroleum, Energy, Corrective Services and Industrial Relations
of the mining chain, as this part of the process is essentially in its DNA.
“Given our evolution from the Hastings Deering Caterpillar dealership, our original focus was using data and analytics to help customers increase productivity from their mining machines,” Spink explained.
“Load-and-haul machinery are key equipment items sold by the dealership, hence this is our heritage.”
Decoda understands that several factors can cause variability in the load-and-haul circuit and is putting that understanding to use to identify insights that help customers continually improve the performance of their load and haul fleets.
“Decoda’s approach also includes ‘looking left and right’ of load-andhaul in the value chain,” Spink said.
Officially launched in July this year, Decoda is a company that has gone from strength to strength in its short life.
Originally a part of Hastings Deering, Decoda was created after the company looked into how it could help its customers improve the performance of their assets through digital technology.
With many miners struggling to improve equipment performance despite having digital initiatives in place, Decoda quickly realised there was a significant gap between most digital initiatives and their operational execution – and that gap is a key contributor to the estimated $350 billion dollars in lost value mining companies are leaving in the ground every year.
“With operational costs rapidly increasing due to inflation, rising wages, poorer ore quality, and availability, this lost value is only going to continue to increase,” Decoda executive general manager George Spink told Australian Mining.
“This is why it is imperative that mining operations begin to extract real value from the data they are collecting and turn that data into actionable insights that can drive performance
improvement across their load and haul circuits.”
Now a leading provider of data and analytics solutions, Decoda works with customers to help them achieve their mine plans through running more efficient and productive operations.
A key tenet of Decoda’s methodology involves adopting a ‘closed loop’ system approach, designed to bridge performance gaps and achieve targets in line with the mine plan.
“Load-and-haul is a key ‘link’ in the mining value chain in terms of either removing overburden or moving the actual commodity itself down the value chain towards processing,” Spink said.
The fact load-and-haul moves the commodity along the value chain makes it an invaluable piece of the puzzle for all mines.
Decoda currently has three key solutions to enable its customers to meet their mine plans: operate for productivity (O4P), operate for reliability (O4R), and short interval control (SIC).
The company can use O4P to provide analytics as a service to a customer. This involves analysing the load-and-haul data and identifying areas for improvement, while providing ongoing monitoring to assist
in providing a cycle of continuous improvement.
“On the other hand, O4R involves us still providing analytics as a service, but with a specific focus on understanding operator-induced events that could impact machine performance or reliability ultimately impacting production,” Spink said.
Decoda’s O4R service offering helps customers in two ways: the first is that it can provide valuable coaching insights to operators to minimise the impact on a machine’s performance, productivity, safety and, potentially, costs; the second is providing operator feedback and coaching on better machine operation that can help with retaining inexperienced operators.
SIC, the third service that Decoda currently provides, is aligned to its O4P service offering and is a forwardlooking decision-support tool.
“Unplanned events happen during a shift. This tool, drawing on near real-time data, allows the production supervisor to run scenario options intra-shift and select the best scenario in terms of hauling and loading unit allocation.” Spink said.
“This ensures production performance remains on track to achieving shift production targets.”
The company has initially focused its efforts on the load-and-haul vertical
“For example, fragmentation from a blast may be impacting the ability for the digging and loading tools to handle the material and this may impact the performance of the load and haul vertical.”
Decoda has found that its customers have been surprised at what their data tells them, which further underpins the company’s drive to provide services to its customers.
“Typically, customers have preconceived ideas as to the performance of their load-andhaul vertical, including machine performance,” Spink said.
“Often these preconceived ideas are based on observation or ‘gut feel’ and may not be based on factual data.
“When operational data is extracted and presented in a way that shows how the load-and-haul circuit is working as a system, there is often surprise at the observations.”
While mine operators may find it challenging to see Decoda’s findings, Spink said it was always nice to see the drive and desire to start implementing improvement initiatives.
“Systems thinking is a key approach for Decoda,” he said.
“To successfully close any gap between actual and plan is to treat the load-and-haul vertical as a system and understand the relationship between the loading tool and the haul trucks as a whole and not separate them into individual parts.”
It’s a common topic of conversation in businesses across Australia, seemingly regardless of industry.
“I can’t find enough staff.”
“We’re still looking for new people.”
“We’re having trouble keeping the team we have.”
“One of our biggest challenges is recruitment and retaining people.”
As Australia continues to move out of and recover from the COVID pandemic, the country is experiencing the type of skills shortage not seen in decades.
According to the Australian Bureau of Statistics (ABS), at the
time of writing there were more than 400,000 job vacancies across various Australian industries.
And the mining industry is among those hit hardest.
A July report from the Australian Resources and Energy Employer Association (AREEA) stated that the mining industry would need 24,000 new workers over the next five years to uphold new projects across the country, with AREEA chief executive officer Steve Knott calling the problem “the worst skills crisis in a generation”.
“This is threatening the continuity of existing operations, resulting in temporary or permanent production downgrades, and driving
other workforce issues including historic levels of staff turnover,” Knott added.
At least 107 projects across coal, gold, and critical minerals are at risk of being severely affected by the worker shortage.
AREEA head of policy and public relations Tom Reid has called the challenge of the skills shortage “significant”.
“We don’t have enough people to continue operations at their full productivity level,” Reid said.
The talk surrounding the skills shortage seems dire, but all is not lost. According to key industry players, the solution might lie in the younger generations.
Starting at a school level
“We need to start with vocational education in TAFE and those sorts of systems to ensure that the skills and qualifications that people are leaving institutions with matches up to what the industry needs,” Reid said.
This statement echoes the thoughts of many companies that have already started targeting those in later high school years as potential new employees in the mining sector.
Komatsu is one company that has successfully put this method to use.
“Our apprentice program is specifically targeted at that highschool-aged group,” Komatsu regional talent acquisition manager,
The Komatsu apprenticeship program, Komatsu Apprentices Development, is a learning pathway to formal qualification while training and working in a job. The program includes eight apprenticeship streams, ranging from mechanic and electrician to fitter and customer support representative.
“We’ve had really good engagement from the local community on the program,” Keating said. “We have over 2000 schools that we’ve approached with the apprenticeship program across Australia and New Zealand.”
The Komatsu apprenticeship program is a way for young people to understand the careers available in the mining industry and grow into them while earning money and working within Komatsu’s culture.
Giving school-leavers knowledge about the sorts of jobs available in mining is often the first hurdle for companies looking to boost their employee numbers.
With ever-increasing access to social media, many young people may have a negative view on what the mining industry does. But, according to Queensland Resources Council (QRC) chief executive Ian Macfarlane, if companies can help to shift this thinking, they may see more benefits.
“The first roadblock to getting young people on board is a constant barrage on social media, which gives them a false impression of the industry and the opportunities that lie in there,” he said.
“There are highly paid jobs waiting for you in an industry that is doing everything it can to improve its environmental and social performance.”
For Samantha Zanevra, who runs the 2022 Komatsu apprenticeship program, success also lies in helping the younger generations understand what sorts of jobs and pathways are out there, and that those options might be broader than people think.
“I had a kid tell me that he was interested in doing something in IT, and so that’s when I had a chat to him about our autonomous range,” she said.
“So it’s really important for kids to find out what’s out there, either through us or through their schools.”
The apprenticeship program is not the only initiative Komatsu runs in an effort to gain more skilled employees.
The company’s employee referral program is an added benefit in which a $5000 payment is given to an employee who successfully recommends someone to fill a vacant role in the company.
“You’ve got to trust your employee’s judgement on a person and employee referrals are one of the top three ways we hire the most people,” Zanevra said.
Komatsu is not alone in turning to alternative recruitment measures.
As job openings become harder to fill, mining companies across the globe are pulling out the stops to attract candidates.
Earlier this year, mining giant Rio Tinto launched two recruitment programs: the Transferable Pathways campaign in Western Australia, and the Women in Leadership Program in New Zealand and eastern Australia.
These programs combined to attract more than 3000 applicants.
Both campaigns targeted women who had not previously worked in the
mining industry, and Rio Tinto chief executive, Australia Kellie Parker said the response was overwhelming.
“Traditional recruitment practices for our industry mean we are hiring women from the same talent pool,” Parker said.
“By opening up our operational roles to women without industry experience but with transferrable skills and talent, we not only increase representation of women in our business but also diversity across the industry as a whole.”
The campaigns mirror Komatsu’s target of 40 per cent female engagement in its apprenticeship program.
METS Ignited chief executive office Adrian Beer said these more modern recruitment methods more effective in attracting new talent.
“Competitive wages are how the industry traditionally attracted new talent,” he told Australian Mining in August.
“It’s a high-paying industry, but it’s no longer a sustainable method.
“Wages have balanced across industry sectors. Work habits have changed – there is more to a career than just the job.
“Employees place a much greater emphasis on social impact and lifestyle factors.”
This is something that Komatsu knows well, with Keating ensuring that she promotes the positive culture that employees will find at Komatsu.
“People want to enjoy coming to work every day,” she said. “It’s not always monetary.”
Going through the recruitment process is one thing, but how do companies ensure they retain employees once they’ve hired them?
Again, Komatsu has an answer: career progression.
“We’re always looking at the next step for each employee,” Zanevra said. “It all depends on which direction they want to go in. There are so many options.”
One part of these options is Komatsu’s dual trade option. If someone is hired as a tradesperson, and they want to expand their skills into a second apprenticeship, they aren’t paid apprenticeship wages –they’re paid tradesperson wages.
As always, however, those in the industry wager that simply throwing money at the issue in the form of higher salaries will not solve it.
Instead, creating a culture of belonging and professional development opportunities, and offering clear career progression is the way to go.
Komatsu’s dual trade program is only one option that the company uses to retain its employees, but combining it with the positive company culture and career progression opportunities means the company is well placed to overcome the recent skills shortage.
“The skills shortage is a global challenge, with high demand across multiple industry sectors,” Beer said.
“While Australia is blessed with an abundance of natural resources and a strong innovative culture, if we don’t effectively commercialise this capability we will become a less significant player on the global stage.
“We must open up our market if we want to attract new skills locally, building a sustainable technology ecosystem for the benefit of all of our major industry sectors. If we don’t, our local businesses will be overtaken by global competition, and this opportunity will go elsewhere.” AM
During a time of uncertainty for the global supply chain and a skills shortages across many industries, uptime is everyone’s most valuable resource.
The mining sector is learning to adapt, employing new technologies and approaches to help equipment communicate through advanced condition monitoring.
According to Motion Australia manager – national sales Grant Gray, even among the growing need for raw materials across infrastructure and construction, operations will need to embrace the benefits of Industry 4.0 if they hope to remain competitive.
“Most consumers are noticing the widespread challenges when veggies are out of stock at the supermarket, or their favourite restaurant is closed two days a week due to staffing issues,” he said.
“But these problems are heavily impacting resource sectors as well, along with an inordinate demand for raw material, so having increased visibility on the health of equipment is paramount.”
In a rugged mining or quarrying environment, gearboxes and other parts are often subject to contaminants, extreme temperatures, and heavy use. Whether it’s a crusher, roller, pump or screen, even the most
reliable equipment can experience unexpected failure.
But, Gray said, it’s all about the smarter allocation of time and people power to stay ahead of the game.
“The increase in material demand also puts more load and stress on quarrying equipment – we’re moving a lot more product now, and we’re moving it faster, for longer,” he said.
“It’s vastly more productive to have maintenance fitters staying on top of equipment upkeep and scheduled change-outs, rather than continually spending time attending to broken gear.
“This is where a remote or online monitoring solution can make all the difference.”
While online condition-monitoring has been a reality for some time, flow-on challenges from the COVID pandemic have forced many businesses to take stock and evaluate the potential strengths of predictive maintenance solutions.
“I think historically there has been a view that this is a tool reserved for the big players within the sector, and that just isn’t the case anymore,” Gray said.
“The costs around implementing it, even on single-site operations, has come down significantly and the return on making that investment is evidently worth it.”
Echoing this sentiment, Motion Australia national business development manager Michael Greelish points out that reliability and consistent production are only capped by the extent of a site’s predictive maintenance plan.
“We do a lot of remote monitoring for quarries, particularly on crusher machines,” he said. “Rather than letting them run to failure, it’s more beneficial to keep an eye on their ongoing performance and address any necessary repair or replacement in a timelier manner.”
Even in smaller operating environments, the integration of online condition analysis to one or two crushing machines has proven beneficial in the long-term. Sensors can replace the need for regular maintenance checks, freeing time that might be better invested elsewhere.
A correctly installed digital framework allows operation managers greater visibility on the health of each piece of equipment, closely analysing factors like speed, vibration, pressure, and temperature of different moving parts.
Compared with traditional frequency-based monitoring approaches that depend on manual labour, the generated data offers an increased likelihood of identifying subtle changes to the machine’s behaviour.
“Catastrophic breakdowns on crushers and screens always start with something small,” Gray said. “A little vibration, or small drip from a seal.
“Then all of sudden the gearbox has got no oil in it, and all the metal parts are grinding without lubrication, so you’ve got excess heat building up. Of course, ultimately, the whole thing explodes, costing hugely in downtime and repair.
“So the question we ask ourselves is: what could we have done if we’d known, if we’d noticed that highfrequency sound coming out of the machine, or slight uptick in temperature before it wasn’t too late?”
As experts in the supply and maintenance of critical quarrying equipment, Motion Australia is well placed to assist with this level of monitoring, analysis and support. The Quarry Roadmap industry guide outlines key pain points on primary and secondary pieces of equipment, suggesting practical solutions based on extensive knowledge.
“Now is the time to be having these conversations with us, so we can come to your site and offer added value to increase your production,” Gray said.
“These issues around supply chain aren’t going away overnight. With the global demand for raw material, we will continue to be heavily invested in ensuring uptime.”
Massey credits Ritchie Bros.’s unreserved auction model as the foundation of business and customer trust, and this trust directly translates into collaboration opportunities.
“We are pleased to be working in collaboration with Emeco to deliver innovative solutions to the dispersal of excess assets,” Massey said.
“With a shared focus on asset solutions, this agreement is the foundation for a strong partnership and compliments our efforts to diversify our sales solutions.”
Emeco general manager Steve Crofts echoed Massey’s thoughts, expressing pride that the multichannel sales approach employed by Ritchie Bros. would help Emeco sell equipment when, how, and where it chooses.
Ritchie Bros. is highly experienced in conducting large-scale mining transactions and delivering significant results by leveraging its global network and comprehensive sales solutions. The company also provides insights and several transaction solutions for commercial assets including Marketplace-E, IronPlanet, and Ritchie Bros. Auctioneers.
These different transaction solutions allow Ritchie Bros. to suit each customer’s need, and it’s this attention to customers that has allowed the company to continue to expand.
Ritchie Bros. has had a bumper second quarter of the year, with a 22 per cent jump in revenue compared to 2021’s second quarter.
After more than a decade of dealings together, Ritchie Bros. and Emeco have collaborated to deliver competitive integrated sales and marketing solutions to the dispersal of heavy earthmoving equipment.
One of Australia’s largest independent equipment rental businesses, Emeco provides resources companies with tailored earthmoving equipment solutions. The company has operations in all of Australia’s key mining regions, which aligns well with the worldwide footprint for Ritchie Bros. is so well known.
As a global asset management and deposition company, Ritchie Bros. offers customers end-to-end solutions for the buying and selling of used equipment, auctioning everything from heavy equipment to trucks in Australia and across the world.
“Emeco chose us to partner with because of our global coverage and our expertise,” Ritchie Bros. sales director Finlay Massey told Australian Mining
The agreement will see Ritchie Bros. deliver excess mining equipment dispersal services to Emeco.
With headquarters in Perth, Emeco brings deep knowledge and an impressive rental fleet and is supported by a network of maintenance and component-rebuilding workshops across the country.
Massey said the relationship between the two companies, which started as a general sales call, had grown steadily over the last decade.
A firm friendship was formed between the Ritchie Bros. team and Emeco chief executive officer Ian Testrow, and the relationship has gone from strength to strength ever since.
With a new joint agreement, Emeco has received a dedicated storefront on Ritchie Bros. IronPlanet, a custombranded seller page that includes Emeco listings for sale. Assets will be sold via both Marketplace-E and IronPlanet auctions, with the approach tailored to deliver the optimal result.
transparent business, allowing customers to view price results, market trends and analytics through its asset solutions.
“We have been in the mining business for 50 years, providing heavy earthmoving equipment to companies and contractors across coal, gold, copper, bauxite and iron ore,” Crofts said.
“We are pleased to start selling surplus assets through Ritchie Bros. to the global mining industry.”
Emeco carries out a comprehensive scope of work from its componentrebuilding company, Force Equipment, to its line boring company, Borex, and underground mining services company, Pit N Portal.
“We are learning and gaining confidence from our growth initiatives and will continue to prudently invest in local yards, sales coverage, and services to accelerate our topline while we advance our marketplace technology,” Ritchie Bros. chief executive officer Ann Fandozzi said in a statement.
This investment will continue with Emeco.
“We are uniquely positioned to deliver Emeco with our substantial resources, industry expertise and extensive buyer database to maximise the return
raises past a safety threshold.
“The direct torque loop control and safety-off feature act as an emergency stop,” Schouw said.
“In the past, if there was a surge, you’d have to completely cut power to the drive. Then there would be a wait time during which the unit would power back on.
“This way, it arrests the output while keeping the drive alive – you still have communications active and there’s no delay on the reset.”
Using liquid-cooled alternatives to air-conditioned drives also contributes to energy cost savings, in tandem with fewer carbon emissions and spatial efficiency. Drive systems are continuously producing heat and run much higher rates of power than typical at-home air conditioners.
“Refrigeration units that service the air conditioners also cost a lot to operate,” Schouw said.
“So if you can take all that heat and run it through water into a chiller exchange, it’s a much more streamlined process and you only have one system to maintain.”
Evoltage variable speed drives (VSDs).
Earth currents flow through a VSD’s earthing systems via the electric induction motor’s grounding points. In the event of a fault within the transformer or VSD, leakage currents pose a major safety concern, which is why they must be closely monitored, with added safety stop protection.
ABB Australia business development manager Adrian Ng said meeting earth leakage protection standards, specifically those outlined by the New South Wales and Queensland governments, was a key design feature of the ABB ACS1000 industrial drive.
The drive creates a ‘protection zone’, covered by the ACS1000’s ground fault supervision. As it is always galvanically isolated from the mains supply by the converter input transformer, it doesn’t matter whether the mains supply is grounded or floating.
In order to avoid group loops where currents can circulate within a galvanically isolated system, only
becomes uncontrolled and attempts to ‘jump’ between conductors.
“If an arc fault cannot be contained or eliminated, it results in an arc blast capable of vaporising metal, creating shockwaves and even fatalities within an instant,” Ng said.
“ABB is at the forefront of arc protection design, and our certified and factory-tested arc-resistant cabinets are quite a unique offering to the Australian industry.”
When installed on the ACS1000, ABB’s Arc Guard System uses optical sensors to detect light from an occurring arc flash, and sends a signal to the circuit breaker within milliseconds.
Ventilation fans and conveyors are two applications that commonly require VSD control in mining operations. According to ABB Australia system drives product manager Luke Schouw, maintaining airflow underground is critical for worker health, so designing a reliable VSD with a proven track record must be a priority.
“Having a drive arrangement that is fully enclosed and liquid-cooled
Breakdown or failure on ventilation systems have a much greater financial impact than a general drive fault.
“Not only will sites have to face downtime loss and maintenance costs, but there are also consequential infringements for evacuations due to breaches of stringent safety protocol,” Schouw said.
When it comes to conveyor applications, Schouw said, the two most important characteristics for modular drives are height and portability. A typical product, even before a cooling fan is installed, will stand over 2m tall, which is usually the height limitation of an underground mine.
“By making a compact and water-cooled casing like the ABB ACS880, it allows skid OEMs greater flexibility,” Schouw said. “These all-compatible single drives are also optimised to protect workers against energy leakage safety risks.”
In addition, the safety torque-off feature limits the impact of stray energy emitting from the drive cable, tripping the system as soon as it
The built-in access gateway on both drive products allows for remote diagnosis and conditionmonitoring, facilitating ABB’s field service. Having full visibility on a drive or entire skid assembly serves to mitigate unplanned downtime and avoid hazardous energy surges.
“The ABB Ability remote condition monitoring can be accessed through a web portal, which acts on a traffic light notification system,” Schouw said. “Most of the time, everything will appear green, but if something needs attention – for example, a cooling circuit requiring an urgent liquid exchange – it will light up yellow.”
“Knowing when to plan maintenance is crucial, because then rather than being reactive, you can mobilise parts to site quickly.”
ABB supplies combined transformer, motor, and drive packages to ensure a fully integrated and compatible solution. By utilising a coordinated line-up, users can minimise risks, guarantee efficiency, and use ABB as a singular point of contact for aftermarket support.
With a heritage dating back 100 years to working on Western Australia’s goldfields
water supply scheme, Black & Veatch continues to advise, develop and deploy resilient and sustainable integrated infrastructure for clients across Australia.
A 100 per cent employeeowned engineering, procurement, construction and consulting company headquartered in Overland Park, Kansas, the company has a full range of solutions across power, water and other critical technologies for the Australian mining sector.
Those solutions are scaled and adapted to clients who have placed an emphasis on decarbonising their operations and adapting to present and emerging climate risks.
Black & Veatch understands that the mines of today are not the mines of tomorrow.
The need to integrate technologies that complement or supersede traditional systems, equipment and processes – while continuing to meet the bottomline requirements of safe, costefficient and productive operations – is where Black & Veatch partners with operators to provide integrated sustainable mining solutions.
“Decarbonisation technologies are moving at an extraordinary pace,” Black & Veatch vice president and managing director Australia Pacific Mick Scrivens told Australian Mining
“And with this innovation comes the need for mining companies to ensure they are undertaking the appropriate levels of strategic thinking and detailed planning, that they are embracing innovation while at the same time developing clear roadmaps that will effectively utilise capital expenditure and maintain flexibility, as regulatory regimes and technology evolve.”
Creating effective decarbonisation roadmaps is a key dimension of the work Black & Veatch’s subject-matter experts undertake when they work with mining companies.
“Our involvement with clients is everything from the pre-feasibility and feasibility phases of projects, through to engineering, procurement, construction and commissioning, as well as remote asset management and pre-planning for asset maintenance,” Scrivens said.
The roadmapping process will help mining companies measure their impact on the global carbon cycle, identify climate risks and opportunities, understand the commercial pathways of emerging technologies, and evaluate competing technologies in order to achieve costeffective decarbonisation results.
Findings from Black & Veatch’s ‘Corporate sustainability goal setting and measurement report 2021’ show that although 80 per cent of US-based companies with revenue in excess of $US250 million had set emission goals, 20 per cent had yet to undertake the commitment, and up to a quarter of chief executive officers were unsure of how they would meet those goals.
At an operational level, Black & Veatch believes responsible mining requires deeper environmental and sustainability commitments.
Mining operations that integrate long-term strategies for the implementation of renewable technologies such as electrification of operations, hydrogen and lithium battery storage systems, and hydrogen vehicles and equipment, can experience improvements in efficiencies, costs and revenue.
“Achieving sustainable outcomes for our mining clients is in complete alignment with Black & Veatch’s mission of building a world of difference,” Scrivens said. “We do that through the provision of expert advice and the implementation of innovative and sustainable infrastructure.
“We help mining companies at every stage of their sustainability journey, from the development of decarbonisation roadmaps and solutions that implement integrated tailings, water and water-reuse processes to electrification of on-site equipment, automation, digital asset management, data analytics and cyber security technology across the entire value chain.”
Black & Veatch’s 2020–23 sustainability strategy guides the company’s work and evaluation
of progress toward the sweeping environmental, social and governance responsibilities championed by the company’s employee–owners.
“A non-negotiable dimension of all our work at Black & Veatch is safety. It’s a core value and our clients require that our safety and injury-prevention performance across all our projects is at the heart of our approach,” Scrivens said.
A key tenet of the company’s sustainability strategy is its pledge to operate at net-zero greenhouse gas emissions by 2025.
“Megatrends such as climate change, decarbonisation and electrification – along with a focus on the principles embodied in the UN Sustainable Development Goals – are reshaping how we engage and co-exist with our clients and communities,” Black & Veatch’s chair and chief executive officer Mario Azar said.
“We appreciate that clients, community partners and other stakeholders not only share in our progress but work with us to identify new opportunities to help change the world through sustainable infrastructure.”
Elphinstone sold its first fully designed and manufactured underground mining product in 1983 and has since grown as one of Australia’s leading manufacturers of high-quality underground mining equipment.
Between 1975 and 1995, Elphinstone delivered underground mining equipment to over 50 locations around Australia and more than 35 global export sites across five continents.
The Elphinstone name became world-renowned for producing reliable, premium-quality underground hard rock mining equipment.
Elphinstone’s success drew the attention of Caterpillar, and the two parties formed a joint venture known as Caterpillar Elphinstone in 1995. Five years later, Caterpillar purchased the business, eventually replacing the Elphinstone name with the worldfamous Caterpillar trademark.
Elphinstone recommenced its underground mining equipment business in 2016, developing a new range of specialised underground support vehicles. That same year, Elphinstone introduced the WR820 Agitator at MINExpo in Las Vegas, signifying its return to the underground hard rock mining sector.
“Our customers see Elphinstone as a value supplier – we build premium quality products that provide a valued service to our customers,” founder and executive chairman Dale Elphinstone said.
“We won’t just build a product to a price; we’ll build a fit-for-purpose, quality solution that gets the job done for the customer”.
Total cost of ownership is a defining factor in the decision-making process when evaluating a machine. The initial cost is the first expense the business will incur throughout the machine’s service life, followed by ongoing ancillary costs.
These costs include maintenance and servicing, machine and facility downtime, annual and hourly running costs, repairs, safety or industryspecific inspections, reliability, and labour costs, including improvements and upgrades.
“If you were to compare our machines to others in the market, our larger, more robust chassis provides greater structural reliability, engineered to outlast our rivals in the field while providing greater value and a lower cost of ownership,” Elphinstone global sales and marketing manager Tim Mitchell said.
The highly configurable WR810 (10-tonne) and WR820 (20-tonne) underground base platforms and the UG20M and UG20K underground graders are engineered to withstand the rigours of the harsh, hard-rock underground environment.
Each machine is integrated with a proven Caterpillar powertrain and reinforced structurally with a larger, more robust chassis.
Component commonality across all platforms and applications provides a high level of reliability and durability, with exceptional parts availability
through the worldwide Caterpillar dealer network, all of which contribute to a reduction in the total cost of ownership.
“Each machine is designed and manufactured to be safe, reliable, productive, ergonomic, and easy to service, maintain and re-build,” Mitchell said.
Integrated into the WR820 and WR810 operator station is a ROPS/ FOPS – roll-over protective structure, falling object protective structure –that offers greater protection.
The WR810 operator cabin seats three people comfortably, allowing an entire crew to travel together rather than deploying an additional light vehicle for personnel transport.
Heading the series is the WR810 Water Cannon, a dual application machine that washes down ore fines, blasts material hang-ups, and fights fires. In addition, the side and rear water sprays suppress haulroad dust and wash down internal surfaces of tunnels.
Offering a flexible transport solution, the WR810 Delivery provides lift-on or lift-off capability, ideal for moving parts, components, equipment, and maintenance personnel safely and securely throughout the mine site.
The WR810 Scissor Lift has a purpose-built underground elevated platform, ideal for safe transportation and installation of components and services into the mine ceiling.
Specialising in transporting smaller batches of concrete to backfill voids, the WR810 Agitator 6m3 has a top
speed at capacity, improving cycle times and increasing production.
The WR810 Fuel and Lube provides in-situ top-up servicing of production machines and equipment within the mine, reducing servicing time and traffic on haul routes.
The WR820 10m3 Agitator specialises in the bulk transport of concrete to backfill voids and transfer of shotcrete to shotcrete machines. The front suspension and increased braking performance allow speeds equal to the production fleet, increasing productivity.
Utilising water spray heads mounted at the rear and sides of the tank, the WR820 Water Tank suppresses haul road dust and washes down internal surfaces of tunnels. The optional water cannon can wet down ore stockpiles, draw points and fight fires.
The role of the UG20M and UG20K underground graders is to maintain haul roads with adequate drainage for increased productivity and reduced operational costs of the haul fleet. Quality haul road maintenance ensures all production, support, and light vehicles can move freely in a safe and controlled manner with optimal efficiency.
Elphinstone continues to develop a high volume of new products, delivering over 270 machines worldwide. As an authorised Caterpillar original equipment manufacturer (OEM), all machine sales, technical assistance and access to spare parts are available and supported through Elphinstone and the global Cat dealer network.
Learn more
Australia’s mining operators can go beyond existing renewable energy power purchasing agreements and small-scale technology deployments.
Discover how the industry can go further, faster and stay ahead of global customers’ expectations for sustainable, zero-emissions products.
the same level of land access to hydraulically apply dust-suppression solutions this effectively.”
Due to the nature of tailings facilities, the equipment and vehicles must be equipped to deal with unique – and often harsh – challenges that are faced at mining operations.
“All Erizon-owned vehicles are fully mine-spec-compliant, and the snow groomer is no exception,” Marshall said.
“Every measure is taken to ensure the safety of the spray technicians who operate the equipment and the environment.
“Pulled by the modified snow groomer, the HydroTrailer has a PSI of 4.8 and utilises its state-of-the-art track system that carries a 15,000L tank. It’s capable of spraying up to 100m using its high-powered dual cannons or localised using the spray bar.”
Cseparation – in either a liquid, solid state or as a collection of fine particles – tailings on a mine site may be harmful and a danger to personal health and the environment if risk management is not applied.
“Tailings storage facilities have the potential to be a significant source of dust,” Erizon national manager Ed Marshall said.
“This dust can then cause issues for on-site personnel, equipment, the environment and local communities, which is why at Erizon we have dustsuppression solutions that help mining operations to continue operating as safely and responsibly as possible.”
Erizon has a customer-focused partnership approach to administering its dust-suppression solutions.
Soil analyses are used in tandem with survey data from the area to confirm the suitability of the product applied, and to ensure the tailings will not compromise or react negatively with the applied dust management.
Focusing on minimising the disruption to facility operations while treating at-risk areas, Erizon has engineered a range of specialised tracked HydroRigs and HydroTrailers that can access areas traditional equipment can’t while also negating the need for expensive aerial application.
These solutions enable mining companies to make sure their
in the event of an unforeseen circumstance, like unpredictable weather.
“These vehicles are safer, more affordable and more accurate than conventional application methods,” Marshall said.
“Safety is a catalyst for innovation with Erizon and the most recent development with regards to dustsuppression technology is our modified snow groomer and HydroTrailer.
some of the most demanding surfaces in Australia safely and efficiently. Initially built for extremely harsh environments and minimal compaction, we have adapted the technology to suit the Australian climate.
“The snow groomer is a powerful and capable machine that produces a PSI (pounds per square inch) of under one in its application of solution. No other vehicle we know can deliver
Supplying solutions beyond dust suppression, with the ability to provide additional support in areas such as erosion control and revegetation projects, Erizon can offer custom approaches that cater to the unique short- and long-term objectives of a mining operation.
With multiple products and application techniques, Erizon works to deliver greater levels of environmental compliance, decreased liability, a reduced effect on communities, and an overall decrease in environmental impact. AM
With operations in Canada, Europe, South America and Australia, Agnico Eagle is a leading global gold producer.
The company’s Fosterville gold mine is working with Sandvik to trial the new LH518B underground loader.
Located just outside of Bendigo, Victoria, the mine is the largest gold producer in the state, employing more than 800 people who are mostly local to the area.
A mining operation as large as Fosterville needs superior equipment to run smoothly.
And that’s where Sandvik comes in. Sandvik’s LH518B is a compact 18-tonne loader and is driven by battery-electric power.
The compact size and powerful motors allow the LH518B to fit in the tightest of tunnels without sacrificing payload or visibility.
The Fosterville operation will become the first mine on Australia’s east coast, and only the second such operation in the country, to take delivery of the LH518B.
“As a company, we’re committed to exploring new technologies to further enhance our extensive health and safety programs and to fully integrate sustainability into everything we do,” Fosterville Gold Mine general manager Lance Faulkner said.
The LH518B has several features that make it an ideal choice for the large gold miner.
The advanced lithium-iron phosphate battery is a particularly exciting feature, as it means the LH518B produces zero underground exhaust emissions and emits significantly less heat than its diesel counterparts.
Another feature of the machine is its 600kW drivetrain, allowing for higher acceleration than conventional loaders. This drivetrain also allows for fast ramp speeds, resulting in short cycle times.
And courtesy of its space-efficient battery system and driveline, the loader is capable of fitting in a 4.5x4.5m tunnel.
“By trialling the Sandvik LH518B, Agnico Eagle is putting itself at the forefront of this emerging technology and showing its environmental credentials,” Sandvik business line manager for load and haul Andrew Dawson said.
Dawson also commented on the advantages that Sandvik batteryelectric vehicles bring in terms of safety, efficiency and sustainability.
“It’s no surprise that they are rapidly gaining popularity among underground operators,” he said.
“Not only does the loader produce no underground emissions and significantly reduced heat, but it also delivers new levels of productivity.
“It all makes for a safer, more comfortable, more controlled underground environment.”
The addition of Sandvik’s AutoSwap technology was another attractive feature of the LH518B loader for Fosterville. This technology allows for a depleted battery to be offloaded
and a fully charged unit loaded in as little as six minutes, with no need for lifting infrastructure.
By utilising the AutoSwap feature, operators at the mine can reduce downtime, which is always an important consideration for mining operations.
“It’s crucial that new technologies are sustainable and safe, but also that they contribute to the efficiency and smooth running of our mining operation,” Faulkner said.
Sustainability has always been a particularly important goal for Sandvik, with Sandvik Australia general manager – sustainability Kate Bills saying the LH518B is a reflection of Sandvik’s determination to lead the market for safe, productive and climate-efficient mining equipment.
“Sandvik is putting its money where its mouth is by investing in batteryelectric vehicles and other technologies that are helping customers achieve their sustainability goals,” Bills said.
“Customers both globally and in Australia are increasingly looking for these kinds of solutions and we are proud to be providing them.”
Sandvik has been engineering solutions for the mining industry for decades and the LH518B is the latest in its large portfolio.
“We’re delighted to be putting the LH518B into service at Fosterville,” Faulkner said. “We’re interested to see just what kind of difference it can make in terms of efficiency and the underground working environment, and we look forward to working closely with Sandvik.”
AS MINING OPERATIONS EVOLVE THEIR DIGITAL INFRASTRUCTURE, AVEVA PROVIDES COMPREHENSIVE AND VALUABLE TECHNOLOGY TO CONSOLIDATE ALL FORMS OF DATA AND RECORDS.
Conflicts in data and records are a cause of concern for the mining industry at large.
Having accurate and up-to-date knowledge of materials, fuel and waste spread far and wide across a mine site is integral to ensure a company maintains a productive and efficient operation.
As businesses focus on realising environmental, social and governance (ESG) targets and limiting downtime on-site, having the digital framework and tools to manage information is imperative.
This is where AVEVA comes to the fore.
“Using a data infrastructure layer, we can bring together all information or data from disparate sources and locations and turn it into digestible, usable information,” AVEVA strategic account executive for mining, minerals and metals John Macdonald told Australian Mining
“In doing so, we have a single digital thread that can stop the data conflicts within different sections of the value chain.
“By treating information this way, arguments about data validity are either minimised or eliminated across the value chain.”
AVEVA’s software also allows for locally stored data, whether physically or digitally, to be uploaded to cloudbased software so all information is available on one data layer.
The scope of AVEVA’s software is dependent on the needs and usages of the site, with customer-centric solutions unique to each operation.
To aid sites that have issues with double-handling of materials at any point in the supply chain, Macdonald said having almost real-time inventory management updates is crucial to reducing operating costs.
“It starts with the rear-end inventory management. Normally, companies would know what their production is
during a certain period of time, like the end of month, for example,” he said.
“The issue, however, is that quantity can and does change, often unexpectedly, in an operation with as many moving parts as mining.
“What we’re able to do with capturing near real-time information is have those stocks validated in a near real-time basis, which allows companies to actually make better decisions, as they are working with the most relevant and upto-date information.”
In turn, the reduced doublehandling of materials enables companies to realise cost savings for themselves and their customers.
Additional tools from AVEVA include the AVEVA Production Management technology, which monitors the uptime, downtime and efficiency of pieces of equipment.
Taking diagnostic information from the consumption of resources such as water and energy, AVEVA’s
technology can make that data classifiable and readable so it can be acted upon.
“By taking classifiable metrics from the equipment, there exists the potential for a root-cause analysis to be undertaken to be able to understand what is happening in the equipment,” Macdonald said.
“From there, our customers can implement a continuous improvement loop, ensuring anything that isn’t working efficiently or as intended doesn’t continue to happen in the future.
“Our systems allow businesses to see the data of how their businesses are running. They can then make the changes they need and continue to monitor that data to ensure the changes are optimal.”
The AVEVA Production Management technology allows businesses to address the difficulties that come with the bulk handling and transport industry.
“AVEVA has the tools to prevent that by optimising the rate of materials passing through that natural bottleneck to keep both workers and the value chain healthy.”
AVEVA customers can receive access to the company’s full portfolio of services through the use of Flex credits. These can be trialled and then kept on or cancelled once the digital solution has been applied by the business.
Flex credits allow customers the ability to see the impact of the software and decide for themselves whether the solution will be a good fit for their operation.
“The solution is fully managed by the customer,” Macdonald said. “They put in the request and can download and use that AVEVA service. We’ve tried to cut out as much of the middleman as possible in delivering these services.”
As automation increases on mine sites, the way companies work with people on-site and across separate locations is changing.
Enabling mining companies to maintain productivity through the natural bottleneck of the value chain, AVEVA Production Management prevents conflicts from arising upstream or downstream by providing accurate data on exported materials.
“Each value chain has a natural place where it will bottleneck,” Macdonald said. “The ideal situation is to maintain a sustainable rate through that bottleneck. That means you’ll have maximum production throughout the whole value chain.
“A lot of the time, there’s conflict either upstream or downstream. That can push people to try and overperform, which will lead to one of two problems: either equipment downtime or quality losses through decreasing recoveries.
AVEVA’s software is fundamentally based around the asset and product data, enabling that data to be actualised on-site so workers are able to adapt and understand the changes taking place and contribute to a safer and more efficient mine operation.
“We aim to provide a seamless integration of data as it flows across the value chain.”
AM
An International Society for Rock Mechanics (ISRM) regional conference, AusRock 2022 is the largest global gathering of rock mechanic practitioners and encourages experts and newcomers alike to interact and elevate the field.
Sponsored by BHP and held in conjunction by UNSW and AusIMM, AusRock attracts a host of invaluable keynote speakers and exhibitors across its three days. The event is also open to physical and virtual attendees.
Ismet Canbulat, a professor of mineral and energy resources engineering and co-chair of AusRock, spoke to Australian Mining key benefits of running and attending the event.
“One of the things that makes AusRock so valuable is the ability to learn from other mining companies,” he said. “That chance to hear about daily experiences of other companies and benchmarking their own operations to other mines and implementation of new technologies is invaluable.
“And then also having the chance to learn about technologies that are available in other industries, such as oil and gas and civil engineering, in terms of what they’re doing and how we can implement those in the mining industry.
“Additionally, being able to learn from the best cases and the worst cases, because we share not only the positive side of things, but also the negatives when we can learn from those incidents.”
AusRock is advantageous for those looking to get a bearing on the broader industry, with experts and speakers on hand to provide a wide spectrum of experiences within the resources sector, from the daily operational issues to general engineering practices to giving newcomers the ability to understand what geotechnical engineering is about.
One of the particular areas of concern within the industry is around rock-burst, an issue present in many
mines sites as technology allows mines to go deeper and deeper.
To discuss this topic, Charlie Li from the Norwegian University of
Science and Technology will be attending the conference as a keynote speaker to discuss his experiences and highlight his work to date.
“The speakers at AusRock do not just have academic experience, but rather they are coming in with practical experience as well,” Canbulat said.
“With speakers from all industries and all backgrounds, we can see that there are so many amazing technologies and developments across other industries that we can share and adapt.
“These transferable pieces of knowledge are so invaluable to solving the puzzle put before us of the ever-changing state of the mining industry.”
Geotechnical engineers have roles that stretch far beyond designing
mine sites for optimal production, often also considering safety measures and the best ways to secure sustainable environmental, social and governance (ESG) targets.
The overlap of other industries and the lessons that can be learned from those who have different experiences in the field are part of what makes attending the AusRock conference so valuable.
“I encourage everyone to attend face-to-face rather than online (if they can), because that’s where the networking comes in,” Canbulat said. “That’s where you get to know people and that’s where you learn from other people from other industries.”
AusRock 2022 will take place in Melbourne between November 29 and December 1 2022.
THE OVERLAP OF OTHER INDUSTRIES AND LESSONS THAT CAN BE LEARNED FROM THOSE WHO HAVE DIFFERENT EXPERIENCES IN THE FIELD ARE PART OF WHAT MAKES ATTENDING THE AUSROCK CONFERENCE SO VALUABLE.”
The Niagara F-Class was built specifically for mining, using double eccentric technology. Unlike traditional inclined vibrating screens, it maintains constant g-force — even during surging — so you can achieve optimal material stratification.
working to develop my technical skills, I also completed a graduate certificate in employment relations.
AFacilitated by the Gold Industry Group, Australian Mining a number of interviews over future issues looking at career profiles of young-generation mining employees and their journeys into gold.
Turning the focus to fly-in, flyout (FIFO) roles, Christina Hartley, a human resources (HR) advisor at the St Barbara Leonora operations in Western Australia, talks about some of her unique experiences in the industry.
Were there any barriers to gaining your position?
As someone brand new to the industry with no FIFO experience, I thought my biggest barrier was going to be at the recruitment stage. I went into the process expecting to be overlooked for opportunities due to my lack of on-site experience, but that wasn’t the case.
empowered people and diverse teams, St Barbara, and my leader
Did you have misconceptions about the gold industry that turned out to be incorrect?
I used to think that most, if not all, mine sites were in the middle of nowhere, but there’s actually a lot of mine sites in the (WA) Goldfields that are close to or connected to towns.
St Barbara is right next to Leonora, which means we get the added bonus of being part of the community and can build relationships with community members and get involved in local activities, which is something rewarding that I didn’t anticipate as part of a FIFO role.
Has there been opportunity to further develop your skills and
I’ve only been working at St Barbara for a few months, but in that time I have had a lot of coaching from the
Additionally, there is a big focus on
Ever since I discovered that you could perform HR roles on-site, I’ve wanted to be in a FIFO role. And since starting my position at St Barbara, I’ve fallen in love with working here.
The operations here are beyond the scope of what I could ever have initially imagined, and I’ve been lucky enough to go on an underground tour of the mine and be exposed to what the gold industry looks like on-site, which is an experience I couldn’t have anywhere else.
It’s incredibly important. The gold industry provides a large number of jobs and it provides those to a diverse range of people in addition to providing job opportunities to remote and regional communities.
At St Barbara, in particular, we have a commitment to empower people in diverse teams and I think
“The new T 274 has been designed and adapted from years of experience in mining truck development,” the company said in a statement.
“The T 274 is a true 305-tonne machine that provides fast cycle times, higher production rates, low fuel consumption, and a low cost per tonne.”
A wide range of options is available for the T 274 and the entire Liebherr haul truck product line, including the next generation of interoperable machine automation solutions, which will be showcased at bauma 2022.
Liebherr commented on how the T 274 will contribute to its zeroemission roadmap.
“Liebherr Mining has committed to offer fossil-fuel-free solutions for its mining applications by 2030,” the company said.
“Two objectives have been defined to achieve this goal.”
W2022 is held in Munich at the end of October, attendees are in for a treat as Liebherr Mining will unveil a brand-new mid-size class hydraulic excavator and its new T 274 305 tonne mining truck.
The excavator, which is yet to be formally named, is the second Generation 8 machine within the Liebherr Mining portfolio.
A pre-series model of the new machine will be exhibited at the Liebherr booth. As the second machine within the Liebherr mining portfolio to receive the Generation 8 label, this new model comes equipped with the latest Liebherr technology products.
The T 274, a 305-tonne mining truck, will also be on display, featuring an impressive demonstration of the trolley assist system.
The trolley assist system uses onboard pantographs to connect the electric-drive system to a mine site’s electrical network, powered by the customer’s energy source of choice.
The trolley assist system offers increased truck fleet productivity, and the potential for reduction in fleet size while maintaining yearly production when compared with standard trucks.
consumption and carbon footprint by decreasing the fleet’s CO2 emissions demonstrates the trolley assist system as an effective first step on the road to zero-emission mine sites.
Liebherr’s portfolio has 56 trucks that have the trolley assist system, making it a tried-and-tested model.
Visitors to bauma 2022 will also experience the latest products and services from Liebherr Mining’s technology product range.
launched and encompasses solutions to enhance safety and overall equipment effectiveness, along with the company’s modular approach to emissions reduction, contributing to a more environmentally oriented development in the mining industry.
Speaking about the new T 274, Liebherr said it was excited to showcase it as part of the company’s collection.
The first objective is to offer mining products with low CO2 emissions by 2022. This goal has already been achieved through the implementation of the trolley assist system and an electric excavator range.
“Both technologies are consistently achieving proven results in the field to lower carbon emissions,” Liebherr said.
The second objective is to eliminate fossil fuels for the majority of Liebherr Mining equipment applications while maintaining machine mobility.
Liebherr has a defined roadmap for this process in the coming years with support from strategic partners.
These two variables mean Liebherr is well placed to offer its customers long-term sustainable solutions for a transition to an emission-free future.
“The basis of the zero-emission Liebherr Mining products is a modular approach, which allows the machines to be energy-type agnostic and drivetrain agnostic, enabling an upgrade or retrofit on existing equipment to zeroemission drives,” Liebherr said.
To further support customers in their zero-emission transformation journey, along with accelerating the research and development process and ensuring the best solutions will be offered, Liebherr has formed key strategic partnerships with industry experts ABB and ENGIE.
The company is excited to showcase its innovative solutions at bauma 2022, with a view to providing continuous updates and developments to its growing portfolio.
To be held at the Perth Conference and Exhibition Centre October 12–13, the WA Mining Conference and Exhibition showcases technical and digital innovation, bringing together suppliers, engineers and thought leaders for a two-day event.
This year’s expanded exhibition will showcase the latest tech and digital solutions across the entire mining value chain.
The conference will bring together experts, industry and academia to illustrate the technical and digital evolution transforming the mining industry in Western Australia, while showcasing the economic importance and the vital contribution the resource sector makes to state and federal economies.
Platinum partner Epiroc encourages industry, tech experts and site personnel to attend, with national sales manager capital equipment Rod Hermann saying that technology helps to move the needle in a number of key areas.
“Epiroc continues to live our motto, ‘dare to think new’, in an industry with rapidly evolving technologies to bring about higher levels of safety, efficiencies and sustainability for our customers,” he said.
“Partnering with WA Mining is just one way that we can help bring technology to the forefront of operations.”
WA Mining’s conference program features a line-up of more than 40 speakers, including conference chair Ric Gros and tech trailblazer Sarah Coleman, chief executive officer of idoba.
The conference’s themes cover critical minerals, digital and autonomous systems, decarbonisation and environmental, social and governance (ESG), and an industry outlook, presented by leaders in government, research, the Minerals Council of Australia, and the private sector.
Gros said it was an honour to chair the conference, which highlights some of the biggest challenges facing the mining industry in WA and across the country.
“WA Mining is an important milestone for the state’s resources sector, as it’s never been more important to share our knowledge for a successful future,” he said.
“We’re in an exciting place postCOVID – while there are certainly difficult things to contemplate like digital risk and the rising importance of ESG, there’s also the bright potential of technology, data science and new research to illuminate the way forward.”
Coleman is looking forward to presenting on the innovation opportunities for the industry. She said the conference and idoba’s goals were very similar: bringing together technology, process and people to co-create sustainable solutions for a better future.
“The world is fast-changing and increasingly more turbulent,” she said.
“The problems and challenges we are facing have too many variables to consider and we’re finding ourselves, our systems and our
traditional problem-solving approaches ineffective in dealing with the depth of these complexities.
“Change is no longer a choice for industries, especially mining – an industry already grappling with the disappointment of digital evolution, while simultaneously navigating the revolution drive by fundamental societal and market shifts across environmental, social and governance.
“Events like the WA Mining Conference and Exhibition are valuable opportunities for us to come together, because no one individual or organisation has the solution to address these complex problems.
“It takes diverse perspectives and skills to challenge the status quo, break down the traditional ways of thinking and the outdated approach to hierarchies so that we can make sense of the issues and adaptively respond to them.”
The conference is complemented by the free-to-attend exhibition, which features technology demonstrations
and workshop sessions presented by leading technology companies.
More than 90 technology and digital suppliers will be on display, including Epiroc, Acubis Technologies, Control Systems Technology, Atlas Copco, Emesent, Schlam, ifm efector and Sage Automation.
Exhibition director Samantha Martin said the team was excited to bring the WA Mining Conference and Exhibition back to Perth after two years of disruption putting the event on hold.
“There’s so much on offer, particularly for site personnel, technology leads and engineers who are interested in integrating technology to work in a safer or smarter way,” she said. “The technologies that are presented are extraordinarily eyeopening and certainly industry-leading.
“We’re proud to make WA Mining Conference and Exhibition an event that really makes attendees think, whether that’s in the conference’s thought-leadership sessions or the expo’s technological attractions.”
The International Mining and Resources Conference (IMARC) is where global mining leaders connect with technology, finance, and the future.
As Australia's largest and most influential mining event, IMARC creates a global conversation, mobilises the industry for collaboration and attracts some of the greatest leaders in the mining, investment, and technology industries for three days of learning, deal-making and unparalleled networking.
Learn from more than 450 mining leaders and resource experts with six concurrent conferences covering the entire mining value chain. Gain strategic insights from c-suite executives on minimising disruptions and building resilience, progressing ESG, accelerating mining’s energy transition and the future workforce. Whilst technical talks will delve into exploration, discovery and project developments, minerals processing, digital technology, and mining innovation.
Discover inspiration and new ideas, find practical solutions, and see demonstrations of the latest products and innovations from startups through to some of the biggest names in the mining industry with more than 470 exhibitors throughout the 17,000m2 expo floor all under the one roof.
Meet over 7,500 decision makers, mining leaders, policy makers, investors, innovators, and educators from more than 100 countries. As the largest gathering of mining professionals in Australia, IMARC provides unmatched networking opportunities, serving as the meeting ground for the mining industry.
Across three days, there are thousands of opportunities to network, brainstorm, and knowledge share, providing the perfect platform to obtain invaluable new business contacts, connect with the industry’s leading figureheads and explore new ideas.
The Australian Mining Prospect Awards were established in 2004 to recognise and reward excellence and innovation across the mining industry.
The 2022 awards mark the first time the event will take place in Perth, celebrating Western Australia’s vibrancy and central place in the country’s mining industry.
Organisers look forward to welcoming attendees to the awards gala on November 17.
• Australian Mine of the Year (sponsored by National Group)
• Lifetime Achievement Award (sponsored by Liebherr)
• O utstanding Mine Performance (sponsored by SEW Eurodrive)
• Mine Project Success of the Year (sponsored by Epiroc)
• Innovative Mining Solution (sponsored by Austmine)
• S afety Advocate Award (sponsored by Flexco)
• Project Lead of the Year (sponsored by Altra Motion)
• Excellence in Mine Safety, OH&S (sponsored by Vocus)
• Discovery of the Year (sponsored by Bonfiglioli)
• Indigenous and Community Engagement Award (sponsored by Schenck Process)
• Excellence in IIoT Application (sponsored by IFM)
• Excellence in Environmental Management (sponsored by Metso Outotec)
Austmine, the leading industry association representing the Australian mining equipment, technology and services (METS) sector, is proud to be a sponsor of the Innovative Mining Solution award.
“We believe that fostering innovation in the sector is crucial to ensuring our industry’s future success,” Austmine chief executive officer Christine Gibbs Stewart told Australian Mining Austmine believes innovation is the key to success for mining and mineral processing companies.
THE 2022 AWARDS WILL BE HELD IN PERTH TO CELEBRATE WA’S CENTRAL PLACE IN THE AUSTRALIAN MINING INDUSTRY.
“With a focus on decarbonisation, climate change and ESG (environmental, social and governance), it’s only through thinking differently and adopting new strategies, technologies and processes that the mining industry will be able to reach their goals and targets,” Gibbs Stewart said.
“New mining technology can take up to 15 years to be integrated into the value chain, which is a veritable lifetime for smaller companies that may not have access to the financial resources of larger players in the market.
“Opening conversations and developing true partnerships to accelerate technology adoption will be key to the industry’s longterm success.”
Liebherr Group is the sponsor of the Lifetime Achievement award. The company’s mining division supplies the industry with large machines for the extraction of raw materials in open-cast mining environments.
“Liebherr is making exciting progress with our developments in several mining projects, including our efforts into achieving zeroemission mining equipment,” executive general manager sales and marketing, mining Grahame Player told Australian Mining
As a third-generation familyowned company, the concept of lifetime achievement is important to Liebherr.
“Our founder Hans Liebherr dedicated his life to building the company that bears his name, and we see many similarities between
Hans Liebherr, his children and now grandchildren, the Liebherr Group, stand for,” Player said.
Metso Outotec, sponsor of the Excellence in Environmental Management award, is a frontrunner in sustainable technologies, end-toend solutions and services for the aggregates, mineral processing and metals refining industries.
“A key focus for us is the development of technologies and services that reduce the consumption of energy, raw materials and water,” vice president of minerals sales Kai Rönnberg told Australian Mining.
“Our extensive offering for the full plant helps our customers improve their profitability and lower their operating costs and risks.
“We have strong R&D (research and development) and innovation capabilities, and we are continuously looking for new ways to introduce
and better technologies and by improving our ways of operating, the mining industry can help to create a more sustainable future and we would like to recognise those who demonstrate this and lead the way in environmental management.”
The Prospect Awards highlight the innovation, excellence and success that abound in the mining industry, and Australian Mining the best of luck.
Truflo Pumps’ dewatering pumps enjoy legendary status in the mining industry for outstanding reliability, efficiency, high performance, and robust build qualities. The pumps are designed, manufactured, and built in regional Australia using only the highest quality metals and componentry available, backed by over 30 years of industry experience. The pumpsets are configured either to a standard application or built bespoke according to the task at hand and to your budget. These pumpsets have stand-out features such as fully automated vac-assisted self-priming, pontoon, skid or trailer-mount options, double bunded in-built fuel tanks, marine-grade paint, remote fuel tank control, web-based pumpset monitoring together with the PumpMaster Control Panel, plus many other features and options.
A&I Coatings, an Australian-owned industrial coatings manufacturing company, has developed a complete system that helps to reduce workplace exposure to harmful chemicals and increase efficiency in the spray booth.
A&I Coatings Vitrephos 560 primer and Vitrethane 650 topcoat are designed to speed up throughput times during application. The V560 primer and V650 topcoat system has excellent wet-on-wet properties, with easy sanding and exceptional drying properties, especially in cold weather, and good film build which has seen a reduction of work hours required to complete works. The V650 topcoat is also reducing labour hours due to its high coverage and presents strong gloss retention to finish, again a very cost-effective option. Added to this are the safety features this system offers, with zero exposure to harmful isocyanate chemicals. Exposure to isocyanates is known to cause both respiratory illness and skin irritation, such as allergic contact dermatitis.
• aicoatings.com.au
CoreSmart is an artificial intelligence system readily trained to predict metal grades directly from hyperspectral data. While the system can be used for drill core analysis, airborne data and in operational mining, the database behind the learning system is itself a vast pool of underutilised data for strategic greenfield exploration.
Metal grades of a wide variety of metals for thousands of drill holes are fully available based on the predictor in addition to assayed segments of the core.
The use of this data combined with the expertise of Dimap and GEOS Engineering in complex data analysis and modelling opens up new approaches for identifying potential industrial and rare metal targets. As the data pool is increasing and new metals are integrated into the CoreSmart Predictor, the use of proxies for lithium and rare earth elements detection improves.
Neousys Nuvo-9000 series is powered by Intel 12th generation Alder Lake Core i processor, supports up to 64GB of DDR5-4800 memory and wide temperature operations, and features flexible expansion and rich I/O ports to digitise your mining operations for equipment such as autonomous dump trucks, excavators, shovels, and for control room and field monitoring applications.
Benefited by the 16-core/ 24 thread configuration of Intel 12th generation Core I processor, Nuvo-9000 presents an incredible boost of performance
The LaseTVM-3D-M (Motion) is a highly accurate 3D laser measurement system for automatic and dynamic measurement of truckload volumes during a passage. The measurement system has high versatility and is used for volume measurement of various materials such as stones, sand, ore or wood products. The LaseTVM-3D-M enables dynamic measurement of the load volume without stopping the vehicle. The laser scanners are mounted on a frame or boom in a central position above the truck lane. One laser scanner measures the transverse profile of the load, and the other laser scanner does the tracking of the truck. The truck is measured once empty and once full (which measurement takes place first depends on the process). The difference between the full and empty truck measurements gives the exact loading volume.
Predict and protect with moneo from ifm. The moneo software platform uses and focuses on the power of digital information generated by smart IO-Link sensors and makes it available as a solid basis for decision-making while indicating the need for action to warn you before it is too late. Planning maintenance according to requirements is important to ensure future machine uptime is efficient, and real-time maintenance is convenient. moneo’s modular concept provides a selection of different, easy-to-handle applications that can be linked together. From sensor parametersetting to condition-monitoring, moneo offers all the features of a future-proof IIoT software. For over 50 years, ifm has been supporting customers as a leading supplier of automation solutions. It now combined its experience in sensor technology with the expert knowledge of our software subsidiaries – this is moneo, “simply made for you”.
RPMGlobal has upgraded ShiftManager with an array of new functions designed to enhance communication and collaboration across mining operations.
The latest version of the planning and task management software comes with the ShiftManager Mobile feature, which has been upgraded to take full advantage of the functional and architectural changes within this new release. The user interface has been overhauled and users can quickly notify their colleagues if a task they are working on will influence other processes within an operation.
The upgraded ShiftManager assists maintenance teams to better organise their priorities and communication with equipment owners, with notifications sent to the latter once a maintenance request for their equipment has been initiated. Another improvement allows for fully configurable and site-specific auditing of all tasks and changes. ShiftManager Mobile is key to the solution’s functionality and can be accessed by both Apple and Android users.
• rpmglobal.com
With an increasing demand for lighter, stronger steel that lasts, mining operators are continually looking for ways to push their earthmoving equipment harder, and for longer. This is where bespoke steel manufacturers come into play with the production of innovative steel designed to withstand the toughest environments. For over 40 years, there is one company that has built a global reputation for its quality, high-performance steel – and it’s proudly Australian. Bisalloy is Australia’s only manufacturer of quenched and tempered steel plate used for wear-resistant, structural, armour and protection steel applications.
The Bisalloy Wear steel range is renowned in mines, exploration and mineral processing operations, and quarries all over the world. Equipment manufacturers require quality steel grades to achieve greater wear resistance and simply get more out of their products, particularly buckets, truck bodies, ground engaging and demolition tools, wear plates and liners for chutes, as well as trommels, screens and crushers.
practices to improve the productivity and safety of mines.
By sharing and disseminating the knowledge gained from operations in Australia and around the world, AusIMM can assist in the provision of the raw materials needed.
The message remains that ventilation controls form much of the effective management of core risk activities in mines. The recognition of this has brought about the requirement of the position of statutory ventilation officers in coal and metalliferous mining sectors in Australia.
Coupled with this is the re-emergence of pneumoconiosis in mine workers. These and other factors should provide the incentive for all underground operations to contribute strongly to this conference.
Significant developments in practice and research in recent years have helped ensure we maintain and improve levels of safety within our underground mining sector.
The conference organising committee aims to provide an opportunity to present these developments so the industry can benefit from this collective knowledge and will call on expertise from industry, academia, researchers and regulators to bring about the 12th in a series of ventilation conferences.
• ausimm.com/conferences-and-events/ minevent/
International Mining and Resources Conference (IMARC)
Sydney | November 2–4
The eighth IMARC comes to Sydney from November 2–4 after being relocated from Melbourne.
A vivid showcase of all the elements that make the mining industry great, IMARC
throughout six concurrent conferences with a program covering the entire mining value chain.
The likes of BHP, Newcrest Mining, Agnico Eagle and Core Lithium will be presenting at the event, along with original equipment manufacturers such as Caterpillar, Epiroc and FLSmidth. For those who registered for the previous event dates, the tickets will have automatically transferred to the new dates.
• imarcglobal.com
Australian Mining Prospect Awards 2022 Perth | November 17
Taking place in Perth for the first time, the Australian Mining Prospect Awards are a great opportunity to recognise and acknowledge the people and companies in the mining sector for their outstanding work.
Having recently celebrated the 2021 Prospect Awards winners, nominations are now open for 2022, with awards honouring categories such as Indigenous and Community Engagement, Mine Project Success of the Year, Outstanding Mine Performance, Sustainability Project of the Year, Discovery of the Year and more. Some of the 2021 award winners included Roy Hill for Australian Mine of the Year and Hard Rock Mine of the Year, Mader Group for Contract Miner of the Year, and Metso Outotec for Minerals Processing of the Year.
This year will be the first time the awards will be held in Western Australia in appreciation of the vibrancy and importance of the state’s thriving mining industry.
• prospectawards.com.au
representatives from industry, research, innovation, education, and government to share knowledge on cutting-edge science and technology in the field of mining biotechnology and discuss innovative solutions and best practice approaches. Drawing from the expertise in biotechnology, chemistry, mineralogy, and engineering, mining biotechnology can benefit the resource sector by enabling the extraction of value from low-grade minerals and wastes streams, providing tools for minerals exploration and environmental monitoring, and mitigating harmful environmental impacts.
The IBS 2022 will be held in hybrid format: face-to-face at Rendezvous Hotel Perth Scarborough in Perth, Western Australia and through an online platform from 20–23 November.
IBS 2022 will be hosted by Australia’s National Science Research Agency, the Commonwealth Scientific and Industrial Research Organisation (CSIRO). The local organising committee includes members from CSIRO and Curtin University.
IBS 2022 is a great opportunity to share the latest scientific advances, find solutions for industry challenges, attend as a sponsor or exhibitor to promote technologies, services and products, and meet experts across the world.
• ibs2022.com.au/
AusRock Conference 2022 Melbourne | November 29 –December 1
Hosted in partnership with AusIMM and UNSW Sydney, AusRock 2022 will be held in conjunction with the International
follows on from earlier conferences that have successfully covered the various aspects of geotechnical engineering servicing the mining industry and shared best practices.
BHP, Jennmar, DSI Underground and GSS have confirmed their support, with exhibitions set to be held by Rocscience, Minova, MineGeoTech and DSI Underground.
AusRock2022 will focus on new technologies and developments, industry needs, operational problem-solving, and practical case studies that will be required for the future.
• ausimm.com/conferences-and-events/ ausrock
Underground Operators Conference 2023
Brisbane | March 27 29
A flagship event in AusIMM’s calendar, the Underground Operators Conference will return in 2023. Bringing together mining engineers, mine operators, technical service managers and consultants, this conference sets the benchmark for sharing underground operational experiences and industry best practice.
With deposits getting deeper or lower in grade, there is increased pressure to find smarter and more cost-effective ways to extract orebodies.
To address this demand, key discussion topics for 2023 centre around the evolution of digital technologies, automation and artificial intelligence, and how these innovations are making it possible to mine at greater depths and lower grades.
• ausimm.com/conferences-and-events/ underground-operators/
Less sediment, less downtime, less trouble.
Slurry sumps can be a constant hassle. Pumps wear hard and fast, and the sumps fill up with sediment. Cantilever pumps are often not up to the task. We know, because that’s when we are called in.
The advanced CFD design of Flygt slurry pumps ensures exceptional levels of abrasion resistance. In addition, we provide an array of measures that keeps sumps clean, even with the heaviest slurries.
Daniel McEvoy is a Reliability Engineer at Motion Australia. His main focus is working with customers to reduce risk and increase reliability of their critical plant. Condition monitoring is one of the ways we effectively do this, and it is part of Daniel’s day-to-day role. The team can help identify, track and trend potential faults on critical pieces of equipment, reporting problems back to the customer so they can be proactive with their maintenance strategy rather than reactive. This helps the customer save money with unnecessary down time. Daniel has a range of skills which enable him to conduct vibration analysis, oil analysis, infrared thermography etc. Daniel also notes that correct installation of parts is a major benefit to plant uptime. as it provides our customer with the best opportunity to maximise service life, and reduce down time and unwanted production losses. Other day-to-day tasks for Daniel include training, consultation, root cause analysis and corrective services.
1 What’s your favourite word?
It would be a toss-up between, sure, mate or grand.
2 If you could win an Olympic medal for any sport, real or fake, what would it be?
Fixing things.
3 If you could change your name, what would it be?
Mr. Fix it!
4 What was your favourite subject in school?
Applied Technology
5 What’s your hidden talent?
Surprisingly, bowls
Daniel has a range of skills which enable him to conduct vibration analysis, oil analysis, infrared thermography etc.
During a time of uncertainty for the global supply chain and skills shortages across many industries, uptime is everyone’s most valuable resource. The mines and quarries sector is learning to adapt, employing new technologies and approaches to help equipment communicate through advanced condition monitoring.
Grant Gray, General Manager –National Sales at Motion Australia, says that even amongst the growing need for raw materials across infrastructure and construction, quarrying operations will need to embrace the benefits of Industry 4.0 if they hope to remain competitive.
“Most consumers are noticing the widespread challenges when veggies are out of stock at the supermarket, or their favourite restaurant is closed two days a week due to staffing issues,” he points out. “But these problems are heavily impacting resource sectors as well, along with an inordinate demand
for raw material – so having increased visibility on the health of equipment is paramount.”
In a rugged quarrying environment, gearboxes and other parts are often subject to contaminants, extreme temperatures, and heavy use. Whether it’s a crusher, roller, pump or screen, even the most reliable equipment can experience unexpected failure. But according to Grant, it’s all about the smarter allocation of time and people power to keep ahead of the game.
“The increase in material demand also puts more load and stress on quarrying equipment – we’re moving a lot more product now, and we’re moving it faster, for longer. It’s vastly more productive to have maintenance fitters staying on top of equipment upkeep and scheduled change-outs, rather than continually spending time attending to broken gear. This is where a remote or online monitoring solution can make all the difference.”
While online condition monitoring has been a reality for some time, Grant says that flow-on challenges from the Covid-19 pandemic have forced many businesses to take stock and evaluate the potential strengths of predictive maintenance solutions.
“I think historically there has been a view that this is a tool reserved for the big players within the sector,” he reflects. “And that just isn’t the case anymore; the costs around
implementing it, even on single site operations, has come down significantly, and the return on making that investment is evidently worth it.”
Echoing this sentiment, Michael Greelish, National Business Development Manager at Motion Australia, points out that reliability and consistent production is only capped by the extent of a site’s predictive maintenance plan.
“We do a lot of remote monitoring for quarries, particularly on crusher machines,” he says. “Rather than letting them run to failure, it’s more beneficial to keep an eye on their ongoing performance and address any necessary repair or replacement in a timelier manner.”
Even in smaller quarrying environments, the integration of online condition analysis to one or two crushing machines has proven beneficial in the long-term. Sensors can replace the need for regular maintenance checks, freeing up time throughout the day that might be better invested elsewhere on site.
A correctly installed digital framework allows operation managers to have greater visibility on the health of each piece of equipment, closely analysing factors like speed, vibration, pressure, and temperature of different moving parts. Compared with traditional, frequency-based monitoring approaches that depend on manual
labour, the generated data offers an increased likelihood of identifying subtle changes to the machine’s behaviour.
“Catastrophic breakdowns on crushers and screens always start with something small,” Grant explains. “A little vibration, or small drip from a seal. Then all of sudden the gearbox has got no oil in it, and all the metal parts are grinding without lubrication, so you’ve got excess heat building up.”
“Of course, ultimately, the whole thing explodes, costing hugely in downtime and repair,” he continues. “So, the question we ask ourselves is, what could we have done if we’d known? If we’d noticed that high frequency sound coming out of the machine, or slight uptick in temperature before it wasn’t too late?”
As experts in the supply and maintenance of critical quarrying equipment, Motion Australia is well placed to assist with this level of monitoring, analysis and support. The Quarry Roadmap industry guide outlines key pain points often seen on primary and secondary pieces of equipment, suggesting practical solutions based on the team’s extensive knowledge.
“Now is the time to be having these conversations with us, so we can come to your site and offer added value to increase your production,” urges Grant. “These issues around supply chain aren’t going away overnight. With the global demand for raw material, we will continue to be heavily invested in ensuring uptime for quarries.”
Scan to take a look at Motion Australia’s Industry Solutions Quarry Roadmap.
belts, so they called us in to organise a solution,” he recounts. “Our power transmission specialists looked over the crusher and identified where there was cracking due to heat, as well as some marking that indicated excessive slippage.”
width. They weigh about half of what a standard V-belt would and are nonself-igniting to mitigate fire risk.”
In many ways, crushers are the heartbeat of a quarrying site, working constantly to break down large pieces of raw material while contending with high vibration, dust and other contaminants. On a recent site visit to a quarrying and materials recycling plant in Melbourne’s west, Motion Australia successfully carried out a drive belt upgrade that has led to significant cost and downtime savings.
The customer’s primary cone crusher was running off a 250KW electric motor and experiencing rapid changeover requirements due to an accelerated wear life on the belt assembly. According to Rob Michelson, National Product Manager for Belts at Motion Australia, the standard V-belts were not capable of meeting the site’s high volume production rate.
“The customer was only getting two to six weeks life out of their previous
“We suggested the Gates® Predator® V-Belts as the best solution going forward,” he continues. “They’ve been running on there for about three months now and in down time alone this change-out has saved them around $90,000. They’re extremely happy with the outcome, as are we.”
Rob suggests that realistically, if belts are requiring replacement more than once a year, a drive analysis is required to assess where improvements can be made.
“The added benefit of this customer’s upgrade is that they were able to go from using ten belts down to six,” he points out. “This has helped provide better overhung load and increase the drive’s bearing life. It’s a bit more compact and creates a much more robust unit.”
Achieving the right amount of tension on any belt application is critical. Too loose, and it will likely experience excess heat or premature wear. Setting them too tightly, however, will result in added strain on the shaft and bearing components.
Rosynes Hernandez, Product Manager for Power Transmission at Gates® Australia, says that while standard belts usually feature polyester tensile cords, the Predator’s aramid alternative offers a maintenance-free solution that won’t require constant re-tensioning.
“The Predator’s aramid core is the strongest available in V-belt construction,” she says. “It’s what pulls and holds the tension to transmit high rates of power. The grip on the pulley is seriously firm, and the curved sidewall ensures a clean, even wear across the
Rather than using a standard rubber material, the Predator® belts are constructed from a chloroprene compound, which boasts superior resistance against both heat and oil. Able to handle up to 2.2 times more power than similarly sized standard V-belts, they also include a bareback cover for added protection.
“The great thing about the double layer fabric cover is that it reduced friction and heat build-up, but also allows for a small degree of potential slippage,” says Rob. “In these crushing units, there is often a lot of high shock load, so if the drive belt can be a little forgiving without losing power capacity, that’s ideal.”
As part of the equipment analysis, Motion Australia’s power transmission specialists used the Gates® Design Flex® Pro™ Software to obtain a comprehensive reading on the drive’s performance and health. This offered a better understanding of the required changes, so that relevant on-site training for installation and aftercare could be carried out.
“All of our power transmission managers are currently travelling around Australia to get this program downloaded into our customer’s systems,” says Rob. “It’s going to give them better visibility over their drive performance on a range of different machines, to make sure that they aren’t
over or under designed.”
The professional Design Flex® Pro™ portfolio allows users to save on time by identifying the most suitable belt products to fit each unique piece of equipment. It can print, email and create PDF files of these design specifications to streamline the
estimation of energy consumption, belt pull, cost savings and overall transmission capacity.
“A lot of people already have their eye on the Gates brand when they come to us for these types of applications,” concludes Rob. “They’ve garnered an incredibly strong reputation in
the Australian industrial market as a robust product that’s designed for the harshest operating environments.”
“These premium belts, hand in hand with such an industry-informed analysis program, truly gives customers the best possible outcomes that will stand to last in the long-term.”
From Rockhampton to the Pilbara, the mining and quarrying networks in Australia are widely spread out, with many operations taking place in geographically remote locations. This can mean that sourcing everyday equipment sometimes proves difficult, and inventory management requires more than a little forward-thinking.
Enter Motion Australia’s diverse selection of vending solutions –designed to combat supply chain costs and downtime by allowing 24/7 access to the most frequently used tools, PPE and consumable products.
According to B2B eCommerce Manager Brenton Finch, overconsumed and misplaced items account for a considerable portion of overspending on many industrial sites, having a serious impact on the bottom line.
“What makes our machines unique is that they work in tandem with the CribMaster software, which is really the key to monitoring stock levels and configuring things like controlled access,” he explains. “It lets the user know exactly what they’ve got on hand, notifying them when they need to reorder. This allows for smarter resource
allocation for each particular job, team or individual employee.”
The On-Site Solutions system can be tailored to suit each user’s requirements and project layout. It can either print a simple stock report on a regular basis, or even generate automatic re-ordering back through the nearest Motion Australia branch.
“Having that added traceability is hugely beneficial in a number of ways,” points out Brenton. “It reduces downtime spent looking for and ordering items, because it can ensure constant product availability. Using this solution, there
should never be an instance where something is inconveniently out of stock, because it will have already flagged the system and triggered a reorder ahead of time.”
Additionally, it allows the business to reduce overall batch quantities, and avoid wasting costs on over-ordering. Instead of the business ending up with three times the amount of bearing lubricant than what is actually required, it will make the whole process more streamlined by reducing redundant stock.
“What’s more,” Brenton says, “it promotes a huge cost saving related to lost or damaged equipment, because it has constant records of who is accessing the machine at what time, for whichever specific task. It does this through individual ID numbers or a swipe card required for access – this is entirely configurable depending on how much information the site manager wants to keep on hand.”
Ideal for high-use consumables, PPE, general shop supplies and cutting tools, the ToolBox unit resembles a regular food and drink coil vending machine. The userfriendly touch screen interface allows individuals with approved access to retrieve items easily throughout the day, mitigating the need to visit a stock room or travel off-site for parts.
Each product is clearly visible through the glass front panel, and stored between coils of varying depth and width. Available in either six or seven shelf options, it can store up to 60 individual SKUs at any given time.
The next step-up in Motion’s vending portfolio is the ProStock – designed to hold small, pre-packaged maintenance, repair and operations (MRO) items. Much like the ToolBox, it can be used to stock PPE, cutting tools and general shop supplies, but is also suitable for welding consumables and electrical components. It has a much higher SKU capacity of up to 560 items, and can be reconfigured as stock rotates through.
Venturing into larger capacity solutions, the WeighStation is a double-door
cabinet which offers more versatility in product size. It can carry about four to five times the stock volume of the standard coil machines, including small to large MRO consumables, abrasives, and general shop supplies.
The precision scale technology offers accurate reporting on changing stock levels, and the easily accessible storage trays ensure timely replenishment.
For storing frequently used tools and larger items in a convenient location on site, the ProLock is a fully configurable storage container with up to 24 individual lockers. Best suited to durable and calibrated tooling, it can also factor restricted access to items requiring inspection prior to use. Cordless power tools can be placed on charge while inside, making it easier to keep track of everything in the one place.
“Larger sites might also consider our upscaled inventory solutions, such as the AccuCab decentralised tool store, or an RFID Storeroom, which features secure gated entry and much larger holding capacity,” says Brenton. “The
1. The end-user takes whichever items they need from the dispensing unit.
2. The process software downloads the usage information throughout each day. It then alerts the local Motion Australia branch about which items need to be replenished.
The quarrying industry can pose significant health and safety risks to employees if quarry managers don’t take steps to ensure a safe working environment.
According to Work Safe Victoria, there are more than 900 quarries in the state of Victoria that range in size from locally owned and operated quarries to large scale operations that are owned by conglomerate investors and global mineral powerhouses.1
Victorian quarries produce a range of materials that supply other Australian industries. Whether it is cement, stone or aggregates like rock, gravel and sand used in the building and construction industry or mineral soil for agriculture, Australians depend on quarried materials for every aspect of their lives.
And yet, regardless of the size of a quarrying operation or the crucial role it plays in Australian life, the risks and hazards quarries pose always remain the same because of the nature of the working environment.
It may seem obvious that falling rocks could be a big risk on quarrying sites, but there are many ways that this can occur on various pieces of quarrying equipment, according to Steve Hittmann, Category Manager for Industrial Drive Systems and Mobile Final Drives at Motion Australia.
“Quarrying equipment is designed to move heavy rock material upwards, downwards, and side to side. This could be in the form of an inclined conveyor belt or a bucket elevator,” says Steve.
“Now imagine for a second that an incline belt conveyor that is about 30 or 40 metres long has heaps of crushed rock on it going uphill to another location on site. In total, that conveyor could have 10 tonnes of crushed rock on the incline.”
“Now if the drive on that conveyor
cuts out for whatever reason– an equipment failure or a power outage–the drive and the conveyor belt will start running backwards down the incline and the 10 tonnes of crushed rock will go with it, landing at the bottom of the conveyor, with any luck nowhere near any pedestrians. But the damage that it can do is catastrophic.”
These kinds of dangerous situations are not uncommon on quarrying applications. As a result, Victoria’s Occupational Health and Safety Act of 2004 issued strict regulations for quarrying sites that ensure these dangers are minimised as much as possible.
Installing backstops and anti-roll back technology on inclined conveyors is just one of the required precautions that every quarry must take on equipment to stay within the bounds of OHS laws, but it is a very important one.
“Australia-wide, any piece of equipment that is inclined by more than four degrees, is required by law to have anti-roll back technology in place,” expounds Steve.
“Fortunately, Motion Australia suppliers that we work with like Regal Rexnord have been proactive in designing solutions to address the dangers of quarrying applications with their Falk True Hold NRT Low-Speed Backstops solution.”
For more than 125 years, Regal Rexnord has been globally recognised for their forward-thinking innovation in the fields of power transmission. Regal
Rexnord acquired the Falk brand in 2005, ushering in a new range of power transmission solutions which now includes safety products for industrial applications.
On a basic level, the Falk True Hold NRT Low-Speed Backstops are a failsafe solution for elevated and inclined equipment, as they allow it to rotate in only one direction. An example is in the case of an inclined quarrying conveyor - the belt line can rotate up the incline,
1. Suitable for dusty environments
Dual, double lip contact seals on each side of unit protect against lubricant leakage and contamination.
2. Longer service life
Grease purgeable exclusion seals create a barrier for contamination and enhances seal life, reducing maintenance costs and extending the life of the seals.
3. Low maintenance generous lubricant capacity
The units maintain optimum oil splash for internals and optimum cooling of the Backstop. The cooler operating temperature enhances oil life and seal life.
4. Visual lubricant check
A standard oil site glass allows operators to verify lubricant levels visually.
but it won’t rotate backwards. If the machine tries to roll back, the Falk True Hold NRT Backstops will stop it. But in addition to providing substantial safety benefits, the Falk True Hold NRT Low-Speed Backstops also have a number of other capabilities, according to Steve.
References: 1. Worksafe Victoria. Quarries health and safety guide. https://www.worksafe.vic.gov.au/ quarries-health-and-safety-guide
5. Performs optimally under variable temperature, humidity, and moisture
The Falk 3-micron Airmax Breather prevents moisture from entering during the inhalation cycle and allows moisture to exit and evaporate as the NRT reaches normal operating temperature. This prevents water contamination and eliminates oxidation of rotating elements.
6. Positive holdback operation Ramp and roller backstopping mechanism performs a wedging action of the cylindrical rollers compressed between the inner cam and outer race assuring immediate prevention of roll back rotation.
7. 100,000 full load cycle rating
Backstop mechanical design capabilities meet or exceed the life of most or all system components. NRTs can run longer than the expected system design life.
Other features and benefits
• Proven speed and load functionality
• Ideal for high vibrational applications
• Dual sets of fasteners and gaskets on seal cages
• Versatile installation potential
• Extended torque capability with load balancing on hydraulic load sharing system
• Maximized tonnage capabilities
• 3-year Heavy Duty Warranty
Falk True Hold NRT Backstops use anti-rollback technology to failsafe quarrying conveyors.
The inside of fluid power machinery is complex, and subject to some of the harshest conditions on mining sites. To address this, Gates® has designed a fit-for-purpose range of industrial-grade hoses, ideal for transporting water and emulsions between hydraulic components.
The Megasys® portfolio offers increased performance and flexibility, facilitating peak plumbing and routing in compact applications. Capable of reducing expenditure by up to 64 per cent, they are easy to install and require fewer bent tube fittings. With such diverse capabilities within the range, it’s important to select the most suitable hose for each individual system.
The Gates® Megasys® range is separated into two main categories:
Wire-braid hose – M3K, M4K, M5K, M6K, MXT, MXT-XTP
These are constructed using high-tensile steel wire and are tested to 600,000 cycles.
Spiral-wire hose – EFG3K, EFG4k, EFG5k, G8K
These are constructed from four to six alternating layers of spiralled, high tensile steel, and are tested to up to one million impulse cycles.
Xpiral hose – MXG4K-XTP, MXG5K-XTP
Built with Gates patented Xpiral™ woven spiral technology, MegaSys MXG™ 4K/5K hydraulic hose is lightweight, highly flexible and qualified to one million impulse cycles. MXG™ 4K/5K exceeds the performance of wire spiral constructions, but with the lower weight and flexibility driven by Gates materials science technology.
Identification laylines are printed along the side of each product, and are used to
communicate critical information about its specifications. This offers increased efficiency for purchasing or organising stock on site. In addition, hoses in the MegaSys® line are distinctly colourcoded to quickly and easily view pressure ratings.
• YELLOW: 8,000 PSI, G8K
• ORANGE: 6,000 PSI, EFG6K
• RED: 5,000 PSI, M5K/EFG5K/MXG5K-XTP
• PURPLE: 4,000 PSI, M4K/EFG4K/ MXG4K-XTP
• BLUE: 3,000 PSI, M3K/EFG3K
Alongside the respective colours, each hose description label will list the I.D number, bend radius, psi working pressure, SAE and European standards, and important features such as flame resistance.
To makes things easy to remember, Gates® recommends using the STAMPED method for running through hose selection criteria:
S = Size
T = Temperature
A = Application
M = Material to be conveyed
P = Pressure
E = Ends or couplings
D = Delivery (volume and velocity)
The inside of a hose diameter can vary, and must align with pressure requirements to avoid excessive turbulence. If possible, check the printed measurement on the side of the old hose that needs replacing. If this has worn off, cut the original hose and carefully measure the internal diameter to match up with the new product.
Both fluid and ambient temperature need to be considered when putting together a new hose assembly. The selected product must withstand the minimum and maximum temperatures that it will experience in service.
Noting where and how the hose assembly is going to be installed will help to determine an optimum selection. Some questions to ask in this process are:
• What is the fluid compatibility?
• What are the environmental conditions and potential risks?
• What are the routing requirements?
• Are the government and industry standards being met?
• Are there unusual mechanical loads?
• Is a non-conductive hose required?
Ensure that the hose tube, cover, couplings, and O-rings are compatible with the water, oil emulsions, or glycol solutions being used. Take care in this selection where gases are present.
Noting the system pressure is one of the most important steps. The published working pressures must be equal to or greater than the relevant system pressure rating. If the hose experiences pressure spikes beyond this, the product life will shorten, so this is not recommended.
Proper sizing of transport efficiency can be ensured by checking the original hose I.D. against the new one. If any relevant aspect of the system has since changed, use the Nemographic Chart to make an exact measurement.
In the quarrying industry, the success of a quarrying operation depends on the performance of equipment in the field. To optimise productivity and keep operational costs down, quarries need to operate like a well-oiled machine with all equipment running at peak performance.
However, due to the nature of a quarrying site and the arduous operating environment, quarrying equipment is subject to a lot of wear and tear from the effects of harsh chemicals, rust and corrosion, and the ingress of moisture and contaminants.
As a result, quarry maintenance departments face a tremendous amount of pressure to keep equipment wellmaintained to curb the costs of incidental breakdowns and premature equipment failures, according to Steve Keown, National Product Manager for Lubricant and Chemicals at Motion Australia.
“Equipment maintenance and repairs significantly impact an operation’s bottom line. A large majority of quarrying equipment is custom made to fit out a site’s specific requirements, so it is an expensive investment,” says Steve.
“In addition to this, any downtime that is experienced on equipment incurs costs to productivity, time, and labour,” says Steve. “Therefore, when equipment and componentry experience an incidental failure– the repair process is critical to controlling operational costs.”
For the team at Motion Australia, helping quarries protect valuable equipment and assets means determining maintenance solutions that can reduce downtime and labour costs. While at the same time, aiming to improve the performance and longevity of equipment and componentry in field.
“There is always a risk during the repair process that a component could be damaged or require a replacement, particularly during disassembly,”
explains Steve. “In the instance that the component manufacturer is overseas, and a part or component needs to be imported, that increases downtime and costs on an operation.”
For a practical solution that addresses some of the quarrying industry’s most critical pain points, Steve recommends the CRC 5.56 Multipurpose Lubricant.
“The CRC 5.56 is a timeless solution that we have supplied to many of our biggest customers in the heavy industrial market over the years,” says Steve. “On quarrying applications it’s ideal for lubricating and protecting fasteners, shackles, pins, bushes and hinges¬ in hard-to-reach locations.”
“It is one of Motion Australia’s bestselling products to the Australian quarrying segment– and well recognised across generations of maintenance workers as an essential ‘toolkit in a can’ on site for its ability to eliminate the need for destructive disassembly on expensive equipment,” furthers Steve.
“The CRC 5.56 facilitates the quick removal of components and releases rusted parts which saves time and labour on repairs.”
According to Melanie Mangos, Head of Industrial Sales at CRC Industries Australia, Australian heavy industry consumes a significant volume of CRC 5.56 every year because the effectiveness of the formula has the ability to save operations thousands of dollars in repairs and downtime– reduced to the cost of a single can of 5.56.
“The CRC 5.56 embodies many of the values and principles that CRC was founded on,” says Melanie. “As a global leader in developing premium quality aerosol lubricants and anti-corrosion formulas, we have built on a foundation of more than 60 years globally of experience supplying premium maintenance products to the heavy
• Saves time and labour on repairs
• Lubricates and penetrates rust and corrosion
• Facilitates quick removal of components
• Assists in non-destructive disassembly of expensive assemblies
• Actuator ‘straw’ nozzle for hard-toreach locations
• Fast acting formula
• Provides an environmental barrier for fasteners, shackles, pins, bushes, and hinges
• Protection from moisture with a protective film
• Self-healing properties
industrial market.”
Ideal for mining and quarrying equipment due to its ability to provide a barrier to strenuous environmental conditions, the CRC 5.56 formula can be used safely on metal, alloy, rubber, plastic and painted equipment. Additionally, the actuator on the nozzle allows for easy access to hardto-reach componentry.
“The product is versatile and unparalleled when it comes to breaking through any rust or corrosion and clearing away scale and dirt. CRC call the product ‘A toolkit in a can,’” explains Melanie. “The formula is fast acting and penetrates rust and corrosion to release parts and components. While at the same time, adding a protective layer of self-healing film that prevents ingress of moisture and contamination.”
“The 5.56 is part of the reason CRC has become a household name and you would be hard pressed not to find one in every MRO workshop in the country,” concludes Melanie. “It’s not uncommon to find a can of 5.56 in a tradie’s truck, toolbox, or workbench, and for older generations to pass this product down to the next generation as a staple.”
The materials extracted from quarrying operations are often transferred to a processing plant, manufacturing facility, warehouse, or workshop where they will be transformed into products. Regardless of where these materials end up, fresh air in these spaces is essential for limiting exposure to the dirt and dust
that come with them.
SafeWork Australia has issued a warning to employers about the health safety risks associated with working in conditions that have inadequate airflow. By law, Australian employers are now required to ensure their working environment has an effective ventilation system.
In a nutshell, ventilation means replacing contaminated air with fresh air. But when it comes to creating safe, healthy working environments, it’s important for site managers to equip their workspaces with powerful, efficient, heavy-duty mechanical ventilation systems, according to Troy Lopez, General Manager at Fanmaster.
fans: For keeping air moving in industrial workspaces
Ventilation methods work by expelling stale air and introducing fresh air from outside. These units can be either fixed or portable. Fixed ventilation methods include hooded roof fans, wall exhaust fans, axial flow fans, and industrial louvered fans designed for industrial sites and agricultural buildings. Portable ventilation units include portable fume collectors, mobile man coolers and compact air blasters.
3. Coolers
The Fanmaster
Hooded roof fan extracts heat, smoke, dust, or fumes from buildings. When used in conjunction with coolers, the hooded roof fan helps to keep the temperature down during hot Australian summers.
“Improper ventilation causes stress on the body, inducing discomfort, exhaustion, and heat stroke in workers. Industrial activities such as welding, drilling, grinding, and even transporting materials emit harmful dust, dirt, and contaminants that can cause long-term respiratory and neurological diseases,” he says.
Cooling units such as evaporative coolers and air conditioners also help improve air quality and air circulation through movement and distribution. Another option is that of misting fans –which supply a fine mist (which quickly evaporates) during operation, helping to create cooling breezes.
Which option works best for you?
and
made from high quality steel
Fortunately, the ventilation, cooling, and extraction experts at Fanmaster have site managers covered with a few effective methods for ventilating industrial workplaces:
1. Industrial fans for air circulation
Fans can make people feel cooler and more comfortable due to the breezy, chilling effect they create. Fans that improve air quality by extracting contaminants and stale air include:
• Mobile Mancoolers: These portable fans that extract contaminants are often used in the mining and quarrying industries because they are suitable for confined spaces on underground operations
• Commercial pedestal fans: Available in a wide range of sizes
• Fixed wall fans: Ideal for use in a range of working environments
• High-volume-low-speed (HVLS) ceiling
In some cases, working environments might require a range of solutions to ensure quality air flow. The best way to start is by speaking to an expert to determine the best solution for your situation.
Fanmaster has been an Australian familyowned-and-operated business for over 21 years. The company specialises in the import and manufacture of cooling, heating, ventilation, and extraction systems and offers extensive knowledge in their field to the industrial sector.
As a supplier to Motion Australia’s network of businesses, this adds an additional layer of technical support and mechanical engineering know-how to Fanmaster’s mission to bring fresh air and thermal comfort to Australian industry.
Visit your local Motion Australia branch and speak to a technical representative today to find the best ventilation system for your quarry.
In many Australian maintenance workshops, the LOCTITE® name is associated with efficient repairs made easy. Now, thanks to LOCTITE PC 7218’s new and improved formula, repairing worn parts and protecting equipment on mining and quarrying applications is easier than ever before.
For more than 20 years, the LOCTITE PC 7218 wearing compound has set the standard for high performance wear resistance for the mining and quarrying industry. LOCTITE PC 7218 is a two-part ceramic filled epoxy paste designed to protect, rebuild and repair high wear areas of processing equipment. Applications such as cyclones and separator bodies, dust collectors and exhausters, pump liners and impellers, fan blades and housings, chutes/ hoppers and elbows/transition points can benefit from the surface protection that LOCTITE PC 7218 wearing compound provides against abrasive materials and erosion.
LOCTITE PC 7218 can also be used for filling gaps, patching and lining pipes, walls, internal surfaces, and tiled areas.
By rebuilding surfaces with LOCTITE PC 7218, maintenance workers can restore
and reinforce them with abrasion resistant coating.
With the recent upgrade and re-release of the LOCTITE PC 7218 formula, LOCTITE has taken maintaining this high-quality standard one step further with improved adhesive and wear resistance capabilities, and the removal of ingredients subject to the 2018 Amended Poisonous and Deleterious Substances Control Law.
To stock up on supply of the LOCTITE® PC 7218, visit your local Motion Australia branch today.
Based on preliminary testing done, LOCTITE materials scientists found that the new LOCTITE PC 7218 formula compares favourably to the former product in three key areas:
1. Strength at high temperature: The new product shows 62% higher tensile shear strength at 80°C.
2. Heat aging property: The new product maintained the same shear strength at 80°C.
3. Abrasion resistance: The new product has improved the weight loss ratio by more than 50%
A leading iron ore ship loader in Western Australia was experiencing wear on the inner face on one of their chutes. The chute was catching iron ore from a fall of approximately six meters lasting only 10 weeks a repair cycle, before requiring patching or replacement.
In under five hours, the inlet chute was prepared and rebuilt using LOCTITE® PC 7218 wearing compound as a ‘cold fix’ requiring no Hot Work Permit. The result was chute life doubled to 20 weeks and the company accrued significant cost savings by avoiding chute replacement and a reduction in labour hours. 10 weeks of production in, the chute was practically still in newly repaired condition.
On a quarrying site, vibrating screens, also known as ‘shaker screens’ play an important role in mineral processing. Much like sifting sand through a sieve, a shaker screen is primarily used for sorting quarried materials to size.
The principle of a shaker screen is relatively simple: they are typically inclined over shafts that have motorised drives that cause the shaker screen to vibrate rapidly.
Depending on the arrangement, the screen moves in a linear or elliptical motion to create centrifugal force. This force causes the smaller particles to crumble and fall to a feed below, while larger sized materials move overhead.
Shaker screens are typically a lowmaintenance, low-cost piece of equipment that allow operators to maintain a good level of control over the flow of material that is otherwise heavy, abrasive, and difficult to handle.
Despite of all the benefits of vibrating screens to the mineral processing industry, the downfalls seem to exceed them in terms of the service life of shaker screens and frequent breakdowns. In short, most shaker screens just don’t work very well.
According to Michael Greelish, the National Business Development Manager at Motion Australia, the most common reason that vibrating screens break so frequently is because the bearings fail.
“The screen manufacturers are not at fault, as they design the screens to withstand immense stress from materials being fed continuously through cycles of crushing and sorting.
If the stress levels remain to testing standards, the screen is likely to be reliable and resilient with the life of the machine,” says Michael.
“The problem is not with the screens themselves; it is with component failure. The internal componentry experiences extreme levels of fatigue and rapid wear under the stress of constant circular, linear, and elliptical forces against abrasive materials,” he continues.
“When the quarried materials are fed onto the screen decks, their movement is relatively volatile, and these uneven movements can put additional stress on internal componentry. The force is hard to predict and even harder to contain–often causing one side of a screen to fail prematurely.”
Michael emphasises that quarries rely
• X-life quality = 70% longer life than standard bearing types
• Bainite heat treatment for temperature stability up to 200°C
• Surface hardened cage for high wear resistance
• Cage guided by outer ring better accommodates centrifugal forces
• Tighter OD and ID dimensional tolerances for better control of fit in housing and on shaft
• Durotect CK hard coating on bore for reduced fretting corrosion and shaft wear
on the performance of their vibrating screen applications for their production.
“A quarry’s overall production output is contingent on the performance of their shaker screens, and the performance of the screens is determined by the suitability of the bearings for the application,” he says.
For quarrying managers, shaker screens pose a difficult engineering problem that often requires outside consult to solve. This is where Motion Australia and their longstanding supply partner Schaeffler enter the equation.
“We have been partnering with Schaeffler to work with quarrying customers for many years, and this includes performing joint site visits and two-fold engineered bearing solutions for shaker screen applications,” says Category Manager for Industrial Bearings at Motion Australia, Tony Tormey.
Tony specialises in providing bearings solutions for heavy industrial applications that “solve problems for customers, rather than create them.”
“A vibrating screen needs to have multidirectional capabilities, so it requires a spherical roller bearing solution that is purpose designed and built to accommodate the extreme stress of these movements,” says Tony.
From their state-of-the-art engineering and manufacturing facilities in Germany, one of Schaeffler’s most recent innovations is their patented Durotect CK bearing surface coating that went into the design of their FAG T41D Shaker Screen Bearings.
“When it comes to bearing solutions for shaker screens, the Schaeffler FAG T41D Shaker Screen Bearings are unparalleled in the market because of the cutting-edge Durotect CK surface technology used in the construction of the bearings,” highlights Tony.
Specifically designed for shaker screen applications, the T41D Bearings have a thin layer chromium bore coating to the inner ring bore which alleviates fretting corrosion, and offers superior wear resistance, greater load carrying capacity and longer service life.
shaker screen applications, the T41D Bearings are part of Schaeffler’s X-Life portfolio, which stands for ‘extended life’ of the bearings.
X-Life bearings are all heat-treated for temperature stability and high wear resistance and resilience under centrifugal force, making them even more well suited for shaker screens.
The T41D Bearings have further surface treated cages and tighter dimensional tolerances for better housing and shaft fitting.
“Quarry managers will often approach us at Motion Australia and ask how they can improve the structural integrity of the shaker screens on their site to reduce stress and avoid production losses,” says Tony.
“I tell them if they want to drastically improve the life of their shaker screens and avoid any loss of productivity, the T41D bearings are the answer,” he concludes. “In some cases, they will even outlive the screen– problem solved.”
In the quarrying industry, off-road light vehicles are often used for the efficient transport of personnel and supplies around or between sites. Some are employed to venture underground, carrying loads of material or equipment through confined and hazardous spaces.
Much like the human body, trucks and cars have a plethora of internal components that work together to keep the whole system moving. Within a light vehicle, the drive shaft serves to deliver torque from the transmission to the differential, then onwards to turn the wheels in motion. A drive shaft designed for a sportscar will be different to that in a quarry site truck, which is where industry knowledge from the team at Hardy Spicer comes in. Michael Walton has been working at Hardy Spicer for over a decade, and has recently stepped into the role as Branch Manager in Townsville. He says that with nine centres located across Queensland, New South Wales and Western Australia, the group is wellplaced to liaise with key players in the quarrying space to ensure the best possible fit for their on-site four-wheel drives.
“Many years ago, we worked with some mining companies to develop a greaseable front CV joint for their fleet’s light vehicles,” he says. “That greaseable front feature meant that they didn’t have to disassemble the whole vehicle to carry out lubrication maintenance.
Around the same time, we innovated our heavy-duty mining specification drive shaft.”
The shaft’s Hardycoat® nylon splines offer 30 per cent longer life than standard steel alternatives. Additionally, the rubber lip seal and boot give superior protection against dirt, dust and water. The complete shafts, universal and greaseable CV joints available from Hardy Spicer are all interchangeable with standard parts from commonly used car makes.
“Our drive shafts are being used in quarries for both above ground and underground applications,” Michael enthuses. “We also have the biggest line of heavy-duty universal joints that are greased through the cap, featuring triple lip seals and teflon thrust pads, giving them a much longer life than a lot of standard OEM replacement parts.”
Each Hardy Spicer service centre is equipped with purpose-build engineering machinery, including press up benches, electronic balancers, and weld lathes. This gives them the capability to balance drive shafts perfectly to meet ISO standards before they go into service, ensuring the prevention of excessive spline wear, yoke, tube or weld failure.
“We can either repair or overhaul existing shafts, or design and build a completely new one to suit almost any application,” says Michael. “Whether it’s a light vehicle or heavy piece of machinery, these custom-built, high performance parts are built to last.”
According to Michael, the team can also carry out fitting of universal joints, couplings and centre bearings, ensuring the safest possible end result for longterm service in the field.
“For example, I’ve recently been working with a customer on a custom job for a two-piece shaft, which has a special parkbreak through the middle,” he explains. “We can do unique flanges, or different shaft lengths. There’s not much we can’t do or won’t try to collaborate with the customer on to find a solution.”
“We’ve supplied these drive shafts to many sites across Australia over the years, and often times people are so happy with their performance that they come back to request fitment on their personal vehicles,” he concludes. “That’s a real demonstration of how satisfied they are.”
Nothing can slow quarry production down like wet conditions. When water permeates the quarrying process, the extracted minerals, gravel, and sand quickly turn to sludge and slurry which are common by-products of daily quarry operations.
As a result, quarries heavily rely on effective pump applications to manage and control the ingress of water on site, and keep production running.
Pump systems in general vary in their ability to withstand the rugged conditions of heavy industrial applications, according to Troy Markland, National Product Manager for Chain and Ironware at Motion Australia.
“The performance of a pump system depends entirely on how it is assembled - from design and manufacture to the sealing and power transmission components,” he says.
“Slurry and sludge pumps use greater or lesser degrees of centrifugal and hydraulic force to displace watered down materials, and in most cases using a specialised dewatering pump is the most efficient and cost-effective solution for a quarry.”
Consequently, it is necessary for quarries to make some considerations when designing and fitting slurry pump assemblies, highlights Troy.
“Slurry pumps typically consist of two shafts– one for driving and the other being driven,” explains. “Power comes from the motor and transfers to the turning shaft through a coupling arrangement.”
“Ensuring a pump system is fitted with the right coupling components is critical to the performance of the application, as any heavy vibrations and loads can cause cracks and fractures on drive equipment,” he explains.
“Furthermore, pump systems are often located underground and requiring heavy lifting and rigging equipment to install. So, they can be difficult to maintain and repair if there is an issue.”
According to Troy, joining two aligning drive shafts is very difficult to do without any deflection and misalignment. Therefore, preventive maintenance on coupling components starts at the point of installation on pump systems.
From Motion Australia’s portfolio, Troy often suggests Fenner coupling solutions to quarrying customers for the most robust drive shaft solutions that can stand up to the abrasive nature of sludge and slurry.
“The Fenner Fenaflex Tyre Couplings are the preferred choice for both aboveground and below ground pump applications due to the Fenaflex tyre, it can accommodate a high degree of misalignment – up to four degrees,” he explains.
For below ground applications, a FRAS rated (Fire Resistant Anti-Static) tyre is recommended.
“The rubber tyre also does a good job of softening vibrational force through absorption,” he adds. “Making them very versatile and flexible on heavy load and high torque applications.”
Working closely with Fenner application engineers, Troy has gained a good understanding of fitting the Fenner Fenaflex Tyre Couplings on quarry pump applications, putting together a brief installation guide for quarry operators to refer to.
•
Firstly, all mating surfaces of the assembly taper balls and flanges, and taper lock bush bores should be cleaned to remove any debris that might impede assembly.
• Before placing the flanges on to the shaft, loosely place the bush into the taper lock bore and align the half holes correctly.
• Remove clamping rings and screws.
• Place loose clamping rings onto the mover and drive machine shaft before locating coupling flanges.
• If keys are required, side fitting keys with top clearance should be used.
• Once the clamping rings and flanges are in place, tighten the fixing screws to the required torque* detailed in the instructions supplied with each bush.
• For keywayed flanges, place on the shaft, locate keyway, and tighten screws.
• Bring the shafts into alignment, taking into consideration end-float and misalignment.
• Measure the gap between the shaft to the appropriate distance.
• Lay a straight edge across the flanges in several areas to check that they are aligned parallel to one another.
• Open the tyre and place over the coupling flanges ensuring it is seated properly, closing the gap of the tyre.
• Replace the clamping rings over the flanges and tighten the clamping ring screws evenly until the correct screw torque is achieved.
• There should be no metal-to-metal contact between coupling flange and clamping ring.
• Run the coupling under load for a test period, if possible and check the torque to ensure it is correct.
*Always refer to the manual for each product for torque ratings.
With sustainability on the forefront of the of the agenda for mining, quarrying and heavy earth moving companies, suppliers have experienced a huge uptick in the demand for zero impact cleaning products in recent years.
“Heavy industry has shifted with the move toward greater Corporate Social Responsibility. New standards and regulations from local and governing bodies have motivated companies to buckle down on their sustainability targets,” says Michael Greelish, Motion Australia’s National Business Development Manager.
“As a result, mining, quarrying and resources managers are now seeking to procure greener product solutions that will offset the environmental footprint of their operations. And in many instances, the green product solutions we supply now take precedence over standard products.”
When it comes to leading the charge on developing greener products for heavy industry, CRC has managed to stay ahead of the curve with the introduction of their Bio-Degreaser formula. Bio-degradable, non-toxic, pH balanced, and water soluble– CRC’s Bio Degreaser offers next generation green cleaning technology without compromising performance.
“With our innovative Bio-Degreaser, we are purposefully demonstrating our commitment to Corporate Social Responsibility and setting a new standard for cleaning and degreasing solutions,” says Melanie Mangos, Head of Industrial Sales at CRC Industries Australia.
On quarrying site where dust, dirt and contaminants are prevalent, it’s necessary to routinely degrease parts and components to keep them in working order.
The CRC Bio-Degreaser is an industrial strength, robust, concentrated formula
that is non-abrasive, non-flammable, non-corrosive, and solvent free. Safe for use on most metal surfaces, the Bio-Degreaser is capable of cleaning engine and motor parts, generators, compressors, bearings, chain, screens and hydraulic systems– quickly and effectively.
“CRC Bio-Degreaser is an extra heavyduty cleaner, its formulation penetrates to dissolve tough grease, oil and contaminants – safely. Our diverse end users love the strength of its cleaning solution,” says Melanie.
“CRC Bio Degreaser is water soluble and works well on all metals and alloys which is one of the reasons our customers trust the product,” she concludes.
As a world leading supplier of premium quality aerosol and bulk lubricants, anti-corrosion and maintenance products, CRC has enjoyed a prosperous working relationship with Motion Australia and their customers in the mining and quarrying sectors for decades. Both companies acknowledge the importance of reducing the environmental footprint of the heavy industrial sector.
For more information on CRC BioDegreaser and CRC’s range of environmentally friendly cleaning and degreasing products, visit your local Motion Australia branch and speak to one of our experts today.
CRC Bio Degreaser is water soluble and works well on all metals and alloys which is one of the reasons our customers trust the product.
Eliminating the risk of fire hazards and combustion is critical to keeping quarrying environments safe. For this reason, where the frequent use of explosives and harsh chemicals takes place, it is important that large pieces of machinery are adequately safeguarded against static charge.
In 2020, Gates® introduced the PowerGrip® GT®4 high-torque synchronous belt to the Australian and New Zealand market. Constructed from rust-resistant ethylene elastomer (EE), this narrow, high-capacity drive belt is meticulously engineered to address durability, efficiency, noise reduction, and streamlined installation.
Importantly, it minimises the amount of friction and the build-up of heat caused by repetitive shock loads. Constructed in alignment with the ISO 9563 testing methods, this belt falls within the specified electrical resistance properties needed to safely operate in an explosive or fire-prone environment. Essentially, it is sufficiently conductive to dissipate electric charge that may form as the drive unit runs.
“One of the biggest challenges that quarries face is making sure that all stages of operation are compliant for the safety and wellbeing of personnel,” points
out Michael Greelish, National Business Development Manager at Motion Australia.
“A straightforward way of doing this is opting for machinery and parts that are up to code, and designed with the industryspecific risks in mind.”
The PowerGrip GT4 is ideal for most types of heavy-duty quarrying equipment, such as driving pumps, fans, conveyor systems, drills and earth moving machinery.
After just a couple of years in the field, the product has already set a new industry benchmark for its impressive power ratings. This is largely due to the company’s extensive research and development efforts, combining decades of technical knowledge with the latest in power transmission science.
Compared to the previous GT®3 series, this newer synchronous belt has boasted superior performance in all operating conditions. To combat a lack of consistent manufacturer standards for developing power rating tables, Gates has undergone a thorough rating development plan to ensure accurate modelling results.
Available in 8MGT and 14MGT pitches, the PowerGrip® GT®4 is a narrower band, without compromising on transmission capacity. This allows for more compact
• High tooth jump resistance
• Reduced environmental impact
• Improved safety and ergonomics
• Lubrication-free capabilities
• Chemical resistance
• Wide temperature range of -40°C to 120°C
• No stretching
• Various available widths of 20, 30, 50, 85mm (8MGT) or 40, 55, 85, 115, 170mm (14MGT)
drive assemblies, and mitigates fatigue or strain during installation and change-outs.
In contrast to many other elastomer synchronous belts currently on the market, they are not fabricated from chloroprene, which harbours performance limitations and can have a negative impact on the environment. Instead, Gates® has pioneered an ethylene elastomer technology, which offers increased resistance to oxidation, heat, extreme weather, brake fluids, oil and grease. Paired with the internal fibreglass tensile cords and patented tooth profile, Michael says they are the next generation for optimum quarrying capacity.
“A fantastic feature to consider is that they require no lubrication or re-tensioning, which reduces huge amounts of downtime and maintenance costs,” he enthuses.
“At Motion Australia, we stock a broad catalogue of Gates® products including compatible sprockets and pulleys, and our power transmission experts are available to carry out site inspections to audit individual customer requirements.”
One of the greatest logistical challenges for quarrying operations is transporting materials from one location to another on site. The heavy loaded, vibrational, and abrasive nature of moving quarried materials requires a sturdy and efficient method of transport– the most convenient of these being a classic belted conveyor system.
Anyone who has visited a quarry, will be familiar with the intricate web of conveyors that spans across the site–some troughed; some flat; and some slanted for uphill and downhill movement. A classic quarry conveyor system consists of belts, pulleys, bearings, and rollers that feed materials in and discharge them out by way of chutes for transport, sorting, and processing.
Of these parts and components, the most critical for the success of a quarrying conveyor system, are the bearingsaccording to Michael Greelish, National Account Manager for Mining, Quarrying and Resources at Motion Australia.
“Bearing failures are one of the primary causes of downtime on quarrying conveyors and this is often due to how they are installed,” he says. “Correctly measuring the internal clearance of the bearing is difficult to get right on installation. In many cases, the bearing ends up being fitted too tightly so it breaks during production, or too loosely so it spins on the shaft.”
“It is very important to install conveyor bearings correctly with the proper fit up, so you can get the optimal performance and service life out of the bearing. A step-by-step fit up that includes checking and using gauges to install the bearings will ensure a prolonged bearing life on quarrying applications,” he emphasises.
For Michael, determining the best bearing solutions for quarrying conveyors and working with suppliers to ensure correct installation is a huge part of Motion Australia’s offering to the quarrying industry.
However, there are some suppliers, like Australian Timken, that set the standard
in terms of providing reliable bearing solutions for these types of applications, he notes.
“In particular, the Timken® Spherical Roller Bearing Solid-Block Housed Unit has established itself in the market as the strongest housed bearing unit of its kind– providing exceptional resilience and strength under extreme operating conditions– and that standard remains unparalleled in the industry,” says Michael.
An example of how the Timken® Spherical Roller Bearing Solid-Block Housed Units perform in quarrying conveyor applications happened recently when a quarrying customer who was experiencing issues with the tail bearings on their quarrying conveyor approached the Motion Australia team.
“The bearings were getting buried by dirt, dust, and contaminants – causing shutdowns every few months and costly bearing replacements,” explains Michael.
“But after a successful trial on one of their conveyors with two Solid-Block Housed units, the customer replaced all
the bearings on their conveyors with the Timken units.”
According to Mark Davies, National Mining Manager at Australian Timken, the success of the Timken® Spherical Roller Bearing Solid-Block Housed Units is due to their superior manufacturing and construction methods.
“The housing is made from solid cast steel and the bearing is fitted inside the housing at the factory level,” explains Mark. “The internal clearance is pre-set at the point of sale, and the sealing arrangement is prefitted to lock in grease and protect from the ingress of dust, dirt, and contaminants.”
“In addition to this, the units are available in a host of shapes, sizes, sealing arrangements and locking systems. We have six different internal locking mechanisms: V-Lock, Double V-Lock, Concentric, Eccentric, Tapered Adapter, and the Double-Nut Tapered Adapter,” elaborates Mark.
“Of these, the Double-Nut Tapered Adapter has been tailored specifically for conveyor pulley applications as an easy screw and lock mechanism that eliminates the need for complicated installation processes.”
In recent years, providing bearing installation training to quarrying sites has become an integral part of Motion Australia’s business offering.
“In the case of the Timken® Spherical Roller Bearing Solid-Block Housed Units, if the installation is done right, it should be a quick and easy process of simply locking the unit onto the shaft with no fitting required,” says Michael.
Furthermore, he notes, Australian Timken plays an active role in working with Motion
• A two-row spherical roller bearing
• Black oxide inner ring
• Six different primary seals against inner ring
• Machined solid feet
• Housing tolerance: J7 > Light Interference fit
• Standard Relief Valve
• Optional open or closed steel or urethane seal covers (bolt on)
• Five axial locking styles
• Easy to change from fixed to floating
• Housing can be supplied with Standard Powder Coat or special order Nickel, Zinc, or Urethane coating
• Housing manufactured from cast steel
Australia’s quarrying customers to provide on-site training for Timken® Solid-Block Housed units.
“We regularly supply Timken® Spherical Roller Bearing Solid-Block Housed Unit installation training to customers,” he says.
“In conjunction with Australian Timken engineers, we teach customers how to correctly install the Timken® Spherical Roller Bearing Solid-Block Housed Units. This training includes all staff on site–from the apprentices to the fitters to the engineers.”
Currently, Motion Australia is also offering their Quarry Training Session– a workshop with a focus on skills sharing and upskilling, that covers training on fitting conveyor bearings, V-Belt tensioning, and alignment procedures.
“This is not an online program. We bring training rigs out to the site and concentrate mainly on the fitting of spherical roller bearings because they are a bit more specialised in their installation requirements. We teach the staff how to measure and calculate radial internal clearance and the reduction of it once the bearing is fitted up by allowing staff to work on the rigs,” says Michael.
“It is a two-hour training session with no digital component or online modules, and no PowerPoints,” he concludes.
“We understand the best way for a lot of tradespeople to learn is by doing. So, this truly a hands-on training.”
For more information on Motion Australia’s Quarry Training Sessions and Timken® Spherical Roller Bearing Solid‑Block Housed Unit training, contact your local Motion Australia branch today.
Lance Brett has been working in mechanical seals for over 35 years. Now a National Product Manager at Seal Innovations, he is excited to bring their new Heavy Duty Slurry Seals onto the market for Australian customers.
“We’re really pleased with the quality of these seals and how they stand up in terms of wear life and reliability,” he enthuses. “It perfectly complements the rest of our product range and offers new potential for our involvement in the mining and quarrying sectors.”
The role of a sealing application cannot be overlooked, especially in resources where they act to secure valuable materials while they are being processed. Slurry is formed when water combines with ferrous and non-ferrous raw material, such as rock and soil between 1mm and 25mm thick. In mining, there are several types of pumps used in the transport of large volumes of slurry to mineral processing plants, where it then undergoes a separation process.
The solids within slurry can often prove highly abrasive, contributing to the accelerated wear life of critical parts, including seals. This problem can be amplified in a hyper saline environment, which may cause crystallisation of material around the surface.
The new Heavy Duty Slurry Pump Seal from Seal Innovations can withstand the harshest operating environments, providing maximum seal life in mining, quarrying and dewatering applications. The abrasion resistant metal components, along with silicone carbide faces, create an open design which reduces flush water and product dilution.
“This seal unit has been specifically designed for handling slurry concentration of up to 40 per cent solids by weight,” explains Lance. “It is an incredibly robust construct mechanical seal which is best suited to rugged mining and quarrying environments. Differently to standard O-ring designs, it is a rotating assembly, offering accurate installation with no special tools required.”
What’s more, the smooth, elastomercoated cone spring increases the product’s reliability with an even spring load to the seal’s faces. This ensures minimal wear or clogging, in operating pressures up to 300 psig (20.7 bar).
“We have introduced this product to fill a prominent need in the market for miningsuited slurry pump parts,” Lance elaborates. “It’s a really exciting addition to our portfolio of industry leading seal products, and we’re already taking it to some of our most
valued customers as an upgrade solution on troublesome equipment.”
He adds that, in addition to a comprehensive catalogue of sealing products, the business also provides aftermarket engineering and repair services from some of their centrally located branches.
“We can repair and overhaul slurry pump units as well as seals from our workshop in Brisbane, and we can repair any type of slurry seal from our Melbourne workshop. Everything is repaired back to manufacturer specification, and thoroughly tested for performance before re-entering the field.”
Technicians from Seal Innovations regularly visit customer sites, utilising their comprehensive knowledge of seal engineering to carry out audits, training and installation services. In line with their motto – “keep industry moving” – they strive to meet each customer’s unique requirements and offer a one-stop-shop for all sealing needs.
Think Water’s foundation principle is that water is our most precious resource and must be treated with efficient management practices. Established in 2007 from a collection of independent businesses, the Think Water group now spans 51 stores across both Australia and New Zealand, specialising in irrigation, pumping, and filtration system design.
“We are heavily involved in our local mine and quarrying industries, and a large part of that is providing the best hosing equipment, which we source through Advanced Industrial Products (AIP),” says Andrew Carrier – Managing Director at Think Water Peats Ridge. “We have been working alongside them for around 25 years, and our own customers have come to trust the excellent quality product for a broad range of applications.”
As part of Motion Australia’s businesses, AIP operates out of its head office in Darra, Queensland, with strategically located branches in Brisbane, Mackay, Wetherill Park, and Sunshine West down in Victoria.
One of the key products that Think Water sources through AIP is the Powaflex Pumpman rubber layflat hose. It is available either as a simple discharge hose, or pump assembly complete with Bauer couplings and Band-It preformed clamps. Designed to meet Australian
industry standards, it demonstrates high performance with extreme reliability.
“Increased levels of rain on the east coast have meant that a lot of underground quarry sites are experiencing flooding, which restricts access and slows down operations,” Andrew explains. “The Pumpman hose offers a very resilient and flexible solution for the efficient dewatering of these areas. Additionally, the high abrasion and temperature resistance defends the product from wear and tear, so the user gets a much longer wear life.”
Capable of transporting both water and slurry in tough operating conditions, the Pumpman rubber layflat is also suitable for washdown and irrigation purposes, with a pressure rating of 150psi (10 bar).
“We have never had any complaints from our customers using the hose, and no news is good news with these sorts of products,” Andrew furthers. “Just the fact that businesses continue to re-order the same units indicates that they are performing really well.”
Stephen Marley, Area Manager at AIP, says that it isn’t unusual for rainwater or seeped groundwater to collect in quarries, so sites need a dependable solution that can handle the transport of large amounts back above ground and away from the area. He adds that a long-
standing relationship with Think Water allows for the best possible solution to reach end-users in Australia’s northeastern quarrying region.
“We take a lot of pride in building close relationships with customers like Think Water, because at the end of the day, this extends beyond a purchase-supply situation,” says Stephen. “We offer technical support and create a sense of reliability that we will deliver on short turnaround times, with a diverse catalogue for almost any application.”
Andrew echoes this sentiment, reflecting on the continual benefits of working together to help customers get premium results with consistency.
“The communication has always been very positive. They are a fantastic company to deal with, and the service that we get is terrific. Our close relationship is a testament to what can be achieved when industry knowledge and customer service come together.”
An extended selection of Powaflex and compatible products are available through AIP’s national supply network, including rubber lay flat hoses, Powaflo valves and Powafit fittings.
On a quarry site, a well-engineered conveyor system can boost productivity by automating much of the transportation process and creating efficiencies that otherwise would not be possible at the ground level.
But engineering a quarrying conveyor system is not a straightforward process. Designing a conveying system for a quarry site requires specialised knowledge to assemble the right parts and components into a working system that will run smoothly once switched on.
According to Motion Australia’s Tony Tormey, a disproportionate number of breakdowns on conveyor systems are due to a bearing’s failure. “Bearing service life is a critical consideration for quarry conveyor systems because a bearings failure can mean a catastrophic halt in production and maintenance costs in the five figures,” he says.
As Category Manager for Industrial Bearings Solutions at Motion Australia, Tony works closely with quarrying customers to deliver bearings solutions that can perform on heavy industrial applications such as conveyor systems used for transporting quarry materials on site.
“The rolling elements on a quarrying conveyor are subject to a large volume of heavy loaded materials and strong vibrations running around the clock during production hours. This is why selecting the right bearings for a quarrying conveyor system is critical to the success of an operation.”
Sharing in his passion for bearings solutions, Tony has the benefit of working
closely with NTN, which has a joint venture with CBC, one of Motion Australia’s businesses.
NTN and CBC have enjoyed more than 50 years of successful partnership in the bearings industry. Together, the two businesses have more than a century of combined technical and engineering knowhow they can draw on for designing and developing bearings solutions for heavy industrial applications.
For this reason, many quarry operators turn to NTN and Motion Australia for assistance in developing tailored bearings solutions for their site.
Most recently, Tony has been directing customers towards the new NTN ULTAGE range of bearings for quarrying conveyor applications, which he says are picking up speed in the quarrying segment due to the performance and longevity.
“The NTN ULTAGE were designed to be the next generation of standard highperformance bearings for the most demanding applications in heavy industry,” says Tony.
Constructed from premium grade steel with a special heat treatment processing, the NTN ULTAGE bearings can support heavy loads, higher operating speeds and maintain stability up to temperatures of 200 degrees Celsius. The result is higher load ratings, greater tolerance to vibrations, reduced operating temperatures and up to three times longer service life when compared to conventional bearings.
Available in a variety of sizes and types, the NTN ULTAGE range is versatile and flexible in offering specialised and industry-specific bearings solutions.
For quarrying conveyors, Tony recommends the NTN Sealed Spherical Roller Bearings, which incorporate unique design lip seals that remain steadfast under misalignment and pressure for preventing any ingress of contaminants or moisture. Additionally, the bearings are pre-lubricated with long-life grease that requires no
cleaning or regreasing after the bearings are fitted.
Bearing’s compact design means less complex housing sealing is used to achieve better results. The internal design consists of a pressed steel cage and a streamlined curvature design that was adopted from the NTN EA series bearings. The EA design is well-recognised in the industry for its lighter and more compact design and topping the industry’s highest load ratings.
NTN and Motion Australia are invested in the design and development of engineered bearings solutions that can be tailored for quarrying sites to speed production and streamline automation.
Industry leading, dynamic load rating
Testing shows over three times extended bearing life
Optimised internal geometry that distributes bearing stress
Heat treated steel construction capable of handling 200°C
20% higher speed capacity
Available in the 223xx series with a cylindrical or tapered bore
Available with bore diameters of between 40mm and 170mm
Available on request for the other series and bore dimensions
Manufactured according to specification EF800
According to Safe Work Australia, noise exposure is the most common preventable cause of hearing loss, which research suggests may contribute to a range of other health concerns including tinnitus, increased heart rate, muscle tension, and fatigue.1
Workers in the mining and quarrying industries are frequently exposed to loud, explosive, grinding, scraping and crushing sounds in close proximities and for extended periods of time. Noise-induced hearing loss (NIHL) is a permanent condition, is a permanent condition, and 100% preventable.
The E-A-R™ Push-Ins™ earplugs from 3M are designed to protect the wearer from noise exposure levels, particularly low-frequency type noise in industrial environments. Constructed with slow recovery polymer foam and joined by a handy PVC cord, they are both washable and reusable with no rolldown required. In addition, these earplugs feature an insertion stem, which eliminates the need to handle the tip when fitting, for a more hygienic approach.
When it comes to critical pieces of PPE, checking that the product meets industry standards can ensure the best possible defence against work-related injury. The E-A-R™ Push-Ins™ are fully compliant with the Australia and New Zealand AS/NZS 1270:2002 certification scheme, and have been tested against the European EN352-2:2002 basic safety requirements.
Fit testing can ensure that users are getting optimal protection from their ear plugs. While most earplugs will have the SLC80 rating printed on the box, this may not be accurate to the size and shape of every worker’s ear canal. Finding the best fit for each individual
will be determined by their Personal Attenuation Rating (PAR).
Designed to be compatible with the E-A-R™ Push-Ins™ and other ear protection products from 3M, the E-A-Rfit™ Dual-Ear Validation System harnesses F-MIRE technology to quantify accurate hearing levels within just five seconds per ear. This can help to eliminate guesswork around the efficacy of different earplugs, with a system that it both portable and durable for on-site testing at any time.
Step 1: Set up the testing station
Install the software onto your computer via the provided flash drive or 3M website. Set up the speaker and microphone assembly, before connecting the system via the USB port.
After set-up is complete, have the test subject insert the earplugs as they normally would before entering the worksite. Then, attach the microphones to each side by inserting the metal probe tube fully into the test plug. Use the subject’s eyewear temple bars to hang the microphones in an upwards pointing direction.
Anybody working in environments where there is a risk of noise induced hearing loss can benefit from thorough fit testing for ear protection.
Position the speaker around 12 inches away from the subject, and then hit ‘run test.’ In less than five seconds, the system will generate a personal attenuation rating, indicating accurate reduction levels provided by the fit. Results will reflect the effectiveness of the person’s fitting method, and whether they require additional training in the use of hearing PPE.
Anybody working in environments where there is a risk of noise-induced hearing loss can benefit from thorough fit testing for ear protection. This might include newly hired employees, employees exposed to high noise areas or to toxic chemicals, and those with assured temporary threshold shift (TTS)/ standard threshold shifts (STS). Ideally, this testing is not a one-time event. Follow up is always recommended to provide opportunity for ongoing and refresher training.
References: 1. https://www.safeworkaustralia.gov.au/ system/files/documents/1702/workrelated_ noise_induced_hearing.pdf
Quarries play a vital role in Australia’s extractive industry, facilitating the production of raw material –such as sand, rock, and gravel – for civil infrastructure and residential construction developments. In contrast to mining, the quarrying landscape comprises of mostly smaller scale sites1 which rely on fewer primary pieces of equipment to bear the load of high intensity output.
Because of this, if a critical part of a machine goes down it is essential that repair can be carried out quickly, as every second of downtime will likely be expensive. To answer this need, CRAM is offering expert repair and overhaul on exciter gearboxes typically used on vibratory screens.
With humble roots in the small NSW town of Unanderra, CRAM is now a globally recognised specialist in fluid power, electro-hydraulics, and tailored engineering services. Their full-spectrum offering entails industryleading refurbishment and repairs on key equipment across the resources, manufacturing and construction industries.
“Exciter boxes essentially sit up the top of a quarrying screen to make the whole thing shake, putting it out of balance so the material gets sifted through,” explains Michael Greelish – National Business Development Manager at Motion Australia.
“So usually what happens when the bearings or other components reach the end of their wear life, is they’ll take the box off and send it back to the screen manufacturer to get repaired. This is usually quite expensive for them, whereas CRAM now have the facilities to strip, inspect and report on these gearboxes with more efficient cost and timeframe parameters.”
According to Michael, CRAM has many years of experience catering to the mines and quarries sector, and an excellent track record of providing holistic solutions for customers. From fabrication and tube work right through to mechanical overhaul and hydraulic schematics, they work closely to Australian standards and are dedicated to troubleshooting complex projects.
“The great thing about the Mackay workshop is that it’s centrally located for so many coal mines and quarrying sites up in Queensland,” he continues. “So instead of having to send their units all the way back to Sydney or Melbourne, they can save on freight and get a much faster turnaround. This can be particularly important for instances where there is no spare gearbox on site, and the machine can’t operate during repair time.”
Tony Harmsworth, Branch Manager at Mackay, says that there are generally two reasons why an exciter may need
attention - either it has experienced an abrupt failure, or it’s up on hours and in need of an overhaul.
“Nine times out of ten, if it’s a premature issue that’s occurred it will be to do with shortened bearing life or lack of lubrication,” explains.
“When it arrives at the workshop, we check all the journals first. Then we go over the condition of the gears and reclaim them back to spec or replace components like bearings and seals where needed. After that, the housing gets blasted, and we do a fresh coat of paint so by the end it’s as good as fresh out of the box.”
Both Michael and Tony agree that this initiative is only the latest benefit to come about from becoming part of the Motion Australia network.
“Because we liaise with the teams across other branches like CBC, Seal Innovations and Hardy Spicer, our customers really benefit form a true one-stop-shop for broad categories of servicing types,” says Tony. “We’re all about creating long lasting relationships, and a strong sense of trust in our commitment to deliver high quality support,” he resolves.
References:
1. https://nationalindustryinsights.aisc.net. au/industries/mining-drilling-and-civilinfrastructure/extractive-industries-quarrying
In the mining industry, draglines are a key piece of excavation equipment that have largely maintained the same design and functionality since they were first invented in 1904 by John W. Page, owner of Page Engineering Company.
Essentially a giant walking shovel– using large buckets, rigged wires, and a boom arm– draglines operate similarly to cranes in their ability to hoist large volumes of extracted materials from pit to pile.
Since their intended purpose has always remained relatively the same, there hasn’t been a lot of technological innovations for draglines that have emerged in the past 100 years– in fact, it’s not uncommon to see draglines that are decades old still in operation.
However, there has been advancements in the part and components used in the operation of draglines, particularly power transmission systems, according to Motion Australia’s Steve Hittmann.
“Draglines can be retrofitted with the latest driven part technology to improve their speed, efficiency, and performance in field,” remarks Steve. “But the most notable issue with draglines is the tremendous amount of power they require to operate them. And as most mine sites have fleets of draglines, these requirements can impact an operation’s bottom line significantly.
As National Category Manager for Mechanical Drive Systems and Mobile Final Drives, Steve’s expertise is vast and includes extensive knowledge of gearing, motors, couplings, brakes and clutches.
“Choosing the right power transmission components is more important than many mining operators may realise,” says Steve. “A good quality power transmission solution for a mining operation is one that can accommodate torque, sheer and compressive forces, vibrations, and high speeds. Ideally, it would also be failsafe, maintenance friendly, and reduce downtime on production.”
Recently, when a major coal mining operation in Queensland approached Motion Australia for a power transmission solution for their dragline fleet, they went
out to the site to assess the application requirements and determine the best course of action.
“We met with the engineers who were responsible for maintaining their dragline fleet,” he explains. “The site was after a solution to minimise maintenance on their fleet and improve operational efficiency. The existing gear couplings required regular lubrication and were expensive to change out, as the complete coupling assembly needed to be replaced when they reached their fatigue life”
Motion Australia deferred to one of their partners in supplying engineered power transmission solutions– Australian Timken–to assist with providing a solution to the coal mining customer, with specific emphasis toward the Timken Quick-Flex® Coupling.
Brad Womersley, Regional Sales Manager at Australian Timken, recommended the Timken Quick-Flex® couplings to power the hoist, drag and propel machinery. “We chose the ‘fit-and-forget’ Timken QuickFlex® 3150 Couplings for their maximum tolerance to force, minimal maintenance, and ease of installation,” says Brad.
“The easy fitment in the envelope design means no metal-to-metal contact and eliminates the need for lubrication. Furthermore, service life of our Quick-Flex® Couplings typically matches that of the equipment itself, which is ideal for draglines that will be in-field for years for reducing the total cost of ownership.”
The Quick-Flex® 3150 Couplings were installed on three of the coal mining site’s draglines. Since then, the customer has reported that the couplings have been operating faultlessly, according to Steve.
“This was a win for both Motion Australia and Australian Timken because the success on the initial machines opens door for the rest of the site’s dragline fleet,” he concludes. “In an industry like coal mining that often operates on legacy equipment, processes, and procedures, this could mean future engineering opportunities and further growth for us in the coal mining sector.”
• Motor to gearbox (low torque/high speed)
• Gearbox to driven equipment (high torque/low speed)
• Motors to pumps
• Any driven shaft
• Versatile design that is interchangeable with most coupling arrangements and can be standardised across a site
• Able to withstand up to two degrees of misalignment
• Dampens vibration and withstands repeated high shock load to the equipment
• Available in standard, single-ended spacer, double-ended spacer, or spined hub designs
• No metal-to-metal contact
• Designed for continuous and peak torque levels. Split cover options help resist axial separating force under high torque.
• Four bore options available to meet customers’ needs: Bored, Bushing, Splined and Mill Motor style.
• Four insert choices for varying torque needs
• Withstand temperature up to 176°C
Choose from Type NRTH for both low speed and semi-high speed applications and Type NRT for heavy-duty high torque applications. Size-for-size TRUE HOLD Backstops provide more system holding power than any other backstop. Plus, Longlife designs and our ability to engineer and manufacture complete, integrated drive packages, assure that you get the ideal system for your needs, whether it’s a single, tandem or multiple backstop configuration.
Titan’s Recovery Puller Winch is ideal for every recovery situation. The rope gripping system is easily disengaged, allowing smooth installation of the wire rope. Allows you to operate the winch without the need for any other powered device, when you are in off-road isolated areas.
These high performance and sealed bearings, belonging to the ULTAGE range, are designed to operate in harsh environments and on equipment requiring extended maintenance intervals. This series is suitable for applications as diverse as steel industry, paper making industry, mines and quarry conveyors, textile, handling equipment as well as elevator transmissions.
Tapered roller bearings can carry radial loads and unidirectional axial loads and offer high capacity. These bearings are used widely in machines with relatively severe loading conditions, usually in various combinations of opposed or combined single-row bearings.
The Fanmaster IHR8-22-6-3 Hooded roof fan extracts heat, smoke, dust, or fumes from buildings. When used in conjunction with coolers, the hooded roof fan helps to keep the temperature down during hot Australian summers.
Schaeffler OPTIME is an easily scalable Condition Monitoring solution, developed for various purposes in industry, recommended for a range of rotating machines with a speed of 120 rpm*-5000 rpm.
ITW’s Molygear has a high load carrying capacity providing lasting lubrication on heavily loaded gear boxes. Formulated from molybdenum disulphide, other applications for the Molygear industrial gear oils include worm drive and conveyor drive gear boxes that are found in the mining, quarrying, heavy earth moving and mineral processing industries.
LOCTITE PC 7218 is a 2-part, grey, epoxy based surface coating for metals. Ideal for protecting against coarse particle abrasion or erosion, or for rebuilding worn parts. It is designed for parts such as cyclones/separator bodies, dust collectors/ exhausters, pump liners/impellers, fan blades and housings, chutes/hoppers and elbows/ transition points.
Specifically designed for shaker screen applications, the T41D Shaker Screen Bearings have a thin layer chromium bore coating the inner ring bore which elevates fretting corrosion, and offers superior wear resistance, greater load carrying capacity and longer service life. These bearings are heat-treated for temperature stability and high wear resistance and resilience under centrifugal force –making them even better suited for shaker screens.
The SUPERDRAULIC HVI HI TEMP range of high viscosity index, high temperature anti wear hydraulic fluids is available in Viscosity Grades 46, 68 and 100. It is formulated using the same chemistry as the Superdraulic range however is formulated with shear stable polymers making it suitable for use in applications where extra harsh conditions and heat are common.
CRC 5.56 is a multi-purpose product with superior penetrating power that breaks through rust and corrosion while it clears away scale and dirt. Eliminates the need for many disassembly operations. Lubricates for smooth action, and silences annoying squeaks and squeals. Protects metals against corrosion and displaces moisture to help start wet engines.
Fenaflex Tyre Couplings are highly elastic, lubrication free couplings that tolerate large amounts of misalignment in all planes as well as offering simple installation and inspection without disrupting the drive. The Fenaflex coupling also has excellent shock absorbing properties while reducing vibration and torsional oscillations.
These push to fit, foam earplugs are easy to use again and again, reducing waste. Poly bag keeps earplugs clean and accessible for re use. Blue stem makes insertion and removal cleaner and easier. Noise Reduction Rating (NRR)* 28 dB. CSA Class AL. Test compatible with 3M™ E A Rfit™ Validation System. *The NRR may overestimate the hearing protection provided during typical use. 3M recommends reducing the NRR by 50% for estimating the amount of noise reduction provided. 3M is Leading the Advancement of Hearing Conservation™.
These extremely popular bearings are made to contend with hot, high-speed and heavy load conditions, offering seven times the service life of generic counterpart products. They can also withstand long periods of lubricant contamination and provide a 20 per cent improvement on seizure resistance. Offering less than half the rate of wear then generic bearing options, the Hi-TF has been designed following comprehensive research and development.
Providing longer operating life due to their improved crack fatigue strength, wear strength and peeling resistance characteristics, especially when the lubricant is contaminated. The EA bearings provide advantages due to their compact design, longer operating life, and longer intervals between maintenance and inspections.
The CRC SmartWasher systems employ a natural process called bioremediation to degrade and remove contaminants from the cleaning fluid, allowing re-use of the cleaning fluid. The CRC SmartWasher is part of the CRC Greenlight program, which offers a diverse range of environmental cleaning products that are smart, safe, and effective.
Heavy-duty ductile iron housing withstands shock loads. Exclusive Magnum no-leak seal design. Horizontal split-housing allows easy disassembly for maintenance. 31 unit sizes, up to 3M lb-in (340 kNm) torque.