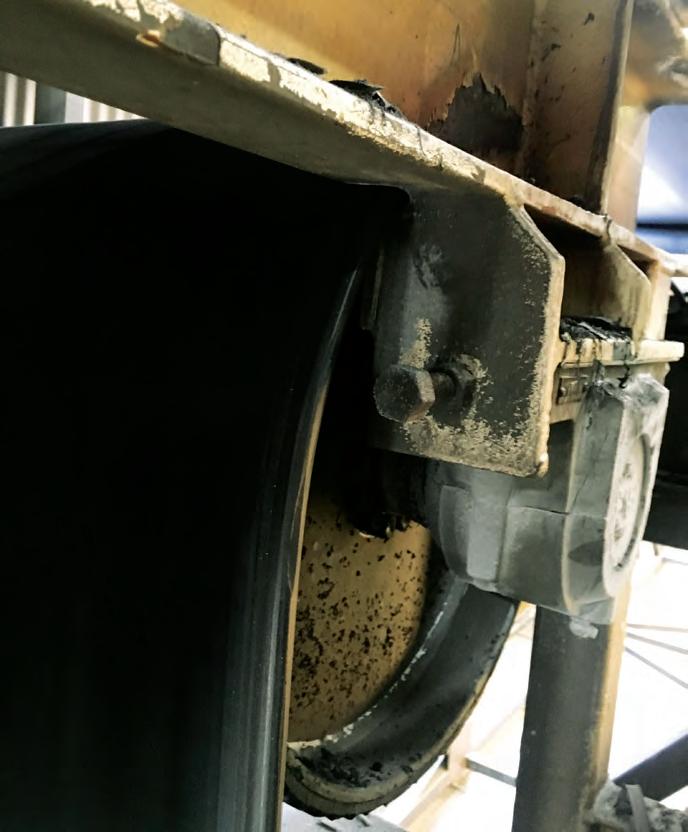
4 minute read
Common causes for conveyor maintenance
Troy Skippings, All Rubber’s Bunbury Area Manager, tells ABHR about some of the common problems plaguing conveyor systems, and what can be done to stop them.
TROY SKIPPINGS HAS BEEN
SPLICING belts for around 15 years. During that time, he’s seen how the bulk handling industry, particularly in Western Australia’s south has developed.
One of the biggest problems he has seen companies deal with is mistracking and belt slippage.
“Mistracking can cause serious damage to the belt and the surrounding
A conveyor belt can cut through steel if not properly maintained. plant. I’ve seen conveyors that have cut through the metal structure around it – the belt being under tension whilst running, can slice through steel,” he says.
“As far as damage to the belt goes, it can delaminate the belt carcass and covers or tear or damage the splice, which can lead to total belt failure.”
Skippings is the Area Manager for conveyor belting specialist, All Rubber. For the past 10 years, he’s been in a managerial role at the company, helping to manage branches, support fly-in fly-out crew and runs the Bunbury, WA branch.
He says another major problem that has been appearing recently is a lack of upkeep of the overall conveyor system, including components such as rollers and scrapers.
“It’s hard to pinpoint the exact causes, but in the areas I work around, a lot can be attributed to a focus on more production as well as a lack of routine maintenance,” he says.
“There’s a lot more demand for higher outputs, but many systems aren’t being upgraded to sustain this. I’ve seen 200 tonne/hr systems now handling 400 tonnes/hr without anything but the motor speed changing.
“With COVID, there’s now also been issues with a lack of personnel in the industry, which makes it harder to source people to schedule shutdowns and prioritise maintenance.”
Worn down equipment can have devastating flow on effects for the rest of a system. If a roller seizes, it can act almost like a knife edge for the belt running on top of it, significantly damaging one of the most expensive parts of the system. Additionally, if scrapers aren’t performing as intended, they can put additional pressure on the drive, as more carryback is experienced.
The point where a small problem can escalate into a major one is also highly variable. Skippings says there have been some belts that have had larger cracks in them that have lasted half a year and others that have had a small nick that grew rapidly in just half a day.
Catching these problems early is critical, and is part of All Rubber’s service offering. The company has a team of
Troy Skippings, All Rubber Area Manager.
fully trained and experienced specialists that have all the necessary equipment to inspect and repair conveyors.
All Rubber can help with all types of breakdowns, from small belt repairs and replacements to large shutdowns and belt change-outs. It is equipped with enough resources to service multiple sites at the same time, 24 hours a day and seven days a week.
Regular checks and maintenance work is a core part of this offering, and aims to prolong the service life of the machinery. Skippings says All Rubber’s technicians can help reduce the likelihood of a breakdown significantly, so that customers can run their businesses smoothly with no unforeseen hiccups - early intervention is key.
Steve Cross, Reliability Supervisor at chemical supplier CSBP says the team at All Rubber helped solve issues the company was having with a conveyor belt in its Fertiliser Super Manufacturing Plant.
“The super phosphate we were conveying is extremely abrasive and was wearing our conveyor belt so much that it was being replaced on a monthly basis,” he says.
“The team at All Rubber came up with a solution and advised us to use their Eagle Maxx Tuff belt with extra CU compound. Now the belt lasts over 12 months or more, which is a huge cost saving to CSBP. They are a very customer focused group, and I would recommend them to any client.”
Skippings says providing a fast response time is critical for companies in the bulk handling sector.
“In a breakdown situation, when a belt goes down, a plant goes down,” he says. “The sooner we get there, the better.”
To provide rapid response capabilities, the company has nine branches located throughout Western Australia. This allows teams to quickly get to sites and helps to build a relationship with the staff there.
A lot of focus goes into this local support, which All Rubber prides itself on. Skippings says it allows the team to know what customers need, making it easier for all involved.
“We’re going to keep growing stronger and cement our footprint in the bottom half of Western Australia,” he says.
“There’s lots of exciting times ahead, as we’re pushing into more rubber lining products and have recently established new branches in Geraldton and Kalgoorlie to support the region.”
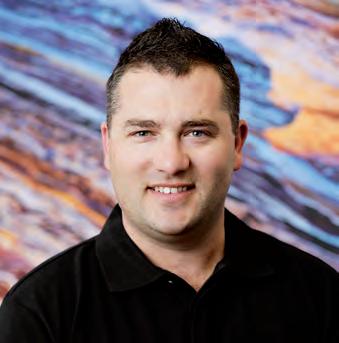
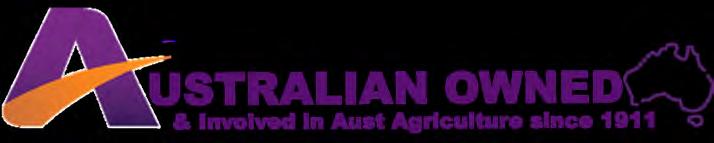
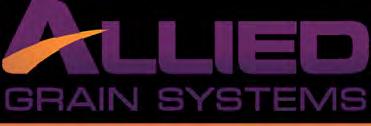
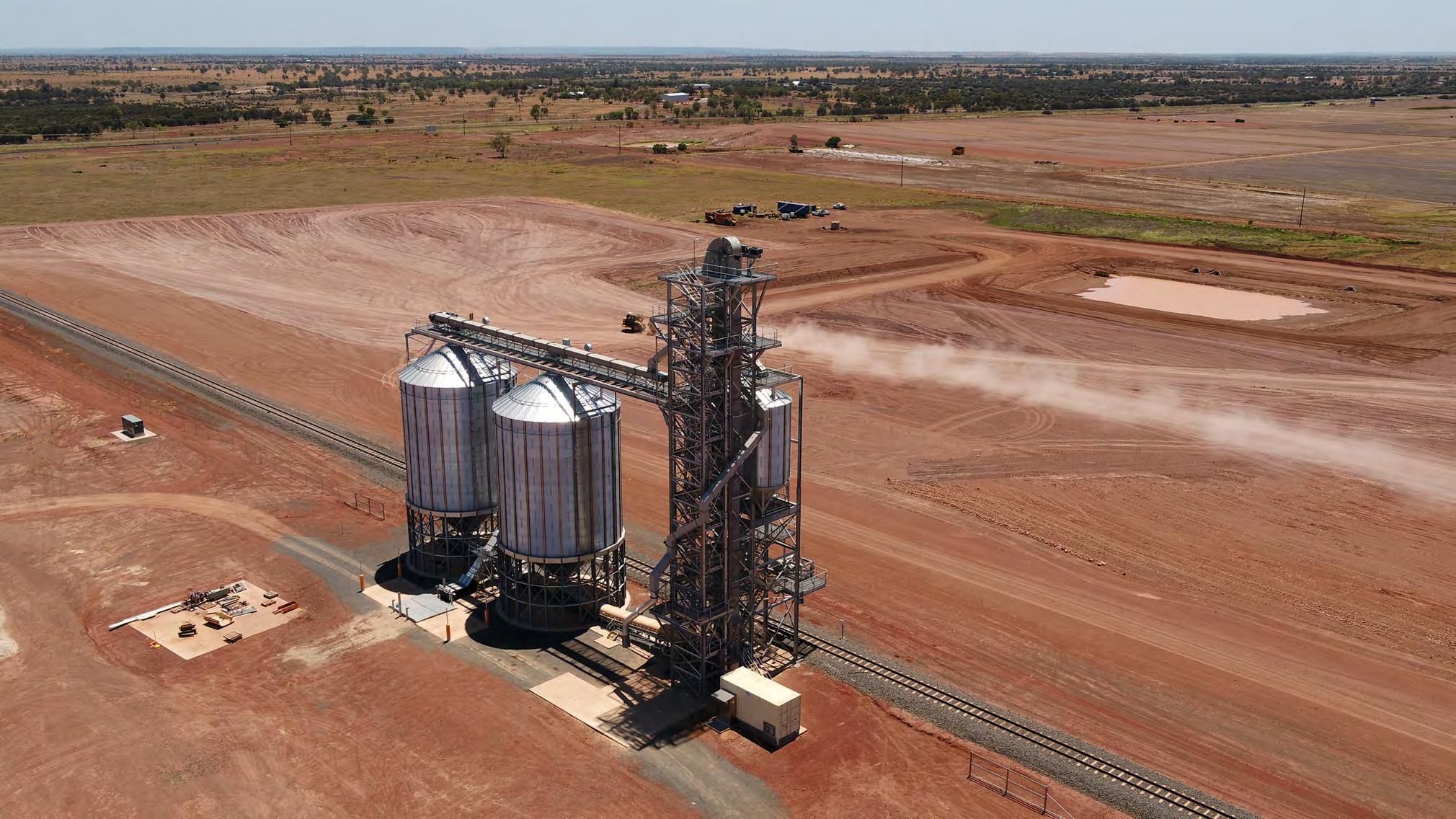