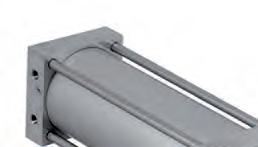
2 minute read
Vortex Global weathers the storm
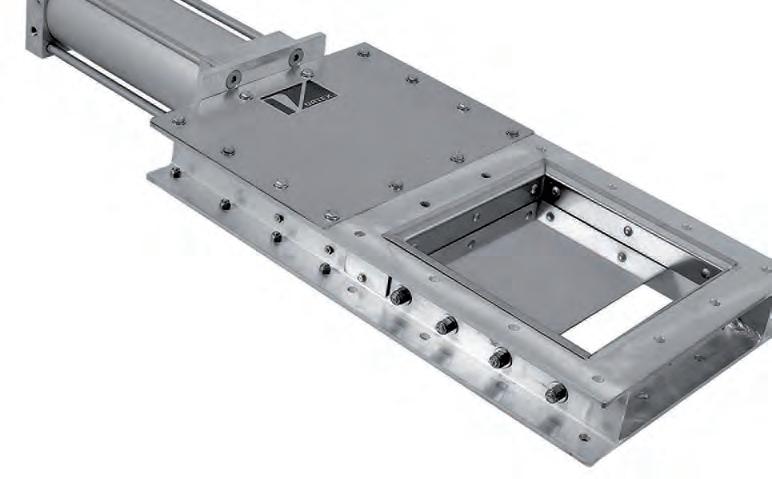
Vortex designs its systems to keep dust limited and can customise its products to fit the application.
Grain can be highly abrasive and releases explosive dusts when handled. Laurence Millington, Managing Director of Vortex Global explains how the company’s equipment excels in this environment.
DEPENDING ON HOW IT IS
CONVEYED, grain can naturally wear equipment away with its highly abrasive nature.
As equipment wears, its service life shortens, maintenance requirements increase, and potential profits are cut into.
Laurence Millington, Managing Director of Vortex Global, says providing robust equipment – whether it is manual or pneumatic – is core to the company’s values.
“When it comes to grain handling, abrasion is one of the major issues, which is why we use a carbon steel material and other materials with abrasion resistance to ensure equipment continues to function.”
This abrasion resistance provides Vortex equipment with significantly longer lifespans. In 1996, the company worked with an animal health company called Alltech in Kentucky, in the United States.
Vortex installed its roller gates at Alltech’s facility, and have required minimal maintenance, other than the replacement of a set of bonnet seals on one of the gates.
“After 24 years of service, we needed to pull one of the gates as it began leaking around the seal,” says Robert Stuart, Maintenance & Facilities Manager at Alltech.
“After dismantling the valve, we were awestruck on how well it looked and held up over the past 24 years as our products are abrasive and have severely worn down many other pieces of equipment over the years.”
The Vortex Roller Gate is designed with several replaceable parts, including blade, clevis, internal seals
The Vortex Roller Gate is designed with several replaceable parts, allowing them to remain in service for decades. and retainers, actuator, position indication switches, and more. If a slide gate is maintained and operated as recommended, these mechanisms should be the only wear parts. In many cases, this maintenance-friendly design has allowed Vortex slide gates to remain in service for many years – and sometimes, even decades.
“When I joined the company around 12 years ago, there was an understanding that machinery needed not only to be easy to install, but easily maintained as well,” he says.
Handling grain also produces explosive dust, which can have disastrous consequences if not properly managed. For that reason, Vortex Global ensure all of its equipment is ATEX and IECEx rated.
Millington says dust doesn’t only pose a risk from explosions.
“Dust migrating on a worksite can build-up, creating hazardous areas in a plant,” he says.
“It can also migrate away in a loading system, potentially causing issues for the nearby environment or neighbours.”
Vortex designs its systems to keep dust limited and can customise its products to fit the application.
Millington says Vortex can provide additional support and maintenance through its local representative, the Brolton Group.
“We offer full sets of spares, fast shipping processes and stay easily contactable to answer any questions,” he says.
“With COVID-19, we can’t visit sites as much as we’d like to, but can still provide support online.”
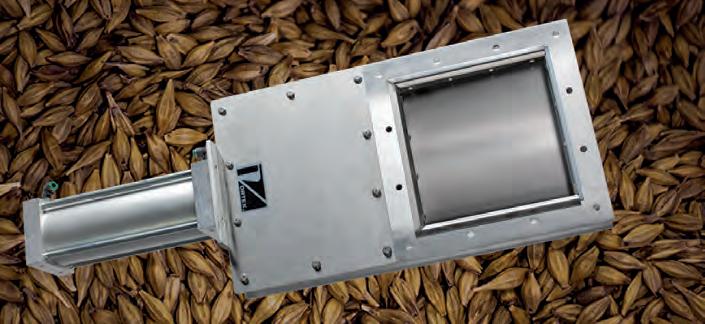