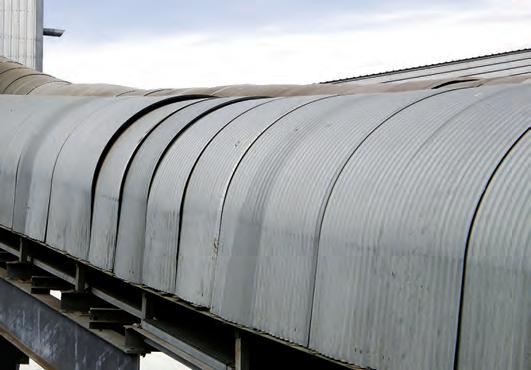
7 minute read
Maintaining belt conveyors
talk
STEVE DAVIS In his regular BULKtalk column, Steve Davis considers the basics of bulk handling that sites often struggle with. Steve has worked in bulk handling for 30 years, for both resource companies and professional engineering firms, in Australia, South Africa, the Middle East and Canada. His experience encompasses such commodities as iron ore, coal, potash, phosphates, petcoke, sulphur, sands and grain.
Maintaining belt conveyors
In the September edition of ABHR, Steve Davis considered the many different types of condition monitoring equipment for conveyors. In this edition of BULKtalk, he examines how the industry can make conveyors more maintainable.
CONDITION MONITORING
SYSTEMS can be installed on existing conveyors to observe, predict, and indicate potential equipment failures.
Predictive maintenance and planned repair are possible and provide the opportunity to get the best possible productivity from these machines.
So far, the only automated online replacement is for idler rolls. This technology seems to be a real possibility, but there are limitations and from review will likely be most effective if the conveyor system is designed specifically to match the replacement method.
In most situations, idlers and all other components will need to be replaced using traditional manual methods. Although some components have been known to last for many years, this is not the norm. Most conveyors will need to be regularly shut down to allow
Covers bolted in place no access to idlers. component change.
The prime consideration should be safety and environment. This results from a combination of initial design and work processes. The better the initial design, the easier the work processes and generally quicker repairs can be made, costing less, and getting conveyors back in service quickly.
Unfortunately, I still see many new conveyor designs that have scant consideration for maintenance. Is this because knowledgeable Operational Readiness (OR) and maintenance personnel are not engaged early enough or do not have sufficient authority? Is it because the concepts are not embedded in the projects from the onset and require additional time and engineering budget to change when identified in workshops? We are certainly improving but there is a long way to go. Rotability of components, especially in chutes, seems to be widespread but having a rotable component that is unsafe or very difficult to exchange is an incomplete concept. Given that shutdown time is always premium time, additional pressure from complex methods and poor access and extended time increases the likelihood of accidents.
As examples: • We can monitor the condition of conveyor pulley bearings such that planned change is implemented before failure, but
long after a scheduled change based on operating hours. - If the plan is to change bearing in-situ and there is poor man access needing scaffold, no consideration of how to remove the bearing, no spare bearing in the spares list we may have an extended and potentially unsafe and expensive bearing change. - If the plan is to rotate the entire pulley for shop repair, and design of the conveyor requires that the belt be cut, structure be modified and complete disassembly of a chute using a large mobile crane due to poor site access, is a four-day outage and an unnecessary resplice or two a good result? • We can monitor idlers and identify when to change rather than waiting for failure. Idler change should be relatively fast with conveyor matched to a good belt lifter and easy access. - Idler change is more complex and time consuming if there is poor access, if roof/cover panels must be removed and the stringer section and arrangement doesn’t match any available belt lifter. The need for additional time and equipment can delay change until roll failure occurs and beyond to where belt damage occurs, and the benefit of monitoring has been lost.
• Rotable sectional chutes are more common in new design, however they are sometimes poorly considered.
Most chutes are semi-vertical, and this dictates a series of stacked chute sections. - Each section must be removable relatively easily. Chute sections with heavy liners might weigh several tonnes and need to be moved horizontally before being craned onto a flatbed. How will it be rigged, where will the crane and flatbed be stationed, and is the size of crane available? - Does the structure have clearances for access without being dismantled?
Is the structure designed for rigging as required and with rated lifting points, rails and rollers etc. Some loads will be eccentric compared to normal operating loads. - What must be removed for rotability? Skirts, cleaners, sprays, pipework, electrical cables etc. Many rotable chutes acquire cable trays and pipes as these are added in the detail design or during construction.
Anything that must be removed adds time and risk.
Are we able to change conveyor design to a more practical approach that would see safer, operable, and maintainable systems? Is the current methodology of basing new design on much of current designs still acceptable? Can we integrate provision for good protection, excellent access, and real maintenance consideration from the onset rather than amending and adding as we progress through the various workshops and run out of time and money to make changes?
Should we engage fully and early with the customer and OR team to understand what can be supplied to assist with operations and maintenance, and what is required, perhaps a menu of options for inclusion in the design basis? Should we update our base concepts for conveyor design to focus on safety and O&M, remembering that we design once (with a few iterations), install once, but the system must be operated and maintained 24/7 for 20 plus years? We have been re-iterating ‘conventional’ designs for many years with minor changes; can we do better?
The approach taken on a recent large iron ore project in WA was a significant improvement on previous projects in the same group. The design team was fully integrated with the customers team. The OR team was on board at the start. Every aspect of the project was reviewed for operation and maintenance access and many good things were incorporated. Is this happening elsewhere perhaps?
Early in the conveyor design we should be considering at least the key safety and O&M aspects that are required. These issues are all common to all conveyors and should be fundamental to designs. Involve personnel that understand maintenance. For example: • What is the minimum access for people, what size cranes will be available, what are the maximum individual weights that can be lifted with available cranes? • What guarding system will be used, will it be perimeter style or close, will it be a maintenance free plastic system or angle and mesh? How will they be removed and stored? • What allowances and access are required to maintain and replace the key items that keep a conveyor functional in the safest and simplest manner; cleaners, skirts, wear liners, chutes, idler rolls, pulley bearings, pulleys, belts, drives, lubrication. If simple solutions are not possible for some reason, what is the fall-back option? • What systems are to be used to monitor condition and how will they be installed? • How will cables be run and where will racks be located? • What will be standardised across the site? • What environmental management methods are to be used? Do we still rely on crude water sprays for suppressing dust and can structural surfaces be orientated to shed accumulation?
As design progresses, we should be looking in more detail at the finer points, for example: • Check that all components are still accessible and removable as above. • Have structures designed for best access and to allow for removal of components. • Are there too many bolts holding flanges together? Is it possible to safely access all bolts and nuts? Is it possible to turn the bolts and nuts with standard tooling? • Are all maintenance points safely accessible, especially for regular online access? Can all local instruments and controls be accessed safely.
Scaffold may be safe, but it is expensive and adds significant time to maintenance. Elevating platforms may be acceptable but must be available and have safe access to the location. 20 years ago, in another country, one of the major conveyor manufacturers supplied me with a conveyor system that included a detailed set of drawings and a manual that covered all main maintenance stages. Every pulley on the system had a detailed methodology for removal without cutting the belt. This was standard with supply.
More recently, also in another country, another of the major suppliers has gone further and animated the maintenance needed in a large conveyor system. The methodology is clearly shown in 3D. On another overseas project, the how to maintain design was clear from the onset.
I would like to see this type of maintenance attention more available in Australia, including incorporation of more of the excellent safety and condition monitoring systems we have available.
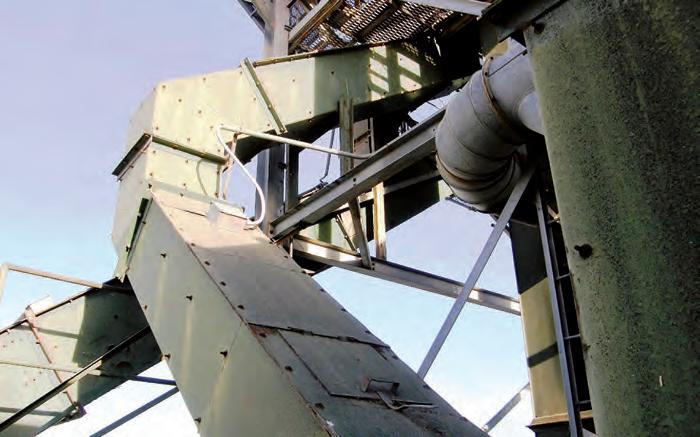
No access to chute liners, inspection hatch or instruments.