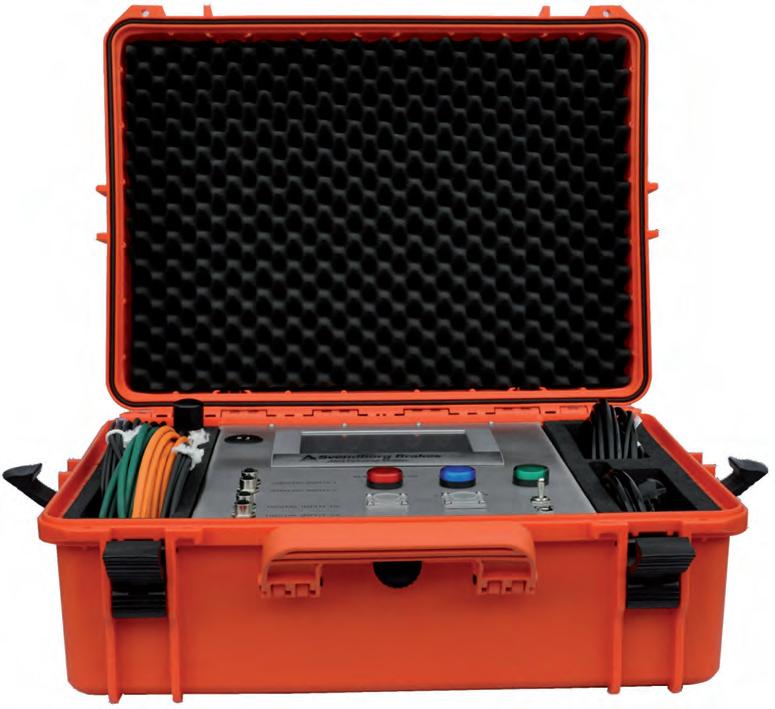
4 minute read
Back in control
Svendborg, an Altra Industrial Motion brand, has developed a case that enables its experts to commission conveyor brakes from their desks.
THE COVID-19 PANDEMIC HAS
thrown a spanner into Altra Industrial Motions’ maintenance and installation plans across conveyor sites, as new safety restrictions limit who can attend a site.
This created a conundrum for Altra Motion which would typically support its customers with face-toface commissioning.The company’s Svendborg Brakes experts ensure the company provides the best service quality possible.
COVID-19 and mobility restrictions threatened this capability, which is why it developed the Universal Control Case (UCCase). The case is a smart technology service tool that enables the remote monitoring of product performance and can help provide insights for maintenance assessment.
Importantly, it allows remote support on standard and SOBO Svendborg Brakes during commissioning and service.
Christoffer Bjerremand, Project Manager for the Svendborg Brakes UCCase, says the case is simple to hook up, requires no training and can be done
Experts can use the UCCase to diagnose brake system behaviour with analytical models. The UCCase is compact and can support high-quality brake commissioning.
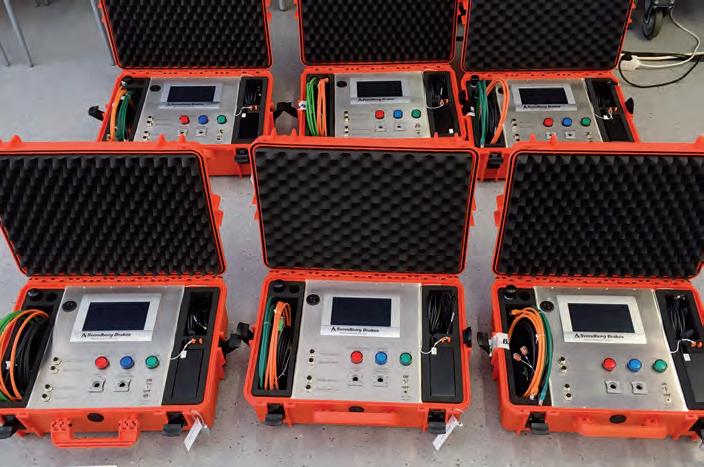
by following instructions in the manual.
“We can send the case to a customer; they connect it to the SOBO PLC and use their phone to connect it to the internet,” he says.
“From there, the sensor sends signals to the cloud, and our team of specialists can take over, using complex algorithms to troubleshoot any faults in the system.”
Altra Motion Australia’s experts, through the UCCase, can diagnose brake system behaviour with analytical models, which they can use to provide advice on which actions to take to prevent a malfunction.
It has already proved immensely useful. For example, in 2020, a customer in Belarus needed support for commissioning. However, due to COVID-19 restrictions and political instability, it wasn’t easy to arrange for a technician to visit the site.
Bjerremand says the project was extensive and couldn’t afford to wait, so Svendborg sent the UCCase.
“Instead of our technician being there, he was at his desk while the customer’s onsite technician used the case to give us remote access.”
The technology has been designed to be backwards compatible and can even work with SOBO units that are decades old.
A drilling ship had a 20-year-old SOBO system that needed planned maintenance at a harbour in Italy. Unfortunately, the customer uninstalled the old system, and a technician was supposed to arrive onsite to reinstall a new one.
Bjerremand says any drillship in downtime is a costly exercise and should be avoided.
“During COVID, we could not travel but it was only going to be in port for only so long. So, because we only had a short window of time to act, we hired out the UCCase for one of their service technicians to operate,” he says.
“Our engineer stayed in close connection with the customer’s local service technician and was able to remotely monitor the situation and guide him onsite to reinstall the old SOBO.
“The data from the UCCase showed that the valves of the hydraulic unit were worn out and needed replacing.”
After the successful remote service check-up, the customer replaced its SOBO system with the latest IQ version. This version can be permanently connected to a Svendborg Brakes cloud, making it possible to constantly measure the behaviour of the brake system and avoid unexpected downtime.
Svendborg Brakes plans to continue developing the case and adding new functionalities, such as an integrated computer running a local cloud. This would allow the case to function independently from the internet in areas such as mine shafts with a poor internet connection.
Altra Industrial Motion’s UCCases are available and ready to support this remote IIOT technology to Australian and Oceanic customers for commissioning, predictive and preventative maintenance.
Svendborg’s SOBO IQ system
The SOBO IQ is a closed loop-controlled system that gives operators constant stopping times and distances. It acts on the gear drives, applying a torque based on the stopping time irrespective of the loads on the conveyor to stop it in a controlled manner. Using a speed reference signal taken from the coupling bolts and a pressure feedback loop, the SOBO IQ can accurately predict what the braking system needs to stop the conveyor. Stopping too hard can cause the material to spill or damage to the belt itself, often one of the most expensive pieces of equipment. The SOBO avoids potential flowon effects, such as blocked chute overflows and gives operators greater control over how the equipment will work. The SOBO control system has a backup that will kick in even if there is a complete loss of power resulting in a safe controlled stop.
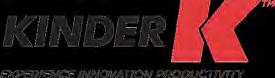
We’re reaching new heights in engineering. The sky’s the limit.
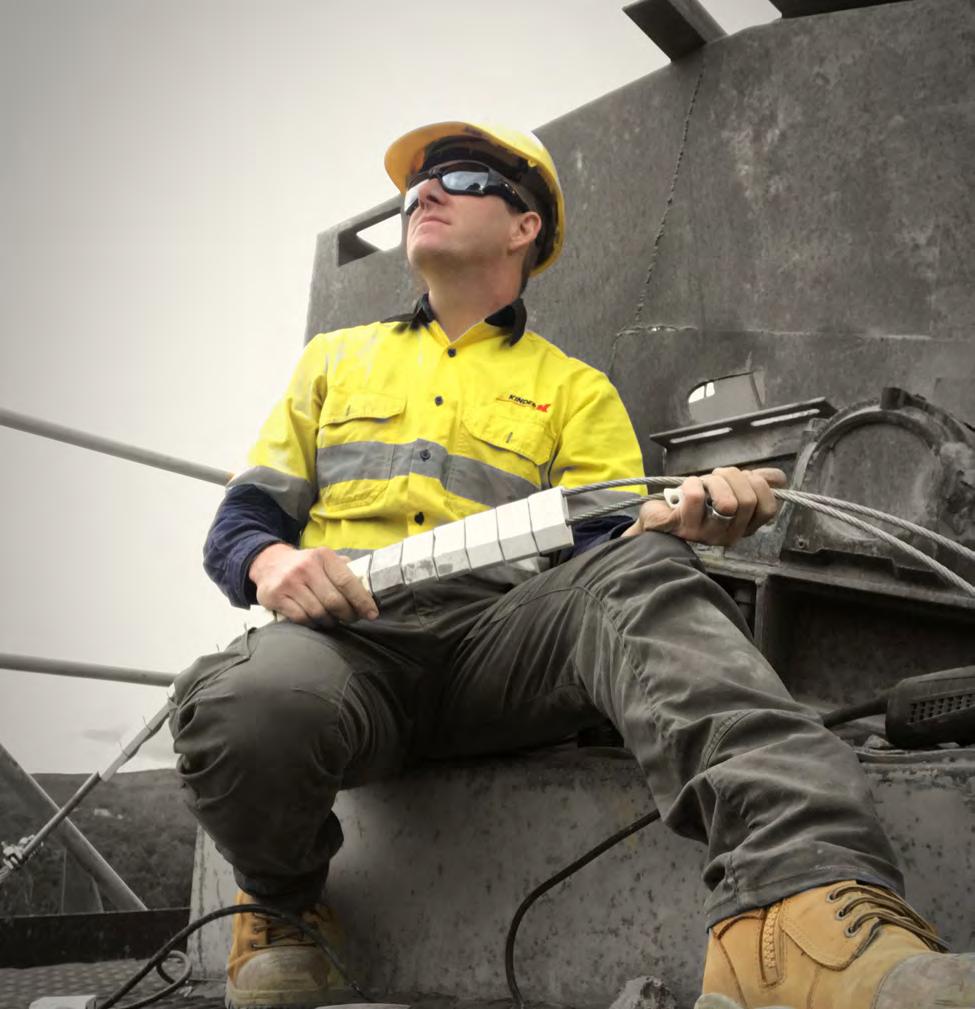
With decades of experience in the field, Kinder Australia supply superior products designed in-house and manufactured from high quality materials to improve your conveyor efficiency.
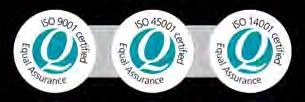