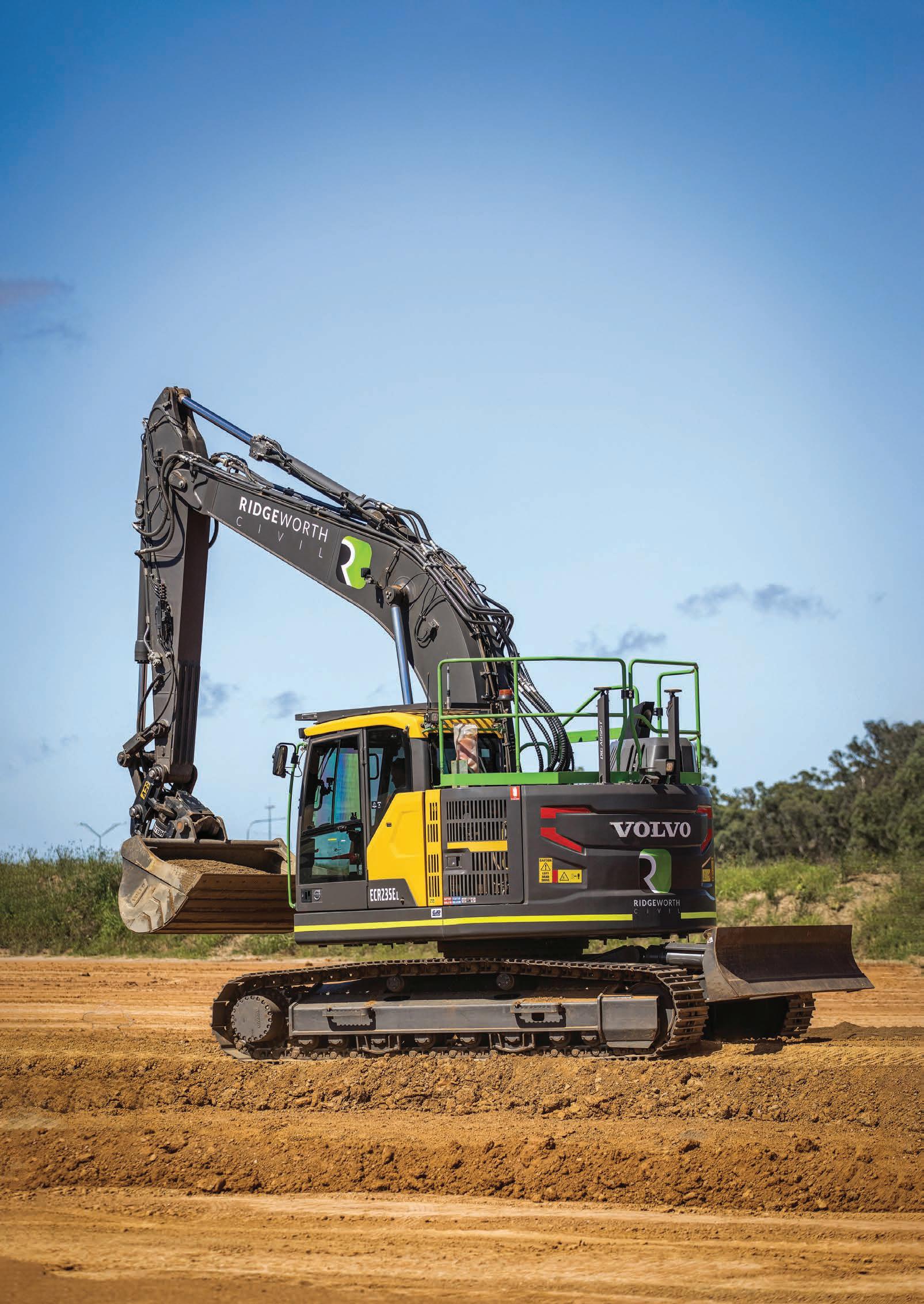
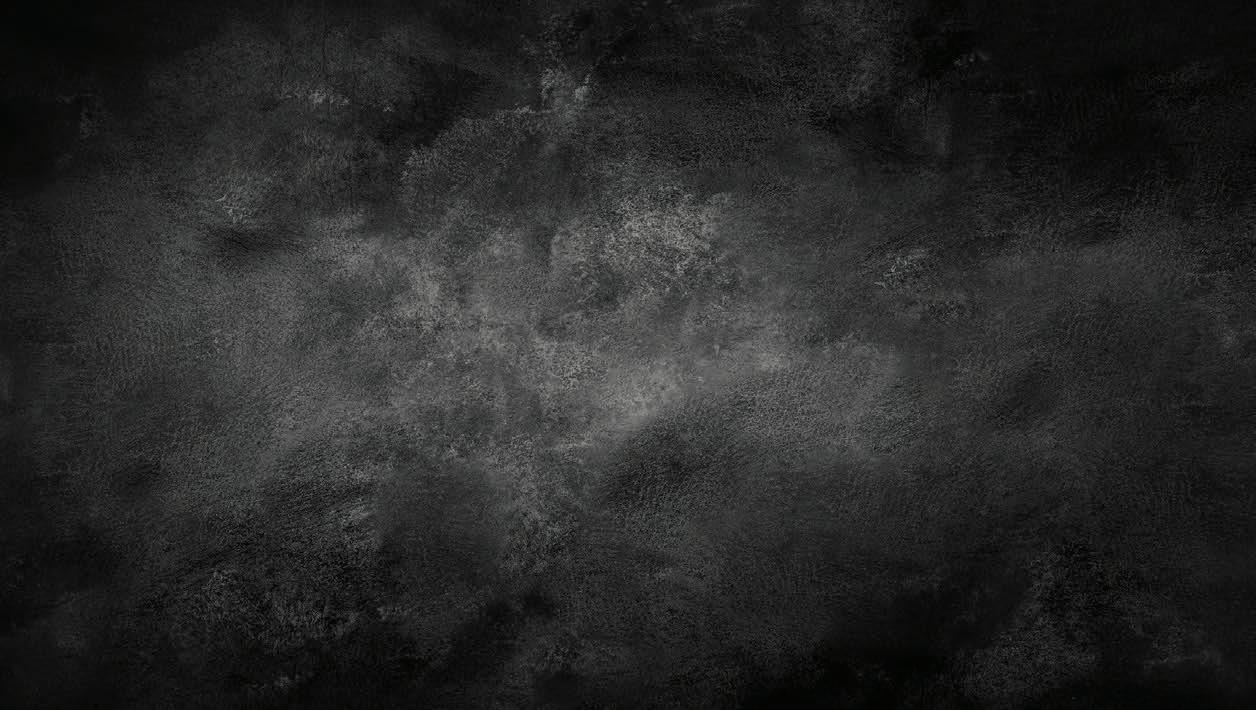

Komatsu’s utility excavators are compact, yet powerful machines designed to carry out a wide range of tasks across a variety of industries. Our exclusive closed-centre hydraulic technology delivers big excavator performance in a small package. And every Komatsu excavator, no matter how small, is covered by our free Komtrax remote monitoring system for complete peace of mind.
The tapestry of the earthmoving industry is woven with threads of unwavering loyalty. Those in our profession, not only in the vast landscapes of Australia but also in every corner of the globe, have stories to tell. Stories that often begin and end with their trust in a single brand.
Such brand loyalty is not mere nostalgia or resistance to change. It is the result of years of experience, countless projects, and the memories of machines that have weathered storms and withstood the test of time. For many, the logos on these machines represent more than a brand; they are symbols of reliability, of days gone by and of projects successfully completed. They stand testament to the very spirit of our profession – a testament to hard work, persistence, and trust.
But what truly makes this industry special is not just the depth of this loyalty, but the mutual respect that underpins it. Our leading manufacturers, well aware of the commitment that professionals show to their brands, never take this loyalty as a given. It’s a bond that is earned, not just once, but every day.
These OEMs, ever in pursuit of excellence, don’t merely rest on their laurels. They understand that behind every piece of machinery is a team of individuals relying on it. They recognise the weight of the responsibility they carry – to support every project, to ensure that every machine performs at its peak, and to stand by their customers through thick and thin. It’s a two-way street.
And so, OEMs go out of their way to support their customers. They invest in research and development to enhance machine reliability and performance. They provide training to ensure that operators can get the best out of their machines. They o er after-sales support
that goes beyond the expected, often transforming customers into lifelong partners along the way.
In our cover story, we visit with the long-time Volvo fans at Victoria’s Riordan Grain Supplies, where a huge fleet of 13 Volvo wheel loaders are doing the heavy lifting, helping the business move vast quantities of grain from field to table.
Loyalty runs deep at Becketts Mining & Civil in northern Tasmania, where Cat® dozers have been the business’ bread and butter for decades – a legacy that continues with the purchase of a new Cat D6 XE. Meanwhile in Adelaide, Rock Cutter Earthworks’ pairing of a Cat 272D3 XE Skid Steer Loader and a Cat SW480 Wheel Saw has taken the business’ rock cutting ability to another level. The EEM team also visits Cat dealer William Adams in Victoria to see the brand-new Cat AP400 wheeled paver in action.
Tasmania’s Zanetto Civil has recently gone bigger than ever with the purchase of a 38-tonne Kobelco SK380XD excavator, which is helping the family business break into new markets, while maximising productivity and e iciency.
Speaking of productivity and e iciency, that’s what’s driving equipment hire company Big Chief Hire’s fruitful relationship with lubrication specialists Alemlube. We visit Big Chief’s Adelaide headquarters to see how it all works. Finally, EEM also goes deep into our feature topics, exploring the latest and greatest in excavators, accessories, and attachments.
Happy digging!
The 38-tonne Kobelco SK380XDLC-10 represents a new direction for Zanetto Civil.
Mark O’Donoghue
Mark O’Donoghue is the CEO and founder of Finlease. Financing over $700mil p/a in equipment finance for private business owners in Civil and related industries.
A family business with a nationwide network, Finlease has a 30-year track record of establishing long term relationships with clients, finding them the best finance solutions to support their business growth. The company’s goal is to make the finance process simpler for businesses so they can focus on what they’re good at.
Scott Lidster
Scott is the Director of Australian Earth Training, a niche operator proficiency training organisation who work across the globe. He has over 25 years’ experience in heavy equipment operation and was an accredited Caterpillar Dealer Instructor (CDI) Trainer-Demonstrator. Scott’s unique skill set enables him to operate and train on a broad range of machines across the mining, construction, quarrying and waste industries, helping his customers to boost their productivity while lowering their owning and operating costs.
Ann has been the Manager of Allied Earthmovers Association for the past 19 years bringing many years’ experience into the role. After gaining business qualifications and managing a retail shopping centre in Sydney CBD, Ann first started her career in earthmoving when she joined the long-established family business in Penrith, which specialised in Caterpillar graders and dozers. Working in a male-dominated industry, Ann brings a di erent aspect to the Association. She has met many people in the industry and knows what the owner operator needs, from the importance of paperwork to machine availability. It’s an industry she respects and is proud to be a part of.
Earthmoving Equipment Magazine is published bimonthly by Prime Creative Media Pty Ltd.
CEO John Murphy
COO
Christine Clancy
Sales Director Bradley Buchanan Editor Leon Cranswick leon.cranswick@primecreative.com.au
Brand Manager
KahChi Liew kahchi.liew@primecreative.com.au 0421 474 407
Production Editor Michelle Alder michelle.alder@primecreative.com.au
Art Director/Design
Daz Woolley, Cat Zappia
Subscriptions
P. +61 3 9690 8766 subscriptions@primecreative.com.au
Website www.earthmovers-magazine.com.au
Copyright Earthmoving Equipment Magazine is owned by Prime Creative Media and published by John Murphy. All material in Earthmoving Equipment Magazine is copyright and no part may be reproduced or copied in any form or by any means (graphic, electronic or mechanical, including information and retrieval systems) without written permission of the publisher. The editor welcomes contributions but reserves the right to accept or reject any material. While every e ort has been made to ensure the accuracy of information, Prime Creative Media will not accept responsibility for errors or omissions, or for any consequences arising from reliance on information published.
The opinions expressed in Earthmoving Equipment Magazine are not necessarily the opinions of, or endorsed by, the publisher unless otherwise stated.
© Copyright Prime Creative Media, 2023
Articles
All articles submitted for publication become the property of the publisher. The editor reserves the right to adjust any article to conform with the magazine format.
Head O ice 379 Docklands Dr, Docklands VIC 3008
P: +61 3 9690 8766 enquiries@primecreative.com.au www.primecreative.com.au
Sydney O ice Suite 3.06, 1-9 Chandos Street Saint Leonards NSW 2065, Australia
P: +61 2 9439 7227
Precision, e iciency, and safety are paramount in the ever-evolving world of construction and excavation. In this dynamic landscape, the Volvo ECR235E excavator emerges as a symbol of innovation, setting new standards for excellence in the industry. This remarkable machine, equipped with optional Volvo Co-Pilot technology, represents the future of excavator operations.
The Volvo ECR235E excavator is equipped with a robust Volvo Stage V D6J engine, boasting an impressive output of approximately 173 hp (129kw). This excavator o ers a versatile range of operating weight, spanning from 25,400kg to 27,200kg. Additionally, its bucket capacity is adaptable to various configurations, typically within 0.6 to 1.2 cubic meters, ensuring versatility to meet diverse job requirements.
One of the standout features of the Volvo ECR235E is its short-swing functionality. Traditional excavators often have long counterweights that extend beyond the tracks, making them less manoeuvrable in tight spaces. The ECR235E, however, boasts a compact design with a reduced swing
radius, allowing operators to work e ectively in confined areas without sacrificing power or performance.
The increased safety and manoeuvrability o ered by the ECR235E short-swing excavators on congested worksites has rapidly created an essential market segment. Today, these versatile machines are put to use on various applications, including utility work, mining and forestry, and general construction.
The ECR235E enables operators to work e iciently in spaces where a conventional excavator would struggle to operate. This feature saves time and minimises the need for additional equipment to access narrow job sites.
The ECR235E excavator is a testament to Volvo's commitment to operator comfort and e iciency. Its ergonomic and spacious design allows operators to work comfortably during extended hours. The cabin layout prioritises intuitive controls and placement, reducing operator fatigue and optimising productivity. The large windows and cleverly positioned mirrors provide exceptional visibility, ensuring
operators can maintain a clear view of their surroundings, enhancing safety and control. Moreover, the rounded shape of the cab is also designed to stay within the rear swing radius, yet remains among the roomiest and most comfortable in the market – as befits Volvo's reputation for providing superior operator comfort.
The machine's advanced hydraulic system operates quietly without compromising power or performance. Volvo's load-sensing hydraulic system combined with its unique ECO mode, Volvo excavators deliver low fuel consumption with high digging power and fast cycle times. The ECO mode reduces fuel consumption by up to 10 per cent without any performance loss in most operating conditions, while the loadsensing hydraulics supply power only when required.
The automatic idling system and automatic engine shut-down function further enhance e iciency by reducing engine speed and shutting down the engine when the controls or machine have been inactive for a pre-set amount of time.
In addition, sound-absorbing materials and innovative engineering techniques have been employed throughout the excavator's design to
How Volvo’s ECR235E short-swing excavator with Co-Pilot technology is setting new standards for precision and e iciency.The Volvo ECR235E’s reduced swing radius allows operators to work e ectively in confined areas.
Dig
minimise noise emissions. This design creates a more comfortable working environment for operators and reduces the impact on the surrounding community, making it an excellent choice for projects in urban areas.
A quieter machine also contributes to improved fuel e iciency. With less noise, operators can better monitor the engine's performance, reducing fuel consumption and lowering emissions. In an era where
environmental concerns are at the forefront, the Volvo ECR235E's noise reduction features make it a responsible and eco-friendly choice for construction professionals.
Unlocking precision and e iciency with Volvo Co-Pilot
For companies like Ridgeworth Civil, staying at the forefront of technology is essential for e icient and flexible work on any job site. Tom
Langridge, the Owner/Director of Ridgeworth Civil, says his experience with the ECR235E and Volvo Dig Assist technology is a testament to the transformative power of innovation in Volvo Construction Equipment (Volvo CE). When Tom decided to purchase his first ECR235E from CJD Equipment Brisbane, what truly sealed the deal for him was the incorporation of Volvo GPS hardware as a standard feature. The integration of GPS
functionality and the cutting-edge Dig Assist technology were pivotal considerations for Tom.
“Having all the essential information right at your fingertips on the screen is simply unmatched in terms of e iciency,” Tom explains. “It also saves on sta ing. With this technology, you can spread your guys across various sites rather than having extra people string lines or use a laser.
“There's no need for a spotter during excavation, as the screen provides precise height information. In my perspective, the future of enhanced e iciency undoubtedly hinges on technological advancements like these.”
Volvo Co-Pilot is the latest intelligent and intuitive technology from Volvo CE. This interactive display allows operators to manage all excavator functions quickly and easily from
a single in-cab system, ensuring the highest e iciency and accuracy in any application.
Whether digging trenches or loading heavyduty material, Volvo Co-Pilot o ers exceptional control, ensuring thorough accuracy and uptime. The generous high-definition 10inch touchscreen features selectable modes of operation to meet the needs of the task, programable joystick buttons and Bluetooth connectivity.
Volvo Co-Pilot also integrates with Volvo Assist, including Dig Assist, Haul Assist, and Load Assist, and provides real-time operational data, resulting in a responsive, harmonious, and highly e icient operating experience.
“The beauty of the Co-Pilot system is that applications can be loaded in a similar way to how you would download an app on a mobile phone,” says CJD Equipment's National Product Manager, Hayden Grant.
Volvo's Dig Assist technology
Volvo Dig Assist is a cutting-edge technology designed to revolutionise excavator operations, and it proves particularly advantageous in the context of the Volvo short-swing ECR235E excavator. This advanced system o ers operators comprehensive tools and features that enhance precision, productivity, and safety during excavation tasks.
One of the primary benefits of Volvo Dig Assist in the ECR235E is its capability to streamline digging operations with remarkable precision. The system provides real-time information and guidance, enabling operators to e ortlessly achieve precise depth, slope, and alignment requirements.
This level of accuracy is invaluable in applications where maintaining exact grades and contours is essential, such as utility trenching, foundation excavation, and
grading. By reducing the need for manual measurements and adjustments, Dig Assist significantly increases operational e iciency and minimises errors, ultimately saving time and resources.
Volvo Dig Assist: 2D technology
Volvo's Dig Assist technology has three levels, o ering a range of capabilities to suit various job requirements. First, the 2D mode is perfect for tasks such as site levelling and slope profiling. With real-time data feedback, operators can quickly gauge when they have reached target depths and slopes, eliminating the need for manual grade and level checks. This technology optimises safety and ensures high precision, faster project completion and reduced over/under excavation. Notably, 2D mode accommodates operators of all skill levels, assisting them to achieve higher levels of productivity with confidence.
Volvo Dig Assist: in-field technology
For more intricate projects, Volvo's In-Field Design mode takes centre stage. It uses GNSS and RTK navigation technology to deliver centimetre-level accuracy for excavation tasks. Operators can e ortlessly define complex shapes in three dimensions using the Volvo Co-Pilot tablet, eliminating the necessity for surveyors to mark out excavation sites. This streamlined process enhances e iciency, enabling operators to dig trenches and tackle intricate projects with unparalleled precision and ease.
Volvo Dig Assist: 3D and TopCon technology
Volvo's 3D mode is the ultimate choice for the most ambitious and large-scale infrastructure projects. With three-dimensional functionality
facilitated by TopCon and Trimble Earthworks for Dig Assist, operators can seamlessly import project designs into the Volvo Co-Pilot system. This integration simplifies the transition from blueprint to action, significantly improving productivity and operational e iciency. With its 2D, In-Field Design, and 3D modes, Volvo's Dig Assist technology empowers excavator operators to tackle a wide range of projects with unparalleled accuracy, e iciency, and confidence.
The Volvo Co-Pilot touch screen in the cab also has data logging and reporting capabilities, allowing operators and project managers to monitor and analyse job progress, which is crucial for optimising e iciency and
cost-e ectiveness. By providing valuable insights into machine performance and job site conditions, Volvo Co-Pilot technology empowers operators to make informed decisions, resulting in more e icient and productive excavations.
In collaboration with Volvo CE, CJD Equipment presents a formidable alliance that caters to your needs, ensuring that your machinery operates safely and at peak e iciency. With an expansive national support network, CJD Equipment stands ready to o er unwavering assistance, regardless of your location or the hour.
For many, acquiring a used machine may be the only viable option, but Tom emphasises the numerous benefits of establishing a lasting partnership with a trustworthy dealer.
“While personal preference plays a role,” he explains, “there are distinct advantages to having all your maintenance and parts and stu like that under the same banner. You've got to go with your gut instinct. I felt comfortable buying a new machine because it's under warranty and gives me a relationship with the dealer.
“I know I'll purchase more machines, so creating that relationship works in my best interests. It works in your favour when it comes to purchasing, servicing, getting parts in on time.”
So, whether you're considering your first purchase or looking ahead to future acquisitions, trust in the partnership between CJD Equipment and Volvo CE. This partnership goes beyond machinery, providing comprehensive solutions and unwavering support for your journey ahead.
JETLAND is a leading supplier of high strength & heavy duty Aluminium loading ramps in Australia. High quality raw material and safety testing systems ensure a safe and reliable product.
No manufacturing delays, all ramps listed online are in stock at our warehouse in Mordialloc, Victoria.
We can also supply Custom built ramps - made to your specifications for your particular needs.
Free Delivery
Australia wide.
When you run your own business or it’s your job to keep equipment running at its peak, time is precious. Using parts.cat.com not only gives you more time to do your job, it gives you more time to do other things in life outside of work. And who wouldn’t want more time to spend with family and friends doing the things you love?
To get the full benefits of parts.cat.com, simply register. The process, like the site itself, is quick and easy. Once you’ve registered, you’ll be connected with your local Cat® dealer. So every time you log in, you’ll have that expert support available when you need it. You can order parts any time, from anywhere, from any device – and have all the essential information on your Cat machines at your fingertips. It’s your 24/7 parts partner.
You can feel confident that you are getting the right parts and instantly access up-to-date maintenance information too. Just add your equipment by entering your machine’s serial number or scanning its QR code. Once you’ve added your machines, you can find genuine Cat parts designed to fit your Cat equipment.
The quick and easy way to buy genuine Cat® parts.
Scan
Order parts from anywhere, any time, and from any device with parts.cat.com.
You can also choose between picking your parts up from your Cat dealer or having them delivered. Thinking of doing your own maintenance or repairs? Planned Maintenance Kits and Self-Service Options give you everything you need to do the work yourself and can easily be ordered on parts.cat.com. Better still, you can customise them so that you only get the parts you need, together with step-by-step instructions, recommended tooling, and technical support. All of this makes scheduling maintenance and repairs easier, giving you more time for your time.
When you’re using parts.cat.com you get all the expert advice you need, when you need it, as well as real time pricing and parts availability. If a part is out of stock, parts.cat.com will give you an estimated availability time. And if you
ever need more information, you can always contact your Cat dealer. You’ll also have access to a dedicated support hotline via phone call or text, as well as downloadable parts manuals and instructions, and a comprehensive FAQ section.
There are even tutorial videos to help you navigate the site e iciently and make sure you have a great experience, whatever you're ordering.
So that’s parts.cat.com – it’s genuinely the quickest and easiest way to get genuine Cat parts, and expert support from your local Cat dealer. And of course, you also get what really matters: more time for your time.
Head to parts.cat.com today or contact your local Cat dealer for more information.
OTR Australia supply earthmover, agricultural, truck, bus and light vehicle tyres and rims from 6” through to 63” in diameter, to blue chip mining, civil contracting, road transport companies, agricultural dealerships and end users.
We maintain a healthy inventory of new and used earthmover tyres of critical sizes and have the ability to custom manufacture Australian Made wheels in 1 of our 10 locations Australia wide.
SALES PHONE 1300 791 672
For any enquiries please visit www.otraustralia.com
Komatsu’s Smart Construction Support Centre was established to give customers the best possible support experience across their Smart Construction product o ering, and since opening in April last year, has resolved more than 2000 customer inquiries.
The centre provides technical support, from machine set up, to operator training on the platform, and remote diagnostics in case of breakdown, as well as access to Customer Technology Advisors to contract out for specific projects that need a higher level of technological support.
Brent Parker, Komatsu Australia’s National Operations Manager – Smart Construction, says this type of support is one that is unique to the Australian market.
“We’re proud that we’re able to o er local support, with our advisors and technicians that know the local market and context of any issues machines could be having – it’s a real di erentiator for Komatsu. We support around 650 machines on a day-to-day basis and have
resolved just over 2100 customer inquiries since launching last April – a massive feat from our team.”
Brent says the most common customer support query from their civil construction customers is around machine set up.
“When a machine moves from one site to another, operators require the new site information loaded and configured on the machine. Typically, this would be done by a surveyor emailing that information to someone on site, then you’d physically visit the machine and configure the information manually. Our Smart Construction solutions allow this to be all done through the platform in the machine, and then our support centre is there for any troubleshooting when loading the site data.
“We also receive calls for machine breakdowns, where we can remotely access the machine to begin the troubleshooting
process and try to get those issues resolved through our service teams as quickly as possible.”
The Smart Construction Support Centre o ers back up for even the most remote locations – where internet connection can be an issue.
“We’ve had a customer in regional Western Australia where their jobsite didn’t have internet coverage, but the customer was able to take his machine tablet back to a site o ice out of the machine, and we were able to remotely load project files and provide the required support, before he left internet coverage to return to the machine and get it started again.”
The centre also has the full backing of Komatsu’s other systems to provide information on a customer’s machine and situation.
“The team can access systems like Komtrax, and see where the machine is on a site, any
fault codes the machine might have, its service history and the nearest branch to contact. These sorts of systems enable our remote support consultants to provide the best possible support outcomes and advice to our customers,” Brent says.
“As more and more customers adopt technology in their business, there are always going to be issues with onboarding and figuring out how to get the most out of the solutions, but our customers know they can rely on Komatsu Australia and the Smart Construction team to work through challenges and keep their team and their fleet working and productive.”
To find out more information about Komatsu’s Smart Construction Support Centre, visit www.komatsu.com.au/ support/smart-construction-supportcentre
During years of di icult market conditions, it is possible for big businesses to forget the importance of their social responsibilities. With economic conditions severely impacting communities in recent years, it’s become more important than ever to rally industry bodies to show support to some great grassroots organisations who are fighting the good fight.
For Pickles, charitable initiatives are a key motivator, and hearkens back to when the company first began – a business founded on mateship and community. And charitable values have remained at the forefront of Pickles’
initiatives, particularly in the hardest of times. As part of this commitment to communities, Pickles often uses its huge network to reach out, encourage and involve any other businesses looking to give back.
Thanks to Pickles’ rich history in Australia, the business holds several long-standing relationships with a number of organisations, one of which is Q H & M Birt. A contractor business based around Australia, Q H & M Birt is home to Australia’s largest privately owned civil scraper fleet.
The family-owned business is large in scale
and in heart, with Managing Director Quentin Birt noting that behind the scenes of their huge industrial operation, giving back is at the heart of their goals. Quentin started his business in 1973, just nine years after Pickles began operating, with both businesses starting out as small, family-owned enterprises. When asked about why he works so closely with Pickles, the answer comes easily to Quentin.
“They’re the most reliable blokes in the business,” he says. “They fulfil their promises, and we trust that they’ll do what they say they will, they talk the talk and walk the walk. I have great relationships with many people from Pickles including James Chauncy, Steven Wainhouse, and others.”
The two companies have historically worked together with great success, with the last sale Pickles hosted for Q H & M Birt resulting in sales of over $15 million worth of earthmoving equipment. Pickles and Q H & M Birt have partnered for several sales during their eightyear relationship, and it was during one of these many collaborations that Pickles’ National Sales Manager, James Chauncy, introduced them to an organisation founded by his sister, School for Life.
School for Life is a grassroots organisation started by Annabelle Chauncy OAM and David Everett OAM in 2008. The initiative raises funds to build schools with quality education resources, employment, and healthcare
The Pickles team breaks down how industry collaboration can be leveraged to give back to communities.Ugandan children involved with School for Life. James Chauncy in Uganda.
solutions to rural Ugandan communities. The organisation, which is supported by Pickles, was introduced to Q H & M Birt, and while Quentin was no stranger to charitable giving through his business, he fell in love with School for Life, its mission, and its dedication to community learning.
It began small, with Q H & M Birt attending one of School for Life’s annual gala dinners, but eventually this led to Quentin embarking on an international trip to Uganda to lend hands to the operation on the ground. Today, after many years and much donating, Q H & M Birt is now a leading supporter of the cause, and their funds are directly responsible for expanding School for Life’s operation and creating more education and healthcare opportunities in Uganda.
When asked about why he gives back with such generosity, Quentin explains how much the organisation has given back to his life.
“I’ve really connected with the Ugandan community, my experiences with them have been incredible,” he says. “I’m getting more back from them than I’m giving. Learning, education – it’s just the most important thing in the world, and I want to support that wherever I can.”
After several years involved with School for Life, Quentin opened his network to the cause, encouraging other industrial organisations to jump aboard the giving train.
With such strong support from large Australian industrial businesses, School for Life has grown in leaps and bounds. To date, the organisation has raised more than A$10 million which has helped educate more than 1700 students annually, employ 120 adults, supply three nutritious meals a day for all sta and students, and provide clean drinking water to the entire Katuuso and Mbazzi communities.
When asked about the impact that industrial companies like Pickles and Q H & M Birt have had on the cause, OEM Annabelle Chauncy sings their praises.
“It’s done huge things for School for Life,” she says. “When big businesses give back it really makes them part of communities, at home and abroad. And the donations stretch such a long way – just 10 Australian dollars provides three meals a day for a whole month for one child. And you couldn’t believe what an impact those meals have on their lives.”
Annabelle says that the circular nature of charitable giving is great for large industrial businesses and the communities they are supporting. It shows that big companies are invested in uplifting communities with education, healthcare, and support. It can also be a great way to show employees and customers that the company they invest themselves with cares about the legacy they leave on the world.
And for companies like Pickles and Q H & M Birt, it’s a big legacy.
For more information on how you, your company or your network can get involved with School for Life, head to www.schoolforlife.org.au. And to find out more about Pickles, head to www.pickles.com.au to find what you need.
Need to offload your used trucks and machinery? DIYinspect is a self-inspection app powered by Pickles. Asset owners can simply download the app, complete an in-app inspection and receive an offer to purchase equipment. Start the process anywhere, at any time.
Why use DIYinspect?
DIYinspect helps customers sell their assets with ease and in their own time and space. By conducting remote inspections, sellers can maximise their time and return on their assets.
Customers receive data-led offers to purchase, eliminating the expense and hassle of conducting in-person asset inspections.
Sellers can offload a range of equipment including trucks, buses, excavators, and loaders.
Head to DIYinspect.com.au for more information, or simply download and get started!
The entire process only takes 15 minutes and you simply follow the steps below to get started.
STEP 1
Download DIYinspect from the App Store or Google Play
STEP 2
Register a business account using your information incl. your ABN
STEP 3
Select the asset type you want inspected
STEP 4
Upload information, notes, photos and videos of your equipment
STEP 5
Submit your DIY inspection and we’ll get back to you within 48 hours!
The Cat D8 (formerly D8T) is the right choice for any business demanding a step up in performance. Caterpillar designed, the Cat D8 dozer has a Tier 4 Final emission and a fully automatic 4-speed transmission is at the heart of performance improvements that take you to a whole new level of productivity and e iciency.
While the name may be a little di erent, the D8 continues to deliver the productivity, e iciency and horsepower needed to help make the most of your equipment investment.
“The nomenclature update from D8T to D8 is part of an e ort to make all Cat dozer model names simpler. The Cat dozer range has been renamed from smallest to largest – D1 to D11 –with one model per size class and no more series letter modifiers like “N,” “K” or “T,” Ho said.
“With expected production increases available through improvements on the D8, operators can expect to move more with little to no overall
increase in operating costs,” he added.
A closer exploration of the D8 illustrates how operators and owners will stand to gain more while spending less.
Firstly, the fully automatic four-speed transmission with lock up torque converter essentially provides an additional gear between the traditional first and second speeds seen in power shift transmissions.
When matched to the exclusive Cat torque converter/divider and combined with a seamless lock-up clutch engagement, this means operators have the ability to shift up and down more smoothly and automatically.
Here the four-speed transmission and torque converter works to continuously optimise the gear selection and engine speed for the task at hand without the need for further operator input.
“The operator simply selects the ground speed and machine will do the rest,” Ho said.
“There is no need for the operator to upshift or downshift.”
It is important to note the D8 model o ers a major productivity advantage – boasting the largest semi-universal blade available in its class at 10.3 cubic metres – o ering a 19 per cent increase in capacity compared to its previous design.
Optimising the powertrain e iciency in this way delivers up to 13 per cent more drawbar power to the ground, improving fuel e iciency for the volume of work being completed. Auto shift works up and down the entire working range, so power and fuel consumption are optimised throughout the dozing cycle.
Secondly, the 10.3 cubic metre SemiUniversal blade with its 19 per cent increase in capacity can also be equipped with an optional performance cutting-edge system for even greater productivity.
Powered by aTier 4
Finalengine,
the newCat® D8 dozer
has been optimised to help customers move more material while burning less fuel. Cat Product Specialist Sean Ho explains how the new machine can save customers money without compromising on the world-class performance o ered by its previous iteration.Operators and owners of the Cat® D8 dozer will stand to gain more while spending less.
“When coupled with a 13 per cent increase in available engine power, operators could experience up to 15 per cent more material moved,” Ho said. “And with optional FirstCut™ Cutting Edges, operators can even increase blade payload by up to 35 per cent, especially in hard ground or rock.”
The optional patented cutting-edge system is designed to better penetrate harder ground or moderate rock, by digging deeper, Ho explained. “This aids blade control, load retention, improves traction and results in reduced track slip. The cutting-edge profile is along a single ‘plane line’ which also delivers excellent grading characteristics that adds to the versatility.”
There is no expected additional wear life cycle costs when compared to standard cutting edge systems, Ho explains. “Just better blade performance when demanded in harder conditions. Moreover, with a 10 per cent increase in steering torque, manoeuvring the larger blade under load is achieved with ease.”
Further reductions in operating costs are gained by use of cartridge style filters and increased service intervals for engine oil changes. Combined, these measures contribute to the design objective of moving more and spending less.
Cat Grade technology remains at the forefront of the machine’s e iciency and productivity.
An optional fitment on the D8 is Cat GRADE with Slope Assist™ – a system that requires no external transmitters or base station.
This feature is factory integrated on smallto medium-size Cat track types and will automatically maintain a single-tilt blades position (as set by the operator) making it an ideal tool for pad construction or creating simple designs ‘on-the-go’.
Ho said it was a relatively simple feature. “An Inertial Measurement Unit (IMU) is fitted to the blade and integrated into the machine's blade control system.”
The operator views the mainfall slope and blade cross slope on the monitoring display, sets their desired blade position and simply activates via a button on the control lever and Slope Assist will maintain that blade position.
“It is a great feature that allows simple jobs to be finished quicker with better surface quality and with less operator input required. And, that helps lower fatigue and improve productivity,” he added.
The optional factory fitment Cat GRADE with 3D is a fully integrated system without the need for a typical GNSS blade mast mount antenna system and is for use with 3D designs.
GRADE with 3D helps improve grading e iciency and accuracy by automating blade movement required in complex 3D designs with reduced operator input.
Two GNSS Antennas are fitted to the top of the cabin (eliminating issues associated with blade mounted masts and cabling) while the receivers are located within the cab structure of the machine.
If GNSS signals are limited, there is also an option of installing blade mounted mast receivers for laser systems or with a Universal Total Station to allow continued productivity.
The range of improved specifications on the D8 are designed to enhance the user experience, reduce fatigue and improve productivity – particularly on repetitive tasks.
blade loads, and helps reduce track slip by automating the blade lift during the cycle. The system also works seamlessly with the integrated GRADE 3D option.
An optional Auto-Ripper control includes a new ‘rip-to-depth’ feature that will automatically adjust the engine speed and ripper depth to reduce track slip.
Integrated machine systems mean the D8 is ready for adoption of technology including ‘Command for Dozing’.
“Command for Dozing allows the machine to be operated in various levels of remote control,” Ho said.
“This provides enhanced operator safety and continued productivity by using either a line of sight, or a remote operator station.
The operator maintains control of the dozer with less out exposure to potential noise, dust, vibration or hazardous applications, or conditions, by utilising deep integration with the machines systems enabling smooth and precise control.
Another option is a heavy-duty Extended Life Undercarriage with DuraLink™ that can improve operating costs in abrasive job-site conditions.
Heavier bushings add up to 25 per cent more wear life and a patented crowned DuraLink™ is hardened to extend life and reduce scalloping to improve operator ride comfort.
Other standard fitments now on the D8 include an electronic fluid level verification system that switches on at start-up to check coolant, engine and powertrain fluids while a programmable auto-reverse cooling fan engages to clear debris from the radiator package.
Optional features include Auto Blade Assist that allows the operator to pre-set the load, carry and spread blade pitch positions.
AutoCarry allows more consistent
The D8 track type and associated technology builds on the pedigree of a long line of Cat track types, and delivers performance and productivity while lowering operating costs. Contact
NSW/ACT: WesTrac – 1300 881 064
VIC/TAS: William – Adams 1300 923 267
Western Australia: WesTrac – 1300 881 064
QLD/NT: Hastings Deering – 131 228
South Australia: Cavpower – 08 8343 1600
NZ: TERRA – 0800 93 39 39
The SK135SR-7 perfectly demonstrates the commitment Kobelco has to designing and manufacturing the most capable excavators available, built with Japanese quality for legendary reliability.
As the #1 selling machine in the 14 tonne class, the SK135SR-7 combines unbeatable performance, fuel efficiency and reliability with a premium operator station and modern machine design.
And now Australia’s most popular short radius heavy excavator is available with a proven Isuzu Tier 3 engine, with no DPF and no AdBlue required, reducing operating costs and increasing convenience.
Starting a new business is an exciting yet challenging endeavour. Whether you're an industry veteran branching out on your own or an employee looking to invest in machinery, the initial steps can be daunting – especially when it comes to financing your first piece of equipment. Traditional banks often hesitate to lend to newcomers, but don't let that deter you. There are alternative paths to secure that crucial first loan.
New businesses often face hurdles when approaching traditional banks for equipment finance. The lack of a track record can be a significant roadblock. But with a skilled broker at your side "there are other ways up the mountain”.
Several second-tier lenders specialise
in equipment finance, including for used machines and private sales. While the interest rates may be slightly higher, these options are often more economical than dry hiring equipment. Plus, they allow you to build equity in your machinery.
A common approach for newcomers is to finance with a second-tier lender for 12 months, often with a 60 per cent or 70 per cent residual. After a year, you'll have "runs on the board", making it easier to refinance with a lower-rate lender.
Some financiers o er competitive rates for clients who can make a small upfront deposit. If you're a homeowner, consider leveraging your home loan to raise this initial amount.
With property values on the rise, this could be a smart move.
If you're planning to start a business, consider registering your Australian Business Number (ABN) sooner rather than later. Having an ABN for over a year can make financing easier, even with mainstream lenders.
At Finlease, we pride ourselves on being more than just brokers; we're your partners in business growth. We o er tailored solutions and build lifelong relationships. If you're contemplating a new venture, it's worth speaking to a reputable finance broker to explore your options.
Learn more by visiting www.finlease.com.au
The Leica iCON iGG3 is an intelligent 3D grading solution that has been designed to revolutionise the way you move material and fine-grade. The solution brings design surfaces inside the cab to let operators work independently, with great accuracy, anywhere on a project design guided by a GNSS system or a robotic total station.
The key benefit of the system is its ability to dramatically increase machine use and productivity and optimise material on any earthmoving and fine-grading contract. The system can be used with a wide range of sensors and combines ease of use, flexibility, and an intuitive user interface.
This flexible solution uses Leica MC1, the
common software and 3D software platform, which reduces complexity in a fleet for all machines. This common software achieves better utilisation of all components across the fleet on a job site. The technology integrates Leica ConX which enables easy data transfer between office and machines, remote communication, fleet management, and earthmoving productivity analysis via the ConX website.
Intuitive user interface
Being easy to use, MC1 software helps operators to move material more efficiently and focus on getting the job done right the first time. They can access all relevant
functions directly on the run screen, and visualise progress with Modify Models – a function which allows for adjustments by tool point interaction while working. The tool’s edge movements are featured on a colourcustomised live heatmap to see the tool edge history to target height distance.
Site managers can now synchronise all as-built data created with surface logging functionality to the ConX 3D page for progress tracking, reporting, volume calculations, and model creation.
As with all Leica 3D machine control software solutions, the iCON iGG3 is compatible with the MCP80 machine control panel. Combined with the intelligent Leica MDC docking station,
The latest technology from Leica Geosystems is a major advance for motor graders in productivity, efficiency, and precision.The Leica iCON iGG3 is designed to optimise efficiency and accuracy.
this provides a one-for-all machine control hardware solution across a range of heavy construction applications.
The MCP80’s common interface also makes it easily interchangeable between any heavy construction machine, meaning operators only need to be trained on one display panel. An eight-inch colour touch screen and backlit buttons adds to ease-ofuse in any conditions.
Users of the Leica iCON iGG3 benefit from maximisation of machine use and return on investment from day one, by getting right to grade the first time and remembering all your settings, saving time by a setup that takes a few minutes. The system creates a reference surface with up to four slopes and its hold slope feature allows precise crown cuts and extending past breaklines when needed.
There is an automatic side shift control for motor graders with Leica’s unique Tri-Sonic or GNSS/TPS sensors. Other benefits include unique mast-tilt compensation which means there is no more re-benching of the motor grader blade between cut and finegrading passes.
The system is fully scalable, which means you can start from basic 2D entry to full 3D capability; and you can add laser, slope,
sonic, GPS, and total station control options later. When you are ready, it’s a simple upgrade step to 3D by buying a 3D-ready panel and upgrade later or rent the GPS/Tracker and 3D software only when needed.
Brad Walker of Walker Grader Hire has used the system and agreed, saying: “Having worked with all GPS brands previous to Leica Geosystems, we have experienced significant e iciency gains by swapping to the Leica Geosystems iGG3 Grader system. The service and support from C.R. Kennedy make the whole experience easy. From the sale to the installation, training and support, our experience with C.R. Kennedy has been
smooth and e ortless.”
Leica Geosystems products are solely distributed in Australia through machine control and positioning specialists C.R. Kennedy. Based in Port Melbourne, C.R. Kennedy has a national network of more than 260 sta across branches in Melbourne, Brisbane, Adelaide, Sydney, Hobart, Perth, and Cairns.
Purchase a full 3D MC1 system (GPS or Total Station Control) and receive a complimentary five- year warranty on all hardware and software (T&Cs apply). For more information, visit:
www.survey.crkennedy.com.au
“We help people work on their business, not just in their business.”
That’s Kurt Herron’s mantra. As one of NTI’s dedicated risk engineers, Kurt knows what he’s talking about, and his colleague Paul Bressan agrees.
“We’re not a regulator,” explained Bressan, “and we’re not there to hit businesses with a hammer. We’re another set of eyes with risk and operations knowledge and industry experience who can provide recommendations on how a business can continually improve.”
It’s an impressive-sounding job description, but what does a risk engineer do?
In a nutshell, it starts with identifying when a client might have a risk problem.
Claims are an obvious indicator, but there are other factors, as Paul outlined: “We also work with clients when they’ve experienced recent growth in their business, or if they’re a potential new client whose history shows they’ve had insurance declined.”
Brokers are another avenue; if they’ve been having conversations with an NTI-insured client about risk, they can access NTI’s riskengineering service.
When on site, risk engineers speak with relevant team members, walk around the premises, and may assist in reviewing training documents, safety controls and other materials.
The visits aren’t too long, typically 60-90 minutes.
“We appreciate how busy our clients are in our industry,” said Paul.
“It’s not a one-size-fits-all activity,” Kurt said,
“but we do have some standard areas we look at because we want to understand the business holistically.
“If I go out and see something that’s claimsrelated, I’ll talk to them about what they do, how they do it, why they do it the way they do. Then I’ll look at subsections. I look at their people; I look at their assets, their maintenance, their care, their technology to get an ‘umbrella’ view of the operation.”
Paul noted it’s essential to talk to the right people. Usually, that’s, “…business owners, if it’s a smaller operation. If they have safety or compliance people, I like them to be there as well.
“If it’s a bigger operation, it’s usually senior managers and operational people.”
Once the visit is done, it’s back to headquarters to assemble a report. That involves research, collaboration, brainstorming and drafting. The NTI team takes time and care, but can usually complete a report in the fortnight after a visit.
“We generally stick to a timeframe of around 14 days,” o ered Paul. “Within that time we like to have the report back in the broker’s hands.”
Once the broker has the report, they can go over it, present their client with it, and be ready for conversations around how to act on any recommendations, and address any questions or concerns.
Kurt emphasised reports aren’t about
telling businesses to spend money on new equipment, training or processes (although they may recommend some, or all, of those measures if needed). Instead, the idea is to get business owners and operators into the right mindset about risk and safety management.
“A lot of what I do is education,” Kurt said. Paul’s take is similar; it’s all about business improvement and understanding the chain of responsibility.
But NTI don’t stop at risk-engineering reports, as Paul noted.
NTI is heavily involved in industry, providing education and support to all sizes and types of businesses.
“We go out to clients. We go to a lot of industry presentations and conferences to keep up with the legislation and compliance standards. We do industryfacing presentations as well, podcasts and video links…if there’s a particular topic, we can address it, like we did in 2022 for flood mitigation.”
Every business can use a helping hand, especially when the ‘help’ consists of experts like Paul and Kurt. And while every business has a degree of risk, there’s no reason to take on more risk than is needed.
If you’d like to learn more about risk management and how to protect your business, contact your insurance broker, or NTI, today. Visit NTI’s Yellow Cover at yellowcover.com.au.
Unique trading accounts with manufacturers, dealers & distributors
ITR Pacific offers a complete range of aftermarket Earthmoving Machinery Parts for most makes & models of Loaders, Graders, Dozers, Excavators, Scrapers & more.
ITR Pacific offers a complete range of aftermarket Earthmoving Machinery Parts for most makes & models of Loaders, Graders, Dozers, Excavators, Scrapers & more.
Enhance
Whether your fleet is big or small, VisionLink® gives your business the insights to take decisive action. With an updated interface and industry-leading features, VisionLink gives you the edge in fuel and time e iciency, uptime, and machine health – meaning greater profitability across the board. Continue reading to find out from customers how VisionLink puts the power of knowledge in your hands.
Keeping customer needs central
Business is advancing rapidly, and Caterpillar customers are embracing technology more than ever – with growing expertise. They understand that to improve operation management they need insights informed by data. Experts in the industry are already extremely good at managing their logistics to improve profitability, but as the industry progresses, technology will be the key to success.
This is where VisionLink proves its value. It helps contractors view their fleet holistically, schedule maintenance and assign tasks. Caterpillar developed these processes with input from customers to optimise fleet e iciency.
The standout customer request was to make the interface easier to use. New VisionLink delivers in spades. It’s simpler and much more intuitive, helping you ensure work is done safely, on time and on budget.
Caterpillar understands the importance of accuracy when bidding for jobs. Overquoting can lose you a job, while underquoting causes
financial strain. That’s why data accuracy is paramount with the new VisionLink.
Turn it up with VisionLink
VisionLink is an integrated full- and mixedfleet management solution. It tracks assets and gives you the information you need to optimise uptime and utilisation. Plus, it integrates fully with Caterpillar’s digital ecosystem. The new interface enables you to manage your entire fleet e iciently. Whether you own, lease or rent your machines, you’ll have access to the data and insights you need to make informed decisions.
VisionLink is cloud-based and accessible via desktop, tablet and mobile. That means metrics such as asset location, fuel level and idle time are available in real time. With a simple dashboard, you can manage assets by group and geofences. You can easily generate tailored reports to simplify activities and pinpoint underutilised machinery.
To simplify fleet management, VisionLink integrates my.cat.com, the Cat® app and past VisionLink applications in one. It also o ers subscription options, so regardless of your fleet size or nature of your work, there’ll be a setup for you.
VisionLink is an integrated full- and mixed-fleet management solution. It tracks assets and gives you the information you need to optimise uptime and utilisation.
“WBHO is one of the biggest construction companies in Africa, with sites all across the continent. Before we used VisionLink we would have guys onsite who would inspect on a daily and weekly basis. But now it’s immediate. If there’s an alert, we can action it immediately. We can look at problems in real time and fix them.”
Zane Baily, WBHO Construction, Johannesburg, South Africa
“Before VisionLink, our equipment management was very reactive. VisionLink has really improved our maintenance program, reduced planned downtime and maximised e iciency.
“We’re using the VisionLink platform and data to help us achieve the absolute highest level of success that we can. Now we can instantly see the hours on each piece of equipment, when the last maintenance was done, and get when the next one is due."
Anthony Guho, Guho Corp, Idaho, USA
Before the rise of little diggers and skid steers, the backhoe was the go-to/must have machine on any construction site. Why? Because they’re quick on their feet and are so bloody versatile, providing you with the best of both worlds. They have a bucket up front and hoe attachment down back, a centaur if you like.
Let’s talk about the front bit – the bucket. In most cases, the bucket has 4 in 1 capability –great for fine grading. They can load a truck, you can use them to backfill trenches, slap a set of forks on them and move pallets, pipes or whatever else takes your fancy.
Let’s look down at the back, to the hoe attachment which can be extendable. Obviously, its main jam is trenching. They can lift and lower pipes into their forever homes, plumb them up, and you can run a hammer or an auger o the end of the hoe attachment.
Now, my knowledge goes only so far about the backhoe. I could use the front half just fine, but the back half, particularly with the old BH control pattern – that used to melt my brain. So, what I’ve done for this top five is reach out to a good mate over in the good old’ US, Frank Cunningham, to pick his brain on backhoeing.
Frank’s been around backhoes since he was a young fella. Operating them on his family farm
in Oklahoma and tagging along with his father who ran a small commercial plumbing business in the area.
Fast forward to 1999, Frank purchased his very first backhoe, New Holland 555E, to start his own backhoe service. He’s been in constant work ever since because he does super outstanding work.
Let’s rip into Frank's top 5 backhoe tips:
1. Easy tiger
Don’t run full throttle. Most people can’t operate at that speed. A slower, steady, smooth pace will get more work done. Work with the machine, don’t fight with it
2. Stay on the level
Don’t raise the tires o the ground, only use enough stabiliser to get level and planted firmly, of course unless you need the height for reach loading trucks
3. Practice, practice, practice
Practice digging level from top to bottom of the ditch, making longer passes when filling the bucket will turn out a better trench than hogging, or trying to fill the bucket in a short pass
4. Where are those tyres at?
Keep the front tyres on the ground when doing loader work. Use the curl when loading, not the boom up
5. Moves like Jagger
Practice moving the machine with the backhoe when trenching. It’s always more e icient if you don’t spend time turning the seat around with every setup.
When asked what some of the things were that have helped him over the years operating, Frank said, “The first backhoe I ran was a total scrap heap, but…it made me a better operator.
“A lot of operators seem to be looking for the next gadget to make them an operator,” he continued. “There is no easy button for being good because it takes hard work and a lot of patience.”
Frank also says that without the support of his better half, his wife of 31 years, Rebekah, his backhoe life would have been a lot more challenging.
Head on over to Frank’s Intsagram page @mrfrankc to check out more of his incredible backhoe work
Australian Earth Training’s Scott Lidster talks about the mighty backhoe – a versatile tool for any construction site.Before the rise of little diggers and skid steers, the backhoe was the go-to/must have machine on any construction site. Backhoe loaders o er a compelling combination of quickness and versatility.
Steelwrist offers tiltrotators for excavators from 2 to 33 tonnes, models X02-X32. Our tiltrotators have a low building height, high tilt angle along with an unbeatable relationship between strength and weight thanks to steel casted components.
Steelwrist tiltrotators greatly increase your productivity and efficiency by enabling you to rotate your work tool 360 degrees and tilt 45 degrees in each direction with top of the class precision and controllability. Combined with our range of mechanical and hydraulic work tools, the Steelwrist tiltrotator becomes the key to unlock your excavator efficiency!
All Steelwrist tiltrotators from X12 upwards can be equipped with our SQ fully automatic technology. The SQ system allows for seamless changes between hydraulic attachments, connecting hydraulic and electrical signals in one movement, no need to get out of the cab for tool changes!
All Steelwrist SQ products follow the Open-S standard for global interchangeability between quick couplers, tiltrotators and work tools for excavators.
We love media training – there’s nothing better than seeing a nervous media newbie (or even a veteran looking for a skills update) feeling confident and ready to own their interviews. Here are Hardman Communications’ top five tips…
1. It’s all about you
The very best thing you can do to maximise your media opportunities is to understand how to tell your own story. It may seem obvious, but there’s an epiphanous moment in every training program we run, where participants recognise how important it is to really, truly understand what you have to say. If you can answer these questions, you’re on the right track:
• Who are you? Not the name, age, whereI-went-to-school stu , but the background directly relevant to what you want to talk about with media
• What do you do? Don’t get lost in the highlevel language here. It’s great you want to save penguins or unleash creativity or empower teams to go further. But what do you actually do? It’s amazing how often people forget the simple, succinct explanation that helps a reporter understand your story. The challenge is knowing how much detail is enough
• Why do you do it? This is partly about what drives you, but it’s also about your goals and impact. “I want to save penguins!” is never going to be as compelling as, “I want every Australian child to have 15 minutes of formal education about the importance of penguins.” Get tangible.
Hardman Communications knows how to make the most of media opportunities.Understanding how to tell your own story will maximise your media opportunities.
A big part of succeeding in the business of customer service is about knowing how to deal with people. The social skills to talk the talk, the integrity to walk the walk, but also the ability and willingness to put yourself in your customer’s shoes.
In the relationships game of earthmoving machinery, mastering these skills will take you far. But equally important – and something that’s impossible to teach – is experience. Experience is what separates a good salesperson from a trusted adviser. And it’s something that Western Sydney’s STM Trucks & Machinery has in spades. Since the business was established by Michael Gerace more than 50 years ago, STM has developed a strong foundation of experience, and a reputation for going the extra mile for customers.
Today, STM specialises in a carefully curated selection of construction machinery brands, including Kobelco excavators, ASV track loaders, D’Avino and CNF site dumpers, Merlo telehandlers, and XCMG access equipment. On the truck front, Iveco and Fuso lead the way. Comprehensive solutions
But of course, supplying a range of machinery from trusted brands is only part of the equation. Dealers like STM are expected to supply everything else a customer will require, both at the point of sale, and ongoing. This is where
STM aims to set itself apart – not just with its range of products, but with an unwavering dedication to providing a complete and seamless service experience to its customers.
According to Group Attachments Manager Jason Willis, STM’s well stocked and
meticulously maintained range of parts, accessories, and attachments puts the business’ customers at a big advantage.
“As a dealer, we have the flexibility to quickly address issues, and we have a large team available to assist customers,” he says.
STM Trucks & Machinery has developed a reputation as one of New South Wales’ most trusted truck and earthmoving machinery dealers – but maintaining that trust is about much more than machinery itself. EEM finds out how STM’s range of spare parts and attachments elevate the business.STM Trucks & Machinery aims to o er complete solutions for customers. STM's accessories range is always well stocked.
“My day-to-day role involves looking after all machinery attachments, including external inquiries from customers and managing orders for our sales team. When a machine is sold, a build sheet comes to me with customerrequested attachments, and I process and track those orders. We also regularly meet with the sales team to anticipate stock needs and sometimes run specials to move inventory.”
Having joined the business less than six months ago, Jason is a relatively new face around STM – and to earthmoving equipment in general. But his automotive experience positioned him well for the lateral step.
“I'm a mechanic by trade,” he says. “I spent the past five years working in New Zealand in the agricultural industry. But there came a point where I wanted to come back home to New South Wales, and the job at STM presented itself as a great opportunity to gain experience in a slightly di erent field.”
Jason says his experience so far has been extremely positive, and he’s enjoyed the opportunity to learn from a dedicated group of colleagues.
“The parts and attachments team is made up of around 20 people, with five full-time phone operators, two inventory controllers, a parts sales rep, two interpreters for the workshop,
and a warehouse team,” he says. “And many of them are long-term STM employees with a wealth of experience and knowledge.
While STM boasts a variety of top-selling products, Jason highlights some of the most
sought-after attachments.
“We sell a lot of buckets – especially for our Kobelco excavators – as well as quick couplers, augers, and hammers,” he says.
As well as genuine parts from major brands
including Iveco, Fuso, Kobelco, ASV, Cummins, and more, STM stocks a comprehensive range of aftermarket parts. And if it’s not available o the shelf, STM's spare parts team will source it.
STM also stocks Shell lubricants, and a wide array of attachments from trusted brands such as Attach2, Epiroc, Digga, Steelwrist, Fecon, Norm Engineering, and Geith, just to name a few. STM is also a SITECH dealer, o ering a full range of Trimble machine and grade control systems.
“We o er a range of oils such as Kobelco, Iveco, and Shell,” Jason adds. “And making sure we always have the right stock at the right time is essential to support our customers.”
What’s more, a broad selection of tools and accessories is also available, including seat covers, floor mates, cleaning kits, weather shields, and more.
And if you find yourself in a pickle onsite, STM also has you covered with pickup and delivery services. Twice daily service runs across metropolitan Sydney and daily afternoon trips to the Southern Highlands/Wollongong region ensures you won’t be out of action for long.
Jason says this all aligns with STM’s approach to ensuring customers always leave with everything they need to get on with their work, as well as the peace of mind in knowing support is never far away.
“Our quality of service sets us apart,” he says. “Many customers come to us for the brands we o er, but they stay for the service.”
To check out STM’s full range of trucks, machinery, attachments, and accessories, visit: www.stm.com.au
With a strong presence across Victoria, South Australia, Queensland, and soon NSW, Big Chief Hire is a big deal in the machinery and truck hire space.
EEM discovers how a productive partnership with lubrication specialists
Alemlube helps keep the Big Chief fleet operating smoothly for its customers.
Nothing is more important to an equipment hire business than ensuring the longevity and e iciency of its fleet. And when a customer is putting their money down for a day of solid work, they expect machinery that can give them their money’s worth.
According to Sergio Eliseo, Workshop Controller at Big Chief Hire, providing this e iciency and value for customers is central to how his employer operates.
Based at Big Chief Hire’s South Australian headquarters in Adelaide’s north, Sergio is responsible for the management of the Big Chief fleet, overseeing its maintenance, and ensuring each machine is running at peak performance for customers. Sergio says it’s a job that keeps him constantly on his toes – almost as much as being a father to two teenage daughters.
“A normal day for me involves meeting with customers, suppliers, running the workshop, as well as liaising with our wet and dry hire managers to prioritise repairs for any machinery that might be going out.
“We work closely with our suppliers and customers to make sure we’re satisfying customer needs, and to address any concerns they have operationally or functionally, and just maintain our workshop – making sure our workshop guys have got what they need, and are clear in what they need to do.”
In his role, Sergio draws on his 30+ years of experience as a mechanic, which began with a passion for all things automotive. An interest in motor racing evolved into a career as a diesel mechanic, which in turn led him to Big Chief Hire, where he progressed into management.
“I really enjoy seeing the personal growth of the sta here at Big Chief,” Sergio says. “And I take pride in increasing the reliability of our machinery.”
As Big Chief Hire continues to grow, Sergio’s team is always kept on their toes as they work
to support an ever-expanding and increasingly diverse fleet.
“The fleet continues growing,” he says. “We can provide anything from a 1.7-tonne excavator up to 50-tonne excavators, bulldozers, and 30-tonne dump trucks. We’ve also got little 2-tonne tippers up to prime mover semi tippers, rollers and compactors from 1.7-tonne to 13-tonne, graders – the list goes on.
“We’ve just started getting into scissor and boom lifts, as well as gensets and mobile water pumps capable of pumping up to 60 litres a second.”
Braeden Johnson, Alemlube Business Development Manager SA/NT, has been with the company for more than 11 years, and he’s looked after Big Chief Hire since 2020.
“In the beginning, I was working with Sergio and his team, supplying some small fittings, greasing supplies, and little bits and pieces around their workshop as needed,” Braeden says.
“It progressed from there to identifying a problem the Big Chief team was having with their trucks.”
Sergio and the Big Chief Hire team had been plagued by the short life spans of their pins and bushes, a challenge for which Braeden figured he had just the right solution.
“We trialled some single cup lubricators to prove the theory behind it,” Braeden says. “Then we progressed into the full Alemlube Lube System across their water tankers, tippers, and excavators – really just progressing through the whole fleet.”
Sergio says the relationship with Alemlube
evolved quickly as the Big Chief team quickly saw the benefits on o er.
“Now, pretty much everything that we buy is fitted with an Alemlube Lube System by our machinery dealer, Northeast Auto Group,” he says. “These systems ensure consistent lubrication into the pins and other critical parts, which helps eliminate any downtime or breakdowns from a lack of grease. And our customers love them because it increases their productivity as well.”
Sergio says it’s a win-win for Big Chief Hire: less downtime, and reduced need for costly repairs – all for what he says amounts to a relatively small investment in Alemlube’s systems.
“Alemlube also supports us really well if we have any breakdowns or issues, their service is pretty well second to none,” Sergio says.
“Braeden is always onto it straight away, and he always makes sure to follow up.
Braeden believes the Big Chief Hire team was quickly won over not just by the level of service provided by the Alemlube team, but by the quality of the products on o er.
“We sell quality products imported from wellknown and respected overseas suppliers,” he says. “Our national footprint includes BDMs in every state, warehouses in every state, and auto lube technicians in every mainland state. And that helps us support Big Chief, as their national footprint marries up well with ours.”
Braeden says the Alemlube Lube System is lightweight, robust, and smart enough to give any competitor on the market a run for its money.
“It’s a quality Italian product backed by Alemlube’s decades of experience in automatic lubrication,” he says. “It’s also backed by our
dedicated team of BDMs, operational sta , technicians, and warehouses.”
According to Braeden, Alemlube is equipped to o er everything from tailored kits designed to a customer’s specifications, through to on-site installation and servicing. Lubrication solutions can also be installed at an OEM level from the start, or retrofitted onto older machines.
“The Alemlube Lube System removes the requirement for manual greasing on the machines as they’re being operated,” Braeden says. “The progressive divided design ensures that grease gets to each point in the quantities required. And the fact that the pump is operating while the machine is in use means that grease is lubricating the entire bearing instead of just the part of the grease point that would otherwise be stationary during greasing.”
This means when a customer hires a Big Chief machine, they don’t have to pay for their operators to spend an hour greasing the machine at the start of every day, significantly reducing downtime.
“Our system is doing it for them,” Braeden says. “That means that Big Chief can get more money from their machines, and it means they aren’t spending as much on maintenance.
“It enhances their o ering for customers: reliable machines that will do the job when and as needed.”
The Alemlube Lube System can be utilised across not just the transport and earthmoving industries that Big Chief Hire services, but in agricultural and fixed plant applications as well – a versatility that Braeden says keeps his job interesting.
“One day I can be working around excavators and loaders, the next day around crushing and
screening equipment, and the next around heavy haulage,” he says. “To work with these industries to provide them with lubrication solutions is challenging, but rewarding.”
Braeden says Alemlube’s progressive, innovative, and customer-centric approach to business only adds to the satisfaction in his work.
“Customer experience and satisfaction are crucial to Alemlube, and vital in fostering trust in our relationships with our customer base,” he says. “Our attention to detail and ‘can do’ attitude combined with quality product are some of the reasons why an ever-expanding customer base trust Alemlube to design, supply, install, commission, and maintain lubrication systems for mobile equipment and fixed plant.”
Alemlube is also a 100 per cent Australian-
owned family business, which Braeden says helps maintain a level of care he says can often be missing from larger multi-national companies.
“Alemlube Lube Systems are also designed and installed with years of experience – and they’re very a ordable too,” he says. “The price of one of these systems pales in comparison to the cost of downtime or unexpected maintenance expenses.
“Whether you’re running one machine or 100, reach out to the Alemlube team in your region and find out what we do for your business.”
For more on Alemlube’s comprehensive workshop and lubrication solutions, visit: www.alemlube.com.au
In a large workshop in Exeter, in Tasmania’s north, Dick Beckett sits flanked by his collection of trucks, cars, Caterpillar® memorabilia, and family photos that tell the story of a long and prosperous career.
Beside him, an engine recovered from an old Cat RD 6 crawler tractor is just a hint at the impressive range of historical Cat machines displayed elsewhere around the
property, regularly drawing the fascination and admiration of earthmoving aficionados visiting on business – or just to experience a taste of history.
If you ask anybody in the area, they’ll tell you that Dick is a legend of the Tasmanian civil and mining industries. Growing up on a farm in Li ey, 30 minutes southwest of Launceston, he’s spent his life watching the state evolve and
grow, and has contributed his 60-year career to the cause – usually from the cab of a Cat Dozer, where he can still regularly be found today.
“All I ever wanted to do was drive bulldozers,” Dick says. “I was able to buy one very early in my life, and started doing jobs around for di erent people.”
This was the beginning of Becketts Mining and Civil, o icially started in 1964 when Dick was just 18 years of age. And outside of a few years working in logging, it’s been mostly dozers ever since.
These days, the business is largely run by Dick’s two sons Jason and Scott. Jason serves as Managing Director – though as he says, it’s still a family business through and through. Jason, Scott, Dick, and Dick’s wife Faye are each 25 per cent shareholders of Becketts, and big business decisions are still talked through as a family.
“While I run the business as Managing Director, the four of us are all still directors,” Jason says. “I’ll table opportunities, and the family is normally happy to accept what I’ve brought forward. But it all still gets discussed as a family, and final decisions made as a family.”
Dick says that today, as when he started, Becketts is equipped to deliver whatever customers require.
Dick Beckett has spent his whole life helping build a better Tasmania from behind the controls of his trusted Cat® dozers. Even with his sons now at the helm of the family business he started in 1964, he still takes every opportunity to roll up his sleeves to do the work he loves.Becketts Mining and Civil's new Cat® D6 XE Dozer. Dick Beckett, Founder, Becketts Mining and Civil.
“Whether it be mining coal, removing overburden, clearing land, or building irrigation dams – whatever,” he says. “That’s how we started, and it’s still how the business goes today.”
Powering Becketts’ range of works is a fleet of predominantly Cat machinery – Dick estimates around 70 pieces – including a large collection of dozers from D6s to D11s, and a full range of everything in between.
Jason says its Becketts’ range of dozers that sets the business apart in the region.
“We think we’ve found a niche here in Tassie,” he says. “We specialise in supplying current and late model Cat dozers to the industry, along with good operators.”
Though the business has gravitated more
towards major civil and mining contracts, Jason says heavy plant hire stills plays a major part in the business.
“We specialise in dry hire as well, which many contractors are reluctant to do,” he says. “But we know that Cat machinery is extremely robust, and can deal with the sort of severe and adverse conditions we work in around the state. And we have the confidence that when we send a Cat dozer out on a job, the job’s going to be done.”
It’s a confidence that Dick has carried with him from the very start – the reliability and e iciency of Cat machinery, and the knowledge that local dealer William Adams will always have the Becketts’ back.
“William Adams has always been a very great
supporter of us and our little business, and the Cat product is the best on the market,” he says. “When we can a ord a Cat machine, we buy a Cat machine. We’ve always preferred them over any other product.”
Beyond simply supplying Cat machinery, Dick says William Adams has been a constant support to Becketts since the 60’s – a partnership that’s been foundational to his business.
“When you’re starting out and you’re trying to build your business up, sometimes you get paid and sometimes you don’t,” he says. “Sometimes you make money, other times you lose it, and sometimes there’s no money to pay your bills at the end of the month.
“But William Adams has trusted us and supported us during those hard times. And you don’t forget that sort of thing – when people treat you like that. And maybe it’s a bit oldfashioned, but that’s why I’ve always been loyal towards them too.”
For William Adams’ Rob Flynn, dealing with the Beckett family on a regular basis has provided benefits far beyond machinery sales.
“I’ve been dealing with the Becketts for the past eight months,” he says. “I’ve learned a lot from them, and they’ve been very helpful for my growth within William Adams as well.”
Rob says the Becketts’ willingness to share their in-depth knowledge of Cat machinery, as well as their understanding of customers’ needs in the region has proven a big bonus for his own professional development.
“Dick has been a leader in the Tasmanian construction and mining industries for a long time, and he’s very passionate about his Cat machinery,” Rob says. “His collection is almost like a Caterpillar museum. There’s a lot of machinery there that they’ve kept rather than sold over the years, so it’s a really good look into the history of the brand.”
Rob was the man Jason and Scott reached out to when the family made the decision to purchase a brand-new Cat D6 XE dozer –partly as a sort of gift for their father, but equally as a calculated business decision.
“We’ve bought a lot of new excavators and very low hour dozers from William Adams over the years, but we’d never actually purchased a brand-new dozer,” Jason says. “But when the opportunity presented itself, it was a good time to do it.
“We’ve always been a bulldozing company, so it was gratifying to be able to place that order for a new D6. There’s a personal satisfaction in making that purchase for the business that our dad started 60 years ago, and it’s a sign of how we’ve grown and progressed in that time.”
And as much as Dick enjoys operating Becketts’ new D6 XE, the e iciency and productivity gains on o er made it a smart business decision too.
According to Rob, it’s this e iciency and productivity that really sets the D6 XE apart –even from many larger dozers.
“The D6 has a considerably smaller footprint compared to the D8, but o ers the same product e iciencies,” he says.
William Adams' Rob Flynn (left), and Dick Beckett.“Fuel e iciency is key with this machine too. You’re reducing all your operating costs per hour, which is a huge benefit to any business. And for the operators, the cab o ers improved visibility and comfort, and a much more ergonomic setup to combat operator fatigue.
“It’s a highly refined machine for today’s market – especially with the 3D technology package on it. It’s a very e icient, productive tool for anyone in the earthmoving business.”
Dick agrees that the investment was a smart decision on Jason and Scott’s part.
“It was a lot of money at the time, but we could a ord it,” Dick says. “And I’m glad we could, because we’ll get our money back with the money we save on fuel. It also enables us to give our customers better value for their money.
“That’s something we’ve always based our business on here – giving customers value for money. If we can’t give you value for your money, we don’t want your business. And with that Cat D6 XE, we can take it onto somebody’s property and wrap a job up that much quicker.”
Dick says the e iciency of the D6 XE, and how it feels to operate, never ceases to impress – high praise from somebody who’s been operating dozers for more than 50 years.
“What it can do for its size and weight is just incredible,” he says. “The way it takes the power from the engine down through the transmission and onto the ground – it’s just fantastic. You’ve got to experience it to understand.
“I just cannot fault it. If I had to find some little thing wrong with it, I don’t know if I could. Visibility, accessibility, and everything else that goes along with it – it’s just super.”
Rob says the Becketts have also taken advantage of WillCare – the Cat Customer Value Agreement (CVA) o ered by William Adams.
“WillCare is one of the market leaders for parts and servicing packages,” he says. “It includes discounted rates, scheduled servicing, capped servicing, all tailored to the needs of the machine and customer for a set price.”
Of course, it’s all good and well to hear that from a sales rep, but Jason is also glowing in his praise for the service and the peace of mind WillCare o ers the family business – especially when it comes to managing maintenance.
“It’s pretty amazing,” he says. “It means we don’t really need to be involved in the maintenance of our new Cat machines –William Adams just takes care of it. They’ve even got coverage on weekends, which means we’re not pulling the machine o jobs during the week. That’s worth gold to us.”
Jason says having the support of the WillCare CVA also means he doesn’t have to find extra people to service Becketts’ fleet as it expands –a real bonus in an era of labour shortages.
“Adding WillCare to the last three or four Cat machines that we’ve bought has meant we haven’t had to hire any more fitters for the business to cover their maintenance – if we could even find them to hire,” he says.
“And that means more cashflow and more margin in our business. There’s a real benefit there for a reasonable fixed cost, and it’s really worked well for us.”
• Ensure safe seperation between machines and humans
• Intelligent, AI-powered cameras accurately detect and track humans, while ignoring inanimate objects.
• Audible and visual alerts warn the operator of pedestrian proximity and exclusion zone breaches
• Up to 360° protection from up to 4 cameras
• Doesn’t require
AI-Powered human detection system
Over the past 25 years, Zanetto Civil has developed into a trusted name in Tasmania’s civil works space. Project Manager Nathan Zanetto explains what makes the family business tick, and how Kobelco’s excavators have contributed to its success.
In 1997, Paul Zanetto left his job as a manager for Boral Construction in Launceston, Tasmania, and went solo. With a view to build a civil works business that could grow along with his young family, he started Zanetto Civil. He started small, a single backhoe loader to his name, delivering small private projects – but things grew quickly.
Since then, having delivered works for clients including the City of Launceston, TasWater, and Launceston Airport just to name a few, the business has put together an extensive and diverse portfolio of works covering bulk earthworks, road construction, subdivisions, retaining structures, and more.
Paul’s son Nathan joined Zanetto Civil as a Project Manager around 18 months ago, bringing his experience as a civil engineer to the family business.
“I’d always hoped Nathan would join the business,” Paul says. “I o ered him the role here two years ago, he took it, and he’s done extremely well.”
For Nathan, it was a natural career progression – and a return to the sort of work he’d grown up around.
“I’ve always enjoyed the variety of work that the civil industry o ers,” Nathan says. “Each day is di erent and there are always unique challenges to overcome with each project.
“An average day for the Zanetto team can include anything from excavation, pipe laying, and transporting material between sites, to dealing with subcontractors, suppliers, and other stakeholders.”
Since Zanetto Civil’s humble single-backhoeloader beginnings, the business’ plant and equipment fleet has grown to include a range of excavators, trucks, rollers, directional drills, vacuum trucks, skid steers, and a broad selection of buckets and rock breaking attachments.
For Nathan, one highlight in his fledgling Zanetto Civil career has been the purchase of a brand-new Kobelco SK380XDLC-10 excavator – a powerful 38-tonne machine that represents a new direction for the business. Paul says Nathan spearheaded the acquisition soon after coming on board, and the decision has proven to be fruitful.
“Nathan ran some figures on the 38-tonner, and figured we could potentially break into some new markets with it,” Paul says. “And it hasn’t stopped working since we’ve had it, so it’s certainly been a good move.”
Nathan adds: “We had some larger earthworks projects in the pipeline, and some tough rock excavation to get through.
We began discussing our needs with local Kobelco dealer DLM Machinery, who helped us select the SK380XD and attachments. From there, they guided us through the timeline, transportation, and handover.”
The purchase is just the latest facilitated by a productive, long-term relationship between the two businesses – one Nathan says stretches back almost 20 years.
“They sold us our first 20-tonne Kobelco excavator, and we have continued to maintain a strong relationship since then,” he says. “We’ve since purchased 12 Kobelco machines over the years, ranging from 3.5-tonne to 38-tonne, and each one has impressed from day one. Of those 12 machines, 11 are still in our fleet today.”
According to DLM Machinery Director Dave Morrison, the Zanetto team was initially drawn to the Kobelco brand for its competitive pricing, but what’s kept them coming back has been a combination of reliability and good backup support – an element of the business that Dave and his wife Leanne have taken pride in since they started the dealership in 1995.
“We became the Kobelco dealer for Tasmania in 2000, and we now have a capable field service team that covers the whole state,” he says.
“Our relationship with Zanetto Civil came about by way of quoting Paul on a new Kobelco
excavator, which he purchased, and we’ve built on that relationship since.”
Paul says DLM’s support has been invaluable from the very start, and that he’s long been happy to trust Dave on his advice and recommendations.
“Dave and the team have been fantastic for us,” Paul says. “Their service and backup support has been second to none. And Dave’s just generally a nice guy. He won’t muck you around – if he says he’s going to do something, he does it.”
Coming in at 37,700kg, Kobelco’s SK380XD is the heaviest excavator in its class. Its 244kN bucket breakout force combined with a slew torque of 120kN o ers top-end productivity, while its reinforced arm and redesigned XD boom ensure longevity in tough working conditions.
While designed for quarry applications, Dave says the SK380XD is also a fantastic choice for civil contractors requiring that bit of extra grunt and toughness.
“The SK380XD is a really great all-rounder,” Dave says. “It gives customers and operators great performance with excellent fuel economy for its class. Operator comfort is also a major contributor to its popularity, and makes it a machine that ticks all boxes for a range of customers.
“With the workload that Zanetto Civil had planned, it was time for them to go the next step up from their 22-tonne machine, and the SK380XD fit the bill very well.”
Nathan says the excavator has impressed the Zanetto team on all levels.
“The reach, digging force, lift capacity, balance, and fuel e iciency all really stand out when compared to our other machines,” he says.
“Our operator Ivan has been in the machine since delivery, and he’s been enjoying every aspect of it. He finds it comfortable, well balanced, powerful, and smooth to operate. And he appreciates the added safety features such as the rear cameras.”
“It’s very important for us to build and maintain strong relationships with our customers,” Dave says. “That way both businesses will be able to grow together. We believe that by looking after our customers with great back up support for great products, good relationships will develop naturally.”
For Nathan, this rings true to how DLM has supported his father’s business over the years.
“They have taken the time to learn about Zanetto Civil as a business, going way beyond what we’d ever expected,” he says.
“Dave and the team always go that extra mile with each interaction – regardless of its size or potential outcomes. They are always responsive and helpful with any of our needs – not only with the purchase of new machines, but also servicing, asset planning, and expert advice.
“They also do all this very quickly, which helps us continue progressing our projects and delivering for our clients.”
Dean Brown from Rock Cutter Earthworks explains how a Cat® 272D3 Skid Steer Loader fitted with a Cat SW480 Wheel Saw is helping him get his work done far quicker, easier, and more efficiently.
Digging trenches for plumbers and electricians through limestone rock can be messy, timeconsuming work. Just ask Dean Brown from Rock Cutter Earthworks. Until recently, Dean had carved out his niche in Coffin Bay, South Australia, using the traditional tools of the trade: excavators, hydraulic hammers, and buckets. But wear and tear on his equipment, as well as the added costs associated with excessive waste material, was taking a toll on his business. So, he decided to find a better way.
In a late-night internet session looking for a solution, Dean came across the Cat® SW480 Wheel Saw. And from what he had seen online, the attachment appeared to be the perfect tool to fast-track his work.
After visiting with the Cavpower Port Lincoln Branch Manager Lou Rawson, the pair researched the Cat Wheel Saw and its full capabilities. Lou did his homework, and came up with the perfect package: the Cat SW480 Wheel Saw paired with a Cat 272D3 Skid Steer Loader.
According to Dean, the combo has proven to be the ideal combination of size, power, and hydraulic flow.
“We specialise in commercial and residential work here in and around Co in Bay, and the SW480 fitted to the 272D3 XE has been a game changer for us, turning previously four or fiveday jobs with hydraulic hammers and buckets into a single day job,” he says.
Dean says another big benefit of the Cat SW480 Wheel Saw is the reduction of site waste.
“The material comes out like sand which can then be used as back-fill once other trades have completed their work,” he says. “So, each site's clean-up job is much cleaner and more e icient. We don't have to cart any rock away, which makes it cheaper for our client again.”
When Dean first picked up the Rock Saw, he thought it was going to be perfect for his standard 250mm power and water trenches, as it has a 250mm cut. But with more and more plumbers looking for trenching 450mm wide to enable better access for work in the trench, Dean and his son soon developed a technique, where they make their first cut then side shift the saw blade and make a second cut directly beside the first. Once this is done, it’s a simple job to clean out the trench.
“The time saving with this technique is brilliant – it’s proved perfect for our plumbers,” Dean says. “In the cab, we utilise the smart creep technology, which not only allows us to dial up or down our machine speed to give
maximum cutting power, it actually connects the machine ECM with the saw ECM, which then automatically adjusts speed. As a result, we are not overworking the saw blade, and we're not underworking it.”
Crucially, Dean says the cuts made by the SW480 are flat and clean, with no ridges or uneven sections – which he credits to the teeth placement on the saw. This, he says, ticks all the boxes for the plumbers laying pipe in the trench.
“Our plumbers don't want to see any ridges that a ect their pipes, and the spacing and placement of the teeth on the saw are spot on,” he says.
Right gear, right support
Dean says when he first took delivery of his new skid steer and wheel saw package, he was a little intimidated by its size.
“But after just a few days in the cab, I was impressed by the manoeuvrability, and the areas we could access in tight spaces around houses,” he says. “The 272D3 has the ability and strength to handle the flow and oil pressure requirements of this power-
hungry attachment, making this pairing of Cat equipment the perfect choice for our needs.”
One of the reasons Dean was keen on finding a solution with Cat machinery was the support provided by his Cat dealer Cavpower. The fact that Cavpower has a nearby service centre in Port Lincoln played a key part in Dean's decision-making process.
Lou says field service backup is a key part of Cavpower’s offering.
“We run four field service vehicles at Port Lincoln, with qualified technicians and tooling to solve most issues in the field,” he says. “We know our customers need to keep moving, so we get them back up and moving as quickly as possible.”
Dean's calendar is now fully booked up to six months in advance, and his Cat 272D3 Skid Steer and SW480 Rock Saw are not missing a beat. His research and decision to bring the unique combination of Cat machinery and attachment to Coffin Bay – as well as the support of Lou and Cavpower – has proven to be an excellent move for Rock Cutter Earthworks.
Daracon revived its workhorse Cat® 825H Soil Compactor – at half of the cost of a new machine.
With operations spread across civil construction, land development, mining, crushing services and more, family-owned NSW business Daracon Group has a large fleet of machines to look after. It’s no easy task for Daracon’s Maintenance Operations Manager, Mick Hingerty, but keeping on top of fleet performance is a must. That includes keeping a trusty Cat® 825H Soil Compactor up to the mark. Until late 2022 the compactor had spent 12 years operating under the Daracon badge on large subdivision jobs between Sydney and Newcastle.
Faced with the decision of what next for ‘The Old Workhorse’, Mick had two options: replace or rebuild.
“Our modelling didn’t stack up in terms of purchasing a new machine,” recalled Hingerty. “We ran the model on the rebuild scenario and that’s where we landed… overwhelmingly in favour of rebuild over replace.
“Part of our decision making was wanting the quickest timeline to have a machine back in service. From a cost/comparison perspective, investing in a rebuild came in at 50 per cent of the price for a new machine – all inclusive.”
So began the conversation with WesTrac, looking to put Daracon’s Cat 825H Soil Compactor through a Certified Power Train (CPT) Plus Rebuild.
Go time
WesTrac Customer Support Manager Lyle Murdoch managed the Daracon rebuild from the moment it was received by the workshop in October 2022 with 16,141 hours on the clock.
In a tip of the hat to Daracon, Lyle pointed out Daracon’s maintenance had been meticulous, with top-notch record keeping and sample
history. Even so, the compactor showing the wear and tear expected in a machine of its age which had been doing the kind of work it was built for – compaction.
“Both WesTrac and Daracon knew where the components were up to and that it was time for a decision to be made,” said Lyle. “At that point, it was pulled in and given a real good birthday with that CPT rebuild.”
WesTrac’s workshop quickly stripped down the 825H, shipped components to its Component Repair Centre (CRC) at Tomago for overhaul, fitted a Cat Reman Engine and overhauled the cab for improved operator comfort.
The Cat 825H chassis, frame and covers underwent crack and rust repairs, and all hoses and machine harnesses were replaced. The machine was then completely re-painted, with new and Daracon and Cat decals installed as finishing touches.
The compactor was returned to Daracon in the first week of January 2023 sporting a new look after its short time in WesTrac’s Tomago workshop.
“To put some context around that, the machine was originally painted lime green,”
laughed Mick. “To have it returned to our job site in Cat yellow, and with all the Cat dress… to say we're impressed is an understatement.”
Lyle estimates Daracon’s Cat 825H Soil Compactor will clock up another 15,000 to 16,000 hours of work following the rebuild, carrying on with the a ectionate nickname it had earned: The Old Workhorse.
“The real benefit was that WesTrac assigned a central point of contact for that build,” Mick said. “That person was intimately involved with where the quotation was, the exacting work scope, and we had daily, If not weekly, communication. So nothing was left to chance. It was very, very transparent. Decisions that needed to be made along the way were made very quickly and e iciently so it didn’t hold up progress with the rebuild.”
Lyle said it’s an aspect of the rebuild process on which WesTrac prides itself.
“We walk through the customer’s expectations of what a rebuild looks like, whether it be a bit of a tidy up, a new engine, if it’s at the end of its life or has completely failed, or they may want to go the full kit and caboodle and basically put a machine back to zero hours so it comes out close to new,” Lyle explained.
From there, WesTrac’s workshop is engaged to run through the scope and a quote is provided to the customer.
Customers can also sit down with workshop technicians and hear direct how the rebuild will unfold and what sort of timeframes will be met.
“Customer involvement is a very important part of the process, right from the beginning,
because it’s their machine,” explained Lyle.
That includes regular progress updates, right through to running checks, final testing and inspection stages before machines are released back to customers.
For those in the construction sector weighing up a rebuild versus a replacement, Mick had some sage advice.
“For me, importantly, you have to understand the inherent rebuild-ability of the machine you’re considering. Not all manufacturers design their machines to have multiple lives. Determining this upfront is critical, especially when I’m considering the purchase price of a machine versus how many lives it could have in the future. There is definitely a place for rebuilding some Cat machines; there is some inbuilt value
you can extract later in life from a rebuild.”
And according to Lyle, the rebuild option is being increasingly favoured by companies operating in the construction sector because the rebuild process is cost-e ective, fast, and allows the company to keep a machine on its fleet that its operators are already comfortable with.
At WesTrac, all work is carried out in-house by dealer-trained Cat-certified technicians, with the latest updates being applied to every machine that goes through a rebuild. The rebuild process with WesTrac is easy, with the Cat dealer providing access to the latest parts, competitive pricing and support all the way through the process, from quoting to getting the machine back in the dirt – where it belongs.
In the domain of material handling equipment, Volvo Construction Equipment (Volvo CE) has carved a niche for itself, delivering solutions that excel in terms of reliability, adaptability, and operational e iciency – particularly in the waste and recycling industry.
Among the specialised o erings tailored to meet the demands of these challenging environments is the Volvo EW200EMH, a robust wheeled excavator designed exclusively for the waste and recycling industry.
Following the success of the EW240E material handler, the EW200EMH, its compact counterpart, quickly gained popularity among construction professionals seeking a more agile and versatile solution for their material handling needs. Volvo meticulously crafts these material handlers at their German factory, subjecting them to specialised engineering to excel in waste and recycling operations, and consistently deliver exceptional performance. With its unique features, impressive specifications, and unwavering support from
CJD Equipment's 24/7 national parts and service assistance, this machine promises to be a game changer in the industry.
Its innovative design and unparalleled functionality set the Volvo EW200EMH material handler apart. This machine boasts a weight of 22.6 tonnes and is powered by a robust and low emission Volvo D6J 6-litre Tier 4 final engine, delivering a formidable 173hp (129kW).
To maintain high productivity and e iciency, the EW200MH comes equipped with a specially adapted hydraulic system. This system, finely tuned to complement the Volvo engine grants these machines an optimal balance between engine RPM and hydraulic performance. Features such as the boom float function and boom cylinder dampening reduce vibrations and secure the grapple firmly in position, enhancing overall stability.
Other modifications – when compared to a
standard excavator – include:
• The hydraulic elevated cab
• Four stabilisers as an option (front blade and rear outriggers as standard)
• Solid rubber tyres.
The Volvo EW200EMH Material Handler's specifications read like a dream for operators in the waste industry. Equipped with three versatile boom and arm configurations, it o ers flexibility. The straight boom can be paired with a 4m gooseneck arm or a 3.5m sorting arm, granting a substantial reach of up to 10 metres. These specifications empower operators with the tools to tackle a wide range of tasks quickly and e iciently.
As the front runner, the EW200EMH demonstrates its intelligence and fuel e iciency through its operational strategies. It incorporates features such as auto idle, which lowers engine speed to idle when controls remain inactive for a redefined duration, and
Combining innovative design, functionality, and e iciency, Volvo’s EW200EMH material handler o ers a compelling package for the waste and recycling industries.Volvo’s EW200EMH is a robust wheeled excavator designed for waste and recycling applications.
an auto engine shutdown mechanism, which reduces fuel consumption. Additionally, the automatic activation of ECO mode further enhances fuel e iciency for the operator.
Volvo's ECO Mode is a new technology that ingeniously controls pump flow to prevent wasteful overflow through overload relief values while ensuring robust hydraulic capabilities and peak swing e iciency. This innovative approach e ectively reduces flow and pressure loss, culminating in up to a 5 per cent enhancement in overall e iciency. ECO Mode's precision and resource-conscious design represent a significant stride towards greener, more economical and environmentally responsible operations.
Volvo has also thoughtfully designed the EW200EMH for seamless maintenance and uninterrupted operation. Greasing points are grouped for easy access, while filters are conveniently placed behind wideopening engine doors, ensuring groundlevel accessibility across all E-series wheel excavators. Enhanced accessibility to areas like the pump compartment simplifies maintenance. Moreover, an optional waste package is available, featuring protective screens and a reversible fan to maintain the cleanliness of the cooling system.
The EW200EMH material handler o ers various convenience features, making it a top operator choice. Accessing and exiting the cab through the outriggers simplifies the work process. In contrast, the cab's impressive ability to elevate up to five metres provides an optimal bird's eye view of the job site. This machine features double-damped cab mounts, ensuring a smooth and comfortable ride and enhancing operator comfort.
Furthermore, the Comfort Drive Control allows joystick steering at speeds up to 19km/h, improving manoeuvrability. With cab and outriggers controlled directly from the joystick, this material handler streamlines operations,
making it a versatile and e icient machine for various tasks.
Additionally, Volvo material handlers come equipped with an adaptable arm-in limitation feature designed to mitigate potential collisions between the operator's cabin and the grapple. Incorporating a height limitation function adds another level of protection, particularly in indoor working environments. Including conspicuously coloured handrails and integrating additional steps into the outriggers have significantly improved cab access for operations. These unique features maximise both power and economy, making it an industry leader in its class.
“The benefit of Volvo machines is that we can customise them to suit our customers' needs,” explains Glenn Martin, General Manager for CJD Equipment Guildford. “We recently customised an EW200EMH for a customer in the waste industry. They required a machine for loading trucks and containers, and the EW200EMH proved to be the ideal choice for their operations.
“One of the primary reasons our customers opt for the EW200EMH is the outstanding visibility, accessibility, and reliability of Volvo machines, complemented by the assurance of our 24/7 national parts and service support network through CJD Equipment.
“I think what we do well is listen to and
understand our customer's requirements and do everything we can to provide them with the right-size machinery and attachments. The EW200EMH is favoured for its customised options; for example, the EW2000EMH features large expanses of glass, providing operators with exceptional all-round visibility. However, to further, enhance safety, customers can choose the Volvo Smart View feature or a one-piece polycarbonate window.”
The Volvo EW200EMH material handler represents innovation and practicality, symbolising Volvo's dedication to providing construction professionals with dependable, versatile, and environmentally conscious heavy machinery.
When you choose Volvo, it’s more than investing in top-tier construction equipment; it means securing comprehensive support from CJD Equipment. Their well-trained team are at your service across Australia, and you can choose from a range of additional services, specifically designed for your machines, allowing you to further increase your profitability, fuel e iciency, and safety solutions for a highly productive operation.
For more information, contact your local CJD branch on 1300 139 804 or visit: www.cjd.com.au
Develon’s 7M series of heavy excavators have begun making their way to local shores, bringing with them all power and toughness to face Australia’s toughest conditions, paired with the Korean company’s commitment to smart technological innovations.
Comprising the three heaviest machines in Develon’s excavator line up – the 38-tonne DX360LC-7M, the 42-tonne DX400LC-7M, and the massive 51-tonne DX490LC-7M – Develon’s 7M series is primed to take on a wide range of tough tasks for customers across a range of heavy industries.
One such customer, David Jacobson, has recently added a Develon DX400LC-7M excavator to his fleet. David manages the Tasmanian company Gadtech, which o ers quarrying, contract crushing, ready mix concrete supply, and civil and earthmoving services.
Having been a Develon customer for years (initially under the manufacturer’s former name, Doosan), David knew what to expect when he placed the order for the powerful new machine through his local dealer JF Machinery.
“We started dealing with Doosan excavators in around 2016 when we took on some used machines as part of a particular contract job,” he says. “Based on that experience, we started to look into new Doosan machines too. And we discovered that their prices were quite a bit cheaper than many of the competitors, and with a more powerful engine.”
One thing led to another, and David and the Gadtech team ended up purchasing a number of Doosan – and now Develon – excavators and wheel loaders, which have been put to use across all other arms of the business.
Earlier on, David says he used to rotate his Doosan machines for new ones quite regularly, not having a good sense of their long-term reliability. But he says if he knew then what he knows now, he wouldn’t have hesitated to hold onto previous machines much longer than he did.
“Looking at it in hindsight, had we known Doosan machines were going to give us such a good run, we probably would have kept each one for twice as long,” David says.
This, he says, is also owing to the level of support Gadtech has received over the years from JF Machinery.
“I’ve known Keith Johnson and Chris Gough there for years now, and we’ve always gotten along really well,” David says. “They o er a really good service, and their backup support has always been superb. We’ve barely had any problems at all with our Doosan machines, but
they’ve always gone over and above for me whenever I’ve needed anything.
“And with parts, they’ve been able to get stu out of Korea in around three days. Whereas with some other brands, sometimes it takes three weeks to get what we need.”
David is a third-generation earthmover, having started his career with his father’s business before going his own way in 1999. Today, his two sons Thomas and Charles Jacobson are following suit, each taking responsibility for di erent areas of the Gadtech business.
Thomas is in charge of Gadtech’s quarrying operations, where the new 42-tonne Develon D400LC-7M is being put to work. David says Thomas has been impressed by the machine’s power and agility for a larger excavator.
“Bigger machines tend to be slower, but that’s the trade-o for power and volume,” David says. “But these Develons are di erent. They feel like you’re driving a 20-tonner. Thomas and the other operators have been pretty amazed by how quick and responsive they are.
“And as far as fuel economy goes, we’ve found the Develons have been using just over half of what we’ve seen with some other excavator brands.”
For more on the Develon range, visit: www.develonequipment.com.au
Develon’s 7M range of heavy excavators introduces a suite of improvements across the board – from power to e iciency to functionality.David says the Develon D400LC-7M is very quick and responsive for its size. The Gadtech team has enjoyed great reliability from their Develon and Doosan machines.
Not many people in the Australian earthmoving industry can count themselves among the list of Guinness World Record holders – but Norman Bartie is one exception.
In early 2019, Norman – Managing Director of iLH-Australia Group (iLHA) – claimed the record for the longest journey in an excavator or digger, when he took a JCB backhoe loader 5649km from Brisbane to Parliament House in Canberra.
An impressive feat, but more importantly, one that helped raised $17,000 and generated some important publicity for his charity – It’s Not Your Fault 4 Kids Incorporated – and spread the word of his cause across Australia’s east coast.
And while this achievement certainly helped raise the profile of Norman and his business, his story starts much earlier.
In 2014, burnt out by a culture of depression and suicide, Norman walked away from his decades-long career in the earthmoving industry. But it wouldn’t be for long – he’d soon return to the industry with a newfound clarity as to his place in the industry, and how he could use his skills to make it better.
After spending his time away focusing on supporting at-risk children, Norman returned to the tools in 2017, when he started iLHA.
Norman describes iLHA as a holistic, traditional indigenous lore-based earthmoving business in the environmental and civil infrastructure space. The business provides
construction, plant and labour hire services, but also runs workplace wellness workshops, as well as cultural awareness training.
In fact, the latter two have become an integral part of the business’ o ering, whereby engaging iLHA on projects requires participation in what Norman calls ‘toolbox sessions’ each morning.
In these sessions, Norman shares learnings from his culture to help workers from all backgrounds appreciate and connect with the environment and people around them. He says this is a key requirement for any project iLHA works on, because it encourages everyone to take a step back and look at the bigger picture. This also means checking on your co-workers, and making sure they’re in the right frame of mind.
“You never know what the people around you might be going through,” Norman says. “One of your work mates might have seen a bad road accident on the way, or maybe his wife’s just left him, and now he’s operating a concrete saw. And if his mind is wandering anywhere but on the task at hand, that’s how someone loses an arm.”
This is the essence of the message that Norman endeavours to spread on every job, in the hope that it will creative positive knock-on e ects throughout the industry.
“It’s about bringing a mindful approach to your everyday work,” he says. “We’re not making people read a book, or knock o early to go see a psychologist.
“I just encourage people to lower their heartrate, raise their frequency, and learn to put their hand up when they need to.”
This is further supported by iLHA’s ‘Wellness Diggers’: hire machines branded and decorated to spark conversation around working mindfully and thoughtfully.
“Throughout the day, when you see one of those machines, they can be real conversation starters,” Norman says. “If you’ve got stu going on, you’re more likely to want to be around that positive energy.”
For Norman, it’s all connected to supporting children in the community – by fostering a happier, healthier workforce, workers have a better shot at supporting a happier, more nurturing family.
“And that positive cycle is something children need,” Norman says. “Kids need it, families need it, all human beings need it – especially in our current world of misinformation and disconnect.
“It’s about connection, the storytelling around that connection, and passing it onto the next generation – that’s what we need to get somewhere as human beings.”
Norman has a lot on his plate day-to-day, but that doesn’t mean he can’t spare a little time to get excited about machinery. He is an earthmoving guy, after all.
And throughout his years in the industry, Norman has developed a loyalty to JCB
Norman Bartie is always trying to give back to his community – whether through his earthmoving business, charity work, or his way of life.The iLHA fleet includes a JCB Hydradig wheeled excavator, and a new 245XR reduced swing excavator.
machinery. This, he says, is down to several reasons. But a big factor is the level of support he’s received from distributor JCB CEA – not just in terms of support for machinery, but for Norman’s way of doing business.
He says the JCB CEA team has demonstrated compassion for his cause, are always looking for ways to provide a platform for his message.
“The team at JCB CEA have great insight and an understanding of what we’re trying to do,” Norman says. “They’re always asking how they
can help with the charity, and they’re sensitive to our cultural di erences as well.
“They don’t make it about money. If someone just wants to talk to me about money, if it’s about greed, then there’s a disconnect in that for me. We all have to make a living, but there’s a right way to do it.”
This has resulted in a fruitful relationship for both parties. The iLHA fleet has become very JCB-heavy, and Norman is always more than proud to talk up and show o his machines.
“JCB’s machines are just in a league of their own,” Norman says. “They’ve always held up really well.”
The two newest pieces of JCB gear in the iLHA fleet are the versatile Teleskid, and the reduced swing 245XR excavator.
“Normally zero-swing machines are a pain,” Norman says. “Without the counterweight, when you’re trying to trim and you go to reach and grab something, you’ll end up with a little dip in your final trimming. But not with the 245XR – it’s just so good. It makes an average operator look great.”
Norman says his partnership with JCB CEA will continue to play a role in his company’s growth over the coming years.
“I’d like to get some of our JCB machines and operators onto larger government projects as a social enterprise,” he says. “That’s my ultimate goal for iLHA. That way, I can run the plant hire side of the business without competing with other big players in the hire space. And the money goes to looking after kids – there shouldn’t be too much opposition to that.”
Of course, none of this is possible without machines you can trust – and this is where Norman says JCB CEA can provide that peace of mind. If he and his operators don’t need to worry about the reliability of their gear, then it frees them up to focus properly on their work.
“Not only are these, in my view, some of the best machines on the market for their safety standards, but their comfort really helps bring operator fatigue down,” Norman says. “This all contributes to a safer workplace, and that’s one thing we’ll never compromise on.”
From a base at Banksmeadow in Sydney, DL Civil has been traversing the greater area to perform the full spectrum of excavations down to backyard swimming pools, as well as handling a wide range of demonstration works.
Dublin-raised David Leonard arrived in Australia from Ireland about 15 years ago, and within about 10 years he has established a business comprising around 30 machines including excavators up to 40 tonnes, seven to eight trucks, and a team of about 20 operators.
Sitting alongside the DL Civil business today is DL Plant Hire and that’s the one the LiuGong equipment is helping to expand.
It recently welcomed a 2.8-tonne, zeroswing 9027F LiuGong excavator and a 3.8-tonne 6032 roller.
David has had a long relationship with Liam King of local LiuGong dealer, Pacific Machinery Group, where he has purchased a range of machine attachments, and, also aided by strong encouragement, he said he could no longer ignore the benefits of the LiuGong brand.
“They are our first LiuGong machines and they are way cheaper than the alternatives,” David says.
“At this smaller end, they probably cost
$20,000-$30,000 less and in the mid-range of excavators, the saving is more like $50,000$70,000.”
The 9027F LiuGong excavator is powered by a 20hp Yanmar engine and suits a range of works including utilities, foundations, landscaping, indoor and outdoor demolitions, and construction.
It is easy to operate and transport and the zero tail and boom swing allows it to dig right alongside its tracks.
“With the zero swing, it can work in tight access areas,” David says.
“For one job, I also took the roof o to work inside a garage. It only required unscrewing a few bolts – it was easy.”
He says the 9027F machine completed some excavation work initially before being set for the dry hire business and heading out to a company to assist demolition works. It uses a quick-hitch for all buckets and also includes a hammer and a grab to pick up rubbish for loading into skip bins.
The 6032 LiuGong roller is the dry hire business’ first roller on civil jobs including road and car park construction and its operators have been highly impressed.
“For their performance in doing the job for a machine price that is $20,000-$30,000 less than others, the LiuGong rollers are really good,” David says.
Power and vibration with the LiuGong 6032 roller are delivered via a reliable Tier 3 Perkins engine, which David said helped to provide even further confidence to operators.
For a young, expanding civil excavation and plant dry hire business, the cost-e ectiveness of adding LiuGong machines to its fleet has been simply too good to pass up.David says the LiuGong 6032 roller o ers strong performance for an extremely competitive price. David Lenard, DL Civil, says the 2.8-tonne, zero-swing 9027F LiuGong excavator is ideal for tight access areas.
HIGH PERFORMANCE
EASY MAINTENANCE
BEST VALUE
The Young Group is a leading Tasmanian, family-owned business spanning the full spectrum of property investment, development, construction, management, and leasing. The company was founded in 2008 by Trent and Nakiya Young who have built the company on family values, integrity, and trust to provide a positive contribution to communities and build spaces for businesses and people to flourish. They work closely with all local stakeholders to provide quality and value in this space. Its commitment lies in building a better future for the community with innovation and sustainability at the core of their work across commercial, retail, industrial and residential sectors.
The Young Group is driven by strong local knowledge and extensive industry expertise, whose team is committed to shaping places that fuel economic and social success.
With this mindset The Young Group were open to exploring the Hidromek range of equipment for the first time. Sean Devine, an operator in the company said that “aside from
seeing them beside the highway”, they had not much knowledge about the brand, nor used any of their equipment on any projects before.
At the moment, it is working on a $60m warehouse development on 6.5 hectares over five years in Hobart's northern suburbs. The site will include local breweries with tastings, shops, community centre, cafes, and a factory which is adjacent to a ordable homes, with stage one starting soon.
“Over time, The Young Group have owned a ‘mix of di erent brands of equipment including Hitachi, Komatsu, Kubota excavators, bobcats, skid steers and a Dynapac roller’,” explained Tim Holloway, Head of Construction. The Group is looking to expand its fleet to complete some of these new projects and were approached by Onetrak to consider Hidromek machinery that suited the needs for their operations.
This was the start of the partnership with Onetrak and the Hidromek brand, during October and November 2022.
“We have added the Hidromek HMK310LC excavator and the HMK110CS roller to our
fleet, which are currently being used for our subdivisions, the quarry on the farm, and roads that lead to the quarry,” Tim explained.
Tim said that they have found the Hidromek equipment to be ‘powerful and fuel e icient, with di erent settings for power modes and it is on par with other brands’.
“The driving experience is excellent. Both machines, the HMK310LC and HMK110CS, are comfortable, spacious, and smoother in the cab, with the HMK310LC excavator being especially comfortable,” Tim said.
He said both machines have great features and everything works well including touchscreens, the Topcon GPS, and Doherty quick-hitch.
“It’s more than a 10 out of 10 for me. Even the cold box for your drink or lunch is cool,” Sean added.
"It didn’t take long for us to get used to the controls because they are standard,” Sean said. “The roller is easy to operate, and it is simple to show someone how to operate it. We were also impressed with the safety features which
include the lock-on controller and having to be in neutral before you started up.”
Sean also described the visibility from the cab as being good due to the cab’s design and wide cab angles.
“You can also take the padfoot o the roller providing a multi-option, which was one of the reasons for buying it,” he said.
In terms of aftersales support, Sean commended Onetrak’s support and service.
“It has been great, with Onetrak’s attention to detail, and quick response time being a highlight,” Sean said. “We deal with the service team at the Bridgewater Branch, and they have been very responsive and great to deal with.”
At the end of it, Sean was more than satisfied with the performance of the machines.
“We get questions all the time about the equipment, with curious people including truck drivers wanting to know what the Hidromeks are like, and we are more than happy to recommend Hidromek and Onetrak to anyone asking because we are pleased with the performance and comfort of the machines,” he said.
If you want to find out more about Hidromek contact Onetrak, your local Hidromek supplier in Australia on 1300 727 520 or visit www.onetrak.com.au
Shandong Lingong Equipment (SDLG) has gained a well-deserved global reputation for its depending performance. With over five decades of industry experience and a presence in more than 130 countries, SDLG stands out as one of China's most rapidly expanding construction equipment manufacturers. Since becoming part of the Volvo Group in 2007, SDLG has seamlessly incorporated Volvo's design principles and stringent quality standards into its machinery, delivering cost-e ective and dependable equipment that prioritises ease of use and maintenance.
“For over a decade, CJD Equipment has been Australia's trusted distributor of SDLG wheel loaders,” explains Andrew Egan, the National Product Manager for SDLG at CJD Equipment. “During this period, our customers across various sectors, including waste and recycling, agriculture, timber plants, and general construction, have achieved remarkable outcomes with these loaders. The consistent feedback from our clientele underscores their exceptional reliability, ease of operation, and adaptability.”
The latest SDLG mini excavator range to be o ered by CJD Equipment consists of three models: ER616F, ER636F, and E660FL.
The ER616F mini excavator from SDLG, launched by CJD Equipment, is a testament to the power of innovation and e iciency. It may be compact, but it's big on performance, versatility, and user-friendliness. In an industry where every second counts and adaptability is critical, the ER616F is a reliable partner for any
construction professional.
The ER616F, the smallest excavator in CJD Equipment's line-up of SDLG excavators, is a compact powerhouse, boasting a mere 1.8-tonne weight, yet packing an impressive punch with its 10kW/13hp Kubota engine. The ER616F has a remarkable excavation force of 15kN, allowing it to e ortlessly handle various attachments, enhancing its versatility for a wide range of applications.
The ER616F has an energy-e icient and fuele icient Kubota engine, ensuring it can operate for extended periods without refuelling. Its zero-tail swing design means it can manoeuvre e iciently in confined spaces, minimising the risk of accidental damage to nearby structures or obstacles.
One of the standard features of the ER616F is the use of high-quality hydraulic components, which provides precise control and greatly enhance overall stability during operation. These components ensure that your work is not only e icient but also carried out with a high degree of accuracy.
Specifically designed for tasks such as landscaping and smaller municipal construction projects, the ER616F is engineered to be robust and dependable. Its simplicity of operation makes it accessible to seasoned professionals and those new to excavating. With an ergonomically positioned mechanical accelerator, pilot handle and control switch, the ER616F helps operators do the job swiftly and precisely. This combination of power, e iciency, and user-friendliness
is an invaluable asset on any job site.
The ER616F excels in its performance and in providing operators with an exceptional field of vision, ensuring they can carry out their tasks with maximum safety and e iciency. Its integrated rollover protection, tip-over protection, and OPG1 standard pressure generation and control components enhance safety, giving operators peace of mind when working in challenging conditions.
The strategic grouping of main components, filters, and lubricant systems under the main engine hood not only showcases the ER616F's commitment to user convenience but also highlights the machine's dedication to minimising maintenance e orts, ultimately benefiting both operators and owners by maximising uptime and reducing operating costs.
CJD Equipment has a long-standing reputation for delivering top-quality machinery with exceptional after-sales support. The SDLG ER616F excavator is no exception. Constructed with robust components and a comprehensive three-year/6000-hour warranty, this excavator guarantees operators a reliable asset for their operations. CJD Equipment's extensive network of service centres across Australia provides prompt and e icient support, ensuring minimal downtime and maximising productivity.
For more information about the SDLG machinery line-up and to find your nearest CJD Equipment branch or SDLG Dealers, please visit www.cjd.com.au or call 1300 139 804.
INCLUDES A 3-YEAR, 6000-HOUR WARRANTY
Newly designed with comfort and reliability at the core, SDLG’s mini excavators deliver optimal power and efficiency at a competitive price without compromising on quality. SDLG has over 50 years of manufacturing expertise and has been a member of the Volvo Group since 2007. SDLG machinery is backed by CJD Equipment’s national branch and SDLG dealer network.
Big Enough to Trust, Small Enough to Care
COMFORT & SAFETY
• Air-conditioned cab
• Pillarless windscreen for ultimate visibility
• Fully certified ROPS/TOPS/OPG1 protection
EFFICIENT & PRODUCTIVE
• 1.8-tonne operating weight
• 10kW/13hp fuel efficient Kubota engine
• Zero-tail swing design
24/7 LOCAL SUPPORT
• 24/7 product support
• Backed by CJD Equipment’s national branch and SDLG dealer network
With a strong focus on technology and the future, the development of the Hitachi Zaxis-7 series of excavators was driven by the goal of creating next-generation solutions. This was accomplished through a thorough review and refinement of its technology, taking into account both natural and work environments. The result is a new level of performance in the industrial world, seamlessly integrating human qualities into the Zaxis-7 series.
In 2022, Hitachi Construction Machinery (Australia) Pty Ltd (HCA) proudly introduced the Zaxis-7 range of medium excavators to the Australian market, empowering customers to take full control of their safety, fleet management, profitability, and comfort thanks to its enhanced reliability, versatility, and productivity.
Among the satisfied customers is Tom Hance, the owner of Southcut Plant & Civil, a Melbourne-based company specialising in equestrian/horse arenas, local council, and civil construction projects. Tom purchased a Hitachi ZX135-7 excavator in late 2022, and he couldn't be happier with his decision.
“The ZX135-7 truly stands out when it comes to completing precise final trim work; it's a
dream to operate,” he says. “The boys are able to complete jobs more e iciently with less fatigue due to the new cab.”
O ering an expansive cab that sets a
new industry standard for spaciousness, coupled with a synchronised console, these enhancements not only increase operator comfort but also reduce fatigue.
Hitachi’s Zaxis-7 series of medium excavators are designed to marry safety, comfort, and productivity, while giving operators full control over their experience.Southcut Plant & Civil specialises in local council and civil construction projects, as well as equestrian arenas. Tom feels like a valued member of Hitachi’s “orange family”.
The redesigned interior significantly enhances operator visibility through features such as LED work lights, an e ective windscreen wiper, generously sized reflective strips, and roller sunshades.
Additional notable features are the inclusion of a standard 270-degree rear camera, complete with an object proximity sensor ensuring a heightened level of safety within the work environment. The ISO standard TOPS and ROPS cab with seat belt further strengthens operator safety and protection.
The excavator comes with built-in Consite capabilities, facilitating real-time monitoring of machine performance. This plays a crucial role in pre-emptive maintenance and prolonging the machine's lifespan. Additionally, an alarm display is integrated to promptly alert the operator to any issues, enabling swift attention.
The ZX135-7's 2D GPS hydraulics have greatly increased its versatility, allowing the Southcut team to e ortlessly tackle various jobs, from final trim applications requiring a super-smooth operation to tree work that demands heavy lifting capabilities. Thanks to the renowned Hitachi hydraulic system, fuel consumption is reduced compared to the previous models.
With upcoming contracts for an equestrian complex past Ballarat, Victoria, and several arena builds scheduled for the spring-summer of 2023, the team at Southcut have a full schedule ahead. The ZX135-7 will primarily be utilised on bulk earthworks and drainage on local council projects.
The decision to purchase the ZX135-7 excavator was driven by its exceptional reliability and the support network it o ered. Tom sought “a machine that would continue to perform well past the factory warranty date” and was pleased to find that dealing with the service and parts team at Hitachi’s Melbourne branch was an exceptional experience, further strengthening his confidence in the global brand.
During his interactions with HCA's Sales Representative Wesley Don, Tom was impressed by the professionalism, punctuality, and transparency demonstrated. Right from the beginning, Tom was treated like a valued member of Hitachi’s “orange family,” inspiring him to make a second purchase – a ZX85 excavator in March 2023.
The Hitachi Zaxis-7 range of excavators has truly made a mark in the industry with its cutting-edge technology and operatorfriendly features. Tom's positive experience with his ZX135-7 speaks volumes about the success of this new generation of excavators.
To check out the range of Zaxis-7 excavators, visit: www.hitachicm.com. au, or call 1300 HITACHI to arrange a test drive.
When it comes to heavy construction equipment, few names resonate as strongly as XCMG. As the world's third-largest construction equipment manufacturer, boasting over 80 years of industry experience, XCMG has solidified its reputation for innovation, reliability, and top-notch performance across its comprehensive range of construction, agriculture, and industrial machinery. A testament to its prowess, XCMG's line-up of large excavators, spanning from 16.6 to 48.1 tonnes, has taken the Australian construction scene by storm, thanks to their unparalleled quality, value for money and bolstered by an industry-leading warranty package.
XCMG heavy excavators are renowned for their exceptional power, lifting capacity, and remarkable reach. Catering to a wide spectrum of requirements and projects, these excavators come in various sizes. The entire range stands out for its hydraulic performance, cycle times and breakout force, setting the bar high for competitors. The integration of premium
Cummins and Isuzu engines, coupled with top-quality components from industry giants like Kawasaki, Nabco, and Miller, ensures that XCMG heavy excavators o er unbeatable value for money.
The XCMG heavy excavator line-up includes models:
• XE155: 16.6t Operating Weight, 2x113LPM
Hydraulic Flow, 121HP Cummins Engine
• XE215: 21.5t Operating Weight, 2x216LPM
Hydraulic Flow, 181HP Cummins Engine
• XE245: 25.7t Operating Weight, 2x241LPM
Hydraulic Flow, 201HP Cummins Engine
• XE310: 30.8t Operating Weight, 2x259LPM
Hydraulic Flow, 226HP Cummins Engine
• XE370: 36.8t Operating Weight, 2x304LPM
Hydraulic Flow, 284HP Isuzu Engine
• XE490: 48.1t Operating Weight, 2x360LPM
Hydraulic Flow, 375HP Cummins Engine. These machines are equipped with auxiliary hydraulic flows fitted as standard, horsepower, and engine options that cater to diverse project demands. Whether it's the XE155's nimbleness
or the XE490's sheer power, each model brings a unique set of capabilities to the table.
Operator comfort is paramount in any heavy machinery, and XCMG's excavators excel in this domain. The spacious and comfortable cabins are designed to accommodate even the longest workdays, with sound dampening and stateof-the-art controls enhancing the operator's experience. XCMG's focus on serviceability and minimal downtime ensures that these machines keep running e iciently, backed by only the most reliable components for extended longevity. Owners seeking a blend of comfort, versatility, and performance at a competitive price would find XCMG heavy excavators irresistible.
One of XCMG's standout features is its comprehensive warranty package, reassuring owners with peace of mind. This warranty is supported by a network of dealerships and service agents spread across Australia. XCMG's commitment goes beyond just selling machines; it's about delivering unmatched after-sales support, ensuring minimal downtime, and o ering premium assistance throughout the machine's lifecycle and beyond.
XCMG heavy excavators e ortlessly check all the boxes for operators who seek powerful performance, ergonomic comfort, and e iciency. With their ability to accommodate various attachments, including those requiring high flow machines, such as mulchers and augers, these excavators o er premium versatility without compromising on a ordability. Their robust design, exceptional hydraulic capabilities, and overall operator satisfaction make them an indispensable asset for a wide array of projects.
XCMG heavy excavators shine as a beacon of innovation, reliability, and performance. With a diverse range of models that cater to di erent project scales, these excavators o er exceptional hydraulic performance, ergonomic comfort, and unparalleled operator satisfaction. The backing of a generous warranty and after-sales support network shows XCMG's commitment to its customers. As XCMG continues to make waves with its exceptional line-up, it's evident that their heavy excavators are not just machines; they're a testament to the brand's dedication to excellence. For those seeking a blend of power, versatility, and comfort in their construction projects, XCMG heavy excavators undoubtedly rise to the occasion.
Find out how XCMG heavy excavators shine as a beacon of innovation, reliability, and performance.XCMG's large excavators have taken the Australian construction industry by storm, thanks to their quality, value for money, and industry-leading warranty package.
If your task involves vegetation control, eradicating invasive flora, establishing fire breaks, or other forestry tasks, Fecon is the brand you need. Fecon takes pride in their machines and attachments as they hold exceptional power, dependability, and heavy duty builds. They ensure that each attachment and machine is engineered to be tough and durable to e ectively manage even the hardest most resilient Australian timbers.
When considering power, Fecon Forestry Tractors stand at the forefront. Fecon has solidified its reputation through its array of remarkable tracked forestry tractors, spanning from 150hp to 300hp. These forestry tractors redefine the land management terrain, o ering exceptional outcomes and end product. Boasting a renowned Cummins engine, these
tractors incorporate top-notch parts and components, translating to reduced downtimes and increased operating periods. Each tractor is fitted with Fecon mulching head and also boasts the capability to accommodate various attachments such as tree shears, Stumpex, root rake, rotary deck mower, dirt bucket, and other high-flow demand implements. They feature a comfortable cabin with an adjustable seat, touchscreen display, and more, perfect for all day operator comfort.
One of the attributes found within the Fecon forestry mulcher lineup is their exceptional force. Equipped with heavy-duty rotors and sturdy implements, these mulchers are crafted to e ectively eliminate dense vegetation, shrubs, trees, and undergrowth. The Fecon Bullhog mulchers are compatible with a wide
array of skid steers and excavator models, o ering versatility through both standard and high-flow options. Available with various rotor types tailored to your precise requirements: the rugged FGT for heavy-duty tasks, the precisionfocused DCR for refined end results, or the swift-cutting FMX. Engineered with hydraulic variable displacement motors, these regulate speed and torque, resulting in enhanced flow and cutting, minimising the risk of stalling. The Fecon Bullhog mulchers indisputably set the standard for excellence in the forestry industry.
Fecon Tree Shears, engineered for use with excavators and skid steers, have revolutionised the craft of tree cutting, hoisting, grouping, and transporting, all within a singular attachment. They were engineered to excel, even against hard Australian timbers. They e ortlessly access areas that would otherwise remain out of reach with ease. With Fecon Tree Shears, you can now engage in forestry management assignments within zones that were once deemed inaccessible. True to the Fecon brand, these tree shears are manufactured with a focus on quality, including their heavy-duty shear knives. These knives are constructed from superior steel to ensure unwavering durability and a prolonged lifespan. The frame is both heavy duty and easy to manoeuvre, guaranteeing agility and e ectiveness during the execution of demanding tasks.
When confronted with old or hard tree stumps, conventional techniques can prove to be time-intensive, untidy, disruptive, and feel impossible. This is where Fecon Stumpex intervenes – a revolutionary stump grinder that introduces an alternative perspective to the process. Tailored for use with both excavators and skid steers, the Fecon Stumpex presents a groundbreaking rotational grinding mechanism resembling an auger, reshaping stumps into finely processed end products with exceptional e iciency and minimal interference. Operating through a deliberate blend of slow rotation and heightened torque, the Stumpex adeptly grinds stumps into a fine end product in a matter of minutes. This approach ensures a safer work environment given its low RPM rotation that prevents flying debris. This creates easy posttask cleanup, compared to most other stump grinders available on the market.
Fecon provides the essential equipment to achieve results with e icacy and rapidity. With summer around the corner Fecon products are the perfect vegetation maintenance tools in bushfire prevention works. Supported by nationwide parts, sales, and support.
Enquire today at: www.fecon.net.au or call 1300 FECON 1.
Fecon has established itself as a widely recognised brand in the forestry sector, owing this to its robust mulching capabilities.Fecon Tree Shears engage in forestry management assignments within zones that were once deemed inaccessible. The Fecon Bullhog mulchers are compatible with a wide array of skid steers and excavator models, o ering versatility through both standard and high-flow options.
Mark Johnson, the motor grader product consultant for John Deere, expresses his enthusiasm for the company's innovative breakthrough. Unlike a standard circle, which necessitates maintenance and wear insert replacements, the Premium Circle is a gamechanger. It boasts a completely sealed bearing system, eliminating the need for shoes, wear inserts, and jack screws. This revolutionary design can only be found on John Deere machines and aligns perfectly with the cuttingedge John Deere SmartGrade mastless GPS system, further enhancing performance.
On a standard circle, the circle is more exposed by design leading to wear over time over the course of the machine’s operation. Wear inserts inside a standard circle require adjustments to keep a good tight circle for accuracy and to prevent damage to the circle before eventually, needing to be replaced. Customers could spend valuable hours in the workshop replacing or shimming the wear inserts as opposed to being on the job, leading to increased downtime over the lifetime of the machine.
In comparison, in the Premium Circle option, there are no shoes, no wear inserts or jack screws exposed with the system completely sealed with the wear inserts being replaced with a sealed bearing. The pinion and circle teeth are also completely sealed from dirt and debris to minimise wear. John Deere’s design was very focused on completely sealing, rather than simply covering the circle pinion drive that can still attract and hold debris.
The option has also been designed to create a more simplified maintenance process. One of the
main di erences is the larger gearbox which has increased the oil change intervals to 4000 hours. The bearing circle has five easy access grease points on the bearings circle, four on the table and one on the pinion. The recommended service intervals on these grease points are every 500 hours, nothing to do on a daily basis here.
The Premium Circle presents a host of advantages that surpass conventional motor grader circles. Most notably, it o ers an increase of up to 15 per cent in circle speed and up to 40 per cent in circle torque compared to the standard option. By eliminating the need for time-consuming maintenance and providing enhanced speed and torque, the Premium Circle significantly boosts productivity and reduces downtime for contractors and government sectors alike.
John Deere has also focused on simplifying the service requirements with the Premium Circle. The larger gearbox on the Premium Circle contributes to its durability, while also extending the service interval for the circle drive system from 2000 to 4000 hours. Additionally, the Premium Circle features five grease points on the bearing circle, providing easy access for maintenance. With four grease CRCs on the top of the table and one on the pinion, technicians can e iciently lubricate these points every 500 hours during routine service intervals.
The Premium Circle o ers substantial value to
both contractors and government sectors. With its enhanced performance, streamlined serviceability, and increased productivity, the Premium Circle enables contractors to complete grading tasks with unparalleled precision and e iciency.
“Customers using grade control systems will notice they no longer have to compensate for wear in the circle or stop the machine to adjust for looseness of the circle when using the Premium Circle option,” says Karen Poulton, Marketing Manager for John Deere Construction & Forestry Division. This is especially impactful when coupled with the innovative John Deere SmartGrade system.
“The same grader can now be used from initial site clearing to final grade without stopping to install masts or downing the machine to adjust for looseness in the circle,” Karen adds.
Government entities can benefit from the reduced maintenance requirements and improved operational capabilities, allowing for optimal utilisation of resources and timely completion of infrastructure projects.
Motor graders continue to play a pivotal role in construction and infrastructure development, and Deere's commitment to innovation and customer satisfaction shines through in this ground-breaking feature.
“The take rate of the Premium Circle is high, and the customer feedback has been that all of their future graders will have it,” Karen says. “The e iciency and lower maintenance it provides is a no-brainer for their businesses. “Deere is still the only manufacturer who o ers this industry exclusive, and it’s available right now on every grader model we make for the Australian market.”
The Premium Circle's sealed bearing system, increased speed and torque, and simplified service requirements exemplify the manufacturer's dedication to pushing the boundaries of motor grader technology. With the Premium Circle leading the way, the future of grading has never been more precise, e icient, and productive.
To find out more about John Deere’s Premium Circle option, fully integrated SmartGrade grade management system, and the automation features that help protect the machine and simplify repetitive work, visit: www.deere.com/en/ campaigns/smartgrade-motor-graders
It’s been nearly three years since John Deere launched its factory-installed Premium Circle option for all John Deere G-Series, GP-Series and SmartGradeTM motor graders.The Premium Circle features a completely sealed bearing system.
Epiroc has now expanded its Bulk Pulveriser range with a smaller and a larger model. Secondary demolition is becoming increasingly important on smaller jobsites and the new BP 1650 and BP 4050 are e ective solutions for secondary breaking of demolition debris and separation of concrete and rebar. They are also a profitable choice for recycling stations and scrapyards.
Suitable for carriers in the weight class 14-23 tonnes, the new BP 1650 weighs 1720kg and has a maximum jaw opening of 760mm. The BP 4050 is suitable for carriers of 40-55 tonnes and has a service weight of 4550kg and a maximum jaw opening of 1200mm.
As with the other Bulk Pulverisers in the range, when developing the BP 1650 and BP 4050, Epiroc focused on fast, e ective operation, minimum maintenance, and long lifetime, all of which help reduce total cost of ownership.
Both models are available in two versions: a standard model and an ‘R’ version with rotation unit. As options they can be equipped with Epiroc’s HATCON™ connectivity tool and a water spraying system.
Epiroc has also released the DP 1820, a smaller Demolition Pulveriser with a new level of performance.
With a service weight of 1820kg, the new DP 1820 is suitable for carriers in the weight class 15-22 tonnes, thus making these attachments a profitable choice for a wider range of carriers. The DP 1820 has a slimmer, more robust design with no cylinder-rod protection needed. Performance is impressive, with up to 20 per cent more crushing force between the jaw tip and the cutting blade. Wear is minimised by an optimised wear part design which, combined with a new speed valve, results in lower maintenance requirements. Cutting blades
and teeth are replaceable and can easily be exchanged onsite.
All models are fitted as standard with a speed valve providing faster cycle times and resulting in greater productivity.
See the Epiroc Bulk Pulveriser range at www.epiroc.com
Urbanization is an ongoing transformation – 7.9 billion people worldwide need housing. Our efficient solutions for demolishing old buildings, and our equipment for foundation work and demolition waste recycling are enabling and accelerating the transformation.
See how we accelerate the transformation
Steelwrist, based in Sweden, is a global manufacturer of tiltrotators, quick couplers, and work tools for excavators. The company’s goal is ‘to be the best in the world to develop, manufacture and sell equipment that increases
e iciency of excavators’, and it prides itself on actively trying to get feedback and suggestions for improvements from customers, suppliers and employees.
In Australia Steelwrist is based in Luscombe, Queensland, and is headed up by Managing Director Australia & New Zealand, Darryn Wilson.
Darryn’s journey to the head of the Australian arm of the fast-growing attachment powerhouse makes for a great story.
“I was with Doherty Couplers & Attachments as the operation manager,” recalls the enormously experienced Queenslander. “Doherty was the dealer for Steelwrist, and when Dohertys was acquired by Kinshofer we had to drop the contract with Steelwrist.
“It was at that point myself and Stefan Stockhaus – the CEO at Steelwrist – got talking about what we needed to do in the Australian market.
“We decided I’d set up Steelwrist Australia as the dealer.”
Darryn, as managing director, set up Steelwrist Australia in 2018 and began growing
the business and in 2021, Steelwrist Sweden acquired Steelwrist Australia, and Darryn stayed on as managing director.
It sounds like a tumultuous few years, but Darryn remembers the focus being unchanged through the period.
“We’d been an Engcon dealer with Dohertys, and then we moved into Steelwrist,” he says. “The focus with both Engcon and Steelwrist was always the tiltrotators and that has not really changed, for me anyway.”
Darryn’s a inity with his product is obvious when he speaks of the evolution of the incredibly versatile attachment.
“Tiltrotators started in Sweden,” he explains, “with a company that is now called Rototilt. At the moment the major manufacturers are all in Sweden.
“Steelwrist started with Stefan Stockhaus and Marcus Nilsson back in 2005. From there, it’s grown to the stage where Steelwrist is now the fastest growing tiltrotator manufacturer in the world. We have representation in Sweden, Finland, Denmark, Norway, Poland, Germany, Netherlands, France, Italy, the US, Canada,
China, Japan, Korea, New Zealand, and Australia. Plus, we have a rest-of-world team that sells into regions where we do not have local representation.
“So we've got a pretty good global coverage.”
Steelwrist also has a Factory Fit program which allows Volvo, JCB and Yanmar machines to arrive in dealer yards already fitted with Steelwrist equipment.
“The evolution of quick couplers in the Australian and New Zealand markets can be summarised in the following stages; standard quick couplers to tilt couplers and now tiltrotators,” Darryn explains. “Looking at the progression, we are now at the stage where I would say that majority of machines are sold with a tilt coupler instead of a standard quick coupler. So the industry has adopted that change and the next phase I believe will be the tiltrotator, similar to evolution in the European and US markets. They’re the next big thing.
“The advantage of a tiltrotator is obviously that it increases e iciency. You don’t have to move the machine around as much, so you save on fuel and track wear, you can do things a lot quicker, and it makes the machine a lot more versatile.”
Year-on-year sales of excavators are increasing, and Darryn thinks the increased popularity is entirely understandable.
“Excavators are a lot more versatile,” he beams.
“You just have to look at any road construction site and count how many excavators are being utilised. They are quickly becoming the machine of choice because they are versatile, and that's where the tiltrotator brings it into another realm altogether.
“The one consistent comment we get from our customers is that ‘I can do so much more with a tiltrotator’ and we love to hear that.”
Darryn is clearly excited about the direction of the construction world, and especially for Steelwrist’s future prospects.
“The whole industry is going through a bit of a change at the moment,” he points out. “Previously we had to install complete control systems to interface with the machine for the tiltrotator.
“A lot of manufacturers now are o ering the option of including a tiltrotator control built in, so the machine is ready to have a tiltrotator fitted without any aftermarket installation required, which is a clear indication of the uptake of the product at the OEM level.
“There was a new machine control system introduced in Bauma last year called MiC-4.0. It will allow any tiltrotator to be connected and controlled from the original machine setup. There’s no installation needed from us. All we do is we supply the tiltrotator. It plugs into the original OEM plug, and then the OEM control system controls everything.
“The list of MiC-4.0 members is growing
and already includes some major excavator manufactures, and I understand it’s being integrated slowly into other manufacturers in Europe as well. It’s all very exciting.”
The other innovation which has Darryn sitting forward in his chair is the Open-S Alliance, an initiative started by Steelwrist, but which now has been embraced by Kinshofer, Rototilt, SMP, ROTAR, KH-Maskin, Agri Manutention, and Volvo.
“We all manufacture our automatic oil couplers and attachments to a certain standard so anybody who purchases a coupler from an Open-S Alliance member can rest assured that
their attachments will fit and work correctly,” he says.
“The beauty of that is the consumer isn’t locked into buying their attachments from the supplier they bought their automatic oil quick coupler from. It’s typical of the Steelwrist mentality with our products. We believe in keeping it all consumer-focussed, and less manufacturer-focussed.
“So that’s where the future is.”
For more information on Steelwrist in Australia, log on to: www.steelwrist.com/ en-au/
the establishment of Undercarriage Track Workshop facilities in Queensland and NSW.
Part of the USCO Group of companies
ITR Pacific is part of the USCO Group of companies and recognised globally as a reputable supplier of earthmoving machinery parts. With ITR Pacific’s passion for parts, the company has established itself as one of the leading suppliers of quality parts through a network of eight branches and two workshops across Australia and New Zealand.
Still strongly invested in the supply of undercarriage parts and components, ground engaging tools, rubber tracks, aftermarket earthmoving machine parts and heavy-duty diesel engine parts, ITR Pacific is targeting a new opportunity with the introduction of Undercarriage Track Workshop facilities in both its NSW and Queensland operations. This development allows ITR Pacific to o er customers an end-to-end service on ITR undercarriage parts and components, as well as ground engaging tools.
ITR Pacific’s two workshops o er another step forward on its mission to provide an endto-end service in the supply and maintenance
of earthmoving machinery parts and components. These services include:
• Supply of new, complete, ITR track groups, rollers, idlers, sprockets, final drives, and much more
• Excavator and dozer track bolt-ups, track plate swaps, and new track chain assemblies
• Complete track frame refurbishments, track frame crack repairs, and modifications
• Robotic, abrasive-resistant tungsten-carbide
As part of the company’s ongoing commitment to the Australian earthmoving industry, ITR has expanded its service o erings withITR Pacific's two workshops o er another step forward towards their mission in providing an end-to-end
servicein the supply and maintenance of earthmoving machinery parts and components. ITR has established itself as a leading supplier of quality parts.
hard facing of ground engaging tools, such as bucket teeth and cutting edges
• Robotic welding of large parts such as track frames and buckets, and
• Hardfacing of dozer track plates with tungsten-carbide grit for added wear resistance.
Over the past few months, the ITR Pacific team has been hard at work setting up impressive workshop equipment, like the 250-tonne and 360-tonne track presses, which will allow customers to have larger track chains resealed with pins and bushes rotated, ensuring maximum life of the chains. Hydraulic-wrench track-bed torque multipliers will ensure all track bolts are correctly torqued to the required specification, ensuring track plates are secure, especially when machines are working in tough conditions.
Heavy-duty track beds and track winders, custom made for Australian conditions, are capable of handling track chains up to 10 tonnes in weight, comfortably covering the large Cat D11 and Komatsu D475 track groups. Using all their knowledge and expertise, the team ensures the process of track lengthening, shortening, new link assembly bolt ups, and pin-and-bush turns are streamlined and e icient for a quick turnaround time.
Just as ITR does not compromise on the quality of the parts, it has certainly not compromised on the quality of its Track Workshop equipment, ensuring each job can be carried out professionally and to exceed customers’ expectations.
“The USCO ITR Group is the largest manufacturer and supplier of aftermarket earthmoving machinery parts in the world,” said an ITR Pacific representative. “Our Yatala and Sydney workshops can handle servicing the smallest steel undercarriage, right up to the largest excavator and dozer undercarriage.”
ITR Pacific knows a large percentage of the cost in owning and operating a track-type machine is related to its undercarriage, therefore ITR recommends being proactive and having the undercarriage on your tracktype machine inspected regularly, allowing you to get the most life from your asset. So, in addition to the large range of undercarriage parts and the new Track Workshop facilities, ITR Pacific also o ers professional undercarriage wear inspections onsite and detailed reports using the ITR WearTek Plus reporting system, allowing a customer full access to its track reports through a mobile app and online web portal.
The substantial growth of ITR over the past 12 months is nothing more than a reflection on the Australian earthmoving industry and the services and parts it is demanding.
To find out more about ITR’s full product o ering and services, give them a call on 1300 820 214 or visit the website: itrpacific.com.au.
TVH has served as a trusted machinery parts specialist since 1969. A Belgian-based company with branches in 90 countries around the world, TVH provides an impressive range of parts for a variety of machines, including a wide range of earthmoving equipment.
The company continues to expand its range and, in addition to mini excavators, skid steer loaders, and compact track loaders, now o ers parts for backhoe loaders.
“We o icially introduced parts and accessories for small earthmovers to our range in 2020,” says Joris Tijtgat, TVH’s Market Management Specialist for small earthmovers. “Of course, that market was not uncharted
territory for us. We were already helping countless owners of small earthmovers and had many fitting parts in stock.
“But at the same time, we noticed that some of our customers weren’t aware that we could also deliver spare parts for small earthmovers. So, we decided to grasp that opportunity with both hands.”
It’s still a work in progress, Joris says, but TVH’s range of parts for small earthmovers is growing steadily across a range of makes.
“At TVH, we take proactive action for parts suitable for nine focus makes: Bobcat, Case, Caterpillar, JCB, John Deere, Kubota, Takeuchi, Volvo, and Yanmar,” Joris says. “Those makes
represent the largest global market share within our submarkets.”
New parts are added to TVH’s catalogue all the time, and the range of parts for small earthmovers is growing steadily, including equipment being developed for other makes like Hitachi, Komatsu, Wacker Neuson, and many others.
TVH Australia has recently made available a range of tracks and undercarriage equipment, adding to the fast-growing range of industrial parts and accessories already available to Australians.
For Brendan Chillingworth, TVH Regional Director for Oceania, this represents a natural progression for the business as it adapts and grows with the local market.
“TVH was always known as a forklift parts and accessories company,” Brendan says. “But we’ve diversified over recent years into parts for agricultural, industrial, and construction equipment.
“The construction side in particular – we’ve seen huge benefits to focusing on that range, and expanding the o ering to undercarriage is the next logical step. It’s also something that our customers have been asking for.”
Brendan says tracks and undercarriage might be new to TVH Australia, but it’s a product range that the company is well grounded in on a global scale. It’s a significant investment, he says, but one guided and informed by well-established industry knowledge.
“It’s an extensive range of products that
we have available,” Brendan says. “We cover a range of rubber tracks and associated undercarriage parts, which includes rollers, idlers, and sprockets. We have introduced a separate warehouse to store it all.”
Brendan says it’s important that customers know TVH Australia is committed to this new range, with the knowledge base, distribution network, stock holding, and most importantly, trusted suppliers and quality products.
“We’ve got the right tools in the toolbox – I think that’s the best way to sum it up,” he says.
Brendan says customers just need to explore TVH’s new e-shop to get a sense of what’s on o er. Customers can look up parts using OEM part numbers, or use the intuitive lookup function, which allows customers to easily search by the make and model of their machine.
This is designed to help streamline the experience of ordering parts to help customers minimise downtime.
“It’s a fantastic tool, one we’ve been developing globally in recent years,” Brendan says. “We’ve substantially grown the userbase, which is now at record numbers.”
But powerful online tools aside, Brendan says TVH customers can be assured that support is always available over the phone for whenever they need to speak to a real person.
“We have a dedicated phone number specifically to support our construction customers,” he says. “They’ll be put straight through to one of our technical parts interpreters, who will be able to answer any questions and provide them with the right solution for their needs.
“It’s all part of o ering that full 360-degree support to our customers as we continue to grow our range.”
To explore TVH Australia’s wide range of parts and accessories, visit: www.tvh.com/en-au
In today’s competitive contracting environment, it has never been more important for excavator operators to maximise productivity, reduce costs, and perform work that fully satisfies their customers.
Owners of excavators in the one-tonne to six-tonne range will welcome the news of immediate stock availability of the all new, industry-leading Miller GTT 180-degree tilting hitch – which o ers guaranteed reliability and maximum performance.
Powered by an advanced, reliable, and heavy-duty helical motor – which requires zero maintenance – this hitch allows full 90-degree left and right rotation with no loss of power while operating at full tilt. The GTT is cast from high-tensile strength steel and because it is cast, there is greater flexibility in the shape of the hitch, meaning that more material can be
put where the strength is needed, and less where it is not required.
This has given the GTT a low profile, minimising the loss of break-out force. The new lightweight, lower-profile design hitch features a shorter pin to point measurement to deliver maximum breakout force for greater productivity and improved machine stability. This also means the machines are not overloaded, allowing them to work to full capacity.
Fully compliant with AS4772 standards, the Miller cast GTT hydraulic quick hitch comprises advanced twin locking technology which enables safe and quick attachment changes to be achieved, all from the comfort of your machine’s cab. Operators have the versatility
and convenience of a 180-degree tilt capability as well as a fully hydraulic hitch that locks on both pins. This means no more having to get o your machine to change an attachment, saving a lot of time and e ort. This added convenience and time saving is particularly apparent on jobs that may require numerous tool changes.
Being able to easily change tools in a couple of minutes without exiting the cab also means operators are more likely to ensure they have attached just the right tool for the job.
The next generation Miller GTT tilting hitch is designed for people who want to work smarter, not harder by transforming an excavator from just a digging machine into a multi-tooled carrier, ideal for performing versatile operations easily from the safety of the cab.
This transformation and new-found flexibility make it ideal for reclaiming, cleaning works and
Miller | NGDF’s new GTT 180-degree tilting hitch o ers a great way for operators to get the most out of their excavators and attachments.The hitch allows full 90-degree left and right rotation without loss of torque.
retrieving, scavenging, drainage of channels, roadside maintenance, and any environmental remediation work. Because it saves time and potentially reduces the number of times the excavator may need to be moved, the GTT 180-degree tilting hitch plays a role in minimising fuel consumption.
A proven industry performer Miller is recognised as a leading manufacturer of earthmoving attachments, including quick hitches and buckets. It says it is trusted by major earthmoving manufacturers, as well as an established independent global distributor network and numerous end-user customers worldwide.
In 2022 the company acquired Victoria based New Generation Design Fabrication (NGDF). Miller says the strategic acquisition combined a wealth of specialist knowledge and experience in both the engineering and manufacturing of hitches and buckets, as well as extensive capabilities in repairs and refurbishment of earthmoving equipment. Hubs with extensive workshop facilities are located in Sydney and Melbourne where skilled and experienced teams o er full end-to-end service and solutions to deliver quick and responsive repair services.
Miller | NGDF also provides a wide range of planned repairs and refurbishment projects to significantly extend the life of earthmoving attachments, as well as o ering customised project solutions. The company enjoys a high profile in the construction, demolition, and material handling markets, as well as grounds maintenance and landscaping, through to civil engineering and utilities, quarrying, and production of aggregates.
For further information, visit: www.millerngdf.com.au or call 1300 744 824.
Compared to the standard fitment five-piece wheels and the Double Gutter seven-piece wheels currently o ered, the OTR Australia QCR System provides an increase NonDestructive test interval period, longer wheel life, improved safety through fewer wheel and component removal/install, resulting in faster tyre change outs and increased uptime.
OTR Australia o ers the QCR System fitted to all six-wheel positions and is available for most makes and models of large mining trucks. Traditionally, the only way to change the inside dual tyre on the rear axle of a large mining truck was to remove the outside wheel and tyre assembly. This process is timeconsuming and downtime results in a loss of production. To overcome this, the Double Lock Ring (DLR) has the same diameter as inner rear dual wheel/rim. This allows the inner and outer tyres to be removed and replaced without the need for any of the rear wheel/rim bases to be removed, improving safety for tyre servicemen and reducing machine downtime which leads to increase productivity.
The DLR fitted to positions three and six consists of the wheel/rim base, two-bead seat bands, two-side flanges, and two-lock rings,
one of which is a two-piece design, while Integrated Lock Rings (ILR) used on positions one, two, four, and five, consists of the wheel/ rim base, two-bead seat bands, two-side flanges, and one-lock ring. The back section of the ILR wheelbase has been modified to include an integrated lock ring and O-ring groove. This accommodates the addition of a second bead seat band, which allows a tyre to be removed without the need for a hydraulic bead breaker tool to separate the inner tyre bead from the wheelbase. As a safety feature, both the ILR and DLR wheels/rims have SurLocs fitted to each of the Bead Seat Bands. Additionally, the Mega Bore tyre inflation system can be incorporated to allow even further reduction in tyre change time by reducing both the deflation and inflation periods. “The Mega Bore system increases the flow area by 2.46 times the current system,” said Travis Parsons, General Manager - Sales.
The advantage of using an ILR wheel on positions one, two, four, and five, against standard five-piece wheel is to allow all tyres positions to be easily rotated to other positions without having to remove or fit
components, making tyre rotations faster and easier. When you combine the ILR and DLR across the machine the benefit of this combination saves time, increasing productivity and improves tyre servicemen safety with the reduction in repetitive tasks such as use of impact guns. Savings can also be calculated by the simple fact that the wheels have not been removed from the truck, so re-torques are not required, increasing truck availability.
Field reports show a positive reaction by customers using the OTR Australia QCR System on o -highway trucks. Customers using the OTR Australia QCR System have reported significant improvements in productivity by decreasing haul truck downtime for tyre servicing, while improving safety for the tyre service personnel. The di erence between the standard rims and the OTR Australia QCR System is significant on a mine site operation. In as little as 12 months, a customer can measure improvements in uptime of the haul truck fleet.
Customer tests indicate that by using the OTR Australia QCR System, tyre servicing times can improve by greater than 50 per cent, combined with improved service personnel safety standards and reduced occurrence of fatigue and injuries associated with tyre service job functions.
The increased productivity that comes from the OTR Australia QCR System in both manpower and moving dirt will comfortably increase profit within the first 12 months and then contribute to additional revenue for the remainder of their service life. OTR wheels and rims also have greater wheel life, lower maintenance costs, and improve safety – the long-term benefits towards profit speak for themselves.
www.miller-ngdf.com.au
Miller I NGDF’s 180° tilting hitch suitable for 1-6T excavators.
Lightweight, low profile design guaranteeing performance and reliability.
Australian built. 3 years warranty.
Backed by Chevron, one of the world’s leading energy companies with more than 70 years of history in Australia, Caltex brings to the marketplace high-quality fuel and lubricants, plus a fleet management system o ering that is fully adaptable for businesses of any size.
Behind this renewed commitment to Australia, Caltex is strengthening its distribution network, ensuring delivery of products to keep the nation moving.
Beyond the retail experience, Caltex brings an all-encompassing product o ering to earthmoving operators that covers all facets of operations.
Leading the charge is the innovative fuel system-cleaning ingredient Techron®, which is available in every fuel grade, helping remove dirt and prevent deposits from forming on critical engine components.
You can also experience Caltex Diesel with Techron D, a premium performance additive suitable for all diesel-powered engines, with the formulation that helps to clean injectors and protect components from corrosion while reducing the possibility of foaming as you fill up.
Accompanying the premium fuel range are the Caltex Delo® lubricants, including earthmoving consumables such as engine oils, hydraulic system oils, transmission oils, engine antifreeze/coolants, gear drive fluid, grease for bearings, and more.
Caltex Delo® contains ISOSYN® Technology, a high-performance additive formulation drawing on over 88 years of development to help protect vital diesel engine parts, provide exceptional soot dispersion, and prevent deposit build-up. It also helps provide engine durability and extend service intervals, ensuring optimal engine performance.
Adding further confidence, Chevron has the capabilities to manufacture lubricants
by producing its own base oil, maintains 21 individual blending plants globally (including joint ventures) and owns Oronite, one of the world’s biggest additive companies.
To keep businesses running smoothly, the Caltex StarCard is a power-packed fuel management card o ering a convenient way to increase fleet management e iciency.
It provides a wide range of adaptable features to manage fleets big and small, control personal expenses, and is perfectly suited to companies engaged in earthmoving, with various vehicle make-ups of trucks, passenger vehicles, and plant machinery.
It has two main options, either ‘Open’ or ‘Closed’ loop. Open loop provides the ultimate coverage allowing access to all Caltex and Puma Energy service stations, and being welcome wherever WEX Motorpass cards are accepted, meaning you can use it at over 6000 service stations and industry partners Australia-wide. Open Loop StarCards can also be used wherever Cabcharge is accepted and for services at Magic Hand Carwashes.
A closed loop card means businesses can avoid paying transaction fees while enjoying access to the range of Caltex with Techron® fuels. Both options can be set up for specific drivers and vehicles, with PIN protection available too.
Additionally, StarCard provides a range of perks and discounts from leading tyre retailers, vehicle parts, and accessory retailers, vehicle servicing providers and accommodation houses.
Caltex is committed to the Australian market and making its products available to customers where and when they need them. Whether you’re running the family business or the company fleet, Caltex is there to support you with expert advice and fuel equipment solutions, quality bulk fuel supply, premium engine oils, and reliable lubricants.
To learn more about Caltex products, visit www.caltex.com/au/business-solutions.
The Caltex brand you know and love has returned, with the brand committing to supporting earthmoving businesses Australia-wide.Caltex brings an all-encompassing product o ering to earthmoving operators that covers all facets of operations. Chevron has the capabilities to manufacture lubricants by producing its own base oil.
One of the major causes of premature failure in rockbreakers is long cycles where an operator continues to hit the button and keep the piston striking for extended periods.
Rammer has readily accessible resources available, including short YouTube videos, product training and manuals, that guide operators through the process of keeping their rockbreaker in prime working condition. These are supported by a dedicated global dealer network with extensive product expertise and access to genuine Rammer parts and products. Correctly operating a rockbreaker isn’t di icult if you follow some simple operational tips, from idle strokes and tool angles to correct greasing and maintenance practices. Watch the Rammer Hammer Operation video at youtube.com/watch?app=desktop&v=LblCt5PvXg
Frequent idle strokes can have a deteriorating e ect on a rockbreaker, hence Rammer rockbreakers are equipped with idle-blow protection as standard to prevent idle strokes. It’s recommended idle-blow protection is switched on during normal operation as the rockbreaker can only be initiated once the tool is pressed against an object. Operators can turn it o when breaking soft material, or in demolition applications where it is di icult to apply su icient feeding force.
It is advised to keep the rockbreaking tool at a 90-degree angle to the surface of the material to be split or broken. If the object moves, or its surface breaks, angle should be corrected immediately. Continued use above or below a 90-degree angle can damage the rockbreaker
and wear out bushings faster.
Striking material near an edge of a surface rather than in the centre can also increase rockbreaking e iciency. Avoid striking in the same spot for more than 15 seconds at a time. If the object does not break, or the tool does not penetrate, stop the rockbreaker and change the position of the tool.
The greasing practice depends on application and operating method.
Tool grease consumption is higher in applications where the tool is penetrating and movements are longer than in impact-breaking applications where the tool is steadily against the thrust ring. Greasing should be increased in dusty applications.
The proper procedure is reached when wet
grease is visible about the length equal to the tool diameter on the tool just beneath the housing bottom plate.
Rammer o ers special tool lubricants and automatic tool-lubrication systems that provide maximum lubrication while only using minimum grease amount, prolonging the tool and bushing life and minimising downtime.
Rammer has also developed Rammer BIO Tool Grease, a high-performance biodegradable grease to help support more sustainable rockbreaking operations.
Rammer is part of Sandvik Rock Processing Solutions, the global engineering leader in mining and rock excavation, metal-cutting and materials technology.
Helping operators work more productively and maintain their rockbreakers safely is supported by a dedicated global dealer network with product expertise and readily accessible genuine Rammer parts and tools.
Rammer customers enjoy added peace of mind knowing their products are fully supported anywhere, anytime, and customers also benefit from exclusive access to available resources such as operational training, manuals and videos, for all Rammer products.
The Rammer authorised dealer network in Australia includes:
• VIC/SA/TAS: Walkers Hammers
• NSW: Groundtec
• QLD/NT/PNG: QLD Rock Breakers
• WA: Total Rockbreaking Solutions
For more information, or to locate your nearest dealer, visit rammer.com or attachmentspecialists.com.au/rammer.
Following simple guidelines when using a rockbreaker can minimise component wear and deterioration.Continued use of the rockbreaker at above or below a 90-degree angle of attack can damage and wear out bushings faster. Correctly operating a rockbreaker isn’t di icult if you follow some simple operational tips.
ALLU
Material Processing
Buckets turn waste into profit by producing aggregates and reusable materials from bricks, concrete, metals, wood, cardboard, glass, asphalt, waste soil or just about anything.
Wet or dry.
One ALLU can produce multiple fragment sizes, with various blade and drum configurations.
For excavators and loaders from 8t to 160t.
A commitment to minimising its ecological footprint has seen the sustainability goals of Scottish articulated hauler manufacturer Rokbak showcase a dedication to environmental stewardship in the heavy machinery industry.
“A lot of work has gone into our sustainability drive over the years,” says Charlie Urquhart, Rokbak Product Manager. “Rokbak’s heritage, knowledge, and resources mean that we’re constantly developing and looking to improve the trucks and the way we operate, in a manner that benefits our customers.”
As part of the Volvo Group, Rokbak is aligned to the Science Based Targets initiative (SBTi). Specific aims include a 30 per cent reduction in CO2 by 2030, a 50 per cent factory operations emission reduction by the same year and becoming net-zero by 2040. These incentives have influenced the design of Rokbak trucks, the daily operation of the Rokbak Motherwell factory and a strict adherence to the Rokbak sustainability roadmap.
Reducing impact on the environment has seen Rokbak employ strategies stemming from fuel consumption analysis, examining alternative fuels, extending maintenance cycles, and lessening maintenance consumables. Furthermore, this research and development in sustainability has led to the
reduction of total cost of ownership (TCO) for Rokbak customers.
Low waste, low cost, high performance
Fuel consumption is the biggest cost of operating a machine and the Rokbak RA30 and RA40’s EU Stage V engines produce a fuel consumption saving of up to 7 per cent, when compared to the previous EU Stage IV engines. This means lower operating costs and, fundamentally, less impact on the environment. Rokbak’s articulated haulers both have lean burning engines and a confirmed low-fuel consumption. The RA40 has a class-leading transmission fluid change interval of 6000 hours, the RA30 o ers an impressive 4000 hours.
Both the RA30 and RA40 are compatible with hydrotreated vegetable oil (HVO), a fuel that allows customers a ‘quick-hit’ on their individual net-zero targets. HVO, also referred to as "Renewable Diesel" or "Green Diesel", is a para inic bio-based diesel fuel originating from animal fats or multiple vegetable oils. HVO fuel has chemical and physical properties like those of diesel fuel, but its fossil-free composition and low carbon content di erentiate it from diesel and make it attractive to those seeking a sustainable fuel option. It is a modern way to produce high-quality bio-based diesel fuels without compromising fuel logistics, engines,
exhaust aftertreatment devices, or exhaust emissions. HVO can provide up to a 90 per cent reduction in CO2 emissions on a well-to-wheel analysis.
Extensive periods between scheduled maintenance, with infrequent parts and fluid changes, mean less material going to landfill. Maintenance and fault alerts allow customers to keep on top of the truck and be informed of the machine’s next required servicing. Instigating the ordering of parts in advance and getting the labour in place increases operational e iciency, not only improving sustainability measures but also reducing TCO.
“When the customer buys a Rokbak hauler, they are acquiring a hauler that has been developed with sustainability in mind,” says Charlie. “It is a hauler that has been manufactured on a site powered by green energy and redirects waste away from landfill.”
Today, the Rokbak factory is completely powered by sustainable sources. Working towards accreditation on a zero-waste-tolandfill policy, 95 per cent of generated waste is now diverted away from landfill.
Rokbak's sustainability initiatives resonate with employees from the factory to the management team and the company’s dealers and customers. Everyone from the factory floor to the head o ice has an eye on energy reduction. Internal trackers inform Rokbak employees how much energy has been used in comparison to the previous week and “green champions” are recruited from throughout the business to promote sustainable practices in their respective work areas.
“It’s to make sure everyone’s doing their bit,” explains Charlie. “Whether you’re monitoring power tools usage or remembering to switch o the lights and air conditioning, you’re part of a united drive.”
Rokbak's sustainability goals and incentives exemplify how we can address environmental challenges within the heavy machinery industry. Rokbak demonstrates the potential for sustainable manufacturing while reaping a host of benefits and stands as an example of how other movers in the manufacturing industry can drive positive change while securing individual success.
“We are creating significant steppingstones towards a sustainable future,” says Charlie. “And this not only results in less waste being generated, but also benefits the Rokbak customer’s wallet.”
At the heart of its sustainability strategy, Rokbak has implemented a set of ambitious goals in operating measures and articulated hauler design and construction. These underscore a determination to reduce environmental impact and promote sustainable practices – all of which benefit the company’s valued customers.The RA30 and RA40’s EU Stage V engines o er fuel consumption savings of up to 7 per cent.
UHI Machinery is always aiming to keep ahead of the game when it comes to innovative access solutions. Its latest releases include a range of ZOOMLION battery powered scissor lifts, electric articulating boom lifts and a heavy-duty diesel-powered articulating boom lift.
The new battery powered AC-L Series range of scissor lifts covers a choice of seven models with lift heights ranging from 7.8m up to 15.7m and platform capacities ranging from 230kg to 350kg. This range of height and weight capacity options makes it easy to find the lift that’s just right for your business.
All models in the range are compliant with CE/ANSI/CSA Standard. The AC system used across the range delivers high performance and superior working e iciency, as well as being maintenance free throughout the equipment’s full life cycle.
Adding to a longer lifespan for the lift range when working in water-prone environments is IP67 rated waterproof protection on the AC wheel motors. The new models also incorporate the latest technology lithium-ion batteries that provide a long service life as well as an impressive 30 per cent increase in running time.
Helping to keep maintenance time and costs to a minimum, the scissor knuckles do not require lubrication and are maintenance free. The battery management system of the AC-L series o ers intelligent connectivity, and the machine control system has dual protection. A swing out tray makes equipment servicing access easy and convenient.
As you would expect from equipment of advanced design, all models in the ZOOMLION scissor lift series have proportionate controls, all-motion alarm, fold-out hand rails for easy accessibility, self-closing entry gate, an autobrake system, emergency descent system, emergency stop button and on-board diagnostics.
Other safety and convenience features include a flashing beacon, an over tilt protection system, active pothole protection and AC power available on the work platform. When the operator needs to move the platform, it is drivable at full lift extension.
If you want more flexibility from the UHI ZOOMLION scissor lift, optional accessories include platform work lights, an air line to the work platform, an overhead protection bar and synthetic biodegradable hydraulic oil.
Continuing the innovation story, the electric ZA10RJE articulating boom lift has a work
height of 11.55m and a 6.85m horizontal outreach, together with a handy up and over height of 4.6m.
The ZA10RJE complies with CE/ANSI/ CSA standards and has a 230kg platform capacity. It features a centre layout for great structural rigidity and small boom deflection. An advanced dual control system comprising a valve and pump control o ers the benefit of energy saving, along with smooth and e icient operation.
There is plenty of power and stability, thanks to the accurate and e icient AC motor, while the 1.24m jib’s plus/minus 90-degree rotation gives you great up and over height to help operators tackle the most challenging tasks. The unit’s compact dimensions of just 1.19m makes it an attractive proposition for applications when you need to reach narrow work spaces.
Advanced design tubular batteries give you an extended working time and are charged from the system’s 35-amp smart charger. Batteries are protected with the assistance of a quantity display and a low electric charge system, while maintenance access is quick and convenient.
Operators will appreciate the ease of operation with the boom lift’s proportional control, auto levelling system and thumb steering joystick. Safety also gets a big tick as features include a self-closing entry rod, emergency descent system, tilt protection system and emergency stop button.
Accessories and options give the operator added convenience and control through
equipment such as a platform light, an electric auxiliary pump and an AC outlet and air line on the work platform. For the environmentally conscious, you can select synthetic biodegradable hydraulic oil.
For bigger lifting jobs anywhere, UHI Machinery has the diesel-powered model ZA14J which has a maximum work height of 15.8m and horizontal outreach of 8.3m. The work platform is rated at 300kg, so you can take some heavy gear up there if needed. The boom lift incorporates a multiple pressure control levelling system for added stability and precise load sensing to improve overload safety operations. An integrated rotary reducer manages rotation stability, and a deadweight lowering system saves energy and provides a very smooth lowering operation.
There are many standard features including a motion alarm, proportional control, selfclosing entry gate, auto levelling system, over tilt protection system and an emergency descent system.
If you want to add further e iciency, optional accessories are available, such as platform work lights, an anti-collision device, and an AC power outlet on the platform.
For full information on the range of UHI scissor lifts and articulating boom lifts, contact UHI Machinery at sales@ unitedheavyindustries.com.au or call 1800 000 844.
If you have work to get done at height, UHI Machinery’s wide range of access solutions has you covered.The lithium-ion battery powered ZOOMLION range o ers long service life and a 30 per cent increase in running time.
Merlo Group Australia is a business on a mission. With its telehandler range wellestablished in the agriculture sector, the business has spent the past two years nurturing its presence in the Australian construction industry.
And it’s been paying o . Through fostering stronger, mutually supportive relationships with dealers new and old, and by doubling down on aftersales support, the team is seeing its e orts translate into sales.
But as Managing Director Michael Lombardo says, this is no time for complacency. Which is why Merlo Group Australia has made the bold move to introduce an entirely new Merlo product line: Cingo multi-purpose transporters and multifunctional models.
“Merlo head o ice in Italy have been eager for us to bring the Cingo range in,” Michael says. “It shows they’re confident in how we’ve set ourselves up over the past few years. They’re happy knowing we’re well set up to introduce this new product the right way, with no false starts.”
Merlo Group Australia is introducing a new product line to the Australian market. EEM learns what the versatile Cingo range can do, who it’s for, and how it will be supported.The Cingo range represents a new challenge for Merlo Group Australia. The Handler 400 attachment transforms the Cingo into a compact telescopic handler.
Chris Wilson, Merlo Group Australia National Dealer Development Manager, says the Cingo product line has been an almost surprise success internationally.
“It was originally manufactured in a section of the Merlo factory in Cueno, Italy,” he says. “But it got to the point where they actually had to remove a car park to build a dedicated factory for the Cingo product range.
“But although this success may have taken Merlo by surprise at first, they’ve also reacted accordingly and adapted to suit the demand.”
Chris says this expanded manufacturing capacity was also part of the catalyst for bringing the range to Australia, where Merlo Group Australia soft launched the Cingo range at Sydney’s HIRE23 exhibition in June.
“The feedback we got from the show was outstanding,” Chris says. “It was probably the most well attended stand we’ve had in the 12 years I’ve been doing the show with Merlo. The Cingos generated a lot of interest from the rental industry, as well as landscaping and other alternative markets. For the multifunctional models, we were hearing people dreaming up all sorts of reasons to use them on various projects.”
Michael says this level of interest has continued to accumulate in the months since –
sometimes from unexpected sources.
“We went out to AgQuip in Tamworth in August, and one of our dealers had been receiving a high volume of inquiries on the Cingo for use on a couple of mining sites,” he says. “They were looking to use the machines to rake underneath their conveyor belts, which is something I would have never considered.”
A rewarding challenge
The Cingos might be compact machines, but introducing the range to the Australian market requires some big adjustments for the Merlo Group Australia team.
Chris says while there is some overlap with telehandlers, Merlo Group Australia will mostly be targeting new industries, and expanding its dealer network to cater accordingly.
“The Cingo range presents opportunities for us and our existing dealer network, but opportunities will also be plentiful for us to appoint new dealers as we expand into some new markets,” he says.
Michael adds that dealers that specialise in larger equipment such as Merlo telehandlers might not be suited for smaller products like the Cingo, which require a whole di erent area of expertise.
“But those who deal in mini excavators and other trailer-transported gear would be a great
fit from a dealer point of view,” he says. “And that’s part of the appeal of the Cingos – they are relatively simple machines. There’s no diagnostics or anything like that required.”
The flipside of this simplicity is the massive range of available accessories that a ords the multifunctional Cingo models their versatility: from dumper bodies and hydraulic hammers to mowers and sprayers – even concrete mixers are available.
This requires Merlo Group Australia and its dealers to be well versed in the attachment range, demand for various attachments across multiple industries, and to ensure the infrastructure is in place to source these products quickly as required.
“It’s been a fun challenge for us though,” Chris says. “It’s been exciting to get away from our bread-and-butter stu to explore di erent avenues and di erent industries.”
Comprising five di erent models, Merlo’s Cingo range has been designed to o er solutions across a diverse array of operations –particularly in tight spaces and uneven terrain, where a combination of compact design and a low centre of gravity provides consistent performance in any environment.
The multipurpose transporter models – the petrol-powered M500 and M700 TD, as well as the diesel-powered M8.3TD EVO – o er the perfect solution for any small-scale material transport and handling operations.
But it’s the multifunctional M8.3EVO and M12.3EVO models where the Cingo range really starts to get interesting. Combined with Merlo’s patented quick-coupling device, users can switch seamlessly between countless attachments, ensuring the machine is always ready for any task – whether it's mowing grass, shredding twigs, or mixing concrete.
Better still, the Cingo M12.3EVO is compatible with the Handler 400 attachment, which transforms the unit into a compact telescopic handler with a 3.4m lift height. This attachment is also equipped with an anti-tipping system to ensure safety for operators and workers.
“In stock currently, we have the petrolpowered M700 TD with the high dump bucket, and the diesel-powered M12.3 EVO with various attachments,” Chris says. “We’ll also be getting in the M500, which is a little walk-behind petrol model, and the diesel M8.3 EVO as well.
“We expect the volume market is going to be in rentals with the petrol versions. Then we’ll be targeting more specific industries with the diesel version and a range of di erent attachments – from bricklayers to pool guys to landscapers. This kind of multi-purpose tool is going to suit them down to the ground.
“And so far, it’s definitely struck a chord with a lot of people from all these industries and more.”
For more on the Cingo range, visit: www.merlo.com/aus/en
If you are interested in dealership opportunities for the Cingo range, contact: info@merlo.com
Shore Hire, a proudly family-owned equipment hire business, began researching and designing the Shore Brace 400 hydraulic bracing system five years ago, after discovering a gap in the market, and released the product last year. It quickly became a customer favourite due to its versatility and strength.
The Shore Brace 400 Hydraulic Brace is a modular system that consists of extension beams of various sizes that are double-pinned and connected to a high-load capacity Hydraulic Ram. The system in question is a bigger version of their Shore Brace 200 system and although the 200 is undeniably e ective, it didn’t quite meet the requirements of clients doing larger-scale excavations.
“Rather than having to use multiple cross struts and deal with complex installation and extraction sequences to accommodate those jobs, we decided, in true Luke Geelan fashion, to make ourselves a brand-new brace,” says Shore Hire’s Research & Development Team.
“It was made out of our Sydney branch over in Condell Park by our product development team and in-house fabrication and manufacturing capability,” says Luke Geelan, Shore Hire’s Executive Chair. “They drew up the design and made many di erent prototypes. Then
they conducted a lot of testing using di erent methods and types of beams. And once we fell in love with a design, that’s the one we rolled out into production.
“We’re all about innovation here. We’re no stranger to taking an existing product and making it better.”
The Shore Brace 400 system is an incredible innovation for the company; it’s powerful,
versatile, and the only hydraulic bracing system made and engineered in Australia.
The system can be designed to support rectangle, square, or really any shaped excavation up to 20m without cross supports, and with the addition of the high load Shore Brace 400 Hydraulic Cross Brace or corner brace, much larger and more complex support projects can be secured.
“It’s by far one of the strongest bracing systems in the market,” explains Luke. “The
In order to shore large four-sided excavations, it is essential to have a system that is not only adaptable and durable, but also designed to withstand the test of time. Shore Hire’s Shore Brace 400 is purpose-built to meet these exact requirements, and more.The Shore Brace 400 was designed to fill a gap in the market. The system can be adapted to suit any shape of excavation.
Shore Brace 400 helps you achieve a clear span, so our clients can drop whatever underground asset they need into a trench without having to navigate around cross struts and corner struts, which would otherwise cause a collapse during installation.”
Another innovative feature of the hydraulic bracing system is that it naturally cambers, meaning that it arches or bends slightly upwards in the middle.
“These systems come in component form, so that camber comes naturally from the joints,
giving it a bit more strength and deflection resilience,” Luke says. “But the unique double pin system we’ve added means the Shore Brace 400 has the same shoring capacity regardless of the direction of the bend - inwards or outwards from the excavation.”
Shore Hire has also recently developed the Shore Strut 400, which is a 1250kN hydraulic strut designed to be used in conjunction with the Shore Brace 400 system to eliminate the need for multiple cross struts in larger excavations.
Sustainability is a key consideration at Shore Hire, and one of the ways in which the Shore Brace 400 demonstrates greater environmental sustainability is by firstly, being a hire product meaning that is constantly reused across multiple years and major projects and secondly, using galvanised steel for even more strength and durability.
The extension beams are also constructed from galvanised steel, meaning they are exceptionally durable and have an extensive life span. This allows for their repeated use across multiple jobs without any damage or requirement for replacement.
Customer support
Feedback from customers has been overwhelmingly positive – not only for the Shore Brace 400 system itself, but also the services Shore Hire offers. This includes providing a 24-hour/7-day full remote monitoring system that will notify customers if there is any unknown movement, and product specialists that are by a customer’s side through the entire process – from tender through to completion.
“We supply the highest quality product and highest quality service every single time,” Luke says. “That’s what keeps people coming back.”
For more information about the Shore Brace 400 or any of our other products visit www.shorehire.com.au, or contact your local Shore Hire branch at 1300 764 734.
FleetSafe, already renowned as Australia's premier supplier of aftermarket automotive technologies, is now steering its expertise to bolster safety standards in construction.
“For almost two decades, we’ve been deeply involved in ensuring vehicular safety,” says Clive Rogers, FleetSafe’s Managing Director. With a history rooted in mobile phone handsfree kits, FleetSafe’s journey has followed the digital evolution closely, moving to parking sensors, reversing cameras, and further.
In 2013, the company broadened its horizons as the national distributor for the Mobileye Advanced Driver Assistance System, aiming to mitigate vehicle collisions.
“Our early days centred on convenience, with a splash of safety. But as we grasped the fact that large vehicles were major culprits in collisions, our focus shifted,” Clive explains.
More recently, FleetSafe has recalibrated its tech prowess to cater specifically to the construction industry, developing state-of-theart human detection systems tailored for heavy machinery.
“Our entry into the earthmoving and construction arena is fresh,” Clive says. “But remember, we've long collaborated with major trucking brands. Safety with colossal machinery isn't new terrain for us.”
From humble hands-free car kits to cutting-edge human detection systems, FleetSafe continues its two-decade-long commitment to advancing vehicular safety — now taking a pivotal step into the earthmoving industry.Mobileye 8 Connect: Advanced collision avoidance for modern machinery. FleetSafe aims to ensure safer environments for vehicle operators and pedestrians alike.
One of FleetSafe's hallmark products, the Spotto BSM-MW, revolutionises blind spot monitoring. Designed meticulously for large vehicles, this technology alerts drivers to obstructions in the notorious blind spot zone. Whether it’s cars, cyclists, or pedestrians, the Spotto's radar detects them all, significantly reducing collision risks.
Another new innovation is the Mobileye 8 Connect, designed as Mobileye’s most sophisticated collision avoidance system yet.
“Mobileye 8 Connect, equipped with the EyeQ4 processor, not only provides an expansive and extended field of view but now detects humans even in dim lighting,” Clive says. Furthermore, the system empowers fleet managers with insights into their team's driving habits, promoting a culture of safety.
The company further augments safety with the Mobileye Shield+, specially designed to protect pedestrians near large vehicles. By covering a 270-degree field around the vehicle, it identifies the most susceptible individuals, ensuring their safety. “Such innovations are paramount for everyone around heavy machinery,” Clive stresses.
FleetSafe's latest introduction, the ProxiCam, is set to redefine safety in the construction domain. “ProxiCam is AI-driven and designed to identify humans specifically," Clive explains. “Despite the myriad of objects on a construction site, it will only notify operators about human proximity.”
Cost has often been an impediment to widespread adoption of safety technologies. Addressing this, Clive states, “We've priced the ProxiCam system very competitively. Safety, which should be fundamental, often comes at a prohibitive cost. Our aim is to democratize access to these life-saving technologies.”
Adding to its user-friendliness, FleetSafe's
equipment boasts easy installation. “Our design is modular, allowing even a regular mechanic to install it. The goal is to make it ubiquitous across construction sites,” Clive says.
As FleetSafe consolidates its position in automotive aftermarket technologies, its foray
For more on FleetSafe, visit: www.fleetsafe.com.au
Tigercat, a leading name in forestry equipment, has been making waves in the skidder market since the release of the 612 series skidder platform earlier this year. This platform's primary focus is on addressing the challenges of selective felling applications, particularly in demanding terrains, while safeguarding the integrity and value of the residual timber stand.
The most recent launch within this series is the 612 dual winch grapple skidder. This versatile machine has been finetuned to operate seamlessly in selective harvesting scenarios, proving especially adept at extracting high-value timber in conditions characterised by steep inclines or environmentally sensitive terrains.
Central to the 612's design are its oscillating centre section and optional blade tongs. The oscillating centre section gives the machine a more compact stance, streamlining its ability to navigate tight forest stands. On the other hand, the blade tongs bring an added layer of versatility to the table, enhancing the skidder's capacity for tasks such as decking wood and performing other secondary duties.
One of the machine's standout features is the Tigercat FPT N67 Stage V engine, boasting a robust 155kW (208hp) output. Paired with Tigercat’s industry-renowned e icient drive system, operators can expect a machine that's not only powerful but also fuel-e icient. This synergy ensures that the 612 grapple skidder can gracefully handle challenging terrains, all while reducing wheel spin.
The design and attention to detail extend into the operator’s cab, which has been crafted for both functionality and comfort. The generous window sizes a ord operators clear sightlines, ensuring safety and precision. Meanwhile, the climate-controlled, heavy-duty air ride suspension seat can be fully adjusted to the operator's preference. Added touches, such as
a climate-controlled cup holder and dedicated storage, underscore Tigercat's commitment to operator convenience.
At the heart of the ergonomic design is the Turnaround seat. This feature is pivotal for e icient machine operation. The Turnaround seat not only enhances comfort but also ensures operators can enter and exit the machine e ortlessly from either side. Furthermore, it grants operators full control over all the skidder's functions within a wide 220-degree range.
Additionally, the 612 series is equipped with an array of features, including an optional dual winch, a movable back shield and fairlead system, and even a crane. These tools are integral for scenarios that require intricate control, like manipulating two separate cables in dense stands. The heavy-duty crane and blade tongs further bolster the machine’s capabilities, making log extraction, manoeuvring, and sorting tasks more streamlined.
Tigercat's 612 series, with its grapple skidder variant, marks a significant step forward in the realm of selective harvesting equipment. Its combination of power, versatility, and operatorfocused design is set to make it a mainstay in challenging forestry operations globally.
Tigercat products are proudly supported in Australia by Onetrak. Onetrak’s national footprint includes sales and service outlets located in Victoria, New South Wales, Queensland, Tasmania, South Australia, and Western Australia.
Home to large brands within the earthmoving, forestry, material handling and extractive industries, the business’ o ering includes new and used machine sales, rental equipment, service, and parts.
For more information, visit: www.onetrak.com.au/forestryequipment/tigercat-skidders
The grapple skidder is the second variation to be built on the Tigercat 612 platform after the release of the European-focused 612 dual winch skidder earlier this year.Key design aspects of the Tigercat 612 include the oscillating centre section and the optional blade tongs. The 612 is powered by a Tigercat FPT N67 Stage V engine.
Toyota Material Handling Australia (TMHA) has announced the completion of its new Melbourne branch in Dandenong South.
The 17,000 square metre space under roof has been specifically designed for TMHA’s material handling operations including the assembly, sales, hire and servicing of forklifts, scissor lifts, skid steer loaders, sweepers and scrubbers, pallet jacks, elevated work platforms, and automatic guided vehicles, and a demonstration area to showcase excavators.
Key areas include 12,140 square metres of warehouse and workshop, 4110 square metres of o ice space, 935 square metres of spare parts area, and 9900 square metres of hardstand. There is also specialised sealed and pressurised paint and preparation booths.
The expansive two-level o ice space includes open plan areas, meeting rooms, lunchrooms, a board room, and a spectacular new reception area with a statement staircase.
TMHA GM Corp Compliance & Project Development Bob Walmsley said the new branch will allow for a greater level of usability and innovation for the brand.
“With features like a dedicated dirt demonstration area, paint booths, and support for parts and service, our new state-of-the-art facility will o er more for our valued Victorian customers,” Walmsley said.
Along with facilitating sales and rental of TMHA forklift and allied equipment, the new facility will serve as a regional base for major and corporate accounts operations; will hold inventories of new material handling and Huski construction equipment; and will o er full support coverage for parts, workshop and field
service, and training facilities. The purpose-designed new facility and the land it is built on is wholly owned by TMHA.
For more information, phone (03) 8795 2500, or visit: www.toyotamaterialhandling.com.au
represent excellent reliability and are stacked with operator features. With 3.8 tonne capacity and high breakout force they offer comfortable and reliable machine operation for the toughest of jobs.
With a great offer available starting at just $39 per day*, there’s never been a better time to finance your new Huski and put you at the head of the pack.
*Prices shown exclude financier documentation fees. 30% balloon payment is payable at the end of the mortgage term. Payments for Huski M-38U Mini Excavator are made monthly in advance (prices shown are rounded up to the nearest dollar) based on a chattel mortgage 60 month term with a 30% balloon. Total minimum purchase price of $71,500.00 exc GST. Huski Finance is provided by MKP Finance Pty Ltd ABN 56 611 706 784 to approved business customers only (must be registered for GST), terms and conditions apply. MKP Finance Pty Ltd reserves the right to change, extend or withdraw an offer at any time. Offer expires while stock last. Any change in interest rates, unit price or government fees, charges or taxes prior to the delivery date may apply. Refer to the website for full terms and conditions.
A DIVISION OF
1800 425 439
huskiconstructionequipment.com.au
Webbair has been a major player in machine control solutions in Australia for years, though focused mainly on supplying to OEMs. EEM finds out how the company is transitioning from behind the scenes to major player in the earthmoving technology space.
Webbair’s IMC system currently comprises two models: an entry-level height limiter only model with proportional hydraulic control and data logging; and a more comprehensive version that adds point-to-point slew limiting, virtual walls, dig depth, cab protection, max radius, and iVoice messaging features.
Additionally, Chris says Webbair’s relationship with Prolec continues to grow from strength to strength, with plans for Prolec to also reciprocate distribution of Webbair’s new products outside of Australia.
This shift in business strategy has also marked another key change for Webbair: from serving predominantly OEMs, to now also selling direct to customers. And with this, the new challenge of brand recognition.
But Chris says his business isn’t starting from scratch – Webbair’s years in the industry has yielded a long list of satisfied customers.
Founded in 1996, Webbair began its journey as a specialised company with a focus on meeting the unique needs of the earthmoving industry, primarily offering services in electrical and air conditioning repair for machinery.
The brainchild of Managing Director Chris Webb, Webbair’s reputation grew as the business evolved.
Over the years, with the advancement of technology and the rising emphasis on safety in the industry, Chris realised the inevitable changes that were approaching the sector and decided to adapt Webbair accordingly.
The company pivoted to meet the newer, technologically driven demands of the industry, focusing on innovative solutions to enhance machinery control and onsite safety. This transformation led to the establishment of Webbair Prolec in 2011, a dedicated branch focusing on machine control.
Chris says Webbair has distributed Prolec machine control products in Australia since 2008, but over the past few years, with rising prices exacerbated by COVID-19, he decided to reposition his business’ place in the industry. And so Webbair has evolved from solely a distributor of high-quality Prolec systems and service provider, to manufacturer of custom solutions and machine control products.
“We’ve taken all our experience, combined that with all the feedback we’ve had from our local customers, and we’ve designed our own machine control system: Intelligent Motion Control (IMC),” Chris says.
“It’s Australian designed and manufactured, easy to use, and offers the latest technology at a cheaper price.”
One long-time Webbair customer is Cain Cooper from Nasi Civil, a multifaceted Melbourne-based earthmoving contractor. Nasi Civil specialises in bulk earthworks, large pipelines, road construction, and plant hire, and has been recently involved in a range of major
projects across Melbourne – including several Level Crossing Removal projects.
Cain says that Nasi Civil’s regular involvement on tight, urban worksites, getting the most out of smaller machinery is important. For this reason, he’s become a strong advocate for Webbair’s Load Management System (LMS), which is designed to maximise a machine’s lifting potential.
“Webbair’s LMS provides a significant benefit in limited access areas,” Cain says. “It gives us the same capability to lift heavier loads where a 30 or 40-ton machine might not be able to fit.
“It essentially increases our machine from 50 per cent of its potential lifting power to probably 80 to 90 per cent. So, with a 23-tonner, we might be able to lift 2.2 tonnes standard out of the factory, but when Webbair applies their LMS, it gives us five-tonne lifting ability.”
Furthermore, Cain says Webbair’s technology is very user friendly – a bonus for less experienced operators.
“You press a couple of buttons to start it, and that’s really the end of it,” he says. “It gives you peace of mind that operators won’t struggle with it.
Cain says the quality of Webbair’s products is
also testament to Chris’ dedication to keeping in touch with the industry his business serves.
“Chris has a combination of understanding of the industry, smarts, knowledge, and his foresight is admirable too,” Cain says. “He can see what’s happening with the industry, putting him ahead of the game. As a result, he's offering something at a decent price, making it available, and backing it up well too."
For these reasons, Cain says every excavator he purchases now goes straight to Webbair by default.
“I think Webbair’s got the best system available right now,” he says. “For backup and availability, Chris’ support is second to none, and he has extensive knowledge of the product. I would 100 per cent recommend Webbair to anyone.
“It's also great to be supporting an Australian business, and we like seeing someone like Chris doing so well in developing advanced and practical solutions for the industry.”
For more on Webbair, visit: www.webbair.com.au
In the world of construction and excavation, safety and e iciency are paramount. This cutting-edge technology combines advanced radar imaging, real-time alerts, and innovative engineering to enhance safety, reduce costs, and improve overall project e iciency.
The heart of the RodRadar Bucket is its Live Dig Radar technology, a patented groundpenetrating radar imaging platform designed to provide real-time, on-site alerts to prevent damage to underground utilities during excavation. This technology marks a significant advancement in utility detection, o ering an unprecedented level of accuracy and reliability. One of the standout features of the RodRadar Bucket is its ability to provide automatic, realtime alerts. This means that as excavation work is carried out, the LDR technology embedded within the bucket scans the subsurface for any signs of buried utilities. If a utility is detected, the system triggers an immediate alert, allowing the operator to take preventive measures and avoid potential utility strikes.
RodRadar's technology is designed to work across a wide range of soil types and utility materials. Whether it's gas, power, communications, water, sewage, or other types of utilities, the LDR technology is equipped to
detect them accurately. This versatility ensures that the system remains e ective regardless of the project requirements. RodRadar helps by assisting operators and contractors with real-time information. The system's easyto-use display, known as LDR Visualize, is situated within the excavator cabin. It employs sophisticated algorithms to classify radar echoes (B-Scan) and provides automated alerts directly to the operator. This means that even operators with limited training can
make informed decisions to avoid damaging underground utilities.
It eliminates the need for o site expert analysis, vacuuming and time-consuming GPR utility scanners by providing immediate insights to operators on-site. This results in a safer working environment, reduces the potential for costly utility strikes and is less time consuming than previous methods. RodRadar's commitment to innovation doesn't end with the current technology. The company's flagship product, LDR Excavate is just the beginning. The company envisions a range of products and services carrying the proprietary LDR technology to modernise excavation practices, improve operator safety, increase productivity, and streamline projects.
Behind the revolutionary RodRadar Bucket is a team of skilled experts from diverse fields dedicated to ensuring the highest quality and performance. RodRadar’s Live Dig Radar bucket represents a transformative leap in excavation safety and e iciency. By providing real-time, automatic alerts for underground utilities during excavation, this innovative solution is set to redefine industry standards. Its easy installation, intuitive operator interface, and capability to detect various utility types in di erent soil conditions make it an essential tool for modern earthworks. As construction and excavation practices continue to evolve, the RodRadar Bucket stands as a testament to how technology can profoundly impact safety, e iciency, and project success.
Nationwide parts, service, and support, enquire today at: www.rodradar.com.au or 1300 837 391.
The RodRadar Live Dig Radar (LDR) Bucket has emerged as a groundbreaking solution that revolutionises the way underground utilities are detected during excavation, ensuring the prevention of utility strikes.RodRadar’s Live Dig Radar bucket represents a transformative leap in excavation safety and e iciency. RodRadar's technology is designed to work across a wide range of soil types and utility materials.
Position Partners announces all-new Topcon MC-X machine control solutions, featuring MC-Mobile 3-in-1 setup for compact machines and MC-Max for excavators, graders, and dozers.
Position Partners, Topcon Positioning Systems’ exclusive Australian distributor, has announced the availability of the new Topcon MC-X platform of machine control solutions.
With all-new control units, updated 3D-MC software and flexible componentry that can be swapped and configured to suit the application, Topcon’s new platform promises increased processing power, speed, accuracy, and reliability.
“We’re excited to roll out Topcon’s new solutions for our customers here in Australia and have been working closely with early adopters to test their suitability for the local market,” said Josh Allan, Civil Business Executive Manager at Topcon.
“The new platform o ers the same userfriendly software and swappable components that customers know and love, but with faster, modern interfaces that connect directly into the machines. Topcon’s solutions have always been machine brand agnostic, but the new platform connects even more seamlessly to the machine and provides faster, more responsive performance that is market leading,” he added.
Now available for excavators, dozers, and graders, Topcon MC-Max can be fitted to all makes and models of heavy earthmoving machines. With flexible mounting solutions and optional automatic blade and bucket control for a variety of machines, the system also provides a full array of positioning technologies to suit the application.
From slope control and laser levelling to multi-constellation Global Navigation Satellite Systems (GNSS) positioning, robotic total station and Topcon’s unique Millimetre GPS technology, Topcon MC-Max gives users the flexibility to mix and match components for the task at hand.
For smaller excavators, skid steers, and compact track loaders, Topcon has designed a new 3-in-1 workflow solution to enable contractors to measure, design, and build with a single system. Topcon MC-Mobile combines the Topcon LN-150 construction total station, machine sensors, and a prism pole, with the option for Global Navigation Satellite System (GNSS) positioning. Users can create and edit designs, set-out, and check as-builts without the need to scale o PDFs and use stringlines.
Backed by the Position Partners’ Tokara remote access technology, customers and support technicians can manage machine design files, communicate with operators, and solve technical problems without visiting machines in person.
“Tokara is able to connect to and support
customers using the new MC-X platform technology to assist customers as they transition and learn the advanced features of the new system,” Allan said.
With more than 350 people in o ices throughout Australia, Southeast Asia, and New Zealand, Position Partners focusses on the distribution and support of intelligent positioning solutions for geospatial, construction, and mining projects. Position Partners is committed to increasing productivity for customers and building lasting business relationships around high calibre positioning activities.
Position Partners distributes Topcon machine
control and positioning systems throughout Australia and Southeast Asia. Complementary solutions from other leading technology innovators include fleet management systems, high precision machine guidance, 3D laser scanners, remotely piloted aircraft, weighing, and proximity detection systems, along with a range of deformation monitoring options. Advanced hardware systems are powered by sophisticated software platforms that enable customers to analyse, monitor, and design e iciently.
A full range of leading instruments and systems is backed by reliable service and industry expertise to give customers the support they need for any project.
For more information, contact Position Partners on 1300 867 266 or visit: www.positionpartners.com.au
Camden Hire has taken delivery of six new Takeuchi TB215R mini excavators to update its fleet. Owner Mark Scarce said, “All our Takeuchi equipment has performed extremely well in terms of satisfying customers’ demands and delivering the return on investment we need. The time has come to upgrade the miniexcavator fleet to ensure the latest machines and technology are available for our valued customers.”
Camden Hire is a family owned business which has been servicing the needs of the do-ityourself enthusiasts and contractors across the Greater Sydney area for over 35 years. The business o ers a huge range of tools, vehicles and equipment, backed by knowledgeable sta totally focused on customer service.
“Our business has grown through a commitment by our excellent team to always deliver genuine helpful service and taking the extra steps to meet customers’ expectations,” explained Scarce. “We now have five locations throughout Sydney’s southwest and employ over 100 people.
“While we mainly operate in the southwest of Sydney, we have clients all across the region, from the Northern Beaches, Blue Mountains, South Coast, Hills District and the Southern Highlands. The majority of our customers are property owners looking for a machine which will give them power needed for landscaping work and small building projects. We also hire equipment to professional contractors who need a small excavator for accessing tight sites, or in times of increased workload.”
Powerful, a ordable and convenient
“Another benefit for people who hire the Takeuchi mini excavators is the convenience of being able to tow them on a trailer, making them easy to pick up and move without the need of a truck,” outlined Scarce. “Also, with building sites becoming ever smaller and access often a challenge for larger machines, these small excavators have become a popular hire item. They are a ordable, convenient, and easy to use.”
“Everyone has limited time these days, so getting the job done quickly is a major appeal. These small but powerful excavators can certainly do that.”
Semco Equipment Sales has supplied the six excavators, with Semco CEO Satch Santilli saying the Takeuchi TB215R 1.5 tonne excavators are ideal for the rental market.
“This model features minimum tail swing to provide great versatility by allowing the machine to work in highly confined applications,” he pointed out. “The engine is powerful and e icient, while meeting the latest emission standards. Equipment supplied as standard includes a multi-informational display, automatic travel shift, pilot operated joystick
controls, a high-capacity cooling system, and convenient filter and service access.”
“People hiring these machines have no problems. Takeuchi equipment is well engineered to take the toughest treatment and the TB215R excavator is ideal for this environment,” said Mark.
“Customers have always been satisfied with the Takeuichi excavators in terms of the amount of power, digging depth, ease of controls and the super-reliable hydraulics. We rent the Takeuchi machines with the standard set of buckets, but sometimes people want small
hammers, boring heads or other attachments. “We normally turn over our excavators at between 2500 and 3000 hours of operation, which normally occurs at about four to five years of age. We’re also happy with the resale value of the old machines when the time comes to retire them, so this is all part of our whole-oflife costing which works out well for us.
“Takeuchi equipment ticks all the boxes required for a successful hire business –performance, durability, serviceability and operator comfort,” Mark added.
Enquiries to Semco Equipment Sales 1800 685 525 or www.takeuchi.com.au.
Lakota Hilbert has been in earthmoving his whole life.
“I grew up around machines, and have been operating since before I could even drive a car,” he says.
Today, from the scenic surroundings of Bacchus Marsh, Victoria, Lakota runs a business that has transformed to meet the demands of the market, and those seeking an eco-friendly solution for their landscaping needs.
Victorian Rockscapes and Excavation specialises in crafting low-carbon, eco-friendly rock walls – born out of Lakota’s passion for working with rocks, nature, and crafting organic settings.
After initially studying to become a greenskeeper, Lakota embarked on his entrepreneurial journey at around the age of 21, when he started Comfy Living Landscapes.
“I started o doing complete landscape packages, from excavation to decking to grass,” he says.
Over time, the business evolved, transitioning first to specialising in concrete and timber retaining walls, before finally narrowing down a focus on eco-friendly rock walls.
“As I started doing more and more of these rock walls, the feedback was really positive," Lakota says. “Before long, it got to the point where we weren’t really doing landscaping
work anymore. And that’s ultimately what led to the name change to Victorian Rockscapes and Excavation.”
Today, Lakota says 99 per cent of his business’ projects focus on crafting natural rock walls. But the change wasn't just a matter of business or following a trend – it was about chasing a passion.
“I've always had a fascination with building natural-looking environments, and I’ve always had an eye for it,” Lakota says. “So I just decided to make the change, and focus on what I’m good at.”
Every business' success depends on not just its
For Lakota Hilbert of Victorian Rockscapes and Excavation, the right equipment is key to o ering a reliable service. EEM finds out how his relationship with Jetland Loading Ramps helps provide the confidence to get his job done.Lakota Hilbert (right) with his partner Alicia.
o erings but also the tools and equipment that facilitate its operations. And when it comes to moving heavy machinery, the importance of reliable loading ramps can't be overstated. This is where Jetland enters the story.
Lakota came across Jetland Loading Ramps just after he’d bought a new truck, and needed to transport a 1.8-tonne and a 3.5-tonne Volvo excavator – so he was on the lookout for a ordable, dependable loading ramps.
Coming across Jetland Loading Ramps, with its wide range, convenient pick-up and delivery options, and robust support, turned out to be a game-changer.
“The product was well priced, it was fair, and Jimmy from Jetland made the process really easy,” Lakota says. “In my books, you’re only as good as the people you deal with – and Jimmy has been great.
“And in the few years since, I’ve bought another two sets of ramps from him.”
Lakota says he chooses to go with 6-tonne ramps to allow himself a degree of flexibility, and that their quality, resilience, and fair pricing have always stood out to him.
“I use them for my 1.8-tonne and 3.5-tonne excavators,” he says. “But when you load the 3.5-tonner up with all the hydraulic grabs and tilt buckets and compaction wheels that I use – it starts to add up. That’s why I went up a weight class with these ramps.”
Lakota says Jetland’s ramps are clearly built to withstand the kind of tough treatment you’d expect from your everyday tradesperson.
“I've tried and tested them well over what they're meant to be doing,” he says. “They are a good quality product.”
In a world where the durability of equipment is paramount, and where business relationships can make or break deals, Lakota says Jetland's rapport with its customers stands out. And because of this, he says he wouldn’t hesitate to recommend Jetland to anybody on the hunt for quality loading ramps.
“Jimmy himself is a great guy, very easy to deal with,” Lakota says. “The products are good, and they’re a ordable compared to a lot
of other brands out there.”
Lakota is also confident in the knowledge that Jetland is ready and willing to support him if any issues ever arise.
“Whatever product you’re buying, you need to know that backup support is there to keep your business moving forward, and to keep your own customers happy,” Lakota says.
“That’s why I’ve chosen to deal with Jimmy, and he’s been awesome from the start. You know Jetland is not just some big company trying to take your money. And that sort of thing makes you want to go back.”
For more Jetland’s range of loading ramps, visit: www.jetlandramps.com.au
Now as well as reconditioning and building engines, Tilly’s climate-controlled, lowdust workshops allow the team to provide customers with complete peace of mind using genuine, fit-for-purpose specs. Producing dyno reports as primary indicators, the team is testing and bringing HP, torque, and RPM all up to required spec.
An increase in demand and a shift in Tilly’s business strategy meant going from one open-
environment workshop to three dedicated bays has not only tripled capacity but is enabling the experienced team to expand its capabilities to C-series engines.
The team was part of the consultative process building the workshop which includes overhead cranes, hydraulic work benches and a substantial investment in more specialised tooling. Each team member has their own space set up to increase e iciency, worker comfort and quality control.
Currently on the benches are a 3306 engine,
130/140G transmission, D9L torque converter and D4 steer clutch, with preparation work underway for a C4 engine arriving shortly.
Leading hand Brian Jeans has been a valued Tilly’s employee for more than 16 years.
Starting in the warehouse and completing a Cert IV in Business Management, Supply Chain and Logistics, Brian then moved to the Dismantling team where he completed his diesel fitter’s trade. His experience across the
A new dedicated refurbishment workshop at Tilly’s Toowoomba headquarters is providing the team with greater opportunities –and Tilly’s customers are reaping the benefits.Tilly’s Refurbishment team is happy to o er mid-life rebuilds and quality, price-competitive services to customers across Australia.
di erent branches of the company means he encourages a learning environment as a collective, rather than each team member keeping their specific skills to themselves.
The Refurbishment team boasts an engineering background, a machine operator and parts interpreter, and they share their knowledge, feel they are all equals on the same path, and that they can cover each other’s skill sets.
A lack of competition within the team ensures they work together to get the job done to an exacting standard, get the part out, and make sure the customer is happy.
Always moving forward
The new workshop also o ers the opportunity for in-house training for other members of the 70-strong Tilly’s team, with Brian encouraging out-of-the-box thinking and problem solving as a key component of the department.
With preventative maintenance essential to long machine life, Tilly’s Refurbishment team is happy to o er mid-life rebuilds and quality, price-competitive services to customers across Australia. This is backed by Tilly’s o ering of over 40,000 new alternative-part lines QA checked and in stock, along with a quality range of undercarriage and attachments.
Tilly’s tagline of ‘always moving forward’ is evident in the company’s investment in more professional outcomes for its team and, in turn, its valued customers.
On a brisk Wednesday afternoon in July 2023, Sage Civil Managing Director Asha Russell arrived at WesTrac Casula in south-western Sydney to pick up a new Cat® 320 Next Gen excavator.
This particular machine was designed to stand out from the rest, with its boom painted pink by WesTrac.
The excavator is the latest addition to Sage Civil’s growing colourful fleet of machinery, fitting in alongside a purple Cat 730C articulated truck, that does more than help drive business outcomes.
The bright, customised machinery is used by Asha – a renowned leader in the civil sector –to spark conversations about attracting women to the civil industry.
Striving to boost female participation across the entire industry, her business is leading the way, with a female participation rate of 33 per cent across the Sage Civil network.
“Although it’s just a colour, it’s not a colour to me,” says Asha. “It reflects what we’re trying to do in this industry, and that is to drive women in civil.
“When people are driving past the job sites,
and you’ve got a whole heap of yellow gear or orange gear, and all of a sudden there’s a pink bit of gear… the conversation starts. For me, it’s the most important thing in this industry.
“It’s my passion to drive women in the industry. I’m not just doing it to tick a box.”
One of those female participants is Asha’s 20-year-old daughter, Paris, who recently started an internship at Sage Civil.
“There are so many more opportunities to be a project engineer or civil engineer that I was never given,” Asha says. “Doing this internship has actually opened her eyes a bit. She’s going to do project management.”
Paris’ story is one of many, with the Civil Contractors Federation New South Wales reporting an increase in female participation across the industry from 4.2 per cent in 2017 to 9.9 per cent currently.
“It’s a massive shift,” Asha comments. “There’s been a lot of movement and it’s not uncommon to see multiple women operating machines on site now rather than just one, so it’s definitely working.”
Role models like Asha provide proof of a career pathway for women in the civil industry,
but Asha believes mentorship is vital in attracting and retaining women in the maledominated industry.
“A lot of people come into the industry and they get thrown into the deep end. They might have a bad experience… where there’s no women or they feel isolated, they don’t get the joys of what this civil industry can really be,” she said.
Asha believes improving diversity in the civil industry is a team e ort, requiring commitment from all involved.
“Diversity just isn’t about one person here, it’s not about Asha Russell, it’s about Sage Civil,” Asha says.
“It’s my whole team that makes it happen,” she says. “It’s the supervisors and the fitters and the other operators who engage in this diversity to make it work.”
WesTrac’s Sustainability Plan – Towards 2030 includes key outcomes dedicated to diversity, with a goal of reaching 25 per cent female participation across the organisation by 2025. WesTrac’s General Manager Construction Industries, Alister Cant, says diversity is a strong focus for the business. Supporting
pathways for women to succeed in the construction and mining industry is a priority.
“We want to see women excel across WesTrac’s operations and we’re proud to have such a targeted goal to be working towards,” Alister says. “WesTrac continues to promote inclusion and diversity through education and training, recruitment targets, and providing a safe and respectful working environment.”
WesTrac is one of three founding sponsors of the Civil Contractors Federation NSW Women in Civil program, and one of the first businesses to sign up to the 50 by 50 commitment, which targets 50-per-cent female participation by 2025 in the civil industry.
“Asha and Sage Civil are exemplars in promoting female participation and set the standard, which is why WesTrac is proud to continue supplying and supporting her womenin-civil movement,” Alister concludes.
Asha has collaborated with WesTrac for her fleet needs for four years and has experienced first-hand the notable number of women working across the organisation.
“WesTrac is the leader of our industry. It’s the one we rely on to make the wheels turn,” Asha comments.
As for women wanting to join the civil industry, Asha’s advice is simple: “Believe in yourself, anything is possible, and once you forge your way in the civil industry, I don’t think you’d ever look back,” she encouraged.
“It doesn’t matter if you’re a woman or a man, if you can operate a machine, you’re good to go.”
Aaron Bollinger started as a service technician with Hydraulink, before moving into mobile service, breakdowns, and installations, then service manager, area sales manager, and now the branch manager at Mackay, Queensland.
“Hydraulink provided me with outstanding support and a clear pathway to progress my career. Along the way I learnt from di erent managers and colleagues, all with di erent styles and ideas, and all of them helped grow my knowledge,” says Aaron.
“In Mackay, we service major industries, such as mining, sugar, and agriculture. The customers we work with want to minimise downtime and ensure safety compliance on their sites, so they trust us to get them moving again,” he added.
Hydraulink and sister company Hydraulink CCR’s extensive national network includes 14 company-owned sites in Australia, 135 network partners, and 150 service vehicles o ering 24/7 onsite and mobile services to the same uniformly high levels of outstanding service, safety, standards compliance, traceability, and diverse machinery and equipment knowledge.
As part of his move to branch manager, Aaron undertook leadership training at the Hydraulink
Academy, which he says was practical and hands on.
“It didn’t feel like we were in a classroom – it felt like we were working with real examples that we might encounter next week on the job. We were also given homework, to bring real examples back to the group and describe how we applied our new learnings. It gives us a chance to learn where we could have done better, so we can continuously improve,” he said.
Hydraulink National Human Resources Manager, Paul Edwards, says whilst we can formally structure di erent career progression pathways, it’s really up to individual employees like Aaron to take initiative and ask the right questions so that we can collaboratively plan the right mix of learning, capability development, and role experiences for our employees to ultimately achieve their career aspirations.
“Aaron is exactly the kind of go-getting employee we encourage at Hydraulink. He has mechanical aptitude, a strong work ethic, and he wants to grow and progress. He knows this business in and out, through growing his understanding from the ground up, so we
were delighted to support him in his career progression,” said Paul.
During his career progression with Hydraulink, Aaron realised that building relationships with people – both within the organisation, and outside of it – was the key to success.
“Customers in the industries we work with aren’t looking to save a couple of dollars – they want someone who knows the site, knows the people, and will do a high quality, e icient job. You only get trusted with these sorts of jobs if you build a relationship over time,” says Aaron.
“Similarly, it’s important to foster relationships within the organisation – I’ve learnt lots from di erent colleagues and managers over the years, and it’s helped me grow as a leader.”
“I’d encourage anyone in any role to take on the opportunity to learn more, and to just give it a go. Even if you don’t feel you have the skills – there are ways to learn them. What’s more important is attitude and desire to grow,” concludes Aaron.
For more information, please contact Hydraulink Australia: 1300 36 37 34.
A man focused on building relationships and solving problems has risen through the ranks to become Mackay branch manager of the national hose, fittings, and hydraulic service organisation, Hydraulink.Hydraulink Mackay branch manager, Aaron Bollinger, says building relationships and solving customer problems are the keys to success that he used to grow his career with Hydraulink.
Owning a skid steer is akin to having a versatile workhorse at your disposal.
These compact machines are celebrated for their agility, manoeuvrability, and the wide range of attachments they can accommodate. However, like any investment, there are both pros and cons to consider.
Enter the world of screening buckets – an innovative attachment revolutionising the skidsteer experience.
Pros and cons
Pros:
• Versatility: skid steers are like a Swiss Army knife of construction equipment. Their compatibility with various attachments makes them invaluable on job sites
• Size: compact design allows skid steers to work e iciently in tight spaces and navigate congested areas with ease
• Attachment variety: from trenchers to forks, there’s an attachment for almost any task, enhancing skid-steer adaptability
• Productivity: skid steers can accomplish
multiple tasks, reducing the need for di erent machines
• Ease of use: intuitive controls make skid steers suitable for operators of varying skill levels. Cons:
• Limited lifting capacity: skid steers may not handle heavy lifting as e ectively as larger machinery
• Rough ride: A smaller frame can lead to a bumpier ride compared to larger equipment, and
• Operating costs: maintenance and fuel costs can add up, impacting overall ownership expenses
The role of screening buckets in skid steer-ownership: Enter screening buckets – an attachment that transforms a skid steer into a productivity powerhouse.
By incorporating a screening bucket like the Flipscreen, skid-steer owners can experience an array of benefits that drastically outweigh the cons.
Benefits of screening buckets for skid steers:
• Cost-e iciency: a screening bucket eliminates the need for separate machines for screening and mixing, saving on operational and maintenance costs
• Waste reduction: precise screening allows for the retention of valuable materials while reducing waste-disposal expenses
• Increased versatility: the Flipscreen’s ability to handle diverse materials, from sand to scrap metal, enhances the skid steer’s usability across di erent projects
• Time and labour savings: automating the screening process reduces manual handling, decreasing labour requirements, and
• Innovative solutions: the Mixing Plate in the Flipscreen brings new possibilities. Imagine o ering custom mixes for landscaping projects or repurposing materials on-site.
Example: Flipscreen’s unique benefit
Consider a skid-steer owner tasked with landscaping a shooting range. The Flipscreen’s ability to quickly screen out slugs, arrowheads, and other debris from the soil streamlines the process. This unique feature not only saves time but also opens doors to niche services like recycling spent slugs.
Such innovative applications set the Flipscreen apart.
Owning a skid steer can be incredibly rewarding with the right attachments. Screening buckets, especially the Flipscreen, bring a new level of productivity and versatility to skid-steer owners. With the potential to reduce costs, increase e iciency, and tap into innovative services, it’s clear screening buckets are changing the game for skid-steer ownership.
Learn more about the Flipscreen Skid Steer Screening Bucket at flipscreen.net and unleash the true potential of your skid steer investment.
Komatsu has introduced a new version of its 50-tonne hydraulic excavator, the PC490LCi-11, to Australia and New Zealand. The excavator comes standard with the manufacturer’s latest machine technology – intelligent Machine Control (iMC) 2.0, which is designed to help operators improve e iciency and accuracy on their projects.
Designed for construction, quarrying, and demolition applications, the PC490LCi-11 features 268kW of horsepower, a bucket capacity of between 1.45 – 2.7 cubic metres, and is Tier 4 emissions certified.
Dean Gaedtke, Komatsu Australia’s Executive General Manager for Construction, says customers can expect a durable and reliable machine in this new addition to the company’s product range.
“The PC490LCi-11 is built for highproduction jobs,” he says. “It’s durable, productive, and most importantly – smart. We’ve been looking forward to bringing this updated model to our Australian and New Zealand customers for some time, and we
know they’ll definitely see the benefits of adding it to their fleets.
“iMC 2.0 uses Komatsu’s unique sensor package and 3D design data loaded in the control box to accurately check your machine and bucket position against the target, helping minimise over-excavation. It’s an integrated, intelligent, and innovative feature that makes every pass count for operators.”
iMC helps operators to work smarter and more e iciently, with several performance improvements from the platform.
“Our research shows that iMC has helped save operators up to 63 per cent of time on site, with iMC helping to reduce staking, grading, and inspection with its 3D design data and semi-automatic grading,” Dean says. “Accuracy is also improved by up to 33 per cent, with iMC providing the ability to continuously monitor your grade, and semi-automatics dig precisely to grade.”
Power is also a key feature of the PC490LCi-11, with the machine equipped with features to boost performance and productivity,
while not compromising on operating costs.
“There are two boom mode settings, which provide power mode for maximum digging force or smooth mode for fine grading operations,” Dean says. “Plus, largedisplacement high-e iciency pumps provide high-flow output at lower engine speeds, improving machine e iciency.
“Komatsu’s Auto Idle Shutdown option helps reduce non-productive engine idle time and reduces operating costs. New engine and hydraulic control technology in this model improves operational e iciency and lowers fuel consumption by up to 11 per cent.
“The machine is backed by service and support of the entire Komatsu Australia and New Zealand network. There is peace of mind in knowing that Komatsu is the one distributor for both countries, and no matter where you are you’re dealing with trusted Komatsu experts.”
For more information, visit: www.komatsu.com.au
The Federal Government’s independent Strategic Review of the Infrastructure Investment Program (IIP) duration would suggest that after 90 days the review would be completed, and all states and territories would know which projects could proceed.
This is in fact a naïve simplification of the actual process.
The Minister for Infrastructure, Transport, Regional Development and Local Government, Catherine King, announced the 90-day review of the $120B 10-year pipeline on 1 May 2023. This information was subsequently published in the Federal budget on 9 May 2023. The Minister has publicly confirmed and has confirmed in-person to CCF that “the $120B pipeline over 10 years is safe”.
The terms of reference of the IIP review includes:
• Making recommendations for transitioning the IIP to a sustainable 10-year rolling pipeline that targets appropriately costed, nationally significant infrastructure projects, as well as assessing:
• Strategies for smoothing the pipeline to manage peaks and troughs
• Whether Commonwealth-state funding arrangements are commensurate with the level of Commonwealth agency in project delivery
• The merits of funding such projects through Commonwealth debt or other arrangements.
• Making recommendations on reforms to ongoing and terminating infrastructure investment sub-programs, including whether sub-programs:
• Are appropriate for delivering the government’s strategic priorities, including supporting safety, resilience and
maintenance outcomes
• Could be delivered more e iciently and e ectively, having regard to the constitutionality of programs.
• Considering other relevant projects or matters as agreed in consultation with relevant jurisdictions.
Since the announcement there has been a hold on all projects which are the subject of the review, and these projects will not progress until the pipeline is finalised. At the time of writing, it has now been 110 days since the start of the review with no conclusion in sight. I have also been informed that at the conclusion of the review there will be a government sign-o process and time will need to be allowed for state agencies to consider the results.
Speaking with representatives from the Department of Transport and Main Roads (‘TMR’), they have not been informed of any resolution and are in the dark as to which projects they could proceed with.
Depending on the outcome of the review, there would need to be a rebalancing of the program to allocate funds from projects no longer supported by the Commonwealth to other projects.
There have been recent suggestions from Commonwealth representatives that the review is also considering market capacity. This comment is out of touch. CCF has
provided the Commonwealth with a market capacity report that demonstrated prior to the review there was latent capacity in the market to deliver the program. The review and the elongation of the timeframe has created additional capacity evidenced by contractors having resources on standby for the review outcomes. As the reviews period continues to lengthen, I am being told that some contractors will have no option but to start laying o personnel. This is more prevalent in regional areas where the current rolling 4-year capital program, Queensland Transport and Roads Investment Program (‘QTRIP’), shows a major bias to South East Queensland at the expense of regional areas.
An analysis of QTRIP shows that every district north of Wide Bay Burnett, including Wide Bay Burnett, has had reductions in their funding in favour of southern regions.
The probable outcome for these northern regions is that the timing of the review conclusion, and subsequent QTRIP finalisation, would mean delayed projects would not go to tender this side of Christmas.
If there is a wet season of any substance, profitable construction would not be able to commence until the conclusion of the wet season which e ectively amplifies the reduction of funding for these regions.
This is a terrible result for an industry that, up until the Commonwealth budget, had line of sight on an increasing pipeline of work and has scaled to meet the challenges.
It is ironic that one of the terms of reference of the 90-day review was to assess strategies to manage peaks and troughs and the review itself has created a significant trough in many regions.
Hopefully the review produces rational conclusions which will support infrastructure development throughout all of Queensland.
The Strategic Review of the Infrastructure Investment Program needs to be put under the microscope, writes Damian Long, CCF QLD CEO.Damian says it has been more than 110 days since the start of the review, with no end in sight.
NOW AVAILABLE
PROUDLY PRESENTED BY MHD
Thurs 20 June, 2024
The Women in Industry Awards recognise outstanding women leaders from across Australia’s industrials sector.
In 1987, 12 backhoe operators got together over a meal at a Chinese restaurant in Castle Hill to see if they could start something that would look after the interests of owner operators. From that meeting was born the Golden Bucket Association, and 36 years later is still serving the needs of the owner operator (albeit less backhoes). The Allied Earthmovers Golden Bucket Association promotes friendship, trades information, assists with compliance and education and shares work around, all under the umbrella of a Code of Ethics.
Our July meeting of the Association saw a near re-creation of that meeting. About 20 members came together at a Chinese restaurant in Warragamba (when was the last time you visited that lovely little town?)
and enjoyed the same camaraderie as their counterparts before them. And the true benefit of our Association was apparent during the evening. It was evident that lasting friendships have been formed and networks have been galvanised. This can only be done when members meet face-to-face and have a personal interaction and that’s where the Association shines.
We are not an on-line facility only; members are encouraged to meet up and be accountable and to discuss industry topics that are relative and current to each member’s situation. Our topics for this meeting were restrictive truck parking in residential areas while working on site and our upcoming Annual General Meeting. Also, during the dinner, our Vice President
Wayne Melrose had the pleasure of welcoming new member Anthony into the Association. The members who sat round the table at that meeting and enjoyed a meal together are the members who get the most out of our Association. What they get out of these types of meetings is priceless – you can’t just go and buy it.
Our Annual General Meeting was held in August and as usual we had no problems filling all vacancies. Our Association is a not-for-profit organisation and is run by a voluntary Board. They do not get paid and, in fact, frequently must reach into their pockets to fulfill their role. All decisions regarding the running of our Association are made by this Board, not by a corporate body who has no connection with the grass roots level of earthmoving sub-contractors. Each Board member know the trials, tribulations and joys associated with working on site. We congratulate Phillip Favaloro for taking on the role of President for a further term.
Currently, membership fees are at an historic low, and it is very easy to save more than double your outlay during the first year with insurance, WorkShare and many other benefits on o er. We look forward to our “Trade Night” meeting at the premises of STM Trucks and Machinery at Smeaton Grange this month and we extend an invitation to anyone interested to come along.
Ann Callaghan ManagerIf you are an owner-operator and are interested in seeing what we are about, just give us a call on 0416 110 024 or email o ice@goldenbucket.com.au. We are a very informal and welcoming bunch. Of course, we are, we’re all owner-operators!
Camaraderie and friendship are invaluable assets in earthmoving. Allied Earthmovers Association Manager Ann Callaghan explains.The Golden Bucket Association is still going strong after 36 years. Membership helps 'dig out' opportunities.
CJD Equipment and Volvo CE are deeply committed to sustainability and environmental responsibility; Volvo’s commitment to circularity starts with its remanufacturing process, bringing new life to worn-out parts. By choosing Approved Used Equipment, you are making an environmentally conscious decision towards a greener future and reducing your carbon footprint.
80%
less energy is required to build a reman component compared to manufacturing a new part. Volvo’s range of remanufacturing services will help keep your machine running for a long time while reducing your owning and operating cost. A Volvo Reman part delivers all the quality and high standards you expect from Volvo.
Find the right part for you with Reman