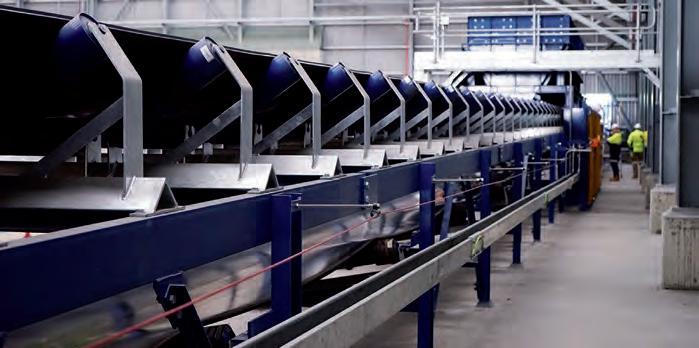
3 minute read
Going ConveyorPro
Transmin’s ConveyorPro range aims to become a one-stop-shop for any business operating conveyors or feeders. ABHR speaks with Amerander Emmadi to learn how it is achieving this goal.
CONVEYOR COMPONENTRY AND
additional accessories are a common request for bulk materials handling supplier Transmin.
When the WA-based company goes out to tender for its conveyor feeders or rockbreakers, often its customers will want additional equipment to supplement the offering.
Amerander Emmadi, Business Development Manager at Transmin says the business already had the design capacity, service capabilities and intense knowledge in the bulk material handling domain, so it made sense to take the next step.
“ConveyorPro started about five years ago, with a goal to become a one-stop shop for everything to do with conveyors,” he says.
“Our goal is to provide a total, 360° offering for spare parts, original equipment manufacturer (OEM) components and other add ons.
“It makes economic sense on both ends, as its easier for the customer and means we can provide the best services possible for them.”
The ConveyorPro brand specialises in providing everything an operator needs for a conveyor, including idlers, rollers, pulleys, impact tables and scrapers. When it comes to belts, the brand offers steel cord, multiple fabric, bucket elevator, corrugated side wall, fire resistant, chevron, rip stop, heat resistant and chemical resistant varieties.
Key account managers will go to sites regularly to gather feedback from current customers. This is then sent through to Transmin’s engineering team, where it is used to design better products.
Emmadi says if a belt is wearing too quickly for a customer, the ConveyorPro team will attempt to find any issues.
The ConveyorPro brand specialises in providing everything an operator needs for a conveyor.
“For example, if the problem seems to be in the loading area, we’ll ensure the material is not being loaded off-centre, relative velocity of incoming material should not be too high or too low and the feeding chutes don’t have any blockages.
“A lot of our customers also mentioned wanting a stronger, longer lasting belt, which is what inspired the ProTough belt.”
ProTough was designed from the ground up to be one of the toughest belts on the market, ideal for hard rock mining, quarrying and the recycling industries. It is made up of a hybrid kevlar and steel mesh composite with special grade anti-abrasive, cut and gouge resistant cover, allowing it to withstand high impact rock falls of three metres.
The belt’s tensile strength exceeds Australian and International Standards. Thanks to its increased durability, the belt is significantly less likely to malfunction and requires less maintenance, reducing operating costs.
Another example of ConveyorPro’s feedback-based development is the ProEdge belt, which is a hot vulcanised edged belt, mainly used on low profile feeders. The edge keeps material away from the track and componentry while also minimising spillage. It also features vastly more strength when compared with a conventional edge strip, capable of withstanding up to 800 newtons before signs of fatigue.
Emmadi says ConveyorPro can also provide additional assistance when it comes to the design selection.
“As part of the service, we can select the right equipment for the application when clients are looking to upgrade or purchase new equipment,” he says.
“We can do all the calculations and design work for a specific application, then provide a quote.
“We’re based in Western Australia, which means we can provide fast, efficient turnarounds. We also carry a range of widely used, fast moving items from our Perth and Brisbane warehouses to also reduce lead times.”
Transmin can supply ConveyorPro products to more than just Australia. It has the capacity to send components to almost anywhere in the world, and has a presence in South Africa, India, and Canada.
The company plans to continue growing its range of products, especially when it comes to rollers, composite rollers and conveyor guarding. Emmadi says the company’s latest high-density polyethylene guarding for low profile feeders has been a major success and has begun looking into providing similar products for conveyors too.
ConveyorPro has also teamed up with American-based Martin Engineering to distribute its conveyor components. In particular, Martin Engineering’s CleanScrape Primary Cleaners are being trialled on several sites.
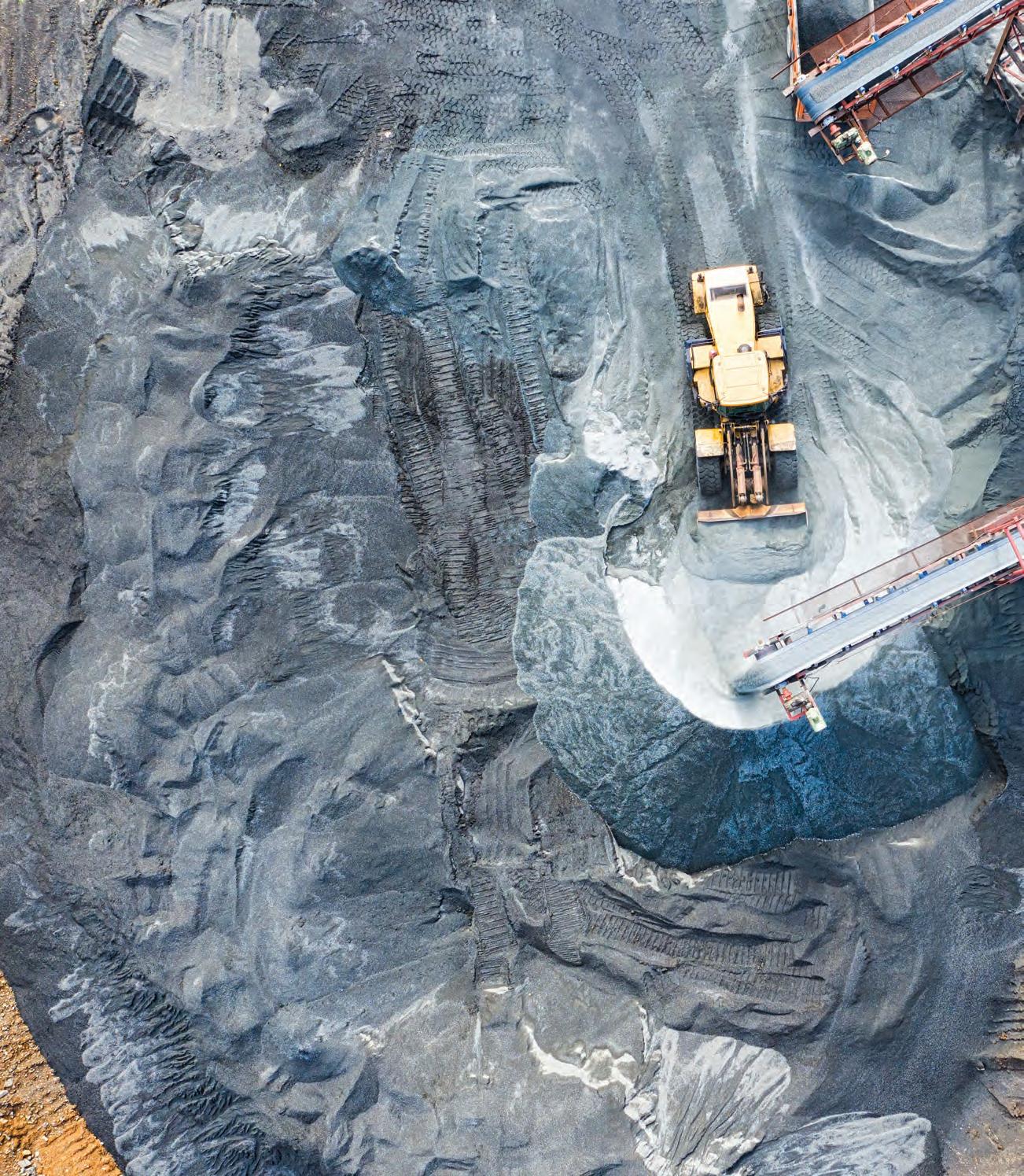