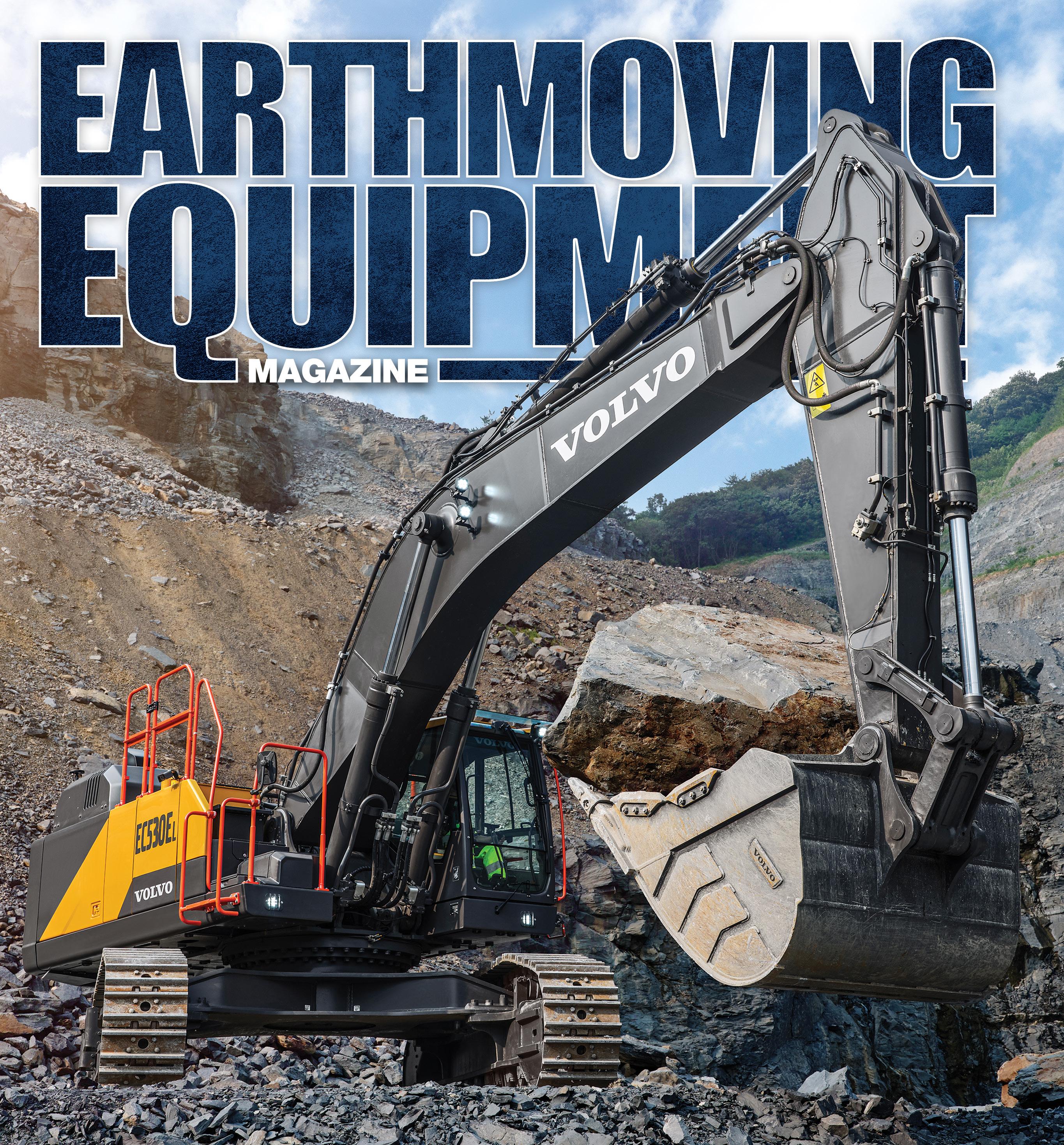
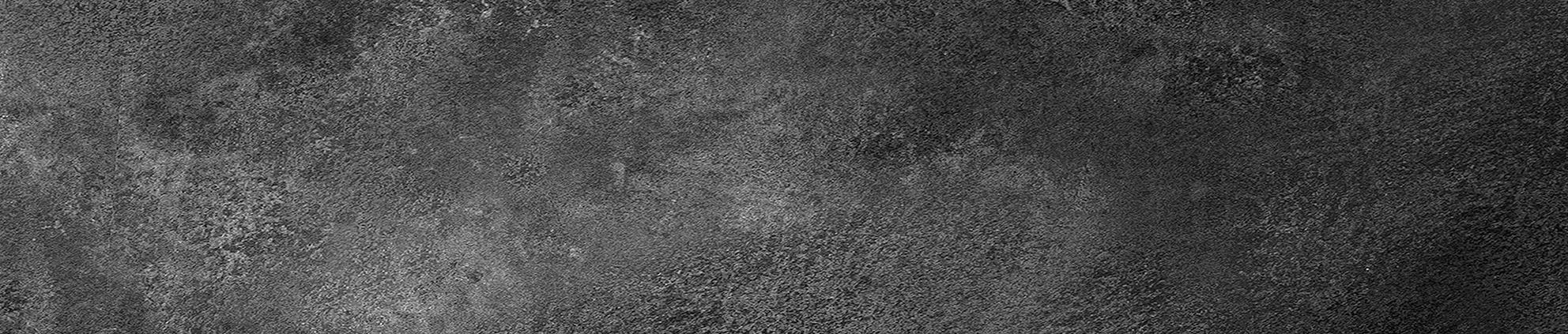
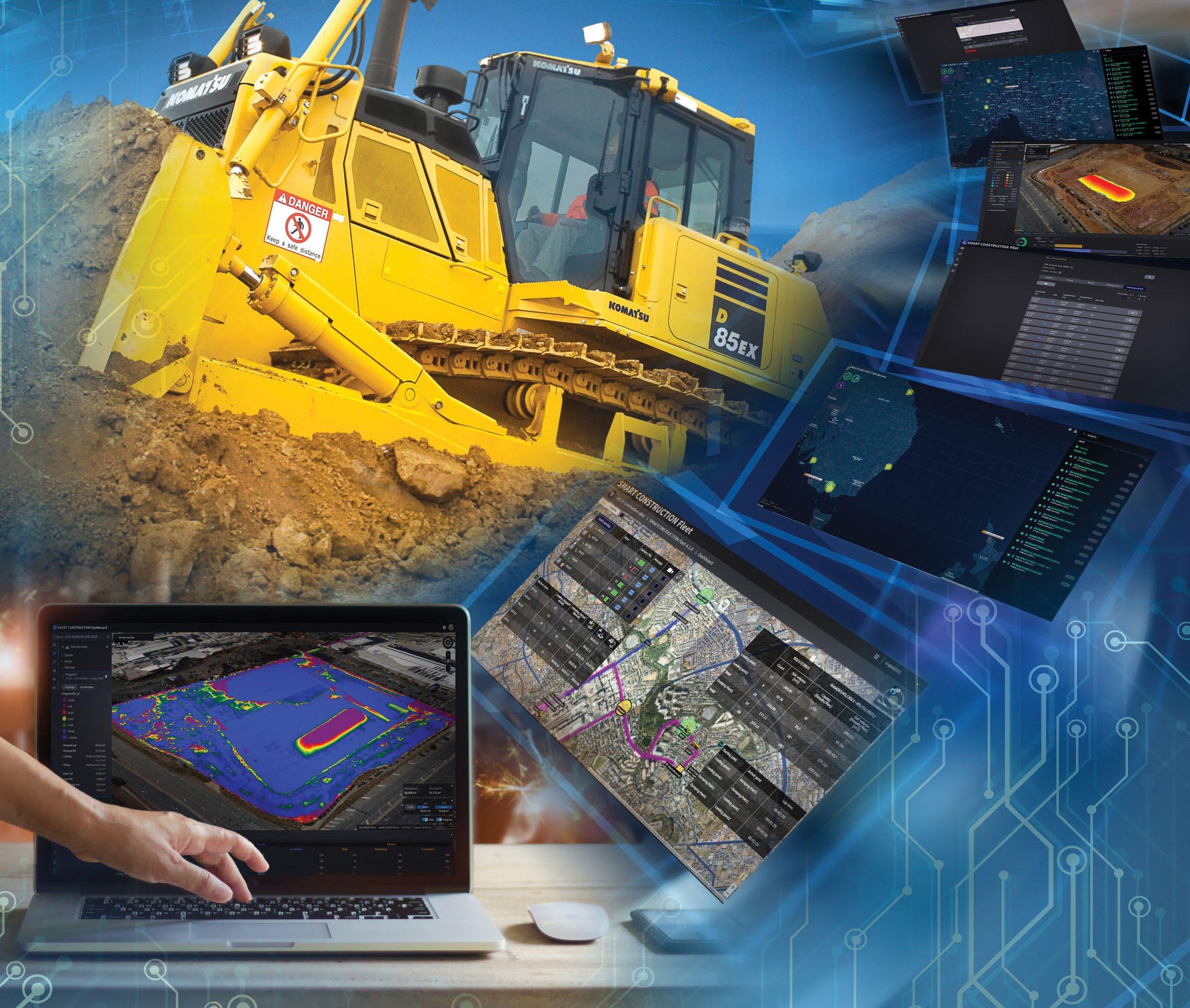

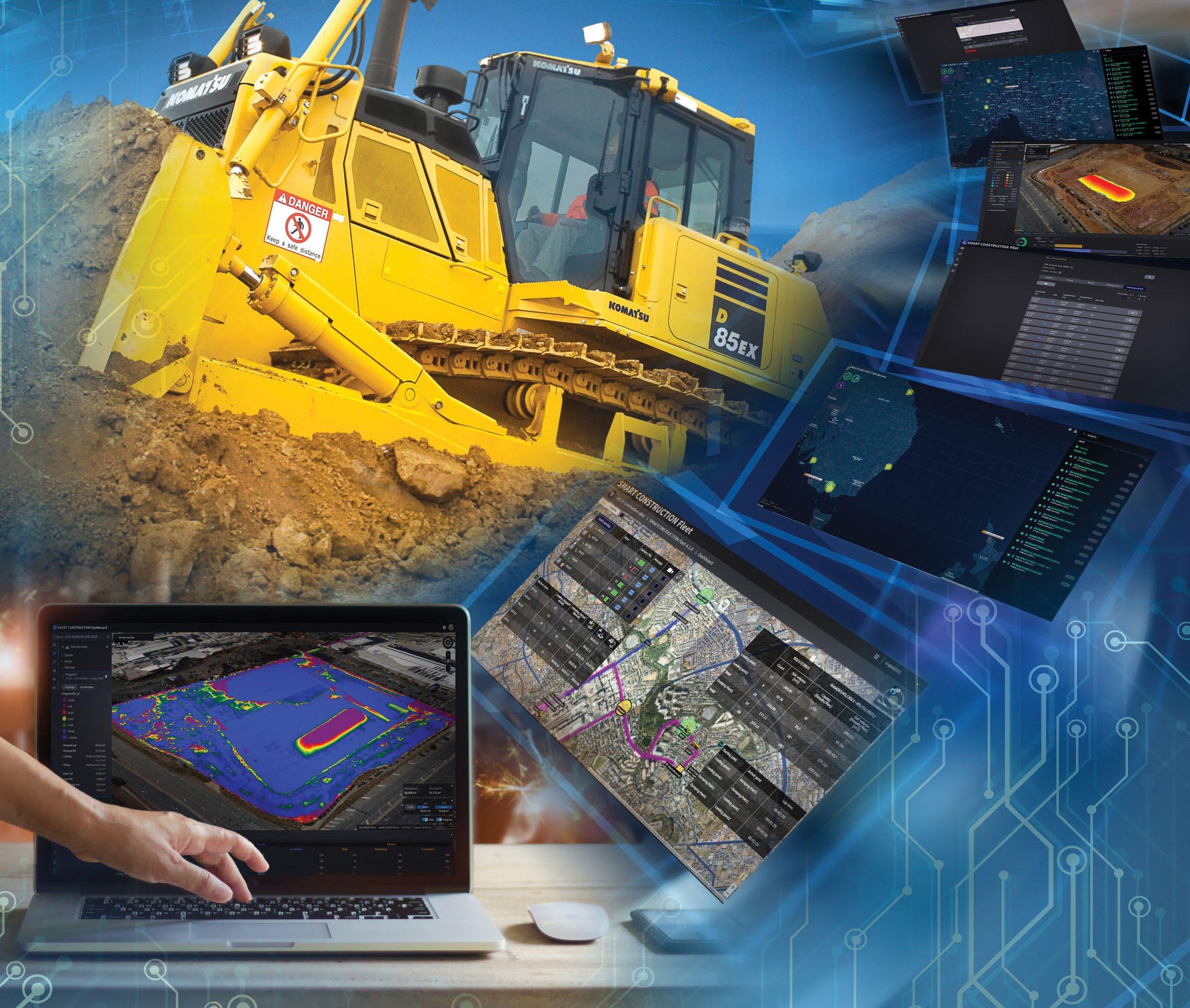
Do you have something you’d like to share with the industry?
Send EEM an email at tom.foster@primecreative.com.au We’re keen to get your thoughts.
It’s all happening here at EEM!
The leading journal of record for Australia’s earthmoving industry has a new owner. Prime Creative Media will now be in the cabin and at the controls of the magazine, and it’s opened up an array of exciting possibilities. That’s for us here in the office and out on the machines. For you folks, the readers, the difference may not be immediately obvious. The magazine will still be full of the latest industry news, hands-on testing of plant, tools and attachments, and of course, advice from experts who understand what it means to run a large business or to need the time to service and maintain hard-working machinery.
While the magazine’s been moving offices and integrating into a new management structure, the team has kept on hunting the big stories, and the cover of this issue is a great example. Nation-wide heavy-machinery
specialists CJD Equipment Pty Ltd, for decades the national distributor of Volvo, is now offering the 50-tonne EC530E. It’s a welcome entry into the 50-tonne category, and EEM spoke to the main players involved in that purchase. It’s clear everyone involved is very happy with the result and the outlook for the future.
There’s also a case study all the way from WA. Picton Civil has been operating for 50 years and recently purchased three Kobelco excavators. There are some interesting thoughts from interesting people shared on those pages as well.
And while everyone loves a competition, things don’t run on a much larger scale than Caterpillar’s Global Operator Challenge.
EEM has been watching with keen interest as the preliminary rounds pitted operators from 40 countries around the world against some amazing challenges. Now the GOC
is at the business end of the whole thing, and five Australian finalists will make their way to Japan to showcase their skills at the Asia-Pacific region semi-finals, hoping for a chance to represent Australia at the final in Japan.
Naturally, EEM will be there, cheering on the Aussie entrants and reminding the world that when it comes to moving earth, Australia is a leading player.
We’ll bring you the report on that event in a future issue.
For now, we’d like to assure our valued readers and partners – it’s not just business as usual, but even better than ever, now that we have a new home with Prime Creative Media!
Onwards and upwards!
Tom Foster Contributing EditorThe Doosan DX140LCR-5 machine builds on Doosan’s enviable reputation for hardworking, reliable and comfortable machines, with this next generation model offering an exceptionally powerful DPF-FREE TIER 4 FINAL engine.
By complying with US Tier 4 regulations, the Tier 4 Final DX140LCR-5 will have no issue operating on jobsites with Tier 4 emission standards - helping future-proof your investment. And with no DPF (Diesel Particulate Filter), you will avoid the maintenance issues experienced by other manufacturers - from time consuming regeneration cycles to expensive DPF servicing issues. This makes the Doosan DX140LCR-5 one of the most productive and reliable machines in its class.
Jamie has been a professional photographer in Sydney for over two decades. He is the owner of Camera, Hammer and Tong, who provides digital content for small businesses in and around the construction industry. He is also a photo journalist & the product feature editor for What Tradies Want Magazine. But he’s just as comfortable with a hammer in his hand as a camera and pen. Undertaking a mature age carpentry apprenticeship in his 40s and still gets the nail bag on when he can.
Scott is the Director of Australian Earth Training, a niche operator proficiency training organisation who work across the globe. He has over 25 years’ experience in heavy equipment operation and was an accredited Caterpillar Dealer Instructor (CDI) Trainer-Demonstrator. Scott’s unique skill set enables him to operate and train on a broad range of machines across the mining, construction, quarrying and waste industries, helping his customers to boost their productivity while lowering their owning and operating costs.
Ann has been the Manager of Allied Earthmovers Association for the past 19 years bringing many years’ experience into the role. After gaining business qualifications and managing a retail shopping centre in Sydney CBD, Ann first started her career in earthmoving when she joined the long-established family business in Penrith, which specialised in Caterpillar graders and dozers.
Working in a male-dominated industry, Ann brings a different aspect to the Association. She has met many people in the industry and knows what the owner operator needs, from the importance of paperwork to machine availability. It’s an industry she respects and is proud to be a part of.
made to ensure the accuracy of information, Prime Creative Media will not accept responsibility for errors or omissions or for any consequences arising from reliance on information published. The opinions expressed in Earthmoving Equipment Magazine are not necessarily the opinions of, or endorsed by the publisher unless otherwise stated.
The 50 t Volvo EC530E crawler excavator has landed in the local market, with Australian construction equipment and trucks distributor CJD Equipment having recently added the purpose-built machine – decked out to tackle a range of heavy-duty applications, including digging, mass excavation and large site preparation – to its product portfolio.
As noted by
Hayden Grant, the introduction of the powerful EC530E sees CJD not only broaden its product offering, but also stake out territory in a new excavator weight class.
“We haven’t had the option of being able to provide our customers with a true 50 t excavator until now,” Hayden told EEM.
“The EC530E was built specifically to compete in this class. Supported by the R&D that goes into the Volvo product, specifically the excavators, operators can expect a fuel-efficient and productive machine with world-class operator comfort.”
In fact, the EC530E – which Volvo advises features the highest engine power in its class, while delivering superior swing torque and tractive force – is geared to provide performance levels normally found in heavier machines.
“The EC530E was made to punch above its weight,” Hayden explained. “It delivers digging forces and a lifting capacity more commonly found in a 60 t machine.”
When it comes to productivity, Volvo advises that the EC530E in conjunction with 30-40 t class Volvo articulated haulers has the capacity to reduce the number of required passes,
CJD National Product Manager, Volvo Construction Equipment,with the potential to dramatically improve cycle times.
Hayden noted that the EC530E sports an extensive range of productivity and fuel-efficiency features, with one of the standout components for him being its advanced hydraulic system
and, in particular, its main control valve.
“The EC530E comes standard with a next-generation electro-hydraulic system with Independent Metering Valve Technology (IMVT),” he commented. “This produces up to a 25% improvement in fuel efficiency.”
Volvo advises that the IMVT system enables intelligent electronic control with more control variability, as compared to a conventional mechanically coupled hydraulic system, resulting in maximum controllability and efficiency in undertaking specific applications.
“The EC530E also features engine pump optimisation, which lowers engine rpm while optimising power, further contributing towards fuel efficiency,” Hayden added.
In addition to this, the EC530E’s productivity and efficiency features include:
• Fuel Efficiency Reports – help to identify areas where improvements can be made, providing insights into the fuel performance of a fleet, across a site or for an individual machine
• Attachments – Volvo attachments are designed to create a single solid and reliable unit, delivering faster and more fuel-efficient cycle times (the EC530E also features the necessary auxiliary piping to power hydraulic attachments)
• On-Board Weighing (optional) – is part of the Dig Assist set of apps, powered by the 10” Volvo Co-Pilot display, providing real-time bucket weight information, ensuring the optimum amount of material is moved with every pass (it also records total tonnage, per shift or per day)
Operator ease of use, safety and comfort are key underlying focus areas spanning the design of the EC530E, effectively providing for both enhanced control and convenient operations, allowing operators to tackle a broad range of tasks with confidence.
As noted by Hayden, the IMVT system not only delivers fuel-efficiency benefits, but also paves the way for “a lot of cool new features”.
“This includes creep mode and motion priority functions, along with reduced boom and arm bouncing, as well as Comfort Drive Control, which is also an option,” he explained. “This makes the EC530E adaptable to any given task by the operator.
“The operator can easily select and adjust a number of functions, depending on personal preferences and the task at hand, including boom/swing and boom and travel priority, which enables prioritisation of one function over another.
“Operators can also easily adjust the boom down speed, which is ideal for precision tasks which require optimum control.”
In addition to this, the EC530E is decked out to deliver when it comes to safety and comfort, with the ROPS cab sporting an integrated air-conditioning and heating system, with pressurised and filtered cab air supplied by an automatically controlled fan.
Additional operator ease of use and comfort features include:
• Visibility – designed to deliver best-in-class visibility, while the optional high-visibility cab and one-piece front window, along with rear and side-view cameras, provide for enhanced visibility (optional Volvo Smart View uses front, rear and side cameras to provide a real-time, overhead view of the machine)
• Reduced shock and vibration levels – hydraulic dampening mounts reduce shock and vibration, while sound-absorbing lining means low noise levels
• Ergonomic operator’s seat – the adjustable seat and joystick console move independently, accommodating the operator, with the seat featuring nine different adjustments plus a seat belt
• Safe access – the cab has a wide door opening for easy access, while bolted anti-slip plates, high-visibility guardrails and handrails ensure enhanced levels of safety when negotiating the machine (an optional foldable cab entrance step and side walkways fold away to enable easier transportation)
The EC530E is designed to keep powering on through when the going gets tough, with it sporting an ultra-durable and reinforced undercarriage, which Volvo states provides the durability and strength expected from a 60 t machine.
In addition to this, it is equipped with a super-strong upper and lower frame, reinforced digging equipment, including a boom and arm with larger pin size, and electric connectors exceeding Ingress Protection 69K waterproofed standards.
Hydraulic pilot lines have also been removed, reducing the number of couplings required, paving the way for increased machine reliability.
“The EC530E will also have a reversible hydraulically driven fan as standard, keeping the cooling pack clean and clear, what is a must in tough conditions,” Hayden told EEM.
When it comes to maintenance, the EC530E provides for quick-and-easy servicing, with features including:
• Upper structure access – three-point right-hand side access
• Convenient servicing access – grouped
filters are accessible from ground-level or the side walkway
• Splash guard – on the UREA/DEF tank
• Long uptime – with less interruptions due to 500-hour engine oil and engine oil filter change intervals
• CareTrack telematic system (optional) –maximise machine uptime and reduce repair costs
The launch of the EC530E coincides with the 30-year milestone of CJD’s partnership with Volvo, with CJD providing its nationwide
customer base access to Volvo’s ever-evolving line of heavy-duty equipment, catering for the specific needs of different industry segments.
Hayden highlighted the strong relationship between the two, with CJD, which presides over a network of dealers and service centres located around the country, supporting its Volvo range with a comprehensive service offering.
“It’s a partnership that keeps getting bigger and better as innovation and technology grows, we couldn’t hope for a better partner in this space,” he commented.
CJD is committed to providing its customer base the most up-to-date product information and service techniques, while its streamlined national supply network sees parts quickly located and dispatched to customers when required.
Meanwhile, despite many of the challenges businesses have faced in recent years, Hayden pointed to the strong momentum CJD has been building throughout 2022, which has seen it continue to deliver its customers a high level of service, from sales through to after-sales.
“This year has been incredible, but also very challenging at the same time,” he said. “This has been the case for most businesses due to things like Covid, shipping, parts and machine delays, not to mention lack of skilled labour.
“As always though, we are staying positive for 2023, doing what we can now to support our customers. Our slogan reads ‘Big Enough to Trust, Small Enough to Care’, and I truly believe this, as I have seen it time and time again over the 13 years that I have worked for CJD.”
The EC530E weighs in at an operating weight of 53.14-57.3 t, with it featuring (based on an EC530EL machine configuration with retractable undercarriage, a 7m boom, 3.35m arm, and 10.6 t counterweight):
• Engine – a 339 kW Volvo D13J engine using Volvo Advanced Combustion Technology (V-ACT), delivering lower emissions, superior performance and fuel efficiency, with precise, high-pressure fuel injectors, a turbocharger and intercooler, and electronic engine controls optimising machine performance
• Bucket capacity – 2.4-4.2m³
• Lifting capacity, along undercarriage – 20.78 t
• Maximum digging reach – 12.18m
• Maximum digging depth – 7.69m
• Breakout force – 251 kN (normal), 269 kN (boost)
Getting the most out of your equipment requires hundreds of decisions, every day. Where should assets be deployed? How can we solve a production bottleneck? What can we do to reduce fuel costs? To be confident that you’re making the right decisions, you need accurate, timely data. Cat® VisionLink® gives you access to all the data you need to keep your equipment on the jobsite and earning money.
As strict emissions regulations become more common, you’ll need to be able to prove that your fleet is running as clean as possible. The VisionLink reporting function lets you monitor and track CO 2 emissions from construction equipment of all kinds. View fleet information online with VisionLink and use it to make informed decisions that boost productivity, lower costs, simplify maintenance, and improve safety on your jobsite.
As governments around the world work to reduce greenhouse gas output, it is falling to the construction companies to provide accurate data to prove they are meeting emissions standards. It may also be used to challenge regulatory rulings when companies feel they have been unnecessarily penalised.
Europe already has strict CO 2 emissions requirements, with heavy fines for non-compliance. Similar regulations are also underway in many other parts of the world.
CO2 REPORTING PER ASSET OR FLEET VisionLink’s Unified Fleet summary page now includes a CO2 Emission column on the Fleet Utilization and Asset Utilization Details pages. It displays the CO2 emissions for each selected asset, calculated by fuel type for the Runtime Fuel Burned each day in a selected date range.
It’s easy to configure this function for the mix of diesel- and gasoline-powered equipment in your fleet. And it enables you to easily run an Emission report for any individual asset, a group of assets or for your entire fleet.
The default fuel type is diesel, but you can change it to gasoline for any asset. You can also display your total Diesel Exhaust Fluid (DEF) Burn and DEF Burn Rate.
Emissions reporting will help you identify when certain machines may not be running as efficiently as possible. If so, you can consider:
• Upgrading maintenance procedures
• Rebuilding components or machines to get the latest technology updates
• Replacing old, less-efficient machines with newer models
CO2 Emissions Tracking: The report you don’t want to skip.Of course, reducing fuel burn, eliminating excess idle time and improving machine efficiency will ultimately save you money. The ability to track and monitor fleet CO 2 output will also help you ‘future proof’ your operation as emissions regulations tighten around the world.
Emissions reporting is just the latest in a long list of benefits reaped from putting telematics data to good use. Analytics software such as VisionLink helps you turn raw data from your equipment into actionable information you can use to build your business success.
For more information on VisionLink contact your local Cat dealer or visit https://www.cat.com/en_AU/ products/new/technology/equipment-management/ equipment-management/102680.html
A Cat® Certified Rebuild can give your machine a second life for a fraction of the cost of new.
All Cat® owners are looking for value, reliability, good service and support. But not all owners fully understand the value they can realise with a Cat Certified Rebuild – available for a range of machines, including 336 excavators, 777 dump trucks and 988 wheel loaders.
Many businesses choose one of the cost-effective rebuild options, including Cat Certified Rebuilds, offered by Cat dealers, but their reasons vary depending on their situation.
Rebuilding can free up capital for other investments. As your business grows, naturally your fleet must evolve with it. Navigating the challenges of this requires making the best use of existing assets, while planning for the future.
Benefit from new technology
You don’t have to buy a new machine to benefit from new technology and other improvements. Rebuilding is an opportunity to add engineering upgrades that will help your fleet run smarter and smoother. Keep using the machines your operators know
When you rebuild, you avoid the issue of training staff on completely new equipment, making it easier to keep productivity on track.
Cat dealers offer a broad range of smart rebuild solutions that work for you, including Cat Certified Powertrain, Cat Machine Component and Cat Full Machine rebuilds. All three solutions are available for 336 excavators, 777 dump trucks and 988 wheel loaders as well as a range of other machines, including motor graders, compactors and dozers.
A Cat Certified Powertrain Rebuild covers your radiator, engine, transmission, torque converter, final drive and axle. All components are disassembled, and all critical engineering updates are incorporated. This option restores your powertrain to like-new performance. Cat Product Link ™ is installed with all Cat Certified Powertrain Rebuilds, meaning your powertrain will generate data that you can use to help boost productivity, reduce costs and manage risks.
A Cat Certified Machine Component Rebuild restores the engine or transmission, plus
the torque converter, to deliver like-new performance for these components. Critical engineering updates are included with this option.
With a Cat Certified Full Machine Rebuild you can recover the performance of your original machine. You’ll benefit from the latest engineering updates and technology, including Cat Product Link™
In addition to Cat Certified Rebuild options, your Cat dealer offers a range of non-certified dealer machine rebuilds, performed by a qualified technician, with tailored financial solutions available.
Whenever a major machine upgrade is required, you have the choice to replace, rebuild or repair. There are many factors that influence this decision, including cashflow and the expected lifespan of the asset.
Advances in technology are also important, helping support productivity gains and reduce costs. Your Cat dealer specialist can provide expert advice on the operational
performance of your machine, to design the best rebuild solution to suit your needs.
A Cat Certified Rebuild is a cost-effective and sustainable way to get your equipment operating like new. Right now, if you rebuild your 336 excavator, 777 dump truck or 988 wheel loader you can take advantage of offers that bring you even more value:
• Performance and technology upgrades
• Extended warranty*
• Competitive low finance rates*
To find out more visit cat.com/rebuild-au or contact your local Cat dealer.
*Terms and conditions apply. See cat.com/rebuild-au for details.
So that it can better service and support new, rental and used equipment customers in the greater Melbourne region, Komatsu has started construction of a new branch at Truganina in Melbourne’s south-west.
The new Truganina branch will be located 30km south-west of Komatsu’s Victorian head office in Campbellfield and 80km north-west of its newly opened Pakenham branch.
Scheduled to open in September, the new branch – at 3 Niton Drive, Truganina – will expand Komatsu’s footprint in the west of metropolitan Melbourne, says John Looker, Komatsu’s Rental Manager for Southern Region.
“This will allow us to better manage the growth in our rental and remarketing operations, and also to alleviate capacity pressures at Campbellfield,” he says.
According to Looker, there are a number of drivers for the creation of a new branch in Melbourne West.
Forthcoming Truganina branch will further enhance customer service and support levels.These include:
• Providing facilities for the expansion of Komatsu’s rental/remarketing operations in Melbourne
• Providing significantly better market coverage for customers in the region
• Improving sales, support and service opportunities for the significant infrastructure development projects planned for Melbourne West over the next five years
• Relieving overcrowding and heavy vehicle congestion issues at Campbellfield
• Increasing field service efficiencies, with field service technicians based at the new branch, and able to get to customer and job sites faster.
“Facilities at our new Melbourne West branch will include a 1400 sq m workshop, storage and warehouse facilities, a paint shop and wash bay, a machinery display area, plus additional concrete hard stand area,” says Looker.
“And in line with Komatsu’s environmental and sustainability principles, it will be a five-star
Green rated building, with solar panels and LED lighting.”
The new facility also aligns better with Komatsu’s Inclusion, Diversity and Equality (IDE) strategy, with equal washroom and toilet facilities for male and female employees.
“In addition, our expansion to this Melbourne West facility will provide new jobs, will help us relieve staff overcrowding issues at Campbellfield, and ensure we continue to offer a modern, safe workplace for our employees,” Looker says.
Many Australians are turning to locally-owned industrial equipment for sale because international production and delivery is delayed. With the industry booming, Pickles has been developing more innovative service solutions to help deliver profitable returns to our industrial sellers.
Pickles makes it simpler for their industrial partners to navigate the flourishing seller’s market. With a continued commitment to making their partnerships more successful, there are plenty of reasons to engage the Pickles sales services.
Pickles proudly boasts in-depth knowledge of all aspects of buying and selling industrial equipment. The Pickles team is the largest and most qualified group of valuers and auctioneers in Australia. This collective expertise extends across multiple industries, including transport, civil construction, agriculture, mining, marine, aviation and rail.
Every year, they sell in excess of 11,500 trucks and trailers and 4500 pieces of earthmoving and mobile plant assets. The process of preparing and presenting assets for sale at our industrial auction facilities is meticulous and recognised as the best in the country.
Pickles local teams are backed by 50 designated industrial representatives
Australia-wide, ensuring that each piece of equipment is represented thoroughly. By bringing in the best industrial team, Pickles sees the best results with combined industrial and vehicle sales in excess of A$550 million a year.
The Pickles team firmly believes that selling should be simple. The process of selling your asset should be simple.
The cost of using Pickles services is transparent and easy to understand so that their customers aren’t faced with surprise hidden costs. This fee transparency allows sellers to make informed decisions about the solutions that work best for them.
Pickles team members can help you realise the price you could get at market for your asset. They provide low and high market estimates on your assets and stand by these quotes. To ensure the asset auctions for the best price, Pickles sets a reserve on all pieces. This makes it simpler and less stressful for vendors to place expensive equipment for sale.
To make the experience even easier for sellers, Pickles simplifies ownership. If your asset has finance owing, Pickles works
directly with lenders to clear title of ownership. They also offer flexible consignment options, so the higher sale price they receive, the more money is returned to you.
There are many reasons why selling with Pickles is the best choice. While their systems and solutions are selling points, nothing beats the returns their vendors receive. Pickles is the best industrial seller on the market because
of the extensive and meticulous work that goes into remarketing assets.
The Pickles website receives approximately one million website users per month. The audience reached is a huge resource of domestic and international buyers. They also execute successful advertising and marketing campaigns on behalf of their sellers using digital and traditional media for maximum exposure. They use tailored marketing, a huge database, and targeted campaigns to maximise returns for their partners.
REMARKETING SOLUTIONS AVAILABLE
• Custom landing pages featured on www.pickles.com.au
• Targeted email and SMS campaigns database of previous registrants
• Display advertising on relevant publisher sites
• Data-led social media campaigns on Facebook, Instagram, and LinkedIn
• Traditional radio, print, magazine, and banner advertisements
If you are ready to sell with a partner with resources, expertise and industry insight, Pickles is available to help. Talk today to the Pickles branch near you to get the ball rolling on the best solutions for your assets.
Visit www.pickles.com.au/about/locations to find the Pickles branch closest to you. Not ready to sell but interested in a quick, hassle-free appraisal?
Visit www.pickles.com.au/sell-through-us/trucksservices-sell , the Pickles DIY inspect app for a simple evaluation of your asset. Download today in the Google Play Store or Apple App Store.
The Pickles team is dedicated to maximising the return on every asset. We have a highly trained team of international valuation experts who have the knowledge, deep experience and tools needed to provide accurate appraisals and specialist advice on how to enhance value. We stand by our valuations, providing sellers the assurance of protection in sale returns.
We understand that every situation is different. Our team brings hundreds of years’ experience in customising solutions that suit the unique needs of our clients. With expertise across multiple sales channels, we will recommend the most effective remarketing strategy based on our deep knowledge of industry trends, potential buyers, and current market conditions, to minimise any risk and maximise the value of every asset put to sale.
Talk to us today about partnering with Pickles.
Safety, productivity and efficiency are vital on any jobsite, and so is having the right tools for the right job - like the purpose-built Cat® Advansys™ system.
Cat Advansys is a range of ground engaging tools (GET) that deliver maximum productivity and one of the lowest bucket lifecycle costs. Designed to perform in even the toughest applications, there are 10 sizes that fit Cat Wheel Loader models 924 through to 994, and Cat Excavator models 311 through to 390/395. The Cat Advansys system can also be used on other brands’ machinery and help standardise all GETs across the jobsite.
“We offer a variety of tips in different point shapes because there are many different applications and machine sizes. For example, an operator wouldn’t use the same tips for sandy conditions or for trenching as in a quarry,” said Desmond Wong, Caterpillar Aftermarket Solutions Consultant for GET.
The Cat Advansys system is also hammerless and tip replacement can be up to 75% faster than previous Cat GET systems. Tips are installed and removed using a ¾” retainer lock that doesn’t require any special tools. A simple half-turn locks and unlocks the CapSure ™ retention. Better still, there are
no loose parts to be concerned about. All of this results in reduced downtime and improved safety on your jobsite.
Thanks to an optimised profile, wear life is improved and tips stay sharper for longer. “Our system has no external pins and
retainers. This is not the case with most of our competitors,” added Wong. “Changing tips faster means more uptime and productivity. Plus, we’ve made enhancements to the shape of the tips to increase performance, improve penetration and accelerate cycle times.”
Insurance is a great way to mitigate the risks to your business, but it’s important to have the right policies in place at the right time. As your business grows and changes, your insurance policies need to change accordingly, and the best way to find out how to get the right coverage is to have an insurance policy review.
Your business is always evolving. Whether it’s new developments in technology, shifting economic pressures or unexpected growth opportunities, things can change pretty quickly in the earthmoving industry. That means the risks you face today are likely to be much different to the risks you faced just a year ago. Having the right insurance policies in place to mitigate these new and emerging risks is vital for the success of your business, and the best way to make sure your business has the proper amount of coverage is to undergo a policy review with an insurance broker.
Did you know that 62% of Australian SMEs are unlikely to have the right insurance in place to protect their business 1, and that 1 in 10 businesses with insurance don’t have enough cover to protect themselves against business interruption, legal liabilities or loss or damage to their assets?2 This is known as “underinsurance” and can greatly increase the threat of a business failing if, or more likely, when, something goes wrong. In the earthmoving industry, the risks businesses face can change quickly. Due to the time pressures owners face in the day-to-day running of their businesses, safeguarding against these new and emerging risks can often be deprioritised, increasing the business’ chances of becoming underinsured. A policy review ensures you have the right level of insurance to protect your business so that it can continue to operate even when the unexpected occurs.
It’s good business practice to not only review your policy each year, but also when there are changes to your usual business operations. There are a number of factors that should trigger a policy review, including:
• New lines of work: remember, what may seem like a small change for you can be viewed as a large change by your insurer;
• Purchasing of new equipment and other business assets;
• New risks to the business due to changes in business operations, including cyber risks;
• Staffing: either increasing or reducing the size of your team;
• Changes in clients or contractors;
• Changes in ownership or directorship.
A policy review with one of MKP’s Earthmoving Insurance experts ensures your business is properly covered moving forward, and can save you valuable time and money.
At MKP, we have over 40 years experience of partnering with earthmoving contractors. We know your industry and understand the challenges your business faces. Our Earthmoving Insurance Experts understand the equipment contractors use, and how critical they are to your business.
MKP uses all this knowledge to tailor the right insurance policy to cover your business and its assets.
We pride ourselves on doing what we say we are going to do, when we say we are going to do it. We don’t use jargon, never rush you into a decision and walk you through why we believe our choice is the best insurance policy for your business.
As your business grows, so do your insurance needs. We advise you every step along the way to make certain you always get the protection your business needs. MKP’s Earthmoving Insurance experts ensure that
you have the right cover in place, so that when accidents happen you can get back to business faster.
We partner with our clients for the long term, and are proud to have multi-decade and multigenerational partnerships with our clients. At MKP, your success is our business, and we value service, integrity and performance above all else. Over forty years, this has meant different things at different times. At certain moments it is helping a client grow their business, at other times it is focused on securing what they already have. In either case, we pride ourselves on being there for you every step of the way.
With MKP Insurance, a review of your business insurance policy can give you the peace of mind that your business is properly protected, with the right types of cover in place.
Call Moody Kiddell & Partners on 1300 000 657 today to have your policy reviewed by one of our Earthmoving Insurance experts.
1 (QBE SMEs and Insurance Report – Pureprofile research study of 609 Australian SMEs completed for QBE Insurance during April 2019).
2 Insurance Council of Australia, Non insurance in the small to medium sized enterprise sector, July 2015.
Since 1981, Moody Kiddell has partnered with Australian businesses, providing finance, insurance and advisory solutions. With four decades of multi-industry experience, we offer businesses the tailored service business owners need to achieve their vision and safeguard its legacy.
At Moody Kiddell & Partners, we see your success as our business.
For forty years, we have partnered with the earthmoving industry to provide finance and insurance solutions for your business.
From enquiry through to paid claim, we dig in with you every step of the way.
Call today to see how one of Moody Kiddell’s equipment finance and insurance experts can tailor solutions for your specific business needs.
What are partners for?
Moody Kiddell. Partners With You
C.R. Kennedy has been appointed the Australian distributor for UK heavy machinery safety specialist Xwatch Safety Solutions, with it bringing the Xwatch XW product portfolio to the local market, including the XW4 Series and XW5 Series, designed to deliver a safe and comfortable working environment.
Since its launch in 2019, Xwatch has set about building a name for itself globally, seeking to raise the bar for safety across a variety of environments, focused on construction, mining and transportation, with its team drawing on extensive machine control and safety systems experience.
It now offers safety solutions in over 20 countries, with the XW Series range variously designed to work in conjunction with excavators, backhoe loaders, truck-mounted cranes, flails and mowers, and special purpose machines.
C.R. Kennedy is also the sole and exclusive distributor for Leica Geosystems in Australia, with the XW Series notably
integrating with Leica’s MC1 machine control software ecosystem, providing operators various insights and enhancing job site safety.
Across its evolving product range, Xwatch provides solutions for modern job sites, with it focused on delivering “forward-thinking integration and simple-to-use operatorfocused hardware with value and flexibility”.
The XW Series runs high-performance, accessible software, requiring minimal operator training, with different models across the range bringing together a variety of features in implementing an additional level of safety on site.
Operation is fail-safe and fully automatic, with function selection never more than two key presses away, while all potential machine high points are monitored and appropriate motions controlled, and full power is always available to move away from a limit.
Motions are controlled with ramped slow-down on approach and soft-stop, with no machine bounce, overshoot or undershoot, while an optional chassis sensor can be installed to correct for terrain slope.
Single/dual parallel wall or angular limitation is available, and when walls are in use the front-end equipment is also monitored and controlled for limit breach, with limits either manually keyed in or set by positioning the machine (if both limits are active, the system will automatically flip to the appropriate display should a hazard approach occur).
Setup is simple, quick and can be protected with an optional access key switch, while all settings are retained and will be active on start-up.
The rated capacity indicator (RCI) ensures the safe operation of lifting equipment throughout the machine’s working envelope, with the system continually measuring the height, radius and load on the machine, allowing operators to work at the maximum
lifting capacity while remaining within the machine’s safe working load.
Along with the height limiting function, the XW Series provides an accurate height value to the bucket pin, and includes a basic dig depth indicator to assist excavator operators in digging to exact levels.
This feature comes in handy when pulling trenches, flat pads and footings because it can eliminate the need for external checking.
Both the XW4 and XW5 feature an IP65 2.8-in or 4.3-in backlit colour LCD display, along with tactile keys, and can be mounted to the window or dash.
The XW4 – which is suitable for operation with excavators, backhoe loaders and special purpose machines – monitors height and slew movement, and can be configured to work in conjunction with a variety of articulated hydraulic plant.
It has been designed to accurately restrict using feather touch, with its height and slew limitation functionality controlled using proportional soft-stop hydraulic valves, paving the way for an accurate and repeatable performance without detriment to the machine.
The XW5 is designed for use with any type of hydraulic excavator, along with special
purpose machines, with it sporting the same height and slew limitation functionality as the XW4, along with an RCI, offering a total safe working envelope around the machine and operator.
A basic dig depth monitor is available when the RCI is not required, while if hazards are encountered, the XW5 will automatically flip to the relevant display page, and tracked machines have automatic sectored lifting duties for over the front/rear operation and over the side.
C.R. Kennedy is focused on providing high-quality products and tailored solutions for industry, supported by its comprehensive national after-sales network, including training, service and repairs, technical support, hire equipment and customer care agreements.
Based out of Port Melbourne, C.R. Kennedy’s national network includes major state offices in Brisbane, Adelaide, Sydney and Perth, with its workforce comprising over 260 staff, including product specialists, qualified surveyors, support staff and factory-trained service technicians.
Incidents involving mobile plant and equipment (MPE) can be expensive.
In the 2021-2022 financial year, NTI – Australia’s leading specialist insurer –recorded 165 significant MPE incidents costing more than $50,000.
In the current climate, replacement parts and plant can be hard to find and slow to replace. Now more than ever, preventing incidents – and reducing the severity and impact should they occur – is a critical business strategy.
Some incidents can’t be prevented, but some can – and they typically fall into one of two categories: human error and maintenance related. Together these two causes account for 70% of incidents.
Based on NTI’s 2021-2022 data, human error accounts for around half of significant MPE incidents. The three leading causes were ‘hit visible machinery/object,’ ‘inappropriate position’ (around 20% each) and ‘loss of traction’ (around 15%).
“Some of these are just momentary lapses of concentration,” says NTI’s MPE Risk Engineer, Hayden Reed. “Some are a lack of training or communication between people working together on a job site.
“More often than not, they come from working around the same equipment day in, day out. You don’t become blind to the risks, but you do become used to them.”
Using the same NTI data set, in 2021-2022 insufficient maintenance accounted for around 20% of incidents. The leading causes were accumulation of debris, electrical faults (around 36% each) and hydraulic faults (around 18%).
“These are basically claims where we’ll get an engineer to look at what’s happened to cause an incident,” Hayden says.
The most common outcomes of maintenancerelated incidents were fire (around 98%) and significant non-structural damage (around 2%).
NTI suggests five steps for businesses looking to reduce the number of preventable incidents: training, safety and operations protocols, maintenance, regular cleaning and investing in new technology.
1. Training: “Most businesses are pretty good at assessing their operators’ competency,” Hayden says. “But that doesn’t mean they shouldn’t be providing training where it’s needed, or looking at certificates of competency.”
It comes down to risk management. Training provided by a legitimate third party gives a fresh look at risks and operational
procedures, and that’s sometimes all that’s needed to avoid a problem.
2. Operations: Good businesses will establish, communicate and enforce safe work and operational practices. Every site should have protocols to log attendance, equipment use, safety and operational procedures, and more.
“It’s up to businesses to decide how frequently to do it,” Hayden says. “You might have a static site with a lot of workers. You could opt to say, ‘we’ll do it six-monthly or yearly.’
“That’s up to the business, but it’s always good to keep messages fresh and to let the team know you’ve got their safety in mind.”
3. Maintenance: Routine maintenance and servicing are a given for most businesses. The point is to go beyond the minimum and establish a preventive maintenance routine based on your operations and equipment. “People might say, ‘oh, it’s just a burst hose,’ and replace it,” Hayden says. “Or if electrical cables are rubbing and causing shorts, they might get an electrician in.
“But when it’s a battery cable that’s unfused it won’t trip fuses or breakers. It’ll just spark till it causes a fire.”
Having checks in place for these components and communicating their importance is critical.
4. Cleaning: Keeping your MPE clean makes you look more professional and gives your team members more pride in their jobs. It also makes it easier to identify faults and avoid incidents – like fires.
This is especially the case for equipment directly exposed to organic materials, such as forestry and agricultural machines; but even for relatively ‘clean’ plant such as cherry pickers and forklifts, cleanliness is a must.
“Have a cleaning regime in place that reflects the nature of the work and the risk,” says Hayden, “consideration should be given towards weather patterns and the machine’s duty cycle.”
5. New technology: Investing in new technology can pay dividends beyond operational improvements. Most (but not all) new plant is safer and easier to operate than older versions, which can immediately impact your business’s risk profile and the likelihood of incidents.
“A lot of newer equipment comes with safety and efficiency improvements,” Hayden says. “You can often geo-fence or input parameters to avoid problems. Automation can pay huge dividends.”
One area often overlooked is businesses investing in technology solutions but not training personnel on use. This is a critical step to ensure you’re maximising your return on investment.
Keeping your equipment clean, wellmaintained, and operated by skilled users with clear protocols can help minimise your claims.
If you’d like to learn more about risk management and how to protect your business, contact your insurance broker, or NTI, today. Visit NTI’s Yellow Cover at www.yellowcover.com.au.
Technology can be a creeping jungle... stand still long enough and it will over run you and leave you behind.
It is extremely important that if we’re to harness the benefits of what tech can offer our industry, the end user (the operator) needs to be trained on how to use it effectively, and not in propeller head jargon either – in straight up language with hands-on learning.
Kommand Machine Control offers exactly that kind of training. A couple of months ago, I got invited over to check out Kommand Machine Control’s Brisbane HQ. Kommand sells, services, and supports a range of GPS solutions, specialising in mixed fleets from Unicontrol, Leica and Hemisphere to Trimble and Topcon.
What is unique about what Kommand are doing in the training space is they have recognised that most operators are kinaesthetic learners, meaning they learn by doing.
So, what have Kommand done? They have set up a little Kobelco SK17SR excavator, kitted out with a Unicontrol GPS system, that they can take to a customer’s site, sit the operators in the seat and while the operators are pulling the leavers, the Kommand representatives walk them through the system... brilliant!
Another benefit is that instead of tying up one of their customer’s excavators for training, the little Kobelco steps in and does all the
heavy lifting as the training mule. This means that there are no production pressures being placed on the training, and the candidate gets more time to wrap their mind around the system, bonus!
Kommand are also working on a suite of bite-sized videos that they’ll be releasing shortly. They also offer onsite coaching with the company’s machine operators and FaceTime sessions to troubleshoot issues. They’re there to help you get on the job quickly and smoothly.
Kommand Machine Control really do live by their mission: To enable anyone that moves dirt to deliver finished results safer, faster, better, easier, and more consistently.
To learn more about what Kommand offer, check out their website: www.kommand.com.au.
NSW
CAPITAL CONSTRUCTION EQUIPMENT
535 Dallinger Road, Lavington NSW, 2641. 02 6025 0444. www.capitalconstruction.com.au
FRANKS SERVICE CENTRE 186 Wakaden Street, Griffith, 2680, NSW 02 6962 6073. www.fscforklifts.com.au/
NORTH WEST FARM MACHINERY 22-26 Whittaker Street, Quirindi, 2343, NSW. 02 6746 3300. www.nwfm.com.au
STM EQUIPMENT Unit 3, 28 Dunn Rd, Smeaton Grange, NSW 2567 02 4728 7500 www.stmequipment.com.au
THREE RIVERS MACHINERY
25 Zora Street, Warren NSW, 2824 02 6847 3111. www.3rm.com.au
SCTM (Canberra)
1/45 Bayldon Road, Queanbeyan, NSW, 2620 02 6299 1500. www.sctm.com.au
SCTM (Wollongong) 6 Mineral Road, Oak Flats, NSW, 2529 024257 1500. www.sctm.com.au
EARTHMOVING EQUIPMENT AUSTRALIA (EEA) 99 Glenwood Drive, Thornton, NSW, 2322. 02 9671 1000. www.eeaustralia.com.au
EARTHMOVING EQUIPMENT AUSTRALIA (EEA) 123 Cobalt Street, Carole Park, QLD, 4300. 1300 753 332. www.eeaustralia.com.au
MCINTOSH & SON (DALBY) 17563 Warrefo Highwyay, Dalby, QLD, 4550. 07 4662 2288. www.mcintoshandson.com.au
MILNE BROS EQUIPMENT (BILOELA) 61-67 Dawson Highway, Biloela, QLD, 4715. 07 4992 1099. www.milnebros.com.au
MILNE
BALLARAT TRACTORS
155 Learmonth Street, Ballarat, VIC, 3350. 03 5334 2444. www.ballarattractors.com.au
KV EQUIPMENT
221 Midland Highway, Epsom, VIC, 3551 03 5445 6999. www.kvequipment.com.au
MELBOURNE TRACTORS 110 Hume Highway, Somerton, VIC, 3062. 03 9303 5777. www.melbournetractors.com.au
MELTRAC MACHINERY
6703 Princes Highway, Terang, VIC, 3264 03 5536 0222. www.meltrac.com.au
PRIMTEC TRACTORS
698 Benetook Ave, Mildura, VIC, 3502. 03 5022 1004. www.primtectractors.com.au
FORKWEST
68 McCombe Road, Bunbury, WA, 6230 08 97254970. www.forkwest.com.au
GEOFF PERKINS MACHINERY
Lot 24 Stewart Street, Narrogin, WA, 6312. 08 9881 2222. www.perkinsmachinery.com.au
MCINTOSH & SON (ALBANY)
189 Chester Pass Road, Albany, WA, 6330 08 9847 4255. www.mcintoshandson.com.au
MCINTOSH & SON (ESPERANCE)
25 Norseman Road, Esperance, WA, 6450. 08 9071 1155. www.mcintoshandson.com.au
MCINTOSH & SON (GERALDTON)
160 Flores Road, Geraldton, WA, 6530. 08 99605500. www.mcintoshandson.com.au
MCINTOSH & SON (KATANNING)
Lot 4 Nyabing Road, Katanning, WA, 6317. 08 9821 7000. www.mcintoshandson.com.au
MCINTOSH & SON (KULIN) 294 Pump Road, Kulin, WA, 6365 08 9880 2556. www.mcintoshandson.com.au
MCINTOSH & SON (MERREDIN) 52 Mitchell Street, Merredin, WA, 6415 08 9041 1099. www.mcintoshandson.com.au
MCINTOSH & SON (PERTH)
547 Great Eastern Highway Redcliffe, WA, 6104 08 9475 1600. www.mcintoshandson.com.au
SOURCE MACHINERY
6 Reggio Rd Kewdale, Kewdale/Karratha, WA, 6105. 08 9358 3389. www.sourcemachinery.com.au
ACCESS SERVICE AUSTRALIA 26 Kilto Crescent, Glendenning, NSW, 2761. 02 9832 9990. www.accessservice.com.au 71 Bradman Street, Acacia Ridge, QLD, 4110. 07 3219 5130. www.accessservice.com.au 32 Healey Road, Dandenong South, VIC, 3175. 03 9768 2155. www.accessservice.com.au
MOTION MACHINERY
1/10 Dickens Place Armadale, WA, 6112. www.motionmachinery.com.au
Melbourne Tractors has built a strong reputation in the local construction and agriculture sectors over the better part of four decades of operations, with the family-owned business firmly focused on supplying its customers a broad variety of world-class machines, complemented by quality parts and attachments.
While a top-notch product line-up is a key attraction for both new and existing customers, General Manager Peter Keley also pointed to Melbourne Tractors’ emphasis on superior customer service, backed by experienced and knowledgeable staff, in helping it stand out in the marketplace.
As noted by Peter – who draws on 37 years of experience in the automotive industry, and who joined Melbourne Tractors 18 months ago – a responsive service, backed by a willingness to “go the extra mile”, ensures customer needs are met from sales through to after-sales.
“At the end of the day, any business is only as good as the people who are in it, and we’re very fortunate to have a great team of people in all areas, whether it’s service, parts, sales or office admin,” Peter told EEM.
“A number of the employees have been long serving. We’ve got a couple of people who have over 30 years of experience with Melbourne Tractors, and then quite a large number at 10 years or more, and that speaks very strongly to both the culture and stability of the business.”
It is this solid foundation that enabled Melbourne Tractors to not only effectively navigate the Covid-related challenges presented over the past couple of years, but also emerge in a stronger position than before.
Peter noted that Melbourne Tractors kept its doors open over this period, modifying its approach where required, as it continued to cater for the varied requirements of its customer base.
“We were able to deliver a customer service that was still appropriate to the needs,” he commented. “It wasn’t without its challenges, we had to be very adaptable in the way we did things, and our staff came along for the ride.
“At the same time, we also increased our sales quite substantially in all of our products. To do that in those circumstances really was down to fantastic staff, who were willing to be involved and do things out of the norm.”
Peter told EEM that, with Melbourne Tractors having first opened its doors in 1983, there is
no substitute for local industry knowledge, while the business also maintains a strong underlying focus on introducing new technologies and innovative products.
In addition to this, he pointed to Melbourne Tractors’ capacity to cater to often urgent and financially pressing customer needs, from the purchase of new machinery to the sourcing of new parts, and machinery service and repairs.
“What makes us different is that we are a family-owned business, and that means we can make decisions very quickly, we don’t have to go through layers of management,” he said. “If there’s a key decision around a customer, we’re able to make those decisions very, very quickly.
“When it comes to putting together a sales proposition, for instance, we can do that very quickly because it’s a streamlined process. Above all, we understand that speed is of the essence and that customer back-up is of the essence.”
Among Melbourne Tractors’ product portfolio, the Merlo range of telehandlers – designed to provide performance, comfort, safety and efficiency benefits – have proven a popular addition, with Peter noting the machines bring together a strong range of features.
Balancing performance with aesthetics, he highlighted the overall appeal of the Merlo range, with the Italian manufacturer –
which draws on a long history of innovative product development stretching back to 1964 – focused on the development of versatile, safe and comfortable machines.
“I think the design and look of the product is second to none,” he said. “Even though these are working machines, it’s a lot easier if you can be proud of the machine that you’re using and it looks the goods, and there’s no doubt that Merlo does that.
“It’s got a great design, stands out, and I think that’s certainly a plus. It makes a statement about your business.”
Along with this, Peter noted that the Merlo range is decked out to thrive in a variety of
conditions, with operators able to confidently tackle different tasks knowing that the machines have been designed to keep on powering through.
“The second part to the Merlo equation is the reliability and durability of the machines, and then having that backed up by great service and parts as well,” he commented.
“And certainly, Merlo is excellent to deal with in that situation.
“Where there has been an issue, we’ve been able to deal with it quickly and efficiently, and again that gives a lot of confidence to not only the owners, but also the sales staff too, because they know it’s well backed.”
Peter noted that demand for the Merlo range, which spans a wide variety of telehandler models, remains consistently strong, with new product arrivals highly sought after among Melbourne Tractors’ customer base.
“Our biggest challenge at the end of the day with Merlo is meeting demand for the product,” he said. “It’s a good challenge to have in as much that as soon as the product lands here it’s sold, and in most cases it’s sold well before it lands here.”
Looking ahead, this augurs well for the remainder of the year, and heading into 2023, with Melbourne Tractors now well positioned to keep building on the hard work put in by its staff over the past couple of years.
Peter told EEM it’s been a particularly busy period of late, with good reason for optimism moving forward.
“We’ve already sold and delivered the same number of machines in the first half of this year than we did for the full year last year,” he said. “We’re seeing a great number of opportunities to continue quoting the machine as we go into the marketplace presenting the credentials of Merlo.”
Events are back, baby! Field days, expos, roundtables, conferences, launches – you name it. Some are still virtual, many are back to in-person and lots of them cost a fortune in time, resources and budget to participate.
What’s great about an event is that it gives you access to a specific target audience. If they’re there, you already know they’re interested in your sector. They’re great for networking and they can also be a lot of fun – something we all need after a few tough years.
What’s not so great about events is that you can easily blow a big chunk of budget on one day, or a few days, and never reach anyone outside the event venue. It can be great for the very hyperlocal location you’re in, but what about the rest of your market?
Not to mention the competition for attention from countless other businesses trying to grab a moment with the same people you are.
So, what do you do?
1. PREPARE PROPERLY
Be clear about what you want from the event. It should be a feel-good opportunity for your team to get out and about – but it also must be more than that.
Make sure your site is eye catching and interesting but is also designed to support the message you want to put to market.
And make sure your staff both at the show and behind the scenes are really well briefed.
What conversations do you want them to have, what data do you want them to collect? Do you need updated collateral? What about business cards?
Perhaps most important of all, make sure people know you will be there. Pre-event communications are critical.
Consider:
• Emails to your database – include info about your stand but also add some messaging for people who won’t actually be there
• Social posts – talk about why you’re going, who’ll be there and why people should connect
• Event platforms – look for opportunities to get into publications produced by event organisers. This is easy if you’re a major sponsor – if not, make sure you have something interesting to say and supported by great visuals.
Make sure your team spends some time walking the floor, checking out other sites, networking, as well as working your stand. Be sure they are well-briefed to qualify visitors so they can quickly distinguish between real
prospects and tyre-kickers. Organise meetings, lunches, dinners, catch ups with as many key contacts as you can. If you’re not exhausted at the end of the event, you haven’t done it right! Make sure you earn that beer after closing.
Don’t forget to communicate during the event:
• Take pics and post to social
• Set up media interviews in person or by phone
• Gather insights for use later
3.
Make the most of your investment in an event by chasing down every lead and by keeping the conversation going. And don’t forget to debrief with your team so you can make a considered evaluation of the ROI. Post event communications can help you convert leads and consolidate networks:
• Send an update email to your database
• Utilise post-event promotion opportunities from the organisers
• Add all those new contacts to LinkedIn and plan your next connection
• Keep rolling out your pics and insights across social
Need support with comms surrounding your next event? We’re here to help! hello@hc.net.au
For almost half a century, STM has made it possible for businesses across NSW to power up – supplying and servicing quality trucks and machinery to meet the demands of any job.
Starting out in a single shed in the 1970s, we know what it takes to build a business – and are passionate about helping you grow yours. Today, our family owned and operated enterprise is proud to offer a multi-site, modern service, with a team of more than 120. We care about giving every customer the best experience possible – with a wide range of trusted brands, flexible finance, spare parts, repairs and personal service.
We may have come a long way from that shed, but our family commitment to quality remains. Whatever your size, whatever your budget, STM is your one stop shop – with everything to keep your business moving.
They began by demonstrating their superior skills at local competitions at Cat® dealerships around the world. Having defeated their peers, they will now move on to the regional semi-final competitions where they will take on even tougher challengers, seeking to break through for a chance to compete in the final in Las Vegas.
Caterpillar initially kicked off its Global Operator Challenge in 2019, hosting more than 10,000 entrants from 30 countries before selecting nine of the world’s most talented equipment operators to compete at CONEXPO-CON/AGG 2020 in Las Vegas. At the conclusion of the event, Jaus Neigum, owner of Industrial Backhoes in Medicine Hat, Alberta, Canada, succeeded in capturing the world champion title.
Now, Caterpillar has once again invited operators from around the world to compete in the Global Operator Challenge 2022/2023 edition. Competitions have been hosted at dozens of Cat dealer sites in nearly 40 countries ahead of the March 2023 finals. The Global Operator Challenge has significantly grown in scope, well beyond the 67 competitions staged over the course of the inaugural event, becoming Caterpillar’s largest construction industry event of its kind.
“More than 80 Cat dealers will host local, one-of-a-kind competitions, celebrating
equipment operators and enabling them to showcase their exceptional skills in fun and dynamic ways,” Tony Fassino, group president of Construction Industries, said earlier this year.
“Whether their expertise lies in digging a trench, moving aggregates or managing demolition, our Global Operator Challenge will be demanding for even the most experienced operators.”
From April through to September, the first round of the Global Operator Challenge consisted of local qualifiers, with participants variously required to execute tasks including digging a trench, loading a precise amount of dirt and manoeuvring equipment through different obstacles. Scoring was awarded based on the operator’s skills, safety awareness and efficiency, as well as competence in using integrated technologies on Cat next generation machines (including Cat Payload, Grade, Command and Grade Assist, and rear-view cameras, return to dig and return to carry) to enhance performance.
The five Australian finalists – representing Western Australia, New South Wales, Victoria, Queensland and South Australia – emerged victorious after a tough test of skill and determination. Putting their remarkable operating talents to work, they beat over 100 entrants across the country at dealer events hosted by WesTrac WA, WesTrac NSW, William Adams, Hastings Deering and Cavpower. They displayed impressive speed, accuracy and best overall operating practices over the course of these hard-fought competitions.
The finalists are:
Jake Myers (MLG Oz) – representing WesTrac WA, Western Australia
Hailing from the Kalgoorlie Goldfields, Jake Myers has always had a keen interest in operating machinery, whether it’s tackling grading projects using the Cat 14M3 motor grader or a weekend cruise on a HarleyDavidson. Jake has over 15 years’ experience working as an operator, and is well equipped with a diverse range of skills that make him a worthy contender in the Global Operator Challenge.
Jake is especially excited about the opportunity to represent Australia, and says winning the challenge and adding to his trophy cabinet would be a great achievement.
Jack Divall (Divall’s Earthmoving and Bulk Haulage) – representing WesTrac NSW, New South Wales
Third-generation heavy machinery operator Jack Divall, from Goulburn, New South Wales, draws on a long family involvement in the earthmoving industry, working in the family business started by his grandfather over 50 years ago. With seven years’ experience as an operator, his favourite machine is the Cat D6T dozer.
Jack knows the family reputation is on the line and aims to bring all of his skills to the fore to take the trophy home.
Patrick Doheny (CRE Group) – representing William Adams, Victoria Originally from Tipperary in Ireland, Patrick Doheny grew up around machinery, with his father running a plant hire and earthmoving business. Patrick has close to three decades of experience in the industry, having studied civil engineering in Ireland, and working for around 15 years in total in Australia, eventually setting up his own business in Melbourne.
Patrick, who has a penchant for Cat dozers and graders, notes that the Global Operator Challenge provides a fantastic opportunity for operators to compete and showcase their skills.
Aiden Lee (Queensland Electrical Solutions), representing Hastings Deering, Queensland
Growing up in Brisbane, Aiden Lee has been around machinery from a young age, having followed a path that eventually saw him become an electrician by trade. He has a passion for machinery and particularly enjoyed getting
behind the controls of the Cat 320 excavator during the Queensland competition, using features such as Grade Assist.
Having made the most of the opportunity to put his skills to the test at a local level, Aiden is now excited to be moving on to the next stage of the Global Operator Challenge in Japan.
Nick Thompson (Modcon Civil) –representing Cavpower, South Australia Born in Modbury and growing up in Kapunda, Nick Thompson has had an interest in machinery since childhood, having spent a good deal of time in the sandpit during recess and lunch. He got his start in the industry at the age of 17, initially working in subdivisions, and has around 15 years’ experience in the game.
Nick, who enjoys getting behind the controls of Cat dozers, diggers and graders, is looking forward to again testing his skills in Japan and would be thrilled to make it to the Las Vegas final.
These five talented operators will gather in Japan for the Global Operator Challenge regional semi-finals, being staged October 19-20, where they will compete with other Asia Pacific finalists. The competition is guaranteed to be hot as they take on three tough challenges at the Caterpillar Demonstration Centre in Chichibu, northwest of Tokyo.
The top three will then go on to represent the Asia Pacific region, competing against six other finalists from Europe and the Americas at Caterpillar’s outdoor Festival Grounds exhibit during CONEXPO-CON/ AGG 2023. There the finalists will test their skills to determine who is the best of the best. Over the course of the finals, operators will again take on challenges testing their agility, mental toughness and versatility, as well as their competence in using Cat integrated technologies to enhance machine performance. The crowned champion will be awarded an all-expense VIP trip for two to a global Caterpillar facility of his or her choice.
The Global Operator Challenge is held to test operators’ skills, showcasing their excellence operating Cat construction equipment and ability to master the equipment safely and efficiently. In staging the event, Caterpillar wishes to celebrate the diversity and skill of all the operators around the world who contribute to the success of our industry. The competition also highlights how Cat Next Generation machines are harnessing new technologies to transform job sites around the world, not only increasing productivity, but also delivering enhanced levels of comfort and ease of operation.
For more information about the Global Operator Challenge, contact your local Cat dealer, visit this site for details: www.cat.com/operatorchallenge and follow the Cat Construction Australia Facebook page.
If you’re looking for a top-shelf specialist in the areas of civil earthworks, wet and dry plant hire, demolition, and asbestos removal in the southwest of WA, you won’t find an outfit with more experience, success and proven track-record than the team at Picton Civil. They have been providing their clients with cost-effective earthmoving services and solutions throughout the southwest and beyond since 1968.
Picton Civil began 50 years ago by four brothers with a Michigan Wheel Loader, which was purchased by their father Jack Cross who founded J.W Cross and Sons.
On a recent trip to Western Australia, EEM took the stunning drive down to Bunbury to catch up with Josh Silver, Workshop Manager at Picton Civil, who has been with the company for 11 years. When I chatted with Josh about his start in the industry, he shared, “Growing up my grandad always had trucks and machines. Watching him work in and on the machines must have made an impressive picture in my mind because I’ve always loved the industry and the people we get to work with on our wide range of projects.”
Josh continued, “At Picton Civil we primarily work with diggers, loaders, graders, and skid steers; and after the business recently gave the Kobelco range of excavators a go, we haven’t looked back. Our team has gone from strength to strength and our operators enjoy the comfort, power and performance of the Kobelco machines.”
The Picton Civil team services a range of clients, from individuals and small businesses to large-scale industry and mining projects. The customer-focused staff are well prepared to cater to the individual requirements of their clients and projects, always giving a high quality of service and workmanship. With their
large, diverse fleet of quality machinery, the team can provide a great variety of tasks to all of their customers. This includes work such as site preparations; demolitions; drainage; asbestos removal; trenching; hard stand construction; pathways; construction and hot mixing car parks and roads; dam building or cleaning; house pads; gravel, hot mix or limestone driveways; delivery of materials; environmental rehabilitation; and work to individual specifications or scope of works.
In recent times Picton Civil has discovered the success and strengths of the Kobelco excavator range, purchasing three machines from LiftRite representative, Dean Bailey, which consisted of the SK55RX-6, SK235SR-2 and SK350LC-10. When I chatted with Josh about both the experience with the Kobelco excavators and the sales and service from LiftRite, he shared, “The Kobelco machines haven’t missed a beat. We run them hard and with over 1200 hours onboard we haven’t had to lift a single spanner outside of the normal servicing requirements. We haven’t had a breakdown or issue, which has been really impressive, and that’s something I can’t say about the other machinery we have used over the years. The thing we love about the Kobelco
range and the reason we gave them a try in the first place was the overall strong and solid construction of the machines, reliability and serviceability. The overall capabilities of the machines are right up there and the operator comfort in the cab is excellent.
“Our operators love the machines. They are quiet and comfortable, but I will admit when we purchased our first Kobelco machine there were a few guys who were not 100 per cent engaged or convinced about the decision, but after spending just an hour or two in the machines our operators were all won over by their performance, specs and technologies. It was simply a matter of spending time in the machine and letting the performance and comfort speak for themselves.”
Josh continued, “We run 3D machine technology in our machines, which means
fewer people on the ground with maximum machine efficiency, less holdups and reduced risk. The fact that we have had zero downtime across all three of our Kobelco machines speaks volumes about the quality of these excavators.”
Josh and the Picton Civil team have been working with Kobelco dealer LiftRite and Sales Manager Dean Bailey – and from all reports the relationship is well and truly off to a great start. “Since starting at LiftRite our rep Dean has shown an interest in our company and regularly reaches out to see if he can assist in any way. The regular comms and updates are handy, so we know what stock LiftRite has and what/when machines are due in. Dean recently let me know they had a 36-tonne excavator in stock, two days later we had a request for a 36-tonne excavator. We already had our other two out and we knew where to find another one… in a hurry!
“As the business continues to grow, we are continually expanding our fleet to give us greater capabilities for large-scale projects. It’s going to be through our relationship with LiftRite and the minimal machine downtime achieved by our quality equipment and quality product support from the LiftRite team that we achieve this. LiftRite and the Kobelco product will be there with us as we update and expand our excavator fleet,” said Josh.
As we fired up the drones and cameras to capture the Kobelco machines ripping into the site at Bunbury I had the chance to ask Dean about his role and working with Josh and the Picton Civil team. “As the area manager for the southern region of WA for LiftRite Hire & Sales in Perth, my background has been in earthmoving for the last 12 years as an operator and user of the Kobelco product. During this time, I’ve
built up significant trust and confidence in the Kobelco brand, which has definitely helped me in my role. It has allowed me to sell the product with confidence and provide solutions to our customers and clients.”
Dean continued, “I’ve been looking after Picton Civil for the last few years dealing with Josh and the managers and directors of the company. The feedback that I receive from the Picton Civil team is that the Kobelco machines are more stable than other machines they have owned previously – the fuel efficiency is second to none in this class, and breakout force is impressive to say the least. There are many opportunities right now for Picton Civil and our other clients here in WA to move forward and build their relationships with LiftRite Hire & Sales and Kobelco. We look forward to continuing to build our relationship with Picton Civil and work together to build both our success moving forward into 2023 and beyond.”
Introducing the new SK45SRX-7 and SK55SRX-7 mini excavators from Kobelco – delivering improved performance and class-leading next generation cabin design. With an extra spacious cabin, improved ergonomics and advanced technology, you’ll be able to make full use of the extra power and speed on offer, all day long. For uncompromising operator comfort and superior productivity, experience the new Kobelco SK45SRX-7 and SK55SRX-7 today –taking performance to the next level.
The job site is no place for equipment failure. Rhino Buckets are built to withstand more. Built with Bisalloy® steel, all welds exceed Australian Standards for guaranteed strength and longevity.
Rhino Excavator Attachments are built for the toughest job sites:
+ Rhino buckets were designed, tested and proven over years on the job in the punishing Pilbara. Thousands of kilometers from a replacement, our customers depend on Rhino delivering quality when and where it matters most.
+ Backed by a 2-year warranty and industry-best support - we don’t hide behind legal fine print.
+ Dual Radius Profile on digging buckets stops excess drag on the bucket and offers dramatic performance advantages
As the world’s third largest construction equipment manufacturer with more than four decades of industry experience, XCMG has built a global reputation for innovation, reliability, and performance throughout its entire range of machinery – including excavators, graders, rollers and so much more.
Two ultra-modern and technologically advanced models within XCMG’s illustrious range of excavators are the 9 tonne XE80U and the 16 tonne XE155UCR. Ideal for small, medium and large-scale construction projects, these highly popular and well-renowned excavators from XCMG are the next generation of digger quality and performance.
With an operating weight of 9.5 tonnes, a powerful yet efficient 73 horsepower Kubota V3307 engine, and 219 litres per minute of hydraulic flow, XCMG’s next-generation XE80U excavator is made to work harder and smarter.
In addition, the XE80U’s minimised tailswing design offers improved safety and better accessibility in tight work environments –meaning you can work effectively where other machines in the same size class simply cannot.
Furthermore, premium quality hydraulic componentry throughout the XE80U ensures smooth control, fast response, low speeds, high torques and low energy consumption across a wide range of operations: digging, dumping, mulching, auger driving, log grappling and much more.
The XE80U’s state-of-the-art next generation cab instantly pleases the operator, with its spacious design, extremely comfortable seat, ergonomic control setup, high-definition colour LCD display screen and premium air conditioning. Large windows on all sides, plus a reverse camera included as standard, offer maximum visibility for machine operation.
Designed and manufactured with particular attention to easy service access, the XE80U offers a single access point for daily maintenance of all main components, a fuel level gauge and refuelling through a lockable cap, plus swing open and swing up engine access doors. In addition, with the backing of
XCMG Australia’s extensive national service network, your machine is always supported by industry experts and its downtime is significantly minimised.
In summary, XCMG’s new XE80U delivers unbeatable value for money in an 8-10 tonne machine and exceeds all the criteria of a quality, reliable, comfortable and operatorfriendly excavator.
A step up in size from the XE80U, yet just as loaded with quality and value, is the renowned XCMG XE155UCR excavator.
Weighing in at 16.7 tonnes, with a powerful and reliable Cummins 121 horsepower engine plus 2x113.4 litres per minute hydraulics and premium Kawasaki componentry, the XE155UCR is a beast made for power and control.
Like the XE80U, an ultra-short tail gyration design of the XE155UCR offers exceptional tight access capability – XCMG really have designed their excavators to work in more places. The XE155UCR also includes Japanese Nabtesco travel motor componentry, for smooth tracking on even challenging terrain, and long-lasting durability.
The operator cab is remarkably spacious and comfortable, with an exceptional climate control system and smooth joystick controls that make machine operation a breeze. The high-definition touchscreen LCD display allows operators to view all key machine information on the fly with a simple press, and the expansive leg and shoulder room delivers all-day comfort to even the largest operators.
With simple and efficient service access forming a fundamental design requirement, the XE155UCR provides a single access point for daily maintenance of all main components, a fuel level gauge and refuelling through a lockable cap, and swing open and swing up engine access doors – plus, the 24/7 backing of XCMG Australia’s national network of service and support, for constant peace of mind.
Safety is also a major focus of the XE155UCR, which includes high-quality wide angle reverse cameras, multiple e-stops accessible from the cab and ground level, audible operation warnings for bystanders, and remarkably short front and rear turning radiuses.
In summary, XCMG’s new generation XE155UCR 16 tonne excavator is an extraordinary amalgamation of intelligent operator-focused design, high quality manufacturing and exceptional durability and performance – resulting in a truly impressive and value-for-money machine, made to dominate any job site in Australia.
For more information about these excavators, or XCMG’s diverse range of construction, mining and agriculture equipment, visit www.xcmg.net.au.
Mulgoa Quarries’ long history in the earthmoving industry spans generations, stretching back the better part of six decades, with the family-owned-and-operated business having built its reputation around providing clients across the Sydney metropolitan region a wide range of high-quality excavation solutions.
Over the years Mulgoa Quarries has branched out from its clay and shale quarrying roots to preside over an increasingly diversified suite of civil engineering services, with it expanding to specialise in areas including major bulk earthworks, controlled filling and remediation projects.
Co-owner Adrian Wearn, who himself has been involved in the industry for close to 40 years, told EEM that while Mulgoa Quarries has grown significantly since its establishment it has very much remained a family enterprise.
“My father started quarrying in 1964, as part of his earthmoving operations, and took over some land at Mulgoa, and then started supplying the brick industry,” Adrian explained of the business’ origins.
“I started out as an apprentice plant mechanic 39 years ago, and 37 years ago myself and four brothers took over the running of Mulgoa Quarries, while for the last 20 years, it’s just been one brother and myself running the business.”
With Adrian and brother Rob at the helm of the business, Mulgoa Quarries has since grown to employ over 110 staff, with an operating fleet spanning more than 75 items of earthmoving equipment, along with 28 truck and trailer combinations of varying payloads.
Mulgoa Quarries caters for its clients’ wideranging civil engineering needs, and also offers bulk haulage and disposal, waste transport and contract quarrying services, providing selective mining and stockpiling of over 1,000,000 tonne of clay and shale per annum
(it has over the years held contracts with clients including Austral Bricks, Boral Bricks and PGH Bricks & Pavers).
In addition to this, it maintains a modern fleet of high-quality earthmoving equipment for hire, decked out to tackle a broad range of tasks, from roadworks to subdivisions, mining, excavation, and building and development projects.
“Our core business is contract quarrying and stockpile management for the brick industry, providing services for a sector that is reasonably unique,” Adrian explained.
“Also, we’ve recently been doing some big quarry rehabilitation work, rehabilitating old quarries in the Western Sydney area.”
Adrian told EEM that Mulgoa Quarries prides itself on putting its clients first, with its team of
highly trained specialists drawing on a wealth of knowledge in undertaking a broad range of excavation and earthmoving projects.
“I think it’s been our consistent and professional operations, running sites in a manner that clients desire, and the culture of our operators and employees to be able to provide that high level of service that gives us repeat business,” he said.
“We’re proud of the professional culture embraced by all of our staff, from general tidiness and safety onsite, to a positive can-do attitude.”
SOPHISTICATED LIEBHERR R 938 G8 CRAWLER
Mulgoa Quarries has recently taken delivery of two Liebherr R 938 G8 crawler excavators, with Adrian noting he had long been aware of the reputation of Liebherr, one of the largest construction equipment manufacturers in the world, prior to purchasing the machines.
Adrian told EEM that in an industry that is extremely demanding day in and day out, with projects needing to be carried out efficiently and effectively, Mulgoa Quarries requires equipment that is not only durable, but also versatile and powerful, with the R 938 G8 excavators fitting the bill.
“We gave an R 938 G8 excavator a demo, and found it to be a very smooth and powerful machine,” he commented. “In addition to this, our operators can customise the machine’s
functions to suit different applications, and they also provide great fuel efficiency.
“Straight away we realised that they are a very sophisticated excavator, and we also found Liebherr’s service to be very keen and prompt.”
As it stands, both of the R 938 G8 excavators have been racking up plenty of operating hours since joining Mulgoa Quarries’ fleet, having been put to work across different projects, and Adrian noted that his operators are more than happy with both the performance and comfort levels provided.
“They’re working a minimum of 50 hours a week, weather depending, across various detailed and bulk excavation applications,” he said. “And they’ve been getting great feedback from the operators, and if they’re happy operating the machines that goes a long way.
“Every indication is that we have very busy times ahead, everyone wants to do business at the moment, and we look forward to moving forward with Liebherr.”
Developed and manufactured by LiebherrFrance SAS, the Liebherr R 938 G8 crawler excavator weighs in at an operating weight
of 37.2-39.05 tonne, with it running a 220 kW Liebherr D944 A7-24 Tier 4 Final engine with an SCR filter (featuring automatic idling/ speed increase, controlled via joystick sensors), and has a bucket capacity of 1.9-3m3
Liebherr advises that the R 938 G8 excavator’s design is characteristic of its new Generation 8 machine range, with its architecture having been completely revamped “to provide even greater comfort, better ergonomics and more enhanced performance”.
The R 938 G8 excavator’s features also include:
• Safety – the ROPS-certified cab sports panoramic visibility with no obstructions, with rear and right-hand-side cameras providing for enhanced safety; an emergency exit
is available via the rear cab window, while the right window and windshield feature laminated and tinted glass, and a tiltable console allows for safe and easy cab access.
• Operator comfort – a spacious, airconditioned workspace features an airsprung seat with vertical and longitudinal suspension, along with an easy-to-use high-resolution 9-inch colour touchscreen, and also comes with LED lighting as standard; in addition to this, the front cab window is completely retractable.
• Undercarriage – there is a choice of two different robust x-shaped undercarriages, equipped with integrated eyes for secure transport, along with maintenance-free track chains and track rollers with lifetime lubrication.
• Maintenance – service points are accessible from ground level, with the engine oil, hydraulic oil, fuel and urea (diesel exhaust fluid) levels visible on the display, with lateral access provided to the uppercarriage, with a large maintenance platform.
For more information, please visit www.liebherr.com.au
Since its foundation, Liebherr has been known as a pioneer in high-quality, breakthrough innovations. With their passion, freedom and visionary mindset, the people at Liebherr will continue creating fascinating solutions and setting new standards. In the area of product development, the Group is already working today to create the solutions of tomorrow.
With its G8 crawler excavator category focusing on safety, increased power and fuel efficiency, as well as durability and overall productivity, Liebherr continues to develop its heavy machinery product offering around an innovative and industry-leading design approach, guaranteeing all Liebherr machines can be deployed with great efficiency and performance in the most challenging and difficult environments.
Customer satisfaction has remained Liebherr’s underlying focus over the course of its long history. With the high-performance G8 excavators featuring improved functionality, engine power, a heavier counterweight for higher bucket capacities and overall reduced fuel consumption, Generation 8 crawler excavators leverage the latest technology to ensure customers can complete jobs with maximum efficiency, the highest level of precision and outstanding performance and exceptional durability. In addition to this, other innovations include a boom concept with a modified head for better boom forces and an optimised load curve, enabling consistent and improved fuel savings.
Mulgoa Quarries has been harnessing these efficiencies since adding two R 938 G8 excavators to its fleet and continues to see the ongoing benefits of the latest technology of Liebherr Equipment.
Deon Cope, JCB CEA’s National Product Manager, explains key features that differentiate the machine from the rest of the market.
With an intuitive design, the 245XR offers users a reduced slewing radius, while also ensuring that other features such as cab space are not compromised.
“This is JCB’s latest release on its X SERIES platform. While the excavator platform weighs 20 to 25 tonnes, the weight comes in at 27 tonnes with the blade,” Cope says.
The 245XR has a tail swing radius of 1.72 metres, which is 40 per cent less than its predecessor, the 220X Excavator.
“One of the main advantages of this feature is the reduced spin, so operators do not need to close off additional freeway lanes when they are working close to live traffic. Operators can also use the machine in tight spaces when working on building and infrastructure projects,” Cope says.
“There is also a safety aspect to the reduced tail swing, as there is less chance of damage to nearby buildings or personnel on site when the machine is in operation.”
With a 40 per cent shorter tail swing and supported by a bucket capacity of 1.25 cubicmetres, the 245XR can optimise operations in difficult working applications.
“The 245XR runs on a similar hydraulic pump system as the 220X, but we have gone with a larger pump, a larger control valve and better fluid dynamics throughout the whole machine,” he says. “So, we still maintain that speed and accuracy while also having increased breakout and performance.”
In designing the 245XR, Cope says JCB’s engineers have allocated weight to key areas of the machine to achieve equilibrium.
Operator feedback also contributed to the design of the 245XR’s cabin, which features double cushioned viscous mounts to reduce the noise to 69 decibels. The seat-mounted joystick and switch controls can also move with the operator.
The 245XR utilises JCB’s DIESELMAX engine, which was released in 2004 and has been proven to be effective in 70 different machines globally.
Cope says the engine, which has a dedicated off-road design, contributes to reducing
running costs for operators. “An advanced cylinder head design means you can get a more efficient burn at the head of the cylinder.
The design also eliminates the need for a diesel particulate filter, which further cuts the maintenance costs.”
The use of AdBlue diesel exhaust fluid further adds to the engine’s performance.
“The 245XR requires approximately three per cent of AdBlue per litre of diesel, which is less than the amount required for comparable excavators,” says Cope.
Selectable Swing Smoothing is a feature that comes as standard with the 245XR and it enables the operator to customise the performance of the vehicle to suit any given application. Cope says that the feature can produce sharper, or more gradual movements, depending on what is required from the job at hand.
“Because of the additional weight of the upper revolving frame, we have selected a larger slew motor and a larger slew brake, which helps increase the torque,” Cope says. “Increased slew braking means operators can accurately slew left or right and then come back onto line when working on projects like installing pipes or cutting trenches.
“We also have the ability to smooth the slew. Where operators may want more speed instead of accuracy, they can switch to softer slew so it doesn’t brake as aggressively and has a smoother action. This is useful for tasks such as loading trucks.”
For more information, visit: www.jcb.com
Introducing our latest addition to the X Series. At just 1,720mm, the new 245XR has a 40% shorter tailswing than the conventional 220X, making it ideal for work in confined urban sites and highways. Despite having reduced tail swing, the 245XR still boasts one of the biggest, most comfortable, quiet and easy to operate cabs on the market, while our proven Tier 4 Final DIESELMAX engine and selectable swing smoothing as standard provide optimum performance in any application.
The Cat® GC product line-up offers a new value proposition for the more cost-conscious customers who do not want to pay for a solution they don’t need without compromising on what matters most to their business. The momentum behind Caterpillar’s range of GC excavators continues to build with the release of the 315 GC – a model proven affordable, durable, reliable and low cost per hour solution.
Caterpillar designed the Cat 315 GC Next Generation compact radius excavator with a larger cab, lower maintenance cost up to 25%, and reduced fuel consumption up to 15% when compared to the previous 315F L model. This new machine is powered by the Cat C3.6 engine that produces 73kW net power.
Similar to the 315 machine, the 315 GC is a 15-metric-tonne excavator, part of Caterpillar’s small excavator lineup, sandwiched between the 13-metric-tonne 313 and the 18-metrictonne 317. This is a machine suitable for use in a wide variety of jobs and industries like grade work, slope work, trenching, loading and utility work.
A compact radius machine with a 1.57m tail swing radius, the 315 GC is easy to manoeuvre and transport. Operators will be able to get into tight spaces for digging and lifting. With a maximum digging depth of 5.99m and a maximum loading height of 7.2m, this machine compares very favourably with much larger machines.
The new electronically controlled hydraulics have made for both faster control response and higher hydraulic flow on the new
GC machine. To the customer, the benefit with the GC model is that you’re getting F-Series level of performance, but now at a lower price point while still getting the big maintenance savings, the big fuel savings and the electro-hydraulic controls on the more expensive standard 315 model.
A key driver in the new design was to reduce maintenance costs by up to 25 per cent over the 315F L with extended and more synchronised maintenance intervals. The new hydraulic oil filter delivers improved filtration and extends filter change intervals to 3000 operating hours, a 50% increase. Both the pilot and case drain filters have been eliminated on the 315GC, with less filters to change that means lower operating costs for the customer.
Operators can conveniently track filter life and maintenance intervals on the in-cab LCD monitor. All daily maintenance checkpoints, including engine oil level, are easily accessible from ground-level, making it safer and easier for the operator.
Just like the 315, the 315 GC larger cab design improves ingress/egress plus boosts operator comfort and productivity. The spacious Cat comfort cab offers a low-profile design plus larger front, rear and side windows with narrow cab pillars to provide a 60 per cent greater vertical visibility compared o the Cat 315F excavator, enhancing safe operation. The viscous cab mounts have also reduced vibration.
The new cab design features a large, 8-inch (203-mm) LCD monitor with touchscreen capability for easy navigation and intuitive operation, boosting productivity for operators of all experience levels. Standard rear-view and right-hand sideview cameras further improve visibility of the operating environment.
Reducing operator fatigue, viscous mounts significantly lessen cab vibration compared to previous designs.
The new cab is key to the customer experience. The ergonomically designed, ROPS cab now sees all controls in front of the operator, a touch screen monitor for ease of use and a seat and consoles offering comfort in even the most aggressive applications. A keyless push start button as well as joysticks with customisable buttons is available for each operator via a unique pin-code system.
This new cab is the standard for operator comfort allowing them to reach the highest productivity levels. It really has to be seen to be believed how much has been packed into one excavator cabin. There are some customers that do not need the added technology features for the work they do. Why pay for something you will never need?
If you’re in the market for a machine that gives you a solid performance with the benefit of lower up-front acquisition costs, lower owning and operating costs and unmatched dealer support, then check out the 315 GC.
Caterpillar expects the customer experience in the 315 GC machines will set a new standard especially for those who consider the Cat brand outside of their price range. They certainly warrant further exploration at your local dealer – a test drive is an experience not to be missed.
For more information about Cat 315 GC, visit your local Cat dealer.
NSW/ACT WesTrac 1300 881 064
VIC/TAS William Adams 1300 923 267
Western Australia WesTrac 1300 881 064
QLD/NT Hastings Deering 131 228
South Australia Cavpower 08 8343 1600
NZ TERRA 0800 93 39 39
St Helens Quarries is owned by Andy & Joanne Griffiths who started the business together in 1998. Twenty-four years later the business is still a small family operated earthmoving and quarrying business. Daughter Elyce joined the business three years ago and PJ Berne joined the team recently. Based in St Helens, the largest town on the north-east coast of Tasmania, St Helens Quarries now includes three quarries in the local area and one in Fingal just under an hour drive south.
One of the quarries is a sand lease while the three rock quarries produce decorative landscaping pebbles and a full range of road materials, including VicRoad compliant Roadbases and high PSV 54 Sealing aggregates. All quarries are phytophthora cinnamomic (PC) free, which means the material produced can be used in sensitive areas such as Tasmania’s national parks.
Joanne’s main role in the business is secretary but as with many family businesses she wears a few different hats depending on what is required on the day.
“In addition to the quarry we supply the major contractors on government projects quarry materials for road upgrades. We also supply material to the local landscaping yards, the council and earthmoving companies in the area,” Joanne adds.
St Helens Quarries currently owns four excavators, two-wheel loaders, two trucks, a crusher and a mobile screening plant.
The newest addition to the fleet is a 31.9 tonne Hidromek HMK310LC H4-Series excavator.
“I saw the Hidromeks in a magazine and thought they looked very impressive. The opportunity arose and we needed another excavator, so we contacted Onetrak,” Andy explains.
“Everyone at Onetrak was great to deal with from the start and invited us to demo a machine so we could test it. We also got the contact details to an earthmoving company here in Tasmania that own a couple of Hidromeks and got a testimonial directly from the owner of that business. From the get-go Onetrak has gone out of their way to help in every way possible. They have even helped with a machine we bought from another company that we have had some challenges with,” Andy continues.
“The Hidromeks are quiet, comfortable and enjoyable to operate. They’re as good as anything else on the market if not better. The HMK310LC is performing better than we expected in our hard rock quarry operation. They’re built extremely solid with reinforced steel components that I have
not seen on any other excavators. The interior of the cabin is great – I reckon I’d happily operate the Hidromek for 12 hours a day without complaining,” Andy adds.
Andy and the team were recently contracted to work on a subdivision project completing trenching and rockbreaking.
“We needed a hire machine just recently and utilised the Hidromek HMK145LCSR zero swing excavator through Onetrak Rental. We were super impressed with that machine –for a machine its size at 16.8 tonnes it was very solid and stable to operate. Great machine,” Andy concludes.
Daughter Elyce officially joined the family business three years ago.
“I was working at the supermarket and just wanted to do something different, which led to me starting to work for the family business. I started in the 8 tonne excavator and then progressed to a 25 tonne and 40 tonne. So far most of the work I’ve done has been in the quarry feeding the crusher, breaking rock or loading the trucks. Outside of that I’ve also worked on some of our other projects excavating trenches,” Elyce says.
When asked what she likes most about the job, Elyce responds, “I like that I just get in the excavator and get on with the job – I put my favourite podcast on and just get the job done.”
Elyce has been operating the new Hidromek HMK310LC since last year.
“I really like the Hidromek. It’s very comfortable with the adjustable air suspension seat and super easy access to everything.”
Elyce has gained quite an impressive following on her Instagram page earning her a few ambassadorships with workwear brands.
“I just started sharing a few posts here and there – of the machines or from my working day and it has just grown from there,” says Elyce.
Check out Elyce’s instagram page: @that_digger_chick.
Onetrak is the official supplier of Hidromek in Australia. Sales and service outlets are in Queensland, Victoria, New South Wales, Tasmania, Western Australia and South Australia.
To learn more about Hidromek or to view the full range of machinery sold and supported by Onetrak, visit www.onetrak.com.au or call 1300 727 520.
MB Plumbing Group this year marks two decades of operations, with the plumbing and plant hire business having expanded its service suite over the years to increasingly cater for the commercial and industrial sectors, building its reputation around tackling projects both large and small with a strong attention to detail.
Michael Brenton told EEM that he had started the business, based out of the Sutherland Shire, in 2002, with it having initially been focused on working high-end residential plumbing projects.
“Prior to that I was playing footy for the Sharks, I broke my shoulder, and then started my plumbing apprenticeship,” he said. “Ever since then I’ve been in business.
“We were in the luxury homes space for at least six or seven years – working properties including James Packer’s house, and the house of Jim Cooney, owner of Sydney to Hobart yacht Brindabella – then we broke out into the commercial sector, and now we’re in the industrial sector.”
In turn, MB Plumbing’s equipment fleet has grown significantly over the years, and Michael pointed to the importance of maintaining efficient and reliable machines.
“I certainly invest a lot of money back into the business, including plant, equipment and specific tools for our trade,” he commented. “It’s not cheap, but you definitely need those pieces of equipment to do the work, that’s for sure.”
Michael told EEM that MB Plumbing is strongly focused on providing a consistently high-quality service when it comes to catering for client requirements, including
maintaining open lines of communication and ensuring it is available when needed.
This involves developing a thorough understanding of client wants and needs, with the business having forged close, ongoing relationships with its client base, which has in turn led to a busy schedule of projects in the industrial sector.
“We specialise in a lot of in-ground sewers, in-ground fire hydrants, in-ground cold water supply and recycled water supply, especially for industrial warehouses, hence why we need all the equipment,” he explained.
Among MB Plumbing’s latest projects, Michael said it has recently finalised work on two big warehouses being developed by industrial, logistics and commercial property developer ESR Australia in Horsley Park, undertaken for construction company Hansen Yuncken.
“We were there for 14 months,” he said. “The one warehouse was about 40,000 square metres and the other one was about 70,000 square metres.
“We’re also currently working on a 100,000 square metre factory at Kemps Creek for Techtronic Industries, which we’re probably
about 50% through, and the builder for that project is also Hansen Yuncken.”
Of course, in undertaking large-scale, highly demanding industrial projects, robust and dependable equipment is required, capable of both powering on through from one day to the next and getting the job done efficiently and effectively.
MB Plumbing’s acquisition of three Kobelco excavators – a 7.5 t SK75SR-7, a 13.5 t SK135SR-7 and a 22.5 t SK225SR-2 – within the space of three months earlier this year has bolstered its operational capacity, providing it versatility in tackling a range of applications.
Michael told EEM that the excavators have been accumulating plenty of operating hours, noting that beyond the significant power and productivity benefits provided, it’s the finer touches that make Kobelco machines a high-quality option.
“I think that all the technology features inside the Kobelcos make them a far superior machine,” he observed. “The excavators have been unbelievable. They haven’t missed a beat; we haven’t had any issues with them at all.”
While the excavators have been hard at work in the field, Michael also noted that STM Trucks & Machinery has provided an exceptional
level of service, giving him confidence that support is on hand if required.
“I can’t speak highly enough of them,” he said. “The team at STM is unreal. It’s a family business and they sort of treat you like family, to be honest.”
As it stands, the excavators are set to continue seeing plenty of action in the near
future, with MB Plumbing enjoying a steady flow of work and set to navigate a busy schedule throughout the remainder of the year and well into 2023.
“Currently right now we’ve got work locked into around April next year and there’s plenty more in the pipeline,” Michael said. “We’re definitely looking to grow in the next 12 months.”
The authorised SANY Dealer in NSW and QLD, is excited to announce the opening of a new YELLO Equipment dealership branch located in Newcastle, NSW. The Newcastle area has a rich industrial heritage and strong demand for capital equipment, making it a meaningful and highly relevant location for the brand to expand within.
The new Newcastle branch will provide invaluable access to the Hunter Region of NSW and act as a gateway into the Central West allowing customers in these vicinities to enjoy localised service and support from YELLO Equipment. The full range of SANY Excavators will be available at the new facility allowing walk-arounds, demos and one-on-one meetings to happen in a more efficient and convenient manner for their customers.
General Manager of YELLO Equipment, Andy Hopcroft, speaks of both the importance this region holds for the NSW Earthmoving sector and the appointment of a new Territory Manager who will have direct responsibility for the operations and sales of the Newcastle branch.
“This is an important and necessary step in the expansion of YELLO Equipment and I’m excited that we will be able to offer our customers in this region a more accessible experience. The demand has been strong, so we listened and acted,” he said.
“I’m also pleased to announce Dino Williams has been appointed as the new YELLO Equipment Territory Manager at this branch. Dino’s knowledge of both the industry and the local area will make him a valuable asset to our team,” explained Hopcroft.
Dino Williams brings with him over 15 years of experience in capital equipment sales and management, having specifically worked within the construction and mining market
segment during this time. He also lives locally and understands the demands and relevant history of this region.
“I proudly live in the Newcastle region and truly love and understand this important part of the state. Heavy equipment is always in high demand due to the booming industries this part of the world is known for. I’m excited to hit the ground running and show customers up here the incredible quality and value we can deliver them with our SANY products and YELLO service commitment,” said Williams.
YELLO Equipment Newcastle will be located at 56 Sandringham Place, Thornton NSW 2322. Beyond Newcastle, the YELLO Equipment team has been busy on the road displaying their fleet at numerous Trade Shows and Field Days.
“Taking our gear on the road to some of these incredible field days is really rewarding,” explained Hopcroft. “Not only is it a great opportunity to showcase the quality of our machines, but more importantly we gather feedback, comments and new connections from people in these communities who may not have previously had the opportunity to get into a SANY machine, have a play and be wowed by what we offer.
“Diesel, Dirt & Turf is always a big event we love, so attending FarmFest in Toowoomba and AgQuip in Gunnedah over the last few months has been awesome,” said Hopcroft.
Hopcroft has noticed a particular interest in their offering from the Civil & Construction, Plumbing and Drainage.
“Word of mouth travels quickly and we have seen first-hand the power of positive testimonials and recommendations to peers by those who have purchased a machine and been blown away by the benefits, power and performance of our machines,” he said.
“A push towards mid-sized and large excavators has also been witnessed with standout models being the SY80U, the SY155U and the SY215C. We knew these models would be well received by the industry the moment they landed in Australia and they have not disappointed. The quality and value we can offer customers on these machines is exceptional. I highly recommend you check them out if you are in the market,” Hopcroft encouraged.
YELLO Equipment will also be present at the upcoming Henty Field Day in Wagga, Murrenbattman Field Day in ACT, Australian National Field Day in Orange and Primex in Casino.
For more information and to meet the team, add these events to your diary.
YELLO Equipment has generated impressive growth during its two short years of operation, a sign that their service approach within the market and the rapidly growing interest in the SANY brand is proving a winning combination.
NSW
Specialising in civil infrastructure projects and heavy plant and equipment hire, ACS delivers high quality earthworks projects to a variety of elite construction companies and service providers.
Its latest task, the construction of a new waste disposal cell at a waste management facility at Nambour on the Sunshine Coast, is the latest to be carried out using Volvo Construction Equipment provided by the team at CJD Equipment.
final trim capabilities.
“CJD will give you that support – it doesn’t matter what day of the week it is.”ACS has turned to the 30 tonne Volvo EC300DL excavator for the bulk and detailed earthworks on the Nambour landfill project, with ACS praising its versatility, for both its bulk handling and final trim capabilities.
“There are many reasons why we run Volvo, one being their service, from sales right through to their remote and regional servicing. The Volvo fuel efficiency, the breakout power, operator comfort and trim capabilities are secondto-none.
“We’ve bought new excavators before [from other manufacturers] and I put Volvo on top when it comes to efficiency, quality and value for money construction equipment.”
Dick says ACS’ penchant for Volvo CE machinery began early and, like the business, has continued to grow ever since. When the business first began in 2017, one of the first machines Dick purchased was a Volvo excavator. “Since then, we’ve worked our way through a variety of other brands and Volvo is definitely up at the top in its class,” Dick says.
They’ll sort of do what they have to do to get to site and get you going as quick as you can,” Dick says. “As far as servicing your machines, they move things to make things happen when best suits and that’s what you need in this industry.
“Even in the early days, CJD still gave me the same service of what you’d only expect for the bigger clients with bulk-buying power.
“They understand that your machines are your teams’ livelihood and that they have to be up and running and, if it’s urgent, they’ll work to get your machines going. “CJD will give you that support – it doesn’t matter what day of the week it is.”
When asked what the future holds for ACS and its relationship with CJD and Volvo CE, Dick offered an honest comment that encapsulates the regard in which he and ACS hold CJD.
“As long as we’re around, we’ll keep buying machines from them,” he says.
ACS has enjoyed a rapid five-year ascent in the earthmoving sector, being awarded major contracts across the eastern seaboard. These include the access, clearing, and earthworks for over 600km of new build transmission line infrastructure across South Australia. A similar project for a new 192km transmission line between Renmark and Robertstown, connecting South Australia and New South Wales, has just commenced for ACS as part of the Energy Connect Transmission Line Project for Downer and ElectraNet.
In all instances, regardless of location and terrain, ACS prefers to use Volvo CE excavators, with Dick saying the company benefits from the second-to-none service and support provided by the team at CJD. “In the off chance that something does break, they’ll be out there.
“There are many reasons why we run Volvo, one being their service, from sales right through to their remote and regional servicing. The Volvo fuel efficiency, the breakout power, operator comfort and trim capabilities are second-to-none.”
The Wacker Neuson range of mini and compact excavators play out their strengths on small landscape and construction sites.
They can be quickly transported and are manoeuvrable on the work site thanks to their compact dimensions so the job can be done more efficiently. The range of Wacker Neuson excavators consists of conventional tracked excavators, mobile excavators and zero tail models without any overhang.
The smallest model in the range also works in zero emissions mode: the mini excavator 803 – what it lacks in size, it makes up in strength. Its compact size
at just 700mm wide makes it ideal for demolition and renovation work within buildings. The rubber tracks do not damage floors and it can easily drive through internal doors.
The EZ17 compact excavator is the best performance zero tail model in its class. The large volume diesel engine combined with LUDV (Load Sensing System) and the new cooling system promise high performance and efficiency. The compact and robust design ensures longer operating life.
Wacker Neuson is setting new standards in the 1.7 tonne to 2.4 tonne class with the ET18. The combination of proven elements and intelligent development approaches provide a plus in performance and efficiency. The Vertical Dig System (VDS) ensures optimum performance and operator comfort.
The Zero Tail excavator EZ25 and EZ26 guarantees modern design, flexibility and ease of use.
Transportation by car trailer to the next construction site?
No problem – the low weight allows transport including attachment tool by means of 3.5-tonne trailer.
The tracked excavator EZ36 – sophisticated drive concept for quick, precise control and shorter work cycles. The 3.5-tonne class impresses with many sophisticated detailed solutions, which increase productivity – from the intuitive operation to the quick maintenance.
Excavating is made easy with the EZ50, which has fantastic performance due to high stability, high lift capacity and digging power, as well as quick working cycles.
Power and efficiency times to the tracked excavators EZ80 and ET90 ensure best work results. The EZ80 combines compact dimensions with excellent digging power – for best performances in a small space. The ET90 impresses with excellent engine and hydraulic performance – concentrated power that remains perfectly under control thanks to the loadsensing system.
As an Australian family-owned company with global reach, Tilly’s is proud to stock over 43,000 new part lines for your earthmoving machinery. Tilly’s quality alternative undercarriage range extends from track groups to idlers, rollers, sprockets and track adjusters suitable for dozers up to D9 and excavators up to 30 tonne.
Tilly's are pleased to now offer a range of quality low-hour machines including General Construction Excavators and Loaders and D6-D8 ex-United States machines.
Tilly's is now offering account customers online ordering of over 30,000 parts for even quicker turnaround time, because we understand that down-time for your machines has a huge impact on your bottom line. That’s why we guarantee the quality of our new parts to ensure you are staying on track.
Fecon is world renowned for building the toughest, most efficient forestry equipment in the industry. Engineered and constructed with unmatched durability and power to tackle even the hardest Australian timbers, Fecon forestry equipment continues to dominate the Australian market for quality, performance and value.
In addition to Fecon Australia’s already legendary ‘Bull Hog’ range of mulching heads for excavators and skid steers, a major favourite within Fecon forestry line-up is the all new FTX150-2 forestry mulching tractor.
Primarily conceived for forestry work, its versatile and powerful design results in the FTX150-2 being a highly adaptable large track loader, capable of many projects outside the forestry scope.
Engineered and manufactured to withstand the full range of mulching demands, the FTX150-2 comprises a high strength, heavy duty steel construction built tough to last, yet without sacrificing ground pressure. A colossal 155hp 4-cylinder water-cooled Cummins F3.8 engine offers extraordinary operating power, and a 227 litres per minute, 5000 psi high flow hydraulic system maximises the performance of any mulcher, slasher, grinder or other attachment. Moreover, this premium hydraulic flow is quickly and easily adjustable in-cab for ultimate operator convenience.
The FTX150-2’s deluxe ROPS/FOPS cab is designed by operators for operators – adjustable joystick pods attached to a suspension seat with 4 points of egress results in absolute comfort, and a large touchscreen IQAN display makes machine operation easy and efficient at the press of a button. The spacious cab is also pressurised with heating, defrosting and air conditioning, delivering all-day every-day comfort for operators.
An expertly designed D3 undercarriage offers 533mm of ground clearance, 6.4kph travel speed, 500mm track width and an impressively-low 4.8psi of ground pressure – meaning you can work harder, faster and
longer in a range of terrain conditions, with minimal ground disturbance.
Even the reduced servicing procedures and requirements of the FTX150-2 are remarkable. Large side compartment doors allow effortless and thorough access to the engine, whilst the moving components of the machine are designed to work longer and more efficiently than other competitor track loaders in its class. The result for owners and operators is the ultimate objective in any machine – minimal downtime, reduced costs and maximised productivity.
The FTX150-2 also comes equipped with a severe duty BH85 Bull Hog mulcher head as
standard, designed for fast, clean and efficient mulching of even Australia’s most challenging hardwood timbers.
As a result, the FTX150-2 has become one of the most coveted machines in the Australian forestry and vegetation management industry, a favourite for land clearing projects big and small. Make a smart investment and expand your business capabilities with the versatile, efficient and reliable FTX150-2 Forestry Mulching Tractor from Fecon Australia.
To learn more about the Fecon FTX150-2 Forestry Tractor, or to book an inspection at your nearest dealer, visit www.fecon.net.au.
Epiroc are excited to announce that their new Epiroc VC 2000 V Cutter has been shortlisted for the World Demolition Award in the category “Manufacturer Innovation, Tools and Attachments”.
The new V-shaped cutter was introduced in April 2022. Its new design allows digging of a trench without having to go side-to-side to make it even. Placing the drums in a V-shape enables a cut with a flat base. This means you can dig a more accurate trench much faster. You work this drum cutter like you would a bucket, just go straight. It saves up to 40% of energy and time savings are substantial. And finally, there is less wear on the carrier, which protects the customer’s investment.
You can find more information on https://epiroc.com/thinkV
The World Demolition Awards are organised by Demolition & Recycling International magazine in co-operation with the European Demolition Association and National Demolition Association of the USA. The independent judges have selected the shortlists out of more than 140 entries.
Winners will be announced at the Demolition Awards ceremony on November 17 in Vienna, Austria. Wish them luck!
2022 was the year that Digga settled into its proverbial skin again. The last three years tested many companies and left many in the industry feeling unsteady. It was this that prompted Digga to focus on building greatness from the inside out. From the CEO to the maintenance staff, from green initiatives, staff welfare programs to life changing fundraising “we want to support our people and our customers just like they have supported Digga during this time,” said Alan Wade, CEO.
landscape. “We are Australians supporting Australians,” said Alan.
manufacturing facility. Digga released an interactive 360-degree tour of their manufacturing facility, which means that anyone, at any time can see behind the scenes work that goes into building a Digga attachment.
This year also saw the launch of MY DIGGA, an online portal for customers accessible through a QR code located inside the cab. Digga Australia has decided to do away with paper and start the transition to a paper-free and digitised support system for all Digga product owners.
Digga Australia has been proudly Australian made for the last four decades and has no plans to change in the future. In keeping their roots firmly planted in Australian soil, the ‘Aussie battler’ spirit came through and kept Digga in production and then some. Currently running the factory 24 hours a day, 6 days a week has enabled Digga to minimise the impacts of the pandemic on their staff and their customers. While this past financial year has seen many Australian businesses fold due to labour shortages, product supply issues and the increasing operating costs, Digga has been able to significantly increase staff numbers and output as demand increased towards a domestically produced product. As a company, Digga said that it works to embody that tough steadfastness that is reflected in their equipment. Their commitment to Australian Industry, which has remained for over 40 years, allows no room for compromise when it comes to designing and producing equipment that is built tough for the diverse and uncompromising Australian
In the last year, on top of keeping fully operational in the new world of the pandemic, Digga continued to invest into their research and development of their products. This year will see the release of the new X-series 4 in 1 bucket, which is a culmination of customer feedback and engineering advancements. This bucket is the first release of a new style in 20 years and starts with the Mini 4-in-1 with the other sizes continuing to be rolled out throughout the year. Digga also released a new bale spear and upgraded their existing skid steer hoe, with more exciting product launches scheduled for later in the year. Perhaps, just in time for a Christmas order.
“It’s a lot bigger than I thought it would be” is the most common sentence heard whenever anyone steps foot into the Queensland
MY DIGGA is the centralised hub for all technical and specifics information, accessible from your mobile phone while you’re on the job. In a further conscious effort to offset their environmental impact, Digga invested in solar panels, with over 1300 panels now installed on the factory based at Yatala.
This June saw Digga partnering with the Ovarian Cancer Research Foundation for a fourth year and the most successful donation drive to date. Digga has an established collaborative partnership with the OCRF after their CEO Suzie Wright lost her battle with the illness four years ago. Digga immediately stepped up to the cause, to help valuable research, including the development of an early detection test. “By the time women are diagnosed with Ovarian Cancer it is often too late,” said Mr Wade. “Helping develop an early detection test is so important to us because it would save so many lives. Current research testing is so promising that it motivates us to help get these tests commercially ready,” he continued.
Through various fundraising programs Digga have contributed over $400,000 towards ovarian research, while assisting to raise much more money through a donation matching initiative every June.
Digga shows no signs of slowing; with all that they have achieved so far and with three months still left in the year there’s no limit to the possibilities. New products? New machines? New technology? All that and more is rumoured to be on the cards for the remainder of the year.
“Great just got better” is one of the taglines Digga use to describe their auger drives when fitted with their new HALO alignment system, but we think it can also be used to describe Digga in 2022.
ITR Pacific is part of the USCO ITR Group - the world’s largest aftermarket supplier of earthmoving machinery parts.
With an extensive geographical footprint of warehousing and workshops in the Australian market and industry experts in each region, ITR Pacific can offer a superior customer experience across a full range of Undercarriage Parts, Rubber Tracks and Pads, Ground Engaging Tools, Repair Parts, Tyres and more.
The unparalleled range held locally, and support from the Group, means ITR Pacific can confidently sell into all sectors of the Australian market, including Mining, Construction, Plant Hire, Agricultural and Forestry Industries.
ITR has one of the most complete Undercarriage ranges on the market, covering components such as track chains, shoes, rollers, sprockets, idlers, and segments which are manufactured within the group’s Asian manufacturing facilities. A fundamental characteristic
Thanks to careful design, technological innovation, and strict process controls, ITR Repair Parts have always been synonymous with high quality. This product range is continuously developing, not only by building up a strong distribution network but also through acquisitions that have helped expand their product offering to cover engine, hydraulic, transmission and frame parts.
bush turns are streamlined and efficient for a quick turnaround time. As ITR does not compromise on the quality of the parts, they have certainly not compromised on the quality of their Track Workshop Equipment, ensuring that each job can be carried out professionally and exceed their customers’ expectations.
ITR Pacific knows that a large percentage of the cost in owning and operating a track-type machine is related to its Undercarriage, therefore it is recommended to be proactive and have your Undercarriage inspected regularly to get the most life from your asset.
Rubber Tracks and Pads have recorded strong and steady growth since first introduced into the group in the 1990s. ITR Rubber Tracks are the fruit of a long road of design studies and tests in the field, which has allowed achieving an excellent quality level and the necessary confidence to brand the product ITR. They can confidently say that ITR carries one of the most complete, product ranges for Mini Undercarriage.
ITR Pacific stocks a full range, covering most makes of Ground Engaging Tools. The product line comprises all the necessary wear parts for manufacturing, reconditioning, and maintenance of bulldozers, excavators, loaders, and graders. The heterogeneous mix consists of teeth and adapters, cutting edges and end-bits, single and double bevel edges, blades, fasteners, and all other components necessary for excavation or levelling, such as rippers and blades for graders.
ITR has developed a range of smaller product lines to meet the market demand. ITR Radial tyres are the best in their class for the mining industry, heavy-duty construction, and industrial applications. Alongside tyres, there is hydraulic hammers, aluminium loading ramps, portable track presses and fuel tanks, buckets for excavators and loaders, and much more.
Expanding past just the parts, ITR Pacific is targeting a new opportunity with the introduction of two new Undercarriage, Workshop facilities into both their QLD and NSW operations. This new development will allow ITR to use all their knowledge and expertise to ensure the process of track lengthening, shortening, new link assembly bolts ups, and pin and
ITR Pacific offer professional Undercarriage Wear Inspections and detailed reports using the ITR WearTek Plus reporting system, allowing customers full access to their track reports through a mobile app and online web portal.
With the acquisition of DTN Equipment in July 2020, ITR Pacific expanded their sales and service arm to include the fitment of excavator and skid-steer loader Rubber Tracks, along with other Undercarriage Parts such as Rubber Pads and Sprockets.
The ITR Mini Undercarriage installation team currently consists of two service vehicles that operate in Southeast Queensland, with plans to expand this service to their Sydney, Melbourne, and Perth branches. With over 53 years of invaluable industry experience and qualified specialists, ITR will use the successful and well-known DTN model when establishing its fitment services Australia-wide.
The substantial growth ITR has seen over the last 12 months is nothing more than a reflection on the Australian earthmoving industry and the services and parts that it is demanding.
To find out more about ITR’s full product offering and services, give them a call on 1300 820 214 or visit their website www.itrpacific.com.au
ITR Pacific offers a complete range of aftermarket Earthmoving Machinery Parts for most makes & models of Loaders, Graders, Dozers, Excavators, Scrapers & more.
Italy-based Simex has been at the forefront of designing and manufacturing highly durable and high-performing excavator and skid steer attachments.
Simex’s range of self-levelling planers are dedicated to road surface restoration, where time is always of the essence as road restrictions from construction are expected to be as minimal as possible.
Simex Planers work to make applications more efficient on site, helping to keep road projects on time and budget.
To ensure speed of execution SIMEX has recently launched the largest road cold planer for compact loaders, the new PL2000 that is equipped with a 2000 mm wide milling drum, the largest currently available on the market.
Designed for milling deteriorated surfaces for resurfacing, the PL2000 is an essential tool for today’s milling and construction industries.
With PL2000 operators can remove the entire layer of asphalt or cement in preparation for trenching or mill deteriorated sections for future resurfacing and create a sustainable outcome by reusing milled material for backfilling trenches.
The PL2000 is designed to be mounted on the new-generation SSL characterised by high hydraulic power and it is equipped with all those features that make a difference on site:
• Independent depth adjustment of the slides on the RH and LH sides, to ensure perfectly flat surfaces with side-by-side passes; an essential feature when, for example, very large areas such as forecourts or car parks need to be milled
• The hydraulic side shift, for convenient milling flush to the walls or sidewalks, a procedure further optimised due to the new completely redesigned slides, with optimised overall dimensions in order to protect the corner-shaped hoses from possible abrasions
• The floating transverse tilt that allows the operator to keep the planer perfectly aligned to the road surface even when the base machine is not parallel to the ground
• The well-known Simex self-levelling system, which guarantees a constant milling depth regardless of the conditions of the road surface
• The dust suppression system with integrated and increased water tank, which avoids a second water tank to be installed on the roof of the base machine
• The exclusive Performer device, which helps the operator to keep the correct advancement of the base machine, thus optimising performance
PL2000 complements the current range of Simex Self Levelling Planers that reach a maximum width of 1200mm and depth of 350mm. Model PL2000 is expected to be available in Australia in 2023.
Simex products have been manufactured in Italy for over 30 years. They are imported to Australia by Queensland-based RD Williams and are available across the country throughout the Simex authorised dealership network:
• QLD Rockbreakers in QLD and NT: (07) 3452 0772, rdw.com.au/qld-rock-breakers
• GroundTec in NSW: (02) 9642 2030, groundtec.com.au
• Walkers Hammers in VIC, SA and TAS: (03) 9315 3788, walkershammers.com.au
• Total Rockbreaking Solutions in WA: 1300 921 498, totalrockbreaking.com.au
Water Spray System to reduce dust and in-built tank in the hook-up plate makes it easy for operators to fill up the tank from the ground.
Performer informs the operator how to work with Simex attachments to maximise power and performance.
•
•
•
•
•
•
• Width up to 2,000mm
•
NSW Groundtec Equipment (02) 9642 2030 groundtec.com.au
Gates X-Series Hydraulic Hoses designed for the demands of the earthmoving equipment industry.
The product of Gates materials science expertise, Gates MegaSys™ X-Series hydraulic hoses are engineered to deliver missioncritical performance in demanding and tough earthmoving equipment applications.
Gates product development teams have created innovative new products that deliver in four core areas:
Gates designed these products to be lower weight for easier handling, quicker installation, and reduced equipment weight.
Gates’ latest innovations require significantly less force to bend for safer, quicker, and less fatiguing routing and installation.
ADVANCED PERFORMANCE
The product of Gates’ materials science expertise, X-Series hoses exceed industry standards for performance and reliability.
Gates has qualified these latest innovations to multiple industry specifications – making it easier to know you have the right hose for the job.
The X-Series range includes:
NEW GATES MEGASYS MXG™ 5K
Recently launched in Australia and New Zealand, Gates MegaSys MXG 5K is a high-pressure 5000 psi hose, yet it is lighter and more flexible than traditional high-pressure equivalents thanks to Gates advanced Xpiral™ technology.
Features:
• MXG 5K is 350 bar (5075 psi) working pressure
• Four layers of patented Xpiral woven spiral technology with high-tensile steel wire reinforcements
• Excellent flexibility and lower force-to-bend for faster and more ergonomic installation (force-to-bend is 25% better and OD is 5% smaller)
• Up to 20% lighter weight for easier handling and installation
• Comes standard with XtraTuff™ Plus cover, providing 25X increased abrasion and 800+ hours of ozone resistance
• Qualified with Gates Global Spiral ™ (GS) couplings to 1,000,000 impulse cycles and with MegaCrimp couplings (-6 & -8) to 600,000 impulse cycles
• Temperature Range: -40°C to +121°C
• Available in sizes -6 to -16
GATES MEGASYS MXG 4K HYDRAULIC
Built with Gates proprietary Xpiral technology, MegaSys MXG 4K hose is lightweight, highly flexible, and qualified to ONE MILLION impulse cycles — it’s a drop-in replacement for conventional spiral hoses.
Features:
• MXG 4K is 280 bar (4060 psi) working pressure
• Four layers of patented Xpiral woven spiral technology with high-tensile steel wire reinforcements
• Excellent flexibility and lower force-to-bend for faster and more ergonomic installation (force-to-bend is 40% better and OD is 8% smaller)
• Up to 30% lighter weight for easier handling and installation
• Comes Standard with XtraTuff Plus cover, providing 25X increased abrasion and 800+ hours of ozone resistance
• Qualified with Gates Global Spiral (GS) couplings to 1,000,000 impulse cycles and with MegaCrimp couplings (-6 to -12) to 600,000 impulse cycles
• Temperature Range: -40°C to +121°C
• Available in sizes -6 to -16
GATES MEGASYS MXT™ WITH XTRATUFF PLUS COVER HYDRAULIC HOSES MXT
Designed to address our customers’ evolving application challenges. Using materials science and process innovation, combined with a patent-pending construction, Gates offers a hydraulic solution that is lighter, stronger and more flexible. MXT is a universally applicable premium product offering performance above industry standards Its diversified application allows you to consolidate inventory while giving you exactly the hose you need, when you need it.
Features:
• Braided high-tensile steel wire reinforcement
• Gates XtraTuff Plus cover available on MXT (optional), providing increased abrasion and ozone resistance
• More flexible with up to 40% lower forceto-bend for faster and more ergonomic installation
• Up to 30% lighter weight for easier handling
• Tested to 3X impulse criteria (600,000 cycles)
• MXT / MXT-XTP compatible with Gates Global Spiral and MegaCrimp Couplings and Gates crimpers
• Temperature Range: -40ºC to +100ºC
• Available in sizes -4 to -16
To promote the launch of Gates MegaSys MXG 5K, Gates Australia is giving you the chance to win a Gates Retro Arcade Drum, simply go to VISIT.GATES.COM/XSERIES and complete the form to enter. You’ll also find more product info, specs and downloads.
The success of your construction business depends on your ability to ensure equipment runs efficiently and reliably.
Whether your construction project involves earthmoving, transporting loads, levelling, compacting or digging, your business relies on your equipment and their lubricated components. Equipment breakdowns can severely compromise your project schedules and prevent your company from earning revenue.
We appreciate that, in the construction industry, you are constantly striving to meet deadlines and lower operating costs. Yet nearly half (43%) of construction companies say they often experience breakdowns because of ineffective lubrication – and 72% say their maintenance teams need more training*.
Construction equipment must be tough and operate in a range of harsh environments. So it’s important to use the right combination of lubricants to get the most out of your engines, transmissions, hydraulic systems and greased components.
By using the right combination of lubricants together, you can improve vehicle and equipment productivity. Lubricant costs can be as little as 1-2% of total maintenance costs, yet optimising lubricant use across all operations can save 30% of operating costs.*
You need a simplified lubricant portfolio that works harder, for longer – helping increase uptime, minimise downtime and extend equipment life. Shell Lubricants for Driveline: are a suite of high-performing lubricants that adds up to more than the sum of its parts – making your equipment more efficient, productive and competitive.
Silvana Farrugia, Lubricants Technical Advisor at Viva Energy, Shell Macro Distributor and valued member of the Technical Helpdesk says they can support customers to optimise their lubricant portfolio and provide advice on the best lubricant for their equipment.
“Our local Technical Helpdesk is available to answer your questions and provide expert equipment lubricant recommendations, as well as advice on rationalisation and lubricant storage. We make sure we recommend products with approved specifications and are the best fit for your construction equipment.”
The Shell Driveline lubricant product suite is designed to meet the needs of the whole machine. Shell’s driveline products meet the appropriate specifications, approvals and recommendations from many of the industry standard and leading sector OEM’s including ACEA, Allison, API, Bosch, CNH, John Deere, Massey Fergusson, Caterpillar, Cummins, Deutz, Scania, Volvo and ZF.
Selecting a less effective lubricant may not result in immediate equipment failure,
but can lead to increased maintenance expenses over time. Businesses seeking real time support can receive a free consult on what lubricant is optimal for their machine through the Viva Energy Technical Help Desk line (Shell Specialists). Enquire about the Shell driveline lubricants today!
Call 1300 134 205 Email technicalhelpdesk@vivaenergy.com.au
Latest generation technology to deliver significantly improved resistance to wear, deposits and oxidation.
Versatile enough to bring you the convenience of a single oil, suitable for virtually all engine ages and vehicle types.
Greater reliability for less downtime and enhanced wear protection.
Smooth and noise-free operation.
Recognised by leading equipment manufacturers.
Increased productivity, with extended oil life and outstanding system efficiency.
Consistent performance over longer periods.
Excellent lasting protection.
With the Flipscreen, you can save on fuel by handling material only once instead of travelling over ground multiple times for each load. You also don’t need to go off-site to create mixes or mix concrete anymore!
Not only can it be used for a variety of tasks, such as sorting, loading, and stockpiling from landscaping to excavating, but it’s also been shown to add profits to the bottom line. The Flipscreen is easy to operate and maintain, and faster and more efficient than traditional methods of screening material, making it an ideal choice for those who want to keep their costs down.
When you’re a professional landscaper, you know that time is money. That’s why the Flipscreen is such a valuable tool to have on-site. With the ability to attach it quickly and easily to your mini excavator or skid steer, you can get to work immediately, without any setup time required.
Using the Flipscreen you can recycle on-site soil and rocks for your projects. In very short order, you can have perfectly good topsoil in one pile, and another pile that can be used for gravel. If you have a large trough or bucket on-site that you can fill with water, you can even wash these rocks or gravel before laying them out. This is an economical way to source materials you need without having to transport them from off-site reducing waste, transfer and tip fees.
The high-volume screening rates of the Flipscreen are due to its large screening surface area, which is the largest in its class. The material is inverted every 2.5 seconds and travels the whole area of the mesh. The unique action of the Flipscreen as it lifts and flips the material means it is able to break up clumps, resulting in an overall higher quality product. After approximately three rotations (7.5 seconds), fines are screened, and the exposed lumps will start to be smashed onto the rear mesh. This enables the operator to either break up the remaining lumps or tip them. The ability to screen and tip in one operation not only increases productivity, but also reduces wear and tear on the machine because there is no need for a second operation to break up the lumps.
With most other screening attachments, as soon as the material is scooped, it will spill through the bucket. The Flipscreen’s base is watertight, enabling the operator to drive around the site with a full load without spilling.
The mixing plate is a versatile addition to the equipment list for any business in the construction or landscaping industry. Being
able to mix cement on-site without the need for additional equipment saves time and money, while the ability to create seed or soil mixtures gives businesses the flexibility to meet customer needs.
The Flipscreen allows users to recycle materials on site. This can save a considerable amount of money on tip fees, as well as hauling-related costs such as fuel and labour. It’s a versatile tool for anyone looking to reduce their environmental impact. The Flipscreen can screen materials such as topsoil, sand, gravel, and demolition waste. It can also be used to sort recyclable materials such as metals, glass, and plastics.
As any landscaper knows, one of the most challenging aspects of the job is dealing with unknown materials. Whether you’re clearing an old lot or digging up a foundation, you never know what you’re going to find. While some materials are easy to deal with, others can be difficult to handle. That’s where the Flipscreen comes in! The Flipscreen is designed to screen anything that you can scoop, whether it’s scrap metal or concrete.
With a Flipscreen you now have a tool that many competitors don’t, which adds a greater service offering to prospective customers. Not only can you screen and sort materials on site, but with the ability to process topsoil, gravel, sand, and other materials, you can offer a one-stop solution for all their needs. This not only saves the customer time and money, but it also gives you a competitive advantage. And with the Flipscreen’s portability and low
maintenance costs, you can offer this service at a fraction of the cost of traditional methods.
Skid steers are among the most common carriers on a job site. They can be outfitted with a variety of attachments, making them perfect for a range of tasks. One of the most popular skid steer attachments is the screening bucket. Screening buckets are ideal for landscaping applications, as they allow you to screen topsoil, mulch, and other materials quickly and easily. The S45 skid steer screening bucket from Flipscreen represents the pinnacle in the market. Featuring a patented design, the S45 is perfect for excavating and screening material on even the most challenging jobsites. With its rugged construction, the S45 is sure to help you get the job done right.
The Flipscreen is the world’s best screening attachment, suitable for use with any carrier. Whether you have a tractor, a backhoe, or even a telehandler.
For more information: https://www.flipscreen.net/
Throughout its more than 50 years in business, Dieci has focused on constantly researching innovative technologies in agricultural, industrial and construction sectors to produce machines that are innovative, operator focused and expertly designed. This quality focus is backed by providing excellent after-sales support and service.
Dieci Australia locally designs, customises and manufactures attachments and machine options to ensure each telehandler is perfect for the specific application while complying with Australian standards. Thanks to a wide range of attachments available, and a reliable service partner (AWD Group), Dieci Australia can work with their customers to produce tailor-made machines to suit any requirement.
Versatile and powerful, Dieci rotating telehandlers can complete tasks traditionally done by telehandlers, elevating work platforms (EWPs) and cranes as a single vehicle.
The Pegasus family is a benchmark for sectors such as construction, quarries, mines and emergency, and for operators seeking maximum reliability and efficiency, combined with unparalleled safety control.
Further characterised by extreme flexibility and robustness, these vehicles outperform many conventional telehandlers in terms of load capacity, reach and the choice of either 360° continuous or non-continuous 400° rotation.
Ranging from 3.8 tonne to 6.0 tonne, and with a maximum lift height of 25 metres, these vehicles can cover an operating area of up to 2122 square metres and are easily maintainable thanks to the use of durable components and cutting-edge materials.
Three engine size choices guarantee optimised output and efficiency with high torque to ensure maximum performance. Full electronic engine control allows limited fuel consumption and reduced emissions.
Access to the engine is made easy with the optimal arrangement of components that make maintenance quick and convenient. Radiators are straight forward and fast to clean, and air filters can be reached without any tools. The interventions required for the change of hydraulic oil are also minimal, as they are only necessary every 2000 hours of operation.
Customers are able to diversify their return on investments through multiple attachment solutions. Lifting hooks, excavation and aggregate buckets, grippers for cylinders, pipes and tyres, centering handlers, and passenger baskets are just some of the accessories available.
When equipped with a man basket, a telehandler can act as an aerial platform, also guaranteeing greater stability, load capacity, and work platform dimensions that can reach up to 6m in height.
The Pegasus’ accurate and sensitive capacitive joystick with deadman sensor enables the turret rotation speed to be adjusted, while the automatic reversal system control makes it possible to travel with a 180° rotated turret for easy navigation inside narrow working areas.
These vehicles are designed to travel and lift with maximum stability and safety on level
ground and off-road. An excellent self-levelling system, adaptive loading software and anti-crash system, eliminate the risks caused by difficult conditions.
Safety is a major priority at Dieci Australia, with more money invested in load charts and design verifications for the complete range of machines than most companies in Australia. They have an independent, external engineer who signs off on every new machine or attachment that comes out, including attachments that they have developed themselves.
To further guarantee safety, an enhanced soft motion system is equipped to make all boom movements easy to control, reducing speed on approaching physical limits, or in pre-alarm conditions. Oscillation of the rear axle is automatically locked when the boom is raised, and the turret is rotated at more than 5°.
Each telehandler comes with a ROPS - FOPS approved cab with a roomy interior, luxurious air seats and powerful integrated air conditioning. These cabs are designed to significantly improve the working conditions and comfort of the operator.
Dieci rotating telehandlers are available across Australia through the Dieci Australia dealer network.
For more information, contact Dieci Australia on 1300 888 479 or visit www.dieciaustralia.com.au
myKomatsu online customer portal provides faster, easier-to-use experience.
Plant hire companies supplying earthmoving and excavating equipment to customers need to know that the machines they provide are in top working order and are not likely to break down or have a key component fail at a critical time.
That’s why major equipment rental companies such as Brooks Hire carry out regular oil analysis of the machines in its fleet of over 700 pieces of earthmoving and construction equipment.
Brooks Hire has been renting earthmoving and construction equipment since 1979, and today has branches not only throughout Western Australia where it started, but also in all state and territory mainland capitals, along with key regional centres.
To stay on top of its mobile equipment fleet maintenance needs, Brooks Hire uses Komatsu’s KOWA (Komatsu Oil Wear Analysis) service – part of its Condition Monitoring Services (CMS) suite of sampling, analysis and diagnostics tools – to carry out regular oil analysis tests on its Komatsu and other branded equipment.
According to Joe Piotrowski, Brooks Hire’s Service Manager WA/NT, the company – which has been using KOWA analysis for the past 16 years – averages more than 220 samples a month nationally.
In fact, the actual number of samples for the Brooks fleet is significantly higher, with many of its customers carrying out their own servicing and sampling on the Brooks machines they have on hire.
Brooks Hire was also an early adopter of the ability to order and manage KOWA samples when Komatsu’s CMS range of offerings became available through the myKomatsu online customer portal (my.komatsu.com.au/ condition-monitoring) in mid 2021.
“In terms of convenience and ease of use, it’s been great to move over to the myKomatsu
reliably, productively and safely.
portal. It’s a very handy tool which our service team uses daily,” he says.
Komatsu set out to make the process of accessing KOWA oil analysis services through myKomatsu faster, more efficient, easier to use and less prone to human error.
“That’s certainly been the case,” says Piotrowski. “We just have to enter the asset number or serial number, and the system shows all sample reports for that asset.
“And the turnaround times for reports once we’ve sent in a KOWA sample for evaluation has been good.”
An important feature of having KOWA samples carried out through myKomatsu is also the ability to have full records of sample histories held in one place for easy access.
“KOWA has always been an important tool in helping us monitor, repair and replace major components. It helps us reduce major failures
onsite, also down time for our customers,” says Piotrowski.
“But with our results now within myKomatsu, we can very easily research our sample histories, so we can check trends and better identify where problem areas may be.”
Andrew Renshaw, Komatsu’s Perth CSSR (Customer Support Sales Representative) provided assistance to get Brooks staff their own individual logins, linked to the Brooks Hire account.
This allows each user to access reports and historical data on their own computer, laptop and mobile devices.
“Our team regularly uses the portal as a tool to access sample histories when required,” says Piotrowski. “In the past, we would call Andrew for details of our CMS histories, but now we can search for just about all the information we need ourselves via the portal.
“It’s all user-friendly and well laid out. In particular, the Advanced Search function is extremely useful,” he says.
The level of detail now in our KOWA reports has improved even further since we moved to managing them through myKomatsu.
“All the reports are very detailed, filled with good, useful information,” Piotrowski says.
For more information about Komatsu’s CMS and its range of KOWA services, visit https://my.komatsu. com.au/condition-monitoring.
Padlock and security products expert, Master Lock, has released their new range of highquality, maximum security Magnum padlocks with longer shackles to ensure greater flexibility of use.
The new Magnum range from Master Lock offers better security application options with the addition of a long shackle design (64mm shackle length), making it easier to safely secure more personal belongings and items
(including with multiple chains and hasps). The range features boron carbide shackles that are 50% harder than hardened steel. The dualarmour construction with stainless steel laminated body provides maximum strength and security, as well as weather and corrosion resistance, even in prolonged extreme weather conditions. Each lock has a 4-pin cylinder for optimal pull and pry resistance.
The new Master Lock Magnum Long Shackle padlock range is available in three variants: M1TLJ (RRP $49.90), M5DLJ (RRP $39.90) and M5TLJ (RRP $69.00).
They have been designed for both commercial and domestic use and can be purposed for a variety of functions including security on worksites, locking up fences, sheds and storage buildings, as well as safeguarding personal belongings.
Master Lock’s Magnum Long Shackle padlocks are available at Bunnings Warehouse.
For more information visit: www.masterlock.com.au/
A fast-growing electrical contracting business based in the Hills District of Dural, New South Wales, MD Industries, has added a new M-16U Huski Construction Equipment mini excavator to its fleet – based on the impressive performance of its longstanding Toyota 5SDK5 Huski skid steer loader.
MD Industries director and project manager, Matt De Bono, started his electrical trade 20 years ago and self-started his current business, which he describes as “Multidisciplinary,” 15 years ago.
“We are mainly electrical contractors, but we cover a lot of fields and also do project work, providing entire customer solutions such as demolition, fit-outs, a whole range of works,” said Mr De Bono. “Because we cover so many areas, we can wrap it up as a package: do all the excavations, trenching, footings, the civil works, concreting, and of course the electrical side of things. We also provide 24-hour everyday quick response.
“At the moment we’re focused on building a network of electric car-charging stations throughout New South Wales. When it’s complete, and it’s due for completion by June 2021, you’ll be able to find one every 150km, all the way to the state borders.”
Given the regional nature of the network, MD Industries faced logistical challenges in terms of transporting a 2.5 tonne excavator to job sites, as Mr De Bono explained: “We go to some pretty far-flung places and it was just too big, heavy and expensive for towing. We were hiring excavators in rural areas but the further we went; it was getting harder and harder to find machines. We were travelling an hour just to get a machine and then an hour back.”
The business needed something lighter and smaller, yet still powerful.
As a long-time satisfied Toyota Huski skid steer loader user, Mr De Bono said his experiences with the 5SDK5 influenced his decision to buy the M-16U Huski mini excavator.
“When we started out, we didn’t have a skid steer loader. But as the business grew, we realised we needed those wide-ranging capabilities that the Huski 5SDK5 provides.
“It has helped us perform duties more efficiently. The Huski skid steer loader definitely makes life a lot easier for us and it’s fair to say that it has helped our business grow.
“Likewise, our business growth and the size of our recent electric car-charging station commitments really spurred the decision to get our new Huski mini excavator, making it quicker and easier to finish our projects.”
A key feature of the M-16U Huski mini excavator is its exceptional power. Mr De Bono considered buying the smallest mini excavator in the Huski range but liaison with Huski Construction Equipment area sales manager – Construction, Peter Bower, revealed the business could choose a highertonnage machine without compromising its transport requirements.
“We needed a smaller machine but one that could also meet our needs in terms of power.
“We looked at the smallest one in the range but after speaking with Peter we realised we could go up in size in order to allow for it doing that bit more, without it affecting our transport.
“The new 1.6 tonne Huski is in a different class to our larger machine but for the size of it, it is very powerful and more so than the 1.6-tonne equivalent from another brand. It performs very well, having excellent break-out force for its size.”
MD Industries also favours Toyota passenger vehicles. Mr De Bono said Toyota reliability is a continuing reason for it to choose the brand. “We also have a HiLux ute which has proven very reliable,” he said. “With the lower weight and compact size of the Huski mini excavator, we can use the HiLux to tow the new Huski digger on a trailer, so that lets us get around without having to worry about trucks.”
Mr De Bono optioned the M-16U Huski mini excavator with a quick hitch for attachments, which he said, “Is handy”, adding that “the zero tail-swing is also a nice feature.”
MD Industries hasn’t had its new Huski mini excavator for long, yet first impressions are positive. “The Huski mini excavator definitely feels smooth to operate,” said Mr De Bono. “And it’s going to give us access to tighter sites because of the smaller size.
“As we expand, we will be adding more Huski and Toyota equipment to our fleet – most likely a forklift. We use the Huski skid steer loader like a forklift but obviously it doesn’t have the same full functionality.”
He said dealing with Toyota Material Handling Australia service technicians and sales managers has been another reason to stick with the brand. “Our relationship with TMHA has been excellent and is a part of the reason we went with the Huski mini excavator as opposed to other brands.
“The major factor, though, was the performance of our Huski skid steer loader. It made the decision simple.”
For more information freecall 1800 425 438 or visit huskiconstructionequipment.com.au
Across various sites, CJD Equipment’s SDLG wheel loaders provide Teys Australia with the versatility its operations need.
Teys Australia is an integrated beef processing business that supplies the domestic and international market. Its origins stretch back to 1946 when four Teys brothers opened their first butcher shop in Woolloongabba, Queensland.
Today, it operates from 14 locations across Australia, including three feedlots, six beef processing plants, two food manufacturing facilities, a hide processing site and a centralised distribution facility, all of which are strategically located along the eastern seaboard.
The Murgon facility, located about 250 km northwest of Brisbane, is a brining and curing operation that processes around 15,000 hides a week, which are mostly exported and end up primarily as automotive and upholstery leathers.
Having utilised the SDLG LG936LA wheel loader from CJD Equipment over the last few years, it performs a variety of tasks around the site and is the ideal utility machine, explains Scott Kapernick, Teys Murgon General Manager.
“The wheel loader isn’t doing massive hours. It will do 10 minutes here, 20 minutes there, then someone else might jump in it for half an hour,” he said.
“Because there’s not one operator sitting in it all day, every day, it needs to be easy to operate.
“We needed something with a good sized bucket, a decent bit of power behind it and a high lift – the SDLG LG936LA ticked all those boxes.”
Powered by a 123hp Weichai Deutz diesel engine, the 2700kg rated LG936LA wheel loader is highly manoeuvrable.
With an air-conditioned steel cab that offers wide visibility and larger operating space, the operator is protected against the elements and enjoys optimum comfort.
“It’s a very adaptive machine, which is crucial for our operations,” Kapernick remarks.
Many of the loads the SDLG LG936LA handles around the Murgon sites, like salts for curing
and compost waste, aren’t particularly heavy, but it’s highly manoeuvrable and easy to operate in tight quarters, according to Kapernick.
“We’ve got 200 acres here as well, so we use it to look after the contours and the roadworks around the property. It’s a great allrounder and has become an integral part of our operations,” he said.
The Teys Australia’s Condamine feedlot in the Western Downs Region of Queensland, around 335km northwest of Brisbane, also run an SDLG wheel loader – the LG938L.
Powered by a 130 hp Deutz diesel engine, it has slightly more horsepower than the LG936LA, and is connected to a tropical cooling package, allowing it to work at full capacity in the toughest conditions.
The cab interior is vast, ensuring operator comfort. But its versatility is what makes it such an important part of the Condamine facility’s day-to-day operations, explains Phil Lambert, Teys Condamine Feedlot General Manager.
“We use the LG938L wheel loader for a variety of jobs around the feedlot: batching rations for the cattle, for pen cleaning and moving material from the pens,” he said.
“We utilise the wheel loader to unload hay trucks, as well as moving the hay around the site. We also use it to move dirt and manure –just a lot of those jobs that are essential to the operation,’ Lambert notes.
Because of the different applications the SDLG LG938L wheel loader is employed in, the Condamine facility runs it with a variety of attachments.
It operates various buckets, as well as a set of hay spears and pallet forks, which are used to unload pallets from trucks and move them around the facility.
The LG938L comes standard with a Volvo compatible quick hitch, which has been designed and built to ensure changing attachments is a simple, straightforward process so that downtime is kept to a minimum.
There are many challenges associated with operating a large business in a rural setting. It can be difficult to get services to site when they are required, which is why strong partnerships are so vital, relates Lambert.
“Teys Australia has a great relationship with CJD Equipment and that is why we’ve been working with them for such a long time,” he said.
“From a sales perspective, they are professional and upfront. They are competitive around pricing, and they always look to go the extra mile to ensure the right product is delivered on time and in line with our needs.
“On the servicing side of things, CJD Equipment do all the servicing on our SDLG and Volvo wheel loaders. We have always found the team very professional; they have good technical knowledge around all the machines, and they get here in a timely fashion for critical breakdowns.
“And, again, from a parts perspective, we couldn’t ask for anymore,” Lambert remarked.
As Teys Australia continues to grow in the future, Lambert has no doubt that CJD Equipment will continue to provide them with all the support they need.
The McDonald family draws on a long history in the Goondiwindi farming and agriculture sector, overseeing a large-scale grain and cattle operation which has built its reputation over the course of generations, and which is very much focused on harnessing new machinery and technologies to continue growing moving forward.
Luke McDonald told EEM that the business, which trades as Jack McDonald Pty Ltd, was originally started by his grandfather Jack, with it having evolved over the years to encompass mixed farming interests.
“The acreage is tied up probably 50/50 between grain and cattle,” Luke said of the business’ areas of focus, adding that it is this type of variety that makes agriculture “in itself an exciting industry to be in”.
“It’s very dynamic and there’s lots of different things we can do in agriculture,” he commented. “There’s different animals and crops, and you’re always trying to think forward, while seasonally it can be extremely variable.
“For this reason, it’s an interesting industry to be in, because you can create your own story, and in some ways you really pick your destiny.”
LOVOL FL962K WHEEL LOADER MAKES AN IMPRESSION WITH PLENTY OF GRUNT
Of course, efficient and reliable machinery is one of the key components underpinning efficient operations, and Luke highlighted the need to keep pace with the latest technology developments, tapping into productivity benefits that can add up significantly over time.
With the business having recently added a Lovol FL962K wheel loader to its fleet, a clear requirement has been high operational efficiency in carrying out various tasks, along with a capacity to power on through in demanding conditions.
Weighing in at an operating weight of 20 t, the FL962K notably sports a Cummins engine
and a Danfoss hydrostatic driveline, as used in Liebherr loaders, providing a smooth operating experience and precise control.
Luke said that the FL962K has thus far been put through its paces across a variety of different applications, impressing with its grunt and robust design.
“We’re mainly using it for earthworks, for erosion control in paddocks, helping to open waterways, fixing roads, cleaning up fence lines and timber, and even loading trucks with grain, doing a bit of grain work in the sheds,” he said.
“It’s got heaps of power, and it’s very well finished in the machining side and the cosmetics. There just seems to be a little bit more refinement in the transmission and everything, and it seems to be well put together.”
LOVOL FL962K WHEEL LOADER: DANFOSS HYDROSTATIC DRIVELINE PROVIDES POWER AND PRECISION Equipment Specialists Operations Manager Lawrence Perkins told EEM that the Danfoss hydrostatic driveline is one of the key features that makes the FL962K a superior loader option, paving the way for high-efficiency operations.
Benefits provided include less wheel slippage, smoother direction changes, increased fuel savings and improved operator comfort, with Lawrence noting that Lovol stands out in the broader loader market due to its integration of high-calibre components at extremely competitive prices.
“Lovol is at the forefront when it comes to hydrostatic wheel loaders, which is the way the industry is going,” he commented.
“The FL962K is a high-quality machine. Along with the game-changing hydrostatic driveline, it is low on plastic and electrically controlled functions, eliminating problematic items and making it extremely reliable.
“It ultimately provides a performance comparable to the big brand names, and there is notably no AdBlue, DPF and EGR.”
The FL962K runs a 170 kW Cummins QSB7 Tier 3 engine, and in addition to the hydrostatic driveline, is equipped with a DANA transfer box and either Meritor wet brake axles or Lovol dry brake axles, with it available with a choice of tyre options.
In addition to this, it features:
• A ROPs and FOPs-certified lined and sealed cab, lessening noise and vibration, decked out with air-conditioning and an air-suspension seat, and also sporting a reverse camera
• A 4 m3 GP bucket (with a choice of GP, rock, coal, grain and bulk buckets), 6 t rated load capacity, 4.2 m bucket lift height and a boom lifting time of 5.2 seconds
• A pilot control joystick incorporating a thumb-action F/N/R function
• A Danfoss steering valve; hydraulic pressure of 3200 psi; fuel tank capacity of 350 l; travel speed of 40 km/h
• A one-piece fully opening side engine cover, enabling ample access (with no bolted covers to remove); fully raised opening rear engine door; patented composite reinforced pivot structure and bushings
• Dimensions: 8.85 m (length), 3.3 m (width) and 3.42 m (height)
Toowoomba-based Equipment Specialists ranges a wide variety of Lovol loaders and excavators, with Lawrence telling EEM this range is poised to grow in the near future, with the 26 t (operating weight) Lovol FL980K loader also due to arrive in the local market soon.
Supporting its equipment range, Equipment Specialists provides access to a range of parts and accessories (not only limited to the brands it stocks), which it sells along with other brands not commonly stocked in Australia, with it capable of sourcing items fast and at cost-effective prices.
Compact, lightweight, able to be towed behind a ute, reliable, efficient, and packed with power and torque, the ASV RT-50 Posi-Track Loader is an ideal machine for many industries.
The RT-50 delivers impressive power in tight areas that most other machines find difficult or impossible to access, making this Posi-Track ideal for any mid-sized machine owner or operator searching for improved site accessibility. Offering a greater performanceto-weight ratio than any machine in its class, the RT-50 features a 900 kilogram rated operating capacity while weighing less than 2400 kilograms. High performance in a lightweight machine means easy transportability and less risk of turf damage. The outcome is more income and profit in a contractor’s pocket.
The RT-50 works hard and fast all day long, thanks to exceptional digging and pushing power resulting from ASV’s Posi-Power system, combined with a 53-horsepower engine, high efficiency drive system and a light overall weight.
Operators can also run demanding attachments with ease, running a highly efficient cooling system and a robust hydraulic setup that includes 3000 psi of auxiliary pressure and 50 litres per minute of flow. The system features large line sizes, hydraulic coolers and direct-drive pumps, transferring more flow and pressure directly to the attachment with maximum efficiency.
Furthermore, ASV has designed and manufactured the RT-50 with features to optimise productivity and quality of work. Operators can use the machine to load landscape trucks and small dump trucks thanks to the loader’s 2784 millimetre pin height. Getting around the jobsite quickly is just as easy, due to the loader’s 11.4 km/h top speed.
The ASV RT-50 Posi-Track is easily towed behind a standard ute or SUV, the result of the machine’s low trailer weight and narrow 1486 millimetre width. Plus, tight area operations, such as working in narrow
backyards, is made easier by this notably slim design.
The lightweight RT-50 Posi-Track also excels in soft ground conditions, allowing operators to get back to work sooner after wet weather, even on sensitive turf. The risk of ground damage is minimised, thanks to the RT-50’s class-leading low ground pressure of just 3.0 psi.
The innovative, patented Posi-Track undercarriage system also offers maximum control, flotation, traction and pushing power in steep, wet, muddy, debris-filled and slippery conditions, thanks to the RT-50’s exceptional 366 millimetres of ground clearance – nearly double that of comparable models from other manufacturers. In addition, track derailment is virtually eliminated thanks to numerous contact points and guide lugs.
The patented Posi-Track undercarriage significantly improves operator comfort, offering a smoother ride over tough terrain made possible by a unique torsion axle suspension setup. The result is significantly less fatigue during a long day in the cab.
Operation is easy and intuitive with standard joystick controls. An optional all-weather cab with heat and A/C allows for year-round comfort while working in extreme temperatures, and for additional comfort ASV also offers an optional suspended seat.
The RT-50 Posi-Track Loader offers exceptional ease of serviceability, minimising machine downtime. Thanks to a large rear-tilting hood, all maintenance points are easily accessible. In addition, a direct-drive pump eliminates the labour-intensive belt servicing that comes with belt-driven pumps. Individually replaceable steel sprocket rollers and metal-face seals as standard to ensure minimised replacement requirements, meaning less downtime and more profitability.
In addition, as with the entire ASV Posi-Track range, the RT-50 comes with an industryleading 2-year/2000-hour warranty, backed by Australia’s renowned ASV national service network.
Find out more about the ASV RT-50 Posi-Track Loader and book an inspection at your local dealer: www.asvaus.com.
The #8560 is the pinnacle of the Blundstone Rotoflex range. The wheat, 6-inch unisex zip-sided safety boot offers new comfort systems and lightweight composite toe protection, all with legendary Blundstone durability and reliability.
There’s a heap of new technologies and features, like SoftCell ® , the overarching comfort system utilising a combination of specialist materials and the unique biomechanical foot-cradling design to increase stability, and AirCell ®, a uniquely constructed, zoned-airflow footbed with specialised breathing channels to activate ventilation and moisture control, as well as provide full-body cushioned comfort. The footbed is anti-bacterial, washable and breathable.
For contractors slogging out long days in the sun, those features quickly add up to a very well-rounded and sophisticated safety boot.
Other new technologies and features include: • Infinergy® from BASF – an E-TPU, super-elastic energy foam, soft but resilient, providing enhanced cushioning and impact reduction every step of the way
• GripTek ® – a biomechanically designed TPU outsole for optimum grip and stability. It’s abrasion-resistant and heat-resistant to 140°C, as well as resistant to oil, acid, organic fat and highly resistant to hydrolysis and microbial attack
• Fortalite® – the broad-fitting, compressionresistant composite toe cap provides safety without weight. It’s airport-friendly and tested to handle a 200-joule impact.
Unisex, side-zip, all-new comfort systems and lightweight composite toe protection – all with legendary Blundstone durability and reliability.
It’s also great to see several components of the boot, including the new lining and laces, are made from recycled PET, with the lining providing moisture-wicking and long-lasting performance.
Graham Groeneveld from SCR, who specialises in all aspects of carpentry and building maintenance, agreed to put the Blundstones to the test for us. Graham’s been in the business for over 25 years and is a gun on the tools.
It’s clear looking at the RotoFlex #8560s that Blundstone has pulled out all the stops with these premium workboots. We caught up with Graham on several different worksites to get a broad feel for the boot’s performance in different environments, everything from scaffolding on 5-level apartment blocks to working at ground level with saws, nail guns and various other power tools.
“The boots feel surprisingly natural and comfortable from the very first wear,” laced Graham. “You need stability and surefootedness climbing through the scaffold at heights. These boots had that in spades. The grip was excellent, and the 150mm boot provided impressive ankle support.
“On the ground, the flexibility of the boot when crouching, kneeling, and generally bending was impressive. A lot of boots I’ve worn just don’t provide this level of comfort and movement.”
After getting familiar with the vast number of features that combine to offer unparalleled levels of safety in a lightweight workboot, there are simply too many features on the #8560 to list in any detail. But after testing and wearing the boots for several weeks, the key elements that jumped out were the reduced risk of ankle rolls, the impressive composite toe cap, the TPU toe covering, and the strength of the GripTek outer sole. Together those last three prevent pretty much anything from penetrating the boot.
Durable, heavy-duty zip with industrial-grade zip fastener.
From intense heat to impressive grip and control, the wearer’s protected from all angles, and the water-resistant nubuck leather upper makes for dry feet on wet jobs.
Bonus!
My feet haven’t felt this secure or comfortable in a work boot before, and a 30-day comfort guarantee, along with a six-month manufacturing warranty, shows the level of confidence Blundstone has in the RotoFlex #8560 workboot. It’s easy to be just a little overwhelmed by all the features, so I’d recommend trying them on next time you’re in the market for boots, and let the experience and comfort do the rest.
It’s been eight years since Greg made the move from the other side of the ditch and set up Ongrade Earthworks, specialising in detailed earthworks in Darwin and its surrounding suburbs. Greg started in another brand of excavator, but after having these machines serviced by the Forecast Machinery team and experiencing various issues, Greg decided it was time to step across into his first Kobelco and hasn’t looked back.
“The thing I love most about my Kobelco machines is the reliability. My first 13-tonne excavator has over 5000 hours on it without a single breakdown. I now have a second machine – the SK135SR-7 – with a new updated cab, improved seat and upgraded controls, and a 10-inch display. It’s very comfortable and feels just like my office with amazing air-conditioning, which doesn’t struggle at all up here in the heat,” said Greg.
What do you do when you’re a gun operator from New Zealand and sick of the cold? Well, if you’re Greg Chant, owner operator of Ongrade Earthworks, you move to Darwin to warm your bones and rip into a pile of work in your new Kobelco machine in Australia’s Northern Territory.
Greg has been operating machinery and excavators since he left school in New Zealand, which means he has decades of experience behind the controls. For his recent purchase, Greg decided to opt in for the GPS services and purchased a tilt rotator. This combination has had a positive effect on his business, expanding his work opportunities into new areas. Greg shared, “I’d be lying if I said the first few months getting the tilt rotator dialled in wasn’t frustrating because it was new territory for me, but once you get used to operating with a tilt rotator there’s no going back – it’s an amazing piece of equipment.”
Dealing with Tom and Andy at Forecast
Machinery has always been a positive experience for Greg. He said they have taken great care of him and gone above and beyond in terms of their level of service. “I’d love to tell you specific stories about how my machine broke down and the Forecast team dropped everything to come save the day, but neither of my Kobelco machines have had a breakdown. The service from the team at Forecast has always been wonderful. If I have service parts or any other required items, they will drop it to my workshop so I don’t have to go to them after hours. I just can’t recommend Tom and Andy enough,” said Greg.
Greg continued, “In terms of power my new Kobelco SK135SR-7 has come ahead leaps and bounds from the previous SK135SR-3. It’s a significantly more powerful machine with faster digging cycles and better breakout force, which means increased productivity. There’s plenty of opportunity coming up in the Territory for Ongrade Earthworks and I’ll certainly be looking to Tom and Andy for my next Kobelco.”
Tom Bate and his wife Andy are the dealer for Kobelco up in the Northern Territory. The pair have done a great job building the dealership in Darwin and its surrounding areas during the
last eight years. When I chatted with Tom about his experience working with Greg, he shared, “We’ve been working with Greg for over eight years now. He started by bringing in other machinery for service and repairs, but when it was time for Greg to look at a new machine –
after doing his research and us sharing with him the strengths of the Kobelco machine – he was quietly impressed and decided to jump into a Kobelco… he hasn’t looked back.
“We have now supplied Greg with his second Kobelco SK135 fitted with an ENGCON tilt
rotating hitch, which has been a bit of a game changer for him, along with setting the machine up with GPS. Greg’s an owner operator who needs machines working at a premium level for his clients. Being able to match the GPS and technical advantages of the Kobelco machines has been right where Greg needed it to be. That, along with the performance and reliability of the Kobelco brand, is why Greg has now
jumped into his second Kobelco machine.” Tom continued, “Our relationship has been nothing but easy because Greg understands small business and the need to plan and forecast his requirements. Being remote in the Northern Territory, having someone that understands the challenges involved has made Greg a pleasure to deal with. We’re looking to grow our relationship and we have already been
talking about some new opportunities and options. We’re looking forward to being able to continue to work with Greg and deliver on a product that can expand his opportunities.” With both the Kobelco range of excavators and the team at Forecast Machinery kicking goals, there’s going to be some busy years ahead for operators and dealerships alike in the Northern Territory.
Vermeer Australia celebrated the winners of their inaugural RDO Vermeer Technician Awards in August, recognising the achievements of service and parts technicians throughout their wide-reaching dealer network.
Justin Spinks took out Service Technician of the Year and Daniel Ryan was awarded Parts Interpreter of the Year, both from Vermeer Australia’s Richlands, Queensland branch. Toby Jones, from the Townsville branch took out Apprentice Service Technician of the Year. Each of the finalists met in Brisbane prior to the awards ceremony to compete in hands-on testing and training across Vermeer’s innovative equipment range, before joining colleagues, management and family members at an awards dinner at Crystalbrook Vincent, Howard Smith Wharves in Brisbane.
Justin Spinks, 2022 Service Technician of the Year: “Thank you to RDO for the opportunity and the privilege to participate in these awards. Congratulations to the other finalists in my category, and I also thank all those who have helped me throughout my career to master the skills I have developed. I’m looking forward to continuing to represent the company, and helping our customers to chip and grind, drill or trench, vacuum or load with the best machines around.”
Daniel Ryan, 2022 Parts Interpreter of the Year: “I feel humbled to have been awarded Parts Technician of the Year and am proud to be part of such a great organisation, full of amazing, talented people who make RDO a fun and fantastic place to work and build a long-lasting career. This past week has been great finally meeting my colleagues from other branches face to face, after spending the past few years only talking on the phone.
I’ve really enjoyed sharing our experiences and learning from the other branches.”
Toby Jones, 2022 Apprentice Service Technician of the Year: “I believe that being awarded as the RDO Vermeer Apprentice Service Technician of the Year is not only a great achievement for myself but also for the tradesmen and managers within the branch. This has been a great opportunity to represent my branch and the great work we do here at RDO Townsville.”
Established this year, the awards were presented to Vermeer Australia’s specialised service technicians and parts interpreters who have excelled in all aspects of their work, from exceptional customer service to excellent technical and diagnostic skills, with nine technicians nominated across the three categories.
Phil Canning, RDO Equipment CEO says the awards are a great opportunity to honour Vermeer Australia’s expert technicians who are constantly delivering to customers.
“We established these awards as we know we have a great team of technicians across our Vermeer network, and we want to recognise their achievements and raise awareness of the amazing career opportunities at RDO Equipment and Vermeer Australia, as well as focusing on continuously developing and training our team,” Phil says.
“Our inaugural winners are a credit to the Vermeer Australia brand and show the depth of experience our entire team has across Vermeer’s market-leading, innovative machinery. From our experienced service techs and parts interpreters to an up-andcoming apprentice, our customers are in capable hands when it comes to their Vermeer equipment.”
Vermeer Australia is part of Vermeer Corporation’s worldwide dealer network of over 3000 team members. Vermeer Corporation, a manufacturer established in Pella, Iowa, in 1948, is a manufacturer of high-quality construction, surface mining, agricultural and environmental equipment.
In 2015, Vermeer Australia became part of what is known today as RDO Equipment Pty Ltd. Across Australia, RDO Equipment proudly employs more than 900 employees across 29 locations in metro and regional Australia, and provides an extensive range of premium equipment and after-sales support to service the agricultural, civil, construction, utility, mining, forestry, and natural resource management industries. This size and breadth means they are able to offer Vermeer Australia customers a range of product, and a level of customer support that is unmatched.
Performance-driven, specially designed elements culminate in RotoFlex—a world-leading biomechanical design system that provides an outstanding level of comfort and safety. These boots are the new benchmark for lightweight safety footwear.
The next generation of safety footwear.
New Hydraulink franchise owner brings strong brand ethics and capabilities to Milperra businesses missing out on local excellence.
A man who spent six months researching the hydraulic hose, fitting and service needs of Milperra’s businesses says he is delighted to have joined a Hydraulink national team dedicated to the same values he holds.
Peter Tsekenis recently became the latest member of the Hydraulink family of franchise operators, which spans more than 400 services points across Australia and New Zealand.
He says Hydraulink – which trades under the market signature “Best Under Pressure” – is an ideal fit for a person such as himself with a strong mechanical background and expert understanding of the importance of safety, precision, attention to detail and a can-do attitude that starts with first understanding customers’ needs.
“We have a huge diversity of industries in Milperra – all dependent upon good hydraulic service to keep mobile and plant machinery functioning reliably without wasting downtime. The robust industry base here extends from distribution, transport and major import and export logistics, through to building, construction, diesel and civil machinery, metalworking, conveying and just about everything mechanical under the sun. Milperra really is a production powerhouse – and nearly all the machinery involved uses hydraulics in one way or another.”
“My research told me all of these could benefit from a door-to-door maintenance and breakdown service that gives them maximum uptime. As someone experienced in the civil engineering industry, I understand that breakdowns and ‘that’ll do’ maintenance cost big money, so I want to bring excellence and quality to the table.”
“When I was doing my research, driving around Milperra and talking to businesses for six months, I found that a lot of local industries were going outside the district to get their service needs. So there seems to me to be a real gap in the market here for someone operating locally within a national group who can bring both global standards of precision and integrity that companies today need – combined with downto-earth family values that integrate services operations into the fabric of the local society.
“All my research pointed me to Hydraulink as the one to give me the national backing and expertise I wanted – Hydraulink is a trusted,
well-respected and continuously growing brand and I wanted to join a team that feels like a family environment. They are proud of their brand and their ethics, and they use top-class products that have been trialled and tested –and they stand by their product and services. Plus, the group has experience across the board, both at local levels as well as in some of the biggest civil, industrial and resources
projects in the country. So, you get the same uniformly excellent standards right across the company, in which reliability, safety and attention to detail are of the utmost importance. This professionalism is a representation of my work ethics as well, so we are a great fit.”
Hydraulink Milperra: 0448 762 667
Hydraulink Australia: 1300 36 37 34
Hydraulink New Zealand: 0800 80 66 66
Onetrak’s Queensland branch is now located on 2/65 Pasturage Road in Caboolture.
The new Caboolture premises includes a large workshop, parts warehouse and offices. The close proximity to the M1 makes it easily accessible.
“We have a very solid team here now in Queensland of team members with broad experience across construction, quarry, mining and forestry. Our customers know us historically as forestry machinery experts, but our customer base now stretches across all different industries. Thanks to the broad experience of our field service team, we are now well-positioned to provide service, maintenance, machine rebuilds and air-conditioning servicing and repairs for all makes and models across all industry sectors,” explains Brad Madden, Regional Manager for Onetrak.
An Open Day was held on August 4, giving new and existing customers a chance to pop in for a visit.
On display in the yard was a range of the latest machinery containing Hidromek construction equipment including excavators, backhoe loaders and wheel loaders. Dressta’s new TD20M Extra dozer was also on display together with a range of Anaconda screens, trommels and scalpers.
In addition to Hidromek, Dressta and Anaconda, Onetrak is also the national dealer for Tigercat forestry machines, Striker crushers and screens, Terex Fuchs material handlers and a range of attachments and accessories including Rotobec grapples, Alicon hammers, Timbermax winch systems, Veriga traction aids and more.
Onetrak Caboolture has a fleet of 4x4 service vehicles available to travel to all customer
sites and is backed by local spare parts expertise and growing parts inventory.
A team of Territory Managers look after the state in terms of new and used machine sales and now also offer rental equipment for customers needing a flexible solution such as Rent-To-Buy or wanting a short-term solution.
Onetrak is an Australian owned company with a national footprint covering Queensland, New South Wales, Tasmania, Victoria, South Australia and Western Australia.
“Our national expansion plan would not have been complete without the important Queensland territory. This move allows us to better service our valued clients in Forestry and Mining where there is already a significant population of Tigercat, Striker and Dressta
The Onetrak team offers heavy machinery sales, service, parts and hire equipment.
customers in the region. It also further allows Onetrak to continue to expand our customer base with the Hidromek and Anaconda brands and provide an even higher level of service support than before. Onetrak’s new Caboolture site has been well resourced with specialised tooling, modern service trucks and increasing parts inventory to allow our very talented team here to get the job done and ensure clients have the best aftersales experience. We look forward to growing together with our valued Queensland customer base and building strong, enduring business relationships,” says David Hazell Managing Director for Onetrak. To find out more about Onetrak visit www.onetrak.com.au or call 1300 727 520 to speak with your nearest Onetrak branch.
Onetrak’s fleet of 4x4 field services team service all makes and models.For every excavator size, there is a crusher bucket model that can transform a construction site into a recycling centre.
Every construction site – whether small or large – generates waste. Inert materials of all kinds have to find a new life, a new use, considering the difficulty in finding raw materials and the time it takes to get them.
Is it possible to recover waste and put it back into the production cycle in a simple, fast, and cost-effective way?
Many may not know the solution lies in the carrier machine already on-site: combined with an MB Crusher bucket to work the material so that it can be immediately reused or repurposed for other uses.
Whether the excavator is large or small, an MB jaw crusher can be easily installed, allowing you to directly reduce the grain size of the material on site.
When the operating machine is small... Czech Republic – A construction company from the Czech Republic needs to recover materials to develop and finish their works on time. On-site, they have an 8-tonne Yanmar B7 Sigma midi excavator. Recovering the material directly on site becomes simple when an MB-C50 crusher bucket is installed on the excavator. With a weight of 0.75 tonnes and a load capacity of 0.15 m 3, it is suitable for excavators and backhoe loaders starting from 7 tonnes and has an hourly production rate up to 10m 3. A small jewel capable of transforming a construction site into a recycling centre: it collects material and crushes it to specific sizes within its range, all on-site. Thus, the material can be reused for works in the urban and road sectors.
Mayotte
In this archipelago of the Indian Ocean, the customer wants to become independent from procuring materials from the quarries, both to save on transport costs and wait times and to avoid the continuous coming and going
of trucks to and from the construction site. There are two carrier machines in his fleet working with MB Crusher equipment: a Bobcat T300 with an MB-L140 crusher bucket and a Kubota KX080 with an MB-S14 basket screening bucket. The combined use of these two pieces of equipment mimics an actual recycling centre: the waste material is screened with the MB-S14, separating the fines from the bulk, then crushed by the jaw crusher, and finally reused directly on-site for filling trenches.
The waste turned into a gain of time and money, but above all, it turned into new material.
If the excavator exceeds 30 tonnes... Czech Republic – We are still in the Czech Republic, but this time the customer’s goal is to save on the costs of landfill disposal or having to purchase or rent a large mobile crusher. The excavator on site is a 36 tonne Doosan DX 350 LC to which an MB Crusher model BF120.4 jaw crusher is installed: a weight
of 48 tonnes for a load capacity of 1.3m3 and production that can reach up to 53 m3/h.
Larger excavator but same results: the material is recycled on-site so there is no need to repurchase or dispose of it in landfills. Transport costs and processing times are also reduced, and you work in total safety since the excavator operator does the operations.
Bulgaria – The redevelopment of the area where the largest steel complex in the country was active for 40 years – the Kremikovtsi plant, whose dimensions were comparable to a city – saw one of the largest models of crusher buckets at work: the BF135.8 on a 45-plustonne Hyundai excavator. Vast quantities of reinforced C&D demolition material had to be processed in an area of approximately 12 million square metres. For this reason, the MB Crusher bucket was chosen – a flexible piece of equipment, easy to transport and use, capable of a high hourly production, and capable of crushing the reinforced material without any problem. The reinforced concrete is crushed to the desired output size, and the iron separates quickly from the aggregate pile. At the same time, a lot of truck trips – and pollution – are reduced.
In short, whether the construction site is large or small, there is always an MB Crusher unit with which it is possible to create a recycling centre that allows the company to be independent in material procurement.
And the cost of producing the recycled aggregate is much lower than that of purchasing virgin aggregate. It is also good for the environment and complies with the latest regulations issued in various countries on the use of recycled aggregates.
Equipment handovers are common, albeit usually low-key affairs for leading Cat® dealer WesTrac.
But a recent ceremony at WesTrac’s South Guildford facility held special meaning for the stakeholders involved.
Indigenous contracting business Civil Road & Rail SX5, part of the broader SX5 Group of companies, will use the new Cat D10T2 Dozer for mine rehabilitation services at Rio Tinto’s mine sites in the Pilbara.
According to SX5 directors Ralph and Cherie Keller, and co-director and Eastern Guruma senior elder Kenzie Smith, the act of rehabilitating the land has grown in significance over recent years.
“We’re making things green again, making Country feel better,” Ralph said.
“In repairing Country, we’re helping repair the trust and relationships with the region’s Traditional Owners.”
As well as being among the Traditional Owners of the land, Kenzie Smith’s family have had a long history of helping modern enterprises utilise and rehabilitate the land. The family once helped break horses and muster cattle on the stations in the region and was permitted to gather any stock left behind to sell themselves. SX5 was the brand applied to those stray cattle before they were taken to market. That set the family on an entrepreneurial path that resulted in Kenzie helping to establish and run SX5’s contracting business.
WesTrac General Manager Cameron Callaway said miners, as well as their suppliers and service providers, understood the vital importance of engaging with the Traditional
Owners on whose country they operate to ensure continual improvement in environmental, social and governance outcomes.
“The world needs miners to supply the mineral resources required for a more sustainable future, and that means we need to support sustainable mining initiatives,” Cameron said.
“Drawing on the knowledge of Traditional Owners and the expertise of knowledgeable, experienced Indigenous organisations such as SX5 is a key aspect of that, and it’s especially rewarding for WesTrac to be involved in projects such as this.”
The Cat D10T2 is a key part of that sustainability story, with onboard technologies
to drive greater efficiency, productivity and fuel economy, as well as improved operator safety and comfort. The D10T2 is also equipped with the building blocks to enable remote and semi-autonomous operations.
Ralph Keller says technology has been key to SX5’s success, and support from Indigenous Business Australia (IBA) has made it possible for the group to continue to purchase equipment with the latest machine control technologies.
“What makes us different is that SX5 continues to reinvent itself every day,” he said.
“It’s all about technology. That’s how you achieve excellence and how you mitigate risk.”
Kobelco has significantly expanded its presence in the South Australian market, partnering with truck specialist Northeast Auto Group (NE Group) in a move that will see the full Kobelco excavator range offered at its Adelaide branches in Burton and Lonsdale, with additional locations around South Australia coming online in the future.
Established in 1978, NE Group presides over a comprehensive dealer network, having built a name for itself as a truck industry leader, carving out a market position as one of the largest Isuzu Truck, Ute and Iveco dealers in the country.
As Managing Director Tony Emanuele told EEM , NE Group prides itself on its strong customer-oriented focus, with its evolving product range backed by an extensive service offering.
“Built from the ground up and backed by family values, we’re the one-stop auto shop that always goes above and beyond, built one customer and one relationship at a time,” Tony stated of NE Group’s approach.
“With sales, service and parts all in one place, in addition to our very own in-house engineering, paint and panel divisions, that’s what makes us unique – the ability to provide a true one-stop shop.”
With NE Group’s broad network and allinclusive service offering providing a
strong foundation, Tony told EEM that branching out to offer a dedicated one-stop solution covering the varied needs of SA earthmoving customers is an “exciting opportunity”.
“Kobelco is a premium excavator product and aligns perfectly with our premium range of trucks,” he commented. “We see a lot of synergies for our customers and Kobelco customers because earthmovers need trucks!
“We will offer the full range of Kobelco excavators from one tonne all the way through to the 85 tonne machines. The big appeal with the Kobelco range is that it is a premium product, and it will meet the expectations our customers demand for reliability, fuel efficiency and support.”
Tony additionally noted that the current local market conditions are extremely conducive for the partnership, with NE Group and Kobelco capable of delivering customers a broad array of options and catering for growing demand moving forward.
“There is a big shift happening in SA at the moment, with plenty of housing and infrastructure set to take place in the coming years,” he said.
“We believe that Kobelco is well positioned to help take our customers into the future with a range of excavators capable of handling small backyard-type work through to large-scale civil, quarrying and mining jobs.”
As the SA market continues to expand, and as customers seek out a streamlined and knowledgeable service offering, Tony said NE Group “is excited to be able to assist our customers’ growth well into the future”.
“NE Group has always been very proud to support local business growth, and we take great pride in supporting customers to achieve their goals,” he said.
“The synergies between Kobelco and the rest of NE Group means that we will offer our customers a one-stop solution for excavators and trucks, with the added convenience of multiple locations for parts, service and support.”
Infrastructure projects in Australia continue to push ahead, with no sign of slowing down in the near future. Even some of the supply chain issues are beginning to ease, indicating that the time is ripe to review your equipment and prepare to meet the approaching needs of the market.
Planning is now well under way for the 2023 National Diesel Dirt & Turf Expo, which is being held for the third time at the Sydney Dragway, Eastern Creek NSW. This premium venue has proved to be a winner with exhibitors and visitors alike, thanks to the great layout, easy navigation to find exhibitors, expansive car parking facilities and other aspects that make for a productive visit.
Expo manager Marti Zivkovich said, “There are many reasons why exhibitors return year after year to participate in Diesel Dirt & Turf. Industry leading brands have embraced the Expo and recognise the value of this wonderful opportunity for face-to-face customer engagement.
“There is real enthusiasm shown by so many exhibitors who look forward to participating each year and always renew their site bookings very quickly to ensure they don’t miss out on this integral part of their sales and marketing activity.
“We are particularly thankful to Komatsu for once again taking on gold sponsorship of this leading industry event. Again, we welcome the gold media sponsorship by Earthmovers & Excavators magazine. Associate sponsorships are a great way to increase your visibility, so if you would like to join our associate sponsors Norm Engineering and Earthmoving Equipment Magazine, contact us now. The Pickles auction has become a key drawcard of Diesel Dirt & Turf. Many visitors will come ready to spend on some of the great deals that Pickles will be offering at the Saturday equipment auction.
“If your business is in site preparation, excavation, installation of public works services,
road maintenance or construction, public space management, turf care, specialised vehicles, site services, specialised tools and attachments or associated finance and services, you will benefit from exhibiting. Sites are now selling, so now is the time to commit,” Marti said.
Note the dates: Diesel Dirt & Turf Expo, Ferrers Road, Eastern Creek, New South Wales on Friday 21st, Saturday 22nd and Sunday 23rd April, 2023.
To enquire or book to secure your exhibitor site contact the Expo manager, Marti on 0411 648 465 or apply online at www.dieseldirtandturf.com.au
Working in his family’s business, Divall’s Earthmoving and Bulk Haulage, Jack took on 11 other finalists from across the State in a series of unique challenges and has won the right to represent NSW at the Asia Pacific Final in Japan next month. He will be joined in Japan by West Australian operator Jake Myers from MLG Oz, who took out the WesTrac-hosted WA final last week, as well as winners from other states and around the APAC region.
The winner of the Japan event will head to Las Vegas next year to vie for the title of best in the world at the Caterpillar Global Operator Challenge final at CONEXPO 2023.
Involving three different challenges, each with a different Cat® machine, competitors showcased skills ranging from precision digging and loading to playing mini golf in an excavator.
WesTrac Heavy Construction Business Manager Jeff Dix said the Global Operator Challenge was launched by Caterpillar in 2019 to recognise and celebrate the skills required to perform tasks safely, efficiently, productively and precisely.
“This is the first year that any Australian Cat dealer including WesTrac has hosted the event,” Mr Dix said.
“We’ve seen that there are some highly skilled operators across the State, and they’ve been able to put their talents on show today. All operators have shown outstanding operator skills, which made it hard for the judges to select an outright winner, but Jack proved he has what it takes.
“We wish him every success as he heads to Japan next month and we hope we’ll see him on the world stage in Las Vegas next year.”
Mr Myers, who works with mine site services provider MLG Oz, outperformed seven other finalists to grab the title of WA’s best and will join other state finalists from around Australia on an all-expenses paid trip to Japan to compete in the Asia Pacific regional final in October.
The winner of that regional event will travel to Las Vegas next year to compete against other finalists from around the world in the Caterpillar Global Operator Challenge final at CONEXPO 2023.
Competitors took part in three different challenges, using a different Cat machine for each, and displayed a broad range of operating skills. That included navigating an obstacle course, using a mini excavator to play golf, digging a trench and loading a truck – all within very tight parameters and to precise specifications.
WesTrac WA General Manager of Construction Cameron Callaway said the Global Operator Challenge was launched by Caterpillar in 2019 to recognise and celebrate one of the key ingredients in
successful use of Cat equipment – the people that operate the machines.
“This year marks the first time that any Australian Cat dealer including WesTrac has had the opportunity to host the event,” Mr Callaway said.
“It’s been an exciting month or two for WesTrac. We started by calling for nominations and received over 50 applications. Then we
whittled that down to 24 operators who met all the criteria to participate and put them to the test last month in a series of heats.
“These eight finalists have shown outstanding operator skills throughout the WA competition, and it was a tough choice to pick an overall winner, but Jake Myers managed to outperform the others to take the prize and we wish him every success in the regional final in Japan and hope to see him make it all the way to Vegas.”
CONEXPO-CON/AGG and the International Fluid Power Exposition (IFPE) recently unveiled the Next Level Awards Program to exhibitors for the March 2023 show.
The CONEXPO-CON/AGG Next Level Awards celebrate exhibiting companies that are pushing the boundaries and developing next-level products, technologies and services designed to advance the construction industry. Ten finalists will be highlighted at CONEXPO-CON/AGG and IFPE, March 14-18, 2023, in Las Vegas, with show attendees voting on-site to determine the Contractors’ Top Choice.
The awards program is open to all 2023 CONEXPO-CON/AGG and IFPE exhibitors in good standing that have created products or services for the construction industry that have one or more of the following characteristics:
• Addresses a common industry need in a unique and innovative way.
• Benefits the industry across multiple applications for industry wide adoption.
• Positively impacts the safety, sustainability, and workforce of the industry.
“We are excited to recognise the innovative construction products that are taking the industry to the next level,” said Dana Wuesthoff, CONEXPO-CON/AGG show director. “Exhibitors, large and small, have an opportunity to be recognised for driving ideas and developing products or services to advance the industry. This is an exciting edition to CONEXPO-CON/AGG and IFPE and we strongly encourage exhibitors to enter.”
The judging will take place by a diverse panel of Associated General Contractors of America (AGC) members. Ten finalists identified by the AGC panel will receive recognition within their booth space. On-site at CONEXPO-CON/AGG and IFPE, show
attendees will have the opportunity to visit the 10 finalists’ booths and vote for their favourite Next Level product or service in the Contractor’s Choice Award.
“AGC is excited to be partnering with the Association of Equipment Manufacturers (AEM) on its Next Level awards initiative to recognise innovation in the construction industry and to highlight tools and solutions that will enable our members to build safer, more efficiently, and more effectively,” said Steve Sandherr, CEO, AGC of America.
Applications are accepted now through to November 30, 2022. Exhibitors should check their dashboard for Rules and Regulations and more information.
On Friday 26 August, CCF Victoria held its annual Earth Awards Presentation Evening – celebrating gold excellence in civil construction.
It was uplifting to everyone there to see this prestigious ceremony once again return to a physical event where members of the civil industry were able to gather in person to acknowledge and celebrate the outstanding civil construction work that had been completed over the past 12 months across Victoria.
The event retuned to the world class setting of Melbourne’s Glasshouse along Olympic Park, and was attended by almost 300 guests, stakeholders, contractors and associate members who were all there to see the incredible standard of work that had been carried out in extremely difficult and challenging circumstances over the past year.
This year, there was a total of 16 finalists over seven Project Value categories, and emotions were high as all the finalists were able to watch their hard work presented to their peers and colleagues over the course of the
evening. While all the projects were worthy of being winners on the night, it was truly inspiring to see the level of humility and graciousness from those that were lucky enough to win and those that were not as each award was presented… a testament to the incredible people that make up our industry.
While the Earth Awards is all about celebrating the outstanding calibre of work on display, the room was also treated to a fun night of laughter and entertainment from none other than Master of Ceremonies and one of Australia’s longest running comedy talents, Paul McDermott who has been at the forefront of Australian entertainment for over 20 years. As writer and presenter of several radio and television shows on the ABC and Triple J, many of you would remember Paul as the host of one of Australia’s most beloved shows “Good News Week”
In addition, the crowd were also treated to an incredible array of music from one of Australia’s best live musical acts, The Baker Boys Band, who had everyone (not just the winners) on their feet by the end of the night showing off their best moves.
As mentioned, all the awards were worthy of being announced as winners, which made the judging process an extremely difficult and challenging one. Throughout the judging process, our Earth Awards judges reviewed a wide-ranging spectrum of project distinction, innovation and practicality throughout the three main competition judging criteria… construction excellence, environmental sustainability and project management.
CCF Victoria would therefore like to especially thank our three judges for the awards in Geoff Reynolds (CCF Victoria HSEQ Advisor and Principal at GRM), Rodney Jackson
(President of ALDE and Principal at Calibre) and Maurice Stabb (former IPWEA Victoria President and Executive Consultant). Geoff, Rodney and Maurice all contributed incredible passion as they brought a wealth of industry knowledge and experience when assessing the varied and outstanding
projects on display. Scores for many of them were very tight and in some cases separated by as little as half a point, which shows the incredibly tough job the judges were faced with.
CCF Victoria would like to congratulate everyone who entered this year’s awards, including the 7 winning projects.
CATEGORY 1 - (PROJECT VALUE UP TO $2 MILLION)
Proudly sponsored by Komatsu
Winner: Ausdecom
Project: Figee Crane Dismantle & Redundant Hopper Demolition
CATEGORY 2 - (PROJECT VALUE $2 MILLION - $5 MILLION)
Proudly sponsored by Komatsu Winner: Ace Contractors Project: Lilydale Station - LXR
CATEGORY 3 - (PROJECT VALUE $5 MILLION - $10 MILLION)
Proudly sponsored by Ecologiq Winner: Ausdecom Project: Demolition & Site Wide Remediation at Toyota Altona North Plant
CATEGORY 4 - (PROJECT VALUE $10 MILLION - $30 MILLION)
Proudly sponsored by Meditac
Winner: Melbourne Water & John Holland-KBR Joint Venture Project: Shakespeare Grove Main Drain Outlet Renewal
CATEGORY 5 - (PROJECT VALUE $30 MILLION - $75 MILLION)
Proudly sponsored by Gallagher Winner: Seymour Whyte Constructions Pty Ltd Project: Upper Yarra Dam Safety Upgrade
CATEGORY 6 - (PROJECT VALUE $75 MILLION - $150 MILLION)
Proudly sponsored by Gallagher
Winner: Metropolitan Roads Program Alliance Fulton Hogan, MTM and LXRP Project: Cardinia Road Level Crossing Removal Project
CATEGORY 7 - (PROJECT VALUE GREATER THAN $150 MILLION)
Proudly sponsored by CCF Victoria
Winner: Major Road Projects Victoria and McConnell Dowell Decmil Joint Venture Project: Mordialloc Freeway
CCF Victoria wishes to congratulate the seven winning projects that will now go on to represent Victoria at the National CCF Earth Awards taking place on Friday 11th November in Canberra. We wish all of you the best of luck and hope you can do us proud.
In addition, CCF Victoria would also like to say a big thank you and acknowledge our amazing business partners in Gallagher, Ecologiq, Komatsu and Meditac. Without your support, events like the Earth Awards, which bring acknowledgment and exposure to the outstanding work being done in our industry, would never be possible.
For those who did not attend this year, we strongly encourage you to make sure you are part of this tradition (which has become one of the year’s most anticipated events for the civil industry), and make sure you nominate a project that you have been part of for next year. The CCF Earth Awards provides you and your business with an opportunity to have your work acknowledged by industry leaders and is a great way to build your reputation.
To view all the winning project videos from the 2022 Earth Awards, visit the CCF Victoria YouTube Channel or website: www.ccfvic.com.au/news/
Australian comedy great and MC Paul McDermott.
The Awards were presented in the following categories:
Industry Training Awards
• Certificate II Student of the Year Award
• Certificate III Trainee/Apprentice of the Year Award
• Certificate IV Student of the Year Award
• Diploma Student of the Year Award
• Encouragement Award
• Outstanding Commitment to Training and Skill Development (Individual) Award
• Outstanding Commitment to Training and Skill Development (Employer) Award
• Overall Student of the Year Award
People’s Awards
• Site Supervisor of the Year
• Project Manager of the Year
• Work Health & Safety Champion of the Year
• Indigenous Employee of the Year Award
• Environmental & Sustainability Champion of the Year
• Construction Industry Person of the Year
CCF QLD CEO Damian Long said: “Our people are the life blood of the civil construction industry in Queensland. We have some of the most highly skilled and qualified people working within our industry building significant infrastructure projects which boost the Queensland economy. It is important for CCF QLD to provide an opportunity to celebrate these people and their achievements.
“In addition to the People’s Awards, we are very excited to be celebrating our Industry
Training Awards once again this year. Training and skill development is key to the successful delivery of projects within Queensland. CCF QLD through our registered training organisation Civil Train are very proud to offer authentic accredited training to industry,” said Mr Long.
Congratulations to the Queensland winners:
• Certificate II Student of the Year: Abdullah Gemicioglu, Nexus Traffic Australia Pty Ltd
• Certificate III Trainee/Apprentice of the Year: Michael Prior, Ventia
• Certificate IV Student of the Year: Scott Bohm, McIlwain Civil Engineering Pty Ltd
• Diploma Student of the Year: Tony Karamatic, Albem Operations Pty Ltd
• Encouragement Award: Brent Johnson, BMD
• Outstanding Commitment to Training and Skill Development (Individual): Tony Karamatic, Albem Operations Pty Ltd
• Outstanding Commitment to Training and Skill Development (Employer): SGQ Pty Ltd
• Overall Student of the Year: Tony Karamatic, Albem Operations Pty Ltd
• Site Supervisor of the Year: Graeme Schulze, Seymour Whyte Constructions Pty Ltd
• Project Manager of the Year: Mark Stone, McIlwain Civil Engineering Pty Ltd
• Work Health & Safety Champion of the Year: Bruce Young, Seymour Whyte Constructions Pty Ltd
• Indigenous Employee of the Year: Ashley Anderson, Albem Operations Pty Ltd
• Environmental and Sustainability Champion of the Year: Claudia Azevedo Fonseca, Civil Mining & Construction
• Construction Industry Person of the Year: Matthew Pollock, Highway Construction
CCF QLD congratulates all this year’s award winners.
These awards recognise the outstanding achievements of the brilliant people who work within the Queensland civil construction industry as well as the outstanding trainees and apprentices trained by Civil Train in the state.
In the last week of September 2022, the Federal Government held its Jobs and Skills Summit and two days earlier the Queensland Government released their Queensland Workforce Strategy. The week prior Construction Skills Queensland (CSQ) released their report, Queensland’s Renewable Future, a study into the investment jobs and skills that will be required to support current net zero targets. Clearly, skills are headlining discussions across the country and no sector is spared.
The CSQ report, focuses on one segment of one industry in one state and the forecast pressure on labour resources is staggering. According to the report Queensland is on the cusp of a renewable energy boom. The boom will be supercharged by the advancement of hydrogen generation and export.
Key findings are:
• Up to 26,700 construction workers from the early 2020s to 2050 could be required to realise Queensland’s renewables boom
• This follows a CAPEX requirement approaching $13.9 billion annually to meet the state’s net zero 2050 target while building a strong hydrogen industry serving both domestic and export needs
• More than half of these construction jobs (13,800) would be in regional Queensland, namely the central and northern parts of the state
This will be in addition to the current infrastructure demands associated with a strong capital expenditure for state infrastructure and the 2032 Olympic Games.
The Federal Government’s Job and Skills Summit is an honourable effort to bring all stakeholders together to brainstorm solutions. Initiatives such as supporting women to reengage with the market and providing incentives for pensioners to work more hours will go some way of addressing labour shortages but when you consider the numbers of construction workers required in Queensland alone these initiatives simply will not be enough.
Approximately 8.7% of the current workforce is engaged in construction. It is fair to say that only a similar percentage of the unlocked workforce will be made available through the above initiatives. Our workforce is aging and regardless of retention strategies beyond retirement the danger is the rate of people leaving the industry will be greater than those entering.
Strategies which attract labour from different industries and or from other states, whilst can be beneficial to our industry, only robs one industry and or state to pay another. The result is bad for Queensland and Australia.
International immigration is a must. It must be targeted to ensure skills sets are matched to our demand. Regardless of the skill international migrants will have there will be a
requirement to train to Australian standards. A well-organised overseas recruitment and domestic training solution will be required to add to the current workforce.
Upskilling of the current workforce so they have the skills to meet the emerging technologies and industries will be essential. There will need to be a holistic training strategy that focuses on attraction, retention and progression. Construction Skills Queensland (CSQ) has recognised these key points. The challenge is to get all policy makers to be aligned around these points.
The next issue to solve will be the shortage of housing for the influx of people we will need. The labour shortage conversation must be held in conjunction with livability issues such as housing and transport infrastructure. This is a challenge in the face of rising interest rates, increasing supply costs and supply challenges.
An outcome of the collective summits and reports is that any solution must address falling productivity. We have seen productivity decrease in the civil construction sector as well as an overall general productivity decrease across industrial services.
Increasing productivity does not involve
decreasing wages, but rather producing more for less. Wages are a small component of the productivity conversation, however how we engage the workforce to assist in producing productive outcomes is critical.
CCF QLD is concerned that the push to revert to industrywide bargaining would be a massive step in the wrong direction as far as productivity goes. Productivity must be at the forefront of these discussions.
If the solutions are right, we will see a lift in real wages, increased productivity, producing better living affordability and standards.
I look forward to real bipartisan leadership on these issues which ignores the noise of self-interested 3rd parties.
In the old days an owner operator with a machine or two would work in the area he lived. He would be known by the locals and wouldn’t need to move into another district for work. If anyone needed earthworks done, they would use one of the local operators, and probably wouldn’t have to wait too long for the job to be done.
It seems these days, owner operators are travelling the state (and sometimes interstate) for work. Work is in abundance at the moment, but still operators are travelling great distances for work. Once upon a time, Sydney area operators wouldn’t dream of travelling to the Central Coast or south to the Southern Highlands for work. These areas had their own operators. However, these days principal contractors are finding it hard to contract the machines they require, and are sourcing operators from further and further afield. But are these operators making money? Is it profitable to travel these distances? When quoting rates, operators factor in fuel, wear and tear on machinery, tolls, accommodation, etc, but what of the other hidden costs. If you are staying away from home, apart from accommodation, there is an additional cost of meals, laundry or home maintenance that you would normally do yourself. If there is a young family, there is a
The cost of working in 2022.
cost to not being around. There may be extra childcare costs if you’re not there to share the load. And what is the cost of not seeing your children daily? What price do you put on that?
It’s very easy to ignore all these extra costs but they do add up and should be taken into account. The exercise of keeping track of all extra expenses due to working away is highly recommended to give the owner operator a true picture of the work’s profitability, not only in a monetary sense, but also in a social sense.
Allied Earthmovers Association exists to help owner operators run their businesses as efficiently as possible. The elimination of unnecessary expenses by the owner operator is crucial if the owner operator doesn’t want to keep chasing his tail. The number one issue with owner operators is insurance costs. Allied Earthmovers Association can save you money on insurance. This saving alone will pay for membership, and then some.
The Association will also help with work shortages or overload, message service system, compliance and networking. Some business costs are a great investment and will return rewards time and time again. Membership of Allied Earthmovers is one of those costs. The Board of the Association has also been able to streamline its costs and now
this not-for-profit organisation is able to offer membership at a greatly reduced rate
If you are an owner operator and would like to see what our Association has to offer, please do not hesitate to give us a call on 0416 110 024 or email us at office@goldenbucket.com.au.
Golden Bucket Allied Earthmovers Association – Run by the Members – For the Members.
Ann Callaghan General ManagerGolden Bucket Allied Earthmovers Association
At CJD Equipment we value our relationships with our customers and manufacturers alike, so much so we believe them to be the cornerstone of our business. This is why we are so proud of the 30 years we have been partnered with Volvo Construction Equipment, a company with nearly 190 years of experience in the industry.
Our relationship has gone from strength to strength over the journey and we look forward to many more years of partnership.
- Alan Barnett, CJD Equipment Managing Director