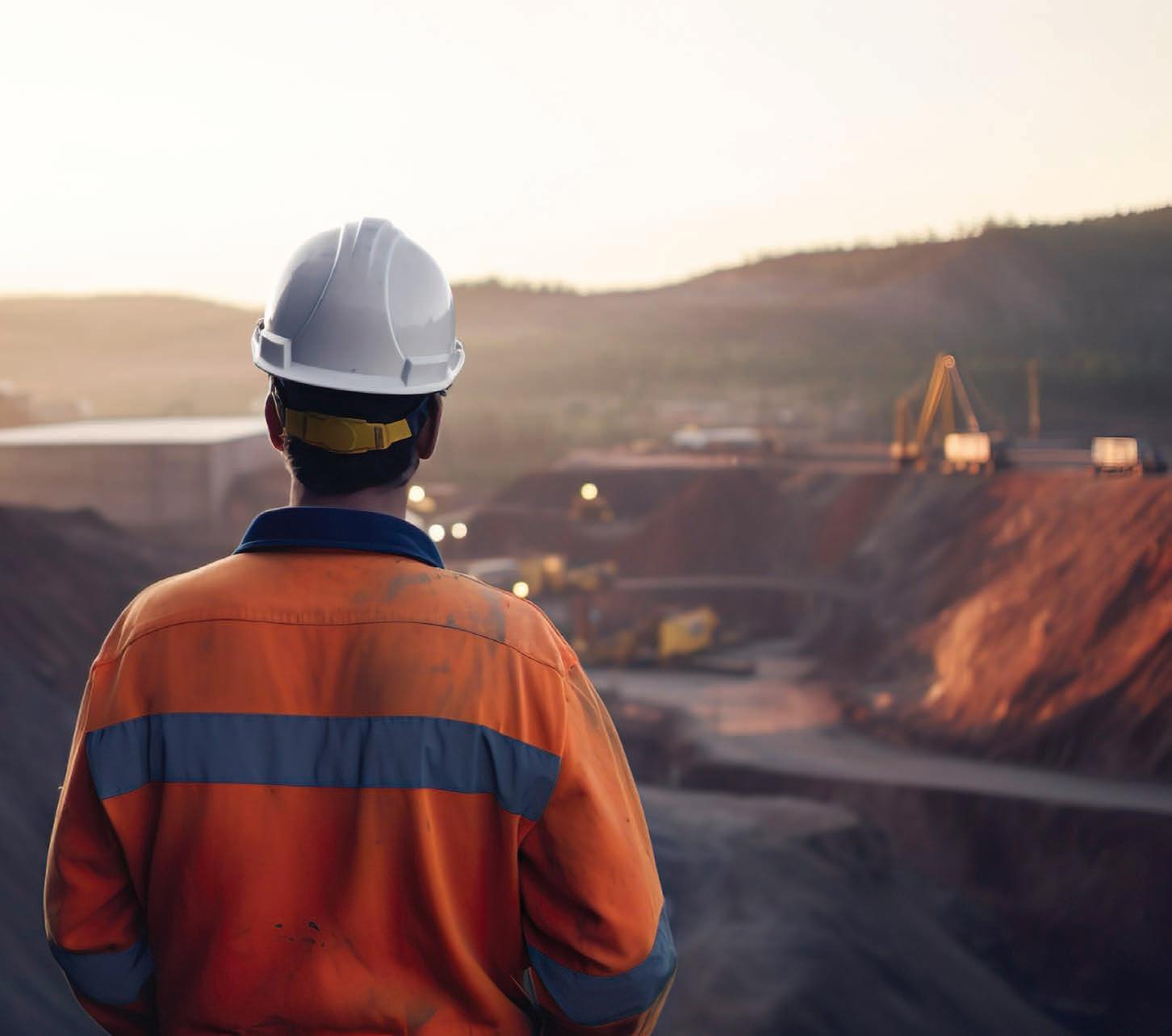
















ifm started over 50 years ago as a sensor company that wanted to do things differently and make technology work for everybody. We’ve kept to this value and run our business as a family does – keeping close to our customers and focusing on a full solutions platform along with quality reliable products and customer service.
ifm started over 50 years ago as a sensor company that wanted to do things differently and make technology work for everybody. We’ve kept to this value and run our business as a family does – keeping close to our customers and focusing on a full solutions platform along with quality reliable products and customer service.
Our goal has always been to protect what’s important to our customers. This hasn’t changed. From mine to port, our automation technology has benefitted customers in the Australian mining industry for many years.
Our goal has always been to protect what’s important to our customers. This hasn’t changed. From mine to port, our automation technology has benefitted customers in the Australian mining industry for many years.
Smart Process instrumentation enabling data-driven decision making for condition-based maintenance.
Collision Awareness systems improving safety around heavy mobile equipment.
Lower your energy costs
Reduce product wastage
Improve efficiencies
Vibration Monitoring maximising asset operational uptime and minimising maintenance costs.
Gain a higher product quality
Reduce downtime
Anomaly Detection enabling enhanced predictive maintenance of critical assets
Sensor2Cloud to collect and monitor from remote assets.
Talk with our team about how we can help to: To
Don’t let it’s compact size fool you. The Scooptram ST14 is a flexible and highly productive 14 metric tonne hauling rig for mid-sized operations. It comes packed with features that make it powerful yet fuel efficient - like the load-sensing variable displacement hydraulic pump and low emission EPA Tier 4 final/EU Stage V engine. Achieve maximum productivity thanks to the new transmission and best operator visibility in it’s class. Take your mining operations to new levels with the Scooptram St14. epiroc.com/en-au
PAUL HAYES paul.hayes@primecreative.com.au
IMARC 2023 GIVES MINERS THE IDEAL CHANCE TO COME TOGETHER TO COLLABORATE ON INDUSTRY TRENDS, INVESTMENT AND INNOVATION.
Entering its 10th year, the International Mining and Resources Conference (IMARC) has long been seen as a key international forum to facilitate continuous improvements and initiatives that are transforming the landscape of the industry.
“One of the great features of IMARC is how it brings out the best in a global industry that shares so many common challenges that can only be addressed at an industry level,” event director Paul Phelan said.
“It is therefore highly collaborative by nature and brings together a wide range of expertise and experience, sharing industry best practice and lessons learnt.
“Unlike many conferences, where it is about sitting and listening to speakers, IMARC facilitates meaningful discussions and leads to real partnerships and real solutions.”
This edition of Australian Mining shines a huge light on the country’s largest mining conference, set to take place in Sydney at the end of October, with a preview of the event, as well as a sneak peak of what many of the industry’s key players will be discussing and what they will have on display.
Described as the conference “where the most influential people in the mining industry come together, delivering ideas, inspiration and serving as a meeting ground for industry leaders”, this year’s IMARC is set to more than deliver on that promise.
CHIEF EXECUTIVE OFFICER JOHN MURPHY
CHIEF OPERATING OFFICER CHRISTINE CLANCY EDITOR PAUL HAYES Email: paul.hayes@primecreative.com.au
ASSISTANT EDITOR ALEXANDRA EASTWOOD
Email: alexandra.eastwood@primecreative.com.au
JOURNALISTS KELSIE HARFORD
Email: kelsie.harford@primecreative.com.au
OLIVIA THOMSON Email: olivia.thomson@primecreative.com.au
Elsewhere in this issue, we train our spotlight bulk material handling.
It can sometimes be easy to forget that once all of those precious ores and minerals are taken from the ground they need to be moved from point A to point B (and usually far beyond).
That process can be a complicated and even dangerous one, and that’s why we look at the some of the latest innovations, techniques and products that make the process as smooth as possible.
We also hear from some of the industry’s key decision-makers, learn about a new BHP research project designed to address issues of workplace culture, and continue to cast our eye to the mining sector of Australia’s closest neighbour, Papua New Guinea.
Astec Australia is a fully integrated business that provides quality new and used equipment, original manufactured parts, service and maintenance, and training support to the mining and bulk materials handling sectors. Founded in 1972, Astec has been servicing the Australian region since 1995.
“Ultimately, our goal is to design and build state-ofthe-art equipment which makes it possible for our customers to supply their customers with industry-leading results profitably,” the company said on its website.
Paul Hayes Managing Editor“For our customers, we will continue to be the most innovative company in our industry, offering the world’s most advanced, productive, durable and environmentally friendly products, coupled with training and education, service and support that is far beyond anything offered by our competition.”
Cover image: Astec
TIM BOND Email: tim.bond@primecreative.com.au
CLIENT SUCCESS MANAGER JANINE CLEMENTS Tel: (02) 9439 7227 Email: janine.clements@primecreative.com.au
SALES MANAGER JONATHAN DUCKETT Tel: (02) 9439 7227 Mob: 0498 091 027 Email: jonathan.duckett@primecreative.com.au
DESIGN PRODUCTION MANAGER MICHELLE WESTON michelle.weston@primecreative.com.au
ART DIRECTOR BLAKE STOREY blake.storey@primecreative.com.au
SUBSCRIPTION RATES Australia (surface mail) $120.00 (incl GST) Overseas A$149.00
For subscriptions enquiries please contact (03) 9690 8766 subscriptions@primecreative.com.au
PRIME CREATIVE MEDIA Suite 303, 1-9 Chandos Street Saint Leonards NSW 2065, Australia www.primecreative.com.au © Copyright Prime Creative Media, 2016
20 INDUSTRY INSIGHT
A record-setting year
While the 2023 financial year may have produced a mixed bag for mining, a number of key players reported impressive results.
26 DECISION-MAKER
Adapting to change
Australian Mining was on hand when Rio Tinto CEO Jakob Stausholm recently discussed the company’s past, present and future.
30 INTERNATIONAL MINING
Reaching across the Pacific
A trommel powerhouse
The MDS M515 mobile track trommel is the jack of all trades when it comes to clearing up a mine site.
54 BULK MATERIAL HANDLING
A paragon in energy-efficient conveying Fenner Conveyors is helping the mining industry decarbonise operations with its green series of conveyor products.
BULK MATERIAL HANDLING
Titan of industry
The new Titan side tipper truck unloader is designed to help remove inefficiencies in bulk material handling.
86 WORKPLACE CULTURE
Empowering on-site change
BHP is working with Monash University to improve physical and psychological safety at its South Flank mine in WA.
5
8
112
114
AUSTRALIAN MINING PRESENTS THE LATEST NEWS FROM THE BOARDROOM TO THE MINE AND EVERYWHERE IN BETWEEN. VISIT WWW.AUSTRALIANMINING.COM.AU TO KEEP UP TO DATE WITH WHAT IS HAPPENING.
AUSTRALIAN MINING GETS THE LATEST NEWS EVERY DAY, PROVIDING MINING PROFESSIONALS WITH UP-TO-THE-MINUTE INFORMATION ON SAFETY, NEWS AND TECHNOLOGY FOR THE AUSTRALIAN MINING AND RESOURCES INDUSTRY.
Thiess Group was awarded a $240 million nickel mining contract with PT Halmahera Sukses Mineral in Central Halmahera, Indonesia, in September.
The contract marks Thiess’ second successful venture in the Indonesian nickel market this year after securing the largest nickel player on Halmahera Island, Weda Bay Nickel.
“We are excited by this new contract award, which underscores Thiess’ expertise and strong track record in the Indonesian mining industry,” Thiess executive chair and
chief executive officer Michael Wright said. “It reaffirms our commitment to providing safe, sustainable and innovative solutions to our clients while contributing to the growth of Indonesia’s nickel industry, a metal critical to enabling the global energy transition.”
The mine is situated just 6km from another Thiess operation, which the company said will lead to the consolidation of its regional footprint and operational efficiency.
Bellevue Gold encountered highgrade mineralisation while it conducted infill drilling in preparation for the start of mining at its flagship Bellevue gold project.
The Bellevue gold project is a historic gold mining operation located approximately 40km north of Leinster in the northern Goldfields region in Western Australia.
Infill drilling was conducted there in preparation for the start of mining. It has returned high-grade results from the Bellevue South area and the Armand Main area. At the upper Armand work area, five
development levels were opened, and long hole stoping was expected to start in early August. This area will contribute to a major portion of early stoping and development ore while access to the higher-grade Armand Main is established.
At the Bellevue South area, ore driving has started from the southern decline by focusing on developing the 1115 and 1095 levels. High-grade development ore has been intersected as expected in the resource model, with both levels encountering consistent zones of mineralisation.
During its three-and-a-half-year contract, Thiess aims to deliver full mining operations, including mine development, haul road construction, ore loading and hauling.
The company said it remains committed to operational excellence and contributing positively to the communities and environments in which it operates.
“This contract win aligns with Thiess’ strategy to diversify our commodities portfolio,” Thiess Group executive – Asia Cluny Randell said.
“Our focus on safety, technological advancement and inclusion sets us apart. We are excited to continue building strong partnerships in the Indonesian nickel sector.”
The company said it will continue its commitment to health and safety, with comprehensive measures to be put in place to ensure the safety and wellbeing of the team.
Thiess has also committed to continuing its dedication to diversity, equity and inclusion by launching its female operator training program, aimed at fostering greater female participation in the mining workforce.
“The Bellevue South lode is a significant component of the production schedule for the 2024 financial year (FY24). Alongside Bellevue South, the Armand, Marceline and Deacon work areas are the other contributors to the FY24 production schedule,” the company said.
“The mining ramp up is proceeding according to the schedule and stoping activities will provide ROM (run of mine) material in advance of gold production, which is expected to occur in the December 2023 quarter.”
Bellevue Gold managing director Darren Stralow said the results provide a valuable insight into what the company can expect as mining ramps up.
“The grades are well above those in the reserve estimation and demonstrate why we are very confident about meeting our key targets as we move into production,” Stralow said.
“The project remains comfortably on time, with first production set for the coming quarter, and our focus is on meeting our targets and ramping up in line with our strategy.”
The Dolphin tungsten mine officially re-opened in August after being closed for three decades.
The mine is located near Grassy, a town on the south-east coast of King Island in the Bass Strait between Victoria and Tasmania. It first operated between 1917 and 1992, but closed due to low tungsten prices, with approximately 50 per cent of the known mineral resource unmined.
Group 6 Metals, an Australian resources exploration and development company, has since recommenced operations at the mine and began commercial
production of tungsten concentrate this year.
Tasmanian Resources Minister Felix Ellis said the reopening of the Dolphin mine has been years in the making.
“With around 95 full-time jobs expected to be supported through this operation, the mine will be King Island’s single biggest employer, keeping roofs over the heads of local families and meals on their tables,” Ellis said.
“It also provides a further economic boost to the local community with flow through to local businesses. Around $5 million will
go into the local economy directly through salaries alone and, for the broader state, around $30 million is expected to be returned to the Tasmanian taxpayer through mining royalties and other payments.”
Ellis said tungsten is a critical mineral due to the fact it is essential for steelmaking, electronics and defence manufacturing, to name a few areas.
“The Dolphin mine is known for hosting the highest-grade tungsten deposit of significant size in the western world,” Ellis said. “In recent years, the tungsten prices have surged significantly, and it is now
classified as a critical mineral by the Australian Government, and others globally.
“The world cannot do without critical minerals, and Tasmania is blessed to have a number of these minerals in abundance. This is also exactly why Tasmania is supporting industry by developing our own critical minerals strategy.”
The Australian Bureau of Statistics announced in June that exploration expenditure in Tasmania had grown significantly, with the latest ABS data showing $44.5 million was spent in the 12 months to March 2023.
August, appointing Rob Brauer, Jason Preston and Rob Kirman as receivers and managers.
The three receivers assumed control of the Kalium Lakes operations, which are set to continue on while an assessment of sale or recapitalisation options is undertaken.
Cheryl Edwardes, Brent Smoothly, Simon Wandke, Robert Adam and
non-executive directors following the announcement.
“The strategic process announced by Kalium Lakes on June 14 2023 is well progressed with wide interest received,” the company said in a statement.
“The receivers will continue the strategic process and immediately pursue the conclusion
Kalium Lakes delivered the first batch of sulphate of potash (SOP) at its Beyondie project in Western Australia in what was believed to be an Australian first in October 2021.
“Kalium Lakes has delivered another major milestone for the Beyondie SOP project, producing
2014,” Kalium Lakes then-chief executive officer Rudolph van Niekerk said at the time.
“It has been a remarkable journey to reach this stage and we thank everyone who has contributed to the success of the project during the past seven years, particularly our longterm shareholders, management team and employees.”
BHP and mineral scanning technology company Orexplore Technologies will collaborate for a field deployment at the Carrapateena copper mine in South Australia.
Valued at $1.55 million, the agreement will see Orexplore deliver site-based drill-core and sample digitisation services. The work will focus on unlocking new rock mass characterisation and geomatallurgical information to advance short- and medium-term mining and operational planning and decision processes.
As part of the agreement, Orexplore will utilise its Smart Domaining (SDM) solution to improve orebody knowledge across the site.
“We are proud to be deploying our technology into BHP’s Carrapateena mine and excited to continue our work with BHP’s team,” Orexplore managing director Brett Giroud said.
“Orexplore is working in close collaboration with the BHP team that is leading the way in the successful adoption of transformational technologies such as the Orexplore
technology platform. We are advancing our mission to improve the sustainability of the mining industry through delivering new technology tools to the field in support of geology and mining professionals transforming their processes and ways of working.”
Orexplore will work with the BHP operations team to embed new information flows into the processes and systems as part of the installation of three GeoCore X10 units at the site.
“This agreement further demonstrates increasing global demand for non-destructive, 3D information sourced rapidly from the field to inform decision processes, drive traditionally siloed collaboration around digital models, and create value within an operating mine,” Giroud said.
“This unique combination powers the company’s broad solution suite that is delivering new value to customers, from exploration to ESG solutions.”
Horizon Minerals and Dundas Minerals have entered into a binding agreement to acquire the Windanya and Baden-Powell/Scotia gold projects in the Kalgoorlie region of WA. Dundas Minerals has also made an application to acquire three prospecting licenses in its own right, contiguous to Horizon’s Banden Powell/Scotia tenements.
“The option to acquire these advanced stage gold exploration
projects in the Kalgoorlie region of Western Australia is an exciting opportunity for Dundas Minerals,” Dundas Minerals managing director Shane Volk said.
“Given the competition for these projects, Dundas is pleased that Horizon viewed us as a worthy partner. We are keen to commence the first phase of exploration in coming weeks.”
The Windanya project is located approximately 50km north of Kalgoorlie, while the Powell/Scotia project is adjacent to the Goldfields Highway, about 60km north of Kalgoorlie. The projects became available due to Horizon’s focus on advancing its Cannon, Penny’s Find and Rose Hill gold projects towards production.
“Being so near to Kalgoorlie, the Goldfields Highway, and several
gold plants, the economics of advancing a gold deposit from within these project areas into production, and generating income for the company are favourable,” Volk said.
Dundas is finalising plans for its first phase of exploration at both projects, which will comprise soil and/or auger sampling programs covering multiple targets ranked by prospectivity.
By utilising the latest technologies we provide an advanced combination of innovative solutions which optimise our customers mining operations performance, sustainability, availability and safety, around the globe.
We supply:
• Wear parts and solutions for mineral processing, mobile and fixed plant operations
• Digital and equipment connectivity
• Asset condition and performance monitoring
• Design, engineering and manufacturing solutions
bradken.com
Gold Road Resources recently released its half-yearly results, reporting record profits. Revenue from gold sales totalled $229 million, up from $196.5 million the previous financial year (FY22).
Gold sales reached 80,115 ounces, outstripping the 79,606 ounces sold the same period in 2022, with production benefiting from record throughput rates.
“The six months to 30 June 2023 has broken several financial records
for Gold Road,” managing director and chief executive officer Duncan Gibbs said.
“The strong result reflects the consistent performance of the processing plant, a supportive Australian dollar gold price and Gold Road’s production being fully unhedged.”
Gold Road’s earnings before interest, taxes, depreciation and amortisation (EBITDA) for the six-month period totalled $122.6
million, with a margin of 54 per cent. Operating cash flow for the six months to June 30 was $110.3 million, smashing the $69.5 million of the previous June 30 period in 2022.
The consolidated net profit after tax for the six months was $55.7 million, compared to the June 2022 after tax profit of $39.9 million.
Gold Road ended the half year with cash and short-term deposits of
$152.6 million, far above the $74.4 million from FY22.
Additionally, Gold Road’s Gruyere exploration project in WA is on target to achieve the restated 2023 annual guidance of 320,000 to 350,000 ounces of gold.
Gold Road also reported a strong exploration and investment portfolio, with strategic listed investments in De Grey Mining and Yandal Resources valued at $416.1 million on 30 June 2023.
Australian Prime Minister Anthony Albanese visited Glencore’s Mt Isa mines in August to discuss the importance of metals and minerals.
The copper-zinc mines are located in Mount Isa, Queensland, and are home to the only copper smelter and refinery in the state.
Glencore head of zinc and copper business Sam Strohmayr said the
company had been looking forward to welcoming the Prime Minister to the site.
“We were delighted to host the Prime Minister and pleased that he was able to take time to visit our zinc operations,” Strohmayr said at the time.
“We were also grateful to have the opportunity to discuss the increasing importance of metals and minerals
in Australia and the contribution our operations make to the region.
“Mt Isa is one of Australia’s most successful mining towns and this is in large part to the support we get from the community.”
Glencore’s Queensland metals business employed over 4400 people in 2022 and contributed $2.4 billion to the economy. This included $1.7 billion
spent on goods and services, which allowed the company to work with approximately 2130 local suppliers.
In 2022, Glencore spent $1.25 billion in investment commitments in transition metals, including spending $475 million to acquire the remaining 56.25 per cent interest in the MARA copper project in the Catamarca province of Argentina.
City of Kalgoorlie-Boulder councillors have voted to lease council land to BHP for temporary worker accommodation, with a total of 1152 new rooms to be built.
Located in Somerville, the three-year lease agreement is touted to bring in $1.3 million a year to the council in rent and rates.
The camp has also been granted three one-year options after the initial leasing period.
BHP will now seek building approval for the camp, which will house
workers for the construction of a furnace rebuild for the company’s nickel smelter as part of its Nickel West division.
“This is a big decision for the city, and we want to do what is best for our community long term,” KalgoorlieBoulder mayor John Bowler said.
“BHP have advised that 60 per cent of its workforce for its Kalgoorlie nickel smelter renewal project would be housed in the temporary village and this would not only ease the burden on residential
Rio Tinto released information on 14 of its global tailings facilities, along with its progress toward conforming to the Global Industry Standard on Tailings Management (GISTM).
Under GISTM classifications, the 14 facilities have been rated as very high or extreme, based on the potential consequences in the event of a failure.
“Since the tragic failure of the tailings facility at Brumadinho in Brazil in 2019, the entire industry
has been working to improve the way we manage tailings facilities,” Rio Tinto chief technology officer Mark Davies said.
“Responsible tailings management is critical to ensure the safety of our people and communities and to protect the environment. It is fundamental for our business and social license. We have made considerable progress since August 2020 towards conformance with the GISTM. We
housing but also have significant benefits for the local economy.”
BHP’s submission was recommended to the council due to the significant financial return it could create in terms of future services for ratepayers.
These funds will be held in city’s future projects reserve for the development of the area as traditional residential housing. Kalgoorlie-Boulder deputy mayor Glenn Wilson told the ABC the camp is necessary to reduce pressure on the city’s housing market.
“We’ve already got $900-a-week rents in Lamington and that will only increase, putting further strain on family budgets,” he said.
BHP’s WA operations supply nickel to world markets for use in electric vehicle batteries and other growing technologies, with an aim to support global decarbonisation.
BHP employs 2500 people across its Nickel West operations, a large portion of which consists of fly-in, flyout (FIFO) workers.
have completed most of the work and have detailed plans to complete outstanding items.
“GISTM has meant a steep change in how the industry manages its tailings facilities. Good tailings management is also about transparent partnership, and we have been working with the local communities near our facilities to increase awareness of our management practices and how we can best work together to continue
to keep people and the environment safe from harm.”
In May of this year, Rio and fellow major BHP invited expressions of interest for a range of new tailings technology partners.
Both companies said the ideas and technologies considered can be market-ready for mining, can involve technologies previously applied in other resource-related industries, or can be original ideas at an early research and development stage.
KEEP UP WITH THE LATEST EXECUTIVE MOVEMENTS ACROSS THE MINING SECTOR, INCLUDING AT FORTESCUE METALS GROUP, RED 5 AND RIO TINTO.
There has been more movement at the top for Fortescue, with three executives announcing their resignation in August and September.
Chief executive officer (CEO) Fiona Hick, chief financial officer (CFO) Christine Morris, and non-executive director Guy Debelle left the company within days of each other. According to the iron ore major, Hick’s departure was a mutual decision.
“We thank Fiona for her valuable efforts since joining Fortescue just under six months ago and wish her all the best with her future pursuits,” Fortescue executive chairman Andrew Forrest said.
Morris resigned from her position after two months and was replaced by group manager finance Apple Paget.
Debelle left Fortescue in September following a four-week notice period.
“I’m moving on,” Debbe told the Australian Financial Review. “I’ve had a great time, learned a lot at Fortescue, it was a great experience but onto other stuff now.”
Red 5 has appointed mining executive David Coyne as its new CFO, allowing
acting CFO Patrick Duffy to transition back into the role of chief corporate development officer.
Coyne has over 30 years of experience in the mining, engineering and construction industries in Australia and internationally.
Red 5 managing director Mark Williams said Coyne is an “outstanding addition” to the company.
“David is well regarded across the mining industry as an accomplished chief financial officer and senior executive and brings a high-level of financial and commercial acumen that will help us maintain a disciplined focus on cost management. David is also well versed in corporate governance and compliance matters,” Williams said.
Tony Mason has joined the ranks of Whitehaven Coal, joining the board of directors as Dr Julie Beeby prepares to depart.
Mason joins as an independent non-executive director with over four decades of experience in the coal mining sector. He has previously worked with some of the largest mining companies in Australia, including Rio Tinto and North Broken Hill.
“We are pleased to expand the experience of the board and welcome a new director who brings significant industry knowledge, commercial acumen and a strong intellect to contribute to strategic discussions and assessments of market dynamics,” Whitehaven chairman Mark Vaile said.
Beeby will step down from her role as non-executive director effective October 26 after serving on the board since July 2015.
“Julie has made a great contribution to the business over the past eight years,” Vaile said.
“With her coal industry experience together with her focus on good governance and consideration across our range of stakeholders, her active contributions to discussions around the board table have been greatly appreciated.”
Rio Tinto has appointed a new CEO of its aluminium business. Jérôme Pécresse will join the company from October 23.
Pécresse will succeed Ivan Vella, who will begin serving as IGO’s CEO in December following the sudden passing of Peter Bradford in October 2022.
Rio Tinto CEO Jakob Stausholm said Pécresse will make a diverse contribution to the company during a critical time for the global mining industry.
“Jérôme brings a wealth of experience across renewable energy, mining, business development and strategy, ideal for shaping our industry-leading aluminium business for a low-carbon future,” Stausholm said.
Pécresse said Rio Tinto’s aluminium business has a key role to play in delivering its strategy, as well as supplying materials needed in a lowcarbon world.
“I am thrilled to be joining Rio Tinto to continue building a stronger and more sustainable global aluminium business with our team around the globe,” Pécresse said.
Pécresse joined General Electric (GE) as CEO of renewable energy when the company completed its acquisition of Alstom’s power and grid businesses for €12.35 billion ($20.76 billion).
Prior to beginning his time at GE and Alstom in 2011, Pécresse spent 13 years in the mining and metals processing industry at Imerys in various roles before becoming its chief operating officer. AM
Combining Sandvik’s expertise in crushing with the screening, feeding and loading know-how of Schenck Process, has strengthened our capacity to deliver high quality equipment and aftermarket support.
We are now better positioned than ever, to develop innovative solutions to the challenges of our industry.
following its $9.63 billion acquisition of OZ Minerals.
$US4.3 billion,” chief executive officer Dino Otranto said.
Major miners made some major moves in the 2023 financial year (FY23), with BHP finalising its acquisition of OZ Minerals and Newcrest preparing to be taken over by Newmont.
But the real records came from the financial results, with Whitehaven Coal and Red 5 producing bumper earnings.
However, miners such as BHP and South32 recorded decreases in profits made in FY23.
BHP
The Big Australian achieved production records at Western Australia Iron Ore (WAIO), as well as Olympic Dam and Spence. Its full year production guidance was also achieved for copper, iron ore, metallurgical and energy coal, and nickel.
The major miner recorded a total revenue of $US53.8 billion; however, this decreased by $US11.3 billion from the
“Our financial results for the year were strong, underpinned by reliable production together with capital and cost discipline as we managed lower commodity prices and inflationary pressures,” BHP chief executive officer (CEO) Mike Henry said.
“Our balance sheet is robust and deliberately positioned to support portfolio growth in commodities the world needs for population growth, urbanisation and decarbonisation.”
Henry said BHP is committed to building an inclusive and highperforming culture, and a more sustainable business.
“Today, more than 35 per cent of our employees are female and we have increased Indigenous employee representation globally,” he said.
“We are taking action to reduce our operational greenhouse gas emissions through renewable electricity supplies and supporting the development of electric trucks, trains and light vehicles.”
“We are investing strategically in new ideas, technologies and countries through exploration and early-stage copper and nickel prospects to capture future growth opportunities,” Henry said.
Fortescue
Fortescue announced that it had achieved underlying net profit after tax (NPAT) of $US5.5 billion, marking its third highest underlying earnings in the company’s two-decade history.
Other financial highlights included delivering underlying earnings before interest, taxes, depreciation and amortisation (EBITDA) of $US10 billion, with an underlying EBITDA margin of 59 per cent, as well as recording a strong balance sheet with cash of $US4.3 billion and net debt of $US1 billion.
Operational highlights included a total recordable injury frequency rate (TRIFR) of 1.8 and record iron ore shipments of 192 million tonnes at the top end of market guidance.
“The team has delivered a fourth consecutive year of record operational performance for FY23, contributing
“Fortescue celebrated a number of significant milestones during the financial year including first production at our Iron Bridge magnetite project, and first ore mined from the Belinga iron ore project in Gabon as part of the early-stage mine development.
“Reflecting our ongoing commitment to delivering enhanced shareholder returns, the board has declared a fully franked final dividend of $1 per share, bringing total dividends declared for FY23 to $1.75 per share. This represents a 65 per cent payout of underlying net profit after tax.”
Red 5
Red 5 delivered record gold production of 165,544 ounces for FY23, which contributed to a gross sales revenue of $422.7 million, a 156 per cent increase from the previous year.
An underlying EBITDA of $96.1 million and a net loss after income tax of $8.7 million was also recorded, which was said to have reflected the ramp-up of the mining done at the King of the Hill (KOTH) site in Western Australia, as well as
WHILE THE 2023 FINANCIAL YEAR MAY HAVE PRODUCED A MIXED BAG FOR MINING, A NUMBER OF KEY PLAYERS REPORTED IMPRESSIVE RESULTS.BHP ACHIEVED PRODUCTION RECORDS AT ITS OLYMPIC DAM SITE IN SA. (IMAGE: BHP)
Westgold broke up its FY23 into two parts: the first half was about stabilising and resetting the company, and the second half was about building cash.
The gold miner consolidated its operations to four underground mines and three processing plants. Through this, 257,116 ounces of gold was produced from its Bryah and Murchison operations in WA, a decrease from FY22’s 270,884 ounces.
However, Westgold delivered $654 million in revenue, a $6 million increase from FY22. It also reduced its TRIFR by 63 per cent, recording a rate of 8.37.
“With new vigour, Westgold’s safety
WESTGOLD CONSOLIDATED ITS OPERATIONS TO FOUR UNDERGROUND MINES AND THREE PROCESSING PLANTS DURING FY23.
Improving mine site maintenance for better efficiency.
“Our three mining operations continue to perform in line with the mine plan, and the processing plant is performing well above nameplate capacity, putting Red 5 on track to achieve our stated production and cost guidance for FY24.”
The Australian gold miner had a “transformative” FY23, most notably due to it being acquired by Newmont for $26.2 billion.
“In FY23 we produced 2.1 million ounces of gold and 133 thousand tonnes of copper, with a significantly improved free cash flow of $404 million and
South32’s statutory profit after tax decreased by $US2.8 billion to a loss of $US173 million in FY23.
Despite the profit slump, South32 increased its supply of commodities critical for a low-carbon future.
“During the year, we delivered strong production growth in commodities that are critical for a low-carbon future. We set three annual production records and realised the benefit of our recent portfolio improvements, increasing aluminium production by 14 per cent, base metals by 17 per cent and manganese by four per cent,” South32 CEO Graham Kerr said.
“This growth, coupled with our continued focus on cost efficiencies, underpinned one of our largest underlying financial results, with underlying EBITDA of $US2.5 billion. This was achieved despite lower commodity prices and industry-wide inflationary pressures.”
statutory and underlying profit of $778 million,” Newcrest interim CEO Sherry Duhe said.
“Our balance sheet remains in excellent shape, sitting comfortably within all our financial policy targets as we continued to invest in our organic portfolio of value generating projects. On the safety front, our injury rates decreased by 26 per cent compared to last year.
“However, we were deeply saddened by the tragic fatality at our Brucejack mine in October and a serious injury at Cadia in June. These incidents
Safety was at the forefront for MinRes in FY23. Managing director Chris Ellison said the tragic death of a contract employee, who lost his life during construction at the Kens Bore site in June, affected everyone at the company.
Ellison said MinRes is determined to learn from the tragedy and safety remained a top priority, with the company recording a TRIFR of 2.08.
Financial highlights for MinRes included its underlying EBITDA increasing 71 per cent to $1.8 billion,
“MinRes continued to execute our high-growth strategy and I’m proud of what our team achieved on the major development projects that will set up MinRes for decades to come,” Ellison said.
“Our flagship Onslow iron project made enormous progress. All major approvals have been received, construction is on track and the project will start generating cash in 12 months.
“In lithium, we demonstrated agility by restructuring our joint ventures in response to the evolving market. The expansion of the Mt Marion plant was completed and a major exploration program revealed strong underground potential.”
MinRes’ $497 million takeover of Norwest was also completed in early June.
The rare earths producer achieved a NPAT of $310.7 million, revenue of $739.3 million and a EBITDA of $377.7 million.
“FY23 was another very productive year for Lynas,” CEO Amanda Lacaze said. “Operational performance was particularly strong, with record concentrate production.
“Whilst strong, (our financial) results were lower than those in FY22 when market prices were at record highs.
“During the year, we invested $595 million in capital projects and completed the year with a cash balance of $1 billion, providing funding certainty for completion of our key growth projects.
“We are well positioned to supply our strategic customers
The coal producer delivered a record NPAT of $2.7 billion for FY23, a 37 per cent increase from FY22. It also recorded an EBITDA of $4 billion, a 30 per cent increase from FY22.
Whitehaven’s record revenue of $6.1 billion was underpinned by an achieved average coal price of $445 per tonne, compared to the $4.9 billion revenue and an average price of $325 per tonne in FY22.
“Record coal prices and our portfolio of high-quality thermal and metallurgical products allowed Whitehaven to optimise the sales mix for FY23 and maximise our exposure to the strong gC NEWC thermal index,” Whitehaven CEO Paul Flynn said.
“With strong underlying market demand for high-CV, high-quality thermal coal and metallurgical coal, coupled with forecast supply tightness, we recognise the opportunity and importance to improve operational performance.”
The miner delivered 1.5 million ounces of gold within its FY23 guidance and sold them at an all-in sustaining cost of $1759 per ounce. It also produced a revenue of $4.1 billion, an underlying EBITDA of $1.5 billion and statutory NPAT of $585 million.
“Northern Star generated a record $1.223 million in cash earnings in the past financial year, the result of our focus on safely delivering operational excellence in parallel to adhering to a disciplined approach to investing shareholders’ funds,” Northern Star managing director Stuart Tonkin said.
“This full-year result also reinforces Northern Star’s strategy to identify growth opportunities
within our strongly endowed geological terrains that can deliver superior returns to shareholders.
“Combined with the on-market share buy-back that was launched during the year, we have increased our capital management returns to shareholders since Northern Star’s creation in FY12 to $1.4 billion.”
Pilbara Minerals saw a 64 per cent increase in the production of spodumene concentrate, recording 620,000 tonnes, up from FY22’s 377,000 tonnes.
This jump in production led to a 68 per cent increase in sales, with Pilbara Minerals selling 607,500 tonnes of spodumene concentrate, up from FY22’s 361,000 tonnes.
These production and price increases resulted in a 242 per cent boost in group revenue, equalling to $4.1 billion for FY23, along with a 307 per cent increase in EBITDA to $3.3 billion, up from FY22’s $800 million.
“The FY23 period has been an exceptional year for Pilbara Minerals across all fronts,” Pilbara CEO Dale Henderson said.
“Strong operational performance within a healthy pricing environment for lithium products has translated to an impressive set of financial outcomes for the business and our shareholders.”
Despite some miners seeing a decrease in their revenue, many were able to celebrate key financial and operational milestones, like high production in areas such as gold, leading to records being hit.
What FY24 holds for the major miners is yet to be seen, but it looks like it could be a positive period for the sector. AM
The next step in the integration of SP Mining (the mining-related business of Schenck Process acquired by global high-tech engineering group Sandvik), has seen SP mining entities change their names to reflect the new ownership.
On October 1, Schenck Process Australia Pty Limited, which became a wholly owned subsidiary of Sandvik in November last year, became Sandvik Rock Processing Australia Pty Limited.
The Australian entity is the largest part of SP Mining’s global business, employing close to 450 people.
Since the acquisition, Sandvik has been focused on bringing together its expertise in crushing with the screening, feeding, weighing and loading know-how of Schenck Process Mining.
Solutions to allow our customers to access our combined expertise in crushing, screening, feeding, weighing and loading,” Withington said.
“Together we aim to deliver even better digitalisation, sustainability and productivity solutions to our industry.
“The end goal of our integration is to allow our customers to place combined crushing, screening, feeding, weighing and loading orders with our new legal entity.”
Withington said the scale of Sandvik’s operations and commercial reach will help to accelerate the combined innovation portfolio of Sandvik Rock Processing Solutions and SP Mining.
“We look forward to continuing to service the business needs of our customers and remain fully focused on the delivery of high-quality
According to Sandvik, the union between its rock processing solutions business area and SP Mining will allow it to provide even more value to the mining industry.
“Since we became part of Sandvik’s rock processing solutions business
“As such, Australia is playing a key role in the overall integration.”
The company saw a key integration milestone in August with around 50 of its Australian employees moving from combined sales, engineering, services and research and development facility in Beresfield, NSW, to the Sandvik Hunter
THE MOVE IS PART OF AN INTEGRATION PROCESS THAT WILL ULTIMATELY SEE SP MINING BECOME A “SEAMLESS PART OF THE SANDVIK ORGANISATION”.SP MINING PRESIDENT ASIA PACIFIC TERESE WITHINGTON. THE NAME CHANGE WILL ALLOW SCHENCK TO BECOME A PART OF THE SANDVIK ORGANISATION WITHOUT ANY CONFUSION.
Industry-leading engineering solutions for metalliferous underground and open pit mobile mining machinery. We design and manufacture high-quality components/ parts/assemblies for the world's best mining equipment. At MASPRO, we optimise parts for safety and reliability so you can drill more metres, move more ore and push your machinery to the limits in harsh mining conditions. maspro.com.au
AUSTRALIAN MINING WAS ON HAND WHEN RIO TINTO CEO JAKOB STAUSHOLM TOOK TO THE STAGE AT THE MELBOURNE MINING CLUB TO LOOK AT THE COMPANY’S PAST, PRESENT AND FUTURE.
With a strong 150year history, Rio Tinto has had its fair share of success all over the world.
To discuss some of the miner’s highs and lows, as well as what’s in store for the future, Rio Tinto chief executive officer (CEO) Jakob Stausholm recently sat down for a discussion at the Melbourne Mining Club.
When Stausholm became CEO of Rio Tinto in January 2021, he outlined four main objectives the company would work towards in the foreseeable future: being the best operator; excelling in development; having impeccable environmental, social and governance (ESG) credentials; and having a strong social license.
One particular objective – to have impeccable ESG credentials – came at a very crucial time for the major miner.
In May 2020, Rio Tinto was searching for iron ore when it blasted two rock shelters, known as Juukan Gorge, in Western Australia.
The incident occurred despite the Traditional Owners of the land, the Puutu Kunti Kurrama and Pinikura people (PKKP), warning of the site’s significance. Since that time, Rio Tinto has aimed to increase transparency around its approach to cultural heritage protection.
“I’m always very careful when making such an assessment because, ultimately, it’s the Traditional Owners who should make that assessment,” Stausholm said of the progress made to repair its relations with First Nations people.
“I was actually very proud to see how (Rio Tinto) had felt, this feeling
that we really must do better here, and that people are prepared to really weigh in and realise what we have got to learn here.”
Stausholm said the PKKP has been instrumental during this rehabilitation process.
“They’ve really invented the concept of co-management of the land,” Stausholm said.
“If you think about it, if you build the right relationships and you really co-develop things, that’s how you create sustainability.
“This year, we have started construction on the Western Range project, which is co-developed with the Yinhawangka people.
“Mine planning today has changed quite a lot in discipline from what it was in the past, and that’s a good thing.”
Improving workplace culture Rio Tinto commissioned a report into workplace culture in 2021 after serious incidents in the mining industry made headlines around Australia.
The report, written by former Australian Sex Discrimination Commissioner Elizabeth Broderick, was released in February 2022.
“In our executive team, we discussed whether this could happen on our mine, and I think the answers were not very convincing. So we realised we need to dig deeper into the issues,” Stausholm said.
“When (Broderick) came out with the report, no matter how disturbing it was, it was really a gift for us because it was factual. Nobody disputed it.”
Rio Tinto’s report was publicised to help aid dialogue with the company’s 50,000 staff members. It outlined 26
recommendations as to how Rio should prevent and respond to discrimination and unacceptable workplace behaviour.
“We were sitting with the report, and we suddenly realised we cannot have the open dialogue without putting it out,” Stausholm said. “It was the only thing we could do to move on internally.”
The report will continue to serve as a guide for Rio Tinto in having these discussions in all corners of the company.
“First, you must recognise that these things are important. Secondly, you need to have a dialogue, and we were not talking about these issues,” Stausholm said.
“But with the report, it was kind of a license to start having the discussions in the offices and on the sites.”
Rio Tinto released its results for the first half of 2023 in late July. The company saw an improvement in operational performance but a significant dip in profits compared to 2022.
The major generated $17.3 billion in earnings before interest, tax, depreciation and amortisation for the first half of 2023, a 25 per cent dip on 2022.
A 10 per cent fall in total sales revenue – to $39.3 billion – led to a dividend payout of $2.62 per share, down 34 per cent from the first half of 2022.
Despite a dip in profits, Rio Tinto saw improved operational performance, highlighted by its Pilbara iron ore
operations returning a seven per cent lift in production and shipments.
“If you can make profitable growth, you create value to the shareholders and you start seeing it, (such as) the iron ore business showing production growth five quarters in a row. We are coming out stronger,” Stausholm said.
March 2022 was a big month for Rio, as it took ownership of the Rincon lithium project in Argentina, its first acquisition in a long time.
“When we bought (Rincon) a year and a half ago, it was our first acquisition in 10 years, and that’s not necessarily a good thing,” Stausholm said.
“I don’t think we need a big acquisition right now, partly because it tends to disturb your focus.
“What we are trying to do is build a smaller portfolio, acquisitions that actually shape the portfolio in a helpful way.”
A key example of this mindset is Rio Tinto’s new joint venture (JV) with Corporación Nacional del Cobre de
• Ideal for processing overburden, riprap/armour rock, limestone mixed with fines, clay and sticky materials
• High capacity, handling up to 500 tons per hour and up to 800mm sized rocks
• Hydraulically adjustable chassis riser for greater stockpile capacity and ease of access
• A tracked machine that’s perfect for moving from site to site
WE HAVE STARTED CONSTRUCTION ON THE WESTERN RANGE PROJECT (IN WA), WHICH IS CO-DEVELOPED WITH THE YINHAWANGKA PEOPLE. MINE PLANNING TODAY HAS CHANGED QUITE A LOT IN DISCIPLINE FROM WHAT IT WAS IN THE PAST, AND THAT’S A GOOD THING.”
Chile (Codelco), the world’s largest copper producer, and its purchase of PanAmerican Silver’s stake in Agua de la Falda, a company with Chilean exploration tenements.
“(The JV is) at the exploration phase, but it’s a very interesting copper deposit. It’s interesting to work closely together with a great company like Codelco,” Stausholm said.
“We do a lot of explorations under the radar, which are so small that you don’t see them, but they are definitely opportunities. You want to try to be a little bit counter cyclical.
“The reality is there’s a lot of hype around lithium and copper right now, so it’s very difficult to go in and buy a lithium or copper company, because you buy it and then you work for 10 years to justify what you’ve paid for it, and you haven’t really created any value.
“But with technology and very often exploration expertise, there might be easier ways to get in.”
To strengthen its alignment with the Paris Agreement and to achieve net-zero emissions by 2050, Rio aims to reduce its Scope 1 and 2 emissions by 15 per cent by 2025 and 50 per cent by 2030.
“In this half-year result, we’ve got the first mine in the world to be 100 per cent on biodiesel at our Boron site in California,” Stausholm said. “We are both a mining and processing company
and 80 per cent of our Scope 1 and 2 emissions are actually in processing.
The key thing is to solve the emissions and processing, and we are making huge technological breakthroughs.”
As Rio Tinto looks ahead to the future, Stausholm was clear that the company would continue to practice adaptability, which he believes is its core strength.
“Being successful in mining is a holistic discipline,” Stausholm said. “You have to get many disciplines right ... (and have) that ability to adjust and accept that the world is changing. AM
With a focus on helping customers achieve production targets faster – and using less fuel in the process, Volvo’s new rigid haulers are made for surface mining and quarrying applications where operation costs and safety are crucial. The R100E is an entirely new 95-tonne rigid hauler that combines market and customer knowledge with proven components, innovative technologies, and a striking new design.
Its power, efficiency, safety, and sustainability combination set new industry standards, making it a top choice for quarry and mining professionals worldwide.
Big Enough to Trust, Small Enough to Care
CONTACT YOUR LOCAL BRANCH FOR MORE INFORMATION
Aeconomic pillars of the country, mining has found a successful home in Papua New Guinea (PNG).
One company that understands this situation well is Hastings Deering, one of the top suppliers of Caterpillar (CAT) products and services to the Pacific nation’s mining sector.
Hastings Deering’s journey in PNG began in 1949, and it has been delivering CAT products and services to the country’s mining industry since that time.
300 employees supporting five business centres located in Port Moresby, Lae, Tabubil and Kimbe, with an operations centre at Lihir Island supporting Australian gold miner Newcrest.
“We have many aspects to our business, with our key objective being to support Caterpillar equipment owners with parts and service support in mining, general construction, power generation and marine industries,” Hastings Deering PNG area manager
Caterpillar line-item parts and access to the Caterpillar global dealer network, we are well positioned for parts distribution to our customer needs.”
Hastings Deering has an in-house training centre in PNG that produces certified CAT technicians through apprenticeships in mechanical and autoelectrician trades.
“The training team based out of Port Moresby and Lae has grown the number of opportunities and offerings in recent
has focused on literature and numeracy testing and parts-warehouse training, being accredited for NC1 and NC2 (National Certificate) for DHEF (Diesel Heavy Equipment Fitting) 1 and 2 and registered with the PNG Department of Higher Education Research Science and Technology.”
The in-house education capability specialists and training staff are taught at a global level under Caterpillar’s standards. To that end, Hastings Deering recently invested more than $250,00 in a state-of-the-art Caterpillar simulator that enables virtual training on excavators and track-type tractors.
Dare is proud of the work the Hastings Deering PNG team has done, especially the changes implemented over recent years to increase the safety of its employees and customer service, an approach that sits at the centre of the company’s continual improvement strategy.
“Our team in Papua New Guinea is doing an incredible job engaging with the local communities and we are very proud of the amazing partnerships they have built,” Dare said.
One of these partnerships is with the Hunters, a professional rugby league club in PNG. Dare said the team aligns with the values of Hastings Deering, embracing diversity, equality and inclusiveness.
“Rugby league is an institution in PNG and the Hunters have the largest footprint for this sport in PNG, so this partnership allows us to connect with our employees, customers and the broader PNG community,” Dare said.
HASTINGS DEERING IS BRINGING MORE THAN JUST CATERPILLAR MACHINERYTO PAPUA NEW GUINEA’S MINING SECTOR. HASTINGS DEERING HAS A ROBUST IN-HOUSE TRAINING CENTRE IN PNG THAT PRODUCES CERTIFIED CAT TECHNICIANS THROUGH APPRENTICESHIPS. HASTINGS DEERING HAS A PARTNERSHIP WITH THE HUNTERS, A PROFESSIONAL RUGBY LEAGUE CLUB IN PNG.
Hastings Deering’s PNG division also sponsors the Port Moresby Kart Club, a go-karting organisation that televises the races across PNG.
“In addition to donating CAT merchandise for prizes, the Hastings Deering PNG team also put on a free barbecue at a recent race, which provided a great opportunity to support and network with the community,” Dare said.
Hastings Deering’s PNG team recently worked with not-for-profit group Buk bilong Pikinini (which roughly translates to ‘books for children’) to create a reader for the book series, When I grow up
The latest in the series, When I grow up I want to be a heavy equipment operator, includes images of children visiting Hastings Deering’s Port Moresby branch.
“Buk bilong Pikinini has published 18 picture books as part of the When I grow up series to ensure PNG children can recognise themselves and their culture in the books they publish,” Dare said. Other PNG causes Hastings Deering is committed to includes the Wild Cats, a Port Moresby netball team that is wholly made up of Hastings Deering PNG employees and their children, and the Port Moresby
annual corporate blood drive since 2015 through sponsorship and a business wide blood donation campaign,” Dare said.
“The Port Moresby General Hospital is the largest hospital in PNG and the impact of this cause has been far-reaching.”
Indeed, with its support of so many causes in PNG, Hastings Deering’s impact in the Pacific nation can also be
Every five years, the Federal Government is required to release an Intergenerational Report.
The reports are a way of assessing how government policies will work over the next 40 years, while mapping out Australia’s outlook for the economy and how this will change future federal budgets.
The 2023 Intergenerational Report may be the most important one yet, as it projects how the world’s shift to net-zero will impact the Australian mining industry.
If the world is to reach net-zero emissions by 2050, reports indicate that the global demand of critical minerals will need to increase by a massive 350 per cent by 2040.
Australia holds many of these critical minerals in its soil. In particular, the country can give the world access to stockpiles of lithium, cobalt and rare earth elements.
“(These minerals) are key inputs to clean energy technologies,” the Intergenerational Report stated.
“With abundant wind, sun and open spaces, Australia also has the potential to generate green energy more cheaply than many countries.”
The report projected substantial growth in the critical minerals sector. Lithium, in particular, was highlighted as a standout, with export volumes expected to double over five years from 2022.
“Australia is already the world’s largest producer of lithium (spodumene concentrate) and is well placed to meet future global demand of lithium,” the report stated.
Lithium is a crucial component of battery manufacturing, especially the lithium-ion batteries that are found in cellular phones, laptops and solar power back-up storage. Australia currently produces nine out of the 10 minerals used in these batteries.
The 10th mineral, graphite, is not yet developed in the country but Australia is seeking to develop refineries for future production.
But by far the biggest consumer of lithium is the electric vehicle.
“Making a 55-kilowatt-hour (kWh) battery and associated systems for a small electric car typically requires over 200kg of minerals, including copper, lithium, nickel, manganese, cobalt and graphite,” the report stated. “This compares to 35kg of copper for the powertrain of a comparable internal combustion engine.
“Electric vehicles and static battery storage have already displaced consumer electronics as the largest consumers
of lithium and are set to overtake stainless steel as the largest end use of nickel by 2040.”
Global sales of electric cars exceeded 10 million in 2022, and those numbers are only projected to grow. Australia already supplies over 50 per cent of total global lithium and if the electric car trend continues, it is set
to supply a lot more. In fact, the year 2028 could see Australia supply 4.5 million tonnes to the world’s netzero effort.
“Global demand for lithium is projected to increase significantly over the next 40 years, significantly expanding Australia’s potential export market,” the report stated.
“Even if global action is only sufficient to limit temperature increases to 3°C, global demand for lithium is projected to quadruple.
“If global actions are consistent with limiting temperature increases to 1.5°C, global lithium demand could be more than eight-times larger than current levels by 2063.”
As new green industries and technologies gain momentum, Australia’s critical minerals industry is set to thrive.
“Climate change and global climate action will have profound impacts on the economy, reshaping Australia’s industry mix and requiring effective mitigation and adaptation to manage the impacts of higher temperatures,” the report stated.
“Australia’s industrial response could harness mineral reserves and abundant sources of renewable energy to supply critical minerals, hydrogen and green metals needed for modern, sustainable economies and to materially affect global climate trajectories.
“The Australian critical minerals industry has the potential to scale up and meet a significant share of this anticipated demand.
“Australia has the scale of resources, established industry, technical expertise and track record as a stable, reliable and responsible supplier to support the scale of investment required.”
As one of the world’s largest exporters of coal, Australia is well placed to continue to meet demand for decades to come.
However, the market has been dealt a challenging hand in the past year.
The Russia–Ukraine war has been the main driver of price volatility for the coal industry, forcing investment plans to focus on maintaining production capacity in the sector. The shift to netzero is also affecting the coal sector.
“The net-zero transformation will impact global energy and resources markets as global demand for lowemission commodities increases,” the report stated.
“While the transition to renewables will boost demand for many of the minerals mined in Australia, creating new growth opportunities, global demand for fossil fuels is projected to decrease over time as global trading partners act to reduce emissions.”
This is especially true for thermal coal which, according to the report, is set to see the largest reduction in global demand.
“If global action limits temperature increases to 1.5°C, the associated reductions in global demand for thermal coal could reduce Australia’s exports to less than one per cent of current levels by 2063,” the report stated.
“Global demand for Australian thermal coal exports is expected to decline as our trading partners move toward netzero emissions.
“However, Australia has some of the world’s largest reserves of critical minerals such as lithium, cobalt and rare earth elements. These are some of the essential ingredients in global emissions reduction as inputs for electric vehicles, batteries and renewable energy generation technologies.”
It is clearer than ever that the world needs Australia’s critical minerals industry to hit net-zero. And with its track record of producing the quantities needed, the country is in position to deliver. AM
Entering its 10th year, the International Mining and Resources Conference (IMARC) has long been seen as a key international forum to facilitate continuous improvements and initiatives in the mining sector.
Conversations around sustainability, net-zero and low carbon emissions are all-important, now more than ever, and that conversation can only happen when the world gets together in one place.
Juergen Wallstabe from the GermanAustralian Chamber of Industry and Commerce said IMARC provides an opportunity to showcase how Germany’s emphasis on environmental protection has led to stringent regulations for mitigating environmental harm.
“Germany’s commitment to remediating and restoring abandoned mining sites demonstrates our dedication to healing environmental wounds,” he said. “IMARC offers a chance to share our experiences and learn from others facing similar challenges.”
Energy security is once again a key term in Europe, partly driven by the ongoing war in Ukraine and its impact on reliable energy supply, but also as a result of shifting political environments in countries like Germany.
And to secure reliable energy for many generations to come, countries across the
continue to be a key player in securing a steady supply of critical minerals,” Wallstabe said.
“Wind turbines need steel, copper and strong magnets with rare earths minerals. Batteries consist of a wide range of critical minerals like lithium,
platinum, iridium or candium.
“All resources that Europe struggles to produce in sufficient quantities.”
IMARC spokesperson Paul Phelan is looking forward to having Germany so strongly represented at the event.
“It is clear that Germany’s public
institutions and companies actively exploring novel technologies to enhance resource extraction efficiency, reduce environmental impacts, and improve worker safety,” Phelan said.
“IMARC offers an opportunity to witness how a technological giant like
THE 2023 INTERNATIONAL MINING AND RESOURCES CONFERENCE WILL HELP TO FACILITATE THE CONVERSATION FOR SUSTAINABLE AND INNOVATIVE MINING OPERATIONS.
IMARC IS DESIGNED TO PROVIDE A FORUM TO EXPLORE OPPORTUNITIES AND TO SHOWCASE THE BEST AND LATEST KNOWLEDGE, INNOVATION AND GROWTH THAT BENEFITS THE WHOLE VALUE CHAIN.”CANADA AND GERMANY ARE JUST TWO OF THE COUNTRIES REPRESENTING THEIR MINING INDUSTRIES AT IMARC. SUSTAINABILITY IS A GLOBAL EFFORT, AND THE TOPIC WILL TAKE CENTRE STAGE AT IMARC 2023.
another mining superpower, will also be in attendance.
Canada Mining Innovation council chief executive officer Carl Weatherell said leadership of the mature mining countries such as Canada and Australia is critical to achieving the mining industry’s global environmental goals.
industry’s energy use, water use and environmental footprint by 50 per cent by 2027, the major players have not only an opportunity but a responsibility to work together on innovations that reduce waste, lower costs and mitigate environmental impacts across all aspects
leaders in the mining industry, with decades of experience and innovation behind them, so they have a natural role in leading mining’s transformation to a more responsive, sustainable and resilient industry.
“It’s incumbent on the two countries
industry in terms of how we collaborate, who we collaborate with, and what we work together on.”
IMARC chief operating officer Anita Richards said the 2023 event is the ideal opportunity for countries like Canada to attract investment, showcase their expertise and engage with mining and METS (mining equipment, technology and services) companies, investors and suppliers to collaborate and develop business opportunities.
“For its part, Canada has a great story to tell as a stable and attractive destination for global investment in the resources the world needs for a cleaner future, and the expertise and leadership it can offer to a transitioning global industry,” Richards said.
“IMARC is designed to provide a forum to explore these opportunities and to showcase the best and latest knowledge, innovation and growth that benefit the whole value chain.
“Standing alongside Australia as one of the world’s largest mining nations with significant role in the future of resources, Canada has always been a strong partner of IMARC throughout our 10-year history and we are delighted to welcome them back once again.” AM
ith a legacy rooted in Australian iron ore processing since the 1950s, Derrick Corporation continues to reshape the industry with cutting-edge solutions.
At the forefront of its offerings is the SuperStack technology, a major advancement that has helped redefine the way iron ore beneficiation plants operate. Derrick Corporation’s trajectory through the annals of iron ore processing has seen the company consistently grow its offerings to stay ahead of the everevolving mining landscape.
Today, its contributions resonate louder than ever as it introduces its SuperStack technology, a vibratory screening machine armed with frontto-back screen panels that provides unparalleled screening capacity, efficiency, and user-friendliness.
“This innovative approach challenges conventional methods of classification, ushering in a new era of efficiency, sustainability and optimised resource utilisation in iron ore processing,” Derrick Australia general manager Garth Hay told Australian Mining
The SuperStack technology offers a host of advantages, and one of its most significant is its enhanced efficiency.
Winefficiencies and sub-optimal outcomes, SuperStack provides a more precise and efficient classification process.
The front-to-back screen panels ensure a thorough separation of particles, leading to higher-quality end products that meet stringent industry standards.
“The SuperStack technology is more than just a technical solution,” Hay said. “It is a statement of commitment to the environment.
“Sustainability has emerged as a central theme in the mining industry and SuperStack is designed to align perfectly with this ethos. Its environmentally conscious design underscores Derrick Corporation’s dedication to responsible and ecofriendly mining practices.”
A key feature of SuperStack is its ability to optimise resource utilisation. By reducing the generation of ultrafines in grinding circuits, the technology not only enhances the quality of the final product but also minimises wastage.
This reduction translates to tangible cost savings and increased operational efficiency, making SuperStack a crucial tool for iron ore processors aiming to maximise their bottom line while minimising their environmental footprint.
“To understand the real-world impact of SuperStack, one need only look at the success story of ArcelorMittal Nippon
Like many players in the industry, AM/NS India faced the challenge of increasing plant capacity without compromising product quality.
Traditional classification systems fell short, jeopardising pellet quality and the integrity of critical infrastructure like slurry pipelines.
“In the face of these challenges, AM/NS India turned to Derrick for a solution,” Jain said.
“Our SuperStack technology stood as the answer to AM/NS India’s pressing needs. Notably, this solution promised an environmentally conscious approach, aligning seamlessly with AM/NS India’s commitment to sustainable practices.
“Through a comprehensive
the exceptional capabilities of their technology.
“Derrick’s wealth of experience in closed grinding circuits and pipeline protection applications added further value to the proposition.”
With the installation of SuperStack machines, the plant saw a 15 per cent increase in mill capacity. Pellet quality soared and the integrity of Asia’s longest continuous slurry pipeline was fortified, ensuring uninterrupted operations. But Derrick Corporation’s contributions extend beyond its SuperStack technology.
“Our iron ore product offerings have consistently elevated the industry’s standards,” Hay said.
“As mining evolves and challenges become more complex, Derrick’s commitment to innovation ensures that our products will continue to shape the future of iron ore processing.”
Derrick Corporation’s legacy is etched in the fabric of iron ore processing. Its journey from the 1950s to the present day has been marked by innovation and unwavering commitment to progress.
The introduction of the SuperStack technology is a testament to its dedication to redefining industry norms and providing solutions that not only enhance operational efficiency but contribute to a more sustainable and responsible mining future.
With SuperStack leading the way, Derrick Corporation continues to be a driving force in revolutionising iron ore processing on a global scale and a reliable partner to responsibly maximise resource efficiency for a greener world. AM
As the resources sector evolves, every facet of the mining value chain is looking for ways to meet its decarbonisation targets.
As a global multi-energy company that has been supplying mines their energy needs for many decades, TotalEnergies has the knowledge and expertise to help companies meet their decarbonisation goals.
“We can leverage our international network to work with a mining company across different countries, products and applications to ensure we have the right product available at the right place and time,” TotalEnergies vice president – global mining segment Dirk de Bruyn said.
“Having the ability to coordinate across customers and regions means we can minimise the costs involved in introducing a new energy supply chain.”
TotalEnergies already supplies fuels and lubricants and offers training, among other essential services to ensure mines are running productively and sustainably.
“Our integrated business model is our strength and is what sets us apart,” de Bruyn said. “We guarantee our customers efficiency, profitability and innovation.
“Thanks to our integrated model, we can reinvent and diversify our energy offering to favour renewable and decarbonised energies and promote the economical and rational use of fossil fuels.”
Currently active in more than 130 countries, TotalEnergies has established itself as a trusted partner for mining companies across the globe. The company’s considerable reach means it can provide solutions to help mines meet their decarbonisation goals within a quick turnaround time.
“Our expansive market presence allows us to have direct global contractual relationships with many of our customers,” de Bruyn said.
“The market proximity allows us to work together to ensure the best operational performance and provide solutions to reduce our customers’ cost of ownership and carbon emissions.
“As a major player in energy transition, we are committed to working towards our ambition of netzero by 2050, together with society.
“We are building the future today by leveraging our strengths. Low-carbon energies will dominate our production and sales mix by 2050.”
To reach net-zero, TotalEnergies is aiming to eliminate the equivalent of 100 million tonnes of CO2 per year through developing a carbon storage service and an industrial e-fuels business.
“It takes a lot of time, cost and effort to develop new solutions,” de Bruyn said. “Our customers appreciate that we have a multi-energy offer that is expanding globally.
“Setting up trials, negotiating new contracts and developing trust can take
a long time, but our direct relationships allow us to transfer best practice across sites and even continents.
“That is essentially valuable to multinational mining companies.”
TotalEnergies will be attending this year’s International Mining and Resources Conference (IMARC) and is looking forward to connecting with the wider mining industry and showing off its recent achievements.
“The presentations at the event will enable us to gain and share insights into
progressing ESG (environmental, social and governance) and environmental resilience and learn about the challenges faced by the industry as a whole,” de Bruyn said.
“The team is looking forward to engaging in fruitful discussions with industry leaders and sharing our multienergy solutions that can support and accelerate mining’s energy transition.” de Bruyn said TotalEnergies’ presence at IMARC would help to further support the company’s decarbonisation mission.
“IMARC is an important event to network and connect with existing global, regional and local clients, as well as showcase the capabilities of TotalEnergies,” he said.
“Through our participation, we hope to educate future mining prospects and discuss with these customers the road to energy transition.
“Having the opportunity to meet face-to-face works wonders for building networks and connecting directly with customers, and we are looking forward to building these networks and fostering deeper collaborations.” AM
THANKS TO OUR INTEGRATED MODEL, WE CAN REINVENT AND DIVERSIFY OUR ENERGY OFFERING TO FAVOUR RENEWABLE AND DECARBONISED ENERGIES AND PROMOTE THE ECONOMICAL AND RATIONAL USE OF FOSSIL FUELS.”TOTALENERGIES IS COMMITTED TO HELPING MINING COMPANIES MEET THEIR DECARBONISATION GOALS. TOTALENERGIES VICE PRESIDENT – GLOBAL MINING SEGMENT DIRK DE BRUYN.
l Optimised design for new pulleys
l Compatible with existing pulley arrangements
l Reliable bearing life
l Simple, robust, easy to install and align
l Ease of maintenance
Specifically designed & developed for conveyor pulleys in Australian mining, minerals processing and bulk materials handling. A reimagining of the traditional SSN and SDD TAC housing ranges.
POSITION PARTNERS WILL HAVE SOLUTIONS ON SHOW AT IMARC TO ENABLE PROACTIVE AND INFORMED DECISIONS THROUGH MEANINGFUL DATA INSIGHTS.
hen the 2023 iteration of the International Mining and Resources Conference (IMARC) kicks off in Sydney at the end of October, Position Partners, a premier provider of intelligent positioning and automation solutions, will be on the ground.
“IMARC is a great opportunity for delegates to learn about the latest developments in technology and how they can make tangible improvements to operational performance on a mine site,” Position Partners executive manager of mining Andrew Granger told Australian Mining.
“Our team also benefits from the event because it gives us insights into industry trends, and into what mine owners and contractors are looking for in terms of operational technology.”
A presence at IMARC helps Position Partners identify needs in the market, which in turn steers its innovation.
“Safety has always been a major theme at IMARC, but what’s gaining recent traction is how technology can improve safety and increase operational performance simultaneously on mine sites,” Granger said.
Position Partners is highlighting a handful of its safety technology solutions, including collision awareness, fleet management, and its next generation automation solution, SafeAI.
W“Autonomy has been around in the mining industry for a little while now, but what we’re looking at is autonomy 2.0, introducing new technologies to add an artificial intelligence (AI) element to these very successful fleets,” Granger said.
“With SafeAI, we’re looking at making sure that these autonomous systems are able to adapt with changes on a mine site in order to keep these machines going.
“Think of it like adding that extra layer of intelligence to prevent the downtime.”
SafeAI can be retrofitted to vehicles from different manufacturers, which Granger said was an essential quality-oflife feature for mining contractors, who often employ varied fleets.
The technology is currently in a proof-of-concept stage with a major contracting group in WA, with work underway to fit autonomy to a mixed fleet of 100 mining trucks..
Position Partners is also focused on listening to feedback on core technology platforms and potential for further industry improvements. Operating as the conduit between site operations and technology suppliers, Position Partners works to provide solutions that are fit for purpose and continuously improving to meet customer needs.
“Our clients value the collaborative approach we take to deploying operational solutions, really understanding the specific challenges and working with our supplier partners to integrate feedback into system development,” Granger said.
Recent examples Position Partners will demonstrate at IMARC include shift scheduling and machine abuse metrics as additional modules to the iVolve fleet management solution.
“Getting the best outcomes from machines and the people that operate
them is critical to safe, productive mine site operations,” Granger said.
“The ability to schedule shifts helps managers coordinate the team and ensure people are allocated jobs as efficiently as possible.”
To reduce maintenance and machine abuse, iVolve fleet management technology can now alert operations managers to metrics like speeding, overloading or excessive braking to enable proactive decision-making.
“This feature is another example of continuous improvement to core technology, giving managers data that helps predict a potential outcome before it becomes a real problem,” Granger said.
“At IMARC, we want to engage with customers to see how we can enhance the solutions that are already on-site and integrate with existing workflows, evolving rather than overhauling.”
Position Partners knows the value of engaging with its industry. Granger said customising and making safety technologies viable for mine sites is driven by the miners.
“Sometimes the technology can be developed in a lab a long way away from site, but we’ve got to make it applicable to the real world, which is something we’re good at,” he said.
“The exciting part of IMARC is that you have genuine mining organisations coming and looking for new technologies and seeking innovation.” AM
On the heels of announcing its new autonomous mining portfolio, Hexagon will be making its presence known at the 2023 International Mining and Resources Conference (IMARC).
Robert Daw, chief technology officer, Hexagon’s Mining division, will take the stage to discuss the company’s partnership with Mineral Resources (MinRes).
The partnership began in late 2021 and involves Hexagon in the development of an autonomous road train solution for the MinRes haulage fleet, starting in Western Australia’s Pilbara region, and then beyond.
In July this year, MinRes announced that it would deploy a fleet of 120 road trains equipped with the autonomous haulage solution developed by Hexagon at its Onslow iron project.
“At IMARC, I will focus on how automation is enabling the mining industry to access remote orebodies, and the future of automation and how it will change the industry for the better,” Daw told Australian Mining
“The narrative has changed what autonomy means to mining. It’s not about replacing people; it’s about removing them from dangerous areas and utilising their skills elsewhere.”
Autonomous mining is in the early stages of evolution, and Daw is excited to see what it can unlock.
“There are more than 1000 autonomous vehicles in mining today; however, we as an industry can continue to think further outside the box,” he said
“We’re starting to see opportunities such as accessing other remote orebodies that previously were never economical.
“It should not be about day-to-day truck driving in a traditional sense. It really is about starting to understand, ‘What does an autonomous mining operation look like, and how does this benefit miners and mines?’”
Hexagon believes autonomy can bring a range of benefits, and those benefits are present in its work with MinRes.
“One of the major benefits is removing people from unsafe environments and manual labour areas,” Daw said.
“Another benefit is the economics and the business opportunity that mining companies have, so how autonomy can actually change business models.
“With some of these uneconomical remote pits, we know the minerals are in the ground but they just aren’t quite feasible to access, and autonomous technologies will unlock some of that potential. There is also an environmental side of autonomy that we’re focusing on, which is the reduction of carbon emissions through better utilisation of our equipment.”
To that end, the autonomous road train configuration created by Hexagon is a world-first on this scale.
“The ability to see a road train that’s pulling over 300 tonnes, three trailers over a 120km road, and to be able to take that from a mine site to port without having to put in any infrastructure like conveyors or rail – it’s just a basic road – is exciting,” Daw said. “All of these solutions and expertise come together to create that world-first. We’re not aware of anywhere else that has these types of road trains operating 24–7, pulling this quantity of material on a 365-day basis.”
Since the inception of the partnership, Hexagon and MinRes have shared a strong working relationship.
“They’ve been a great partner for us in terms of being able to work collaboratively on the road train itself, from access to vehicle sand sites to testing to working with people who are equally dedicated to success,” Daw said. “Hexagon couldn’t have achieved this successful milestone without MinRes and vice versa.” AM
ONE SUPPLIER FOR THE LIFE OF YOUR CONVEYOR
With so many moving parts and heavy loads, our highly talented engineers, belt splicers, mechanical technicians, and customer support specialists are always available when you need them most.
Backed by our local manufacturing facilities and industry-leading conveyor monitoring technology, you can trust our team to ensure maximum productivity from your operations.
Operating Australia’s largest network of field service centres, Fenner Conveyors are only a phone call away.
Phone 1800 Fenner (336 637)
fenner.com.au | sales@fenner.com.au
Inspections & Audits
Belt Splicing & Refurbishment
Mechanical Conveyor Maintenance
Belt Installs & Change-Outs
Equipment Overhaul & Refurbishment
System Redesign
Diagnostics & Intelligent Conveying Technology
AUSTRALIAN MINING SAT DOWN WITH INTERNATIONAL TELECOMMUNICATIONS COMPANY VOCUS TO DISCUSS WHY PRIVATE 4G/5G NETWORKS ARE SO IMPORTANT TO A MINING OPERATION.
Wi-Fi is such a typical, necessary part of everyday life that many wouldn’t think twice about the little black box that provides internet to their entire home or workplace.
But within that black box, millions of radio waves are being transmitted to ensure users can enjoy browsing on their private networks to their heart’s content.
A mine’s wireless network is the same concept, just on a much larger scale.
Vocus head of wireless Simon Lardner said that as mining continues to become more technologically advanced, networks need to ensure they keep up with the demand.
“Mines are essentially a big factory,” he said. “People need to be in constant communication with each other and with their equipment.
“If a regular person spends a couple of hundred dollars on a Wi-Fi modem and it stops working, it’s annoying, but in a mine, if the network stops working, that can have some tragic consequences.”
The solution to such an issue is a Vocus 4G/5G private network.
“Mines come to us trying to solve a connectivity problem, usually to do with autonomous trucks or equipment.” Lardner said. “They require a sophisticated network, and that’s where we get involved.”
The most crucial aspect of a private 4G/5G network is the communication it enables. Some mines are so large that it can take several hours of driving to get from one side to the other, which presents a potential barrier to communication unless they have an effective network.
“Connectivity is such a simple concept, but on a mine site it means everything,” Lardner said.
“It enables the use of new technology which in turn enables improved safety, and improved systems being implemented means autonomous trucks can run without crashing into each other, it means people can express ideas or warnings about dangerous situations.
“Good communication translates to an efficient, productive mine.”
Lardner hailed Beach Energy as the first oil and gas company to build a private network using Vocus’ expertise. Having launched in 2015, it is now one of the longest operating private 4G/5G networks in the world. Beach Energy’s site, located in the Cooper Basin in SA, is about as isolated as one can get.
In a modern automated environment, mining equipment operators don’t necessarily need to be sitting inside the truck to do their jobs. Many control the equipment from an operating room hundreds of kilometres away.
But in order to control the equipment correctly, a network must be strong enough to ensure unplanned downtime is avoided, especially if employees aren’t close to the mine site to fix it.
“The benefits of a private 4G/5G network are pretty easy to calculate, which is why every mine is starting to implement them,” Lardner said.
“If we can take humans out of dangerous areas and put them in areas where they can use their brain power and avoid injury, that’s a good thing.”
Lardner also highlighted the interpersonal benefits that employees can gain from working on a mine with a well-designed private network.
In particular, those who used to have to complete fly-in, fly-out (FIFO) work may now have the opportunity to work in a remote centre in the city, where they can be close to loved ones.
“Being on a FIFO roster – for example, on-site for 10 days and then
home for six – can be really demanding physically and mentally,” Lardner said. “But if you can offer people the opportunity to operate remotely and work from their home town due to improved connectivity, those people are probably more likely to stay in their job.”
Vocus’ extensive fibre and private networks are an ideal choice for mine operators who want to control their sites with confidence and peace of mind.
“There are two types of network traffic: one is within the mine with machines talking to each other, and another is between the mine site and
the main corporate hub in Perth, for example,” Lardner said.
“And that’s where Vocus’ broader fibre networks and low earth orbit satellite services get leveraged because we’re able to provide that all-important connectivity back to the big cities and make sure an operator’s screen doesn’t suddenly lose all its real-time data.
“Networks sound complicated, but it’s common sense. It needs to work, because without it, a mine doesn’t work.” AM
Derrick screens have been used in iron ore processing since the 1950’s. While needed in numerous applications to solve unique customer problems, today, over 1000 Derrick fine screens are serving the iron ore industry for applications including:
• Increased concentrate grade
• Improved grinding classification
• Sizing
• Fine iron recovery
In many installations, Derrick fine screens achieve more than one of the benefits listed above. All as part of our mission to empower our global family to responsibly maximize resource efficiency for a greener world.
Improve your bottom line. Contact Derrick today to learn how you can benefit from this game-changing technology.
Mining companies are analysing more alternatives to tailings storage facilities (TSF) earlier for new projects as they respond to the global industry standard on tailings management (GISTM) and stakeholder expectations.
Launched in August 2020, the GISTM sets a global benchmark for environmental, social and technical outcomes from tailings management. The goal is zero harm to communities and the environment from tailings facilities worldwide.
The GISTM has been widely adopted by members of the International Council on Mining and Metals (ICMM). These companies had until August 2023 to conform to the GISTM for tailings facilities, with “extreme’” or “very high” potential consequences for not doing so. All other tailings facilities have until 2025 to conform.
Requirement 3.2 of the GISTM necessitates operators of new tailings facilities to undertake a multi-criteria alternative analysis of all feasible sites, technologies and strategies for tailings management. They should consider TSF alternatives over the project life cycle and
address environmental, technical and socioeconomic impacts.
The goal is twofold: select a TSF alternative that minimises risks to people and the environment through the TSF life cycle, and minimise the volume of tailings and water placed in external tailings facilities.
The GISTM requires the process to be reviewed independently and disclosed to stakeholders in order to aid public accountability.
SRK Consulting senior tailings engineer Sam Kendall said the GISTM’s requirement for the early evaluation of alternative tailings technologies and strategies has significant implications for new and established mining companies.
“In the context of GISTM compliance, there is increased attention being paid to the assessment of best available practices and/or best available technologies; however, some established mining houses have long been applying these principles,” Kendall said.
“Some miners are drawn to shortterm capex (capital expenditure) and opex (operational expenditure) without sufficiently considering the longer-term, less tangible aspects of TSF design, which also derive value.
“For newer companies at the very early stages of project development, the initial selection of a low-cost, status quo tailings management solution can be appealing, particularly when considering time and budget constraints.
“During the initial stages of project development, it can be easy for project managers without specific tailings experience to favour selecting a familiar, cost-effective solution; however, with large-scale uptake of the GISTM, the industry is being encouraged to invest in optimising tailings management to find more sustainable, long term, cost effective solutions.”
Kendall believes expectations are changing with the implementation of the GISTM and all miners developing new TSFs are expected to demonstrate that they are working towards a defensible evaluation of management options.
“This is an important consideration for mining companies, particularly those looking for early-stage investment from institutions which expect GISTM compliance,” Kendall said.
“More broadly, this process also influences perceptions from regulators, communities and the public. Companies should understand this change and be taking steps now to adapt to it.”
According to Kendall, the long-term benefits of comparing TSF alternatives can far outweigh the extra cost and risk, particularly when there are unique project drivers or TSF constraints.
“Examining alternative TSF technologies will help mining companies to implement the optimal result on mine-waste design, now and in the future,” he said.
“Fundamentally, it’s about being future-focused and open-minded about TSF technologies.”
Documenting and disclosing the process used to consider TSF alternatives has other benefits, Kendall said, including project transparency and stakeholder collaboration. Similarly, adopting this approach helps to demonstrate environmental, social and governance (ESG) principles in TSF and cultivate a more holistic view of tailings management going forward.”
Arguably, the main benefit of this approach is the potential to “futureproof” TSF design.
“Given life of mine is often 10-plus years, it is well worth exploring options that have the potential to improve the risk profile of the operation and licence to operate into the future,” Kendall said.
“Business-as-usual-type facilities might not be able to maintain acceptability, as ongoing public disclosure requirements set a high bar for the mining industry in general.”
Kendall acknowledges, however, that this approach adds extra cost and risk for smaller mining companies. Assessing more TSF alternatives requires greater internal resources or use of industry consultants. Documenting the process to select a TSF technology and strategy, and having it independently reviewed, adds other costs.
The main risk for smaller miners when selecting alternative tailings management approaches, such as large-scale filtration (reducing the amount of water transported from a processing plant to a TSF) or codisposal (combining tailings and waste rock), is reliability and the potential for operational delays.
“These are important considerations that can be addressed with time,” Kendall said.
“Mining companies that don’t adhere to GISTM requirements around TSFs will find it increasingly hard to attract capital from investors or will have to pay a higher cost for that capital.”
Stakeholders have demanded more rigorous and stringent TSF processes after the catastrophic tailings dam collapse at Vale’s Córrego do Feijão mine in Brumadinho, Brazil, in January 2019.
“Investors are scrutinising TSFs in more detail than ever,” Kendall said. “They recognise the immense reputational risk that can arise from a tailings failure, and the potential destruction of mine value.”
Kendall believes it is a good sign that mining companies are starting to adopt GISTM principles for tailing facilities.
“Like many things in mining, change usually starts at the top and works its way down,” he said. “There’s no onesize-fits-all approach.”
The key is a different mindset.
“It’s easy to view a TSF as only a cost and focus mostly on its impact on project economics. It’s harder to identify and value the long-term, less tangible benefits of a successful TSF strategy and the damage caused if something goes wrong,” Kendall said.
“The GISTM provides an opportunity for mining companies to show stakeholders the process they went through to choose their TSF. That’s good for the company, communities, investors, and the environment.”
SRK Consulting is a leading, independent international consultancy that advises clients mainly in the earth and water resource industries. Its mining services range from exploration to mine closure. SRK experts are leaders in fields such as due diligence, technical studies, mine waste and water management, permitting, and mine rehabilitation. AM
Start early: For new facilities, the GISTM calls for early assessment of available technologies. Companies looking for institutional investment should be able to demonstrate that they are working to address best applicable technologies and best available practices principles, and identifying tailings disposal options.
Engage stakeholders: The GISTM proposes identifying the optimal preferred solution through the use of a project-specific multiple accounts analysis framework. This requires engagement by a number of stakeholders from technical and non-technical backgrounds to consider alternatives.
Be open-minded: It can be easy to influence early evaluation of tailings technologies and strategies with subconscious bias. Each site, project and client has different criteria and objectives. Starting the assessment early and approaching it with an open mind allows for a pragmatic, measured approach.
Look beyond cost: Selecting a low-cost system can be appealing; however, if not coupled with the consideration of risks such as permitting, community acceptance, governance, ongoing regulations and compliance, chances are actual costs may escalate beyond what would have been acceptable if a more balanced approach was applied.
CEO AMANDA LACAZE HAD A CLEAR MESSAGE TO YOUNG AUSTRALIANS WHEN SPEAKING AT DIGGERS & DEALERS: FIND WORK WITH PURPOSE IN MINING.
Following a recent $20 million Federal Government grant and $390 million project investment from the US, it’s hard to believe Lynas Rare Earths is a company in its relative infancy.
Only 10 years old, Lynas has proved its hunger for progress. The miner has expanded across Western Australia and Malaysia in its pursuit of providing rare earth metals, with an emphasis on sustainability and environmental responsibility.
“Australia used to run on the sheep’s back. And today it stands on the digger’s shoulders,” Lynas Rare Earths managing director and chief executive officer Amanda Lacaze said in an address at the recent Diggers & Dealers Forum in the WA goldfields.
Lacaze discussed a common misunderstanding of mining by young Australians who might question the industry’s necessity. As these young people enter the job market, she said, many discover a strong future in mining, one with an emphasis on clean energy, sustainability, and environmental and social governance (ESG).
“For those of us who work in the industry, it is our duty to treat this gift with respect, to mine safely, to limit our footprint wherever possible, to care for our people in our communities, and to rehabilitate land at the end of mine life.” Lacaze said.
“We work with selected partners to provide mine-to-magnet traceability. We conduct lifecycle assessments, and we participate in external sustainability and verification initiatives.”
Established as a world-leading ethical and environmentally responsible producer of rare earth minerals, Lynas has enjoyed several stand-out years with strong demand and high profits.
“We’ve been in production for a decade and have faced every type of challenge that could be thrown at us,” Lacaze said.
But Lynas keeps coming back stronger, with a recent upgrade project to its Kalgoorlie processing facility in WA entering Stage 4 development and a new filter building and dissolution facility in Malaysia, which is the only plant producing separated rare earth materials outside of China.
One of the highest-grade rare-earth deposits in the world, the Mt Weld mine in Kalgoorlie is the crown jewel of Lynas’ 2025 growth plan.
“This is a significant project for Kalgoorlie and for the state of Western Australia and it will provide the foundation for a critical minerals processing hub in the goldfields region,” Lacaze said.
Lacaze said mining contributes almost 10 per cent of Australia’s gross domestic product (GDP), supports more than 1.1 million jobs over 200 sites, and pays an average salary of $144,000.
It also contributed $59 billion in company tax and $24 billion in royalties last financial year, she said, with $295 billion paid in company tax and royalties in the last 10 years.
“Mining matters. Without the minerals we mined and process, none of us can live the lifestyles we desire – and we cannot meet the challenge of reducing the devastating effect we humans are having on the planet,” Lacaze said.
“And if our younger generations want to do work with purpose, then they can find that in the mining industry.”
The $20 million grant awarded to Lynas earlier this year is part of the Federal Government’s Modern Manufacturing Initiative, which will contribute to the development of new
processing capabilities for apatite-rich ores from Mt Weld.
It will also partially fund the Apatite Leach Circuit project Lynas is undertaking in collaboration with the Australian Nuclear Science and Technology Organisation (ANSTO). The project create 90 new jobs across its production, and Lynas is committed to engaging with Australian universities to give skills to science and engineering students as they enter the workforce.
“It is very pleasing that this project will be undertaken in collaboration with ANSTO and with the involvement of students from Australian universities, who are the future of the critical minerals industry,” Lacaze said.
Lacaze welcomed a promising future for Lynas, and mining at large, in the face of industry challenges.
“We are seeing lower market prices at present,” she said. “But we see many of these trends as relatively short lived and expect that, in the medium term, market pricing will return to a more normalised level.”
Lacaze underlined the idea that always considering the challenges for mining is necessary, pointing to the importance of building a rare earths industry outside of China.
“We’ve now signed an updated contract with the United States Department of Defense (DoD) for our US heavy rare earths plant (HRE),” Lacaze said.
The $390 million investment from the DoD is an increase from the $181 million the US Government pledged in June 2022 and will be used for the construction of the HRE component of Lynas’ US rare earths processing facility project in Texas.
The project will be constructed on a 149-acre greenfield site in Seadrift, Texas, and is set to be operational in the 2026 financial year.
“We are delighted to work with the US DoD to deliver our US HRE
separation plant in Texas, which is a key pillar of Lynas’ growth strategy,” Lacaze said.
“This further support by the DoD demonstrates the priority being given to developing robust and resilient rare earth supply chains.”
Once complete, material from Lynas’ Mt Weld mine in Kalgoorlie will be transported and processed
at the Texas facility, as well as at the company’s plant in Malaysia.
“We really look forward to getting to know the community and working to create advanced manufacturing jobs and economic opportunities for local people.” Lacaze said.
Closing her address, Lacaze called on delegates and the future of the Australian mining workforce to
be proud of one of their country’s leading industries.
“My advice to you is do what is right. Listen to your people and meet each challenge as an opportunity to get better,” she said.
“And whilst there will be days where you wonder if it’s all worth it, I’m happy to stand here as proof that it is.” AM
SKF has built its reputation on developing, designing and manufacturing state-ofthe-art bearings, seals and lubrication systems.
With products found in almost every corner of the global mining industry, SKF takes the responsibility of leading its customers toward a more sustainable future very seriously.
Sustainability, carbon emissions and the push for net-zero are becoming increasingly important for companies within the resources sector.
But there is still a reliance on a takemake-waste cycle, whereby resources are taken from the ground, used in products and then discarded at the end of their usage.
SKF is looking to change this longentrenched approach with a forwardleaning and ambitious new purpose statement, ‘Together, we re-imagine rotation for a better tomorrow’.
This statement directly amplifies the company’s stance on a circular economy, with commitment to creating intelligent and clean solutions for people and the planet.
“We look at a circular economy through a lifecycle lens,” SKF principal application engineer Dario Rodriguez told Australian Mining
“A total of 20 per cent of all energy used in the world is wasted in overcoming friction. Our main focus is to minimise that waste.
“Once we have designed a bearing arrangement for an asset and we’re
learning how it’s performing out in the field, then we can feed those learnings back into the design phase and improve our product even further.
“This allows us to both improve asset life and use less energy.”
Through in-depth analysis during the design (eg right bearing, right lubricant type and amount, right sealing system, etc) and usage phase (eg proper installation, correct alignment, optimal settings, etc), SKF can achieve additional reductions in friction. This means power losses are minimised, energy consumption is further reduced, which in turn reduces CO2 emissions.
SKF is committed to reducing energy consumption across the entire manufacturing value chain, a mindset the company has embedded throughout its operations.
“We aim to be net-zero from our own operations by 2030,” Rodriguez said.
“We have several initiatives and programs in our factories looking to improve our processes to reduce energy consumption and have even celebrated the milestones of having several factories energy-neutral.
“That means several of our factories are operating solely on green energy supplied by solar and wind for all their production requirements.”
With its strong sustainability profile, SKF is well-placed to deliver new technological advancements in a move toward net-zero.
SKF Bearing Select software is a free-to-use application that allows customers to explore how choosing
bearing arrangements that minimise friction and reduce lubricant consumption can have a significant effect on their CO2 footprint.
“The reports can be used to illustrate how emissions can differ in various configurations for the same application,” Rodriguez said.
“You can look at any machine in the mining process and they will all have different technical alternatives. For example, some use grease lubrication, some use oil, and so on.
“Users can add these data points in Bearing Select and get a better understanding on CO2 emissions.”
The Bearing Select software also allows users to engage directly with SKF’s application engineers, who can provide a more detailed view on specific emissions from the bearing.
“It’s one of the best tools to use for regular technical evaluation of different bearing solutions,” Rodriguez said.
“Whenever we are involved in advising the manufacturer or equipment end user what the best technical options are, we can use this software to illustrate our options.”
SKF is using the Bearing Select technology in combination with its ability to remanufacture bearings to get even more out of the life of a product.
“Remanufacturing gives us the opportunity to inspect the bearing at the right time and do the rework it needs so it can go back in operation with a full second life,” Rodriguez said.
“Depending on the amount of work needed, a remanufactured bearing reduces the carbon footprint by up to 90 per cent compared to a new one.”
The 2023 International Mining and Resources Conference (IMARC) will see SKF promote sustainable rotation and showcase how the company can help its customers move towards a circular economy.
“Remanufacturing contributes to reducing lifecycle costs of many critical assets, and at the same time reduces environmental impact,” Rodriguez said. “(Remanufacturing) is going to be one important element that we’re going to showcase at IMARC, but another one is SKF’s RecondOil – a truly circular use of oil.”
RecondOil technology allows for cleaner oil without having to change it. By re-using the same oil, customers can enjoy more sustainable operations.
“The ideal solution for our customer is extending as much as possible the performance of their machines,” Rodriguez said. “IMARC attendees will see how our condition monitoring solutions not only help to predict and alert about premature failures but let
us learn more about why assets fail. We use that knowledge to develop the next generation of products.”
One such solution is SKF’s OnDemand Lubrication system, which combines predictive maintenance with lubrication automation, resulting in a system that modifies its cycle according to the bearing condition.
“We were asking ourselves, how do you optimise the usage of lubrication
rather than just using it and letting it go to waste?” Rodriguez said.
“How can we make sure that our customers’ equipment is working correctly, so they can have it running for as long as possible, with minimal lubrication, with minimal energy consumption, and with the lowest environmental impact?
“So that’s the end goal that we are aiming for.” AM
Unleash the future of compressed air technology with the Atlas Copco E-Air Compressor Range. Designed to redefine efficiency, reliability, and performance, the E Air is the ultimate solution for your industrial and commercial needs. Boasting state-of-the-art technology that ensures optimal energy consumption the Atlas Copco E-Air range can adapt intelligently to your workload demand, reducing operational costs while maximising output and reducing your carbon footprint.
Experience uninterrupted operations and minimal downtime, and all while your compressor delivers consistent and precise airflow, ensuring your operations maintain peak performance day in and day out.
Available in a variety of models and capacities, there’s a perfect fit for every application. From compact designs to high-capacity solutions, customise your compressed air system to match your unique requirements effortlessly.
LIKE TO KNOW MORE? SPEAK TO OUR TEAM TODAY
PH: 1800 733 782 www.atlascea.com.au
WE HAVE SEVERAL INITIATIVES AND PROGRAMS IN OUR FACTORIES LOOKING TO IMPROVE OUR PROCESSES TO REDUCE ENERGY CONSUMPTION AND HAVE EVEN CELEBRATED THE MILESTONES OF HAVING SEVERAL FACTORIES ENERGY-NEUTRAL.”Suitable for use with exploration drilling, maintenance, construction, blasting and underground ventilation systems. REMANUFACTURING WILL BE A KEY TOPIC FOR SKF AT IMARC. THE RECONDOIL BOX ALLOWS SKF CUSTOMERS TO GET CLEANER OIL IN THEIR APPLICATIONS.
As the only exclusive dealer of the MDS M515 mobile track trommel in Western Australia, South Australia, the Northern Territory, Papua New Guinea and New Caledonia, Lincom has made it its business to know the ins and outs of the heavy-duty machine.
A flagship model, the M515 is the ideal machine for recovering rocks mixed with sticky materials like clay.
Lincom general manager Western Australia Mark Crestani told Australian Mining the M515 is set to solve a range of bulk handling challenges for the industry.
“We’ve seen the M515 perform really well on all mine sites, but particularly where a mine has sticky, hard-to-process material. That’s where it really shines,” Crestani said.
“Sticky materials would normally bind up in a vibrating screen, but the action of the trommel screen helps clean them up.
“In the worst applications, we can fit a drum cleaner to the M515 so the material can continue to flow.”
The M515 has been a staple of the industry for several years, so when MDS wanted to grow into the Western Australian mining scene, Lincom was the obvious choice for an exclusive dealership.
“Lincom saw this as a significant opportunity to add value to our current brands,” Crestani said. “Not only does it add to what we already offer, but it creates more value for our customers.”
Mine sites would generally screen out larger rocks with a scalping machine, but even the largest scalping machines can’t match what the M515 can do.
“We’re seeing a lot of sites pick out larger rocks manually, because their current equipment can’t handle the larger sizes,” Crestani said. “Obviously that’s not great for productivity and it can lead to inefficiencies.”
800mm in size, so on-site workers no
longer have to be tasked with sorting these by hand.
“There’s a lot of really strong downstream benefits from the M515,” Crestani said. “A lot of the time, overburden is pushed to one side without being processed, but the M515 allows this to be processed efficiently.
“We’re even seeing people create a revenue stream from being able to process rocks from overburden that, without the M515, would just be a waste product.”
Thanks to the versatility of the tracks on which it sits, the M515 can easily be moved from site to site, and the conveyors fold out efficiently so mines no
And with Lincom’s after-sales service, customers can be assured that any problems will be solved quickly.
“We have our own fitters who can provide any sort of technical assistance or breakdown assistance,” Crestani said. “We also hold spare parts for any model that we supply, so we’re well covered when it comes to servicing.
“We also have field service across the areas that we supply to. Even though the M515 is a relatively simple machine to operate, we want to be available to alleviate any of those growing pains that come with implementing a new machine.”
Lincom attended factory training with MDS before taking delivery of the M515 to ensure its teams were up to date with the machine.
“We also conduct operator and safety training on the same day the machine is delivered, and that’s a service we provide no matter what,” Crestani said. “But the fact that the machine is simple to install is a real advantage.”
In an industry where bulk handling is such a common, everyday occurrence, miners need to be assured their equipment is up for the task.
The M515 can provide that assurance, especially with Lincom’s experience and skill backing it all the way.
“The M515 is heavy-duty by nature,” Crestani said. “It’s big. It’s solid. And, most importantly, it’s going to deliver.” AM
ROX Mining Parts is a division of the Bend-tech Group dedicated to the supply of Open cut and Underground machine replacement parts. ROX is committed to eliminating downtime, improving performance, and increasing longevity of parts through innovation. The ROX team has been restructured with customer experience in mind and with dedicated supporting departments such as research and development, engineering, and logistics, the ROX division is poised to transform mining parts supply.
ROX
A riff on the substrate mobile equipment mine (Rocks). Combined with the animal the Aurochs or Ox for its characteristics in defence, agility, and protection.
Representing the strengths of the division and the parts we supply the Aurochs is known as an agile, athletic, and strong animal capable of defending themselves against predators such as wolves.
We are excited to introduce our reimagined identity – a transformation born from our unwavering commitment to provide even greater value to our customers and a realisation that our provision of OEM replacement parts division has become much more than just a business unit. Our journey began with a simple idea, and today, that idea is evolving into a brand-new experience that reflects our dedication to innovation, quality, minimising downtime, and customer experience.
Every great journey has its origins. What has become ROX today started in the late 2000’s when we began supplying OEM replacement handrails for Underground machines. This quickly evolved into supplying more handrails, then more parts. Which then evolved into servicing the Open cut machine market, supplying components such as handrails, fenders and guards, platform modules and fuel tanks. Through the years, we've remained dedicated to serving our customers, adapting to their needs, and leveraging new technologies to improve their experience.
Our new identity is not just a logo or a name – it's a reflection and commitment of our vision for the future. We envision a world where all our customers’ required parts are stocked, downtime is eliminated, parts are innovated and improved, and we are the relied upon supplier for mining equipment replacement parts. This vision is the driving force behind every decision we've made in shaping our rebrand.
Our promise to you remains unchanged. Just as we've stood by your side in the past, we will continue to be your trusted partner on this journey of sustained value and minimising downtime. Our commitment to all parts being stocked, downtime eliminated, innovated parts and improved performance, and becoming the relied upon supplier for mining equipment replacement part supply remains steadfast, serving as the bedrock of our rebrand and the road ahead.
As time passed, the division continued to grow both in parts and services provided as well as our human resources and supporting divisions such a research and development (R&D). We realised that providing what the industry needs and mitigating customer pain points meant embracing change. Our rebrand is the result of an evolution – a transformational process that has seen us listen to your feedback, learn from our experiences, and begin a journey towards continued innovation to create something even more exceptional.
Our rebrand isn't just for us – it's for you. We've reimagined our service with you in mind, with the mission of creating an experience that is more streamlined, innovative, and dedicated than ever before. With our new identity, we're poised to elevate your experience and empower you like never before. With a restructured team, more robust R&D, and a new, dedicated website in the works we are poised to deliver the best service in the industry.
In closing, we're excited to embark on this new chapter with you. Our rebrand of our OEM Replacement Parts division is more than a new name, new colours, or new logo – it's a testament to our dedication to continuous improvement, innovation, and growth. Thank you for being a part of our story so far, and we look forward to the exciting journey ahead, hand in hand.�
The term ‘decarbonise’ gets a lot of traction in the mining industry these days. But excessive use can sometimes dilute the meaning of a word.
Serious mining industry customers are more likely to care about verifiable results than a catchy tagline, and Fenner Conveyors has the backing, expertise and products to deliver what customers are after.
Fenner Conveyors draws on its rigorously designed Green Series of conveyor products, PowerSaver and Yeloroll-HD, to show customers exactly how much they’ll be saving on energy consumption and carbon emissions when it comes to overland conveyor systems for mines.
“PowerSaver is a rubber compound that is applied to the pulley (bottom) cover of the conveyor belt to effectively reduce energy loss due to the indentation of the pulley cover moving over the idler roll,” Fenner general manager,
technology Tim Briggs told Australian Mining. “The reduction of energy loss is achieved by improving viscoelastic properties of the PowerSaver compound.
“Various factors go into developing the PowerSaver compound for us to be able to predict the power saving of a belt for our customers. We’re proud to have the in-house technical experts who are able to interpret this data accurately.
“To measure indentation rolling resistance, our team looks at idler roll diameter, belt loading, cover thickness and the viscoelastic properties of the bottom cover. On top of this, we must consider the operating conditions such as temperature, belt speed, and belt load.
“Indentation rolling resistance accounts for approximately 60 per cent of the power draw of typical overland conveyor systems, which is why reducing this is a key factor.
“The Australian mining industry needs more and more material conveyed by their systems. We can’t change the throughput, and we can’t change the
distance, but we can change is the viscoelasticity of the rubber.”
The unique compound design of PowerSaver helps to reduce energy consumption, as it supports the system to operate across longer distances and with higher tonnage.
“When designing a new system and looking to reduce power consumption on your belt, you’re able to step down your tensions, your drive motors get smaller, your pulleys get smaller. The whole conveyor benefits,” Briggs said.
Whether fitting to a new or existing system, the PowerSaver compound helps conveyor belts carry load more efficiently, reducing energy consumption. This translates to lower operating costs, increased asset life, and reduced carbon emissions.
“The first generation of PowerSaver shows a verifiable 28 per cent reduction in indentation loss when applied to M-grade conveyor belts,” Briggs said.
“Our second iteration, PowerSaver 2.0, improves this by an additional
12 per cent, or 40 per cent compared to M-grade.”
A third generation of the product is currently under development.
The second tool in Fenner Conveyors’ Green Series toolkit is the Yeloroll-HD. Engineered by Conveyor Products and Solutions – a company Fenner Conveyors acquired in 2022 – Yeloroll-HD rollers are 40 per cent lighter than equivalent steel idlers.
Key to the product’s efficiency is its composite shell, making it beltfriendly, corrosion- and impactresistant, and lightweight.
“We’ve been specialising in highperformance composite conveyor rollers for over 20 years,” Conveyor Products and Solutions general manager of engineering operations Warren Sexton told Australian Mining
“As conveyor loads go up, you require larger bearings and an increased diameter of your rollers to keep material moving efficiently.
“But both of those increase the mass of your rollers significantly. For large surface operations, these rollers are typically over 40kg each.
“We’re able to reduce that weight by 30 per cent, sometimes up to 50 per cent, by using these composite materials. You end up getting better performance with lower energy consumption.”
The Yeloroll-HD rollers are beltfriendly, removing the risk of ripping associated with typical steel idlers.
“Particularly in long conveyor operations, there’s a significant risk to the customer that if one of the units fails and puts a rip in the belt, you’re going to destroy millions of dollars of material,” Sexton said.
Owing to the light weight, YelorollHD idlers can be transported with significantly less fuel burn than steel.
The rollers also operate quietly, minimising noise impacts on workers and the environment. This also helps mine sites with noise restrictions keep running at higher tonnage rates than permissible with typical steel idlers.
When large, sharp lumps strike the conveyor, belt damage occurs at load zones. This results in premature component failure through belt punctures, damage to idlers and structure, and decreased material containment.
Installing impact beds at load zones reduces damage to the conveyor belt, surrounding structure and idlers. Other advantages include effective belt sealing, which reduces material spillage and reduced belt drag.
Yeloroll-HD is best used in tandem with PowerSaver. The two products come together to create a paragon in overland conveyor systems.
Briggs said that the PowerSaver compound, while system-agnostic, is being developed to be optimised for Yeloroll-HD idlers.
“We can bring these products together to show our customers exactly how much they’ll be saving on power and carbon emissions,” Briggs said.
A lot of work is being done at Fenner Conveyors to design products that help customers reduce their environmental footprint and decarbonise manufacturing in the process.
“PowerSaver and Yeloroll-HD are only the start,” Briggs said. “We are so fortunate to have some of the best brains in the industry within the Fenner group in Australia and look forward to sharing more innovations in the pipeline with our customers.
“With sustainability, we aren’t about short-term wins. We’re about making an impact.” AM
ESS introduces a new modular impact bed design for medium and light-duty applications!
ESS Modular Impact Bed features include;
• Modular support frames for easy maintenance
• Polyethylene surface to reduce friction
• Rubber body to absorb impact
Benefits of the ESS Modular Impact Bed include;
• Shorter manufacturing & lead time
• Suitable for a wide range of conveyor belt applications
• Reduced downtime
• Reduced maintenance and repair costs
FOR MORE INFORMATION ABOUT ESS IMPACT CRADLES VISIT www.esseng.com.au
Miners in the Pilbara region of Western Australia haul thousands of tonnes of ore every day.
A central point in this haulage cycle is a mine’s conveyor system, but issues tend to arise when an overworked machine meets the often hot and dusty climate of the Pilbara.
When a major iron ore mine experienced carryback issues (where material was being caught on the underside of its conveyor belt) back in 2021, it called in Flexco to develop a tailored washbox solution.
Two years later, the washbox is going still strong, as are the dozens of others that Flexco has installed throughout the country.
“A washbox is another way of adding an additional cleaning element into the conveyor belt,” Flexco Pilbara industry manager Jason Coe told Australian Mining
“A washbox is an effective way to maximise belt hygiene and cleaning efficiency. They eliminate material build-up on rollers, which creates mistracking, belt damage and premature roller failure, as well as carryback that causes environmental issues.”
Just before he spoke with
washboxes, one on each conveyor,” Coe said. “Within 12 hours of the first washbox being installed, you could see the instant drop in carryback along the system.
“When I spoke to the mine superintendent, he said that the results
in the Pilbara site in 2021, it customengineered it to suit the mine’s needs.
Mounted to the return side of the belt, the washboxes were fitted with pressure rollers, spray bars, two secondary cleaners and a recovery system.
This process of customising washboxes to fit each mine’s needs is a standard practice for Flexco.
“We get our sites to fill out data sheets, which are then reviewed by our engineering team,” Coe said.
“That team determines the size and scope of the project.
“Then it comes down to us field specialists to identify which cleaners would work best for each project.”
It’s important that each washbox is designed to suit the application, because an incorrectly installed washbox can be detrimental to the life of the conveyor belt.
Coe explained that Flexco can use different cleaners to suit different needs.
“We have multiple different types of cleaners, spray bars and rollers. We can configure a combination of them to suit the application,” he said.
“There are so many different configurations possible that no two mines ever get the same washbox.”
Being installed in large Australian mine sites means the washboxes have
Luckily, this is something the Flexco team has taken into account.
“Our washboxes last because they’re made with high-grade stainless steel,” Coe said. “If a client has a $5 million conveyor belt that’s supposed to last 10 years, we need the washboxes to also live up to this. And not only are they meeting the belt life of a conveyor, but they are actually increasing the life, too.”
At the Pilbara site, installing the washbox meant Flexco was able to reduce the mine’s clean-up around the beltline, saving time and money.
The washbox added a further 12 months to the life of the overlander belt beyond its typical three-year life.
The washboxes are manufactured and configured in Australia, which means customers don’t have to wait long to have their material handling problems solved. Being on home soil also means that if there are any issues, the team can be out to a site in a matter of hours to check how things are running.
“The most important thing for us is that the washboxes are performing as they should for our customers,” Coe said. “So if that means heading back out to site to check on any problems, we’ll do it.
“We understand the frustration caused by a belt not running properly, and we want to be part of the solution.” AM
Combining sensor, software and autonomous technologies, Hexagon helps mines solve complex challenges by streamlining workflows.
Digital transformation demands more than partial solutions. Hexagon is the complete solution, connecting all parts of your mine.
One platform. One partner. For the life of your mine.
Get in touch to learn more!
| Visit hexagon.com/mining
THEJO’S INTELLIGENT BELT MONITORING PROGRAM HAS BEEN DESIGNED TO EXTEND CONVEYOR BELT LIFE AND IMPROVE SAFETY AND SUSTAINABILITY OF MATERIAL HANDLING PLANTS.
Conveyor belts are widely used across various industries for the transportation of materials and products, and the mining industry is no exception.
These belts play a crucial role in facilitating efficient production and logistics processes. And like any other machinery, they are subject to wear and tear, and operational damages and breakdowns can lead to enormous production losses and safety risks.
With a goal of making material handling more sustainable, Thejo’s intelligent belt monitoring (IBM) program is designed to increase the belt life, improve safety, and enhance efficiency.
IBM uses advanced sensors and analytics to provide real-time insights into the condition of conveyor belts, detect faults, and monitor performance.
But proper conveyor belt monitoring can go beyond the life of the plant, contributing to environmental, social and governance (ESG) initiatives in several ways.
“Conveyor belt scrap is amongst the highest contributors toward nonbiodegradable waste produced by material handling plants,” Thejo told Australian Mining
“IBM helps minimise belt wastage and promote sustainability efforts, reducing the need to replace conveyor belts frequently by reducing the risk of belt failure. IBM helps reduce greenhouse gas emissions and promote energy conservation by running conveyor belts more efficiently.”
Like any faulty machinery, a conveyor belt that hasn’t been looked after can fail or break. But IBM can continuously monitor the health of the belts, identifying potential issues before they can lead to a catastrophic failure.
“IBM ensures proper functioning of the conveyor belt, reducing the risk of workplace injuries, thus promoting a safe work environment,” Thejo said.
“It ensures efficient operation of the conveyor belt, minimising downtime and allowing workers’ time to be used more productively. Implementation of IBM ensures high-quality production output which benefits all stakeholders.”
Applying IBM also means mines can ensure their processes meet regulatory standards.
“IBM also helps asset tracking by monitoring the location and operation of the conveyor, aiding in the optimisation of production processes in terms of efficiency and cost reduction,” Thejo said.
“Conveyor belt health monitoring systems are essential
for ensuring the safety of workers and preventing accidents.”
IBM utilises belt scanners installed on the conveyor to detect anomalies or deviations from normal operation. It typically consists of sensors, dataacquisition devices and software algorithms that analyse data to provide insights into the condition of the belt.
“The scanner works on the logic that any damage on the conveyor belt can be represented as a three-dimensional image,” Thejo said.
“The scanners use laser beams to create a profile of the belt surface and capture the profile image with the help of an optical camera at a very high frequency.
“The system software then combines these profiles to create an image of the belt surface.”
By continuously monitoring the belt, the scanner can detect anomalies like longitudinal belt rips, belt wear, edge damages, side rips, tears, through holes, grooves, splice fatigue or belt misalignment.
On detecting critical damages, IBM immediately raises and alarm and stops the conveyor for repairs. For noncritical damages, an alarm is raised and details are stored in the database so they can be attended to during planned maintenance stoppages.
IBM also features an integrated online wear monitoring module.
“The system generates a wear map of the belt, highlighting the wear profile at various sections of the belt,” Thejo said.
“The wear monitor automatically adapts to new and old belts and provides valuable data that can be used to analyse belt wear patterns, predict belt service life, and make informed decisions about maintenance, replacement or upgradation of conveyor belts.
“It helps in reducing the conveyor belt inventory, allowing purchasers to plan and order belts in a timely manner, and eliminating hasty purchase decisions.”
IBM is suitable for any type of conveyor belt regardless of the reinforcement or the belt grade.
It is a non-contact system without any loops, coils or any other modification to the belt. It is also a fully automatic, online system which does not need any user intervention.
“In a nutshell, IBM helps improve the reliability and lifespan of conveyor belts by enabling early detection of potential issues and facilitating timely maintenance interventions,” Thejo said.
“This can result in cost savings, increased productivity, and enhanced safety in conveyor belt operations.” AM
Enabling new possibilities for the resources industry across regional and remote Australia.
UNSCHEDULED STOPS AND SHUTDOWNS CAN CAUSE MAJOR LOSSES IN PRODUCTIVITY AND INCOME, AND THAT MAKES KEEPING CONVEYOR BELTS CLEAN ESSENTIAL.
As a leader in manufacturing and supplying conveyor products, DYNA Engineering understands the ins and outs of the industry – and is across all of the details.
The company is acutely aware, for example, of the importance of utilising spray bars to ensure residue is not stuck to the belt surface.
Most material being transported along a conveyor belt is discharged at the head pulley, but a small amount, known as carryback, will stick to the belt surface.
This can lead to spillage along the return strand of the conveyor, which can quickly drop off and build up, potentially causing a variety of increasingly serious and expensive problems if left unchecked.
That’s why cleaning and maintaining a conveyor belt is so essential – and DYNA Engineering has a vast range of belt tools to help mining operations stay on top of the situation.
One of these tools is the company’s DYNAFastFit spray bar, which not only helps mine sites keep conveyor belts clean but also provides a number of operational and financial benefits.
A spray bar is a pipe arrangement with several spray nozzle fittings that are used to disperse a liquid (usually water) in a desired pattern to assist with cleaning the conveyor belt or suppressing dust particles.
“The DYNAFastFit spray bars are designed to be safer and easier
to maintain,” DYNA Engineering general manager Thomas Greaves told Australian Mining
“They have a unique design that employs a fully retractable bar, mounted in a stationary shaft to form a two-part assembly. This allows the bar to be safely removed and returned to its original position while the conveyor is running, without the need for highly skilled labour.
“When the spray bar is removed, maintenance can be performed in a safe and ergonomic location. This allows maintenance personnel to quickly remove any sediment build-up from the pipe and unblock any clogged nozzles.”
Stainless steel DYNAFastFit spray bars are configured to suit almost any function, so they can be used for a range of applications, flow rates and supply pressures.
The long-lasting nature of the stainless steel means mining operations won’t have to spend thousands to maintain or replace the spray bars.
Generally speaking, the sticky material caught on the conveyor hardens when it dries, clogging conventional spray bars. But the retractability of the DYNAFastFit spray bars changes that equation.
“A major bauxite miner in the south-west of Western Australia uses DYNAFastFit spray bars to effectively clean sticky carryback from their conveyor belts,” Greaves said.
“The miner was previously using conventional spray bars, but they were
constantly clogging with the hardened material. This caused downtime and safety hazards, as ground operators had to climb onto the conveyor belt to clear the blockages.”
The DYNAFastFit spray bars’ unique design means ground operators can safely clear the blockages from a groundlevel location without having to climb onto the conveyor belt.
“The (WA) miner has reported that the DYNAFastFit spray bars have significantly reduced downtime and improved safety,” Greaves said.
“They are also more effective at cleaning the conveyor belts, which
has helped to extend the lifespan of the belts.”
The DYNAFastFit spray bars have received positive feedback from many customers.
“Customers have reported that the DYNAFastFit spray bars are more effective at cleaning conveyor belts than other spray bars, as they are made from high-quality materials and are designed to distribute water evenly across the width of the conveyor belt,” Greaves said. “The DYNAFastFit spray bars are designed to be safe and easy to maintain, which is in line with the overall focus of our DYNAFastFit range.” AM
CAPS offers mine-spec skid packages as standard to better accommodate safety and performance in extreme conditions.
INGERSOLL RAND AIR & POWER TOOLS
Time-proven, quality tools specially designed for assembly, industrial and vehicle service.
01 02 03 04
Ingersoll Rand, CAPS, and Hertz brand electric compressors available as oilflooded or oil-free.
Mine-spec AIRMAN portable diesel air compressors and power generators, air treatment, and specialist equipment.
05
24/7 service nationwide for maintenance and emergency breakdowns.
CALL 1800 800 878 OR VISIT CAPS.COM.AU
for most conveyor systems. Everything from ambient temperature to changes in material grade can impact belt alignment, causing spillage and belt damage.
But mistracking is as much a safety issue as an efficiency and spillage issue, so monitoring belt drift to avoid contact with the structure is critical.
The Australian/New Zealand standard, AS/NZS 4024.3611-2015 – Conveyors, offers instructions to control belt wander in section 2.8.2.6. Tracking devices are required to stop excessive lateral movement that would allow uneven loading or where the belt might contact the stationary steel structure, which can cause spillage, frictional heating, or damage to the belt and/or structure.
Wsigns of mistracking – material spillage, belt and structural damage – were likely already occurring. When these signs are noticed, immediate tracking remediation is required before returning the system to production.
Failure to review and address causes of misalignment may result in permanent belt damage or even structural collapse. Temporary fixes are often employed but, for safety and longterm economic reasons, a permanent solution should involve a modern tracking system.
Operators need to know when misalignment becomes actionable and what to do about it. A new document from the Conveyor Equipment Manufacturers Association (CEMA),
CEMA’s guide and the International Organization for Standardization (ISO) standards 14890 and 15236-1 are very similar in their recommendations for normal belt deviation from the central path. The CEMA guide is based on standard CEMA components and the ISO standards on the conveyor belt construction tolerances such as camber and troughability.
According to the ISO allowance, the conveyor belting, when running on a correctly aligned conveyor with centred loading, should not deviate from the central track by more than ±40mm for a belt width up to ≤800mm, or by more than ±5 per cent of the belt width of over >800mm with a maximum of ±75mm.
tracking is bound to happen on any system, and the CEMA allowable tolerance was established for normal running conditions.
Actionable mistracking happens when operational or environmental factors influence belt tracking to the point where spillage or damage to the belt and/or structure occurs.
Best-in-class operators will plan action to correct this level of mistracking as soon as practical.
Critical mistracking is a second-level fault that creates an immediate and serious risk of substantial damage and injury to personnel. It must be corrected immediately to avoid additional spillage, belt or structural damage and other safety incidents.
Consistent belt tracking is a system issue that must be addressed at every stage, from specifications to the conveyor’s initial design, installation, operation and maintenance.
The project specification should state the mistracking allowance as it affects the selection of the belting, structural clearances and rotating components.
The belting should be new and sourced from a manufacturer of highquality equipment. Used belting will have wear, tear and stretching from its previous system, and low-quality belting may not be manufactured to Rubber Products Manufacturers Association or ISO requirements. Incorrectly specified belting might not trough properly, resulting in poor contact with the idlers.
The width of the belt should be based on 85 per cent of the CEMA standard cross-sectional loading to allow for variations in loading and adequate free belt edge so the belt does not run out from under the sealing system.
The CEMA mistracking allowances are based on standard CEMA idlers.
Consideration should be given to using offset return idler brackets, because the return run is lower in tension and the idlers therefore have less effect on maintaining a centre track and greater mistracking is possible.
The main pulleys should be selected so the belt doesn’t run off the face.
This may mean specifying a wider pulley face than a standard CEMA pulley.
The structure should allow a free path for the belt, including the mistracking allowances.
Installation of the conveyor structure and alignment of the rotating components are the foundations of a system designed to track properly. When replacing a belt, components are often moved out of the way and not reset in the proper position. Mixing idler brands to save a few dollars or in search of the “perfect” idler can affect belt-to-idler contact and loading point spillage.
CEMA installation tolerances should be followed in the fabrication,
erection and mounting of the rotating components. Benchmarks should be established, especially for the main pulleys, so in the event of chronic mistracking there is a reference for confirming the main pulleys are level and square as a starting point for correcting mistracking.
The same is true for resetting the idlers square to the centreline, as they are often haphazardly knocked and shimmed in an attempt to treat symptoms rather than root causes of mistracking.
Carry side mistracking is usually not constrained by the idler roll length or load zone structural supports but rather by the possibility of spillage.
CEMA specifies a standard belt edge (Bwe = 0.055 x belt width + 0.9 inches) designed to prevent spillage due to belt sag between carrying idlers outside the load zone when the belt is centrally loaded.
CEMA standard 100 per cent full area is based on the idler geometry, the standard belt edge, Bwe, and the surcharge angle. The standard area times the belt speed and bulk density give the CEMA standard capacity, Q.
CEMA best practice is to design for 85 per cent of the theoretical 100 per cent full loading to accommodate surge loading and changing bulk material properties.
Return side mistracking is limited by the width of the CEMA 502 standard return rollers.
The structure for mounting the return rollers is usually based on the carry idler base dimensions. The standard
mounting brackets for return rollers are very close to the ends of the rollers in most designs.
If the belt travels into the return bracket, it can quickly be cut in half by the friction of the belt edge. Serious injuries have resulted from failed brackets causing falling return idlers.
CEMA pulley misalignment tolerances are based on ANSI/CEMA B105.1 standard pulley face widths. When greater tracking variance is required, engineered pulleys are an option.
Personnel should be trained on how overloading and off-centre loading affects mistracking.
Belt tracking works primarily through gravity (centre loading) and friction (a minimum of 50 per cent
and carryback must be controlled for consistent tracking, as build-up on idlers and pulleys changes the geometry of rolling components and can reduce beltto-idler friction.
Spillage in the load zone due to mistracking is a common problem, and there are many different sealing systems available to address the issue.
Depending on the spacing of the skirtboards and the thickness of the sealing system, there could be differences in the amount of free belt edge needed for allowable mistracking in the load zone. If there is a history of actionable or critical mistracking that cannot be mitigated, an even wider free belt edge is warranted.
Modern skirting designs are engineered to minimise spillage by creating a sealed environment within the loading zone. Depending on the type and allowable space of the belt, they can have a double seal that rides the belt, offering greater sealing, but that can take up extra space on the belt edge.
Skirtboards can lower maintenance costs by self-adjusting as they wear rather than having to be unbolted and adjusted manually amid spillage.
Accessories to deal with mistracking may come standard with conveyor systems. These are often “brute force” trainers that prevent the belt from coming in contact with the structure and are not actually training systems but protective barriers. Modern belt trainers use sensing arms to detect slight variations in the belt path. These arms are attached to a pivoting idler that immediately reacts to these variations and trains the belt back into alignment.
fashion but without a troughed roller. Training idlers are set slightly above the belt plane, allowing the weight of the belt to offer some additional tension on the roller. As the sensing arm detects the belt drift, it turns the roller in the opposing direction to train it back into alignment.
Since the low-tension belt return can easily become misaligned, a return tracker is especially effective when placed near the tail pulley.
The CEMA allowable mistracking recommendations are for properly loaded, unloaded, cleaned, maintained and operated conventional troughed conveyors. The recommendations do not apply to horizontal curves or specialty belts.
A good starting point for designing for misalignment is to examine current operating and maintenance practices.
Conveyors bought on 100 per cent loading and price alone often experience tracking issues.
Knowledgeable conveyor designers should consult the owner on the significance of design allowances, and the costs and benefits associated with wider belts and less than 100 per cent loading best practices.
Training operators and maintenance personnel in techniques to reduce mistracking is an effective way to mitigate mistracking issues.
Laser alignment of components to CEMA installation standards is now a common technique for establishing conveyor alignment benchmarks. Positioning training idlers at critical locations is specified but commonly has limited ability to change the path of the belt when maintenance practices are poor, there are extreme environmental conditions, or there is a build-up on the rolling components. AM
Water Resilience. Electrification. Hydrogen and Alternative Fuels. Australia’s mining and metal processing companies can go beyond existing renewable energy deployments and drive a sustainable future. Discover how the industry can go further, faster and stay ahead of global customers’ expectations for sustainable, zero-emissions products.
SCHLAM’S
SCHLAM PROVIDES SOME ADVICE ON HOW TO OVERCOME THE PAYLOAD CHALLENGES ASSOCIATED WITH HARD ROCK MINING.
It’s somewhat surprising –refreshing, even – to see the growing number of electric vehicles (EVs) on city streets EVs are now commonplace around the world, especially in Europe. With many governments around the world encouraging the adoption of EVs, and with more manufacturers emerging, demand is expected to continue.
Most of today’s EVs use lithiumion batteries, and with EV production growing 26 per cent annually, global lithium demand is growing at 20 per cent per year.
In 2022, 60 per cent of lithium, 30 per cent of cobalt and 10 per cent of nickel demand was attributed to EVs.
At the same time, we are also seeing a growing demand for residential and commercial battery storage.
In combination, this has spurred a growth in lithium mining around the globe, especially in Australia. Western Australia has fast become
the centre of global lithium mining, accounting for 21 per cent of the world’s reserves and 55 per cent of the world’s production in 2022.
A key challenge in the Australian lithium production sector is competitive commodity pricing as the market exits it ‘bullish’ stage to one of normality. This has required mining operators to improve production efficiencies.
In WA, lithium is sourced from spodumeme and petalite. Both are rated as ‘hard’ minerals comparative to magnetite, the iron ore notorious for affecting the life and performance of fixed and mobile plant machinery.
“Maximising the life and use of assets is vital to mining productivity. Lithium producers are realising the harsh effects of hard rock, especially on dump truck bodies,” Schlam Sales and Business Development Manager – West, Tom Smith, told Australian Mining
“Abrasion, wear and impact on dump bodies can significantly affect mining
productivity in many ways, including unscheduled downtime and maintenance and operating costs, including fuel.
its inception over 26 years ago, the company has established itself as a key supply partner to leading Tier 1 hard rock mining companies in Australia, as well as other mining centres around the world.
The company’s innovative curvedshape Hercules open-cut dump body is demanded by major iron ore miners in WA and found across hard rock mine sites across Australia and beyond.
Designed to be lighter than traditional dump bodies, without sacrificing structural integrity, Hercules has enabled some miners to experience payload gains above 20 per cent.
“Schlam assists all mining tiers with hauling lithium, magnetite, blue rock and the ever-challenging mixed ores to help manage wear and to improve payload productivity.”
Schlam is widely recognised for its commitment to making mining equipment more productive. Since
Hard rock miners generally use the weight saving to allow for the installation of wear packages, without affecting payload and fleet productivity.
“The Hercules dump truck body was developed around the needs of hard rock miners,” Smith said. “Our rapid growth stems from our ability to uniquely engineer every Hercules body to combat the challenges of the site it operates in.”
OUR RAPID GROWTH STEMS FROM OUR ABILITY TO UNIQUELY ENGINEER EVERY HERCULES BODY TO COMBAT THE CHALLENGES OF THE SITE IT OPERATES IN.”
HERCULES OPEN-CUT DUMP BODY HAS ENABLED MANY HARD ROCK MINERS TO EXPERIENCE SIGNIFICANT PAYLOAD GAINS.
Schlam is continuing to help hard rock miners, including lithium miners, to improve their payload productivity.
Here’s some of the key issues being faced by these miners, as well as considerations offered by the Schlam team based on its extensive industry experience.
Hard minerals have the potential to cause wear and abrasion on dump truck bodies, affecting asset longevity and performance.
“Spodumeme and petalite are extremely hard minerals, so it’s important to factor in wear right from the start,” Smith said.
“We do this at the design and engineering stages, taking into consideration site-specific wear characteristics.”
With traditional dump bodies, many miners use a ‘band-aid’ approach to wear mitigation. The unplanned patching of cracks, gouges and highwear areas results in significant asset downtime and unreliability.
“Every time a dump body is being repaired, it’s not being productive. Plus, your incurring additional labour and material costs, and increasing safety risk exposure,” Smith said. “These costs add up over time, so investing in a suitable
wear solution, right up front, makes good economic sense.”
To avoid expensive body replacements, most mining operators plan for a long asset life.
Schlam assists operators by designing the right wear package, and also offering a wear maintenance program.
Wear packages are designed based on site-specific requirements and are installed at the time of manufacture. Packages can include standard plates and the weight saving patented Schlam Hex tile.
The fact the Hercules body is lighter means it can accommodate a wear package without sacrificing body weight and payload performance. In fact, according to Schlam, a Hercules tray fitted with a bespoke wear package can sometimes weigh less than a standard dump body.
“We place a lot of effort in engineering site-specific wear solutions to minimise the effects of wear and impact, and to maximise material flow,” Smith said. “Quite simply, we add thicker hardened steel where it’s needed the most, and lighter steel in surrounding areas, providing stability, performance and durability.”
Schlam also offers clients an optional wear management program. This service includes site visits and inspections
where wear rates are measured, enabling corrective measures to be prescribed.
“The program has assisted many hard rock miners in extending the life of their dump truck bodies – sometimes exceeding 10 years,” Smith said.
Schlam works closely with its clients to address site-specific variables, including wear, material flow and asset lifecycle management.
“Every mine site is different. While one mine site may be challenged by abrasion, another site 50km away could be contending with material hang-up,” Smith said.
“That’s why we design and engineer every Hercules body individually.”
With fewer experienced operators available, and with the push to increase mine productivity, many sites are now opting for larger dump trucks and excavator buckets.
Lithium miners are continuing to introduce 240-tonne class vehicles into their fleet, the same used by iron ore miners.
Schlam works closely with all of the leading OEM dump truck suppliers, providing hard rock miners the benefit of collaborative experience and delivery of a site-specific vehicle and dump body solution.
Schlam is the only large-scale manufacturer of open-cut dump bodies in WA, providing the state’s hard rock miners with local supply and a dedicated service team that provides technical and engineering support, whether remotely or on-site.
All Hercules dump truck bodies supplied in WA are manufactured in Perth, using local labour and worldrenowned steel products. This means Hercules bodies are delivered to WA mine sites in considerably less time than those sourced from overseas suppliers.
“We’re here to assist all lithium and hard rock miners, whether they’re in the production or development stage of the mining cycle,” Smith said. “We understand the challenges of hard rock mining and we’re here to guide miners in improving their payload productivity.”
KNOWN GLOBALLY AS A LEADING SUPPLIER OF BULK MATERIAL HANDLING SOLUTIONS, TAKRAF OWES ITS REPUTATION TO ITS ADVANCED TECHNOLOGIES AND QUALITY CLIENT SUPPORT.
TAKRAF’s technical expertise, work planning and execution skills help to ensure successful project delivery. But the company is also one of the industry’s largest and most competent full-service suppliers of bulk material equipment, boasting significant experience in the maintenance, refurbishment and upgrade of a wide variety of equipment
As a result, the company is now in demand to support material handling equipment that is no longer being supported by its original equipment manufacturer (OEM).
“In times where many players seem to move away from materials handling projects, we at TAKRAF live for this and, by doing so, we help our customers secure the metal supply of the future in a sustainable way,” TAKRAF Group chief executive officer Thomas Jabs said.
TAKRAF (an acronym for Tagebau-Ausrüstungen, Krane und Förderanlagen) provides customised maintenance solutions for its equipment from the locations in which it operates. Material handling equipment it supports includes the full range from conveyors and spreaders to all stockyard, loading/un-loading equipment and port machines. Of particular note is the group’s refurbishments and upgrades of equipment such as stackers and reclaimers to extend machine life, upgrade equipment to the latest standards, and increase capacity.
Just as operational efficiency is a focus area in TAKRAF’s maintenance solutions, achieving such efficiency with increased safety is a non-negotiable of the group’s holistic approach to maintenance.
With the philosophy that an improved maintenance solution must always have a safety upside and increased safety does not need to come at the expense of maintenance efficiency, TAKRAF has shown that efficiency and safety do in fact complement one another.
In line with its holistic approach, TAKRAF addresses maintenance requirements and the associated safety risks from the start of the engineering process. For example, numerous accidents and even fatalities can occur while replacing a chute liner. These can be the result of a range of risks, from falling material to the unsafe handling of tools and equipment.
One method to reduce risks is to design chutes with modular sections (or rotable chutes) that not only provide a significant improvement in safety but also reduce downtime from an eighthour shift to 60 minutes.
However, TAKRAF’s ultimate safety approach in this regard is to make it possible to stay outside of the chute at all times during maintenance with, for example:
• the lip liner being accessible from the outside
• wear plates with external access
• u ltrasonic measurement of liner thickness, and therefore wear, from outside the chute to allow for planned maintenance.
Other benefits of this approach include significant savings in downtime as liner exchange can start immediately after the operational stop, since no scaffolding is required.
Conducting maintenance on belt conveyors and the replacement of worn or damaged rolls (idlers), which can run into thousands on long overland conveyors, is challenging. This is especially true on steep slopes, in tunnels
or on elevated structures. TAKRAF’s maintenance cart was therefore developed to access any location along a conveyor belt in the shortest possible time and in the safest manner.
At a major copper project in North America, a TAKRAF maintenance cart services a steep 26 per cent decline section of a 4350m overland conveyor. This 1250m section features more than 3700 rolls.
A similar TAKRAF maintenance cart for a large copper mine in South America was of interest to the client due to the increased safety it would provide over its complicated 6000m overland conveyor. Featuring a number of horizontal curves, this conveyor required bridges to be built on more than 50 per cent of its length, making it extremely difficult for maintenance to be conducted.
Recognised as a leading technology brand in bulk material handling, TAKRAF’s solutions cater to clients’ unique requirements from the supply of individual machines to complete integrated systems.
Recent projects across the globe have continued to demonstrate TAKRAF’s technology prowess. In Australia, for example, the group’s rail-mounted stacker at a bulk terminal is one of the largest ever delivered and, with its unique design features, one of the most technically advanced.
The stacker boasts an initial stacking capacity of 6300 tonnes per hour (tph) and a massive 62m curved boom, but was designed at the outset to accommodate a peak volumetric rate of up to 10,700 square metres per hour (equal to 9600tph) for a scheduled future upgrade.
In the design of the world’s most powerful belt conveyor system for a major copper miner in Chile, the numerous innovations developed during the project resulted in six patents. The application of gearless drives on the two main underground conveyors (totalling more than 6300m) and the overland conveyor (more than 5300m) represented a major step forward, as it significantly reduced the number of main wear parts and reduced the drive system’s footprint and emissions.
The 11,000tph system boasts a total installed drive power of 58MW (58,000kW) – the underground conveyors feature 10,000kW of installed drive power per drive pulley and 20,000kW per conveyor, while the overland conveyor features three 5000kW direct drive motors.
These highly efficient electric drive motors replace diesel truck engines, cutting CO2 emissions produced when transporting the material by more than two thirds for the same copper volume.
“This project highlights TAKRAF’s commitment to more sustainable and environmentally friendly installations,” the company said.
Other recent projects in South America include supply of a 13,200tph belt conveyor system for copper ore and a 7200tph bucket-wheel reclaimer for iron ore.
In North America, TAKRAF replaced a 6000tph rail-mounted stacker for limestone in southern Mexico, designing a robust machine that could operate in the hot, humid and corrosive environment, and in high-velocity
winds. This machine was replaced in just three days.
Following the successful delivery of a contract for Phase 1 of a bauxite expansion project in Guinea, Africa, TAKRAF is supplying a further two conveyors to the project. The Phase 1 contract included delivery of a greenfield wagon unloading and primary crushing station, a secondary crushing station and a complex brownfield conveyor system. The structure of the unloading station is constructed entirely from steel, which presented a major engineering challenge, considering the high dynamic loads
and forces resulting from the continual passage of trains.
Four portal reclaimers supplied to a new multi-commodity power plant in Japan are some of the largest ever built. Due to the redundancy required – two reclaimers are required to work on the same rail in the same warehouse – a dedicated safety and anti-collision system was implemented.
Each machine has a dedicated platform to carry a small bulldozer, which it can drop off at any location along the stockpile for cleaning purposes. AM
Industrial vibrators are essential components in ore processing plants on mine sites. Vibrators are employed at various points along the chain, helping material travel between hoppers, screens, conveyors and crushers.
Vibrators’ main job at a mine is to keep things moving. Without them, everything grinds to a halt.
That’s why Oli Vibrators makes its vibrators to last. And with an international backing and agents all across Australia, the company can deliver the goods anywhere, anytime.
Oli Vibrators specialises in industrial vibration technology, providing highquality, European-built industrial electric and pneumatic vibrators, frequency converters, flow aids and aerators.
“You’ll find our vibrators on grizzly screens, scalping screens, conveyors, pan feeders, dewatering systems and much more across all sorts of mining operations,” Oli Vibrators general manager Mark Thompson told Australian Mining. “Our products have applications in coal, hard rock, and gold operations – and of course in any mineral processing plant.”
Oli Vibrators manufactures its product in Malta and Italy. The company’s headquarters is located in Modella,
Italy, where the equipment goes through rigorous testing and quality control to ensure it can handle extreme conditions, such as heat, cold, abrasion and heavy use.
The company has a lot of products in its toolkit, but the brute force MVE electric vibrator motor range is its vibrator of choice for the Australian mining industry.
These vibrators can generate between 3–26,000kg of centrifugal force, which can be adjusted with ease. The MVE range is also available with multiple voltage options, making the vibrators suitable to dexterous and heavy-duty tasks.
“The MVE electric vibrators are standard IECEx, Zone 21 rated and ideal for any hazardous conditions because they’re built extremely tough and durable, with a fully optimised electrical design,” Thompson said. “We also have an increased safety and explosion proof in our range for those sensitive areas.
“They’re built for heavy-duty, continuous work in harsh environments.
“The amount of force on the vibrator itself can be adjusted quite easily, and there’s lots of different voltages and frequencies available.”
One of the product’s main advantages is its ‘greased for life’ feature, which
means exactly what the term implies. Thanks to Oli’s extensive research and development, the vibrators don’t need re-greasing, which means no scheduled maintenance and less downtime.
“The MVE range is manufactured to a high F-class insulation, using world-class materials and bearings,” Thompson said.
F-class insulation is a universal measure of temperature resistance, making them perfect for hot mine sites throughout Australia.
An ingress protection rating of IP66, coupled with a positive temperature coefficient thermistor fitted to every unit, keeps the vibrators protected from water and dust, as well as temperature.
And thanks to a range of footprints, the vibrators are compatible with many machines and can be retrofitted or builtin at the manufacturing level.
With over 35 global warehouses, 26 trading subsidiaries, and three manufacturing plants around the world, Oli Vibrators can supply essential vibration solutions when and where they are needed. In Australia, the company has warehouses in Perth, Brisbane, Sydney and Melbourne.
“The benefit of being such a large company is that we’ve got a very strong supply line,” Thompson said. “We’ve got a 24-hour service where we’re ready to go all the time.
“Our customers can rest assured that they’re not going to be waiting months for industrial vibrators. We’ve got the gear on hand, and it can be dispatched within 24 hours.”
Backed by a vast supply network and rigorous European design standards, Oli Vibrators’ reliable, brute force vibrators are keeping things moving in the Australian mining industry. AM
WITH ITS RANGE OF BRUTE FORCE MVE ELECTRIC VIBRATORS, OLI VIBRATORS IS PROVIDING THE AUSTRALIAN MINING INDUSTRY WITH A RELIABLE AND VERSATILE VIBRATION SOLUTION.OLI VIBRATORS FITTED TO A DEWATERING SCREEN. OLI’S VIBRATORS ARE BUILT FOR CONTINUOUS HEAVY-DUTY WORK IN HARSH ENVIRONMENTS
Hardox® 500 Tuf is the latest grade of Hardox® wear plate. It combines the hardness of Hardox® 500 with the toughness of Hardox® 450. The wear resistance of Hardox® 500 Tuf makes it possible to increase the load capacity by using a thinner plate and still have the same outstanding service life. Or stay with the same thickness and increase service life by 30% or more.
Hardox® 500 Tuf can also double as a structural steel. Its high yield strength and toughness allow for lighter mining bodies that are resistant to dents and can take impact loads with less supporting structures.
Get the full story of Hardox® 500 Tuf at www.hardox.com
LESS FUEL ON EMPTY RUNS
Brokk robots are designed specifically for high-performance demolition and maintenance works and improve effectiveness, uptime, and profitability for operators.
Within a mine, Brokk robots are able to perform various tasks such as oversize rock breaking, scaling, drilling, digging, and shaft sinking.
www.brokk.com/au
The OPS Group offers a diverse and extensive range of mineral processing and handling equipment in Australia, and one of its key brands is Telestack.
Through the equipment and products it supplies, OPS aims to remove inefficiencies in bulk material handling processes.
“We see opportunities anywhere where can eliminate loaders or haul trucks, reduce labour requirements or save fuel,” OPS area manager of capital sales Gerry McGuigan told Australian Mining.
“We already offer some really unique track-mounted solutions such as the Telestack Titan T1600-8 mobile truck unloader that can accept rigid haul trucks up to CAT 777 size and the popular Telestack HF24T.
“The HF24T was developed for OPS by Telestack to provide an easily
side tippers to discharge directly into conveying systems.
“The side tipper truck pulls alongside the unit. It can tip its entire (single) trailer contents into the unit and move to next trailer,” McGuigan said.
“The sider tipper unit will then receive the full trailer load onto its apron belt feeder and feed this into a conveyor system for ship-loading at a controlled rate.”
Deep-pit or underground truck tipping hoppers usually require costly civil work to install and cannot be moved or relocated as a plant expands. Reartipping truck unloaders are also at a disadvantage since set-up cycle times are longer than a side-tip solution setup.
However, a surface feeder provides operators with a semi-permanent solution that can be being fixed during operation and relocated later.
Enter the Titan side tipper unloader, a semi-permanent installation that can be
Removing water from tailings - dewatering - is an key step to ensuring a plant continues to run smoothly while reducing environmental risks and improving sustainability.
And a necessary step in the tailings dewatering process is adding polymers to improve the solid-liquid separation.
However, many mining companies still have operators manually complete this step, often leading to the polymer dose being set and unchanged throughout the shift, even when adjustment is necessary.
To help solve this problem, ANDRITZ developed Metris addIQ RheoScan, an optical measurement system designed to detect the texture of the slurry and adjust the polymer accordingly through the use of artificial intelligence (AI).
“The system automatically adjusts and optimises the polymer dosage 24–7 and provides maximum flexibility to control and monitor the entire operation remotely,” ANDRITZ global service product group manager Stefan Peter said.
“This eliminates the need for on-site supervision.”
The ANDRITZ service team works closely with its customers and, when it began to hear that operators were often
overloaded and needed elsewhere, it came up with Metris addIQ RheoScan.
“We’re always aiming to improve and optimise our equipment with further developments,” ANDRITZ regional manager (ANZ) Paul Stevens told Australian Mining. “Using feedback from operators, we came up with the idea of using intelligence solutions.
“In this case, we came up with a camera system to take over the permanent optical effort of the operators to optimise machine performance. We called that system Metris addIQ RheoScan.
“It works on all makes and models of belt filter presses, gravity belt tables, and polymer dosing systems.”
ANDRITZ is currently focusing this solution on mining operations that want to optimise their plant using belt presses and gravity belt thickeners. Both types of machines help to thicken slurry and remove wastewater.
“We have successfully proven the technology in the dewatering process of environmental and industrial sludges, as well as coal and sand tailings,” Peter said.
“Our customers are telling us that they’ve seen a reduction in overspills and an increase in plant safety and performance after employing the Metris addIQ RheoScan.”
The Metris addIQ RheoScan will be making its conference debut at this year’s International Mining and Resources Conference (IMARC), and ANDRITZ is excited to showcase the technology. demonstrate a smart solution for a common industry issue when using these types of equipment, but we also want to communicate to the attendees that interesting solutions are created in cooperation between clients and OEMs (original equipment manufacturers),”
“Collaboration to strengthen innovation in mining and driving safety and productivity through digital transformation are two of the key themes of IMARC, and they are also two key ANDRITZ’s strategy to support not only our equipment, but to partner our customers with our automation and digitalisation team and the Metris
There are a multitude of features that come with employing the Metris addIQ RheoScan, but Peter highlighted
“Cost-saving is a big benefit,” Peter said. “Due to the reduction of
polymer consumption by up to 30 per cent, sites are saving a high amount of money and seeing a significant reduction in overspills.
“They are also seeing an increase in operation stability and plant reliability, along with operation going off without a hitch because there’s no need for supervision; the AI takes care of that. We can say that it’s an almost independent intelligent machine.”
Peter also highlighted the Metris addIQ RheoScan’s squeeze control with an optional second camera. This patented technology brings the machine almost to an independent system without any need of active operator actions.
“Metris addIQ control systems – the brain behind the ANDRITZ equipment operation – include the latest stateof-the-art IIoT (Industrial Internet of Things),” Peter said.
“addIQ control systems are part of Metris, the ANDRITZ brand for digital solutions that includes both IIoT solutions and smart services which can be tailored to fit each customer’s requirement.
“Our aim is always going to be to listen closely to our customers to ensure we are developing the right technologies to fit their growing needs.” AM
TAKRAF Group’s service & maintenance teams are problem solvers and boast significant experience in the maintenance, refurbishment and upgrade of a wide variety of equipment.
In addition to our own previously supplied equipment, we also support customers with equipment that is no longer supported by its original supplier.
Our expertise:
Asset integrity
Technical support & site services
Repair & maintenance
Refurbishments & upgrades
Spare parts
Understanding that each user’s requirements are different and that technology adoption is not always linear, SICK works closely with customers to provide systems that grow and adapt to keep up with end users’ needs. SICK’s solutions can boost the mine productivity, assisting mine operators with gaining process transparency and enabling predictive maintenance to help avoid standstills and equipment faults or downtime. SICK’s Green Intelligence systems cover the energy generation side of operations, increasing transparency and efficiency in green energy supply-digital service for integration. www.sick.com/au/en/mining
TS Global’s acquisition of Mackay Conveyor Equipment (MCE) earlier this year marked a significant moment in its journey to becoming a leading manufacturer of premium-grade conveyor accessories and polyurethane components, dedicated to delivering cutting-edge solutions to its customers.
“We are specialists in the underground mining market from a product and conveyor solutions aspect,” MCE founder and TS Global Queensland operations manager Jason Kelly told Australian Mining.
“We’re focused on reducing the amount of people required to install anything that we’ve designed and manufactured, ultimately reducing the risk and potential harm to those installing and operating the equipment.”
A key example of the company’s innovation is the Jibaroo, a product transfer system that optimises efficiency and safety.
“By utilising the Jibaroo, they’re getting the benefits multiple times as opposed to a one-off installation,” Kelly said.
“One of our clients suggested that their savings in labour and equipment … is about $200,000 per installation.
“If you’ve got a piece of equipment that’s going to be relocated four or five times in its lifetime, then you’re potentially saving $1 million, and while reducing manual handling risks.”
Another standout is the Wombelt reeling system. Capable of holding 250–300m of conveyor belt, the system is distinguished by its ability to receive and install a belt in the appropriate orientation for transport.
“Benefits of our design compared to others is that it completely removes manual handling,” Kelly said. “It’s got lots of grunt to pull the belt straight out of the loop take-up without relying on pinch roller assemblies.
“It can alter the torque of the drive, depending on the roll diameter of the belt, so that when the belt diameter is small the torque of the drive is reduced to ensure the belt is not damaged.”
Designed primarily for underground coal mines, the DD series development drives offer a mobile conveyor system ideal for temporary installations.
“Our development drives have been crafted for enhanced flexibility and interchangeability, empowering mines to navigate unforeseen challenges with greater adaptability” Kelly said.
“We have two series: a light series that is capable of 75–185kW, and a heavy series that is capable of 200–400 kW, suitable for EXD or NERZ depending on the client’s requirements.”
In addition, TS Global’s knockdown switch is designed to safeguard major conveyor components and minimise downtime. Its design ensures that any substance lying on the conveyed material won’t impact the outbye conveyor terminals.
“If anything large comes through that may smash into the coffin seal, for example, it will hit the knockdown switch, which flips up a heavy steel plate
gate, knocks an wander switch and stops the belt,” Kelly said.
TS Global’s belt spindle allows for empty belt spindles to be handled safely and reduces manual handling in loading spindles into their belt reelers.
“It’s at the right diameter, so it won’t damage the belt,” Kelly said.
“It also has fork pockets, so workers can take it underground on a forklift and it can’t roll off.”
The inclusion of MCE in its portfolio means TS Global has the ability to design and manufacture its own boot ends for all belt widths, as well as conveyor pulleys.
“We have two variations – a retractable roller type and a solid bar type – which can be supplied with or without electrics, tailored to client requests,” Kelly said.
“We can design, refurbish and manufacture all pulley types, from 200–2350mm diameter, weighing from 200kg to 25 tonnes.”
Incorporating the MCE range has propelled TS Global forward in its mission to provide innovative and efficient conveyor solutions.
“Our ability to adapt quickly and prioritise client timelines ensures we’re there when clients need us the most,” Kelly said. AM
ALREADY A LEADING UNDERGROUND CONVEYOR EQUIPMENT PROVIDER, TS GLOBAL NOW OFFERS ONE OF THE MOST EXTENSIVE SELECTIONS OF CUTTING-EDGE SOLUTIONS IN THE INDUSTRY.THE DD SERIES DEVELOPMENT DRIVE HAS SIMPLE INSTALLATION AND MAXIMUM CONFIGURATION FLEXIBILITY. THE TS GLOBAL RANGE OF CONVEYOR PULLEYS AND EQUIPMENT IS AVAILABLE NATIONALLY.
BEND-TECH OFFERS A TAILORED SOLUTION FOR EFFICIENCY AND SAFETY IN THE USE OF INTERMEDIATE BULK CONTAINERS.
In various industries, the use of intermediate bulk containers (IBCs) has become indispensable for storing and transporting liquids. However, the conventional practices of IBC storage and drainage often lead to inefficiencies, safety hazards, and resource wastage.
Australian Mining spoke with engineering company Bend-tech to examine the existing issues associated with IBC storage and present an innovative solution that is designed to transform the way these containers are utilised.
Sub-optimal storage and drainage
A common challenge arises in the form of inappropriate IBC storage.
IBCs are frequently placed on makeshift stands that lack the essential certification for their intended purpose. These structures are often assembled on-site without adherence to established safety regulations and industry standards, endangering the stability of the IBCs and the safety of workers. Compounding the problem, IBCs are often stored in a horizontal position, resulting in difficulties when extracting the last remnants of liquid as the container nears depletion. The liquid tends to collect in one end, making complete drainage cumbersome and time-consuming.
In response, on-site teams resort to manual tipping of IBCs, a process that not only consumes labour but exposes workers to potential physical risks.
To confront these challenges headon, a forward-thinking solution has emerged, aimed at not only addressing storage concerns but also enhancing drainage efficiency. Here’s a breakdown of this innovative approach.
The foundation of the solution rests on certified IBC stands featuring a carefully designed 15° tilt on top. This inclination ensures that the liquid naturally gravitates toward the outlet, facilitating complete drainage without the need for manual intervention.
Recognising the diverse applications of IBCs, the solution incorporates adjustable-height legs.
This adaptability allows IBCs to be positioned at the ideal height for a particular task, minimising strain and enhancing operational convenience.
Fork pockets for easy mobility
Mobility is a key aspect of modern industry. The solution therefore integrates fork pockets into the stands and the IBCs, enabling effortless lifting, transportation and relocation.
Extra-heavy-duty construction for mining Industries like mining demand sturdier solutions due to their often-harsh operating conditions. Accordingly, the solution introduces extra heavyduty construction tailored for mining, ensuring durability and reliability.
By embracing this innovative approach, a paradigm shift in IBC storage and drainage is achieved, yielding a host of benefits:
• Improved drainage efficiency – the 15° tilt in certified stands expedites liquid drainage, eliminating the need for manual tipping and saving time
• Enhanced safety – the ergonomic design and adjustable-height legs mitigate the manual handling risks typically associated with IBCs
• Tailored application – the adjustableheight feature ensures IBCs can be set at the optimal height for a given task, enhancing precision and comfort
• Versatility in mobility – fork pockets empower seamless
transportation, enabling the IBCs to be easily relocated across various operational areas.
The challenges posed by conventional IBC storage and drainage practices demand innovative solutions.
The combination of all aspects in the innovative solution means industries can revolutionise the way IBCs are stored, utilised and drained. This approach not only bolsters efficiency and safety but also showcases a commitment to embracing advancements that drive positive change in the industrial landscape.
As the industry embraces this new era of IBC management, the stage has been set for a more productive, safer and streamlined future. AM
The Schlam Hercules open-cut dump body continues to improve the payload capacity of all classes of haul trucks, across all commodities, the world over.
Engineered to meet the challenges of hard rock mining, the unique Hercules curved design offers a lighter body, with outstanding strength and durability.
Being lighter means your fleet can carry more payload every trip. With a payback period of as little as a few months, you’ll be rewarded with a solution that will keep delivering for longer.
Every Hercules is custom engineered to meet your unique site-specific requirements. We can also design and supply the right wear package, and even a wear maintenance program, to further extend the life of your Hercules body.
Overcome the challenges of hard rock mining with the Schlam Hercules dump body.
schlam.com/hercules
AUSTRALIA’S UNOFFICIAL GOLD-MINING CAPITAL ONCE AGAIN PLAYED HOST TO SOME OF THE BIGGEST NAMES IN MINING FOR THE DIGGERS AND DEALERS FORUM.
The Diggers and Dealers forum has once again heralded mining giants from across the country – and the world – to the main stage for its 32nd year.
Held in the heart of Western Australia’s gold mining industry in Kalgoorlie, this year’s event saw the biggest and best come together in August to rub shoulders and share the latest their enterprises have to offer.
More than 2600 miners, explorers, bankers, brokers, investors, financiers and mining service professionals from around the world were in attendance, all looking to network, raise finance, invest in projects and generally engage with the resources sector.
The event was a display of mining accomplishment culminating in the gala dinner on the final night, where the winners of the Diggers and Dealers Awards were announced.
This year, Dr Linda Yueh kicked off the three-day forum with her keynote address. An economist, writer and broadcaster, as well as a fellow in economics at Oxford University and an adjunct professor of economics at the London Business School, Yueh’s address reflected the key themes of progress, sustainability and collaboration.
Yueh’s speech was followed by Pilbara Minerals’ managing director and chief executive officer Dale Henderson.
Joining Pilbara Minerals in 2017, Henderson has experience in mining operations and developing the resources sector and has worked for a range of major resource operators.
“We have had the biggest year ever,” Henderson said of Pilbara Minerals’ 64 per cent growth in production and $3.3 billion cash margin for the financial year (FY23).
“Now the leading growth stock in the ASX 50 this past year, with over 114 per cent growth, it’s a story of grit, survival, teamwork and a big dose of good luck. We finished the financial
year with 620,000 tonnes produced and we’re estimated to be eight per cent of the global lithium supply, which is a remarkable feat given the young age of the company and what lies ahead.”
Henderson said Pilbara Minerals planned to double its produce tonnes over the next 18–24 months at its Pilgangoora project in
And the company is on track, with a construction underway for a 680,000-tonne step-up in production, as well as another project set for commissioning that will bring production up to one million tonnes per quarter, aiming to be operational by 2025.
The future is looking especially green for Pilbara Minerals, as Henderson discussed the company’s future focus on renewables, with its 6MW solar farm now operating on site with community investment.
Another mining giant looking to renewables this year was Westgold Resources, sharing a 56 per cent reduction in emissions, 34 per cent power-generating capacity supplied by green energy, and a 38-million-litre reduction in diesel fuel usage.
Taking the Diggers and Dealers stage for Westgold was managing director Wayne Bramwell, a metallurgist and
mineral economist with nearly three decades of industry experience.
“Westgold is an innovator,” Bramwell said. “In the last 12 months, we set about constructing 82MW of hybrid power stations across our operations.”
With over 100km of core drilled and a production rate of 257,000 ounces of gold over the last 12 months, Westgold is setting itself up for serious expansion. Bramwell said the company has expanded two mines and optimised another two, while putting three into care and maintenance.
Westgold is also investing $60 million in the development of three new mines, including the Great Fingall gold mine in WA, which has previously hosted a significant mine production of about 1.2 million ounces.
Westgold has also put its workers to the fore over the past 12 months, with a 63 per cent reduction in injuries.
“We are continuing to invest in our people,” Bramwell said. “At 1400-strong, people don’t realise how big our workforce is – 965 staff and over 300 contractors. It’s these people that have delivered the mission for the shareholders in FY23.”
Westgold was not the only giant focused on expansion at Diggers and Dealers.
29Metals impressed with expansions across all mining operations, particularly the Golden Grove copper mine in WA and the Capricorn copper mine in Queensland.
It was 29Metals managing director and chief executive officer Peter Albert, with over 35 years of experience in the mining industry across multiple commodities spanning Australia, Asia, Africa and Europe, who shared expansion insights with the crowd.
“We continue to invest in our future, continue to invest with ventilation
(PILBARA MINERALS) FINISHED THE FINANCIAL YEAR WITH 620,000 TONNES PRODUCED AND WE’RE ESTIMATED TO BE EIGHT PER CENT OF THE GLOBAL LITHIUM SUPPLY, WHICH IS A REMARKABLE FEAT GIVEN THE YOUNG AGE OF THE COMPANY AND WHAT LIES AHEAD.”DIGGERS AND DEALERS BROUGHT TOGETHER BIG PLAYERS FROM THE GLOBAL MINING INDUSTRY.
upgrades, cooling plant upgrades and, most importantly, the underground development to our extremely rich oreody Xantho extended,” Albert said.
Xantho is an extended orebody at 29Metals’ Golden Grove mine with a reported 9.9 million tonnes of ore at 7.9 per cent zinc and two per cent copper.
“The plan is to extend it to about a million tonnes per annum over the next two or three years,” Albert said.
29Metals is also looking to extend its Scuddles mine at Golden Grove with its Cervantes project commencing a prefeasibility study.
“We have committed to another 7km of drilling at Cervantes this year,” Albert said.
But 29Metals isn’t stopping there, looking to add a third mining front to its Golden Grove operation with feasibility studies completed on its Gossan Valley project.
“What’s really exciting about Gossan Valley is that it’s about 7km from existing operations,” Albert said. “We anticipate it could do exactly what Gossan Hill and Scuddles has done over the last 30 years.”
Turning to 29Metals’ Capricorn copper mine, Albert told the Diggers and Dealers audience about its exciting future.
“We have got 1900 square kilometres of tenement that has not had the
opportunity to be explored with modern exploration methodologies,” he said.
“We have strategically well positioned roads, rail, power and right next door to the mine is the Mount Isa smelter, which is only 140km away.”
With an additional 10-year mine life for Capricorn, 29Metals can focus on its sizeable metal endowment of over one million tonnes of copper and significant amounts of silver and cobalt.
“We’ve got the right ground, the right skills, the right team and the right metals,” Albert said.
A leader that knows a thing or two about team building is Liontown
managing director and chief executive officer Tony Ottaviano.
Having held previous executive positions at Rio Tinto and BHP, Ottaviano is no stranger to the industry and has seen to it that Liontown’s mining operations have either commenced or are being stockpiled.
Ottaviano told Diggers and Dealers delegates that the company’s Kathleen Valley project in WA is now less than 12 months away from achieving its target of first production in mid-2024.
“Liontown Resources is powering to production and recent achievements reinforce the commitment to realising the full potential for Kathleen Valley and growing our company,” Ottaviano said.
“We are on track to award our most significant contract, the underground mining services contract, on schedule in the September quarter along with the structural and mechanical piping contract.”
Ottaviano highlighted Liontown’s commitment to creating value and testing the supply chain with its delivery of a direct shipping ore (DSO) product as an early source of revenue ahead of first concentrate production from the Kathleen Valley project.
“Executing the DSO project enables us to realise the dual benefit of unlocking early revenue and de-risking the
project by field testing our ore sorting and logistics solutions ahead of first concentrate production,” Ottaviano said.
Ottaviano also emphasised the importance of environmental, social and governance (ESG) to Liontown’s operations.
“ESG is our core DNA,” he said. “We’ve started construction on our hybrid renewable farm, one of the largest in Australia at 95MW.
“We will be installing 31,000 solar panels in the coming months and five of the largest inland wind turbines are on the ship on the way out to Geraldton as we speak.”
After the speeches, Diggers and Dealers attendees were treated to visits to mine sites in the GoldfieldsEsperance region around Kalgoorlie to soak up what is perhaps Australia’s most iconic mining foundation.
It was against this backdrop that the winners of this year’s Diggers and Dealers Awards were announced.
One to watch in the coming years is Patriot Battery Metals, taking away the Best Emerging Company Award. Pilbara Minerals and Allkem were also crowned Digger of the Year and Dealer of the Year, respectively.
The next Diggers and Dealers forum will be hosted in Kalgoorlie in 2024, from August 5–7. AM
LIONTOWN RESOURCES IS POWERING TO PRODUCTION AND RECENT ACHIEVEMENTS REINFORCE THE COMMITMENT TO REALISING THE FULL POTENTIAL FOR KATHLEEN VALLEY AND GROWING OUR COMPANY.”LIONTOWN RESOURCES MANAGING DIRECTOR AND CHIEF EXECUTIVE OFFICER TONY OTTAVIANO.
Having been in Australia since the early 2000s, SSAB has prioritised understanding the needs of the country’s mining industry. And one of the primary needs within the sector is a wear plate that stands the test of time.
“We are always looking to produce new products and improve the ones we already have,” SSAB area sales manager – Australia and New Zealand Matthew Spiteri told Australian Mining. “One of the ways we do this is with Hardox 500 Tuf.
“With its unique combination of hardness and toughness, Hardox 500 Tuf allows for the optimised design of all kinds of truck and trailer bodies.” Hardox 500 Tuf also allows mine sites to haul more and save more.
“The examples of savings by upgrading to Hardox 500 Tuf are based on a truck travelling 100,000km per year for six years,” Spiteri said.
“The increased load capacity and other benefits in operation and production are the result of changing from 6mm-thick Hardox 450 to 5mmthick Hardox 500 Tuf.
“It’s amazing what a different 1mm makes.”
According to Spiteri, the weight benefits of reducing plate thickness are easy to calculate.
“Not only does it make the body of the machine 17 per cent lighter, but you need to purchase, store and handle 17 per cent less steel,” he said.
“A 17 per cent reduction in plate thickness cuts down on welding time and the need for welding consumables.”
Hardox 500 Tuf has a hardness interval of 475–505 HBW (Brinell hardness calculation) for high wear resistance in the most challenging abrasive applications.
The toughness makes Hardox 500 Tuf perform as a structural wear steel, keeping dump bodies in good shape and standing up to impacts from large and heavy objects striking the plate.
“Hardox 450 has been the workhorse for wear applications for a long time,” Spiteri said. “Now it’s time for the next step with the arrival of Hardox 500 Tuf.
“The hardness of this steel has jumped more than 10 per cent compared to Hardox 450. And since wear resistance isn’t a linear phenomenon, the increase
in hardness can give an increase in wear life as high as 50 per cent – depending on the abrasive material and operating conditions, of course.
“So if you’re looking for a longerlasting body, Hardox 500 Tuf is the way to go.”
Whether Hardox 500 Tuf is welded, bent or machined, customers can expect the steel to deliver predictable performance. Hardox 500 Tuf comes with guarantees for narrow flatness and thickness tolerances and bending performance, ensuring cost efficiency and product quality in the workshop. Using thinner dimensions means less bending force is required.
“The Hardox 500 Tuf has been on the market since 2017,” Spiteri said. “Our end-users and mines love the material because of its impact toughness.
“We’ve made sure that our teams are on hand to support our customers who might be upgrading from Hardox 450 to 500 Tuf.”
Spiteri said this type of support has changed the game for SSAB’s customers.
“It sounds simple, but local technical support can really go a long way,” Spiteri said. “Technical support comes
in all different facets, but whenever the customer needs us, we’ll be there.”
SSAB is also making efforts to minimising its carbon footprint and reducing global emissions.
“We know that steel production is one of the highest producers of CO2,” Spiteri said.
“Our first step toward minimising CO2 within our steel production is the introduction of SSAB Zero.”
SSAB Zero steel is made of recycled steel and produced with fossil-free electricity and biogas. The result is steel with virtually no carbon emissions.
Spiteri said it’s important for SSAB to continue providing solutions for the global energy transition to ensure the mining industry stays competitive and able to produce the high-quality ore for which it is known.
“I think being net-zero or fossilfuel-free is a big thing to aspire to, but it’s also a big thing to look forward to,” Spiteri said.
“We’re not just looking at Australia, we’re looking at the entire world. That’s a lot of CO2 we can reduce and a lot of help we give the environment for future generations.” AM
BHP’s South Flank mine has seen great success since opening its doors.
The Pilbara operation delivered its first ore in May 2021 and has created approximately 9000 direct and indirect jobs, and 600 operational roles.
Located south of the existing Mining Area C, South Flank’s nameplate output of 80 million tonnes per year will lift production from the combined operations to 145 million tonnes of iron ore annually, making it the largest operating iron ore hub in the world.
Since inception, the mine has aimed to improve diversity, culture and safety.
BHP has partnered with Monash University on a research project, ‘BHP South Flank: Using science to drive meaningful change to behaviours’, which aims to further drive positive social and cultural change on-site.
The research was conducted with BehaviourWorks Australia, a leading behaviour-change research enterprise within the Monash Sustainable Development Institute, in collaboration with the Faculty of Education.
“This project started in October 2022, and it was conceived to design and assess programs to encourage positive workplace behaviours, and to decrease negative behaviours such as sexual harassment and bullying,” BehaviourWorks Australia senior research fellow Dr Denise Goodwin told Australian Mining.
The project comes as mining companies and various state governments introduce initiatives to foster healthier work environments within the resources sector.
A key example of these efforts is the WA Government launching two programs – ‘SPEAK UP, REPORT IT’ and ‘Respect in Mining’ – to create safer workplaces and to drive cultural change within the state’s resources sector.
However, issues of workplace culture are not limited to the mining industry.
“There’s a number of industries that are dealing with these issues in the workplace. But it’s come to light because of some high instances in mining,” Goodwin said.
South Flank was chosen for the project because it is a relatively new
mine and having these conversations at a new site can create more opportunity for change.
“As the mine is still in the final stages of ramp-up, there’s a real opportunity to say, ‘How can we change the environment?’ and ‘How can we put things in place that enable the behaviour change?’,” Goodwin said.
Researchers surveyed a large cohort of employees and contractors at South
initiatives to build a physically and psychologically safe workplace.
“As part of our process, we then spoke to 76 people from South Flank. This was across the whole mine site, from roles in production to mobile and fixed plant maintenance,” Goodwin said.
“We spoke to people in all those areas, across all levels and genders as well, so it wasn’t just senior staff.
“We have also done some extensive
so it’s quite a significant portion of the workforce.
“The research team also spent time on-site, so we’ve been able to immerse ourselves in everything that’s going on.”
Other findings from the research include that increasing the percentage of women in male-dominated industries, such as fly-in, fly-out (FIFO) mining, can reduce discrimination and anti-social behaviour, and having more women onsite can lead to occupational health and safety (OH&S) improvements.
“Gender balance was one of the big areas that we were looking at, (including) how can it be achieved,” Goodwin said. “It was viewed quite positively within the staff.
“We had some really good responses from people who said, ‘This is the way of the future and this is what a mine site should be’.”
Since the research stage of the project, South Flank has implemented many positive changes.
“We’ve put a lot of effort into respectful behaviours and then thinking about how we can manage them respectfully,” BHP South Flank mine general manager Steve Campbell told Australian Mining.
“Today we have around 40 per cent female and 15 per cent Indigenous participation, and if you look around the village and the workplace, we have a population that more closely resembles general society – people of different races, religions, backgrounds and sexual orientations.
“They all bring something different to the table, and that is something that we’re extremely proud of.”
However, Campbell understands that there is still work to do.
“By using science-based and datadriven techniques, Monash are helping us understand what is working and where we can refocus our efforts to improve any measures or controls that we already have in place, as well as develop new ones to help change the way people behave.”
Socially speaking, improving gender balance has been viewed in a mostly positive light. However, concerns regarding gender balance negatively affecting men have been raised.
“Any time a system undergoes change
feel that way and they can understand that this is a good thing for all moving forward,” Goodwin said.
BHP is committed to continuing its work with Monash University to find solutions to reduce any concerns regarding gender balance at South Flank.
“A gender-balanced workforce is more inclusive and respectful and recognises the value everyone brings. When people feel respected, they feel appreciated, they feel like they belong, and they are happier in their work,” Campbell said.
While South Flank is already a leader in the industry when it comes to building diverse and inclusive teams, Goodwin said the lessons from the project have shown strong leadership is needed across all aspects of the business.
“I don’t mean leadership at the top like CEOs; it’s got to be on-site and across all levels,” she said.
And that will be the next step in the project: continuing work with leaders and crew members directly across the South Flank site.
“I think interventions at site then couple with the policies that have already been in place for quite some time,” Goodwin said.
“But it’s enacting those within the sites by working directly with the teams.”
Campbell believes the lessons that have been learnt at South Flank can be translated beyond BHP’s WA iron ore operations.
“I think the biggest thing I learnt a long time ago is that it takes time to change culture,” he said.
“For everyone to really understand and embrace diversity, and everything it brings to the workplace, it’s not just one discussion, it’s many discussions with lots of people over a long period of time.”
Goodwin echoed those sentiments.
“There isn’t a-one-size-fits-all,” she said.
“It’s about working with the crews to listen, understand and develop interventions that ensure it is a safe place for everybody both physically and psychosocially. AM
Water is fundamental to life on earth, and its role in the mining industry is no less salient. It plays an integral role in the processing and treatment of ore, among other areas.
But a warming climate presents issues for mine sites when it comes to responsible water stewardship.
Black & Veatch’s business development director Mike Russell explained some of the trends the engineering, procurement, consulting and construction company was seeing in the mining industry.
“Water has historically been a low priority for mines, but it’s becoming more critical for companies as an essential part of producing their end product,” Russell said.
“We’re seeing more companies wanting to move away from relying on rainfall and stormwater collection to climate-independent sources such as seawater or brackish groundwater, using tailored water treatment and desalination to secure that water supply.
“As Australia’s mining sector moves to capture the green energy revolution with better quality iron ore, lithium and more, there is an increased demand on the quantity and quality of water.”
Green minerals and metals often require more treatment and processing, which means mine sites need better water, and more of it, than ever.
Remote inland operations face their own set of challenges.
“We’ve seen quite a few industrial hubs cropping up in various areas of Australia; suddenly there are multiple industries operating in an area, so there’s a lot more competition for a water source, not only between projects but also with the urban provider,” Russell said.
“There is a big ESG (environmental, social and governance) aspect to this, as well. Clients are having to really consider their environmental footprint in terms of what impact it’s going to have on the groundwater resource, local communities, and other industries in the region.”
The weight of this situation was demonstrated when Black & Veatch built a major seaside desalination plant supply, with a lot of competition for the limited water resource,” Black &
Veatch water treatment section head Dr Srinivas Veerapaneni said.
“Taking it from the ground would have devastating impacts on the people and environment, so the project was aimed at creating a climateindependent water supply through seawater desalination.
“We did all the preliminary work right through to the detailed design and the commissioning of that plant. We were invited back to expand that desalination plant a number of years later.”
While some sites battle too little water, others face excess.
“The iron ore sector in the Pilbara faces a unique challenge, which is mining below the water table,” Russell said.
“Not only do you have to worry about removing water to access your orebody, but you’ve suddenly got the additional issue of figuring out what to do with the surplus.”
Mining operations also create waste streams from treatment processing, such as tailings, which would traditionally be stored in dams. Miners are now searching for creative
alternatives when it comes to reusing excess water.
“Waste stream disposal is a very significant issue for any inland site,” Russell said. “I recently worked on a project at an inland desalination plant where the site was trying to figure out how to dispose of the salty water created from the desalination process.
“We determined that their only option was to go down a zero-liquid-discharge pathway. It’s expensive, but it means the site can now operate without restriction. We’re exploring similar zero-discharge technologies for tailings dams.
“Desalination projects for seawater and brackish water are the core of what we do. We have significant experience in the engineering, procurement and delivery of these large-scale projects.”
Pairing expertise with a technologyagnostic approach, Black & Veatch considers each project’s individual needs before deciding on a course of action. This method allows the company to determine the best technology for each application and bring value to projects through careful planning, risk mitigation and forward-thinking solutions.
AM
“Our sensors integrate artificial intelligence (AI) technology to give operators a depth of vision and allow them to see what’s ahead,” Baron said.
“For example, if a person is approaching the protected zone of equipment, the AI would identify how many metres away that person is, and that number would decrease as they keep walking away.
“Furthermore, if there is an object in the field of view (FOV) that is preventing full body image detection, the AI can smartly ignore the object and still detect the potential intruder of the protection zone, so the machine operator can receive an alarm in time without object distractions in the FOV.”
SICK’s long history of designing, refining and updating its sensor technology means the company’s customers can purchase the equipment with confidence.
Amine is a worksite with a lot of moving parts, so it is imperative that workers keep all guards on machinery and equipment, and act confidently from the remote operating centres.
To tackle the challenges and a more sustainable future, remote sensing solutions are required. One of these technologies is LiDAR (light detection and ranging).
LiDAR sensors are not a new product in the industry, but companies like SICK are constantly developing them to ensure they meet the standards and evolving needs of the sector.
“There are a lot of LiDAR products on the market, but SICK has a reputation for having fit-for-purpose sensors for the mining space,” SICK market product manager Tim Baron told Australian Mining.
“Harsh environments like mining need reliable products that will continue to operate no matter what the space throws at them. SICK understands this, so we develop our products accordingly.”
A mine site can use a LiDAR sensor for multiple applications. The technology can capture geological data to create 3D models, scan the surrounding environment to help control autonomous vehicles, and even detect changes in the underground environment that can’t be seen by the naked eye.
“Using LiDAR sensors on a mine site not only improves safety but it also improves uptime,” Baron said.
“If you have two pieces of autonomous machinery that collide, no one will be injured but you’ll be down hours of productivity while you work to get them fixed.
“The growing demands of these products speak for themselves. Our LiDAR sensors are dynamic and they do the job.”
Having developed LiDAR sensors for a number of years, SICK understands that technology must constantly be redeveloped as the mining industry adapts smarter ways of working.
That’s why the company will be featuring its new and innovative product line at the upcoming 2023 International Mining and Resources Conference (IMARC) in Sydney. One of these products is called SARA (SICK Augmented Reality Assistant).
“With SARA, we’re utilising standard mobile devices like your smartphone and overlaying data to help customers quickly diagnose a problem on their equipment,” Baron said.
SARA merges visualised sensor data with the real-world environment, allowing the user to simply hold up their phone to see the equipment and any safety concerns that were previously invisible to them, such as a load displacement or a hazard obstructing the way.
“While using SARA, your phone or your tablet becomes this virtual world where you’re seeing the real equipment but also all the information that the sensor is putting out,” Baron said. “We’ll be showing IMARC attendees just how easy it is to use.”
SICK’s LiDAR product family has something for every need, from the very basic to high-end configurations. But no matter what product a mine chooses, it can be assured it’s getting some of the best performance on the market.
“We have a wide installation base in Australia so we’re able to provide a strong understanding to mean time to failure (a maintenance metric that measures the average amount of time a non-repairable asset operates before it fails), which allows our customers to really realise their return on investment,” Baron said.
“Companies have utilised our equipment because of its high reliability and our confidence that this system works as intended and is Germanengineered to keep working for many years to come.
“Our customers are happy with our LiDAR sensors and that’s one of the most important things for us, because if they’re happy then we’re happy.” AM
The sight of flames on a mine site is usually the cause of considerable alarm.
But when a Queensland Fitzroy Mining Operations site recently went up in flames, there was no such distress: it was simply the start of the Queensland Mines Rescue Services’ (QMRS) second State Cup.
Eight mine rescue teams from across Queensland took part in a series of exercises from search-and-rescue scenarios to simulated vehicle collisions and firefighting.
And though all teams gave it their best, only one could be crowned winner.
That honour went to the rescue team from Anglo American’s Grosvenor coal mine in Moranbah, whose members will go on to compete in the Australia-wide competition in October.
This was not the first time that Anglo American’s mine rescue team had taken out a top prize. In 2019, the team was named national champions of that year’s competition.
Then-team captain Boyd Buschmann said the simulations in events like the QMRS State Cup represent an important opportunity for all teams to test their skills.
“These competitions help ensure we have absolute confidence in our skills if we’re ever called on to undertake a rescue,” he said at the time.
“I’m very proud of the team’s hard work, dedication and professionalism. We’re also the first mixed-gender team to ever win the competition, which is a fantastic achievement.”
Coming in hot on Anglo American’s heels in 2019 and 2023 was Moranbah North, placing second on both occasions.
This year saw the team from Broadmeadow come in third, while Oaky North took out fourth place.
QMRS operations manager Luke Ludlow emphasised the importance of such industry events.
“These annual competitions provide a chance to acknowledge these teams for their contribution to mine safety and the opportunity to execute learnings for future training,” Ludlow said.
Fitzroy Mining Operation’s chief executive officer Brian MacDonald said he was pleased to show the broader industry Fitzroy’s operation and capabilities.
“We at Fitzroy are honoured to have hosted the State Cup for the first time at our Carborough Downs mine,” he said.
Mine rescue has been a necessity ever since the first tonnes of coal were exported in Australia in 1799. But it wasn’t until 1909 that the first mines rescue brigade was formed.
That first brigade found its home in the Ipswich coal fields in central Queensland, building the first permanent mines rescue station there in 1923. Stations were then built further afield in Collinsville, Blackwater, Moura and Dysart.
From the early days of mines rescue teams, they have been an integral part of the Australian mining landscape. And as the sector diversifies, so too do the teams.
Anglo American formed the first ever all-female mines rescue team at its Capcoal open-cut mine near Middlemount, Queensland, in March of this year.
The team is made up of seven women, who have named the team ‘Women of Steel’.
Team captain and Capcoal emergency response team coordinator Kiri Blanch said she had wanted to put together an all-female team for some time.
“Our team is a dedicated group of women who really gel together,” she said. “Everyone has been very supportive,
continues to both support mines rescue and empower the women we work with.
“This has inspired our team to commit to the challenge, improve our health and fitness and achieve the best results possible whilst representing women in mining.
“We will train closely with the Capcoal open-cut men’s team and support each other during competitions.”
of the Women of Steel.
“We’re so pleased to support this outstanding group of women as they get set to make a real mark on Queensland’s mines rescue circuit,” he said.
“Our mines rescue teams play a critical role in any incident response or rescue, and these competitions help ensure their skills are well honed if called upon to undertake a rescue.” AM
THESE COMPETITIONS HELP ENSURE WE HAVE ABSOLUTE CONFIDENCE IN OUR SKILLS IF WE’RE EVER CALLED ON TO UNDERTAKE A RESCUE.”MINES RESCUE TEAMS HAVE BEEN A VITAL PART OF THE INDUSTRY SINCE 1909. THE TEAMS COMPETED IN UNDERGROUND AND SURFACE MINING SITUATIONS.
One of the biggest challenges facing mining in Australia is ensuring the next generation of workers has the right skills and experience to continue delivering the essential resources on which we rely.
In a move to tackle this issue, mining giant BHP has unveiled its new FutureFit Academy in Forrestfield, Perth, as part of the company’s commitment to building the skills workers need for modern mining.
Through its academies in Western Australia and Mackay, Queensland, BHP aims to create 2500 new traineeships and apprenticeships over five years.
“Minerals and mining are critical to Australia’s economy and the global energy transition,” BHP Australia president Geraldine Slattery said.
“We have an enormous opportunity but also challenges to overcome to keep competing in the global arena, among them the need to build the skills needed in a modern mining sector.”
Launched in 2020 with a $300 million commitment from BHP, the FutureFit project offers paid training pathways into the mining industry for workers at any stage of their career or for those without previous mining experience.
“Our new BHP FutureFit Academy in Perth will provide an even better learning experience for the next wave of Australia’s tradespeople, technicians and maintenance professionals,” Slattery said.
To date, more than 1100 people have joined the FutureFit program and more than 500 have graduated with qualifications and a guaranteed job with BHP.
The Forrestfield and Mackay academies feature immersive virtual reality technology combined with workshop learning to develop skills and knowledge, giving students the edge they need in a rapidly developing industry.
The new academy is more than double the size of its predecessor in Welshpool, with an additional 110,000 square metres of workshop space and a much larger capacity for students.
Kael, a proud Noongar man from Perth, is 10 months into an apprenticeship with the academy. For 10 years prior to joining FutureFit, Kael worked in a pawnbroker shop.
“At 33, I never thought I wanted to go for an apprenticeship. It was one of those things that I thought was out of my grasp,” Kael said.
“But with FutureFit apprenticeships being closer to two years and based here in Perth, it was something that I jumped at the opportunity to get on board with.”
FutureFit Academy also offers an expanded curriculum that will allow students to become trained in high-risk work licensing, maintenance associate and trade programs in auto electrical, fabrication mechanical fitting, and heavy diesel.
It is now also delivering an apprentice program for BHP’s Western Australia Iron Ore and Nickel West operations. The academy offers three entry pathways for students. The trade apprenticeship takes place over 24 months and equips graduates with a full trade qualification and the skills to perform preventive maintenance, diagnostics and repairs. The other two pathways are 12-month courses in either production or maintenance.
Production sees students learn how to operate equipment essential to mine sites, ensuring products are delivered safely and efficiently.
The maintenance pathway is designed for those who enjoy working with their hands and figuring out how things work, learning the skills needed to keep on-site equipment such as conveyors and trucks running smoothly.
Perth local Britnee was working in customer service before deciding she wanted to follow her dream of a career in the mining industry and is now four months into her traineeship as a maintenance associate.
“When the opportunity arose to apply for FutureFit, I decided I was just going to go for it and when I got the call, I just couldn’t believe it,” Britnee said.
“To have paid training, working with people who’ve also had no experience in mining, from all different walks of life, all different ages, and a lot of other females, it’s just so empowering.” AM
DYNA Engineering has developed a “chamfered mesh pattern”, designed to reduce washdown splash back and increase visibility through the guard panels.
This design feature is a major “point of difference” compared to standard HDPE mesh and will improve inspection and cleaning operations.
Washdown Mesh
• Up to 50% additional spray-through for washdown.
Increased Visibility
• Up to 25% additional viewing angle and see-through visability.
ROBUST ✓ LIGHTWEIGHT ✓ ECONOMICAL ✓DECODA HAS ITS SIGHTS SET ON MAKING THE MINING INDUSTRY AS TECHNOLOGICALLY ADVANCED AS POSSIBLE.
Mining has been around for centuries, and this means miners across the globe have long relied on tried-and-true methods of extracting ore from the ground.
But Decoda is seeking to challenge the status quote of these methods by developing new and innovative technology that makes mining smoother, faster and safer for everyone in the industry.
“I believe a non-mining-type mindset is what’s needed to challenge the idea of traditional mining,” Decoda executive general manager George Spink told Australian Mining.
“That type of mindset will challenge some of the long-held beliefs in the sector and really allow the industry to embrace new technology.”
Decoda is no stranger to producing innovative technology for the mining industry. Its RockAware and Integrated Performance Management (IPM) technology solutions are challenging the traditional ways of industry.
RockAware, a leading artificial intelligence (AI) system that helps detect obstacles before they can impact and
shorten a haul truck’s tyre life, will also deliver positive environmental benefits.
“Obviously there’s a massive safety and cost benefit to utilising RockAware on a mine site,” Spink said. “But the underlying environmental benefits are just as important.”
“If less haul truck tyres are getting shredded by rocks and are achieving a longer life, that means less are ending up in landfill. If less tyres are in landfill, less tyres need to be purchased, saving the energy it takes to manufacture them, resulting in a reduced carbon footprint.” Decoda is well-versed in crafting datadriven solutions for its mining clients. Its IPM solution is just one example.
The software allows miners to visualise their value chain as a cohesive system, highlighting operational and financial risks and providing a single source of truth for data-driven decisions.
“Relevant data generated across a mine site is ‘ingested’ into our IPM solution, helping miners make timely decisions about their operation,” Spink said. “With new generations of miners coming through, they’ll have an expectation of utilising technology. Unless mines and miners continue to modernise, they run the risk of not being able to attract and retain new employees.
DECODA’S IPM AND ROCKAWARE TECHNOLOGY SOLUTIONS HELP TO DELIVER POSITIVE ENVIRONMENTAL AND PRODUCTION BENEFITS.
“Sojitz, a trusted development partner for the past 18 months, has played a pivotal role in collaborating with us to build its IPM solution from inception.”
Sojitz Blue general manager –assets, innovation and growth Darren Woodward highlighted the industry’s need to stay ahead in terms of technology adoption.
“We’re witnessing a shift where mining companies must proactively adopt innovative technology,” Woodward said. “It’s no longer enough to simply rely on traditional methods; we have the means to achieve more.”
Decoda’s IPM software is a key example of how technology can be harnessed to drive efficiency and accuracy in mining operations.
IPM empowers mining operators to gain comprehensive insights into their entire operation, thereby minimising operational risks.
“To achieve this, you need to understand risk and forecast sensitivities across the entire process chain,” Woodward said.
“Decoda’s expertise in this area, born out of a deep understanding of information flow from machinery up, is invaluable.”
Spink agreed with this point.
“The key lies in correctly contextualizing the vast amounts of data generated in mining operations,” Spink said. “IPM excels in this aspect, ensuring the right data is collected and utilised for data-driven decision-making.”
In a world where data is abundant but discerning insights from it can be challenging, Decoda stands as a trusted partner for mining companies seeking clarity and actionable intelligence.
Decoda and Sojitz will be sharing the stage at the 2023 International Mining and Resources Conference (IMARC) to discuss the topic ‘decoding production forecasting’.
“Decoda is striving to create an intelligent mining environment and ecosystem,” Spink said. “We want IMARC attendees to leave the conference knowing that Decoda is an innovative, technology-driven company that is driving us toward the future.
“I want to challenge the mining industry to be bold and courageous in exploring and adopting new technology, and to partner with companies like Decoda to embrace this.” AM
IMARC 2023 will be held at ICC Sydney from October 31 – November 2.
It’s no secret that mines require a regular supply of treated water for their operations.
But what happens when a fixed water treatment plant fails or goes out of commission for a time?
Enter Veolia.
“Our mobile water technologies are pre-engineered and pre-packaged with the flexibility to have these units deployed quickly to support the needs of our customers,” Veolia Water Technologies business development manager for mobile water services Damon Good said.
“Once we have completed a water analysis at the customer’s site, we can start to discuss the right system for their needs.”
There are multiple reasons an operation might require a mobile water treatment solution from Veolia, but among all, there is the desire to reduce water levels in tailings dams.
“One example is a gold mining company from Queensland who reached out to us for support to harness the power of water management technology in order to optimise its operations,” Good said.
“That was quite a challenging period for the company because there had just
been some really heavy rainfall, so the mobile system played a crucial role in regulating the tailings dam and reducing the water to prevent overflow.”
The fact that many Australian mine sites are located in remote corners of the country means it can be tricky to get large pieces of equipment – like a water plant – mobilised quickly.
Veolia’s mobile water systems help to address this tyranny of distance.
“A permanent structure can sometimes take a year or two to be fully operational,” Good said. “But you cannot wait that long if you are trying to solve a time-critical problem.
“In contrast, our mobile water technologies feature plug-and-play connections and are mounted on trailers, containers or skids so they can be set up and ready to run quickly.”
When it comes to technology evolution, Veolia is driven by the desire to help its customers optimise resource management for more sustainable and cost-effective solutions.
“We are moving towards a hybrid system approach,” Good said. “That means the units are not just capable of traditional water treatment methods but will also incorporate some newer
cutting-edge techniques to enhance efficiency and effectiveness.
“All this adaptability ensures that a wide range of water quality issues can be addressed, from simple filtration to more complex contaminant removal processes.”
Veolia has also leveraged the Starlink communications network to enable remote access capabilities in its mobile water treatment systems.
“With satellite technology, we can access the systems from anywhere in the country with real-time monitoring,” Good said. “With this, we can make immediate adjustments and troubleshoot.”
By employing Veolia mobile water treatment equipment with remote access, sites can deploy the staff that would normally be monitoring the equipment elsewhere, saving time and money.
The technology is also making positive waves in the environmental management of mine sites.
“By ensuring consistent water supply for mineral processing and implementing dust control measures, our mobile water treatment systems can play a pivotal role in minimising the environmental footprint of mining activities,” Good said.
“Miners and their operations are growing every day, and we want to be able to assist them in not only growing their sites but also ensuring that we are being as sustainable as possible.”
Veolia has over 350 proprietary water and wastewater treatment technologies available, and the company takes pride in working with its customers to understand their requirements and goals.
“We have the back-up support, the technical know-how, and an extensive pool of global resources to call on for our customers,” Good said.
“If our mobile water treatment system is not the right fit for a customer, we can address their business needs by mapping it to the range of solutions that we offer.
“What Veolia does well is provide the expertise to ensure our customers are getting the best solutions to meet their objectives every time.” AM
Just as a gear unit is an integral component of any motor, customer satisfaction and growth are at the heart of any business striving for success. At Flender, these foundations are more than just ideals. With the company’s latest expansion to a new service centre in Sydney, joining its locations in Perth, Melbourne and Rockhampton in Queensland, Flender aims to set the industry standard for customer care while its gear units and couplings continue to power some of Australian mining’s heaviest machines.
“We hope that by having a facility here we’ll be able to support our customers not only with a service centre but with technical support, project engineering, project management engineering and sales support all located close to the mining centre of New South Wales,” Flender managing director for Australia Kareem Emara said.
“We wanted to future-proof the business long-term by increasing our footprint from one facility and a network of offices around Australia to four key service workshops strategically placed to support our customers throughout the lifecycle of our products.”
That plan means delivering continued support beyond the sale of the gear units and couplings and considering
how the company can keep offering value to its customers.
“We are also looking at ways to create value-driven data for our customers,” Emara said.
“The digital enabler of all measurements and optimisations is our new gear unit intelligence AIQ. It gives us flexibility to listen to customer feedback and adapt our portfolio to suit their needs.”
The new system provides customers with diagnostic information on conveyors, mills and other key assets at their mine sites, including how their machines are operating and the lifecycle of the product.
With countless industry applications on the books, including belt conveyors, drills, slewing drives, feeders, crushers and mills, Flender has been servicing the mining sector with high-quality gears and couplings for decades.
The company’s expansion on the east coast is critical to increasing its availability to customers in one of Australia’s most influential mining regions.
Flender is focused heavily on grinding and milling operations, with its products powering some of the largest geared mills and highpressure grinding rolls (HGPR) in Australia.
reached customers across 33 countries, selling more than 1.9 million gear units.
“We have got the largest standard range of any gear unit manufacturer,” Emara said. “We’ve got multiple 2.5-megawatt drives scattered throughout the country.
“Some of the most complex conveyance systems around Australia are driven by Flender products – that encompasses gear units, couplings and other accessories.”
individual conveyor, compared to any of our competition,” he said.
“We are able to adapt our portfolio to meet our customers’ needs rather than just giving them products off the shelf, and our customers like the agility we’ve been able to provide which has been reflected in the growth we’ve seen as a business.
“Our vision at Flender is to set the global benchmark when it comes toservice.” AM
ELPHINSTONE RECENTLY ACQUIRED THE BELTOR PULLER, AN UNDERGROUND MINE EXTRACTION DEVICE DESIGNED TO SAFELY RECOVER BURIED EQUIPMENT WITH MINIMAL DISRUPTION TO OPERATIONS.
Operator safety and mine productivity have always been priorities at Elphinstone, a company with a long and successful history designing and manufacturing underground hard rock mining equipment.
From its headquarters in Burnie, Tasmania, Elphinstone has been supplying the mining industry with equipment since 1975, when Dale Elphinstone founded the company.
“Dale is the executive chairman of Elphinstone and his legacy of over 45 years in the underground mining realm continues in the ethos and values of the company he founded,” Elphinstone global sales and marketing manager Tim Mitchell told Australian Mining Elphinstone’s dedication to the business and contribution to the METS (mining equipment, technology and services) sector received public recognition when he was awarded the Champion of Innovation award at Austmine 2023.
“The award celebrates an individual who has pioneered and championed innovation and has changed the course of the mining industry through their outstanding vision, inspirational leadership, passion for innovation and advancement of mining equipment, safety, technology and services,” Mitchell said.
Elphinstone’s ongoing commitment to safety and mine productivity was further demonstrated in March of this year, when it announced the acquisition of MED Pty Ltd, the owner of the intellectual property for the underground mine extraction device (MED), also known as the Beltor puller.
The Beltor puller was developed by the founder of Beltor Engineering, Aldo Beletich, back in the 1980s.
“The MED was invented in response to underground miners needing a way to extract buried or bogged equipment in a safe and efficient manner without damaging the mine or negatively impacting production,” Mitchell said.
When Beletich invented the first Beltor mine extraction device – or MED Puller as it’s commonly called
– mining equipment was much lighter than it is today.
The first MED, with a pulling capacity of 90 tonnes, was introduced to the market in 1988 to meet the needs of the underground thermal coal miners in and around Newcastle.
“With the increase in size and weight of underground mining equipment, there was a need for larger extraction devices to recover buried or bogged equipment,” Mitchell said. “As a result, higher capacity MEDs were introduced to ensure that underground mining operations could return to full production with minimum delay.”
The 150-tonne (MED150) and 210-tonne (MED210) versions of the device were subsequently introduced in line with the industry’s growth.
In addition to the retrieval of buried equipment, the higher capacity models are also capable of extracting drill rods embedded in the rock face.
And the expansion did not stop there.
“In 2020, the largest version of the extraction device was launched, the MED360,” Mitchell said. “It has a pulling capacity of 360 tonnes for
much larger underground coal and hard rock machinery.
“What makes the (Elphinstone) MED unique is that it eliminates the need, damage and disruption of using other production equipment to remove the buried machine and operates in a more controlled and safe way.”
Mitchell explained how the MED works on a mine site.
“When the MED is towed into position in the mine, the boom is raised against the roof and the wheels are lowered on the floor, effectively wedging the machine into position,” he said.
“A bridle assembly is interlocked into the teeth of the MED racks, which are then pulled via hydraulic cylinders.
“The process is conducted in relative silence, allowing the operators to hear and see exactly what is happening during the extraction – a stark contrast to the traditional method with wheeled or tracked tow vehicles that produce noise and dust.”
The MED will be sold and serviced by Elphinstone direct to end users from the company’s manufacturing facility in Burnie. AM
The International Mining and Resources Conference (IMARC) is where the most influential people in the mining industry come together, delivering ideas, inspiration and serving as a meeting ground for the industry. From ground-breaking technology and world-class content to a vivid showcase of all the elements that make the mining industry great, IMARC is an opportunity to learn from more than 500 mining leaders and resource experts with a program covering the entire mining value chain.
The world-class conference program now features seven concurrent streams with more than 340 technical talks, panel discussions and strategic keynote presentations taking place throughout the three days. Gain strategic insights from c-suite executives on topics including reshaping the mining value chain, progressing ESG and environmental resilience, accelerating mining’s energy transition and so much more.
Attend one of the many networking events or simply catch up with industry colleagues on the 18,500m2 expo show floor featuring 470+ leading companies. There are thousands of opportunities to network, brainstorm, and knowledge share across the three days at the ICC Sydney from 31 October - 2 November 2023.
IMARC 2023 will also see us celebrate 10 years of IMARC and industry, reflecting on the progress the industry has made, and the new directions that mining companies, METS, Governments, and its value chain partners are embarking on to prepare for the future.
There are several ways you can get involved in IMARC, from accessing the full conference on a Delegate Pass, adding on networking events including the Gala Dinner or confirming your Expo Pass for as little as $15.
PLEASE USE CODE PRIME10 TO SAVE 10% ON DELEGATE PASSES. IMARCGLOBAL.COM
dump trucks, earthmovers, and wheel loaders to conveyors, tunnel-boring machines, infrastructure, pipework, and upstream equipment.
It goes without saying that in a heavyduty, high-risk environment such as a mine site, accuracy of torque applied is critical.
Bolt fastening has traditionally been a labour-intensive and costly exercise, using impact wrenches that can overtorque joints; hydraulic wrenches that are externally powered and bulky, requiring two people to operate; or air and corded electric nutrunners, which require changing torque via a bench torque tester.
Still, inefficient operation is only part of the challenge, with the added issues of indeterminate control and monitoring. Many companies are currently using dated guesswork of manually recording torque goals with paper and pencil in the field.
Time may be valuable for productivity, but accuracy, consistency and traceability of performance are the cornerstones of a compliant and safe work site. Without a precise auditing method, how can you be sure your tool is doing its job?
Fortunately, commercial and compliance difficulties often drive innovation, and in recognition of these challenges Ingersoll Rand developed the QX Series cordless torque multiplier. This ground-breaking tool has been specifically designed to replace less accurate manual fastening methods with a traceable method that is quicker and more effective.
Relatively new to the Australian market, the QX Series torque multiplier employs advanced technology, communication and control features to ensure accurate, repeatable bolting for industrial applications. The tool is available in a range from 200–4000Nm in 20V and 40V options.
The multiplier features a brushless motor paired with a premium Norbar gearbox. At the heart of the torque multiplier is the Ingersoll Rand closedloop transducer, which is the key to delivering torque precision, supreme accuracy and traceable results.
The tool operates on the Ingersoll Rand IQV20 and 40V Series battery system and each 20V battery charge will rundown an average of 100 bolts.
The multi-function display module provides visual feedback via red, yellow and green lights to signal whether the bolt has met the specified torque limit or angle, or if the proper gang count was reached. The only tool using a closedloop transducer for precision, it delivers accuracy to +/- 0.1Nm without use of a test bench.
Operators will benefit from improved efficiency and ability to hit nuts in faster sequence.
Multiple user-programmable configurations such as torque (Nm, Ft-lbs, in-lbs, prevailing), angle and gang count reduce the number of tools needed for multiple applications. Up to 32 presets can be stored, and these functions can be navigated directly on the tool or programmed from the Insight app, a computer or data controller, or remotely via web.
The quiet, cordless and compact QX torque multiplier eliminates the need for a hydraulic pump or breaker bar and reduces noise and vibration levels.
The risk of injury and operator strain is minimised as users move freely without the inconvenience of bulky air or hydraulic hoses or power packs, and the 360° adjustable handle provides a comfortable grip and provisions for a tethering point, allowing maximum flexibility when working on multiple joints and accessing odd angles.
Replacing potentially flawed and time-consuming manual record-keeping practices, the multiplier tool itself can store records for up to 1200 fastenings, which can be downloaded to a computer via a USB cable or wirelessly transferred to a dedicated process communication module. Reliable compliance data is now available for review, analysis and record keeping at any time.
The CAPS commitment
CAPS is the only Australian distributor of the Ingersoll Rand QX torque multiplier, which has successfully been utilised across mining, heavy equipment, rail, construction, infrastructure, military, and process automation industries around the world.
Established in 1980, CAPS boasts more than 43 years of experience in compressed air and power generation. With 10 branches around Australia and 24–7 service for maintenance and emergency breakdowns, CAPS endeavours to lead the industry in service and solutions.
The QX Series of smart tools also includes right angle wrenches, pistol wrenches and precision screwdrivers, all offering improved process control, operator comfort, and data communication while increasing productivity, lowering costs, and ensuring quality. AM
You might be hard pressed to find a leader as community-minded as Rebecca Tomkinson.
As chief executive officer of the Chamber of Minerals and Energy of Western Australia, Tomkinson is on the frontline of the mining industry and the crucial shift toward critical minerals.
And she is acutely aware that no single jurisdiction can forge this kind of path alone.
“Stepping in to lead the Chamber of Minerals and Energy has been a real privilege,” Tomkinson told Australian Mining. “I’m very proud to be able to join it at a critically important time.
“Currently, we need to do more mining than we have done in the past. And we need our organisations and the community to be part of that with us.”
Used in everything from electric vehicles to banknotes, the world needs more critical minerals than ever before – and Australia has some of the largest deposits needed to make that happen.
“The Federal Minister for Resources Madeleine King has said that the road
to net-zero runs through Australia’s resources sector,” Tomkinson said.
“But I would take that a step further and say that it actually runs through Western Australia.
“We are very privileged to have all the rare and critical minerals required to decarbonise, but the most immediate challenge for us right now is getting enough industrial-ready land to mine these minerals.”
The challenges and the opportunities facing the sector will be key topics in Tomkinson’s keynote speech at AusIMM’s Critical Minerals Conference 2023.
Held in Perth from November 21–23, the conference has been created by the industry, for the industry. It will address the challenges facing the sector as it transitions to cleaner energy.
“I’m very excited to talk about the work we’ve been doing in this space,” Tomkinson said. “I’m especially keen to engage with young people to encourage them to join the industry.”
A 2018 survey of young graduates conducted by Youth Insight found that 40 per cent of
respondents believed jobs in mining were in decline. Tomkinson is hoping to change that perception.
“We need the brightest and the best to partner with us on this pathway to reaching net-zero by 2050, and to do that we need more people to join us in the mining industry,” she said.
“I want to ensure that at the end of my keynote, everyone in attendance knows just how significant Western Australia is to the critical minerals industry, and what we’re capable of delivering on a global stage.”
Tomkinson said that in order to meet the target of net-zero by 2050, all aspects of the Australian mining industry must to work together.
“We need to ensure that Australia continues to lead the world in the critical minerals space,” she said.
“But to do that we need to work with federal and state governments and all member organisations.
“Approximately 82 per cent of the world’s energy is generated from some form of fossil fuel source and we need to transition out of that and build the new greener energy sources.”
stewardship of sorts.
“You want to leave something as strong as you found it, if not stronger,” she said. “It’s about demonstrating the contributions our industry makes. Those contributions make the country stronger.
“If we get public policy settings, sustainability, environmental approvals, and work we’re doing with First Nations people right, then we can deliver on our promise of net-zero by 2050.
“The health and wellbeing of everyone depends on the future, and the future needs critical minerals.”
CRITICAL MINERALS ARE THE BEDROCK ON WHICH THE WORLD’S TRANSITION TO NET-ZERO SITS. AND NO ONE UNDERSTANDS THIS BETTER THAN CHAMBER OF MINERALS AND ENERGY OF WESTERN AUSTRALIA CEO REBECCA TOMKINSON.REBECCA TOMKINSON, CEO OF THE CHAMBER OF MINERALS AND ENERGY OF WESTERN AUSTRALIA. THE CONFERENCE WILL ADDRESS CHALLENGES THE SECTOR FACES AS IT TRANSITIONS TO CLEANER ENERGY. THE 2023 CRITICAL MINERALS CONFERENCE WILL FOCUS ON THE FUTURE OF AUSTRALIA’S CRITICAL MINERALS INDUSTRY.
THE TEAM OF HIGHLY TRAINED ENGINEERS AND THOUGHTLEADERS AT MASPRO STRIVE TO OFFER THE BEST SERVICE AND SOLUTIONS TO AUSTRALIA’S MINES.
Safety, reliability and productivity are the pillars of mining technology manufacturer MASPRO’s approach to providing solutions to the challenges in today’s resources sector
“We’re passionate about manufacturing a quality product and we saw a gap in the hard-rock mining scene in Australia,” MASPRO managing director Greg Kennard told Australian Mining. “We pride ourselves on being able to deliver on innovation and collaboration with our clients, offering industry-leading engineering solutions for underground and open-pit mobile mining equipment.
“We have an experienced, agile team of engineers using cutting-edge technology with all their design and
technology space. He said the company’s engineering maximises the operating hours of new technologies.
MASPRO engineers recently redesigned a rotation head for an openpit surface drill for a client that wanted to extend the life of heads that were achieving 500–1500 hours. MASPRO worked with the client to create an upgraded version within a month, and the new head increased scheduled changeout intervals to 6000 hours.
Productivity and safety are big concerns in mining and MASPRO remains committed to working with clients to keep workers safe and operations running efficiently.
of the product. We collaborate with the maintenance and safety teams on-site to design solutions that keeps everyone safe while also extending the lifecycles of the components we redesign.”
MASPRO engineers recently put these values into action in designing what they call the Development Drill Bolting upgrade 2.0.
This unit is designed to improve the capability of a development drill intended for the standard tunnelling market in Australia, and has been upgraded to better handle the rigours of meshing and bolting.
The MASPRO team designed a complete upgrade to the major components of the drill to mitigate against fatigue or failure, while also increasing safety features. A new redundancy feature was introduced into the MASPRO design to ensure the feed rail could not detach while being used for the meshing and bolting process.
“Maintaining a high level of customer service and being solutions-driven is what sets us apart from others,” Kennard said. “We partner with our customers to build lasting solutions that support their stringent operational targets.
“We aim to provide more durability, safety and extend the life of the products we design. By listening to our customers, our designs address the problems our customers face on and in the ground.”
According to Kennard, expanding the company’s offering is also a key objective for MASPRO, with research and development ramping up into improving several products.
“MASPRO’s focus continues to be on development drills and will expand to offering other mobile equipment,” Kennard said.
Kennard also discussed MASPRO’s manufacturing capability from its multiple manufacturing facilities, and its enduring commitment to pursuing the latest in technology.
“We’ve got robotic welders and robotic machine loaders, as well as next-generation quality inspection, including automated 3D metrology,” he said. “We’re riding the technology wave and seeing the value it can bring to the business and our customers, with continuous operations now a reality.”
For MASPRO, it always comes back to the customers. The company is driven to ensure it is providing the best products and service on the market coupled with the latest engineering capabilities that can tailor a solution to any challenge.
“With MASPRO, our customers are experiencing a more agile, flexible and reactive team,” Kennard said.
“We put ourselves in the customer’s shoes and deliver superior solutions quicker and more efficiently.” AM
WE HAVE AN EXPERIENCED, AGILE TEAM USING CUTTINGEDGE TECHNOLOGY WITH ALL THEIR DESIGN AND ENGINEERING PROJECTS. THAT ALLOWS THEM TO GET STUCK INTO A PROBLEM AND COME UP WITH SOLUTIONS QUICKLY AND EFFICIENTLY.”MASPRO TAKE SAFETY, RELIABILITY AND PRODUCTIVITY SERIOUSLY. MASPRO IS RIDING THE MINING TECHNOLOGY WAVE.
The 2023 iteration of the Women in Industry Awards was a remarkable event. A sold-out gala dinner, 160 nominations and a 55 per cent increase in attendance on the previous year were some of the standouts. But the real highlights were the exceptional women whose success was showcased throughout the night. Held in Melbourne, the 2023 awards
who have achieved success through leadership and innovation.
There are 11 categories in play in 2024, including Excellence in Mining, and the esteemed Woman of the Year award.
Giselle Phillips, HSEQ (health, safety environment and quality) advisor at Fredon, was named Woman of the Year at the 2023 awards.
“This is a celebration not only for me
“So this is not only for me, but also for every woman that is in the room.”
Past sponsors Atlas Copco, SEW Eurodrive, Fulton Hogan and PACCAR Australia have confirmed sponsorship for 2024, with more to be announced.
Atlas Copco, which sponsored the 2023 Rising Star of the Year award, believes diversity is a key contributor to the long-term success of a business.
“The Women in Industry Awards is a special way in which we can show our commitment to advancing the gender balance in industry,” Atlas Copco said.
“As a global company, Atlas Copco recognises the link between diversity and innovation, and contributing to these awards is just one way that we can show that Atlas Copco recognises the talent and achievement of females across our industry.”
The 2023 Excellence in Mining award, sponsored by Weir Minerals, was presented to Ashara Moore from BHP.
“I would love to start with thanking Weir Minerals for sponsoring this award,” Moore said in her speech on the night.
“The video they played this evening really embodies how I feel about resources.
“They spoke quite a lot to STEM (science, technology, engineering and math). And it’s something I’m very passionate about as an engineer myself and a PhD student in sustainable management in the mining sector.”
Sophia Kurianski was named Rising Star of the Year in 2023 and said she was incredibly honoured to receive the award.
“I’d like to say thank you and congratulate every single woman in this
room,” she said. “You’re doing really amazing things and I’m just so honoured to be in a room full of such amazing women in this industry.”
With such a successful event behind it, there is no doubt the 2024 iteration of the awards will be better than ever. Nominations are now open and close April 19 2024.
Categories accepting nominations:
• Excellence in Mining
• Safety Advocacy Award
• R ising Star of the Year (sponsored by Atlas Copco)
• Business Development Success of the Year
• Industry Advocacy Award
• Mentor of the Year
• Excellence in Manufacturing (sponsored by PACCAR Australia)
• Excellence in Transport
• Excellence in Engineering (sponsored by SEW-EURODRIVE)
• Excellence in Construction
Winners will be announced at a gala dinner in Sydney on June 20 2024. AM
When an Industry 4.0-ready device is installed on a mine site, it needs to be able to handle the extreme industry environment. If dust or water make their way into a splitter box, module or field master, it can damage the vital electronics within. That’s why ifm has designed a range of protective caps for use in wet and dusty areas. Their robust, high-quality stainless-steel design protects what is important. Other dust caps, ifm said, may be removed or can be knocked off, revealing the sockets and pins to the elements. The E12542 protective caps screw onto the sockets and form a complete seal, while the E12598 caps protect plugs on sensors and IO-link masters.
The caps can operate in ambient temperatures between -25°C to 100°C and ensure the protection rating, even if sockets are not used. They come in a bag of four and are available online.
• ifm.com/au/en/product/E125
The MAXXDRIVE XD industrial gear unit is available as a three- and fourstage helical gear unit. The housing design follows the proven UNICASE housing principle and has been specially optimised for external loads. Due to the elongated arrangement of gear stages, the housing has a large centre distance, enabling a U-shaped drive design. Especially with lifting gear drives, the cable drum and the motor can easily be arranged on the same gear side of the gearbox. Furthermore, the housings are equipped with an inspection cover as standard. This is made possible due to NORD’s extensive knowledge of the specific requirements for every application, as well as optimised stocking of components.
• nord.com
Turn to the water logistics experts at Crusader Hose for reliable accessories when dewatering with a submersible pump. The rated five tonne lifting clamp is designed and tested to withstand the specific load, reducing the risk of accidents, drops or damage to the riser, equipment, and personnel. Crusader Hose’s lifting clamps are an essential accessory for the safe installation of the Flexibore rising main. The clamps are engineered to provide secure and stable attachment points to the riser, allowing it to be lifted and precisely positioned.
The rated five tonne lifting clamp consists of two steel beams secured together by two swing bolts at either end. It is equipped with an eye bolt for easy chain attachment during installation. For smaller jobs, rated 1.2 lifting clamps are available. Crusader Hose designs and manufactures Flexibore in a range of diameters, up to 10 inches and with deep bore pumping capabilities to depths of 400m.
• crusaderhose.com.au/flexibore-hose
The Marland ABC sprag backstop results from a collaboration between Regal Rexnord’s brands.
The new sprag design features indexed sprags to distribute force evenly and have less internal friction between the inner and outer races.
It also features lower operating temperatures when compared with similar units. The ABC series backstops are designed for installation on low-speed shafts with typical dimensional tolerances and clearances.
The components and bearings are continuously self-lubricated in a shielded oil chamber. A double lip seal is positioned adjacent to the bearings to keep oil and environmental contaminants out of the backstop chamber.
In addition, a periodic check of the oil level and purity can be performed utilising the oil level indicator during operation or at rest. If the inspection reveals impurities in the oil, draining, flushing and refilling can be easily accomplished using piping, T-connections and traps.
• regalrexnord.com
WOMEN IN INDUSTRY NOMINATIONS ARE NOW OPEN. Now is your chance to nominate an industry leader who you believe is advocating for positive change and deserves to be recognised.
PROUDLY PRESENTED BY
Thurs 20 June, 2024
The Women in Industry Awards recognise outstanding women leaders from across Australia’s industrials sector.
EVENT SUBMISSIONS CAN BE EMAILED TO EDITOR@AUSTRALIANMINING.COM.AU
IMARC
Sydney | October 31 – November 2
International Mining and Resources Conference (IMARC) creates a global conversation, mobilises the industry for collaboration, and attracts some of the greatest leaders in the mining, investment and technology industries for three days of learning, deal-making and unparalleled networking. Learn from more than 500 mining leaders and resource experts with seven concurrent conferences covering the entire mining value chain. Gain strategic insights from C-suite executives on progressing ESG and environmental resilience, accelerating mining’s energy transition and the digitisation of mines. Technical talks will delve into exploration, discovery and project developments, mineral processing, digital technology, and mining innovation. Discover inspiration and new ideas, find practical solutions, and see demonstrations of the latest products and innovations from start-ups through to some of the biggest names in the mining industry with more than 470 exhibitors throughout the 18,500m² expo floor all under the one roof.
• imarcglobal.com
Brisbane | November 9
Taking place in Brisbane in 2023, the Australian Mining Prospect Awards are a great opportunity to recognise and acknowledge the people and companies in the mining sector for their outstanding work.
Nominations are now open for 2023, with awards honouring categories such as Indigenous and Community Engagement, Mine Project Success of the Year, Outstanding Mine Performance, Sustainability Project of the Year, Discovery of the Year and more. Some of the 2022 award winners included Kestrel Coal for Australian Mine of the Year, Roy Hill for Mine Project Success of the Year, and Flexco Australia for Excellence in IIoT Application. This year, the awards will return to Brisbane in appreciation of the vibrancy and importance of the state’s thriving mining industry.
• prospectawards.com.au
Perth | November 21–23
Critical minerals are essential components in many of today’s rapidly growing clean energy technologies – from wind turbines and electricity networks to electric vehicles.
The increasing appetite and rapid pace of the transition to cleaner energy sources continues to drive the growth in demand for these minerals, and in response the supporting industries are also growing at unprecedented rates.
To address this rapid growth, AusIMM will launch its inaugural Critical Minerals Conference in 2023.
The event will include a multi-stream format and seek to engage with a larger audience from multiple disciplines as well as a wide range of industry.
• ausimm.com/conferences-and-events/ critical-minerals/
The Women in Industry awards are an opportunity to celebrate the success of women who work in the mining industry. The awards night, to be held in Sydney on June 20 2024, features multiple categories that showcase exceptional examples of industry advocacy, mentorship and broad sector excellence. The Women in Industry Awards recognise outstanding women from across a range of industrials sectors; for example, those who work in mining, transport, manufacturing, engineering, logistics, bulk handling, waste management, rail and construction and infrastructure – all traditionally maledominated sectors.
This is an opportunity to recognise the women who are driving change in industry and, in doing so, breaking down barriers and creating new possibilities for the next generation.
• womeninindustry.com.au
The Queensland Mining and Engineering Exhibition (QME) connects leading suppliers and technical experts with those seeking better efficiency, better productivity, and increased optimisation for their business and site.
QME will feature over 250 suppliers. Beyond the exhibition floor, the event will host a free-to-attend seminar series that will give attendees the opportunity to hear from industry professionals who
will address the current needs of the industry. With live demonstrations and topical presentations, QME will be the ultimate destination for the Queensland mining industry.
QME is a key place for the industry to come together to be inspired, innovate and connect over three days. In one of the world’s most dynamic industries, QME has maintained its relevance and importance within the mining sector. It’s the event you simply cannot miss.
• queenslandminingexpo.com.au
The 2024 PNG Industrial and Mining Resources Exhibition will showcase over 100 local, national and international manufacturers and suppliers with the latest innovations in the supply of services and equipment for the industrial, mining, and oil and gas sectors.
The two-day exhibition is the premier meeting place to connect and network with thousands of industry decision-makers across a broad industry reach, including senior management, procurement, government personnel, engineers, contractors and trade technicians.
With extensive support from key stakeholders in government, associations and industry, PNG2024 is a premier meeting place for industry trade and a forum for establishing high-quality customer contacts and conducting business.
• pngexpo.com
Less sediment, less downtime, less trouble.
Slurry sumps can be a constant hassle. Pumps wear hard and fast, and the sumps fill up with sediment. Cantilever pumps are often not up to the task. We know, because that’s when we are called in.
The advanced CFD design of Flygt slurry pumps ensures exceptional levels of abrasion resistance. In addition, we provide an array of measures that keeps sumps clean, even with the heaviest slurries.